Flir BelgiumBA DP12KW Light Marine Navigational Radar User Manual
Raymarine UK Ltd. Light Marine Navigational Radar
Radar installation manual
Digital Radar
Installation
Manual
Document number: 87087-2
Date: December 2007

i
Important Information ...............................................................1
Intended use ................................................................................. 1
Raymarine Support ...................................................................... 3
System Overview .......................................................................7
1.1 Introduction ................................................................................... 7
System configuration .................................................................... 8
1.2 EMC installation guidelines ........................................................... 9
Connections to other equipment ................................................. 10
1.3 Unpacking and inspecting the components ................................ 11
What‘s in the box? .......................................................................11
What tools do I need? ..................................................................11
1.4 Selecting the digital radar unit site ............................................... 12
Digital radar dimensions ............................................................. 12
1.5 Mounting Surfaces ...................................................................... 15
Sailboats ..................................................................................... 15
Power Boats ............................................................................... 15
1.6 Setting the radiation plane ........................................................... 16
1.7 Cable requirements ..................................................................... 17
Digital Radar cable ..................................................................... 17
1.8 Power requirements .................................................................... 20
Voltage Converter Module (VCM100) ......................................... 21
1.9 Grounding the digital radar system .............................................. 23
1.10 Circuit breaker and fuse ratings ................................................. 24
Installing the Digital Radar Components .................................25
2.1 Digital radar ................................................................................. 25
2.2 Installing the VCM 100 ................................................................ 26
2.3 Securing the pedestal to the mounting platform .......................... 27
2.4 Removing the lifting eyes ............................................................ 31
2.5 Fitting the open array to the pedestal .......................................... 31
2.6 System Connections ................................................................... 34
Connecting the digital radar cable .............................................. 34
Digital Radar Connections .......................................................... 35
Data Connections ....................................................................... 35
Power Connections .................................................................... 35
Maintenance and Troubleshooting ..........................................37
3.1 EMC Conformance ..................................................................... 37
3.2 System Checks ........................................................................... 37
3.3 Set up, alignment and timing checks ........................................... 38
Switch on and initial set up .......................................................... 38
Checking transmission ............................................................... 38
Bearing alignment ....................................................................... 38
Display timing adjustment ........................................................... 38

ii
Parking alignment .......................................................................39
3.4 Maintenance ............................................................................... 40
Routine Checks ..........................................................................40
Servicing and Safety ...................................................................41
3.5 Problem Solving ......................................................................... 42
VCM100 status LED sequence’s ................................................43
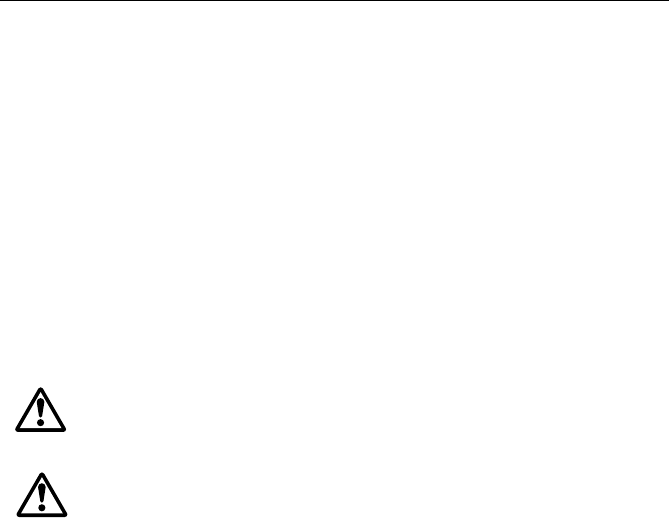
1
Important Information
Digital Radar Owners Handbook
June 2007
Intended use
This product is a radar scanner intended for use within a naviga-
tional radar system. The intended application is for leisure marine
boats and work boats not covered by IMO/SOLAS carriage
requirements.
Safety Notices
WARNING: Electrical safety
Ensure you have the power supply switched and locked off
before you start installing/servicing this product.
WARNING: Navigational safety
Although we have designed this product to be accurate and
reliable, many factors can affect its performance. Therefore, it
should serve only as an aid to navigation and should never
replace commonsense and navigational judgement. Always
maintain a permanent watch so you can respond to situations
as they develop.
CAUTION:
Before installing the Digital radar system, check that individual
components are the correct voltage for your boat’s supply.
As correct performance is critical for safety, we STRONGLY
RECOMMEND that an Authorized Raymarine Service
Representative fits this product. You will only receive full warranty
benefits if you can show that an Authorized Raymarine Service
Representative has installed or commissioned this product.
This radar equipment must be installed, commissioned and
operated in accordance with the Raymarine instructions provided.
Failure to do so could result in personal injury, damage to your boat
and/or poor product performance. In particular
1. High Voltage. The scanner unit contains high voltages. Adjust-
ments require specialized service procedures and tools only avail-

2
able to qualified service technicians – there are no user serviceable
parts or adjustments contained in this product. The operator should
never remove the digital radar units internal covers, or attempt to
service the equipment.
2. Radio Frequency Radiation Hazard. The radar antenna emits
electromagnetic radio frequency (RF) energy which can be harmful
particularly to your eyes. DO NOT look at the antenna at close
range. It is important that the radar is turned off whenever personnel
are required to come close to the scanner assembly or associated
equipment. It is recommended that the radar scanner is mounted
out of range of personnel (above head height). Distances from the
face of the radar at which RF radiation levels of 100 W/m2 and 10W/
m2 exist, are given below.
When properly installed and operated, the use of this radar will con-
form to the requirements of:
• ANSI/IEEE C95.1-2005 Standard for Safety Levels with Respect
to Human Exposure to Radio Frequency Electromagnetic Fields,
3 Hz to 300 GHz.
• ICNIRP Guidelines 1998 - International Commission on Non-Iro-
nising Radiation Protection: Guidelines for limiting exposure to
time-varying electric, magnetic and electromagnetic fields (up to
300Ghz) 1998.
3. Navigation Aid. This radar unit is only an aid to navigation. Its
accuracy can be affected by many factors, including equipment fail-
ure or defects, environmental conditions, improper handling, instal-
lation or use. It is the user’s responsibility to exercise common
prudence and navigational judgements. This radar unit should not
be relied upon as a substitute for such prudence and judgement.
Model Distance to 100 W/m2 point Distance to 10 W/m2 point
RA1048HD
(4 kW) Nil Worst case
1.0 M
RA1072HD
(4kW) Nil Worst case
1.0 M
RA2048SHD
(12 kW) Nil Worst case
1.0 M
RA3072SHD
(12 kW) Nil Worst case
1.0 M

3
Raymarine Support
Raymarine products are supported by a network of Authorized
Service Representatives. For information on Raymarine products
and services, contact either of the following:
United States Raymarine Inc.
21 Manchester Street
Merrimack
NH 03054-4801, USA
Telephone +1 603 881 5200
Fax +1 603 864 4756
www.raymarine.com
Europe Raymarine Ltd.
Anchorage Park
Portsmouth
Hampshire PO3 5TD
England
Telephone +44 (0)23 9269 3611
Fax +44 (0)23 9269 4642
www.raymarine.com
Copyright © Raymarine Ltd. 2007
The technical and graphical information contained in this handbook,
to the best of our knowledge, was correct as it went to press.
However, the Raymarine policy of continuous improvement and
updating may change product specifications without prior notice. As
a result, unavoidable differences between the product and
handbook may occur from time to time, for which liability cannot be
accepted by Raymarine.
SeaTalk is a registered trademark of Raymarine Ltd.

4
Preface
The handbook contains very important information on the
installation and operation of your new equipment. In order to obtain
the best results in operation and performance, please read this
handbook thoroughly.
Raymarine’s Technical Support representatives or your local dealer
will be available to answer any questions you may have.
This handbook is divided into three chapters as follows:
Chapter One provides information to help you plan the digital radar
installation.
Chapter Two provides detailed instructions on how to mount and
electrically connect your digital radar.
Chapter Three provides instructions on how to perform the system checks,
alignment and adjustments. It also provides information on maintenance
and trouble-shooting.
Warranty
To register your new Raymarine product, please fill out the warranty
card included in the box or go to: www.raymarine.com
It is important that you complete the owner information and return
the card to receive full warranty benefits, including notification of
software updates if they are required.
Certified Installation
Raymarine recommends certified installation by a Raymarine
approved installer. A certified installation qualifies for enhanced
warranty benefits. Contact your Raymarine dealer for further details
and refer to the separate warranty card packed with your product.
Servicing Raymarine equipment
The digital radar contains no user serviceable parts. For any
servicing required, see you local authorized Raymarine service
agents for information.They will ensure that service procedures and
parts will not affect the units performance.
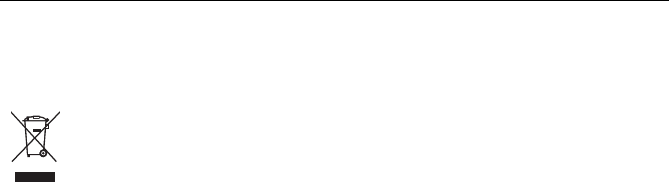
5
Waste Electrical and Electronic Equipment (WEEE)
Directive
The European WEEE Directive requires that waste electrical and electronic
equipment is recycled.
Products carrying the crossed out wheeled bin symbol (illustrated)
must not be disposed of in general waste or landfill, but in
accordance with local regulations for such products.
Although the WEEE Directive does not apply to all Raymarine
products, we support its policy and ask you to be aware of the
correct method for disposing of such products.
Please contact your local dealer, national distributor or Raymarine
Technical Services for information on product disposal.
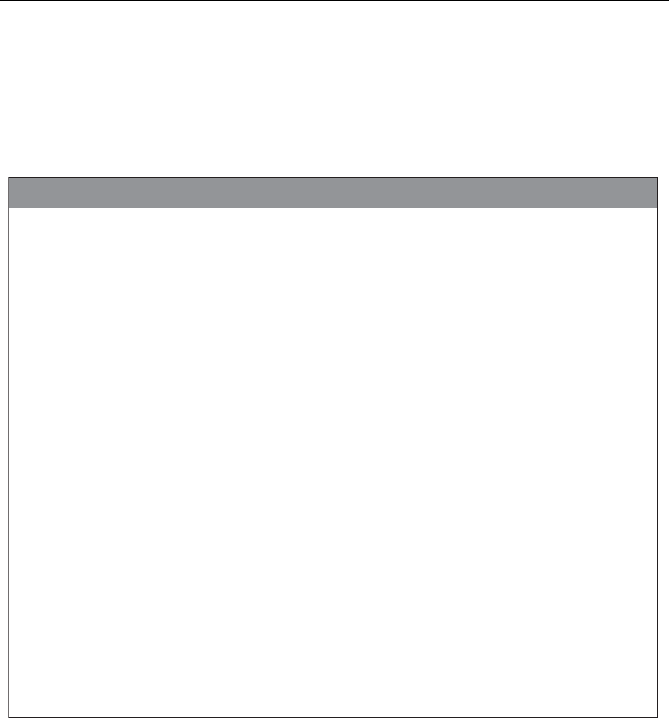
6
EMC Conformance
Raymarine equipment and accessories conform to the appropriate
Electromagnetic Compatibility (EMC) regulations for use in the
recreational marine environment. Correct installation is required to
ensure that EMC performance is not compromised.
General information
D10368_1
Approvals
FCC and Industry Canada information
The 4kW & 12kW Digital Radars comply with US CFR47 part 80 Rules and with IC Standard
RSS138. Operation is subject to the following two conditions: (1) these devices may not
cause harmful interference and (2) these devices must accept interference received,
including interference that may cause undesired operation.
Changes or modifications to these devices not expressly approved in writing by Raymarine
could violate compliance with FCC or IC rules, and void the user's authority to operate the
equipment.
Declaration of Conformity
Raymarine UK Ltd. hereby declares that the 4kW & 12kW Digital Radars are in compliance
with the essential requirements and other relevant provisions of the R&TTE Directive
1999/5/EC.
The original Declarations of Conformity may be viewed on the relevant product pages at
www.raymarine.com.
EU R&TTE Directive 1999/5/EC
USA FCC Part 80 FCC ID: PJ5-DP4KW (4kW) PJ5-DP12KW (12kW)
Industry Canada RSS138 ID IC:4069B-DP4KW (4kW) IC:4069B-DP12KW (12kW)

