Fomotech TWISTER2X Industrial Remote Control User Manual Twister2X 99 910MHZ channels
Fomotech International Corp. Industrial Remote Control Twister2X 99 910MHZ channels
Fomotech >
user manual
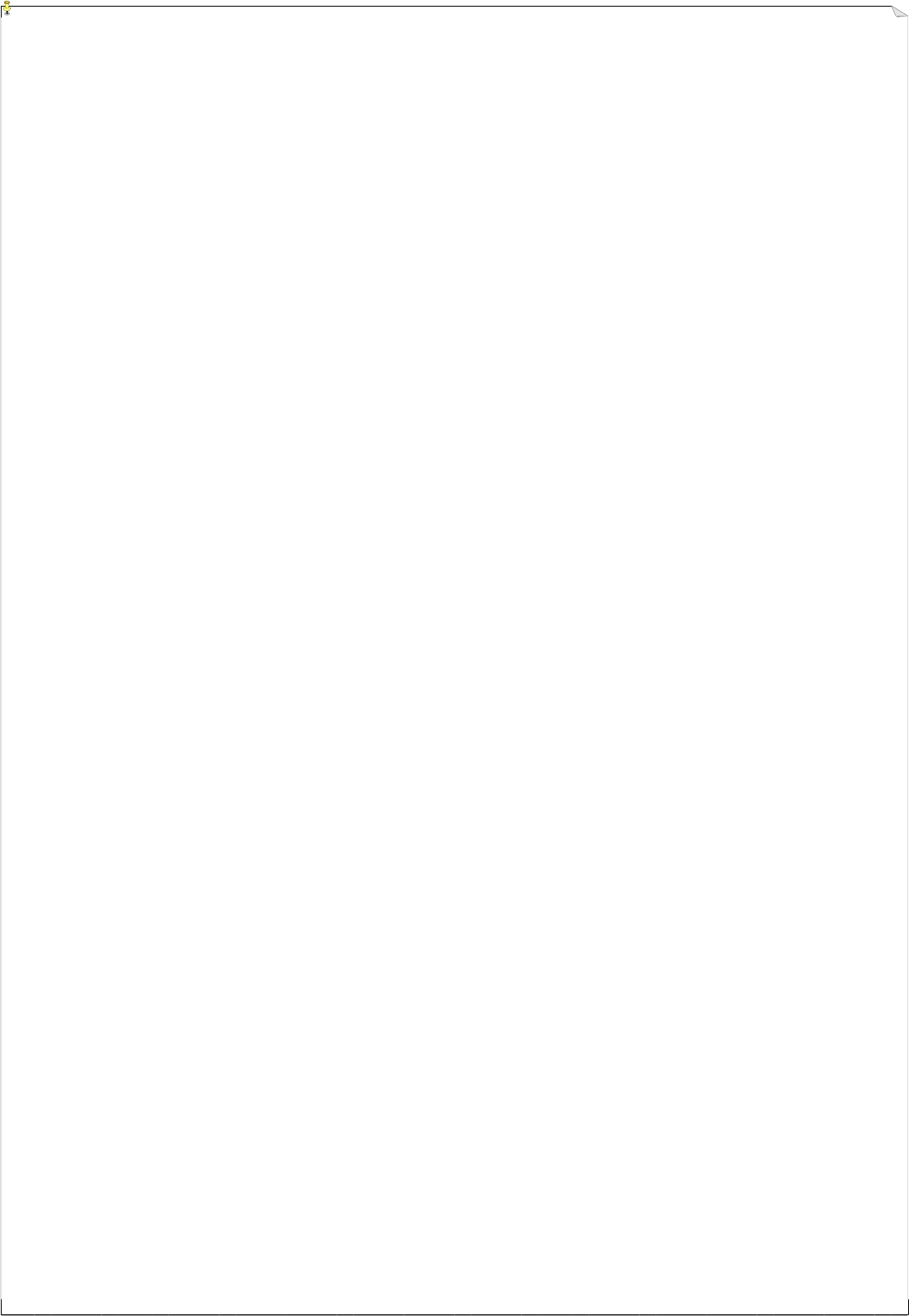
1
T
TA
AB
BL
LE
E
O
OF
F
C
CO
ON
NT
TE
EN
NT
TS
S
Page
1. INTRODUCTION ................................................................................................. 2
2. SAFETY INSTRUCTIONS ................................................................................... 3
3. SYSTEM FUNCTIONS
3.1 TRANSMITTER JOYSTICK DESCRIPTIONS ........................................... 4
3.2 TRANSMITTER PUSHBUTTON DESCRIPTIONS ................................... 5
3.3 GENERAL FUNCTION DESCRIPTIONS ................................................... 6
4. TRANSMITTER OUTLINE
4.1 TRANSMITTER EXTERNAL DESCRIPTIONS ......................................... 7
4.2 TRANSMITTER EXTERNAL DESCRIPTIONS ......................................... 8
5. RECEIVER OUTLINE
5.1 RECEIVER EXTERNAL & INTERNAL DESCRIPTIONS ......................... 9~11
5.2 RECEIVER MOUNTING DIMENSION ....................................................... 12
6. SYSTEM SETTINGS
6.1 TRANSMIITTER ID CODE SETTINGS ..................................................... 13
6.2 TRANSMITTER FREQUENCY CHANNEL SETTINGS ........................... 13
6.3 RECEIVER LCD STATUS DISPLAYS ......................................................... 14
6.4 RECEIVER ID CODE & FREQUENCY CHANNEL SETTINGS ............... 15
6.5 FREQUENCY CHANNEL TABLE ............................................................... 16
7. RECEIVER SYSTEM STATUS DISPLAYS ......................................................... 17~18
8. RECEIVER INSTALLATION
8.1 PREPARATION ............................................................................................. 19
8.2 STEP-BY-STEP INSTALLATION ................................................................. 19
8.3 SYSTEM TESTING ....................................................................................... 20
9. OPERATING INSTRUCTION
9.1 POWER “ON” THE SYSTEM ....................................................................... 21
9.2 DUAL HOIST/TROLLEY OPERATION ..................................................... 22
9.3 TRANSMITTER SYSTEM STATUS DISPLAYS ........................................... 23
10. BATTERY CHARGING ....................................................................................... 24
11. SYSTEM SPECIFICATIONS ............................................................................... 25~26
12. PARTS LIST ........................................................................................................... 27
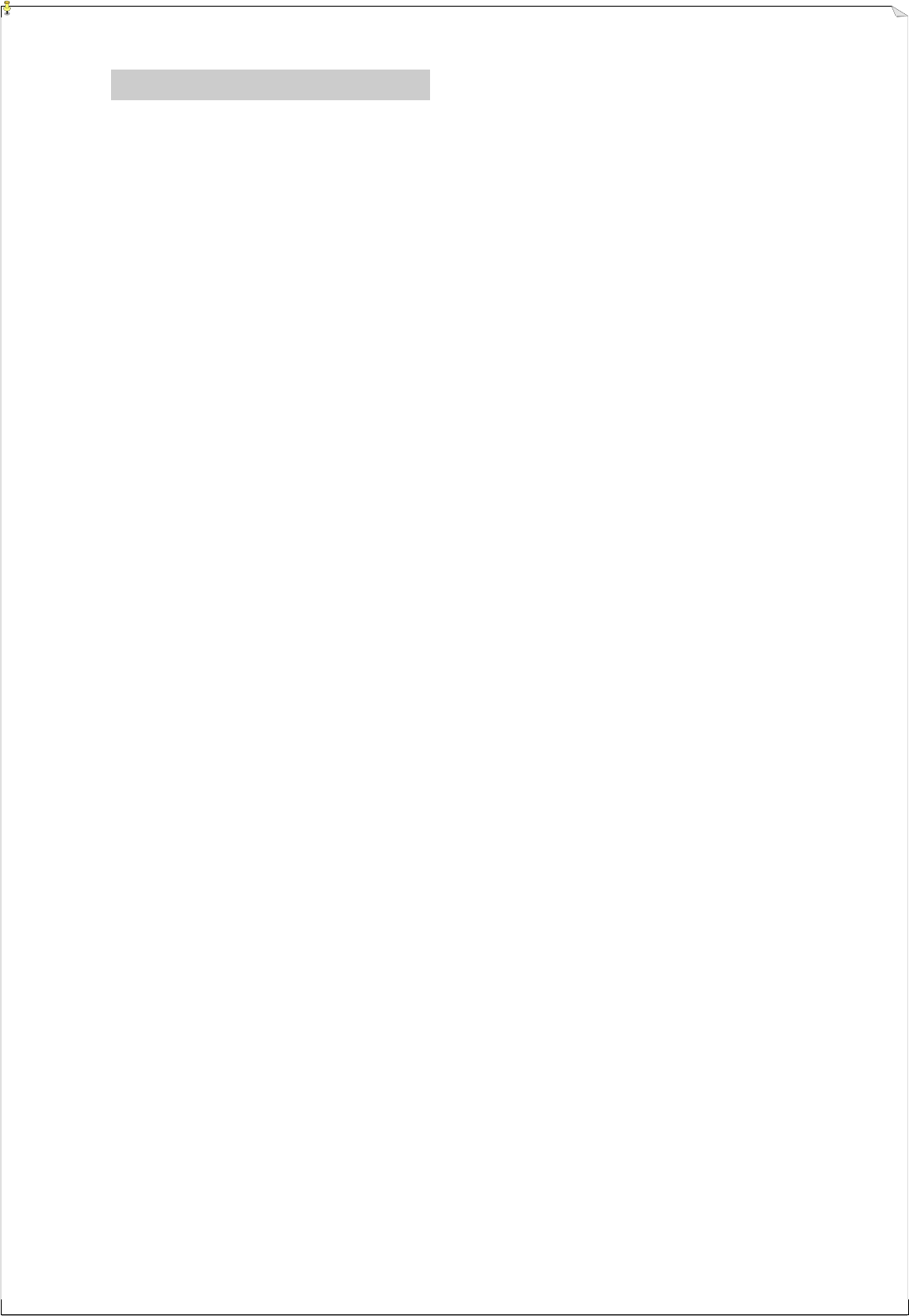
2
1. INTRODUCTION
The Twister 2X is a highly sophisticated industrial radio remote control system. The versatile
features of Twister 2X permit its usage in a wide range of industrial applications. The system can
be used to control all types of industrial cranes, tower cranes, building construction equipment,
automatic control systems, mining equipment, and many others.
The Twister 2X incorporates numerous advanced safety features and software programming that will
ensure maximum security and safety in the workplace. The major features of Twister 2X industrial
radio remote control system are as follow:
* The system is equipped with highly evolved software that has redundant error checking and
correcting capabilities to ensure 100% error-free transmission, decoding, and control of all
output relays. This highly evolved software includes CRC (Cyclical Redundancy Check) and
Hamming Codes (Error Recovery) programming.
* The encoding system utilizes advanced microprocessor control for 100% error-free data
transmission. The availability of 65,536 sets of unique security ID codes + 20 distinct RF
channels will ensure that only commands from a matching control transmitter can be carried out
without any interference from other radio systems.
* The decoding system utilizes dual-microprocessor control, which will ensure 100% error-free
calculating, bit checking and correcting of all incoming data.
* The system also utilizes an additional central microprocessor for data comparison and
crosschecking between the two decoding microprocessors. When faults are detected via this
central microprocessor, for maximum safety, the entire system will be shutdown immediately to
avoid possibility of any accidents occurring.
* The system utilizes PLL synthesized RF transmission. It allows the user to select from 20 sets
of frequency channels best suited for the environment. The frequency channel is selected via
simple dip-switch settings inside the transmitter unit. The frequency channel for the receiver
is selected via simple button setting on the receiver LCD control panel. The receiver also has
the ability to auto-scan from these 20 sets of frequency channels. The receiver will search and
locked on to the intended matching control transmitter.
* For added safety the receiver also utilizes dual Safety Relay for the receiver MAIN relay circuit.
If the receiver MAIN relay is defective (example: fails to open or close during operation or not
responding to a “Stop” command) a fault will be detected and the system will be shut down
immediately to avoid possibility of any accidents occurring.
* The Twister 2X is equipped with numerous self-diagnosing functions, which include transmitter
low-voltage detection/warning, faulty pushbutton/joystick detection, faulty safety MAIN relays
detection, faulty relay boards detection, faulty EEPROM detection, faulty RX module detection,
incorrect ID code detection, and receiver MAIN auto-deactivation when transmitter low-voltage
is detected, when encountering strong radio interference, and when the transmitter/operator is
out of receiving range.
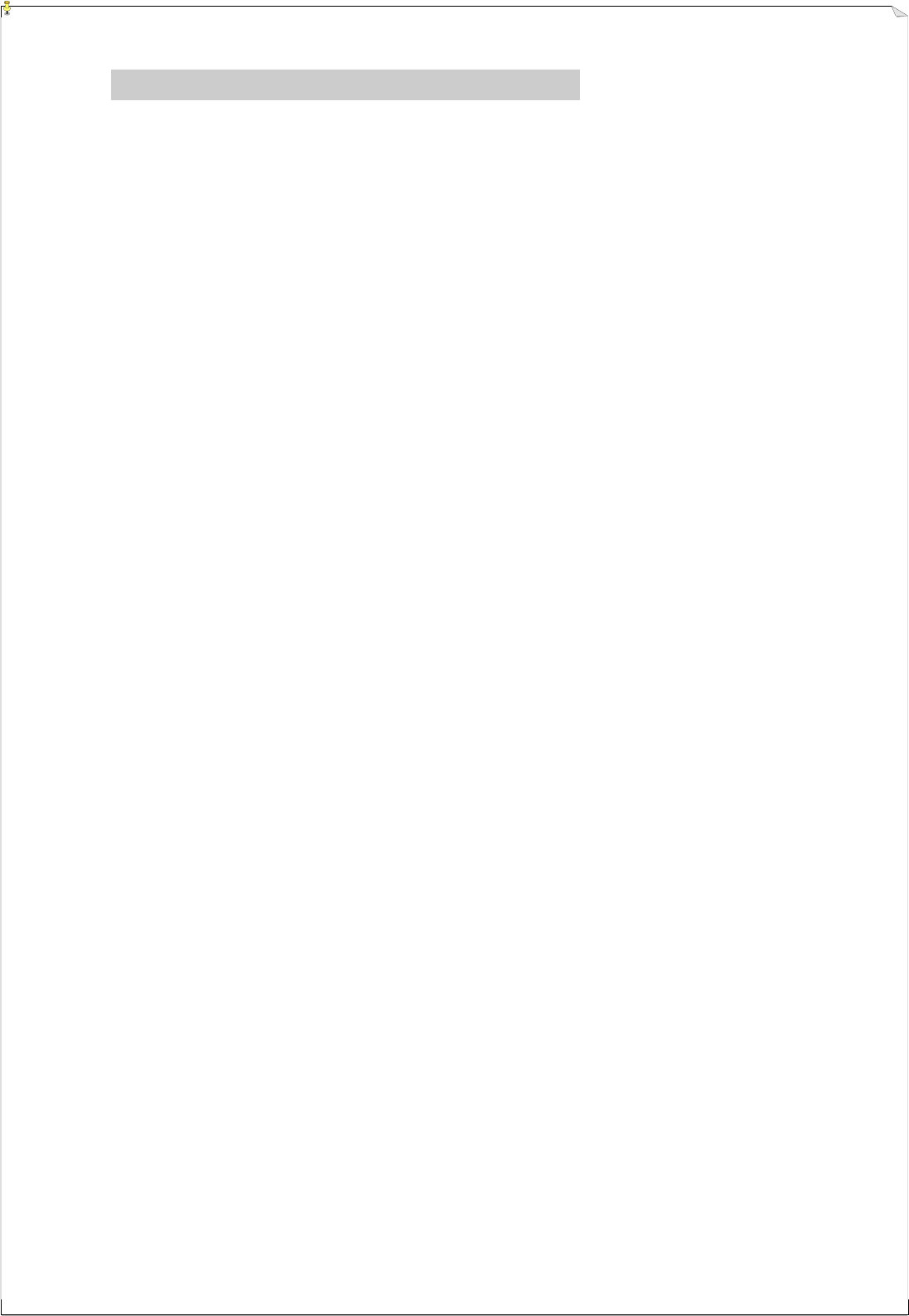
3
2. SAFETY INSTRUCTIONS
The Twister 2X system is relatively simple to use. However, it is very important to observe the
proper safety procedures before, during, and after operation. When use properly the Twister 2X
systems will enhance productivity and efficiency in the workplace.
The following instructions should be strictly followed:
1. Make a daily check of the transmitter casing, joysticks and pushbuttons. Should it appear that
anything could inhibit the proper operation of the transmitter unit, it should be immediately
removed from service.
2. The transmitter voltage should be checked on a daily basis. If the voltage is low, the battery
pack should be recharged or replaced (refer to page 23 for battery power status LED display).
3. The emergency stop button (EMS) should be checked at the beginning of each shift to ensure
they are in the proper working order.
4. In the event of an emergency, activate the emergency stop button immediately by pressing the
red EMS button down. This will immediately disconnect the transmitter power and receiver
MAIN relays. Then turned the power “off” from the main power source of the equipment.
5. The transmitter power key, which is located on the right side of the transmitter box, should be
turned “off” after each use and should never left the power key in “on” position when the unit is
unattended.
6. Do not use the same frequency channel and ID code as any other unit in use at the same facility
or within distance of 300 meters.
7. Ensure the waist belt and the shoulder strap is worn at all time during operation to avoid
accidental damages to the transmitter box.
8. Never operate a crane or equipment with two (2) transmitter units at the same time with same
frequency channel and ID code.
