Foster Freezer LC125 Meatwell LDU15 & AT1 5 Service Manual (re1010)
User Manual: Foster Freezer LC125
Open the PDF directly: View PDF .
Page Count: 15
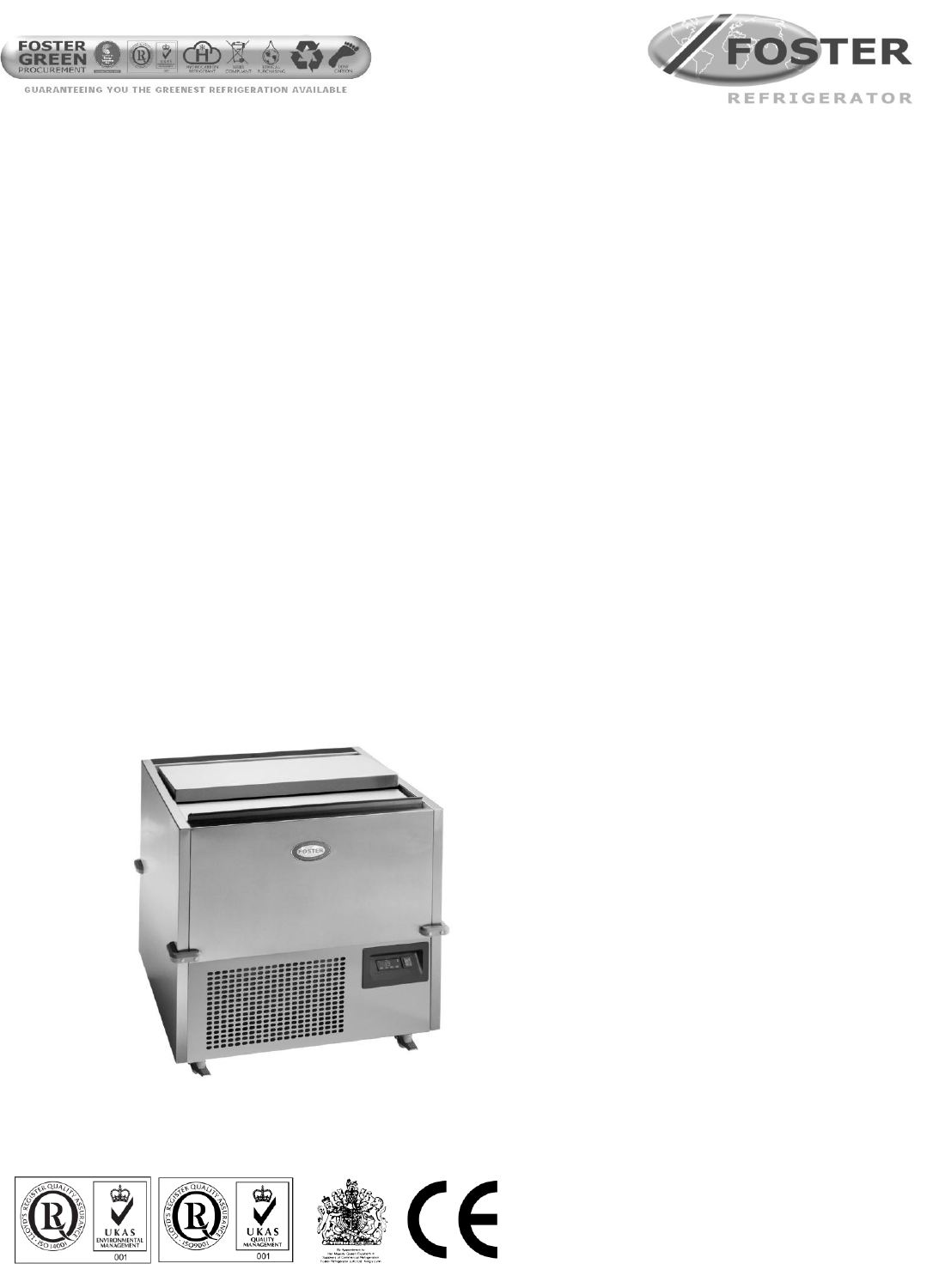
LC125 Meatwell
with
LDU15 Controller (Feb
‘04 till July ‘09)
then
AT1-5 Controller (July
‘09 onwards)
Service Manual
Re-Issued October 2010
Original Aug 09
ISO 14001
ISO 9001
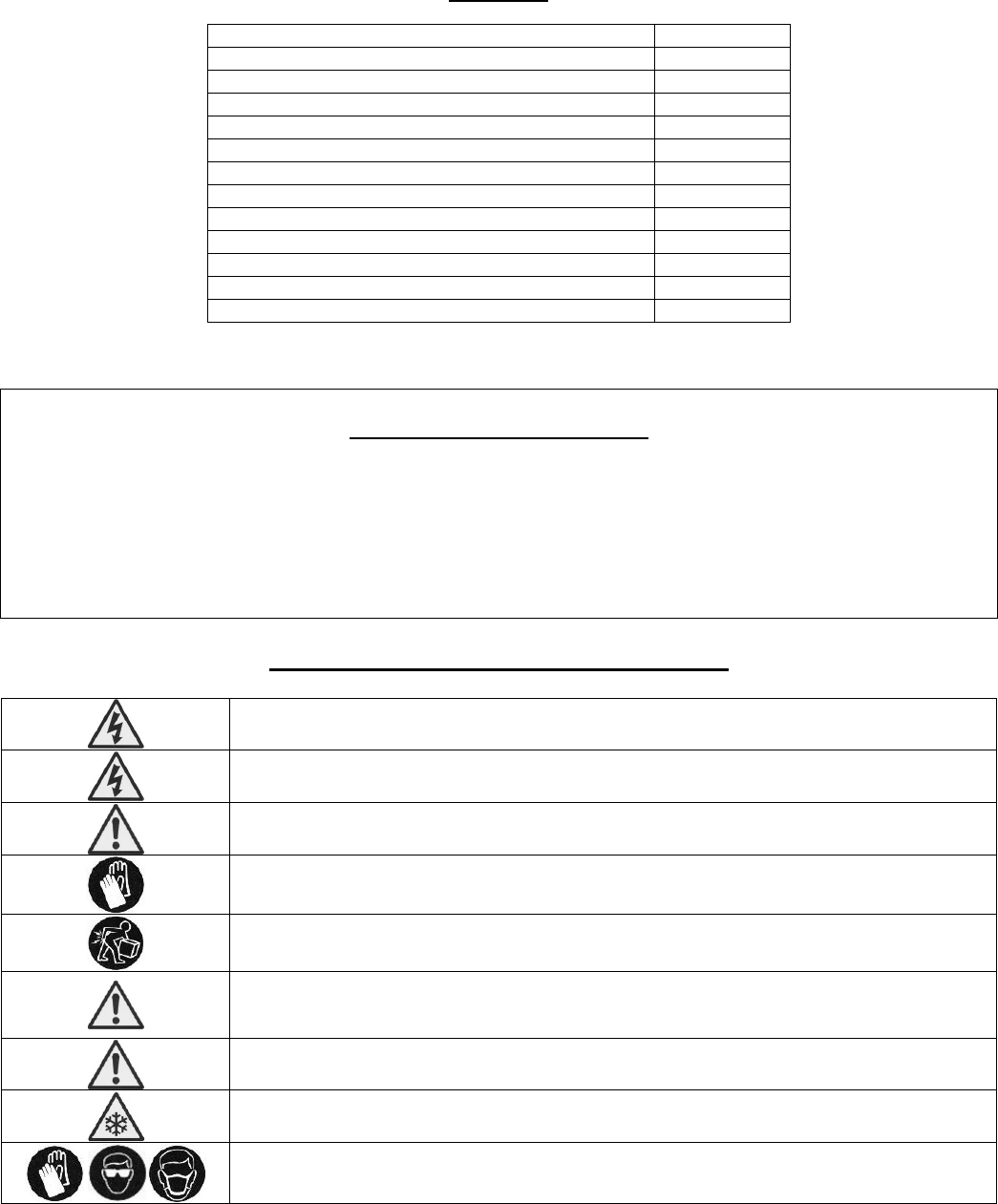
1
Contents
Manual Information & Health & Safety Notes
1
Environmental Management Policy
2
Disposal Requirements
2
Important Controller Change Information
3
Description, Maintenance & Technical Information
3
AT1-5 Controller Information
3 to 4
Alarms and Warnings
4 to 5
Probe Setting, Parameters & Adjustments
5 to 6
AT1-5 Wiring Diagram
7
LDU15 Controller Information
8
Parameters & Electrical Connections
9
LDU15 Wiring Diagram
10
Troubleshooting & Notes
11 to 13
Service Manual Information
The products and all information in this manual are subject to change without prior notice.
