DYNATORQUE Valve Magazine Fall 2002 Article
User Manual: DYNATORQUE Valve Magazine Fall 2002 Article Resource Library
Open the PDF directly: View PDF .
Page Count: 8

FALL 2002 1
MAGAZINE
FALL 2002
VOLUME 14, NO. 4
Advances in Valve & Actuator Technologies
190697klc 2/25/03, 2:06 PM1
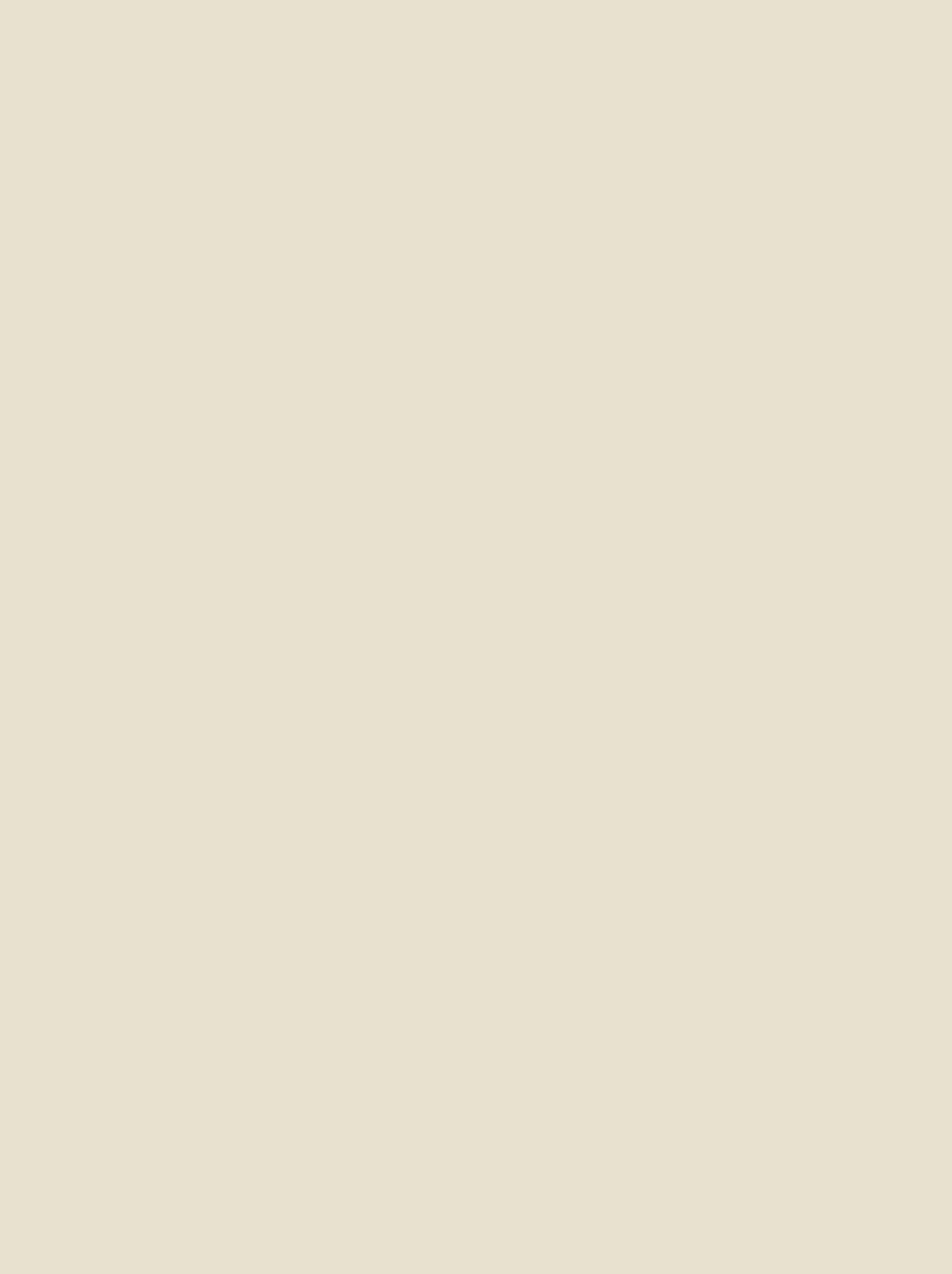
2 VALVE MAGAZINE
by Mike Mitchell There is a storm forming on the horizon for offshore
rigs, refineries, and all other industrial process
plants that have automated valves in their safety
systems. Like the rumble of distant thunder, they
know it is coming—but they’re just now cranking-up their radar
to find out how the storm will affect them. One thing is certain:
when this storm finally hits, no plant will remain untouched by
its fury....What’s causing the storm to brew?
