PerformaCv Performa Cv962 Control User Manual
User Manual: Performa Cv962 Control User Manual
Open the PDF directly: View PDF .
Page Count: 48
- Table of Contents
- 1.0 Performa Cv System
- 2.0 Performa Cv 962 Control
- 3.0 Performa Cv Filter Valve and Controls, 962F, 962FTC, 942F
- 4.0 Performa Cv Performance Charts and Graphs
- 5.0 Performa Cv Service and Troubleshooting
- 6.0 Performa Cv Parts

Softener/Filter
Water Control System
Installation, Operation and Maintenance Manual
Autotrol Performa Cv
®™
This system installed by:

2
Table of Contents
1.0 Performa Cv System . . . . . . . . . . . . . . . . . . . . . . . . . . . . . . . . . . . . . . . . . . . . . . . . . . . . .3
1.1 Specifications . . . . . . . . . . . . . . . . . . . . . . . . . . . . . . . . . . . . . . . . . . . . . . . . . . . . . . . . . . . . . .3
1.2 Installation . . . . . . . . . . . . . . . . . . . . . . . . . . . . . . . . . . . . . . . . . . . . . . . . . . . . . . . . . . . . . . . . .5
1.3 Placing Performa Cv Softener/Filter into Operation . . . . . . . . . . . . . . . . . . . . . . . . . . . . . . . . .7
1.4 Disinfection of Water Conditioners . . . . . . . . . . . . . . . . . . . . . . . . . . . . . . . . . . . . . . . . . . . . . .8
2.0 Performa Cv 962 Control. . . . . . . . . . . . . . . . . . . . . . . . . . . . . . . . . . . . . . . . . . . . . . . . . .9
2.1 Introduction to the Performa CV Softener and Filter Systems . . . . . . . . . . . . . . . . . . . . . . . . .9
2.2 Programming and Application . . . . . . . . . . . . . . . . . . . . . . . . . . . . . . . . . . . . . . . . . . . . . . . . .10
2.3 Softener Programming Tables . . . . . . . . . . . . . . . . . . . . . . . . . . . . . . . . . . . . . . . . . . . . . . . . .16
3.0 Performa Cv Filter Valve and Controls, 962F, 962FTC, 942F. . . . . . . . . . . . . . . . . . . . . .18
3.1 Programming and Application . . . . . . . . . . . . . . . . . . . . . . . . . . . . . . . . . . . . . . . . . . . . . . . . .18
3.2 Explanation of Parameter Values for the 962 Single and Parallel Tank Controls . . . . . . . . . .24
4.0 Performa Cv Performance Charts and Graphs . . . . . . . . . . . . . . . . . . . . . . . . . . . . . . . .27
4.1 General Specification . . . . . . . . . . . . . . . . . . . . . . . . . . . . . . . . . . . . . . . . . . . . . . . . . . . . . . .27
4.2 Injector Curves. . . . . . . . . . . . . . . . . . . . . . . . . . . . . . . . . . . . . . . . . . . . . . . . . . . . . . . . . . . . .28
4.3 Performa Cv Softener Performance Data . . . . . . . . . . . . . . . . . . . . . . . . . . . . . . . . . . . . . . . .31
5.0 Performa Cv Service and Troubleshooting . . . . . . . . . . . . . . . . . . . . . . . . . . . . . . . . . . .34
5.1 Historical Data . . . . . . . . . . . . . . . . . . . . . . . . . . . . . . . . . . . . . . . . . . . . . . . . . . . . . . . . . . . . .34
5.2 Preventative Maintenance . . . . . . . . . . . . . . . . . . . . . . . . . . . . . . . . . . . . . . . . . . . . . . . . . . . .35
5.3 Removing the Valve Assembly for Servicing . . . . . . . . . . . . . . . . . . . . . . . . . . . . . . . . . . . . . .36
5.4 Removing the Control . . . . . . . . . . . . . . . . . . . . . . . . . . . . . . . . . . . . . . . . . . . . . . . . . . . . . . .36
5.5 Identification of Control Valving. . . . . . . . . . . . . . . . . . . . . . . . . . . . . . . . . . . . . . . . . . . . . . . .38
5.6 Valve Disc Principle of Operation . . . . . . . . . . . . . . . . . . . . . . . . . . . . . . . . . . . . . . . . . . . . . .38
5.7 Performa Cv Softener Flow Diagrams . . . . . . . . . . . . . . . . . . . . . . . . . . . . . . . . . . . . . . . . . . .38
5.8 Performa Cv Filter Flow Diagrams. . . . . . . . . . . . . . . . . . . . . . . . . . . . . . . . . . . . . . . . . . . . . .40
5.9 Troubleshooting . . . . . . . . . . . . . . . . . . . . . . . . . . . . . . . . . . . . . . . . . . . . . . . . . . . . . . . . . . . .41
6.0 Performa Cv Parts . . . . . . . . . . . . . . . . . . . . . . . . . . . . . . . . . . . . . . . . . . . . . . . . . . . . . .44
6.1 Valve Component Exploded View . . . . . . . . . . . . . . . . . . . . . . . . . . . . . . . . . . . . . . . . . . . . . .44
6.2 Parts List . . . . . . . . . . . . . . . . . . . . . . . . . . . . . . . . . . . . . . . . . . . . . . . . . . . . . . . . . . . . . . . . .45
6.3 Performa Cv Controls . . . . . . . . . . . . . . . . . . . . . . . . . . . . . . . . . . . . . . . . . . . . . . . . . . . . . . .46

3
1.0 Performa Cv System
1.1 Specifications
1.1.1 Performa Cv Softener
Flow Rates (Valve Only)
Service @ 15 psi (1.03 bar) . . . . . . . . . . . . . . . . . . . . . . . . . . . . . . . . . . . . . . . . . . . . . . . . . . . . . . 25.0 gpm (5.7 m3/h)
Backwash (Softener) @ 25 psi (1.72 bar) drop . . . . . . . . . . . . . . . . . . . . . . . . . . . . . . . . . . . . . . . 20.0 gpm (4.5 m3/h)
Service . . . . . . . . . . . . . . . . . . . . . . . . . . . . . . . . . . . . . . . . . . . . . . . . . . . . . . . . . . . . . . . . . . . . . Cv = 6.5 (Kv = 5.58)
Backwash Softener. . . . . . . . . . . . . . . . . . . . . . . . . . . . . . . . . . . . . . . . . . . . . . . . . . . . . . . . . . . . Cv = 4.0 (Kv = 3.46)
Control Configurations
962 Microprocessor Demand System and 962 Electronic Timeclock
Backwash . . . . . . . . . . . . . . . . . . . . . . . . . . . . . . . . . . . . . . . . . . . . . . . . . . . . . . . . . . . . . . . . . . . . . . . 4 to 60 minutes
Brine . . . . . . . . . . . . . . . . . . . . . . . . . . . . . . . . . . . . . . . . . . . . . . . . . . . . . . . . . . . . . . . . . . . . Electronically calculated
Slow rinse . . . . . . . . . . . . . . . . . . . . . . . . . . . . . . . . . . . . . . . . . . . . . . . . . . . . . . . . . . . . . . . . . . . . . .7 to 125 minutes
Fast rinse . . . . . . . . . . . . . . . . . . . . . . . . . . . . . . . . . . . . . . . . . . . . . . . . . . . . . . . . . . . . . . . . . . . . . . . 2 to 19 minutes
External Brine Valve Required - Timed Fill
Valve Connections/Dimensions
Tank Thread . . . . . . . . . . . . . . . . . . . . . . . . . . . . . . . . . . . . . . . . . . . . . . . . . . . . . . . . . . . . . . . .2-1/2 inches - 8, male
Inlet/Outlet . . . . . . . . . . . . . . . . . . . . . . . . . . . . . . . . . . . . . . . . . . . . . . . . . . . . . . . . 1-3/4 inches - 12 UNC-2A, male
Drain Line . . . . . . . . . . . . . . . . . . . . . . . . . . . . . . . . . . . . . . . . . . . . . . . . . . . . . . . . . . . . . . . . . . . . 3/4-inch NPT, male
Brine Line . . . . . . . . . . . . . . . . . . . . . . . . . . . . . . . . . . . . . . . . . . . . . . . . . . . . . . . . . . . . . . . . . . . . 3/8-inch NPT, male
Distributor Tube O.D. . . . . . . . . . . . . . . . . . . . . . . . . . . . . . . . . . . . . . . . . . . . . . . . . . . . . . . . . . 1.050 inches (27 mm)
Distributor Tube Length . . . . . . . . . . . . . . . . . . . . . . . . . . . . . . 1/2 ± 1/2 inches (13 mm ± 13 mm) above top of tank
Operating
Valve Body . . . . . . . . . . . . . . . . . . . . . . . . . . . . . . . . . . . . . . . . . . . . . . . . . . . . . . . . . . . . . . . . . . . Glass-Filled Noryl*
Rubber Components . . . . . . . . . . . . . . . . . . . . . . . . . . . . . . . . . . . . . . . . . . . . . . . . . . . .Compounded for cold water
Weight (Valve with Control) . . . . . . . . . . . . . . . . . . . . . . . . . . . . . . . . . . . . . . . . . . . . . . . . . . . . . . . . . . 4.5 lbs (2.0 kg)
Transformer Output. . . . . . . . . . . . . . . . . . . . . . . . . . . . . . . . . . . . . . . . . . . . . . . . . . . . . . . . . 12 VAC 400 mA (4.6 vA)
Transformer Input . . . . . . . . . . . . . . . . . . . . . . . . . . . . . . . . . . . . . . . . . . . . . . . . . . . . 115V 50/60 Hz, 230V 50/60 Hz
100 V 50/60 Hz
Operating Pressure. . . . . . . . . . . . . . . . . . . . . . . . . . . . . . . . . . . . . . . . . . . . . . . . . . . .20 to 120 psi (1.37 to 8.27 bar)
Canada: 20 to 100 psi (1.37 to 6.89 bar)
Water Temperature . . . . . . . . . . . . . . . . . . . . . . . . . . . . . . . . . . . . . . . . . . . . . . . . . . . . . . . . . 35° to 100°F (2° to 38°C)
Options
Bypass Valve, Model 1265 . . . . . . . . . . . . . . . . . . . . . . . . . . . . . . . . . . . . . . . . . . . . . 1-3/4 inches - 12 UNC-2A male
Bypass Fitting Kits:
Copper, Sweat Tube Adapter . . . . . . . . . . . . . . . . . . . . . . . . . . . . . . . . 1-1/4-inch, 1-inch, 3/4-inch, 28-mm, 22-mm
CPVC, Solvent Weld Tube Adapter. . . . . . . . . . . . . . . . . . . . . . . . . . . . . . . . . . . . . . . . . . . . .1-inch, 3/4-inch, 25-mm
Plastic NPT or BSPT Pipe Adapter. . . . . . . . . . . . . . . . . . . . . . . . . . . . . . . . . . . . . . . . . . .1-inch male, 3/4-inch male
Brass NPT or BSPT Pipe Adapter . . . . . . . . . . . . . . . . . . . . . . . . . . . . . . . . . . . . . . . . . . .1-inch male, 3/4-inch male
Flow Meter 962 Control . . . . . . . . . . . . . . . . . . . . . . . . . . . . . . . . . . . . . . . . . . . . . . . . . . . . . 1-inch Autotrol Turbine
*Noryl is a trademark of the General Electric Company.