We assume by the information given that the person(s) working on these refrigeration units are fully trained and
skilled in all aspects of their workings. Also that they will use the appropriate safety equipment and take or meet
precautions where required.
The service manual does not cover information on every variation of this unit; neither does it cover the installation
or every possible operating or maintenance instruction for the units.
Health & Safety Warnings and Information
Make sure the power supply is turned off before making any electrical repairs.
To minimise shock and fire hazards, please do not plug or unplug the unit with wet
hands.
During maintenance and cleaning, please unplug the unit where required.
Care must be taken when handling or working on the unit as sharp edges may cause
personal injury, we recommend the wearing of suitable PPE.
Ensure the correct moving and lifting procedures are used when relocating a unit.
Do NOT use abrasive cleaning products, only those that are recommended. Never
scour any parts of the refrigerator. Scouring pads or chemicals may cause damage by
scratching or dulling polished surface finishes.
Failure to keep the condenser clean may cause premature failure of the
motor/compressor which will NOT be covered under warranty policy.
Do NOT touch the cold surfaces in the freezer compartment. Particularly when hands
are damp or wet, skin may adhere to these extremely cold surfaces and cause frostbite.
Please ensure the appropriate use of safety aids or Personnel Protective Equipment
(PPE) are used for you own safety.

2
Environmental Management Policy for Service Manuals and Duets.
Product Support and Installation Contractors
Foster Refrigerator recognises that its activities, products and services can have an adverse impact upon the
environment.
The organisation is committed to implementing systems and controls to manage, reduce and eliminate its adverse
environmental impacts wherever possible, and has formulated an Environmental Policy outlining our core aims. A
copy of the Environmental Policy is available to all contractors and suppliers upon request.
The organisation is committed to working with suppliers and contractors where their activities have the potential to
impact upon the environment. To achieve the aims stated in the Environmental Policy we require that all suppliers
and contractors operate in compliance with the law and are committed to best practice in environmental
management.
Product Support and Installation contractors are required to:
1. Ensure that wherever possible waste is removed from the client‟s site, where arrangements are in place all
waste should be returned to Foster Refrigerator‟s premises. In certain circumstances waste may be disposed
of on the client‟s site; if permission is given, if the client has arrangements in place for the type of waste.
2. If arranging for the disposal of your waste, handle, store and dispose of it in such a way as to prevent its
escape into the environment, harm to human health, and to ensure the compliance with the environmental law.
Guidance is available from the Environment Agency on how to comply with the waste management „duty of
care‟.
3. The following waste must be stored of separately from other wastes, as they are hazardous to the environment:
refrigerants, polyurethane foam, and oils.
4. When arranging for disposal of waste, ensure a waste transfer note or consignment note is completed as
appropriate. Ensure that all waste is correctly described on the waste note and include the appropriate six-digit
code from the European Waste Catalogue. Your waste contractor or Foster can provide further information if
necessary.
5. Ensure that all waste is removed by a registered waste carrier, a carrier in possession of a waste management
licence, or a carrier holding an appropriate exemption. Ensure the person receiving the waste at its ultimate
destination is in receipt of a waste management licence or valid exemption.
6. Handle and store refrigerants in such a way as to prevent their emission to atmosphere, and ensure they are
disposed of safely and in accordance with environmental law.
7. Make arrangements to ensure all staff who handle refrigerants do so at a level of competence consistent with
the City Guilds 2078 Handling Refrigerants qualification or equivalent qualification.
8. Ensure all liquid substances are securely stored to prevent leaks and spill, and are not disposed of to storm
drains, foul drain, or surface water to soil.
