第一章 FD Servo_User_Manual Servo User Manual
User Manual: FD Servo_User_Manual
Open the PDF directly: View PDF .
Page Count: 171 [warning: Documents this large are best viewed by clicking the View PDF Link!]
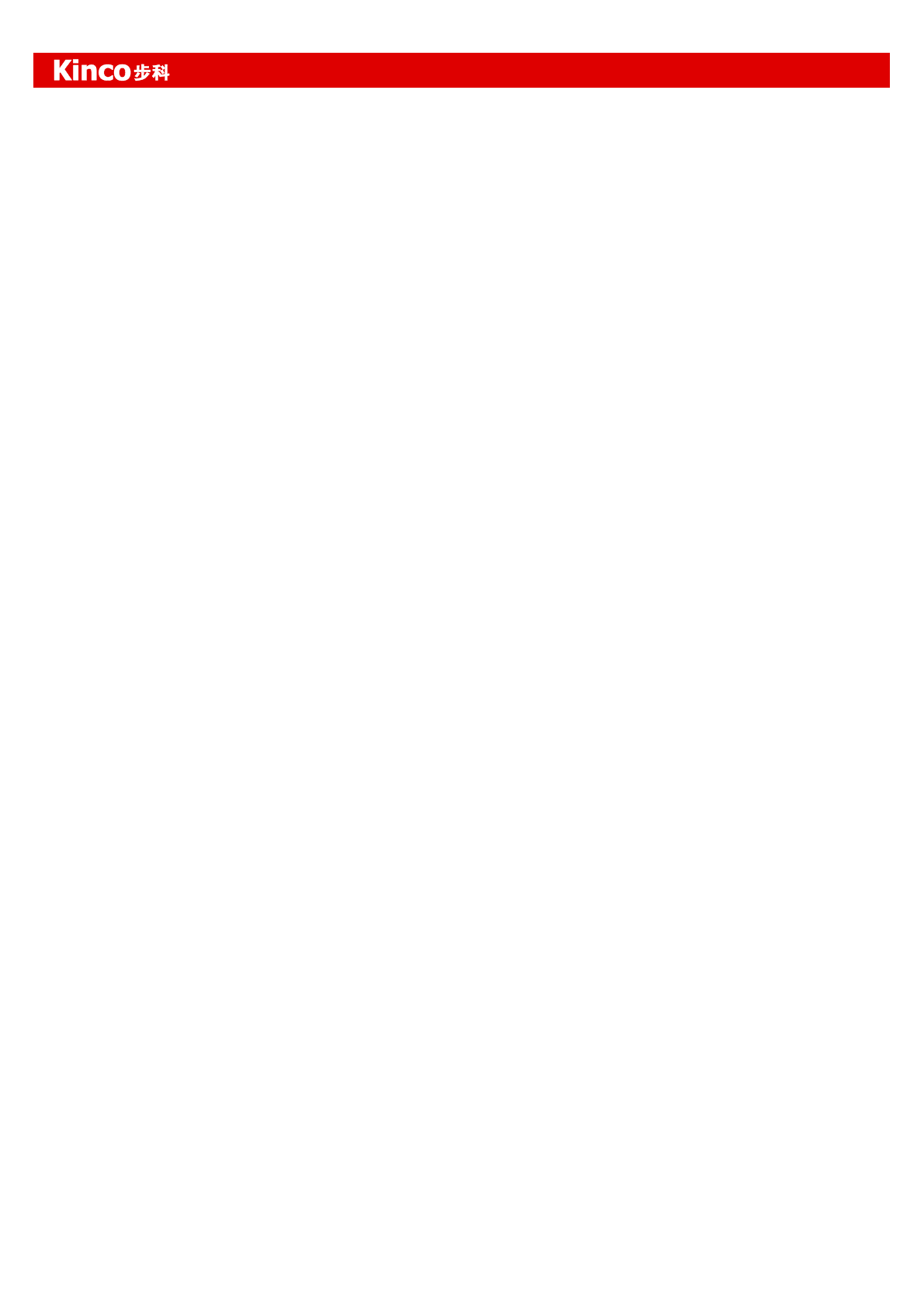
1
Kinco FD Series Servo User Manual
Content
Chapter 1 Product Acceptance & Model Description ........................................................................................ 5
1.1 Product Acceptance ................................................................................................................................. 5
1.1.1 Items for Acceptance (Wires Included) ............................................................................................. 5
1.1.2 Nameplate of Servo Driver ................................................................................................................ 6
1.1.3 Nameplate of Servo Motor ................................................................................................................ 6
1.2 Component Names .................................................................................................................................. 7
1.2.1 Component Names of FD Series Servo Driver ................................................................................. 7
1.2.2 Component Names of Servo Motor .................................................................................................. 8
1.3 Model Description of Servo Motors and Drivers ...................................................................................... 8
1.3.1 Servo Drivers .................................................................................................................................... 8
1.3.2 Servo Motors ..................................................................................................................................... 8
1.3.3 Power, Brake and Encoder cable of Motors ..................................................................................... 9
Chapter 2 Precautions and Installation Requirements .................................................................................... 10
2.1 Precautions ............................................................................................................................................ 10
2.2 Environmental Conditions ...................................................................................................................... 10
2.3 Mounting Direction & Spacing ................................................................................................................ 10
Chapter 3 Interfaces and Wirings of FD Driver................................................................................................ 12
3.1 Interface and wiring of FD122 ................................................................................................................ 12
3.1.1 Panel and Interfaces Description of FD122 .................................................................................... 12
3.1.2 External Wiring of FD122 ................................................................................................................ 13
3.1.3 Interface Wiring Defination of FD122 .............................................................................................. 14
3.2 Interface and wiring of FD412/FD422/FD432/FD622 ............................................................................ 18
3.2.1 Interface Description ........................................................................................................................... 18
3.2.2 External Wirings .................................................................................................................................. 20
3.2.3 I/O Interface ........................................................................................................................................ 21
3.2.4 Power Interface of FD Driver (FD412/FD422/X3, FD432/FD622/X3 and X7) .................................... 22
3.2.5 X4~X6 Interface .................................................................................................................................. 22
3.2.5.1 X4 Interface(RS485/CAN) ............................................................................................................ 23
3.2.5.2 X5 Interface(RS232) .................................................................................................................... 24
3.2.5.3 X6 Interface (Encoder in) ............................................................................................................. 24
Chapter 4 Digital Operation Panel ................................................................................................................... 25
4.1 Introduction ............................................................................................................................................ 25
4.2 Operation on Digital Operation Panel .................................................................................................... 27
Chapter 5 KincoServo Software Introductions................................................................................................. 29
5.1 Software Installation ............................................................................................................................... 29
5.2 Quick Start ............................................................................................................................................. 29
5.2.1 Hardware Configuration for Running KincoServo Software............................................................ 29
5.2.2 KincoServo Software Online ........................................................................................................... 29
5.3 Menu Introductions ................................................................................................................................ 32
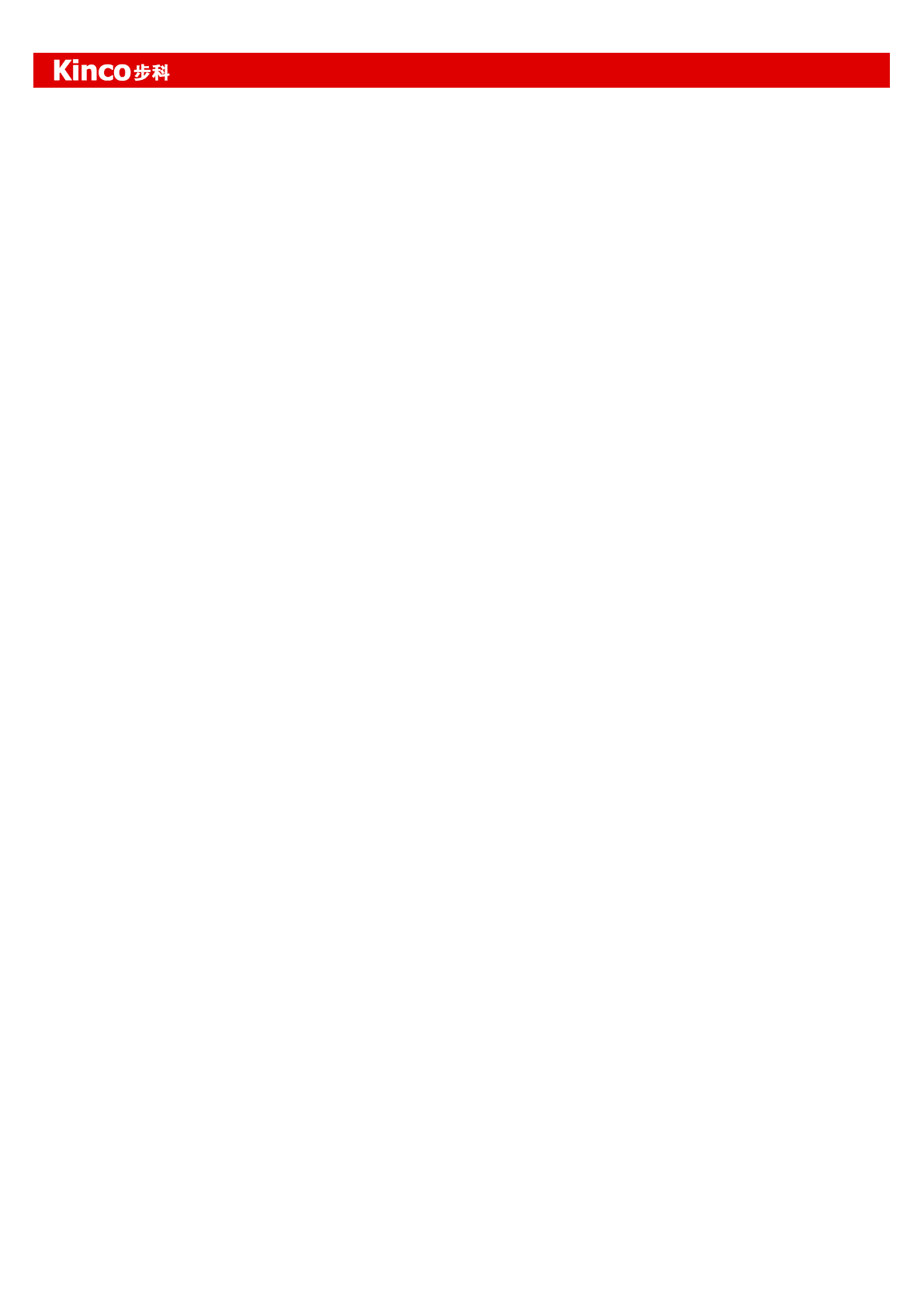
2
Kinco FD Series Servo User Manual
5.4 Driver Control ......................................................................................................................................... 33
5.4.1 Basic Operate ................................................................................................................................. 33
5.4.2 Control Loop .................................................................................................................................... 34
5.4.3 I/O Port ............................................................................................................................................ 35
5.4.4 Operation Mode .............................................................................................................................. 37
5.4.5 Data Object ..................................................................................................................................... 37
5.4.6 Driver Config ................................................................................................................................... 39
5.4.7 ECAN Setting(CANopen PDO Setting) ...................................................................................... 39
5.4.8 Oscilloscope .................................................................................................................................... 40
5.4.9 Error Control .................................................................................................................................... 44
5.4.10 Error History .................................................................................................................................. 45
5.4.11 Control Panel ................................................................................................................................. 45
5.4.12 Initialize/Save ................................................................................................................................ 45
5.4.13 Driver Property .............................................................................................................................. 45
Chapter 6 Motor Selection,Trial Operation and Parameter List ...................................................................... 46
6.1 Driver and motor configuration .............................................................................................................. 46
6.1.1 Configuration Table for FD Servo Driver and Motor ........................................................................ 46
6.1.2 Procedure for Motor configuration .................................................................................................. 47
6.2 Trial Operation ....................................................................................................................................... 48
6.2.1 Objective ......................................................................................................................................... 48
6.2.2 Precautions ..................................................................................................................................... 48
6.2.3 Operating Procedure ....................................................................................................................... 48
6.2.4 Diagram of Trial Operation .............................................................................................................. 49
6.3 Descriptions of Parameters ................................................................................................................... 49
Parameter List: Group F000 (To Set Driver Instructions) ......................................................................... 49
Parameter List: Group F001 (To Set Real-Time Display Data) ................................................................ 50
Parameter List: Group F002 (To Set Control Loop Parameters) ............................................................. 52
Parameter List: Group F003 (To Set Input/Output & Pattern Operation Parameters) ............................. 53
Parameter List: Group F004 (To Set Motor Parameters) ......................................................................... 57
Parameter List: Group F005 (To Set Driver Parameters) ........................................................................ 58
Chapter 7 Operation on Input/Output Ports ..................................................................................................... 60
7.1 Digital Input ............................................................................................................................................ 60
7.1.1 Polarity Control on Digital Input Signals.......................................................................................... 60
7.1.2 Simulation of Digital Input Signals .................................................................................................. 61
7.1.3 Status Display of Digital Input Signals ............................................................................................ 62
7.1.4 Addresses & Functions of Digital Input Signals .............................................................................. 62
7.1.5 Wirings of Digital Input Port ............................................................................................................ 66
7.2 Digital Output ......................................................................................................................................... 67
7.2.1 Polarity Control on Digital Output Signals ....................................................................................... 67
7.2.2 Simulation of Digital Output Signals(More details please refer to 7.1.2) ................................... 68
7.2.3 Status Display of Digital Output Signals .......................................................................................... 68
7.2.4 Addresses and Functions of Digital Output Signals ........................................................................ 68
7.2.5 Wiring of Digital Output Port ........................................................................................................... 69
Chapter 8 Operation Mode .............................................................................................................................. 71
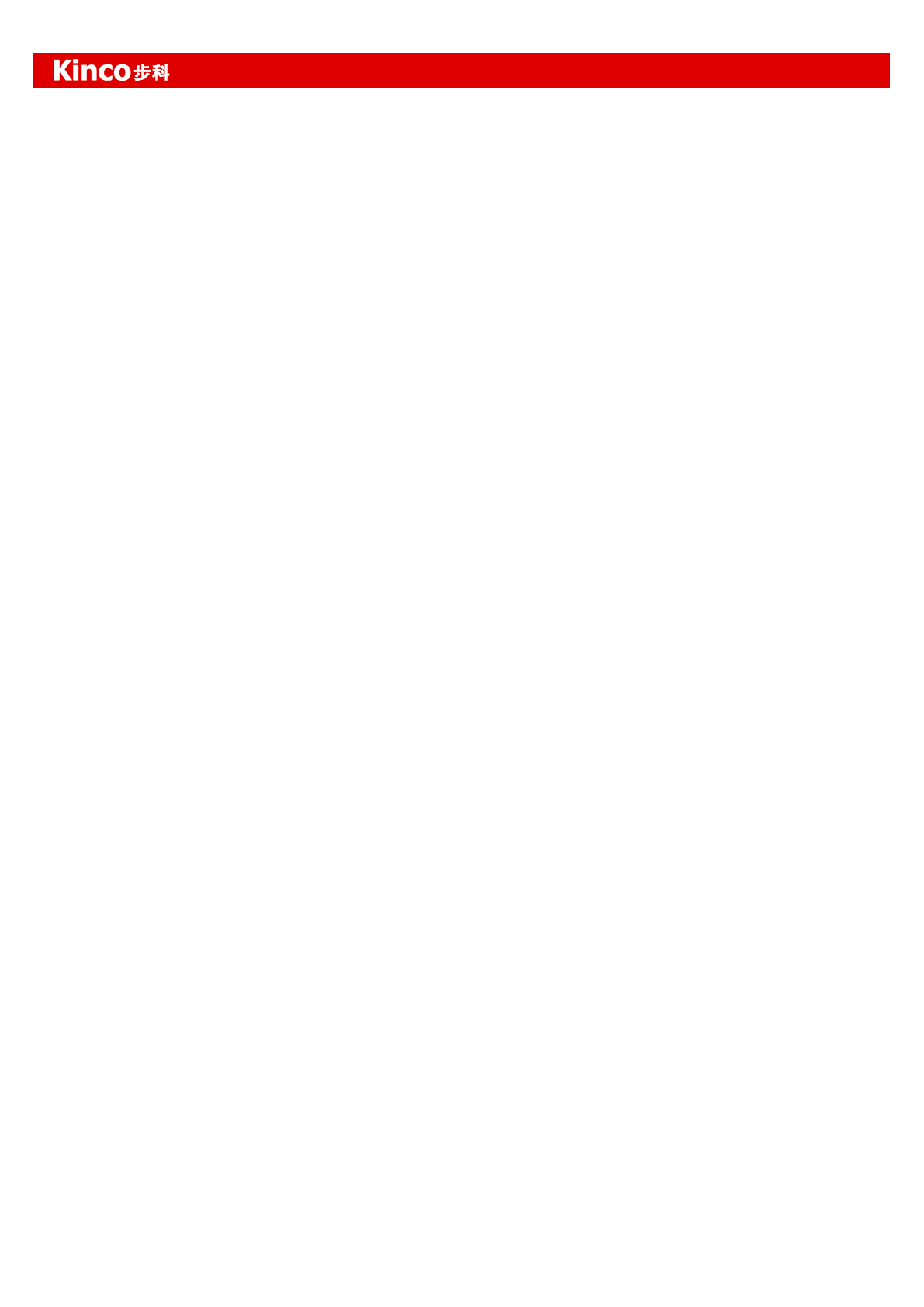
3
Kinco FD Series Servo User Manual
8.1 Pulse Control Mode (“-4” Mode) ............................................................................................................ 71
8.1.1 Wiring in Pulse Control Mode ......................................................................................................... 71
8.1.2 Parameters for Pulse Control Mode ................................................................................................ 72
8.1.3 Examples of Pulse Control Mode .................................................................................................... 75
8.2 Speed Mode (“-3” or “3” Mode) .............................................................................................................. 77
8.2.1 Wiring in Analog – Speed Mode ............................................................................................................. 78
8.2.2 Parameters for Analog – Speed Mode ............................................................................................ 78
8.2.3 Analog Signal Processing ............................................................................................................... 79
8.2.4 Calculation Procedure for Analog – speed Mode ........................................................................... 80
8.2.5 Examples of Analog – Speed Mode ................................................................................................ 81
8.3 Torque Mode (“4” Mode) ........................................................................................................................ 86
8.3.1 Wiring in Analog – Torque Mode ..................................................................................................... 86
8.3.2 Parameters for Analog – Torque Mode ........................................................................................... 86
8.3.3 Analog Signal Processing ............................................................................................................... 87
8.3.4 Calculation Procedure for Analog – Torque Mode .......................................................................... 88
8.3.5 Examples of Analog – Torque Mode ............................................................................................... 88
8.4 Internal Multi-position Control Modes (“1” Mode) .................................................................................. 91
8.5 Internal Multi-speed Control Modes (“-3” or “3” Mode) .......................................................................... 94
8.6 Internal Torque Control Mode (“4” Mode) .............................................................................................. 95
8.7 Homing Mode (“6” Mode) ....................................................................................................................... 95
Chapter 9 Control Performance ..................................................................................................................... 109
9.1 Auto Reverse ....................................................................................................................................... 109
9.2 Driver Performance Tuning ................................................................................................................... 110
9.2.1 Manual Adjustment......................................................................................................................... 110
9.2.2 Auto Adjustment (Only for Velocity Loops) .................................................................................. 113
9.3 Oscillation Inhibition .............................................................................................................................. 115
9.4 Debugging Example ............................................................................................................................. 116
9.4.1 Oscilloscope ................................................................................................................................... 116
9.4.2 Procedure for Parameter Adjustment............................................................................................. 118
Chapter 10 Communication ........................................................................................................................... 124
10.1 RS232 Communication ...................................................................................................................... 124
10.1.1 RS232 Communication Interface ................................................................................................ 124
10.1.2 RS232 Communication Parameters ........................................................................................... 125
10.1.3 Transport Protocol ....................................................................................................................... 125
10.1.3.1 Data Protocol ........................................................................................................................... 126
10.1.4 RS232 Communication Address of Servo Parameters ............................................................... 127
10.2 RS485 Communication ...................................................................................................................... 128
10.2.1 RS485 Communication Interface ................................................................................................ 128
10.2.2 RS485 Communication Parameters ........................................................................................... 128
10.2.3 MODBUS RTU ............................................................................................................................ 128
10.2.4 RS485 Communication Address of Servo Parameters ............................................................... 130
10.3 CANopen Communication ................................................................................................................. 130
10.3.1 Hardware Introduction ................................................................................................................. 131
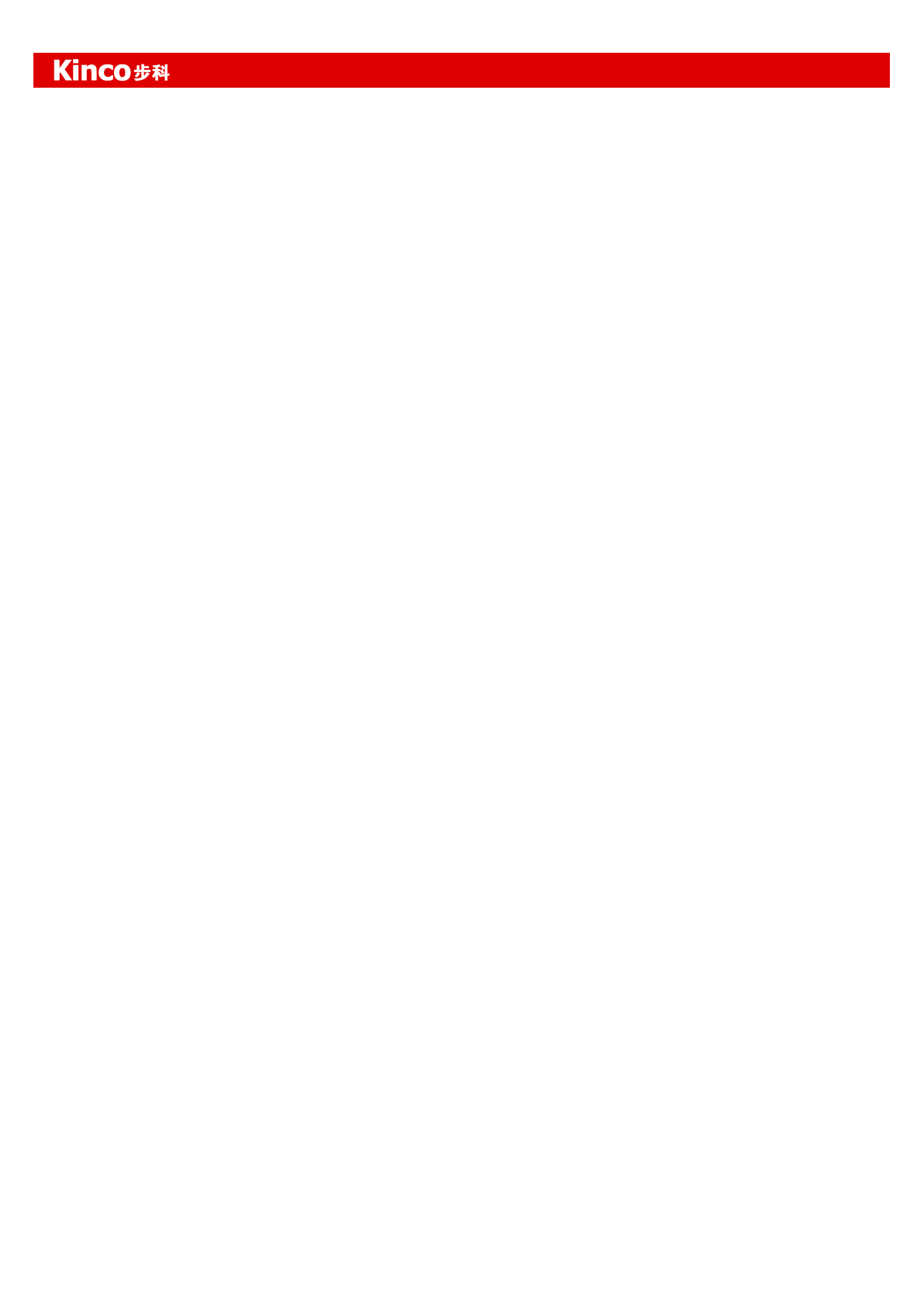
4
Kinco FD Series Servo User Manual
10.3.2 Software Introduction .................................................................................................................. 132
10.3.1.1 EDS .......................................................................................................................................... 132
10.3.1.2 SDO ......................................................................................................................................... 132
10.3.1.3 PDO ......................................................................................................................................... 132
10.3.3 CANopen Communication Parameters ....................................................................................... 135
10.3.4 CANopen Communication Address of Servo Parameters .......................................................... 136
Chapter 11 Alarm and Troubleshooting ......................................................................................................... 137
11.1 Alarm Messages ................................................................................................................................. 137
11.2 Alarm Causes & Troubleshooting ....................................................................................................... 138
Chapter 12 Appendix ..................................................................................................................................... 139
Appendix 1 Instructions of operation mode via Communication ............................................................... 139
1. Position mode(Mode 1) ...................................................................................................................... 139
2. Speed Mode(Mode -3 or 3) ................................................................................................................ 139
3. Master-slave mode(Mode -4) ............................................................................................................. 140
4.Torque Mode(Mode 4) ......................................................................................................................... 140
5. Homing mode(Mode 6) ...................................................................................................................... 141
6. Driver Status Display .......................................................................................................................... 142
Appendix 2:Example for CANopen Communication .................................................................................. 142
1.Canopen communication between Kinco F1 PLC and FD Servo ....................................................... 142
2.CANopen Communication between FD Servo and Peak CAN. ......................................................... 149
Appendix 3:Example for RS485 Communication ...................................................................................... 151
1.Modbus Communication Between FD Servo and Kinco HMI ............................................................. 151
2. Modbus Communication Between FD Servo and Siemens S7-200 .................................................. 154
Appendix 4:Example for RS232 Communication ...................................................................................... 156
1.Communication between FD Servo and Kinco HMI. .......................................................................... 156
Appendix 5: Use KincoServo software to import and export driver parameters. ....................................... 159
Appendix 6: Conversion between engineering unit and internal unit of common objects. ........................ 162
Appendix 7: Common Objects List ............................................................................................................ 163
Appendix 8: Selection for Brake Resistor .................................................................................................. 170
Appendix 9: Selection for Fuse .................................................................................................................. 171

5
Kinco FD Series Servo User Manual
Chapter 1 Product Acceptance & Model Description
1.1 Product Acceptance
1.1.1 Items for Acceptance (Wires Included)
Table 1-1 Product acceptance
Item for Acceptance
Remark
Whether the model of a delivered FD series
servo system is consistent with the
specified model
Check the nameplate of a servo motor and
that of a servo driver
Whether the accessories included in the
packing list are complete
Check the packing list
Whether any breakage occurs
Check the external appearance completely
for any losses that are caused by
transportation
Whether any screws are loose
Check for loose screws with a screwdriver
Whether the motor wiring is correct
Purchase motor accessory packages if no
wirings are purchased
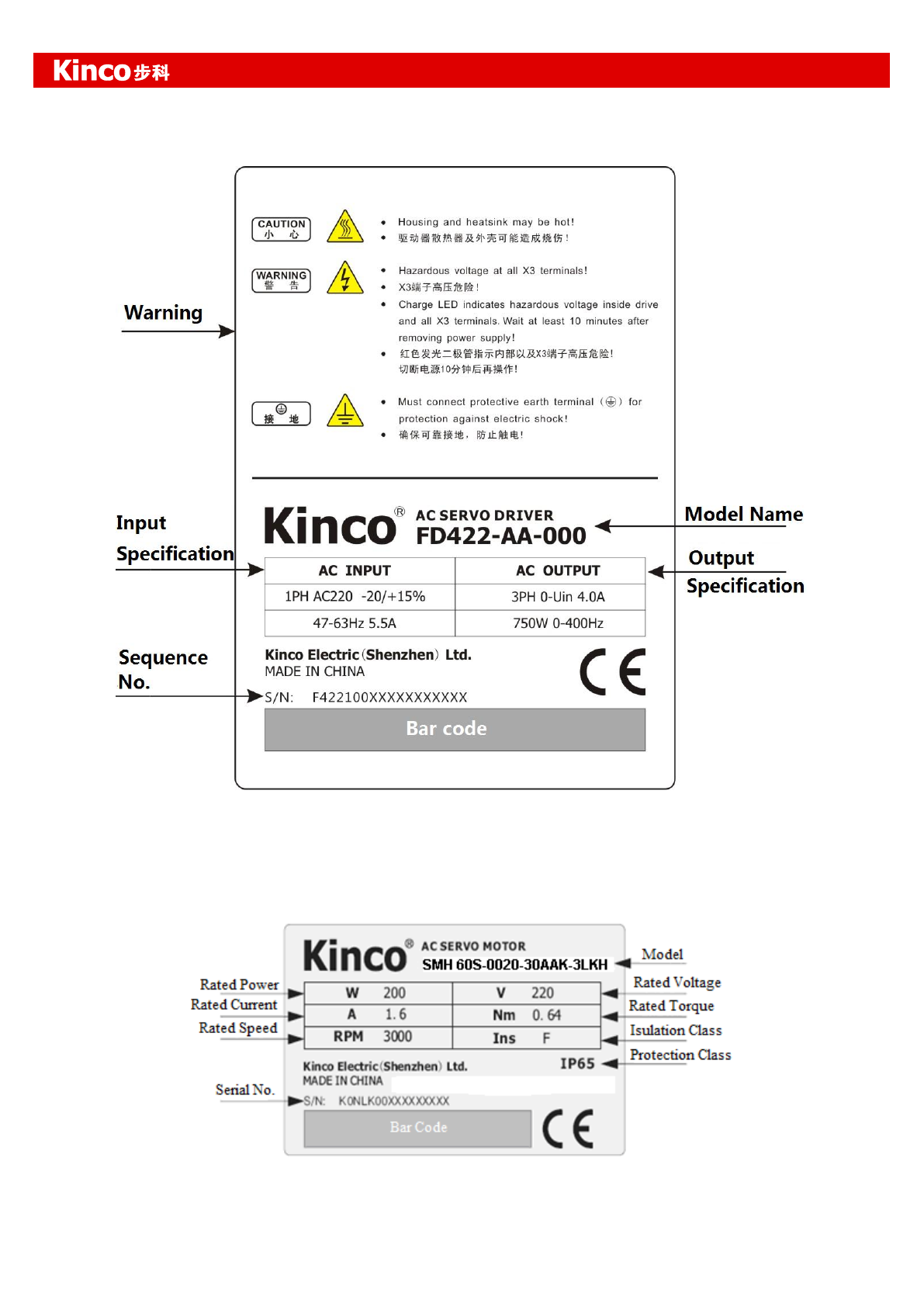
6
Kinco FD Series Servo User Manual
1.1.2 Nameplate of Servo Driver
Fig. 1-1 Nameplate of a servo driver
1.1.3 Nameplate of Servo Motor
Fig. 1-2 Nameplate of a servo motor
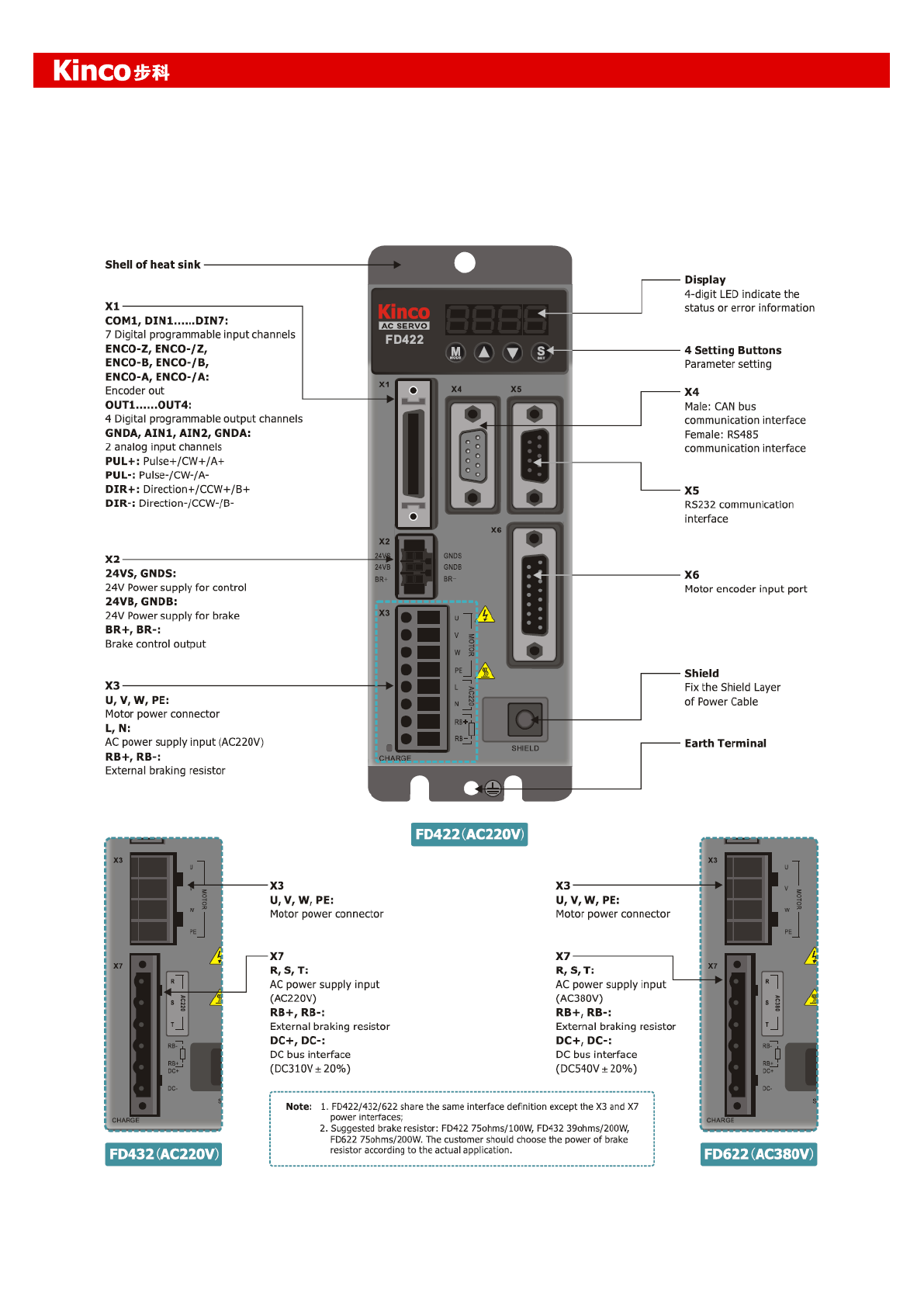
7
Kinco FD Series Servo User Manual
1.2 Component Names
1.2.1 Component Names of FD Series Servo Driver
Fig. 1-3 Component Names of FD Series Servo Driver
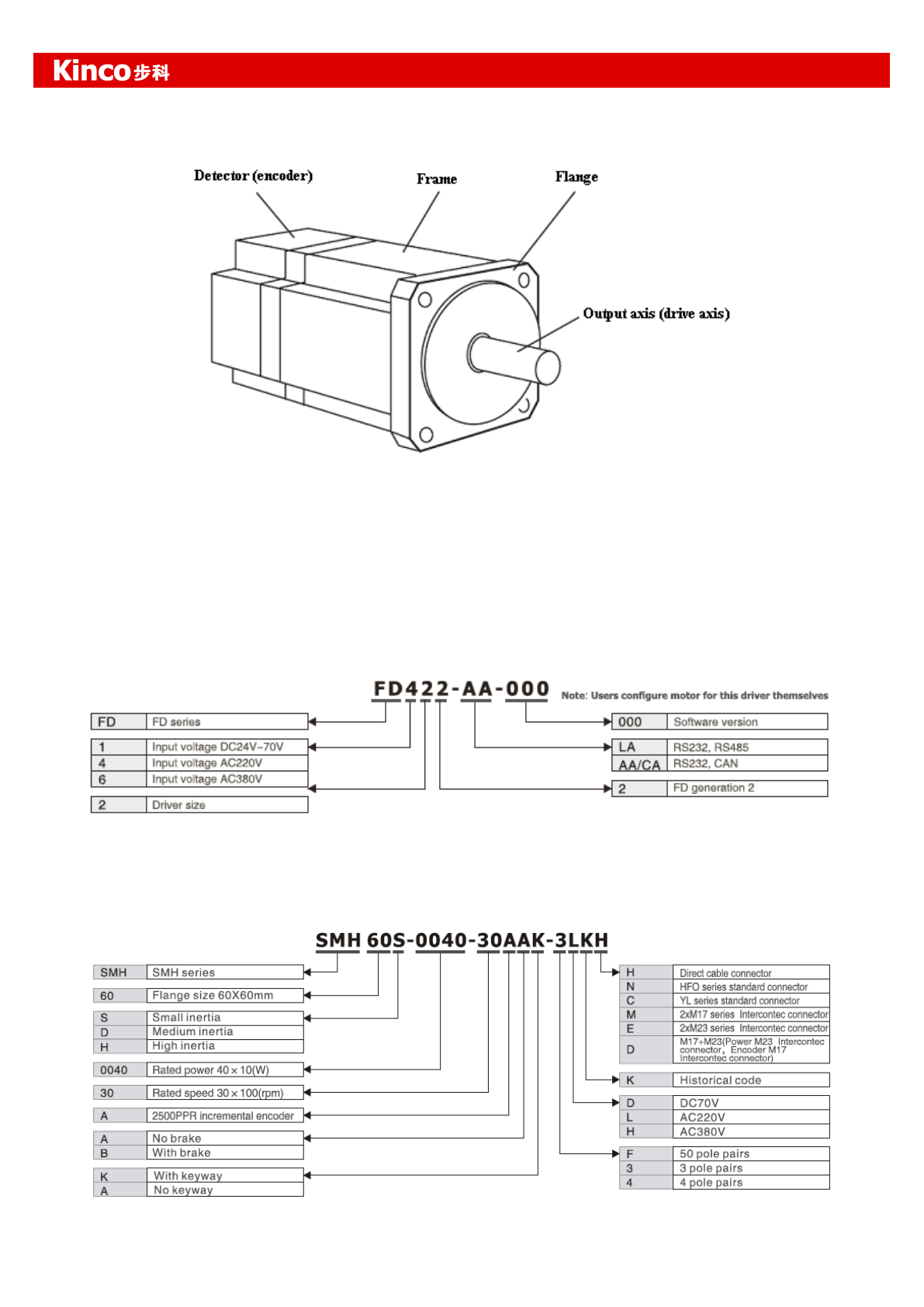
8
Kinco FD Series Servo User Manual
1.2.2 Component Names of Servo Motor
Fig. 1-4 Component names of a servo motor (brakes excluded)
1.3 Model Description of Servo Motors and Drivers
1.3.1 Servo Drivers
1.3.2 Servo Motors
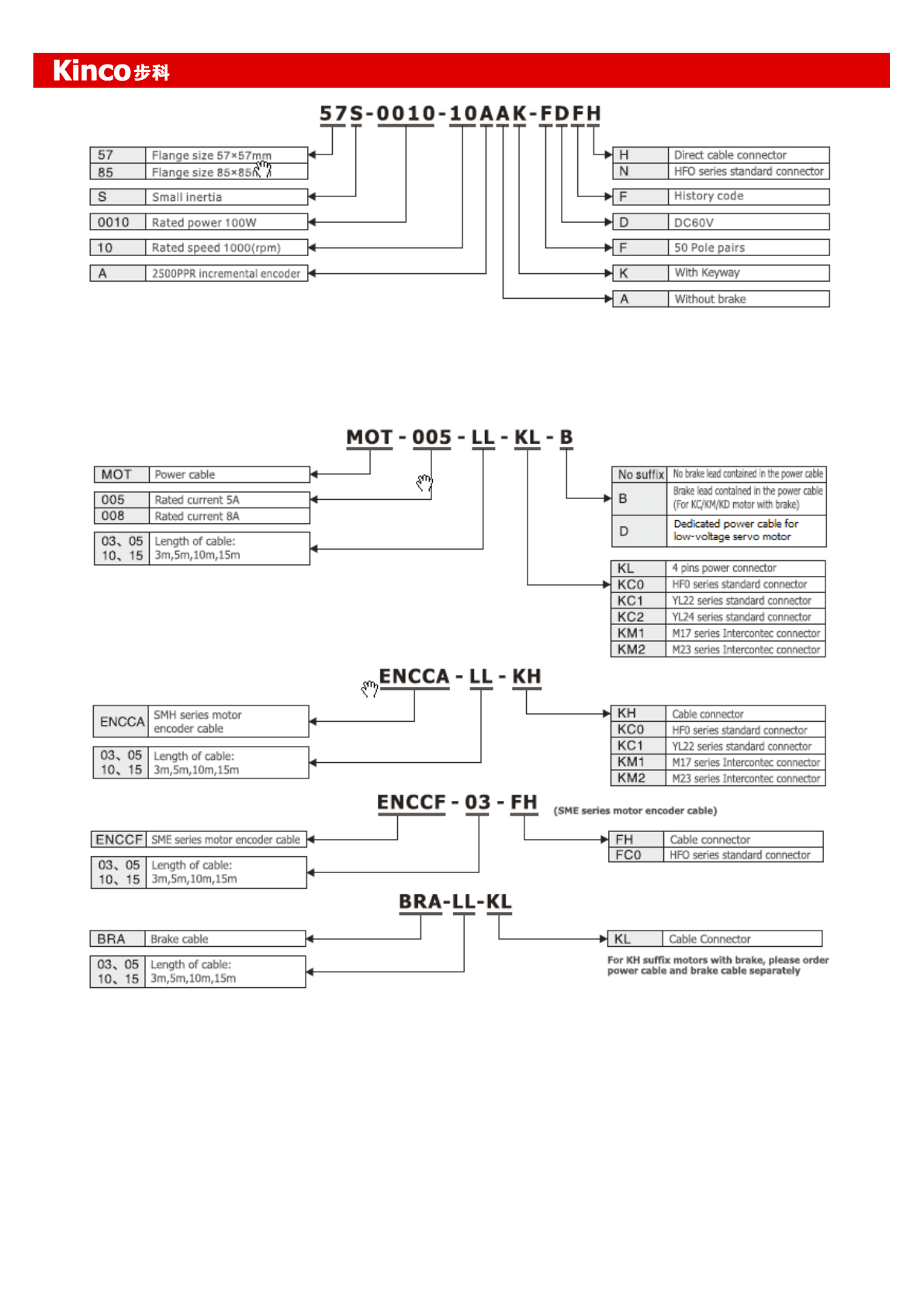
9
Kinco FD Series Servo User Manual
1.3.3 Power, Brake and Encoder cable of Motors
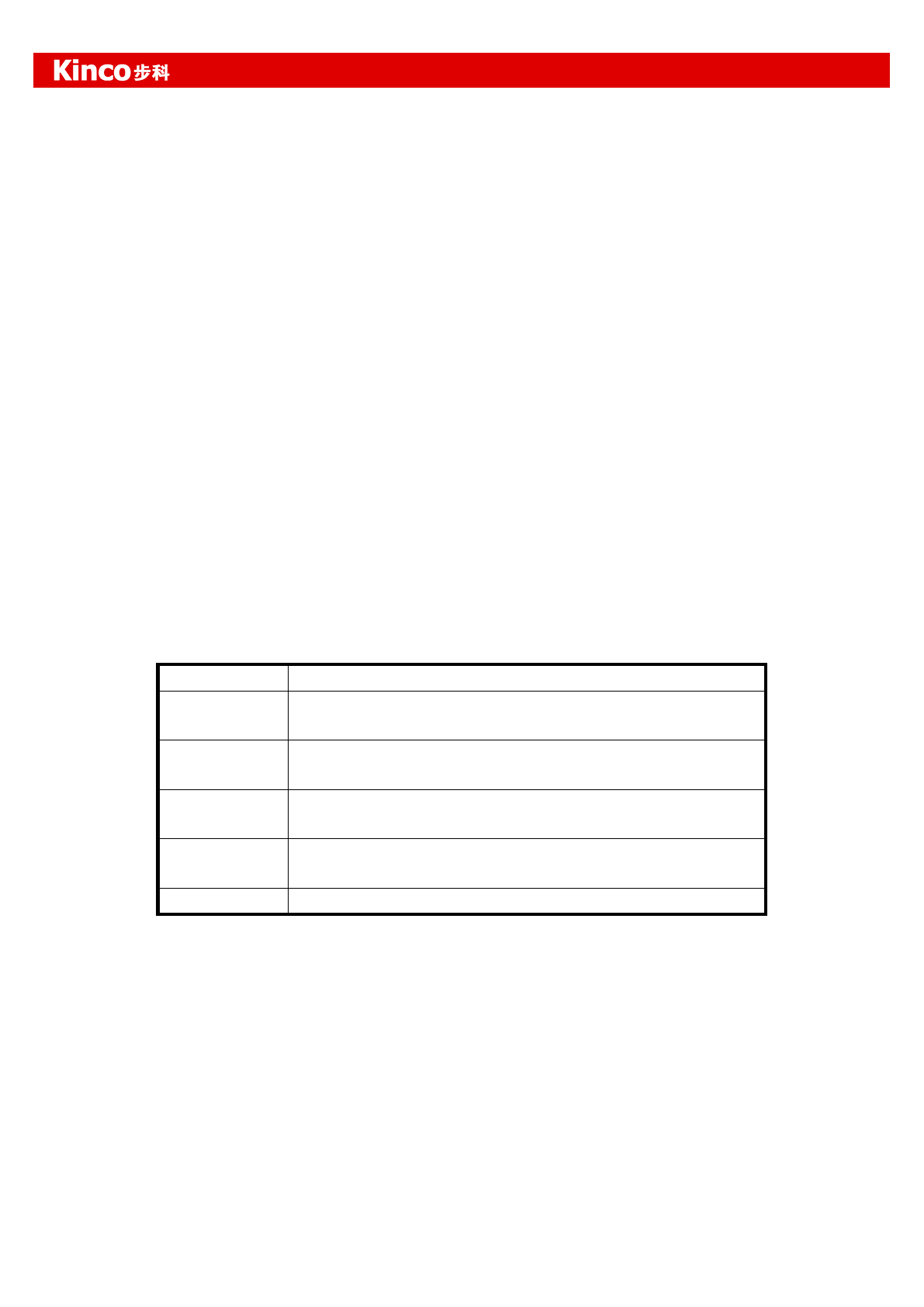
10
Kinco FD Series Servo User Manual
Chapter 2 Precautions and Installation
Requirements
2.1 Precautions
- Tightly fasten the screws that fix the motor;
- Make sure to tightly fasten all fixed points when fixing the driver;
- Do not tighten the cables between the driver and the motor/encoder;
- Use a coupling shaft or expansion sleeve to ensure that both the motor shaft and equipment shaft
are properly centered;
- Do not mix conductive materials (such as screws and metal filings) or combustible materials (such
as oil) into the servo driver;
- Avoid the servo driver and servo motor from dropping or striking because they are precision
equipment;
- For safety, do not use any damaged servo driver or any driver with damaged parts.
2.2 Environmental Conditions
Table 2-1 Environmental conditions
Environment
Condition
Temperature
Operating temperature: 0C - 40C (ice free)
Storage temperature: - 10C - 70C (ice free)
Humidity
Operating humidity:5~ 90% RH (non-condensing)
Storage humidity: 5~90% RH (non-condensing)
Air
Indoor (No direct sunlight), no corrosive gas or combustible gas
No oil vapor or dust
Height
Below 2000 m above the sea level,it needs power derating after
1000m
Vibration
5.9 m/s2
2.3 Mounting Direction & Spacing
Please install the servo driver correctly according to following figure,or it will cause faults.
The servo driver should be vertically installed on wall.Take fully into account heat dissipation when using
any heating components (such as braking resistors) so that the servo driver is not affected.
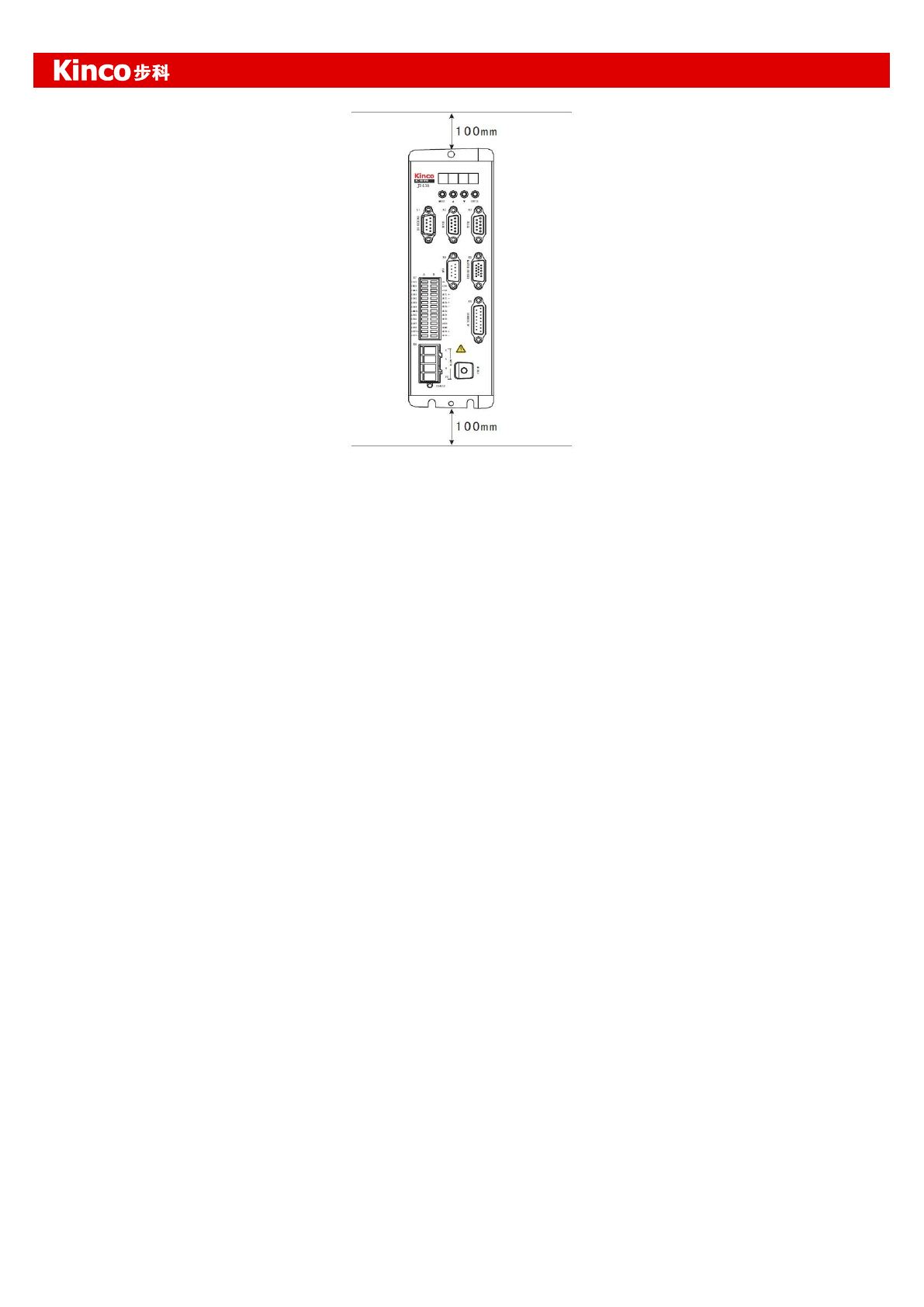
11
Kinco FD Series Servo User Manual
Fig. 2-1 Installing a servo driver
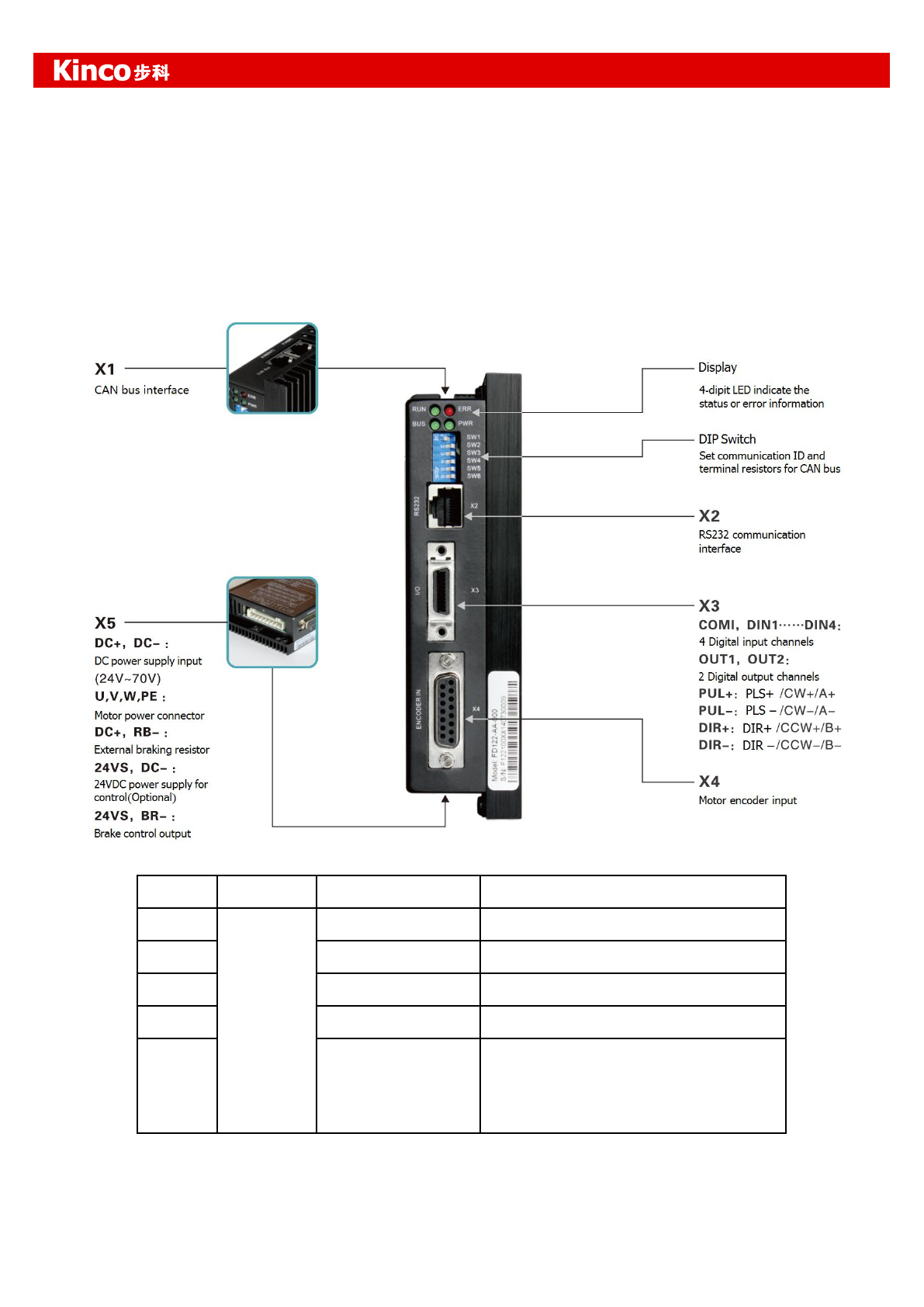
12
Kinco FD Series Servo User Manual
Chapter 3 Interfaces and Wirings of FD Driver
3.1 Interface and wiring of FD122
3.1.1 Panel and Interfaces Description of FD122
Interface
Driver
Function
Description
X1
FD122
CAN
CAN bus interface
X2
RS232
RS232 interface
X3
I/O
I/O port
X4
Encoder input
Motor encoder input interface
X5
Motor and power
supply interface
24V~70VDC power supply, motor power,
brake power supply, brake resistor
interface
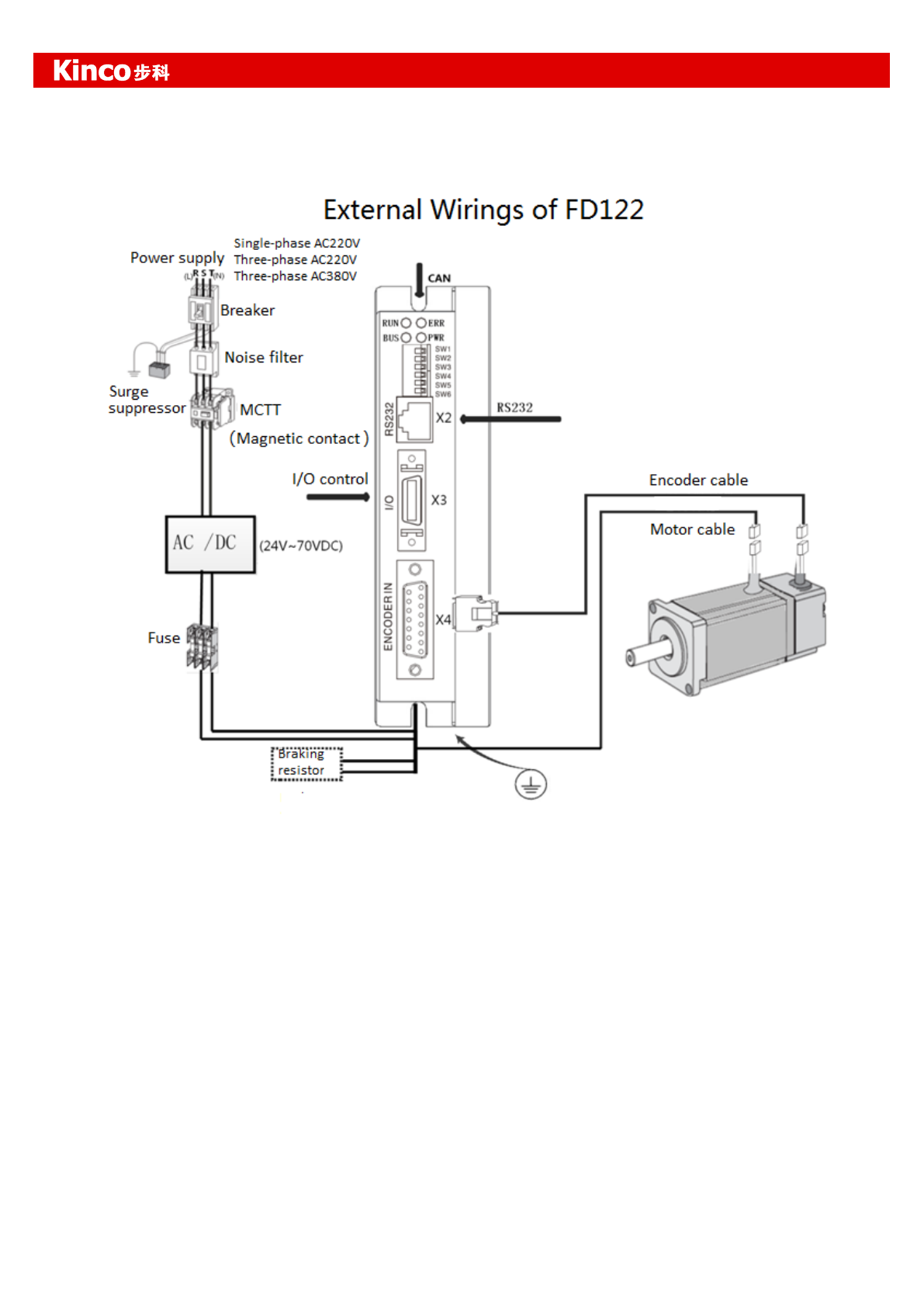
13
Kinco FD Series Servo User Manual
3.1.2 External Wiring of FD122
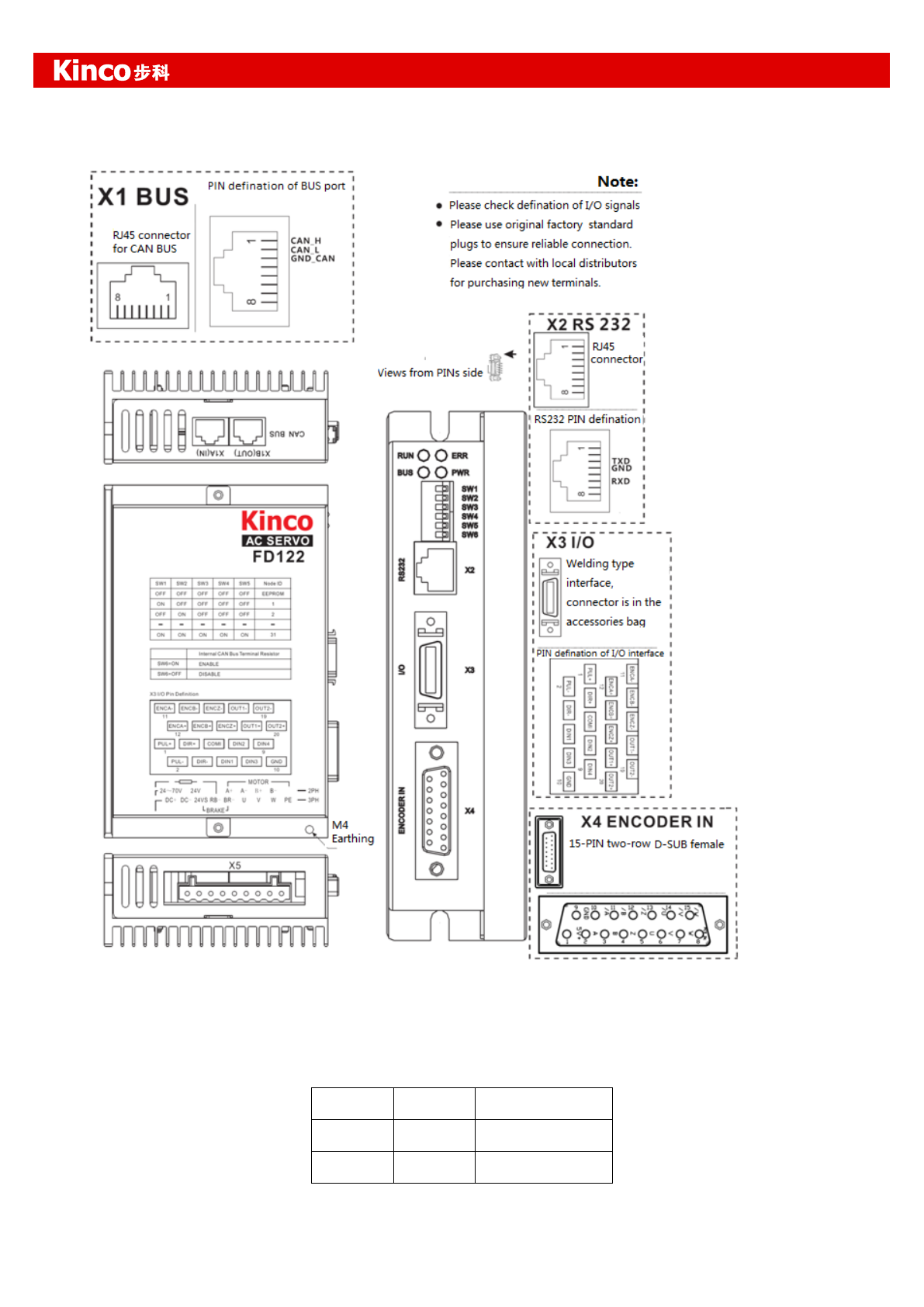
14
Kinco FD Series Servo User Manual
3.1.3 Interface Wiring Defination of FD122
3.1.3.1 CAN Bus Interface(X1)
Fig. 3-1 CAN Bus interface PINs defination
No.
Name
Function
1
CAN_H
CAN bus high
2
CAN_L
CAN bus low
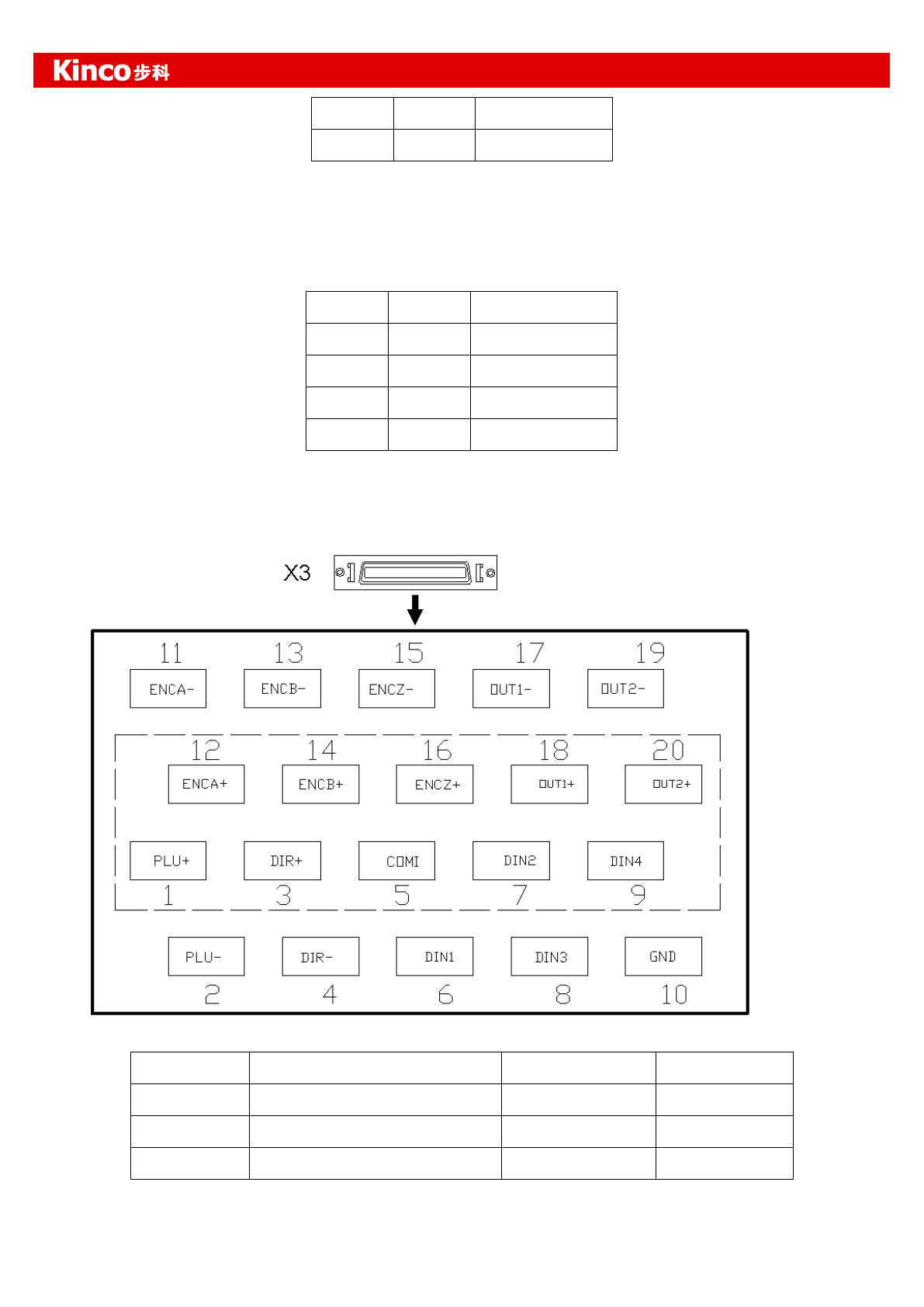
15
Kinco FD Series Servo User Manual
3
GND
Signal ground
Others
NC
Undefined
3.1.3.2 Communication Interface(X2)
Fig. 3-2 RS232 communication interface PINs defination
No.
Name
Function
3
TXD
Send data
4
GND
Signal ground
6
RXD
Receive data
Others
NC
Undefined
3.1.3.3 I/O Interface(X3)
Name
Function
Name
Function
COMI
Common port of digital input
PUL+/PUL-
Pulse input
DIN1~DIN4
Digtal input
DIR+/DIR-
Direction input
OUT1+/OUT1-
Digital output
ENCO-Z/ENCO-/Z
Encoder signal
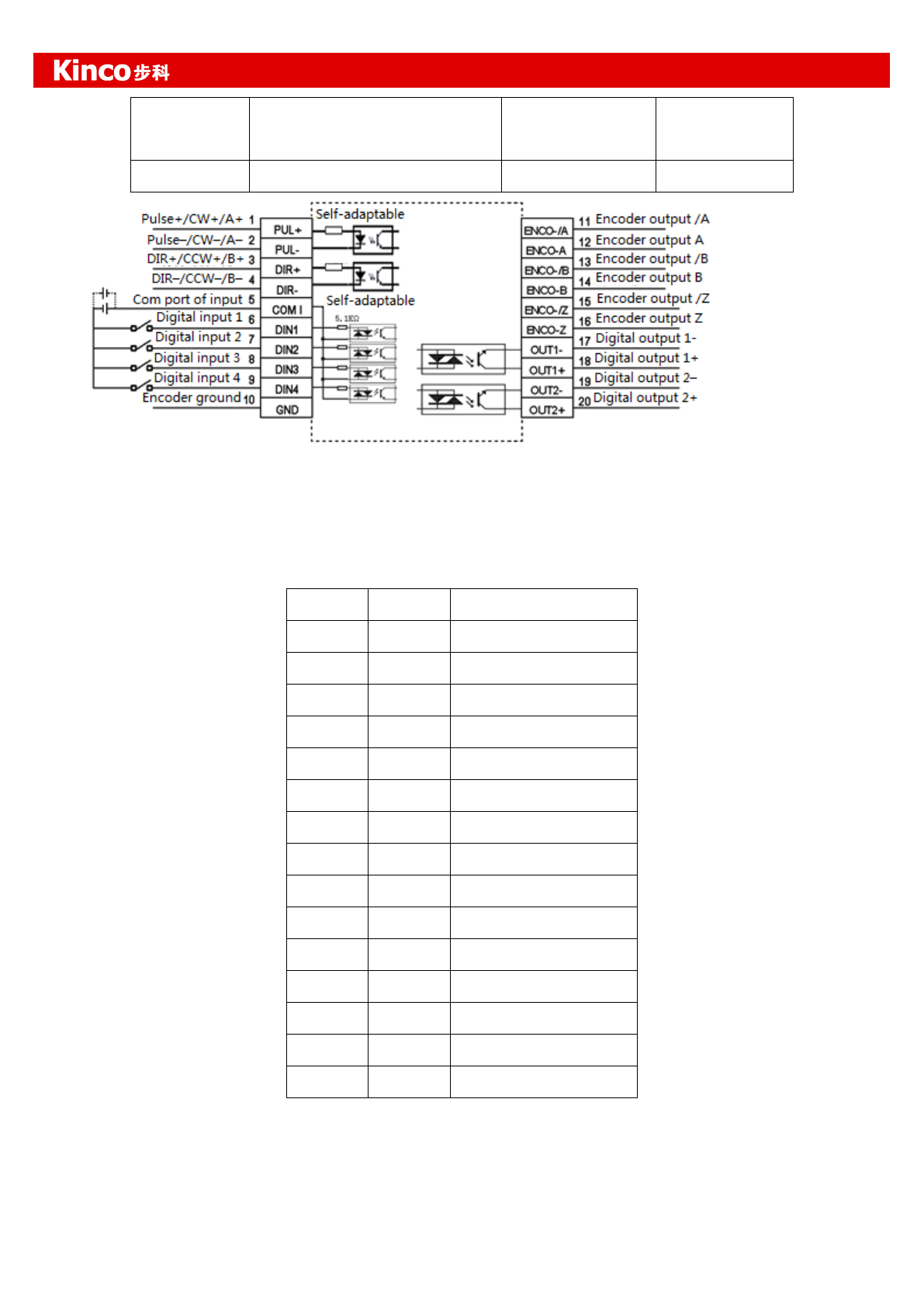
16
Kinco FD Series Servo User Manual
OUT2+/OUT2-
ENCO-B/ENCO-/B
ENCO-A/ENCO-/A
output
GND
Digital signal ground
3.1.3.4 Encoder Input Interface(X4)
Fig. 3-3 Encoder input interface PINs defination
No.
Name
Function
1
5V+
5V output
2
A
A phase of encoder input
3
B
B phase of encoder input
4
Z
Z phase of encoder input
5
U
U phase of encoder input
6
V
V phase of encoder input
7
W
W phase of encoder input
8
PTC_IN
Undefined
9
GND
Ground of encoder signal
10
/A
A phase of encoder input
11
/B
B phase of encoder input
12
/Z
Z phase of encoder input
13
/U
U phase of encoder input
14
/V
V phase of encoder input
15
/W
W phase of encoder input
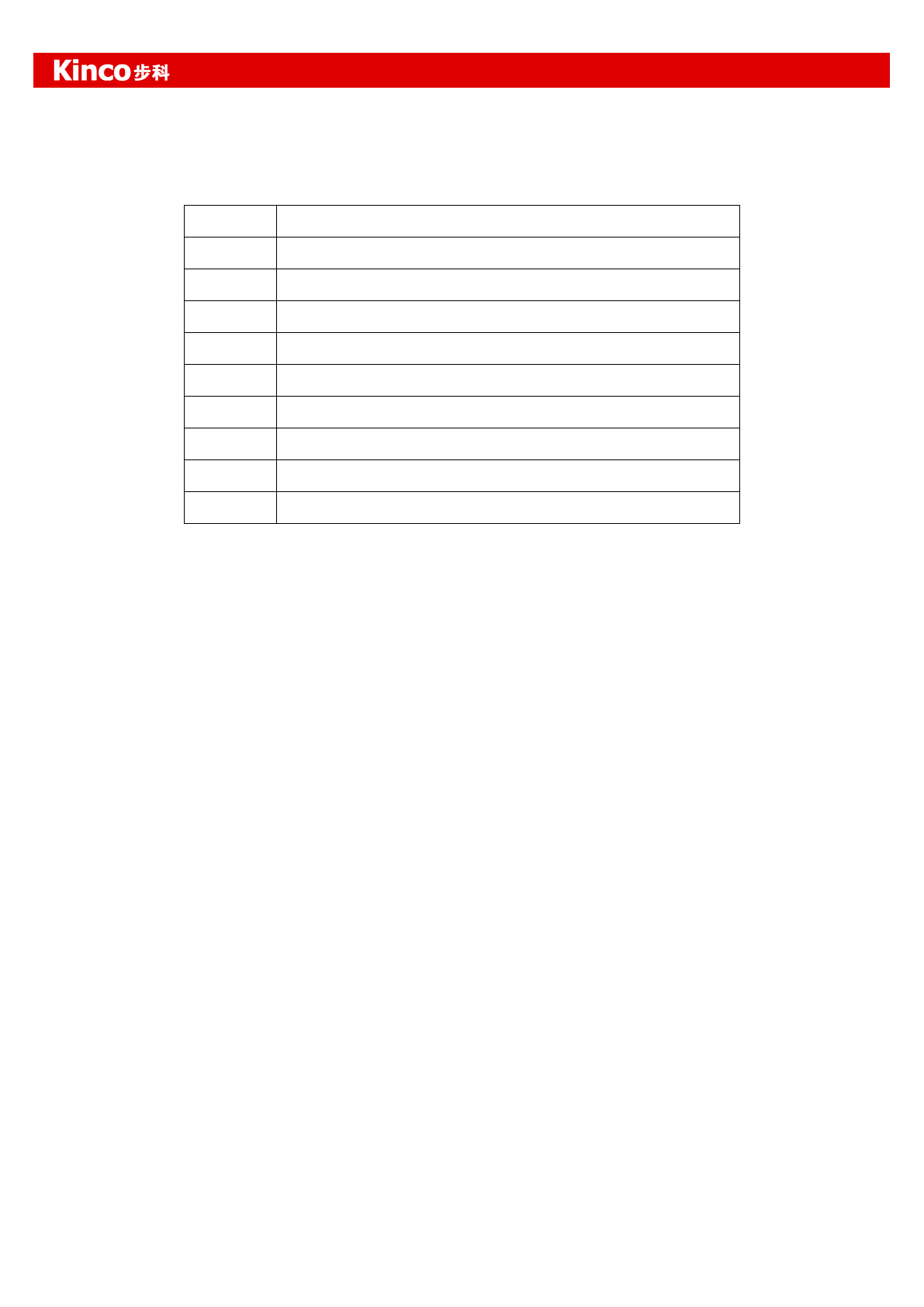
17
Kinco FD Series Servo User Manual
3.1.3.5 Motor/Power Supply Interface (X5)
Fig. 3-4 Motor power supply interface
PIN name
PIN function
DC+
Positive terminal of DC power supply and braking resistor
DC-
Negtive terminal of DC power supply and 24VDC power supply
24VS
Positive terminal of 24VDC power supply and braking
RB-
Negtive terminal of braking resistor
BR-
Negtive terminal of braking, A- phase of motor output
U
U phase of motor output, A- phase of motor output
V
V phase of motor output, B+ phase of motor output
W
W phase of motor output, B- phase of motor output
PE
Motor earthing
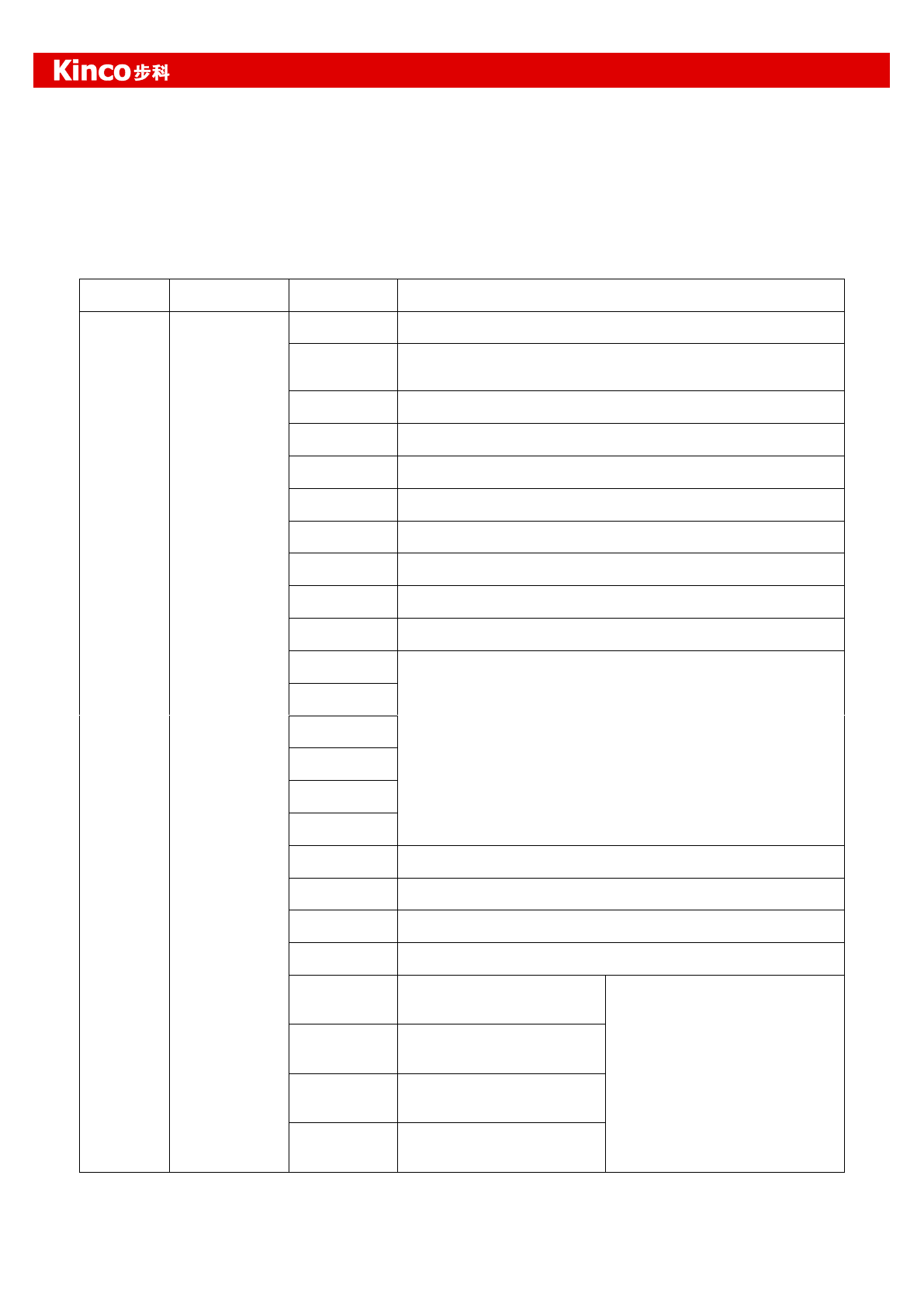
18
Kinco FD Series Servo User Manual
3.2 Interface and wiring of FD412/FD422/FD432/FD622
3.2.1 Interface Description
Table 3-1 Interfaces of FD412/FD422/FD432/FD622
Interface
Driver
Symbol
Function
X1
FD412
FD422
FD432
FD622
COMI
Common terminal of digital inputs
DIN1~DIN7
Digital inputs. Valid signal:12.5V~24V.Invalid signal:<5V
OUT1+
Digital output 1+
OUT1-
Digital output 1-
OUT2+
Digital output 2+
OUT2-
Digital output 2-
OUT3
Digital output 3
OUT4
Digital output 4
COMO
Common terminal of digital outputs
GND
Ground signal
ENCO-Z
Motor encoder output interface
ENCO-/Z
ENCO-B
ENCO-/B
ENCO-A
ENCO-/A
AIN1
Analog signal input 1. Input impedance: 200 K
GNDA
Ground signal of analog
AIN2
Analog signal input 2. Input impedance: 200 K
GNDA
Ground signal of analog
PUL+
Pulse or positive pulse
interface (+)
Input voltage range: 5V~24V
PUL-
Pulse or positive pulse
interface (-)
DIR+
Direction or negative
pulse interface (+)
DIR-
Direction or negative
pulse interface (-)
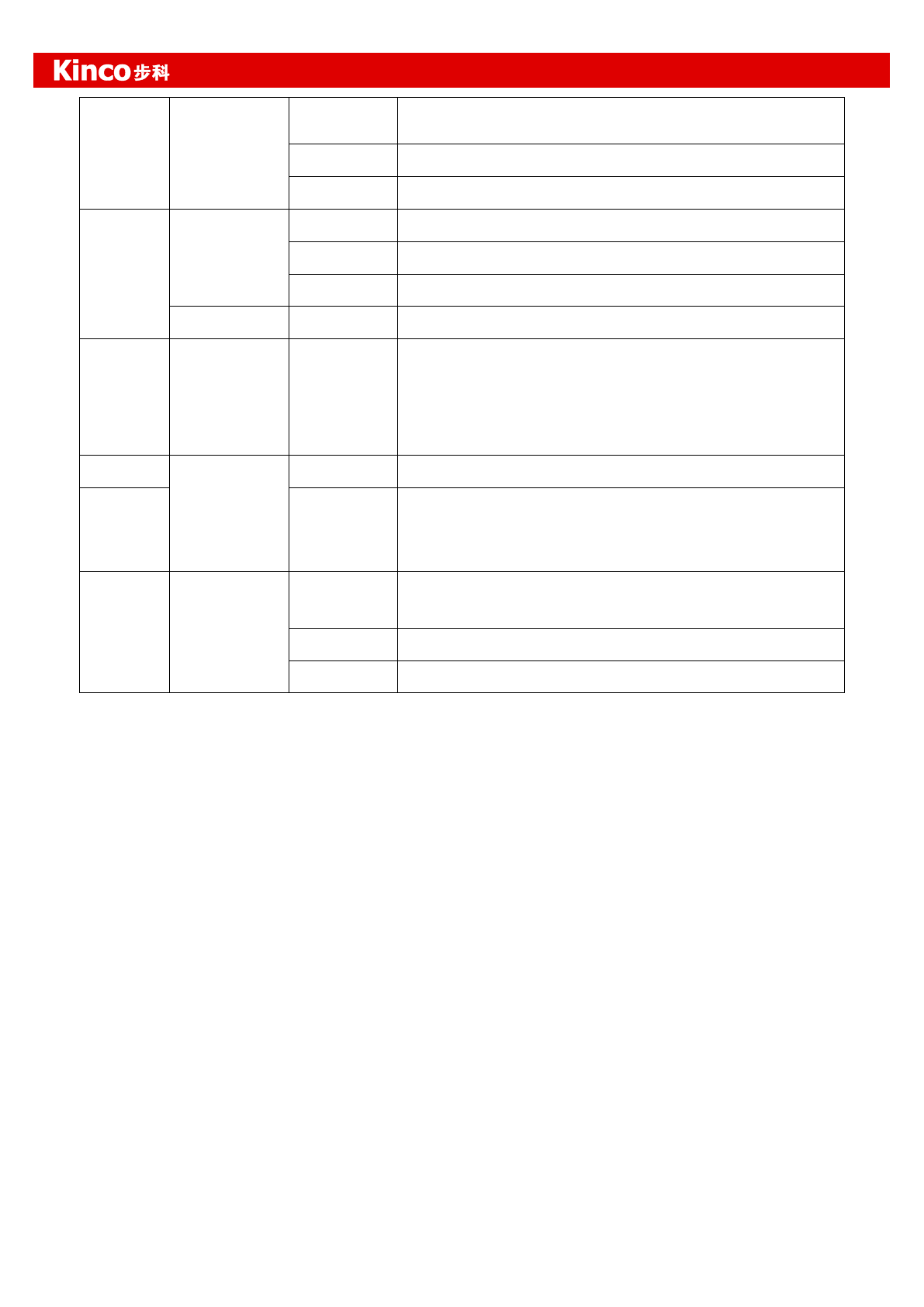
19
Kinco FD Series Servo User Manual
X2
24VS/GNDS
Logic power supply:24 V ± 15%, >0.5A
24VB/GNDB
Power supply for brake ,DC18~30V 2A
BR+/BR-
Brake interface
X3
FD412
FD422
U/V/W/PE
Motor cable interface
L/N
Main power supply (Single-phase AC220V)
RB+/RB-
Braking resistor interface
FD432/FD622
U/V/W/PE
Motor cable interface
X4
FD412
FD422
FD432
FD622
BUS
RS485 or CAN interface
X5
FD412
FD422
FD432
FD622
RS232
RS232 interface
X6
ENCODER
IN
Encoder cable interface
X7
FD432
FD622
R/S/T
Main power supply (CD432: Single phase or 3-phase
AC220V, CD622: 3-phase AC380V)
RB+/RB-
Braking resistor interface
DC+/DC-
DC bus power supply(Cannot use together with R/S/T)
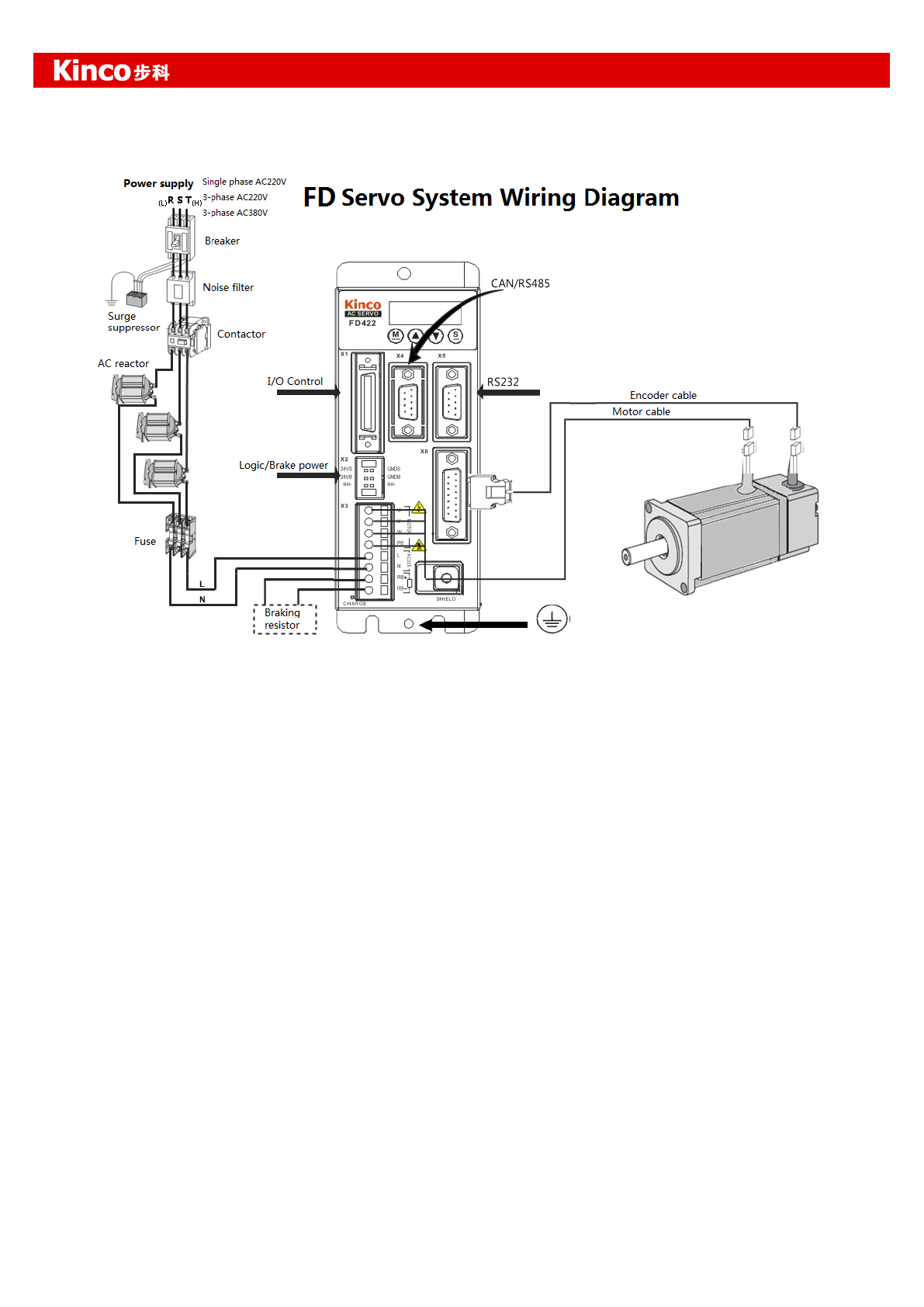
20
Kinco FD Series Servo User Manual
3.2.2 External Wirings
Fig. 3-1 External wirings diagram of FD drive
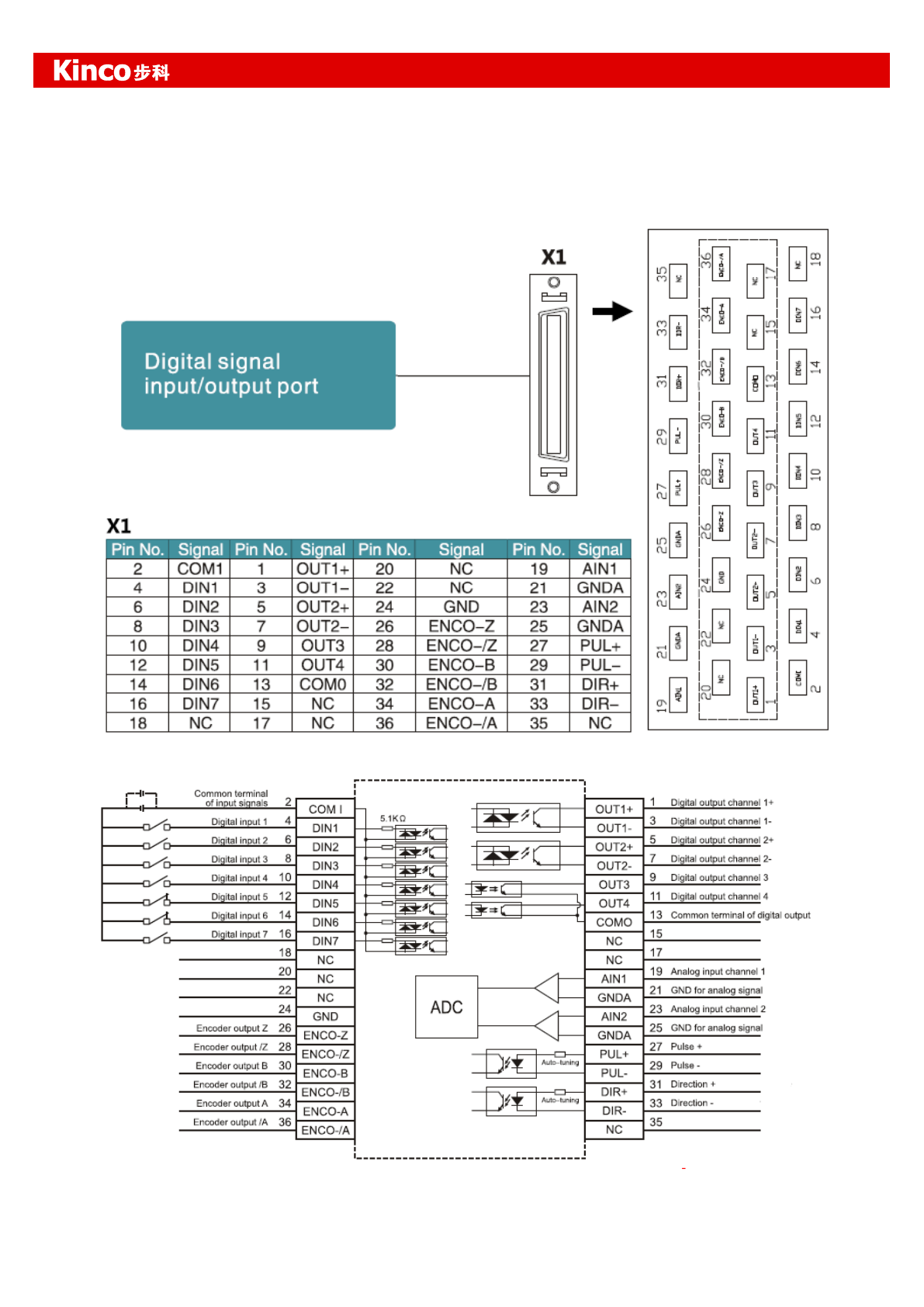
21
Kinco FD Series Servo User Manual
3.2.3 I/O Interface
Fig. 3-2 I/O interface of FD driver
Fig. 3-3 Wirings of the I/O interface of FD driver
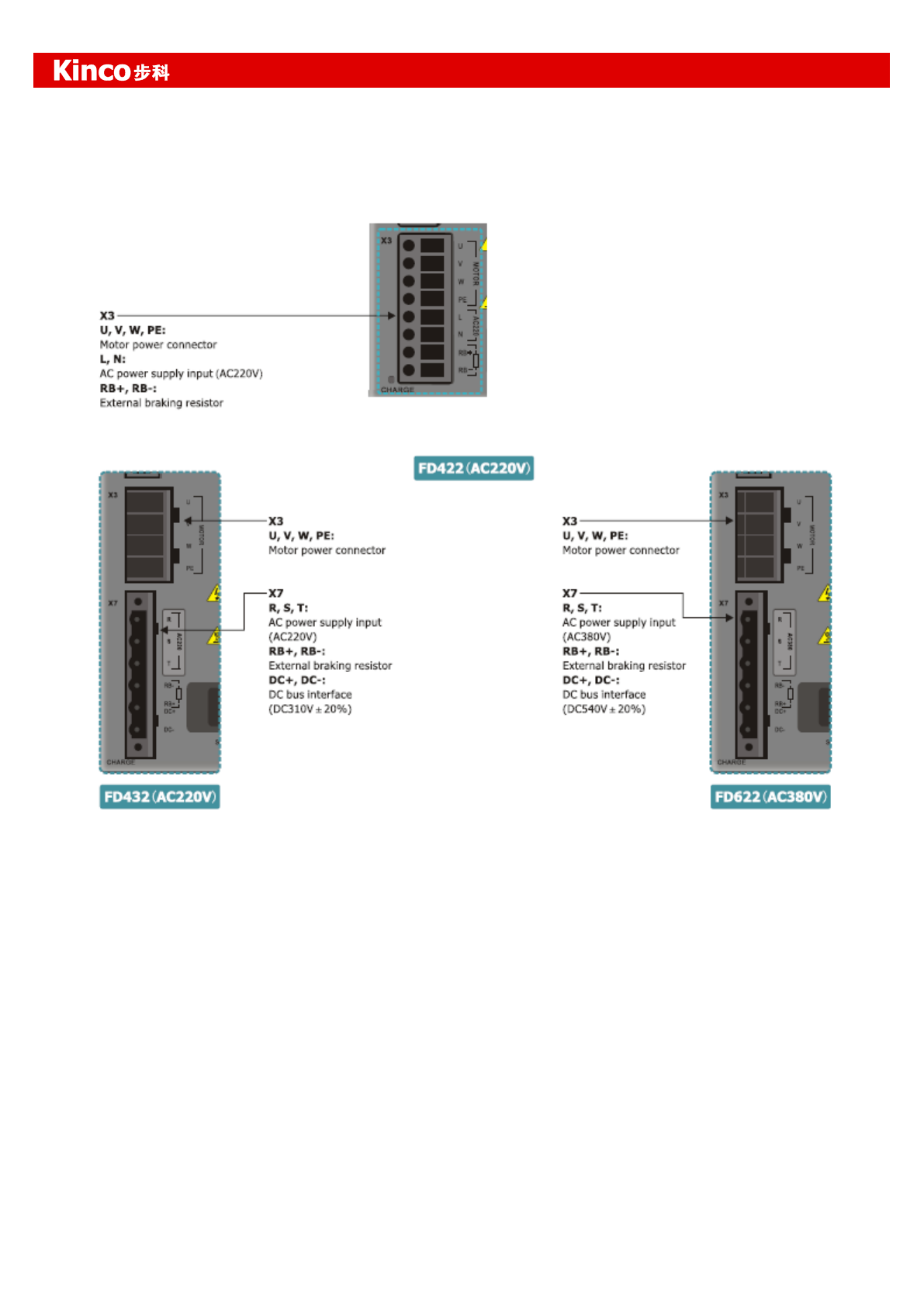
22
Kinco FD Series Servo User Manual
3.2.4 Power Interface of FD Driver (FD412/FD422/X3, FD432/FD622/X3
and X7)
3.2.5 X4~X6 Interface
X4~X6 interface of FD driver use D-SUB connector.The styles of different D-SUB connectors are
shown in following figure.
