Friedrich Air Conditioner Eq08M11 Users Manual Xstar_ServMan_02 21 11
XQ05M10 to the manual 8800c6a3-bee2-46a0-87cc-ea4c3810f2ad
2015-02-02
: Friedrich Friedrich-Friedrich-Air-Conditioner-Eq08M11-Users-Manual-428249 friedrich-friedrich-air-conditioner-eq08m11-users-manual-428249 friedrich pdf
Open the PDF directly: View PDF .
Page Count: 47
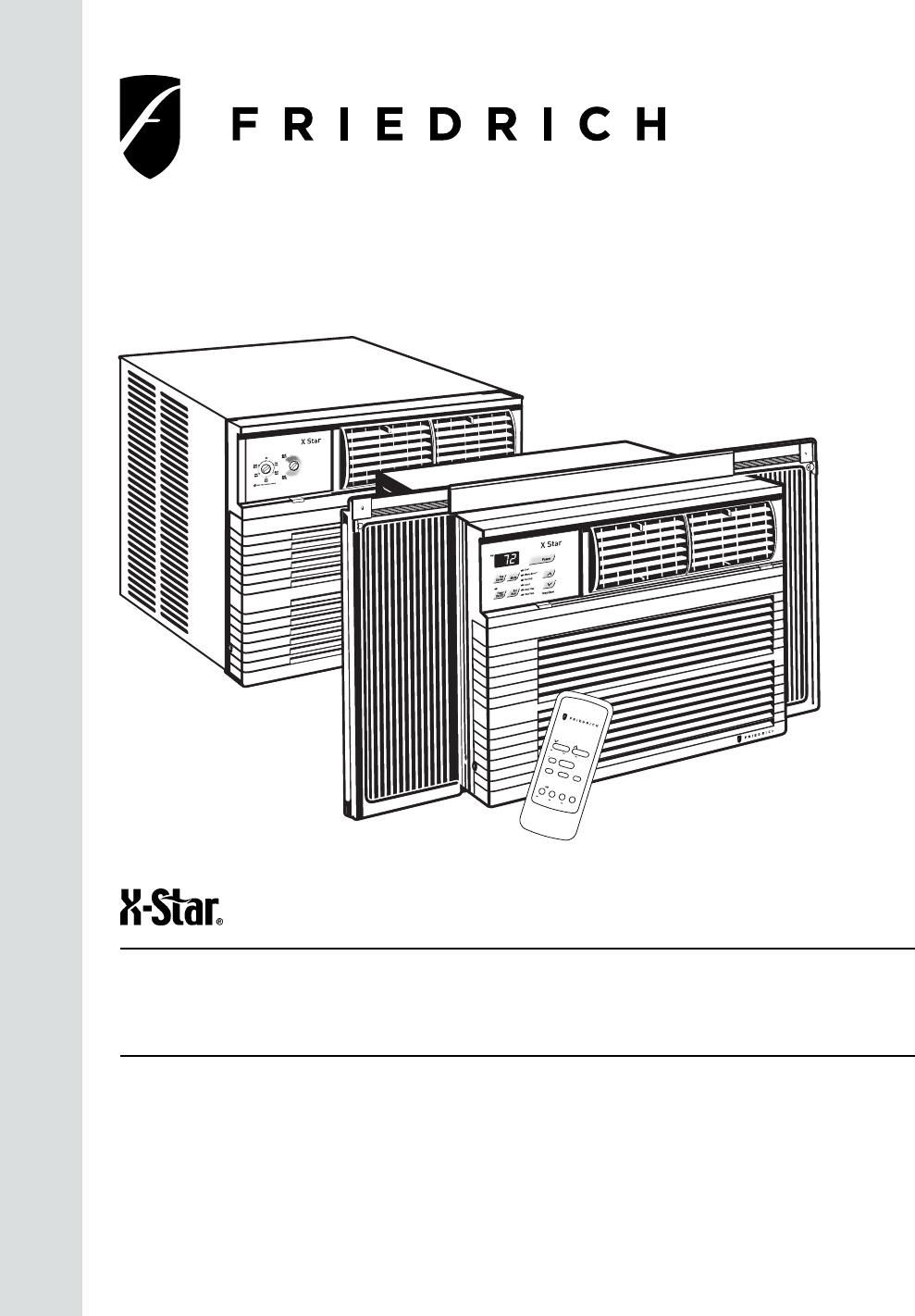
Service Manual
R-410A Models
Room Air Conditioners
2 0 1 1
Cool Only
Cool with Electric Heat
X-Star-ServMan (1-11)
115-Volt: XQ05M10*, XQ06M10*, XQ08M10*, XQ10M10*
115-Volt: EQ08M11*
* Last character may vary.
M oney
Fa
n
Set Hr
.
Stop
St
a
rt
Tem pera
ture
Fa
n
Cool
On/
Cooler Warm e
r
Onl
y S
peed Saver
®
P
ower
Tim e
r Ope
r
ation
1
Table Of Contents
Important Safety Information .......................................................................................................................................... 2-4
Unit Identifi cation ............................................................................................................................................................... 5
Performance Data ............................................................................................................................................................. 6
Chassis Specifi cations ...................................................................................................................................................... 6
Installation Information/Sleeve Dimensions ...................................................................................................................... 6
Electrical Data ................................................................................................................................................................... 7
Before Operating the Unit ................................................................................................................................................. 8
For Best Cooling Performance and Energy Effi ciency ...................................................................................................... 8
How to Operate the XQ ..................................................................................................................................................... 9
How to Use the XQ Remote Control ............................................................................................................................... 10
How to Operate the EQ ................................................................................................................................................... 10
Electronic Control Sequence of Operation ...................................................................................................................... 11
Functional Component Defi nition .................................................................................................................................... 12
Components Testing .................................................................................................................................................. 13-16
Refrigeration Sequence of Operation ............................................................................................................................. 17
R-410A Sealed System Repair Considerations .............................................................................................................. 18
Sealed Refrigeration System Repairs ........................................................................................................................ 19-22
Compressor Checks ................................................................................................................................................... 23-24
Compressor Replacement .......................................................................................................................................... 25-26
Routine Maintenance ................................................................................................................................................. 27-28
Performance Test Data Sheet ......................................................................................................................................... 29
Troubleshooting ......................................................................................................................................................... 30-36
Wiring Diagrams ........................................................................................................................................................ 37-38
Instructions for using Cooling Load Estimate Form ........................................................................................................ 39
Cooling Load Estimate Form ........................................................................................................................................... 40
Heat Load Form ......................................................................................................................................................... 41-42
Warranty .......................................................................................................................................................................... 43
Technical Assistance ....................................................................................................................................................... 44

IMPORTANT SAFETY INFORMATION
The information contained in this manual is intended for use by a qualifi ed service technician who is familiar
with the safety procedures required for installation and repair, and who is equipped with the proper tools and
test instruments required to service this product.
Installation or repairs made by unqualifi ed persons can result in subjecting the unqualifi ed person making
such repairs as well as the persons being served by the equipment to hazards resulting in injury or electrical
shock which can be serious or even fatal.
Safety warnings have been placed throughout this manual to alert you to potential hazards that may be
encountered. If you install or perform service on equipment, it is your responsibility to read and obey these
warnings to guard against any bodily injury or property damage which may result to you or others.
PERSONAL INJURY OR DEATH HAZARDS
ELECTRICAL HAZARDS:
• Unplug and/or disconnect all electrical power to the unit before performing inspections,
maintenance, or service.
• Make sure to follow proper lockout/tag out procedures.
• Always work in the company of a qualifi ed assistant if possible.
• Capacitors, even when disconnected from the electrical power source, retain an electrical charge
potential capable of causing electric shock or electrocution.
• Handle, discharge, and test capacitors according to safe, established, standards, and approved
procedures.
• Extreme care, proper judgment, and safety procedures must be exercised if it becomes necessary
to test or troubleshoot equipment with the power on to the unit.
Your safety and the safety of others are very important.
We have provided many important safety messages in this manual and on your appliance. Always read
and obey all safety messages.
All safety messages will tell you what the potential hazard is, tell you how to reduce the chance of injury,
and tell you what will happen if the instructions are not followed.
This is a Safety Alert symbol.
This symbol alerts you to potential hazards that can kill or hurt you and others.
All safety messages will follow the safety alert symbol with the word “WARNING”
or “CAUTION”. These words mean:
You can be killed or seriously injured if you do not follow instructions.
You can receive minor or moderate injury if you do not follow instructions.
A message to alert you of potential property damage will have the
word “NOTICE”. Potential property damage can occur if instructions
are not followed.
WARNING
CAUTION
NOTICE
2
• Do not spray or pour water on the return air grille, discharge air grille, evaporator coil, control panel,
and sleeve on the room side of the air conditioning unit while cleaning.
• Electrical component malfunction caused by water could result in electric shock or other electrically
unsafe conditions when the power is restored and the unit is turned on, even after the exterior is dry.
• Never operate the A/C unit with wet hands.
• Use air conditioner on a single dedicated circuit within the specifi ed amperage rating.
• Use on a properly grounded outlet only.
• Do not remove ground prong of plug.
• Do not cut or modify the power supply cord.
• Do not use extension cords with the unit.
• Follow all safety precautions and use proper and adequate protective safety aids such as: gloves,
goggles, clothing, adequately insulated tools, and testing equipment etc.
• Failure to follow proper safety procedures and/or these warnings can result in serious injury or death.
REFRIGERATION SYSTEM HAZARDS:
• Use approved standard refrigerant recovering procedures and equipment to relieve pressure before
opening system for repair.
• Do not allow liquid refrigerant to contact skin. Direct contact with liquid refrigerant can result in minor
to moderate injury.
• Be extremely careful when using an oxy-acetylene torch. Direct contact with the torch’s fl ame or hot
surfaces can cause serious burns.
• Make sure to protect personal and surrounding property with fi re proof materials.
• Have a fi re extinguisher at hand while using a torch.
• Provide adequate ventilation to vent off toxic fumes, and work with a qualifi ed assistant whenever
possible.
• Always use a pressure regulator when using dry nitrogen to test the sealed refrigeration system for
leaks, fl ushing etc.
• Make sure to follow all safety precautions and to use proper protective safety aids such as: gloves,
safety glasses, clothing etc.
• Failure to follow proper safety procedures and/or these warnings can result in serious injury or death.
MECHANICAL HAZARDS:
• Extreme care, proper judgment and all safety procedures must be followed when testing,
troubleshooting, handling, or working around unit with moving and/or rotating parts.
• Be careful when, handling and working around exposed edges and corners of sleeve, chassis, and
other unit components especially the sharp fi ns of the indoor and outdoor coils.
• Use proper and adequate protective aids such as: gloves, clothing, safety glasses etc.
• Failure to follow proper safety procedures and/or these warnings can result in serious injury or death.
3

PROPERTY DAMAGE HAZARDS
FIRE DAMAGE HAZARDS:
• Read the Installation/Operation Manual for this air conditioning unit prior to operating.
• Use air conditioner on a single dedicated circuit within the specifi ed amperage rating.
• Connect to a properly grounded outlet only.
• Do not remove ground prong of plug.
• Do not cut or modify the power supply cord.
• Do not use extension cords with the unit.
• Failure to follow these instructions can result in fi re and minor to serious property damage.
WATER DAMAGE HAZARDS:
• Improper installation maintenance, or servicing of the air conditioner unit, or not following the above
Safety Warnings can result in water damage to personal items or property.
• Insure that the unit has a suffi cient pitch to the outside to allow water to drain from the unit.
• Do not drill holes in the bottom of the drain pan or the underside of the unit.
• Failure to follow these instructions can result in result in damage to the unit and/or minor to serious
property damage.
4
INTRODUCTION
This service manual is designed to be used in conjunction with the operation and installation manual provided
with each unit.
This service manual was written to assist the professional HVAC service technician to quickly and accurately
diagnose and repair any malfunctions of this product.
This manual, therefore, will deal with all subjects in a general nature. (i.e. All text will pertain to all models).
IMPORTANT:It will be necessary for you to accurately identify the unit you are
servicing, so you can be certain of a proper diagnosis and repair.
(See Unit Identifi cation.)
System Controls
Return Air Grille/Filter
Condenser Fan Blade
Compressor
Condenser Coil
Discharge Air
Outdoor Grille
Sleeve
Basepan
Blower Motor
Blower Wheel
Evaporator Coil
Front Cover