Disposal Requirements
If not disposed of properly all refrigerators have components that can be harmful to the environment. All old
refrigerators must be disposed of by appropriately registered and licensed waste contractors, and in accordance
with national laws and regulations.

3
IMPORTANT CONTROLLER CHANGE INFORMATION
AS OF FEB 2004 THIS UNIT HAD THE LDU15 (00-555357) CONTROLLER.
AS OF 22ND JULY 2009 THIS HAS NOW BEEN REPLACED WITH AN AT1-5 (00-556223) CONTROLLER.
PLEASE NOTE THAT IF YOU ARE REPLACING THE LDU15 CONTROLLER TO THE NEW AT1-5
CONTROLLER YOU WILL ALSO HAVE TO REPLACE THE AIR PROBE WITH SN4K150P1 (00-556187).
This manual provides information on both controllers.
Meatwell Description
This is a one piece foam shell with a skin evaporator and bottom mount condensing system. The condensing
system uses R134a refrigerant. The cabinet is designed for the storage of frozen products and is top loading.
It is fitted with four 60mm castors, rubber bumpers to each corner and a front smash bar is available as an added
option (but fitted as standard to Burger King units).
Routine Maintenance
In order to keep the unit operating reliably and efficiently periodical cleaning of the condenser is necessary. (The
frequency being determined by site conditions)
This operation is to be carried out with the unit turned OFF.
We advise the use of a soft long haired brush on the outside of the condenser taking care not to damage the fins.
Warning: Condenser fins have sharp edges so care must be taken to avoid injury
Technical Information
Temperature Set Point
-21ºC
Refrigerant
R134A
Refrigerant Charge
180grms
Capillary
4.4mts x 042
Power Supply
230/50/1
Controller Information for models using the LAE AT1-5BS6E-FS1 Controller (00-556223)
Operation Guidelines –
Please note the unit has a rest time of 10mins before start up will begin.
Initial Start Up
Start Up & self Test:
The indication is only displayed during the first three seconds following the mains electrical power being applied to
the unit. During this period the controller performs a self-check.
Once the self-check has been completed will be displayed.
Press and hold for three seconds. The unit will start and the air temperature will be displayed.
Check temperature set point.
To make adjustments to the set point it is necessary to access the parameter and alter SPL and SPH accordingly.
OFF

4
Check set point by pressing the button
To increase set point press + until required temperature is displayed.
To decrease set point press + until required temperature is displayed.
Exit from set up occurs after 10 seconds if no button is pressed.
Manual Defrost
To initiate a manual defrost press and hold .
will be displayed release .
On completion of the defrost will be displayed until the cabinet temperature is achieved and then it will
revert to displaying the normal cabinet temperature.
Set Unit to Standby
Press , in the display will show
This indication is displayed while the unit is not operating but with mains power applied to the unit. This mode may
be used for internal cleaning regimes and short periods when the unit is not required.
For extended periods of inactivity the mains supply should be isolated.
Alarm and Warnings
High Temperature Alarm
Will be displayed.
The alarm will sound but can be silenced by pressing any of the buttons, however it will return after the pre-set
designated period. The unit will return to normal operating temperature and will automatically cancel the alarm.
Possible Causes: The evaporator fan is not working; there is a restricted airflow through the air duct. The
evaporator is iced up or the compressor is not working.
Low Temperature Alarm.
Will be displayed.
The alarm will sound but can be silenced by pressing any of the buttons, however it will return after the pre-set
designated period. The unit will return to normal operating temperature and will automatically cancel the alarm
Possible Causes: Controller is faulty (not switching compressor off). The compressors secondary relay will not de-
energise (low temperature models).
Air Temperature Probe Failure
Will be displayed.
The alarm will sound but can be silenced by pressing any button.
There is no further action that can be taken by the user in this instance. During this period the unit will continue to
operate but have a reduced performance.
Action: Replace Probe.
Information Menu
Pressing and releasing activates the information menu. From this menu you can display the
temperature relating to T1 (air probe), T2 (evaporator probe, if fitted) and T3 (condenser probe, if fitted).
The maximum temperature (THI) and the minimum temperature (TLO) the cabinet has achieved since it was last
re-set.