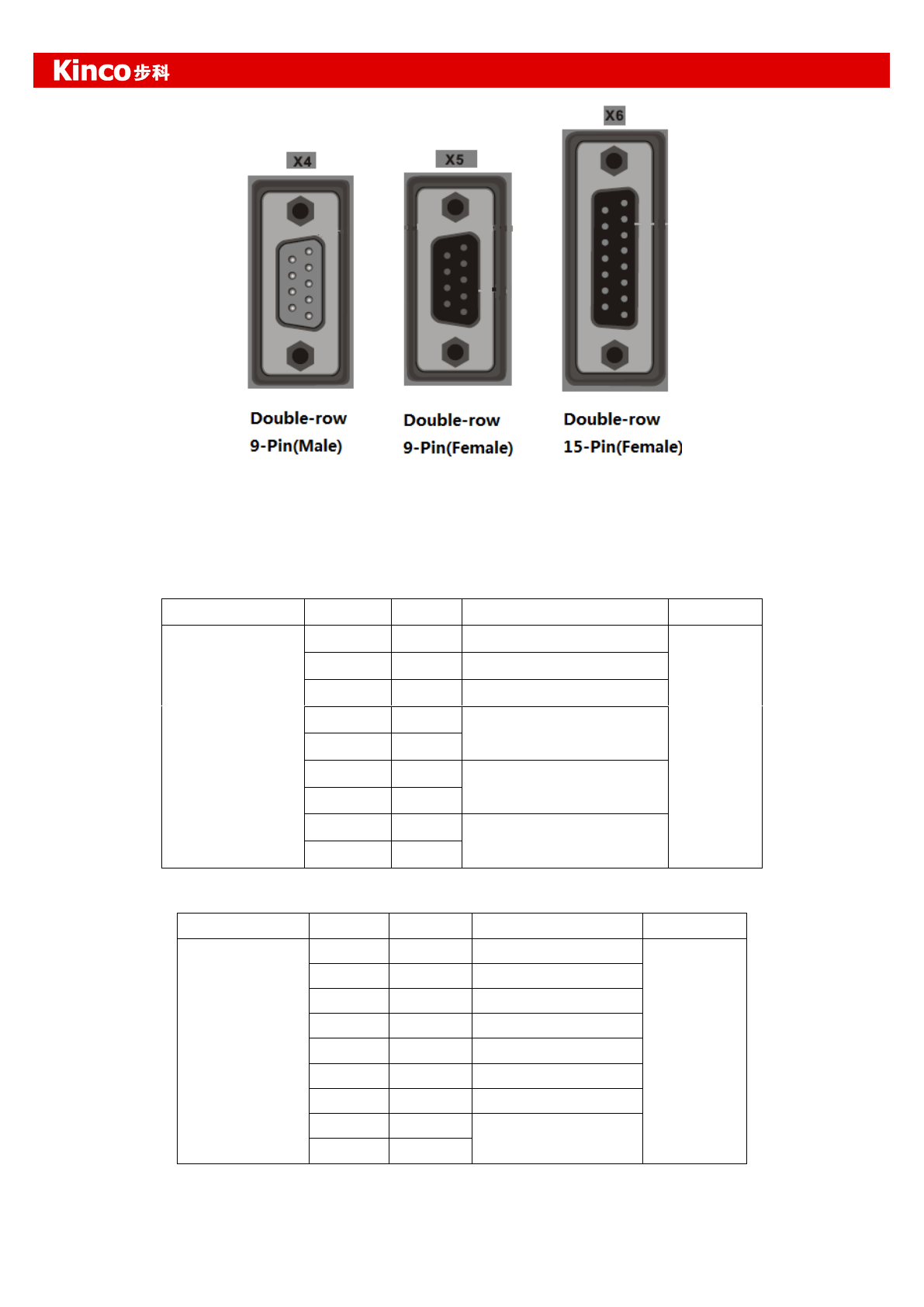
23
Kinco FD Series Servo User Manual
Fig.3-6 D-SUB connector diagram of driver
3.2.5.1 X4 Interface(RS485/CAN)
RS485:
CAN:
Name
Pin
Signal
Descriptions
Function
RS485
(9-Pin female)
1
NC
N/A
RS485
interface
5
GND
Signal ground
6
+5V
Power
2
RX
Receive data
7
/RX
3
TX
Send data
8
/TX
4
NC
N/A
9
NC
Name
Pin
Signal
Descriptions
Function
CAN
(9-Pin male)
1
NC
CAN bus
interface
5
NC
6
NC
2
CAN_L
CAN_L
7
CAN_H
CAN_H
3
GND
Signal ground
8
NC
4
NC
9
NC
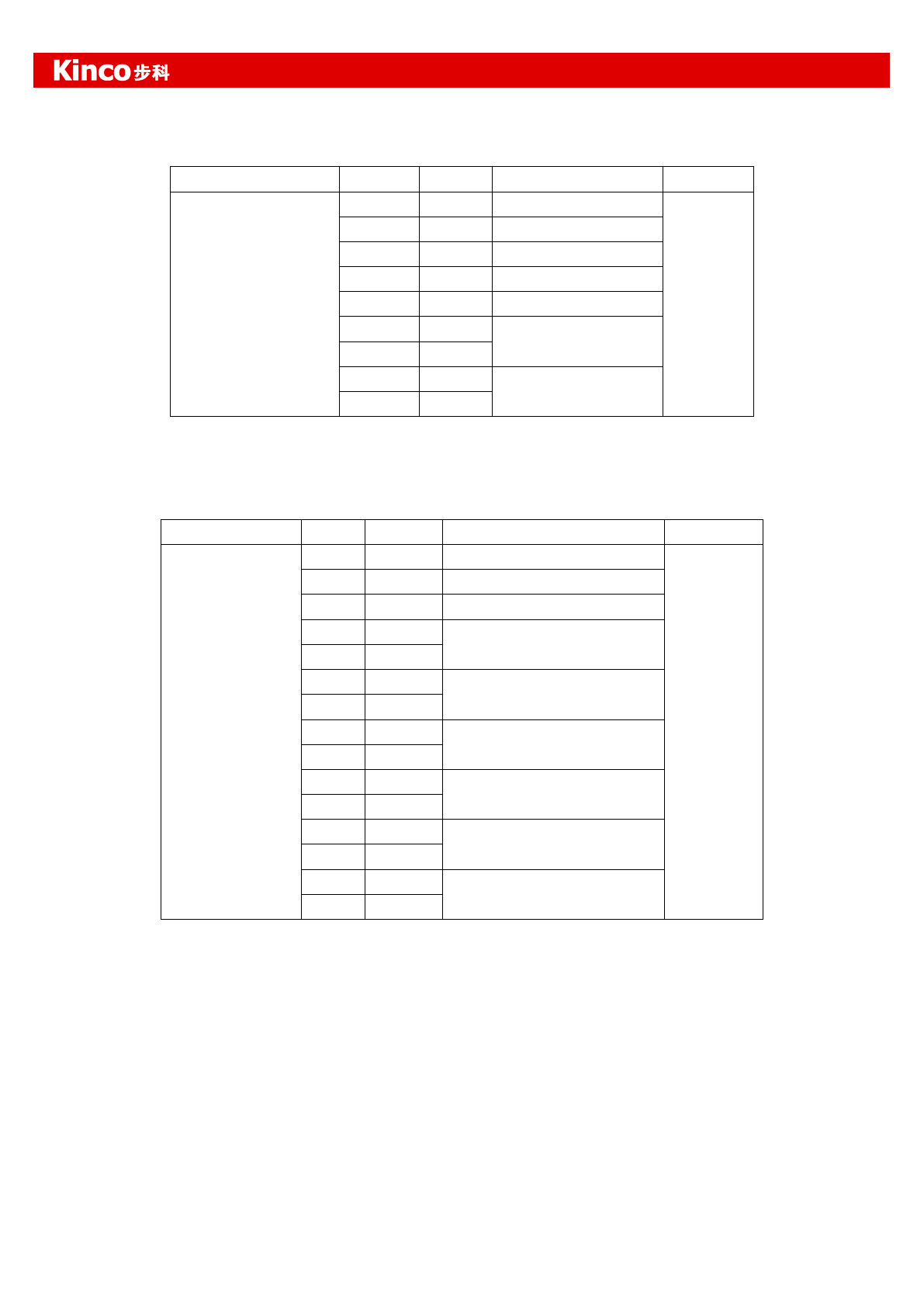
24
Kinco FD Series Servo User Manual
3.2.5.2 X5 Interface(RS232)
3.2.5.3 X6 Interface (Encoder in)
Name
Pin
Signal
Descriptions
Function
RS232
(9-Pin female)
1
NC
N/A
RS232
interface
2
TX
Send data
3
RX
Receive data
4
NC
N/A
5
GND
Signal ground
6
NC
N/A
7
NC
8
NC
N/A
9
NC
Name
Pin
Signal
Descriptions
Function
Encoder in
(Double rows
15-Pin female)
1
+5V
5V output
Motor
encoder
input
9
GND
0V
8
PTC_IN
PTC of motor input
2
A
A phase of encoder input
10
/A
3
B
B phase of encoder input
11
/B
4
Z
Z phase of encoder input
12
/Z
5
U
U phase of encoder input
13
/U
6
V
V phase of encoder input
14
/V
7
W
W phase of encoder input
15
/W
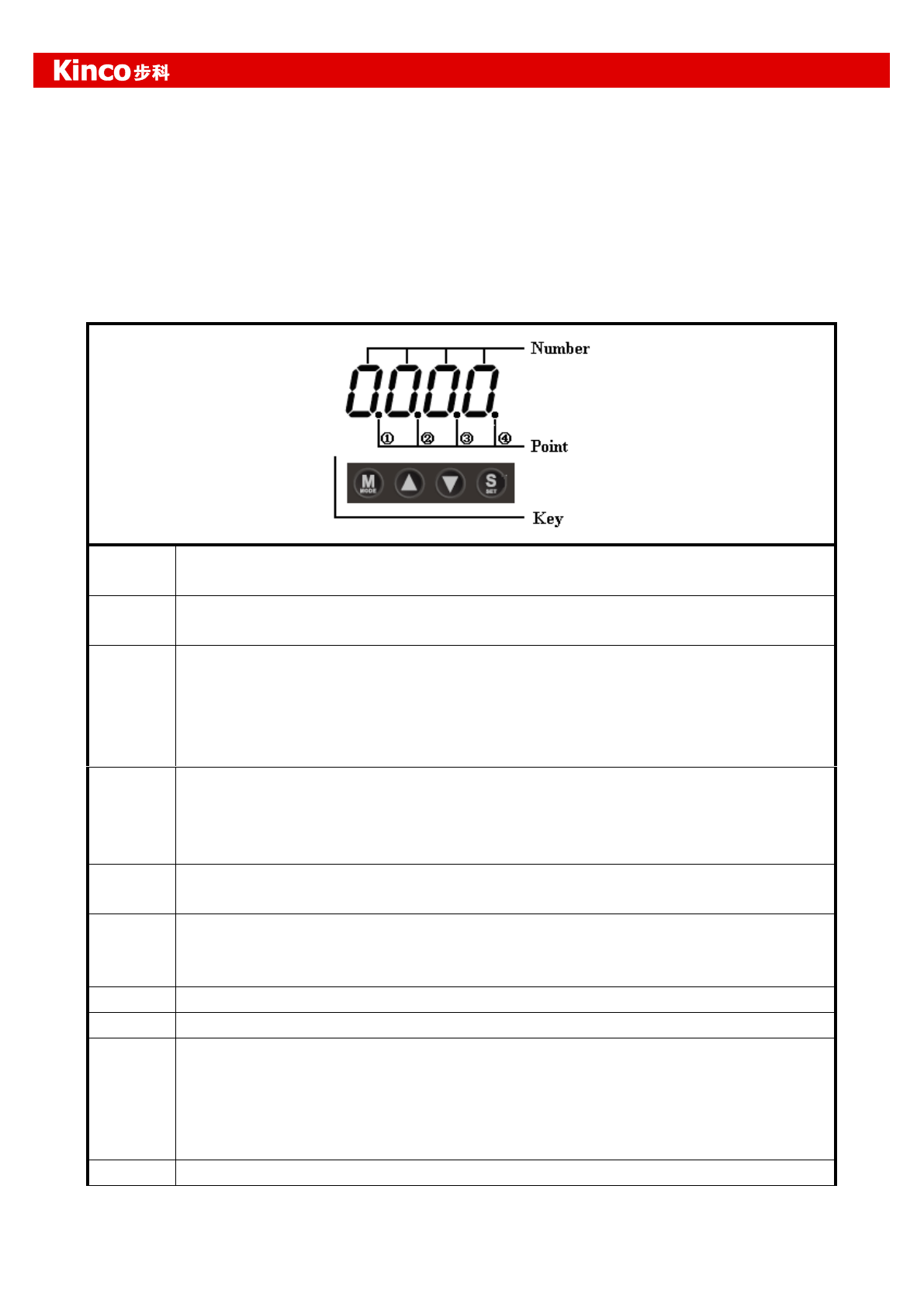
25
Kinco FD Series Servo User Manual
Chapter 4 Digital Operation Panel
4.1 Introduction
A digital operation panel functions to set user parameters in a servo driver, execute instructions, or
display parameters. Table 4-1 describes all display contents and functions of the digital operation panel.
Table 4-1 Display contents and functions of a digital operation panel
Number/
Point/Key
Function
①
Indicates whether data is positive or negative. If it is on, it indicates negative; otherwise it
indicates positive.
②
Distinguishes the current object group and the address data in this object group during
parameter settings.
Indicates the higher 16 bits of the current 32-bit data when internal 32-bit data is displayed
in real time.
Indicates the earliest error when history records of errors (F007) are displayed.
③
Indicates a data display format when parameters are displayed and adjusted in real time.
If it is on, it indicates the data is displayed in hexadecimal; otherwise it indicates the data
is displayed in decimal.
Indicates the latest error when the history records of errors (F007) are displayed.
④
If it is on, it indicates that internal data is currently displayed.
If it flickers, it indicates that the power part of the driver is in the working status.
MODE
Switches basic menus.
During the adjustment of parameters, short presses the key to move the bit to be
adjusted, and long presses the key to return to the previous state.
▲
Presses ▲ to increase set values; long presses ▲ to increase numbers promptly.
▼
Presses ▼ to decrease set values; long presses ▼ to decrease numbers promptly.
SET
Enters the selected menu by pressing this key.
Keeps current parameters in the enabled status.
Confirms input parameters after parameters are set.
Long presses this key to switch to higher/lower 16 bits when internal 32-bit data is
displayed in real time.
P..L
Activates position positive limit signals.
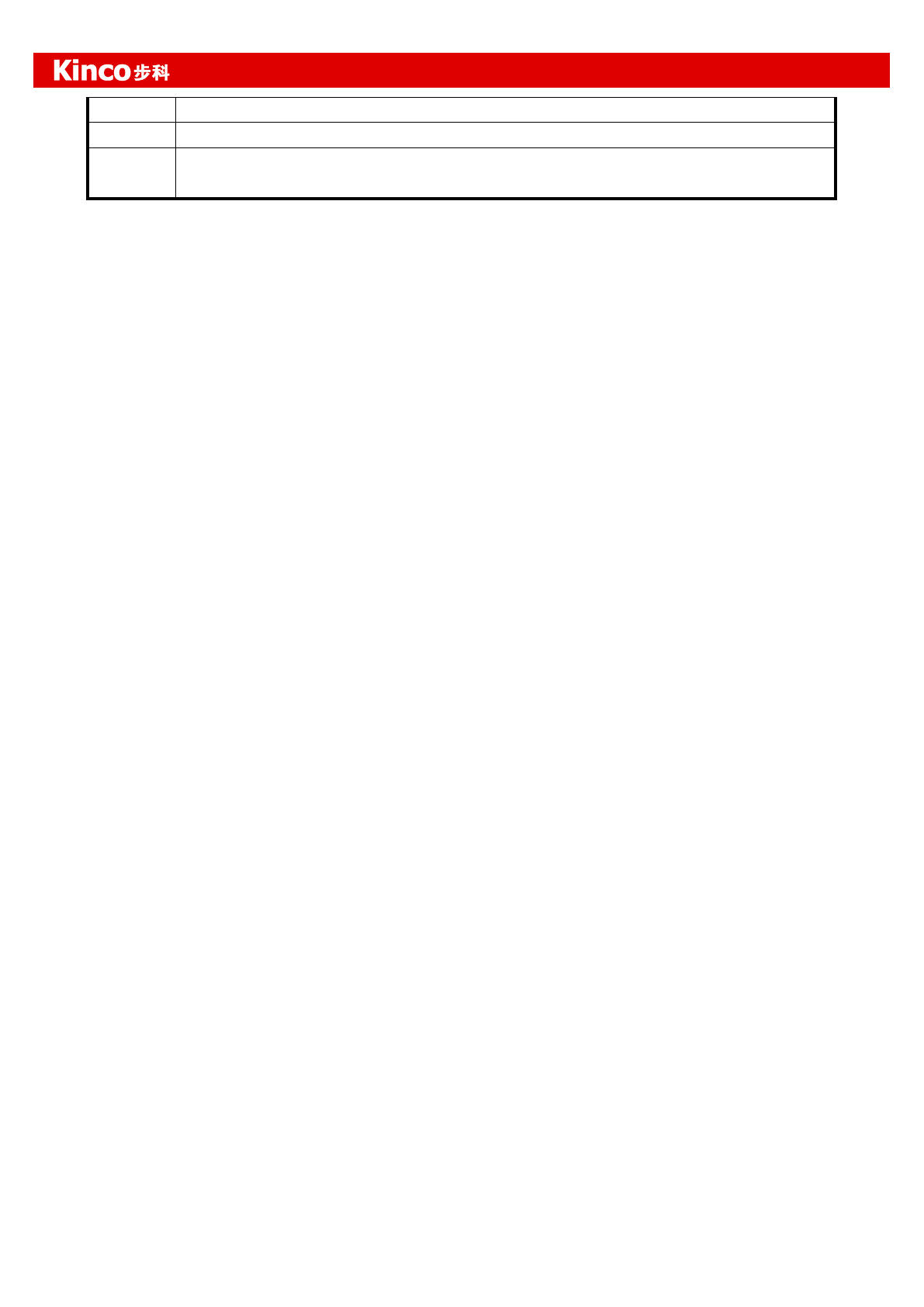
26
Kinco FD Series Servo User Manual
n..L
Activates position negative limit signals.
Pn.L
Activates position positive/negative limit signals.
Overall
Flicking
Indicates that an error occurs on the driver, and is in the alarm state.
If the parameter adjusting display mode is featured by the decimal system:
When the units place is flickering, press ▲ to add 1 to the current value; press ▼ to deduct 1 from the
current value. When the tens place is flickering, press ▲ to add 10 to the current value; press ▼ to
deduct 10 from the current value. When the hundreds place is flickering, press ▲ to add 100 to the
current value; press ▼ to deduct 100 from the current value. When the thousands place is flickering,
press ▲ to add 1000 to the current value; press ▼ to deduct 1000 from the current value.
If the parameter adjusting display mode is featured by the hexadecimal system:
When the units place is flickering, press ▲ to add 1 to the current value; press ▼ to deduct 1 from the
current value. When the tens place is flickering, press ▲ to add 0X10 to the current value; press ▼ to
deduct 0X10 from the current value. When the hundreds place is flickering, press ▲ to add 0X100 to the
current value; press ▼ to deduct 0X100 from the current value. When the thousands place is flickering,
press ▲ to add 0X1000 to the current value; press ▼ to deduct 0X1000 from the current value.
When adjusting decimal parameters, the display mode is automatically switched to the hexadecimal
system if the data is greater than 9999 or less than -9999. In this case, the 3rd decimal point from left to
right is highlighted.
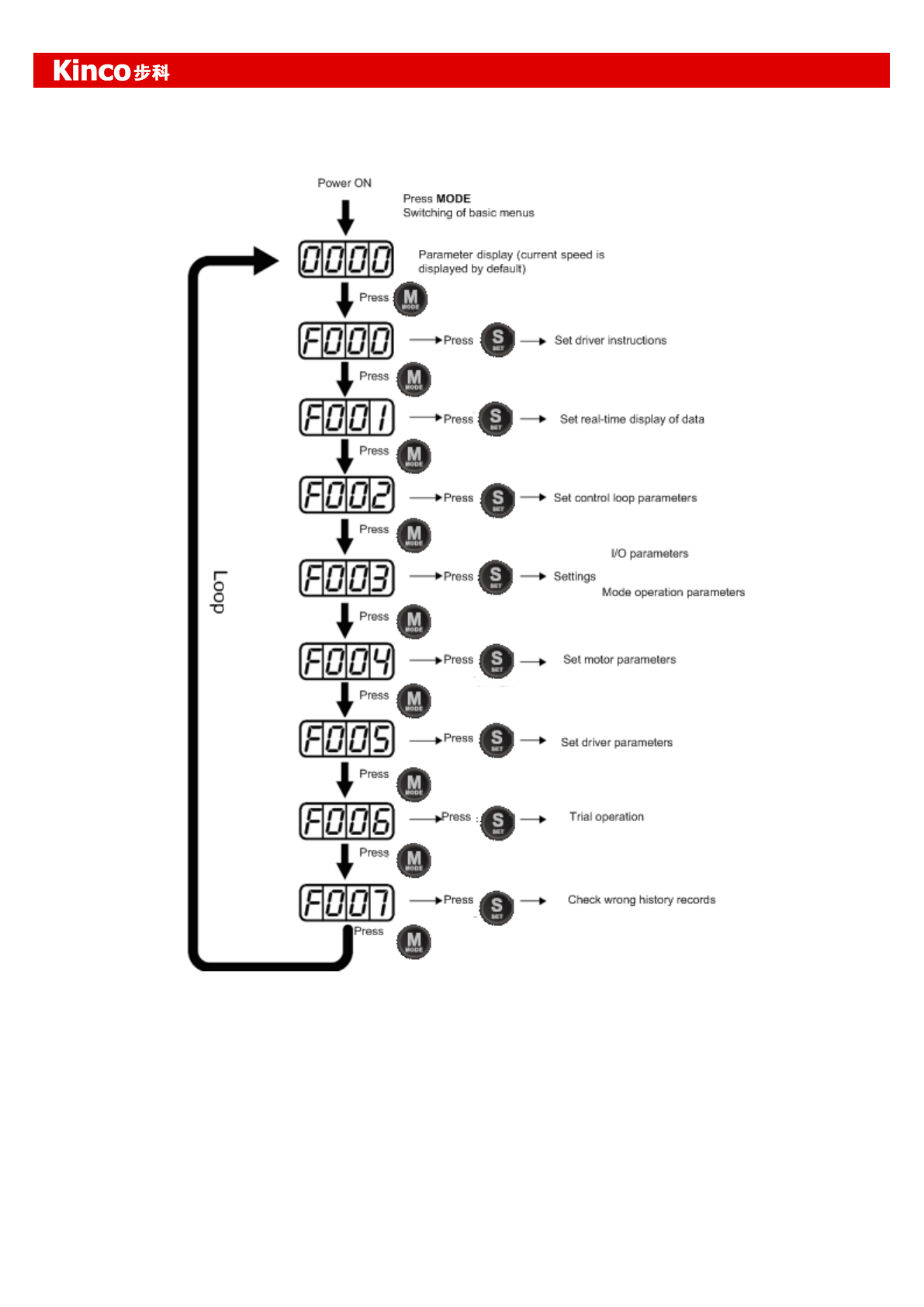
27
Kinco FD Series Servo User Manual
4.2 Operation on Digital Operation Panel
Figure 4-1 Operation on a digital operation panel
Note: If a non real-time display interface is displayed for the control panel, and no key operation occurs,
the real-time display interface is automatically skipped after 20 seconds to avoid misoperation.
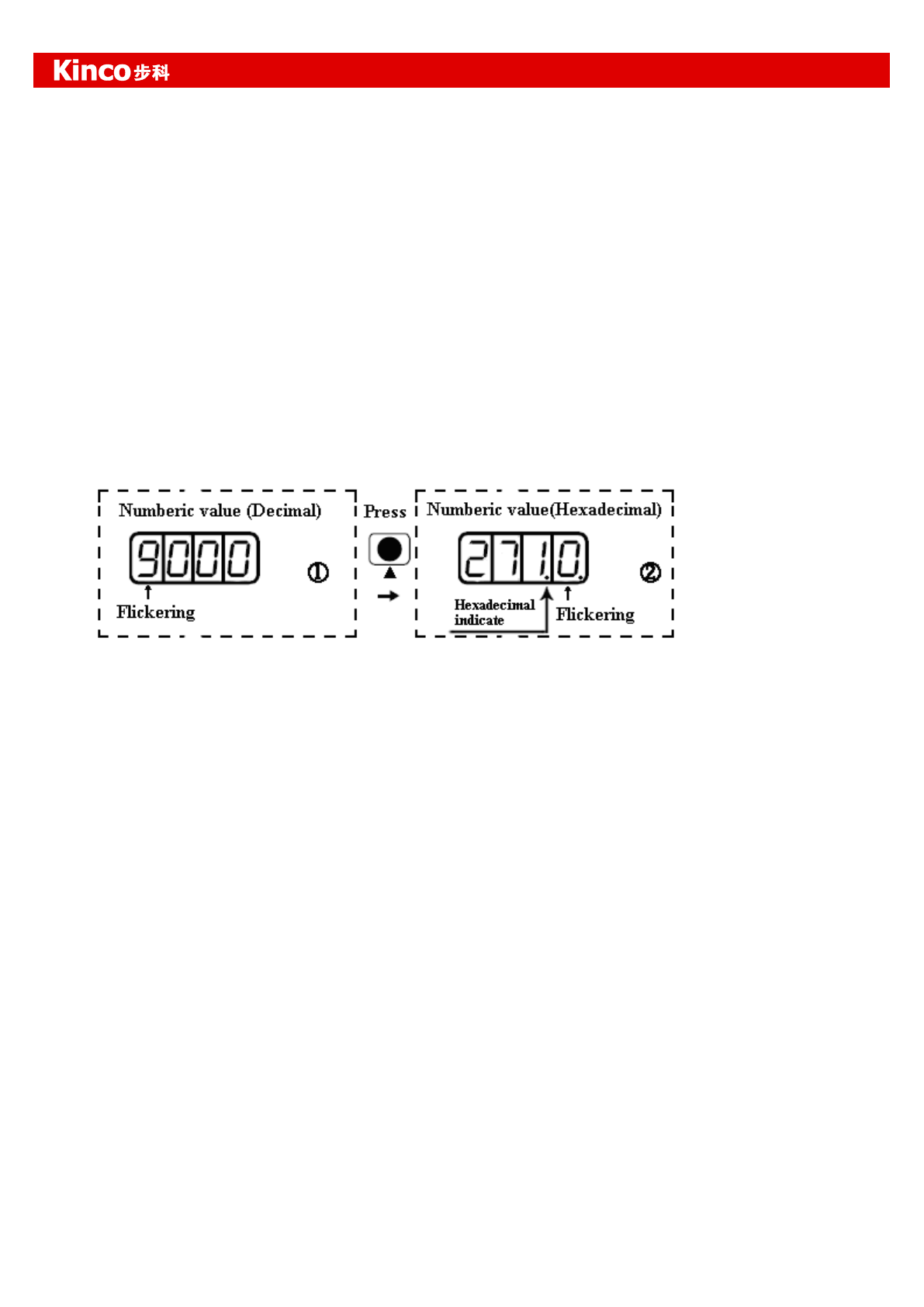
28
Kinco FD Series Servo User Manual
Example 4-1: Set the denominator of electronic gear ratio to 10000 with
number system switching
Press MODE. The main menu is displayed. Choose F003.
Press SET. The interface for selecting addresses is displayed.
Press ▲ to adjust data as d3.35.
Press SET to display the current value d3.35. Press SET again to modify the value d3.35. In this case,
the 1st number at the right side is flickering. Short press MODE for three times to move to the first
position on the left. Then press ▲. The value is increased to 9000. In this case, the current data is
decimal.
Press ▲ again. The content of numeric display changes to “271.0”, and the 3rd decimal point (from left to
right) flickers. In this case, the data is hexadecimal. Press SET to confirm the current value. The 1st
decimal point on the right flickers. In this case, the denominator of the electronic gear ratio is modified to
10000.
Figure 4-2 Number system conversion
Example 4-2: Set the speed to 1000 RPM/-1000 RPM with separate
regulation of bits
Press MODE. The main menu is displayed. Choose F000.
Press SET. The interface for selecting addresses is displayed.
Press ▲ to adjust data as d0.02.
Press SET to display the current value d0.02. Press SET again to modify the value d0.02. In this case,
the 1st number at the right side is flickering.
Short press MODE for three times to move to the 1st position on the left. Press ▲ to modify the value to 1.
Press SET to confirm the current value. The 1st decimal point on the right flickers. In this case, the speed
is 1000 RPM.
Press ▼ to modify the value to -1. In this case, the 1st decimal point on the left flickers, indicating that the
current data is negative. Press SET to confirm the current value. The 1st decimal point on the right
flickers. In this case, the speed is -10000 RPM.
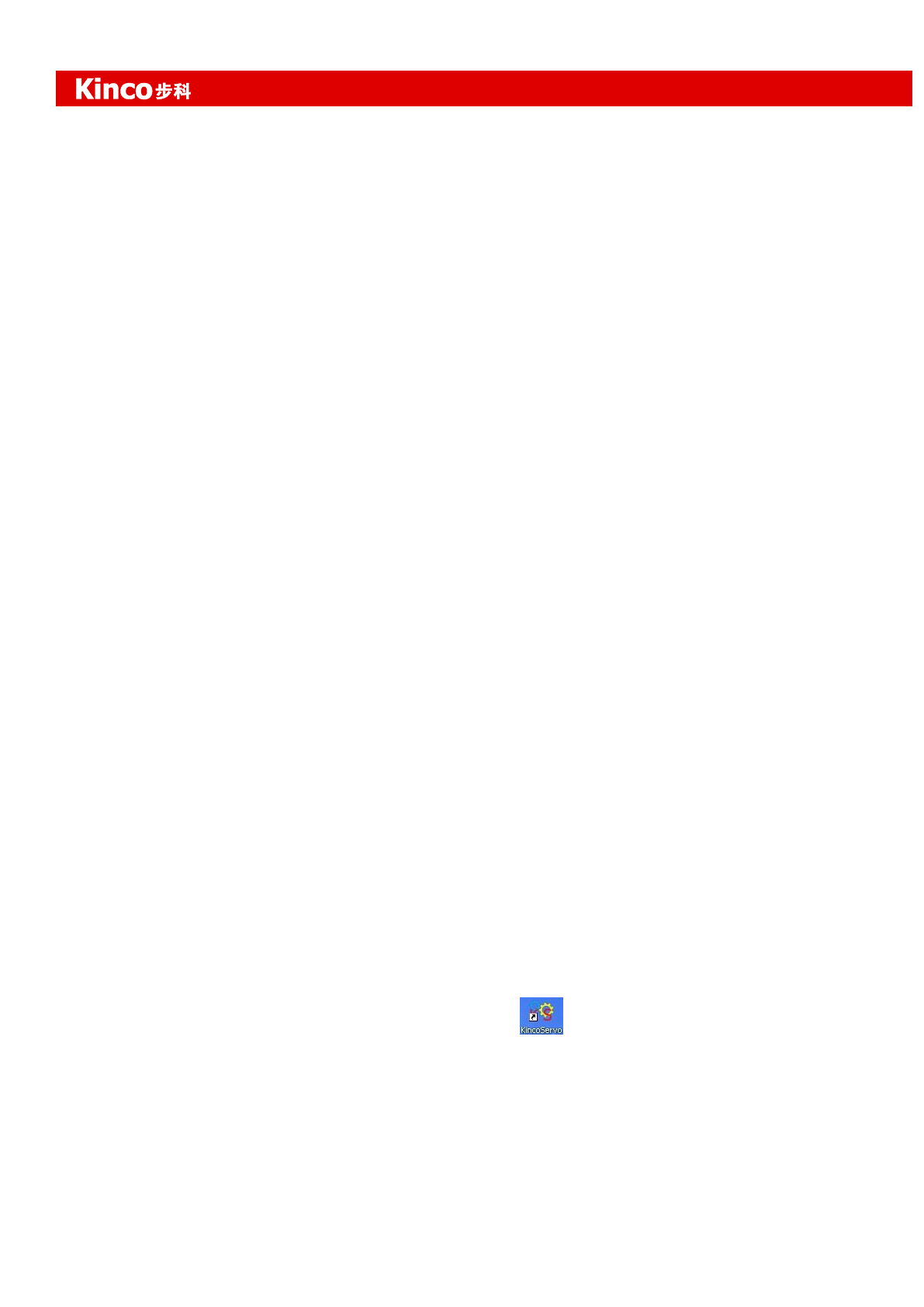
Kinco FD Series Servo User Manual
Chapter 5 KincoServo Software Introductions
5.1 Software Installation
This software doesn’t need to install.Users can download KincoServo software from our website:
www.kinco.cn.
5.2 Quick Start
5.2.1 Hardware Configuration for Running KincoServo Software
KincoServo software can be used to configure all the parameters of FD Series servo driver via
RS232 or CANopen port.Please refer to Chapter 3 to connect servo driver and motor before using
it.
● System configuration for programming via RS232.
24VDC power supply for driver.
Serial programming cable,whose wiring diagram is as following figure.
PC FD Servo RS232 Interface(X5)
RxD 2 ---------------------------------- TXD 2
TxD 3 ---------------------------------- RXD 3
GND 5 ---------------------------------- GND 5
● System configuration for programming via CANopen.
24VDC power supply for driver.
PEAK series USB or LPT adapter from PEAK company.
CANopen communication cable,its wiring diagram is as following figure:
Pecan FD Servo CAN Interface(X4)
CAN_L 2 ---------------------------------- CAN_L 2
CAN_H 7 ---------------------------------- CAN_H 7
5.2.2 KincoServo Software Online
1.Open the folder of KincoServo and double click the icon ,then it will open the window as following
figure:

Kinco JD 伺服系列使用手册
30
Kinco FD Series Servo User Manual
2.New Project.
3.It will popup dialog box “Commutation Way”,if it uses serial port,then select “RS232C”and click “Next”.
If it uses CAN tools such as PEAK-CAN,then select “CAN” and click “Next”.
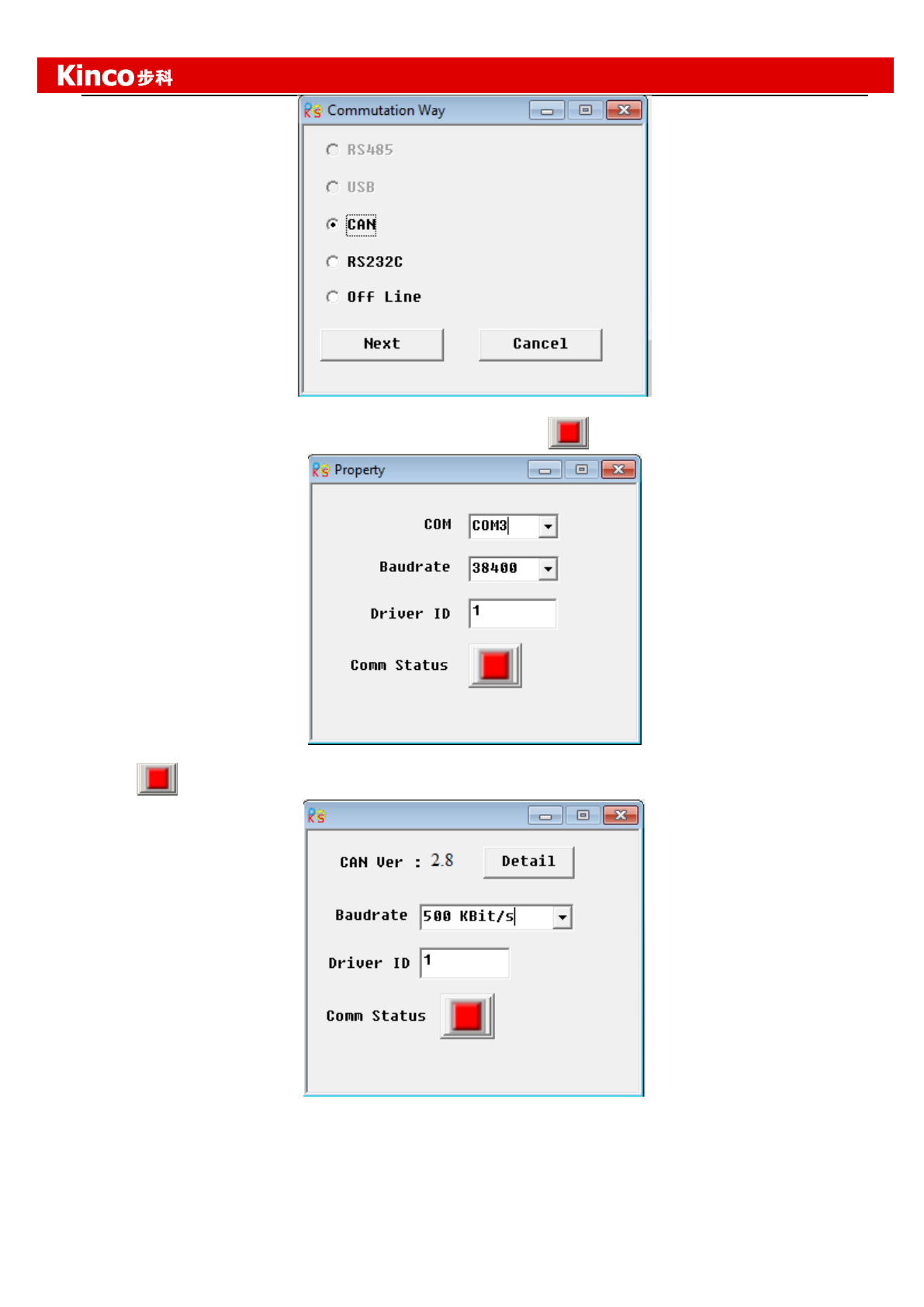
Kinco JD 伺服系列使用手册
31
Kinco FD Series Servo User Manual
4.Enter communication property interface.Set the parameters like COM,Baudrate,Driver ID corresponding to
the actual value in servo driver.Then click Comm Status button 。
If it uses CAN connection,set the parameters like Baudrate,Driver ID.Then click Comm Status
button .
5.Check the informations in the lower-right side.If the informations are like “Comm Status:Open COM1
38400” and the Comm Status turns green,it means KincoServo software is online successfully.
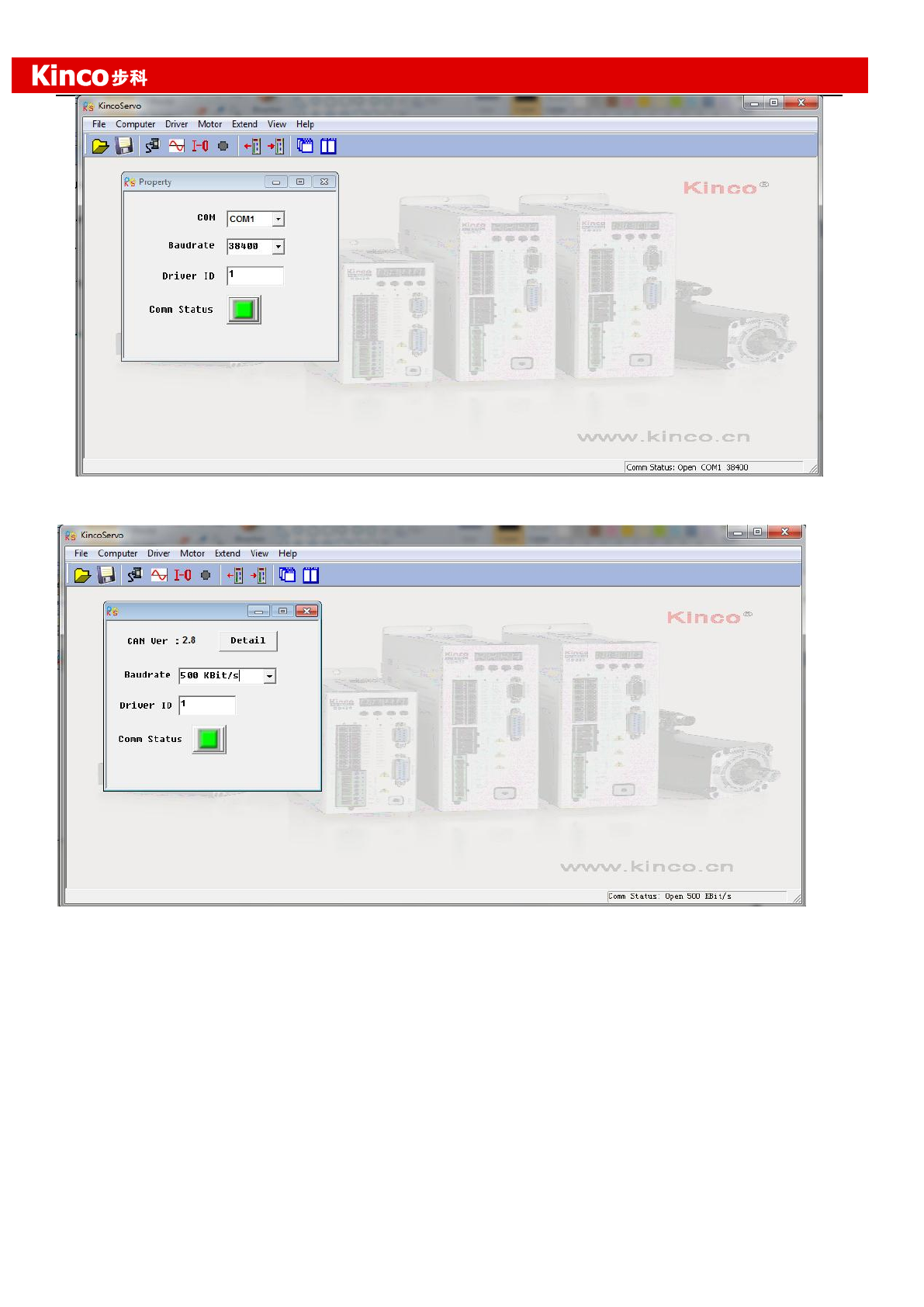
Kinco JD 伺服系列使用手册
32
Kinco FD Series Servo User Manual
When it uses CAN connection,if the informations in the lower-right side are like “Comm Status:Open 500K
Bit/S” and the Comm Status turns green,it means KincoServo software is online successfully.
5.3 Menu Introductions
Open KincoServo software as following figure:

Kinco JD 伺服系列使用手册
33
Kinco FD Series Servo User Manual
The descriptions of Menu bar are as following table.
Name
Descriptions
File
Used to New,Open,Save project.
Computer
Used to set communication property.
Driver
Used to control driver,more details please refer to 5.4
Motor
Used to configure motor parameters,more detail please refer to 6.1.3
Extend
Used to change language and read/write driver parameters.
5.4 Driver Control
5.4.1 Basic Operate
In this menu,it can do some basic control operation for driver.About more details of operation
mode,please refer to Chapter8.
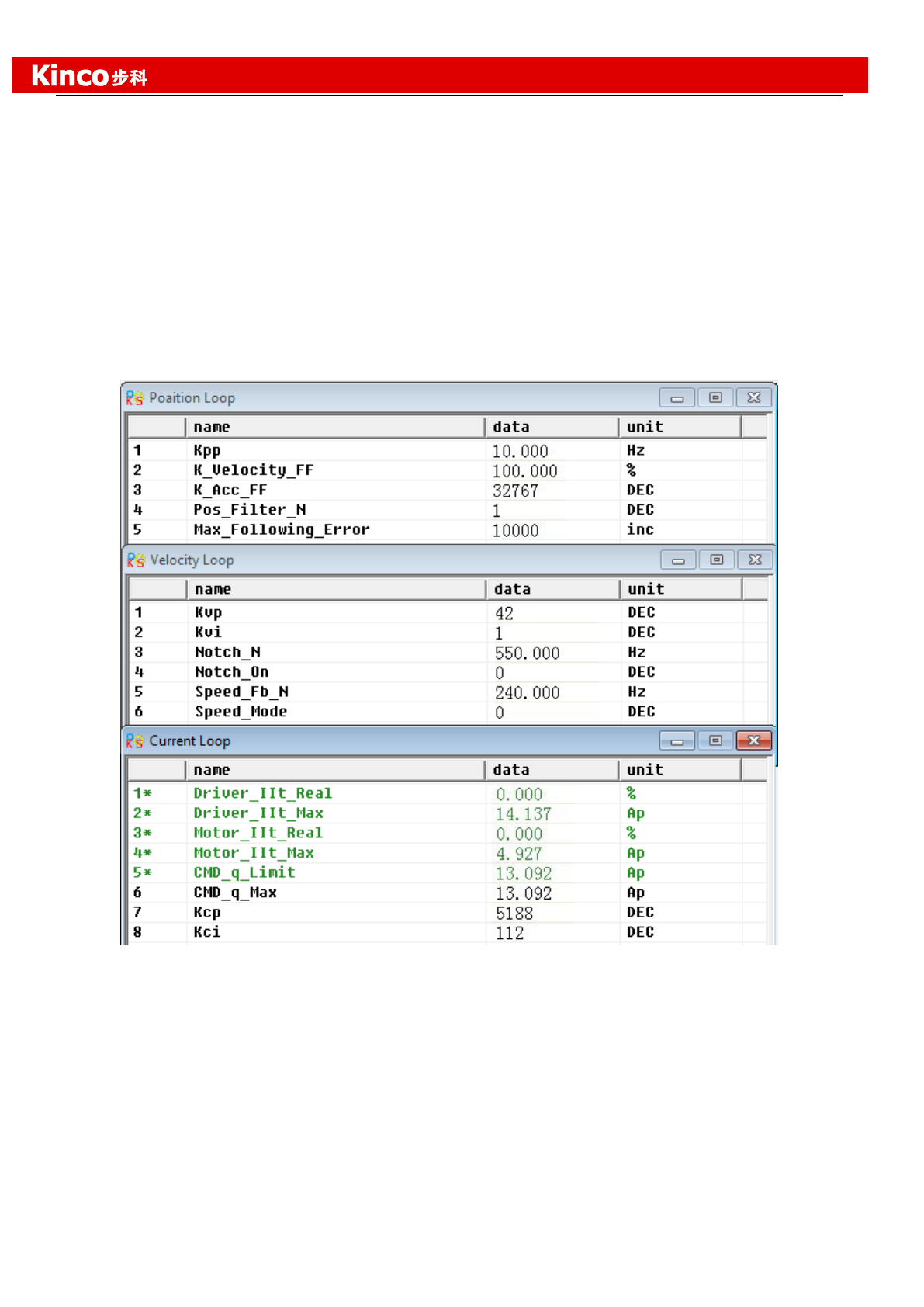
Kinco JD 伺服系列使用手册
34
Kinco FD Series Servo User Manual
Example 5-1: Use KincoServo software to control servo running in speed
mode by manual.
Step 1: Cancel the default setting of DIN1 and DIN3 according to Example 5-2.
Step 2: Set the basic parameters according to “Speed Mode” in Chapter 8.As shown on the red
line in the figure,it means the driver is in speed mode.And the speed is 100RPM.Set the
SpeedDemand_RPM as negative value when need to run reversed.
5.4.2 Control Loop
In this menu,it is used to adjust parameters for driver’s control performance.More details please refer to
chapter 9.
Please be careful for parameters setting in Current Loop!If users use FD Servo driver together with the servo
motors provided by Kinco Company,then it needn’t set the parameters in Current Loop.
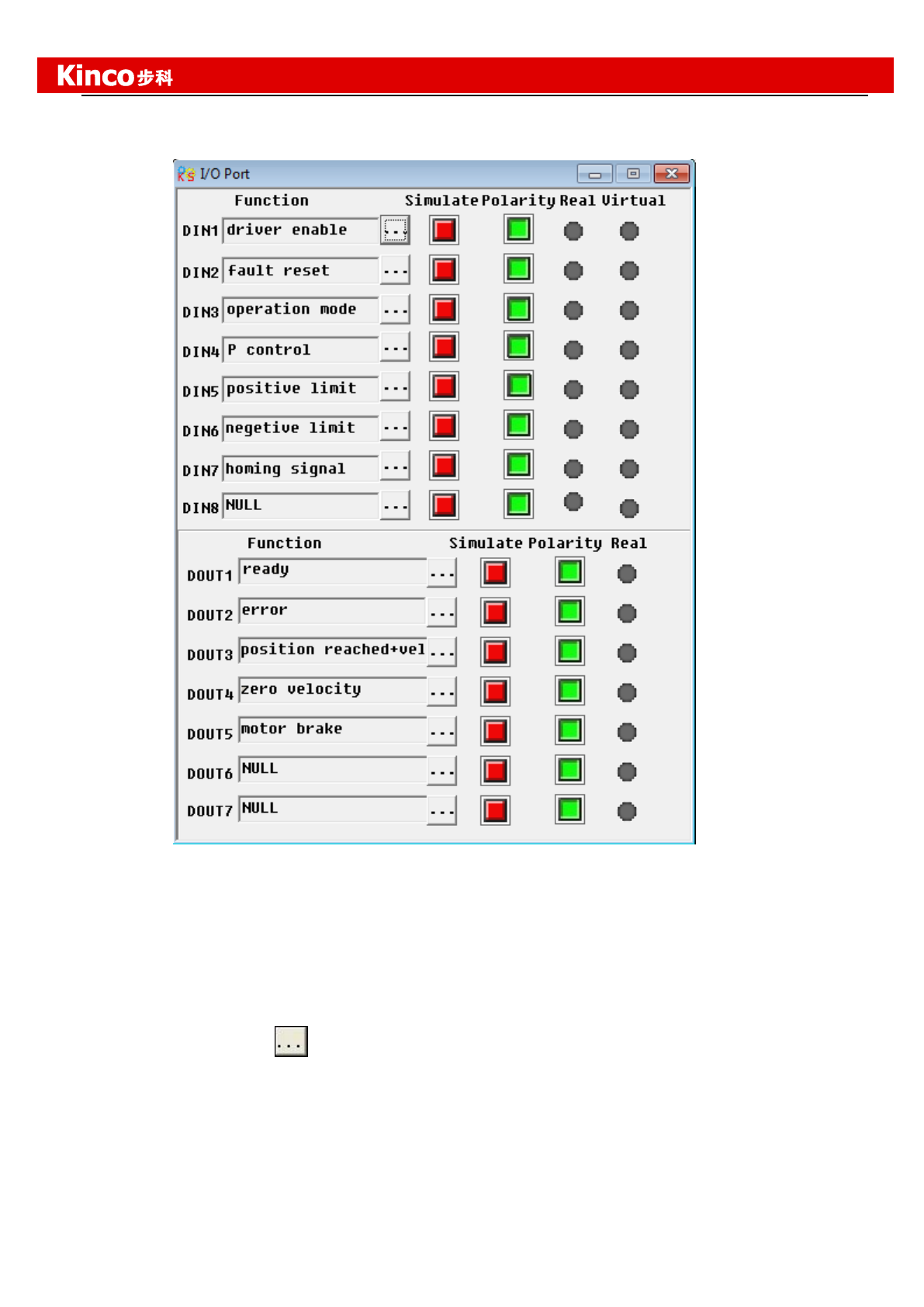
Kinco JD 伺服系列使用手册
35
Kinco FD Series Servo User Manual
5.4.3 I/O Port
In this menu,it is used to set the functions and polarity of I/O ports,monitor the status of I/O ports and simulate
the I/O ports.
Example 5-2:Use KincoServo software to set the functions of I/O port
Requirement: Cancel the functions of DIN1, DIN3 and DIN5.Set DIN2 as default reset,DIN4 as emergency
stop and OUT2 as Reference found.Others are set as default.
Step 1: Click the button beside DIN1.Cancel the function “Driver enable” in the popup window as
following figure, then click OK.
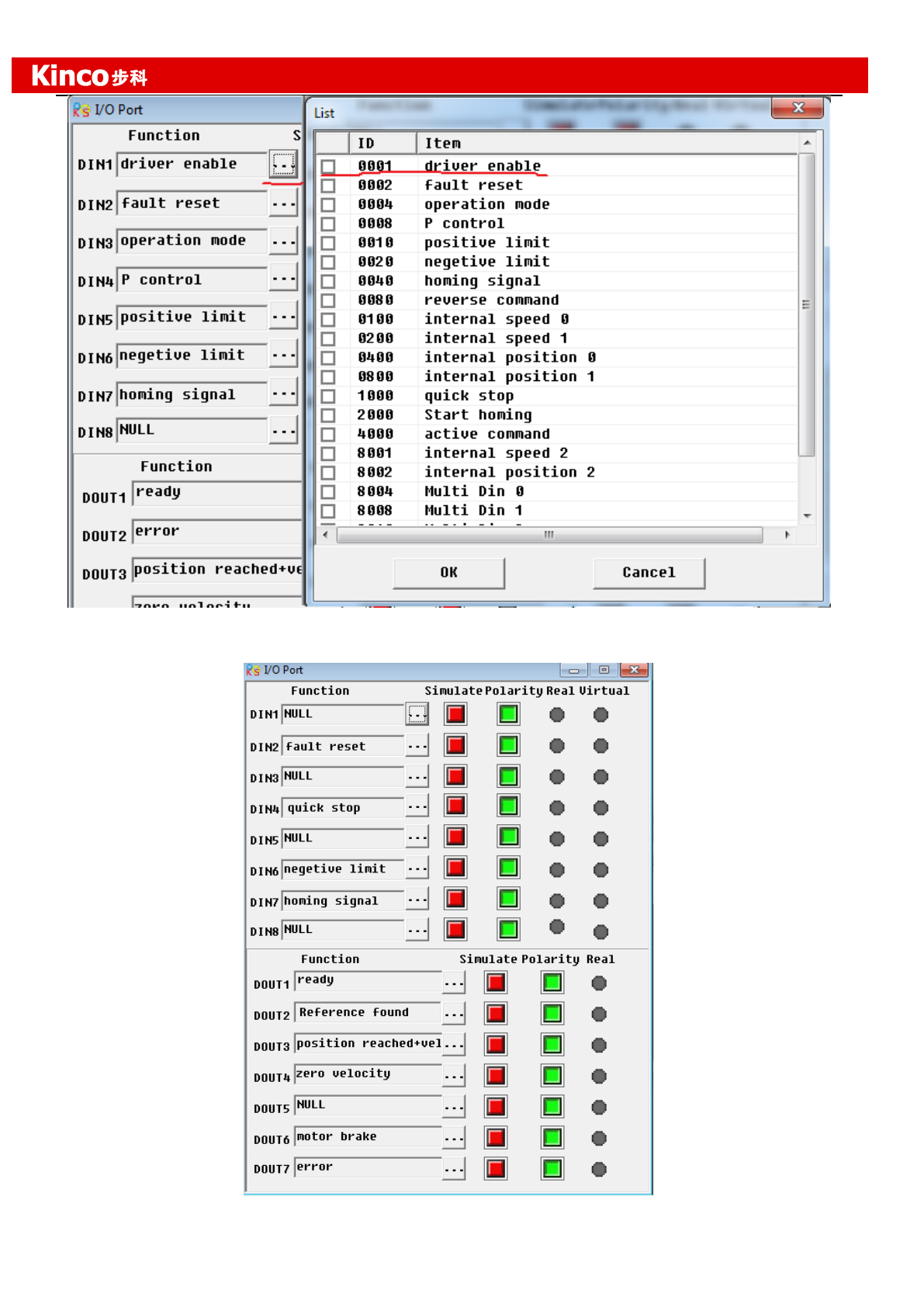
Kinco JD 伺服系列使用手册
36
Kinco FD Series Servo User Manual
Step 2:Set all the functions of other I/O ports with the similar operations as step 1.Then select
Driver -> Initialize/Save and click “Save control parameters”.The final settings of I/O ports
are as following figure:
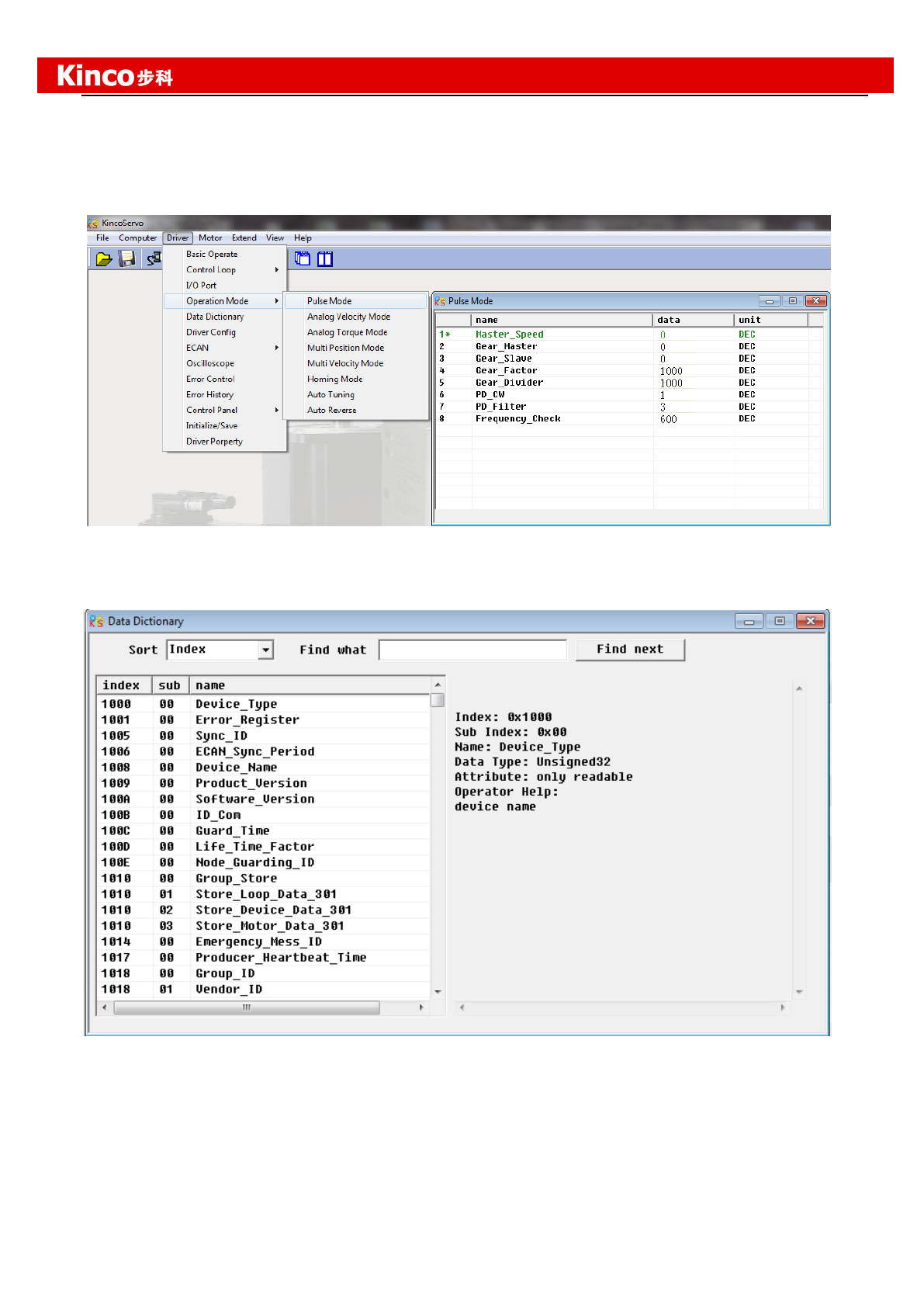
Kinco JD 伺服系列使用手册
37
Kinco FD Series Servo User Manual
5.4.4 Operation Mode
In this menu,it is used to set and monitor the objects in each operation mode.More details please refer to
chapter 9.Following figure is the menu for pulse mode.
5.4.5 Data Object
In this menu,it can be used to query the address and descriptions of all the objects in FD driver.As
shown in above picture,there are Index,Subindex address and the name of the objects on the left
side.On the right side,there are the descriptions of the object.
Example 5-3:Use KincoServo Software to Add an Object
Requirement:Add an address in any menu.Here we will add “CANopen baudrate” in “Basic Operate”.
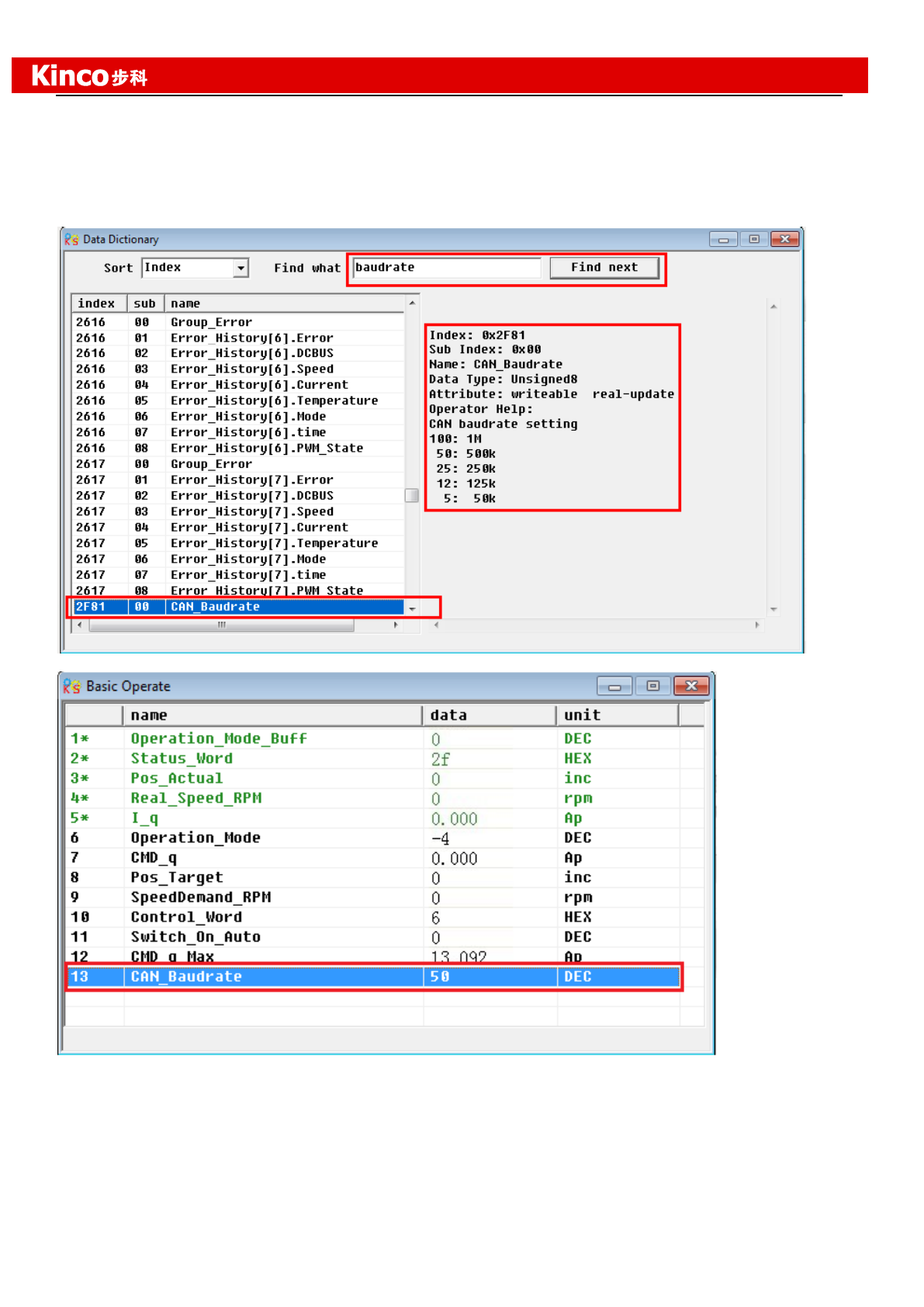
Kinco JD 伺服系列使用手册
38
Kinco FD Series Servo User Manual
Step 1:Open “Basic Operate”,then righ click in the window of “Basic Operate”.Select
“add”,then it will popup a window of “Data Object”.
Step 2:Enter “baudrate” in “Find what”,then click “Find next”.It will jump to the object
“CAN_Baudrate” whose index address is 2F81.There are the descriptions of this object in the
rightside. As shown in following figure.
Step 3:Double click the object to add this object into “Basic operate” menu.
Step 4:If you need to delete the object in the menu.Right click the object and select “del”to
delete the object.If you need to know more details of the object,then right click the object
and select “help” to show the details.
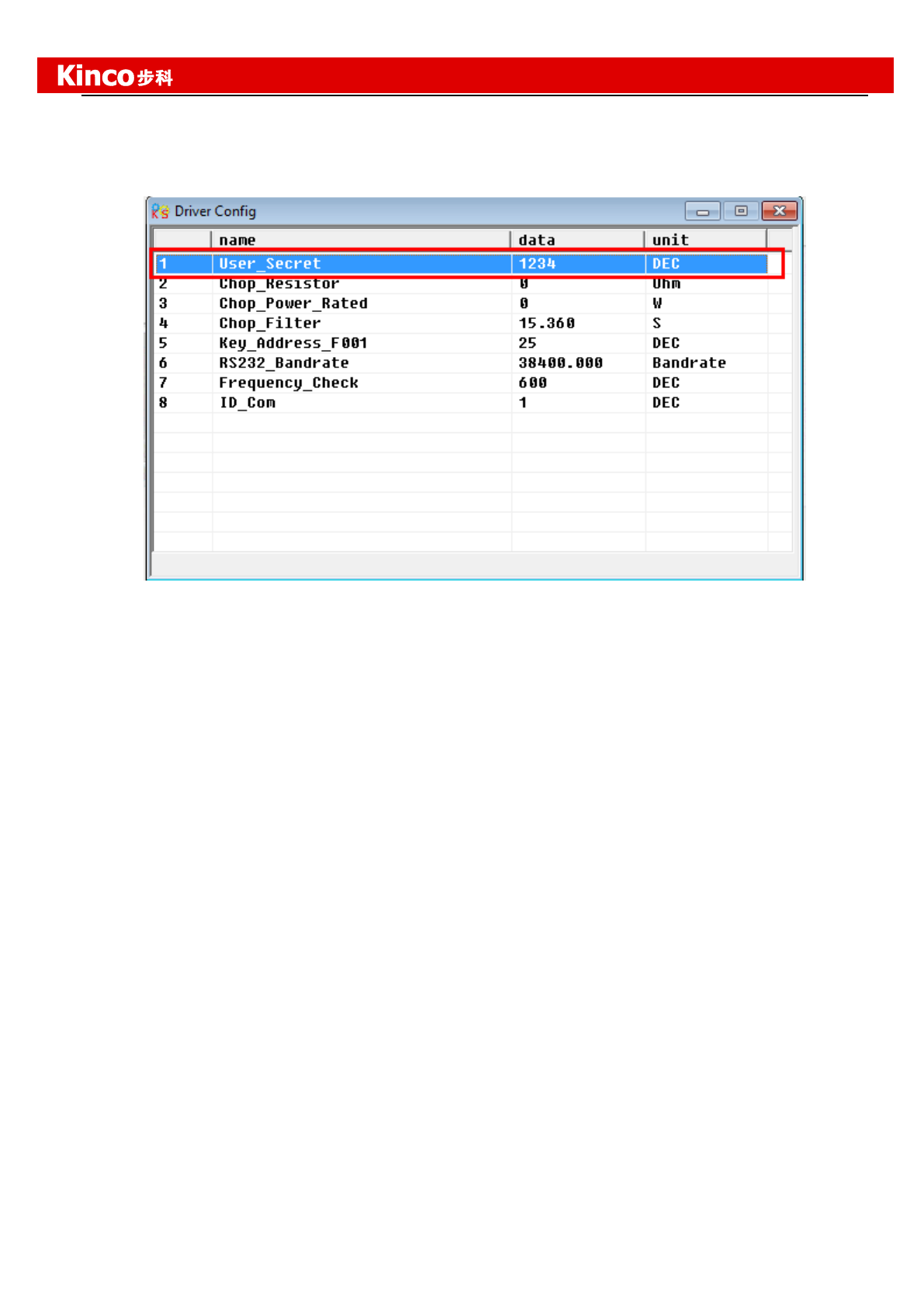
Kinco JD 伺服系列使用手册
39
Kinco FD Series Servo User Manual
5.4.6 Driver Config
In this menu,it is used to set the parameters such as User Password,Brake resistor,RS232 communication
and so on.
Example 5-4:Use KincoServo to set an User Password
Step 1:Set the number “1234”as password in the object “User_Secret” as shown in the red
box in the figure above.
Step 2:Click “Save all control parameters” in Driver->Initialize/Save to save parameters,then
Click “Reboot driver”.
Step 3:The password will be activated after rebooting driver.Then users can not set any parameters before
entering the correct password in the object “User_Secret”in “Driver Config”.
Step 4:Enter 0 in the object “User_Secret” to cancel the password after entering correct password.
5.4.7 ECAN Setting(CANopen PDO Setting)
This menu is used to set CANopen communication parameters.About details please refer to chapter 10.
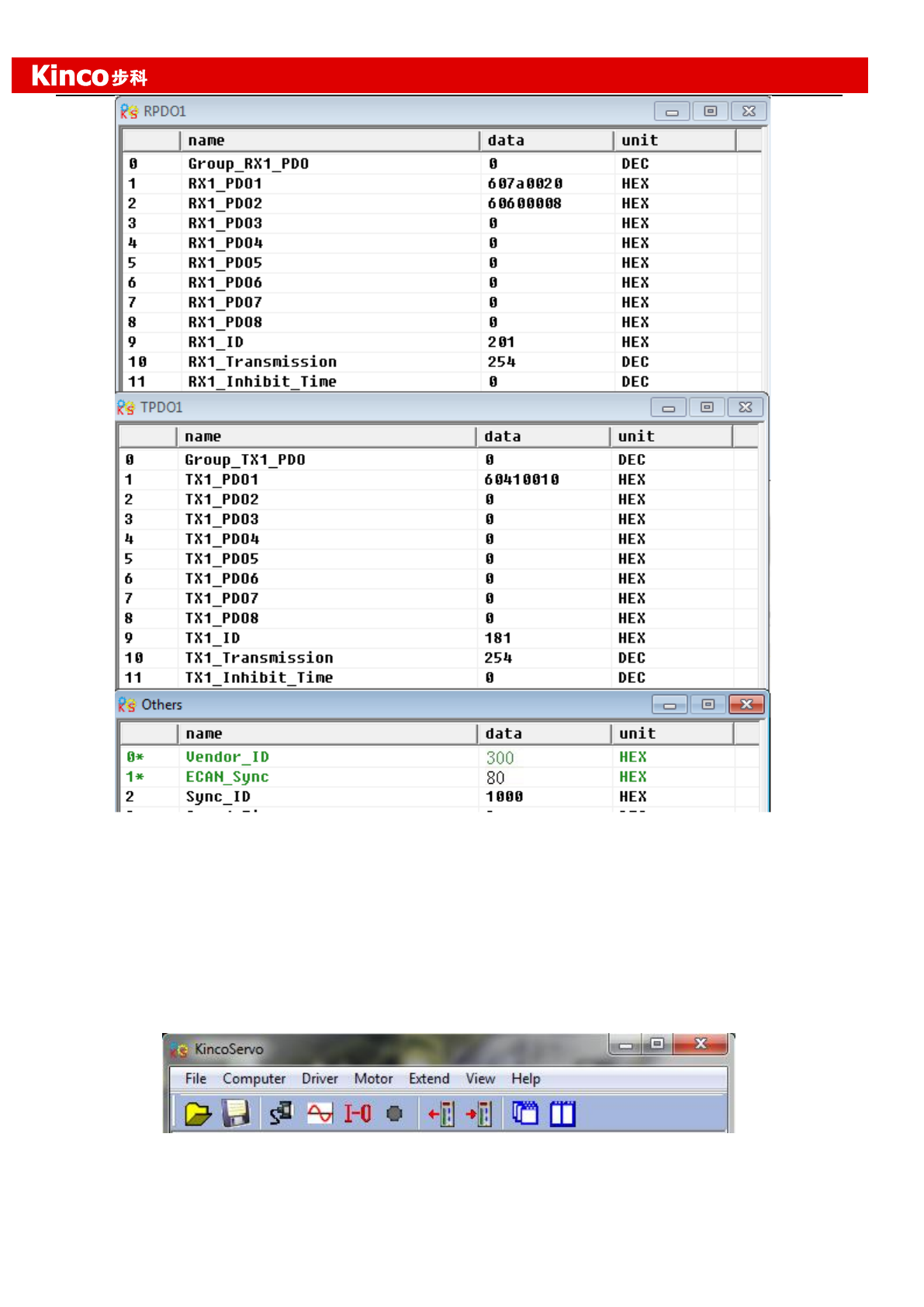
Kinco JD 伺服系列使用手册
40
Kinco FD Series Servo User Manual
5.4.8 Oscilloscope
Oscilloscope can help you adjust servo’s parameters better by observing the curve of speed,position and so
on.
There are two ways to open oscilloscope as following figures.
Fig.1.Oscilloscope shotcut in toolbar
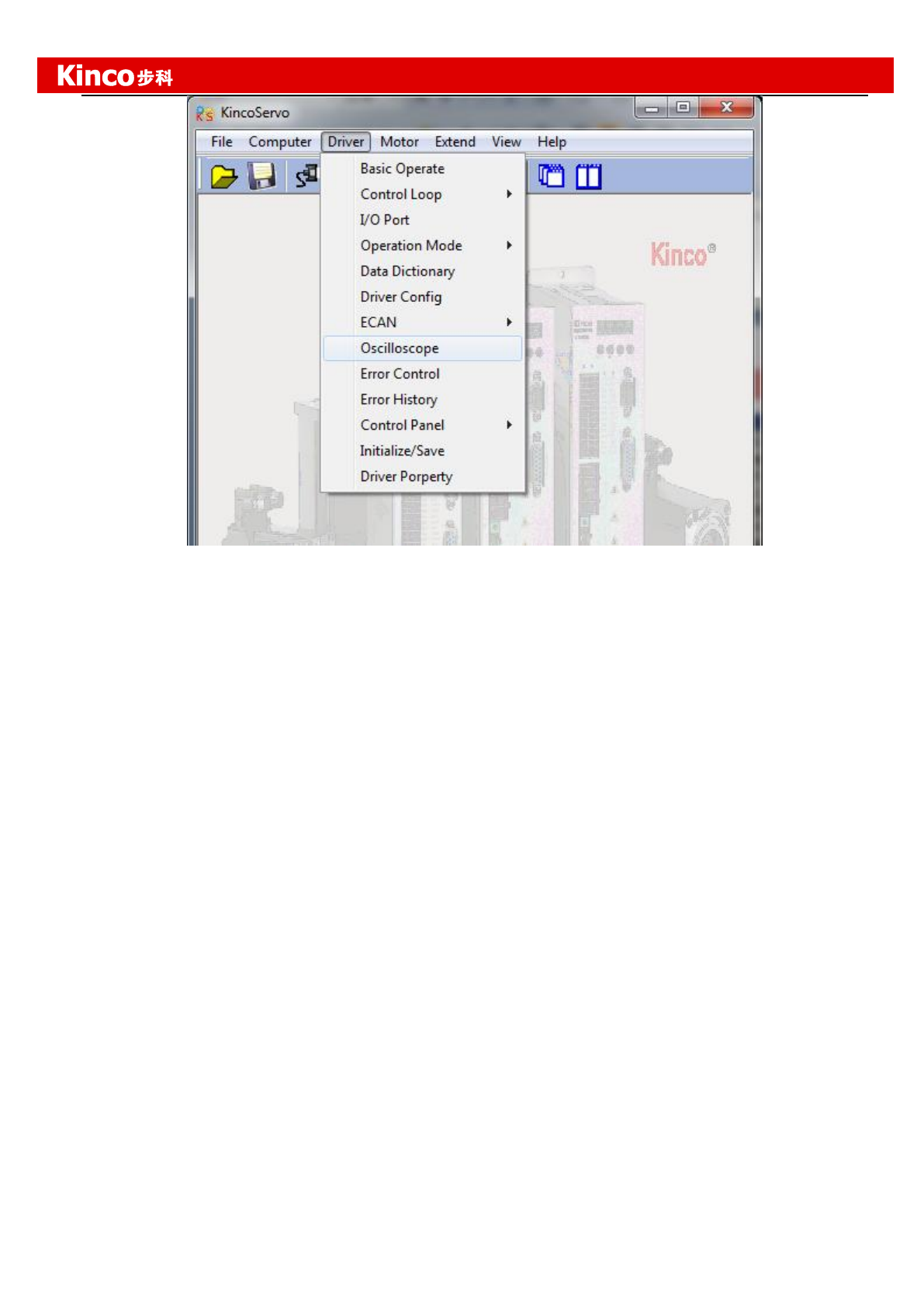
Kinco JD 伺服系列使用手册
41
Kinco FD Series Servo User Manual
Fig.2.Menu bar---Driver--Oscilloscope
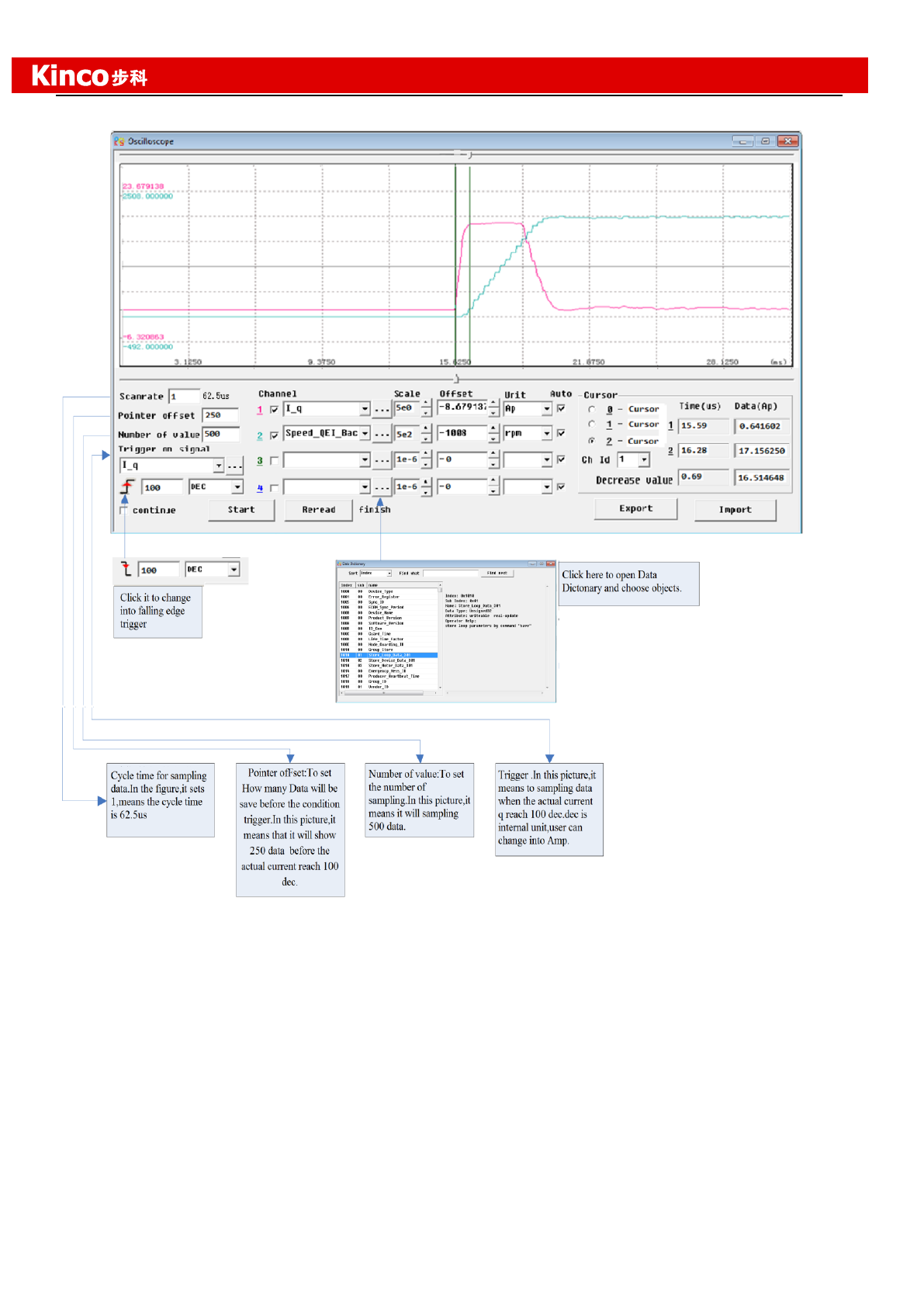
Kinco JD 伺服系列使用手册
42
Kinco FD Series Servo User Manual
Follows are the parameters instructions in Oscilloscope.
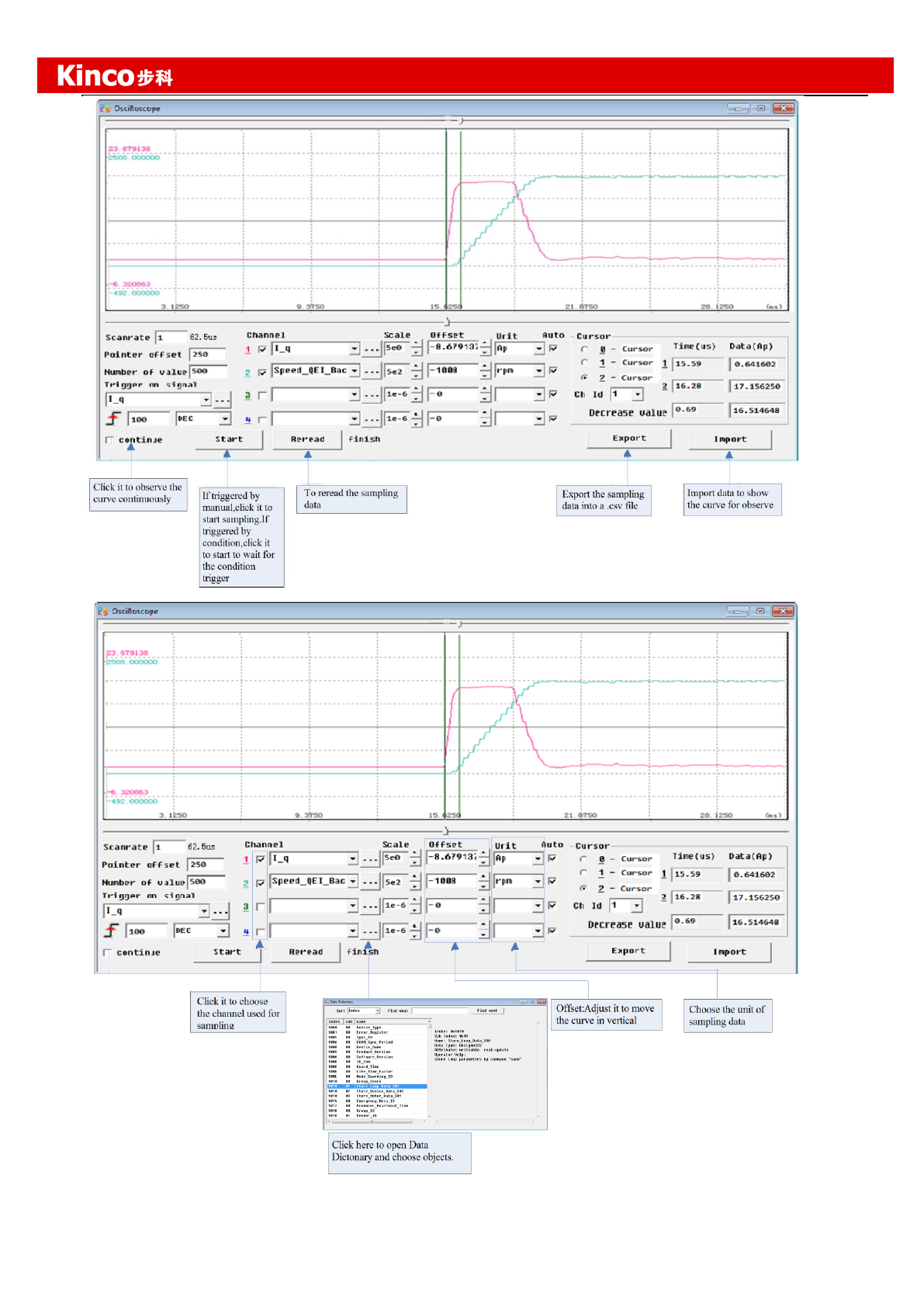
Kinco JD 伺服系列使用手册
43
Kinco FD Series Servo User Manual
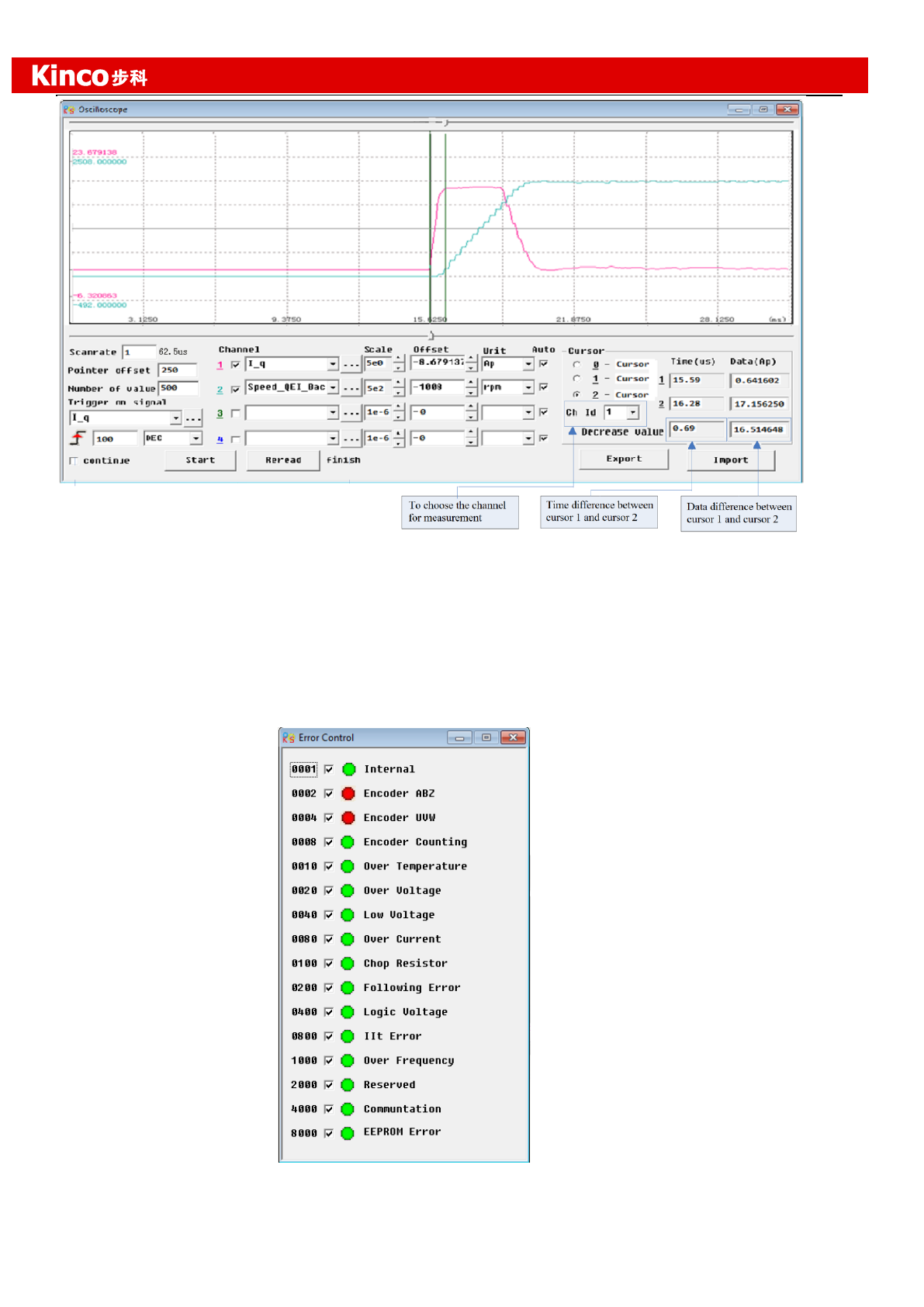
Kinco JD 伺服系列使用手册
44
Kinco FD Series Servo User Manual
5.4.9 Error Control
This menu is used to monitor the current error information.As shown in following figure,The Hex data is the
same error code as shown in LED display on servo driver.The small box is used to choose whether to shield
error or not.There is error when the lamp is red.The text is the descriptions of error.About more details please
refer to chapter 11.
Note:Please be careful for shielding error,and not all the errors can be shielded.
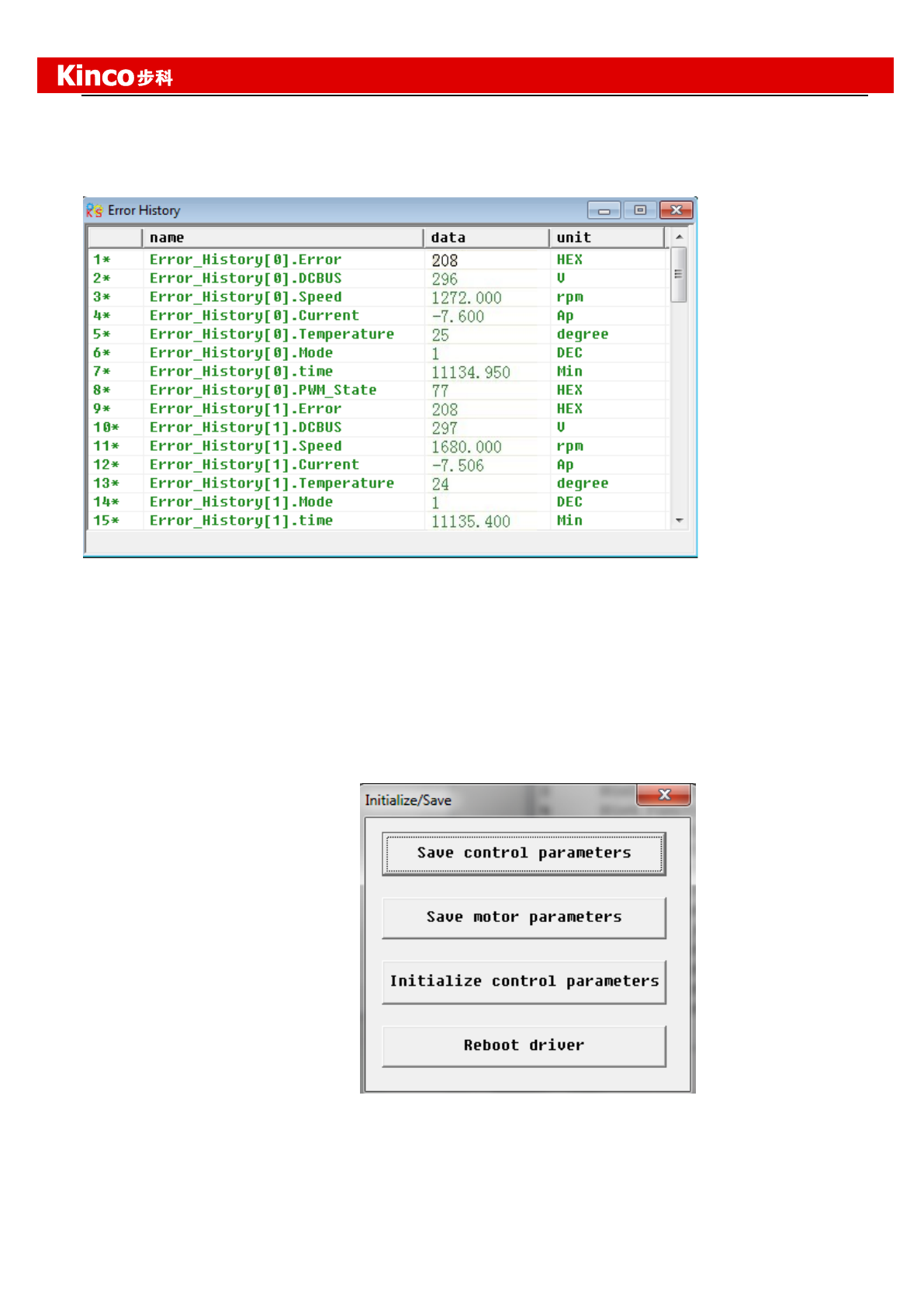
Kinco JD 伺服系列使用手册
45
Kinco FD Series Servo User Manual
5.4.10 Error History
FD Servo driver provides 7 groups of historical error informations.Users can query the informations such as
error code,voltage,current,temperature,speed,operation mode,driver accumulated working time and so on.
5.4.11 Control Panel
This menu is used to set and query all the parameters which are corresponding to the parameters
from Group F000 to F007 in servo driver.
5.4.12 Initialize/Save
This menu is used to save and initialize parameters and reboot servo driver.
5.4.13 Driver Property
This menu is used to display the informations such as driver model,software version,serial number and so on.
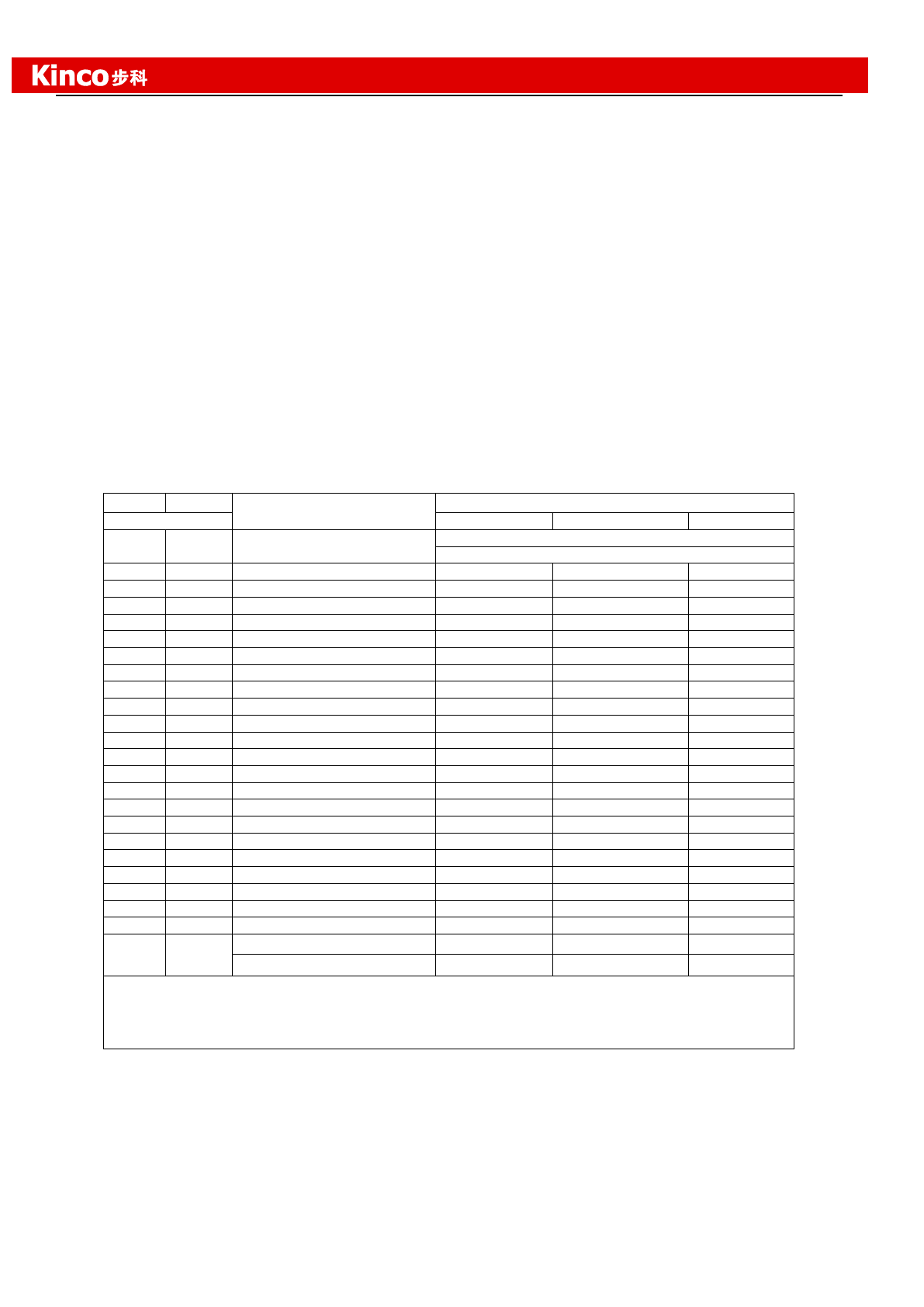
Kinco JD 伺服系列使用手册
46
Kinco FD Series Servo User Manual
Chapter 6 Motor Selection,Trial Operation and Parameter
List
6.1 Driver and motor configuration
There is no default motor type set in driver,so users need to set the motor model before using the
driver.Please refer to the selection table in 6.1.1 when setting the motor model.
6.1.1 Configuration Table for FD Servo Driver and Motor
PC
LED
Motor Model
Suitable Servo
LED Code:d4.19
FD422
FD432
FD622
K@
404.b
Do not configure motor
Display FFF.F if not enable (CD120 displays FF)
Display 800.0 if enable (CD120 displays 16)
K0
304.b
SMH60S-0020-30A■K-3LK□
√
K1
314.b
SMH60S-0040-30A■K-3LK□
√
K2
324.b
SMH80S-0075-30A■K-3LK□
√
K3
334.b
SMH80S-0100-30A■K-3LK□
√
K4
344.b
SMH110D-0105-20A■K-4LK□
√
K5
354.b
SMH110D-0125-30A■K-4LK□
√
K6
364.b
SMH110D-0126-20A■K-4LK□
√
K7
374.b
SMH110D-0126-30A■K-4HK□
√
K8
384.b
SMH110D-0157-30A■K-4HK□
√
K9
394.b
SMH110D-0188-30A■K-4HK□
√
KB
424.b
SMH130D-0105-20A■K-4HK□
√
√
KC
434.b
SMH130D-0157-20A■K-4HK□
√
√
KD
444.b
SMH130D-0210-20A■K-4HK□
√
KE
454.b
SMH150D-0230-20A■K-4HK□
√
E0
304.5
SME60S-0020-30A■K-3LK□
√
E1
314.5
SME60S-0040-30A■K-3LK□
√
E2
324.5
SME80S-0075-30A■K-3LK□
√
S0
305.3
130D-0105-20AAK-2LS
√
√
S1
315.3
130D-0157-20AAK-2LS
√
S2
325.3
130D-0157-15AAK-2LS
√
S3
335.3
130D-0200-20AAK-2HS
√
S4
345.3
130D-0235-15AAK-2HS
√
F8
384.6
85S-0045-05AAK-FLFN
√
85S-0045-05AAK-FLFO-KT
√
Note: ■=A: No brake □= H:Direct cable connector √:Recommended Configuration
=B: With brake =N:HFO series standard connector of Servo and Motor
= C:YL22 series standard connector
= M:2*M17 series Intercontec connector
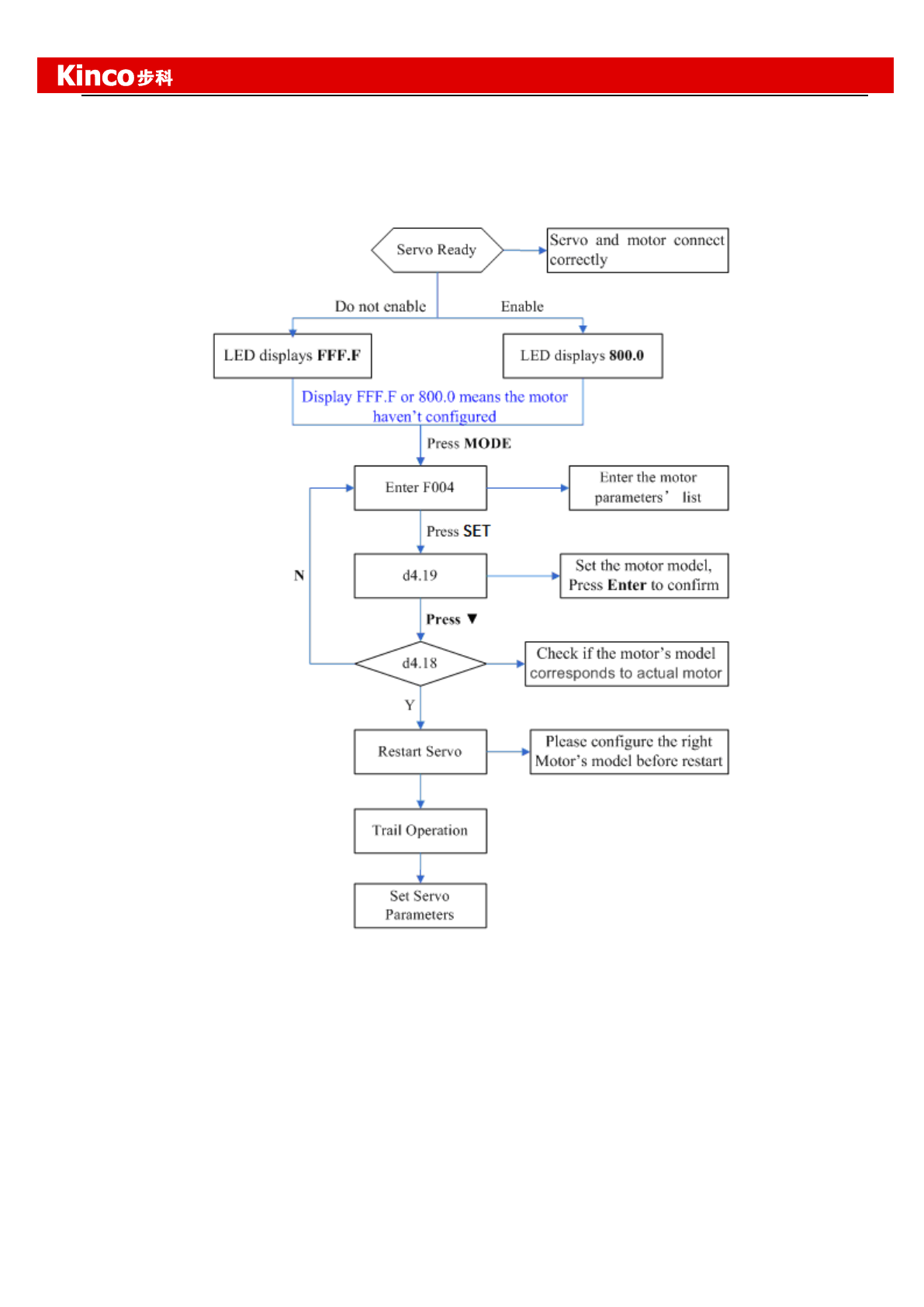
Kinco JD 伺服系列使用手册
47
Kinco FD Series Servo User Manual
6.1.2 Procedure for Motor configuration
If there is no motor type set in driver,then the driver will appear error FFF.F or 800.0.There are two ways to set
the motor type in driver as follows:
1.Panel operation.
Please configure the right motor’s model before restart. If customers want to reset the motor model,
they should set D4.19 to 303.0 (Press SET to confirm) and then d4.00 to 1(Save motor parameters), after
restart the servo they can reset motor model and servo parameters according to the above chart
2.KincoServo software operation
Connect the servo to PC, open the KincoServo, then Menu—Driver—Control Panel—F004, in the F004, in
the F004, set the 19th operation: Motor Num (Please refer to the servo and motor configuration table), after
that press Enter to confirm, then restart servo.
Please configure the right Motor’s model before restart. If the customers want to reset the motor
model, they should set d4.19 (Motor Num in F004) to 00(Press SET to confirm), then enter the Initialize/Save
page, click the Save motor parameters. After restart the servo, they can reset the motor model and set
servo parameters.
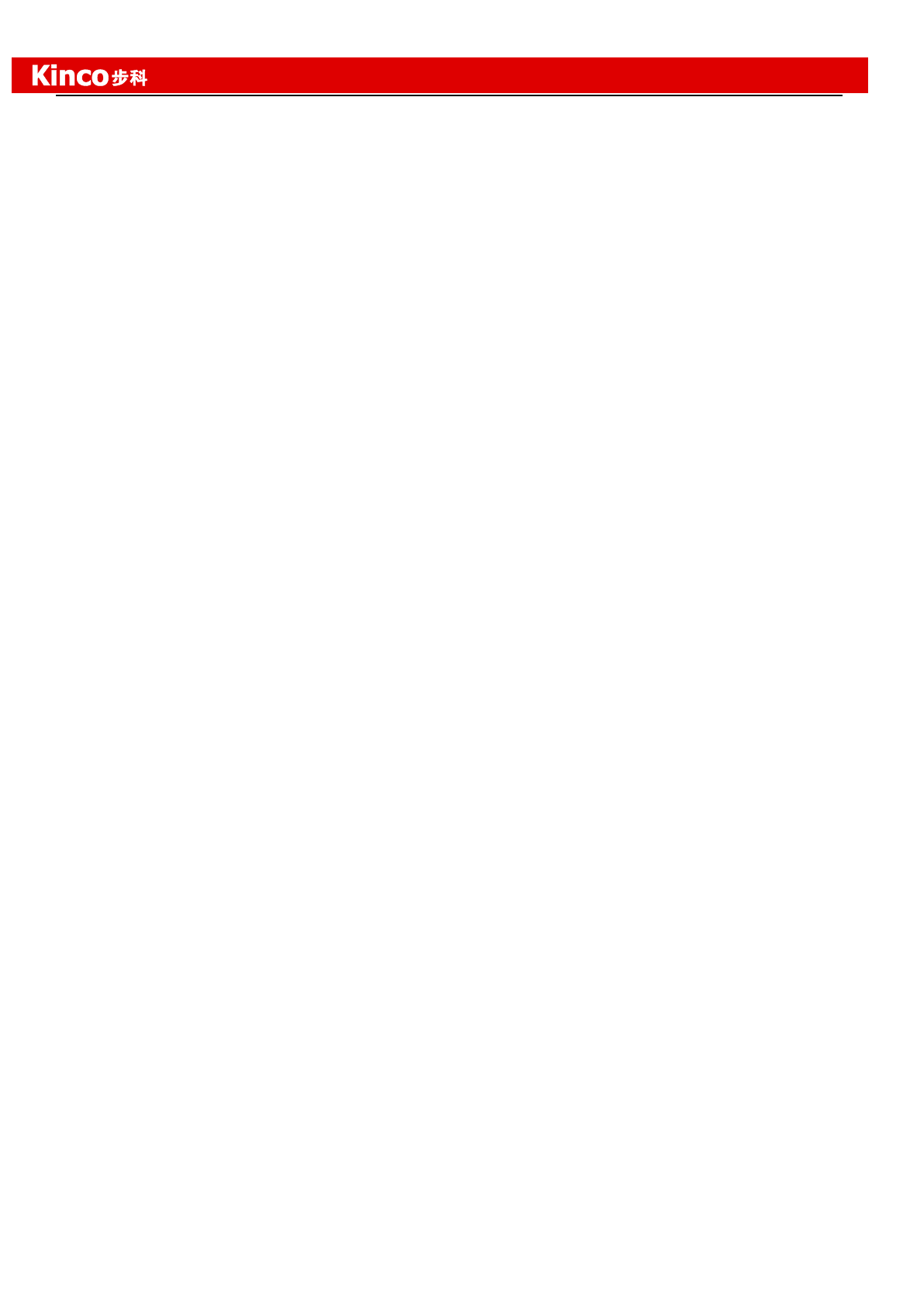
Kinco JD 伺服系列使用手册
48
Kinco FD Series Servo User Manual
6.2 Trial Operation
6.2.1 Objective
The trial operation allows you to test whether the driver works properly, and whether the motor runs stably.
6.2.2 Precautions
Ensure the motor type is set correctly.
Ensure that the motor is running without load. If the motor flange is fixed on the machine, ensure that the
motor shaft is disconnected from the machine.
Ensure that motor cables, motor encoder cables, and power circuits (power lines and control power lines) are
properly connected. For details, see Chapter 3.
During the trial operation, if you long press ▲ or ▼ when the motor is running, pulse signals, digital input
signals, and analog signals of the external controller are temporarily unavailable, so safety must be ensured.
During the trial operation, the system automatically adopts the instantaneous speed mode, that is, the “-3”
mode.
After the trial operation, Group F006 exits automatically. To enter Group F006 again, you must re-activate the
trial operation.
If motor/encoder cables are wrongly connected, the actual rotation speed of the motor may be the possible
maximum rotation speed, or the rotation speed is 0 and the actual current value is the maximum value. In this
case, make sure to release the button; then check cable connection and test it again.
If there is problem in the keys,then trial operation can not be used.
6.2.3 Operating Procedure
Please make sure the correct wiring of STO(refer to chanpter 3.4.3) before using trial operation,or the driver
will display error 200.0.
Operate by panel:
Press MODE to enter Group F004. Select the object address “d4.18”, and check the motor type.
Press MODE to enter Group F000. Select the object address “d0.02”, and set the target speed to
“SpeedDemand_RPM".
Press MODE to enter Group F006. Arrange a test for keys, with the default value of d6.40. Firstly, press ▼ to
adjust the data to d6.31. Then, press ▼, the data automatically changes to “d6.15”. Finally, press ▲ to adjust
the data to d6.25.
Press SET to activate trial operation. In this case, the numeric display is “adc.d”, and the motor shaft releases.
When long pressing ▲ or ▼, the motor automatically locks, and runs according to “+SpeedDemand_RPM” or
“-SpeedDemand_RPM” separately. During the trial operation, the numeric displays the motor speed in real
time.
The motor set counter clockwise as positive direction.If the direction is not fit for the requirement ,users can
change the direction through the parameter d2.16 in Group F002.
Operate by CD-PC software:
1:Set motor mode in “Motor” in the software.
2:Refer to Fig.5-1 to operate by manual.