7
Chapter 1: System Overview
1.1 Introduction
This handbook provides instructions to assist you in the installation
of the following digital radars:
• 4 kW High definition open array digital radar
• 4kW Super high definition open array digital radar
• 12kW Super high definition open array digital radar
Each of the above radars is available with either:
• 48” array scanner
• 72” array scanner
Note: Digital radars work with G and E-Series systems (for E-Series
systems to be compatible with digital radar, software version 4.0 or
above is required). For advanced operating procedures please refer
to G and E-Series handbooks or contact technical support.
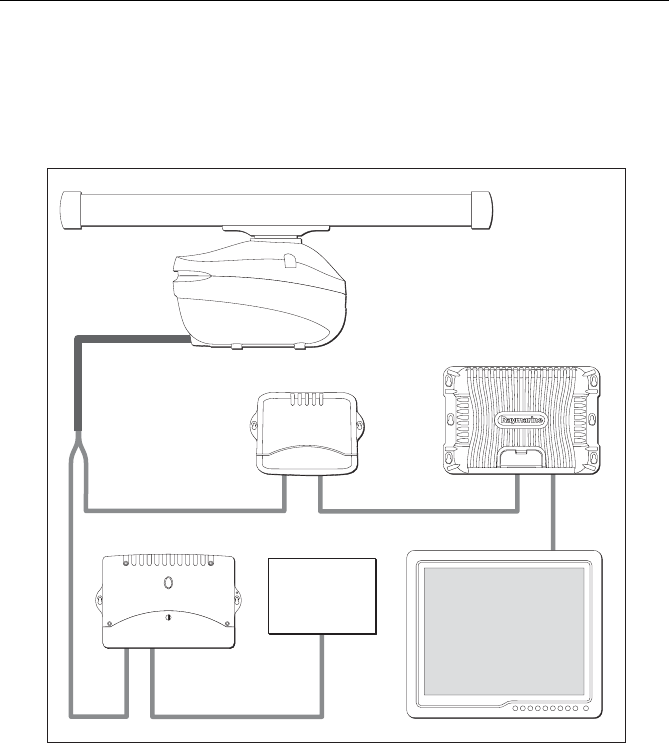
8
System configuration
Examples of digital radar systems as illustrated below. For more
detailed systems please see your individual display Owner’s
Handbook.
D10430-1
GPM400
Radar
Power
VCM100 Display
SeaTalkhs switch
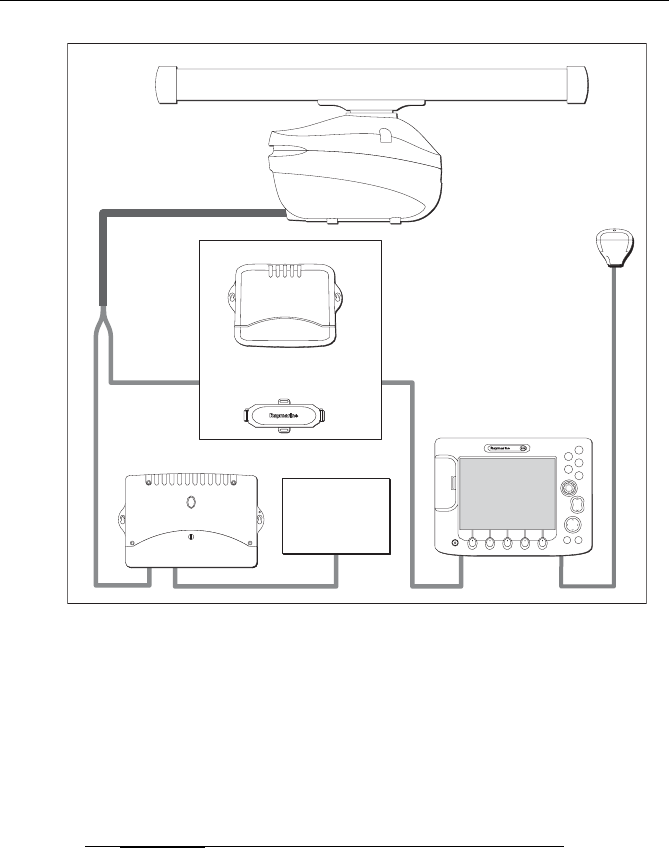
9
1.2 EMC installation guidelines
Raymarine equipment and accessories conform to the appropriate
Electromagnetic Compatibility (EMC) regulations. This minimises
electromagnetic interference between equipment, which could
otherwise affect the performance of your system.
Correct installation is required to ensure that EMC performance is
not compromised.
For optimum EMC performance, we recommend that:
• Raymarine equipment and the cables connected to it are:
• At least 3 ft (1 m) from any equipment transmitting or cables
carrying radio signals e.g. VHF radios, cables and antennas.
In the case of SSB radios, the distance should be increased
to 7 ft (2 m).
D10509-1
Radar
Power
VCM100
SeaTalkhs switch
GPS
antenna
E series display
CANCELOK
RANGE
IN
OUT
PAGE
ACTIVE
WPTS
MOB
MENU
DATA
OR
SeaTalkhs crossover coupler
(direct from digital radar)
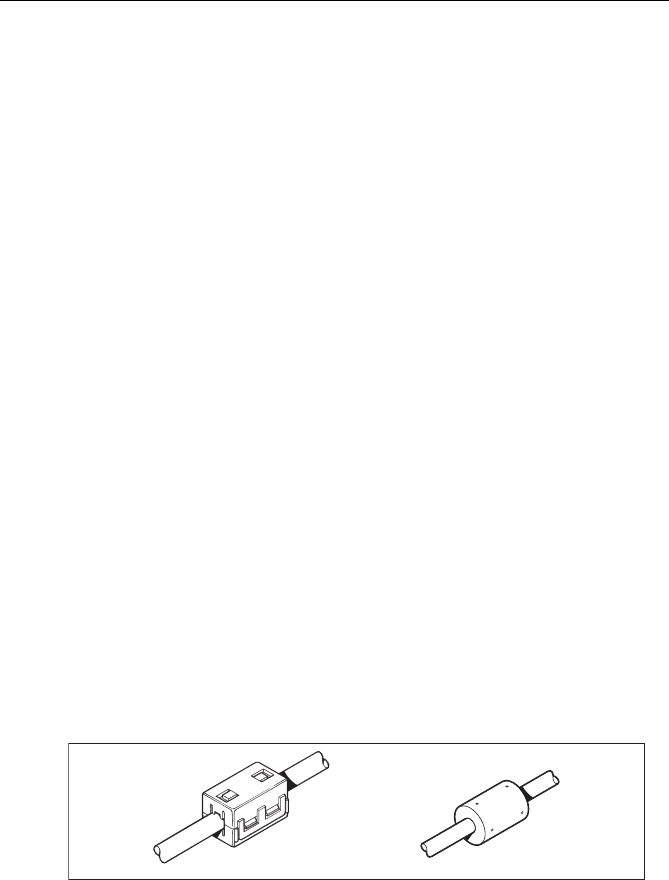
10
• More than 7 ft (2 m) from the path of a radar beam. A radar
beam can normally be assumed to spread 20 degrees above
and below the radiating element.
• The product is supplied from a separate battery from that used
for engine start. This is important to prevent erratic behavior and
data loss, which can occur if the engine start does not have a
separate battery.
• Raymarine specified cables are used.
• Cables are not cut or extended unless doing so is detailed in the
installation manual.
Remember
Where constraints on the installation prevent any of the above
recommendations:
• Always allow the maximum separation possible between
different items of electrical equipment. This will provide the best
conditions for EMC performance for the installation.
Suppression ferrites
Raymarine cables may be fitted with suppression ferrites. These
are important for correct EMC performance. Any ferrite removed to
facilitate installation must be replaced in the original position
immediately when installation is complete.
Use only ferrites of the correct type, supplied by Raymarine
authorised dealers.
The following illustration shows a typical range of suppression
ferrites fitted to Raymarine equipment.
Connections to other equipment
If Raymarine equipment is to be connected to other equipment
using a cable not supplied by Raymarine, a suppression ferrite
MUST always be fitted to the cable close to the Raymarine unit.
D3548-8
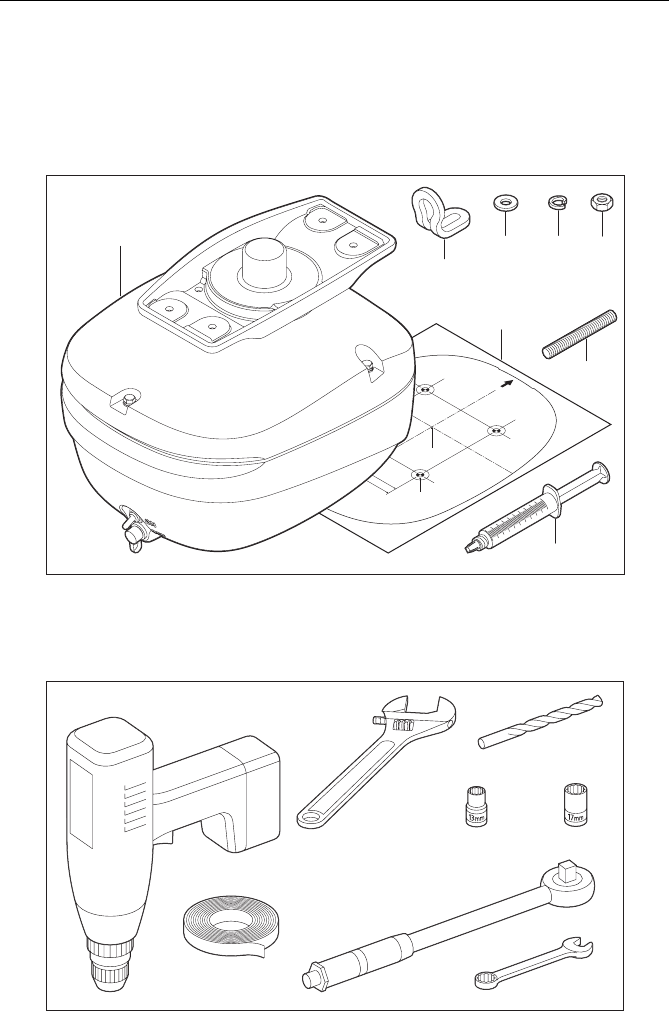
11
1.3 Unpacking and inspecting the components
Unpack your system carefully, to prevent damage to the equipment.
Check that you have all the correct system components.
What‘s in the box?
What tools do I need?
Parts supplied
D10495-1
Stud
(x4)
Pedestal
Template
Plain
washer
(x4)
Spring
washer
(x4)
Nut
(x8)
Denso paste
Drill 11 mm
diameter hole
(4 positions)
Centre of Rotation
FORWARD
Cable Entry
140 mm
70 mm
150 mm
57 mm
Maximum
outline of
pedestal
IMPORTANT
Secure pedestal
before opening lid
Digital Pedestal
Mounting Template
Lifting
eye
(x3)
Tools required
D10516-1
Power drill
Large
adjustable
spanner 13 mm socket 17 mm socket
11 mm drill
17 mm spanner
Torque wrench
Adhesive tape
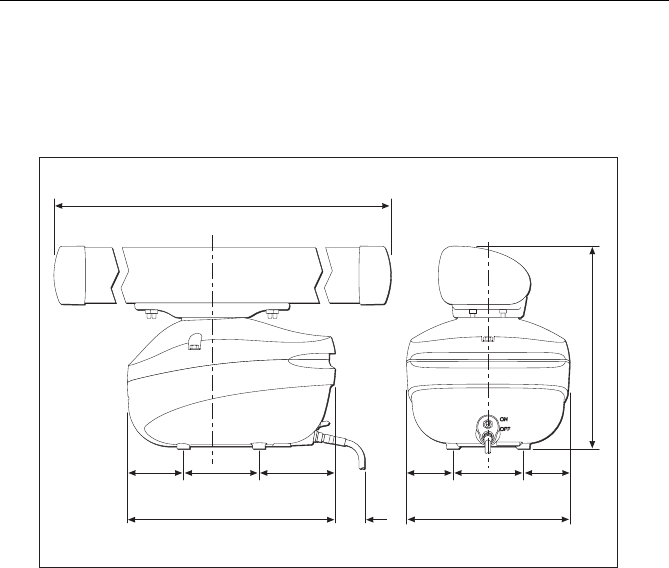
12
1.4 Selecting the digital radar unit site
Digital radar dimensions
CAUTION:
If two digital radars are installed at different locations in a dual
radar system, care should be taken to allow for the difference
in position of the radars when switching between the two on
your display, this is especially noticeable at short ranges on
larger vessels.
Selecting the best location for the digital radar unit requires careful
consideration of the following points, to ensure reliable and trouble
free operation:
•Height: The digital radar unit should normally be mounted as
high as practical above the waterline, for three reasons:
• For safety reasons the digital radar should be out of range of
personnel, preferably above head height. This avoids
mechanical danger and electromagnetic contact, particularly
with the eyes.
D10487-1
Centre of rotation Centre of rotation
Maximum rotation
48"- 1330 mm (52.4 in), 72"- 1950 mm (76.8 in)
402 mm (15.8 in)
324 mm (12.75 in)
111 mm
(4.4 in)
150 mm
(5.9 in)
151 mm
(5.95 in)
92 mm
(3.62 in)
140 mm
(5.5 in)
92 mm
(3.62 in)
412 mm (16.2 in) 59 mm
(2.3 in) minimum

