Carrier 48Tfd008 014 Users Manual
48TFF008-012 to the manual a800217e-ac22-4a34-8b65-f3daa3ba0313
2015-01-24
: Carrier Carrier-48Tfd008-014-Users-Manual-310670 carrier-48tfd008-014-users-manual-310670 carrier pdf
Open the PDF directly: View PDF .
Page Count: 48

Manufacturer reserves the right to discontinue, or change at any time, specifications or designs without notice and without incurring obligations.
Catalog No. 004-816 Printed in U.S.A. Form 48TF-C1SI Pg 1 1-01 Replaces: New
Book 1 4
Ta b 1 a 6 a
Installation, Start-Up and
Service Instructions
CONTENTS
Page
SAFETY CONSIDERATIONS . . . . . . . . . . . . . . . . . . . . . . 1
INSTALLATION . . . . . . . . . . . . . . . . . . . . . . . . . . . . . . . . 1-33
Step 1 — Provide Unit Support . . . . . . . . . . . . . . . . . . . 1
•ROOF CURB
• SLAB MOUNT
Step 2 — Field Fabricate Ductwork . . . . . . . . . . . . . . . 2
Step 3 — Install External Trap for
Condensate Drain. . . . . . . . . . . . . . . . . . . . . . . . . . . . . . 2
Step 4 — Rig and Place Unit . . . . . . . . . . . . . . . . . . . . . 2
• POSITIONING
Step 5 — Install Flue Hood . . . . . . . . . . . . . . . . . . . . . . . 8
Step 6 — Install Gas Piping . . . . . . . . . . . . . . . . . . . . . . 8
Step 7 — Make Electrical Connection . . . . . . . . . . . . 8
• FIELD POWER SUPPLY
• FIELD CONTROL WIRING
• HEAT ANTICIPATOR SETTINGS
Step 8 — Adjust Factory-Installed Options . . . . . . 11
• APOLLO CONTROL
• MANUAL OUTDOOR-AIR DAMPER
• OPTIONAL DURABLADE ECONOMIZER
• OPTIONAL ECONOMI$ER
Step 9 — Adjust Evaporator-Fan Speed . . . . . . . . . 20
START-UP . . . . . . . . . . . . . . . . . . . . . . . . . . . . . . . . . . . . 34-36
SERVICE . . . . . . . . . . . . . . . . . . . . . . . . . . . . . . . . . . . . . 36-41
TROUBLESHOOTING. . . . . . . . . . . . . . . . . . . . . . . . . 42-46
START-UP CHECKLIST . . . . . . . . . . . . . . . . . . . . . . . . CL-1
SAFETY CONSIDERATIONS
Installation and servicing of air-conditioning equipment can
be hazardous due to system pressure and electrical compo-
nents. Only trained and qualified service personnel should
install, repair, or service air-conditioning equipment.
Untrained personnel can perform basic maintenance func-
tions of cleaning coils and filters and replacing filters. All other
operations should be performed by trained service personnel.
When working on air-conditioning equipment, observe precau-
tions in the literature, tags and labels attached to the unit, and
other safety precautions that may apply.
Follow all safety codes. Wear safety glasses and work
gloves. Use quenching cloth for unbrazing operations. Have
fire extinguishers available for all brazing operations.
INSTALLATION
Unit is shipped in the vertical discharge configuration. To
convert to horizontal configuration, remove screws from side
duct opening covers and remove covers. Using the same
screws, install covers on vertical duct openings with the insula-
tion side down. Seals around duct openings must be tight. See
Fig. 1.
Step 1 — Provide Unit Support
ROOF CURB — Assemble and install accessory roof curb in
accordance with instructions shipped with curb. See Fig. 2. In-
stall insulation, cant strips, roofing felt, and counter flashing as
shown. Ductwork must be attached to curb. If gas, electric
power or control power is to be routed through the curb, attach
the accessory thru-the-curb service connection plates to the
roof curb in accordance with the accessory installation instruc-
tions. Connection plates must be installed before unit is set in
roof curb.
Curb should be level. Unit leveling tolerances are shown in
Fig. 3. This is necessary for unit drain to function properly. Re-
fer to Accessory Roof Curb Installation Instructions for addi-
tional information as required.
Disconnect gas piping from unit when leak test-
ing at pressure greater than 3.4 kPa (1/2 psig).
Pressures greater than 3.4 kPa (1/2 psig) will
cause gas valve damage resulting in hazardous
condition. If gas valve is ever subjected to pres-
sure greater than 3.4 kPa (1/2 psig), it must be
replaced before use. When pressure testing
field-supplied gas piping at pressures of 3.4 kPa
(1/2 psig) or less, a unit connected to such piping
must be isolated by manually closing the gas
valve(s).
Before performing service or maintenance operations on
unit, turn off main power switch to unit. Electrical shock
could cause personal injury.
IMPORTANT: The gasketing of the unit to the roof curb
is critical for a watertight seal. Install gasket supplied
with the roof curb as shown in Fig. 2. Improperly
applied gasket can also result in air leaks and poor unit
performance.
48TFD008-014
48TFE008-014
48TFF008,012
Single-Package Rooftop Heating/Cooling Units
50 Hz

2
SLAB MOUNT (Horizontal Units Only) — Provide a level
concrete slab that extends a minimum of 152 mm (6 in.)
beyond unit cabinet. Install a gravel apron in front of con-
denser coil air inlet to prevent grass and foliage from obstruct-
ing airflow.
NOTE: Horizontal units may be installed on a roof curb if
required.
Step 2 — Field Fabricate Ductwork — Secure all
ducts to roof curb and building structure on vertical units. Do
not connect ductwork to unit. For horizontal applications, field-
supplied flanges should be attached to horizontal discharge
openings and all ductwork secured to the flanges. Insulate and
weatherproof all external ductwork, joints, and roof openings
with counter flashing and mastic in accordance with applicable
codes.
Ducts passing through an unconditioned space must be in-
sulated and covered with a vapor barrier.
If a plenum return is used on a vertical unit, the return
should be ducted through the roof deck to comply with applica-
ble fire codes.
A minimum clearance is not required around ductwork.
Cabinet return-air static shall not exceed –87 Pa (–.35 in. wg)
with Durablade economizer, –26 Pa (–.30 in. wg) with
EconoMi$er or –112 Pa (–.45 in. wg) without economizer.
These units are designed for a minimum heating operation
continuous return-air temperature of 10 C (50 F) (dry bulb), or
an intermittent operation down to 7 C (45 F) (dry bulb), such as
when used with a night set-back thermostat.
Step 3 — Install External Trap for Condensate
Drain — The unit’s 19-mm (3/4-in.) condensate drain con-
nections are located at the bottom and side of the unit. Unit dis-
charge connections do not determine the use of drain connec-
tions; either drain connection can be used with vertical or hori-
zontal applications.
When using the standard side drain connection, make sure
the plug (Red) in the alternate bottom connection is tight before
installing the unit.
To use the bottom drain connection for a roof curb installa-
tion, relocate the factory-installed plug (Red) from the bottom
connection to the side connection. See Fig. 4. The piping for
the condensate drain and external trap can be completed after
the unit is in place.
All units must have an external trap for condensate drain-
age. Install a trap at least 102-mm (4-in.) deep and protect
against freeze-up. If drain line is installed downstream from the
external trap, pitch the line away from the unit at 25 mm (1 in.)
per 3 m (10 ft) of run. Do not use a pipe size smaller than the
19-mm (3/4-in.) unit connection.
Step 4 — Rig and Place Unit — Inspect unit for
transportation damage. File any claim with transportation
agency. Keep unit upright and do not drop. Spreader bars are
not required if top crating is left on unit. Rollers may be used to
move unit across a roof. Level by using unit frame as a refer-
ence. See Tables 1A and 1B and Fig. 5 for additional informa-
tion. Operating weight is shown in Tables 1A and 1B and
Fig. 5.
Lifting holes are provided in base rails as shown in Fig. 5
and 6. Refer to rigging instructions on unit.
POSITIONING — Maintain clearance around and above unit
to provide minimum distance from combustible materials,
proper airflow, and service access. See Fig. 6.
Do not install unit in an indoor location. Do not locate unit
air inlets near exhaust vents or other sources of contaminated
air.
Be sure that unit is installed so that snow will not block the
combustion intake or flue outlet.
Unit may be installed directly on wood flooring or on Class
A, B, or C roof-covering material when roof curb is used.
(Copy continued on page 4.)
All panels must be in place when rigging.
Fig. 1 — Horizontal Conversion Panels
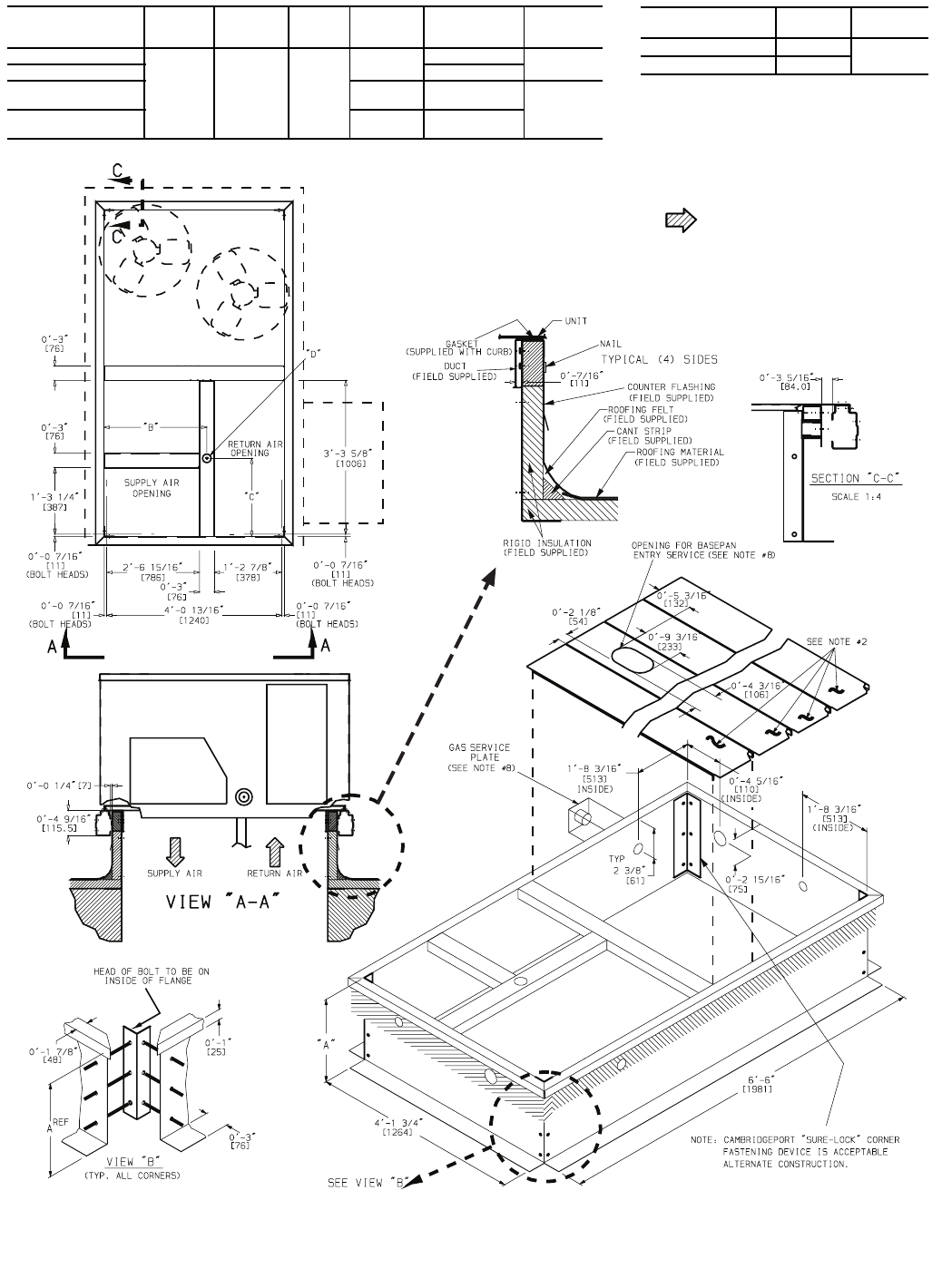
3
CONNECTOR
PKG. ACCY. BC
D ALT
DRAIN
HOLE
GAS POWER CONTROL
CRBTMPWR001A00
2′-87/16″
[827]
1′-1015/16″
[583]
13/4″
[44.5]
3/4″
[19] NPT
3/4″ [19] NPT 1/2″
[12.7]
CRBTMPWR002A00 11/4″ [31.7]
CRBTMPWR003A00 1/2″
[12.7] NPT 3/4″ [19] NPT 1/2″
[12.7]
CRBTMPWR004A00 3/4″
[19] NPT 11/4″ [31.7]
NOTES:
1. Roof curb accessory is shipped disassembled.
2. Insulated panels: 1-in. [25] thick polyurethane
foam, 13/4 lb density.
3. Dimensions in [ ] are in millimeters.
4. Roof curb: 16-gage steel.
5. Attach ductwork to curb (flanges of duct rest on
curb).
6. Service clearance 4 ft [1219] on each side.
7. Direction of airflow.
8. Connector packages CRBTMPWR001A00 and
2A00 are for thru-the-curb gas type. Packages
CRBTMPWR003A00 and 4A00 are for thru-
the-bottom type gas connections.
ROOF CURB
ACCESSORY “A” UNIT SIZE
48TF
CRRFCURB003A00 1′-2″ [356] 008-014
CRRFCURB004A00 2′-0″ [610]
Fig. 2 — Roof Curb Details

4
Although unit is weatherproof, guard against water from
higher level runoff and overhangs.
Position unit on roof curb so that the following clearances
are maintained: 7 mm (1/4-in.) clearance between roof curb and
base rails on each side and duct end of unit; 84 mm (35/16-in.)
clearance between roof curb and condenser coil end of unit.
(See Fig. 2, section C-C.)
Locate mechanical draft system flue assembly at least
1219 mm (48 in.) from any opening through which combustion
products could enter the building, and at least 1219 mm (48 in.)
from an adjacent building or combustible material. When unit
is located adjacent to public walkways, flue assembly must be
at least 2.13 m (7 ft) above grade.
Flue vent discharge must have a minimum horizontal clear-
ance of 1219 mm (48 in.) from electric and gas meters, gas reg-
ulators, and gas relief equipment.
Flue gas can deteriorate building materials. Orient unit so
that flue gas will not affect building materials.
Adequate combustion-air space must be provided for proper
operation of this equipment. Be sure that installation complies
with all local codes and Section 5.3, Air for Combustion and
Ventilation, NFGC (National Fuel Gas Code), ANSI (Ameri-
can National Standards Institute), latest revision, U.S.A.
Standards.
(Copy continued on page 8.)
DRAIN PLUG
MAXIMUM ALLOWABLE
DIFFERENCE mm (in.)
A-B B-C A-C
13 (0.5) 25 (1.0) 25 (1.0)
Fig. 3 — Unit Leveling Tolerances
NOTE: Drain plug is shown in factory-installed position.
Fig. 4 — Condensate Drain Pan
NOTES:
1. Dimension in ( ) is in millimeters.
2. Hook rigging shackles through holes in base rail as shown in
detail ‘‘A.’’ Holes in base rails are centered around the unit cen-
ter of gravity. Use wooden top skid when rigging to prevent rig-
ging straps from damaging unit.
3. Weights include base unit without economizer. See Tables 1A
and 1B for economizer weights.
All panels must be in place when rigging.
Fig. 5 — Rigging Details
UNIT
48TF
MAX
WEIGHT
DIMENSIONS
‘‘A’’ ‘‘B’’ ‘‘C’’
lb kg in. mm in. mm in. mm
D/E/F008 870 395 87.38 2219 40.25 1022 41.31 1050
D/E/F012 1035 469 87.38 2219 40.25 1022 49.31 1253
D/E014 1050 476 87.38 2219 40.25 1022 49.31 1253

5
Table 1A — Physical Data (SI)
LEGEND *Weight of 356 mm (14-in.) roof curb.
NOTE: The 48TF units have a loss-of-charge (low pressure) switch located in
the liquid line.
UNIT SIZE 48TF 008 012 014
Low Heat (D), Medium Heat (E), High Heat (F) D E F D E F D E
NOMINAL CAPACITY (kW) 21.5 29.2 35.9
OPERATING WEIGHT (kg)
Unit 395 469 476
Durablade Economizer 20 20 20
EconoMi$er 28 28 28
Roof Curb* 65 65 65
COMPRESSOR TYPE Hermetic Hermetic Scroll
Quantity 222
Oil (ml) 1479 ea 1479 ea 1597 ea
REFRIGERANT TYPE R-22
Operating Charge (kg)
Circuit 1 2.10 3.08 3.49
Circuit 2 2.22 3.22 3.49
CONDENSER COIL Enhanced Copper Tubes, Aluminum Lanced Fins
Rows...Fins/m 1...669 2...669 2...669
Total Face Area (sq m) 1.90 1.92 2.30
CONDENSER FAN Propeller Type
Nominal L/s 2880 3050 3050
Quantity...Diameter (mm) 2...559 2...559 2...559
Motor BkW...r/s .19...15.5 .19...15.5 .19...15.5
EVAPORATOR COIL Enhanced Copper Tubes, Aluminum Double-Wavy Fins, Acutrol™ Feed Device
Rows...Fins/m 3...590 3...590 4...590
Total Face Area (sq m) 0.74 0.93 1.03
EVAPORATOR FAN Centrifugal Type
Quantity...Size (mm x mm) 1...381 x 381 1...381 x 381 1...381 x 381
Type Drive Belt Belt Belt
Nominal L/s 1230 1700 1980
Motor kW 1.12 1.50 2.24
Maximum Continuous BkW 1.79 1.79 2.76
Motor Frame Size 56 56 56
Fan r/s Range 8.2-11.7 9.5-13.0 12.0-15.0
Motor Bearing Type Ball Ball Ball
Maximum Allowable r/s 26.7 26.7 26.7
Motor Pulley Pitch Diameter Min/Max (mm) 61/86 71/97 102/127
Nominal Motor Shaft Diameter (mm) 16 16 22
Fan Pulley Pitch Diameter (mm) 178 178 203
Nominal Fan Shaft Diameter (mm) 25 25 25
Belt, Quantity...Type...Length (mm) 1...A...1245 1...A...1245 1...A...1346
Pulley Center Line Distance (mm) 425-489 403-445 403-445
Speed Change per Full Turn of
Movable Pulley Flange (r/s) .70 .70 .60
Movable Pulley Maximum Full Turns
From Closed Position 555
Factory Setting 555
Factory Speed Setting (r/s) 8.2 9.5 12.0
Fan Shaft Diameter at Pulley (mm) 25 25 25
FURNACE SECTION
Rollout Switch Cutout Temp (C) 90.6 90.6 90.6
Burner Orifice Diameter (mm)
Natural Gas — Std 3.05 3.05 3.05 3.28 3.05 3.28
Liquid Propane — Alt 2.44 2.44 2.44 2.59 2.44 2.59
Thermostat Heat Anticipator Setting (amps)
400 v Stage 1 .14 .14 .14 .14 .14
Stage 2 .14 .20 .20 .20 .20
Gas Input (kW) Stage 1 21.1 31.9 39.8 31.9 39.8 43.9 39.8 43.9
Stage 2 31.4 50.4 59.8 50.4 59.8 65.6 59.8 65.6
Efficiency (Steady State) (%) 80 80 80
Temperature Rise Range (C) –6-10 2-18 7-24 2-18 7-24 4-21 7-24 4-21
Manifold Pressure (kPa)
Natural Gas — Std 8.3 8.3 8.3
Liquid Propane — Alt 8.3 8.3 8.3
Field Gas Connection Size (mm) 13 19 19 19 19 19 19 19
HIGH-PRESSURE SWITCH (kPa)
Standard Compressor
Internal Relief (Differential) 3103 ± 345 3448 ± 345
Cutout 2951
Reset (Auto.) 2206
LOW-PRESSURE SWITCH (kPa)
Cutout 48 ± 21
Reset (Auto.) 152 ± 48
FREEZE PROTECTION THERMOSTAT
Opens (C) –1 ± 3
Closes (C) 7 ± 3
OUTDOOR-AIR INLET SCREENS Cleanable
Quantity...Size (mm) 1...508 x 635 x 25
1...406 x 635 x 25
RETURN-AIR FILTERS Throwaway
Quantity...Size (mm) 4...406 x 508 x 51 4...508 x 508 x 51 4...508 x 508 x 51
Bhp — Brake Horsepower
BkW — Fan Input Watts x Motor Efficiency

