Image Sensing Systems RTMS-X3 RTMS X3 User Manual USERS MANUAL
Image Sensing Systems, Inc. RTMS X3 USERS MANUAL
USERS MANUAL
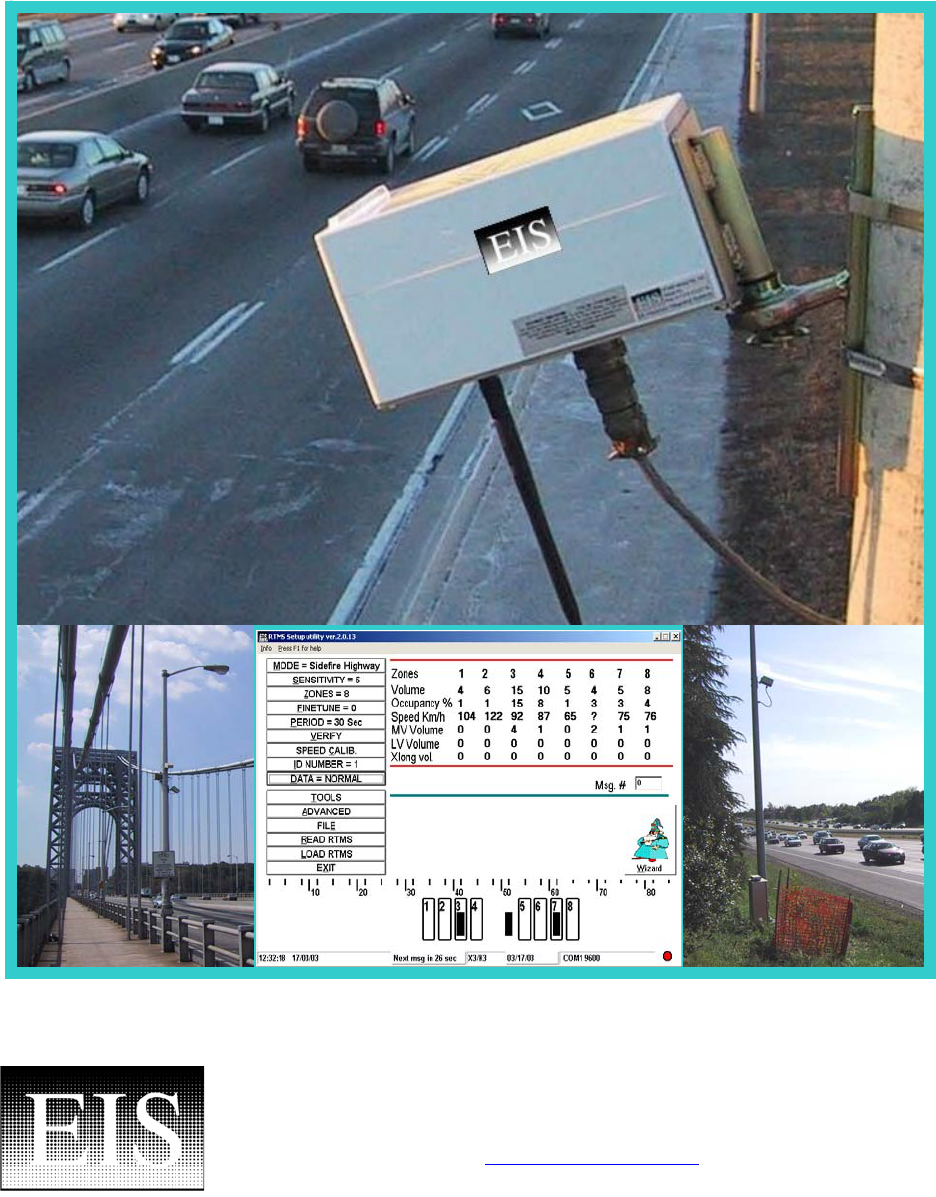
RTMS User Manual
TM
EIS Electronic Integrated Systems Inc.
150 Bridgeland Avenue, Toronto, Ontario, Canada M6A 1Z5
Tel. (416) 785-9248
www.rtms-by-eis.com
Issue 3.2.1
©
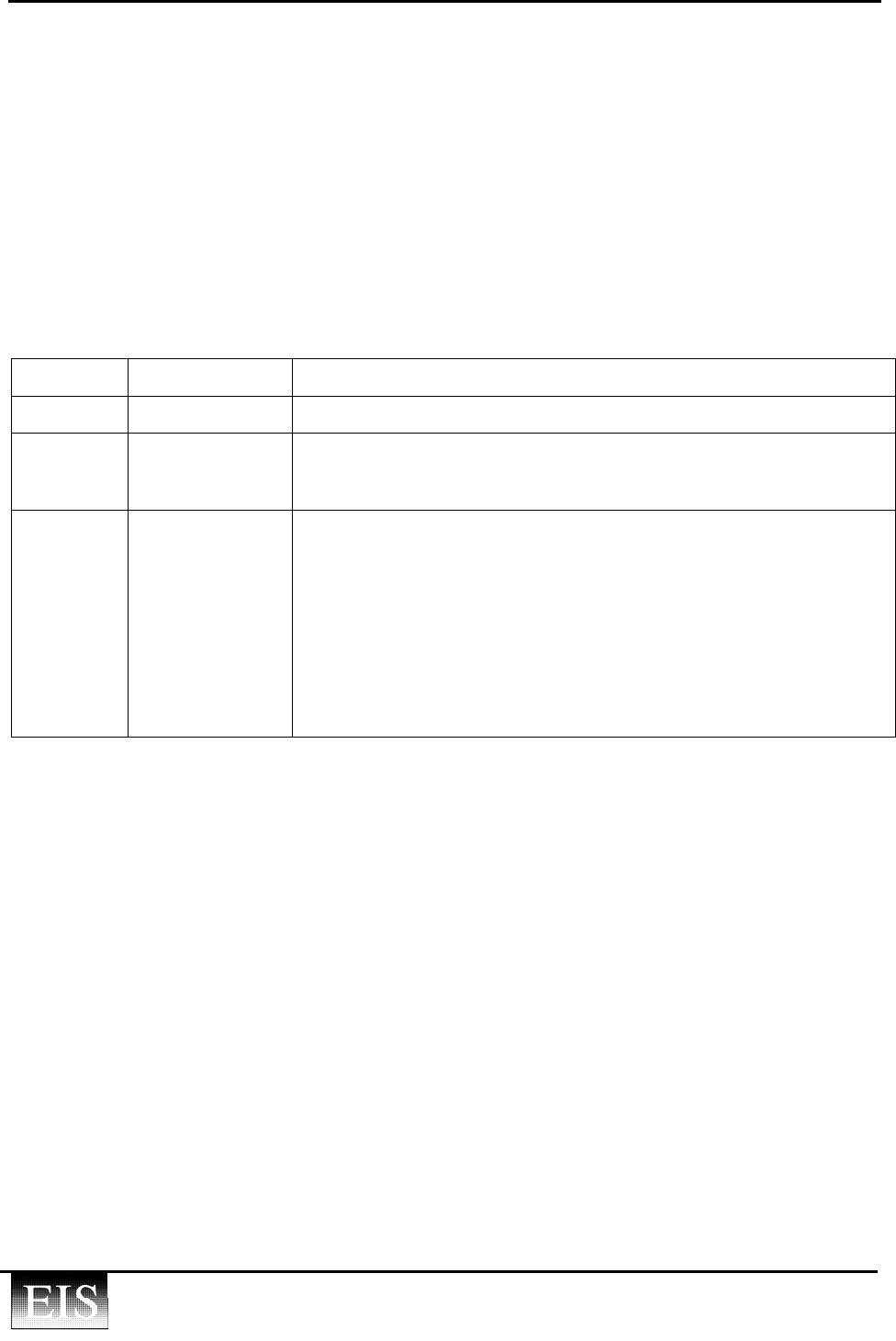
RTMS User Manual Issue 3.2 i
EIS Electronic Integrated Systems Inc.
Scope of the Document
This issue of the RTMS User Manual is limited in scope to installation, setup and troubleshooting
of the RTMS sensor. Deeper and detailed information on its operation, applications and
installation design can be found in the ITS Designers Guide to EIS products.
• The setup procedures rely on the new RTMS Setup Utility program, running under MS
Windows. They apply to Models X2/K2 and the newer Models X3/K3.
• Features specific to Model X3/K3 are identified.
Revision History
Issue No. Issue date Reason for issue
Issue 3.0 September 2002 Revised as described in Purpose of the Document
Issue 3.1 March 2003 • Adds details of RTMS F/W Rev 6.1 features
• Adds Appendix 1 – Miscellaneous Cabling Requirements
Issue 3.2 April, 2004 • Add information on RTMS options
• Add Wizard setup feature of the RTMS Setup Utility Ver. 3.0
• Show reduced set-back requirements for Model X3
• Revise cabling details of RS-485 option
• Add details for TCP/IP interface option
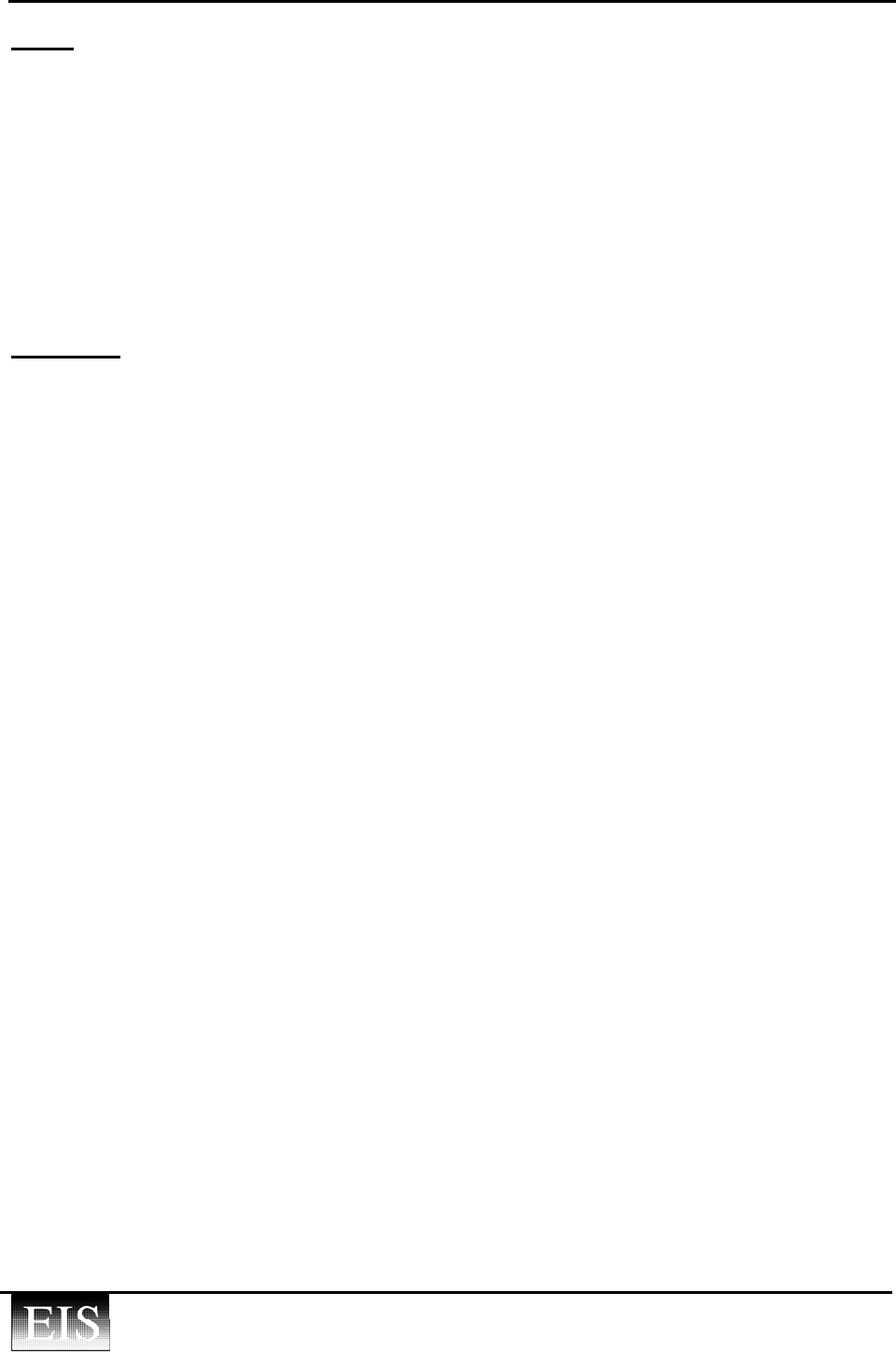
RTMS User Manual Issue 3.2 ii
EIS Electronic Integrated Systems Inc.
NOTE
This equipment has been tested and found to comply with the limits for a Class A
digital device, pursuant to Part 15 of the FCC Rules. These limits are designed to
provide reasonable protection against harmful interference when the equipment is
operated in a commercial environment. This equipment generates, uses, and can
radiate radio frequency energy and, if not installed and used in accordance with
the instruction manual, may cause harmful interference to radio communications.
Operation of this equipment in a residential area is likely to cause harmful
interference in which case the user will be required to correct the interference at
his own expense.
WARNING
Changes or Modifications not expressly approved by EIS Electronic Integrated
Systems Inc. could void the user's authority to operate the equipment.