13
• Radar operates at the line-of-sight, so a high mounting
position gives better long range performance.
• Surrounding large objects, in the same horizontal plane, can
interfere with the radar signal and cause blind areas or
shadow sectors and false targets on the radar screen (see
below in ‘mounting surfaces’).
However, do not mount the digital radar so high that it is affected
by the pitching and rolling of the vessel. In addition, you may
need to lower the digital radar to avoid creating a shadow sector
underneath the digital radar’s beam.
•Access: The digital radar unit site should be easily accessible to
allow maintenance to be carried out safely. Particular attention
should be paid to space above the install site to ensure you can
open the radar lid fully.
•Magnetic compass: Mount the digital radar unit at least 1 m
away from a magnetic compass.
•Cable run: The maximum length of cable between the battery
and the Voltage Converter Module unit (VCM100) should not
normally exceed 19.6 ft. (6 M). All power cable lengths should be
kept as short as possible. If you need to use a longer cable,
power and data cable lengths must be considered, (see 1.8,
Power requirements p.20 and Table 1-1 p.18).
•Shadow sectors and false echoes: Mount the digital radar
away from large structures or equipment, such as large engine
stacks, searchlights, horns, or masts. It is particularly important
to avoid shadow sectors near the bow. Raising or even lowering
the digital radar may help to reduce these effects.
In shadow areas beyond the obstruction there will be a reduction
of the beam intensity, although not necessarily a complete cut-
off; there will be a blind sector if the subtended angle is more
than a few degrees. In some shadow sectors the beam intensity
may not be sufficient to obtain an echo from a very small object,
even at close range, despite the fact that a large vessel can be
detected at a much greater range. For this reason the angular
width and relative bearing of any shadow sector must be deter-
mined at installation. Sometimes shadowing can be seen by
increasing the radar gain until noise is present. Dark sectors indi-
cate possible shadowed areas. This information should be

14
posted near the display unit and operators must be alert for tar-
gets in these blind sectors.
It should also be noted that wet sails create shadow areas and
thus sail boat operators should be aware that radar performance
may reduce in rain.
If you mount the digital radar on a mast, echoes from the mast
may appear on the radar display. These can be minimized by
placing absorbing material, such as a block of wood, between
the digital radar and mast.
•Platform rigidity/stability: The radar platform should not twist
(causing bearing errors) or be subject to excessive vibration.
•Heat/fumes: Mount the digital radar away from the top of
exhaust stacks, since the array and cables can be damaged by
excessive heat and the corrosive effects of exhaust gases.
•Mounting Platform: The platform must be mechanically secure
and capable of supporting the mass and inertia of the open array
scanner. The complete digital radar unit (Open array and
Pedestal) weighs: 48" scanner - 25 kg (55.1 lb); 72" scanner - 29
kg (63.9 lb).
• The site must be clear of ropes and moving rigging.
• Sufficient clearance must be allowed to fully open the open array
pedestal for maintenance/service (see Digital radar dimensions
on page ).
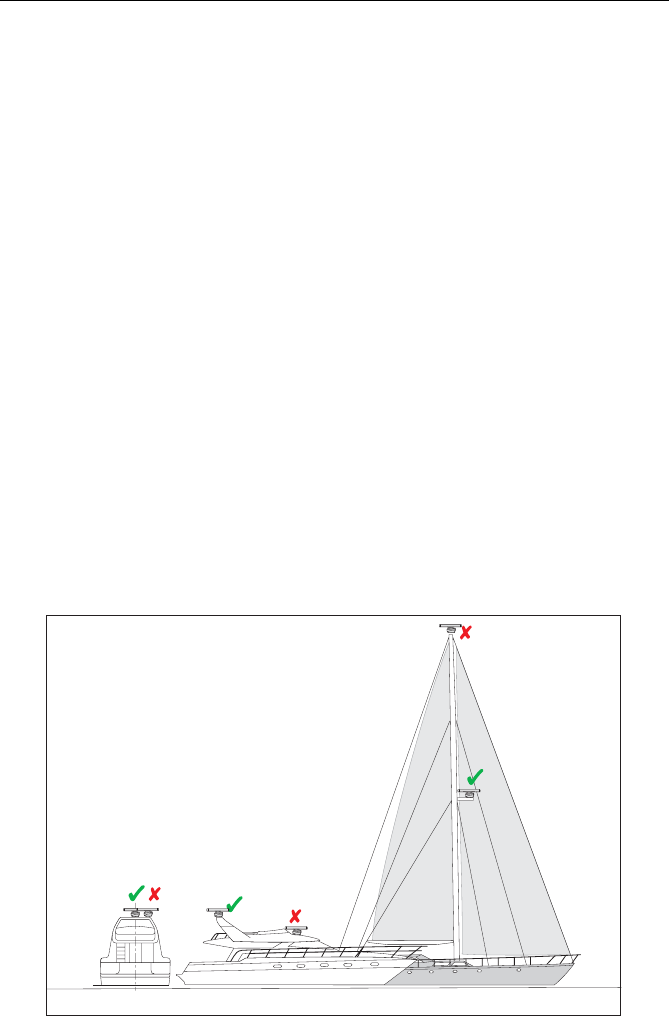
15
1.5 Mounting Surfaces
The digital radar unit can be installed on a mast platform, an arch, or
a bridge structure. Make sure that the platform surface is flat and
the units drain hole is not obstructed.
If there is any doubt concerning the appropriate type of hardware,
consult your boat dealer or representative for their
recommendations.
Sailboats
Depending on the type of sailboat, a radar guard should be installed
if the sails or any rigging could touch the digital radar or mounting
platform. Without a proper radar guard the mounting platform and
the digital radar could be severely damaged.
Power Boats
On many small vessels the digital radar unit can be installed on an
arch, or a bridge structure, but take care to follow the site
guidelines, particularly regarding height. If necessary, construct a
suitable mounting platform to obtain a sufficiently high mounting
position. Make sure that the platform surface is flat. Ensure the
platform is strong enough to support the maximum likely shock
loads of the radar whilst at sea.
D10486-1
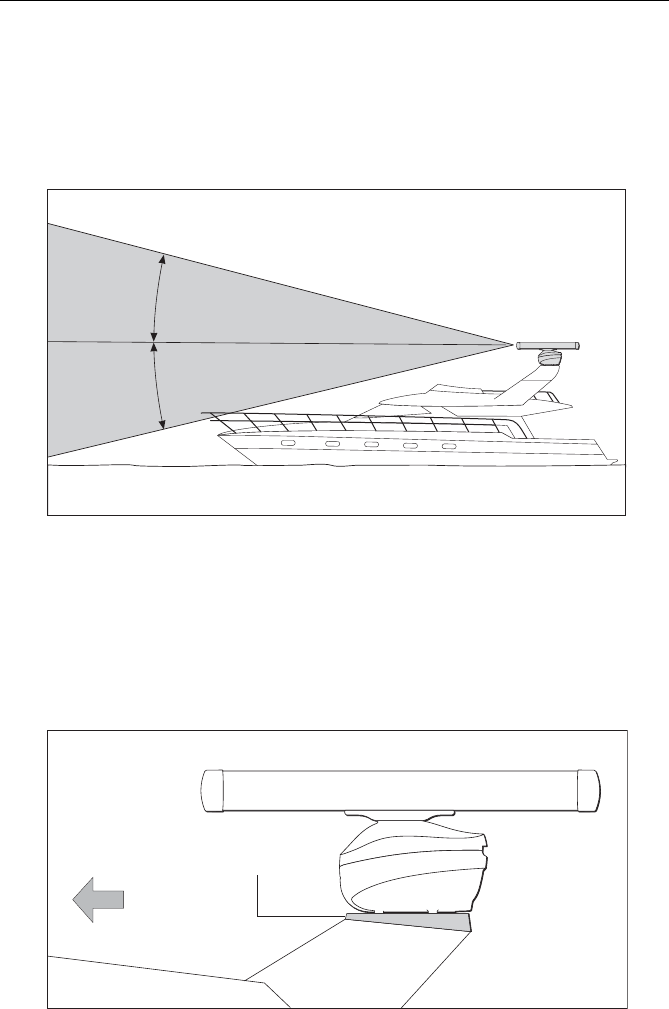
16
1.6 Setting the radiation plane
The digital radar unit should be mounted so that the array rotates
parallel to the waterline. The radar beam is approximately 25° wide
in the vertical direction, providing good target detection during the
vessel’s pitching and rolling.
Planing hull vessels, and some displacement hull vessels, adopt a
higher bow angle when the vessels is at its cruising speed. In many
cases this substantially alters and raises the radar’s main radiation
plane, and can cause poor detection of nearby targets. It may be
helpful to lower the radar beam back towards the parallel, by
shimming the rear of the digital radar, so that the beam points
slightly downwards with respect to the waterline when the vessel is
at rest.
12.5°
12.5°
Waterline
Ideal Radiation Plane
D10488-1
Wedge or
washers
Using shims to lower the main beam
Forward
D10489-1

