Flir BelgiumBA S1000 S1000 Autopilot with radio interface node User Manual Logo World Leaders B W 38mm eps
Raymarine UK Ltd. S1000 Autopilot with radio interface node Logo World Leaders B W 38mm eps
Contents
- 1. Installation Manual
- 2. Operation Manual
Installation Manual
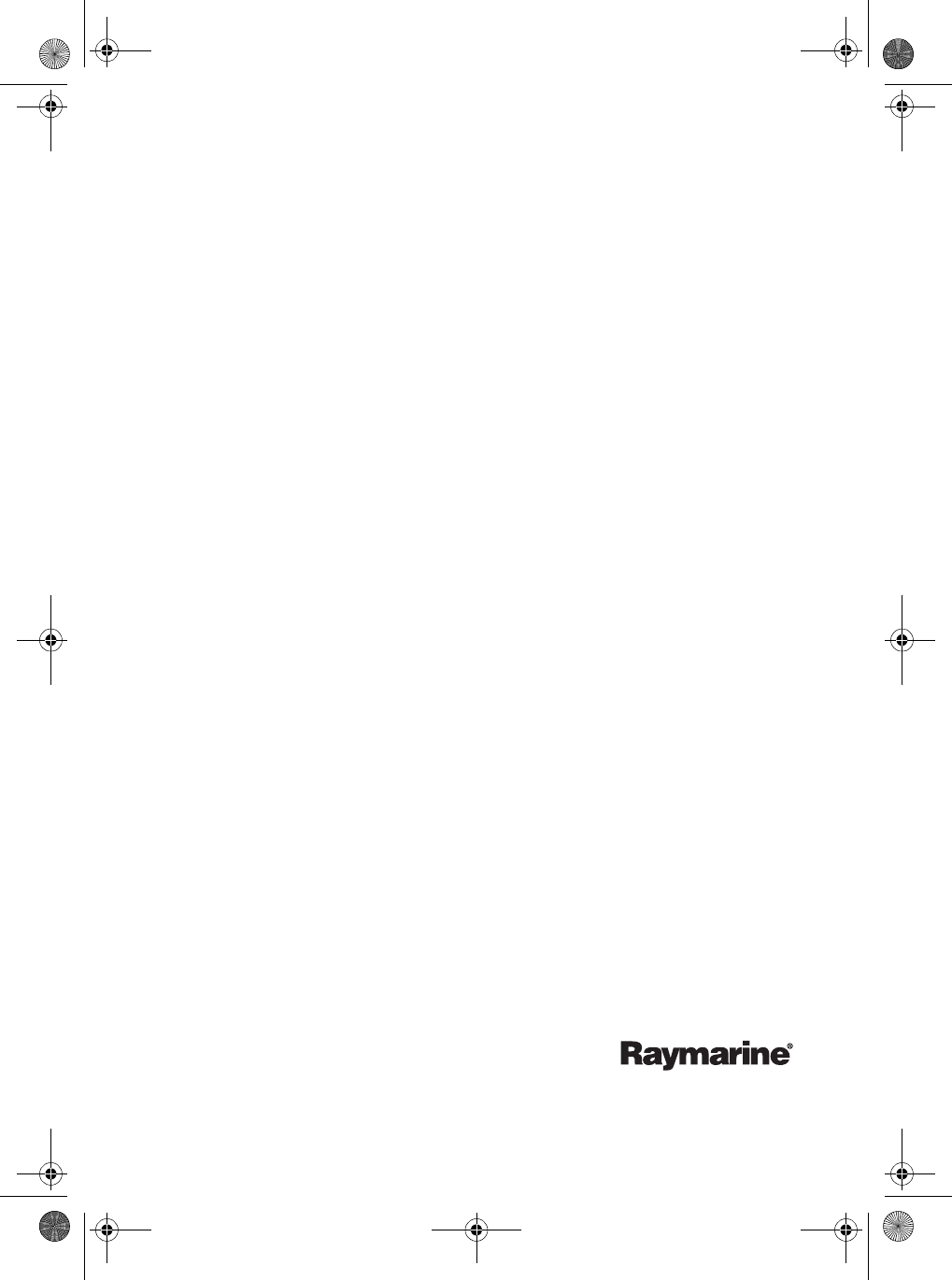
SmartPilot
S1000 Autopilot
Installation Guide
Document Number: 87040-1
Date: December 2004
87040_1.book Page 1 Wednesday, December 22, 2004 12:32 PM

Welcome to the Raymarine S1000 Autopilot
Congratulations on having bought a Raymarine S1000 Autopilot. This state-of-the-art
product is specifically designed to be easily integrated with your boat’s steering system, and
enable you to automatically control the steering.
The S1000 Autopilot is intended for use in:
• HC5345, HC5347, HC5348, and HC5358 SeaStar steering systems.
• Systems with HC4600, HC4645, HC4647, HC4648, and HC4658, BayStar steering rams.
• Systems with Hynautic K6 steering rams.
SeaTalk® is a Registered Trademark of Raymarine
All other trademarks used in this document are acknowledged.
© Copyright Raymarine UK Limited 2004
Existing hydraulic steering system
Buzzer
Pump control
S1000 Autopilot System
S100 Remote
Course
computer
Autopilot
pump
D7501-1
S100 REMOTE
MODE
STANDBY PILOT
GPS input
The S100 requires
GPS data (SeaTalk or
NMEA compatible),
to operate correctly
Alarm
87040_1.book Page 2 Wednesday, December 22, 2004 12:32 PM
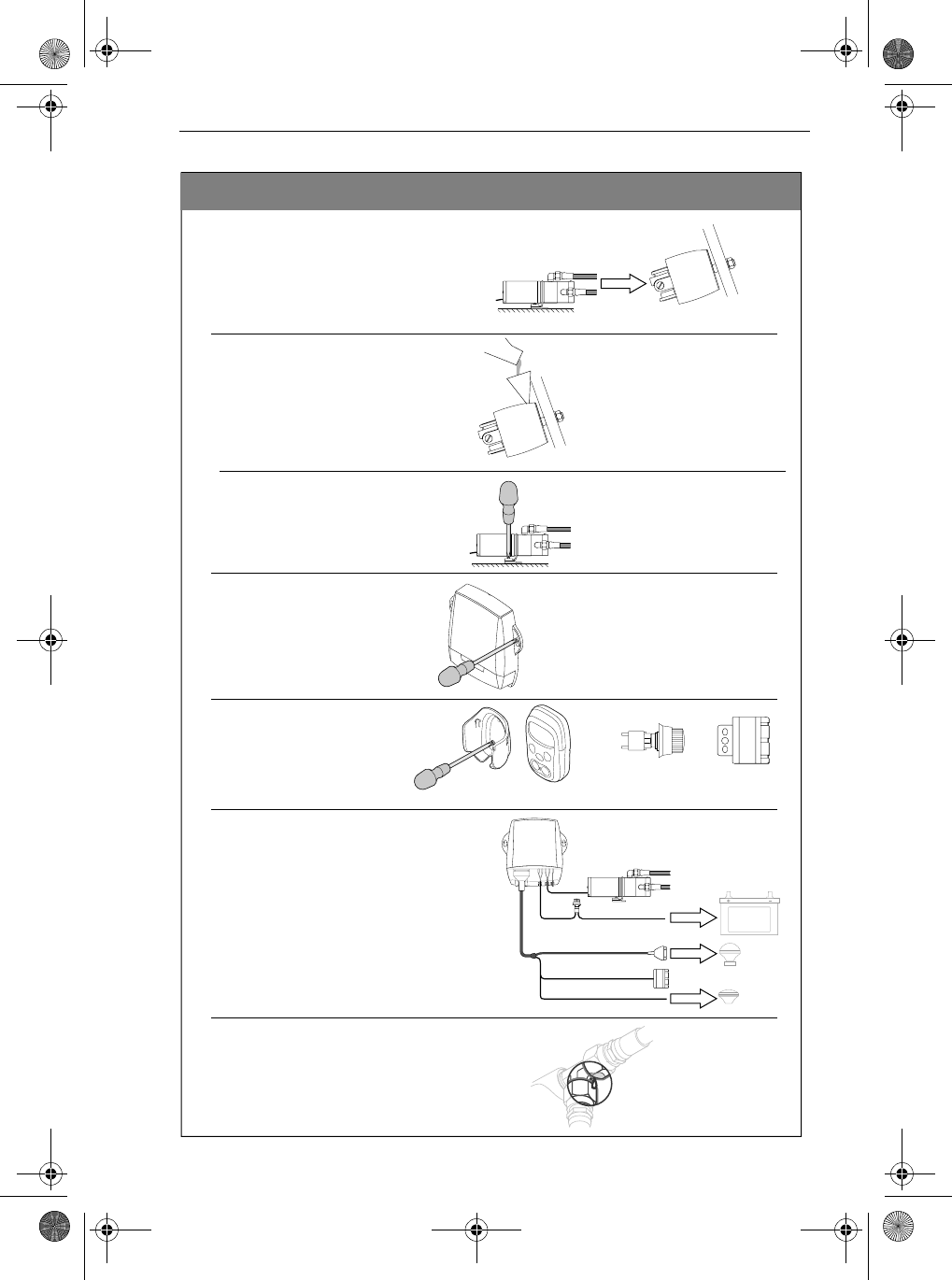
S1000 Autopilot Installation Guide 1
Connect the autopilot pump
to your existing steering system.
Bleed the steering system.
Secure the autopilot pump.
Fit the course computer.
1.
2.
3.
4.
Fit miscellaneous items
5.
Make electrical connections
6.
Carry out post installation checks
7.
In-line power switch Buzzer
Installation overview
D7583-1
Page 9
Page 12
Page 16
Page 17
Page 18
Page 21
Page 28
S100 Remote
87040_1.book Page 1 Wednesday, December 22, 2004 12:32 PM
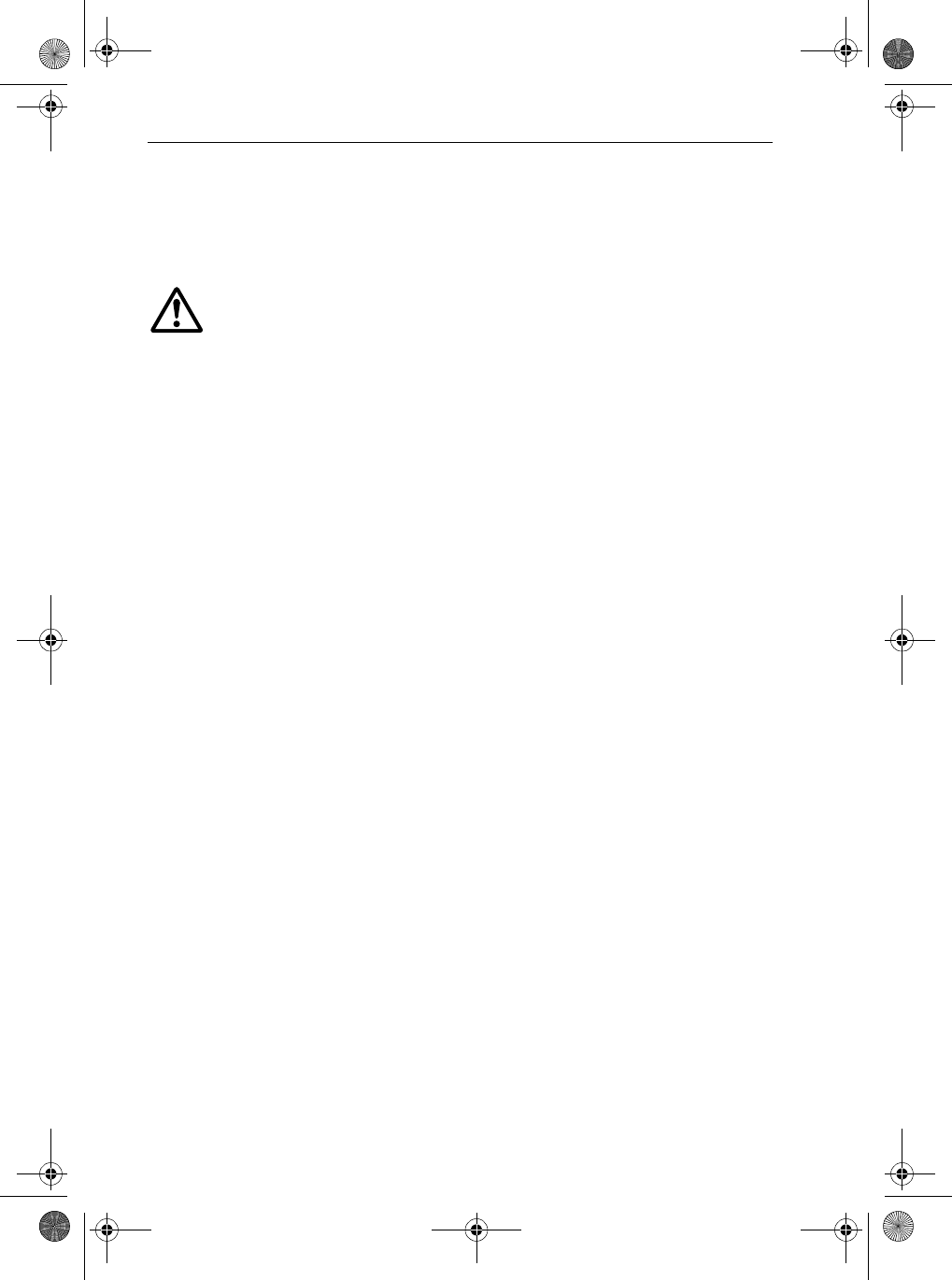
2 S1000 Autopilot Installation Guide
This guide
Before starting to install your S1000 Autopilot, please take time to read this guide. In particu-
lar, please take note of the safety and electromagnetic compatibility (EMC) information at the
end of this guide.
WARNING:
This product must be installed and operated in accordance with the
Raymarine instructions provided. Failure to observe this could
result in personal injury, damage to the boat and/or poor product
performance.
The installation procedures are described in a rational sequence, but because of variations in
boat design, space available etc, you may need to adapt the sequence to suit your particular
circumstances.
Before you start fitting your S1000 Autopilot, we recommend you:
•Unpack your S1000 Autopilot and check that all parts are present.
•Plan your S1000 Autopilot installation so that you fit the components in the best possible
locations.
Important note
The S1000 Autopilot must receive position information from a suitable GPS in
order to function correctly. GPS systems compatible with SeaTalk or NMEA or
both, are suitable. If you need advice as to which GPS to use, please contact
your Raymarine dealer.