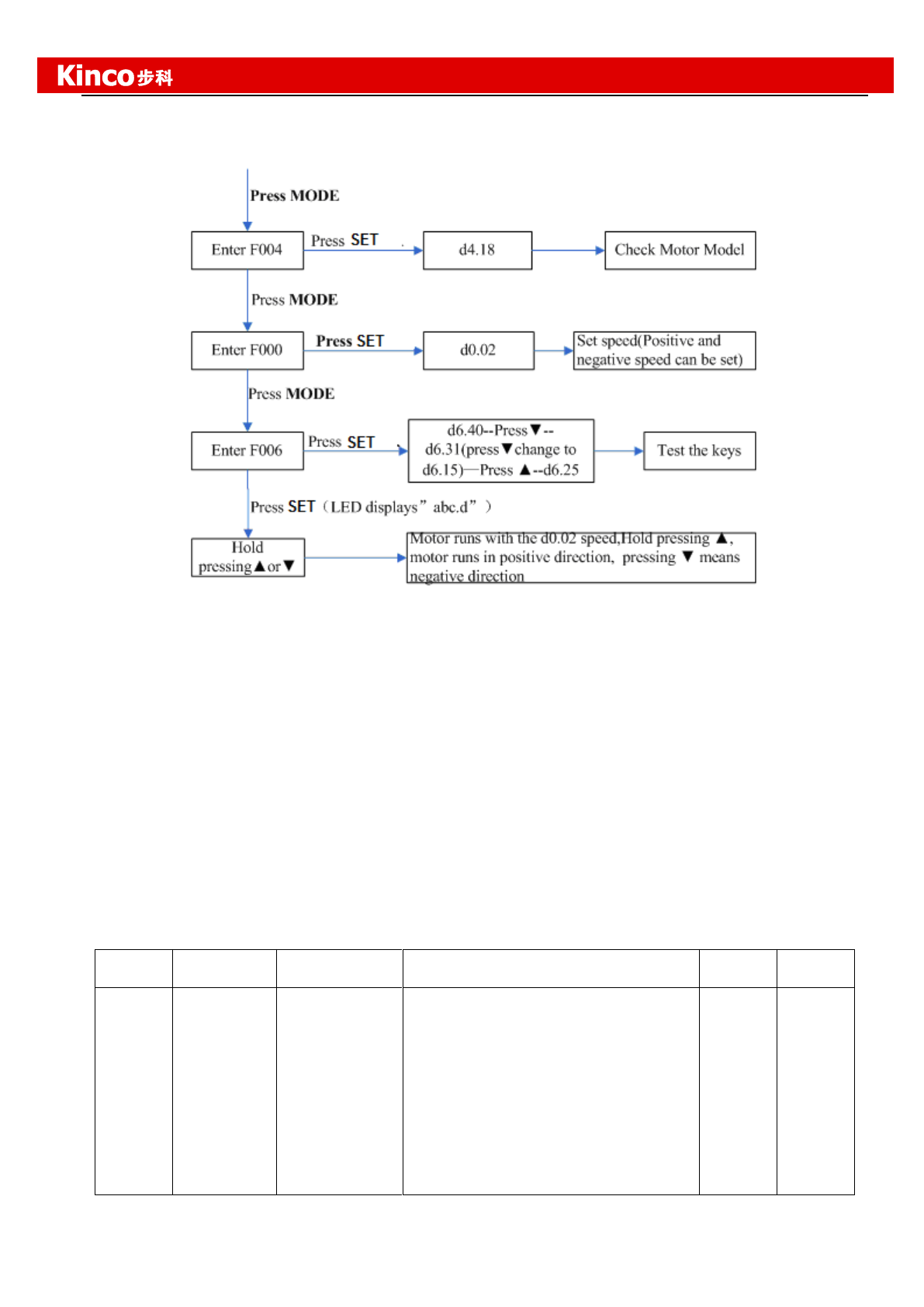
Kinco JD 伺服系列使用手册
49
Kinco FD Series Servo User Manual
6.2.4 Diagram of Trial Operation
Fig.6-1 Trial operation
6.3 Descriptions of Parameters
Group F000 represents an instruction group, and the parameters in this group cannot be saved.
The address d4.00 is used to save the motor parameters set for Group F004. Note that this group of
parameters must be set when customers choose third-party motors, but these parameters need not to be set
for the motors delivered and configured by our company.
d2.00, d3.00 and d.5.00 represent the same address, and are used to save all setup parameters except those
of motors (Group F001/F002/F003/F004/F005). Three numeric objects (d2.00/d3.00/d5.00) are developed to
facilitate customers.
Parameter List: Group F000 (To Set Driver Instructions)
Numeric
Display
Internal
Address
Variable Name
Meaning
Default
Value
Range
d0.00
60600008
Operation_Mo
de
0.004 (-4): Pulse control mode,
including pulse direction (P/D) and
double pulse (CW/CCW) modes. 0.003
(-3): instantaneous speed mode
0001 (1): Internal position control
mode
0003 (3): Speed mode with
acceleration/deceleration
0004 (4): Torque mode
Note: Only applied in the working
mode where no external signals
-4
/
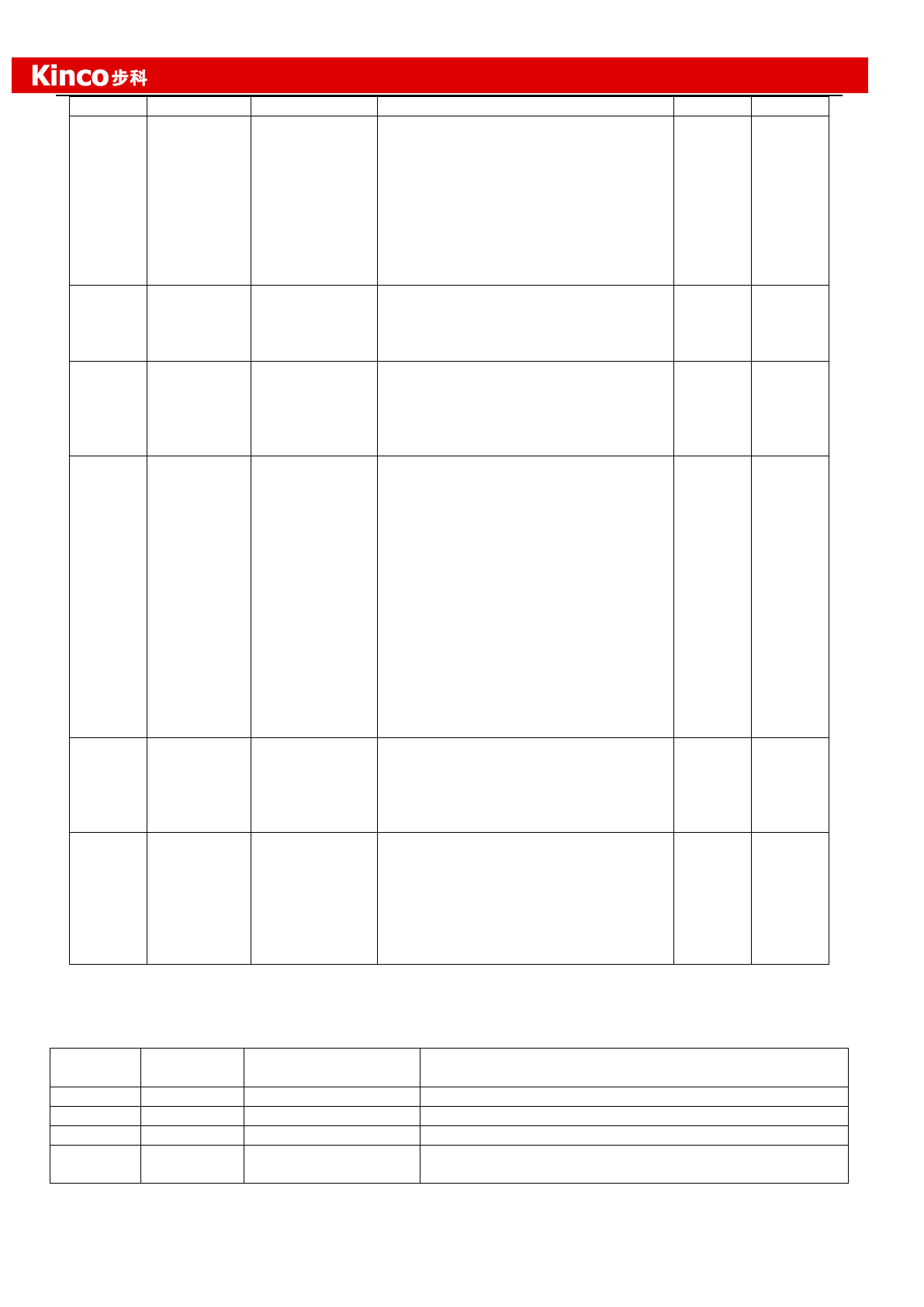
Kinco JD 伺服系列使用手册
50
Kinco FD Series Servo User Manual
control the driver.
d0.01
2FF00508
Control_Word_
Easy
000.0: Releases the motor
000.1: Locks the motor
001.0: Clears errors
Note: Only applied in the situation
where enabling a driver or wrong
resetting is not controlled by external
signals. After the wrong reset of the
driver, the motor must be enabled
again.
0
/
d0.02
2FF00910
SpeedDemand
_RPM
Sets the motor’s target rotation speed
when the driver works in the “-3” or “3”
mode and the address d3.28 is set to 0
(without external analog control).
0
/
d0.03
60710010
Target_Torque
%
Sets input torque instructions (current
instructions) when the driver works in
the “4” mode and the address d3.30 is
set to 0 (without external analog
control).
0
-2047~
2047
d0.04
2FF00A10
Vc_Loop_BW
Sets the velocity loop bandwidth. The
unit is Hz.
This variable can only be set after auto
tuning is performed properly; otherwise
the actual bandwidth goes wrong,
which causes abnormal working of the
driver.
If the auto tuning result is abnormal,
setting this parameter may also cause
abnormal working of the driver.
Note: This parameter cannot be
applied when auto tuning is
unavailable. After setting this
parameter, apply d2.00 to save the
settings as required.
/
0~600
d0.05
2FF00B10
Pc_Loop_BW
Sets the position loop bandwidth. The
unit is Hz.
Note: After setting this parameter,
apply d2.00 to save the settings as
required.
/
/
d0.06
2FF00C10
Tuning_Start
If the variable is set to 11, auto tuning
starts. All input signals are neglected
during auto tuning. The variable is
automatically changed to 0 after auto
tuning is completed.
Sets the variable to other values to end
auto tuning.
0
/
Parameter List: Group F001 (To Set Real-Time Display Data)
Numeric
Display
Internal
Address
Variable Name
Displayed Content
d1.00
2FF00F20
Soft_Version_LED
Software version of numeric display
d1.01
2FF70020
Time_Driver
Accumulated working time of the driver (S)
d1.02
2FF01008
Motor_IIt_Rate
Ratio of real iit to the maximum iit of a motor
d1.03
60F61210
Motor_IIt_Real
Actual data of motor overheat protection
The formula of conversion between display value and

Kinco JD 伺服系列使用手册
51
Kinco FD Series Servo User Manual
Numeric
Display
Internal
Address
Variable Name
Displayed Content
actual current(Average value):
peak
rms
I
Motor_IIt_Real*512
I*
2047 2
peak
I
is the max. peak value of the output current
of driver.
d1.04
2FF01108
Driver_IIt_Rate
Ratio of real iit to the maximum iit of a driver
d1.05
60F61010
Driver_IIt_Real
Actual data of driver overheat protection
d1.06
2FF01208
Chop_Power_Rate
Ratio of actual power to rated power of a braking resistor
d1.07
60F70D10
Chop_Power_Real
Actual power of a braking resistor
d1.08
60F70B10
Temp_Device
Temperature of a driver (°C)
d1.09
60790010
Real_DCBUS
Actual DC bus voltage
d1.10
60F70C10
Ripple_DCBUS
Fluctuating value of the bus voltage (Vpp)
d1.11
60FD0010
Din_Status
Status of an input port
d1.12
20101410
Dout_Status
Status of an output port
d1.13
25020F10
Analog1_out
Filter output of external analog signal 1
d1.14
25021010
Analog2_out
Filter output of external analog signal 2
d1.15
26010010
Error_State
Error state
d1.16
26020010
Error_State2
Error state word 2
d1.17
60410010
Status_Word
Driver status word
bit0:Ready to switch on
bit1:Switch on
bit2:Operation enable
bit3:Falt
bit4:Voltage Enable
bit5:Quick Stop
bit6:Switch on disable
bit7:Warning
bit8:Reserved
bit9:Reserved
bit10:Target reach
bit11:Internal limit active
bit12:Step.Ach./V=0/Hom.att.
bit13:Foll.Err/Res.Hom.Err.
bit14:Commutation Found
bit15:Referene Found
d1.18
60610008
Operation_Mode_Buff
Efficient working mode of a driver
d1.19
60630020
Pos_Actual
Actual position of a motor
d1.20
60FB0820
Pos_Error
Position following error
d1.21
25080420
Gear_Master
Count of input pulses before electronic gear
d1.22
25080520
Gear_Slave
Count of executed pulses after electronic gear
d1.23
25080C10
Master_Speed
Pulse speed entered by the master axis (pulse/mS)
d1.24
25080D10
Slave_Speed
Pulse speed of the slave axis (pulse/mS)
d1.25
606C0010
Real_Speed_RPM
Real speed (rpm)
Internal sampling time: 200 mS
d1.26
60F91910
Real_Speed_RPM2
Real speed (0.01 rpm)
Internal sampling time: 200 mS
d1.27
60F91A10
Speed_1mS
Speed data (inc/1 mS)
Internal sampling time: 1 mS

Kinco JD 伺服系列使用手册
52
Kinco FD Series Servo User Manual
Numeric
Display
Internal
Address
Variable Name
Displayed Content
d1.28
60F60C10
CMD_q_Buff
Internal effective current instruction
d1.29
60F61710
I_q
Actual current
The formula of conversion between display value
andactual current:
peak
rms
I
_
I*
2047 2
Iq
peak
I
is the max. peak value of the output current
of driver.
d1.30
60F90E10
K_Load
Load parameter
d1.31
30100420
Z_Capture_Pos
Position data captured by encoder index signals
Parameter List: Group F002 (To Set Control Loop Parameters)
Numeric
Display
Internal
Address
Variable
Name
Meaning
Default
Value
Range
d2.00
2FF00108
Store_Lo
op_Data
1: Stores all setup parameters except those of
a motor
10: Initializes all setup parameters except
those of a motor
0
/
d2.01
60F90110
Kvp
Sets the response speed of velocity loop
0~
32767
d2.02
60F90210
Kvi
Time used to adjust speed control to
compensate minor errors
0~
16384
d2.03
60F90308
Notch_N
Notch/filtering frequency setting for a velocity
loop, used to set the frequency of the internal
notch filter, so as to eliminate the mechanical
resonance produced when the motor drives
the machine. The formula is
F=Notch_N*10+100.
For example, if the mechanical resonance
frequency is F = 500 Hz, the parameter should
be set to 40.
45
0~90
d2.04
60F90408
Notch_O
n
Enable or disable the notch filter
0: Disable the trap filter
1: Enable the trap filter
0
/
d2.05
60F90508
Speed_F
b_N
You can reduce the noise during motor
operation by reducing the feedback bandwidth
of velocity loop. When the set bandwidth
becomes less, the motor responds slower.
The formula is F=Speed_Fb_N*20+100.
For example, to set the filter bandwidth to "F =
500 Hz”, you need to set the parameter to 20.
0~45
d2.06
60F90608
Speed_M
ode
0: Speed response after traveling through a
low-pass filter
1: Direct speed response without filtering
2: Feedback on output feedback
0
/
d2.07
60FB0110
Kpp
Proportional gains on position loop Kpp
1000
0~
16384
d2.08
60FB0210
K_Speed
_FF
0 indicates no feedforward, and 256 indicates
100% feedforward
256
0~
256
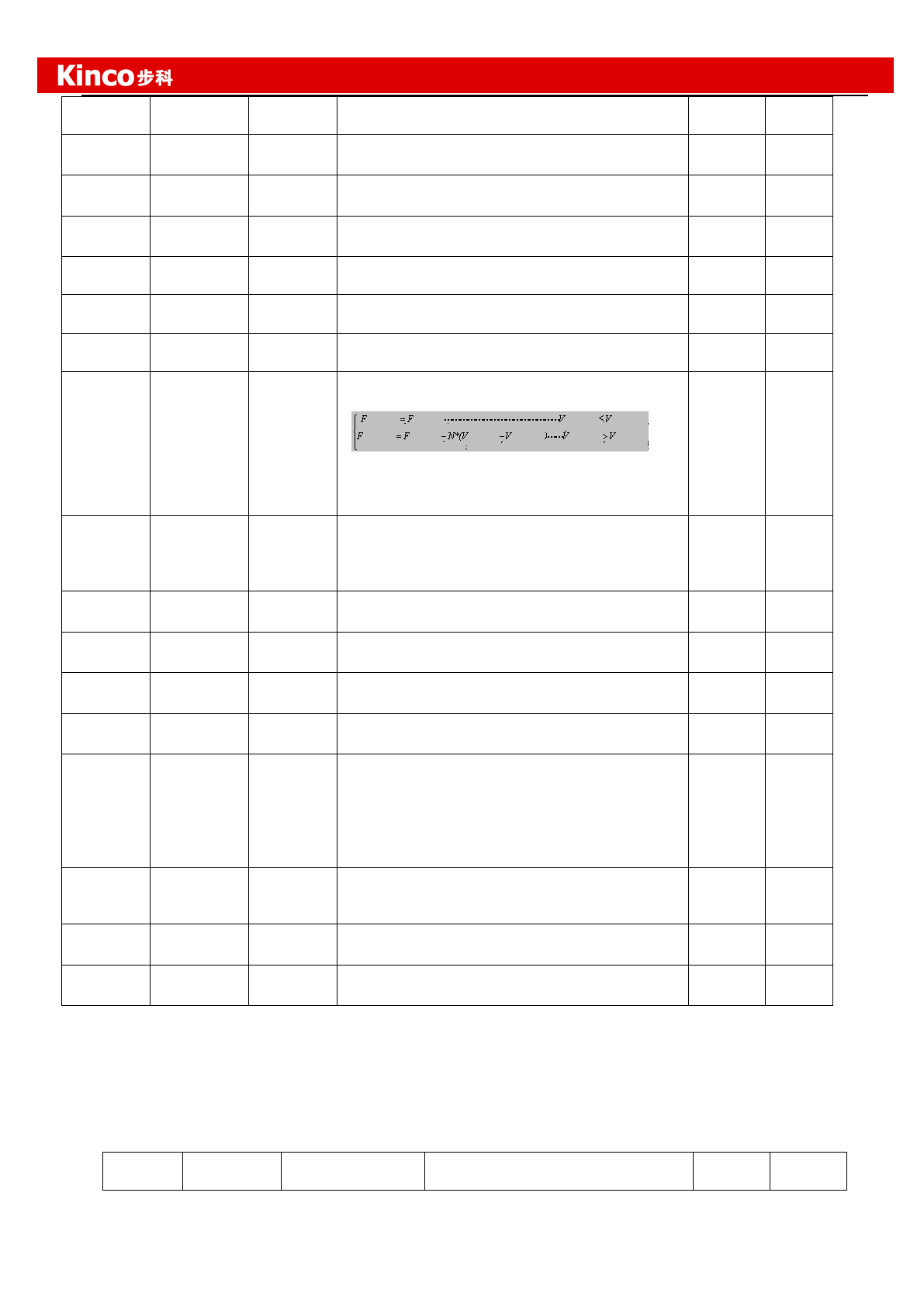
Kinco JD 伺服系列使用手册
53
Kinco FD Series Servo User Manual
Numeric
Display
Internal
Address
Variable
Name
Meaning
Default
Value
Range
d2.09
60FB0310
K_Acc_F
F
The data is inversely proportional to the
feedforward
7FF.F
32767
~10
d2.10
2FF00610
Profile_A
cce_16
To set trapezoidal acceleration (rps/s) in the
“3” and “1” modes
610
0~
2000
d2.11
2FF00710
Profile_D
ece_16
To set trapezoidal deceleration (rps/s) in the
“3” and “1” modes
610
0~
2000
d2.12
60F60110
Kcp
To set the response speed of the current loop
and this parameters does not require adjusting
/
/
d2.13
60F60210
Kci
Time used to adjust current control to
compensate minor errors
/
/
d2.14
60730010
CMD_q_
Max
Indicates the maximum value of current
instructions
/
/
d2.15
60F60310
Speed_Li
mit_Fact
or
The factor that limits the maximum speed in
the torque mode
Actual torque Set torque
Actual torque Set torque Actual speed Maximum speed
Actual speed
Actual speed
Maximum speed
Maximum speed
V the maximum speed complies with d2.24
Max_Speed_RPM parameter settings
10
0~
1000
d2.16
607E0008
Invert_Dir
Runs polarity reverse
0: Counterclockwise indicates the forward
direction
1: Clockwise indicates the forward direction
0
/
d2.17
60F90E10
K_Load
Indicates load parameters
/
20~
15000
d2.18
60F90B10
Kd_Virtu
al
Indicates the kd of observers
1000
0~
32767
d2.19
60F90C10
Kp_Virtu
al
Indicates the kp of observers
1000
0~
32767
d2.20
60F90D10
Ki_Virtual
Indicates the ki of observers
0
0~
16384
d2.21
60F91010
Sine_Am
plitude
Proper increase in this data will reduce the
tuning error, but machine vibration will become
severer. This data can be adjusted properly
according to actual conditions of machines. If
the data is too small, the auto tuning error
becomes greater, or even causes a mistake.
64
0~
1000
d2.22
60F91110
Tuning_S
cale
It is helpful to reduce the auto tuning time by
reducing the data, but the result may be
unstable.
128
0~
16384
d2.23
60F91210
Tuning_F
ilter
Indicates filter parameters during auto-tuning
64
1~
1000
d2.24
60800010
Max_Spe
ed_RPM
Limits the maximum rotation speed of motors
5000
0~
6000
Parameter List: Group F003 (To Set Input/Output & Pattern Operation
Parameters)
Numeric
Display
Internal
Address
Variable Name
Meaning
Default
Value
Range
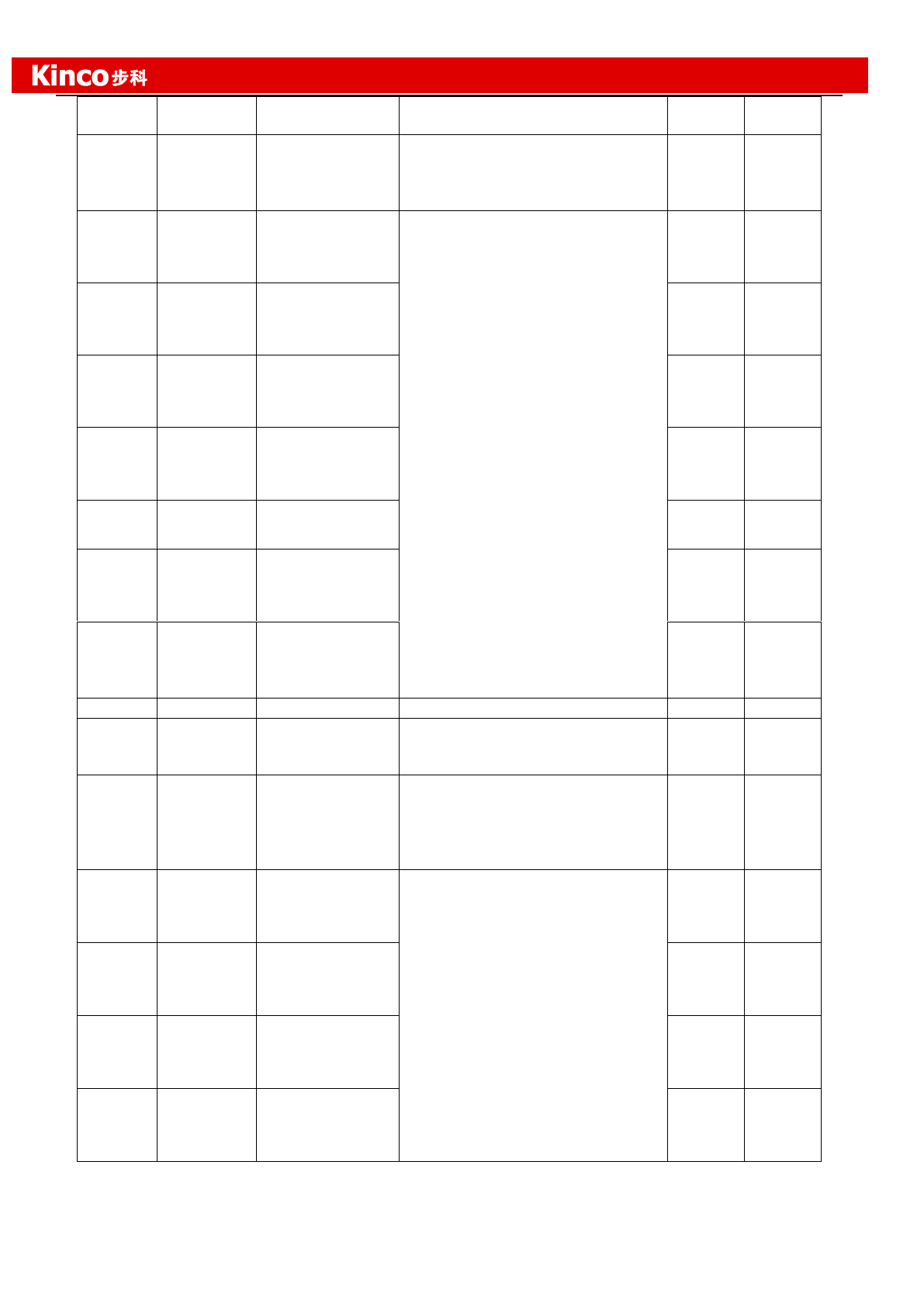
Kinco JD 伺服系列使用手册
54
Kinco FD Series Servo User Manual
Numeric
Display
Internal
Address
Variable Name
Meaning
Default
Value
Range
d3.00
2FF00108
Store_Loop_Dat
a
1: Stores all setup parameters
except motors
10: Initializes all setup parameters
except motors
0
/
d3.01
20100310
Din1_Function
000.1: Driver enable
000.2: Driver fault reset
000.4: Operation mode control
000.8: P control for velocity loop
001.0: Position positive limit
002.0: Position negative limit
004.0: Homing signal
008.0: Reverse speed demand
010.0: Internal speed control 0
020.0: Internal speed control 1
800.1: Internal speed control 2
040.0: Internal position control 0
080.0: Internal position control 1
800.2: Internal position control 2
800.4 Multi Din 0
800.8 Multi Din 1
801.0 Multi Din 2
802.0 Gain switch 0
804.0 Gain switch 1
100.0: Quick stop
200.0: Start homing
400.0: Activate command
Note:DinX_Function(X is 1-7) is
used to define the function of
digital inputs.
000.1
/
d3.02
20100410
Din2_Function
000.2
/
d3.03
20100510
Din3_Function
000.4
/
d3.04
20100610
Din4_Function
000.8
/
d3.05
20100710
Din5_Function
001.0
/
d3.06
20100810
Din6_Function
002.0
/
d3.07
20100910
Din7_Function
004.0
/
d3.08
2FF00D10
Dio_Polarity
Sets IO polarity
0
/
d3.09
2FF00810
Dio_Simulate
Simulates input signals, and
enforce output signals for
outputting
0
/
d3.10
20000008
Switch_On_Auto
Automatically locks motors when
drivers are powered on
0: No control
1: Automatically locks motors
when drivers are powered on
0
/
d3.11
20100F10
Dout1_Function
000.1: Ready
000.2: Error
000.4: Position reached
000.8: Zero velocity
001.0: Motor brake
002.0:Velocity reached
004.0: Index
008.0: The maximum speed
obtained in the torque mode
010.0: PWM ON
020.0: Position limiting
040.0: Reference found
080.0: Reserved
100.0: Multi Dout 0
200.0: Multi Dout 1
000.1
/
d3.12
20101010
Dout2_Function
000.0
/
d3.13
20101110
Dout3_Function
00a.4
/
d3.14
20101210
Dout4_Function
000.8
/
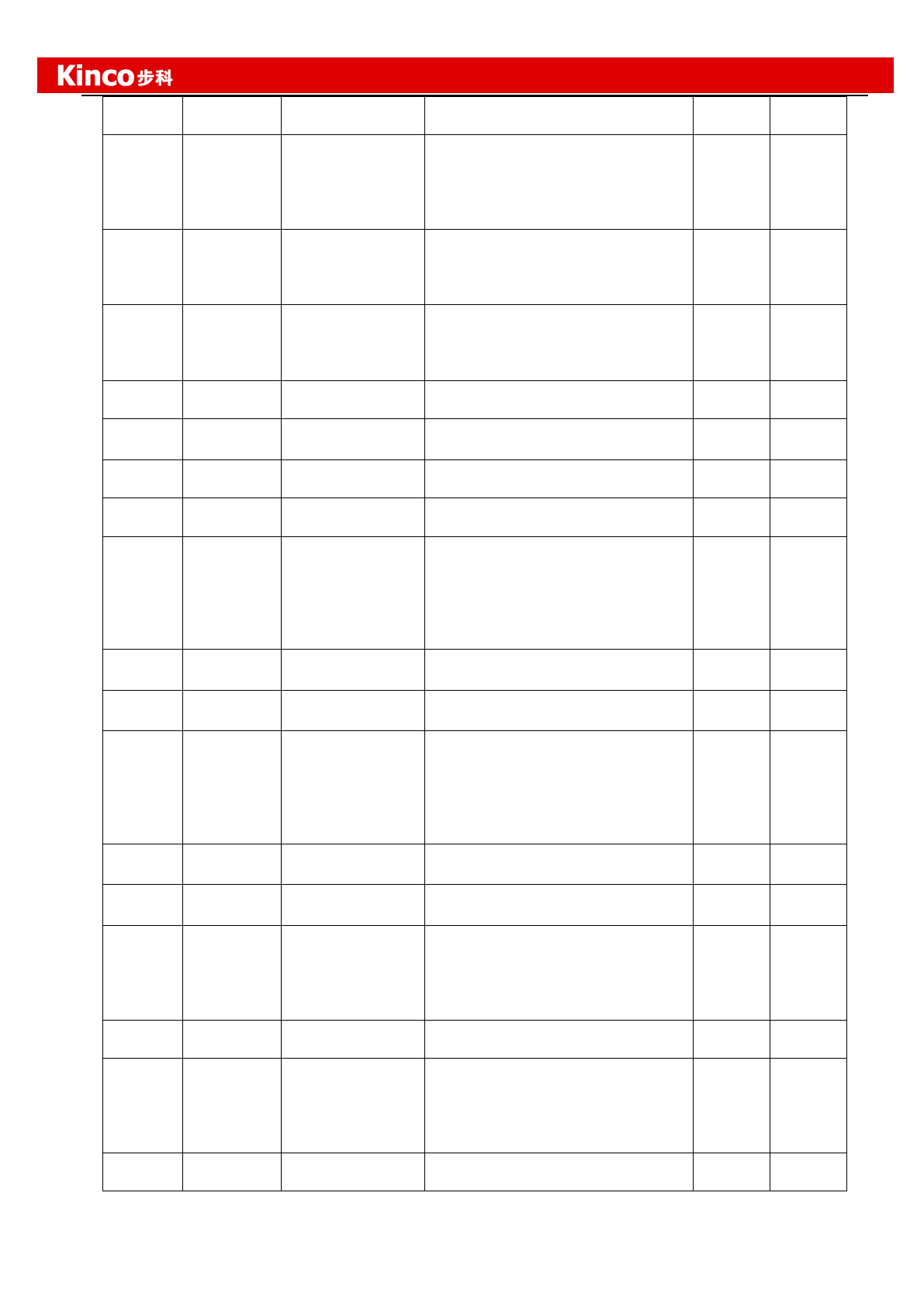
Kinco JD 伺服系列使用手册
55
Kinco FD Series Servo User Manual
Numeric
Display
Internal
Address
Variable Name
Meaning
Default
Value
Range
d3.15
20101310
Dout5_Function
400.0: Multi Dout 2
Note:DoutX_Function(X is 1-5) is
used to define functions of the
digital outputs.
000.0
/
d3.16
20200D08
Din_Mode0
If a digital input is defined as
Operation mode control,then this
operation mode is selected when
the input signal is invalid
-4
/
d3.17
20200E08
Din_Mode1
If a digital input is defined as
Operation mode control,then this
operation mode is selected when
the input signal is valid
-3
/
d3.18
20200910
Din_Speed0_RP
M
Multi-speed control: 0 [rpm]
0
/
d3.19
20200A10
Din_Speed1_RP
M
Multi-speed control: 1 [rpm]
0
/
d3.20
20200B10
Din_Speed2_RP
M
Multi-speed control: 2 [rpm]
0
/
d3.21
20200C10
Din_Speed3_RP
M
Multi-speed control: 3 [rpm]
0
/
d3.22
25020110
Analog1_Filter
Used to smooth the input analog
signals
F (Filter Frequency) = 4000/ (2π*
Analog1_Filter)
Τ (Time Constant) =
Analog1_Filter/4000 (S)
5
1~127
d3.23
25020210
Analog1_Dead
Sets dead zone data for external
analog signal 1
0
0~
8192
d3.24
25020310
Analog1_Offset
Sets offset data for external analog
signal 1
0
-8192
~8192
d3.25
25020410
Analog2_Filter
Used to smooth the input analog
signals
Filter frequency: f=4000/(2π*
Analog1_Filter)
Time Constant: T =
Analog1_Filter/4000 (S)
5
1~127
d3.26
25020510
Analog2_Dead
Sets dead zone data for external
analog signal 2
0
0~
8192
d3.27
25020610
Analog2_Offset
Sets offset data for external analog
signal 2
0
-8192
~8192
d3.28
25020708
Analog_Speed_
Con
Chooses analog-speed channels
0: Invalid analog channel
1: Valid analog channel 1 (AIN1)
2: Valid analog channel 2 (AIN2)
Valid mode -3 and 3
0
/
d3.29
25020A10
Analog_Speed_F
actor
Sets the proportion between
analog signals and output speed
1000
/
d3.30
25020808
Analog_Torque_
Con
Chooses analog-torque channels
0: Invalid analog channel
1: Valid analog channel 1 (AIN1)
2: Valid analog channel 2 (AIN2)
Valid mode 4
0
/
d3.31
25020B10
Analog_Torque_
Factor
Sets the proportion between
analog signals and output speed
1000
/
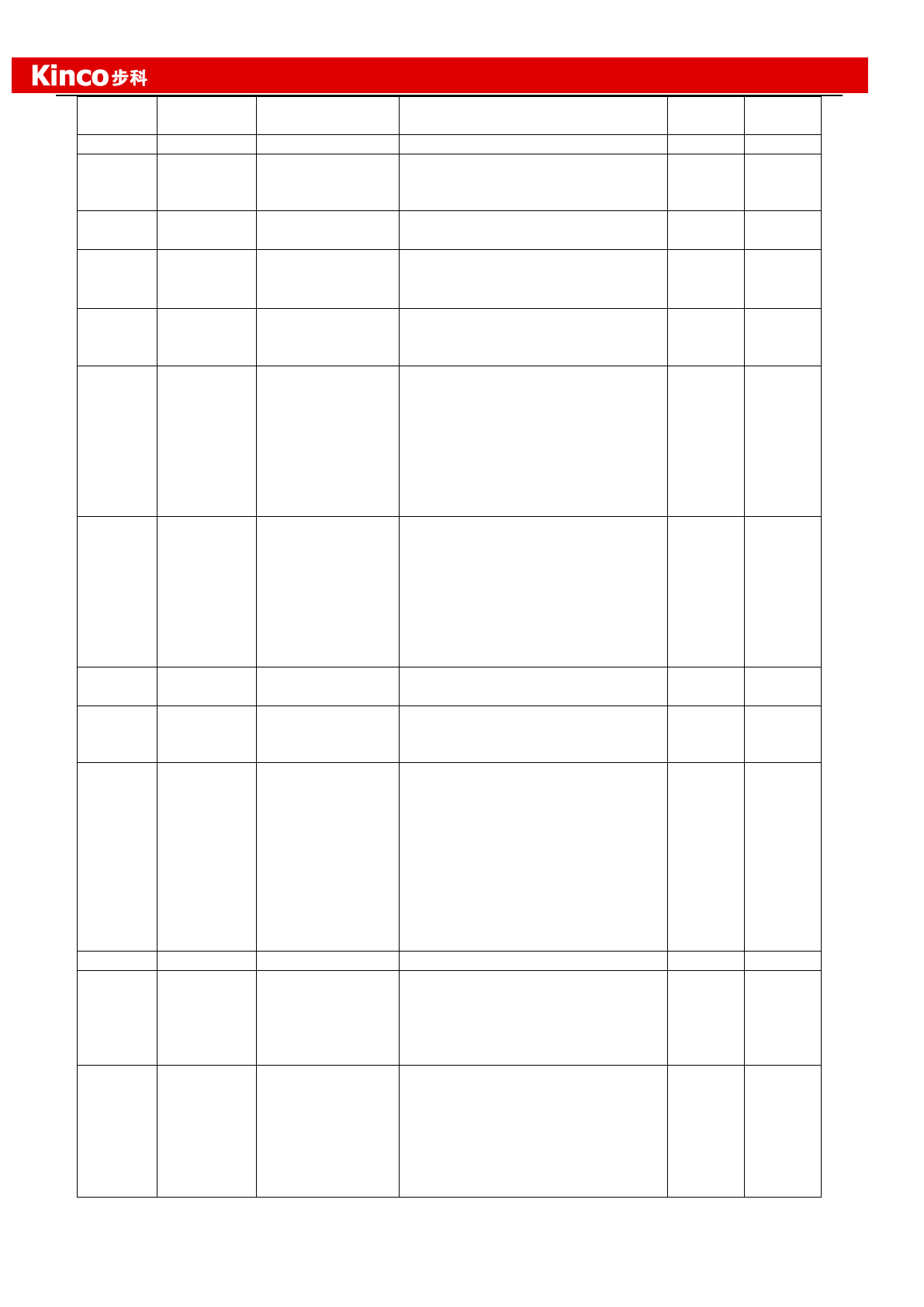
Kinco JD 伺服系列使用手册
56
Kinco FD Series Servo User Manual
Numeric
Display
Internal
Address
Variable Name
Meaning
Default
Value
Range
(current)
d3.32
25020908
Analog_MaxT_C
on
0: No control
1: Max. torque controlled by AIN 1
2: Max. torque controlled by AIN 2
0
/
d3.33
25020C10
Analog_MaxT_F
actor
Indicates the max torque factor on
analog signal control
8192
/
d3.34
25080110
Gear_Factor
Indicates the numerator to set
electronic gears when the
operation mode is -4
1000
-32767
~
32767
d3.35
25080210
Gear_Divider
Indicates the denominator to set
electronic gears when the
operation mode is -4
1000
1~
32767
d3.36
25080308
PD_CW
Pulse mode control
0...CW/CCW
1...Pulse/Direction
2...Incremental encoder
Note:After changing this
parameter,it needs to save by
d2.00/d3.00/d5.00 and then reboot
driver.
1
/
d3.37
25080610
PD_Filter
To flat the input pulse.
Filter frequency: f=1000/(2π*
PD_Filter)
Time constant: T = PD_Filter/1000
Unit: S
Note: If you adjust this filter
parameter during the operation,
some pulses may be lost.
3
1~
32767
d3.38
25080810
Frequency_Chec
k
Indicates the limitation on pulse
input frequency (k Hz)
600
0~600
d3.39
25080910
PD_ReachT
Indicates the position reached time
window in the pulse mode
Unit: mS
10
0~
32767
d3.40
2FF10108
Din_Position_Sel
ect_L
Select which internal position will
be set.(The range of L is 0-7)
Din_Pos0
Din_Pos1
Din_Pos2
Din_Pos3
Din_Pos4
Din_Pos5
Din_Pos6
Din_Pos7
0
d3.41
2FF10210
Din_Position_M
Refer to d3.42
0
d3.42
2FF10310
Din_Position_N
The position of internal position set
in Din_Position_Select_L
Din_Pos =
Din_Position_M*10000+Din_Positi
on_N
0
d3.43
20200F10
Din_Control_Wor
d
Absolute positioning/Relative
positionin gsetting
2F:Absolute positioning
4F:Relative positioning
Note:This parameter needs to
save and reboot driver after
change.
2F
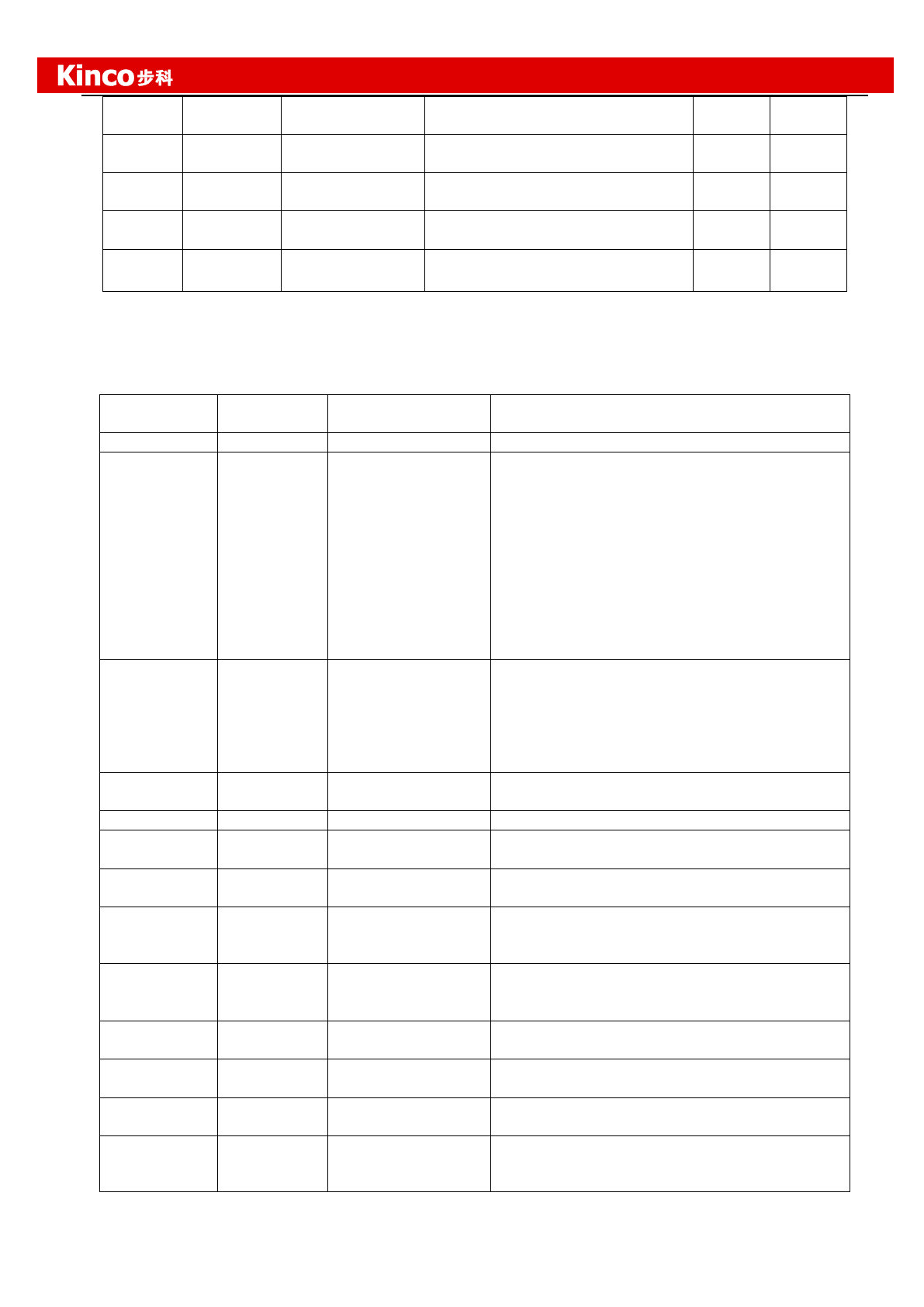
Kinco JD 伺服系列使用手册
57
Kinco FD Series Servo User Manual
Numeric
Display
Internal
Address
Variable Name
Meaning
Default
Value
Range
d3.44
20201810
Din_Speed4_RP
M
Multi-speed control: 4 [rpm]
0
d3.45
20201910
Din_Speed5_RP
M
Multi-speed control: 5 [rpm]
0
d3.46
20201A10
Din_Speed6_RP
M
Multi-speed control: 6 [rpm]
0
d3.47
20201B10
Din_Speed7_RP
M
Multi-speed control: 7 [rpm]
0
Parameter List: Group F004 (To Set Motor Parameters)
Numeric
display
Internal
Address
Variable Name
Meaning
d4.00
2FF00308
Store_Motor_Data
1: Stores the set motor parameters
d4.01
64100110
Motor_Num
Host computer (ASCII code) numerical
display (hexadecimal)
“00”..... ..... ...303.0
About the motor number please refer to chapter
6.1.1.
Note: 1.Set the motor parameters refer to
chapter 6 before operating.
2.It must use capital letter when set this
parameter by PC.
3.It needs to save by d4.00 and reboot driver
after changing this parameter.
d4.02
64100208
Feedback_Type
Type of encoders
001.1: Differential ABZ and differential UVW
signals
001.0: Differential ABZ and UVW signals of TTL
000.1: ABZ of TTL and differential UVW signals
000.0: ABZ of TTL and UVW signals of TTl
d4.03
64100508
Motor_Poles
Number of motor poles pairs
[2p]
d4.04
64100608
Commu_Mode
Searching excitation mode
d4.05
64100710
Commu_Curr
Searching excitation current
[dec]
d4.06
64100810
Commu_Delay
Delay in searching excitation
[mS]
d4.07
64100910
Motor_IIt_I
Indicates current settings on overheat
protection of motors
Ir[Arms]*1.414*10
d4.08
64100A10
Motor_IIt_Filter
Indicates time settings on overheat protection
of motors
Time: N*256/1000 Unit: S
d4.09
64100B10
Imax_Motor
Indicates max peak current of motors
I[Apeak]*10
d4.10
64100C10
L_Motor
Indicates phase inductance of motors
L[mH]*10
d4.11
64100D08
R_Motor
Indicates phase resistance of motors
R[Ω]*10
d4.12
64100E10
Ke_Motor
Indicates the reverse electromotive force of
motors
Ke[Vp/krpm]*10
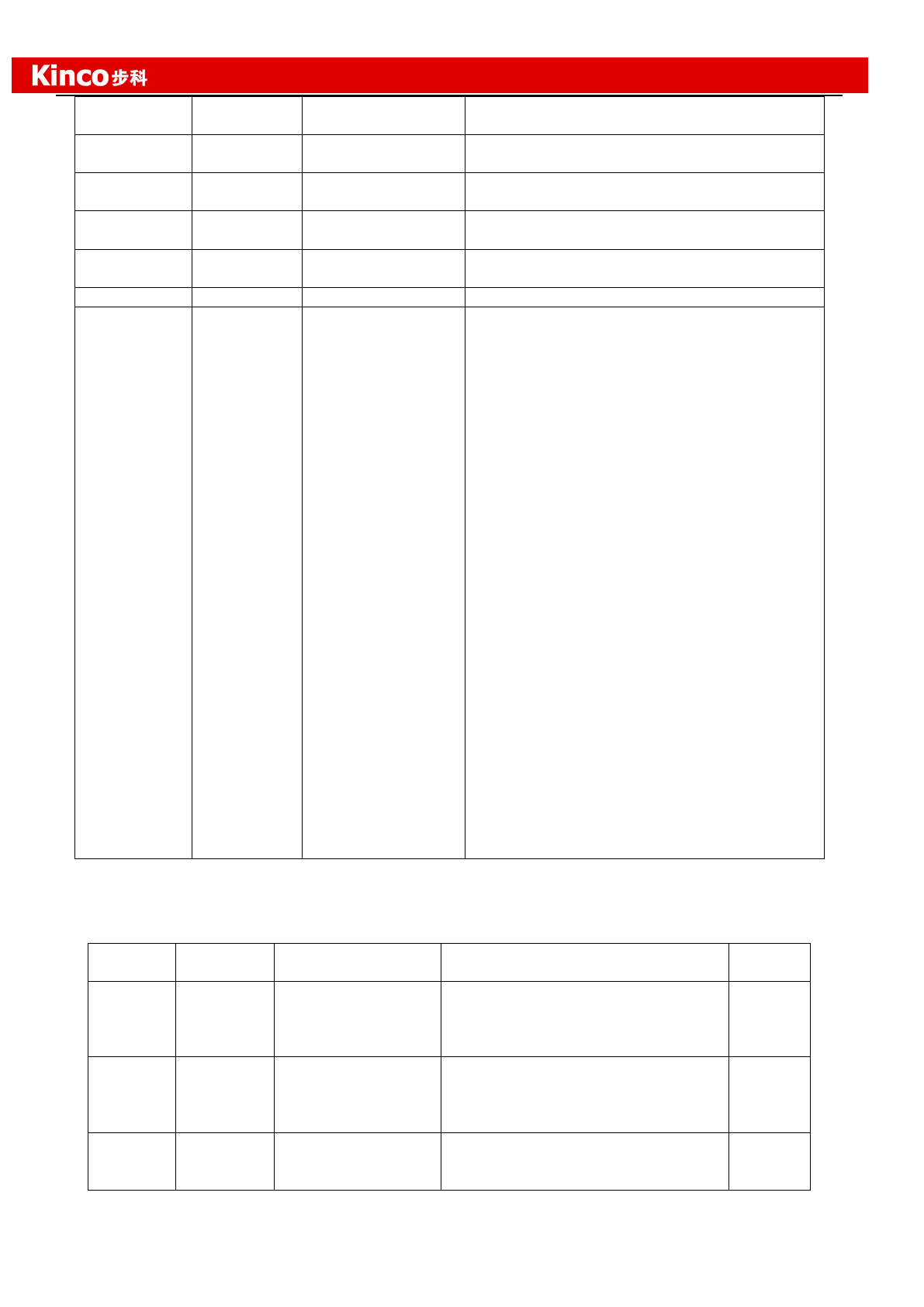
Kinco JD 伺服系列使用手册
58
Kinco FD Series Servo User Manual
Numeric
display
Internal
Address
Variable Name
Meaning
d4.13
64100F10
Kt_Motor
Indicates the torque coefficient of motors
Kt[Nm/Arms]*100
d4.14
64101010
Jr_Motor
Indicates the rotor inertia of motors
Jr[kgm^2]*1 000 000
d4.15
64101110
Brake_Duty_Cycle
Indicates the duty cycle of contracting brakes
0~2500[0…100%]
d4.16
64101210
Brake_Delay
Indicates the delay time of contracting brakes
Default value: 150 ms
d4.17
64101308
Invert_Dir_Motor
Indicates the rotation direction of motors
d4.18
64101610
Motor_Using
Current using motor type.
PC Software Numeric Display Model
"K0"....................304.B…....SMH60S-0020-30
"K1"...................314.B…….SMH60S-0040-30
"K2"...................324.B…….SMH80S-0075-30
"K3"...................334.B…….SMH80S-0100-30
"K4"...................344.B……SMH110D-0105-20
"K5"...................354.B……SMH110D-0125-30
"K6"..................364.B….....SMH110D-0126-20
"K7"……….......374.B…….SMH110D-0126-30
"K8"…………...384.B.........SMH110D-0157-30
"K9"..................394.B…....SMH110D-0188-30
KB"……..……...424.B…....SMH130D-0105-20
“KC"…………...434.B…….SMH130D-0157-20
“KD"…………...444.B…….SMH130D-0210-20
“KE"…………...454.B…....SMH150D-0230-20
"S0"………...305.3…..130D-0105-20AAK-2LS
"S1"..............315.3…..130D-0157-20AAK-2LS
"S2"………...325.3….130D-0157-15AAK-2LS
"S3"..............335.3….130D-0200-20AAK-2HS
"S4"..............345.3….130D-0235-15AAK-2HS
"F8"………...384.6…..85S-0045-05AAK-FLFN
"E0"..............304.5………..SME60S-0020-30
"E1"..............314.5……........SME60S-0040-30
"E2".................324.5…………..SME80S-0075-30
Parameter List: Group F005 (To Set Driver Parameters)
Numeric
Display
Internal
Address
Variable Name
Meaning
Default
Value
d5.00
2FF00108
Store_Loop_Data
1: Stores all control parameters
except motor parameters
10: Initializes all control parameters
except motor parameters
0
d5.01
100B0008
ID_Com
Station No. of Drivers
Note: To change this parameter, you
need to save it with the address
“d5.00”, and restart it later.
1
d5.02
2FE00010
RS232_Bandrate
Set the baud rate of RS232 port
540 19200
270 38400
270
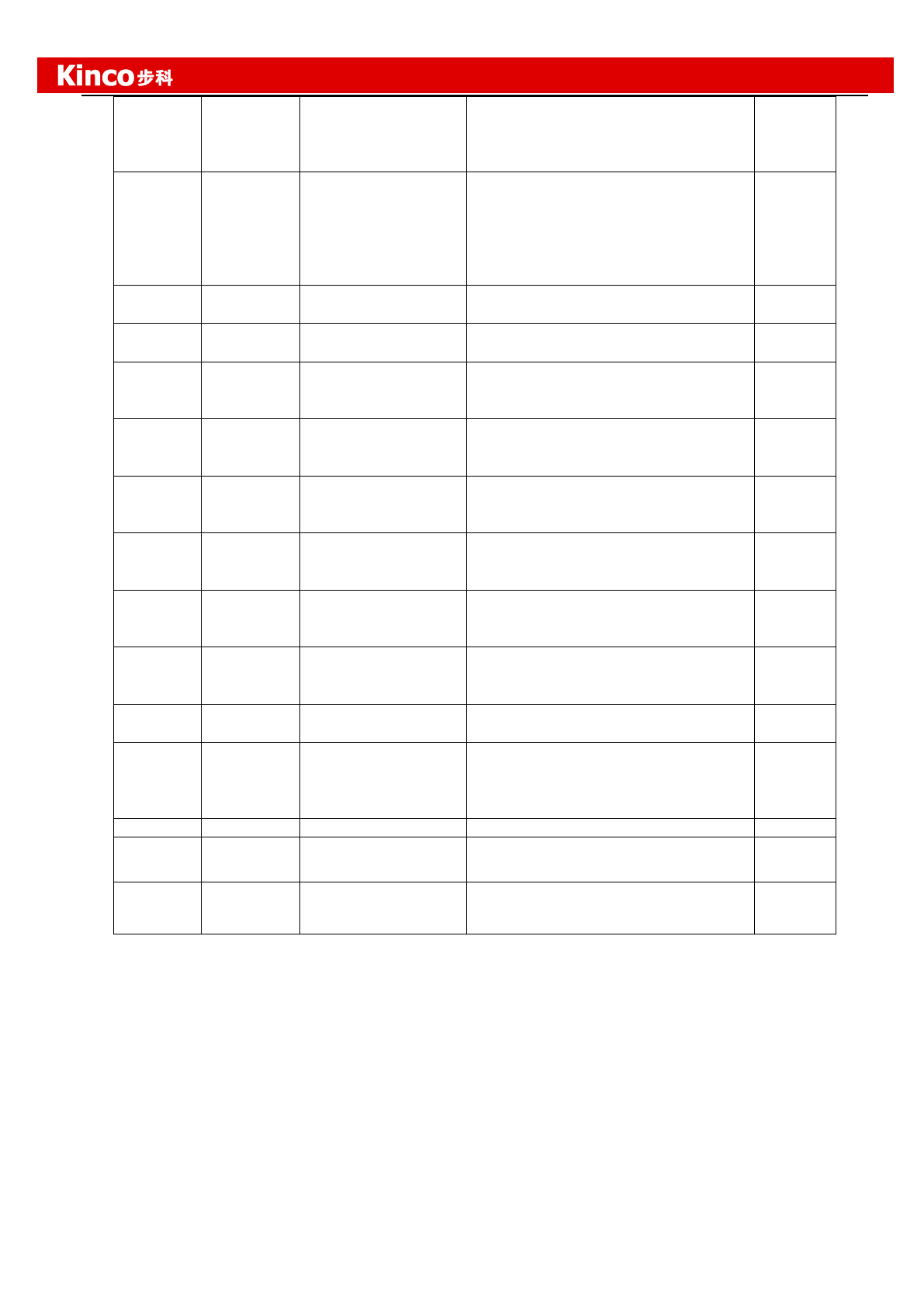
Kinco JD 伺服系列使用手册
59
Kinco FD Series Servo User Manual
90 115200
Note: To change this parameter, you
need to save it with the address
“d5.00”, and restarts it later.
d5.03
2FE10010
U2BRG
Sets the baud rate of RS232 port
540 19200
270 38400
90 115200
You need not restart it,but it can’t be
saved.
270
d5.04
60F70110
Chop_Resistor
Indicates the values of braking
resistors
0
d5.05
60F70210
Chop_Power_Rated
Indicates the nominal power of a
braking resistor
0
d5.06
60F70310
Chop_Filter
Indicates the time constant of a
braking resistor
Time: N*256/1000 Unit: S
60
d5.07
25010110
ADC_Shift_U
Indicates data configuration of U
phase shift.
Note:Factory parameters
/
d5.08
25010210
ADC_Shift_V
Indicates data configuration of V
phase shift
Note:Factory parameters
/
d5.09
30000110
Voltage_200
ADC original data when DC bus
voltage is 200 V
Note:Factory parameters
/
d5.10
30000210
Voltage_360
ADC original data when DC bus
voltage is 360 V
Note:Factory parameters
/
d5.11
60F60610
Comm_Shift_UVW
Indicates the excitation pointer of a
motor
Note:Factory parameters
/
d5.12
26000010
Error_Mask
Indicates error masks
Note:Factory parameters
FFF.F
d5.13
60F70510
RELAY_Time
Indicates the relay operating time of
capacitor short-circuits
Unit: mS
Note:Factory parameters
150
d5.14
2FF00408
Key_Address_F001
Sets numeric display data
/
d5.15
65100B08
RS232_Loop_Enabl
e
0:1 to 1
1:1 to N
0
d5.16
2FFD0010
User_Secret
User password.16bits.
0~
65535
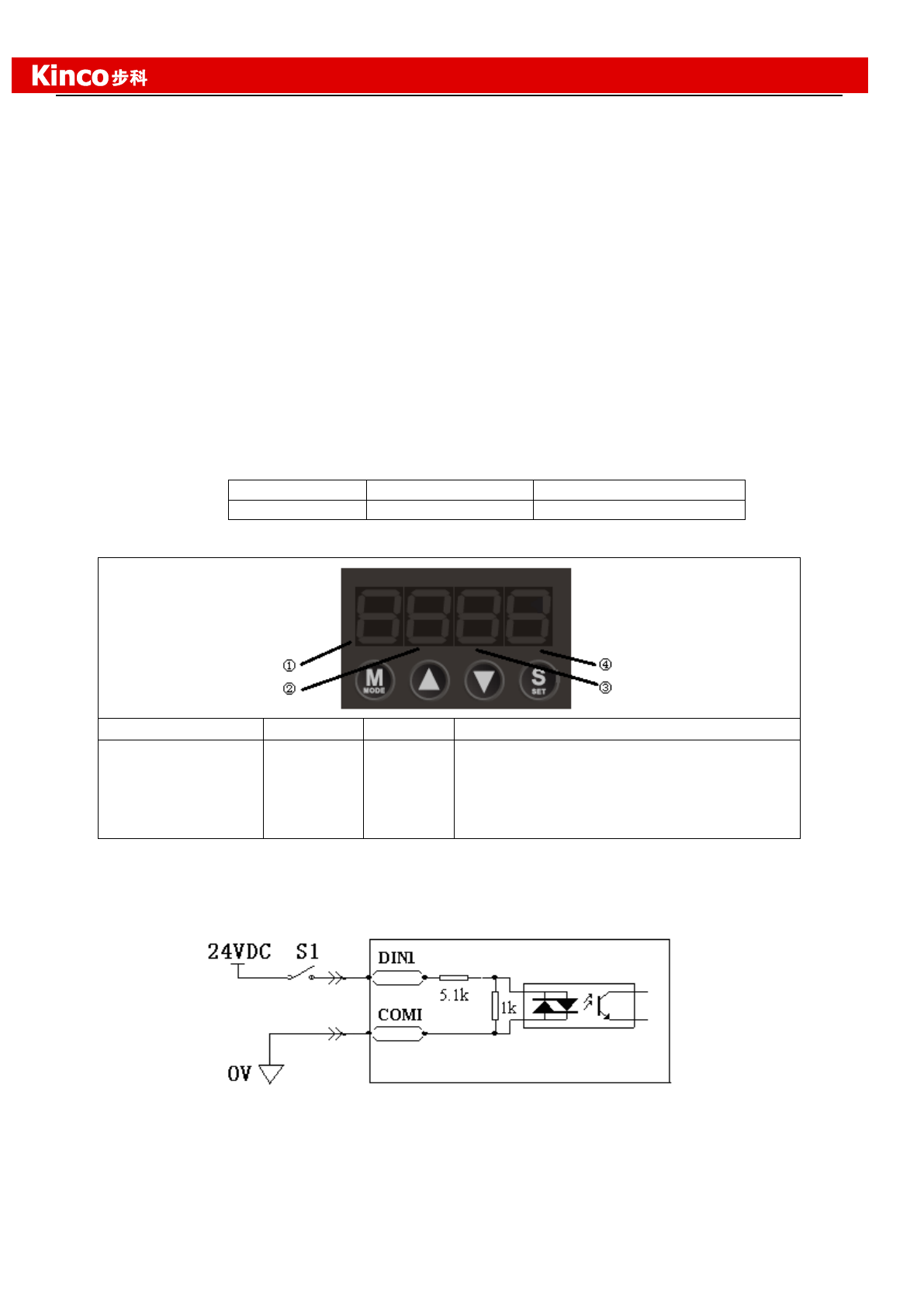
Kinco JD 伺服系列使用手册
60
Kinco FD Series Servo User Manual
Chapter 7 Operation on Input/Output Ports
KINCO FD servo driver has 7 digital input ports (a digital input port can receive high-level or low-level
signals, depending on whether high-level or low-level signals are chosen at the COM terminal) and 5 digital
output ports,OUT1-OUT4 ports can drive 100 mA load, and BR port can drive 500 mA load, and can directly
drive the internal contracting brake device. You can freely configure all functions on digital input/output ports
according to application requirements.
7.1 Digital Input
7.1.1 Polarity Control on Digital Input Signals
Note:all the digital inputs are normally open by default.
Table 7-1 Simplified IO polarity setting variables
Numeric Display
Variable Name
Meaning
d3.08
Dio_Polarity
Sets IO polarity
Table 7-2 Polarity setting methods for digital input signals
①
②
③
④
Input/output port
selection
0: Output port
1: Input port
Channel
selection
Input: 1-8
Output: 1-7
Reserved
0:The inputs are normally close
1:The inputs are normally open
Others:Check the current status
Example 7-1: Polarity Setting for Digital Input Signal DIN1
Fig.7-1 Polarity setting for digital input signal DIN1
7.1.1.1 Use panel to change the polarity
Table 7-3 Polarity setting for digital input signal DIN1
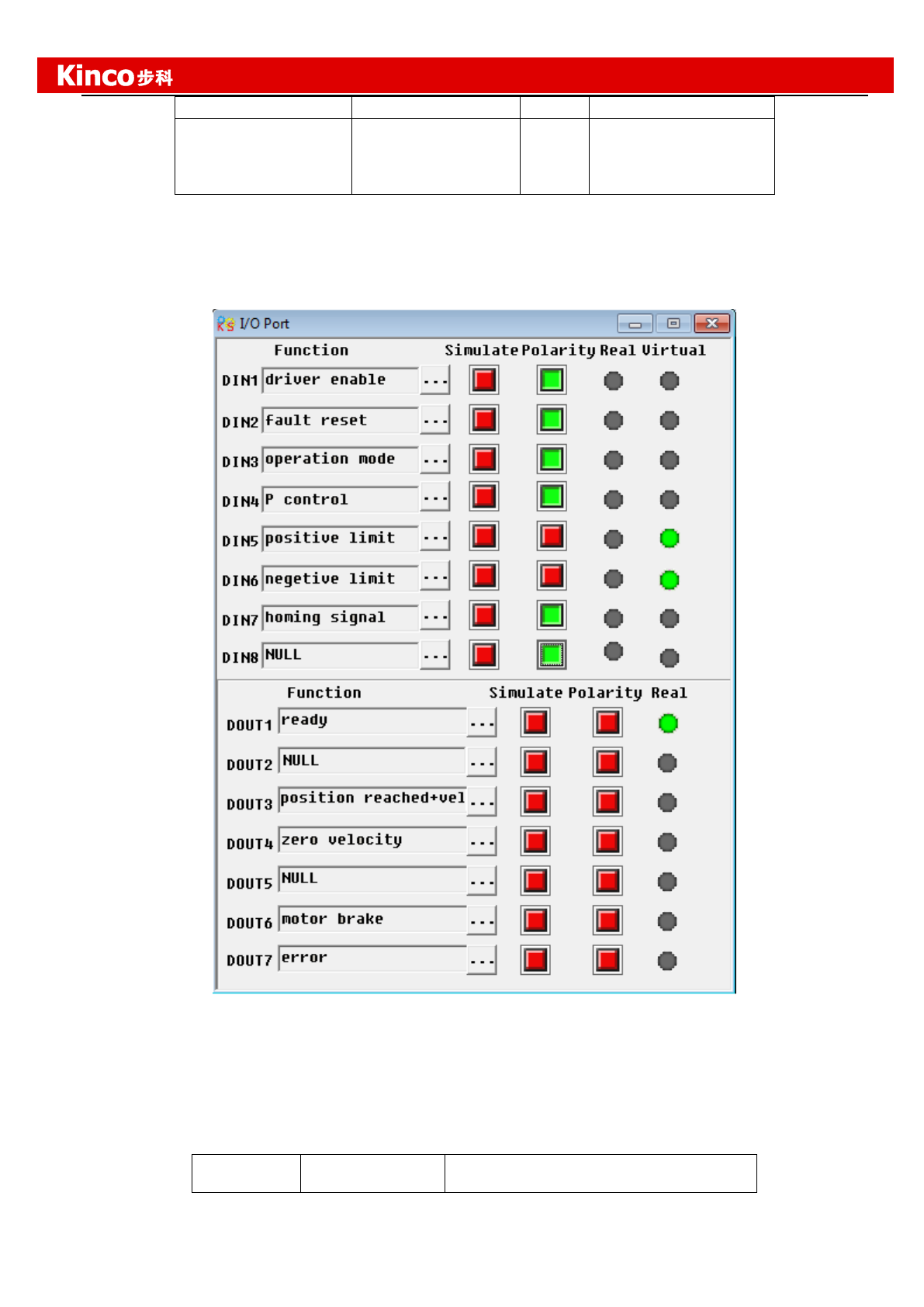
Kinco JD 伺服系列使用手册
61
Kinco FD Series Servo User Manual
①
②
③
④
Input/output port
selection
Set to 1 (input port
selected)
Channel selection
Set to 1 (DIN 1
selected)
Reserv
ed
0: DIN1 is enabled
when S1 opens
1: DIN1 is enabled
when S1 closes
Namely, if d3.08 is set to “110.0”, it indicates that DIN1 is normally close.If d3.08 is set to “110.1”, it indicates
that DIN1 is normally open.
7.1.1.2:Use PC software to change polarity
Use the PC software to connect to FD Servo and then open I/O port.The LED under polarity are green,it
indicates that the inputs are normally open.As following figure,if you change the LED of DIN5 and DIN6 into
red,it indicates that DIN5 and DIN6 are normally close.
Fig.7-2 Digital I/O in PC software
7.1.2 Simulation of Digital Input Signals
Table 7-4 IO simulation variable
Numeric
Display
Variable Name
Meaning
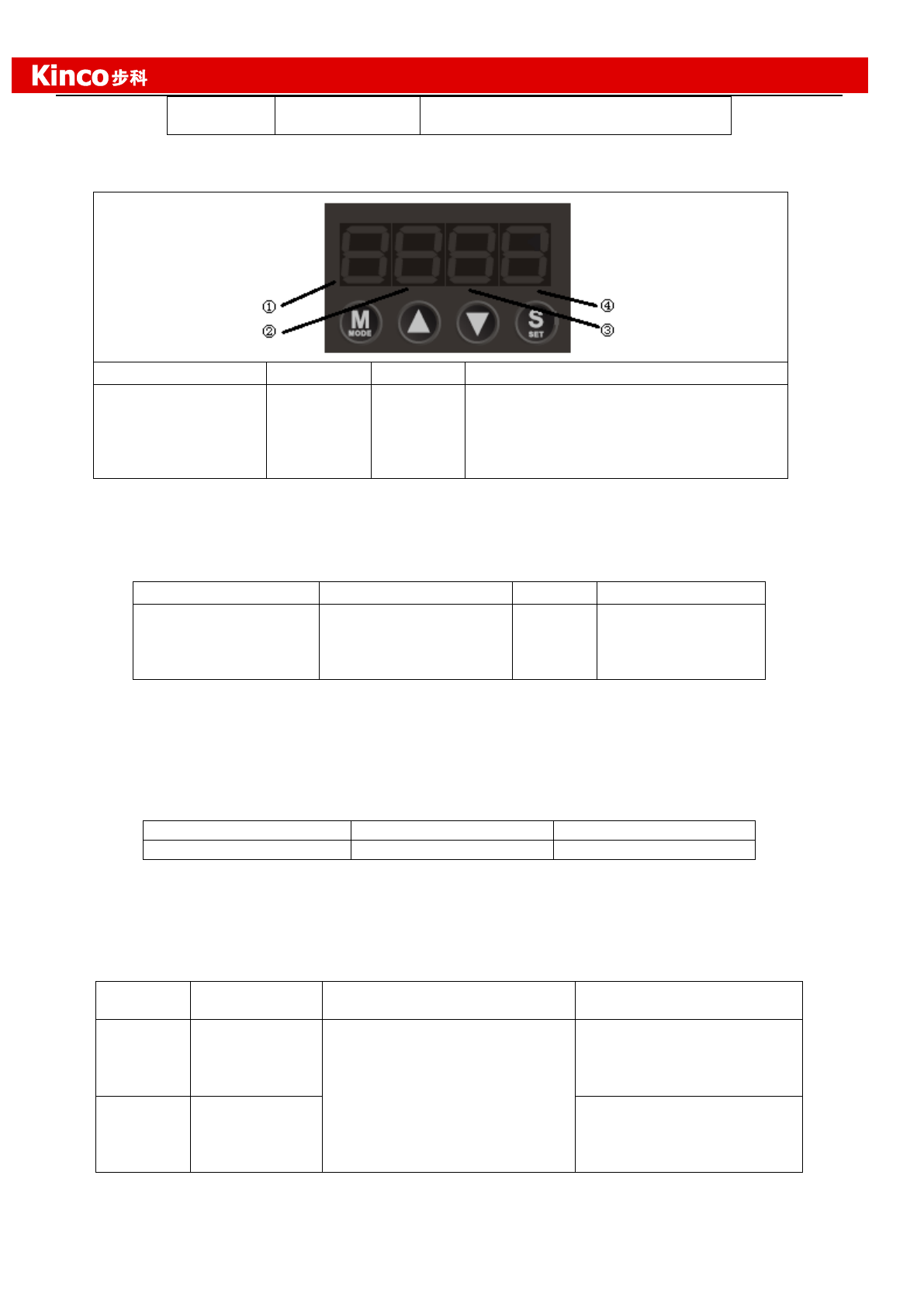
Kinco JD 伺服系列使用手册
62
Kinco FD Series Servo User Manual
d3.09
Dio_Simulate
Simulates input signals, and enforces
output signals for outputting
Dio_Simulate (IO simulation) is for the software to simulate inputting of a valid signal. “1” indicates that the
input signal is valid, and “0” indicates that the input signal is invalid.
Table 7-5 Settings on simulation of digital input signals
①
②
③
④
Input/output port
selection
0: output port
1: input port
Channel
selection
Input: 1-8
Output: 1-7
Reserved
0: No input signal is simulated, and no
output signal is compulsorily outputted
1: Input signal is simulated, and output
signal is outputted compulsorily
Other: Check the current status
Example 7-2: Simulate digital input DIN1
Table 7-6: Simulate digital input DIN1
①
②
③
④
Input/output port
selection
Set to 1 (input port
selected)
Channel selection
Set to 1 (DIN 1 selected)
Reserve
d
0: Invalid DIN1
simulation
1: Valid DIN1
simulation
Namely, if d3.09 is set to “110.0”, it indicates that no DIN1 input signals are simulated; if d3.09 is set to “110.1”,
it indicates that DIN1 input signals are simulated.
7.1.3 Status Display of Digital Input Signals
Table 7-7 Variables for status display of digital input signals
Numeric Display
Variable Name
Meaning
d1.11
Din_Status
Status of input ports
Din_Status (hexadecimal) is used to display the status of the actually input external signals in real time.
7.1.4 Addresses & Functions of Digital Input Signals
Table 7-8 Addresses & default functions of digital input signals
Numeric
Display
Variable Name
Meaning
Default Value
d3.01
Din1_Function
000.1: Driver enable
000.2: Driver fault reset
000.4: Operation mode control
000.8: P control for velocity loop
001.0: Position positive limit
002.0: Position negative limit
004.0: Homing signal
008.0: Reverse speed demand
000.1 (Driver enable)
d3.02
Din2_Function
000.2 (Driver fault reset)
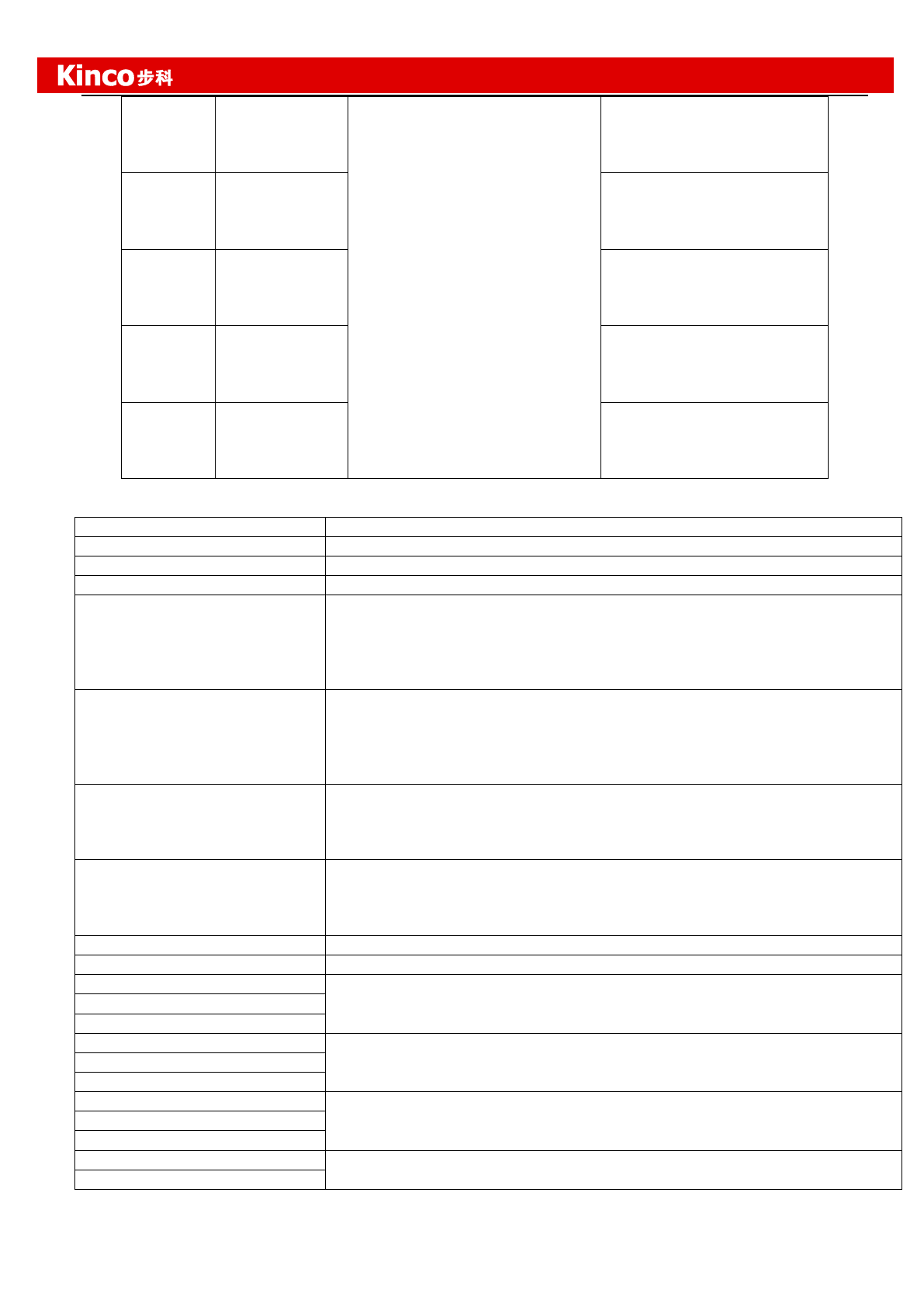
Kinco JD 伺服系列使用手册
63
Kinco FD Series Servo User Manual
d3.03
Din3_Function
010.0: Internal speed control 0
020.0: Internal speed control 1
800.1: Internal speed control 2
040.0: Internal position control 0
080.0: Internal position control 1
800.2: Internal position control 2
800.4 Multi Din 0
800.8 Multi Din 1
801.0 Multi Din 2
802.0 Gain switch 0
804.0 Gain switch 1
100.0: Quick stop
200.0: Start homing
400.0: Activate command
Note:DinX_Function(X is 1-7) is
used to define the function of
digital inputs.
000.4 (Operation mode
control)
d3.04
Din4_Function
000.8 (P control for velocity
loop)
d3.05
Din5_Function
001.0 (Position positive limit)
d3.06
Din6_Function
002.0 (Position negative
limit)
d3.07
Din7_Function
004.0 (Homing signal)
Table 7-9 Meaning of defined functions of digital input signals
Function
Meaning
Disable
Used to cancel the function of this digital input.
Driver enable
By default, the driver enable signal is valid, and the motor shaft is locked.
Driver fault reset
Signals on the rising edge are valid, and alarms are cleared.
Operation mode control
To switch between two operation modes.
You can freely determine the operation modes corresponding to valid signals
and invalid signals by performing settings through d3.16 Din_Mode0 (choose
0 for operation mode) of Group F003 and Din_Mode1 (choose 1 for operation
mode) of Group F003.
P control for velocity loop
Indicates the control on stopping integration in velocity loop. The control is
applied in the occasion where high-speed system stop occurs, but
overshooting is not expected.
Note: In the “-3” mode, if the signal is valid, fixed errors occur between the
actual speed and target speed.
Position positive limit
Indicates the limit of forward running of motors (normally closed contact by
default).
By default, the driver regards position positive limits as valid, and polarity can
be modified to adjust to normally open switches.
Position negative limit
Indicates the limit of inverted running of motors (normally closed contact by
default).
By default, the driver regards position negative limits as valid, and polarity can
be modified to adjust to normally open switches.
Homing signal
To find origins of motors.
Reverse speed demand
To reverse the target speed in the speed mode ("-3" or “3”).
Internal speed control 0
To control internal multiple speeds.
Note: For details, see Section 7.5 Internal Multi-Speed Control.
Internal speed control 1
Internal speed control 2
Internal position control 0
To control internal multiple positions.
Note: For details, see Section 7.4 Internal Multi-Position Control.
Internal position control 1
Internal position control 2
Multi Din 0
To switch multiple electronic gear
Multi Din 1
Multi Din 2
Gain switch 0
To switch multiple gain parameters(P-gain of velocity loop,i-gain of velocity
loop,p-gain of position loop)
Gain switch 1
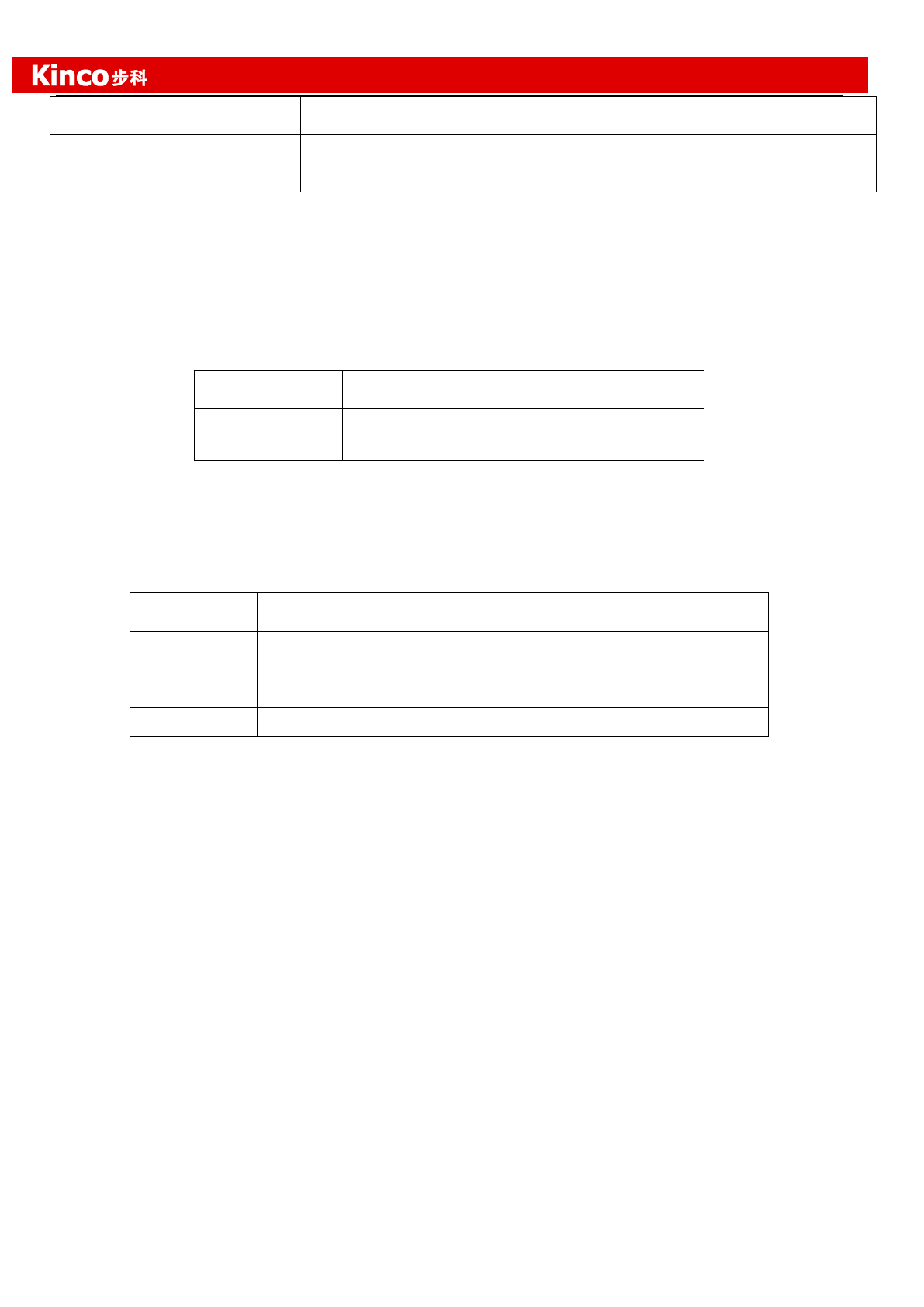
Kinco JD 伺服系列使用手册
64
Kinco FD Series Servo User Manual
Quick stop
When the signal is valid, the motor shaft releases.
After the signal is removed, the driver requires re-enabling.
Start homing
When the rising edge of the signal is detected,it will start homing command.
Activate command
When the rising edge of the signal is detected,it will activate the internal
position control
Example 7-3: Driver Enable Setting
Requirement: The “driver enable” function is controlled through an external digital output port. In this example,
the digital input port DIN1 is defined as the “driver enable” function. Table 7-10 shows the setup method.
Table 7-10 Digital Input Port DIN1 Defined as the “Driver Enable” Function
Numeric Display
Variable Name
Parameter
Settings
d3.01
Din1_Function
Set to 000.1
d3.00
Store_Loop_Data
Set to 1
Note: Any digital output of DIN1-7 can be defined as “driver enable”, and is set to 000.1, that is, bit 0 is valid.
Requirement: Enable the function of automatically powering on the driver by setting internal parameters in
drivers instead of external digital input ports. Table 7-11 describes the setup method.
Table 7-11 Enabling the function of automatically powering on the driver by setting internal parameters in
drivers
Numeric
Display
Variable Name
Parameter Settings
d3.01- d3.07
DinX_ Function
(1~7)
None of the digital input port can be set to
000.1, that is, the Enable function is not
controlled by any digital input port.
d3.10
Switch_On_Auto
Set to 1
d3.00
Store_Loop_Data
Set to 1
Users can also use PC software to define I/O functions.Open the I/O port menu,click the button in
red box as shown in following figure,then select the required function.
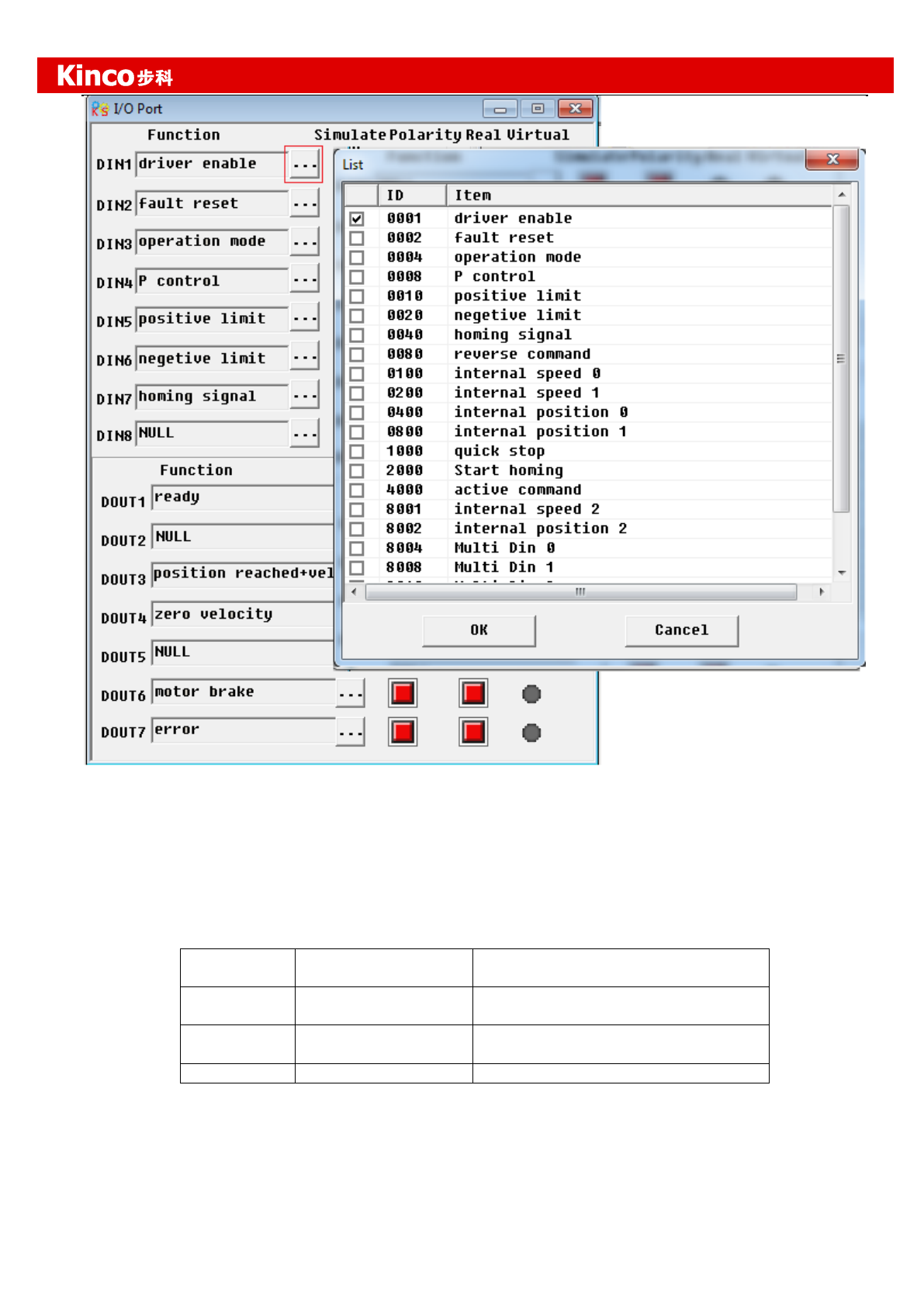
Kinco JD 伺服系列使用手册
65
Kinco FD Series Servo User Manual
Fig.7-2 Set digital I/O function in PC software
Example 7-4: Disabling Position Positive/Negative Limit Settings
When the driver is delivered, the DIN5 of the motor is the position positive limit and DIN6 is the position
negative limit by default. If there are no external position positive/negative limit switches, this function must be
disabled so that the servo driver can work properly. Table 7-12 describes the setup method.
Table 7-12: Disabling position positive/negative limit settings
Numeric
Display
Variable Name
Parameter Settings
d3.05
Din5_Function
Change the default value 001.0
(position positive limit) to 000.0
d3.06
Din6_Function
Change the default value 002.0
(position negative limit) to 000.0
d3.00
Store_Loop_Data
Set to 1
Example 7-5: Operation Mode Control on Drivers
Requirements: Defines the input port DIN3 as the operation mode control on drivers, and the operation mode
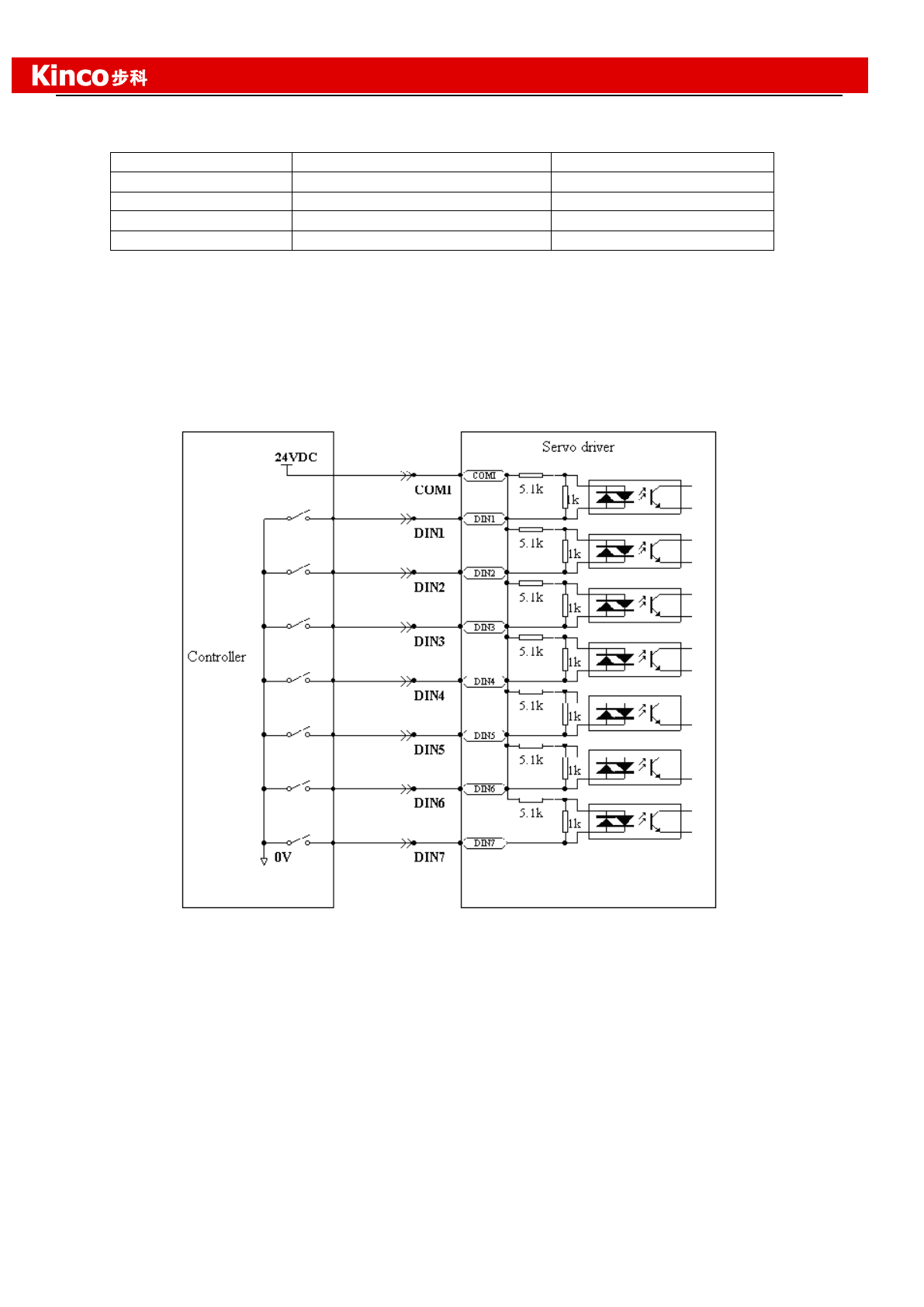
Kinco JD 伺服系列使用手册
66
Kinco FD Series Servo User Manual
is “-4” (pulse control mode) when DIN3 fails, and is “-3” (instantaneous speed mode) when DIN3 is valid.
Table 7-13 describes the setup method.
Table 7-13 Settings on operation mode control on drivers
Numeric Display
Variable Name
Parameter Settings
d3.03
Din3_Function
Set to 000.4
d3.16
Din_Mode0
Set to 0.004 (-4)
d3.17
Din_Mode1
Set to 0.003 (-3)
d3.00
Store_Loop_Data
Set to 1
Note: If the driver is required to operate in some mode with power on, one of the digital input must be set as
function “Operation Mode Control”. Then you can set the operation modes that require in the parameters
d3.16 or d3.37 in Group F003.
7.1.5 Wirings of Digital Input Port
1. NPN wiring diagram (to the controller that supports low level output)
Fig.7-4 NPN wiring diagram (to the controller that supports low level output)
2. PNP wiring diagram (to the controller that supports high level output)
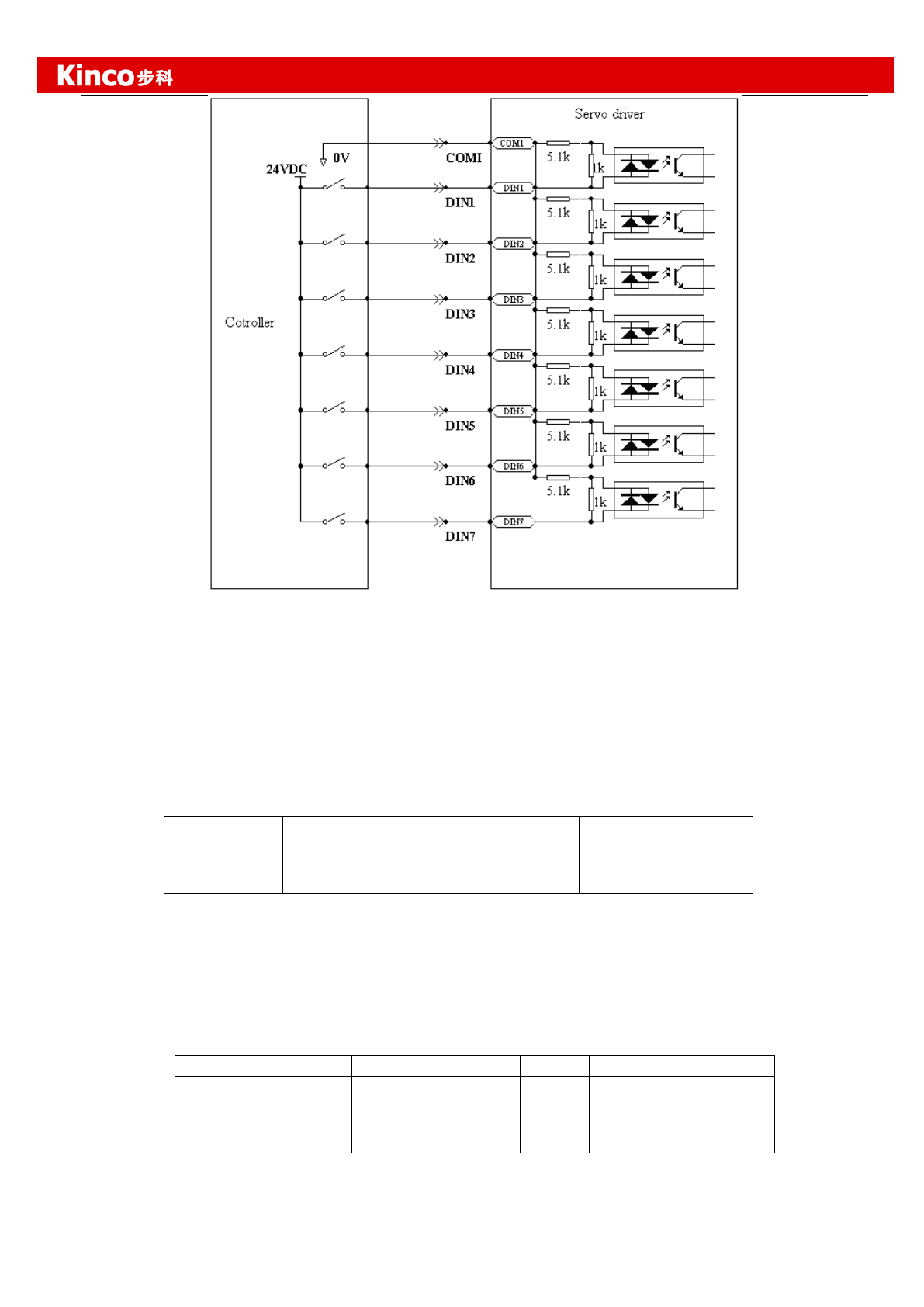
Kinco JD 伺服系列使用手册
67
Kinco FD Series Servo User Manual
Fig.7-5 PNP wiring diagram (to the controller that supports high level output)
7.2 Digital Output
7.2.1 Polarity Control on Digital Output Signals
Note:All the digital output are normally open by default.
Table 7-14 Variables for setting simplified IO polarity
Numeric
Display
Variable Name
Meaning
d3.08
Dio_Polarity
Sets IO polarity
Dio_Polarity (simplified IO polarity settings) is used to set the polarity of valid digital output signals. The
number “1” indicates normally open, and “0” indicates normally close.Default is 1.
Example 7-6: Polarity setting for digital output OUT1
7.2.1.1:Use panel to change polarity
Table 7-15 Polarity setting for digital output OUT1(Default is ready function)
①
②
③
④
Input/output port
selection
Set to 0 (Output port
selected)
Channel selection
Set to 1 (OUT1
selected)
Reserv
ed
0: OUT1 is normally
close
1: OUT1 is normally
open.
Namely, if d3.08 is set to “010.0”, it indicates that OUT1 is normally close.If d3.08 is set to “010.1”, it indicates
that OUT1 is normally open.
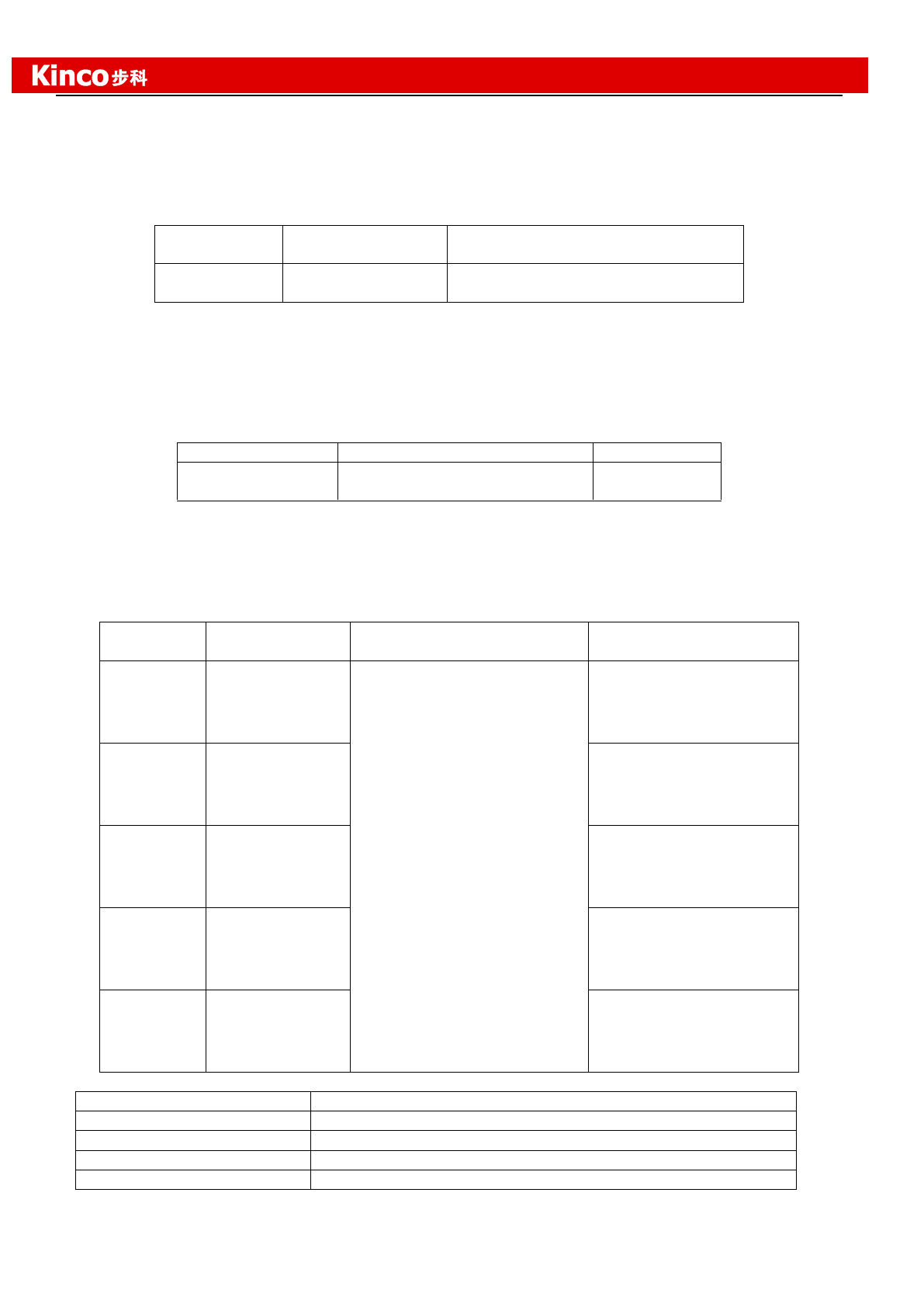
Kinco JD 伺服系列使用手册
68
Kinco FD Series Servo User Manual
7.2.1.2:Use PC software to change polarity,please refer to 7.1.1.2.
7.2.2 Simulation of Digital Output Signals(More details please refer to 7.1.2)
Table 7-16 IO simulation variables
Numeric
Display
Variable Name
Meaning
d3.09
Dio_Simulate
Simulates input signals, and force the
output signal
Dio_Simulate (IO simulation) is to simulate the output of a valid signal. The number “1” indicates that the
output signal is valid, and “0” indicates that the output signal is invalid.
7.2.3 Status Display of Digital Output Signals
Table 7-17 Variables for status display of digital output signals
Numeric Display
Variable Name
Meaning
d1.12
Dout_Status
Status of an
output port
Din_Status (hexadecimal) displays the status of actual external output signals in real time.