6
Table 1B — Physical Data (English)
LEGEND *Weight of 356 mm (14-in.) roof curb.
NOTE: The 48TF units have a loss-of-charge (low pressure) switch located in
the liquid line.
UNIT SIZE 48TF 008 012 014
Low Heat (D), Medium Heat (E), High Heat (F) D E F D E F D E
NOMINAL CAPACITY (tons) 6.1 8.3 10.2
OPERATING WEIGHT (lb)
Unit 870 1035 1050
Durablade Economizer 44 44 44
EconoMi$er 62 62 62
Roof Curb* 143 143 143
COMPRESSOR TYPE Hermetic Hermetic Scroll
Quantity 222
Oil (oz) 50 ea 50 ea 54 ea
REFRIGERANT TYPE R-22
Operating Charge (lb-oz)
Circuit 1 4-10 6-13 7-11
Circuit 2 4-11 7- 2 7- 8
CONDENSER COIL Enhanced Copper Tubes, Aluminum Lanced Fins
Rows...Fins/in. 1...17 2...17 2...17
Total Face Area (sq ft) 20.50 20.50 25.00
CONDENSER FAN Propeller Type
Nominal Cfm 6100 6500 6500
Quantity...Diameter (in.) 2...22 2...22 2...22
Motor BkW...Rpm 1/4...930 1/4...930 1/4...930
EVAPORATOR COIL Enhanced Copper Tubes, Aluminum Double-Wavy Fins, Acutrol™ Feed Device
Rows...Fins/in. 3...15 3...15 4...15
Total Face Area (sq ft) 8.0 10.0 11.1
EVAPORATOR FAN Centrifugal Type
Quantity...Size (in.) 1...15 x 15 1...15 x 15 1...15 x 15
Type Drive Belt Belt Belt
Nominal Cfm 2600 3500 4200
Motor Hp 11/223
Maximum Continuous Bhp 2.40 2.40 3.70
Motor Frame Size 56 56 56
Fan Rpm Range 492-700 571-779 717-900
Motor Bearing Type Ball Ball Ball
Maximum Allowable Rpm 1600 1600 1600
Motor Pulley Pitch Diameter Min/Max (in.) 2.4/3.4 2.8/3.8 4.0/5.0
Nominal Motor Shaft Diameter (in.) 5/85/87/8
Fan Pulley Pitch Diameter (in.) 7.0 7.0 8.0
Nominal Fan Shaft Diameter (in.) ———
Belt, Quantity...Type...Length (in.) 1...A...49 1...A...49 1...A...53
Pulley Center Line Distance (in.) 16.75-19.25 15.85-17.50 15.85-17.50
Speed Change per Full Turn of
Movable Pulley Flange (rpm) 41 41 36
Movable Pulley Maximum Full Turns
From Closed Position 555
Factory Setting 555
Factory Speed Setting (rpm) 492 571 717
Fan Shaft Diameter at Pulley (in.) 111
FURNACE SECTION
Rollout Switch Cutout Temp (F) 195 195 195
Burner Orifice Diameter (in. ...drill size)
Natural Gas — Std .120...31 .120...31 .120...31 .129...30 .120...31 .129...30
Liquid Propane — Alt .096...41 .096...41 .096...41 .102...38 .096...41 .102...38
Thermostat Heat Anticipator Setting (amps)
400 v Stage 1 .14 .14 .14 .14 .14
Stage 2 .14 .20 .20 .20 .20
Gas Input (Btuh) Stage 1 72,000 109,000 136,000 109,000 136,000 150,000 136,000 150,000
‘107,000 172,000 204,000 172,000 204,000 224,000 204,000 224,000
Efficiency (Steady State) (%) 80 80 80
Temperature Rise Range (F) 20-50 35-65 45-75 35-65 45-75 40-70 45-75 40-70
Manifold Pressure (in. wg)
Natural Gas — Std 3.5 3.5 3.5
Liquid Propane — Alt 3.5 3.5 3.5
Field Gas Connection Size (in.) 1/2 3/4 3/43/43/4
HIGH-PRESSURE SWITCH (psig)
Standard Compressor
Internal Relief (Differential) 450 ± 50 500 ± 50
Cutout 428
Reset (Auto.) 320
LOW-PRESSURE SWITCH (psig)
Cutout 7 ± 3
Reset (Auto.) 22 ± 7
FREEZE PROTECTION THERMOSTAT
Opens (F) 30 ± 5
Closes (F) 45 ± 5
OUTDOOR-AIR INLET SCREENS Cleanable
Quantity...Size (in.) 1...20 x 25 x 1
1...16 x 25 x 1
RETURN-AIR FILTERS Throwaway
Quantity...Size (in.) 4...16 x 20 x 2 4...20 x 20 x 2 4...20 x 20 x 2
Bhp — Brake Horsepower
BkW — Fan Input Watts x Motor Efficiency

7
BOTTOM POWER CHART, THESE HOLES
REQUIRED FOR USE WITH ACCESSORY
PACKAGES — CRBTMPWR002A00 (POWER
AND CONTROL) AND CRBTMPWR004A00
(POWER, CONTROL, AND GAS)
THREADED
CONDUIT
SIZE
WIRE
USE
REQURED
HOLE SIZES
(MAX.)
1/2″
″ ″
″ [12.7] 24 V 7/8″
″″
″ [22.2]
11/4″
″ ″
″ [31.7] Power 13/4″
″″
″ [44.4]
3/4″
″ ″
″ [19] FPT Gas 15/8″
″″
″ [41.3]
UNIT
48TF
STANDARD
UNIT WEIGHT
DURABLADE
ECONOMIZER
WEIGHT
ECONOMI$ER
WEIGHT
CORNER
WEIGHT (A)
CORNER
WEIGHT (B)
CORNER
WEIGHT (C)
CORNER
WEIGHT (D) “H” “J” “K” “L”
Lb Kg Lb Kg Lb Kg Lb Kg Lb Kg Lb Kg Lb Kg ft-in. [mm] ft-in. [mm] ft-in. [mm] ft-in. [mm]
D/E/F008 870 395 44 20 62 28 189 86 161 73 239 109 280 127 1-27/8[378] 3-5
5/16 [1050] 2-911/16 [856] 2- 27/16 [672]
D/E/F012 1035 469 44 20 62 28 225 102 192 87 285 129 333 151 2-57/8[759] 4-1
5/16 [1253] 3-03/8[924] 2-107/16 [875]
D/E014 1050 476 44 20 62 28 228 103 195 88 289 131 338 153 1-27/8[378] 4-1
5/16 [1253] 3-03/8[924] 2-107/16 [875]
CONNECTION SIZES
A13/8″
″″
″ Dia [35] Field Power Supply Hole
B21/2″
″″
″ Dia [64] Power Supply Knockout
C13/4″
″″
″ Dia [44] Charging Port Hole
D7/8″
″″
″ Dia [22] Field Control Wiring Hole
E3/4″
″ ″
″ [19] - 14 NPT Condensate Drain
F
1/2″
″″
″ [13] - 14 NPT Gas Connection 48TFD008
3/4″
″ ″
″ [19] - 14 NPT Gas Connection 48TFE,F008
48TFD,E012 & 014, 48TJF012
G2″
″″
″ Dia [51] Power Supply Knockout
NOTES:
1. Dimensions in [ ] are in millimeters.
2. Center of gravity.
3. Direction of airflow.
4. On vertical discharge units, ductwork to be attached to
accessory roof curb only. For horizontal discharge units,
field-supplied flanges should be attached to horizontal dis-
charge openings, and all ductwork should be attached to
the flanges.
5. Minimum clearance (local codes or jurisdiction may prevail):
a. Between unit, flue side and combustible surfaces,
36 in. [914].
b. Bottom of unit to combustible surfaces (when not using
curb), 1 in. [25]. Bottom of base rail to combustible sur-
faces (when not using curb) 0 inches.
c. Condenser coil, for proper airflow, 36 in. [914] one side,
12 in. [304] the other. The side getting the greater clear-
ance is optional.
d. Overhead, 60 in. [1624] to assure proper condenser fan
operation.
e. Between units, control box side, 42 in. [1067] per NEC
(National Electrical Code).
f. Between unit and ungrounded surfaces, control box
side, 36 in. [914] per NEC.
g. Between unit and block or concrete walls and other
grounded surfaces, control box side, 42 in. [1067] per
NEC.
h. Horizontal supply and return end, 0 inches.
6. With the exception of the clearance for the condenser coil
and combustion side as stated in notes 5a, b and c, a
removable fence or barricade requires no clearance.
7. Units may be installed on combustible floors made from
wood or Class A, B, or C roof covering material if set on
base rail.
8. The vertical center of gravity is 1′-7″ [483] for 008, 1′-11″
[584] for 012 and 014 up from the bottom of the base rail.
Fig. 6 — Base Unit Dimensions

8
Step 5 — Install Flue Hood — Flue hood is shipped
screwed to the burner compartment access panel. Remove
from shipping location and, using screws provided, install flue
hood and screen in location shown in Fig. 7.
Step 6 — Install Gas Piping — Unit is equipped for
use with type of gas shown on nameplate. Refer to local
building codes.
For natural gas applications, gas pressure at unit gas connec-
tion must not be less than 13.5 kPa (4.0 in. wg) (17.0 kPa
[5.0 in. wg] in high heat units) or greater than 44.0 kPa
(13.0 in. wg) while unit is operating. For liquid propane applica-
tions, the gas pressure must not be less than 17.0 kPa (5.0 in. wg)
or greater than 44.0 kPa (13.0 in. wg) at the unit connection.
Size gas supply piping for 1.7 kPa (0.5 in. wg) maximum
pressure drop. Do not use supply pipe smaller than unit gas
connection.
NOTE: When installing gas piping to gas valve inlet, use prop-
erly sized back-up wrench on inlet flange flats.
Support gas piping as shown in the table in Fig. 8. For ex-
ample, a 19 mm (3/4-in.) gas pipe must have one field-
fabricated support beam every 2.4 m (8 ft).
See Fig. 8 for typical pipe guide and locations of external
manual gas shutoff valve.
Step 7 — Make Electrical Connections
FIELD POWER SUPPLY — All units are factory wired for
the voltage shown on the nameplate.
Refer to unit label diagram for additional information. Pig-
tails are provided for field service.
When installing units, provide a disconnect per local codes.
Use copper conductors only when splice connectors are used.
All field wiring must comply with local requirements.
Install conduit through side panel openings indicated in
Fig. 6. Route power lines through connector to terminal con-
nections as shown in Fig. 9.
Voltages between phases must be balanced within 2% and
the current within 10%. Use the formula shown in Table 2,
Note 2 to determine the percentage of voltage imbalance. Op-
eration on improper line voltage or excessive phase imbalance
constitutes abuse and may cause damage to electrical compo-
nents. Such operation would invalidate any applicable Carrier
warranty.
NOTE: If field-installed thru-the-bottom connections are used,
refer to the accessory installation instructions for power wiring.
Refer to Fig. 6 for drilling holes in basepan.
FIELD CONTROL WIRING — Install a Carrier-approved
accessory thermostat assembly according to installation in-
structions included with the accessory. Locate thermostat
assembly on a solid wall in the conditioned space to sense aver-
age temperature in accordance with thermostat installation
instructions.
NOTE: For wire runs up to 15 m (50 ft), use no. 18 AWG
(American Wire Gage) insulated wire (35 C minimum). For 15
to 23 m (51 to 75 ft), use no. 16 AWG insulated wire (35 C
minimum). For over 23 m (75 ft), use no. 14 AWG insulated
wire (35 C minimum). All wire larger than no. 18 AWG cannot
be directly connected to the thermostat and will require a junc-
tion box and splice at the thermostat. Refer to Table 3 for wire
conversions.
Unit cabinet must have an uninterrupted, unbroken electri-
cal ground to minimize the possibility of personal injury if
an electrical fault should occur. This ground may consist of
electrical wire connected to unit ground lug in control com-
partment, or conduit approved for electrical ground when
installed in accordance with NEC (National Electrical
Code), ANSI/NFPA (National Fire Protection Associa-
tion), latest edition (U.S.A. Standards), and local electrical
codes. Do not use gas piping as an electrical ground. Fail-
ure to follow this warning could result in the installer being
liable for personal injury of others.
BASE UNIT
BASE RAIL
FROM GAS METER
ROOF CURB
DRIP LEG PER NFGC*
FIELD-FABRICATED
SUPPORT*
1219 mm (48") MINIMUM
228 mm (9") MINIMUM CLEARANCE
FOR PANELREMOVAL
MANUAL GAS
SHUTOFF VALVE*
GAS
REGULATOR*
X
Fig. 8 — Gas Piping Guide (With Accessory
Thru-the-Curb Service Connections)
SPACING OF SUPPORTS
STEEL PIPE NOMINAL DIAMETER
mm (in.)
X
DIMENSION
m (ft)
13 (1/2)
19 or 25 (3/4 or 1)
32 or larger (11/4 or larger)
1.8 (6)
2.4 (8)
3.0 (10)
LEGEND
*Field supplied.
NOTE: Follow all local codes.
NFGC — National Fuel Gas Code (U.S.A. Standard)
Fig. 7 — Flue Hood Details

9
Table 2 — Electrical Data
LEGEND
*Fuse or HACR circuit breaker.
NOTES:
1. In compliance with NEC requirements (U.S.A. Standard) for
multimotor and combination load equipment (refer to NEC Arti-
cles 430 and 440), the overcurrent protective device for the unit
shall be fuse or HACR breaker.
2. Unbalanced 3-Phase Supply Voltage
Never operate a motor where a phase imbalance in supply volt-
age is greater than 2%. Use the following formula to determine
the percent of voltage imbalance.
% Voltage Imbalance
Example: Supply voltage is 400-3-50.
AB = 393 v
BC = 403 v
AC = 396 v
= 397
Determine maximum deviation from average voltage.
(AB) 397 – 393 = 4 v
(BC) 403 – 397 = 6 v
(AC) 397 – 396 = 1 v
Maximum deviation is 6 v.
Determine percent of voltage imbalance.
% Voltage Imbalance = 100 x
= 1.5%
This amount of phase imbalance is satisfactory as it is below the
maximum allowable 2%.
Route thermostat cable or equivalent single leads of colored
wire from thermostat subbase terminals to low-voltage connec-
tions on unit (shown in Fig. 10) as described in Steps 1-4
below.
1. If unit is mounted on roof curb and accessory thru-the-
curb service plate connection is used, route wire through
connection plate.
2. Pass control wires through the hole provided on unit (see
connection D in Connection Sizes table in Fig. 6).
3. Feed wires through the raceway built into the corner post
to the 24-v barrier located on the left side of the control
box. See Fig. 11. The raceway provides the UL-required
(Underwriters’ Laboratories) clearance between high-
and low-voltage wiring.
4. Connect thermostat wires to screw terminals on low-
voltage connection board.
HEAT ANTICIPATOR SETTINGS — Set heat anticipator
settings at .14 amp for the first stage and .20 amp for second-
stage heating, except for 008 low heat. Set both first and sec-
ond stage heat anticipator settings for 008 at .14 amp.
Table 3 — American/European Wire Conversions
LEGEND
UNIT
48TF
NOMINAL
VOLTAGE
(50 Hz)
VOLTAGE
RANGE
COMPR
(ea)
OFM
(ea) IFM POWER SUPPLY MINIMUM UNIT
DISCONNECT
Min Max RLA LRA FLA FLA MCA MOCP* FLA LRA
008 400
(3 phase) 360 440 6.4 42.0 0.3 2.6 17.6 20 18 108
012 400
(3 phase) 360 440 8.9 52.0 0.3 2.6 23.2 30 24 128
014 400
(3 phase) 360 440 10.4 73.0 0.7 5.4 29.4 35 31 192
FLA — Full Load Amps
HACR — Heating, Air Conditioning and Refrigeration
IFM — Indoor (Evaporator) Fan Motor
LRA — Locked Rotor Amps
MCA — Minimum Circuit Amps
MOCP — Maximum Overcurrent Protection
NEC — National Electrical Code (U.S.A.)
OFM — Outdoor (Condenser) Fan Motor
RLA — Rated Load Amps
= 100 x max voltage deviation from average voltage
average voltage
Average Voltage = 393 + 403 + 396
3
= 1192
3
IMPORTANT: If the supply voltage phase imbalance is
more than 2%, contact your local electric utility company
immediately.
6
397
AMERICAN EUROPEAN
Industry
Standard Size
American
Conversion
Size (mm2)
Industry
Standard
Size (mm2)
18 AWG 0.82 1.0
16 AWG 1.30 1.5
14 AWG 2.08 2.5
12 AWG 3.30 4.0
10 AWG 5.25 6.0
8 AWG 6.36 10.0
6 AWG 13.29 16.0
4 AWG 21.14 25.0
3 AWG 26.65 —
2 AWG 33.61 35.0
1 AWG 42.39 50.0
1/0 AWG 53.49 —
2/0 AWG 67.42 70.0
3/0 AWG 85.00 95.0
4/0 AWG 107.19 120.0
250 kcmil 126.64 150.0
300 kcmil 151.97 —
350 kcmil 177.90 185.0
400 kcmil 202.63 240.0
500 kcmil 253.29 300.0
600 kcmil 303.95 —
AWG — American Wire Gage
kcmil — Thousand Circular Mils

10
INTEGRATED
GAS UNIT
CONTROLLER
(IGC)
RACEWAY
UNIT LOW VOLTAGE
CONNECTION
BOARD
COMPRESSOR
NO.1
COMPRESSOR
NO. 2
Fig. 9 — Power Wiring Connections
LEGEND
C—
Contactor
IFC — Indoor (Evaporator)
Fan Contactor
NEC — National Electrical Code
(U.S.A. Standard)
Splice Connection
(Factory Supplied)
Equipment Ground
Field Wiring
Factory Wiring
Fig. 10 — Low-Voltage Connections
LEGEND
AHA — Adjustable Heat Anticipator
CC — Cooling Compensator
Field Wiring
Factory Wiring
Fig. 11 — Field Control Wiring Raceway
and Compressor Location
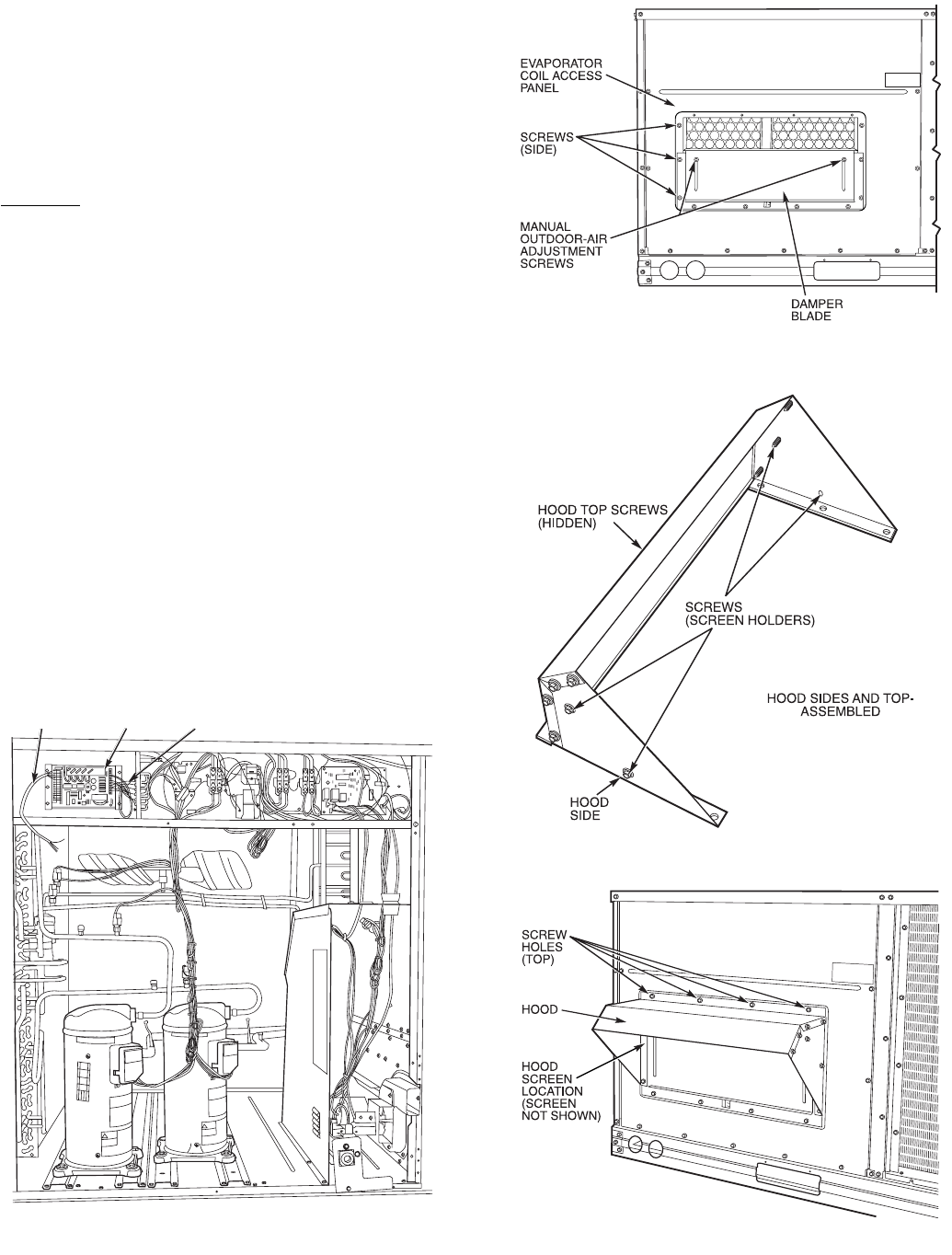
11
Step 8 — Adjust Factory-Installed Options
APOLLO CONTROL — The optional Apollo control is used
to actively monitor all modes of operation as well as indoor
(evaporator) fan status, filter status, and indoor-air quality. The
Apollo control is designed to work with Carrier TEMP and
VVT® systems.
The thermostat must be wired to the Apollo control before
starting the unit. Refer to the Apollo control installation
instructions for information on installing the thermostat. See
Fig. 12 for Apollo location.
MANUAL OUTDOOR-AIR DAMPER — The outdoor-air
hood and screen are attached to the basepan at the bottom of
the unit for shipping.
Assembly:
1. Determine quantity of ventilation required for building.
Record amount for use in Step 8.
2. Remove and save evaporator coil access panel and
screws. See Fig. 13.
3. Separate hood and screen from basepan by removing the
screws and brackets securing them. Save all screws and
discard brackets.
4. Replace evaporator coil access panel using screws from
Step 2.
5. Place hood on front of evaporator coil access panel. See
Fig. 14 for hood details. Secure top of hood with the
screws removed in Step 3. See Fig. 15.
6. Remove and save 6 screws (3 on each side) from sides of
the manual outdoor-air damper. Remove and save 2 man-
ual outdoor-air adjustment screws (one on each side of
damper blade).
7. Align screw holes on hood with screw holes on side of
manual outdoor-air damper. See Fig. 14 and 15. Secure
hood with 6 side screws from Step 6.
8. Adjust minimum position setting of the damper blade by
adjusting the 2 manual outdoor-air adjustment screws on
the front of the damper blade. See Fig. 13. Slide blade
vertically until it is in the appropriate position determined
by Fig. 16. Tighten screws.
9. Remove and save screws currently on sides of hood.
Insert screens. Secure screens to hood using the screws.
See Fig. 15.
WIRING TO
THERMOSTAT APOLLO
CONTROL
CONTROL
WIRING
Fig. 12 — Apollo Control Factory-Installed
in Typical Unit
Fig. 13 — Damper Panel with Manual
Outdoor-Air Damper Installed
Fig. 14 — Outdoor-Air Hood Details
Fig. 15 — Damper with Hood Attached

