FREQUENTIS USA F4E60F92 Voice communication system User Manual FREQUENTIS
FREQUENTIS USA Inc. Voice communication system FREQUENTIS
Contents
- 1. short user manual
- 2. safety guidelines
- 3. Product description VCS
safety guidelines

FREQUENTIS
SAFETY GUIDELINES
00A46 E500.12
COPYRIGHT FREQUENTIS 2000
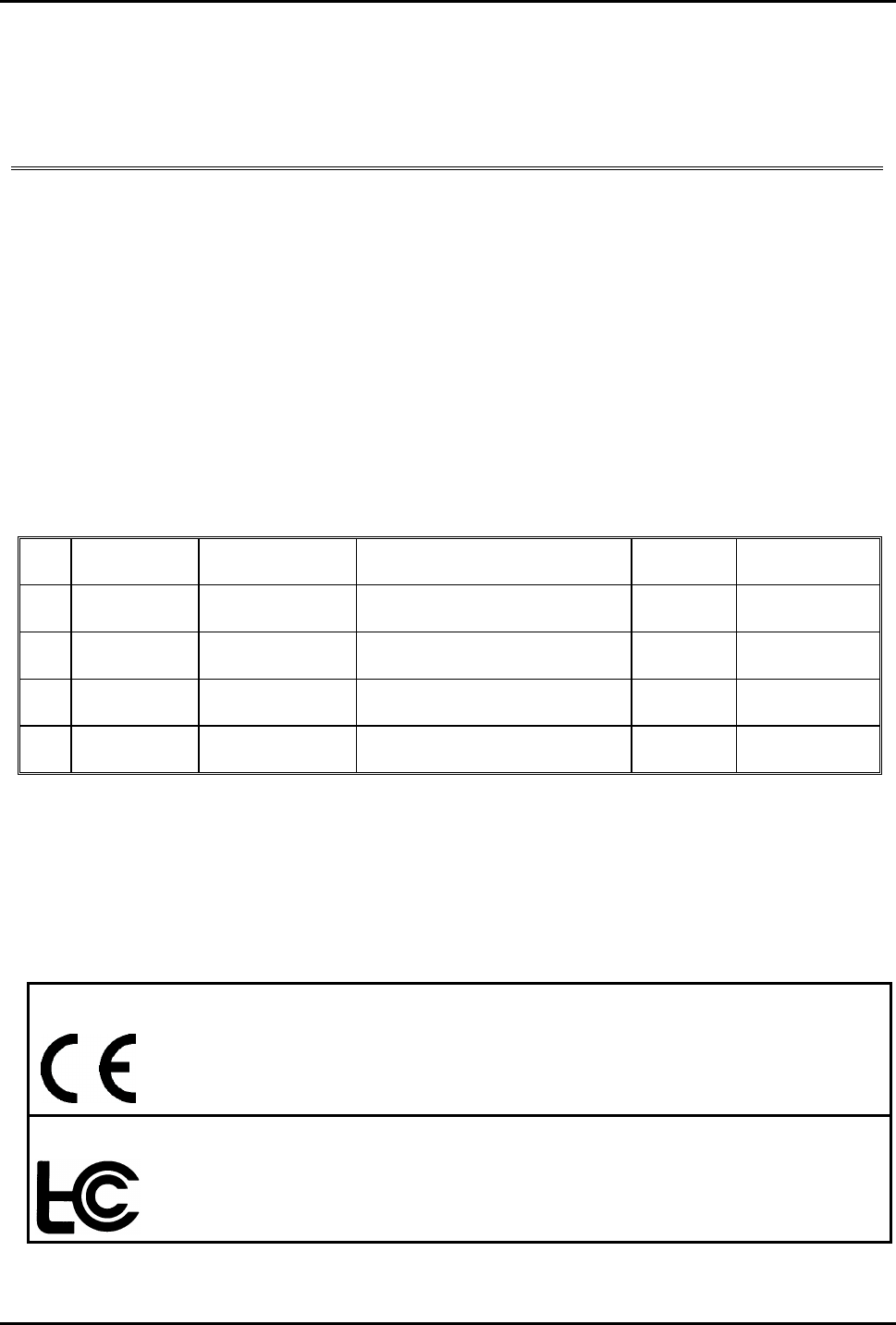
FREQUENTIS GmbH
Spittelbreitengasse 34, A-1120 Vienna, DVR 0364797
D-1 File: SGL REV.1.2.DOC FREQUENTIS SAFETY GUIDELINES
No: 00A46 E500.12 Author: S. Meisel COPYRIGHT FREQUENTIS 2000
History Chart
Rev. Date Changed Page(s) Cause of Change Implemented
1.0 00-11-29 All sections New Document S. Meisel
1.1 01-07-20 All sections Wording & Corrections S. Meisel
1.2 04-02-01 D-1, 5, 6, 8, 9, 34, 35 UL- & EN-Requirements;
VCS >> "system"
S. Meisel
No. Action Name Signature Date Department
1 Prepared S. Meisel 04-07-12 TCI
2 Approved G. Herndl 04-07-16 SSG
3 Approved H. Schicht 04-07-13 TQC
4 Released F. Kalwitz 04-07-16 TCI
The information in this document is subject to change without notice.
All rights reserved. No part of the document may be reproduced or transmitted in any form or
by any means, electronic or mechanical, for any purpose, without the written permission of
FREQUENTIS GmbH.
Company or product names mentioned in this document may be trademarks or registered
trademarks of their respective companies.
Confirmed by the CE-label, the system complies with following EC-directives and EC-standards:
● 73/23/EC “Low Voltage”
● 89/336/EEC “Electromagnetic Compatibility”
● 99/5/EC “R&TTE” (Annex 2 Class I Equipment)
● EN 60950-1 (01)
● EN 55022 (98)
● EN 55024 (98)
The system complies with Part 15 of the FCC Rules. Operation is subject to the following 2 conditions:
(1) this device may not cause harmful interference, and
(2) this device must accept any interference received, including interference that may
cause undesired operation.
Dieses Dokument ist elektronisch freigegeben.
This document is released electronically.
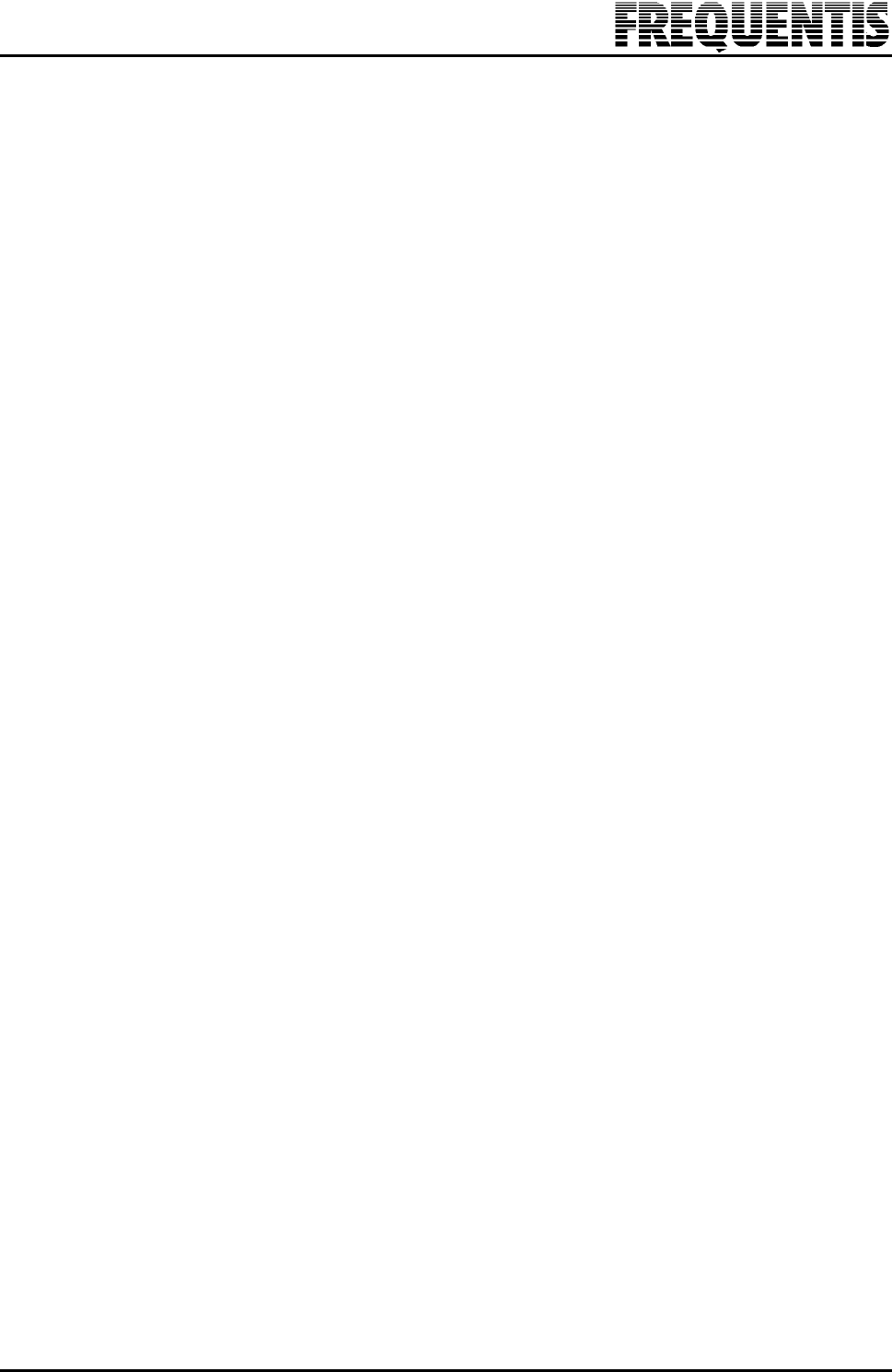
SAFETY GUIDELINES FREQUENTIS File: SGL REV.1.2.DOC C-2
COPYRIGHT FREQUENTIS 2000 Author: S. Meisel No: 00A46 E500.12
Contents
1. Introduction .......................................................................... 4
1.1. Purpose.............................................................................................................4
1.2. Target Group.....................................................................................................4
1.3. Requirements Concerning Warranty.................................................................4
1.4. Description of the Warning Symbols .................................................................5
1.5. Definition of Terms and Synonyms ...................................................................6
1.6. Major Warnings .................................................................................................6
2. Safety Instructions...............................................................7
2.1. Safety-Critical Phases of Installation and Maintenance .................................... 7
2.2. Personal Safety.................................................................................................8
2.2.1. Fire Hazard .......................................................................................................8
2.2.2. Electric Shock ...................................................................................................8
2.2.2.1. Causes and Prevention of Electric Shock .........................................................9
2.2.2.2. Inspection to Prevent Electric Shock...............................................................10
2.2.3. Injuries.............................................................................................................11
2.3. Handling Safety...............................................................................................11
2.4. Equipment Safety............................................................................................12
2.4.1. Mechanical Requirements...............................................................................12
2.4.2. Electrical Requirements ..................................................................................13
2.4.2.1. Safety Requirements.......................................................................................13
2.4.2.2. Redundancy Requirements (if applicable) ......................................................14
2.4.2.3. Protective Earthing..........................................................................................15
3. Electrostatic Discharge (ESD) ..........................................16
3.1. Definition .........................................................................................................16
3.2. ESD-Protection of Sensitive Assembly Parts..................................................16
3.3. Handling of Devices Sensitive to Electrostatic Discharge...............................17
3.3.1. General Rules for Handling Electronic Assemblies.........................................17
3.4. ESD-protection at the Equipment Area ...........................................................17
3.5. ESD-Protected Workplace ..............................................................................19
3.6. ESD-Protection during Shipping and Storage.................................................20
3.6.1. Packaging of Electronic Assemblies ...............................................................20
3.7. ESD-Regulations for Visitors...........................................................................20
4. Overvoltage Caused by Electrical Transients / Lightning. 21
5. Electromagnetic Compatibility (EMC) .............................. 22
5.1. Generic Electromagnetic Compatibility Requirements....................................22
5.2. Specific Electromagnetic Compatibility Requirements....................................22
5.2.1. Electromagnetic Fields Emitted by Visual Display Units .................................23
5.2.2. Check of Aerials and Receivers Adjacent to the Equipment...........................23
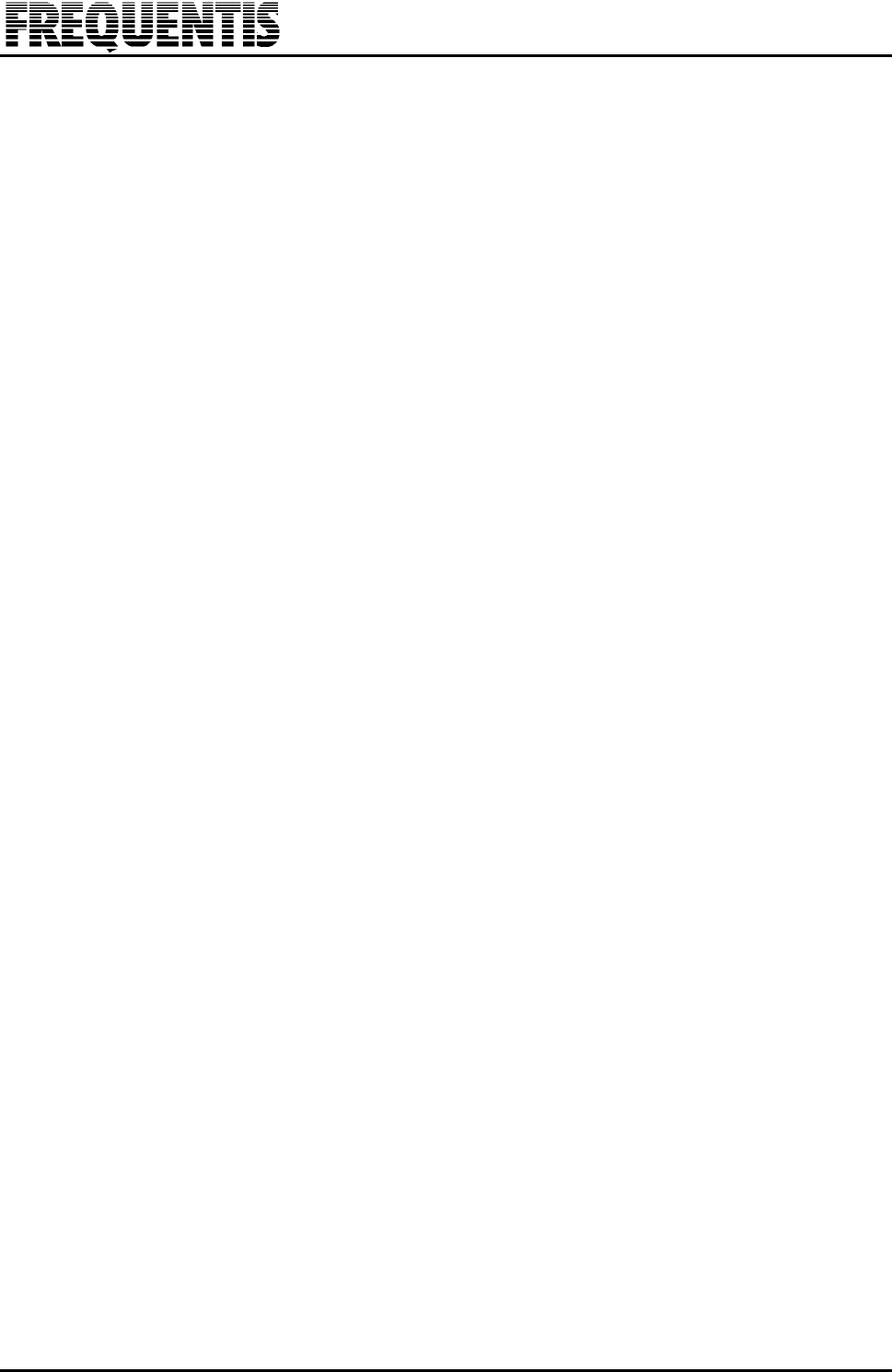
C-3 File: SGL REV.1.2.DOC FREQUENTIS SAFETY GUIDELINES
No: 00A46 E500.12 Author: S. Meisel COPYRIGHT FREQUENTIS 2000
6. Equipment Labelling.......................................................... 24
6.1. Adhesive FREQUENTIS Equipment Labels ...................................................24
6.1.1. Labels Indicating Product Categories .............................................................25
6.1.2. Labels Indicating Standards............................................................................26
6.2. Cable Identification..........................................................................................27
6.2.1. Cable Identifier Tags.......................................................................................27
6.2.2. Cable Types ....................................................................................................27
6.2.2.1. Connector Plan ...............................................................................................28
6.2.2.2. Wiring List .......................................................................................................28
6.2.3. Labelling with Printed Sheathing.....................................................................28
7. Handling of Equipment...................................................... 29
7.1. Required Tools................................................................................................29
8. Abbreviations ..................................................................... 30
9. Appendix............................................................................. 32
9.1. References to Standards ................................................................................32
9.2. Tables Concerning Safety Regulations...........................................................34
Illustrations
Fig. 3-1: Layout of Markings for Earth Bonding Points (Examples)............................... 18
Fig. 3-2: Earth Bonding Point at the Front of a Cabinet (Example) ...............................18
Fig. 3-3: Wrist Cable Connected to Grounding Point ....................................................19
Fig. 6-1: ESD-Label and Structure of Serial Numbers ..................................................24
Fig. 6-2: Serial Number Label of a Board......................................................................25
Fig. 6-3: Example of the Two Cable Identifiers for One Cable ......................................27
Fig. 6-4: Complete Cable Designation ..........................................................................27
Fig. 6-5: Position of a Cable Identifier Tag....................................................................28
Fig. 6-6: Cable Sheath Printing ..................................................................................... 28
Fig. 7-1: ESD Field Service Kit......................................................................................29
Fig. 9-1: Structure of EN Standards (Example)............................................................. 32
Tables
Tab. 2-1: Causes and Prevention of Electric Shock .........................................................9
Tab. 6-1: Labels Indicating Product Categories .............................................................25
Tab. 6-2: Labels Indicating Standards............................................................................26
Tab. 9-1: Typical Static Charge Sources........................................................................34
Tab. 9-2: Typical Static Voltage Generation...................................................................34
Tab. 9-3: Maximum Resistance vs. Discharge Time for Static Safe Operations............34
Tab. 9-4: Minimum Sizes of Conductors in Power Supply Cords...................................35
Tab. 9-5: Ranges of Conductor Cross-Sections.............................................................35
---------- END OF SECTION ----------
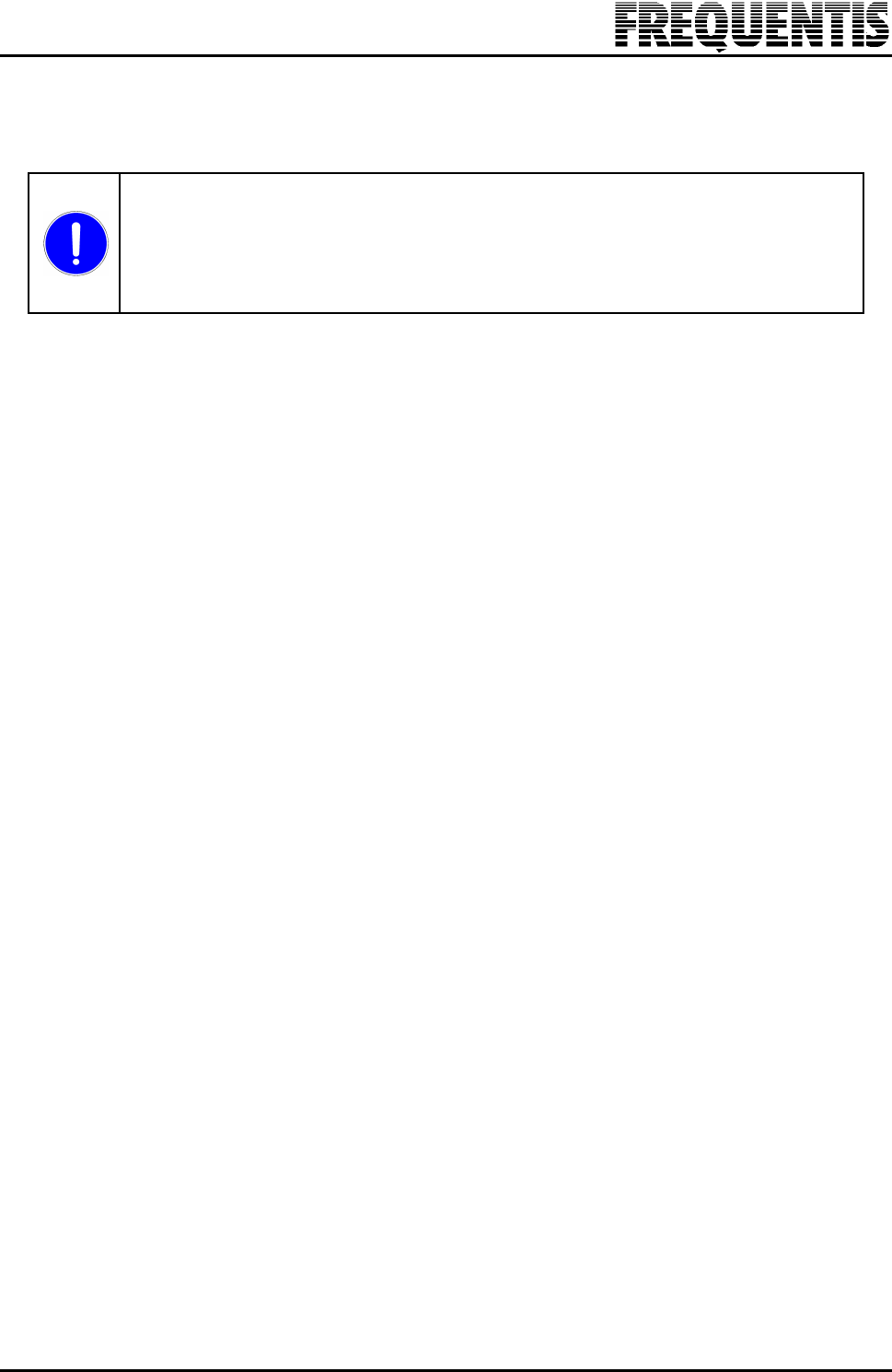
SAFETY GUIDELINES FREQUENTIS File: SGL REV.1.2.DOC 4
COPYRIGHT FREQUENTIS 2000 Author: S. Meisel No: 00A46 E500.12
1. Introduction
Only trained personnel authorised by the customer and/or FREQUENTIS
may handle the system.
Always read this manual carefully before starting to install or service the
system.
For easy access, keep the Safety Guidelines at hand on site.
1.1. Purpose
These Safety Guidelines explain the precautions and basic information required
for correct handling of a system from the range of released products of
FREQUENTIS (e.g. VCS 3020 Series, VCX, DICORA). For details of the actual
configuration, please refer to the System Configuration document.
These Safety Guidelines are concerned with workplace and equipment safety not
including the reliability of the system.
1.2. Target Group
The Safety Guidelines contain precautions to be taken by the trained installation
and/or maintenance staff when servicing the system. They are intended for
everyone involved in preparing for the infrastructure, installing the system and/or
maintaining its components. Moreover, this manual is aimed at anyone who deals
physically with the system.
The staff is expected to be aware of obvious hazards. Furthermore, they have to
be appropriately trained for and experienced enough to recognise hazards in
their daily work, and to minimise risks to themselves and others.
The staff must be trained and observe, among others, appropriate ESD-practices
and procedures for handling the cabinets, boards and cabling. A FREQUENTIS
training course covering the technical part (basics and maintenance) of the
system is essential to achieve the correct handling of the system.
1.3. Requirements Concerning Warranty
Only trained personnel authorised by the customer and/or FREQUENTIS may
prepare the site, install, put into operation and maintain the system.
All warnings and instructions contained in the applicable documents supplied
must be observed. The meaning of the warning symbols used is described in
chapter 1.4. Major warnings e.g. concerning risks of injuries or damage to the
equipment are listed in chapter 1.6.
Violation or non-observance of the Safety Guidelines in this document cancels or
restricts the warranty provided by FREQUENTIS. In particular, FREQUENTIS
shall not be responsible for any resultant operational errors or any damages
caused to persons, properties or whatsoever.