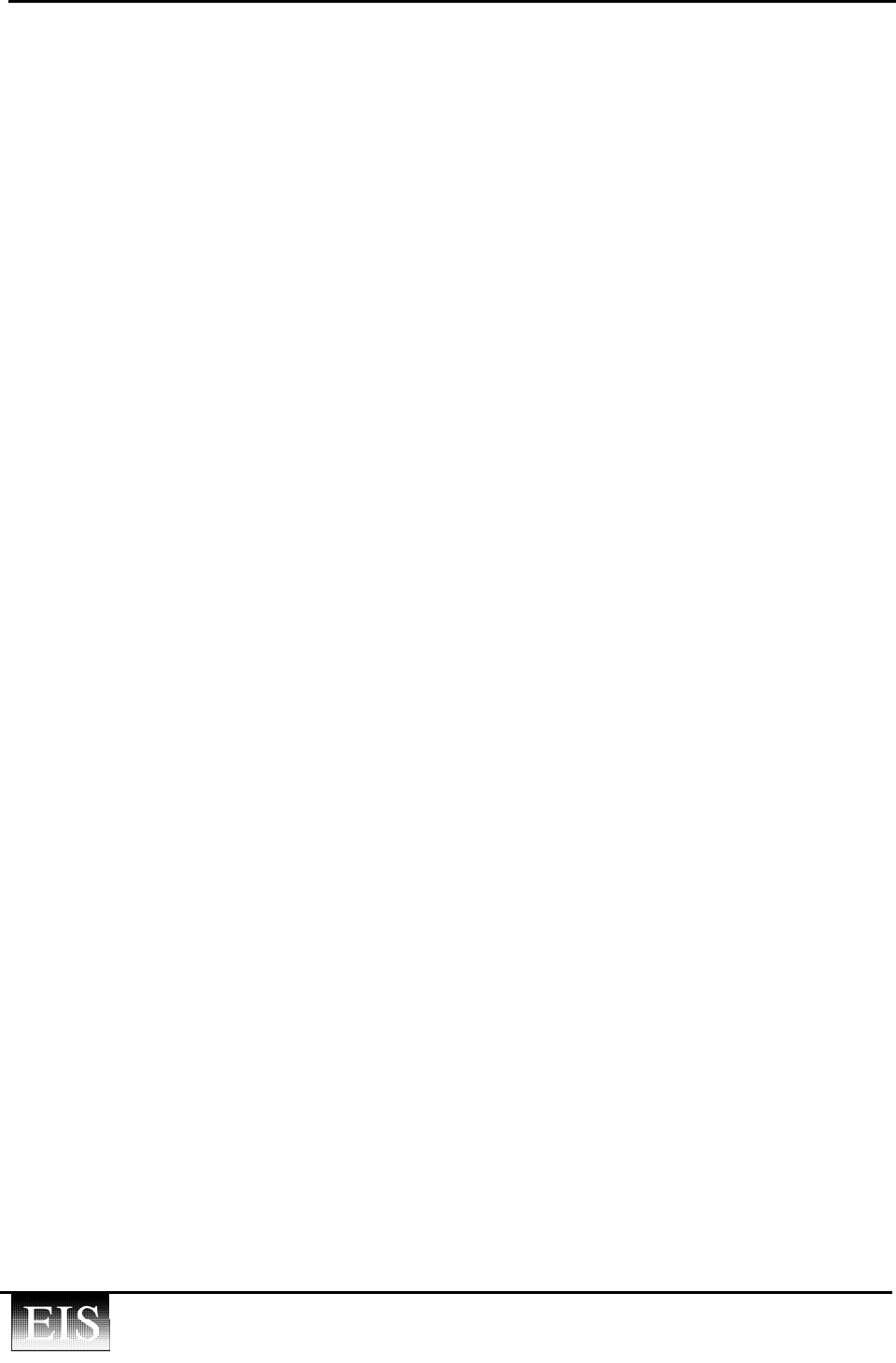
RTMS User Manual Issue 3.2 iii
EIS Electronic Integrated Systems Inc.
Table of Content
1 OPERATION OF RTMS ..................................................................................................................................1
VEHICLE DETECTION .................................................................................................................................................2
OUTPUTS ...................................................................................................................................................................2
2 RTMS OPTIONS ...............................................................................................................................................3
POWER OPTIONS ........................................................................................................................................................3
DATA COMMUNICATION OPTIONS .............................................................................................................................3
3 RTMS INSTALLATION...................................................................................................................................3
INCOMING INSPECTION ..............................................................................................................................................3
INSTALLATION STEPS .................................................................................................................................................3
RTMS MOUNTING AND AIMING................................................................................................................................5
Sidefired Configuration........................................................................................................................................5
Set-back and Mounting Height ......................................................................................................................................... 5
Initial Aiming Instruction.................................................................................................................................................. 6
Pointing RTMS away from heavy structures .................................................................................................................... 6
Sidefired mounting in Intersection Stop Bar Detection..................................................................................................... 7
Forward-looking configuration ............................................................................................................................8
Offset of RTMS in Forward-looking configuration .......................................................................................................... 8
4 SETUP OF THE RTMS ....................................................................................................................................9
THE PC REQUIREMENTS ............................................................................................................................................9
THE RTMS SETUP UTILITY (WINRTMS) ...................................................................................................................9
Installation............................................................................................................................................................9
Direct and Multi-drop Communication Modes....................................................................................................9
GETTING STARTED ..................................................................................................................................................10
WinRtms Setup Utility Screen ...........................................................................................................................11
SETUP SEQUENCE ....................................................................................................................................................12
Automated Wizard setup....................................................................................................................................13
Aiming Verification and Manual Sensitivity setting..........................................................................................13
RTMS Operating Modes....................................................................................................................................14
ZONE SETUP – SIDEFIRED MODES ...........................................................................................................................15
Automatic Zone Setup .......................................................................................................................................15
Manual Zone Setup ............................................................................................................................................15
Fine Tune ...........................................................................................................................................................16
Fine Tune Setup .................................................................................................................................................18
ZONE SETUP – FORWARD-LOOKING MODE .............................................................................................................18
Manual Zone Setup – Forward-looking Mode ...................................................................................................18
ADVANCED PARAMETERS........................................................................................................................................19
ADDITIONAL FORWARD-LOOKING PARAMETERS ....................................................................................................21
Height and Offset...............................................................................................................................................21
Alarm Speed Limit.............................................................................................................................................21
Speed bins ..........................................................................................................................................................21
COUNT VERIFICATION .............................................................................................................................................22
SPEED CALIBRATION ...............................................................................................................................................23
Sidefired Speed Calibration ...............................................................................................................................23
Sidefired Automatic Speed Calibration........................................................................................................................... 23
Sidefired Manual Speed Calibration ............................................................................................................................... 24
Forward-Looking Speed calibration...................................................................................................................24
Per Vehicle Speed........................................................................................................................................................... 24
DATA MODE ............................................................................................................................................................25
CUSTOMIZATION OF TRAFFIC DATA (RTMS X3/K3 REV 6.1 AND UP).....................................................................26
THE TRAFFIC STATISTICS DISPLAY AREA................................................................................................................26
Sidefired Data Definitions..................................................................................................................................27
Forward-looking Data Definitions .....................................................................................................................28
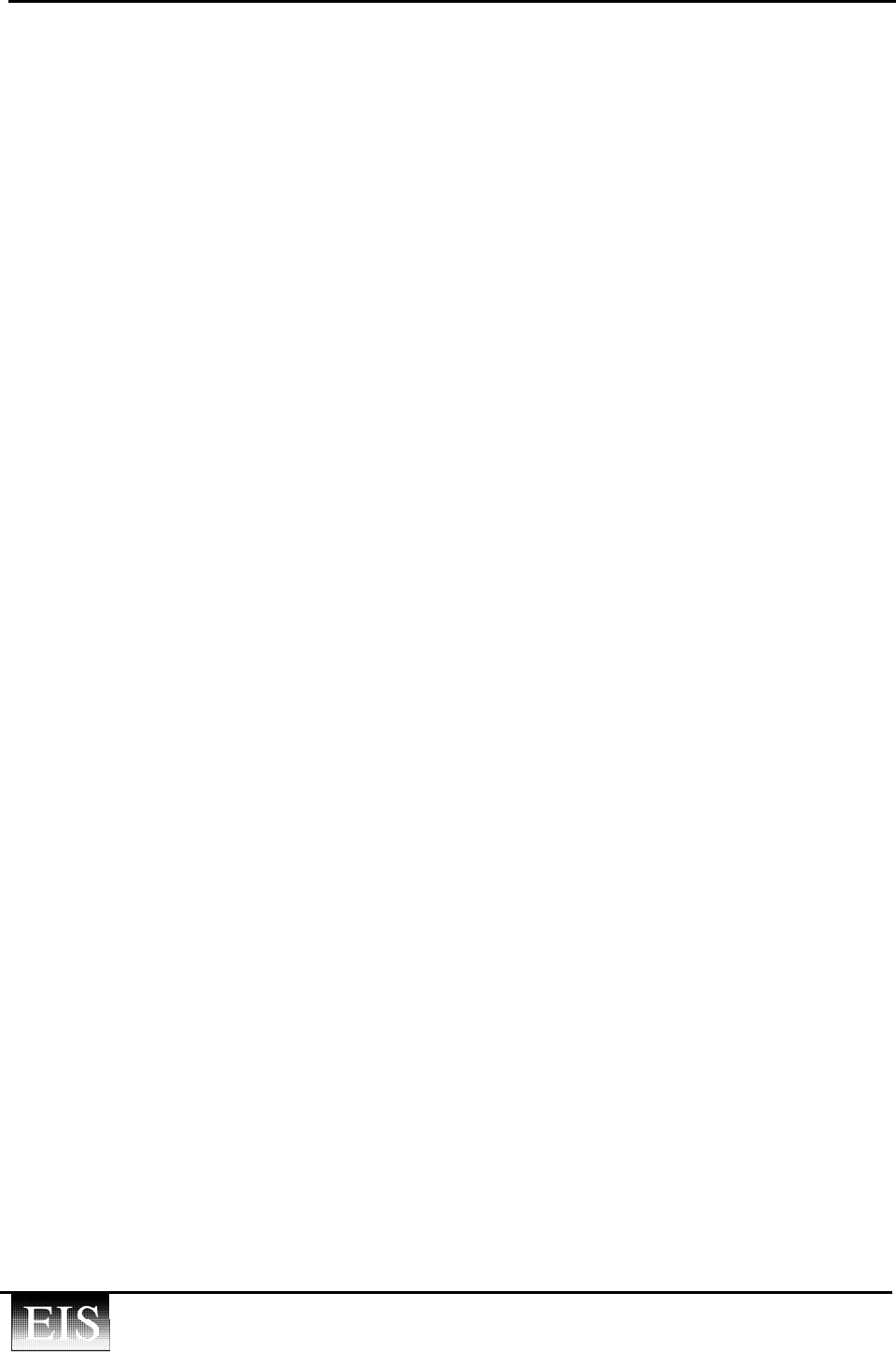
RTMS User Manual Issue 3.2 iv
EIS Electronic Integrated Systems Inc.
5 NON-SETUP FUNCTIONS OF THE RTMS SETUP UTILITY ................................................................29
SETTING THE RTMS SETUP UTILITY COMMUNICATION MODE ...............................................................................29
SETTING THE PC COMMUNICATION.........................................................................................................................29
Setup of Integral Digital Spread Spectrum Modem ...........................................................................................30
COMMUNICATING WITH MULTIPLE RTMS UNITS IN MULTI-DROP MODE................................................................30
ACCESSING A SPECIFIC SENSOR IN MULTI-DROP MODE...........................................................................................30
SAVING AND RETRIEVING SETUP FILES....................................................................................................................31
DATA RECORDING ...................................................................................................................................................31
SELF-TEST DIAGNOSTIC...........................................................................................................................................32
SUPPORT FOR OTHER LANGUAGES ..........................................................................................................................32
6 CABLES ........................................................................................................................................................33
THE RTMS CABLE...................................................................................................................................................33
RTMS MS Connector pin out ............................................................................................................................34
Power Cabling notes ..........................................................................................................................................34
RTMS SERIAL COMMUNICATIONS AND CABLING ...................................................................................................35
Standards and Nomenclature........................................................................................................................................... 35
RTMS Serial Port Wiring...................................................................................................................................36
RS-232 Port wiring ......................................................................................................................................................... 36
RS-232 Port wiring – for RTMS with DSS Option......................................................................................................... 36
RS-485 Serial Port Wiring ( Models X3/K3 only)......................................................................................................... 37
TCP/IP (Ethernet) Port Wiring..........................................................................................................................37
Modem cabling ..................................................................................................................................................38
7 SERVICE AND WARRANTY .......................................................................................................................39
SERVICE INFORMATION ...........................................................................................................................................39
EIS WARRANTY ......................................................................................................................................................39
8 TECHNICAL SPECIFICATIONS.................................................................................................................40
MICROWAVE SIGNAL AND COVERAGE AREA ...........................................................................................................40
MEASUREMENTS, THEIR ACCURACIES AND RANGES ...............................................................................................40
MECHANICAL ..........................................................................................................................................................40
INTERFACES.............................................................................................................................................................40
Contacts..............................................................................................................................................................40
Data Ports...........................................................................................................................................................41
POWER REQUIREMENTS AND CONSUMPTION ............................................................................................................41
SURGE IMMUNITY ....................................................................................................................................................41
ENVIRONMENTAL CONDITIONS ...............................................................................................................................41
ELECTROMAGNETIC INTERFERENCE ........................................................................................................................41
RELIABILITY ............................................................................................................................................................41
ACCURACY PERFORMANCE CONDITIONS!...............................................................................................................42
9 RTMS TROUBLESHOOTING GUIDE........................................................................................................43
APPENDIX 1 WIRING CONFIGURATIONS FOR MULTIPLE RTMS.......................................................45
MODEM SHARING ....................................................................................................................................................45
MODEM-SHARING CABLE CONSTRUCTION..............................................................................................................45
MULTI-DROP WIRING ..............................................................................................................................................46
APPENDIX 2 SETTING RTMS IP ADDRESS..................................................................................................47
PROGRAMMING AN IP ADDRESS ..............................................................................................................................47
RECOVERY PROCEDURES.........................................................................................................................................48
Recovery of MAC address.................................................................................................................................48
Recovery of IP address (MAC address known) .................................................................................................48
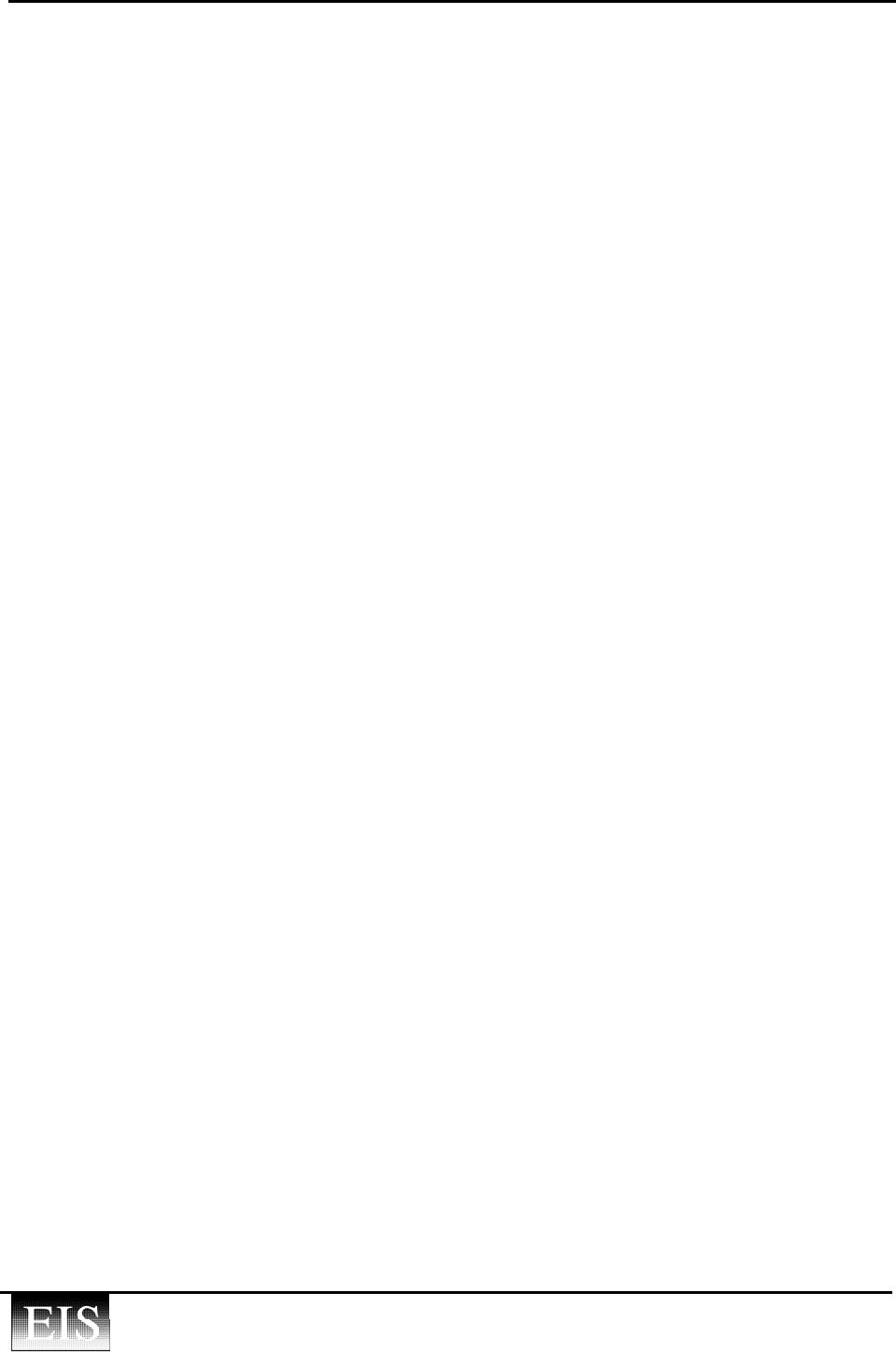
RTMS User Manual Issue 3.2 v
EIS Electronic Integrated Systems Inc.
