Craftsman 113244401 User Manual 10 INCH BAND SAW Manuals And Guides L0811258
CRAFTSMAN Saw Band Manual L0811258 CRAFTSMAN Saw Band Owner's Manual, CRAFTSMAN Saw Band installation guides
User Manual: Craftsman 113244401 113244401 CRAFTSMAN CRAFTSMAN 10-INCH BAND SAW - Manuals and Guides View the owners manual for your CRAFTSMAN CRAFTSMAN 10-INCH BAND SAW #113244401. Home:Tool Parts:Craftsman Parts:Craftsman CRAFTSMAN 10-INCH BAND SAW Manual
Open the PDF directly: View PDF .
Page Count: 24

Save This Manual
For Future Reference
MODEL NO.
11 3.244401
Serial
Number__
Model and serial
number may be found
at the right-hand side
of the frame.
You should record both
model and serial number
in asafe place for
future use.
CAUTION:
Read GENERAL and
ADDITIONAL SAFETY
INSTRUCTIONS
carefully
IO-INCH DIRECT
BAND SA WDRIVE
"assembly
eoperating
=repair parts
Sold by SEARS, ROEBUCK AND CO., Chicago, IL. 60684 U.S.A.
Part No. 691 87 Printed in U.S,A.
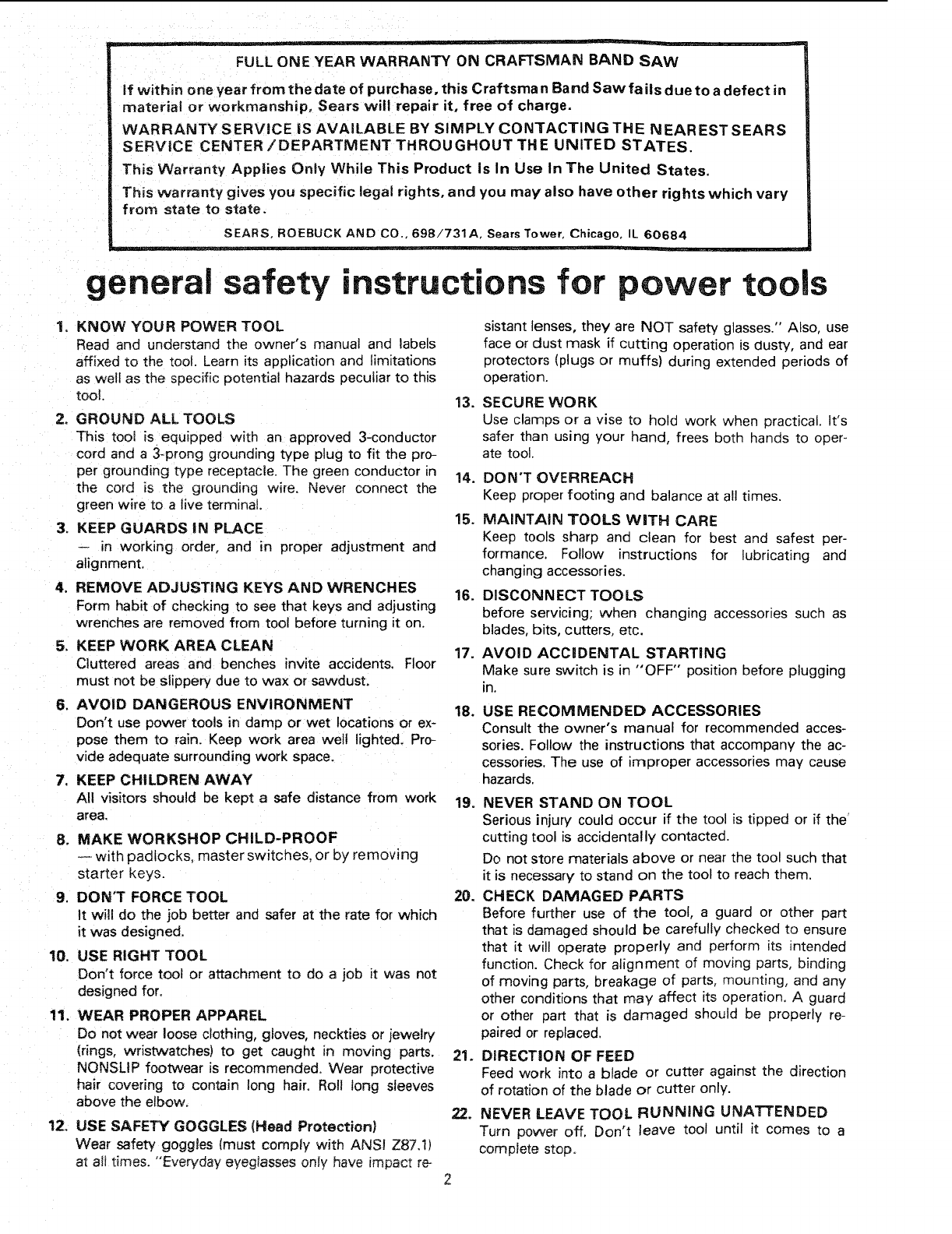
- - =L ..... =
FULL ONE YEAR WARRANTY ON CRAFTSMAN BAND SAW
if within one year from the date of purchase, this Craftsman Band Saw fails due to adefect in
material or workmanship, Sears will repair it, free of charge.
WARRANTY SERVICE iS AVAILABLE BY SIMPLY CONTACTING THE NEARESTSEARS
SERVICE CENTER/DEPARTMENT THROUGHOUT THE UNITED STATES.
This Warranty Applies Only While This Product Is In Use In The United States.
This warranty gives you specific legal rights, and you may also have other rights which vary
from state to state.
SEARS, ROEBUCK AND CO., 698/731A. Sears Tower, Chicago, IL 60684
general safety instructions for power tools
1, KNOW YOUR POWER TOOL
Read and understand the owner's manual and labels
affixed to the tool. Learn its application and limitations
as well as the specific potential hazards peculiar to this
tool.
2. GROUND ALL TOOLS
This tool is equipped with an approved 3-conductor
cord and a 3-prong grounding type plug to fit the pro-
per grounding type receptacle. The green conductor in
the cord is the grounding wire. Never connect the
green wire to a live terminal.
3. KEEP GUARDS tN PLACE
-- in working order, and in proper adjustment and
alignment,
4. REMOVE ADJUSTING KEYS AND WRENCHES
Form habit of checking to see that keys and adjusting
wrenches are removed from tool before turning it on.
5. KEEP WORK AREA CLEAN
Cluttered areas and benches invite accidents. Floor
must not be slippery due to wax or sawdust.
6. AVOID DANGEROUS ENVIRONMENT
Don't use power tools in damp or wet locations or ex-
pose them to rain_ Keep work area well lighted. Pro-
vide adequate surrounding work space.
7, KEEP CHILDREN AWAY
All visitors should be kept a safe distance from work
area.
8. MAKE WORKSHOP CHILD-PROOF
with padlocks, master switches, or by removing
starter keys.
9. DONq" FORCE TOOL
It will do the job better and safer at the rate for which
it was designed
10. USE RIGHT TOOL
Don't force tool or attachment to do a job it was not
designed for.
11. WEAR PROPER APPAREL
Do not wear loose clothing, gloves, neckties or jewelry
(rings, wristwatches) to get caught in moving parts.
NONSLtP footwear is recommended. Wear protective
hair covering to contain long hair. Roll long sleeves
above the elbow.
12. USE SAFETY GOGGLES (Head Protection)
Wear safety goggles Imust comlJly with ANSi Z87,1)
a_alt times. "Everyday eyegfasses only have impact re-
13.
sistant lenses, they are NOT safety glasses." Also, use
face or dust mask if cutting operation is dusty, and ear
_Jrotectors (plugs or muffs) during extended periods of
operation.
SECURE WORK
Use clamps or a vise to hold work when practical. It's
safer than using your hand, frees both hands to oper-
ate tool.
14. DON'T OVERREACH
Keep proper footing and balance at all times.
15. MAINTAIN TOOLS WiTH CARE
Keep tools sharp and clean for best and safest per-
formance. Follow instructions for lubricating and
changing accessories.
16. DISCONNECT TOOLS
before servicing; when changing accessories such as
blades, bits, cutters, etc.
17. AVOID ACCIDENTAL STARTING
Make sure switch is in "OFF" position before plugging
in.
18. USE RECOMMENDED ACCESSORIES
Consult the owner's manual for recommended acces-
sories. Follow the instructions that accompany the ac-
cessories. The use of improper accessories may cause
hazards.
19. NEVER STAND ON TOOL
Serious injury could occur if the tool is tipped or if the"
cutting tool is accidentally contacted.
Do not store materials above or near the tool such that
it is necessary to stand on the tool to reach them.
20. CHECK DAMAGED PARTS
Before further use of the tool, a guard or other part
that is damaged should be carefully checked to ensure
that it will operate properly and perform its intended
function. Check for alignment of moving parts, binding
of moving parts, breakage of parts, mounting, and any
other conditions that may affect its operation. A guard
or other part that is damaged should be properly re-
paired or replaced.
21. DiRECTiON OF FEED
Feed work into a blade or cutter against the direction
of rotation of the blade or cutter only.
22° NEVER LEAVE TOOL RUNNING UNATTENDED
Turn power off. Don't _eave tool until it comes to a
complete stop,