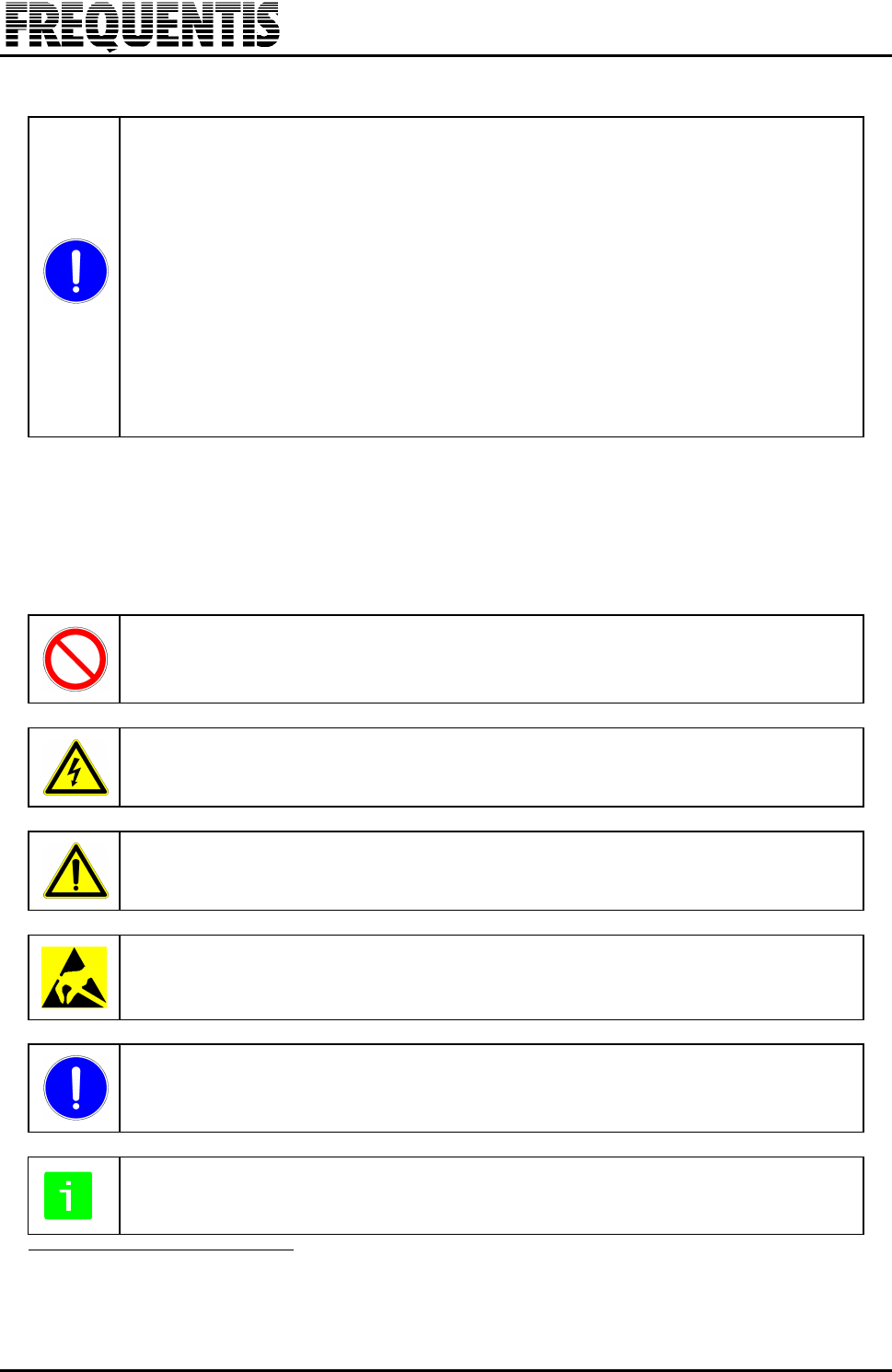
5File: SGL REV.1.2.DOC FREQUENTIS SAFETY GUIDELINES
No: 00A46 E500.12 Author: S. Meisel COPYRIGHT FREQUENTIS 2000
If the customer wishes to make major changes to the system (i.e. any
system modification not described in the relevant revision of the System
Configuration document, Installation Manual or Maintenance Manual), for
instance, if the customer wants
● to move the system or parts of the core system to different locations,
● to extend, reduce or modify the system configuration,
● to connect third-party equipment to the system supply circuits,
● to change to power supplies not delivered by FREQUENTIS,
● to change the grounding concept,
FREQUENTIS must be informed in writing giving sufficient advance notice.
The customer then has to wait for written permission from FREQUENTIS
before carrying out such changes.1)
1.4. Description of the Warning Symbols
The Safety Guidelines and the other User Documentation contain warnings,
recommendations and safety precautions as defined in ISO 3864-1984 (E).
Disallowed - Interdict - Prohibition!
Risk of an electric shock.
Risk of serious injury or of severe damage to equipment.
Risk of severe damage to electrostatic sensitive devices.
Mandatory for operation.
This symbol emphasises extra information.
1) Any change of the system configuration must be incorporated adequately in the accompanying
system- and user-documentation without delay agreed with FREQUENTIS.
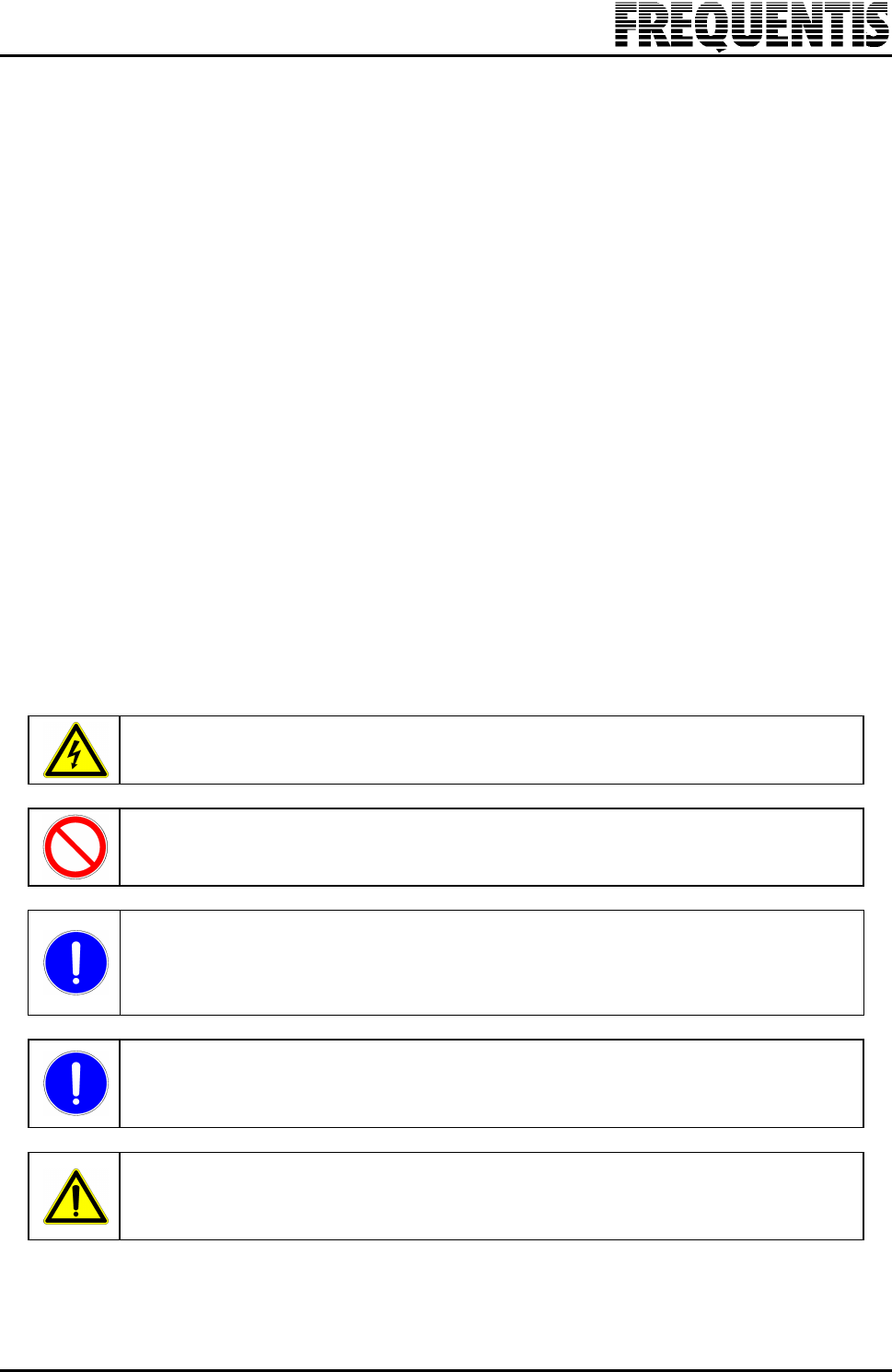
SAFETY GUIDELINES FREQUENTIS File: SGL REV.1.2.DOC 6
COPYRIGHT FREQUENTIS 2000 Author: S. Meisel No: 00A46 E500.12
1.5. Definition of Terms and Synonyms
Handling Dealing with or manipulating the system or its components in a
technical context.
Installation Initial set-up of the system hardware or parts of it, and operating
system configuration.
Maintenance Any action for keeping the system in working order (acc. to the
relevant maintenance level).
Service All actions taken to set-up or to keep the system in good operating
condition, including monitoring of the technical infrastructure,
maintenance and repair work.
Because of potential inconsistency in terminology, the following terms on the left
can be considered as synonyms for the terms on the right:
A/G-Communication ~ Radio Communication
G/G-Communication ~ Telephone Communication
Operator Position (OP) ~ Controller Working Position (CWP)
Project Specification ~ System Configuration Document
Documentation, DOC, (output) ~ Recording, REC, (output)
1.6. Major Warnings
The following warnings and precautions have to be observed strictly:
Some of the devices (e.g. power supplies and panels) operate at lethal
voltages.
Do not work on live system parts. De-energise all power supplies first then
follow the appropriate procedures.
The equipment is to be installed in Restricted Access Areas only
(dedicated equipment rooms, wall-mounting equipment cabinets, or the like)
in accordance with National Electric Code, ANSI/NFPA 70 (110-16 to 18). It is
suitable for mounting on concrete or other non-combustible surfaces only.
Only persons who are properly trained and capable of handling electronic
devices may service the system.
Observe the ESD- and EMC-regulations (refer to section 3 and 5).
Do not utilise non-released SW or HW additional to or instead of SW resp.
HW of the system configuration released by FREQUENTIS.
Do not apply wrong supply voltages.
---------- END OF SECTION ----------

7File: SGL REV.1.2.DOC FREQUENTIS SAFETY GUIDELINES
No: 00A46 E500.12 Author: S. Meisel COPYRIGHT FREQUENTIS 2000
2. Safety Instructions
Above all, basic prerequisites must be considered concerning safety instructions,
protection against electrostatic discharge, overvoltage caused by electrical
transients or lightning, electromagnetic compatibility, infrastructure planning, site
survey and area identification.
This section covers the safety-critical service phases: personal safety, fire
hazards, electrical shocks, injuries, handling safety and equipment safety.
2.1. Safety-Critical Phases of Installation and Maintenance
Only a fully trained technical crew may service the system as the crewmembers
may be exposed to potential hazards of various types while performing their
duties. These hazards must be eliminated or reduced to ensure that the staff is at
minimum risk.
All installation personnel shall be briefed on the potential hazards involved in
installing the system. Awareness of these hazards shall be promoted by the site
safety officer (person responsible for safety at the site), who shall be present
during all safety-critical phases of installation:
1) Unloading of equipment on site
2) Transport of equipment to final location
3) Installation of heavy system parts
4) Initial power application to fully-installed system
5) Changing of boards
The service life cycle consists of the following phases:
1) (Trans)shipment to site
2) Unloading on-site
3) Transport to final location
4) Erection and mechanical assembly at the final location
5) Cabling at the final location
6) Initial equipment power-up
7) Test and integration of fully powered system
8) Adding, changing or removing components
Each of these phases contains some or all of the hazards identified in the
following chapters. Detailed countermeasures are described for each type of
hazard.
The staff have to be aware of the typical hazards already identified and the action
required. The list is in no way conclusive and unforeseen hazards may occur at
any time. Each crewmember is responsible for identifying further hazards and
reporting them to the site safety officer.
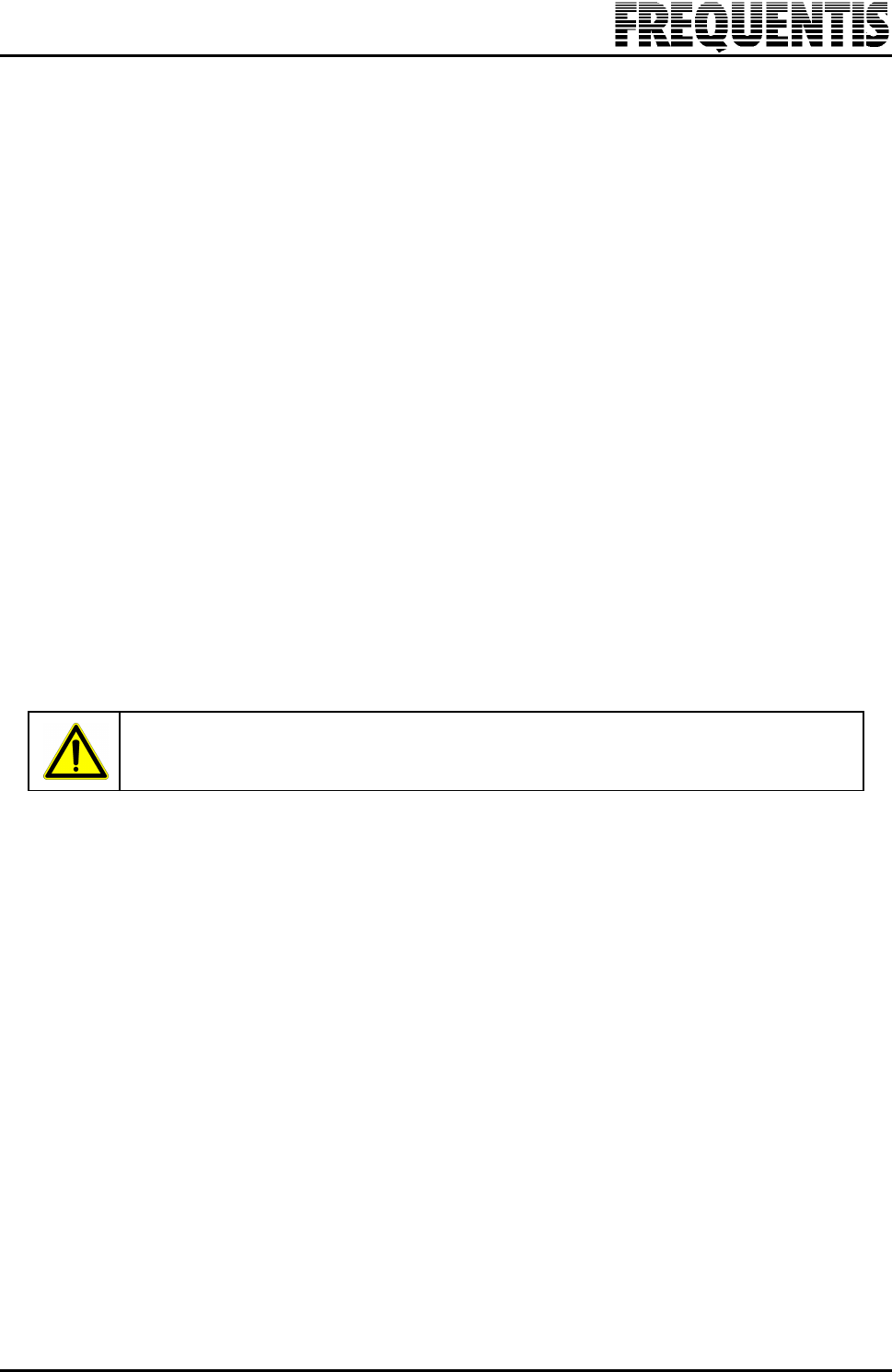
SAFETY GUIDELINES FREQUENTIS File: SGL REV.1.2.DOC 8
COPYRIGHT FREQUENTIS 2000 Author: S. Meisel No: 00A46 E500.12
2.2. Personal Safety
It is of utmost importance not to expose the personnel to unnecessary risks
during their work. Where essential activities involve a safety risk of any kind, the
site safety officer has to be informed. The site safety officer has to take measures
to provide adequate precautions against the hazard, such as fire extinguishers or
medical supervision. The following hazards are predictable:
● Fire hazard Chapter 2.2.1
● Electrical shock Chapter 2.2.2
● Injuries (e.g. tripping over cables or cuts from sharp objects) Chapter 2.2.3
2.2.1. Fire Hazard
Fire hazards can never be totally eliminated, but preventive measures should
ensure that any damage or injury is avoided.
● In particular, the correct type of fire extinguisher always has to be available in
the vicinity of current activities. The personnel shall be instructed by the
person responsible for site safety on the correct use of an extinguisher in an
emergency, the various types and their physical location.
● Burns and/or inhalation of fumes caused by fire must be reported immediately
for treatment by the medical staff.
● Smoking in the facility during the service period is not permitted.
To reduce the risk of fire, use only No. 26 AWG (>0.4 mm ∅) or larger wires
for telecommunication lines.
2.2.2. Electric Shock
Despite the care taken by skilled personnel at work, exposure to electric shock
due to unpredictable events can, however, never be excluded. Line driving and
ringing voltage are health hazards to the personnel. They therefore have to work
with special care during and after the initial power-up, particularly at the
backplanes of the core and interface racks.
Though the following safety precautions should prevent such potential hazards,
the power may be turned on inadvertently by third parties or electrical power may
already be available in other parts of the system.
● Each system component must be correctly connected to ground to minimise
personnel exposure to shock hazards. This must be completed before power of
any voltage is applied. The facility power engineer must ensure that all
grounding points are properly connected to the central bonding rail (the
building’s earth).
● Service activities after connection of the system to the main facility power shall
be co-ordinated by means of mobile communication between the
crewmembers and the facility power engineer, who is responsible for ensuring
that power application at a particular location does not affect other locations.
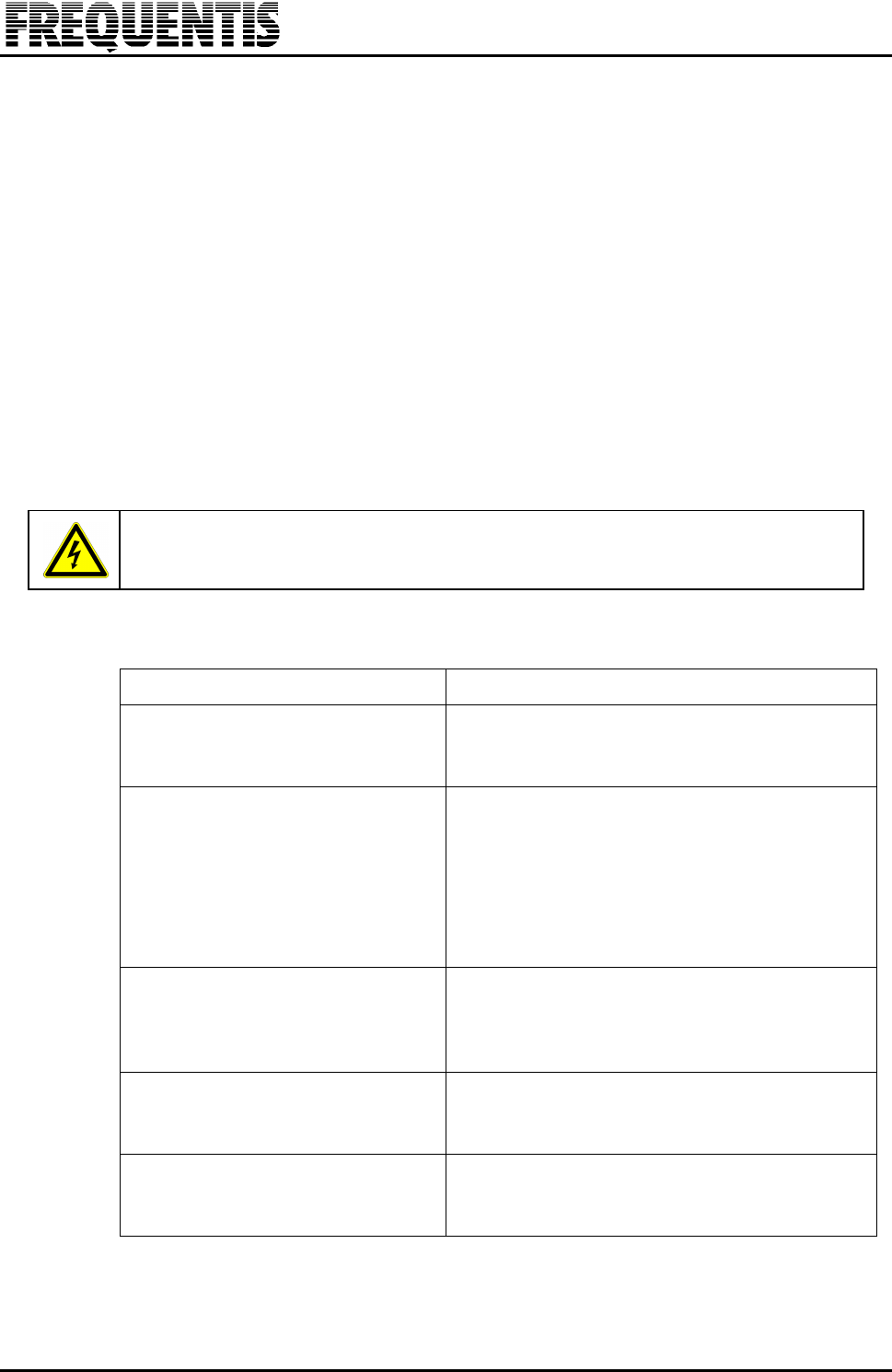
9File: SGL REV.1.2.DOC FREQUENTIS SAFETY GUIDELINES
No: 00A46 E500.12 Author: S. Meisel COPYRIGHT FREQUENTIS 2000
● Medical supervision should be provided, but first-aid counter-measurements
will provide the most effective treatment for electrical shock victims. Artificial
respiration is the prime recognised means of resuscitating an electrical shock
victim. All crewmembers must be trained in this method.
● A victim must be separated from live power contacts before resuscitation
measures are employed. If the source of power cannot be accessed or turned
off, a dry, insulated object, such as a broom, must be used to minimise the
risk that the person providing aid is not similarly exposed to the same hazard.
● Qualified medical attention must be sought in all cases of electrical shock
exposure to ensure that no symptoms remain. The site safety officer must be
immediately informed of an accident to notify the appropriate authorities.
● Provision must be made in the grounding system to protect the personnel
from live circuitry due to carelessness or equipment failure. A survey must be
performed of the available voltage sources that could be encountered at the
equipment area to provide adequate protection from electrical hazards.
The equipment may have more than one power supply cord! To avoid
electric shock, disconnect all power supplies before servicing the system.
2.2.2.1. Causes and Prevention of Electric Shock
Causes of Electric Shock Prevention
Contact with parts normally
at hazardous voltage.
Prevent access to parts at hazardous voltage
by fixed or locked covers, interlocks, etc.
Discharge capacitors at hazardous voltages.
Breakdown of insulation between
parts normally at hazardous
voltage and accessible conductive
parts.
● Connect the accessible conductive parts to
earth to limit the voltage to safe values and
the circuit breaker will disconnect the parts
having low impedance faults.
● Use double or reinforced insulation between
accessible conductive parts and parts which
are at hazardous voltages in normal use.
Breakdown of insulation between
parts at hazardous voltages,
applying it to accessible parts.
Segregate hazardous voltage circuits.
Separate by earthed metal screens or
reinforced insulation. Earth any circuits capable
of carrying fault currents.
Breakdown of insulation guarding
parts at hazardous voltage.
Insulation for parts at hazardous voltage acces-
sible to the authorised representative must
have adequate mechanical/electrical strength
Leakage current from parts at
hazardous voltage to the casing.
Failure of PE-connection.
Limit leakage current to body to a safe value,
or provide high integrity protective earth
connection.