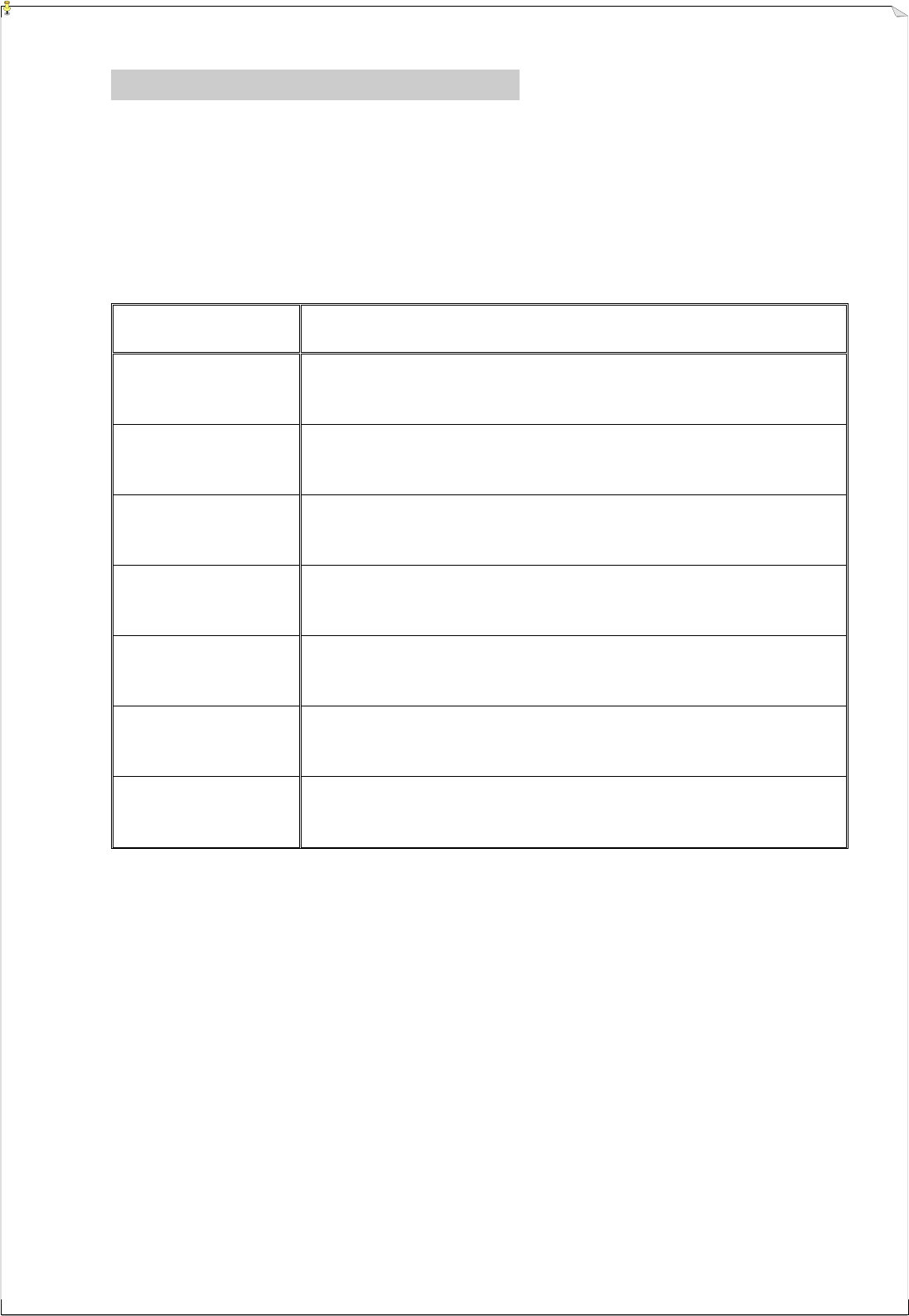
4
3. SYSTEM FUNCTIONS
3.1 Transmitter Joystick Descriptions
All transmitter units are equipped with two joysticks, in single or double axis configurations. The
table below illustrates the number of steps or speeds available for the Twister 2X in relation to each
speed’s output contact relay configuration:
TYPE FUNCTION
1-Speed 1 speed output contact relay for both forward and reverse motion
(total of 2 output relays per axis or motion)
2-Speed Shared 2nd speed output contact relay for each forward and
reverse motion (total of 3 output relays per axis or motion)
2-Speed* Separate 2nd speed output contact relay for each forward and
reverse motion (total of 4 output relays per axis or motion)
3-Speed Shared 2nd and 3rd speed output contact relays for each forward
and reverse motion (total of 4 output relays per axis or motion)
4-Speed Shared 2nd, 3rd and 4th speed output contact relays for each forward and
reverse motion (total of 5 output relays per axis or motion)
5-Speed Shared 2nd, 3rd, 4th and 5th speed output contact relays for each forward
and reverse motion (total of 6 output relays per axis or motion)
0-Speed** Addition of 0-speed (neutral position) output contact relay for
connection to crane’s braking system
* Separate 2nd speed output contact relay - For travel motion that required individual output contact relay for the 2nd speed function
(example: hoist motion with dual motors).
** By adding a 0-speed output contact relay, when the joystick is at center or neutral position, this 0-speed relay will be energized.
This feature is best suited for cranes or equipment with special breaking system.
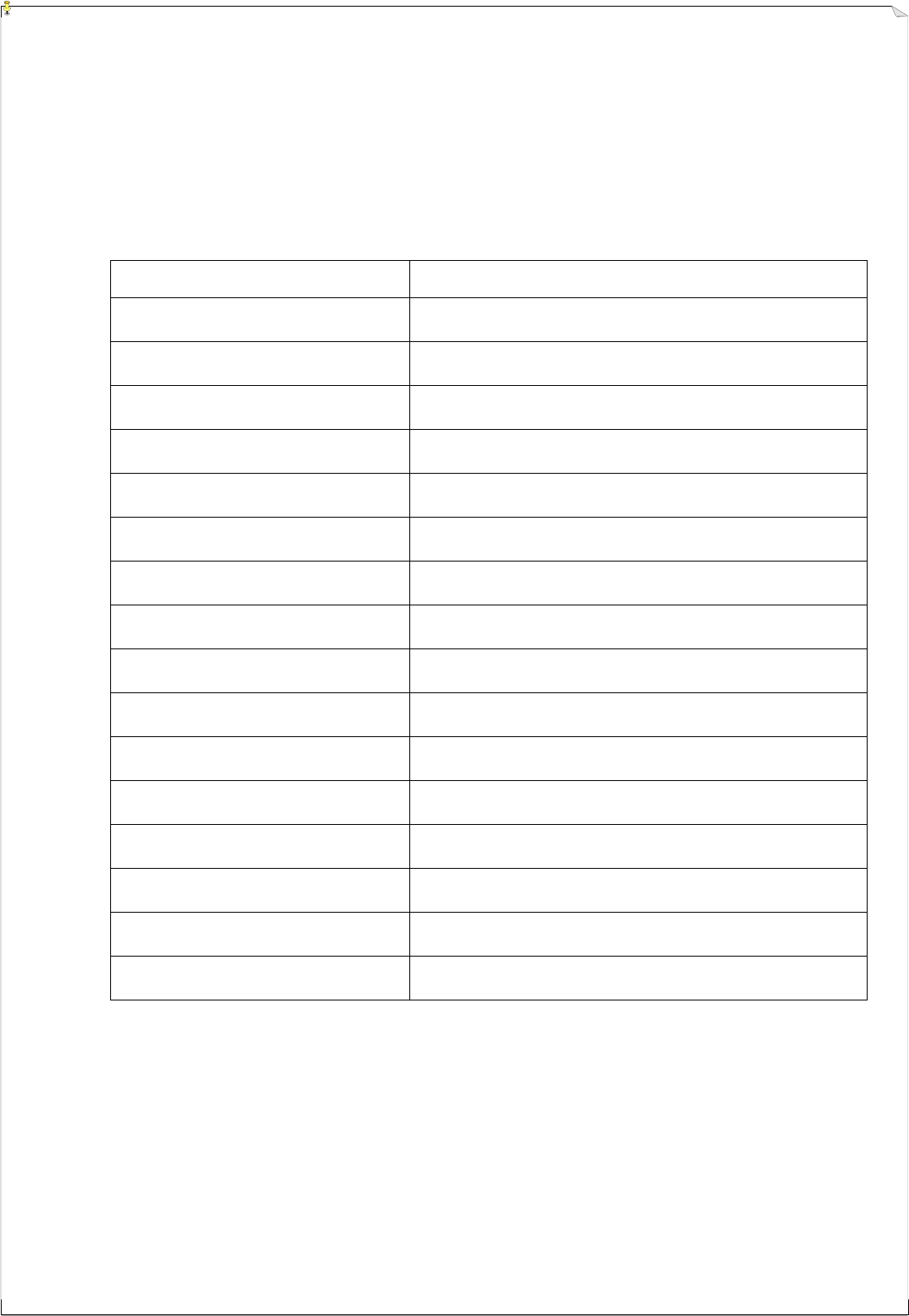
5
3.2 Transmitter Pushbutton Descriptions
There are many different types of pushbuttons and switches available for the Twister 2X, please refer
to the chart below.
TYPE FUNCTION
1-Step Pushbutton Pushbutton with momentary output contact relay
1-Step Electronic Toggled Pushbutton Resets itself when the transmitter unit is turned
“off” or when EMS button is activated
Mechanical Toggled Pushbutton Maintained toggled even after transmitter unit is turned
“off” or when EMS button is activated
2-Stage Mechanical Rocker Switch 0-T (refer to note 1 & 2)
2-Stage Mechanical Rocker Switch 0-R (refer to note 1)
3-Stage Mechanical Rocker Switch T-0-T (refer to note 1 & 2)
3-Stage Mechanical Rocker Switch R-0-T (refer to note 1 & 2)
3-Stage Mechanical Rocker Switch T-0-R (refer to note 1 & 2)
3-Stage Mechanical Rocker Switch R-0-R (refer to note 1)
2-Stage Mechanical Selector Switch 0-T (refer to note 1 & 2)
2-Stage Mechanical Selector Switch 0-R (refer to note 1)
3-Stage Mechanical Selector Switch T-0-T (refer to note 1 & 2)
3-Stage Mechanical Selector Switch T-0-R (refer to note 1 & 2)
3-Stage Mechanical Selector Switch R-0-T (refer to note 1 & 2)
3-Stage Mechanical Selector Switch R-0-R (refer to note 1)
“ON/OFF” 1-Step Pushbuttons Will reset to “off” position when transmitter unit is
turned “off” or after EMS reset
Note 1: 0 → Neutral position.
T → Maintained position (toggled contact).
R → Retract back to 0-position (momentary contact).
Note 2: 1-step pushbuttons, 2 & 3 stage mechanical rocker and selector switches with maintained toggled function (T) will remained
energized (or closed) even when the power of the transmitter is turned off or when EMS is activated (Receiver Hold function).
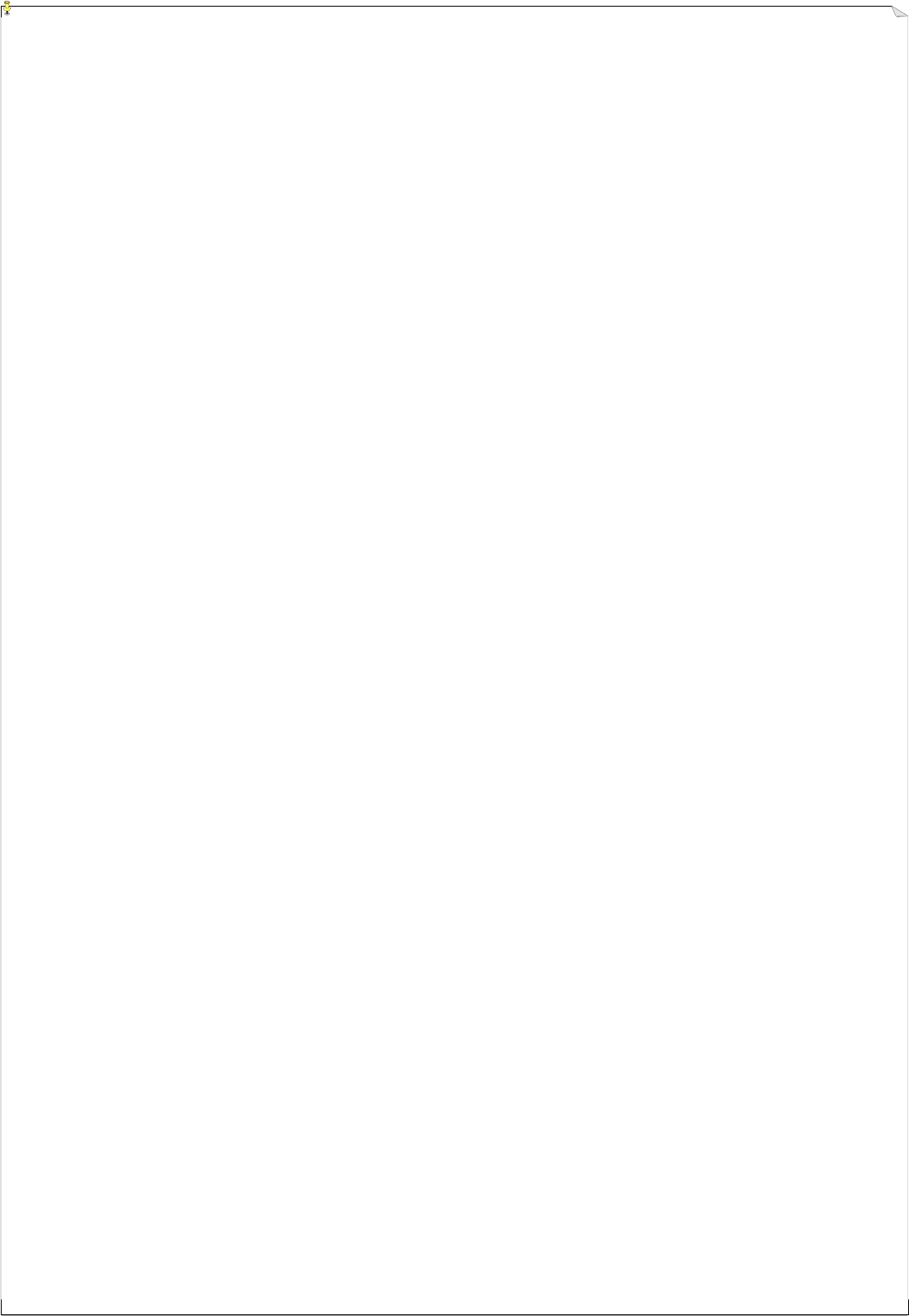
6
3.3 General Function Descriptions
Emergency Stop Button (Standard Equipped)
In case of an emergency, press down the red emergency stop button (EMS) will immediately
deactivates the transmitter power and the receiver safety MAIN contact relays (refer to section 4.1 on
page 7).
Transmitter Power Key (Standard Equipped)
All transmitters are equipped with two detachable power keys (one for spare) for turning the
transmitter power “on” and “off” (refer to section 4.1 on page 7).
START button (Standard Equipped)
All transmitters are equipped with a START button for purpose of activating the receiver MAIN
contact relay after turning on the transmitter power. After turning “on” the transmitter unit via the
transmitter power key, press and hold the START button for up to a second will activate the receiver
MAIN contact relay.
After resetting the EMS button, by twisting the button 1/4 turn clockwise, the operator must also
press and hold the START button for up to a second to reenergize the receiver MAIN contact relay.
Also, when the system is left unattended for 5 minutes or longer (system will go into sleep mode), the
operator must again press and hold the START button for up to a second to reenergize the receiver
MAIN contact relay.
Removable Relay Cards (Standard Equipped)
Special designed relay cards provided easy service maintenance and as well as for simplifying the
inventory of spare parts.
Auto-Scanning Receiver (Standard Equipped)
When transmitter’s frequency channel (from channel 01 ~ 20) is changed via simple dip-switch
setting inside the transmitter belly box, the receiver will search and locked on to the intended
matching transmitter.
Tandem Feature / Dual-Crane Operation Feature (optional)
This feature allows two operators controlling two crane systems independently or one operator
controlling two crane systems simultaneously (Crane A, Crane B, Crane A+B).
“Pitch And Catch” Feature (optional)
This feature allows two operators controlling one crane system from opposite ends of a long or cross
travel.
Random Access Feature (optional)
This feature allows for up to 8 operators randomly accessing up to 8 crane systems via a 16-position
mechanical selector switch and operate pitch/catch function via START/PITCH button.
Infrared Initial Startup Feature (optional)
The feature allows system activation under or in close proximity to the crane or receiver via infrared
transmission. After infrared initial system activation, the frequency transmission will take over.
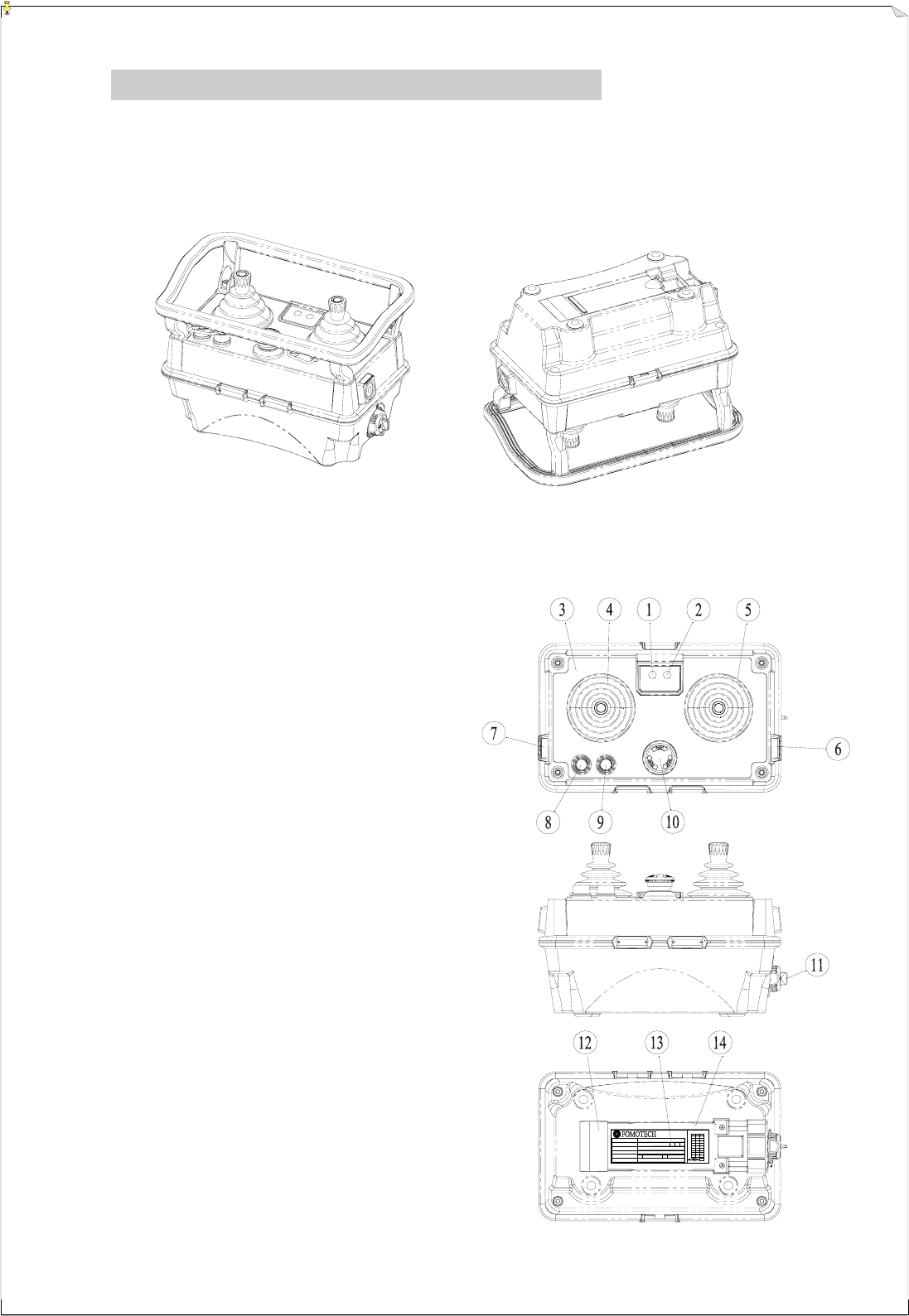
7
4. TRANSMITTER OUTLINE
4.1 Transmitter External Descriptions
(Fig. 1) Transmitter Top View (Fig. 2) Transmitter Bottom View
1. Battery Power LED Display
2. Status LED Display
3. Information Top Plate (engraved)
4. Left Joystick
5. Right Joystick
6. START Pushbutton
7. AUX/RES Pushbutton (side panel)
8. AUX/RES Pushbutton (top panel)
9. AUX/RES Pushbutton (top panel)
10. Emergency Stop Button (EMS)
11. Power Key (detachable)
12. Battery Contact (gold-plated)
13. System Information
14. Battery slot
(Fig. 3) Transmitter Exterior Views
MODEL
VOLTAGE
BAND
POWER
S/NO.
