Honeywell Universal Remote Pub1012S Users Manual 63 2689—05 Spyder® BACnet® Programmable Controllers
PVB0000AS to the manual 4c37fbb3-7b7c-4d61-9c6b-18cced4cb5af
2015-01-23
: Honeywell Honeywell-Honeywell-Universal-Remote-Pub1012S-Users-Manual-262606 honeywell-honeywell-universal-remote-pub1012s-users-manual-262606 honeywell pdf
Open the PDF directly: View PDF .
Page Count: 24

PRODUCT DATA
63-2689-05
Spyder® BACnet®
Programmable Controllers
PRODUCT DESCRIPTION
The PUB and PVB controllers are part of the Spyder family.
These controllers are BACnet MS/TP network devices
designed to control HVAC equipment. These controllers
provide many options and advanced system features that
allow state-of-the-art commercial building control. Each
controller is programmable and configurable through software.
The Spyder BACnet controllers require the Spyder BACnet
Programmable Feature to be licensed in the WEBpro
workbench tool and the WEBS AX JACE Controller for
programming and downloading. The Spyder BACnet Models
are also available as Individually Licensed Controllers (ILC).
The ILC versions are identical in design and capability in every
detail except for the licensing. The Individual Licensing of the
Spyder ILCs (the License is built in) allows them to be
programmed and downloaded with any brand of the Niagara
Workbench or JACE controller. The Spyder ILCs are identified
with a suffix on the Part Number of -ILC. Example:
PUB6438S-ILC follows all the same Installation Instructions
information as the PUB6438S.
These controllers are for use in VAV (Variable Air Volume),
Unitary and advanced HVAC control applications. Each
controller has flexible, universal inputs for external sensors,
digital inputs, and a combination of analog and digital Triac
outputs. All the models are described in Table 1. The photo to
the left is the model PVB6436AS, which includes the actuator.
Table 1. Controller configurations.
Each controller communicates via an EIA-485 BACnet MS/TP communications network, capable of baud rates between 9.6 and
115.2 kbits/s.
Controllers are field-mountable to either a panel or a DIN rail.
Controller
Model
Programmable
Type
Universal
Inputs
(UI)
Digital
Inputs
(DI)
Analog
Outputs
(AO)
Digital
Outputs
(DO)
Velocity
Pressure
Sensor
(Microbridge)
Series 60
Floating
Actuator
PUB1012S Unitary 1 0 1 2 NO NO
PUB4024S Unitary 4 0 2 4 NO NO
PUB6438S Unitary 6 4 3 8 NO NO
PVB0000AS VAV 0 0 0 0 YES YES
PVB4022AS VAV 4 0 2 2 YES YES
PVB4024NS VAV 4 0 2 4 YES NO
PVB6436AS VAV 6 4 3 6 YES YES
PVB6438NS VAV 6 4 3 8 YES NO

SPYDER® BACNET® PROGRAMMABLE CONTROLLERS
63-2689—05 2
ORDERING INFORMATION
When purchasing replacement and modernization products from your TRADELINE® wholesaler or distributor, refer to the
TRADELINE® Catalog or price sheets for complete ordering number. If you have additional questions, need further information,
or would like to comment on our products or services, please write or phone:
1. Your local Honeywell Environmental and Combustion Controls Sales Office (check white pages of your phone directory).
2. Honeywell Customer Care
1985 Douglas Drive North
Minneapolis, Minnesota 55422-4386
3. http://customer.honeywell.com or http://customer.honeywell.ca
International Sales and Service Offices in all principal cities of the world. Manufacturing in Belgium, Canada, China, Czech
Republic, Germany, Hungary, Italy, Mexico, Netherlands, United Kingdom, and United States.
SPECIFICATIONS
General Specifications
Rated Voltage: 20–30 Vac; 50/60 Hz
Power Consumption:
100 VA for controller and all connected loads (including the
actuator on models PVL0000AS, PVL4022AS and
PVL6436AS).
Controller Only Load: 5 VA maximum; models PUB1012S,
PUB4024S, PUB6438S, PVB4024NS and PVB6438NS.
Controller and Actuator Load: 9 VA maximum; models
PVL0000AS, PVL4022AS and PVL6436AS.
External Sensors Power Output: 20 Vdc ±10% @ 75 mA
maximum.
VAV Operating & Storage Temperature Ambient Rating
(models PVB0000AS, PVB4022AS, PVB4024NS,
PVB6436AS and PVB6438NS):
Minimum 32 ºF (0 ºC); Maximum 122 ºF (50 ºC)
Unitary Operating & Storage Temperature Ambient Rating
(models PUB1012S, PUB4024S and PUB6438S):
Minimum -40 ºF (-40 ºC); Maximum 150 ºF (65.5 ºC)
Relative Humidity: 5% to 95% non-condensing
LED: Provides status for normal operation, controller down-
load process, alarms, manual mode, and error conditions
Velocity Pressure Sensor (models
PVB0000AS, PVB4022AS, PVB4024NS,
PVB6436AS and PVB6438NS)
Operating Range: 0 to 1.5 in. H2O (0 to 374 Pa)
Series 60 Floating Actuator (models
PVB0000AS, PVB4022AS and PVB6436AS)
Rotation Stroke: 95° ± 3° for CW or CCW opening dampers
Torque Rating: 44 lb-in. (5 Nm)
Run Time for 90° rotation: 90 seconds at 60 Hz
Operating Temperature: -4 ºF to 140 ºF (-20 to 60 ºC)
Real Time Clock
Operating Range: 24 hour, 365 day, multi-year calendar
including day of week and configuration for automatic day-
light savings time adjustment to occur at 2:00 a.m. local
time on configured start and stop dates
Power Failure Backup:
24 hours at 32°F to 100°F (0°C to
38°C), 22 hours at 100°F to 122°F (38°C to 50°C)
Accuracy: ±1 minute per month at 77
°
F (25
°
C)
Digital Input (DI) Circuits
Voltage Rating: 0 to 30 Vdc open circuit
Input Type: Dry contact to detect open and closed circuit
Operating Range: Open circuit = False; Closed circuit = True
Resistance: Open circuit > 3,000 Ohms; Closed circuit < 500
Ohms
Digital Triac Output (DO) Circuits
Voltage Rating: 20 to 30 Vac @ 50/60Hz
Current Rating: 25 mA to 500 mA continuous, and
800 mA (AC rms) for 60 milliseconds
Analog Output (AO) Circuits
Analog outputs can be individually configured for current or
voltage.
ANALOG CURRENT OUTPUTS:
Current Output Range: 4.0 to 20.0 mA
Output Load Resistance: 550 Ohms maximum
ANALOG VOLTAGE OUTPUTS:
Voltage Output Range: 0.0 to 10.0 Vdc
Maximum Output Current: 10.0 mA
Analog outputs may be configured as digital outputs and
operate as follows:
– False (0%) produces 0 Vdc, (0 mA)
– True (100%) produces the maximum 11 Vdc, (22 mA)
Universal Input (UI) Circuits
See Table 2 for the UI circuit specifications.
Table 2. Universal input circuit specifications.
Input
Type
Sensor
Type
Operating
Range
Room/Zone
Discharge Air
Outdoor Air
Temperature
20K Ohm
NTC
-40 to 199
°
F
(-40 to 93
°
C)
Outdoor Air
Temperature C7031Ga-40 to 120
°
F
(-40 to 49
°
C)
C7041Fa-40 to 250
°
F
(-40 to 121
°
C)
PT1000
(IEC751 3850)
-40 to 199
°
F
(-40 to 93
°
C)

SPYDER® BACNET® PROGRAMMABLE CONTROLLERS
363-2689—05
BEFORE INSTALLATION
The controller is available in three models (see Table 1).
Review the power, input, and output specifications on page 2
before installing the controller.
— Hardware driven by Triac outputs must have a minimum
current draw, when energized, of 25 mA and a maximum
current draw of 500 mA.
— Hardware driven by the analog current outputs must have a
maximum resistance of 550 Ohms, resulting in a maximum
voltage of 11 volts when driven at 20 mA.
If resistance exceeds 550 Ohms, voltages up to 18 Vdc are
possible at the analog output terminal.
WARNING
Electrical Shock Hazard.
Can cause severe injury, death or property damage.
Disconnect power supply before beginning wiring or
making wiring connections to prevent electrical shock
or equipment damage.
INSTALLATION
The controller must be mounted in a position that allows
clearance for wiring, servicing, removal, connection of the
BACnet MS/TP Molex connector and access to the MS/TP
MAC address DIP switches (see Fig. 15 on page 12).
The controller may be mounted in any orientation.
IMPORTANT
Avoid mounting in areas where acid fumes or other
deteriorating vapors can attack the metal parts of the
controller, or in areas where escaping gas or other
explosive vapors are present. Fig. 6–Fig. 7 on page 5
for mounting dimensions.
For the PVB6436AS model, the actuator is mounted first and
then the controller is mounted. For the other models, go to
“Mount Controller” on page 5 to begin the installation.
Mount Actuator onto Damper Shaft
(PVB0000AS, PVB4022AS and
PVB6436AS)
PVB0000AS, PVB4022AS and PVB6436AS controllers include
the direct-coupled actuator with Declutch mechanism, which is
shipped hard-wired to the controller.
The actuator mounts directly onto the VAV box damper shaft
and has up to 44 lb-in. (5 Nm) torque, 90-degree stroke, and 90
second timing at 60 Hz. The actuator is suitable for mounting
onto a 3/8 to 1/2 in. (10 to 13 mm) square or round VAV box
damper shaft. The minimum VAV box damper shaft length is 1-
9/16 in. (40 mm).
The two mechanical end-limit set screws control the amount of
rotation from 12° to 95°. These set screws must be securely
fastened in place. To ensure tight closing of the damper, the
shaft adapter has a total rotation stroke of 95° (see Fig. 1).
NOTES:
1. The actuator is shipped with the mechanical end-
limit set screws set to 95 degrees of rotation.
Adjust the two set screws closer together to
reduce the rotation travel. Each “hash mark” indi-
cator on the bracket represents approximately 6.5°
of rotation per side.
2. The Declutch button, when pressed, allows you to
rotate the universal shaft adapter (see Fig. 1).
IMPORTANT
Determine the damper rotation and opening angle
prior to installation. See Fig. 2 below and Fig. 3 on
page 4 for examples.
Fig. 1. Series 60 Floating Actuator.
TR23
Setpoint
Potentiometer
500 Ohm
to
10,500 Ohm
-4° DDC to +4° DDC
(-8° DDF to +7° DDF)
or
50 F to 90 F
(10 C to 32 C)
Resistive Input Generic 100 Ohms to 100K Ohms
Voltage
Input
Transducer,
Controller
0–10 Vdc
Discrete Input Dry Contact
closure Open Circuit > 3000 Ohms
Closed Circuit < 3000 Ohms
aC7031G and C7041F are recommended for use with these
controllers, due to improved resolution and accuracy when
compared to the PT1000.
Input
Type
Sensor
Type
Operating
Range
UNIVERSAL SHAFT
CLAMPING BOLTS (2)
M23568
UNIVERSAL
SHAFT ADAPTER
MECHANICAL
END LIMIT SET
SCREWS (2)
DECLUTCH
BUTTON

