Fluke 43B Case Studies
2015-09-09
: Fluke Fluke-43B-Case-Studies-809754 fluke-43b-case-studies-809754 fluke pdf
Open the PDF directly: View PDF .
Page Count: 4

Application Note
Energy savings
make the case for
an HVAC upgrade
Profile: Mike Klingler, Service Mgr.,
Farber Corporation
Tools: Fluke 1735 Three-Phase
Power Logger and Fluke 975
AirMeter™ test tool
Measurements: Energy consumption,
air quality
From the Fluke Digital Library @ www.fluke.com/library
Business needs: An older six-story building requires
cooling even in winter. To condition the air, a 200-ton
refrigeration unit operates year round, consuming major
amounts of energy. The client wants to reduce HVAC
energy usage without increasing the temperature.
Solution: Service contractor Farber Corp. measures
energy usage and air quality. Tests show that installing
a heat exchanger and shutting down a 200-ton chiller
during winter months will save the building owner $9,954
in annual energy costs.
Tools used: The Fluke 1735 Power Logger measures
energy consumed by the chiller. The Fluke 975 AirMeter
tester measures indoor air quality before and after the
installation to verify system performance.
Field
Applications
Case
Study

2 Fluke Corporation Energy savings make the case for an HVAC upgrade
Klingler had a plan in mind,
but didn’t want to guess how
much energy the big chiller
was consuming. The return on
investment (ROI) for his system
optimization program would
hinge on energy savings.
The law building uses hot
water heating and chilled
water cooling, with a dual-duct
system for air distribution. Hot
and cold air travel to termi-
nal units (also called mixing
boxes) which mix flows to
the required supply tempera-
ture. Water chilled to 45 °F
is pumped to the air handler,
where it cools supply air. In
the process, excess building
heat is transferred to the water,
warming it to about 55 °F. That
warmer water then returns to
the chiller, where it is cooled
back down to 45 °F and
pumped back through the loop.
In the original configuration,
the chiller used the refrigera-
tion cycle to transfer the waste
heat to another water loop on
the condenser side. Condenser
water at about 85 °F was then
pumped through rooftop cooling
towers that rejected the heat
into the outside air.
Taking the guesswork out
“What if I figure another way to
cool the system?” Klingler asked
himself. There was plenty of
cold air available outside during
the Columbus winter, where
temperatures average 33.5 °F in
December, 28.3 °F in January,
32 °F in February and 42 °F in
March. Klingler figured he could
bypass the chiller entirely.
We can use the water from
the cooling towers on the roof,
he reasoned, to cool the chilled
water. Instead of running the
chiller, why not use the cooling
towers to cool the condenser
side water down to 45 °F, and
simply pump it through a plate
and frame heat exchanger to
extract waste heat from the
chilled water loop? Instead of
Cool it: There must be a
better way
It was a familiar challenge for
Mike Klingler, service manager
for Farber Corporation, an
HVAC/R contractor in Columbus,
Ohio: Prove to a customer that
investment in a major HVAC
system upgrade would pay for
itself in energy savings, without
compromising occupant comfort
or indoor air quality (IAQ).
“I work in all kinds of build-
ings,” says Klingler, “and I
am often asked to reduce the
energy costs of the HVAC
systems.” The subject this time
was an older six-story build-
ing that once housed an insur-
ance company, but now serves
students at a Columbus-area
law school.
Working on a project to
replace two outdoor cooling
towers and install variable-
frequency drives in the build-
ing’s HVAC system, Klingler
noticed that one of the facility’s
two big 200-ton capacity chill-
ers was kept running to supply
cold water for the system, even
in winter.
“A lot of buildings we can
cool with outside air,” Klingler
says. “When we get down to
50-52 °F and below, we can
just draw that outside air in
and use it for free cooling. But
because of the setup of the law
school building, they had to run
one of the chillers even when it
was 20-25 °F outside. Because
of the duct distribution system
we couldn’t rely on outside air
in certain areas of the building.”
As a result, one chiller kept
running to supply water chilled
to 45 °F to the air handling
units and keep the building’s
occupied spaces comfortable.
The big motors powering the
device were consuming a lot
of energy and money—power
and cost the school could save
if Klingler could find a better
way to cool. Of course the
solution would have to deliver
acceptable indoor air quality.
the chiller’s powerful compres-
sor motors, the system would
run with just a small pump. The
cost of the upgrade would be
significant, but Klingler felt he
could prove it financially with
accurate data on the potential
energy savings. (see illustration)
Finding the ideal balance
between building energy
consumption and indoor air
quality requires a careful
balance of multiple factors. “One
of the areas we look to are
ventilation rates for the build-
ing,” Klingler said. “Decreasing
ventilation rates may reduce
overall energy consumption
and reduce operating costs, but
at the same time we have to
maintain good indoor air quality
standards too. There’s usually a
very tight ventilation standard
that the service provider has
to control in order to reduce
energy costs and maintain
quality indoor air conditions.
