Honeywell Sleep Apnea Machine L404A D Users Manual 4b Pressuretrol
L404A-D to the manual 5dac9070-5b9e-4c2d-afcb-bf8177f575e8
2015-01-23
: Honeywell Honeywell-Honeywell-Sleep-Apnea-Machine-L404A-D-Users-Manual-261816 honeywell-honeywell-sleep-apnea-machine-l404a-d-users-manual-261816 honeywell pdf
Open the PDF directly: View PDF .
Page Count: 10
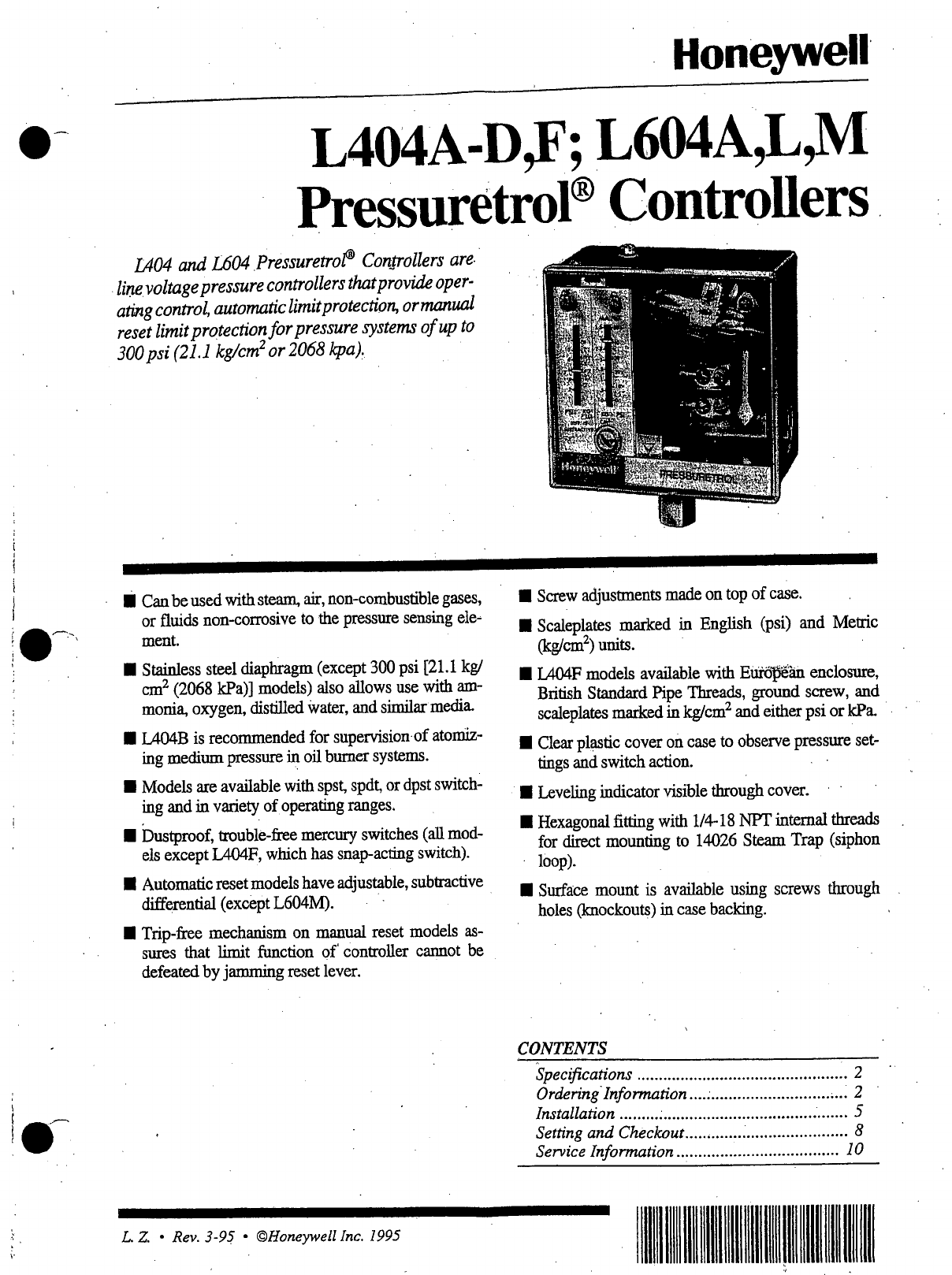
I
I
i
i
I
I
Honeywell
L404A
D
F
L604A
L
M
Pressuretrol@
Controllers
IA04
and
L604
PressuretrofFJ
Con
trollers
are
li7J
evoltage
pressure
controllers
thatprovide
oper
ating
control
automatic
limit
protection
ormanual
reset
limit
protection
for
pressure
systems
of
up
to
300
psi
21
1
kglcm2
or
2068
kpa
Ii
Can
be
used
with
steam
air
non
combustible
gases
or
fluids
non
corrosive
to
the
pressure
sensing
ele
ment
Stainless
steel
diaphragm
except
300
psi
21
1
kg
cm2
2068 kPa
models
also
allows
use
with
monia
oxygen
distilled
water
and
similar
media
IA04B
is
recommended
for
supervision
of
atomiz
ing
medium
pressure
oil
burner
systems
Models
are
available
with
spst
spdt
or
dpst
switch
ing
and
in
variety
of
operating
ranges
Dustproof
trouble
free
mercury
switches
all
mod
els
except
lA04F
which
has
snap
acting
switch
Automatic
reset
models
have
adjustable
subtractive
differential
except
L604M
Trip
free
mechanism
on
manual
reset
models
as
sures
that
limit
function
of
controller
cannot
be
defeated
by
jamming
reset
lever
Screw
adjustments
made
on
top
of
case
Scaleplates
marked
in
English
psi
and
Metric
kg
cm2
units
lA04F
models
available
with
Euro
pean
enclosure
British
Standard
Pipe
Threads
ground
screw
and
scaleplates
marked
in
kglcm2
and
either
psi
or
kPa
Clear
plastic
cover
on
case
to
observe
pressure
set
tings
and
switch
action
Leveling
indicator
visible
through
cover
Hexagonal
fitting
with
1
4
18
NPT
internal
eads
for
direct
mounting
to
14026 Steam
Trap
SIphon
loop
Surface
mount
is
available
using
screws
through
holes
knockouts
in
case
backing
CONTENTS
Specifications
2
Ordering1nformation
2
Installation
5
Setting
and
Checkout
8
Service
Information
10
L
Z
Rev
3
95
@Honeywelllnc
1995
11111111111111111
II
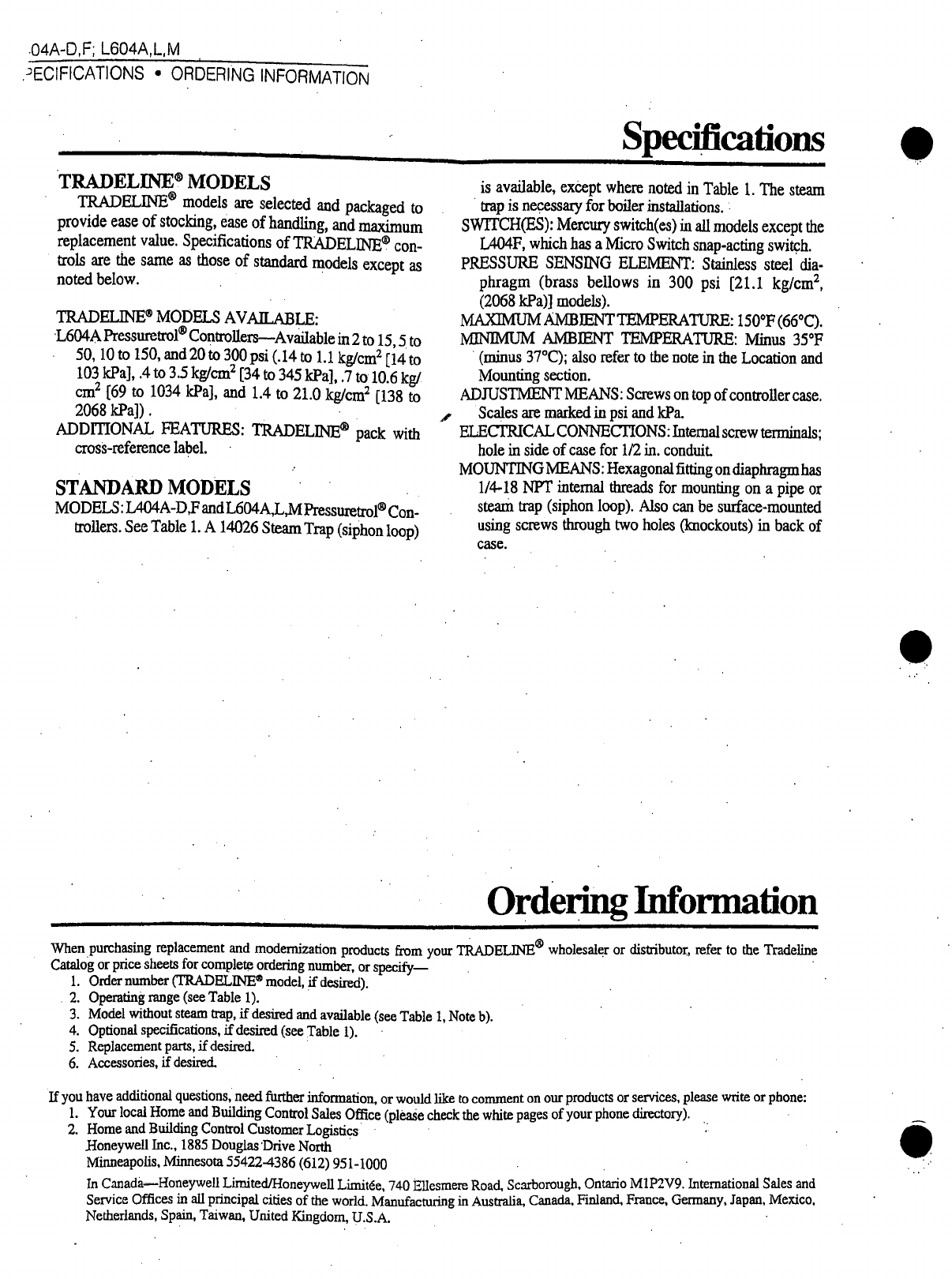
04A
D
F
L604A
L
M
JECIFICATIONS
ORDERING
INFORMATION
TRADELINE@
MODELS
TRADELINE@
models
are
selected
and
packaged
to
provide
ease
of
stocking
ease
of
handling
and
maximum
replacement
value
Specifications
of
TRADELlNE@
con
trols
are
the
same
as
those
of
standard
models
except
as
noted
below
TRADELINE@
MODELS
A
V
All
ABLE
L604A
Pressuretrol@
Controllers
Available
in
2
to
15
5
to
50
10
to
150
and
20
to
300
psi
14
to
11
kg
cm2
14to
103
kPa
4
to
35
kg
cm2
34
to
345
kPa
7
to
10
6kg
cm2
69
to
1034
kPa
and
14
to
21
0
kg
cm2
138
to
2068
kPa
ADDmONAL
FEATURES
TRAnELINE@
pack
with
cross
reference
label
STANDARD
MODELS
MODELS
IA04A
D
F
andL604A
L
MPressuretrol@Con
trollers
See
Table
1
A
14026 Steam
Trap
siphon
loop
Specitications
is
available
exCept
where
noted
in
Table
1
The
steam
trap
is
necessary
for
boiler
installations
SWITCH
ES
Mercury
switch
es
in
all models
except
the
IA04F
which
has
a
Micro
Switch
snap
acting
swit9h
PRESSURE
SENSING
ELEMENT
Stainless
steel
dia
phragm
brass
bellows
in
300
psi
21
1
kg
cm2
2068
kPa
models
MAXIMUM
AMBIENTTEMPERA11JRE
1500F
660C
MINlMUM
AMBIENT
TEMPERATURE
Minus
350F
minus
370C
also
refer
to
the
note
in
the
