Honeywell Tradeline R182J Users Manual 69 0791 R182J, R482J, R845A, R847A, RA89A, RA832A Switching Relays
RA832A to the manual 2f02a257-716d-42e2-94df-683b737d61f3
2015-01-23
: Honeywell Honeywell-Tradeline-R182J-Users-Manual-261952 honeywell-tradeline-r182j-users-manual-261952 honeywell pdf
Open the PDF directly: View PDF .
Page Count: 4

1 69-0791—3J.H. • Rev. 10-94 • ©Honeywell Inc. 1994 • Form Number 69-0791—3
R182J, R482J, R845A,
R847A, RA89A, RA832A
Switching Relays
Application
These relays can be used for a variety of switching applications. Typically they provide control of line- or low-voltage
devices by a low voltage controller. See Table 1.
TABLE 1—SWITCHING RELAY SPECIFICATIONS.
TRADELINE®
Voltage Switch Control
Coil
Voltage
(Vac at Relay Coil
Current
Contact
Ratings (A)
Models Application (50/60 Hz) Action Circuit 50/60 Hz) (A) AFL ALR
R182J For 24V thermostat 120 Dpdt 3-wire 24 0.40
a
7.4 44.4
control of line voltage
devices. 240 3.7 22.2
R482J Controlled by a line 120 2-wire 120 0.08 7.4 44.4
voltage controller 208/240 208/240 0.04 3.7 22.2
R845A For hot water zone control
systems or spst control of
two separate loads.
120 Dpst 24 0.40 7.4 44.4
R847A Provides switching for 120 22 100
high-current loads such as
cooling compressors. 240 10 50
RA89A For switching one line
voltage load. 120 Spst 10.2 61.2
RA832A For switching two line 120 Dpst 7.4 44.4
voltage loads with a
common power source. 240 3.7 22.2
a IMPORTANT: The transformer on the R182 can over-
heat when used with a series 20 thermostat if the
total resistance of the thermostat circuit exceeds
2.5 ohms. If the measured resistance of the thermo-
stat (including thermostat wire and thermostat con-
tact resistance) exceeds 2.5 ohms, add a 100 ohm,
10 watt resistor between the W and R terminals.
Table 2 gives maximum thermostat wire runs; if
longer runs are necessary, measure the resistance or
add a 100 ohm, 10 watt resistor across terminals W
and R.
TABLE 2—LENGTH OF WIRE.
AWG
Wire
Size
Total Wire
Length
Length of Run
to Thermostat
(Wires)
(Number) Feet Meters Feet Meters
22 120 38.0 60 18.0
20 200 61.0 100 30.5
18 300 91.5 150 45.5
16 500 152.5 250 76.0
14 800 244.0 400 122.0
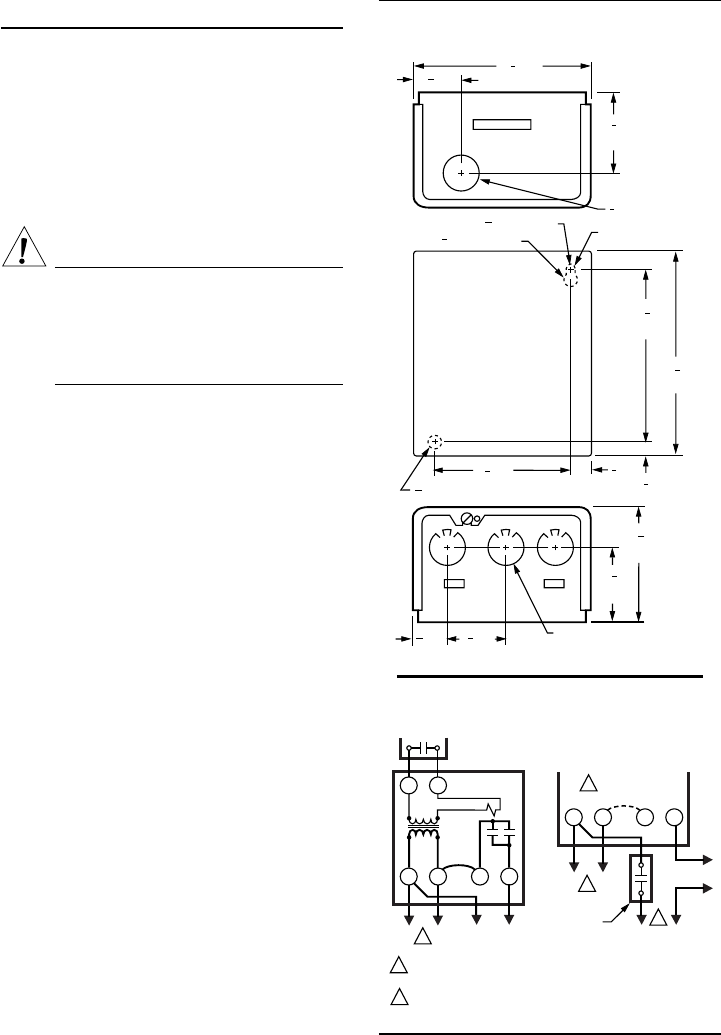
69-0791—32
Installation
WHEN INSTALLING THIS PRODUCT…
1. Read these instructions carefully. Failure to follow
instructions can damage product or cause a hazardous
condition.
2. Check the ratings given in the instructions and on the