4
1.1.2 Performa Cv Filter Specifications
Flow Rates (Valve Only)
Service @ 15 psi (1.03 bar) drop . . . . . . . . . . . . . . . . . . . . . . . . . . . . . . . . . . . . . . . . . . . . . . . . . 25.0 gpm (5.7 m3/h)
Backwash (Filter) @ 25 psi (1.72 bar) drop. . . . . . . . . . . . . . . . . . . . . . . . . . . . . . . . . . . . . . . . . . 25.0 gpm (4.5 m3/h)
Service . . . . . . . . . . . . . . . . . . . . . . . . . . . . . . . . . . . . . . . . . . . . . . . . . . . . . . . . . . . . . . . . . . . . . .Cv = 6.5 (Kv = 5.58)
Backwash Filter . . . . . . . . . . . . . . . . . . . . . . . . . . . . . . . . . . . . . . . . . . . . . . . . . . . . . . . . . . . . . . .Cv = 5.0 (Kv = 5.78)
Control Operation
942F Mechanical Clock Timer - 7 Day or 12 Day
Backwash. . . . . . . . . . . . . . . . . . . . . . . . . . . . . . . . . . . . . . . . . . . . . . . . . . . . . . . . . . . . . . . . . . . . . . . . . 8-30 minutes
Fixed Fast Rinse. . . . . . . . . . . . . . . . . . . . . . . . . . . . . . . . . . . . . . . . . . . . . . . . . . . . . . . . . . . . . . . . . . . . . . .9 minutes
962F Microprocessor Demand
Backwash. . . . . . . . . . . . . . . . . . . . . . . . . . . . . . . . . . . . . . . . . . . . . . . . . . . . . . . . . . . . . . . . . . . . . . . 4 to 60 minutes
Fast Rinse. . . . . . . . . . . . . . . . . . . . . . . . . . . . . . . . . . . . . . . . . . . . . . . . . . . . . . . . . . . . . . . . . . . . . . . 2 to 19 minutes
962 FTC Electronic Time Clock
Backwash. . . . . . . . . . . . . . . . . . . . . . . . . . . . . . . . . . . . . . . . . . . . . . . . . . . . . . . . . . . . . . . . . . . . . . . 4 to 60 minutes
Fast Rinse. . . . . . . . . . . . . . . . . . . . . . . . . . . . . . . . . . . . . . . . . . . . . . . . . . . . . . . . . . . . . . . . . . . . . . . 2 to 19 minutes
Interval Regeneration. . . . . . . . . . . . . . . . . . . . . . . . . . . . . . . . . . . . . . . . . . . . . . . . . Day of the Week Regeneration
Valve Connections/Dimensions
Tank Thread . . . . . . . . . . . . . . . . . . . . . . . . . . . . . . . . . . . . . . . . . . . . . . . . . . . . . . . . . . . . . . . . 2-1/2 inches - 8, male
Inlet/Outlet . . . . . . . . . . . . . . . . . . . . . . . . . . . . . . . . . . . . . . . . . . . . . . . . . . . . . . . . .1-3/4 inches - 12 UNC-2A, male
Drain Line . . . . . . . . . . . . . . . . . . . . . . . . . . . . . . . . . . . . . . . . . . . . . . . . . . . . . . . . . . . . . . . . . . . . 3/4-inch NPT, male
Brine Line . . . . . . . . . . . . . . . . . . . . . . . . . . . . . . . . . . . . . . . . . . . . . . . . . . . . . . . . . . . . . . . . . . . . 3/8-inch NPT, male
Distributor Tube O.D. . . . . . . . . . . . . . . . . . . . . . . . . . . . . . . . . . . . . . . . . . . . . . . . . . . . . . . . . . 1.050 inches (27 mm)
Distributor Tube Length . . . . . . . . . . . . . . . . . . . . . . . . . . . . . . 1/2 ± 1/2 inches (13 mm ± 13 mm) above top of tank
Operating
Valve Body . . . . . . . . . . . . . . . . . . . . . . . . . . . . . . . . . . . . . . . . . . . . . . . . . . . . . . . . . . . . . . . . . . . . . Glass-filled Noryl
Rubber Components . . . . . . . . . . . . . . . . . . . . . . . . . . . . . . . . . . . . . . . . . . . . . . . . . . . . Compounded for cold water
Weight (Valve with Control). . . . . . . . . . . . . . . . . . . . . . . . . . . . . . . . . . . . . . . . . . . . . . . . . . . . . . . . . . .4.5 lbs (2.0 kg)
Transformer Output . . . . . . . . . . . . . . . . . . . . . . . . . . . . . . . . . . . . . . . . . . . . . . . . . . . . . . . . . 12VAC 400 mA (4.6 vA)
Transformer Input . . . . . . . . . . . . . . . . . . . . . . . . . . . . . . . . . . . . . . . . . . . . . . . . . . . . .115V 50/60 Hz, 230V 50/60 Hz
100V 50/60 Hz
Operating Pressure . . . . . . . . . . . . . . . . . . . . . . . . . . . . . . . . . . . . . . . . . . . . . . . . . . . 10 to 120 psi (1.37 to 8.27 bar)
Canada: 20 to 100 psi (1.37 to 6.89 bar)
Water Temperature . . . . . . . . . . . . . . . . . . . . . . . . . . . . . . . . . . . . . . . . . . . . . . . . . . . . . . . . .34° to 100°F (1° to 38°C)
Options
Bypass Valve, Model 1265 . . . . . . . . . . . . . . . . . . . . . . . . . . . . . . . . . . . . . . . . . . . . 1-3/4 inches - 12 UNC - 2A male
Bypass Inlet/Outlet Fitting Kits:
Copper, Sweat Tube Adapter . . . . . . . . . . . . . . . . . . . . . . . . . . . . . . . . . 1-1/4-inch, 1-inch, 3/4-inch, 28-mm, 22-mm
CPVC, Solvent Weld Tube Adapter . . . . . . . . . . . . . . . . . . . . . . . . . . . . . . . . . . . . . . . . . . . . 1-inch, 3/4-inch, 25-mm
Plastic NPT or BSPT Pipe Adapter . . . . . . . . . . . . . . . . . . . . . . . . . . . . . . . . . . . . . . . . . . 1-inch male, 3/4-inch male
Brass NPT or BSPT Pipe Adapter . . . . . . . . . . . . . . . . . . . . . . . . . . . . . . . . . . . . . . . . . . . 1-inch male, 3/4-inch male
Flow Meter 962 Control . . . . . . . . . . . . . . . . . . . . . . . . . . . . . . . . . . . . . . . . . . . . . . . . . . . . 1-inch Autotrol Turbine
See Section 4.1 for specification drawings.

5
1.2 Installation
All plumbing and electrical connections must conform
to local codes.
Inspect unit carefully for carrier shortage or shipping
damage.
Location Selection
1. The distance between the unit and a drain should be
as short as possible.
2. If it is likely that supplementary water treatment
equipment will be required, make certain adequate
additional space is available.
3. Since salt must be added periodically to the brine
tank, the location should be easily accessible.
4. Do not install any unit closer to a water heater than
a total run of 10 feet (3 m) of piping between the
outlet of the conditioner and the inlet to the heater.
Water heaters can sometimes overheat to the
extent they will transmit heat back down the cold
pipe into the unit control valve.
Hot water can severely damage the conditioner. A
10-foot (3-m) total pipe run, including bends,
elbows, etc., is a reasonable distance to help
prevent this possibility. A positive way to prevent
hot water flowing from heat source to the
conditioner, in the event of a negative pressure
situation, is to install a check valve in the soft
water piping from the conditioner. If a check valve
is installed, make certain the water heating unit
is equipped with a properly rated temperature
and pressure safety relief valve. Also, be
certain that local codes are not violated.
5. Do not locate unit where it or its connections
(including the drain and overflow lines) will ever be
subjected to room temperatures under 34oF (1oC)
or over 120oF (49oC).
6. Do not install unit near acid or acid fumes.
7. The use of resin cleaners in an unvented enclosure
is not recommended.
Water Line Connection
The installation of a bypass valve system is
recommended to provide for occasions when the water
conditioner must be bypassed for hard water or for
servicing.
The most common bypass systems are the Autotrol
Series 1265 bypass valve (Figure 1.1) and plumbed-in
globe valves (Figure 1.2). Though both are similar in
function, the Autotrol Series 1265 bypass offers
simplicity and ease of operation.
Figure 1.1 - Autotrol Series 1265 Bypass Valve
Figure 1.2 - Typical Globe Valve Bypass System
Drain Line Connection
Note: Standard commercial practices are expressed
here. Local codes may require changes to the following
suggestions.
1. Ideally located, the unit will be above and not more
than 20 feet (6.1 m) from the drain. For such
installations, using an appropriate adapter fitting,
connect 1/2-inch (1.3-cm) plastic tubing to the drain
line connection of the control valve.
2. If the backwash flow rate exceeds 5 gpm
(22.7 Lpm) or if the unit is located more than 20 feet
(6.1 m) from drain, use 3/4-inch (1.9-cm) tubing for
runs up to 40 feet (12.2 m). Also, purchase
appropriate fitting to connect the 3/4-inch tubing to
the 3/4-inch NPT drain connection.
3. If the unit is located where the drain line must be
elevated, you may elevate the line up to 6 feet
(1.8 m) providing the run does not exceed
15 feet (4.6 m) and water pressure at conditioner is
not less than 40 psi (2.76 bar). You may elevate an
additional 2 feet (61 cm) for each additional
10 psi (0.69 bar).
B
Y
P
A
S
S
B
Y
P
A
S
S
B
Y
P
A
S
S
B
Y
P
A
S
S
Not in Bypass In Bypass
Water
Conditioner
In Out
Water
Conditioner
In Out
Water Water
Not in Bypass In Bypass
Water
Conditioner
Water
Conditioner

6
4. Where the drain line is elevated but empties into a
drain below the level of the control valve, form a
7-inch (18-cm) loop at the far end of the line so that
the bottom of the loop is level with the drain line
connection. This will provide an adequate siphon
trap.
5. Where the drain empties into an overhead sewer
line, a sink-type trap must be used.
IMPORTANT: Never insert drain line into a drain, sewer
line or trap. Always allow an air gap between the drain
line and the wastewater to prevent the possibility of
sewage being back-siphoned into the conditioner.
Figure 1.3
Note: Standard commercial practices have been
expressed here. Local codes may require changes to
these suggestions.
Brine Line Connection
It will be necessary to install the brine line for a
Performa Cv softener to the brine fitting on the valve
(3/8-inch NPT).
Be sure all fittings and connections are tight.
Overflow Line Connection
In the absence of a safety overflow and in the event of
a malfunction, the BRINE TANK OVERFLOW will direct
“overflow” to the drain instead of spilling on the floor
where it could cause considerable damage. This fitting
should be on the side of the cabinet or brine tank.
To connect overflow, locate hole on side of brine tank.
Insert overflow fitting (not supplied) into tank and
tighten with plastic thumb nut and gasket as shown
(Figure 1.4). Attach length of 1/2-inch (1.3-cm) I.D.
tubing (not supplied) to fitting and run to drain. Do not
elevate overflow line higher than 3 inches (7.6 cm)
below bottom of overflow fitting. Do not tie into drain
line of control unit. Overflow line must be a direct,
separate line from overflow fitting to drain, sewer or
tub. Allow an air gap as per drain line instructions
(Figure 1.3).
Figure 1.4
Battery Back-Up
All 962 family controls are battery backup capable. A
9-volt rechargeable battery is available from Osmonics,
P/N 1075768. The battery is a VARTA, TYPE V7/8H
(AccuPlus Nickle Hydride Ni-mh 9v 150 mAH, No.
5522). A standard non-rechargeable battery is an
option for backup but needs to be replaced
periodically, Figure 1.5.
Figure 1.5
Right Way
Brine Tank
Overflow Fitting
Installed
Connect 1/2-inch (1.3-cm)
Tubing or Hose and Run
to Drain
Battery

7
1.3 Placing Performa Cv Softener/Filter
into Operation
After all previous steps have been completed, the unit
is ready to be placed into operation. Follow these steps
carefully.
1. Remove control valve cover by first depressing the
plastic clips from the front of the cover. Pull front of
cover up.
Note: The following steps will require turning the
cycle indicator to various positions. Manually
rotate the camshaft COUNTERCLOCKWISE only
until cycle indicator points to desired position.
(See manual regeneration sections for each
control’s manual operation.)
2. Rotate cycle indicator COUNTERCLOCKWISE
until it points directly to the word BACKWASH.
3. Fill media tank with water.
a. With water supply off, place the bypass valve(s)
into the “service” position.
b. Open water supply valve very slowly to
approximately the 1/4 open position.
IMPORTANT: If opened too rapidly or too far, media
may be lost. In the 1/4 open position, you should hear
air escaping slowly from the drain line.
Softener
a. When all of the air has been purged from the
tank (water begins to flow steadily from the
drain), open the main supply valve all the way.
b. Allow water to run to drain until clear.
c. Turn off water supply and let the unit stand for
about five minutes. This will allow all trapped air
to escape from the tank.
4. Add water to brine tank (initial fill).
With a bucket or hose, add approximately
4 gallons (15 liters) of water to brine tank. If the
tank has a salt platform above the bottom of the
tank, add water until the level is approximately
1 inch (25 mm) above the platform.
5. Place the conditioner into operation.
a. With the water supply valve completely open,
carefully advance the cycle indicator
COUNTERCLOCKWISE to the center of the
BRINE REFILL position. Hold at this position
until water starts to flow through the brine line
into the brine tank. Do not run for more than
two minutes.
b. Advance the cycle indicator
COUNTERCLOCKWISE until it points to the
center of the BRINE/SLOW RINSE position.
c. With the conditioner in this position, check to
see if water is being drawn from the brine tank.
The water level in the brine tank will recede very
slowly. Observe water level for at least three
minutes. If the water level does not recede, or if
it goes up, reference the Troubleshooting
section.
d. Advance the cycle indicator
COUNTERCLOCKWISE to the
REGENERATION COMPLETE position and
run water from a nearby faucet until the water is
clear and soft.
Filter
All filter medias except carbon:
a. After the air has been purged from the tank
(water begins to flow steadily from the drain)
open the main supply all the way. Backwash
media for a minimum of 15 minutes or longer if
necessary. Water running to the drain should be
clear.
Carbon media should be allowed to soak for a
minimum of 12 hours to allow air bubbles to
escape prior to backwashing.
b. After the backwash is complete plug in control
and allow it to advance to BACKWASH
COMPLETE.
Electrical Connection
100 VAC, 115 VAC, and 230 VAC units: Remove twist
tie from the power cord and extend cord to its full
length. Make sure power source matches the rating
printed on the control. Be certain a wall switch does not
control the outlet.
12 VAC: Connect the plug of the transformer (supplied)
secondary cable to the mating socket at the rear or
bottom of the timer housing. Be certain the transformer
is secure and is plugged into a power source of correct
voltage that is not controlled by a wall switch.

8
1.4 Disinfection of Water Conditioners
The materials of construction of the modern water
conditioner will not support bacterial growth, nor will
these materials contaminate a water supply. However,
the normal conditions existing during shipping, storage
and installation indicate the advisability of disinfecting
a conditioner after installation, before the conditioner is
used to treat potable water. In addition, during normal
use, a conditioner may become fouled with organic
matter or in some cases with bacteria from the water
supply.
Thus every conditioner should be disinfected after
installation, some will require periodic disinfection
during their normal life, and in a few cases disinfection
with every regeneration would be recommended.
Depending upon the conditions of use, the style of
conditioner, the type of ion exchanger, and the
disinfectant available, a choice can be made among
the following methods.
Sodium or Calcium Hypochlorite
Application
These materials are satisfactory for use with
polystyrene resins, synthetic gel zeolite, greensand and
bentonites.
5.25% Sodium Hypochlorite
These solutions are available under trade names such
as Clorox Bleach*. If stronger solutions are used, such
as those sold for commercial laundries, adjust the
dosage accordingly.
1. Dosage
a. Polystyrene resin: 1.2 fluid ounces per cubic
foot.
b. Non-resinous exchangers: 0.8 fluid ounce per
cubic foot.
2. Brine tank conditioners
a. Backwash the conditioner and add the required
amount of hypochlorite solution to the brine
well of the brine tank. (The brine tank should
have water in it to permit the solution to be
carried into the conditioner.)
b. Proceed with the normal regeneration.
Calcium Hypochlorite
Calcium hypochlorite, 70% available chlorine, is
available in several forms including tablets and
granules. These solid materials may be used directly
without dissolving before use.
1. Dosage
a. Two grains (approximately 0.1 ounce) per cubic
foot.
2. Brine tank conditioners
a. Backwash the conditioner and add the required
amount of hypochlorite to the brine well of the
brine tank. (The brine tank should have water in
it to permit the chlorine solution to be carried
into the conditioner.)
b. Proceed with the normal regeneration.
*Clorox Bleach is a trademark of the Clorox Company.