0
1
2
3
4
5
6
7
8
9A
CHANNEL A B C
BC
:
:
:
:
:
:
V
mMHz
RXWTXW
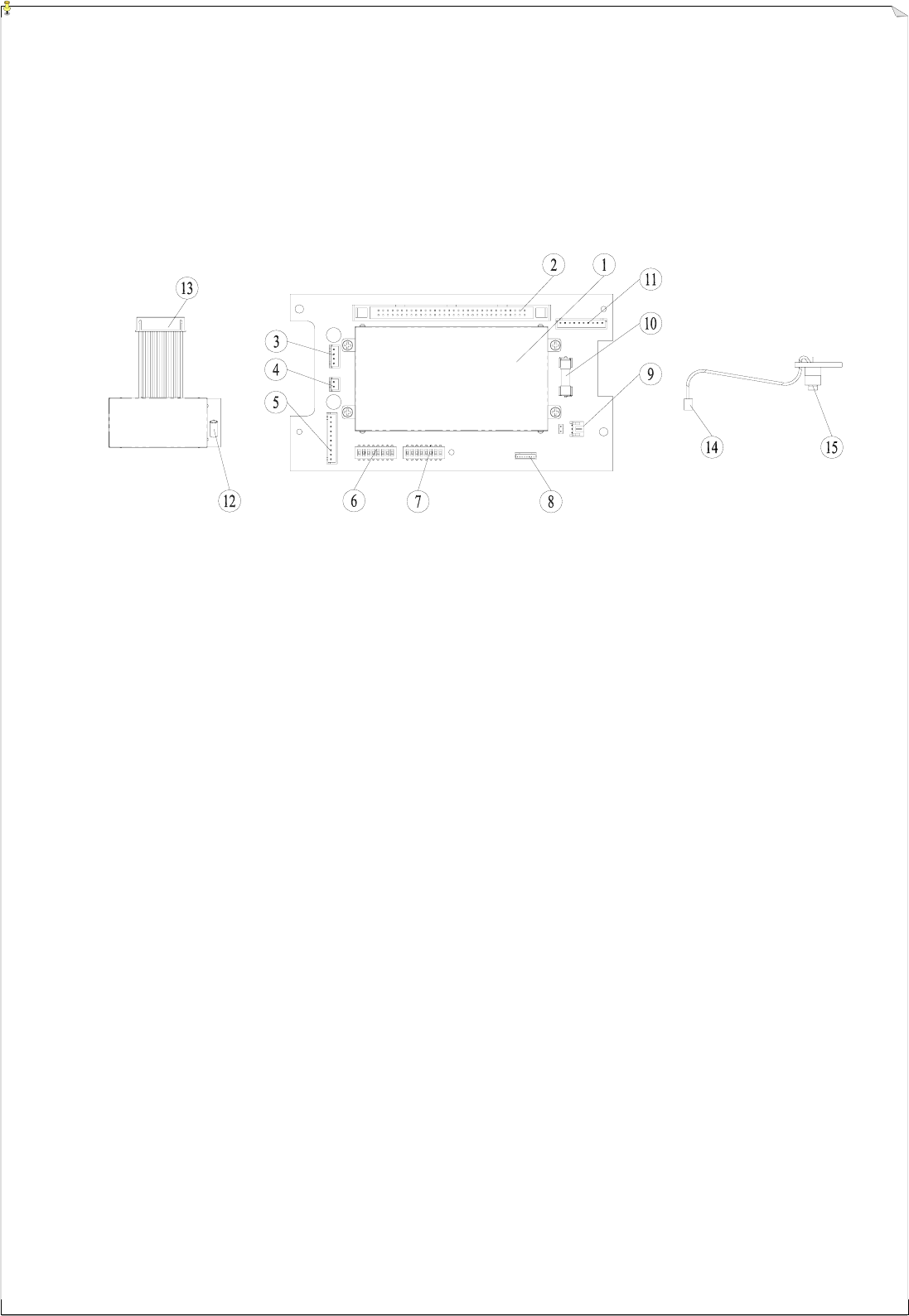
8
4.2 Transmitter Internal Descriptions
(Fig. 4) RF Module, Encoder Board and Power Switch Views
1. Encoder Shielding Plate 9. Power Key Switch Connector Port
2. Ribbon Type Connector Port 10. Power Fuse (0.5A)
3. Power Input Connector Port 11. Infrared Startup Interface Port
4. Charger Connector Port 12. Antenna Port
5. TX Module Connector Port 13. TX module Connector
6. ID Code Dip-Switch 14. Power Key Switch Connector
7. Frequency Channel Dip-Switch 15. Power Key Switch
8. External Programming Port
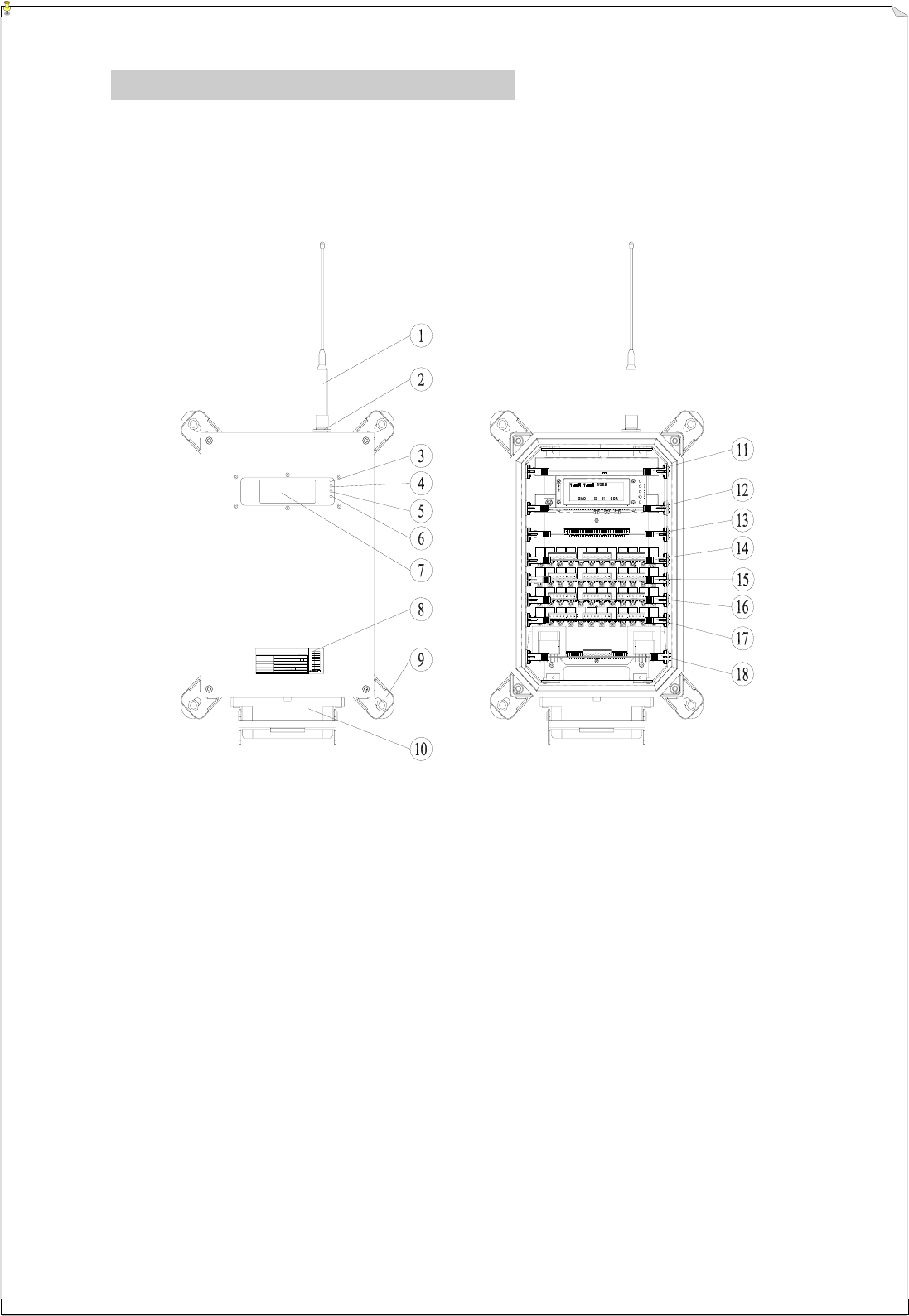
9
0
00
00
00
00
00
00
00
00
00
00
00
00
00
00
00
00
00
00
00
0
FTEC I T 'P
>>>>>>
MODEL
VOLTAGE
BAND
POWER
S/NO.
0
1
2
3
4
5
6
7
8
9A
CHANNEL A B C
BC
:
:
:
:
:
:
V
mMHz
RXWTXW
5. RECEIVER OUTLINE
5.1 Receiver External and Internal Descriptions
(Fig. 5) Receiver External and Internal View
1. Antenna 10. Multi-Pin Cable Connector (optional)
2. Antenna Port 11. RX Module Card
3. AC Power Display 12. Decoder Card
4. SQ-1 Display (for RX-1) 13. Reserved Relay Card Slot
5. SQ-2 Display (for RX-2 / optional) 14. Relay Card #1
6. Central CPU Status Display 15. Relay Card # 2
7. System LCD Display 16. Relay Card # 3
8. System Information Plate 17. Relay Card # 4
9. Mounting Bracket + Shock Absorber 18. Power Supply Card
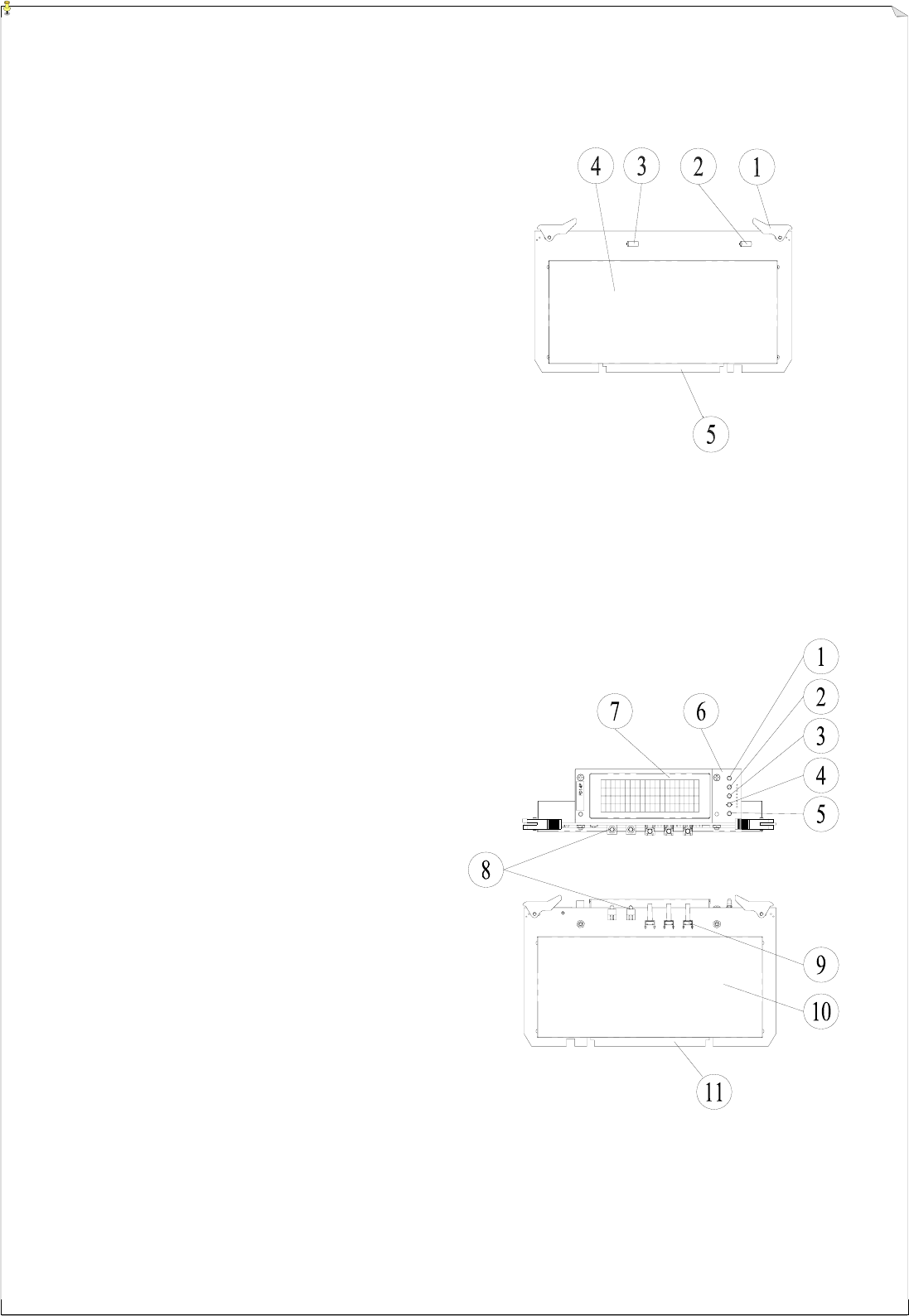
10
RX Module Card
1. RX Module Card Release Clip
2. RX-1 Antenna Port
3. RX-2 Antenna Port (optional)
4. RX module Shielding Plate
5. RX Module Card-to-Motherboard
Connector
(Fig. 6) Receiver RX Module Card
Decoder Card
1. Power Display (LED #1)
2. SQ-1 Display (LED #2)
3. SQ-2 Display (LED #3)
4. Central CPU Status Display (LED #4)
5. Reserved Function Display (LED #5)
6. LED Display Panel
7. LCD Screen
8. Dual Decoding CPU Status Display
(LED #6 and LED #7)
9. Function Settings Buttons
10. Decoder Shielding Plate
11. Decoder Card-to-Motherboard
Connector
(Fig. 7) Receiver Decoder Card
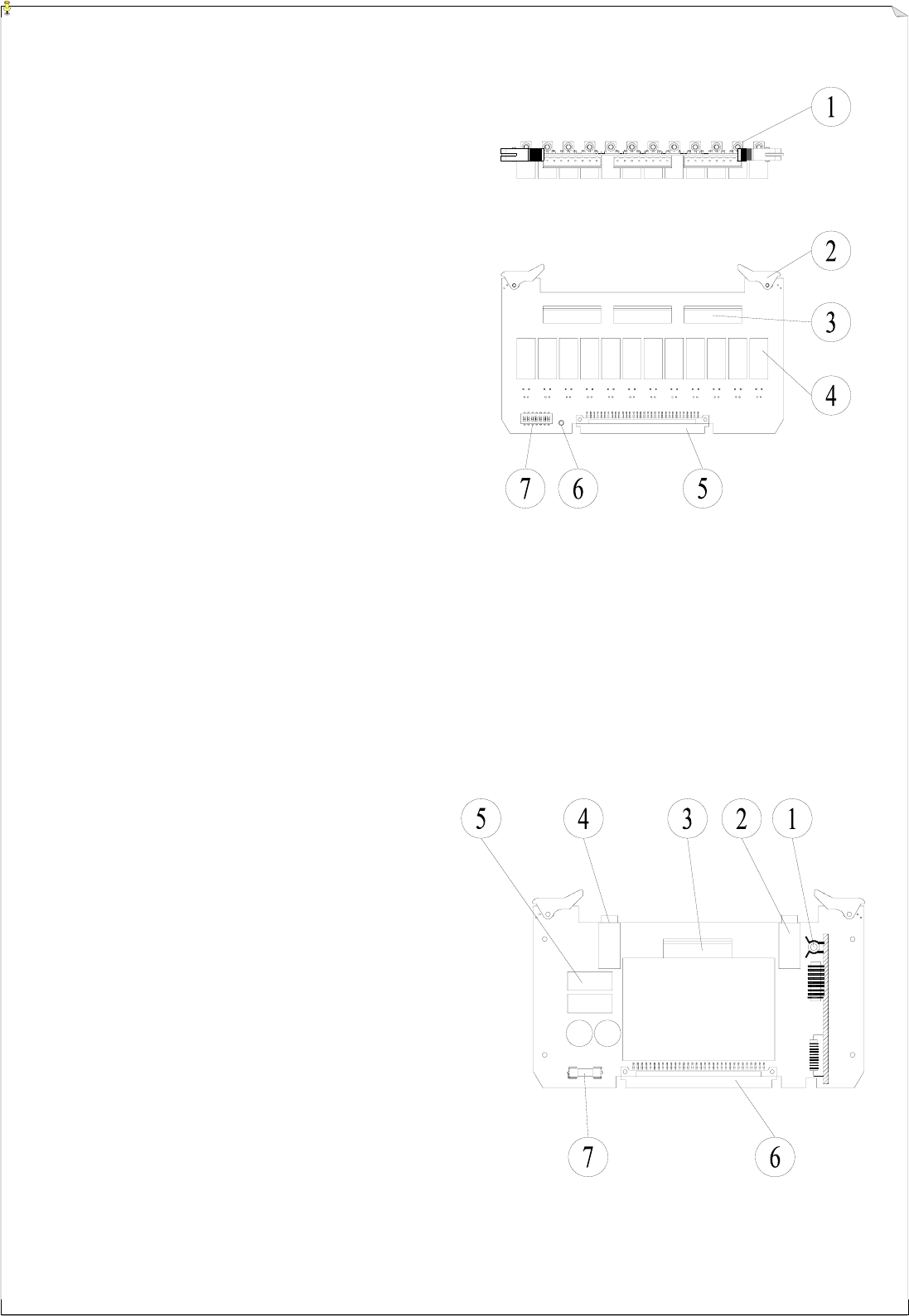
11
Output Relay Card
1. Relay LED Display
2. Relay Card Release Clip
3. Relay Output Contact Connector Port
4. Contact Relays
5. Relay Card-to-Motherboard Connector
6. Relay Power LED Display
7. Relay Card Position/Address
Dip-Switch (see note below).