In “the good old days” process plant operations managers had
the luxury of shutting down their facility every year or two for
what is now fondly remembered as the “maintenance shutdown”.
This was a period of time set aside to close down production and
perform maintenance on the plant’s equipment. So the produc-
tion stream was “turned off” and the maintenance crew was free
to disassemble, clean and/or replace equipment. The control
systems engineer, safety engineer, and reliability engineers were
able to test their process control and safety equipment without
the worry of dealing with process flow. That was when companies
could devote the time and resources to perform this task in the
most efficient and complete manner.
Times have changed, and to succeed in today’s aggressive
business climate, we must change along with the times. One of
the most obvious changes in the process industries in recent years
is the demise of the planned periodical maintenance shutdown.
Closing down the plant, for whatever reason, also shuts down the
revenue stream. The process industries are under incredible
pressure to increase revenues and these “shutdowns” of the
revenue flow are not acceptable to management and other
stakeholders. The result is an emphasis on running industrial
process plants on a 24-hour-a-day, 7-day-a-week basis for as many
years as possible-without maintenance shutdowns.
CONSIDER
Mechanical Partial S
FOR PROCESS ESD
190697klc 2/25/03, 2:07 PM2

FALL 2002 3
Among the most critical valves affected by less frequent
maintenance are the Emergency Shutdown (ESD) Valves and
other fail-safe valves in safety related applications. These
valves may typically incorporate a spring-to-fail actuator to
stroke a valve in the event of an upset process condition. If
the ESD valve does not perform its function to close (or in rare
applications, open the valve) at the time of an upset event, the
consequences to property and life can be catastrophic. [Note:
For the purpose of simplifying this discussion, when referring
to pneumatically or hydraulically operated ESD and safety
valves, the convention of “air-to-open valve, spring-to-close
valve, de-energize to trip” will be used].
This new emphasis on continual process revenue genera-
tion has led the Occupational Safety and Health Administra-
tion (OSHA), insurance companies, other regulatory agen-
cies, and safety engineers to take a fresh look at how this new
operating philosophy impacts plant safety. These agencies
posed the question to the process plants: If the plant is going
to remain operational for an extended period of time, how can
we be assured the valve safety systems will function correctly
when called upon?
The industry has responded to this question with “accepted
industry standards” (essentially self-governing) such as ISA-
S84.01 (Application of Safety Instrumented Systems for the
Safety-Related Valves
Process Industries) and IEC 61508 (Functional Safety Of E/E/
PE Safety-Related Systems) to determine acceptable levels of
performance of these systems.
This article examines mechanical Partial Stroke Test
Devices as a preferred methodology for assuring compliance
with new standards. These standards define requirements for
Safety Instrumented Systems (SIS) and allow the end user to
establish Safety Integrity Levels (SIL) for specific applications.
One means of showing conformance is to test all the various
SIS components such as solenoid valves, quick exhaust valves,
relays, valve to stem integrity, and valve actuator without
actually closing the valve.
By the nature of the application, the ESD valve is subject
to flowing process fluid. If the ESD were to be full-stroke
tested while the plant is operational, the “flow of revenue”
(i.e., process flow) would come to a halt. One methodology of
overcoming this dilemma is to install a bypass valve and
piping around the ESD valve. When the bypass valve is open,
the ESD valve and its safety system may be fully tested
without affecting process flow. This option sounds effective,
and it is. However, piping dimensional constraints (particularly
on offshore drilling and production rigs) and the cost associated
with installing a dual system at every ESD valve make a
bypass system generally not preferred.
