Cattron North America MKU915A Remote Transmitter User Manual MKU System Manual
Laird Controls North America Inc. Remote Transmitter MKU System Manual
Contents
- 1. manual
- 2. manual 2
manual 2
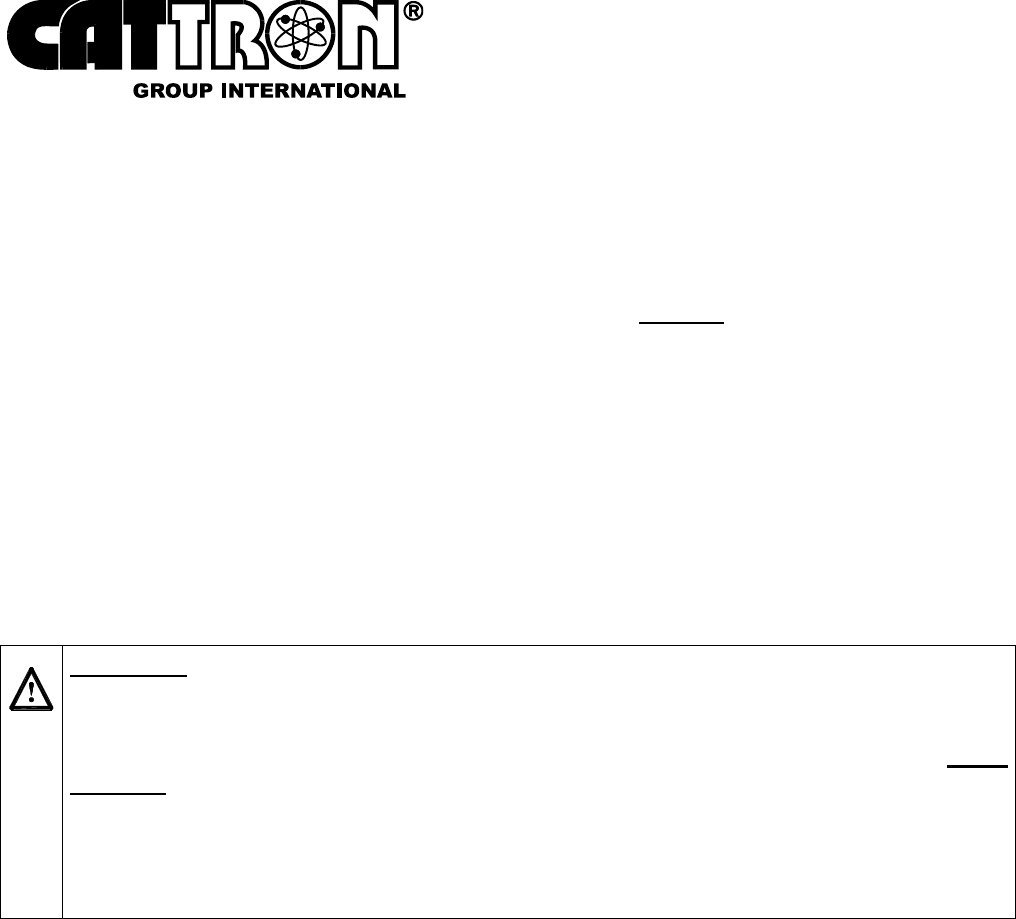
Page 34 Part # 68C-MKU, Edition 01/2007, Version 1.0
1. Insert the correct ‘TransKey’. This coded electronic key sets the unique operating
parameters for a given control system. These parameters include, address code,
operating frequency and function key (pushbutton) configurations. Note that an OCU
will not operate without a ‘TransKey’ installed.
NOTE: If your controller uses the bottom row of keypad switches for ‘ON’,
‘OFF’, and ‘STOP’ functions, proceed directly to step 5 of this
procedure.
2. Set red STOP Switch to ‘RUN’. Pulling this switch upward enables power to be
applied to the OCU. If the switch has been pushed down to the ‘STOP’ position, you
will first have to unlatch the switch knob by rotating in a clockwise direction.
3. Set ON/OFF Switch to ‘ON’. Rotating this switch clockwise applies power to the
OCU. If the multicolor STATUS LED illuminates green and two short beeps are
heard, the OCU is ready for use and a power up message has been sent to the
target MCU. The targeted MCU will respond by energizing the mainline contactor of
your controlled machine.
WARNING:
BEFORE ATTEMPTING TO USE THE REMOTE CONTROL SYSTEM, VERIFY THE
TARGET CRANE OR MACHINE YOU WISH TO OPERATE IS UNDER THE DIRECT
COMMAND OF YOUR OCU. THIS IS ACCOMPLISHED BY OPERATING A NON-
MOTION OCU FUNCTION SUCH AS A HORN OR LAMP AND OBSERVING THAT
THE RESPECTIVE FUNCTION ON THE TARGETED CRANE OR MACHINE
RESPONDS.
FAILURE TO IMPLEMENT THE ABOVE MAY RESULT IN PERSONAL INJURY OR
DEATH TO PERSONNEL AND DAMAGE TO EQUIPMENT.
4. Press a non-motion Function Key (pushbutton) such as a horn or lamp and
observe that the targeted crane or machine responds. The OCU is now fully
operational and transmitting a signal as indicated by the green ‘TRANSMIT’ LED
flashing. Operate the keypad control and auxiliary pushbuttons as required,
remembering that each pushbutton must be maintained in order for the function to
continue to operate. Any or all functions may be operated simultaneously if the
controlled machine permits such operation.
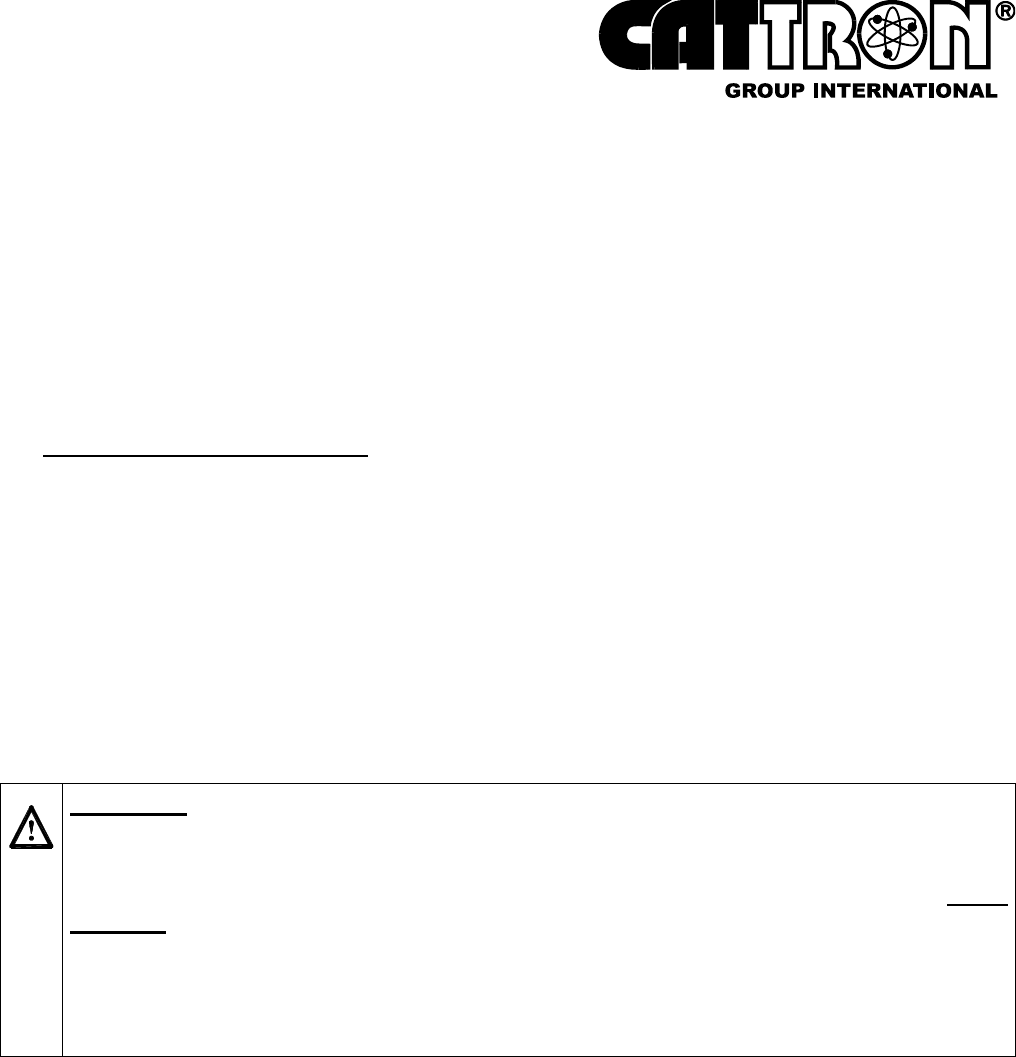
Part # 68C-MKU, Edition 01/2007, Version 1.0 Page 35
NOTES: A system STOP may be initiated at any time during the control function
by pushing the red STOP switch downwards. It should be further
noted that in “pitch and catch” control operations where two OCUs are
used, only the OCU that sets the ‘STOP’ condition will re-set the ‘RUN’
condition.
When all control functions have been completed, we recommend you
initiate a system STOP (push red STOP switch down) before setting the
ON/OFF switch to the ‘OFF’ position.
5. Alternative Power-up procedure using bottom row keypad switches:
Referring to Figure 15 overleaf:
a. Press the ‘ON’ keypad pushbutton once and observe the multicolor STATUS
LED illuminates red.
b. Press the ‘STOP’ keypad pushbutton once (1st & 2nd step) and observe the
multicolor STATUS LED illuminates orange.
c. Press the ‘ON’ keypad pushbutton once again and observe the multicolor
STATUS LED illuminates green..
NOTE: The above Power-up sequence must be completed within 10 seconds.
WARNING:
BEFORE ATTEMPTING TO USE THE REMOTE CONTROL SYSTEM, VERIFY THE
TARGET CRANE OR MACHINE YOU WISH TO OPERATE IS UNDER THE DIRECT
COMMAND OF YOUR OCU. THIS IS ACCOMPLISHED BY OPERATING A NON-
MOTION OCU FUNCTION SUCH AS A HORN OR LAMP AND OBSERVING THAT
THE RESPECTIVE FUNCTION ON THE TARGETED CRANE OR MACHINE
RESPONDS.
FAILURE TO IMPLEMENT THE ABOVE MAY RESULT IN PERSONAL INJURY OR
DEATH TO PERSONNEL AND DAMAGE TO EQUIPMENT.
6. Press a non-motion Function Key (pushbutton) such as a horn or lamp and
observe that the targeted crane or machine responds. The MKU controller is now
fully operational and transmitting a signal as indicated by the multicolor STATUS
LED flashing green. Operate the keypad control and auxiliary pushbuttons as
required, remembering that each pushbutton must be maintained in order for the
function to continue to operate. Any or all functions may be operated simultaneously
if the controlled machine permits such operation.