adamdonam safety instructions for band saw
Safety is a combination of operator common sense and
alertness at all times when the band saw is being used.
WARNING: FOR YOUR OWN SAFETY, DO NOT
ATTEMPT TO OPERATE YOUR BAND SAW UNTIL
IT IS COMPLETELY ASSEMBLED AND INSTALL-
ED ACCORDING TO THE INSTRUCTIONS ... AND
UNTIL YOU READ AND UNDERSTAND THE FOL-
LOWING:
PAGE
3. General Safety instructions for Power Tools... 2
2. Getting To Know Your Band Saw ............ 16
3. Basic Band Saw Operation .................. 17
4. Maintenance ............................... 18
5. Stabinity of Machine.
Your band saw must be bolted securely to a stand or
work bench. In addition, if there is any tendency for
the band saw to tip over or move during certain op-
erations such as cutting long heavy boards, bolt your
band saw stand or workbench to the floor.
6. Location
This band saw is intended for indoor use only.
7. Protection: Eyes, Hands, Face, Ears, Body
a. Wear safety goggles that comply with ANSI
Z87.1 and aface shield if operation is dusty.
Wear ear plugs or muffs during extended
periods of operation. Do not wear gloves.., roll
long sleeves abo_e the elbow.
b. Do not cut pieces of material too small to hold by
hand.
c. Avoid awkward hand positions where a sudden
slip could cause a hand to move into the blade.
d. Never turn your band saw "ON" before clearing
the table of all Objects (tools, scraps of wood,
etc.) except for the workpiece and related feed or
support devices for the operation planned.
e. Make sure the blade runs downward toward the
table. Always adjust tracking wheel correctly so
that the blade does not run off the wheels.
f,
g.
Always adjust blade tension correctly.
ALWAYS adjust the upper blade guide and blade
guard to just clear the workpiece to protect the
operator, to keep blade breakage to a minimum,
and to provide maximum support for blade.
,
h,
i.
j.
k.
m.
n.
o.
p.
q,
When cutting a large piece of material, make sure
it is supported at table height,
Hold the work firmly against the table,
Do not feed the material too fast while cutting.
Only feed the material fast enough so that the
blade will cut. Keep fingers away from the blade.
Use caution when cutting off material which is
irregular in cross section which could pinch the
blade before the cut is completed. A piece of
molding for example must lay flat on the table and
not be permitted to rock while being cut.
Use caution when cutting off round material such
as dowel rods, or tubing. They have a tendency to
roll while being cut causing the blade to "bite".
Always use a "V" block, or clamp round material
to a miter guage.
When backing up the workpiece, the blade may
bind in the kerf (cut)... this is usually caused by
sawdust clogging up the kerf or because the
blade comes out of the guides. If this happens:
I, Turn off the band saw.., remove plug from
power source outlet.., remove cover from
band saw. Insert a screwdiver or wedge in the
kerf.., rotate the wheels by hand while back-
ing up the workpiece.
Never leave the band saw work area with the
power on, before the machine has come to a com-
plete stop, or without removing and storing the
switch key.
Never operate band saw with cover removed.
Do not perform layout, assembly, or setup work
on the table while the cutting toot is rotating.
Turn saw "off" and remove plug from power sup-
ply outlet before installing or removing an acces-
sory or attachment.
Should any part of this band saw be missing, bend,
or fail in any way, or any electrical component fail to
perform properly, shut off power switch and remove
plug from power supply outlet. Replace damaged,
missing, and/or failed parts before resuming opera-
tion.
9. Think Safety.
Safety is a combination of operator common sense
and alertness whenever the band saw is in operation.
!0. This band saw is not designed to cut meta!.
WARNING: DO NOT ALLOW FAMILIARITY (GAINED FROM FREQUENT USE OF YOUR BAND SAW} TO
BECOME COMMONPLACE. ALWAYS REMEMBER THAT A CARELESS FRACTION OF A SECOND iS
SUFFICIENT TO INFLICT SEVERE INJURY.
3

additional safety instructions for band saw
YOUR
The operation of any power tool can result in foreign
objects being thrown into the eyes, which can result in
severe eye damage. Always wear safety goggles com-
plying with ANSI Z87.1 (shown on Package) before
commencing power tool operation. Safety Goggles are
available at Sears retail or catalog stores.
READ AND FOLLOW THE INSTRUCTIONS APPEARING ON THE INSTRUCTION PLATE ON
THE FRONT OF THE BAND SAW.
_DIRECT DRIVE SAW
-- - --- = iii , -- -
motor specifications and electrica|
requirements
This machine is designed to use, and is equipped with,
a 1725 RPM motor. It is wired for operation on 110-120
volts, 60 Hz., alternating current. (TOOL MUST NOT BE
CONVERTED TO OPERATE ON 230 VOLT).
For replacement motor refer to parts list in this manual;
CONNECTING TO POWER SUPPLY OUTLET
This machine must be grounded while in use to protect
the operator from electric shock.
Ptug power cord into a 110-120V properly grounded
type outlet protected by a15-amp. dual element
time delay or Circuit-Saver fuse or circuit breaker.
If you are not sure that your outlet is properly grounded,
have it checked by a qualified electrician.
WARNING: DO NOT PERMIT FINGERS TO TOUCH
THE TERMINALS OF PLUGS WHEN INSTALLING
OR REMOVING THE PLUG TO OR FROM THE
OUTLET.
WARNING: IF NOT PROPERLY GROUNDED THIS
POWER TOOL CAN CAUSE AN ELECTRICAL
SHOCK PARTICULARLY WHEN USED IN DAMP
LOCATIONS CLOSE TO PLUMBING. IF AN ELEC-
TRICAL SHOCK OCCURS THERE IS THE POTEN-
TIAL OF ASECONDARY HAZARD SUCH AS
YOUR HANDS CONTACTING THE SAW BLADE.
if power cord is worn or cut, or damaged in any way,
have it replaced immediately.
Your unit is for use on 110.120 volts, and has a plug
that looks like below.
PROPERLY.
GROUNDED
3-PRONG OUTLET--_
3-PRONG
PLUG
GROUNDING
4 PRONG