(Fig. 8) Receiver Output Relay Card
Note: The relay card position (address) dip-switch must be adjusted according to the wiring diagram sheet located on the last page of
this manual and on the backside of the receiver cover plate.
Relay Card Position 1 → Address: 0000000 Relay Card Position 4 → Address: 0000011
Relay Card Position 2 → Address: 0000001 Relay Card Position 5 → Address: 0000100
Relay Card Position 3 → Address: 0000010
Power Supply Card
1. Power AC Fuse #1 (2.0A)
2. Power AC Fuse #2 (2.0A)
3. VAC Input / VDC Output Connector
4. MAIN Contact Relay Fuse (3.0A)
5. Dual MAIN Contact Relays
6. Power Supply Card-to-Motherboard
Connector
7. VDC Fuse
(Fig. 9) Receiver Power Supply Card
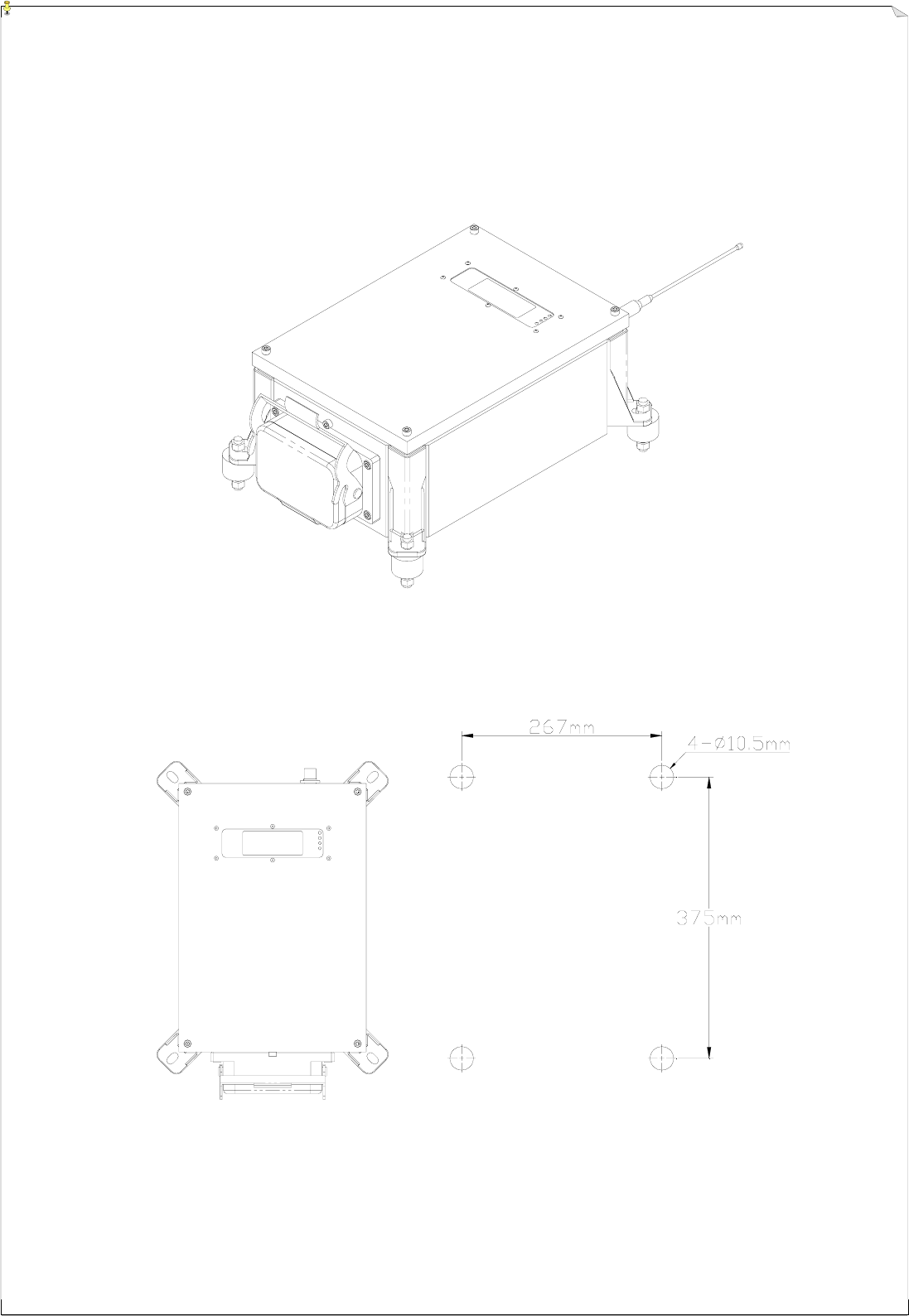
12
5.2 Receiver Mounting Dimension
(Fig. 10) Receiver Exterior View
(Fig. 11) Receiver Mounting Dimension
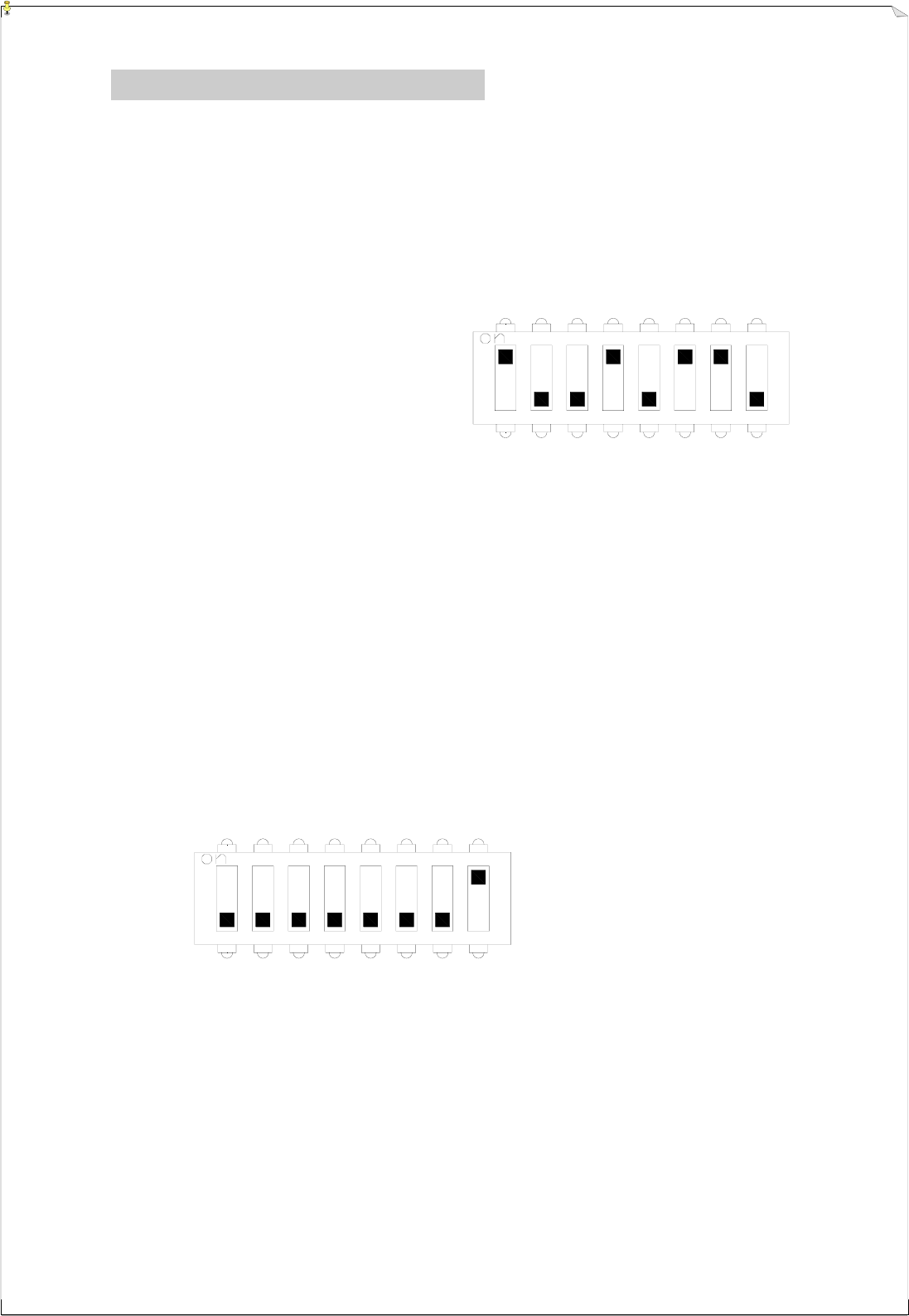
13
6. SYSTEM SETTINGS
6.1 Transmitter ID Code Settings
Transmitter ID code are set via an 8-position dip-switch located on the encoder board (refer to
fig. 4 on page 8). For receiver ID code settings please refer to section 6.3 & 6.4.
Example: ID code → 10010110
Top location : “1”
Bottom location : “0”
Note: When transmitter ID code is altered please also make sure to readjust the receiver ID code accordingly. System will not
operate if the ID code on both the transmitter and receiver are different.
6.2 Transmitter Frequency Channel Settings
The transmitter frequency channel is also set via an 8-position dip-switch located on the
encoder board (refer to fig. 4 on page 8). For receiver frequency channel settings please refer
to section 6.3 & 6.4.
For the below dip-switch with 00000001 setting, the RF channel is “01”, which also represents
frequency “910.500MHz” (refer to frequency channel table on page 16).
Top location : “1” Bottom location : “0”
Note: When the frequency channel of the transmitter is altered please also make sure to readjust the receiver frequency channel
accordingly. System will not operate if the frequency channel on both the transmitter and receiver are different.
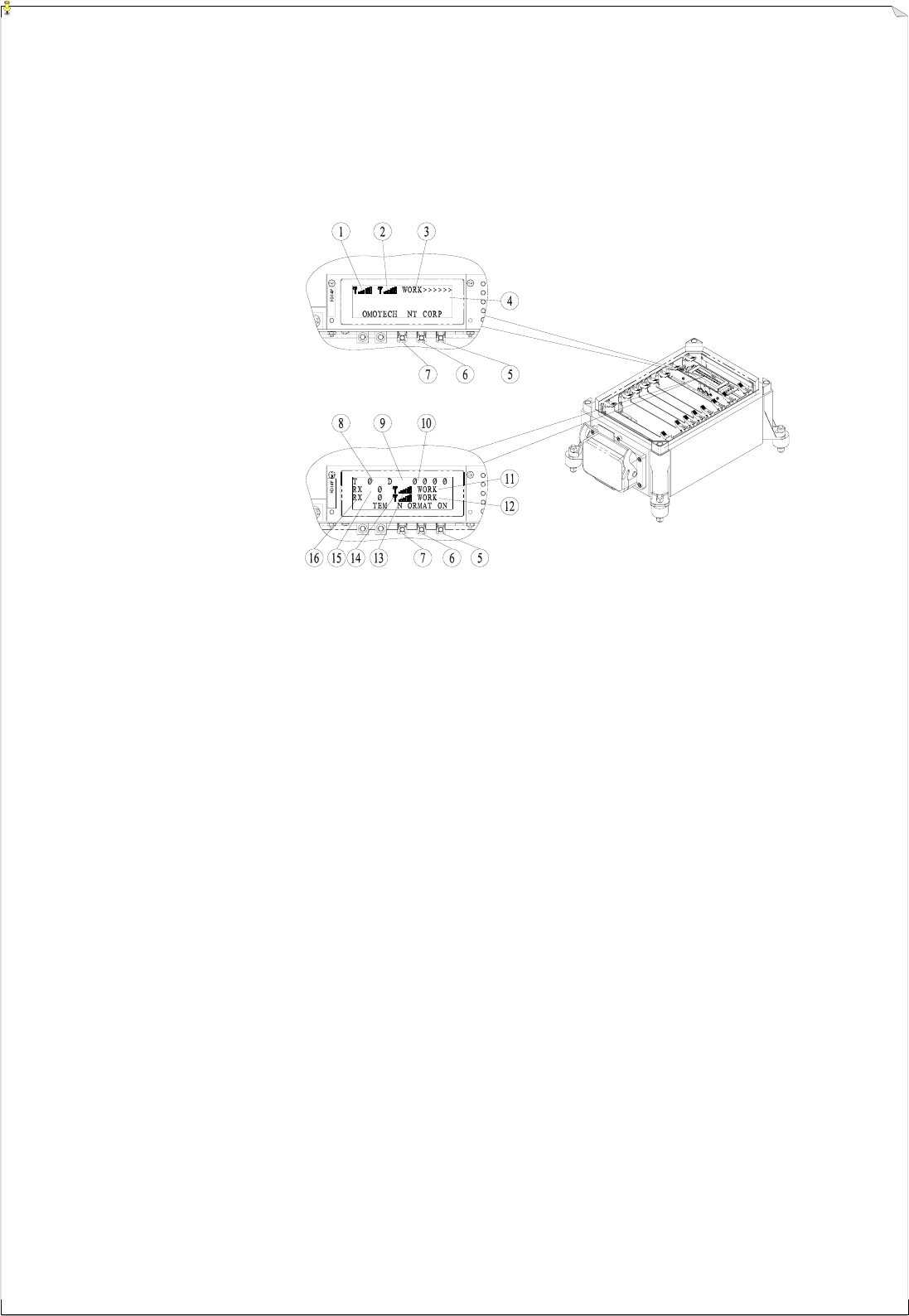
14
F I '
0
00
00000 0000 0000 0000 0000 0000 0000
0000
0000
YS S
1:
F
5
I
2:5
P:1I:77-1111
I
6.3 Receiver LCD Status Displays
(Screen “1”)
(Screen “2”)
(Fig. 12) Receiver LCD Screen
1. RX-1 Signal Strength 9. ID Code-1 (regional code)
2. RX-2 Signal Strength (optional) 10. ID Code-2 (system ID code)
3. System at Work 11. Decoder System-1
4. Contact Relay Activation Display 12. Decoder System-2
“0”→ relay OFF; “1”→ relay ON 13. RX–1 Signal Strength
5. EXIT/DOWN (-) Button (PS1) 14. RX–2 Signal Strength (optional)
6. EDIT/UP (+) Button (PS2) 15. RX–1 Frequency Channel
7. MODE/ENTER Button (PS3) 16. RX–2 Frequency Channel (optional)
8. System Type
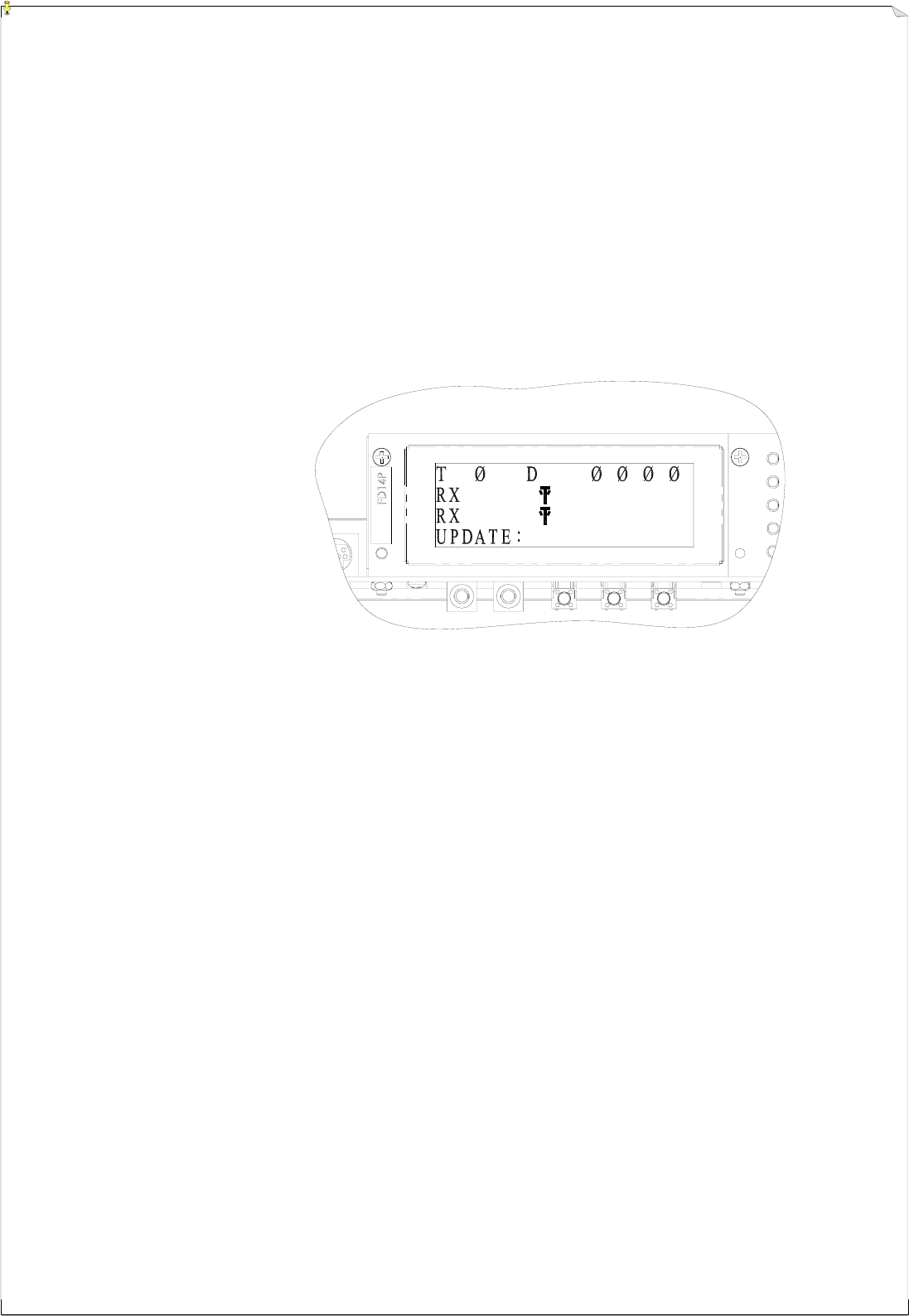
15
1:
2:
P:1I:77-1111
__
__ _
___
_
_
6.4 Receiver ID Code & Frequency Channel Settings
Unlike the dip-switch setting on the transmitter, the receiver ID code and frequency channel can
be easily adjusted via the LCD control panel on the receiver unit. Please follow the
step-by-step instructions illustrated below on how to change receiver ID code and frequency
channel.