ERING
al Stroke Test Devices
&
190697klc 2/28/03, 8:32 AM3
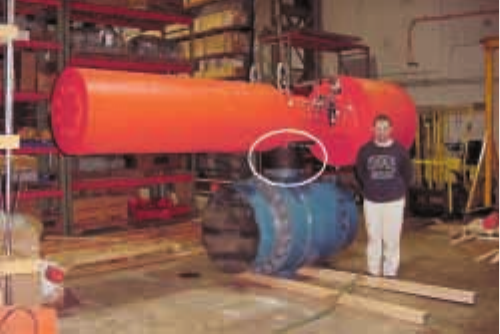
4 VALVE MAGAZINE
Figure 1: Typical example of a “sandwich-mount” product
installed between the pneumatic actuator and valve.
One of the terms associated with these ISA and IEC
standards is “partial stroke testing” (Reference ISA-S84.01,
paragraph 9.7.5.2.b). A “partial stroke” might be defined as, for
example, allowing the safety system to close a valve only 20%
(this would be the set point). In that case, all of the control
elements are being tested, but obviously the valve never fully
closes during the test.
The overall assumption is that a given number of “partial
strokes” can be applied as a statistical “credit” against “full
stroke tests”. Thus, the end user may be capable of either 1)
lowering the Probability of Failure on Demand (PFD) of a given
SIS by doing partial stroke tests between full stroke tests; or 2)
by doing partial stroke testing between full stroke tests, the end
user may be able to maintain or lower his PFD and enjoy a
greater interval of time between full stroke test intervals.
The background for safety testing has been explained in a
previous Valve Magazine (See “Getting Closure on Compli-
ance, Putting Valve-Related Safety Standards in Perspective”,
Valve Magazine, Summer 2002 Edition, Volume 14, Number
3). The technical analysis supporting the benefits of Partial
Stroke Testing have also been examined in detail at VMA
Seminars (Reliability, Safety, Integrity Today, March 7-8,
2002, Houston, TX), and ISA conferences (Safety Instru-
mented Systems for the Process Industry, May 14-16, 2002,
Baltimore, MD) and numerous websites (see, for example,
www.iec.ch/zone/fsafety/; www.instrument-net.co.uk/silansi.htm).
Thus, it would be redundant to cover that material here.
The purpose of this discussion is to examine the benefits of
mechanical Partial Stroke Test Devices as a preferred method-
ology for functional testing of the SIS when a full stroke of the
valve is not practical.
At both the consulting engineer and end user levels,
responsibility for process flow control and valve safety systems
generally fall under the authority of Control Systems Engi-
neering (Instrumentation) because the valves are automated.
Often times this engineering discipline attempts to affect a
Partial Stroke through the use of ancillary controls and
instrumentation. This often results in making the SIS more
complex, expensive, and subject to complicated software
programming, installation, and commissioning.
The following criteria should be considered when consider-
ing methodology for affecting the Partial Stroke Test of a SIS,
including the associated ESD valve:
Keep it a Simple System (KISS)
Because a mechanical Partial Stroke Test Device does not
require the addition of extensive extraneous controls, several
important user benefits are realized. There are no require-
ments to add additional power, wiring or control systems to
perform a partial stroke function test. The benefit is obviously
a reduction in capital cost and system complexity. Secondly,
mechanical interlock systems are generally considered a more
positive method of achieving the partial stroke. This option is
discussed further in “Mechanical Characteristics”, below.
Lastly, we can make these systems as complicated as we want
to, but more times than not, it is important to keep things
simple and safe. In the real world, often times the less
complex the system, the fewer things will go wrong.
Mechanical Characteristics
Perhaps the primary advantage of the mechanical Partial
Stroke Test Device is just that: It’s mechanical. A typical
installation of a mechanical Partial Stroke Test Device would
be to mount the device “sandwich” style between the valve
bonnet (mounting flange) and the drive face (or bottom) of a
pneumatic valve actuator. (See Figure 1). Within the device
there is a drive mechanism that, once engaged, prevents the
de-energized actuator from causing the valve to stroke more
than a specified percentage of full travel—thus accomplishing
the partial stroke. There is no mandatory device requirement
to integrate it into the control loop or add ancillary controls.