9
2.0 Performa Cv 962 Control
2.1 Introduction to the Performa CV
Softener and Filter Systems
2.1.1 Performa Cv Softener Valve (278)
The Performa Cv softener valve is available with one of
two controls. The 962 electronic demand system
control and the 962TC electronic time clock control.
The Performa Cv system offers a true 1-inch valve with
superior flow characteristics. The Performa Cv softener
valve will deliver a service flow of 25 gpm (94.6 Lpm) at
a pressure drop of 15 psi (service Cv = 6.5, Kv = 5.6).
The Performa Cv softener is capable of backwashing at
the rate of 20 gpm (75.6 Lpm) with a pressure drop of
25 psi (backwash Cv = 4.0, Kv = 3.5). The application
for this valve will be on softener systems with mineral
tanks up to 21 inches in diameter.
2.1.2 Performa Cv Filter Valve (273)
The Performa Cv filter valve is available with one of
three controls. The 962F electronic demand system
control, the 962FTC electronic time clock control, and
the 942F mechanical time clock control in a 12-day
configuration. The Performa Cv filter valve has the
same service flow capability as the softener valve
however the backwash Cv is higher (Cv = 5.0, Kv = 5.8)
resulting in the capability of backwashing at 25 gpm
(94.6 Lpm) with a 25 psi pressure drop. The Performa
Cv filter valve can be used on carbon filters with media
tank sizes up to 24 inches in diameter. Other filter
media backwash requirements will determine
maximum media tank dimensions. Refer to the
backwash flow requirements in Table 4.5 and Table 4.6.
The Performa Cv softener valve and the Performa Cv
filter valve can be identified by a label attached to the
right side of the valve.

10
2.2 Programming and Application
This section covers all aspects of programming the 962
control.
Note that some parameters have a single unit of
measure option such as the Rinse Time which is only
entered in minutes. Other parameters have dual units
such as Salt Amount which can be entered in pounds
or kilograms. To select which units are active, look for a
comment in the NOTES column of Table 2.1 and Table
2.4. It will reference another parameter that selects
which units are active. For example, Parameter P12
(Table 2.4) selects U.S. units if it is set to “0” and metric
if it is set to “1.”
Level I Parameters (Table 2.1)
Level I Parameters are identified as those that have an
LED indicator on the front panel. The green indicator
illuminates next to the name of the active control
setting. The end user has access to all of these
parameters. In general, pressing the DOWN ARROW
(↓) button displays the Level I Parameters in the
following order:
•Time of Day
•Time of Regeneration
•Hardness
•Salt Amount
•Capacity
If you continue to press the DOWN ARROW (↓) button,
the parameters start over with Time of Day. Pressing
the UP ARROW (↑) button displays the parameters in
reverse order. Refer to Table 2.1 for a description of
these parameters and the available ranges for each
parameter.
Press the SET button and the far right number on the
display starts flashing. If you want to change this
number, press the UP ARROW (↑) button to increase
the number or the DOWN ARROW (↓) button to
decrease the number. To skip the number without
changing, press the LEFT ARROW (←) button. When
you reach the far left digit, pressing the LEFT ARROW
(←) button will return you to the far right digit.
Note: If you press and hold either the UP ARROW (↑)
button or the DOWN ARROW (↓) button for more than
one second, the flashing number will increment or
decrement at the rate of 10 counts per second.
When the number is correct, press the LEFT ARROW
(←) button. The first number stops flashing and the next
number starts flashing. You can only change the
flashing number. Continue changing numbers until you
reach the desired setting. Press the SET button. The
numbers stop flashing and the control accepts the new
setting. After approximately 30 seconds, the control
starts alternating the display between Time of Day and
Capacity.
Note: If a beep sounds, the new setting is not accepted
because it was outside the allowable range. The old
value will be displayed.
Day of Week/Time of Day
Press the SET button. The display will show the Time
of Day with the minutes digit blinking. If you want to
change this number, press the UP ARROW (↑) button
to increase the number or the DOWN ARROW (↓)
button to decrease the number. To skip the number
without changing, press the LEFT ARROW (←) button.
The first number stops flashing and the next number
starts flashing. You can only change the flashing
number. When you have reached the far left digit,
pressing the LEFT ARROW (←) button returns you to
the far right digit. The day of the week is displayed with
the time of day in the far left digit. It is programmed at
P1, the same as the time of day. The day of week will
automatically increment at midnight. This will allow
correlation to the daily usage history stored in L7
through L13 to days of the week. Customer should use
day 1 = Sunday through day 7 = Saturday. Continue
changing numbers until you reach the desired setting.
Press the SET button to save the value.
Time of Regeneration/Time of Backwash/Time of
History
The next value displayed is the Time of Regeneration/
Backwash/History. It has a default value of 2:00 a.m. If
this is not acceptable, press the SET button and
change the number. Press the SET button to save the
value. If 2:00 a.m. is acceptable, press the DOWN
ARROW (↓) button. Time of History is the time at which
all data that have been accumulated during the
previous 24 hours, are updated. This designation is
used on the Performa Cv 962M only.
Hardness
Hardness is the next value displayed. This value is the
water hardness expressed in grains per gallon
(milligrams per liter). The default value is
0 grains/gallon (0 mg/L). This parameter must be
programmed with the correct water hardness for the
control to operate properly. Press the SET button and
enter a new value. Any value between 3 and 250 grains
per gallon (30 and 2500 milligrams per liter) is allowed.
Press the SET button to save the new value.

11
Salt Amount
Salt Amount is the next value displayed. The default
value for Salt Amount is 6 pounds (2.7 kilograms) of
salt; refer to Table 2.2 for suggested salt settings.
Note: This is the total amount of salt used for a
regeneration, not pounds per cubic foot. If 6 pounds is
not acceptable, press the SET button and change the
numbers. If 6 pounds is acceptable, press the DOWN
ARROW (↓) button.
Capacity
Capacity is the next value displayed and is expressed
in kilograins (kilograms). Refer to Table 2.2 for the
capacity setting that corresponds to the resin bed
volume and salt amount. The default value is 0. Press
the SET button and enter a new value. Any value
between 1 and 2600 kilograins (.1 and 260.0 kilograms)
is allowed.
Table 2.1 - Level I Programming Performa Cv 962 Parallel Multi Tank or Single Tank Softener
Parameter Range of Values Minimum
Increments
Factory
Value
Units of
Measure Notes
Name Description
P1 Time of Week
and Time of day
(1-7)
1:00 to 12:59
AM or PM Metric
(1-7)
00:00 to 23:59
(1 day)
1 minute None Hour:minute
Range depends on value
selected for P13.
For day of week SUN=1,
MON=2, TUE=3, WED=4,
THU=5, FRI=6, SAT=7.
P2
Time of day to
start
regeneration
1:00 to 12:59
AM or PM
00:00 to 23:59
1 2:00 AM Hour:minute
Range depends on value
selected for P13. Use only if
P15 = 0, 1 or 2.
P3 Hardness of
water
3 to 250
30 to 2500
1
10
0
0
Grains/gallon
ppm
Unit of measure depends on
value selected for P12.
P4 Salt amount 0.5 to 125.0
0.2 to 50.0
0.5
0.2
6
2.6
Pounds
Kilograms
Select from Table 2.2 on
page 12.
P5 Capacity of unit 1 to 2600
0.1 to 260.0
1.0
0.1 0Kilograins
Kilograms
Select from Table 2.2 on
page 12.

12
Table 2.2 - Suggested Settings for P4, P5, P6, P7
P5 Capacity
Setting
Kilograins
(Kilograms)
Resin Volume per Tank (liters)
3 ft3 (85) 4 ft3 (113) 5 ft3 (142) 6 ft3 (170) 7 ft3 (198)
P4 Salt Setting: Pounds (kg) of Salt
60 (3.9) 18 (8.2) - - - -
80 (5.2) - 24 (10.9) - - -
84 (5.4) 30 (13.6) - - - -
90 (5.8) 45 (20.4) - - - -
100 (6.4) - - 30 (27.2) - -
112 (7.2) - 40 (18.1) - - -
120 (7.7) - 60 (27.2) - 36 (16.3) -
140 (9.0) - - 50 (22.7) - 42 (19)
150 (9.7) - - 75 (34) - -
168 (10.8) - - - 60 (27.2) -
180 (11.6) - - - 90 (40.8) -
196 (12.7) - - - - 70 (31.8)
210 (13.6) - - - - 105 (47.6)
P6 Refill Setting: 14 inch tank = 74 (.74 gpm)
16 inch thru 21 inch tanks = 130 (1.39 gpm)
P7 Brine Draw Setting. All values are based on 50 psi (3.5 bar) inlet pressure. For pressure other than 50 psi refer to brine
draw charts in Section 4.0.
Tank Diameter Injector Part Number P7 equals Color
14 in (35.5 cm) M 1055737 60 Brown
16 in (40.6 cm) Q 1035739 80 Purple
18 in (45.7 cm) Q 1035739 80 Purple
21 in (53.3 cm) R 1035884 83 Dark Grey

13
Level II Parameters (Table 2.4)
The Level II Parameters are P6 through P22 in Table
2.4. To access Level II Parameters, simultaneously
press and hold the DOWN ARROW (↓) and UP
ARROW (↑) buttons for three seconds. A “P” number
will display.
Refer to Table 2.4 to find the parameter associated
with each “P” number. Use the UP ARROW (↑) button
or the DOWN ARROW (↓) button to move from one
parameter to the next. The display cycles through the
“P” numbers shown in Table 2.1 and Table 2.4. When
you reach P22, the next P number will go back to P1.
When the parameter number you want to change is on
the display, press the LEFT ARROW (←) button to
display the data assigned to that parameter. Press the
SET button and the far right number on the display
starts flashing. If you want to change this number, press
the UP ARROW (↑) button or the DOWN ARROW (↓)
button. To skip the number without changing, press the
LEFT ARROW (←) button. When the number is correct,
press the SET button. The numbers stop flashing and
the control accepts the new setting. If a beep sounds,
the new setting was not accepted. Refer to Table 2.4
for allowable values for that parameter.
To change or view other parameters, press the LEFT
ARROW (←) button to have the display show “P”
numbers. Now use the UP ARROW (↑) button or the
down arrow (↓) button to move to the parameter
number you wish to change.
To exit the Level II programming mode, simultaneously
press and hold the DOWN ARROW (↓) and UP
ARROW (↑) buttons for three seconds, or wait 30
seconds without pressing a button. The control starts
alternating the display between Tank in Service, Flow
Rate and Capacity.
Settings for all parameters can be written on the label
provided with the control. The label has an adhesive
backing so it can be attached to the inside rear cover
of this manual for future service reference.
Level II Programming
•Parameter P6 is used by the control to calculate the
Refill Time. Press SET button and enter a new
value. Refer to Table 2.2 for the correct value.
•Parameter P7 is used by the control to calculate the
brine draw time. Press the SET button and enter a
new value. Refer to Table 2.2 for the correct value.
The control calculates the brine draw time using
this value and the salt amount. The brine draw time
is added to the Rinse Time (P10) to determine the
total Brine Draw/Slow Rinse Time.
•This control does not use Parameter P8. No entry
is needed for this parameter.
•Parameter P12 selects the units of measure. Be
sure that this is set to the correct value before
entering any data for Parameters P3, P4 or P5.
•Parameter P13 selects the clock display mode. If
the 12-hour mode is selected, a PM indicator is
used. If the 24-hour mode is selected, the PM
indicator is not used.
•Parameter P15 has four allowable values. Values 0
or 1 will cause the control to wait for Parameter P2,
time of day of regeneration, to begin the
regeneration. Values 2 or 3 will cause the control to
start the regeneration as soon as the capacity is
exhausted.
•When Parameter P15 selects a smart reserve type,
0 or 2, Parameter P16 is used to calculate the initial
seven average daily water usage values. The
control multiplies the total capacity by the
percentage entered for Parameter P16 and uses
that value as the initial average daily usage for each
day of the week until water usage establishes new
averages, refer to Reserve Options, page 15.
•Parameter 17 must be programmed following the
appropriate programming table. Improper
regenerations will occur if P17 is set to any other
number.
•Parameter P18 allows the installer to lock the Salt
Amount and Capacity values so they cannot be
changed. When Parameter 18 is set to 1, those two
settings can only be viewed when the control is in
the Level II mode. The settings will be skipped
when the control is in the Level I mode. When
Parameter 18 is set to zero, the Salt Amount and
Capacity can be viewed and changed in either
Level I or Level II.
•Parameter P19 selects the flow sensor that is to be
used with the system. The factory preset value is 1
for a 1-inch turbine. The range is 1 - 4. 1 = Autotrol
1-inch turbine, 2 = Autotrol 2-inch turbine, 3 = user
programmable K-factor, 4 = user programmable
pulse equivalent. The K-factors or pulse
equivalents for individual meters should be
supplied by the respective meter manufacturer.
•Parameter P20 is programmed only if P19 = 3 or 4.
P20 is where the factory supplied K-factor or pulse
equivalent number is programmed.
•Parameter P21 allows the user to tell the control
how long a signal must be present at the remote
regeneration input for it to be valid. For example; a
differential pressure switch may send false signals
of short duration many times before a filter really
does need to be backwashed. Programming P21
allows the control to start a backwash only when it
is required and not respond to false signals.