87040_1.book Page 2 Wednesday, December 22, 2004 12:32 PM
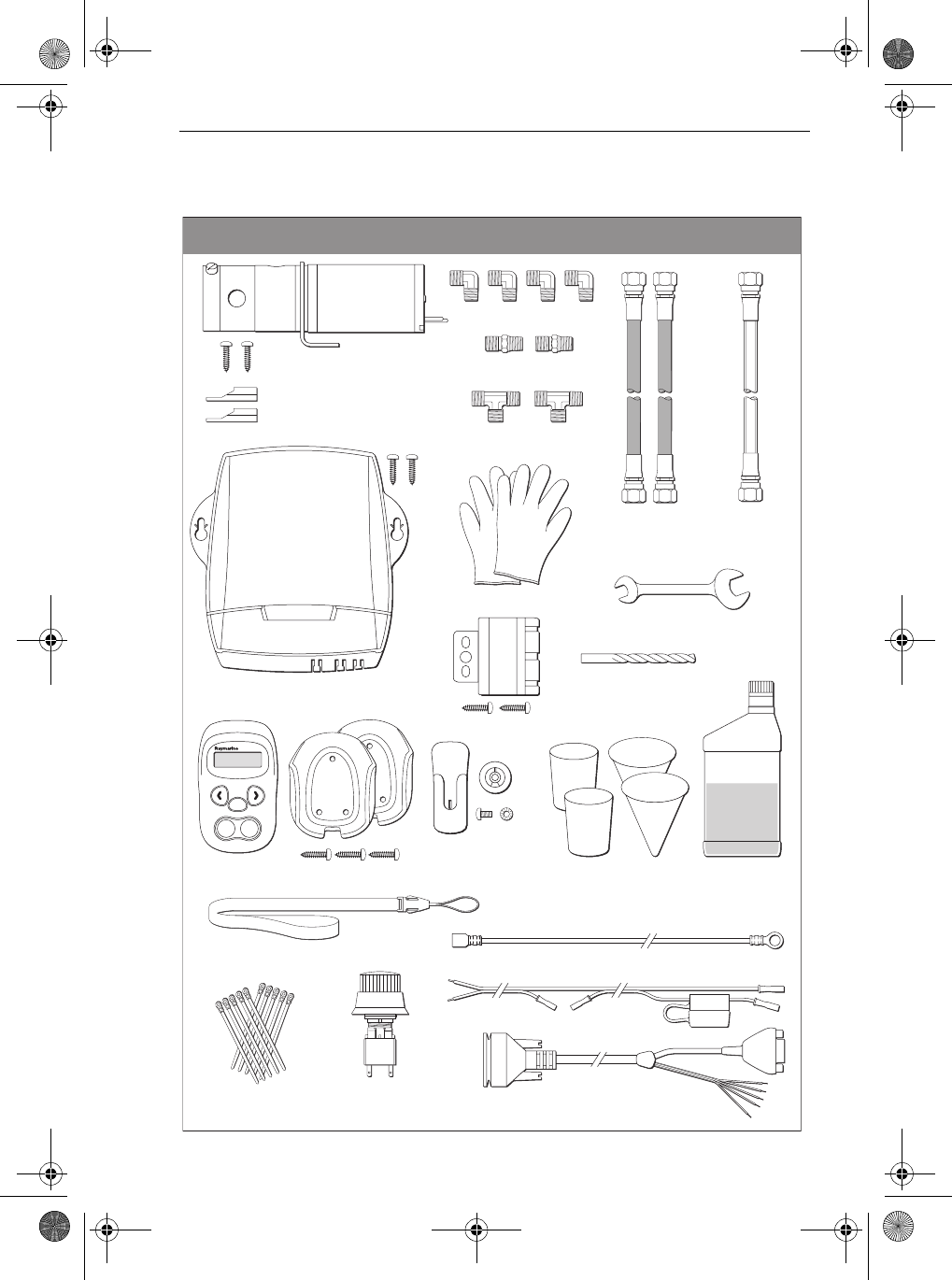
S1000 Autopilot Installation Guide 3
What you need
Elbow fitting, x 4
'T' fitting x 2
High pressure
steering hoses
(x 2)
Low pressure
transparent
bleeding hose
Straight fitting x 2
Nitrile gloves
Autopilot Pump
Anti-vibration mounts x 2
Course Computer
Wrench 12 mm AF x 19 mm AF
In-line power
switch
Drill 3.4 mm
Cable Tie x 10
D7330-1
S100 Remote & 2 x cradles 1 pint (0.5 liter)
hydraulic fluid
Belt clip assembly
Fill cups
Buzzer
Parts supplied
S100 REMOTE
MODE
STANDBY PILOT
Ground lead
Data cable
Power cable
Drain cups
Lanyard
87040_1.book Page 3 Wednesday, December 22, 2004 12:32 PM
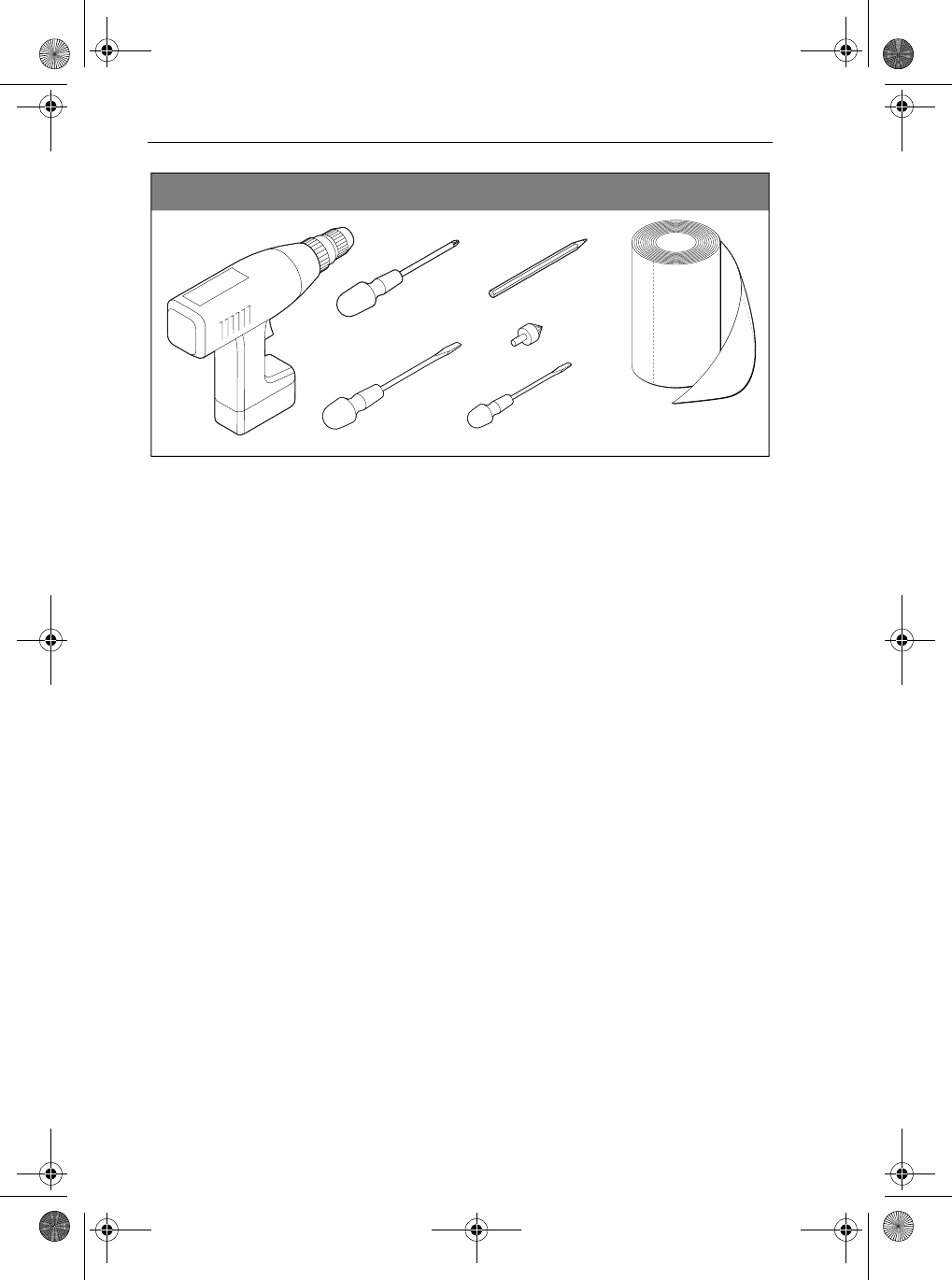
4 S1000 Autopilot Installation Guide
D7331-1
Tools & materials required
Screwdriver,
No. 2 Pozidriv
Screwdriver,
medium,
flat blade
Screwdriver,
small,
flat blade
Countersink
bit
Pencil
Drill
Absorbent,
disposable wipes
87040_1.book Page 4 Wednesday, December 22, 2004 12:32 PM
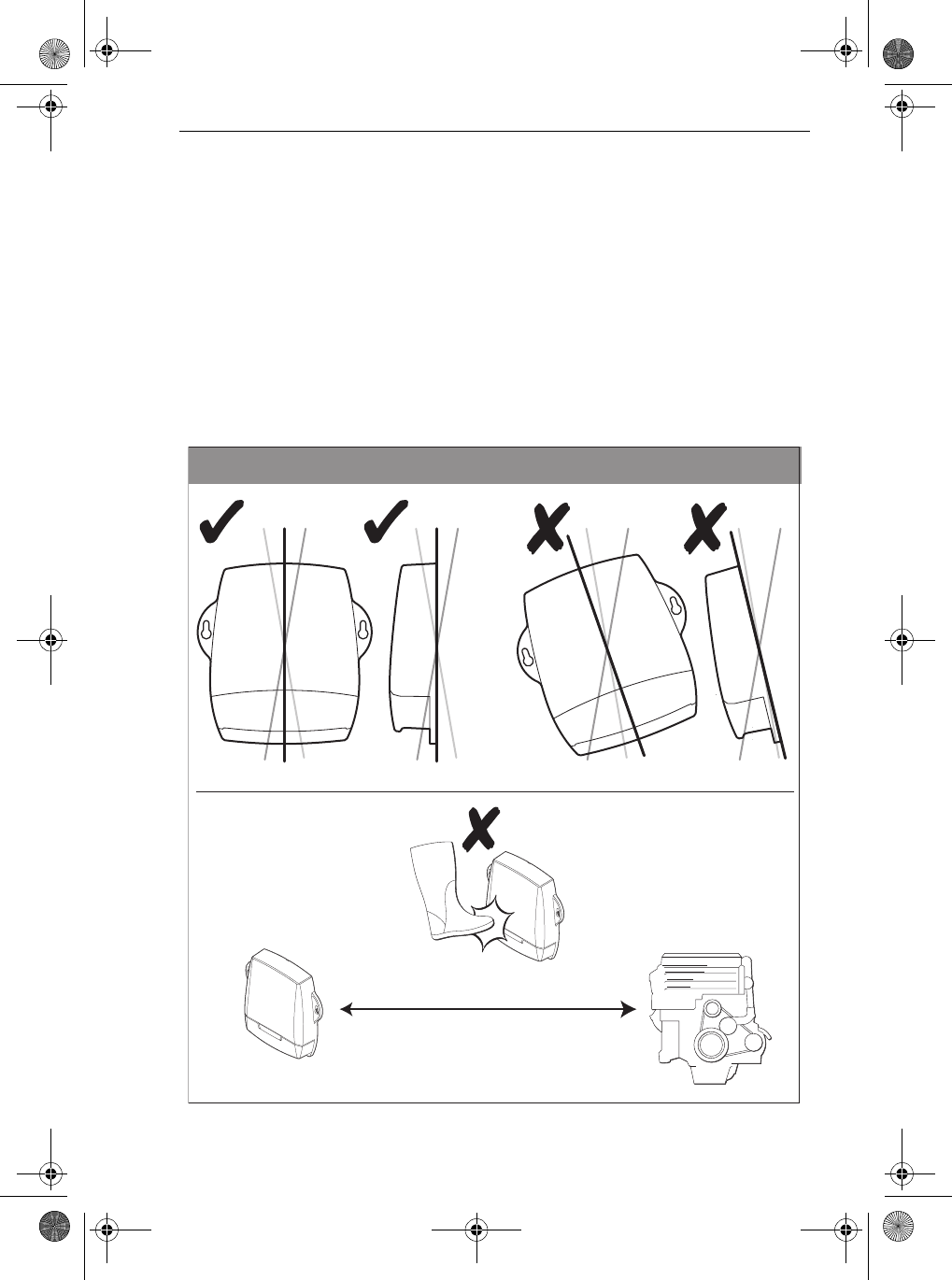
S1000 Autopilot Installation Guide 5
Planning
In order to make the installation as trouble free as possible, we strongly recommend you
spend adequate time planning the best locations for your autopilot components. This is
particularly important when considering the position of the autopilot pump, as hydraulic
hoses are supplied in fixed lengths, so there are some limitations on the positioning of the
autopilot pump with respect to the boat’s helm pump.
If you have internet access, please view the installation video on line at www.raymarine.com.
Before you disturb your hydraulic steering system, we strongly recommend that you consult
the manufacturer and read the steering system manuals.
5˚ 5˚
D7552-1
5˚ 5˚ 5˚ 5˚ 5˚ 5˚
At least 3 ft (1 meter)
Locating the course computer
87040_1.book Page 5 Wednesday, December 22, 2004 12:32 PM
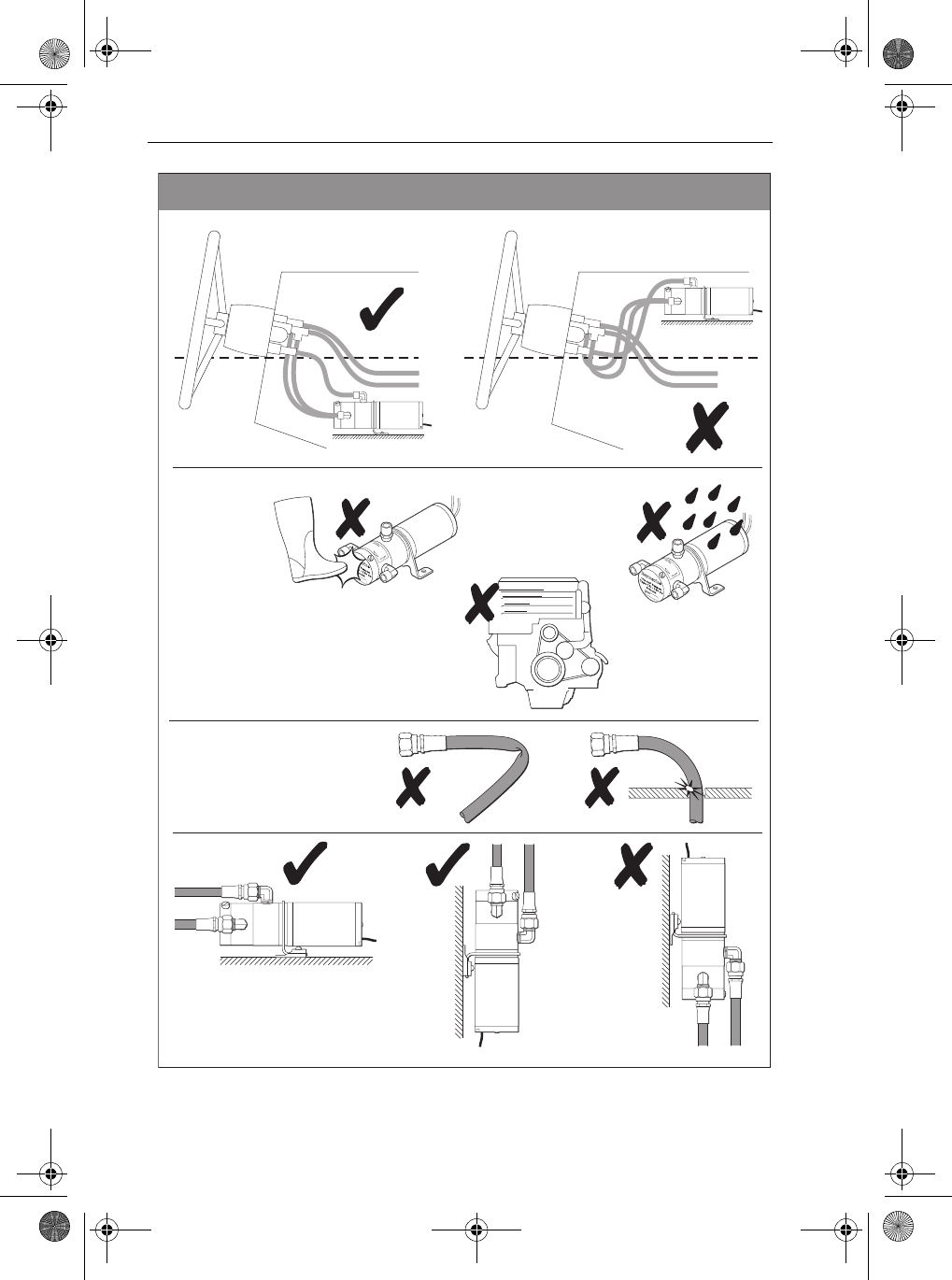
6 S1000 Autopilot Installation Guide
R
e
s
e
v
i
r
r
o
B
l
e
e
w
S
c
r
e
d
Port
Port
R
e
s
e
v
i
r
r
o
B
l
e
e
w
S
c
r
e
d
Port
Port
D7350-1
Autopilot pump to be lower
than helm pump
No sharp bends, kinks or
chafing of tube
Locating autopilot pump
Provide protection
from physical
damage.
Mount pump location either
horizontally or with connector end up.
Do not mount pump with connector
end down.
Install in a dry location.
Do not fit in engine compartments, near
fuel tanks or in any other area where fuel
vapor is likely.
87040_1.book Page 6 Wednesday, December 22, 2004 12:32 PM
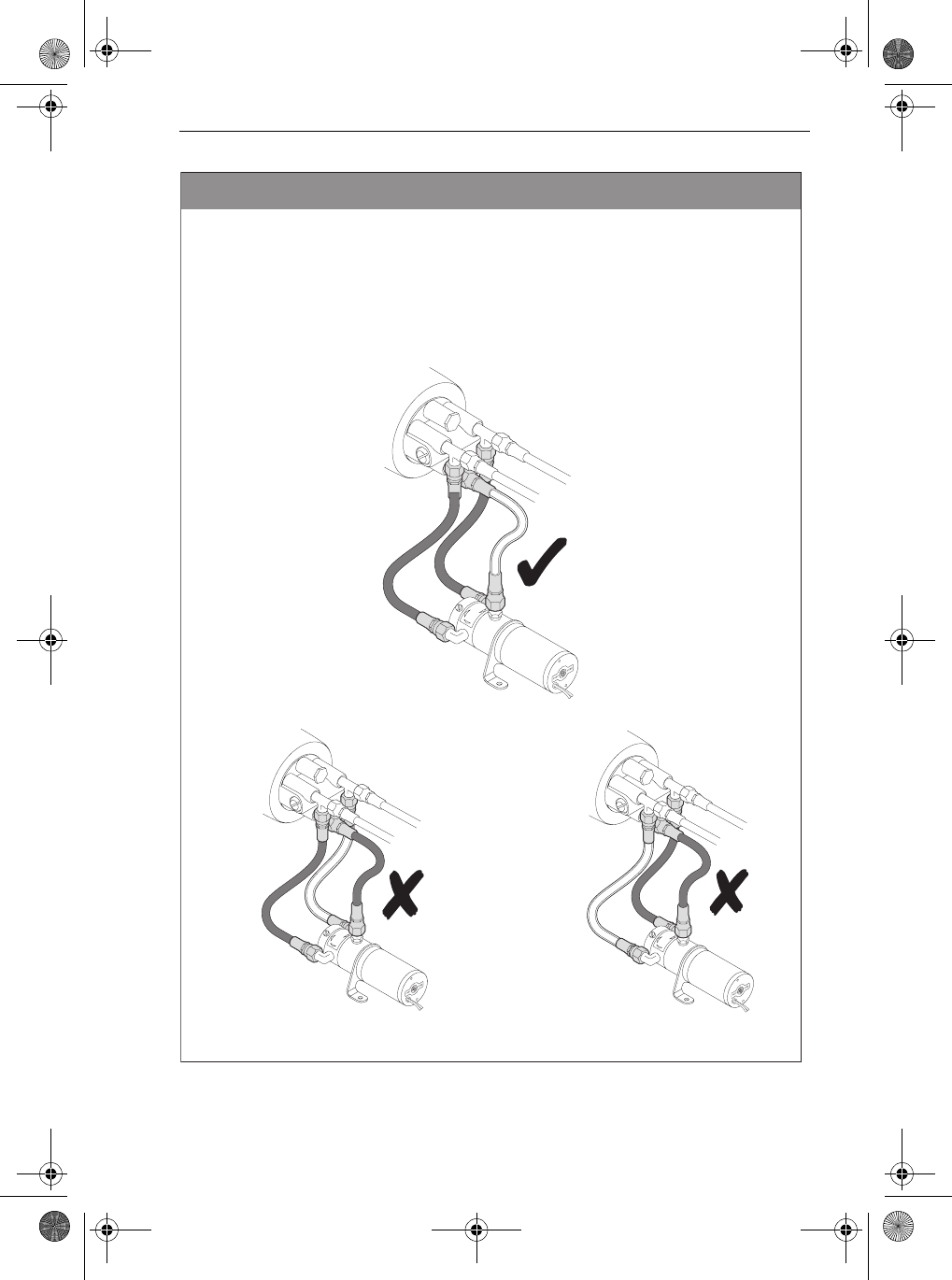
S1000 Autopilot Installation Guide 7
Port
Port
B
r
e
c
S
d
e
e
l
r
i
o
v
r
e
e
s
R
w
Using the hydraulic hoses
D7553-1
Three, pre-assembled hydraulic hoses are supplied. Two of these are dark-colored, high
pressure steering hoses and the third is a transparent low-pressure hose.
The transparent hose is intended to help you check for air bubbles when bleeding the
system and must be used only to connect the autopilot pump reservoir to the lower
connector on the helm pump. It must NOT be used anywhere else in the system.
Port
Port
B
r
e
c
S
d
e
e
l
r
i
o
v
r
e
e
s
R
w
Port
Port
B
r
e
c
S
d
e
e
l
r
i
o
v
r
e
e
s
R
w
87040_1.book Page 7 Wednesday, December 22, 2004 12:32 PM
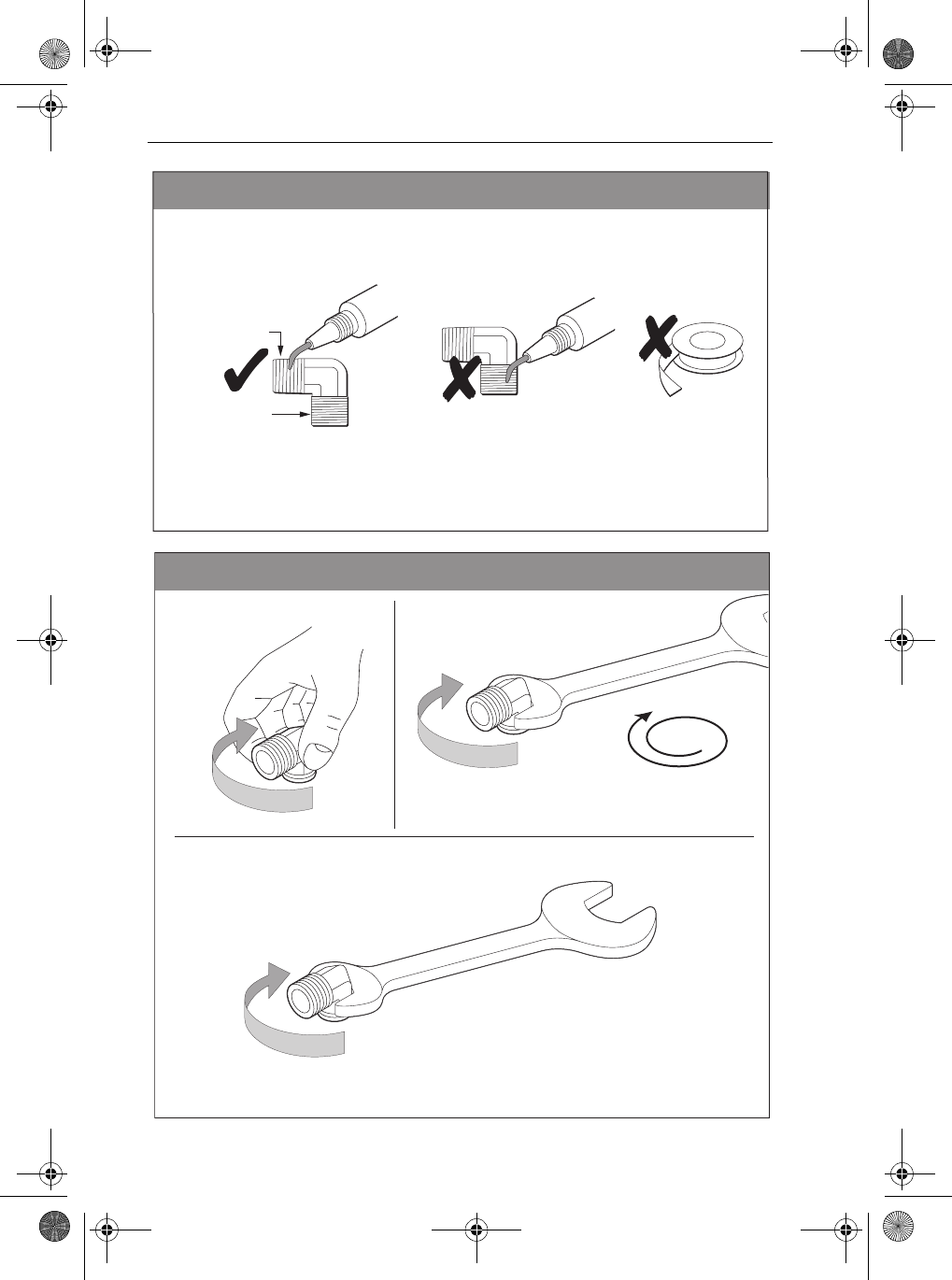
8 S1000 Autopilot Installation Guide
Tapered thread
Thread for hose
connection
Sealing hydraulic joints
Do not apply sealant to
hose connection thread
Note: The hydraulic fittings supplied with the autopilot pump have sealant pre-
applied to the tapered threads. You only need you to apply sealant to any extra
joints you may obtain. The recommended sealant for doing this, is Loctite 542.