7.2.4 Addresses and Functions of Digital Output Signals
Table 7-18 Addresses and default functions of digital output signals
Numeric
Display
Variable Name
Meaning
Default Value
d3.11
Dout1_Function
000.1: Ready
000.2: Error
000.4: Position reached
000.8: Zero velocity
001.0: Motor brake
002.0:Velocity reached
004.0: Index
008.0: The maximum speed
obtained in the torque mode
010.0: PWM ON
020.0: Position limiting
040.0: Reference found
080.0: Reserved
100.0: Multi Dout 0
200.0: Multi Dout 1
400.0: Multi Dout 2
000.1 (Ready)
d3.12
Dout2_Function
000.2 (Error)
d3.13
Dout3_Function
00a.4 (Position
reached/Velocity
reached/Max. velocity
limit)
d3.14
Dout4_Function
000.8 (Zero velocity)
d3.15
Dout5_Function
001.0 (Motor brake)
Table 7-19 Meanings of the functions defined by digital output signals
Function
Meaning
Disable
Cancel the function of this digital output
Ready
The driver is ready for operation.
Error
Alarm signals are output, indicating that the driver is faulty.
Position reached
In the “-4” mode of pulse control, the target position data keeps
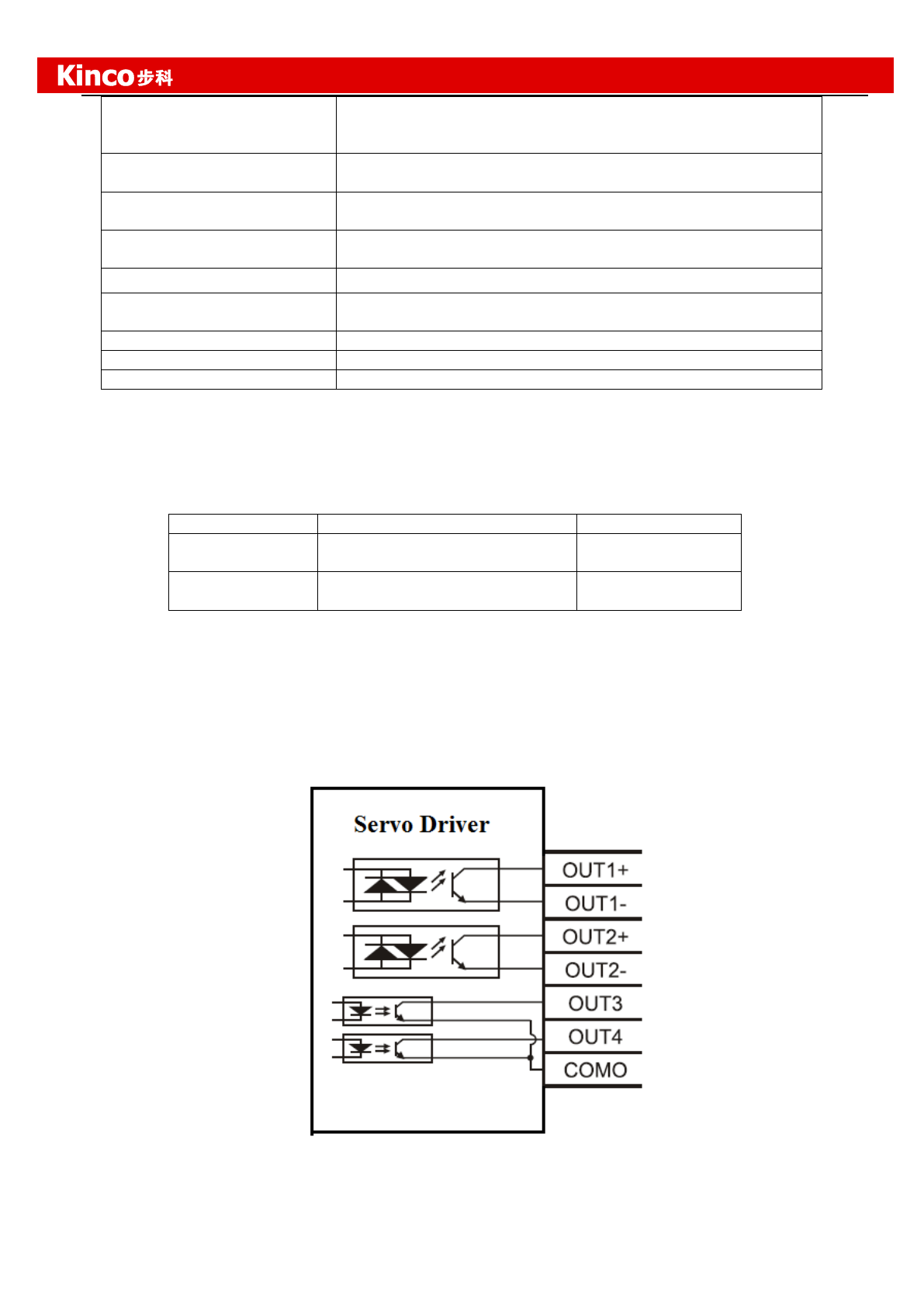
Kinco JD 伺服系列使用手册
69
Kinco FD Series Servo User Manual
unchanged in the window (d3.39) of the time of reaching the
target position, and position errors are within the window of
reaching the target position.
Zero velocity
After the motor is enabled, it is outputted when the motor speed
is 0.
Motor brake
The driver enables the motor, and contracting brake output is
valid.
Velocity reached
In the “-3” or "3” internal speed control mode, signals are output
after they reach the target speed.
Index
Z phase signal output (the speed should not be too high).
Max. velocity limit
In the “4” analog – torque mode, signals are output after the max
restricted speed is reached.
PWM ON
The driver enables the motor.
Motor limiting
Motor is in the status of position limiting.
Reference found
Homing is finished.
Example 7-7: “Ready” settings
Requirement: The OUT1 is defined as the “Ready” function. For details on settings, see Table 7-19。
Table 7-20 “Ready” settings
Numeric Display
Variable Name
Parameter Settings
d3.11
Dout1_Function
Set to 000.1
d3.00
Store_Loop_Data
Set to 1
7.2.5 Wiring of Digital Output Port
1. Internal circuit diagram of digital output ports
Fig.7-6 Internal circuit diagram of digital output
Note:1.OUT3 and OUT4 use the same common terminal(COMO).
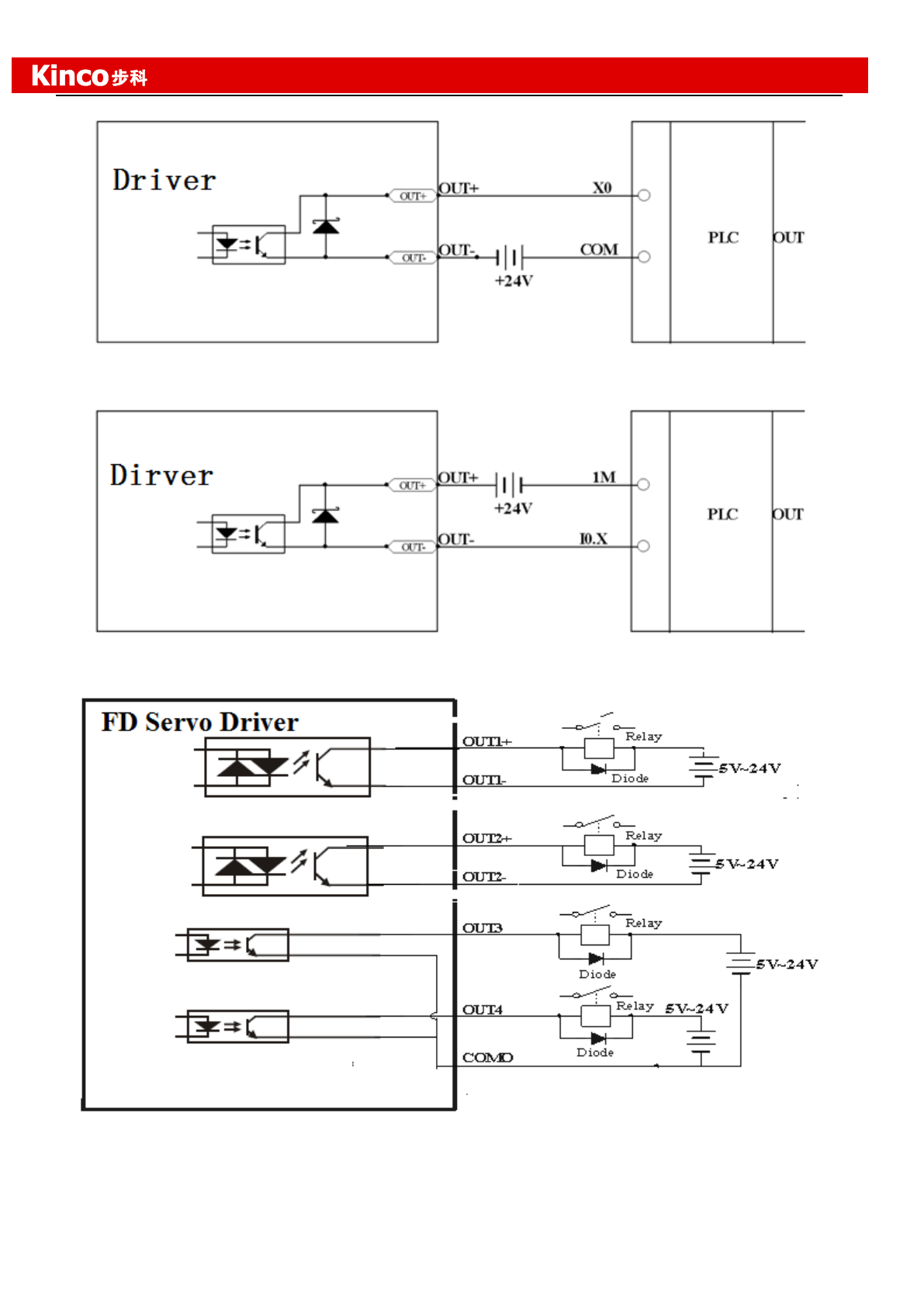
Kinco JD 伺服系列使用手册
70
Kinco FD Series Servo User Manual
2.NPN Wiring Diagram(OUT1-OUT7 all support this)
Fig.7-7 NPN wiring diagram (to controllers that support valid low level input)
3. PNP wiring diagram (Only OUT1,OUT2 and OUT7 support this wiring)
Fig.7-8 PNP wiring diagram (to controllers that support valid low level input))
4. To connect a relay to the digital output port, do remember to connect a diode in inverse parallel, as shown
in Fig.7-9.
Fig.7-9 Connect a relay to the digital output port
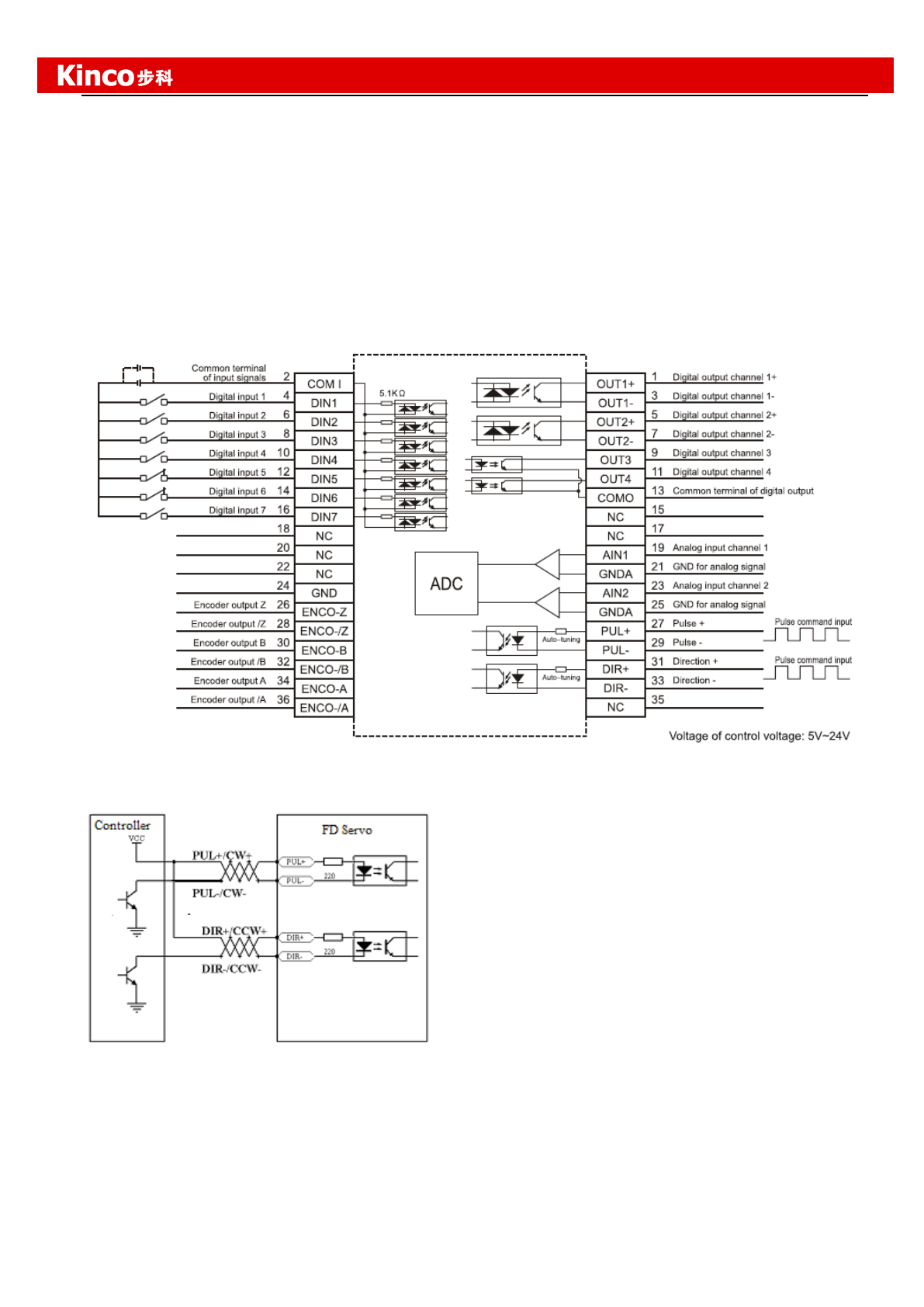
Kinco JD 伺服系列使用手册
71
Kinco FD Series Servo User Manual
Chapter 8 Operation Mode
8.1 Pulse Control Mode (“-4” Mode)
8.1.1 Wiring in Pulse Control Mode
1. Wiring diagram of FD driver in pulse control mode
Fig. 8-1 Wiring diagram of FD driver in pulse control mode
2.Common anode connection (to controllers that support valid low level output)
Fig. 8-2 Common anode connection (to controllers that support valid low level output)
3. Common cathode connection (to controllers that support valid high level output)
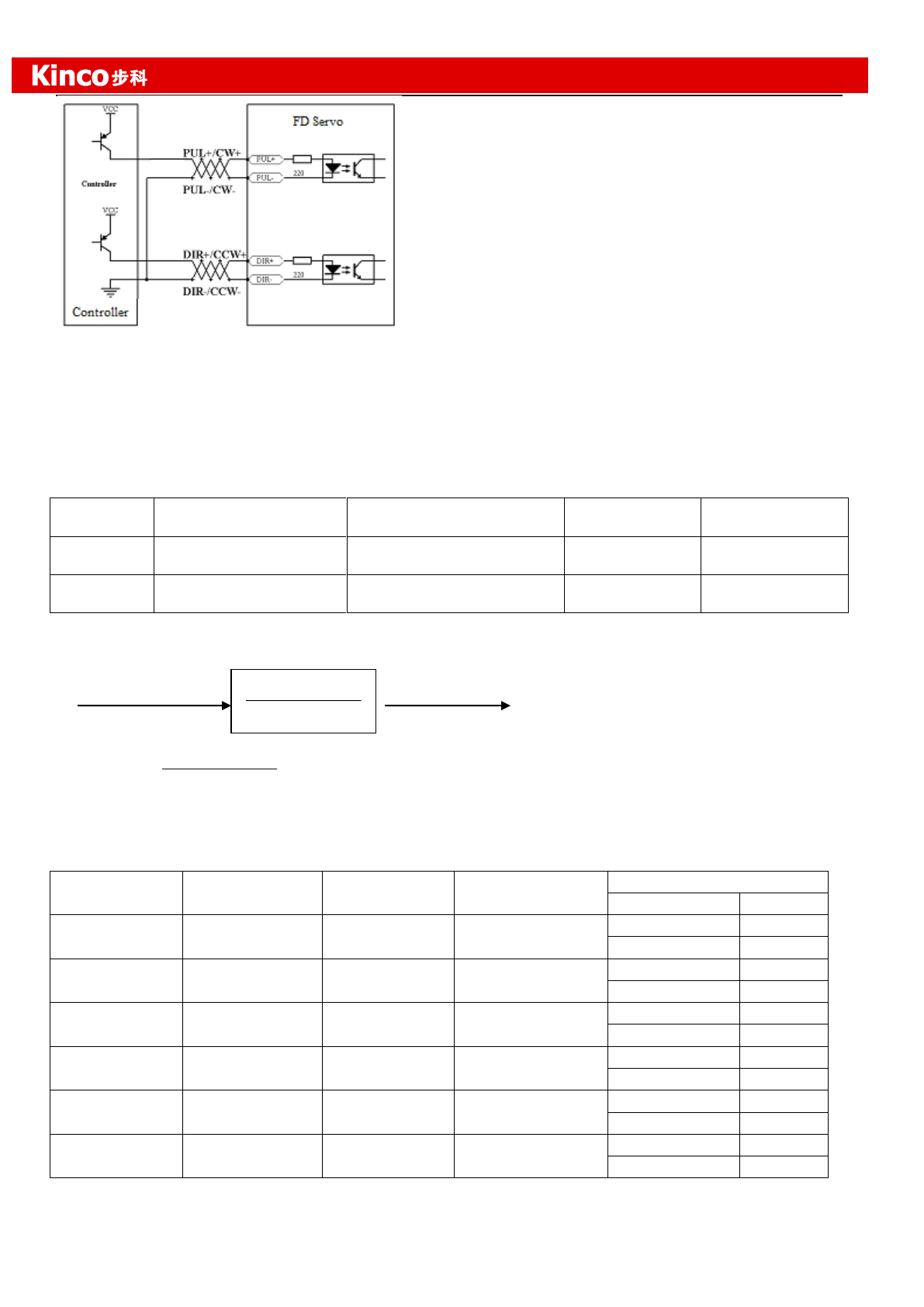
Kinco JD 伺服系列使用手册
72
Kinco FD Series Servo User Manual
Fig. 8-3 Common cathode connection (to controllers that support valid high level output)
8.1.2 Parameters for Pulse Control Mode
1. Parameters for electronic gear ratio
Table 8-1 Parameters for electronic gear ratio
Numeric
Display
Variable Name
Meaning
Default Value
Range
d3.34
Gear_Factor
Numerator of electronic
gear 0 in mode -4
1000
-32767~32767
d3.35
Gear_Divider
Denominator of electronic
gear 0 in mode -4
1000
1~32767
Parameters for electronic gear ratio are used to set the numerator and denominator of electronic gears when
the driver operates in mode -4.
Command pulse input Command pulse output
F1 F2
Namely: F2=
DividerGear
FactorGear
_
_
* F1
If the electronic gear ratio is 1:1, 10000 pulses are inputted externally (the resolution of encoders is 2500
PPR, quadruple), and the motor turns a circle. If the electronic gear ratio is 2:1, 10000 pulses are inputted
externally, and the motor turns two circles.
Multi electronic gears can be defined by DIN with function “Multi DinX” as shown in following table.
Multi Din 2
Multi Din 1
Multi Din 0
Descriptions
Parameter
Name
Address
0
0
0
Electronic gear 0
Gear_Factor 0
25080110
Gear_Divider 0
25080210
0
0
1
Electronic gear 1
Gear_Factor 1
25090110
Gear_Divider 1
25090210
0
1
0
Electronic gear 2
Gear_Factor 2
25090310
Gear_Divider 2
25090410
0
1
1
Electronic gear 3
Gear_Factor 3
25090510
Gear_Divider 3
25090610
1
0
0
Electronic gear 4
Gear_Factor 4
25090710
Gear_Divider 4
25090810
1
0
1
Electronic gear 5
Gear_Factor 5
25090910
Gear_Divider 5
25090A10
DividerGear
FactorGear
_
_
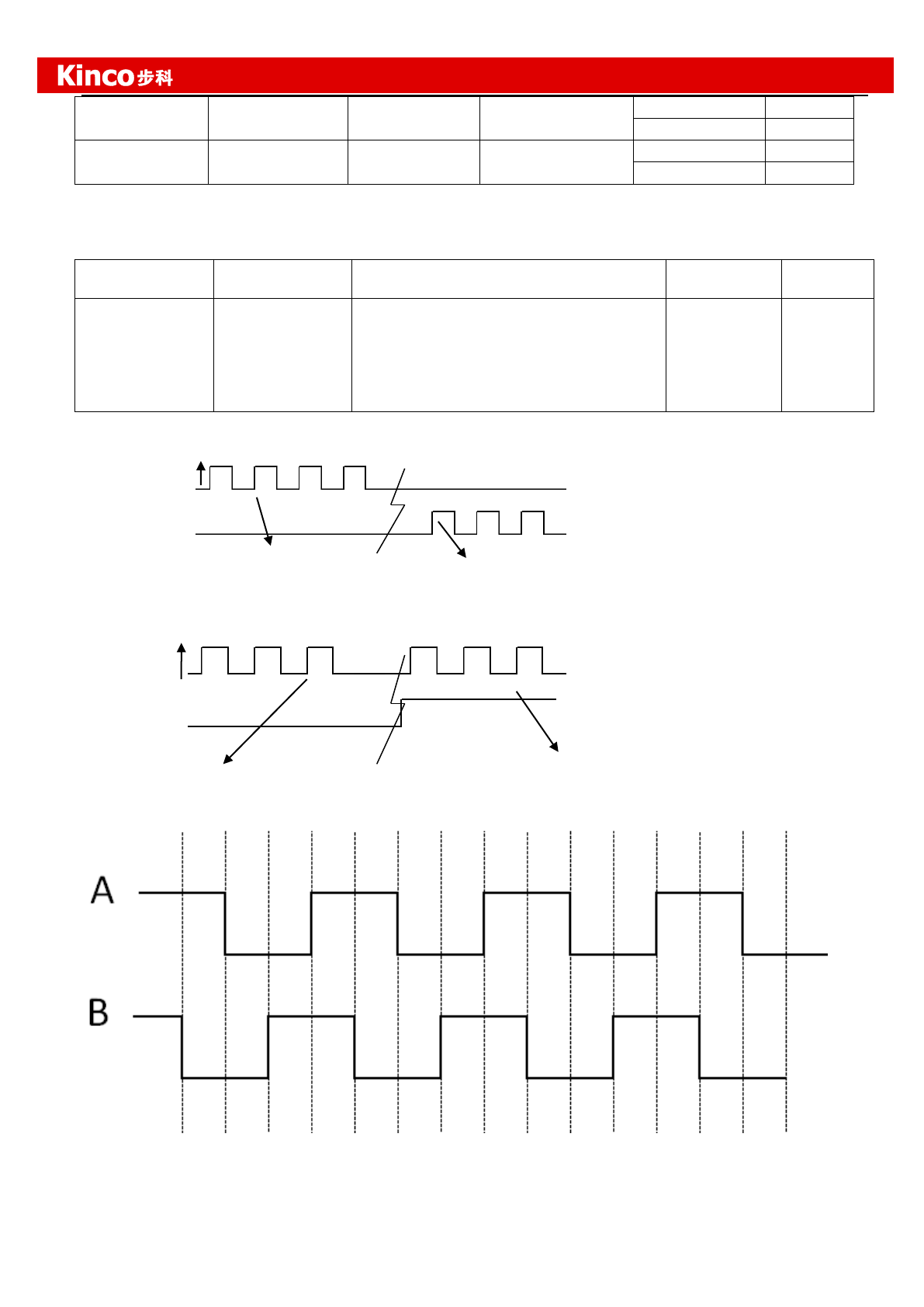
Kinco JD 伺服系列使用手册
73
Kinco FD Series Servo User Manual
1
1
0
Electronic gear 6
Gear_Factor 6
25090B10
Gear_Divider 6
25090C10
1
1
1
Electronic gear 7
Gear_Factor 7
25090D10
Gear_Divider 7
25090E10
The default value of Gear_Factor and Gear_Divider are 1000.
2. Parameters for pulse mode selection
Table 8-2 Parameters for pulse mode selection
Numeric
Display
Variable Name
Meaning
Default
Value
Range
d3.36
PD_CW
0: Double pulse (CW/CCW) mode
1. Pulse direction (P/D) mode
2. Incremental encoder mode
Note: To change this parameter, you
need to save it with d3.00, and restarts it
later.
1
N/A
Double pulse (CW/CCW) mode (d3.36 = 0)
Pulse direction (P/D) mode (d3.36 = 1)
Incremental encoder mode (d3.36=2)
Forward rotation
Reverse rotation
Forward rotation
Reverse rotation
Effective on the
rising edge
Effective on the
rising edge
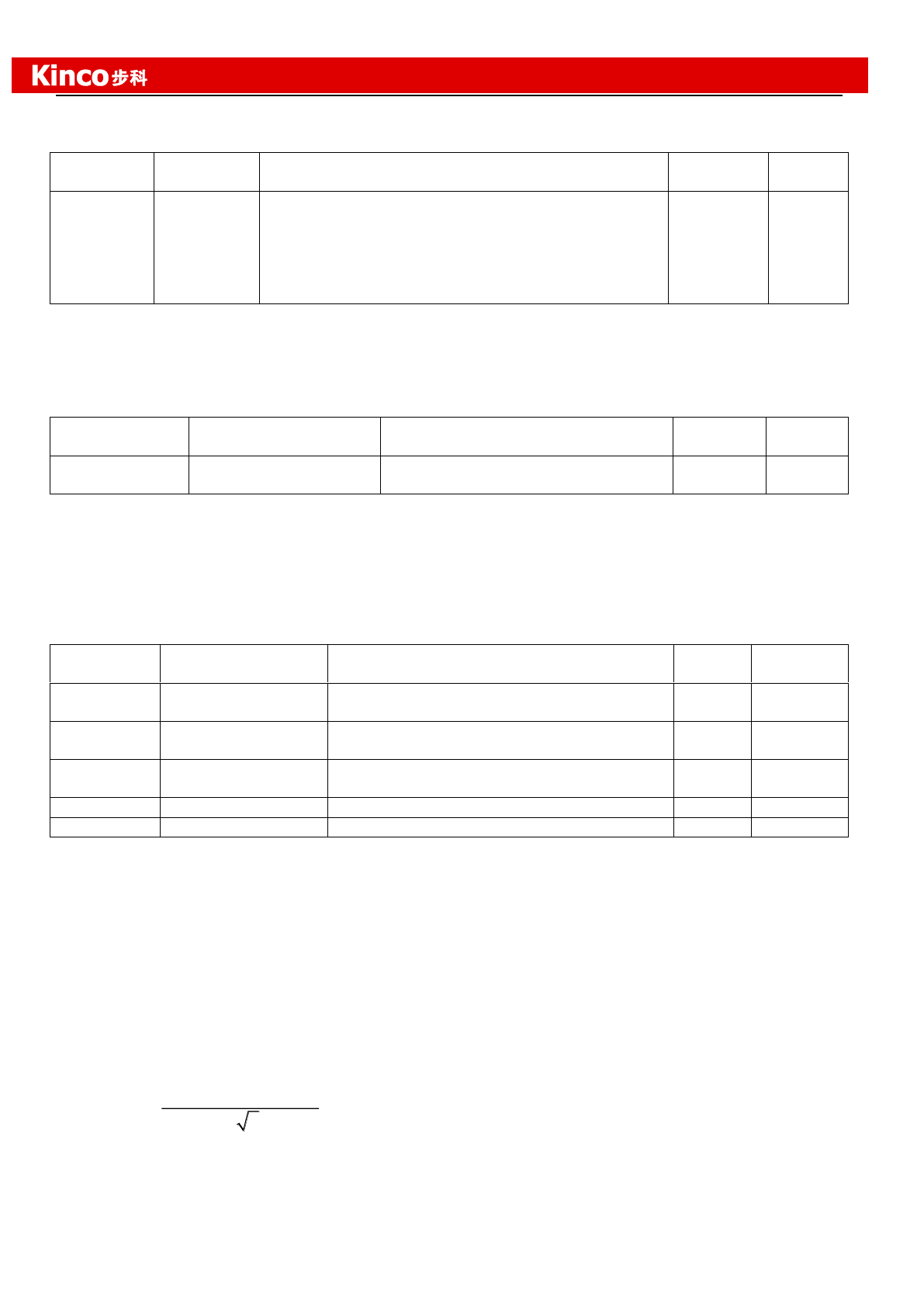
Kinco JD 伺服系列使用手册
74
Kinco FD Series Servo User Manual
Parameters for pulse filtering coefficient
Table 8-3 Parameters for pulse filtering coefficient
Numeric
Display
Variable
Name
Meaning
Default
Value
Range
d3.37
PD_Filter
Used to smooth the input pulses.
Filter frequency: f = 1000/(2π* PD_Filter)
Time constant: T = PD_Filter/1000
Unit: S
Note: If you adjust this parameter during the operation,
some pulses may be lost.
3
1~3276
7
When a driver operates in the pulse control mode, if the electronic gear ratio is set too high, it is required to
adjust this parameter to reduce motor oscillation; however, if the parameter adjustment is too great, motor
running instructions will become slower.
Parameters for pulse frequency control
Table 8-4 Parameters for pulse frequency control
Numeric Display
Variable Name
Meaning
Default
Value
Range
d3.38
Frequency_Check
Indicates the limitation on pulse input
frequency (kHz)
600
0~600
5. Parameters for gain control on position loops and velocity loops
Current loops are related to motor parameters (optimal parameters of the selected motor are default for the
driver and no adjusting is required).
Parameters for velocity loops and position loops should be adjusted properly according to loading conditions.
During adjustment of the control loop, ensure that the bandwidth of the velocity loop is at least twice of that of
the position loop; otherwise oscillation may occur.
Table 7-5 Parameters for gain control on position loops
Numeric
Display
Variable Name
Meaning
Default
Value
Range
d2.07
Kpp
Indicates the proportional gain Kpp 0 of the
position loop
1000
0~16384
d2.08
K_Velocity_FF
0 indicates no feedforward, and 256 indicates
100% feedforward
256
0~256
d2.09
K_Acc_FF
The value is inversely proportional to the
feedforward
32767
32767~10
d0.05
Pc_Loop_BW
Sets the bandwidth of the position loop in Hz.
0
/
d2.26
Pos_Filter_N
Average filter parameter
1
/
Proportional gains of the position loop Kpp: If the proportional gain of the position loops increases, the
bandwidth of the position loop is improved, thus reducing both the positioning time and following errors.
However, too great bandwidth may cause noise or even oscillation. Therefore, this parameter must be set
properly according to loading conditions. In the formula Kpp=103* Pc_Loop_BW,Pc_Loop_BW indicates the
bandwidth of the position loop. The bandwidth of a position loop is less than or equal to that of a velocity loop.
It is recommended that Pc_Loop_BW be less than Vc_Loop_BW /4 (Vc_Loop_BW indicates the bandwidth of
a velocity loop).
Velocity feedforward of the position loop K_Velocity_FF : the velocity feedforward of a position loop can be
increased to reduce position following errors. When position signals are not smooth, if the velocity
feedforward of a position loop is reduced, motor oscillation during running can be reduced. Acceleration
feedback of the position loop K_Acc_FF (adjustment is not recommended for this parameter): If great gains of
position loops are required, the acceleration feedback K_Acc_FF can be properly adjusted to improve
performance.
* * _
K_Acc_FF 250000* 2 * *
pt
t
I K Encoder R
J
Note: K_Acc_FF is inversely proportional to the acceleration
feedforward.
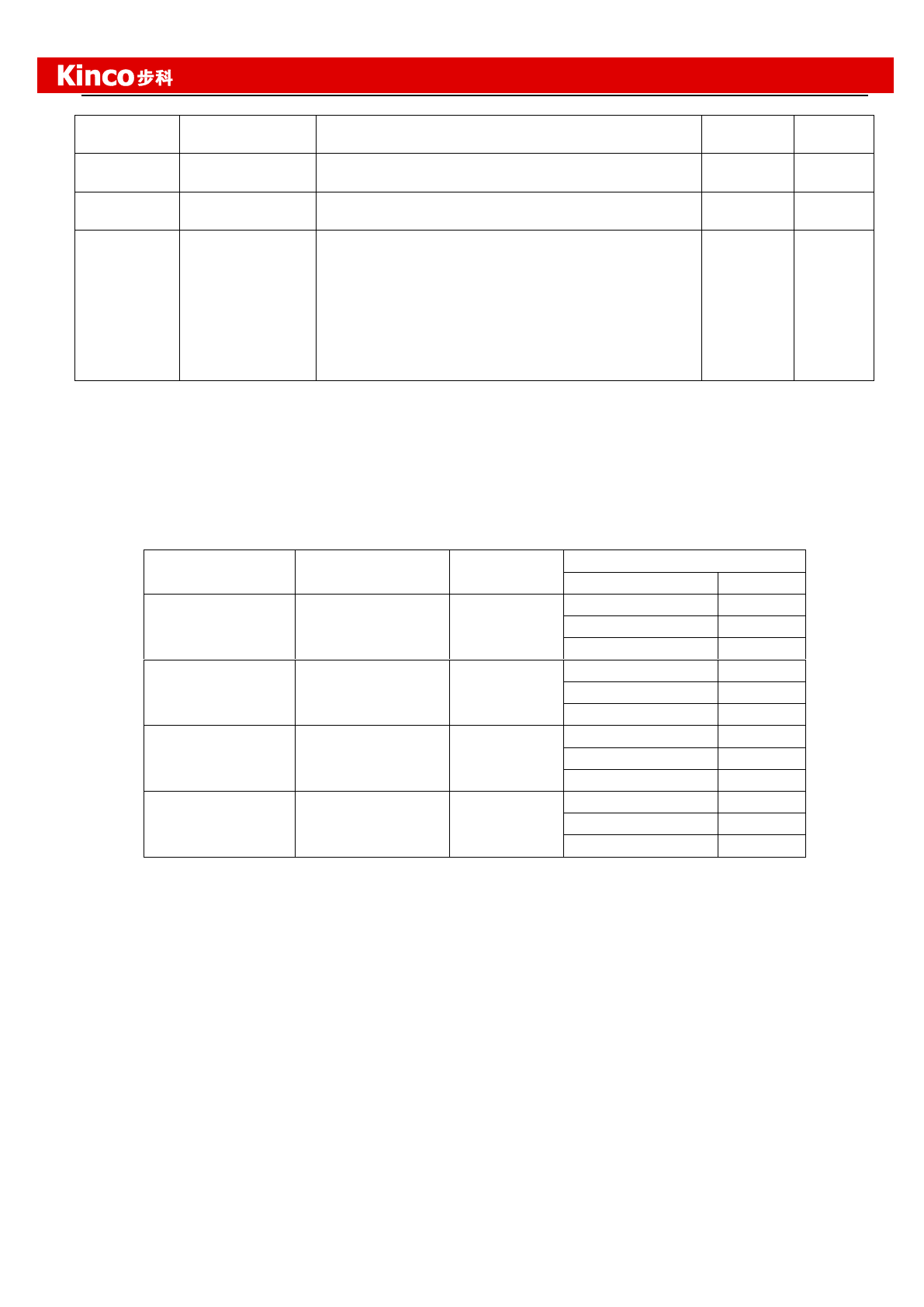
Kinco JD 伺服系列使用手册
75
Kinco FD Series Servo User Manual
Table 8-6 Parameters for gain control on position loops
Numeric
Display
Variable Name
Meaning
Default
Value
Range
d2.01
Kvp
Sets the response speed of a velocity loop
100
0~3276
7
d2.02
Kvi
Adjusts speed control so that the time of minor
errors is compensated
2
0~1638
4
d2.05
Speed_Fb_N
You can reduce the noise during motor operation
by reducing the feedback bandwidth of velocity
loops (smoothing feedback signals of encoders).
When the set bandwidth becomes smaller, the
motor responds slower. The formula is
F=Speed_Fb_N*20+100.
For example, to set the filter bandwidth to "F = 500
Hz”, the parameter should be set to 20.
45
0~45
Proportional gain of velocity loop Kvp: If the proportional gain of the velocity loop increases, the responsive
bandwidth of the velocity loop also increases. The bandwidth of the velocity loop is directly proportional to the
speed of response. Motor noise also increases when the velocity loop gain increases. If the gain is too great,
system oscillation may occur.
Integral gain of velocity loop Kvi: If the integral gain of the velocity loop increases, the low-frequency intensity
is improved, and the time for steady state adjustment is reduced; however, if the integral gain is too great,
system oscillation may occur.
Multiple gains can be defined by DIN with the function “Gain Switch 0” and “Gain Switch 1” as shown in
following table.
Gain Switch 1
Gain Switch 0
Descriptions
Parameters
Name
Address
0
0
Gain 0
Kvp of Gain 0
60F90110
Kvi of Gain 0
60F90210
Kpp of Gain 0
60FB0110
0
1
Gain 1
Kvp of Gain 1
23400410
Kvi of Gain 1
23400510
Kpp of Gain 1
23400610
1
0
Gain 2
Kvp of Gain 2
23400710
Kvi of Gain 2
23400810
Kpp of Gain 2
23400910
1
1
Gain 3
Kvp of Gain 3
23400A10
Kvi of Gain 3
23400B10
Kpp of Gain 3
23400C10
If DIN is defined as “Gain Switch” function,then the parameter “PI_Switch” will disable.
Parameter “PI_Point”(60F92808) is used to display the current gain.
Auto-tuning can only be used to set Gain 0.
Vc_Loop_BW and Pc_Loop_BW are only corresponding to Gain 0.Other Gain needs to set by manual.
“PI_Switch” is used to switch Gain 0 and Gain 1.In mode -4,1 and 3,it will use Gain 1 when “Position reached”
signal is valid,and use Gain 0 when “Position reached” signal is invalid.
8.1.3 Examples of Pulse Control Mode
In the pulse control mode, follow the steps below to configure a driver:
Step 1: Confirm whether the functions of the driver require enabling through external digital input ports. To
enable the driver through external digital input ports, see Table 6-12 in Example 6-3 for settings. If it is not
necessary to enable the driver through external digital input ports, you can disable the enabling control
function of external digital input ports by referring to Table 6-13 of Example 6-3, and enable the driver by
setting its internal parameters.
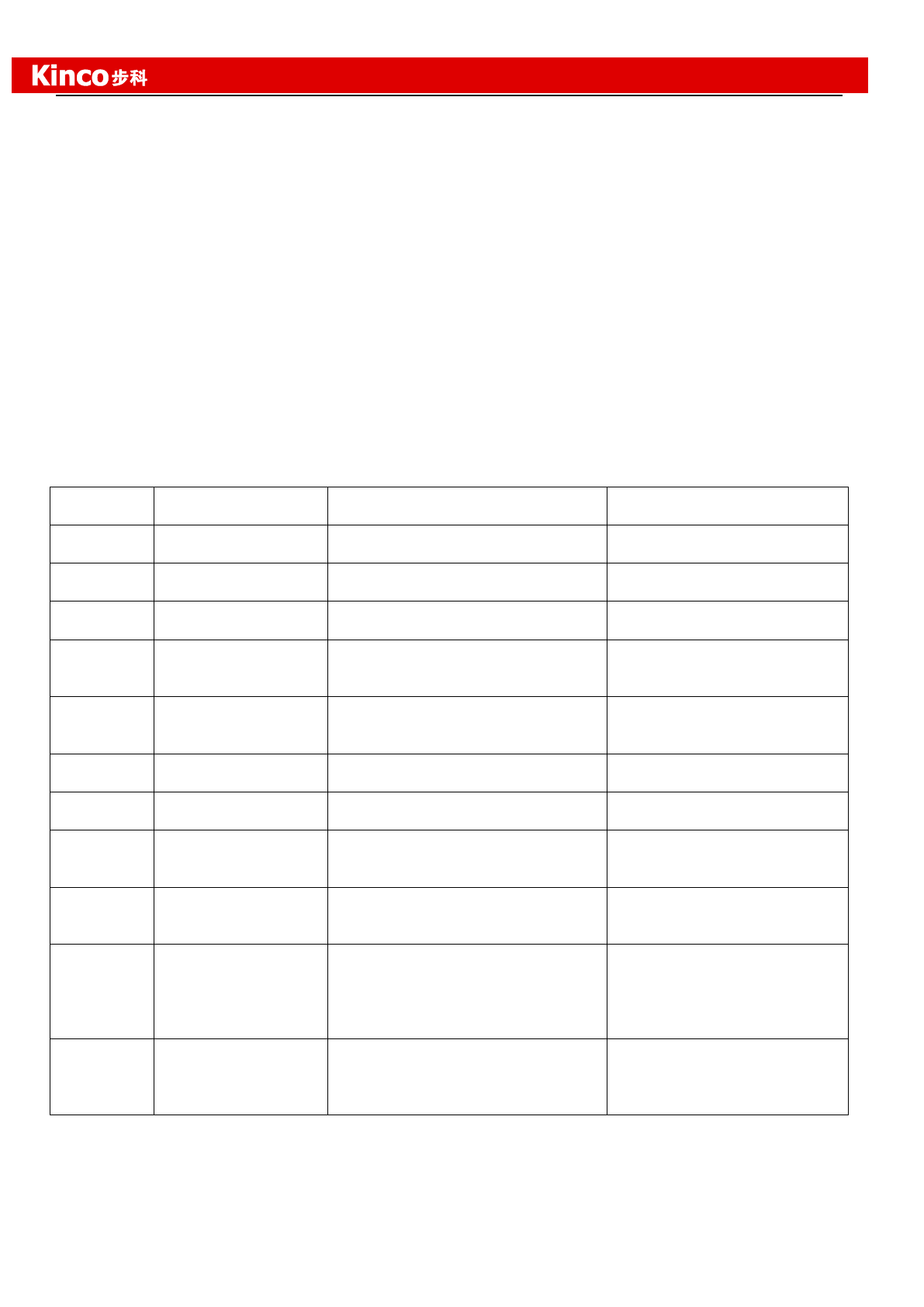
Kinco JD 伺服系列使用手册
76
Kinco FD Series Servo User Manual
Step 2: Confirm whether limit switches are required. By default, the driver operates in the limit status after
being powered on. In this case, the numeric display has limit status display. If there is no limit switches,
please disable the function of limit switches by referring to Example 6-4.
Step 3: Confirm mode switching bits and operation modes by referring to the settings in Example 6-5. The
factory default settings of the driver are as follows: When no signal is inputted on DIN3, the driver operates in
the “-4” mode (pulse control mode).
Step 4: After function configuration on digital input ports, it is required to set parameters such as pulse modes
and electronic gear ratio.
Step 5: Save parameters.
Example 8-1: Pulse control mode “-4” – enable the driver through external
digital input
Requirement: DIN1 is used for enabling the driver, DIN2 is used for error resetting, and DIN3 controls the
operation modes of the driver (the mode is “-4” when no signal is inputted, and the mode is “-3” when signal is
inputted). Limit switches are unavailable. The pulse form is pulse/direction, and the electronic rear ratio is 2:1.
Table 8-7 describes the setup method.
Table 8-7: Pulse control mode “-4” – enable the driver through external digital input
Numeric
Display
Variable Name
Meaning
Parameter Settings
d3.01
Din1_Function
Defines the functions of digital input
port 1
000.1 (Driver enable)
d3.02
Din2_Function
Defines the functions of digital input
port 2
000.2 (Fault reset)
d3.03
Din3_Function
Defines the functions of digital input
port 3
000.4 (Operation mode
control )
d3.05
Din5_Function
Defines the functions of digital input
port 5
The default value 001.0
changes to 000.0 (position
positive limits are disabled)
d3.06
Din6_Function
Defines the functions of digital input
port 6
The default value 002.0
changes to 000.0 (position
negative limits are disabled)
d3.16
Din_Mode0
Select this operation mode when
input signals are invalid
Set to 0.004 (-4) mode
(pulse control mode)
d3.17
Din_Mode1
Select this operation mode when
input signals are valid
Set to 0.003 (-3) mode
(instantaneous speed mode)
d3.34
Gear_Factor
Indicates the numerator to set
electronic gears in the “-4” operation
mode (pulse control mode)
Set to 2000
d3.35
Gear_Divider
Indicates the denominator to set
electronic gears in the “-4” operation
mode (pulse control mode)
Set to 1000
d3.36
PD_CW
0: Double pulse (CW/CCW) mode
1. Pulse direction (P/D) mode
Note: To change this parameter, you
need to save it with the address
“d3.00”, and restarts it later.
Default value is 1
(pulse direction)
d3.00
Store_Loop_Data
1: Storing all configured parameters
for the control loop
10: Initializing all parameters for the
control loop
Set to 1
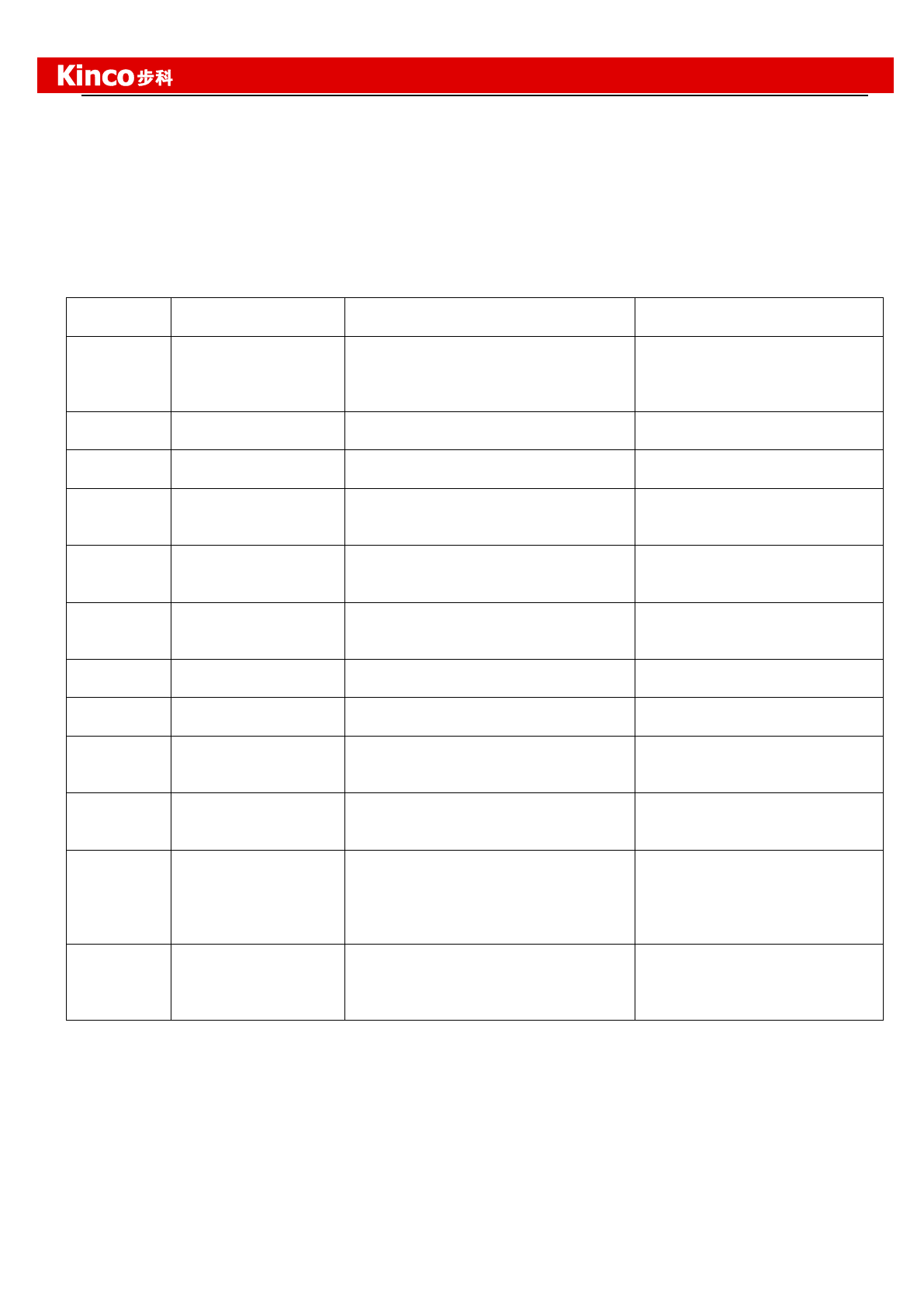
Kinco JD 伺服系列使用手册
77
Kinco FD Series Servo User Manual
Example 8-2 Pulse control mode “-4” – enable the driver automatically after
driver power on
Requirement: The auto power-on function of the driver is enabled, DIN2 is used for error resetting, and DIN3
controls the operation modes of a driver (the mode is “-4” when no signal is inputted, and the mode is “3”
when signal is inputted). Limit switches are unavailable. The pulse form is pulse/direction, and the electronic
rear ratio is 1:2. Table 8-8 describes the setup method.
Table 8-8 Pulse control mode “-4” – enable driver automatically after driver power on
Numeric
Display
Variable Name
Meaning
Parameter Settings
d3.01-
d3.07
DinX_ Function
(1~7)
Defines the functions of digital input
ports 1-7
None of the digital input port
can be set to 000.1, that is, the
Enable function is not controlled
by any digital input port.
d3.02
Din2_Function
Defines the functions of digital input
port 2
000.2 (Error resetting)
d3.03
Din3_Function
Defines the functions of digital input
port 3
000.4 (Control on operation
modes for the driver)
d3.05
Din5_Function
Defines the functions of digital input
port 5
The default value 001.0
changes to 000.0 (position
positive limits are disabled)
d3.06
Din6_Function
Defines the functions of digital input
port 6
The default value 002.0
changes to 000.0 (position
negative limits are disabled)
d3.10
Switch_On_Auto
0: No control
1:Automatically locks the motor when
the driver is powered on
Set to 1
d3.16
Din_Mode0
Select this operation mode when
input signals are invalid
Set to 0.004 (-4) mode
(pulse control mode)
d3.17
Din_Mode1
Select this operation mode when
input signals are valid
Set to 0.003 (-3) mode
(instantaneous speed mode)
d3.34
Gear_Factor
Indicates the numerator to set
electronic gears in the “-4” operation
mode (pulse control mode)
Set to 1000
d3.35
Gear_Divider
Indicates the denominator to set
electronic gears in the “-4” operation
mode (pulse control mode)
Set to 2000
d3.36
PD_CW
0: Double pulse (CW/CCW) mode
1. Pulse direction (P/D) mode
Note: To change this parameter, you
need to save it with the address
“d3.00”, and restarts it later.
Default value is 1
(pulse direction)
d3.00
Store_Loop_Data
1: Storing all configured parameters
for the control loop
10: Initializing all parameters for the
control loop
Set to 1
8.2 Speed Mode (“-3” or “3” Mode)
In the instantaneous speed mode (“-3” mode), the actual speed reaches the target speed instantly. As a
contrast, in the speed mode with acceleration/deceleration (“3” mode), the actual speed gradually increases
until it reaches the target speed. Both the acceleration and deceleration (trapeziform shape) are configured
respectively by d2.10 and d2.11. In the “3" mode, you can set Kpp to enable/disable position loops. If a
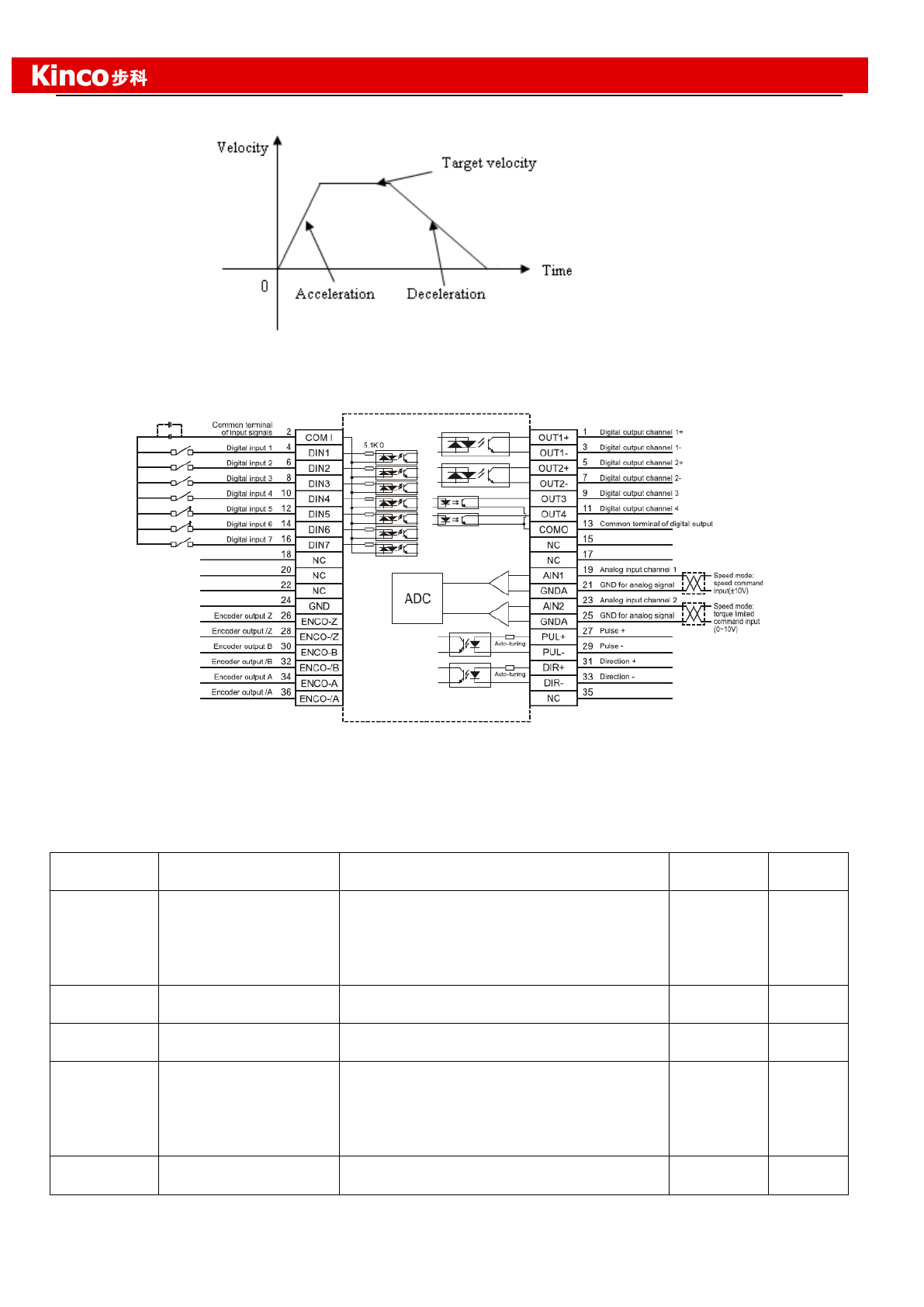
Kinco JD 伺服系列使用手册
78
Kinco FD Series Servo User Manual
position loop is enabled, speed oscillation is less than that when the loop is disabled. If Kpp is 0, it indicates
that the position loop is closed.
Fig. 8-4 The speed mode “3” with acceleration/deceleration
8.2.1 Wiring in Analog – Speed Mode
Fig. 8-5 Wiring diagram of FD Servo in analog–speed mode
8.2.2 Parameters for Analog – Speed Mode
Table 8-9 Parameters for analog – speed mode
Numeric
Display
Variable Name
Meaning
Default
Value
Range
d3.22
Analog1_Filter
Used to smooth the input analog signals.
Filter frequency: f=4000/(2π*
Analog1_Filter)
Time Constant (T) = Analog1_Filter/4000
(S)
5
1~127
d3.23
Analog1_Dead
Sets dead zone data for external analog
signal 1
0
0~8192
d3.24
Analog1_Offset
Sets offset data for external analog signal 1
0
-8192~8
192
d3.25
Analog2_Filter
Used to smooth the input analog signals.
Filter frequency: f=4000/(2π*
Analog1_Filter)
Time Constant (T) = Analog2_Filter/4000
(S)
5
1~127
d3.26
Analog2_Dead
Sets dead zone data for external analog
signal 2
0
0~8192
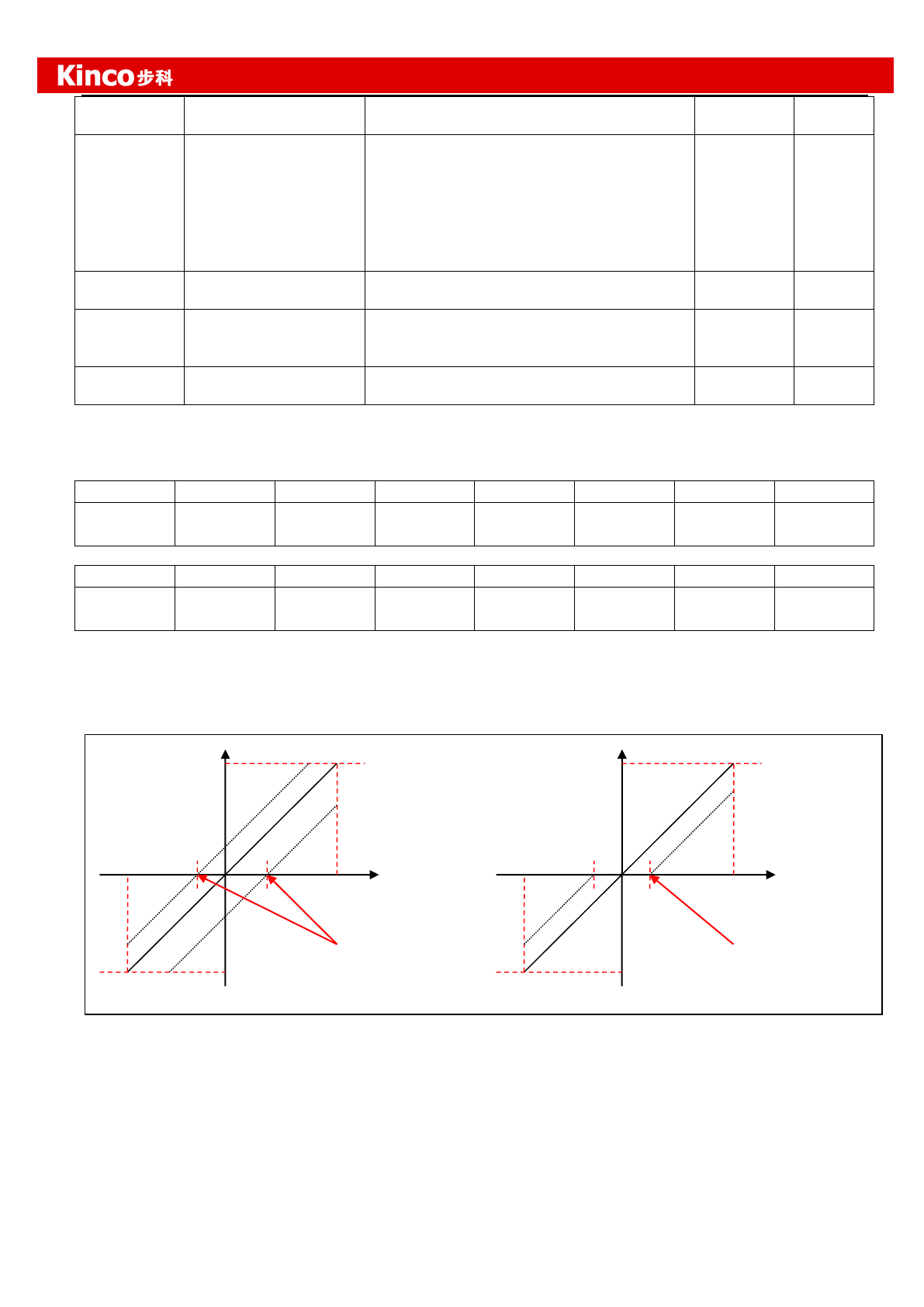
Kinco JD 伺服系列使用手册
79
Kinco FD Series Servo User Manual
d3.27
Analog2_Offset
Sets offset data for external analog signal 2
0
-8192~8
192
d3.28
Analog_Speed_Con
Chooses analog-speed channels
0: Invalid analog channel
1: Valid analog channel 1 (AIN1)
2: Valid analog channel 2 (AIN2)
10~17:AIN1 for “Din_Speed (X-10)”
20~27:AIN2 for “Din_Speed (X-20)”
Valid in mode -3, 3 and 1.
0
N/A
d3.29
Analog_Speed_Factor
Sets the proportion between analog signals
and output speed
1000
N/A
d3.32
Analog_MaxT_Con
0: No control
1: Max torque that Ain1 can control
2: Max torque that Ain2 can control
0
N/A
d3.33
Analog_MaxT_Factor
Indicates the max torque factor for analog
signal control
8192
N/A
When d3.28 is 1 or 2,mode 1 is invalid,mode 3 and -3 are valid.
When d3.28 is 10~17 or 20~27,mode 1,3 and -3 are valid.
When d3.28 is 10~17(AIN1 for “Din_Speed (X-10)”),the corresponding speed is as following table.
10
11
12
13
14
15
16
17
Din_Speed
0
Din_Speed
1
Din_Speed
2
Din_Speed
3
Din_Speed
4
Din_Speed
5
Din_Speed
6
Din_Speed
7
When d3.28 is 20~27(AIN1 for “Din_Speed (X-10)”),the corresponding speed is as following table.
20
21
22
23
24
25
26
27
Din_Speed
0
Din_Speed
1
Din_Speed
2
Din_Speed
3
Din_Speed
4
Din_Speed
5
Din_Speed
6
Din_Speed
7
8.2.3 Analog Signal Processing
Fig. 8-6 Analog signal processing
Electrical control on internal variables is available only after ADC conversion and offset of external analog
signals, and judgment of dead zone signals.
For offset processing, see the left part in Fig. 8-6; for dead zone processing, see the right part in Fig. 8-6.
Mathematical equation for offset processing:
shiftexternalernal UUU
int
2047
-2048
shift
U
-10v
10v
1
0
2047
-2048
2
dead
U
-10v
10v
external
U
external
U
ernal
Uint
ernal
Uint
Offset
Dead zone
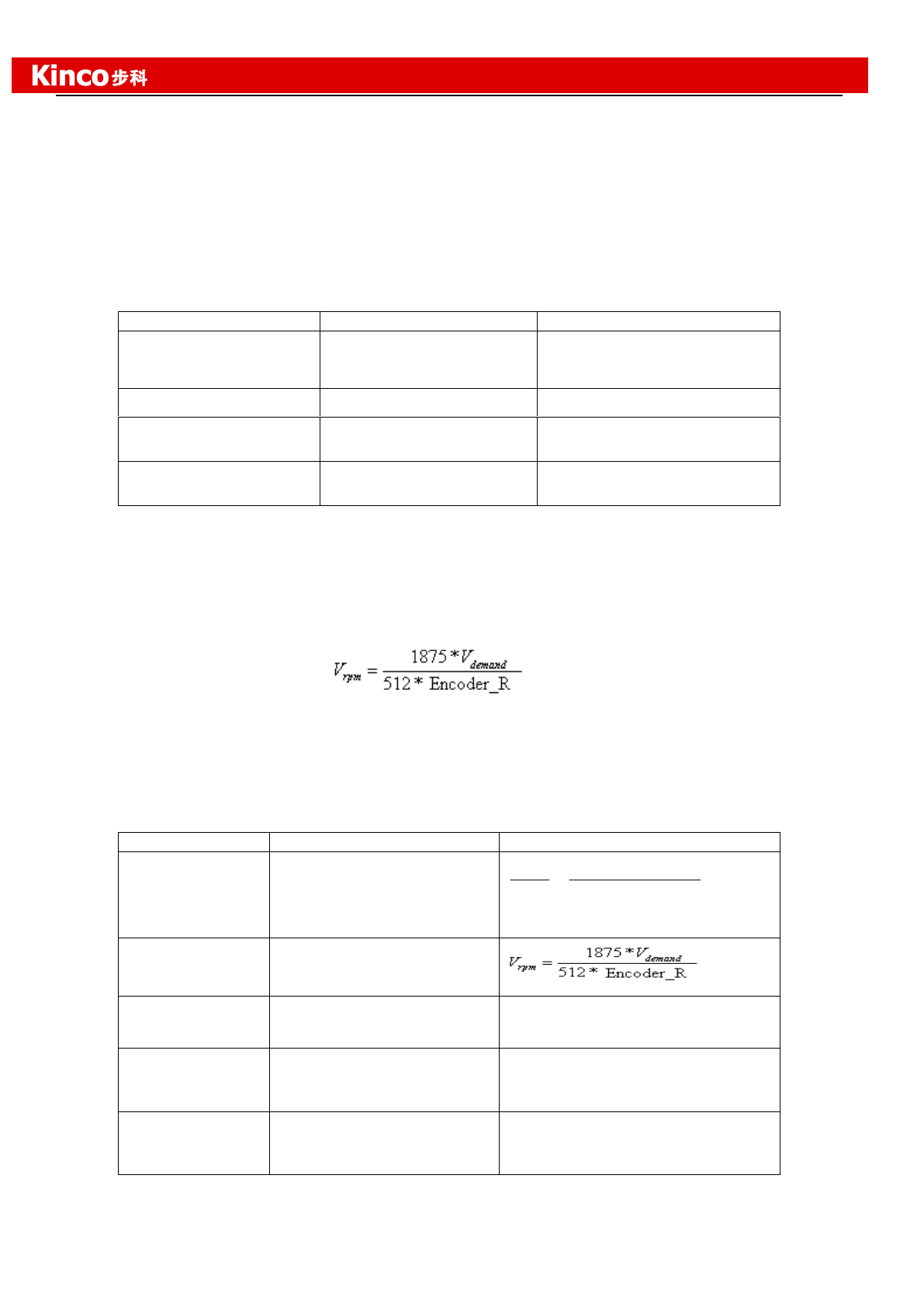
Kinco JD 伺服系列使用手册
80
Kinco FD Series Servo User Manual
Mathematical equation for dead zone processing:
externaldead
externaldead
deadexternalernal
deadexternaldeadernal
UU
UU
UUU
UUUU
int
int 0
Mathematical equation for integrated processing (offset and dead
zone)
shiftexternaldead
shiftexternaldead
deadshiftexternalernal
deadshiftexternaldeadernal
UUU
UUU
UUUU
UUUUU
int
int 0
Table 8-10 Analog signal variables
Variable
Meaning
Range
internal
U
Internal data corresponding
to the external voltage
-10 V – 10 V corresponds to
-2048 – 2047 when no offset or
dead zone voltage exists
tex ernal
U
External input voltage
-10V – 10V
shift
U
Offset voltage
0 – 10 V corresponds to
log_Ana Offset
0~8191
dead
U
Dead zone voltage
0 – 10 V corresponds to
log_Ana Dead
0~8191
The obtained analog signal
internal
U
obtains
filter
U
after passing through a first-order low-pass filter, and is
applied by the internal programs again.
In the analog – speed mode, if the analog signal
filter
U
that passes through the filter is multiplied by a factor,
this signal will be regarded as the internal target speed
demand
V
.
Mathematical formula:
20472048* filterfilterdemand UUFactorV
demand
V
Formula for
rpm
V
conversion:
Note: The resolution unit of an encoder is inc/r.
8.2.4 Calculation Procedure for Analog – speed Mode
Table 8-11 Calculation procedure for analog – speed mode
Procedure
Method
Formula
Step 1
Calculate
filter
U
according
to the offset voltage and dead
zone voltage that require
settings
2047
10 10
filter
shift dead
U
v v U U
Step 2
Calculate
demand
V
according
to the required speed
rpm
V
Step 3
Calculate
Factor
according
to
filter
U
and
demand
V
filterdemand UFactorV *
Step 5
Calculate
log_Ana Dead
according to the required
dead zone voltage
8191/10 log_ / dead
v Ana Dead U
Step 5
Calculate
log_Ana Offset
according to the required
offset voltage
8191/10 log_ / shift
v Ana Offset U
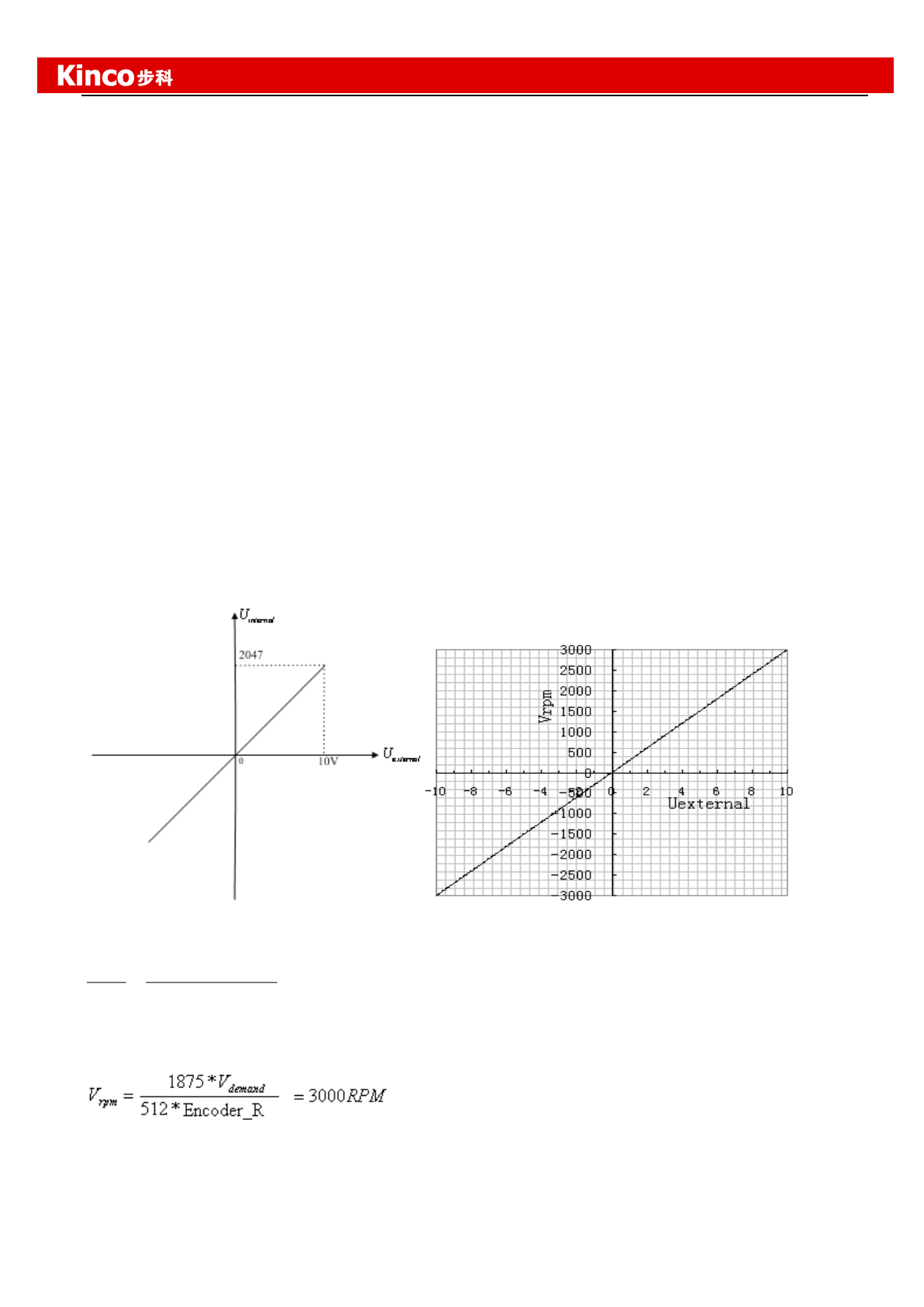
Kinco JD 伺服系列使用手册
81
Kinco FD Series Servo User Manual
8.2.5 Examples of Analog – Speed Mode
In the analog – speed mode, follow the steps below to set a driver:
Step 1: Confirm whether it is necessary to enable the driver through external digital input ports. To enable the
driver through external digital input ports, see Table 6-12 in Example 6-3 for settings. If the driver does not
require enabling through external digital input ports, you can disable the enabling function of external digital
input ports by referring to Table 6-13 of Example 6-3, and enable the auto power-on function of the driver by
setting its internal parameters.
Step 2: Confirm whether limit switches are required. By default, the driver operates in the limit status after
being powered on. In this case, the numeric display has limit status display. If limit switches are unavailable,
please disable the function of limit switches by referring to Example 6-4.
Step 3: Confirm the mode switching positions and operation modes by referring to the settings in Example 6-5.
The factory default settings are as follows: When no signal is inputted to DIN3, the driver operates in the “-4”
mode (d3.16 = -4); when signal is inputted to DIN3, the driver operates in the “-3” mode (d3.17 = -3). If the
driver is required to operate in the speed mode after being powered on, set d3.16 to -3 or 3.
Step 4: After configuring functions on digital input ports, select the analog – speed channel, and set
parameters such as analog – speed factors, dead zone, offset and filtering.
Step 5: Save parameters.
Example 8-3: Analog – speed mode (without setting the dead zone voltage and
offset voltage)
Requirement: DIN1 is used for enabling the driver, DIN2 is used for error resetting, and DIN3 controls the
operation modes of the driver (the mode is “-3” when no signal is inputted, and is “3” when signal is inputted).
Limit switches are unavailable. The voltage 10V corresponds to the rated rotation speed of 3000 rpm, and
-10V corresponds to the rated rotation speed of -3000 rpm. Select analog channel 1 (AIN1) to control the
speed.
Fig. 8-7 Schematic diagram of Example 8-3
Calculate
filter
U
according to the offset voltage and dead zone voltage that require settings:
2047
10 10
filter
shift dead
U
v v U U
(In this example,
0
dead
U
, and
0
shift
U
)
Result:
filter
U
=2047
Calculate
demand
V
according to the required speed
rpm
V
:
(Encoder_R is 10000 inc/r)
Result:
8192000
demand
V
Calculate
Factor
according to
filter
U
and
demand
V
:
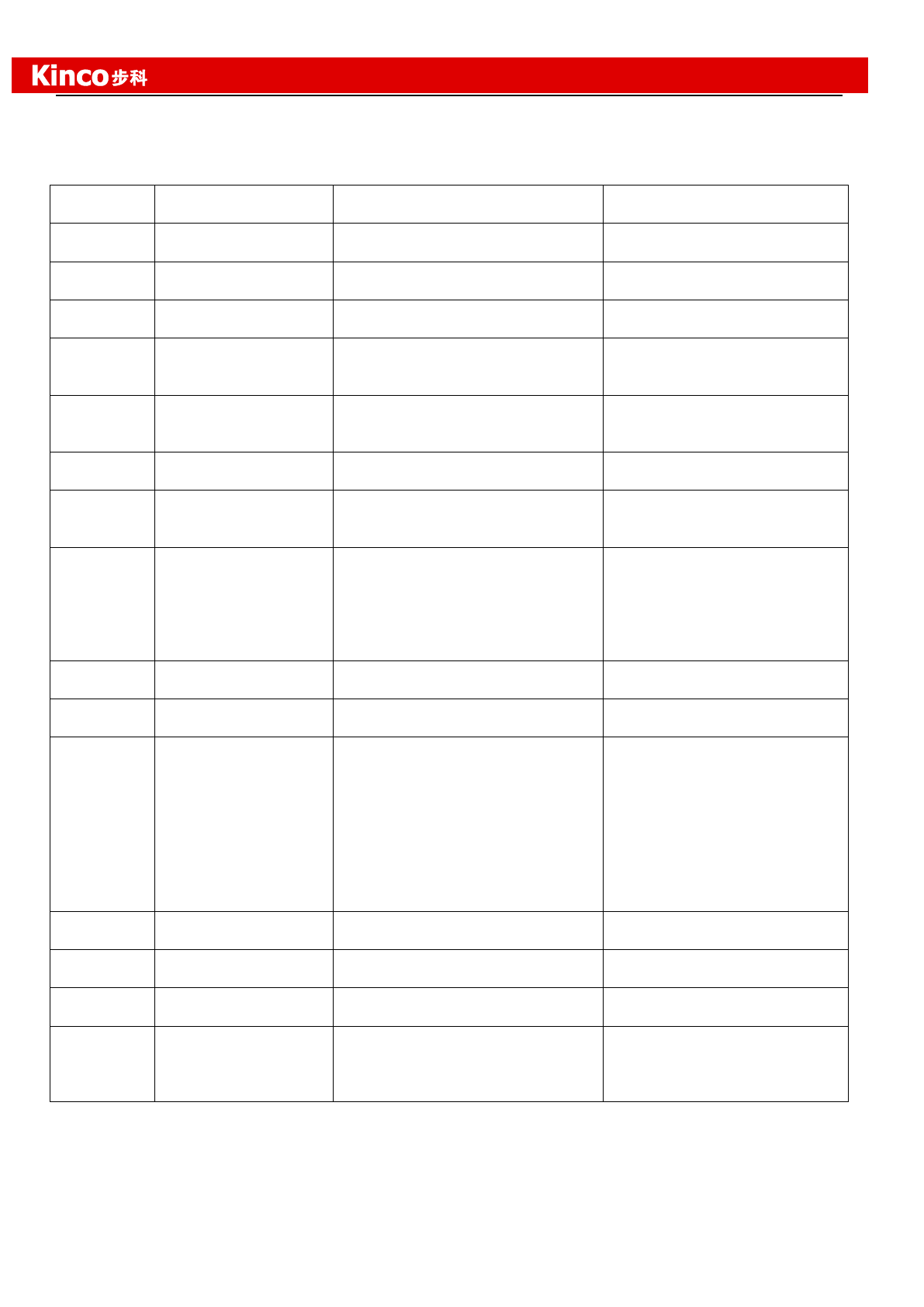
Kinco JD 伺服系列使用手册
82
Kinco FD Series Servo User Manual
*
demand filter
V Factor U
Result:
4000Factor
Table 8-12 Parameter settings in Example 8-3
Numeric
Display
Variable Name
Meaning
Parameter Settings
d3.01
Din1_Function
Define the functions of digital input
port 1
000.1 (Driver enable)
d3.02
Din2_Function
Define the functions of digital input
port 2
000.2 (Error resetting)
d3.03
Din3_Function
Define the functions of digital input
port 3
000.4 (Control over operation
modes of drivers)
d3.05
Din5_Function
Define the functions of digital input
port 5
The default value 001.0
changes to 000.0 (position
positive limits are disabled)
d3.06
Din6_Function
Define the functions of digital input
port 6
The default value 002.0
changes to 000.0 (position
negative limits are disabled)
d3.16
Din _Mode0
Select this operation mode when
input signals are invalid
Set to 0.003 (-3) mode
(instantaneous speed mode)
d3.17
Din _Mode1
Select this operation mode when
input signals are valid
Set to 0.003 (3) mode
(speed mode with
acceleration/deceleration)
d3.22
Analog1_Filter
Used to smooth the input analog
signals.
Filter frequency: f=4000/(2π*
Analog1_Filter)
Time Constant (T) =
Analog1_Filter/4000 (S)
d3.23
Analog1_Dead
Set dead zone data for external
analog signal 1
Set to 0
d3.24
Analog1_Offset
Set offset data for external analog
signal 1
Set to 0
d3.28
Analog_Speed_Con
Chooses analog-speed channels
0: Invalid analog channel
1: Valid analog channel 1 (AIN1)
2: Valid analog channel 2 (AIN2)
10 ~17 :AIN1 for “Din_Speed
(X-10)”
20 ~27 :AIN2 for “Din_Speed
(X-20)”
Valid in mode -3, 3 and 1.
Set to 1
d3.29
Analog_Speed_Factor
Set the proportion between analog
signals and output speed
Set to 4000
d2.10
Profile_Acce_16
Set the acceleration in operation
mode 3 and 1.(rps/s)
610 by defaut
d2.11
Profile_Dece_16
Set the deceleration in operation
mode 3 and 1.(rps/s)
610 by defaut
d3.00
Store_Loop_Data
1: Storing all configured
parameters for the control loop
10: Initializing all parameters for
the control loop
Set to 1
Example 8-4 Analog – speed mode (setting the dead zone voltage)
Requirement: The dead zone voltage ranges from - 0.5 V to 0.5 V, that is, the speed is 0 when the voltage
ranges from - 0.5 V to 0.5 V. The voltage 10 V corresponds to 3000 rpm, and -10 V corresponds to -3000 rpm.
Select analog channel 1 (AIN1) to control the speed.
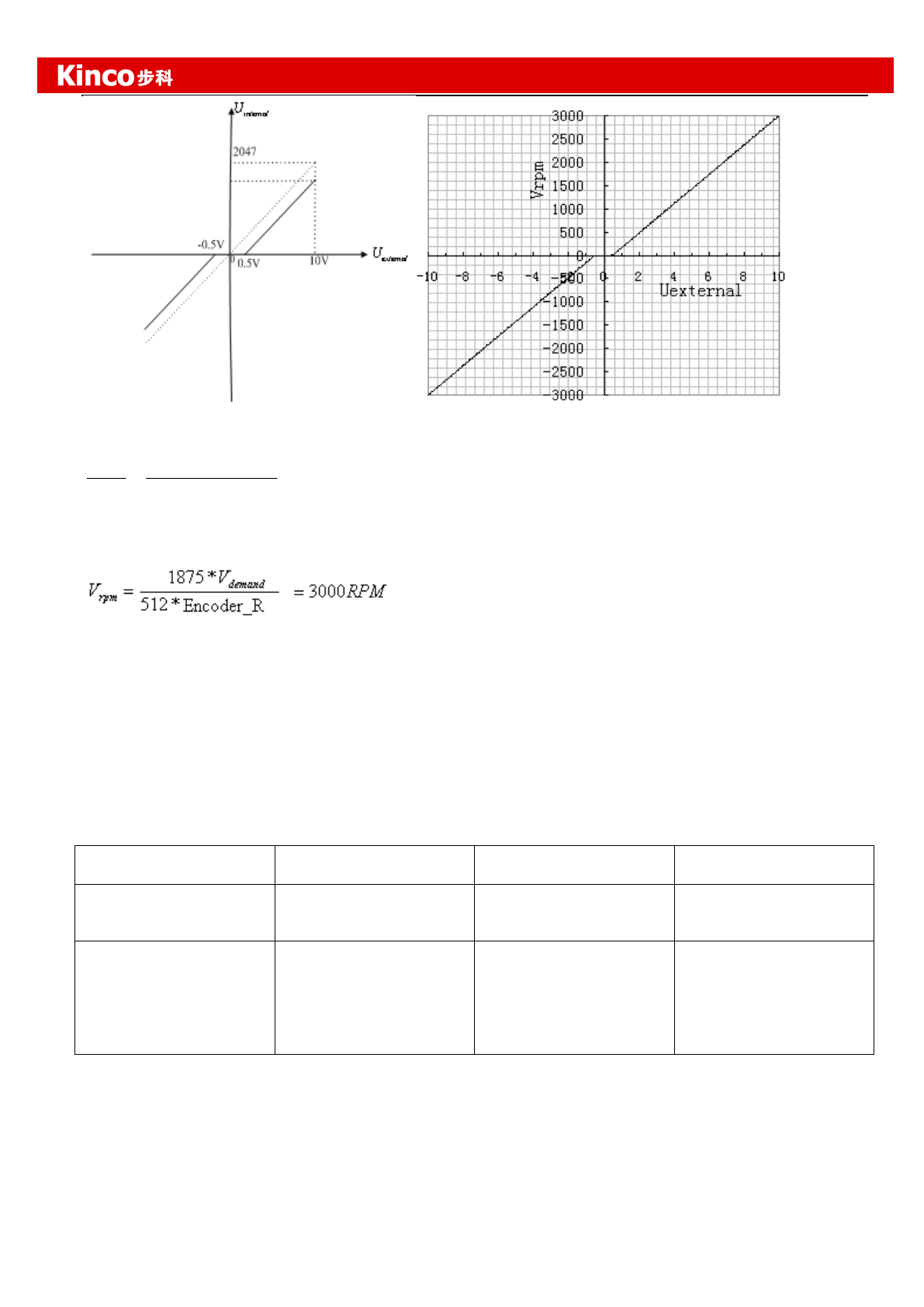
Kinco JD 伺服系列使用手册
83
Kinco FD Series Servo User Manual
Fig. 8-8 Schematic diagram of Example 8-4
Calculate
filter
U
according to the offset voltage and dead zone voltage that require settings:
2047
10 10
filter
shift dead
U
v v U U
(In this example,
0
dead
U
.5, and
0
shift
U
)
Result:
filter
U
=1944
Calculate
demand
V
according to the required speed :
rpm
V
, (Encoder_R:10000 inc/r)
Result:
8192000
demand
V
Calculate
filter
U
according to
demand
V
and
Factor
:
*
demand filter
V Factor U
Result:
Factor
=4213
Calculate
log1_Ana Dead
according to the required dead zone voltage:
8191/10 log1_ / dead
v Ana Dead U
Result:
log1_Ana Dead
=410
The following changes are required on the basis of Example 8-3.
Table 8-13 Parameter settings in Example 8-4
d3.23
Analog1_Dead
Sets dead zone data for
external analog signal 1
Set to 410
d3.29
Analog_Speed_Factor
Sets the proportion
between analog signals
and output speed
Set to 4213
d3.00
Store_Loop_Data
1: Storing all configured
parameters for the
control loop
10: Initializing all
parameters for the
control loop
Set to 1
Example 8-5 Analog – speed mode (setting the offset voltage)
Requirement: The offset voltage is 1 V, that is, the speed is positive when the voltage is greater than 1 V, and
is negative when the voltage is less than 1 V. In this case, the voltage 10 V corresponds to 3000 rpm, and -9
V corresponds to -3000 rpm (in case of -10 V, the corresponding speed is less than -3000 rpm). Select analog
channel 1 (AIN1) to control the speed.
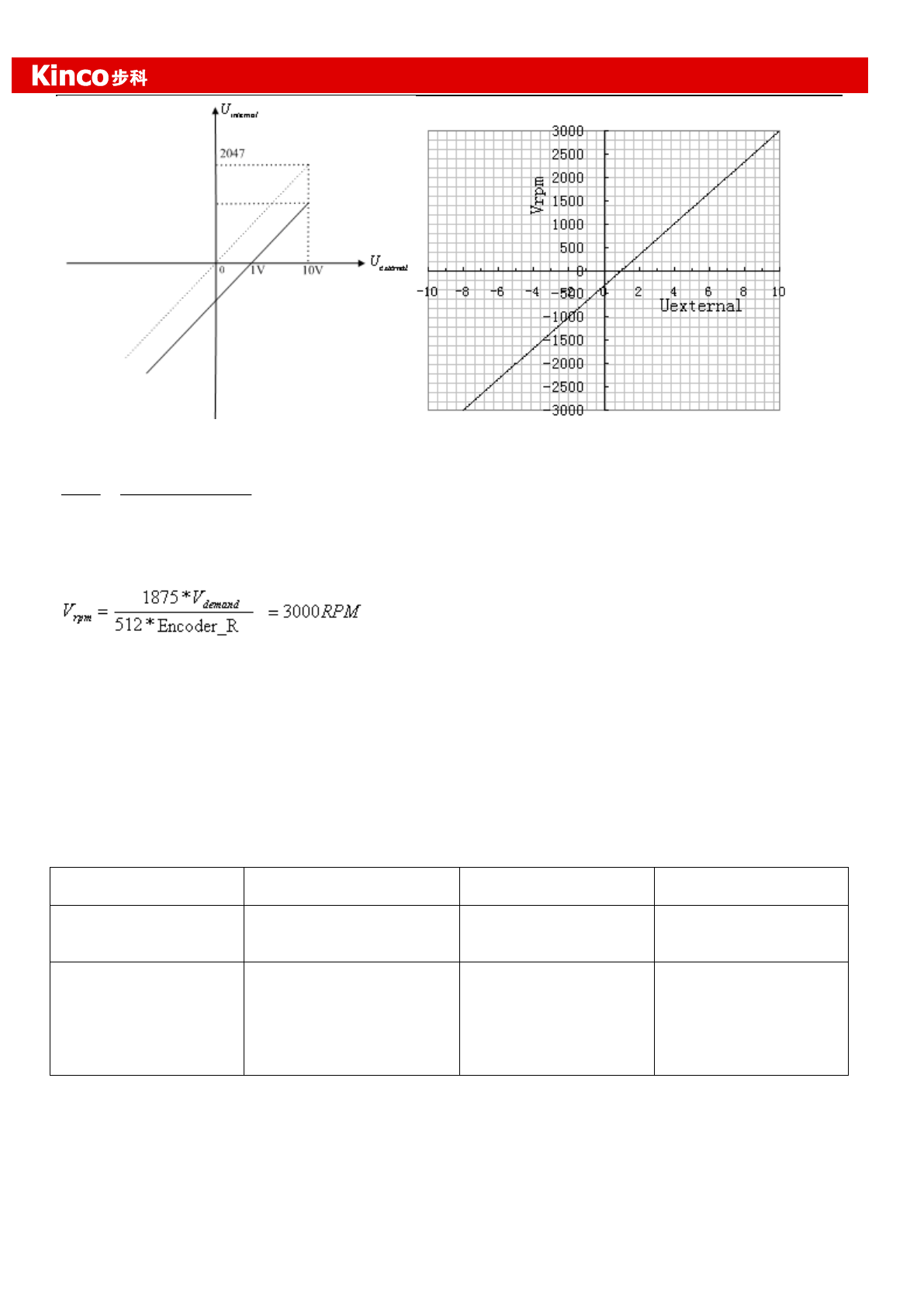
Kinco JD 伺服系列使用手册
84
Kinco FD Series Servo User Manual
Fig. 8-9 Schematic diagram of Example 8-5
Calculate
filter
U
according to the offset voltage and dead zone voltage that require settings:
2047
10 10
filter
shift dead
U
v v U U
(In this example,
0
dead
U
, and
1
shift
U
)
Result:
1842
filter
U
Calculate
demand
V
according to the required speed :
rpm
V
, (Encoder_R:10000 inc/r)
Result:
8192000
demand
V
Calculate
filter
U
according to
demand
V
and
Factor
:
*
demand filter
V Factor U
Result:
Factor
=4447
Calculate
log1_Ana Offset
according to the required offset voltage:
8191/10 log1_ / shift
v Ana Offset U
Result:
log1_Ana Offset
=819
The following changes are required on the basis of Example 8-3.
Table 8-14 Parameter settings in Example 8-5
d3.24
Analog1_Offset
Sets offset data for
external analog signal 1
Set to 819
d3.29
Analog_Speed_Factor
Sets the proportion
between analog signals
and output speed
Set to 4447
d3.00
Store_Loop_Data
1: Storing all configured
parameters for the
control loop
10: Initializing all
parameters for the
control loop
Set to 1
Example 8-6: Analog – speed mode (setting the dead zone voltage and offset
voltage)
Requirement: Set the offset voltage to 1V, the dead zone voltage to 0.5V to 1.5V, and the max speed
corresponding to 10V to 3000 rpm. Select analog channel 1 (AIN1) to control the speed.
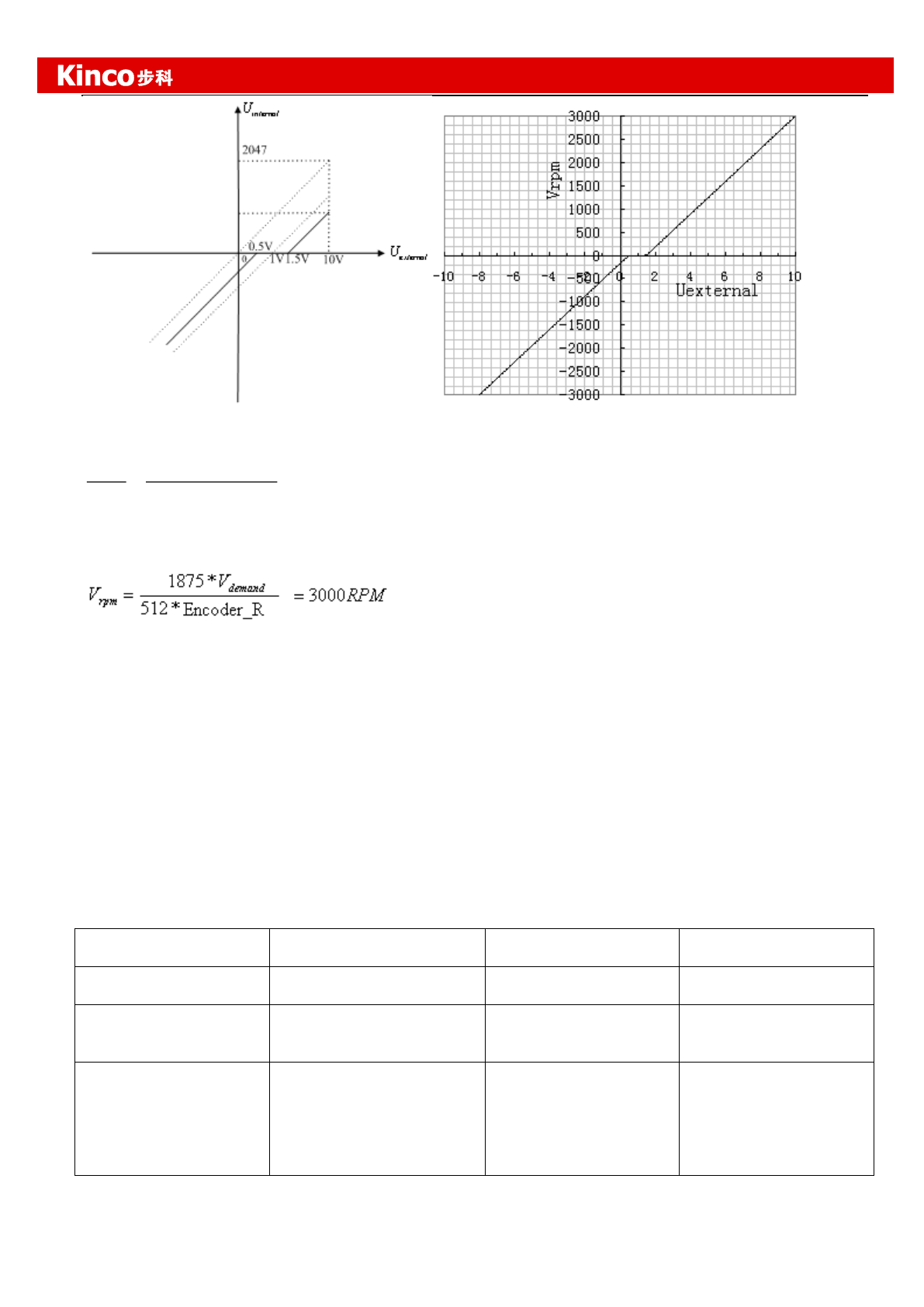
Kinco JD 伺服系列使用手册
85
Kinco FD Series Servo User Manual
Fig. 8-10 Schematic diagram of Example 8-6
Calculate
filter
U
according to the offset voltage and dead zone voltage that require settings:
2047
10 10
filter
shift dead
U
v v U U
(In this example,
0
dead
U
.5, and
1
shift
U
)
Result:
filter
U
=1740
Calculate
demand
V
according to the required speed :
rpm
V
, (Encoder_R:10000 inc/r)
Result:
8192000
demand
V
Calculate
Factor
according to
filter
U
and
demand
V
:
*
demand filter
V Factor U
Result:
Factor
=4708
Calculate
log1_Ana Dead
according to the required dead zone voltage:
8191/10 log1_ / dead
v Ana Dead U
Result:
log1_Ana Dead
=409
Calculate
log1_Ana Offset
according to the required offset voltage:
8191/10 log1_ / shift
v Ana Offset U
Result:
log1_Ana Offset
=819
The following changes are required on the basis of Example 8-3.
Table 8-15 Parameter settings in Example 8-6
d3.23
Analog1_Dead
Sets dead zone data for
external analog signal 1
Set to 409
d3.24
Analog1_Offset
Sets offset data for
external analog signal 1
Set to 819
d3.29
Analog_Speed_Factor
Sets the proportion
between analog signals
and output speed
Set to 4708
d3.00
Store_Loop_Data
1: Storing all configured
parameters for the
control loop
10: Initializing all
parameters for the
control loop
Set to 1
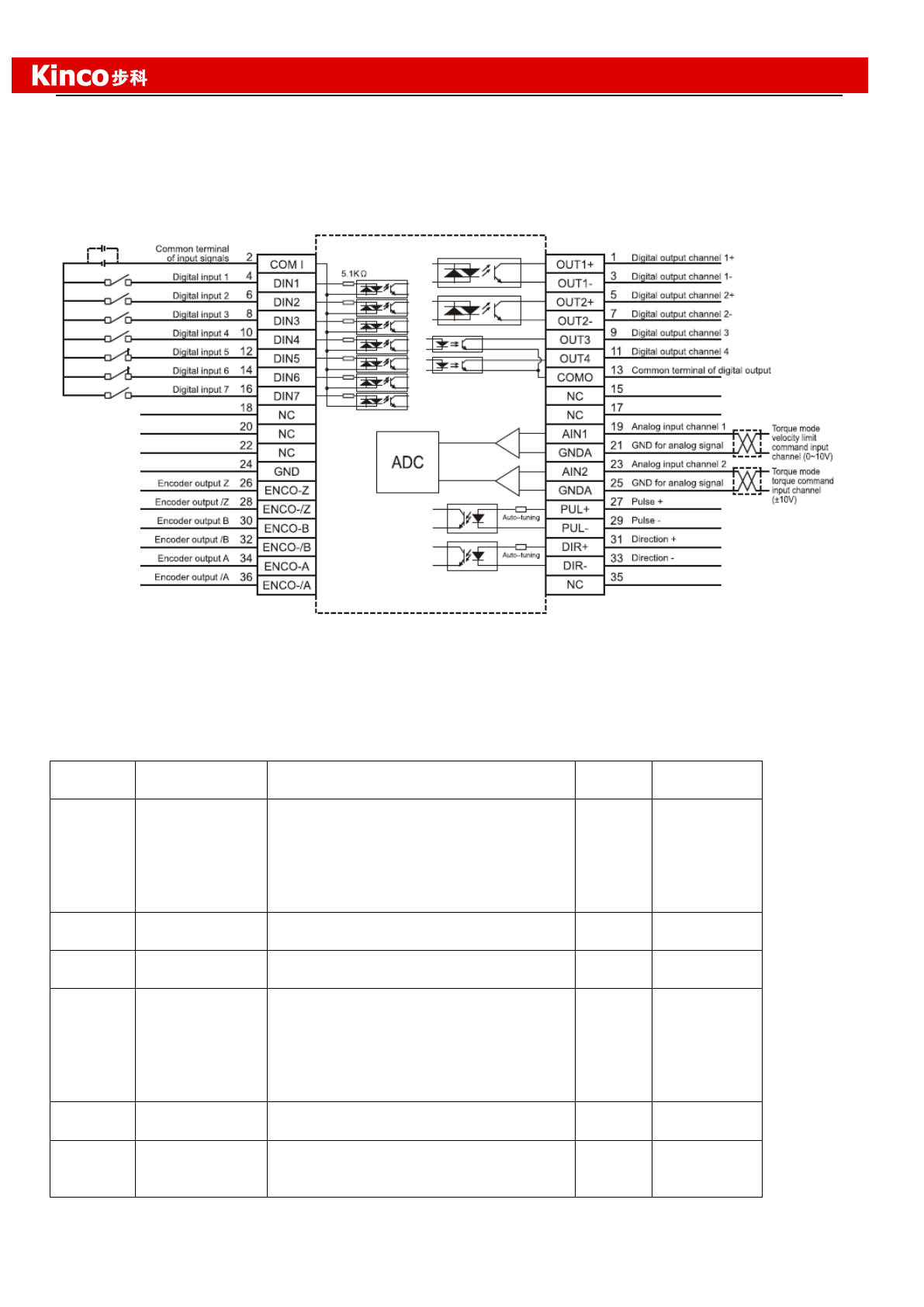
Kinco JD 伺服系列使用手册
86
Kinco FD Series Servo User Manual
8.3 Torque Mode (“4” Mode)
8.3.1 Wiring in Analog – Torque Mode
Fig. 8-11 Wiring diagram of FD Servo in analog – torque mode
8.3.2 Parameters for Analog – Torque Mode
Table 8-16 Parameters for analog – torque mode
Numeric
Display
Variable Name
Meaning
Default
Value
Range
d3.22
Analog1_Filter
Used to smooth the input analog
signals.
Filter frequency: f=4000/(2π*
Analog1_Filter)
Time Constant: τ = Analog1_Filter/4000
(S)
5
1~127
d3.23
Analog1_Dead
Sets dead zone data for external analog
signal 1
0
0~8192
d3.24
Analog1_Offset
Sets offset data for external analog
signal 1
0
-8192~8192
d3.25
Analog2_Filter
Used to smooth the input analog
signals.
Filter frequency: f=4000/(2π*
Analog1_Filter)
Time Constant (T) =
Analog2_Filter/4000 (S)
5
1~127
d3.26
Analog2_Dead
Sets dead zone data for external analog
signal 2
0
0~8192
d3.27
Analog2_Offset
Sets offset data for external analog
signal 2
0
-8192~8192
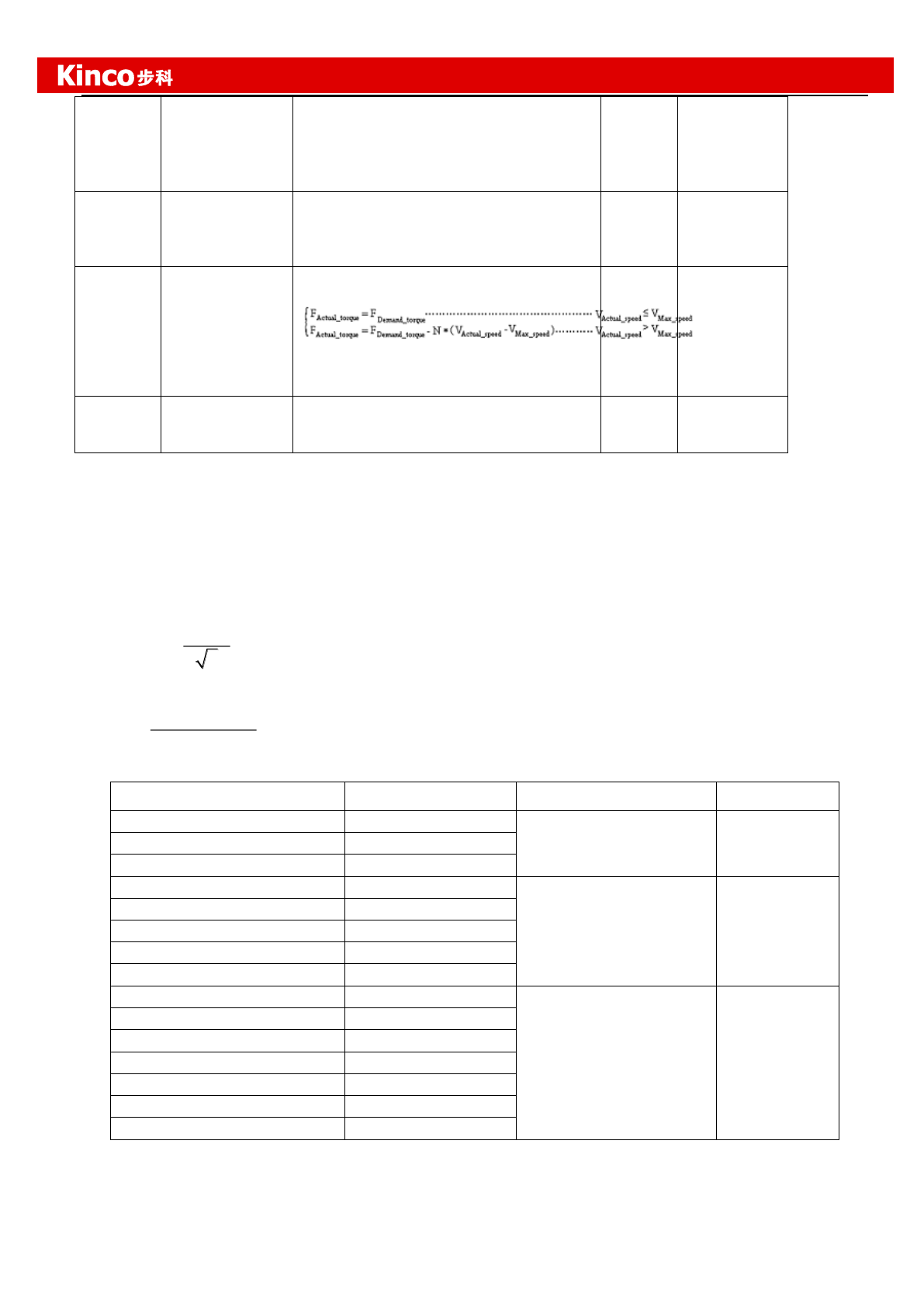
Kinco JD 伺服系列使用手册
87
Kinco FD Series Servo User Manual
d3.30
Analog_Torque
_Con
Selects analog - torque channels
0: Invalid analog channel
1: Valid analog channel 1 (AIN1)
2: Valid analog channel 2 (AIN2)
Valid mode 4
0
N/A
d3.31
Analog_Torque
_Factor
Sets the proportion between analog
signals and output torque (current)
1000
N/A
d2.15
Speed_Limit_F
actor
The factor that limits the maximum
speed in the torque mode
Vmax_speed complies with d2.24
Max_Speed_RPM parameter settings.