14
•Parameter P22. Special codes are entered at the
factory to program all of the pertinent P locations
for specific controls; Metric for example. This
parameter should never be changed by the end
user.
Electronic Time Clock Operation
Programming automatic regeneration frequency:
The Electronic Time Clock has two regeneration
options: Interval Regeneration and Day of Week
Regeneration.
To initiate an automatic regeneration one or both of the
options must be chosen. The system may also be
regenerated manually by pressing the Regeneration
button for three seconds.
Interval Regeneration — The Electronic Time Clock
may be programmed to regenerate in intervals of up to
30 days. This feature is Parameter P14 Calendar
Override (see Table 2.4). Example: If 5 is programmed
into P14 then the system will regenerate every five days
at the time programmed into P2.
Day of Week Regeneration — The Electronic Time
Clock may be programmed to regenerate on a specific
day or on specific days of the week. The instructions for
this option are found in Table 2.3 on page 15.
Application
The Performa Cv 962 Softener and the Performa Cv
962F Filter may be operated as a single, dual, or triplex
system.
Dual and Triplex Softeners and Filters
The dual and triplex systems require a different cam
than the cam that is used in the single unit systems.
They also require an interconnecting lock out cable.
This allows the unit that is in regeneration or backwash
to signal the other units and prevents them from
starting a regeneration or backwash until the first unit is
finished. Dual and triplex units should be plumbed in
parallel with each other. In a multi-unit system the
backwash water is supplied by the other unit or units in
the system. In a dual filter system consideration must
be given that the unit in service is able to satisfy service
requirements and be able to supply sufficient
backwash water to the other filter while it is in the
backwash cycle. There is a selection guide, Table 4.6,
in Section 4.0 to assist in qualifying the choice of a dual
or triplex system. This selection guide is based on
media backwash requirements and tank diameter.
A parallel kit must be purchased for multi-unit
operation. The kit numbers are:
•Dual Parallel Softener P/N 1035923
•Triplex Parallel Softener P/N 1035925
•Dual Parallel Filter P/N 1035924
•Triplex Parallel Filter P/N 1035926
Kits include parallel operation cams and the proper
interconnect cable.
Manual Start Regeneration
To force the control to perform a regeneration, press
the REGEN button. This button is located on the front
of the control. When you press the REGEN button, the
control performs a full regeneration of the conditioner.
If you press this button again more than one minute
after regeneration begins, but before the
regeneration is complete, a second regeneration
will start when the first regeneration is finished. The
display will freeze and only show the Regen Time
Remaining as an indication that the second
regeneration will be performed. When the first
regeneration is complete, the second one will begin
and the display will alternate between Flow and Regen
Time Remaining.
Automatic Regeneration
There are three ways to have the control automatically
start a regeneration: calendar override, having the
control monitor the water usage, or programming day
of the week regeneration.
Calendar Override
This feature is set in Parameter P14. It can be set for
one to 30 days. If it is set to zero, this feature is
disabled. When this feature is active, the control keeps
track of the number of days since the last regeneration
and when that number equals the value set in P14, a
regeneration is automatically started at the Time of
Regeneration set in P2.
Control Monitors the Water Usage
The control compares the water usage to the
calculated volume capacity of the system. The control
then uses the Capacity Parameter P5 divided by the
Hardness Parameter P3 to calculate the volume
capacity of the system. It also uses a reserve value to
determine if a regeneration is necessary. If the water
usage since the last regeneration is greater than the
system capacity minus the reserve, a regeneration is
needed.

15
Programming Day of the Week Regeneration/
Backwash
Enter Day of the Week Regeneration/backwash
programming by depressing the LEFT ARROW (←)
button and the DOWN ARROW (↓) button
simultaneously for 3 seconds. The days are shown as
d1, d2, d3, etc., on the display. Select the days of the
week regeneration/backwash should occur. To activate
that day, change the 0 to a 1. The programming mode
will be exited if no keys are pressed for 30 seconds. If
this feature is used in conjunction with calendar
override the calender override timer will be reset at the
end of this regeneration/backwash.
Reserve Options
There are two types of reserve options for this control:
fixed reserve and smart reserve (historical water usage
pattern). They are selected with Parameter P15.
Fixed Reserve
When fixed reserve is selected, the control multiplies
the maximum system capacity by the percent value set
in Parameter P16 and uses the result as a reserve.
Smart Reserve (water usage pattern)
The other reserve option allows the control to adjust the
reserve based upon the historical water usage pattern
of the system. The control keeps track of the water
usage for each day of the week and uses that day’s
average usage multiplied by 1.2 as the reserve for that
day. Every day at the Time of Regeneration, the control
recalculates the day’s average water usage. If less than
10% of a day’s average water usage is used, the
control will not change the day’s average. If more than
twice the day’s average is used, the control uses the
actual usage in the reserve calculation.
Since a new installation has no history of water usage,
the control multiplies the percent of capacity value set
in Parameter P16 by the total system capacity to
determine starting average for each day of the week.
The factory set value for P16 is 30 which means that
30% of the total system capacity is used for the starting
average for each day.
Program Parameter P15 is also used to select whether
the control waits until the Time of Regeneration set in
Parameter P2 to start a regeneration, or if the control
should begin a regeneration immediately when the
capacity remaining is less than the reserve.
Table 2.3 - Day of Week Regeneration/Backwash
# Description of Parameter Set as required
0 = No - 1 = yes Notes
d1 Sunday As required 0 = no day of week regeneration 1 = backwash this day
d2 Monday As required 0 = no day of week regeneration 1 = backwash this day
d3 Tuesday As required 0 = no day of week regeneration 1 = backwash this day
d4 Wednesday As required 0 = no day of week regeneration 1 = backwash this day
d5 Thursday As required 0 = no day of week regeneration 1 = backwash this day
d6 Friday As required 0 = no day of week regeneration 1 = backwash this day
d7 Saturday As required 0 = no day of week regeneration 1 = backwash this day

16
2.3 Softener Programming Tables
Go to Section 3.2 for detailed explanation of the programming parameters on this page.
Table 2.4 - Level II Programming Performa Cv 962 Parallel Multi Tank or Single Tank Softener
Parameter Description Range of
Values
Minimum
Increment
Recommended
Program Value
Units of
Measure Notes
P6 Refill controller 2-200 1 Selected from
Table 2.2
This number tells the controller the rate
of refill based on the refill control
installed. Refill dwell time is calculated
to refill the proper amount of water into
brine tank.
P7 Brine draw rate 2-200 1 Selected from
Table 2.2
This number tells the controller the draw
rate based on the injector size. The
dwell time in the draw position is then
calculated.
P9 Backwash time 4-60 1 14* Minutes *May be adjusted for application
P10 Slow Rinse time 7-125 1 40* Minutes
*May be adjusted for application. This
time does not include the calculated
brine draw time.
P11 Fast Rinse time 2-60 1 4* Minutes *May be adjusted for application
P12 Units of measure 0-1 1 00 = US, 1 = Metric
P13 Clock mode 0-1 1 00 = 12 hour clock, 1 = 24 hour clock
P14
Interval
Regeneration
(Calendar override)
0-30 1 0Days 0 = no calendar override
P15 Reserve Type 0-3 1 0
0 = Smart Reserve, 1 = Fixed Reserve,
2 = Smart Reserve with immediate
regeneration, 3 = Fixed Reserve with
immediate regeneration
P16
Initial average
usage or fixed
reserve
0-70 1 30
This number is used to establish the
fixed reserve. It is also used to establish
the initial Daily Average
P17 Operation type 0-7 1 33 = Single or Parallel Softener, 4 =
Single or Parallel Filter
P18 Salt/Capacity
Change Lock out 0-1 1 00 = none, 1 = Salt/Capacity change
locked out
P19 Flow Sensor select 1-4 1 1
1 = 1.0” Autotrol, 2 = 2.0” Autotrol, 3 =
User defined K-factor, 4 = User defined
pulse equivalent
P20 K-factor or Pulse
equivalent 0.00-255.00 .01 Number used for Meter K-factor or
Pulse equivalent
P21
Remote
Regeneration
switch delay
0-254 1 60 Seconds Time remote switch must be active to
start a regeneration
P22 Factory Use Only -
DO NOT CHANGE 99

17
Go to Section 3.2 for detailed explanation of the programming parameters on this page.
Table 2.5 - Programming Performa Cv 962TC Electronic Time Clock Softener
Parameter Description Range of
Values
Minimum
Increment
Recommended
Program
Value
Units of
Measure Notes
P1 Day of Week and
Time of Day
(1-7)
1:00-12:59
AM or PM
Metric
(1-7)
0:00-23:59
(1 day)
1 Minute
Current Day and
Time
Hour
Minute
Range depends on value selected
for P13. For day of week SUN=1,
MON=2, TUE=3, WED=4, THU=5,
FRI=6, SAT=7,. THIS IS THE LEFT
MOST DIGIT ON THE DISPLAY
P2 Time of day to start
regeneration
1:00-12:59 AM
or PM
00:00-23:59
As required Hour
Minute
Range depends on value selected
for P13
P3 As recommended 10
P4 Salt amount
.5-125.0
.2-50.0 .5
.2
Selected from Table
2.2
Pounds
Kilograms
P5 Program as
Recommended 10
P6 Refill controller 2-200 1 Selected from Table
2.2
This number tells the controller the
rate of refill based on the refill
control installed. Refill dwell time is
calculated to refill the proper
amount of water into brine tank.
P7 Brine draw rate 2-200 1 Selected from Table
2.2
This number tells the controller the
draw rate based on the injector
size. The swell time in the draw
position is then calculated.
P9 Backwash time 4-60 1 14* Minutes *May be adjusted for application
P10 Slow Rinse time 7-125 1 40* Minutes
*May be adjusted for application.
This time does not include the
calculated brine draw time.
P11 Fast Rinse time 2-60 1 4* Minutes *May be adjusted for application
P12 Units of measure 0-1 1 00 = US, 1 = Metric
P13 Clock mode 0-1 1 00 = 12 hour clock, 1 = 24 hour clock
P14 Interval Regeneration
Calendar override 0-30 1 0Days between
regeneration
0 = no interval chosen - *May be
adjusted for application.
P15 Does not apply for
Timeclock operation 0
P16 Does not apply for
Timeclock operation 30
P17 Operation type 3-4 1 66 = Single 962TC
P18 Salt Change Lock out 0-1 1 00 = none, 1 = Salt/Capacity change
locked out
P19 Does not apply for
Timeclock operation
P20 Does not apply for
Timeclock operation
P21
Remote
Regeneration Switch
Delay
0-254 1 60 Seconds Time remote switch must be active
to start a regeneration
P22 Factory Use Only -
DO NOT CHANGE 99

18
3.0 Performa Cv Filter Valve and Controls, 962F, 962FTC, 942F
3.1 Programming and Application
This section covers all aspects of programming the control.
Go to Section 2.2 for detailed explanation of the programming parameters on this page.
Table 3.1 - Programming Performa Cv 962F Three Cycle Filter
Parameter Description Range of
Values
Minimum
Increment
Recommended
Program
Value
Units of Measure Notes
P1 Day of week and
time of day
(1-7)
1:00-12:59
AM or PM
Metric
(1-7)
0:00-23:59
(1 day)
1 Minute
Current Day and
Time
Hour
Minute
Range depends on value selected
for P13. For day of week SUN=1,
MON=2, TUE=3, WED=4, THU=5,
FRI=6, SAT=7,. THIS IS THE
LEFT MOST DIGIT ON THE
DISPLAY
P2 Time of day to start
backwash
1:00-12:59 AM
or PM
00:00-23:59
As required Hour
Minute
Range depends on value selected
for P13
P3 Program as
recommended
10
100
U.S.
Metric
P4 Program as
recommended 0.5
P5 Filter capacity As required
U.S.
Metric
Divide the volumetric capacity
(gallons) of the filter by 100 and
enter this number into P5.
Divide the volumetric capacity
(cubic meters) by 10 and enter this
number into P5.
P6 Program as
recommended 200
P7 Program as
recommended 200
P9 Backwash time 7-60 1 14* Minutes *May be adjusted for application.
P10 Program as
recommended 8
P11 Fast Rinse time 9-60 1 9* Minutes *May be adjusted for application.
P12 Units of measure 0-1 1 00 = US, 1 = Metric
P13 Clock mode 0-1 1 00 = 12 hour clock,
1 = 24 hour clock
P14
Interval
Regeneration 0-30 1 0Days 0 = no interval chosen - *May be
adjusted for application
P15 Reserve Type 0-3 1 0
For a detailed
explanation go to
“Explanation of
Parameter Values”
P2 on page 24.
0 = Smart Reserve, 1 = Fixed
Reserve, 2 = Smart Reserve with
Immediate Regeneration, 3 =
Fixed Reserve with Immediate
Regeneration.
P16 Fixed reserve
percentage 0-70 1 30 This number is used to establish
initial Daily Average.
P17 Operation type 0-7 1 44 = Filter Performa Cv
P18 Salt Change Lock
out 0-1 1 00 = none, 1 = Salt/Capacity change
locked out
P19 Flow Sensor
Select 1-4 1 1
1 = 1” Autotrol Turbine, 3 = User
Defined K-factor, 2 = 2” Autotrol
Turbine, 4 = User Defined Pulse
Equivalent
P20 K-factor or Pulse
Equivalent 0.01-255.0 0.01 0.01 Number used for Meter K-factor or
Pulse Equivalent.
P21
Remote
Regeneration
Switch Delay
0-254 1 60 Seconds Time remote switch must be active
to start a backwash
P22 Factory Use Only -
DO NOT CHANGE 99
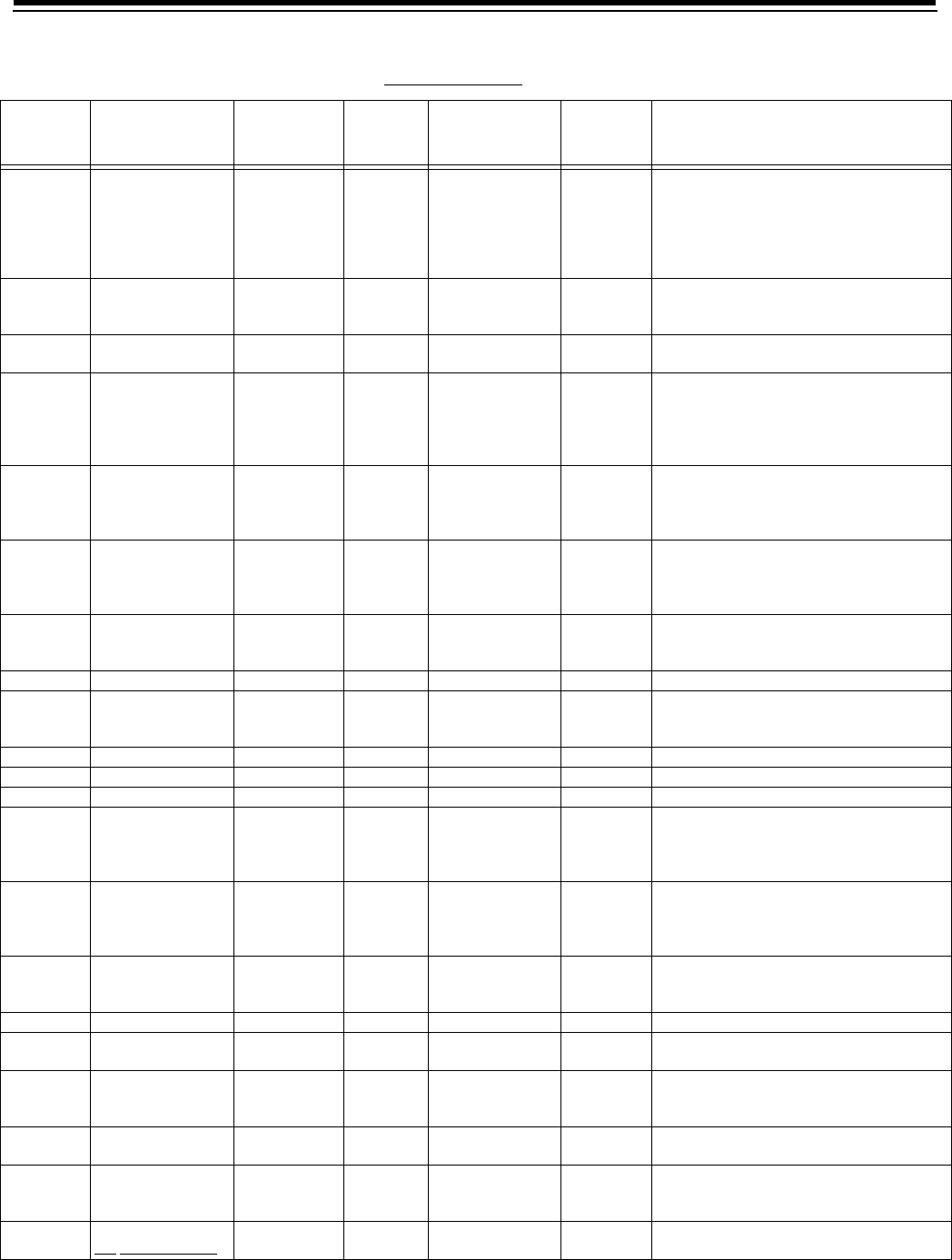
19
Go to Section 2.2 for detailed explanation of the programming parameters on this page.
Table 3.2 - Programming Performa Cv 962F Five Cycle Filter
Parameter Description Range of
Values
Minimum
Increment
Recommended
Program
Value
Units of
Measure Notes
P1 Day of week and
time of day
(1-7)
1:00-12:59
AM or PM
Metric
(1-7)
0:00-23:59
(1 day)
1 Minute
Current Day and
Time
Hour
Minute
Range depends on value selected for P13.
For day of week SUN=1, MON=2, TUE=3,
WED=4, THU=5, FRI=6, SAT=7,. THIS IS
THE LEFT MOST DIGIT ON THE DISPLAY
P2 Time of day to start
regeneration
1:00-12:59 AM
or PM
00:00-23:59
As required Hour
Minute Range depends on value selected for P13
P3 As recommended 10
100
P4
Potassium
Permanganate
KMnO4
.5-125.0
.2-50.0
.5
.2 As required
A potassium permanganate feeder with a float
must be used.
Number programmed into P5 equals gallons
of dissolved potassium permanganate,
multiplied by 3.
P5 Filter capacity As required
U.S.
Metric
Divide the volumetric capacity (gallons) of the
filter by 100 and enter this number into P5.
Divide the volumetric capacity (cubic meters)
by 10 and enter this number into P5.
P6 Refill controller 2-200 1 Selected from
Table 2.2
This number tells the controller the rate of
refill based on the refill control installed. Refill
dwell time is calculated to refill the proper
amount of water into the tank.
P7 Brine draw rate 2-200 1 Selected from
Table 2.2
This number tells the controller the draw rate
based on the injector size. The dwell time in
the draw position is then calculated.
P9 Backwash time 4-60 1 20* Minutes *May be adjusted for application.
P10 Slow rinse time 7-125 1 50* Minutes
*May be adjusted for application. This time
does not include the calculated brine draw
time.
P11 Fast Rinse time 2-60 1 8* Minutes *May be adjusted for application.
P12 Units of measure 0-1 1 00 = US, 1 = Metric
P13 Clock mode 0-1 1 00 = 12 hour clock, 1 = 24 hour clock
P14
Interval
Regeneration
(Calendar override) 0-30 1 0Days 0 = no interval selected
P15 Reserve Type 0-3 1 0
0 = Smart Reserve, 1 = Fixed Reserve, 2 =
Smart Reserve with Immediate Regeneration,
3 = Fixed Reserve with Immediate
Regeneration.
P16 Fixed reserve
percentage 0-70 1 30
This number is used to establish the fixed
reserve. It is also used to establish the initial
Daily Average.
P17 Operation type 0-7 1 33 = Single or Parallel Conditioner
P18 Salt/Capacity
Change Lock out 0-1 1 00 = none, 1 = Salt/Capacity change locked out
P19 Flow Sensor Select 1-4 1 1
1 = 1” Autotrol Turbine, 3 = User Defined K-
factor, 2 = 2” Autotrol Turbine, 4 = User
Defined Pulse Equivalent
P20 K-factor or Pulse
Equivalent 0.00-255.00 .01 Number used for Meter K-factor or Pulse
Equivalent.
P21
Remote
Regeneration Switch
Delay
0-254 1 60 Seconds Time remote switch must be active to start a
backwash
P22 Factory Use Only -
DO NOT CHANGE 99