Therefore, there is no complexity added to what might already
be a rather sophisticated control loop or shutdown system.
Field Retrofits/No Calibration
Although Partial Stroke Test Devices are often supplied
with a new valve/actuator package, they are also field
retrofitable to existing valves. As mentioned previously,
typical installation of these products is to sandwich them
between the valve and actuator. Mechanical partial stroke
devices can be furnished with mounting surfaces premachined
to fit an existing valve and actuator interface. This makes the
installation of the device simple and cost effective. In fact,
depending on the specific valve and actuator, in many
190697klc 2/28/03, 8:33 AM4
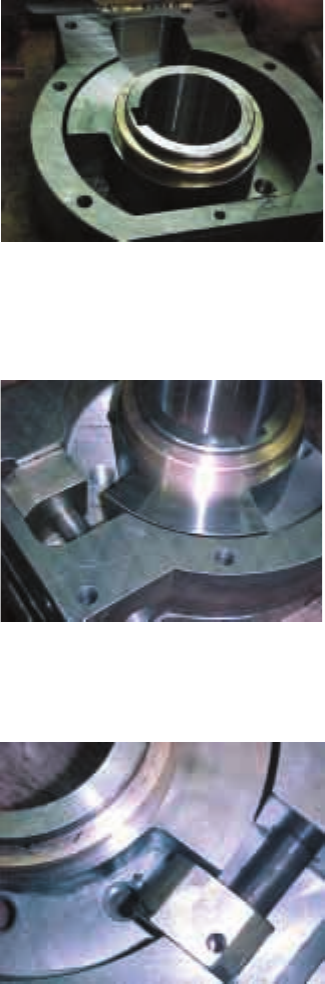
FALL 2002 5
instances the sandwich-style device can
actually replace typical valve/actuator
mounting hardware.
Instrumentation personnel and
software programmers are not required to
install the devices, nor is commissioning
or routine calibration of controls
required, because there aren’t any. Most
process plants have qualified in-house
mechanics or Valve Automation Centers
nearby and, since there are no additional
controls required, installation cost savings
can be realized when compared to
electrical or controls-driven test systems.
Real World Automation
Although the point behind partial
stroke testing is to establish a statistical
analysis for lowering the Probability of
Failure on Demand, as one industry
speaker recently put it: “Calculations are
not necessarily reality!” Therefore, the
process operators must take care to assure
that real world conditions are considered
when selecting a methodology for partial
stroke testing.
ESD valves are often large and are
typically operated by pneumatic or
hydraulic piston cylinder actuators, or
electric motor operators. Due to the
critical nature of the application, one
would expect the ESD valve to seldom
operate. Although piston cylinder
actuators are considered extremely
reliable, in the real world these devices
are not always smooth-acting. The less
often they are stroked (as in the case of a
typical ESD valve application), the less
smooth is their operation. This might be
caused by the elastomeric piston o-rings
taking a set against the interior surface of
the cylinder.
Most of the non-mechanical Partial
Stroke Test Devices assume a relatively
smooth movement of the valve actuator
and that the SIS will act in a consistent manner, indepen-
dent of environmental conditions such as temperature and
humidity or how long the valve rests between test cycles.
This is rarely the case. The primary function of a mechanical
Partial Stroke Test Device is to stop valve movement at a
specified percentage or degree of valve
closure and will not give spurious SIS
trips (alarms) based on extraneous
conditions.
Further, when using non-mechanical
or controls-driven partial stroke test
systems there is an assumption that the
test device or system will actually
prevent the actuator from driving the
valve past the set point to the fully
closed position. In the real world, the
stored energy in an actuator may drive
the valve past the set point and actually
allow the valve to close, forcing a
process shut down. Mechanical devices
physically prevent the valve from
moving past the specified test point.
Once the test device is engaged, the
valve cannot move past the set point.