Tab. 2-1: Causes and Prevention of Electric Shock
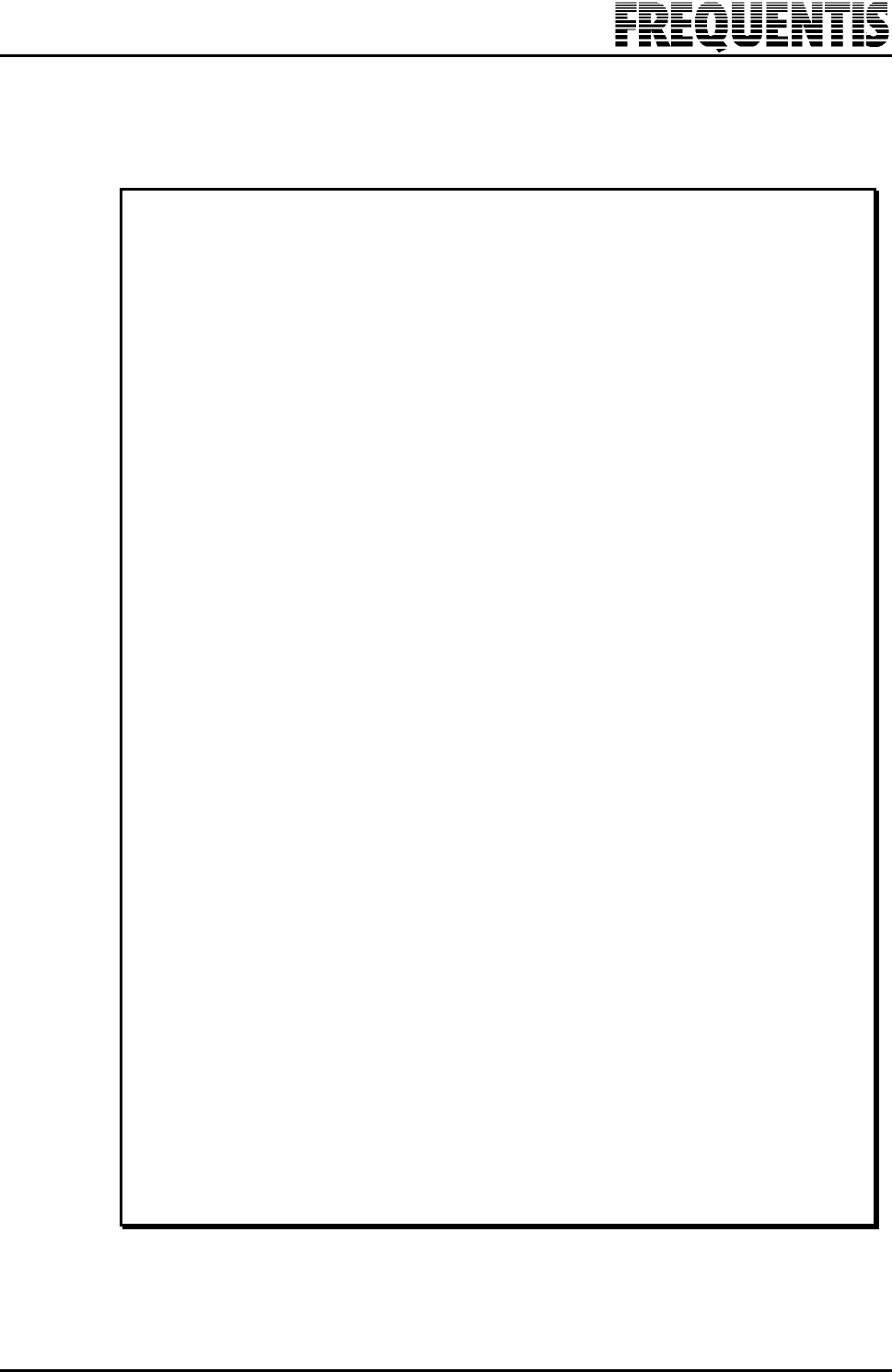
SAFETY GUIDELINES FREQUENTIS File: SGL REV.1.2.DOC 10
COPYRIGHT FREQUENTIS 2000 Author: S. Meisel No: 00A46 E500.12
2.2.2.2. Inspection to Prevent Electric Shock
Check, that
1) Protective devices comply with the site-specific requirements in accordance
with the (inter)national regulations.
•Protective earthing (PE) and equipotential bonding conductors meet the
required minimum cross-sections.
•PE- and neutral(N)-conductors are marked suitably and unmistakably.
•PE-conductors contain no switches, fuses or circuit breakers.
•Protective contacts of all plug-and-socket connections work efficiently.
•PE or neutral connection and disconnect points are identified.
2) Cross-sections of cords and cabling are appropriate to current consumption
at maximum load.
3) Connections are made in accordance with to the regulations.
4) Disconnect devices are implemented and suitably placed.
5) Inspection of the appliances shows no obvious lapse from safety provisions.
•All appliances meet the site specific environmental conditions and safety
requirements.
•All appliances are easily accessible for operation and maintenance.
•Warning labels for multiple supplies and/or multiple disconnection are
applied according to the respective appliances.
6) Personnel must be prevented from accessing
•bare parts normally operating at ELV or hazardous voltages and
•operational or basic insulation of such parts or wiring.
7) Generally, between an unearthed accessible conductive part and a primary
circuit double or reinforced insulation must be applied.
8) Conductive handles or their shafts, which are manually moved and earthed
only through a pivot or bearing must be separated from hazardous voltages
•by creepage distances and clearances of double or reinforced insulation,
•by supplementary insulation over accessible parts.
9) Insulation of internal wiring at hazardous voltages accessible to personnel
must not be
•subject to damage or stress,
•needed to be handled in normal operation routines,
•routed or fixed in such a way that unearthed metal parts are touchable.
10) Conductive parts of the equipment exposed to hazardous voltage in the event
of a single insulation fault must be reliably connected to a PE-terminal
resistant to significant corrosion.
11) Fire enclosures and fire prevention sheets are applied according to the
regulations.
12) Documentation for installation and maintenance is available at site.
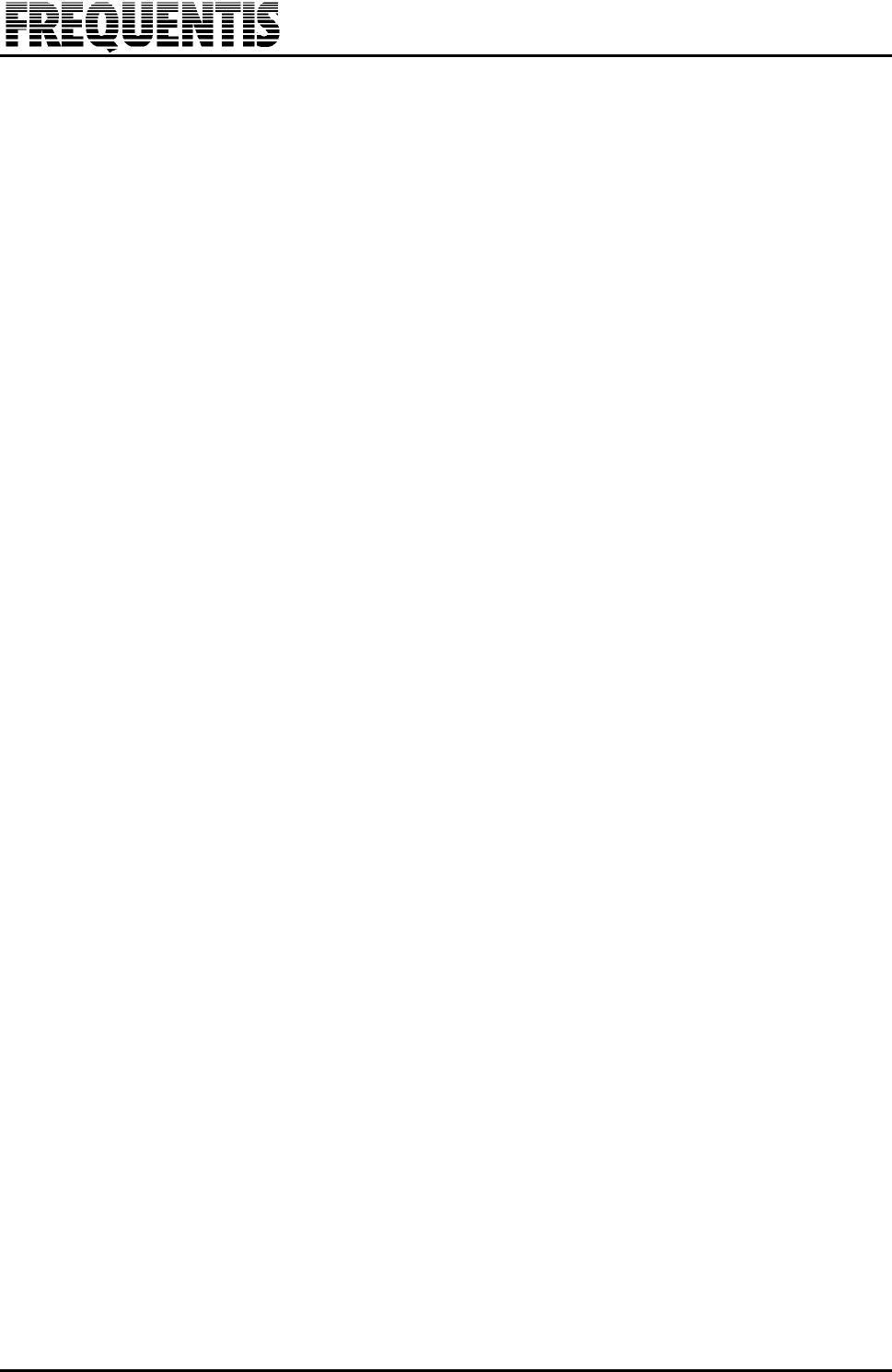
11 File: SGL REV.1.2.DOC FREQUENTIS SAFETY GUIDELINES
No: 00A46 E500.12 Author: S. Meisel COPYRIGHT FREQUENTIS 2000
2.2.3. Injuries
Whenever installation or maintenance work is performed, there is a risk of injury
due to mechanical parts. These injuries might be caused by moving parts, falling
items, tripping over cables, tools, sharp edges or working in confined spaces.
● Incautious or accidental movements can result in cuts, bruises and abrasions.
At all times crewmembers must be aware of their environment, the objects in
their vicinity and the presence or proximity of their team colleagues.
● When someone is working in a confined space, such as inside a controller
working position or under the raised false floor, a second person must be
present to supervise the inaccessible person, to check regularly his/her
physical condition and react quickly if there is any suspicion of injury.
● First-aid treatment of physical injuries shall be the prime defence against
further deterioration of the victim's condition. A first-aid box shall be made
available to the personnel on-site.
● Qualified medical attention must be sought in all cases of physical injury to
ensure that there is no risk of contamination or infection of a wound. To this
effect, the site safety officer shall be immediately informed of an accident and
he will notify the appropriate authorities.
2.3. Handling Safety
Moving parts of the equipment must not lead to injury under normal conditions. In
the case of parts accessible to personnel, constructive precautions have to
provide that -
● hazardous parts cannot be mounted with any enclosure part removed,
● enclosure parts are secured to the assembly requiring a tool for removal,
● interlocks protect against access to the potential hazard.
A suitable warning label protects from an obvious hazard caused by the moving
part. De-energising means have to carry warnings readily visible in a prominent
position where the risk of injury is highest.
In particular hard hats, heavy-duty leather gloves and steel-capped safety boots
shall be worn during all activities involving manhandling of corresponding
equipment. The phases of installation/maintenance intended for manhandling
activities are as described in chapter 2.1. No crewmember present in the zone of
operation shall be permitted to perform his/her tasks without taking these
precautionary measures:
● At all times during these phases, precautions shall be taken against human
strain. Sufficient manpower shall be secured when off-loading heavy
equipment, such as the racks, to ensure that no individual is overburdened.
● All individually transportable units must bear a label clearly indicating the
weight of that item, in order to enable the crew to identify the manhandling
resources necessary for that item. The crewmembers must always take
notice of the weight indications attached to the transport items.
● No person must lift equipment that is heavier than 20 kg. Several persons
may lift more than 20 kg, but their individual portion of the total load may not
exceed this weight.
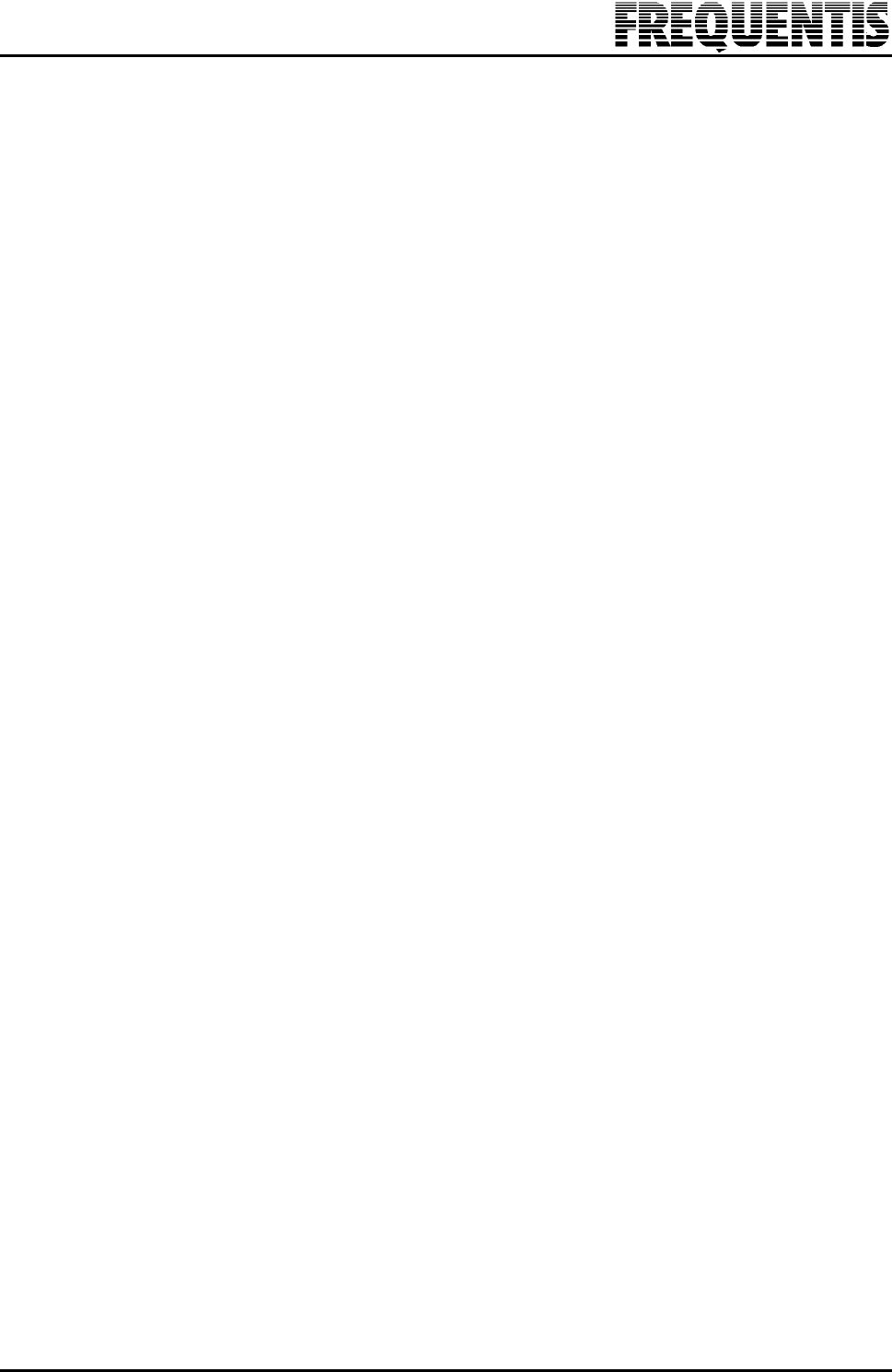
SAFETY GUIDELINES FREQUENTIS File: SGL REV.1.2.DOC 12
COPYRIGHT FREQUENTIS 2000 Author: S. Meisel No: 00A46 E500.12
● Lifting gear must be employed in all cases where the total load exceeds
50 kg. Where lifting gear is used, the immediate vicinity must be cleared of all
personnel except the authorised representative, to ensure that no hazards
exist due to incorrect loading.
● If the item is to be lifted by the eyebolts mounted on top of the racks, care
shall be taken to ensure that these are completely screwed in.
● Where pallets are used, the load shall be equally distributed over the
available pallet area to reduce the risk of accidental shifting. No personnel,
apart from the authorised representatives, are permitted to accompany the
equipment being transported, such as riding on a forklift truck, crane or hoist.
2.4. Equipment Safety
2.4.1. Mechanical Requirements
Mechanical equipment safety hazards can be caused by:
● Damage to the equipment during transport causing unexpected behaviour.
● Access to internal components using incorrect tools.
● Incorrect mechanical mating of connectors.
These safety hazards can be mitigated by applying the following rules:
● The equipment must be adequately secured during shipment/transport using
retaining lines and pallets if necessary. Smaller units must be packed to
prevent denting or perforation of the unit itself.
● All units must be inspected for obvious damage on arrival at the facility.
Those units with damaged packing shall be reported to the team leader, who
will initiate any insurance claims and further inspection of the damaged item.
At his discretion, the item may be released for installation or returned to the
company for replacement.
● Access to internal system components for adjustment purposes must always
be performed with the correct tools. For instance, a potentiometer may only
be accessed through perforated covers with an insulated screwdriver.
● Connectors can easily be damaged during mechanical mating activities. In
order to prevent this, both pin and socket (or both sides) connector halves
must be manually inspected for damage before attempting the mate.
● If a connector, its pins or sockets are damaged in any way, no attempt must
be made to connect the connector. This fact must be reported to the team
leader, who will initiate repair actions.
● If no damage is visible, both connector halves must be gently brought
together in such a way that the keying (if applicable) is lined-up. Mating is
achieved by constant pressure to the connector shell evenly over the mating
area until further movement is no longer possible and the connector can be
secured.
● If a connector is applied to the wrong connection point, serious damage may
occur to the equipment. For this reason, the cable label must match the
destination point. However, insert the connector to its destination shell with
care. If a mismatch is suspected, the mating operation must be stopped for
further technical investigation.
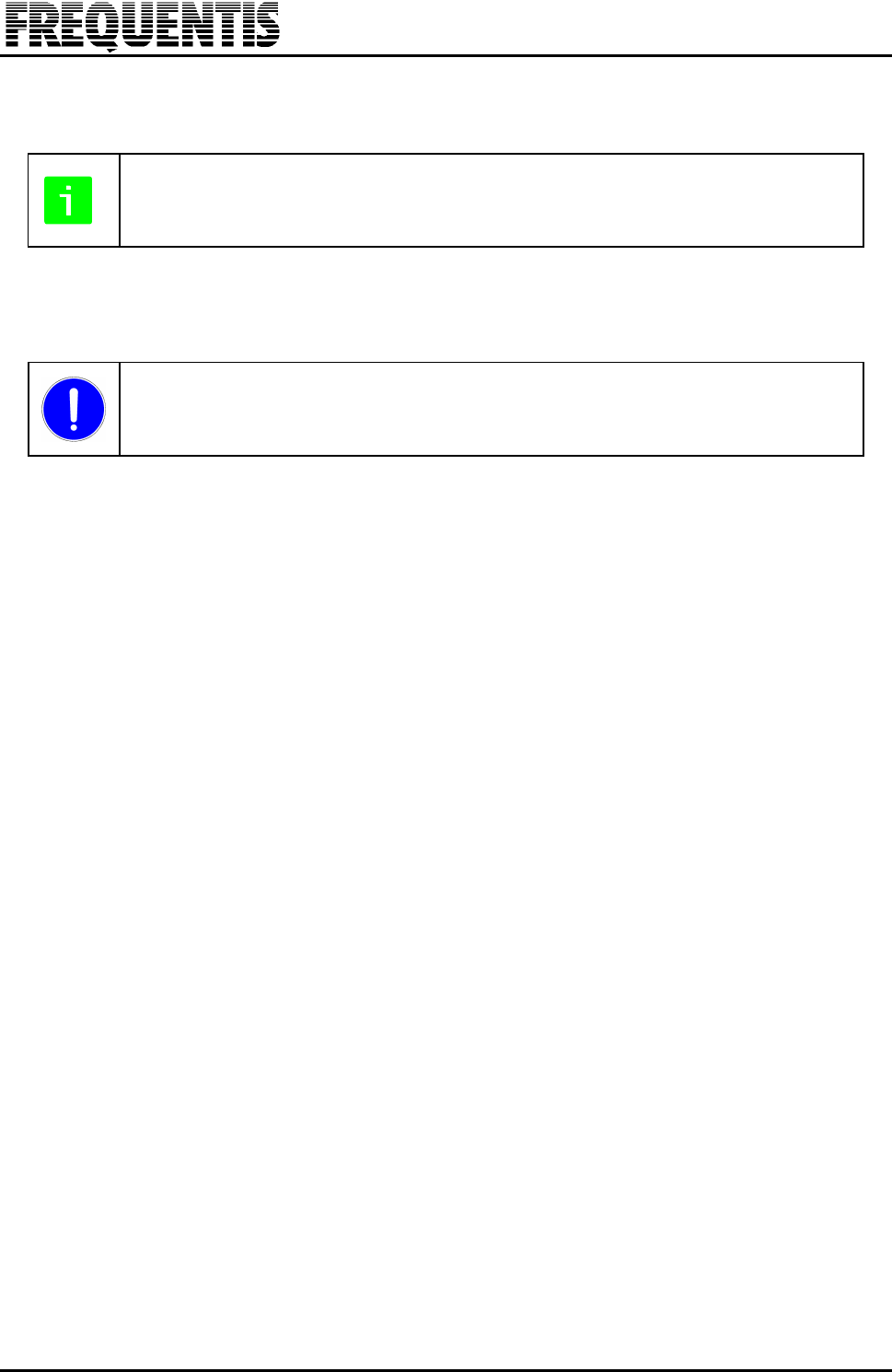
13 File: SGL REV.1.2.DOC FREQUENTIS SAFETY GUIDELINES
No: 00A46 E500.12 Author: S. Meisel COPYRIGHT FREQUENTIS 2000
2.4.2. Electrical Requirements
The Installation Manual provides the required information to set-up the system
for safe and reliable operation, including the power supply concept and the
equipotential bonding and grounding concept.
2.4.2.1. Safety Requirements
Installation and construction of the power supply system must comply with the
international standards and national regulations.
Installation of the building’s power supply system must at least observe
the requirements in IEC 60364 or equivalent national regulations (for
instance, VDE 0100 in Germany, and ÖVE/ÖNORM E 8001 in Austria).
Subject to the specific national regulations, the equipment must still be connected
in accordance with (i.e. not contravening) IEC 60950, so that compliance with the
standard is maintained.
● If a plug on a power supply cord is used for disconnection, the according
socket with earthing contact must be located near the system and easily
accessible. The supply plug, if used as the disconnect device, must connect
the PE earlier than the supply connections and must break it later than the
supply connections. Device inlets must meet the following conditions,
compliant to IEC 60320:
● Hazardous voltages are not accessible during handling with connectors.
● Connectors can be inserted easily.
● Sockets are not used for mechanical securing.
● The PE-terminal for each appliance is connected to the PE-terminal inside
the equipment.
● Power supply cords shall not be exposed to sharp points or cutting edges.The
conductors have to be relieved from strain, including twisting. Compression
bushings must not be used as cord anchorage. If the flexible cord should
slip in its anchorage, causing the conductors to be strained, the protective
earthing conductor, if any, must be the last to take the strain.
● Cords must not be clamped by screws; knots must not be applied. When an
anchorage is made of conducting material, it must be supplementary
insulated from accessible metal parts. The insulation of the conductors must
be protected from abrasion.
● For equipment with a non-detachable power supply cord, which is intended to
be moved while in operation, cord guards of insulating material must be
applied at the power supply cord inlet opening, protecting against excessive
bending for at least five times the cross-section of the whole cable.
● Screws and nuts, which clamp external power supply conductors, must
comply with standards ISO 261 or 262 and the like, fixing not any other
component. Terminal strands must not be able to contact unearthed
conductive parts, even when these parts are separated by basic insulation
from other accessible conductors.