APPENDIX 3 INTERNAL DSS MODEM SETUP ............................................................................................49
APPENDIX 4 RECOMMENDED RTMS SETUP SHEETS...............................................................................1
RTMS SET UP SHEET – HIGHWAY - COMPLETED SAMPLE ................................................................................1
RTMS SET UP SHEET – INTERSECTION - COMPLETED SAMPLE ......................................................................2
INDEX ..........................................................................................................................................................1
Table of Figures
FIG 1 RTMS MICROWAVE BEAM AND ITS FOOTPRINT......................................................................... 1
FIG 2. RTMS MOUNTING CONFIGURATIONS .............................................................................................1
FIG 3 REFLECTED SIGNALS WITHIN THE RTMS BEAM ........................................................................ 2
FIG 4. INSTALLATION OF RTMS BRACKET ............................................................................................... 3
FIG 5. SET-BACK AND HEIGHT REQUIREMENTS...................................................................................... 5
FIG 6. AIMING TO THE FIRST 1/3 OF THE MONITORED LANES ........................................................... 6
FIG 7. SIDEFIRED MOUNTING ON HEAVY STRUCTURES....................................................................... 6
FIG 8. MOUNTING RTMS AT INTERSECTIONS...........................................................................................7
FIG 9. MOUNTING ON OVERHEAD STRUCTURE IN FORWARD-LOOKING CONFIGURATION. .. 8
FIG 10. CORRECT AND INCORRECT AIMING IN FORWARD-LOOKING CONFIGURATION ........... 8
FIG 11. OFFSET FORWARD-LOOKING RTMS MOUNTING........................................................................ 8
FIG 12. RTMS SETUP UTILITY COMMUNICATING WITH THE SENSOR ............................................. 11
FIG 13. ZONE ICONS AND TARGET BLIPS ................................................................................................... 16
FIG 14. THE EFFECT OF FINE TUNE CONTROL ON VEHICLE BLIPS .................................................. 17
FIG 15. CUSTOMIZATION OF TRAFFIC DATA ............................................................................................ 26
FIG 16. SIDE-FIRED MODE SETUP AND TRAFFIC DATA (F/W REV 6.1) ............................................... 27
FIG 16. SIDEFIRED STATISTICAL TRAFFIC DATA.................................................................................... 27
FIG 17. FORWARD-LOOKING MODE TRAFFIC DATA .............................................................................. 28
FIG 18. SAMPLE RECORDED FILE FORMAT............................................................................................... 32
FIG 19. MS CONNECTOR VIEWS ..................................................................................................................... 34
FIG 20. PIN NUMBERING OF D-TYPE CONNECTORS................................................................................ 35
FIG 21. RTMS RS-232 PORT WIRING .............................................................................................................. 36
FIG 22. RTMS RS-485 PORT WIRING .............................................................................................................. 37
FIG 23. RTMS ETHERNET PORT WIRING..................................................................................................... 37
FIG 24. RTMS TO MODEM CABLES................................................................................................................ 38
FIG 25 MODEM SHARING Y-CABLES ........................................................................................................... 45
FIG 26. MULTI-DROP WIRING CONFIGURATION...................................................................................... 46
FIG 27. RS-485 PORT MULTI-DROP WIRING................................................................................................ 46
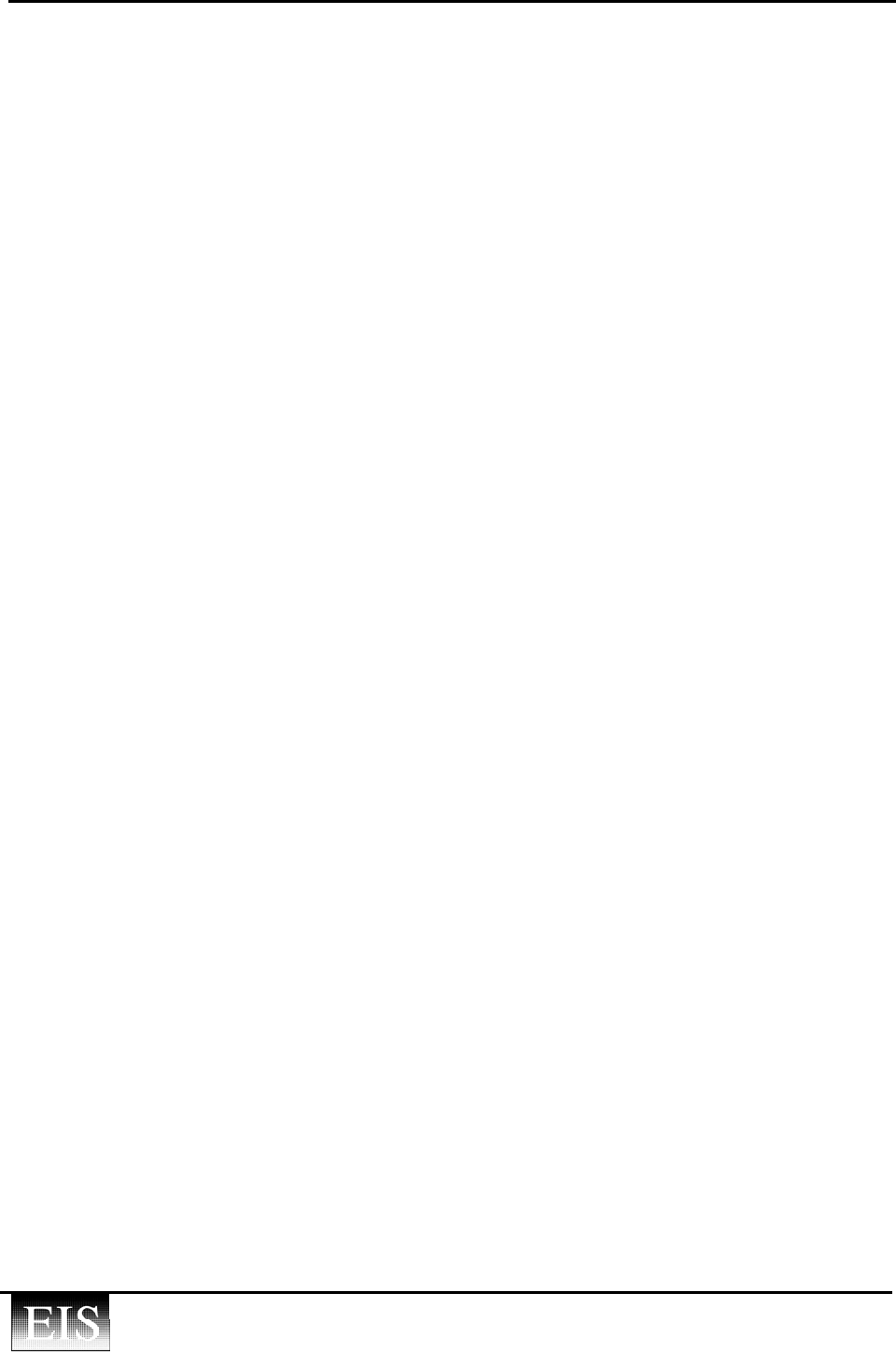
RTMS User Manual Issue 3.2 vi
EIS Electronic Integrated Systems Inc.
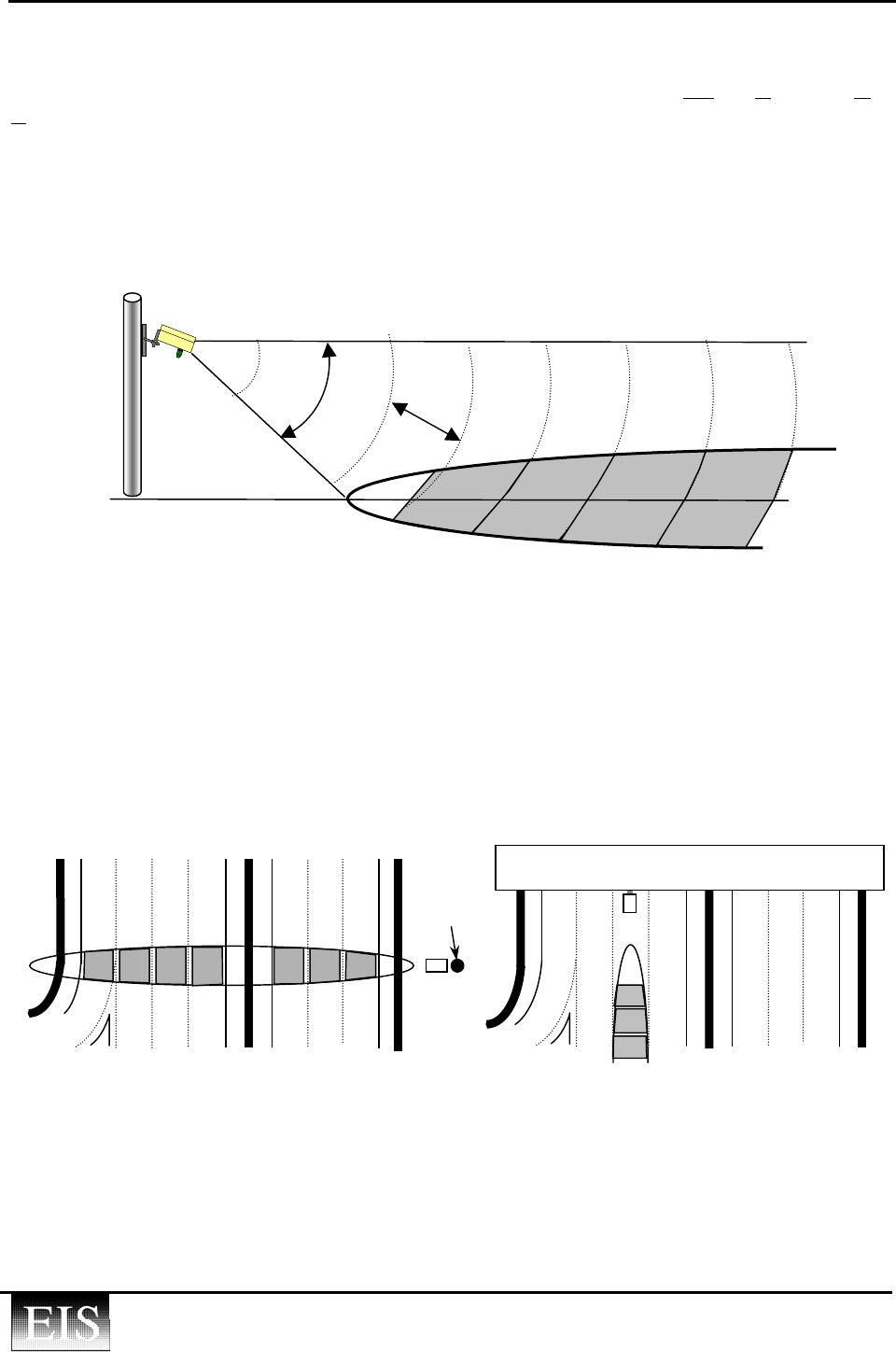
RTMS User Manual Issue 3.2 1
EIS Electronic Integrated Systems Inc.
1 OPERATION OF RTMS
The RTMS (Remote Traffic Microwave Sensor) is a true RADAR (RAdio Detection And
Ranging) device, specially designed for traffic sensing applications. It measures the distance to
objects in the path of its microwave beam. The ranging capability allows the RTMS to detect
stationary and moving vehicles in multiple detection zones.
The RTMS microwave beam is approximately 40° high and 15° wide. Its range of 60m (200 feet)
is divided into 32 range-slices, each 2m (7ft.) wide. When pointed onto a roadway, it projects an
oval footprint, in which detection zones can be defined using the range slices.
Fig 1. RTMS microwave beam and its footprint
The RTMS has two mounting configurations and several operating modes.
SIDEFIRED configuration, mounted on a roadside pole, aimed perpendicular to the traffic lanes.
Range-slices corresponding to the location of traffic lanes are defined as detection zones as part of
the setup process. A maximum of 8 detection zones can be defined. Each detection zone may
consist of one or more range slices. Its length is determined by the width of the beam’s footprint.
FORWARD-LOOKING configuration, RTMS is mounted on an overhead structure aimed
parallel to the lane. In this configuration the sensor cannot discriminate between lanes and the
aiming angle must be carefully adjusted to confine the footprint to a single lane.