10
0~1000
d2.24
Max_Speed_R
PM
Limits the max rotation speed of the
motor
5000
0~6000
8.3.3 Analog Signal Processing
In the analog – torque mode, external analog command signals are directly inputted to the current loops
in the driver, thus directly controlling target current through the internal current loop. Analog signal is
processed in the same way as that in the analog – speed mode.
In the analog – torque mode,
demand
I
is calculated according to the specified
demand
T
with the formula of
*2
demand
demand t
I
TK
(
t
K
is a torque constant).
Factor
is calculated according to
demand
I
and
filter
U
with the formula of
**
2048*2048
filter
demand
Factor U
I Ipeak
(
Ipeak
indicates the peak current of a driver).
Table 8-17
t
K
and
Ipeak
parameters
Motor Model
t
K
(Nm/A)
Driver Model
Ipeak
(A)
SMH60S-0020-30AXK-3LKX
0.48
FD422
15
SMH60S-0040-30AXK-3LKX
0.48
SMH80S-0075-30AXK-3LKX
0.662
SMH80S-0100-30AXK-3LKX
0.562
FD432
27.5
SMH110D-0105-20AXK-4LKX
0.992
SMH110D-0126-20AXK-4LKX
1.058
SMH130D-0105-20AXK-4HKX
1.1578
SMH130D-0157-20AXK-4HKX
1.191
SMH110D-0126-30AXK-4HKX
1.058
FD622
25
SMH110D-0157-30AXK-4HKX
0.992
SMH110D-0188-30AXK-4HKX
1.058
SMH130D-0105-20AXK-4HKX
1.1578
SMH130D-0157-20AXK-4HKX
1.191
SMH130D-0210-20AXK-4HKX
1.3232
SMH150D-0230-20AXK-4HKX
1.65
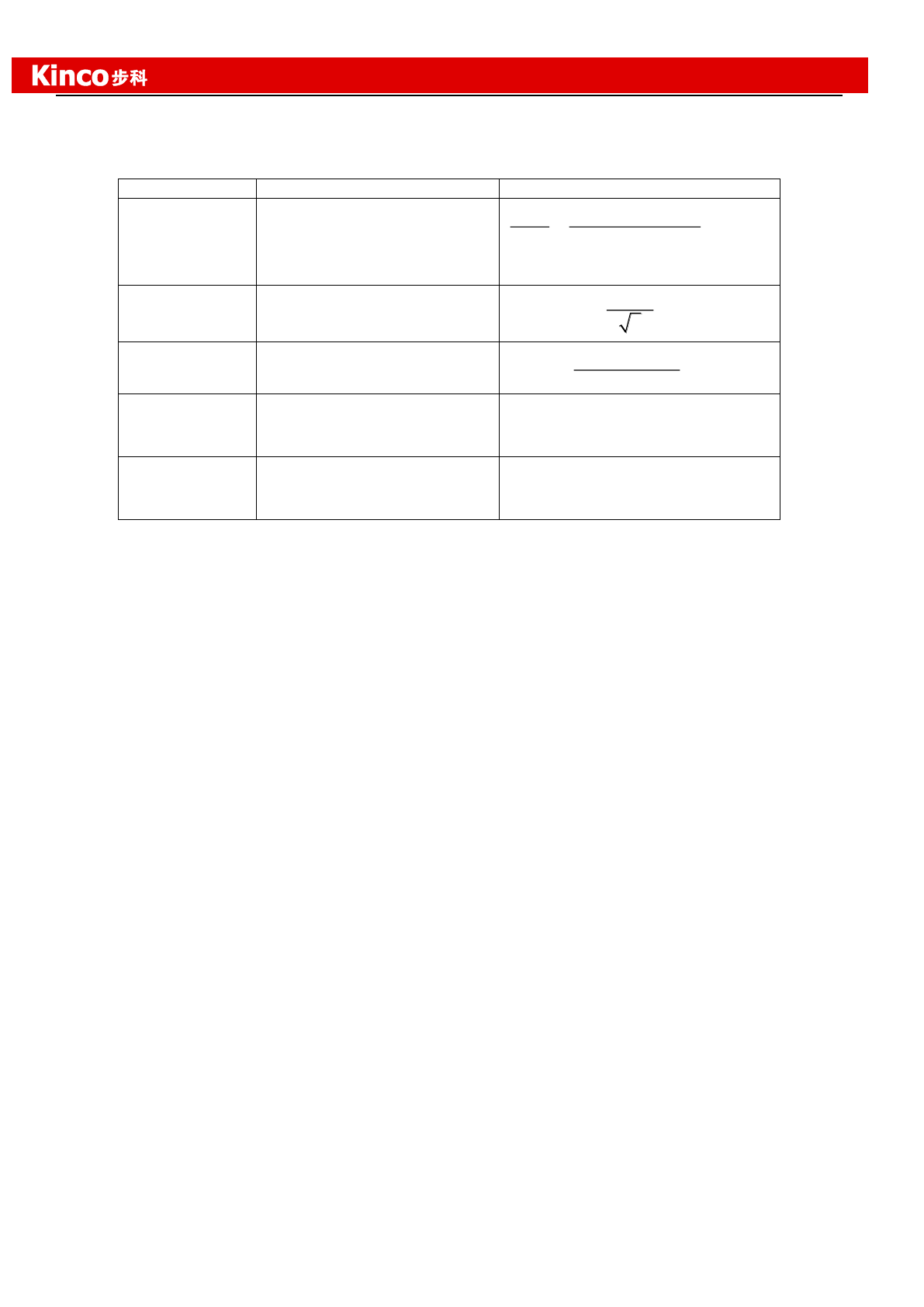
Kinco JD 伺服系列使用手册
88
Kinco FD Series Servo User Manual
8.3.4 Calculation Procedure for Analog – Torque Mode
Table 8-17 Calculation procedure for analog – torque mode
Procedure
Method
Formula
Step 1
Calculate
filter
U
according to
the offset voltage and dead
zone voltage that require
settings
2047
10 10
filter
shift dead
U
v v U U
Step 2
Calculate
demand
I
according to
the required torque
demand
T
*2
demand
demand t
I
TK
Step 3
Calculate
Factor
according to
filter
U
and
demand
I
**
2048*2048
filter
demand
Factor U
I Ipeak
Step 4
Calculate
log_Ana Dead
according to the required dead
zone voltage
8191/10 log_ / dead
v Ana Dead U
Step 5
Calculate
log_Ana Offset
according to the required offset
voltage
8191/10 log_ / shift
v Ana Offset U
8.3.5 Examples of Analog – Torque Mode
In the analog – torque mode, follow the steps below to configure a driver:
Step 1: Confirm whether it is necessary to enable the driver through external digital input ports. To enable the
driver through external digital input ports, see Table 6-12 in Example 6-3 for settings. If the driver does not
require enabling through external digital input ports, you can disable the enabling function of external digital
input ports by referring to Table 6-13 of Example 7-3, and enable the auto power-on function of the driver by
setting its internal parameters.
Step 3: Confirm mode switching positions and operation modes by referring to the settings in Example 6-5.
The factory default settings for the driver are as follows: When no signal is inputted to DIN3, the driver
operates in the “-4” mode (d3.16 = -4); when signal is inputted to DIN3, the driver operates in the “-3” mode
(d3.17 = -3). If the driver is required to operate in the torque mode (“4” mode), please set d3.16 or d3.17 to 4.
In case d3.16 = 4, if DIN3 has no input signals when the driver is powered on, the driver operates in the “4”
mode. In case d3.17 = 4, if DIN3 has input signals, the driver operates in the “4” mode.
Step 3: After configuring functions on digital input ports, select the analog – torque channel, and set
parameters such as analog – torque factors, dead zone, offset, filtering, speed limit factors, and max speed
limits.
Step 4: Save parameters.
Example 8-7: Analog – torque mode (without setting the dead zone voltage and
offset voltage)
Requirement: DIN1 is used for enabling the driver, DIN2 is used for error resetting, and DIN3 controls the
operation modes of the driver (the mode is “4” when no signal is inputted, and is “3” when signal is inputted).
The motor Kt is 0.48 Nm/A, and the peak current of drivers is 15 A. The analog input voltage -10 V
corresponds to -0.64 Nm, and 10 V corresponds to 0.64 Nm. Select analog channel 2 (AIN1) to control the
torque.
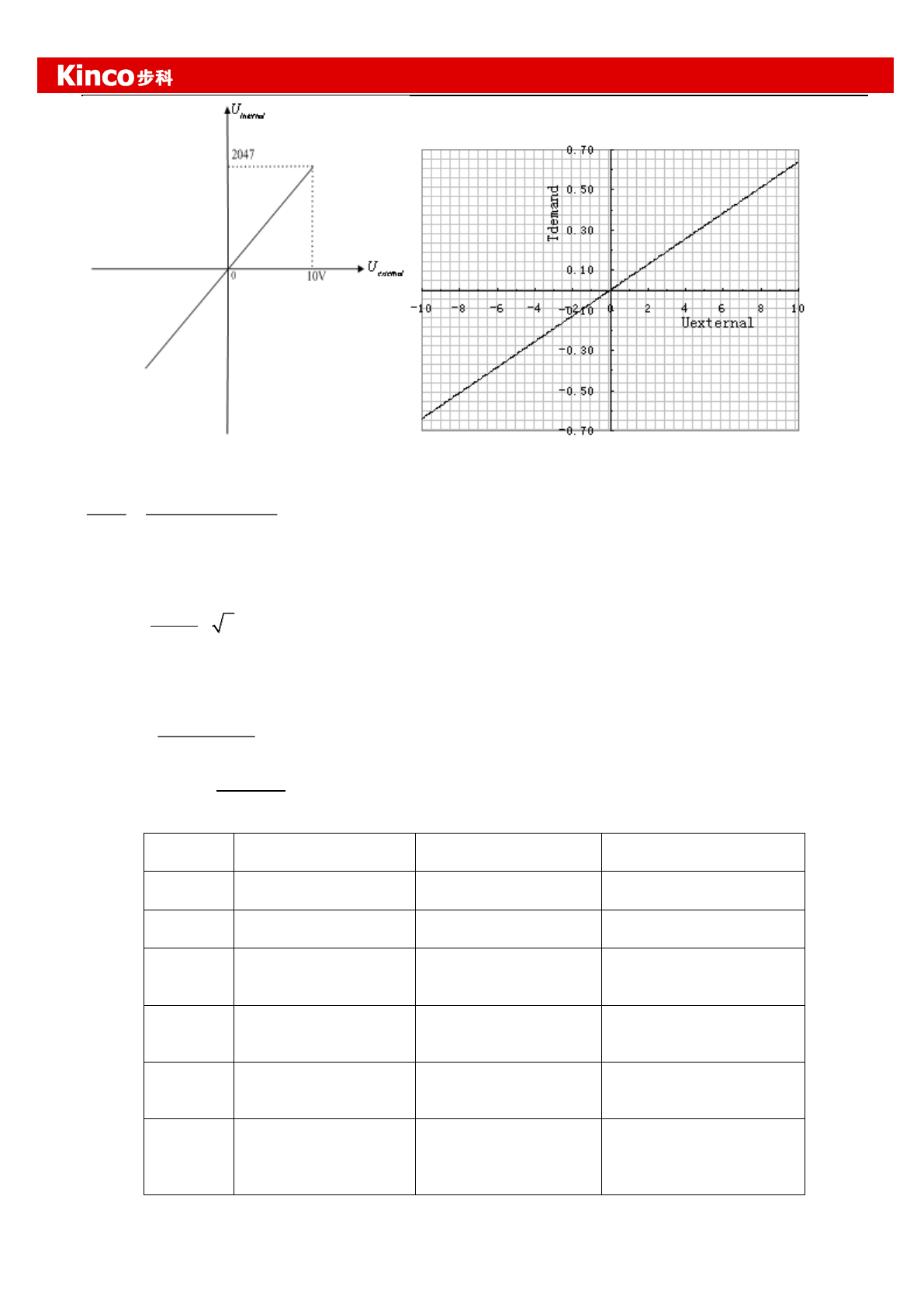
Kinco JD 伺服系列使用手册
89
Kinco FD Series Servo User Manual
Fig. 8-13 Schematic diagram of Example 8-7
Calculate
filter
U
according to the offset voltage and dead zone voltage that require settings:
2047
10 10
filter
shift dead
U
v v U U
(In this example,
0
dead
U
, and
0
shift
U
)
Result:
filter
U
=2047
Calculate
demand
I
according to the required torque
demand
T
:
*2
demand
demand
t
T
IK
Result:
demand
I
=1.89
Calculate
Factor
according to
filter
U
and
demand
I
:
*2048*4096
*
demand
filter
I
Factor U Ipeak
Result:
1.89 *2048*4096 515
2047*15
Factor
Table 8-18 Parameter settings in Example 8-7
Numeric
Display
Variable Name
Meaning
Parameter Settings
d3.01
Din1_Function
Defines the functions of
digital input port 1
000.1 (Driver enable)
d3.02
Din2_Function
Defines the functions of
digital input port 2
000.2 (Error resetting)
d3.03
Din3_Function
Defines the functions of
digital input port 3
000.4 (Control over
operation modes of
drivers)
d3.16
Din _Mode0
Select this operation
mode when input
signals are invalid
Set to 0004 (4) mode
(torque mode)
d3.17
Din _Mode 1
Select this operation
mode when input
signals are valid
Set to 0.003 (3) mode
(speed mode with
acceleration/deceleration)
d3.25
Analog2_Filter
Used to smooth the
input analog signals.
Filter frequency:
f=4000/(2π*
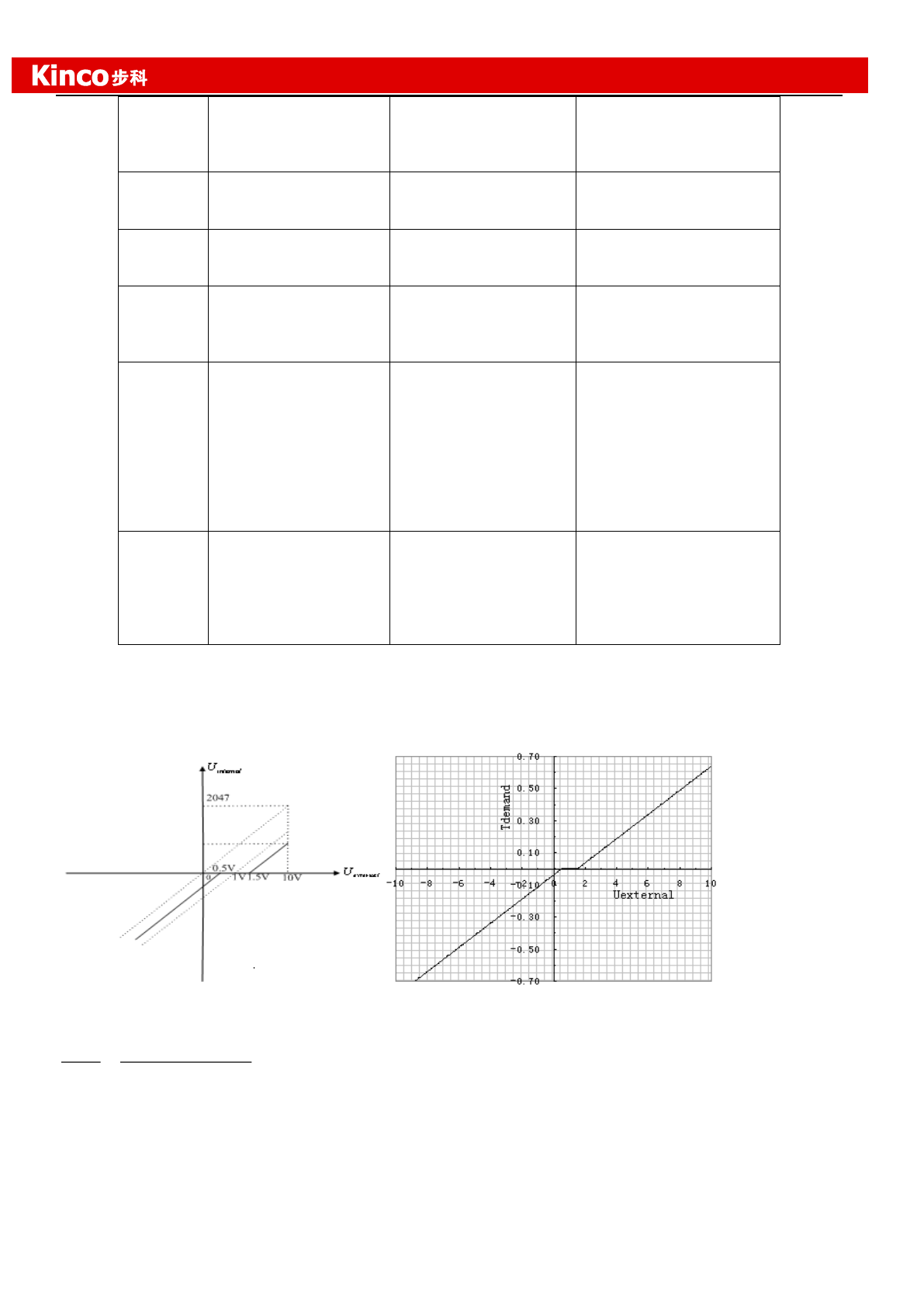
Kinco JD 伺服系列使用手册
90
Kinco FD Series Servo User Manual
Analog1_Filter)
Time Constant: T =
Analog2_Filter/4000
(S)
d3.26
Analog2_Dead
Sets dead zone data
for external analog
signal 2
Set to 0
d3.27
Analog2_Offset
Sets offset data for
external analog signal
2
Set to 0
d3.31
Analog_Torque_Factor
Sets the proportion
between analog signals
and output torque
(current)
Set to 515
d3.30
Analog_Torque_Con
Selects analog - torque
channels
0: Invalid analog
channel
1: Valid analog channel
1 (AIN1)
2: Valid analog channel
2 (AIN2)
Valid mode 4
Set to 2
d3.00
Store_Loop_Data
1: Storing all configured
parameters for the
control loop
10: Initializing all
parameters for the
control loop
Set to 1
Example 8-8: Analog – torque mode (setting the dead zone voltage and offset
voltage)
Requirement: The offset voltage is 1V, and the dead zone voltage is 0.5V. The motor Kt is 0.48 Nm/A, and the
peak current of the driver is 15A. The analog input voltage 10V corresponds to 0.64Nm. Select analog
channel 2 (AIN2) to control the torque.
Fig. 8-14 Schematic diagram of Example 8-8
Calculate
filter
U
according to the offset voltage and dead zone voltage that require settings:
2047
10 10
filter
shift dead
U
v v U U
(In this example,
0
dead
U
.5, and
1
shift
U
)
Result:
filter
U
=1740
Calculate
demand
I
according to the required torque
demand
T
:
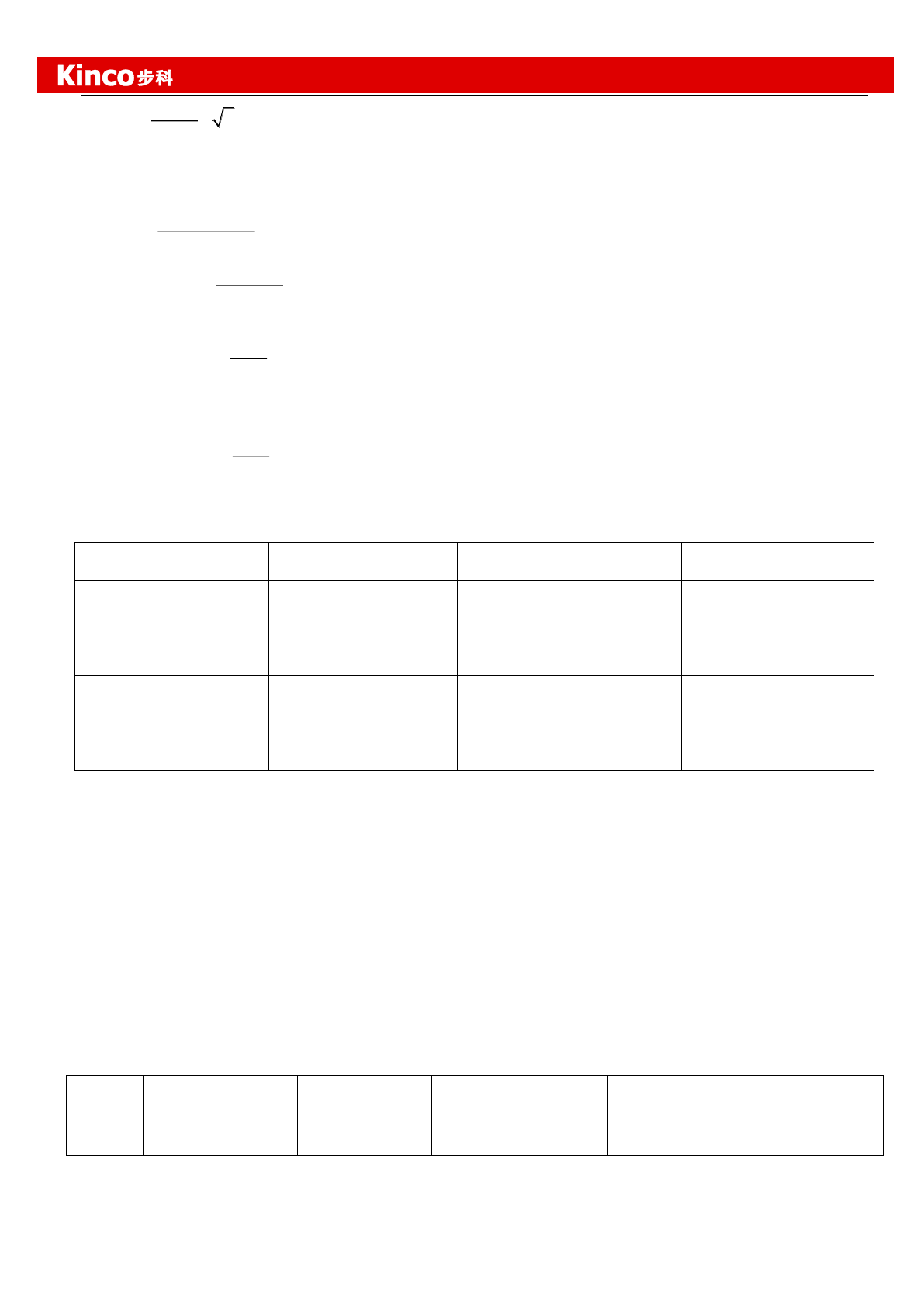
Kinco JD 伺服系列使用手册
91
Kinco FD Series Servo User Manual
*2
demand
demand
t
T
IK
Result:
demand
I
= 1.89
Calculate
Factor
according to
filter
U
and
demand
I
:
*2048*4096
*
demand
filter
I
Factor U Ipeak
Result:
1.89 *2048*4096 606
1740*15
Factor
Calculate
log2_Ana Dead
according to the required dead zone voltage:
8191
2_ *
10 dead
Analog Dead U
v
Result:
log2_Ana Dead
= 410
Calculate
log2_Ana Offset
according to the required offset voltage:
8191
2_ *
10 shift
Analog Offset U
v
Result:
log2_Ana Offset
=819
The following changes are required on the basis of Example 8-7.
Table 8-19 Parameter settings in Example 8-8
d3.26
Analog2_Dead
Sets dead zone data for
external analog signal 2
Set to 410
d3.27
Analog2_Offset
Sets offset data for external
analog signal 2
Set to 819
d3.31
Analog_Torque_Factor
Sets the proportion between
analog signals and output
torque (current)
Set to 2362
d3.00
Store_Loop_Data
1: Storing all configured
parameters for the control
loop
10: Initializing all parameters
for the control loop
Set to 1
8.4 Internal Multi-position Control Modes (“1” Mode)
In Internal multi-position control mode, we can activate internal set target position though an external signal to
control motors. The activation has two preconditions:
1, multi-position control mode can only be activated in Mode 1, it can’t be activated in other modes.
2, At least one of the external input signal is defined as “Internal position control 0”, “Internal position control 1
“ or “Internal position control 2 “, which means at least one address of digital tubes-d3.01 ~ d3.07 is set to
“040.0”’, “080.0” or “800.2.
“Internal position control 0” , “Internal position control 1” and “Internal position control 2 “, these three
signals will be combined into binary codes used to select a target position between “Position 0~7”.
Internal
position
0
Internal
position
1
Internal
position
2
Corresponding
position
Position section
numberic display
Corresponding
speed
Speed
section
numberic
display
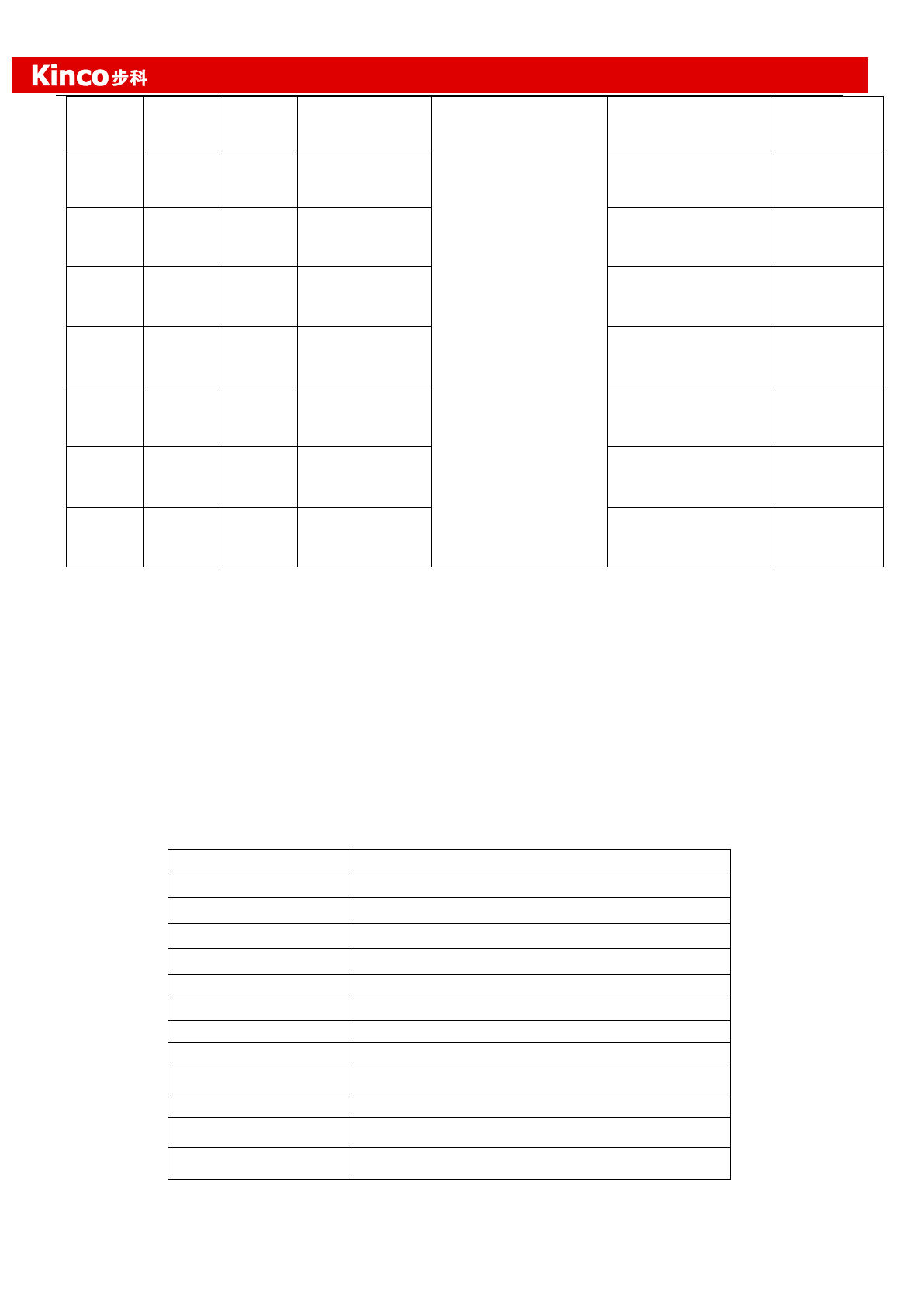
Kinco JD 伺服系列使用手册
92
Kinco FD Series Servo User Manual
Table 8-20 Internal Multi-position Control Mode Parameter Table
Note: In this control mode, “position section X” can be positive or negative, it can be flexibly set; while the
corresponding speed must be positive. Other parameters such as acceleration, deceleration, etc, can use the
default value; also can be changed through digital tube.
Example 8-9: Internal multi-position control mode
A motor needs to go eight position sections. In position section 0, it should reach the 5000 pulse location at
the speed of 100RPM.In position section 1, it should reach the 15000 pulse location at the speed of
150RPM.In position section 2, it should reach the 28500 pulse location at the speed of 175RPM.In position
section 3, it should reach the -105000 pulse location at the speed of 200RPM. In position section 4, it should
reach the -20680 pulse location at the speed of 300RPM. In position section 5, it should reach the -30550
pulse location at the speed of 325RPM. In position section 6, it should reach the 850 pulse location at the
speed of 275RPM. In position section 7, it should reach the 15000 pulse location at the speed of 460RPM.
Table 8-21 Internal Multi-position Control Mode Demand
DIN1
The driver is enabled, the motor shaft is locked
DIN3
Driver working mode(invalid 1,valid-3)
DIN4
Internal position 0
DIN5
Internal position 1
DIN6
Internal position 2
DIN6:DIN5:DIN4=0:0:0
Select position and speed in section 0
DIN6:DIN5:DIN4=0:0:1
Select position and speed in section 1
DIN6:DIN5:DIN4=0:1:0
Select position and speed in section 2
DIN6:DIN5:DIN4=0:1:1
Select position and speed in section 3
DIN6:DIN5:DIN4=1:0:0
Select position and speed in section 4
DIN6:DIN5:DIN4=1:0:1
Select position and speed in section 5
DIN6:DIN5:DIN4=1:1:0
Select position and speed in section 6
DIN6:DIN5:DIN4=1:1:1
Select position and speed in section 7
0
0
0
Din_Pos0
d3.40select position
section sequence
number
d3.41select position
section high bit
d3.42select position
section low bit
Din_Speed0_RPM
d3.18
0
0
1
Din_Pos1
Din_Speed1_RPM
d3.19
0
1
0
Din_Pos2
Din_Speed2_RPM
d3.20
0
1
1
Din_Pos3
Din_Speed3_RPM
d3.21
1
0
0
Din_Pos4
Din_Speed4_RPM
d3.44
1
0
1
Din_Pos5
Din_Speed5_RPM
d3.45
1
1
0
Din_Pos6
Din_Speed6_RPM
d3.46
1
1
1
Din_Pos7
Din_Speed7_RPM
d3.47
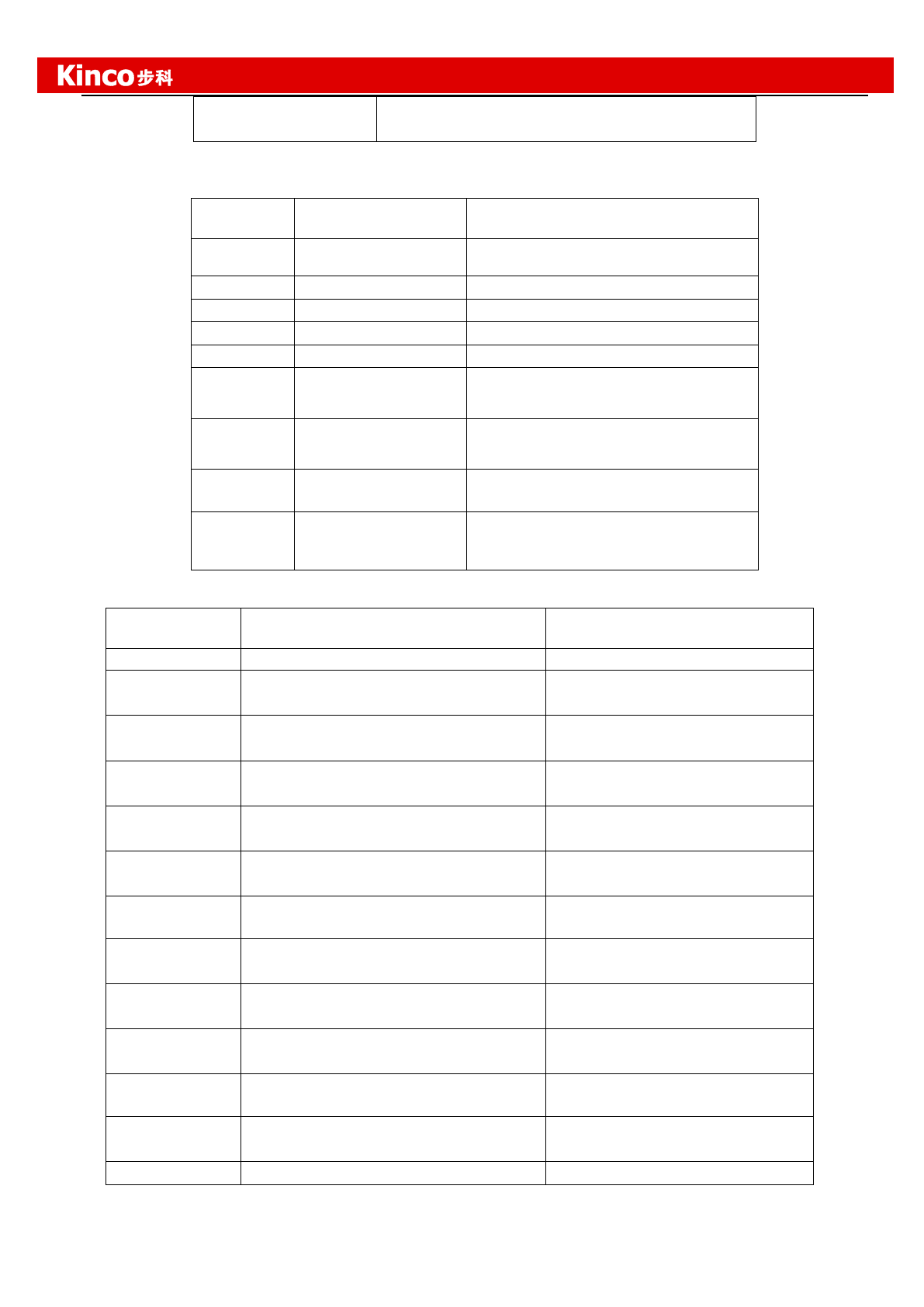
Kinco JD 伺服系列使用手册
93
Kinco FD Series Servo User Manual
DIN6
Activate command (execute the selected
position section)
Define the meanings of the input points:
Table 8-22 Internal Multi-position Control Mode Configuration
Numberic
display
Variable name
Configuration way
d3.01
Din1_Function
000.1(Driver enabled)
d3.03
Din3_Function
000.4(Set driver mode)
d3.04
Din4_Function
040.0(Internal position control 0)
d3.05
Din5_Function
080.0(Internal position control 1)
d3.06
Din6_Function
800.2 (Internal position control 2)
d3.07
Din7_Function
400.0(Activate command)
d3.16
Din_mode 0
Set 0001(1)Mode
Internal multi-position control mode
d3.17
Din_mode 1
Set 0.004 (-4) Mode
Pulse-control mode
d3.00
Storage parameters
1(Storage configuration parameters)
Set position and speed:
Table 8-23 Internal Multi-position and Speed Configuration
Numberic
display
Variable Name
Parameters Settings
d3.43
Relative / Absolute position selection
Set to 2F(absolute location)
d3.40
Set the position section number to 0
Set to 0(select position section
0)
d3.41
Set the high bit of position section
(N*10000)
Set to 0
d3.42
Set the low bit of position section
Set to 5000(set the position of
section 0 t0 5000)
d3.18
Set the speed of section 0
Set to 100(set the speed of
section 0 to 100)
d3.40
Set the position section number to 1
Set to 1(select position section
1)
d3.41
Set the high bit of position section
(N*10000)
Set to 1
d3.42
Set the low bit of position section
Set to 15000(set the position of
section 1 t0 15000))
d3.19
Set the speed of position section 1
Set to 150(set the speed of
section 1 to 150)
d3.40
Set the position section number to2
Set to 2(select position section
2)
d3.41
Set the high bit of position section
(N*10000)
Set to 2
d3.42
Set the low bit of position section
Set to 28500(set the position of
section 2 t0 28500)
d3.20
Set the speed of position section 1
Set to 175(set the speed of
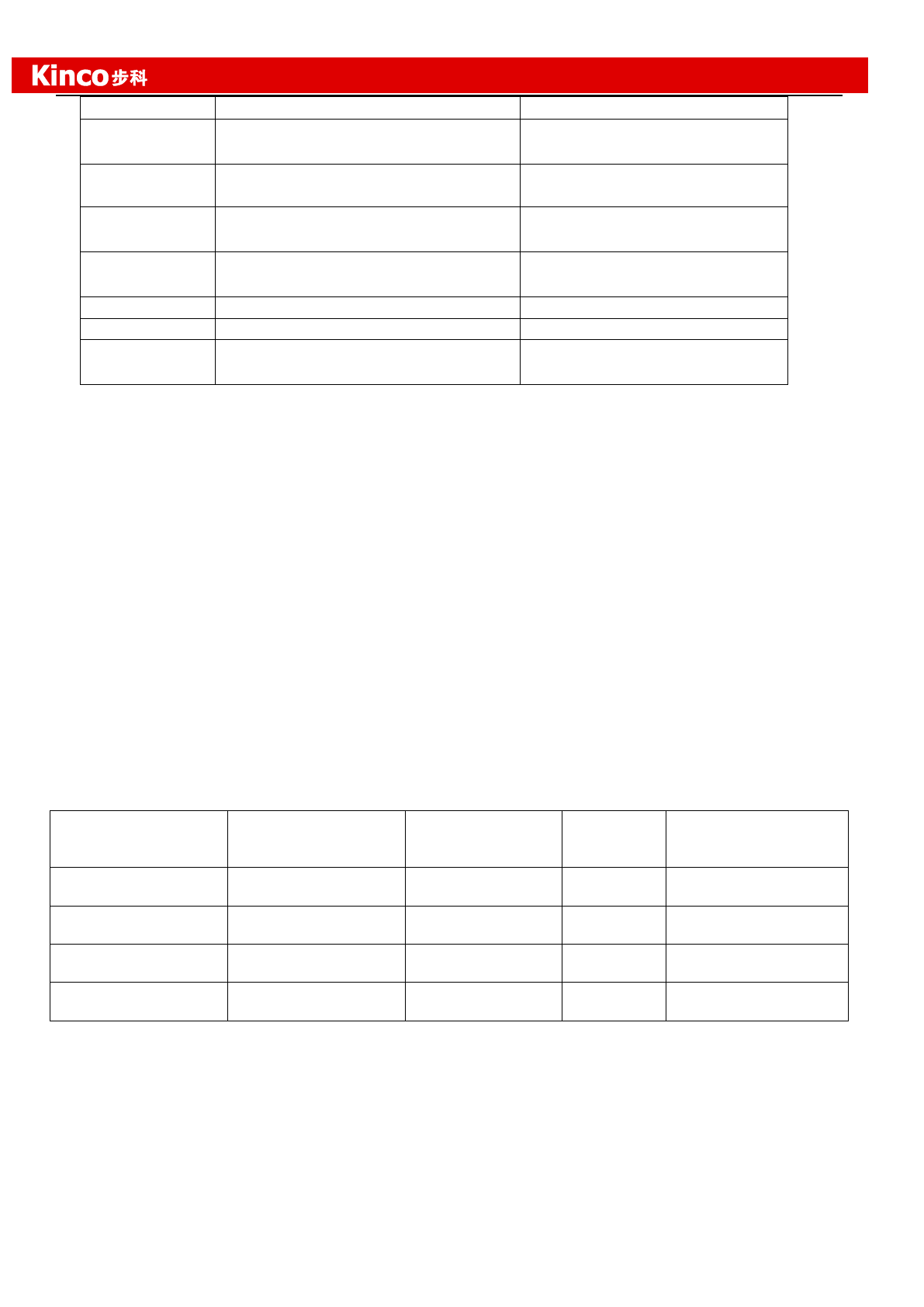
Kinco JD 伺服系列使用手册
94
Kinco FD Series Servo User Manual
section 2 to 175)
d3.40
Set the position section number to 3
Set to 3(select position section
3)
d3.41
Set the high bit of position section
(N*10000)
Set to 3
d3.42
Set the low bit of position section
Set to 10500(set the position of
section 3 t0 10500)
d3.20
Set the speed of position section 3
Set to 200(set the speed of
section 3 to 200)
d2.10
Acceleration
Default 610 rps/s
d2.11
Deceleration
Default 610 rps/s
d3.00
Storage parameter
1(storage configuration
parameters)
Set all these parameters, then:
1. Enable the driver, which means to make the digital input DIN1 high-level.
2. Select the position section, which means to change the electrical level of DIN4,DIN5 and DIN6.
3. Activate instructions and execute the program, which means to make the digital input DIN7 high-level.
Notice:
In multi-position control mode, select location method by setting the different value of the digital tube d3.43.If
you choose absolute positioning mode, set it to “F”; if the instructions require immediate updating, set it
to “2F”; if you choose relative positioning method, set it to “4F”.To change these parameters successfully,
you have to save the value of d3.00,and then restart.
8.5 Internal Multi-speed Control Modes (“-3” or “3” Mode)
In this control mode, external input signals are used to activate the internally configured target speed to
control the motor. There are two prerequisites for activation:
1. Multi-speed control is available in the “-3” or “3” mode, and is unavailable in other modes.
2. Set d3.28 to 0. In this case, the analog – speed channel is invalid.
3. At least one external input signal DinX_Function defines Bit8 or Bit9.
For example, define Din2_Function corresponding to Din2 as 010.0, and Din3_Function corresponding
to Din3 as 020.0. In this way, the combination of the two above signals is used to choose any one of
Din_Speed0_RPM, Din_Speed1_RPM, Din_Speed2_RPM or Din_Speed3_RPM as the target speed.
Table 8-24 Parameters for internal multi-speed control modes
Internal Speed
Control 0
(Din_Sys.Bit8)
Internal Speed
Control 1
(Din_Sys.Bit9)
Meaning
Numeric
Display
Valid Object
(numeric display
operation)
0
0
Multi-speed
control: 0 [rpm]
d3.18
Din_Speed0_RPM
1
0
Multi-speed control
1 [rpm]
d3.19
Din_Speed1_RPM
0
1
Multi-speed control
2 [rpm]
d3.20
Din_Speed2_RPM
1
1
Multi-speed control
3 [rpm]
d3.21
Din_Speed3_RPM
Note: If you need to set the target speed precisely, it is required to set Din_Speed0, Din_Speed1, Din_Speed2
and Din_Speed3 with a host computer. The four data units are internal units and are suitable for users who
are familiar with drivers. Din_SpeedX_RPM indicates the data after converting Din_SpeedX into the unit of
rpm to facilitate users. Conversion involves both the reading and writing processes, and does not require
calculation by users.
Example 8-10: Internal multi-speed control
Requirement: You need to define the digital input ports DIN6 and DIN7 as internal speed control, DIN1 as
driver enabling and DIN2 as operation mode control of the driver (the mode is “3” when the driver is valid, and
is “-3” when the driver is invalid). For detailed requirements, see Table 8-25. For the setting method, see
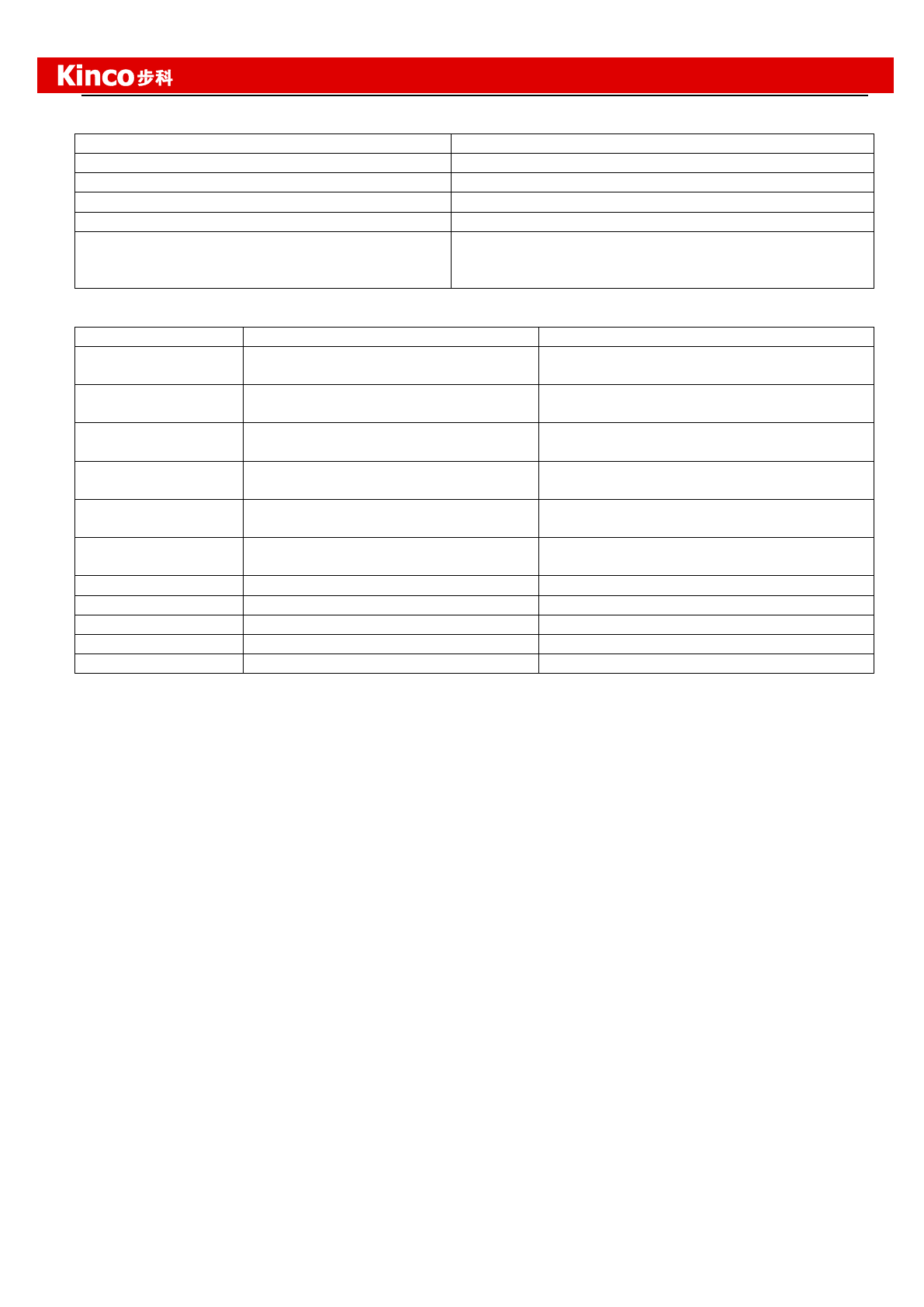
Kinco JD 伺服系列使用手册
95
Kinco FD Series Servo User Manual
Table 7-26.
Table 8-25 Requirements on internal multi-speed control
DIN6:DIN7=0:0
To execute the multi-step 1 speed (100 rpm)
DIN6:DIN7=1:0
To execute the multi-step 2 speed (200 rpm)
DIN6:DIN7=0:1
To execute the multi-step 3 speed (300 rpm)
DIN6:DIN7=1:1
To execute the multi-step 3 speed (400 rpm)
DIN1
To enable the driver, and lock the motor shaft
DIN2
To control operation modes of the driver (the mode is “3”
when the driver is valid, and is “-3” when the driver is
invalid)
Table 8-26 Setting methods for internal multi-speed control
Numeric Display
Variable Name
Setting Method
d3.01
Din1_Function
Set to 000.1
(Driver enable)
d3.02
Din2_Function
Set to 000.4
(control over operation modes of drivers)
d3.06
Din6_Function
Set to 010.0
(internal speed control 0)
d3.07
Din7_Function
Set to 020.0
(internal speed control 1)
d3.16
Din_Mode0
Set to 0.003 (3) mode
(speed mode with acceleration/deceleration)
d3.17
Din_Mode1
Set to 0.003 (-3) mode
(instantaneous speed mode)
d3.18
Din_Speed0_RPM
Set to 100 [rpm]
d3.19
Din_Speed1_RPM
Set to 200 [rpm]
d3.20
Din_Speed2_RPM
Set to 300 [rpm]
d3.21
Din_Speed3_RPM
Set to 400 [rpm]
d3.00
Store_Loop_Data
Set to 1
8.6 Internal Torque Control Mode (“4” Mode)
In the internal torque mode, only the current loop of the driver operates. Set d0.03 (CMD_q target current)
parameter directly to obtain the desired target torque. The prerequisite is that d3.30 must be set to 0. In this
case, the analog–torque channel is invalid.
8.7 Homing Mode (“6” Mode)
1, Summary
To make a system execute positioning in accordance with its absolute positioning, the first step is to define
the origin. For instance, as shown in the following XY plane, to navigate to (X, Y) = (100mm, 200mm), you
must define the origin of the machine firstly. It’s necessary to define the origin.
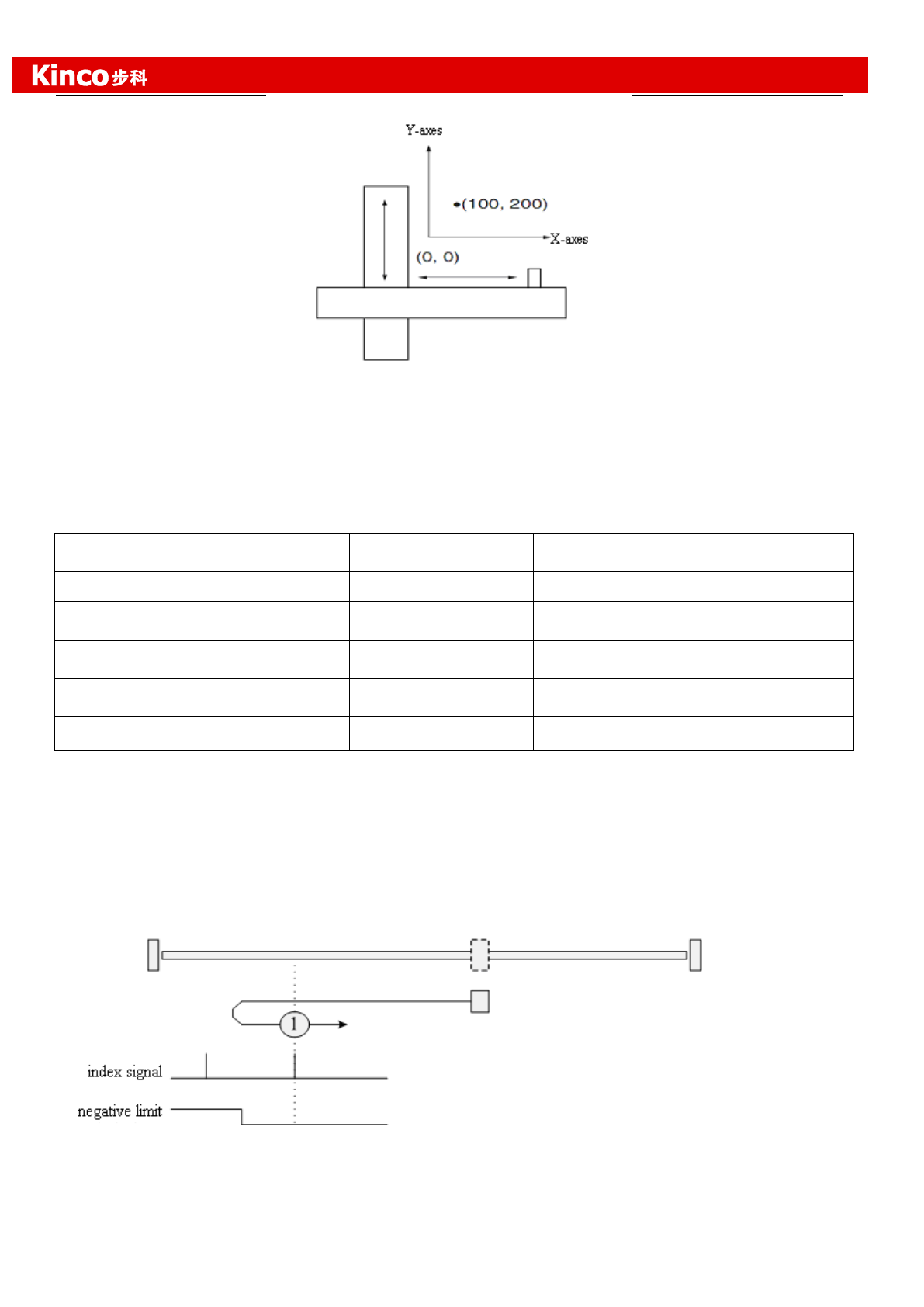
Kinco JD 伺服系列使用手册
96
Kinco FD Series Servo User Manual
2, Procedure of homing
Use the following steps to homing:
1. Set the external I / O parameters, and then save.
2. Set the data for homing, and then save.
3. Execute homing.
3, Configuration of the data for homing
Here are simple descriptions of the data for executing homing.
CD has 27 methods for homing, referring the CANopen’s definition of DSP402.
1st-14th methods use Z signal as homing signal.
17th-30th methods use external signal as homing signal.
Method 1: Homing on the negative limit switch and index pulse
Using this method, the initial direction of movement is leftward if the negative limit
switch is inactive (here shown as low). The home position is at the first index pulse to the
right of the position where the negative limit switch becomes inactive.
Method 2: Homing on the positive limit switch and index pulse
0x607C0020
Home_Offset
Home offset
In Homing mode, set the offset relative to
the zero point.
0x60980008
Homing_Method
Homing method
Select the homing method
0x60990120
Homing_Speed_Switch
Speed for searching
the limit switch
Set the speed for searching the limit
switch which defined as homing signal.
0x60990220
Homing_Speed_Zero
Speed for searching
the Zero point.
Only valid when find Index signal.
0x60990308
Homing_Power_On
Homing when power
on
Every time after power on,it will start
homing once.
0x609A0020
Homing_Accelaration
Homing acceleration
Control the acceleration of homing
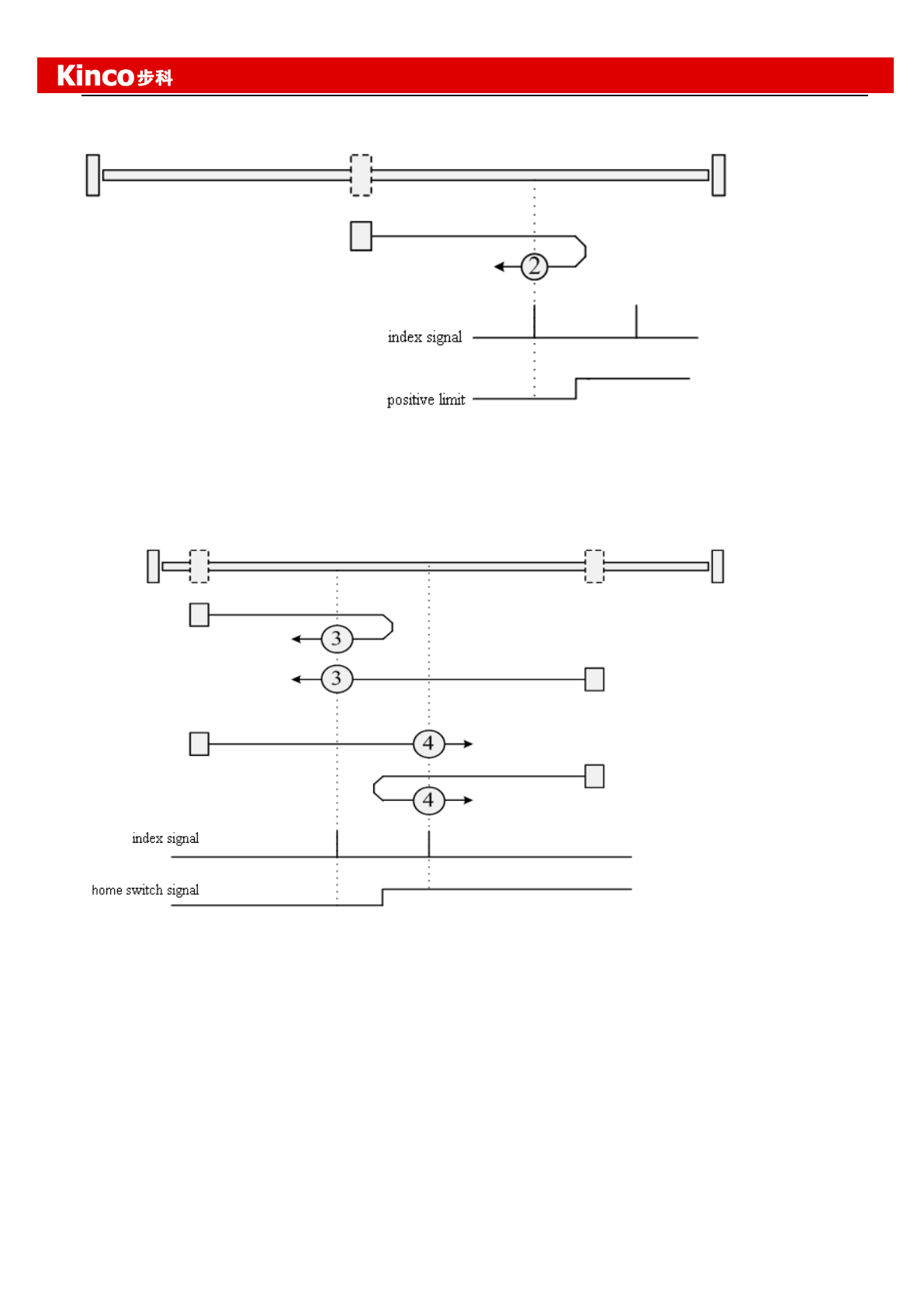
Kinco JD 伺服系列使用手册
97
Kinco FD Series Servo User Manual
Using this method, the initial direction of movement is rightward if the positive limit
switch is inactive (here shown as low). The position of home is at the first index pulse to
the left of the position where the positive limit switch becomes inactive.
Methods 3 and 4: Homing on the positive home switch and index pulse
Using methods 3 or 4, the initial direction of movement is dependent on the state of the
home switch. The home position is at the index pulse to either the left or right of the pint
where the home switch changes state. If the initial position is sited so that the direction of
movement must reverse during homing, the point at which the reversal takes place is
anywhere after a change of state of the home switch.
Methods 5 and 6: Homing on the negative home switch and index pulse
Using methods 5 or 6, the initial direction of movement is dependent on the state of the
home switch. The home position is at the index pulse to either the left or the right of the
point where the home switch changes state. If the initial position is sited so that the
direction of movement must reverse during homing, the point at which the reversal takes
place is anywhere after a change of state of the home switch.
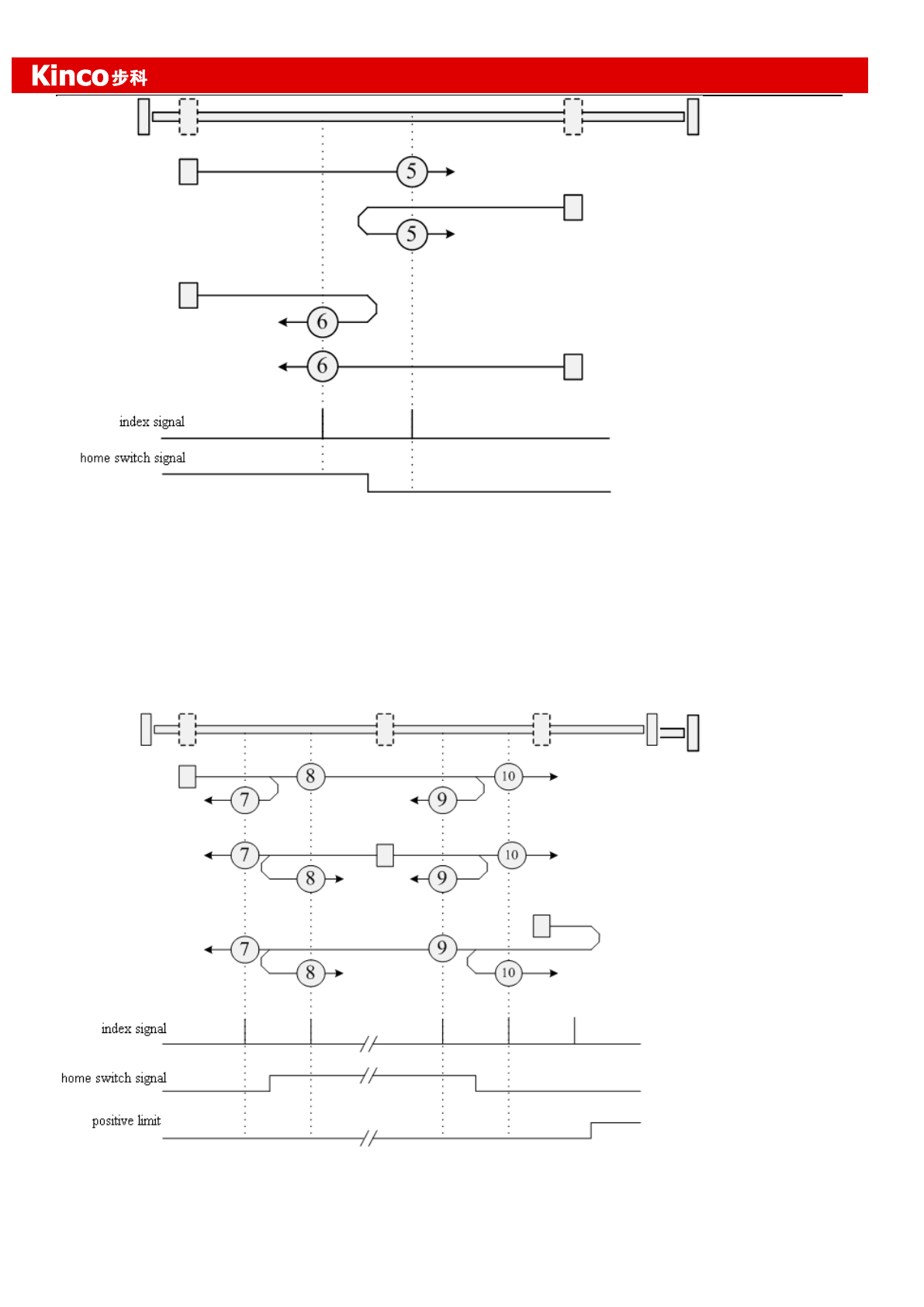
Kinco JD 伺服系列使用手册
98
Kinco FD Series Servo User Manual
Methods 7 to 14: Homing on the home switch and index pulse
These methods use a home switch that is active over only a portion of the travel; in effect
the switch has a “momentary” action as the axle position sweeps past the switch.
Using methods 7 to 10, the initial direction of movement is to the right, and using
methods 11 to 14, the initial direction of movement is to the left, except if the home
switch is active at the start of motion. In this case, the initial direction of motion is
dependent on the edge being sought. The home position is at the index pulse on either
side of the rising or falling edges of the home switch, as shown in the following two
diagrams. If the initial direction of movement leads away from the home switch, the
drive must reverse on encountering the relevant limit switch.
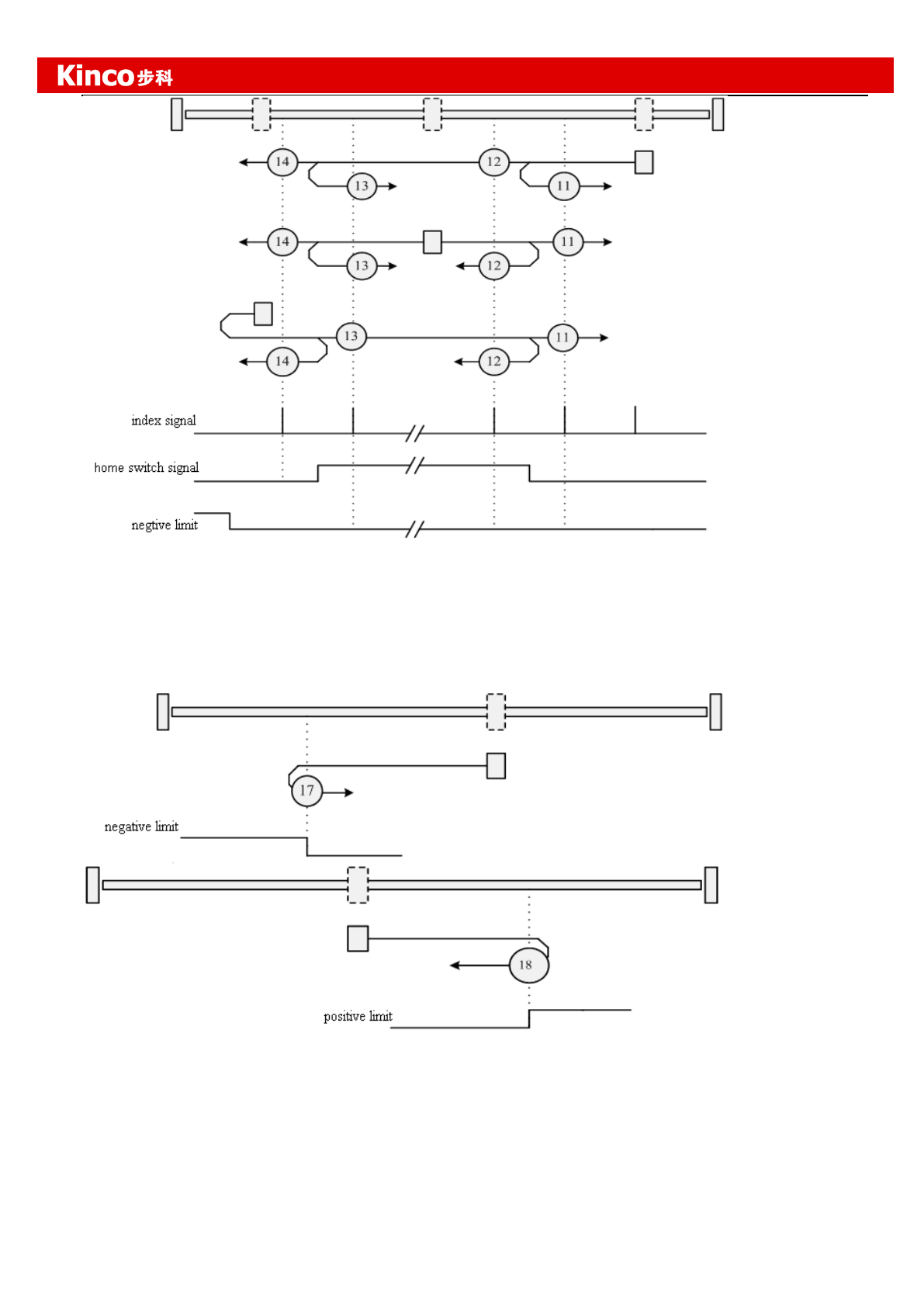
Kinco JD 伺服系列使用手册
99
Kinco FD Series Servo User Manual
Methods 15 and 16: Reserved
These methods are reserved for future expansion of the homing mode.
Methods 17 to 30: Homing without an index pulse
These methods are similar to methods 1 to 14, except that the home position is not
dependent on the index pulse; it is dependent only on the relevant home or limit switch
transitions. For example, methods 19 and 20 are similar to methods 3 and 4, as shown in
the following diagram:
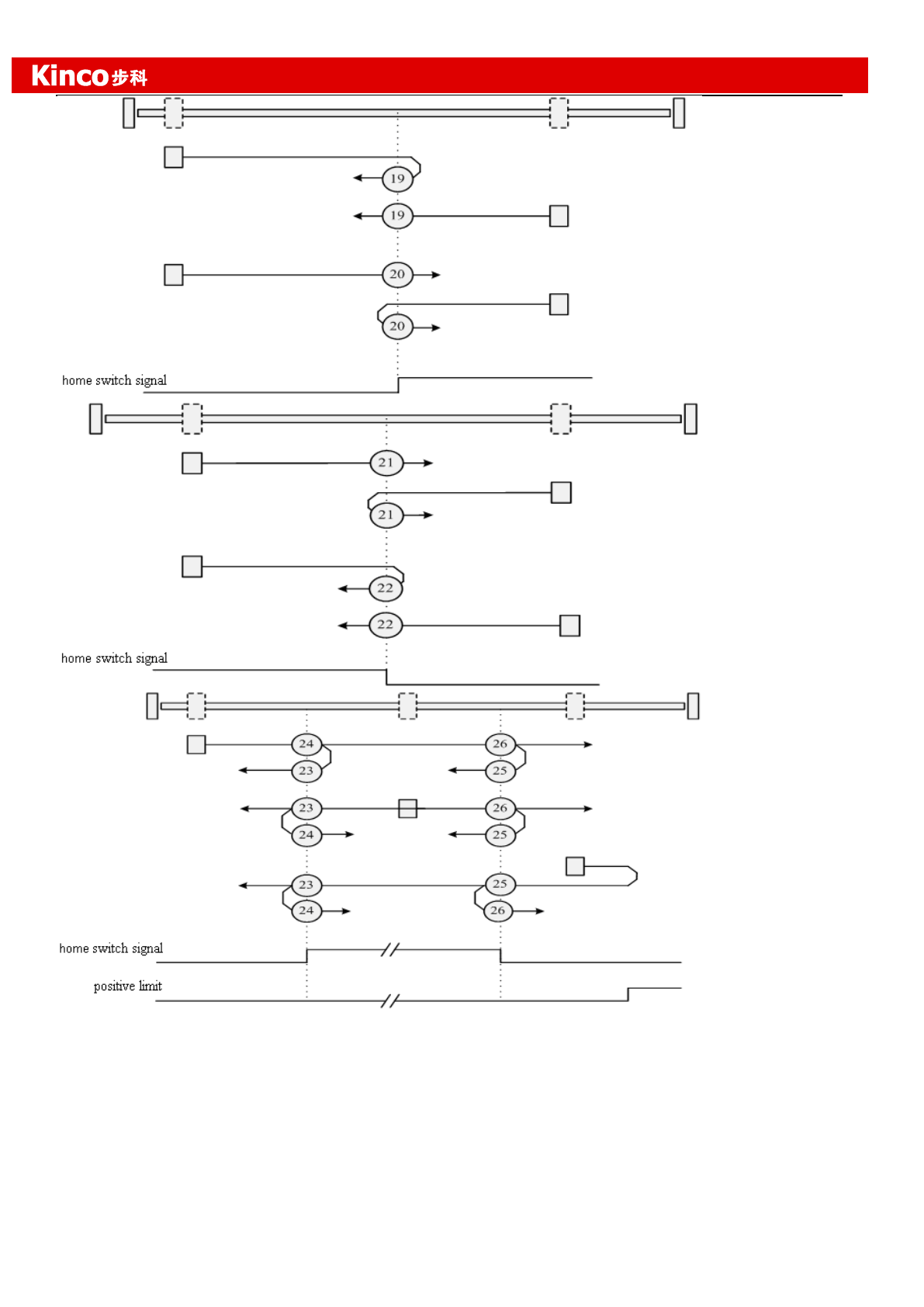
Kinco JD 伺服系列使用手册
100
Kinco FD Series Servo User Manual
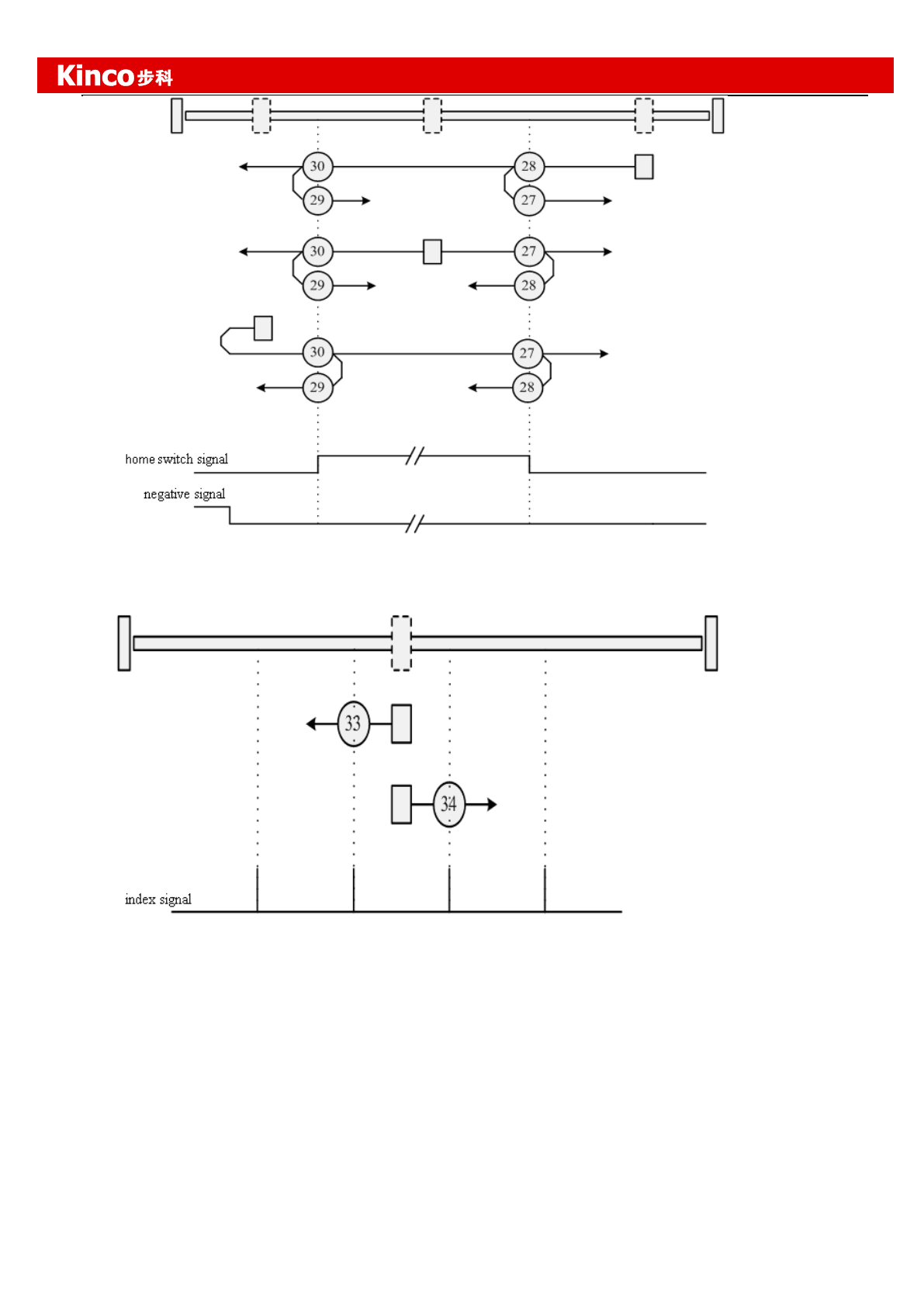
Kinco JD 伺服系列使用手册
101
Kinco FD Series Servo User Manual
Methods 31 and 32: Reserved
These methods are reserved for future expansion of the homing mode.
Methods 33 and 34: Homing on the index
Method 35: Homing on the current position
In this method, the current position is taken to be the home position.
Methods -17 and -18: Use the mechanical terminal as reference point
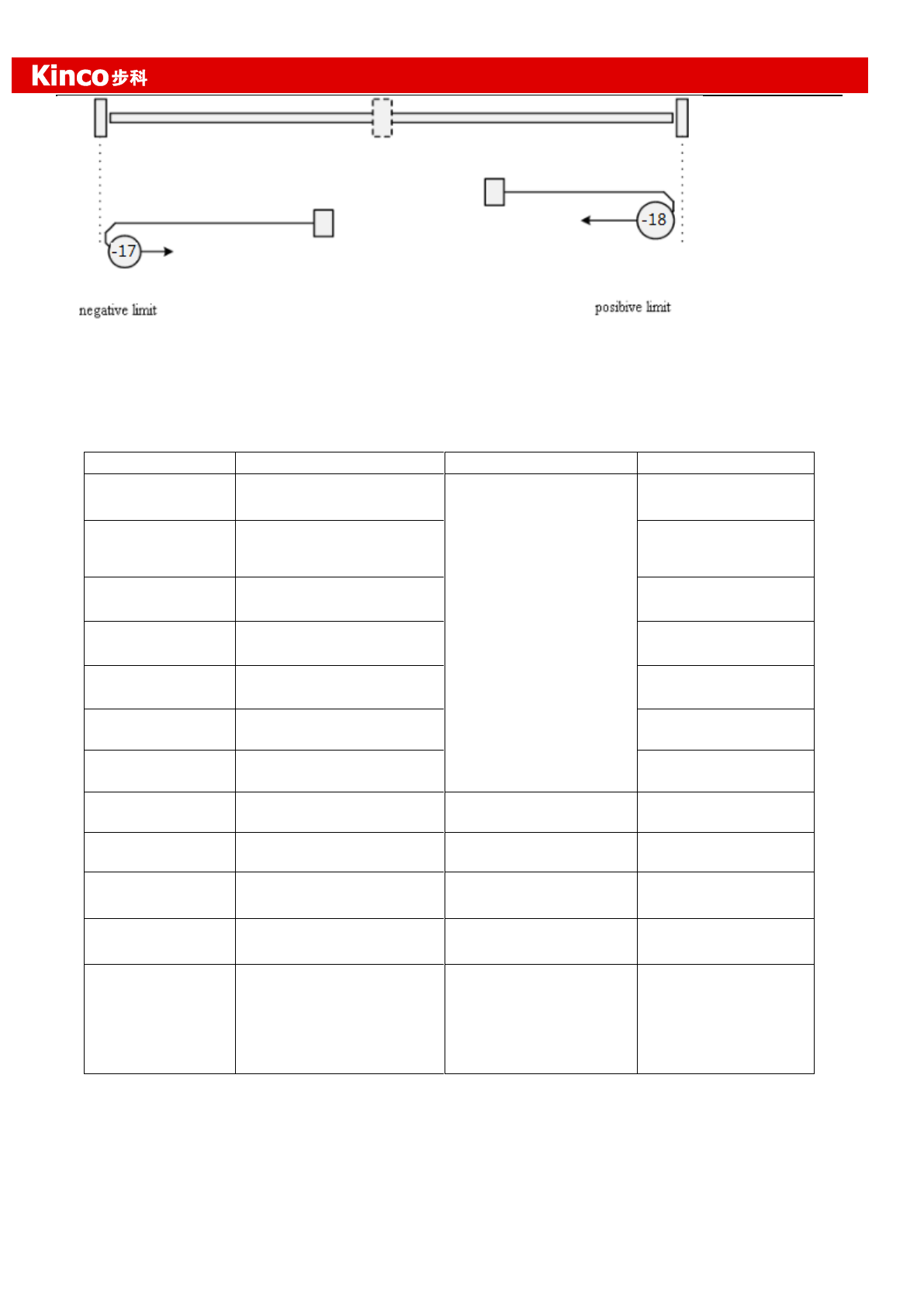
Kinco JD 伺服系列使用手册
102
Kinco FD Series Servo User Manual
Example 8-11:Using method 7 for homing.
Set parameters.
Numberic display
Parameter Name
meaning
Setting Value
d3.01
Din1_Function
000.1: Driver enabled
000.2: Driver error reset
000.4: Operation mode
001.0:Positive limit
002.0:Negative limit
004.0:Origin signal
200.0:Start homing
000.1
(Driver enabled)
d3.02
Din2_Function
000.2
(Driver error reset)
d3.03
Din3_Function
000.4
(Driver model control)
d3.04
Din4_Function
200.0
(Start homing)
d3.05
Din5_Function
001.0
(Positive limit)
d3.06
Din6_Function
002.0
(Negative limit)
d3.07
Din7_Function
004.0
(Home signal)
d3.14
Dout4_Function
004.0:Index signal appears
004.0
(Index signal appears)
d3.15
Dout4_Function
040.0:Origin found
040.4
(origin found)
d3.16
Din_Mode0
Select this mode when the
input signal is invalid
0.004 (-4)
d3.17
Din_Mode1
Select this mode when the
input signal is valid
0.003 (-3)
d3.00
Store_Loop_Data
1:Storage all the setting
parameters except those of
motor
10:Initialize all the setting
parameters except those of
motor
0001 (1)
At this time, computer software shows:
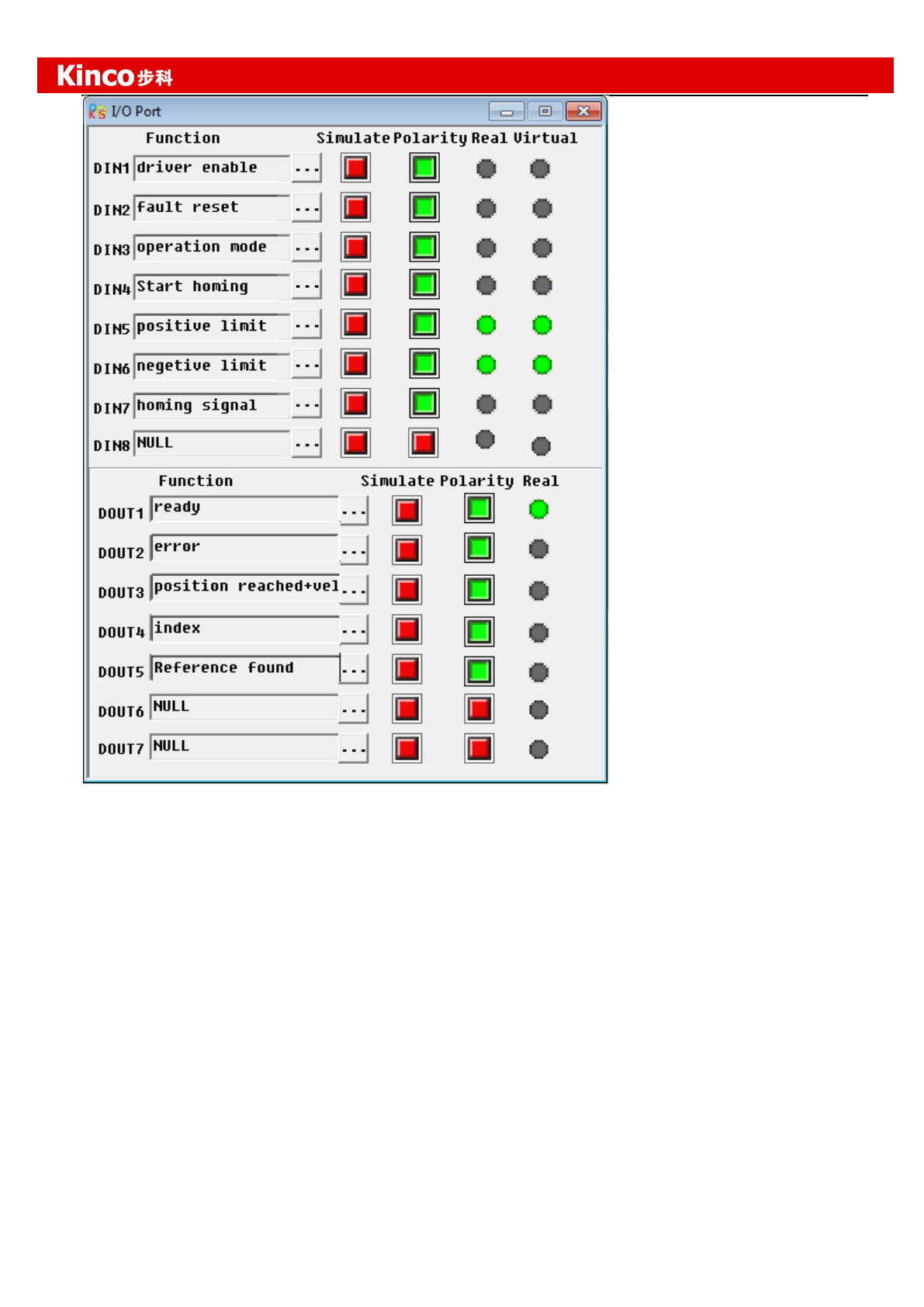
Kinco JD 伺服系列使用手册
103
Kinco FD Series Servo User Manual
Notice: The positive and negative limits are default to normally closed point. Otherwise, the Panel will alarm
and display P.L (positive limit) and N.L (No limit). Only when the alarm is eliminated, the origin control mode
can be normally used.
Computer monitoring status is:
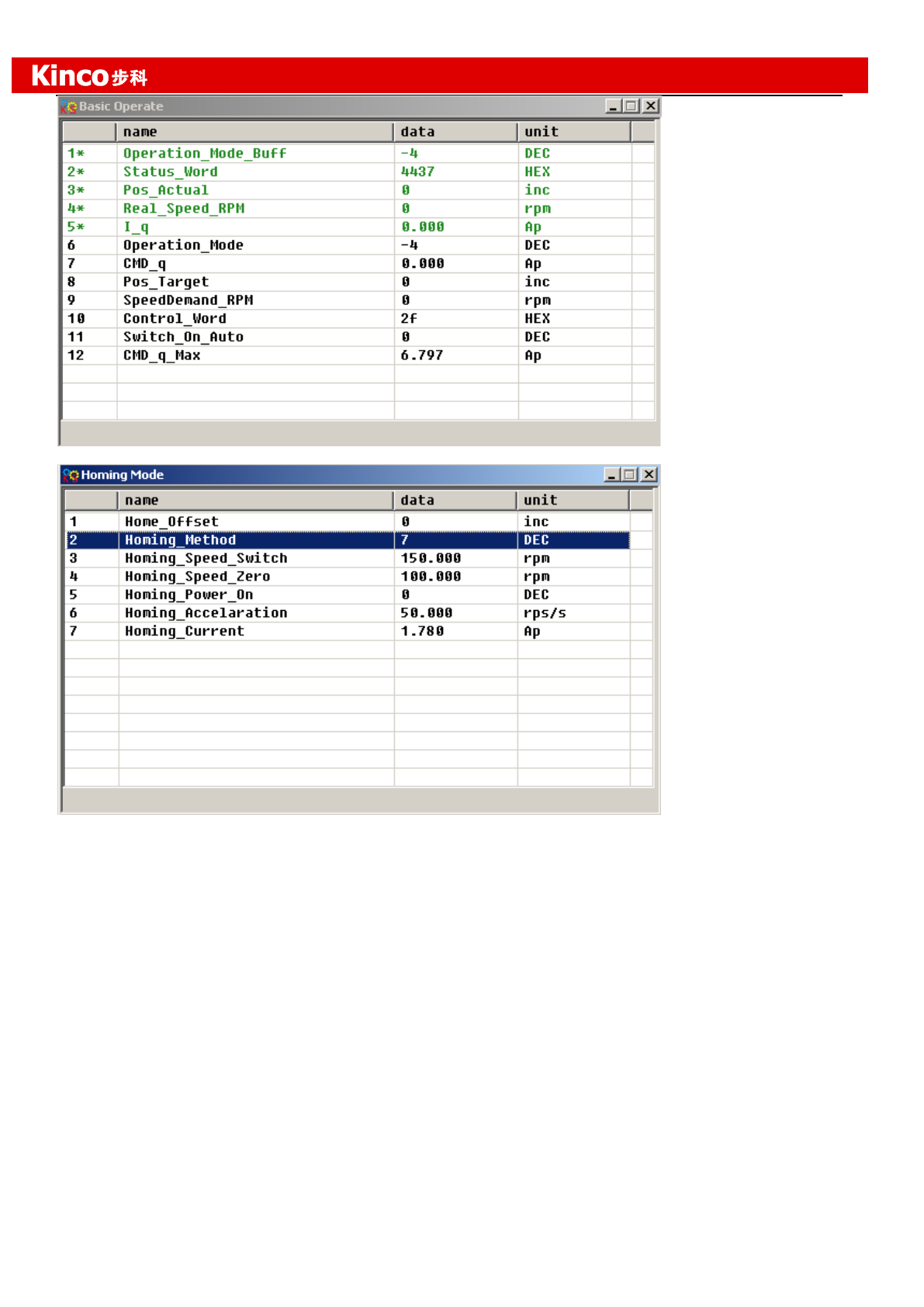
Kinco JD 伺服系列使用手册
104
Kinco FD Series Servo User Manual
Set parameters for homing.
In common circumstance, only need to set up the model of origin and the rest of the parameters are default.
In some case, “Electrify and then find the origin” is set to 1, at the same time the definition-- “Start finding the
origin” is eliminated.
Start homing.
(1). Enable motor, which means the digital input point 1 is set to high-level. The computer motoring picture is
shown below:
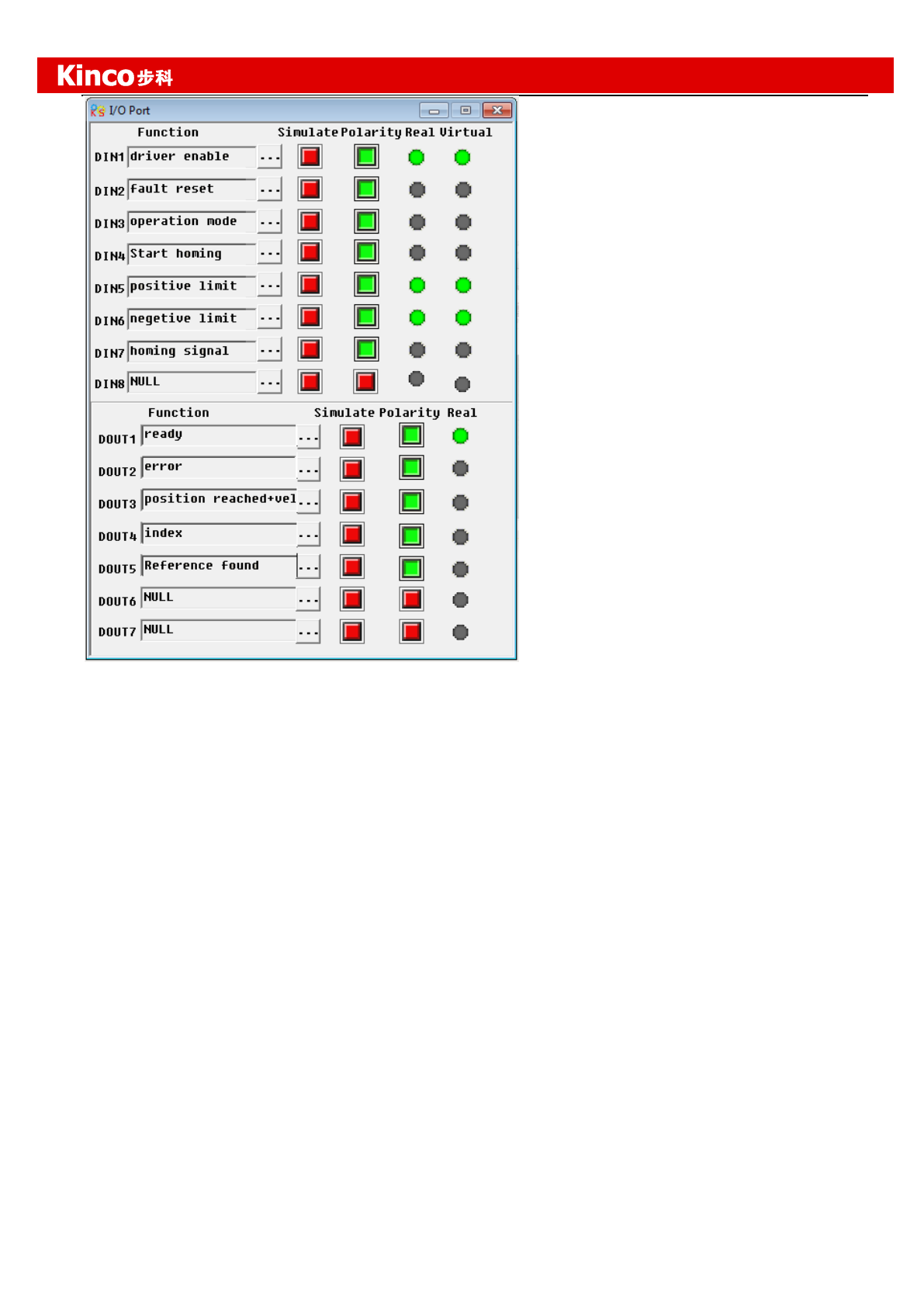
Kinco JD 伺服系列使用手册
105
Kinco FD Series Servo User Manual
(2). Send “Start finding the origin” signal to motor, which means the digital input point 4 is set to high-level.
The computer motoring picture is shown below:
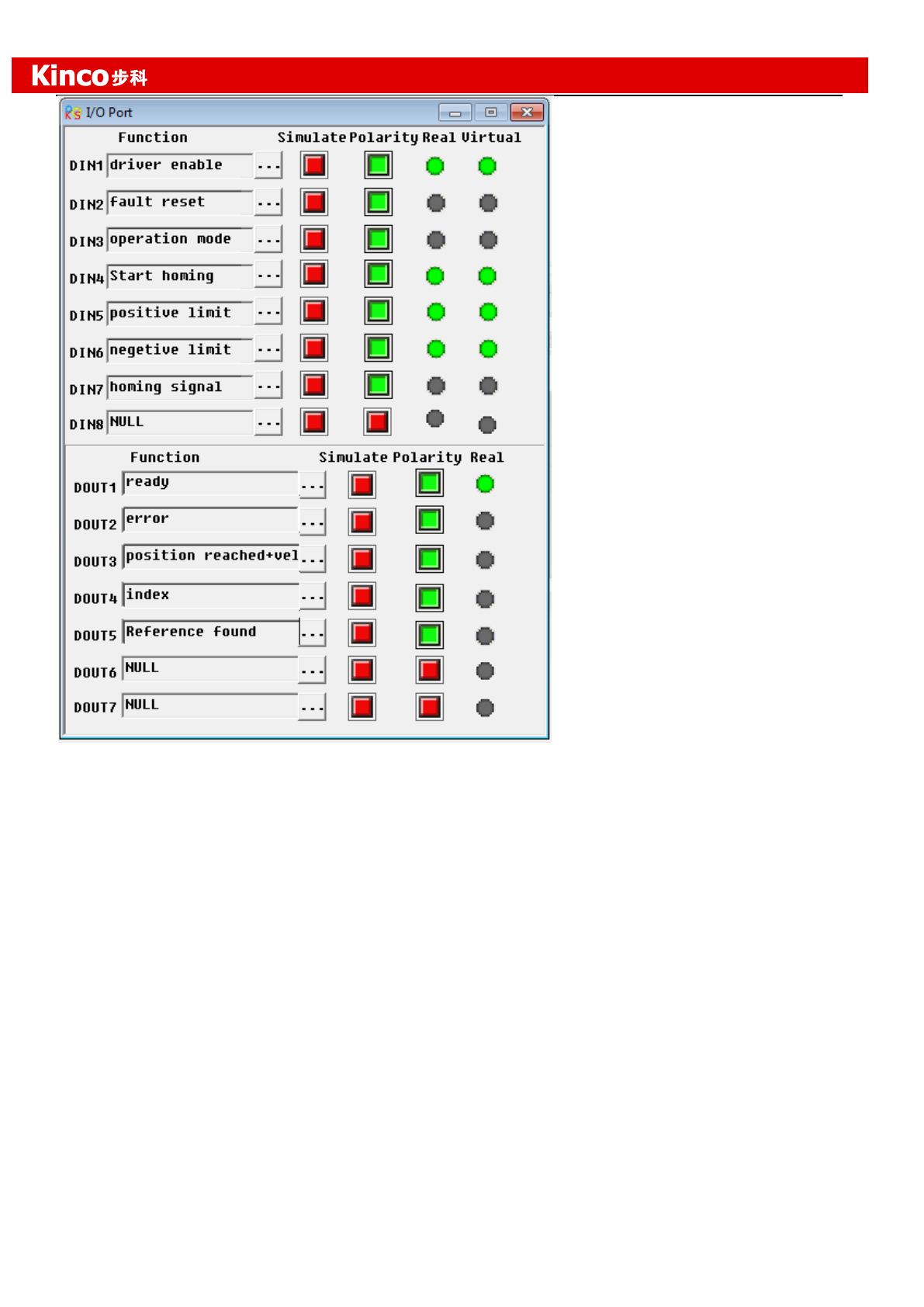
Kinco JD 伺服系列使用手册
106
Kinco FD Series Servo User Manual
Note: “Start finding the origin” signal is a pulse signal, requires only a rise, not need to always be on. If you
want to start next time, a rise pulse is enough.
(4). After the external find the origin, computer monitoring picture is as follows:
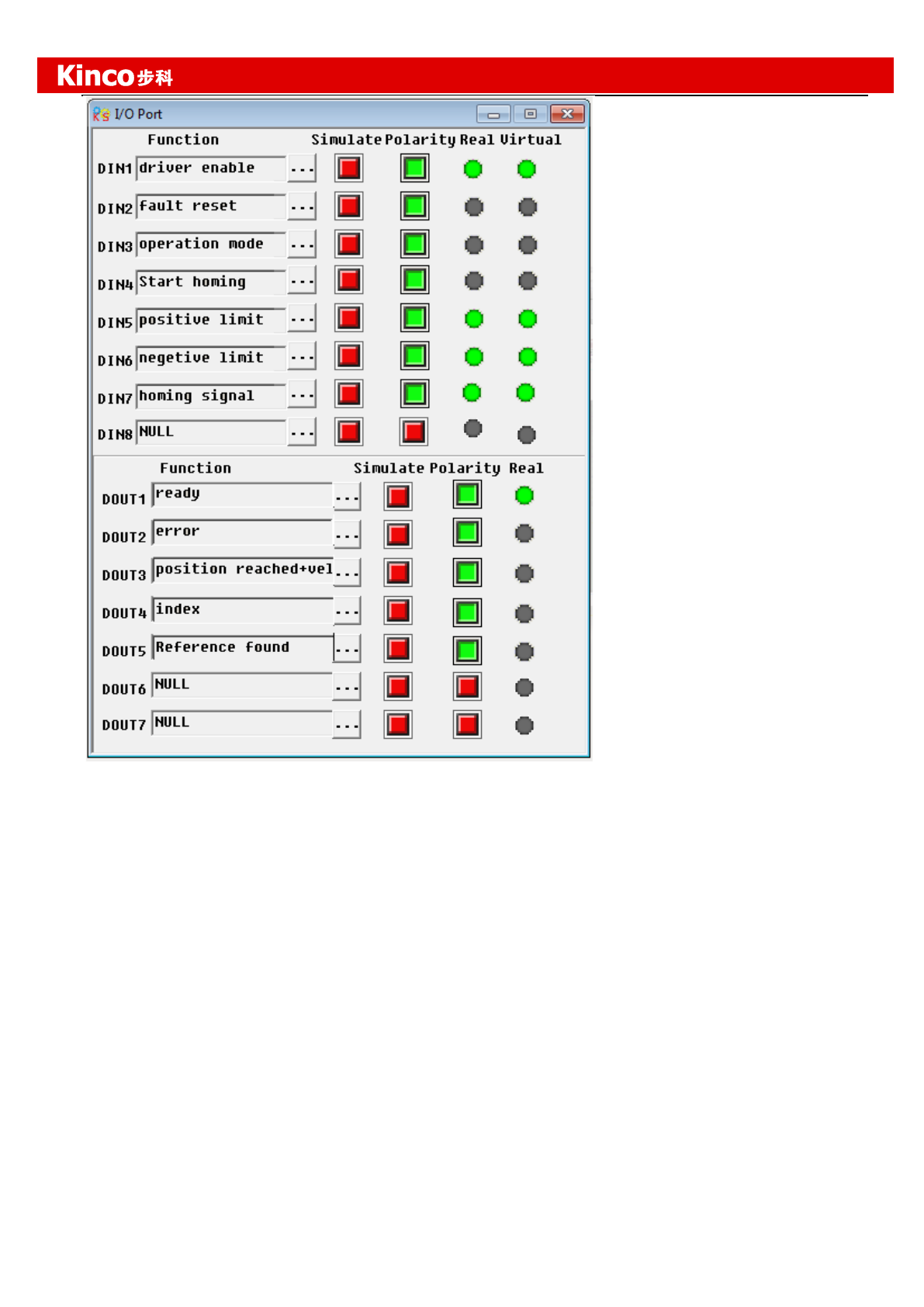
Kinco JD 伺服系列使用手册
107
Kinco FD Series Servo User Manual
(5). Driver searches the Z phase signal in mode 7, and ultimately find the origin. Computer monitoring picture
is shown as follows:
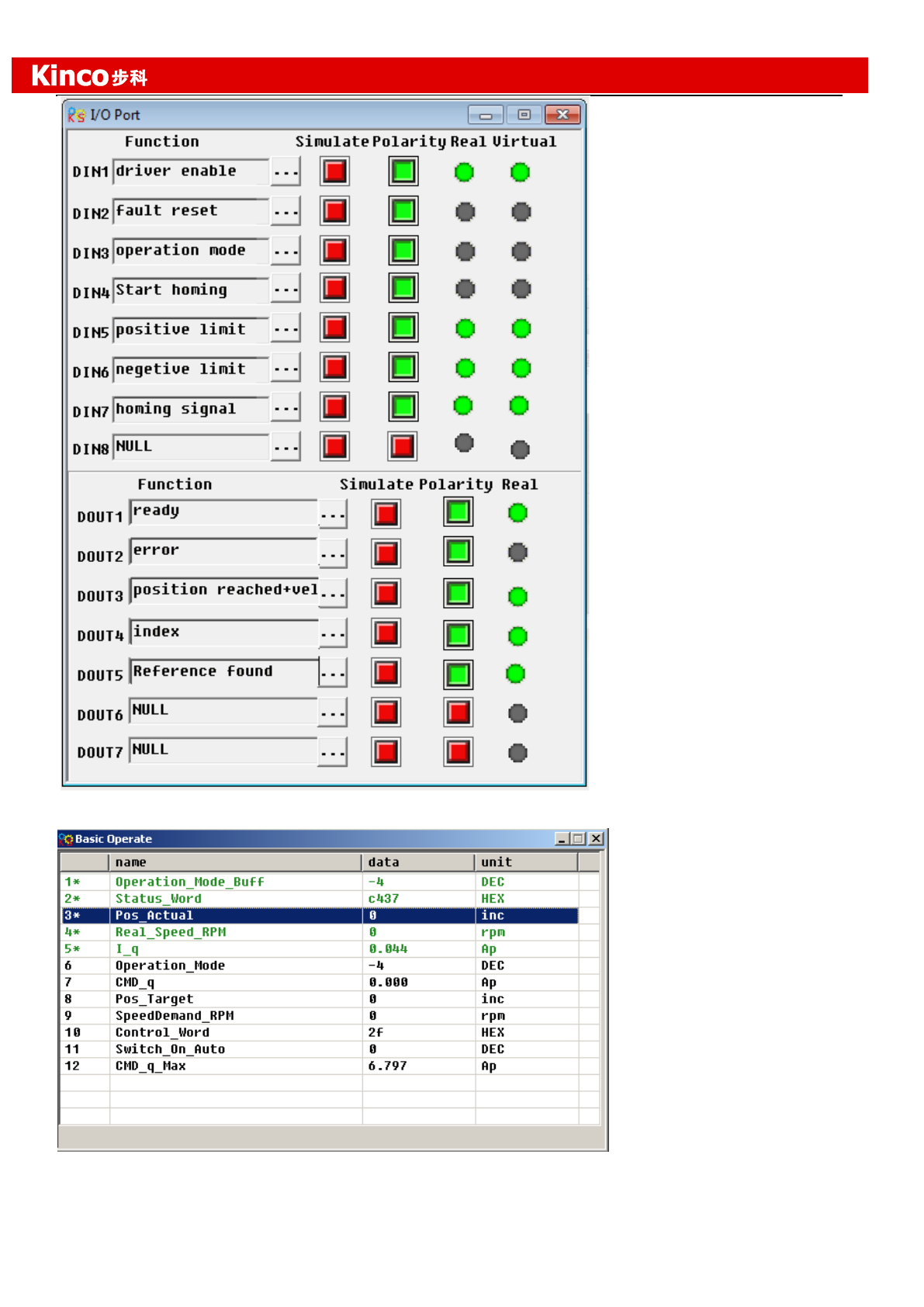
Kinco JD 伺服系列使用手册
108
Kinco FD Series Servo User Manual
At this point, you have completed the origin search function, then the drive position is automatically set to
zero, and the current position is default to origin. Computer monitoring picture is as shown:
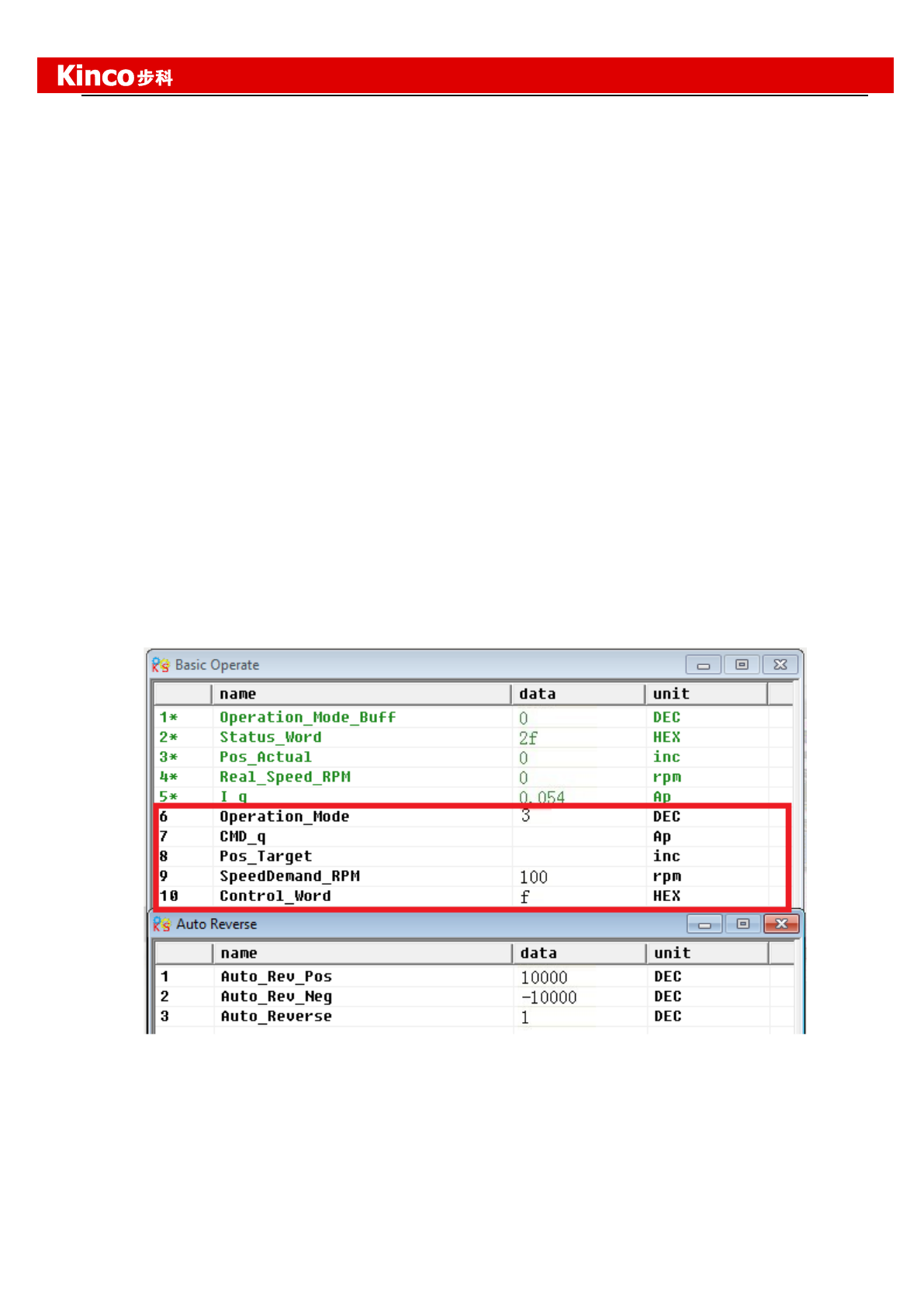
Kinco JD 伺服系列使用手册
109
Kinco FD Series Servo User Manual
Chapter 9 Control Performance
9.1 Auto Reverse
In this mode,motor will run forward and reverse continuously according to the setting mode.User
can set parameters in velocity loop and position loop in this mode.Please make sure auto forward/reverse is
allowed in the machine before using this mode and make sure the power of driver can be cut off anytime to
advoid accident.