12
OPTIONAL DURABLADE ECONOMIZER — The option-
al economizer hood assembly is packaged and shipped in the fil-
ter section. Damper blades and control boards are installed at the
factory and the economizer is shipped in the vertical discharge
position.
NOTE: Horizontal discharge block-off plate is shipped with
the air hood package. If unit is to be used for vertical discharge
application, discard this plate.
Assembly
1. Determine if ventilation air is required in building. If so,
determine the minimum amount to be supplied by each
unit and record quantity of ventilation air needed for use
in Step 8.
2. Remove filter access panel by raising panel and swinging
panel outward. Panel is now disengaged from track and
can be removed. No tools are required to remove filter ac-
cess panel. Remove outdoor-air opening panel. Save pan-
els and screws. See Fig. 17. Remove optional economizer
and outdoor-air damper hood package from filter section.
3. Assemble outdoor-air hood top and side plates as shown
in Fig. 18. Install seal strips on hood top and sides. Put
aside screen retainer and retainer screw for later assem-
bly. Do not attach hood to unit at this time.
4. On 012 and 014 units, install vertical discharge block-off
plate on right side over return air duct opening. See
Fig. 19.
5. a. Slide economizer into unit and secure with screws.
See Fig. 20.
NOTE: Be sure to engage rear economizer flange under tabs at
rear of vertical return-air opening.
b. Remove screw and discard from barometric relief
damper. See Fig. 20.
6. To convert to horizontal discharge application:
a. Rotate the economizer 90 degrees until the econo-
mizer motor faces the condenser section (see
Fig. 21).
b. Rotate the barometric relief damper hinge
90 degrees. Barometric relief damper should open
vertically to operate properly.
c. Install horizontal discharge block-off plate over
the opening on the access panel. (Block-off plate
MUST be installed before installing hood assem-
bly.) See Fig. 22.
7. Insert economizer plug into economizer harness. Remove
tape from barometric relief damper. See Fig. 20.
8. If ventilation air is not required, proceed to Step 9. If ven-
tilation air is required, determine the minimum position
setting for required airflow. See Fig. 23. Adjust minimum
position setting by loosening the screws on the position
setting bracket. See Fig. 24. Slide bracket until the top
screw is in the position determined by Fig. 23. Tighten
screws.
9. Remove tape from outdoor-air thermostat (OAT). Fasten
OAT to inside of hood using screws and speed clips pro-
vided. See Fig. 25. Make sure OAT terminals are posi-
tioned up.
10. Replace outdoor-air opening panel using screws from
Step 2. Replace filter access panel. Ensure the filter ac-
cess panel slides along the tracks and is securely engaged.
11. Fasten hood top and side plate assembly to outdoor-air
opening panel with screws provided.
12. Place knob supplied with economizer on OAT. See
Fig. 25. Set OAT for 1.7° C (3° F) below indoor room
thermostat setting. If accessory enthalpy control (EC) is
used in place of OAT, see instructions shipped with EC
for installation and adjustment. See Fig. 25.
13. Connect OAT per Fig. 26.
14. Slide outdoor-air inlet screens into screen track on hood
side plate. While holding screens in place, fasten screen
retainer to hood using screws provided.
NOTE: Refer to Fig. 27 for Durablade economizer barometric
relief damper characteristics.
1" (25 mm) OPEN
2" (51 mm)
3" (76 mm)
4.4" (112 mm)
024 68
10 12
OUTDOOR AIRFLOW (cfm x 100)
0100 200 300 400 500
OUTDOOR AIRFLOW (L/s)
0.2
0.4
0.6
0.8
1.0
NEGATIVE PRESSURE (Pa)
0
50
100
150
200
250
NEGATIVE PRESSURE (in. wg)
Fig. 16 — Position Setting
OUTDOOR-AIR
OPENING PANEL
FILTER ACCESS
PANEL
Fig. 17 — Access Panel Locations
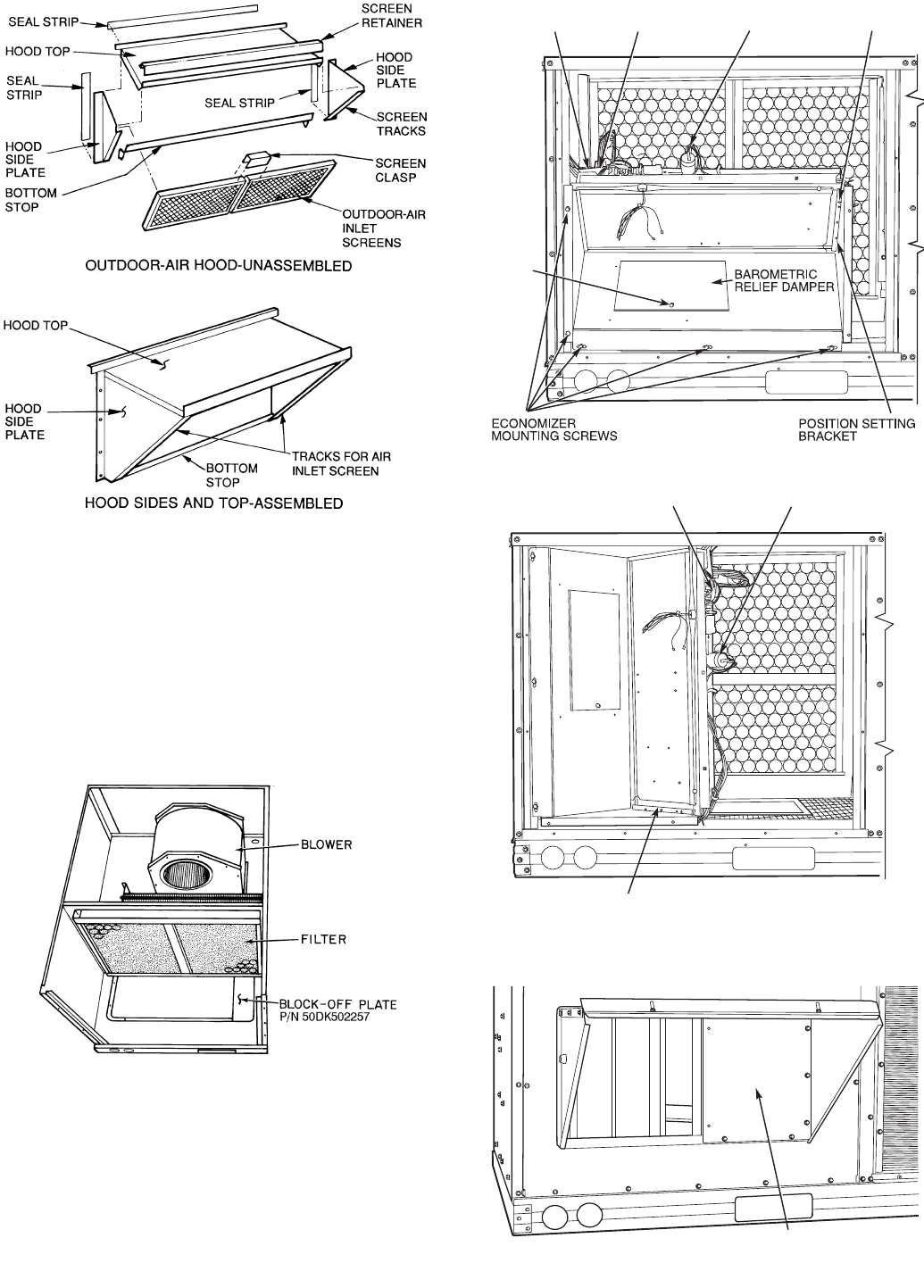
13
ECONOMIZER
CONTROL BOARD
ECONOMIZER
PLUG
ECONOMIZER
MOTOR
TOP
SCREW
SHIPPING
SCREW
ECONOMIZER CONTROL BOARD ECONOMIZER MOTOR
POSITION SETTING BRACKET
BLOCK-OFF PLATE
Fig. 18 — Outdoor-Air Hood Details
Fig. 19 — Vertical Discharge Block-Off Plate
(48TF012, 014 Units Only)
Fig. 20 — Durablade Economizer Installed in Unit
Fig. 21 — Horizontal Durablade Economizer
Installation (90 Degree Rotation)
Fig. 22 — Horizontal Discharge Block-Off Plate

14
43210
5
6
7
8
9
UNIT
TOP
OAT
(TERMINALS ARE UP)
OUTSIDE AIR
SCREEN
MINIMUM
POSITION
OPEN
3
1
T
P
P1
T1
4
2
5
S
S
O
D
C
TR
B
REV.B
198818A
%
H
U
M
I
D
I
T
Y
90
70
60
30
10
DCBA
60 65 70
75
55
50 85
80
DAMPER
DAMPER
CLOSED
OPEN
OUTDOOR TEMP.°F
REV
.
97-3672
CW–SETPOINTS–CCW
CONTACTS SHOWN IN HIGH ENTHALPY
RUSHAT 24VAC
3 mA MIN. AT 11 VDC
CONTACT RATINGS: 1.5A RUN, 3.5A IN
OR UNPOWERED STATE
1
2
3
TR
TR1
24V
AC
ENTHALPY CONTROL
ENTHALPY
CONTROL
HOOD
Example:
Given —
Negative Pressure . . . . . . . . . . . . . . . . . . . . . . . . . 25 Pa (0.1 in. wg)
Outdoor Airflow . . .. . . . . . . . . . . . . . . . . . . . . . . . 520 L/s (1100 cfm)
Determine —
Setting = 150 mm (6 in.)
Fig. 23 — Durablade Economizer Damper Minimum
Position Setting
Fig. 24 — Durablade Economizer Minimum
Position Damper Setting
Fig. 25 — Outdoor-Air Thermostat/
Enthalpy Control Installation

15
OPTIONAL ECONOMI$ER — See Fig. 28 for EconoMi$er
component locations.
1. To remove the existing unit filter access panel, raise the
panel and swing the bottom outward. The panel is now
disengaged from the track and can be removed. Remove
the indoor coil access panel and discard. See Fig. 29.
NOTE: If installing an optional Power Exhaust Assembly,
refer to the EconoMi$er Power Exhaust Installation Instruc-
tions, then proceed to Step 6. Controller should be mounted in
vertical position as shown in Fig. 28.
2. To assemble the hood assembly remove the EconoMi$er
hood from its packaging. Locate the outdoor air opening
panel. See Fig. 30.
3. Install the 19 mm x 19 mm (3/4 x 3/4-in.) seal strip on the
exhaust air hood top panel. Install the 3 mm x 22 mm
(1/8 x 7/8-in.) seal strip on the exhaust air hood side panels
and bottom brackets. Assemble the exhaust air hood to
the outdoor air opening panel as shown in Fig. 30, using
the screws provided. Do not attach hood assembly to unit
at this time.
4. Install the 3 mm x 22 mm (1/8 x 7/8-in. seal strip on the
outdoor air hood top and side panels. Assemble the out-
door air hood to the outdoor air opening panel as shown
in Fig. 31, using the screws provided. Do not attach com-
pleted hood (Fig. 32) assembly to the unit at this time.
L/s
0.00 200 400 600 800 1000 1200
CFM
0.70
0.60
0.50
0.40
0.30
0.20
0.10
PRESSURE DROP (in. wg)
0 100 200 300 400 500 570
175
150
125
100
75
50
25
0
PRESSURE DROP (Pa)
Fig. 27 — Durablade Economizer Barometric Relief
Damper Characteristics
Fig. 26 — Wiring Connections for
Outdoor-Air Thermostat
CONTROLLER
BAROMETRIC
RELIEF DAMPERS
OUTDOOR AIR
TEMPERATURE
SENSOR
GEAR-DRIVEN
DAMPER
ACTUATOR
ECONOMI$ER
PLUG
Fig. 28 — EconoMi$er Component Locations
OUTDOOR-AIR
OPENING PANEL
FILTER ACCESS
PANEL
Fig. 29 — Typical Access Panel Locations
OUTDOOR AIR
OPENING PANEL
SEAL STRIP
EXHAUST AIR SCREEN
EXHAUST AIR
HOOD TOP
SCREEN
RETAINER
EXHAUST AIR
HOOD SIDES
EXHAUST AIR
BOTTOM BRACKET
Fig. 30 — Exhaust Air Hood Assembly

16
5. Slide the outdoor air inlet screens into the screen track on
the hood side panels. While holding the screens in place,
fasten the screen retainer to the hood using the screws
provided. Repeat the process for the barometric exhaust
air screen. Do not attach hood assembly to unit at this
time.
6. For 48TF014 units, install the return air block-off plate
over the return air duct opening. See Fig. 33.
NOTE: For 48TF008 and 012 units, remove the factory-
installed block-off plate. See Fig. 33.
7. Slide the EconoMi$er assembly into the rooftop unit. See
Fig. 34 and 35.
NOTE: Be sure to engage rear EconoMi$er flange under tabs in
return air opening of the unit base. See Fig. 34.
8. Install the outdoor air block-off plate, then secure the
EconoMi$er with the screws provided. See Fig. 35.
9. Remove and store the 12-pin jumper plug from the unit
wiring harness located in the upper left corner and insert
the EconoMi$er plug into the unit wiring harness. Refer
to wiring diagram Fig. 36 and 37. Also refer to Fig. 38 if
installing an accessory power exhaust.
10. Install the complete hood assembly on the unit and secure
using the screws provided.
11. Remove the indoor fan motor access panel.
12. Mount the supply air temperature sensor to the lower left
portion of the indoor blower housing with the two (2)
screws provided (see Fig. 39). Connect the violet and
pink wires to the corresponding connections on the sup-
ply air temperature sensor. Replace the indoor fan motor
access panel.
SEAL STRIP
SEAL STRIP
OUTDOOR AIR
HOOD TOP
SCREEN
RETAINER
OUTDOOR AIR
INLET
SCREENS
OUTDOOR AIR
HOOD SIDES
ASSEMBLED
EXHAUST HOOD
OUTDOOR AIR
OPENING
PANEL
Fig. 31 — Outdoor Air Hood Assembly
Fig. 32 — Completed Hood Assembly
WIRING HARNESS
OUTDOOR AIR
BLOCK-OFF PLATE
Fig. 35 — EconoMi$er Installed in
48TF008 and 012 Units
ECONOMIZER
ECONOMIZER REAR
FLANGE
UNIT BASE
UNIT FILTER
RACK
ECONOMIZER CLIP
HVAC UNIT
Fig. 34 — Rear EconoMi$er Flange Installation
BLOWER
FILTER
RETURN AIR
BLOCK-OFF
PLATE
REMOVE FACTORY INSTALLED
BLOCK-OFF PLATE
(008 AND 012 UNITS ONLY)
INSTALL
Fig. 33 — Return Air Block-Off Plate Installation
(48TF014 Units Only)

17
OUTDOOR
AIR
SENSOR
TEMP
TEMP
COM
OUT
PWR
BROWN
VIOLET
WHITE
RED
BROWN TEMP
TEMP
COM
OUT
PWR
RETURN
AIR
SENSOR
VIOLET
WHITE
RED
OAT
COM
OAH
+15 V
RAT
COM
RAH
+15 V
ECONOMI$ER
CONTROLLER
PINK TEMP
TEMP
VIOLET
SUPPLY AIR
TEMPERATURE SENSOR
V+ 24
COM VAC
SENSOR
CO2
(+)
COM
DAT
COM
REM POT
COM
LED
COM
CO2
CO2
Fig. 36 — EconoMi$er Wiring
Fig. 37 — EconoMi$er Sensor Wiring
LEGEND
OAT —Outdoor-Air Thermostat

18
SUPPLY AIR
TEMPERATURE
SENSOR
MOUNTING
LOCATION
SUPPLY AIR
TEMPERATURE
SENSOR
4-PIN
CONNECTOR
PLUG
L1
L2
GREEN
1
1
22
33
44
GND
230 VAC
1 PHASE
GREEN/
YELLOW
3
2
1
58
69B
A
7
4
LT. BLUE
BLACK
BROWN
C1
BLUE
GREEN/
YELLOW
3
2
1
58
69B
A
7
4
LT. BLUE
BLACK
BROWN
C1
BLUE
FAN 2
FAN 1
BLACK
BLACK
BLACK
R1
24 VAC
R2
24 VAC
BLACK
BLUE
1
2
3
BROWN
ORANGE
3-PIN
CONNECTOR
PLUG
YELLOW
RED YEL
H1
BLU GRAY
H4
SECONDARY
230VAC
X4 X1
HT01AH850
(460 VAC)
BLACK L1
BLUE L2
FIELD SUPPLIED
WIRING
GREEN GND
2 x 4 IN.
HANDY BOX
H2
H3
X2 X3
TO FUSED
DISCONNECT
Fig. 39 — Supply Air Sensor Placement
Fig. 38 — Wiring Diagram for Power Exhaust System

19
CO2 Control Set Up — If a CO2 sensor is not being used, pro-
ceed to the next section. If a CO2 sensor is being used, perform
the following:
1. Determine the value at which you want the minimum
position of the dampers to begin opening to allow a great-
er amount of outdoor air to enter. The range is 800 to
1,400 ppm.
2. Locate the CO2 SP (PPM) potentiometer and adjust to the
desired set point. See Fig. 40.
Mechanical Cooling Lockout — Determine the outdoor-air
temperature at which you want the mechanical cooling (com-
pressors) to be disabled. Locate the mechanical cooling lockout
(MECH CLG LOCKOUT) potentiometer. To disable this fea-
ture, turn the potentiometer counterclockwise (CCW) to the
OFF position. Otherwise, set the value between –12 and 15 C
(10 and 60 F). Mechanical cooling will not operate when the
outdoor air temperature is below this value. See Fig. 40.
Dry Bulb Changeover Set Up — Determine the dry bulb
changeover set point from Table 4. The settings are A, B, C and
D. Locate the ECON SP potentiometer and set the dry bulb
changeover set point. See Fig. 40. When the OAT is above this
set point, the damper is limited to minimum position setting.
Table 4 — Changeover Set Points
*Field-installed accessory.
If a potentiometer fails, its setting will default to the values
in Table 5.
Table 5 — Default Potentiometer Settings
Ventilation Air (Minimum Position Set Up) — If ventilation
air is not required, proceed to Step 5. If ventilation air is re-
quired, perform the following:
1. The indoor fan must be on to set the ventilation air. Either
put the thermostat in the continuous fan mode or jumper
the R and G terminals at the rooftop unit connection
board.
2. Locate the minimum position (MIN POS) potentiometer.
Turn the potentiometer full CCW to fully close the out-
door air dampers. Turn the potentiometer gradually
clockwise (CW) to the desired position. See Fig. 40.
3. Replace the filter access panel. See Fig. 21. Ensure the fil-
ter access panel slides along the tracks and is securely
engaged.
4. Calculate the minimum airflow across the EconoMi$er.
a. Calculate % of outside air using the following
formula.
% Outdoor air through EconoMi$er
b. Multiply total CFM by percentage outdoor air, this
gives outdoor air volume in CFM.
5. Turn on base unit power.
NOTE: The EconoMi$er begins operation three min-
utes after power up.
6. See Fig. 41 for barometric relief damper characteristics.
SETTINGS ABCD
Dry Bulb C (°F) 23
(73)
21
(69)
19
(66)
17
(63)
Single Enthalpy* KJ/Kg (Btu/lb) 63
(27)
58
(25)
56
(24)
51
(22)
Differential Temperature* C
(°F, Not Adjustable)
1.1
(2)
1.1
(2)
1.1
(2)
1.1
(2)
Differential Enthalpy* KJ/Kg
(Btu/lb, Not Adjustable)
2
(1)
2
(1)
2
(1)
2
(1)
POTENTIOMETER DEFAULT SETTING
CO2 SP (PPM) 1,000
MECH CLG LOCKOUT, C (F) 8.3 (47)
ECON SP D
MIN POS (%) 20
% Outdoor air = Mixture Temp – Return Air Temp
Outdoor Temp – Return Air Temp
Personal Injury Hazard. Avoid possible injury by keep-
ing fingers away from damper blades.
0400 800 1200 1600 2000 2400
FLOW (CUBIC FEET/MINUTE)
0.5
0.4
0.3
0.2
0.1
0
STATIC PRESSURE (IN.WG)
PRESSURE DROP (Pa)
FLOW (L/s)
0200 400 600 800
125
100
75
50
25
0
1000 1200
Fig. 40 — EconoMi$er Control Adjustment
Potentiometers (Factory Settings)
Fig. 41 — EconoMi$er Barometric Relief Capacity

20
Step 9 — Adjust Evaporator-Fan Speed — Ad-
just evaporator-fan speed to meet jobsite requirement.
Table 6 shows motor performance. Tables 7 and 8 show fan
rpm at motor pulley settings, Table 9 shows motor efficiencies
and Tables 10 and 11 give accessory static pressure drops. Re-
fer to Tables 12-23 to determine fan speed settings. Fan motor
pulleys are factory set for speed shown in Table 1A or 1B.
To change fan speed:
1. Shut off unit power supply and install lockout tag.
2. Loosen belt by loosening fan motor mounting plate nuts
(see Fig. 42 and 43).
3. Loosen movable pulley flange setscrew (see Fig. 44).
4. Screw movable flange toward fixed flange to increase fan
speed and away from fixed flange to decrease fan speed.
Increasing fan speed increases load on motor. Do not ex-
ceed maximum speed specified in Table 1A or 1B.
5. Set movable flange at nearest flat of pulley hub and tight-
en setscrew (see Table 1A or 1B for speed change for
each full turn of pulley flange).
To align fan and motor pulleys:
1. Loosen fan pulley setscrews.
2. Slide fan pulley along fan shaft.
3. Make angular alignment by loosening motor from
mounting plate.
To adjust belt tension (see Fig. 42 and 43):
1. Loosen fan motor mounting nuts.
2. Size 008 — Slide motor mounting plate away from fan
scroll for proper belt tension (13 mm [1/2-in.] deflection
with 3.6 to 4.5 kg [8 to 10 lbs] of force) and tighten
mounting nuts. See Fig. 42.
Sizes 012,014 — Slide motor mounting plate downward
to tighten belt tension (13 mm [1/2-in.] deflection with 2.3
to 4.5 kg [5 to 10 lbs] of force) and tighten mounting nuts.
See Fig. 43.
3. Adjust bolt and nut on mounting plate to secure motor in
fixed position. See Fig. 44.
Realign fan and motor pulleys:
1. Loosen fan pulley setscrews.
2. Slide fan pulley along fan shaft.
3. Make angular alignment by loosening motor from
mounting plate.
Table 6 — Evaporator-Fan Motor Performance
LEGEND *Extensive motor and electrical testing on these units ensures that
the full range of the motors can be utilized with confidence. Using
your fan motors up to the ratings shown in this table will not result in
nuisance tripping or premature motor failure. Unit warranty will not
be affected.
UNIT
48TF
UNIT RATED
VOLTAGE
MAXIMUM ACCEPTABLE
CONTINUOUS
BkW*
MAXIMUM ACCEPTABLE
CONTINUOUS
BHP*
MAXIMUM ACCEPTABLE
OPERATING
WATTS
MAXIMUM
AMP DRAW
008 400 2.76 2.90 2615 3.6
012 400 2.76 3.70 3313 5.0
014 400 2.76 3.70 3313 5.0
BHP —Brake Horsepower
BkW —kW x Motor Efficiency
MOTOR MOUNTING
PLATE NUTS
Fig. 42 — Typical Belt-Drive Motor Mounting
for Size 008
Fig. 43 — Typical Belt-Drive Motor Mounting
for Sizes 012,014
Fig. 44 — Evaporator-Fan Pulley Adjustment