(Screen “3”)
1) To enter into screen “2”, press MODE/ENTER button one time.
2) To enter into Screen “3”, press EDIT/UP (+) button for up to 5 seconds.
3) TP (System type) and Country code cannot be changed (manufacture preset).
4) Press EXIT/DOWN (-) button and EDIT/UP (+) buttons to change the ID code.
5) Press MODE/ENTER button to proceed to the RX-1 setting column.
6) Press EXIT/DOWN (-) button and EDIT/UP (+) button to change frequency channel
of RX-1.
7) Press MODE/ENTER button to proceed to RX-2 setting column.
8) Press EXIT/DOWN (-) button and EDIT/UP (+) button to change frequency channel
of RX-2.
9) Press MODE/ENTER button to proceed to the UPDATE setting column.
10) Press EDIT/UP (+) button to input “YES” as to save changes.
11) Press EXIT/DOWN (-) button to input “NO” as to cancel changes.
12) Press MODE/ENTER button to exit screen “3”.
Note A: If new values are not inputted within 25 seconds, the system will exit the setup screen (screen “3”) and returned
to screen “1”.
Note B: If your system is not equipped with dual RX module, please skip step 7 through 8 described above.
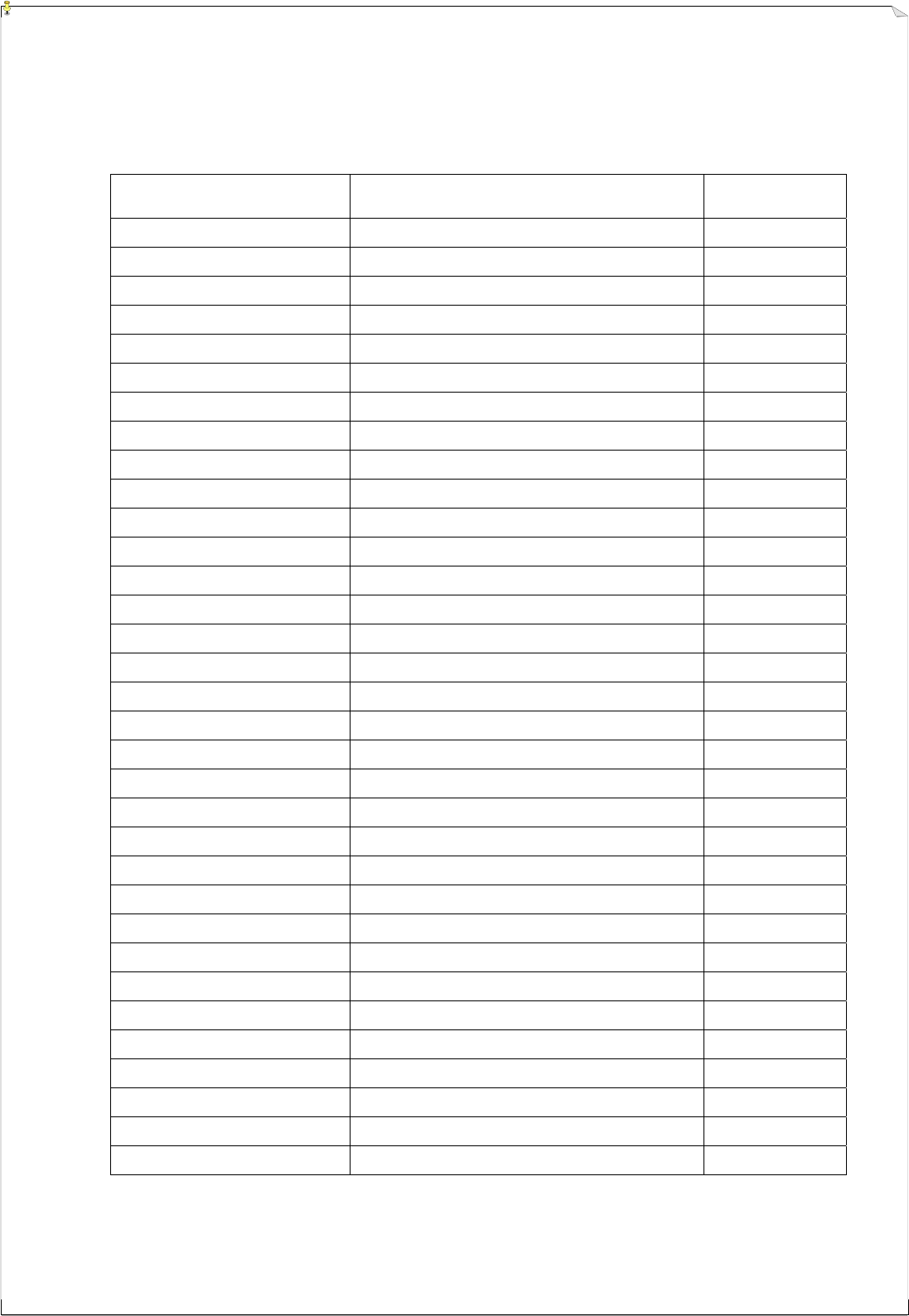
16
6.5 Frequency Channel Table
FREQUENCY DIP-SWITCH SETTING CHANNEL
910.500 MHz 00000001 01
910.550 MHz 00000010 02
910.600 MHz 00000011 03
910.650 MHz 00000100 04
910.700 MHz 00000101 05
910.750 MHz 00000110 06
910.800 MHz 00000111 07
910.850 MHz 00001000 08
910.900 MHz 00001001 09
910.950 MHz 00001010 10
911.000 MHz 00001011 11
911.050 MHz 00001100 12
911.100 MHz 00001101 13
911.150 MHz 00001110 14
911.200 MHz 00001111 15
911.250 MHz 00010000 16
911.300 MHz 00010001 17
911.350 MHz 00010010 18
911.400 MHz 00010011 19
911.450 MHz 00010100 20
911.500 MHz 00010101 21
911.550 MHz 00010110 22
911.600 MHz 00010111 23
911.650 MHz 00011000 24
911.700 MHz 00011001 25
911.750 MHz 00011010 26
911.800 MHz 00011011 27
911.850 MHz 00011100 28
911.900 MHz 00011101 29
911.950 MHz 00011110 30
912.000 MHz 00011111 31
912.050 MHz 00100000 32
912.100 MHz 00100001 33
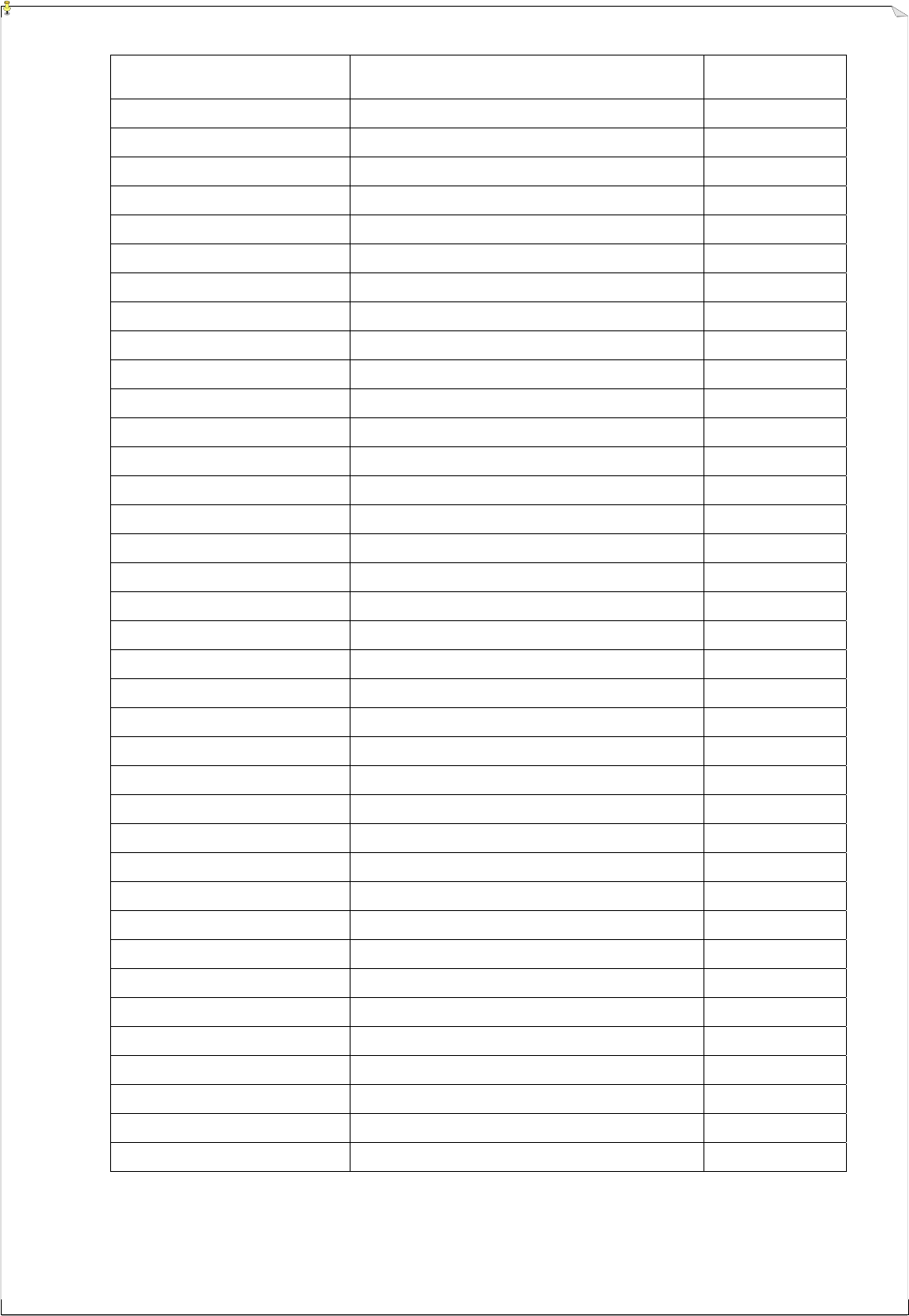
17
FREQUENCY DIP-SWITCH SETTING CHANNEL
912.150 MHz 00100010 34
912.200 MHz 00100011 35
912.250 MHz 00100100 36
912.300 MHz 00100101 37
912.350 MHz 00100110 38
912.400 MHz 00100111 39
912.450 MHz 00101000 40
912.500 MHz 00101001 41
912.550 MHz 00101010 42
912.600 MHz 00101011 43
912.650 MHz 00101100 44
912.700 MHz 00101101 45
912.750 MHz 00101110 46
912.800 MHz 00101111 47
912.850 MHz 00110000 48
912.900 MHz 00110001 49
912.950 MHz 00110010 50
913.000 MHz 00110011 51
913.050 MHz 00110100 52
913.100 MHz 00110101 53
913.150 MHz 00110110 54
913.200 MHz 00110111 55
913.250 MHz 00111000 56
913.300 MHz 00111001 57
913.350 MHz 00111010 58
913.400 MHz 00111011 59
913.450 MHz 00111100 60
913.500 MHz 00111101 61
913.550 MHz 00111110 62
913.600 MHz 00111111 63
913.650 MHz 01000000 64
913.700 MHz 01000001 65
913.750 MHz 01000010 66
913.800 MHz 01000011 67
913.850 MHz 01000100 68
913.900 MHz 01000101 69
913.950 MHz 01000110 70
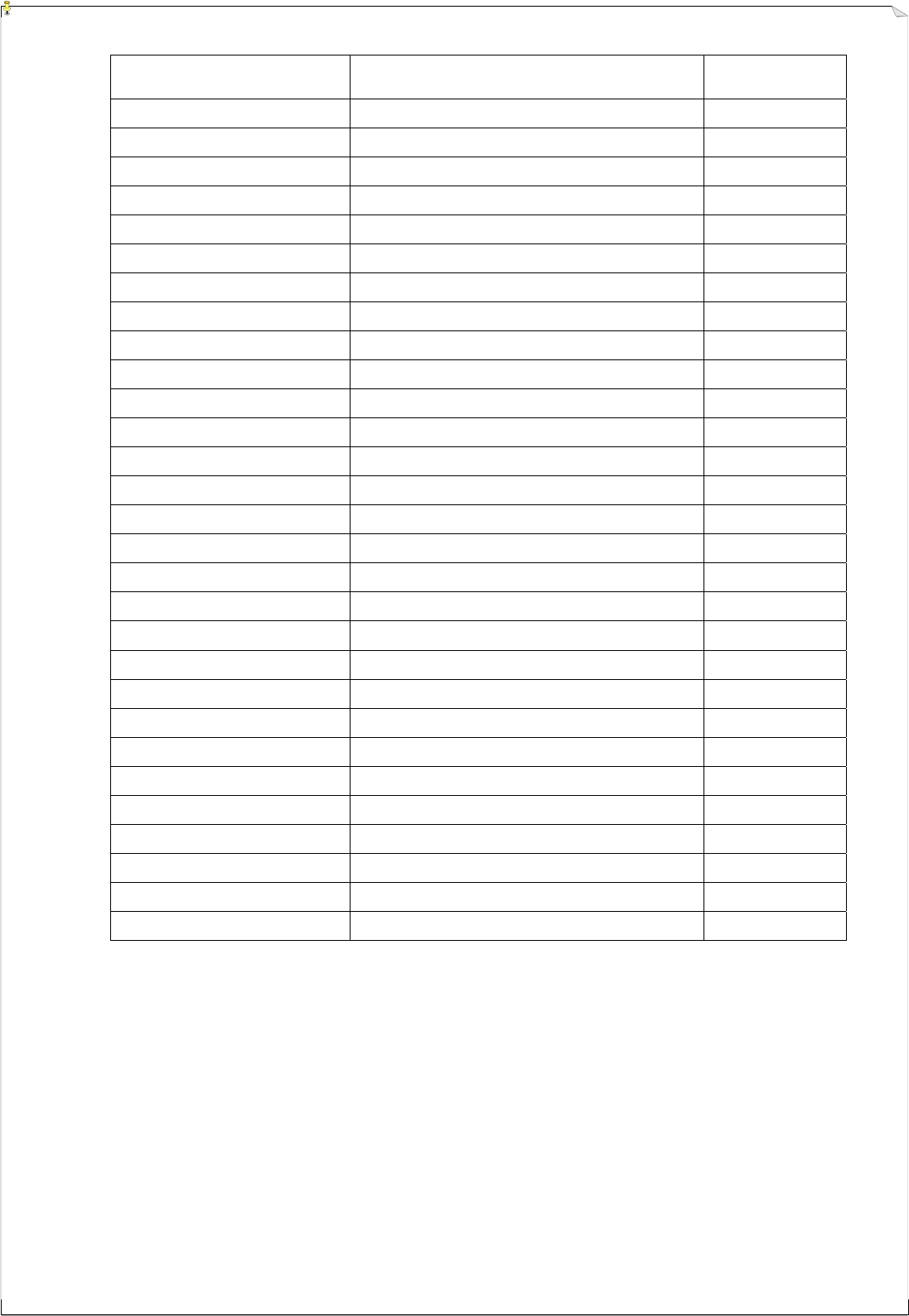
18
FREQUENCY DIP-SWITCH SETTING CHANNEL
914.000 MHz 01000111 71
914.050 MHz 01001000 72
914.100 MHz 01001001 73
914.150 MHz 01001010 74
914.200 MHz 01001011 75
914.250 MHz 01001100 76
914.300 MHz 01001101 77
914.350 MHz 01001110 78
914.400 MHz 01001111 79
914.450 MHz 01010000 80
914.500 MHz 01010001 81
914.550 MHz 01010010 82
914.600 MHz 01010011 83
914.650 MHz 01010100 84
914.700 MHz 01010101 85
914.750 MHz 01010110 86
914.800 MHz 01010111 87
914.850 MHz 01011000 88
914.900 MHz 01011001 89
914.950 MHz 01011010 90
915.000 MHz 01011011 91
915.050 MHz 01011100 92
915.100 MHz 01011101 93
915.150 MHz 01011110 94
915.200 MHz 01011111 95
915.250 MHz 01100000 96
915.300 MHz 01100001 97
915.350 MHz 01100010 98
915.400 MHz 01100011 99
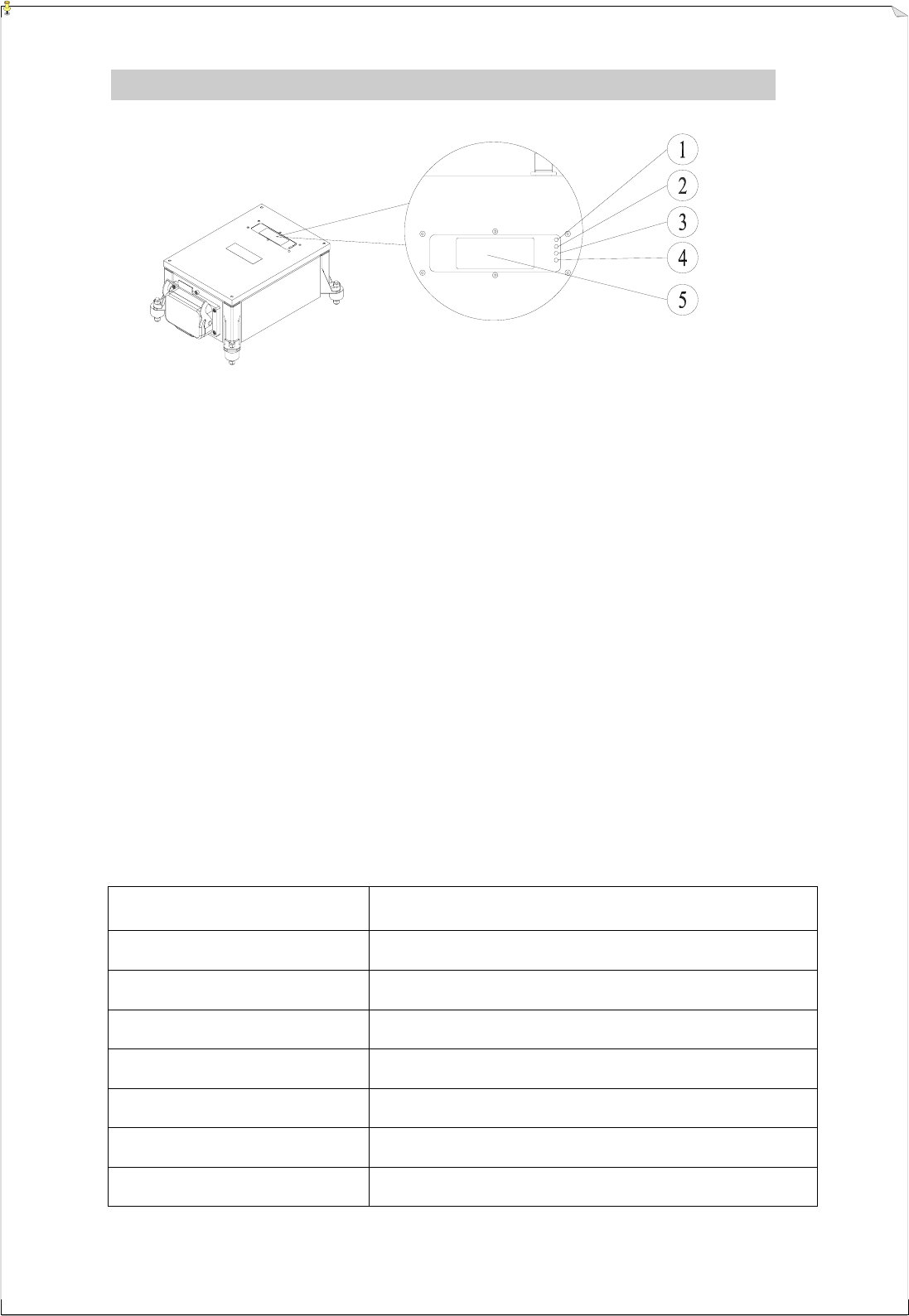
19
7. RECEIVER STATUS LED DISPLAYS
(Fig 13) Receiver Status LED Display
1. Receiver Power Display 4. Central CPU Status Display
2. SQ-1 (RX-1) Status Display 5. LCD System Information Display
3. SQ-2 (RX-2) Status Display
Receiver Power Display
Should be lighted at all time when the system is turned on, if not, please check the input power
source.