17
The shims may be made from aluminium plate wedges, simple flat
washers, or an angled wooden block. For thick shims, you may
need longer securing bolts than the M10 studding supplied, (see
note in Installing the Digital Radar Components on p.26).
1.7 Cable requirements
This section provides details on selecting the appropriate cables for
your system. Permissible cable lengths depend on the digital radar
type and the boat’s power system. Information on the combined
inter-unit and power cables is provided in the following sections.
You need to consider the following before installing the cables:
• You need to connect the digital radar to the SeaTalkhs switch, or
SeaTalkhs crossover coupler for data, and the Voltage Converter
Module (VCM100) unit for power. The cable required depends
on the distance between the digital radar, VCM100 and data
connections.
• All cables should be adequately clamped and protected from
physical damage and exposure to heat - avoid running cables
through bilges or doorways, or close to moving or hot objects.
• Acute bends in any cable must be avoided. Minimum bend
radius = 2.5 inch (60mm).
• Where a cable passes through an exposed bulkhead or
deckhead, a watertight gland or swan neck tube should be used.
• Do not cut and re-join cables.
Digital Radar cable
The digital radar cable combines inter-unit data (SeaTalkhs) and
power cores. One has a plug for connecting in to the SeaTalkhs
network, the other is for connecting to the power output of the
VCM100 (see Voltage Converter Module (VCM100) on page ). The
digital radar cable connector plug is situated at the rear of the digital
radar unit.
4 cable lengths and 2 extension cable length’s are available (see
Table 1-1 p.18).
All figures are for cable lengths between digital radar to VCM100
and SeaTalkhs connections.
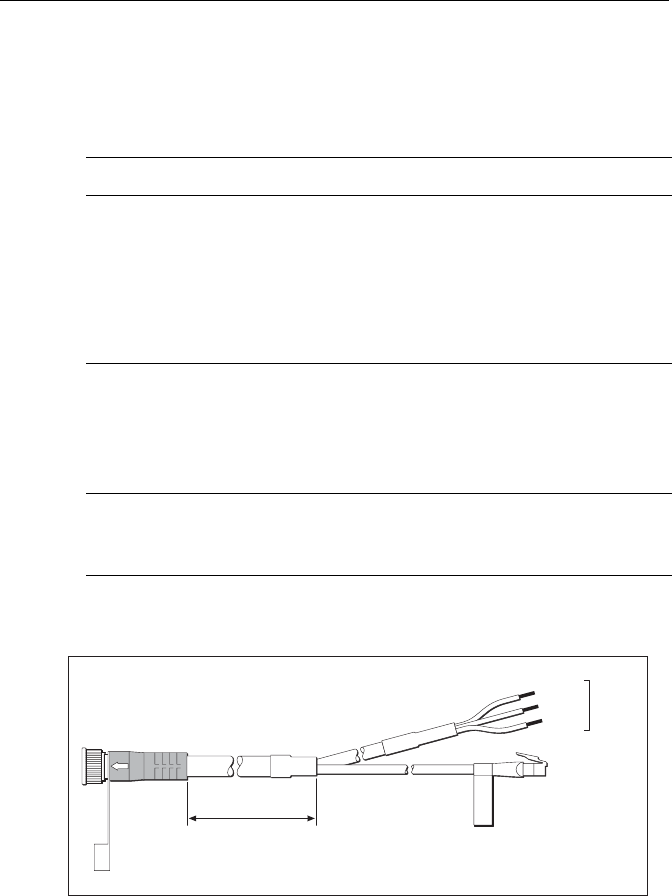
18
These cable lengths should be sufficient to complete the cable run
required on most vessels, part numbers for cables are shown in the
table below.
The radar cables power and data connectors described above are
illustrated in the following diagram.
Table 1-1:
Item Part No. Option for:
4 kW digital radar Pedestal
4 kW digital radar Pedestal
12 kW digital radar Pedestal
48" Open Array
72" Open Array
48" Open Array
72" Open Array
E52069
E52081
E52082
E52083
E52084
E52092
E52093
High definition
Super high definition
Super high definition
High definition
High definition
Super high definition
Super high definition
Digital cables
16.4 ft. (5 M) Digital cable
32.8 ft. (10 M) Digital cable
49.2 ft. (15 M) Digital cable
82.0 ft. (25 M) Digital cable
A55076
A55077
A55078
A55079
Cable options for all
digital radar
configurations.
Digital extension cables
16.4 ft. (5 M) Digital extension cable
32.8 ft. (10 M) Digital extension cable
A55080
A55081
D10497-1
Cable length
To
SeaTalkhs
switch
To
VCM100
Red
Black
Screen

19
Running the cable to the digital radar
CAUTION:
Do not pull the cable through bulkheads using a cord
attached to the connector. This could damage the
connections.
The digital connector plug is at the rear of the digital radar unit. If the
unit is mounted on a hollow structure the cable may be run up on
the inside and then fed through to the digital radars cable connector.
Make sure that the cable does not chafe where it enters and exits
the mounting structure.
Cable bend requirements
The minimum bends permitted are:
Minimum bend, 2.5 in (60 mm) radius
Extending cables
Data
You should NOT cut and re-join any of the supplied cables. If it is
necessary to extend the SeaTalkhs data cable you should use a
Raymarine supplied extension cable (see Table 1-1:, p.18 ).
For the SeaTalkhs data cable extensions you must:
•G-series: Connect the digital radar cable’s SeaTalkhs data plug
to the SeaTalkhs switch. The output of the SeaTalkhs switch
should then be connected to the G-series GPM’s SeaTalkhs port
for a networked system (see System configuration on page 8).
•E-series: If you have a single SeaTalkhs device to connect into
your E-series, use a SeaTalkhs cross-over coupler to route to the
display as a direct connection of the digital radars data output is
not possible (ensure you have 2 SeaTalkhs data cables for either
side of the cross-over coupler). If you have multiple SeaTalkhs
devices, you should route to your display via a SeaTalkhs switch.
Connect the output of the switch to the E-series display for a
networked system, (see System configuration on page 9).
Note: Please ensure you have the correct software version in your E-
series display for use with the digital radar. For upgrade procedure
information and correct software levels, see your E-series