21
Table 7 — Fan R/s at Motor Pulley Settings (SI)
Table 8 — Fan Rpm at Motor Pulley Settings (English)
Table 9 — Evaporator-Fan Motor Efficiency
NOTE: Convert watts to bhp using the following formula:
Table 10 — Accessory/FIOP Static Pressure Drop (Pa) — 48TF008-014
Table 11 — Accessory/FIOP Static Pressure Drop (in. wg) — 48TF008-014
UNIT
48TF
MOTOR PULLEY TURNS OPEN
01/211
1/222
1/233
1/244
1/25
008 11.70 11.35 11.00 10.65 10.30 9.95 9.60 9.25 8.90 8.55 8.20
012 13.00 12.65 12.30 11.95 11.60 11.25 10.90 10.55 10.20 9.85 9.50
014 15.00 14.70 14.40 14.10 13.80 13.50 13.20 12.90 12.60 12.30 12.00
UNIT
48TF
MOTOR PULLEY TURNS OPEN
01/211
1/222
1/233
1/244
1/25
008 700 681 660 639 618 597 576 555 534 513 492
012 779 760 739 718 697 676 655 634 613 592 571
014 900 883 865 843 825 807 789 771 753 735 717
MOTOR
48TF EFFICIENCY (%)
D/E/F008 80
D/E/F012 80
D/E014 85
bhp = watts input x motor efficiency
746
UNIT 48TF RATED VOLTAGE L/s DURABLADE ECONOMIZER
PRESSURE DROP ECONOMI$ER
008-014 All
1100 5 —
1200 6 —
1300 7 —
1400 8 31
1500 9 35
1600 10 41
1700 11 50
1800 12 59
1900 13 67
2000 14 75
2100 15 84
2200 16 90
2300 17 97
FIOP —Factory-Installed Option
UNIT 48TF RATED VOLTAGE CFM DURABLADE ECONOMIZER
PRESSURE DROP ECONOMI$ER
008-014 All
2200 .02 .07
2500 .02 .09
3000 .03 .13
3500 .04 .18
4000 .05 .23
4500 .06 .30
5000 .07 .36
5500 .08 —
6000 .09 —
FIOP —Factory-Installed Option

22
Table 12 — Fan Performance, 48TF008 — Vertical Discharge Units (SI)
LEGEND
NOTES:
1. Boldface indicates field-supplied drive required. (See Note 5.)
2. indicates field-supplied motor and drive are required.
3. Values include losses for filters, unit casing, and wet coils.
4. Use of a field-supplied motor may affect wire sizing. Contact
your Carrier representative to verify.
5. Standard drive range is 8.2 to 11.7 r/s. All other speeds require
a field-supplied drive.
6. Maximum continuous BkW is 1.79. Extensive motor and electri-
cal testing on these units ensures that the full range of the
motor can be utilized with confidence. Using the fan motors up
to the ratings shown will not result in nuisance tripping or pre-
mature motor failure. Unit warranty will not be affected.
7. Interpolation is permissible. Do not extrapolate.
AIRFLOW
(L/s)
EXTERNAL STATIC PRESSURE (Pa)
50 100 150 200
R/s BkW R/s BkW R/s BkW R/s BkW
1150 8.8 0.45 10.1 0.62 11.2 0.79 12.2 0.96
1200 9.0 0.47 10.3 0.65 11.4 0.82 12.4 1.02
1275 9.3 0.53 10.5 0.70 11.6 0.89 12.6 1.08
1300 9.6 0.58 10.8 0.78 11.9 0.96 12.8 1.17
1400 9.9 0.63 11.1 0.85 12.1 1.02 13.1 1.26
1450 10.1 0.68 11.3 0.86 12.3 1.09 13.2 1.29
1500 10.4 0.78 11.5 0.96 12.6 1.18 13.5 1.38
1550 10.7 0.81 11.8 1.06 12.8 1.25 13.7 1.48
1600 11.0 0.90 12.0 1.10 13.0 1.35 14.0 1.56
1650 11.3 0.99 12.4 1.22 13.3 1.43 14.2 1.67
1700 11.5 1.06 12.6 1.30 13.6 1.54 14.4 1.78
1750 11.8 1.16 12.9 1.38 13.8 1.65 14.7 1.88
1800 12.2 1.24 13.2 1.49 14.1 1.75 14.9 2.00
1850 12.4 1.35 13.4 1.60 14.4 1.84 15.1 2.10
1900 12.8 1.47 13.7 1.70 14.6 1.97 15.4 2.24
AIRFLOW
(L/s)
EXTERNAL STATIC PRESSURE (Pa)
250 300 350 400
R/s BkW R/s BkW R/s BkW R/s BkW
1150 13.2 1.15 14.1 1.39 15.1 1.73 15.8 1.96
1200 13.3 1.21 14.1 1.41 15.2 1.76 15.9 2.00
1275 13.5 1.28 14.3 1.46 15.3 1.76 16.1 2.17
1300 13.8 1.37 14.6 1.55 15.2 1.72 16.3 2.17
1400 14.0 1.45 14.7 1.65 15.5 1.84 16.5 2.10
1450 14.1 1.53 14.9 1.73 15.6 1.88 16.7 2.10
1500 14.4 1.61 15.2 1.84 15.8 2.04 16.4 2.18
1550 14.5 1.72 15.4 1.95 16.1 2.15 16.5 2.34
1600 14.8 1.80 15.6 2.07 16.3 2.29 17.0 2.49
1650 15.0 1.92 15.8 2.15 16.6 2.42 17.2 2.66
1700 15.2 2.01 16.0 2.27 16.7 2.56 17.5 2.80
1750 15.5 2.14 16.2 2.41 16.9 2.65 17.6 2.92
1800 15.7 2.24 16.4 2.52 17.2 2.82 ——
1850 15.9 2.37 16.7 2.66 17.4 2.92 ——
1900 16.2 2.51 16.9 2.78 ————
BkW —Fan Input kW x Motor Efficiency
R/s —Revolutions Per Second of Blower Wheel

23
Table 13 — Fan Performance, 48TF012 — Vertical Discharge Units (SI)
LEGEND
NOTES:
1. Boldface indicates field-supplied drive required. (See Note 5.)
2. indicates field-supplied motor and drive are required.
3. Values include losses for filters, unit casing, and wet coils.
4. Use of a field-supplied motor may affect wire sizing. Contact
your Carrier representative to verify.
5. Standard drive range is 9.5 to 13.0 r/s. All other speeds require
a field-supplied drive.
6. Maximum continuous BkW is 1.79. Extensive motor and electri-
cal testing on these units ensures that the full range of the
motor can be utilized with confidence. Using the fan motors up
to the ratings shown will not result in nuisance tripping or pre-
mature motor failure. Unit warranty will not be affected.
7. Interpolation is permissible. Do not extrapolate.
AIRFLOW
(L/s)
EXTERNAL STATIC PRESSURE (Pa)
50 100 150 200 250
R/s BkW R/s BkW R/s BkW R/s BkW R/s BkW
1500 9.8 0.55 10.9 0.67 12.0 0.79 12.9 0.92 13.8 1.04
1550 10.0 0.60 11.2 0.74 12.2 0.86 13.1 0.98 13.9 1.11
1600 10.3 0.66 11.4 0.80 12.4 0.92 13.3 1.05 14.2 1.18
1650 10.6 0.72 11.7 0.86 12.6 0.98 13.6 1.12 14.4 1.25
1700 10.9 0.78 12.0 0.93 12.8 1.06 13.7 1.20 14.6 1.34
1750 11.1 0.86 12.2 1.00 13.1 1.14 14.0 1.28 14.8 1.42
1800 11.4 0.93 12.5 1.08 13.3 1.22 14.2 1.36 15.0 1.52
1850 11.7 1.00 12.7 1.15 13.6 1.31 14.4 1.44 15.2 1.60
1900 12.0 1.08 12.9 1.23 13.8 1.40 14.6 1.53 15.4 1.70
1950 12.2 1.16 13.2 1.31 14.1 1.49 14.8 1.63 15.6 1.79
2000 12.5 1.25 13.4 1.40 14.3 1.59 15.1 1.74 15.9 1.90
2050 12.8 1.34 13.7 1.50 14.6 1.69 15.3 1.85 16.1 2.00
2100 13.1 1.44 13.9 1.60 14.9 1.80 15.6 1.97 16.3 2.12
2150 13.3 1.53 14.2 1.71 15.1 1.91 15.8 2.09 16.5 2.24
2200 13.6 1.64 14.5 1.82 15.3 2.02 16.1 2.21 16.8 2.37
2250 13.9 1.75 14.7 1.94 15.6 2.13 16.3 2.34 ——
2300 14.2 1.86 15.0 2.06 15.8 2.25 16.6 2.47 ——
2400 14.5 1.98 15.3 2.19 16.1 2.38 —— — —
2450 14.8 2.10 15.6 2.32 ——————
AIRFLOW
(L/s)
EXTERNAL STATIC PRESSURE (Pa)
300 350 400 450 500
R/s BkW R/s BkW R/s BkW R/s BkW R/s BkW
1500 14.6 1.15 15.3 1.26 16.1 1.38 16.9 1.45 17.7 1.68
1550 14.8 1.23 15.5 1.35 16.2 1.47 17.1 1.60 17.8 1.81
1600 15.0 1.30 15.7 1.44 16.4 1.55 17.1 1.68 17.9 1.86
1650 15.1 1.39 15.9 1.52 16.6 1.65 17.3 1.77 18.0 1.91
1700 15.3 1.47 16.1 1.61 16.8 1.74 17.4 1.88 18.1 2.00
1750 15.5 1.56 16.3 1.70 17.0 1.85 17.6 1.98 18.2 2.11
1800 15.8 1.66 16.4 1.80 17.2 1.95 17.8 2.09 18.4 2.22
1850 16.0 1.75 16.6 1.90 17.3 2.05 18.0 2.20 18.6 2.34
1900 16.2 1.86 16.9 2.01 17.5 2.16 18.2 2.31 ——
1950 16.4 1.96 17.1 2.12 17.7 2.26 18.4 2.43 ——
2000 16.6 2.07 17.3 2.24 17.9 2.39 —— — —
2050 16.8 2.18 17.5 2.36 ——————
2100 17.0 2.30 ————————
2150 17.2 2.41 ————————
2200 —— — — — ——— — —
2250 —— — — — ——— — —
2300 —— — — — ——— — —
2400 —— — — — ——— — —
2450 —— — — — ——— — —
BkW —Fan Input kW x Motor Efficiency
R/s —Revolutions Per Second of Blower Wheel

24
Table 14 — Fan Performance, 48TF014 — Vertical Discharge Units (SI)
LEGEND
NOTES:
1. Boldface indicates field-supplied drive required. (See Note 5.)
2. indicates field-supplied motor and drive are required.
3. Values include losses for filters, unit casing, and wet coils.
4. Use of a field-supplied motor may affect wire sizing. Contact
your Carrier representative to verify.
5. Standard drive range is 12.0 to 15.0 r/s. All other speeds
require a field-supplied drive.
6. Maximum continuous BkW is 2.76. Extensive motor and electri-
cal testing on these units ensures that the full range of the
motor can be utilized with confidence. Using the fan motors up
to the ratings shown will not result in nuisance tripping or pre-
mature motor failure. Unit warranty will not be affected.
7. Interpolation is permissible. Do not extrapolate.
AIRFLOW
(L/s)
EXTERNAL STATIC PRESSURE (Pa)
50 100 150 200 250
R/s BkW R/s BkW R/s BkW R/s BkW R/s BkW
1900 12.5 1.10 13.5 1.27 14.4 1.42 15.3 1.63 16.1 1.81
1950 12.7 1.18 13.7 1.36 14.6 1.52 15.5 1.73 16.4 1.92
2000 13.0 1.27 14.0 1.46 14.9 1.62 15.7 1.81 16.6 2.02
2050 13.3 1.36 14.3 1.56 15.1 1.72 16.0 1.91 16.8 2.14
2100 13.6 1.46 14.5 1.66 15.4 1.84 16.2 2.01 17.0 2.25
2150 13.9 1.56 14.8 1.78 15.7 1.95 16.5 2.13 17.3 2.37
2250 14.2 1.67 15.1 1.89 15.9 2.07 16.7 2.24 17.5 2.48
2300 14.5 1.78 15.4 2.00 16.2 2.19 17.0 2.37 17.7 2.60
2350 14.8 1.89 15.7 2.13 16.4 2.32 17.2 2.51 18.0 2.72
2400 15.0 2.01 15.9 2.25 16.7 2.46 17.5 2.64 18.2 2.85
2450 15.4 2.16 16.2 2.38 17.0 2.60 17.7 2.79 18.5 2.99
2500 15.7 2.28 16.5 2.52 17.3 2.75 18.0 2.95 18.7 3.13
2550 15.9 2.43 16.8 2.65 17.5 2.90 18.2 3.10 18.0 3.29
2600 16.2 2.58 17.1 2.81 17.8 3.05 18.5 3.26 19.2 3.47
2650 16.5 2.72 17.3 2.95 18.1 3.22 18.8 3.43 19.4 3.64
2700 16.8 2.89 17.6 3.12 18.4 3.39 19.0 3.60 19.7 3.83
2750 17.1 3.05 17.9 3.28 18.7 3.56 19.3 3.80 20.0 4.01
2800 17.4 3.21 18.2 3.45 18.9 3.74 19.6 3.98 20.2 4.19
2850 17.7 3.40 18.5 3.64 19.2 3.93 19.9 4.18 20.5 4.41
2900 18.0 3.57 18.8 3.81 19.5 4.11 20.2 4.37 ——
2950 18.3 3.76 19.1 4.02 19.8 4.29 —— — —
3000 18.6 3.96 19.4 4.21 20.1 4.51 —— — —
3050 18.9 4.15 19.6 4.40 ——————
3100 19.2 4.38 ————————
AIRFLOW
(L/s)
EXTERNAL STATIC PRESSURE (Pa)
300 350 400 450 500
R/s BkW R/s BkW R/s BkW R/s BkW R/s BkW
1900 17.0 2.00 17.9 2.21 18.7 2.39 19.4 2.58 20.1 2.74
1950 17.2 2.11 18.0 2.31 18.8 2.51 19.6 2.71 20.3 2.88
2000 17.4 2.22 18.2 2.43 19.0 2.63 19.8 2.84 20.5 3.02
2050 17.6 2.33 18.4 2.54 19.2 2.76 19.9 2.97 20.7 3.17
2100 17.8 2.45 18.6 2.66 19.3 2.89 20.1 3.10 20.8 3.32
2150 18.0 2.59 18.8 2.79 19.5 3.01 20.3 3.24 21.0 3.46
2250 18.2 2.71 19.0 2.93 19.7 3.15 20.4 3.37 21.2 3.60
2300 18.5 2.85 19.2 3.05 19.9 3.29 20.6 3.52 21.3 3.76
2350 18.7 2.99 19.4 3.21 20.1 3.43 20.8 3.67 21.5 3.92
2400 18.9 3.12 19.6 3.36 20.3 3.59 21.0 3.82 21.7 4.08
2450 19.2 3.27 19.8 3.53 20.5 3.74 21.2 3.99 ——
2500 19.4 3.38 20.1 3.67 20.7 3.93 21.4 4.15 ——
2550 19.6 3.54 20.3 3.83 21.0 4.09 21.6 4.33 ——
2600 19.9 3.69 20.5 4.01 21.2 4.27 —— — —
2650 20.1 3.86 20.8 4.16 21.4 4.44 —— — —
2700 20.4 4.03 21.0 4.32 ——————
2750 20.6 4.21 ————————
2800 20.9 4.40 ————————
2850 ——————————
2900 ——————————
2950 ——————————
3000 ——————————
3050 ——————————
3100 ——————————
BkW —Fan Input kW x Motor Efficiency
R/s —Revolutions Per Second of Blower Wheel