product to make sure the product is suitable for your
application.
3. Make sure installer is a trained, experienced service
technician.
4. After completing installation, use these instructions
to check out product operation.
WARNING
ELECTROCUTION HAZARD CAN
CAUSE PROPERTY DAMAGE, SEVERE
INJURY, OR DEATH.
Transformer core not bonded.
Disconnect power supply before wiring to pre-
vent electrical shock or equipment damage.
MOUNTING
For replacement, mount the relay in the same location as
the old relay. If this is a new installation, locate the relay
vertically on a solid wall or partition as close as possible to
the device to be controlled. Select a location that is easily
accessible for installation and service.
NOTE: To reduce the possible transformer hum and relay
noise that is sometimes amplified by mounting surfaces
such as sheetmetal, plasterboard, and similar materials,
place rubber or felt washers between the case and the
mounting surface.
1. Position the relay and mark the mounting holes. See
Fig. 1.
2. Start a screw for the keyhole type mounting hole in
the upper right corner. Screw it down within about 1/8 in.
[3 mm] of the surface.
3. Hang the relay on the screw, position the case, and
start the bottom screw.
4. Tighten both screws.
WIRING
All wiring must comply with all applicable electrical
codes, ordinances, and regulations. Follow any instructions
furnished with the controlled equipment.
IMPORTANT: The switching relay terminals are ap-
proved for use with copper wires only.
See Figs. 2 through 9 for hookup diagrams for these
relays. When two or more devices are to be controlled in
parallel, the total current must not exceed the relay load
rating. Fig. 11 is an internal view of the RA832A showing
terminal locations and barriers.
Never connect load terminals to a load that takes more
current than the amount listed in the electrical ratings on the
relay.
Fig. 1—Approximate mounting dimensions in
in. [mm].
4
[114]
1
2
1
[48]
7
8
3
8[10]
3
8[10]
5
32
1 [29]
1
4
4 [108]
1
2
3 [89]
5
[133]
1
4
3
32 [2] DIAMETER
1
2[13] DIAMETER KEYHOLE TYPE
MOUNTING HOLE
7
8[22] DIAMETER
7
32 [6] DIAMETER MOUNTING HOLE
1
[48]
7
8
25
32 [20] KNOCKOUT FOR
1/2 (13) CONDUIT (3)
3
8
1 [35]
M3823
2
[75]
15
16
L1
HOT
L2
TT
21 34
1
1
TO LOAD
LOW VOLTAGE (CLASS 2)
2-WIRE THERMOSTAT
RA89A (SPST)
JUMPER
L1
HOT
L2
21 34
1TO LOAD
RA89A
JUMPER REMOVED
2
CONTROLLER
(IF USED) 1
POWER SUPPLY. PROVIDE OVERLOAD PROTECTION
AND DISCONNECT MEANS AS REQUIRED.