SPYDER® BACNET® PROGRAMMABLE CONTROLLERS
63-2689—05 4
Fig. 2. Damper with 90 degree CW rotation to open.
IMPORTANT
Mount actuator flush with damper housing or add a
spacer between the actuator mounting surface and
damper box housing.
Before Mounting Actuator onto Damper
Shaft (PVB0000AS, PVB4022AS and
PVB6436AS)
Tools required:
— Phillips #2 screwdriver - end-limit set screw adjustment
— 8 mm wrench - centering clamp
Before mounting the actuator onto the VAV box damper shaft,
determine the following:
1. Determine the damper shaft diameter. It must be
between 3/8 in. to 1/2 in. (10 to 13 mm).
2. Determine the length of the damper shaft. If the length of
the VAV box damper shaft is less than 1-9/16 in.
(40 mm), the actuator cannot be used.
3.
Determine the direction the damper shaft rotates to open
the damper (CW or CCW) (see Fig. 3). Typically, there is
an etched line on the end of the damper shaft that indi-
cates the position of the damper. In Fig. 2, the indicator
shows the damper open in a CW direction.
4. Determine the damper full opening angle (45, 60, or 90
degrees). In Fig. 2, the damper is open to its full open
position of 90 degrees.
Fig. 3. Determining the rotation direction (CW or CCW)
for damper opening.
Mounting Actuator Onto Damper Shaft
(PVB0000AS, PVB4022AS and PVB6436AS)
The unit is shipped with the actuator set to rotate open in the
clockwise (CW) direction to a full 95 degrees. The extra 5
degrees ensures a full opening range for a 90 degree damper.
The installation procedure varies depending on the damper
opening direction and angle:
1. If the damper rotates clockwise (CW) to open, and the
angle of the damper open-to-closed is 90 degrees:
a. Manually open the damper fully (rotate clockwise).
b. Using the Declutch button, rotate the universal shaft
adapter fully clockwise.
c. Mount the actuator to the VAV damper box and shaft.
d. Tighten the two bolts on the centering clamp
(8 mm wrench; 70.8–88.5 lb-in. [8–10 Nm] torque).
When the actuator closes, the damper rotates CCW
90 degrees to fully close.
2. If the damper rotates clockwise (CW) to open, and the
angle of the damper open-to-closed is 45 or 60 degrees:
a. Manually open the damper fully (rotate clockwise).
b. The actuator is shipped with the mechanical
end-limits set at 95 degrees. Adjust the two
mechanical end-limit set screws to provide the
desired amount of rotation. Adjust the two set screws
closer together to reduce the rotation travel.
c. Tighten the two mechanical end-limit screws (Phillips
#2 screwdriver; (26.5–31 lb-in. [3.0–3.5 Nm] torque).
d. Using the Declutch button, rotate the universal shaft
adapter fully clockwise.
e. Mount the actuator to the VAV damper box and shaft.
f. Tighten the two bolts on the centering clamp
(8 mm wrench; 70.8–88.5 lb-in. [8–10 Nm] torque).
g. When the actuator closes, the damper rotates CCW
either 45 or 60 degrees to fully close.
3.
If the damper rotates counterclockwise (CCW) to open, and
the angle of the damper open-to-closed is 90 degrees:
a. Manually open the damper fully (rotate counterclock-
wise).
b. Using the Declutch button, rotate the universal shaft
adapter fully counterclockwise.
c. Mount the actuator to the damper box and shaft.
d. Tighten the two bolts on the centering clamp (8 mm
wrench; 70.8–88.5 lb-in. [8–10 Nm] torque). When
the actuator closes, the damper rotates CW
90 degrees to fully close.
4.
If the damper rotates counterclockwise to open, and the
angle of the damper open-to-closed is 45 or 60 degrees:
a. Manually open the damper fully (rotate counterclock-
wise).
b. The actuator is shipped with the mechanical
end-limits set at 95 degrees. Adjust the two
mechanical end-limit set screws to provide the
desired amount of rotation. Adjust the two set screws
closer together to reduce the rotation travel.
c. Tighten the two mechanical end-limit screws
(Phillips #2 screwdriver; (26.5–31 lb-in. [3.0–3.5 Nm]
torque).
d. Using the Declutch button, rotate the universal shaft
adapter fully counter-clockwise.
e. Mount the actuator to the VAV damper box and shaft.
f. Tighten the two bolts on the centering clamp
(8 mm wrench; 70.8–88.5 lb-in. [8–10 Nm] torque).
g. When the actuator closes, the damper rotates CW
either 45 or 60 degrees to fully close.
M23569
DAMPER SHAFT
ROTATES
CLOCKWISE
TO OPEN
DAMPER
AIR
FLOW
AIR
FLOW
CW TO OPEN, CCW TO CLOSE
CCW TO OPEN, CW TO CLOSE
M2067B
TYPE A DAMPER
TYPE B DAMPER
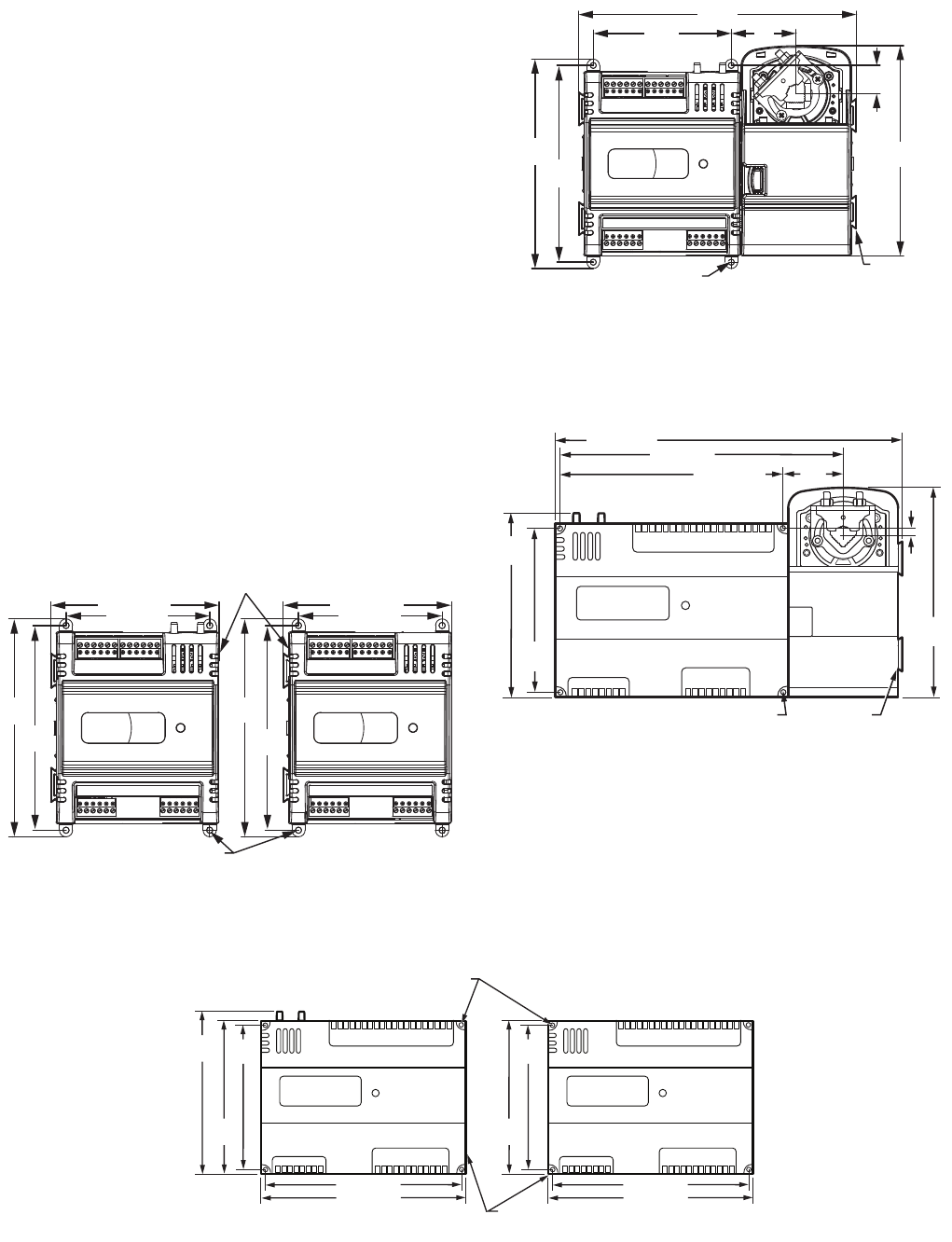
SPYDER® BACNET® PROGRAMMABLE CONTROLLERS
563-2689—05
IMPORTANT
Special precautions must be taken for dampers that
open in a CCW direction. The actuator is shipped with
its rotation direction set to CW to Open, which applies
to the damper direction in steps 1 and 2 above. If the
damper shaft rotates in the CCW direction to open, the
controller software must be programmed to change
the rotation to “Reverse to Open,” which applies to the
damper direction in steps 3 and 4 above.
IMPORTANT
It is advisable to leave the dampers in an open
position after installation to avoid the possibility of
over-pressurizing the duct work on fan startup. Use
the Declutch button (see Fig. 1 on page 3) to open the
box damper on controllers that are powered down, to
prevent over-pressurization in the duct work on fan
startup. To Declutch, press and hold the button to
disengage the motor. Turn the damper shaft until the
damper is open and release the button. When power
is restored to the controller, the controller
synchronizes the damper actuator, so that the damper
is in the correct position upon startup.
Mount Controller
NOTE: The controller may be wired before mounting to a
panel or DIN rail.
Terminal blocks are used to make all wiring connections to the
controller. Attach all wiring to the appropriate terminal blocks
(see “Wiring” on page 8).
Fig. 4. Panel mounting - controller dimensions in inches
(mm) for PUB1012S, PUB4024S and PVB4024NS only
(PUB4024S and PVB4024NS shown).
Fig. 5. Panel mounting - controller and actuator
dimensions in inches (mm) for PVB0000AS and
PVB4022AS only (PVB4022AS shown).
Fig. 6. Panel mounting - controller and actuator
dimensions in inches (mm) for PVB6436AS.
Fig. 7. Panel mounting - controller dimensions in inches (mm) for models PUB6438S and PVB6438NS.
M31531
NOTE: CONTROLLER CAN BE MOUNTED IN ANY ORIENTATION.
3/16 (4.5) PANEL MOUNTING HOLE (4X)
DEPTH IS 2-1/4 (57)
4-13/16 (122)
4-1/8 (105)
6-1/4
(159)
5-7/8
(149)
4-13/16 (122)
4-1/8 (105)
6-1/4
(159)
5-7/8
(149)
1 2 3 4 5 6 7 8 9
10
11
12
1 2 3 4 5 6 7 8 9
10
11
12
13 14 15 16 17 18
19 20 21 22 23 24 13 14 15 16 17 18
19 20 21 22 23 24
NOTE: CONTROLLER CAN BE MOUNTED IN ANY ORIENTATION.
M31532
8-9/32
(211) 1-15/16
(49)
6-9/32
(159)
3/16 (4.5) PANEL
MOUNTING HOLE (4X)
27/32
(21)
4-1/8
(105)
6-1/4
(159)5-7/8
(149)
DEPTH IS
2-1/4 (57)
1 2 3 4 5 6 7 8 9
10
11
12
13
14
15
16
17
18
19
20
21
22
23
24
12345678 109 234567
11 111111
12345678 0
9
2
22
222222 3
3
12345678 0
9
3
33
33
33
34
5-3/4
(146)
10-5/16 (262)
NOTE: CONTROLLER CAN BE MOUNTED IN ANY ORIENTATION.
PANEL MOUNTING HOLE
(4X) 3/16 IN. (4.5)
M29329
5-3/64
(128)
8-5/16 (211)
6-29/64 (164) 1-55/64
(47)
6-17/64
(159)
7/16
(11)
DEPTH IS
2-1/4 (57)
1 2 3 4 5 6 7 8 1 0 9 2 3 4 5 6 7 8 0 9
1 1 1 1 1 1 1 1 1 2 1
1 2 3 4 5 6 7 8 0
9
2
2 2
2 2 2 2 2 2 3
3
1 2 3 4 5 6 7 8 0
9
3
3 3
3 3
3 3
3 4
5-3/4
(146)
6-27/32 (174)
NOTE: CONTROLLER CAN BE MOUNTED IN ANY ORIENTATION.
PANEL MOUNTING HOLE
(4X) 29/64 IN. (12)
M29330
5-3/64
(128)
6-29/64 (164)
5-29/64
(139)
1 2 3 4 5 6 7 8 1 0 9 2 3 4 5 6 7 8 0 9
1 1 1 1 1 1 1 1 1 2 1
1 2 3 4 5 6 7 8 0
9
2
2 2
2 2 2 2 2 2 3
3
1 2 3 4 5 6 7 8 0
9
3
3 3
3 3
3 3
3 4
6-27/32 (174)
5-3/64
(128)
6-29/64 (164)
5-29/64
(139)
PVB6438NS PUB6438S
DEPTH IS
2-1/4 (57)