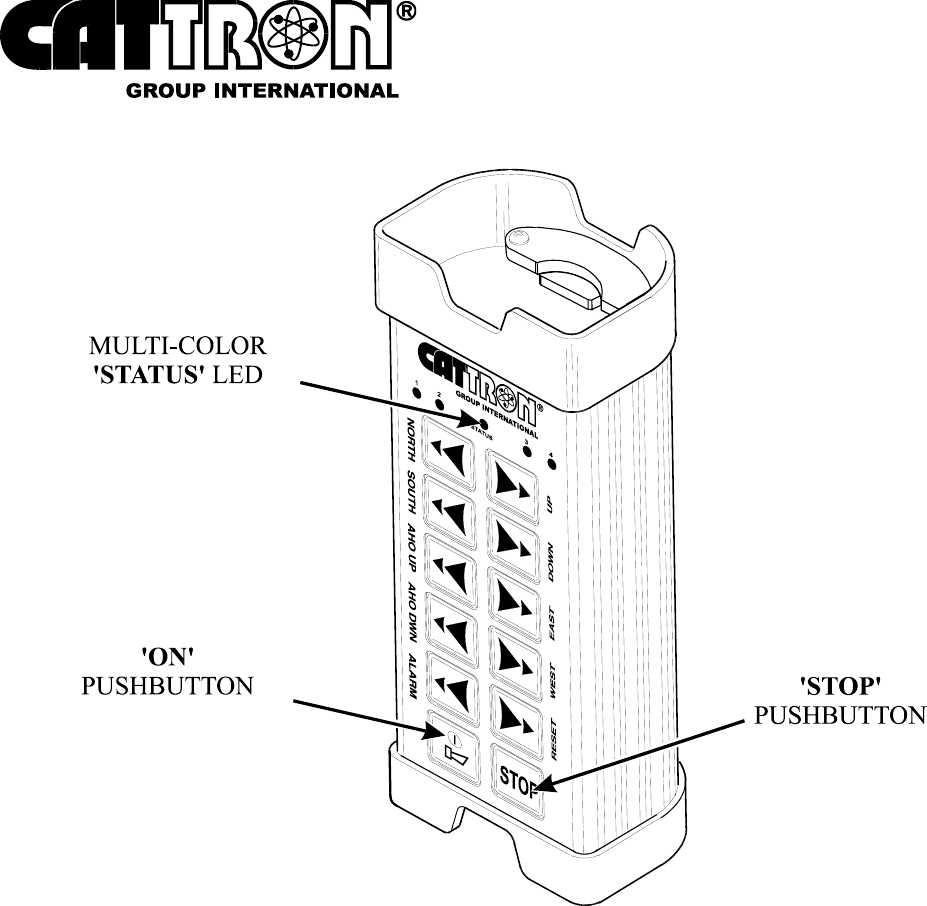
Page 36 Part # 68C-MKU, Edition 01/2007, Version 1.0
Figure 15. Alternative MKU Controller - Power-up using bottom row keypad switches
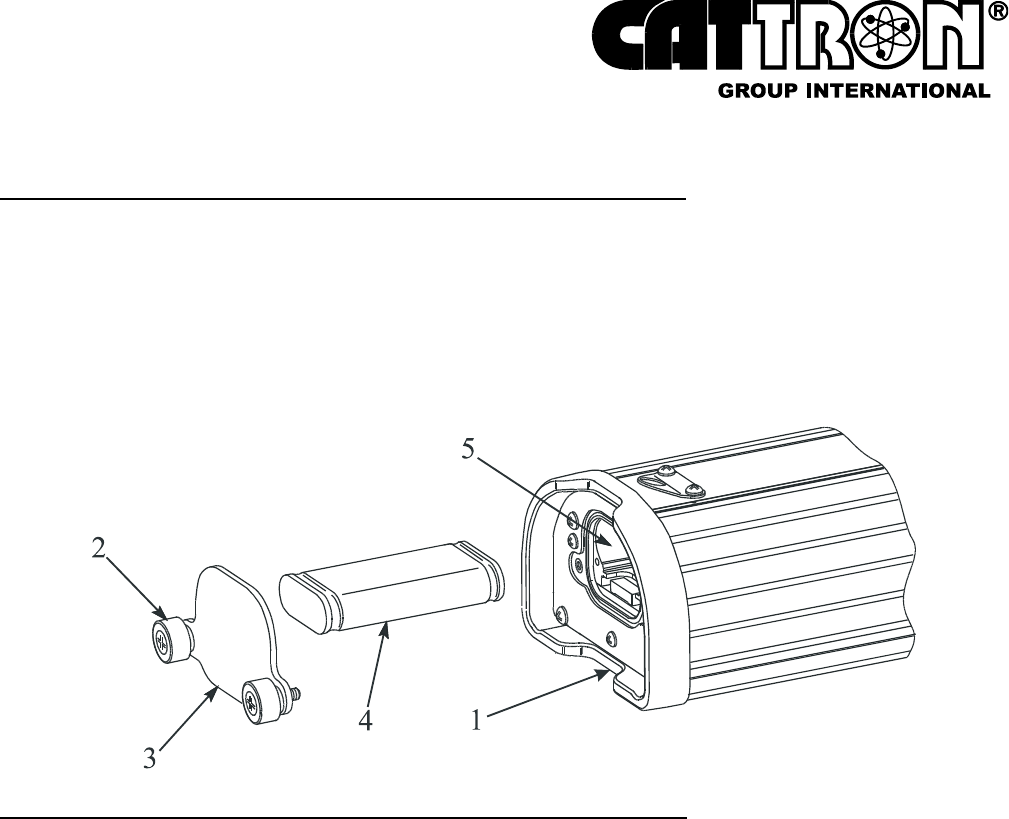
Part # 68C-MKU, Edition 01/2007, Version 1.0 Page 37
6.4 CHANGING THE BATTERY PACK
Referring to Figure 16 below, remove the battery pack as follows:
a. Lay MKU controller (1) face down.
b. Release two knurled thumbscrews (2) and withdraw cover-plate (3).
c. Withdraw battery pack (4) from battery compartment (5).
Figure 16. Battery Pack, removal and replacement
Referring to Figure 16 above, replace the battery pack as follows:
a. Position battery pack (4) with the four contact strips facing down and forwards.
Install battery pack (4) by pushing fully home inside the battery compartment (5).
b. Install cover-plate (3) and secure by evenly hand tightening two knurled
thumbscrews (2). Do not overtighten - a snug fit is all that is necessary.
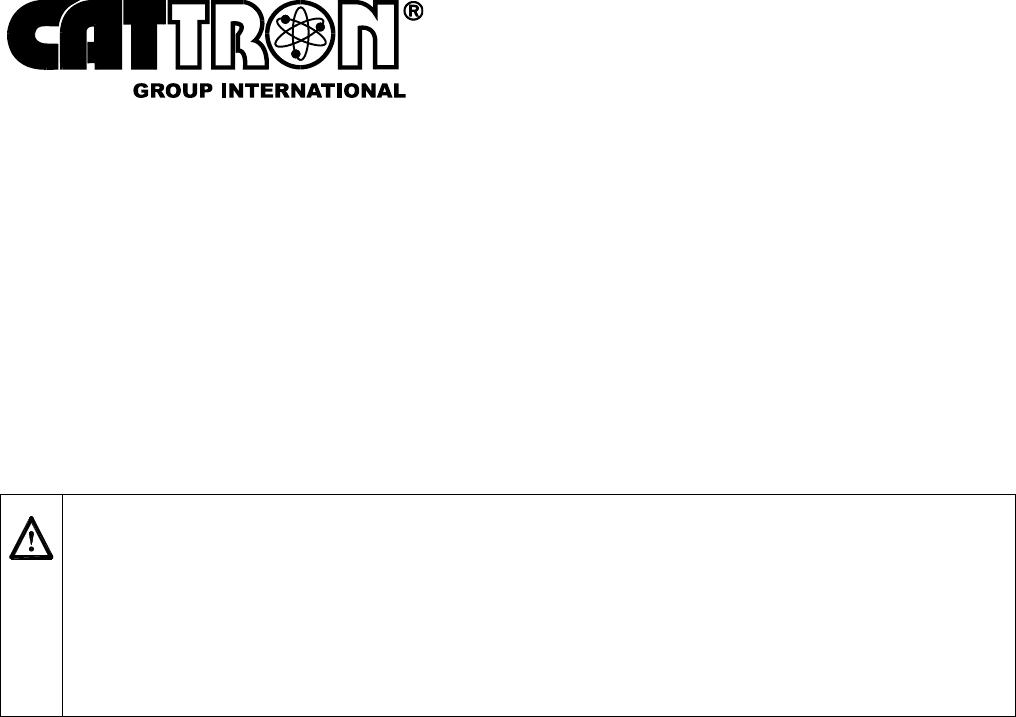
Page 38 Part # 68C-MKU, Edition 01/2007, Version 1.0
6.5 CHARGING THE BATTERY PACK
NOTES: Do not re-charge the battery pack until the OCU’s LED indicates
‘low battery’.
A CATTRON® External Battery Charging Unit (Part # 70C-0003) will
be required for battery charging or conditioning.
A CATTRON® ‘Standard’ Battery Charger (Part # 70C-0001) enables a Ni-Cad battery pack
to be charged within a period of 10 hours from a 110-120 VAC mains supply. Standard rate
chargers include a yellow LED to indicate charge mode.
A CATTRON® ‘state of the art’ Battery Conditioner (Part # 70C-0002) is also available for use
with Ni-Cad battery packs only. For details, refer to Battery Pack Conditioning, below.
CAUTIONS:
CATTRON® MKU Battery Conditioners and External Charging Units are designed
for use with CATTRON® Ni-Cad Battery Packs only.
Battery Packs must be removed or disconnected from Battery Conditioners/
External Charging Units within 48-hours of achieving the fully charged state.
Failure to comply with these Cautions may result in equipment and/or battery
damage and will void our warranty.
Battery Pack Charging: To charge a Ni-Cad Battery Pack, refer to Figure 17 opposite and
connect the CATTRON® Battery Charger to the mains power supply. Install the charging jack
to the external battery charging unit socket. Simply drop the battery pack into the battery
charging unit, ensuring the battery pack contacts are positioned as shown. When the Ni-Cad
battery pack is properly installed, the appropriate charging indicator on the connected battery
charger will illuminate.
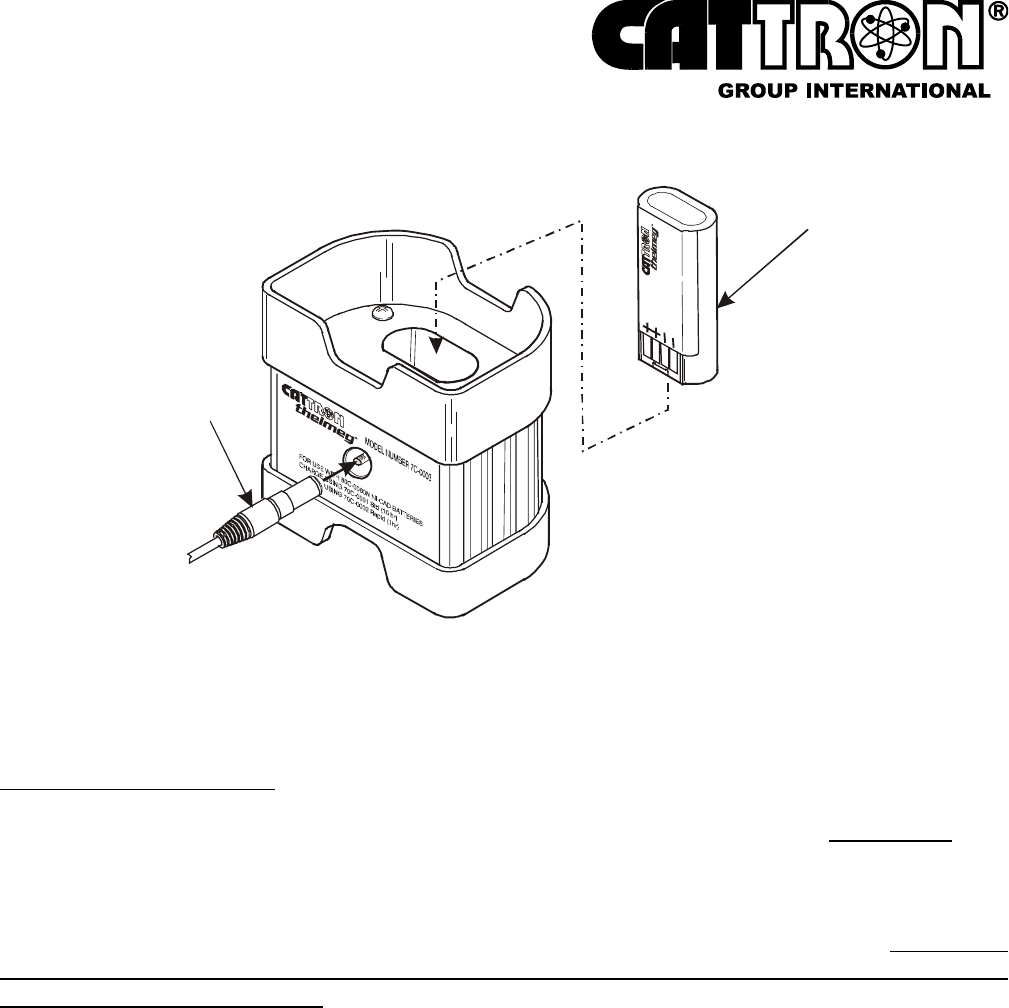
Part # 68C-MKU, Edition 01/2007, Version 1.0 Page 39
Figure 17. External Ni-Cad Battery Pack Charging
6.6 CONDITIONING THE BATTERY PACK
A ‘state of the art’ CATTRON® Battery Conditioner (Part # 70C-0002) is available for use with
Ni-Cad battery packs only.