motor specifications and
requirements
electrical
This power tool is equipped with a 3-conductor cord
and grounding type plug which has agrounding prong,
approved by Underwriters' Laboratories and the Cana-
dian Standards Association. The ground conductor has
a green jacket and is attached to the too! housing at
one end and to the ground prong in the attachment
plug at the other end.
This plug requires a mating 3oconductor grounded type
outlet as shown.
If the outlet you are planning to use for this power tool
is of the two prong type DO NOT REMOVE OR ALTER
THE GROUNDING PRONG IN ANY MANNER. Use an
adapter as shown below and always connect the
grounding lug to known ground.
It is recommended that you have a qualified electrician
replace the TWO prong outlet with a properly grounded
THREE prong outlet.
A temporary adapter as shown below is avaimable for
connecting plugs to 2-prong receptacles. The green
grounding lug extending from the adapter must be
connected to a permanent ground such as to a
properly grounded outlet box.
A temporary adapter as illustrated is available for
connecting plugs to 2-prong receptacles. The
temporary adapter should be used only until a properly
grounded outlet can be installed by a qualified
electrician.
WARNING: THE GREEN GROUNDING LUG
EXTENDING FROM THE ADPATER MUST BE
CON N ECTED TO A PERMAN ENT GROUND SUCH
GROUNDmNG LUG
/
3-PRONG _._ /!...o J-,-.44---I¢t_n_Ts=n T_ AI_k-_-._jII MAKE SURE THIS _$
ADAPTER
AS TO A PROPERLY GROUNDED OUTLET BOX.
NOT ALL OUTLET BOXES ARE PROPERLY
GROUNDED.
If you are not sure that your outlet box is properly
grounded, have it checked by a qualified electrician.
NOTE: The adapter illustrated is for use only if you
already have a properly grounded 2-prong receptacle.
The use of any extension cord wilt cause some loss of
power. To keep this to a minimum and to prevent over-
heating and motor burn-out, use the table below to de-
termine the minimum wire size (A.W.G.) extension cord.
Use only 3 wire extension cords which have 3-prong
grounding type plugs and 3-pole receptacles which
accept the plug on the saw.
Extension Cord Length Wire Size A.W.G,
Up to 100 Ft. 16
100 - 200 Ft. 14
200 - 400 Ft. 10
CONTENTS
POWER TOOL WARRANTY ................... 2
GENERAL SAFETY INSTRUCTIONS FOR
POWER TOOLS ............................. 2
ADDITRONAL SAFETY INSTRUCTIONS
FOR BAND SAW ............................ 3
MOTOR SPEC0FiCATJONS AND ELECTRICAL
REQUIREMENTS ............................ 4
UNPACKING AND CHECKING CONTENTS ... 6
ASSEMBLY
Mounting Band Saw to Workbench ........... 7
Installing the Table ........................... 8
Installing the Blade .......................... 8
Tracking the Blade .......................... 10
Adjusting the Table Square to Blade ......... 11
Adjusting
Adjusting
Adjusting
Adjusting
Adjusting
Adjusting
Adjusting
Guide Bar ........................ 12
Front to Back Squareness ......... 12
Side to Side Squareness .......... 13
Upper Blade Guide Assembly ...... 13
Upper Blade Guides ............... 13
Upper Thrust Roller ............... 14
Lower Blade Guide Assembly ...... 14
Adjusting Lower Blade Guides ............... 14
Adjusting Lower Thrust Roller ............... 15
Adjusting Table ............................. 15
GETTING TO KNOW YOUR BAND SAW
Tension Adjustment Knob ................... t 6
Tension Setting ............................. 16
Guide Bar Lock Screw ...................... 16
Thrust Roller Adjustment ................... 16
Table Lock Knob ............................ 16
Tilt Scale ................................... 16
Blade Guides ............................... 16
On-Off Switch .............................. 16
BASIC BAND SAW OPERATION
Sawing ..................................... 1 7
Blade Selection Guide ...................... 17
MAINTENANCE ............................. 18
Lubrication ................................. 18
RECOMMENDED ACCESSORIES ........... 18
TROUBLESHOOTING ....................... 19
REPAIR PARTS ............................. 20

unpacking and checking contents
-- - TOOLS NEEDED .... _-- -_-
COMBINATION SQUARE
MEDIUM SCREWDRIVER {_8=:====
Model 113.244401 Band Saw is shipped complete in
one carton but DOES NOT INCLUDE Steel Legs.
Separate all parts from packing materials and check
each item with illustration and "Table of Loose Parts".
Make certain all items are accounted for, before discard-
ing any packing material.
7/16 INCH WRENCH
3/8 INCH WRENCH
1/2 INCH WRENCH
5/! 6 INCH WRENCH
5/32 INCH SET SCREW
#2 PHILLIPS SCREWDRIVER If any parts are missing, do not attempt to assemble the
band saw, plug in the power cord, or turn the switch on
until the missing parts are obtained and installed cor-
rectly.
COMBINATION SQUARE MUST BE TRUE
DRAW LIGHT
LINE ON BOARD
ALONG THIS EDGE
STRAIGHT EDGE OF
BOARD 3/4" THICK
THIS EDGE MUST BE
PERFECTLY STRAIGHT
WRENCH
/
SHOULD BE NO GAP OR OVERLAP HERE WHEN
SQUARE IS FLIPPED OVER IN DOTTED POSITION
¢
/
!ITEM
i
A
B
C
D
E
F
TABLE OF LOOSE PARTS QTY.
Basic saw assembly ............... 1
Owners Manual ................... 1
Saw Table ........................ 1
Blade, Saw 1/4 ................. ,. 1
Insert, Table ...................... 1
Bag Assembly Part - #691 32
Containing the following parts:
Roller, Blade Thrust ............... 2
Switch, Key ....................... 1
iNut, Wing 1/4-20 ................. 1
Screw, Truss Hd. 1/4-20 x 1 ....... 1
Washer 17/64 x 5/8 x 1/16 ....... 1
Screw, Hex Hd. 5/16-18 x 3/4 ..... 2
External Lockwasher, 5/16 ........ 2
Wrench, Hex "L'" 5/32 ............ 1

assernbly
MOUNTING BAND SAW TO WORKBENCH
If band saw is to be used in a permanent location, it
should be fastened securely to a firm supporting
surface such as a workbench or accessory leg set,
If mounting to aworkbench, holes should be drilled
through supporting surface of the workbench using
dimensions illustrated.
!. Each foot should be bolted securely using 1/4"
diameter machine screws, washer, Iockwashers,
and 1/4" hex nuts. Bolts must be of sufficient
length to accommodate legs of saw, washers, hex
nuts, and thickness of supporting surface.
2. Locate and mark holes where band saw is to be
mounted.
3. Drill (4) 11/32" din. holes through workbench.
4. Remove band saw cover by releasing latches.
5. Place band saw on workbench aligning holes in feet
with holes drilled in workbench.
6. Insert all four screws, Iockwashers and nuts and
tighten.
T
5" 9/32" DJA.(4)
[_. HOLES _,
12-1/8"--
An alternate method of mounting is to fasten band saw
to a mounting board. The board should be of sufficient
size to avoid tipping of saw while in use. Any good
grade of plywood or chipboard with a 3/4" minimum
thickness is recommended.
1. Follow instructions for mounting to workbench,
substituting a board 1 8" x 24" minimum size and
using 1/4 inch flat head screws, flat washers,
Iockwashers, and hex nuts. Screws must be of
sufficient length to accommodate legs of saw,
washers, hex nuts, and thickness of supporting
board.
NOTE: Holes must be counter sunk so screw heads
are flush with surface of supporting board.
2. Securely clamp board to workbench using C
clamps.
NOTE: Supporting surface where band saw is mounted
should be examined carefully after mounting to insure
that no movement during use can result. If any tipping
or walking is noted, secure workbench, legs, or support-
ing surface before operating band saw.
18"
MIN.
24" MIN.
5" 9/32" IDIA. (4)
HOLES