Fig 2. RTMS Mounting Configurations
Sidefired Configuration Forward-Looking Configuration
Pole
Overhead structure
40° Range slice
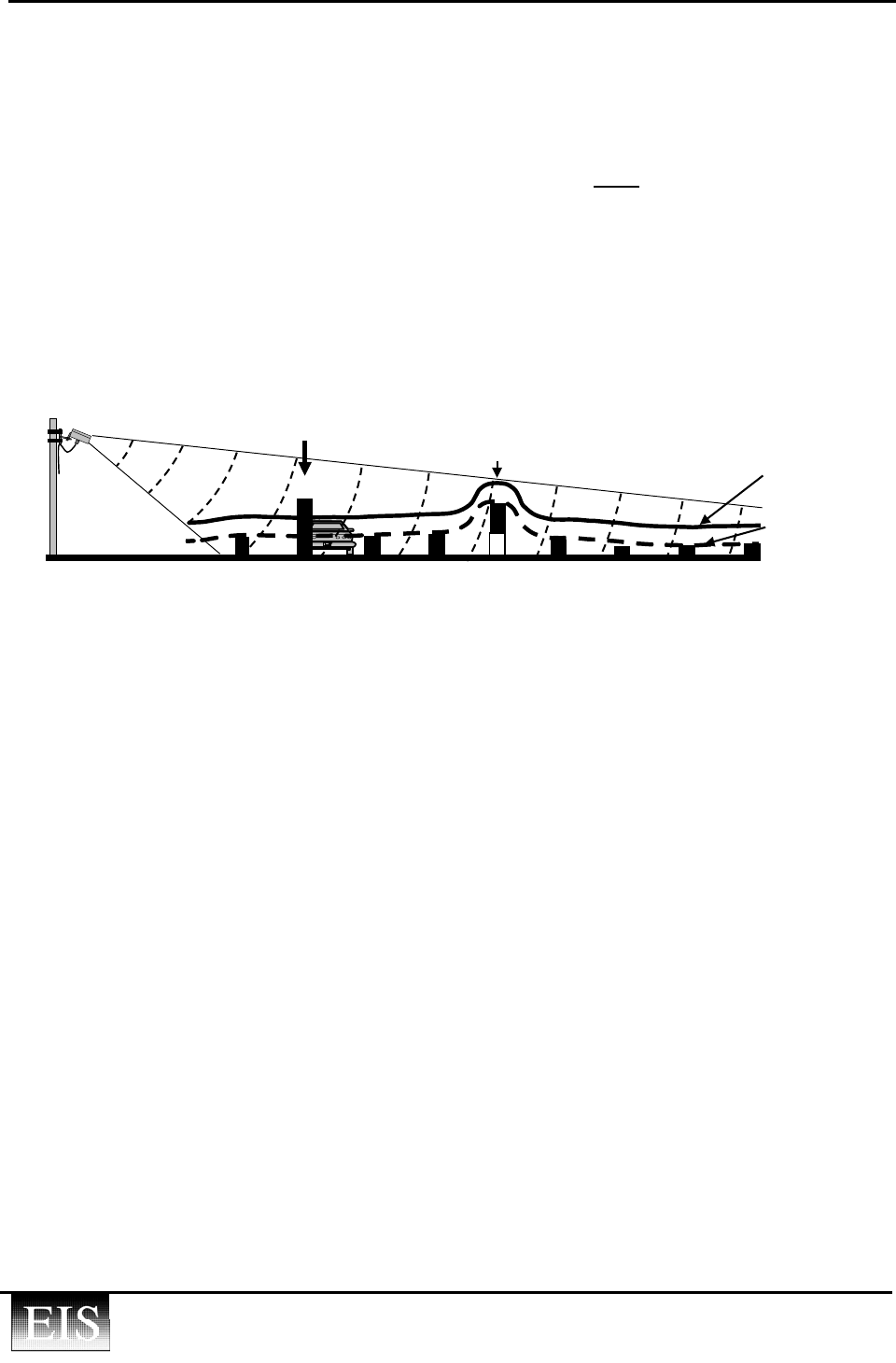
RTMS User Manual Issue 3.2 2
EIS Electronic Integrated Systems Inc.
Vehicle Detection
Use of long-wave microwave and ranging, enables accuracy in severe weather, strong vibrations
and detection of vehicles completely occluded by other vehicles. Mounting can be relatively low.
The RTMS receives reflected signals from all surfaces within its beam - pavement, barriers,
vehicles and trees. It maintains a background signal level from fixed objects in each range slice.
Vehicles are detected when their reflected signal exceeds the background level in their range slice
by a certain threshold level. If that range slice is part of a defined detection zone, its contact is
closed during the detection time to indicate detection and internal counters are incremented.
The background level “capture” requires 30 seconds to fully settle during setup. It is continually
adjusted during normal operation. As an example, signals from a stalled vehicle will be
incorporated into the background after about 30 minutes and detection will cease (zone contact
will open). However, when the vehicle is removed, the background level falls rapidly to the
original level, resuming detection at full sensitivity within seconds.
Fig 3. Reflected signals within the RTMS beam
The strongest signals are reflected from vertical surfaces of vehicles. Horizontal surfaces (e.g.
roofs) tend to scatter the microwaves away from the sensor, reflecting weaker signal.
Signal levels from vehicles vary depending on the shape of the vehicle and can dip below the
detection threshold during brief intervals called nulls. To prevent multiple counting due to nulls,
the RTMS signal processing includes an Extension Delay Time (EDT) to bridge the nulls and
hold the presence indication. The RTMS system corrects for the effects of EDT to obtain the
correct Occupancy measurement. RTMS X3/K3 Rev 6.1 and up can emulate a 6 ft loop.
The Threshold level and EDT are two of several parameters, set to default values when the Mode
of Operation is selected. These parameters optimize the operation for the selected application.
Outputs
The detection of a vehicle in any zone is registered in two independently operating outputs:
• Zone Contacts: 8 contact pairs corresponding to the detection zones are closed for as long as
detection persists. They can be connected to Traffic Controllers to indicate presence (in
intersection applications) or to Counters for traffic measurement. An external Interface Card can
add Fail-Safe operation, EDT correction and Dual-loop speed trap emulation.
• Data Port: Detection status in each range slice is transmitted via “target” messages sent 10
times per second. RTMS internal firmware uses vehicle detection to accumulate Volume,
Occupancy, Average Speed and Classification by length over a user-defined Period. At the end of
the period the accumulated data, containing measurements for all zones, is transmitted.
• Data Port Options: Besides RS-232, RS-485 and TCP/IP Ethernet interface options, Model
X3/K3 units support an optional internal DSS wireless modem, which can transmit either statistic
measurements or contact closure information directly from the unit.
Background
Signal
Threshold
(blanket)
Barrier
Each vertical bar represents a separate range slice
Detection
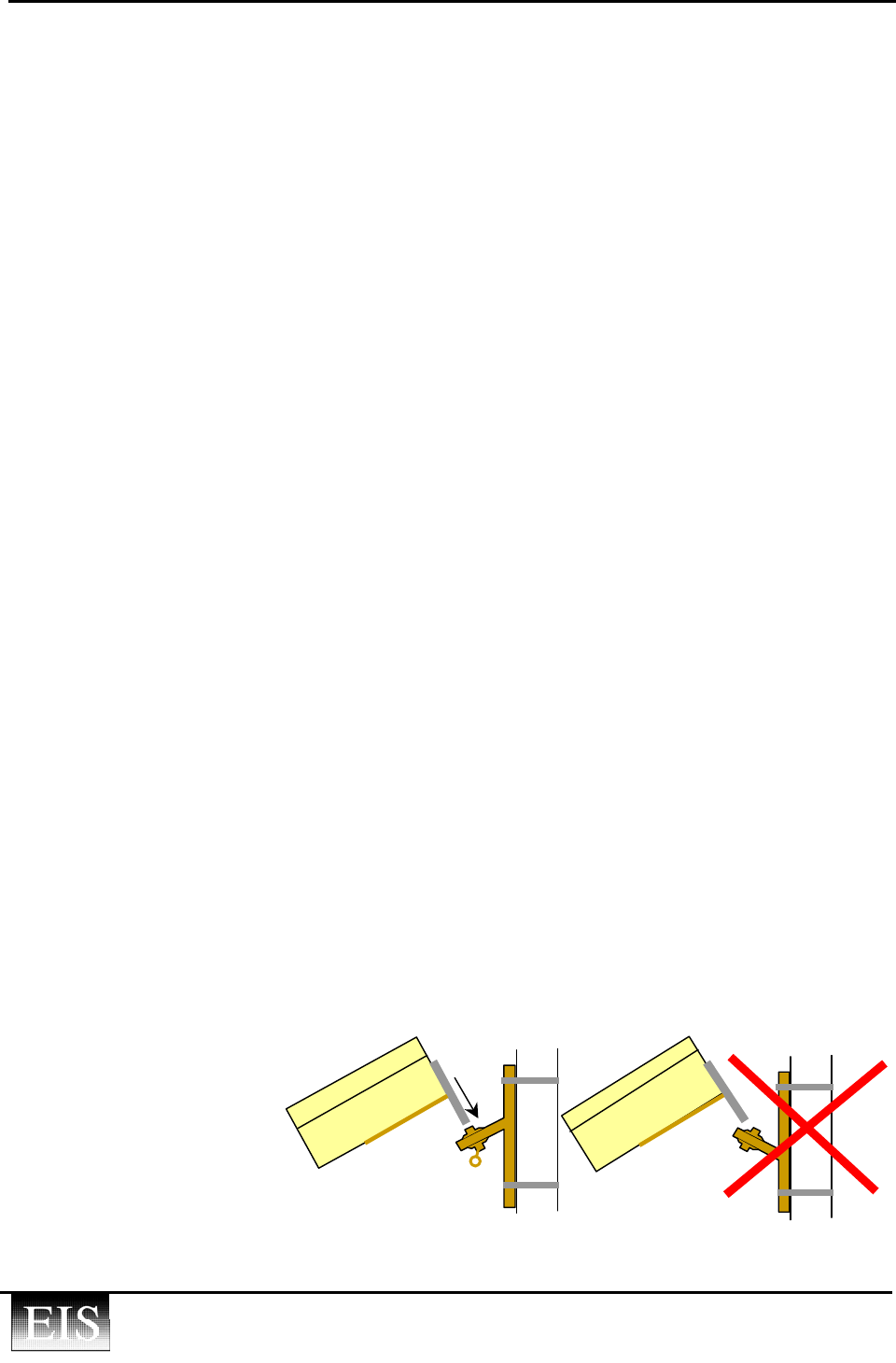
RTMS User Manual Issue 3.2 3
EIS Electronic Integrated Systems Inc.
2 RTMS OPTIONS
The RTMS may be ordered with the following options
Power options
• Low voltage 12-24V AC or DC ------------------------- Standard
Data Communication Options
• Serial Port
• RS-232 ---------------------------------------------------------- Standard
• RS-485 Serial Port --------------------------------------------- Factory setting option
• Integrated Digital Spread Spectrum (DSS) transceiver ------- Optional
• Integrated TCP/IP Ethernet Interface ---------------------------- Optional
Note: The DSS and TCP/IP communication options are incompatible with 115VAC power option
3 RTMS INSTALLATION
Incoming Inspection
The RTMS standard shipment contains:
• The RTMS sensor with lynch pin.
• Ball-joint mounting bracket
• Connector kit: MS and DB-9F connectors with female crimp pins, backshells and pin
insertion/extraction tool.
• RTMS Setup Utility software on CD
• If an internal DSS modem is included (indicated by labels), a small whip antenna is added
If the contents are incomplete or there is mechanical damage, please notify EIS Inc.
immediately.
Installation steps
• Secure mounting bracket to the pole or overhead structure facing the traffic lanes to be
monitored, using stainless steel bands or bolts. See RTMS Mounting and Aiming section for
the required set-back and mounting height.
• The ball-joint must point downwards as illustrated.
Fig 4. Installation of
RTMS bracket
• Insert the RTMS mounting pin into the ball-joint, taking care not to kink the rubber grommet.
Lubrication is recommended (e.g. WD40).
•
•
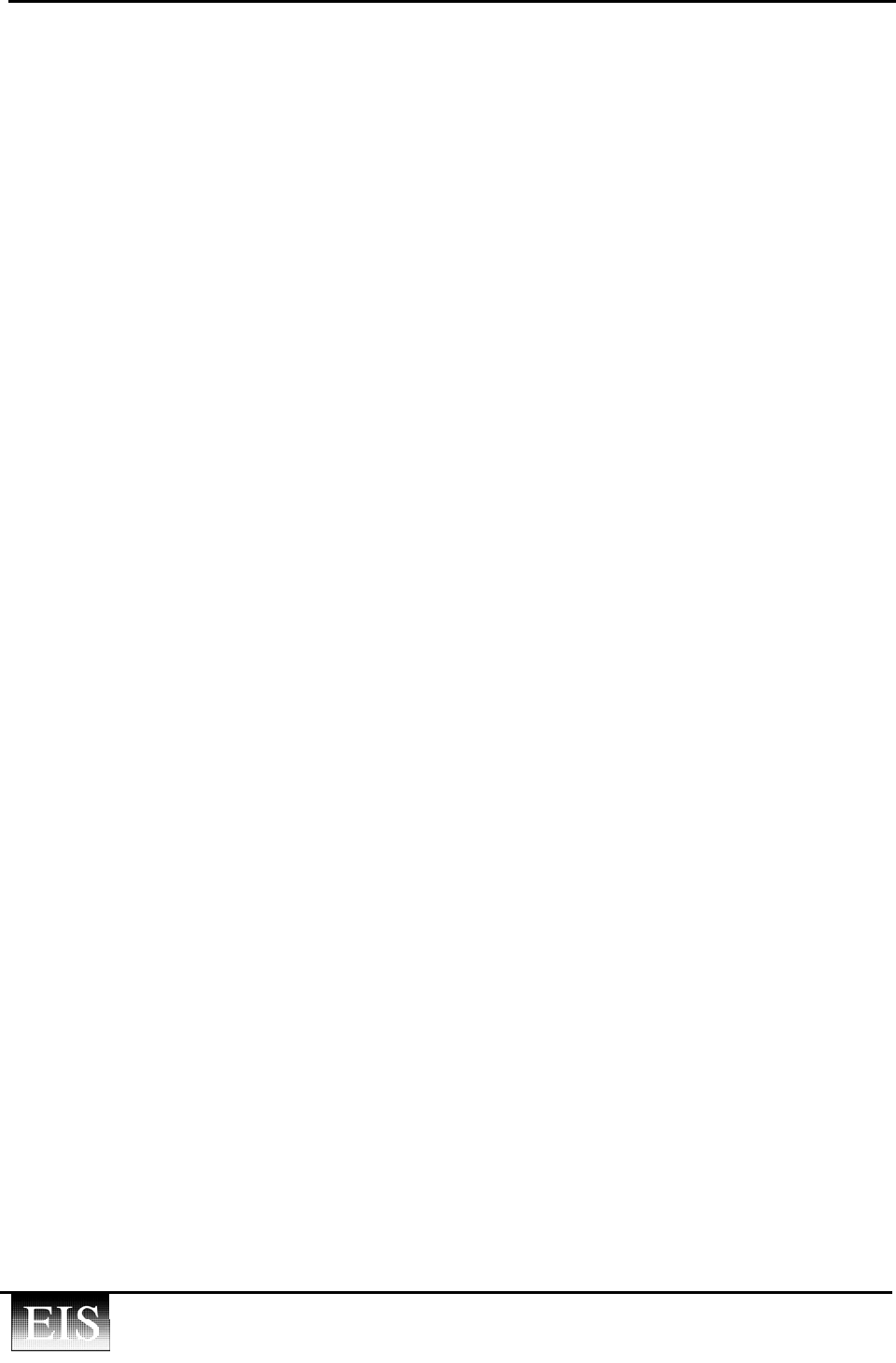
RTMS User Manual Issue 3.2 4
EIS Electronic Integrated Systems Inc.