Operation procedure for auto reverse:
1:Use KincoServo software to online according to chapter 5.
2:Set speed mode control according to 5.4.1.
3:Click the menu “Driver-Operation mode-Auto Reverse” and set the parameter for auto reverse.
Set “Auto_Reverse” as 0 for no control.
Set “Auto_Reverse” as 1 for position control.The motor will run between the position “Auto_Rev_Pos”
and”Auto_Rev_Neg”.The unit is inc.The speed depends on target velocity.
Set “Auto_Reverse” as 3 for time control.The motor will run between time “Auto_Rev_Pos”
and”Auto_Rev_Neg”.The unit is ms.The speed depends on target velocity.
Following figure shows the parameters need to set.In this figure,the servo will run between -10000 inc and
10000 at speed 100RPM.
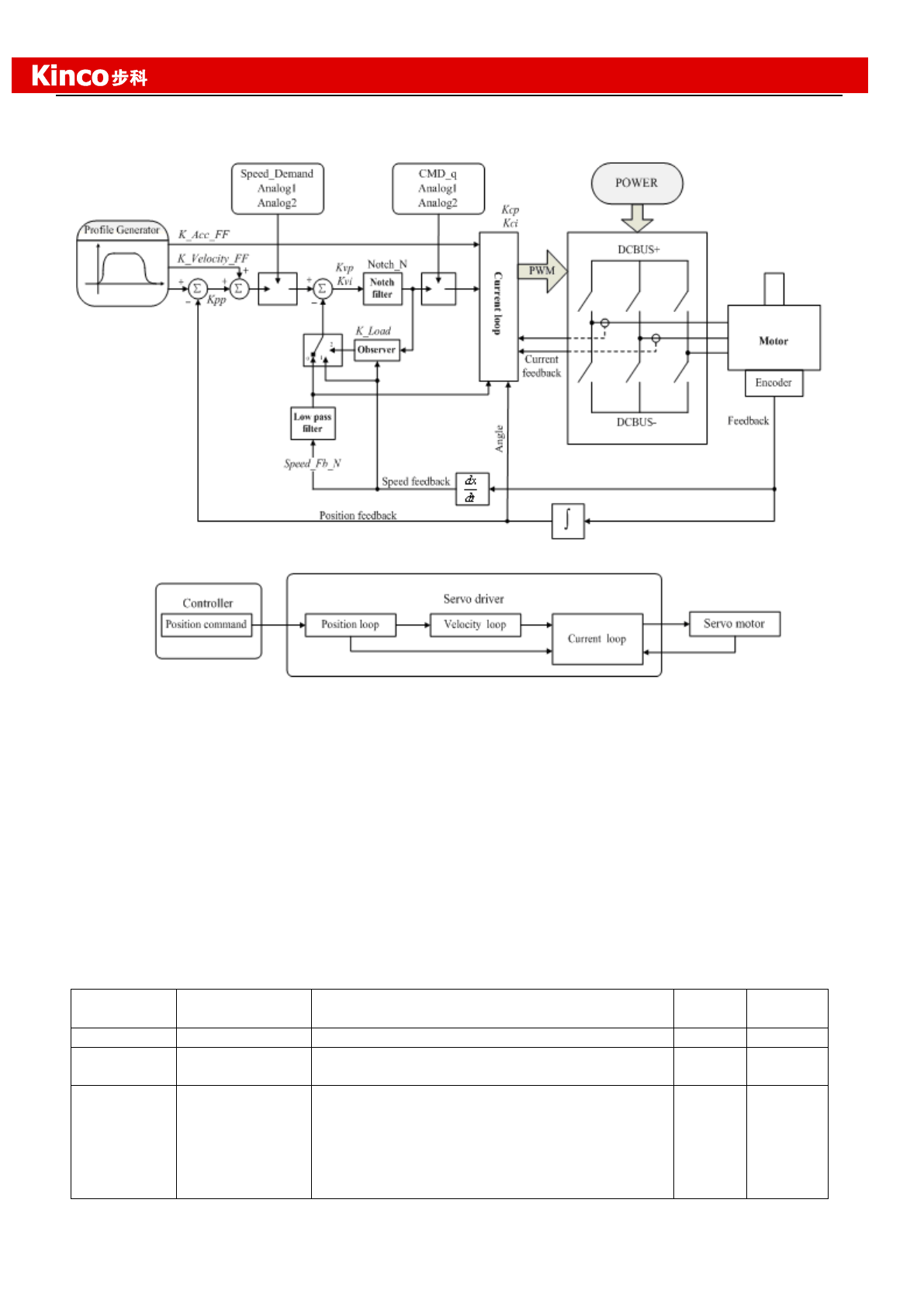
Kinco JD 伺服系列使用手册
110
Kinco FD Series Servo User Manual
9.2 Driver Performance Tuning
Fig. 9-1 Schematic diagram for control loop adjustment
As shown in Fig. 9-1, a typical servo system contains three control loops, namely, position loop, velocity loop,
and current loop.
Current loop are related to motor parameters (optimal parameters of the selected motor are default for the
driver and no adjusting is required).
Parameters for velocity loop and position loop should be adjusted properly according to load conditions.
During adjustment of the control loop, ensure that the bandwidth of the velocity loop is at least twice of that of
the position loop; otherwise oscillation may occur.
9.2.1 Manual Adjustment
1. Parameters for velocity loop
Table 9-1 Parameters for velocity loop
Numeric
Display
Variable Name
Meaning
Default
Value
Range
d2.01
Kvp
Sets the response speed of a velocity loop
100
0~32767
d2.02
Kvi
Adjusts speed control so that the time of minor
errors is compensated
2
0~16384
d2.05
Speed_Fb_N
Reduces the noise during motor operation by
reducing the feedback bandwidth of velocity
loops (smoothing feedback signals of
encoders). When the set bandwidth becomes
smaller, the motor responds slower.
The formula is F=Speed_Fb_N*20+100.
45
0~45
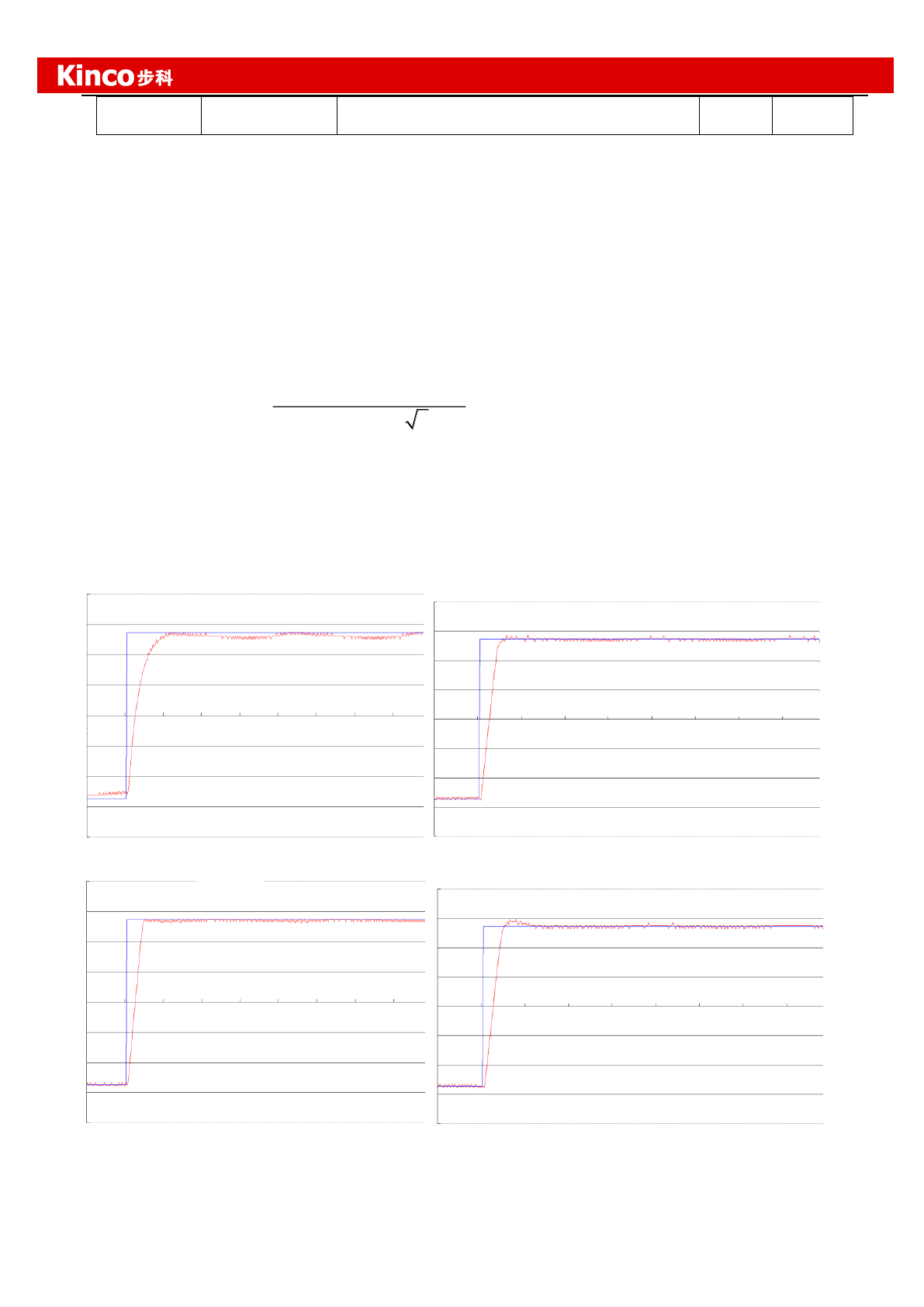
Kinco JD 伺服系列使用手册
111
Kinco FD Series Servo User Manual
For example, to set the filter bandwidth to "F =
500 Hz”, you need to set the parameter to 20.
Proportional gain of velocity loop Kvp: If the proportional gain of the velocity loop increases, the responsive
bandwidth of the velocity loop also increases. The bandwidth of the velocity loop is directly proportional to the
speed of response. Motor noise also increases when the velocity loop gain increases. If the gain is too great,
system oscillation may occur.
Integral gain of velocity loop Kvi: If the integral gain of the velocity loop increases, the low-frequency intensity
is improved, and the time for steady state adjustment is reduced; however, if the integral gain is too great,
system oscillation may occur.
Adjustment steps:
Step 1: Adjust the gain of velocity loop to calculate the bandwidth of velocity loop
Convert the load inertia of the motor into the inertia Jl of the motor shaft, and then add the inertia Jr of the
motor itself to obtain Jt = Jr + Jl. Put the result into the formula:
* * _
Vc_Loop_BW Kvp * *204800000* 2 *2
pt
t
I K Encoder R
J
To calculate the bandwidth of the velocity loop
Vc_Loop_BW
according to the adjusted the gain of velocity loop Kvp, only adjust Kvi according to actual
requirements.
Adjust the impact of Kvp and Kvi, as shown in Fig.9-2.
For the effect of Kvp adjustment, see the first to the fourth from left of Fig. 9-2. Kvp gradually increases from
the first to the fourth from left. The value of Kvi is 0.
For the effect of Kvi adjustment, see the first to the fourth from right of Fig. 9-2. Kvi gradually increases from
the first to the fourth from right. The value of Kvp remains unchanged.
Left 1
Right 1
Left 2
Right 2
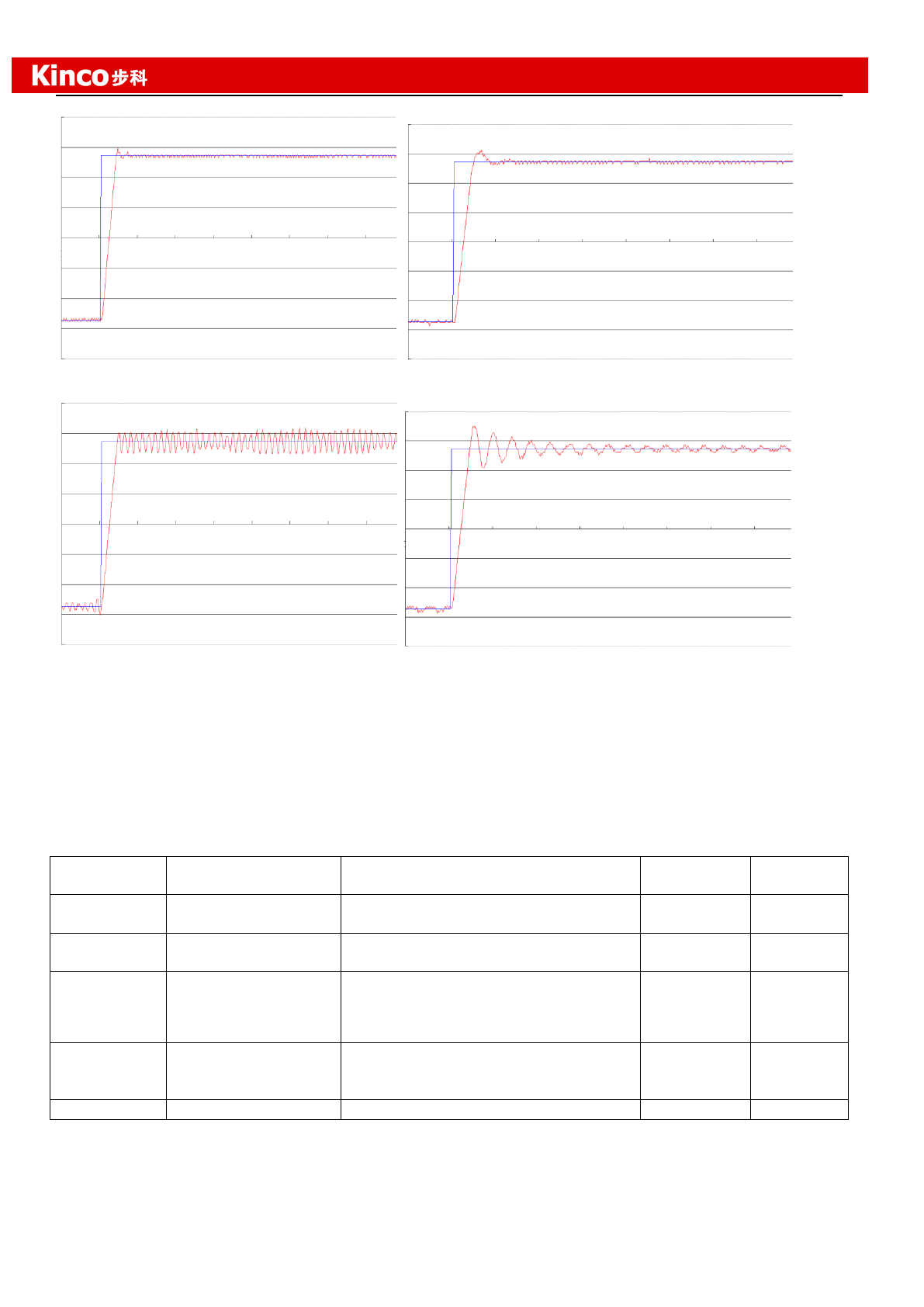
Kinco JD 伺服系列使用手册
112
Kinco FD Series Servo User Manual
Fig.9-2 Schematic diagram of gain adjustment of velocity loop
Step 2: Adjust parameters for feedback filter of velocity loop
During gain adjustment of a velocity loop, if the motor noise is too great, you can properly reduce the
parameter Speed_Fb_N for feedback filter of the velocity loop; however, the bandwidth F of the feedback filter
of velocity loop must be at least three times of the bandwidth of velocity loop; otherwise oscillation may occur.
The formula for calculating the bandwidth of feedback filter of velocity loop is F = Speed_Fb_N*20+100 (Hz).
2. Parameters for position loop Table 9-2 Parameters for position loop
Numeric
Display
Variable Name
Meaning
Default
Value
Range
d2.07
Kpp
Indicates the proportional gain of the
position loop Kpp
1000
0~16384
d2.08
K_Velocity_FF
0 indicates no feedforward, and 256
indicates 100% feedforward
256
0~256
d2.09
K_Acc_FF
The value is inversely proportional to
the feedforward
7FF.F
32767~10
d0.05
Pc_Loop_BW
Sets the bandwidth of the position
loops in Hz
0
N/A
/
Pos_Filter_N
Set the average filter
1
1~255
Proportional gain of the position loop Kpp: If the proportional gain of the position loop increases, the
bandwidth of the position loop is improved, thus reducing both the positioning time and following errors.
However, too great bandwidth may cause noise or even oscillation. Therefore, this parameter must be set
Left 4
Right 4
Right 3
Left 3
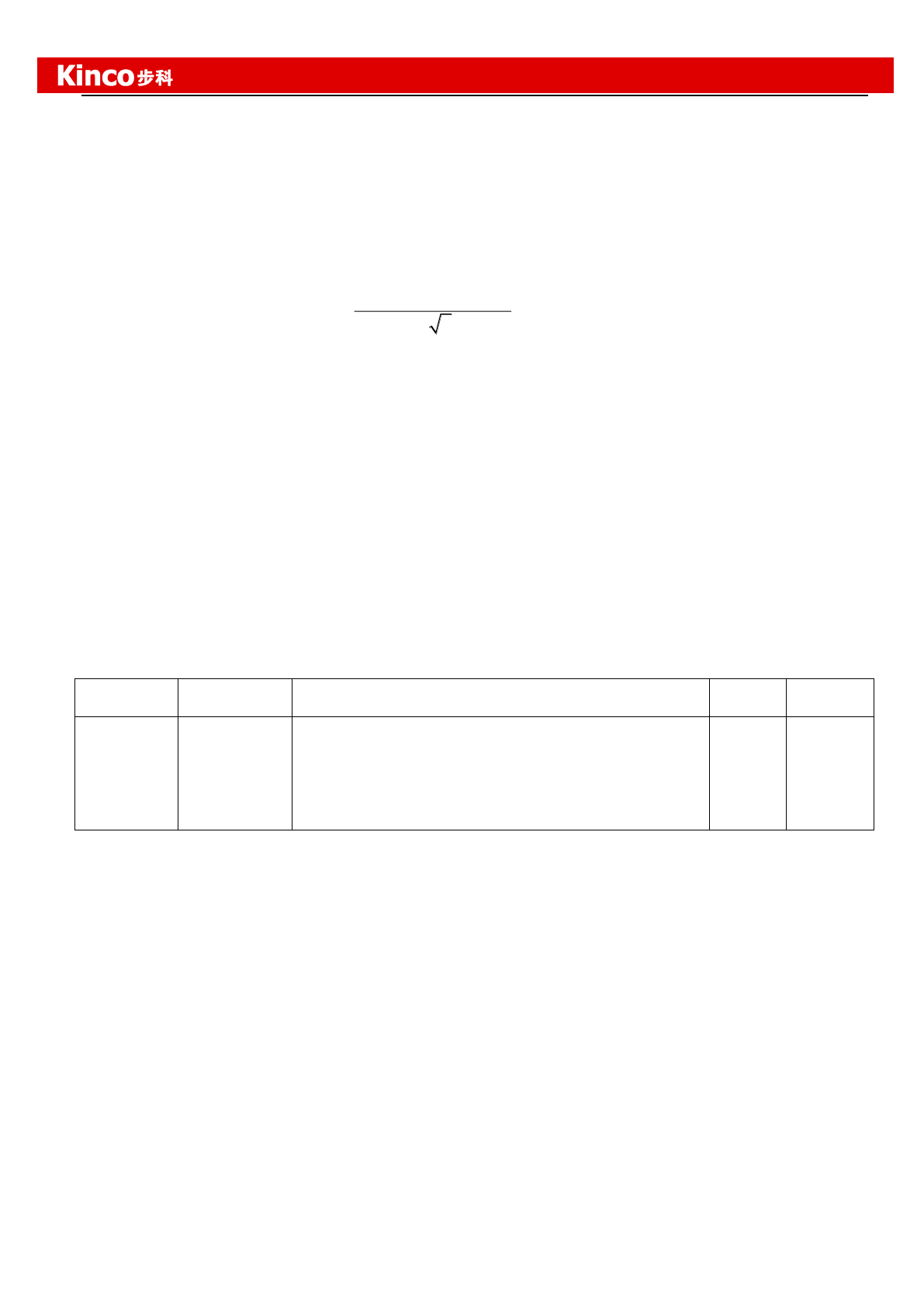
Kinco JD 伺服系列使用手册
113
Kinco FD Series Servo User Manual
properly according to loading conditions. In the formula Kpp=103* Pc_Loop_BW, Pc_Loop_BW indicates
the bandwidth of the position loop. The bandwidth of a position loop is less than or equal to that of a velocity
loop. It is recommended that Pc_Loop_BW be less than Vc_Loop_BW /4 (Vc_Loop_BW indicates the
bandwidth of a velocity loop).
Velocity feedforward of the position loop K_Velocity_FF: the velocity feedforward of a position loop can be
increased to reduce position following errors. When position signals are not smooth, if the velocity
feedforward of a position loop is reduced, motor oscillation during running can be reduced.
Acceleration feedback of the position loop K_Acc_FF (adjustment is not recommended for this parameter): If
great gains of position rings are required, the acceleration feedback K_Acc_FF can be properly adjusted to
improve performance.
* * _
K_Acc_FF 250000* 2 * *
pt
t
I K Encoder R
J
Note: K_Acc_FF is inversely proportional to the
acceleration feedforward.
Pos_Filter_N is used for average filter of the speed produced by target position.Setting this parameter as N
means to average N data.
Adjustment procedure:
Step 1: Adjust the proportional gain of a position loop.
After adjusting the bandwidth of the velocity loop, it is recommended to adjust Kpp according to actual
requirements (or directly fill in the required bandwidth in Pc_Loop_BW, and the driver will automatically
calculate the corresponding Kpp). In the formula Kpp = 103*Pc_Loop_BW, the bandwidth of the position loop
is less than or equal to that of the velocity loop. For a common system, Pc_Loop_BW is less than
Vc_Loop_BW /2; for the CNC system, it is recommended that Pc_Loop_BW is less than Vc_Loop_BW /4.
Step 2: Adjust velocity feedforward parameters of the position loop.
Velocity feedforward parameters (such as K_Velocity_FF) of the position loop are adjusted according to
position errors and coupling intensities accepted by the machine. The number 0 represents 0% feedforward,
and 256 represents 100% feedforward.
3. Parameters for pulse filtering coefficient
Table 9-3 Parameters for pulse filtering coefficient
Numeric
Display
Variable
Name
Meaning
Default
Value
Range
d3.37
PD_Filter
Used to smooth the input pulses.
Filter frequency: f = 1000/(2π* PD_Filter)
Time constant: T = PD_Filter/1000
Unit: S
Note: If you adjust this filter parameter during the
operation, some pulses may be lost.
3
1~32767
When a driver operates in the pulse control mode, if the electronic gear ratio is set too high, this parameter
must be adjusted to reduce motor oscillation; however, if the parameter adjustment is too great, motor
running instructions will become slower.
9.2.2 Auto Adjustment (Only for Velocity Loops)
Auto adjustment is only available for velocity loops (see Section 8.11 for manual adjustment of position loops)
when both forward rotation and reverse rotation of a motor are allowable, and the loadings do not change
much during the operation. You can determine the total inertia of motor loadings through gain auto tuning,
and then manually enter the desired bandwidth. The driver will automatically calculate appropriate Kvp and
Kvi values. The motion curve is in the shape of a sine curve, as shown in Fig. 9-3.
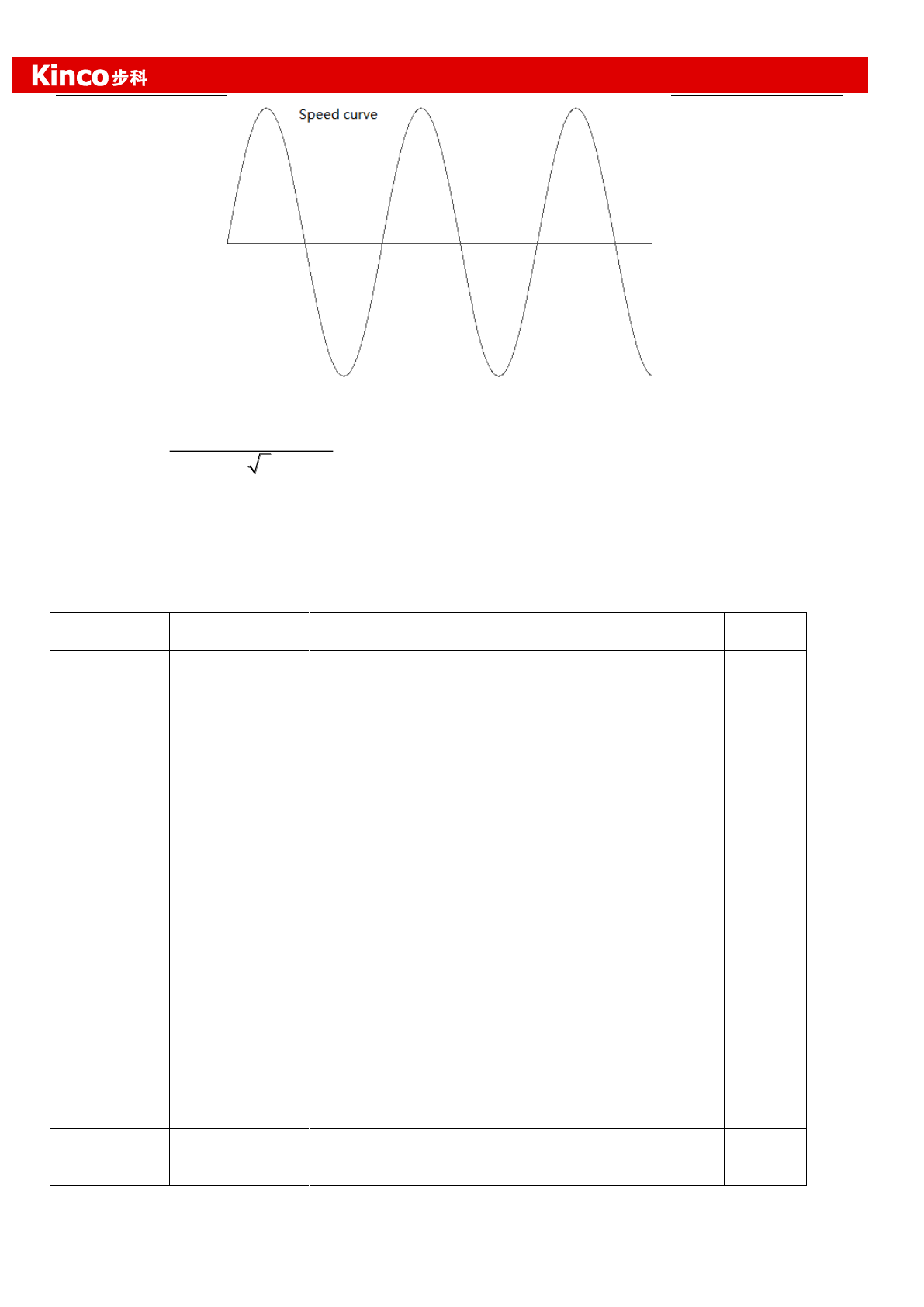
Kinco JD 伺服系列使用手册
114
Kinco FD Series Servo User Manual
Fig.9-3 Speed curve
K_Load represents the internal data that displays the actual inertia of the system.
* * _
_62500* 2 *
pt
t
I K Encoder R
K Load J
In the above formula:
Ip represents the maximum peak output current in units of “A”;
Kt represents the torque constant of the motor in units of “Nm/Arms”;
Encoder_R represents the resolution of a motor encoder in units of “inc/r”;
Jt represents the total inertia of the motor and loadings in units of “kg*m^2”.
Table 9-4 Parameters for controlling gain auto tuning
Numeric
Display
Variable Name
Meaning
Default
Value
Range
d0.06
Tuning_Start
Auto tuning starts after the variable is set to
11. All input signals are ignored during
auto tuning. The variable is automatically
changed to 0 after auto tuning is completed.
Sets the variable to other values to end auto
tuning.
0
/
d0.04
Vc_Loop_BW
Sets the bandwidth of the velocity loop in
Hz. The variable can only be set after auto
tuning is performed properly; otherwise the
actual bandwidth goes wrong, which causes
abnormal working of the driver. If the auto
tuning result is abnormal, setting this
parameter may also cause abnormal
working of the driver.
Note: This parameter cannot be applied
when auto tuning is unavailable.
0
0~600
d2.17
K_Load
Indicates loading parameters
/
20~1500
0
d2.21
Sine_Amplitude
Proper increase in this data will reduce the
tuning error, but machine vibration will
become severer. This data can be adjusted
64
0~1000
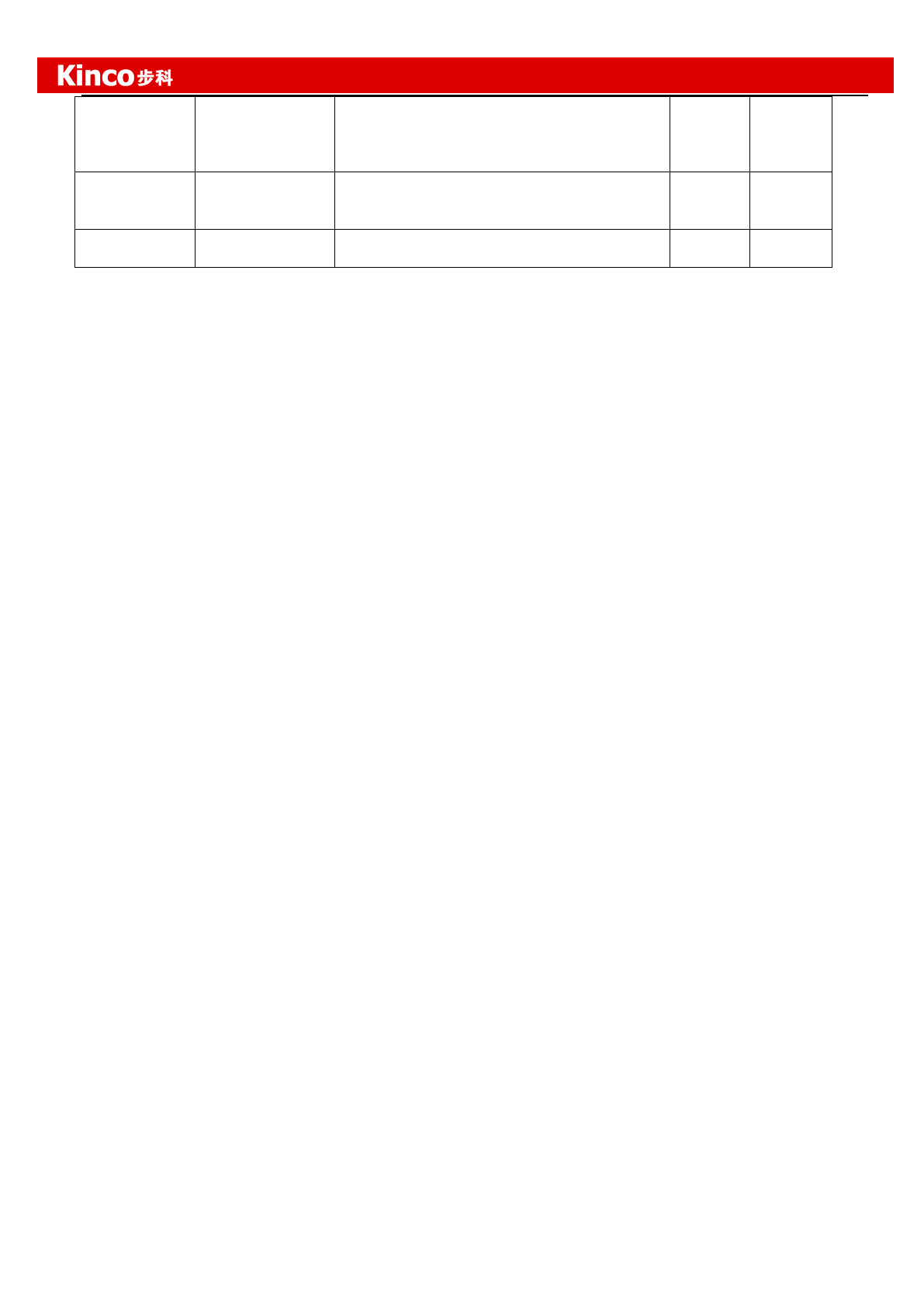
Kinco JD 伺服系列使用手册
115
Kinco FD Series Servo User Manual
properly according to actual conditions of
machines. If the data is too small, the auto
tuning error becomes greater, or even
causes a mistake
d2.22
Tuning_Scale
It is helpful to reduce the auto tuning time by
reducing the data, but the result may be
unstable.
128
0~16384
d2.23
Tuning_Filter
Indicates filter parameters during
auto-tuning
64
1~1000
Auto tuning is a process where the suitable and stable K_Load value is automatically calculated. In the auto
tuning mode, the data of numeric display is automatically switched to the real-time display mode of K_Load
data. When K_Load data gradually becomes stable, the driver automatically adjusts Kvp and Kvi data of a
velocity loop, so that the actual bandwidth of the velocity loop is 50Hz. When K_Load data becomes stable,
the driver automatically stops auto tuning operation; then you need to customize Vc_Loop_BW, representing
the desired bandwidth of the velocity ring. Finally, run the test system in the actual environment, and save the
parameters.
Precautions:
Auto tuning applies when both forward rotation and reverse rotation of a motor are allowable, and the
loadings do not change much during the operation. When forward rotation or reverse rotation of the motor is
not allowable on a device, it is recommended to adjust the parameters manually.
During auto tuning operation, pulse signals, digital input signals, and analog signals of the external controller
are temporarily unavailable, so safety must be ensured.
Before auto tuning operation, it is recommended to properly adjust the Kvp, Kvi and Speed_Fb_N (a
feedback filter parameter) values of the velocity loop to prevent visible oscillations when the system works in
the speed mode. If necessary, adjust the data of d2.03 notch filter to inhibit resonance.
The time for different load tuning varies, and generally a few seconds is required. The auto tuning time can be
reduced by presetting the K_Load value to a predicted value that is close to the actual value.
Vc_Loop_BW can be written only after successful auto tuning, otherwise the driver may work improperly.
After you write the desired bandwidth of the velocity loop in Vc_Loop_BW, the driver automatically calculates
the corresponding values of Kvp, Kvi and Speed_Fb_N. If you are dissatisfied with low-speed smoothness,
you can manually adjust Kvi. Note that auto tuning does not automatically adjust the data of a notch filter.
In the following circumstances, auto tuning parameters should be adjusted:
When the friction in a rotation circle of the motor is uneven, it is required to increase the amplitude of d2.21
sine wave to reduce the impacts caused by uneven friction. Note that d2.21 increases when the oscillation
amplitude of the loadings increase.
If auto tuning lasts for a long time, initial evaluation of the total inertia is available. It is recommended to set
K_Load to an evaluation value before auto tuning.
If auto tuning is unstable, the stability of auto tuning increases when d2.22 increases properly, but the time for
auto tuning slightly increases.
In the following conditions, auto adjustment goes wrong. In this case, you can only set parameters manually:
The load inertia is featured by great fluctuation.
Mechanical connection rigidity is low.
Clearances exist in the connection between mechanical elements.
The load inertia is too great, while Kvp values are set too low.
If the load inertia is too great, K_Load data will be less than 20; if the load inertia is too little, K_Load data will
be greater than 15000.
9.3 Oscillation Inhibition
If resonance occurs during machine operation, you can adjust a notch filter to inhibit resonance. If resonance
frequency is known, you can directly set Notch_N to (BW-100)/10. Note that you need to set Notch_On to 1 to
enable the notch filter. If you do not know exactly the resonance frequency, you can firstly set the max value
of d2.14 current instruction to a low one, so that the oscillation amplitude is within the acceptable range; then
try to adjust Notch_N to check whether resonance disappears.
If machine resonance occurs, you can calculate the resonance frequency by observing the waveform of the
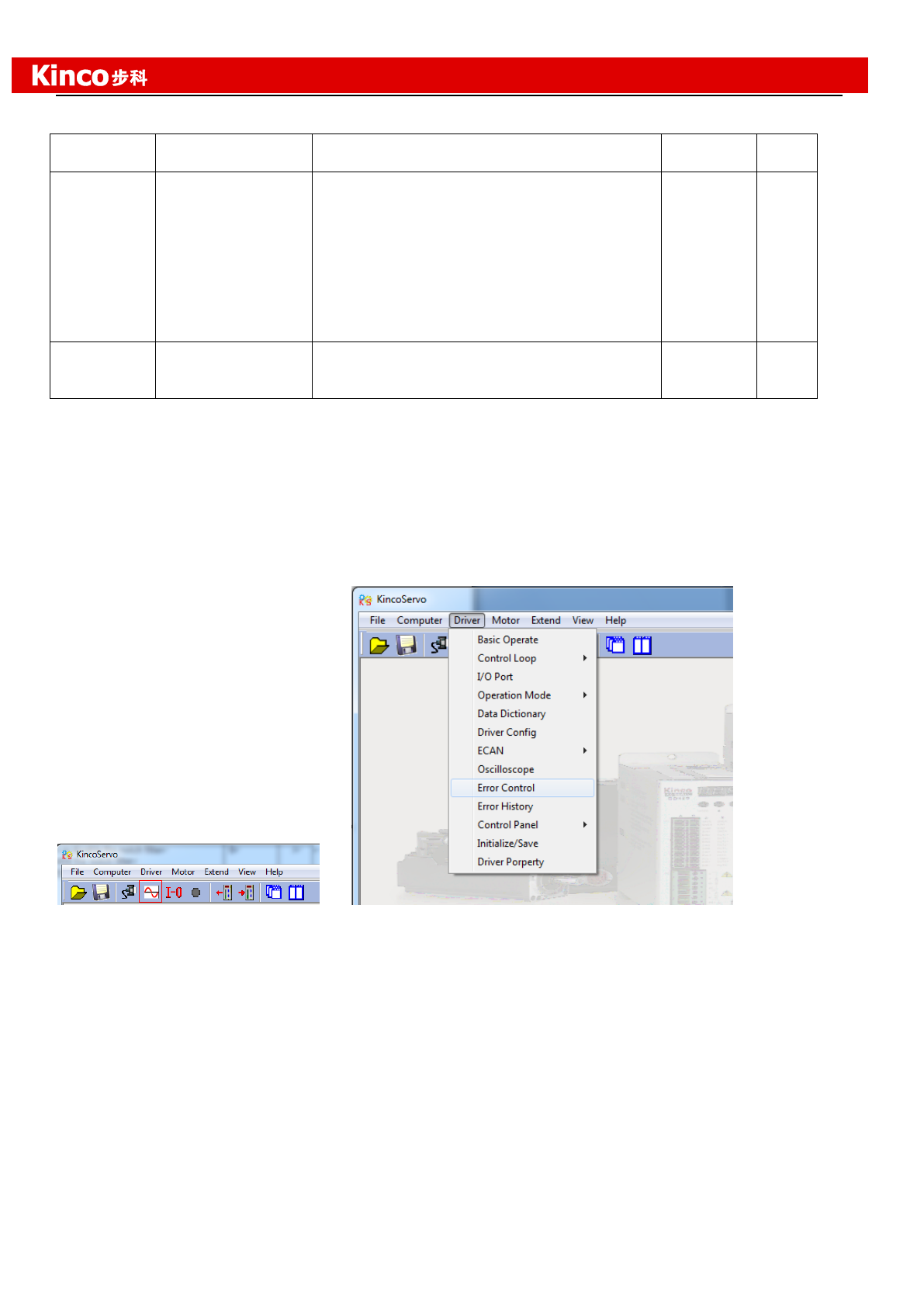
Kinco JD 伺服系列使用手册
116
Kinco FD Series Servo User Manual
target current with the oscilloscope function of the driver.
Table 9-5 Parameters for oscillation inhibition
Numeric
Display
Variable Name
Meaning
Default
Value
Rang
e
d2.03
Notch_N
Notch/filtering frequency setting for a velocity
loop, used to set the frequency of the internal
notch filter, so as to eliminate the mechanical
resonance produced when the motor drives
the machine. The formula is F = Notch_N*10 +
100.
For example, if the mechanical resonance
frequency is F = 500 Hz, the parameter should
be set to 40.
45
0~90
d2.04
Notch_On
Enable or disable the notch filter
0: Disable the notch filter
1: Enable the notch filter
0
/
9.4 Debugging Example
9.4.1 Oscilloscope
1.Enter oscilloscope
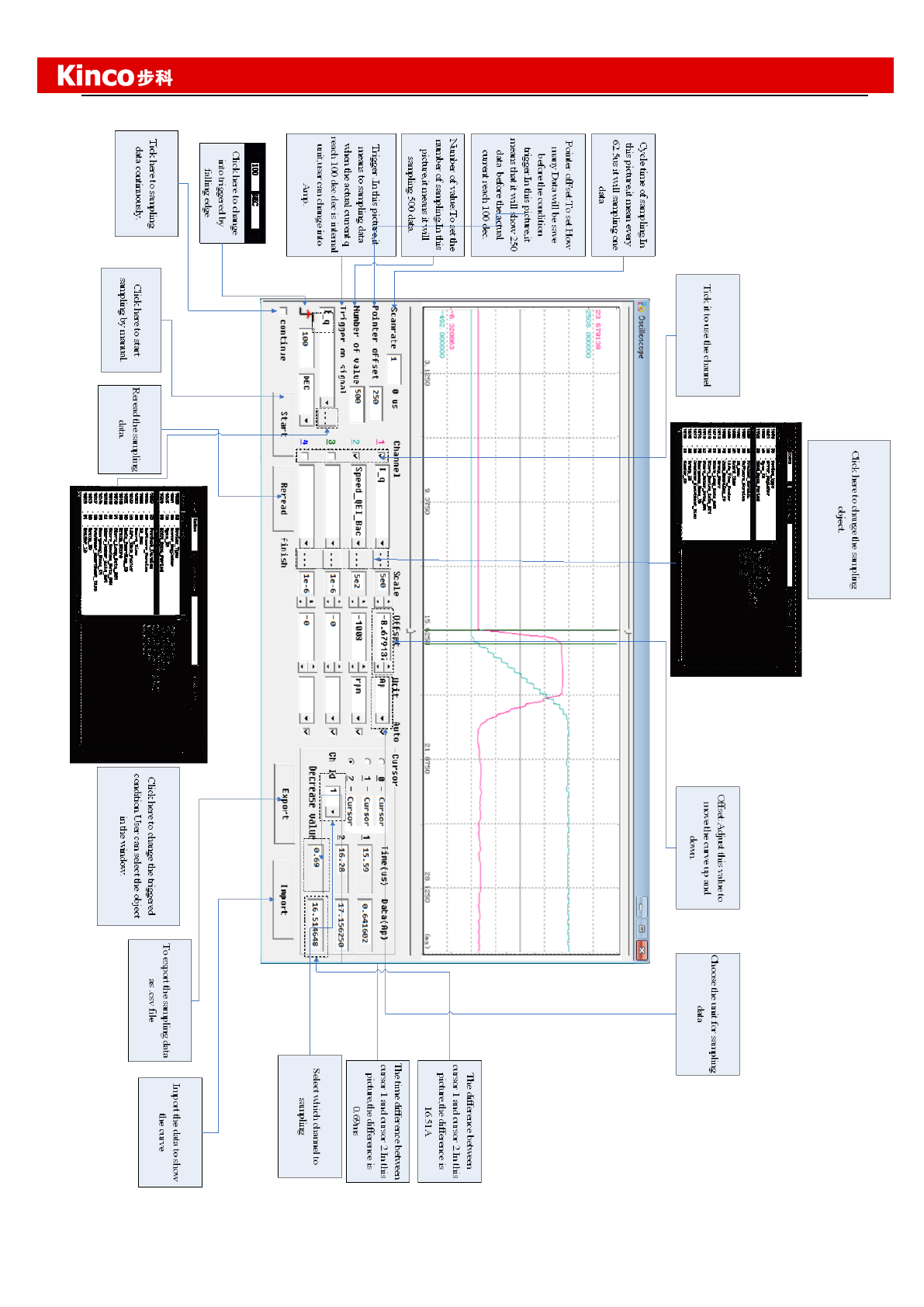
Kinco JD 伺服系列使用手册
117
Kinco FD Series Servo User Manual
2.Parameters for Oscilloscope
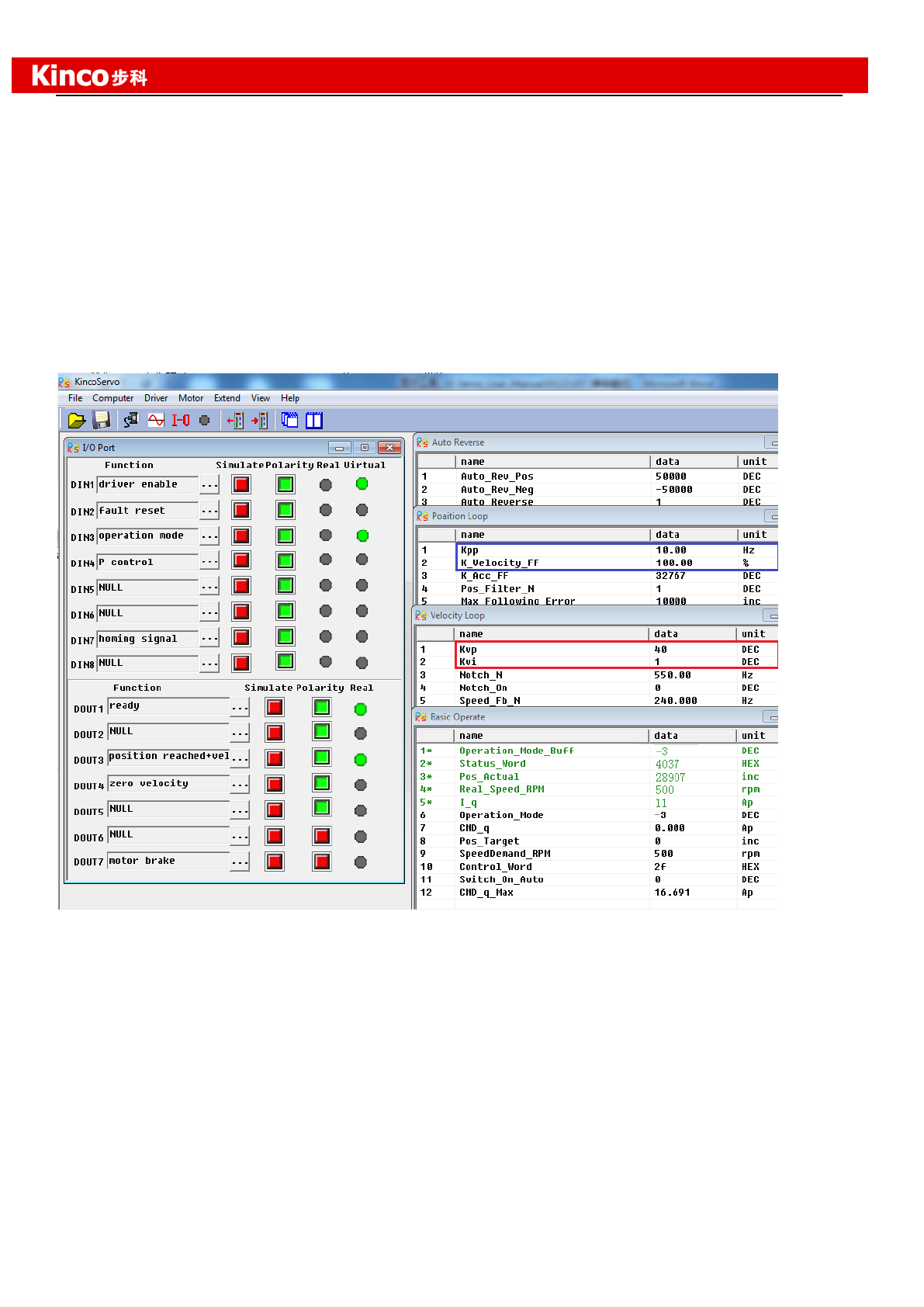
Kinco JD 伺服系列使用手册
118
Kinco FD Series Servo User Manual
9.4.2 Procedure for Parameter Adjustment
1、Velocity Loop Adjustment
(1) Adjust Kvp according to the load.
① Set motor running at Auto Reverse mode by position(Operation mode -3),then open oscilloscope and set
the parameters to observe the curve.As shown in following figures.
② Adjust Kvp and observe the speed curve.Following figures show the different curve in different
Kvp.According to the curve,it shows that the bigger value of Kvp,the faster response of speed.
(2) Adjust Kvi according to load.
(3) Adjust Speed_Fb_N to reduce system noise.
Speed_Fb_N:This parameter is used to reduce system noise.But the bigger value of this parameter,the
slower response of system.
In Auto Reverse mode,Kvp=40
The oscilloscope is shown as follows:actual speed response is 33.88ms
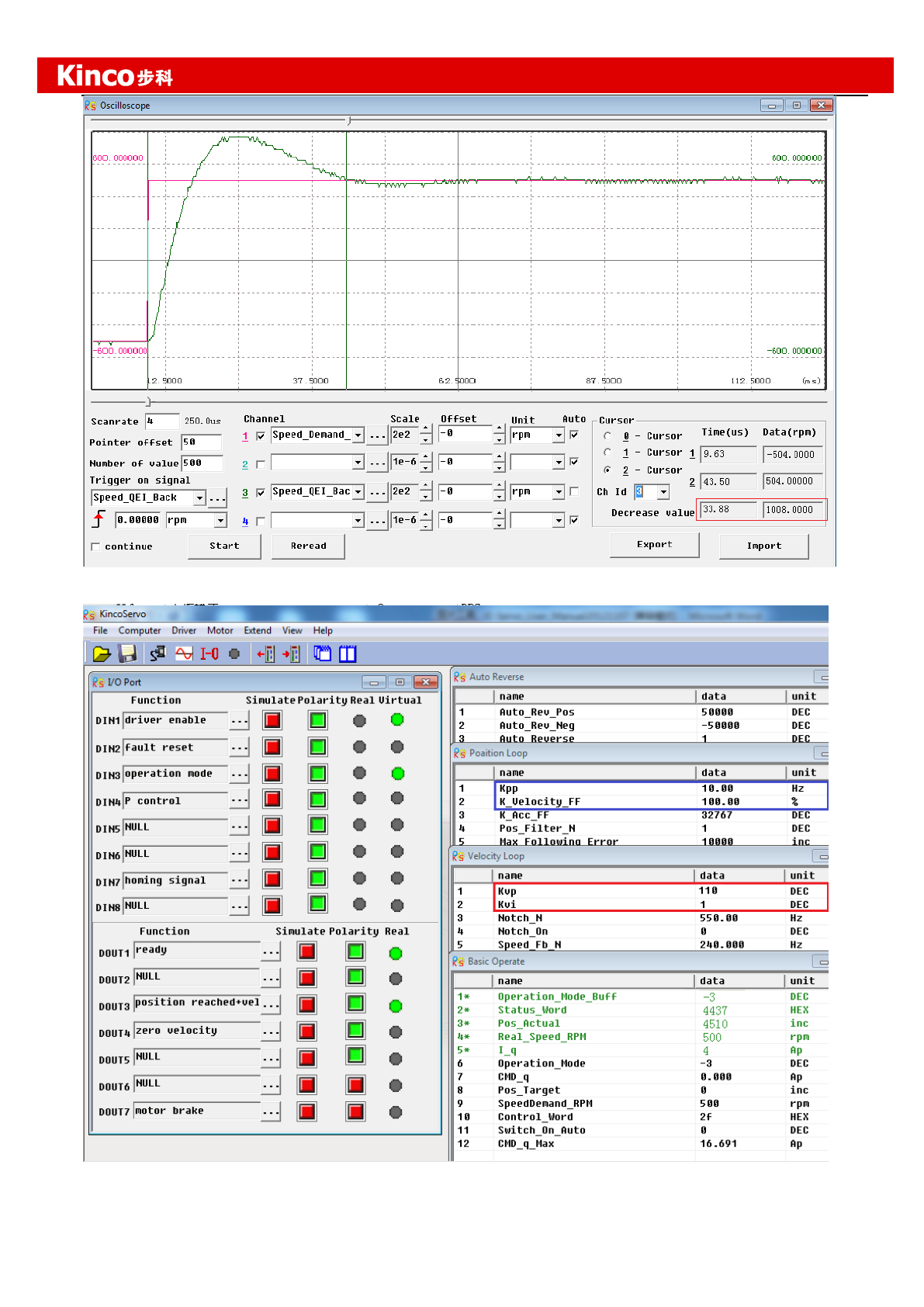
Kinco JD 伺服系列使用手册
119
Kinco FD Series Servo User Manual
In Auto Reverse mode,Kvp=110
The oscilloscope is shown as follows:actual speed response is 10.00ms
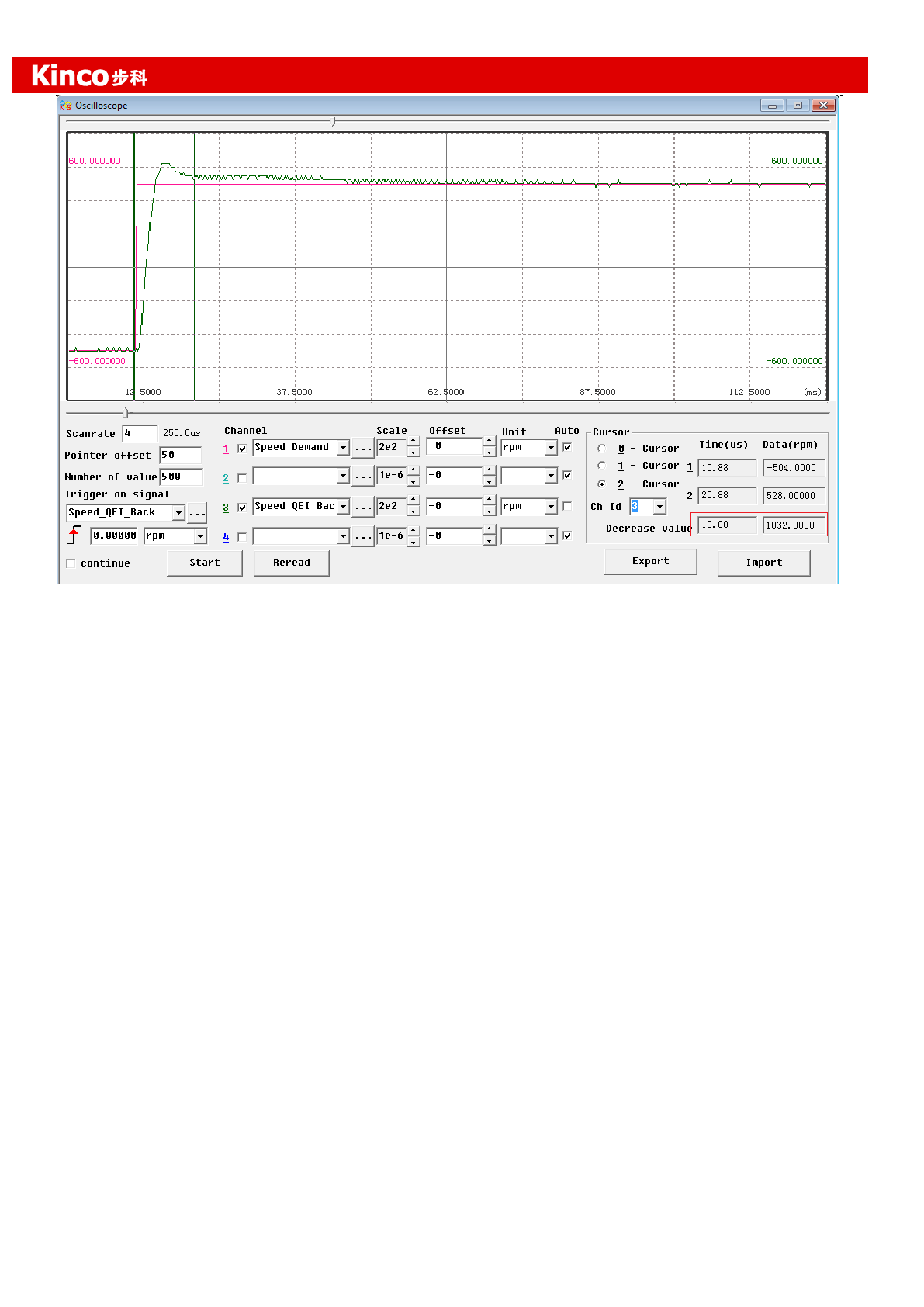
Kinco JD 伺服系列使用手册
120
Kinco FD Series Servo User Manual
2.Position Loop Adjustment
(1) Adjust Kpp.
(2)Adjust Vff(K_Velocity_FF)
Adjust Vff parameter according to the allowable position error and coupling performance of machine.
Normally Vff is 100%.If system doesn’t need high response for position,then this parameter can
be decreased to reduce overshoot.
(3)Use oscilloscope to observe curve.
Set motor running at Auto Reverse mode by time (Operation mode 3),set parameters of oscilloscope
as following figure.
In Fig.(1) and Fig.(2),Vff is 100%,When Kpp is 30,the response of position loop is faster than the
one when Kpp is 10.Meanwhile the following error is also less,but overshoot is bigger.
Fig.(3),Kpp is 30,Vff is 50%.Compare with Fig.(2),the following error is bigger,but response becomes
slower and there is almost no overshoot.
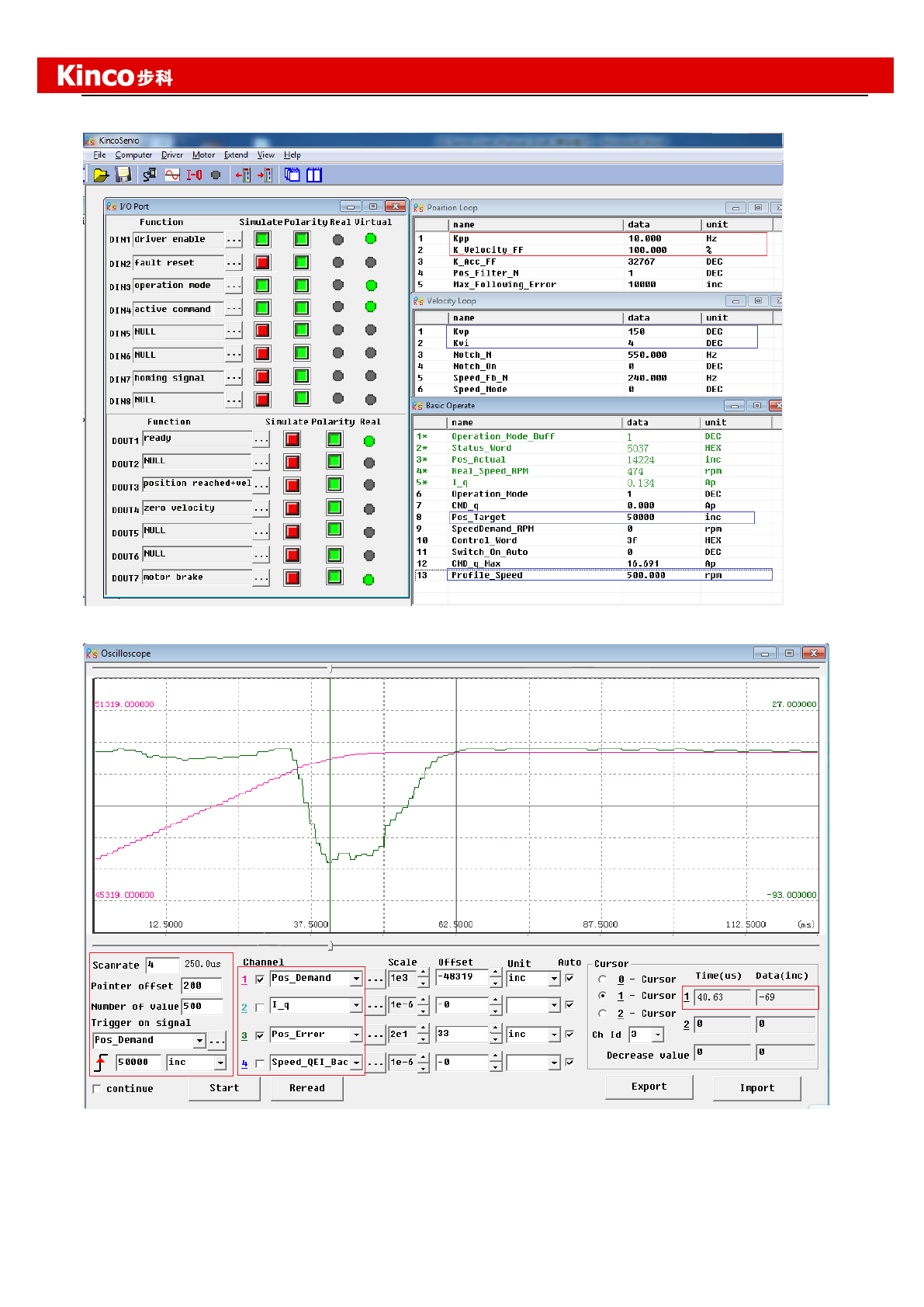
Kinco JD 伺服系列使用手册
121
Kinco FD Series Servo User Manual
Internal position mode,target position is 50000 inc.
Fig.(1) Kpp=10,Vff=100%
The oscilloscope is as following: max. following error is 69 inc.
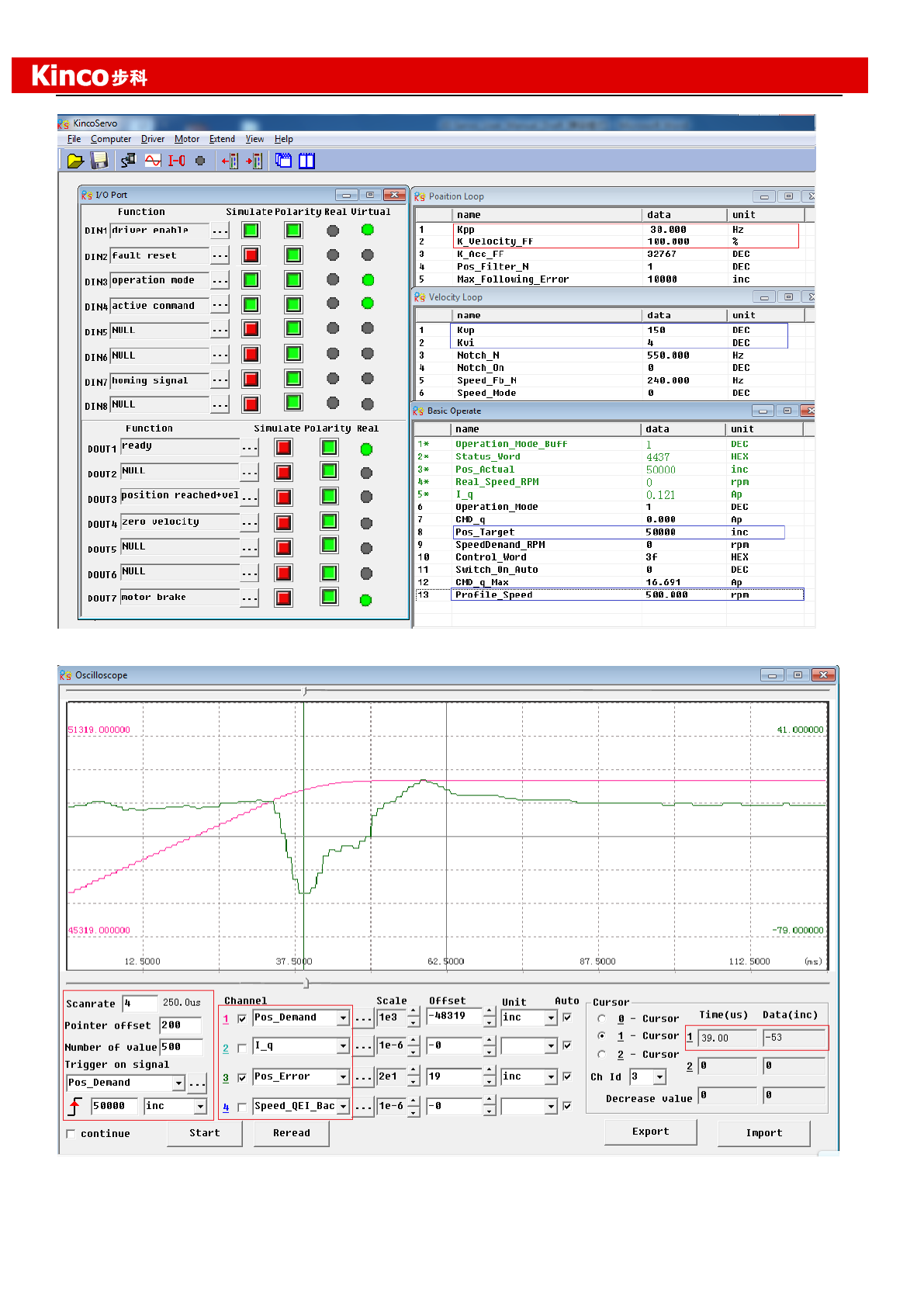
Kinco JD 伺服系列使用手册
122
Kinco FD Series Servo User Manual
Fig.(2) Kpp=30,Vff=100%
The oscilloscope is as following:max. following error is 53 inc.
Fig.(3) Kpp=30,Vff=50%
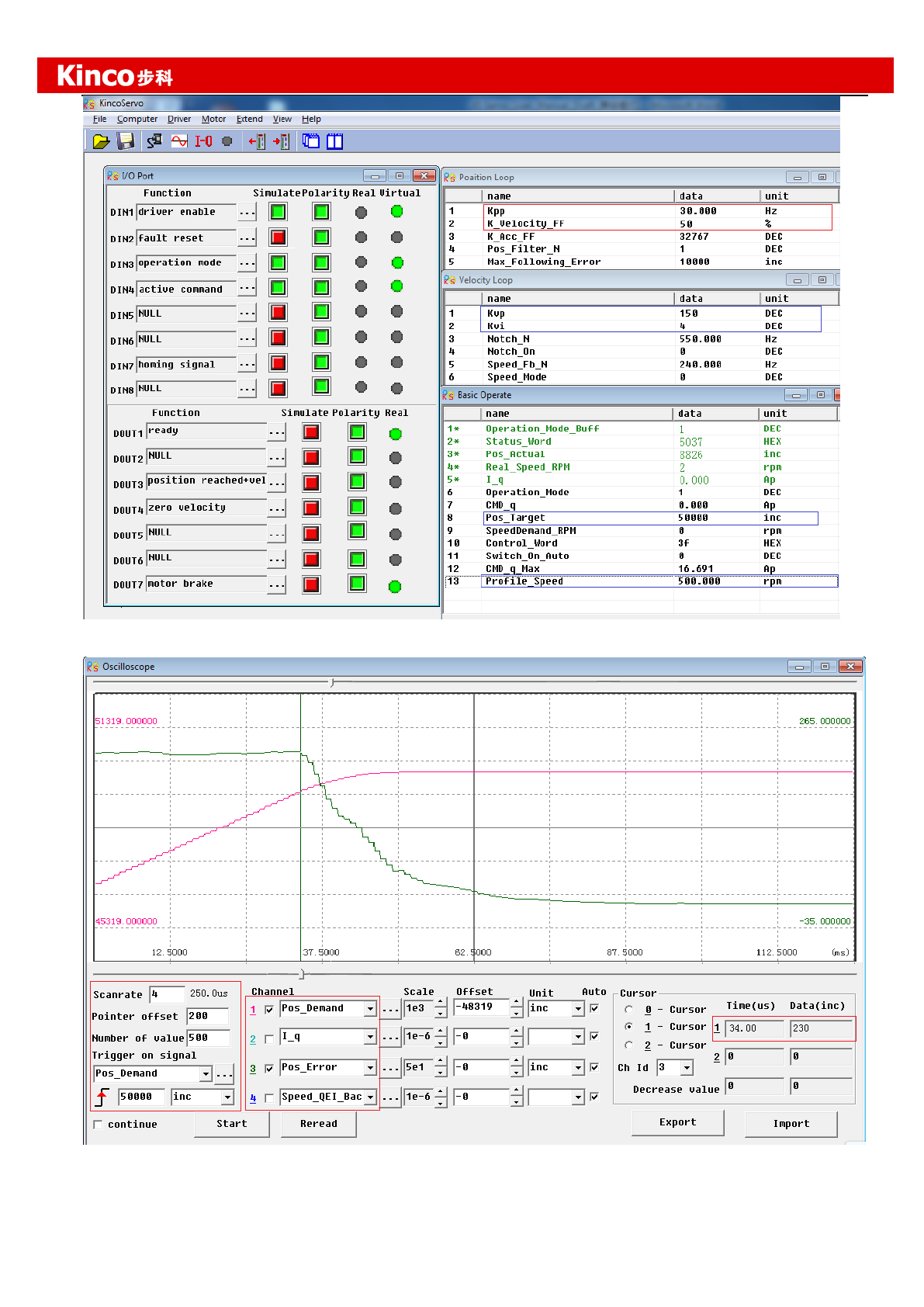
Kinco JD 伺服系列使用手册
123
Kinco FD Series Servo User Manual
The oscilloscope is as following:max. following error is 230 inc.
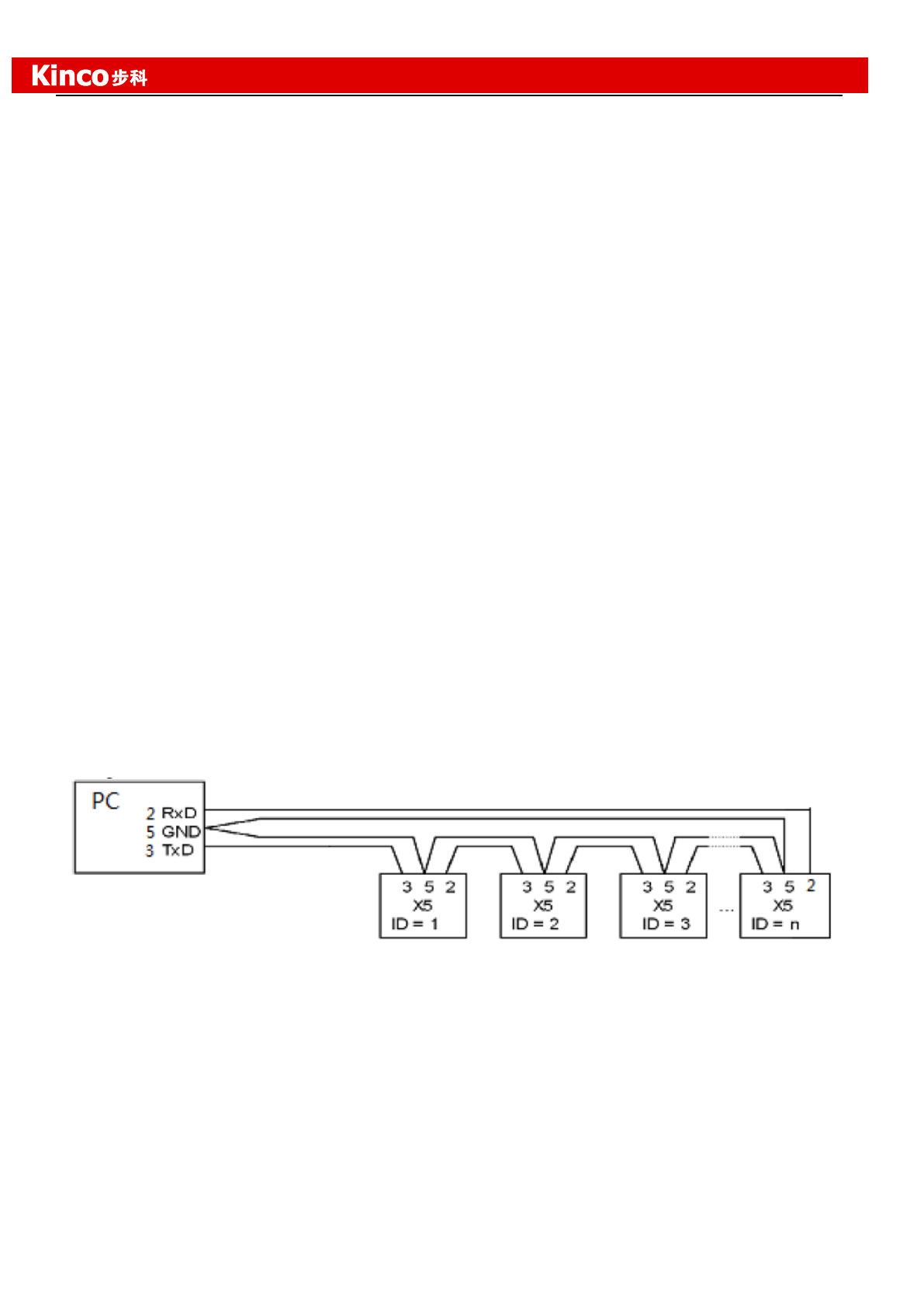
Kinco JD 伺服系列使用手册
124
Kinco FD Series Servo User Manual
Chapter 10 Communication
FD Servo supports powerful communication capabilities and adopts the control mode based on an object
dictionary. All controls come down to the configuration of internal objects. The configuration can be
implemented by multiple methods including RS232, RS485 and CANopen. It supports the connection of
multiple sites and simultaneous operation of multiple communication ports.
Notice:
1.DIN1 is set as driver enable function and DIN3 is set as operation mode control function by default.Before
using communication control,it must cancel the functions of these two DIN.
2.There are internal unit and engineering unit.All the parameters use internal unit when using communication
control,so it need to convert the unit.About more details about the relationship of the units please refer to
Appendix.
3.When using read/write function of SDO of CANopen,RS232 and RS485 communication,make sure there is
only one command in the network at the same time,and good communication error handling, etc., in order to
avoid communication into an infinite loop.
10.1 RS232 Communication
10.1.1 RS232 Communication Interface
The wiring diagram between PC and single FD Servo is as following:
PC FD Servo RS232(X3)
2 RxD ---------------------------------- TXD 2
3 TxD ---------------------------------- RXD 3
5 GND --------------------------------- GND 5
The wiring diagram between PC and multiple FD Servo is as following:( D05.15 must be set as 1,and restart
driver after setting)
FD SERVO
Note:1.It is the same way to connect FD Servo to HMI or other controllers.(The PIN definition of HMI or other
controllers may be different from PC’s).
2.When using the wiring of multiple FD Servo,all the FD Servo will receive the command at the same time.
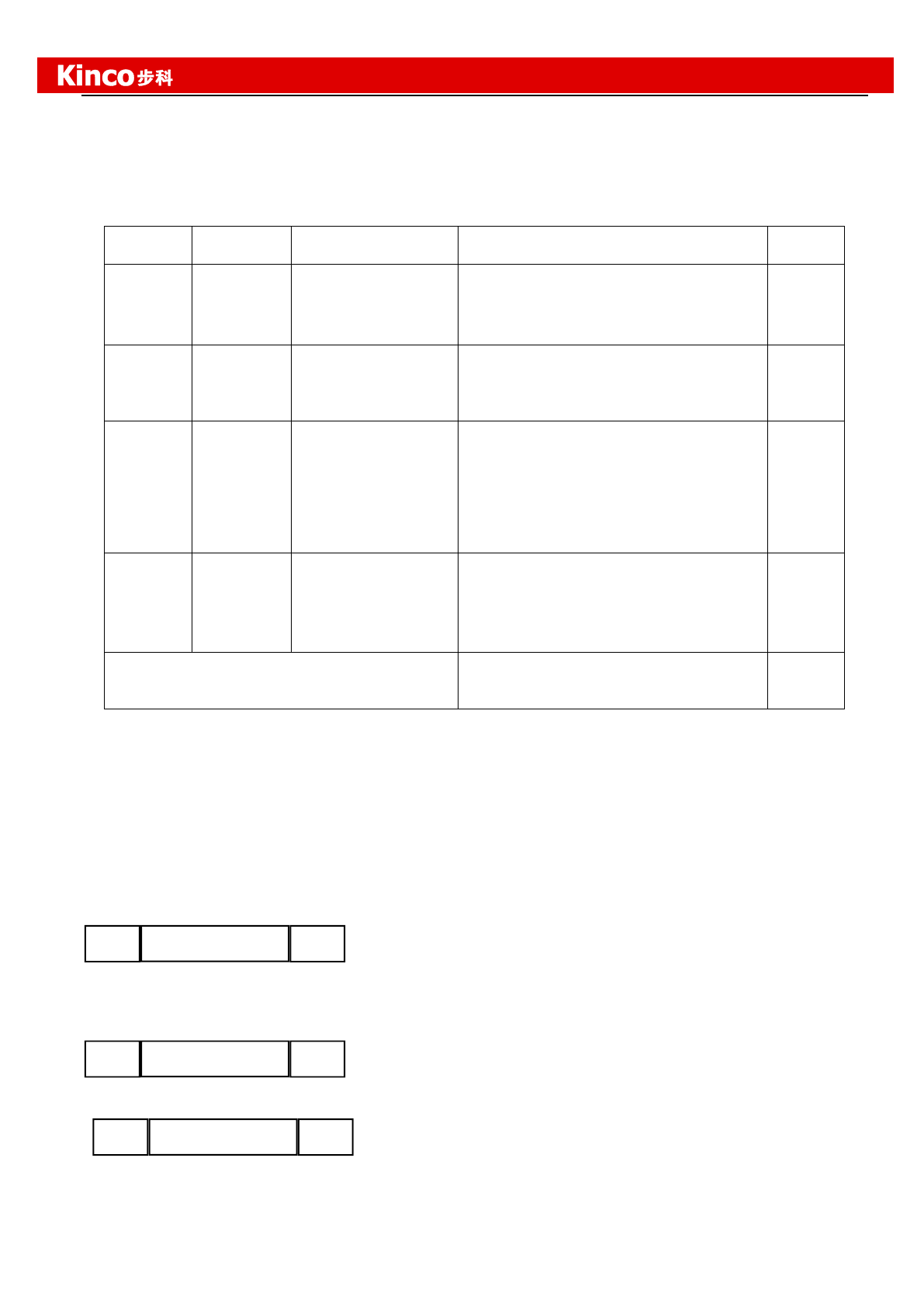
Kinco JD 伺服系列使用手册
125
Kinco FD Series Servo User Manual
10.1.2 RS232 Communication Parameters
LED
Display
Internal
Address
Name
Meaning
Default
value
d5.00
2FF00108
Store_Loop_Data
1:Store all control parameters except
motor parameters
10 :Initialzie all control parameters
except motor parameters
0
d5.01
100B0008
ID_Com
Station No. of Drivers
Note: To change this parameter, you
need to save it with the address “d5.00”,
and restart it later.
1
d5.02
2FE00010
RS232_Bandrate
Set the baud rate of RS232 port
540 19200
270 38400
90 115200
Note: To change this parameter, you
need to save it with the address “d5.00”,
and restarts it later.
270
d5.15
65100B08
RS232_Loop_Enabl
e
0:1:1
1:1:N
Note:It needs to restart driver after
changing
this parameter.
0
Other parameters
Data bit = 8
Stop bit = 1
Parity = None
Consta
nt
10.1.3 Transport Protocol
The RS-232C communication of the FD Servo driver strictly follows a master/slave protocol. The host
computer can send any data to FD driver. The driver configured with ID No. will calculate such data and
return a reply.
This transport protocol of RS232 uses a data packet with fixed length of10 bytes.
ID CHKS8 byte data
byte 0 byte 9
ID is the ID No. of the slave
CHKS = - SUM(byte0,…,byte8), CHKS is the lowest byte of the calculation result.
The host sends:
ID CHKS8 byte host data
byte 0 byte 9
When D5.15 is 0,FD Servo sends:
ID CHKS8 byte slave data
byte 0 byte 9
When D5.15 is 1,FD Servo sends:
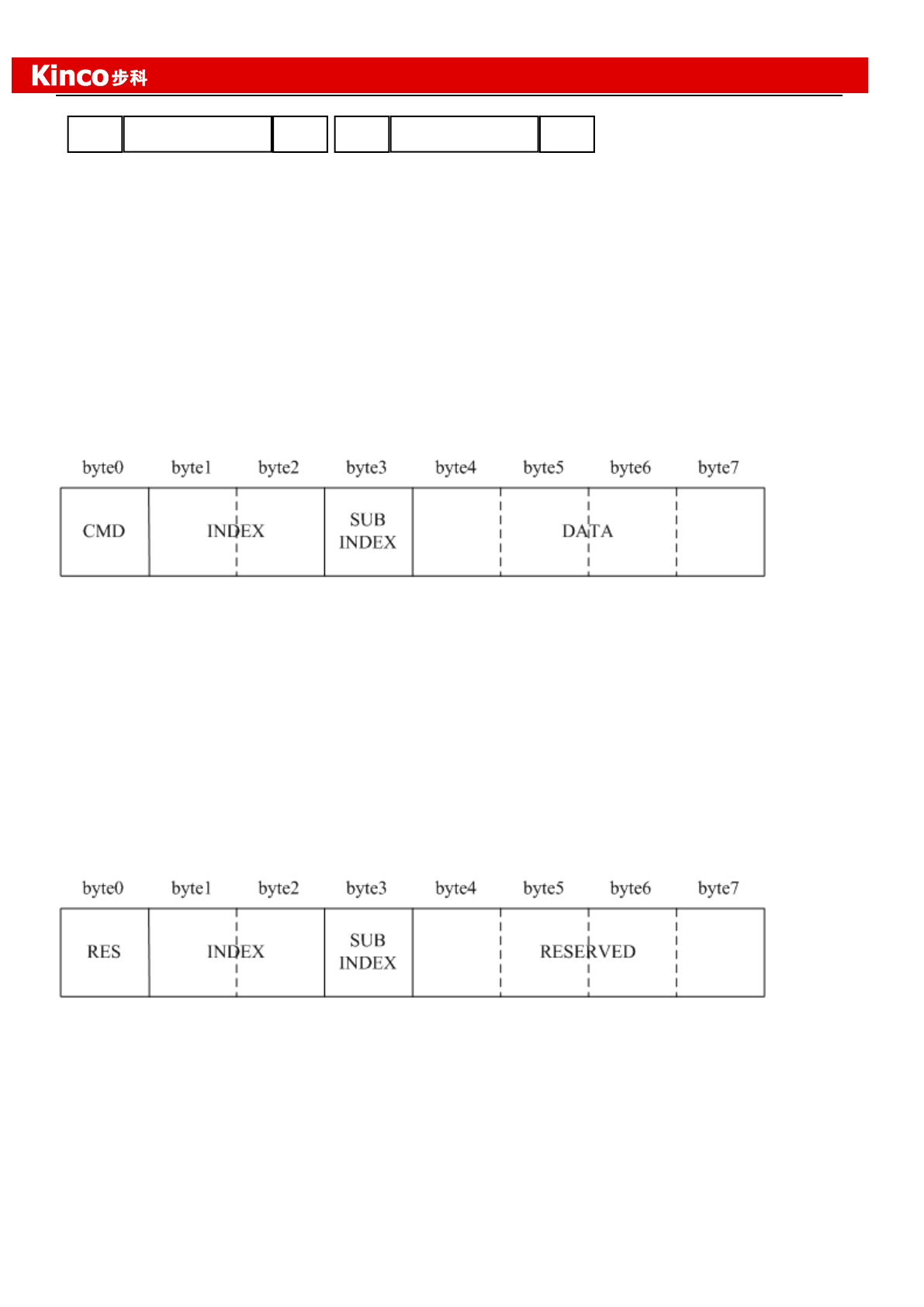
Kinco JD 伺服系列使用手册
126
Kinco FD Series Servo User Manual
ID CHKS8 byte host data
byte 0 byte 9
ID CHKS8 byte slave data
byte 0 byte 9
Note: Each 10-byte packet has its own CHKS.
If the host sends an ID not existed in the network to the FD Servo driver, no FD Servo driver will make a reply.
After the host sends the data correctly, the slave will find the data packets in compliance with its own ID and
check the CHKS value. If the checksum does not match, the slave will not make a response.
10.1.3.1 Data Protocol
A data protocol is different from a transport protocol. It contains 8 bytes of all 10 bytes of the above RS-232.
Definition of CD servo driver internal data complies with the CANopen international standard. All parameters,
values and functions are expressed by index and subindex.
A:Download. the host sends a command to write values into the objects in the slave, and the host generates
an error message when the value is downloaded to a non-existent object.
The host sends:
CMD Specifies the direction of data transfer and the volume of data.
23(0x16) Sends 4-byte data (bytes 4...7 contain 32 bits)
2b(0x16) Sends 2-byte data (bytes 4, 5 contain 16 bits)
2f(0x16) Sends 1-byte data (bytes 4 contains 8 bits)
INDEX Index in the object dictionary where data should be sent
SUB INDEX Subindex in object dictionary where data should be sent
In all four bytes in data, the lower-order bits are arranged before the higher-order bits. To write 7650 inc into
“Target Position” in the slave, the unit of 607A0029 is inc, 7650 is in decimal system, and 1DE2 is in
hexadecimal system.Since the length of the object to be written is 4 bytes and the calculation result 1D E2
has only 2 bytes,zero shall be filled to the higher-order bits. Therefore, the final result = 00 00 1D E2.
DATA: byte4=E2
byte5=1D
byte6=00
byte7=00
Slave responds:
RES: Displays slave response:
60(0x16) Data successfully sent
80(0x16) Error, bytes 4…7 contain error cause
INDEX 16-bit value, same as that sent by the master
SUBINDEX 8-bit value, same as that sent by the master
RES Reserved
For example:
Host sends:
01 23 7A 60 00 E2 1D 00 00 03 (This command is to write data into target position 607A0020)
Slave responds:
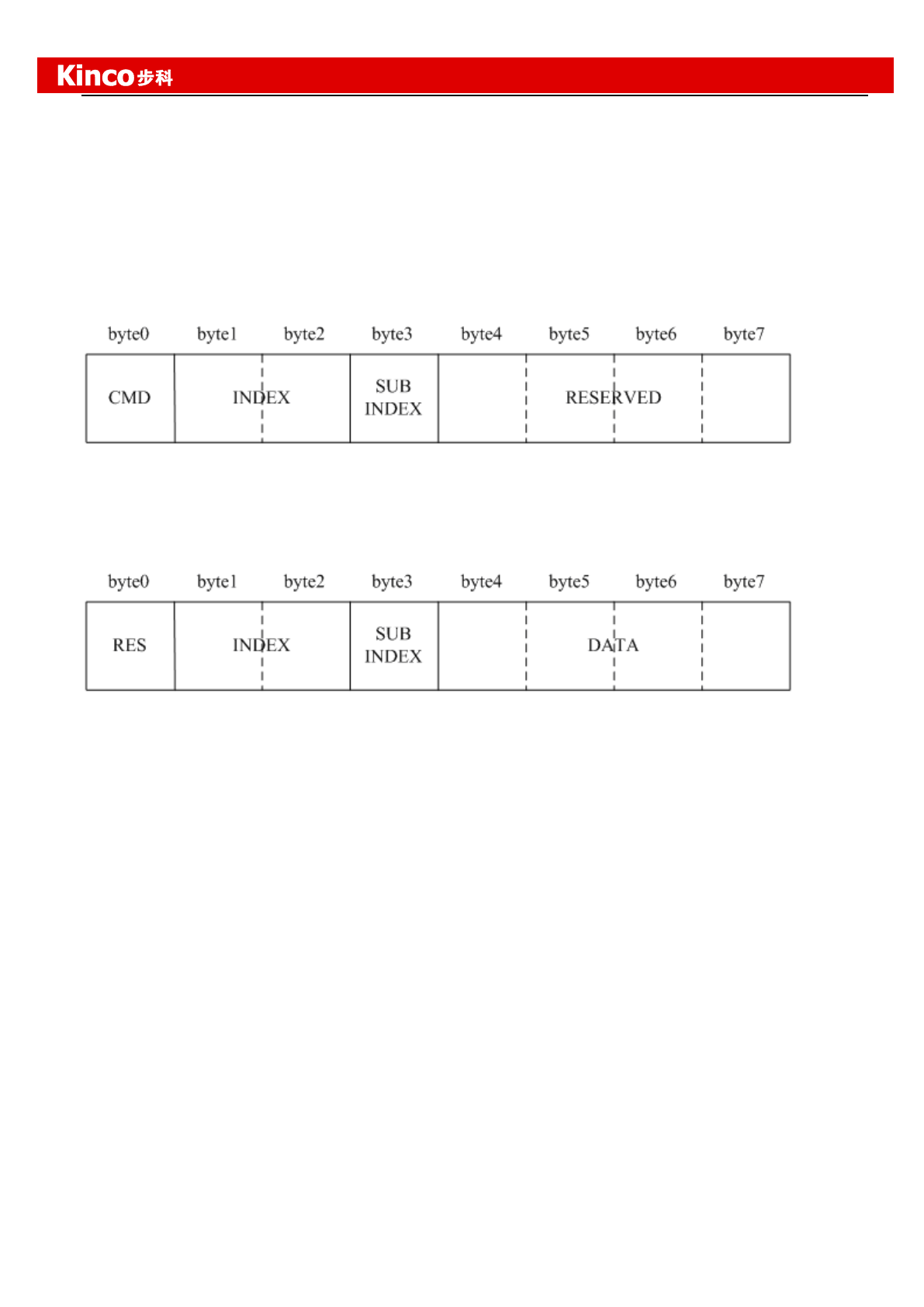
Kinco JD 伺服系列使用手册
127
Kinco FD Series Servo User Manual
01 60 7A 60 00 E2 1D 00 00 C6
Means:
01-Station No. of slave is 1
60-Data successfully sent.And data are saved in byte4…byte5.
byte4=E2,byte5=1D,byte6=00,byte7=00
Then,DATA= byte7 byte6 byte5 byte4 = 1DE2(hex)=7650 inc
B:Upload. Upload refers to that the master sends a command to read object address in the slave and the
master will generate an error if a non-existent target address is uploaded.
The host sends:
CMD Specifies the direction of data transfer
40(0x16)
INDEX 16-bit value
SUBINDEX 8-bit subindex
RESERVED Bytes 4…7 not used
The slave responds:
RES Displays slave response:
43(0x16) bytes 4...7 contain 32-bit data
4B(0x16) bytes 4, 5 contain 16-bit data
4F(0x16) byte 4 contains 8-bit data
80(0x16) error, bytes 4…7 contain error cause
INDEX 16-bit value, same as that sent by the master
SUBINDEX 8-bit value, same as that sent by the maste
If the data contains no error, byte 4…byte 7 save the object value read from the slave, with the lower-order
bits arranged before the higher-order bits. Correct value = byte7, byte6, byte5, byte4. If there is an error, data
contained in these four types is no longer object values read from the slave.
For example:
Host sends:
01 40 7A 60 00 00 00 00 00 E5 (This command is to read data of target position 607A0020)
Slave responds
01 43 7A 60 00 E2 1D 00 00 E3
Means:
01-Station No. of slave is 1
43-Receive 4 bytes of data and save into byte4…byte5.
byte4=E2,byte5=1D,byte6=00,byte7=00
Then DATA= byte7 byte6 byte5 byte4 = 1DE2(hex)=7650 inc
10.1.4 RS232 Communication Address of Servo Parameters
About the objects of each operation mode please refer to chapter8.
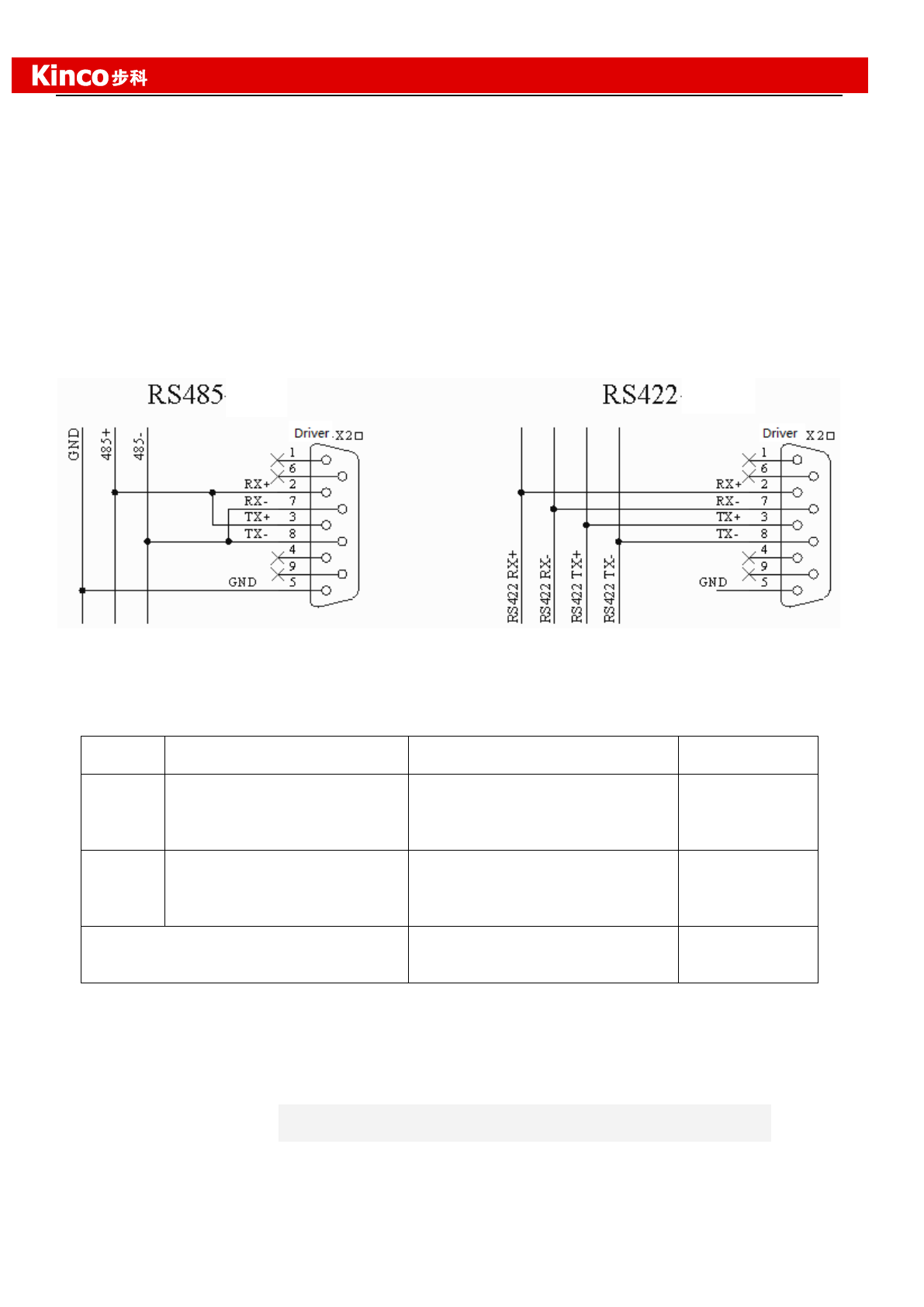
Kinco JD 伺服系列使用手册
128
Kinco FD Series Servo User Manual
About common object address please refer to object list in Appendix.
About all the communication address please refer to parameters list.
About RS232 communication example please refer to Appendix.
10.2 RS485 Communication
10.2.1 RS485 Communication Interface
The X2 interface of FD Servo driver supports RS485 and RS422 communication.The wiring diagram is shown
in following figure.
10.2.2 RS485 Communication Parameters
LED
Display
Name
Meaning
Default Value
d5.01
ID_Com
Station No. of Drivers
Note: To change this parameter,
you need to save it with the
address “d5.00”, and restart it later.
1
RS485_Bandrate
Set the baud rate of RS485 port
Note: This parameter must be
changed in KincoServo software.
540
Other parameters
Data bit = 8
Stop bit = 1
Parity = None
Constant
10.2.3 MODBUS RTU
The RS485 interface of FD Servo driver supports Modbus RTU protocol.
Modbus RTU protocol format
Start(No less than 3.5
characters of
messages interval)
Station
No.
Function
code
Data
CRC
1 Byte
1 Byte
N Bytes
2 Bytes
Function code of Modbus
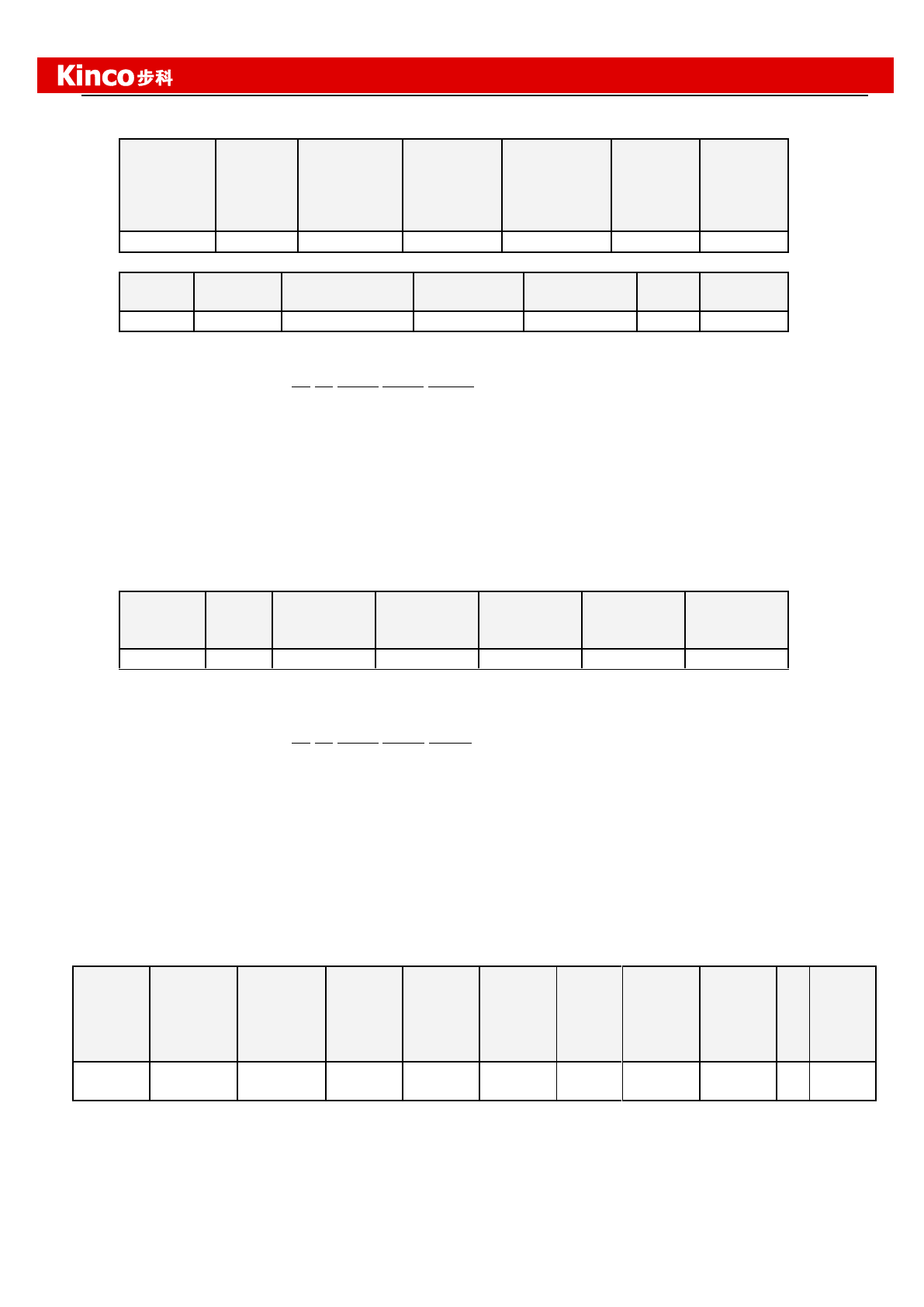
Kinco JD 伺服系列使用手册
129
Kinco FD Series Servo User Manual
0x03:Read data registers
Request format:
Station No.