SPYDER® BACNET® PROGRAMMABLE CONTROLLERS
63-2689—05 6
Panel Mounting
The controller enclosure is constructed of a plastic base plate
and a plastic factory-snap-on cover.
NOTE: The controller is designed so that the cover does
not need to be removed from the base plate for
either mounting or wiring.
The controller mounts using four screws inserted through the
corners of the base plate. Fasten securely with four No. 6 or
No. 8 machine or sheet metal screws.
The controller can be mounted in any orientation. Ventilation
openings are designed into the cover to allow proper heat
dissipation, regardless of the mounting orientation.
DIN Rail Mounting (PUB1012S, PUB4024S,
PUB6438S, PVB4024NS and PVB6438NS)
To mount the PUB1012S, PUB4024S, PUB6438S,
PVB4024NS and PVB6438NS controllers on a DIN rail
[standard EN50022; 1-3/8 in. x 9/32 in. (7.5 mm x 35 mm)],
refer to Fig. 8 and perform the following steps:
1. Holding the controller with its top tilted in towards the DIN
rail, hook the two top tabs on the back of the controller
onto the top of the DIN rail.
2. Push down and in to snap the two bottom flex connectors
of the controller onto the DIN rail.
IMPORTANT
To remove the controller from the DIN rail, perform the
following:
1. Push straight up from the bottom to release the top
tabs.
2. Rotate the top of the controller out towards you and
pull the controller down and away from the DIN rail to
release the bottom flex connectors.
Fig. 8. Controller DIN rail mounting (models PUB1012S,
PUB4024S, PUB6438S, PVB4024NS and PVB6438NS).
Piping (PVB0000AS, PVB4022AS,
PVB4024NS, PVB6436AS and
PVB6438NS)
Air flow Pickup
For PVB0000AS, PVB4022AS, PVB4024NS, PVB6436AS and
PVB6438NS, connect the air flow pickup to the two restrictor
ports on the controller (see Fig. 9).
NOTES:
— Use 1/4 inch (6 mm) outside diameter, with a 0.040
in. (1 mm) wall thickness, plenum-rated 1219 FR
(94V-2) tubing.
— Always use a fresh cut on the end of the tubing
that connects to the air flow pickups and the
restrictor ports on the controller.
Connect the high pressure or upstream tube to the plastic
restrictor port labeled (+), and the low pressure or downstream
tube to the restrictor port labeled (-). See labeling in Fig. 9.
When twin tubing is used from the pickup, split the pickup
tubing a short length to accommodate the connections.
NOTES:
— If controllers are mounted in unusually dusty or dirty
environments, an inline, 5-micron disposable air
filter (
use 5-micron filters compatible with
pneumatic controls)
is recommended for the high
pressure line (marked as
+
) connected to the air
flow pickup.
— The tubing from the air flow pickup to the controller
should not exceed three feet (0.914 m). Any length
greater than this will degrade the flow sensing
accuracy.
— Use caution when removing tubing from a connec-
tor. Always pull straight away from the connector or
use diagonal cutters to cut the edge of the tubing
attached to the connector. Never remove by pulling
at an angle.
Fig. 9. Air flow pickup connections (PVB0000AS,
PVB4022AS, PVB4024NS, PVB6436AS and PVB6438NS).
Power
Before wiring the controller, determine the input and output
device requirements for each controller used in the system.
Select input and output devices compatible with the controller
and the application. Consider the operating range, wiring
requirements, and the environment conditions when selecting
input/output devices. When selecting actuators for modulating
applications consider using floating control. In direct digital
control applications, floating actuators will generally provide
control action equal to or better than an analog input actuator
for lower cost.
Determine the location of controllers, sensors, actuators and
other input/output devices and create wiring diagrams. Refer to
Fig. 17–Fig. 23 beginning on page 14 for illustrations of typical
controller wiring for various configurations.
DIN RAIL
TOP TABS
BOTTOM FLEX
CONNECTORS M16815
M23556A
AIR FLOW
PICKUP
ΔP
1 2 3 4 5 6 7 8 1 0 9 2 3 4 5 6 7 8 0 9
1 1 1 1 1 1 1 1 1 2 1
1 2 3 4 5 6 7 8 0
9
2
2 2
2 2 2 2 2 2 3
3
1 2 3 4 5 6 7 8 0
9
3
3 3
3 3
3 3
3 4
RESTRICTOR
PORT
RESTRICTOR
PORT
CONNECTOR
TUBING

SPYDER® BACNET® PROGRAMMABLE CONTROLLERS
763-2689—05
The application engineer must review the control job
requirements. This includes the sequences of operation for the
controller, and for the system as a whole. Usually, there are
variables that must be passed between the controller and other
Spyder BACnet controller(s) that are required for optimum
system wide operation. Typical examples are the TOD, Occ/
Unocc signal, the outdoor air temperature, the demand limit
control signal, and the smoke control mode signal.
It is important to understand these interrelationships early in
the job engineering process, to ensure proper implementation
when configuring the controllers. Refer to the controller
Application Guides.
Power Budget
A power budget must be calculated for each device to
determine the required transformer size for proper operation. A
power budget is simply the summing of the maximum power
draw ratings (in VA) of all the devices to be controlled. This
includes the controller itself and any devices powered from the
controller, such as equipment actuators (ML6161 or other
motors) and various contactors and transducers.
IMPORTANT
• When multiple controllers operate from a single
transformer, connect the same side of the transformer
secondary to the same power input terminal in each
device. The earth ground terminal (terminal 3) must
be connected to a verified earth ground for each
controller in the group (see Fig. 12 on page 9).
• Half-wave devices and full-wave devices must not use
the same AC transformer. If a Spyder controller will
share its power supply with another device, make
sure the other device utilizes a half-wave rectifier and
that the polarity of the wiring is maintained.
POWER BUDGET CALCULATION EXAMPLE
Table 3 is an example of a power budget calculation for a
typical PVB6436AS controller. While the example is shown for
only this model, the process is applicable for all controller
models.
Table 3. Power budget calculation example.
The system example above requires 30.7 VA of peak power.
Therefore, a 100 VA AT92A transformer could be used to
power one controller of this type. Because the total peak power
is less than 33 VA, this same transformer could be used to
power three of these controllers and meet NEC Class 2
restrictions (no greater than 100 VA).
See Fig. 11–Fig. 12 beginning on page 9 for illustrations of
controller power wiring. See Table 4 for VA ratings of various
devices.
Table 4. VA ratings for transformer sizing.
For contactors and similar devices, the in-rush power ratings
should be used as the worst case values when performing
power budget calculations. Also, the application engineer must
consider the possible combinations of simultaneously
energized outputs and calculate the VA ratings accordingly.
The worst case, which uses the largest possible VA load,
should be determined when sizing the transformer.
Each controller requires 24 Vac power from an energy-limited
Class II power source. To conform to Class II restrictions (U.S.
only), transformers must not be larger than 100 VA. A single
transformer can power more than one controller.
GUIDELINES FOR POWER WIRING ARE AS FOLLOWS:
— For multiple controllers operating from a single
transformer, the same side of the transformer
secondary must be connected to the same power input
terminal in each device. The earth ground terminal
must be connected to a verified earth ground for each
controller in the group (see Fig. 12 on page 9).
Controller configurations are not necessarily limited to
three devices, but the total power draw, including
accessories, cannot exceed 100 VA when powered by
the same transformer (U.S. only).
— See Fig. 11 on page 9 for controller power wiring used
in UL 1995 equipment (U.S. only).
— Many controllers require all loads to be powered by the
same transformer that powers the controller.
— Keep the earth ground connection wire run as short as
possible (refer to Fig. 11–Fig. 12 beginning on page 9).
— Do not connect earth ground to the controller’s digital or
analog ground terminals (refer to Fig. 11 and Fig. 12).
— Unswitched 24 Vac power wiring can be run in the
same conduit as the LONWORKS® Bus cable.
Line-Loss
Controllers must receive a minimum supply voltage of 20 Vac.
If long power or output wire runs are required, a voltage drop
due to Ohms Law (I x R) line-loss must be considered. This
line-loss can result in a significant increase in total power
Device VA
Information Obtained From
PVB6436AS
controllers (include
Series 60 Floating
Damper Actuator)
9.0 See “Specifications” on
page 2.
R8242A Contactor
fan rating
21.0 TRADELINE® Catalog
inrush rating
D/X Stages 0.0 For example, assume
cooling stage outputs are
wired into a compressor
control circuit and have no
impact on the budget.
M6410A Steam
Heating Coil Valve
0.7 TRADELINE® Catalog,
0.32A 24 Vac
TOTAL 30.7
Device Description VA
PVB6436AS
controllers and
Series 60 Floating
Damper Actuator
Controller and Actuator 9.0
PUB6438S or
PVB6438NS
Controller 5.0
ML684 Versadrive Valve Actuator 12.0
ML6161 Damper Actuator, 35 lb-in. 2.2
ML6185 Damper Actuator SR 50 lb-in 12.0
ML6464 Damper Actuator, 66 lb-in. 3.0
ML6474 Damper Actuator, 132 lb-in. 3.0
R6410A Valve Actuator 0.7
R8242A Contactor 21.0

