Rosemount 8711 Flow Tube User Manual
User Manual: Rosemount 8711 Flow Tube User Manual
Open the PDF directly: View PDF .
Page Count: 53

Series 8700
Magnetic Flowmeter
Flowtubes
00809-0100-4727
English
Rev. DA

Product Manual
1Series 8700 Magnetic
Flowmeter Flowtubes
Rosemount, the Rosemount logotype, and SMART FAMILY are registered trademarks of Rosemount Inc.
DeltaV is a trademark of the Fisher-Rosemount group of companies.
HART is a registered trademark of the HART Communication Foundation.
Tefzel and Teflon are registered trademarks of E.I. du Pont de Nemours & Co.
Ryton is a registered trademark of the Phillips Petroleum Co.
Fluoraz is a registered trademark of Greens, Tweed & Co., Inc.
Hastelloy C and Hastelloy C-22 are registered trademarks of Haynes International,
FOUNDATION is a trademark of the Fieldbus Foundation.
Cover photo: 8711-004AC
Read this manual before working with the product. For personal and system
safety, and for optimum product performance, make sure you thoroughly
understand the contents before installing, using, or maintaining this product.
Within the United States, Rosemount Inc. has two toll-free assistance numbers.
Customer Central: 1-800-999-9307 (
7:00 a.m. to 7:00 p.m. CST)
Technical support, quoting, and order-related questions.
North American 1-800-654-7768 (
24 hours a day – Includes Canada)
Response Center: Equipment service needs.
For equipment service or support needs outside the United States, your local
Rosemount representative.
The products described in this document are NOT designed for
nuclear-qualified applications.
Using non-nuclear qualified products in applications that require
nuclear-qualified hardware or products may cause inaccurate readings.
For information on Rosemount nuclear-qualified products, contact your local
Rosemount Sales Representative.
SNF-0004
NOTICE
Fisher-Rosemount satisfies all obligations coming from legislation
to harmonize product requirements in the European Union.
Rosemount Inc.
8200 Market Boulevard
Chanhassen, MN 55317 USA
Tel 1-800-999-9307
Fax (952) 949-7001
© 2000 Rosemount Inc.
Printed in the USA.
http://www.rosemount.com
P
R
I
N
T
E
D
IN
U.
S.
A.

Table of Contents
Procedures and instructions in this manual may require special precautions to
ensure the safety of the personnel performing the operations. Refer to the
safety messages at the beginning of each section before performing
any operations.
IMPORTANT
i
SECTION 1
Introduction
Manual Scope . . . . . . . . . . . . . . . . . . . . . . . . . . . . . . . . . . . . . . . . . . . 1-1
System Description . . . . . . . . . . . . . . . . . . . . . . . . . . . . . . . . . . . . . . . 1-2
Safety Messages
SECTION 2
Installation
Safety Messages . . . . . . . . . . . . . . . . . . . . . . . . . . . . . . . . . . . . . . . . . 2-1
Step 1: Handling . . . . . . . . . . . . . . . . . . . . . . . . . . . . . . . . . . . . . . . . . 2-2
Step 2: Mounting . . . . . . . . . . . . . . . . . . . . . . . . . . . . . . . . . . . . . . . . . 2-2
Calibration . . . . . . . . . . . . . . . . . . . . . . . . . . . . . . . . . . . . . . . . . . 2-2
Upstream/Downstream Piping . . . . . . . . . . . . . . . . . . . . . . . . . . 2-3
Flowtube Orientation . . . . . . . . . . . . . . . . . . . . . . . . . . . . . . . . . . 2-3
Flow Direction . . . . . . . . . . . . . . . . . . . . . . . . . . . . . . . . . . . . . . . 2-5
Step 3: Installation of Model 8705 and Model 8707 High-Signal . . . 2-5
Gaskets . . . . . . . . . . . . . . . . . . . . . . . . . . . . . . . . . . . . . . . . . . . . . 2-5
Flange Bolts . . . . . . . . . . . . . . . . . . . . . . . . . . . . . . . . . . . . . . . . . 2-6
Step 3: Installation of Model 8711 . . . . . . . . . . . . . . . . . . . . . . . . . . . 2-8
Gaskets . . . . . . . . . . . . . . . . . . . . . . . . . . . . . . . . . . . . . . . . . . . . . 2-8
Alignment and Bolting . . . . . . . . . . . . . . . . . . . . . . . . . . . . . . . . . 2-8
Flange Bolts . . . . . . . . . . . . . . . . . . . . . . . . . . . . . . . . . . . . . . . . . 2-9
Step 4: Grounding . . . . . . . . . . . . . . . . . . . . . . . . . . . . . . . . . . . . . . . . 2-10
Step 5: Wiring . . . . . . . . . . . . . . . . . . . . . . . . . . . . . . . . . . . . . . . . . . . 2-13
Conduit Ports and Connections . . . . . . . . . . . . . . . . . . . . . . . . . . 2-13
Cable Preparation . . . . . . . . . . . . . . . . . . . . . . . . . . . . . . . . . 2-15
Flowtube to Model 8712C/U Transmitter Connections . . . . . . . 2-16
High-Signal Flowtube to High-Signal Transmitter
Connections . . . . . . . . . . . . . . . . . . . . . . . . . . . . . . . . . . . . . . . . . . 2-17
Flowtube to Integral Mount Transmitter Connections . . . . . . . 2-18
Step 6: Process Leak Protection (Model 8705 and Model 8707
High-Signal Only) . . . . . . . . . . . . . . . . . . . . . . . . . . . . . . . . . . . . . . . . 2-19
Standard Housing Configuration . . . . . . . . . . . . . . . . . . . . . . . . 2-19
Relief Valves . . . . . . . . . . . . . . . . . . . . . . . . . . . . . . . . . . . . . . . . . 2-20
Process Leak Containment . . . . . . . . . . . . . . . . . . . . . . . . . . . . . 2-21
Step 7: Start-up and Operation . . . . . . . . . . . . . . . . . . . . . . . . . . . . . 2-22
Flowtube Calibration Number . . . . . . . . . . . . . . . . . . . . . . . . . . . 2-22
Quick Start-up . . . . . . . . . . . . . . . . . . . . . . . . . . . . . . . . . . . . . . . 2-22
SECTION 3
Troubleshooting
Safety Messages . . . . . . . . . . . . . . . . . . . . . . . . . . . . . . . . . . . . . . . . . 3-1
Independent Flowtube and Transmitter Replacement . . . . . . . . . . . 3-1
Flowtube Troubleshooting . . . . . . . . . . . . . . . . . . . . . . . . . . . . . . . . . 3-2
Return of Materials . . . . . . . . . . . . . . . . . . . . . . . . . . . . . . . . . . . . . . . 3-4

ii
SECTION 4
Specifications:
Model 8705 and
Model 8707
High-Signal Flowtubes
Specifications
Functional Specifications . . . . . . . . . . . . . . . . . . . . . . . . . . . . . . . . 4-1
Performance Specifications . . . . . . . . . . . . . . . . . . . . . . . . . . . . . . 4-3
Physical Specifications . . . . . . . . . . . . . . . . . . . . . . . . . . . . . . . . . . 4-4
SECTION 5
Specifications:
Model 8711 Flowtube
Specifications
Functional Specifications . . . . . . . . . . . . . . . . . . . . . . . . . . . . . . . . 5-1
Performance Specifications . . . . . . . . . . . . . . . . . . . . . . . . . . . . . . 5-3
Physical Specifications . . . . . . . . . . . . . . . . . . . . . . . . . . . . . . . . . . 5-3
APPENDIX A
Field-Removable
Electrodes
Safety Messages . . . . . . . . . . . . . . . . . . . . . . . . . . . . . . . . . . . . . . . . . A-1
Remove the Electrode Assembly . . . . . . . . . . . . . . . . . . . . . . . . . . . . A-1
Replace the Electrode Assembly . . . . . . . . . . . . . . . . . . . . . . . . . . . . A-2
INDEX I-1

Section
1-1
1Introduction
MANUAL SCOPE The Rosemount® Series 8700 Magnetic Flowmeter System combines
separate flowtube and transmitter units. This manual is designed to assist
in the installation and operation of Rosemount Model 8705, Model 8707
High-Signal, and Model 8711 Magnetic Flowmeter Flowtubes.
Specific transmitter information is located in the product manual
for the Model 8712C/U/H (document 00809-0100-4729), Model 8732C
(document 00809-0100-4725), or Model 8742C (document 00809-0100-4793)
Magnetic Flowmeter Transmitters.
Section 2: Installation
• installation instructions
Section3:Start-UpandOperation
• flowtube calibration number
• flowtube configuration information.
Section 4: Troubleshooting
• troubleshooting procedures
• electrical circuit diagrams
Section 5: Model 8705 and Model 8707 High-Signal
Flowtube Specifications
• specifications for Model 8705 and Model 8707
• reference tables
• dimensional drawings
Section 6: Model 8711 Flowtube Specifications
• specifications for Model 8711
• reference tables
• dimensional drawings
Appendix A: Field-Removable Electrodes
• instructions for removing and replacing the field-removable
electrode assembly
Attempting to install and operate Model 8705, Model 8707 High-Signal, or Model
8711 Magnetic Flowmeter Flowtubes without reviewing the instructions contained in
this manual could result in personal injury or equipment damage.

Rosemount Series 8700 Magnetic Flowmeter Flowtube
1-2
SYSTEM DESCRIPTION Rosemount Series 8700 Magnetic Flowmeter Systems measure
volumetric flow rate by detecting the velocity of a conductive liquid that
passes through a magnetic field. Magnetic Flowmeter Systems consist
of a flowtube and a transmitter.
There are three Rosemount magnetic flowmeter flowtubes:
• Flanged Model 8705
• Flanged High-Signal Model 8707
• Wafer-Style Model 8711
There are three Rosemount magnetic flowmeter transmitters:
• Model 8712C/U/H
• Model 8732C
• Model 8742C
The flowtube is installed in-line with process piping — either vertically
or horizontally. Coils located on opposite sides of the flowtube create the
necessary magnetic field. A conductive liquid moving through the
magnetic field generates a voltage that is detected by two electrodes.
The transmitter drives the coils to generate a magnetic field and
electronically conditions the voltage detected by the electrodes. The
transmitter then produces output signals proportional to the
liquid velocity.
SAFETY MESSAGES Procedures and instructions in this manual may require special
precautions to ensure the safety of the personnel performing the
operations. Refer to the safety messages listed at the beginning of each
section before performing any operations.

Section
2-1
2Installation
SAFETY MESSAGES This section covers the steps required to physically install the flowtube.
Instructions and procedures in this section may require special
precautions to ensure the safety of the personnel performing the
operations. Please refer to the following safety messages before
performing any operation in this section.
Failure to follow these installation guidelines could result in death or serious injury:
Installation and servicing instructions are for use by qualified personnel only.
Performing any servicing other than that contained in this manual may
result in death or serious injury. Do not perform any servicing other than
that contained in the operating instructions, unless qualified.
The flowtube liner is vulnerable to handling damage. Never place anything through
the flowtube for the purpose of lifting or gaining leverage. Liner damage can render
the flowtube useless.
To avoid possible damage to the flowtube liner ends, do not use metallic or
spiral-wound gaskets. If frequent removal is anticipated, take precautions to protect the
liner ends. Short spool pieces attached to the flowtube ends are often used for
protection.
Correct flange bolt tightening is crucial for proper flowtube operation and life. All bolts
must be tightened in the proper sequence to the specified torque limits. Failure to
observe these instructions could result in severe damage to the flowtube lining and
possible flowtube replacement.