(Figure 2 - Figure 4)
Many process plants also use electric
Motor Operated Valves (MOVs) in
critical process applications. Although
most MOVs have internal mechanisms
that can be set to stop valve movement
at a specified percentage of stroke, plant
operators often select a mechanical
Partial Stroke Test Device to prevent
valve closure should the internal
mechanism malfunction.
Man-Machine Interface?
Partial Stroke Testing is receiving
increased attention as the aforemen-
tioned industrial standards are consid-
ered by industry. Progressive refineries,
process plants, pipeline companies, etc.,
are going through an evolutionary
process of developing the methodology
by which they will comply with the
standards and how those methodologies
will be implemented. One of the
considerations is, to what extent should
plant personnel be proactively involved
in performing the test of process valve
Safety Instrumented Systems?
One philosophy of methodology calls for a Man-Machine
interface. In the simplest format, mechanical Partial Stroke Test
Devices provide for a plant maintenance person to locally
engage the device using a controlled key (See Figure 5).
Figure 2: Fabricated body of a Partial
Stroke Test Device. Valve Stem would be
connected to the device through the bore
and keyway.
Figure 3: During normal operation, the
device is passive and will allow the valve
to ESD on demand.
Figure 4: When a partial stroke test is
required, the device is “engaged” and the
ESD valve will only travel to the specified
percentage of stroke. The device
mechanically prevents movement past the
interlock.
190697klc 2/28/03, 8:33 AM5
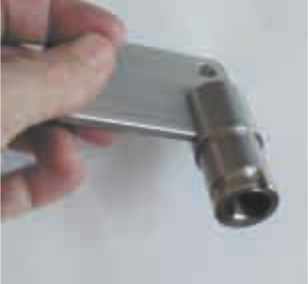
6 VALVE MAGAZINE
Figure 5: For manual operation, a
controlled key is used to engage the
Partial Stroke Test Device. The key
cannot be removed from the mechanical
testing device while it is in the test
position. If plant operating personnel
know the key is in their control and not
in the test device, then they also know
the device cannot be accidentally
engaged.
By design, the key cannot be removed
from the mechanical testing device while
it is in the test position. If plant opera-
tions personnel know the key is in their
control and not in the test device, then
they also know the device cannot be
engaged. When it is time to test the
valve, the maintenance person inserts the
controlled key into the device, engages
the device and then informs the control
room that the valve is now ready to test.
When the SIS test is simulated, the
person witnesses and reports the event,
usually by radio, to the control room, and
then resets the system. Plant operations,
safety engineers and management are
assured the of the system’s reliability
because “the man saw it function”.
(Figure 6, Figure 7a, and Figure 7b)
Management philosophies at other
plants may hold a different view: They
want the entire system to be automatic
with absolutely no human interface. Many mechanical Partial
Stroke Test Devices provide for automatic operation as an
option to the Man-Machine interface. Under this methodol-
ogy, a remotely controlled mechanism is used to engage and
disengage the device and there is no key control system. The
ESD valve can then be tested either by a signal generated by
the control room or any number of other sources without field
personnel involvement.
Mechanical Partial Stroke Test Devices offer plant opera-
tions and maintenance management both manual or auto-
matic operating options as their philosophies dictate. In either
case, diagnostic devices can be integrated into the system to
report specific operating details of the SIS function.
Integrated Data Systems
Some end users are beginning to investigate diagnostic
technology for valve maintenance considerations. The data
acquired from these systems may be helpful in determining the
operational status of an automated valve. Even though
mechanical Partial Stroke Test Devices do not require ancil-
lary controls, such controls may be added if the end user
specifies them (Figure 8). For example, if the user would like
to have a data acquisition system to determine if the valve/
actuator package is experiencing a change in run time trends,
the actuator top works can use standard diagnostic technology
to report that information. But because the mechanical
device is engaged during the test, the end user has assurance
that the actuator will not stroke the valve
past the set point.