Serial Number
Decade Manufactured
L=0 C=3 F=6 J=9
A=1 D=4 G=7
B=2 E=5 H=8
A A A Y 00001
Production Run Number
Year Manufactured
A=1 D=4 G=7 K=0
B=2 E=5 H=8
C=3 F=6 J=9
Product Line
X-Start
Month Manufactured
A=Jan D=Apr G=Jul K=Oct
B=Feb E=May H=Aug L=Nov
C=Mar F=Jun J=Sept M=Dec
1st Digit – Function
E = Electric Heat
X = Straight Cool
2nd Digit
Q = Chassis Size
3rd and 4th Digit - Approximate
BTU/HR in 1000s (Cooling)
Heating BTU/Hr capacity listed in the
Specifi cation/Performance Data Section
7th Digit – Options
0 = Straight Cool
1 = 1 KW Heat Strip, Nominal
6th Digit – Voltage
1 = 115 Volts
Model Number Code
X Q 08 M 1 0 A - A
RAC Serial Number Identifi cation Guide
UNIT IDENTIFICATION
5
8th Digit – Marketing Suffi x
Indicates Modifi cation
(Subject to change)
9th Digit – Engineering Suffi x
Indicates Modifi cation
(Subject to change)
5th Digit - Model Series / Year Introduced
M=2010

PERFORMANCE DATA *
Installation Information / Sleeve Dimensions
* Minimum extensions when mounted in a window.
** Minimum widths achieved using one side curtain assembly as opposed to both in a standard installation.
Circuit Rating/ Breaker
(B)
(C)
Front
SIDE VIEW
Model
Circuit Rating
Breaker or
T-D Fuse
Plug
Face
(NEMA#)
Power Cord
Length (ft.)
Wall Outlet
Appearance
XQ05M10*, XQ06M10*,
XQ08M10*, XQ10M10*
EQ08M11*
7
125V - 15A 5 - 15P 6
Sleeve Height Width
Depth
with Front
Shell Depth to
Louvers Minimum
Extension
Into Room*
Minimum
Extension
Outside*
Window Width
Thru-the-wall Installation
Finished Hole
Minimum** Maximum Height Width Max. Depth
Q14" 19
¾
"21
3/8
"8
½"
5
½"
10
¾"
22" 42" 14 ¼" 20" 8 ½”
All models use
environmentally
friendly R-410A
refrigerant.
R-410A
As an ENERGY STAR® partner, Friedrich Air Conditioning Co. has determined that the selected ENERGY STAR® (H) models
meet the ENERGY STAR®
Estimated yearly operating cost based on a 2007 national average electricity cost of 10.65 cents per kWh.
† The estimated yearly operating cost of this model was not available at the time the range was published.
Model
Cooling
Capacity Btu
Heating
Capacity Btu
Volts
Rated
Cooling
Amps
Cooling
Watts
Heating
Amps
Heating
Watts COP
Energy
Ratio
EER
Estimated
Yearly
Operating
Cost
Moisture
Removal
Pints/HR
Room Side
Air
Circulation
CFM Sleeve
Net
Weight
Lbs
XStar ®
XQ05M10*5500 — 115 4.5 491 — — 11.2 $39 1.0 170 Q 72
XQ06M10*6000 — 115 4.9 500 — — 12.0 † 1.0 175 Q 72
XQ08M10*7500 — 115 6.9 701 — — 10.7 $56 1.7 175 Q 71
XQ10M10*9500 — 115 9.0 970 — — 9.8 $56 2.5 180 Q 71
XStar ®
Electric Heat
EQ08M11*7500 4000 115 6.3 701 11.2 1290 2.8 10.7 $56 1.9 175 Q 72
Window Mounting Kits
Heat/Cool Models Kit No.
EQ08M11*WIKQ
Friedrich heat/cool models include accessories for
thru-the-wall installation only. Window mounting requires
use of optional accessory kit as listed above.
6
COOLING
PERFORMANCE DATA**
EVAP. AIR TEMP. DEG. F CONDENSER
TEMPERATURE DEG. F Discharge Temp Suction Temp Super Heat Sub-Cooling
OPERATING PRESSURES ELECTRICAL RATINGS R-410A
REF. Voltage
BREAKER FUSE
Discharge Air Temp.
Drop F. Suction Discharge Amps Cool Amps Heat Locked Rotor
Amps
Charge in
OZ. 60 Hertz Amps
Q-Chassis
XQ05M10*57 23 117 133 60 5 19 157 410 4.5 24.0 27.0 115 15
XQ06M10*54 26 120 152 63 12 18 150 410 4.9 25.0 21.0 115 15
XQ08M10*51 29 119 160 63 13 25 138 420 6.3 32.0 25.5 115 15
XQ10M10*47 33 131 176 59 12 32 132 490 9.8 57.0 24.0 115 15
EQ08M11*49 31 120 162 60 14 27 133 420 7.0 7.6 32.0 25.5 115 15
** Rating Conditions: 80 degrees F, room air temp. & 50% relative humidity, with 95 degree F, outside air temp & 40% relative humidity, all systems use R410A.
* Due to continuing research in new energy-saving technology, performance data and 8th and 9th character are subject to change without notice.

ELECTRICAL DATA
ELECTRIC SHOCK HAZARD
WARNING
Turn off electric power before service or
installation.
All electrical connections and wiring MUST be
installed by a qualifi ed electrician and conform to
the National Electrical Code and all local codes
which have jurisdiction.
Failure to do so can result in personal injury or
death.
Not following the above WARNING could result in fi re or
electically unsafe conditions which could cause moderate
or serious property damage.
Read, understand and follow the above warning.
NOTICE
FIRE HAZARD
Wire Size Use ONLY wiring size recommended for single outlet branch circuit.
Fuse/Circuit Breaker Use ONLY the correct HACR type and size fuse/circuit breaker. Read electrical ratings on unit’s
rating plate. Proper circuit protection is the responsibiity of the homeowner.
Grounding Unit MUST be grounded from branch circuit through service cord to unit, or through separate
ground wire provided on permanently connected units. Be sure that branch circuit or general
purpose outlet is grounded.
Receptacle The fi eld supplied outlet must match plug on service cord and be within reach of service cord.
Do NOT alter the service cord or plug. Do NOT use an extension cord. Refer to the table above
for proper receptacle and fuse type.
The consumer - through the AHAM Room Air Conditioner Certifi cation Program - can
be certain that the AHAM Certifi cation Seal accurately states the unit’s cooling and
heating capacity rating, the amperes and the energy effi ciency ratio.
*HACR: Heating Air Conditioning and Refrigeration
7

ELECTRICAL SHOCK HAZARD
WARNING
Make sure your electrical receptacle has the same
configuration as your air conditioner’s plug. If
different, consult a Licensed Electrician.
Do not use plug adapters.
Do not use an extension cord.
Do not remove ground prong.
Always plug into a grounded 3 prong outlet.
Failure to follow these instructions can result in
electrical shock, serious injury or death.
8

To start unit
siti,elc at pec erreporpaotnideggulpdnadellatsnisirenoitidnocriaruoyfI
ready to go. The first time the unit is started, the compressor will delay for three
minutes. See Automatic Component Protection on the following page.
1Touch the Power button once. The unit will automatically be in Cool
mode with the temperature set at 75°F (24°C) and the fan speed at
F1, the sleep setting.
To set mode of operation
When you rst turn the unit on, it will be in the Cool mode (light on), with
constant fan.
2Touch the Mode button once to activate the MoneySaver®(light on).
MoneySaver®ros serp mocehthtiwnafehtselcyctahterutaefasi
so that the fan does not run all the time. This saves energy and
eromrofnaftnats nocreferpyamuoyrO.noit ac i dim uh edsevorpmi
ehthcuot,naftnatsnocotnruterot(tnem evomria Mode button two
more times).
In order to run the fan by itself, do the following:
3Continuing from MoneySaver®mode (light on), touch theMode button
once to activate the FAN ONLY feature (light on).
The FAN ONLY setting will circulate air in the room without the com-
pressor coming on.
To adjust temperature
4Use the Mode button to select either the COOL or MoneySaver®
function
5COOLER – Touch the button to lower the room air temperature.
6WARMER – Touch the button to raise the room air temperature.
7Press both the and ehthctiwsotemitemasehttasnottub
temperature readout from Fahrenheit (°F) to Celsius (°C).
Repeat step 7 to switch from °C back to °F.
To adjust fan speed
8Touch the Fan Speed button to see the current setting. Touch it again
to change speed. F1 is the lowest setting (SLEEP SETTING / LOW),
F2 is MEDIUM, and F3 is HIGH.
To activate Smart Fan
9There is a fourth option, SF, when selecting the fan speed. This is
the SMART FAN function. SMART FAN DOES NOT OPERATE IN
CONJUCTION WITH THE FAN ONLY MODE.
Smart Fan will adjust the fan speed automatically to maintain the
desired comfort level. For example, if the outside doors in your home
are opened for an extended period of time, or more people enter a
room, Smart Fan may adjust to a higher fan speed to compensate
for the increased heat load. This keeps you from having to adjust the
fan speed on your own.
How to operate the Friedrich room air conditioner (XQ models)
PM
Temp/Hour
Cool
MoneySaver
®
Fan Only
Clock
StartTime
Stop Time
Power
Fan
Speed Mode
Timer Set
Hour
10 11 12
13
7
3 4
56
18 9 2 Figure 5
To set the hour clock
10 Touch the Set Hour button to see the current setting (clock light
comes on). The number that is displayed is the approximate time
(hour only). Use the and buttons to change the settings. BE
SURE TO SET A.M. AND P.M. ACCORDINGLY. (P.M. is indicated
by a red light in the upper left corner of the display).
To set the timer
NOTE: Set the HOUR CLOCK before attempting to set timer functions.
You can set the START and STOP times a minimum of one hour apart, and
a maximum of twenty-three hours apart.
11 After setting the time, press the Set Hour button once (Start light
comes on). Use the and buttons to select the time that the
unit will START.
12 After selecting the START time, press the Set Hour button once more
(Stop light comes on). Use the and buttons to select the time
that the unit will STOP. After selecting the stopping time, press the
Set Hour button once.
13 Press the Timer On/Off button (light turns on) to activate the timer
function. To deactivate this function, press the Timer On/Off button
once again (light turns off). Once the on and off times have been
selected, they will remain in memory and cycle daily until changed.
NOTE: If the unit is unplugged or the power is interrupted, the HOUR
must be reset or the Timer On/Off will not function when desired.
Automatic component protection
Your unit is equipped with Automatic Component Protection. To protect the
compressor of the unit, there is a three minute start delay if you turn the unit
off or if power is interrupted. The fan operation will not be affected. Also, if you
switch from Cool mode to Fan Only, and switch back to Cool mode, there
is a three minute delay before the compressor comes back on.
9
Figure 3
PM
X Star
Temp/Hour
Cool
Money Saver
®
Fan Only
Clock
Start Time
Stop Time
Power
Fan
Speed Mode
Timer
On/Off Set
Hour
10 11 12
13 7
3 4
56
18 9 2

To set the timer
NOTE: You can set the START and STOP times a minimum of one hour
apart, and a maximum of 23 hours apart.
9TIMER START - Press Start .gniloocrofemittratstnerrucehtweivot
Continue pressing the Start button until you arrive at the start time
you desire. The start time for cooling will then be set.
10 TIMER STOP - Press the Stop button. Continue pressing the Stop
button until you arrive at the stop time you desire. The stop time for
cooling will then be set.
11 TIMER ON / OFF - Press the On/Off button to activate (light on) or
deactivate (light off) the timer. Once the on and off times have been
selected, they will remain in memory and cycle daily until changed.
NOTE: If the unit is unplugged or the power is interrupted, the Set Hr.
function must be reset or the On/Off function will not work.
How to use the remote control
To start unit
1POWER - Press the Power button once. The unit will automatically
start in the mode and fan speed it was last left on.
To set mode of operation
2COOL - Press the Cool button to automatically switch the operating
mode to COOL.
3FAN ONLY - Press the Fan Only button if you want to run the fan
only.
4MoneySaver®- Press the MoneySaver®button to activate the
MoneySaver®feature. This feature cycles the fan with the compres-
sor so that the fan does not run all the time.
To adjust temperature setting
5WARMER - Press the Warmer button to raise the temperature
setting.
6COOLER - Press the Cooler button to lower the temperature
setting.
To adjust fan speed
7FAN SPEED - Press the Fan Speed button to see the current set-
ting. Press again to change the fan speed. F1 is the lowest setting
(SLEEP / LOW), F2 is MEDIUM,F3 is HIGH, and SF is the SMART
FAN setting.
To set the hour clock
8SET HOUR CLOCK - Press Set Hr. once to see the current clock
setting. Continue pressing the button until you arrive at the current
time (Hour only). Minutes are not shown on the display. Make sure
that the A.M. / P.M. setting is correct. Additional RC1 wireless remote controls can be purchased from your Friedrich dealer.
(XQ models)
Money
Fan
Set Hr.
Stop
Start
Temperature
Fan
Cool
On/O
Cooler Warmer
Only Speed Saver®
Power
Timer Operation
8
10
7
11
9
43
12
56
10
How To Operate The EQ08
Function Control Knob
The left knob is a six position control that allows you to
select heat or cool in either low speed or high speed. Plus
you can select fan only if you wish.
Thermostat Knob
The right hand knob is the thermostat - turn it clockwise for
cooler, counter-clockwise for warmer.