The Battery Conditioner automatically conditions the battery pack by first discharging it at
750mA for 1.5 hours before applying a rapid charge for 1.2 hours. The conditioner
incorporates end of charge detection circuitry to accurately sense when the battery pack is fully
charged. When this condition has been detected, the conditioner switches to a ‘trickle’ mode
that keeps the battery pack fully charged and ready to use for up to 48-hours. To prevent
damage to the battery pack, it should be removed from the conditioner within 48-hours of
achieving a fully charged state.
The CATTRON® Battery Conditioner incorporates an LED that indicates status as follows:
Amber Color – indicates the battery pack is being discharged.
Red Color - indicates the battery pack is being charged at a rapid rate.
Green Color - indicates the battery pack is fully charged and that a ‘trickle’ charge is
being applied to maintain the fully charged state. The battery pack is ready for use and
should be removed from the conditioner within 48-hours.
CHARGING JACK
FROM BATTERY
CHARGER
NI-CAD BATTERY PACK ONLY
PART # 60C-0060N
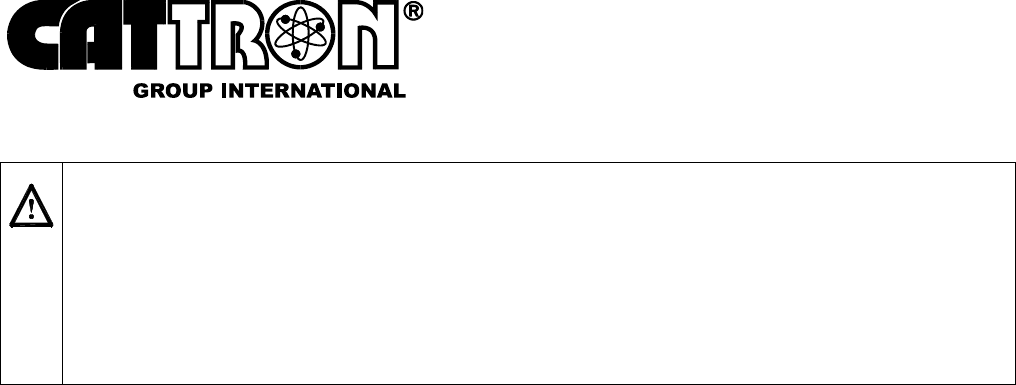
Page 40 Part # 68C-MKU, Edition 01/2007, Version 1.0
CAUTIONS:
CATTRON® MKU Battery Conditioners and External Charging Units are designed
for use with CATTRON® Ni-Cad Battery Packs only.
Battery Packs must be removed or disconnected from Battery Conditioners/
External Charging Units within 48-hours of achieving the fully charged state.
Failure to comply with these Cautions may result in equipment and/or battery
damage and will void our warranty.
The Battery Conditioner includes a Mains VAC Adaptor that enables the conditioner to operate
from mains supply voltages between 100 and 240 VAC @ 50/60 kHz. Referring to Figure 18
opposite, this adaptor is connected as shown. Similarly, when connecting the Battery
Conditioner to the External Battery Charging Unit, refer to Figure 18 for the appropriate
connections.
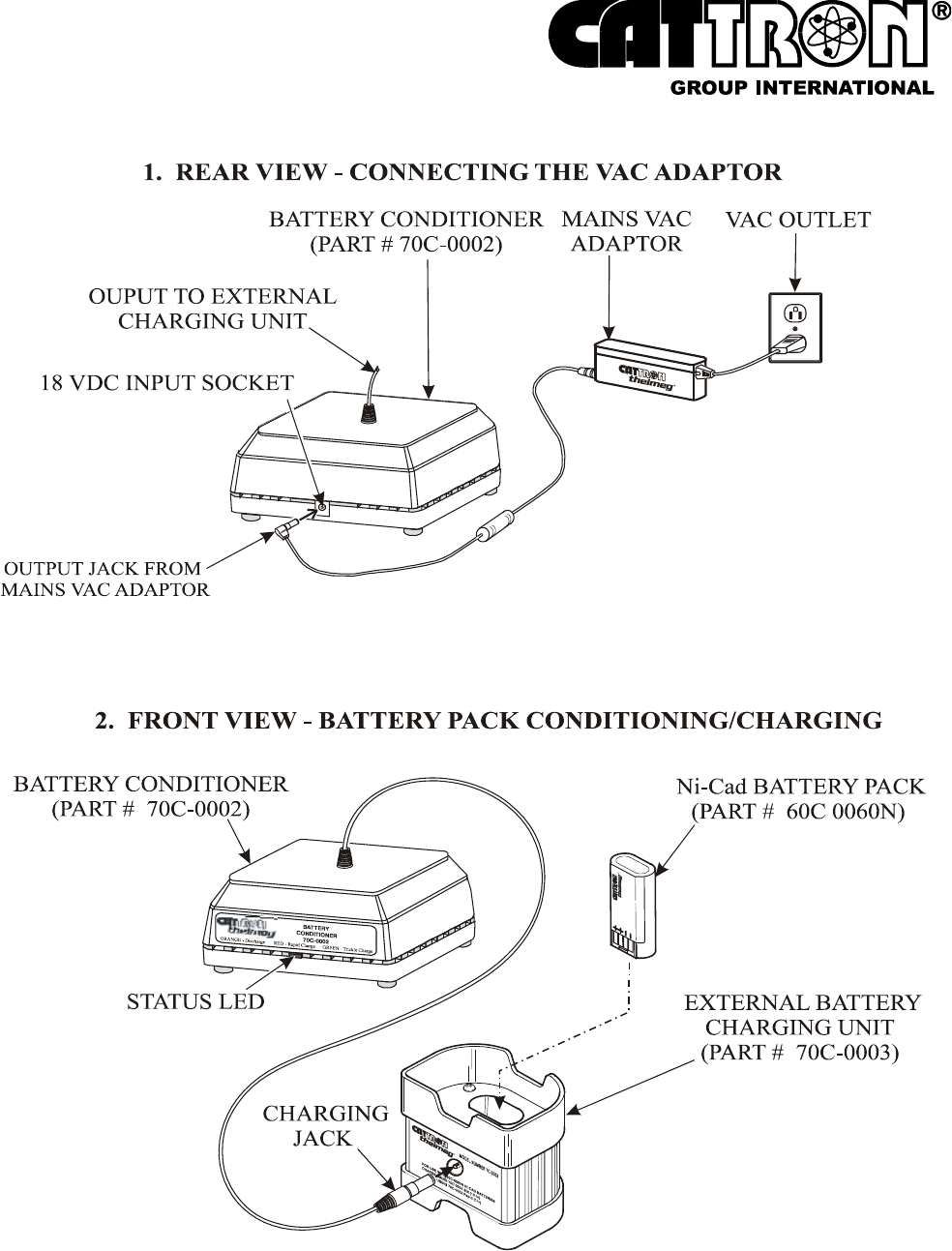
Part # 68C-MKU, Edition 01/2007, Version 1.0 Page 41
Figure 18. Battery Pack Conditioning – interconnection details
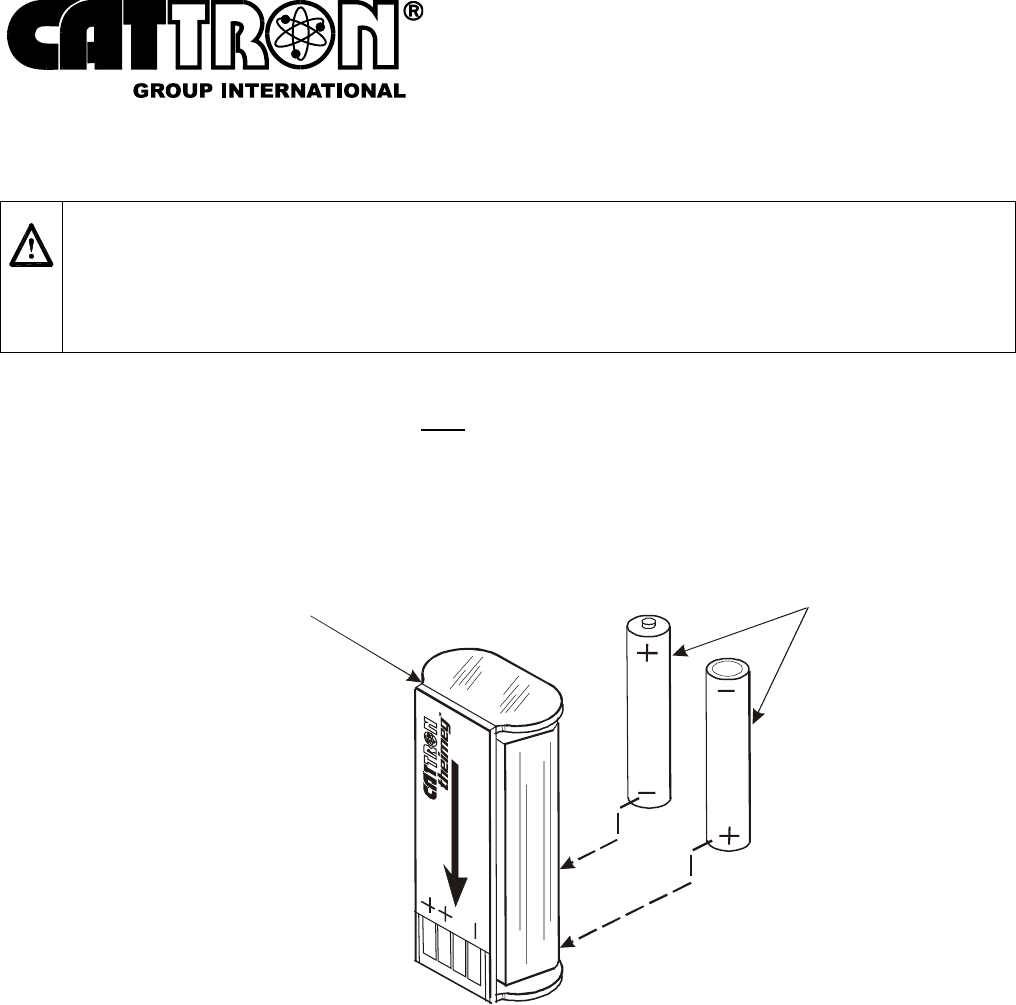
Page 42 Part # 68C-MKU, Edition 01/2007, Version 1.0
6.7 ALKALINE BATTERY ADAPTER
CAUTION:
CATTRON® MKU Battery Adapters are designed for use with non re-chargeable
‘AAA’ size Alkaline Batteries only. Carbon/Zinc, Lithium, or Ni-Cad Batteries are
not to be used with this adapter. Damage to batteries will occur if this adapter is
used for battery charging.
Referring to Figure 19 below, a CATTRON® Battery Adapter is available which will accept two
‘AAA’ size Alkaline 1.5-volt batteries only. It should be noted that when using ‘AAA’ size
Alkaline 1.5-volt batteries with this adapter, battery life will only be 40% of that provided by a
CATTRON® Alkaline Battery Pack.
