User manual
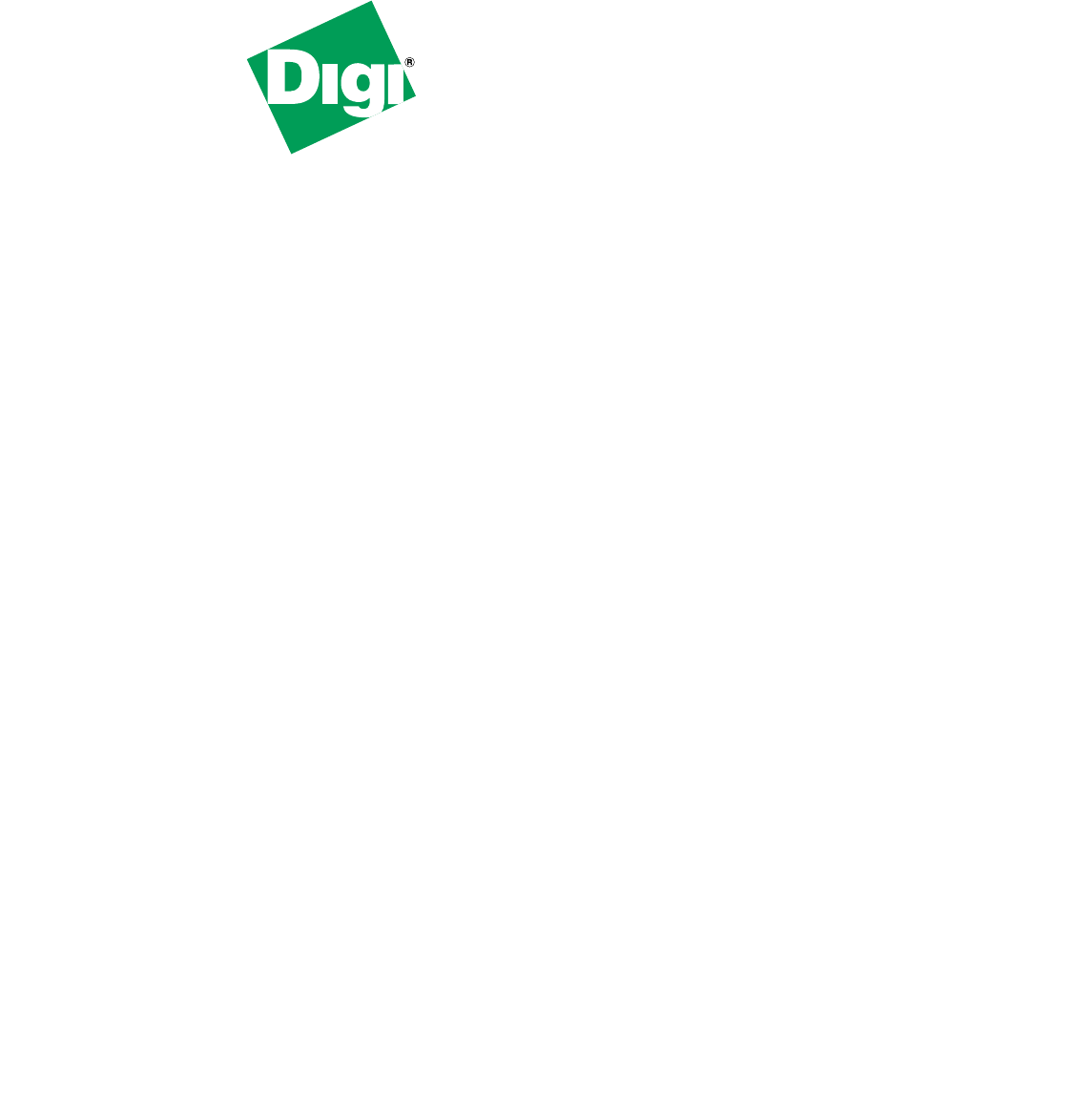
Digi Connect®Wi‐EM9210
HardwareReference
Part number/version 90000955_A
Release date: August 2008
www.digiembedded.com
© Digi International Inc. 2008. All Rights Reserved.
The Digi logo and Digi Connect are registered trademarks of Digi International, Inc.
Connectware and Digi Connect Wi-EM are trademarks of Digi International, Inc.
NetSilicon, NET+Works, NET+OS, and NET+ are trademarks of NetSilicon, Inc.
All other trademarks mentioned in this document are the property of their respective owners.
Information in this document is subject to change without notice and does not represent a commitment on the part of Digi
International.
Digi provides this document “as is,” without warranty of any kind, either expressed or implied, including, but not limited to,
the implied warranties of fitness or merchantability for a particular purpose. Digi may make improvements and/or changes
in this manual or in the product(s) and/or the program(s) described in this manual at any time.
This product could include technical inaccuracies or typographical errors. Changes are periodically made to the information
herein; these changes may be incorporated in new editions of the publication.

5
Contents
About This Guide .....................................................................................................................7
Scope of Reference Manual .............................................................................................7
Related Documentation....................................................................................................7
Support Information .........................................................................................................7
Chapter 1: About the Embedded Module............................................................................9
Overview ..........................................................................................................................9
Types of Modules...........................................................................................................10
Connectors: Power and Serial Interface.........................................................................11
Connectors: Antenna......................................................................................................13
Reset Switch...................................................................................................................14
Module LEDs .................................................................................................................14
Chapter 2: About the Development Board ........................................................................17
Overview ........................................................................................................................17
Basic Description ...........................................................................................................17
Ports................................................................................................................................19
Connectors and Blocks...................................................................................................20
Power Jack (P17)............................................................................................................25
Switches..........................................................................................................................26
Development Board LEDs .............................................................................................28
Test Points......................................................................................................................29
Chapter 3: Programming Considerations..........................................................................33
GPIO...............................................................................................................................33
About Embedded Module LEDs....................................................................................39
Embedded Module Reset................................................................................................40

6
Memory..........................................................................................................................40
Appendix A: Specifications ................................................................................................. 43
Network Interfaces......................................................................................................... 43
Serial Interface............................................................................................................... 44
Data Rates (bps)............................................................................................................. 44
Flow Control Options..................................................................................................... 44
Environmental................................................................................................................ 44
DC Characteristics ......................................................................................................... 44
Mechanical .................................................................................................................... 46
Layouts and Dimensions................................................................................................ 46
Antenna Information...................................................................................................... 51
RF Exposure Statement.................................................................................................. 56
Safety Statements........................................................................................................... 56
Notes to original equipment manufacturer (OEM ) integrators..................................... 57
Appendix B: Certifications ................................................................................................. 59
FCC Part 15 Class B ...................................................................................................... 59
Industry Canada ............................................................................................................. 60
Declaration of Conformity............................................................................................. 61
International EMC Standards......................................................................................... 62
Appendix C: Sample Application: TTL Signals to EIA-232............................................ 63
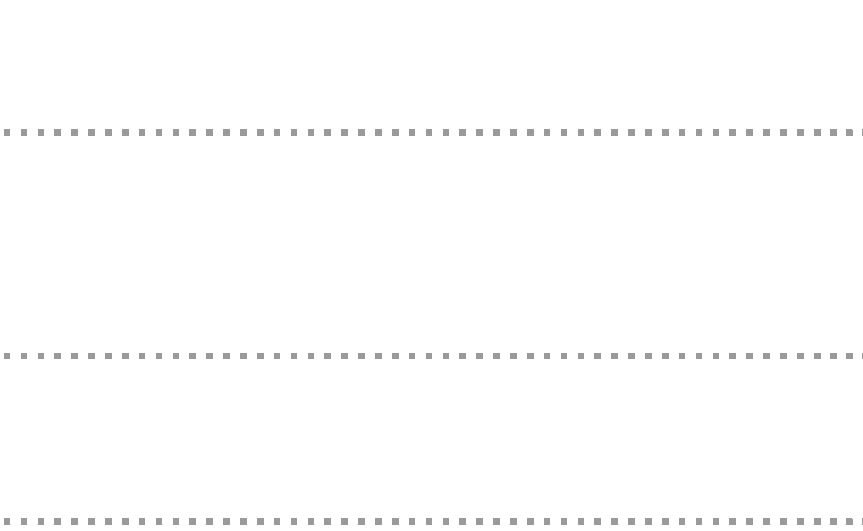
7
•••••••••••••••••••••••••••••••••••••••••••••••••••
About This Guide
Scope of Reference Manual
The scope of this guide is to enable developers to integrate the Digi Connect Wi-
EM 9210 modules into other devices. Graphics illustrate the placement and
dimensions of components for both the modules and the development board.
Related Documentation
See the NS 9210 Hardware Reference for information on the NS 9210 chip.
Support Information
To get help with a question or technical problem or make comments and
recommendations about Digi products and documentation, use the following
contact information.
General Customer Service and Support
Digi International
11001 Bren Road East
Minnetonka, MN 55343
U.S.A.
United States: 1 877-912-3444
Other Locations: 1 952-912-3444
www.digiembedded.com/support
www.digiembedded.com

Support Information
8
Digi Connect EM & Wi-EM Hardware Reference
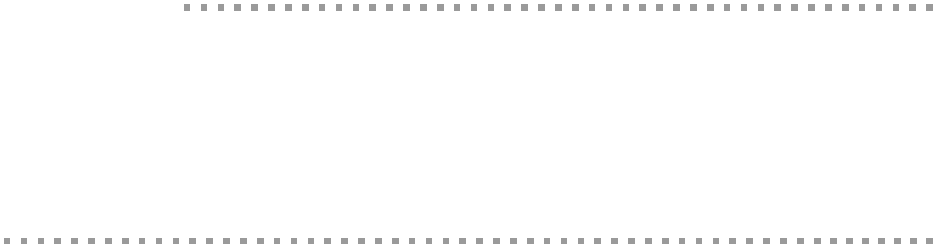
9
About the Embedded
Module
CHAPTER 1
Overview
Digi Connect Wi-EM 9210 Overview
The embedded modules are part of the Digi Connect family of device servers that provide
simple, reliable and cost-effective network connections for serial devices. They provide
fully transparent serial device connectivity over industry-standard wireless connections and
allow both equipment manufacturers and systems integrators to network-enable products at
a fraction of the time and cost required to develop a custom solution. It is a highly flexible
and compact single component solution with a robust on-board TCP/IP stack and wireless
support. Features include the following:
32-bit Digi Wi-EM 9210 processor with ARM926EJ-S core
4MB Flash and 8MB RAM on board
2 High Speed Serial Ports
SPI Master Mode Interface
9 General Purpose Input/Output Port Options
NetSilicon NET+Works platform for embedded software development
From medical systems to building control and industrial automation, in virtually any
application where embedded serial connectivity over WLAN is needed, the embedded
module is the ideal choice, delivering high-performance functionality.
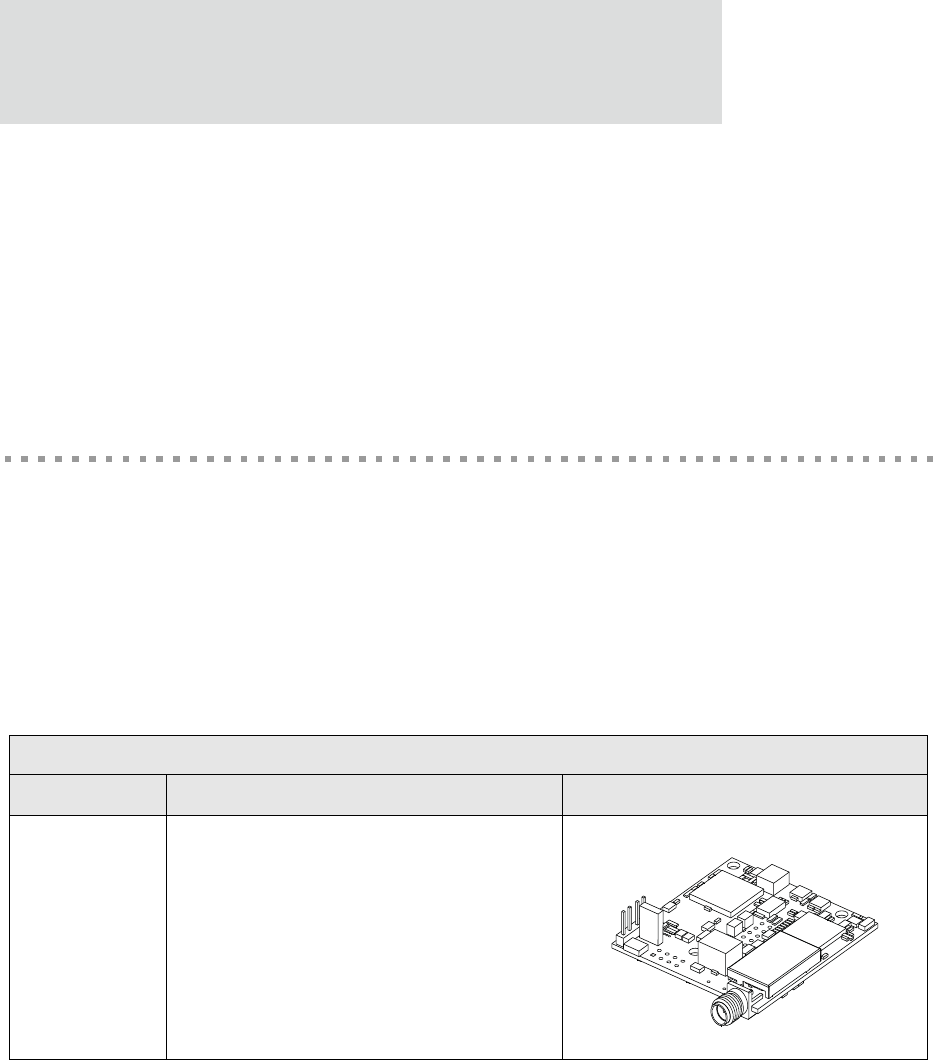
Types of Modules
10
Digi Connect Wi-EM 9210 Hardware Reference
Cautions
To guard against damage to the module due to electrostatic discharge (ESD), do not
remove it from its protective packaging until you have been properly grounded. To ground
yourself, put the wrist strap on (included in the package) and then attach the clip to a metal
surface.
Input voltage for the module is 3.3 VDC.
Types of Modules
The following describes the available types of Digi Connect Wi-EM 9210 modules:
Choosing a Module for Your Product
Although any of the embedded modules can be designed into your product, a JTAG header
would typically be used only for debugging during the development process. The following
shows all available Digi Connect Wi-EM 9210 product options.
DC-EM-02T-ST.C
Digi Connect Wi-EM Modules
Model Description Figure
DC-WEM-9210-JT
--- Used for development purposes only
--- JTAG interface
--- Pin headers LED functionality
--- Single RP-SMA Antenna Connector.
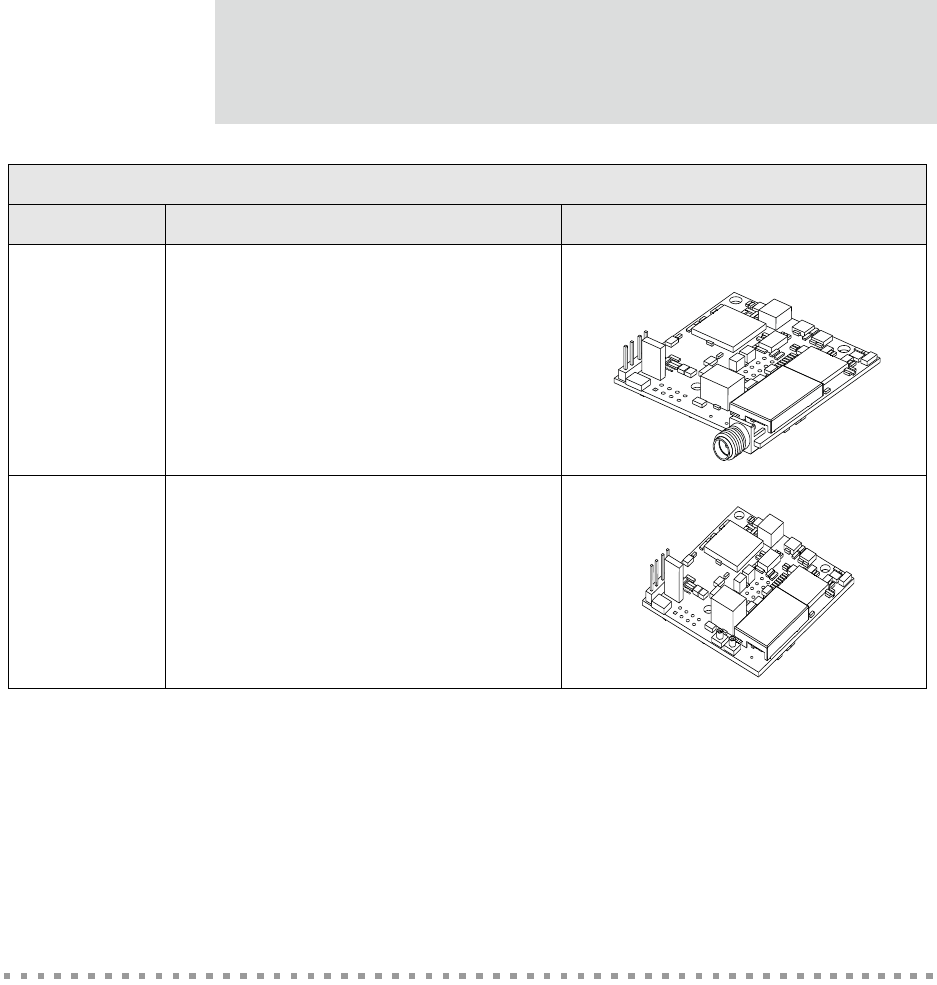
11
About the Embedded Module
Digi Connect Wi-EM Antennae
The Digi Connect Wi-EM 9210 is available with U.FL dual-diversity or single RP-SMA
antenna connectors. In case of dual diversity, the right antenna (P2) is always used for
transmit and receive. The left antenna is receive only. The antenna will choose the best
signal.
Connectors: Power and Serial Interface
This single 12-pin, serial interface port (P5) supports 2 TTL serial interfaces, data rates up
to 921 Kbps and full-modem control (on port 1). See the figure for help locating pins and
the table for pin assignments.
DC-WEM-9210-
IN-1
--- No JTAG interface
--- Pin headers LED functionality
--- Single RP-SMA Antenna Connector
--- Ordered independently of
development kit for use in your
implementation
DC-WEM-9210-
SB-1
--- No JTAG interface
--- No LED array/pin header
--- Dual U.FL Antenna Connector
--- Ordered independently of either
development or integration kit for use
in your implementation.