Rosemount Series 8700 Magnetic Flowmeter Flowtube
2-2
STEP 1: HANDLING Handle all parts carefully to prevent damage. Whenever possible,
transport the system to the installation site in the original shipping
containers. Teflon®-lined flowtubes are shipped with end covers that
protect it from both mechanical damage and normal unrestrained
distortion. Remove the end covers just before installation.
Flanged 6- through 36-inch flowtubes come with a lifting lug on each
flange. The lifting lugs make the flowtube easier to handle when it is
transported and lowered into place at the installation site. Flanged ½-
to 4-inch flowtubes do not have lugs. They must be supported with a
lifting sling on either side of the housing.
Figure 2-1 shows flowtubes correctly supported for handling and
installation. Notice the plywood end pieces are still in place to protect
the flowtube liner during transportation.
FIGURE 2-1. Flowtube Support for
Handling and Installation
STEP 2: MOUNTING Physical mounting of a flowtube is similar to installing a typical section
of pipe. Conventional tools, equipment, and accessories (bolts, gaskets,
and grounding hardware) are required.
Calibration Rosemount flowtubes are wet calibrated at the factory. They do not
need further calibration during installation.
See Safety Messages on page 2-1 for complete warning information.
½- through 4-Inch
Flowtubes 6- through 36-Inch
Flowtubes
8705-0281D02A, 0281E02A

2-3
Installation
Upstream/
Downstream Piping
To ensure specification accuracy over widely varying process conditions,
install the flowtube a minimum of five straight pipe diameters
upstream and two pipe diameters downstream from the electrode plane
(see Figure 2-2).
FIGURE 2-2. Upstream and
Downstream Straight Pipe Diameters
Flowtube Orientation The flowtube should be installed in a position that ensures the flowtube
remains full during operation. Horizontal or inclined positions are
preferred. Figures 2-3, 2-4, and 2-5 show the proper flowtube orientation
for the most common installations.
The following orientations ensure that the electrodes are in the
optimum plane to minimize the effects of entrapped gas. Further
information on electrode orientation can be found in Appendix A.
As illustrated in Figures 2-4B and 2-5B, avoid downward flows where back
pressure does not ensure that the flowtube remains full at all times.
FIGURE 2-3.
Horizontal Flowtube Orientation
8
705-0281F02A.EPS
5PipeDiameters 2PipeDiameters
FLOW
FLOW
8705-0005F01A

Rosemount Series 8700 Magnetic Flowmeter Flowtube
2-4
FIGURE 2-4.
Vertical Flowtube Orientation
FIGURE 2-5.
Incline or Decline Orientation
FLOW
B
8705-0005G01A, 0005G01B
A
FLOW
FLOW
FLOW
B
8705-0005E01A, 0005E01B
A

2-5
Installation
Flow Direction The flowtube should be mounted so that the FORWARD end of the flow
arrow, shown on the flowtube identification tag, points in the direction
of flow through the tube (see Figure 2-6). In this mounting
configuration, the conduit ports point upstream.
FIGURE 2-6. Flow Direction
STEP 3: INSTALLATION OF
MODEL 8705 AND MODEL
8707 HIGH-SIGNAL
The following drawings should be used as a guide in the installation of
the Model 8705 and Model 8707 High-Signal Flowtubes. Refer to page
2-8 for installation of the Model 8711 Flowtube.
Gaskets The flowtube requires a gasket at each of its connections to adjacent devices
or piping. The gasket material selected must be compatible with the process
fluid and operating conditions. Metallic or spiral-wound gaskets can
damage the liner. If the gaskets will be removed frequently, protect the
liner ends.
A gasket is required on each side of the grounding ring, as shown in
Figure 2-7. All other applications (including lining protector and
grounding electrode) require only one gasket on each end connection, as
shown in Figure 2-8.
FLOW
Flow Direction Arrow
8705-0281H02F
See Safety Messages on page 2-1 for complete warning information.

Rosemount Series 8700 Magnetic Flowmeter Flowtube
2-6
FIGURE 2-7. Gasket Placement with
Non-attached Grounding Rings
FIGURE 2-8. Gasket Placement
Flange Bolts Flowtube sizes and torque values for both ASME B16.5 (ANSI) Class
150 and Class 300 flanges are listed in Table 2-1. Consult factory for
other flange ratings and types. Tighten flange bolts in the incremental
sequence as shown in Figure 2-9. See Table 5 and Table 7 for bolt sizes
and hole diameters.
Always check for leaks at the flanges after tightening the flange bolts.
Failure to use the correct flange bolt tightening methods can result in
severe damage. All flowtubes require a second torquing twenty-four
hours after initial flange bolt tightening.
Gasket (Supplied by user)
Grounding Ring
Gasket (Supplied by user)
8705-0038D
8705-0040E
Gasket (Supplied by user)
See Safety Messages on page 2-1 for complete warning information.

2-7
Installation
FIGURE 2-9. Flange Bolt
Torquing Sequence
TABLE 2-1. Flange Bolt Torque
Specifications for Model 8705 and
Model 8707 High-Signal Flowtubes
4-Bolt 8-Bolt
12-Bolt 14-Bolt
20-Bolt
8701-0870G02A
Torque the flange bolts
in increments according to
the above numerical sequence.
Size Code Line Size Class 150
(pound-feet) Class 300
(pound-feet)
005
010
015
020
030
040
060
080
100
120
140
160
180
200
240
300
360
½-inch (15 mm)
1inch(25mm)
1½ inch (40 mm)
2inch(50mm)
3inch(80mm)
4inch(100mm)
6inch(150mm)
8inch(200mm)
10 inch (250 mm)
12 inch (300 mm)
14 inch (350 mm)
16 inch (400 mm)
18 inch (450 mm)
20 inch (500 mm)
24 inch (600 mm)
30 inch (750 mm)
36 inch (900 mm)
10
10
17
25
45
35
60
80
70
80
100
90
125
125
150
150
200
10
10
22
17
35
50
65
60
65
80
–
–
–
–
–
–
–

Rosemount Series 8700 Magnetic Flowmeter Flowtube
2-8
STEP 3: INSTALLATION OF
MODEL 8711
The following section should be used as a guide in the installation of the
Model 8711 Flowtube.
Gaskets The flowtube requires a gasket at each of its connections to adjacent devices
or piping. The gasket material selected must be compatible with the process
fluid and operating conditions. Metallic or spiral-wound gaskets can
damage the liner. If the gaskets will be removed frequently, protect the
liner ends. If grounding rings are used, a gasket is required on each
side of the grounding ring.
Alignment and Bolting 1. On 1½ - through 8-inch (40 through 200 mm) line sizes, place
centering rings over each end of the flowtube. The smaller line
sizes, 0.15- through 1-inch (4 through 25 mm), do not require
centering rings.
2. Insert studs for the bottom side of the flowtube between the pipe
flanges. Stud specifications are listed in Table 2-2 Using carbon
steel bolts on smaller line sizes, 0.15- through 1-inch (4
through 25 mm), rather than the required stainless steel
bolts, will degrade performance.
TABLE 2-2. Stud Specifications
3. Place the flowtube between the flanges. Make sure that the
centering rings are properly placed in the studs. The studs should
be aligned with the markings on the rings that correspond to the
flange you are using.
4. Insert the remaining studs, washers, and nuts.
5. Tighten to the torque specifications shown in Table 2-1 Do not
overtighten the bolts or the liner may be damaged.
NOTE
On the 4- and 6-inch PN 10–16, insert the flowtube with rings first and then
insert the studs. The slots on this ring scenario are located on the inside of
the ring.
See Safety Messages on page 2-1 for complete warning information.
Nominal Flowtube Size Stud Specifications
0.15 – 1 inch (4 – 25 mm) 316 SST ASTM A193, Grade B8M Class 1 threaded mounted studs
1½ – 8 inch (40 – 200 mm) CS, ASTM A193, Grade B7, threaded mounting studs

2-9
Installation
FIGURE 2-10. Gasket Placement with
Centering Rings
Flange Bolts Flowtube sizes and torque values for both Class 150 and Class 300
flanges are listed in Table 2-3. Tighten flange bolts in the incremental
sequence, shown in Figure 2-9.
Always check for leaks at the flanges after tightening the flange
bolts. All flowtubes require a second torquing 24 hours after initial
flange bolt tightening.
TABLE 2-3. Torque specifications
Customer-supplied
Gasket
8732-0002A1A
Centering Rings
FLOW
Installation, Studs
Nuts and Washers
Size Code Line Size Pound-feet Newton-meter
15F
30F
005
010
015
020
030
040
060
080
0.15 inch (4 mm)
0.30 inch (8 mm)
½-inch (15 mm)
1inch(25mm)
1½ inch (40 mm)
2inch(50mm)
3inch(80mm)
4 inch (100 mm)
6 inch (150 mm)
8 inch (200 mm)
5
5
5
10
15
25
40
30
50
70
6.8
6.8
6.8
13.6
20.5
34.1
54.6
40.1
68.2
81.9

Rosemount Series 8700 Magnetic Flowmeter Flowtube
2-10
STEP 4: GROUNDING Grounding the flowtube is one of the most important details of flowtube
installation. Proper grounding ensures that only the voltage induced in
the magnetic field of the flowtube is measured. Use Table 2-4 to
determine which grounding option to follow for proper installation.
Attached grounding rings should be grounded equivalently to
non-attached grounding rings.
NOTE
Consult factory for installations requiring cathodic protection or situations
where there are high currents or high potential in the process.
The flowtube case should always be grounded in accordance with
national and local electrical codes. Failure to do so may impair the
protection provided by the equipment. The most effective grounding
method is direct connection to earth ground with minimal impedance.
The Internal Ground Connection (Protective Ground Connection)
located in side the junction box is the Internal Ground Connection
screw. This screw is identified by the ground symbol:
TABLE 2-4. Grounding Installation
Grounding Options
Type of Pipe No Grounding Options Grounding Rings Grounding Electrodes Lining Protectors
Conductive Unlined Pipe See Figure 2-11 Not Required Not Required See Figure 2-12
Conductive Lined Pipe Insufficient Grounding See Figure 2-12 See Figure 2-11 See Figure 2-12
Non-Conductive Pipe Insufficient Grounding See Figure 2-13 See Figure 2-14 See Figure 2-13

2-11
Installation
FIGURE 2-11. No Grounding Options
or Grounding Electrode in Lined Pipe
FIGURE 2-12. Grounding with
Grounding Rings or Lining Protectors
Earth
Ground
8705-0040C
Earth
Ground
8705-0038C
Grounding Rings
or
Lining Protectors

Rosemount Series 8700 Magnetic Flowmeter Flowtube
2-12
FIGURE 2-13. Grounding with
Grounding Rings or Lining Protectors
FIGURE 2-14. Grounding with
Grounding Electrodes
8705-0038E
Grounding Rings
or
Lining Protectors
Earth
Ground
Earth
Ground
8705-0040D

2-13
Installation
STEP 5: WIRING The conduit connections needed for installation depend on transmitter
location. A conduit run between the flowtube and transmitter is not
required if the transmitter is integrally mounted on the flowtube.
Conduit Ports
and Connections
Both the flowtube and transmitter junction boxes have ports for ¾-inch
NPT conduit connections. These connections should be made in
accordance with local or plant electrical codes. Unused ports should be
sealed with metal plugs. Housing damage will result if metal plugs
are overtightened.
Flanged and wafer flowtubes have two conduit ports as shown in
Figures 1, 2, 3, and 1. Either one may be used for both the coil drive and
electrode cables. Use the stainless steel plug that is provided to seal the
unused conduit port.
Series 8700 Flowtubes use a pulsed-dc signal generated by Model
8712C/U/H, Model 8732C, or Model 8742C Magnetic Flowmeter
Transmitter. Connect the Model 8712H High-Signal Magnetic
Flowmeter Transmitter only to the Model 8707 High-Signal Flowtube.
A single dedicated conduit run for the coil drive and electrode cables is
needed between a flowtube and a remote transmitter. Bundled cables in
a single conduit are likely to create interference and noise problems in
your system. Use one set of cables per conduit run. See Figure 2-15 for
proper conduit installation diagram and Table 2-5 for
recommended cable.
Use wire rated for the proper temperature application. For connections
in ambient temperatures above 140 °F (60 °C), use a wire rated for
176 °F (80 °C). For ambients greater than 176 °F (80 °C), use a wire
rated for 230 °F (110 °C).
This is a pulsed dc magnetic
flowmeter. Do not connect ac
power to the flowtube or to
terminals 1 and 2 of the
transmitter, or replacement of the
electronics board will be necessary.