assembly
INSTALLING THE TABLE
Applying a coat of automobile wax to the table and
inside surfaces of trunnion that slide on frame will
ease sliding on these surfaces.
1. Loosen the guide bar lock screw and position the
upper guide assembly all of the way up. Tighten
lock screw.
2. Locate two (2) 5/16 - 18 x 3/4 inch hex head screws
and external Ioc kwashers among loose parts.
3. Position trunnion at the 0degree position and tight-
en table lock knob.
4. Place table on trunnion so that the slots in trunnion
line up with the mounting holes in table as illus-
trated.
5. Insert hex head screw and Iockwasher through
front hole of trunnion )nto table and tig hten.
6. Loosen table Lock Knob and position Trunnion at
the 45 degree position.
7. Insert hex head screw and Iockwasher through rear
hole of trunnion into table and tighten.
8. Return table to the 0 degree position and tighten
table lock knob.
| _ --APPLY WAX
TO NSaDE
____,_ _ SURFACES
TABLE _F_ _ F-'TRUNN'ON
\
_--TABLE _'_
__ LOCK KNOB
_--- EXTERNAL
___ LOCKWASH ER
5/16-18 HEX HEAD SCREW
INSTALLING THE BLADE GUIDE BAR LOCK SCREW_
1. Loosen the two mounting screws and remove the BLADE --, t11 1_-7--'--'_
blade guard. MOUNTING
2. Loosen the guide bar lock screw and position the SCREWS_ ! } I 11!1_ _J_
upper guide assembly approximately two inches _----_LI l_lltl_----__._ _
__ __'_ GUIDE BAR
abOVescrew,the table as shown and tighten the Iock UPPER B L/_p,.Eo,._,____-_ Z_._
GUIDE ASSEMBLY -"-_ _[;Z_- ._,':"_-'_
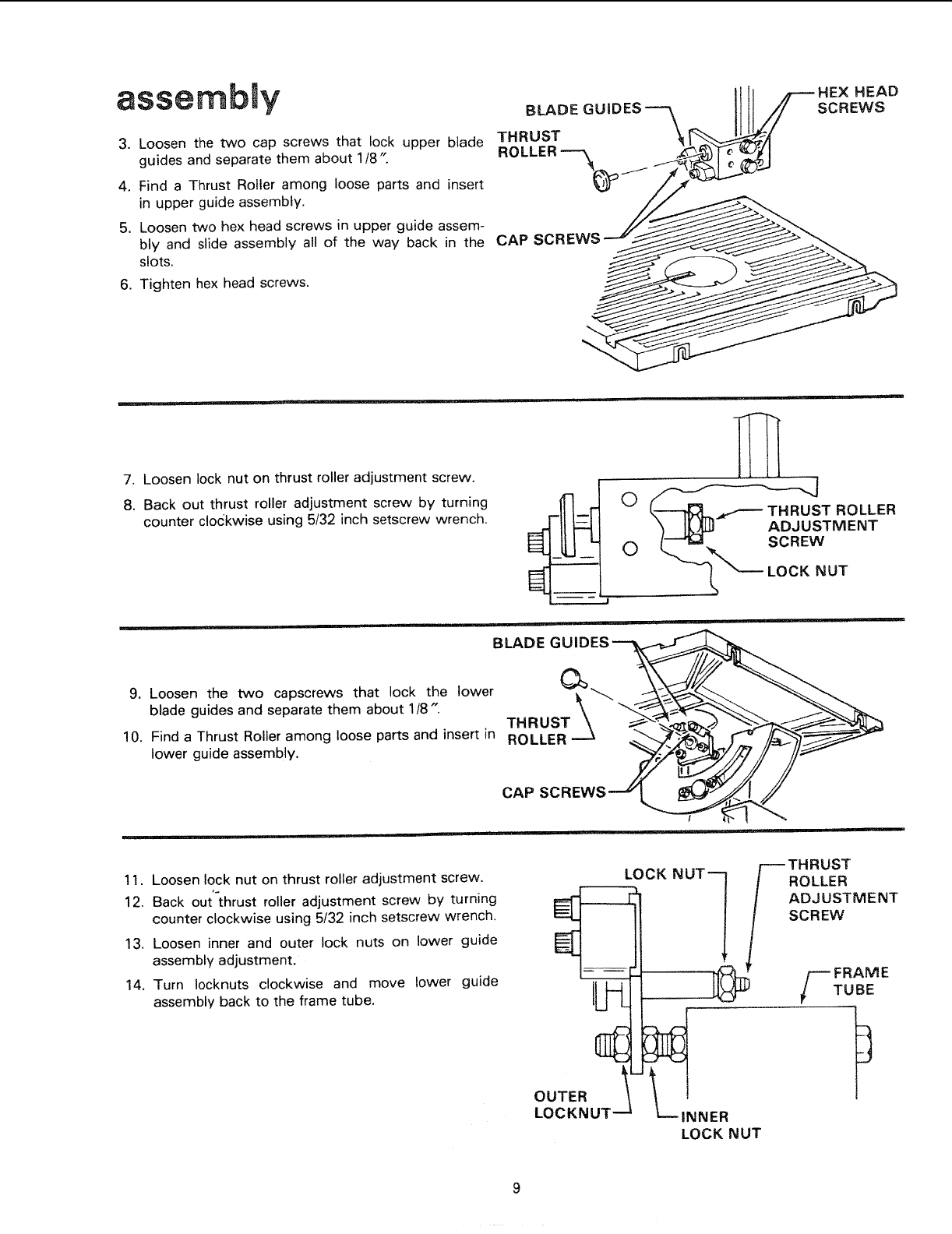
assembly
3. Loosen the two cap screws that lock upper blade
guides and separate them about 1/8 ':
4. Find a Thrust Roller among loose parts and insert
in upper guide assembly.
BLADE GUIDES--_
THRUST
R© LLER ----_:_ _..
5. Loosen two hex head screws in upper guide assem-
bly and slide assembly all of the way back in the CAP SO
slots.
6. Tighten hex head screws.
HEX HEAD
SCREWS
7. Loosen lock nut on thrust roller adjustment screw.
8. Back out thrust roller adjustment screw by turning
counter clo(:kwise using 5/32 inch setscrew wrench.
©
©
______ THRUST ROLLER
_____ ADJUSTMENT
L_-LOCK NUT
BLADE GL
9. Loosen the two capscrews that lock the lower ""_'_
blade guides and separate them about 1/8" THRUST
10. Find a Thrust Roller among loose parts and insert in ROLLER
lower guide assembly.
11. Loosen lock nut on thrust roller adjustment screw.
12. Back out"thrust roller adjustment screw by turning
counter clockwise using 5/32 inch setscrew wrench.
!3. Loosen inner and outer lock nuts on lower guide
assembly adjustment.
14. Turn Iocknuts clockwise and move lower guide
assembly back to the frame tube.
CAP S
I
LOCK NUT-- r-_THRUST
ROLLER
,=_'--_-] ::)] /ADJUSTMENT
SCREW
LOCK NUT
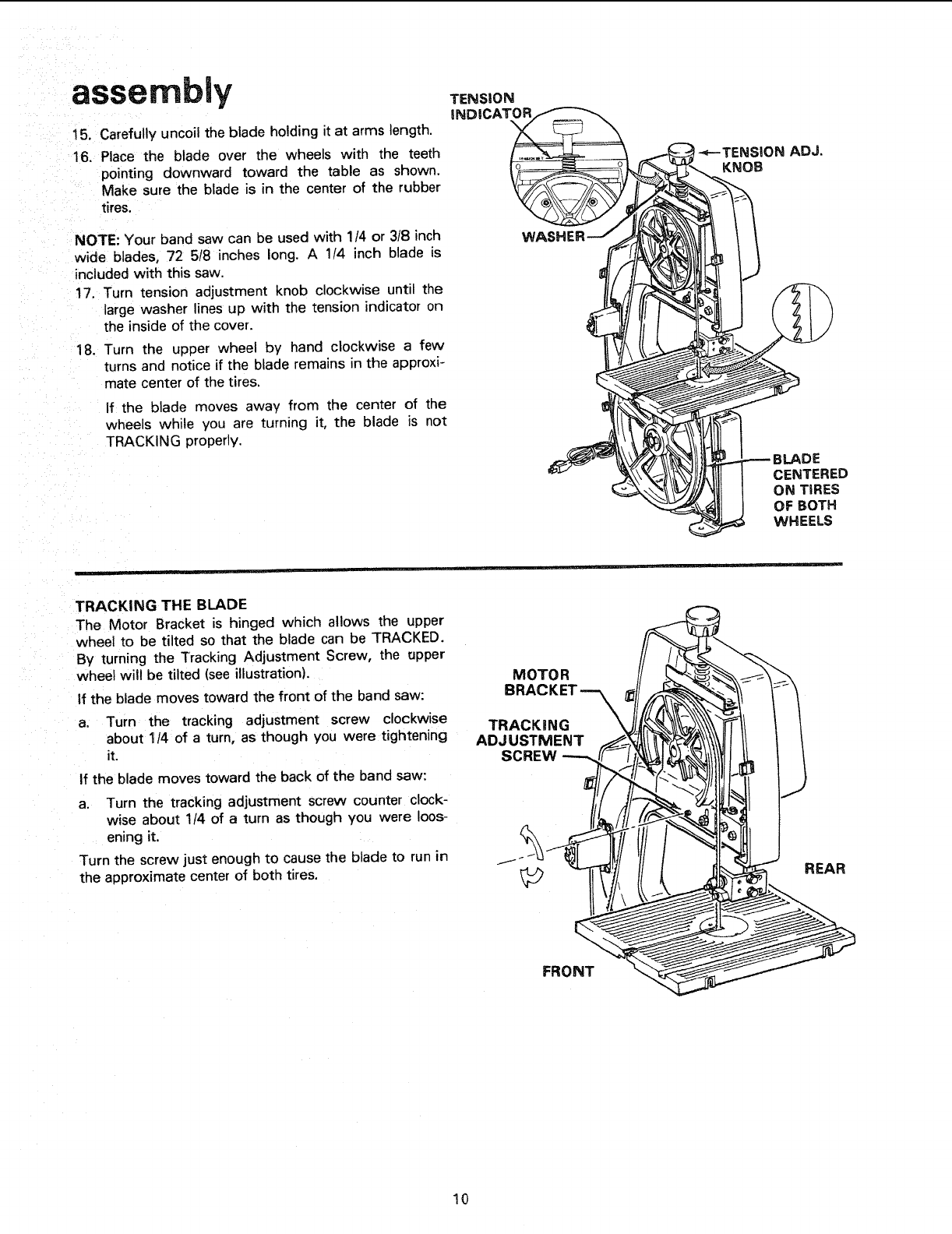
assembly
15. Carefully uncoil the blade holding it at arms length.
!6, Place the blade over the wheels with the teeth
pointing downward toward the table as shown.
Make sure the blade is in the center of the rubber
tires.
NOTE: Your band saw can be used with 1/4 or 3/8 inch
wide blades, 72 5/8 inches long. A 1/4 inch blade is
included with this saw.
17. Turn tension adjustment knob clockwise until the
large washer lines up with the tension indicator on
the inside of the cover.
18. Turn the upper wheel by hand clockwise a few
turns and notice if the blade re mains in the approxi-
mate center of the tires.
If the blade moves away from the center of the
wheels while you are turning it, the blade is not
TRACKING properly.
TENSION
INDICAT__ _
WASHERJ
DE
CENTERED
ON TIRES
OFBOTH
WHEELS
TRACKING THE BLADE
The Motor Bracket is hinged which allows the upper
wheel to be tilted so that the blade can be TRACKED.
By turning the Tracking Adjustment Screw, the upper
wheel will be tilted (see iliustration).
if the blade moves toward the front of the band saw:
a. Turn the tracking adjustment screw clockwise
about 1/4 of a turn, as though you were tightening
it.
If the blade moves toward the back of the band saw:
a. Turn the tracking adjustment screw counter clock-
wise about 114 of a turn as though you were loos-
ening it.
Turn the screw just enough to cause the blade to run in
the approximate center of both tires.
MOTOR
TRACKING
ADJUSTMENT
SCREW ---,,
REAR
FRONT
10