Do not use sealing tape on any part of a hydraulic system, as this can disintegrate
and the resulting particles can cause blockages in the hydraulic system.
CAUTION:
D7545-1
2.
3.
1.5 turns
D7546-1
From hand tight, use a wrench to tighten the joint a
further 1.5 turns. This should make it leakproof.
To change the orientation of the joint to align it with the
hose, further tighten the joint, to a maximum of one
further turn, until the joint is facing the required
direction.
1.
Hand tighten
CAUTION:
Do not exceed 13 ft/lbs
(17.6 Nm) torque.
CAUTION:
Do not exceed 13 ft/lbs (17.6 Nm) torque. DO NOT
EXCEED 2.5 TURNS in total, from hand tight.
Installing tapered thread fittings
87040_1.book Page 8 Wednesday, December 22, 2004 12:32 PM
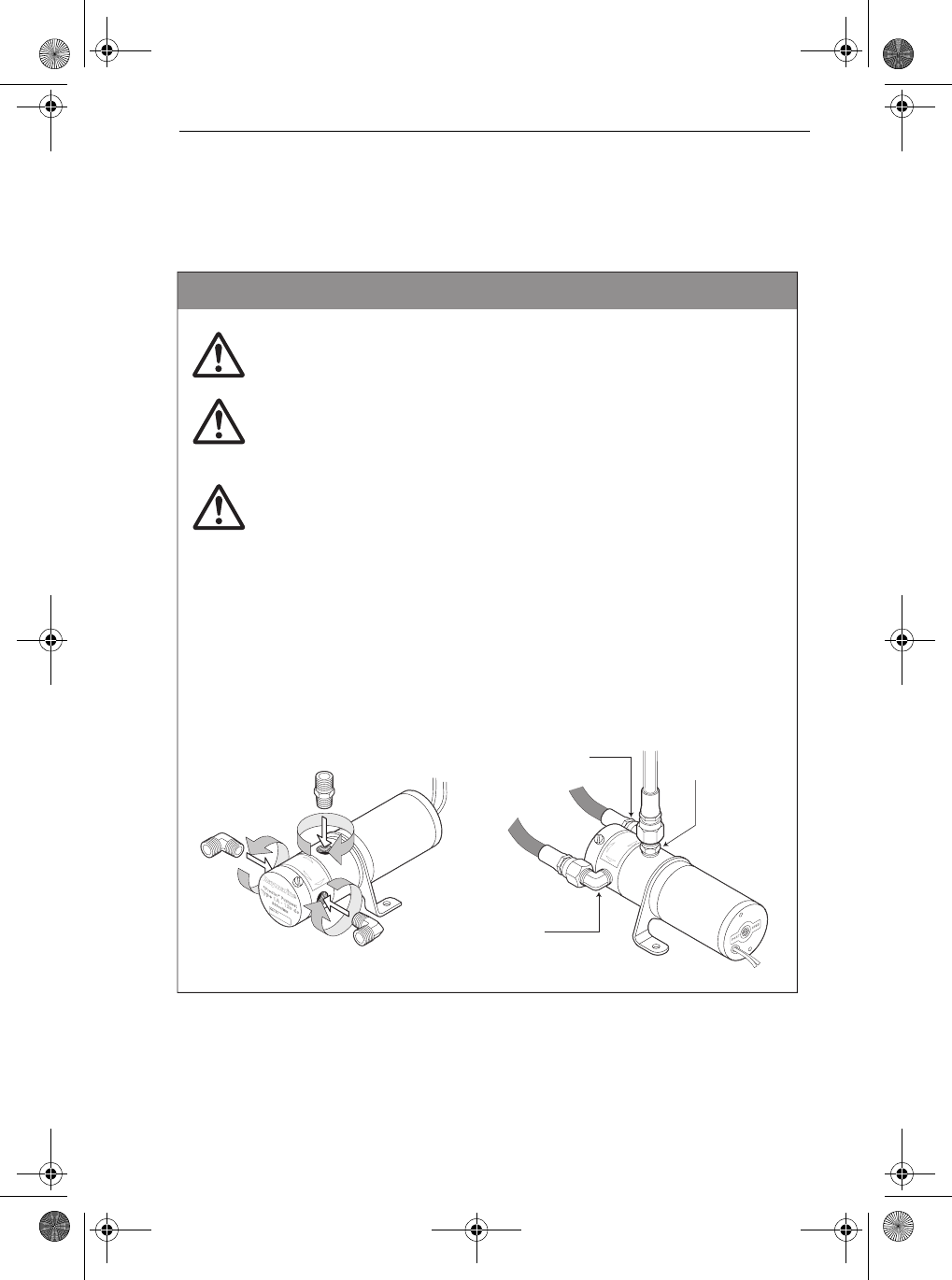
S1000 Autopilot Installation Guide 9
Installation procedures
1. Connecting the autopilot pump
O
Port
Port
B
r
e
c
S
d
e
e
l
r
i
o
v
r
e
e
s
R
w
R
e
s
e
v
i
r
r
o
B
l
e
e
w
S
c
r
e
d
Port
Port
1. 2.
Secure the required hydraulic joints
(elbow or straight) into the autopilot
pump, as described under Fitting
hydraulic joints.
CAUTION:
Do not use the transparent hose for connecting any part of the steering
system other than between the autopilot pump reservoir and the lower
connector on the helm pump.
Connect hydraulic hoses to autopilot
pump. Ensure the transparent hose is
connected to the reservoir connector.
WARNING:
Do not allow hydraulic fluid to come into contact with your skin. Wear the
protective nitrile gloves provided when working with hydraulic fluid.
WARNING:
A sudden release of pressure from a hydraulic system could result in personal
injury. Before disconnecting any part of a hydraulic steering system, safely
release any pressure in accordance with the manufacturer’s instructions.
WARNING:
The autopilot pump is not suitable for use in the vicinity of engines, fuel
tanks or in any other area where fuel vapor is likely to be present.
Connecting the autopilot pump, sheet 1
D7345-1
Port
connector
Starboard
connector
Reservoir
connector
87040_1.book Page 9 Wednesday, December 22, 2004 12:32 PM

10 S1000 Autopilot Installation Guide
0
D7483-1
5.
Remove & retain the plug from the
helm pump lower port and drain the
fluid into one of the cups provided.
Discard the drained fluid in
accordance with local regulations.
6.
Label the port ram hose to aid future
reassembly, then disconnect both ram
hoses & straight connectors from the
helm pump.
Remove & retain the helm pump
breather cap.
4.
Set steering to dead ahead
and do not move it until
instructed.
3.
7.
Using the
Fitting hydraulic joints
procedure, fit 'T'
connectors to the helm pump port (P) and
starboard (S) connectors, and a straight connector
to the helm pump lower connector.
Connecting the autopilot pump, sheet 2
D7483-1
5.
Remove & retain the plug from the
helm pump lower port and drain the
fluid into one of the cups provided.
Discard the drained fluid in
accordance with local regulations.
6.
Label the port ram hose to aid future
reassembly, then disconnect both ram
hoses & straight connectors from the
helm pump.
Remove & retain the helm pump
breather cap.
4.
Set steering to dead ahead
and do not move it until
instructed.
3.
7.
Using the
Fitting hydraulic joints
procedure, fit 'T'
connectors to the helm pump port (P) and
starboard (S) connectors, and a straight connector
to the helm pump lower connector.
Connecting the autopilot pump, sheet 2
87040_1.book Page 10 Wednesday, December 22, 2004 12:32 PM
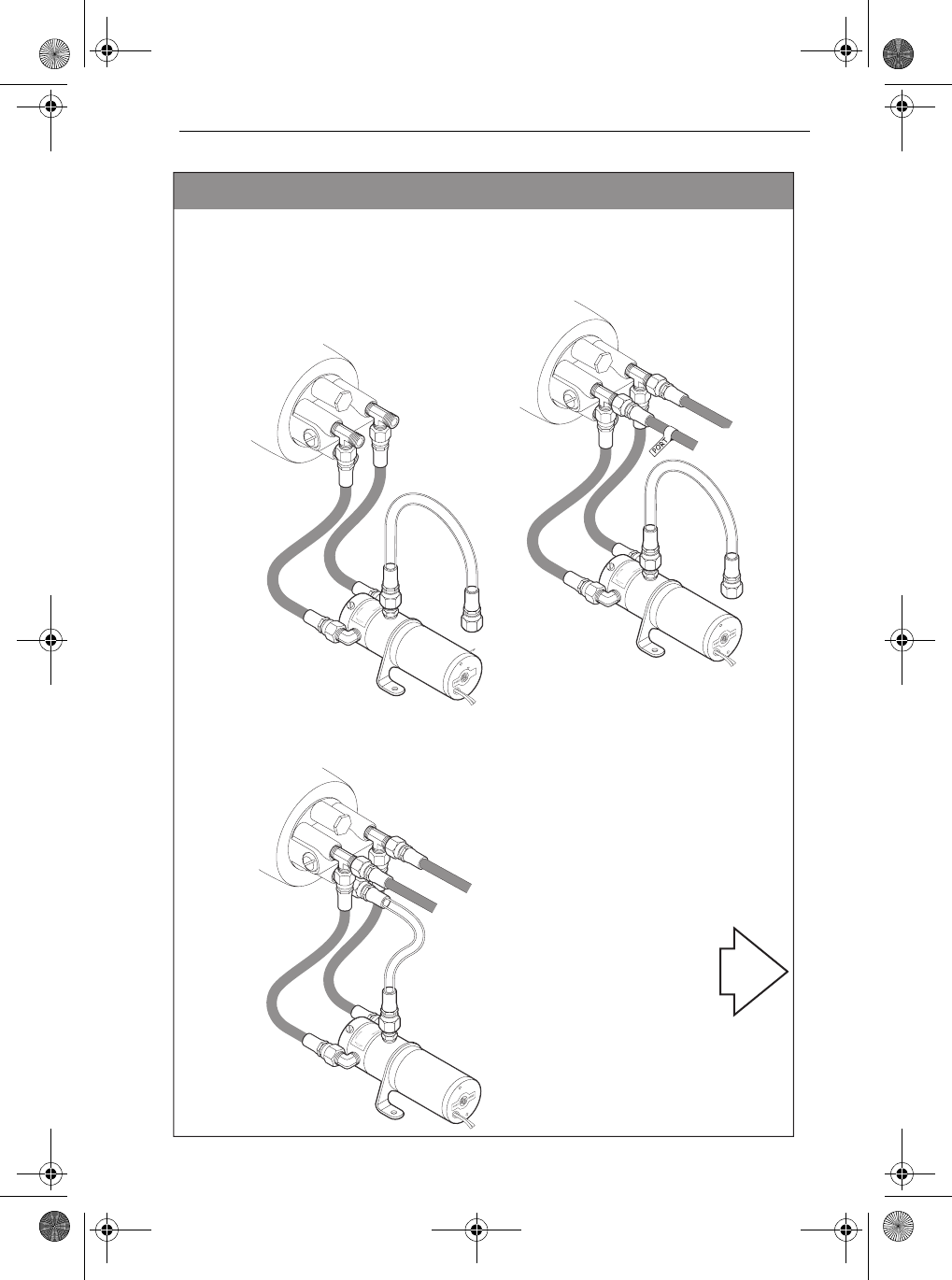
S1000 Autopilot Installation Guide 11
Port
Port
B
r
e
c
S
d
e
e
l
r
i
o
v
r
e
e
s
R
w
Port
Port
B
r
e
c
S
d
e
e
l
r
i
o
v
r
e
e
s
R
w
9. Re-connect the ram hoses to the
appropriate helm pump 'T' connectors.
10. Connect the transparent hose from autopilot pump reservoir hose to the
straight connector at the helm pump lower connector.
This completes the connection
of the autopilot pump.
Now bleed the steering system.
to steering
ram
Port
Port
B
r
e
c
S
d
e
e
l
r
i
o
v
r
e
e
s
R
w
D7484-1
Connecting the autopilot pump, sheet 3
8. Connect hydraulic steering hoses from
autopilot pump Port and Starboard
connectors to the Port and Starboard
connectors on the helm pump, so that
Port connects to Port, and Starboard
connects to Starboard .
87040_1.book Page 11 Wednesday, December 22, 2004 12:32 PM
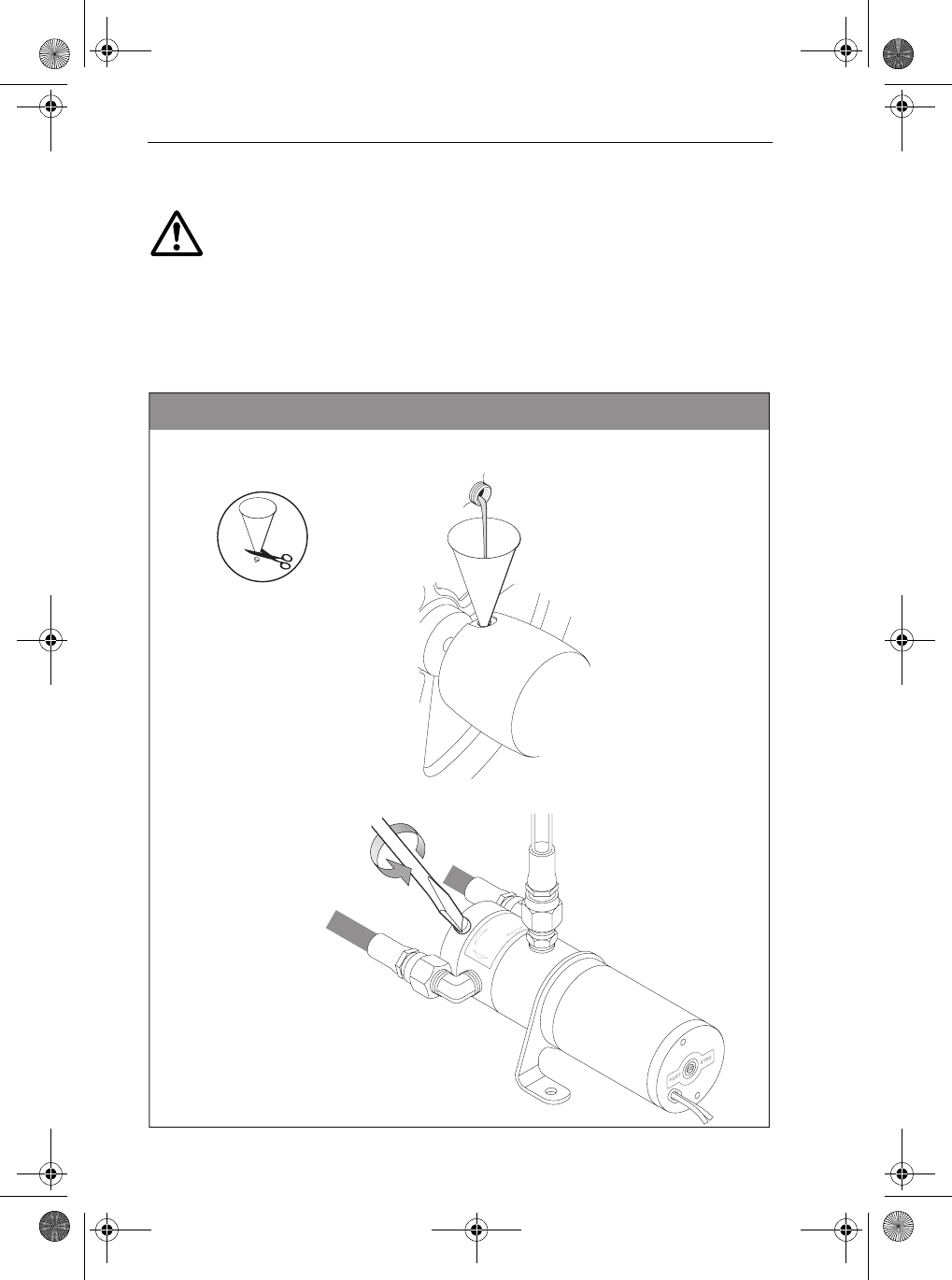
12 S1000 Autopilot Installation Guide
2. Bleeding the steering system
WARNING:
Do not allow hydraulic fluid to come into contact with your
skin. Wear the protective nitrile gloves provided when
working with hydraulic fluid.
Connecting the autopilot pump will introduce air into the steering system, making it feel
‘spongy’ and ‘lumpy’ to operate. To return the steering system to smooth operation, use the
procedure given here to bleed the air from the system.
Por t
Port
B
r
e
c
S
d
e
e
l
r
i
o
v
r
e
e
s
R
w
Bleed procedure, sheet 1
2.
Loosen autopilot pump
bleed screw 2 full turns
2.
Top up helm pump with hydraulic fluid
D7336-1
87040_1.book Page 12 Wednesday, December 22, 2004 12:32 PM
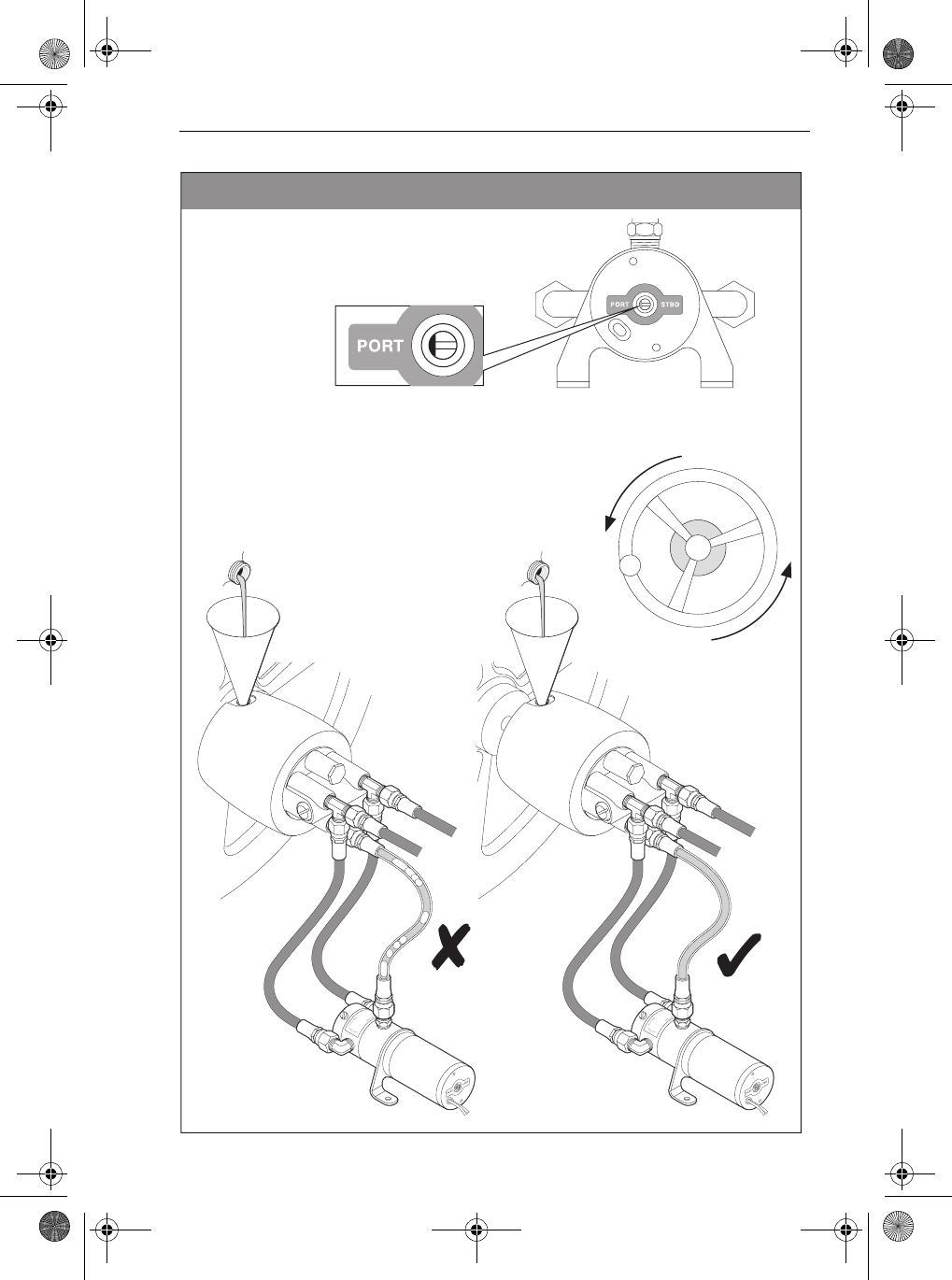
S1000 Autopilot Installation Guide 13
Port
Port
B
r
e
c
S
d
e
e
l
r
i
o
v
r
e
e
s
R
w
Port
Port
B
r
e
c
S
d
e
e
l
r
i
o
v
r
e
e
s
R
w
Bleed procedure, sheet 2
D7339-1
4. SLOWLY turn the wheel counter-clockwise and observe
the bubbles in the transparent tube. Keep the helm
pump reservoir topped up while doing this. Keep
turning the wheel counter-clockwise until there are no
more bubbles i.e. so the hydraulic fluid in the
transparent tube is clear.