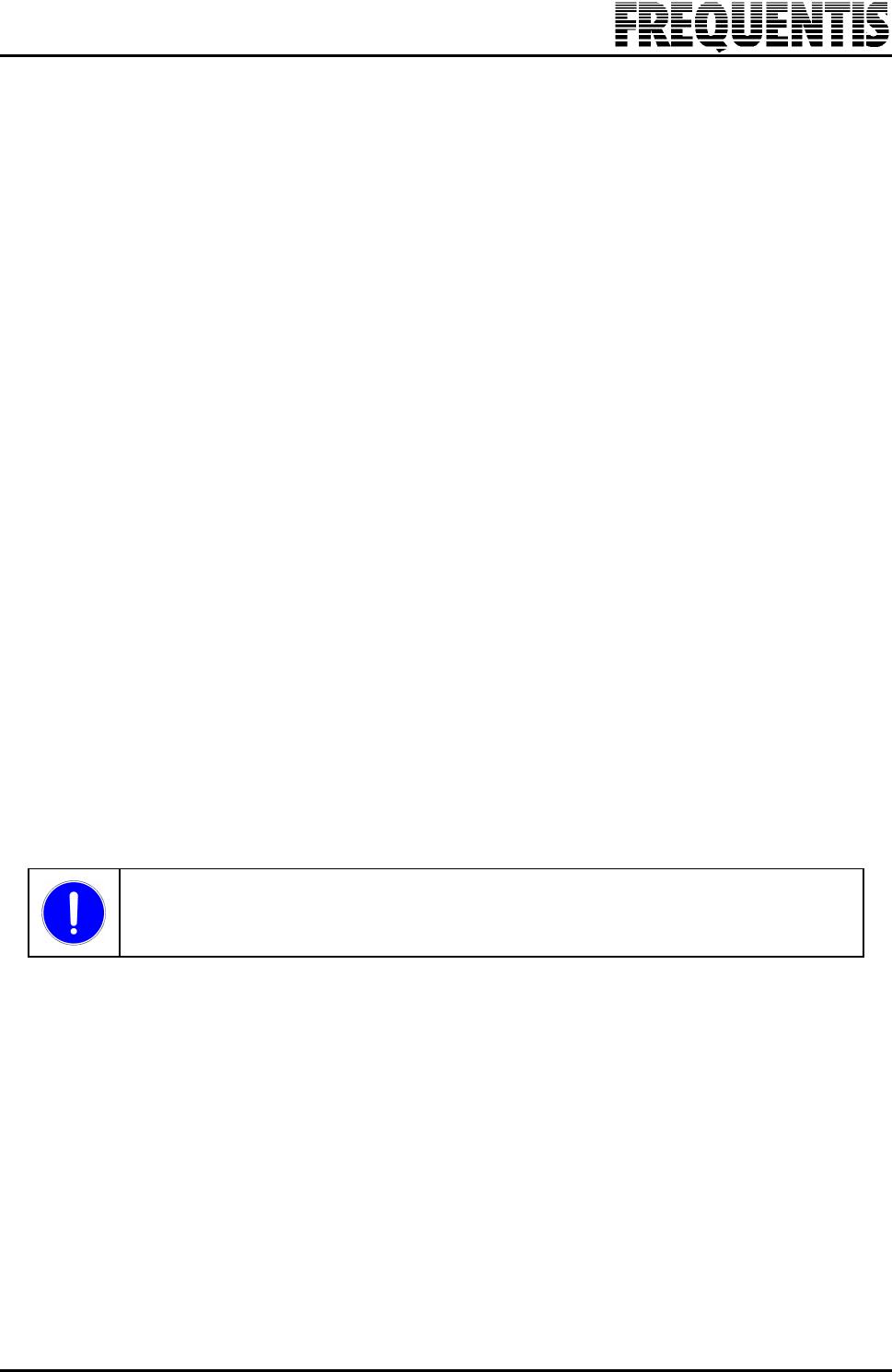
SAFETY GUIDELINES FREQUENTIS File: SGL REV.1.2.DOC 14
COPYRIGHT FREQUENTIS 2000 Author: S. Meisel No: 00A46 E500.12
● Where cord terminals are used for permanently connected equipment (non-
detachable power supply cords), the cord cross sections must fit the
respective clamps, otherwise, appropriate adapters must be applied (e.g. in
the case of increased WCS for long distances). Terminals must clamp with
sufficient contact pressure without damaging the conductor when tightened or
loosened, but so that the conductor cannot slip out, the terminal itself does
not work loose and the internal wiring is not subjected to stress (this aspect
has to be taken into account especially at the operator positions).
● Power supply cords consist of -
● a green/yellow PE-conductor electrically connected to the PE-terminal
inside the equipment and connected to the PE-contact of the plug, if
applicable, and
● conductors with minimum cross-sectional areas compliant to the standards
(see Tab. 9-4 and Tab. 9-5), corresponding to the maximum possible
current consumption (for examples refer to Tab. 9-5 in the Appendix).
Protective Devices
● Protective devices against excess current, short circuits and earth faults in
primary circuits, have to be included as integral parts of the equipment, or
part of the building installation.
● Where more than one phase conductor of a supply is used, any protective
device breaking the neutral conductor must break all phase conductors, too.
Devices for different conductors of the same supply shall be located together.
● For commercial (single-phase) equipment connected to standard supply
outlets, the building’s installation is regarded as providing protection in
accordance with the rating of the wall outlet.
● Fuses must be marked so that it is obvious to which circuit the fuse applies,
including its type, rated current, and voltage. Special fusing characteristics
must also be indicated.
In any case, AC or DC power supplies must be installed and maintained
according to the respective national regulations.
2.4.2.2. Redundancy Requirements (if applicable)
The system is designed for highest redundancy and availability. Therefore,
systems are typically installed with resilience against any single failure. This
redundancy concept is fully supported by the power supply concept.
The system provides the connections to two separate supply lines provided by
the site. If one power unit (or whole circuit) fails, alternate power units supply the
system without any malfunction or loss of performance during the downtime of
the failed supply.
Power distribution systems are usually structured radially and circuit breakers
have to be added at any point where the wire cross section is reduced.
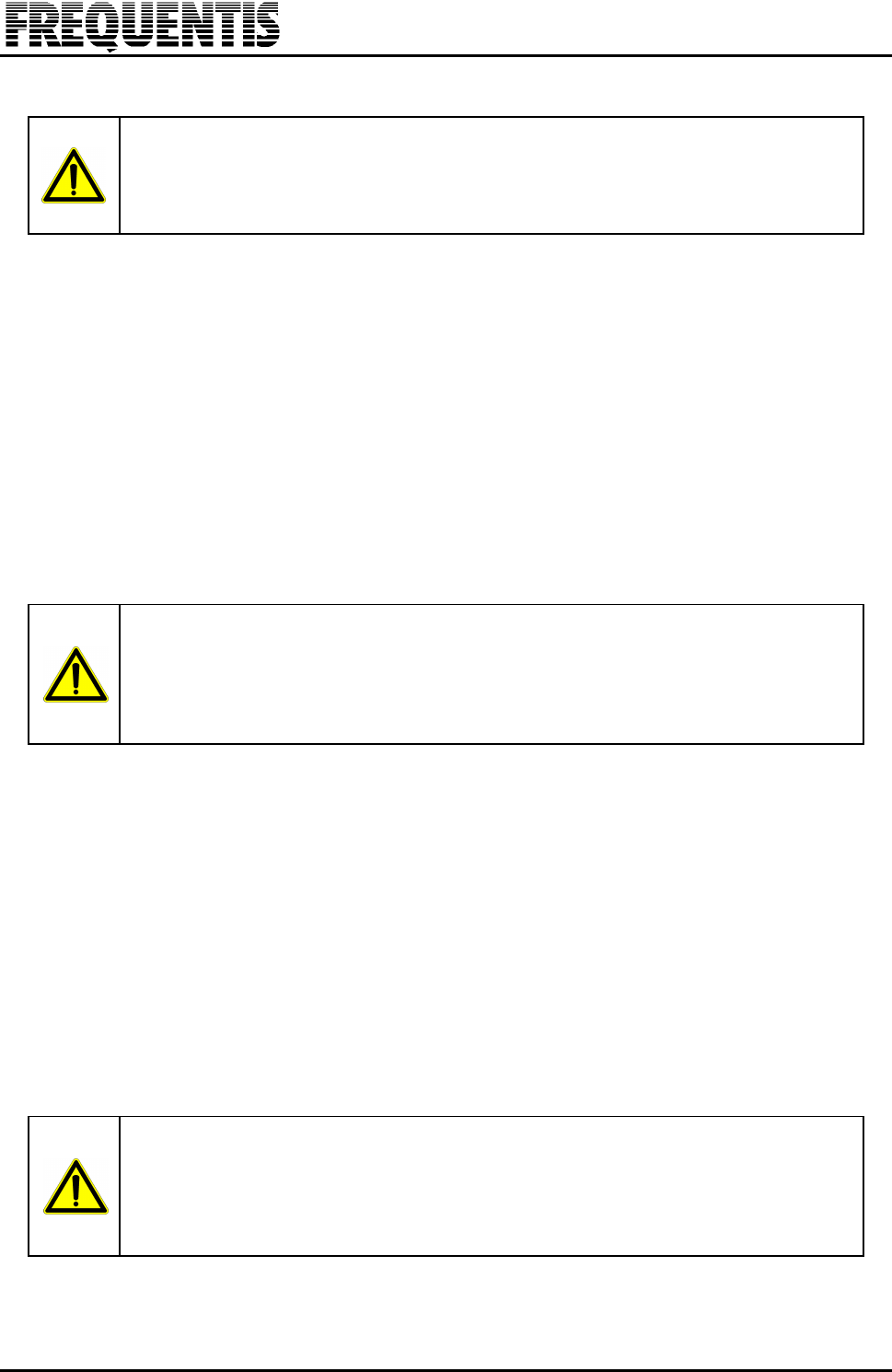
15 File: SGL REV.1.2.DOC FREQUENTIS SAFETY GUIDELINES
No: 00A46 E500.12 Author: S. Meisel COPYRIGHT FREQUENTIS 2000
The resulting series connection of overcurrent circuit breakers shall be
selective, which means that only the device next to the fault is triggered.
In addition, unwanted triggering of the main ground fault interrupters must
be avoided to ensure that other branches maintain energy flow.
General Rules
● Several branches with overcurrent circuit breakers connected to one ground
fault interrupter consider that a single defective unit can power down all
systems connected.
● Series connections of ground fault interrupters or overcurrent circuit breakers
operating on magnetic principles are not recommended because selectivity is
not ensured except under special conditions.
● Use slow blow fuses or special circuit protectors for heavy loads as the main
overcurrent protectors.
● Selectivity also depends on the characteristics of the (magnetic) circuit
breakers or the pre-arcing I²t of the fuses (Joule heat value), therefore always
follow the manufacturers instructions.
● Preferably, use combined ground fault/overcurrent circuit breakers.
Set up the power distribution system with utmost care regarding
availability. Especially, the redundant supplies A and B for the core
component cabinets must not both fail due to a single fault, i.e.
● they must not be disconnected simultaneously.
● no other equipment must be connected to the system's supplies
2.4.2.3. Protective Earthing
According to the safety standards, accessible conductive parts of the equipment,
that might assume a hazardous voltage in the case of a single insulation fault,
must be -
● reliably connected to a protective earthing terminal within the equipment, or
● at a fail-safe distance from these voltages by reinforced insulation.
The earthing conductors must be used on the power supply cords to protect the
personnel against electrical hazards from the cabinet equipment. Each power
supply must have its own grounding (protective earthing) in accordance with
EN 60950 or IEC 60950 (and the respective national regulations, if required). The
resistance of the earthing connection between the central earth connection point,
and each part required to be earthed must not exceed 0.1 Ω (without the
PE-resistance of the power supply cord).
Warning labels have to indicate to the personnel all the non-earthed parts
that have to be checked for hazardous voltages before being touched.
Vice versa, all parts of the system labelled with the earthing symbol must
remain permanently connected to the grounding system (together with
their subordinate components).
----------- END OF SECTION -----------
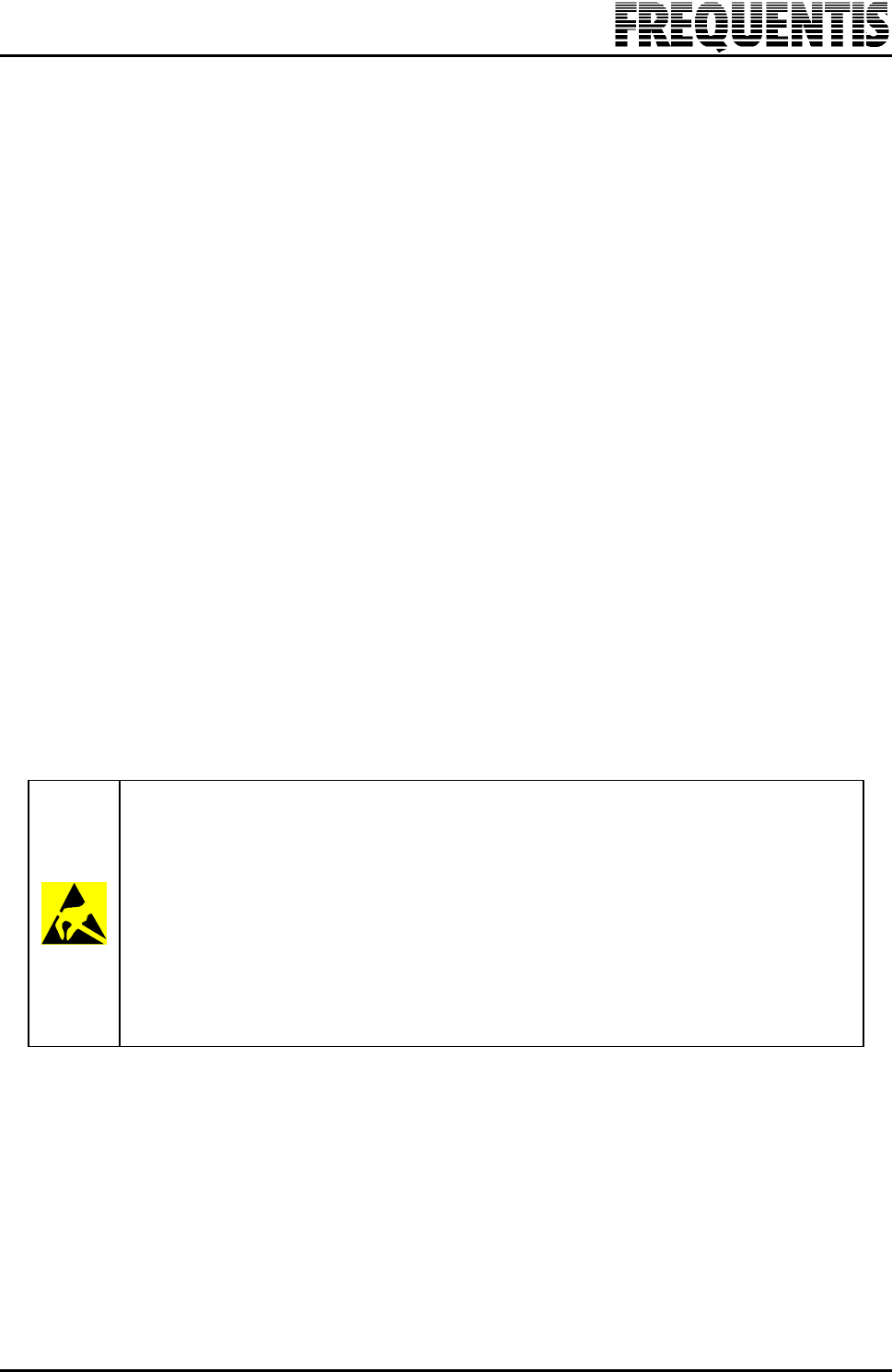
SAFETY GUIDELINES FREQUENTIS File: SGL REV.1.2.DOC 16
COPYRIGHT FREQUENTIS 2000 Author: S. Meisel No: 00A46 E500.12
3. Electrostatic Discharge (ESD)
3.1. Definition
Electrostatic sensitive devices are components and assemblies, which can be
damaged, latently damaged or even destroyed by Electrostatic Discharge (ESD).
ESD is the fast discharge of electrical energy created by static sources. A device
sensitive to electrostatic discharge is affected by these high-energy surges,
dependent upon its construction and materials. In assembly areas, where,
unprotected electronic assemblies are attached to the electrostatic sensitive
components, future system failures may be caused by ignoring the basic
protective measures.
The damage due to ESD occurring during handling (e.g., see Tab. 9-2) or
processing can be the same as from electrically powered processes. Affected
components can fail to operate immediately or latently to operate or change in
value. The consequences of latent failure are the most serious, because the
product may fail after delivery although it passed the inspection.
Common materials such as plastic bags or containers are serious static
generators. Do not use these materials (e.g., see Tab. 9-1) in especially static
safe operating areas. Peeling an adhesive tape from a roll can generate 20 kV.
Even compressed air over insulating surfaces generates charges.
Static charges can be induced on nearby conductors (like human skin), and
discharged into other conductors (like boards). Electrostatic discharges are
normally too low to be felt (less than 3.5 kV), but still able to damage sensitive
components.
When working with boards, observe the following precautions for
handling devices sensitive to electrostatic discharge (ESDS-
components).
1) ESD sensitive devices are labelled with the symbol, shown left.
2) Special training is required for working with ESD sensitive devices.
3) Do not touch boards without taking ESD-precautions.
4) Transport and packaging must also provide full ESD-protection.
5) Improper handling cancels warranty and liability on the part of
FREQUENTIS.
3.2. ESD-Protection of Sensitive Assembly Parts
When built-in, each part of the system resists electrostatic discharge (no damage,
no malfunction, and no loss of performance). Sensitive spare parts (e.g. interface
or microprocessor boards) will be delivered in conducting packing material that
prevents damage caused by electrostatic discharge.
All electronic assemblies of systems from FREQUENTIS are tested in accordance
with EN 61000-4-2 with 4 kV contact discharge. Parts, which are touched by
personnel (e.g. touch panels) are additionally tested with 8 kV air discharge.
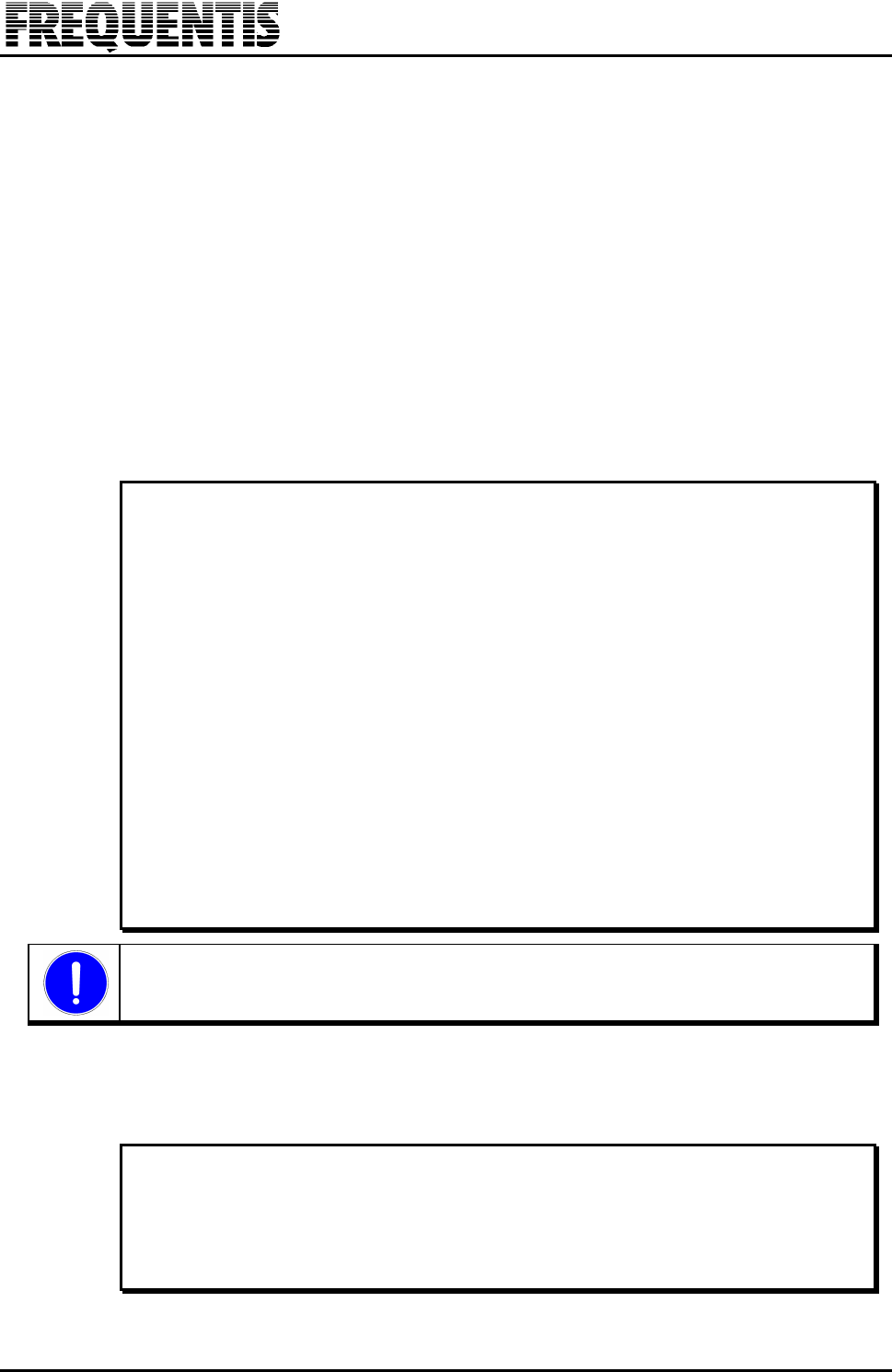
17 File: SGL REV.1.2.DOC FREQUENTIS SAFETY GUIDELINES
No: 00A46 E500.12 Author: S. Meisel COPYRIGHT FREQUENTIS 2000
3.3. Handling of Devices Sensitive to Electrostatic Discharge
Before handling or processing electrostatic discharge sensitive (ESDS)
components, tools and equipment need to be tested carefully to ensure that they
do not generate damaging energy, including spike voltages. As required by most
ESD-specifications, periodic testing is recommended as a precaution because
equipment performance may degrade with use over time. The best ESD-damage
prevention is
● first to prevent, and
● then eliminate static charges if they do occur.
The amount of electrostatic energy generated depends on the characteristics of
the source, and many factors such as material, relative motion by contacting,
separation, or rubbing of the material, humidity etc...
3.3.1. General Rules for Handling Electronic Assemblies
1) Personnel must be trained in and follow the appropriate ESD-practices.
2) Minimise the handling of electronic components to prevent damage.
3) Keep workplaces clean. Avoid any food; do not smoke in the equipment area.
4) In general, handle electronic assemblies with clean hands or gloves (not
common plastics). Touch the board only at the edges and with full ESD-
protection. Do not use hand creams or lotions containing silicone since they
can cause solderability problems and conformal coating adhesion problems.
When gloves are used, they need to be changed frequently.
5) Solderable surfaces are not to be handled with bare fingers. Lotions reduce
solderability, promote corrosion and dendritic growth. They can also cause
poor adhesion of subsequent coatings or encapsulates.
6) Never stack electronic assemblies because physical damage may occur. For
temporary storage, special racks need to be provided in assembly areas.
7) Do not take ESDS-components close to display screens.
8) Always assume the items are ESDS-components even if they are not
marked.
9) Never transport ESDS-components unless proper packaging is applied.
If there is any doubt about the sensitivity of an assembly, it must be
handled as a sensitive device until it is determined otherwise.
3.4. ESD-protection at the Equipment Area
ESDS-components must only be handled on condition that the floor conductivity
is sufficient (acc. to IEC 61340-4-1) when
1) a grounding strip is worn around the wrist
2) and/or ESD-shoes (which have to be checked before handling) are worn,
or when
3) the component/assembly is located on an ESD-protected workplace.
4) In addition, wearing a cotton coat it is recommendable.