assembly
NOTE: IF BLADE CANNOT BE MADE TO RUN IN THE APPROXIMATE CENTER OF THE LOWER WHEEL, tT
MAY BE NECESSARY TO REPOSITION THE UPPER WHEEL ON THE MOTOR SHAFT.
i. Loosen the set screw in the upper wheel.
a, If the blade is running to the front of lower wheel - Slide upper wheel to the rear toward the motor.
b, If the blade is running to the rear of lower wheel - Slide upper whee! to the front away from the motor.
2. Tighten the set screw in the upper wheel.
3, Track the blade by turning the tracking adjustment screw in or out as needed.
ADJUSTING THE TABLE SQUARE TO BLADE
NOTE: The combination square must be "true". See
start of "assembly" section for checking method.
1. Loosen guide bar lock screw and raise the upper
blade guide assembly all the way up. Tighten guide
bar lock screw.
2. Place a square on the table against the rear edge of
the blade as illustrated.
3. If adjustment is required, loosen the two screws in
the trunnion stop brackets and tap table up or
down until table is square with blade.
4. Tighten screws.
5. Loosen table lock knob.
6. Place a square on the table against the blade as
illustrated,
7. Tilt table up or down to atign table 90 degrees to
blade (0 degree position} and tighten table lock
knob.
8. Loosen the two screws in the trunnion stop brac-
kets and slide bracket under lock knob until it rests
against end of slot in trunnion.
9. Tighten screws.
10. Check squareness of blade to table, Make readjust-
ments if necessary.
11. Loosen table lock knob.
12. Tilt table to 45 degree position and check using a
combination square.
!3. Loosen the two screws in the trunnion stop brac-
kets and slide bracket on opposite side of lock
knob until it rests against end of slot in trunnion.
NOTE: Be careful not to change position of slide
bracket under lock knob that set the 0 degree position.
14. Tighten screws.
t5. Check blade to table at the 45 degree position.
!6. Loosen table lock knob and position table at 0 de-
gree position; recheck squareness.
17. Make readjustments if necessary.
_-" COMBINATION SQUARE
t______,
;I . --SAWBU,OE
STOP BRACKET
SCREWS
11

assembly
ADJUSTING GUIDE BAR
NOTE: When the upper guides are raised or lowered,
they must not deflect the blade front to back or side-
ways. This means that the guide bar must be parallel to
the blade.
1. Lower guide bar until it is approximately 1-3/4
inches above table. Tighten guide bar lock screw,
2. Hold asquare on table against guide bar as shown
to check side to side squareness.
3. Hotd square on table against guide bar as shown to
check front to back squareness.
NOTE: Square must rest on the guide bar and not on
the upper guide bracket, Note illustration.
ADJUSTING FRONT TO BACK SQUARENESS
NOTE: When making adjustments, guide bar lock
screw must be loosened. To check squareness it must
be tightened.
a. Loosen guide bar lock screw and lower guide bar
until it rests on table. Leave lock screw loose,
b. Loosen two hex head screws on the top of frame
tube.
c. Loosen lock nuts on guide bar bracket adjustment
screws.
NOTE: Turning guide bar bracket adjustment screws
clockwise will move quide bar toward front of saw.
Turning screws counter clockwise will move guide bar
to rear of saw.
d, Turn guide bar bracket adjustment screws 1/4
turn using phillips screwdriver.
e, Tighten hex head screws on top of frame tube.
f. Raise guide bar I-3/4 inches and tighten guide
bar lock screw.
g. Check squareness. Readjust if necessary,
hA Hold guide bar bracket adjustment screws with
phillips screwdriver and tighten lock nuts.
GUIDE BAR _11
BRACKET \"_J
ADJUSTMENT \_
SCREWS _-
LOCKNUTS__
_.._-- HEX HEAD
7SCREWS
FGUIDE BAR
iBRACKET
12