A mechanical sandwich-type Partial
Stroke Test Device may also come
equipped with its own data point device
(such as limit switches) for positive
annunciation to the control room
indicating whether the device is engaged
for testing the Safety System. Some may
want to use such a device to gather
information for the data acquisition
system such that auditable reports,
testifying to time and date of the test, can
be generated (Reference ISA-S84.01,
paragraph 9.8.1).
Controls can also be configured to
automatically disengage a Partial Stroke
Test Device in the unlikely event of an
ESD occurring during the test.
True Safety System Tests
As previously stated, a mechanical
Partial Stroke Test Device requires no extraneous controls or
devices to be added in the safety control loop. When the
device is tested, all the actual SIS components, controls and
elements used in an ESD or safety valve will be activated.
The user has real information about the exact controls that
will be relied upon to protect his plant and personnel.
Valverciser™
An additional feature of mechanical Partial Stroke Test
Devices is that they are not only applicable to safety related
applications, but can also be used to enhance the operation of
the valve. In many process applications the chemical
composition of the flowing fluid causes material to build-up
on the valve internal body and trim surfaces. Over time, this
build-up may cause the valve to “stick” in position and not
stroke. Partial Stroke Test Devices can be used to simply
“exercise” the valve by allowing it to partially stroke, keeping
the valve surfaces that are required to move free from material
build-up.
Many mechanical Partial Stroke Test Devices can also be
configured to accommodate maintenance lock-in, tag-out
requirements as well.
All Things Considered...
Now that we have fully explored the benefits of mechanical
Partial Stroke Test Devices it should be clear that the simplic-
ity, safety, reliability, and cost advantages of the devices far
190697klc 2/28/03, 8:33 AM6

FALL 2002 7
outweigh the whiz-bang factor of adding more controls and
instrumentation to what is probably already a sophisticated
valve safety system. Consideration and use of the mechanical
devices will lead to “sunny days ahead” when battling the
oncoming storm of standards compliance!
The author is Vice President, Sales, DynaTorque Inc.,
Muskegon, MI; 231.739.1431; www.dynatorque.com;
mmitchell@dynatorque.com.