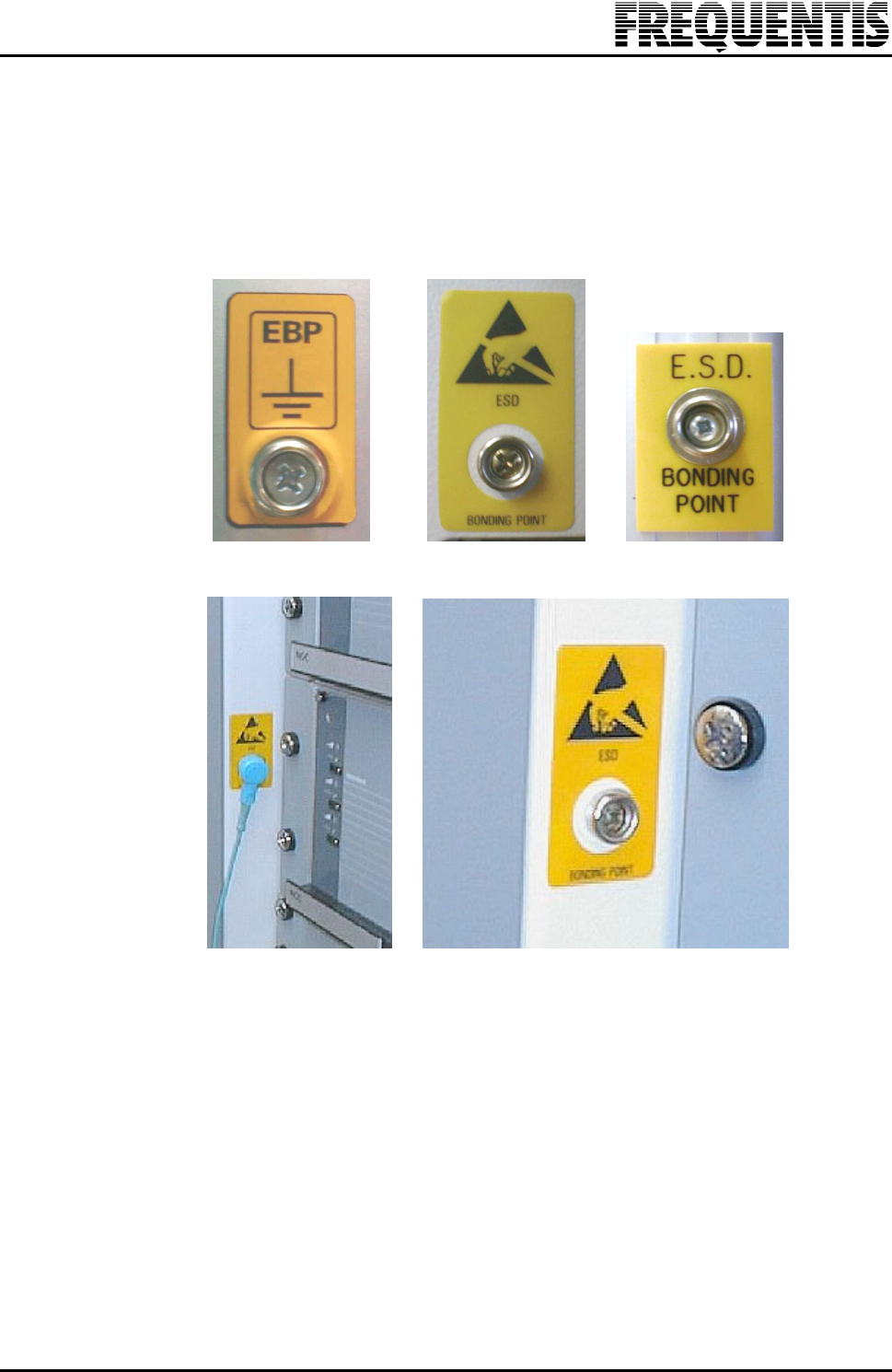
SAFETY GUIDELINES FREQUENTIS File: SGL REV.1.2.DOC 18
COPYRIGHT FREQUENTIS 2000 Author: S. Meisel No: 00A46 E500.12
EN 100015-1 specifies: The leakage resistance of respective parts must be in the
range between 1 MΩ and 35 MΩ, otherwise suitable action must be taken (e.g.
ESD-shoes, ESD-carpet).
For correct handling of ESDS-components, FREQUENTIS cabinets have a
dedicated grounding point (for the path-to-ground). These earth bonding points
are usually located at the front of the cabinet frame as shown in Fig. 3-2.
Fig. 3-1: Layout of Markings for Earth Bonding Points (Examples)
Fig. 3-2: Earth Bonding Point at the Front of a Cabinet (Example)
When removing boards from the system, first connect the wrist cable to the
grounding point as shown in Fig. 3-3. If no dedicated grounding point is available,
for instance, if a component is to be handled outside the cabinet(s), ESD-shoes
must be worn in all cases (proper floor conductivity must be provided).
Moving Electronic Assemblies
Handling assemblies with bare fingers contaminates the board/component and
causes soldering and coating problems. Fingerprints are hard to remove and will
often show up after exposure to humidity. Body oils and acids reduce
solderability, promote corrosion and dendritic growth, causing poor adhesion of
subsequent coatings or encapsulants. The best solution is to use gloves or other
protective handling devices to prevent such contamination.
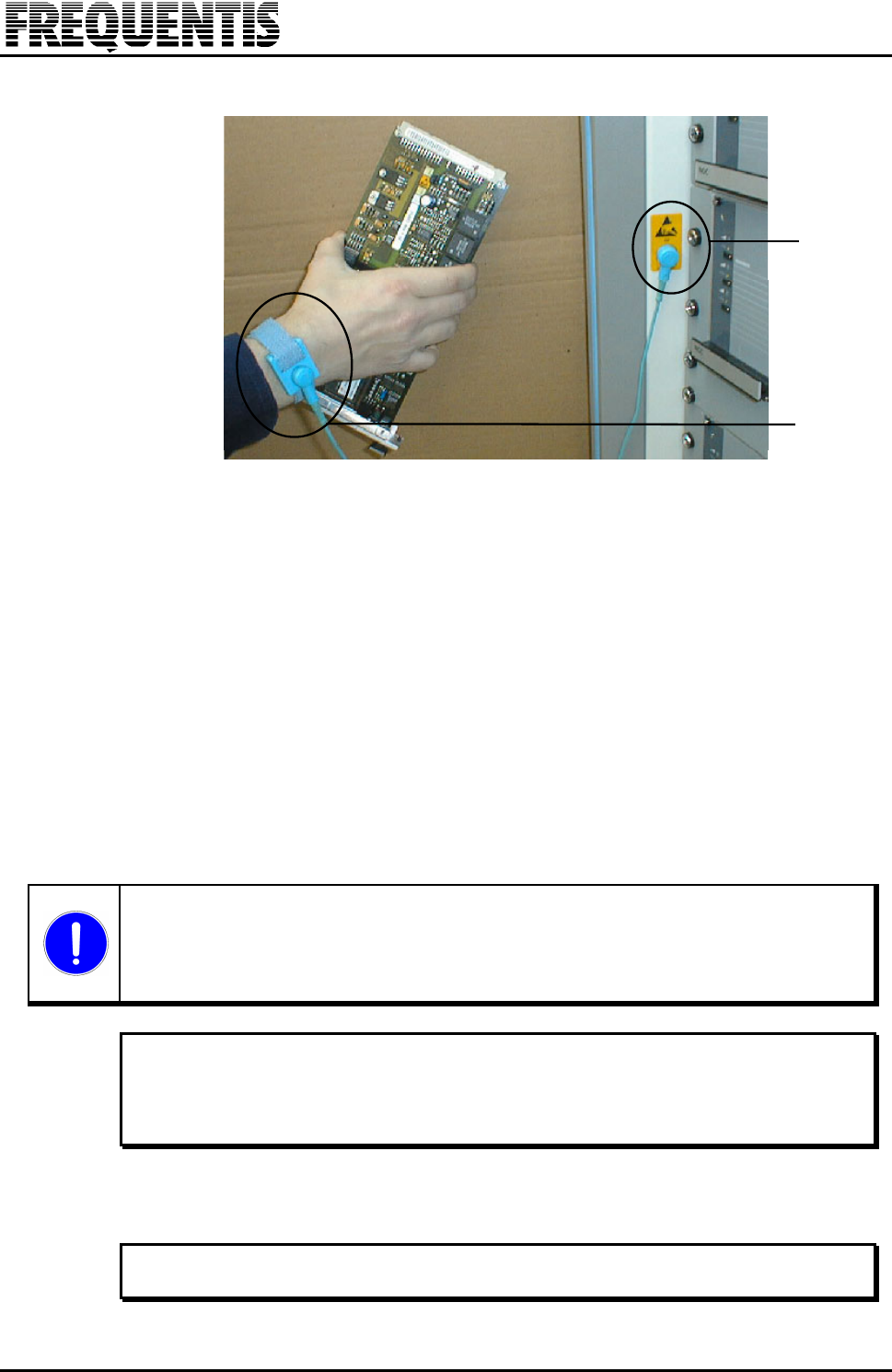
19 File: SGL REV.1.2.DOC FREQUENTIS SAFETY GUIDELINES
No: 00A46 E500.12 Author: S. Meisel COPYRIGHT FREQUENTIS 2000
grounding
cable at wrist
grounding
point
Fig. 3-3: Wrist Cable Connected to Grounding Point
3.5. ESD-Protected Workplace
Soldering irons, solder extractors and testing instruments can emit sufficient
energy to destroy ESDS-components or seriously degrade them. An ESD-
protected workplace is capable of preventing ESD-damage to ESDS-components
by providing –
● a line to earth for neutralising and draining off surges,
● static dissipative or antistatic working plates connected to a common ground,
● a wrist strap to drain off charges generated on the operator’s skin or clothing.
Provisions in the grounding system commonly succeed (through resistance in line
with the ground path) in slowing down the charge decay time preventing sparks
or surges of energy from static charged sources. Values for maximum allowable
resistance and discharge times are given in Tab. 9-3).
Ensure personnel safety.
Consider an adequate decay or discharge time for ESD-potentials.
Keep any workplace free of static generating materials, especially untested
domestic appliances (see Tab. 9-1).
1) Periodically check ESD-protected workplaces to make sure they work.
2) Periodically check and maintain tools and equipment to avoid EOS/ESD-
hazards for assemblies or personnel caused by improper grounding methods
or oxide on grounding connectors.
In the case of DC-circuits, a floating neutral can have a potential of 80 to 100 V
instead of workbench or earth potential, and can damage ESDS-components or
even put someone's life at risk.
3) Therefore, use earth-fault protected electrical outlets at ESD-protected
workplaces.
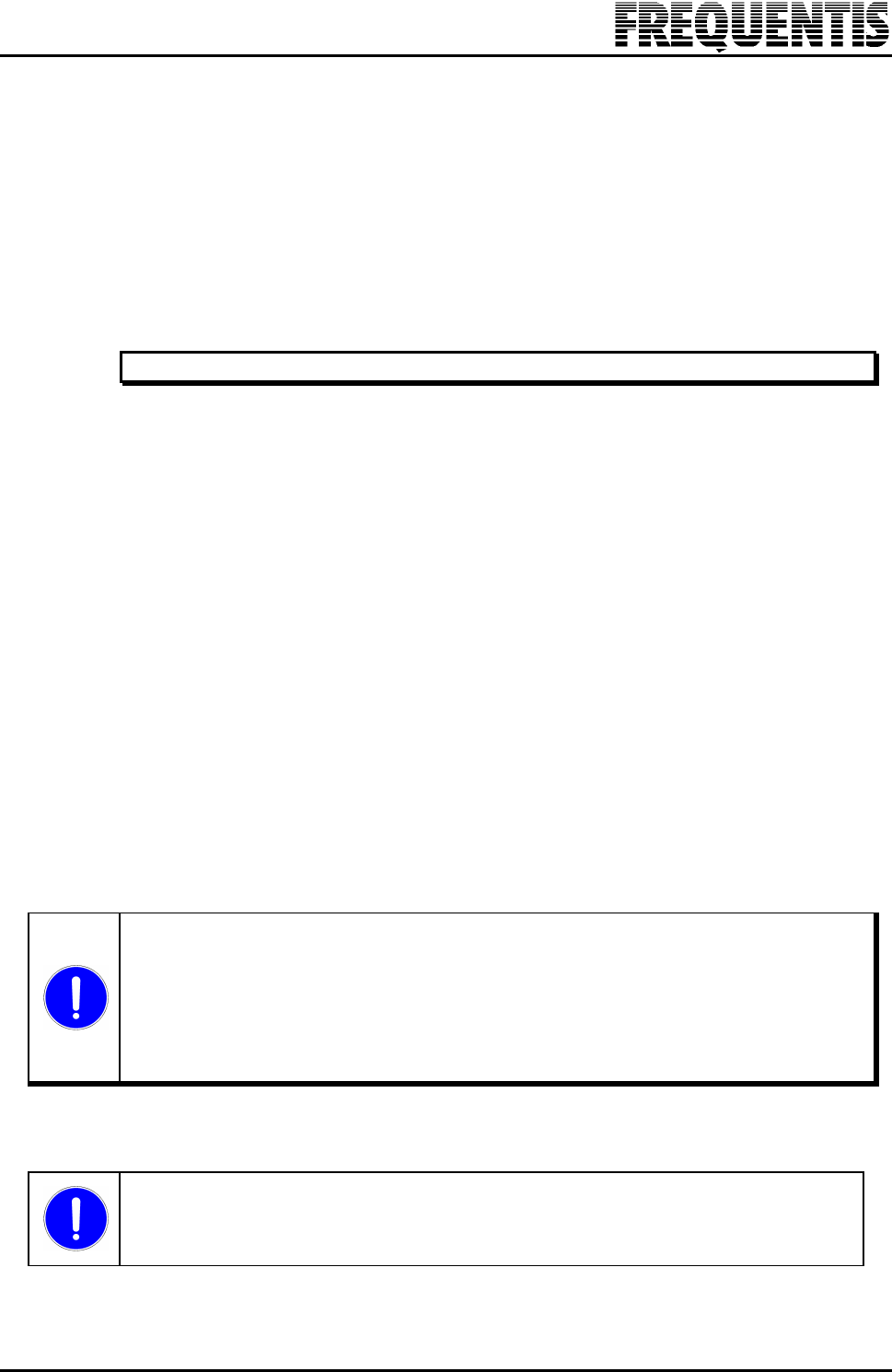
SAFETY GUIDELINES FREQUENTIS File: SGL REV.1.2.DOC 20
COPYRIGHT FREQUENTIS 2000 Author: S. Meisel No: 00A46 E500.12
3.6. ESD-Protection during Shipping and Storage
Devices, which are sensitive to electrostatic discharge (boards, sub-boards,
position electronics etc.) must be covered for transport or storage by conducting
protective sheathing (ESD-boxes).
When leaving devices on an ESD-protected workplace, they must be packed with
static shielding (e.g. shielded bags with ESD protection marking).
Exceptions from this regulation are products housed within closed conducting
cases, mechanical parts and cables.
1) Use enclosures with full ESD-protection when moving ESDS-components.
ESDS-components must always be protected from static sources when they are
not at ESD-protected workplaces. This protection can be conductive static
shielding boxes, bags or wraps. ESDS-components may only be pulled out of
their protective enclosures at ESD-protected workplaces.
3.6.1. Packaging of Electronic Assemblies
There are three different types of protective enclosure material:
● static shielding (or barrier packaging)
● antistatic materials
● static dissipative materials
Static shielding packaging prevents an electrostatic discharge from passing
through the package and into the assembly causing damage.
Antistatic packaging materials are used to provide inexpensive cushioning and
intermediate packaging for ESDS-components. Antistatic materials do not
generate charges when motion is applied. However, if an electrostatic discharge
occurs, it could pass through the packaging and into the component or assembly,
causing ESD-damage.
Static dissipative materials provide sufficient conductivity to dissipate applied
charges over the surface avoiding energy spots.
2) For transport or storage, any device sensitive to electrostatic discharge
(boards, sub-boards, position electronics etc.) must be covered by
conducting protective sheathing (ESD-boxes).
3) Parts leaving an ESD-protected workplace must be packed static
shielded. Complete the protection with static dissipative and antistatic
materials inside.
3.7. ESD-Regulations for Visitors
Visitors to ESD-protected areas shall be provided with cotton coats.
They have to be informed about the ESD-regulations and must follow all
the procedures mentioned above.
----------- END OF SECTION -----------
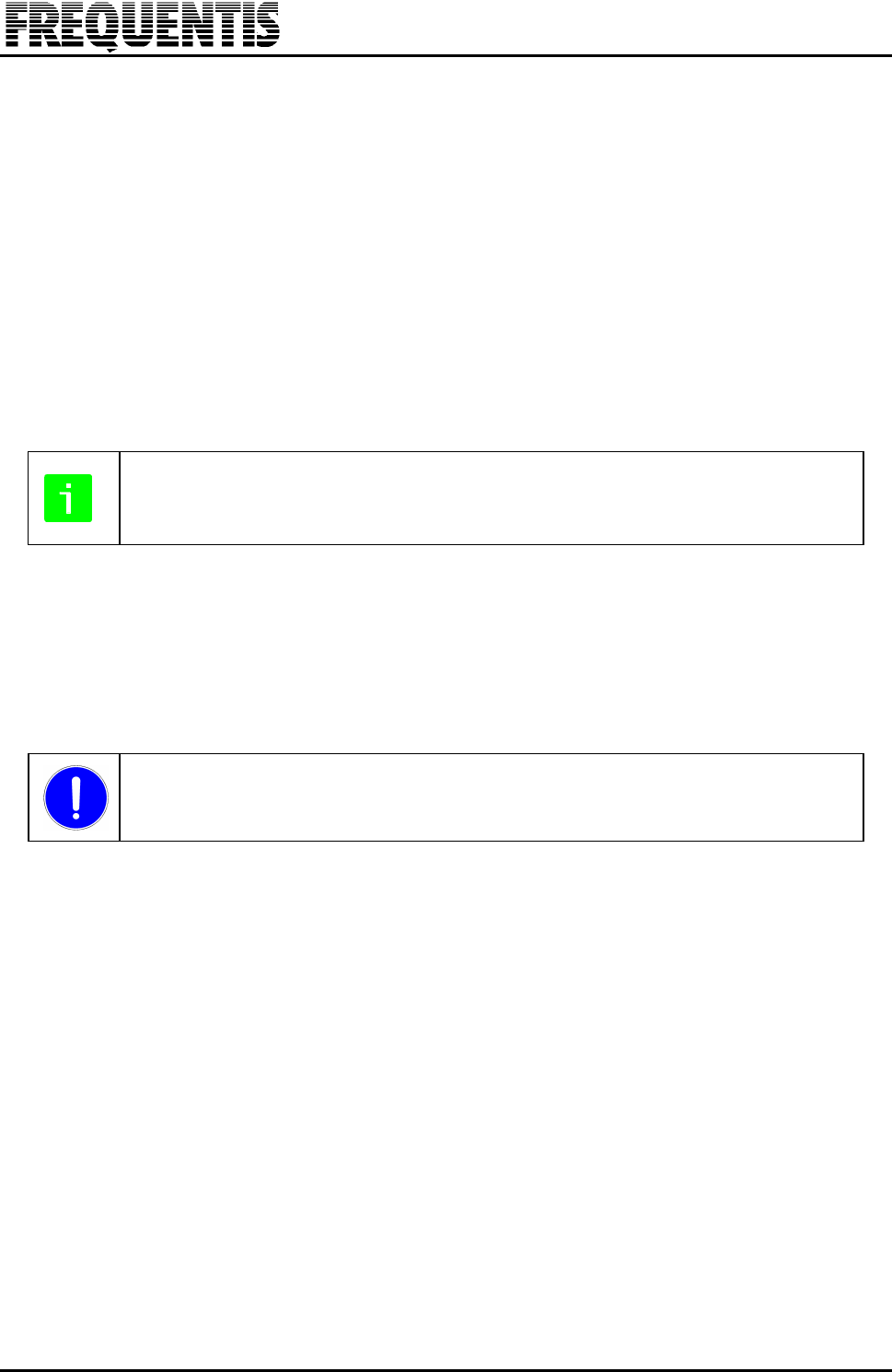
21 File: SGL REV.1.2.DOC FREQUENTIS SAFETY GUIDELINES
No: 00A46 E500.12 Author: S. Meisel COPYRIGHT FREQUENTIS 2000
4. Overvoltage Caused by Electrical Transients / Lightning
International standards for voice communication systems were applied during the
development of FREQUENTIS systems. Third-party components (e.g. monitors)
have to meet the respective industrial standards. To protect the system against
malfunction and destruction caused by indirect stroke, a combination of both
voltage and current limiting devices is implemented. FREQUENTIS offers
operational reliability for the following environmental operating conditions. There
are always two steps in protection:
● Coarse protection: All telecommunication cables leaving the building have
to be supplied with arresters, usually gas-filled protectors, against transient
overvoltages. Rating and design must meet the local requirements, and must
be state-of-the-art.
Coarse protection is not included in the scope of the delivery and has to
be provided by the customer for each site. The overvoltage arresters have
to support a rated spark-over voltage of at least 150 V (up to 230 V).
● Fine protection: All FREQUENTIS system interfaces are equipped with both
voltage and current limiters connected on the load side of the coarse
protection, to minimise the residual energy of an indirect stroke, so that the
subsequent connected electronics are not damaged.
Using specially designed power supplies, the FREQUENTIS equipment is able to
resist surge pulses according to ITU-T recommendation K.21 (EN 61000-4-5).
Overvoltage protectors in interfaces correspond to ITU-T recommendation G.703.
Lightning protective measures have to be adjusted to the earthing concept
in compliance with national regulations.
----------- END OF SECTION -----------
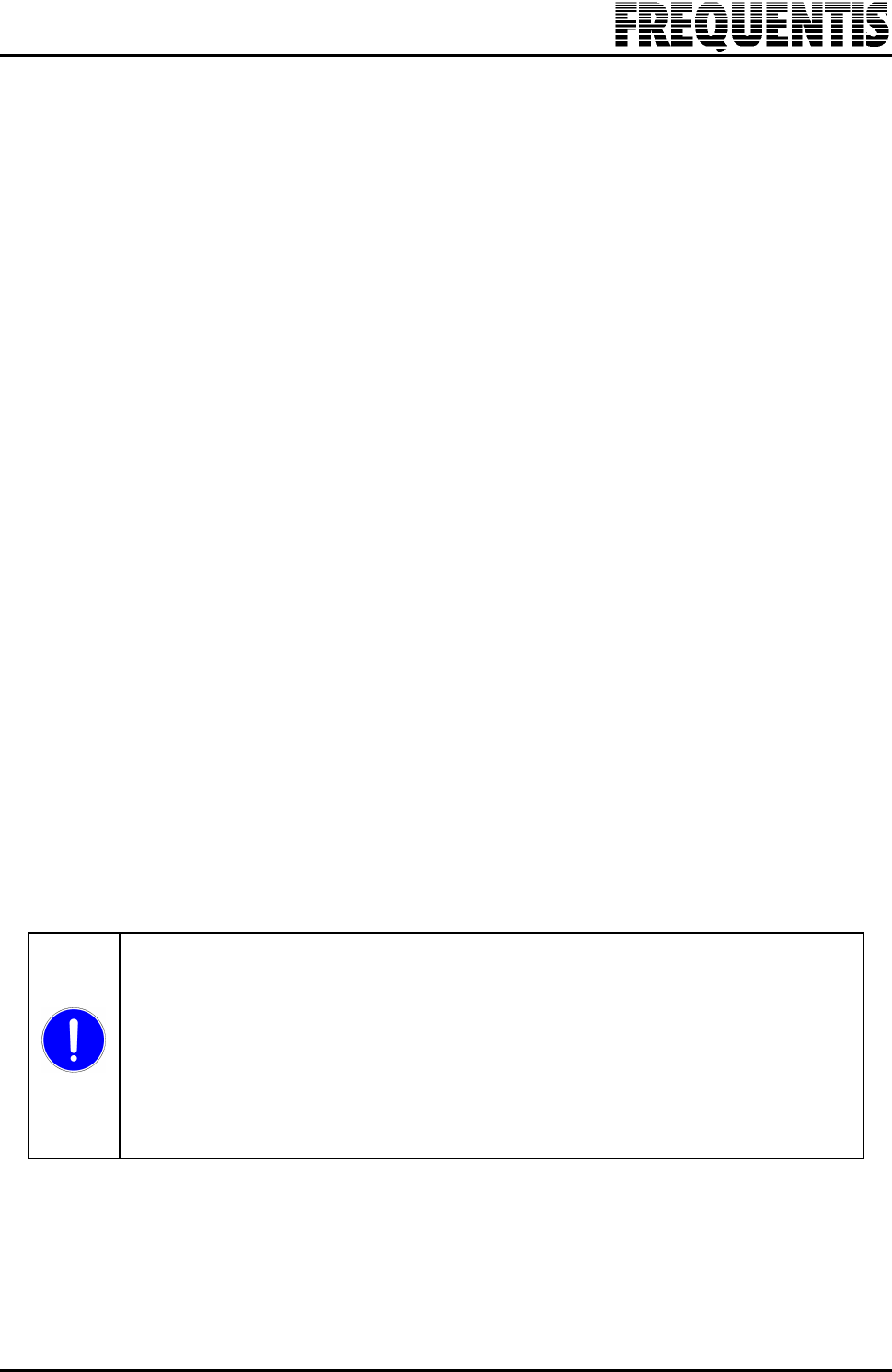
SAFETY GUIDELINES FREQUENTIS File: SGL REV.1.2.DOC 22
COPYRIGHT FREQUENTIS 2000 Author: S. Meisel No: 00A46 E500.12
5. Electromagnetic Compatibility (EMC)
Electromagnetic Compatibility (EMC) is the satisfactory working of an
apparatus, an installation or a system in an electromagnetic environment without
causing electromagnetic disturbances, which are unacceptable for other devices
in this environment.
Electromagnetic Immunity (EMI) from disturbance is the capability of
equipment to continue operating normally when an electromagnetic disturbance
occurs.