Location
and
Mounting
section
ADJUSTMENT
MEANS
Screws
on
top
of
controller
case
Scales
are
marked
in
psi
and
kPa
ELECfRICAL
CONNECTIONS
Internal
screw
tenninals
hole
in
side
ofcase
for
12
in
conduit
MOUNTING
MEANS
Hexagonal
fitting
on
diaphragm
has
1
4
18
NPT
internal
threads
for
mounting
on
a
pipe
or
steariJ
trap
siphon
loop
Also
can
be
surface
mounted
using
screws
through
two
holes knockouts
in
back
of
case
Ordering
Information
When
purchasing
replacement
and
modernization
products
from
your
TRADELlNE@
wholesal
r
or
distributor
refer
to
the
Tradeline
Catalog
or
price
sheets
for
comple
ordering
number
or
specify
1
Order
number
TRADELINE4D
model
if
desired
2
Operating
range
see
Table
1
3
Model
without
steam
trap
if
desired
and
available
see
Table
I
Note
b
4
Optional
specifications
if
desired
see
fable
1
5
Replacement
parts
if
desired
6
Accessories
if
desired
If
you
have
additional
questions
need
further
infonnation
or
would
like
to
conunent
on
our
products
or
services
please
write
or
phone
1
Your
local
Home
and
Building
Control
Sales
Office
please
check
the
white
pages
of
your
phone
directory
2
Home
and
Building
Control
Customer
Logistics
Honeywell
Inc
1885
Douglas
Drive
North
Minneapolis
Minnesota
55422
4386
612
951
1000
In
Cmlada
Honeywell
LimitedIHoneywell
Limitee
740
Ellesmere
Road
Scarborough
Ontario
M1P2V9
International
Sales and
Service
Offices
in
all
principal
cities
of
the
world
Manufacturing
in
Australia
Canada
Finland France
Germany
Japan
Mexico
Netherlands
Spain
Taiwan
United
Kingdom
U
SA
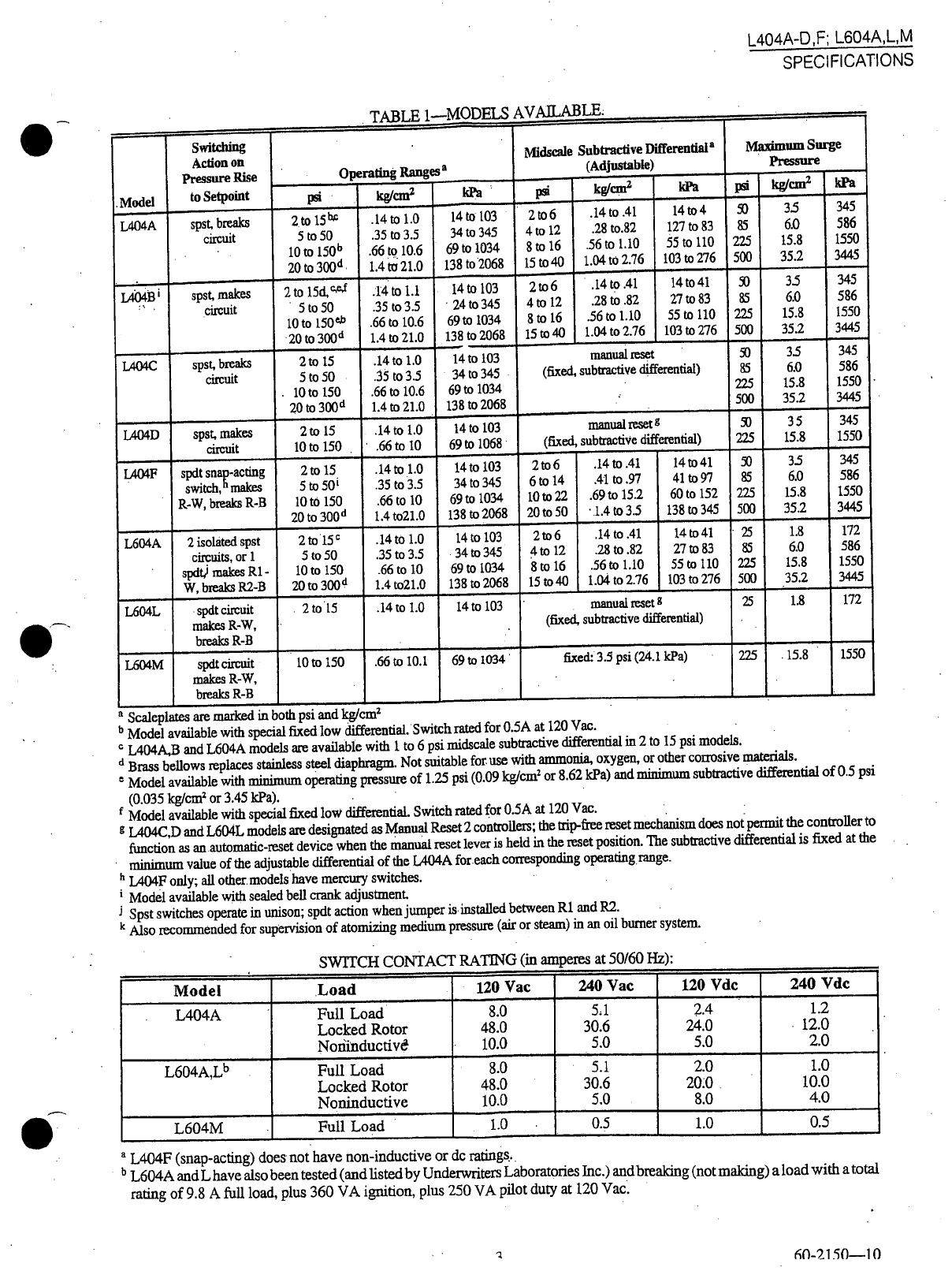
L404A
D
F
L604A
L
M
SPECIFICATIONS
I
I
I
Switching
Midscale
Subtractive
Differential
a
Maximum
Surge
Action
on
Pressure
Rise
Operating
Ranges
a
Adjustable
Pressure
Model
to
Setpoint
psi
kglem2
kPa
psi
kgfcm2
kPa
psi
kglem2
kPa
L404A
spst
breaks
2to
15b
c
14to1
0
14
to
103
2to6
14to
41
14to4
35
345
circuit
5
to
50 35
to
3 5
34
to
345
4
to
12 28
to
82
127
to
83
85 6
0
586
10
to
150b
66
to
10
669
to
1034
8
to
16
56
to
1
10
55
to
110 225
15 8
1550
20
to
300d
14
to
21
0
138
to
2068
15
to
40
1
04
to
2
76
103
to
276
500
35
2
3445
I
A04
8
i
spst
makes
2
to
15d
c
e
f
14
to
11
14
to
103
2to6
14
to
41
14
to
41
35
345
circuit
5
to
50
35
to
35
24
to
345
4
to
12
28
to
82 27
to
83
85 6
0
586
10
to
150e
b
66
to
10
6
69
to
1034
8
to
16
56
to
1
10
55
to
110 225
15
8
1550
20
to
300d
14
to
21
0
138
to
2068
15
to
40
1
04
to
2
76
103
to
276 500
35
2
3445
I
A04C
spst
breaks
2
to
15
14 to
1
0
14
to
103
manual
reset
35
345
circuit
5
to
50
35
to
35
34
to
345
fixed
subtractive
differential
85 6
0
586
10
to
150
66
to
10
6
69
to
1034
225
15 8
1550
20
to
300d
1
4
to
21
0
138
to
2068
500
35
2
3445
lA04D
spst
makes
2
to
15
14 to
1
0
14
to
103
manual
reset
g
35
345
circuit
10
to
150
66
to
10 69
to
1068
fixed
subtractive
differential
225
15 8 1550
lA04F
spdt
snaR
acting
2
to
15
14 to
1
0
14
to
103
2to6
14 to
41
14
to
41
35
345
switch
makes
5
to
50i
35to
3 5
34
to
345
6
to
14
41
to
97 41
to
97
85
60
586
R
W
breaks
R B
10
to
150
66
to
10 69
to
1034
10
to
22 69
to
15
2
60
to
152 225
15 8
1550
20
to
300d
14
to21
0138
to
2068
20
to
50
1
4
to
3
5 138
to
345 500
35
2
3445
L604A
2
isolated
spst 2
to15C
14 to
1
014
to
103
2to6
14
to
41 14
to
41
25
1
8
172
circuits
or
15
to
50
35
to
3 5
34
to
345
to
12
28
to
82 27
to
83
85 6
0
586
spdt
makes
R1
10
to