3. Using a suitable screwdriver, turn the
autopilot pump shaft so that the flat on the
shaft is toward the PORT side of the pump
87040_1.book Page 13 Wednesday, December 22, 2004 12:32 PM
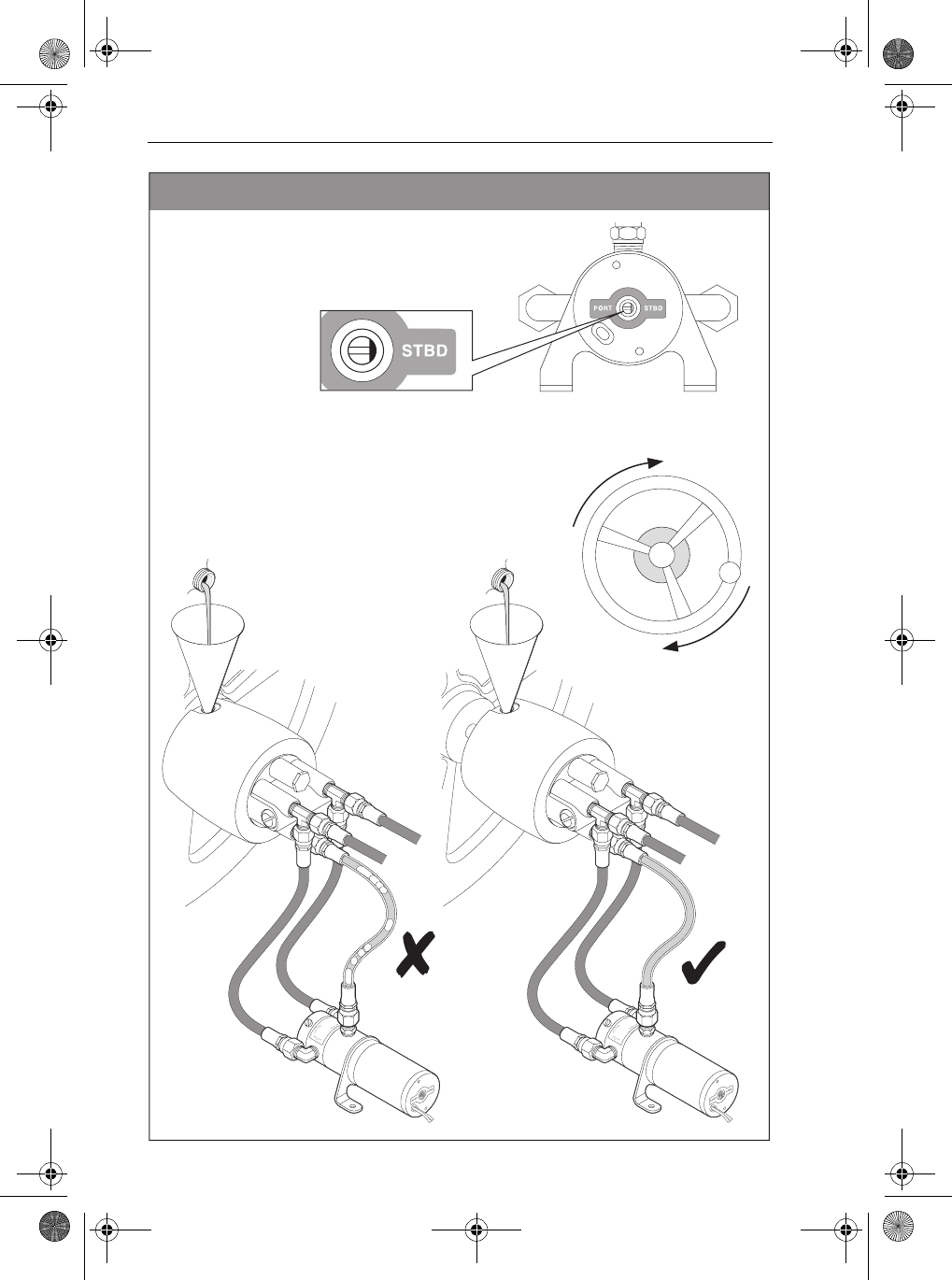
14 S1000 Autopilot Installation Guide
Port
Port
B
r
e
c
S
d
e
e
l
r
i
o
v
r
e
e
s
R
w
Port
Port
B
r
e
c
S
d
e
e
l
r
i
o
v
r
e
e
s
R
w
Bleed procedure, sheet 3
6. SLOWLY turn the wheel clockwise and observe the bubbles
in the transparent tube. Keep the helm pump reservoir
topped up while doing this. Keep turning the wheel
counter-clockwise until there are no more bubbles i.e. so
the hydraulic fluid in the transparent tube is clear.
D7337-1
5. Using a suitable screwdriver, turn the autopilot
pump shaft so that the flat on the shaft is toward
the starboard (STBD) side of the pump
87040_1.book Page 14 Wednesday, December 22, 2004 12:32 PM
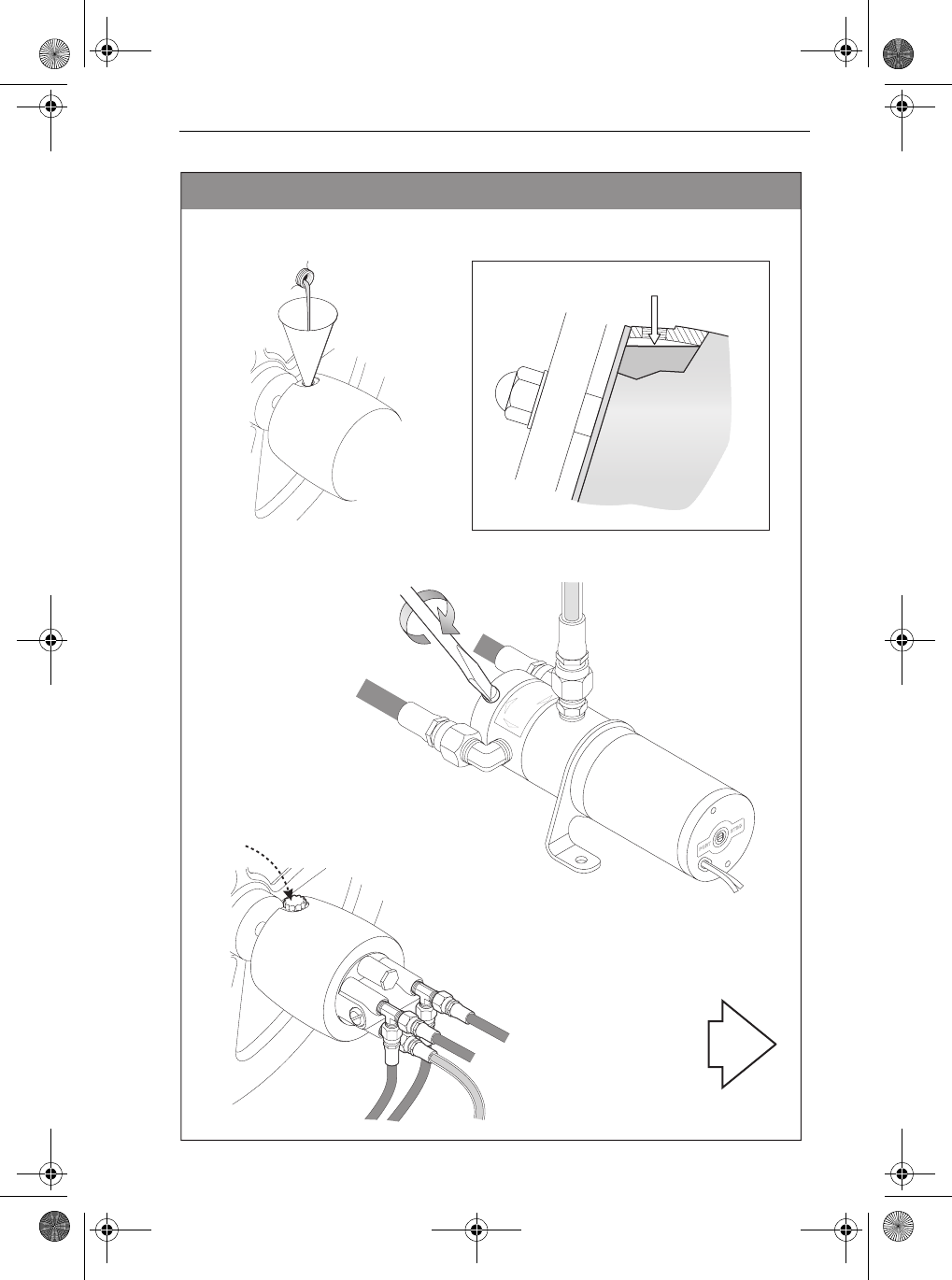
S1000 Autopilot Installation Guide 15
Por t
Port
B
r
e
c
S
d
e
e
l
r
i
o
v
r
e
e
s
R
w
Bleed procedure, sheet 4
8. Turn the autopilot pump bleed screw, fully clockwise, and hand-tighten it.
7. Top up the hydraulic fluid.
9. Replace the helm pump breather cap.
D7486-1
This completes the
bleed procedure.
Now secure the pump.
Correct fluid level
Helm pump
87040_1.book Page 15 Wednesday, December 22, 2004 12:32 PM
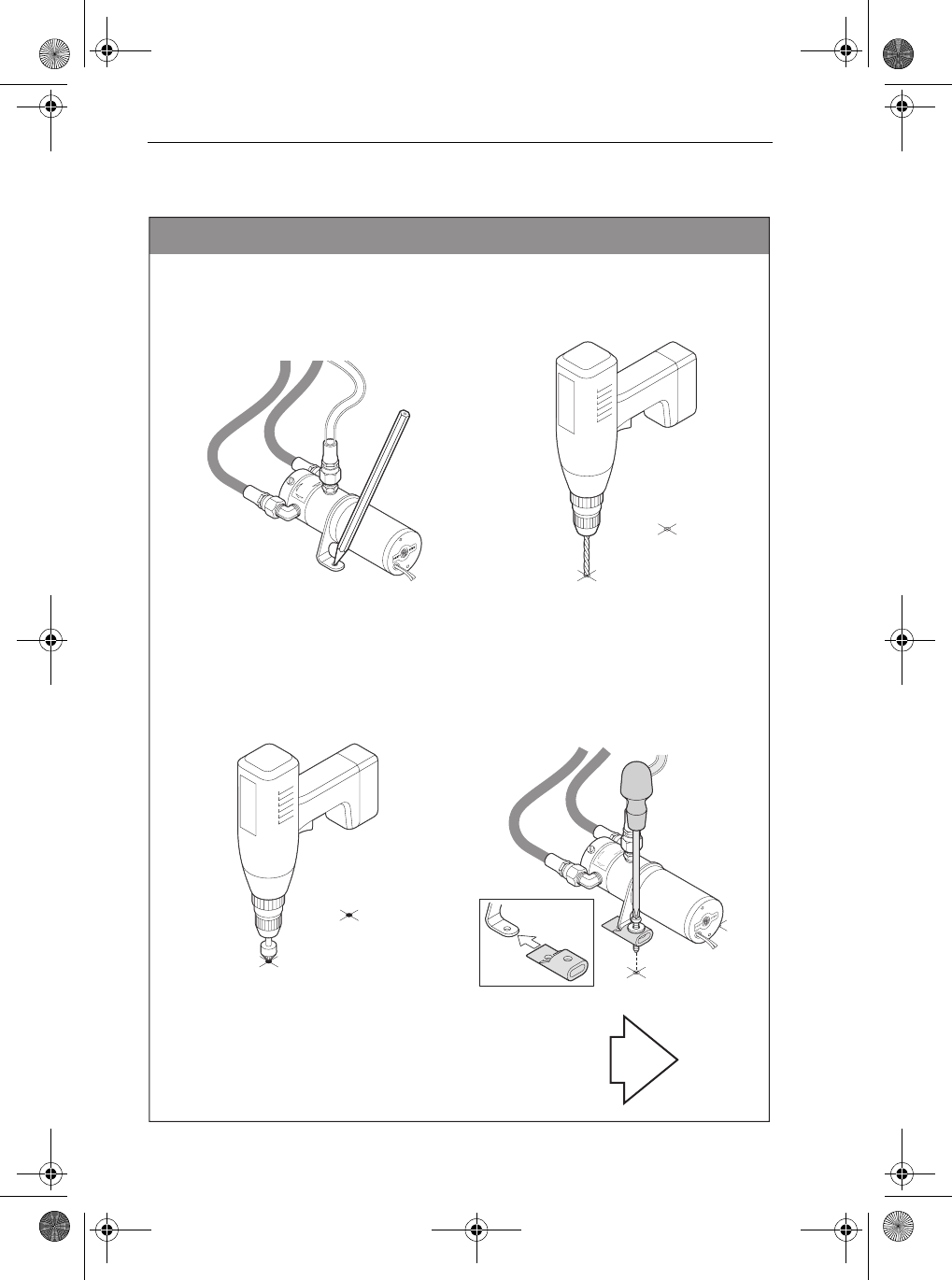
16 S1000 Autopilot Installation Guide
3. Securing the pump
3. 4.
D7488-1
Slide the anti-vibration mounts onto
the pump bracket feet, then secure
the pump with the screws provided.
Countersink pilot holes to prevent
damage to the mounting surface.
The autopilot pump should now be secure.
Now fit the course computer.
Port
Port
B
r
e
c
S
d
e
e
l
r
i
o
v
r
e
e
s
R
w
Securing the pump
1. 2.
Drill two 1/8" (3.4 mm) pilot holes
for the fixing screws
Place the pump at the intended
location and mark holes for the
fixing screws.
Port
Port
B
r
e
c
S
d
e
e
l
r
i
o
v
r
e
e
s
R
w
87040_1.book Page 16 Wednesday, December 22, 2004 12:32 PM
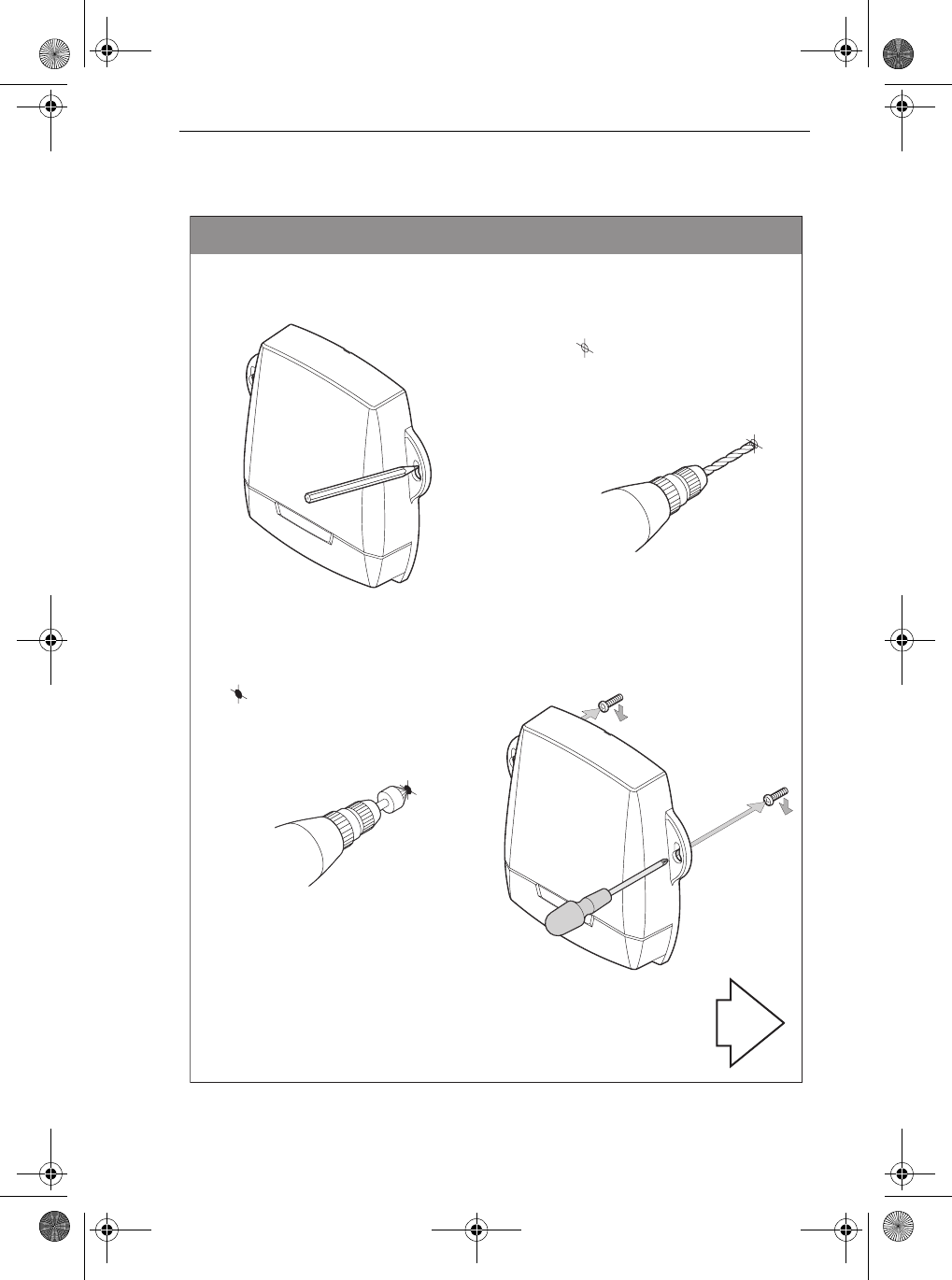
S1000 Autopilot Installation Guide 17
4. Fitting the course computer
D7338-1
Securing course computer
1. 2.
4.
3.
Mark holes for fixing screws. Drill two 1/82" (3.4 mm) pilot holes
for fixing screws
Partially screw in the screws provided,
then slot the course computer onto the
screws, and tighten screws.
Countersink pilot holes to prevent
damage to the mounting surface.
The course computer is now secure.
87040_1.book Page 17 Wednesday, December 22, 2004 12:32 PM
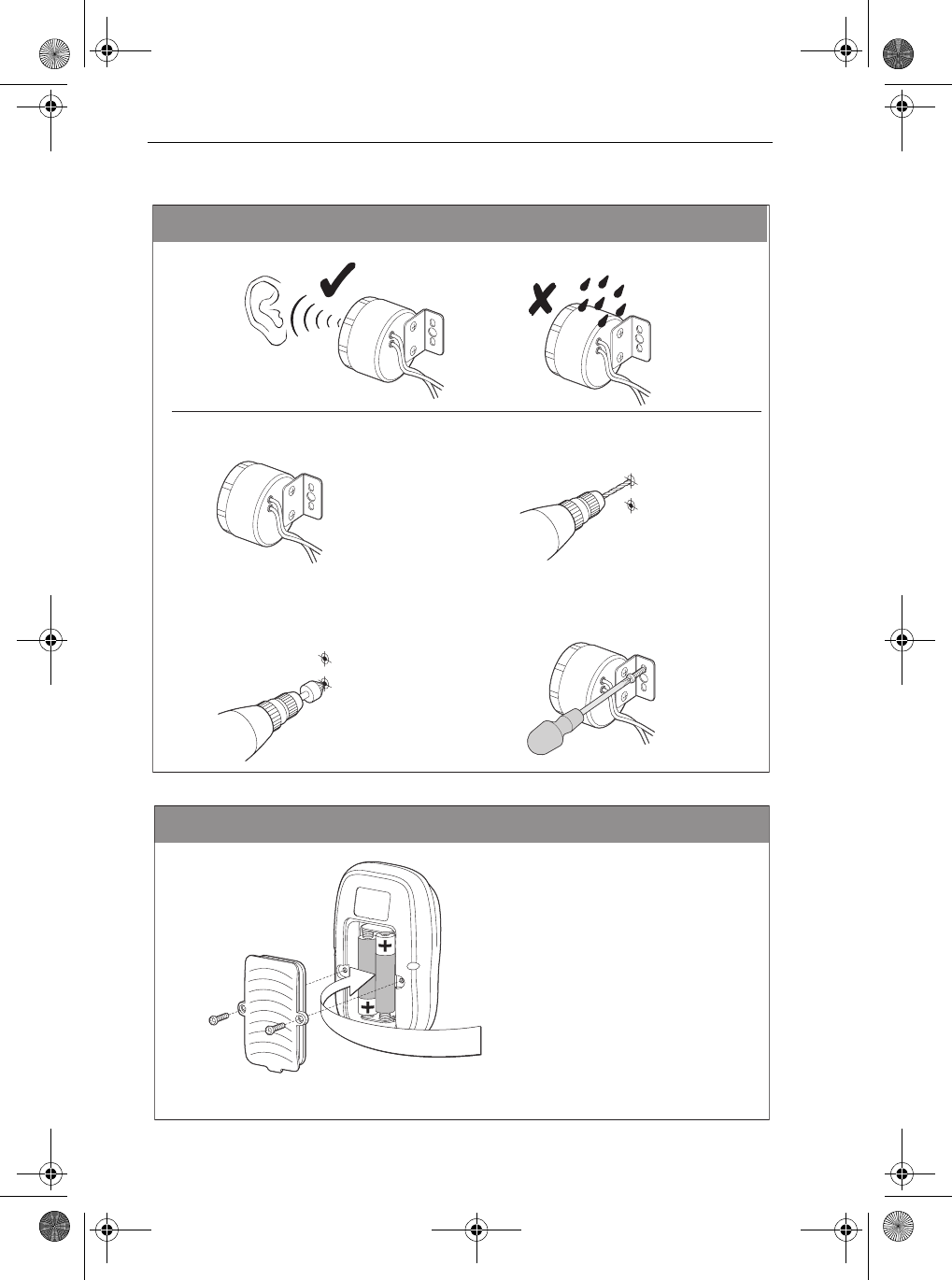
18 S1000 Autopilot Installation Guide
5. Fitting miscellaneous items
D7607-1
Buzzer
1. 2.