Digi Connect Wi-EM Modules
Model Description Figure
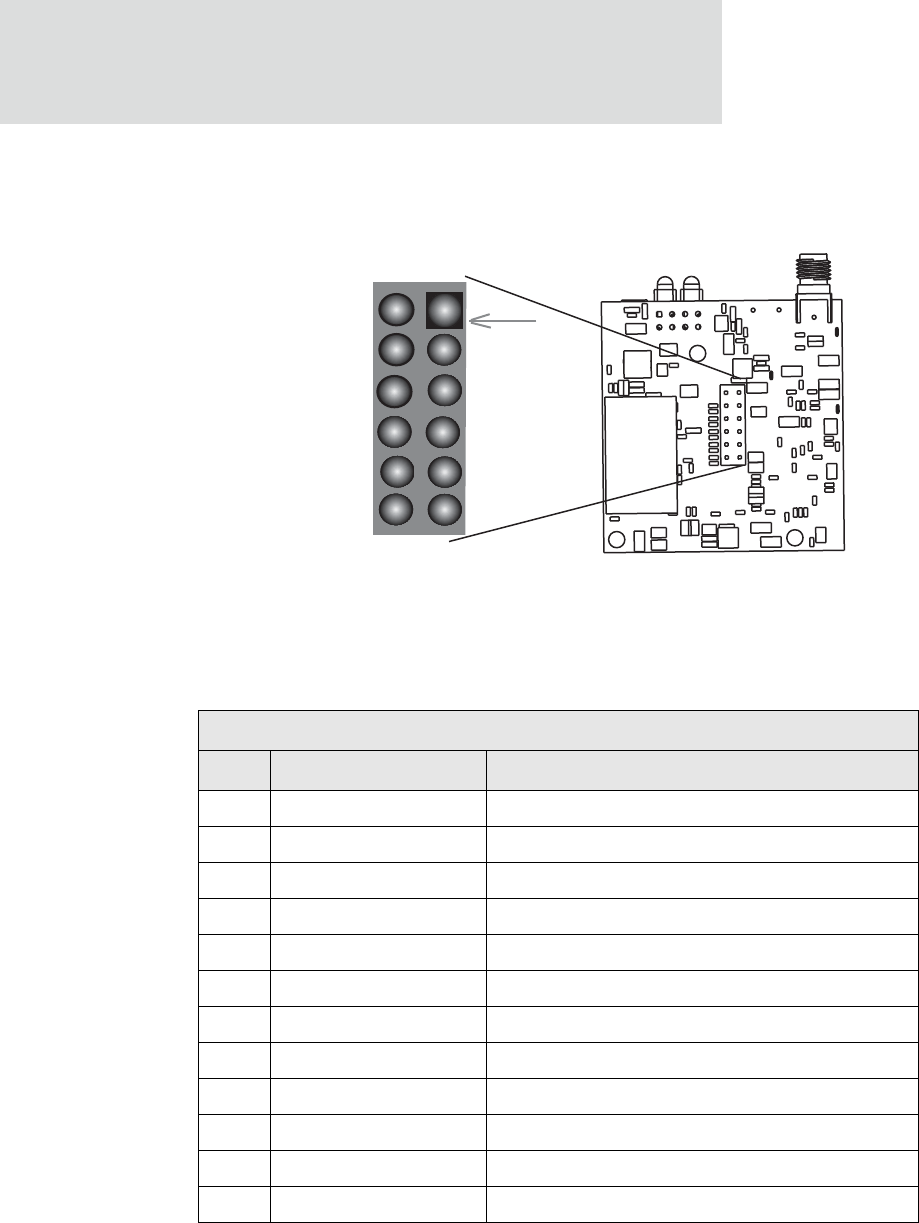
Connectors: Power and Serial Interface
12
Digi Connect Wi-EM 9210 Hardware Reference
Power and Serial Interface
Power and Serial Interface Pin Assignments
Pin Signal Name Description and Notes
1 VCC +3.3 VDC (input only)
2 GND Reference Ground for input power
3 RXD/GPIO-7 Port 1 RXD (input)/GPIO-7
4 TXD/GPIO-6 Port 1 TXD (output)/GPIO-6
5 RTS/GPIO-4/SPI_CLK Port 1 RTS/GPIO-4/SPI clock
6 DTR/GPIO-5 Port 1 DTR (output)/GPIO-5
7 CTS/GPIO-2 Port 1 CTS (input)/GPIO-2
8 DCD/GPIO-1/SPI_EN Port 1 DCD (input)/GPIO-1/SPI enable
9 DSR/GPIO-3 Port 1 DSR (input)/GPIO-3
10 /RST Reset (input)
11 RXD/GPIO-9 Port 2 RXD (input)/GPIO-9
12 TXD/GPIO-8 Port 2 TXD (output)/GPIO-8
pin 1
23
45
top view
11
7
9
8
10
12
6
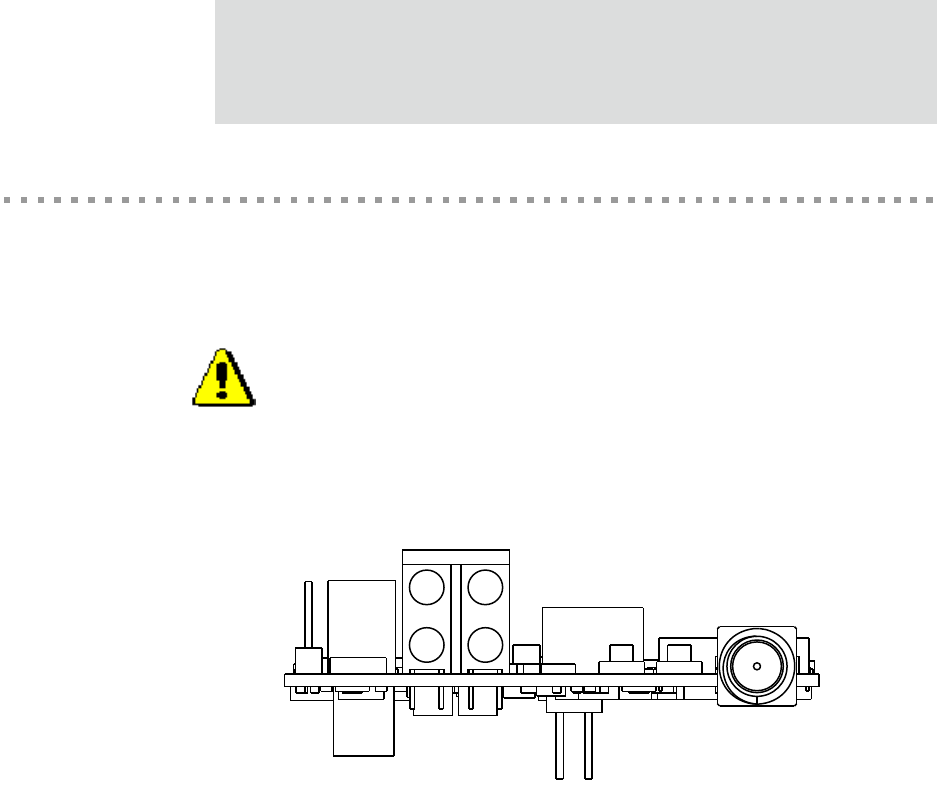
13
About the Embedded Module
Connectors: Antenna
The Digi Connect Wi-EM is available in two antenna configurations: (1) two U.FL antenna
connectors for dual-diversity, or (2) a single RP-SMA antenna connector.
Wi-EM Antenna Connectors
.
Caution: This Part 15 radio device operates on a non-interference basis
with other devices operating at this frequency when using the antennae
listed in the Antenna Specification table. Any changes or modification to
user’s authority to operate the device.
the product not expressly approved by Digi International could void the
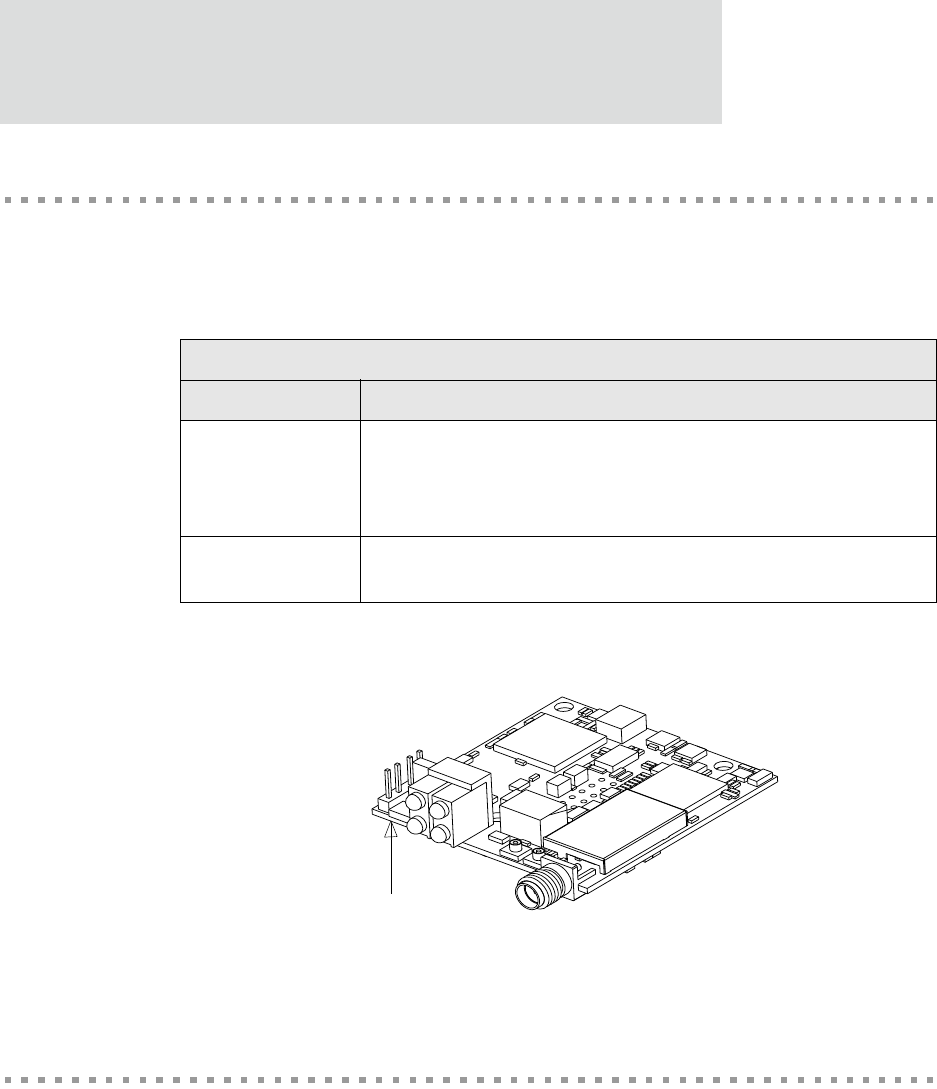
Reset Switch
14
Digi Connect Wi-EM 9210 Hardware Reference
Reset Switch
The behavior of the reset switch is determined by software, which means that it has a
predefined behavior in the integration kit. In the development kit, its behavior is
determined by your implementation. See the following table for details.
Reset Switch Location
Module LEDs
The modules provide two hardware options for LEDs, with or without on board LED array.
The integration kit provides predefined LED behavior. With the development kit, some
LED behavior can be determined by your implementation. See the following table for more
information..
Reset Switch Behavior
Kit Behavior
Integration The reset switch does one of the following:
If pressed and released immediately, the device is rebooted.
If pressed and held down (for about 20 seconds) during power-up, the
device is rebooted and restored to the default configuration.
Development The behavior of the switch is user-defined.
See "Embedded Module Reset" on page 40 for more information.
Reset switches
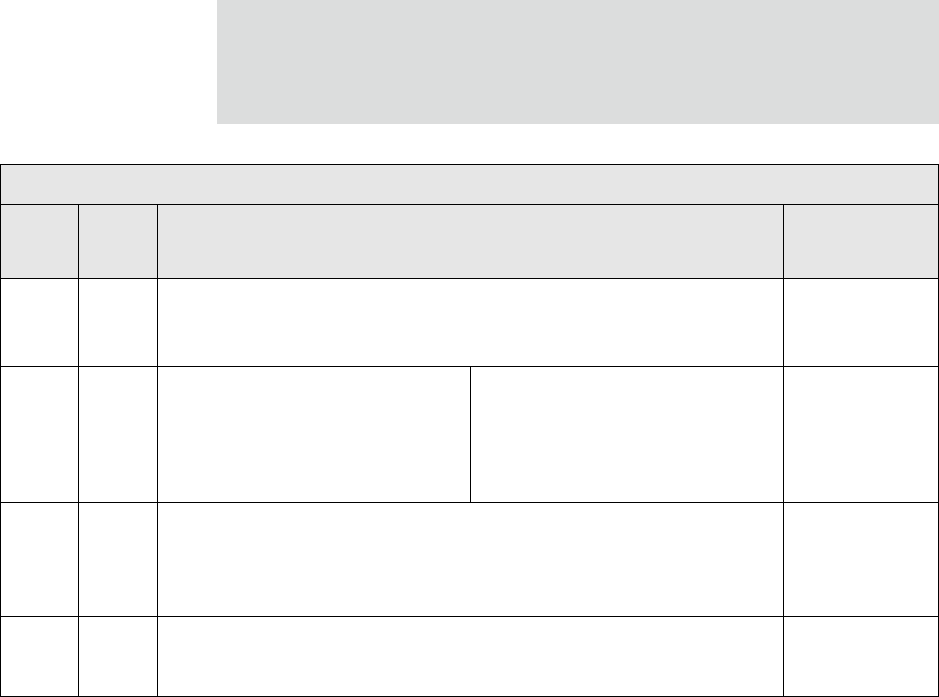
15
About the Embedded Module
LED Behaviors
LED Pin
Header
EM Description Notes
Top left
(green)
1 (+)
3(-)
Serial port activity:
Off - the serial channel is idle.
Blinking - serial data is transmitted or received.
This LED is
software
programmable
Top
right
(green)
5 (+)
7 (-)
Network link status:
Off - no link has been detected.
On - a link has been detected.
Network link status:
On - unit is associated with an access point
Blinking slowly - unit is in ad hoc mode
Blinking quickly - unit is scanning for a
network
Same as
Integration Kit
(Network link
status)
Bottom
left (red)
2 (+)
4 (-)
Diagnostics:
Blinking 1-1-1 - starting the operating system.
Blinking 1-5-1 - configuration has been returned to factory defaults.
Note: If other blinking patterns occur, contact Digi Technical Support.
This LED is
software
programmable
Bottom
right
(yellow)
6 (+)
8 (-) Blinking - network data is transmitted or received This LED is
software
programmable
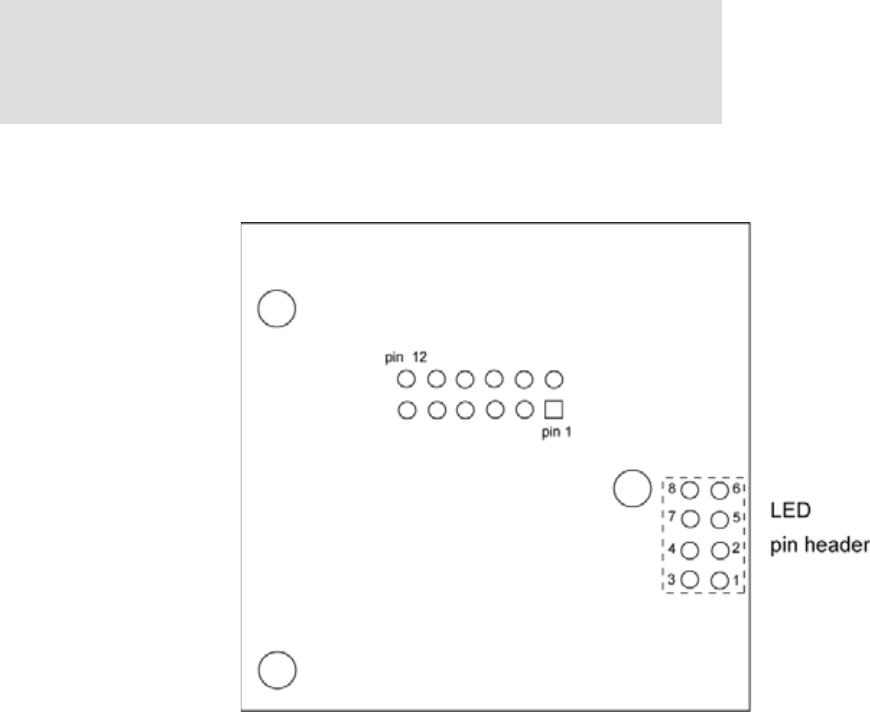
Module LEDs
16
Digi Connect Wi-EM 9210 Hardware Reference
Digi Connect Wi-EM 9210 Pin Header Locations (Top view)
LED pin header
LED pins and pin header configuration are described in the "LED Behaviors" table on
page 15.
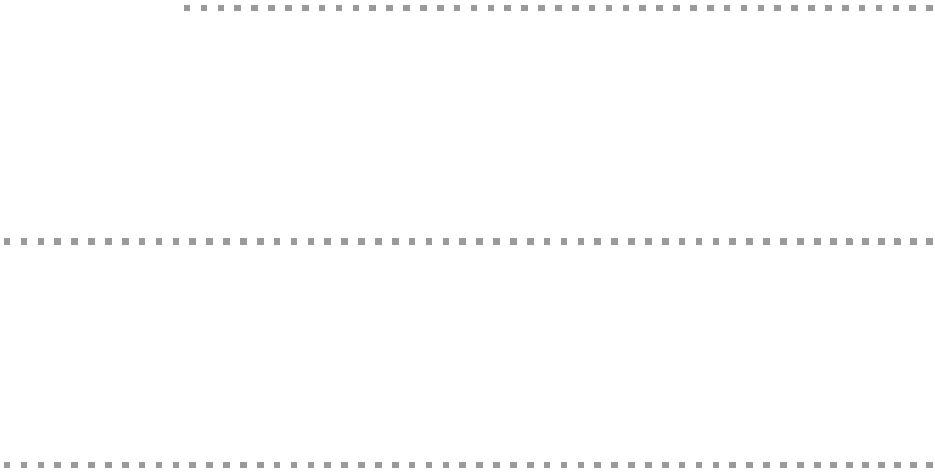
17
About the Development
Board
CHAPTER 2
Overview
This chapter provides information on the development board, a hardware platform from
which you can determine how to integrate the embedded module into your design. For
additional information, see the schematic and mechanical drawings.
Basic Description
The following graphic is a layout of the development board.
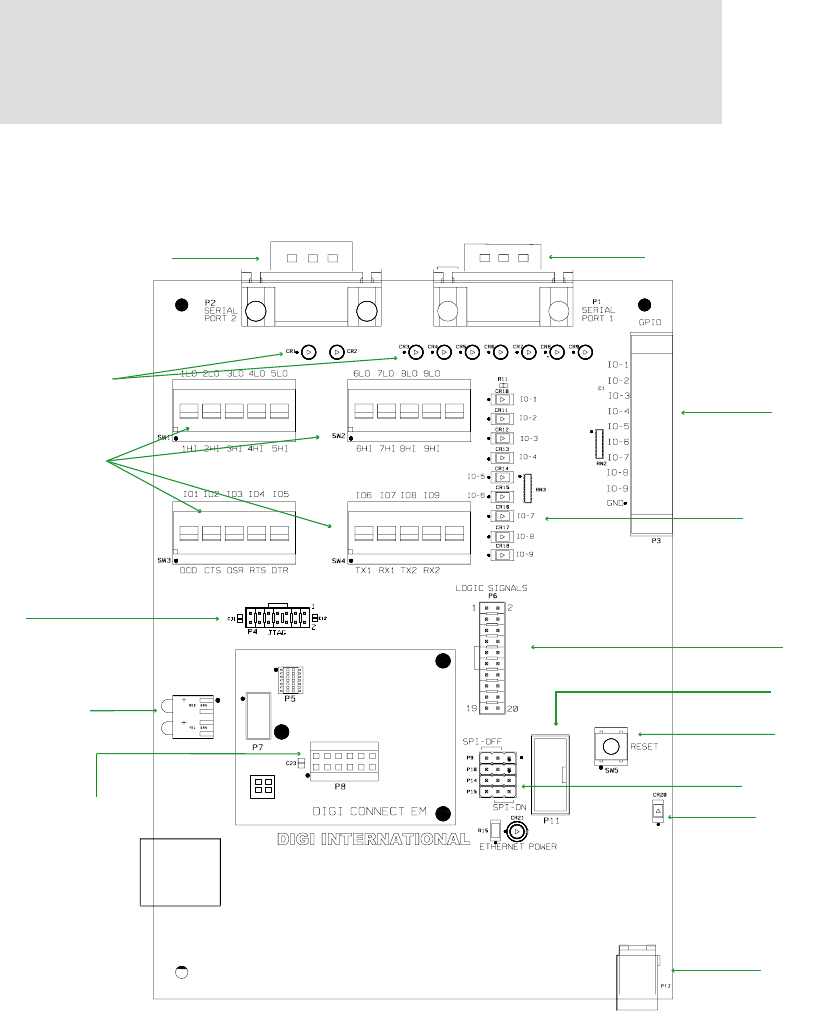
Basic Description
18
Digi Connect Wi-EM 9210 Hardware Reference
Basic Description
Serial port 2 Serial port 1
GPIO/serial
switch
banks
JTAG connector
for debugger
Status
LEDs
Main
Digi Connect Wi-EM 9210
connector
Logic signal
connector
Reset switch
SPI connector
Power jack
GPIO ports
GPIO
LEDs
Serial signaling
LEDs
3.3V LED
SPI jumpe
r
block
P12
CR19
P13
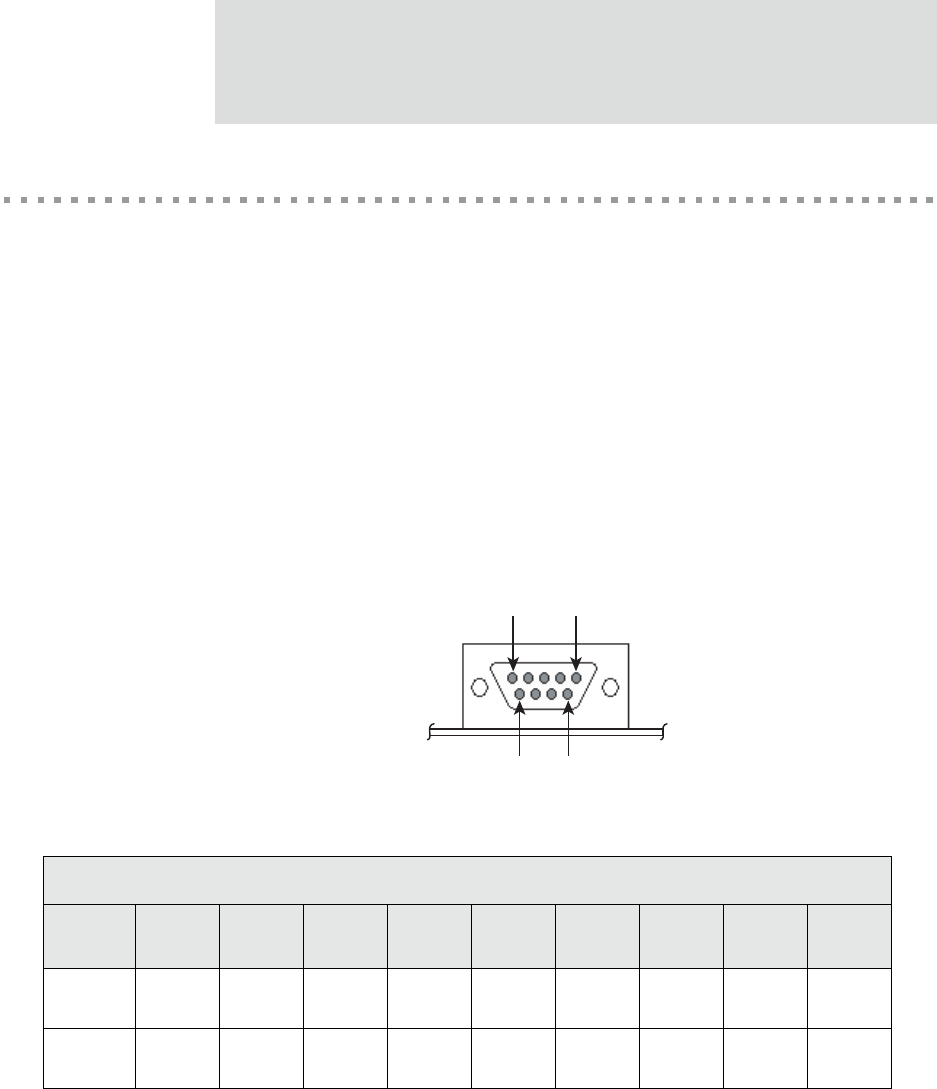
19
About the Development Board
Ports
The development board provides the following ports:
Serial Port 1 (P1) and Serial Port 2 (P2)
Ethernet Port (P12)
GPIO Port (P3)
Serial Port 1 (P1) and Serial Port 2 (P2)
Serial port 1 and port 2 are DB-9 male connectors labeled P1 and P2. Use the following
figure and table for pin orientation and pin assignment information.