20
Go to Section 2.2 for detailed explanation of the programming parameters on this page.
Table 3.3 - Programming Performa Cv 962 TC Electronic Time Clock Filter
Parameter Description Range of
Values
Minimum
Increment
Recommended
Program
Value
Units of
Measure Notes
P1 Day of week and
time of day
(1-7)
1:00-12:59
AM or PM
Metric
(1-7)
0:00-23:59
(1 day)
1 Minute
Current Day and
Time
Hour
Minute
Range depends on value selected for P13.
For day of week SUN=1, MON=2, TUE=3,
WED=4, THU=5, FRI=6, SAT=7,. THIS IS
THE LEFT MOST DIGIT ON THE DISPLAY
P2 Time of day to start
backwash
1:00-12:59 AM
or PM
00:00-23:59
As required Hour
Minute Range depends on value selected for P13
P3 Program as
recommended
10
100
U.S.
Metric
P4 Program as
recommended 0.5
P5 Program as
recommended As required U.S.
Metric
P6 Program as
recommended 2-200 1 200
P7 Program as
recommended 2-200 1 200
P9 Backwash time 7-60 1 14* Minutes *May be adjusted for application.
P10 Program as
recommended 7Minutes
P11 Fast Rinse time 9-60 1 9* Minutes *May be adjusted for application.
P12 Units of measure 0-1 1 00 = US, 1 = Metric
P13 Clock mode 0-1 1 00 = 12 hour clock, 1 = 24 hour clock
P14 Interval
Regeneration 0-30 1 0Days 0 = no interval selected. *May be adjusted for
application.
P15 Does not apply for
Time Clock operation
P16 Does not apply for
Time Clock operation
P17 Operation type 0-7 1 77 = Single 962FTC
P18 Salt/Capacity
Change Lock out 0-1 1 00 = none, 1 = Salt/Capacity change locked out
P19 Does not apply for
Time Clock operation
P20 Does not apply for
Time Clock operation
P21
Remote
Regeneration Switch
Delay
0-254 1 60 Seconds Time remote switch must be active to start a
backwash
P22 Factory Use Only -
DO NOT CHANGE 99

21
Electronic Time Clock Operation
To initiate an automatic backwash one or both of the
following options must be chosen. The system may be
backwashed manually by pressing the Backwash
button for three seconds.
Programming automatic regeneration frequency:
The Electronic Time Clock has two regeneration
options: Interval Regeneration and Day of Week
Backwash.
Interval Backwash — The Electronic Time Clock may
be programmed to regenerate at intervals up to 30
days. This feature is also known as Calendar Override.
It is located at P14. Example: If 5 is programmed into
P14 then the system will backwash every five days at
the time programmed into P2.
Day of Week Backwash — The Electronic Time Clock
may be programmed to backwash on a specific day or
specific days of the week. The instruction for this
option is found in Table 2.3 on page 17.
Application
The Performa Cv 962 Softener and the Performa Cv
962F Filter may be operated as a single, dual, or triplex
system.
Dual and Triplex Softeners and Filters
The dual and triplex systems require a different cam
than the cam that is used in the single unit systems.
They also require an interconnecting lock out cable.
This allows the unit that is in regeneration or backwash
to signal the other units and prevents them from
starting a regeneration or backwash until the first unit is
finished. Dual and triplex units should be plumbed in
parallel with each other. In a multi-unit system the
backwash water is supplied by the other unit or units in
the system. In a dual filter system consideration must
be given that the unit in service is able to satisfy service
requirements and be able to supply sufficient
backwash water to the other filter while it is in the
backwash cycle. There is a selection guide, Table 4.6,
in Section 4.0 to assist in qualifying the choice of a dual
or triplex system. This selection guide is based on
media backwash requirements and tank diameter.
A parallel kit must be purchased for multi-unit
operation. The kit numbers are:
•Dual Parallel Softener P/N 1035923
•Triplex Parallel Softener P/N 1035925
•Dual Parallel Filter P/N 1035924
•Triplex Parallel Softener P/N 1035926
Kits include parallel operation cams and the proper
interconnect cable.

22
3.2 Mechanical
Series 942F Mechanical Control
The Series 942F mechanical control provides
mechanical timeclock function for filter applications.
Figure 3.1
3.2.1 Settings
Setting the Time of Day, the Days of Backwash and
performing manual backwashing with the 942F
controls.
Setting the Time of Day
Rotate the Clock Dial clockwise until the pointer
indicates the correct time of day. With the time of day
set, the conditioner will backwash at approximately
2:00 a.m. If it is desired to have the unit backwash at an
earlier or later time, simply offset the current time of day
accordingly. For example, to have the unit backwash at
4:00 a.m., set the Clock Dial 2 hours later than the
actual current time of day.
Note: Do not rotate the Calendar Cap by hand. The
Clock Dial indexes the Calendar Cap daily. To manually
index the Calendar Cap, rotate the Clock Dial
clockwise one complete turn for every day to be
indexed. Day pins should be in the outward position
during Clock Dial rotation to prevent an undesired
backwash. Reset day pins when completed.
Setting the Days of Backwash
Setting the days that the conditioner will backwash is
accomplished in two simple steps:
1. Pull all of the day pins outward.
2. Push in the day pin(s) for the day(s) on which a
backwash is desired.
NOTE: The NEXT DAY pin is noted on the control face.
Pushing this pin will insure a backwash the next day at
approximately 2:00 a.m. since the Calendar Cap
progresses in a clockwise direction, pushing the day
pin immediately following the NEXT DAY pin
counterclockwise will insure a backwash occurs the
following day at approximately 2:00 a.m. This
progression is noted on the control face as “FUTURE
DAYS”.
Manual Backwash
Excessive water usage or other service related issues
may create the need to manually backwash the filter.
This function is performed by rotating the Indicator
Knob COUNTERCLOCKWISE to the “START”
position. Once in this position, the filter will begin a
backwash within a few minutes. The normal schedule,
established with the pushed in day pins, will not be
disrupted by a manual backwash.
24 Hour Clock
The Performa Cv Series 942F control utilizes a 24 hour
clock dial. This is typically referred to as “Military Time”.
The hours of the day between 12:00 a.m. (midnight)
and 12:00 p.m. (noon) are designated on the clock dial
by the numbers 1 through 12, with 1 being 1:00 a.m.
The hours of the day between 12:00 p.m. (noon) and
12:00 a.m. (midnight) are designated on the clock dial
by the numbers 13 through 24, with 13 being 1:00 p.m.
Be sure to set the correct time of day accordingly.
Performa Cv 942F
Indicator Knob
Day Pin
Calendar Cap
Clock Dial

23
Adjusting the Backwash Setting
The Backwash Dial (Figure 3.2) controls the backwash
time. With the Indicator Knob in the BACKWASH
COMPLETE position, rotate the Backwash Dial
counterclockwise at least one full turn to cancel out the
current setting. A light clicking sound will be replaced
by a heavier clicking sound when the previous setting
is cancelled. Once the heavier clicking is heard, the
new setting may be set by rotating the Backwash Dial
to the desired setting. The numbers on the Backwash
Dial represent “MINUTES” of backwash time.
Figure 3.2 Backwash Complete
Table 3.4 - Cycle Times for 942F Control
Cycle Time (Minutes)
Backwash 8 - 30
Purge 9
Backwash Dial

24
3.3 Explanation of Parameter Values for the 962 Single and Parallel Tank Controls
This section contains a detailed explanation of the programming parameters in the 962 electronic control.
Number Description of
Program Values Explanation
P1 * Time of Day The day of the week is displayed with the time of day in the far left digit. It
is programmed at P1 the same as the time of day. The day of week will
automatically increment at midnight. This will allow correlation to the daily
usage history stored in L7 through L13 to days of the week. Customer
should use day 1 = Sunday through day 7 = Saturday. Then L7 will hold
the usage history for Sunday through L13 holding the usage history for
Saturday. The daily averages stored in the L-values will still be updated at
the time of regeneration, not midnight. This is required to keep an
accurate record for reserve capacity needed at the time of regeneration.
Customers should understand that the L-value displayed for the average
water usage for Sunday “day one” will be the average water usage for
Sunday at 2:00 a.m. to Monday at 2:00 a.m., assuming the time of
regeneration is set for 2:00 a.m. Customers can reduce this two hour shift
by setting the time of regeneration to 12:01 a.m.
P2 * Time of
Regeneration
If P15 is set at 0 (smart reserve), the unit will check at the P2 time to see if
the smart reserve capacity has been reached. If it has, the unit WILL
regenerate at the specified P2 time. If the capacity display reaches zero
gallons (m3) at any time during the day, the unit will NOT regenerate until
the specified P2 time is reached.
If P15 is set at 1 (fixed reserve), the unit will check at the P2 time to see if
the fixed reserve capacity (P16) has been reached. If it has, the unit WILL
regenerate at the specified P2 time. If the capacity display reaches zero
gallons (m3) at any time during the day, the unit will NOT regenerate until
the specified P2 time is reached.
If P15 is set at 2 (smart reserve with immediate regen), the unit will check
at the P2 time to see if the smart capacity has been reached. If it has, the
unit will regenerate at the specified P2 time. If the capacity display
reaches zero gallons (m3) at any time during the day, the unit WILL
regenerate immediately. It will ALSO continue checking at the specified
P2 time to see if the smart reserve capacity has been reached, initiating a
regeneration at the P2 time if it has.
If P15 is set at 3 (fixed reserve with immediate regen), the unit will check
at the P2 time to see if the fixed reserve capacity has been reached. If it
has, the unit will regenerate at the specified P2 time. If the capacity
display reaches zero gallons (m3) at any time during the day, the unit WILL
regenerate immediately. It will ALSO continue checking at the specified
P2 time to see if the fixed reserve capacity has been reached, initiating a
regeneration at the P2 time if it has. If the fixed reserve is set to zero, the
unit will ONLY regenerate when the capacity display reaches zero.
If calendar override is used (P14), the unit will regenerate every 1 to 30
days at the specified P2 time.
Fixed Reserve: Fixed percentage of capacity defined by user
(gallons)(m3).
Smart Reserve: 120% of the daily average (gallons) (m3) calculated from
historical values stored in NOVRAM.
P3 ** Hardness of water If the 962 controller is programmed at P12 to use U.S. units, enter
hardness in grains per gallon (gpg). If the 962 controller is programmed at
P12 to use metric units, enter hardness in parts per million (ppm).