5.1. Generic Electromagnetic Compatibility Requirements
The FREQUENTIS system equipment is produced in accordance with the
regulations of the European community, i.e. the system do not generate an
environment that is dangerous to the personnel.
For EMC, the EC Directive 89/336 Electromagnetic Compatibility amended by
EEC Directive 92/31 and EEC-Directive 93/68, and Part 15 of the FCC Rules,
apply. All the equipment therefore meets the European standards EN 55022
(Radio disturbance characteristics measurement) as well as EN 55024 (Immunity
characteristics measurement).
5.2. Specific Electromagnetic Compatibility Requirements
Compliance with EMC-limits no longer applies when –
● any door or enclosure part of an EMC-cabinet is opened,
● components not supplied by FREQUENTIS are installed in an EMC-cabinet
supplied by FREQUENTIS (e.g. supplementary installations to increase/filter
the airflow),
● racks and interfaces are not installed in an EMC-cabinet (e.g. non-protected
cabinet or stand-alone, i.e. non-FREQUENTIS cabinets).
Any modification of a FREQUENTIS-released system configuration
cancels EMC and EMI assured by FREQUENTIS.
Only cabinets supplied by FREQUENTIS may be used for the FREQUENTIS
core and interface equipment.
The cabinet doors must be closed to ensure EMC and EMI in the system.
When opening a cabinet or rack (e.g. for service purposes), first check the
operational state of adjacent equipment for potential risks due to
electromagnetic interferences.
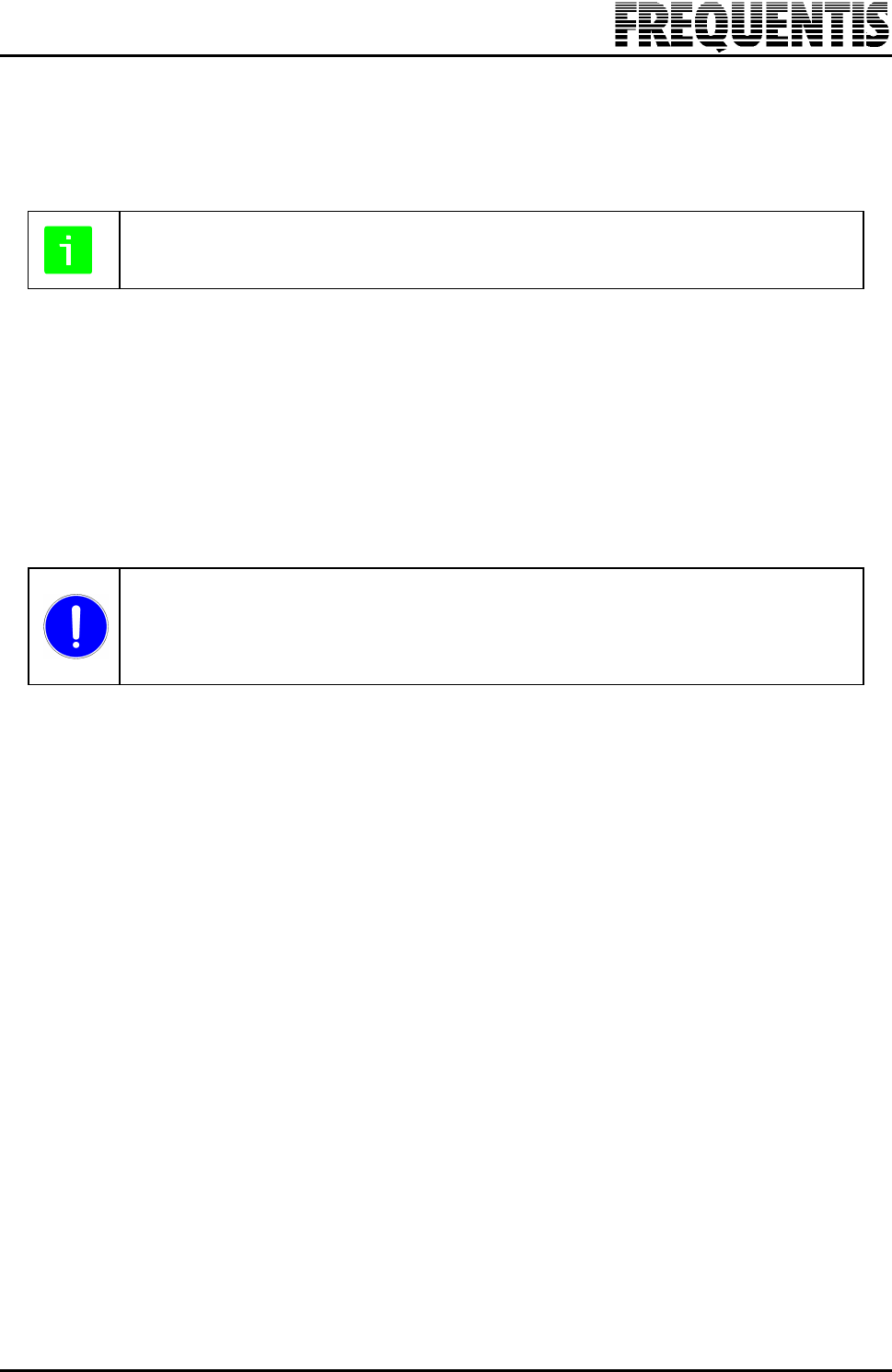
23 File: SGL REV.1.2.DOC FREQUENTIS SAFETY GUIDELINES
No: 00A46 E500.12 Author: S. Meisel COPYRIGHT FREQUENTIS 2000
5.2.1. Electromagnetic Fields Emitted by Visual Display Units
The only visual display unit (VDU), which might be equipped with a Cathode Ray
Tube (CRT) is/are the monitor(s) of the TMCS.
The TMCS-monitors are commercial off-the-shelf units, which meet the
requirements listed above (e.g. TCO 99) and the specific national standards.
The other VDUs are equipped with non-CRT devices (flat screen displays, e.g.
colour active matrix LCD-modules incorporating amorphous silicon TFT [Thin
Film Transistor], TFD [Thin Film Diodes] or passive LCD [Liquid Crystal Display],
all with backlights and resistive touch surface). These VDUs do not therefore emit
substantial electromagnetic fields.
5.2.2. Check of Aerials and Receivers Adjacent to the Equipment
Type and characteristics of aerials / receivers adjacent to the system, their
sensitivity and the applied frequencies have to be identified. Check the potential
risks due to disturbance of these third-party appliances.
To avoid potential interference problems do not install receiving or
emitting aerials and highly sensitive receivers within a certain distance of
the system's equipment, in particular closer than 50 m to the position
electronics and interface cabling.
---------- END OF SECTION ----------
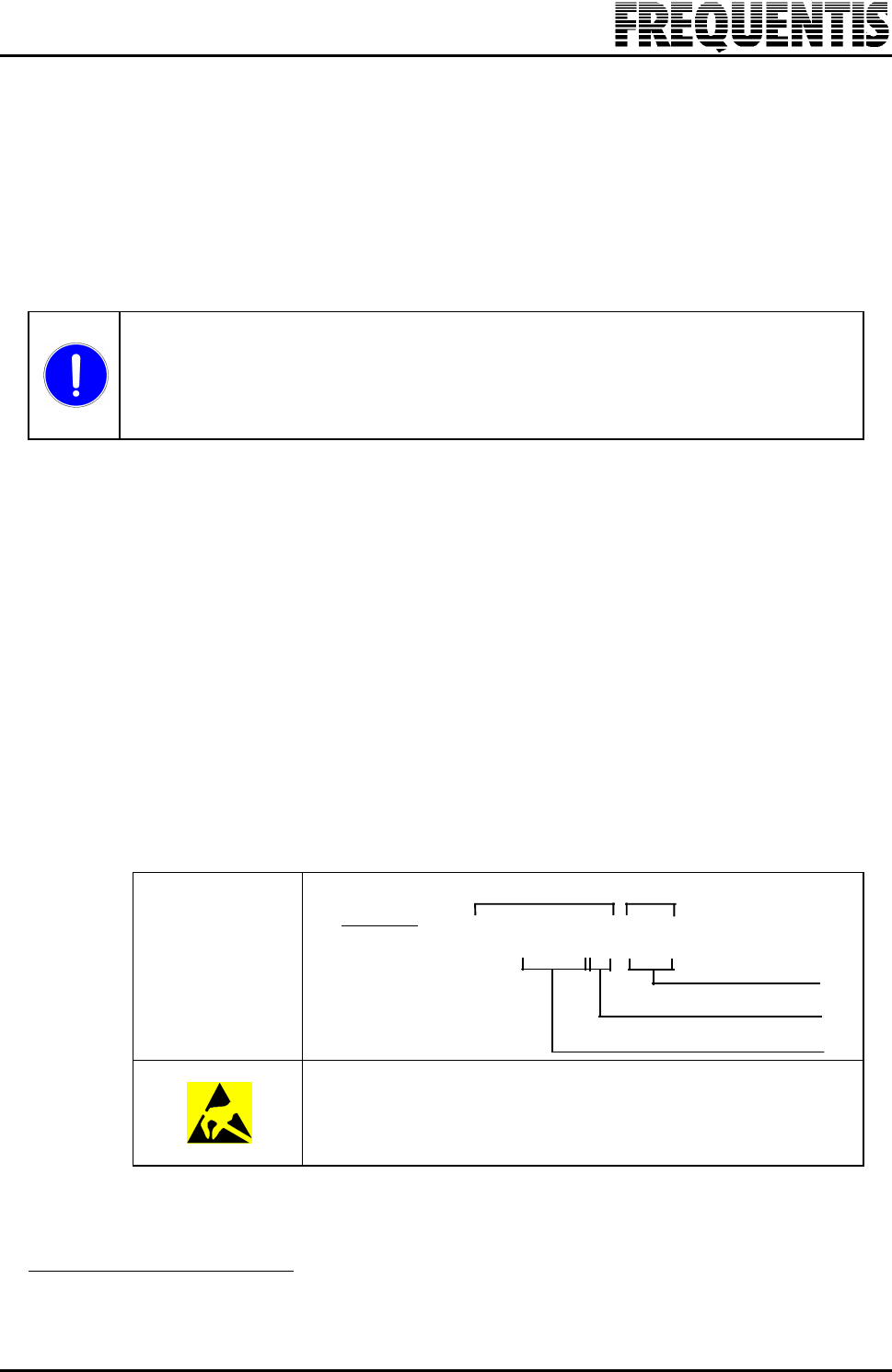
SAFETY GUIDELINES FREQUENTIS File: SGL REV.1.2.DOC 24
COPYRIGHT FREQUENTIS 2000 Author: S. Meisel No: 00A46 E500.12
6. Equipment Labelling
Equipment labelling of the delivered system is essential for identifying the system
state.
The hardware can be traced back down to component level by means of serial
numbers while the software/firmware can be traced back down to module level by
means of the label and version number.
If any equipment labels get damaged during operation, the customer is
responsible for replacing them with intact ones in the same positions.
To comply with the relevant standards (specific colours, materials or font
sizes), use original labels in all cases.
Safety instructions and the respective equipment marking must be durable and
legible, and in the customary language. Marking in English is acceptable for
equipment accessible to maintenance only. Labels must not be placed on
removable parts so that the marking is not ambiguous when the part is removed.
Generally, the equipment must be marked with the power rating for selecting the
correct voltage, frequency and current-carrying capacity. If the device can be
operated at several voltage ranges, the switch conditions must be described.
Labels not visible from outside the equipment must be directly visible when a
door or enclosure is opened, attached to the equipment to clearly indicate the
location of the marking. Devices not to be connected directly to the main supply
need not be marked with their rated current.
6.1. Adhesive FREQUENTIS Equipment Labels
Quality control labels are applied to the specific FREQUENTIS-components.
Checked samples are signed manually.
Serial Numbers
Finished: 30-
Semi-finished: 40- YYNNNVV - sssss
Serial numbe
r
Variant
Year+Counte
r
HW-Numbe
r
Counte
r
Product:
The ESD-sensitivity symbol is used to indicate that an
electrical or electronic device or assembly is susceptible to
damage from an ESD-event. Each ESDS-component
(board, PCB, module,…) is marked with this label.2
Fig. 6-1: ESD-Label and Structure of Serial Numbers
2 The ESD-symbol may also be integrated in the marking of the earth bonding points (see Fig. 3-1).
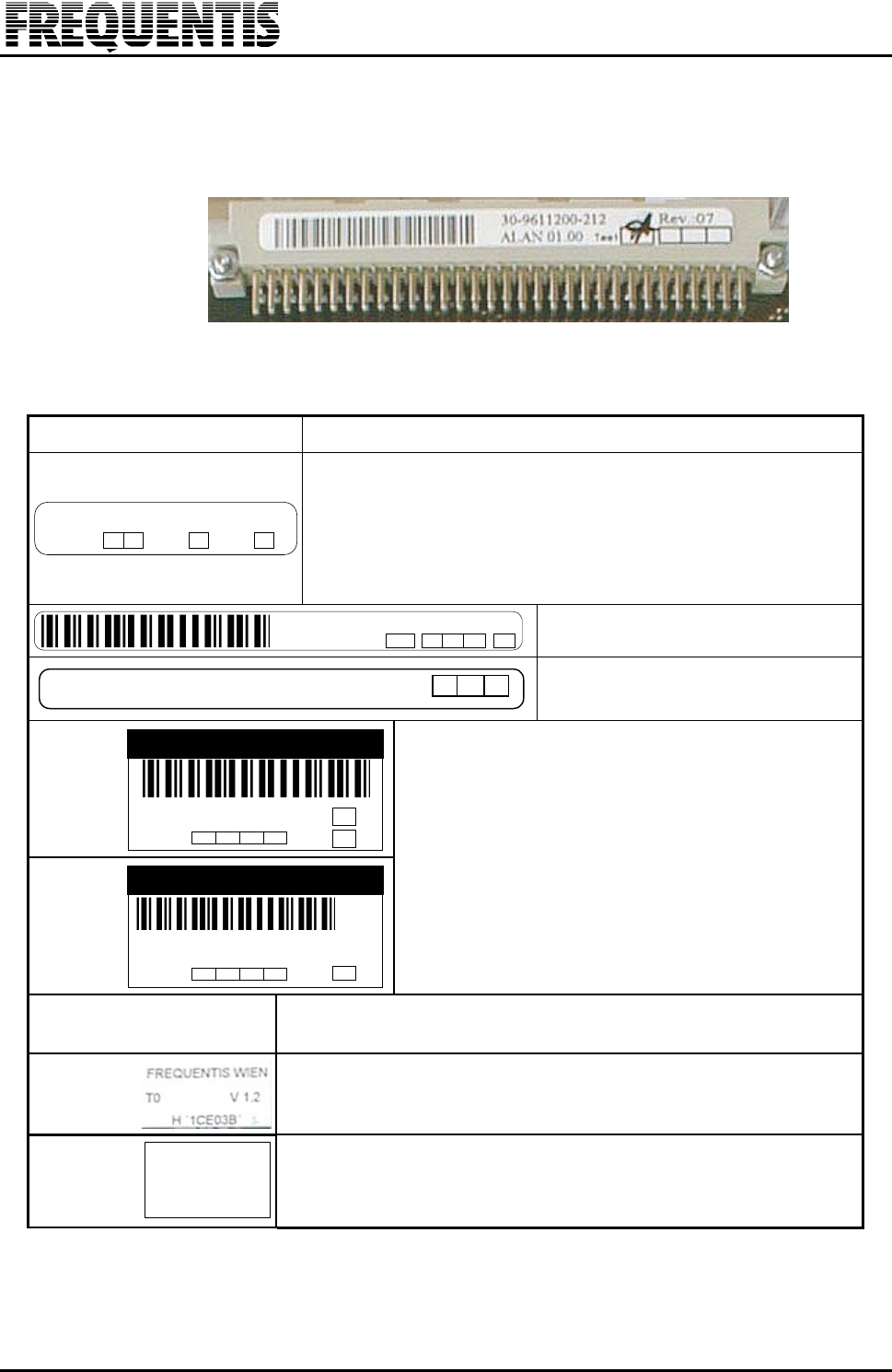
25 File: SGL REV.1.2.DOC FREQUENTIS SAFETY GUIDELINES
No: 00A46 E500.12 Author: S. Meisel COPYRIGHT FREQUENTIS 2000
The serial numbers of racks and boards are labelled on the components in plain
text and as a barcode (code 128) (see Fig. 6-2). The serial numbers of power
supplies are printed on the rear of the components.
Fig. 6-2: Serial Number Label of a Board
6.1.1. Labels Indicating Product Categories
Label Component / Description of Labelling
PIP 02.00 30-960600
198
REV:02 QC Test
Sub-boards: The drawing number of the PCB-layout is used
for identifying of small PCBs (no label).
Minimum identification if an appropriate label fits on the sub-
board: Serial number, revision and bar code (128 Bit).
For larger sub-prints, the product name and the
FREQUENTIS Logo are usually added.
40-9705101-889
4CPPC 02.00
TEST REV.: 02 QC
Boards: Label with serial number
FREQUENTIS
Produktnummer: 1998002130
Bezeichnung: POS 3025
00
Boards and modules:
Label with product number
Module
FREQUENTIS
30-9204503-006
SPM20.21
Rev.:01
Test
QC
Rack
FREQUENTIS
30-9515502-006
BGT DATA 02
Rev.:00
QC
For both, serial and product numbers, the last two
digits of the product number identifying the product
revision, have to be filled into the first box after
“Rev.”.
If the revision is increased (e.g. change of
software/firmware), the new revision number is
entered in the next box.
Cabinets If there is no specific definition in the System Configuration on
customer request, the board’s identification system is applied.
Firmware Name, version, checksum on EPROM and/or EPLD
Cables 1.007
CAB1/21/X29
CAB1/18/X103
108-K-15 (1)
Label with type and length of cable. In the case of outsourcing
included in the order (see chapter 6.2).
Tab. 6-1: Labels Indicating Product Categories
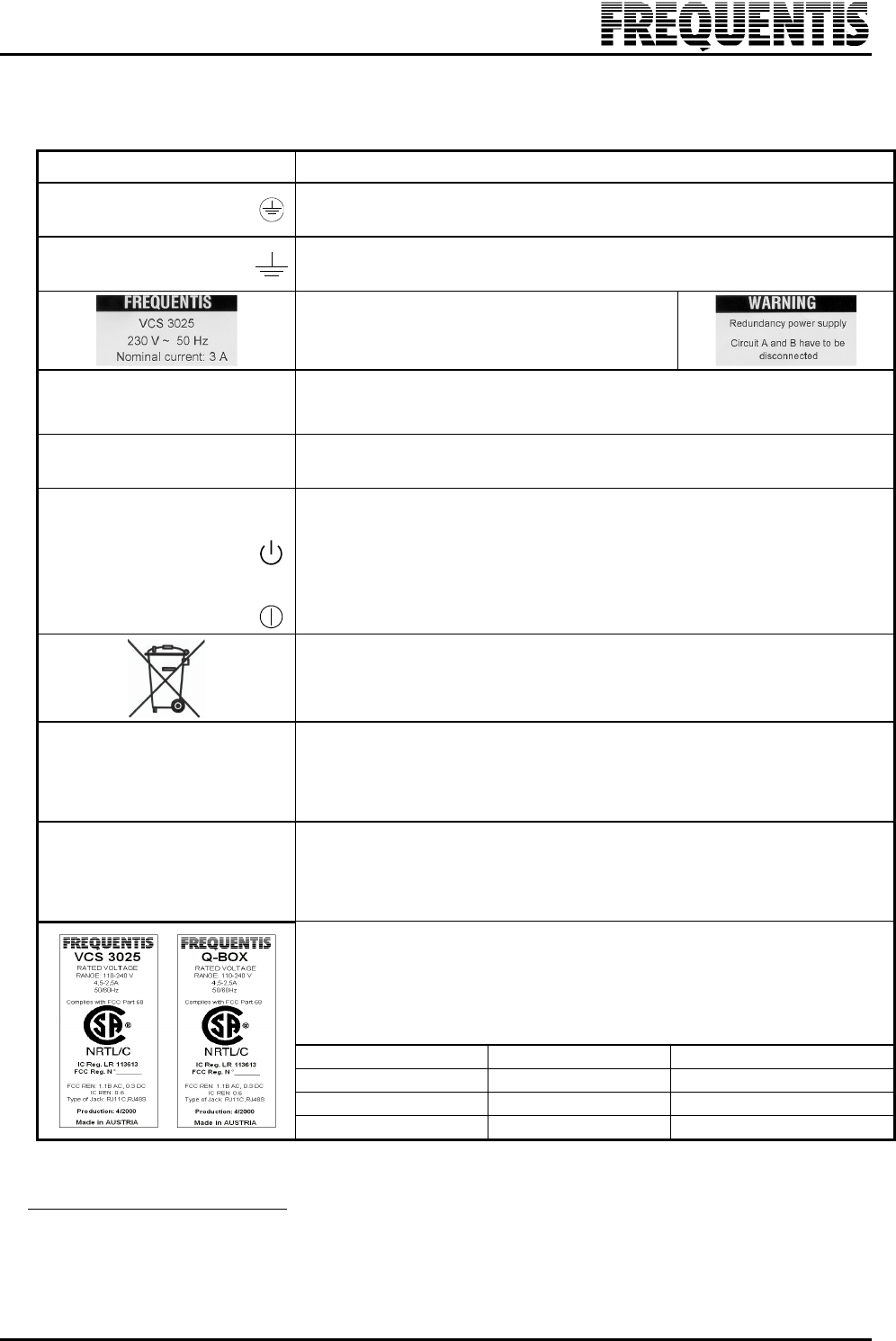
SAFETY GUIDELINES FREQUENTIS File: SGL REV.1.2.DOC 26
COPYRIGHT FREQUENTIS 2000 Author: S. Meisel No: 00A46 E500.12
6.1.2. Labels Indicating Standards
Label (Example) Description
PE (Protective Earth) Main earth connection point of the FREQUENTIS-cabinets.
This symbol is reserved for the protective earth only.
Earth connection point Earth terminal of each C-Box and each PowerPanel. All other sub-
ordinate FREQUENTIS earth connection points remain unmarked.
The power rating marking as well as the
disconnection warning must be applied
near the connecting supply terminal.
HIGH LEAKAGE CURRENT
Earthing is essential
before connecting supply
Leakage Current exceeding 3.5 mA must carry a warning label like
this (acc. to IEC 60364-7-707).
230 V ~ 50 Hz
Maximum Load 500 W
Power supply outlet sockets accessible to the operator must be
marked with the maximum connectable load.
Plugs & Switches
OFF
Stand-by
ON
Push/push
IEC 60417, 5007…10-a require adjacent marking of switches clearly
indicating their function, using the following symbols:
O and | may be used as OFF and ON markings on any primary
power switches, including isolating switches. If figures are used to
indicate different status, OFF is indicated by 0 (zero).
'+' and '–' are used to indicate in/decreasing adjustment values.
The symbol for separate collection of electric and electronical
devices marks components, which require special disposal
according to Directive 2002/96/EC.
CE-Labelling
(LVD-, EMC- and R&TTE-
Compliance)
For all systems delivered in Europe, the CE-conformity must be
marked by the CE-label representing the DOC issued by
FREQUENTIS. The label is applied nearby the connecting supply
terminal on the resp. cabinet.
PSTN-Label
(if applicable)
System approval numbers (outside EC) specific to national standards
are placed on the cabinet(s) or on one of the racks. If only parts of the
system are approved, relevant interface approval numbers are placed
on each board, if applicable.
FCC-Label (USA): The equipment complies with Part 68 of the FCC
(US Federal Communications Commission) rules. A label is located
on the rear of the unit containing the FCC registration number and/or
the Ringer Equivalence Number (REN)3. For instance, the following
information is provided to the local telephone company on request:
Loopstart Leased line DSU
FIC 02LS2 (BCB) FIC Metallic (ERIF) FIC 04DU5-64 (NI64)
JT RJ11C SOC 7.0Y SOC 6.0N
REN 1.1B AC, 0.3 DC JT RJ48S JT RJ48S
Tab. 6-2: Labels Indicating Standards
3) The REN determines the quantity of devices, which may be connected to the telephone line. Excessive RENs on the telephone line
may result in the devices not ringing in response to an incoming call. In most, but not all areas, the sum of RENs should not exceed five
(5.0). To be certain of the number of devices that may be connected to a line, as determined by the total RENs, contact the local PSTN.