Figure 19. ‘AAA’ Alkaline Battery Adapter
USE ‘AAA’ ALKALINE
BATTERIES ONLY
BATTERY ADAPTER, 3 VOLT
(QUANTITY 2 x ‘AAA’ SIZE)
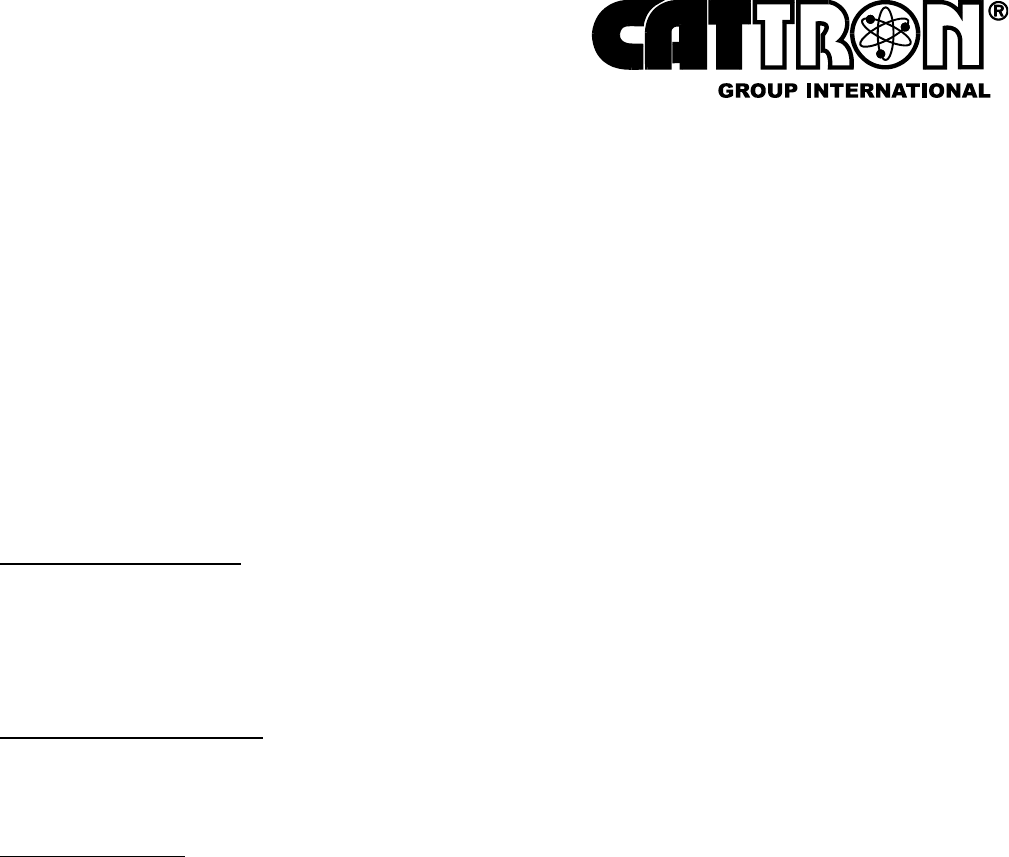
Part # 68C-MKU, Edition 01/2007, Version 1.0 Page 43
7 MAINTENANCE INSTRUCTIONS
Unless customer technicians have received formal maintenance training from CATTRON®, our
maintenance philosophy is that inoperative OCUs and MCUs be returned as complete units to
our workshops for repair. This is because each system has been customized at our factory for
a particular application, thus it is highly unlikely that two control systems will be the same.
NOTE: When returning an OCU for repair, the original 'TransKey' supplied
with the unit should be removed and retained for use with your spare
unit.
7.1 PREVENTIVE MAINTENANCE
Preventive maintenance for MKU systems is minimal because they are extremely durable and
reliable units. Preventive maintenance is limited to the following:
Daily Visual Inspection:
Before use, visually inspect the OCU and MCU for cleanliness, physical damage, and
security of external parts (screws, switches, rubber grips, etc.). CATTRON® emphasizes
that regular visual inspections not only mean quickly locating a source of potential
problems, but also may prevent serious problems from developing later.
Cleaning the Transmitter:
The OCU should be cleaned with a moist cloth (if necessary, with a little washing-up liquid),
then wiped dry with a clean paper towel. DO NOT IMMERSE THE OCU IN WATER.
Functional Check:
A functional check is accomplished by operating the OCU in accordance with the Operating
Procedures in Para. 6.3 on page 32 of this manual. Insure all system control functions are
fully operational.
7.2 TRANSMITTER FAULT MESSAGES
The OCU has a multicolor STATUS LED indicator that displays the current system status to
the operator. When an OCU fault is detected, the multicolor STATUS LED will illuminate red
and signal this with a series of blinks. Refer to Table 2 overleaf for the blink sequence and the
corresponding fault messages.
Note that any repairs or replacements should only be made by CATTRON® trained
technicians.
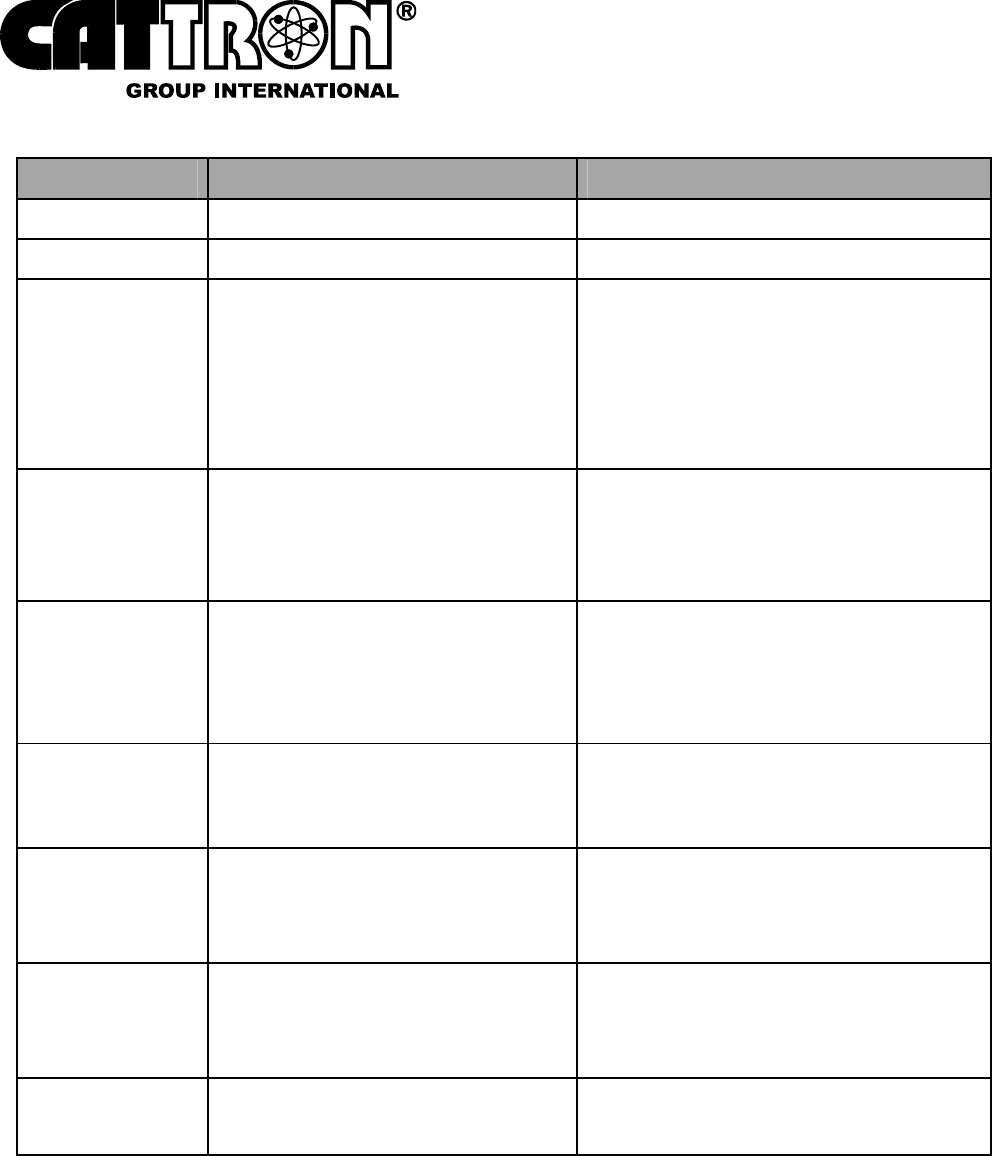
Page 44 Part # 68C-MKU, Edition 01/2007, Version 1.0
Table 2. OCU Fault Messages - multicolor STATUS LED
LED Indication Fault Action
2-flashes TransKey missing Plug in the Transkey
3-flashes TransKey cannot be read Check the Transkey configuration*
4-flashes Fault in the low-voltage test
during switch-on Switch the OCU off then on again.
Replace/Charge Battery Pack
If fault persists, investigate fault*
Change Transmitter board*
Return OCU for repair
5-flashes Switch-on sequence not
performed correctly Insure the STOP pushbutton is
released
Switch the OCU OFF then ON
again.
6-flashes Fault during reading of
command initiator
Investigate fault*
Change Transmitter
board/Keyboard*
Return OCU for repair
7-flashes Incorrect RF module or RF
module incorrectly configured Replace the RF module or correct
the configuration*
Return OCU for repair
8-flashes General system fault Investigate fault*
Change Transmitter board*
Return OCU for repair
9-flashes Low Power Supply voltage Replace/Charge Battery Pack
Change Transmitter board*
Return OCU for repair
10-flashes Hardware Fault Change Transmitter board*
Return OCU for repair
*CATTRON® customer trained technicians only. If necessary, contact the factory for the
replacement part number applicable to your system configuration - refer to the rear cover of
this manual for telephone numbers and e-mail addresses.
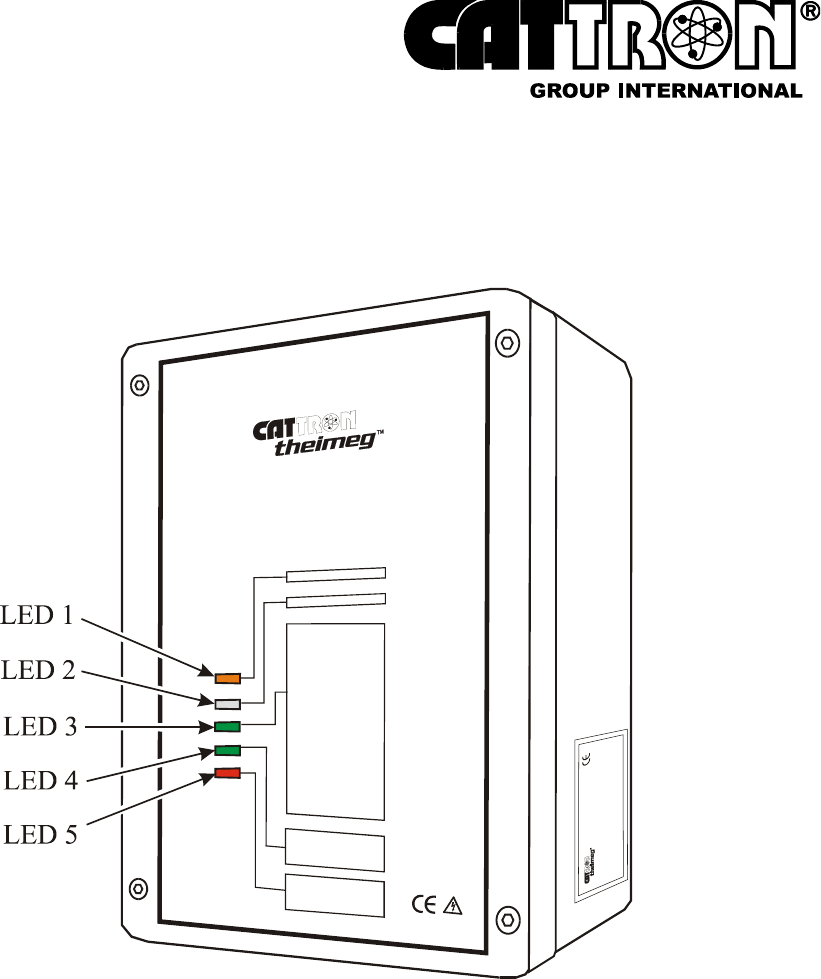
Part # 68C-MKU, Edition 01/2007, Version 1.0 Page 45
7.3 RECEIVER FAULT MESSAGES
The MCU has five externally visible LED indicators that display the current system status to the
operator. Referring to Figure 20 below and Table 3 overleaf, these are:
Figure 20. MCU System Status LEDs

Page 46 Part # 68C-MKU, Edition 01/2007, Version 1.0
Table 3. MCU External Status LEDs
LED Description
1. Power On Illuminates orange when the MCU receiver has voltage
2. Scan Mode
Not used when
system is
configured for fixed
frequency
Flashes red/orange in Scan Mode
3. RF Reception Illuminates green when valid data from the OCU is received and
both OPR relays are energized
Illuminates orange if valid data from the OCU is received and the
OPR relays are de-energized
Illuminates red if data from another OCU (with invalid address) is
received
4. Command Illuminates green when commands are received from the OCU
(normal condition)
5. Fault indication Blinks red when the MCU detects a fault (refer to Table 4 below
for the blink sequence and the corresponding fault messages).