assembmy
ADJUSTBNG S_DE TO $_DE SQUARENESS
NOTE: When making adjustments, guide b_r iock
screw must be loosened. To check squareness it must
be tightened.
a. Loosen guide bar lock screw and lower g_Jide bar
until it rests on table. Leave lock screw loose,
b. Loosen two hex head screws on top of frame tube.
c. Grasp guide bar as illustrated and move to the side
needed to square it with table. -[his wilt slide the
guide bar bracket into position.
d. Tighten hex head screws on the top of frame tube,
e. Raise guide bar 1-3/4 inches and tighter_ _j_ide bar
lock screw.
f. Check squareness. Readjust if necessary.
tP
!/y--- HEX HEAD
_ SCREWS
_ _GUiDEBAR
i _" 8RACKET
ADJUSTING UPPER BLADE GUIDE ASSEMBLY
NOTE: The upper and lower blade guides support the
blade and keep it from twisting during operation. An ad-
justment is necessary when bRades are changed or re-
placed.
1. Loosen two hex head screws in upper blade guide
assembly and slide assembly forward in the slots
until the front edge of the blade guides are approxi-
mately 1/32"from the GULLET of the saw blade.
2. Tighten two hex head screws.
NOTE: It may be necessary to back out thrust roller ad-
justment to allow thrust roller to move back from blade
to get 1/32" clearance from the gullet to edge of blade
guide.
GULLET--_Z "Z
l
Z
_""-...-- B LAD EGUIDE
!l
""_ I'_'---APPROX,
1132
q
ADJUSTING UPPER BLADE GUIDES
1. Loosen the two cap screws that lock the upper
blade guides and press the two guides evenly
against thesides of the blade but do not pinch the
blade. ReJease the guides and rotate the upper
wheel slightly clockwise moving the blade down,-
ward. Make sure one guide is not further away
from the blade than the other. Tighten both cap
screws.
SAW BLADE
CAP
SCREW
BLADE
GUBDE{ CAP
SCREW
13

assembly
ADJUSTING UPPER THRUST ROLLER
NOTE: The thrust toilers support the b}ade from the
rear and w_ll rotate when the blade is pushed against
them wh_le you are cutting. As soon as you stop cut-
ting, the rotters should stop rOtating,
t To be sure the thrust roller is properly supporting
the blade, turn the thrust roller adjustment screw
using 5/32" setscrew wrench so that the roller
moves towar(_ the blade and almost touches.
2, Whiie turn_ng th_ upper wheel clockwise by hand,
adjust the thrust roller until it barely touches the
blade and starts to rotate. Now move the roller
back shghtly until it stops rotating while upper
wheel is rotated.
3. T_gn[er,. lock nut while holding thrust roller adjust,
ment screw with setscrew wrench.
THRUST
ROLLER --7
/
/
/
}°0
_--- BLADE
ADJUSTING LOWER BLADE GUIDE ASSEMBLY
1. Turn Iock nuts on lower blade guide assembly
counter clockw=se and move lower blade guide
assembly forward until the front edge of the blade
guides are app{oximately 1/32" from the GULLET
of the _w bfade,
NOTE: It may be necessary to back out thrust roller ad-
lustment to allow thrust roller to move back from the
blade to get !132" clearance from the gullet to edge of
blade guide.
2. Tighten lock nuts,
GUIDE
LOCK NUT
rHRUST ROLLER
ADJUSTMENT
SCREW
APPROX.
_ 1t32" THRUST ROLLER
Z _ "2_ ADJUSTMENT
°i
ADJUSTING LOWER BLADE GUIDES
1. Loosen the two cap screws that lock the lower
blade guides and press the two guides evenly
against the s_des of the blade but do not pinch the
blade. Release the guides and rotate the upper
wheet stightty clockwise moving the blade down-
ward. Make sure one guide is not further away
from the blade than the other, Tighten both cap
SCre_¢S.
SAW _ _4"-" B LAD E
BLADE "I_ _GUIDES
" CAP SCREWS
14

assembty
ADJUSTING LOWER THRUST ROLLER
t. To be sure the thrust rotler is properly supporting
the biade, turn the thrust rol!er adiustment screw
using 532" setscrew wrench so that the roller
moves toward the blade and a!most touches,
2, Whiie turning the upper wheel clockwise by hand,
adjust the thrust roller unti! it barely touches the
blade and starts to rotate. Now move the roller
back si;ghtly untii it stops rotating while upper
wheei is rotated,
3, Tighten iock nut whi!e ho!ding thrust roller adjust-
ment screw with setscrew wrench.
4, Rotate the upper wheei a few times by hand and
check the blade guides and thrust rollers. Make re-
adiustments if necessary,
THRUST ROLLER
ADJUSTMENT
!! _CREW
THRUST ROLLER t
ADJUST|NG THE TABLE
I Replace the blade guard on the upper guide assem-
bly and tighten screws.
2. Locate the table insert and place it in the opening in
the tabte,
3. Locate a 1/4 - 20 x ! " truss head screw, a flat wash-
er, and a 1/4 -. 20 wing nut among loose parts, in-
sert screw into hoie in table top as illustrated.
4. From the underside of the table, install washer and
wing nut onto the truss head screw and tighten
finger tight. This wit! keep the table flat and in
alignment,
5. Replace the cover.
TRUSS
HEAD
SCREW---_
!
HER
GUARD
6, Blade should be in approximate center of slot in
_nsert.
7. If blade runs to one side, loosen hex head screws
that mount table to trunnion and shift table to cen-
ter blade in table insert.
8. Tighten screws,
t5

getting to know your band saw
8
ON-OFF SWITCH
\\\
COVER
J
j_
1
//---- TENSION ADJUSTMENT KNOB "-_
COVER RETAINING
CLIP (5 USED)
7
LOWER
BLADE
GUIDES
3
GUIDE BAR
LOCK SCREW
FBLADE GUARD
TABLE -_
/
\
/
4
UPPER THRUST
ROLLER ADJUSTMENT
7BLADE
GUIDES
6
TILT
SCALE
2
TENSSON SETTING
(gNSODE}
4
LOWER THRUST
ROLLER ADJUSTMENT
5
TABLE LOCK KNOB
FRONT BACK
1. TENSION ADJUSTMENT KNOB...Tightening
the knob will increase the tens=on on the blade,
Loosening it wilt decrease the tension.
2. TENSION SETTING...The marking indicates the
correct blade tension for the blade. For example,
when installing the blade, tighten the tension ad-
justment knob until the indicator washer is pointing
to the marking on the inside of cover.
3. GUIDE BAR LOCK SCREW... The upper blade
guides should just clear the workpiece while cut-
ting. Always adjust the upper guide assembly and
tock the guide bar by tightening the guide bar lock
screw before turning on the band saw.
4. THRUST ROLLER ADJUSTMENT...Turning
the adjustment screw moves the thrust roller in or
out to support the blade from the rear while cut-
ting,
5. TABLE LOCK KNOB ...Turning the knob allows
the table to be tilted and locks it in place.
6. TILT SCALE .,. Shows degree table is tilted,
7. BLADE GUIDES.,. Supports the blade and keeps
it from twisting during operation. An adjustment is
necessary when blades are changed or replaced.
8, ON-OFF SWITCH... See below and next page.
ONOFF SWITCH
The On-Off Switch has a locking feature, THiS FEA-
TURE IS iNTENDED TO PREVENT UNAUTHORIZED
AND POSSI8LY HAZARDOUS USE BY CHILDREN
AND OTHERS.
1, insert key into switch.
NOTE: Key is made of yellow plastic.
LLON I
16