20
documentation, display upgrade procedure booklet 81299, or go
online at www.raymarine.com.
Power
To extend the power cable (see Table 1-2:, p.21 for maximum
extension lengths), use a splash proof junction box. The junction
box should provide a terminal strip with sufficient space for power
connections. The terminal strip should be a minimum of 20 Amp
rating for power cores. It is essential that both power cores and the
screen are connected and that the connection is of very low
resistance as considerable power passes through this connection.
CAUTION:
The digital radar connector at one end of the cable is a
moulded plug that should not be removed. DO NOT remove
this moulded plug.
1.8 Power requirements
The digital radar system is intended for use on ships’ DC power
systems operating from 12 to 24 Volts DC.
12 V and 24 V systems
Extensions to the supplied power cable should be kept to the
minimum length possible. Raymarine recommends that the power
should be fed directly from the output of the battery isolator switch
or DC distribution panel via its own dedicated cable system to the
VCM100. It is also recommended that no additional power switch is
included in this power cable.
All power connections must be of high quality to minimize their re-
sistance and to remove the risk of accidental shorts. Recommended
total power cable lengths and gauges are given in the table below.
These figures relate to the maximum distance of cables from the
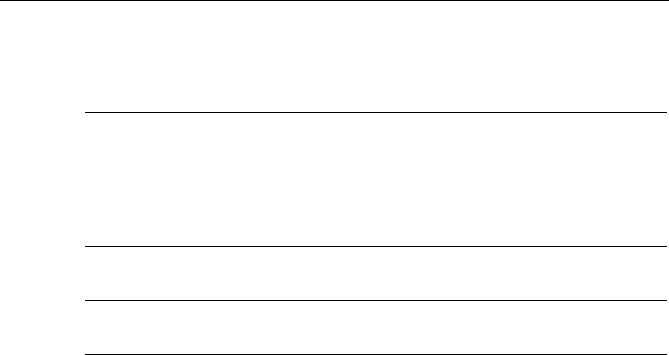
21
battery isolator switch/DC distribution panel to the VCM100. Do not
exceed these lengths as unreliable operation may result.
Note: If the required extensions result in unacceptably large diameter
cables, use two or more smaller gauge wires to achieve the
required copper wire cross-section. For example, using two pairs of
2 mm2 is equivalent to using two single 4.0 mm2 cables.
Voltage Converter Module (VCM100)
The VCM100 is exclusively used to convert the ships supply,
nominally operating at ranges from 12 to 24 V with a higher voltage
output of 42 V to the digital radar. The unit is a below decks unit only
and is designed to be splash-proof only!
Notes:
• Only one digital radar can be powered per VCM100.
• For dual digital radar systems, use one digital radar per
VCM100.
Power in
Power from the battery isolator/DC distribution panel goes to the
‘POWER IN’ port, making sure to use the screen port to effectively
ground the radar (see Grounding the digital radar system on
page 23).
Power out
The ‘POWER OUT’ port is used to connect the digital radar power
cable to supply the 42 V required, also ensure that the screen port is
used.
Table 1-2:
*Max total distance from
power supply to Voltage
Converter Module
(VCM100)
AWG (American Wire Gauge)11 10 8 7
Maximum distance (12 V
supply) 6.0 M
(19.6 ft.) 8.0 M
(26.2 ft.) 10.0 M
(32.8 ft.) 15.0 M
(49.2 ft.)
Maximum distance (24V
supply) 24.0 M
(78.7 ft.) 32.0 M
(104.9 ft.) 40.0 M
(131.2 ft.) 55.0 M
(180.4 ft.)
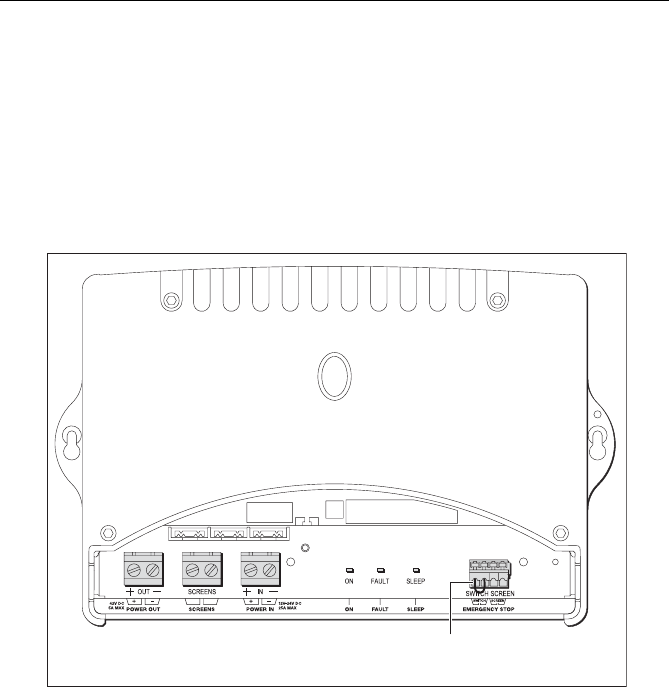
22
VCM100 Status LED’s
The VCM100 has status LED’s fitted (see Table 3-2:, p.43 for
trouble-shooting advice).
Emergency stop button
The VCM100 unit has an option for an emergency stop button. If
this is used, the factory fitted wire link (bridge) should be removed
and replaced with the emergency stop button’s connector wires.
.
CAUTION:
The digital radar has been designed to be used in conjunction
with a VCM100 and is NOT compatible with a direct battery
connection
D10490-1
Ensure either the wire link,
or emergency stop button is fitted