Serial Port Pin Orientation
0
0000006
Pin 1 Pin 5
Pin 6 Pin 9
Serial Pin Assignment
Port Signal
Pin 1 Signal
Pin 2 Signal
Pin 3 Signal
Pin 4 Signal
Pin 5 Signal
Pin 6 Signal
Pin 7 Signal
Pin 8 Signal
Pin 9
1DCD RXD TXD DTR GND DSR RTS CTS Not
Connected
2Not
Connected RXD TXD Not
Connected GND Not
Connected
Not
Connected
Not
Connected
Not
Connected
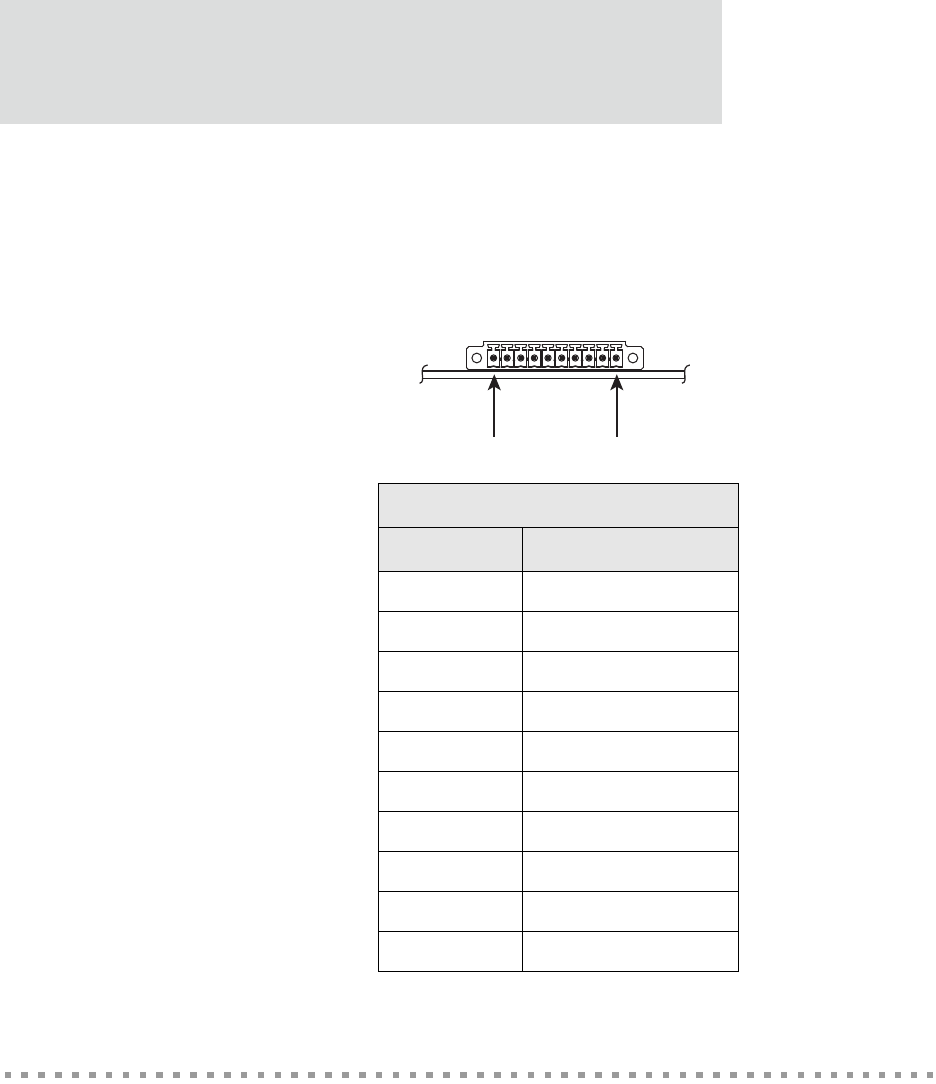
Connectors and Blocks
20
Digi Connect Wi-EM 9210 Hardware Reference
GPIO Port (P3)
The GPIO port is a 10-pin male right-angle connector (labeled P3). See the following
figure and table for pin orientation and pin assignments.
GPIO Port Pin Orientation
Connectors and Blocks
The development board provides the following connectors and blocks:
JTAG Debugger Connector (P4)
SPI Connector (P11) and SPI Jumper Block
GPIO Port Pin Assignments
Pin Signal Name
1GND
2GPIO-9
3GPIO-8
4GPIO-7
5GPIO-6
6GPIO-5
7GPIO-4
8GPIO-3
9GPIO-2
10 GPIO-1
Pin 1 Pin 10
0
0000020
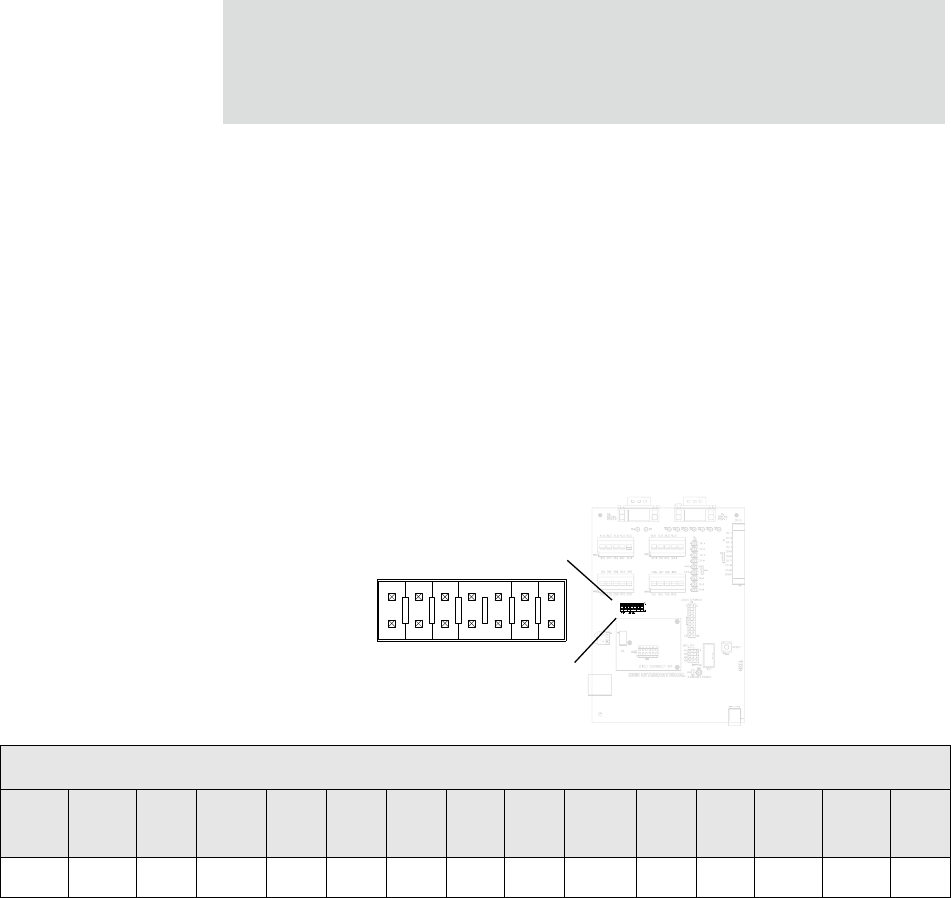
21
About the Development Board
Logic Signal Analyzer Header (P6)
Main Connector (P8)
JTAG Debugger Connector (P4)
This 14-pin male vertical header labeled P4 mates with a JTAG debugger plug (for
example, a Digi JTAG Link). It is used with the development kit only. See the following
figure and table for pin orientation and assignments.
JTAG Debugger Connector Pin Orientation
SPI Connector (P11)
This connector is used for a Serial Peripheral Interface (SPI) connection. When enabled,
signals are disconnected from serial port 1 and GPIO connectors. See the following figure
and table for pin orientation and pin assignments.
pin
1
2
13
14
JTAG Debugger Connector Pin Assignments
Pin
1Pin
2Pin
3Pin
4Pin
5Pin
6Pin
7Pin
8Pin
9Pin
10 Pin
11 Pin
12 Pin
13 Pin
14
Signal VCC+ GND /TRST GND TDI GND TMS GND TCK GND TDO /SRST VCC+ GND

Connectors and Blocks
22
Digi Connect Wi-EM 9210 Hardware Reference
SPI Connector Pin Orientation
SPI Jumper Block
The SPI jumper block determines whether the SPI connector is connected or not. If SPI is
off (the default), serial and GPIO signals are routed to switch banks 1 through 4. (See
"Serial/GPIO Switch Bank 3 (SW3) and Switch Bank 4 (SW4)" on page 26 and "GPIO
Switch Bank 1 (SW1) and 2 (SW2)" on page 27.) If SPI is on, SPI signals are routed to the
SPI connector (P11).
The following figures demonstrate how to set the SPI jumper block
Pin 1Pin 2
Pin 7
Pin 8
SPI Pin Assignments
Pin
1Pin
2Pin
3Pin
4Pin
5Pin
6Pin
7Pin
8Pin
9Pin
10
Signal SPI-EN GND SPI-CLK GND SPI-TX GND SPI-RX GND Not
connected
Not
connected
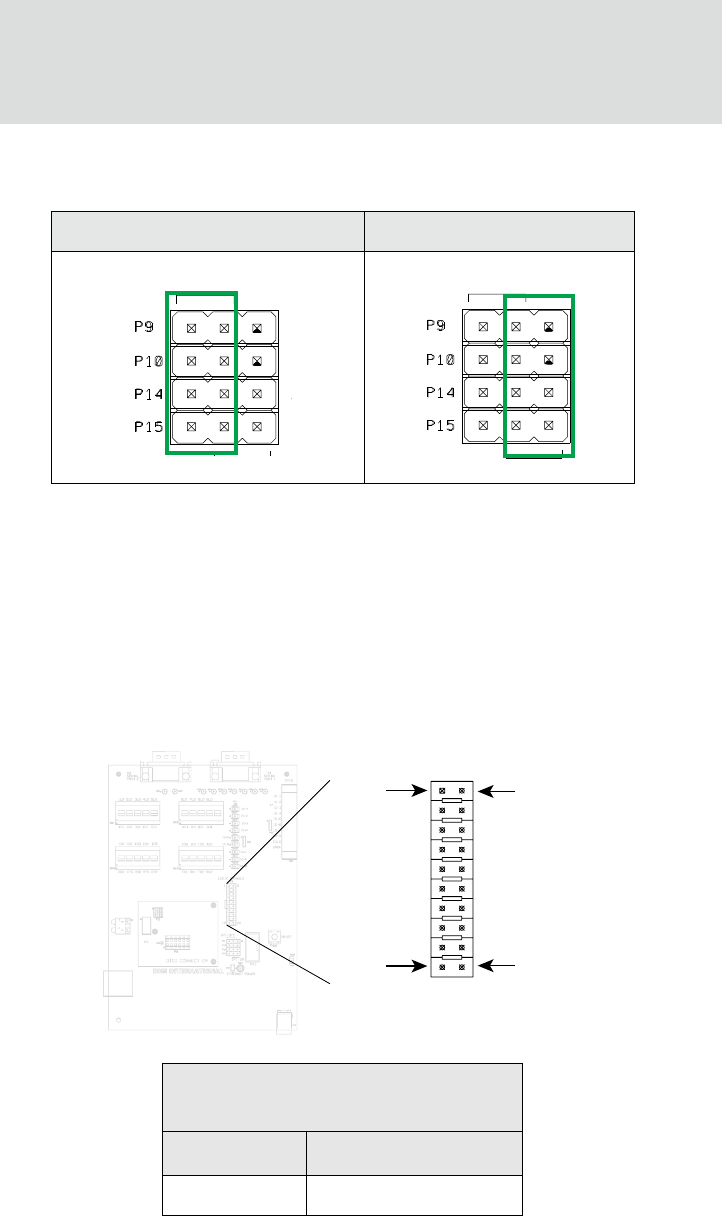
23
About the Development Board
SPI Jumper Settings
Logic Signal Analyzer Header (P6)
This 20-pin male vertical header (labeled P6) connects a digital signal analyzer (for
example, a logic analyzer) to the development board. It is used with the development kit
only. See the following figure and table for pin orientation and pin assignments.
Logic Analyzer Header Pin Orientation
SPI OFF SPI ON
oo
Logic Analyzer Header Pin
Assignments
Pin Signal
1 - 8 Not connected
Pin 2
Pin 20
Pin 1
Pin 19
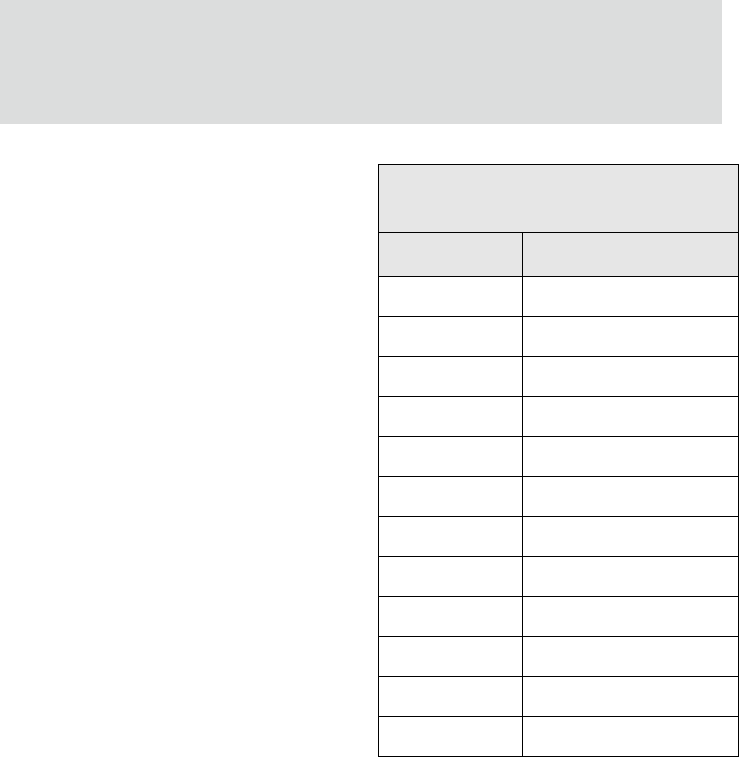
Connectors and Blocks
24
Digi Connect Wi-EM 9210 Hardware Reference
Main Connector (P8)
This 12-pin connector is used to interface with the embedded module. See the following
figure for pin orientation.
9/RST
10 Not connected
11 DTR/GPIO-5
12 TXD-2/GPIO-8
13 CTS/GPIO-2
14 RXD-2/GPIO-9
15 DSR/GPIO-3
16 TXD-1/GPIO-6
17 RTS/GPIO-4/SPI_CLK
18 RXD-1/GPIO-7
19 DCD/GPIO-1/SPI_EN
20 GND
Logic Analyzer Header Pin
Assignments
Pin Signal
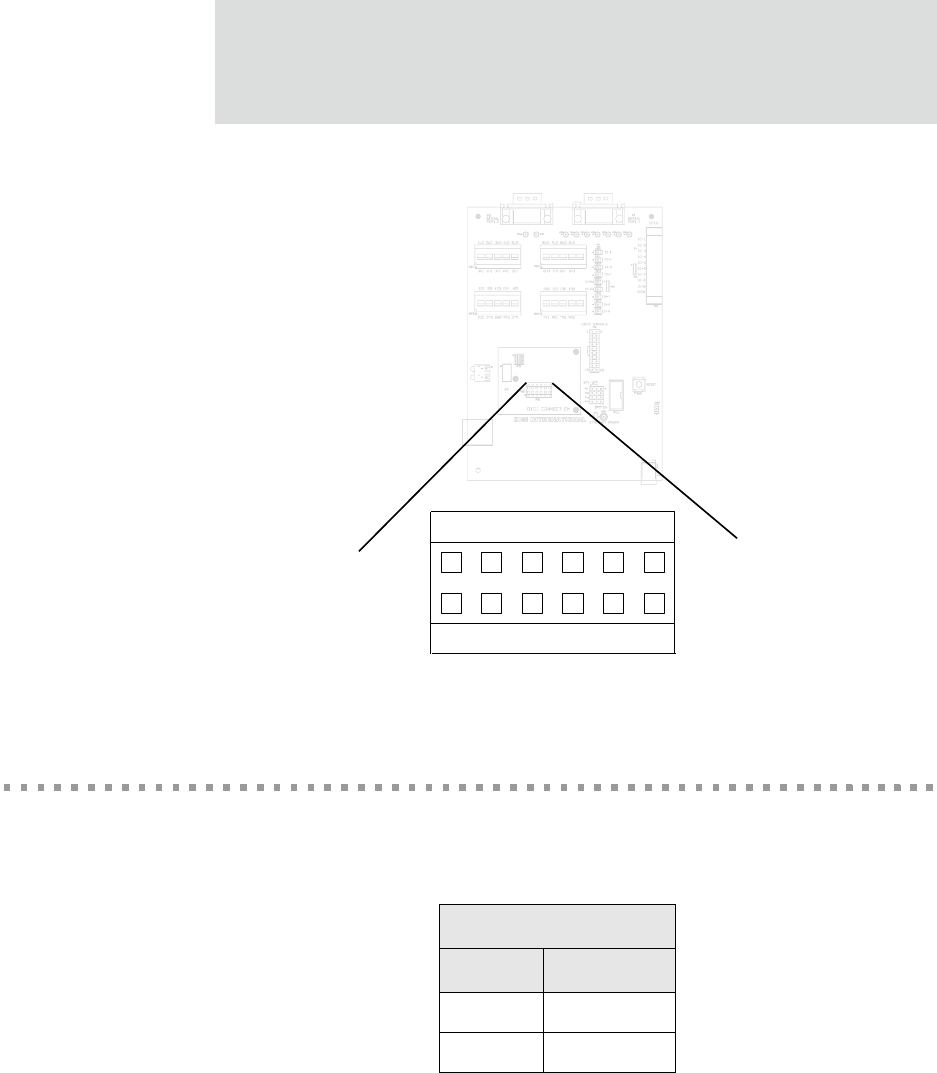
25
About the Development Board
Main Connector Pin Orientation
Power Jack (P17)
The Power Jack is a barrel connector that accepts 9 to 30 VDC +/- 5%. The jack is labeled
P17. The following table shows the polarity of the power jack.