25
P4 **
page 12
Salt amount Enter your TOTAL salt amount per regeneration. For example, salting at
10 lb (4.5 kg) per cubic foot on a unit with 3 cubic feet of resin, enter 30.
(10 lb/ft3) x (3 ft3)= 30 lb. salt. [(4.5 kg/ ft3) x (3 ft3)= 13.6 kg salt].
P5
page 12
Capacity of unit Enter the capacity of the unit here, in kilograins (kilograms). For example,
a 3 ft3 unit with a resin capacity of 25,000 grains (1620 grams) per ft3,
enter 75 here. (25,000 grains/ ft3) x (3 ft3) = 75,000 grains = 75 kilograins.
[(1620 grams/ ft3) x (3 ft3) = 4860 grams = 4.86 kilograms].
Note: 15 lb/cu ft salting yields 30,000 grains/cu ft resin
10 lb/cu ft salting yields 25, 000 grains/cu ft resin
6 lb/cu ft salting yields 20,000 grains/cu ft resin
Reduced salting yields a reduced capacity
1 kilograin (1000 grains) = 0.0648 kilograms (64.8 grams)
P6
page 12
Refill control Enter value from Table 2.1 - Suggested Settings on page 12 of manual.
This value is the refill flow rate times 100, rounded to the next whole
number. For example, on a 16-inch tank, the refill control has a flow rate
of 1.3 gpm. Enter 130 (1.3 gpm x 100 = 130).
P7
page 12
Brine draw rate Enter value from Table 2.1 - Suggested Settings on page 12 of manual.
This is the injector draw rate times 100, rounded to the next whole
number. For example, on a 16-inch tank, the injector has a draw rate of
0.8 gpm. Enter 80 (0.8 gpm x 100 = 80).
P8 Not used P8 is reserved for future use.
P9 Backwash time Self explanatory. Generally, 5 to 15 minutes or until water runs clear or
specific water conservation needs are met.
P10 Slow rinse Time, in minutes, to achieve adequate slow rinse volume for resin type
used. Resin manufacturers recommend one to two and one half bed
volumes of slow rinse water. The required amount of time is calculated
using the injector performance curves provided in Section 4.0 of this
manual.
For example, assuming 4 cubic feet of resin and two bed volumes of slow
rinse water for a 16 x 65, 50 psi inlet pressure, program 43 minutes in
Parameter P10. (4 cubic feet) x (7.5 gallons/cubic foot) x 2 (bed volumes)
= 60 gallons of slow rinse water. A “Q” injector is recommended for a 16-
inch tank. From the “Q” injector performance chart the nominal slow rinse
rate is 1.4 gpm. 60 gallons divided by 1.4 gallons per minute equals 42.8
minutes. Round up to 43 minutes and enter in P10.
P11 Fast rinse Time, in minutes, to achieve adequate fast rinse volume for resin type
used. For example, for standard softening resin (Ionac C-249), fast rinse
at 30 gallons (0.11 m3) per cubic foot of resin. A unit with 3 ft3 of resin will
require 90 gallons (0.34 m3) of water to obtain the resin manufacturer’s
recommended fast rinse. (30 gal/ ft3 x 3 ft3) = 90 gallons. (0.11 m3/ ft3 x 3
ft3 = 0.34 m3). The fast rinse flow rate is controlled by the drain line flow
control. For this example, assume a 5 gpm (1.14 m3/hr) drain line flow
control. Enter 18 minutes in P10. (90 gallons/5 gpm) = 18 minutes (0.34
m3/1.14 m3 /hr = 0.3 hr/ x 60 min = 18 minutes).
P12 Units of measure Self explanatory. Enter 0 for U.S., enter 1 for metric.
P13 Clock mode Self explanatory. Enter 0 for 12-hour clock, enter 1 for 24-hour clock.
P14 Calendar override 0 = No calendar override. 1 - 30 = Maximum number of days between
regeneration/backwash.
P15 Reserve type
Immediate or delay
regeneration
See P2. Not used in Alternating mode.
Number Description of
Program Values Explanation

26
* The 962 controller functions in either a 12-hour or
24-hour clock mode. Programming P13 (clock mode) before
P1 or P2 will eliminate any confusion when setting these
parameters.
** The 962 controller functions in either U.S. or metric units.
Programming P12 (units of measure) before P3 or P4 will
eliminate any confusion when setting these parameters.
*** The calculated gallon amount loaded into the daily
registers (L7 through L13) at START-UP, uses this percentage
of capacity. Example: 90,000 grains in P5 ñ 10 grains in P3,
90,000 / 10 = 9,000 gallon capacity, 9,000 x .3 (30% in P16)
= 2700 gallons, which is loaded into L7 through L13, the
daily averages. For this example, the smart reserve at
START-UP, would be 2700 gallon x 1.2 (120% of the daily
average) = 3240 gallon. This daily average will change as
actual water usage information is gathered.
P16 *** Fixed Reserve
capacity
If P15 is set at 1 or 3, enter the fixed reserve capacity (in gallons) (m3) that
the unit will look for as explained in sections P2 and P15 above. Not used
in Alternating mode.
P17 Operation type Self explanatory. 3 = Single or parallel Softener or Tank; 4 = Single or
Parallel Filter.
P18 Salt/capacity
lockout
Allows for the lock out of P4 and P5 so that NO unauthorized changes to
the programmed values can be made.
P19 Flow Sensor Select This parameter is used to select the flow sensor that is to be used with
the system. The factory-preset value is 1 for a 1-inch turbine. The range is
1 - 4.
1 = Autotrol 1-inch turbine, 2 = Autotrol 2-inch turbine, 3 = user
programmable K-factor, 4 = user programmable pulse equivalent. The
respective meter manufacturer should supply the K-factors or pulse
equivalents for individual meters.
P20 K-factor or pulse
equivalent
The range is 000.01 to 255.00 in 0.01 steps. How this number is used is
defined by the values stored in P12 (units of measure) and P19 (flow
sensor select). P12 is used to define gallons or liters (0 = gallons, 1 =
liters). P19 is used to define K-factor or pulse equivalent (3 = K-factor, 4 =
pulse equivalent). K-factor is defined as pulses per gallon or pulses per
liter. Signet and Sea-Flow are two flow sensor manufacturers that publish
a K-factor. The control can now use any flow sensor as long as the
programmed K-factor is correct. The pulse equivalent is defined as
gallons or liters per pulse. The control will register 5 gallons of flow for
every pulse if P12 = 0, P19 = 4 and P20 = 5.00. Badger Meter is one
manufacturer that uses a pulse equivalent. The control will not show flow
rate if P19 = 4 (pulse equivalent). This is because pulses are accumulated
over 10 seconds and flow rate is displayed in gallons per minute. The
control will alternate between time of day and capacity remaining or
regeneration time remaining during normal operation.
P21 Remote
regeneration/
backwash switch
delay
This parameter is used to program the length of signal time required to
initiate a regeneration/backwash using a differential pressure switch or
remote start button/contact. The range is 1 to 254 seconds in 1-second
steps. The default is 60 seconds. A counter starts when there is a closed
dry contact (no voltage) to this input. A regeneration/backwash will start
when the contacts remain closed for the programmed time. The counter
will reset to zero when the contacts open for at least 0.02 seconds. The
remote regeneration input cannot be used to perform a double manual
regeneration. The remote regeneration input is ignored during a
regeneration/backwash.
P22 Factory use only DO NOT CHANGE
Number Description of
Program Values Explanation

27
4.0 Performa Cv Performance Charts and Graphs
4.1 General Specification
Hydrostatic Test Pressure . . . . . . . . . . . . . . . . . . . . . . . . . . . . . . . . . . . . . . . . . . . . . . . . . . . . . . . . 300 psi (20.69 bar)
Working Pressure. . . . . . . . . . . . . . . . . . . . . . . . . . . . . . . . . . . . . . . . . . . . . . . . . . . . . . . . 20-120 psi (1.38 - 8.27 bar)
Standard Electrical Rating. . . . . . . . . . . . . . . . . . . . . . . . . . . . . . . 962: series wall transformer 12V 60 Hz, 12V 50 Hz
942F: 7 day or 12 day/24 hour 50 Hz 12 V transformer, 60 Hz 120 Vac or 12 V transformer
Electrical Cord (standard rating) . . . . . . . . . . . . . . . . . . . . . . . . . . . . . . . . . . . . . . . . 60-inch (1.5-m) 3-wire with plug
Pressure Tank Thread . . . . . . . . . . . . . . . . . . . . . . . . . . . . . . . . . . . . . . . . . . . . . . . . . . . . . . . . . . .2-1/2-inch—8 male
Riser Pipe Diameter Required . . . . . . . . . . . . . . . . . . . . . . . . . . . . . . . . . . . . . . . . . . . . . . . . 1.050-inch OD (26.7-mm)
Riser Pipe Length . . . . . . . . . . . . . . . . . . . . . . . . . . 1/2 inch ±1/2 inch (13 mm ± 13 mm) higher than the top of tank
Standard Connection . . . . . . . . . . . . . . . . . . . . . . . . . . . . . . . . . . . . . . . . . . .1-inch (25.4-mm) copper tube adapters
Optional Connections . . . . . . . . . . . . . . . . . . . . . . . 1-1/4-inch, 3/4-inch, 22-mm, and 28-mm copper tube adapters
3/4-inch BSPT, 1-inch BSPT, 1-inch NPT brass pipe adapters
3/4-inch, 1-inch, 1-1/4-inch, 25-mm CPVC tube adapters
Brine Line Connection . . . . . . . . . . . . . . . . . . . . . . . . . . . . . . . . . . . . . . . . . . . . . . . . . . . . . . . . . . . 3/8-inch NPT male
Drain Line Connection. . . . . . . . . . . . . . . . . . . . . . . . . . . . . . . . . . . . . . . . . . . . . . . . . . . . . . . . . . . 3/4-inch NPT male
Optional Bypass Valve. . . . . . . . . . . . . . . . . . . . . . . . . . . . . . . . Rotating handles, full 1-inch porting, reinforced Noryl
Control Module, Tank Adapter. . . . . . . . . . . . . . . . . . . . . . . . . . . . . . . . . . . . . . . . . . . . . . . . . . . . . . . Reinforced Noryl
Rubber Goods . . . . . . . . . . . . . . . . . . . . . . . . . . . . . . . . . . . . . . . . . . . . . . . . . . Compounded for cold water service
Program Clock (Timer) 942F: Available in 7- to 12-day English, German, French, Italian, Spanish, Japanese
962, 962F, 962TC, 962FTC: Available in English, German, French, Italian, Spanish, Japanese
Brine Refill Control. . . . . . . . . . . . . . . . . . . . . . . . . . . . . . . . . . . . . . . . . . . . . . . . . . . . . . . . . . . . . . .0.74 and 1.3 GPM
External Backwash Controllers . . . . . . . . . . . . 5, 7, 10, 12, 15, 20 GPM. Beyond 20 GPM must be outside sourced.

28
4.2 Injector Curves
Injector "L" in a Performa Cv Valve
Injector "M" in a Performa Cv Valve

29
Injector "N" in a Performa Cv Valve
Injector "Q" in a Performa Cv Valve

30
Injector "R" in a Performa Cv Valve

31
4.3 Performa Cv Softener Performance Data
Table 4.1 - Performa Cv Injector Performance Chart
Injectors L - R Flow Rate Charts (gpm)
PSI L M N Q R
Draw Rinse Draw Rinse Draw Rinse Draw Rinse Draw Rinse
20 0.26 0.4 0.3 0.5 0.4 0.65 0.4 0.9 0.45 1.2
30 0.3 0.45 0.4 0.55 0.45 0.75 0.5 0.95 0.5 1.3
60 0.5 0.6 0.6 0.8 0.75 1 0.82 1.4 0.9 1.75
80 0.6 0.65 0.7 0.85 0.8 1.1 0.9 1.6 1 2
100 0.6 0.76 0.7 0.9 0.8 1.6 0.95 1.8 1.1 2.2
Injectors L - R Flow Rate Charts (Lpm)
Bar L M N Q R
Draw Rinse Draw Rinse Draw Rinse Draw Rinse Draw Rinse
1.4 0.98 1.5 1.1 1.9 1.5 2.5 1.5 3.4 1.7 4.5
2.1 1.1 1.7 1.5 2.1 1.7 2.8 1.9 3.6 1.9 4.9
4.2 1.9 2.3 2.3 6 2.8 3.8 3.1 5.3 3.4 6.6
5.6 2.3 2.5 2.6 3.2 3 4.2 3.4 6 3.8 7.6
7 2.3 2.9 2.6 3.4 3 4.9 3.6 6.8 4.2 8.3
Table 4.2 - Service and Backwash Flow Performance Data
Flow vs Pressure Drop (gpm) Flow vs Pressure Drop (Lpm)
PSI Service (Cv 6.5) Backwash (Cv 4.0) Bar Service (Cv 6.5) Backwash Cv 4.0)
5 15 9 0.35 56 34
10 20 13 0.7 76 49
15 25 16 1 95 61
20 29 18 1.4 109 68
25 32 20 1.7 121 76
30 35 22 2.1 132 83
Table 4.3 - Recommended Drain Flow Controls (Backwash Anion and Cation Resin @ 55°F (12.7°C) Water
Temperature
Tank Diameter
Inches (mm)
Bed Area
sq. ft.
Anion Resin @ 3 gpm/sq ft
(m3h/sq ft)
Cation Resin @ 5 gpm/sq
ft
(m3h/sq ft)
14 (35.6) 1.02 3 (.7) 5 (1.1)
16 (40.6) 1.38 4 (.9) 7 (1.5)
18 (45.7) 1.76 5 (1.1) 8 (1.8)
21 (53.3) 2.4 7 (1.5) 12 (2.7)