MODE CONTROL
The mode control pad(s) allow the selection of the operating
modes of the unit.
There is a two second delay before the mode activates its
appropriate relay.
OPERATING SEQUENCE / CHARACTERISTICS
AND FEATURES
Compressor Operation
The run state of the compressor is determined by the
difference between the indoor ambient temperature and
the set temperature. See specifi c mode of operation for
details.
Compressor Time Delay: 180 seconds
This feature is initiated every time the compressor is de-
energized, either due to:
(1) satisfying the temperature set point
(2) changing mode to fan only
(3) a power interruption or
(4) turning the unit off
The compressor is also time delayed for 3 minutes when the
control is fi rst plugged in or power is restored after failure.
When the compressor cycles off as a result of satisfying the
“load”, the time delay is typically timed out during the off
cycle. Compressor time delay is bypassed by “Test Mode”.
Return Air Temperature Sensor
The control range is 60°F to 90°F +/- 2.0°F.
Frost Protection Sensor
Temperature settings:
Disable the compressor when sensing 30° +/- 3°F for 2
minutes continuously.
Enable compressor @ 55° +/- 5°F.
The fan should not be affected by the Frost Protection. It
should continue to function normally if freeze protection is
called for.
COOL MODE FOR XQ MODELS
When in the COOL mode, the control will turn on the
compressor when the indoor temperature is 1.5°F above the
set point and turn off the compressor when the ambient gets
below the set point by 1.5°F. The fan will run continuously.
MONEY SAVER MODE
When in MONEY SAVER mode, the system will be turned
on when the indoor temperature gets above the set point by
0.75°F and turns off when the indoor temperature gets below
the set point by 0.75°F. The fan will turn on 5 seconds before
the compressor and turn off 5 seconds after the compressor
stops. If the compressor is delayed the fan will continue to
run while the compressor restarts. If the thermostat remains
satisfi ed for more than approximately 9 minutes, the fan will
turn on for a period of 90 seconds for air sampling. Operation
in MONEY SAVER mode will light both the MONEY SAVER
and COOL indicators.
ELECTRONIC CONTROL SEQUENCE OF OPERATION
11
FAN ONLY MODE
When in the FAN ONLY mode, the compressor will not
operate. The fan will run continuously at the user-selected
speed (see “Fan Speed Set” below). Smart Fan is not
available in FAN ONLY Mode.
FAN SPEED SET
XQ fan speed is changed by pressing FAN SPEED button
and scrolling through F1, F2, F3 and SF (Smart Fan) in the
digital display.
There will be a 2 second delay before the fan speed changes
to prevent unnecessary switching of the relays during fan
speed selection.
SMART FAN
On the XQ model, smart fan is activated by pressing the
FAN SPEED button and scrolling through speeds until
“SF” appears in the digital display. Using the remote
control, Smart Fan is selected by the fourth push of Fan
Speed button.
Smart fan changes fan speeds based on the temperature
differential between the ambient and set temperatures.
CHECKING ROOM TEMPERATURE
Check the room temperature at the electronic control
pad by pressing the “FAN SPEED” button and the
“TEMP ” button at the same time on XQ models.
The indoor temperature will display for 10 seconds. Indoor
temperature can be viewed in all modes, including the
TEST mode. The display can be changed back to SET
temperature by pressing any key, except the ON/OFF
button, or after 10 seconds has elapsed.
KEEP ALIVE
The electronic control has a memory to retain all functions
and status as set up by the user in the event of a power
failure. Once power is restored to the unit there is a two
second delay before the fan comes on and approximately
three minutes delay before the compressor is activated,
providing that the mode was set for cooling and the set
point temperature has not been met in the room.
REBOOT/RESET THE CONTROL BOARD
With unit on, press “MODE” and “TEMP/HOUR ” buttons
simultaneously for 10 seconds. If the panel will reboot, you
will hear the fan come on and the temperature window
will read 60°F. If this happens, turn the unit off for about
10 seconds and then turn it back on to fi nish the reboot
cycle. If the panel does not reboot, you possibly need to
replace it.

MECHANICAL COMPONENTS
Plenum assembly Diffuser with directional louvers used
to direct the conditioned airfl ow.
Blower wheel Attaches to the indoor side of the fan motor
shaft and is used for distributing unconditioned, room side
air though the heat exchanger and delivering conditioned
air into the room.
Slinger fan blade Attaches to the outdoor side of the fan
motor shaft and is used to move outside air through the
condenser coil, while slinging condensate water out of the
base pan and onto the condenser coil, thus lowering the
temperature and pressures within the coil.
ELECTRICAL COMPONENTS
Thermostat Used to maintain the specifi ed room side
comfort level
System switch Used to regulate the operation of the fan
motor, the compressor or to turn the unit off. For troubleshoot-
ing, refer to the wiring diagrams and schematics in the back
of this service manual.
Capacitor Reduces line current and steadies the voltage
supply, while greatly improving the torque characteristics of
the fan motor and compressor motor.
MoneySaver® switch When engaged, it sends the power
supply to the fan motor through the thermostat, which allows
Smart Fan Automatically adjusts the fan speed to main-
tain the desired room temp.
for a cycle-fan operation.
Fan Motor Dual-shafted fan motor operates the indoor
blower wheel and the condenser fan blade simultaneously.
Heating element Electric resistance heater, available in
EQ08 model.
Heat anticipator Used to provide better thermostat and
room air temperature control.
HERMETIC COMPONENTS
Compressor Motorized device used to compress refrigerant
through the sealed system.
Capillary tube A cylindrical meter device used to evenly dis-
tribute the fl ow of refrigerant to the heat exchangers (coils.)
FUNCTIONAL COMPONENT DEFINITIONS
12

13
TESTING THE ELECTRONIC CONTROL
BOARDS FOR XQ MODELS
Activating Test Mode:
Activate test mode by pressing at the same time the
“MODE” button and the “TEMP ” button on XQ
models. LEDs for Hour, Start, and Stop will blink 1 bps
while Test Mode is active.
Test Mode has duration of 90 minutes. Test Mode can
be activated under any conditions, including Off. Test
Mode is cancelled by pressing the On/Off button,
unplugging the unit, or when the 90 minutes is timed
out. All settings revert to the factory default settings of
Cool, 75 degrees F, Timer and Set Hour features are
nonfunctional.
Test Mode overrides the three-minute lockout, all
delays for compressor and fan motor start / speed
change, and no delay when switching modes.
During Test Mode, the default settings are; Unit ON,
Money Saver ON, 60°F, and High fan speed.
IMPORTANT: Error Codes are cleared from the
log by exiting from Error Code Mode. To exit on XQ
models, press Timer On/Off button. Or unplug unit to
exit Error Code Mode. Plug unit in after 5 seconds to
resume normal operation of unit.
Activating Error Code Mode: (Submode of Test Mode)
Unit must be in Test Mode to enter Error Code Mode
1. Activate Error Code Mode by pressing the “TIMER ON/
OFF” button on XQ models. LED for the “TIMER ON/OFF”
will fl ash 1 bps while Error Code Mode is active. Pressing
the “TEMP/HR ” button will display 00. Consecutive
presses will scroll through all error codes logged. Press
the “TEMP/HR ” button to see the reverse order of all
error codes logged. When the end of logged error codes is
reached the temperature set point will appear.
COMPONENTS TESTING
ERROR CODE LISTINGS
E1 SHORT CYCLE SITUATION: Defi ned as (compressor
powered on before the three minute time delay ten times in
one hour. Investigate and correct short cycling problem.
E2 KEYBOARD STUCK ERROR: If key button(s) are
pressed continuously for twenty seconds or more. If MODE
key is stuck, unit will default to cool. Exit Error Code
Mode to see if error “E2” is no longer displayed and unit is
functioning. Replace board if “E2” still displays after exiting
Error Code Mode.
E3 FROST PROBE OPEN: Normal operation is allowed.
Ohm frost probe. Replace probe if ohm value not read. If
ohm value is present replace board.
E4 FROST PROBE SHORT: Normal operation allowed.
Replace probe.
E5 INDOOR PROBE OPEN: Control assumes indoor
ambient temperature is 90 degree F and unit will operate.
Ohm indoor probe. Replace probe if ohm value not read.
E6 INDOOR PROBE SHORT: Control assumes ambient
temperature is 90 degree F and unit will operate. Replace
probe.
NOTE: All Error Code displays for Frost & Indoor Probe
will allow unit to operate. Unit may or will ice up if faulty
components not replaced.
FROST PROBE SENSOR: disables compressor at 35
degrees F.
INDOOR PROBE SENSOR: Control range is 60°F to 90°F
+/- 2°F.
Indoor temperature will be displayed by pressing:
(XQ units) The Fan Speed button and the “TEMP ”
button.
The indoor temperature will be displayed for 10 seconds.
The display will change back to the Set Point temperature
by pressing any key button except for the On/Off button.
The indoor temperature can be viewed in all modes,
including test mode.
PM
X Star
Temp/Hour
Cool
Money Saver
®
Fan Only
Clock
Start Time
Stop Time
Power
Fan
Speed Mode
Timer
On/Off Set
Hour

TEST:
1. Remove leads from thermostat.
2. Turn thermostat knob clockwise to its coldest
position.
3. Test for continuity between the two terminals. Contacts
should be closed.
4. Turn thermostat knob counterclockwise to its warmest
position.
5. Test for continuity - contacts should be open.
NOTE: The thermostat must be within the temperature
range listed to open and close.
To maintain the comfort level desired, a cross ambient type
thermostat is used. The thermostat has a range from 60°
±2°F to 92° ±3°F. The thermostat bulb is positioned in front
of the evaporator coil to sense the return air temperature.
Thermostat malfunction or erratic operation is covered in
the troubleshooting section of this manual.
THERMOSTAT (“EQ08” Models)
(See Figure 17)
This thermostat is single pole-double throw, cross ambient
with a range of 60° to 92°F and a differential of ±2°F. Terminal
“2” is common.
Figure 17
Thermostat
(EQ Model)
Figure 18
Thermostat
TEST:
Cooling/Heating Models: Remove wires from thermostat
and check continuity between terminal “2” (common) and
“3” for cooling. Check between terminals “2” (common)
and “1” for heating. Also check that contacts in thermostat
open after placing in either position. NOTE: Temperature
must be within range listed to check thermostat. Refer to
the troubleshooting section in this manual for additional
information on thermostat testing.
THERMOSTAT ADJUSTMENT
No attempt should be made to adjust thermostat. Due
to the sensitivity of the internal mechanism and the
sophisticated equipment required to check the calibration,
it is suggested that the thermostat be replaced rather than
calibrated. Thermostat bulb must be straight to insure
proper performance.
THERMOSTAT BULB LOCATION
The position of the bulb is important in order for the
thermostat to function properly. The bulb of the thermostat
should be located approximately 45° to a maximum of 60°
from horizontal. Also, do not allow the thermostat bulb to
touch the evaporator coil. (See Figures 17 and 18)
Thermostat sensor holder 020
to be positioned between the
4th and 5th and 6th and 7th
rows of tubes from the bottom
of the coil at dimension shown
Figure 19
Thermostat Bulb Location
(EQ Model)
COMPONENTS TESTING (Continued)
ELECTRIC SHOCK HAZARD
WARNING
Disconnect power to the unit before
servicing. Failure to follow this warning
could result in serious injury or death.
EQ08 SYSTEM CONTROL SWITCH - TEST
“EQ08” SYSTEM CONTROL SWITCH – TEST
Turn knob to phase of switch to be tested. There must be
continuity as follows:
1. “Fan Only” Position – between terminals “MS” and “H”
2. “Hi Cool” Position – between terminals “L1” and “C” and
“MS” and “H”
3. “Low Cool” Position – between terminals “L1” and “C”
and “MS” and “LO”
4. “Low Heat” Position – between terminals “L2” and “2”
and “MS” and “LO”
5. “Hi Heat” Position – between terminals “L2” and “2” and
“MS” and “H”
L1
MS
2
H
LO
C
L2
B1
System Control Switch
(EQ Models)
14