Considering the dynamic
changes in a building and a
functioning HVAC system, in
many cases, it’s not real easy.”
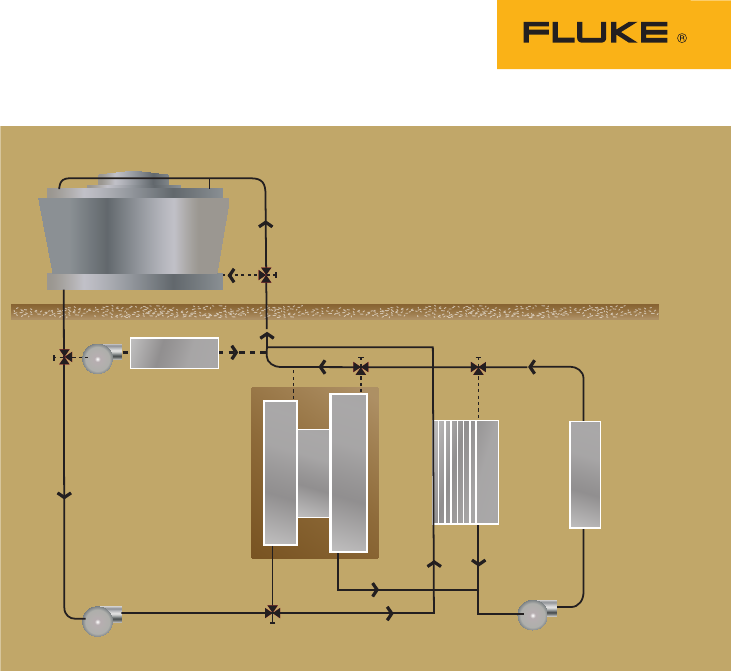
3 Fluke Corporation Energy savings make the case for an HVAC upgrade
But Klingler was well
equipped to find the balance
point. He could measure
multiple IAQ factors before the
upgrade, then check afterward
to ensure air quality was not
compromised, using the Fluke
975 AirMeter™ test tool. And he
didn’t have to estimate energy
consumption, or guess. He
logged actual kWh consumption
at the chiller over multiple 12-
hour cycles, using a beta test
version of the new Fluke 1735
Power Logger.
“I’m saying okay, I have to
run that 100-horsepower motor
in the winter time,” Klingler
said. “What’s the real kWh?
Then I can go back to the
owner and say, here’s how
much is it costing us to run
that chiller. The Fluke 1735
will measure and monitor over
time and tell me the real power
consumption of that equipment.
It takes the guesswork out of
it. Before having the power
analyzer, you would have to
say well, it’s probably consum-
ing about this much power. But
you can set this tool up and
walk away, then come back
and get the information. You
can see what your real power
consumption is for any equip-
ment in your building, and then
equate that to real dollars.”
Proving in the payback
Klingler’s measurements with
the Fluke 1735 showed that the
big chiller averaged 790 kWh
of power consumption over a
12-hour period. He computed a
total power consumption over
the four cold-weather months
of 189,600 kWh. At a cost of
six cents per kWh, running that
chiller was costing the law
school $11,376 every winter.
Klingler figured his alternate
approach would cut that bill
by 87.5 percent, for an annual
energy saving of $9,954.
He estimated that installing
the heat exchanger, piping,
valves and controls would
cost $46,000. That meant the
payback period for the project
would be just 4.62 years. And
that estimate did not include
possible savings due to reduced
wear and tear on the chiller
unit.
While he’s waiting for a
response on his proposal for a
system upgrade, Klingler has
found lots of other uses for the
Fluke 1735 and the 975 AirMe-
ter. Beyond simply measuring
power consumption, the Fluke
Power Logger collects all kinds
of power quality information
that Klingler figures will help
him do his job. And the AirMe-
ter makes it a snap to calcu-
late percentage of outside air
required to meet standards.
Working on a one-floor
remodel in a ten-story office
building, Klingler had to calcu-
late the percentage of outside
air delivered to a newly laid
out conference room. “We go
to ASHRAE 62 and the local
building code, and they say 15
percent of the air delivered to
the space needs to be outside
air,” he said. “How do you know
that 15 percent is really outside
air? You have to go back to the
big air handler, take a reading
and say, how’s this air handler
set up right now? What’s the
percentage of outside air we’re
providing to the entire build-
ing?