getting to know" your
2. To turn machir_e on, insert finger under switch 'ew!}_
arid pu4 e_d of switch out,
band
3. To turnmachh_e OFF .. PUSH lever ir_.
NEVER LEAVE THE MACHINE UNATTENDED
UNTIL IT HAS COME TO A COMPLETE STOP. ii'
4. To lock switch in OFF position.,, hold switch IN
with one hand .,, REMOVE key with other hand,
WARNING: FOR YOUR OWN SAFETY, ALWAYS
LOCK THE SWITCH "OFF" WHEN MACHINE IS
NOT IN USE... REMOVE KEY AND KEEP IT IN A
SAFE PLACE... ALSO...IN THE EVENT OF A
POWER FAILURE (ALL OF YOUR LIGHTS GO OUT)
TURN SWITCH OFF.., REMOVE THE KEY AND
STORE DTREMOTE FROM BAND SAW. THIS WILL
PREVENT THE MACHINE FROM STARTING UP
AGAIN WHEN THE POWER COMES BACK ON.
basic band saw operation
A band saw is basically a "curve cutting" machine. It is also used for straight-line cutting operations such as cross-
cutting, ripping, mitering, beveling, compound cutting, and resawing, tt is not capable of doing inside curing.
This band saw is not designed to cut metal.
SAWING
1. Adjust the upper guide assembly to just clear the
workpiece.
2. Use both hands while feeding the work into the
blade. Hold the workpiece firmly against the table.
Use gentle pressure, and do not force the work, but
allow the blade to cut.
BLADE SELECTION GUIDE FOR
MINIMUM CIRCLE CUTTING
,The smallest diameter circle that can be cut out is
determined by the width of the blade. For example,
a 1/4" wide blade will cut a minimum diameter of
approximately 1-1/2 £(See Chart)
BLADE SIZE 114" 3,!8,,
t7

maintenance
WARNING: FOR YOUR OWN SAFETY. TURN
SWITCH "OFF" AND REMOVE PLUG FROM
POWER OUTLET BEFORE MAINTAINING OR
LUBRICATING YOUR BAND SAW.
TIRES
Pitch and sawdust that accumulate on the tires should
be removed with a stiff brush or scraped off with a
piece of wood. Do not use a sharp knife or any kind of
solvent,
When the t_res become worn they should be replaced.
_%'hen replacing the tires, stretch them around the
wheels but do not g_ue them on.
GENERAL
Keep your Band Saw clean.
Remove sawdust from the inside.
Do not altow pitch to accumulate on the table, blade in-
sert. blade guides, or thrust rollers. Clean them with
Craftsman Gum and Pitch Remover.
Apply a thin coat of automobile-type wax on the table
so tt_e wood slides easily while cutting. Also apply wax
to the _nside surfaces of the trunnion.
MOTOR
Frequently vacuum or blow out any sawdust from the
motor,
If the power cord is worn, cut, or damaged in any way,
have it replaced immediately.
LUBRICATION
All of the BALL BEARINGS are packed with grease at
the factory. They require no further lubrication.
BLACK
MOTOR
RECOMMENDED ACCESSORIES
Item Cat. No.
Floor Stand ............................... 9-2221 3
Miter Gauge .............................. 9-29929
Rip Fence ................................ 9-23433
Blades ................................ See Catalog
Steel Leg Set ........................... 9-22244
Circle Cutting Attachment ................... 9-24301
Table Extension ........................... 9-24302
Power Tool Know How Handbooks
Radial Saw ................................ 9-2917
Table Saw ................................. 9-2918
The above recommended accessories are current
and were available at the time this manual was
printed.
18

troubleshooting
WARNING: FOR YOUR OWN SAFETY, TURN SWITCH "OFF" AND REMOVE PLUG FROM POWER
SOURCE OUTLET BEFORE TROUBLESHOOTING YOU_ BAND SAW.
TROUBLE PROBABLE CAUSE REMEDY
Motor will not run, I.
Blade does not run in the
approximate center of the
upper wheel,
Blade does not run in the
approximate center of the
lower wheel.
Band Saw s_ows down
when cutting.
Blades breaking.
2,
Defective OnOff switch.
Defective switch cord.
Defective switch box receptacle.
Motor Defective,
1, Not tracking properly.
Upper wheel not positioned
correctly on shaft.
1, Cutting too small a radius.
2. Dull blade.
1. Too much tension,
2. Kink in blade caused by cutting
too small a radkJs or turning the
material too fast when cutting.
t, Replace defective parts before using
Band Saw again,
2. Consut[ Sears Service. Any attempt, to repair
this motor may create a HAZARD unJess
repair is done by a qualified serv}ce techniciar'.
Repair service is available at your nearest Sears
Store,
1. Adjust tracking, see Assembly Sectior_,
"Tracking the Blade."
1, Reposition tile wheel, see Assembly
Section, "Tracking the Blade."
1. Stop feeding, and back up to the material
slightly, until the band saw speeds up.
2. Replace blade.
1. Adjust tension. See Getting To Know
Your Band Saw "Tension Setting".
2. Use correct cutting technique. See Basic
Band Saw Operation Section.
19