Rosemount Series 8700 Magnetic Flowmeter Flowtube
2-14
FIGURE 2-15. Conduit Preparation
TABLE 2-5. Cable Requirements Transmitter Input Power
Remote transmitter installations require equal lengths of signal and
coil drive cables. Integrally mounted transmitters are factory wired and
do not require interconnecting cables.
Lengths from 5 to 1,000 feet (1.5 to 300 meters) may be specified, and
will be shipped with the flowtube.
Cable longer than 100 feet (30 meters) is not recommended for
high-signal magmeter systems.
Coil Drive and Electrode
Cables Coil Drive and Electrode
Cables
Power
Outputs
Power
Outputs
WRONG CORRECT
Power
Outputs
Power
Outputs
8705-0005CDGA, DDGA
Description Part Number
Signal Cable (20 AWG)
Belden 8762, Alpha 2411 equivalent
08712-0061-0001
Coll Drive Cable (14 AWG)
Belden 8720, Alpha 2442 equivalent
08712-0060-0001
Combination Signal and Coil
Drive Cable (18 AWG)(1)
Belden 9368 equivalent
(1) Combination signal and coil drive cable is not recommended for
high-signal magmeter system. For remote mount installations,
combination signal and coil drive cable should be limited to less
than 100 ft (30 m).
08712-0750-0001

2-15
Installation
Cable Preparation Prepare the flowtube ends of the coil drive and electrode cables, as
shown in Figure 2-16.
NOTE
The maximum length for unshielded wire in the wiring compartment is ½-inch.
Correct cable preparation is important for a successful installation. The
cable shield should be stripped back no more than 0.50 inch. If more wire is
exposed, electrical noise will increase and create unstable meter readings.
FIGURE 2-16. Cable
Preparation Detail
IMPORTANT
Failure to connect the cable shields will result in improper operation.
Series 8700 Flowtube Systems require that the cable shields be
connected at the flowtube for proper operation.
0.50inc
h
Cable Shield
8705-0041B

Rosemount Series 8700 Magnetic Flowmeter Flowtube
2-16
Flowtube to Model 8712C/U
Transmitter Connections
Connect coil drive and electrode cables as shown in Figure 2-17.
FIGURE 2-17. Wiring Diagram to
Model 8712C/U Transmitter
8712-04A
This is a pulsed dc
magnetic flowmeter. Do
not connect ac power
to the flowtube or to
terminals 1 and 2 of
the transmitter,or
replacement of the
electronics board will be
necessary.
TABLE 2-6. Flowtube to Remote
Mount Transmitter
Rosemount
Model 8712C/U
Transmitters
Rosemount Model
8705/8707/8711
Flowtubes
11
22
17 17
18 18
19 19

2-17
Installation
High-Signal Flowtube
to High-Signal
Transmitter Connections
Connect coil drive and electrode cables as shown in Figure 2-18.
FIGURE 2-18. Wiring Diagram to
Model 8712H High-Signal Transmitter
8712-03A
This is a pulsed dc
magnetic flowmeter. Do
not connect ac power
to the flowtube or to
terminals 1 and 2 of
the transmitter,or
replacement of the
electronics board will
be necessary.
TABLE 2-7. High-Signal Flowtube to
High-Signal Transmitter
Rosemount
Model 8712H
Transmitters
Rosemount Model
8707 Flowtubes
11
22
17 17
18 18
19 19

Rosemount Series 8700 Magnetic Flowmeter Flowtube
2-18
Flowtube to Integral Mount
Transmitter Connections
Connect coil drive and electrode cables as shown in Figure 2-19.
FIGURE 2-19. Wiring Diagram to
Model 8732C/8742C Transmitter
8732-8732B01A
Electronics Board
W
This is a pulsed dc
magnetic flowmeter. Do
not connect ac power
to the flowtube or to
terminals 1 and 2 of
the transmitter,or
replacement of the
electronics board will
be necessary.
TABLE 2-8. Flowtube to Integral
Mount Transmitter
Rosemount Model
8732C/8742C
Rosemount
Model 8705/8711
Flowtubes
11
22
17 17
18 18
19 19
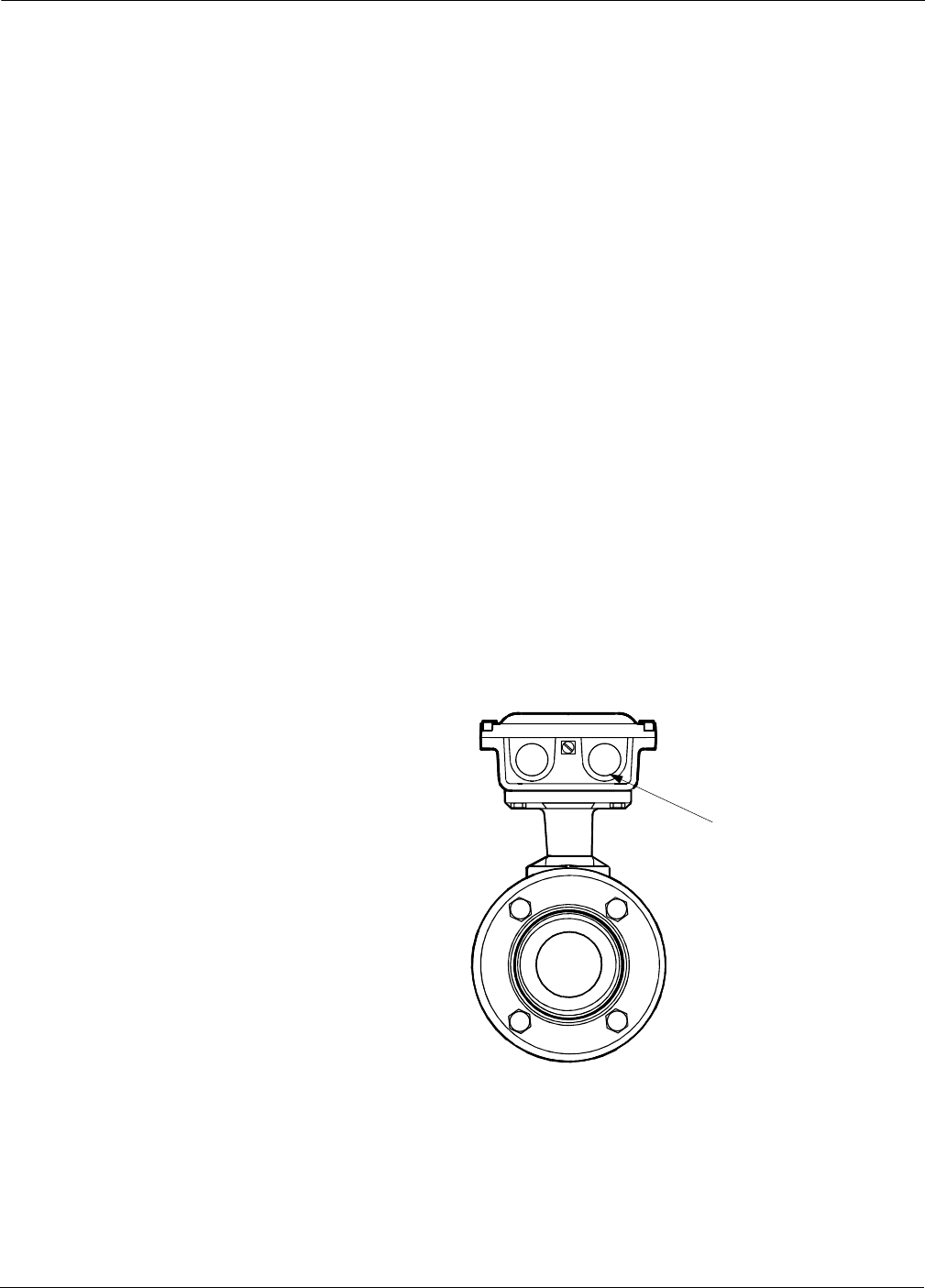
2-19
Installation
STEP 6: PROCESS LEAK
PROTECTION
(MODEL 8705 AND MODEL
8707 HIGH-SIGNAL ONLY)
The Model 8705 and Model 8707 High-Signal Flowtube housing is
fabricated from carbon steel to perform two separate functions. First, it
provides shielding for the flowtube magnetics so that external
disturbances cannot interfere with the magnetic field and thus affect
the flow measurement. Second, it provides the physical protection to
the coils and other internal components from contamination and
physical damage that might occur in an industrial environment. The
housing is completely welded and gasket-free.
The three housing configurations are identified by the W0, W1, or W3
in the model number option code when ordering. Below are brief
descriptions of each housing configuration, which are followed by a
more detailed overview.
•Code W0 — sealed, welded coil housing (standard configuration)
•Code W1 — sealed, welded coil housing with a relief valve
capable of venting fugitive emissions to a safe location (additional
plumbing from the flowtube to a safe area, installed by the user, is
required to vent properly)
•Code W3 — sealed, welded coil housing with separate electrode
compartments capable of venting fugitive emissions (additional
plumbing from the flowtube to a safe area, installed by the user, is
required to vent properly)
Standard Housing
Configuration
The standard housing configuration is identified by a code W0 in the
model number. This configuration does not provide separate electrode
compartments with external electrode access. In the event of a process
leak, these models will not protect the coils or other sensitive areas
around the flowtube from exposure to the pressure fluid.
FIGURE 2-20. Standard Housing —
Configuration Sealed Welded Housing
(Option Code W0)
¾–14 NPT Conduit
Connection
(no relief valve)
8705-1002A05D

Rosemount Series 8700 Magnetic Flowmeter Flowtube
2-20
Relief Valves The first optional configuration, identified by the W1 in the model
number option code, uses a completely welded coil housing. This
configuration does not provide separate electrode compartments with
external electrode access. This optional housing configuration provides
a relief valve in the housing to prevent possible overpressuring caused
by damage to the lining or other situations that might allow process
pressure to enter the housing. The relief valve will vent when the
pressure inside the flowtube housing exceeds 5 psi. Additional piping
(provided by the user) may be connected to this relief valve to drain any
process leakage to safe containment (see Figure 2-21).
FIGURE 2-21. Coil-Housing
Configuration — Standard Welded
Housing With Relief Valve
(Option Code W1)
Optional:
Use drain port to
plumb to a safe area
(Supplied by user) ¾–14 NPT Conduit
Connection
8705-0021A05B
¼''NPT–5psi
Pressure Relief Valve