CAPACITORS
ELECTRIC SHOCK HAZARD
WARNING
Turn off electric power before servicing.
Discharge capacitor with a 20,000 Ohm 2 Watt
resistor before handling.
Failure to do so may result in personal injury,
or death.
Many motor capacitors are internally fused. Shorting the
terminals will blow the fuse, ruining the capacitor. A 20,000
ohm 2 watt resistor can be used to discharge capacitors
safely. Remove wires from capacitor and place resistor
across terminals. When checking a dual capacitor with
a capacitor analyzer or ohmmeter, both sides must be
tested.
Capacitor Check with Capacitor Analyzer
The capacitor analyzer will show whether the capacitor is
“open” or “shorted.” It will tell whether the capacitor is within
its micro farads rating and it will show whether the capacitor
is operating at the proper power-factor percentage. The
instrument will automatically discharge the capacitor when
the test switch is released.
Capacitor Connections
The starting winding of a motor can be damaged by a
shorted and grounded running capacitor. This damage
usually can be avoided by proper connection of the running
capacitor terminals.
From the supply line on a typical 230 volt circuit, a 115 volt
potential exists from the “R” terminal to ground through a
possible short in the capacitor. However, from the “S” or
start terminal, a much higher potential, possibly as high as
400 volts, exists because of the counter EMF generated
in the start winding. Therefore, the possibility of capacitor
failure is much greater when the identifi ed terminal is
connected to the “S” or start terminal. The identifi ed
terminal should always be connected to the supply line, or
“R” terminal, never to the “S” terminal.
When connected properly, a shorted or grounded running
capacitor will result in a direct short to ground from the “R”
terminal and will blow the line fuse. The motor protector
will protect the main winding from excessive temperature.
Dual Rated Run Capacitor Hook-up
FIGURE 24
BLOWER/FAN MOTOR - TEST
1. Determine that capacitor is serviceable.
2. Disconnect fan motor wires from fan speed switch or
system switch.
3. Apply “live” test cord probes on black wire and common
terminal of capacitor. Motor should run at high speed.
4. Apply “live” test cord probes on red wire and common
terminal of capacitor. Motor should run at low speed.
5. Apply “live” test cord probes on each of the remaining
wires from the speed switch or system switch to test
intermediate speeds. If the control is in the “MoneySaver”
mode and the thermostat calls for cooling, the fan will
start - then stop after approximately 2 minutes; then the
fan and compressor will start together approximately 2
minutes later.
Figure 23
Blower/Fan Motor
FAN MOTOR
A single phase permanent split capacitor motor is used to drive
the evaporator blower and condenser fan. A self-resetting
overload is located inside the motor to protect against high
temperature and high amperage conditions. (See Figure 23)
ELECTRIC SHOCK HAZARD
WARNING
Disconnect power to the unit before
servicing. Failure to follow this warning
could result in serious injury or death.
COMPONENTS TESTING (Continued)
15

HEATING ELEMENT (See Figure)
All electric heat models are equipped with a heating element.
The EQ08 has a 1.15 KW element.
The heating element contains a fuse link and a heater limit
switch. The fuse link is in series with the power supply and
will open and interrupt the power when the temperature
reaches 199°F or a short circuit occurs in the heating
element. Once the fuse link separates, a new fuse link
must be installed.
NOTE: Always replace with the exact replacement.
The heater element has a high limit control. This control
is a bimetal thermostat mounted in the top of the heating
element.
Should the fan motor fail or fi lter become clogged, the high
limit control will open and interrupt power to the heater
before reaching an unsafe temperature condition.
The control is designed to open at 110°F ±6°F. Test
continuity below 110°F and for open above 110°F.
TESTING THE HEATING ELEMENT
Testing of the elements can be made with an ohmmeter
across the terminals after the connecting wires have been
removed. A cold resistance reading of approximately 10.11
ohms for the 1.15 KW heater should be registered.
Figure
Heating Element
DRAIN PAN VALVE
During the cooling mode of operation, condensate which
collects in the drain pan is picked up by the condenser fan
blade and sprayed onto the condenser coil. This assists
in cooling the refrigerant plus evaporating the water.
During the heating mode of operation, it is necessary that
water be removed to prevent it from freezing during cold
outside temperatures. This could cause the condenser
fan blade to freeze in the accumulated water and prevent
it from turning.
To provide a means of draining this water, a bellows type
drain valve is installed over a drain opening in the base
pan.
This valve is temperature sensitive and will open when
the outside temperature reaches 40°F. The valve will
close gradually as the temperature rises above 40°F to
fully close at 60°F.
Figure 26
Bellows Assembly
Drain Pan Valve
COMPONENTS TESTING (Continued)
ELECTRIC SHOCK HAZARD
WARNING
Disconnect power to the unit before
servicing. Failure to follow this warning
could result in serious injury or death.
16

Suction
Line
Evaporator
Coil
Metering
Device
Refrigerant
Strainer
Discharge
Line
Condenser
Coil
Compressor
Refrigerant Drier Liquid
Line
A good understanding of the basic operation of the
refrigeration system is essential for the service technician.
Without this understanding, accurate troubleshooting of
refrigeration system problems will be more diffi cult and time
consuming, if not (in some cases) entirely impossible. The
refrigeration system uses four basic principles (laws) in its
operation they are as follows:
1. “Heat always fl ows from a warmer body to a cooler
body.”
2. “Heat must be added to or removed from a substance
before a change in state can occur”
3. “Flow is always from a higher pressure area to a lower
pressure area.”
4. “The temperature at which a liquid or gas changes state
is dependent upon the pressure.”
The refrigeration cycle begins at the compressor. Starting
the compressor creates a low pressure in the suction line
which draws refrigerant gas (vapor) into the compressor.
The compressor then “compresses” this refrigerant, raising
its pressure and its (heat intensity) temperature.
The refrigerant leaves the compressor through the discharge
Line as a hot High pressure gas (vapor). The refrigerant
enters the condenser coil where it gives up some of its
heat. The condenser fan moving air across the coil’s fi nned
surface facilitates the transfer of heat from the refrigerant to
the relatively cooler outdoor air.
When a suffi cient quantity of heat has been removed from
the refrigerant gas (vapor), the refrigerant will “condense”
(i.e. change to a liquid). Once the refrigerant has been
condensed (changed) to a liquid it is cooled even further by
the air that continues to fl ow across the condenser coil.
The RAC design determines at exactly what point (in the
condenser) the change of state (i.e. gas to a liquid) takes
place. In all cases, however, the refrigerant must be
totally condensed (changed) to a Liquid before leaving the
condenser coil.
The refrigerant leaves the condenser Coil through the liquid
line as a warm high pressure liquid. It next will pass through
the refrigerant drier (if so equipped). It is the function of the
drier to trap any moisture present in the system, contaminants,
and large particulate matter.
The liquid refrigerant next enters the metering device. The
metering device is a capillary tube. The purpose of the
metering device is to “meter” (i.e. control or measure) the
quantity of refrigerant entering the evaporator coil.
In the case of the capillary tube this is accomplished (by
design) through size (and length) of device, and the pressure
difference present across the device.
Since the evaporator coil is under a lower pressure (due to
the suction created by the compressor) than the liquid line,
the liquid refrigerant leaves the metering device entering the
evaporator coil. As it enters the evaporator coil, the larger
area and lower pressure allows the refrigerant to expand
and lower its temperature (heat intensity). This expansion is
often referred to as “boiling”. Since the unit’s blower is moving
indoor air across the fi nned surface of the evaporator coil,
the expanding refrigerant absorbs some of that heat. This
results in a lowering of the indoor air temperature, hence the
“cooling” effect.
The expansion and absorbing of heat cause the liquid
refrigerant to evaporate (i.e. change to a gas). Once the
refrigerant has been evaporated (changed to a gas), it is
heated even further by the air that continues to fl ow across
the evaporator coil.
The particular system design determines at exactly what
point (in the evaporator) the change of state (i.e. liquid to a
gas) takes place. In all cases, however, the refrigerant must
be totally evaporated (changed) to a gas before leaving the
evaporator coil.
The low pressure (suction) created by the compressor
causes the refrigerant to leave the evaporator through the
suction line as a cool low pressure vapor. The refrigerant then
returns to the compressor, where the cycle is repeated.
REFRIGERATION SEQUENCE OF OPERATION
17

• R-410A pressure is approximately 60% higher than R-22 pressure.
• R-410A cylinders must not be allowed to exceed 125 F, they may leak or rupture.
• R-410A must never be pressurized with a mixture of air, it may become
fl ammable.
• Servicing equipment and components must be specifi cally designed for use with R-410A and
dedicated to prevent contamination.
• Manifold sets must be equipped with gauges capable of reading 750 psig (high side) and 200
psig (low side), with a 500-psig low-side retard.
• Gauge hoses must have a minimum 750-psig service pressure rating
• Recovery cylinders must have a minimum service pressure rating of 400 psig, (DOT 4BA400
and DOT BW400 approved cylinders).
• POE (Polyol-Ester) lubricants must be used with R-410A equipment.
• To prevent moisture absorption and lubricant contamination, do not leave the refrigeration
system open to the atmosphere longer than 1 hour.
• Weigh-in the refrigerant charge into the high side of the system.
• Introduce liquid refrigerant charge into the high side of the system.
• For low side pressure charging of R-410A, use a charging adaptor.
• Use Friedrich approved R-410A fi lter dryers only.
The following is a list of important considerations when working with R-410A equipment
R-410A SEALED SYSTEM REPAIR CONSIDERATIONS
Do not puncture, heat, expose to fl ame or incinerate.
Only certifi ed refrigeration technicians should
service this equipment.
R410A systems operate at higher pressures than
R22 equipment. Appropriate safe service and
handling practicces must be used.
Only use gauge sets designed for use with R410A.
Do not use standard R22 gauge sets.
WARNING
Refrigeration system under high pressure
18

Proper refrigerant charge is essential to proper unit operation.
Operating a unit with an improper refrigerant charge will
result in reduced performance (capacity) and/or effi ciency.
Accordingly, the use of proper charging methods during
servicing will insure that the unit is functioning as designed
and that its compressor will not be damaged.
Too much refrigerant (overcharge) in the system is just as bad
(if not worse) than not enough refrigerant (undercharge). They
both can be the source of certain compressor failures if they
remain uncorrected for any period of time. Quite often, other
problems (such as low air fl ow across evaporator, etc.) are
misdiagnosed as refrigerant charge problems. The refrigerant
circuit diagnosis chart will assist you in properly diagnosing
these systems.
An overcharged unit will at times return liquid refrigerant
(slugging) back to the suction side of the compressor eventually
causing a mechanical failure within the compressor. This
mechanical failure can manifest itself as valve failure, bearing
failure, and/or other mechanical failure. The specifi c type of
failure will be infl uenced by the amount of liquid being returned,
and the length of time the slugging continues.
Not enough refrigerant (undercharge) on the other hand, will
cause the temperature of the suction gas to increase to the point
where it does not provide suffi cient cooling for the compressor
motor. When this occurs, the motor winding temperature will
increase causing the motor to overheat and possibly cycle open
the compressor overload protector. Continued overheating of
the motor windings and/or cycling of the overload will eventually
lead to compressor motor or overload failure.
Sealed Refrigeration System contains refrigerant
and oil under high pressure.
Proper safety procedures must be followed,
and proper protective clothing must be worn
when working with refrigerants.
Failure to follow these procedures could
result in serious injury or death.
WARNING
HIGH PRESSURE HAZARD
Unplug and/or disconnect all electrical power
to the unit before performing inspections,
maintenances or service.
Failure to do so could result in electric shock,
serious injury or death.
WARNING
RISK OF ELECTRIC SHOCK
R-410A SEALED REFRIGERATION SYSTEM REPAIRS
SEALED SYSTEM REPAIRS TO COOL-ONLY MODELS REQUIRE THE INSTALLATION OF A LIQUID LINE DRIER.
IMPORTANT
EQUIPMENT REQUIRED:
1. Voltmeter
2. Ammeter
3. Ohmmeter
4. E.P.A. Approved Refrigerant Recovery System
5. Vacuum Pump (capable of 200 microns or less
vacuum.)
6. Acetylene Welder
7. Electronic Halogen Leak Detector capable of
detecting HFC (Hydrofl uorocarbon) refrigerants.
8. Accurate refrigerant charge measuring device such
as:
a. Balance Scales - 1/2 oz. accuracy
b. Charging Board - 1/2 oz. accuracy
9. High Pressure Gauge - (0 to 750 lbs.)
10. Low Pressure Gauge - (-30 to 200 lbs.)
11. Vacuum Gauge - (0 - 1000 microns)
12. Facilities for fl owing nitrogen through refrigeration tubing
during all brazing processes.
EQUIPMENT MUST BE CAPABLE OF:
1. Recovering refrigerant to EPA required levels.
2. Evacuation from both the high side and low side of the
system simultaneously.
3. Introducing refrigerant charge into high side of the
system.
4. Accurately weighing the refrigerant charge introduced
into the system.
Refrigerant Charging
NOTE: Because the XStar system is a sealed system,
service process tubes will have to be installed. First install a
line tap and remove refrigerant from system. Make necessary
sealed system repairs and vacuum system. Crimp process
tube line and solder end shut. Do not leave a service valve in
the sealed system.
19