4.
3.
Mark holes for fixing screws. Drill two (3.4 mm) pilot holes.
18
/
"
Secure the buzzer with the screws
provided.
Countersink pilot holes to prevent
damage to the mounting surface.
Locating
Securing
D7504-2
Fitting batteries in S100 Remote
2 x AAA batteries (supplied).
When replacing, use only high-quality
alkaline, AAA size batteries.
87040_1.book Page 18 Wednesday, December 22, 2004 12:32 PM
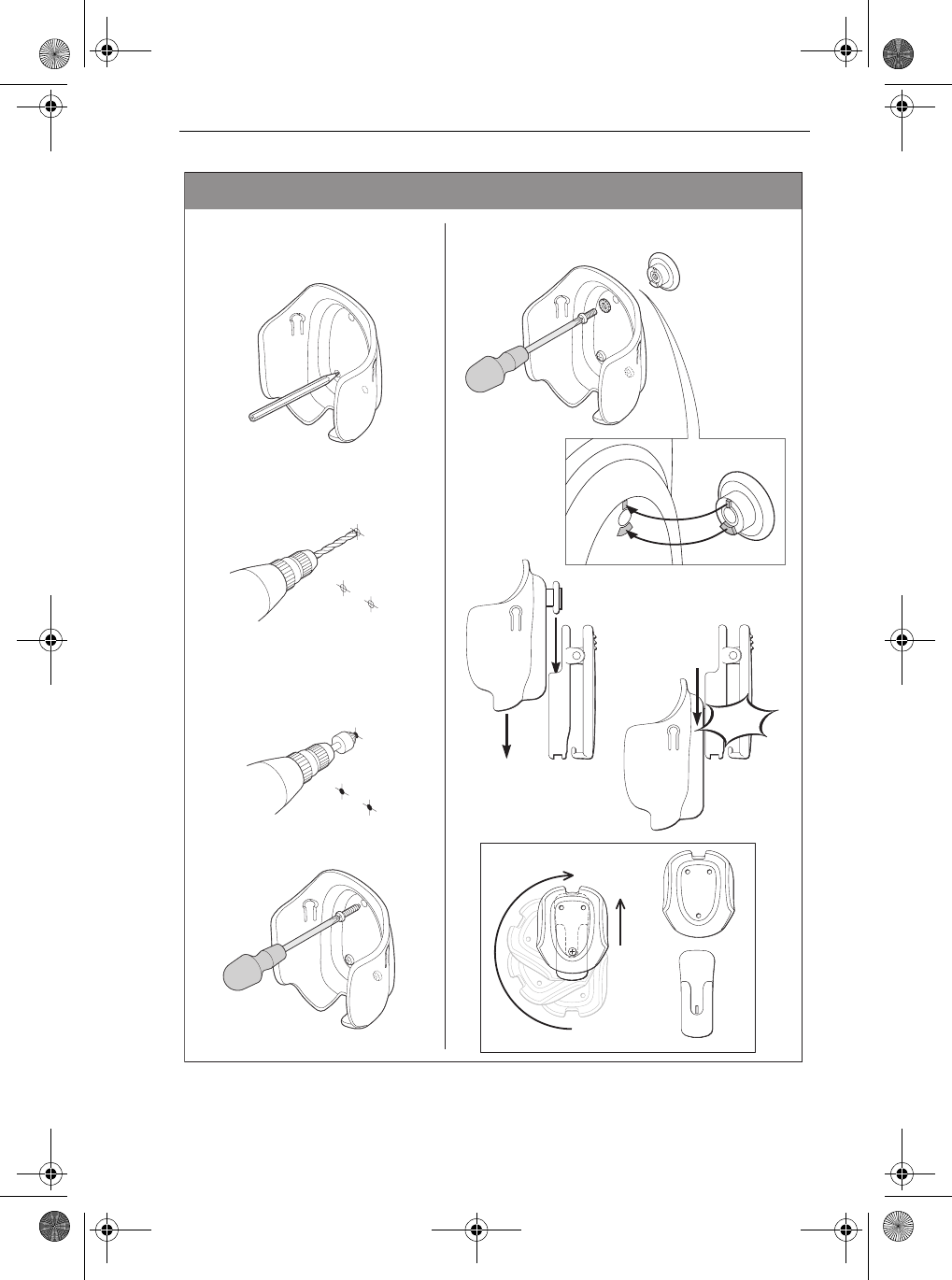
S1000 Autopilot Installation Guide 19
1.
3.
2.
1.
2.
D7683-1
3.
4.
Mark holes for the fixing screws.
Drill three (3.4 mm) pilot holes for
the fixing screws
Fitting S100 Remote cradle
Secure the cradle.
At fixed position On belt clip
18
/
"
Countersink the pilot holes to prevent
damage to the mounting surface.
To separate cradle from clip
C
l
i
c
k
87040_1.book Page 19 Wednesday, December 22, 2004 12:32 PM
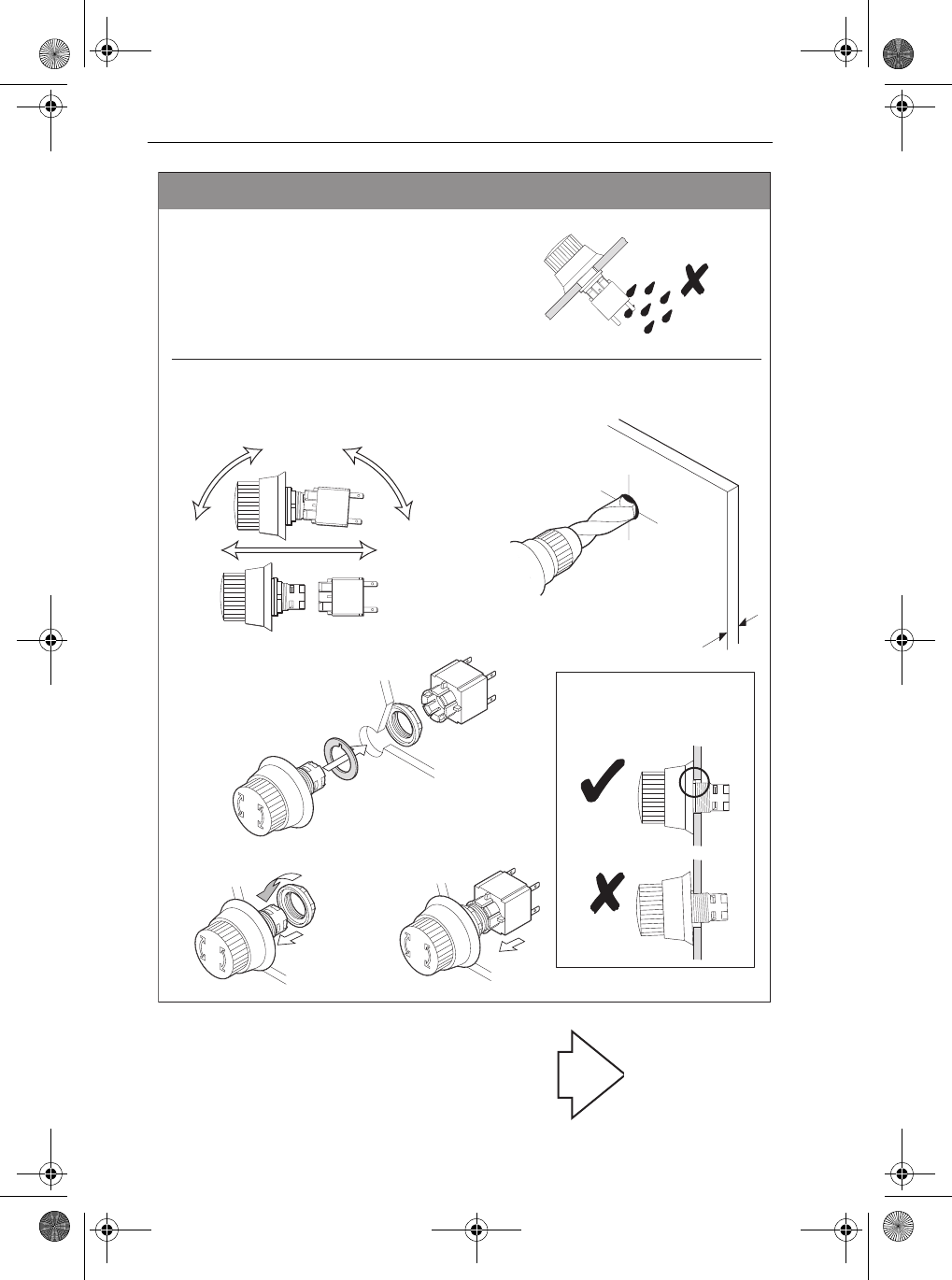
20 S1000 Autopilot Installation Guide
[
In-line power switch
D7591-1
inch (5 mm)
maximum
Ensure the protrusion on the
switch barrel goes fully into
the mounting hole.
1. 2.
3.
4. 5.
Cut inch (18 mm)
1116
/
15
/
Locating
Securing
Fit the in-line power switch in an
easily-accessible location.
When all items have been fitted,
connect up the system electrics.
87040_1.book Page 20 Wednesday, December 22, 2004 12:32 PM
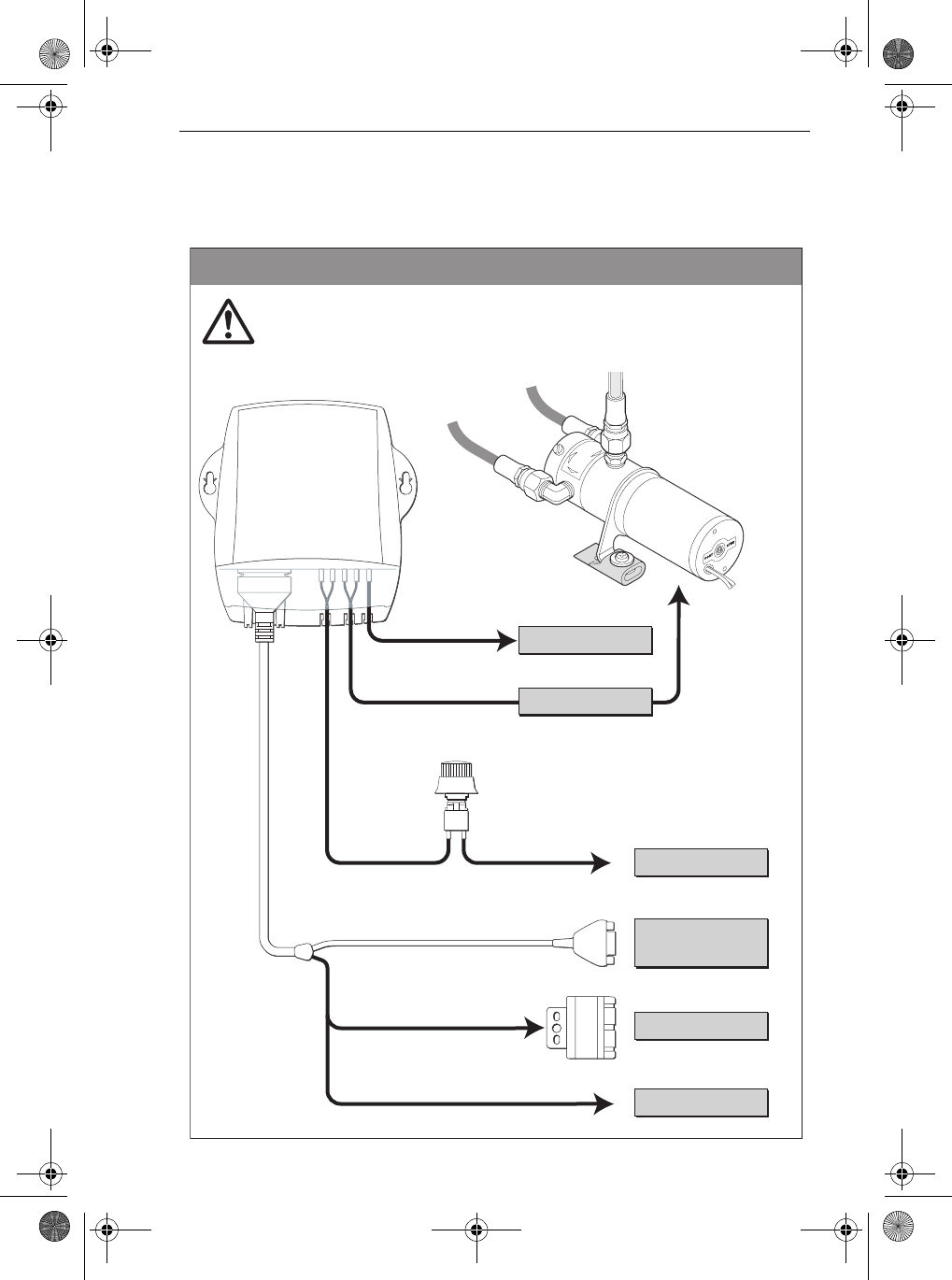
S1000 Autopilot Installation Guide 21
6. Electrical connections
Overview
SeaTalk
See Diagram A
D7522-1
RF ground
Buzzer
NMEA Spur
Course Computer
Autopilot
Pump
Data
cable
See Diagram B
See Diagram B
See Diagram C
& Diagram D
See Diagram C
See Diagram C
Summary
WARNING:
Before making electrical connections to any part of the S1000 system,
ensure the power source for the system is switched off.
In-line power switch
Port
Port
B
r
e
c
S
d
e
e
l
r
i
o
v
r
e
e
s
R
w
87040_1.book Page 21 Wednesday, December 22, 2004 12:32 PM
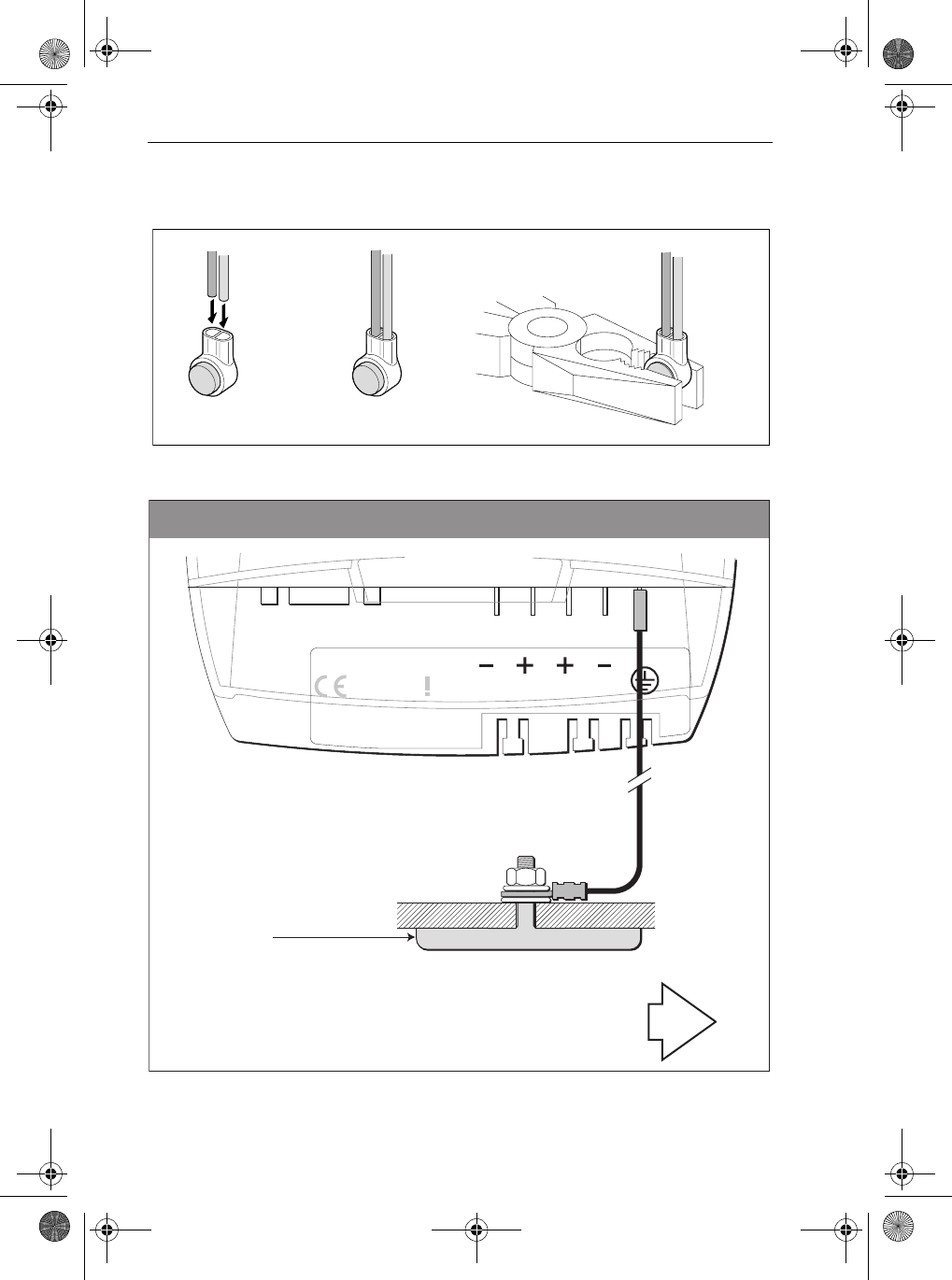
22 S1000 Autopilot Installation Guide
Connecting wires
When you need to join thin, data wires, use the Scotchlock connectors provided.