The following figure schematically represents the polarity of the power jack
Pin 2 Pin 12
Pin 1 Pin 11
Top view
Power Jack Polarity
Contact Polarity
Center +9 to +30 VDC
Outer Ground
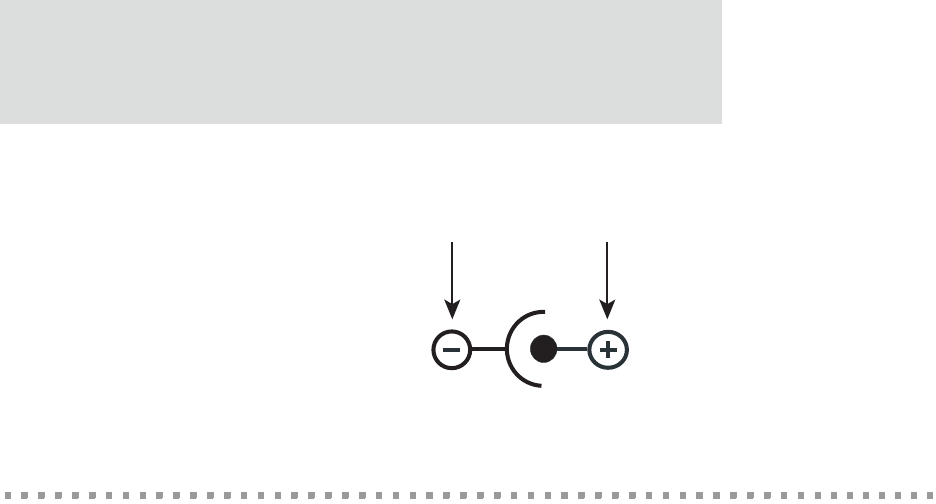
Switches
26
Digi Connect Wi-EM 9210 Hardware Reference
Power Jack Polarity Schematic.
Switches
The development board provides the following switches:
Reset Switch (SW5)
Serial/GPIO Switch Bank 3 (SW3) and Switch Bank 4 (SW4)
GPIO Switch Bank 1 (SW1) and 2 (SW2)
Reset Switch (SW5)
This push button switch is labeled SW5. Pressing it sets the module's /RST line low,
holding the module in a hard reset until the switch is released.
Note:
This is a "hard" reset using the /RST pin on the main connector, not a "soft"
reset. The reset button on the embedded module performs a "soft" reset (see
also "Main Connector (P8)" on page 24).
Serial/GPIO Switch Bank 3 (SW3) and Switch Bank 4 (SW4)
Each switch bank holds five slide switches that enable either serial or GPIO signaling
between the development board and the module. When set for GPIO signaling, SW3 works
in conjunction with SW1, and SW4 works with SW2. See "GPIO Switch Bank 1 (SW1)
and 2 (SW2)" on page 27 for more information. See the following table for SW3 and SW4
switch definitions.
Ground +9 to +30 VDC
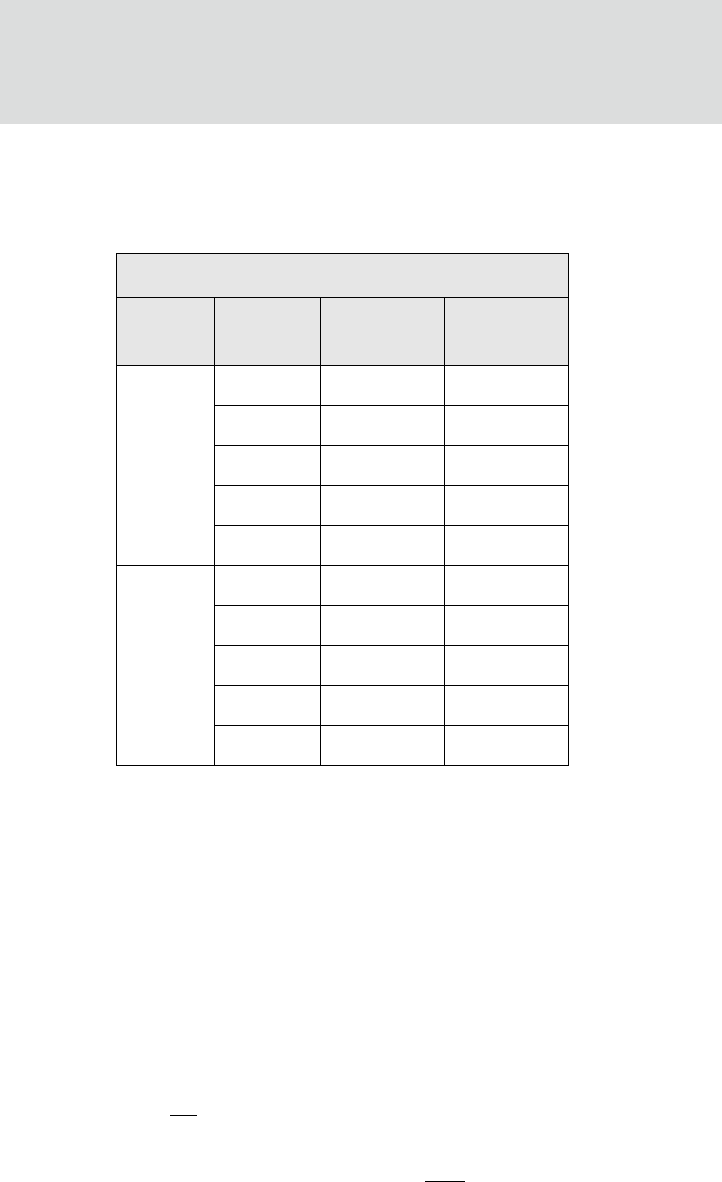
27
About the Development Board
Note:
These switches control where the development board routes a signal. They do not
reconfigure the Wi-EM 9210 processor. Software should be configured to track
with switch settings. See "GPIO" on page 33 for more information.
GPIO Switch Bank 1 (SW1) and 2 (SW2)
GPIO Switch Bank 1 and Switch Bank 2, labeled SW1 and SW2, are two sets of five slide
switches that set GPIO inputs to logic levels of high (switch to left) or low (switch to
right).
If the GPIO port is configured as an output, then the switch should always be to the left. If
there is an external device connected to P3, the switch should always be set to the left.
Each GPIO port can be used independently.
Notes:
These switches do not determine whether the GPIO is an input or output. That
is determined by the module software.
If GPIO is set to an output by software, switches must be set to the left (high).
These switches are used in conjunction with SW3 and SW4.
GPIO Switch Banks 3 and 4 Settings
Switch
Bank Switch
Number Left
Position Right
Position
SW3
1 DCD GPIO-1
2 CTS GPIO-2
3 DSR GPIO-3
4 RTS GPIO-4
5 DTR GPIO-5
SW4
6 TXD-1 GPIO-6
7 RXD-1 GPIO-7
8 TXD-2 GPIO-8
9 RXD-2 GPIO-9
10 Not connected Not connected
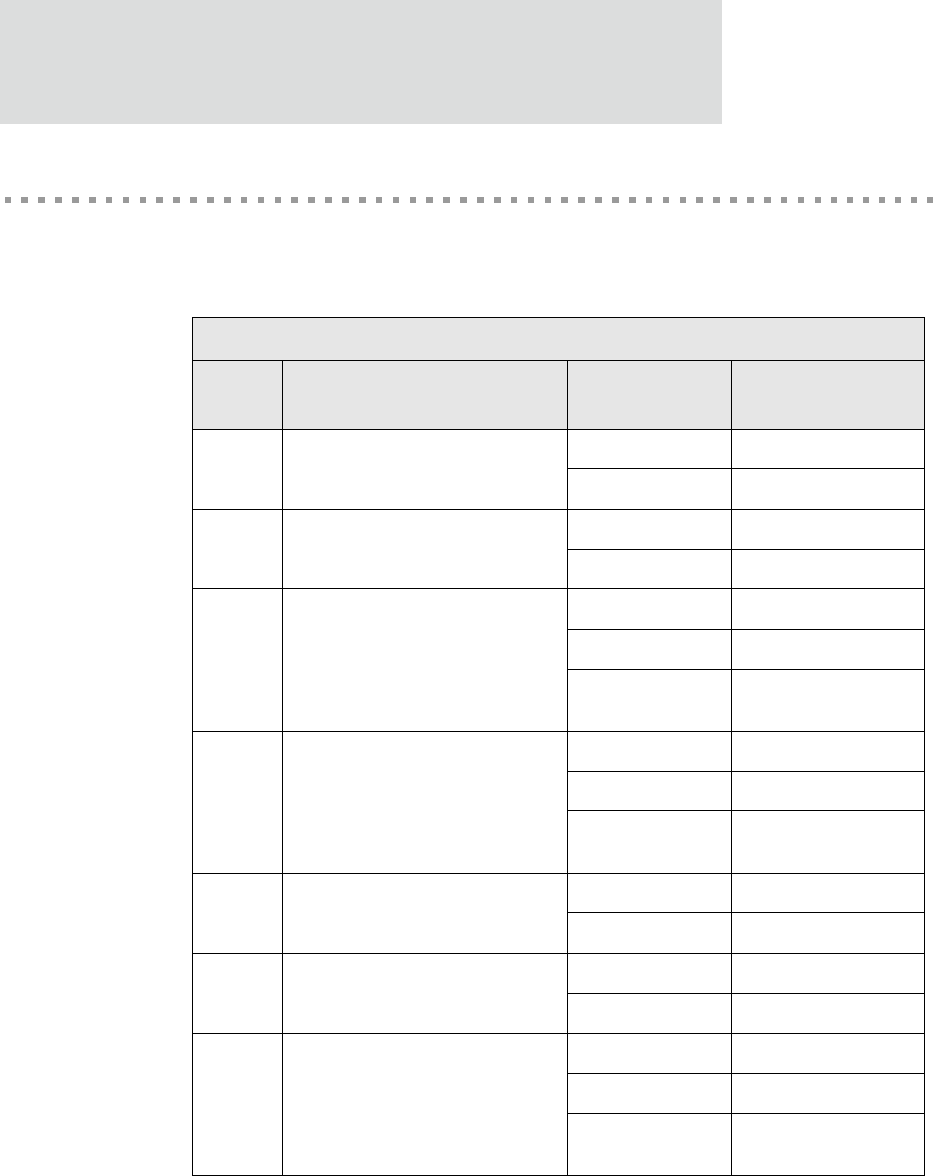
Development Board LEDs
28
Digi Connect Wi-EM 9210 Hardware Reference
Development Board LEDs
The development board contains 21 LEDs labeled CR1 through CR21. The following table
lists and describes the LEDs.
LED Descriptions
Board
Label Description
Color or State
Indication
CR1 TXD-2 Flickering Serial activity
Green Inactive
CR2 RXD-2 Flickering Serial activity
Green Inactive
CR3 CTS
Yellow Active
Green Inactive
Off Not connected or signal
not being driven
CR4 DTR
Yellow Active
Green Inactive
Off Not connected or signal
not being driven
CR5 TXD-1 Flickering Serial activity
Green Inactive
CR6 RXD-1 Flickering Serial activity
Green Inactive
CR7 RTS
Yellow Active
Green Inactive
Off Not connected or signal
not being driven
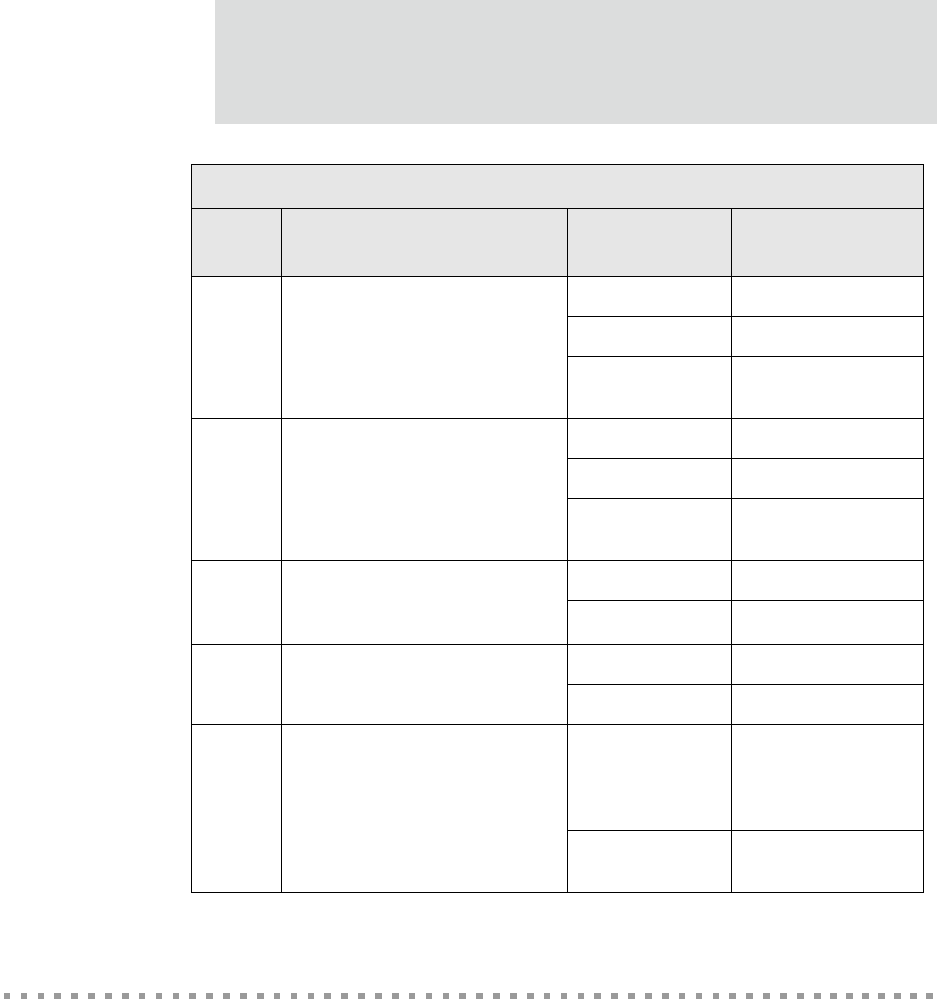
29
About the Development Board
Test Points
The development board provides 25 test points that can be identified by board label or test
point number. The board labels are adjacent to each test point on the board. The test point
numbers are in the development board schematic drawings. The following table lists the
test point number, board label, and a brief description of each test point.
CR8 DCD
Yellow Active
Green Inactive
Off Not connected or signal
not being driven
CR9 DSR
Yellow Active
Green Inactive
Off Not connected or signal
not being driven
CR10 -18 GPIO-1 through GPIO-9.
(CR10=GPIO-1, CR11=GPIO-2, etc.
All can be used for input or output.)
On Logic high
Off Logic low
CR20 3.3V Indicator On Power on
Off Power off
CR21 EPWR, Powered Ethernet Enabled
On
Ethernet power present
from external powered
Ethernet connector
(Ethernet hub or switch)
Off No powered Ethernet
voltage
LED Descriptions
Board
Label Description
Color or State
Indication
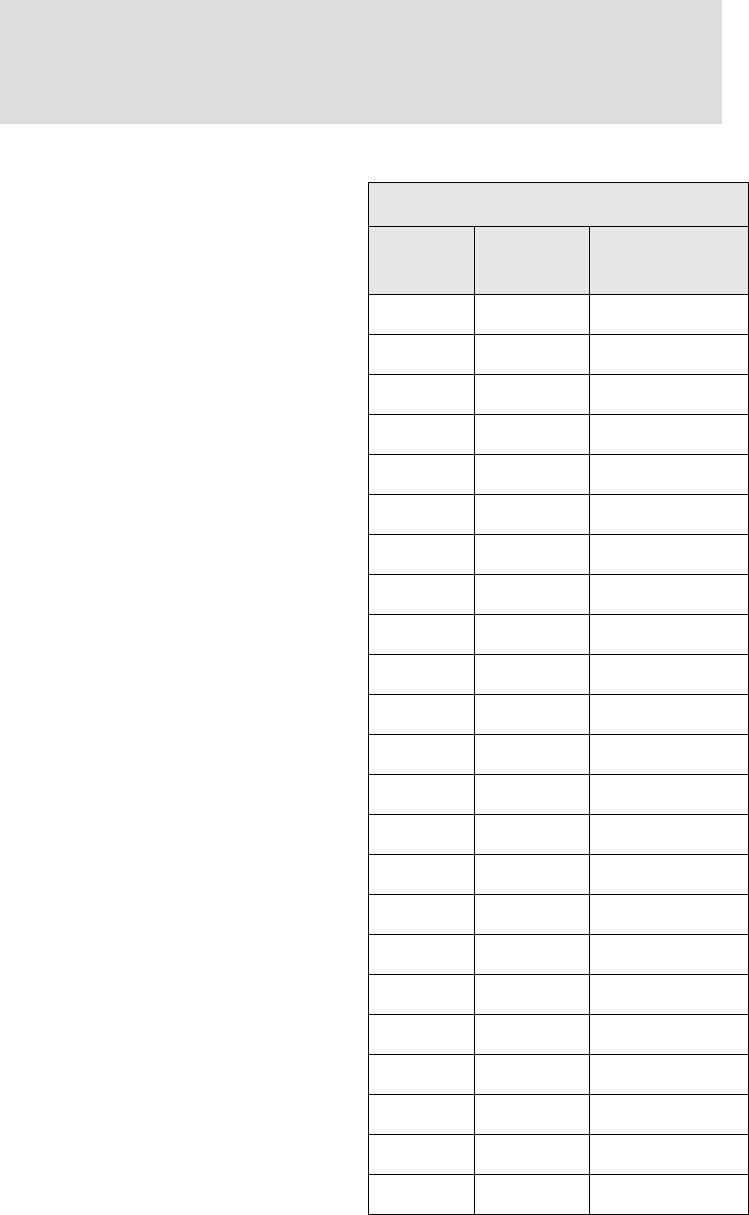
Test Points
30
Digi Connect Wi-EM 9210 Hardware Reference
Test Point Descriptions
Test
Point Board
Label Description
TP2 TXD TXD-2
TP3 RXD RXD-2
TP4 CTS CTS
TP5 DTR DTR
TP6 TXD TXD-1
TP7 RXD RXD-1
TP8 RTS RTS
TP9 DCD DCD
TP10 DSR DSR
TP11 IO-1 GPIO-1
TP12 IO-2 GPIO-2
TP13 IO-3 GPIO-3
TP14 IO-4 GPIO-4
TP15 IO-5 GPIO-5
TP17 3.3V 3.3V Supply
TP20 RESET Reset (active low)
TP21 E+ Ethernet Power +
TP22 E- Ethernet Power -
TP23 V-IN 9-30 VDC Input
TP24 GND Ground
TP25 GND Ground
TP26 IO-8 GPIO-8
TP27 IO-7 GPIO-7
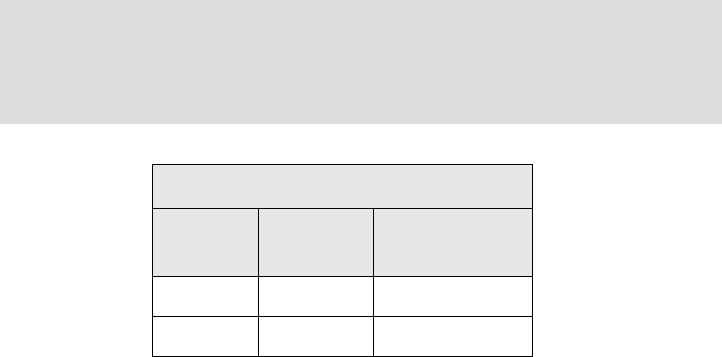
31
About the Development Board
TP28 IO-6 GPIO-6
TP29 IO-9 GPIO-9
Test Point Descriptions
Test
Point Board
Label Description

Test Points
32
Digi Connect Wi-EM 9210 Hardware Reference
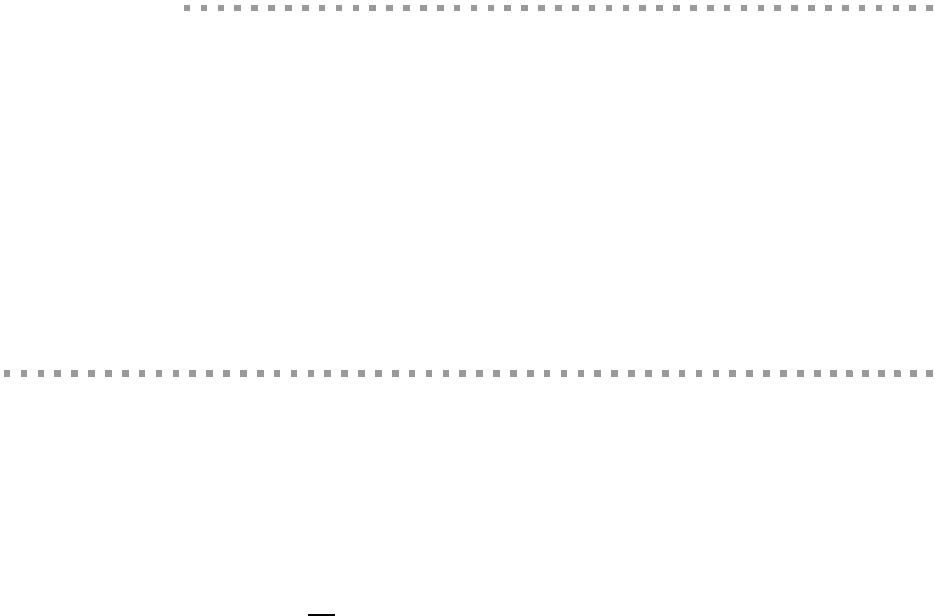
33
Programming
Considerations
CHAPTER 3
This chapter addresses the embedded modules programming considerations.