Referring to Figure 21 below, an additional PROCESSOR FAULT LED indicator is mounted on
the MCU processor board and may be viewed by removing the MCU front cover.
Figure 21. MCU Status and Fault LEDs

Part # 68C-MKU, Edition 01/2007, Version 1.0 Page 47
The PROCESSOR FAULT LED blinks orange if the receiver does not detect a transmitter, and
green when valid RF Transmissions are received. If the processor detects a fault, it will signal
this by blinking in red. Refer to Table 4 below for the blink sequence and the corresponding
fault messages.
Note that any repairs or replacements should only be made by CATTRON® trained
technicians.
Table 4. MCU Fault Messages
LED Indication Fault Action
2-flashes TransKey missing Plug in the Transkey
3-flashes TransKey cannot be read Check the Transkey configuration*
4-flashes Fault in the low-voltage test
during switch-on Switch the MCU off then on again.
If fault persists, investigate fault*
Change Processor Board*
Return MCU for repair
5-flashes OPR relay fault Check the OPR Relay(s)*
Change the OPR Relay(s)*
Return MCU for repair
6-flashes Relay board fault Investigate fault*
Change Relay Motherboard*
Return MCU for repair
7-flashes Incorrect RF module or RF
module incorrectly configured Replace the RF module or correct
the configuration*
Return MCU for repair
8-flashes General system fault Investigate fault*
Change appropriate board*
Return MCU for repair
9-flashes Low Power Supply voltage Check power inputs and outputs*
Change appropriate board*
Return MCU for repair
10-flashes Processor fault Change Processor Board*
Return MCU for repair
*CATTRON® customer trained technicians only. If necessary, contact the factory for the
replacement part number applicable to your system configuration - refer to the rear cover of
this manual for telephone numbers and e-mail addresses.

Page 48 Part # 68C-MKU, Edition 01/2007, Version 1.0
8 ACCESSORIES AND CONSUMABLE ITEMS
Contact CATTRON® sales department for availability and pricing of the following accessories
and consumable items. These items are itemized in Table 5 below and illustrated on the
following pages.
Table 5. Optional Accessories
Item # Part Number Order
Quantity Item Description
1 60C-0060A 1 Battery pack, alkaline, non-rechargeable, 3-volt, 2,500
mAH
2 60C-0060N 1 Battery pack, Ni-Cad, re-chargeable, 2.4-volt, 1,100
mAH
3 42C-0066 1 Carrying Strap, Belt, loop, 2", nylon, black
4 70C-0001 1 Battery Charger, Ni-Cad, standard charge (10-hour),
110 VAC
5 70C-0002 1 Battery Conditioner, 100-240 VAC input