2-21
Installation
Process Leak Containment The second optional configuration, identified as option code W3 in the
model number, divides the coil housing into three compartments: one
for each electrode and one for the coils. Should a damaged liner or
electrode fault process fluid to migrate behind the electrode seals, the
fluid is contained in the electrode compartment. The sealed electrode
compartment prevents the process fluid from entering the coil
compartment where it would damage the coils and other
internal components.
The electrode compartments are designed to contain the process fluid at
full line pressure. An o-ring sealed cover provides access to each of the
electrode compartments from outside the flowtube; drainports are
provided in each cover for the removal of fluid.
NOTE
The electrode compartment could contain full line pressure and it must
be depressurized before the cover is removed.
FIGURE 2-22. Housing Configuration
— Sealed Electrode Compartment
(Option Code W3)
If necessary, capture any process fluid leakage, connect the appropriate
piping to the drainports, and provide for proper disposal (see Figure
2-22).
Fused Glass Seal
Sealed Electrode Compartment
¼–NPT
O-Ring Seal
Optional:
Use drain port to
plumb to a safe area
(Supplied by user)
8705-0007ADGB
Grounding Electrode Port

Rosemount Series 8700 Magnetic Flowmeter Flowtube
2-22
STEP 7: START-UP
AND OPERATION
Start-up and operation is dependent upon the transmitter selected to
complement the flowtube. For transmitter start-up information, refer to
the Model 8712C/U/H manual (document 00809-0100-4729), the Model
8732C manual (document 00809-0100-4725), or the Model 8742C
manual (document 00809-0100-4793).
Flowtube
Calibration Number
A unique flowtube calibration number, imprinted on the flowtube tag,
enables any flowtube to be used with any Rosemount transmitter
without further calibration. Rosemount flow lab tests determine
individual flowtube output characteristics. The characteristics are
identified by a 16-digit calibration number.
The 16-digit calibration number can be programmed into the Model
8712C/U/H or Model 8732C transmitter using the Local Operator
Interface (LOI) or the Model 275 HART® Communicator. Refer to the
appropriate transmitter product manual for complete instructions. In a
FOUNDATION™ fieldbus environment, the Model 8742C can be
configured using the DeltaV™ configuration tool or another
FOUNDATION fieldbus configuration device.
The calibration number is more than a correction factor, or K- factor, for
the flowtube. The first five digits represent the low frequency gain. The
ninth through thirteenth digits represent the high frequency gain. Both
numbers are normalized from an ideal number of 10000. Standard
configurations use the low frequency gain, but in noisy applications it
may be worthwhile to switch to the higher frequency. An additional
transmitter procedure, called Auto Zero, is required to perform at the
higher coil drive frequency. The full procedure can be found in the
appropriate transmitter manual. The seventh and eigth digits
represent the zero offset at both frequencies where the nominal value
is 50. Empty pipe functionality is a transmitter feature that is
controlled by the flowtube calibration number. To turn off this feature,
change the fourteenth digit to the number 7.
Quick Start-up To initiate a basic transmitter start-up, only four parameters are required:
• Tube calibration number
•Tube size
•Units
• Analog output range (URV)
Refer to the Model 8712C/U/H, Model 8732C, or Model 8742C product
manuals for complete transmitter start-up instructions.

Section
3-1
3Troubleshooting
SAFETY MESSAGES Instructions and procedures in this section may require special
precautions to ensure the safety of the personnel performing the
operations. Refer to the following safety messages before performing
any operation in this section.
INDEPENDENT
FLOWTUBE AND
TRANSMITTER
REPLACEMENT
Rosemount flow lab tests determine individual flowtube characteristics
and account for them with the 16-digit calibration number. Flowtube
interchangability reduces the need for spare transmitters. It also
ensures factory-calibrated accuracy without additional calibration
procedures or equipment. The unique calibration number is loaded into
the transmitters, enabling the interface of a Rosemount flowtube to
communicate with a Rosemount transmitter. A description of the
flowtube calibration number is included on page 2-22.
Failure to follow these installation guidelines could result in death or serious injury:
Installation and servicing instructions are for use by qualified personnel only.
Performing any servicing other than that contained in this manual may result in death
or serious injury. Do not perform any servicing other than that contained in the
operating instructions, unless qualified.
Mishandling products exposed to a hazardous substance may result in death or
serious injury. If the product being returned was exposed to a hazardous substance
as defined by OSHA, a copy of the required Material Safety Data Sheet (MSDS) for
each hazardous substance identified must be included with the returned goods.

Rosemount Series 8700 Magnetic Flowmeter Flowtube
3-2
FLOWTUBE
TROUBLESHOOTING
The Model 8712C/U/H, Model 8732C, or Model 8742C Magnetic
Flowmeter Transmitters perform self diagnostics on the entire
magnetic flowmeter system: the transmitter, the flowtube, and the
interconnecting wiring. While most of the diagnostics are related
to the transmitter microprocessor, some tests diagnose specific
flowtube problems.
NOTE
Before performing any of the flowtube tests, cut off power and
disconnect all connections inside the flowtube junction box.
If a problem with the flowtube is identified, the following chart can
assist in troubleshooting the flowtube.
Take all readings from inside the junction box with a multimeter.
Readings taken at the transmitter terminals may provide incorrect or
inconclusive information and should be avoided.
A flowtube circuit diagram is shown in Figure 3-1.

3-3
Troubleshooting
TABLE 3-1. Flowtube Troubleshooting
Test A–Flowtube Coil
Step 1 Step 2 Step 3
Disconnect power from the transmitter
by removing the fuse. Disconnect wires
1and2fromthetransmitter.
➤Measure the resistance across wires 1
and 2 going to the flowtube, using the
lowest ohms scale. The reading should
be between 2 and 18 V.
➤A reading outside this range indicates
that the coils or cables may be open
or shorted.
Test B– Coil Shield to Coil
Step 1 Step 2 Step 3
Disconnect power from the transmitter
by removing the fuse. Disconnect wires
1, 2, and ground from the transmitter.
➤Measure the resistance from the coil
shield (ground) to wires 1 and 2 using
the highest scale. Both readings should
be overrange.
➤Any reading on the scale indicates that
the coils are shorted to the housing.
Test C– Electrode Shield to Electrode (See Note Below)
Step 1 Step 2 Step 3
Disconnect power from the transmitter
by removing the fuse. Disconnect wires
17, 18, and 19 from the transmitter. Test
with process in the flowtube (either flow
or no flow).
➤Measuretheresistancefromwire17to
18 and 17 to 19. This reading will
change as you hold the leads on the
wires, so use the initial reading.
These readings should both be between
1kVand 3 MVand close to each other.
➤A reading near 68kVor 0Vindicates a
possible shorted electrode. A stable
reading indicates a shorted electrode.
A high reading indicates a possible
coated electrode, non-conductive
process, or electrode not in contact
with process.
Test D– Positive to Negative Electrode (See Note Below)
Step 1 Step 2 Step 3
Disconnect power from the transmitter
by removing the fuse. Disconnect wires
18, and 19 from the transmitter. Test with
process in the flowtube (either flow or
no flow).
➤Measure the resistance between wires
18 and 19. This reading should be in the
range between 100 kVand 2MV.
➤An overrange reading indicates a coated
electrode, non-conductive process,
or electrode not in contact with the
process.
Test E– Coils to Electrode
Step 1 Step 2 Step 3
Disconnect power from the transmitter
by removing the fuse. Disconnect all
wires from the transmitter.
➤Measure the resistance between wires 1
or 2 and 18 and between 1 or 2 and 19.
Both readings should be in overrange.
➤Any reading on scale indicates a
resistive path from the coils to electrode.

Rosemount Series 8700 Magnetic Flowmeter Flowtube
3-4
FIGURE 3-1.
Flowtube Circuit Diagram
RETURN OF MATERIALS To expedite the return process outside the United States, contact the
nearest Fisher-Rosemount representative.
The North American Response Center (1-800-654-7768) will assist you
with any needed information or materials and is available for users
within the United States and Canada, 24 hours a day.
The center will ask for product model and serial numbers, and will
provide a Return Material Authorization (RMA) number. The center
will also ask for the name of the process material the product was last
exposed to. Mishandling products exposed to a hazardous substance
may result in death or serious injury. A copy of the Material Safety
Data Sheet may be required, depending on the nature of the hazardous
substance as defined by OSHA.
The North American Response Center will provide the additional
information and procedures necessary to return goods exposed to
hazardous substances.
8712-0007E04A
68.1kV (not applicable for flowtubes
with N0 hazardous certification
approval option code)
Flowtube Housing
68.1kV
See Safety Messages on page 3-1 for complete warning information.

Section
4-1
4Specifications:
Model 8705 and Model 8707
High-Signal Flowtubes
SPECIFICATIONS
Functional Specifications Service
Conductive liquids and slurries
Line Sizes
1/2–36 inch (15–900 mm) for Model 8705
3–36 inch (80–600 mm) for Model 8707
Interchangeability
Model 8705 flowtubes are interchangeable with Model 8712C/U, Model
8732, and Model 8742C Transmitters. Model 8707 High-Signal
Flowtubes are interchangeable with Model 8712H High-Signal
Transmitters. System accuracy is maintained regardless of line size or
optional features. Each flowtube nameplate has a sixteen-digit
calibration number that can be entered into a transmitter through the
Local Operator Interface (LOI) or the HART Communicator on the
Model 8712C/U/H and the Model 8732C. In a FOUNDATION™ fieldbus
environment, the Model 8742C can be configured using the DeltaV™
fieldbus configuration tool or another FOUNDATION fieldbus
configuration device. No further calibration is necessary.
Upper Range Limit
30 ft/s (10 m/s)
Process Temperature Limits
Teflon (PTFE) Lining
–20 to 350 °F (–29 to 177 °C)
Tefzel (ETFE) Lining
–20 to 300 °F (–29 to 149 °C)
Polyurethane Lining
0 to 140 °F (–18 to 60 °C)
Neoprene Lining
0 to 185 °F (–18 to 85 °C)
Linatex Lining (Not available for Model 8707)
0 to 158 °F (–18 to 70°C)
Ambient Temperature Limits
–30 to 150 °F (–34 to 65 °C)
Ambient Conditions
Overvoltage category I. Pollution Degree 2

Rosemount Series 8700 Magnetic Flowmeter Flowtubes
4-2
Pressure Limits
See Table 1 and Table 2 for flange limits. (Verify that the process
temperature does not exceed liner material specifications.)
Pressure and Vacuum Limits
Full vacuum at maximum lining material temperature; consult factory
for vacuum applications that require Teflon (PTFE) lining material and
line sizes greater than 6 inches (150 mm) or larger
Submergence Protection
IP 68. Continuous to 30 feet (10 meters)
Enclosure Rating
NEMA 4x. CSA 4
Electrical Rating (Model 8707 only)
Coil drive: 185 V pulse dc, 6 Hz, 250 W
Electrode: 5 V 1 W
Hazardous Location Certifications
N0 Factory Mutual (FM) Approval Dust-ignition proof for Class II/III,
Division 1 Groups E, F, and G; Non-incendive for Class I, Division
2 Groups A, B, C, and D; T5 temperature code; For non-flammable
process fluid service only
AND
Canadian Standards Association (CSA) Approval Suitable for use
in Class I, Division 2 Groups A, B, C, and D; Dust-ignition proof for
Class II/III, Division 1, Groups E, F, and G hazardous locations
AND
CE Marking (Model 8705 only)
TABLE 4-1. Flowtube Temperature vs. Pressure Limits
for ASME B16.5 Class Flanges (1/2- to 24-inch line sizes)(1)
Flange Material Flange Rating
Pressure
@ -20 to 100 °F
(-29 to 38 °C) @ 200 °F
(93 °C) @ 300 °F
(149 °C) @ 350 °F
(177 °C)
Carbon Steel Class 150 255 psi 260 psi 230 psi 215 psi
Class 300 740 psi 675 psi 655 psi 645 psi
304 Stainless Steel Class 150 275 psi 235 psi 205 psi 190 psi
Class 300 720 psi 600 psi 530 psi 500 psi
(1) 30- and 36-inch AWWA C207 Table 2 Class D rated to 150 psi at 150 °F (66 °C).
TABLE 4-2. Flowtube Temperature vs. Pressure Limits
for DIN Flanges (15 to 600 mm line sizes)
Flange Material Flange Rating
Pressure
@ -29 to 50 °C
(-20 to 122 °F) @ 100 °C
(212 °F) @ 150 °C
(302 °F) @ 175°C
(347 °F)
Carbon Steel
PN 10(1) 10 bar 10 bar 9.6 bar 9 bar
PN 16 16 bar 16 bar 15.2 bar 14.2 bar
PN 25 25 bar 25 bar 24 bar 22.5 bar
PN 40 40 bar 40 bar 37.1 bar 34.5 bar
304 Stainless Steel PN 10(1) 10 bar 8.4 bar 7.6 bar 7.2 bar
PN 16 16 bar 13.5 bar 12.2 bar 11.6 bar
PN 25 25 bar 21.2 bar 19.1 bar 18.2 bar
PN 40 31.1 bar 27.5 bar 25.8 bar 25.1 bar
(1) Minimum temperature is -10 °C (14 °F).