COMPLETE WIRING AS SHOWN ABOVE.
2
M3819
Fig. 2—Internal schematic and typical hookup
for RA89A.
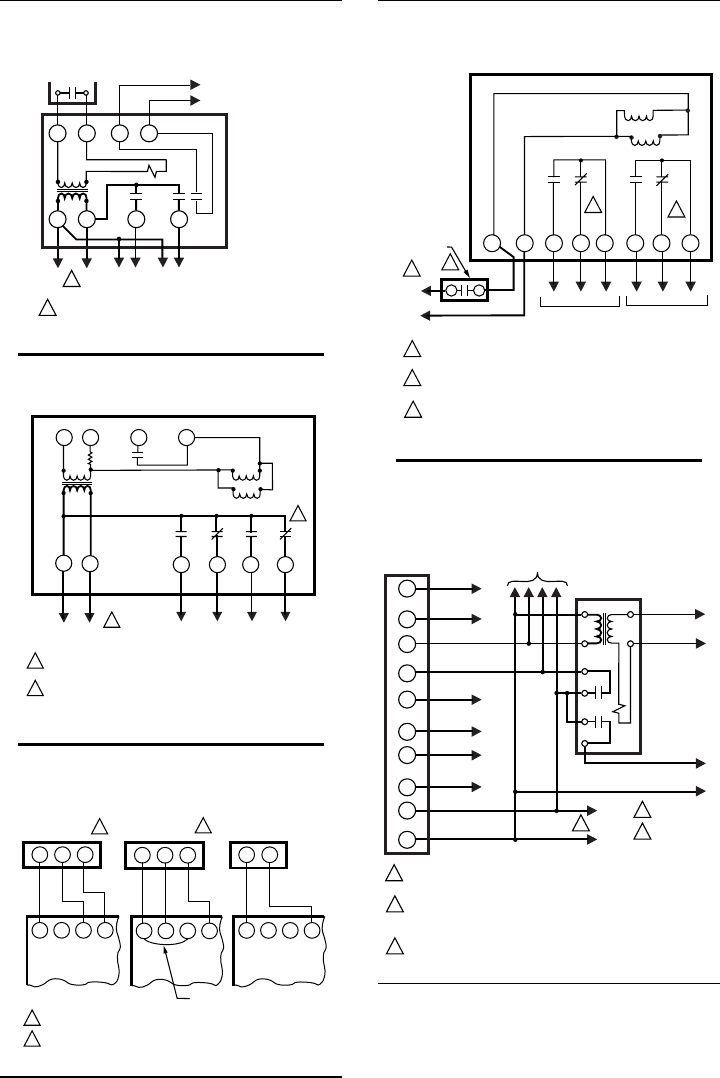
3 69-0791—3
Fig. 3—Internal schematic and typical hookup
for RA832A.
L1
HOT
L2
TT
21 34
1
1
LOAD 2
(OPTIONAL)
LOW VOLTAGE (CLASS 2)
2-WIRE THERMOSTAT
RA832A
POWER SUPPLY. PROVIDE OVERLOAD PROTECTION
AND DISCONNECT MEANS AS REQUIRED. M3821
LOAD 1
XX
AUXILIARY TO LOW
OR MILLIVOLTAGE
(POWERPILE) LOAD
Fig. 6—Internal schematics and typical hookup
for R482J.
12
3
3
3
1
2
R482J
N.O.
N.C. N.C.
537
6
N.O.
421 8
POWER SUPPLY. PROVIDE OVERLOAD PROTECTION
AND DISCONNECT MEANS AS REQUIRED.
CONTROLLER (IF USED) MUST BE SNAP ACTION OR
MERCURY SWITCH TYPE.
N.O. CONTACTS MAKE BEFORE N.C CONTACTS BREAK,
AND N.C. CONTACTS MAKE BEFORE N.O. CONTACTS BREAK.