SPYDER® BACNET® PROGRAMMABLE CONTROLLERS
63-2689—05 8
required and thereby affect transformer sizing. The following
example is an I x R line-loss calculation for a 200 ft. (61m) run
from the transformer to a controller drawing 37 VA and using
two 18 AWG (1.0 sq mm) wires.
The formula is:
Loss = [length of round-trip wire run (ft.)] x [resistance in
wire (ohms per ft.)] x [current in wire (amperes)]
From specification data:
18 AWG twisted pair wire has a resistance of 6.52 ohms per
1000 feet.
Loss = [(400 ft.) x (6.52/1000 ohms per ft.)] x [(37 VA)/(24V)]
= 4.02 volts
This means that four volts are going to be lost between the
transformer and the controller. To assure the controller
receives at least 20 volts, the transformer must output more
than 24 volts. Because all transformer output voltage levels
depend on the size of the connected load, a larger transformer
outputs a higher voltage than a smaller one for a given load.
Fig. 10 shows this voltage load dependence.
In the preceding I x R loss example, even though the controller
load is only 37 VA, a standard 40 VA transformer is not
sufficient due to the line-loss. Looking at Fig. 10, a 40 VA
transformer is just under 100 percent loaded (for the 37 VA
controller) and has a secondary voltage of 22.9 volts. (Use the
lower edge of the shaded zone in Fig. 10 that represents the
worst case conditions.) When the I x R loss of four volts is
subtracted, only 18.9 volts reaches the controller. This is not
enough voltage for proper operation.
In this situation, the engineer has three alternatives:
1. Use a larger transformer. For example, if an 80 VA model
is used, an output of 24.4 volts, minus the four volt line-
loss, supplies 20.4V to the controller (see Fig. 10).
Although acceptable, the four-volt line-loss in this exam-
ple is higher than recommended.
IMPORTANT
No installation should be designed where the line-loss
is greater than two volts. This allows for nominal oper-
ation if the primary voltage drops to 102 Vac (120 Vac
minus 15 percent).
2. Use heavier gauge wire for the power run. 14 AWG
(2.0 sq mm) wire has a resistance of 2.57 ohms per
1,000 ft. Using the preceding formula results in a line-
loss of only 1.58 volts (compared with 4.02 volts). This
would allow a 40 VA transformer to be used. 14 AWG
(2.0 sq mm) wire is the recommended wire size for 24
Vac wiring.
3. Locate the transformer closer to the controller. This
reduces the length of the wire run, and the line-loss.
The issue of line-loss is also important in the case of the output
wiring connected to the Triac digital outputs. The same formula
and method are used. Keep all power and output wire runs as
short as practical. When necessary, use heavier gauge wire, a
bigger transformer, or install the transformer closer to the
controller.
To meet the National Electrical Manufacturers Association
(NEMA) standards, a transformer must stay within the NEMA
limits. The chart in Fig. 10 shows the required limits at various
loads.
With 100 percent load, the transformer secondary must supply
between 23 and 25 volts to meet the NEMA standard. When a
purchased transformer meets the NEMA standard DC20-1986,
the transformer voltage regulating ability can be considered
reliable. Compliance with the NEMA standard is voluntary.
Fig. 10. NEMA Class 2 transformer voltage output limits.
The Honeywell transformers listed in Table 5 meet the NEMA
standard DC20-1986.
Table 5. Honeywell transformers that meet
NEMA standard DC20-1986.
NOTE: The AT88A and AT92A transformers do not meet
the voluntary NEMA standard DC20-1986.
Wiring
All wiring must comply with applicable electrical codes and
ordinances, or as specified on installation wiring diagrams.
Controller wiring is terminated to the screw terminal blocks
located on the top and the bottom of the device.
WARNING
Electrical Shock Hazard.
Can cause severe injury, death or property damage.
Disconnect power supply before beginning wiring or
making wiring connections, to prevent electrical shock
or equipment damage.
NOTES:
— For multiple controllers operating from a single
transformer, the same side of the transformer
secondary must be connected to the same power
input terminal in each controller. Controller
configurations will not necessarily be limited to
three devices, but the total power draw, including
accessories, cannot exceed 100 VA when
powered by the same transformer (U.S. only). For
power and wiring recommendations, See “Power”
Transformer Type VA Rating
AT40A 40
AT72D 40
AT87A 50
AK3310 Assembly 100
27
26
25
24
23
22
21
20
19
18
17
16
15
14
0 50 100 150
% OF LOAD
SECONDARY VOLTAGE
200
M993
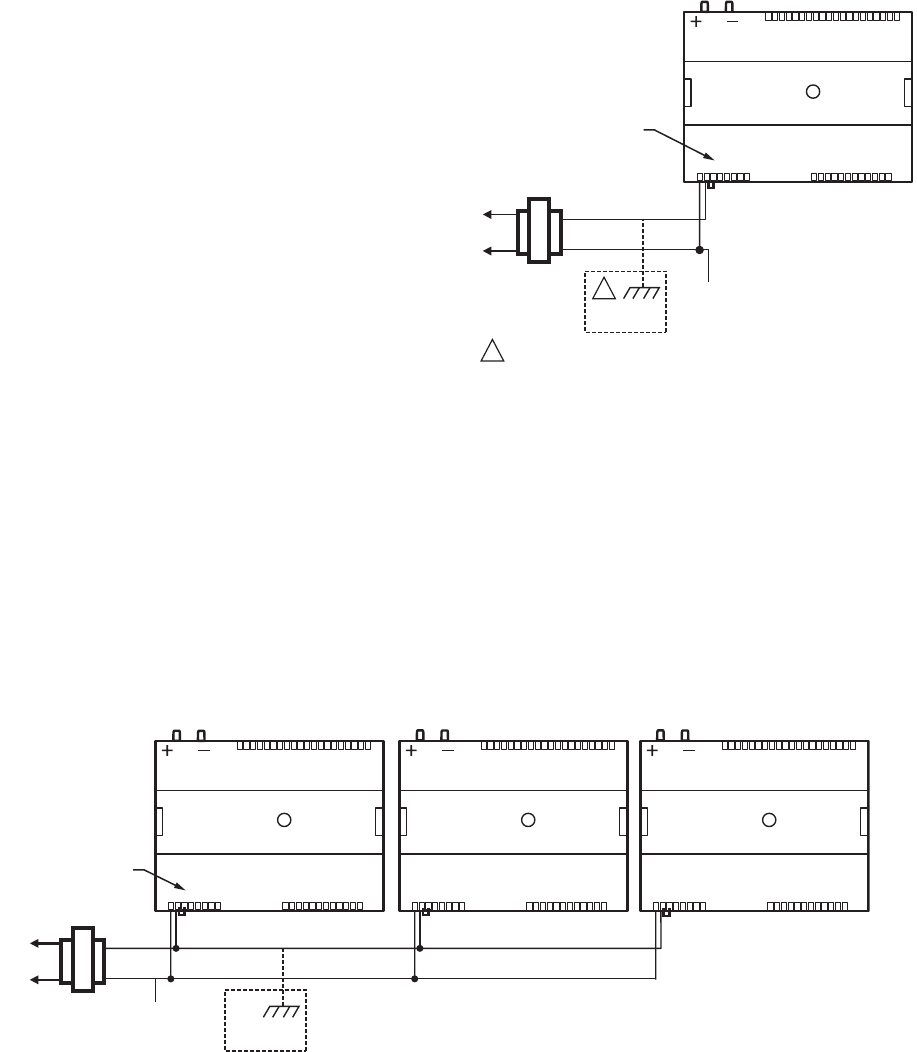
SPYDER® BACNET® PROGRAMMABLE CONTROLLERS
963-2689—05
on page 6. The earth ground terminal (terminal 3)
must be connected to a verified earth ground for
each controller in the group (see Fig. 12 on
page 9).
— All loads on the controller must be powered by the
same transformer that powers the controller itself.
A controller can use separate transformers for
controller power and output power.
— Keep the earth ground connection (terminal 3) wire
run as short as possible.
— Do not connect the universal input COM terminals,
analog output COM terminals or the digital input/
output COM terminals to earth ground. Refer to
Fig. 16–Fig. 21 beginning on page 13 for wiring
examples.
The 24 Vac power from an energy limited Class II power
source must be provided to the controller. To conform to Class
II restrictions (U.S. only), the transformer must not be larger
than 100 VA.
Fig. 11 depicts a single controller using one transformer.
IMPORTANT
Power must be off prior to connecting to or removing
connections from the 24 Vac power (24 Vac/24 Vac
COM), earth ground (EGND), and 20 Vdc power (20
Vdc) terminals.
IMPORTANT
Use the heaviest gauge wire available, up to 14 AWG
(2.0 sq mm), with a minimum of 18 AWG (1.0 sq mm),
for all power and earth ground wiring.
Screw-type terminal blocks are designed to accept up
to one 14 AWG (2.0 sq mm) conductor or up to two 18
AWG (1.0 sq mm) conductors. More than two wires
that are 18 AWG (2.0 sq mm) can be connected with
a wire nut. Include a pigtail with this wire group and
attach the pigtail to the terminal block.
IMPORTANT
Connect terminal 2, (the 24 Vac common [24 VAC
COM] terminal) to earth ground (see Fig. 11).
NOTE: Unswitched 24 Vac power wiring can be run in the
same conduit as the LONWORKS® cable.
Fig. 11. Power wiring details for one controller per
transformer.
More than one controller can be powered by a single
transformer. Fig. 12 shows power wiring details for multiple
controllers.
NOTE: Controller configurations are not necessarily lim-
ited to three devices, but the total power draw,
including accessories, cannot exceed 100 VA
when powered by the same transformer (U.S.
only). For power wiring recommendations, see
“Power” on page 6.
Fig. 12. Power wiring details for two or more controllers per transformer.
Communications
Each controller uses a BACnet MS/TP communications port.
The controller’s data is presented to other controllers over a
twisted-pair MS/TP network, which uses the EIA-485 signaling
standard capable of the following baud rates: 9.6, 19.2, 38.4,
76.8 or 115.2 kilobits per second (configured at global
controller). The Spyder BACnet controllers are master devices
on the MS/TP network. Each Spyder BACnet controller uses a
high-quality EIA-485 transceiver and exerts 1/4 unit load on the
MS/TP network.
M29684A
TRANSFORMER
OUTPUT
DEVICE
POWER
ΔP
12345678 109 2345678 09
11 1111111 21
12345678 0
9
2
22
222222 3
312345678 0
9
3
33
33
33
34
EARTH
GROUND
1
LINE VOLTAGE
GREATER
THAN 150 VAC
WHEN CONNECTIONG POWER TO THE SPYDER BACnet
CONTROLLER, CONNECT THE COM LEG OF THE VAC SECONDARY
CIRCUIT TO A KNOWN EARTH GROUND.
1
COM
24 VAC
CONNECT POWER TO
TERMINALS 1 AND 2
M29685A
120/240
VAC
TRANSFORMER OUTPUT
DEVICE
POWER
ΔP
12345678 109 2345678 09
11 1111111 21
12345678 0
9
2
22
222222 3
312345678 0
9
3
33
33
33
34
COM
24 VAC
ΔP
12345678 109 2345678 09
11 1111111 21
12345678 0
9
2
22
222222 3
312345678 0
9
3
33
33
33
34 ΔP
12345678 109 2345678 09
11 1111111 21
12345678 0
9
2
22
222222 3
312345678 0
9
3
33
33
33
34
CONNECT POWER TO
TERMINALS 1 AND 2
EARTH
GROUND

SPYDER® BACNET® PROGRAMMABLE CONTROLLERS
63-2689—05 10
Cabling should be selected that meets or exceeds the BACnet
Standard which specifies the following: An MS/TP EIA-485
network shall use shielded, twisted-pair cable with
characteristic impedance between 100 and 130 ohms.
Distributed capacitance between conductors shall be less than
100 pF per meter (30 pF per foot). Distributed capacitance
between conductors and shield shall be less that 200 pF per
meter (60 pF per foot). Foil or braided shields are acceptable.
The Honeywell tested and recommended MS/TP cable is
Honeywell Cable 3322 (18 AWG, 1-Pair, Shielded, Plenum
cable), alternatively Honeywell Cable 3251 (22 AWG, 1-Pair,
Shielded, Plenum cable) is available and meets the BACnet
Standard requirements (www.honeywellcable.com).
The maximum BACnet MS/TP network Bus segment length is
4,000 ft. (1,219 m) using recommended wire. Repeaters must
be used when making runs longer than 4,000 ft. (1,219 m). A
maximum of three repeaters can be used between any two
devices.
Setting the MS/TP MAC address
The MS/TP MAC address for each device must be set to a
unique value in the range of 0-127 on an MS/TP network
segment (address 0, 1, 2, & 3 should be avoided as they are
commonly used for the router, diagnostic tools, and as spare
addresses). DIP switches on the Spyder BACnet controller are
used to set the controller's MAC address.
To set the MS/TP MAC address of a Spyder BACnet controller:
1. Find an unused MAC address on the MS/TP network to
which the Spyder BACnet controller connects.
2. Locate the DIP switch bank on the Spyder BACnet for
addressing. This is labeled MAC Address
3. With the Spyder BACnet Controller powered down, set
the DIP switches for the MAC Address you want. Add the
value of DIP switches set to ON to determine the MAC
address. See Table 6. Example, if only DIP switches 1, 3,
5, and 7 are enabled the MAC address would be 85 (1 +
4 + 16 + 64 = 85).
NOTE: See Fig. 15 on page 12 for DIP switch orienta-
tion and arrangement.
Setting the Device Instance Number
The Device Instance Number must be unique across the entire
BACnet system network because it is used to uniquely identify
the BACnet devices. It may be used to conveniently identify the
BACnet device from other devices during installation. The
Spyder BACnet Controllers Device Instance Number is
automatically set when it is added to a WEBStation-AX project.
The Device Instance Number can be changed by the user,
which may be necessary when integrating with a third party or
when attempting to replace an existing controller and it is
desired to maintain the existing Device Instance Number.
To edit the Device Instance Number using WEBs AX:
1. Identify an unused Device Instance Number on the BAC-
net Network, in the range of 0 - 4194302.
2. Open the Spyder Bacnet Device Mgr View
a. Double click on the BacnetNetwork located in the
Nav tree.
b. Select the Spyder Controller to be modified.
c. Click on the Edit button.
d. Enter an unused value in the Device Id field.
e. Select OK
3. Right Click on the Spyder Controller and select Actions >
Write Device Instance to complete the update
Termination Resistors
Matched terminating resistors are required at each end of a
segment bus wired across (+) and (-). Use matched precision
resistors rated 1/4W ±1% / 80 - 130 Ohms. Ideally, the value of
the terminating resistors should match the rated characteristic
impedance of the installed cable. For example, if the installed
MS/TP cable has a a listed characteristic impedance of 120
Ohm, install 120 Ohm matched precision resistors.
NOTE: The controller does not provide any network bias-
ing.
Shield Terminating
Following proper MS/TP cabling shield grounding procedures
is important to minimize the risk of communication problems
and equipment damage caused by capacitive coupling.
Capacitive coupling is caused by placing MS/TP cabling close
to lines carrying higher voltage. The shield should be grounded
on only one end of the MS/TP segment (typically the router
end). Tie the shield through using the SHLD (terminal 4) on the
Spyder BACnet Controller.
Sylk™ Bus
Sylk is a two wire, polarity insensitive bus that provides both 18
VDC power and communications between a Sylk-enabled
sensor and a Sylk-enabled controller. Using Sylk-enabled
sensors saves I/O on the controller and is faster and cheaper
to install since only two wires are needed and the bus is
polarity insensitive. Sylk sensors are configured using the
latest release of the Spyder Tool for WEBPro and WEBStation.
Table 6. DIP Switch Values For MS/TP MAC Address.
DIP 7654321
VALUE 6432168421