23
1.9 Grounding the digital radar system
It is important that an effective RF ground is connected to the radar
system.
You must ground the radar by connecting the drain/screen wire
(green) of the power cable to the ground point (screen) of the
VCM100, the ship’s RF ground system should be connected to the
other screen point on the VCM100 when running the power cables.
Refer to your display unit Owner’s Handbook for details.
If you need to extend the drain (screen) wire, the extension wire
should be an 8 mm braid or AWG 10 (6.0 mm2) multi-stranded
cable.
If your vessel does not have an RF system, connect the drain wire
to the negative battery terminal.
The DC system should be either:
• Negative grounded, with the negative battery terminal connected
to the ship’s ground.
• Floating, with neither battery terminal connected to the ship’s
ground.
CAUTION:
This radar is not intended for use on ‘positive’ ground
vessels. The power cable Earth screen connections must be
connected to the ship’s ground.
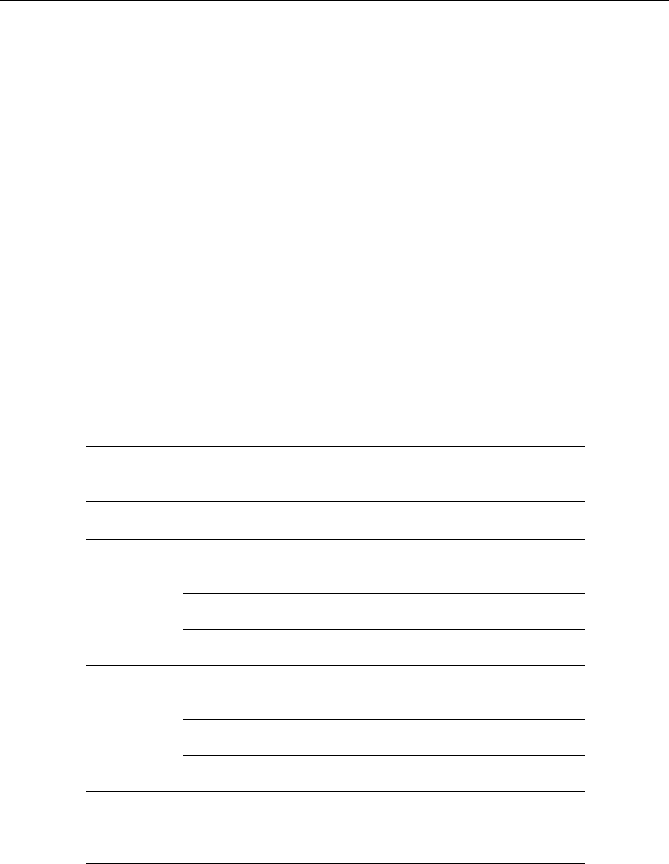
24
1.10Circuit breaker and fuse ratings
It is recommended that power is fed directly to the VCM100 via its
own dedicated cable system and MUST be protected by a thermal
circuit breaker or fuse, fitted close to the power connection, then run
power from the output of the VCM100 to the digital radar, (the
connection from the output of the VCM100 to the digital radar does
not need any fuse or circuit breakers connecting). Refer to the table
below for isolator switch, circuit breaker or fuse value ratings. Check
and ensure all terminal connections are clean.
CAUTION:
If you do not have a thermal circuit breaker or fuse in your
power circuit, e.g. fitted to the DC distribution panel, you MUST
fit an in-line breaker or fuse to the positive lead of the power
cable.
Table 1-3:
Vessels
Supply Device Open Array Systems
4 kW 12 kW
12 V
Isolator Switch min.
rating 30 A 30 A
Thermal Breaker rating 15 A 15 A
Fuse value 20 A 20 A
24 V
Isolator Switch min.
rating 15 A 15 A
Thermal Breaker rating 8 A 10 A
Fuse value 10 A 15 A
Digital radars cannot be directly connected to the battery.
Power connections are made from the VCM100 POWER OUT
port.
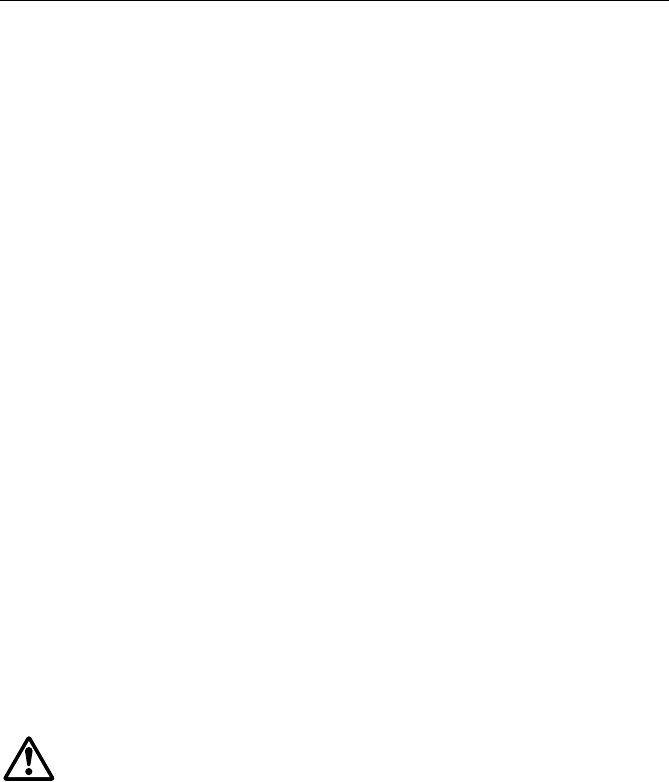
25
Chapter 2: Installing the Digital Radar
Components
2.1 Digital radar
CAUTION:
Correct performance of the boat’s navigation equipment is
critical for safety, we STRONGLY RECOMMEND that an
Authorized Raymarine Service Representative fits this product.
You will only receive full warranty benefits if you can show that an
authorized Raymarine service representative has installed or
commissioned this product.
Installation of the digital radar should only be undertaken by a
competent installer. If you have any difficulty with the installation,
please contact your local Raymarine dealer or distributor.
The digital radar system is supplied in three sections; the pedestal
unit, the antenna and the Voltage Converter Module (VCM100). The
pedestal unit is secured from below the mounting platform. The
open array is then secured to the pedestal, and the VCM100 is fitted
where it is accessible Full details for mounting the digital radar are
given below.
CAUTION:
The pedestal unit has a cap fitted over the open array
mounting shaft to protect the delicate protuding co-axial pin.
This cap must be left in place until the open array antenna is
ready to be fitted and fixed.
WARNING:
The digital radar weighs in total (with antenna fitted): 48" Radar
- 25 kg (55.1 lb); 72" Radar - 29kg (63.9 lb). For safety reasons it
is recommended that the unit is not lifted by one person.
The unit is supplied with lifting eyes (maximum SWL = 40 kg) to
facilitate the use of standard lifting accessories, e.g. rope, chain or
strop. The Safe Working Load (SWL) of the lifting accessories
should be a minimum of 150 kg. Suitable lifting equipment could
include a crane, hoist, or an appropriate rigid, overhead structure.
You should not attach the antenna to the digital radar prior to lifting,
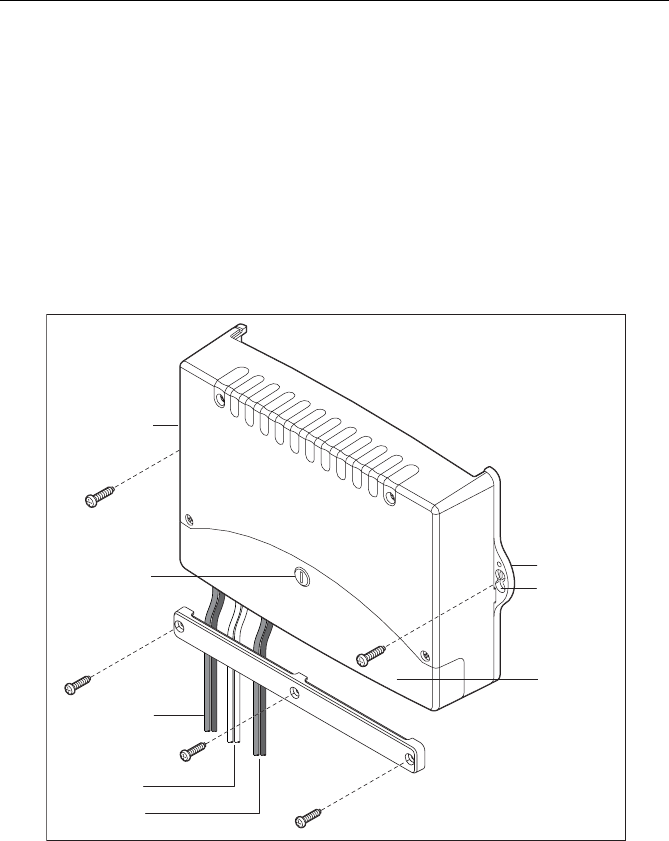
26
lift and fix the digital radar in place before fixing the antenna. You
should never lift the unit by the attached open array antenna.
Please read and understand chapter 1 before you start to install any
of the components of the digital radar system.
2.2 Installing the VCM 100
CAUTION:
It is important to keep the cable run from the DC distribution
panel/circuit breaker to the VCM100 as short as possible. (see
Table 1-2, p.21).
).
Ensure the VCM100 unit is level on it’s horizontal plane. Once
situated, fit in position with the 2 mounting screws provided
CAUTION:
The VCM100 is a ‘below decks’ piece of equipment. It is
designed to be splash-proof only!
D10496-1
Mounting lug
Keyhole slot
Main cover
Connector
cover
Connector
cover catch
Power in
Power out
Screens
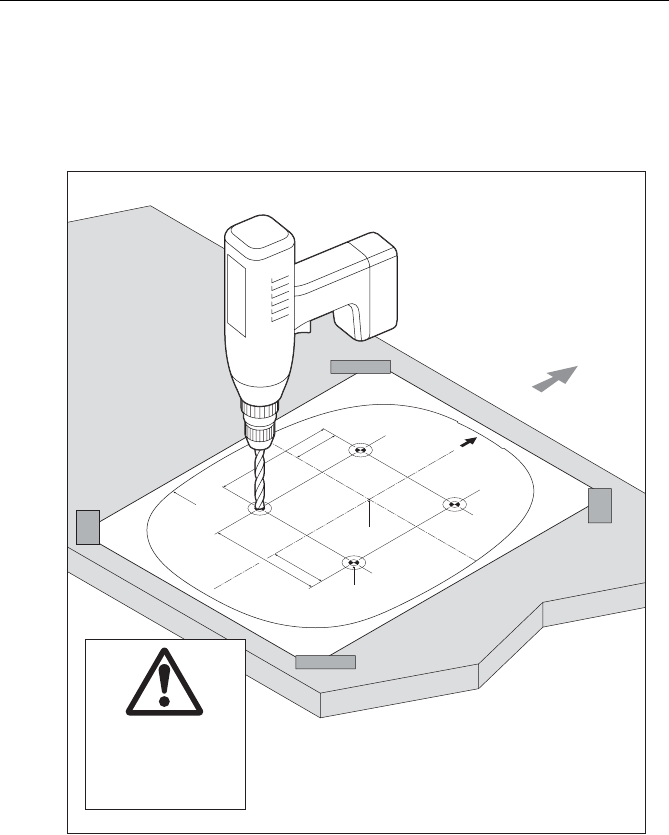
27
2.3 Securing the pedestal to the mounting platform
1. Using the paper template supplied with the mounting kit, mark the
flat mounting surface in-line with the holes, and drill as indicated on
the template.
2. Ensure the lifting eyes are securely fitted to the top of the pedestal,
and the yellow protective cap is in place.
Preparing mounting holes
D10491-1
Drill 11 mm
diameter hole
(4 positions)
Centre of Rotation
FORWARD
Cable Entry
140 mm
70 mm
150 mm
57 mm
Maximum
outline of
pedestal
IMPORTANT
Secure pedestal
before opening lid
Digital Pedestal
Mounting Template
FORWARD
Mounting platform
1. Tape template to mounting platform.
2. Using template, drill 11 mm diameter hole in four positions.
IMPORTANT
Ensure mounting platform
is adequately robust for
this installation.
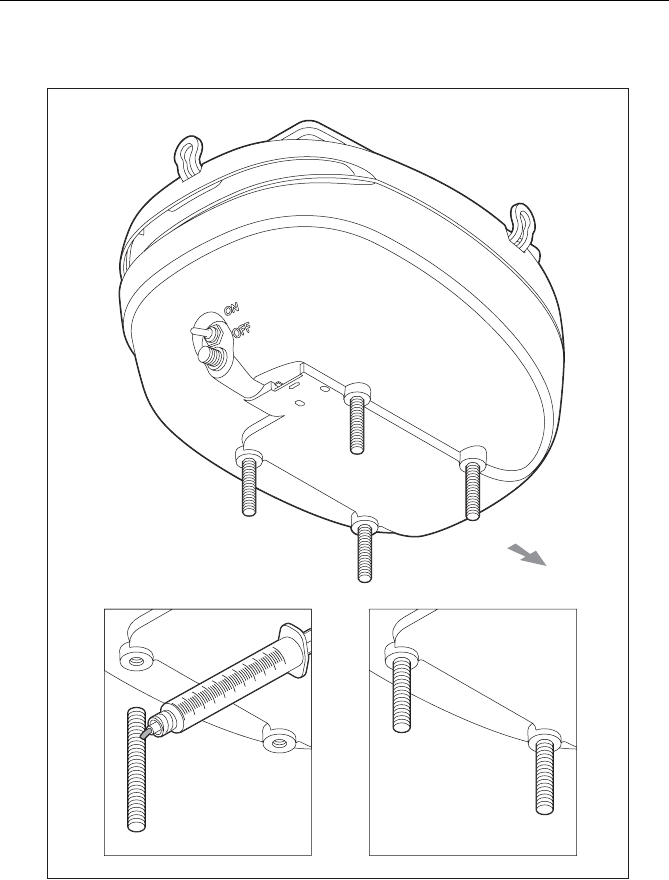
28
3. Grease the studs with Denso paste (supplied) then in turn, hand
tighten the 4 studs into the pedestal.
Note: If the studding supplied is not long enough for the mounting surface
thickness, use M10 stainless steel, grade A4-70 studding of a
suitable length. Refer to the following illustrations for details.
FORWARD
Preparing mounting studs
D10492-1
Apply Denso Paste
to stud.
Hand tighten
stud into
pedestal.
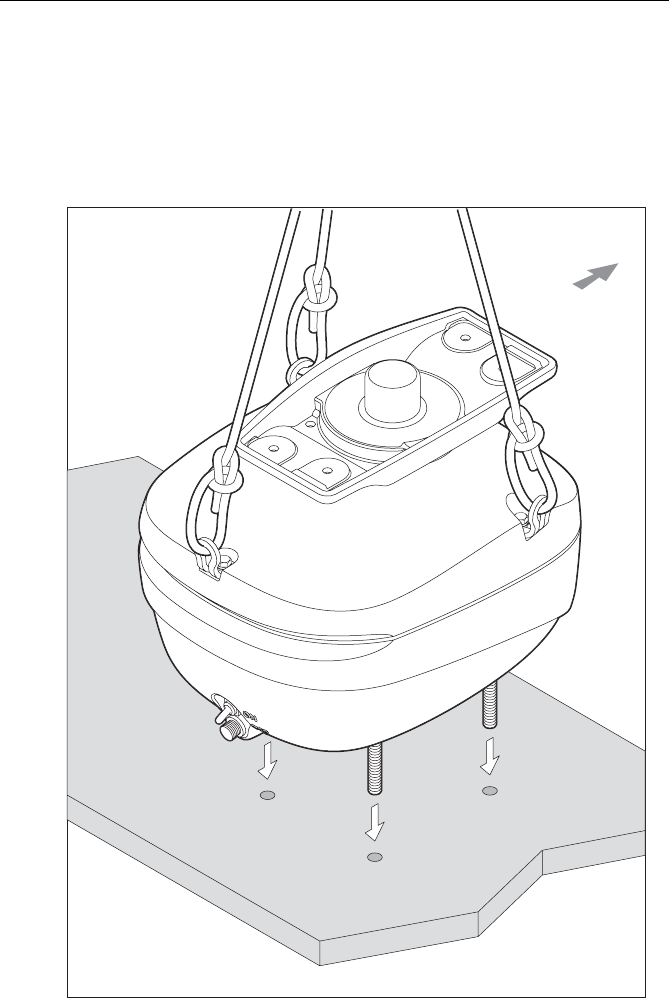
29
CAUTION:
DO NOT lift the unit with the open array antennae attached.
4. Using suitable lifting equipment (see warning on page -25), raise the
pedestal over the mounting surface. Carefully lower into position,
taking care that the studs pass through the holes without damaging
the threads. Ensure that the digital connector plug is pointing aft.
Positioning pedestal
D10493-1
Position pedestal
onto mounting platform.
FORWARD
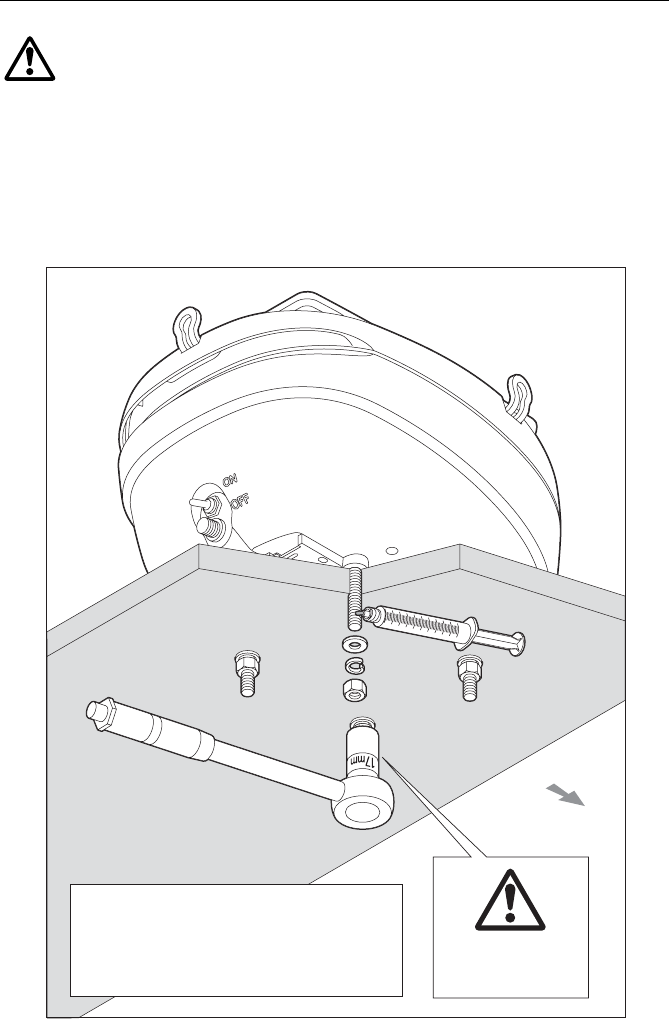
30
WARNING:
Support the pedestal unit until it has been secured to the
mounting platform. It is important that all four sets of nuts and
washers are used to secure the pedestal to the mounting
platform.
5. Referring to the following illustration, use the four nuts and
associated washers to secure the pedestal. Grease the studs with
Denso paste (supplied). Tighten to 22.1 lb ft. (30NM) torque; ensure
the radar is tightly fitted. If required, cut-off any excess stud.
FORWARD
D10494-1
IMPORTANT
Ensure nut torques are
periodically checked.
1. Apply Denso Paste to the four studs.
2. Secure pedestal to mounting platform using the
plain washers, spring washers and nuts.
3. Tighten the nuts to 30 Nm (22.1 lb ft).
Check torques