Procedures
D7547-1
Boat hull Boat hull
RF Ground Plate
Diagram A: Connecting RF ground - preferred method
D7539-1
If the boat does not have a ground plate, use
the alternative method shown in the following
diagram, to connect the RF ground. Now connect the power
& the autopilot pump
Course computer
POWER PUMP
S1000 Autopilot
Raymarine Ltd
Portsmouth PO3 5TD England
FCC ID PJ5S1000
IC: 4069B-S1000
0191
Product Code: A18107 O
87040_1.book Page 22 Wednesday, December 22, 2004 12:32 PM
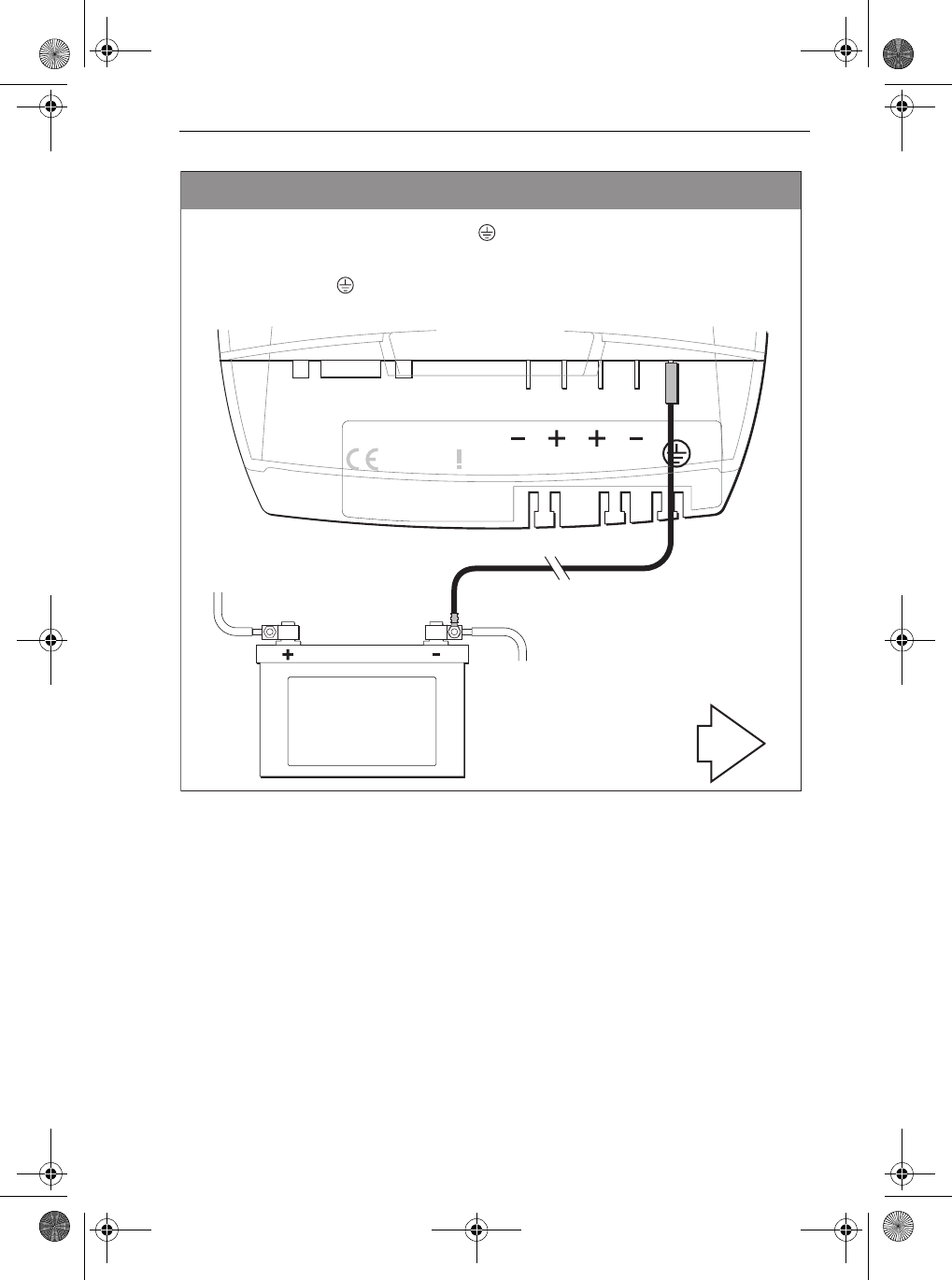
S1000 Autopilot Installation Guide 23
Connecting RF ground - alternative method
Note: Use this method of connecting the terminal, ONLY if the boat does not have
an RF grounding plate.
Do NOT connect the terminal to any other point.
D7540-1
Now connect the power &
the autopilot pump
Course computer
Product Code: A18107
POWER PUMP
S1000 Autopilot
Raymarine Ltd
Portsmouth PO3 5TD England
FCC ID PJ5S1000
IC: 4069B-S1000
0191
Product Code: A18107 O
87040_1.book Page 23 Wednesday, December 22, 2004 12:32 PM
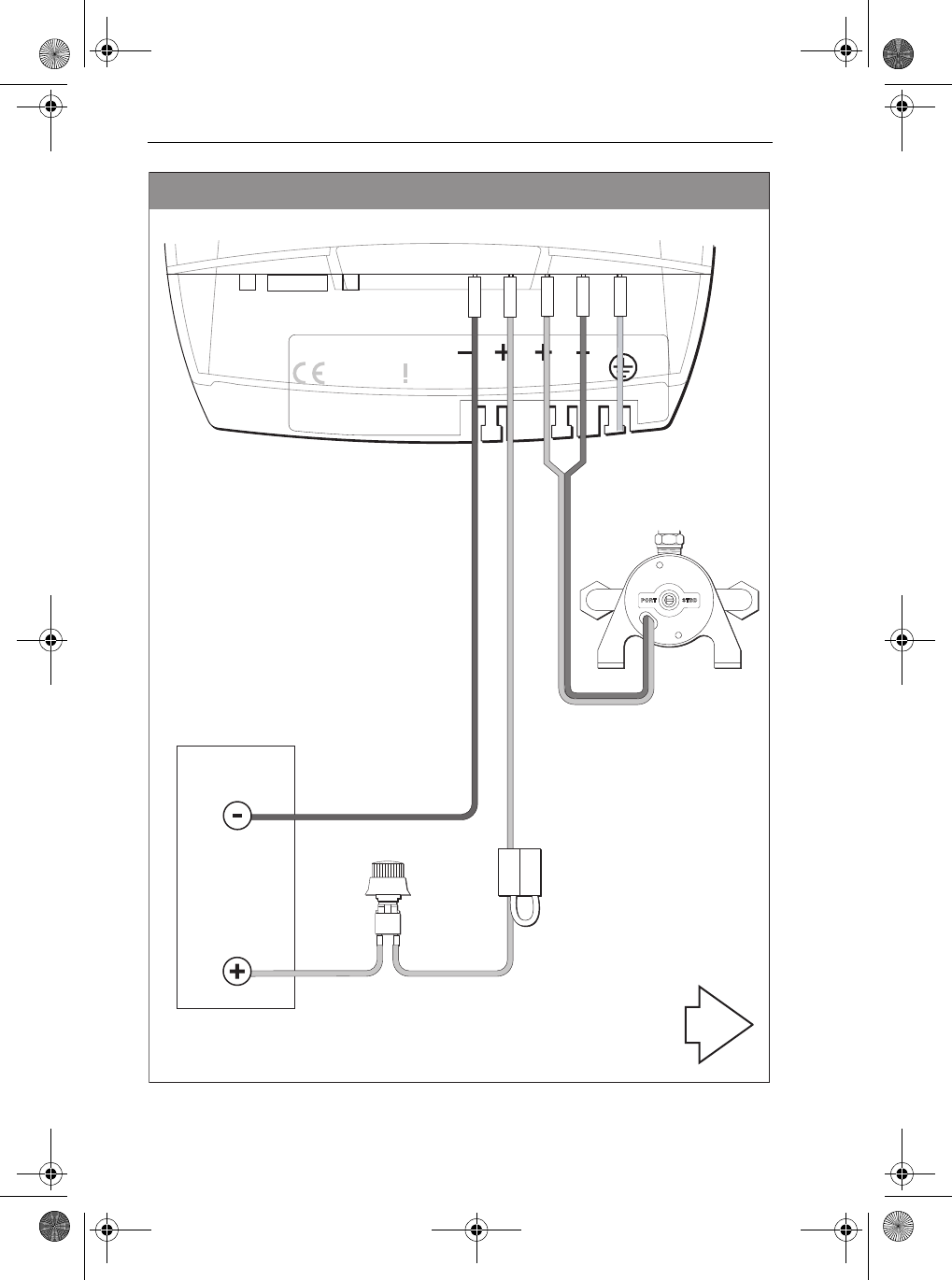
24 S1000 Autopilot Installation Guide
Red
Red
Black
Black
Integral
10 A fuse
POWER PUMP
S1000 Autopilot
Raymarine Ltd
Portsmouth PO3 5TD England
FCC ID PJ5S1000
IC: 4069B-S1000
0191
Product Code: A18107 O
In-line power switch
12 V
Power supply
Autopilot pump
D7541-1
Course computer
Diagram B: Connecting power & autopilot pump
Now make the necessary
Data Cable connections
87040_1.book Page 24 Wednesday, December 22, 2004 12:32 PM
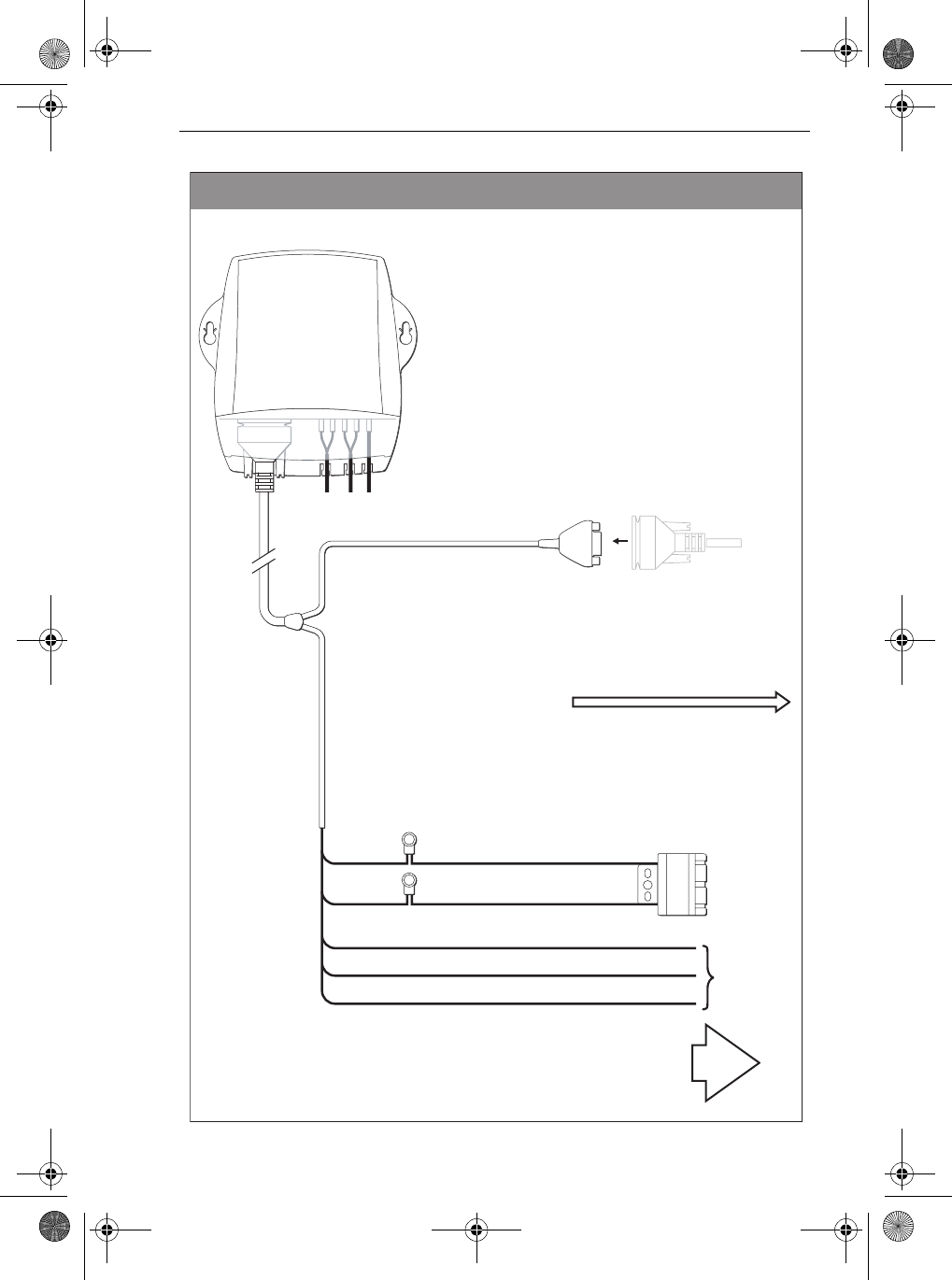
S1000 Autopilot Installation Guide 25
Yellow: SeaTalk Data
Red: SeaTalk +12 V
Black: SeaTalk 0 V
SeaTalk
Each time power is applied to an S1000 Autopilot connected to a
Raymarine GPS (via NMEA or SeaTalk), the S1000 will set the GPS
filtering to WEAK.
D7549-1
Purple Red
Black
Scotchlock connector
White Scotchlock connector
NMEA connector (not
supplied), from GPS
GPS requirement
The S1000 must receive GPS information, to function
correctly. Use the Data Cable supplied, to connect the
Course Computer to a GPS, using either of the
following methods:
1. To a Raymarine GPS via SeaTalk connections.
2. To a Raymarine GPS via NMEA spur.
3. To a non-Raymarine GPS via NMEA spur.
External
buzzer
NMEA Spur
Course Computer
Data
cable
For details of the NMEA Spur
connections, refer to Diagram D
Diagram C: Connecting the Data Cable
When connecting NMEA data from an external source, always
connect via the NMEA spur on the Data Cable. Do NOT connect
NMEA data from an external source directly to the connector on the
Course Computer.
When you have completed the electrical
connections, secure the wires at the
Course Computer
87040_1.book Page 25 Wednesday, December 22, 2004 12:32 PM
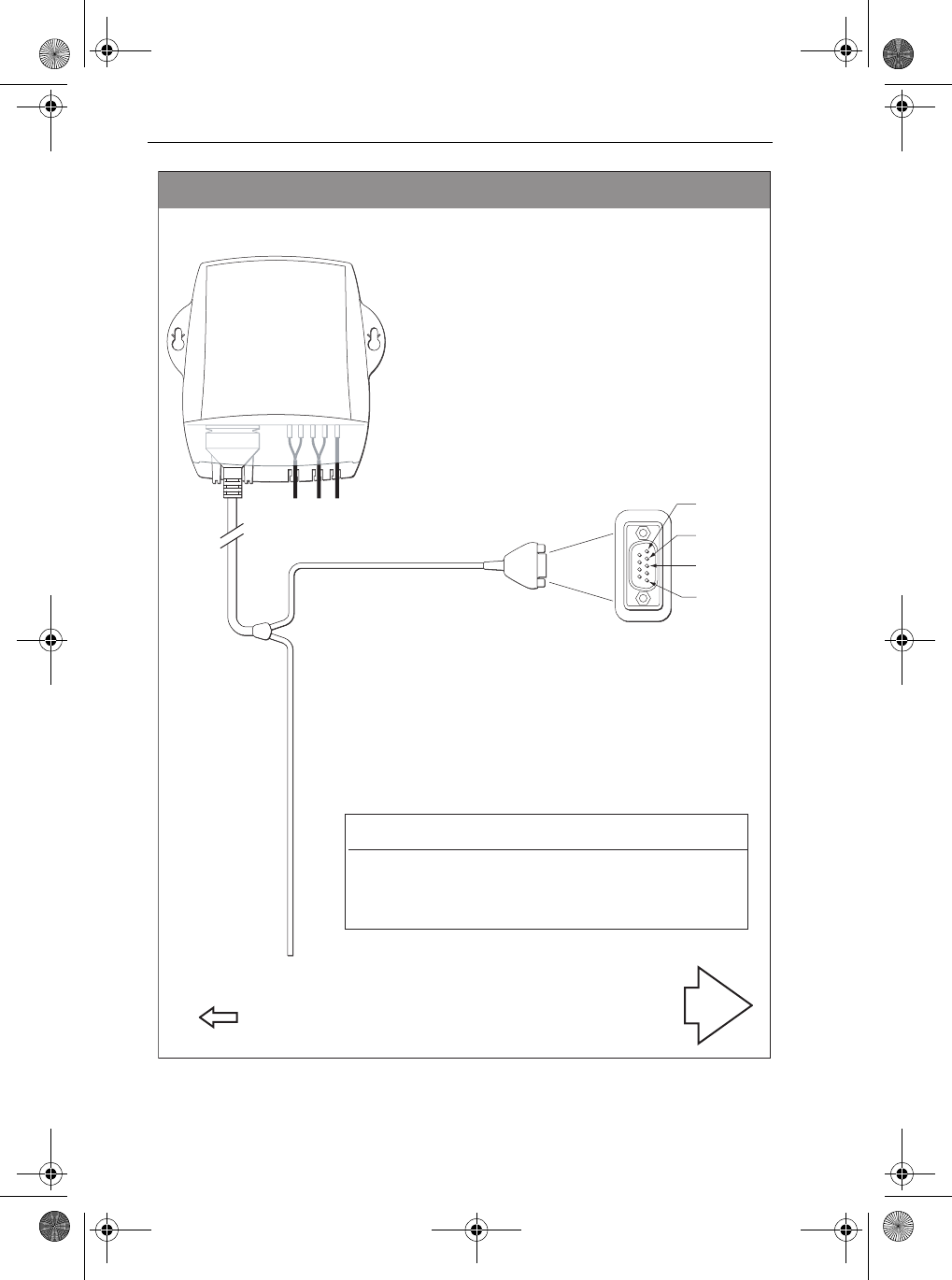
26 S1000 Autopilot Installation Guide
SeaTalk & buzzer
connections
(see Diagram C)
When you have completed the electrical
connections, secure the wires at the
Course Computer
D7596-1
Pin
number
Wire
color
NMEA signal
at S1000
Connection at
3rd party GPS
Brown
Green
Orange
Blue
1
2
3
5
-- ve out
+ve out
+ve in
-- ve in
NMEA --ve receive
NMEA +ve receive
NMEA +ve transmit
NMEA --ve transmit
NMEA Spur
NMEA
Connector
Course Computer
Data
cable
If it is more convenient to connect the NMEA spur to the GPS
without using the NMEA connector, you can remove the
connector and prepare the cable end as appropriate for your
preferred method of connection. Refer to the wire identification
table below, as necessary
CAUTION:
Before making any changes to the Data Cable,
disconnect it from the Course Computer.
Pin 1
Pin 2
Pin 3
Pin 5
Diagram D: NMEA connections
If a Raymarine GPS (such as the Raystar 120 or 125)
is to be connected to the S1000 Autopilot via NMEA,
the
NMEA in
and
out, +ve
and
-ve
lines must all be
correctly connected.
Each time power is applied to an S1000 Autopilot
connected to a Raymarine GPS (via NMEA or SeaTalk),
the S1000 will set the GPS filtering to WEAK.
Using with Raymarine GPS
87040_1.book Page 26 Wednesday, December 22, 2004 12:32 PM
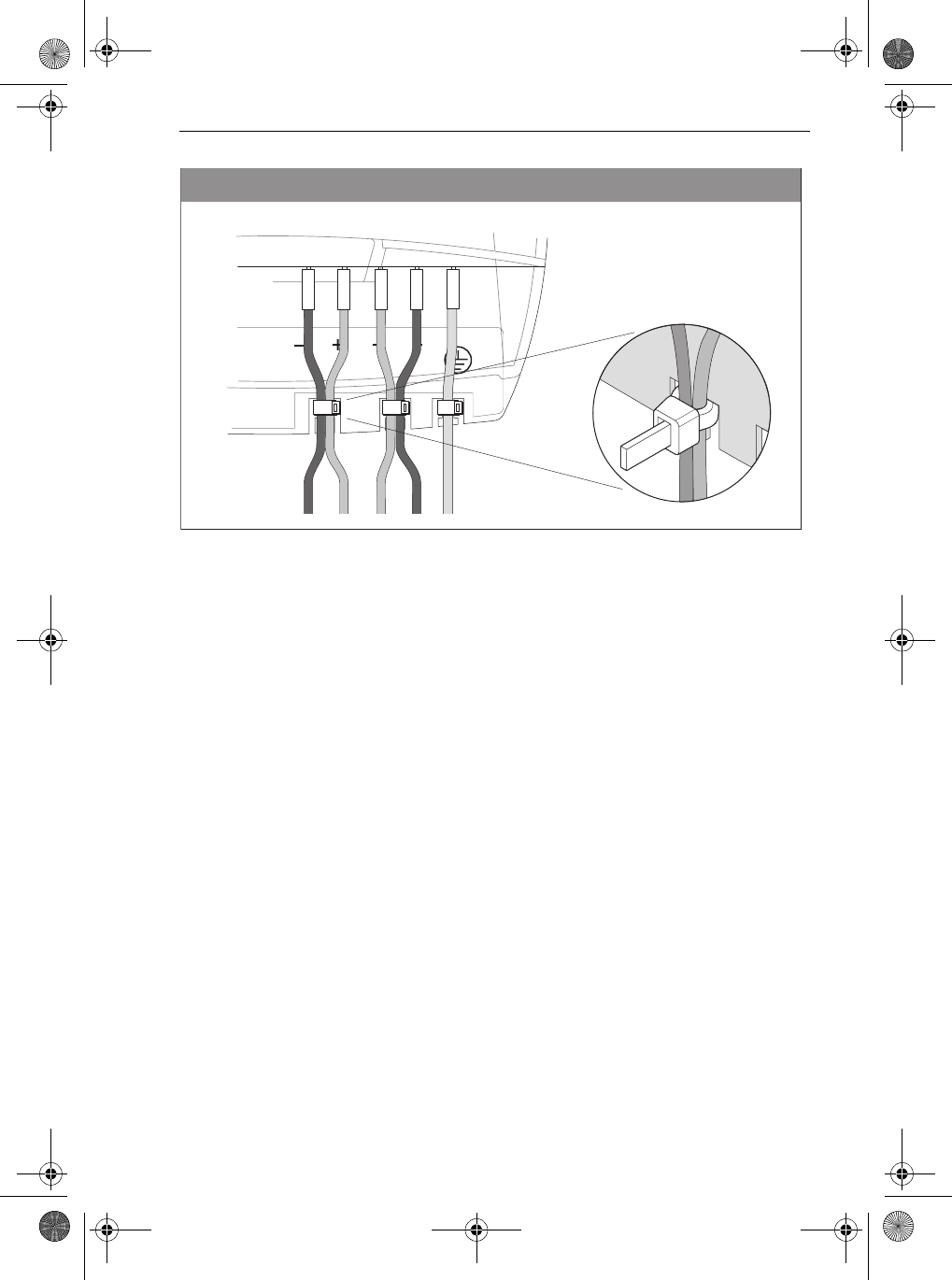
S1000 Autopilot Installation Guide 27
This completes the installation procedure. Now carry out the
Post installation
procedures
(below).