Function
Code
High Byte
of Start
Address
Low Byte
of Start
Address
High byte of
Address
Length
(Word)
Low byte
of
Address
Length
(Word)
CRC
check
1 Byte
03
1 Byte
1 Byte
1 Byte
1 Byte
2 Bytes
Normal response format:
Station
No.
Function
Code
Return data
length(Bytes)
High byte of
Register 1
Low byte of
Register 1
…
CRC
check
1 Byte
03
1 Byte
1 Byte
1 Byte
…
2 Bytes
If there is error such as non-exist address,then it will return function code 0x81.
For example:Send message 01 03 32 00 00 02 CA B3
Meaning:
01: Station NO.
03: Function code:read data registers
32 00 :Read address starting from 4x3200(Hex).This is the modbus address corresponding to
parameter“Status word”(60410010)
00 02:Read 2 words of data
CA B3:CRC check.
0x06:Write single data register
Request format:
Station
No.
Functi
on
Code
High Byte
of Register
Low Byte of
Register
High byte of
writing
value
Low byte of
writing
value
CRC check
1 Byte
06
1 Byte
1 Byte
1 Byte
1 Byte
1 Bytes
Response format:If writing successful,then return the same message.
If there is error such as address over range,non-exist address and the address is read only,then it will return
function code 0x86.
For example:Send message 01 06 31 00 00 0F C7 32
Meaning:
01: Station No.
06: Function code,write single WORD
31 00 : Modbus address for writing data.This is the address corresponding to parameter “control
word”(60400010)
00 0F: Write data 000F(Hex)
C7 32: CRC check.
0x10:Write multiple registers
Request format:
Station
No.
Function
Code
High Byte
of Start
Address
Low
Byte of
Start
Address
High
byte of
Address
Length
(Word)
Low
byte of
Address
Length
(Word)
Data
length
(Bytes
)
High
byte of
Data 1
Low
byte of
Data 1
…
CRC
check
1 Byte
10
1 Byte
1 Byte
1 Byte
1 Byte
1 Byte
1 Byte
1 Byte
…
2
Bytes
Normal respons format:
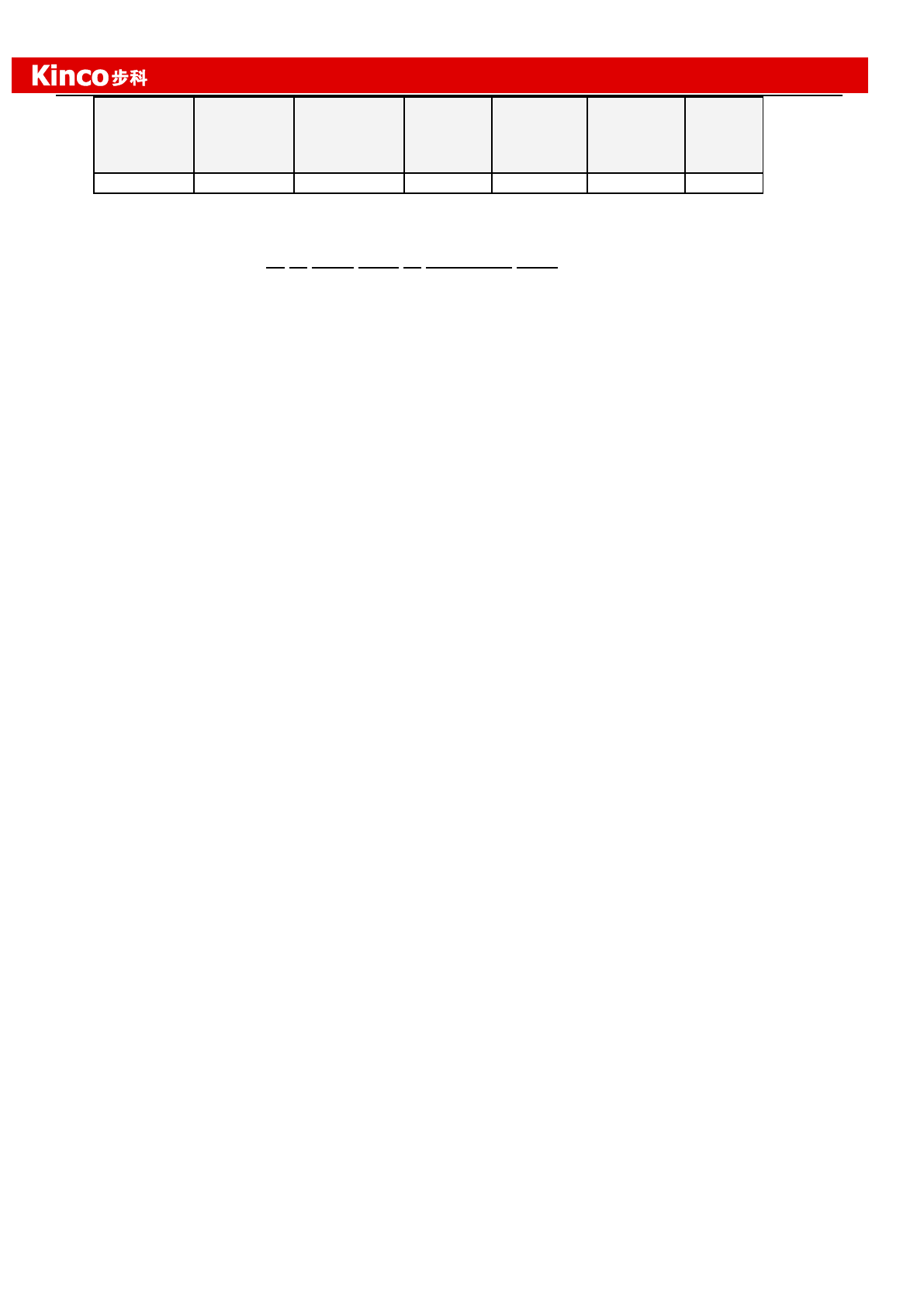
Kinco JD 伺服系列使用手册
130
Kinco FD Series Servo User Manual
Station No.
Function
Code
High Byte of
Start
Address
Low Byte
of Start
Address
High byte
of Address
Length
(Word)
Low byte
of Address
Length
(Word)
CRC
check
1 Byte
10
1 Byte
1 Byte
1 Byte
1 Byte
2 Bytes
If there is error such as address over range,non-exist address and the address is read only,then it will return
function code 0x90
For example:Send message 01 10 6F 00 00 02 04 55 55 00 08 1A 47
Meaning:
01: Station No.
10: Function code,write multiple WORDs
6F 00: Modbus address for writing data. This is the address corresponding to parameter “Target
Velocity”(60FF0020)
00 02: Address length is 2 WORD.
04: Data length is 4 Bytes(2 words)
55 55 00 08:Write data 00085555(Hex) into address.
1A 47: CRC check
10.2.4 RS485 Communication Address of Servo Parameters
About the objects of each operation mode please refer to Appendix.
About common object address please refer to object list in Appendix.(Not all the objects support RS485)
About RS485 communication example please refer to Appendix.
10.3 CANopen Communication
CANopen is one of the most famous and successful open fieldbus standards.It has been widely recognized
and applied a lot in Europe and USA. In 1992,CiA (CANinAutomation) was set up in Germany,and began to
develop application layer protocol CANopen for CAN in automation. Since then, members of CiA developed a
series of CANopen products,and applied in a large number of applications in the field of machinery
manufacturing such as railway, vehicles, ships, pharmaceutical, food processing etc..Nowadays CANopen
protocol has been the most important industrial fieldbus standard EN-50325-4 in Europe
The FD series servo supports standard CAN (slave device), strictly follow CANopen2.0A / B protocol, any
host computer which support this protocol can communicate with it. FD Servo uses of a strictly defined object
list, we call it the object dictionary, this object dictionary design is based on the CANopen international
standards, all objects have a clear definition of the function. Objects said here similar to the memory address,
we often say that some objects, such as speed and position,can be modified by an external controller, some
object were modified only by the drive itself, such as status and error messages.
These objects are as following:
For example:
Index Sub Bits Attribute Meaning
6040 00 16(=0x10) RW Control word
6060 00 8(=0x08) RW Operation mode
607A 00 32(=0x20) W Target position
6041 00 16(=0x10) MW Status word
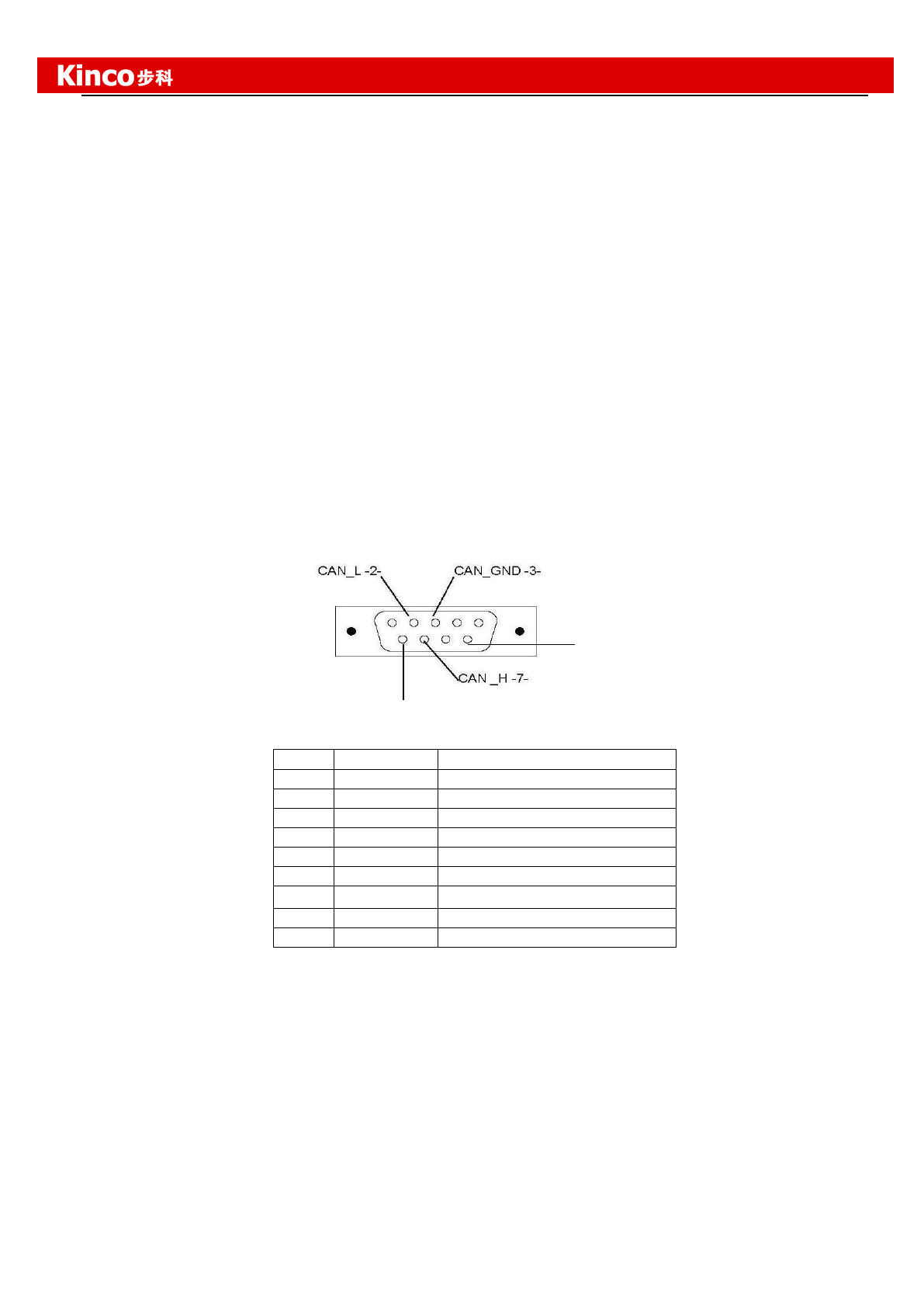
Kinco JD 伺服系列使用手册
131
Kinco FD Series Servo User Manual
The attributes of objects are as follows:
1. RW:The object can be both read and written.
2. RO:The object can be read only
3. WO:The object can be written only.
4. M:The object can be mapping,similar to indirect addressing.
5. S:The object can be stored in Flash-ROM without lost after power failure.
10.3.1 Hardware Introduction
CAN communication protocol describes a way of transmitting information between devices, The definition of
CAN layer is the same as the open systems interconnection model OSI, each layer communicates with the
same layer in another device, the actual communication takes place adjacent layers in each device,but the
devices only interconnect by the physical media of thephysical layer in the model.CAN standard defines data
link layer and physical layer in the mode. The physical layer of CAN bus is not strictly required, it can use a
variety of physical media such as twisted pair Fibre. The most commonly used is twisted pair signal, sent by
differential voltage transmission (commonly used bus transceiver). The two signal lines are called CAN_H
and CAN_L. The static voltage is approximately 2.5V, then the state is expressed as a logical 1, also called
hidden bit. It represents a logic 0 when CAN_H is higher than the CAN_L, we called it apparent bit,then the
voltage is that CAN_H = 3.5V and CAN_L= 1.5V,apparent bit is in high priority.
The standard CAN interface is as following figure:
Pin
Name
Description
1
NC
Reserved
2
CAN_L
CAN_L bus (low dominant )
3
CAN_GND
CAN ground
4
NC
Reserved
5
CAN_SHLD
Optional shield for CAN
6
GND
Optional ground
7
CAN_H
CAN_H bus(high dominant )
8
NC
Reserved
9
CAN_V+
NC
■Note:
1、All CAN_L and CAN_H of slaves connect directly by using series connection, not star connection.
2、There must be connected a 120 ohm resistance in start terminal(master) and end terminal(slave).
3、All FD Servo driver don’t need external 24VDC supply for CAN interface.
4、Please use the shield wires for communication cable,and make good grounding(Pin.3 is advised to
grounding when
communication is in long distance and high baudrate).
5、The max. distance at different baudrate are shown in following table:
GND
CAN_V+
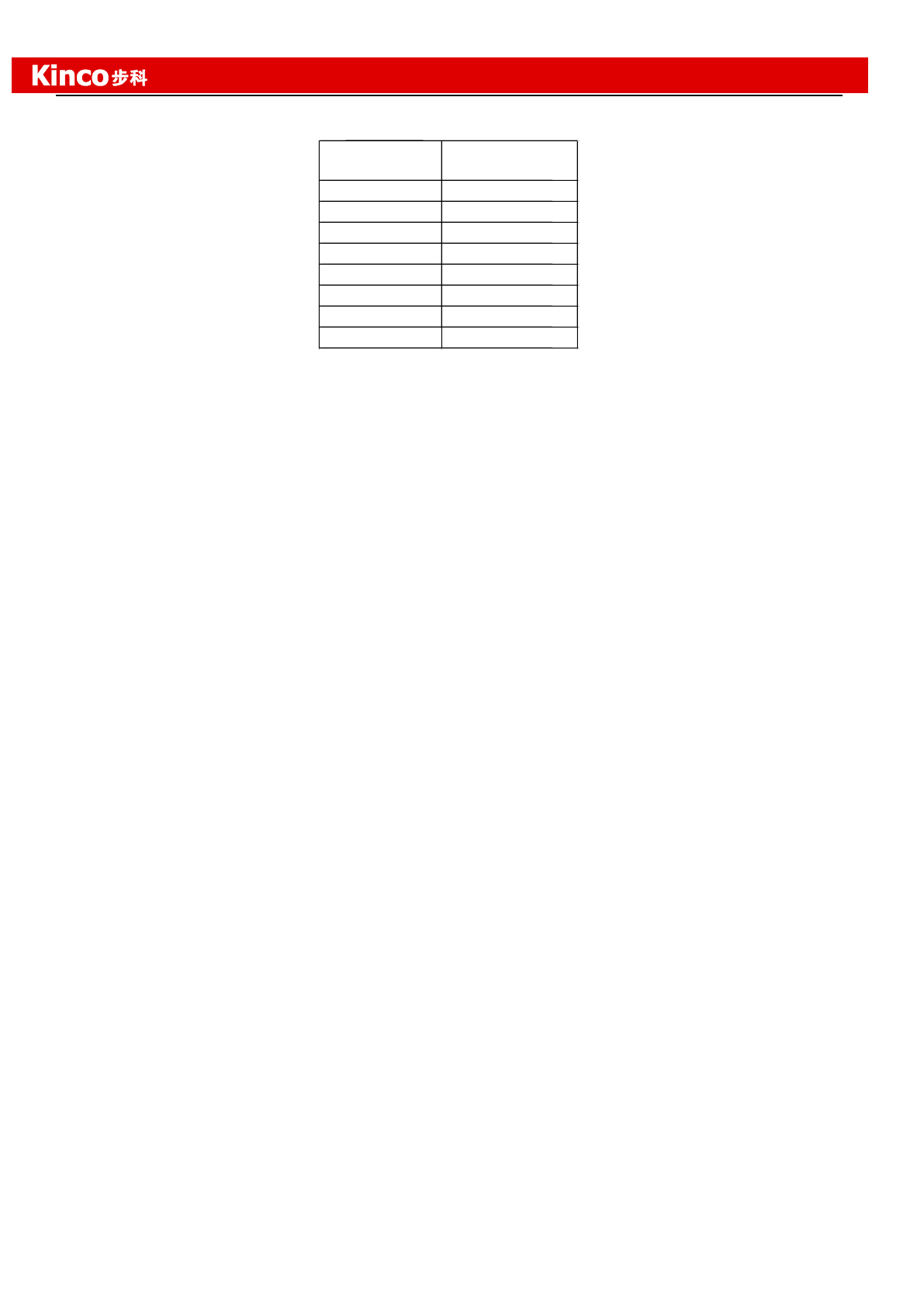
Kinco JD 伺服系列使用手册
132
Kinco FD Series Servo User Manual
10.3.2 Software Introduction
10.3.1.1 EDS
EDS(Electronic Data Sheet)file is an identification documents or similar code of slave device,to identify what
kind of slave device is(Like 401,402 and 403,or which device type of 402).This file includes all information of
slaves,such as manufacturer,sequence No.,software version,supportable baudrate,mappable OD and
attributes of each OD and so on,similar to the GSD file for Profibus.Therefore,we need to import the EDS file
of slave into the software of master before we configure the hardware.
10.3.1.2 SDO
SDO is mainly used in the transmit the low priority object between the devices, typically used to configure
and mange the device,such as modifying PID parameters in current loop,velocity loop and position loop,and
PDO configuration parameters and so on.This data transmission mode is the same as Modbus,that is it
needs reponse from slave when master sends data to slave.This communication mode is suitable for
parameters setting,but not for data transmission frequently.
SDO includes upload and download.The host can use special SDO instructions to read and write the OD
of servo.
10.3.1.3 PDO
PDO can transport 8 bytes of data at one time,and no other protocol preset(Mean the content of the data
are preset),it is mainly used to transmit data in high frequency.PDO uses brand new mode for data
exchange,it needs to define the data receiving and sending area before the transmission between two
devices,then the data will transmit to the receiving area of devices directly when exchanging data.It greatly
increase the efficiency and ultilization of the bus communication.
Baudrate
Distance
1Mbit/s
25M
800Kbit/s
50M
500Kbit/s
100M
250Kbit/s
250M
125Kbit/s
500M
5
0
Kbit/s
600M
25Kbit/s
800M
10Kbit/s
1000M
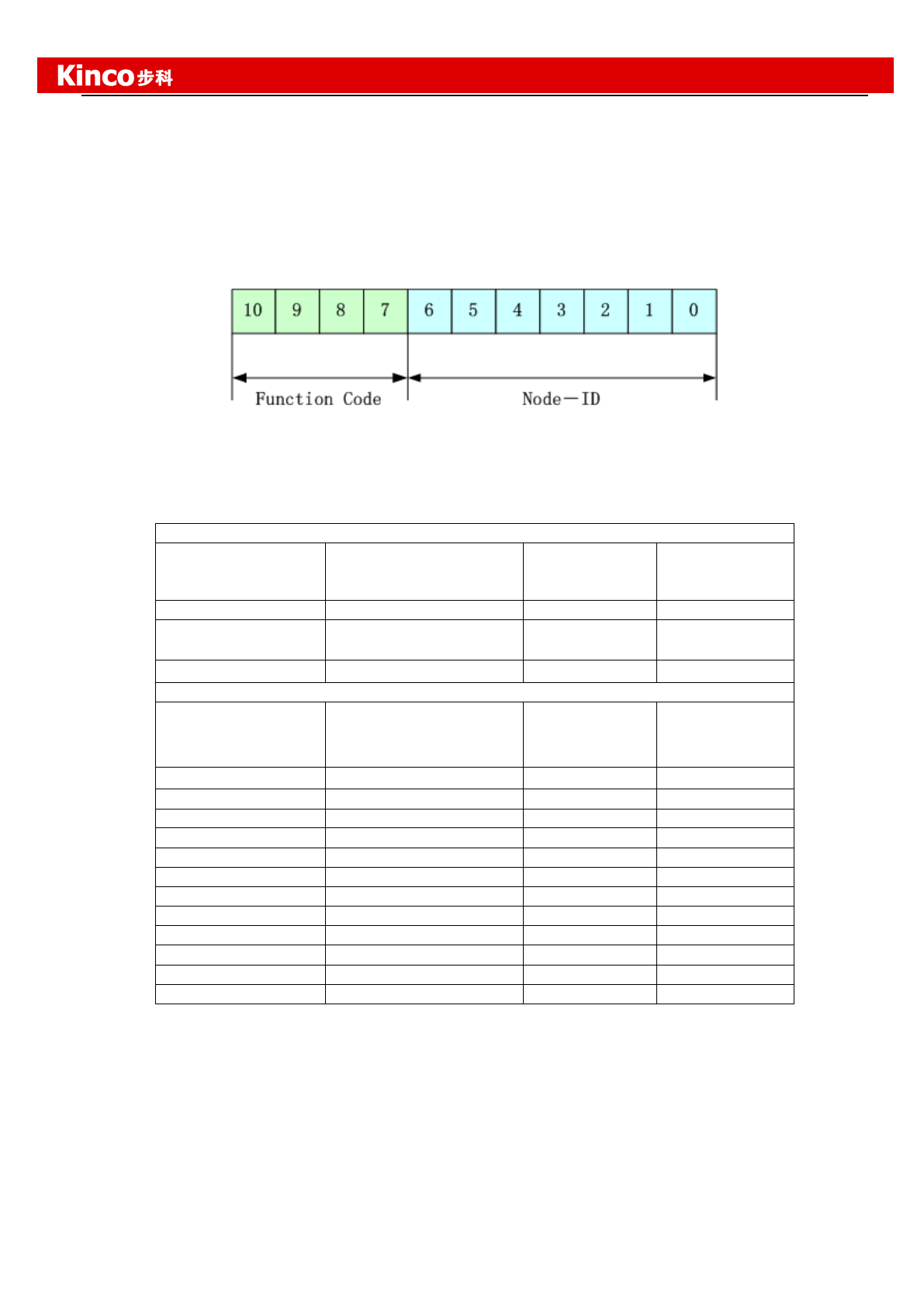
Kinco JD 伺服系列使用手册
133
Kinco FD Series Servo User Manual
PDO COB-ID
COB-ID is a unique way of CANopen communication protocol,it is the short name
of Communication Object Identifier. These COB-ID defines the respective transmission levels for PDO, These
transport level, the controller and servo will be able to be configured the same transmission level and the
transmission content in the respective software.Then both sides know the contents of data to be transferred,
there is no need to wait for the reply to check whether the data transmission is successful or not when
transfering data.
The default ID allocation table is based on the CAN-ID(11 bits) defined in CANopen 2.0A(The COB-ID of
CANopen 2.0B protocol is 27 bits),include function code(4 bits) and Node-ID(7 bits) as shown in following
figure:
Node-ID is defined by system integrators,such setting by the DIP switch on the devices(Like servo’s station
No.).The range of Node-ID is 1~127(0 is forbidden).
Function Code:The function code for data transmission define the transmission level of PDO,SDO and
management message.The smaller the function code,the higher the priority.
The allocation table for CAN identifiers in master/slave connection set predefined by CANopen is as follows:
Broadcast objects
Object
Function code
(ID-bits 10-7)
COB-ID
Index of
communication
parameter in OD
NMT Module Control
0000
000H
-
SYNC
0001
080H
1005H,1006H,
1007H
TIME SSTAMP
0010
100H
1012H,1013H
Reciprocity objects.
Object
Function code
(ID-bits 10-7)
COB-ID
Index of
communication
parameter in OD
Emergency
0001
081H-0FFH
1024H,1015H
PDO1(Send)
0011
181H-1FFH
1800H
PDO1(Receive)
0100
201H-27FH
1400H
PDO2(Send)
0101
281H-2FFH
1801H
PDO2(Receive)
0110
301H-37FH
1401H
PDO3(Send)
0111
381H-3FFH
1802H
PDO3(Receive)
1000
401H-47FH
1402H
PDO4(Send)
1001
481H-4FFH
1803H
PDO4(Receive)
1010
501H-57FH
1403H
SDO(Send/Server)
1011
581H-5FFH
1200H
SDO(Receive/Client)
1100
601H-67FH
1200H
NMT Error Control
1110
701H-77FH
1016H-1017H
Note:
1. The smaller the COB-ID,the higher the priority.
2. The function codes of COB-ID in every level are fixed.
3. COB-ID of 00H, 80H, 100H, 701H-77FH, 081H-0FFH are system management format.
The COB-ID supported by FD Servo:
Send PDO(TXPDO)
Send PDO of servo means servo sends out data,and these data are received by PLC.The function codes
of send PDO (COB-ID) are as follows:
1、 0x180+Station No. of Servo
2、 0x280+ Station No. of Servo
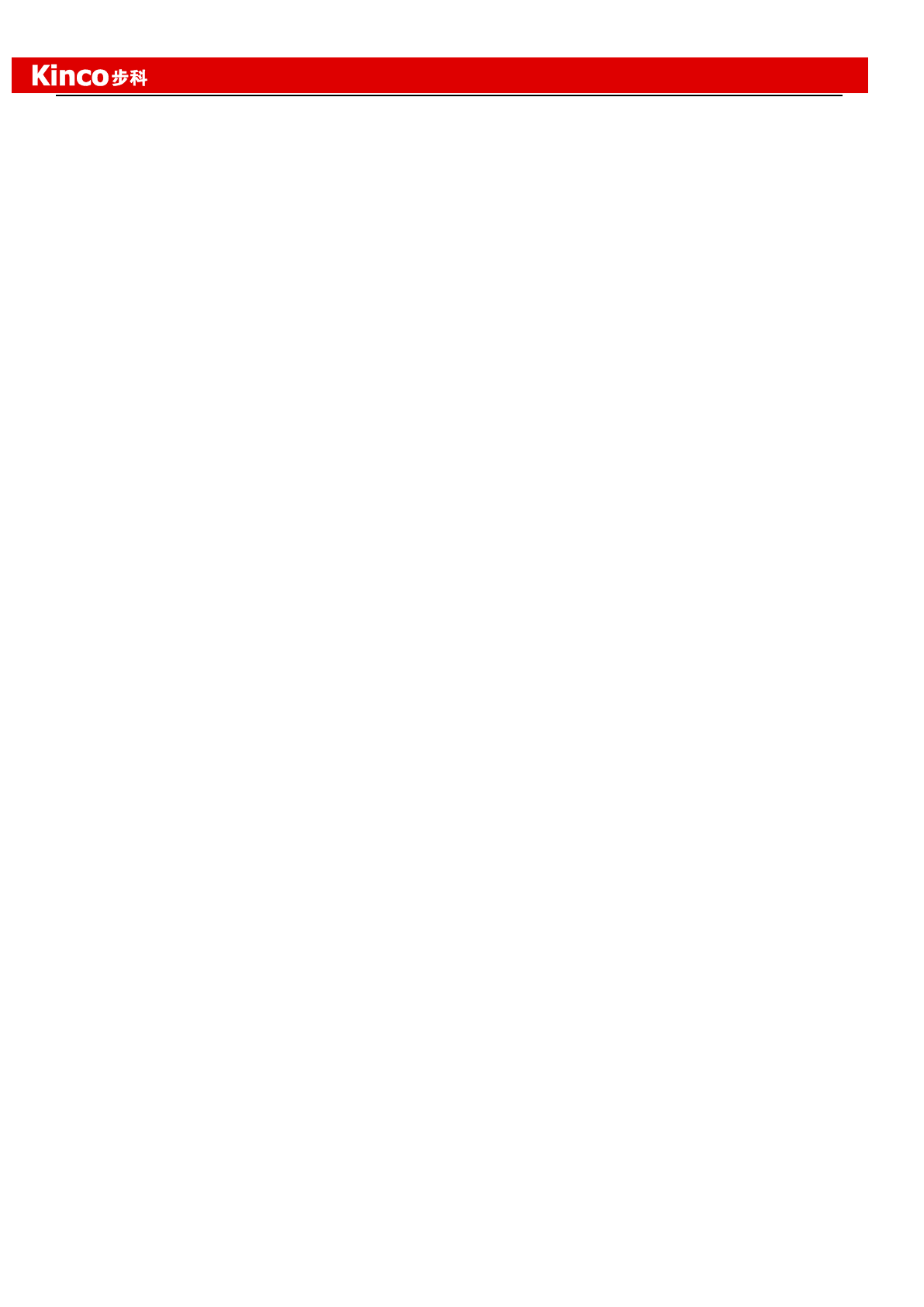
Kinco JD 伺服系列使用手册
134
Kinco FD Series Servo User Manual
3、 0x380+ Station No. of Servo
4、 0x480+ Station No. of Servo
Receive PDO(RXPDO)
Receive PDO of servo means servo receive data,and these data are sent by PLC.The function codes of
receive PDO(COB-ID) are as follows:
1、 0x200+ Station No. of Servo
2、 0x300+ Station No. of Servo
3、 0x400+ Station No. of Servo
4、 0x500+ Station No. of Servo
FD Servo is designed according to the standard of CANopen 2.0A protocol,and it also supports CANopen
2.0B protocol.Therefore,if 8 PDOs are not enough,users can define new PDO,for example,set 0x43FH as the
communication PDO of Station No.1,but it needs the controllers and servo define PDO by the same rule.
PDO transmission types:
PDO supports two transmission mode:
SYNC: Transmission is triggered by the synchronization message(Transmission type:0-240)
In this transmission mode, controller must have the ability to send synchronous messages(The message is
sent periodically at a maximum frequency of 1KHz),and servo will send after receiving the synchronous
message.
Acyclic:Pre-triggered by remote frame,or by specific event of objects speicficed by the equipment
sub-protocol.In this mode,servo will send out data as soon as receiving the data of synchronous message
PDO.
Cyclic:Triggered after sending 1 to 240 SYNC messages.In this mode,servo will send out data in PDO after
receiving n SYNC messages.
ASYNC(Transmission Type:254/255):
Slave sends out message automatically as soon as the data change,and it can define an interval time
between two messages which can advoid the one in high priority always sending message.(The smaller
number of PDO,the higher its priority)
PDO Inhibit Time:
Each PDO can define an inhibit time,that is the minimum interval time between two continuous PDO
transmission.It is used to advoid the PDO in higher priority always occupying the communication.The inhibit
time is 16bit unsigned integer,its unit is 100us.
Protection mode(Supervision type)
Supervision type is to choose which way master uses to check slave during operation,and check whether
slave is error or not and handle the error.
Heartbeat message:Slave send message to master cyclically during supervision time.If master hasn’t
received the message from slave after heartbeat time,then master will consider slave as error.
Message format
(0x700+NodeID)+Status
Status:
0:Start 4:Stop 5:Run 127:Pre-operational
Node Guarding: Slave send message to master cyclically during supervision time.If master hasn’t received
the message from slave after supervision time,then master will consider slave as error.
The format of master request message:
(0x700+NodeID)( No data in this message)
Format of slave response message:
(0x700+NodeID)+Status:
Status:
The bit7 of the data is triggered bit.This bit will alternately set to 0 or 1 in the response message.It will be set
to 0 at the first request of node guarding.The bit0 ~ bit6 indicate the status of node.
Status: 0:Initialization 1:No connection 2.Connection 3:Operational 4:Stop 5:Run
127:Pre-operational
Normally standard CAN slave only one protection mode,but FD Servo can support both.
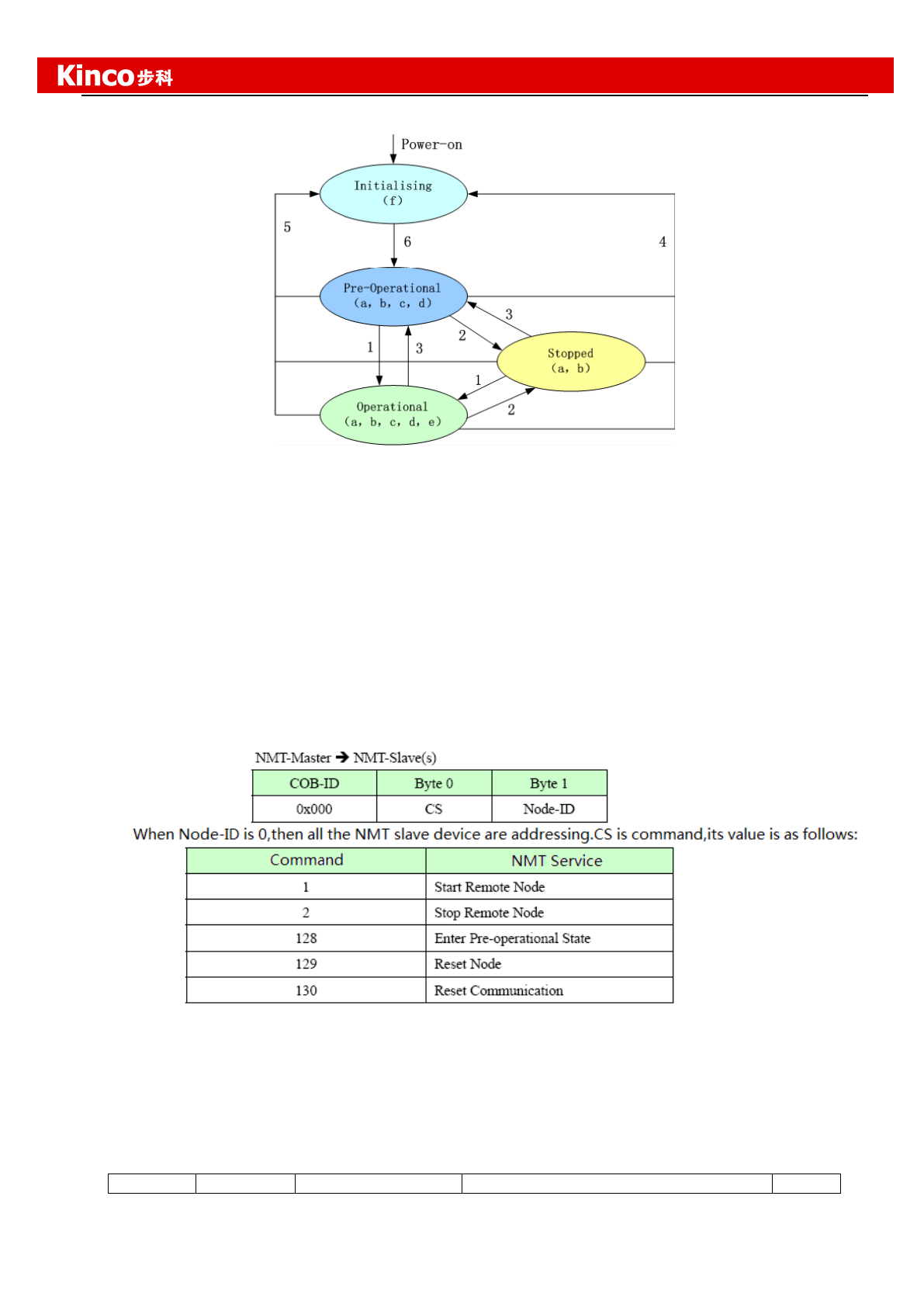
Kinco JD 伺服系列使用手册
135
Kinco FD Series Servo User Manual
Boot-up process
The boot-up process is shown in following figure.
Note:
►The letters in the parenthesis means the objects which can used in this status:
a. NMT ,b. Node Guard ,c. SDO ,d. Emergency ,e. PDO ,f. Boot-up
► State transition(1-5 are sent by NMT service),NMT command as shown in the parenthesis:
1:Start_Remote_node (0x01)
2:Stop_Remote_Node (0x02)
3:Enter_Pre-Operational_State (0x80)
4:Reset_Node (0x81)
5:Reset_Communication (0x82)
6:Initialization finish,enter pre-operational status and send boot-up message.
NMT management message can be used to change the modes.Only NMT-Master node can send NMT
Module Control message,and all slave must support NMT Module Control service,meanwhile NMT Module
Control message needn’t response.The format of NMT message is as follows:
For example, If you want a node in the operational status to return to the pre-operational status,then the
controller needs to send following message:
0x000:0x80 0x02
10.3.3 CANopen Communication Parameters
LED
Internal
Name
Meaning
Default
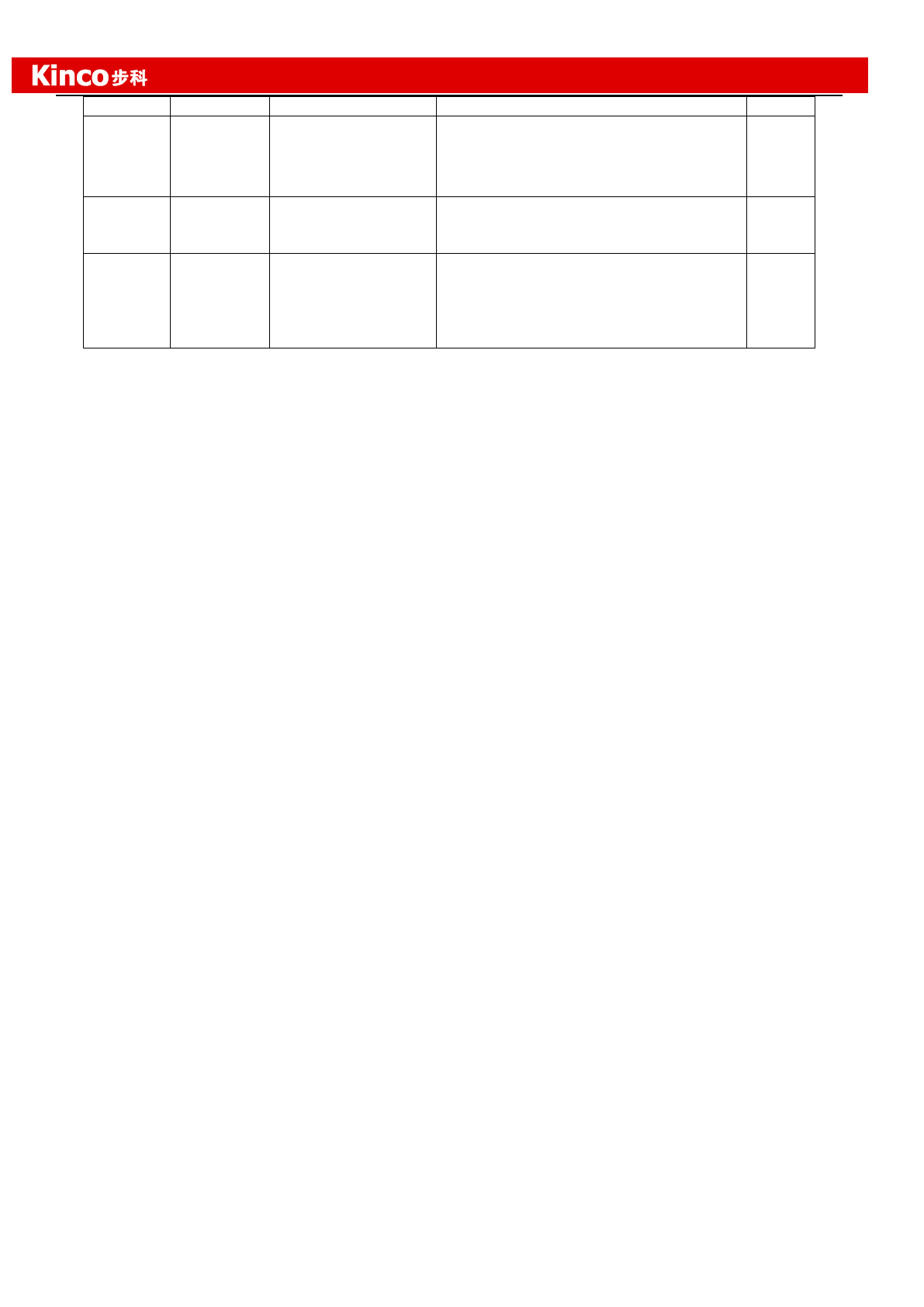
Kinco JD 伺服系列使用手册
136
Kinco FD Series Servo User Manual
Display
Address
Value
d5.00
2FF00108
Store_Loop_Data
1:Save all control parameters except
motor parameters
10 :Initialize all control parameters
except motor parameters
0
d5.01
100B0008
ID_Com
Driver station No.
Note:It needs to save and restart driver
after changing this parameter.
1
2F810008
CAN_Bandrate
Baudrate of CAN port:
Note: It needs to save and restart driver
after changing this parameter.This
parameter can only set in KincoServo
software.
50
10.3.4 CANopen Communication Address of Servo Parameters
About the objects of each operation mode please refer to Appendix.
About common object address please refer to object list in Appendix.
About all the communication address please refer to parameters list.
About CANopen communication example please refer to Appendix.
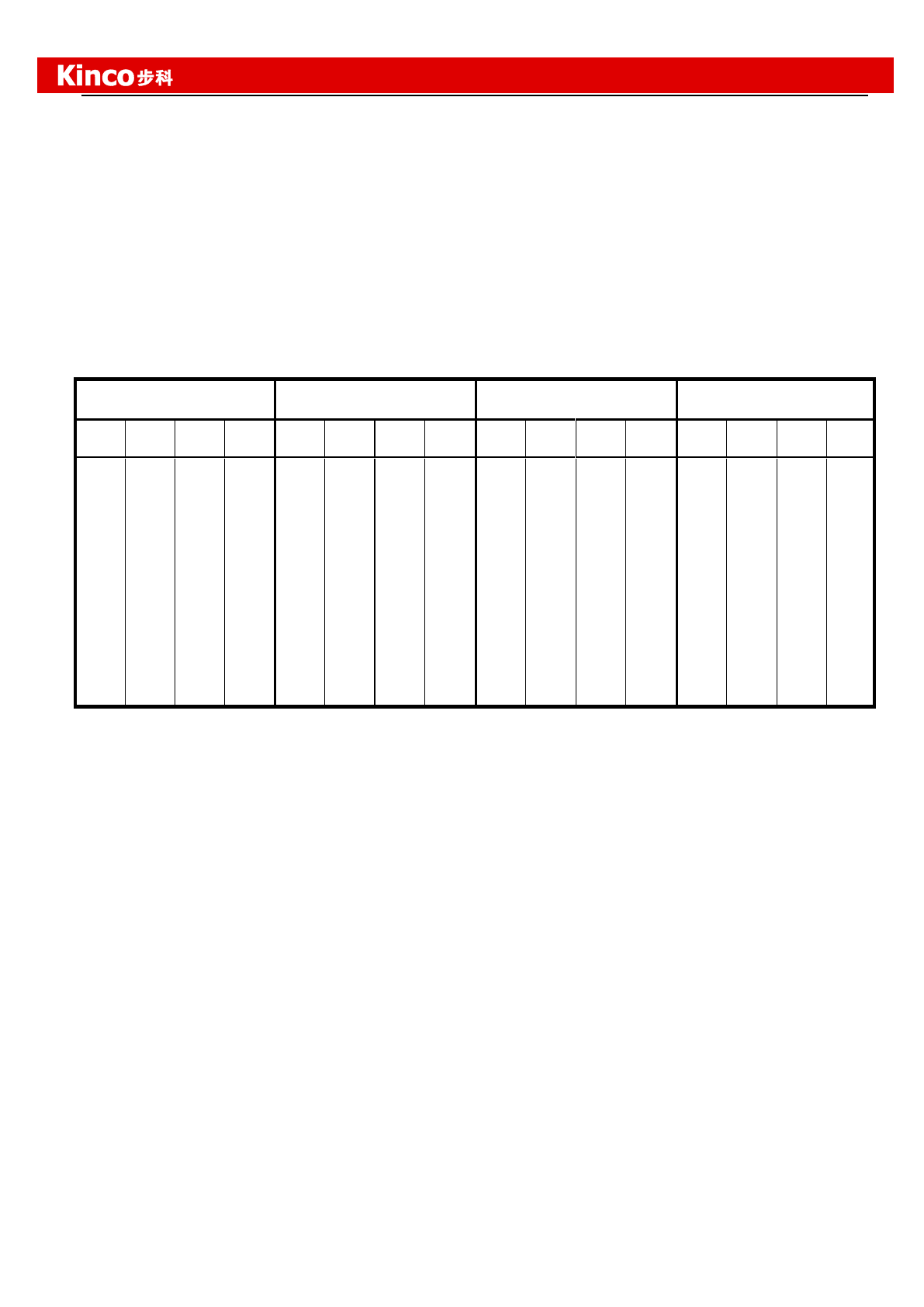
Kinco JD 伺服系列使用手册
137
Kinco FD Series Servo User Manual
Chapter 11 Alarm and Troubleshooting
11.1 Alarm Messages
Digital flickering on the display indicates that an alarm occurs indicating that the driver is faulty. For
details about faults, see Table 11-1 “Fault codes”. A code of the alarm message is represented by a
hexadecimal data, and four numeric displays appear. If the driver is faulty, the corresponding bits in the alarm
codes are set to “1”. For example, if an encoder is not connected, the 1st and 2nd bits of the faulty code are set
to “1”. As a result, “0006” is displayed. Table 11-1 Fault codes
1st bit in numeric display
(left)
2nd bit in numeric display
3rd bit in numeric display
4th bit in numeric display
(right)
15
14
13
12
11
10
9
8
7
6
5
4
3
2
1
0
EEPROM Error
Commutation
STO Error
Over Frequency
IIt Error
Logic Voltage
Following Error
Chop Resistor
Over Current
Low Voltage
Over Voltage
Over Temperature
Encoder Counting
Encoder UVW
Encoder ABZ
Internal
A maximum of 7 generated alarms can be stored in the driver. For details, enter the menu of Group F007.
Press Enter. The interface of faulty codes is displayed. The errors that you first discovered are those that
have occurred most recently. Press ▲ or ▼ to browse the messages of historical alarms. If the decimal point
at the lower right corner in the second bit of the numeric display is on, it indicates that the earliest alarm
message is just browsed; if the decimal point at the lower right corner in the third bit of the numeric display is
on, it indicates that the latest alarm message is just browsed.
For details on error messages, you need to access PC software via a communication port to check the
working status of the driver when an error occurs. Here are some messages of the driver for your reference:
1. Error codes;
2. Bus voltage when an error occurs;
3. Motor speed when an error occurs;
4. Motor current when an error occurs;
5. Driver temperature when an error occurs;
6. Working mode of the driver when an error occurs;
7. Accumulated working time of the driver when an error occurs;
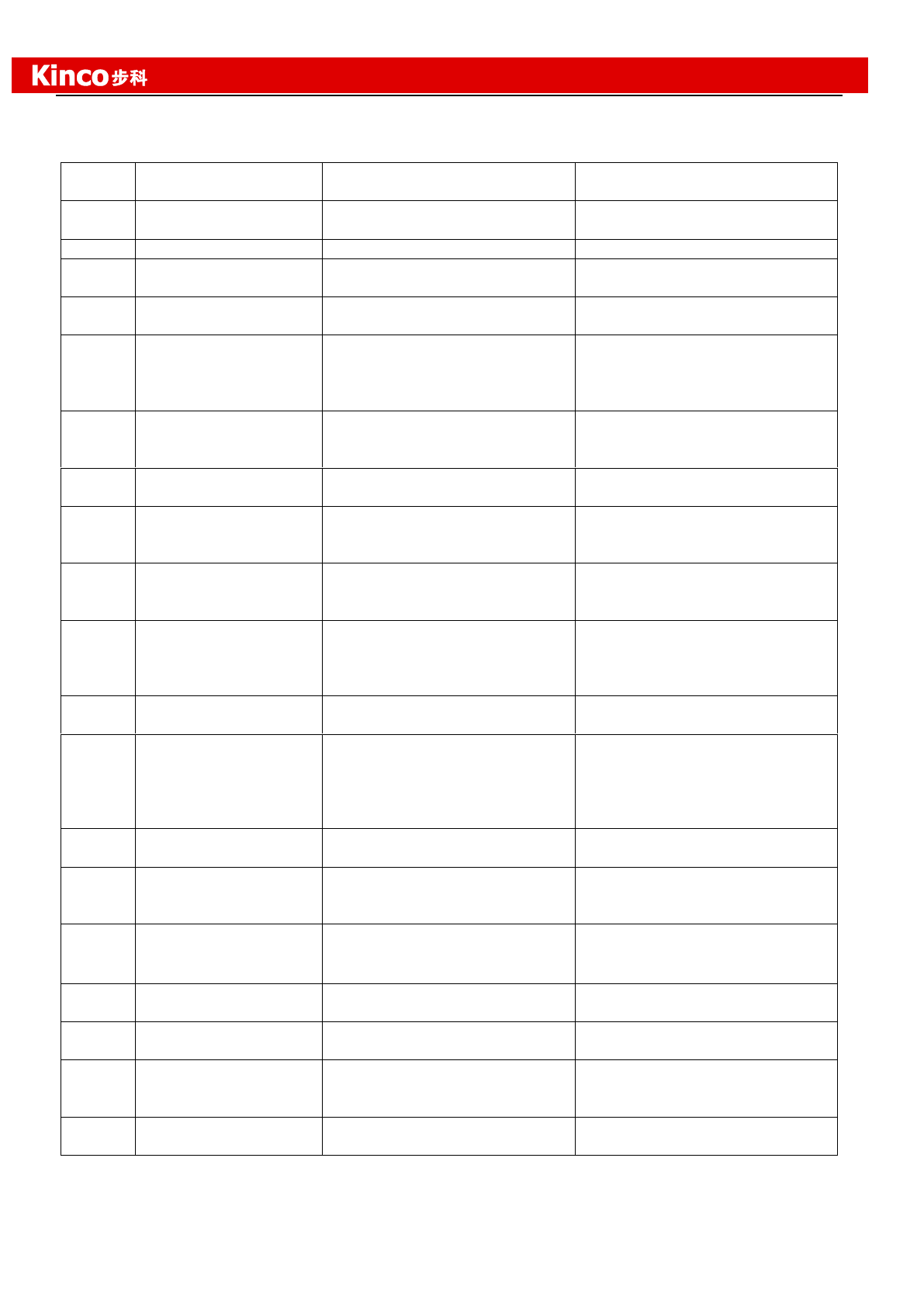
Kinco JD 伺服系列使用手册
138
Kinco FD Series Servo User Manual
11.2 Alarm Causes & Troubleshooting
Alarm
code
Alarm Information
Alarm Cause
Troubleshooting
FFF.F
/800.0
No motor configured
There is no motor type set in servo
driver
Set the motor type in d4.01.
000.1
Internal
Internal problem
Please contact manufacturer
000.2
Encoder ABZ
The ABZ signal cable is
disconnected.
Check the cable.
000.4
Encoder UVW
The UVW signal cable is
disconnected.
Check the cable.
000.8
Encoder Counting
Interferences are suppressed.
Encoder cable problem
Check encoder cable.
Remove interference(Such as
connect the motor cable to SHIELD
terminal etc.)
000.6
Encoder Error
ABZ and UVW signals of the
encoders incur error
simultaneously.
Check the cable.
001.0
Over Temperature
The driver temperature exceeds
83°C.
Check whether the selected driver
has enough power.
002.0
Over Voltage
The bus voltage of the driver
exceeds the allowable range.
Check the input voltage,or determine
whether a braking resistor is
connected.
004.0
Low Voltage
The voltage of the driver bus is
below the allowable range.
Check the input power.
Power on AC first,then power DC.
Reduce deceleration.
008.0
Over Current
The power tube in the driver is
faulty, or short circuit occurs on the
phase line of the motor.
Check motor wires. If the motor
works properly, it can be judged that
faults occur on the power tube in the
driver.
010.0
Chop Resistor
The actual power of brake resistor
is larger than rated power
Change brake resistor.
020.0
Following Error
Control loop parameters setting
problem.
Overload or block.
Encoder signal problem.
Set VFF (d2.08) as 100%,increase
kpp(d2.07) and kvp(d2.01).
Choose bigger power motor or check
whether the load is blocked.
Check the encoder cable.
040.0
Logic Voltage
The logic voltage is lower than
18V.
Check the logic power supply 24V.
080.0
IIt Error
Control loop parameters setting
problem.
Overload or block.
Increase kvp(d2.01).
Choose bigger power motor or check
whether the load is blocked.
100.0
Over Frequency
The input pulse frequency exceeds
the allowable maximum value.
Check the input pulse frequency and
the maximum permissible value of
the frequency.(d3.38)。
200.0
STO Error
STO Error
Check the wiring according to
Chapter 3.4.
400.0
Commutation
UVW signal of encoder cable
problem
Check encoder cable.
800.0
EEPROM Error
Because of updating firmware.
Driver internal problem.
Initialize all control parameters and
save,then restart driver.
Contact manufacturer.
888.8
Driver abnormal working
states
Logic power supply problem.
Driver internal problem.
Check 24VDC power supply.
Contact manufacturer.
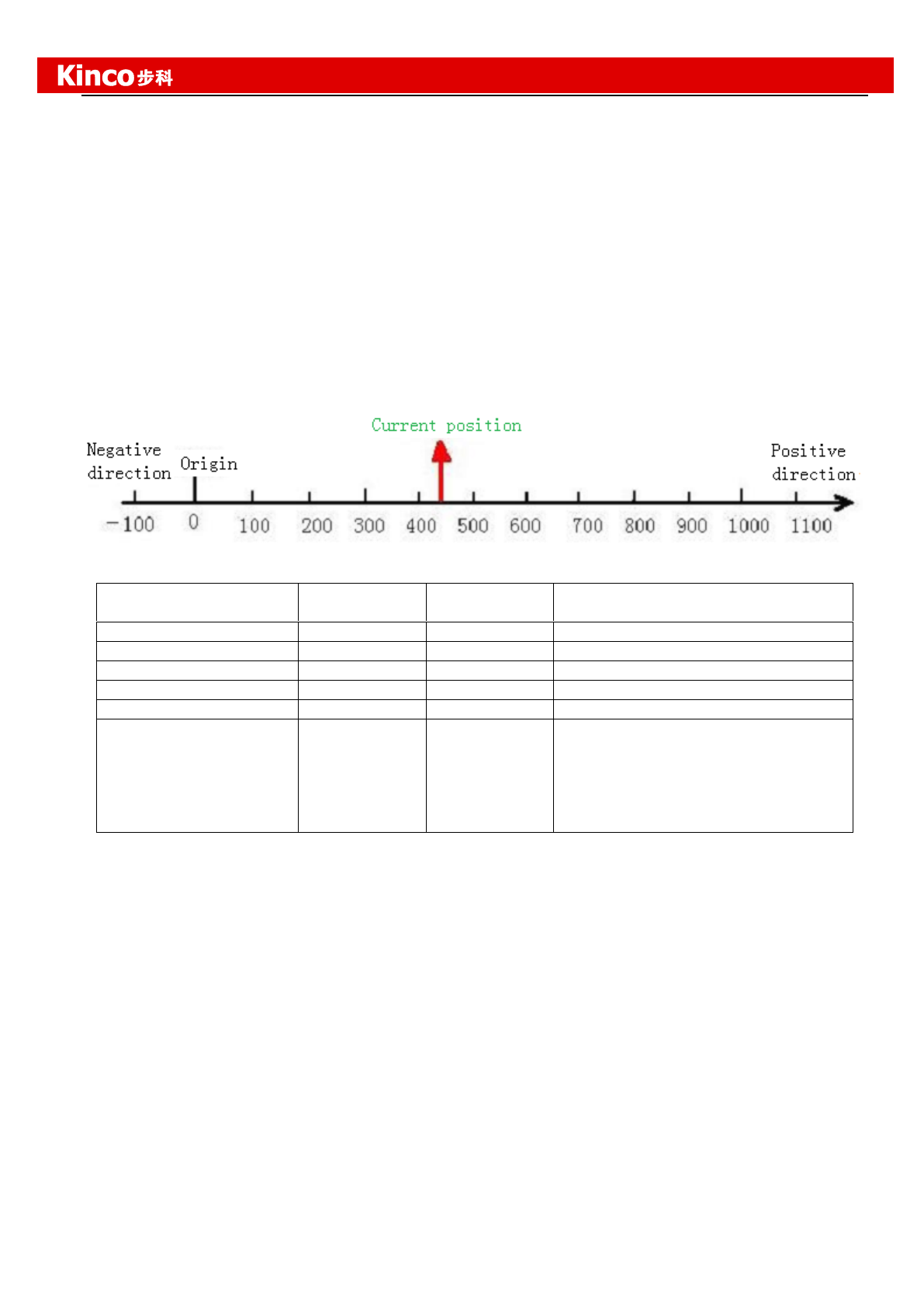
Kinco JD 伺服系列使用手册
139
Kinco FD Series Servo User Manual
Chapter 12 Appendix
Appendix 1 Instructions of operation mode via Communication
1. Position mode(Mode 1)
Take this mode for example: In the coordinate system shown below, the red arrow indicates the current
position = 450. If it is defined as absolute motion, when the target position is set to 700, the motor will move to
the position of coordinate = 700; if it is defined as relative motion, when the target position is set to 700, the
motor will move to the position of coordinate = 1150.
Fig.1 Absolute/Relative positioning
In mode 1, the following objects have to be defined :
CANopen Address
Modbus
Address
Value
Meaning
60600008
0x3500
1
Set as position mode
60810020
0x4A00
User setting
Profile velocity
60830020
0x4B00
User setting
Acceleration
60840020
0x4C00
User setting
Deceleration
607A0020
0x4000
User setting
Target position
60400010
0x3100
2F -> 3F
4F -> 5F
103F
105F
Start absolute positioning
Start relative positioning
Start absolute positioning while target
position change
Start relative positioning while target
position change
More details please refer to “Mode and Control” and “Target Object” in Appendix.
About position mode controlled by communication,please refer to communication example in Appendix.
2. Speed Mode(Mode -3 or 3)
Mode 3 implements velocity control over the motor. The operation curve consists of three sequences:
acceleration, uniform velocity, and deceleration, as shown below. The acceleration time can be calculated on
the basis of initial velocity, uniform velocity, and acceleration velocity.
Vt=Vo+at Vt-Uniform velocity
Vo-Initial velocity
a - Acceleration or deceleration
t - Acceleration time

Kinco JD 伺服系列使用手册
140
Kinco FD Series Servo User Manual
S=Vot + (1/2) at2 S-Acceleration displacement
In mode -3, when a new value is assigned to the target velocity, the motor will run at the new velocity
immediately, without a definable acceleration/deceleration as described in mode 3.
In speed mode, the following objects have to be defined:
CANopen 地址
Modbus
Address
Value
Meaning
60600008
0x3500
3 or -3
Set as speed mode
60FF0020
0x6F00
User setting
Target velocity
60830020
0x4B00
User setting
Acceleration
60840020
0x4C00
User setting
Deceleration
60400010
0x3100
F
Start running
More details please refer to “Mode and Control” and “Target Object” in Appendix.
About position mode controlled by communication,please refer to communication example in Appendix.
3. Master-slave mode(Mode -4)
In this mode, the movement of the motor is directly controlled by the external encoder, pulse/direction,
CW/CCW pulse signal from the X1 interface of the drive. If the system receives signal from the external
encoder, set the drive to master/slave mode. The drive will serve as the slave and the motor shaft will be the
slave shaft to follow the encoder master shaft signal of the X1 interface to perform the following movement.
The velocity rate of the following movement can be set by the electronic gear ratio.
In mode -4, the following objects have to be defined:
CANopen
Address
Modbus
Address
Value
Meaning
60600008
0x3500
-4
Set as master-slave mode
25080110
0x1910
User setting
Factor of electronic gear
25080210
0x1920
User setting
Divider of electronic gear
25080310
0x1930
User setting
Pulse mode
0...CW/CCW mode
1... Pulse/Direction mode
2...Incremental encoder mode
Note:This parameter must save
after change.
60400010
0x3100
F
Start running
More details please refer to “Mode and Control” , “Target Object” and “Master-slave mode” in Appendix.
4.Torque Mode(Mode 4)
In this mode, the motor will output at constant torque. The output torque depends on the value of target
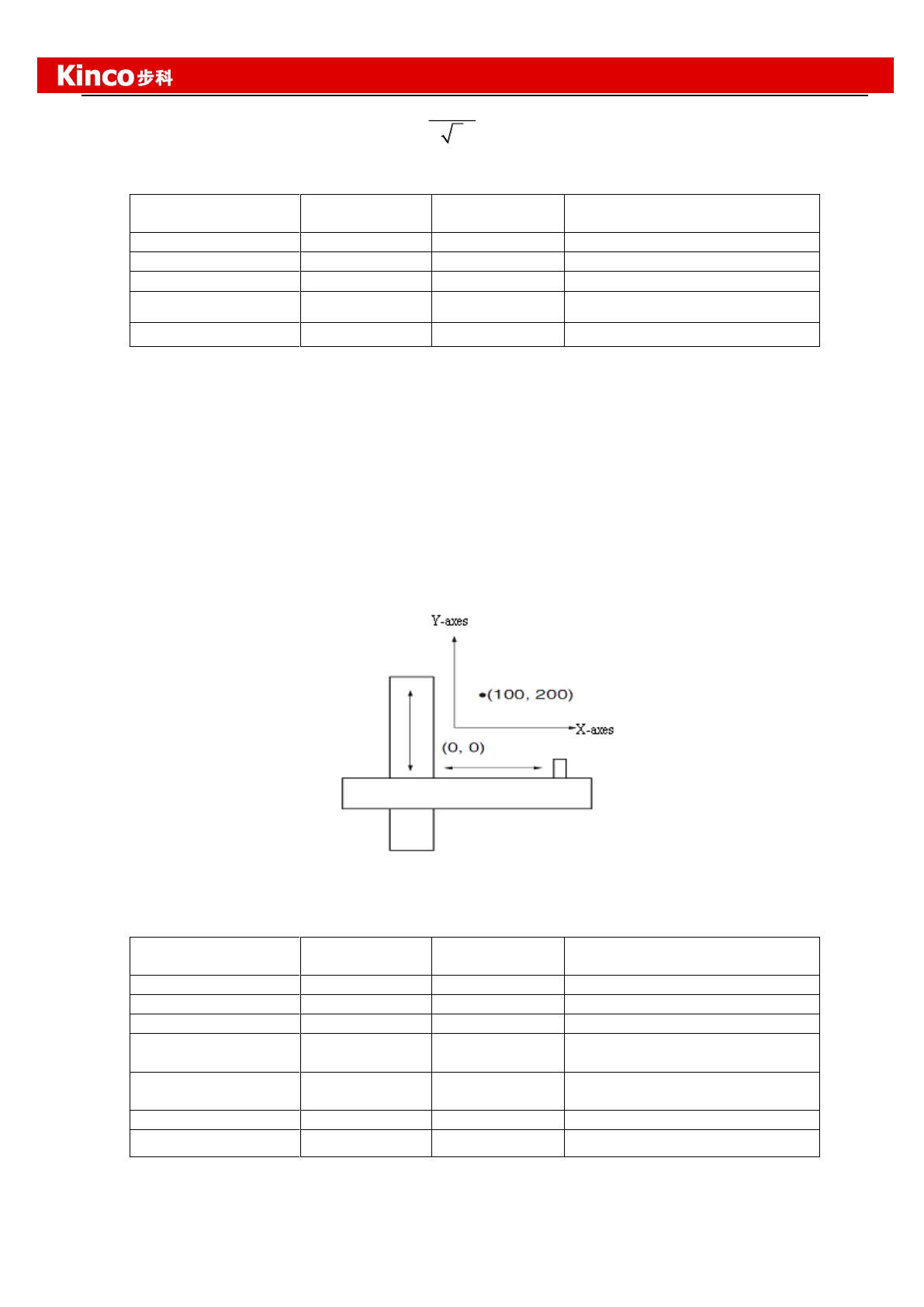
Kinco JD 伺服系列使用手册
141
Kinco FD Series Servo User Manual
torque.The conversion formula is
*2
demand
demand t
I
TK
,
t
K
is torque constant,users can find it in the
catalog.
demand
I
is peak current.
In mode 4, the following objects have to be defined:
CANopen
Address
Modbus
Address
Value
Meaning
60600008
0x3500
-4
Set as torque mode
60710010
0x3C00
User setting
Target torque
60730010
0x3D00
User setting
Max. current
60800010
0x4900
User setting
Max. speed
60400010
0x3100
F
Start running
More details please refer to “Mode and Control” and “Target Object” in Appendix.
Warning: Before locking the motor shaft, pay attention to the drive. Because it has constant torque output,
the motor velocity is only restricted by the value of target torque. Make sure the load is correctly installed and
in normal operation before any operation. Remember to set the maximum velocity.
5. Homing mode(Mode 6)
To make a system execute positioning in accordance with its absolute positioning, the first step is to define
the origin. For instance, as shown in the following XY plane, to navigate to (X, Y) = (100mm, 200mm), you
must define the origin of the machine firstly. It’s necessary to define the origin.
In mode 6, the following objects have to be defined:
CANopen
Address
Modbus
Address
Value
Meaning
60600008
0x3500
6
Set as homing mode
607C0020
0x4100
User setting
Home offset
60980008
0x4D00
User setting
Homing method
60990120
0x5010
User setting
Homing speed for searching
home signal
60990220
0x5020
User setting
Homing speed for searching
index signal
609A0020
0x5200
User setting
Homing acceleration
60400010
0x3100
F->1F
Start running
More details about homing method please refer to homing methods in Appedix.
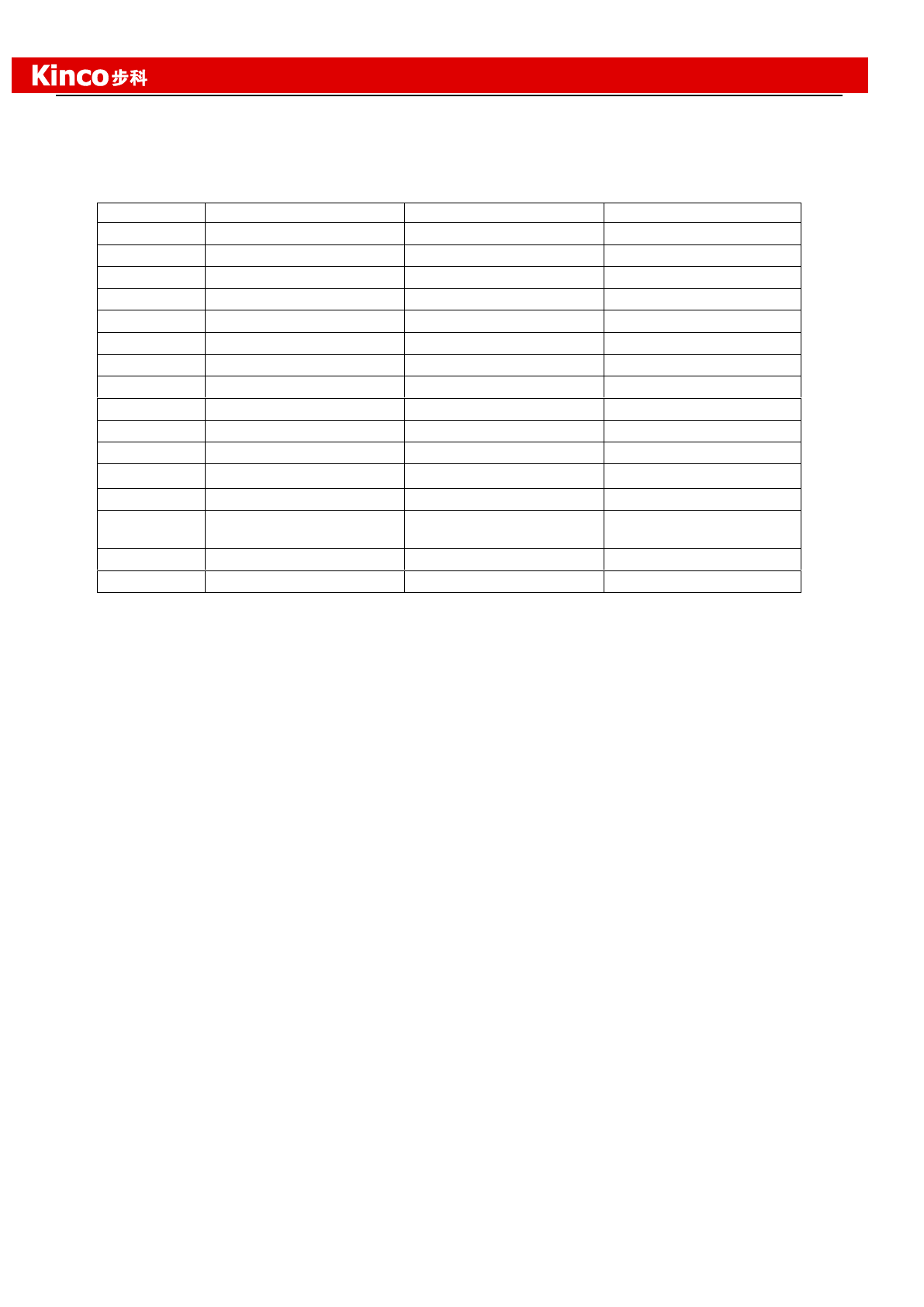
Kinco JD 伺服系列使用手册
142
Kinco FD Series Servo User Manual
6. Driver Status Display
FD Servo driver uses object 60410010(Modbus address is 0x3200) to indicate the current status
of driver.The definitions of every bit are as following:
bit
Definition
Meaning
Value
0
Ready to Switch on
Ready to switch on
60410010=0x0001
1
Switched On
Already switched on
60410010=0x0002
2
Operation Enable
Operation enable
60410010=0x0004
3
Fault
Driver fault
60410010=0x0008
4
Voltage Disable
Voltage output disable
60410010=0x0010
5
Quick Stop
Emergency stop
60410010=0x0020
6
Switch On Disable
Switch on disable
60410010=0x0040
7
Warning
Warning
60410010=0x0080
8
Manufacturer specific 1
Reserved
60410010=0x0100
9
Reserved 1
Reserved 1
60410010=0x0200
10
Target Reached
Target position reach
60410010=0x0400
11
Internal Limit Active
Internal limit active
60410010=0x0800
12
Setp.Ach./v=0/Hom.att.
Pulse response
60410010=0x1000
13
Foll.Err./Res.Hom.Err.
Following
error/Reference error
60410010=0x2000
14
Commutation Found
Commutation found
60410010=0x4000
15
Reference Found
Reference found
60410010=0x8000
Appendix 2:Example for CANopen Communication
1.Canopen communication between Kinco F1 PLC and FD Servo
1.1 Wiring diagram
F1 PLC CAN port FD CAN port (X4)
CAN_L 2 ---------------------------------- CAN_L 2
CAN_H 7 ---------------------------------- CAN_H 7
■Note:
1.It must use series connection for multiple slaves.
2.CAN1 and CAN2 of F1 PLC are separately,can be used at the same time.
3.There are terminal resistors in PLC which set by DIP switch.Therefore,it needs a 120ohm terminal resistor
in the end of the communication cable(In the last slave).
1.2 Parameter setting.
About the settings of FD parameters such as baudrate and station No.,please refer to the chapter of
CANopen.
1.3 Software program
(1)Create new project,select Kinco F122-D1608T and click OK.
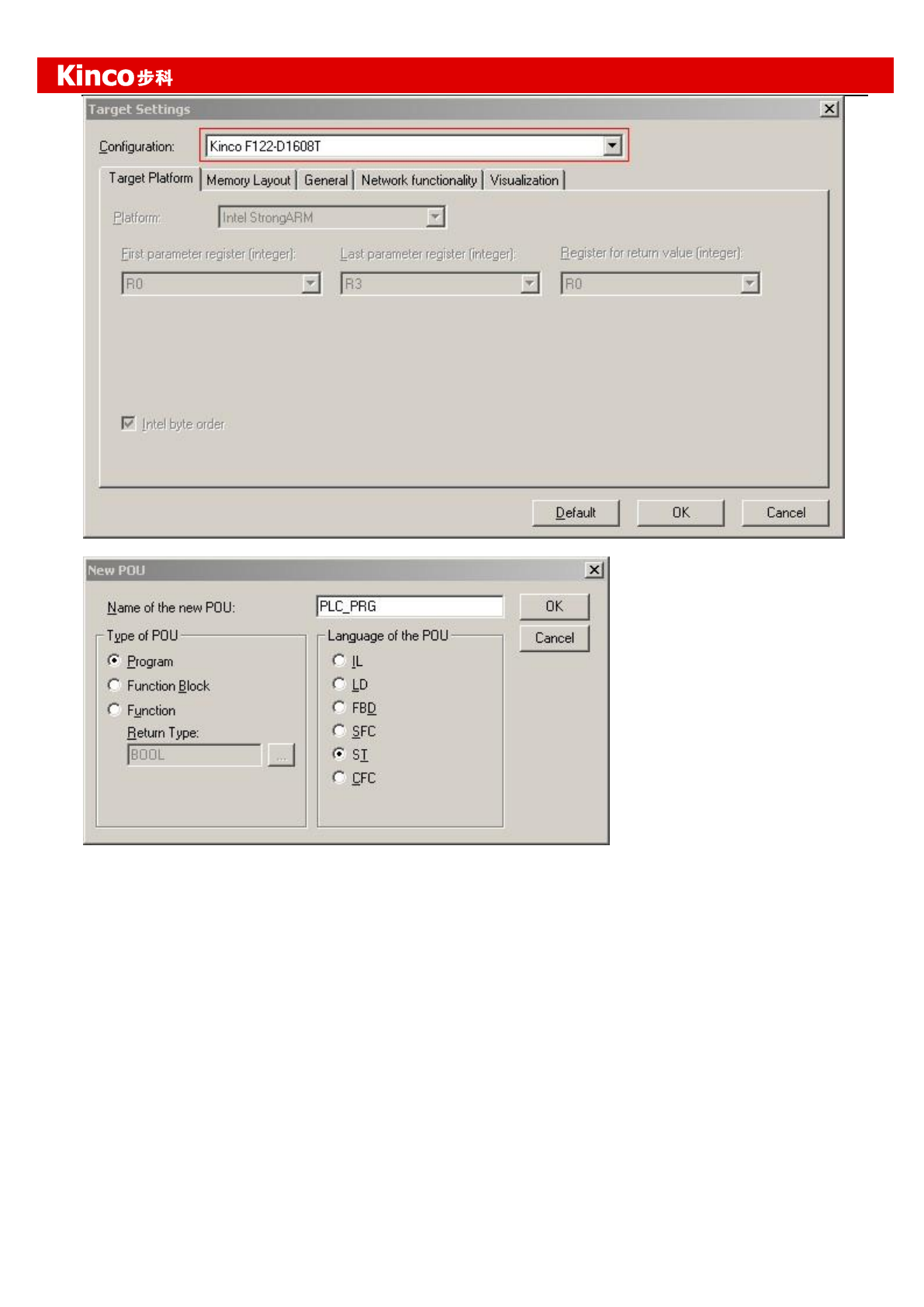
Kinco JD 伺服系列使用手册
143
Kinco FD Series Servo User Manual
(2)Select program language according to your habit.Then click OK.
(3)Select “Resources” option and click “PLC Configuration”.
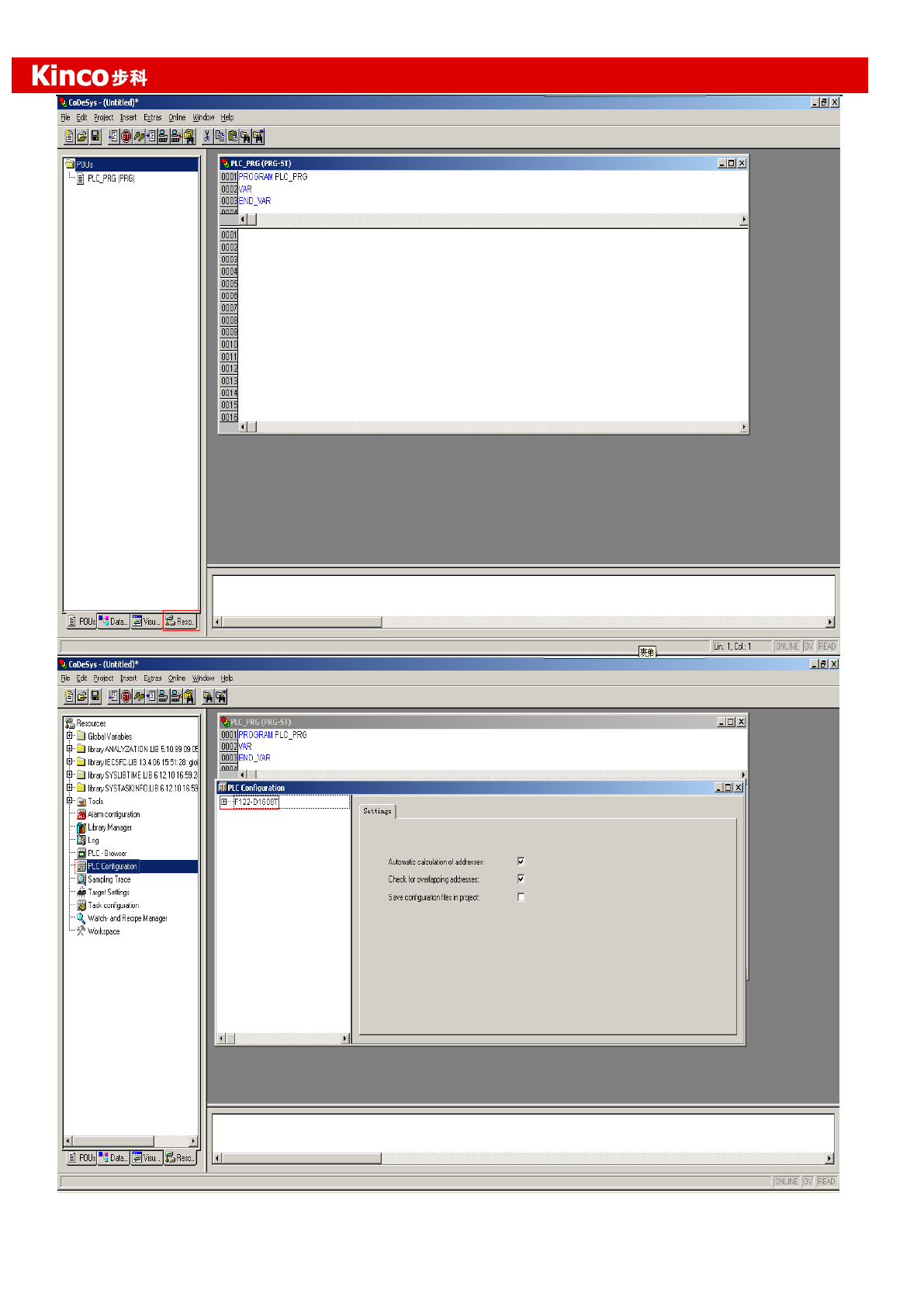
Kinco JD 伺服系列使用手册
144
Kinco FD Series Servo User Manual
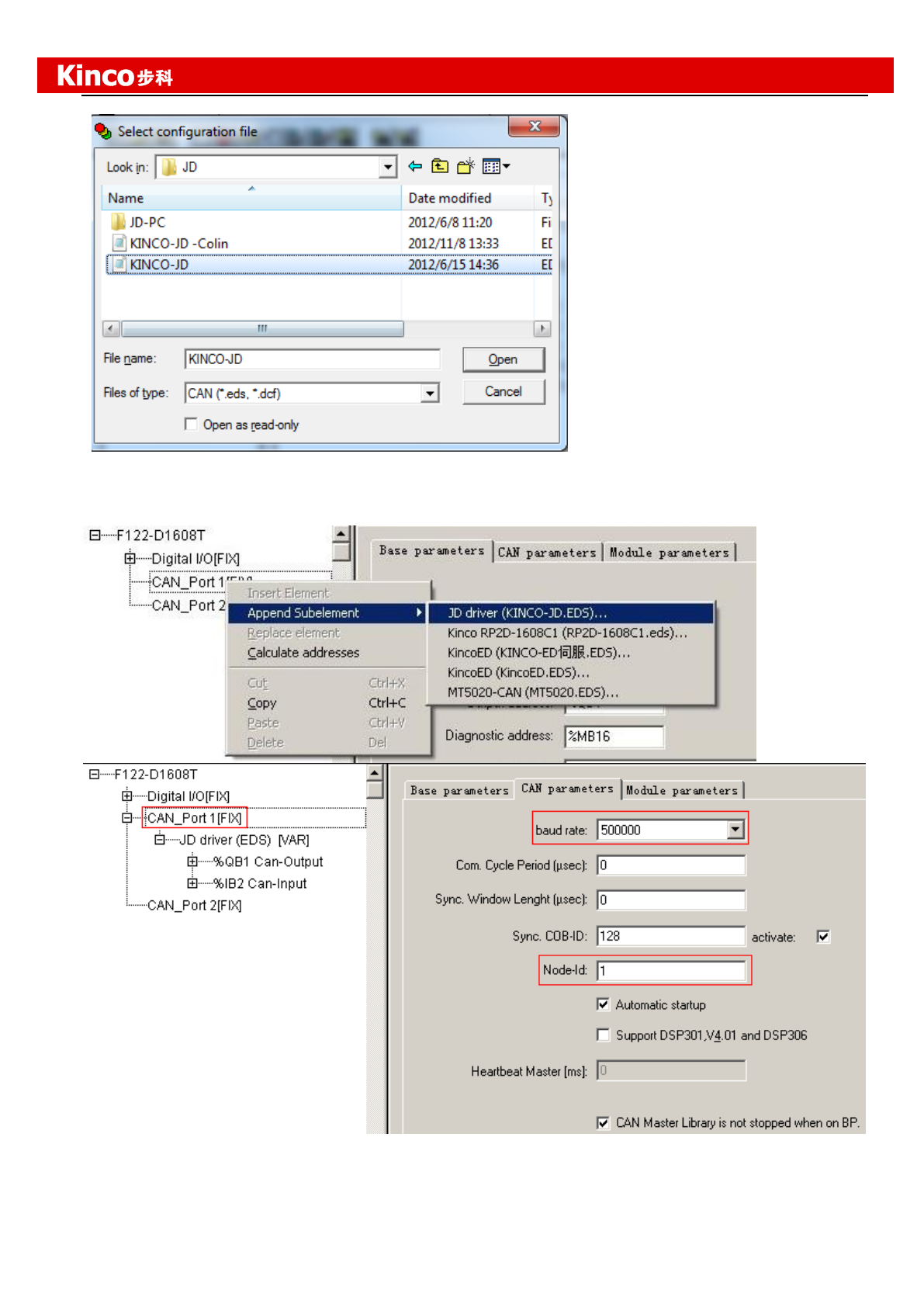
Kinco JD 伺服系列使用手册
145
Kinco FD Series Servo User Manual
(4)Click “Extras->add configuration file” to add EDS file of FD Servo.
(5)There are two CAN ports in F1 PLC.Both of them can be used as master. Set baudrate and Node-ID for
CAN port.If you need synchronous message,please click “activate” ,then set “Com.Cycle period” and
“Sync.COB-ID”.
(6) Right click CAN port and select “Append Subelement->FD driver” to add slaves.Then set parameters such
as Node ID,Nodeguarding,RX-PDO and TX-PDO.
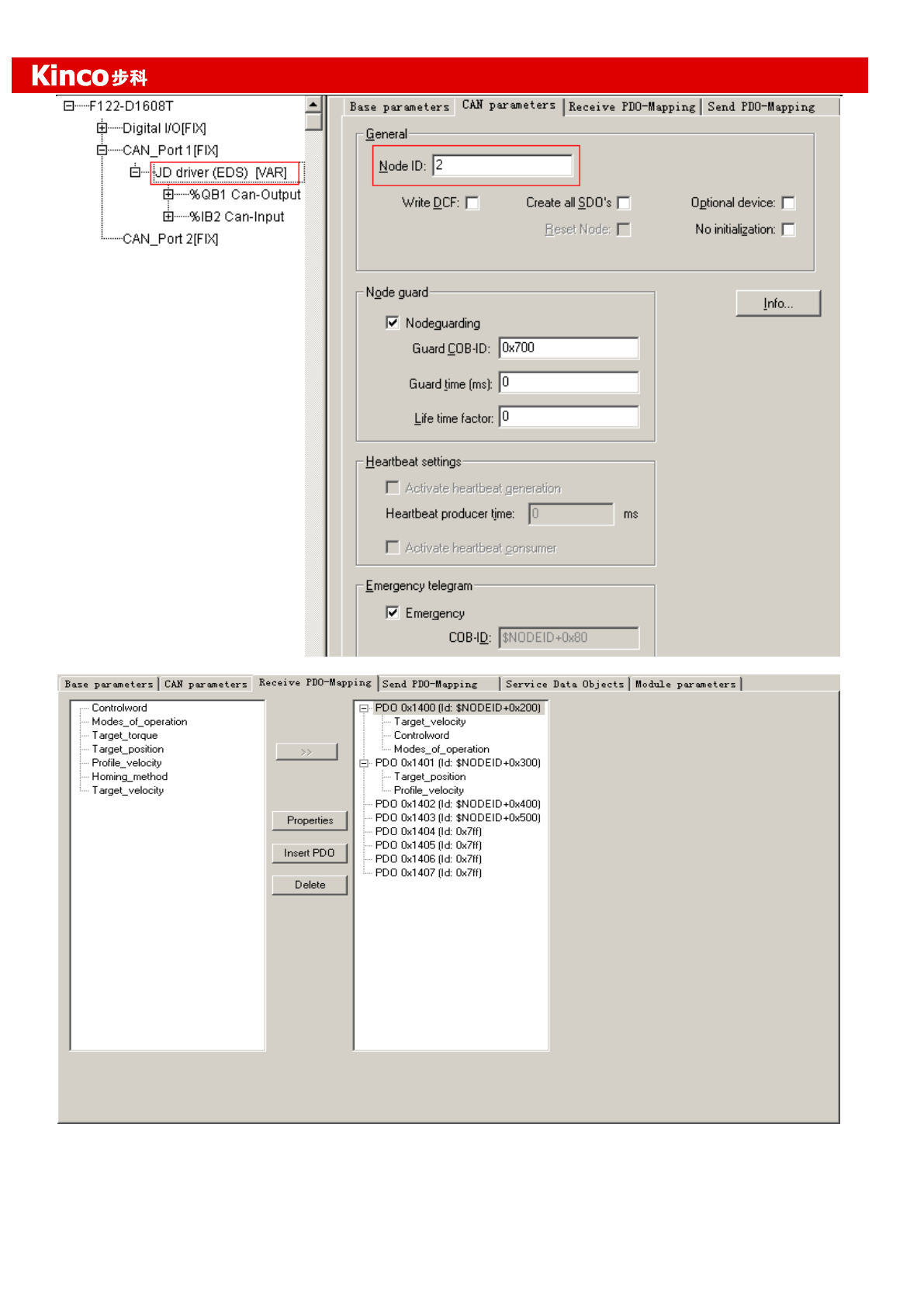
Kinco JD 伺服系列使用手册
146
Kinco FD Series Servo User Manual
(7)Configure PDO objects according to the requirement.
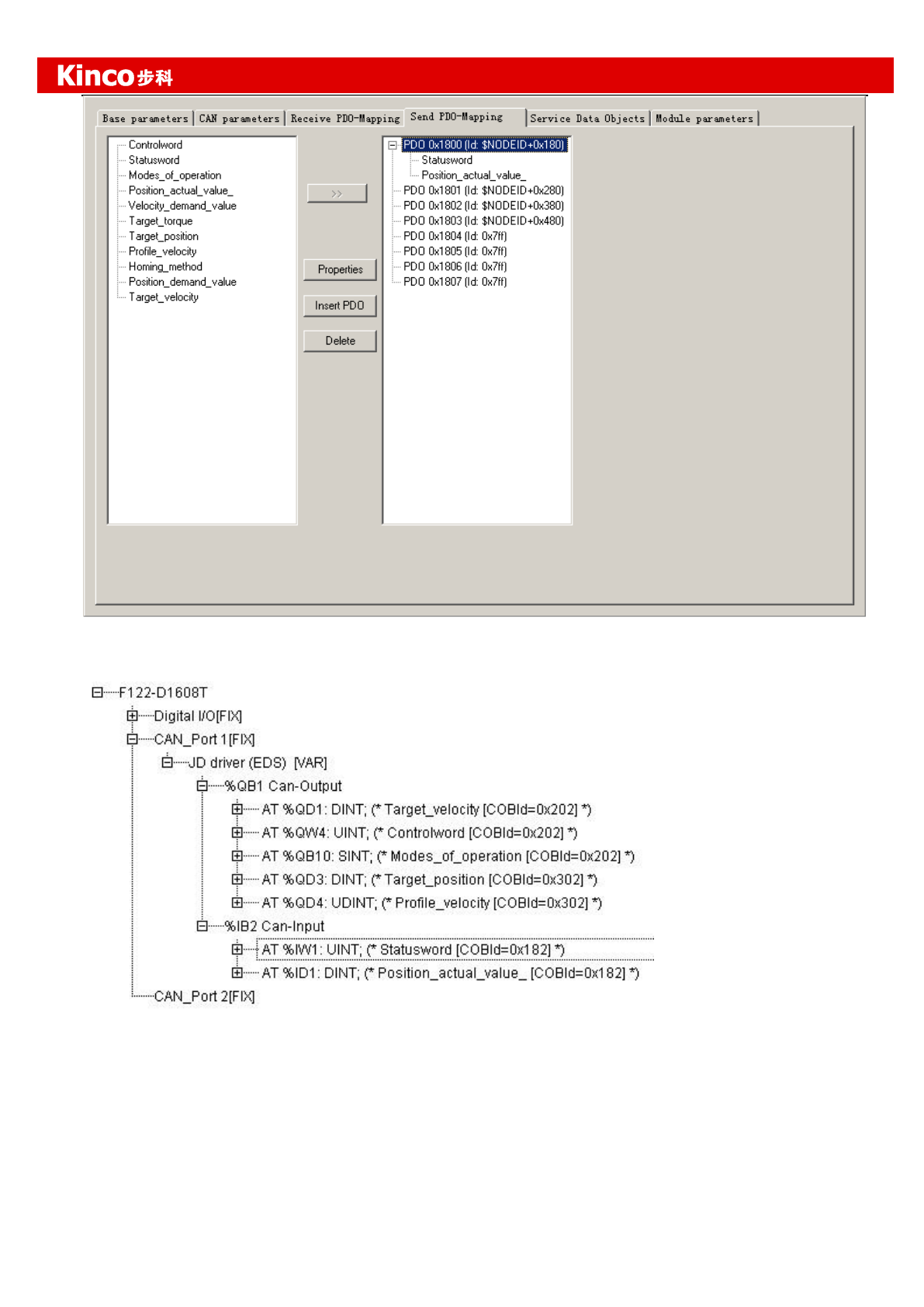
Kinco JD 伺服系列使用手册
147
Kinco FD Series Servo User Manual
(8)After configure all the parameters,there will be all the registers corresponding to all the OD
as shown in following figure.For example,the register for Controlword is QW4,and the register
for Statusword is IW1.8.
(9)Configure other slaves according to procedure above.Then we can start to program.In the program,we can
use the register directly or define gloable variables.
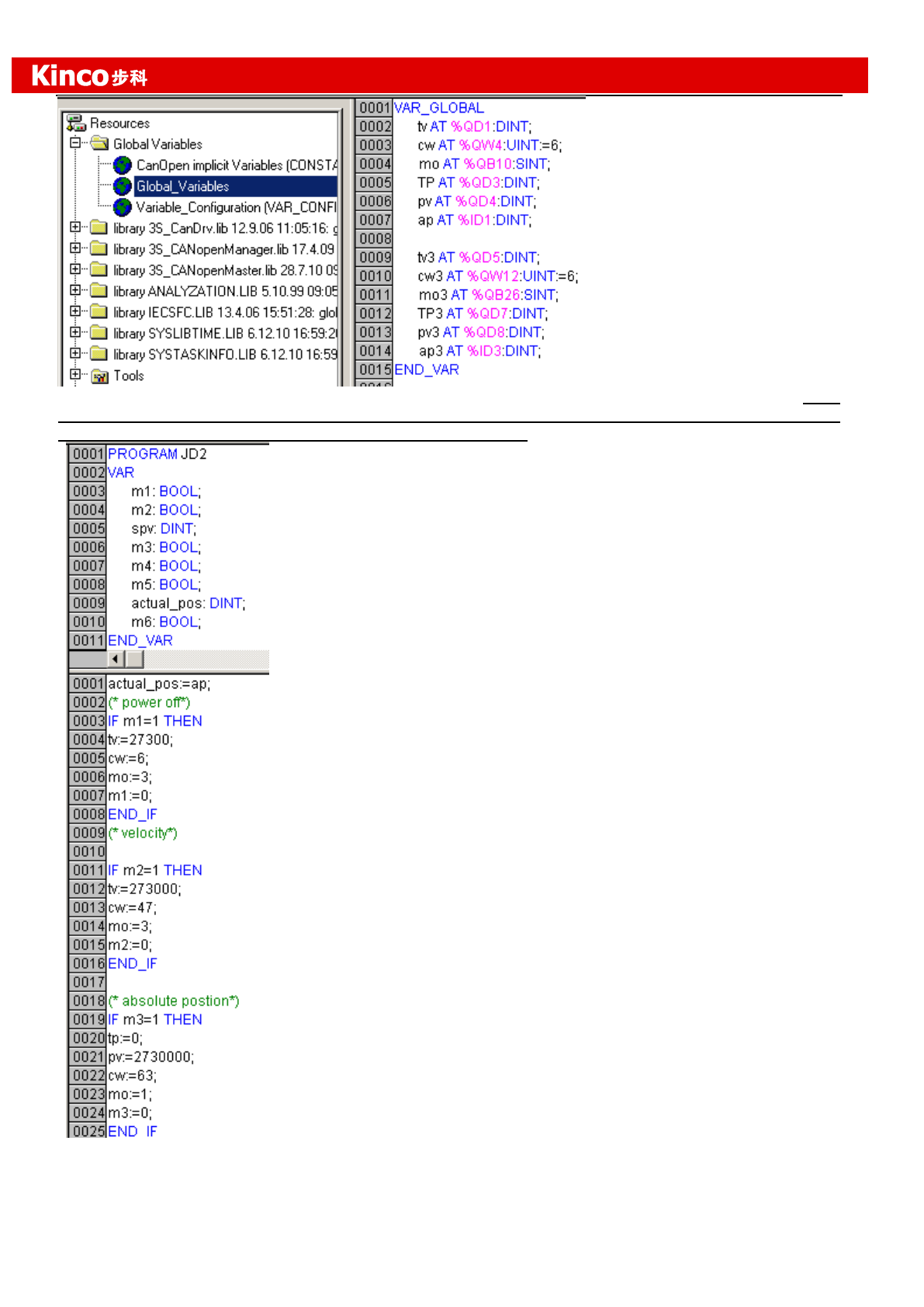
Kinco JD 伺服系列使用手册
148
Kinco FD Series Servo User Manual
(10)The program is as following figure.More details please refer to the chapter of operation mode.After
creating communication between F1 PLC and servo,it needs to set a initial value 6 to the object
“Controlwrod”,or other command can’t be effective in servo.
If the objects are not in the EDS file or not commonly use,then we can use SDO to read and write these
ojectes,as shown in following figure.
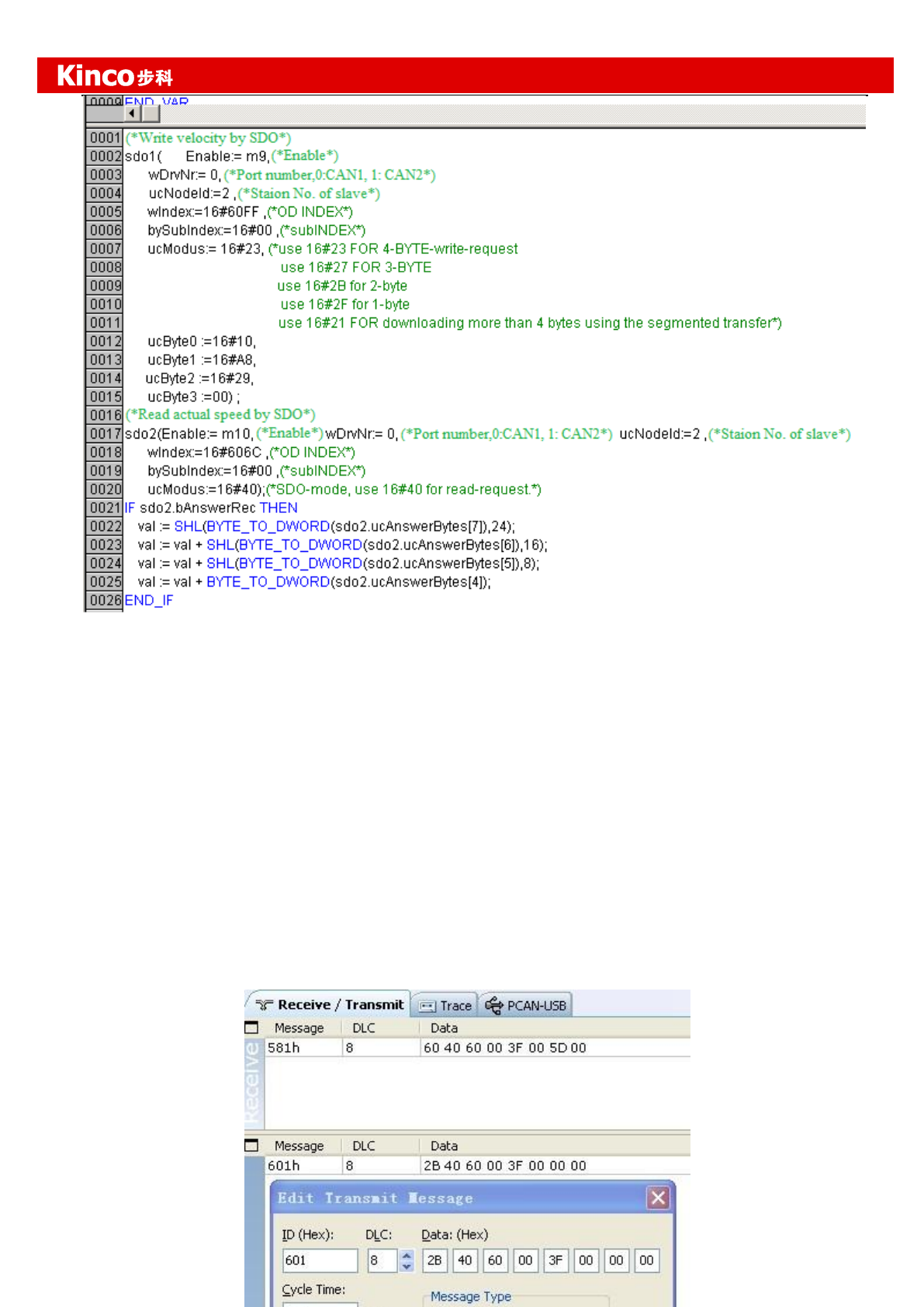
Kinco JD 伺服系列使用手册
149
Kinco FD Series Servo User Manual
2.CANopen Communication between FD Servo and Peak CAN.
Peak company has many kinds of CAN adapter such as ISA,PCI,USB-CAN and so on.This example is to use
PCAN-USB connected to FD Servo.
2.1 Wiring
Master Slave 1 Slave 2 ----- Slave N
PCAN_USB CAN 口 FD X4 port FD X4 port FD X4 port
2 CAN_L 2CAN_L 2CAN_L 2CAN_L
7 CAN_H 7CAN_H 7CAN_H 7CAN_H
It needs to add a 120-150 ohm resistor between PIN2 and PIN7 in the terminal(Slave N).
2.2 Set the communication parameters such as baudrate,ID according to FD Servo.Then open
PCAN-VIEW(Software for PCAN-USB) to send and receive data.
Following figure is the example to send command to set 6040 as 3F.The lower part of the figure is to send
data,the upper part of the figure is to receive data.
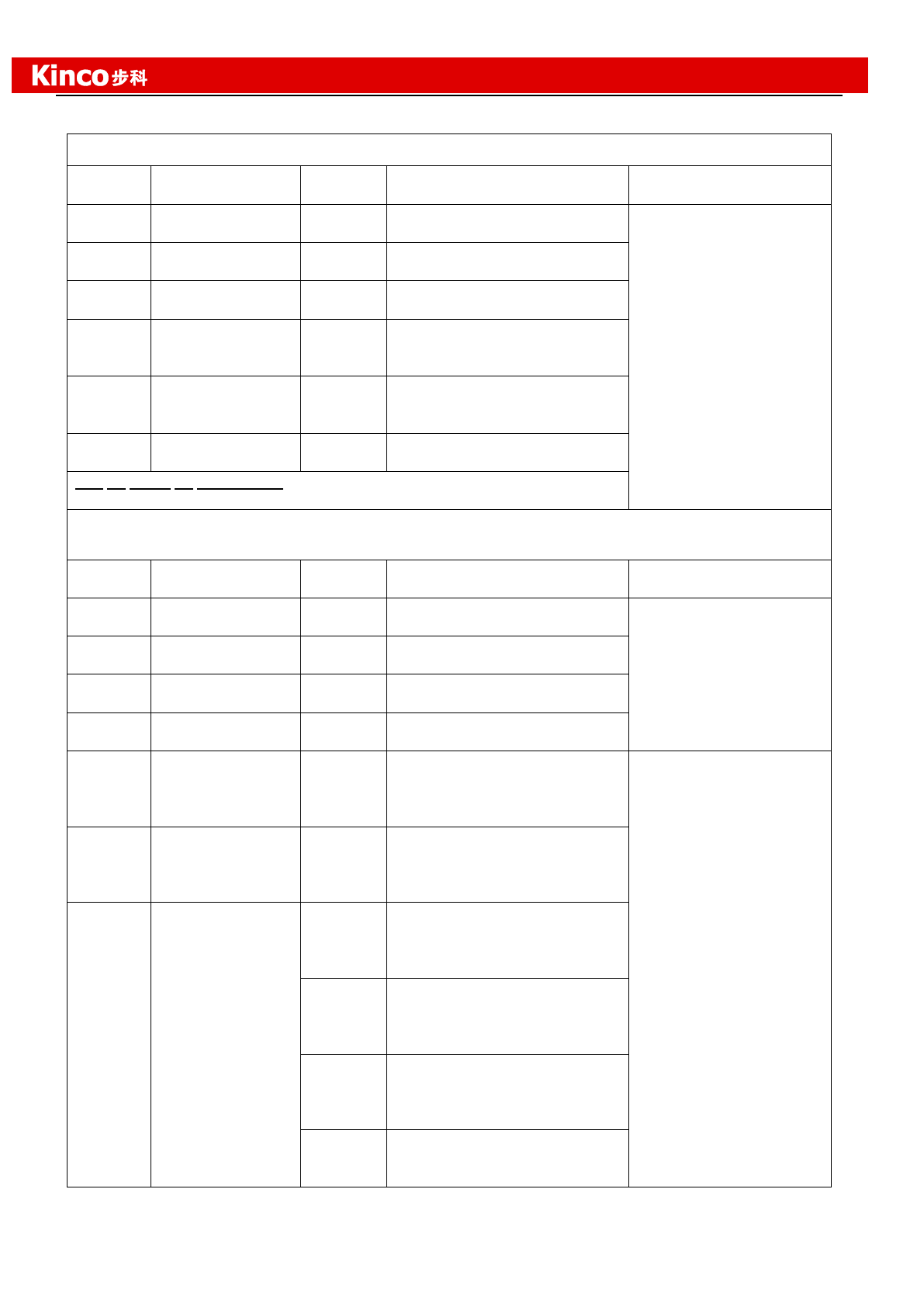
Kinco JD 伺服系列使用手册
150
Kinco FD Series Servo User Manual
Following is the example about sending and receiving messages for different operation mode.(The
sataion No. is 1)
Homing mode(The controlword should change from F to 1F)
Internal
Address
Name
Setting
value
Message(ID=1)
Note
6040001
0
Control word
F
601 2B 40 60 00 0F 00
581 60 40 60 00 0F 00
DEC=[(RPM*512*Encode
r_resolution)/1875]
6060000
8
Operation mode
6
601 2F 60 60 00 06 00
581 60 60 60 00 06 00
6098000
8
Homing method
33
601 2F 98 60 00 21 00
581 60 98 60 00 21 00
6099012
0
Velocity for
searching limit
switch
200RPM
601 23 99 60 01 55 55 08 00
581 60 99 60 01 55 55 08 00
6099022
0
Velocity for
searching
phase-N signal
150RPM
601 23 99 60 02 00 40 06 00
581 60 99 60 02 00 40 06 00
6040001
0
Control word
1F
601 2B 40 60 00 1F 00
581 60 40 60 00 1F 00
601 40 41 60 00 00 00 00 00 Read status word,C037 means reference
found.