SPYDER® BACNET® PROGRAMMABLE CONTROLLERS
11 63-2689—05
Fig. 13. Termination modules.
Wiring Method
WARNING
Electrical Shock Hazard.
Can cause severe injury, death or property damage.
Disconnect power supply before beginning wiring, or
making wiring connections, to prevent electrical shock
or equipment damage.
NOTE: When attaching two or more wires to the same
terminal, other than 14 AWG (2.0 sq mm), be sure
to twist them together. Deviation from this rule
can result in improper electrical contact (see Fig.
14).
Each terminal can accommodate the following gauges of wire:
— Single wire: from 22 AWG to 14 AWG solid or stranded
— Multiple wires: up to two 18 AWG stranded, with 1/4 watt
wire-wound resistor
Prepare wiring for the terminal blocks, as follows:
1. Strip 1/2 in. (13 mm) insulation from the conductor.
2. Cut a single wire to 3/16 in. (5 mm). Insert the wire in the
required terminal location and tighten the screw.
3. If two or more wires are being inserted into one terminal
location, twist the wires together a minimum of three
turns before inserting them (see Fig. 14).
4. Cut the twisted end of the wires to 3/16 in. (5 mm) before
inserting them into the terminal and tightening the screw.
5. Pull on each wire in all terminals to check for good
mechanical connection.
Fig. 14. Attaching two or more wires at terminal blocks.
Wiring Details
Each controller is shipped with the digital outputs, which switch
the 24 Vac to the load (High Side).
The three analog outputs (AO) are used to control modulating
heating, cooling and economizer equipment. Any AO may be
used as a digital output, as follows:
— False (0%) produces 0 Vdc, (0 mA)
— True (100%) produces the maximum 11 Vdc (22 mA)
The wiring connection terminals described in Table 7 are
shown in Fig. 15 starting on page 12.
AO-1
COM
AO-2
AO-3
COM
UI-1
COM
UI-2
UI-3
COM
UI-4
UI-5
COM
UI-6
DI-1
DI-2
COM
DI-3
20V DC
DI-4
BAC –
BAC +
SHLD
EGND
24 VAC
24VAC COM
DO-1
COM
DO-2
DO-3
DO-4
DO-5
COM
DO-6
COM
M29331
ADD APPROPRIATE TERMINATION
RESISTOR BETWEEN THE BAC+
AND THE BAC– TERMINALS.
BACnet MS/TP–
BAC+
SHLD
BAC–
NOTE: ALL BACnet MS/TP CONNECTIONS ARE MADE TO:
1 2 3 4 5 6 7 8 1 0 9 2 3 4 5 6 7 8 0 9
1 1 1 1 1 1 1 1 1 2 1
1 2 3 4 5 6 7 8 0
9
2
2 2
2 2 2 2 2 2 3
3
1 2 3 4 5 6 7 8 0
9
3
3 3
3 3
3 3
3 4
AO-1
COM
AO-2
AO-3
COM
UI-1
COM
UI-2
UI-3
COM
UI-4
UI-5
COM
UI-6
DI-1
DI-2
COM
DI-3
20V DC
DI-4
BAC –
BAC +
SHLD
EGND
24 VAC
24VAC COM
DO-1
COM
DO-2
DO-3
DO-4
DO-5
COM
DO-6
COM
1 2 3 4 5 6 7 8 1 0 9 2 3 4 5 6 7 8 0 9
1 1 1 1 1 1 1 1 1 2 1
1 2 3 4 5 6 7 8 0
9
2
2 2
2 2 2 2 2 2 3
3
1 2 3 4 5 6 7 8 0
9
3
3 3
3 3
3 3
3 4
AO-1
COM
AO-2
AO-3
COM
UI-1
COM
UI-2
UI-3
COM
UI-4
UI-5
COM
UI-6
DI-1
DI-2
COM
DI-3
20V DC
DI-4
BAC –
BAC +
SHLD
EGND
24 VAC
24VAC COM
DO-1
COM
DO-2
DO-3
DO-4
DO-5
COM
DO-6
COM
1 2 3 4 5 6 7 8 1 0 9 2 3 4 5 6 7 8 0 9
1 1 1 1 1 1 1 1 1 2 1
1 2 3 4 5 6 7 8 0
9
2
2 2
2 2 2 2 2 2 3
3
1 2 3 4 5 6 7 8 0
9
3
3 3
3 3
3 3
3 4
DO-7
DO-8
COM
DO-7
DO-8
COM
SBUS1
SBUS2
SBUS1
SBUS2
SBUS1
SBUS2
BACnet MS/TP+
SHIELD
BACnet MS/TP–
BACnet MS/TP+
SHIELD
1/2
(13)
STRIP 1/2 IN. (13 MM)
FROM WIRES TO
BE ATTACHED AT
ONE TERMINAL.
1.
2.
TWIST WIRES
TOGETHER WITH
PLIERS (A MINIMUM
OF THREE TURNS).
3.
CUT TWISTED END OF WIRES TO 3/16 IN. (5 MM)
BEFORE INSERTING INTO TERMINAL AND
TIGHTENING SCREW. THEN PULL ON EACH
WIRE IN ALL TERMINALS TO CHECK FOR
GOOD MECHANICAL CONNECTION. M17207

SPYDER® BACNET® PROGRAMMABLE CONTROLLERS
63-2689—05 12
Table 7. Description of wiring terminal connections for
PUB6438S, PVB6436AS, and PVB6438NS.
IMPORTANT
If the controller is not connected to a good earth
ground, the controller's internal transient protection
circuitry is compromised and the function of protect-
ing the controller from noise and power line spikes
cannot be fulfilled. This could result in a damaged cir-
cuit board and require replacement of the controller.
Refer to installation diagrams for specific wiring.
All controllers have the terminal arrangements similar to the
examples shown in Fig. 15 as described in Table Table 7 on
page 12.
MS/TP MAC ADDRESS DIP SWITCHES
The MS/TP MAC address DIP switches are used to set the
unit's MAC address. Each Spyder BACnet on an MS/TP
network must have a unique MAC address in the range of 0-
127 (address 0 should be avoided as it is the Honeywell factory
default MAC address for all MS/TP devices).
MS/TP SERVICE CONNECTOR PINS
Local device MS/TP network connection is provided via the
molex connector pins (0.100-in. molex connector—part
number: 22-01-2035).
Fig. 15. Controller Terminal Connections, MS/TP MAC
address DIP switches, MS/TP service connector pins, and
BACnet Status LED for the PUB's and PVB's (PVB6438NS
shown).
Wiring Applications (Examples)
Fig. 16–Fig. 22, beginning on page 13, illustrate controller
wiring for the following configurations.
• Typical controller wiring for VAV application using the TR23
Wall Module and a C7770A Air Temperature Sensor (see
Fig. 16 on page 13).
• Typical controller wiring for VAV application with staged
reheat (see Fig. 17 on page 14).
• Typical controller wiring for PWM reheat and PWM
peripheral heat valve actuator (see Fig. 18 on page 15).
• Typical controller wiring for AHU application (see Fig. 19 on
page 16).
• Typical controller wiring for 4 to 20 mA enthalpy sensors and
digital inputs (see Fig. 20 on page 17).
Terminal Label Connection
INPUT POWER & GROUND
1 24 Vac 24 Vac Power
2 24 Vac COM 24 Vac Power
3 EGND Earth Ground
4 SHLD MS/TP Shield
5SBUS 1 Sylk
6SBUS 2 Sylk
NETWORK CONNECTIONS
7BAC + LONWORKS® communications
8BAC - LONWORKS® communications
DIGITAL OUTPUTSa
9 DO-1 Digital Output
10 DO-2 Digital Output
11 COM Common
12 DO-3 Digital Output
13 DO-4 Digital Output
14 COM Common
15 DO-5 Digital Output
16 DO-6 Digital Output
17 COM Common
18 DO-7 Digital Output
19 DO-8 Digital Output
20 COM Common
ANALOG OUTPUTSb
21 AO-1 Analog Output
22 COM Common
23 AO-2 Analog Output
24 AO-3 Analog Output
25 COM Common
DIGITAL INPUTSc
26 DI-1 Digital Input
27 DI-2 Digital Input
28 COM Common
29 DI-3 Digital Input
30 DI-4 Digital Input
ATTACHED DEVICE(S) POWER
31 20 Vdc 20 Vdc Power
UNIVERSAL INPUTS
32 UI-1 Universal Input
33 COM Common
34 UI-2 Universal Input
35 UI-3 Universal Input
36 COM Common
37 UI-4 Universal Input
38 UI-5 Universal Input
39 COM Common
40 UI-6 Universal Input
aFor the PVB6436AS controller ONLY, terminals 18, 19, and 20 (DO7,
DO8, & COM) are not present. The actuator is internally hardwired to
these terminals.
bAnalog outputs may be configured as digital outputs and operate as fol-
lows:
– False (0%) produces 0 Vdc, (0 mA)
– True (100%) produces the maximum 11 Vdc (22 mA)
cDigital inputs: Open circuit = False; Closed circuit = True
BACnet MS/TP MAC
A
DDRESS DIP SWITCHES
TERMINALS 1-8 TERMINALS 9-20
TERMINALS 21-40
AO-1
COM
AO-2
AO-3
COM
UI-1
COM
UI-2
UI-3
COM
UI-4
UI-5
COM
UI-6
DI-1
DI-2
COM
DI-3
20V DC
DI-4
NET-2
NET-1
SHLD
EGND
24 VAC
24VAC COM
DO-1
COM
DO-2
DO-3
DO-4
DO-5
COM
DO-6
COM
1 2 3 4 5 6 7 8 1 0 9 2 3 4 5 6 7 8 0 9
1 1 1 1 1 1 1 1 1 2 1
1 2 3 4 5 6 7 8 0
9
2
2 2
2 2 2 2 2 2 3
3
1 2 3 4 5 6 7 8 0
9
3
3 3
3 3
3 3
3 4
M29332
DO-7
DO-8
COM
SBUS1
SBUS2
LOCAL BACnet MS/TP
MOLEX CONNECTOR PINS

SPYDER® BACNET® PROGRAMMABLE CONTROLLERS
13 63-2689—05
• Typical controller wiring for 4 to 20 mA heating, cooling, and
model ML6161 floating motor control (see Fig. 21 on
page 18).
• Typical controller wiring for a pneumatic transducer, model
RP7517B (see Fig. 22 on page 19).
Fig. 16. Controller wiring diagram (model PVB6438NS shown) for typical VAV application, using the TR23 wall module and
a C7770A air temperature sensor. (For note 2, refer to Fig. 14.)
2
1
3
TO ASSURE PROPER ELECTRICAL CONTACT, WIRES MUST BE TWISTED TOGETHER BEFORE INSERTION INTO THE TERMINAL BLOCK.
CONTACTS MUST BE SUITABLE FOR DRY SWITCHING, 5V AT 10 mA. USE SEALED TYPE, GOLD FLASHED OR PIMPLED CONTACTS.
M31169C
AO-1
DI-1
UI-1
UI-2
UI-4
COM
24 VAC
24 VAC
COM
+
-
DO-1
DO-2
DO-3
DO-4
SERIES OR
PARALLEL FAN
CONTACTOR
REHEAT
STAGE
CONTACTORS
ML6161 DAMPER
ACTUATOR
CW COM CCW
OCCUPANCY SENSOR
(CONTACTS CLOSED
EQUALS OCCUPIED)
WINDOWS CONTACTS
(CONTACTS CLOSED
EQUALS WINDOW CLOSED)
DI-2
COM
2
DO-5
DO-6
C7770A
AIR
TEMPERATURE
SENSOR
UI-3
COM
AIR FLOW
PICKUP
ΔP
33
DAMPER OPEN
DAMPER CLOSE
REHEAT STAGE 1 (OR OPEN)
REHEAT STAGE 2 (OR CLOSE)
COM
REHEAT STAGE 3
DI-3
COM
COM
SBUS1
SBUS2
AO-1
COM
AO-2
AO-3
COM
UI-1
COM
UI-2
UI-3
COM
UI-4
UI-5
COM
UI-6
DI-1
DI-2
COM
DI-3
20V DC
DI-4
SHLD
EGND
24 VAC
24VAC COM
DO-1
COM
DO-2
DO-3
DO-4
DO-5
COM
DO-6
COM
12345678 109 2345678 09
11 1111111 21
12345678 09
22 2222222 3312345678 09
333333334
DO-7
DO-8
COM
BAC+
BAC–
SHIELD
BACnet MS/TP+
BACnet MS/TP–
2
DIP SWITCH S3
(TR23 AND TR24 ONLY.)
ON
SW1 SW2 SW3
DIP SWITCH S2
ON
SW1 SW2
DIP SWITCH
S1
ON
SW1 SW2
DIP SWITCH S1 FOR HUMIDITY MODELS ONLY. SEE TR23 INSTALLATION INSTRUCTIONS, FORM NO. 62-0267,
FOR CONFIGURATION DETAILS.
TR23-H ONLY
DO NOT CHANGE THIS
SWITCH POSITION.
10 8643
GND
SENSOR
LON +
LON -
SETPT
LED
OVERRIDE
HUM
24 VAC
97521
11
12
1