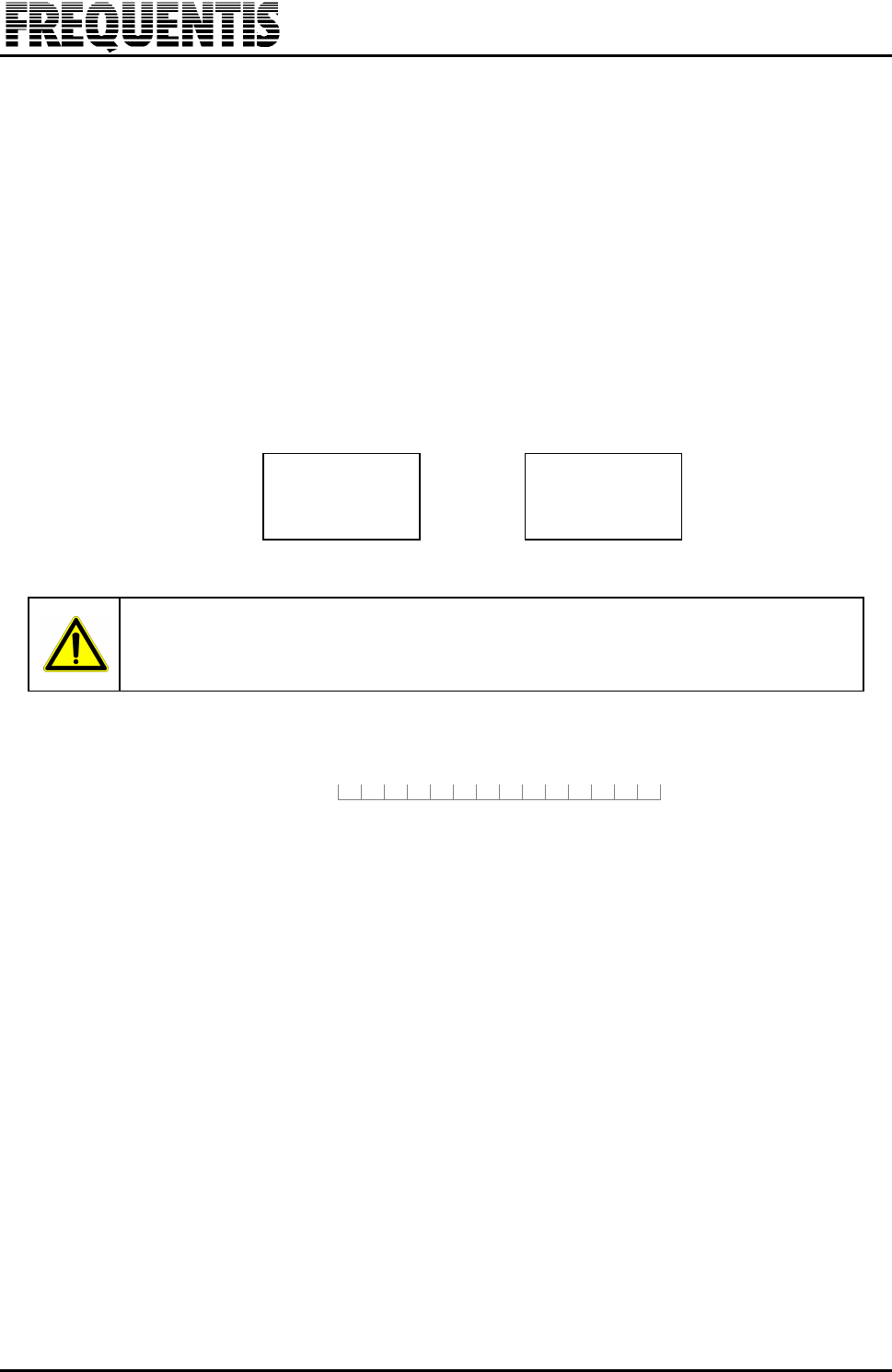
27 File: SGL REV.1.2.DOC FREQUENTIS SAFETY GUIDELINES
No: 00A46 E500.12 Author: S. Meisel COPYRIGHT FREQUENTIS 2000
6.2. Cable Identification
6.2.1. Cable Identifier Tags
All cables (except earthing wires, peripheral TMCS-cables and those to
footswitches) are labelled at both ends close to the connectors with identifier tags
containing the following information:
1st line Particular project specific cable number (column 10 in the Cabling List)
2nd line Destination of cable at connector 1 (columns FROM in the Cabling List)
(Cabinet Number / Cabinet Level / Connector name on target component)
3rd line Origin of cable at connector 2 (columns TO in the List of Cables)
4th line Type of cable with the length in the unit [dm = 10 cm]. The connector
number as used in the System Configuration is given in parentheses.
1.007 1.007
CAB1/21/X291 CAB1/18/X103
CAB1/18/X103 CAB1/21/X291
108-K-15 (1) 108-K-15 (2)
Fig. 6-3: Example of the Two Cable Identifiers for One Cable
Ensure that the correct cable end is attached to the corresponding
connector. Wrong connection can lead to a fault or damage of the
connected equipment.
6.2.2. Cable Types
Cables of the same physical configuration are identified by a unique term:
K
}
Number
}
Type
x
}
Length (dm)
xxxx1- -
Fig. 6-4: Complete Cable Designation
● Number each cable type different in the used components (parts list),
connector plan or wiring list is numbered consecutively.
● Type reflects the safety category:
K Cable with standard PVC-Insulation
S Special cable (e.g. variant of a standard cable for special use)
LSF Low inflammable, halide-free insulation (Low Smoke and Fume)
HLF Halide-free insulation
● Length is the length of the particular cable in [dm].
The Connector Plan, Wiring List and Parts List form part of the standard
FREQUENTIS Hardware Documentation, which is available on request. All
information necessary for proper connection of the pre-assembled cabling
supplied is covered by the System Configuration Document.
The identifier tags must be applied so that they can be read easily as shown in
Fig. 6-5 (reading direction towards the viewer, app. four cm from the connector).
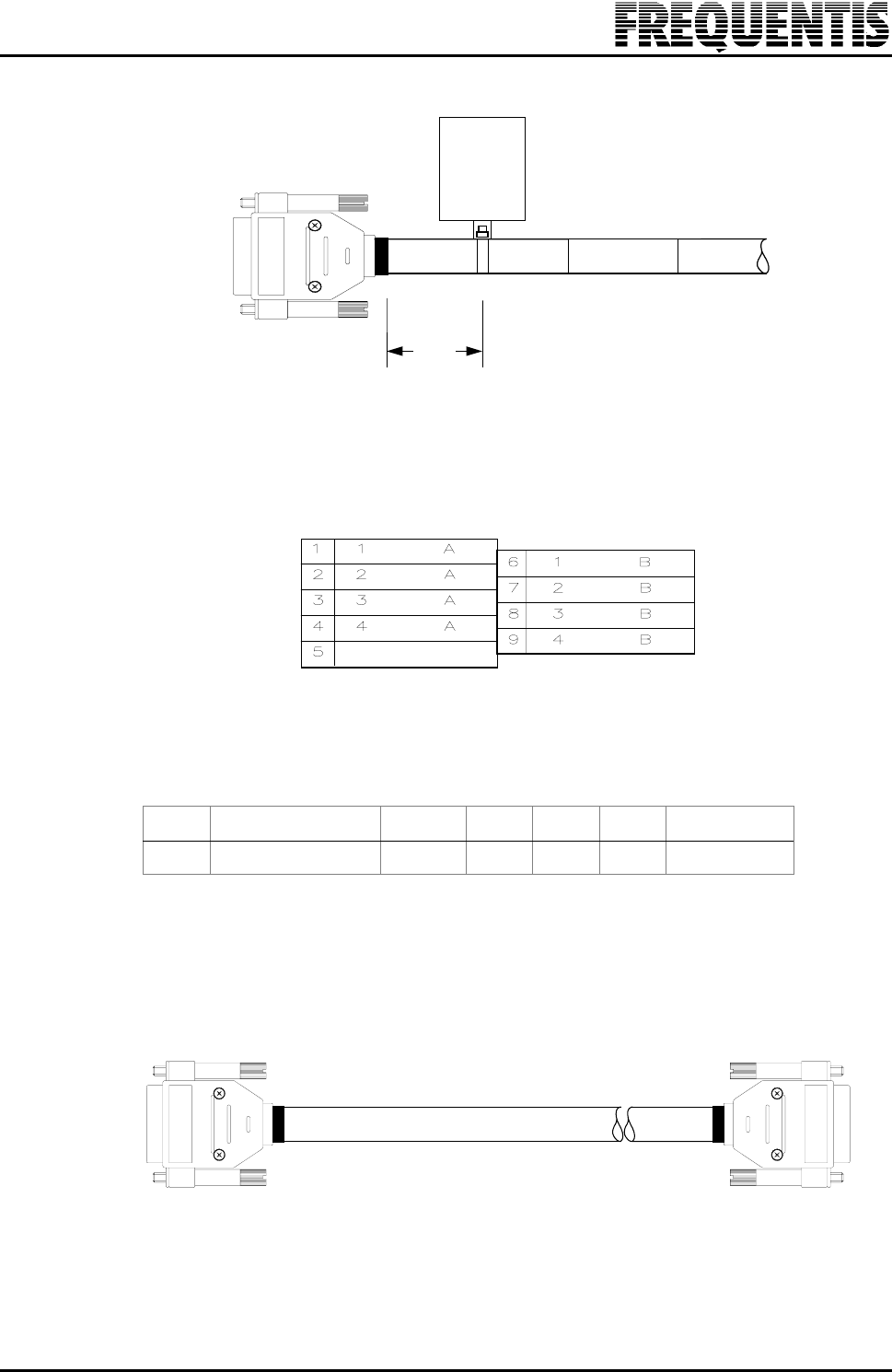
SAFETY GUIDELINES FREQUENTIS File: SGL REV.1.2.DOC 28
COPYRIGHT FREQUENTIS 2000 Author: S. Meisel No: 00A46 E500.12
3 cm
1002
CAB3/4/X17
CAB3/7/X361
1-K-15 (1)
1-K-015
08/00 - Test O.K.
Rev. 2.0
Fig. 6-5: Position of a Cable Identifier Tag
6.2.2.1. Connector Plan
The pinning of a 9-pin Min-D socket to a quadruple paired cable is shown as an
example (A and B are not exchangeable):
6.2.2.2. Wiring List
The Wiring List, part of the FREQUENTIS Hardware Documentation, describes
the circuit interconnection wiring for all connectors on the respective cable
according to the Connector Plan, including the wire cross sections in mm2.
No. Cross Section From Pin To Pin Comment
1 twisted pair 0.14 ST1 1, 6 ST2 1, 6
Additional cable layer plans can be provided for cables that split up into several
connectors at one side.
6.2.3. Labelling with Printed Sheathing
This non-abrasive labelling is applied along the cable coating. It is acid- and
grease-proof, and includes all information mentioned above.
FREQUENTIS VOICE COMMUNICATION SYSTEM
1−K−015
08/00 Rev 2.0 Test O.K.
Fig. 6-6: Cable Sheath Printing
----------- END OF SECTION -----------
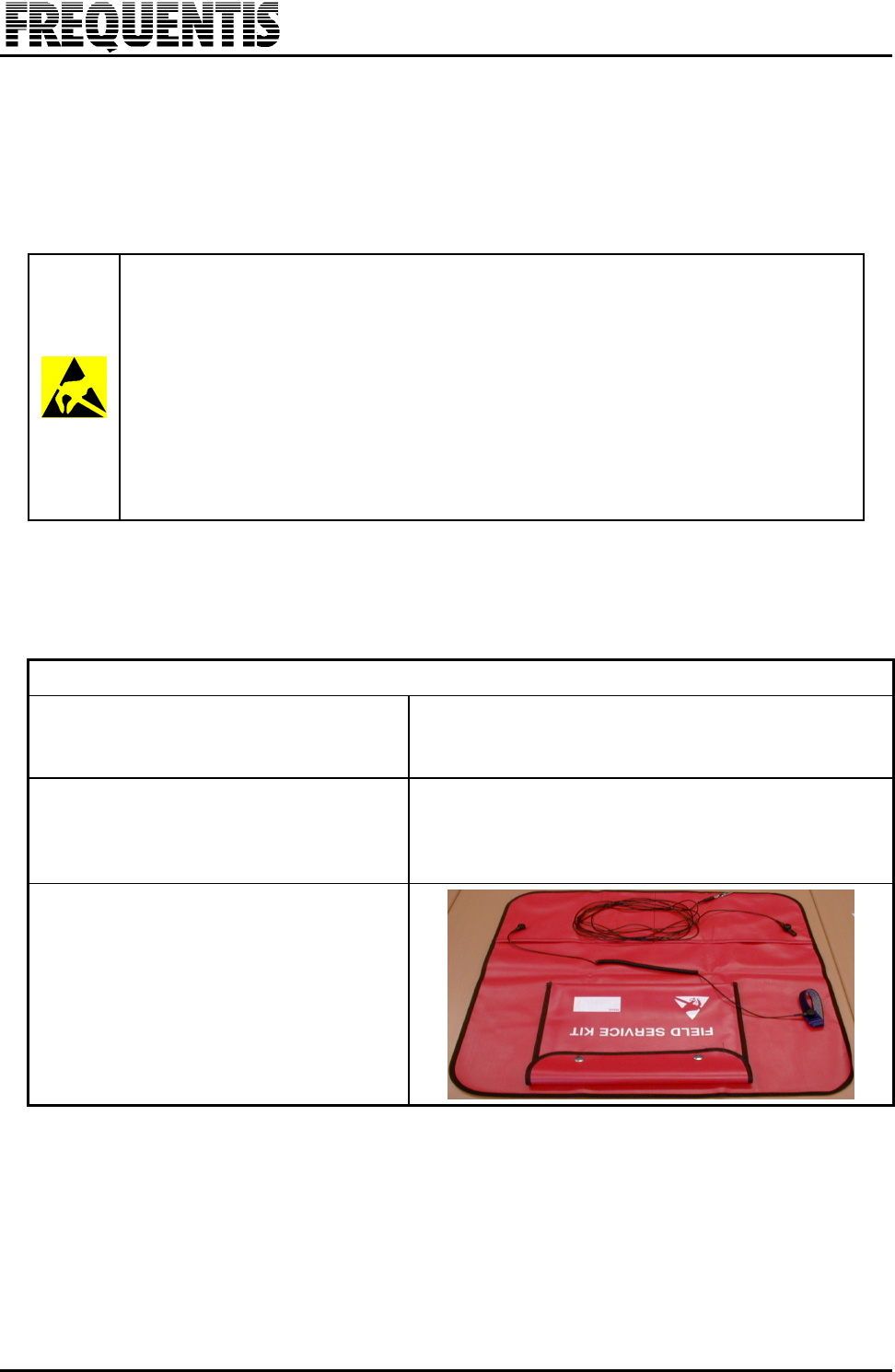
29 File: SGL REV.1.2.DOC FREQUENTIS SAFETY GUIDELINES
Author: S. Meisel No: 00A46 E500.12 COPYRIGHT FREQUENTIS 2000
7. Handling of Equipment
Boards of the same type can be replaced only if they have the same jumper
settings (see Maintenance Manual) and the same firmware (see System
Configuration document).
When working with boards, remember the following precautions for
handling components sensitive to electrostatic discharge:
1) ESD sensitive devices are labelled with the symbol shown left.
2) Special training is required for working with ESD sensitive devices.
3) Do not touch boards without taking ESD-precautions.
4) Transport and packaging must also provide full ESD-protection.
5) Improper handling cancels warranty and liability on the part of
FREQUENTIS.
For detailed information, please refer to Section 3
7.1. Required Tools
Check the availability of the required tools (no special tools or test equipment are
required to set up the system, except for safety and test purposes):
Standard Tools (all tools insulated complying with ESD-requirements)
Operational Maintenance Screwdrivers of several sizes
Philips screwdrivers of several sizes
Wrenches of several sizes
Intermediate Maintenance Various (diagonal cutting) pliers
Soldering iron
Solder extraction tool
Soldering tin
ESD Field Service Kit (recommended)
1 ESD-blanket with
1 spiral-shaped cable and
1 wrist strap with cable clip
1 connecting cable to
the protective contact of a
2-pole and earth-socket outlet
1 connecting cable with crocodile clip
Fig. 7-1: ESD Field Service Kit
----------- END OF SECTION -----------
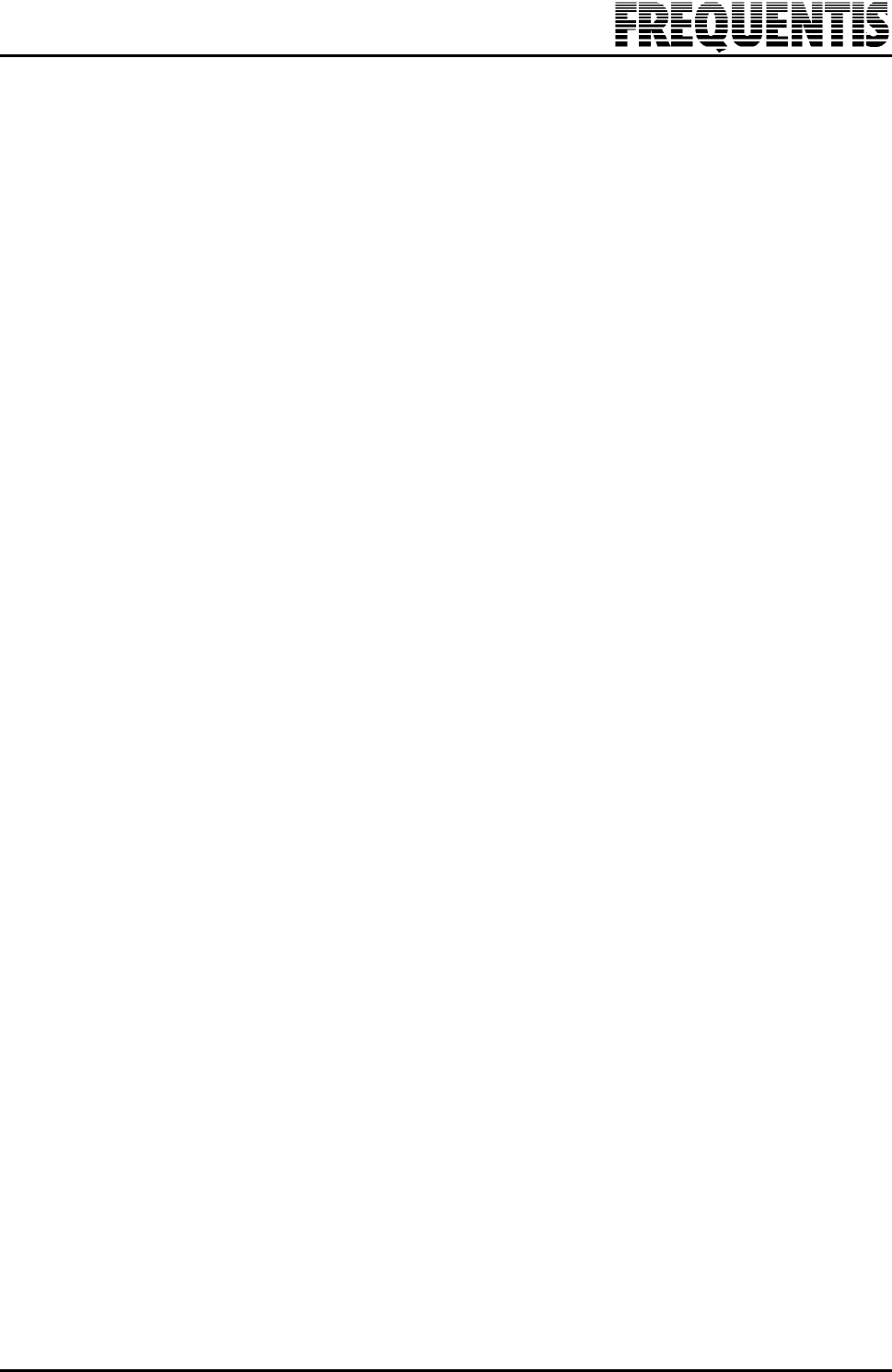
SAFETY GUIDELINES FREQUENTIS File: SGL REV.1.2.DOC 30
COPYRIGHT FREQUENTIS 2000 Author: S. Meisel No: 00A46 E500.12
8. Abbreviations
AC Alternating Current
acc. according
approx. approximately
AWG American Wire Gauge
BCB Battery Central Type B; analog 2-wire interface connecting to telephone line
CAB Cabinet
CE Conformité Européene; European conformity
CRT Cathode Ray Tube
CSA Canadian Standardization Association
CWP Controller Working Position
D/A Digital to Analog
DC Direct Current; Data Coupler
DICORA Dispatcher Communication Railway
DOC Output for recording (summarised context for the use of recording outputs);
Declaration of Conformity
DSU Data/Digital Service/Signalling Unit
e.g. exempli gratia; for instance
EBP Earth Bonding Point
EC European Community
EEC European Economic Community
ELV Extra Low Voltage
EMC Electromagnetic Compatibility
EMI Electromagnetic Immunity; Electromagnetic Interference
EN European Norm
EOS Electrical Overstress
EPLD Electrically (EPROM based) Programmable Logic Device
EPROM Erasable Programmable Read Only Memory
ERIF Extended Radio Interface (analog 4-wire interface)
ESD Electrostatic Discharge; Electrostatic Damage
ESDS Electrostatic Discharge Sensitive (components)
FCC Federal Communications Commission (US)
FIC Facility Interface Code
FRQ FREQUENTIS
G/G Ground to Ground communication
HLF Halide-Free Insulation
HW Hardware
IEC International Electrotechnical Commission
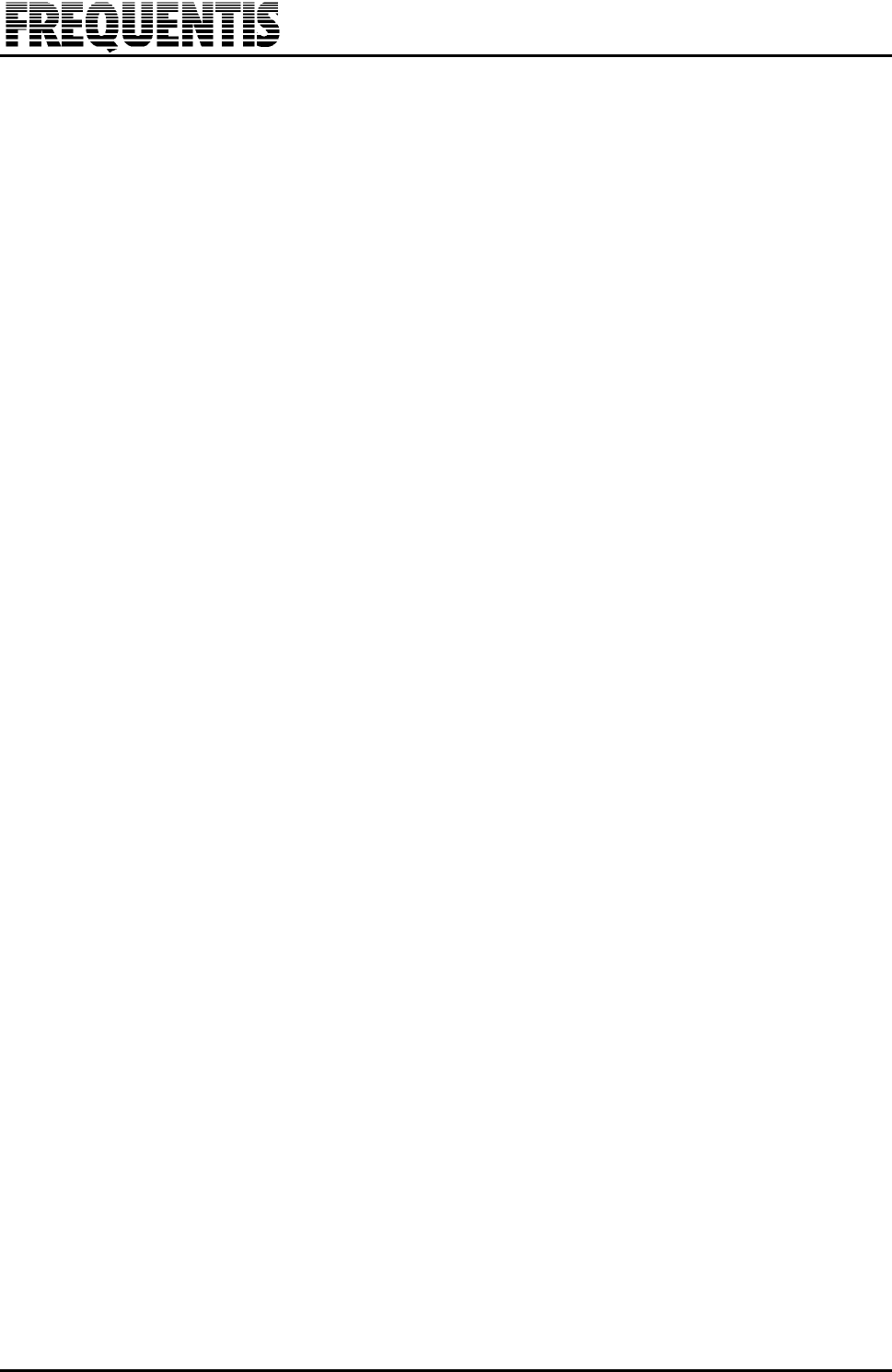
31 File: SGL REV.1.2.DOC FREQUENTIS SAFETY GUIDELINES
No: 00A46 E500.12 Author: S. Meisel COPYRIGHT FREQUENTIS 2000
IF Interface
ISDN Integrated Services Digital Network
ISO International Standardisation Organisation
ITU-T International Telecommunications Union - Telecommunications Sector
JT Jack Type
LAN Local Area Network
LCD Liquid Crystal Display
LED Light Emitting Diode
LSF Low Smoke and Fume (low inflammable, halide-free insulation)
LVD Low Voltage Directive
NI64 Network Interface, 64 kBit/s
NFPA National Fire Protection Association
ÖNORM Österreichische Norm; Austrian standard
OP Operator Position
ÖVE Österr. Verband für Elektrotechnik; Austrian electrical engineering association
PCB Printed Circuit Board
PE Protective Earth
PS Power Supply
PSTN Public Switched Telephone Network
R&TTE Radio and Telecommunications Terminal Equipment
REC Recording (output)
REN Ringer Equivalent Number (US)
resp. respectively
Rev. Revision
SI Système International; international system for measurement units
SOC Service Ordering Code
STxx Stecker xx; Connector XX
SW Software
TCO Tjänstemännens Central Org. (Swedish Confederation of Professional Employees)
TFD Thin Film Diodes
TFT Thin Film Transistors
TMCS Technical Monitoring and Control System
VCS Voice Communication System
VCX Voice Communication Exchange
VDE Verband Deutscher Elektrotechniker; German Association of Electrotechnicians
VDU Visual Display Unit
WCS Wire Cross Section
----------- END OF SECTION -----------
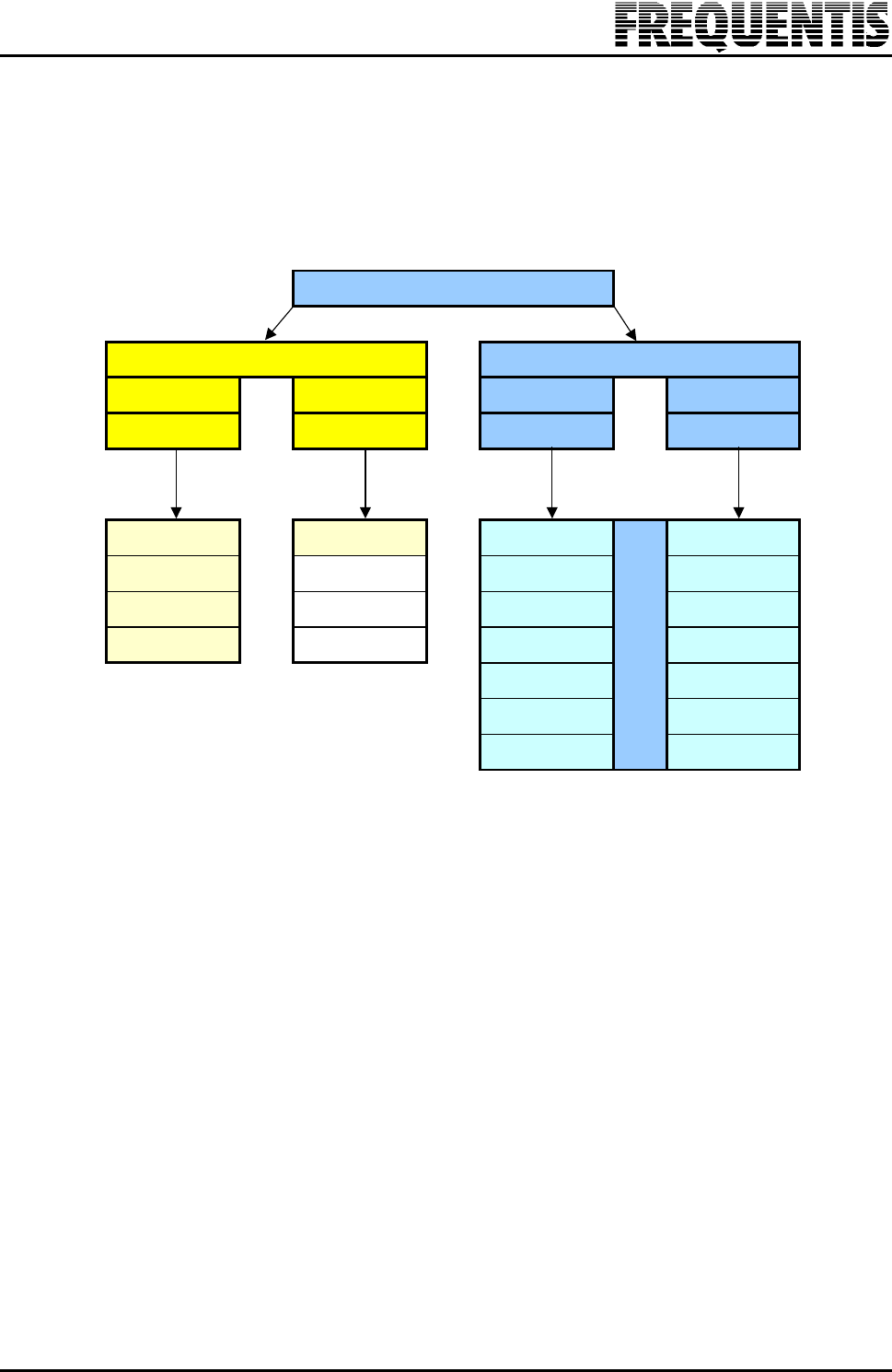
SAFETY GUIDELINES FREQUENTIS File: SGL REV.1.2.DOC 32
COPYRIGHT FREQUENTIS 2000 Author: S. Meisel No: 00A46 E500.12
9. Appendix
The contents of this section are for information only.