Note:
This chapter applies only to development kit customers.
GPIO
General Information
The Wi-EM 9210 processor supports 16 general purpose I/O (GPIO) lines, some of which
are reserved for specific functions and some of which can be customized. These GPIO lines
fall into three categories:
Those labeled “Reserved” in the following table are reserved for a specific use
and must not be reprogrammed, or the unit may not operate correctly. Often,
these lines are not connected to external interfaces.
Those labeled “Allocated” in the following table are exposed to an external
interface and allocated to a specific use by the software, but they can be
customized safely with code modifications.
Those labeled “Available” are exposed to an external interface, not controlled
directly by the software, and can be customized.
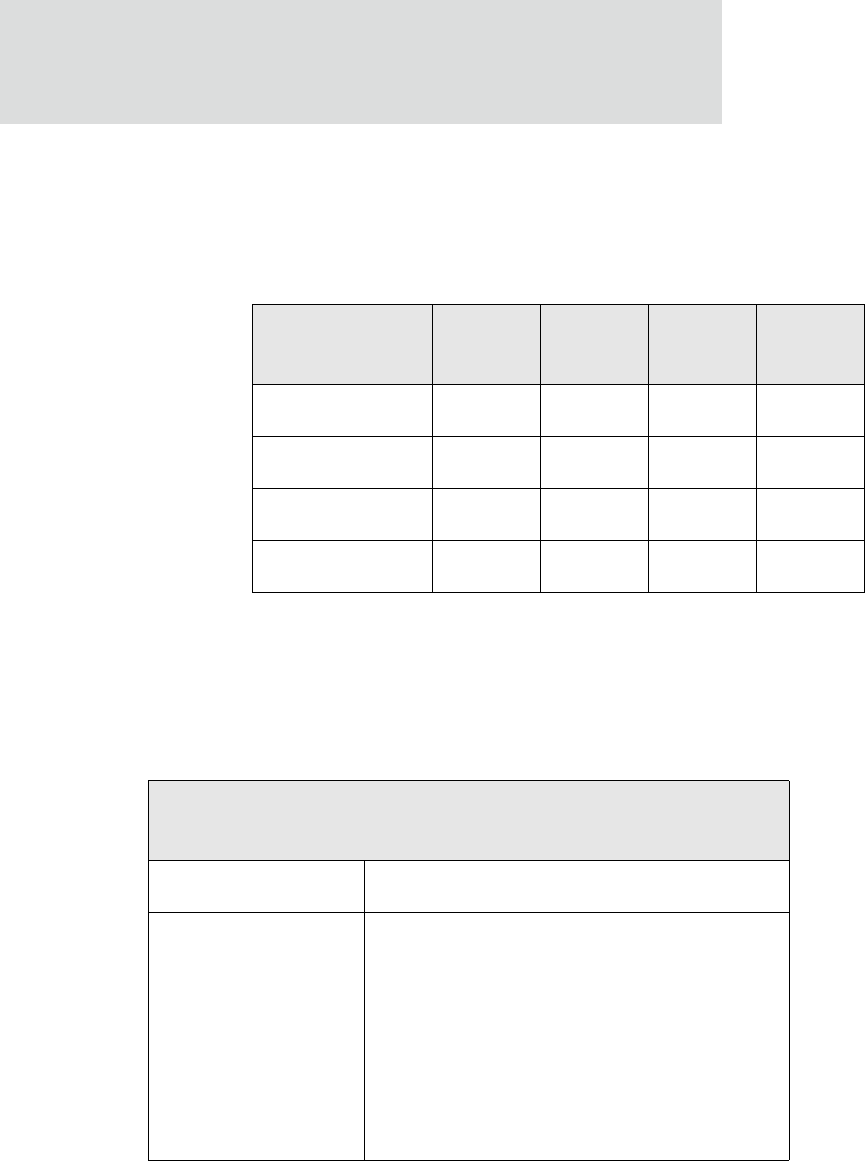
GPIO
34
Digi Connect Wi-EM 9210 Hardware Reference
GPIO Registers
Six registers govern the 16 GPIO pins. There are four configuration registers. Each has
eight bits dedicated to the configuration of each GPIO.
.
Each GPIO configuration section is set up the same way. The following table shows the
settings using bits D07:00; the same settings apply to the corresponding bits in D31:24,
D23:D16, and D15:08.
GPIO pin configuration registers
Register D31:24 D23:D1
6D15:08 D07:00
A090 2000, config 0 GPIO [15] GPIO [14] GPIO [13] GPIO [12]
A090 2004, config 1 GPIO [11] GPIO [10] GPIO [9] GPIO [8]
A090 2008, config 2 GPIO [7] GPIO [6] GPIO [5] GPIO [4]
A090 200C, config 3 GPIO [3] GPIO [2] GPIO [1] GPIO [0]
GPIO Configuration
Setings using bits D07:00
D07:06 Reserved N/A
D05:03 FUNC
Use these bits to select the function you want to use. For
a detailed description of each function see the NS 9210
HRM in the Pinout chapter under "General purpose I/O
(GPIO)" and the "GPIO pin use" table in this manual.
000 Function #0
001 Function #1
010 Function #2RESET_DONE - default for GPIO[12]
011 Function #3GPIO - default, except for GPIO[12]
100 Function #4
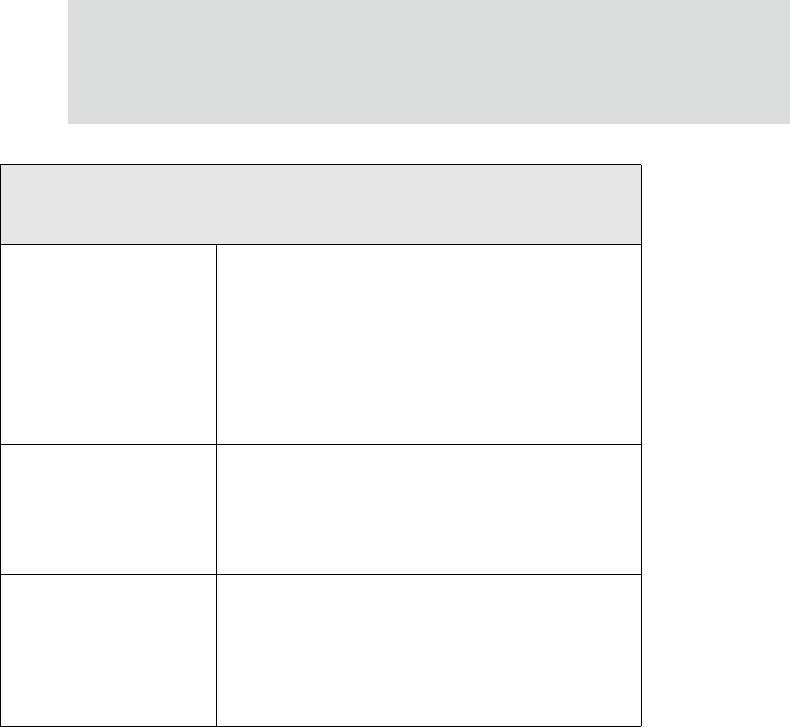
35
Programming Considerations
D02 DIR
Controls the pin direction when the FUNC field is
configured for GPIO mode, function #3.
0 Input
1 Output
All GPIO pins reset to the input state.
Note: The pin direction is controlled by the selected
function in modes #0 through #2.
D01 INV
Controls the inversion function of the GPIO pin.
0 Disables the inversion function
1 Enables the inversion function
This bit applies to all functional modes.
D00 PUDIS
Controls the GPIO pin pullup resistor operation.
0 Enables the pullup
1 Disables the pullup
Note: The pullup cannot be disabled on GPIO[9],
GPIO[12]
GPIO Configuration
Setings using bits D07:00
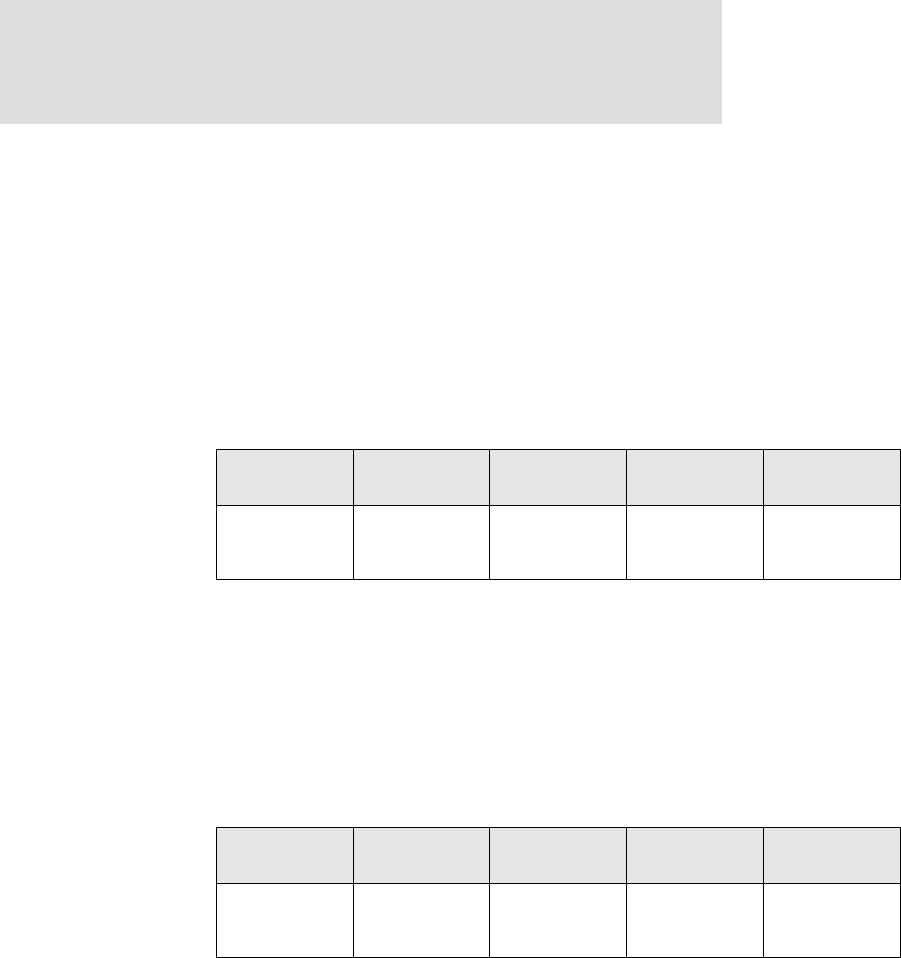
GPIO
36
Digi Connect Wi-EM 9210 Hardware Reference
GPIO [15:0] Control Register
There is one GPIO control Register that governs all 16 GPIO pins. When a GPIO pin is
configured as a GPIO output, the corresponding bit in the GPIO Control Register is driven
out the GPIO pin. In all configurations, the CPU has read/write access to these registers.
Register bits D31:16 are unused GPIO pins. These pins are being used as memory data bits
15:00. It is safest to read all 32 bits, modify the bit(s) corresponding to the GPIO(s) of
interest, and then write back the full 32 bits. In this way the behavior of the other GPIO
lines will be preserved.
GPIO [15:0] Status Register
There is one GPIO Status Register. This register contains the status information for each of
the 16 GPIO pins. Bits D31:16 are used as memory data therefore their status will not be
meaningful. In all configurations, the value on the GPIO input pin is brought to the status
register and the CPU has read-only access to this register.
Register D31:24 D23:D16 D15:08 D07:00
A090 206C GPIO [31:24]
not used] GPIO [23:16]
not used GPIO [15:8] GPIO [7:0]
Register D31:24 D23:D16 D15:08 D07:00
A090 207C GPIO [31:24]
not used] GPIO [23:16]
not used GPIO [15:8] GPIO [7:0]
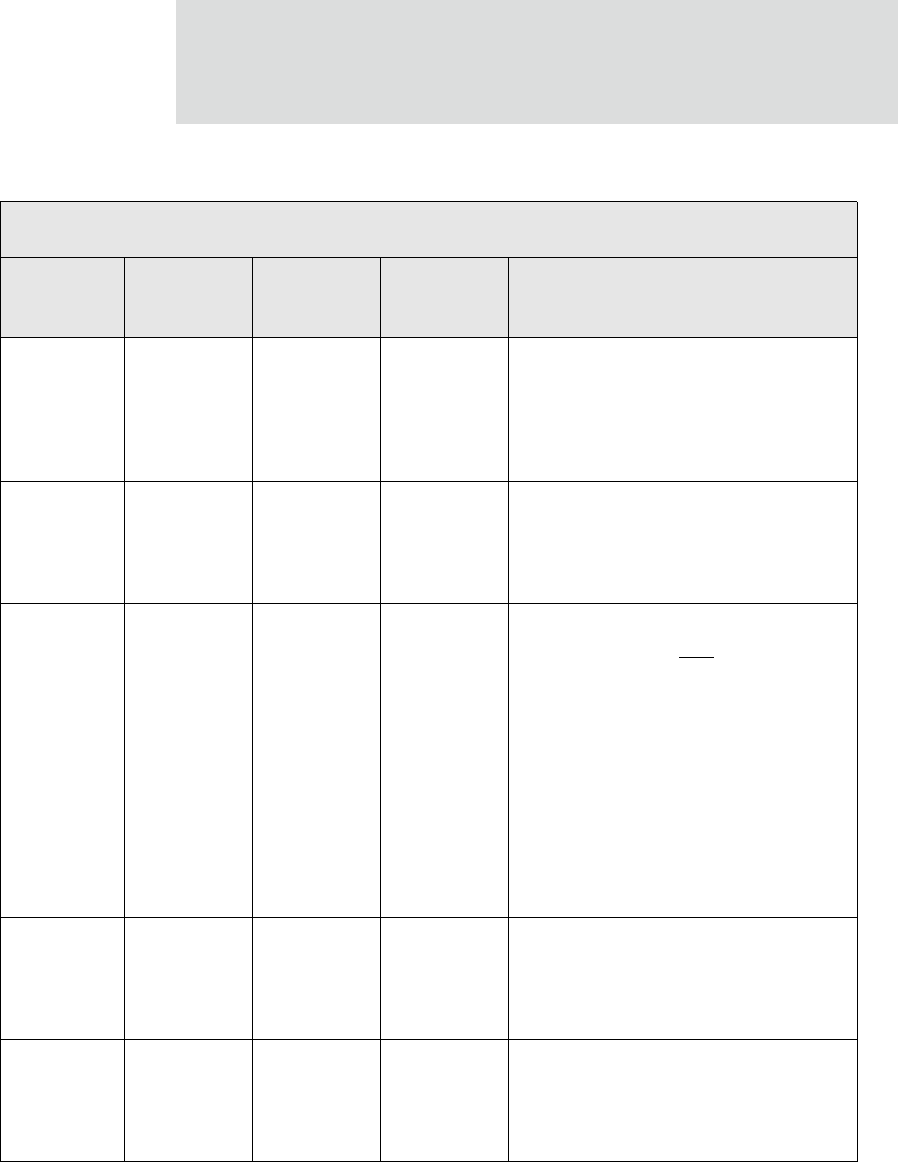
37
Programming Considerations
GPIO pin use table
GPIO Pin Use
Name Register
Bit Category External
Interface Description
TXSD/
SPI_TX/
GPIO-6 GPIO[7] Allocated Pin 4 on the
main header
Used for the serial TXD or SPI_TX, but
could be reassigned as a GPIO, timer out 7 or
in 8.
If used with the development board, this pin
maps to GPIO-6.
DTR/GPIO-
5GPIO[6] Allocated Pin 6 on the
main header
Usedc for the serial DTR but could be
reassigned as a GPIO, or timer in 7.
If used with the development board, this pin
maps to GPIO-5.
RTS/
SPI_CLK/
GPIO-4 (See
description)
GPIO[5]or
GPIO[4] Allocated Pin 5 on the
main header
Since these two processor pins map to the
same header pin, one must be configured as
an input to avoid contention.
UART: GPIO[5] is confiured for RTS and
GPIO[4] for GPIO input.
SPI: GPIO[5] for GPIO input and GPIO[4]
for SPI_CLK.
Other: GPIO[5] supports IRQ3 and timer out
6.
GPIO[4] supports IRQ2 and timer in 6.
If used with the development board, header
pin 5 maps to GPIO-4.
RXD/
SPI_RX/
GPIO-7 GPIO[3] Allocated Pin 3 on the
main header
Used for the serial RXD or SPI_RX, but
could be reassigned as a GPIO or PICO-3.
If used with the development board, this pin
maps to GPIO-7.
DSR/GPIO-
3GPIO[2] Allocated Pin 9 on the
main header
Used for the serial DSR, but could be
reassigned as a GPIO or PICO-2.
If used with the development board, this pin
maps to GPIO-3.
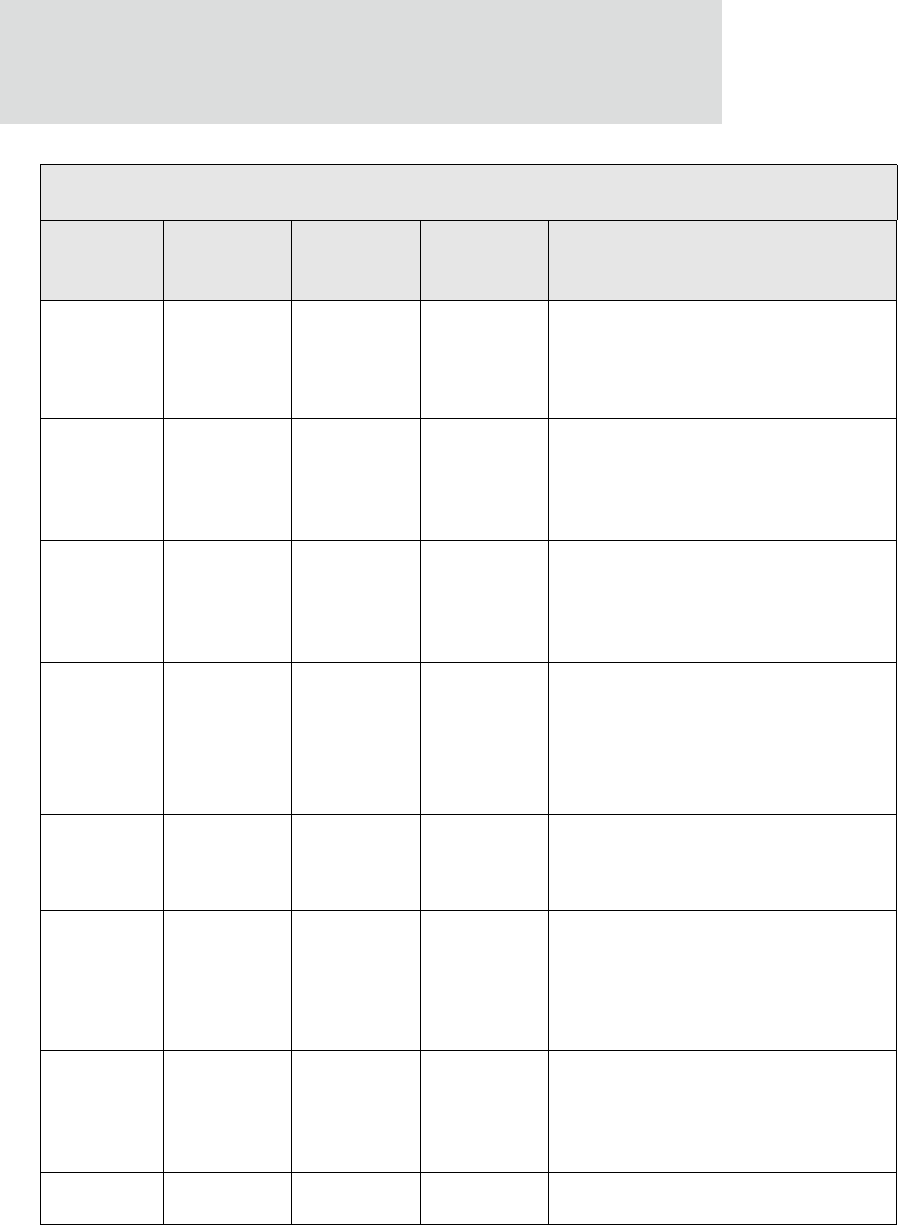
GPIO
38
Digi Connect Wi-EM 9210 Hardware Reference
CTS/GPIO-
2GPIO[1] Allocated Pin 7 on the
main header
Used for the serial CTS, but could be
reassigned as a GPIO, IRQ0 or PICO-1. If
used with the development board, this pin
maps to GPIO-2.