4-3
Specifications: Model 8705 and Model 8707 High-Signal Flowtubes
N5 Factory Mutual (FM) Approval Dust-ignition proof for Class II/III,
Division 1 Groups E, F, and G; Non-incendive for Class I, Division
2 Groups A, B, C, and D; T5 temperature code; For flammable
process fluid service
KD KEMA/CENELEC (Model 8705 only)
EEx e ia IIC T3...T6 (See Table 3)
AND
CE Marking (Model 8705 only)
Conductivity Limits
Process liquid must have a conductivity of 5 microsiemens/cm (5
micromhos/cm) or greater for Model 8705. Process liquid must have a
conductivity of 50 microsiemens/cm (50 micromhos/cm) for Model 8707
(excludes the effect of interconnecting cable length in remote mount
transmitter installations).
Performance
Specifications (System specifications are given using the frequency output and with the
unit at referenced conditions.)
Accuracy
Model 8705 with Model 8712C/U, Model 8732C, or Model 8742C
±0.5% of rate from 1 to 30 ft/s (0.3 to 10 m/s); includes combined
effects of linearity, hysteresis, repeatability, and calibration
uncertainty; accuracy is ±0.005 ft/s (±0.0015 m/s) from low-flow
cutoff to 1.0 ft/s (0.3 m/s)
Model 8707 with Model 8712C/U/H, Model 8732C, or Model 8742C
±0.5% of rate from 3 to 30 ft/s (1 to 10 m/s); include combined effects
of linearity, hysteresis, repeatability and calibration uncertainty;
accuracy is ±0.015 ft/s (±0.0045 m/s) from low-flow cutoff to 3.0 ft/s
(1 m/s)
TABLE 4-3. Relation Between Ambient Temperature, Process
Temperature, and Temperature Class(1)
(1) This table is applicable for KEMA/CENELEC approval only.
Meter Size
(inches) MaximumAmbient
Temperature Maximum Process
Temperature Temperature
Class
1/2149 °F (65 °C) 240 °F (116 °C) T3
1
1
149 °F (65 °C)
95 °F (35 °C)
248 °F (120 °C)
95 °F (35 °C)
T3
T4
11/2
11/2
149 °F (65 °C)
140 °F (60 °C)
257 °F (125 °C)
140 °F (60 °C)
T3
T4
2
2
2
149 °F (65 °C)
149 °F (65 °C)
104 °F (40 °C)
257 °F (125 °C)
167 °F (75 °C)
104 °F (40 °C)
T3
T4
T5
3-4
3-4
3-4
3-4
149 °F (65 °C)
149 °F (65 °C)
131 °F (55 °C)
104 °F (40 °C)
266 °F (130 °C)
167 °F (75 °C)
194 °F (90 °C)
104 °F (40 °C)
T3
T4
T5
T6
6
6
6
6
149 °F (65 °C)
149 °F (65 °C)
149 °F (65 °C)
140 °F (60 °C)
175 °F (79 °C)
167 °F (75 °C)
230 °F (110 °C)
140 °F (60 °C)
T3
T4
T5
T6
8-36
8-36
8-36
8-36
149 °F (65 °C)
149 °F (65 °C)
149 °F (65 °C)
149 °F (65 °C)
284 °F (140 °C)
240 °F (116 °C)
176 °F (80 °C)
149 °F (65 °C)
T3
T4
T5
T6

Rosemount Series 8700 Magnetic Flowmeter Flowtubes
4-4
Vibration Effect
IEC 770 Pipeline Installation Conditions
Mounting Position Effect
None when installed to ensure flowtube remains full.
Physical Specifications Non-Wetted Materials
Flowtube Housing
Welded, AISI Type 304 SST or Type 316L SST
Flanges
Carbon steel, AISI Type 304 SST, or Type 316L SST
Paint
Polyurethane
Process Wetted Materials
Lining
Teflon (PTFE), Tefzel (ETFE), polyurethane, neoprene, Linatex
Electrodes
316L SST, Hastelloy C-276, tantalum, 90% platinum-10% iridium,
titanium
Process Connections
ASME B16.5 (ANSI) Class 150, Class 300, or Class 600
0.5- to 24-inch
AWWA C207 Table 2 Class D
30- and 36-inch
DIN PN 10, 16, 25, and 40
PN10: Not available for flange sizes from 15 to 150 mm
PN16: Not available for flange sizes from 15 to 80 mm
PN 25: Not available for flange sizes from 15 to 150 mm
PN40: Available for all flange sizes
AISI Type 304 SST Sanitary Tri-Clover
3-A approved quick disconnect ferrule-mounted to ASME B16.5
(ANSI) Class 150 flange; 0.5- to 3-inch
Electrical Connections
Two ¾–14 NPT connections with number 8 screw terminals are
provided in the terminal enclosure for electrical wiring.
Grounding Electrode
A grounding electrode is installed similarly to the measurement
electrodes through the flowtube lining. It is available in all electrode
materials.
Grounding Rings
Grounding rings are installed between the flange and the tube face on
both ends of the flowtube. They have an I.D. slightly larger than the
flowtube I.D. and an external tab to attach ground wiring. Grounding
rings are available in 316L SST, Hastelloy-C, titanium, and tantalum.

4-5
Specifications: Model 8705 and Model 8707 High-Signal Flowtubes
Lining Protectors
Lining protectors are installed between the flange and the tube face on
both ends of the flowtube. The leading edge of lining material is
protected by the lining protector; lining protectors cannot be removed
once they are installed. Lining protectors are available in 316L SST,
Hastelloy-C, and titanium.
Flowtube Dimensions
See Table 5, Table 7, Table 6
See Figure ?-??, Figure ?-??, and Figure ?-??
Weight
See Table 4
TABLE 4-4. Flowtube Weight
CF = Consult Factory
Nominal Line Size(1)
Inches (mm)
(1) 30- and 36-inch AWWA C207 Table 2 Class D rated to
150 psi at 150 °F (66 °C).
Flowtube Flange
Rating Flowtube Weight
lb (kg)
ASME
B16.5
(ANSI) DIN
½ (15)
½ (15)
150
300
PN 40 20 (9)
22 (10)
1 (25)
1 (25)
150
300
PN 40 20 (9)
22 (10)
1½ (40)
1½ (40)
150
300
PN 40 22 (10)
24 (11)
2 (50)
2 (50)
150
300
PN 40 26 (12)
28 (13)
3 (80)
3 (80)
150
300
PN 40 40 (18)
47 (21)
4 (100)
4 (100)
150
300
PN 16 48 (22)
65 (30)
6 (150)
6 (150)
150
300
PN 16 81 (37)
93 (42)
8 (200)
8 (200)
150
300
PN 10 110 (50)
162 (74)
10 (250)
10 (250)
150
300
PN 10 220 (98)
300 (136)
12 (300)
12 (300)
150
300
PN 10 330 (150)
435 (197)
14 (350)
16 (400)
150
150
PN 10
PN 10
370 (168)
500 (227)
18 (450)
20 (500)
150
150
PN 10
PN 10
600 (272)
680 (308)
24 (600) 150 PN 10 1,000 (454)
30 (750)
36 (900)
125
125
CF
CF
1,400 (637)
1,975 (898)