Figure 6: During normal
operation, key is kept in a
controlled environment
and device is free to
operate and is
transparent to the ESD
valve operation.
Figure 7b: ...the device is then “engaged”
and maintenance informs the control room
that the ESD is now ready to test.
Figure 7a: When
it is time to test
the ESD,
maintenance
inserts the
controlled key
into the device...
Figure 8: Although mechanical Partial Stroke Test Devices do not
require ancillary controls, they may be added if specified.
© Fall 2002 Valve Magazine and Valve Manufacturers Association of
America (VMA), Washington, DC. All trademarks, trade names, service
marks and logos reference herein belong to their respective companies and
the VMA. Valve magazine articles or content may not be reprinted or
reproduce in any format without written permission from the VMA. For
more information, please visit www.vma.org.
VM
190697klc 2/28/03, 8:33 AM7
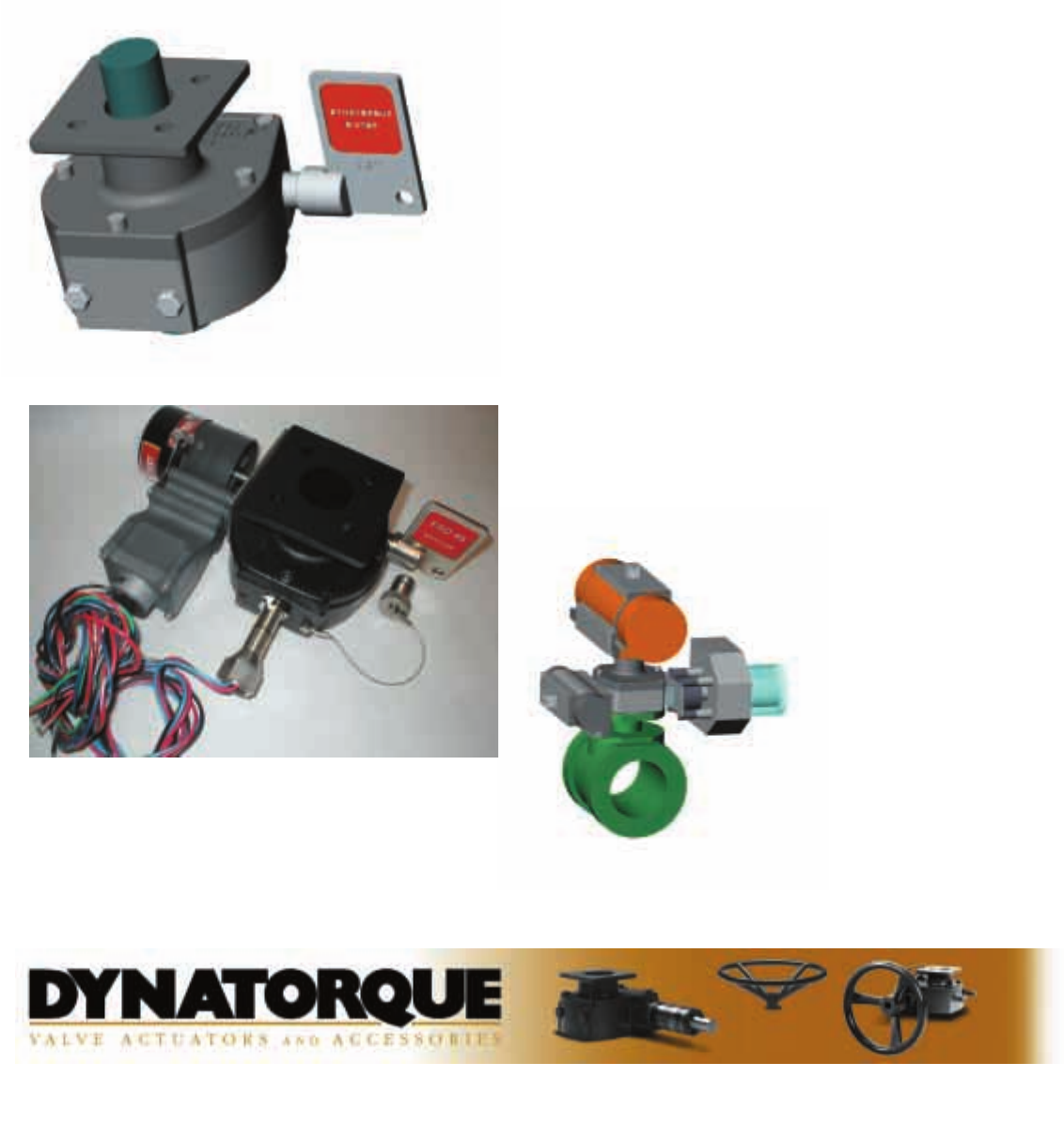
8 VALVE MAGAZINE
Plants need to make sure ESD and other critical safety
valves function properly now that maintenance shutdowns
for “full-stroke testing” are less frequent.
The DynaTorque D-Stop™ (Patent Pending) allows safety
control elements to be tested, but does not allow the valve
to fully-close during the test so the “revenue flow” is not
affected. Partial Stroke Testing may lower the Probability of
Failure on Demand (PFD) or may increase the time interval
required between full-stroke tests.
The D-Stop™ covers actuator torque ranges from 3000 lb-
in to 4,000,000 lb-in. It is a reliable mechanical device. Di-
agnostics and ancillary controls can be added, but they are
not required. No software or commissioning, so capital
costs are low.
Most important? The D-Stop™ keeps the system simple
and safe. In the real world, the less complex the system,
the fewer things can go wrong!
Critical Valve Test?
D-STOP™ it!
For remote and/or auto-
mated applications the
key and safety release
are not required. The
top actuator controls
the valve, while the
smaller actuator on left
engages/disengages
the D-Stop™.
Limit Switches (left and bottom) may be added to provide
feedback to I/O system indicating the D-Stop™ has been
engaged and that the device is in the
test
position. Data
points can be fed to a data acquisition system for the Par-
tial Stroke Test audit trail.
Ph. 231-739-1431 Fax. 231-739-4514 www.dynatorque.com/dstop info@dynatorque.com
190697klc 2/28/03, 8:33 AM8