150
66
to
10 69
to
1034
8
to
16
56
to
1
10
55
to
110 225
15 8 1550
W
breaks
R2
B
20
to
300d
1
4
to21
0
138
to
2068
15
to
40 1
04
to
2
76
103
to
276 500
35
2
3445
L604L
spdt
circuit
2
to
15
14
to
1
0
14
to
103
manual
reset
g25
1
8
172
makes
R
W
fixed
subtractive
differential
breaks
R B
L604M
spdt
circuit
10
to
150
66
to
10
1
69
to
1034
fixed
3 5
psi
24
1
kPa
225
15 8
1550
makesR
W
breaks
R
B
TABLE
1
MODELS
AV
All
ABLE
a
Scaleplates
are
marked
in
both
psi
and
kglcm2
b
Model
available
with
special
fixed
low
differential
Switch
rated
for
O
5A
at
120
Vac
C
L404A
B
and L604A
models
are
available
with
1
to
6
psi
midscale
subtractive
differential
in
2
to
15
psi
models
d
Brass
bellows
replaces
stainless
steel
diaphragm
Not
suitable
for
use
with
ammonia
oxygen
or
other
corrosive materials
e
Model
available
with
minimum
operating
pressure
of
1
25
psi
0 09
kglcm2
or
8
62
kPa
and
minimum
subtractive
differential
of
0
5
psi
0
035
kglcm2
or
3
45
kPa
f
Model
available
with
special
fixed
low
differential
Switch
rated
for
0
5A
at
120
Vac
g
L404C
D
and
L604L
models
are
designated
as
Manual
Reset
2
controllers
the
trip
free
reset
mechanism
does
not
permit
the
controller
to
function
as
an
automatic
reset
device
when
the
manual
reset
lever
is
held
in
the
reset
position
The
subtractive
differential
is
fixed
at
the
minimum
value
of
the
adjustable
differential
of
the
L404A
for
each
corresponding
operating
range
h
L404F
only
all
other
models
have
mercury
switches
Model
available
with
sealed
bell
crank
adjustment
J
Spst
switches
operate
in
unison
spdt
action
when
jumper
is
installed
between
Rl
and
R2
k
Also
recommended
for
supervision
of
atomizing
medium
pressure
air
or
steam
in
an
oil
burner
system
I
I
Model
Load
120
Vae
240
Vac
120
V
de
240
V
de
L404A Full
Load
80
51
4
12
Locked
Rotor
48
0
30
6
24
0
12
0
Norimductiv
10
050
5
0
20
L604A
Lb
Full
Load
8
0 5
1
2 0
10
Locked
Rotor
48
0
30
6
20
0
10
0
Noninductive
10
05 0 8 0
40
L604M
Full
Load
1
0
05 1
0
05
SWITCH
CONTACT
RATING
in
amperes
at
50 60
Hz
a
L404F
snap
acting
does
not
have
non
inductive
or
dc
ratings
b
L6
4A
and
L
have
also
been
tested
and
listed
by
Underwriters
Laboratories
Inc
and
breaking
not
making
a
load
with
a
total
ratmg
of
9
8
A full
load
plus
360
VA
ignition
plus
250
VA
pilot duty
at
120
Vac
1
flO
21
50
1
0
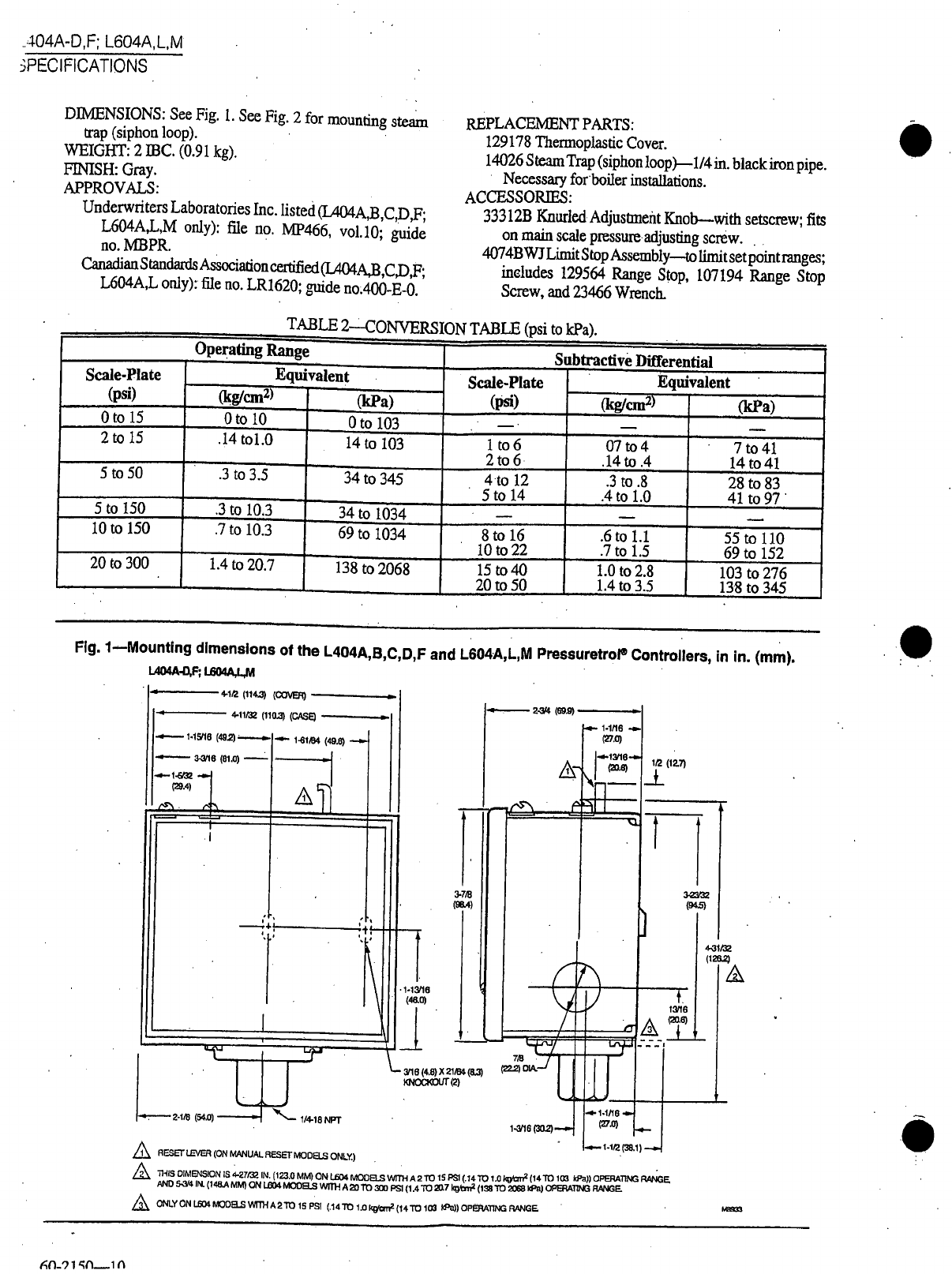
404A
D
F
L604A
L
M
JPECIFICA
nONS
DIMENSIONS
See
Fig
1
See
Fig
2
for
mounting
s
trap
siphon
loop
WEIGHT
2
me
0
91
kg
FINISH
Gray
APPROVALS
Underwriters
Laboratories
Inc
listed
IA04
AB
C
D
F
L604A
L
M
only
file
no
MP466
v01
l0
guide
no
MBPR
Canadian
Standards
Associationcertified
LA04A
B
CD
F
L604A
L
only
file
no
LR1620
guide
noAOO
E
O
REPLACEMENT
PARTS
129178
Thermoplastic
Cover
14026 Steam
Trap
siphon
loop
l
4
in
black
iron
pipe
Necessary
for
boiler
installations
ACCESSORlES
33312B
Knurled
Adjustment
Knob
with
setscrew
fits
on
main
scale
pressure
adjusting
screw
4074BWJLimitStop
Assembly
to
limit
set
point
ranges
ineludes
129564
Range
Stop
107194
Range
Stop
Screw
and
23466
Wrench
TABLE
2
ONVERSION
TABLE
psi
to
kPa
I
Operating
Range
Subtractive DitTerential
Scale
Plate
Equivalent
Scale
Plate
Equivalent
psi kglcm2
kPa
psi kglcm2
kPa
o
to
15
OtolO
o
to
103
2
to
15
14
to1
0
14
to
103
1
to
6
07to4
7
to
41
2to
6
14
to
4
14
to
41
5
to
50
3
to
3
5
34
to
345
4to
12
3