25
Table 15 — Fan Performance, 48TF008 — Horizontal Discharge Units (SI)
LEGEND
NOTES:
1. Boldface indicates field-supplied drive required. (See Note 5.)
2. indicates field-supplied motor and drive are required.
3. Values include losses for filters, unit casing, and wet coils.
4. Use of a field-supplied motor may affect wire sizing. Contact
your Carrier representative to verify.
5. Standard drive range is 8.2 to 11.7 r/s. All other speeds require
a field-supplied drive.
6. Maximum continuous BkW is 1.79. Extensive motor and electri-
cal testing on these units ensures that the full range of the
motor can be utilized with confidence. Using the fan motors up
to the ratings shown will not result in nuisance tripping or pre-
mature motor failure. Unit warranty will not be affected.
7. Interpolation is permissible. Do not extrapolate.
AIRFLOW
(L/s)
EXTERNAL STATIC PRESSURE (Pa)
50 100 150 200 225
R/s BkW R/s BkW R/s BkW R/s BkW R/s BkW
1075 8.1 0.34 9.5 0.49 10.7 0.66 11.8 0.81 12.4 0.92
1125 8.4 0.39 9.7 0.53 10.9 0.71 12.0 0.89 12.5 0.98
1150 8.6 0.42 9.9 0.58 11.1 0.76 12.2 0.96 12.7 1.05
1200 8.9 0.46 10.2 0.64 11.3 0.81 12.4 1.02 12.8 1.11
1250 9.1 0.51 10.4 0.70 11.5 0.87 12.6 1.08 13.0 1.19
1300 9.4 0.56 10.7 0.75 11.7 0.93 12.7 1.14 13.2 1.25
1400 9.7 0.62 10.9 0.82 12.0 0.99 12.9 1.22 13.4 1.33
1450 10.0 0.67 11.2 0.88 12.2 1.07 13.2 1.27 13.6 1.40
1500 10.2 0.74 11.4 0.94 12.4 1.15 13.4 1.36 13.8 1.48
1550 10.5 0.80 11.7 1.02 12.7 1.23 13.6 1.44 14.0 1.56
1600 10.8 0.88 11.9 1.09 12.9 1.32 13.8 1.53 14.2 1.65
1650 11.1 0.97 12.2 1.17 13.2 1.41 14.0 1.63 14.4 1.75
1700 11.4 1.04 12.4 1.25 13.4 1.51 14.3 1.73 14.7 1.85
1750 11.7 1.12 12.7 1.35 13.7 1.61 14.5 1.85 14.9 1.97
1800 12.0 1.23 13.0 1.45 13.9 1.70 14.8 1.95 15.1 2.07
1850 12.2 1.33 13.2 1.54 14.2 1.81 15.0 2.08 15.4 2.20
1900 12.5 1.42 13.5 1.65 14.4 1.92 15.2 2.20 15.6 2.34
AIRFLOW
(L/s)
EXTERNAL STATIC PRESSURE (Pa)
250 300 350 400
R/s BkW R/s BkW R/s BkW R/s BkW
1075 12.9 1.03 13.9 1.29 15.0 1.60 15.7 1.89
1125 13.0 1.08 14.0 1.34 15.1 1.68 15.9 1.92
1150 13.1 1.13 14.1 1.38 15.2 1.69 16.0 1.96
1200 13.3 1.21 14.3 1.42 15.2 1.74 16.0 2.01
1250 13.5 1.29 14.4 1.48 15.3 1.78 16.2 2.06
1300 13.7 1.37 14.5 1.56 15.4 1.81 16.3 2.09
1400 13.9 1.44 14.7 1.66 15.5 1.84 16.4 2.19
1450 14.1 1.52 14.9 1.77 15.7 1.97 16.5 2.18
1500 14.3 1.60 15.1 1.86 15.9 2.08 16.6 2.29
1550 14.2 1.68 15.3 1.94 16.1 2.21 16.8 2.43
1600 14.8 1.77 15.5 2.04 16.3 2.31 17.0 2.55
1650 14.9 1.86 15.7 2.13 16.5 2.42 17.2 2.70
1700 15.1 1.97 15.9 2.24 16.6 2.52 17.4 2.82
1750 15.3 2.08 16.1 2.35 16.3 2.64 17.6 2.94
1800 15.5 2.20 16.3 2.45 17.0 2.76 17.7 3.05
1850 15.8 2.32 16.5 2.58 17.2 2.87 17.9 3.19
1900 16.0 2.46 16.7 2.70 17.5 2.99 18.1 3.31
BkW —Fan Input kW x Motor Efficiency
R/s —Revolutions Per Second of Blower Wheel
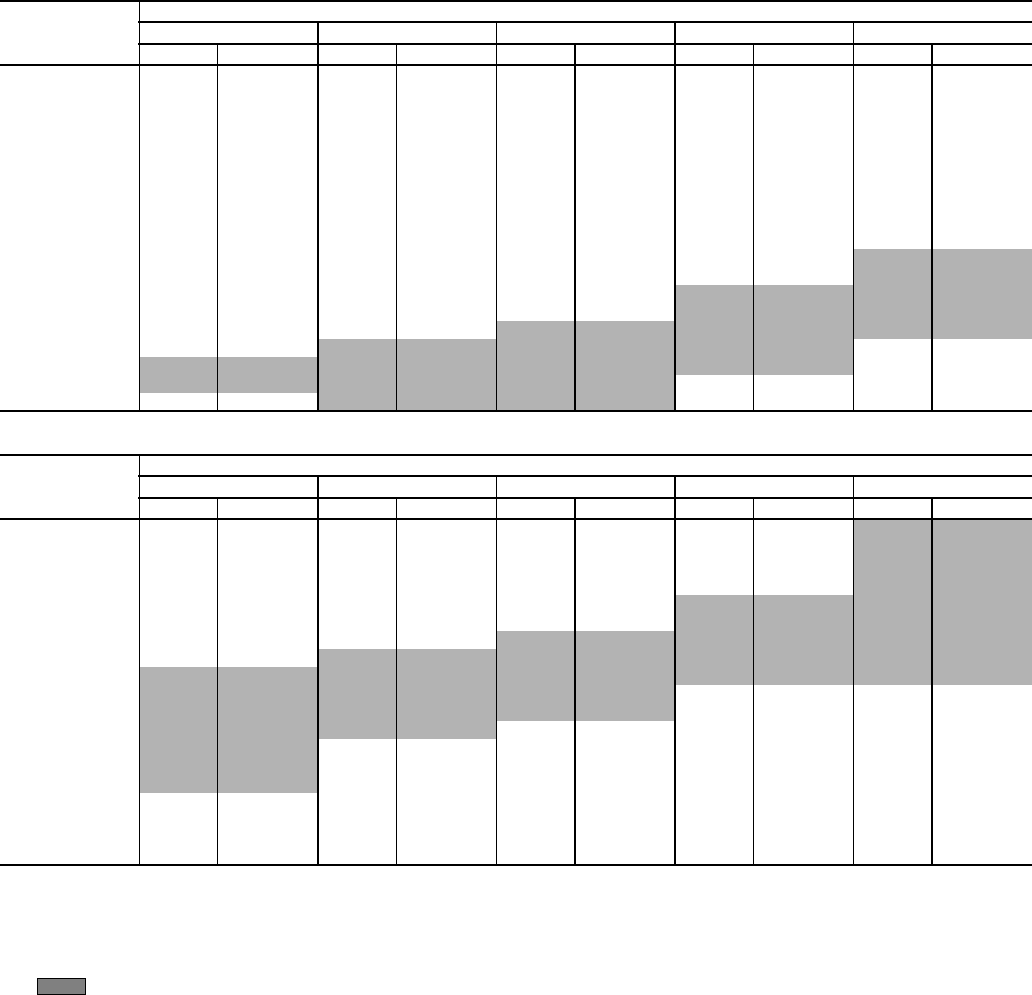
26
Table 16 — Fan Performance, 48TF012 — Horizontal Discharge Units (SI)
LEGEND
NOTES:
1. Boldface indicates field-supplied drive required. (See Note 5.)
2. indicates field-supplied motor and drive are required.
3. Values include losses for filters, unit casing, and wet coils.
4. Use of a field-supplied motor may affect wire sizing. Contact
your Carrier representative to verify.
5. Standard drive range is 9.5 to 13.0 r/s. All other speeds require
a field-supplied drive.
6. Maximum continuous BkW is 1.79. Extensive motor and electri-
cal testing on these units ensures that the full range of the
motor can be utilized with confidence. Using the fan motors up
to the ratings shown will not result in nuisance tripping or pre-
mature motor failure. Unit warranty will not be affected.
7. Interpolation is permissible. Do not extrapolate.
AIRFLOW
(L/s)
EXTERNAL STATIC PRESSURE (Pa)
50 100 150 200 250
R/s BkW R/s BkW R/s BkW R/s BkW R/s BkW
1500 9.1 0.49 10.5 0.63 11.6 0.77 12.6 0.89 13.5 0.99
1550 9.4 0.54 10.7 0.68 11.8 0.82 12.8 0.96 13.7 1.06
1600 9.6 0.59 10.9 0.73 12.0 0.88 13.0 1.02 13.9 1.14
1650 9.8 0.65 11.1 0.80 12.2 0.95 13.2 1.09 14.1 1.22
1700 10.1 0.71 11.3 0.86 12.4 1.01 13.4 1.16 14.2 3.10
1750 10.3 0.77 11.5 0.92 12.6 1.07 13.5 1.23 14.4 1.38
1800 10.6 0.84 11.7 0.98 12.8 1.14 13.7 1.30 14.6 1.47
1850 10.8 0.92 11.9 1.04 13.0 1.21 13.9 1.39 14.8 1.55
1900 11.1 1.00 12.1 1.14 13.2 1.29 14.1 1.47 15.0 1.64
1950 11.3 1.09 12.3 1.22 13.4 1.38 14.3 1.55 15.2 1.72
2000 11.6 1.18 12.6 1.31 13.6 1.47 14.5 1.65 15.3 1.82
2050 11.9 1.28 12.8 1.40 13.8 1.56 14.7 1.73 15.5 1.92
2100 12.1 1.38 13.0 1.50 14.0 1.64 14.9 1.82 15.8 2.02
2150 12.4 1.49 13.2 1.60 14.2 1.73 15.1 1.93 15.9 2.13
2200 12.7 1.61 13.4 1.70 14.4 1.83 15.3 2.04 16.1 2.24
2300 12.9 1.74 13.7 1.81 14.6 1.93 15.5 2.15 ——
2350 13.2 1.86 13.9 1.93 14.8 2.03 15.7 2.27 ——
2400 13.5 2.00 14.2 2.05 15.0 2.14 ————
2500 ——
14.4 2.14 15.2 2.25 ————
AIRFLOW
(L/s)
EXTERNAL STATIC PRESSURE (Pa)
300 350 400 450 500
R/s BkW R/s BkW R/s BkW R/s BkW R/s BkW
1500 14.5 1.13 15.2 1.22 16.1 1.40 16.8 1.54 17.7 1.82
1550 14.6 1.20 15.4 1.30 16.2 1.43 16.9 1.60 17.8 1.86
1600 14.8 1.26 15.6 1.40 16.3 1.50 17.1 1.68 17.9 1.91
1650 14.9 1.33 15.7 1.48 16.5 1.60 17.2 1.72 18.0 1.97
1700 15.0 1.42 15.9 1.56 16.7 1.70 17.3 1.81 18.0 1.97
1750 15.2 1.51 16.0 1.64 16.8 1.79 17.5 1.91 18.2 2.04
1800 15.4 1.61 16.2 1.73 17.0 1.89 17.7 2.03 18.3 2.15
1850 15.6 1.71 16.3 1.84 17.1 1.98 17.8 2.15 18.5 2.27
1900 15.8 1.80 16.5 1.94 17.2 2.07 18.0 2.24 18.7 2.40
1950 16.0 1.91 16.7 2.06 17.4 2.19 ————
2000 16.2 2.01 16.9 2.17 17.6 2.31 ————
2050 16.3 2.10 17.1 2.29 ——————
2100 16.5 2.21 ————————
2150 16.7 2.32 ————————
2200 16.9 2.43 ————————
2300 ——————————
2350 ——————————
2400 ——————————
2500 ——————————
BkW —Fan Input kW x Motor Efficiency
R/s —Revolutions Per Second of Blower Wheel

27
Table 17 — Fan Performance, 48TF014 — Horizontal Discharge Units (SI)
LEGEND
NOTES:
1. Boldface indicates field-supplied drive required. (See Note 5.)
2. indicates field-supplied motor and drive are required.
3. Values include losses for filters, unit casing, and wet coils.
4. Use of a field-supplied motor may affect wire sizing. Contact
your Carrier representative to verify.
5. Standard drive range is 12.0 to 15.0 r/s. All other speeds
require a field-supplied drive.
6. Maximum continuous BkW is 2.76. Extensive motor and electri-
cal testing on these units ensures that the full range of the
motor can be utilized with confidence. Using the fan motors up
to the ratings shown will not result in nuisance tripping or pre-
mature motor failure. Unit warranty will not be affected.
7. Interpolation is permissible. Do not extrapolate.
AIRFLOW
(L/s)
EXTERNAL STATIC PRESSURE (Pa)
50 100 150 200 225
R/s BkW R/s BkW R/s BkW R/s BkW R/s BkW
1900 11.5 0.96 12.7 1.14 13.7 1.32 14.7 1.49 15.6 1.71
1950 11.8 1.04 12.9 1.22 13.9 1.40 14.9 1.57 15.8 1.80
2000 12.1 1.12 13.2 1.29 14.2 1.49 15.1 1.65 16.0 1.89
2050 12.3 1.18 13.4 1.38 14.4 1.59 15.3 1.75 16.2 1.96
2100 12.6 1.27 13.6 1.46 14.6 1.68 15.5 1.86 16.4 2.05
2150 12.8 1.36 13.9 1.56 14.9 1.78 15.7 1.96 16.6 2.15
2200 13.1 1.44 14.1 1.66 15.1 1.88 16.0 2.07 16.8 2.26
2250 13.3 1.53 14.4 1.75 15.3 1.99 16.2 2.20 17.0 2.36
2325 13.6 1.63 14.6 1.87 15.5 2.10 16.4 2.30 17.2 2.50
2400 13.9 1.74 14.9 1.98 15.8 2.20 16.6 2.44 17.4 2.64
2450 14.1 1.84 15.1 2.10 16.0 2.31 16.8 2.56 17.6 2.77
2500 14.4 1.95 15.4 2.22 16.2 2.44 17.1 2.69 17.8 2.90
2550 14.7 2.07 15.6 2.34 16.5 2.56 17.3 2.83 18.1 3.05
2600 14.9 2.18 15.8 2.47 16.7 2.69 17.5 2.96 18.3 3.20
2650 15.2 2.32 16.1 2.60 16.9 2.83 17.8 3.11 18.5 3.34
2700 15.4 2.44 16.4 2.74 17.2 2.96 18.0 3.26 18.7 3.51
2750 15.7 2.57 16.6 2.89 17.4 3.11 18.2 8.38 19.0 3.67
2800 15.9 2.71 16.9 3.03 17.7 3.27 18.4 3.55 19.2 3.84
2850 16.2 2.86 17.1 3.18 17.9 3.46 18.7 3.70 ——
2900 16.5 2.98 17.3 3.32 18.2 3.57 18.9 3.85 ——
2950 16.7 3.11 17.6 3.46 18.4 3.72 ————
3000 17.0 3.25 17.8 3.60 18.7 3.87 ————
3050 17.3 3.38 18.1 3.74 ——————
3100 17.5 3.52 18.3 3.89 ——————
AIRFLOW
(L/s)
EXTERNAL STATIC PRESSURE (Pa)
300 350 400 450 500
R/s BkW R/s BkW R/s BkW R/s BkW R/s BkW
1900 16.6 1.91 17.5 2.11 18.2 2.29 18.9 2.44 19.3 2.55
1950 16.7 2.00 17.6 2.21 18.4 2.41 19.1 2.58 19.6 2.71
2000 16.9 2.11 17.8 2.31 18.6 2.52 19.3 2.71 19.9 2.87
2050 17.1 2.20 17.9 2.42 18.7 2.64 19.5 2.84 20.1 3.02
2100 17.2 2.30 18.1 2.53 18.9 2.76 19.6 2.97 20.3 3.17
2150 17.4 2.42 18.2 2.64 19.0 2.88 19.8 3.10 20.5 3.31
2200 17.6 2.52 18.4 2.76 19.2 2.99 20.0 3.23 20.7 3.45
2250 17.8 2.61 18.6 2.88 19.4 3.11 20.1 3.37 20.9 3.60
2235 18.0 2.71 18.8 3.00 19.5 3.26 20.3 3.49 21.0 3.75
2400 18.2 2.83 18.9 3.13 19.7 3.39 20.5 3.64 21.2 3.89
2450 18.4 2.97 19.1 3.24 19.9 3.52 20.6 3.77 ——
2500 18.6 3.09 19.3 3.35 20.0 3.66 20.8 3.93 ——
2550 18.8 3.25 19.5 3.49 20.2 3.81 ————
2600 19.0 3.42 19.7 3.63 20.4 3.95 ————
2650 19.2 3.58 19.9 3.81 ——————
2700 19.4 3.73 20.1 3.92 ——————
2750 19.7 3.91 ————————
2800 ——————————
2850 ——————————
2900 ——————————
2950 ——————————
3000 ——————————
3050 ——————————
3100 ——————————
BkW —Fan Input kW x Motor Efficiency
R/s —Revolutions Per Second of Blower Wheel

28
Table 18 — Fan Performance, 48TF008 — Vertical Discharge Units (English)
LEGEND
NOTES:
1. Boldface indicates field-supplied drive required. (See Note 5.)
2. indicates field-supplied motor and drive are required.
3. Values include losses for filters, unit casing, and wet coils.
4. Use of a field-supplied motor may affect wire sizing. Contact
your Carrier representative to verify.
5. Standard drive range is 492 to 700 rpm. All other rpms require
a field-supplied drive.
6. Maximum continuous bhp is 2.4. Extensive motor and electrical
testing on these units ensures that the full range of the motor
can be utilized with confidence. Using the fan motors up to the
ratings shown will not result in nuisance tripping or premature
motor failure. Unit warranty will not be affected.
7. Interpolation is permissible. Do not extrapolate.
AIRFLOW
(Cfm)
EXTERNAL STATIC PRESSURE (in. wg)
0.2 0.4 0.6 0.8
Rpm Bhp Rpm Bhp Rpm Bhp Rpm Bhp
2200 506 0.52 586 0.72 656 0.95 718 1.18
2250 514 0.55 593 0.76 662 0.99 724 1.22
2300 521 0.56 600 0.79 668 1.02 730 1.26
2400 536 0.63 613 0.85 680 1.09 741 1.34
2500 551 0.69 626 0.93 693 1.17 753 1.43
2550 559 0.72 634 0.97 700 1.21 759 1.48
2600 567 0.75 641 1.00 706 1.25 764 1.52
2700 582 0.83 655 1.08 719 1.34 776 1.61
2800 598 0.90 670 1.17 732 1.43 789 1.71
2900 614 0.98 684 1.25 745 1.53 802 1.81
3000 630 1.07 699 1.35 759 1.63 815 1.92
3100 646 1.16 714 1.45 773 1.74 828 2.04
3200 662 1.26 729 1.55 787 1.86 841 2.16
3300 679 1.36 744 1.66 801 1.98 854 2.29
3400 695 1.47 759 1.78 816 2.10 867 2.42
3500 712 1.59 774 1.90 830 2.23 881 2.56
3600 729 1.71 790 2.03 845 2.37 895 2.71
3700 745 1.84 805 2.17 860 2.52 909 2.87
3750 754 1.91 813 2.24 868 2.59 917 2.95
AIRFLOW
(Cfm)
EXTERNAL STATIC PRESSURE (in. wg)
1.0 1.2 1.4 1.6
Rpm Bhp Rpm Bhp Rpm Bhp Rpm Bhp
2200 776 1.43 838 1.78 898 2.21 935 2.58
2250 781 1.78 841 1.81 902 2.25 939 2.60
2300 786 1.50 843 1.83 905 2.28 943 2.62
2400 796 1.59 849 1.88 910 2.31 952 2.74
2500 808 1.69 859 1.96 912 2.31 963 2.81
2550 814 1.74 864 2.01 915 2.34 968 2.81
2600 819 1.79 869 2.06 918 2.37 973 2.81
2700 831 1.89 880 2.17 927 2.47 976 2.84
2800 842 2.00 892 2.29 938 2.58 983 2.92
2900 854 2.11 903 2.42 949 2.71 993 3.03
3000 866 2.23 915 2.54 961 2.85 1003 3.17
3100 878 2.35 926 2.67 972 3.00 1015 3.32
3200 891 2.48 938 2.81 983 3.14 1026 3.47
3300 904 2.61 950 2.95 995 3.30 ——
3400 917 2.75 963 3.10 1007 3.45 ——
3500 930 2.90 976 3.25 ————
3600 943 3.05 988 3.41 ————
3700 956 3.22 ——————
3750 963 3.30 ——————
Bhp —Brake Horsepower at Motor Shaft
Rpm —Revolutions Per Minute of Blower Wheel

29
Table 19 — Fan Performance, 48TF012 — Vertical Discharge Units (English)
LEGEND
NOTES:
1. Boldface indicates field-supplied drive required. (See Note 5.)
2. indicates field-supplied motor and drive are required.
3. Values include losses for filters, unit casing, and wet coils.
4. Use of a field-supplied motor may affect wire sizing. Contact
your Carrier representative to verify.
5. Standard drive range is 571 to 779 rpm. All other speeds
require a field-supplied drive.
6. Maximum continuous bhp is 2.4. Extensive motor and electrical
testing on these units ensures that the full range of the motor
can be utilized with confidence. Using the fan motors up to the
ratings shown will not result in nuisance tripping or premature
motor failure. Unit warranty will not be affected.
7. Interpolation is permissible. Do not extrapolate.
AIRFLOW
(Cfm)
EXTERNAL STATIC PRESSURE (in. wg)
0.2 0.4 0.6 0.8 1.0
Rpm Bhp Rpm Bhp Rpm Bhp Rpm Bhp Rpm Bhp
3000 592 0.76 661 0.93 722 1.09 779 1.26 829 1.42
3100 607 0.83 676 1.01 734 1.17 791 1.34 840 1.51
3200 622 0.90 690 1.09 746 1.25 803 1.43 852 1.60
3300 638 0.98 705 1.17 759 1.33 815 1.52 864 1.70
3400 653 1.06 719 1.26 772 1.43 826 1.62 876 1.81
3500 669 1.15 733 1.35 786 1.53 838 1.72 888 1.91
3600 684 1.24 747 1.44 800 1.64 850 1.82 900 2.03
3700 700 1.33 760 1.54 814 1.75 863 1.92 912 2.14
3800 715 1.43 774 1.64 828 1.86 875 2.04 924 2.26
3900 731 1.54 787 1.74 843 1.98 888 2.16 936 2.30
4000 747 1.65 801 1.85 857 2.10 902 2.30 948 2.51
4100 763 1.76 816 1.97 872 2.23 916 2.44 960 2.64
4200 778 1.88 831 2.10 886 2.36 929 2.58 972 2.78
4300 794 2.00 846 2.23 900 2.50 943 2.73 985 2.93
4400 810 2.13 861 2.37 913 2.64 958 2.89 999 3.09
4500 826 2.27 876 2.52 927 2.78 973 3.04 1012 3.26
4600 842 2.41 892 2.67 940 2.92 987 3.21 ——
4700 858 2.55 907 2.83 954 3.08 1002 3.38 ——
4800 874 2.70 922 2.99 968 3.24 ————
4900 890 2.86 938 3.16 ——————
5000 906 3.03 953 3.33 ——————
AIRFLOW
(Cfm)
EXTERNAL STATIC PRESSURE (in. wg)
1.2 1.4 1.6 1.8 2.0
Rpm Bhp Rpm Bhp Rpm Bhp Rpm Bhp Rpm Bhp
3000 880 1.58 924 1.73 970 1.89 1019 2.00 1066 2.30
3100 890 1.68 935 1.84 977 2.00 1026 2.17 1070 2.44
3200 900 1.77 946 1.95 987 2.11 1029 2.28 1075 2.51
3300 910 1.88 957 2.06 998 2.23 1037 2.40 1082 2.58
3400 921 1.98 967 2.17 1009 2.35 1047 2.53 1087 2.70
3500 933 2.10 976 2.29 1020 2.48 1058 2.66 1095 2.84
3600 945 2.22 986 2.41 1030 2.61 1069 2.80 1106 2.98
3700 957 2.34 998 2.54 1039 2.74 1081 2.94 1117 3.13
3800 969 2.47 1010 2.67 1049 2.87 1091 3.08 1128 3.29
3900 981 2.60 1022 2.81 1060 3.02 1100 3.23 ——
4000 993 2.74 1034 2.96 1072 3.17 1110 3.38 ——
4100 1005 2.88 1046 3.11 1084 3.32 ————
4200 1016 3.03 1058 3.26 ——————
4300 1028 3.17 ————————
4400 1040 3.32 ————————
4500 ——————————
4600 ——————————
4700 ——————————
4800 ——————————
4900 ——————————
5000 ——————————
Bhp —Brake Horsepower at Motor Shaft
Rpm —Revolutions Per Minute of Blower Wheel