• Align the holes in the bracket with the RTMS mounting-pin holes and insert the lynch pin.
Do not use undue force or tools. When fully inserted, flip its ring to snap into place around the
ball-joint
• Using a 7/16” wrench, loosen the bracket bolt to release the ball-joint and aim the RTMS per
the Mounting and Aiming section. Tighten the locking bolt firmly. Once properly aimed,
RTMS can be quickly replaced without need to repeat the aiming process.
• Mate the cable’s MS Connector (see Section 5 for Cabling instructions) to the RTMS with the
wide connector key pointing to the front of the sensor. Twist the MS Connector outer ring
clockwise half a turn until it locks with a click. If an internal DSS modem is included, screw
on the supplied antenna.
• Connect the RTMS cable data port connector to a laptop PC and perform Setup per
instructions in Section 3. During setup, aiming corrections may be required.
• Recording details of the RTMS setup and location is recommended. See Appendix 2 for
completed samples of forms, which can be made available.
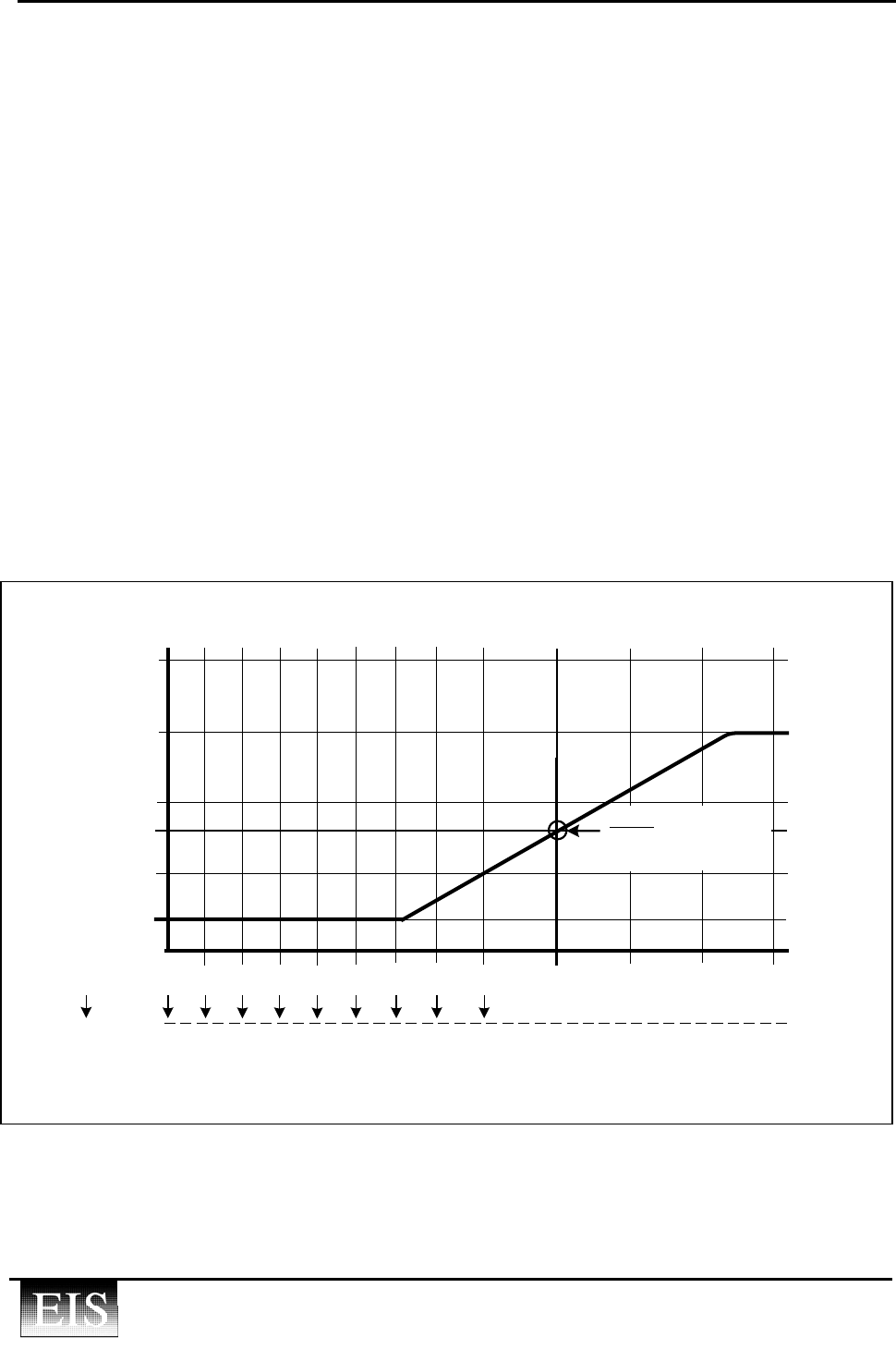
RTMS User Manual Issue 3.2 5
EIS Electronic Integrated Systems Inc.
RTMS Mounting and Aiming
The mounting site selection should take into consideration the set-back and height requirements.
For best results, mount the sensor at the correct height and aim it initially as shown below.
Sidefired Configuration
Set-back and Mounting Height
To include all lanes of interest within its beam footprint, the RTMS must be set back from the
detection zones.
For set-backs less than 20 feet (6m) RTMS should be mounted at 17 foot (5m) height above the
road surface. Minimum set-backs for monitoring the required number of equivalent lanes are as
shown by Fig. 5.
Equivalent lanes include median strips, e.g. an eight lane road with a two lane wide median strip
has 10 equivalent lanes. The span of 13 equivalent lanes plus the required minimum 25 foot
set-back approaches the range limit of the RTMS.
If the set-back is more than 20 ft, the height may be increased approximately 3 feet per 5 foot
increase in set-back to a maximum of 30 feet, as shown by the graph. The 30 foot set-back and
23 foot height represents an ideal location for any highway application.
Fig 5. Set-back and Height requirements
Set-Back (Meters) - to first lane
35'
17'
35'
Height (Feet) - above road
Set-Back (Feet) - to first lane
45'
5m
10.5
10.5m 13.5m2.5m
Height (Meters) - above road
8'
3
Set-Back =
of Lanes
Max. No. =
X3 - Max. # of Equivalent Lanes for Set-Back
yyyy
25'
7.5m
13 (8 lanes + 5 equiv. lane median)
22'
12
20'
6.2m
11
y
18'
10
16'
8
5.5m
y
14'
6
12'
5
3.7m
y
10'
4
40'
12m
y
Ideal mounting for
most highway
applications
23' 7m
20' 6m
25' 7.5
30' 9m
30'
9m
y
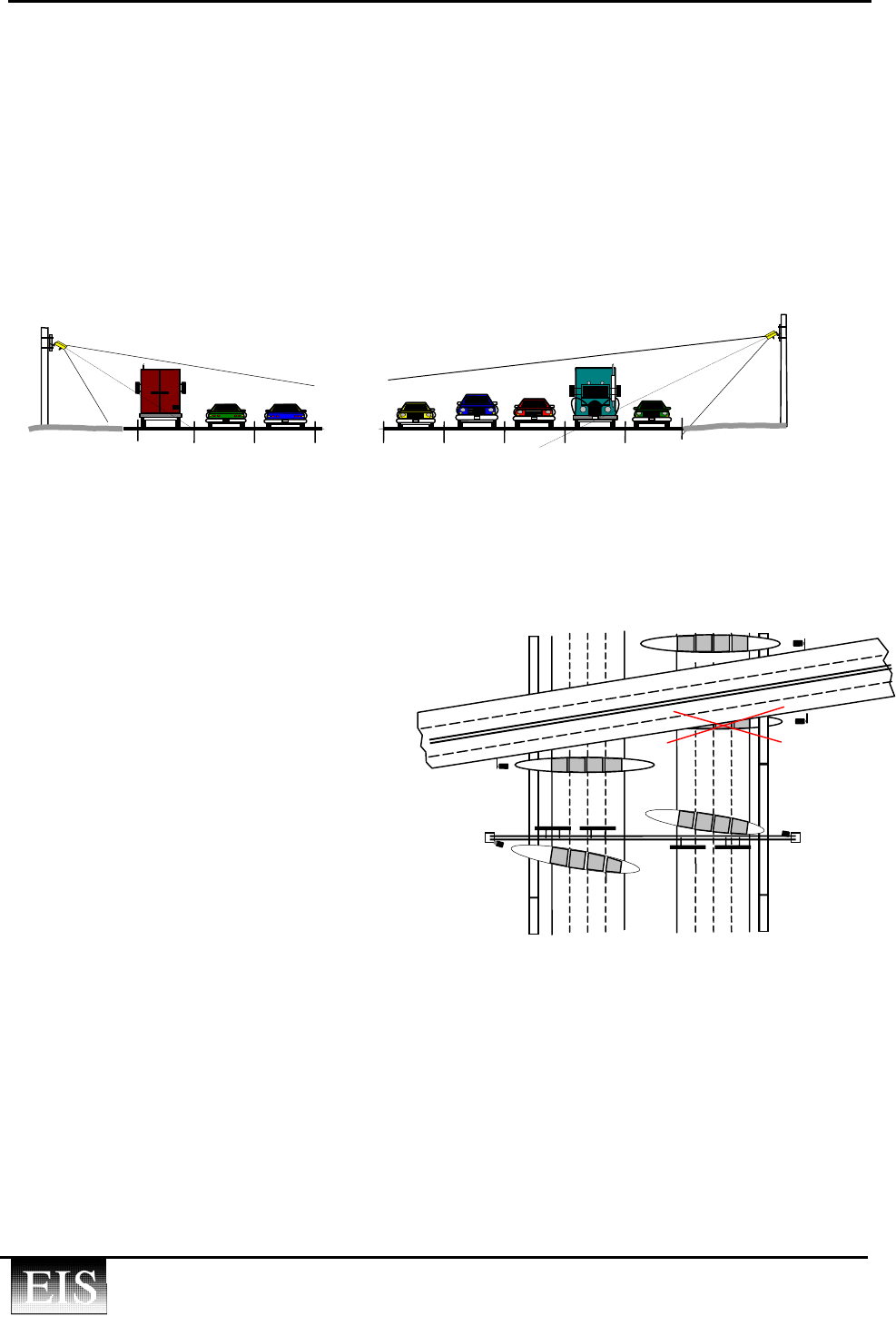
RTMS User Manual Issue 3.2 6
EIS Electronic Integrated Systems Inc.
Initial Aiming Instruction
The following guidelines are recommended for good coverage of all lanes to be monitored.
• Look from behind the unit and use the top and sides as a guide to “eyeball” its boresight
direction:
• Adjust the sideways sway of the RTMS to be perpendicular to the travel lanes.
• Tilt down so that the top of the RTMS is aimed to the first 1/3 of the monitored lanes.
• Keep the RTMS level, side to side.
Note: Final verification of aiming is performed during the setup procedure (See Section 3)
Fig 6. Aiming to the first 1/3 of the monitored lanes
Pointing RTMS away from heavy structures
When deploying RTMS on heavy structures such as overpasses and some sign-bridges, mount
them so that the microwave beam clears the structures to avoid multi-path distortion of the beam:
• Do not mount directly on perpendicular
(or preferably angled) overpasses. Use
separate poles at least 7m (20 feet) away.
• When having to mount on angled
overpasses, take advantage of the angle,
as shown and use 5 ft extension arms.
• Mount sensors on the “clean” side of
heavy-structured sign bridges, away
from catwalks and lighting at a small
angle as shown (not exceeding 15°).
Extension arms are also recommended.