31
2.4 Removing the lifting eyes
Note: Complete this step on each bolt, one by one.
1. Loosen the first self retaining bolt securing the lifting eye to the
pedestal lid, do this enough to remove the lifting eye.
2. Once the lifting eye is removed, re-tighten the bolt to 5.2 lb ft. (7
NM) torque. Move to the next bolt, repeat the steps until all three
lifting eyes are removed.
2.5 Fitting the open array to the pedestal
CAUTION:
Before attaching the open array antenna to the digital radar
unit ensure that the pedestal base is securely fixed to the
platform. Also ensure the cable is not attached and no power is
applied to the display unit or it’s attached system. The digital
radars power switch should be in the OFF position.
The pedestal unit has a cap fitted over the open array mounting shaft
to protect the protuding co-axial pin. This cap must be left in place until
you’re ready to fit the open array to the pedestal unit.
Important Information:
CAUTION:
Extreme caution is required to ensure that the open array
antennae does not come into contact with the delicate
protruding coaxial pin. This is a critical component and should
be treated with caution. Ensure that the alignment guides are
used and all instructions below are adhered to!
1. Fit the 4 threaded alignment guides to the studs on the underside of
the antenna until they bottom out. The alignment guides are
essential to help prevent damage to the coaxial pin.
2. Remove and retain the protective cap from the open array shaft.

32
Note: Retain the protective cap, for use if the open array is removed from
the pedestal in the future. If the pin is damaged during the following
operation you should contact your service dealer.
3. Move the antenna mounting bracket so it sits on the Port to
Starboard axis of the digital radar. Lift the open array into position,
taking care it is in the correct orientation and that the threaded
alignment guides are fitted. Carefully align, then slowly lower the
array.
Note: The antenna mounting bracket is designed so that the array can
only be fitted to the pedestal in the correct orientation.
4. Once the antenna is seated, remove the alignment guides.
5. Grease the four securing studs with Denso paste (supplied).
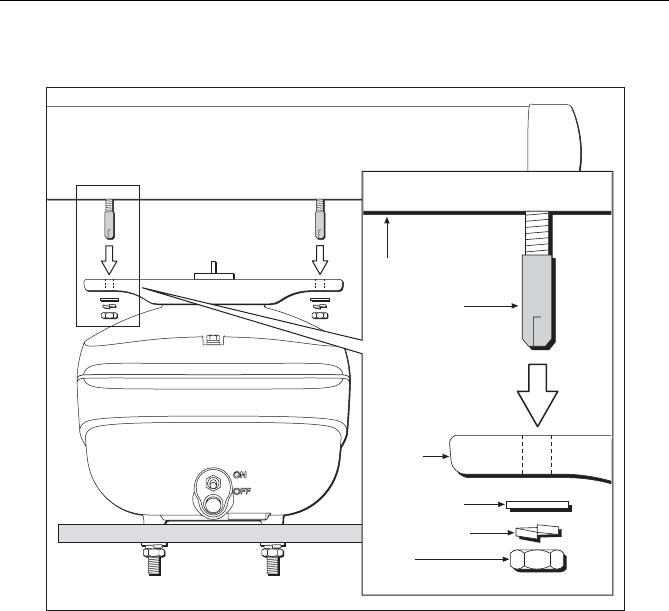
33
6. Use the four nuts and associated washers supplied to secure the
array to the pedestal as shown in the diagram below.
D10425-1
M8 plain washer
Array
Alignment guide
Pedestal
M8 spring washer
M8 nut
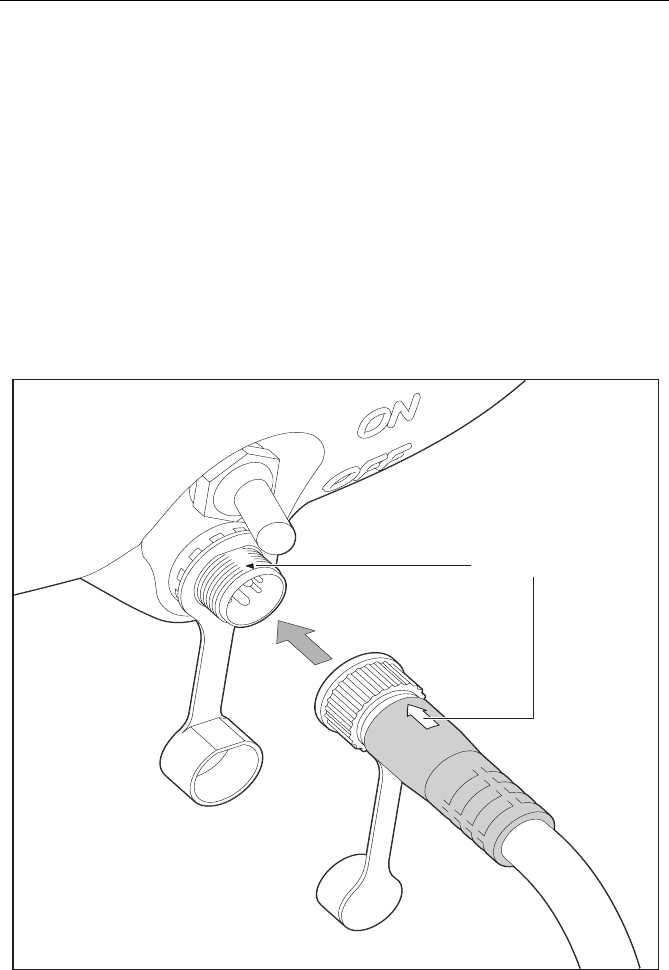
34
2.6 System Connections
CAUTION:
The digital radar connector (situated at one end of the cable) is
a moulded plug that should not be removed. DO NOT remove
this moulded plug.
Connecting the digital radar cable
Line up the two arrows (one on the radar cable, one on the radar
connector, on the base). With the two arrows aligned, push the
connector in, once the connector is sited turn the threaded collar
clockwise to lock the cable into position. Ensure the connector is
fully home and tightened.
D10511-1
Alignment arrows
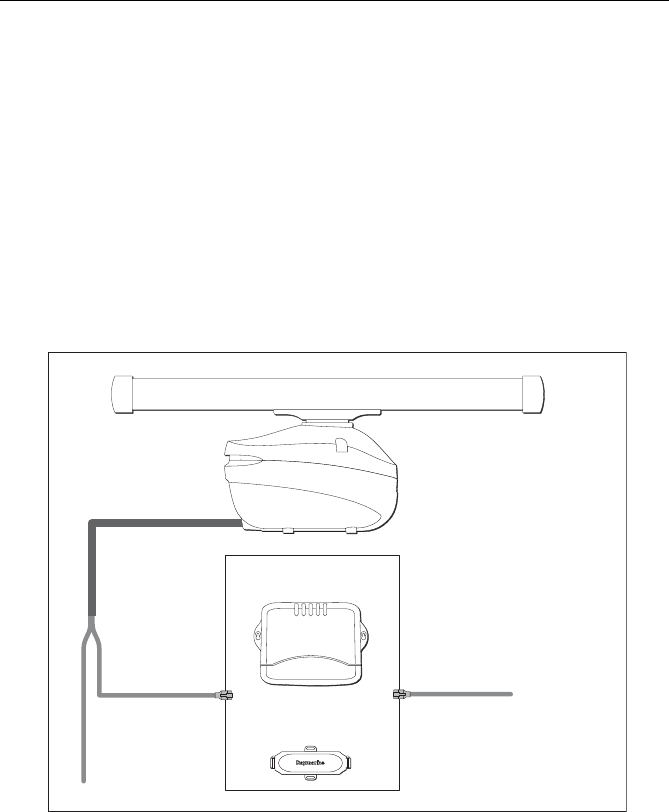
35
Digital Radar Connections
The digital radar cable consists of 2 parts, power and data. The
moulded connector plugs in to the digital radar. The cable’s power
cores are routed to the VCM100. The RJ45 data connector goes to
the SeaTalkhs connection as described in Installing the Digital
Radar Components on p.35.
Data Connections
The digital radar data connection should go into the SeaTalkhs data
bus via the SeaTalkhs switch/crossover coupler. Connect the display
system into the SeaTalkhs data bus from the switch/cross-over
coupler so data can be shared throughout the system.
Power Connections
DC power requirements are described in Power requirements on
page 20).
Power for a digital radar is supplied via the VCM100. The digital
radar has a power switch fitted to it. This switch can normally be left
ON. However, if the scanner is being serviced, or if anyone needs to
SeaTalkhs switch
(multiple devices)
OR
Crossover coupler
(Single SeaTalkhs device)
D10512-1
Radar
Power
Data To E/G-Series
SeaTalkhs
connections