3. Install a process tube to sealed system.
4. Make necessary repairs to system.
5. Evacuate system to 200 microns or less.
6. Weigh in refrigerant with the property quantity of R410-A
refrigerant.
7. Start unit, and verify performance.
8. Crimp the process tube and solder the end shut.
Proper safety procedures must be followed,
and proper protective clothing must be worn
when working with a torch.
Failure to follow these procedures could
result in moderate or serious injury.
Proper safety procedures must be followed,
and proper protective clothing must be worn
when working with liquid refrigerant.
Failure to follow these procedures could
result in minor to moderate injury.
WARNING
CAUTION
BURN HAZARD
FREEZE HAZARD
Proper safety procedures must be followed,
and proper protective clothing must be worn
when working with a torch.
Failure to follow these procedures could
result in moderate or serious injury.
WARNING
BURN HAZARD
Method Of Charging / Repairs
The acceptable method for charging the RAC system is the
Weighed in Charge Method. The weighed in charge method is
applicable to all units. It is the preferred method to use, as it is
the most accurate.
The weighed in method should always be used whenever
a charge is removed from a unit such as for a leak repair,
compressor replacement, or when there is no refrigerant
charge left in the unit. To charge by this method, requires the
following steps:
1. Install a piercing valve to remove refrigerant from the
sealedsystem. (Piercing valve must be removed from the
system before recharging.)
2. Recover Refrigerant in accordance with EPA regulations.
20

Undercharged Refrigerant Systems
An undercharged system will result in poor performance
(low pressures, etc.) in both the heating and cooling
cycle.
Whenever you service a unit with an undercharge of
refrigerant, always suspect a leak. The leak must be
repaired before charging the unit.
To check for an undercharged system, turn the unit on,
allow the compressor to run long enough to establish
working pressures in the system (15 to 20 minutes).
During the cooling cycle you can listen carefully at the exit
of the metering device into the evaporator; an intermittent
hissing and gurgling sound indicates a low refrigerant
charge. Intermittent frosting and thawing of the evaporator
is another indication of a low charge, however, frosting
and thawing can also be caused by insuffi cient air over
the evaporator.
Checks for an undercharged system can be made at
the compressor. If the compressor seems quieter than
normal, it is an indication of a low refrigerant charge.
Overcharged Refrigerant Systems
A check of the amperage drawn by the compressor
motor should show a lower reading. (Check the Unit
Specifi cation.) After the unit has run 10 to 15 minutes,
check the gauge pressures. Gauges connected to system
with an undercharge will have low head pressures and
substantially low suction pressures.
of the evaporator will not be encountered because the
refrigerant will boil later if at all. Gauges connected to
system will usually have higher head pressure (depending
upon amount of over charge). Suction pressure should be
slightly higher.
Compressor amps will be near normal or higher.
Noncondensables can also cause these symptoms. To
confi rm, remove some of the charge, if conditions improve,
system may be overcharged. If conditions don’t improve,
Noncondensables are indicated.
Whenever an overcharged system is indicated, always
make sure that the problem is not caused by air fl ow
problems. Improper air fl ow over the evaporator coil may
indicate some of the same symptoms as an over charged
system.
An overcharge can cause the compressor to fail, since it
would be “slugged” with liquid refrigerant.
The charge for any system is critical. When the compressor
is noisy, suspect an overcharge, when you are sure that
the air quantity over the evaporator coil is correct. Icing
ELECTRIC SHOCK HAZARD
WARNING
Turn off electric power before service or
installation.
Extreme care must be used, if it becomes
necessary to work on equipment with power
applied.
Failure to do so could result in serious injury or
death.
Sealed Refrigeration System contains refrigerant
and oil under high pressure.
Proper safety procedures must be followed,
and proper protective clothing must be worn
when working with refrigerants.
Failure to follow these procedures could
result in serious injury or death.
WARNING
HIGH PRESSURE HAZARD
21

Restricted Refrigerant System
Troubleshooting a restricted refrigerant system can be
diffi cult. The following procedures are the more common
problems and solutions to these problems. There are two
types of refrigerant restrictions: Partial restrictions and
complete restrictions.
A partial restriction allows some of the refrigerant to
circulate through the system.
With a complete restriction there is no circulation of
refrigerant in the system.
Restricted refrigerant systems display the same symptoms
as a “low-charge condition.”
When the unit is shut off, the gauges may equalize very
slowly.
Gauges connected to a completely restricted system will
run in a deep vacuum. When the unit is shut off, the gauges
will not equalize at all.
A quick check for either condition begins at the evaporator.
With a partial restriction, there may be gurgling sounds
at the metering device entrance to the evaporator. The
evaporator in a partial restriction could be partially frosted
or have an ice ball close to the entrance of the metering
device. Frost may continue on the suction line back to the
compressor.
Often a partial restriction of any type can be found by feel,
as there is a temperature difference from one side of the
restriction to the other.
With a complete restriction, there will be no sound at the
metering device entrance. An amperage check of the
compressor with a partial restriction may show normal
current when compared to the unit specifi cation. With a
complete restriction the current drawn may be considerably
less than normal, as the compressor is running in a deep
vacuum (no load.) Much of the area of the condenser will
be relatively cool since most or all of the liquid refrigerant
will be stored there.
The following conditions are based primarily on a system
in the cooling mode.
22

Locked Rotor Voltage (L.R.V.) Test
Locked rotor voltage (L.R.V.) is the actual voltage available
at the compressor under a stalled condition.
Single Phase Connections
Disconnect power from unit. Using a voltmeter, attach one
lead of the meter to the run “R” terminal on the compressor
and the other lead to the common “C” terminal of the com-
pressor. Restore power to unit.
Determine L.R.V.
Start the compressor with the volt meter attached; then stop
the unit. Attempt to restart the compressor within a couple
of seconds and immediately read the voltage on the meter.
The compressor under these conditions will not start and will
usually kick out on overload within a few seconds since the
pressures in the system will not have had time to equalize.
Voltage should be at or above minimum voltage of 197 VAC,
as specified on the rating plate. If less than minimum, check
for cause of inadequate power supply; i.e., incorrect wire
size, loose electrical connections, etc.
COMPRESSOR CHECKS
ELECTRIC SHOCK HAZARD
WARNING
Turn off electric power before service or
installation. Extreme care must be used, if it
becomes necessary to work on equipment with
power applied.
Failure to do so could result in serious injury or
death.
Amperage (L.R.A.) Test
The running amperage of the compressor is the most impor-
tant of these readings. A running amperage higher than that
indicated in the performance data indicates that a problem
exists mechanically or electrically.
Single Phase Running and L.R.A. Test
NOTE: Consult the specification and performance section
for running amperage. The L.R.A. can also be found on the
rating plate.
Select the proper amperage scale and clamp the meter
probe around the wire to the “C” terminal of the compres-
sor. Turn on the unit and read the running amperage on
the meter. If the compressor does not start, the reading
will indicate the locked rotor amperage (L.R.A.).
External Overload
The compressor is equipped with an external overload
which senses both motor amperage and winding tem-
perature. High motor temperature or amperage heats the
overload causing it to open, breaking the common circuit
within the compressor.
Heat generated within the compressor shell, usually due
to recycling of the motor, is slow to dissipate. It may take
anywhere from a few minutes to several hours for the
overload to reset.
Checking the External Overload
With power off, remove the leads from compressor termi-
nals. If the compressor is hot, allow the overload to cool
before starting check. Using an ohmmeter, test continu-
ity across the terminals of the external overload. If you
do not have continuity; this indicates that the overload is
open and must be replaced.
Certain unit components operate at
temperatures hot enough to cause burns.
Proper safety procedures must be followed,
and proper protective clothing must be
worn.
Failure to follow this warning could result
in moderate to serious injury.
WARNING
BURN HAZARD
ELECTRIC SHOCK HAZARD
WARNING
Turn off electric power before service or
installation. Extreme care must be used, if it
becomes necessary to work on equipment
with power applied.
Failure to do so could result in serious injury or
death.
23

Single Phase Resistance Test
Remove the leads from the compressor terminals and set
the ohmmeter on the lowest scale (R x 1).
Touch the leads of the ohmmeter from terminals common
to start (“C” to “S”). Next, touch the leads of the ohmmeter
from terminals common to run (“C” to “R”).
Add values “C” to “S” and “C” to “R” together and
check resistance from start to run terminals (“S” to “R”).
Resistance “S” to “R” should equal the total of “C” to “S”
and “C” to “R.”
In a single phase PSC compressor motor, the highest
value will be from the start to the run connections (“S” to
“R”). The next highest resistance is from the start to the
common connections (“S” to “C”). The lowest resistance
is from the run to common. (“C” to “R”) Before replacing a
compressor, check to be sure it is defective.
GROUND TEST
Use an ohmmeter set on its highest scale. Touch one
lead to the compressor body (clean point of contact as
a good connection is a must) and the other probe in turn
to each compressor terminal. If a reading is obtained the
compressor is grounded and must be replaced.
Check the complete electrical system to the compressor
and compressor internal electrical system, check to be
certain that compressor is not out on internal overload.
Complete evaluation of the system must be made
whenever you suspect the compressor is defective. If
the compressor has been operating for sometime, a
careful examination must be made to determine why the
compressor failed.
Many compressor failures are caused by the following
conditions:
1. Improper air fl ow over the evaporator.
2. Overcharged refrigerant system causing liquid to be
returned to the compressor.
3. Restricted refrigerant system.
4. Lack of lubrication.
5. Liquid refrigerant returning to compressor causing oil
to be washed out of bearings.
6. Noncondensables such as air and moisture in
the system. Moisture is extremely destructive to a
refrigerant system.
7. Defective capacitors.
24

Recommended procedure for compressor
replacement
1. Be certain to perform all necessary electrical and
refrigeration tests to be sure the compressor is
actually defective before replacing.
2. Recover all refrigerant from the system though
the process tubes. PROPER HANDLING OF
RECOVERED REFRIGERANT ACCORDING TO
EPA REGULATIONS IS REQUIRED. Do not use
gauge manifold for this purpose if there has been
a burnout. You will contaminate your manifold and
hoses. Use a Schrader valve adapter and copper
tubing for burnout failures.
3. After all refrigerant has been recovered, disconnect
suction and discharge lines from the compressor and
remove compressor. Be certain to have both suction
and discharge process tubes open to atmosphere.
4. Carefully pour a small amount of oil from the suction
stub of the defective compressor into a clean
container.
9. Evacuate the system with a good vacuum pump capable
of a fi nal vacuum of 200 microns or less. The system
should be evacuated through both liquid line and suction
line gauge ports. While the unit is being evacuated, seal
all openings on the defective compressor. Compressor
manufacturers will void warranties on units received not
properly sealed. Do not distort the manufacturers tube
connections.
10. Recharge the system with the correct amount of
refrigerant. The proper refrigerant charge will be
found on the unit rating plate. The use of an accurate
measuring device, such as a charging cylinder,
electronic scales or similar device is necessary.
COMPRESSOR REPLACEMENT
5. Using an acid test kit (one shot or conventional kit), test
the oil for acid content according to the instructions
with the kit.
6. If any evidence of a burnout is found, no matter how
slight, the system will need to be cleaned up following
proper procedures.
7. Install the replacement compressor.
8. Pressurize with a combination of R410-A and nitrogen
and leak test all connections with an electronic or
Halide leak detector. Recover refrigerant and repair
any leaks found.
Repeat Step 8 to insure no more leaks are present.
Unplug and/or disconnect all electrical power
to the unit before performing inspections,
maintenances or service.
Failure to do so could result in electric shock,
serious injury or death.
WARNING
RISK OF ELECTRIC SHOCK
Sealed Refrigeration System contains refrigerant
and oil under high pressure.
Proper safety procedures must be followed,
and proper protective clothing must be worn
when working with refrigerants.
Failure to follow these procedures could
result in serious injury or death.
WARNING
HIGH PRESSURE HAZARD
Extreme care, proper judgment and all safety
procedures must be followed when testing,
troubleshooting, handling or working around
unit while in operation with high temperature
components. Wear protective safety aids
such as: gloves, clothing etc.
Failure to do so could result in serious burn
injury.
WARNING
HIGH TEMPERATURES
The use of a torch requires extreme care and proper
judgment. Follow all safety recommended precautions
and protect surrounding areas with fi re proof materials.
Have a fi re extinguisher readily available. Failure to follow
this notice could result in moderate to serious property
damage.
NOTICE
FIRE HAZARD
The use of nitrogen requires a pressure
regulator. Follow all safety procedures and
wear protective safety clothing etc.
Failure to follow proper safety procedures
result in serious injury or death.
WARNING
EXPLOSION HAZARD
Proper safety procedures must be followed,
and proper protective clothing must be worn
when working with liquid refrigerant.
Failure to follow these procedures could
result in minor to moderate injury.
CAUTION
FREEZE HAZARD
25