•
Fig 7. Sidefired mounting on heavy structures
EIS
EIS EIS EIS
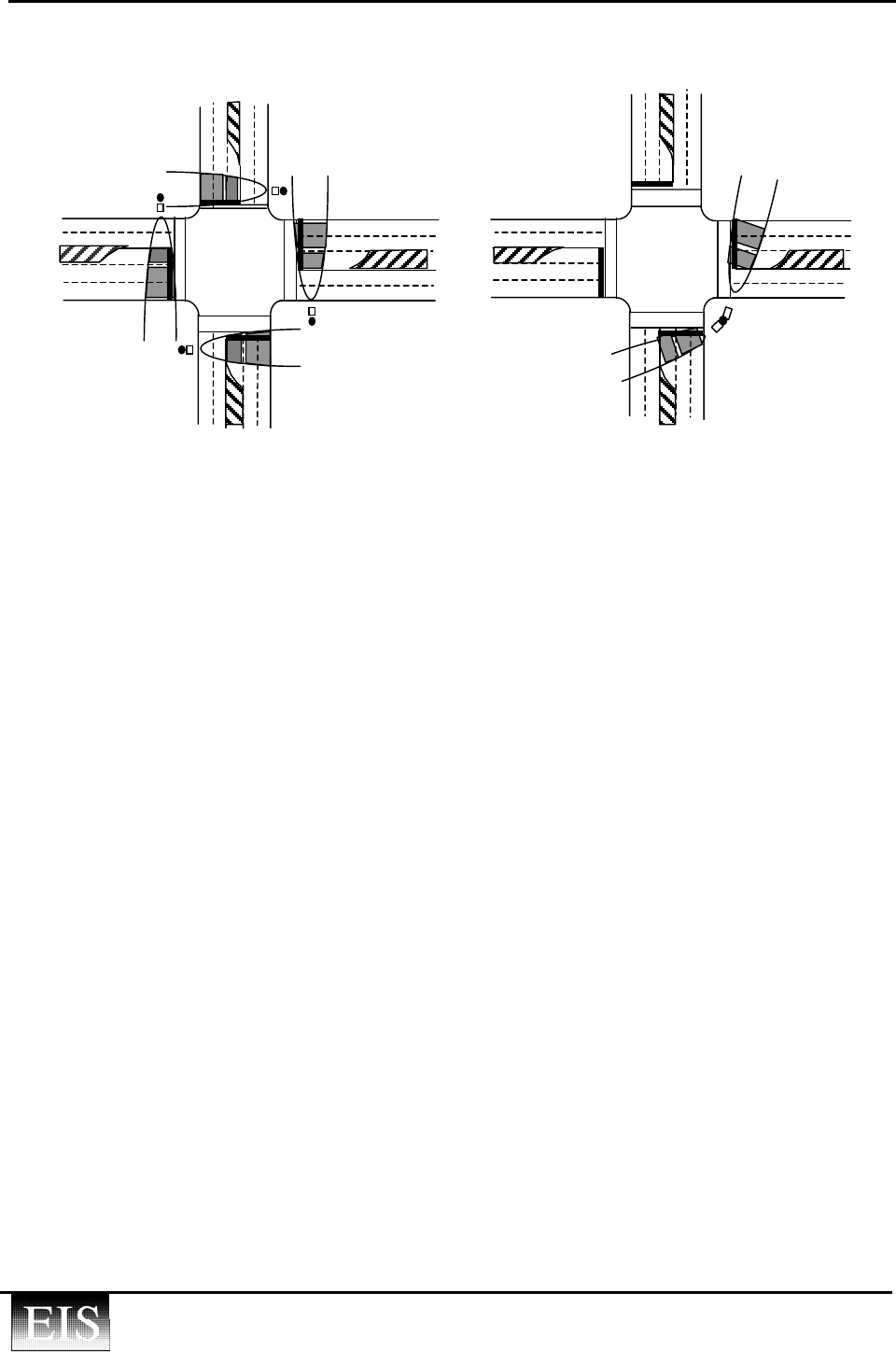
RTMS User Manual Issue 3.2 7
EIS Electronic Integrated Systems Inc.
Sidefired mounting in Intersection Stop Bar Detection
Fig 8. Mounting RTMS at intersections
• Poles at optimal locations allow aiming at the stop bar while perpendicular to the traffic lanes
• Mounting across the road from the detection zones widens the footprint by increasing the set-
back, makes the beam more perpendicular and ensures no occlusion of Left-turn lane.
When existing poles are not in optimal position, use of extension arms is recommended to
alleviate outlined problems and improve performance
• Mounting of sensors on poles close to the detection zones, narrows the footprint due to limited
set-back and increases occlusion in the Left-turn lane.
• The larger offset angle (over 15° from perpendicular) scatters the microwave beam and causes
detection misalignment into unwanted areas.
• It reduces the reflected signal, and therefore, the performance.
•
Optimal pole
locations
Non-optimal pole
location
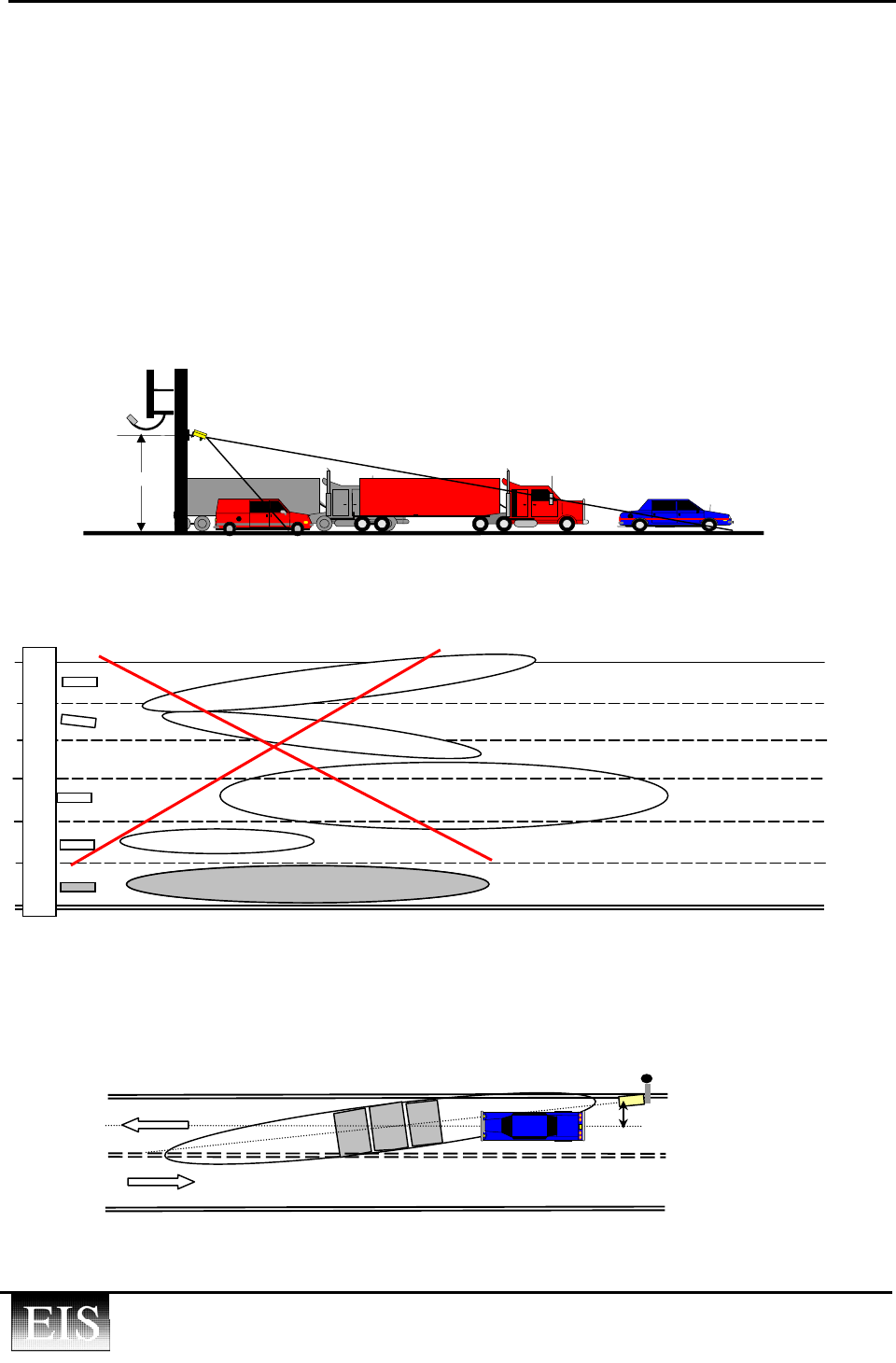
RTMS User Manual Issue 3.2 8
EIS Electronic Integrated Systems Inc.
Forward-looking configuration
In highway traffic monitoring applications, sensors are mounted on a sign-bridge or overpass
away from interfering structures, as shown below. The sensor can be aimed at approaching or
receding traffic, but aiming at receding traffic is preferable.
• Mount the sensor above the center of the lane at the recommended height of 5m (17 feet) but
not exceeding 6m (20 feet).
• Point it parallel to the monitored lane
• Mount it level side to side
Looking from behind the unit, “eyeball” - aim it to a point about 10m (30 – 35 feet) from the
sensor. This will ensure a sufficiently long footprint but restrict its width to a single lane.
Fig 9. Mounting on overhead structure in Forward-looking configuration.
Incorrect aiming will result in poor accuracy. Aiming adjustments may be needed during setup,
where verification is performed using a PC.
Fig 10. Correct and incorrect aiming in Forward-looking configuration
Offset of RTMS in Forward-looking configuration
Forward-looking RTMS may be mounted on a roadside pole, if the offset (distance from sensor to
lane centerline) is less than 3m (10 feet). Extension arms can be used to reduce offset.
Fig 11. Offset Forward-Looking RTMS Mounting
20 ft max.
Extension arm on pole
Offset
Sensor not level
–
foot
p
rint is skewed
Sensor aiming not parallel to lane – footprint
extends into
neighboring lane
Sensor mounted too high or aimed too far –
footprint is wider than one lane
Sensor aimed correctly – footprint contained within one
lane and is lon
g
enou
g
h
Sensor aimed at a sharp angle– footprint is
short, beam is aimed at roofs of vehicles
Correct
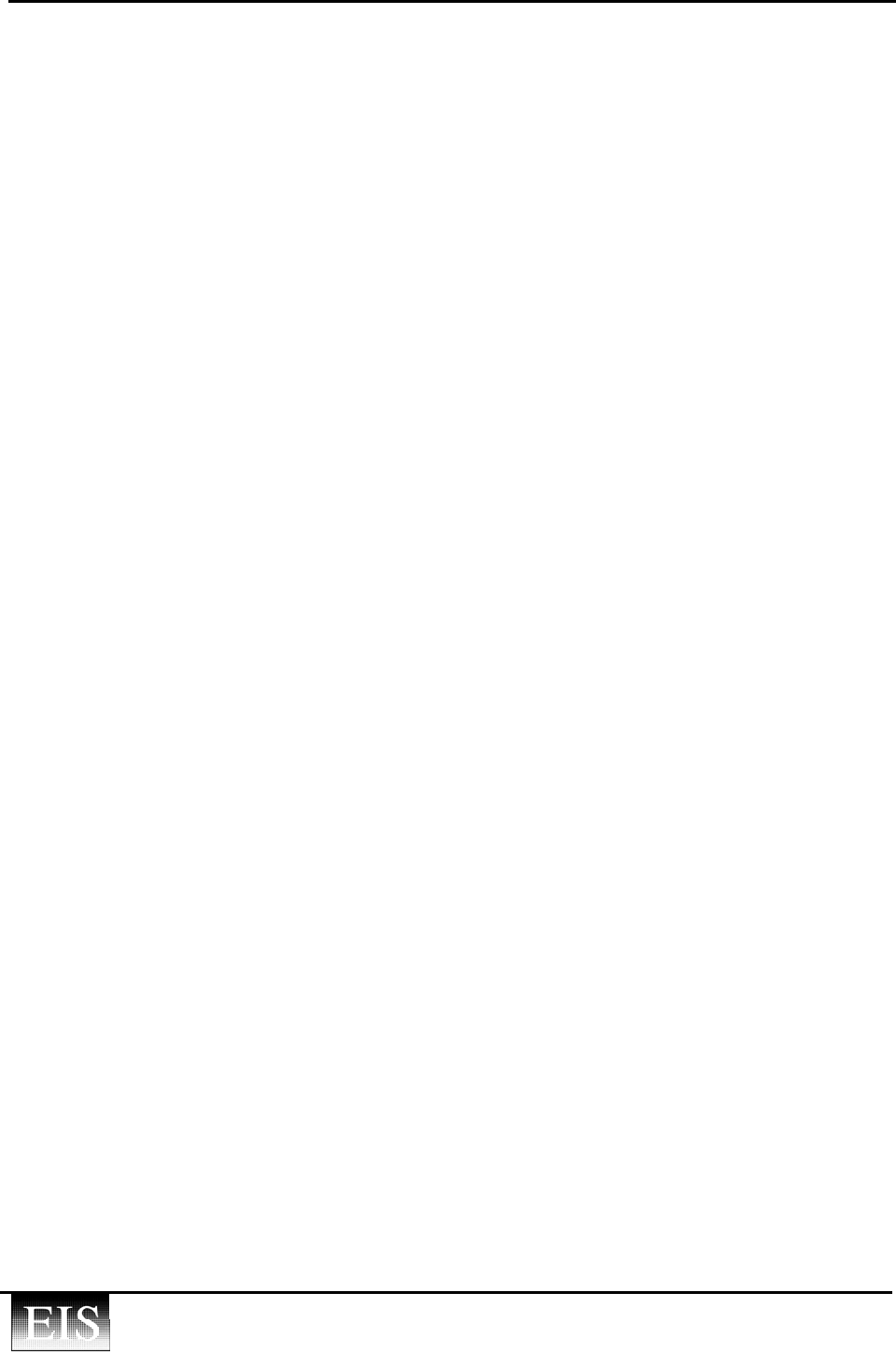
RTMS User Manual Issue 3.2 9
EIS Electronic Integrated Systems Inc.
4 SETUP OF THE RTMS
The PC requirements
Installed RTMS sensors are calibrated using a laptop PC operating under MS Windows. The
operator connects the PC to the RTMS Serial port and runs the interactive RTMS Setup Utility
“WinRtms” program while viewing the monitored road traffic. Therefore, cabling arrangements
must provide access to that port within view of the monitored lanes.
A PC equipped with a USB port only, requires a converter to RS-232. Care must be taken that the
converter driver is correct for the Operating System employed, e.g. driver for Windows 2000 may
not work with Windows XP.
The RTMS Setup Utility (WinRtms)
Installation
RTMS Setup Utility program is provided on a CD. Insert CD into your CD-ROM. If “Autorun” is
enabled, the content of the CD will be shown. For Windows 98/2000/NT4/2000/Me system, open
the ‘Software’ folder, double click ‘WinRTMSInst.exe” icon and follow installation instructions.
The WinRtms install utility will install the WinRtms program and two files in the RTMS folder.
Rtms.ini configuration file retains the main program settings (e.g. speed, mode of operation, etc).
The Rtmslng.txt file contains all screen legends and can be edited to accommodate other
languages. See Section 5 - Non-setup Functions of the Setup Utility for further details
Direct and Multi-drop Communication Modes
The WinRtms program communicates in Direct and Multi-drop modes.
• Direct mode is employed for individual RTMS setup, outlined in this section.
• Multi-drop mode allows communication with several RTMS sensors connected to a common
communication line, e.g. for the purpose of data collection. See Section 5 - Non-setup
Functions of the Setup Utility to configure WinRtms program for this function
• An RTMS equipped with TCP/IP interface (identified by a label on the bottom of the
enclosure), may be accessed via the Internet. Winrtms must be set to communicate using an
IP address rather than the Serial Port. See Section 5 - Non-setup Functions of the Setup
Utility to configure WinRtms program for this function
For direct access, the RTMS must be unplugged from the hub and connected to the PC
network card. PC networking setup must be changed to static IP address. See Appendix 2 on
PC setup and setting of the RTMS IP address.