32
*May exceed 25 psi or 1.72 bar pressure drop.
Table 4.4 - Performa Filter
Pressure Loss vs Flow (gpm)
PSI Service (Cv 6.5) Backwash (Cv 5.0)
515 11
10 20 16
15 25 19
20 29 22
25 32 25
30 35 27
Pressure Loss vs Flow (Lpm)
Bar Service (Kv 5.6) Backwash (Kv 5.8)
0.35 56 42
0.7 76 61
195 72
1.4 109 83
1.7 121 95
2.1 132 102
Table 4.5 - Typical Backwash Flow Requirements for Various Filter Medias (based on 55°F (12.7°C) water
temperature)
GAC/CARBON FILTER-AG, CALCITE
GREENSAND
BIRM
SAND, MULTI-MEDIA
Tan k D ia .
inches (mm)
Bed Area
sq. ft.
8 gpm/sq ft
(Lpm/sq ft)
10 gpm/sq ft
(Lpm/sq ft)
12 gpm/sq ft
(Lpm/sq ft)
15 gpm/sq ft
(Lpm/sq ft)
14 (35.6) 1.02 8 (30) 10 (38) 12 (45) 15 (57)
16 (40.6) 1.38 11 (42) 13 (49) 16 (61) 20 (76)
18 (45.7) 1.76 14 (53) 17 (64) 21 (79) *26 (98)
21 (53.3) 2.4 19 (72) 24 (91) *29 (98)
24 (60.9) 3.14 25 (95)

33
* May exceed 25 psi or 1.72 bar pressure drop during backwash of second unit.
NR = Not Recommended. A flow control on the service outlet of each valve may be required to insure proper
backwash volume to backwashing unit.
Table 4.6 - Performa Cv Filter Sizing Selection Guide for Dual Unit Filters.
Typical backwash flow requirements for various filter medias (based on 55°F (12.7°C) water temperature.
GAC/CARBON FILTER-AG, CALCITE
GREENSAND
BIRM
SAND, MULTI-MEDIA
Tan k D ia .
inches (mm)
Bed Area
sq. ft.
8 gpm/sq ft
(Lpm/sq ft)
10 gpm/sq ft
(Lpm/sq ft)
12 gpm/sq ft
(Lpm/sq ft)
15 gpm/sq ft
(Lpm/sq ft)
14 (35.6) 1.02 8 (30) 10 (38) 12 (45) NR
16 (40.6) 1.38 11 (42) 13 (49) NR NR
18 (45.7) 1.76 *14 (53) NR NR NR
21 (53.3) 2.4 NR NR NR NR

34
5.0 Performa Cv Service and Troubleshooting
5.1 Historical Data
Level III Memory Locations
To assist in troubleshooting the Water Conditioning
System, the contents of the controller memory can be
examined to determine the status of the control and the
history of water usage. To view the controller’s memory
locations “L1” to “L15” described in Table 5.1, the
location viewing mode must be selected. This mode
can be selected by simultaneously pressing the
LEFT ARROW (←) and the UP ARROW (↑) buttons.
The control will then show “L1” on the display.
Locations can be stepped through in the same method
as described for Level II programming. However, the
[SET] button is inactive except for L4. If [SET] is
pressed when L4 is displayed, Peak Flow is reset to
zero. If [SET] is pressed when any other location is
displayed, the control will beep.
Table 5.1 - Level III Historical Data
Regeneration Cycle Advance
A function is used to advance the control to the next
stop position during a regeneration. Pressing and
holding the LEFT ARROW ( ← ) button after the control
has stopped at a cycle position (BACKWASH for
example) will cause the control to cancel the park time
in that position and advance to the next cycle park
position (BRINE DRAW for example). The regeneration
time remaining will decrease by the amount of park
time that was skipped. This function will not work when
the motor is on. The control will beep if the LEFT
ARROW ( ← ) button is held for 2.5 seconds and the
motor output is on.
Regeneration/Backwash Cancel
The regeneration/backwash may be cancelled at any
time during the operation by pressing the SET button
and the LEFT ARROW ( ← ) for 3 seconds. ERR 3 will
appear on the display and the control will advance to
the Complete position. The control may be manually
advanced by turning the cam shaft
COUNTERCLOCKWISE to the complete position.
Location Range Description
L1 1 - 7 Day
L2 0 - 255 Days since last regeneration
L3 1:00-12:59 AM/PM
0:00-23:59 Time of day that peak flow occurred
L4 0-200 (0-50.0) Peak Flow in gallons per minute (m3/hr) since location reset
L5 0-655360(0-6553.6) Water used today in gallons (m3) since time of regeneration
L6 0-655360(0-6553.6) Water used since last regeneration in gallons (m3)
L7 0-655360(0-6553.6) Average water usage for Day 1 in gallons (m3)
L8 0-655360(0-6553.6) Average water usage for Day 2 in gallons (m3)
L9 0-655360(0-6553.6) Average water usage for Day 3 in gallons (m3)
L10 0-655360(0-6553.6) Average water usage for Day 4 in gallons (m3)
L11 0-655360(0-6553.6) Average water usage for Day 5 in gallons (m3)
L12 0-655360(0-6553.6) Average water usage for Day 6 in gallons (m3)
L13 0-655360(0-6553.6) Average water usage for Day 7 in gallons (m3)
L14 0-999990(0-99999.9) Total water used since controller installed in gallons or (m3)(least significant
digits)
L15 0-167(0-16) Total water used since controller installed in gallons x 106 or (m3)(most
significant digits)

35
5.2 Preventative Maintenance
Injector Screen and Injector
Inspect and clean brine tank and screen filter on end of
brine pickup tube once a year or when sediment
appears in the bottom of the brine tank.
Clean injector screen and injector once a year:
1. Unplug the wall-mount transformer.
2. Shut off water supply or put bypass valve(s) into
bypass position.
3. Relieve system pressure by opening valve No. 7
(at rear) with a screwdriver.
4. Using a screwdriver, remove injector screen and
injector cap (Figure 5.1).
5. Clean screen using a fine brush. Flush until clean.
6. Using a needle-nose pliers, pull injector straight
out.
7. Flush water into the injector screen recess of the
valve body to flush debris out through the injector
recess.
8. Clean and flush the injector.
9. Lubricate the O-rings on the injector, injector cap
and injector screen with silicone lubricant only!
10. Reinstall the injector, injector cap and injector
screen.
IMPORTANT: Do not overtighten the plastic cap. Seat
the cap lightly into position. Overtightening may cause
breakage of the plastic cap that may not be
immediately evident.
11. Plug the wall-mount transformer into outlet; reset
clock if necessary.
12. Slowly open water supply valve or return bypass
valve(s) to the “service” position.
Figure 5.1
Water Meter Maintenance
The metering device used with the 962 Cv demand
controls may require simple maintenance. In rare
instances, the turbine wheel of the water meter can
collect small particles of oxidized iron, eventually
preventing the wheel from turning.
1. Shut off the water supply or put the bypass valve(s)
into the bypass position.
2. Relieve pressure by opening the Backwash Drain
Valve (the seventh back from the control) with a
screwdriver.
3. Loosen and remove the pipe/tube adapters or
1265 bypass from the inlet and outlet of the valve
body.
4. Using a needle-nose pliers, remove the turbine
from the outlet housing. Grasp one of the four
vanes of the outer gland and pull straight out to
remove turbine assembly from the outlet of the
valve (Figure 5.1).
5. Carefully remove the turbine wheel from the
housing. Use a toothbrush to lightly scrub the iron
off the magnet. Iron buildup on the surfaces can be
removed by soaking the wheel in a mild sodium
hydrosulfite (such as RoVer*) solution for a few
minutes. Flush thoroughly with water.
6. Carefully reinstall the turbine wheel into the turbine
cage housing. Make sure that the shaft of the wheel
seats into the bearing of the cage. Reassemble the
turbine cage and check that the wheel rotates
freely.
7. Reinstall the turbine cage into the outlet of the
valve.
8. Reinstall the pipe/tube adapters or 1265 bypass to
the inlet and outlet of the valve.
9. Turn on the water supply or put the bypass valve(s)
into the service position and purge the air out of the
system.
To check for proper meter operation, open a
downstream faucet and observe the water flow
indication, blinking colon, on the control display.
*RoVer is a trademark of Hach Chemical Company.
Injector
Injector Screen
Cap
Turbine

36
5.3 Removing the Valve Assembly for
Servicing
1. Unplug the power cord.
2. Shut off water supply or put bypass valve(s) into
bypass position.
3. Remove cover and with screwdriver, relieve tank
pressure by pushing open valve No. 7 (rear flapper)
on control as shown (Figure 5.2).
Figure 5.2
4. When used with a globe valve bypass, loosen and
detach the inlet, outlet, brine and drain lines from
the valve. If using the 1265 bypass, loosen and
remove valve from bypass as well as loosening and
removing the brine and drain lines.
5. Unscrew (counterclockwise) and remove valve
from tank.
6. To replace the control valve, reverse the above
procedure.
5.4 Removing the Control
Complete the following steps to remove the 960
ProSoft control for servicing:
1. Unplug the wall-mount transformer.
2. Shut off the water supply or put the bypass valve(s)
into bypass position.
3. Remove the rear cover by depressing the two tabs
provided on the cover, Figure 5.3. Lift the front of
the cover and remove to expose the valve body.
Figure 5.3
4. Relieve system pressure by opening the Backwash
Drain Valve (the seventh valve back from the
control) with a screwdriver, Figure 5.4.
Figure 5.4
5. To remove the camshaft or to reinstall it, the arrow
on the rear of the cam shaft must be pointing at the
line on the rear “hoop” of the top plate. This occurs
when the cycle indicator is rotated to the refill
position. Press down on the back of the camshaft
to disengage it from the rear “hoop” of the top
plate, Figure 5.5.
Slide the camshaft back to disengage it from the
timer, Figure 5.6.
Figure 5.5
Tab

37
Figure 5.6
6. Disconnect the turbine probe from the turbine
assembly.
7. Lift the control off the valve, Figure 5.7. To replace
the control, reverse the above procedure. Note that
the camshaft needs to be positioned correctly
before it can be inserted into the back of the
control. There is a locating arrow on the camshaft.
Position the arrow on the top of the shaft and slide
the camshaft into the control. Push up on the end
of the camshaft, furthest from the timer, snapping it
into place.
Figure 5.7

38
5.5 Identification of Control Valving
1 Brine Valve
2 Bypass Valve
3 Inlet Valve
4 Outlet Valve
5 Refill Valve
6 Rinse Drain Valve
7 Backwash Drain Valves
5.7 Performa Cv Softener Flow Diagrams
1Brine
Adjustment
Inlet
Outlet
Drain
Brine
Tank
Tank
Riser Tube
2
3
4
5
67
Valve No.
1 - Closed
2 - Closed
3 - Open
4 - Open
5 - Closed
6 - Closed
7 - Closed
Name
Brine
By-Pass
Inlet
Outlet
2nd Tank Top
Purge
Backwash
Auxiliary D
Auxiliary B
Auxiliary A
Auxiliary C
2 Backwash Position
1 Service Position
1
Brine
Adjustment
Inlet
Outlet
Drain
Brine
Tank
Tank
Riser Tube
2
4
5
6
Valve No.
1 - Closed
2 - Open
3 - Closed
4 - Open
5 - Closed
6 - Closed
7 - Open
Name
Brine
By-Pass
Inlet
Outlet
2nd Tank Top
Purge
Backwash
Auxiliary D
Auxiliary B
Auxiliary A
Auxiliary C
7
3
5.6 Valve Disc Principle of Operation

39
4 Fast Rinse Position
3 Brine/Slow Rinse Position
1
Brine
Adjustment
Inlet
Outlet
Drain
Brine
Tank
Tank
Riser Tube
2
4
5
6
Valve No.
1 - Open
2 - Open
3 - Closed
4 - Closed
5 - Open
6 - Open
7 - Closed
Name
Brine
By-Pass
Inlet
Outlet
2nd Tank Top
Purge
Backwash
Auxiliary D
Auxiliary B
Auxiliary A
Auxiliary C
7
3
1
Brine
Adjustment
Inlet
Outlet
Drain
Brine
Tank
Tank
Riser Tube
2
4
5
6
Valve No.
1 - Closed
2 - Open
3 - Open
4 - Closed
5 - Open
6 - Open
7 - Closed
Name
Brine
By-Pass
Inlet
Outlet
2nd Tank Top
Purge
Backwash
Auxiliary D
Auxiliary B
Auxiliary A
Auxiliary C
7
3
1
Brine
Adjustment
Inlet
Outlet
Drain
Brine
Tank
Tank
Riser Tube
2
4
5
6
Valve No.
1 - Open
2 - Closed
3 - Open
4 - Open
5 - Closed
6 - Closed
7 - Closed
Name
Brine
By-Pass
Inlet
Outlet
2nd Tank Top
Purge
Backwash
Auxiliary D
Auxiliary B
Auxiliary A
Auxiliary C
7
3
5 Refill Position

40
5.8 Performa Cv Filter Flow Diagrams
1 Backwash Position
2 Fast Rinse Position
1
Brine
Adjustment
Inlet
Outlet
Drain
Brine
Tank
Tank
Riser Tube
2
4
5
Valve No.
1 - Open
2 - Open
3 - Closed
4 - Open
5 - Open
6 - Closed
7 - Open
Name
Brine
By-Pass
Inlet
Outlet
2nd Tank Top
Purge
Backwash
Auxiliary D
Auxiliary B
Auxiliary A
Auxiliary C
7
3
Plug
Plug
6
1
Brine
Adjustment
Inlet
Outlet
Drain
Brine
Tank
Tank
Riser Tube
2
5
Valve No.
1 - Closed
2 - Open
3 - Open
4 - Closed
5 - Closed
6 - Open
7 - Closed
Name
Brine
By-Pass
Inlet
Outlet
2nd Tank Top
Purge
Backwash
Auxiliary D
Auxiliary B
Auxiliary A
Auxiliary C
3
Plug
Plug
67
4
page no.