30
Table 20 — Fan Performance, 48TF014 — Vertical Discharge Units (English)
LEGEND
NOTES:
1. Boldface indicates field-supplied drive required. (See Note 5.)
2. indicates field-supplied motor and drive are required.
3. Values include losses for filters, unit casing, and wet coils.
4. Use of a field-supplied motor may affect wire sizing. Contact
your Carrier representative to verify.
5. Standard drive range is 717 to 900 rpm. All other rpms require
a field-supplied drive.
6. Maximum continuous bhp is 3.7. Extensive motor and electrical
testing on these units ensures that the full range of the motor
can be utilized with confidence. Using the fan motors up to the
ratings shown will not result in nuisance tripping or premature
motor failure. Unit warranty will not be affected.
7. Interpolation is permissible. Do not extrapolate.
AIRFLOW
(Cfm)
EXTERNAL STATIC PRESSURE (in. wg)
0.2 0.4 0.6 0.8 1.0
Rpm Bhp Rpm Bhp Rpm Bhp Rpm Bhp Rpm Bhp
3700 729 1.36 790 1.58 847 1.79 902 2.06 955 2.29
3800 745 1.46 805 1.69 861 1.89 915 2.17 967 2.41
3900 761 1.56 820 1.80 875 2.02 928 2.29 979 2.55
4000 777 1.67 836 1.92 889 2.14 941 2.40 991 2.68
4100 793 1.79 851 2.05 904 2.27 955 2.42 1004 2.82
4200 810 1.91 867 2.18 918 2.41 968 2.54 1017 2.96
4300 826 2.04 883 2.32 933 2.55 982 2.79 1030 3.11
4400 842 2.17 898 2.46 948 2.70 996 2.93 1043 3.25
4500 859 2.31 914 2.60 962 2.85 1010 3.09 1056 3.40
4600 876 2.46 930 2.76 977 3.01 1024 3.26 1070 3.55
4700 892 2.60 945 2.91 992 3.18 2039 3.43 1083 3.71
4800 909 2.77 961 3.07 1008 3.36 1053 3.61 1097 3.88
4900 926 2.93 977 3.24 1024 3.54 1068 3.80 1111 4.06
5000 942 3.11 993 3.41 1039 3.73 1080 3.90 1126 4.25
5100 959 3.29 1009 3.60 1055 3.92 1097 4.19 1139 4.46
5200 976 3.47 1025 3.78 1071 4.12 1112 4.40 1153 4.67
5300 993 3.67 1041 3.98 1086 4.33 1127 4.61 1168 4.90
5400 1010 3.87 1057 4.18 1102 4.54 1142 4.84 1182 5.13
5500 1027 4.07 1073 4.39 1118 4.76 1157 5.07 1197 5.36
5600 1043 4.29 1090 4.61 1133 4.99 1173 5.31 1211 5.61
5700 1060 4.51 1106 4.83 1149 5.22 1189 5.55 ——
5800 1077 4.74 1122 5.07 1165 5.46 ————
5900 1094 4.98 1139 5.41 1181 5.70 ————
6000 1111 5.22 1155 5.55 ——————
6100 1128 5.48 ————————
6200 1145 5.74 ————————
AIRFLOW
(Cfm)
EXTERNAL STATIC PRESSURE (in. wg)
1.2 1.4 1.6 1.8 2.0
Rpm Bhp Rpm Bhp Rpm Bhp Rpm Bhp Rpm Bhp
3700 1008 2.55 1060 2.80 1108 3.05 1152 3.27 1190 3.46
3800 1019 2.67 1070 2.94 1118 3.19 1163 3.44 1203 3.65
3900 1029 2.80 1079 3.07 1128 3.34 1173 3.60 1214 3.83
4000 1040 2.94 1089 3.22 1137 3.49 1183 3.76 1225 4.00
4100 1052 3.08 1100 3.36 1147 3.65 1193 3.93 1236 4.19
4200 1064 3.23 1110 3.51 1157 3.81 1202 4.09 1245 4.38
4300 1076 3.40 1121 3.67 1167 3.97 1212 4.27 1255 4.56
4400 1088 3.56 1133 3.84 1178 4.14 1222 4.44 1265 4.74
4500 1101 3.73 1144 4.00 1188 4.31 1232 4.62 1274 4.93
4600 1114 3.90 1157 4.19 1199 4.49 1242 4.81 1284 5.13
4700 1126 4.07 1169 4.38 1210 4.68 1252 5.00 1294 5.33
4800 1140 4.25 1181 4.58 1222 4.87 1263 5.20 ——
4900 1153 4.41 1194 4.77 1234 5.09 1274 5.40 ——
5000 1166 4.59 1207 4.97 1247 5.30 1286 5.62 ——
5100 1180 4.78 1220 5.18 1259 5.52 ————
5200 1194 4.98 1233 5.38 1272 5.74 ————
5300 1208 5.19 1246 5.58 ——————
5400 1221 5.41 ————————
5500 1235 5.64 ————————
5600 ——————————
5700 ——————————
5800 ——————————
5900 ——————————
6000 ——————————
6100 ——————————
6200 ——————————
Bhp —Brake Horsepower at Motor Shaft
Rpm —Revolutions Per Minute of Blower Wheel
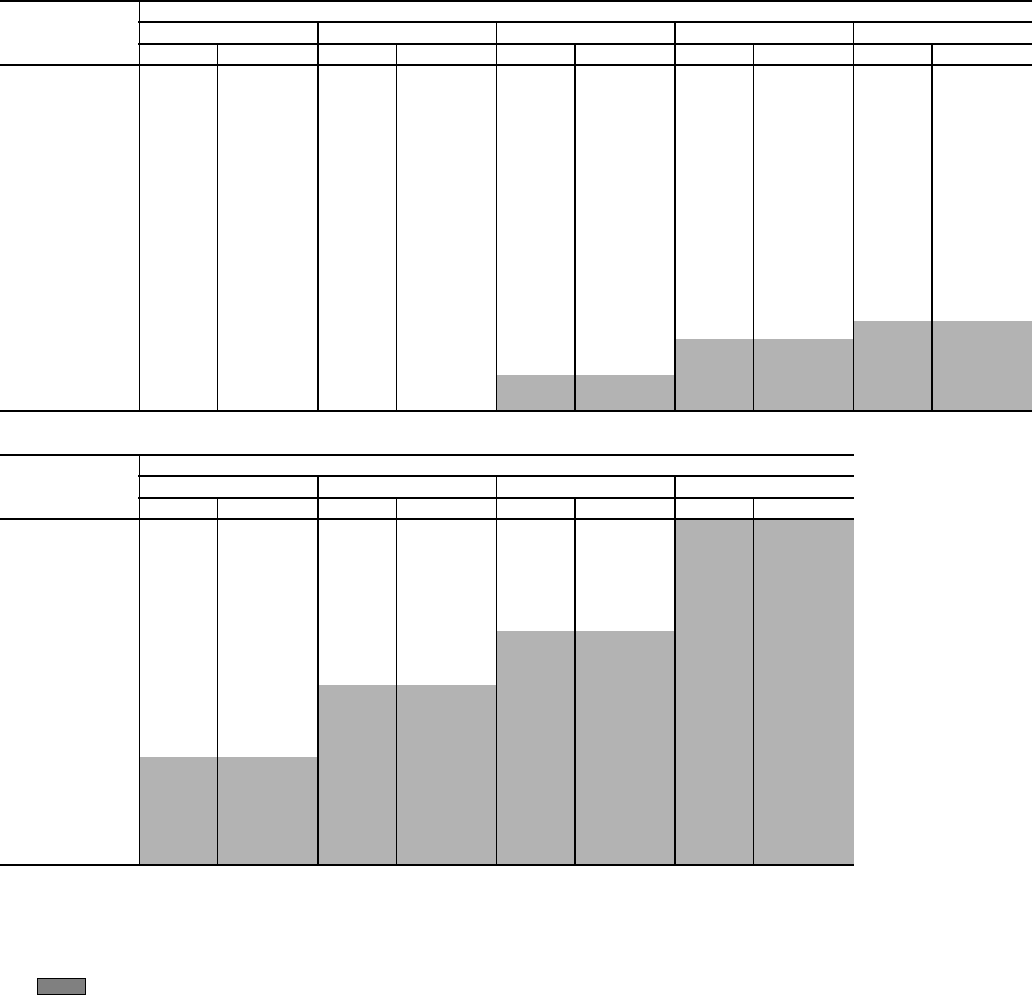
31
Table 21 — Fan Performance, 48TF008 — Horizontal Discharge Units (English)
LEGEND
NOTES:
1. Boldface indicates field-supplied drive required. (See Note 5.)
2. indicates field-supplied motor and drive are required.
3. Values include losses for filters, unit casing, and wet coils.
4. Use of a field-supplied motor may affect wire sizing. Contact
your Carrier representative to verify.
5. Standard drive range is 492 to 700 rpm. All other rpms require
a field-supplied drive.
6. Maximum continuous bhp is 2.4. Extensive motor and electrical
testing on these units ensures that the full range of the motor
can be utilized with confidence. Using the fan motors up to the
ratings shown will not result in nuisance tripping or premature
motor failure. Unit warranty will not be affected.
7. Interpolation is permissible. Do not extrapolate.
AIRFLOW
(Cfm)
EXTERNAL STATIC PRESSURE (in. wg)
0.2 0.4 0.6 0.8 0.9
Rpm Bhp Rpm Bhp Rpm Bhp Rpm Bhp Rpm Bhp
2200 499 0.50 580 0.70 652 0.94 717 1.17 748 1.30
2250 507 0.53 586 0.73 658 0.97 722 1.22 752 1.34
2300 513 0.55 592 0.76 663 1.00 727 1.26 756 1.38
2400 528 0.60 606 0.83 674 1.06 738 1.34 766 1.46
2500 542 0.66 619 0.90 686 1.13 748 1.41 777 1.55
2550 550 0.69 627 0.94 692 1.17 754 1.45 783 1.60
2600 557 0.72 634 0.97 698 1.21 759 1.49 787 1.64
2700 573 0.79 648 1.05 711 1.29 770 1.58 798 1.73
2800 588 0.86 662 1.13 723 1.38 782 1.66 809 1.82
2900 604 0.94 676 1.21 737 1.48 794 1.76 821 1.92
3000 620 1.02 690 1.30 750 1.58 806 1.86 832 2.02
3100 636 1.11 704 1.39 764 1.69 818 1.97 844 2.13
3200 652 1.21 718 1.49 778 1.80 831 2.09 856 2.25
3300 668 1.31 732 1.59 793 1.92 844 2.21 869 2.37
3400 684 1.41 747 1.70 807 2.04 857 2.35 882 2.51
3500 701 1.53 762 1.82 821 2.16 871 2.48 895 2.64
3600 717 1.65 777 1.94 835 2.29 885 2.63 908 2.79
3700 733 1.77 792 2.07 849 2.42 899 2.78 922 2.95
3750 742 1.84 800 2.14 856 2.49 907 2.86 929 3.03
AIRFLOW
(Cfm)
EXTERNAL STATIC PRESSURE (in. wg)
1.0 1.2 1.4 1.6
Rpm Bhp Rpm Bhp Rpm Bhp Rpm Bhp
2200 779 1.43 839 1.78 905 2.21 951 2.57
2250 783 1.46 843 1.81 908 2.25 955 2.59
2300 786 1.49 846 1.84 910 2.25 959 2.61
2400 795 1.58 853 1.88 912 2.31 967 2.68
2500 806 1.68 859 1.94 919 2.37 971 2.73
2550 812 1.74 864 1.99 920 2.39 974 2.76
2600 816 1.79 868 2.04 921 2.41 976 2.78
2700 827 1.88 878 2.16 928 2.45 983 2.88
2800 837 1.98 889 2.29 937 2.57 986 2.91
2900 848 2.08 900 2.41 947 2.70 993 3.01
3000 849 2.18 910 2.52 958 2.85 1002 3.15
3100 870 2.29 920 2.64 968 2.99 1012 3.30
3200 882 2.40 931 2.76 979 3.13 1023 3.47
3300 894 2.53 942 2.89 989 3.26 1034 3.63
3400 907 2.66 954 3.02 1000 3.40 1044 3.79
3500 919 2.80 966 3.15 1011 3.55 1054 3.94
3600 932 2.95 978 3.30 1022 3.69 1065 4.10
3700 945 3.11 990 3.45 1034 3.84 1076 4.28
3750 952 3.20 997 3.54 1040 3.93 1082 5.27
Bhp —Brake Horsepower at Motor Shaft
Rpm —Revolutions Per Minute of Blower Wheel

32
Table 22 — Fan Performance, 48TF012 — Horizontal Discharge Units (English)
LEGEND
NOTES:
1. Boldface indicates field-supplied drive required. (See Note 5.)
2. indicates field-supplied motor and drive are required.
3. Values include losses for filters, unit casing, and wet coils.
4. Use of a field-supplied motor may affect wire sizing. Contact
your Carrier representative to verify.
5. Standard drive range is 571 to 779 rpm. All other rpms require
a field-supplied drive.
6. Maximum continuous bhp is 2.4. Extensive motor and electrical
testing on these units ensures that the full range of the motor
can be utilized with confidence. Using the fan motors up to the
ratings shown will not result in nuisance tripping or premature
motor failure. Unit warranty will not be affected.
7. Interpolation is permissible. Do not extrapolate.
AIRFLOW
(Cfm)
EXTERNAL STATIC PRESSURE (in. wg)
0.2 0.4 0.6 0.8 1.0
Rpm Bhp Rpm Bhp Rpm Bhp Rpm Bhp Rpm Bhp
3000 552 0.68 632 0.87 701 1.05 761 1.22 816 1.36
3100 565 0.74 644 0.93 711 1.12 772 1.31 825 1.45
3200 578 0.81 656 1.00 723 1.20 782 1.39 835 1.55
3300 591 0.88 668 1.08 734 1.28 793 1.47 845 1.65
3400 605 0.96 680 1.16 745 1.36 803 1.56 856 1.75
3500 619 1.04 691 1.23 755 1.44 813 1.65 867 1.86
3600 633 1.13 703 1.31 766 1.52 824 1.74 877 1.97
3700 648 1.23 714 1.39 777 1.61 835 1.85 887 2.07
3800 662 1.33 726 1.51 789 1.72 846 1.95 897 2.18
3900 677 1.44 738 1.61 801 1.82 857 2.06 908 2.29
4000 692 1.55 750 1.73 813 1.94 868 2.17 918 2.40
4100 707 1.67 762 1.84 825 2.05 878 2.28 929 2.53
4200 722 1.80 775 1.97 837 2.16 889 2.40 941 2.66
4300 737 1.94 787 2.09 848 2.27 900 252 952 2.80
4400 752 2.08 800 2.21 860 2.39 912 2.66 962 2.93
4500 768 2.24 814 2.35 871 2.51 924 2.80 973 3.07
4600 783 2.40 827 2.50 883 2.64 937 2.95 983 3.21
4700 799 2.56 841 2.64 894 2.77 949 3.10 994 3.36
4800 814 2.74 855 2.80 906 2.91 961 3.26 ——
4900 ——
868 2.90 918 3.05 972 3.40 ——
5000 ——
883 3.10 931 3.21 ————
AIRFLOW
(Cfm)
EXTERNAL STATIC PRESSURE (in. wg)
1.2 1.4 1.6 1.8 2.0
Rpm Bhp Rpm Bhp Rpm Bhp Rpm Bhp Rpm Bhp
3000 871 1.54 918 1.67 967 1.89 1010 2.09 1063 2.46
3100 879 1.63 928 1.78 973 1.94 1018 2.17 1070 2.51
3200 887 1.71 937 1.90 981 2.04 1026 2.26 1075 2.57
3300 895 1.80 946 2.00 991 2.16 1032 2.32 1080 2.64
3400 904 1.91 953 2.10 1000 2.29 1041 2.44 1083 2.65
3500 914 2.03 961 2.20 1009 2.41 1051 2.57 1090 2.74
3600 924 2.15 970 2.32 1017 2.53 1061 2.72 1099 2.88
3700 935 2.28 980 2.45 1024 2.64 1069 2.87 1109 3.03
3800 946 2.40 989 2.58 1033 2.76 1077 2.99 1118 3.20
3900 956 2.53 1000 2.73 1042 2.91 1085 3.12 1127 3.36
4000 967 2.66 1010 2.87 1052 3.06 1093 3.24 ——
4100 977 2.78 1021 3.02 1062 3.22 1102 3.41 ——
4200 987 2.91 1032 3.17 1072 3.38 ————
4300 999 3.04 1042 3.32 ——————
4400 1008 3.19 ————————
4500 1019 3.34 ————————
4600 ——————————
4700 ——————————
4800 ——————————
4900 ——————————
5000 ——————————
Bhp —Brake Horsepower at Motor Shaft
Rpm —Revolutions Per Minute of Blower Wheel

33
Table 23 — Fan Performance, 48TF014 — Horizontal Discharge Units (English)
LEGEND
NOTES:
1. Boldface indicates field-supplied drive required. (See Note 5.)
2. indicates field-supplied motor and drive are required.
3. Values include losses for filters, unit casing, and wet coils.
4. Use of a field-supplied motor may affect wire sizing. Contact
your Carrier representative to verify.
5. Standard drive range is 717 to 900 rpm. All other rpms require
a field-supplied drive.
6. Maximum continuous bhp is 3.7. Extensive motor and electrical
testing on these units ensures that the full range of the motor
can be utilized with confidence. Using the fan motors up to the
ratings shown will not result in nuisance tripping or premature
motor failure. Unit warranty will not be affected.
7. Interpolation is permissible. Do not extrapolate.
AIRFLOW
(Cfm)
EXTERNAL STATIC PRESSURE (in. wg)
0.2 0.4 0.6 0.8 1.0
Rpm Bhp Rpm Bhp Rpm Bhp Rpm Bhp Rpm Bhp
3700 677 1.20 748 1.43 810 1.65 869 1.89 928 2.17
3800 691 1.28 761 1.52 822 1.75 880 1.98 937 2.28
3900 705 1.37 773 1.62 834 1.86 891 2.08 947 2.39
4000 720 1.47 786 1.71 847 1.97 902 2.19 956 2.50
4100 734 1.56 800 1.82 860 2.09 914 2.31 967 2.60
4200 749 1.66 813 1.92 873 2.21 926 2.44 978 2.71
4300 764 1.77 826 2.04 886 2.33 938 2.57 989 2.83
4400 779 1.88 840 2.16 899 2.46 951 2.71 1000 2.96
4500 793 1.99 854 2.28 912 2.59 963 2.86 1012 3.09
4600 808 2.11 868 2.42 925 2.73 975 3.00 1024 3.25
4700 822 2.24 882 2.56 937 2.86 988 3.16 1036 3.42
4800 837 2.37 896 2.71 950 3.00 1001 3.32 1048 3.59
4900 852 2.51 910 2.86 963 3.15 1014 3.48 1060 3.76
5000 867 2.65 924 3.01 977 3.30 1027 3.65 1073 3.94
5100 882 2.79 938 3.17 990 3.46 1040 3.82 1085 4.12
5200 896 2.95 952 3.33 1003 3.63 1053 4.00 1098 4.30
5300 911 3.11 967 3.50 1017 3.80 1066 4.18 1111 4.50
5400 926 3.27 981 3.68 1030 3.98 1079 4.35 1124 4.70
5500 940 3.44 995 3.86 1044 4.17 1092 4.54 1137 4.91
5600 955 3.62 1010 4.04 1058 4.38 1105 4.73 1150 5.12
5700 970 3.80 1024 4.23 1072 4.59 1118 4.93 1163 5.34
5800 985 3.99 1039 4.42 1086 4.80 1131 5.14 1176 5.56
5900 1000 4.18 1053 4.62 1100 5.02 1144 5.36 ——
6000 1015 4.39 1068 4.83 1114 5.25 1158 5.58 ——
6100 1030 4.59 1083 5.04 1128 5.48 ————
6200 1046 4.81 1097 5.26 1142 5.71 ————
AIRFLOW
(Cfm)
EXTERNAL STATIC PRESSURE (in. wg)
1.2 1.4 1.6 1.8 2.0
Rpm Bhp Rpm Bhp Rpm Bhp Rpm Bhp Rpm Bhp
3700 984 2.43 1036 2.68 1080 2.90 1114 3.07 1135 3.17
3800 993 2.55 1046 2.81 1092 3.05 1129 3.25 1156 3.39
3900 1002 2.66 1055 2.94 1102 3.20 1143 3.42 1174 3.59
4000 1011 2.79 1064 3.07 1112 3.34 1155 3.59 1190 3.80
4100 1021 2.91 1072 3.20 1121 3.49 1165 3.76 1203 3.99
4200 1030 3.04 1081 3.34 1130 3.64 1175 3.92 1215 4.18
4300 1040 3.18 1090 3.48 1139 3.79 1185 4.08 1226 4.36
4400 1050 3.31 1100 3.63 1148 3.94 1194 4.25 1236 4.54
4500 1061 3.43 1109 3.78 1156 4.09 1203 4.42 1246 4.72
4600 1071 3.56 1119 3.93 1166 4.26 1212 4.58 1255 4.91
4700 1082 3.70 1129 4.09 1175 4.43 1221 4.76 1264 5.09
4800 1093 3.86 1139 4.24 1185 4.60 1230 4.93 1273 5.28
4900 1105 4.02 1150 4.38 1194 4.77 1239 5.12 1282 5.47
5000 1117 4.20 1161 4.54 1204 4.95 1248 5.31 1291 5.66
5100 1129 4.40 1172 4.71 1214 5.13 1257 5.61 ——
5200 1141 4.60 1183 4.91 1225 5.29 1267 5.70 ——
5300 1153 4.80 1194 5.08 1236 5.47 ————
5400 1166 5.01 1206 5.29 1247 5.65 ————
5500 1178 5.22 1218 5.52 ——————
5600 1190 5.44 1230 5.75 ——————
5700 1203 5.67 ————————
5800 ——————————
5900 ——————————
6000 ——————————
6100 ——————————
6200 ——————————
Bhp —Brake Horsepower at Motor Shaft
Rpm —Revolutions Per Minute of Blower Wheel

34
START-UP
Unit Preparation — Make sure that unit has been in-
stalled in accordance with these installation instructions and
applicable codes. Make sure that Start-Up Checklist, located on
back page of this booklet, has been completed and filled out.
Return-Air Filters — Make sure correct filters are in-
stalled in filter tracks (see Tables 1A and 1B). Do not operate
unit without return-air filters.
Outdoor-Air Inlet Screens — Outdoor-air inlet screens
must be in place before operating unit.
Compressor Mounting — Compressors are internally
spring mounted. Do not loosen or remove compressor hold-
down bolts. On 48TF014 units, remove the tiedown bands that
hold the compressors together.
Internal Wiring — Check all electrical connections in
unit control boxes. Tighten as required. Ensure wiring does not
come into direct contact with refrigerant tubing.
Refrigerant Service Ports — Each refrigerant sys-
tem has 4 Schrader-type service gage ports: one on the suction
line, one on the liquid line, and two on the compressor dis-
charge line. Be sure that caps on the ports are tight. One
Schrader-type valve is located under both the high-pressure
switch and the low-pressure switch when ordered as an option.
High Flow Valves — Located on the compressor hot gas
and suction tubes are High Flow Valves. Large black plastic
caps distinguish these valves with O-rings located inside the
caps. These valves cannot be accessed for service in the field.
Ensure the plastic caps are in place and tight or the possibility
of refrigerant leakage could occur.
Compressor Rotation — On 3-phase units with scroll
compressors, it is important to be certain compressor is rotating
in the proper direction. To determine whether or not compres-
sor is rotating in the proper direction:
1. Connect service gages to suction and discharge pressure
fittings.
2. Energize the compressor.
3. The suction pressure should drop and the discharge pres-
sure should rise, as is normal on any start-up.
If the suction pressure does not drop and the discharge pres-
sure does not rise to normal levels:
1. Note that the evaporator fan is probably also rotating in
the wrong direction.
2. Turn off power to the unit and install lockout tag.
3. Reverse any two of the unit power leads.
4. Reapply power to unit. Reenergize compressor.
The suction and discharge pressure levels should now move
to their normal start-up levels.
NOTE: When the compressor is rotating in the wrong direc-
tion, the unit will make an elevated level of noise and will not
provide cooling.
Cooling — To start unit, turn on main power supply. Set
system selector switch at COOL position and fan switch at
AUTO. position. Adjust thermostat to a setting below room
temperature. Compressor, indoor and outdoor fans start on clo-
sure of contactors.
Check unit charge. Refer to Refrigerant Charge section,
page 37. Unit must operate a minimum of 15 minutes before
adjusting charge.
Reset thermostat at a position above room temperature.
Compressor and outdoor fans will shut off. Evaporator fan will
shut off after 30-second delay.
TO SHUT OFF UNIT — Set system selector switch at OFF
position. Resetting thermostat at a position above room tem-
perature shuts unit off temporarily until space temperature ex-
ceeds thermostat setting.
Main Burners — Main burners are factory set and should
require no adjustment.
TO CHECK ignition of main burners and heating controls,
move thermostat set point above room temperature and verify
that the burners light and evaporator fan is energized. After en-
suring that the unit continues to heat the building, lower the
thermostat setting below the room temperature and verify that
the burners and evaporator fan turn off (fan will turn off only if
fan selector switch is in the AUTO. position). Refer to Table 24
for the correct orifice to use at high altitudes.
NOTE: Upon a call for heat, the main burners will remain on
for a minimum of 60 seconds.
ADJUST GAS INPUT — The gas input to the unit is deter-
mined by measuring the gas flow at the meter or by measuring
the manifold pressure. Manifold pressure should be 872 Pa
(3.5 in. wg).
NOTE: Unit uses a 2 stage gas valve. There is no need to
adjust the “Low Fire” manifold pressure.
Measure Gas Flow (Natural Gas Units) — Minor adjustment
to the gas flow can be made by changing the manifold pressure.
The manifold pressure must be 872 Pa (3.5 in wg). Normal
manifold pressure is 872 Pa (3.5 in. wg) in high fire, W1 and
W2 inputs to gas valve.
Proceed as follows:
1. Turn off gas supply to unit.
2. Remove pipe plug on manifold then connect manometer
at this point. Turn on gas to unit. Ensure gas valve is in
high fire operation.
Observe manifold pressure and proceed as follows to adjust
gas input:
1. Remove cover screw over regulator adjustment screw on
gas valve. Ensure gas valve is operating in high fire
mode.
2. Turn regulator adjustment screw clockwise to increase
gas input, or turn regulator adjustment screw counter-
clockwise to decrease input. High fire manifold pressure
must be 872 Pa (3.5 in. wg).
3. Replace cover screw cap on gas valve.
4. Turn off gas supply to unit. Remove manometer from
pressure tap and replace pipe plug on gas valve. Turn on
gas to unit and check for leaks.
Heating
1. Purge gas supply line of air by opening union ahead of
gas valve. When gas odor is detected, tighten union and
wait 5 minutes before proceeding.
2. Turn on electrical supply and open manual gas valve.
3. Set system switch selector at HEAT position and fan
switch at AUTO. or ON position. Set heating temperature
lever above room temperature.
4. The induced-draft motor will start, purging heat
exchangers.
Unsafe operation of the unit may result if manifold pres-
sure is outside 847 to 897 Pa (3.4 to 3.6 in. wg) range. Per-
sonal injury or unit damage may result.