to
8
28
to
83
5
to
14
4
to
1
0
41
to
97
5
to
150
3
to
10
3
34
to
1034
10
to
150
7
to
10
3
69
to
1034
8
to
16
6
to
11
55
to
110
10
to
22
7
to
1
5
69
to
152
20
to
300
1
4
to
20
7
138
to
2068
15
to
40
1
0
to
2 8
103
to
276
20
to
50
1
4
to
3 5
138
to
345
Flg 1
Mountlng
dimensions
of
the
L404A
B
C D
F
and
L604A
L
M
pressuretroP
Controllers
in in
mm
LA04A
Fj
I
604A
L
M
RESET
LEVER
ON
MANUAL
RESET
MOOas
ONLY
iHISOIMENSION
IS
27132IN
t23
0MM
ON
l
Ji04MOOasWITHA21O
1SPSl
14
TO
1
0kg
an
1410103
kPa
OPERATINGRANae
AND
53
4
N
l48
AMM ON
t
eo4MOOas
WlTHA2010
300
PSI
1
4
TO
2A7
iqycm2
13810
2068Jd
a
OPERATING
RANGE
ONLY
ON
Ui04MOOasWITHA2TO
15
PSI
1410
1
0
kgIan2
14
10
103
kPo
OPEAAllNG
RANGE
4 1
l
114
3
COVER
4
1132
110
3
CASE
1
1S16
49
2
Hl1164
49
6
3
G
16
81
0
j
1
32
1
29A
1r
1
1M6
48
0
J
L
Me
4
6
X
21164
63
KNOCKOl1T
2
3 76
lI8
4
2
at4
69
9
I
3
2332
94
5
4
31
32
126
2
1
1f
38
1
n
hO
1
1
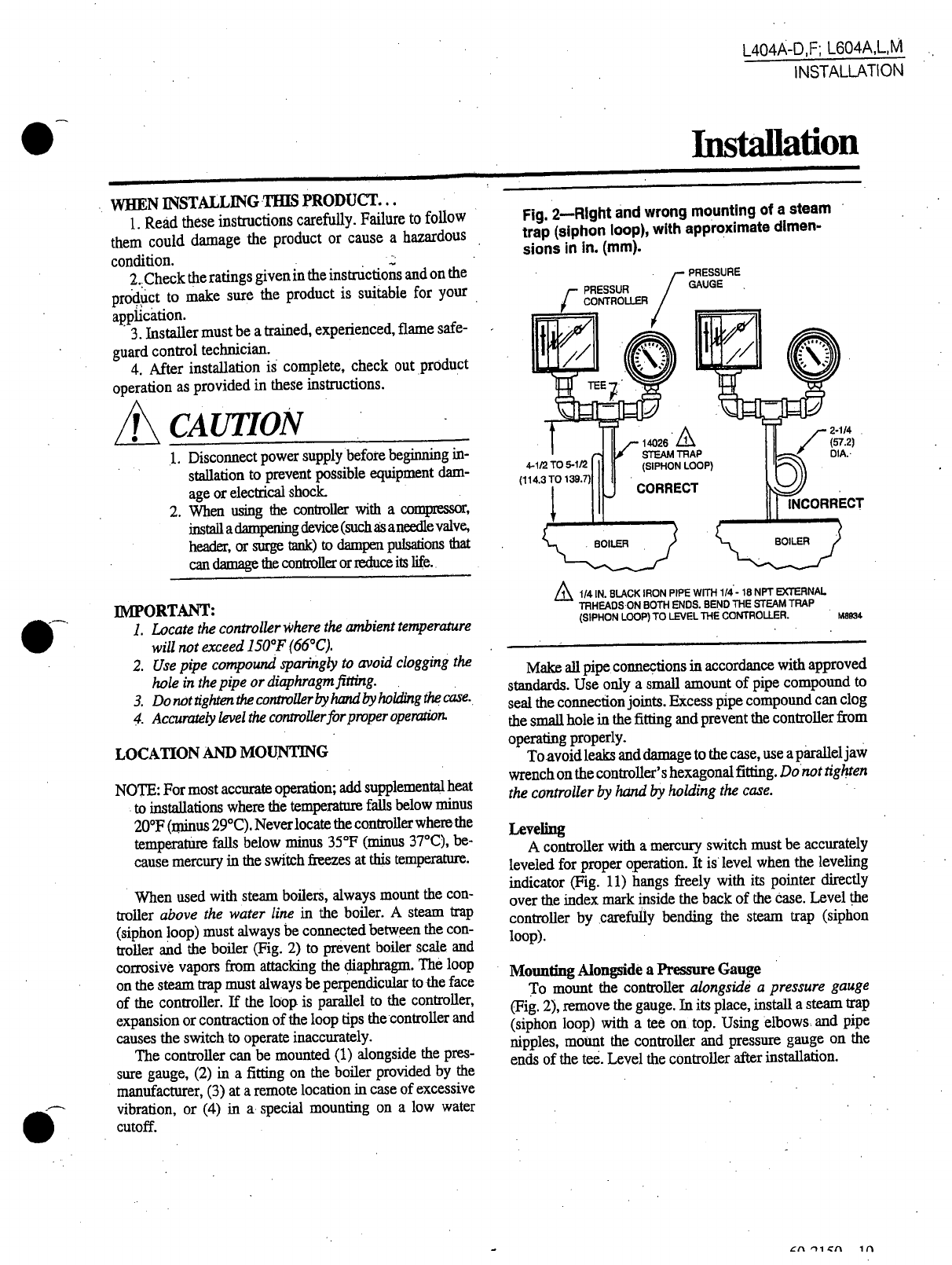
l404A
D
Fl604A
l
M
INSTALLATION
Installation
WHEN
INSTALLING
TIllS
PRODUCT
1
Read
these instructions
carefully
Failure
to
follow
them
could
damage
the
product
or
cause
a
hazardous
condition
2
Check
the
ratings
given
in
the
instructions
and
on
the
prod
ct
to
make
sure
the
product
is
suitable
for
your
application
3
Installer
must
be
a
tramed
expenenced
flame
safe
guard
control
technician
4
After
installation
is
complete
check
out
product
operation
as
provided
in
these
instructions
ffi
CAUTION
1
Disconnect power
supply
before
beginning
in
stallation
to
prevent
possible
equipment
dam
age
or
electrical
shock
2
When
using
the
controller
with
a
compressor
install
a
dampening
device
such
as
aneed1e
valve
header
or
surge
tank
to
dampen pulsations
that
can
damage
the
controller
or
reduce its
life
IMPORTANT
1
Locate
the
controller
where
the
ambient
temperature
will
not
exceed
1500F
660C
2
Use
pipe
compound
sparingly
to
avoid
clogging
the
hole
in
the
pipe
or
diaphragm
fitting
3
Do
not
tighten
the
controller
by
hand
by
holding
the
case
4
Accurately
level
the
controller
for
proper
operation
LOCATION
AND
MOUNTING
NOTE
For
most
accurate
operation
add
supplemental
heat
to
installations
where
the
temperature
falls
below minus
200P
minus 290C
Never
locate
the
controller
where
the
temperatUre
falls
below minus
350P
minus
370C
be
cause
mercury
in
the
switch
freezes
at
this
temperature
When
used
with
steam
boilers
always
mount
the
con
troller
above
the
water
line in
the
boiler
A
steam
trap
siphon loop
must
always
be
connected
between
the
con
troller
and
the
boiler
Fig 2
to
prevent
boiler
scale and
corrosive
vapors
from
attacking
the
diaphragm
The
loop
on
the
steam
trap
must
always
be
perpendicular
to
the
face
of
the
controller
If
the
loop
is
parallel
to
the
controller
expansion
or
contraction
of
the
loop
tips
the
controller
and
causes
the
switch
to
operate
inaccurately
The
controller
can
be
mounted
1
alongside
the
pres
sure
gauge
2
in
a
fitting
on
the
boiler
provided
by
e
manufacturer
3
at
a
remote
location
in
case of
excesSIve
vibration
or
4
in
a
special
mounting
on
a
low
water
cutoff
Fig
2
Rlght
and wrong
mounting
of
a
steam
trap
siphon
loop
with
approximate
dimen
sions
in in
mm
1
4
IN
BLACK
IRON
PIPE
WITH
1
4
18
NPT
EXTERNAL
TRHEADSON
BOTHENDS
BEf
lD
THE
STEAM
TRAP
SIPHON
LOOP
TO
LEVEL
THE
CONTROLLER
M8934
Make
all
pipe
connections
in
accordance
with