37
Chapter 3: Maintenance and
Troubleshooting
Once you have installed your digital radar unit, and made all the
connections, you need to check your installation. You can then set
up the radar system, align the scanner and check the display timing.
In addition, for a 72" open array scanner you need to set the
antenna size to ensure the scanner rests in the correct position
when rotation stops.
Set up, alignment and timing checks are performed from the radar
system display unit. The procedures are outlined below; full details
are provided in the display unit/system Owner’s Handbook.
Reading the relevant Multifunctional display/system Owner’s
Handbook will help you to familiarize yourself with the operation of
the radar.
3.1 EMC Conformance
Always check the installation before going to sea to make sure that
it is not affected by radio transmissions, engine starting etc.
To do this:
• Turn on all transmitting equipment (radar, VHF radio etc.).
• Check that all electronic systems are operating correctly without
undue interference or noise.
3.2 System Checks
Before performing the functional test, check the following:
• All securing bolts are fully tightened and mechanical locking
arrangements as specified are in place
• All connections have been made
• All connecting wires are secured and protected as necessary
Note: We recommend that an certified and authorized Raymarine agent
checks the installation before going to sea.

38
3.3 Set up, alignment and timing checks
Switch on and initial set up
On the digital radar, ensure the power switch is set to ON. Switch on
the display unit. The magnetron warm-up sequence should start,
after which the unit should enter Standby mode. If necessary, adjust
the lighting and contrast. If required, change the default language
settings.
Checking transmission
WARNING:
The radar scanner transmits electromagnetic energy. Ensure that the
scanner has been installed according to the recommendations given,
and that all personnel are clear of the scanner, before switching to
transmit mode.
Run through the radar operations described in the display unit
Owner’s Handbook and check that all the expected data is
displayed.
Bearing alignment
When the system is correctly installed, you must check the bearing
alignment to ensure that targets appear at their correct bearing
relative to the ship’s bow, and adjust the alignment if necessary,
(see display unit Owner’s Handbook for information on bearing
alignment).
Display timing adjustment
The display timing setting can be used to set/change the range
accuracy shown on the display, if required. It is possible to check
the display timing before using the system for navigation. To fine
tune the radar for accuracy if required see your display unit Owner’s
Handbook.

39
Parking alignment
When the radar is in standby or powered down, the antenna should
park (rest) facing forward, (so you can see the Raymarine logo
when looking towards the scanner from the front of the boat). A
parking offset angle determines where the scanner parks, and you
can set this, so the scanner parks correctly.
To set the correct offset angle ensure that:
• The display is switched on with the radar page selected.
• The radar is powered up.
• The radar is in standby mode.
1. Press MENU.
2. Select Radar Setup.
3. Select Scanner Setup.
4. Select the Parking Offset option, then set the correct offset angle
so the antenna parks facing forward.
5. Select OK until you return to the radar display page.
6. Visually check that the radar is suitably parked.
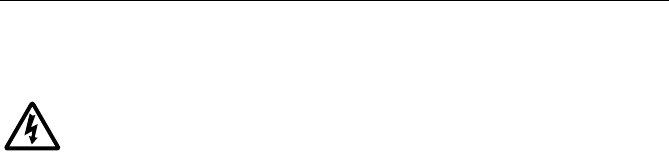
40
3.4 Maintenance
WARNING: HIGH VOLTAGE
The display and digital radar units contain high voltage. Do not
remove the rear cover from the display or any covers from the
scanner.
Adjustments require specialized service procedures and tools only
available to qualified service technicians - there are no user
serviceable parts or adjustments and the operator should not
attempt to service the equipment.
Always turn the radar system off before carrying out any routine
maintenance on the scanner or nearby equipment. Switch off the
display unit before removing the power cord.
Suppression ferrites
Raymarine cables may be fitted with suppression ferrites. These are
important for correct EMC performance. Any ferrite removed for
maintenance purposes must be replaced in the original position
once the maintenance is complete.
Use only ferrites of the correct type, supplied by Raymarine
authorized dealers.
Routine Checks
The radar scanners are sealed units. Maintenance procedures are
therefore limited to the following periodical checks:
• Examine the cables for signs of damage, such as chafing, cuts or
nicks.
• Check that the cable connectors are firmly attached.
• Make sure the scanner and pedestal are still attached securely to
the mounting.
• Once a year, remove, grease and re-attach the mounting bolts
securing the scanner and pedestal.

41
Servicing and Safety
• Raymarine equipment should only be serviced only by authorized
Raymarine service technicians. They will ensure that service pro-
cedures and replacement parts used will not affect performance.
There are no user serviceable parts in any Raymarine product.
• Some products generate high voltages, so never handle the
cables/connectors when power is being supplied to the equip-
ment.
• Undue noise and interference may be a symptom of an EMC
related problem, Always report any EMC-related problem to your
nearest Raymarine dealer. We use such information to improve
our quality standards.
• To minimise any EMC related problems and ensure the best pos-
sible performance from your Raymarine equipment, follow the
guidelines given in the installation instructions.
• In some installations, it may not be possible to prevent the equip-
ment from being affected by external influences. In general this will
not damage the equipment but it can lead to spurious resetting
action, or momentarily may result in faulty operation.
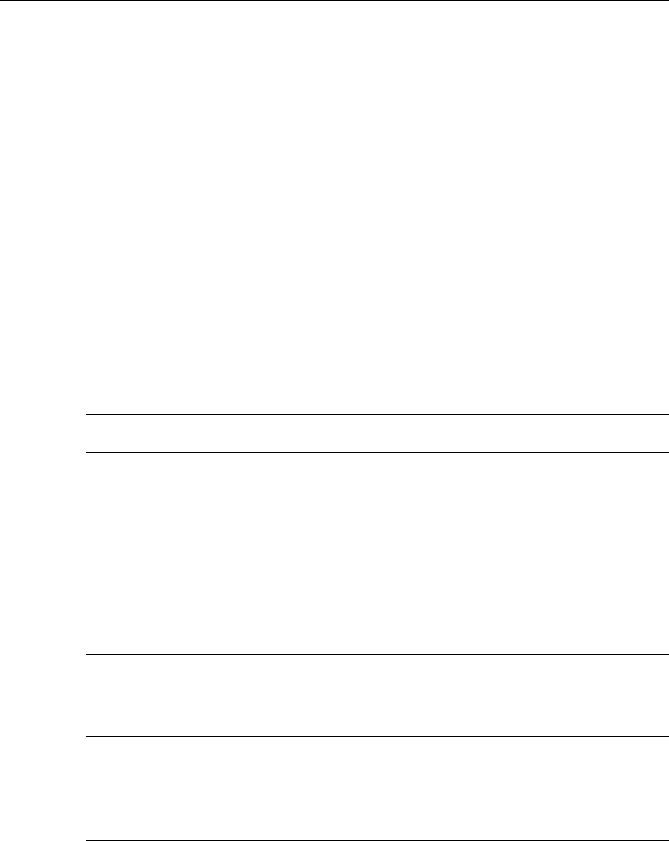
42
3.5 Problem Solving
All Raymarine products are subjected to comprehensive test and
quality assurance programmes prior to packing and shipping.
However, if this radar unit or VCM100 should develop a fault, please
refer to the following table’s to identify the most likely cause and the
corrective action required to restore normal operation.
If you still have a problem after referring to the table below, contact
your local dealer, national distributor or Raymarine Product Support
Department for further advice.
Always quote the product serial numbers. The display unit serial
number is printed on the back of the unit, and the digital radar serial
number is on the rear of the scanner near the connector socket.
Table 3-1:
Problem Correction
“No Data Source” mes-
sage Check that all the SeaTalkhs cable
connections from the digital radar to
the SeaTalkhs hub/crossover coupler
and from the SeaTalkhs hub/crossover
coupler to the display system is firmly
attached, and undamaged. Check
that the polarity of the cables is cor-
rect.Check the
The bearing displayed on
the radar display is not the
same as the actual bearing
Perform the bearing alignment proce-
dure described in the display unit
Owner’s Handbook
The 72” antenna stops in
the wrong position when I
power down or go to
standby.
Refer to Parking alignment on
page 39.
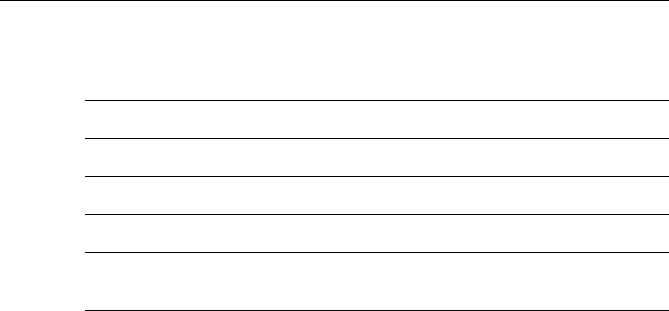
43
VCM100 status LED sequence’s
Table 3-2:
LED name Operating color Working condition
On Green (solid) Radar operating normally
Fault Red (solid) Fault condition
Sleep Yellow (flashing) (Radar in Standby)
Yellow (solid) Fault condition, self
recovers after 20 seconds

44