CRAFTSMAN 10-INCH BAND SAW, MODEL 113.244401
o
/
/12
46
\42
40
41
\
3
14 1_, 11 12 13
\
/
44 45
FIGURE 1
16
\
18

I
CRAFTSMAN 10-INCH BAND SAW, MODEL 113.244401
Always order by Part Number - not by Key Number
FIGURE 1 PARTS LIST
I'O
KEY
NO.
1
2
3
4
5
6
7
8
9
10
1!
12
!3
!4
15
16
17
!8
19
20
2!
22
23
24
25
PART
NO. NAME
69031
60386
60430
69109
STD600603
63467
69118
60256
62442
69119
STD375006
STD601103
STD 55121
60289
69123
69128
69127
60419
60321
60432
!60323
STD551025
STD54t625
69129
69133
Knob Asm, Tension
Washer, 15/32 x 1-3/8 x 3/64
Washer .47 x 2.5 x .06
*Spring, Tension
*Screw, Pan Cross Type T6-32 x 3/8
Cap-Flag Terminal
Cover, Switch
Key, Switch
Switch
Cord
*Connector, Wire
*Screw, Pan Rec Type T 10-32 x 3/8
*Lockwasher, Ext. NIO
Ring, Hog
Cord with Plug
Seal, Motor Foam
Cover, Motor
Screw, Pan Hd. Plastite 8-16 x 1/2
Screw, Thumb 5/16-18 x 1-1/2
Spacer, 7/16 ID x 1800
Screw, Truss Hd. 1/4-20x 1
*Washer, 17/64 x 5/8 x 1/16
*Nut, Wing 1/4-20
Table
Table Insert
KEY PART
NO. NO. NAME
26
27
28
29
30
31
32
33
34
35
36
37
38
39
40
41
42
43
44
45
46
47
69120
69121
60076
63387
109751
STD551031
STD541110
STD551131
STD523107
60431
69084
139377
STD541031
273229
69110
18232
193250
69114
69112
69115
69126
STD551008
69187
69132
Trunnion
Guide, Trunnion
Washer, .505 x 7/8 x t/16
Knob
Bolt, Carriage 5/16-18 x 2-3/4
*Washer, 21/64 x 7/8 x 1/8
*Nut, Hex 10-32
*Lockwasher, 5/16
*Screw, Hex Hd. 5/16-18 x 3/4
Screw, Soc Cap 10-32 x 2-1/2
Foot, Frame
Screw, Hex Soc Set 5/16-18-1
Nut, Hex 5/16-!8
Screw, Hex Type T 1/4-20 x 1/2
Bar, Guide
Roller, Blade Thrust
Screw, Hex Soc Cap 10-32 x 7/8
Guide, Blade
Bracket Asm, Upper
Guard, Blade
Cover Asm., Front
*Washer, 3/16 x 3/8 x 1/16
Owners Manual (Not Illustrated)
Bag Of Loose Parts (Not Illustrated)
"Standard Hardware Item - May Be Purchased Locally.
tStock item -- May be secured through the Hardware Department of most Sears or Simpsons-Sears Retail Stores or Catalog
Order Houses.
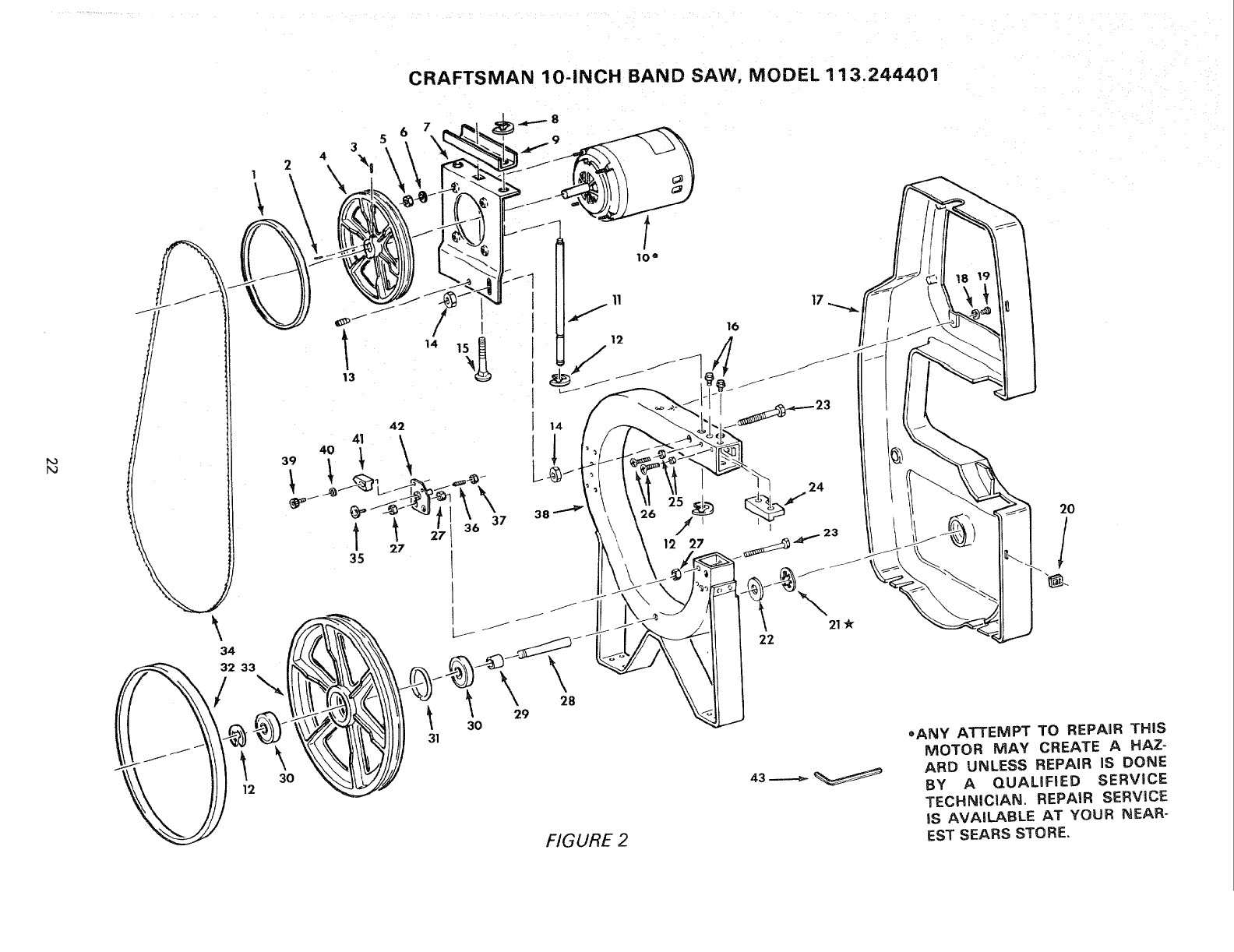
CRAFTSMAN 10-iNCH BAND SAW, MODEL 113.244401
43 i--,--_
FIGURE 2
2O
i
oANY ATTEMPT TO REPAIR THIS
MOTOR MAY CREATE A HAZ-
ARD UNLESS REPAIR IS DONE
BY A QUALIFIED SERVICE
TECHNICIAN. REPAIR SERVICE
IS AVAILABLE AT YOUR NEAR-
EST SEARS STORE,

CRAFTSMAN 10-iNCH BAND SAW, MODEL 113,244401
FIGURE 2PARTS LIST
I'J
KEY I PART
NO. INO.
t69117
STD503105
4 69116
5 !STD541008
6 STD551208
769106
8 STD581050
9 69108
10 69137
11 69107
12 STD581062
13 102584
t4 STD541425
15 109129
16 273229
17 69124
18 STD551010
19 STD601105
20 69125
2! 60525
22 37838
NAME
Tire
*Key, Square 3/16 x 15/16
*Screw, Hex Soc 5/16-18 x 5/8
Wheel, Drive
*Nut, Hex 8-32
*Lockwasher, Ext. N8
Motor Mount Assembly
*Ring, Retaining 1/2
Bracket, Guide Rod
®Motor
Rod, Guide
*Ring, Retaining 5/8
Screw, Set Hex Cup 5/16-18 x 3/4
Lock Nut, 1/4-20
Bolt, Carriage 7/16-14 x 3
Screw, Hex Type T 1/4-20 x 1/2
Cover, Rear
*Washer, 13/64 x 7/16 x 1/16
_Screw, Pan Rec. Type T 10-32 x 1/2
Latch
_rRing, Retaining 5/8
Washer,.629 x 7/8 x 1/64
KEY
NO.
23
24
25
26
27 i
28 1
291
30 I
31 I
32 I
33 I
34 I
35 I
36 I
37 I
38 I
391
40
41
42
43
PART
NO.
814584
69111
STD5411!0
9416390
STD541025
69142
60433
STD315228
41812
41815
69028
69130
18232
139377
STD541031
69105
193250
STD551210
69114
69113
37837
NAME
Screw, Spl. Hex Hd. 1/4-20 x 3-1/4
Bracket, Guide Bar
*Nut, Hex 10-32
Screw, Pan Cross Type "'T'" 10-32 x 5/8
Nut, Hex 1/4-20
Shaft, Wheel (Includes Key 2!)
Spacer
*Bal! Bearing
Ring, Retaining
Tire
Wheel, idler
tBlade, Band Saw 1/4 x 72-5/8
Roller, Blade Thrust
Screw, Hex Soc Set 5/16-18 x 1
Nut, Hex 5/16-18
Frame Assembly
Screw, Hex Soc Cap 10-32 x 7/8
*Lockwasher, Int. N10
Guide, Blade
Bracket Asm., Lower
!-Wrench, Hex "L" 5/32
*Standard Hardware Item - May Be Purchased Locally,
tStock Item -- May be secured through the Hardware Department of most Sears Retail Stores or Catalog
Order Houses.
_-If this part is removed, discard and replace with a new Retaining Ring,

SERVICE
M ODEL NO.
1 1 3.244401
HOW TO ORDER
REPAIR PARTS
10-1NCH NO SAW
Now that you have purchased your l O-inch Band Saw
should a need ever exist for repair parts or service, sim-
ply contact any Sears Service Center and most Sears,
Roebuck and Co. stores. Be sure to provide all pertinent
facts when you call or visit.
The model number of your lO-Inch Band Saw will be
found on a plate at the right-hand side of the saw.
WHEN ORDERING REPAIR PARTS, ALWAYS GIVE THE
FOLLOWING INFORMATION:
PART NUMBER PART DESCRIPTION
MODEL NUMBER
113.244401
NAME OF ITEM
lO-Jnch Band Saw
All parts listed may be ordered from any Sears Service
Center and most Sears stores. If the parts you need are
not stocked locally, your order wil be electronically
transmitted to a Sears Repair Parts Distribution Center
for handling.
Sold by SEARS, ROEBUCK AND CO., Chicago, IL. 60684 U.S.A.
Part No. 69187 Form No SP501 !-t Printed in U.S.A. 10/86