approved
standards
Use
only
a
small
amount
of
pipe
compound
to
seal
the
connection
joints
Excess
pipe
compound
can
clog
the
small
hole
in
the
fitting
and
prevent
the
controller
from
operating
properly
To avoid
leaks
and
damage
to
the
case
use
a
parallelJaw
wrench
on
the
controller
s
hexagonal
fitting
Donot
tig
ten
the
controller
by
hand
by
holding
the
case
LeveUng
A
controller
with
a
mercury
switch
must
be
accurately
leveled
for
proper
operation
It
is
level
when
the
leveling
indicator
Fig
11
hangs
freely
with
its
pointer
directly
over
the
index
mark
inside
the
back
of
the
case
Level
the
controller
bycarefu11y
bending
the
steam
trap
siphon
loop
Mounting
Alongside
a
Pressure
Gauge
To
mount
the
controller
alongside
a
pressure
gauge
Fig
2
remove
the
gauge
In
its
place
install
a
steam
ap
siphon
loop
with
a
tee
on
top
Using
elbows
and
pIpe
nipples
moUnt
the
controller
and
pressure gau
e
on
the
ends
of
the
tee
Level
the
controller
after
installattOn
I
11
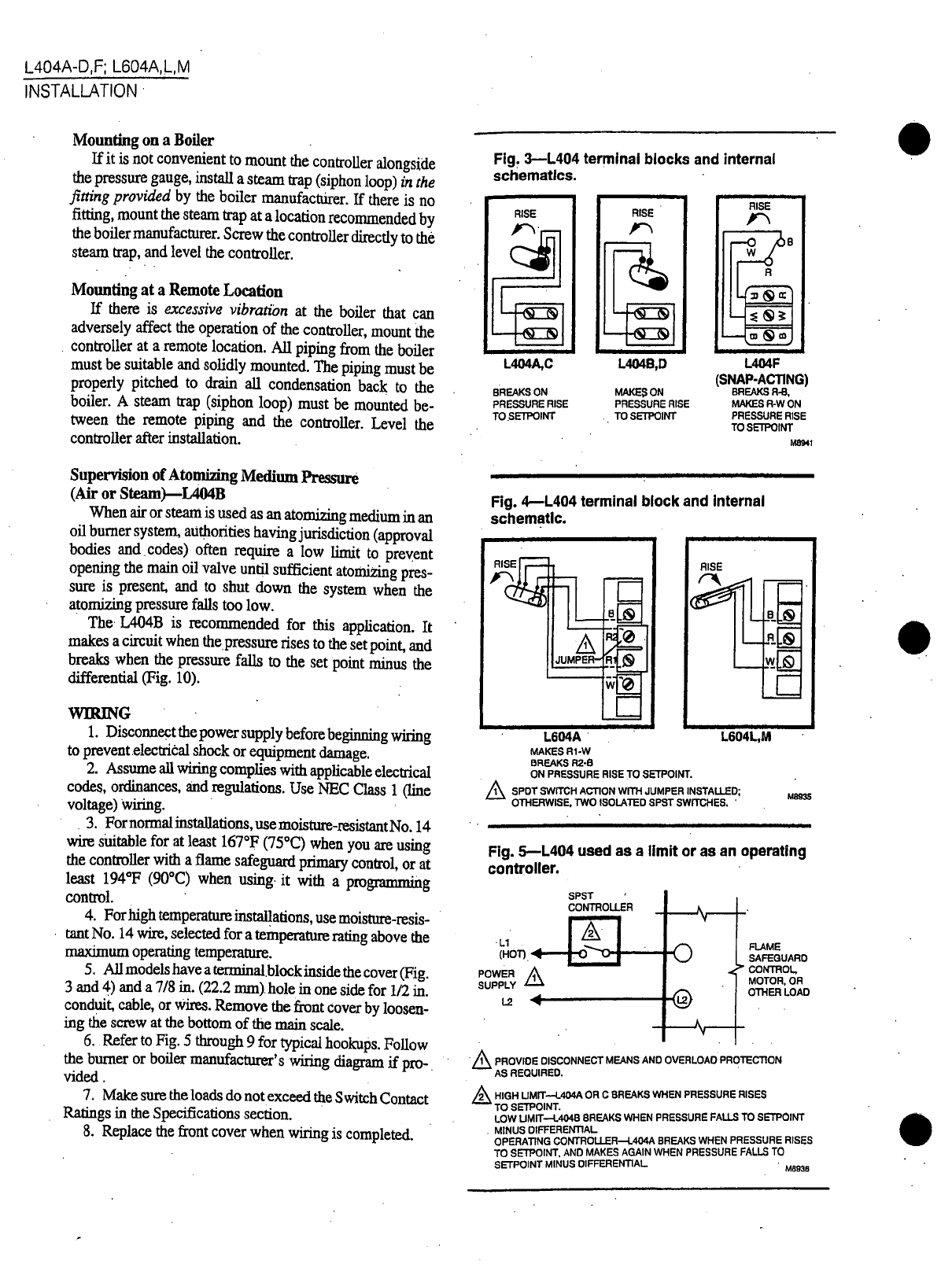
L404A
D
F
L604A
L
M
INSTALLATION
Mounting
on a
Boiler
If
it
is
not
convenient
to
mount
the
controller
alongside
the
pressure
gauge
install
a
steam
trap
siphon
loop
in
the
fitting
provided
by
the
boiler
manufactUrer
If
there is
no
fitting
mount
the
steam
trap
at
a
location
recommended
by
the
boiler
manufacturer
Screw
the
controller
directly
to
the
steam
trap
and
level
the
controller
Mounting
at
a
Remote
Location
If
there
is excessive vibration at
the
boiler
that
can
adversely
affect
the
operation
of
the
controller
mount
the
controller
at
a
remote
location
All
piping
from
the
boiler
must
be
suitable
and
solidly
mounted
The
piping
must
be
properly
pitched
to
drain
all
condensation
back
to
the
boiler
A
steam
trap
siphon
loop
must
be
mounted
be
tween
the
remote
piping
and
the
controller
Level
the
controller
after
installation
Supervision
of
Atomizing
Medium
Pressure
Air
or
Steam
L404B
When
air
or
steam
is used
as
an
atomizing
medium
in
an
oil
burner
system
authorities
having
jurisdiction
approval
bodies
and
codes
often
require
a
low
limit
to
prevent
opening
the
main
oil
valve
until
sufficient
atomizing
pres
sure
is
present
and
to
shut
down
the
system
when
the
atomizing
pressure
falls
too
low
The
L404B
is
recommended
for
this
application
It
makes
a
circuit
when
the pressure
rises
to
the
set
point
and
breaks
when
the pressure
falls
to
the
set
point
minus
the
differential
Fig
10
WlRING
1
DiscoDDe
t
the
power
supply
before
beginning
wiring
to
preventelectrical
shock
or
equipment
damage
2
Assume
all
wiring
complies
with
applicable
electrical
co
ordinances
and
regulations
Use
NEC
Class 1
line
voltage
wiring
3
Fornormalinstallations
use
moisture
resistant
No
14
wire
sUitable
for
at
least
1670
1
750C
when
you
are
using
the
controller
with
a
flame
safeguard
primary
control
or
at
least
1940F
900C
when
using
it
with
a
programming
control
4
For
high
temperature
installations
use
moisture
resis
tant
No
14
wire
selected
for
a
temperature
rating
above
the
maximum
operating
temperature
5
All
models
have
a
terminal
block
inside
the
cover
Fig
3
and
4
and
a
7 8
in
22
2
mm
hole
in
one
side
for
1
2
in
condui
cable
or
wires
Remove
the
front
cover
by
loosen
ing tIi
e
screw
at
the
bottom
of
the
main
scale
6
Refer
to
Fig
5
through
9
for
typical
hookups
Follow
the
burner
or
boiler
manufacturer