DCD//
SPI_EN/
GPIO-1 GPIO[0] Allocated Pin 8 on the
main header
Used for the serial DCD or SPI_EN, but
could be reassugned as a GPIO or PICO-0.
If used with the development board, this pin
maps to GPIO-1.
TXD2/
GPIO-8 GPIO[15] Allocated Pin 12 on the
main header
Used for the serial2 TXD, but could be
reassigned as a GPIOor timer in 9.
If used with the development board, this pin
maps to GPIO-8.
Network
link Green
LED GPIO[14] Reserved
Connected to
the Green
LED above
the Yellow
LED
Network link status:
On - unit is associated with an access point
Blinking slowly - unit is in ad hoc mode
Blinking quickly - unit is scanning for a
network
/INIT GPIO[13] Available Connected to
the button on
the module Should be configured as a GPIO input.
Serial Port
activity
LED/MFGO GPIO [12] Allocated
Connected to
the green
LED above
the red LED
Used as the NET+OS green LED, but can be
reassigned as a general purpose LED. It must
remain a GPIO output for the LED to operate
correctly. The LED is lit when the signal is
low.
RXD2/
GPIO-9 GPIO[11] Allocated Pin 11 on the
main header
Used for the serial2 RXD, but could be
reassigned as a GPIO or IRQ2.
If used with the development board, this pin
maps to GPIO-9.
IRQ1 GPIO[10] Reserved N/A N/A
GPIO Pin Use
Name Register
Bit Category External
Interface Description
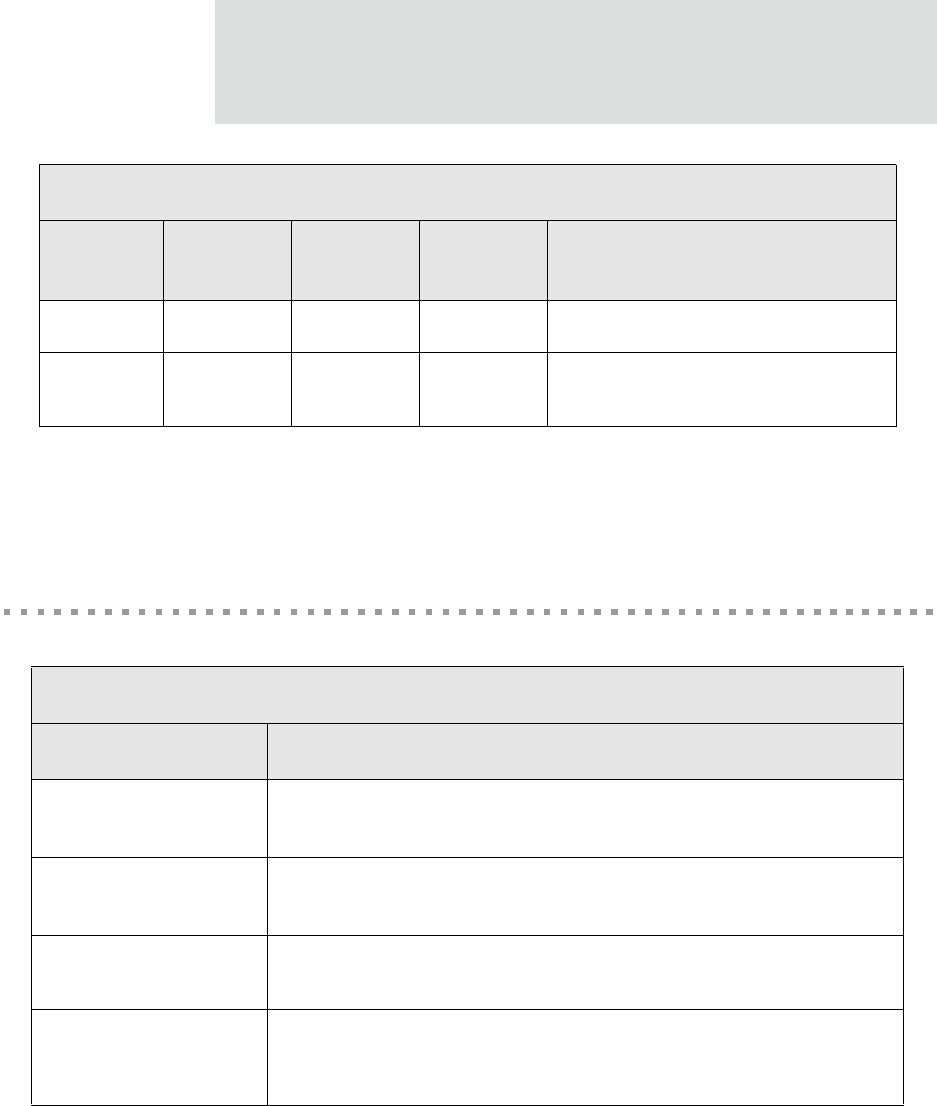
39
Programming Considerations
Note: The Wi-EM 9210 signals PIC0-[0:3] provided by the programmable FIMs
(DRPIC) are only applicable when running NET+OS.
About Embedded Module LEDs
MFGI GPIO[9] Reserved N/A N/A
Red LED GPIO[8] Allocated Connected to
the Red LED Used for diagnostics and power on
indication.
GPIO Pin Use
Name Register
Bit Category External
Interface Description
Embedded Module LED Description
LED Description
Green
(above yellow LED) This LED is wired to the network hardware and provides an indication of link status.
Green
(the one above the red LED)
This LED is software programmable and is wired to processor GPIO register bit
GPIO[12] and wired to be lit when low. Use for serial port activity.
Yellow This LED is wired to the network hardware and provides an indication of network
activity.
Red This LED is software programmable, wired to processor GPIO register bit GPIO[8],
and wired to be lit when low. LED ON indicates power on and is in addition used for
diagnostics.
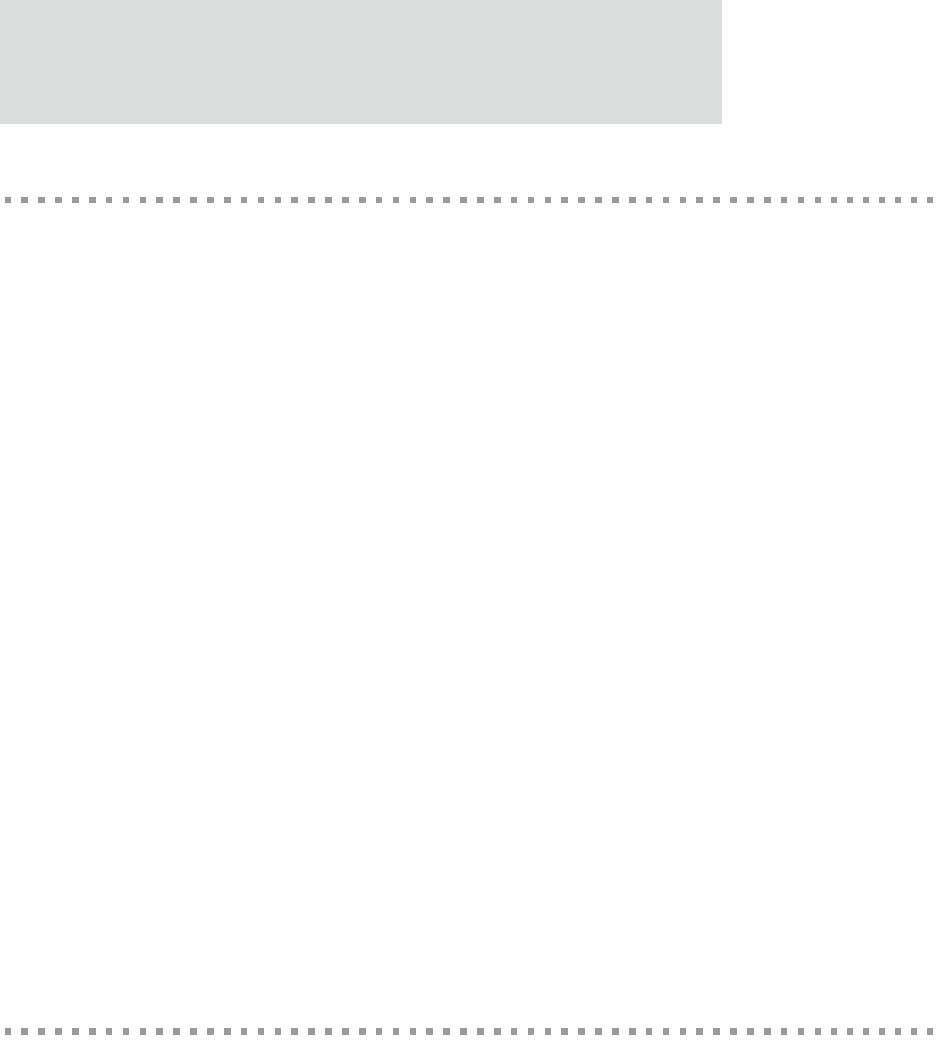
Embedded Module Reset
40
Digi Connect Wi-EM 9210 Hardware Reference
Embedded Module Reset
Hard Reset
The embedded modules support a hardware reset on pin 10 of the 12-pin header. The unit
will be forced into a hard reset if this pin is pulled low. When used with the development
board, this pin is wired to reset button SW5, which means it acts as a hard reset button.
The JTAG version of the Wi-EM 9210 EM module has a 3-pin jumper (JP1) to allow two
modes of operation.
Shorted 1-2: The CPU and other registers are reset. The PLL, GPIOs, and memory are not.
Debugger connection is maintained. This is the same as SRST# from the debugger.
Shorted 2-3: The entire module is reset. Debugger connection will need to be re-
established.
Soft Reset
NET+OS provides an internal facility to enact a soft reset, but it is the responsibility of a
specific implementation to choose a reasonable trigger to invoke it. One choice is to use a
GPIO pin as a signal to trigger a soft reset. The embedded modules have one GPIO pin
GPIO[13] which is not normally assigned to any other task named "/INIT." It is an ideal
candidate for use as a signal for soft reset. The signal is wired to the push button on the
module (next to the LEDs), and is pulled high unless the button is pushed.
The "naresetapp" sample application demonstrates a simple mechanism for monitoring a
GPIO pin and then initiating a soft reset when the pin achieves a particular value.
Memory
Flash
The Wi-EM 9210 module has 4 MB of flash memory, which is controlled by chip select 2
(default = st_cs1) located at 0x50000000.

41
Programming Considerations
SDRAM
The Wi-EM 9210 module has 16 MB of SDRAM memory, controlled by chip select 1
(default = dy_cs0), located at 0x00000000.

Memory
42
Digi Connect Wi-EM 9210 Hardware Reference
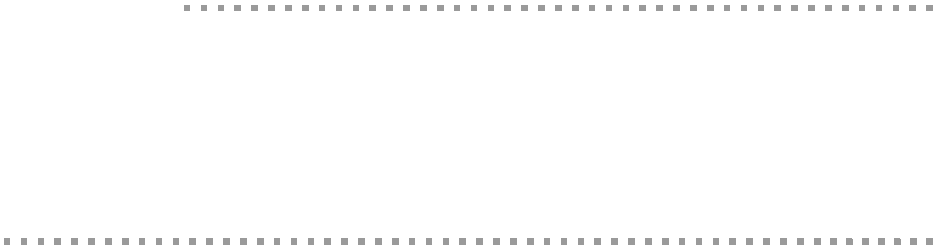
43
Specifications
APPENDIX A
Network Interfaces
Standard: IEEE802.11b/g
Frequency: 2.4 GHz
Data rate: Up to 54 Mbps with fallback
Modulation: DBPSK (1 Mbps), DQPSK (2 Mbps), CCK (5.5, 11 Mbps), BPSK
(6, 9 Mbps), QPSK (12, 18 Mbps), 16-QAM (24, 36 Mbps), 64-QAM (48, 54
Mbps)
Transmit power: 16 dBm typical
Receive sensitivity: -73 dBm @ 54 Mbps
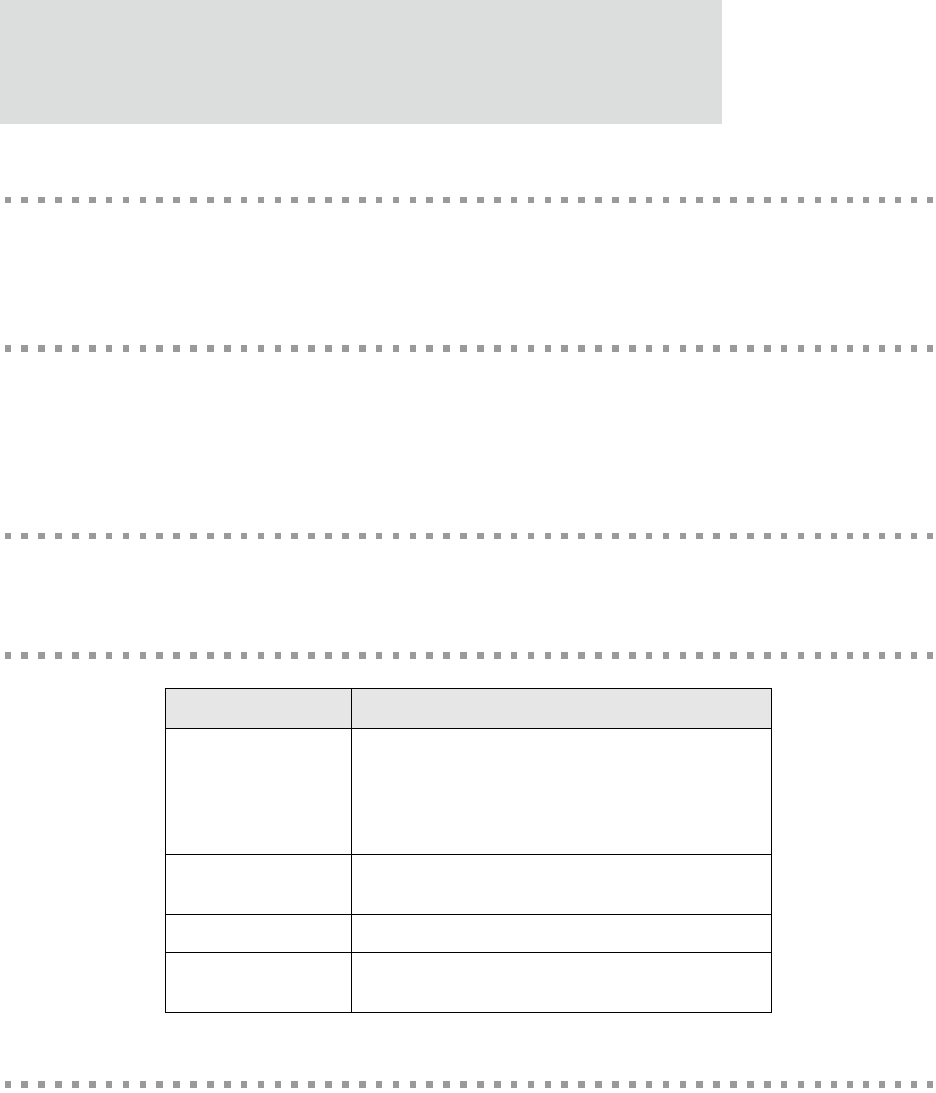
Serial Interface
44
Digi Connect Wi-EM 9210 Hardware Reference
Serial Interface
Two serial ports, one with full modem control signals and the other with TXD and RXD
only.
Data Rates (bps)
50, 110, 134, 150, 200, 300, 600, 1200, 2400, 3600, 4800, 9600, 19200, 38400, 57600,
115200, 230400, 460000, 921600
Flow Control Options
RTS/CTS, XON/XOFF, None
Environmental
DC Characteristics
The following tables provide DC characteristics for operating conditions, inputs, and
outputs.
Digi Connect Wi-EM 9210
Ambient Temperature
-22oF to 140oF
(-30oC to 60oC)
600C max at 100% duty cycle
650C max at 50% duty cycle
700C max at 30% duty cyce .
Storage Temperature -400F to 2570F
(-400C to 1250C)
Humidty 5% to 90%
Altitude 12000 feet
(3657.60 meters)
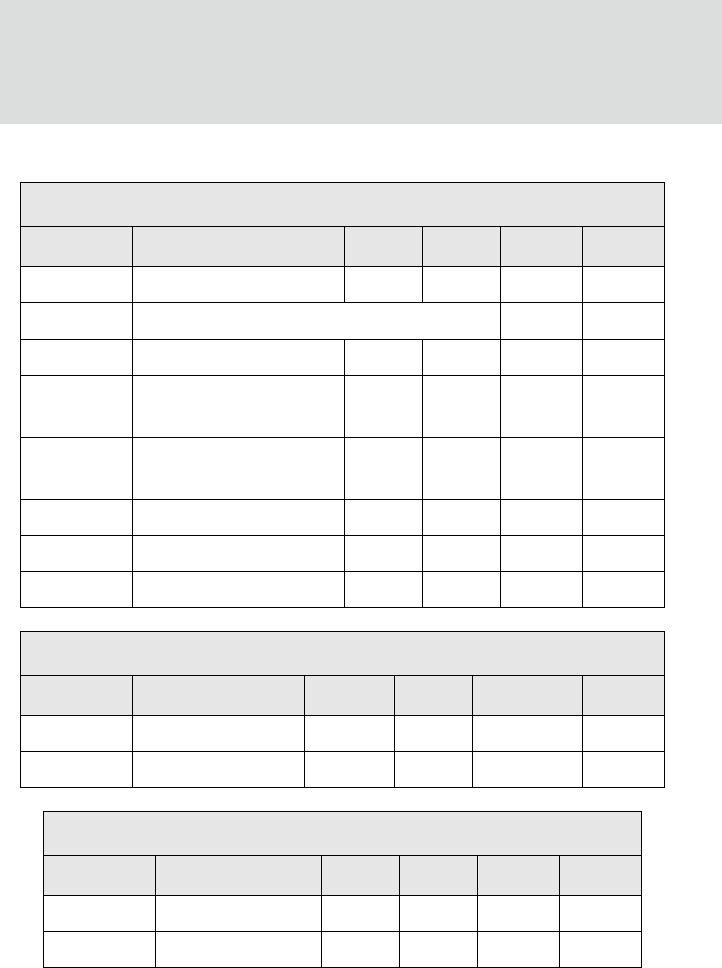
45
Specifications
Note: The embedded modules use a supervisory circuit with a 2.93V reset threshold. When
VCC falls to the threshold voltage, a reset pulse is issued, holding the output in active state.
When power rises above 2.93V, the reset remains for approximately 200 ms to allow the
system clock and other circuits to stabilize.
Warning: The rise time of the 3.3v power supply must be between 700 mS and 140ms and
the inrush current must be limited to less than 2 A. A rise time outside of these limits may
cause the device to malfunction and give a 3-1-3 diagnostic error.