SQ-1 and SQ-2 Status Displays
Lights “on” → Transmitted signals detected and received.
Lights “off” → No transmitted signals detected.
Blinking lights when transmitter is turned “off” → Other radio interference.
Dual Decoding CPU Status Display (refer to Fig. 7 on page 10)
Lights “on” 0.1 second and “off” 1.0 second → Decoders on Standby.
Lights “on” 0.1 second and “off” 0.1 second → Decoding in Process.
Receiver Central CPU Status LED Display
LED INDICATION REASON
Slow Blinks (Green) Standby
Fast Blinks (Green) Transmitted signals received
Fast Blinks (Red) MAIN contact relays jammed or defective
3 Fast Blinks (Red) RX module defective
4 Fast Blinks (Red) EEPROM error
5 Fast Blinks (Red) Incorrect transmitted ID code
6 Fast Blinks (Red) Incorrect system type
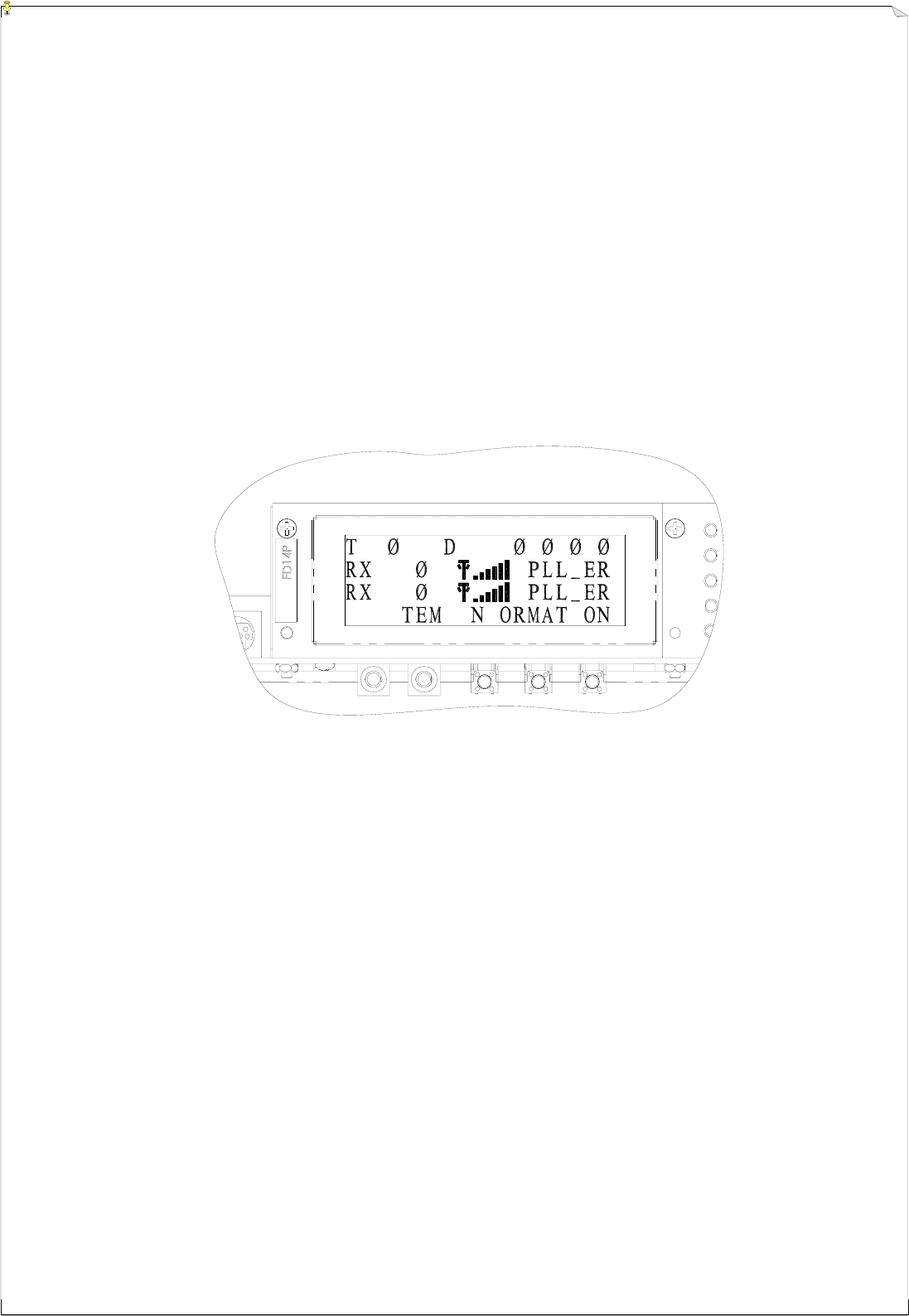
20
YS S
1:
F
5
I
2:5
P:1I:77-1111
I
Receiver Central CPU Status LCD Display
Some of the system status indications described on page 17 are also displayed on the receiver LCD
screen for easy readout (screen “2”).
1) ID_ER → Incorrect transmitted ID code
2) MAIN_ER → Defective MAIN contact relay or relays
3) PLL_ER → Defective RX module
4) WORK → Transmitted signals received and decoded
5) SEARCH → System on standby
6) SCAN → System scanning for new frequency channel
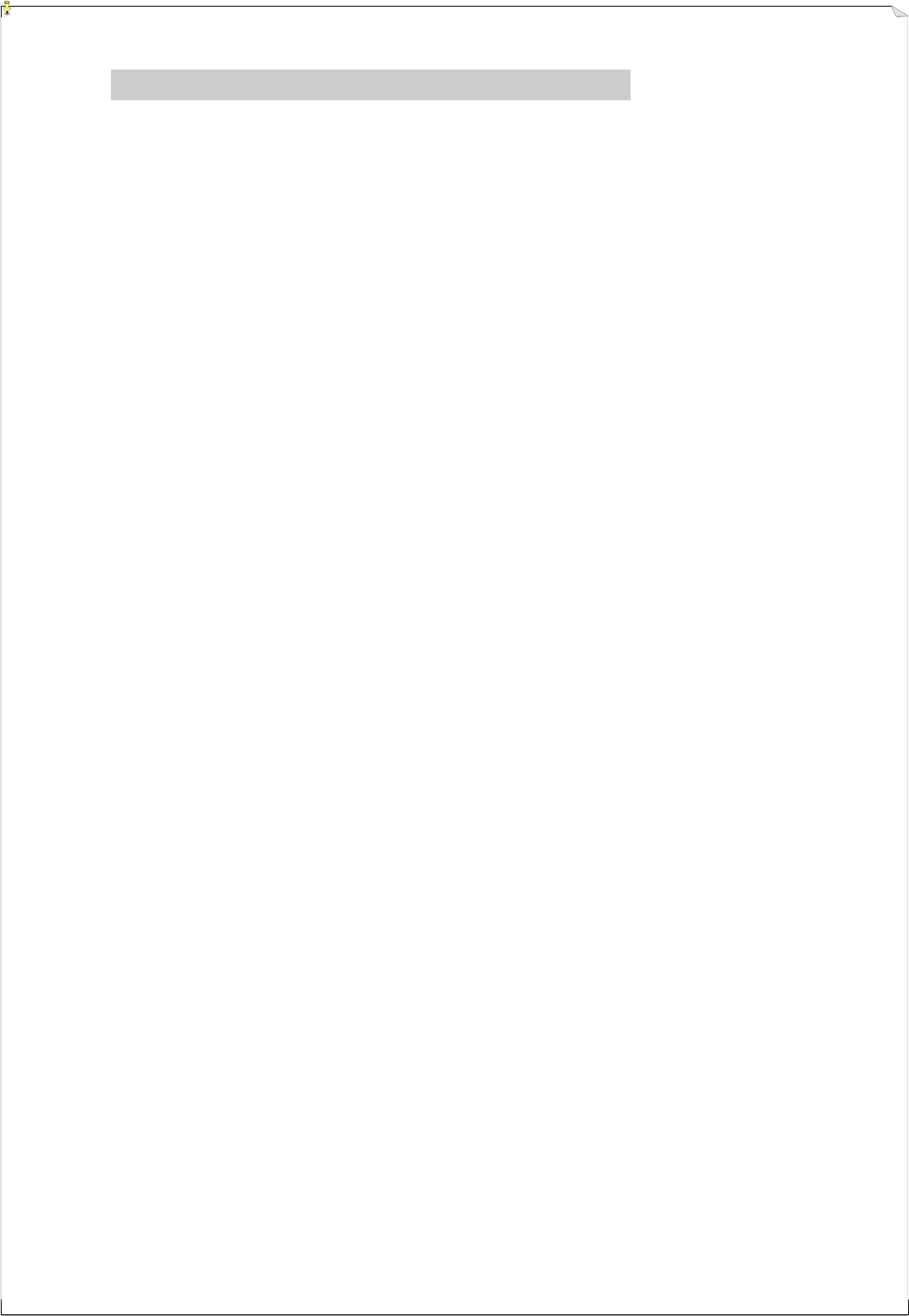
21
8. RECEIVER INSTALLATION
8.1 Preparation
1. Required Tools:
1) Flat Head Screwdriver (- )
2) Phillips Head Screwdriver (+)
3) Multi-Meters
4) 14 mm Wrench X 2
5) Power Drill with 10.5 ~ 11mm Drill-Bit
6) Output Cables
2. Ensure receiver is not set to the same frequency channel and ID code as any other units in
use at the same facility or within distance of 300 meters.
3. Prior to installation, make sure that the crane system itself is working properly.
4. Use the multi-meter to check the voltage source available and ensure receiver voltage
setting is correct for this voltage.
5. Prior to installation, switch off the main power source to the equipment.
8.2 Steps-By-Steps Installation
1. Select a suitable location to mount the receiver.
2. As much as possible, the location selected should have the antenna visible from all areas
where the transmitter is to be used.
3. The location selected should not be exposed to high levels of electrical noise.
4. Ensure the selected location has adequate space to accommodate the receiver enclosure.
5. The distance between the antenna and the control panel should be as far apart as possible.
6. Drill four holes on the control panel (10.5mm).
7. Tightened all screws provided.
8. For system wiring, please refer to the wiring diagram located on the last page of this
manual and on the backside of the receiver cover plate.
9. Ensure all wiring is correct and safely secured and all screws are fastened.
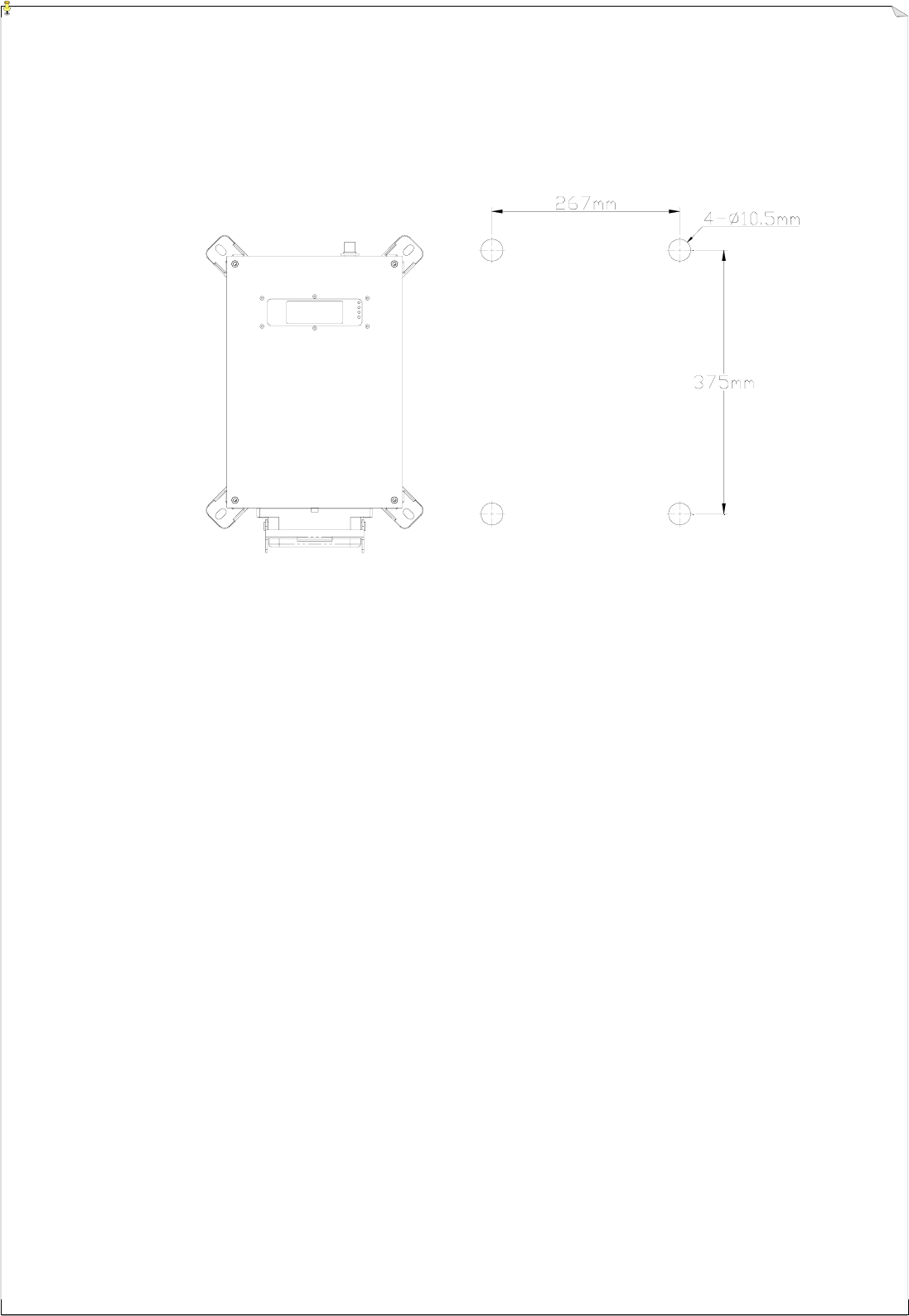
22
8.3 System Testing
1. Connect the power source to the receiver and test the operation of each function to
ensure it operates in the same manner as the pendant controller.
2. Ensure the MAIN contact relay can be properly controlled by the remote control.
3. Ensure the limit switches on the crane that limit all travels are working properly.
4. Ensure the pendant controller is located in a safe location where it would not interfere
with remote operation.