s
wiring
diagram
if
pro
vided
7
Make
sure
the
loads
do
not
exceed the
Switch
Contact
Ratings
in
the
Specifications
section
8
Replace
the
front
cover
when
wiring
is
completed
Fig
3
L404
terminal
blocks
and
internal
schematics
RISE
L404AC
L404B
D
BREAKS
ON
PRESSURE RISE
TO
SETPOINT
MAKE ON
PRESSURE
RISE
TO
SETPOINT
RISE
B
L404F
SNAP ACTING
BREAKS
R
a
MAKES
R
WON
PRESSURE
RISE
TO
SETPOINT
M8941
Fig
4
L404
terminal
block
and
Internal
schematic
L604A
L604L
M
MAKES
Rl
W
BREAKS
R2
8
ON
PRESSURE RISE
TO
SETPOINT
SPDT
SWITCH
ACTION
WITH
JUMPER
INSTALLED
M8935
OTHERWISE
TWO
ISOLATED
SPST SWITCHES
Fig
S
L404 used
as
a
limit
or
as
an
operating
controller
SPST
CONTROLLER
Ll
HOT
POWER
1
SUPPLY
Lll
U
FlAME
SAFEGUARD
CONTROL
MOTOR
OR
OTHER
LOAD
PROVIDE
DISCONNECT
MEANS
AND
OVERLOAD
PROTECTION
AS
REQUIRED
HIGH
UMIT
l
404A
OR
C
BREAKS
WHEN
PRESSURE
RISES
TO
SETPOINT
LOW
UMIT
t
4048
BREAKS WHEN
PRESSURE
FALLS
TO
SETPOINT
MINUS
DIFFERENTIAL
OPERATING
CONTROLLER
t
404A
BREAKS
WHEN
PRESSURE
RISES
TO
SETPOINT AND
MAKES
AGAIN WHEN
PRESSURE
FALLS
TO
SETPOINT
MINUS
DIFFERENTIAL
M8936
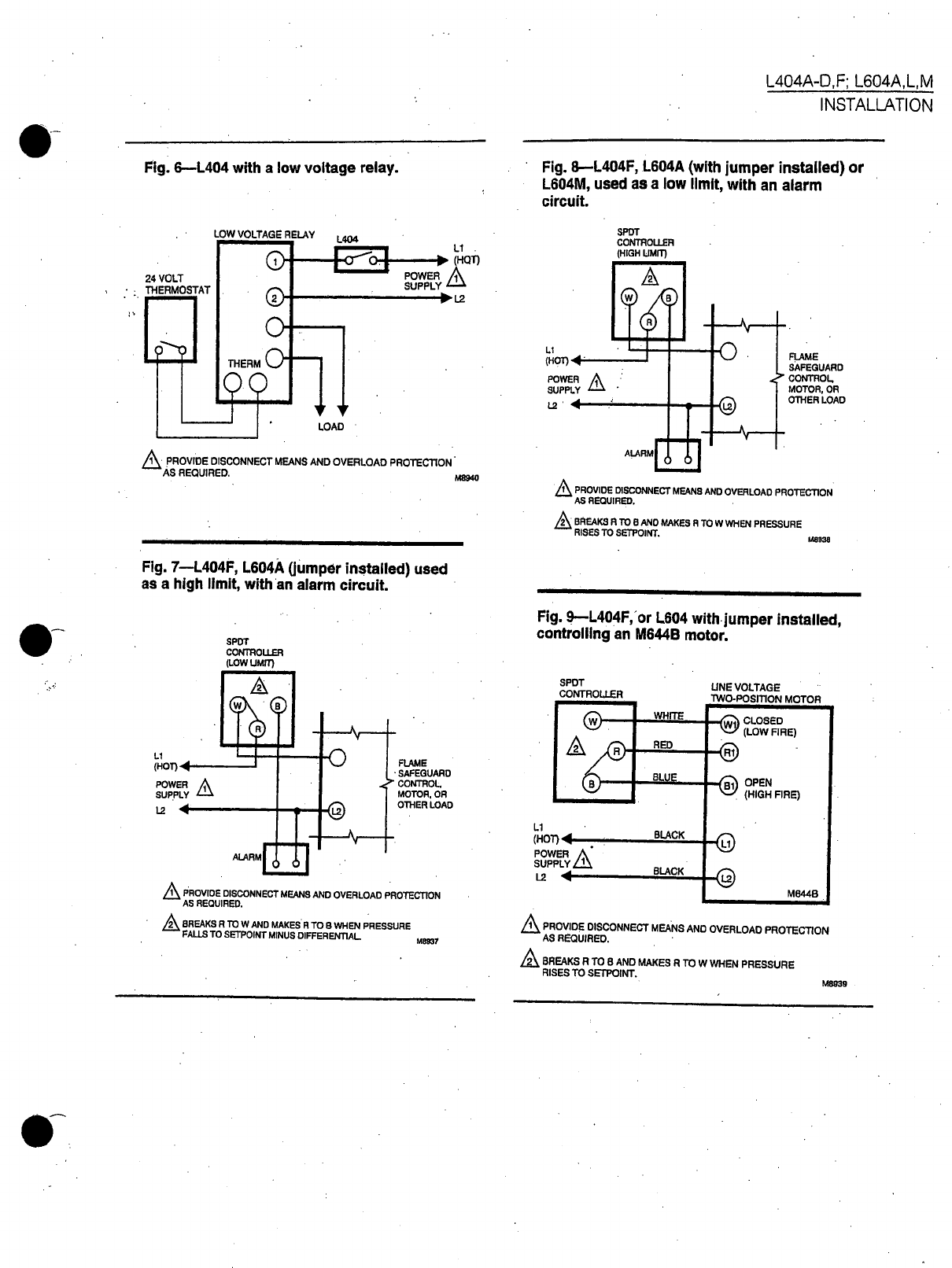
Fig
6
l404
with
a
low
voltage relay
LOW
VOLTAGE
RELAY
24
VOLT
THERMOSTAT
L1
HOT
POWER
1
SUPPLY
a
L2
LOAD
PROVIDE
DISCONNECT
MEANS
AND
OVERLOAD
PROTECTION
AS
REQUIRED
M8940
Fig
7
l404F
l604A
Oump
r
installed
used
as
a
high
limit with
an
alarm
circuit
SPOT
CONTROUER
LOW
UMfT
Ll
HOT
POWER
SUP
PLY
12
FlAME
SAFEGUARD
CONTROL
MOTOR
OR
OTHER
LOAD
PROVIDe
DISCONNEct
MEANS
AND
OVERLOAD
PROTECTION
AS
REQUIRED
BREAKS
R
TO
W
AND
MAKES
R
TO
B
WHEN
PRESSURE
FALLS
TO
SETPOINT
MINUS
DIFFERENTIAL
MB937
L404A
D
F
L604A
L
M
INSTALLATION
Fig
8
l404F l604A
with
jumper
installed
or
l604M
used
as
a
low
limit with
an
alarm
circuit
SPOT
CONTROUER
HIGH
UMIT
Ll
HOT
POWER
SUPPLY
Lb
12
FlAME
SAFEGUARD
CONTROl
MOTOR
OR
OTHER
LOAD
ALARM
PROVIDE
DISCONNECT
MEANB
AND
OVERLOAD
PROTECTION
AS
REQUIRED
BREAKS
R
TO
B
AND
MAKES
R
TO
W
WHEN
PRESSURE
RISES
TO
SETPOINT
M8938
Fig
9
L404F
or
L604
wlth
jumper
installed
controlling
an
M644B
motor
SPOT
CONTROLLER
UNEVOLTAGE
lWO
POsmON
MOTOR
CLOSED
LOW
ARE
W
WHITE
OPEN
HIGH
FIRE
Ll
HOT
POWER
SUPPLY
ill
L2
BLACK
BLACK
MB44B
PROVIDE
DISCONNECT
MeANS
AND
OVERLOAD
PROTECTION
AS
REQUIRED
BREAKS
R
TO
B
AND
MAKES
R
TO
W
WHEN
PRESSURE
RISES
TO
SETPOINT
M8939
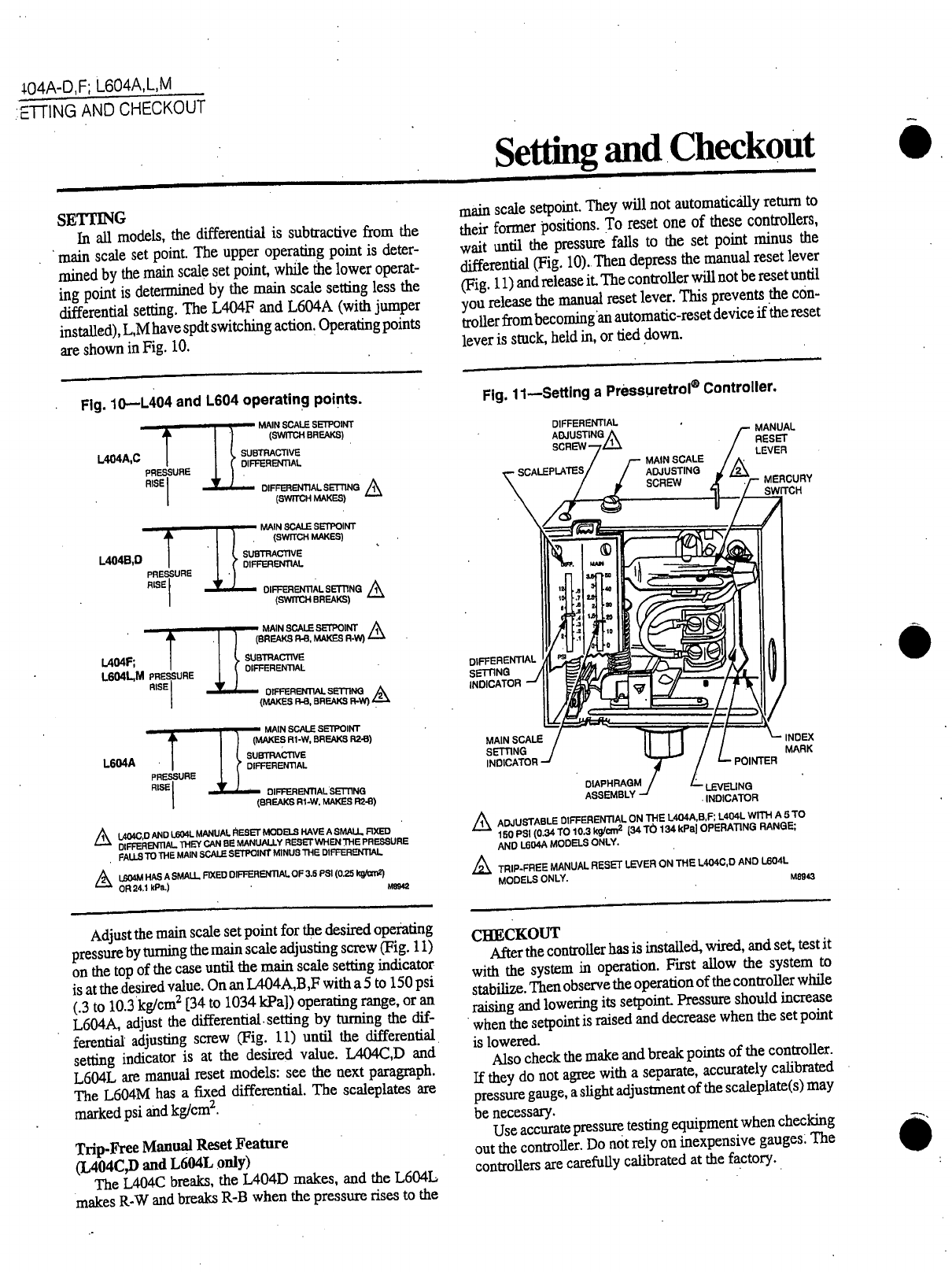
04A
D
F
L604A
L
M
ETTING
AND
CHECKOUT
Setting
and
Checkout
SETIING
In
all
models
the
differential
is
subtractive
from
the
main
scale
set
point
The
upper
operating
point
is
deter
mined
by the
main
scale
set
point
while
the
lower
operat
ing
point
is
determined
by
the
main
scale
setting
less
the
differential
setting
The
L404F
and
L604A
with
jumper
installed
L
M
have
spdt
switching
action
Operating points
are
shown
in
Fig
10
Fig
1o
L404
and
L604
operating
points
L404A
C
PRESSURE
RISE
I
MAIN SCALE SETPOINT
SWITCH
BREAKS
SUBTRACTIVE
DIFFERENTIAL
DIFFERENTIAL
SETTING
SWITCH
MAKES
L404B
D
PRESSURE
RISE
I
MAIN
SCALE
SETPOINT
SWITCH
MAKES
SUBTRACTIVE
DIFFERENTIAL
DIFFERENTIAL
SETTING
4
SWITCH
BREAKS
ill
MAIN
SCALE
SETPOINT
4
BREAKS
RB
MAKES
RW
ill
SUBTRACTIVE
DIFFERENTIAL
L404F
L604
M
PRESSURE
RISE
I
DIFFERENTIAL
SETTING
a
MAKES
RB
BREAKS
R
W
L604A
MAIN SCALE SETPOINT
MAKE
Rl W
BREAKS
R2
8
SUBTRACTIVE
DIFFERENTIAL
PRESSURE
RISE
DIFFERENTIAL
SETTING
BREAKS
Rl W
MAKES