The total operating time of the condenser (CND) since it was last cleaned, and the keyboard status (LOC).
The information to be displayed can be selected sequentially by pressing repeatedly or scrolling
E1
LO
OFF
REC
dEF
HI

5
through the menu using the or buttons.
Once selected press to display the value.
Exit from the info menu by pressing or it will automatically exit after 6 seconds if no buttons are
pressed.
To reset the temperature settings recorded in THI and TLO and the hours counted in CND, access the info menu
press to display the value plus simultaneously for resetting to be completed.
To check the LOC status scroll through to LOC, press to display status – YES to lock keys. – NO to
leave keys accessible.
NOTE: with the keys locked it is not possible to turn the unit OFF or ON or to check the set point.
Parameter Setting and Adjustment
It is strongly advised that before adjusting any Service Parameters a thorough understanding of the
following instructions should be obtained.
The parameters are accessed by pressing the following keys in succession +
and keeping them pressed for 5 seconds.
After this period the first parameter ‘SCL’ will be displayed.
Press button to pass from one parameter to the next and button to go back.
Press to display the value followed by or to change it.
Exit from set up is by pressing or automatic if no buttons are pressed for 30 seconds.
Probe Identification
The probe fitted to this controller is the 10k NTC type (LAE SN4K15P1, Part number 00-556187) with red letter
identification.
LAE NTC10K Temperature Resistance Table
Temperature(°C)
R-mid (K)
Temperature(°C)
R-mid (K)
Temperature(°C)
R-mid (K)
-25
87.559
-5
33.892
15
14.674
-20
68.237
0
27.219
20
12.081
-15
53.65
5
21.63
25
10
-10
42.506
10
17.926
30
8.315

6
LAE AT1-5BS6E-FS1 Controller Parameter List
Mnem.
Definition
Min
Max
Default
Dim
Setting