Rosemount Series 8700 Magnetic Flowmeter Flowtubes
4-6
TABLE 4-5. Model 8705 and Model 8707 Dimensions in Inches (Millimeters).
Refer to Dimensional Drawings, Figure 1, Figure 2, and Figure 3
Line Size(1)
and Flange
Rating
(ASME B
16.5)
Liner Face
Diameter
“A”
Process
Flange Rad.
“B”
Overall
Flowtube
Length
“L”(2) Body Height
“C” Body Width
’“D”
Centerline to
Conduit
“E”
Bolt Hole
Circle
Diameter Bolt Hole
Diameter
Number
and Size
of Bolts
0.5–150
0.5 –300
1.38 (35)
1.38 (35)
1.75 (44)
1.88 (48)
7.88 (200)
7.88 (200)
8.75 (222)
8.75 (222)
6.88 (175)
6.88 (175)
5.16 (131)
5.16 (131)
2.38 (60)
2.62 (67)
0.62 (16)
0.62 (16)
4–1/2
4–1/2
1 –150
1 –300
2.00 (51)
2.00 (51)
2.13 (54)
2.44 (62)
7.88 (200)
7.88 (200)
8.75 (222)
8.75 (222)
7.34 (186)
7.34 (186)
5.16 (131)
5.16 (131)
3.12 (79)
3.50 (89)
0.62 (16)
0.75 (19)
4–1/2
4–5/8
1.5 –150
1.5 –300
2.88 (73)
2.88 (73)
2.50 (64)
3.06 (78)
7.88 (200)
7.88 (200)
9.52 (242)
9.52 (242)
7.05 (179)
7.05 (179)
5.57 (141)
5.57 (141)
3.88 (99)
4.50 (114)
0.62 (16)
0.88 (22)
4–1/2
4–3/4
2 –150
2 –300
3.62 (92)
3.62 (92)
3.00 (76)
3.25 (83)
7.88 (200)
7.88 (200)
9.52 (242)
9.52 (242)
7.47 (190)
7.47 (190)
5.57 (141)
5.57 (141)
4.75 (121)
5.00 (127)
0.75 (19)
0.75 (19)
4–5/8
8–5/8
3 –150
3 –300
5.00 (127)
5.00 (127)
3.75 (95)
4.13 (105)
7.88 (200)
8.63 (219)
11.52 (293)
11.52 (293)
9.57 (243)
9.57 (243)
6.57 (167)
6.57 (167)
6.00 (152)
6.62 (168)
0.75 (19)
0.88 (22)
4–5/8
8–3/4
4 –150
4 –300
6.19 (157)
6.19 (157)
4.50 (114)
5.00 (127)
9.84 (250)
10.88 (276)
12.22 (310)
12.22 (310)
10.01 (254)
10.01 (254)
6.92 (176)
6.92 (176)
7.50 (191)
7.88 (200)
0.75 (19)
0.88 (22)
8–5/8
8–3/4
6 –150
6 –300
8.50 (216)
8.50 (216)
5.50 (140)
6.25 (159)
11.81 (300)
13.06 (332)
14.39 (366)
14.39 (366)
10.41 (264)
10.41 (264)
8.05 (204)
8.05 (204)
9.50 (241)
10.62 (270)
0.88 (22)
0.88 (22)
8–3/4
12–3/4
8 –150
8 –300
10.62 (270)
10.62 (270)
6.75 (171)
7.50 (191)
13.78 (350)
15.60 (396)
16.33 (415)
16.33 (415)
11.38 (289)
11.38 (289)
9.02 (229)
9.02 (229)
11.75 (298)
13.00 (330)
0.88 (22)
1.00 (25)
8–3/4
12–7/8
10 –150
10 –300
12.75 (324)
12.75 (324)
8.00 (203)
8.75 (225)
15.00 (381)
17.13 (435)
19.11 (485)
19.11 (485)
17.00 (432)
17.00 (432)
10.44 (265)
10.44 (265)
14.25 (362
15.25 (387)
1.00 (25)
1.12 (28)
12–7/8
16–1
12 –150
12 –300
15.00 (381)
15.00 (381)
9.50 (241)
10.25 (260)
18.00 (457)
20.14 (512)
21.27 (540)
21.27 (540)
19.16 (487)
19.16 (487)
11.52 (293)
11.52 (293)
17.00 (432)
17.75 (451)
1.00 (25)
1.25 (32)
12–7/8
16–11/8
14 –150
14 –300
16.25 (413)
16.25 (413)
10.50 (267)
11.50 (292)
21.00 (533)
23.25 (591)
23.39 (594)
23.39 (594)
21.28 (541)
21.28 (541)
12.58 (320)
12.58 (320)
18.75 (476)
20.25 (514)
1.12 (28)
1.25 (32)
12–1
20–11/8
16 –150
16 –300
18.50 (470)
18.50 (470)
11.75 (298)
12.75 (324)
24.00 (610)
26.25 (667)
25.41 (645)
25.41 (645)
23.30 (592)
23.30 (592)
13.59 (345)
13.59 (345)
21.25 (540)
22.50 (572)
1.12 (28)
1.38 (35)
16–1
20–11/4
18 –150
18 –300
21.00 (533)
21.00 (533)
12.50 (318)
14.00 (356)
27.00 (686)
30.12 (765)
27.93 (709)
27.93 (709)
25.82 (656)
25.82 (656)
14.85 (377)
14.85 (377)
22.75 (578)
24.75 (629)
1.25 (32)
1.38 (35)
16–11/8
24–11/4
20 –150
20 –300
23.00 (584)
23.00 (584)
13.75 (349)
15.25 (387)
30.00 (762)
33.25 (845)
29.95 (761)
29.95 (761)
27.84 (707)
27.84 (707)
15.86 (403)
15.86 (403)
25.00 (635)
27.00 (686)
1.25 (32)
1.38 (35)
20–11/8
24–11/4
24 –150
24 –300
27.25 (692)
27.25 (692)
16.00 (406)
18.00 (457)
36.00 (914)
39.64 (1007)
34.50 (876)
34.50 (876)
32.39 (823)
32.39 (823)
18.14 (461)
18.14 (461)
29.50 (749)
32.00 (813)
1.37 (35)
1.62 (41)
20–11/4
24–11/2
30
36
33.80 (859)
40.27 (1023)
19.38 (492)
23.00 (584)
37.25 (946)
40.75 (1035)
40.41 (1026)
48.29 (1227)
38.50 (928)
46.38 (1178)
21.31 (541)
25.25 (641)
36.00 (914)
42.75 (1086)
1.38 (35)
1.63 (41)
28–11/4
32–11/2
Dimensions with ASME B16.5 (ANSI) Flanges
(1) 30- and 36-inch AWWA C207 Table 2 Class D rated to 150 psi at 150 °F.
(2) When grounding rings (2 rings per meter) are specified, add 0.25 inch (6.35 mm) for 0.50- through 14-inch (15 through 350 mm) flowtubes,
add 0.50 inch (12.7 mm) for 16-inch (400 mm) and larger. When lining protectors are specified, add 0.25 inch (6.35 mm) for ½- through 12-inch
(15 through 300 mm) flowtubes, add 0.50 inch (12.7 mm) for 14- through 36-inch (350 through 900 mm) flowtubes.
TABLE 4-6. Flowtube Dimensions in inches (millimeters)
Line Size and Flange
Rating Nominal Tri-Clamp
Diameter Process Flange Rad.
“B” Body Height “C” Max Centerline to Conduit
“E”
Overall Flowtube
Length
“L”
0.5–150 lb. 1.00 (25) 1.75 (44) 8.38 (213) 5.16 (131) 13.78 (350)
1–150 lb. 1.50 (40) 2.13 (54) 8.38 (213) 5.16 (131) 13.78 (350)
1.5–150 lb. 2.00 (50) 2.50 (64) 9.00 (229) 5.56 (141) 13.78 (350)
2–150 lb. 3.00 (80) 3.00 (76) 9.00 (229) 5.56 (141) 13.78 (350)
3–150 lb. 4.00 (100) 3.75 (95) 12.00 (305) 6.57 (167) 13.78 (350)
Dimensions with ASME B16.5 (ANSI) Flanges and Tri-Clamp Adapters.

4-7
Specifications: Model 8705 and Model 8707 High-Signal Flowtubes
TABLE 4-7. Model 8705 Flowtube Dimensions with DIN Flanges in Millimeters (Inches)
Line Size(1)
and Flange
Rating
Liner Face
Diameter
“A”
Process
Flange
Rad. “B”
Overall
Flowtube
Length
“L”(2)
Body
Height
“C”
Body
Width “D”
with Port
Centerline
to Conduit
“E”
Bolt Hole
Circle
Diameter
Bolt Hole
Diameter Number of
Bolts
15 mm PN 10–40 45 (1.77) 47 (1.87) 200 (7.88) 222 (8.75) 175 (6.88) 131 (5.16) 65 (2.56) 14 (0.55) 4
25 mm PN 10–40 68 (2.68) 58 (2.27) 200 (7.88) 222 (8.75) 186 (7.34) 131 (5.16) 85 (3.35) 14 (0.55) 4
40 mm PN 10–40 88 (3.46) 75 (2.96) 200 (7.87) 242 (9.52) 179 (7.05) 141 (5.57) 110 (4.33) 18 (0.71) 4
50 mm PN 10–40 102 (4.02) 83 (3.25) 200 (7.87) 242 (9.52) 190 (7.47) 141 (5.57) 125 (4.92) 18 (0.71) 4
80 mm PN 10–40 138 (5.43) 100 (3.94) 200 (7.87) 293 (11.52) 243 (9.57) 167 (6.57) 160 (6.30) 18 (0.71) 8
100 mm PN 10–16 158 (6.22) 110 (4.33) 250 (9.84) 310 (12.22) 254 (10.01) 176 (6.92) 180 (7.09) 18 (0.71) 8
100 mm PN 25–40 162 (6.38) 117 (4.63) 250 (9.84) 310 (12.22) 254 (10.01) 176 (6.92) 190 (7.48) 22 (0.87) 8
150 mm PN 10–16 212 (8.35) 142 (5.61) 300 (11.81) 366 (14.39) 264 (10.41) 204 (8.05) 240 (9.45) 22 (0.87) 8
150 mm PN 25 218 (8.58) 150 (5.91) 300 (11.81) 366 (14.39) 264 (10.41) 204 (8.05) 240 (9.45) 22 (0.87) 8
150 mm PN 40 218 (8.58) 150 (5.91) 332 (13.06) 366 (14.39) 264 (10.41) 204 (8.05) 240 (9.45) 22 (0.87) 8
200 mm PN 10 268 (10.55) 170 (6.70) 351 (13.81) 415 (16.33) 289 (13.38) 229 (9.02) 295 (11.61) 22 (0.87) 8
200 mm PN 16 268 (10.55) 170 (6.70) 351 (13.81) 415 (16.33) 289 (13.38) 229 (9.02) 295 (11.61) 22 (0.87) 8
200 mm PN 25 278 (10.94) 180 (7.09) 350 (13.78) 415 (16.33) 289 (13.38) 229 (9.02) 310 (12.20) 26 (1.02) 12
200 mm PN 40 285 (11.22) 187 (7.38) 396 (15.60) 415 (16.33) 289 (13.38) 229 (9.02) 320 (12.60) 30 (1.18) 12
250 mm PN 10 320 (12.60) 197 (7.70) 381 (15.00) 485 (19.11) 432 (17.00) 265 (10.44) 350 (13.78) 22 (0.87) 12
250 mm PN 16 320 (12.60) 202 (7.97) 381 (15.00) 485 (19.11) 432 (17.00) 265 (10.44) 355 (13.98) 26 (1.02) 12
250 mm PN 25 335 (13.19) 213 (8.39) 381 (15.00) 485 (19.11) 432 (17.00) 265 (10.44) 370 (14.67) 30 (1.18) 12
250 mm PN 40 345 (13.58) 225 (8.86) 435 (17.13) 485 (19.11) 432 (17.00) 265 (10.44) 385 (15.16) 33 (1.30) 12
300 mm PN 10 370 (14.57) 223 (8.76) 457 (18.00) 540 (21.27) 487 (19.16) 265 (10.44) 400 (15.75) 22 (0.87) 12
300 mm PN 16 378 (14.88) 230 (9.06) 457 (18.00) 540 (21.27) 487 (19.16) 293 (11.52) 410 (16.14) 26 (1.02) 12
300 mm PN 25 395 (15.55) 242 (9.55) 457 (18.00) 540 (21.27) 487 (19.16) 293 (11.52) 430 (16.93) 30 (1.18) 16
300 mm PN 40 410 (16.14) 258 (10.12) 512 (20.14) 540 (21.27) 487 (19.16) 293 (11.52) 450 (17.72) 33 (1.30) 16
350 mm PN 10 430 (16.93) 252 (9.94) 534 (21.03) 594 (23.39) 541 (21.28) 293 (11.52) 460 (18.11) 22 (0.87) 16
350 mm PN 16 438 (17.24) 260 (10.24) 534 (21.03) 594 (23.39) 541 (21.28) 320 (12.58) 470 (18.50) 26 (1.02) 16
350 mm PN 25 450 (17.72) 277 (10.93) 534 (21.03) 594 (23.39) 541 (21.28) 320 (12.58) 490 (19.29) 33 (1.30) 16
350 mm PN 40 465 (18.31) 290 (11.42) 591 (23.25) 594 (23.39) 541 (21.28) 320 (12.58) 510 (20.08) 36 (1.42) 16
400 mm PN 10 482 (18.98) 282 (11.12) 610 (24.00) 645 (25.04) 592 (23.30) 345 (13.59) 515 (20.28) 26 (1.02) 16
400 mm PN 16 490 (19.29) 290 (11.42) 610 (24.00) 645 (25.04) 592 (23.30) 345 (13.59) 525 (20.67) 30 (1.18) 16
400 mm PN 25 505 (19.88) 310 (12.21) 610 (24.00) 645 (25.04) 592 (23.30) 345 (13.59) 550 (21.65) 36 (1.42) 16
400 mm PN 40 535 (21.06) 330 (12.99) 667 (26.25) 645 (25.04) 592 (23.30) 345 (13.59) 585 (23.03) 39 (1.54) 16
450 mm PN 10 532 (20.94) 308 (12.13) 686 (27.00) 709 (27.93) 656 (25.82) 377 (14.85) 565 (22.24) 26 (1.02) 20
450 mm PN 16 550 (21.65) 320 (12.60) 686 (27.00) 709 (27.93) 656 (25.82) 377 (14.85) 585 (23.03) 30 (1.18) 20
450 mm PN 40 560 (22.05) 343 (13.50) 765 (30.12) 709 (27.93) 656 (25.82) 377 (14.85) 610 (24.02) 30 (1.18) 20
500 mm PN 10 585 (23.03) 335 (13.19) 762 (30.00) 761 (29.95) 707 (27.84) 403 (15.86) 620 (24.41) 26 (1.02) 20
500 mm PN 16 610 (24.02) 358 (14.08) 762 (30.00) 761 (29.95) 707 (27.84) 403 (15.86) 650 (25.59) 33 (1.30) 20
500 mm PN 25 615 (24.21) 365 (14.37) 762 (30.00) 761 (29.95) 707 (27.84) 403 (15.86) 660 (25.98) 36 (1.42) 20
500 mm PN 40 615 (24.21) 378 (14.88) 845 (33.25) 761 (29.95) 707 (27.84) 403 (15.86) 670 (26.38) 42 (1.65) 20
600 mm PN 10 685 (26.97) 390 (15.36) 914 (36.00) 885 (34.85) 823 (32.39) 461 (18.14) 725 (28.54) 30 (1.18) 20
600 mm PN 16 725 (28.54) 420 (16.54) 914 (36.00) 877 (34.51) 823 (32.39) 461 (18.14) 770 (30.31) 36 (1.42) 20
600 mm PN 25 720 (28.35) 423 (16.64) 914 (36.00) 877 (34.51) 823 (32.39) 461 (18.14) 770 (30.31) 39 (1.54) 20
600 mm PN 40 735 (18.94) 445 (17.52) 1,007 (39.64) 886 (34.88) 823 (32.39) 461 (18.14) 795 (31.30) 48 (1.88) 20
Dimensions with DIN Flanges
(1) Consult factory for larger line sizes.
(2) When grounding rings (2 rings per meter) are specified, add 6.35 mm (0.25 in.) for 15 mm through 350 mm (½- through 14 in.) flowtubes or
12.7 mm (0.50 in.) for 400 mm (16 in.) and larger. When lining protectors are specified, add 6.35 mm (0.25 in.) for 15 mm through 300 mm
(½- through 12-in.) flowtubes, 12.7 mm (0.50 in.) for 350 mm through 900 mm (14- through 36-in.) flowtubes.