SPYDER® BACNET® PROGRAMMABLE CONTROLLERS
63-2689—05 14
Fig. 17. Controller wiring diagram (model PVB6436AS shown) for typical VAV application with staged reheat.
(For note 2, refer to Fig. 14.)
AO-1
DI-1 UI-3
UI-2
UI-1
COM
COM
24 VAC
24 VAC
COM
+
-
DO-1
DO-2
DO-3
OCCUPANCY SENSOR
(CONTACTS CLOSED
EQUALS OCCUPIED)
WINDOWS CONTACTS
(CONTACTS CLOSED
EQUALS WINDOW CLOSED)
DI-2
2
AIR FLOW
PICKUP
ΔP
33
DI-3
COM
LINE
POWER
STAGE 1
STAGE 2
STAGE 3
AO-1
COM
AO-2
AO-3
COM
UI-1
COM
UI-2
UI-3
COM
UI-4
UI-5
COM
UI-6
DI-1
DI-2
COM
DI-3
20V DC
DI-4
BAC–
BAC+
SHLD
EGND
24 VAC
24VAC COM
DO-1
COM
DO-2
DO-3
DO-4
DO-5
COM
DO-6
COM
12345678 109 2345678 09
11 1111111 21
12345678 09
22 2222222 3312345678 09
333333334
SBUS1
SBUS2
SHIELD
BACnet MS/TP+
BACnet MS/TP–
2
2
1
3
TO ASSURE PROPER ELECTRICAL CONTACT, WIRES MUST BE TWISTED TOGETHER BEFORE INSERTION INTO THE TERMINAL BLOCK.
CONTACTS MUST BE SUITABLE FOR DRY SWITCHING, 5V AT 10 mA. USE SEALED TYPE, GOLD FLASHED OR PIMPLED CONTACTS. M31172C
DIP SWITCH S3
(TR23 AND TR24 ONLY.)
ON
SW1 SW2 SW3
DIP SWITCH S2
ON
SW1 SW2
DIP SWITCH
S1
ON
SW1 SW2
DIP SWITCH S1 FOR HUMIDITY MODELS ONLY. SEE TR23 INSTALLATION INSTRUCTIONS, FORM NO. 62-0267, FOR CONFIGURATION DETAILS.
TR23-H ONLY
DO NOT CHANGE THIS
SWITCH POSITION.
10 8643
GND
SENSOR
LON +
LON -
SETPT
LED
OVERRIDE
HUM
24 VAC
921
12
5
711
1