POWER PUMP
D7551-1
Course Computer
Secure wires
87040_1.book Page 27 Wednesday, December 22, 2004 12:32 PM
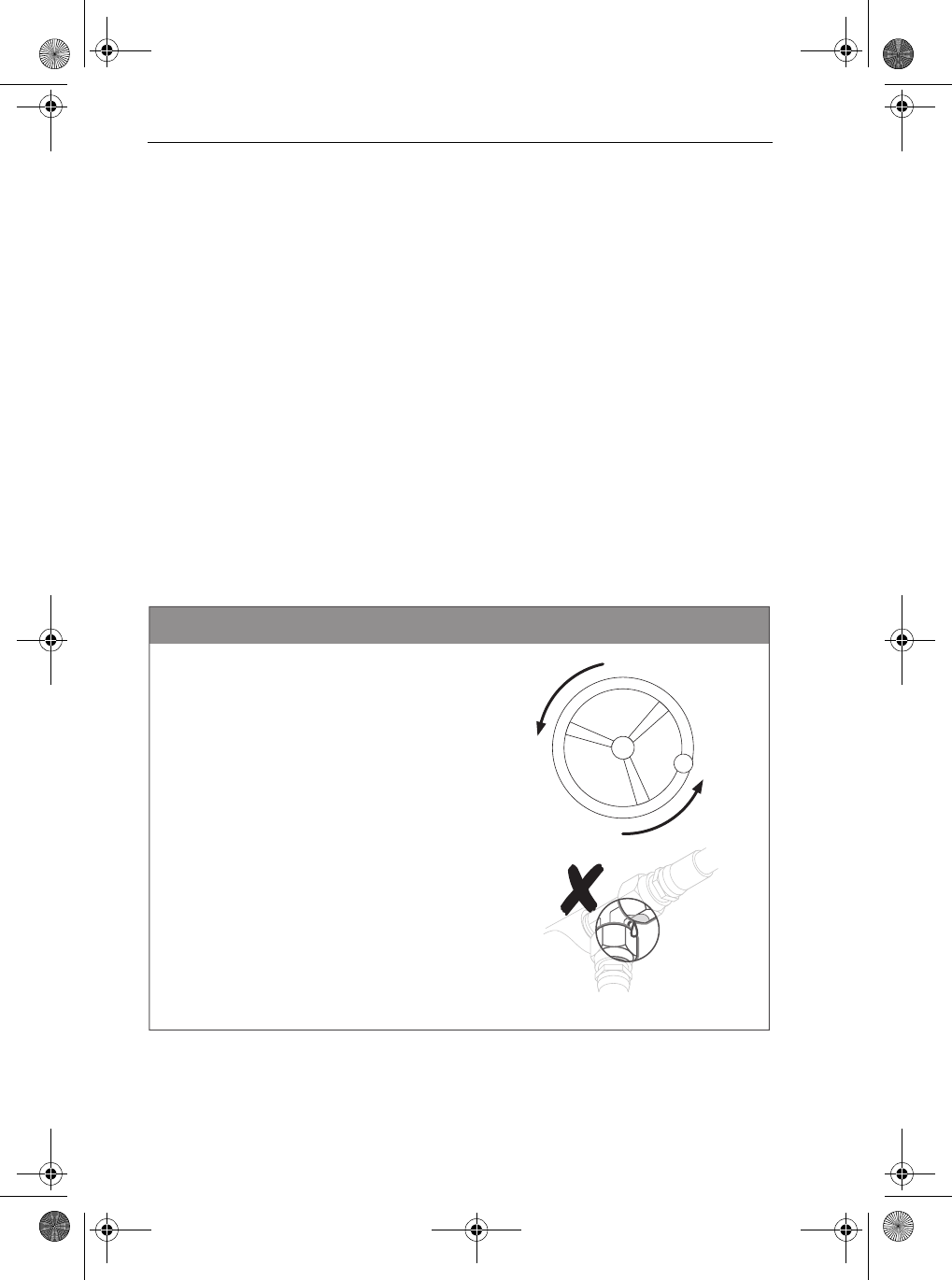
28 S1000 Autopilot Installation Guide
7. Post installation
When you have completed the installation of your S1000 Autopilot, use the following
procedures to:
•Check the steering operation.
•Check the system for leaks.
•Switch on the autopilot, then use the commissioning procedure, to correctly set up the
autopilot.
Steering operation
Turn the wheel from hard over port, to hard over starboard. If the steering operates
satisfactorily, proceed with the other post installation checks.
If the steering feels uneven and/or less responsive than it was before you installed your S1000
Autopilot, you may need to bleed the entire steering system. To do this, use the purge
procedure at the following web address:
http://www.seastarsteering.com/OUTBOARD/oboard.htm?../FILL_PURGE/FillPurge.htm&1
Checking for leaks
Checking for leaks (sheet 1)
Ensure all hydraulic joints are secure, then turn
the wheel to port. When the hard over point is
reached, continue turning to port to pressurize the
port lines, until the safety valve releases. At this
point, the fluid in the port lines will be at
maximum pressure and the wheel has a 'lumpy'
feel when turned to port.
1.
D7502-1
With the port lines at maximum pressure, check
the port lines for leaks, paying particular
attention to the joints.
If a leak occurs, turn the wheel to starboard to
release the pressure, then repair the leak and
repeat step 1.
2.
87040_1.book Page 28 Wednesday, December 22, 2004 12:32 PM
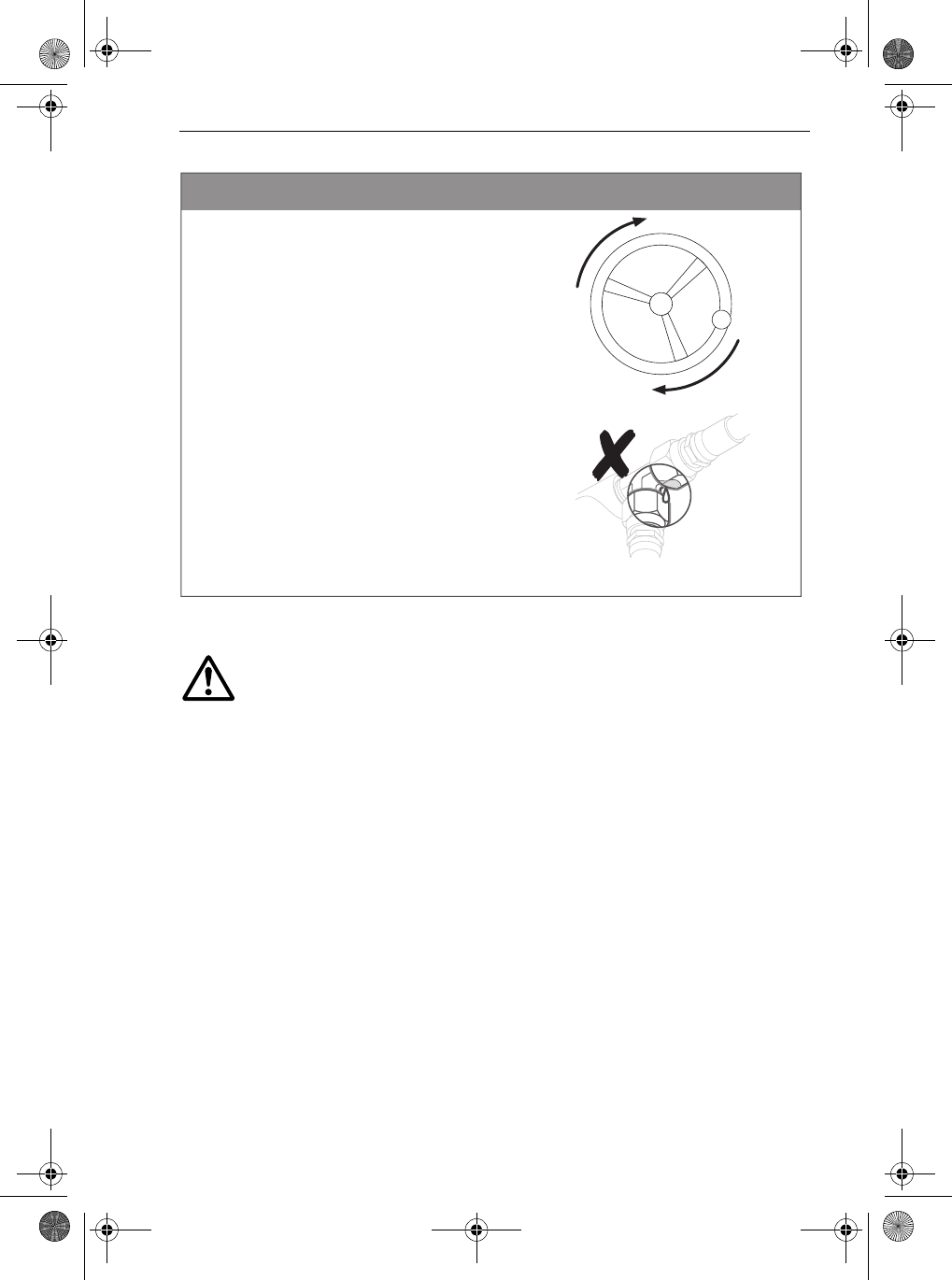
S1000 Autopilot Installation Guide 29
Switch on & commissioning
WARNING:
Before switching on power to the course computer, make
sure that personnel are clear of the steering gear and that
the boat is securely moored.
1. Switch on power to the S1000 system.
2. Carry out the commissioning procedure.
Checking for leaks (sheet 2)
After 24 hours, re-check the steering system to
ensure there are still no hydraulic fluid leaks.
5.
D7550-1
With the starboard lines at maximum pressure,
check the starboard lines for leaks, paying
particular attention to the joints.
If a leak occurs, turn the wheel to port to release
the pressure, then repair the leak and repeat step 3.
4.
Turn the wheel to starboard, and when the hard
over point is reached, continue turning to
starboard to pressurize the starboard lines, until
the safety valve releases. At this point, the fluid in
the starboard line will be at maximum pressure
and the wheel has a 'lumpy' feel when turned to
starboard.
3.
87040_1.book Page 29 Wednesday, December 22, 2004 12:32 PM
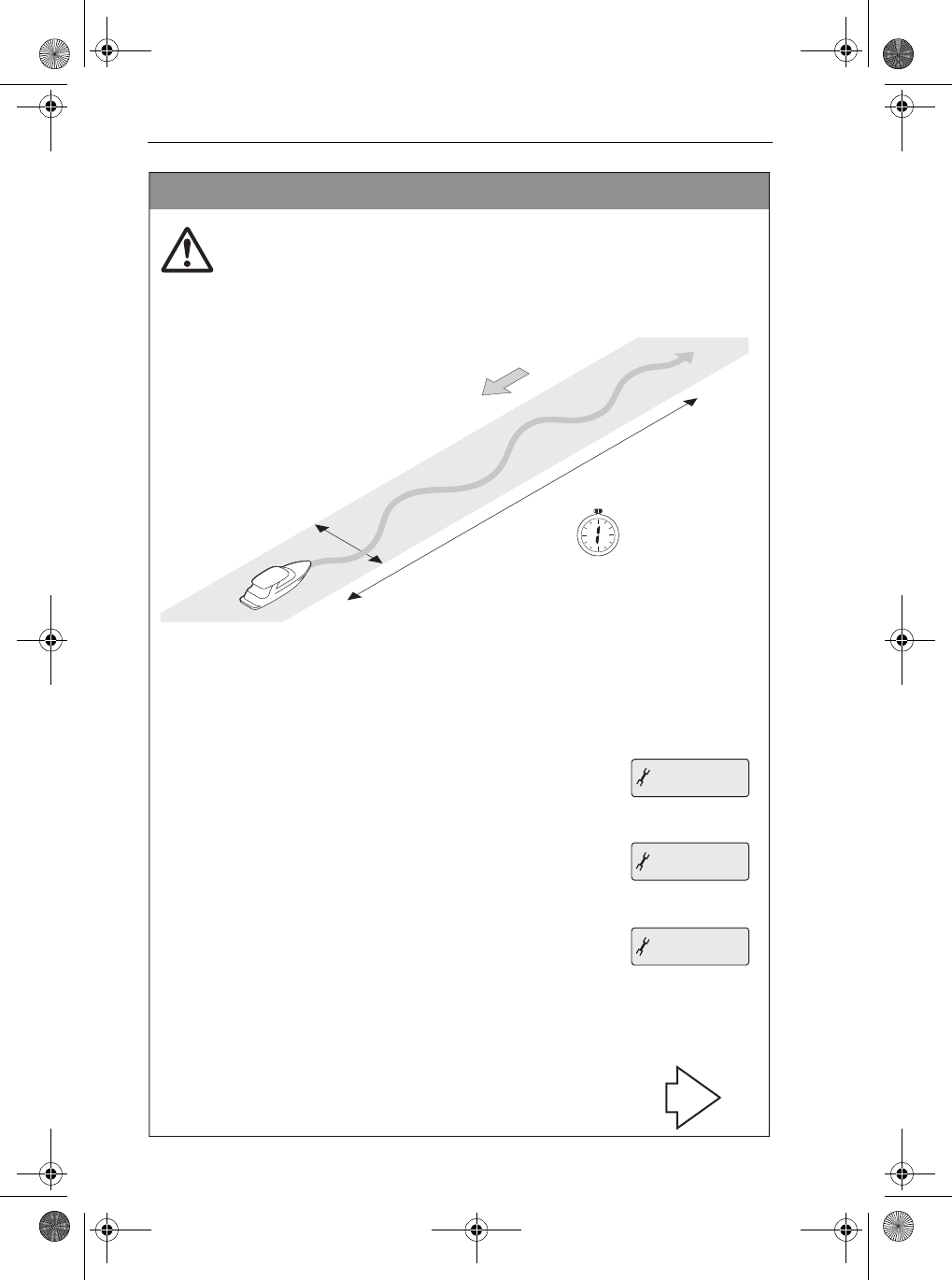
30 S1000 Autopilot Installation Guide
Commissioning using Autolearn - sheet 1
WARNING:
At least 0.25 nm (500 m) of clear sea space
At least 0.04 nm (100 m)
of clear sea space
1 minute
(approximately)
Wind
To regain control of the boat at any time during Autolearn,
press STANDBY.
Continue on sheet 2
The Autolearn process takes your boat through a series of
zig-zag maneuvers, so a significant amount of CLEAR SPACE
is required in front of your boat. Do NOT start Autolearn
unless this space is available.
1.
Before you use the autopilot, run the inbuilt Autolearn facility to set up the
autopilot for your boat:
At the S100 remote, hold down STANDBY for 2 seconds,
to enter Pilot Setup mode
2. Press MODE the necessary number of times to display
AUTOLEARN.
3. Press PILOT to initiate Autolearn.
Pilot Setup
AUTOLEARN
CLEAR TO
MANEUVER?
D7508-1
4. Ensure you have sufficient sea room to carry out the Autolearn, then steer
straight ahead and set the speed between 8 and 15 knots. Ensure the boat
is OFF the plane.
87040_1.book Page 30 Wednesday, December 22, 2004 12:32 PM
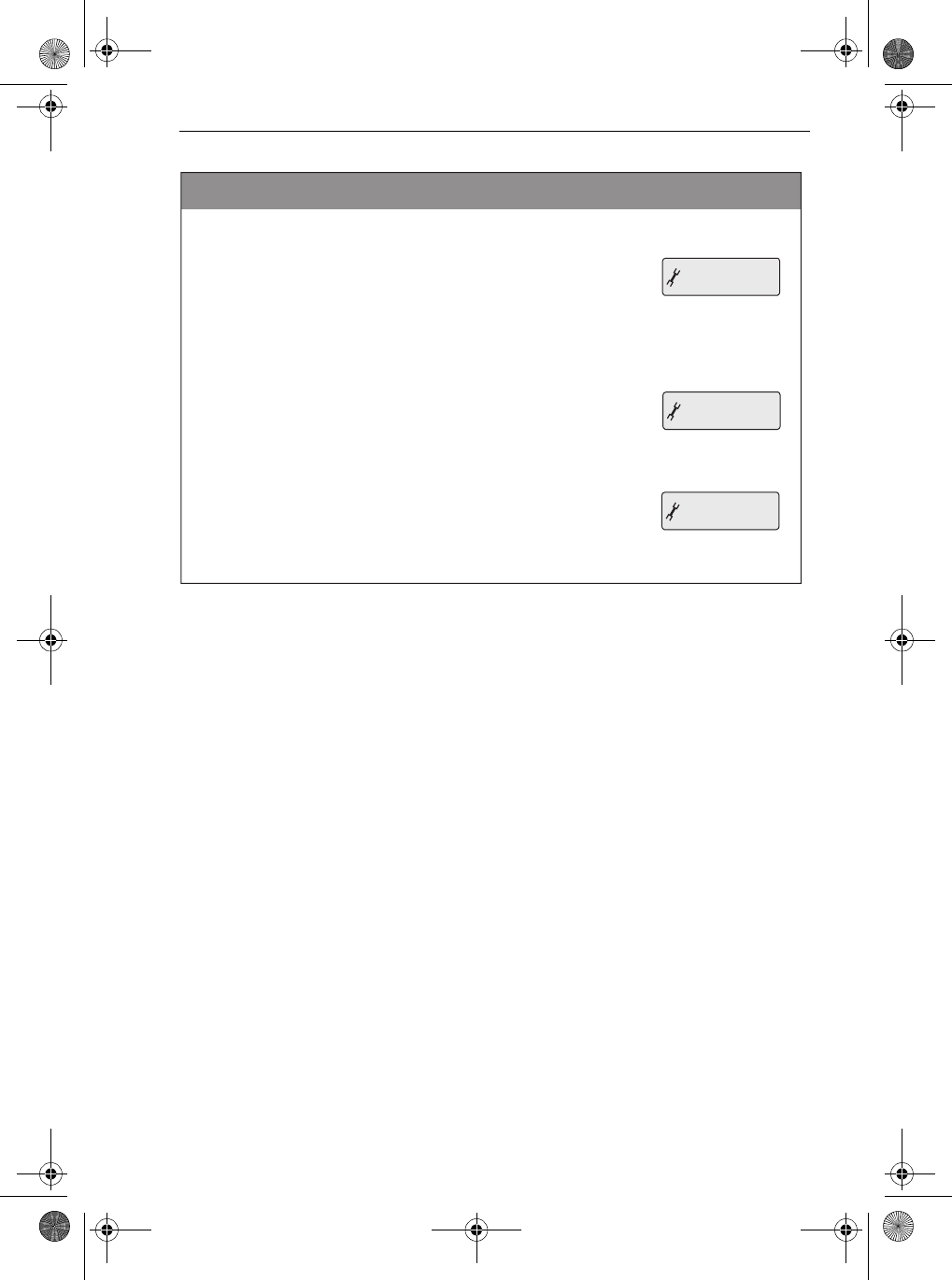
S1000 Autopilot Installation Guide 31
Commissioning using Autolearn - sheet 2
D7557-1
5. Press PILOT to begin. Your boat will then make a series of
zig-zag turns and the S100 display will show the Autolearn
step numbers (counting up). A typical Autolearn process
takes from 7 to 27 steps.