M8234
CONTROLLER
L1
(HOT)
L2 TO LOAD TO LOAD
COM. COM.
Fig. 4—Internal schematic and typical hookup
for R182J.
Fig. 7—Schematic diagram showing R845A in
multizone, forced hydronic heating system.
This arrangement is suitable for any number of
additional zones.
L1
HOT
L2
2
1
3
4
1
1
RA845A RELAY
POWER SUPPLY. PROVIDE OVERLOAD PROTECTION
AND DISCONNECT MEANS AS REQUIRED.
IF CONTROLLING TWO LOADS, USE:
3 AND 4 FOR LINE VOLTAGE LOAD
5 AND 6 FOR LINE OR LOW VOLTAGE LOAD
IF USING LOW VOLTAGE, USE A SEPARATE TRANSFORMER.
M3822
T
T
THERMOSTAT
ZONE 1
ZC
ZP
B1
B2
C1
C2
1
2
BURNER
CIRC.
LINE
THERM.
BURNER
CONTROL
CIRCULATOR
ZONE 1
2
3
THERMOSTAT
ZONE 2
CIRCULATOR
ZONE 2
TO ADDITIONAL R845A
RELAYS FOR OTHER ZONES
HYDRONIC HEATING
CONTROL TERMINALS
2
3
5
6
L1
(HOT) L2 1
2
1
2
N.O. N.C. N.O. N.C.
WX RB
L1 L2 437 6
R182J
K1
K1
K1
K2
K2
POWER SUPPLY. PROVIDE OVERLOAD PROTECTION AND
DISCONNECT MEANS AS REQUIRED.
N.O. CONTACTS MAKE BEFORE N.C CONTACTS BREAK,
AND N.C. CONTACTS MAKE BEFORE N.O. CONTACTS BREAK.
M8232
LOAD LOAD
3
OHMS
Fig. 5—Thermostat connections for R182J.
W
W
R
R
BWRB
BX
R182J
WRBX
R182J
WRBX
R182J
THREE-WIRE
LOW VOLTAGE
(SERIES 10)
THERMOSTAT
THREE-WIRE
LOW VOLTAGE
(SERIES 20)
THERMOSTAT
TWO-WIRE
LOW VOLTAGE
(SERIES 80)
THERMOSTAT
12
1
2
MAKES CONTACT ON TEMPERATURE FALL ONLY.
MAKES CONTACT ON BOTH A TEMPERATURE RISE AND FALL.
M8233A
JUMPER
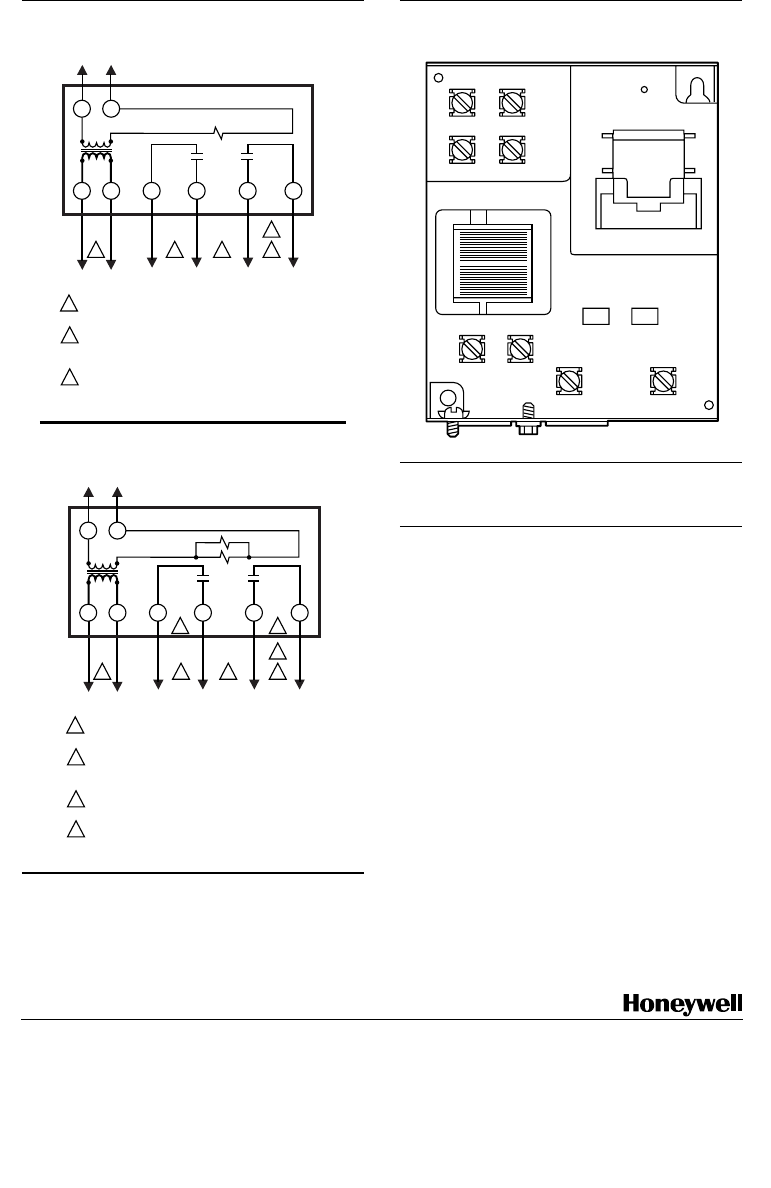
69-0791—34
QUALITY IS KEY
Home and Building Control Home and Building Control Helping You Control Your World
Honeywell Inc. Honeywell Limited—Honeywell Limitée
1985 Douglas Drive North 740 Ellesmere Road