SPYDER® BACNET® PROGRAMMABLE CONTROLLERS
15 63-2689—05
Fig. 18. Controller wiring diagram (model PUB6438S shown) for typical PWM reheat and PWM peripheral heat valve
actuator. (For note 2, refer to Fig. 14.)
NOTE: Make sure to set the Configuration DIP Switch as
shown in Fig. 18. Switches 1 through 3 set the tim-
ing of the ML7984B valve actuator to match the
controller outputs (0.1 second minimum with a
maximum time of 25.6 seconds). Switch 4 deter-
mines the action of the actuator (Off = Direct Act-
ing, On = Reverse Acting).
1234
2
ON
OFF
ML7984B
CONFIGURATION
DIP SWITCHES
(LOCATED ADJACENT
TO THE INPUT
TERMINAL BLOCK)
1
1
2
TO ASSURE PROPER ELECTRICAL CONTACT, WIRES MUST BE TWISTED TOGETHER BEFORE INSERTION INTO THE TERMINAL BLOCK.
TURN POWER OFF BEFORE SETTING THE DIP SWITCHES.
MAKE SURE ALL TRANSFORMER/POWER WIRING IS AS SHOWN: REVERSING TERMINATIONS WILL RESULT IN EQUIPMENT
MALFUNCTION.
M29335C
24 VAC
24 VAC
COM
+
-
DO-1
DO-2
DO-3
3
3
24 VAC COM
1
1
24 (H)
24 (N)
PWM
(H 24 VAC)
PWM OUTPUT
FROM CNTRL
PWM VALVE ACTUATOR
ML7984B
T6 T5 C B W R
REHEAT
VALVE ACTUATOR
24 (H)
24 (N)
PWM
(H 24 VAC)
PWM OUTPUT
FROM CNTRL
PWM VALVE ACTUATOR
T6 T5 C B W R
PERIPHERAL HEAT
VALVE ACTUATOR
24 VAC
3
3
AO-1
COM
AO-2
AO-3
COM
UI-1
COM
UI-2
UI-3
COM
UI-4
UI-5
COM
UI-6
DI-1
DI-2
COM
DI-3
20V DC
DI-4
BAC–
BAC+
SHLD
EGND
24 VAC
24VAC COM
DO-1
COM
DO-2
DO-3
DO-4
DO-5
COM
DO-6
COM
12345678 109 2345678 09
11 1111111 21
12345678 0
9
22 2222222 3312345678 0
9
333333334
DO-7
DO-8
COM
SBUS1
SBUS2
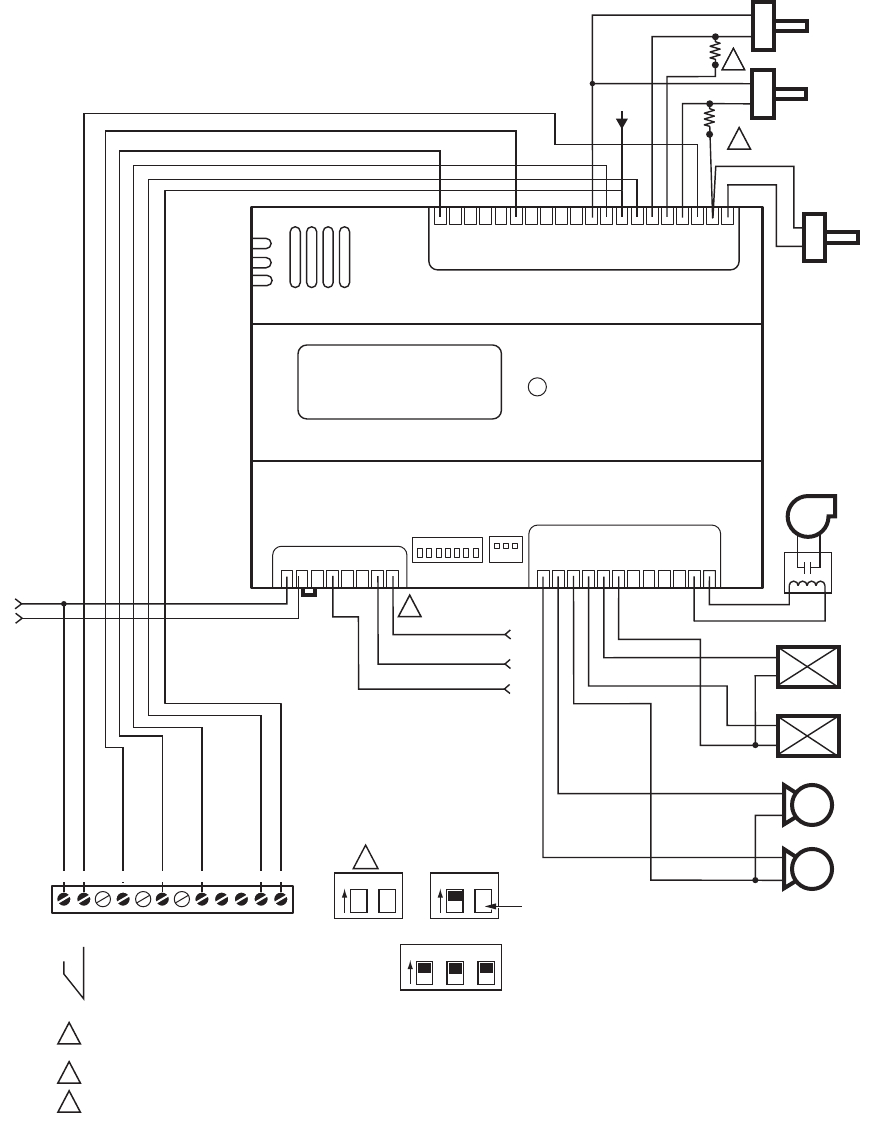
SPYDER® BACNET® PROGRAMMABLE CONTROLLERS
63-2689—05 16
Fig. 19. Controller wiring diagram (model PUB6438S shown) for typical AHU application.
(For note 2, refer to Fig. 14.)
2
AO-1
DI-1
UI-2
UI-1
UI-5
24 VAC
24 VAC
COM
+
-
DO-1
DO-2
DO-3
DO-4
DO-8
UI-3
COM
COM
COM
COM
DISCHARGE
AIR TEMP
COM
COM
UI-6
OUTDOOR
ENTHALPY
RETURN
ENTHALPY
20 VDC
20 VDC
3
499
2
COMP2
COMP 1
HEAT 2
HEAT 1
FAN
UI-4
499
SBUS1
SBUS2
AO-1
COM
AO-2
AO-3
COM
UI-1
COM
UI-2
UI-3
COM
UI-4
UI-5
COM
UI-6
DI-1
DI-2
COM
DI-3
20V DC
DI-4
SHLD
EGND
24 VAC
24VAC COM
DO-1
COM
DO-2
DO-3
DO-4
DO-5
COM
DO-6
COM
12345678 109 2345678 09
11 1111111 21
12345678 0
9
22 2222222 3312345678 0
9
333333334
DO-7
DO-8
COM
BAC+
BAC–
SHIELD
BACnet MS/TP+
BACnet MS/TP–
2
1
3
TO ASSURE PROPER ELECTRICAL CONTACT, WIRES MUST BE TWISTED TOGETHER BEFORE INSERTION INTO THE TERMINAL BLOCK.
CONTACTS MUST BE SUITABLE FOR DRY SWITCHING, 5V AT 10 mA. USE SEALED TYPE, GOLD FLASHED OR PIMPLED CONTACTS.
M31176B
DIP SWITCH S3
(TR23 AND TR24 ONLY.)
ON
SW1 SW2 SW3
DIP SWITCH S2
ON
SW1 SW2
DIP SWITCH
S1
ON
SW1 SW2
DIP SWITCH S1 FOR HUMIDITY MODELS ONLY. SEE TR23 INSTALLATION INSTRUCTIONS, FORM NO. 62-0267,
FOR CONFIGURATION DETAILS.
TR23-H ONLY
DO NOT CHANGE THIS
SWITCH POSITION.
10 8643
GND
SENSOR
LON +
LON -
SETPT
LED
OVERRIDE
HUM
24 VAC
12
11 9 7 521
1
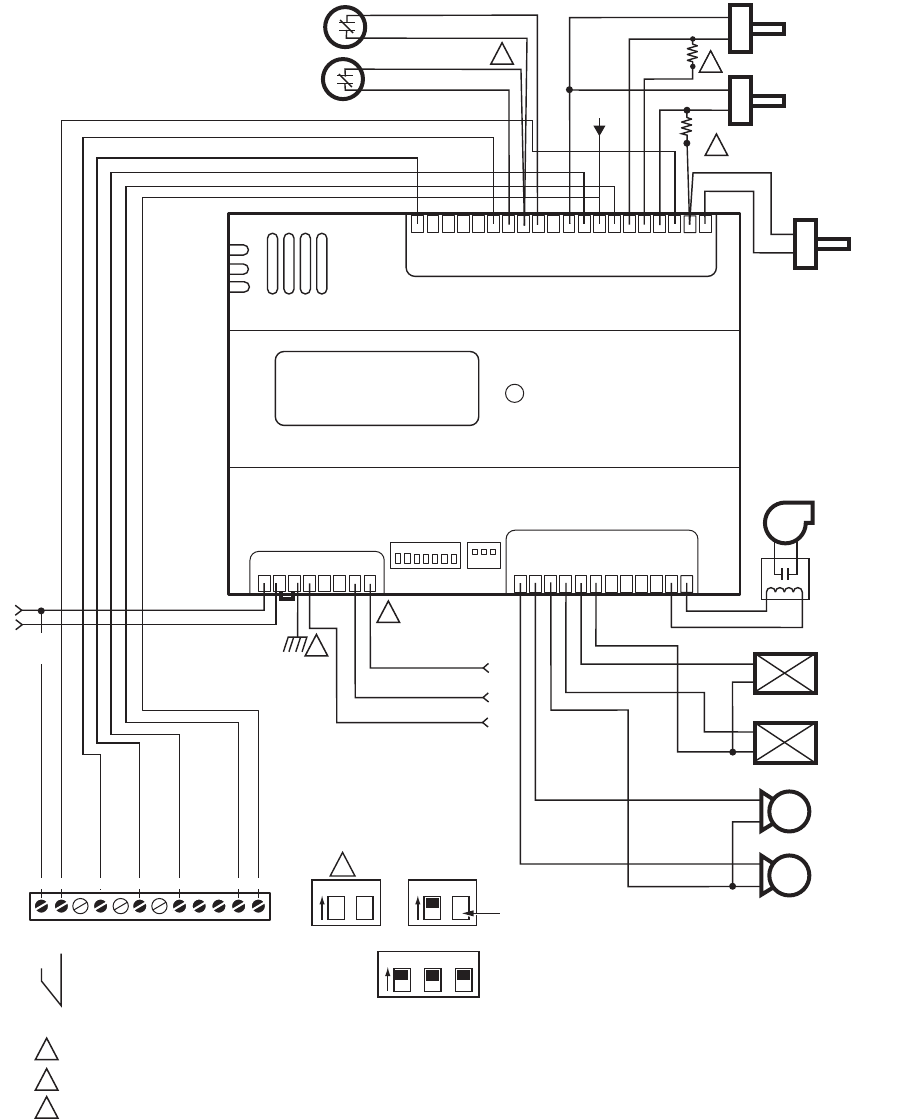
SPYDER® BACNET® PROGRAMMABLE CONTROLLERS
17 63-2689—05
Fig. 20. Controller wiring diagram (model PUB6438S shown) with 4 to 20 mA enthalpy sensors and digital inputs.
(For note 2, refer to Fig. 14.)
AO-1
DI-1
UI-2
UI-1
UI-5 COM
2
1
3
TO ASSURE PROPER ELECTRICAL CONTACT, WIRES MUST BE TWISTED TOGETHER BEFORE INSERTION INTO THE TERMINAL BLOCK.
CONTACTS MUST BE SUITABLE FOR DRY SWITCHING, 5V AT 10 mA. USE SEALED TYPE, GOLD FLASHED OR PIMPLED CONTACTS.
DIP SWITCH S3
(TR23 AND TR24 ONLY.)
ON
SW1 SW2 SW3
DIP SWITCH S2
ON
SW1 SW2
DIP SWITCH
S1
ON
SW1 SW2
DIP SWITCH S1 FOR HUMIDITY MODELS ONLY. SEE TR23 INSTALLATION INSTRUCTIONS, FORM NO. 62-0267, FOR CONFIGURATION DETAILS.
TR23-H ONLY
DO NOT CHANGE THIS
SWITCH POSITION.
10 8643
GND
SENSOR
LON +
LON -
SETPT
LED
OVERRIDE
HUM
24 VAC
12
11 9 7 521
1
2
3
M31177B
24 VAC
+
-
DO-1
DO-2
DO-3
DO-4
DO-8
UI-3
COM
COM
COM
COM
DISCHARGE
AIR TEMP
COM
UI-6
OUTDOOR
ENTHALPY
RETURN
ENTHALPY
20 VDC
20 VDC
4
499
2
COMP2
COMP 1
HEAT 2
HEAT 1
FAN
UI-4
499
OCCUPANCY SENSOR
(CONTACTS CLOSED
EQUALS OCCUPIED)
WINDOWS CONTACTS
(CONTACTS CLOSED
EQUALS WINDOW CLOSED)
3
DI-2
COM
DI-3
AO-1
COM
AO-2
AO-3
COM
UI-1
COM
UI-2
UI-3
COM
UI-4
UI-5
COM
UI-6
DI-1
DI-2
COM
DI-3
20V DC
DI-4
SHLD
EGND
24 VAC
24VAC COM
DO-1
COM
DO-2
DO-3
DO-4
DO-5
COM
DO-6
COM
12345678 109 2345678 09
11 1111111 21
12345678 0
9
22 2222222 3312345678 0
9
333333334
DO-7
DO-8
COM
SBUS1
SBUS2
BAC–
BAC+
SHIELD
BACnet MS/TP+
BACnet MS/TP–
24 VAC
COM
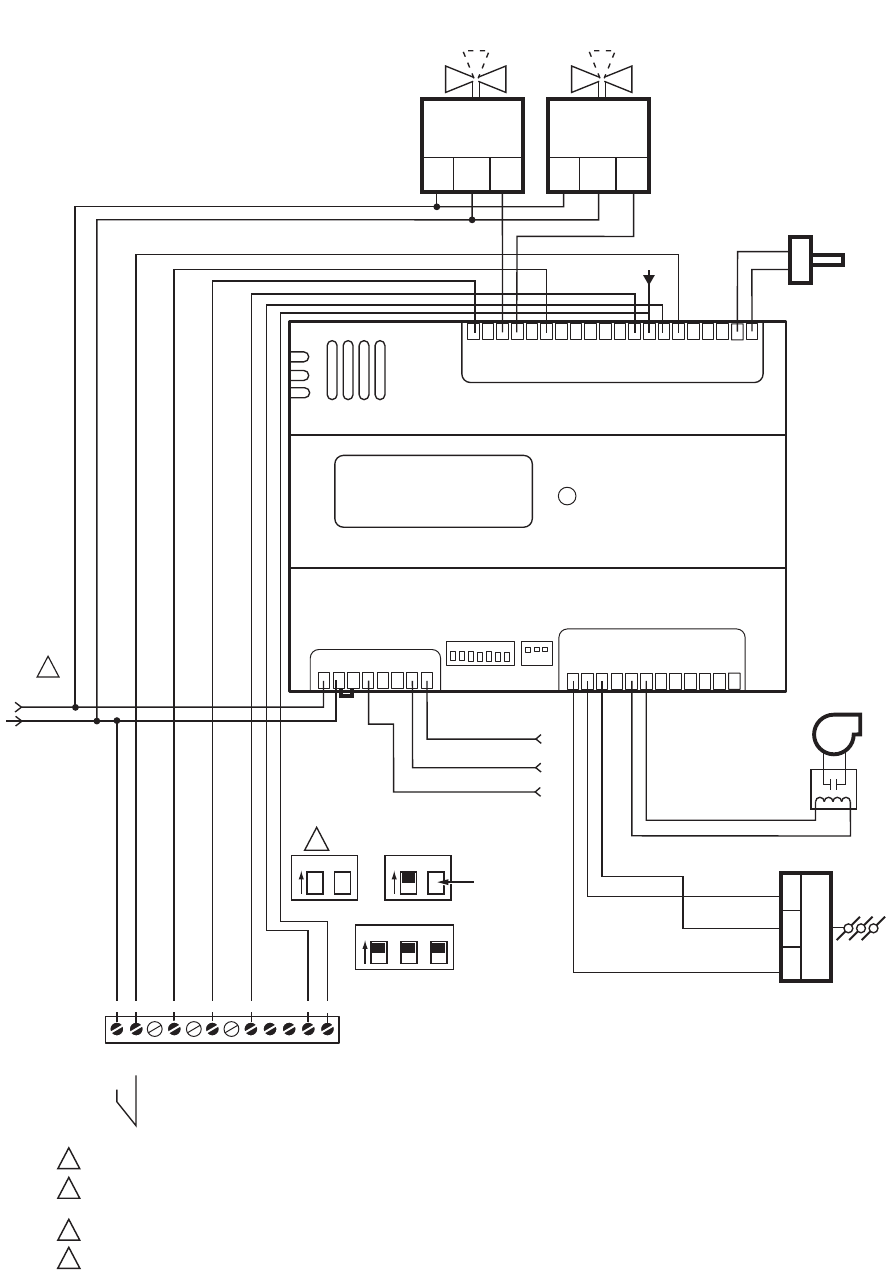
SPYDER® BACNET® PROGRAMMABLE CONTROLLERS
63-2689—05 18
Fig. 21. Controller wiring diagram (model PUB6438S shown) with 4 to 20 mA heating, cooling, and model ML6161 damper
actuator. (For note 2, refer to Fig. 14.)
COM
COM
DO4
COM
UI-6
FAN
SERIES 70
VALVE
ACTUATOR
24
VAC
IN-
PUT
COM
TWO - OR
THREE-WAY
CHILLER
WATER VALVE
SERIES 70
VALVE
ACTUATOR
24
VAC
IN-
PUT
COM
TWO - OR
THREE-WAY
HOT WATER/
STEAM VALVE
AO-3
3
ML6161 DAMPER
ACTUATOR
CW COM CCW
DAMPER OPEN
DAMPER CLOSED
DISCHARGE
AIR TEMP
AO-2
AO-1
UI-2
UI-1
DI-1 UI-3
AO-1
COM
AO-2
AO-3
COM
UI-1
COM
UI-2
UI-3
COM
UI-4
UI-5
COM
UI-6
DI-1
DI-2
COM
DI-3
20V DC
DI-4
24 VAC
24VAC COM
DO-1
COM
DO-2
DO-3
DO-4
DO-5
COM
DO-6
COM
12345678 109 2345678 09
11 1111111 21
12345678 0
9
22 2222222 3312345678 0
9
333333334
DO-7
DO-8
COM
BAC–
BAC+
SHIELD
BACnet MS/TP+
BACnet MS/TP–
SHLD
EGND
SBUS1
SBUS2
2
1
3
EARTH GROUND WIRE LENGTH SHOULD BE HELD TO A MINIMUM. USE THE HEAVIEST GAUGE WIRE AVAILABLE, UP TO 14 AWG (2.O MM2) WITH
A MINIMUM OF 18 AWG (1.O MM2), FOR EARTH GROUND WIRE.
TO ASSURE PROPER ELECTRICAL CONTACT, WIRES MUST BE TWISTED TOGETHER BEFORE INSERTION INTO THE TERMINAL BLOCK.
CONTACTS MUST BE SUITABLE FOR DRY SWITCHING, 5V AT 10 mA. USE SEALED TYPE, GOLD FLASHED OR PIMPLED CONTACTS.
M31178A
4
DIP SWITCH S3
(TR23 AND
TR24 ONLY.)
ON
SW1 SW2 SW3
DIP SWITCH S2
ON
SW1 SW2
DIP SWITCH
S1
ON
SW1 SW2
DIP SWITCH S1 FOR HUMIDITY MODELS ONLY. SEE TR23 INSTALLATION INSTRUCTIONS, FORM NO. 62-0267, FOR CONFIGURATION DETAILS.
TR23-H ONLY
DO NOT
CHANGE THIS
SWITCH
POSITION.
10 8643
GND
SENSOR
LON +
LON -
SETPT
LED
OVERRIDE
HUM
24 VAC
9
24 VAC
24 VAC
COM
+
-
1
COM
2
5
711
12
1
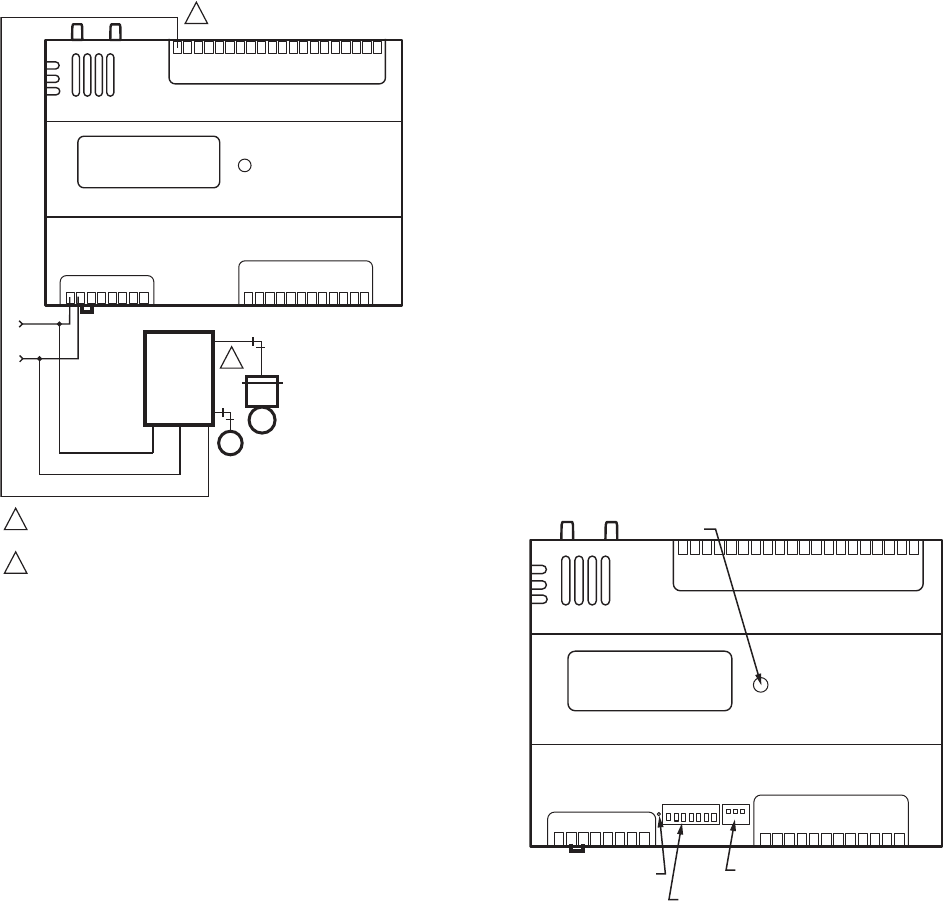
SPYDER® BACNET® PROGRAMMABLE CONTROLLERS
19 63-2689—05
Fig. 22. Controller wiring diagram (model PUB6438S
shown) for RP7517B pneumatic transducer.
CHECKOUT
Step 1. Check Installation and Wiring
Inspect all wiring connections at the controller terminals, and
verify compliance with installation wiring diagrams. If any wiring
changes are required, first be sure to remove power from the
controller before starting work. Pay particular attention to:
— 24 Vac power connections. Verify that multiple controllers
being powered by the same transformer are wired with the
transformer secondary connected to the same input
terminal numbers on each controller. Use a meter to
measure 24 Vac at the appropriate terminals (see Fig. 12
on page 9). Controller configurations are not necessarily
limited to three devices, but the total power draw, including
accessories, cannot exceed 100 VA when powered by the
same transformer (U.S. only).
— Be sure that each controller has terminal 3 wired to a
verified earth ground, using a wire run as short as possible
with the heaviest gauge wire available, up to 14 AWG (2.0
sq mm) with a minimum of 18 AWG (1.0 sq mm) for each
controller in the group (see Fig. 12 on page 9).
— Check that the MS/TP network polarity has been connected
properly on each controller. BACnet MS/TP is polarity
sensitive; communication will be lost for the entire segment
if one controller is connected improperly (see Fig. 13 on
page 11).
— Verify that Triac wiring of the digital outputs to external
devices uses the proper load power and 24 Vac common
terminal (digital output common terminals) for High-Side
switching.
NOTE: All wiring must comply with applicable electrical
codes and ordinances or as specified on installa-
tion wiring diagrams.
For guidelines for wiring run lengths and power budget, see
“Power” on page 6.
VERIFY END-OF-LINE TERMINATION RESISTOR
PLACEMENT
The installation wiring diagrams should indicate the locations
for placement of the end of line termination resistors. See
Fig. 13 on page 11.
Correct placement of the end-of-line termination resistors is
required for proper LONWORKS® Bus communications.
Step 2. Startup
Refer to Fig. 23 and the following text for startup information.
Fig. 23. LED, service, and network connection locations.
SET THE MS/TP MAC ADDRESS
The MS/TP MAC address DIP switches are used to set the
unit's MAC address. Each Spyder BACnet on an MS/TP
network must have a unique MAC address in the range of 0-
127 (address 0 should be avoided as it is the Honeywell factory
default MAC address for all MS/TP devices).
CONTROLLER STATUS LED:
The LED on the front of the controller provides a visual
indication of the status of the device. When the controller
receives power, the LED appears in one of the following
allowable states, as described in Table 8.
AO-1
COM
AO-2
AO-3
COM
UI-1
COM
UI-2
UI-3
COM
UI-4
UI-5
COM
UI-6
DI-1
DI-2
COM
DI-3
20V DC
DI-4
NET-2
NET-1
SHLD
EGND
24 VAC
24VAC COM
DO-1
COM
DO-2
DO-3
DO-4
DO-5
COM
DO-6
COM
12345678 109 2345678 09
11 1111111 21
12345678 0
9
22 2222222 3312345678 0
9
333333334
M29339B
24 VAC
AO1
24 VAC
COM
1
2
USE 1/4 IN (6 MM) PNEUMATIC TUBING. MINIMUM BRANCH LINE
MUST BE 6 FT. (1.8M) OR LONGER.
TERMINALS 21, 23, AND 24 ARE ANALOG OUTPUTS.
+
-
BLUE
BLACK
BROWN
PNEUMATIC
VALVE
ACTUATOR
RP7517B
1M
2B
M
2
1
DO-7
DO-8
COM
SBUS1
SBUS2
BACnet MS/TP MAC
ADDRESS DIP SWITCHES
TERMINALS 1-8 TERMINALS 9-20
TERMINALS 21-40
AO-1
COM
AO-2
AO-3
COM
UI-1
COM
UI-2
UI-3
COM
UI-4
UI-5
COM
UI-6
DI-1
DI-2
COM
DI-3
20V DC
DI-4
NET-2
NET-1
SHLD
EGND
24 VAC
24VAC COM
DO-1
COM
DO-2
DO-3
DO-4
DO-5
COM
DO-6
COM
1 2 3 4 5 6 7 8 1 0 9 2 3 4 5 6 7 8 0 9
1 1 1 1 1 1 1 1 1 2 1
1 2 3 4 5 6 7 8 0
9
2
2 2
2 2 2 2 2 2 3
3
1 2 3 4 5 6 7 8 0
9
3
3 3
3 3
3 3
3 4
M29340A
HOST
STATUS LED
DO-7
DO-8
COM
SBUS1
SBUS2
BACnet
STATUS LED
LOCAL BACnet MS/TP
MOLEX CONNECTOR PINS