35
5. After a call for heating, the main burners should light
within 5 seconds. If the burners do not light, then there is
a 22-second delay before another 5-second ignition try.
If the burners still do not light, the time delay is repeated.
If the burners do not light within 15 minutes, there is a
lockout. To reset the control, break the 24 v power to W1.
6. The evaporator-fan motor will turn on 45 seconds after
the burners are ignited.
7. The evaporator-fan motor will turn off 45 seconds after
the thermostat temperature is satisfied.
8. Adjust airflow to obtain a temperature rise within the
range specified on the unit nameplate and in Table 1A
or 1B.
Table 24 — Altitude Compensation*
*As the height above sea level increases, there is less oxygen.
Therefore, heat input rate should be reduced at higher altitudes.
†Orifice available through your local distributor.
Integrated Gas Controller (IGC) Operation
NOTE: The default value for the evaporator-fan motor ON and
OFF delay is 45 seconds. The Integrated Gas Controller (IGC)
modifies this value when abnormal limit switch cycles occur.
Based upon unit operating conditions, the ON delay can be
reduced to 0 seconds and the OFF delay can be extended to
180 seconds.
When one flash of the LED (light-emitting diode) is ob-
served, the evaporator-fan ON/OFF delay has been modified.
If the limit switch trips at the start of the heating cycle during
the evaporator ON delay, the time period of the ON delay for
the next cycle will be 5 seconds less than the time at which the
switch tripped. (Example: If the limit switch trips at 30 sec-
onds, the evaporator-fan ON delay for the next cycle will occur
at 25 seconds.) To prevent short-cycling, a 5-second reduction
will only occur if a minimum of 10 minutes has elapsed since
the last call for heating.
The evaporator-fan OFF delay can also be modified. Once
the call for heating has ended, there is a 10-minute period dur-
ing which the modification can occur. If the limit switch trips
during this period, the evaporator-fan OFF delay will increase
by 15 seconds on the next cycle. A maximum of 9 trips can oc-
cur, extending the evaporator-fan OFF delay to 180 seconds.
To restore the original default value, reset the power to the unit.
TO SHUT OFF UNIT — Set system selector switch at OFF
position. Resetting heating selector lever below room tempera-
ture will shut unit off temporarily until space temperature falls
below thermostat setting.
Safety Relief — A soft-solder joint at the suction line
Schrader port provides pressure relief under abnormal tempera-
ture and pressure conditions.
Ventilation (Continuous Fan) — Set fan and system
selector switches at ON and OFF positions, respectively.
Evaporator fan operates continuously to provide constant air
circulation. When the evaporator-fan selector switch is turned
to the OFF position, there is a 30-second delay before the fan
turns off.
Operating Sequence
COOLING, UNITS WITHOUT ECONOMIZER — When
thermostat calls for cooling, terminals G and Y1 are energized.
The indoor (evaporator) fan contactor (IFC) and compressor
contactor no. 1 (C1) are energized, and evaporator-fan motors,
compressor no. 1, and both condenser fans start. The condenser-
fan motor runs continuously while unit is cooling. If the thermo-
stat calls for a second stage of cooling by energizing Y2, com-
pressor contactor no. 2 (C2) is energized and compressor no. 2
starts.
When the thermostat is satisfied, C1 and C2 are deener-
gized and the compressors and outdoor (condenser) fan motors
(OFM) shut off. After a 30-second delay, the indoor (evapora-
tor) fan motor (IFM) shuts off. If the thermostat fan selector
switch is in the ON position, the evaporator motor will run
continuously.
HEATING, UNITS WITHOUT ECONOMIZER — When
the thermostat calls for heating, terminal W1 is energized. In
order to prevent thermostat short-cycling, the unit is locked
into the Heating mode for at least 1 minute when W1 is ener-
gized. The induced-draft motor (IDM) is then energized and
the burner ignition sequence begins. The indoor (evaporator)
fan motor (IFM) is energized 45 seconds after a flame is ignit-
ed. On units equipped for two stages of heat, when additional
heat is needed, W2 is energized and the high-fire solenoid on
the main gas valve (MGV) is energized. When the thermostat
is satisfied and W1 and W2 are deenergized, the IFM stops af-
ter a 45-second time-off delay.
COOLING, UNITS WITH DURABLADE ECONO-
MIZER — When the outdoor-air temperature is above the
OAT (outdoor-air thermostat) setting and the room thermostat
calls for cooling, compressor contactor no. 1 is energized to
start compressor no. 1 and the outdoor (condenser) fan motor
(OFM). The indoor (evaporator) fan motor (IFM) is energized
and the economizer damper moves to the minimum position.
Upon a further call for cooling, compressor contactor no. 2 will
be energized, starting compressor no. 2. After the thermostat is
satisfied, the damper moves to the fully closed position when
using an auto fan or to the minimum position when using a
continuous fan.
When the outdoor-air temperature is below the OAT setting
and the thermostat calls for cooling, the economizer dampers
move to the minimum position. If the supply-air temperature is
above 14 C (57 F), the damper continues to open until it reach-
es the fully open position or until the supply-air temperature
drops below 11 C (52 F).
When the supply-air temperature falls to between 14 C
(57 F) and 11 C (52 F), the damper will remain at an intermedi-
ate open position. If the supply-air temperature falls below
11 C (52 F), the damper will modulate closed until it reaches
the minimum position or until the supply-air temperature is
above 11 C (52 F). When the thermostat is satisfied, the damp-
er will move to the fully closed position when using an auto fan
or to the minimum position when using a continuous fan.
ELEVATION
m or km
(ft)
31.4, 50.4, AND 59.8 kW
(107,000, 172,000 AND
204,000 BTUH
NOMINAL INPUT
65.6 kW
(224,000 BTUH)
NOMINAL INPUT
Natural
Gas
Orifice
Size†
Liquid
Propane
Orifice
Size†
Natural
Gas
Orifice
Size†
Liquid
Propane
Orifice
Size†
0-610 m (0-2,000) 3.0 (31) 2.4 (41) 3.2 (30) 2.5 (38)
610 m (2,000) 2.9 (32) 2.3 (42) 3.2 (30) 2.5 (39)
914 m (3,000) 2.9 (32) 2.3 (42) 3.0 (31) 2.4 (40)
1.22 km (4,000) 2.9 (32) 2.3 (42) 2.9 (32) 2.4 (41)
1.52 km (5,000) 2.8 (33) 2.2 (43) 2.8 (33) 2.3 (42)
1.83 km (6,000) 2.8 (34) 2.2 (43) 2.8 (34) 2.2 (43)
2.13 km (7,000) 2.8 (35) 2.1 (44) 2.8 (35) 2.2 (43)
2.44 km (8,000) 2.7 (36) 2.1 (44) 2.7 (36) 2.1 (44)
2.74 km (9,000) 2.6 (37) 2.0 (45) 2.6 (37) 2.1 (44)
3.05 km (10,000) 2.5 (38) 2.0 (46) 2.5 (38) 2.0 (45)
3.35 km (11,000) 2.5 (39) 1.9 (47) 2.5 (39) 2.0 (45)
3.66 km (12,000) 2.4 (40) 1.9 (47) 2.4 (40) 2.0 (46)
3.96 km (13,000) 2.4 (41) 1.9 (48) 2.4 (41) 1.9 (47)
4.27 km (14,000) 2.3 (42) 1.9 (48) 2.3 (42) 1.9 (47)

36
If the outdoor air alone cannot satisfy the cooling require-
ments of the conditioned space, economizer cooling is integrat-
ed with mechanical cooling, providing second-stage cooling.
Compressor no. 1 and the condenser fan will be energized and
the position of the economizer damper will be determined by
the supply-air temperature. Compressor no. 2 is locked out.
When the second stage of cooling is satisfied, the compres-
sor and OFM will be deenergized. The damper position will be
determined by the supply-air temperature.
After a 30-second delay, the IFM shuts off. If the thermostat
fan selector switch is in the ON position, the IFM will run
continuously.
COOLING UNITS WITH ECONOMI$ER — When the
OAT is above the ECON SP set point and the room thermostat
calls for Stage 1 cooling (R to G + Y1), the indoor fan motor
(IFM) is energized and the EconoMi$er damper modulates to
minimum position. The compressor contactor is energized to
start the compressor and outdoor-fan motor (OFM). After the
thermostat is satisfied, the damper modulates to the fully closed
position when the IFM is deenergized.
When the OAT is below the ECON SP setting and the room
thermostat calls for Stage 1 cooling (R to G + Y1), the
EconoMi$er modulates to the minimum position when the
IFM is energized. The EconoMi$er provides Stage 1 of cooling
by modulating the return and outdoor air dampers to maintain a
13 C (55 F) supply air set point. If the supply-air temperature
(SAT) is greater than 14 C (57 F), the EconoMi$er modulates
open, allowing a greater amount of outdoor air to enter the unit.
If the SAT drops below 12 C (53 F), the outdoor air damper
modulates closed to reduce the amount of outdoor air. When
the SAT is between 12 C (53 F) and 14 C (57 F), the
EconoMi$er maintains its position.
If outdoor air alone cannot satisfy the cooling requirements
of the conditioned space, and the OAT is above the MECH
CLG LOCKOUT set point, the EconoMi$er integrates free
cooling with mechanical cooling. This is accomplished by the
strategies below.
NOTE: Compressors have a two-minute Minimum On, Mini-
mum Off, and interstage delay timer.
1. If Y1 is energized, and the room thermostat calls for Y2
(2-stage thermostat), the compressor and OFM are ener-
gized. The position of the EconoMi$er damper is main-
tained at its current value.
2. If Y1 is energized for more than 20 minutes, and Y2 is
not energized (whether or not a 2-stage thermostat is
used), the compressor and OFM are energized. The posi-
tion of the EconoMi$er damper is maintained at its cur-
rent value.
3. If Y1 is energized, and compressor no. 1 is already ener-
gized (see Step 2) and the room thermostat calls for Y2,
compressor no. 1 continues to operate. If Y2 remains
energized for more than 20 minutes, compressor no. 2 is
energized.
NOTE: Compressor no. 2 cannot be energized unless there is a
signal for Y2 from the space thermostat.
4. If compressor no. 2 is energized, and the Y2 signal from
the thermostat is satisfied, compressors 1 and 2 are deen-
ergized. Re-asserting Y2 will start compressor no. 1 and
(after a 20-minute interstage delay) compressor no. 2.
5. If compressor no. 1 is energized and the thermostat is sat-
isfied, compressor no. 1, the OFM, and IFM are deener-
gized and the EconoMi$er modulates closed.
When the OAT is below the MECH CLG LOCKOUT set
point, the compressors remain off.
SERVICE
Cleaning — Inspect unit interior at the beginning of each
heating and cooling season or more frequently as operating
conditions require.
EVAPORATOR COIL — Clean coil as required. Inspect coil
at beginning of heating and cooling seasons.
1. Turn unit power off. Remove evaporator coil access panel.
2. If economizer is installed, remove economizer by discon-
necting Molex plug and removing economizer mounting
screws. Refer to Accessory Economizer Installation In-
structions or Optional Economizer sections on pages 12
and 15 for more details.
3. Remove filters from unit.
4. Clean coil using a commercial coil cleaner or dishwasher
detergent in a pressurized spray canister. Wash both sides
of coil and flush with clean water. For best results, back-
flush toward return-air section to remove foreign materi-
al. Caution should be taken as to not overflow the evapo-
rator drain condensate pan.
5. Flush condensate pan after completion.
6. Reinstall economizer and filters.
7. Reconnect wiring.
8. Replace access panels.
CONDENSER COIL — Inspect coil monthly. Clean con-
denser coil annually, and as required by location and outdoor-
air conditions.
One-Row Coils — Wash coil with commercial cleaner. Clean
outer surfaces with a stiff brush in the normal manner. It is not
necessary to remove top panel.
2-Row Coils — Clean coil as follows:
1. Turn off unit power.
2. Remove top panel screws on condenser end of unit.
3. Remove condenser coil corner post. See Fig. 45. To hold
top panel open, place coil corner post between top panel
and center post. See Fig. 46.
4. Remove screws securing coil to center post.
5. Remove fastener holding coil sections together at return
end of condenser coil. Carefully separate the outer coil
section 3 to 4 in. from the inner coil section. See Fig. 47.
6. Use a water hose or other suitable equipment to flush
down between the 2 coil sections to remove dirt and de-
bris. Clean the outer surfaces with a stiff brush in the nor-
mal manner.
7. Secure inner and outer coil rows together with a field-
supplied fastener.
8. Reposition the outer coil section and remove the coil cor-
ner post from between the top panel and center post.
9. Reinstall the coil corner post and replace all screws.
CONDENSATE DRAIN — Check and clean each year at
start of cooling season. In winter, keep drain dry or protect
against freeze-up.
FILTERS — Clean or replace at start of each heating and cool-
ing season, or more often if operating conditions require it. Re-
placement filters must be same dimensions as original filters.
BELTS — Adjust belt tension and pulley alignment at least
twice a year or more frequently as operating conditions require.
Refer to Step 9 — Adjust Evaporator for Fan Speed
for procedures.
When servicing unit, shut off all electrical power to unit to
avoid shock hazard or injury from rotating parts.

37
Lubrication
COMPRESSORS — Each compressor is charged with the
correct amount of oil at the factory.
FAN-MOTOR BEARINGS — Fan-motor bearings are of
the permanently lubricated type. No further lubrication is re-
quired. No lubrication of condenser- or evaporator-fan motors
is required.
Condenser-Fan Adjustment (Fig. 48)
1. Shut off unit power supply and tag disconnect.
2. Remove condenser-fan assembly (grille, motor, motor
cover, and fan) and loosen fan hub setscrews.
3. Adjust fan height as shown in Fig. 48.
4. Tighten setscrews and replace condenser-fan assembly.
Manual Outdoor-Air Damper — If outdoor-air damp-
er blade is required, see Manual Outdoor-Air Damper section on
page 12.
Economizer Adjustment — Refer to Optional Dura-
blade Economizer section on page 14.
Condenser Coil Grille — Condenser coil grille is
shipped factory-installed. No adjustments are required.
Refrigerant Charge — Amount of refrigerant charge is
listed on unit nameplate (also refer to Tables 1A and 1B). Refer
to Carrier GTAC 2-5 Charging, Recovery, recycling, and recla-
mation training manual and the following procedures.
Unit panels must be in place when unit is operating during
charging procedure.
NO CHARGE — Use standard evacuating techniques. After
evacuating system, weigh in the specified amount of refriger-
ant (refer to Tables 1A and 1B).
LOW CHARGE COOLING — Using the Cooling Charging
Charts, Fig. 49-51 vary refrigerant until the conditions of the
appropriate chart are met. Note the charging charts are differ-
ent from the type normally used. The charts are based on
charging the units to the correct superheat for the various oper-
ating conditions. Accurate pressure gage and temperature sens-
ing device are required. Connect the pressure gage to the
service port on the suction line. Mount the temperature sensing
device on the suction line and insulate it so that outdoor ambi-
ent temperature does not affect the reading. Indoor-air cfm
must be within the normal operating range of the unit.
TO USE COOLING CHARGING CHARTS — Take the out-
door ambient temperature and read the suction pressure gage.
Refer to appropriate chart to determine what suction tempera-
ture should be. If suction temperature is high, add refrigerant.
If suction temperature is low, carefully reclaim some of the
charge. Recheck the suction pressure as charge is adjusted.
Example (Fig. 51, Circuit 1):
Outdoor Temperature. . . . . . . . . . . . . . . . . . . . . . . . .13 C (55 F)
Suction Pressure. . . . . . . . . . . . . . . . . . . . . . . .483 kPa (70 psig)
Suction Temperature should be. . . . . . . . . . . . . . . . .23 C (74 F)
(Suction temperature may vary ± 3 C [5 F].)
Fig. 45 — Cleaning Condenser Coil
Fig. 46 — Propping Up Top Panel
Fig. 47 — Separating Coil Sections
Fig. 48 — Condenser-Fan Adjustment
48TF UNIT VOLTAGE FAN HEIGHT “A” (in.)
400 V 89 (3.50)

38
Fig. 49 — Cooling Charging Charts, 48TF008 Units
Fig. 50 — Cooling Charging Charts, 48TF012 Units

39
Flue Gas Passageways — To inspect the flue collec-
tor box and upper areas of the heat exchanger:
1. Remove the combustion blower wheel and motor assem-
bly according to directions in Combustion-Air Blower
section below.
2. Remove the flue cover to inspect the heat exchanger.
3. Clean all surfaces as required using a wire brush.
Combustion-Air Blower — Clean periodically to as-
sure proper airflow and heating efficiency. Inspect blower
wheel every fall and periodically during heating season. For the
first heating season, inspect blower wheel bimonthly to deter-
mine proper cleaning frequency.
To inspect blower wheel, shine a flashlight into draft hood
opening. If cleaning is required, remove motor and wheel as
follows:
1. Slide burner access panel out.
2. Remove the 6 screws that attach induced-draft motor
housing to vestibule plate (Fig. 52).
3. The blower wheel can be cleaned at this point. If addi-
tional cleaning is required, continue with Steps 4 and 5.
4. To remove blower from the motor shaft, remove
2 setscrews.
5. To remove motor, remove the 4 screws that hold blower
housing to mounting plate. Remove the motor cooling fan
by removing one setscrew. Then remove nuts that hold
motor to mounting plate.
6. To reinstall, reverse the procedure outlined above.
Limit Switch — Remove blower access panel (Fig. 6).
Limit switch is located on the fan deck.
Burner Ignition — Unit is equipped with a direct spark
ignition 100% lockout system. Integrated Gas Unit Controller
(IGC) is located in the control box (Fig. 11). Module contains a
self-diagnostic LED (light-emitting diode). A single LED on
the IGC provides a visual display of operational or sequential
problems when the power supply is interrupted. When a break
in power occurs, the module will be reset (resulting in a loss of
fault history) and the indoor (evaporator) fan ON/OFF times
will be reset. For additional information, refer to the Start-Up,
Heating section on page 34. The LED error code can be ob-
served through the viewport. During servicing refer to the label
on the control box cover or Table 25 for an explanation of LED
error code descriptions.
If lockout occurs, unit may be adjusted by interrupting pow-
er supply to unit for at least 5 seconds.
Table 25 — LED Error Code Description*
LEGEND
*A 3-second pause exists between LED error code flashes. If more
than one error code exists, all applicable codes will be displayed in
numerical sequence.
†Indicates a code that is not an error. The unit will continue to oper-
ate when this code is displayed.
**Indicates internal processor fault and will reset itself in 1 hour.
LED INDICATION ERROR CODE DESCRIPTION
ON Normal Operation
OFF Hardware Failure
1 Flash†Evaporator Fan On/Off Delay Modified
2 Flashes Limit Switch Fault
3 Flashes Flame Sense Fault
4 Flashes 4 Consecutive Limit Switch Faults
5 Flashes Ignition Lockout Fault
6 Flashes Induced-Draft Motor Fault
7 Flashes Rollout Switch Fault
8 Flashes Internal Control Fault
9 Flashes** Temporary 1 hour automatic reset fault
LED —Light-Emitting Diode
IMPORTANT: Refer to Troubleshooting Tables 26-30 for addi-
tional information.
CIRCUIT NO. 2
CIRCUIT NO. 1
Fig. 51 — Cooling Charging Chart; 48TF014 Units

40
Main Burners — At the beginning of each heating sea-
son, inspect for deterioration, blockage due to corrosion or oth-
er causes. Observe the main burner flames and replace burners
if necessary.
REMOVAL AND REPLACEMENT OF GAS TRAIN
(Fig. 52 and 53)
1. Shut off manual gas valve.
2. Shut off power to unit and tag disconnect.
3. Slide out burner section side panel (not shown).
4. Disconnect gas piping at unit gas valve.
5. Remove wires connected to gas valve. Mark each wire.
6. Remove wires from ignitor and sensor wires at the Inte-
grated Gas Unit Controller (IGC).
7. Remove the 2 screws that attach the burner rack to the
vestibule plate.
8. Slide the burner tray out of the unit (Fig. 53).
9. To reinstall, reverse the procedure outlined above.
CLEANING AND ADJUSTMENT
1. Remove burner rack from unit as described in Removal
and Replacement of Gas Train section on this page.
2. Inspect burners; if dirty, remove burners from rack.
3. Using a soft brush, clean burners and cross-over port as
required.
4. Adjust spark gap. See Fig. 54.
5. Reinstall burners on rack.
6. Reinstall burner rack as described in Removal and Re-
placement of Gas Train section.
Replacement Parts — A complete list of replacement
parts may be obtained from any Carrier distributor upon
request.
When working on gas train, do not hit or plug orifice
spuds.
INDUCED-
DRAFT
MOTOR
MOUNTING
PLATE
INDUCED-
DRAFT
MOTOR
MANIFOLD
PRESSURE
TAP
VESTIBULE
PLATE
FLUE
EXHAUST
ROLLOUT
SWITCH
BLOWER
HOUSING
GAS
VALVE
BURNER
SECTION
Fig. 52 — Burner Section Details
Fig. 53 — Burner Tray Details