Operating Conditions
Symbol Description Min Typ Max Unit
VCC Supply Voltage 3.14 3.3 3.45 V
n/a Power Supply Ripple 40 mVpp
ICC Supply Current — 390 630 mA
IIL Input Current as “0”
(16.5K equivalent pull-up) — — 200 μA
IIH Input Current as “1”
(16.5K equivalent pull-up) -10 — 10 μA
IOZ HighZ Leakage Current -10 — 10 μA
IOD Output Drive Strength — — 2 mA
CIO Pin Capacitance (VO=0) — — 4 pF
Inputs
Symbol Description Min Typ Max Unit
VIH Input High Voltage 2 — VCC+0.3 V
VIL Input Low Voltage VSS-0.3 — 0.2*VCC V
Outputs
Symbol Description Min Typ Max Unit
VOH Output High Voltage 2.4 — 3.45 V
VOL Output Low Voltage 0 — 0.4 V
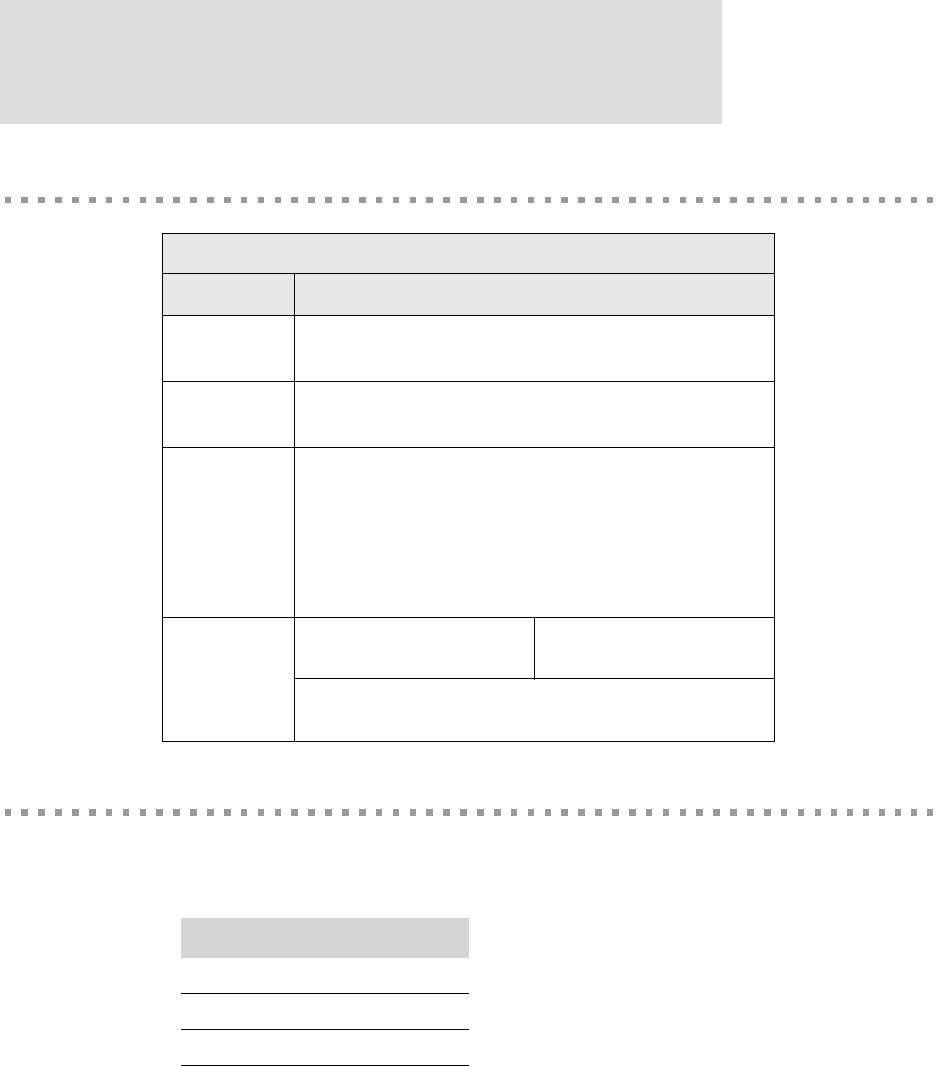
Mechanical
46
Digi Connect Wi-EM 9210 Hardware Reference
Mechanical
Layouts and Dimensions
All dimensions are in inches. These are the tolerances for the drawings shown in this
section:
Module Dimensions
Dimension Digi Connect Wi-EM
Length: 2.287 in
(58.09 mm)
Width: 1.885 in
(47.879 mm)
Height:
Fully populated
0.785 in
(19.939 mm)
Pin header model
0.653in
(16.586 mm)
Weight
Antenna -.408 oz.
(11.567 g)
.672 oz.
(19.051 g)
Total - 1.080 oz.
(30.617 g)
Measure Tolerance
.XX ± .02
.XXX ± .010
Angles ± 2 degrees

47
Specifications
Digi Connect Wi-EM (w/LED Array)
Top
(2X) .100
.100
1.935
1.855
.639
1.375
1.430
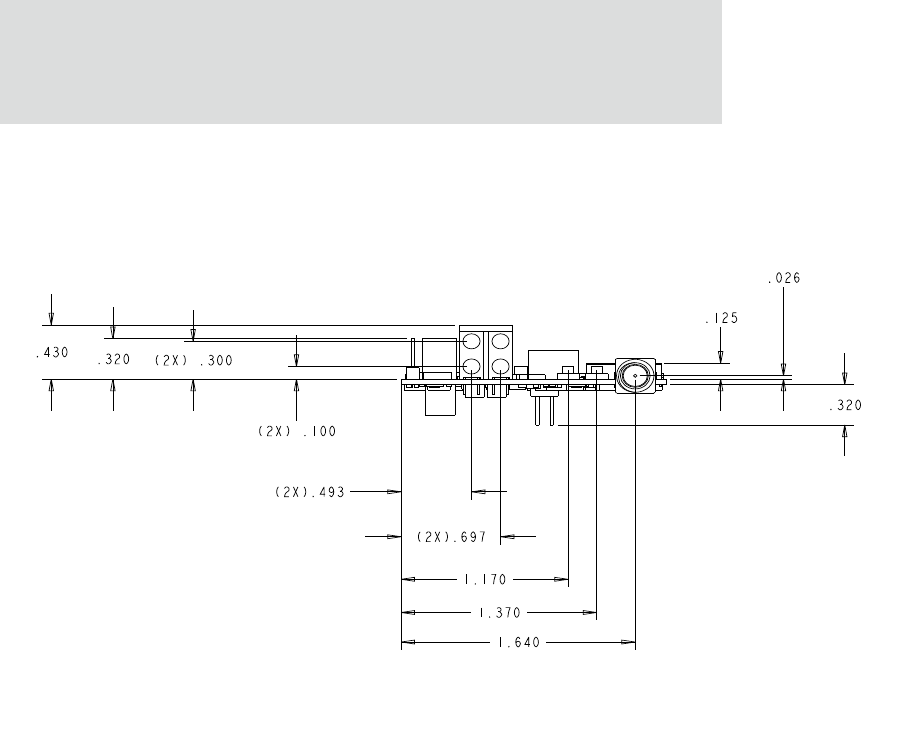
Layouts and Dimensions
48
Digi Connect Wi-EM 9210 Hardware Reference
Front
(2X) .100
(2X) .300
.430
(2X).493
(2X).697
1.170
1.370
1.640
.320
.026
.125
.320
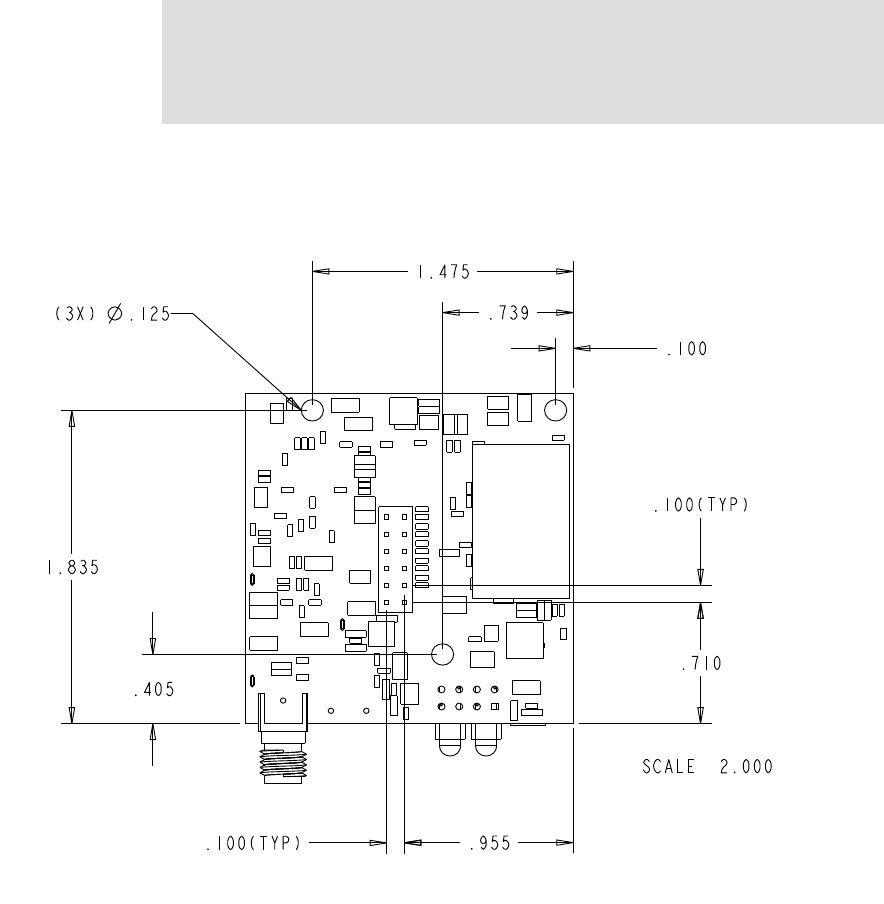
49
Specifications
Bottom
.100
.739
1.475
.955
.405
1.835
.710
(TYP).100
(TYP).100
SCALE 2.000
(3X) .125
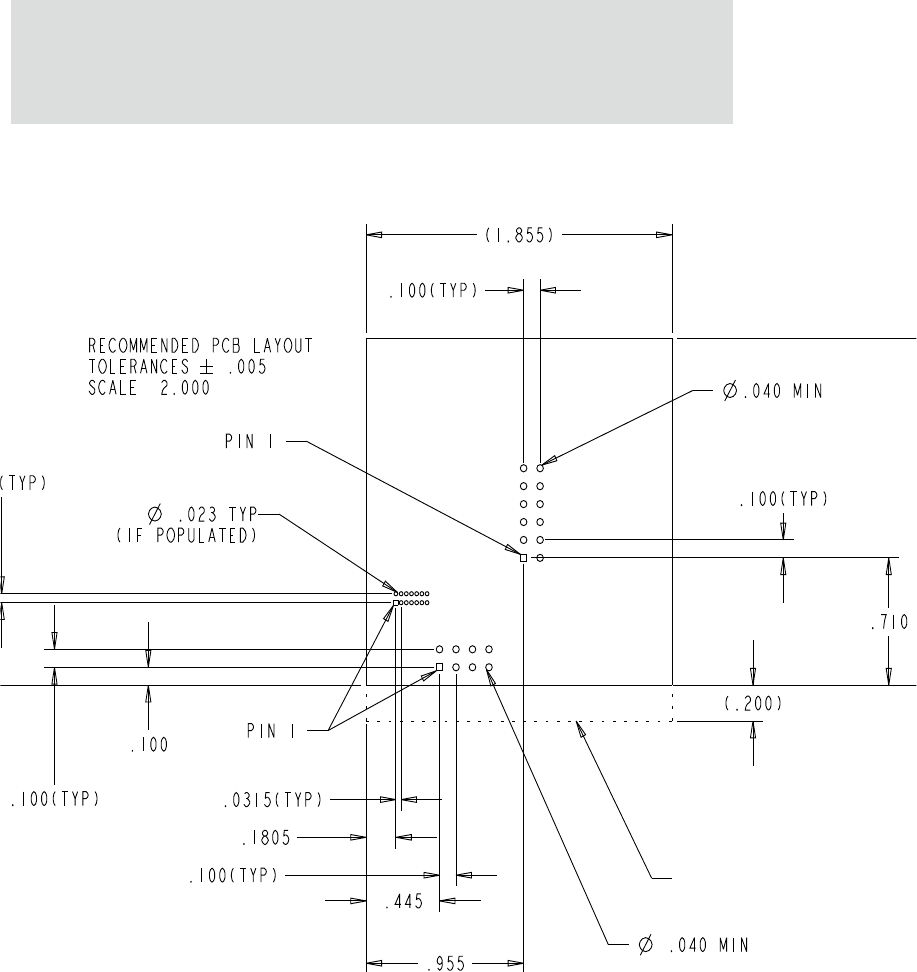
Layouts and Dimensions
50
Digi Connect Wi-EM 9210 Hardware Reference
Digi Connect Wi-EM (w/LED Pin Headers)
LED ARRAY AREA
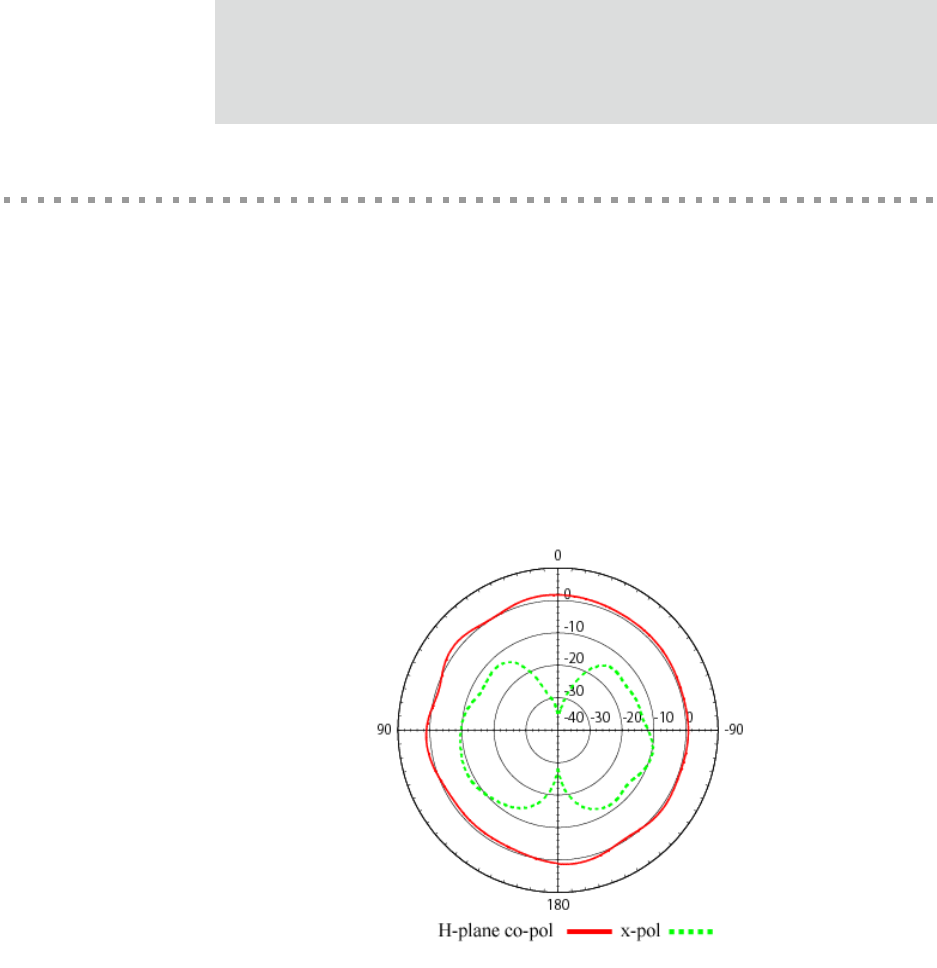
51
Specifications
Antenna Information
Antenna Strength
The following diagram demonstrates the strength of the signal received by the antenna on
both a horizontal and vertical plane. The diagram shows the magnetic field when the
antenna is in a vertical position. The red line represents the horizontal plane and the dotted
green lined represents the vertical plane. You can see in the illustration that at 90degrees,
the signal strength is (as expected) 0.
Radiation Patterns

Antenna Information
52
Digi Connect Wi-EM 9210 Hardware Reference
Radiation Patterns for PCB Mount Antenna
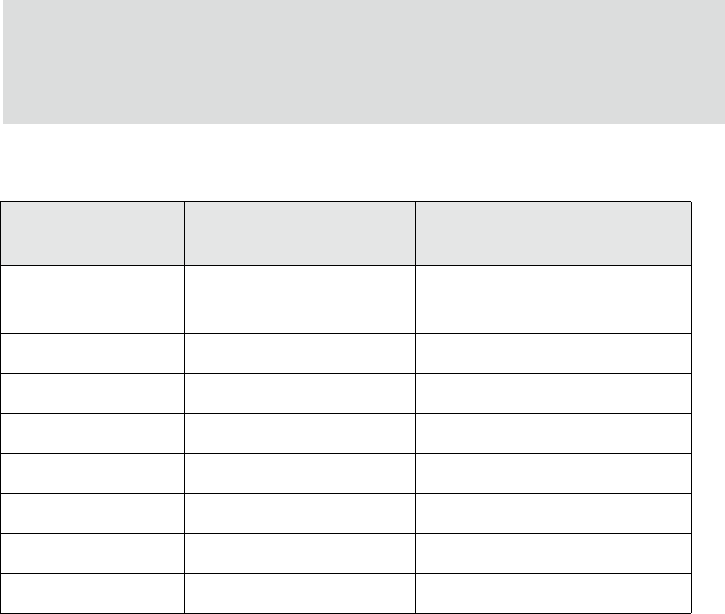
53
Specifications
Antenna Specifications for North America
In the United States, any antenna matching the in-band and out-of-band signal patterns and
strengths of the antenna, whose characteristics are given in the Antenna Description table
and the Radiation pattern graphic, may be used with the Digi Connect Wi-EM 9210.
Antenna
Description Dipole PCB Mount
Frequency 2.4~2.5GHz 2.4~2.5 GHz
4.9~5.9GHz
Power Output 2W 10W
DB Gain 2dBi >2dBi
VSWR < or = 2.0 < 2.5
Dimension 108.5 mm x 10.0 mm 24.13 x 10.67 mm
Weight 10.5g < 1g
Connector RP-SMA U.FL
Part Number DG-ANT-20DT-BG DG-ANT-20CB-AG
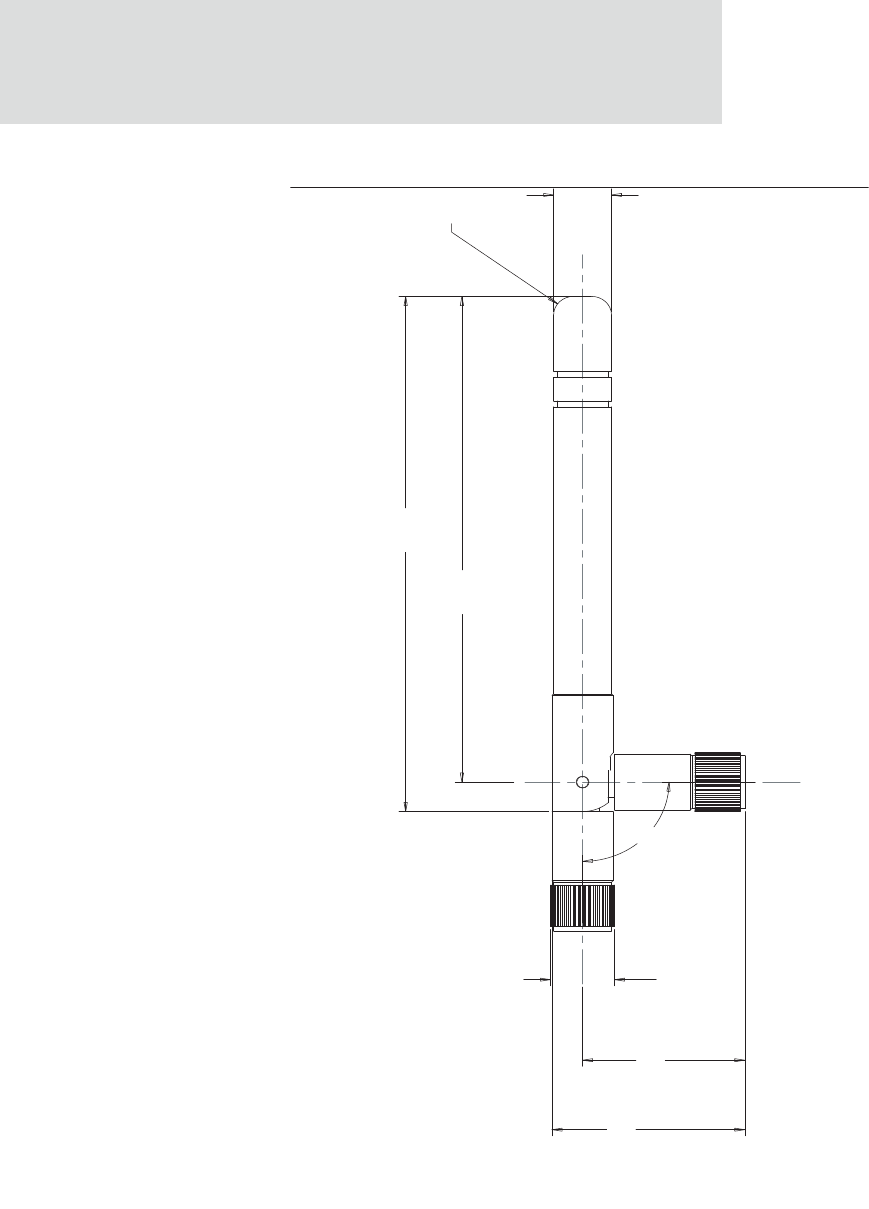
Antenna Information
54
Digi Connect Wi-EM 9210 Hardware Reference
Dipole Antenna Dimensions
bOBITRON
SCALE 3.000
UNITS: mm
90.0˚
(9.1)
.360
(88.9)
3.500
(30.5)
1.200
(25.4)
1.010
(83.8)
3.300
(10.1)
.399
R
(3.2)
.125
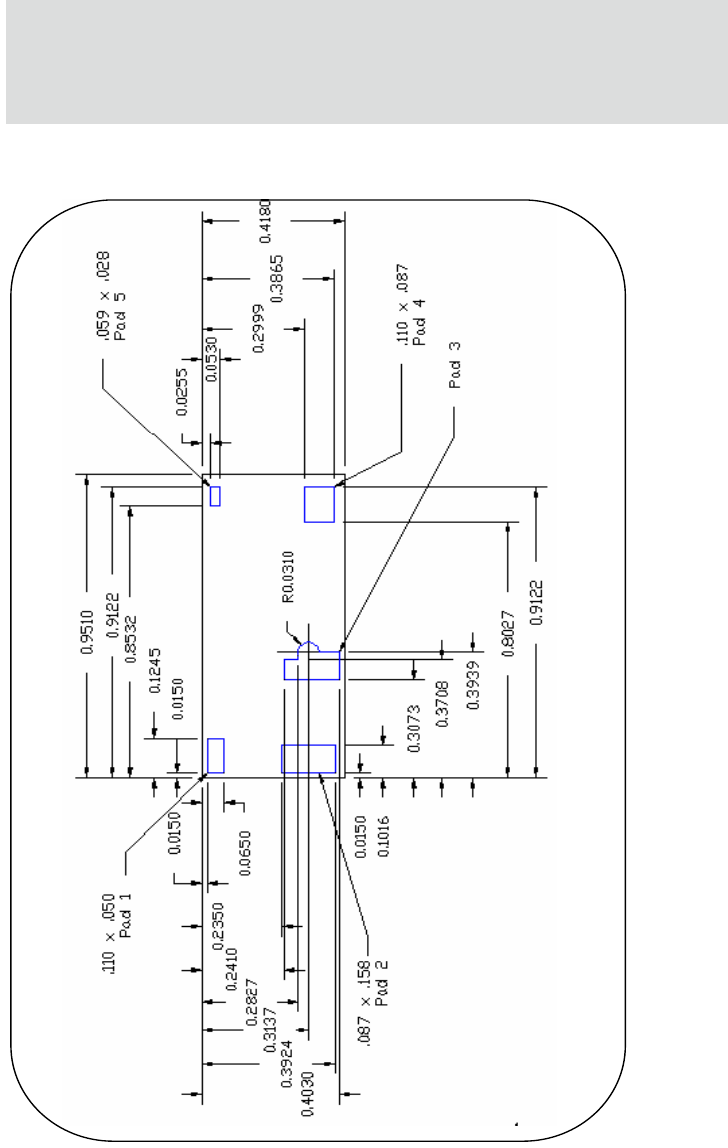
55
Specifications
PCB Mount Antenna Dimensions
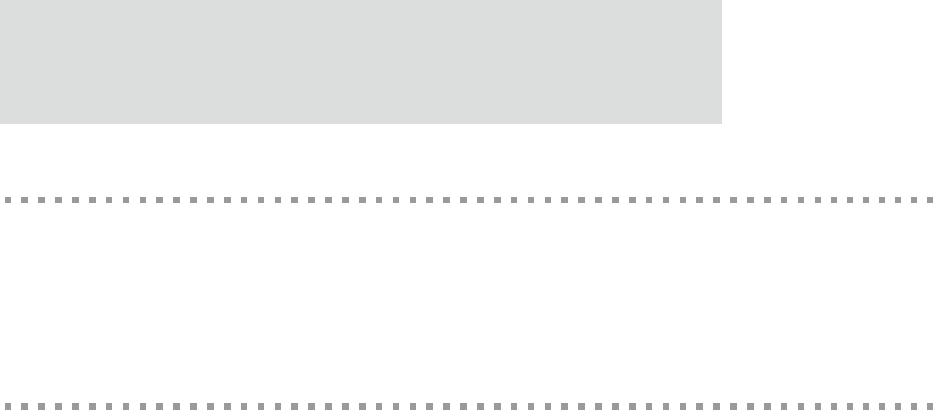
RF Exposure Statement
56
Digi Connect Wi-EM 9210 Hardware Reference
RF Exposure Statement
The Digi Connect Wi-EM 9210 module complies with the RF exposure limits for humans
as called out in RSS-102. It is exempt from RF evaluation based on its operating frequency
of 2.4 GHz, and effective radiated power less than the 3 watt requirement for a mobile
device (>20 cm separation) operating at 2.4 GHz.