“With the 975 AirMeter, the
service company can go right
into the air handler and take
those readings and it will tell
us, based on temperature or
carbon dioxide. It’s a very quick,
easy, labor-saving tool.”
On the power quality side,
the Power Logger measures
voltage on three phases and
current on three phases and
neutral. It records multiple
parameters that can help deter-
mine system load, including
voltage, current, frequency, real
power (kW), apparent power
(kVA), reactive power (kVAR),
power factor, and energy
(kWh). It can also perform
power quality measurements.
And the Fluke 1735 downloads
to a PC and comes with soft-
ware for creating reports.
Cooling
Tower
Heat Exchanger
Load
Basin
Heater
(Optional)
CWP CHWP
Evaporator
Comp.
Condenser
Figure 1. Proposed new system with heat exchanger.

4 Fluke Corporation Energy savings make the case for an HVAC upgrade
Fluke Corporation
PO Box 9090, Everett, WA USA 98206
Fluke Europe B.V.
PO Box 1186, 5602 BD
Eindhoven, The Netherlands
For more information call:
In the U.S.A. (800) 443-5853 or
Fax (425) 446-5116
In Europe/M-East/Africa +31 (0) 40 2675 200 or
Fax +31 (0) 40 2675 222
In Canada (800)-36-FLUKE or
Fax (905) 890-6866
From other countries +1 (425) 446-5500 or
Fax +1 (425) 446-5116
Web access: http://www.fluke.com
©2007 Fluke Corporation. All rights reserved.
Specifications subject to change without notice.
Printed in U.S.A. 5/2007 3034723 A-EN-N Rev A
Fluke. Keeping your world
up and running.®
A more savvy contractor
“The power logger makes it
real easy for the contractor or
engineering group to come in
and measure power consump-
tion on individual components
in a building, a plant or an
industrial facility,” Klingler
said. “When you start to look
at the individual components,
it allows you to think in terms
of control strategies: how can I
control this piece of equipment
to reduce energy consumption?
How much is it costing me and
what can I do for savings?”
Beyond such applications,
Klingler sees the Fluke 1735 as
a tool that can help him move
his business to a higher level.
“For a mechanical contractor
such as myself, you’re adding
service offerings through the
use of this product,” he said. “It
allows you to be a more savvy
contractor. It allows you to be
more advanced and offer the
additional services that I think
we should be providing to our
customers. You can export the
data to spreadsheets, which
you can use for presentations
to the building owners. That’s a
big feature when I sit down at
the table.”
In addition to measuring
power consumption, as Klingler
did at the law school, the Fluke
1735 measures and logs volt-
age, amps, frequencies, wave-
forms, harmonics and power
anomalies. “For maintenance
and servicing, it’s a trouble-
shooting tool,” Klingler said.
“You can see if you’re having a
problem with power, or when
you’re not sure what’s happen-
ing and you can’t see it with a
snapshot from your meter. You
can measure it, record it and
view it with this device.
“As a contractor, I would use
it as a diagnostic tool, and it
would be just as valuable to
me in that regard as it is as a
power consumption tool. I can
use it both ways.”
Tips for optimizing your HVAC system
1. Measure airflow
Use duct traverses to measure air pressure,
velocity and flow. If pressure is too high and/
or airflow too low, check dirty coils, fans and
filters that could be blocking the system.
2. Check ventilation
Many buildings are either under-ventilated
(bad IAQ) or over-ventilated (expensive).
Readjust to ASHRAE standards.
3. Add VFDs
Variable air volume systems use variable
frequency drives (VFDs) to more efficiently
regulate motors and pumps. An upfront
installation cost in exchange for long term
energy savings.
ASHRAE 55 and 61
Guidelines for creating comfortable,
affordable, indoor environments
ASHRAE Standard 55, “Thermal
Environmental Conditions for Human
Occupancy”, explains how to create an
indoor environment that satisfies 80
percent of a building’s occupants. You
do it with a combination six factors: air
temperature, radiant temperature, air
speed, humidity, metabolic rate, and
clothing insulation.
Similarly, ASHRAE Standard 62,
“Ventilation for Acceptable Indoor Air
Quality”, lists the minimum ventilation
rates and air quality parameters that are
acceptable to occupants. It also explains
how to use ventilation to control air
contaminants.
Combined, the two standards provide
a set of thresholds for you to compare
customer systems against. Optimize
toward ASHRAE and you’ll probably
improve both air comfort and energy
usage.