41
NOTE: Dimensions in ( ) are millimeters.
Fig. 54 — Spark Gap Adjustment
48TFD008
31.4/21.1 kW INPUT (107,000/72,000 BTUH)
48TFE008, 48TFD012
50.4/31.9 kW INPUT/ (172,000/109,000 BTUH)
48TFD014, 48TFE012, 48TFF008
59.8/39.8 kW INPUT
(204,000/136,000 BTUH)
48TFE014, 48TFF012
65.6/43.9 kW INPUT
(224,000/150,000 BTUH)

42
TROUBLESHOOTING
Table 26 — LED Error Code Service Analysis
LEGEND
PROBLEM CAUSE REMEDY
Hardware failure.
(LED OFF)
Loss of power to control module (IGC). Check 5- amp fuse on IGC, power to unit, 24-v circuit breaker,
and transformer. Units without a 24-v circuit breaker have an
internal overload in the 24-v transformer. If the overload trips,
allow 10 minutes for automatic reset.
Limit switch fault.
(LED 2 flashes)
High temperature limit switch is open. Check the operation of the indoor (evaporator) fan motor.
Ensure that the supply-air temperature rise is in accordance with
the range on the unit nameplate.
Flame sense fault.
(LED 3 flashes)
The IGC sensed flame that should not be
present.
Reset unit. If problem persists, replace control board.
4 consecutive limit switch trips.
(LED 4 flashes)
Inadequate airflow to unit. Check operation of indoor (evaporator) fan motor and that supply-air
temperature rise agrees with range on unit nameplate information.
Ignition lockout.
(LED 5 flashes)
Unit unsuccessfully attempted ignition for
15 minutes.
Check ignitor and flame sensor electrode spacing, gaps, etc.
Ensure that flame sense and ignition wires are properly termi-
nated. Verify that unit is obtaining proper amount of gas.
Induced-draft motor fault.
(LED 6 flashes)
IGC does not sense that induced-draft
motor is operating.
Check for proper voltage. If motor is operating, check the
speed sensor plug/IGC Terminal J2 connection. Proper
connection: PIN 1— White, PIN 2 — Red, PIN 3 — Black.
Rollout switch fault.
(LED 7 flashes)
Rollout switch has opened. Rollout switch will automatically reset, but IGC will continue to
lock out unit. Check gas valve operation. Ensure that induced-
draft blower wheel is properly secured to motor shaft. Reset unit
at unit disconnect.
Internal control fault.
(LED 8 flashes)
Microprocessor has sensed an error in
the software or hardware.
If error code is not cleared by resetting unit power, replace the
IGC.
Temporary 1 hour automatic reset
fault. (LED 9 flashes)
Stray radio frequency signals in ?? Processor will be reset after 1 hour.
IGC —Integrated Gas Unit Controller
LED —Light-Emitting Diode
If the IGC must be replaced, be sure to ground yourself to dissi-
pate any electrical charge that may be present before handling
new control board. The IGC is sensitive to static electricity and
may be damaged if the necessary precautions are not taken.
IMPORTANT: Refer to Table 28 — Heating Service Trouble-
shooting for additional troubleshooting information.

43
Table 27 — Cooling Service Troubleshooting
PROBLEM CAUSE REMEDY
Compressor and
condenser fan
will not start.
Power failure. Call power company.
Fuse blown or circuit breaker tripped. Replace fuse or reset circuit breaker.
Defective thermostat, contactor, transformer,
or control relay.
Replace component.
Insufficient line voltage. Determine cause and correct.
Incorrect or faulty wiring. Check wiring diagram and rewire correctly.
Thermostat setting too high. Lower thermostat setting below room temperature.
Compressor will not start
but condenser fan runs.
Faulty wiring or loose connections in com-
pressor circuit.
Check wiring and repair or replace.
Compressor motor burned out, seized, or
internal overload open.
Determine cause. Replace compressor.
Defective run/start capacitor, overload, or
start relay.
Determine cause and replace.
One leg of 3-phase power dead. Replace fuse or reset circuit breaker. Determine
cause.
Compressor cycles (other than
normally satisfying thermostat).
Refrigerant overcharge or undercharge. Recover refrigerant, evacuate system, and
recharge to nameplate.
Defective compressor. Replace and determine cause.
Insufficient line voltage. Determine cause and correct.
Blocked condenser. Determine cause and correct.
Defective run/start capacitor, overload, or
start relay.
Determine cause and replace.
Defective thermostat. Replace thermostat.
Faulty condenser-fan motor or capacitor. Replace.
Restriction in refrigerant system. Locate restriction and remove.
Compressor operates continuously. Dirty air filter. Replace filter.
Unit undersized for load. Decrease load or increase unit size.
Thermostat set too low. Reset thermostat.
Low refrigerant charge. Locate leak, repair, and recharge.
Leaking valves in compressor. Replace compressor.
Air in system. Recover refrigerant, evacuate system, and
recharge.
Condenser coil dirty or restricted. Clean coil or remove restriction.
Excessive head pressure. Dirty air filter. Replace filter.
Dirty condenser coil. Clean coil.
Refrigerant overcharged. Remove excess refrigerant.
Air in system. Recover refrigerant, evacuate system, and
recharge.
Condenser air restricted or air short-cycling. Determine cause and correct.
Head pressure too low. Low refrigerant charge. Check for leaks, repair, and recharge.
Compressor valves leaking. Replace compressor.
Restriction in liquid tube. Remove restriction.
Excessive suction pressure. High heat load. Check for source and eliminate.
Compressor valves leaking. Replace compressor.
Refrigerant overcharged. Recover excess refrigerant.
Suction pressure too low. Dirty air filter. Replace filter.
Low refrigerant charge. Check for leaks, repair, and recharge.
Metering device or low side restricted. Remove source of restriction.
Insufficient evaporator airflow. Increase air quantity. Check filter and replace if
necessary.
Temperature too low in conditioned area. Reset thermostat.
Field-installed filter drier restricted. Replace.
Compressor no. 2 will not run. Unit in economizer mode. Proper operation; no remedy necessary.
Compressor makes excessive
noise (48TF014 scroll only).
Compressor rotating in wrong direction. Reverse the 3-phase power load as described in
Start-Up, Compressor Rotation section on
page 34.

44
Table 28 — Heating Service Troubleshooting
Table 29 — EconoMi$er Troubleshooting
LEGEND
PROBLEM CAUSE REMEDY
Burners will not
ignite.
Misaligned spark electrodes. Check flame ignition and sensor electrode positioning.
Adjust as needed.
No gas at main burners. Check gas line for air purge as necessary. After purging
gas line of air, allow gas to dissipate for at least 5 minutes
before attempting to relight unit.
Check gas valve.
Water in gas line. Drain water and install drip leg to trap water.
No power to furnace. Check power supply, fuses, wiring, and circuit breaker.
No 24 v power supply to control circuit. Check transformer. Transformers with internal overcurrent
protection require a cool down period before resetting.
Miswired or loose connections. Check all wiring and wirenut connections.
Burned-out heat anticipator in thermostat. Replace thermostat.
Broken thermostat wires. Run continuity check. Replace wires, if necessary.
Inadequate heating. Dirty air filter. Clean or replace filter as necessary.
Gas input to unit too low. Check gas pressure at manifold. Clock gas meter for input. If too
low, increase manifold pressure, or replace with correct orifices.
Unit undersized for application. Replace with proper unit or add additional unit.
Restricted airflow. Clean filter, replace filter, or remove any restrictions.
Blower speed too low. Use high speed tap, increase fan speed, or install optional
blower, as suitable for individual units.
Limit switch cycles main burners. Check rotation of blower, thermostat heat anticipator settings,
and temperature rise of unit. Adjust as needed.
Too much outdoor air. Adjust minimum position.
Check economizer operation.
Poor flame
characteristics.
Incomplete combustion (lack of Check all screws around flue outlets and burner compartment.
combustion air) results in: Tighten as necessary.
Aldehyde odors, CO, sooting flame, or floating flame. Cracked heat exchanger.
Overfired unit — reduce input, change orifices, or adjust
gas line or manifold pressure.
Check vent for restriction. Clean as necessary.
Check orifice to burner alignment.
Burners will not Unit is locked into Heating mode for a Wait until mandatory one minute time period has
turn off. one minute minimum. elapsed or power to unit.
PROBLEM POTENTIAL CAUSE REMEDY
Damper Does Not
Open
Indoor (Evaporator) Fan is Off Check to ensure that 24 vac is present at Terminal C1 (Common Power)
on the IFC (Indoor [Evaporator] Fan Contactor) or that 24 vac is present at
the IFO (Indoor [Evaporator] Fan On) terminal. Check whether 24 vac is
present at PL6-1 (red wire) and/or PL6-3 (black wire). If 24 vac is not
present, check wiring (see unit label diagram).
Check proper thermostat connection to G on the connection board.
No Power to EconoMi$er Controller Check to ensure that 24 vac is present across Terminals 24 VAC and
24 V COM on the EconoMi$er control. If 24 vac is not present, check wiring
(see unit label diagram). If 24 vac is present, STATUS light should be on
constantly.
No Power to G Terminal If IFM is on, check to ensure 24 vac is present on G Terminal of the
EconoMi$er controller. If 24 vac is not present, check wiring (see unit
label diagram).
Controller Fault If STATUS light is flashing one flash, the EconoMi$er controller is
experiencing a fault condition. Cycle power to the controller. If condition
continues, replace the EconoMi$er controller.
Thermostat Fault If STATUS light is flashing two flashes, the EconoMi$er controller senses
the thermostat is wired incorrectly. Check wiring between the thermostat
and the connection board in the electrical panel. The fault condition is
caused by Y2 being energized before Y1.
Actuator Fault Check the wiring between the EconoMi$er controller and the actuator.
Hold CONFIG button between 3 and 10 seconds to verify the
actuator’s operation. (This process takes 3 minutes to complete.)
EconoMi$er
Operation Limited to
Minimum Position
Minimum Position Set Incorrectly Verify that the MIN POS (%) is set greater than zero. Adjust MIN POS (%)
to 100% to verify operation, and then set to correct setting.
EconoMi$er Changeover Set Point Set Too
High or Too Low
Set at correct value. See Table 4.
Supply Air Temperature Sensor Faulty If STATUS light is flashing 4 flashes, Supply Air Temperature Sensor is
faulty. Check wiring or replace sensor.
Outdoor Air Temperature Sensor Faulty If STATUS light is flashing 5 flashes, Outdoor Air Temperature Sensor is
faulty. Check wiring or replace sensor.
Damper Position
Less than Minimum
Position Set Point
Supply Air Low Limit Strategy Controlling The supply-air temperature is less than 7 C (45 F), causing the minimum
position to be decreased. Refer to the Start-Up instructions. Verify correct
setting of MIN POS (%). If correct, EconoMi$er is operating correctly.
Damper Does Not
Return to Minimum
Position
CO2 Ventilation Strategy Controlling If a CO2 sensor is being used, and the damper position is greater than
minimum position, the ventilation control strategy is controlling. Refer to
the Start-Up instructions. EconoMi$er is operating correctly.
Damper Does Not
Close on Power Loss
Damper Travel is Restricted Check to ensure the damper is not blocked.
IFM —Indoor Fan Motor
PL —Plug

45
Table 30 — Durablade Economizer Troubleshooting
LEGEND
PROBLEM CAUSE REMEDY
Damper does not
open.
Indoor (evaporator) fan is off. 1. Check to ensure that 24 vac is present at terminal C1 on the IFC or
that 24 vac is present at the IFO terminal. Check whether 24 vac is
present at PL6-1 (red wire) and/or PL6-3 (black wire). If 24 vac is
not present, check wiring (see unit label diagram).
2. Check proper thermostat connection to G on the connection board.
No power to economizer motor. 1. Check that SW3 is properly making contact with the damper
blade. Check that SW1 is in the NC (normally closed) position.
2. Check diode D1. If diode is not functioning properly, replace D1.
3. Confirm that the economizer control board is grounded properly at
PL6-4 (brown wire) and at brown terminal of the economizer control
board (brown wire). The economizer motor must also be grounded
properly at the negative motor terminal (brown wire).
4. Verify SW1 and SW3 are working and wired properly (see unit label
diagram).
5. Check for 24 vac input at both PL6-1 (red wire) and PL6-3 (black
wire). If 24 vac not present, check unit wiring (see unit label dia-
gram). If 24 vac is found in both places, check for 24 vac at the
yellow terminal of the economizer control board (yellow wire). If
24 vac power is not present, replace the economizer control board.
Economizer motor failure. If the indoor (evaporator) fan and economizer motor are energized,
verify that there is a minimum of 18 vdc at the positive motor
terminal. If the motor is not operating, replace the motor.
Economizer
operation
limited to minimum
position.
OAT or EC set too high. 1. Set at correct temperature (1.7 C [3 F] below indoor space
temperature).
2. Check OAT or EC by setting above outdoor temperature or humidity
level. If the OAT or EC switches do not close, replace OAT or EC.
Verify economizer control board is
correctly wired and works properly.
1. Perform the following tests when OAT or EC is closed, Y1 is called
for and damper is at minimum position. Confirm 24 vac on gray ter-
minal of the economizer control board (gray wire). If 24 vac is not
present, check wiring (see unit label diagram).
2. Verify that SW1 and SW3 are wired correctly and working properly
(see unit label diagram).
3. Check to ensure that 24 vac exists at PL6-2 (blue wire). If
24 vac is not present, check wiring (see unit wiring label diagram).
4. Check 24 vac output at PL6-10 (white wire). If 24 vac is not
present, replace economizer control board.
Check SAT. 1. After verifying that the OAT and EC settings and the economizer
control board wiring are correct, check to ensure that the 24 vac
terminal of the SAT has 24 vac (white wire). If OAT, EC, and control
board are functioning and wired properly and no 24 vac exists,
check wiring (see unit label diagram).
2. If supply-air temperature is greater than 14 C (57 F), 24 vac should
be found at terminal T2 on the SAT (pink wire). If 24 vac is not
present, replace SAT.
Damper does not
close.
Incorrect wiring of economizer. 1. Verify that SW2 and SW4 are wired and working properly (see unit
label diagram).
2. Check diode D2. If diode is not functioning properly, replace D2.
Verify economizer control board is
functioning properly.
1. After verifying that the wiring is correct, modulate the damper to the
minimum position. Remove the call for G (evaporator fan).
2. If the damper does not move, check for 24 vac at PL6-1 (red wire).
If 24 vac is not present, check wiring (see unit label diagram).
3. If damper still does not move, check for 24 vac at blue terminal of
economizer control board (blue wire). If 24 vac is not present,
replace the economizer circuit board.
Check SAT. 1. After verifying that the wiring is correct and the economizer control
board is functioning properly, place the OAT or EC switch in the
closed position. Place a call for Y1 and open the damper to the fully
open position. Confirm that the 24 vac terminal of the SAT has
24 vac (white wire). If 24 vac is not present, check wiring (see unit
label diagram).
2. If supply-air temperature is less than 11 C (52 F), 24 vac should be
found at terminal T1 on the SAT (violet wire). If 24 vac not found,
replace SAT.
Economizer motor failure. If economizer control board and SAT are functioning properly, verify
that there is a minimum of 18 vdc at the positive motor terminal. If a
minimum if 18 vdc is present and the motor is still not operating,
replace the motor.
Economizer damper
does not close on
power loss.
Verify that close-on-power-loss and
economizer control board are func-
tioning properly.
1. Check voltage potential across batteries. If lower than 14 vdc,
replace close-on-power-loss power supply (9-v alkaline batteries). It
is recommended that you check this emergency power supply on a
regular basis or whenever the filters are changed.
2. If the close-on-power-loss and economizer control board are func-
tioning properly, check for 14 vdc or higher at the blue terminal of
the economizer control board (blue wire) when power is discon-
nected from unit. If 14 vdc is not present, replace the control board.
C1 —Common Power OAT —Outdoor-Air Thermostat
EC —Enthalpy Control PL —Plug
IFC —Indoor (Evaporator) Fan Contactor SAT —Supply-Air Thermostat
IFO —Indoor (Evaporator) Fan On SW —Economizer Position Switch

Manufacturer reserves the right to discontinue, or change at any time, specifications or designs without notice and without incurring obligations.
Catalog No. 004-816 Printed in U.S.A. Form 48TF-C1SI Pg 46 1-01 Replaces: New
Book 1 4
Ta b 1 a 6 a
Copyright 2001 Carrier Corporation
Fig. 55 — Typical Unit Wiring Schematic
LEGEND
AHA —Adjustable Heat Anticipator
BR —Blower Relay
C—Contactor, Compressor
CAP —Capacitor
CB —Circuit Breaker
CC —Cooling Compensator
COMP —Compressor Motor
CR —Combustion Relay
D—Diode
EC —Enthalpy Control
ECON —Economizer
EPS —Emergency Power Supply
(9-Volt Battery)
EQUIP —Equipment
ER —Economizer Relay
FPT —Freeze-Up Protection Thermostat
FSS —Filter Status Sensor
GND —Ground
GVR —Gas Valve Relay
HPS —High-Pressure Switch
HS —Hall-Effect Sensor
I—Ignitor
IDM —Induced-Draft Motor
IFC —Indoor-Fan Contactor
IFM —Indoor Fan Motor
IGC —Integrated Gas Unit Controller
LPS —Low-Pressure Switch
LS —Limit Switch
MGV —Main Gas Valve
MTR —Motor
OAT —Outdoor-Air Thermostat
OFM —Outdoor-Fan Motor
P—Plug
PL —Plug Assembly
QT —Quadruple Terminal
R—Relay
RS —Rollout Switch
SAT —Supply-Air Thermostat
SEN —Sensor
SW1 —Switch Fully Open
SW2 —Switch Fully Closed
SW3 —Switch Min. Vent Position
SW4 —Switch Max. Vent Position
TC —Thermostat-Cooling
TH —Thermostat-Heating
TRAN —Transformer
Field Splice
Marked Wire
Terminal (Marked)
Terminal (Unmarked)
Terminal Block
Splice
Splice (Marked)
Factory Wiring
Field Control Wiring
Field Power Wiring
Accessory or Optional Wiring
To indicate common potential
only. Not to represent wiring.
NOTES:
1. If any of the original wire furnished must be replaced, it must be
replaced with Type 90 C wire or its equivalent.
2. Three-phase motors are protected under primary single phasing
conditions.
Thermostat: HH07AT170, 172, 174 and P272-2783
Subbase: HH93AZ176, 178 and P272-1882, 1883
3. Set heat anticipator for first stage at 0.14 amp, second stage at
0.2 amp, except for 008 low heat, set both first and second stage at
0.14 amp.
4. Use copper conductors only.

Manufacturer reserves the right to discontinue, or change at any time, specifications or designs without notice and without incurring obligations.
Catalog No. 004-816 Printed in U.S.A. Form 48TF-C1SI Pg CL-1 1-01 Replaces: New
Book 1 4
Ta b 1 a 6 a
Copyright 2001 Carrier Corporation
- - - - - - - - - - - - - - - - - - - - - - - - - - - - - - - - - - - - - - - - - - - - - - - - - - - - - - - - - - - - - - - - - - - - - - - - - - - - - - - - - - - - - - - - - - - - - - - - - - - - - - - - - - - - - - - - - - - - - - - - - - - - - - - - - - - - - - - - - - - - - - - - - - - - - - - - - - - - - - - - - - - - - - - - - - - - -- - - - - - - - - - - - - - - - - - - -
CUT ALONG DOTTED LINE CUT ALONG DOTTED LINE
START-UP CHECKLIST
(Remove and Store in Job File)
I. PRELIMINARY INFORMATION
MODEL NO.:________________________________ SERIAL NO.: ___________________________________
DATE:______________________________________ TECHNICIAN: __________________________________
JOB LOCATION: _______________________________
II. PRE-START-UP (insert checkmark in box as each item is completed)
VERIFY THAT ALL PACKING MATERIALS HAVE BEEN REMOVED FROM UNIT
REMOVE ALL SHIPPING HOLDDOWN BOLTS AND BRACKETS PER INSTALLATION INSTRUCTIONS
VERIFY THAT CONDENSATE CONNECTION IS INSTALLED PER INSTALLATION INSTRUCTIONS
CHECK ALL ELECTRICAL CONNECTIONS AND TERMINALS FOR TIGHTNESS
CHECK GAS PIPING FOR LEAKS
CHECK THAT INDOOR-AIR FILTERS ARE CLEAN AND IN PLACE
VERIFY THAT UNIT INSTALLATION IS LEVEL
CHECK FAN WHEELS AND PROPELLERS FOR LOCATION IN HOUSING/ORIFICE AND SETSCREW TIGHTNESS
AND DRIVE BELTS TENSION.
III. START-UP
ELECTRICAL
TEMPERATURES
PRESSURES
VERIFY REFRIGERANT CHARGE USING CHARGING TABLES
VERIFY THAT 3-PHASE SCROLL COMPRESSOR ROTATING IN CORRECT DIRECTION (014 ONLY)
SUPPLY VOLTAGE L1-L2 L2-L3 L3-L1
COMPRESSOR AMPS L1 L2 L3
COMPRESSOR AMPS L1 L2 L3
INDOOR-FAN AMPS L1 L2 L3
OUTDOOR-AIR TEMPERATURE DB
RETURN-AIR TEMPERATURE DB WB
COOLING SUPPLY AIR DB
GAS HEAT SUPPLY AIR DB
GAS INLET PRESSURE kPa (IN. WG)
GAS MANIFOLD PRESSURE kPa (IN. WG) (HI FIRE)
REFRIGERANT SUCTION Pa (PSIG) — CIRCUIT NO. 1
Pa (PSIG) — CIRCUIT NO. 2
REFRIGERANT DISCHARGE Pa (PSIG) — CIRCUIT NO. 1
Pa (PSIG) — CIRCUIT NO. 2