R2
8
lA04C
D
AND
l604L
MANUAL
RESET
MeDB
S
HAVE
A
SMALL
AXED
DIFFERENTIAL
THEY
CAN
BE
MANUALLY
RESET
WHEN
THE
PRESSURE
FALLS
TO
THE
MAIN
SCALE
SETPOINT
MINUS
THE
DIFFERENTlAL
l
604M
HAS
A
SMALl
AXED
DIFFEAENTlAL
OF
3 5
PSI
0
25
kgIcm2
W
Adjust
the
main
scale
set
point
for
the
desired
operating
pressure
by turning
the
main
scale
adjusting
screw
Fig
11
on
the
top
of
the
case
until
the main
scale
setting
indicator
is
at
the
desired
value
On
an
L404A
B F
with
a
5
to
150
psi
2
3
to
10
3
kg
cm
34
to
1034
kPa
operating
range
or
an
L604A
adjust
the
differential
setting
by
turning
the
dif
ferential
adjusting
screw
Fig
11
until
the
differential
setting
indicator
is at
the
desired value
L404C
D
and
L604L
are
manual
reset
models
see
the
next
paragraph
The
L604M
has
a
fixed
differential
The
scaleplates
are
marked
psi
arid
kg
cm2
Trip
Free
Manual
Reset
Feature
L404C
D
and
L604Lonly
The
L404C
breaks
the
L404D
makes
and
the
L604L
makes R
W
and
breaks
R
B
when
the
pressure
rises
to
the
main
scale
setpoint
They
will
not
automatic
illy
return
to
their
fonner
positions
To
reset
one
of
these
controllers
wait
until
the
pressure
falls
to
the
set
point
minus
the
differential
Fig
10
Then
depress
the
manual
reset
lever
Fig
11
and
release
it
The
controller
will
not
be
reset
until
you
release the
manual
reset
lever
This
prevents
the
con
troller
from
becoming
an
automatic
reset
device
if
the
reset
lever
is
stuck
held
in
or
tied
down
Fig
11
Setting
a
Press
Jretrollli
Controller
DIAPHRAGM
ASSEMBLY
INDICATOR
ADJUSTABLE
DIFFERENTIAL
ON
THE
L404A
B
F
L404L
WITH
A
5
TO
150
PSI
0
34
TO
103
kglcm2
34
TO
134
kPal
OPERATING
RANGE
AND
L604A MODELS
ONLY
TRIP
FREe
MANUAL
RESET LEVER
ON
THE
L404C
D
AND
L604L
MODELS
ONLY
MIlIl43
CHECKOUT
After
the
controller
has
is installed
wired
and
set
test
it
with
the
system
in
operation
First
allow
the
system
to
stabilize
Then
observe
the
operation
of
the
controller
while
raising
and
lowering
its
setpoint
Pressure
should
increase
when
the
setpoint
is
raised
and
decrease
when
the
set
point
is
lowered
Also
check
the
make
and
break
points
of
the
controller
If
they
do
not
agree
with
a
separate
accurately
calibrated
pressure
gauge
a
slight
adjusnnent
of
the
scaleplate
s
may
be
necessary
Use
accurate
pressure
testing
equipment
when
checking
out
the
controller
Do
not
rely
on
inexpensive
gauges
The
controllers
are
carefully
calibrated
at
the
factory
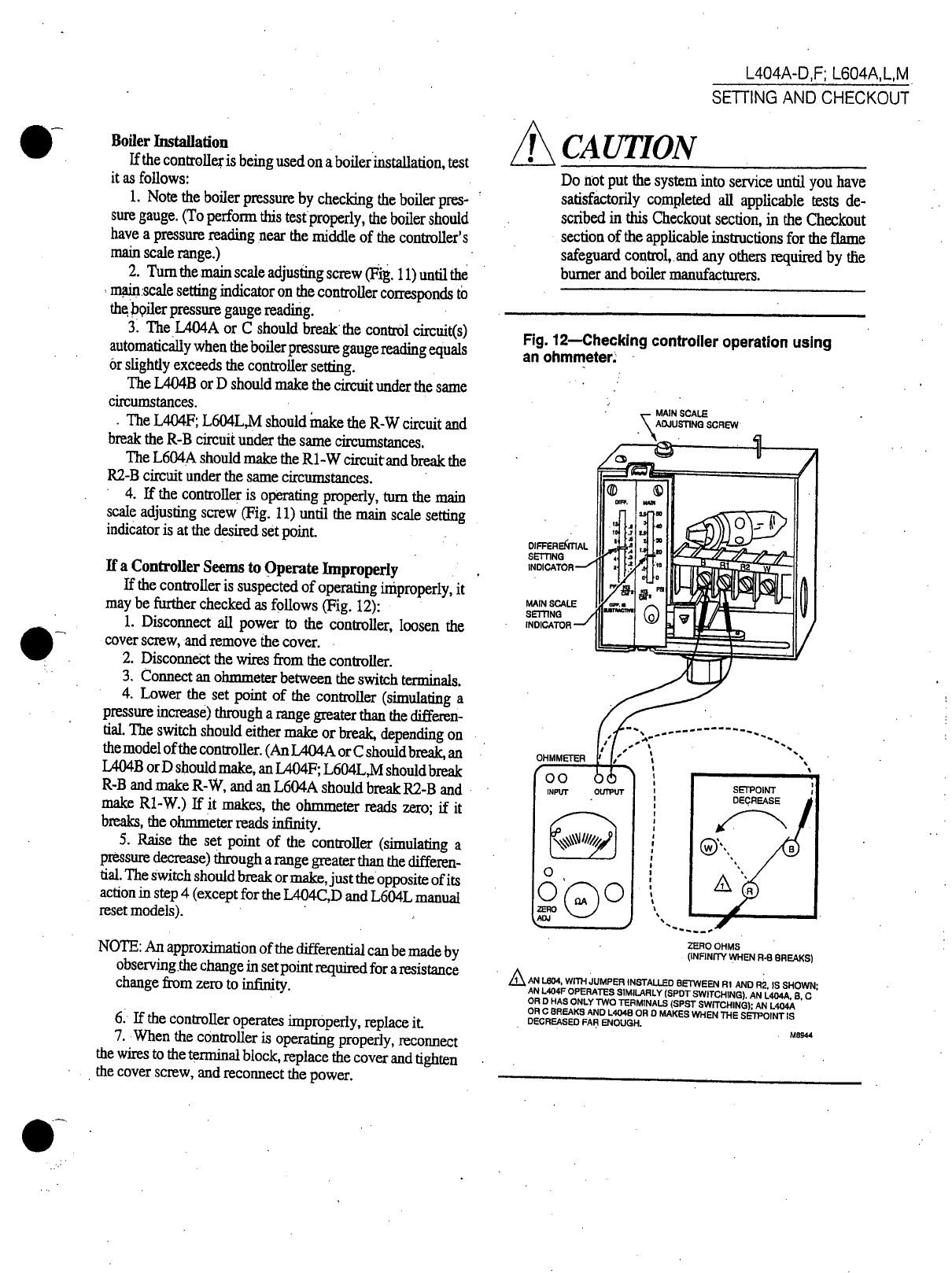
Boiler
Installation
If
the
controller
is
being
used
on
a
boiler
installation
test
it
as
follows
1
Note
the
boiler
pressure
by
checking
the
boiler
pres
sure
gauge
To
perform
this
testproperly
the
boiler
should
have
a
pressure
reading
near
the
middle
of
the
controller
s
main
scale
range
2
Turn
the
main
scale
adjusting
screw
Fig
11
until
the
m
rlnscale
setting
indicator
on
the
controller
corresponds
to
th
b9iler
pressure
gauge
readiri
g
3
TheL404A
or
C
should
break
the
control
circuit
s
automatically
when
the
boiler
pressure
gauge
reading
equals
or
slightly
exceeds
the
controller
setting
The
L404B
or
D
should
make
the
circliit
under
the
same
circumstances
The
L404F
L604L
M
should
inake
the
R
W
circuit
and
break
the
R
B
circuit
under
the
same
circumstances
The
L604A
should
make
the
RI
W
circuit
and
break
the
R2 B
circuit
under
the
same
circumstances
4
If
the
controller
is