Golden Valley, MN 55422 Scarborough, Ontario
M1P 2V9
Printed in U.S.A.
Fig. 8—R845A hookup for controlling two loads.
L1
HOTL2
TT
21 34
1
1
TO
POWER
LOW VOLTAGE (CLASS 2)
2-WIRE THERMOSTAT
R845A
POWER SUPPLY. PROVIDE OVERLOAD PROTECTION
AND DISCONNECT MEANS AS REQUIRED.
WHEN CONTROLLING TWO LOADS, USE 3 AND 4
FOR LINE VOLTAGE LOAD AND 5 AND 6 FOR LINE
OR LOW VOLTAGE LOAD.
IF USING LOW VOLTAGE, USE A SEPARATE
TRANSFORMER.
2
M3820
65
LOAD 1
TO
POWER LOAD 2
1 1
2
3
3
Fig. 9—Internal schematics and hookup for
R847A.
Fig. 10—Internal view of RA832A Switching
Relay.
M3824
24V TRANSFORMER
RELAY
12
34
T
T
X
X
L1
(HOT)
L2
TT
L2 L1 34
1
1
TO
POWER
LOW VOLTAGE (CLASS 2)
2-WIRE THERMOSTAT
R847A
POWER SUPPLY. PROVIDE OVERLOAD PROTECTION
AND DISCONNECT MEANS AS REQUIRED.
WHEN CONTROLLING TWO LOADS, USE 3 AND 4
FOR LINE VOLTAGE LOAD AND 5 AND 6 FOR LINE
OR LOW VOLTAGE LOAD.
IF USING LOW VOLTAGE, USE A SEPARATE
TRANSFORMER.
10 AMP CONTACT RATING OR 20 AMP WHEN POLES
ARE CONNECTED IN PARALLEL.
2
M8231B
67
LOAD 1
TO
POWER LOAD 2
1 1
2
3
44
3
4
Service and Checkout
1. Never use oil on any part of the relay coil or contacts.
2. Keep the cover on the relay during normal operation
and remove only for service and checkout.
3. Relay contacts require no cleaning; they are arranged
so they close with a wiping action and are self-cleaning.
The contacts may turn black after being in service for some
time; this discoloration does not prevent proper operation.
4. After installation is complete, operate system through
at least one cycle from the controller to make certain the
relay controls the equipment as intended.