SCL
Readout Scale
1ºC ; 2 ºC ; F º
2
flag
2 ºC
SPL
Minimum Set Point (1)
-50
SPH
-5
ºC
-21
SPH
Maximum Set Point (1)
SPL
120
5
ºC
-21
SP
Set Point (1)
SPL
SPH
0
ºC
-21
C-H
Refrigeration / Heating
REF
HEA
REF
flag
REF
HYS
Thermostat Hysteresis
1
100
3
ºK
3
CRT
Minimum Compressor Rest Time
0
30
3
min
10
CT1
Compressor Run with T1 Failure
0
30
3
min
7
CT2
Compressor Stop With T1 Failure
0
30
6
min
3
CSD
Compressor Stop Delay From Door Opening
0
30
1
min
1
DFR
Defrost Frequency / 24h
0
24
3
1/24
0
DLI
Defrost End Temperature
-30
30
6
ºC
15
DTO
Maximum Defrost Duration
1
120
20
min
20
DTY
Defrost Type
OFF; ELE; GAS
ELE
Flag
OFF
DDY
Defrost Display Control
0
60
10
Min
20
ATM
Alarm Threshold Control
NON; ABS; REL
ABS
flag
REL
ALA(’R)
Low Temperature Alarm Threshold
-50 (-120)
+120 (0)
-50
ºC/ ºK
-25
AHA(‘R)
High Temperature Alarm Threshold
-50 (0)
+120 (120)
120
ºC/ ºK
-10
ALR
Low Temperature Alarm Differential
-12
0
ºK
-5
AHR
High Temperature Alarm Differential
0
12
ºK
5
ATD
Alarm Temperature Delay
0
120
30
min
90
ADO
Door Alarm Delay
0
30
5
min
5
ACC
Condenser Cleaning Period
0
52
0
wks
0
SB
Button 0/1 Enabling
YES
NO
YES
flag
YES
DS
Door Switch Enabling
YES
NO
NO
flag
NO
OAU
AUX Output Control
NON;0-1:LGT;FAN;AL1
LGT
flag
NON
INP
SN4 / ST1
SN4; ST1
SN4
flag
SN4
OS1
T1 (air) Probe Offset
-125
125
0
ºK
0
T2
T2 (evaporator) Probe Enabling
YES
NO
NO
flag
NO
OS2
T2 (evaporator) Probe Offset
-125
125
0
ºK
0
TLD
Delay for Minimum / Maximum Temperature Storage
1
30
5
min
5
SIM
Display Slowdown
0
100
0
exp
50
ADR
Unit Peripheral Address
1
255
1
exp
1
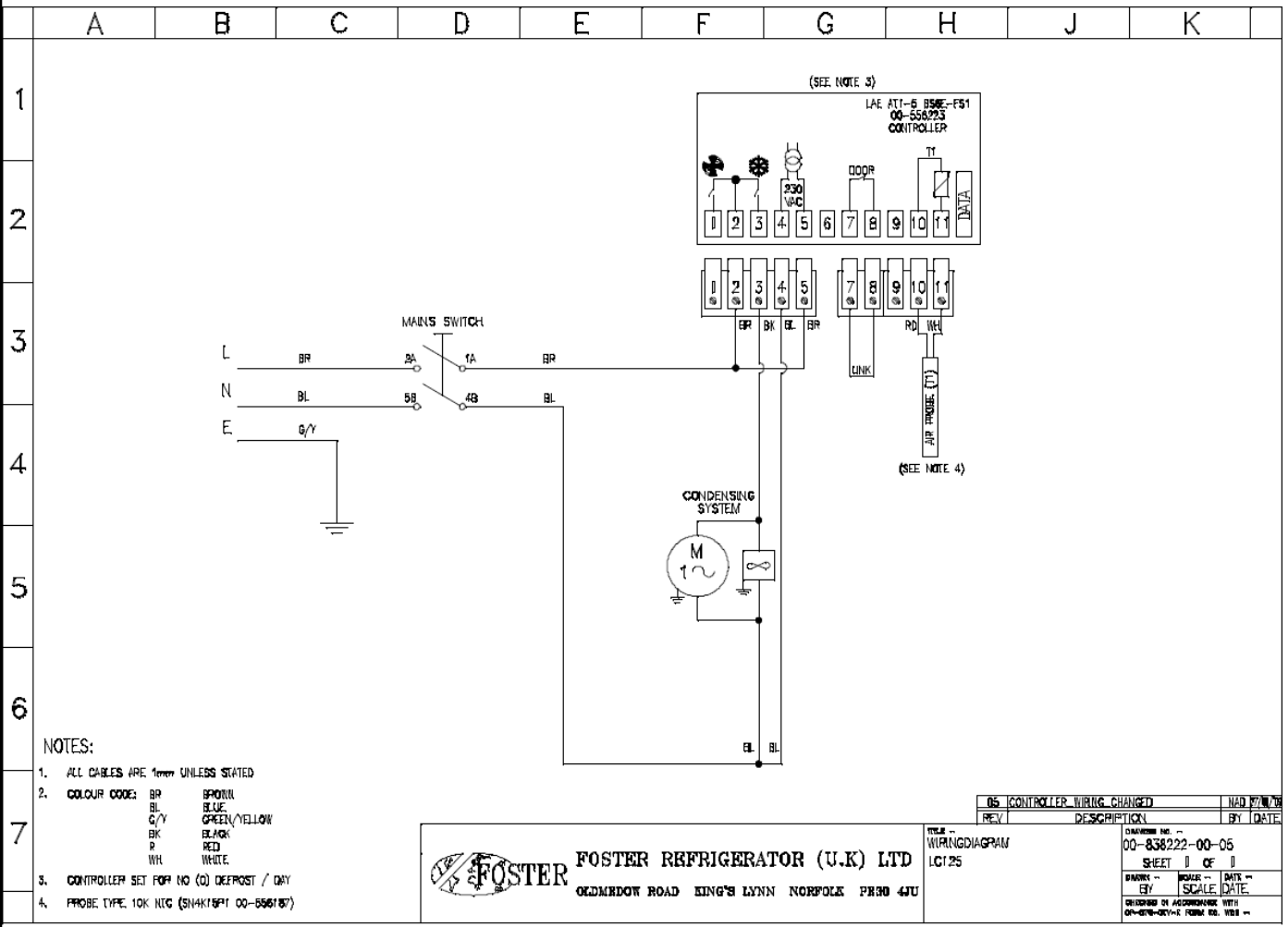
7
LC125 Wiring Diagram with the LAE AT1-5BS6E-FS1 Controller

8
Controller Information for models using the LDU 151E-BG Controller (00-555357)
When the controller is switched on a single line appears on the display for 3 seconds to indicate the autotest
period.