The WinRtms program is designed for use outdoors, where screen visibility is reduced by the sun
glare. While supporting “point and click” mouse functionality, most functions may be performed
using the UP/DOWN, LEFT/RIGHT arrow keys, the ENTER key and keyboard shortcuts
(keying underlined letters). Setup actions are identified by ⇒
RTMS equipped with higher revisions of firmware, may require latest versions of WinRtms.
WinRtms Ver. 3.0 and up features automated or assisted setup through its Wizard.
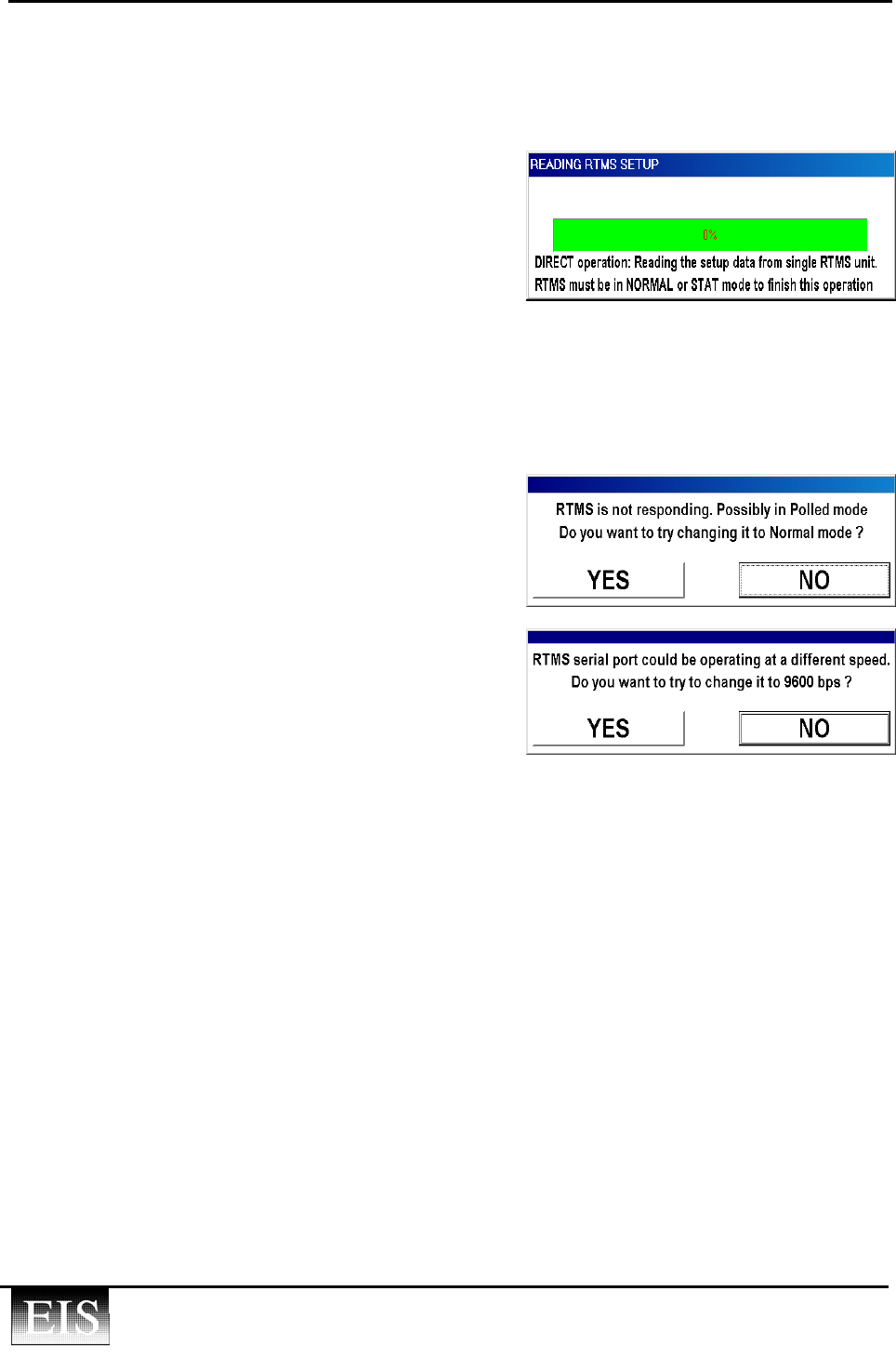
RTMS User Manual Issue 3.2 10
EIS Electronic Integrated Systems Inc.
Getting Started
With the RTMS sensor connected to the PC as appropriate to the data interface, click the
WinRtms.exe icon to launch the RTMS Setup Utility program.
The RTMS Setup program, initially set to its Direct
mode, attempts to establish communication with the
RTMS and displays the message on the right, while
attempting to read the current RTMS setup.
If WinRtms is set to its Multi-drop mode, it will display a window presenting a polling range of
first and last Sensor IDs. See Section 5, Non-Setup Functions of the Setup Utility on changing
the mode of communication to Direct.
If WinRtms in Direct Mode is unable to read the RTMS setup, it will display the messages below
suggesting a course of action to recover. Possible reasons for failure to read may be:
• RTMS is not connected to the PC or is not powered
• PC RS-232 Serial port is not working or is not free
(e.g. used by another application) or wrong cable is
used to connect other data interfaces
• RTMS is set to Polled mode
⇒ Select YES on these windows to try reading again
after attempting to change Data mode or port speed.
Selecting NO will display a default RTMS Setup screen with COM Port and Speed settings
shown at the bottom right corner of the screen. They may be changed, if incorrect. See Section 5,
Non-setup Functions of the Setup Utility for details.
Once communication with RTMS is established (Data mode is NORMAL), the main screen
display will show the following:
• A blinking circle/square messaging “lamp” in the lower-right screen-corner indicates that
WinRtms is receiving data from RTMS. (RTMS transmits “Target” messages 10 times per
second)
• Sensor parameter settings are shown on the Setup screen buttons. If not, Select READ
RTMS. If unsuccessful, See Section 9 – Trouble Shooting.
• Detection zone icons below the range scale, based on the present setup
• Target “blips” are displayed in their correct range when vehicles cross the sensor beam
• Per zone traffic data is updated at the end of every Message Period, along with a distinctive
sound.
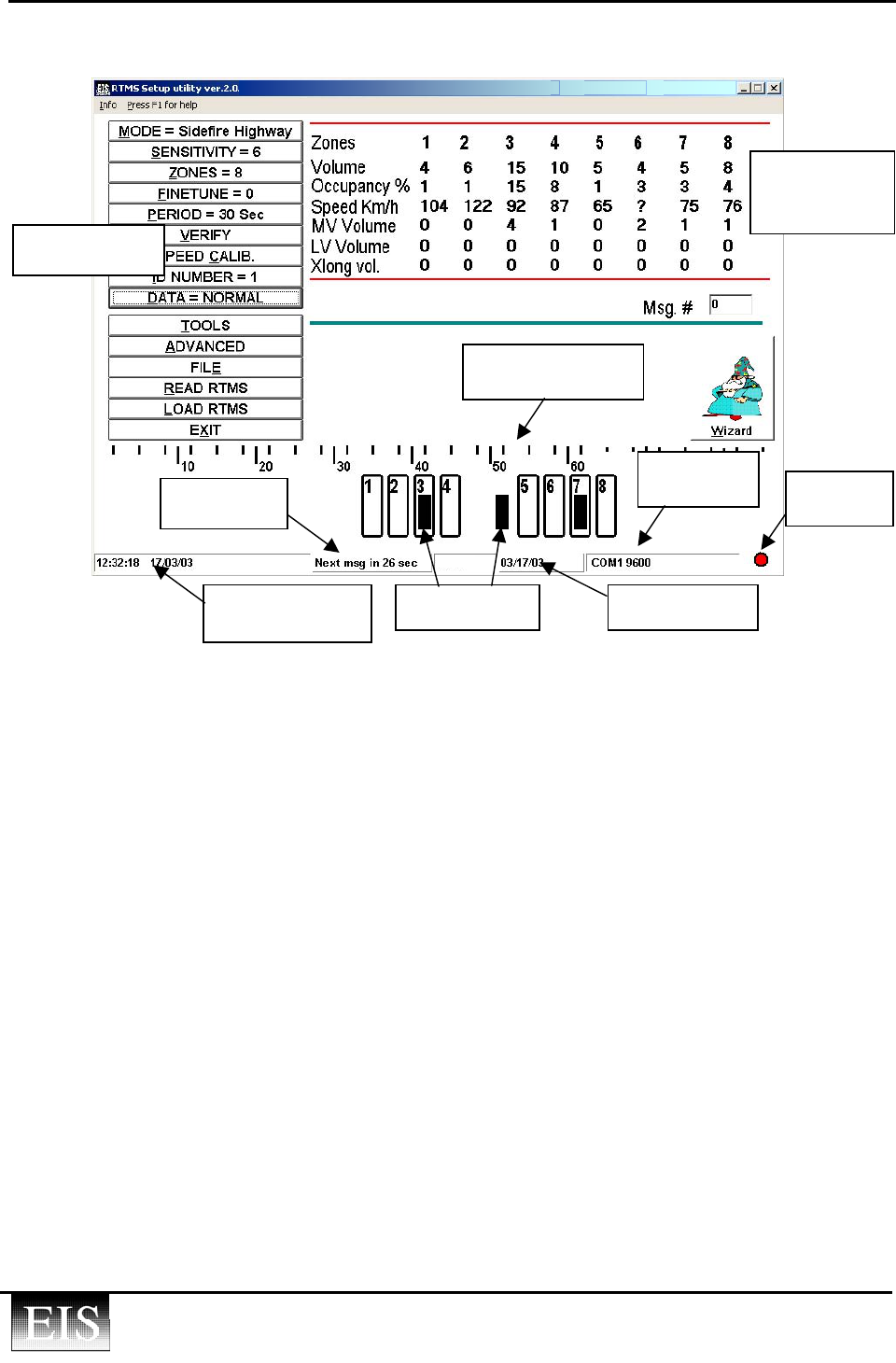
RTMS User Manual Issue 3.2 11
EIS Electronic Integrated Systems Inc.
WinRtms Setup Utility Screen
Fig 12. RTMS Setup Utility communicating with the sensor
The screen bottom line display depends on the Model and Revision version of the RTMS.
Always shown are the PC COM port, its speed and the setup date.
RTMS Model X3/K3 with Rev 6.1 or higher displays additional info at the bottom of the screen:
• RTMS serial number and Rev. version whenever the RTMS setup is read
• If RTMS output includes real time clock, the above is displaced by date and time of day,
• Time remaining to next message
• Input power voltage.
Note: The displayed voltage is the DC measured at the input (if powered by AC, its voltage
multiplied by 1.4). If voltage exceeds 25.5V, the Model identification will be
displayed instead, e.g. X3
⇒ Date of last setup change in the RTMS.
Traffic data for RTMS X3/K3 with Rev. 6.1 and higher (shown) reflects expanded vehicle
classification. See Section 4 -The Traffic Statistics Display Area for further details
Target “blips”
Range scale
(
meters or
y
ards
)
Flashing
“lamp”
PC Comm.
Port setting
Traffic data
(Last Message
Period)
Buttons display
p
arameters
Last setup date
RTMS “Real time”
or S/N and Rev No.
Message
Count down
12.5V
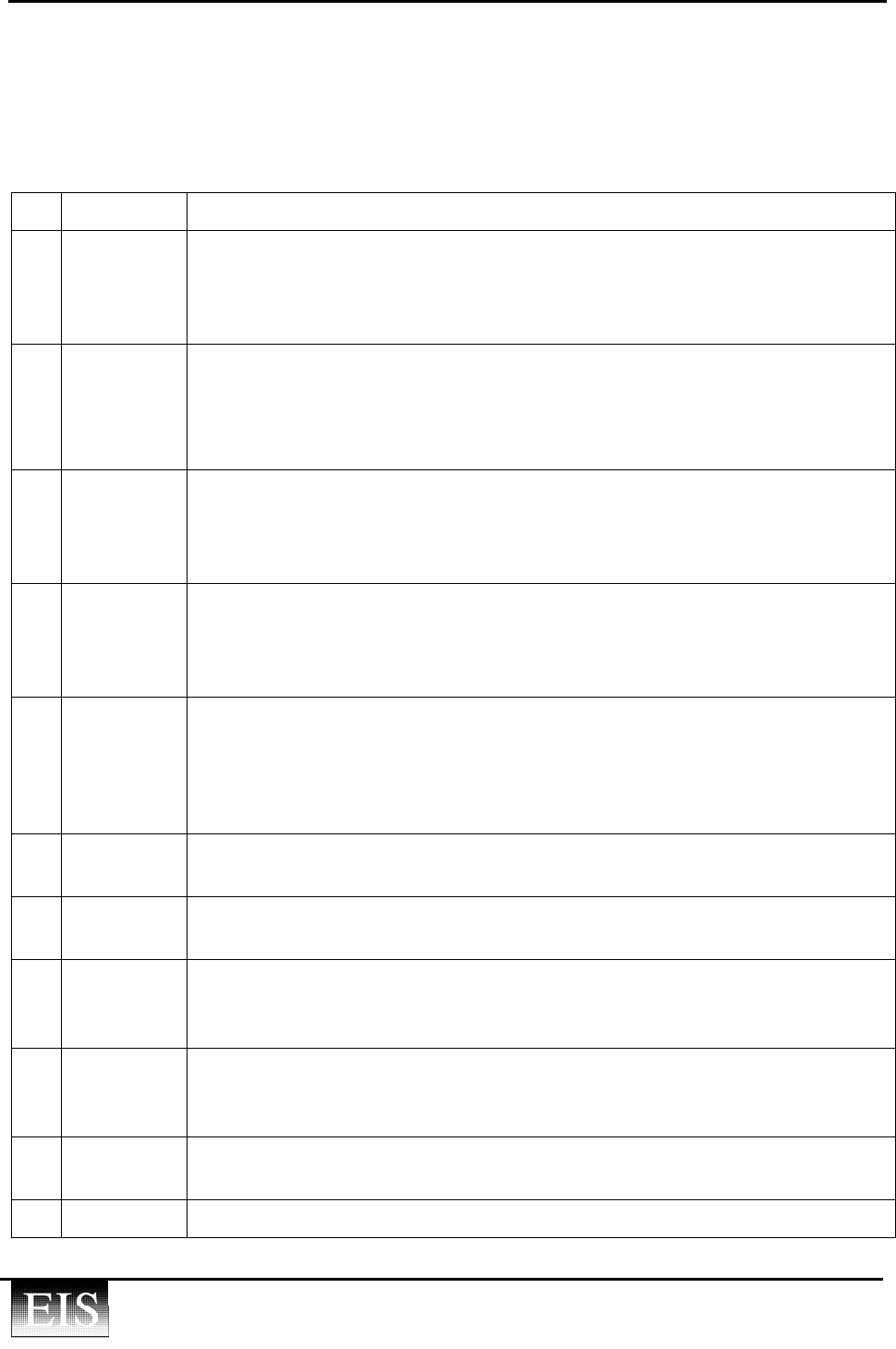
RTMS User Manual Issue 3.2 12
EIS Electronic Integrated Systems Inc.