6 42C-0057 1 Carrying strap, shoulder
7 70C-0003 1 External Battery Charging Unit (use with items 2, 4, &
5)
8 60C-0062 1 Battery Adapter, 3-volt (for qty. 2 ‘AAA’ Alkaline
batteries only)
9 54C-0088A 1 Standard Label Kit, English Text*
10 54C-0088SPA 1 Special Label Kit, English Text*
*Non-English language text labels are available. Contact CATTRON® sales department for
details - refer to the rear cover of this manual for telephone numbers and e-mail addresses.

Part # 68C-MKU, Edition 01/2007, Version 1.0 Page 49
8.1 ACCESSORIES/CONSUMABLE ITEMS - ILLUSTRATIONS
White color
Item 1. Battery pack, alkaline, non-rechargeable, 3-volt, 2,500 mAH – Part # 60C-0060A
Yellow color
Item 2. Battery pack, Ni-Cad, re-chargeable, 2.4-volt, 1,100 mAH – Part # 60C-0060N
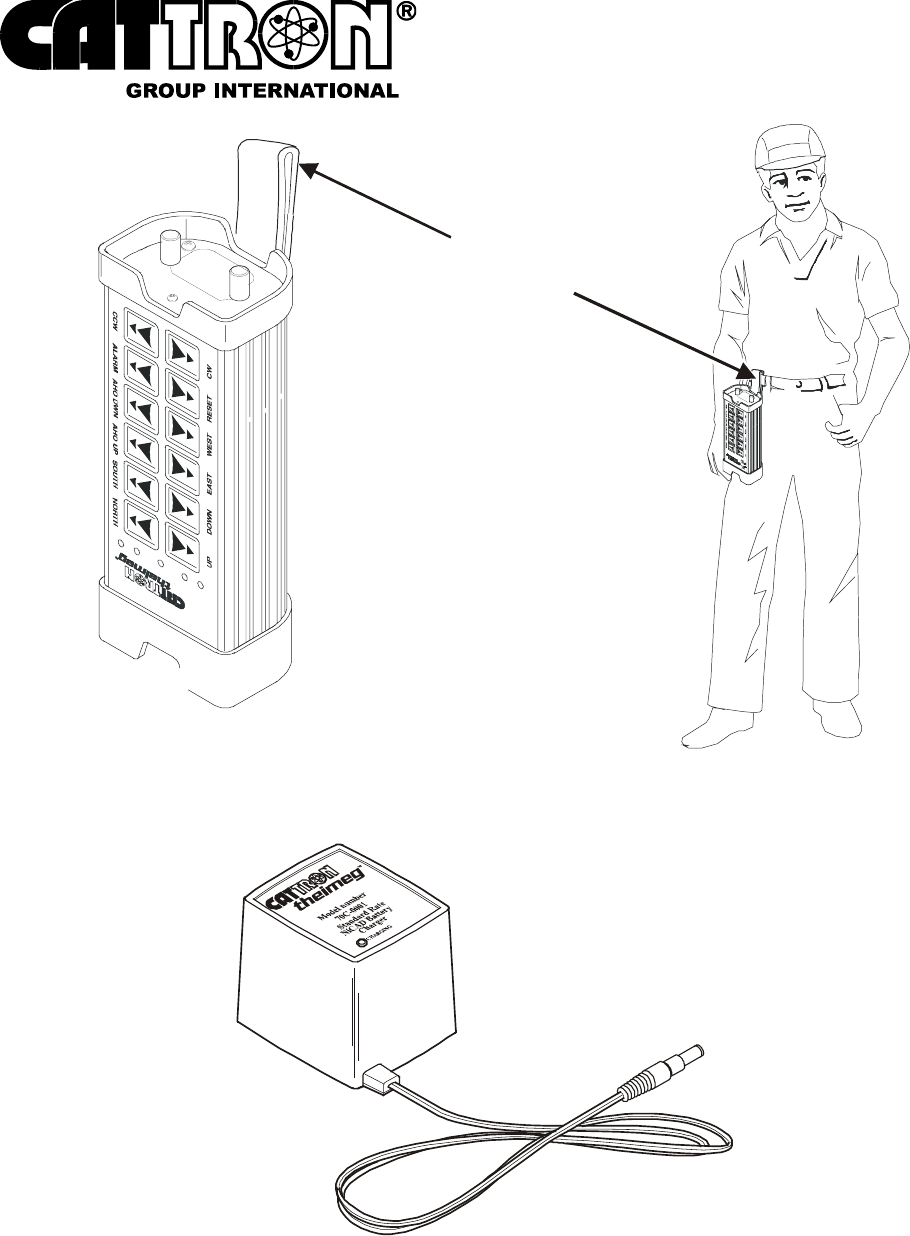
Page 50 Part # 68C-MKU, Edition 01/2007, Version 1.0
BELT LOOP STRAP
Item 3. Carrying strap, belt, loop, 2", nylon, black - Part # 42C-0066
Item 4. Battery Charger, Ni-Cad, standard charge (10-hour), 110 VAC - Part # 70C-0001
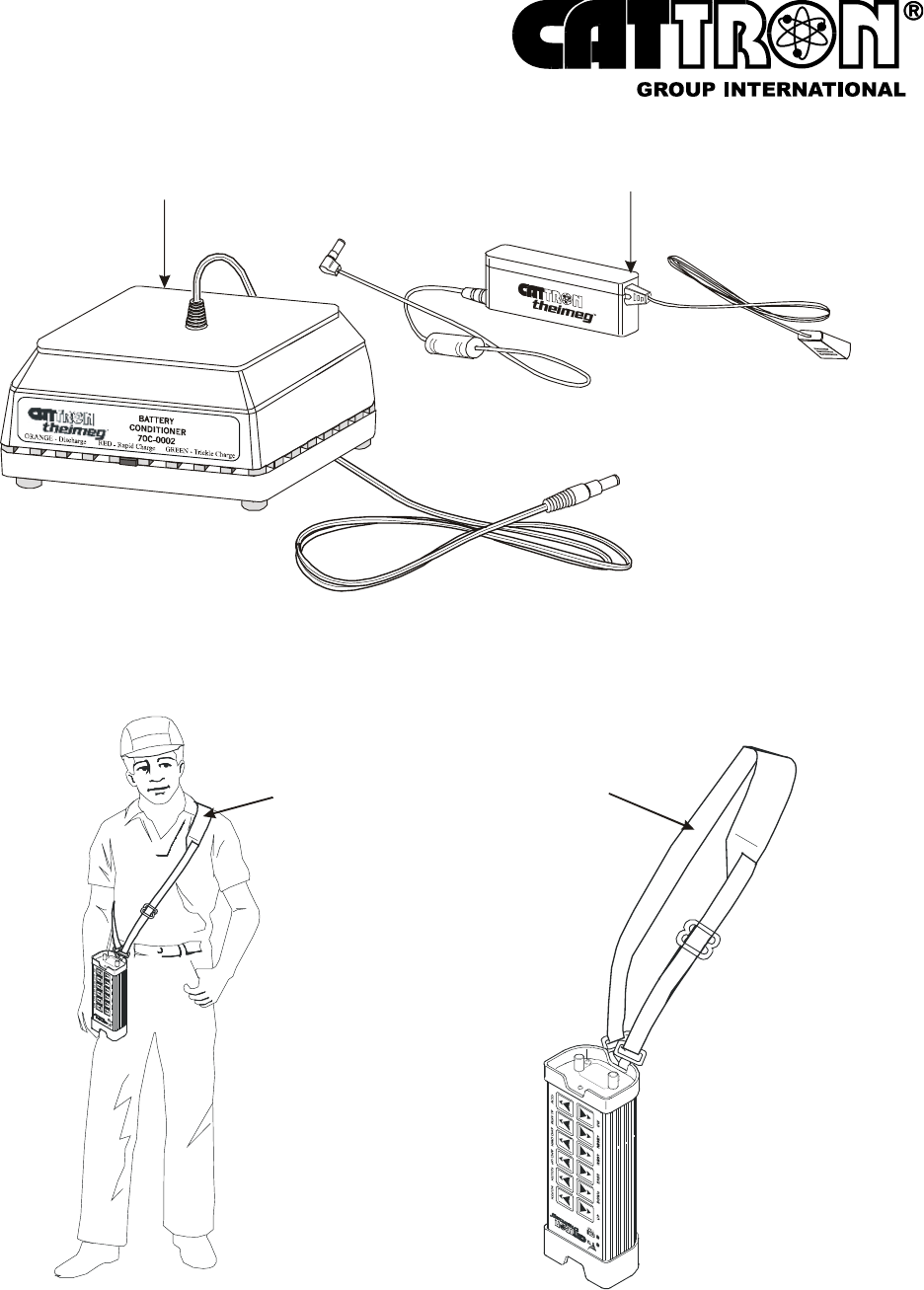
Part # 68C-MKU, Edition 01/2007, Version 1.0 Page 51
MULTI-VOLTAGE ADAPTERBATTERY PACK CONDITIONER
Item 5. Battery Conditioner, 100-240 VAC input, complete with multi-voltage adapter - Part # 70C-0002
SHOULDER CARRYING STRAP
Item 6. Carrying strap, shoulder - Part # 42C-0057
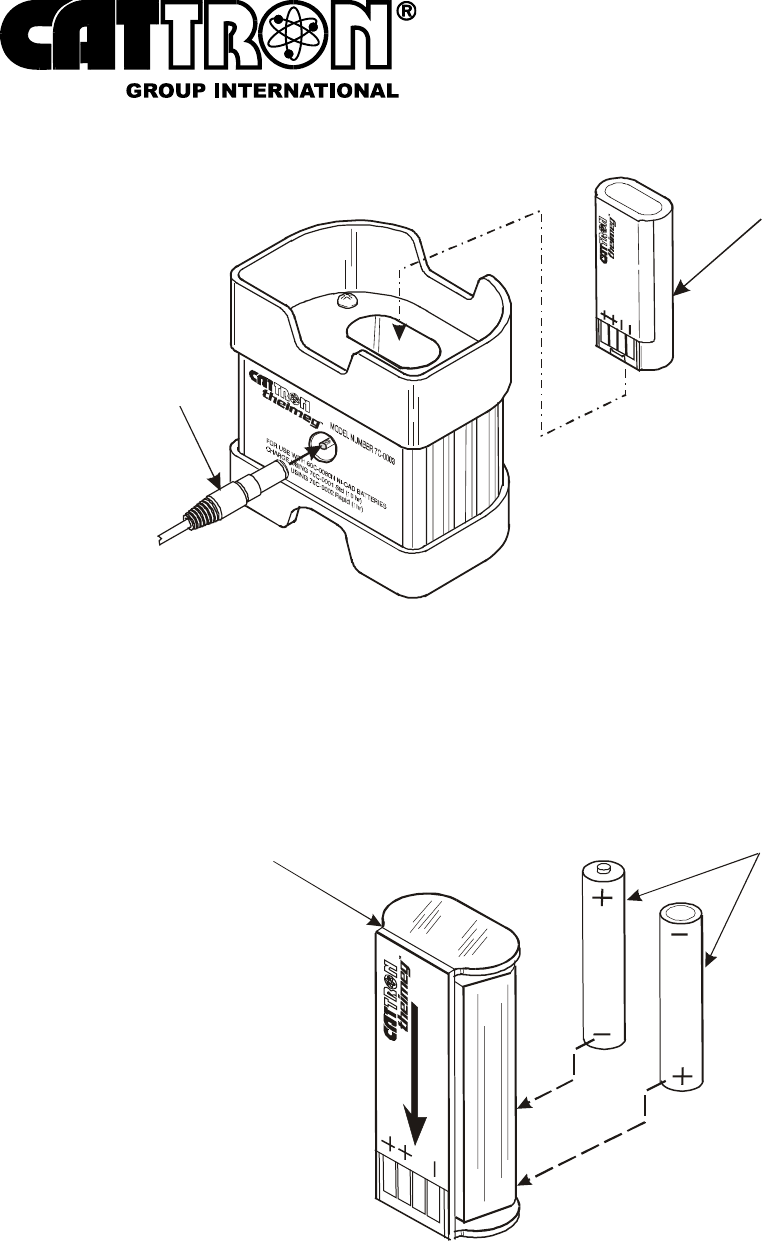
Page 52 Part # 68C-MKU, Edition 01/2007, Version 1.0
CHARGING JACK
FROM BATTERY
CHARGER
NI-CAD BATTERY PACK ONLY
PART # 60C-0060N
Item 7. External Battery Charging Unit (used with items 2, 4, & 5 above) - Part # 70C-0003
Item 8. Battery Adapter for Quantity 2 x ‘AAA’ Alkaline Batteries - Part # 60C-0062
USE ‘AAA’ ALKALINE
BATTERIES ONLY
BATTERY ADAPTER, 3 VOLT
(QUANTITY 2 x ‘AAA’ SIZE)
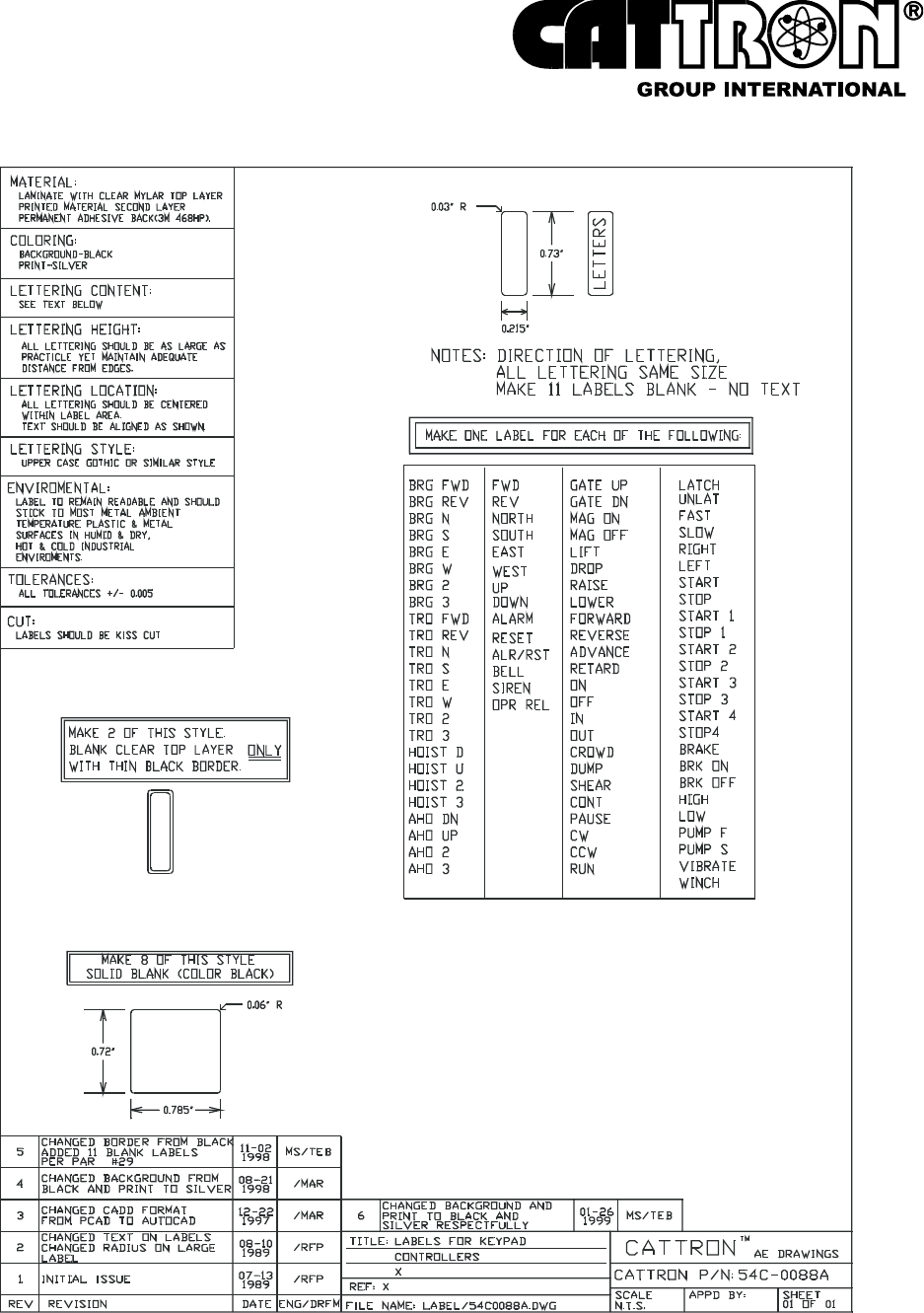
Part # 68C-MKU, Edition 01/2007, Version 1.0 Page 53
Item 9. Standard Label Kit, English Text - Part # 54C-0088A
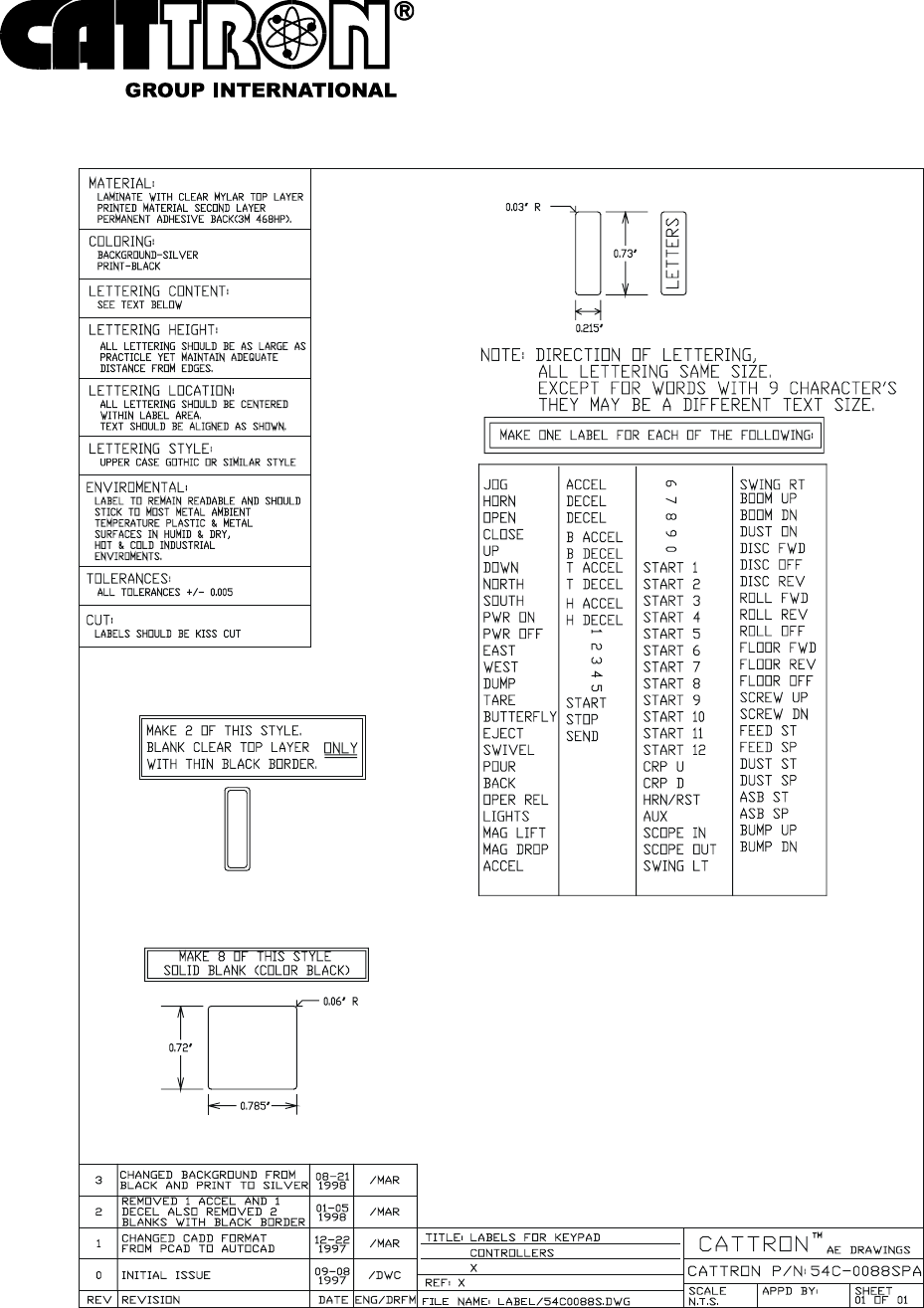
Page 54 Part # 68C-MKU, Edition 01/2007, Version 1.0
Item 10. Special Label Kit, English Text - Part # 54C-0088SPA
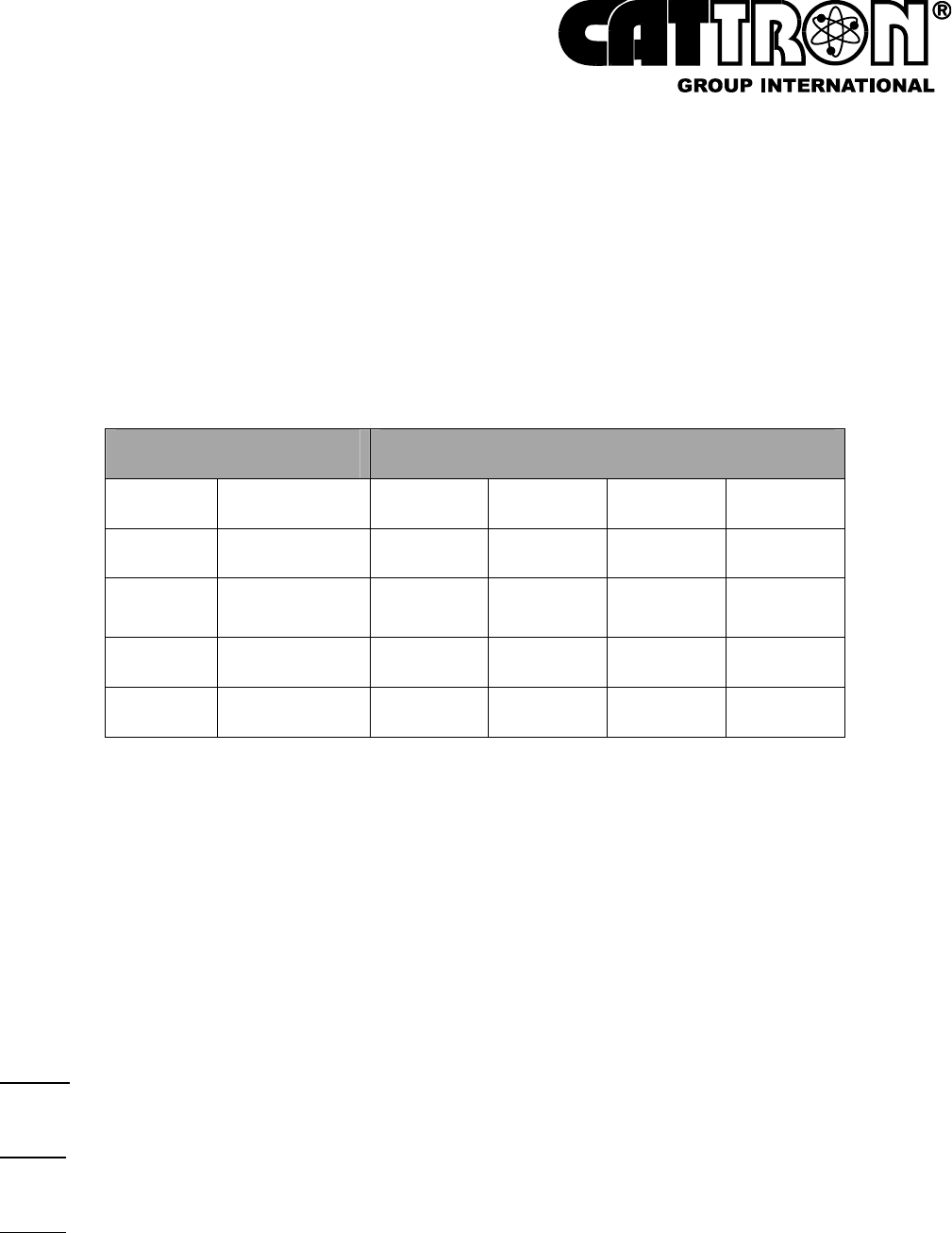
Part # 68C-MKU, Edition 01/2007, Version 1.0 Page 55
APPENDIX ‘A’ – OCU CHANNEL CHANGING OPTION
Occasionally, a change of RF channel may be necessary due to radio interference or the fact
that the factory pre-programmed RF channel is already in use.
This is normally accomplished by reprogramming the TransKey (external programming).