Safety Statements
To avoid contact with electrical current:
Never install electrical wiring during an electrical storm.
Use a screwdriver and other tools with insulated handles.
You and those around you should wear safety glasses or goggles.
Installation of inside wire may bring you close to electrical wire, conduit,
terminals and other electrical facilities. Extreme caution must be used to avoid
electrical shock from such facilities. You must avoid contact with all such
facilities.
Protectors and grounding wire placed by the service provider must not be
connected to, removed, or modified by the customer.
Do not touch or move the antenna(s) while the unit is transmitting or receiving.
Do not hold any component containing a radio such that the antenna is very
close to or touching any exposed parts of the body, especially the face or eyes,
while transmitting.
Do not operate a portable transmitter near unshielded blasting caps or in an
explosive environment unless it is a type especially qualified for such use
Any external communications wiring you may install needs to be constructed to all
relevant electrical codes. In the United States this is the National Electrical Code Article
800. Contact a licensed electrician for details.
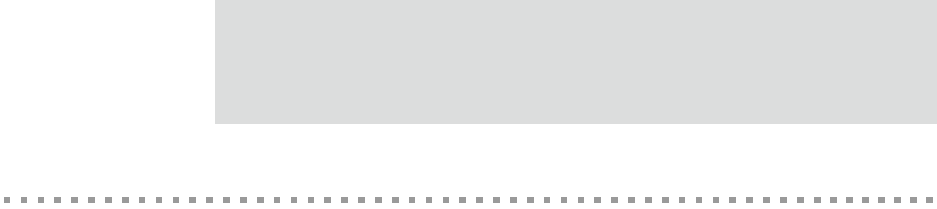
57
Specifications
Notes to original equipment manufacturer (OEM ) integrators
This device is intended only for OEM integrators under the following conditions:
1) The antenna must be installed such that 20 cm is maintained between the antenna and
users for all installations, and
2) The transmitter module may not be co-located with any other transmitter or antenna, and
3) The Module is approved using the FCC ‘unlicensed modular transmitter approval’
method.
Therefore the module must only be used with the originally approved antennas. As long as
the 3 conditions above are met, further transmitter testing will not be required.
However, the OEM integrator is still responsible for testing their end-product for any
additional compliance requirements required with this module installed (for example,
digital device emissions, PC peripheral requirements, etc.).
NOTE: In the event that any of these conditions can not be met (for example portable
configurations, co-location with another transmitter, or use of a different antenna), then the
FCC authorization is no longer considered valid and the FCC ID can not be used on the
final product. In these circumstances, the OEM integrator will be responsible for re-
evaluating the end product (including the transmitter) and obtaining a separate FCC
authorization.

Notes to original equipment manufacturer (OEM ) integrators
58
Digi Connect Wi-EM 9210 Hardware Reference
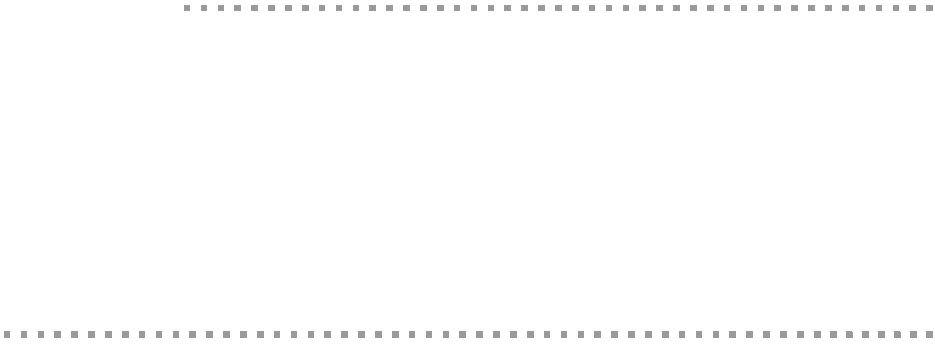
59
Certifications
APPENDIX B
These products comply with the following standards.
FCC Part 15 Class B
Radio Frequency Interference (RFI)(FCC 15.105)
The Digi Connect Wi-EM 9210 embedded modules have been tested and found to comply
with the limits for Class B digital devices pursuant to Part 15 Subpart B, of the FCC Rules.
These limits are designed to provide reasonable protection against harmful interference in a
residential environment. This equipment generates, uses, and can radiate radio frequency
energy, and if not installed and used in accordance with the instruction manual, may cause
harmful interference to radio communications. However, there is no guarantee that
interference will not occur in a particular installation. If this equipment does cause harmful
interference to radio or television reception, which can be determined by turning the
equipment off and on, the user is encouraged to try and correct the interference by one or
more of the following measures:
Reorient or relocate the receiving antenna.
Increase the separation between the equipment and the receiver.
Connect the equipment into an outlet on a circuit different from that to which
the receiver is connected.
Consult the dealer or an experienced radio/TV technician for help.
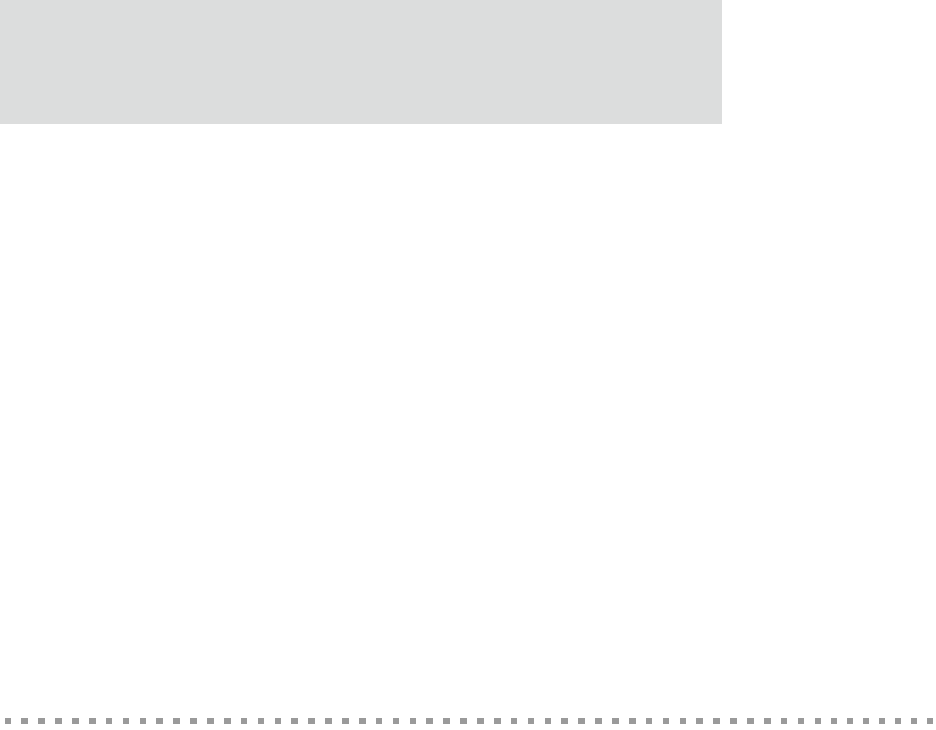
Industry Canada
60
Digi Connect Wi-EM 9210 Hardware Reference
Labeling Requirements (FCC 15.19)
This device complies with Part 15 of FCC rules. Operation is subject to the following two
conditions: (1) this device may not cause harmful interference, and (2) this device must
accept any interference received, including interference that may cause undesired
operation.
If the FCC ID / IC ID is not visible when installed inside another device, then the outside of
the device into which the module is installed must also display a label referring to the
enclosed module FCC ID / IC ID. This exterior label can use wording such as the
following: “Contains Transmitter Module FCC ID: MCQ-501538” / IC: 1846A-
50M1538”.
Modifications (FCC 15.21)
Changes or modifications to this equipment not expressly approved by Digi may void the
user's authority to operate this equipment.
Industry Canada
This digital apparatus does not exceed the Class B limits for radio noise emissions from
digital apparatus set out in the Radio Interference Regulations of the Canadian Department
of Communications.
Le present appareil numerique n'emet pas de bruits radioelectriques depassant les limites
applicables aux appareils numeriques de la class B prescrites dans le Reglement sur le
brouillage radioelectrique edicte par le ministere des Communications du Canada.
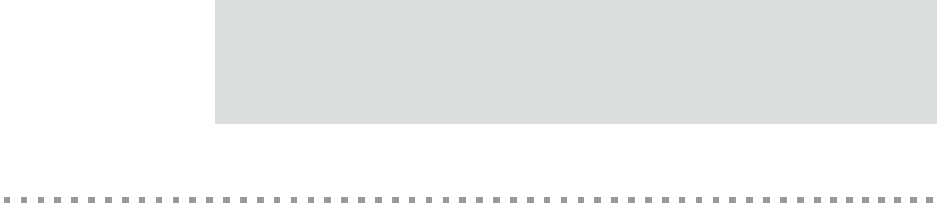
61
Certifications
Declaration of Conformity
(In accordance with FCC Dockets 96-208 and 95-19)
Digi International declares, that the products:EM-02T-JT
to which this declaration relates, meet the requirements specified by the Federal
Communications Commission as detailed in the following specifications:
Part 15, Subpart B, for Class B Equipment
FCC Docket 96-208 as it applies to Class B personal
Computers and Peripherals
The products listed above have been tested at an External Test Laboratory certified per
FCC rules and has been found to meet the FCC, Part 15, Class B, Emission Limits.
Documentation is on file and available from the Digi International Homologation
Department.
Manufacturer's Name: Digi International
Corporate Headquarters: 11001 Bren Road East
Minnetonka MN 55343
Manufacturing Headquarters: 10000 West 76th Street
Eden Prairie MN 55344
Product Name: Digi Connect Wi-EM 9210
Model Numbers: 50001538-xx
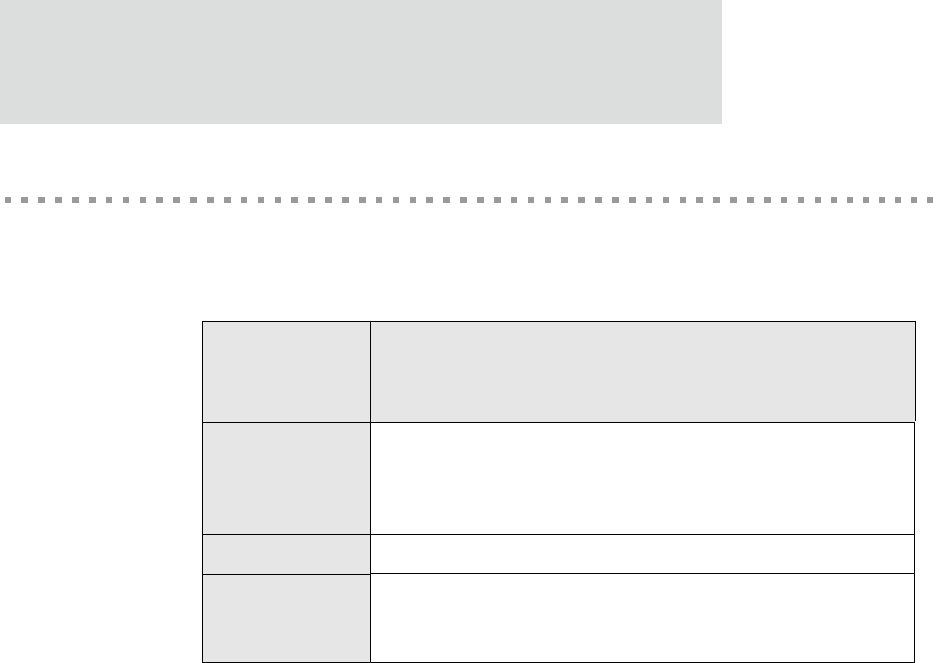
International EMC Standards
62
Digi Connect Wi-EM 9210 Hardware Reference
International EMC Standards
The Digi Connect Wi-EM 9210 meet the following standards:
Standards Digi Connect
Wi-EM 9210
Emmissions
FCC Part 15 Subpart C
RSS-210 Issue 7 and RSS-GEN Issue 2
FCC ID: MCQ-50M1538
IC: 1846A-50M1538
Immunity EN 55024
Safety UL 60950-1
CSA 22.2 No. 60950--1
EN 60950-1

63
Sample Application:
TTL Signals to EIA-232
APPENDIX C
The following schematic is an example of how to convert the module’s TTL signals to
EIA-232.
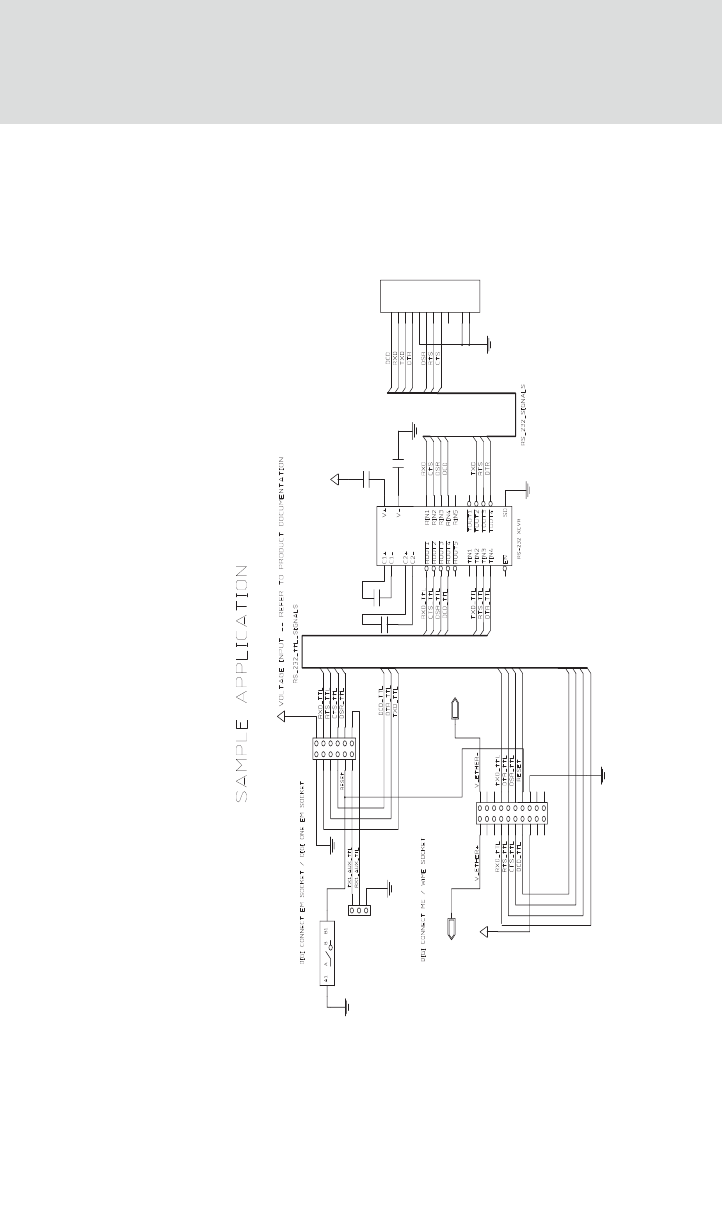
64
Digi Connect EM & Wi-EM Hardware Reference
0.1uF
1
2
0.1uF
1
2
0.1uF
1
2
0.1uF
2
1
GND
11
10
9
8
7
6
5
4
3
2
1
DB9 CONNECTOR
SHIELD
SHIELD
GND
17
13
25
24
16
15
14
12
2821
120
36
27
19 18
22 23
26 27
54
89
GND
1112
10
9
87
65
4
3
12
SOCKET 2X6
3
2
1
ADDITIONALSIGNALS / OPTIONAL
GND
RESET SWITCH
12
GND
GND
SOCKET2X10
12
34
56
78
91
0
11 12
13 14
15 16
17 18
19 20
V_ETHER-
V_ETHER+
POWERED ETHERNET -- SEE PRODUCTDOCUMENTATION
V
OLTAGE INPUT -- REFER TO PRODUCT DOCUMENTATION
GND
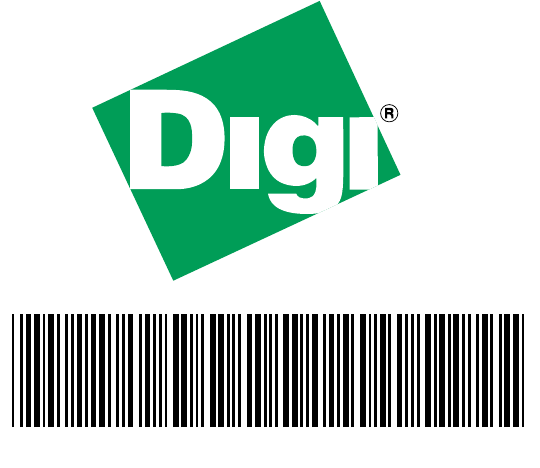
PN (1P): 90000955 A