6. At the end of a successful Autolearn process, the display
shows LRN PASS. When this occurs, hold down
STANDBY for 2 seconds, to save the Autolearn values and
enter autopilot Standby Mode.
If an Autolearn process fails, the display shows LRN FAIL.
Press and release STANDBY to return to Autolearn and
repeat the process.
LEARNING...
STEP 1
LRN PASS
LRN FAIL
87040_1.book Page 31 Wednesday, December 22, 2004 12:32 PM
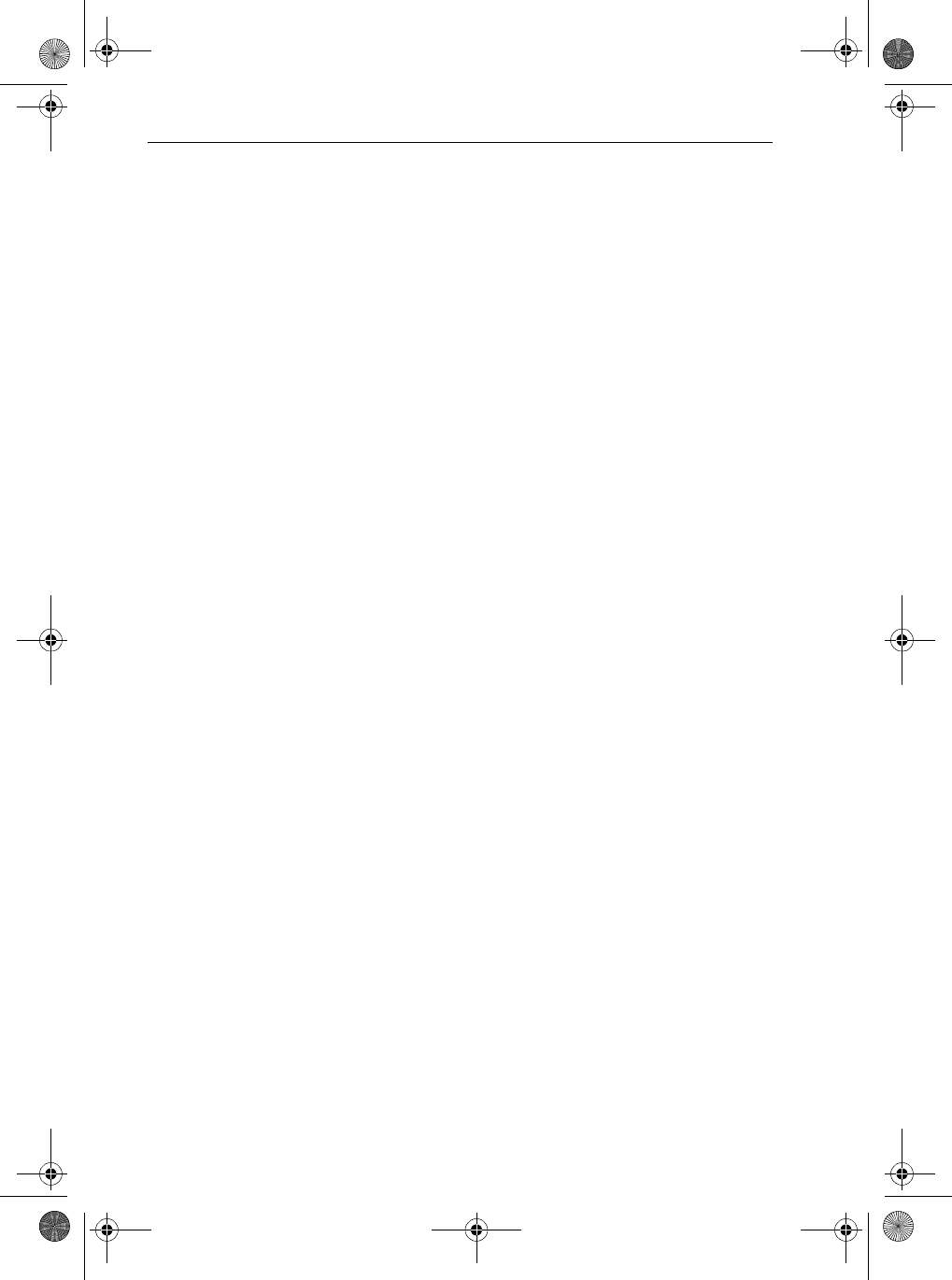
32 S1000 Autopilot Installation Guide
87040_1.book Page 32 Wednesday, December 22, 2004 12:32 PM
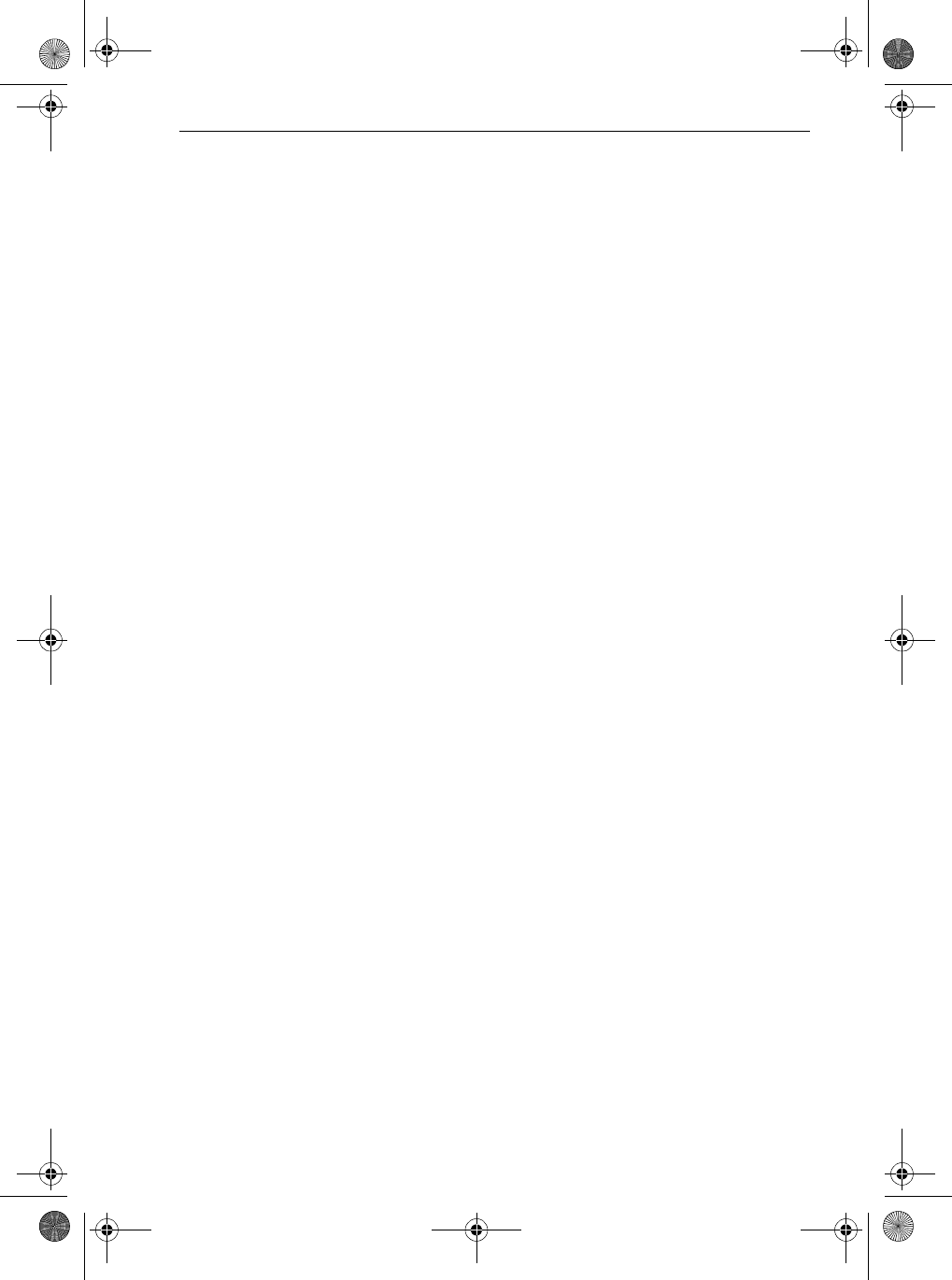
S1000 Autopilot Installation Guide 33
Specifications
System
Approvals: FCC, EMC, CE, IC
Autopilot pump
Voltage:10.5 V dc to 13.8 V dc
Current consumption: 4 A at 100 psi (69 kP), 7 A at 500 psi (3449 kP)
Dimensions: 6.5in (165mm) x 2.5in (65mm) x 3.2in (82mm)
Weight: 3 lbs (1.4 kg)
Course computer
Voltage: 12 V dc
Current consumption: 10 A, maximum
4 A, nominal
Dimensions: 6.5 in (165 mm) x 6.7 in (170 mm) x 1.73 in (44 mm)
Data In/Out: SeaTalk, NMEA 0183
S100 Remote
Voltage: 3 V, supplied by two internal, ‘AAA’ batteries.
Dimensions: S100 Remote only: 101 mm x 60.5 mm x 35 mm
Remote in cradle:103 mm x 66 mm x 44 mm
Waterproofing: IPX 6
Hydraulic fittings
Tapered thread: ¼ NPT (National Pipe Thread)
Hose connection thread: 9/16 UNEF (Unified Extra Fine)
Hydraulic fluid
Recommended Types: Canmet Steering Fluid. High VI, ISO 15 Hydraulic Oil
SeaStar/BayStar Marine Steering Fluid
Other suitable Types: Texaco HO15
Shell Aero 4
Esso Univis N15
Chevron Aviation Fluid A
Mobil Aero HFA
Fluids meeting MIL H5606 specifications
87040_1.book Page 33 Wednesday, December 22, 2004 12:32 PM
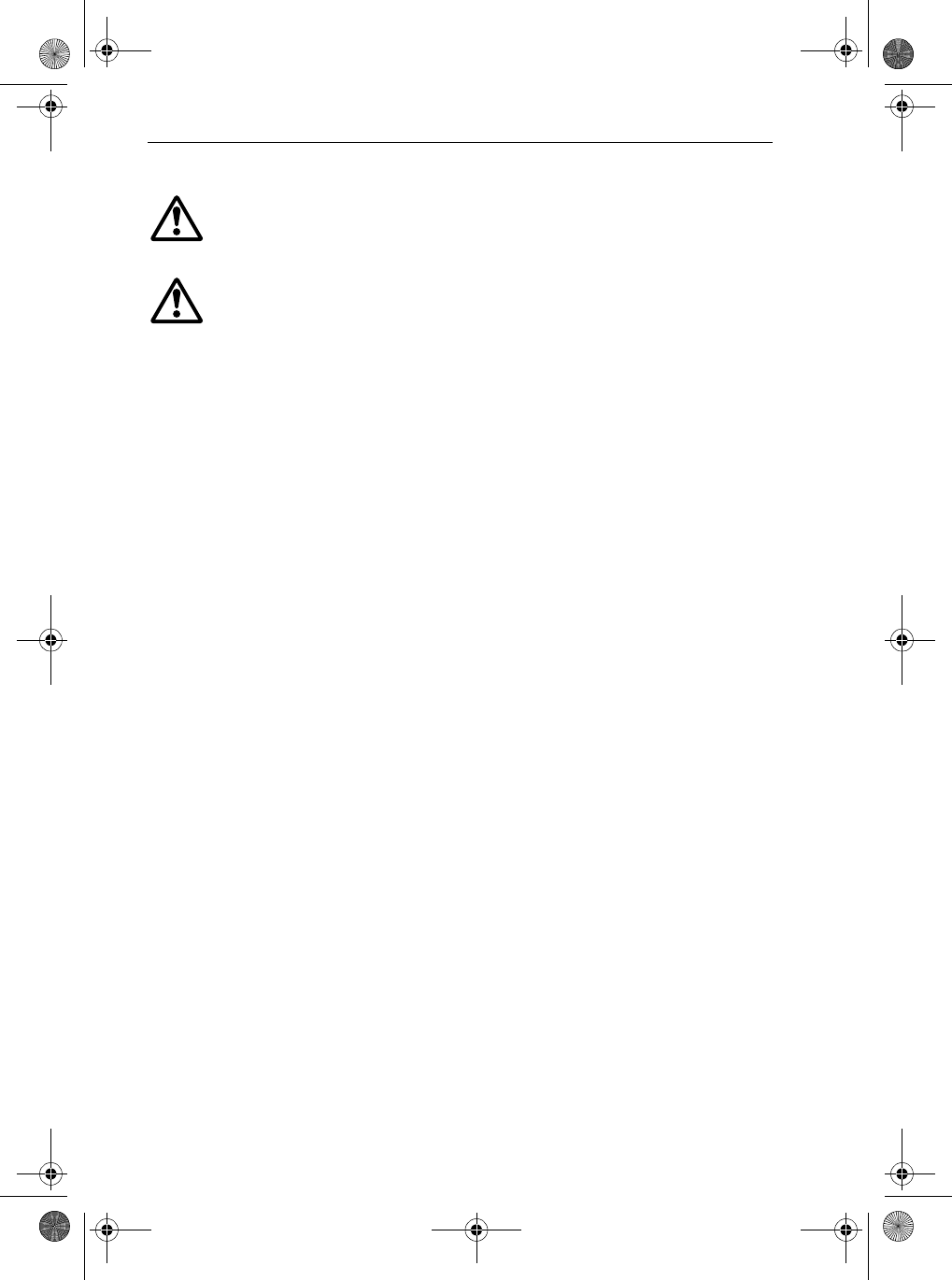
34 S1000 Autopilot Installation Guide
Safety notices
WARNING: Product installation & operation
This equipment must be installed and operated in accordance with the Raymarine
instructions provided. Failure to do so could result in personal injury, damage to
your boat and/or poor product performance.
WARNING: Electrical safety
Make sure you have switched off the power supply before you start installing this
product.
Information
To the best of our knowledge, the information in this guide was correct when it went to press. However, Raymarine
cannot accept liability for any inaccuracies or omissions it may contain.
In addition, our policy of continuous product improvement may change specifications without notice. Therefore,
Raymarine cannot accept liability for any differences between the product and this guide.
EMC Installation Guidelines
All Raymarine equipment and accessories are designed to the best industry standards for use in the recreational
marine environment.
Their design and manufacture conforms to the appropriate Electromagnetic Compatibility (EMC) standards, but
correct installation is required to ensure that performance is not compromised. Although every effort has been taken
to ensure that they will perform under all conditions, it is important to understand what factors could affect the
operation of the product.
The guidelines given here describe the conditions for optimum EMC performance, but it is recognized that it may not
be possible to meet all of these conditions in all situations. To ensure the best possible conditions for EMC
performance within the constraints imposed by any location, always ensure the maximum separation possible
between different items of electrical equipment.
For optimum EMC performance, it is recommended that wherever possible:
•Raymarine equipment and cables connected to it are:
•At least 3 ft (1 m) from any equipment transmitting or cables carrying radio signals e.g. VHF
radios, cables and antennas. In the case of SSB radios, the distance should be increased to 7
ft (2 m).
•More than 7 ft (2 m) from the path of a radar beam. A radar beam can normally be assumed
to spread 20 degrees above and below the radiating element.
•The equipment is supplied from a separate battery from that used for engine start. Voltage drops below 10 V in
the power supply to our products, and starter motor transients, can cause the equipment to reset. This will not
damage the equipment, but may cause the loss of some information and may change the operating mode.
•Raymarine specified cables are used. Cutting and rejoining these cables can compromise EMC performance and
must be avoided unless doing so is detailed in the installation manual.
•If a suppression ferrite is attached to a cable, this ferrite should not be removed. If the ferrite needs to be
removed during installation it must be reassembled in the same position.
87040_1.book Page 34 Wednesday, December 22, 2004 12:32 PM

S1000 Autopilot Installation Guide 35
Suppression Ferrites
The following illustration shows typical cable suppression ferrites used with Raymarine equipment. Always use the
ferrites supplied by Raymarine.
Connections to Other Equipment
If your Raymarine equipment is to be connected to other equipment using a cable not supplied by Raymarine, a
suppression ferrite MUST always be attached to the cable near the Raymarine unit.
D3548-6
87040_1.book Page 35 Wednesday, December 22, 2004 12:32 PM
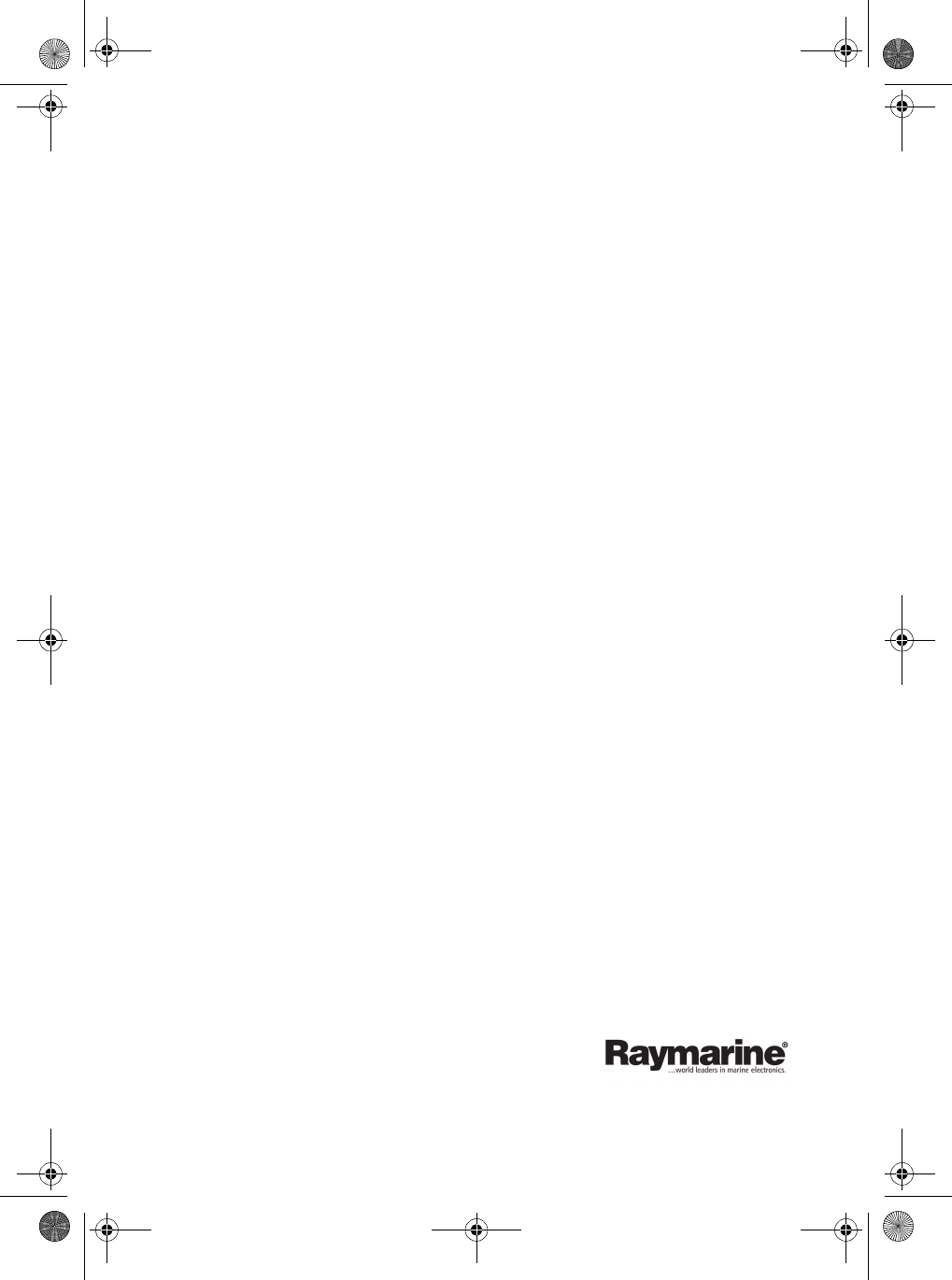
Raymarine Inc,
22 Cotton Road,
Unit D, Nashua,
New Hampshire 03063-4219,
USA.
Tel: +1 603.881.5200
Fax: +1 603.864.4756
www.raymarine.com
Raymarine UK Ltd,
Quay Point,
Northarbour Road
Portsmouth,
Hampshire PO6 3TD,
United Kingdom.
Tel: +44 (0) 23 9269 3611
Fax: +44 (0) 23 9269 4642
www.raymarine.com
87040_1.book Page 36 Wednesday, December 22, 2004 12:32 PM