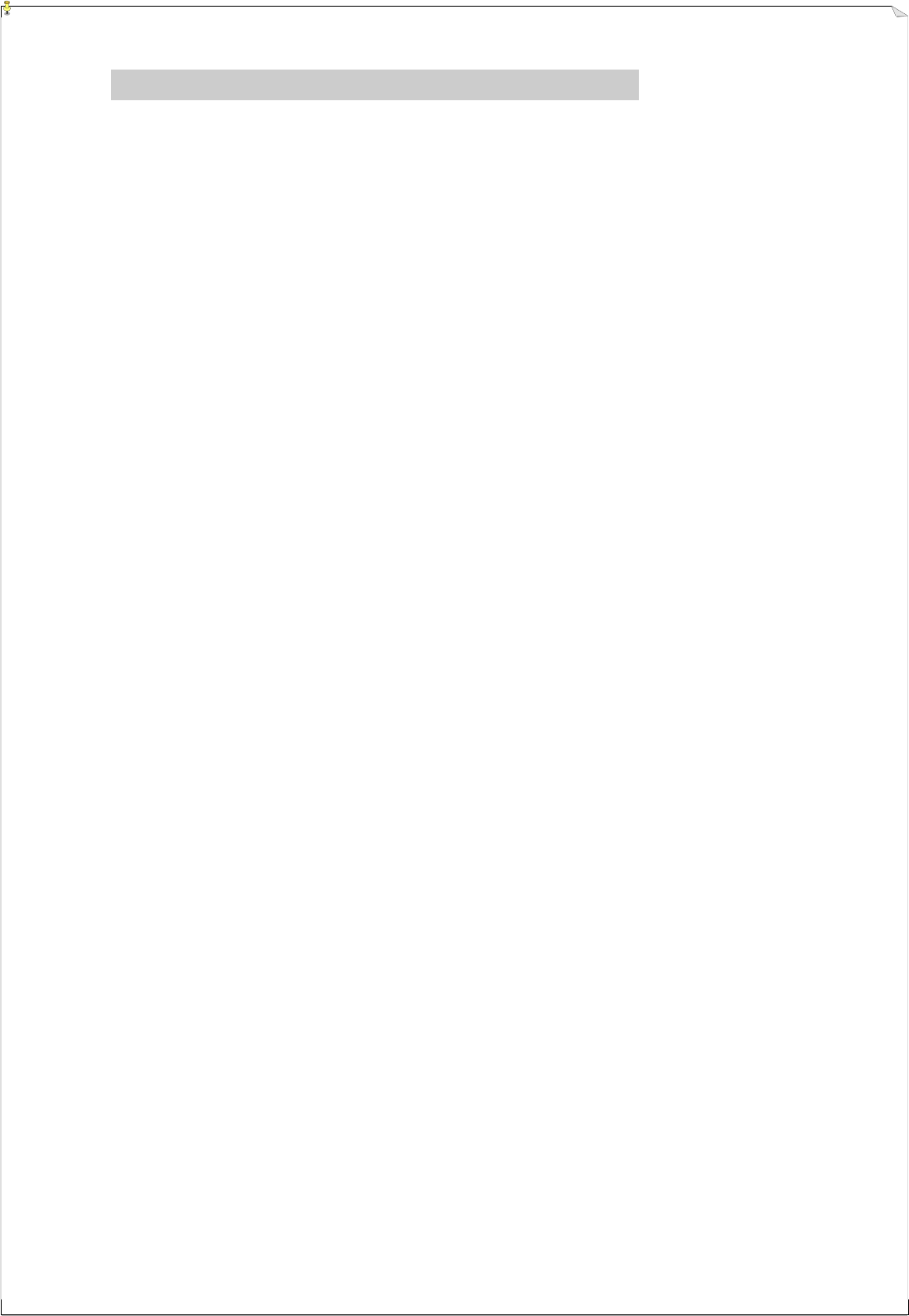
23
9. OPERATING INSTRUCTION
9.1 Power “ON” the System
1. Insert the transmitter power key into the key-switch slot located on the right side of the
transmitter belly box.
2. Push the transmitter power key inward and then rotate it clockwise to “1” position.
“1” → “ON” “0” → “OFF”
3. Make sure both joysticks are in their neutral (0-speed) position when transmitter power is
turned “on”. If the transmitter is turned “on” with the joystick in a non-neutral position,
the transmitter will be temporarily disabled to avoid any unexpected crane movement at
system startup. If this situation occurs, just turn the transmitter power key “off” and then
back “on” again with joystick in neutral position.
4. Make sure that the red emergency stop button (EMS) is elevated before the transmitter
power is turned on.
5. To activate the receiver MAIN relay, press and hold the “START” pushbutton for up to 1.0
second. The START pushbutton is located on the right side of the belly box, above the
transmitter power key switch.
6. After receiver MAIN relay activation (relay closed), if the operator did not give any
command by pressing any pushbuttons or moving the joysticks to a non-neutral position,
after 5 minutes of inactivity, the transmitter unit will go into “sleep mode” with receiver
MAIN relay temporarily deactivated (relay opened). To resume operation after 5
minutes of inactivity, just press and hold the “START” pushbutton again to reactivate the
system.
7. After 1 hour of inactivity, the transmitter power will be temporarily deactivated to save
power.
8. If the frequency channel of the transmitter unit is altered via simple dip-switch setting
inside the transmitter (refer to page 13), you must then also change the frequency RF
channel in the receiver (refer to page 15~16). Since the receiver is equipped with
frequency channel auto-scanning feature, after changing the frequency channel in the
transmitter, you must then press and hold the START pushbutton for up to 20 seconds after
turning “on” the transmitter power in order for the auto-scanning receiver to identify the
newly selected channel.
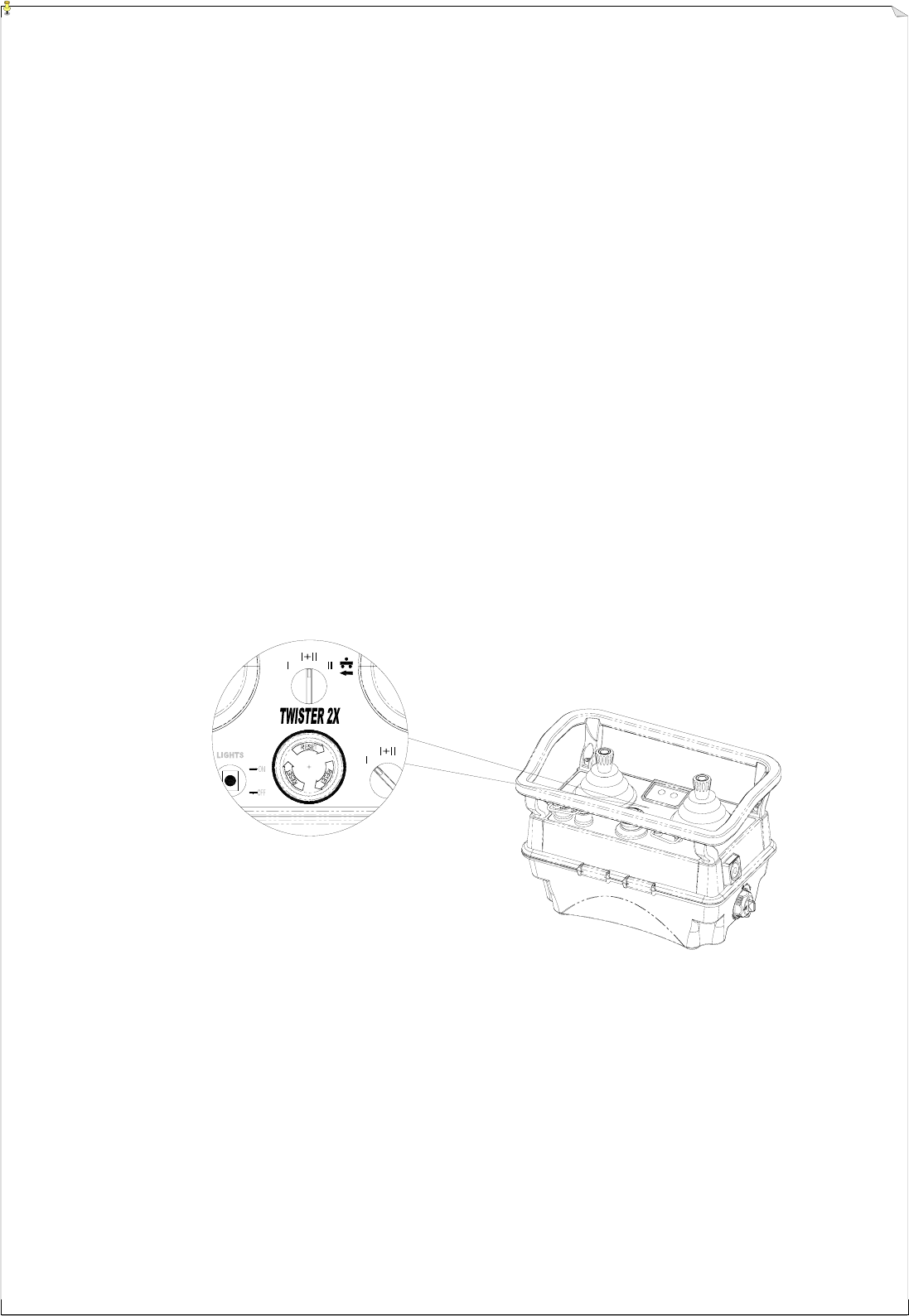
24
9.2 Dual Hoist/Trolley Operation
For system with dual hoist/trolley operation, use the 3-stage mechanical selector switch located
between the two joysticks (refer to diagram below) to select which hoist and/or trolley to
operate. At position “I”, the main hoist and/or trolley are activated. At position “II”, the
auxiliary hoist and/or trolley are activated. At position “I+II”, both main and auxiliary hoists
and/or trolleys are activated with simultaneous travel movement.
During system wiring, make sure to connect the Select-I output to the main hoist and/or trolley
and Select-II output to auxiliary hoist and/or trolley. When the selector switch is at position
“I”, Select-I contact relay will close. At position “II”, Select-II contact relay will close. At
position “I+II”, both Select-I and Select-II contact relay will close. For system wiring, please
refer to the system wiring schematic located on the last page of this manual or on the inner side
of the receiver cover.
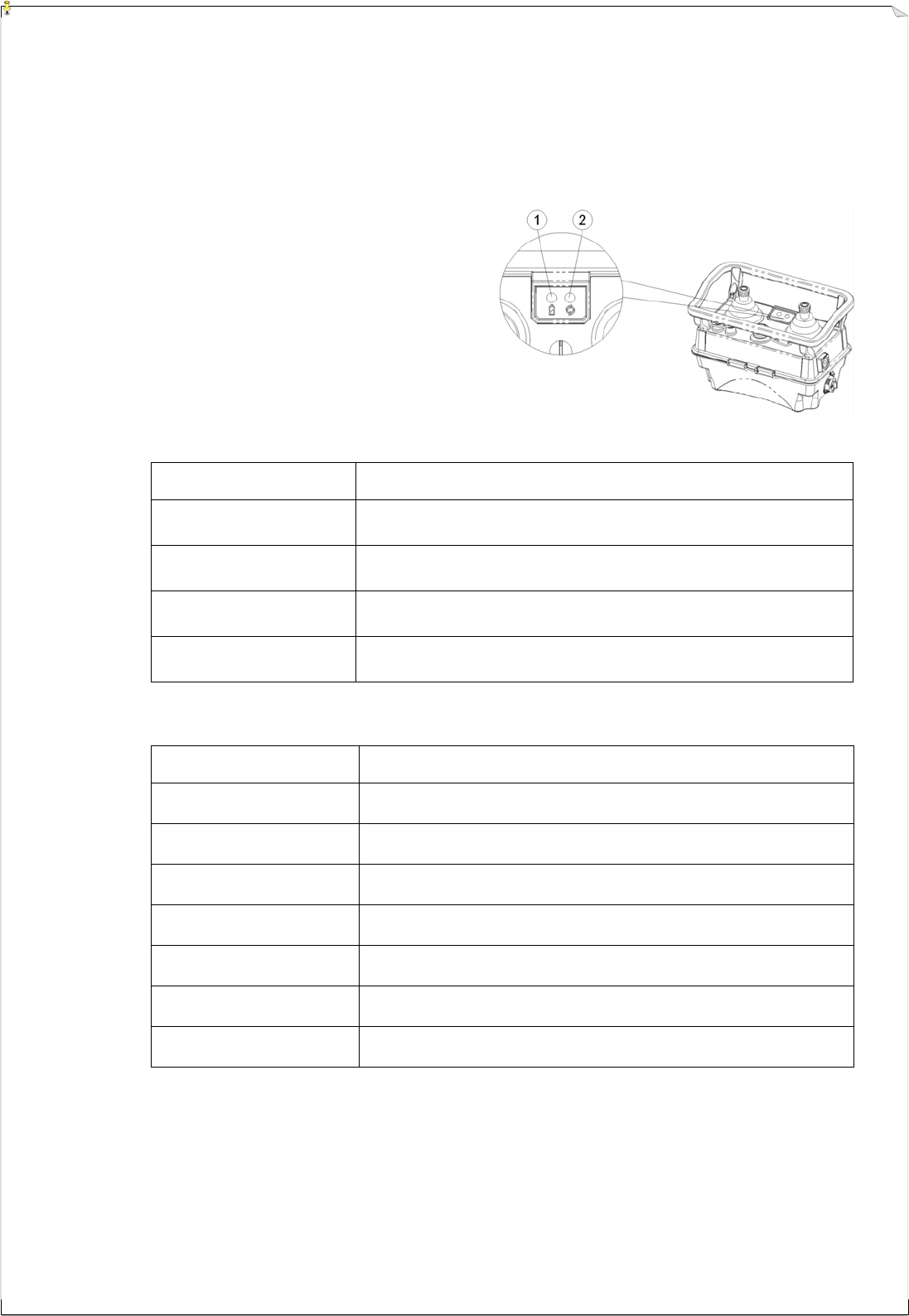
25
9.3 Transmitter System Status Displays
1. Battery Power LED Display
2. Transmitter Status LED Display
Transmitter Battery Power LED Display
POWER DISPLAY REASON
Constant Green Battery level normal
Slow Blinking Red Low battery power (1st warning)
Fast Blinking Red Low battery power (2nd warning)
Transmitter unit will stop transmitting at anytime
Constant Red Low battery power (3rd warning)
Transmitter power and receiver MAIN relay deactivated
Transmitter Status LED Display
STATUS DISPLAY REASON
No Light Displayed Transmitter in sleep mode with receiver MAIN relay deactivated
Slow Blinks (Green) Transmitter on standby
Fast Blinks (Green) Transmitter active
Constant Red Light Jammed or defective pushbutton, switch or joystick contacts
Fast Blinks (Red) The contact point currently in use is operative (refer to note A)
3 Fast Blinks (Red) PLL TX module defective
4 Fast Blinks (Red) EEPROM error
Note A: When there is a defective or jammed pushbutton, switch or joystick contacts, the transmitter status LED will display a
constant red light without flashes. To find out which contact is defective or jammed, activate each pushbuttons,
switches or joysticks a step at a time by holding at each position for up to 2 seconds. If a flashing red light (blinks
rapidly) is displayed at a specific position, it means that the contact point for that particular position is operative. If the
lights remained constantly red at a certain position, then it means that this position’s contact is either jammed or
defective. The main purpose of function is to let the user realize which contact on the transmitter is not working
properly and required service immediately.
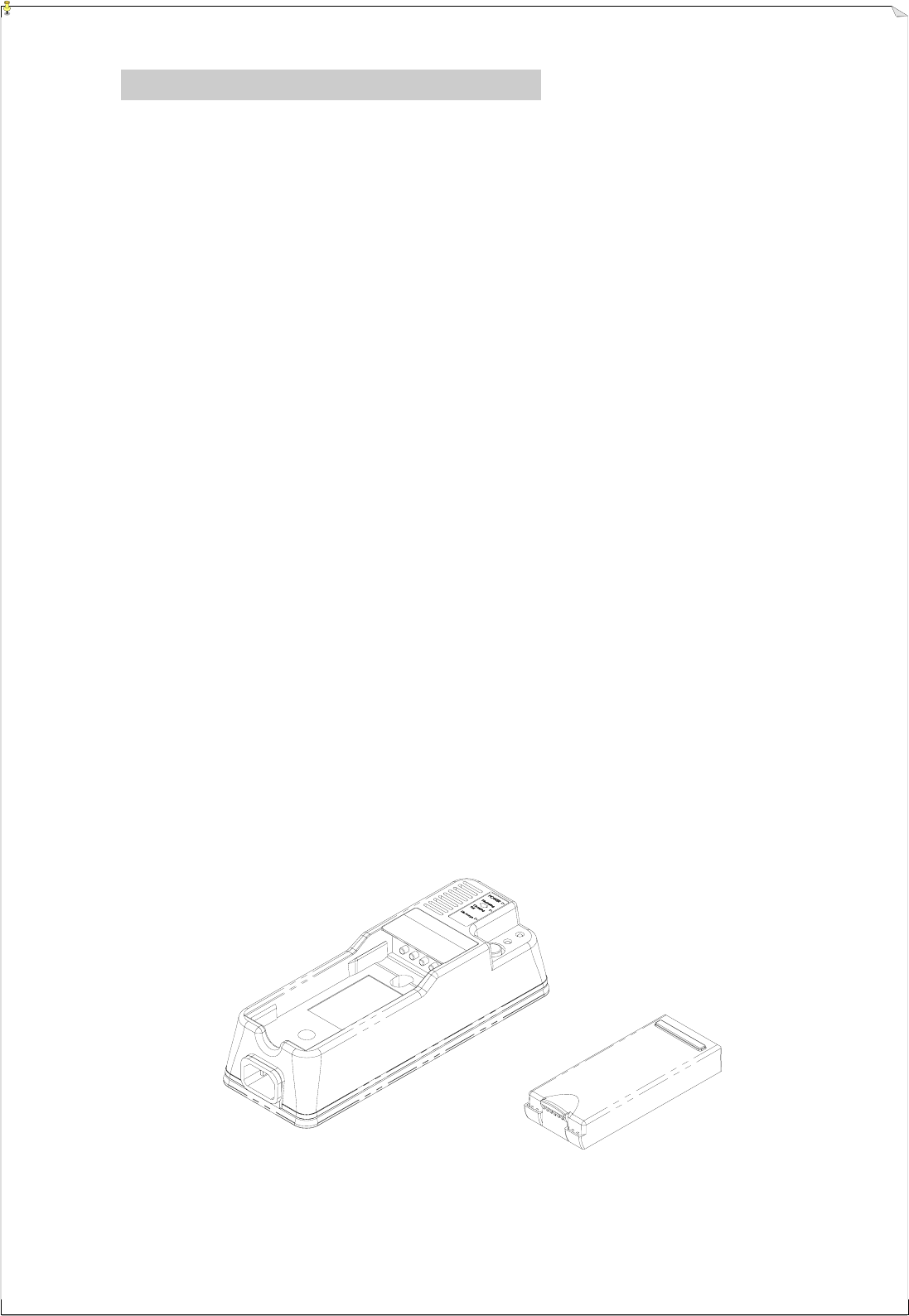
26
10.BATTERY CHARGING
1. Plug in the power cord and the power indicator will light up.
2. When a battery pack is inserted, the green charging light will blink to indicate charging is taking
place at the current moment.