9.1. References to Standards
Domestic/Office Industry Domestic/Office Industry
Generic EN61000-6-3 EN61000-6-4 EN61000-6-1 EN61000-6-2
Test
Emission IEC/CISPR14/1 =
EN55014-1
IEC/CISPR 11 =
EN 55011 EN61000-4-2 EN61000-4-2 ESD
Emission IEC/CISPR22 Cl.B
= EN55022 EN61000-4-3 EN61000-4-3 Radiated HF-Fields
incl.”900MHz”
Harmonics EN61000-3-2 EN61000-4-4 EN61000-4-4 Burst
Flicker EN61000-3-3 EN61000-4-5 EN61000-4-5 Surge
EN61000-4-6 EN61000-4-6 Injected HF-Currents
EN61000-4-8 EN61000-4-8 Magnetic LF-Fields
EN61000-4-11 EN61000-4-11 Voltage Variations
EMC Directive 89/336/EC
Differentiation by measured
quantity of test disturbance
EN 55024
Emission Immunity
Fig. 9-1: Structure of EN Standards (Example)
Connection between the respective International (IEC), European (EN) and
German (VDE) regulations (if applicable):
IEC 1000-4-x = EN 61000-4-x = VDE 0847-x
Directive 73/23/EEC on the harmonisation of the laws of Member States
relating to electrical equipment designed for use within
certain voltage limits. 19 February 1973
amended by Directive 93/68/EEC of 22 July 1993
Directive 89/336/EEC on the approximation of the laws of the Member States
relating to electromagnetic compatibility. 3 May 1989
amended by Directive 92/31/EEC 26 April 1992
and by Directive 93/68/EEC 22 July 1993
Directive 99/5/EC on Radio equipment and telecommunications terminal
equipment (R&TTE) and the mutual recognition of their
conformity. 9 March 1999
ANSI/NFPA 70 National Electric Code, 110-16 to 18; 1999
CAN/CSA C22.2 No.950-95 Safety of information technology equipment 1995
EN 55022 Information technology equipment - Radio disturbance
characteristics - Limits and methods of measurement.1998.
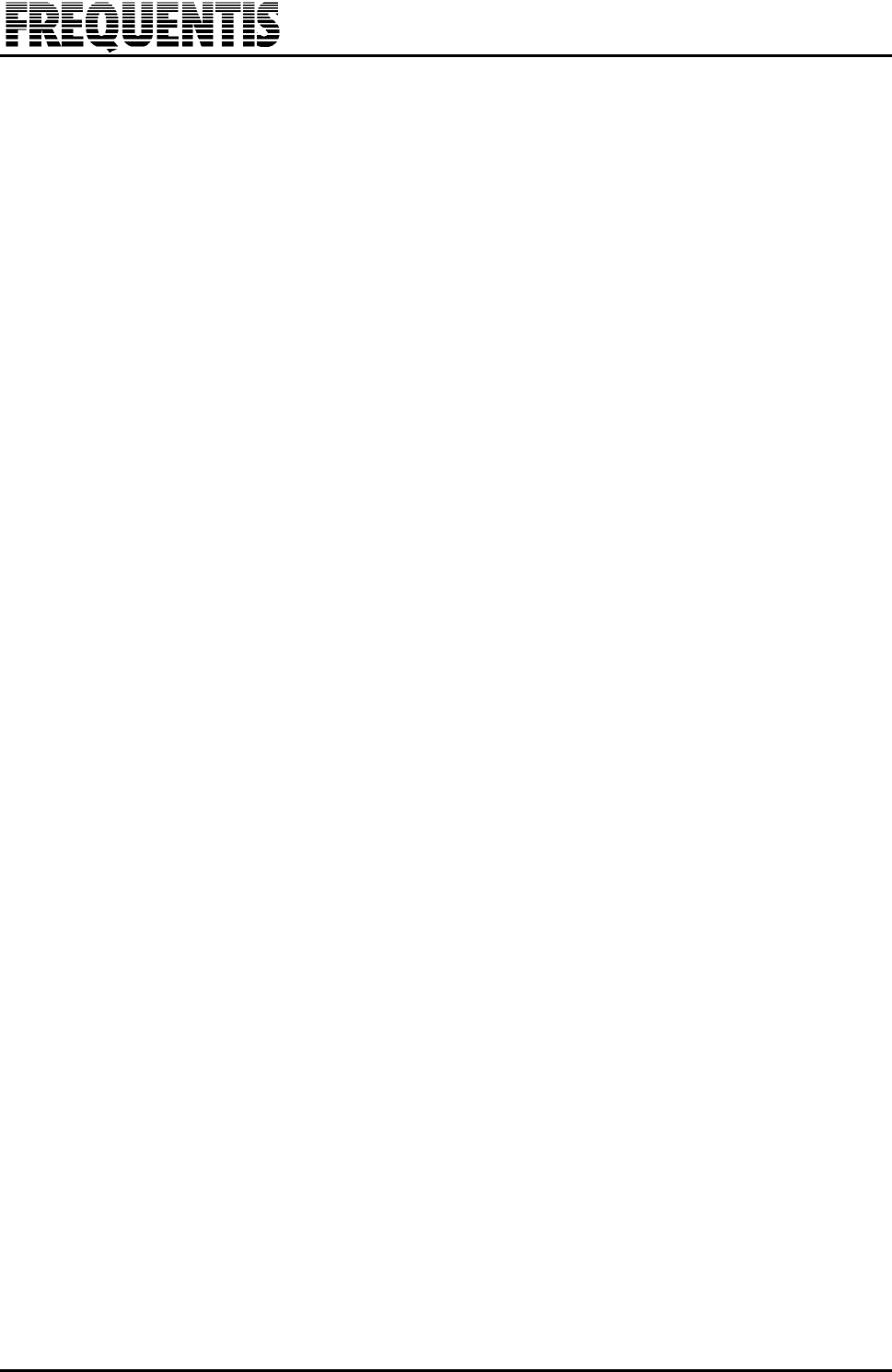
33 File: SGL REV.1.2.DOC FREQUENTIS SAFETY GUIDELINES
No: 00A46 E500.12 Author: S. Meisel COPYRIGHT FREQUENTIS 2000
EN 55024 Information technology equipment - Immunity
characteristics - Limits and methods of measurement 1998
EN 60950 Safety of information technology equipment including
electrical business equipment. 1999
EN 61000-4-2 Electromagnetic compatibility (EMC) -
Part 4: Testing and measurement techniques -
Section 2: Electrostatic discharge immunity test. 1995
EN 100015-1 Harmonised system of quality assessment for electronic
components. Basic specification: Protection of
electrostatic sensitive devices. General requirements.6/93
IEC 60320 Appliance couplers for household and similar general
purposes - Part 1: General requirements 6/94
Part 2-2: Interconnection couplers for household and
similar equipment 8/98
IEC 60364-5 Electrical installation of buildings – Selection and erection
of electrical equipment 02/82 – 08/01
IEC 60364-7 Electrical installations of buildings. Part 7: Requirements
for special installations or locations. 12/84 – 02/01
IEC 60417 Graphical symbols for use on equipment. 8/98 – 10/00
IEC 61340-4-1 Electrostatics – Part 4: Standard test methods for specific
applications – Section 1: Electrostatic behaviour of floor
coverings and installed floors. 1995
IEC 61340-5-1 Protection of electronic devices from electrostatic
phenomena - General requirements. Dec. 98
IEC 61340-5-2 Protection of electronic devices from electrostatic
phenomena - User guide. Feb. 99
IEC 60950 Safety of information technology equipment. 4/99
ISO 261 ISO general-purpose metric screw threads -
General plan. 1998
ISO 262 ISO general-purpose metric screw threads -
Selected sizes for screws, bolts and nuts. 1998
ISO 3864 Safety colours and safety signs. 1984
ITU-T Recommendation G.703 General aspects of digital transmission systems.
Terminal equipment. Physical/electrical characteristics
of hierarchical digital interfaces. 1991
ITU-T Recommendation K.21 Resistibility of subscriber’s terminal to overvoltages and
overcurrents. 10/96
ÖVE/ÖNORM E 8001 Erection of electrical installations with nominal voltages of
up to 1000 V AC and 1500 V DC. 2000
TCO 99 Ergonomics, safety, energy consumption and
environmental compatibility of displays and other PC
equipment 1999
VDE 0100 Power installations with nominal voltages of up to 1 kV 1994
UL 1950, 3rd Edition Safety of information technology equipment 1995
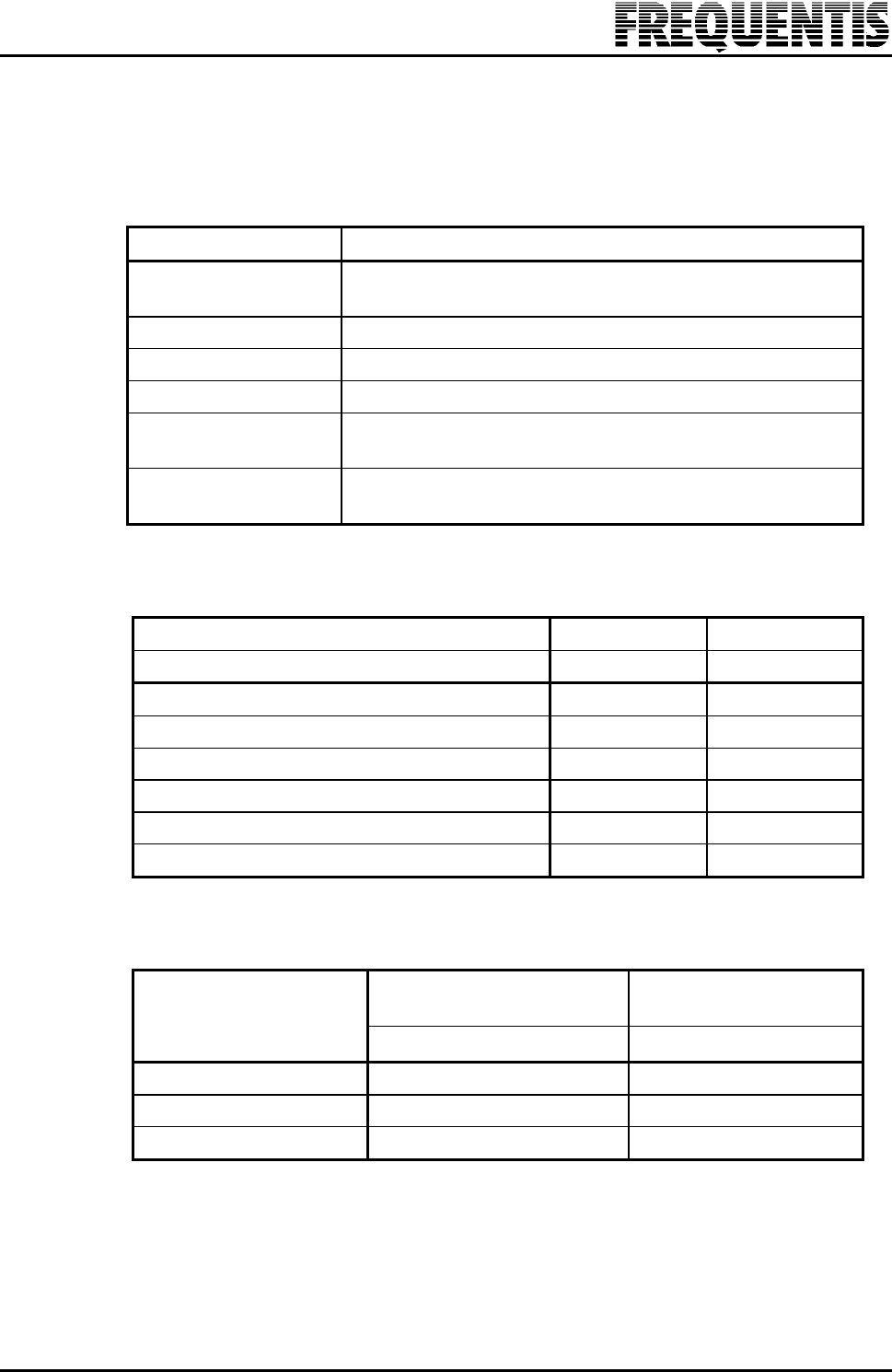
SAFETY GUIDELINES FREQUENTIS File: SGL REV.1.2.DOC 34
COPYRIGHT FREQUENTIS 2000 Author: S. Meisel No: 00A46 E500.12
9.2. Tables Concerning Safety Regulations
This chapter gives examples for recommended electrical and mechanical
guidelines based on the standards EN 100015, IEC 61340-5-x and EN 60950.
Category Examples
Work surfaces Waxed, painted or varnished surfaces, untreated vinyl
and plastics, glass
Floors Sealed concrete, waxed/finished wood, tile and carpeting
Clothes and personnel Non-ESD overalls and shoes, synthetic materials, hair
Chairs Finished wood, vinyl, fibreglass, non-conductive wheels
Packaging and
handling materials
Plastic bags, wraps, envelopes, foam, non-ESD trays,
boxes, parts, bins
Assembly tools and
materials
Pressure sprays, compressed air, synthetic brushes,
heat guns, blowers, copiers, printers
Tab. 9-1: Typical Static Charge Sources
Air Humidity 10-20% 65-90%
Process [V] [V]
Walking on carpet 35000 1500
Walking on vinyl flooring 12000 250
Operator at a bench 6000 100
Vinyl envelopes (e.g. Installation Manual) 7000 600
Plastic bag picked up from a workbench 20000 1200
Work chair with foam pad 18000 1500
Tab. 9-2:Typical Static Voltage Generation
Maximum Tolerable
Resistance
Maximum Acceptable
Discharge Time
From Operator
through [MΩ][s]
Floor mat to ground 1000 < 1
Table mat to ground 1000 < 1
Wrist strap to ground 100 < 0.1
Tab. 9-3:Maximum Resistance vs. Discharge Time for Static Safe Operations
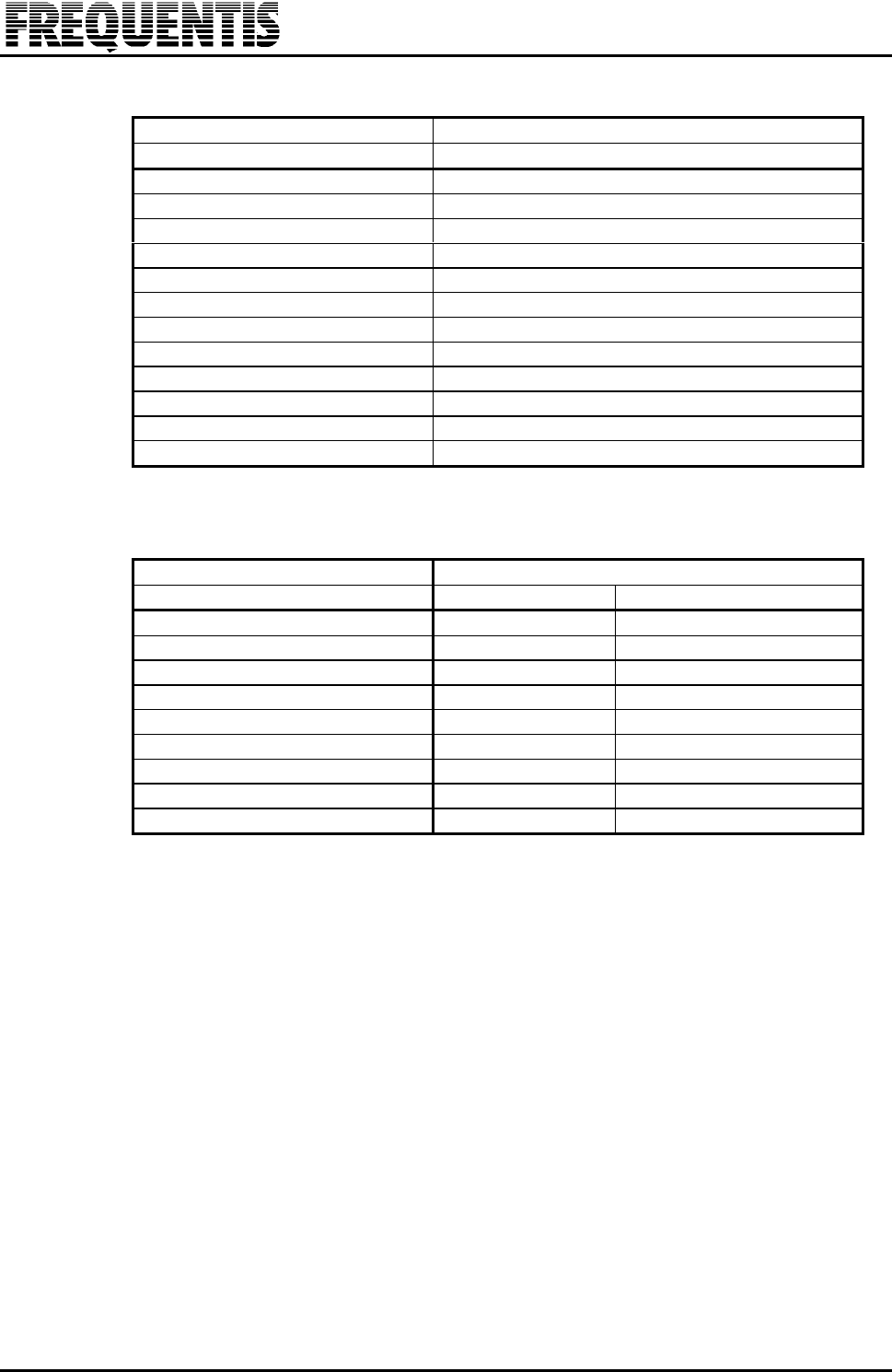
35 File: SGL REV.1.2.DOC FREQUENTIS SAFETY GUIDELINES
No: 00A46 E500.12 Author: S. Meisel COPYRIGHT FREQUENTIS 2000
Rated Current Nominal Cross-sectional Area
[ A ] [ mm2 ]
60.75
10 1.00
13 1.25
16 1.5
25 2.5
32 4
40 6
63 10
80 16
100 25
125 35
160 50
Tab. 9-4: Minimum Sizes of Conductors in Power Supply Cords
Max. Rated Current Nominal Cross-sectional Area [ mm2 ]
[ A ] Flexible Cables Other Cables
3 0.5 to 0.75 1 to 2.5
6 0.75 to 1 1 to 2.5
10 1 to 1.5 1 to 2.5
13 1.25 to 1.5 1.5 to 4
16 1.5 to 2.5 1.5 to 4
25 2.5 to 4 2.5 to 6
32 4 to 6 4 to 10
40 6 to 10 6 to 16
63 10 to 16 10 to 25
Tab. 9-5: Ranges of Conductor Cross-Sections
----------- END OF DOCUMENT -----------