Rosemount Series 8700 Magnetic Flowmeter Flowtubes
4-8
Figure 4-1. Dimensional Drawing of Model 8705 and Model 8707 Flowtubes,
Typical of 1/2- through 4-inch (15 through 100 mm) Line Sizes with Option Code W1, Housing Configuration
Figure 4-2. Dimensional Drawing of Model 8705 and Model 8707 Flowtubes,
Typical of 6- through 36-inch (150 through 900 mm) Line Sizes with Option Code W3, Housing Configuration
3/4–14 NPT Conduit
Connection
2.00
(51)
1.00
(25)
4.75
(121)
“C”
“L”
“A”
8705-1002A05A,1002B05A1
“B”
NOTES
Dimensions are in inches (millimeters).
See Table 5 and 7 for variable dimensions.
2.10
(53)
2.10
(53)
0.66
(17)
1.35
(34)
“E”
Relief Valve
8705-1002A06A,1002B06A
“B”
NOTES
Dimensions are in inches (millimeters).
Consult factory for larger line sizes.
See Table 5 and 7 for variable dimensions.
4.75
(121)
“C”
“L”
“A”
“D”
2.10
(53)
2.00
(51) 1.00
(25)
2.10
(53)
0.66
(17)
1.35
(34)
“E”
3/4–14 NPT
Conduit
Connection
Separate Electrode
Compartments

4-9
Specifications: Model 8705 and Model 8707 High-Signal Flowtubes
Figure 4-3. Dimensional Drawing of Model 8705 Sanitary Flowtubes,
Typical of 1/2- through 3-inch (15 through 86 mm) Line Sizes with Option Code W0, Housing Configuration
3/4–14 NPT
Conduit
Connection
2.00
(51)
1.00
(25)
4.75
(121)
“E”
8705-1002A05B, 1002B05C
NOTES
Dimensions are in inches (millimeters).
See Table 7 for variable dimensions.
“C”
“B”
“L”
0.66
(17)
2.10
(53)
1.35
(34)

Section
5-1
5Specifications:
Model 8711 Flowtube
SPECIFICATIONS
Functional Specifications Service
Conductive liquids and slurries
Line Sizes
0.15- through 8-inch (4 through 200 mm)
Interchangeability
Model 8711 Flowtubes are interchangeable with Model 8712C/U, Model
8732, and Model 8742C Transmitters. System accuracy is maintained
regardless of line size or optional features. Each flowtube nameplate
has a sixteen-digit calibration number that can be entered into a
transmitter through the Local Operator Interface (LOI) or the HART
Communicator on the Model 8712C/U/H and the Model 8732C. In a
FOUNDATION fieldbus environment, the Model 8742C can be configured
using the DeltaV fieldbus configuration tool or another FOUNDATION
fieldbus configuration device. No further calibration is necessary.
Upper Range Limit
30 ft/s (10 m/s)
Process Temperature Limits
Tefzel (ETFE) Lining
–20 to 300 °F (–29 to 149 °C) for 0.5- through 8-inch (15–200 mm)
line sizes
–20 to 200 °F (–29 to 93 °C) for 0.15- and 0.3-inch (4 and 8 mm)
line sizes
Teflon (PTFE) Lining
-20 to 350 °F (-29 to 177 °C)
Ambient Temperature Limits
–30 to 150 °F (–34 to 65 °C)
Ambient Conditions
Overvoltage Category I. Pollution Degree 2
Pressure and Vacuum Limits
Line sizes 0.5- through 8-inch (15 through 200 mm): full vacuum to 740
psi (51.0 bar); line sizes 0.15- through 0.30-inch (4 through 8 mm): full
vacuum to 288 psi (19.8 bar); consult factory for vacuum applications
that require Teflon (PTFE) lining material
Enclosure Rating
NEMA 4x. CSA Type 4

Rosemount Series 8700 Magnetic Flowmeter Flowtubes
5-2
Hazardous Location Certifications
N0 Factory Mutual (FM) Approval Dust-ignition proof for Class II/III,
Division 1 Groups E, F, and G; Non-incendive for Class I, Division
2 Groups A, B, C, and D; T5 temperature code; For non-flammable
process fluid service only
AND
Canadian Standards Association (CSA) Approval Suitable for use
in Class I, Division 2 Groups A, B, C, and D; Dust-ignition proof for
Class II/III, Division 1, Groups E, F, and G hazardous locations
AND
CE Marking.
N5 Factory Mutual (FM) Approval; Dust-ignition proof for Class II/III,
Division 1 Groups E, F, and G hazardous locations; Non-incendive
for Class I, Division 2 Groups A, B, C, and D; T5 temperature code;
For flammable process fluid service
E5 Factory Mutual (FM) Approval Explosion Proof for Class I,
Division 1, Groups C and D; T6 temperature code; flammable
process fluid service; Available for remote mount transmitter or
integral mount Model 8732C transmitters
CD KEMA/CENELEC Approval
EEx e ia IIC T3...T6 (See Table 5-1)
Conductivity Limits
Process liquid must have a conductivity of 5 microsiemens/cm (5
micromhos/cm) or greater for Model 8711. Excludes the effect of
interconnecting cable length in remote mount transmitter installations
TABLE 5-1. Relation Between Ambient Temperature,
Process Temperature, and Temperature Class(1)
(1) This table applicable for KEMA/CENELEC approval only.
Meter Size
(inches)
Maximum
Ambient
Temperature Maximum Process
Temperature Temperature
Class
1/2149 °F (65 °C) 240 °F (116 °C) T3
1
1
149 °F (65 °C)
95 °F (35 °C)
248 °F (120 °C)
95 °F (35 °C)
T3
T4
11/2
11/2
149 °F (65 °C)
140 °F (60 °C)
257 °F (125 °C)
140 °F (60 °C)
T3
T4
2
2
2
149 °F (65 °C)
149 °F (65 °C)
104 °F (40 °C)
257 °F (125 °C)
167 °F (75 °C)
104 °F (40 °C)
T3
T4
T5
3-4
3-4
3-4
3-4
149 °F (65 °C)
149 °F (65 °C)
131 °F (55 °C)
104 °F (40 °C)
266 °F (130 °C)
167 °F (75 °C)
194 °F (90 °C)
104 °F (40 °C)
T3
T4
T5
T6
6
6
6
6
149 °F (65 °C)
149 °F (65 °C)
149 °F (65 °C)
140 °F (60 °C)
175 °F (79 °C)
167 °F (75 °C)
230 °F (110 °C)
140 °F (60 °C)
T3
T4
T5
T6
8-36
8-36
8-36
8-36
149 °F (65 °C)
149 °F (65 °C)
149 °F (65 °C)
149 °F (65 °C)
284 °F (140 °C)
240 °F (116 °C)
176 °F (80 °C)
149 °F (65 °C)
T3
T4
T5
T6

5-3
Specifications: Model 8711 Flowtube
Performance
Specifications (System specifications are given using the frequency output and with the
unit at referenced conditions.)
Accuracy
Model 8711 with Model 8712C/U, Model 8732C, or
Model 8742C Transmitters
±0.5% of rate from 3 to 30 ft/s (1 to 10 m/s); include combined effects
of linearity, hysteresis, repeatability and calibration uncertainty;
accuracy is ±0.015 ft/s (±0.0045 m/s) from low-flow cutoff to 3.0 ft/s
(1 m/s)
Vibration Effect
IEC 770 Pipeline Installation Conditions
Mounting Position Effect
None when installed to ensure flowtube remains full.
Physical Specifications Non-Wetted Materials
Flowtube
303 SST (ASTM A-743)
Coil Housing
Investment cast steel (ASTM A-27)
Paint
Polyurethane
Process-Wetted Materials
Lining
Tefzel (ETFE), Teflon (PTFE)
Electrodes
316L SST, Hastelloy C-276, tantalum, 90% platinum—10% iridium,
titanium
Process Connections
Mounts between these Flange Configurations
ASME B16.5 (ANSI): Class 150, 300.vv
DIN: PN 10 and 25
BS: 10 Table D, E, and F

Rosemount Series 8700 Magnetic Flowmeter Flowtubes
5-4
Studs, Nuts, and Washers(1)
ASME B16.5 (ANSI)
Line sizes 0.15- through 1-inch (4 through 25 mm):
316 SST, ASTM A193, Grade B8M, Class 1 threaded mounting studs;
ASTM A194, Grade 8M heavy hex nuts; SAE per ANSI B18.2.1, Type
A, Series N flat washers
Line sizes 1.5- through 8-inch (40 through 200 mm):
CS, ASTM A193, Grade B7, Class 1 threaded mounting studs; ASTM
A194, Grade 2H heavy hex nuts; SAE per ANSI B18.2.1, Type A,
Series N flat washers; all items clear, chromate zinc-plated
DIN
Line sizes 4 through 25 mm (0.15- through 1-inch):
316 SST ASTM A193, Grade B8M Class 1 threaded mounting studs;
ASTM A194, Grade 8M, DIN 934 H=D, metric heavy hex nuts; 316
SST, A4, DIN 125 flat washers
Line sizes 40 through 200 mm (1.5- through 8-inch):
CS, ASTM A193, Grade B7 threaded mounting studs; ASTM A194,
Grade 2H, DIN 934 H=D, metric heavy hex nuts; CS, DIN 125 flat
washers; all items yellow zinc-plated
Electrical Connections
Two ¾–14 NPT connections with number 8 screw terminals are
provided in the terminal enclosure for electrical wiring.
Grounding Electrode
A grounding electrode is installed similarly to the measurement
electrodes through the flowtube lining. It is available in all electrode
materials.
Grounding Rings
Grounding rings are installed between the flange and the tube face on
both ends of the flowtube. They have an I.D. slightly larger than the
flowtube I.D. and an external tab to attach ground wiring. Grounding
rings are available in 316L SST, Hastelloy C-276, titanium, and
tantalum.
Flowtube Dimensions and Weight
See Table 1
(1) 0.15 and 0.30 inch (4 and 80 mm) flowtubes mount between 1/
2
-inch (13 mm) flange.
TABLE 1. Flowtube Dimensions and Weight
Nominal
Line Size
Inches (mm)
Flowtube Housing Dimensions Flowtube Length
“D” Inside Diameter Weight
lb (kg)
“A” Max. “B” “C”
0.15
0.30
(4)
(8)
4.00
4.00
(102)
(102)
5.44
5.44
(138)
(138)
3.56
3.56
(90)
(90)
2.17
2.17
(55)
(55)
.165
.287
(4)
(7)
4
4
(2)
(2)
0.5
1
1.5
(15)
(25)
(40)
4.00
4.31
4.42
(102)
(109)
(112)
5.44
6.06
7.41
(138)
(154)
(188)
3.56
4.50
3.28
(90)
(114)
(83)
2.17
2.17
2.73
(55)
(55)
(69)
.595
.959
1.50
(15)
(24)
(38)
4
5
5
(2)
(2)
(2)
2
3
4
(50)
(80)
(100)
4.64
5.26
5.87
(118)
(134)
(149)
7.94
9.19
10.41
(202)
(233)
(264)
3.91
5.16
6.38
(99)
(131)
(162)
3.26
4.68
5.88
(83)
(119)
(149)
1.95
2.98
3.90
(50)
(76)
(99)
7
13
22
(3)
(6)
(10)
6
8
(150)
(200)
6.97
8.00
(177)
(2003)
12.60
14.66
(320)
(372)
8.56
10.63
(217)
(270)
6.87
8.86
(174)
(225)
5.825
7.87
(148)
(200)
35
60
(16)
(27)