1.
2.
3.
4.
5.
ELECTRIC SHOCK HAZARD
WARNING
Turn off electric power before service or
installation.
Failure to do so may result in personal injury,
or death.
Sealed Refrigeration System contains refrigerant
and oil under high pressure.
Proper safety procedures must be followed,
and proper protective clothing must be worn
when working with refrigerants.
Failure to follow these procedures could
result in serious injury or death.
WARNING
HIGH PRESSURE HAZARD
The use of nitrogen requires a pressure
regulator. Follow all safety procedures and
wear protective safety clothing etc.
Failure to follow proper safety procedures
result in serious injury or death.
WARNING
EXPLOSION HAZARD
Recover all refrigerant and oil from the system.
Remove compressor, capillary tube and fi lter drier
from the system.
Flush evaporator condenser and all connecting
tubing with dry nitrogen or equivalent. Use approved
fl ushing agent to remove all contamination from
system. Inspect suction and discharge line for
carbon deposits. Remove and clean if necessary.
Ensure all acid is neutralized.
Reassemble the system, including new drier strainer
and capillary tube.
Proceed with step 8-10 on previous page.
SPECIAL PROCEDURE IN THE CASE OF MOTOR
COMPRESSOR BURNOUT
Basically, troubleshooting and servicing rotary compres-
sors is the same as on the reciprocating compressor with
only one main exception:
NEVER, under any circumstances, liquid charge a rotary
compressor through the LOW side. Doing so would cause
permanent damage to the new compressor.
ROTARY COMPRESSOR SPECIAL TROUBLESHOOTING
AND SERVICE
26

ROUTINE MAINTENANCE
AIR FILTER
Clean the unit air intake fi lter at least every 300 to 350 hours
of operation. Clean the fi lters with a mild detergent in warm
water and allow to dry thoroughly before reinstalling.
COILS AND BASE PAN
The indoor coil (evaporator coil), the outdoor coil (condenser
coil) and base pan should be inspected periodically
(yearly or bi-yearly) and cleaned of all debris (lint, dirt,
leaves, paper, etc.). Clean the coils and base pan with a soft
brush and compressed air or vacuum. If using a pressure
washer, be careful not to bend the aluminium fi n pack. Use
a sweeping up and down motion in the direction of the verti-
cal aluminum fi n pack when pressure cleaning coils. Cover
all electrical components to protect them from water or spray.
Allow the unit to dry thoroughly before reinstalling it in the
sleeve.
BLOWER WHEEL / HOUSING / CONDENSER FAN /
SHROUD
Inspect the indoor blower housing, evaporator blade, con-
denser fan blade and condenser shroud periodically (yearly
or bi-yearly) and clean of all debris (lint, dirt, mold, fungus,
etc.). Clean the blower housing area and blower wheel with
an antibacterial / antifungal cleaner. Use a biodegradable
cleaning agent and degreaser on condenser fan and con-
denser shroud. Use warm or cold water when rinsing these
items. Allow all items to dry thoroughly before reinstalling
them.
ELECTRONIC / ELECTRICAL / MECHANICAL
Periodically (at least yearly or bi-yearly): inspect all control
components: electronic, electrical and mechanical, as well as
the power supply. Use proper testing instruments (voltmeter,
ohmmeter, ammeter, wattmeter, etc.) to perform electrical
tests. Use an air conditioning or refrigeration thermometer
to check room, outdoor and coil operating temperatures.
Use an electronic tester to measure wet bulb temperatures
indoors and outdoors.
Units are to be inspected and serviced by qualifi ed service
personnel only. Use proper protection on surrounding
property. Failure to follow this notice could result in
moderate or serious property damage.
NOTICE
EXCESSIVE WEIGHT HAZARD
WARNING
Use two people to lift or carry the unit, and wear
proper protective clothing.
Failure to do so may result in personal injury.
Do not use a caustic coil cleaning agent on coils or base
pan. Use a biodegradable cleaning agent and degreaser,
to prevent damage to the coil and/or base pan.
NOTICE
ELECTRIC SHOCK HAZARD
WARNING
Turn off electric power before inspections,
maintenances, or service.
Extreme care must be used, if it becomes
necessary to work on equipment with power
applied.
Failure to do so could result in serious injury
or death.
CUT/SEVER HAZARD
WARNING
Be careful with the sharp edges and corners.
Wear protective clothing and gloves, etc.
Failure to do so could result in serious injury.
27

SLEEVE / DRAIN
Inspect the sleeve and drain system periodically (at least yearly or bi-yearly) and clean of all obstructions and
debris. Clean both areas with an antibacterial and antifungal cleaner. Rinse both items thoroughly with water and
ensure that the drain outlets are operating correctly. Check the sealant around the sleeve and reseal areas as
needed.
FRONT COVER
Clean the front cover when needed. Use a mild detergent. Wash and rinse with warm water. Allow it to dry
thoroughly before reinstalling it in the chassis.
CLEARANCES
Inspect the surrounding area (inside and outside) to ensure that the unit’s clearances have not been compromised or
altered.
ROUTINE MAINTENANCE (Continued)
Do not drill holes in the bottom of the drain pan or the
underside of the unit. Not following this notice could
result in damage to the unit or condensate water leaking
inappropriately which could cause water damage to
surrounding property.
NOTICE
28
System Controls
Return Air Grille/Filter
Condenser Fan Blade
Compressor
Condenser Coil
Discharge Air
Outdoor Grille
Sleeve
Basepan
Blower Motor
Blower Wheel
Evaporator Coil
Front Cover

29 29
Due to variations in room design, climate zone and occupancy, larger areas
may require the use of multiple units to provide the optimal cooling solution.
This is a general guide.
Please consult manual J or M for exact load calculations.
1. If heavily shaded, reduce capacity 10%.
2. If very sunny, add 10%.
3. Add 500 BTU/H per person over 2 people.
4. Add 4,000 BTU/H if area is a kitchen.
ROOM AIR CONDITIONER UNIT
PERFORMANCE TEST DATA SHEET
DATE: _______________ MODEL:_______________ SERIAL:________________
YES NO
IS THERE A FRIEDRICH SLEEVE INSTALLED? ____ ____
IS THERE A CHASSIS SEAL GASKET INSTALLED? ____ ____
IS MAINTENANCE BEING PERFORMED? ____ ____
If NO is checked use back of sheet for explanation
ELECTRICAL:
LINE VOLTAGE (STATIC) --------- VOLTS
START UP VOLTAGE --------- VOLTS
AMPERAGE DRAW --------- AMPS (COOL)
AMPERAGE DRAW --------- AMPS (HEAT)
COMPRESSOR
LOCKED ROTOR AMPS --------- AMPS
RUNNING AMPS --------- AMPS
LOCKED ROTOR VOLTAGE --------- VOLTS
INDOOR TEMPERATURES:
INDOOR AMBIENT TEMPERATURE -------- F
RELATIVE HUMIDITY (RH) INDOOR -------- %
COOL HEAT
DISCHARGE AIR TEMPERATURE (INDOOR) ---------- F --------- F
RETURN AIR TEMPERATURE (INDOOR) ---------- F --------- F
DIFFERENTIAL ---------- F --------- F
OUTDOOR TEMPERATURE:
OUTDOOR AMBIENT TEMPERATURE --------- F
RH OUTDOOR --------- %
CONDENSER:
DISCHARGE AIR TEMPERATURE (OUTDOOR) --------- F ---------- F
INTAKE AIR TEMPERATURE (OUTDOOR --------- F ---------- F
DIFFERENTIAL --------- F ---------- F
APPLICATION USE ------------------------- ROOM (RESIDENTIAL OR COMMERCIAL)

Problem Possible Cause Possible Solution
Unit does not operate.
The unit is turned to the off position, Turn the unit to the on position and raise or
lower temperature setting (as appropriate) to
call for operation.
The LCDI power cord is unplugged.
Plug into a properly grounded 3 prong
receptacle. See “Electrical Rating Tables” on
pg. 6 for the proper receptacle type for your
unit.
The LCDI power cord has tripped
(Reset button has popped out).
Press and release RESET (listen for click;
Reset button latches and remains in) to resume
operation.
The circuit breaker has tripped or
the supply circuit fuse has blown.
Reset the circuit breaker, or replace the fuse as
applicable. If the problem continues, contact a
licensed electrician.
There has been a local power
failure.
The unit will resume normal operation once
power has been restored.
Unit Trips Circuit Breaker or
Blows Fuses.
Other appliances are being used on
the same circuit.
The unit requires a dedicated outlet circuit, not
shared with other appliances.
An extension cord is being used. Do NOT use an extension cord with this or any
other air conditioner.
The circuit breaker or time-delay
fuse is not of the proper rating.
Replace with a circuit breaker or time-delay
fuse of the proper rating. See “Electrical
Rating Tables” on pg. 6 for the proper circuit
breaker/fuse rating for your unit. If the problem
continues, contact a licensed electrician.
LCDI Power Cord Trips (Reset
Button Pops Out).
The LCDI power cord can trip
(Reset button pops out) due to
disturbances on your power supply
line.
Press and release RESET (listen for click;
Reset button latches and remains in) to resume
normal operation.
Electrical overload, overheating, or
cord pinching can trip (Reset button
pops out) the LCDI power cord.
Once the problem has been determined and
corrected, press and release RESET (listen for
click; Reset button latches and remains in) to
resume normal operation.
NOTE: A damaged power supply cord must be replaced with a new power supply cord
obtained from the product manufacturer and must not be repaired.
Unit Does Not Cool/Heat
On And Off Too Frequently.
The return/discharge air grille is
blocked.
Ensure that the return and/or discharge air
paths are not blocked by curtains, blinds,
furniture, etc.
Windows or doors to the outside are
open.
Ensure that all windows and doors are closed.
The temperature is not set at a cool
enough/warm enough setting.
Adjust the Temperature control to a cooler or
warmer setting as necessary.
remove obstruction.
The indoor coil or outdoor coil is
dirty or obstructed.
Clean the coils, (See Routine Maintenance), or
remove obstruction.
There is excessive heat or moisture
(cooking, showers, etc.) in the room.
Be sure to use exhaust vent fans while cooking
or bathing and, if possible, try not to use heat
producing appliances during the hottest part of
the day.
The temperature of the room you
are trying to cool is extremely hot.
Allow additional time for the air conditioner to
cool off a very hot room.
GENERAL TROUBLESHOOTING TIPS
30

Unit Does Not Cool/Heat
On And Off Too Frequently
(continued).
The outside temperature is below
60° F (16° C).
Do not try to operate your air conditioner in the
cooling mode when the outside temperature
is below 60° F (16° C). The unit will not cool
properly, and the unit may be damaged.
The digital control is set to fan
cycling mode.
Since the fan does not circulate the room
air continuously at this setting, the room air
does not mix as well and hot (or cold) spots
may result. Using the continuous fan setting
is recommended to obtain optimum comfort
levels.
cooling capacity to match the heat
gain of the room.
Check the cooling capacity of your unit to
ensure it is properly sized for the room in which
it is installed. Room air conditioners are not
designed to cool multiple rooms.
heating capacity to match the heat
loss of the room.
Check the heating capacity of your unit. Air
conditioners are sized to meet the cooling load,
and heater size is then selected to meet the
heating load. In extreme northern climates,
room air conditioners may not be able to be
used as a primary source of heat.
Unit Runs Too Much.
This may be due to an excessive
heat load in the room.
If there are heat producing appliances in use
in the room, or if the room is heavily occupied,
the unit will need to run longer to remove the
additional heat.
It may also be due to an improperly
sized unit.
Be sure to use exhaust vent fans while cooking
or bathing and, if possible, try not to use heat
producing appliances during the hottest part of
the day.
This may be normal for higher
your new air conditioner may result in the
unit running longer than you feel it should.
This may be more apparent, if it replaced an
compared to older models.
You may notice that the discharge
air temperature of your new air
conditioner may not seem as cold
as you may be accustomed to from
older units. This does not, however,
indicate a reduction in the cooling
capacity of the unit.
capacity rating (Btu/h) listed on the unit’s rating
GENERAL TROUBLESHOOTING TIPS (CONTINUED)
Problem Possible Cause Possible Solution
31