After this period the air temperature measured by the T1 probe is displayed.
It is strongly advised that before adjusting any Service Parameters a thorough understanding of the
following instructions should be obtained.
LDU 15 Controller
Check temperature set point.
Check set point by pressing the “set” button
To increase set point press “set” +
To decrease set point press “set” +
Factory Temperature Set Point -21°C.
Exit from set up occurs after 10 seconds if no button is pressed.
Manual Defrost.
To initiate a manual defrost press buttons and simultaneously.
Controller Set Up.
The parameters are accessed by pressing the following keys in succession + “set” + and keeping
them pressed for 3 seconds.
Access to the parameters has been achieved with the first parameter SCL being displayed.
To pass from one parameter to the next press either the or key.
To display the value press. “set”
To change the value press “set” + to increase, or “set” + to decrease.
Exit from set up by pressing “aux” or is automatic after 30 seconds if no buttons are pressed.
Alarms and Warnings
HI
High Temperature Alarm
LO
Low Temperature Alarm
E1
T1 Probe Failure
DF
Defrosting in Progress
CLN
Condenser
aux
lae
set
aux

9
Parameters for Cabinets with the LDU15 1E-B Controller
Display
Parameter
LDU151E-B
Default Values
LC 125
SCL
Readout Scale
2°C
2°C
SPL
Minimum Temperature Set Point
05
-25
SPH
Maximum Temperature Set Point
01
-15
SP
Effective Temperature Set Point
03
-21
HYS
Hysteresis
3
+3
CRT
Compressor Rest Time (minutes)
10
0
CDC
Compressor Regulation with T1 Fail
20
7
DFR
Defrosting Frequency (/24 hours)
4
0
DTO
Defrosting Duration (minutes)
20
20
DDY
Defrost Display Control
1
1
ATL
Low Alarm Differential
-5
-10
ATH
High Alarm Differential
5
10
ATD
Temperature Alarm Delay (minutes)
60
90
ACC
Condenser Clean Interval
05
0
OAU
Auxiliary Output Mode of Operation
30
NON
BAU
Auxiliary Button Mode of Operation
05
NON
OS1
T1 Offset
00
00
SIM
Display Slowdown
00
00
ADR
Address
01
01
LDU 151E-BG Electrical Connections
PWR
1 2 3 4 5 6 7 8 9 10
11
AUX
T1
DATA

10
Wiring Diagram for Models Using the LDU15 Controller

11
Troubleshooting
Problem
Possible Cause
Solution
Compressor will not start
No voltage in socket
Use voltmeter to check
Electrical conductor or wires may be
cut
Use ohmmeter to check for
continuity
Defective electrical component:
thermostat, relay, thermal protector
etc
Replace defective component
Compressor motor has a winding
open or shorted
Measure ohmic resistance of main
and auxiliary winding using
ohmmeter. Compare with correct
values
Compressor stuck
Change compressor
Temperature control contacts are
open
Repair or replace the contacts
Incorrect wiring
Check wiring diagram and correct
Fuse blown or circuit breaker
tripped.
Replace fuse or reset circuit breaker
Power cord unplugged
Plug in power cord.
Controller set too high
Set controller to lower temperature.
Cabinet in defrost cycle
Wait for defrost cycle to finish
The temperature is too cold
Controller is set at a very cold
position
Set to warmer position and check if
the compressor stops according to
controllers operating range.
Controller does not disconnect the
condensing unit
Check the insulation of the
thermostat. If problem persists,
change the thermostat
Control contacts are stuck closed
Change the control. Check
amperage load
Defective or incorrect temperature
control
Determine correct control and
replace.
The temperature is not cold
enough
Controller is set at a very warm
position
Adjust to colder setting
Condenser is dirty
Clean condenser
The refrigerator has been placed at
an inadequate location
The unit must not be near stoves,
walls that are exposed to the sun, or
places that lack sufficient air flow.