SPYDER® BACNET® PROGRAMMABLE CONTROLLERS
63-2689—05 20
Table 8. Status LED States.
BACNET STATUS LED:
The LED on the front of the controller, between the BACnet
MS/TP terminals and MAC Address DIP Switches, provides a
visual indication of the BACnet MS/TP communication status.
When the controller receives power, the LED appears in one of
the following allowable states, as described in Table 9.
Table 9. BACnet Status LED States.
Step 3. Checkout Completion
At this point the controller is installed and powered. To
complete the checkout, the NIAGARA FRAMEWORK® application
(run on a PC) is used to configure the I/O and functions of the
controller. Refer to the Programming Tool User Guide, form no.
63-2662, for controller configuration and programming details.
CONTROLLER REPLACEMENT
There are no serviceable or repairable parts inside the
controller.
WARNING
Fire, Explosion, or Electrical Shock Hazard.
Can cause severe injury, death or property damage.
Do not attempt to modify the physical or electrical
characteristics of this device in any way. Replace the
controller if troubleshooting indicates a malfunction.
WARNING
Electrical Shock Hazard.
Can cause severe injury, death or property damage.
Disconnect power supply before beginning controller
replacement to prevent electrical shock or equipment
damage.
Terminal Block Removal
To simplify controller replacement, all terminal blocks are
designed to be removed with the wiring connections intact and
then re-installed on the new controller. See Fig. 24 and refer to
the following procedure:
IMPORTANT
To prevent bending or breaking the alignment pins on
longer terminal blocks, insert the screwdriver at
several points to evenly and gradually lift up the
terminal block.
Insert the screwdriver blade no more than 1/8 in.
(3 mm) to prevent damage to the terminal block align-
ment pins on the controller circuit board.
Fig. 24. Removing Terminal Blocks.
1. Use a thin-bladed screwdriver to evenly raise the
terminal block from its alignment pins:
a. For short terminal blocks (1 to 5 terminals), insert
screwdriver blade in the center of the terminal block
and use a back and forth twisting motion to gently
raise the terminal block from its alignment pins 1/4 in.
(6.35 mm).
b. For long terminal blocks (6 or more terminals), insert
screwdriver blade on one side of the terminal block
and gently rotate the blade 1/4 turn. Then, move to
the other side of the terminal block and do the same.
Repeat until the terminal block is evenly raised 1/4 in.
(6.35 mm) from its alignment pins.
LED State Blink Rate Status or Condition
OFF Not applicable No power to processor,
LED damaged, low
voltage to board, first
second of power up or
loader damaged.
ON ON steady;
not blinking
Processor not operating.
Application Program CRC
being checked. This takes
1-2 seconds and occurs
on each restart (power
up, reset and reflash, and
following configuration file
download).
Very Slow Blink
(continuous)
1 second ON,
1 second OFF
Controller is operating
normally.
Slow Blink
(continuous)
0.5 second ON,
0.5 second OFF
Controller alarm is active
or controller in process of
configuration file
download.
Medium Blink
(continuous)
0.3 second ON,
0.3 second OFF
Controller is in reflash
mode or awaiting/
receiving reflash data via
the BACnet network.
BACnet LED Status Status or Condition
Solid on Controller has power, loader is not
running.
Solid on, blinking off
once in 2.5 sec.
Controller is in reflash mode, no MS/
TP communication.
Solid on, blinking off
twice in 2.5 sec.
Controller is in reflash mode, MS/TP
communication present.
Solid on, blinking off
thrice in 2.5 sec
Controller is in reflash mode, MS/TP
communication data transfer in
progress.
Solid off, there is no
power
No power to processor, LED
damaged, low voltage to board, or
loader damaged.
Solid off, blinking on
once in 2.5 sec.
Controller is running, no MS/TP
communication.
Solid off, blinking on
twice in 2.5 sec.
Controller is running, MS/TP
communication present.
Solid off, blinking on
thrice in 2.5 sec
Controller is running, MS/TP
communication data transfer in
progress.
SHORT TERMINAL BLOCK LONGTERMINAL BLOCK M23563
SPYDER® BACNET® PROGRAMMABLE CONTROLLERS
21 63-2689—05
2. Once the terminal block is raised 1/4 in. (6.35 mm) from
its alignment pins, grasp the terminal block at its center
(for long terminal blocks grasp it at each end) and pull it
straight up.
Controller Replacement (PVB0000AS,
PVB4022AS and PVB6436AS)
For PVB0000AS, PVB4022AS and PVB6436AS controllers,
which are hard-wired to an actuator, perform the following
actions to replace the complete assembly (controller and
actuator):
1. Remove all power from the controller.
2. Remove the two air flow pickup connections from the
pressure sensor.
3. Remove the terminal blocks (See “Terminal Block
Removal” ).
4. Remove the old controller and actuator assembly from its
mounting.
• Loosen the two bolts on the actuator clamp to release
the actuator from the shaft.
• Remove the controller’s mounting screws.
• Gently pull the controller and actuator assembly
straight out, until the assembly is clear of the actuator
shaft.
5. Mount the new controller and actuator assembly (See
“Installation” on page 3.).
6. Reconnect the two air flow pickup tubes to the pressure
sensor (See “Piping (PVB0000AS, PVB4022AS,
PVB4024NS, PVB6436AS and PVB6438NS)” on
page 6.).
7. Replace the terminal blocks:
• Insert each terminal block onto its alignment pins.
• Press straight down to firmly seat it.
• Repeat for each terminal block.
8. Restore power to the controller.
9. Perform “Checkout” on page 19.
Controller Replacement (PVB4024NS
and PVB6438NS)
Perform the following to replace the PVB4024NS and
PVB6438NS controllers:
1. Remove all power from the controller.
2. Remove the two air flow pickup connections from the
pressure sensor.
3. Remove the terminal blocks.
• See “Terminal Block Removal” on page 20..
4. Remove the old controller from its mounting.
IMPORTANT
(FOR CONTROLLERS MOUNTED TO A DIN RAIL):
1. Push straight up from the bottom to release the top
pins.
2. Rotate the top of the controller outwards to release
the bottom flex connectors (see Fig. 8 on page 6).
5. Mount the new controller.
• See “Installation” on page 3.
6. Reconnect the two air flow pickup tubes to the pressure
sensor (See “Piping (PVB0000AS, PVB4022AS,
PVB4024NS, PVB6436AS and PVB6438NS)” on
page 6.).
7. Replace the terminal blocks:
• Insert each terminal block onto its alignment pins.
• Press straight down to firmly seat it.
• Repeat for each terminal block.
8. Restore power to the controller.
9. Perform “Checkout” on page 19.
Controller Replacement (PUB1012S,
PUB4024S, and PUB6438S)
Perform the following to replace the PUB1012S, PUB4024S
and PUB6438S controllers:
1. Remove all power from the controller.
2. Remove the terminal blocks (See “Terminal Block
Removal” on page 20.).
3. Remove the old controller from its mounting.
IMPORTANT
(FOR CONTROLLERS MOUNTED TO A DIN RAIL):
1. Push straight up from the bottom to release the top
pins.
2. Rotate the top of the controller outwards to release
the bottom flex connectors (see Fig. 8 on page 6).
4. Mount the new controller (See “Installation” on page 3.).
5. Replace the terminal blocks:
• Insert each terminal block onto its alignment pins.
• Press straight down to firmly seat it.
• Repeat for each terminal block.
6. Restore power to the controller.
7. Perform “Checkout” on page 19.
SPYDER® BACNET® PROGRAMMABLE CONTROLLERS
63-2689—05 22
SPYDER® BACNET® PROGRAMMABLE CONTROLLERS
23 63-2689—05

SPYDER® BACNET® PROGRAMMABLE CONTROLLERS
Automation and Control Solutions
Honeywell International Inc.
1985 Douglas Drive North
Golden Valley, MN 55422
customer.honeywell.com
® U.S. Registered Trademark
© 2012 Honeywell International Inc.
63-2689—05 M.S. Rev. 01-12
Printed in United States
BACnet® is a registered trademark of ASHRAE.
BTL® is a registered trademark of the BACnet International.
NIAGARA FRAMEWORK® and the Niagara framework logo are registered trademarks of Tridium, Inc.