COOLING ONLY ROOM AIR CONDITIONERS: TROUBLESHOOTING TIPS
noitcA esuaC elbissoP melborP
Compressor
does not run
Low voltage Check voltage at compressor. 115V & 230V
units will operate at 10% voltage variance
T-stat not set cold enough or
inoperative or electronic control
board is bad
Set t-stat to coldest position. Test t-stat &
replace if inoperative
Compressor hums but cuts off on
overload
Hard start compressor. Direct test compressor.
If compressor starts, add starting components
Open or shorted compressor
windings Check for continuity & resistance
Open overload Test overload protector & replace if inoperative
Open capacitor Test capacitor & replace if inoperative
Inoperative system switch,
thermistor or electronic board
Test for continuity in all positions. Replace if
inoperative switch or electronic board.
Broken, loose or incorrect wiring Refer to appropriate wiring diagrams to check
wiring
noitcA esuaC elbissoP melborP
Fan motor
does not run
Inoperative system switch Test switch & replace if inoperative
Broken, loose or incorrect wiring Refer to applicable wiring diagram
Open capacitor Test capacitor & replace if inoperative
Fan speed switch open Test switch & replace if inoperative
Inoperative fan motor Test fan motor & replace if inoperative (be sure
internal overload has had time to reset)
noitcA esuaC elbissoP melborP
Does not cool or
only cools slightly
Undersized unit Refer to industry standard sizing chart
T-stat open or inoperative
Thermistor or electronic board is bad, Set to coldest position. Test t-stat or electronic
control board & replace if necessary.
Dirty fi launaM s’renwO ni dednemmocer sa naelC retl
Dirty or restricted condenser or
evaporator coil
Use pressure wash or biodegradable cleaning
agent to clean
Poor air circulation Adjust discharge louvers. Use high fan speed
Fresh air or exhaust air door open
on applicable models
Close doors. Instruct customer on use of this
feature
Low capacity - undercharge Check for leak & make repair
Compressor not pumping properly Check amperage draw against nameplate. If
not conclusive, make pressure test
32

COOLING ONLY ROOM AIR CONDITIONERS: TROUBLESHOOTING TIPS
noitcA esuaC elbissoP melborP
Unit does not run
Fuse blown or circuit tripped
Replace fuse, reset breaker. If repeats, check
fuse or breaker size. Check for shorts in unit
wiring & components
Power cord not plugged in Plug it in
System switch in “OFF” position Set switch correctly
Inoperative system switch or open
electronic control board Test for continuity
Loose or disconnected wiring at
switch, control board or other com-
ponents
Check wiring & connections. Reconnect per
wiring diagram
noitcA esuaC elbissoP melborP
Evaporator coil
freezes up
Dirty fi launaM s’renwO ni dednemmocer sa naelC retl
Restricted airfl ow
Check for dirty or obstructed coil. Use
pressure wash or biodegradable cleaning
agent to clean
Inoperative t-stat or thermistors Test for continuity
Short of refrigerant De-ice coil & check for leak
Inoperative fan motor Test fan motor & replace if inoperative
Partially restricted capillary tube
De-ice coil. Check temp. differential (delta T)
across coil. Touch test coil return bends for
same temp. Test for low running current
noitcA esuaC elbissoP melborP
Compressor runs
continually & does
not cycle off
Excessive heat load Unit undersized. Test cooling performance &
replace with larger unit if needed
Restriction in line Check for partially iced coil & check
temperature split across coil
Refrigerant leak
Check for oil at silver soldered connections.
Check for partially iced coil. Check split across
coil. Check for low running amperage
T-stat contacts stuck Check operation of t-stat. Replace if contacts
remain closed.
T-stat incorrectly wired Refer to appropriate wiring diagram
Thermistor shorted Replace thermistor or electronic control board
noitcA esuaC elbissoP melborP
T-stat does not
turn unit off
T-stat contacts stuck
Disconnect power to unit. Remove cover
of t-stat & check if contacts are stuck. If so,
replace t-stat
T-stat set at coldest point Turn to higher temp. setting to see if unit
cycles off
Incorrect wiring Refer to appropriate wiring diagrams
Unit undersized for area to be
cooled Refer to industry standard sizing chart
Defective thermistor Replace thermistor or electronic control board
33

COOLING ONLY ROOM AIR CONDITIONERS: TROUBLESHOOTING TIPS
noitcA esuaC elbissoP melborP
Compressor runs
for short periods
only. Cycles on
overload
Overload inoperative. Opens too
soon
Check operation of unit. Replace overload if
system operation is satisfactory
Compressor restarted before
system pressures equalized
Allow a minimum of 2 minutes to allow
pressures to equalize before attempting to
restart. Instruct customer of waiting period
Low or À uctuating voltage
Check voltage with unit operating. Check for
other appliances on circuit. Air conditioner
should be in separate circuit for proper voltage
& fused separately
Incorrect wiring Refer to appropriate wiring diagram
Shorted or incorrect capacitor Check by substituting a known good capacitor
of correct rating or test cap
Restricted or low air À ow through
condenser coil or evaporator coil
Check for proper fan speed or blocked
coils
Compressor running abnormally
hot
Check for kinked discharge line or restricted
condenser. Check amperage
noitcA esuaC elbissoP melborP
T-stat does not
turn unit on
Loss of charge in t-stat bulb
(EQ08M11)
Place jumper across t-stat terminals to check if
unit operates. If unit operates, replace t-stat.
Loose or broken parts in t-stat Check as above
Incorrect wiring Refer to appropriate wiring diagram
Defective thermistor Replace thermistor or electronic control board
noitcA esuaC elbissoP melborP
Noisy operation
Poorly installed Refer to Installation Manual for proper
installation
Fan blade striking chassis Reposition - adjust motor mount
Compressor vibrating
Check that compressor grommets have not
deteriorated. Check that compressor mounting
parts are not missing
Improperly mounted or loose
cabinet parts refrigerant tubes
Check assembly & parts for looseness,
rubbing & rattling. Correct as needed
noitcA esuaC elbissoP melborP
Water leaks into
the room
Evaporator drain pan overÀ owing Clean obstructed drain trough
Condensation forming underneath
base pan
Evaporator drain pan broken or cracked.
Reseal or replace. No chassis gasket installed.
Install chassis gasket
Poor installation resulting in rain
entering the room
Check installation instructions. Reseal as
required
Condensation on discharge grille
louvers
Dirty evaporator coil. Use pressure wash
or biodegradable cleaning agent to clean.
Environmental phenomena: point supply
louvers upward
Chassis gasket not installed Install gasket, per Installation manual
Downward slope of unit is too
steep inward
Refer to installation manual for proper
installation
34

COOLING ONLY ROOM AIR CONDITIONERS: TROUBLESHOOTING TIPS
noitcA esuaC elbissoP melborP
Water “spitting”
into room
Sublimation:
When unconditioned saturated,
outside air mixes with conditioned
air, condensation forms on the
cooler surfaces
Ensure that foam gaskets are installed in
between window panes & in between the
unit & the sleeve. Also, ensure that fresh
air/exhaust vents (on applicable models) are in
the closed position & are in tact
Downward pitch of installation is
too steep towards back of unit
Follow installation instructions to ensure that
downward pitch of installed unit is no less than
1/4” & no more than 3/8”
Restricted coil or dirty fi lter Clean & advise customer of periodic cleaning
& maintenance needs of entire unit
noitcA esuaC elbissoP melborP
Excessive
moisture
Insuffi cient air circulation thru area
to be air conditioned Adjust louvers for best possible air circulation
noitisop ”revaSyenoM“ ni etarepO tinu dezisrevO
Inadequate vapor barrier in building
structure, particularly fl oors Advise customer
noitcA esuaC elbissoP melborP
T-stat or
thermistor
short cycles
Defective thermistor Replace thermistor or electronic control board
T-stat differential too narrow Replace t-stat
Plenum gasket not sealing,
allowing discharge air to short
cycle t-stat
Check gasket. Reposition or replace as
needed
Restricted coil or dirty fi lter Clean & advise customer of periodic cleaning
& maintenance needs of entire unit
noitcA esuaC elbissoP melborP
Prolonged off
cycles (automatic
operation)
Heat anticipator (resistor) wire
disconnected at t-stat or system
switch
Refer to appropriate wiring diagram
Heat anticipator (resistor) shorted or
open
Disconnect plus from outlet. Remove resistor
from bracket. Insert plug & depress “COOL”
& “FAN AUTOMATIC” buttons. Place t-stat to
warmest setting. Feel resistor for temperature.
If no heat, replace resistor
Partial loss of charge in t-stat bulb
causing a wide differential Replace t-stat
Defective thermistor Replace thermistor or electronic control board
noitcA esuaC elbissoP melborP
Outside water
leaks
Evaporator drain pan cracked or
obstructed Repair, clean or replace as required
Water in compressor area Detach shroud from pan & coil. Clean &
remove old sealer. Reseal, reinstall & check
Obstructed condenser coil Use pressure wash or biodegradable cleaning
agent to clean
Fan blade/slinger ring improperly
positioned
Adjust fan blade to 1/2” of condenser coil fi n
pack
35

HEAT / COOL ONLY ROOM AIR CONDITIONERS: TROUBLESHOOTING TIPS
noitcAesuaC elbissoPmelborP
Room temperature
uneven
(Heating cycle)
Heat anticipator (resistor) shorted (on applicable
models)
Disconnect power to unit. Remove resistor from
t-stat bulb block. Plug in unit & allow to operate.
Feel resistor for heat. If not heat, replace resistor
Wide differential - partial loss of t-stat bulb charge Replace t-stat
Incorrect wiring
Refer to appropriate wiring diagram. Resistor is
energized during "ON" cycle of compressor or
fan.
noitcAesuaC elbissoPmelborP
Does not heat
adequately
Opened doors or windows Close doors or windows.
Dirty filaunaM s'renwO ni dednemmocer sa naelCretl
Unit undersized
Check heat rise across coil. If unit operates
effi ciently, check if insulation can be added
to attic or walls. If insulation is adequate,
recommend additional unit or larger one
Heater hi-limit control cycling on & off Check for adequate fan air across heater. Check
control for open at 110°F & close at 100°F
Shorted or opened heater Ohmmeter/continuity check
margaid gniriw elbacilppa kcehCgniriw tcerrocnI
36
* NOTE: Heater size on the EQ08M11 is: 1.15 KW.
*