5-5
Specifications: Model 8711 Flowtube
Figure 5-1. Model 8711 Dimensional Drawings (1.5-inch through 8-inch line sizes)
2.10
(53)
0.66
(17)
1.35(34)
0.5
(13) 4.75
(121)
NOTE
Dimensions are in
inches (millimeters).
See Table 1 for
variable dimensions.
8711-1012B04A, 1012A04A
“C”
Flow
“D”
“B”
“A”

Rosemount Series 8700 Magnetic Flowmeter Flowtubes
5-6
Figure 5-2. Model 8711 Dimensional Drawings (0.15-inch through 1-inch line sizes).
“A” “B”
4.5
(121)
2.00
(51)
0.87
(22)
3.37
(86)
2.10
(53)
0.50
(13)
Flow
4.75
(121)
“D”
Grounding
Clamp
¾–14 NPT
Conduit
Connection
(2 places)
“C”
0.66
(17)
1.35
(34)
NOTE
Dimensions are in
inches (millimeters).
See Table 1 for
variable dimensions.
8711-1012B03A, 1012A03A

Appendix
A-1
AField-Removable Electrodes
SAFETY MESSAGES Instructions and procedures in this section may require special
precautions to ensure the safety of the personnel performing
the operations.
The field-removable electrode option allows the user to remove the
electrode assembly with the flowtube still mounted in the line.
Frequently, this option will be used for cleaning the electrode head
when coating is of concern.
The flowtube should be drained of any process fluid prior to disassembly of
the electrodes. To avoid personal injury, care should be taken when
handling electrodes that have been in contact with corrosive process fluids.
Take care to avoid rotating the electrode when removing it to avoid
damage to the o-ring. Some resistance may be experienced due to the
tight o-ring fit.
REMOVE THE
ELECTRODE ASSEMBLY
Use the following procedure to remove the electrode assembly
from the flowtube.
1. Drain the flowtube of any process fluid prior to disassembly
of the electrodes.
2. Remove the screws that secure the electrode cover.
3. Remove the electrode cover and o-ring. It is generally
recommended that new o-rings be installed on the electrode and
the electrode cover during reassembly.
4. Remove the electrode lead screw that secures the signal wire to
the electrode.
5. Remove the electrode retaining nut.
6. Take the electrode from the electrode housing by pulling it
straight out, with firm pressure, along the axis of the electrode.
Failure to follow these installation guidelines could result in death or serious injury:
Installation and servicing instructions are for use by qualified personnel only.
Performing any servicing other than that contained in this manual may
result in death or serious injury. Do not perform any servicing other than
that contained in the operating instructions.

Rosemount Series 8700 Magnetic Flowmeter Flowtube
A-2
REPLACE THE
ELECTRODE ASSEMBLY
Use the following procedure to replace the electrode assembly
into the flowtube.
1. Lubricate the o-ring.
2. Install the o-ring on the electrode.
3. Insert the electrode into the electrode housing. Push straight in
until the electrode is seated. Avoid rotating the electrode or the
electrode housing as this could result in leakage.
4. Secure the electrode into the housing with the retaining nut and
lock washer. Tighten the retaining nut to 15 in/oz of torque.
Failure to tighten the fasteners can cause loss of liquid tight seal
and result in damage to the unit.
5. Secure the signal wire to the electrode with the electrode
lead screw.
6. Install the o-ring into the electrode cover.
7. Secure the electrode cover to the flowtube with the screws.
FIGURE A-1.
The Field-Replaceable Electrode
Electrode Lead
Screw
Lock Washer
Housing Nut
O-rIng
Nut
Lock Washer
Housing
Electrode
Insulator Cap
Lockwasher
Spring
8705-1002B03A

I-1
Index
A
Accuracy
Ensuring ..................... 2-3
Model 8705/8707 .............. 5-3
Model 8711 ................... 6-3
C
Cable Preparation .............. 2-15
Calibration .................2-2,2-22
Canadian Standards Association
Approval
Model 8705/8707 ...........5-2,6-2
Conductivity
Model 8705/8707 .............. 5-3
Model 8711 ................... 6-2
Conduit Ports and Connections .. 2-13
D
Dedicated Conduit .............. 2-13
Dimensional Drawing
Model 8705/8707 ...........5-8,5-9
Model 8711 ................6-5,6-6
Dimensions
Model 8705/8707 .............. 5-5
Model 8711 ................... 6-4
Direction ....................... 2-4
Downstream/Upstream Piping .... 2-3
Drawings
Model 8705 ................... 2-5
Model 8707 High-Signal ........ 2-5
Model 8711 ................... 2-8
E
Electrical Considerations
Input Power ................. 2-14
Electrical Rating ................ 5-2
Empty pipe functionality ........ 2-22
Enclosure Rating ................ 5-2
F
Factory Mutual Approval
Model 8705/8707 .......5-2,5-3,6-2
Flange Bolts .................... 2-6
Flanges
Class 150 .................2-6,2-9
Class 300 .................2-6,2-9
Flow Direction ...............2-4,2-5
Flowtube Calibration Number ... 2-22
16-digit Calibration Number .... 2-22
empty pipe functionality ....... 2-22
Flowtube Orientation ............2-3
G
Gaskets ..................... 2-5,2-8
Spiral-wound ..................2-1
Grounding .....................2-10
Grounding Electrodes ..........2-10
Grounding Rings ..............2-10
Lining Protectors .............2-10
Grounding Rings .................2-5
H
Handling ........................2-2
Hazardous Locations Certifications
Model 8705/8707 ...............5-2
Model 8711 ...................6-2
I
Independent Replacement ........4-1
Input Power ....................2-14
Installation ......................2-1
Installation Drawings
Model 8705 ...................2-5
Model 8707 High-Signal .........2-5
Model 8711 ...................2-8
K
KEMA/CENELEC Approval
Model 8705/8707 ...............5-3
Model 8711 ...................6-2
L
Lining Protectors ...............2-10
M
Model 8712C/U
Transmitter Connections .......2-16
Mounting .......................2-2
Model 8705/8707 ...............5-4
Model 8711 ...................6-3
O
Operation ......................2-22
Orientation ......................2-3
P
Piping ..........................2-3
Positioning Flowtube
Horizontal/Inclined .............2-3

Rosemount Series 8700 Magnetic Flowmeter Flowtubes
I-2
Pressure
limits ........................ 5-2
Model 8705/8707 .............. 5-2
Process Leak
Containment ................ 2-21
Protection ................... 2-19
Q
Quick Start-up ................. 2-22
R
Relief Valves ....................A-2
Return of Materials .............. 4-4
S
Safety ..........................A-1
Specifications
Model 8705 and Model 8707 ..... 5-1
accuracy .................. 5-3
ambient temperature limits .. 5-1
ASME/ANSI .............. 5-4
conductivity limits ......... 5-3
dimensional drawing . . . .5-8, 5-9
electrical connections ....... 5-4
electrodes ................ 5-4
enclosure rating ........... 5-2
flowtube dimensions ........ 5-5
functional specifications ..... 5-1
grounding electrode ........ 5-4
grounding rings ........... 5-4
hazardous locations ........ 5-2
interchangeability ......... 5-1
line sizes ................. 5-1
lining .................... 5-4
lining protectors ........... 5-5
mounting position effect ..... 5-4
non-wetted materials ....... 5-4
performance specifications ... 5-3
physical specifications ...... 5-4
pressure limits ............ 5-2
process conditions .......... 5-4
process temperature limits .. 5-1
process wetted materials .... 5-4
service ................... 5-1
submergence protection ..... 5-2
upper range limit .......... 5-1
vacuum limits ............. 5-2
vibration effect ............ 5-4
weight ................... 5-5
Model 8707
electrical rating ............ 5-2
Model 8711 ................... 6-1
accuracy .................. 6-3
ambient conditions ......... 6-1
ambient temperature limits .. 6-1
ASME/ANSI ...............6-3
conductivity limits ..........6-2
dimensional drawings ... 6-5,6-6
electrical connections .......6-4
electrodes .................6-3
enclosure rating ............6-1
flowtube dimensions ........6-4
functional specifications .....6-1
grounding electrode .........6-4
grounding rings ............6-4
hazardous locations .........6-2
interchangeability ..........6-1
line sizes ..................6-1
lining ....................6-3
mounting position effect .....6-3
non-wetted materials .......6-3
performance specifications ...6-3
physical specifications .......6-3
pressure and vacuum limits ..6-1
process conditions ..........6-3
process temperature limits ...6-1
process-wetted materials ....6-3
service ...................6-1
upper range limit ...........6-1
vibration effect .............6-3
weight ....................6-4
Spiral-wound Gaskets ............2-1
Start-up ........................2-22
T
Temperature ...................2-13
Model 8705/8707 ...............5-1
Model 8711 ...................6-1
Transmitter Connections
High-Signal ..................2-17
Model 8712C/U ...............2-16
Model 8732C .................2-18
Transporting System .............2-2
Troubleshooting .................4-1
Chart ........................4-2
U
Upstream/Downstream Piping ....2-3
V
Vacuum Limits ..................5-2
Vibration
Model 8705/8707 ...............5-4
Model 8711 ...................6-3
W
Warning . 1-1, 2-1, 2-13, 2-16, 2-17, 2-18,
4-1

00809-0100-4727 Rev. DA 4/00
Rosemount Inc.
8200 Market Boulevard
Chanhassen, MN 55317 USA
Tel 1-800-999-9307
Fax (952) 949-7001
© 2000 Rosemount Inc.
P
R
I
N
T
E
D
IN
U.
S.
A.
http://www.rosemount.com
¢00809-0100-4727X¤
Fisher-Rosemount Flow
Groeneveldselaan 6-8
3909 AZ
3900 AB Veenendaal
The Netherlands
Tel 31 (0) 318 549 549
Fax 31 (0) 318 549 559
Fisher-Rosemount
Singapore PTE LTD
1 Pandan Crescent
Singapore 128461
Tel 31 (65) 777-8211
Fax 31 (65) 777-0947
email: AP.RMT-Specialist@frco.com
This document is available electronically at www.rosemount.com.