However, some OCUs are equipped with a Channel Changing Option that allows the operator
to change the RF channel using the OCU keypad. If this option is available, an RF Frequency
Color Code Table similar to the example shown below will be supplied with your Remote
Control System.
Table A-1. Example RF Frequency Color Code Table
902 MHz LED
Channel Frequency 1 2 3 4
0 902.000 - - red -
1 902.100 - - - red
2 902.200 - - - green
3 902.300 - - - orange
NOTES: Regardless of the OCU model (6, 8, 10 or 12 buttons), in addition to the
‘ON’ and ‘STOP’ buttons, only the top two rows of buttons are used to
change the RF channel.
The programming mode can be exited at any time by pressing the
STOP button. In this case the previously stored RF channel will remain
in effect.
A.1 ACTIVATING THE PROGRAMMING MODE.
Refer to Figure A-1, overleaf
Step 1: Switch the OCU OFF and then keep the ‘ON’ button pressed for approximately 5-
seconds until the red ‘STATUS’ LED switches from permanently red to fast blinking red.
Step 2: Within 3 seconds press the ‘UP’ and ‘DOWN’ buttons (in the top row), first and second
step, at the same time.
Step 3: The OCU is now in the programming mode. The ‘STATUS’ LED blinks orange and the
set RF channel is indicated via a color code (see example Table A-1, above) using the 4 LEDs.
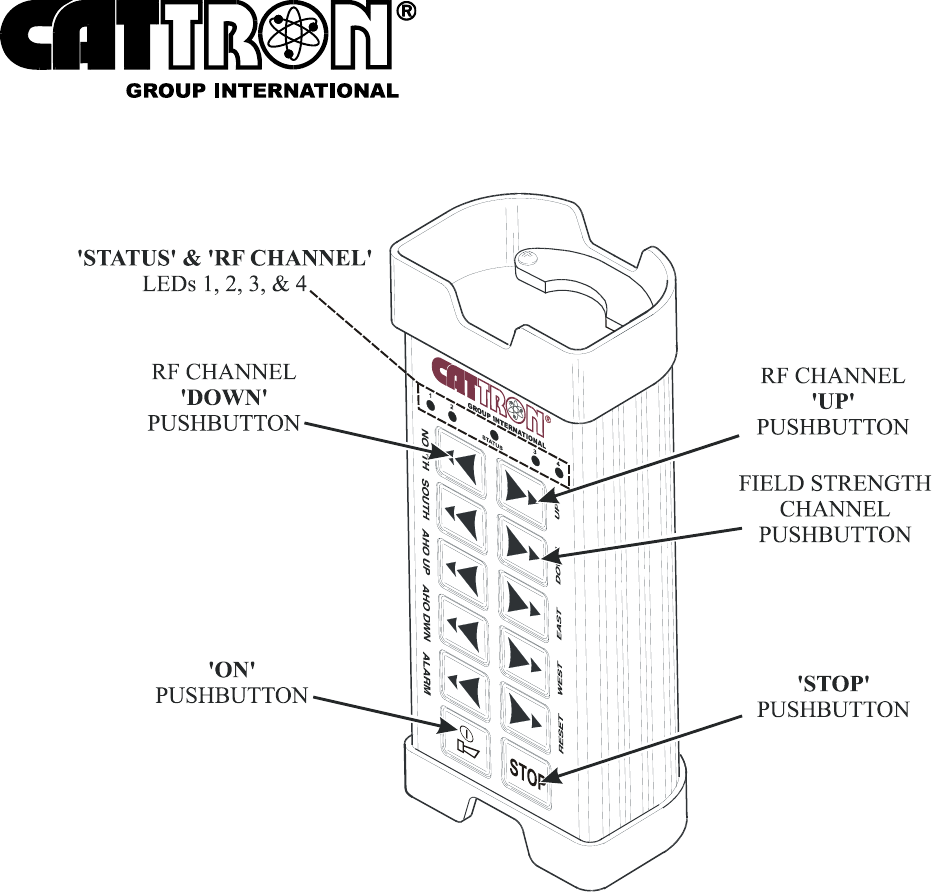
Page 56 Part # 68C-MKU, Edition 01/2007, Version 1.0
Figure A-1. RF Programming Mode Pushbuttons and LEDs
A.2 SELECTING THE RF CHANNEL
Pressing the first level of the UP and DOWN buttons selects the next higher or next lower RF
channel respectively.
Alternatively, holding down the second level initiates a fast run (approx. 0.3 seconds per
channel) in order to set the system to the desired RF channel (see example Table A-1, above).
When the desired RF channel has been selected, pressing the ON button stores the selected
RF channel in the OCU, exits the programming mode and switches off the OCU.
When the OCU is switched on again it then transmits on the selected channel.
NOTE: After the first activation of the OCU following an RF channel change, it
can take up to 1-minute before the MCU is ready for operation.
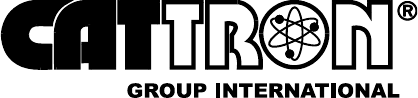
Part # 68C-MKU, Edition 01/2007, Version 1.0 Page 57
A.3 RE-ACTIVATING THE TRANSKEY RF CHANNEL
Pressing the first level of the Field Strength Channel Pushbutton and the ‘ON’ Pushbutton re-
activates the RF channel originally configured in the TransKey (basic configuration). This
action exits the programming mode and switches off the OCU.