Compressor is inefficient or there is
a high pressure due to the air in the
system
If there is air in the system, purge
and recharge
Iced up evaporator coil
Check temperature control,
refrigerant charge, and defrost
mechanism. Remove all ice
manually and start over.
Restriction in system
Locate exact point of restriction and
correct
The refrigerator has been used
improperly
The shelves must never be covered
with any type of plastic or other
material that will block the
circulation of cold air within the
refrigerator.
Too many door openings
Advise user to decrease if possible
Excessive heat load placed in
cabinet
Advise user not to put in products
that are too hot.

12
The refrigerator has been
overcharged with the refrigerant gas
Check to see if condensation or ice
crystals have formed on the suction
line. If so, charge with the correct
amount of gas.
The refrigerant gas is leaking
Find the location of gas leak in order
to seal and replace the defective
component. Change the drier.
Perform a good vacuum and
recharge unit.
The evaporator and/or condenser
fans are not working
Check electrical connections and
make sure that the fan blade isn‟t
stuck. Replace the fan motor if it
doesn‟t work.
Blocking air flow
Re-arrange product to allow for
proper air flow. Make sure there is
at least four inches of clearance
from evaporator.
Fuse blown or circuit breaker tripped
Replace fuse or reset circuit
breaker.
Electrical Shocks
Wires or electrical components are
in direct contact with metallic parts.
Check for appropriate insulation on
the connections of each component.
Noise
The refrigerator is not properly
levelled
Check if the noise goes away after
you level the refrigerator
The condenser is not fastened
correctly. Copper tubing is in contact
with metal
While the compressor is working,
check to see if metal parts are in
contact with one another and/or if
the screws that fasten the
condenser are tightened.
The evaporator and/or condenser
fans are loose
Check if the fans are securely
fastened. Also, check if the fan
blades are loose, broken or
crooked. If so, change the faulty
blade.
Compressor has an internal noise
If the noise persists after all other
measures have been taken, it may
be originating from the compressor.
Loose part(s)
Locate and tighten loose part(s)
Extreme condensation inside the
refrigerator
Controller is set at a very cold
position
Set the controller to a warmer
position & check to see if
compressor stops as should.
The outside environment‟s relative
humidity is very high (over 75%)
This type of occurrence is caused
by local climatic conditions and not
by the refrigeration unit.
The refrigerator door wont shut
completely
Check the door and/or the magnetic
gasket. Adjust the door hinges if
needed; replace the gasket if
broken.
The refrigerator had been placed at
an inadequate location
The unit must not be near sources
that produce too much heat.
No illumination (Glass door
models only)
The light switch is “off” position
Press the light switch to “on”
position
False contact on the light switch, the
fluorescent tube, or the ballast
Inspect all connections
Light switch, ballast and/or
fluorescent tube are damaged
Replace the damaged component.

13
Condensing unit runs for
long periods of time
Excessive amount of warm product
placed in cabinet
Advise user to leave adequate time
for products to cool down
Prolonged door opening or door ajar
Advise user to ensure doors are
closed when not in use and to avoid
opening doors for long periods of
time.
Door gasket(s) not sealing properly
Ensure gaskets are snapped in
completely. Remove gasket and
wash with soap and water. Check
condition of gasket & replace if
necessary
Dirty condenser coil
Clean condenser coil
Evaporator coil iced over
Unplug unit and allow coil to defrost.
Make sure thermostat is not set too
cold. Ensure that door gasket(s) are
sealing properly. Select manual
defrost and ensure system works.
Notes

14
Foster European Operations
France
Foster Refrigerator France SA
Tel: (33) 01 34 30 22 22. Fax: (33) 01 30 37 68 74.
Email: commercial@fosterfrance.com
Germany
Foster Refrigerator Gmbh,
Tel: (49) 781 990 7840. Fax (49) 781 990 7844.
Email: info@foster-gmbh.de
Foster Refrigerator
Oldmedow Road
Kings Lynn
Norfolk
PE30 4JU
Tel: 0843 216 8833
Fax: 0843 216 4707
Website: www.fosterrefrigerator.co.uk
Email: support@foster-uk.com
a Division of „ITW (UK) Ltd‟
LCU15/LDU15 & ATI-5/SM 10/10