3. If discharging of battery pack is desired (strongly recommended for 600mA NiCd battery pack),
press the “DISCHARGE” button. At discharging mode, the green blinking light will now
turned into a constant red light indicating that the battery pack is now being discharged. If you
want to cancel the discharge, just press “DISCHARGE” button again.
4. When discharging is completed, the charger will automatically switch to the charging mode
where the green blinking light will reappear again.
5. The charging time for a 600mA NiCd battery pack is approximately 3 ~ 6 hours. As for the
1450mA NiMH battery pack, the charging time is approximately 7 ~ 9 hours.
6. When charging is completed, a constant green light will appear to indicate that the battery pack
is fully charged.
7. When the battery pack is at 90% charged state, trickle charging will take over to ensure the
longevity of the battery pack and as well as to ensure the battery pack is 100% charged.
8. When the battery pack’s temperature exceeds 50℃, the charger will go into protective mode
and charging will be discontinued.
9. To prolong the life of the battery pack (600mA NiCd battery pack), it is recommended that the
battery pack be fully discharged prior to every re-charging.
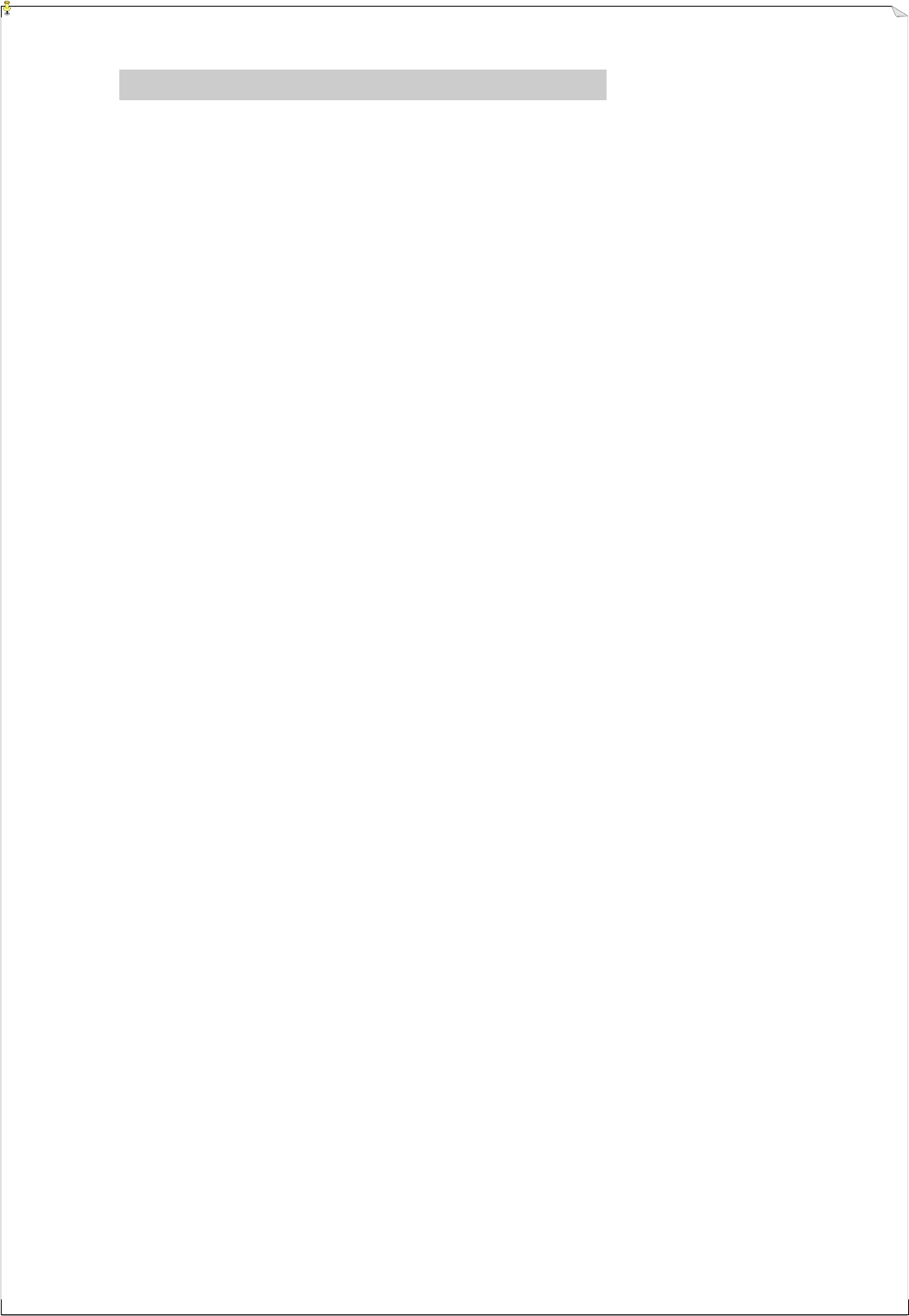
27
11.SYSTEM SPECIFICATION
Transmitter Unit
Frequency Range : PLL 910.500 ~915.400 MHz
Transmitting Range: : 100 Meters
Continuous Operating Time : 37.7+ Hours (1650mA)
Security ID Code : 65,536 sets (16 + 1 bit)
Channel Spacing : 50KHz
Hamming Distance : ≧ 6
Frequency Control : Synthesizer (PLL)
Frequency Drift : < 3ppm @ -25℃ ~ 75℃
Frequency Deviation : < 1ppm @ 25℃
Spurious Emission : > 60dBc
Transmitting Power :
0.043mW
Emission : F1D
Antenna Impedance : 50 ohms
Enclosure Rating : IP-66
Source Voltage : 7.2 V (1650mA)
Current Drain : ~80mA
Operating Temperature : -10℃ ~ 75℃
Dimension : 247mm X 154mm X 182mm
Weight : 1,600g (with 1650mA battery pack)
Note: Longer or shorter transmitting ranges are available upon request.
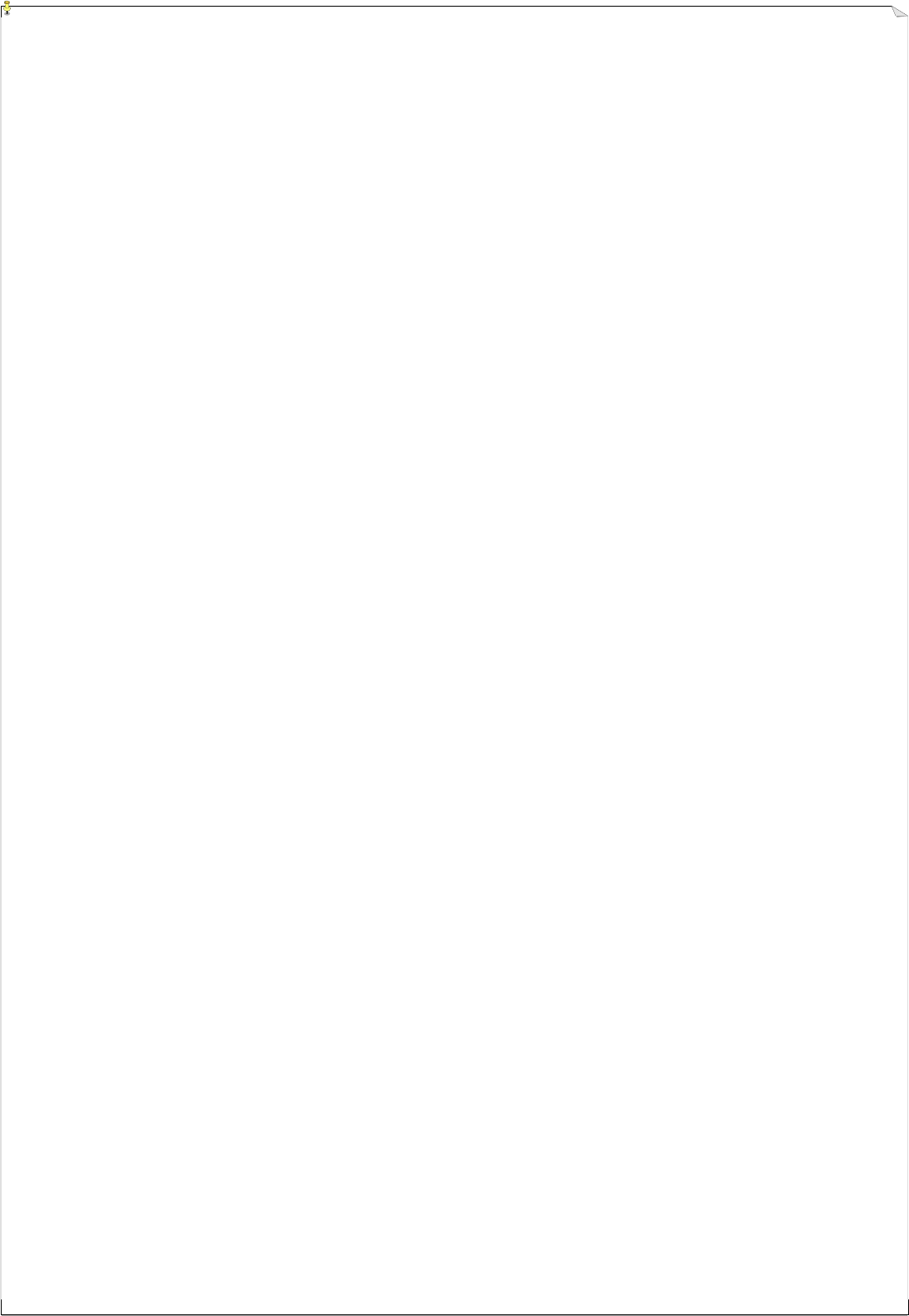
28
Receiver Unit
Frequency Range : PLL910.500 ~915.400 MHz
Channel Spacing : 50KHz
Hamming Distance : ≧ 6
Frequency Control : Synthesizer (PLL)
Frequency Drift : < 3ppm @ -10℃ ~ 75℃
Frequency Deviation : 1ppm @ 25℃
Sensitivity : -115dBm
Decoding Reference : FSK
Antenna Impedance : 50 ohms
Data Decoder Reference : Quartz Crystals
Responding Time : 100mS ~ 300mS
Enclosure Rating : IP-66
Source Voltage : 100 ~ 240VAC @ 50/60 Hz. (standard equipped)
Power Consumption : 36VA
Operating Temperature : -10℃ ~ 75℃
Output Contact Rating : 250V @ 10A
Dimension : 417mm X 309mm X 167mm
Weight : 8,800g (without the output cable)
Note: Other types of source voltages are available upon request.
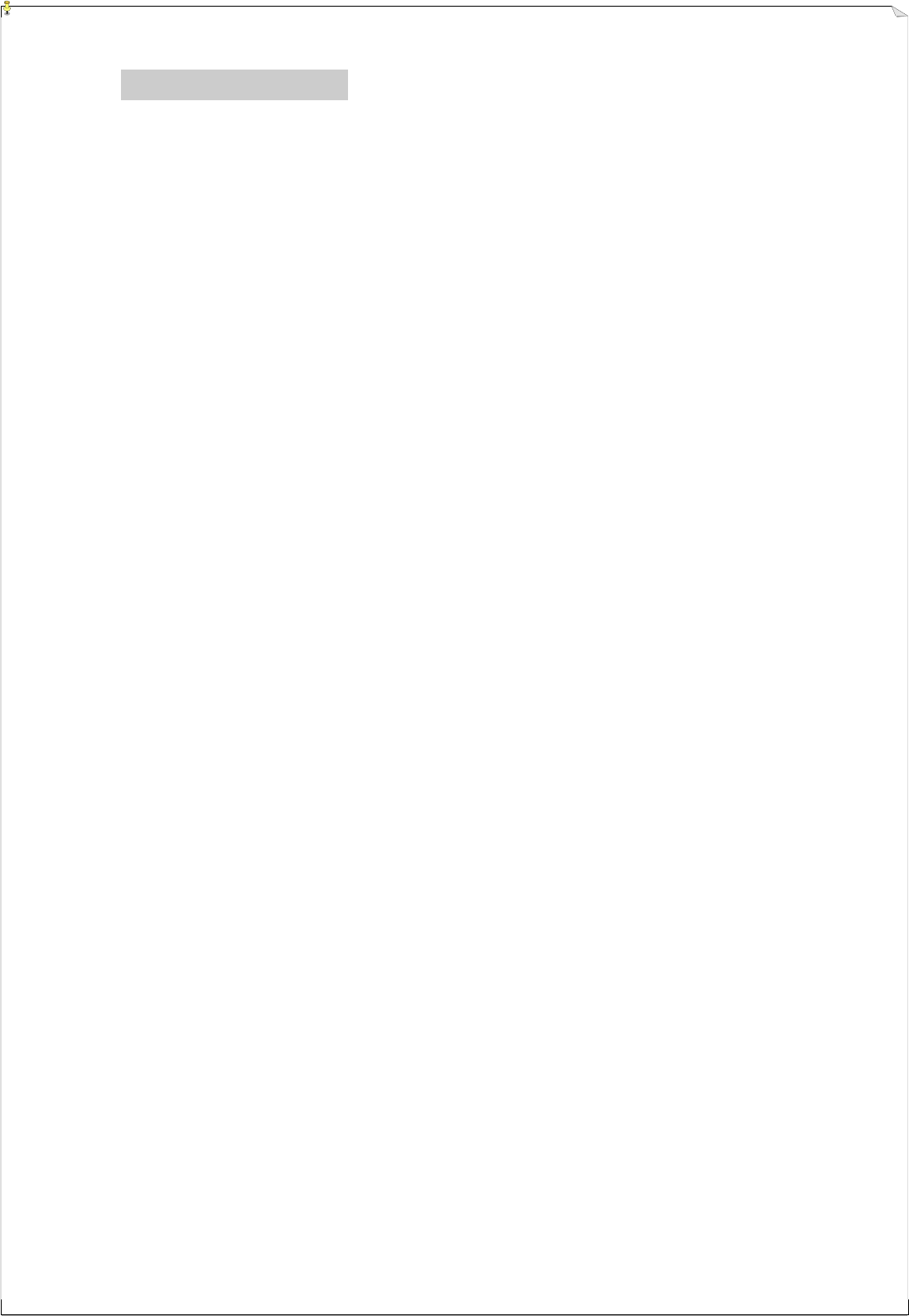
29
12.PARTS LIST
1. TX module (please specify frequency band) TX5000
2. RX module card (please specify frequency band) RX5000
3. Encoder board EN5000
4. Decoder card DE5000
5. Relay card RY5000
6. Power supply card (100 ~ 240VAC) PS5000
Power supply card (48VAC) PS5001
Power supply card (24VDC) PS5002
Power supply card (380VAC) PS5003
Power supply card (400 ~ 420VAC) PS5004
7. Single axis joystick unit (complete)
2 speeds / steps JOY-12
3 speeds / steps JOY-13
4 speeds / steps JOY-14
5 speeds / steps JOY-15
8. Double axis joystick unit (complete)
2 speeds / steps JOY-22
3 speeds / steps JOY-23
4 speeds / steps JOY-24
5 speeds / steps JOY-25
9. 1-step pushbutton (side panel) PB-1S
10. 1-step pushbutton (top panel) PB-1T
11. 2-stage selector switch SW-2T
12. 3-stage selector switch SW-3T
13. 2-stage toggle switch TW-2T
14. 3-stage toggle switch TW-3T
15. Emergency stop button EM5000
16. Transmitter casing (complete) TC5000
18. Transmitter protective guardrail PG5000
19. Transmitter power key PW5000
20. 1650mA NiMH battery pack BAT1650
21. Receiver antenna (433 MHz ~ 434 MHz) ANT433
22. Receiver antenna (910.500 ~915.400 MHz) ANT910
23. Receiver enclosure (complete) RC5000
24. Intelligent charger (please specify voltage) CH5000
25. Waist Belt WB5000
26. Shoulder Strap SS5000
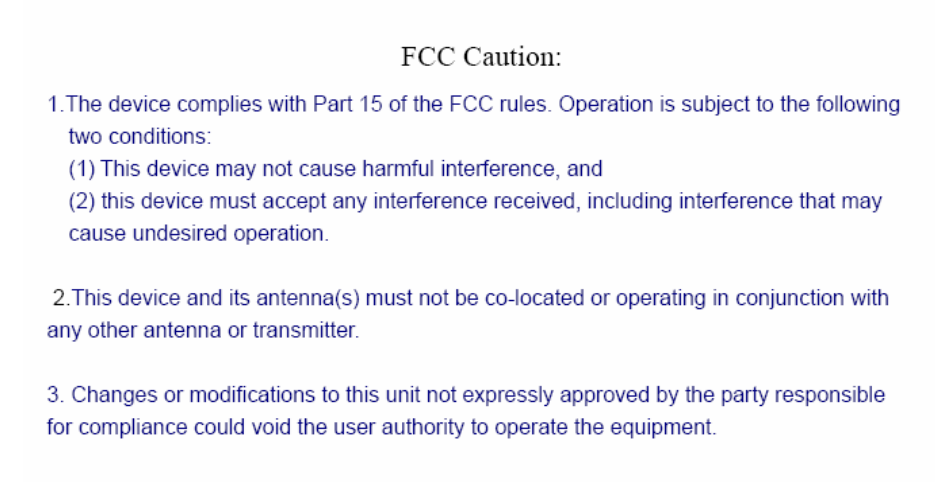