operating
properly
turn
the
main
scale
adjusting
screw
Fig
11
until
the
main
scale
setting
indicator
is at
the
desired
set
point
If
a
Controller
Seems
to
Operate
Improperly
If
the
controller
is
suspected
of
operating
iniproperly
it
may
be
further
checked
as
follows
Fig
12
1
Disconnect
all
power
to
the
controller
loosen
the
cover
screw
and
remove
the
cover
2
DisconneCt
the
wires
from
the
controller
3
Connect
an
ohmmeter
between
the
switch
terminals
4
Lower
the
set
point
of
the
controller
simulating
a
pressure
increase
through
a
range
greater
than
the
differen
tial
The
switch
should
either
make
or
break
depending
on
the
model
of
the
controller
AnL404A
orC
should
break
an
L404B
or
D
should
make
an
IA04F
L604L
M
should
break
R
B
and
make
R
W
and
an
L604A
should
breakR2
B
and
make
RI
W
If
it
makes
the
ohmmeter
reads
zero
if
it
breaks
the
ohmmeter
reads
infinity
5
Raise
the
set
point
of
the
controller
simulating
a
pressure
decrease
through
a
range
greater
than
the
differen
tial
The
switch
should
break
or
make
just
the
opposite
of
its
action
in
step
4
except
for
the
L404C
D
and
L604L
manual
reset
models
NOTE
An
approximation
of
the
differential
can
be
made
by
observing
the
change
in
set
point
required
for
a
resistance
change
from
zero
to
infinity
6
If
the
controller
operates
improperly replace
it
7
When
the
controller
is
operating
properly
reconnect
the
wires
to
the
terminal
block
replace
the
cover
and
tighten
the
cover
screw
and
reconnect
the
power
L404A
D
F
L604A
L
M
SETTING
AND
CHECKOUT
ffi
CAUTION
Do
not
put
the
system
into
service
until
you
have
satisfactorily
completed
all
applicable
tests
de
scribed
in
this
Checkout
section
in
the
Checkout
section
of
the
applicable
instructions
for
the
flame
safeguard
control
and any
others
required
by
tlie
burner
and
boiler
manufacturers
Fig
12
Checking
controller
operation
using
an
ohmmeter
MAIN
SCALE
SETllNG
INDICATOR
00
INPUT
OUTPUT
o
280
ADJ
MAIN
SCALE
ADJUSTlNG
SCREW
I
I
I
I
I
I
I
I
I
I
I
I
I
I
I
I
I
I
I
ro
SETPOINT
DEqREASE
ZERO
OHMS
INANITY
WHEN
RB
BREAKS
AN
l
604
WITH
JUMPER
INSTALLED
BElWEEN
Rl
AND
R
IS SHOWN
AN
L404F
OPERATES
SIMIlJ
RL
Y
SPOT
SWITCHING
AN
L404A
B C
OR
0
HAS
ONLY
TWO
TERMINALS
SPST SWITCHING
AN
L404A
OR
C
BREAKS
AND
L404B
OR
0
MAKES
WHEN
THE
SETPOINT
IS
DECREASED
FAfl
ENOUGH
M8944

Q4A
D
F
L604A
L
M
RVICE
INFORMATION
Service
Information
CALmRATION
The
controller
was
carefully
calibrated
during
manufac
turing
and
should
not
require
recalibration
Most
calibra
tion
errors
are
caused
by
improper
leveling
The
controller
should
be
level
when
the
pointer
on
the
leveling
indicator
is
directly
over
the
index
mark
Fig
11
In
some
cases
the
leveling
indicator
may
not
be
accurate
enough
The
pointer
may
be
over
the
index
mark
but
the
controller
still
may
not
be
operating
within
the
tolerance
of
its
scale
setting
In
this
case
carefully
bend
the
steam
trap
siphon
loop
until
the
controller
switches
properly
MAINTENANCE
The
cover
of
the
controller
should
be
in
place
at
all
times
to
protect
the
internal
components
from
dirt
dust
and
physical
damage
Routine
maintenance
should
consist
of
occasional
inspection
and
blowing
or
brushing
away
any
accumulated
dirt and
dust
To
ensure
proper
functioning
of
the
controller
at
all
times
perform
an
operational
check
of
the
entire
system
during
routine
maintenance
checks