Position mode(Control word should change from 2F to 3F for absolute positioning,and change from
4Fto5F for relative positioning.103F or 105F means activate immediately when position change.)
Internal
Address
Name
Setting
value
Message(ID=1)
Note
6040001
0
Control word
F
601 2B 40 60 00 0F 00
581 60 40 60 00 0F 00
DEC=[(RPM*512*Encode
r_resolution)/1875]
6060000
8
Operation mode
1
601 2F 60 60 00 01 00
581 60 60 60 00 01 00
607A002
0
Target velocity
50000inc
601 23 7A 60 00 50 C3 00 00
581 60 7A 60 00 50 C3 00 00
6081002
0
Profile velocity
200RPM
601 23 81 60 00 55 55 08 00
581 60 81 60 00 55 55 08 00
6083002
0
Acceleration
Default
value
610.352r
ps/s
NULL
DEC=[(RPS/S*65536*En
coder_resolution)/1000/
4000]
6084002
0
Deceleration
Default
value
610.352r
ps/s
NULL
6040001
0
Control word
2F(Absol
ute
positionin
g)
601 2B 40 60 00 2F 00
581 60 40 60 00 2F 00
3F(Absol
ute
positionin
g)
601 2B 40 60 00 3F 00
581 60 40 60 00 3F 00
4F(Relati
ve
positionin
g)
601 2B 40 60 00 4F 00
581 60 40 60 00 4F 00
5F(Relati
ve
positionin
601 2B 40 60 00 5F 00
581 60 40 60 00 5F 00
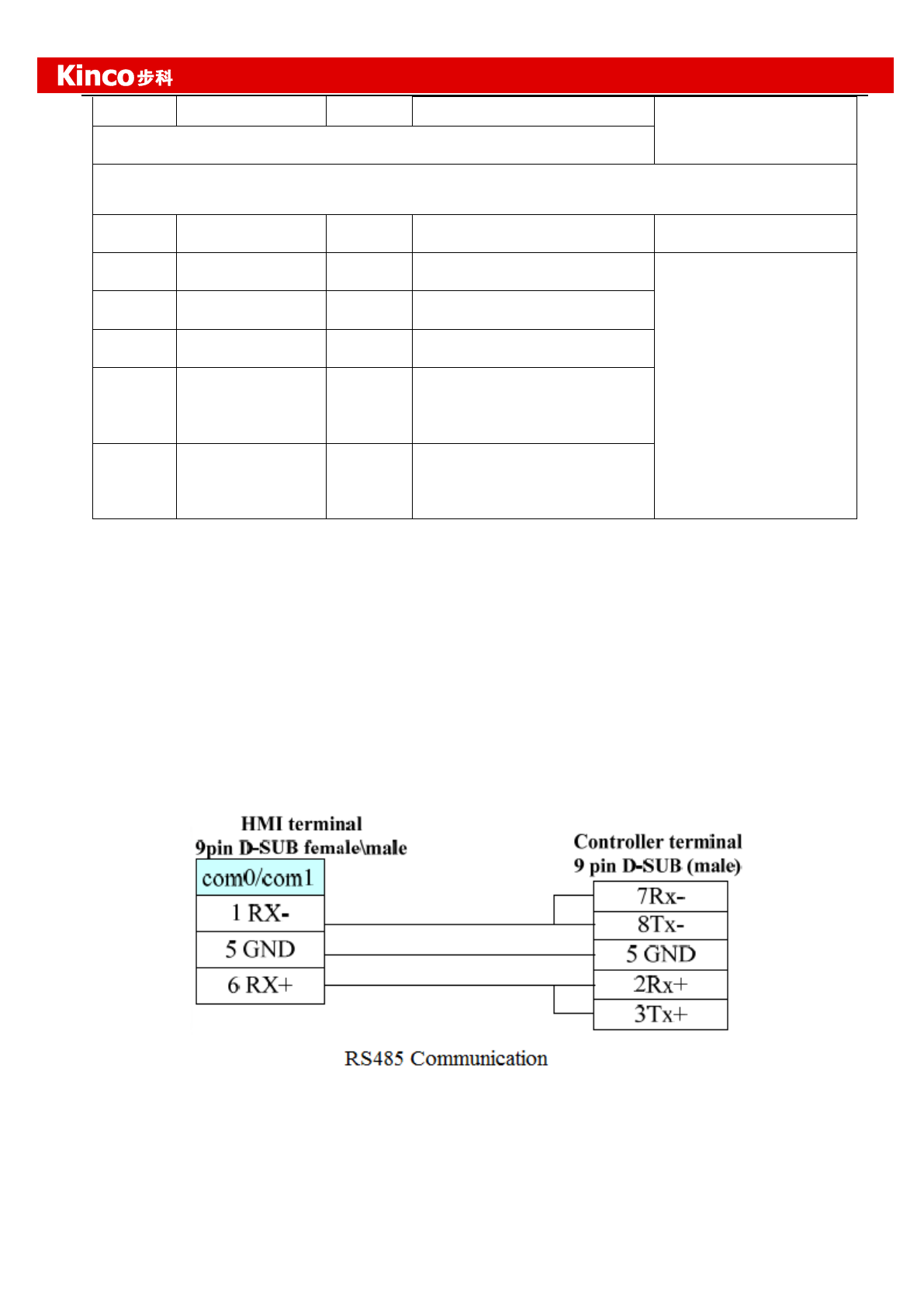
Kinco JD 伺服系列使用手册
151
Kinco FD Series Servo User Manual
g)
601 40 41 60 00 00 00 00 00 Read status word.D437 means target
position reach.
Speed mode
Internal
Address
Name
Setting
value
Message(ID=1)
Note
6060000
8
Operation mode
3
601 2F 60 60 00 03 00
581 60 60 60 00 03 00
DEC=[(RPM*512*Encode
r_resolution)/1875]
DEC=[(RPS/S*65536*En
coder_resolution)/1000/
4000]
60FF002
0
Target velocity
150RPM
601 23 FF 60 00 00 40 06 00
581 60 FF 60 00 00 40 06 00
6040001
0
Control word
F
601 2B 40 60 00 0F 00
581 60 40 60 00 0F 00
6083002
0
Acceleration
Default
value
610.352r
ps/s
NULL
6084002
0
Deceleration
Default
value
610.352r
ps/s
NULL
Note:All the data are Hexadecimal format when using communication.
Appendix 3:Example for RS485 Communication
1.Modbus Communication Between FD Servo and Kinco HMI
(1) HMI control single FD Servo.
a.Wiring diagram
b. Parameters setting
It needs to choose Modbus RTU in HMI software,the communication parameters are as following figure.The
PLC station No. must be set the same as the ID of FD Servo.
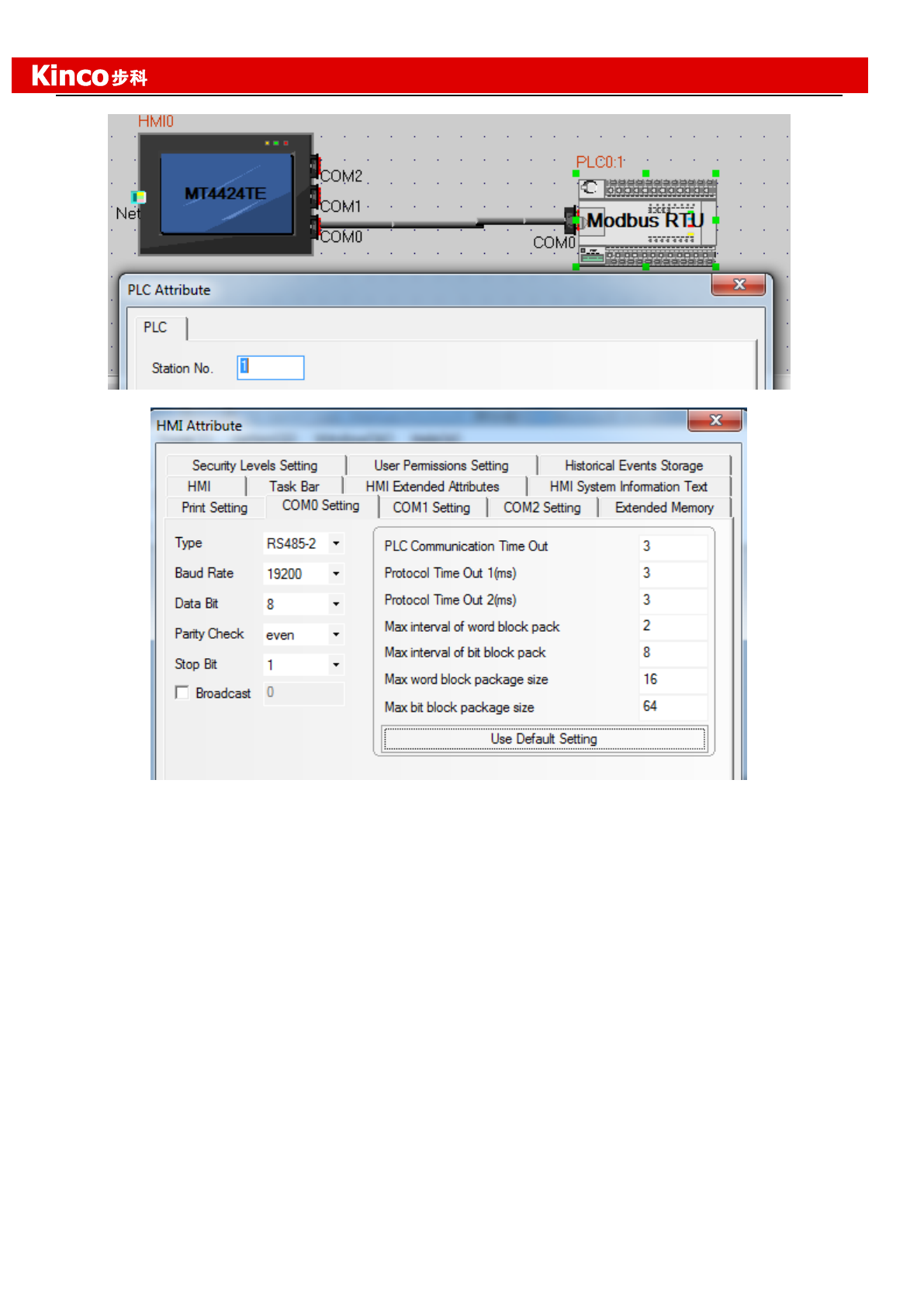
Kinco JD 伺服系列使用手册
152
Kinco FD Series Servo User Manual
c. Address setting
It needs to use address type 4X in HMI program(All the objects of FD Servo are corresponding to
4X).According to Modbus address of objects in the Common Object List,the Modbus address of the object
“Target velocity”(60FF0020) is 0x6F00,its decimal value is 28416.When we use this address in HMI,we need
to add 1,so in HMI the address for “Target velocity” is 28417 as shown in following figure.
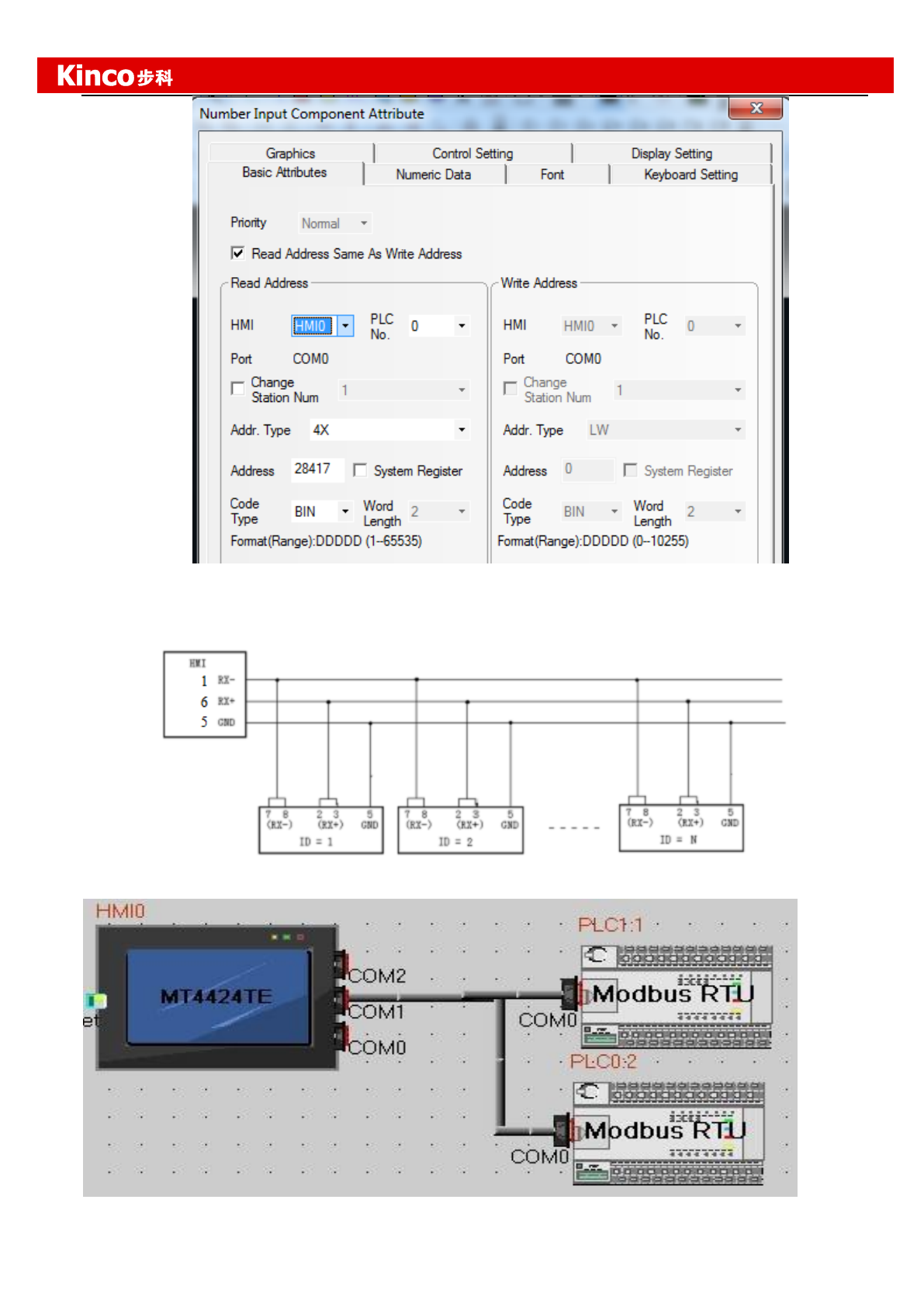
Kinco JD 伺服系列使用手册
153
Kinco FD Series Servo User Manual
(2)HMI control multiple FD Servo
a、Wiring diagram
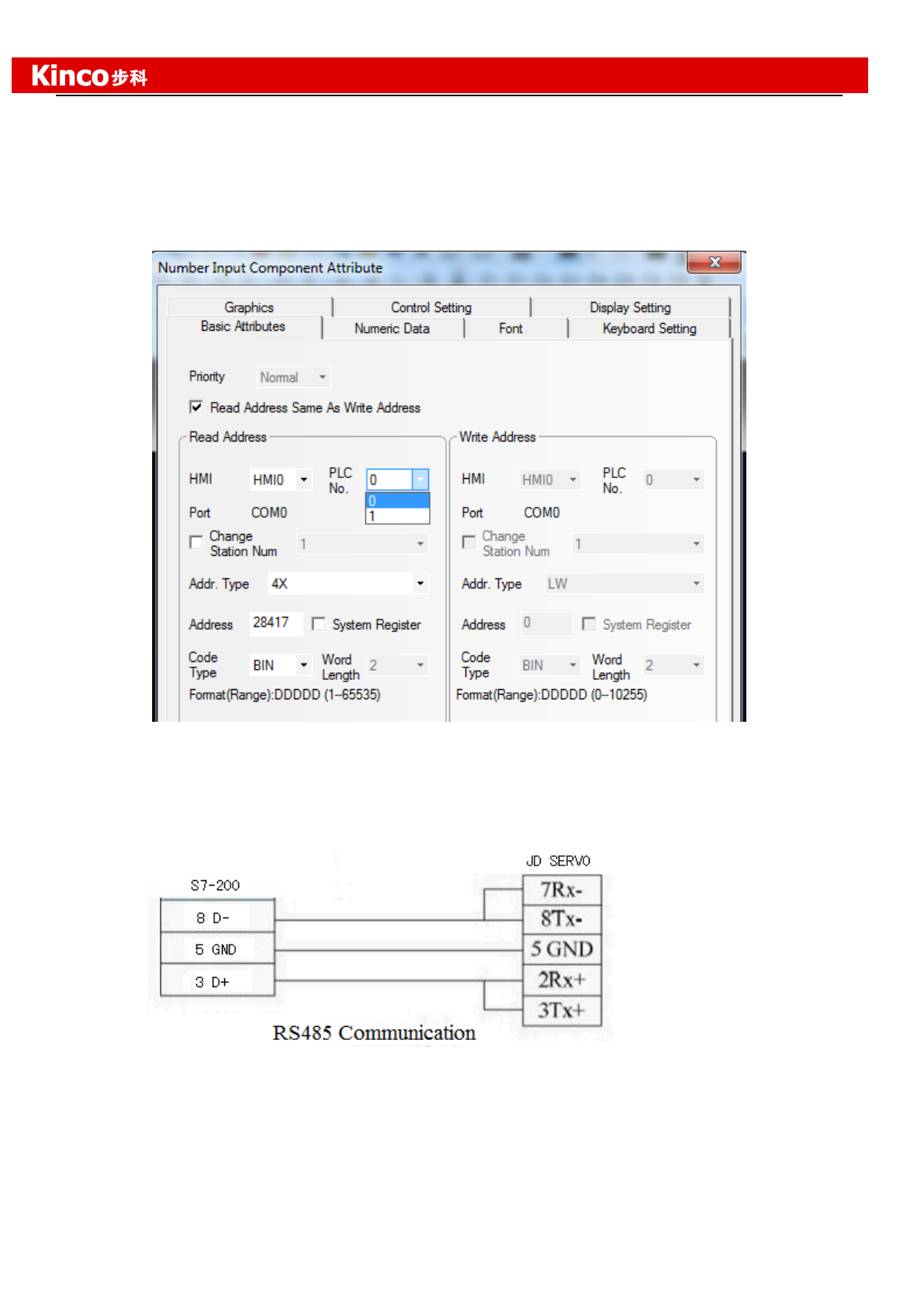
Kinco JD 伺服系列使用手册
154
Kinco FD Series Servo User Manual
b. Parameter setting
The parameters setting in HMI is the same as above example,the difference is to set different station no. for
different servo.In the attribute of components in HMI,it needs to select the PLC No. for different servo.(The
PLC No. is not the servo station No.,as shown in the figure above,PLC0:2 means the PLC No. is 0,and
station No. is 2)
2. Modbus Communication Between FD Servo and Siemens S7-200
(1)Wiring diagram
(2)Parameter setting.
About the parameter setting of FD Servo please refer to Chapter 10.2.The default parameters are Modbus
RTU,19200,8,None,1.
In the software of S7-200 PLC,there is a library function used to set communication parameters as shown in
following figure.
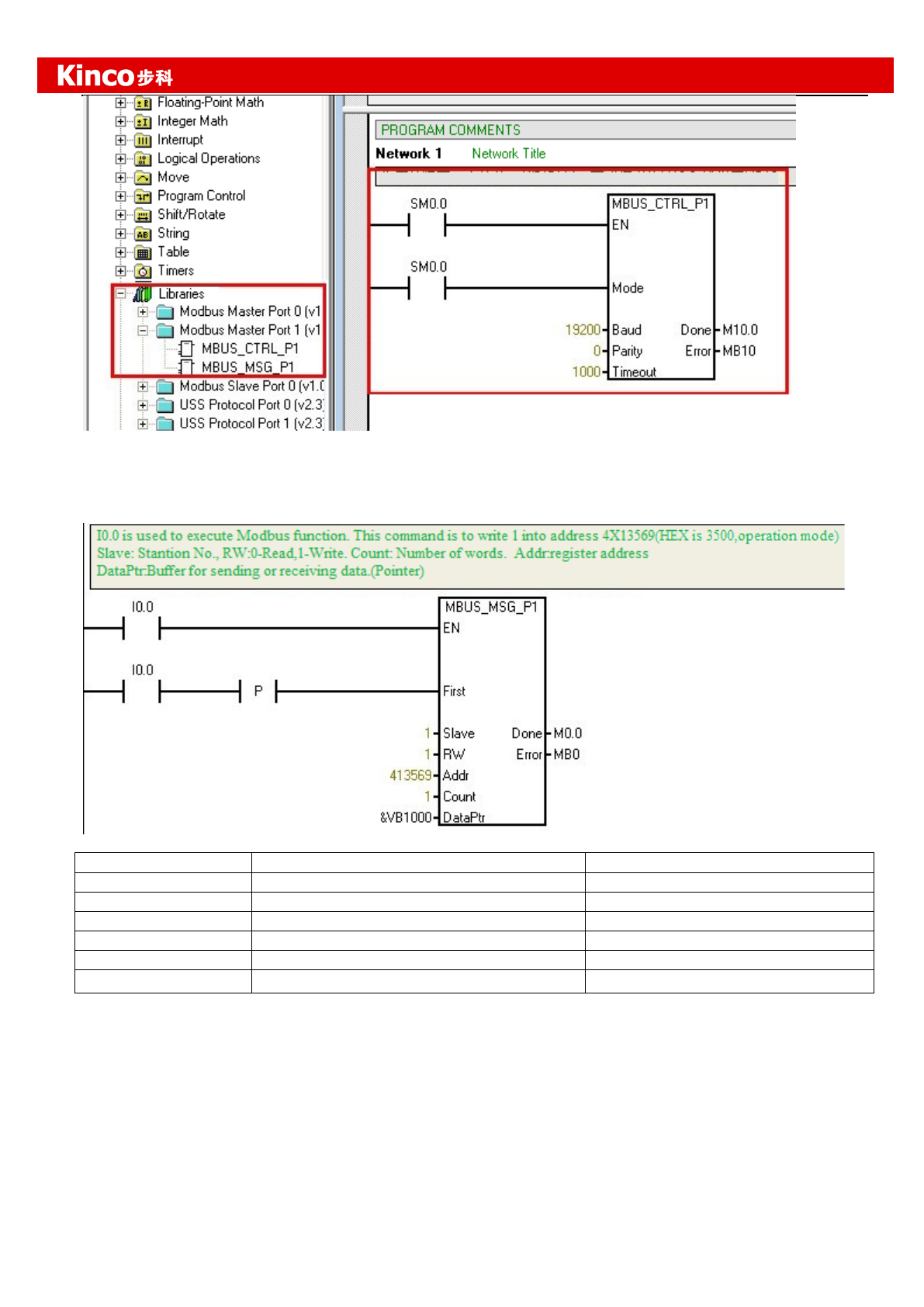
Kinco JD 伺服系列使用手册
155
Kinco FD Series Servo User Manual
(3)Program
It needs to use the Modbus function (MODBUS_MSG) to send and receive data.The descriptions of Modbus
function are shown in following figure.
(4)Example descriptions
S7200 plc Inputs
Function
Description
I0.0
Write 60600008=1
Set as position mode
I0.1
Wirte 607A0020=10000
Set the target position
I0.2
Write 60810020=1000rpm
Set the profile velocity
I0.3
Write 60400010=0x4F first,then 0x5F
Start relative positioning
I0.4
Read 60630020
Read the actual position
I0.5
Read 60410010
Read the status word
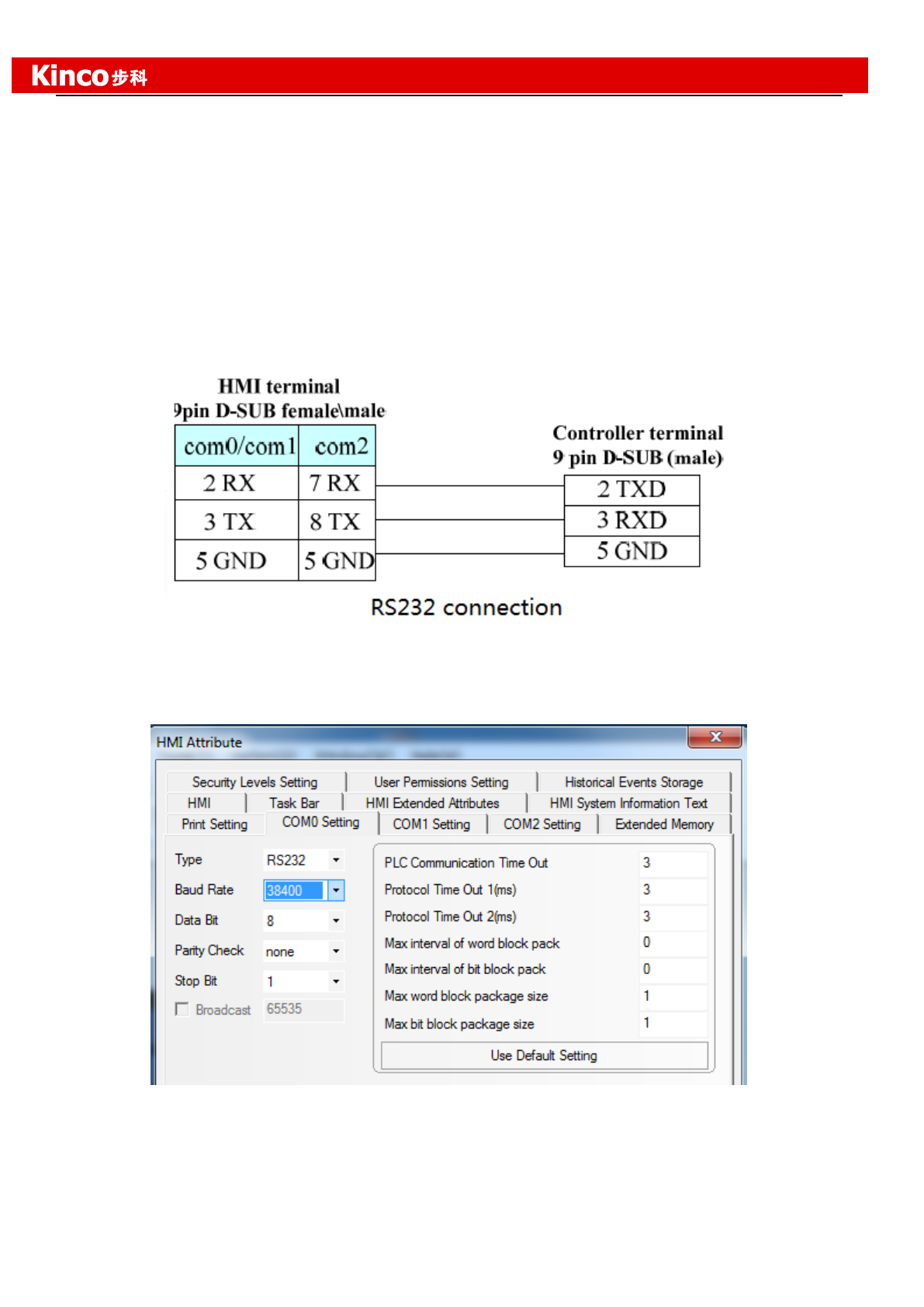
Kinco JD 伺服系列使用手册
156
Kinco FD Series Servo User Manual
Appendix 4:Example for RS232 Communication
1.Communication between FD Servo and Kinco HMI.
Kinco MT4000 and MT5000 series HMI can communicate with RS232 port of FD Servo.Users can set
internal parameters of FD Servo and display the status of FD Servo.Kinco HMI can communicate with single
FD Servo,and also can communicate with multiple FD Servo via RS232.
(1) HMI control single FD Servo
a.Wiring diagram
b. Communication parameters setting
It needs to choose Kinco Servo Series driver in HMI.The parameters setting are shown in following figure.
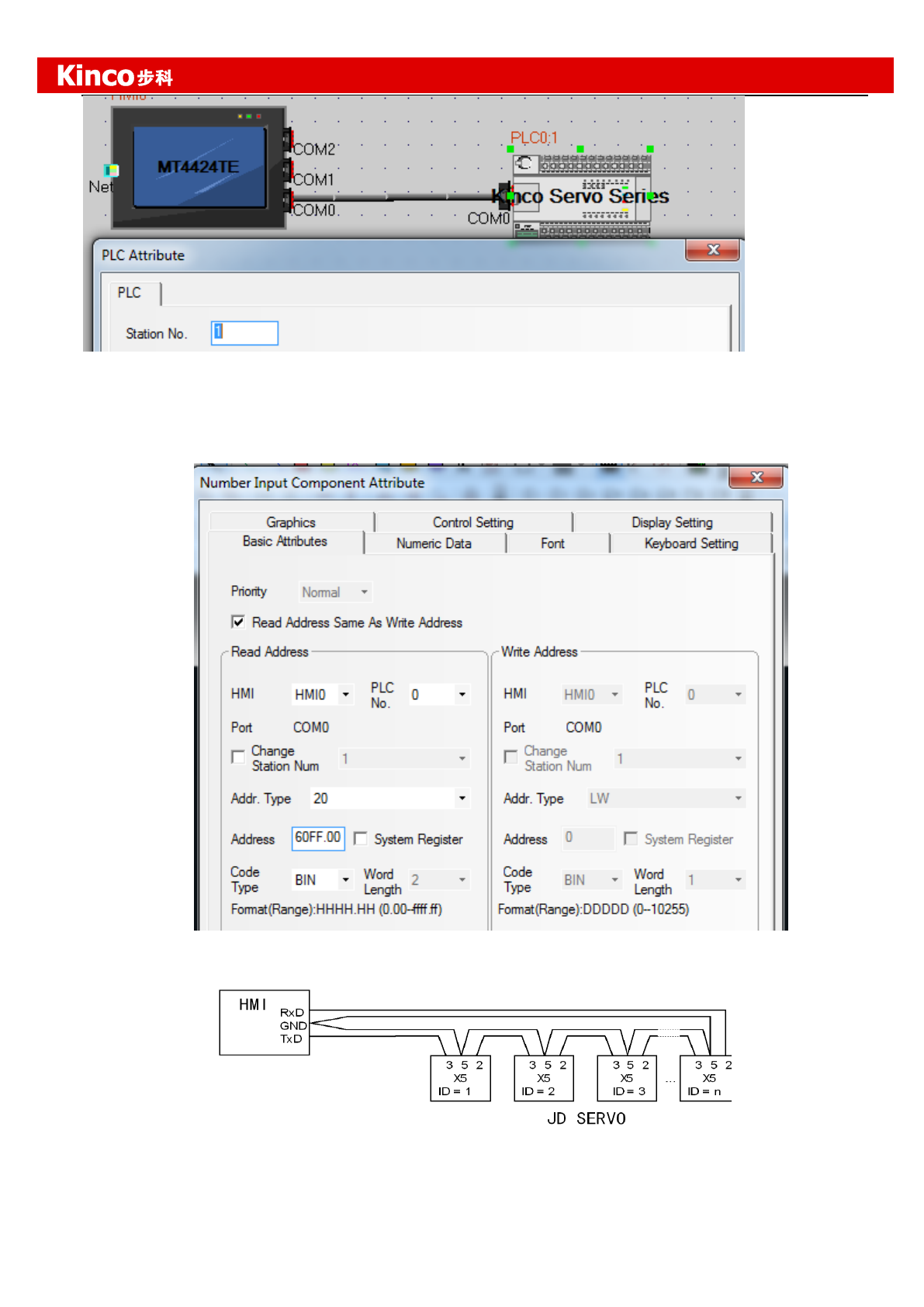
Kinco JD 伺服系列使用手册
157
Kinco FD Series Servo User Manual
c. Address setting
There are three address types in HMI software which are corresponding to the data length of the objects in
FD Servo.These address types are 08(8 bits),10(16 bits) and 20 (32 bits).The format of the address is
Index.Subindex.Following figure is an example for using object 60FF0020(Target velocity)
(2)HMI controls multiple FD Servo (D05.15 must set as 1)
a、Wiring diagram
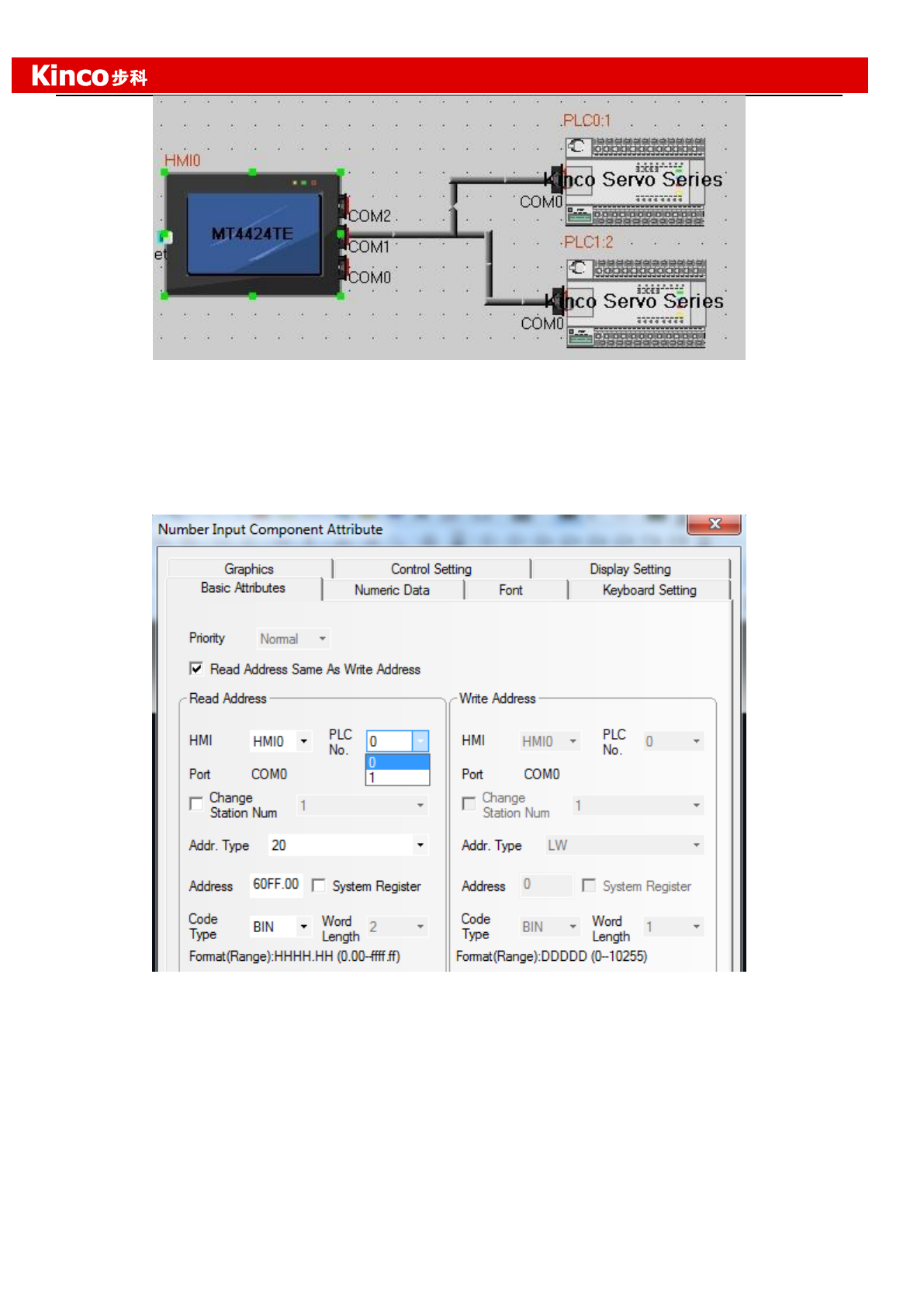
Kinco JD 伺服系列使用手册
158
Kinco FD Series Servo User Manual
b. Parameters setting
The parameters setting in HMI is the same as above example,the difference is to set different station no. for
different servo.In the attribute of components in HMI,it needs to select the PLC No. for different servo.(The
PLC No. is not the servo station No.,as shown in the figure above,PLC0:1 means the PLC No. is 0,and
station No. is 1)
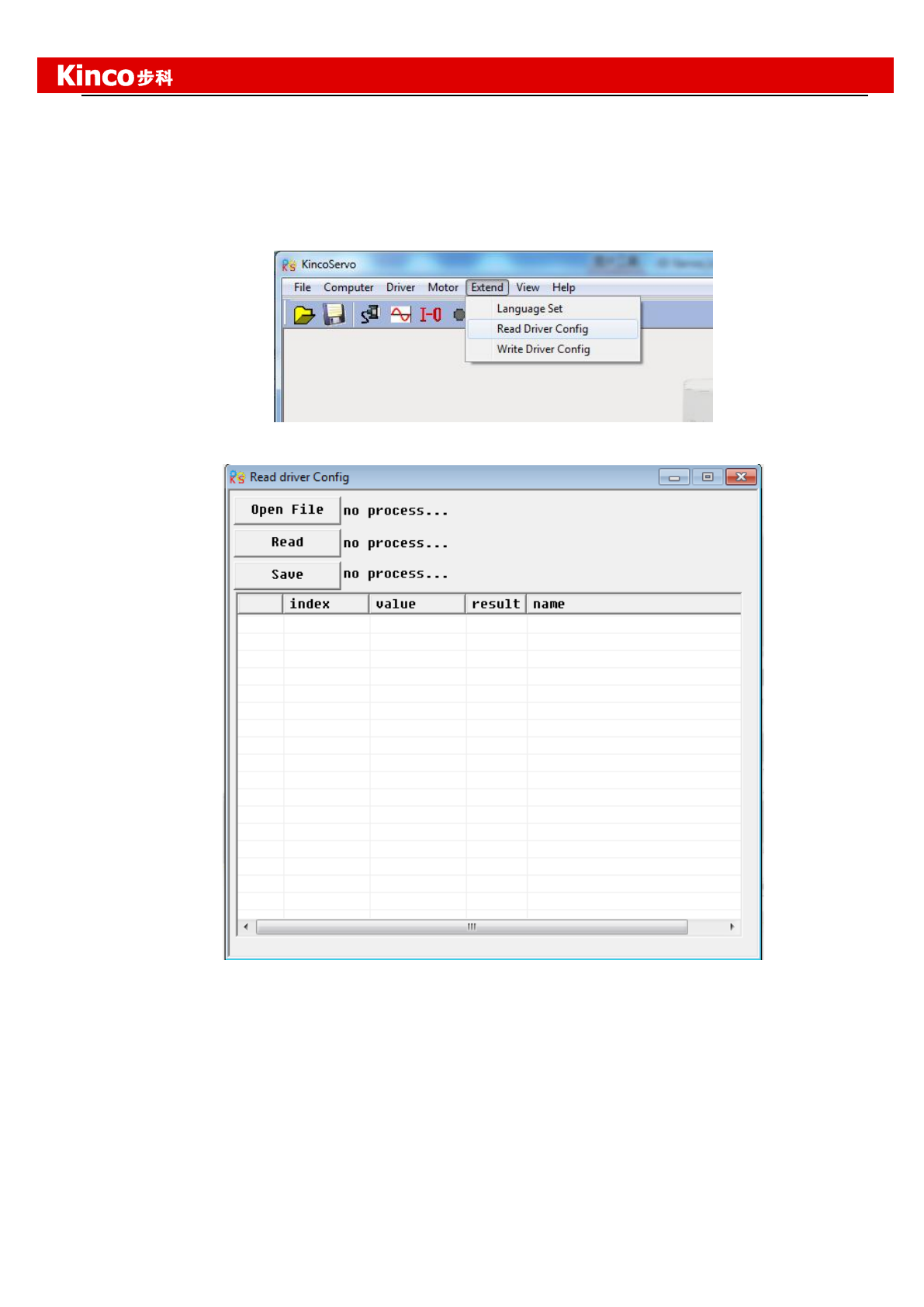
Kinco JD 伺服系列使用手册
159
Kinco FD Series Servo User Manual
Appendix 5: Use KincoServo software to import and export driver
parameters.
Export: It means to upload the parameters from driver and save in PC.
1.Select the Menu->Extend->Read Driver Config;
2.Open the window as the following picture:
3.Click the Open File, pop up a dialog box like that:
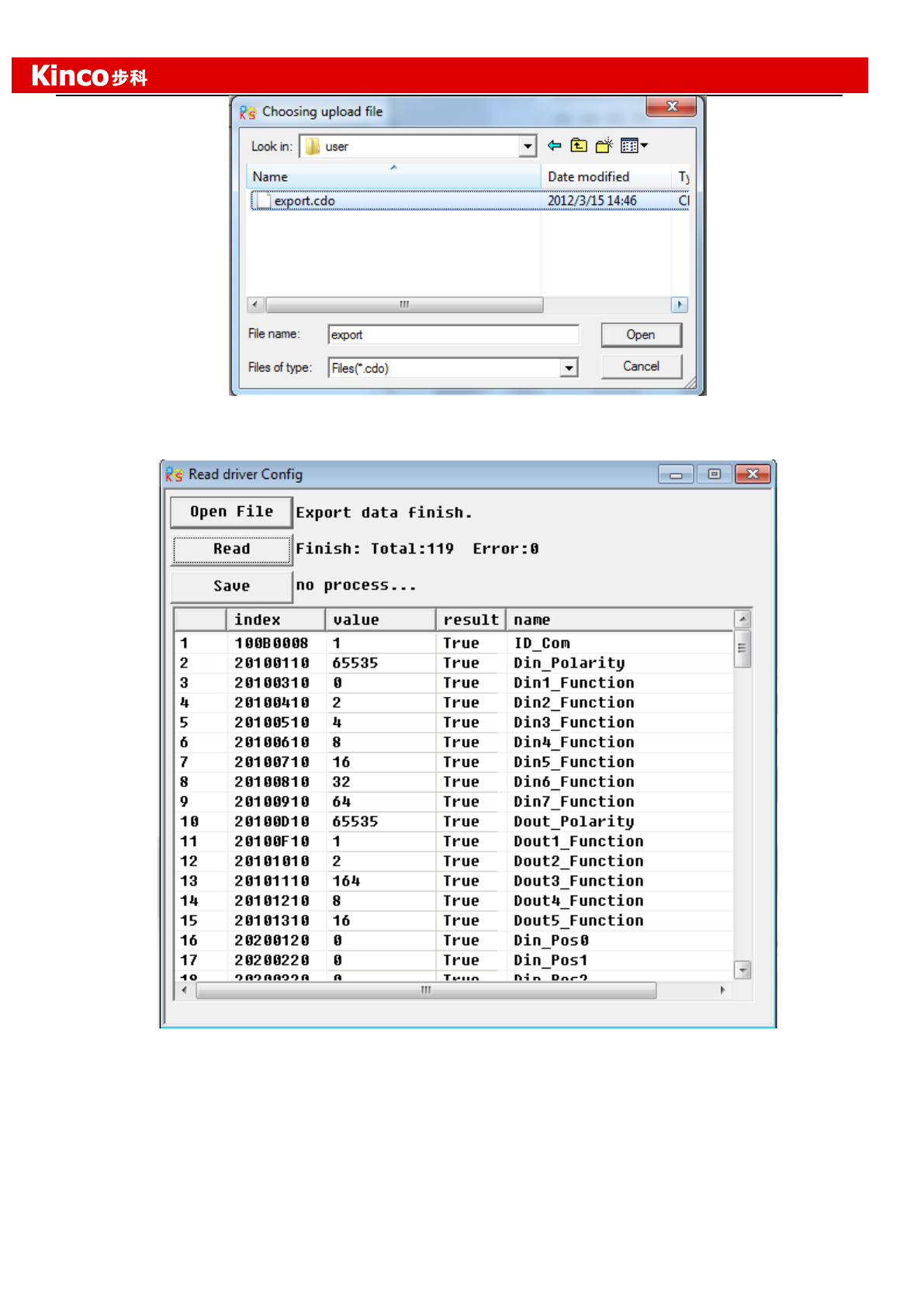
Kinco JD 伺服系列使用手册
160
Kinco FD Series Servo User Manual
4.Select the export.cdo, click the Open, the parameters will be listed in the window, and then
click the Read, and values of parameters will be shown in following the window:
5.At last, choose the Save, and input the file name, so the data in driver is uploaded.
Import: It means to download the parameters into servo driver.
1.Select the Menu->Extend->Write Driver Config:
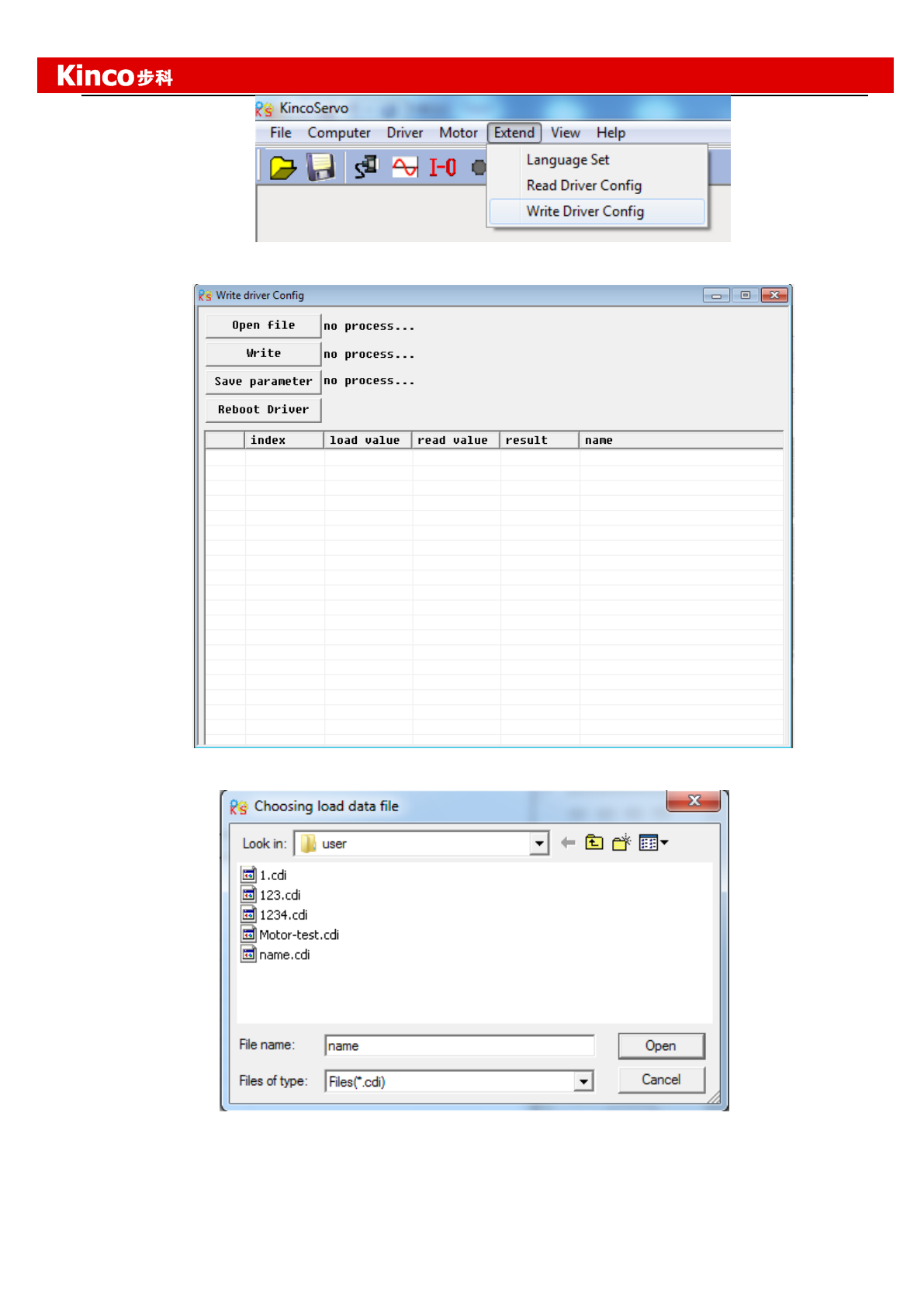
Kinco JD 伺服系列使用手册
161
Kinco FD Series Servo User Manual
2.Open the window as the following picture.
3.Click the Open File, then pop up a dialog window to select file.
4.Select one of the file that needed to be download to driver. For example we choose
Motor-test.cdi, Click Open. The parameters and their values in this file will be shown in the
window:
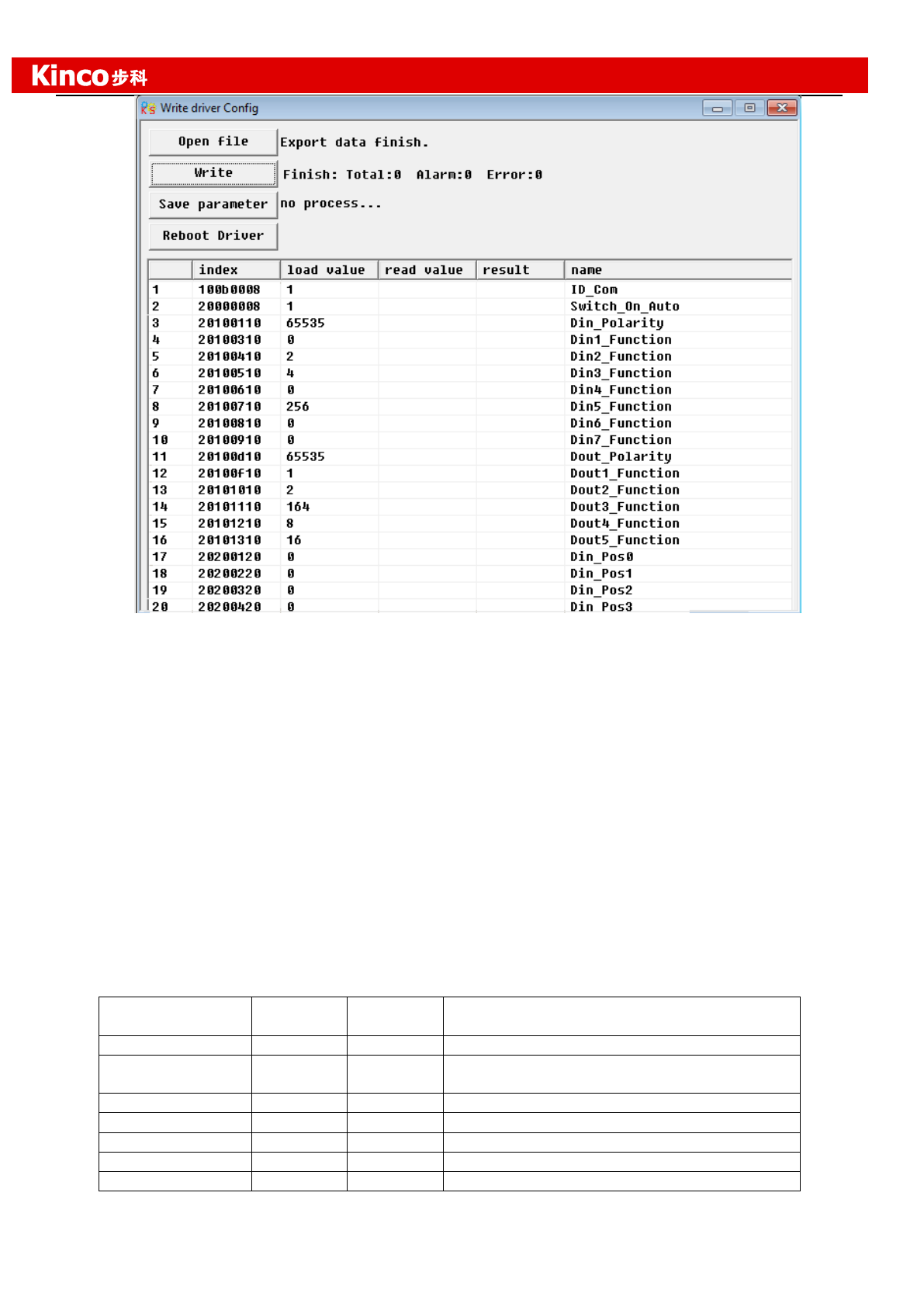
Kinco JD 伺服系列使用手册
162
Kinco FD Series Servo User Manual
5.Then click the Write, so the parameters are downloaded to driver. After that do not forget to
click Save Parameter, then the parameters are saved in driver.
Appendix 6: Conversion between engineering unit and internal unit of
common objects.
There are engineering unit and internal unit for some internal objects in FD Servo.When driver is controlled by
communication,some objects use internal unit,therefore it needs to convert the unit.For example,the
engineering unit for speed is RPM,and the internal unit is dec.Their conversion formular is
1RPM=2730dec(Resolution of encoder is 10000).Suppose to set speed as 10 RPM,then you need to send
data 27300dec to the driver when using communication control.
Following table is the list of common conversion unit.
Parameter Name
Engineerin
g Unit
Internal
Unit
Conversion Fomular
Velocity
RPM
dec
dec=[(RPM*512*Encoder_resolution)/1875]
Acceleration
r/s*s
dec
dec=[(RPS/S*65536*
Encoder_resolution)/4000000]
Kpp
hz
dec
1 hz= 100dec
K_Velocity_FF
%
dec
100%=256dec
Notch_N
hz
dec
Hz=dec*45+100
Speed_Fb_N
hz
dec
Hz=dec*20+100
Current
A
dec
1 Arms=1.414 Ap=105dec
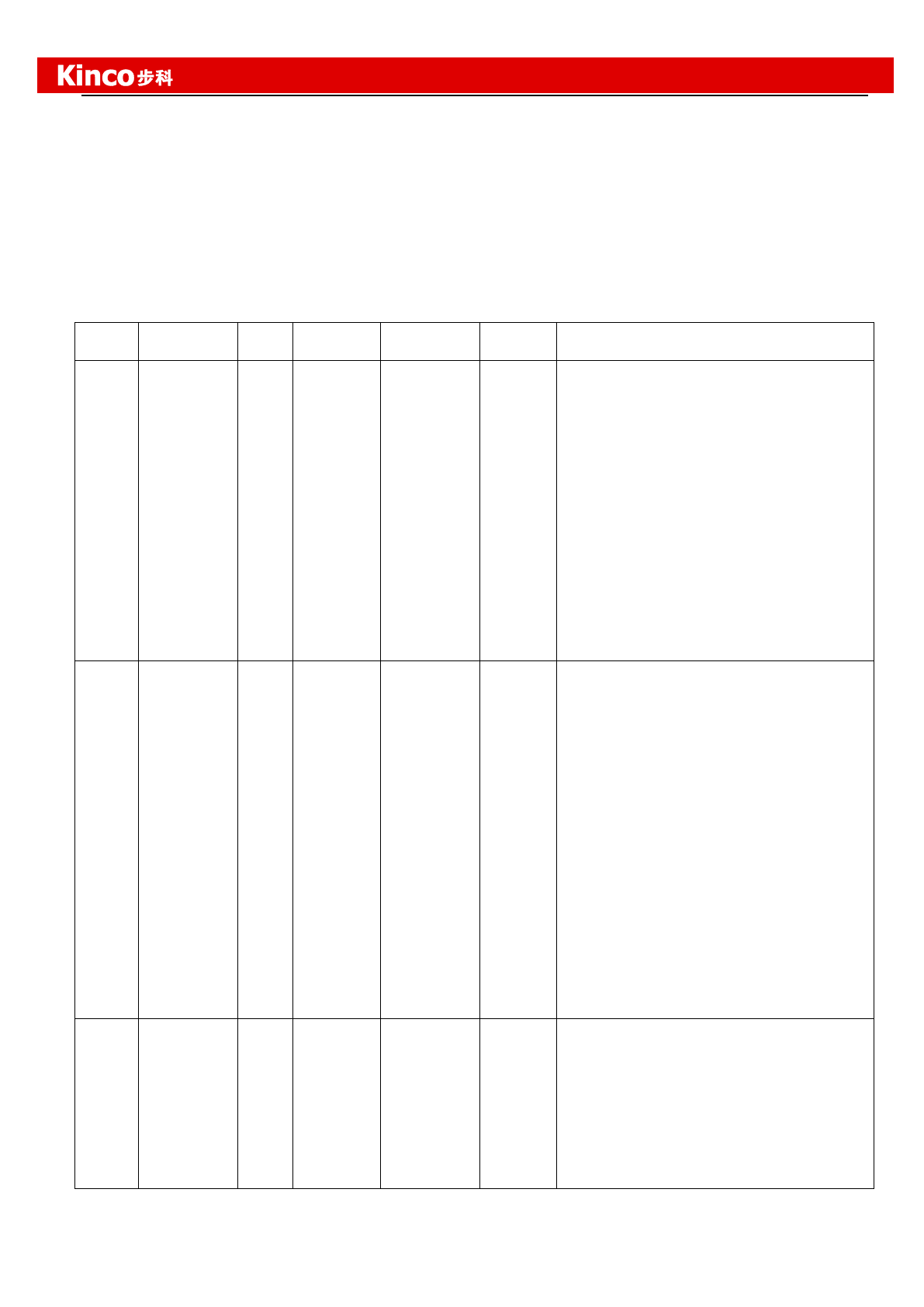
Kinco JD 伺服系列使用手册
163
Kinco FD Series Servo User Manual
Appendix 7: Common Objects List
Based on the data communication protocols described in Chapter 10,all parameter values are transferred in
hexadecimal data. In the later sections of this document, we adopt the hexadecimal system and use Index
(16-bit index) and Subindex (8-bit subindex) to represent the register addressing. The digit 08 indicates the
register will store data up to 1 byte, and the digit 10 indicates that the register will store data up to 2 bytes,
and the digit 20 indicates the register will store data up to 4 bytes. It also covers the storage digits and
read/write property of the register, read or write flag (RW), read-only or write-only flag (RO, WO), and
mapping flag (M).
Modes and Control:
Index
Subindex
Bits
Modbus
Address
Command
Type
Unit
Descriptions
6040
00
10
0x3100
RW
bitcode
Use control word to change status of
drive =>machine state
0x06 Motor power off
0x0F Motor power on
0x0B Quick stop, load tops-voltage
switched off
0x2F-3F Start absolute positioning
immediately
0x4F-5F Start relative positioning
immediately
0x103F Start absolute positioning
while target position changes.
0x105F Start relative positioning
while target position changes
0x0F-1F Start homing
0X80 Clear internal error.
6041
00
10
0x3200
RO
bitcode
Status byte shows the status of drive
bit0:ready to switch on
bit1:switch on
bit2:operation enable
bit3:falt
bit4:Voltage Enable
bit5:Quick Stop
bit6:switch on disable
bit7:warning
bit8:internal reserved
bit9:reserved
bit10: target reach
bit11: internal limit active
bit12: Step.Ach./V=0/Hom.att.
bit13: Foll.Err/Res.Hom.Err.
bit14: Commutation Found
bit15: Referene Found
6060
00
08
0x3500
WO
number
Operation modes:
1 Positioning with position loop
3 Velocity with position loop
-3 Velocity loop (immediate velocity
mode)
-4 Master/slave or pulse/direction control
mode
6 Homing
7. CANOPEN based motion interpolation
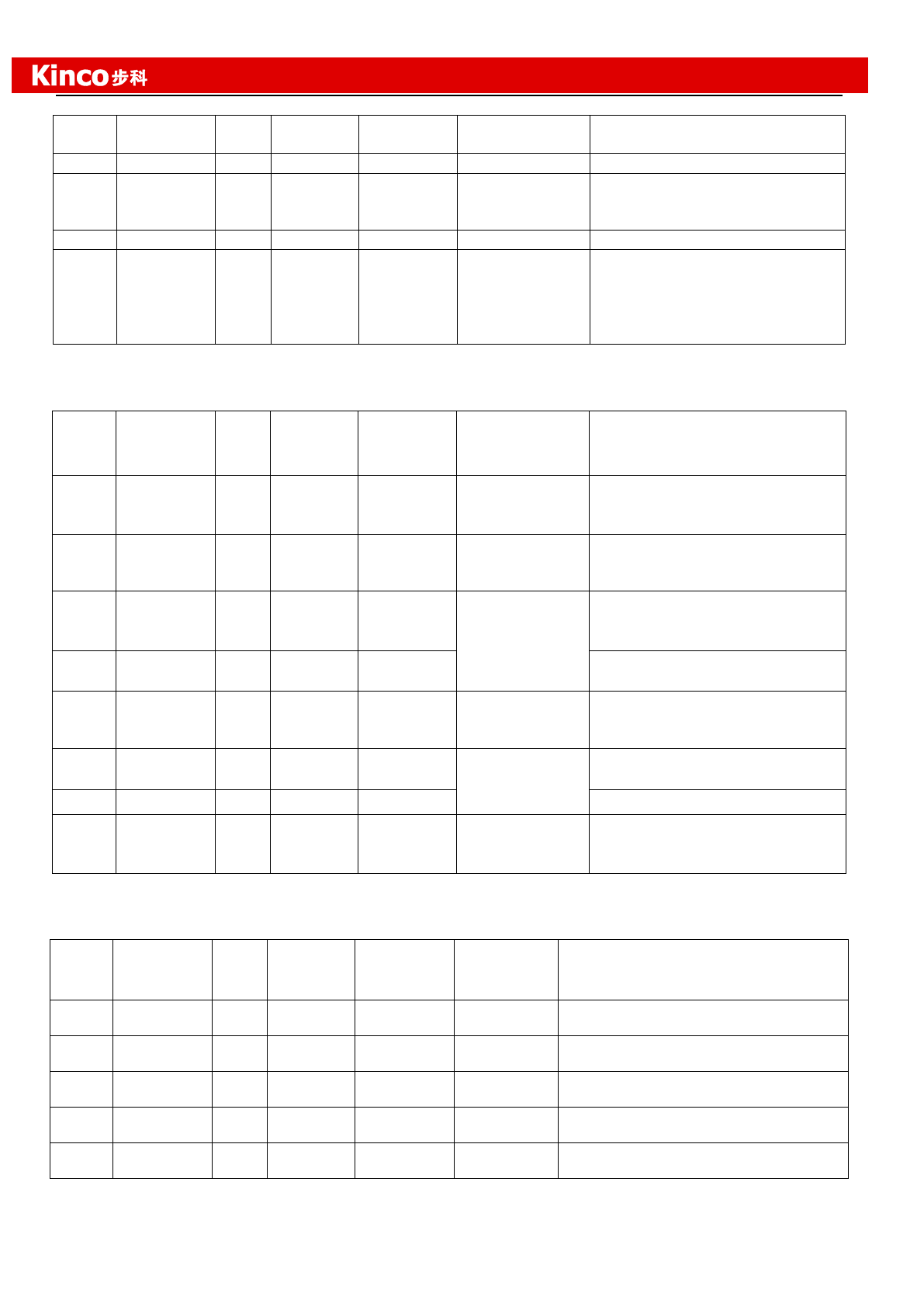
Kinco JD 伺服系列使用手册
164
Kinco FD Series Servo User Manual
Measurement data:
Target object:
Multiple position,multiple speed.
Index
Subindex
Bits
Modbus
Address
Command
Type
Unit
Descriptions
6063
00
20
0x3700
RO
inc
Actual position value
606C
00
20
0x3b00
RO
DEC=[(RPM*51
2*Encoder_res
olution)/1875]
Actual velocity value
6078
00
10
0x3E00
RO
number
Actual current value
60FD
00
20
0x6D00
RO
bitcode
Status words for digital inputs
bit0: Negative limit signal status
bit1: Positive limit signal status
bit2: Home signal status
bit3: Hardware lock signal status
Index
Subindex
Bits
Modbus
Address
Command
Type
Unit
Descriptions
607A
00
20
0x4000
RW
inc
Target position in operation
mode 1, shift to demand position
if control word starts motion
6081
00
20
0x4A00
RW
DEC=[(RPM*51
2*Encoder_res
olution)/1875]
Maximum velocity of trapezium
profile in mode 1
6083
00
20
0x4B00
RW
DEC=[(RPS/S*
65536*Encoder
_resolution)/40
00000]
Acceleration of the trapezium
profile
Default value:610.352rps/s
6084
00
20
0x4C00
RW
Deceleration of trapezium profile
Default value:610.352rps/s
60FF
00
20
0x6F00
RW
DEC=[(RPM*51
2*Encoder_res
olution)/1875]
Target velocity in mode 3, -3, or 4
6071
00
10
0x3C00
RW
1Arms=1.414
Ap=105dec
Target current
6073
00
10
0x3D00
RW
Maximum current
6080
00
20
0x4900
RW,M
RPM
Maximum velocity.
Actual velocity in mode 4.
Maximum velocity in other mode.
Index
Subindex
Bits
Modbus
Address
Command
Type
Unit
Descriptions
2020
01
20
0x0C10
RW
DEC
Multiple position control 0
2020
02
20
0x0C20
RW
DEC
Multiple position control 1
2020
03
20
0x0C30
RW
DEC
Multiple position control 2
2020
04
20
0x0C40
RW
DEC
Multiple position control 3
2020
10
20
0x0D00
RW
DEC
Multiple position control 4
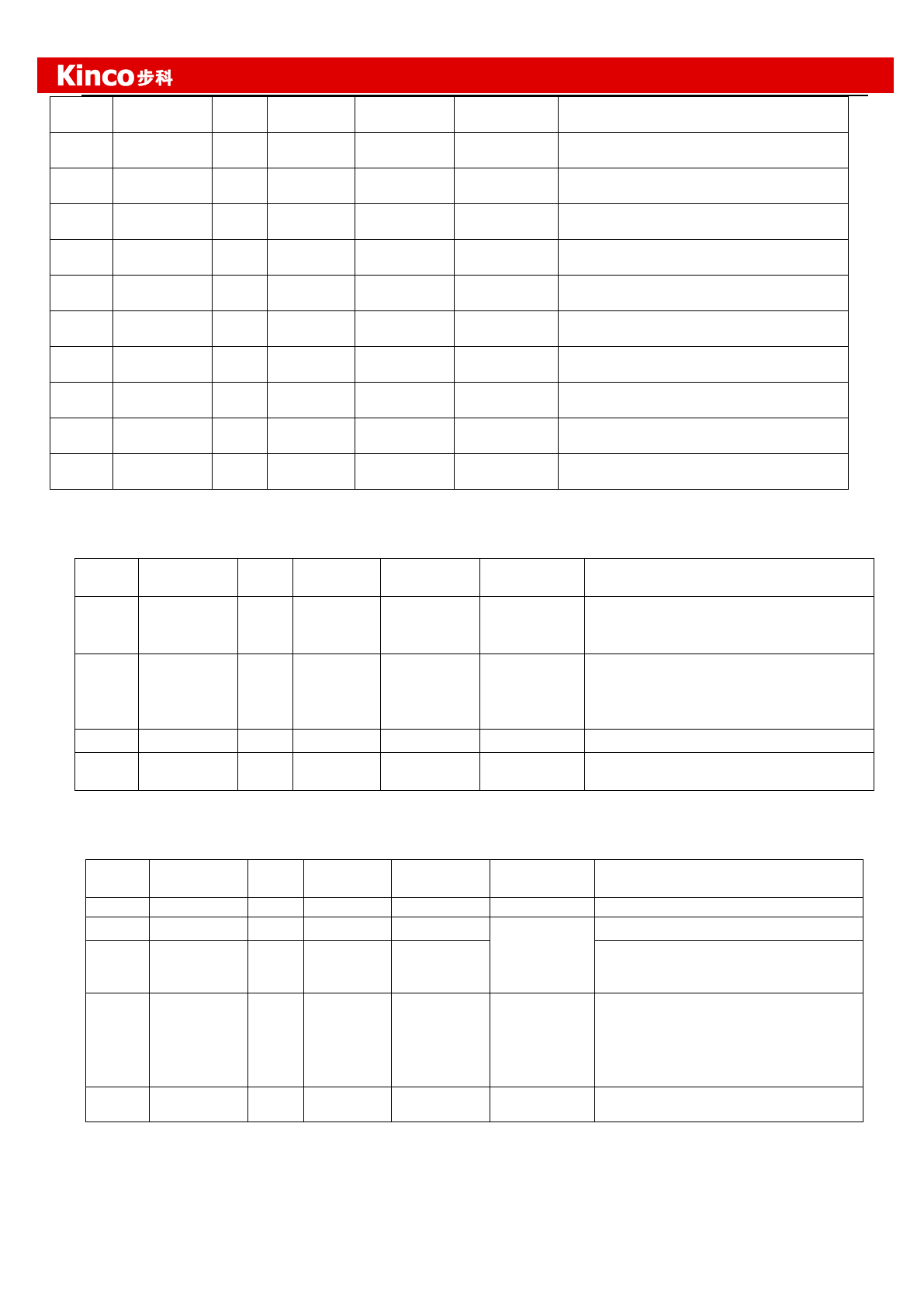
Kinco JD 伺服系列使用手册
165
Kinco FD Series Servo User Manual
Performance object
Homing
Velocity loop object:
2020
11
20
0x0D10
RW
DEC
Multiple position control 5
2020
12
20
0x0D20
RW
DEC
Multiple position control 6
2020
13
20
0x0D30
RW
DEC
Multiple position control 7
2020
05
20
0x0C50
RW
RPM
Multiple speed control 0
2020
06
20
0x0C60
RW
RPM
Multiple speed control 1
2020
07
20
0x0C70
RW
RPM
Multiple speed control 2
2020
08
20
0x0C80
RW
RPM
Multiple speed control 3
2020
14
20
0x0D40
RW
RPM
Multiple speed control 4
2020
15
20
0x0D50
RW
RPM
Multiple speed control 5
2020
16
20
0x0D60
RW
RPM
Multiple speed control 6
2020
17
20
0x0D70
RW
RPM
Multiple speed control 7
Index
Subindex
Bits
Modbus
Address
Command
Type
Unit
Descriptions
6065
00
20
0x3800
RW,M
inc
Maximum following error at which the
drive generates an alarm
Default value 10000inc
6067
00
20
0x3900
RW,M
inc
Position reach window
position range for “target reached”
flag
Default value 10inc
607D
01
20
0x4410
RW,M
inc
Soft positive limit
607D
02
20
0x4420
RW,M
inc
Soft negative limit.
(if both are zero, there is no limit)
Index
Subindex
Bits
Modbus
Address
Command
Type
Unit
Descriptions
6098
00
08
0x4D00
RW
integer
Homing methods
6099
01
20
0x5010
RW
DEC=[(RP
M*512*Enc
oder_resolu
tion)/1875]
Velocity for searching limit switch
6099
02
20
0x5020
RW
Velocity for searching phase-N
signal
609A
00
20
0x5200
RW
DEC=[(RPS
/S*65536*E
ncoder_res
olution)/400
0000]
Acceleration
607C
00
20
0x4100
RW
inc
Home offset
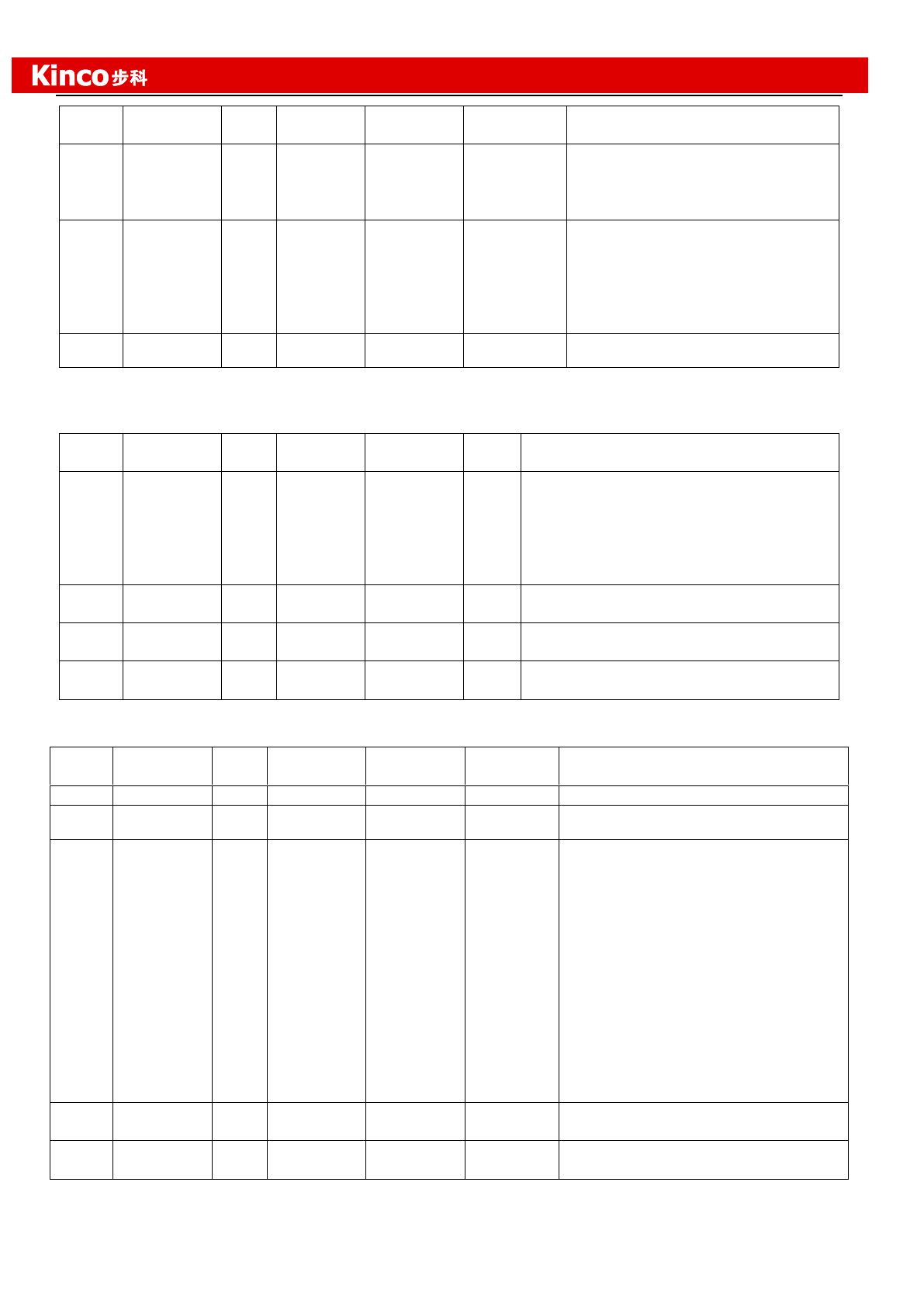
Kinco JD 伺服系列使用手册
166
Kinco FD Series Servo User Manual
Position loop object:
Pulse input parameters:
Index
Subindex
Bits
Modbus
Address
Command
Type
Unit
Descriptions
60F9
01
10
0x6310
RW
inc/s
VC_KP proportional gain of velocity
loop
50 soft gain
200 hard gain
60F9
02
10
0x6320
RW
integer
VC_KI integral gain of velocity loop
0 no correction of transient
deviations
1 default value
2 strong correction, can cause
oscillation
60F9
05
10
0x6350
RW
integer
Speed feedback filter
Index
Subindex
Bits
Modbus
Address
Command
Type
Unit
Descriptions
60FB
01
10
0x6810
RW
unsig
ned
PC_KP proportional value of position
loop, for example:
1000 default value, soft correction
3000 value for middle performance
8000 good performance value, with low
following error, high position stiffness
60FB
02
10
0x6820
RW
integ
er
Velocity feedforward
60FB
03
10
0x6830
RW
integ
er
Acceleration feedforward
60FB
05
10
0x6850
RW
integ
er
Smooth filter
Index
Subindex
Bits
Modbus
Address
Command
Type
Unit
Descriptions
2508
01
10
0x1910
RW
integer
Numerator of electronic gear ratio
2508
02
10
0x1920
RW
unsigned
Denominator of electronic gear ratio
2508
03
08
0x1930
RW
integer
Pulse mode control
0...CW/CCW
1...Pulse/Direction
2...Incremental encoder
10..CW/CCW(RS422 type)
11..Pulse/Direction(RS422 type)
12.. Incremental encoder (RS422
type)
Note:0,1,2 are used for
PIN4,5,9,10,14,15 of Master_Encoder
interface,they are TTL signal.
10,11,12 are used for
PIN6,7,8,11,12,13,they are differential
signal.
2508
04
20
0x1940
RW
inc
Input pulse amount before electronic
gear.
2508
05
20
0x1950
RW
inc
Execute pulse amount after electronic
gear
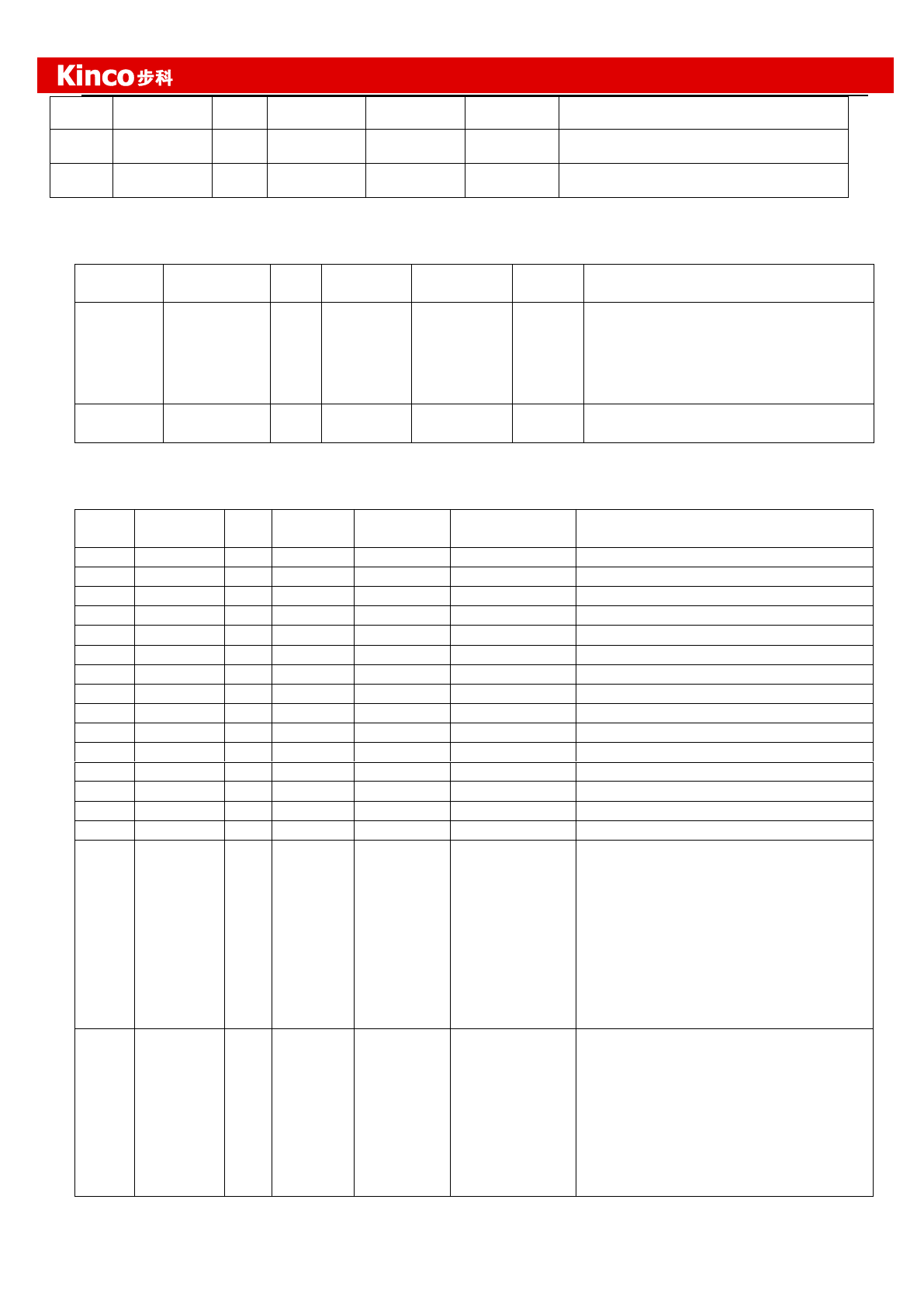
Kinco JD 伺服系列使用手册
167
Kinco FD Series Servo User Manual
Storage parameters:
Input and output parameters:
2508
06
10
0x1960
RW
DEC
Filter for pulse input
2508
0C
10
0x19C0
RW
pulse/mS
Pulse speed of master
2508
0D
10
0x19D0
RW
pulse/mS
Pulse speed of slave
Index
Subindex
Bits
Modbus
Address
Command
Type
Unit
Descriptions
2FF0
01
08
0x2910
RW
unsign
ed
1:Save all control parameters
10:Initialize all control parameters.
Note :Only for control
parameters,exclude motor
parameters.
2FF0
03
08
0x2930
RW
unsign
ed
1:Save motor parameters
Index
Subindex
Bits
Modbus
Address
Command
Type
Unit
Descriptions
2010
03
10
0x0830
RW
unsigned
Function definition of digital input 1
2010
04
10
0x0840
RW
unsigned
Function definition of digital input 2
2010
05
10
0x0850
RW
unsigned
Function definition of digital input 3
2010
06
10
0x0860
RW
unsigned
Function definition of digital input 4
2010
07
10
0x0870
RW
unsigned
Function definition of digital input 5
2010
08
10
0x0880
RW
unsigned
Function definition of digital input 6
2010
09
10
0x0890
RW
unsigned
Function definition of digital input 7
2010
1D
10
0x09D0
RW
unsigned
Function definition of digital input 8
2010
0F
10
0x08F0
RW
unsigned
Function definition of digital output 1
2010
10
10
0x0900
RW
unsigned
Function definition of digital output 2
2010
11
10
0x0910
RW
unsigned
Function definition of digital output 3
2010
12
10
0x0920
RW
unsigned
Function definition of digital output 4
2010
13
10
0x0930
RW
unsigned
Function definition of digital output 5
2010
1E
10
0x09E0
RW
unsigned
Function definition of digital output 6
2010
1F
10
0x09F0
RW
unsigned
Function definition of digital output 7
2010
0A
10
0x08A0
RO
bitcode
Status of digital input
bit0:Din1
bit1:Din2
bit2:Din3
bit3:Din4
bit4:Din5
bit5:Din6
bit6:Din7
bit7:Din8
2010
14
10
0x0940
RO
bit code
Status of digital output
bit0:Dout1
bit1:Dout2
bit2:Dout3
bit3:Dout4
bit4:Dout5
bit5:Dout6
bit6:Dout7
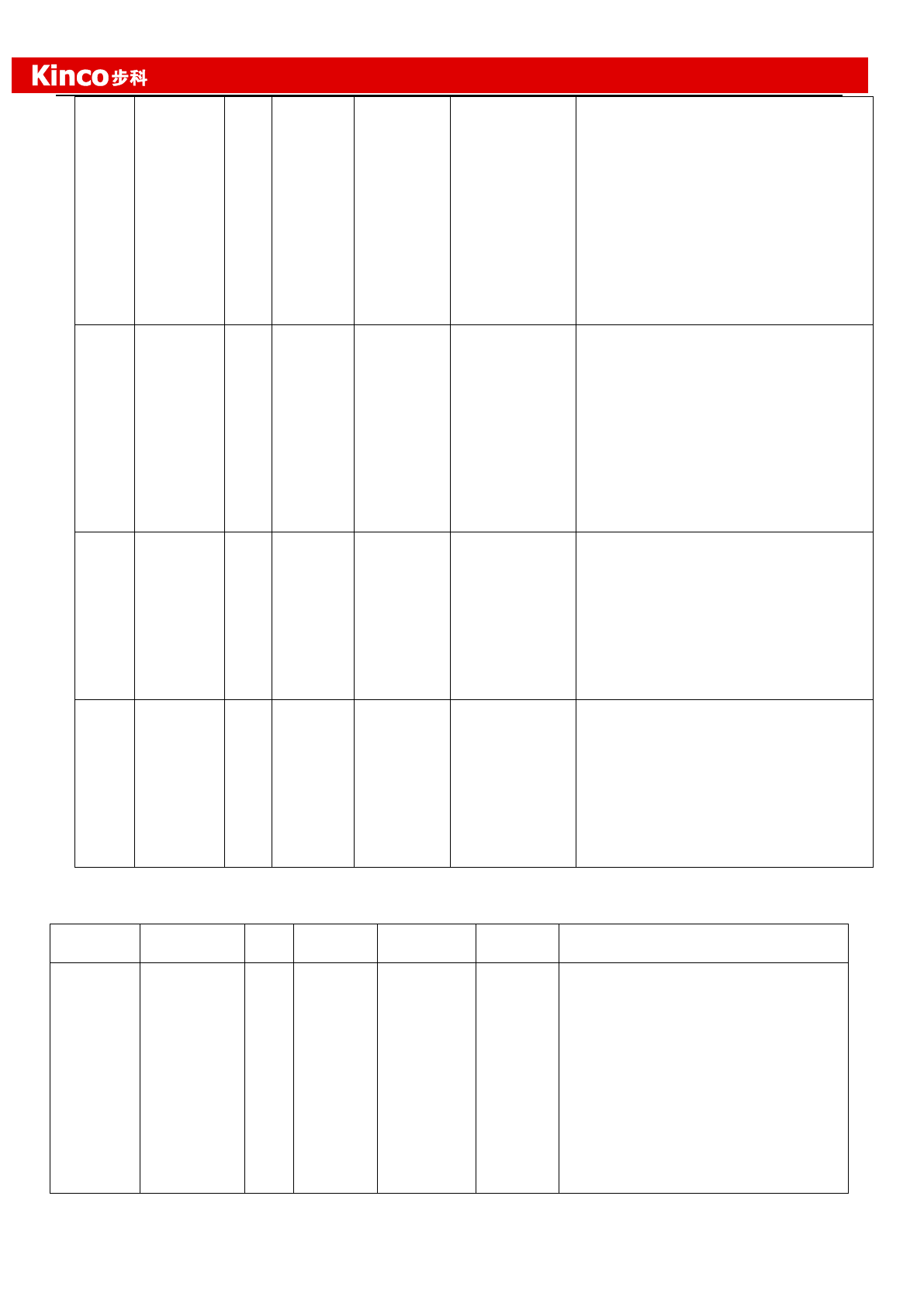
Kinco JD 伺服系列使用手册
168
Kinco FD Series Servo User Manual
Error code:
Index
Subindex
Bits
Modbus
Address
Command
Type
Unit
Descriptions
2601
00
10
0x1F00
RO
unsigne
d
Current error code:
bit0:Internal
bit 1:Encoder ABZ
bit 2:Encoder UVW
bit 3:Encoder counting
bit 4:Over temperature
bit 5:Over voltage
bit 6:Low voltage
bit 7:Over current
bit 8:Chop resistor
bit 9:Following error
2010
01
10
0x0810
RW
bitcode
Polarity of digital input
0:Normally-open;1:Normally-close
bit0:Din1
bit1:Din2
bit2:Din3
bit3:Din4
bit4:Din5
bit5:Din6
bit6:Din7
bit7:Din8
Default value is FF
2010
0D
10
0x08D0
RW
bitcode
Polarity of digital output
0:Normally-open;1:Normally-close
bit0:Dout1
bit1:Dout2
bit2:Dout3
bit3:Dout4
bit4:Dout5
bit5:Dout6
bit6:Dout7
Default value is FF
2010
02
10
0x0820
RW
bitcode
Simulation of digital input
bit0:Din1
bit1:Din2
bit2:Din3
bit3:Din4
bit4:Din5
bit5:Din6
bit6:Din7
2010
0E
10
0x08E0
RW
bitcode
Simulation of digital output
bit0:Dout1
bit1:Dout2
bit2:Dout3
bit3:Dout4
bit4:Dout5
bit5:Dout6
bit6:Dout7
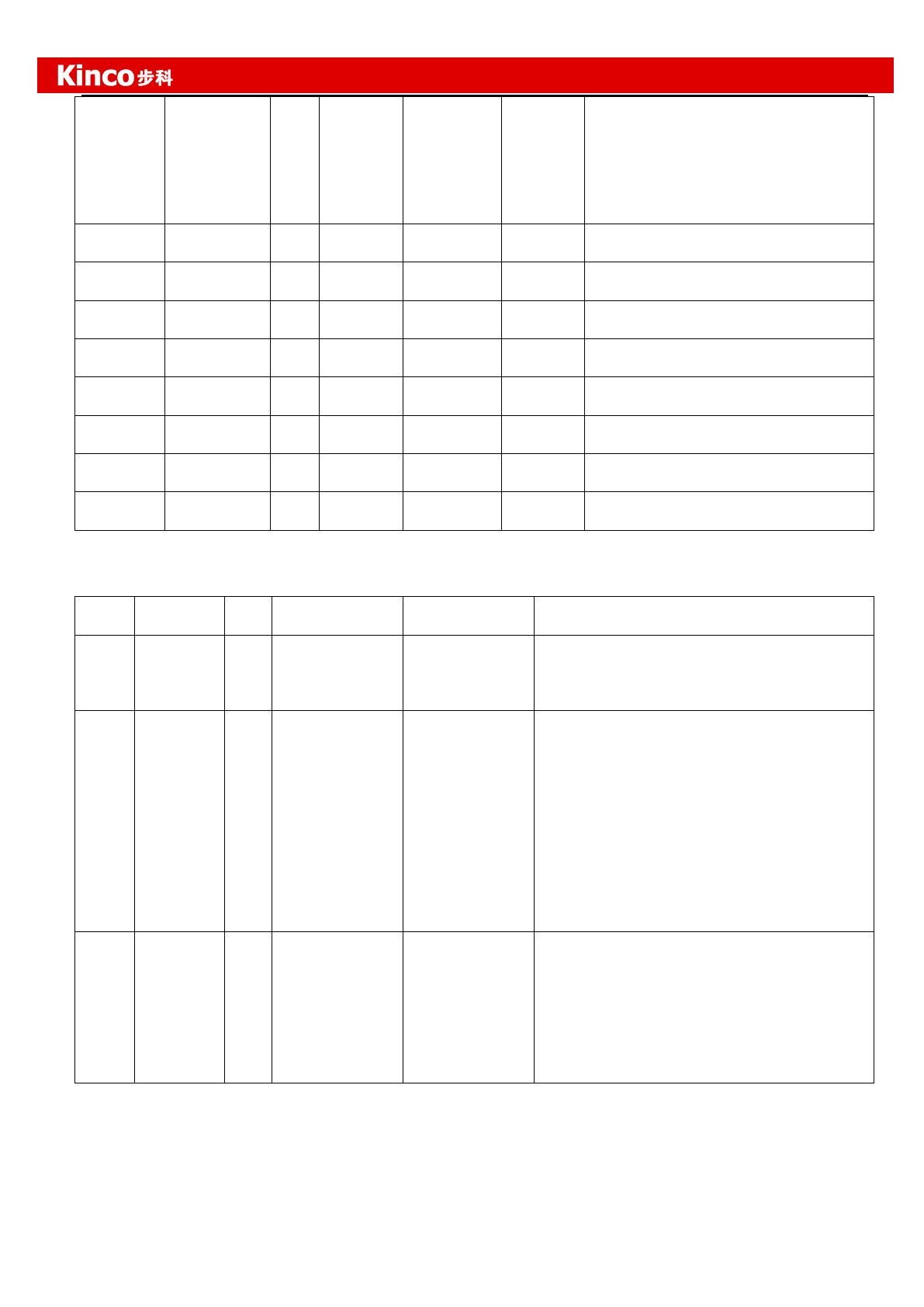
Kinco JD 伺服系列使用手册
169
Kinco FD Series Servo User Manual
bit 10:Logic voltage
bit 11:IIt error
bit 12:Over frequency
bit 13:Reserved
bit 14:Commutation
bit 15:EEPROM
2610
00
10
/
RO
unsigne
d
Error code of historical alarm 0
2611
00
10
/
RO
unsigne
d
Error code of historical alarm 1
2612
00
10
/
RO
unsigne
d
Error code of historical alarm 2
2613
00
10
/
RO
unsigne
d
Error code of historical alarm 3
2614
00
10
/
RO
unsigne
d
Error code of historical alarm 4
2615
00
10
/
RO
unsigne
d
Error code of historical alarm 5
2616
00
10
/
RO
unsigne
d
Error code of historical alarm 6
2617
00
10
/
RO
unsigne
d
Error code of historical alarm 7
Bus specification parameters:
Index
Subindex
Bits
Command
Type
Command
Type
Unit
100B
00
08
RW
unsigned
Station No. of driver
Default value:1
Note:it needs to save and restart driver after
change.
2F81
00
08
RW
unsigned
Baudrate for CAN
Setting value Baudrate
100: 1M
50: 500k
25: 250k
12: 125k
5: 50k
1: 10k
Default value: 50
Note:it needs to save and restart driver after
change.
2FE0
00
10
RW
unsigned
Baudrate for RS232
Setting value Baudrate
540 19200
270 38400
90 115200
Default value: 270
Note:it needs to save and restart driver after
change.
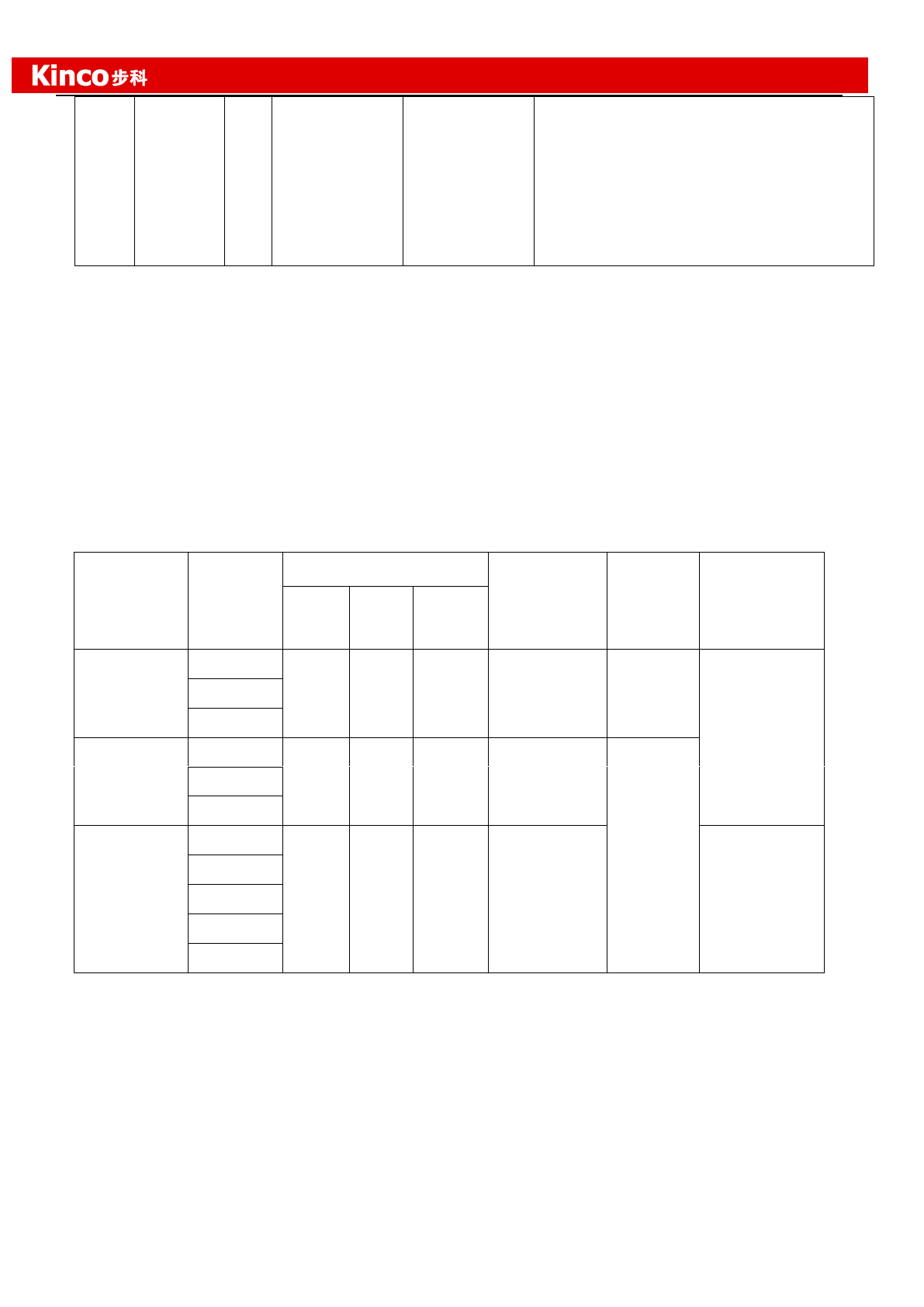
Kinco JD 伺服系列使用手册
170
Kinco FD Series Servo User Manual
CAN-PDO parameters:0X1400-0X1A00
0X1400-7(RX-Parameter/Read)
0X1600-7(RX-Mapping)
0X1800-7(TX-Parameter/Write)
0X1A00-7(TX-Mapping)
Appendix 8: Selection for Brake Resistor
Driver
Model
Driver
Power[W]
Brake Resistor[Ω]
Brake
Resistor
Model(Ref.)
Brake
Resistor
Power[W]
(Ref.)
Brake
Resistor
Withstand
Voltage[VDC]
(Min.)
Min.
Max.
Ref.
FD422-AA-000
200W
39
100
75
T-75R-100
100
500
400W
750W
FD432-AA-000
1.0KW
27
51
39
T-39R-200
200
1.05KW
1.26KW
FD622-AA-000
1.26KW
47
150
75
T-75R-200
800
1.57KW
1.88KW
2.1kw
2.3kw
Note:Please set brake resistor value and power in d5.04 and d5.05 when using brake resistor.
Please select brake resistor power according to real application.
2FE2
00
10
RW
unsigned
Baudrate for RS485
Setting value Baudrate
1080 9600
540 19200
270 38400
90 115200
Default value: 540
Note:it needs to save and restart driver after
change.
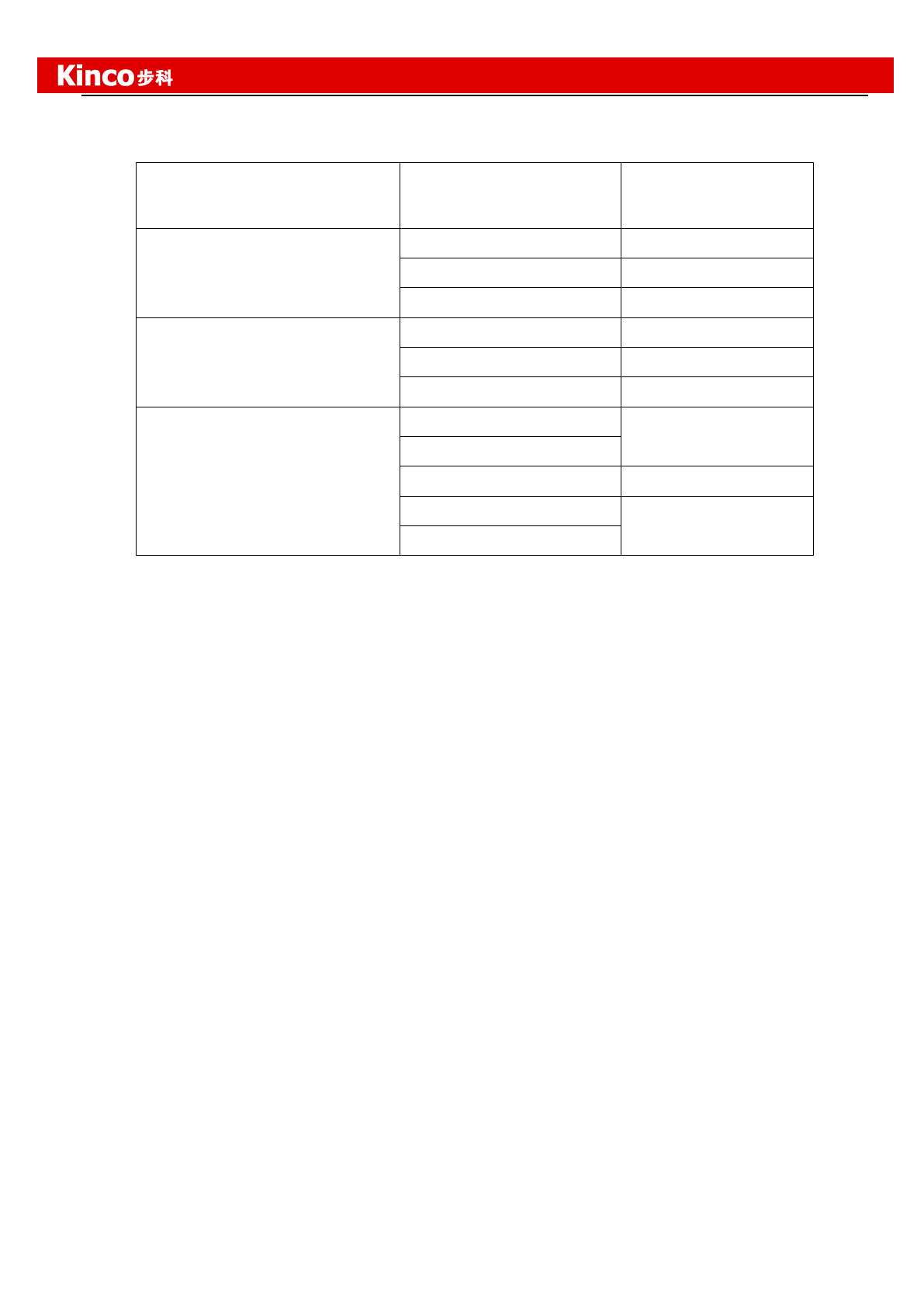
Kinco JD 伺服系列使用手册
171
Kinco FD Series Servo User Manual
Appendix 9: Selection for Fuse
Driver Model
Driver Power[W]
Specification
FD422-AA-000
200W
3.5A/250VAC
400W
7A/250VAC
750W
15A/250VAC
FD432-AA-000
1000W
20A/250VAC
1.05KW
20A/250VAC
1.26KW
25A/250VAC
FD622-AA-000
1.26KW
15A/500VAC
1.57KW
1.88KW
20A/500VAC
2.1KW
25A/250VAC
2.3KW