41
5.9 Troubleshooting
The technology upon which the Autotrol Performa
control valve is based is well established and proven in
service over many years. However, should a problem or
question arise regarding the operation of the system,
the control can be serviced easily. For parts mentioned,
refer to exploded views in the Replacement Parts
section of this manual.
IMPORTANT: Service procedures that require the
water pressure to be removed from the system are
marked with a ! after the possible cause. To remove
water pressure from the system, put the bypass valve
or three-valve bypass into the bypass position and
open the backwash drain valve (the seventh valve back
from the control) with a screwdriver. Restore system
water pressure when the service work is completed.
Valve Troubleshooting
Problem Possible Cause Solution
1. Control will not draw brine. a. Low water pressure.
b. Restricted drain line.
c. Injector plugged !
d. Injector defective !
e. Valve (2 and/or 4) not closed.
f. Damaged injector O-ring.
a. Set pump to maintain 30 psi at conditioner.
b. Remove restriction.
c. Clean injector and screen.
d. Replace injector.
e. Remove foreign matter from disc and check
disc for closing by pushing in on stem. Replace
if needed.
f. Replace injector O-ring.
2. Brine tank overflow. a. Brine valve (1) being held open.
b. Uncontrolled brine refill flow rate !
c. Valve (3 or 4) not closed during brine draw
causing refill.
d. Air leak in brine line.
a. Manually operate valve stem to flush away
obstruction.
b. Remove variable salt controller to clean.
c. Flush out foreign matter by holding disc open
and manually operating valve stem.
d. Check all connections in brine line for leaks.
Refer to instructions.
3. System using more or less salt
than salt control is set for.
a. Inaccurate setting.
b. Foreign matter in controller causing
incorrect flow rates !
c. Defective controller.
a. Correct setting.
b. Remove variable salt controller and flush out
foreign matter. Manually position control to
brine draw to clean controller (after so doing,
position control to “purge” to remove brine
from tank).
c. Replace controller.
4. Intermittent or irregular brine
draw.
a. Low water pressure.
b. Defective injector !
a. Set pump to maintain 30 psi at conditioner.
b. Replace both injector and injector cap.
5. No conditioned water after
regeneration.
a. Unit did not regenerate.
b. No salt in brine tank.
c. Plugged injector !
a. Check for power.
b. Add salt.
c. Clean injector. Flush with water.
6. Control backwashes at
excessively low or high rate.
a. Incorrect backwash controller used.
b. Foreign matter affecting controller
operation !
a. Replace with correct size controller.
b. Remove controller and ball. Flush with water.
7. Flowing or dripping water at
drain or brine line after
regeneration.
a. Drain valve (6 or 7) or brine valve (1) held
open by foreign matter or particle.
b. Valve stem return spring on top plate
weak.
a. Manually operate valve stem to flush away
obstruction.
b. Replace spring.
8. Hard water leakage during
service.
a. Improper regeneration.
b. Bypass flapper held open.
c. Leaking of bypass valve !
d. O-ring around riser tube
damaged !
a. Repeat regeneration making certain that the
correct salt dosage is set.
b. Valve needs cleaning. Contact the installer.
c. Replace O-ring.
d. Replace O-ring.

42
962 Control Troubleshooting
Alarms
The Model 962 continuously monitors itself and sounds
an alarm if it detects something wrong. The alarm is a
beep that is on for one second and then off for nine
seconds.
When the alarm sounds, the display shows the letters
“Err” with a number from 1 to 4. The table below lists
the Err numbers, a description of each error, the cause
of the error, and the solutions. To silence the alarm,
press any button on the control. If the error still exists,
the control will go back to the alarm condition after 30
seconds.
Model 960 Alarms
Indication Description Cause Solution
Err1 Electronics Failure Control settings need
reprogramming.
Press any key to load default values. Refer
to “Programming the Model 960 Control”.
Err2 Improper start of
regeneration (limit switch
closed when it should be
open).
Valve camshaft has been
manually rotated during a
regeneration.
Valve camshaft has been
manually rotated out of
“regeneration complete”
position.
Faulty motor.
Faulty motor drive.
Faulty switch.
Press any key to silence the alarm. (Note:
Alarm automatically clears at “TIME OF
REGEN”.)
The control will turn the motor on and drive
the camshaft to the proper location.
Replace the control.
Replace the control.
Replace the control.
Err3 Improper finish of
regeneration (limit switch
open when it should be
closed).
Valve camshaft has been
manually rotated out of
“regeneration complete”
position.
Faulty motor.
Faulty motor drive.
Faulty switch.
The control will turn the motor on and drive
the camshaft to the proper location.
Replace the control.
Replace the control.
Replace the control.
Err4 Improper control settings
(one or more settings out of
the allowable range).
One or more settings out of
the allowable range.
Hardness: Adjust range: 3 to 250.
Capacity: Adjust range: 0.1 to 140.0.
Refill control: Adjust range: 1 to 99.
Brine draw value: Adjust range per
Table 4.1.
Problem Possible Cause Solution
1. Capacity display stays at 9999
even through there is water
usage.
a. Total system capacity was calculated to
be a value greater than 9999.
a. As the water usage continues, the remaining
capacity will drop below 9999 and then other
values will be shown.
2. Timer beeps when left arrow
button is pressed.
a. Button is only active in the programming
mode.
a. Refer to the Programming section.
3. Timer does not respond to
REGEN button.
a. Button is not active in the programming
mode.
a. Refer to the Regeneration section.
4. Timer does not display time of
day.
a. Transformer is unplugged.
b. No electric power at outlet.
c. Defective transformer.
d. Defective circuit board.
a. Connect power.
b. Repair outlet or use working outlet.
c. Replace transformer.
d. Replace control.
5. Timer does not display correct
time of day.
a. Outlet operated by a switch.
b. Power outages.
a. Use outlet not controlled by switch.
b. Reset Time of Day.

43
Problem Possible Cause Solution
6. No water flow display when
water is flowing (colon does
not blink).
a. Bypass valve in bypass position.
b. Meter probe disconnected or not fully
connected to meter housing.
c. Restricted meter turbine rotation due to
foreign material in meter !
d. Defective meter probe.
e. Defective circuit board.
a. Shift bypass valve into service position.
b. Fully insert probe into meter housing.
c. Remove meter housing, free up turbine and
flush with clean water. Turbine should spin
freely. If not, refer to the Water Meter
Maintenance section.
d. Replace control.
e. Replace control.
7. Control display is frozen at
Regen Time Remaining.
a. Back to back regenerations were
requested.
a. Refer to the Manual Regeneration section.
8. Control regenerates at the
wrong time of day.
a. Power outages.
b. Time of day set incorrectly.
c. Time of regeneration set incorrectly.
a. Reset time of day to correct time of day.
b. Reset time of day to correct time of day.
c. Reset time of regeneration.
9. Timer stalled in regeneration
cycle.
a. Motor not operating.
b. Motor runs backwards.
c. No electric power at outlet.
d. Incorrect voltage or frequency (Hz).
e. Broken gear.
f. Defective switch.
g. Air leak in brine connections (pressure
locked flapper).
h. Binding of camshaft.
i. Water pressure greater than 125 psi
during regeneration.
j. Defective circuit board.
a. Replace control.
b. Replace control.
c. Repair outlet or use working outlet.
d. Replace timer and/or transformer with one of
correct voltage and frequency (Hz).
e. Replace control.
f. Replace control.
g. Check all junction points and make
appropriate corrections.
h. Remove foreign object obstruction from valve
discs or camshaft.
i. Install pressure regulator to reduce pressure.
j. Replace control.
10. Continuous regeneration.
Camshaft does not stop at the
end of regeneration.
a. Broken projection on drive gear.
b. Defective switch.
a. Replace control.
b. Replace control.
11. Control does not regenerate
automatically or when REGEN
button is depressed.
a. Transformer unplugged.
b. No electric power at outlet.
c. Defective motor.
d. Broken gear.
e. Binding in gear train.
f. Defective switch.
a. Connect power.
b. Repair outlet or use working outlet.
c. Replace control.
d. Replace control.
e. Replace control.
f. Replace control.
12. Control does not regenerate
automatically but does
regenerate when REGEN
button is depressed.
a. If water flow display is not operative, refer
to item 5 in this table.
b. Incorrect hardness and capacity settings.
c. Defective circuit board.
a. Refer to item 5 in this table.
b. Set new control values. Refer to the
Programming section.
c. Replace control.
13. Run out of soft water between
regenerations.
a. Improper regeneration.
b. Fouled resin bed.
c. Incorrect salt setting.
d. Incorrect hardness or capacity settings.
e. Water hardness has increased.
f. Restricted meter turbine rotation due to
foreign material in meter housing !
g. Excessive water usage below 1/5 gallon
per minute.
a. Repeat regeneration making certain that
correct salt dosage is used.
b. Use resin cleaner.
c. Set salt control to proper level. Refer to the
Programming section in this manual.
d. Set to correct values. Refer to the
Programming section in this manual.
e. Set to new value. Refer to the Programming
section in this manual.
f. Remove meter housing, free up turbine, and
flush with clean water. Turbine should spin
freely, if not, replace meter.
g. Repair leaky plumbing and/or fixtures.

44
6.0 Performa Cv Parts
6.1 Valve Component Exploded View
2
Performa Valve
3
4
14
9
1
5
6
10
11
7
8
12
12
13
15

45
6.2 Parts List
* Not Shown
Code
Part
No. Description Qty. Code
Part
No. Description Qty.
1 1000413 Performa Cv Softener Valve Assy, w/o 1 10 1010429 O-Ring 1
Flow Controls 11 1035622 Tank Ring 1
1000418 Performa Cv Filter Valve Assy, w/o Flow Control 12 Plumbing Adapter Kits: 1
2 1035611 962 Softener Cam Assy, Single Unit 1 1001606 3/4-inch Copper Tube Adapter Kit
1030377 962 Softener Cam Assy, Multi Unit 1001670 1-inch Copper Tube Adapter Kit
1030380 962F Filter Cam Assy, Single Unit 1041210 1-1/4-inch Copper Tube Adapter Kit
1030384 962F Filter Cam Assy, Multi Unit 1001608 22-mm Copper Tube Adapter Kit
3 Drain Control Assembly: 1 1001609 28-mm Copper Tube Adapter Kit
1030355 DLFC Assy, 5 gpm 1001613 3/4-inch CPVC Tube Adapter Kit
1030356 DLFC Assy, 6 gpm 1001614 1-inch CPVC Tube Adapter Kit
1030357 DLFC Assy, 7 gpm 1001615 25-mm CPVC Tube Adapter Kit
1030358 DLFC Assy, 8 gpm 1001769 3/4-inch NPT Plastic Pipe Adapter Kit
1030359 DLFC Assy, 9 gpm 1001603 1-inch NPT Plastic Pipe Adapter Kit
1030360 DLFC Assy, 10 gpm 1001604 3/4-inch BSPT Plastic Pipe Adapter Kit
1000406 DLFC Assy, 12 gpm 1001605 1-inch BSPT Plastic Pipe Adapter Kit
1000407 DLFC Assy, 15 gpm 1001611 3/4-inch BSPT Brass Pipe Adapter Kit
1000408 DLFC Assy, 17 gpm 1001610 1-inch NPT Brass Pipe Adapter Kit
1000409 DLFC Assy, 20 gpm 1001612 1-inch BSPT Brass Pipe Adapter Kit
1000410 DLFC Assy, 25 gpm 13 1033444 Turbine Assembly 1
4 1030502 Ball, Flow Control 2 14 1001580 Spring, Flapper Valve
5 Injector Assembly (includes O-Rings): 1 15 1030372 Cover 1
1035736 “L” Injector - Orange * Valve Disc Kit:
1035737 “M” Injector - Brown 1041174 Standard
1035738 “N” Injector - Green 1041175 Severe Service
1035739 “Q” Injector - Purple * 1034312 Interconnect Cable, Dual Operation
1035884 “R” Injector - Dark Grey 1035593 Interconnect Cable, Triplex Operation
6 1000269 Injector Cap Assembly (includes O-RIngs): 1 * 1075768 Battery, 9-Volt Rechargable
7 Brine Refill Control 1 * Parallel Kits, Multi-unit Operation
1000224 .74 gpm * 1035923 Dual Parallel Softener Kit
1000519 1.3 gpm * 1035925 Triplex Parallel Softener Kit
8 1002449 Drain Fitting Elbow (3/4” hose barbed) 1 * 1035926 Triplex Parallel Filter
9 1000226 Screen/Cap Assembly 1

46
6.3 Performa Cv Controls
B
Y
P
A
S
S
B
Y
P
A
S
S
5
1265 Bypass
Performa Cv 962F TC
BACKWASH COMPLETE TIME OF DAY
TIME OF BACKWASH
BACKWASH CYCLE
TIME REMAINING
B
A
C
K
W
A
S
H
F
A
S
T
R
I
N
S
E
BACKWASH
DAY PM
SET
Clear
Window
TM
Performa Cv 962
REGENERATION COMPLETE
TIME OF DAY
TIME OF REGEN
HARDNESS
SALT AMOUNT
CAPACITY
REGEN TIME
REMAINING
B
A
C
K
W
A
S
H
R
I
N
S
E
REGEN
FLOW PM
SET
TM
B
R
I
N
E
/
S
L
O
W
R
I
N
S
E
F
A
S
T
R
E
F
I
L
L
Performa Cv 962TC
REGENERATION COMPLETE
TIME OF DAY
TIME OF REGEN
SALT AMOUNT
REGEN TIME
REMAINING
B
A
C
K
W
A
S
H
R
I
N
S
E
REGEN
DAY PM
SET
TM
B
R
I
N
E
/
S
L
O
W
R
I
N
S
E
F
A
S
T
R
E
F
I
L
L
Clear
Window
Performa Cv Filter
BACKWASH COMPLETE TIME OF DAY
TIME OF REGEN
SET VALUE TO 10
SET VALUE TO .5
CAPACITY
REGEN TIME
REMAINING
B
A
C
K
W
A
S
H
F
A
S
T
R
I
N
S
E
REGEN
FLOW PM
SET
Clear
Window
TM
Code
Part
No. Description Qty.
1 1053810 Performa Cv 962 50 Hz Control 1
1053811 Performa Cv 962 60 Hz Control
2 1053812 Performa CV 962FTC 50 Hz Control 1
1053813 Performa CV 962FTC 60 Hz Control
3 1053814 Performa CV 962TC 50 Hz Control 1
1053815 Performa CV 962TC 60 Hz Control
4 1053808 Performa CV 962F 50 Hz Control 1
1053809 Performa CV 962F 60 Hz Control
51040930 1265 Bypass 1
*1053780 Performa Cv 942F, 120V, 60 Hz, 7 Day Control 1
1053781 Performa Cv 942F, 120V, 60 Hz, 12 Day Control
* 1000811 Transformer 1
* 1000907 Transformer Extension Cord, 15 feet (4.6 m) 1
* 1034264 Y-Splitter (run 2 units from 1 transformer) 1
* Not Shown
34
21

47

© Copyright 2004 GE Water Technologies & Infrastructure
Printed in USA P/N 1228354 Rev. D