37
ELECTRONIC CONTROL
COOL ONLY MODELS:
XQ05M10* XQ06M10* XQ08M10* XQ10M10*
*Last character may vary.

38
ELECTROMECHANICAL CONTROL
COOL WITH ELECTRIC HEAT MODEL:
EQ08M11*
*Last character may vary.

4
INSTRUCTIONS FOR USING COOLING LOAD ESTIMATE
FORM FOR ROOM AIR CONDITIONERS
(AHAM PUB. NO. RAC-1)
A. This cooling load estimate form is suitable for estimating the cooling load for comfort air conditioning installations
which do not require specifi c conditions of inside temperature and humidity.
B. The form is based on an outside design temperature of 95°F dry bulb and 75°F wet bulb. It can be used for areas
in the continental United States having other outside design temperatures by applying a correction factor for the
particular locality as determined from the map.
C. The form includes “day” factors for calculating cooling loads in rooms where daytime comfort is desired (such as
living rooms, offi ces, etc.)
D. The numbers of the following paragraphs refer to the corresponding numbered item on the form:
1. Multiply the square feet of window area for each exposure by the applicable factor. The window area is the
area of the wall opening in which the window is installed. For windows shaded by inside shades or venetian
blinds, use the factor for “Inside Shades.” For windows shaded by outside awnings or by both outside aw-
nings and inside shades (or venetian blinds), use the factor for “Outside Awnings.” “Single Glass” includes
all types of single thickness windows, and “Double Glass” includes sealed airspace types, storm windows,
and glass block. Only one number should be entered in the right hand column for Item 1, and this number
should represent only the exposure with the largest load.
2. Multiply the total square feet of all windows in the room by the applicable factor.
3a. Multiply the total length (linear feet) of all walls exposed to the outside by the applicable factor. Doors should
be considered as being part of the wall. Outside walls facing due north should be calculated separately from
outside walls facing other directions. Walls which are permanently shaded by adjacent structures should be
considered “North Exposure.” Do not consider trees and shrubbery as providing permanent shading. An
uninsulated frame wall or a masonry wall 8 inches or less in thickness is considered “Light Construction.” An
insulated wall or masonry wall over 8 inches in thickness is considered “Heavy Construction.”
3b. Multiply the total length (linear feet) of all inside walls between the space to be conditioned and any uncondi-
tioned spaces by the given factor. Do not include inside walls which separate other air conditioned rooms.
4. Multiply the total square feet of roof or ceiling area by the factor given for the type of construction most nearly
describing the particular application (use one line only.)
5. Multiply the total square feet of fl oor area by the factor given. Disregard this item if the fl oor is directly on the
ground or over a basement.
6. Multiply the number of people who normally occupy the space to be air conditioned by the factor given. Use
a minimum of 2 people.
7. Determine the total number of watts for light and electrical equipment, except the air conditioner itself, that
will be in use when the room air conditioning is operating. Multiply the total wattage by the factor given.
8. Multiply the total width (linear feet) of any doors or arches which are continually open to an unconditioned
space by the applicable factor.
NOTE: Where the width of the doors or arches is more than 5 feet, the actual load may exceed the calculated
value. In such cases, both adjoining rooms should be considered as a single large room, and the room air
conditioner unit or units should be selected according to a calculation made on this new basis.
9. Total the loads estimated for the foregoing 8 items.
10. Multiply the subtotal obtained in item 9 by the proper correction factor, selected from the map, for the particular
locality. The result is the total estimated design cooling load in BTU per hour.
E. For best results, a room air conditioner unit or units having a cooling capacity rating (determined in accordance
with the NEMA Standards Publication for Room Air Conditioners, CN 1-1960) as close as possible to the estimated
load should be selected. In general, a greatly oversized unit which would operate intermittently will be much less
satisfactory than one which is slightly undersized and which would operate more nearly continuously.
F. Intermittent loads such as kitchen and laundry equipment are not included in this form.
39

5
COOLING LOAD ESTIMATE FORM
HEAT GAIN FROM
1. WINDOWS: Heat gain from the sun.
Northeast
East
Southeast
South
Southwest
West
Northwest
North
2. WINDOWS: Heat by conduction
(Total of all windows.)
Single glass
Double glass or glass block
3. WALLS: (Based on linear feet of wall)
a. Outside walls
North Exposure
Other than North exposure
b. Inside Walls (between conditioned and
unconditioned spaces only.)
4. ROOF OR CEILING: (Use one only)
a. Roof, uninsulated
b. Roof, 1 inch or more insulation
c. Ceiling, occupied space above
d. Ceiling, insulated, with attic space above
e. Ceiling, uninsulated, with attic space above
5. Floor: (Disregard if fl oor is directly on ground or
over a basement.
6. NUMBER OF PEOPLE
7. LIGHTS AND ELECTRICAL EQUIPMENT IN USE
8. DOORS AND ARCHES CONTINUOUSLY
OPENED TO UNCONDITIONED SPACE: (TOTAL
LINEAR FEET OF WIDTH.)
9. SUBTOTAL
10. TOTAL COOLING LOAD (BTU per hour to be used
for selection of room air conditioner(s).)
No
Shades*
60
80
75
75
110
150
120
0
___ _sq. ft.
___ _sq. ft.
____sq. ft.
____sq. ft.
____sq. ft.
____sq. ft.
____sq. ft.
____sq. ft.
____sq. ft.
____sq. ft.
____ ft.
____ ft.
____sq. ft.
____sq. ft.
____sq. ft.
____sq. ft.
____sq. ft.
____sq. ft.
____sq. ft.
____
____watts
____ft.
*****
Inside
Shades*
25
40
30
35
45
65
50
0
Outside
Awnings*
20 ____
25 ____
20 ____
20 ____
30 ____
45 ____
35 ____
0 ____
(Area
X Factor)
Use
only
the
largest
load.
Use
only
one.
____
____
____
____
____
____
____
____
QUANTITY BTU/Hr.
(Quantity x Factor)
14
7
30
19
8
3
5
12
3
600
3
300
*****
Light Construction
30
60
Heavy Construction
20
30
_____
_____
_____
_____
_____
_____
_____
_____
_____
_____
_____
_____
_____
_____
_____
* These factors are for single glass
only. For glass block, multiply the
above factors by 0.5; for double
glass or storm windows, multiply the
above factors by 0.8.
FACTORS
DAY
____ Total in Item 9 X ____ (Factor from Map) = ____
40

6
Following is an example using the heat load form:
A space to be conditioned is part of a house geographically
located in an area where the lowest outdoor ambient winter
temperature is 40°F. The calculated heat loss is 184 BTU/
Hr./°F.
Subtract 40°F (lowest outdoor ambient temperature for the
geographical location) from 70°F (inside design temperature
of the unit) for a difference of 30°F. Multiply 184 by 30 for a
5500 BTU/Hr. total heat loss for the calculated space.
On the graph, plot the base point (70°) and a point on the
40°F line where it intersects with the 5500 BTU/Hr. line on
the left scale. Draw a straight line from the base point 70
through the point plotted at 40°F. This is the total heat loss
line.
Knowing that we have a 5500 BTU/Hr. heat loss, and
we expect that our heat pump will maintain a 70°F inside
temperature at 40°F outdoor ambient, we plot the selected
unit capacity BTU/Hr. of the unit between 35° and 60° on the
graph and draw a straight line between these points. Where
the total heat loss line and the unit capacity line intersect,
read down to the outdoor ambient temperature scale and
fi nd that this unit will deliver the required BTU/Hr. capacity
to approximately 30°F.
The heat load form on the following page may be used by
servicing personnel to determine the heat loss of a conditioned
space and the ambient winter design temperatures in which
the unit will heat the calculated space.
The upper half of the form is for computing the heat loss of
the space to be conditioned. It is necessary only to insert
the proper measurements on the lines provided and multiply
by the given factors, then add this result for the total heat
loss in BTU/Hr./°F.
The BTU/Hr. per °F temperature difference is the 70°F
inside winter designed temperature minus the lowest outdoor
ambient winter temperature of the area where the unit is
installed. This temperature difference is used as the multiplier
when calculating the heat loss.
The graph shows the following:
Left Hand Scale Unit capacity BTU/Hr. or heat loss
BTU/Hr.
Bottom Scale Outdoor ambient temperature, base
point.
Heat Pump Model BTU/Hr. capacity heat pump will
deliver at outdoor temperatures.
Balance Point Maximum BTU/Hr. heat pump
will deliver at indicated ambient
temperature.
HEAT LOAD FORM
41

7
HEATING LOAD FORM
FRIEDRICH ROOM UNIT HEAT PUMPS
BTU/HR PER
WALLS: (Linear Feet) °F TEMP. DIFFERENCE
2” Insulation Lin. Ft. x 1.6
Average Lin. Ft. x 2.6
WINDOWS & DOORS (Area, sq. ft.)
Single Glass: Sq. Ft. x 1.13
Double Glass: Sq. Ft. x 0.61
INFILTRATION - WINDOWS & DOORS: AVG. Lin. Ft. x 1.0
Loose Lin. Ft. x 2.0
CEILING: (Area, Sq. Ft.)
Insulated (6”) Sq. Ft. x 0.07
Insulated (2”) Sq. Ft. x 0.10
Built-up Roof (2” insulated Sq. Ft. x 0.10
Built-up Roof (1/2” insulated) Sq. Ft. x 0.20
No Insulation Sq. Ft. x 0.33
FLOOR: (Area, Sq. Ft.)
Above Vented Crawl space
Insulated (1:) Sq. Ft. x 0.20
Uninsulated Sq. Ft. x 0.50
* Slab on Ground Lin. Ft. x 1.70
1” Perimeter insulation Lin. Ft. x 1.00
* Based on Linear Feet of outside wall TOTAL HEAT LOSS PER °F BTU/HR/°F
Multiply total BTU/HR/°F X 30 and plot on the graph below at 40°F. Draw a straight line from
the 70 base point thru the point plotted at 40°F. The intersection of this heat loss line with the
unit capacity line represents the winter design heating load.
42

43
Friedrich Air Conditioning Company
10001 Reunion Place, Suite 500
San Antonio, TX 78216
1-800-541-6645
www.friedrich.com
ROOM AIR CONDITIONERS
LIMITED WARRANTY
FIRST YEAR
ANY PART: If any part supplied by FRIEDRICH fails because of a defect in workmanship or material within twelve months from date of original
purchase, FRIEDRICH will repair the product at no charge, provided room air conditioner is reasonably accessible for service. Any additional labor
cost for removing inaccessible units and/or charges for mileage related to travel by a Service Agency that exceeds 25 miles one way will be the
responsibility of the owner. This remedy is expressly agreed to be the exclusive remedy within twelve months from the date of the original purchase.
SECOND THROUGH FIFTH YEAR
SEALED REFRIGERANT SYSTEM:
because of a defect in workmanship or material within sixty months from date of purchase, FRIEDRICH will pay a labor allowance and parts
necessary to repair the Sealed Refrigeration System; PROVIDED FRIEDRICH will not pay the cost of diagnosis of the problem, removal, freight
charges, and transportation of the air conditioner to and from the Service Agency, and the reinstallation charges associated with repair of the
Sealed Refrigeration System. All such cost will be the sole responsibility of the owner. This remedy is expressly agreed to be the exclusive remedy
within sixty months from the date of the original purchase.
APPLICABILITY AND LIMITATIONS: This warranty is applicable only to units retained within the Fifty States of the U.S.A., District of Columbia,
and Canada. This warranty is not applicable to:
1. A
2. Products on which the model and serial numbers have been removed.
3. Products which have defects or damage which results from improper installation, wiring, electrical current characteristics, or
installed in a corrosive atmosphere, default or delay in performance caused by war, government restrictions or restraints, strikes,
material shortages beyond the control of FRIEDRICH, or acts of God.
OBTAINING WARRANTY PERFORMANCE: Service will be provided by the FRIEDRICH Authorized Dealer or Service Organization in your
area. They are listed in the Yellow Pages. If assistance is required in obtaining warranty performance, write to: Room Air Conditioner Service
Manager, Friedrich Air Conditioning Co., P.O. Box 1540, San Antonio, TX 78295-1540.
LIMITATIONS: THIS WARRANTY IS GIVEN IN LIEU OF ALL OTHER WARRANTIES. Anything in the warranty notwithstanding, ANY
IMPLIED WARRANTIES OF FITNESS FOR PARTICULAR PURPOSE AND/OR MERCHANTABILITY SHALL BE LIMITED TO THE DURATION
OF THIS EXPRESS WARRANTY. MANUFACTURER EXPRESSLY DISCLAIMS AND EXCLUDES ANY LIABILITY FOR CONSEQUENTIAL
OR INCIDENTAL DAMAGE FOR BREACH OF ANY EXPRESSED OR IMPLIED WARRANTY.
Performance of Friedrich’s Warranty obligation is limited to one of the following methods:
1. Repair of the unit
2. A refund to the customer for the prorated value of the unit based upon the remaining warranty period of the unit.
3. Providing a replacement unit of equal value
NOTE: Some states do not allow limitations on how long an implied warranty lasts, or do not allow the limitation or exclusion of consequential or
incidental damages, so the foregoing exclusions and limitations may not apply to you.
OTHER:
PROOF OF PURCHASE: Owner must provide proof of purchase in order to receive any warranty related services.
All service calls for explaining the operation of this product will be the sole responsibility of the consumer.
All warranty service must be provided by an Authorized FRIEDRICH Service Agency, unless authorized by FRIEDRICH prior to repairs being made.
(10-08)

TECHNICAL SUPPORT
CONTACT INFORMATION
44
FRIEDRICH AIR CONDITIONING CO.
10001 Reunion Place, Ste. 500, San Antonio, TX 78216
(210) 546-0500 877-599-5665 x 261 FAX (210) 546-0731
Email: tac@friedrich.com
www.friedrich.com
Printed in the U.S.A.


X-Star-ServMan (1-11)
FRIEDRICH AIR CONDITIONING CO.
10001 Reunion Place, Ste. 500, San Antonio, TX 78216
P 210-546-0500 | F 210-546-0731
www.friedrich.com
Printed in the U.S.A.