When the OCU is switched on again, it will transmit on the RF Channel stored in the TransKey
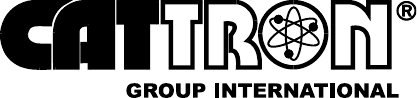
Page 58 Part # 68C-MKU, Edition 01/2007, Version 1.0
This page intentionally left blank
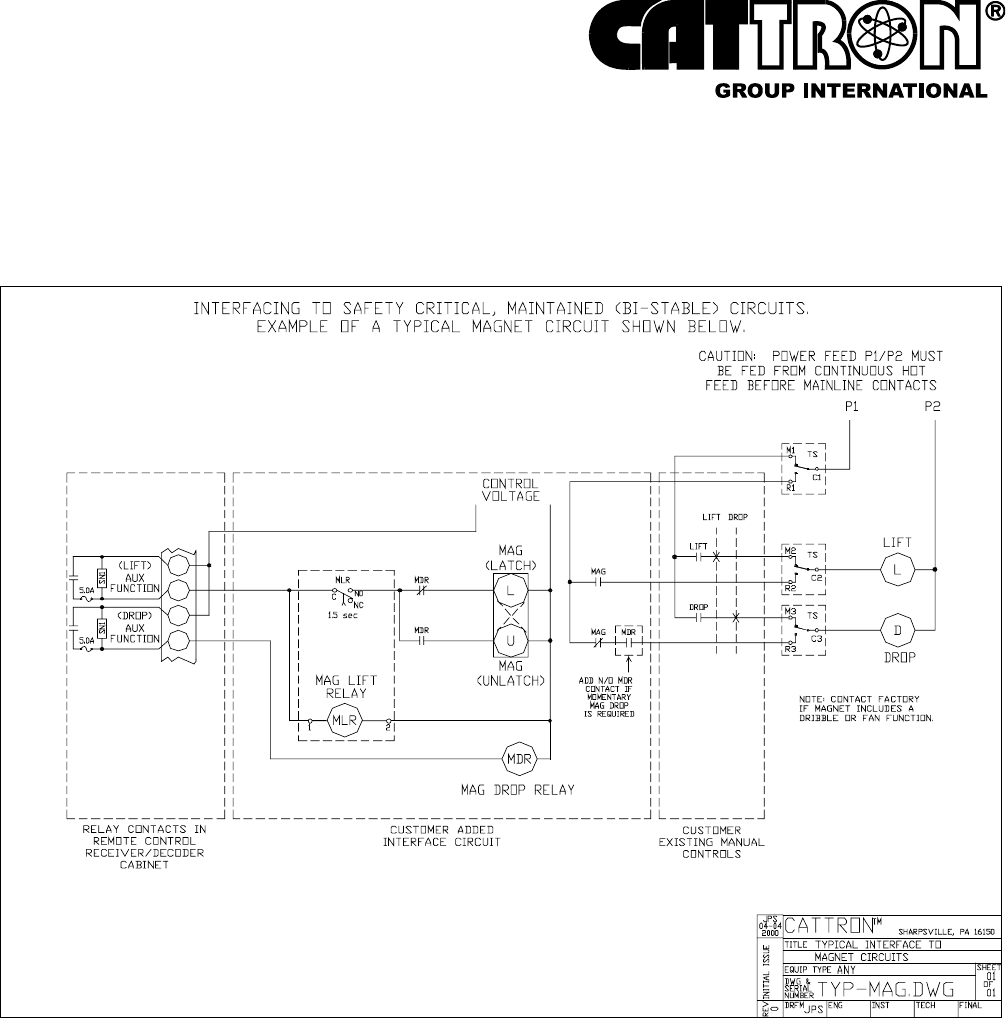
Part # 68C-MKU, Edition 01/2007, Version 1.0 Page 59
APPENDIX ‘B’ – INTERFACING TO SAFETY CRITICAL MAINTAINED BI-
STABLE CIRCUITS
B.1 EXAMPLE CIRCUIT DIAGRAM - MAGNET
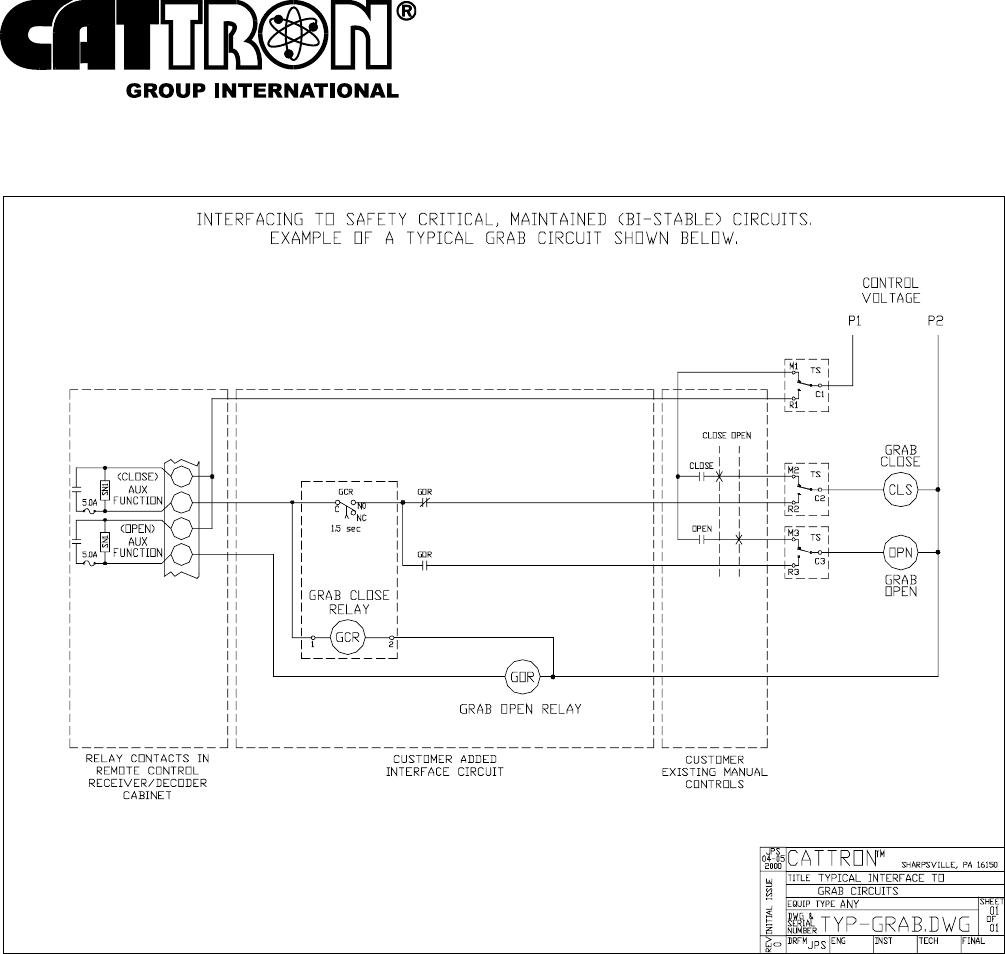
Page 60 Part # 68C-MKU, Edition 01/2007, Version 1.0
B.2 EXAMPLE CIRCUIT DIAGRAM - GRAB
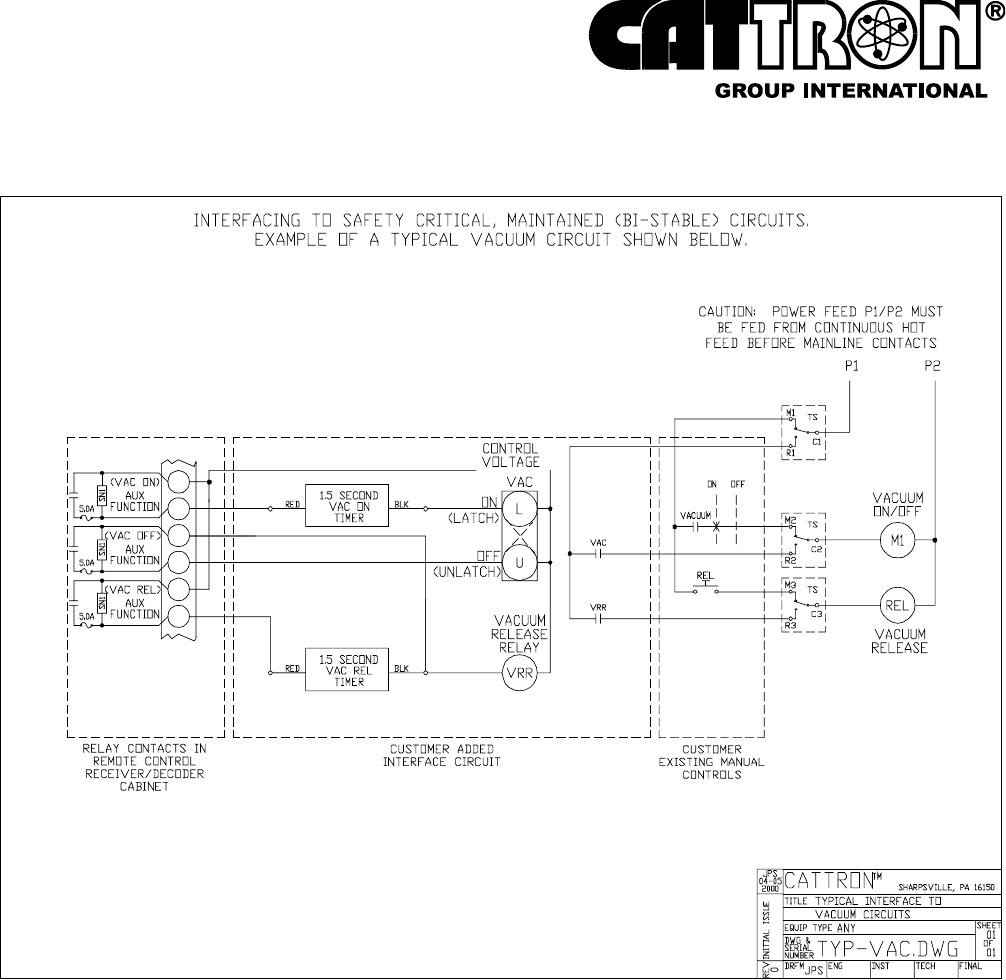
Part # 68C-MKU, Edition 01/2007, Version 1.0 Page 61
B.3 EXAMPLE CIRCUIT DIAGRAM - VACUUM
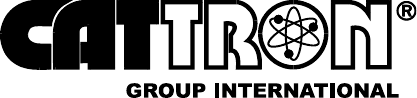
Page 62 Part # 68C-MKU, Edition 01/2007, Version 1.0
This page intentionally left blank
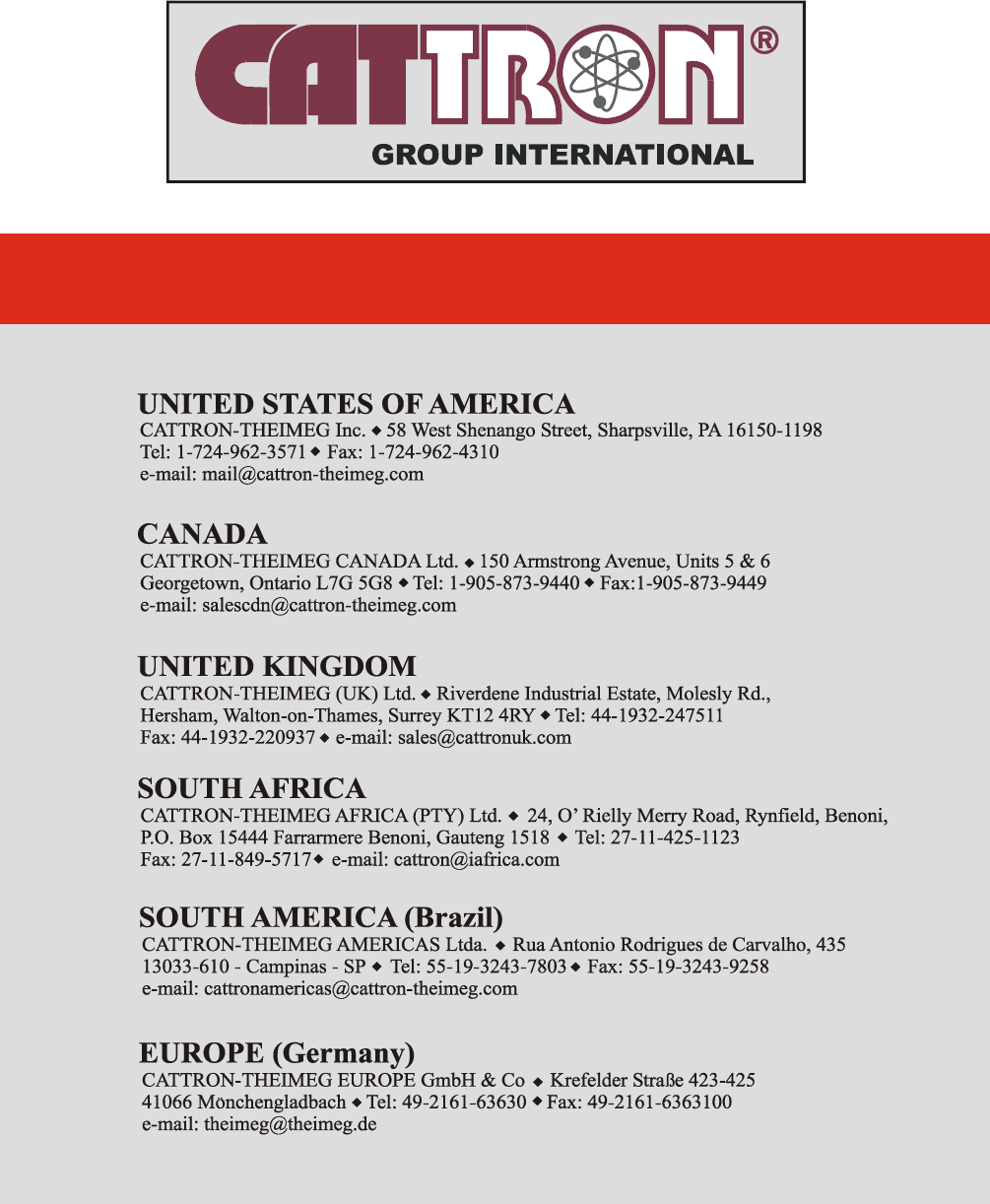
This manual is Confidential and Proprietary to CATTRON® Group International. The entire document including
any or all of the information contained therein is not to be reproduced, disclosed, or used in whole or in part for
any purpose without prior written authorization of CATTRON® Group International.