Setup Sequence
The automated Wizard can execute or assist setup of Steps 2 to 5 (RTMS X3/K3 Rev. 6.1 and up
only), just verify aiming first. (See Wizard for details)
The manual setup procedure follows the sequence shown below. Further details of each step are
provided in referenced sections of this Manual.
# Action Procedure
1
2
Verify
aiming and
set
Sensitivity
Ensure that all vehicles in first and last lanes of the detection range are
detected (showing blips).
See Aiming Verification and Sensitivity setting for details.
3 Set RTMS
operating
Mode
Select MODE button. Select the required application from the list. See
RTMS Operating Modes section, or press F1 for onscreen HELP tips.
If Forward-looking mode is selected, see Additional Forward-look
Parameters for details.
4 Perform
zone setup
Select ZONES button. Set the number, position and size of all detection
zones interactively. Zone setup procedure differs between Sidefired and
Forward-looking modes. Alternately, click the Auto button to initiate
automatic zone setup. See Zone Setup section for details.
5 Fine Tune
to correct
“splashing”
Select FINE TUNE button. Use the Fine Tune control to correct “splashing”
(single vehicle causing two blips in adjacent detection zones). Alternately,
click the Auto button to initiate automatic Fine tune setup. Correct zone
location if necessary. See Fine Tune section for details
6
Verify
count
accuracy
Select PERIOD. Set to 30 seconds. Select VERIFY button and verify setup
by comparing to manual vehicle counts on each lane.
See Count Verification for details
* If your application uses the RTMS Serial Data, continue. Otherwise Exit.
7 Select
Speed units
If Speed units need changing, select ADVANCED button, then select Km/h
– MPH, to set the desired speed unit.
8 Calibrate
Speed
Select SPEED CALIB. Button. Calibration compares measured speeds to a
reference speed in each lane. See Speed Calibration for details
9 Set
Message
Period
Select PERIOD button and set the message period to the desired value
(range 10-600sec.) using UP/DOWN and ENTER keys.
8 Set the
Data Mode
Select DATA to set the required Data mode. It may be different than the
Normal mode required for setup, depending on the communications system
and application. See section on Data Mode for details
9 Set ID
number
Select ID NUMBER button. To set the displayed ID to desired number use
UP/DOWN and ENTER keys
12 Exit Select the EXIT button when setup is finished
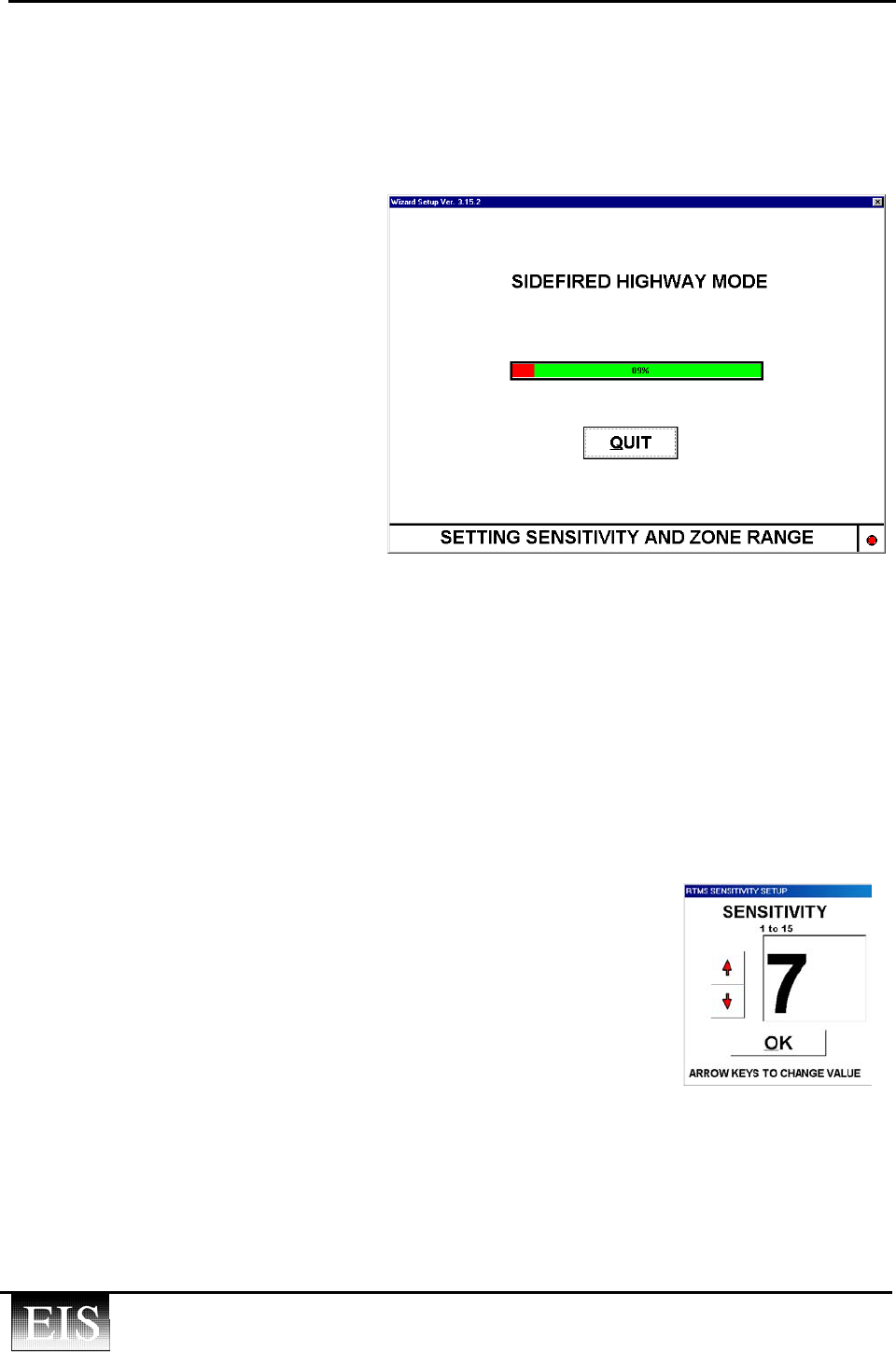
RTMS User Manual Issue 3.2 13
EIS Electronic Integrated Systems Inc.
Automated Wizard setup
The WinRTMS Wizard feature (RTMS X3/K3 Rev.6.1 and up only) automates the setup stages:
Sensitivity, Fine tune and Zone setup, allowing the operator to make interactive corrections in
SideFired mode. Before proceeding to full Wizard setup, ensure that aiming is correct, i.e. target
blips corresponding to vehicles in lanes of interest are visible on the screen.
⇒ Click the Wizard icon to initiate
automatic setup.
⇒ Select the RTMS operating mode
from the presented window (see
next page for details of the RTMS
modes)
The Wizard will proceed to set
Sensitivity and initial Zone Setup,
defining up to 8 zones in range
slices where traffic is detected,
presenting its recommendation for
approval.
Verify visually (using vehicle blips)
whether zones were placed on all lanes
of interest. If they are, press SKIP. If not, press OK to manually change the number of zones and
their location. Specifically, correct the position of the closest and farthest zones, then Click OK to
proceed. This step ensures optimization of the setup on the lanes of interest only. See Zone Setup
section.
NOTE: Don’t worry about some splashing at this point. The Wizard will continue the automatic
setup with Fine Tune and final Zone Setup.
At the conclusion of the Wizard setup, some lane reconfiguration may be required due to traffic
conditions. Finally speed calibration or other additional parameters can be executed.
Aiming Verification and Manual Sensitivity setting
Select the SENSITIVITY button to open the RTMS SENSITIVITY SETUP window.
⇒ Use UP/DOWN keys or click UP/DOWN arrows on screen to set to
a medium value of 7. (Set to 5 if only a few close lanes are
monitored)
⇒ Increase Sensitivity if needed to detect small vehicles in the middle
lanes of interest. Reduce setting if a “Sensitivity too High” warning
is displayed continuously.
If small vehicles in either close or far lanes are missed, aiming
should be adjusted. Tilt the sensor towards the zones of poor detection.
Do not increase Sensitivity to compensate for improper aiming.
⇒ For manual setup, to force the “capture” of a new background quickly after aiming changes,
increase the Sensitivity by one and restore it back.
⇒ Press ENTER or click OK to activate the new value and exit this window
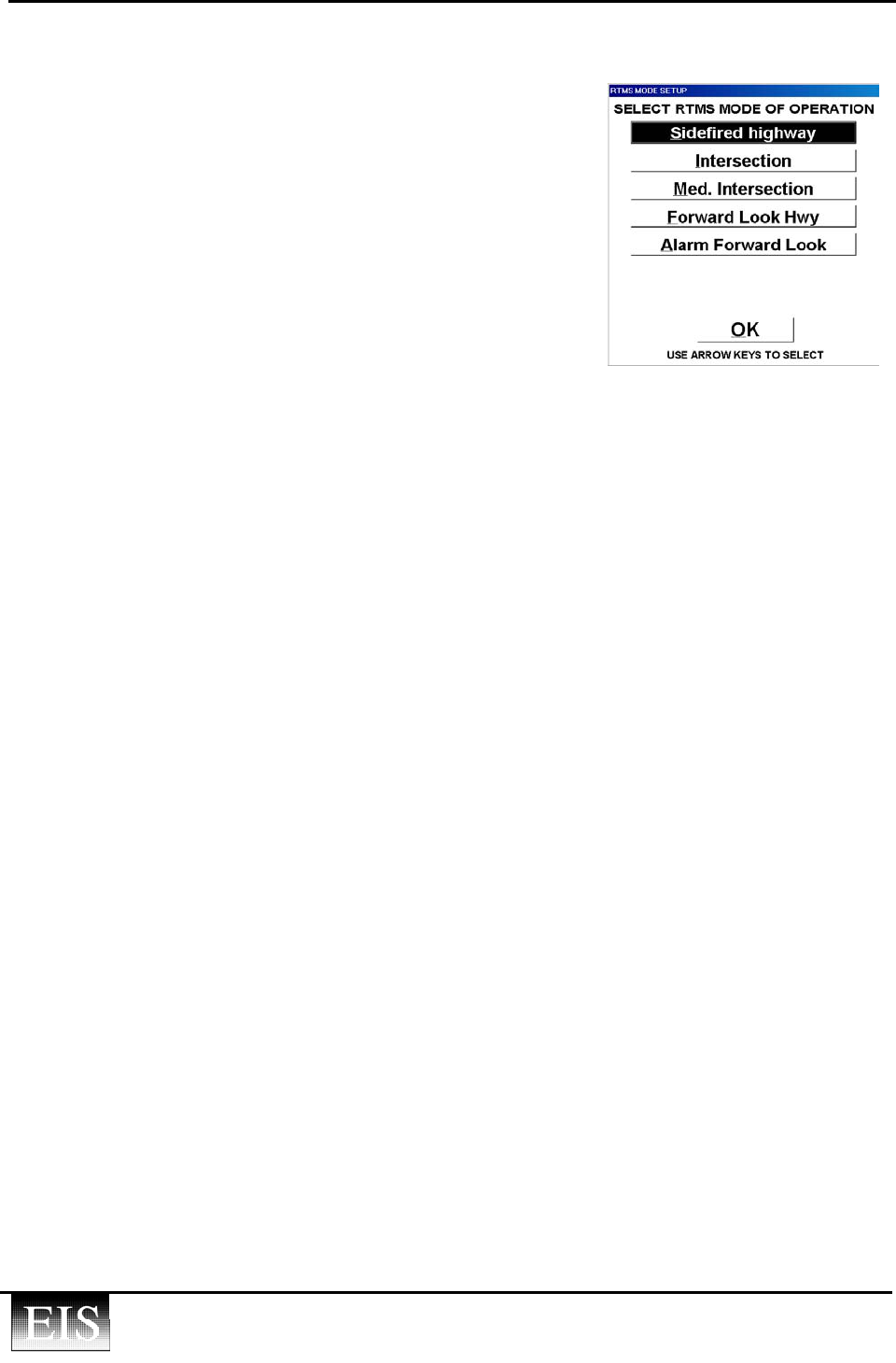
RTMS User Manual Issue 3.2 14
EIS Electronic Integrated Systems Inc.
RTMS Operating Modes
⇒ Select MODE button to open the RTMS MODE SETUP
window.
⇒ Select the required mode for your application.
The Mode selection loads the RTMS with several
parameters, optimizing its performance for the selected
application.
The characteristics of available modes and their default
settings are:
Sidefired Highway Sidefired sensor detects presence and generates traffic data in up to
8 zones. Used in highway and counting applications.
RTMS X2/K2 to X3/K3 Rev 6.0 provided two length
classifications. Rev 6.1 and up provide two more classes. See
Advanced Parameters for further details.
Default settings: EDT = 200 msec, Threshold = Normal
Intersection Sidefired sensor detects presence only (no traffic data is generated)
in multiple zones. Used in Stop-bar detection
Default settings: EDT = 1000 msec, Threshold =Low.
Mid. Intersection Similar to Sidefired Highway mode, this mode is for use in mid-
block detection in urban settings.
Default settings: EDT= 1000 msec for up to Rev 5.5,
300 msec for Rev 6.1 and up
Threshold = Medium.
Forward Look Hwy Used in applications demanding high accuracy of speed
measurements such as Speed Enforcement. Zones 1, 2 and 3 are set
as a speed trap for accurate speed measurements.
RTMS X2 Rev 4.3 or higher, provide per vehicle Doppler-based
speed measurement when speeds exceed 15Km/h (10MPH).
Volume data in up to 7 speed-bins is available. See Advanced
Parameters for further details
Default settings: EDT= 200 msec, Threshold = Normal
Alarm Forward Look Similar to Forward-Looking Hwy mode in RTMS firmware version
5.X and higher. Adds programmable Speed threshold and real time
contact #8 closure (for 20ms) when a vehicle exceeds threshold.
Intended for use in speed enforcement and warning applications.
Default settings: EDT= 200 msec, Threshold = Normal.
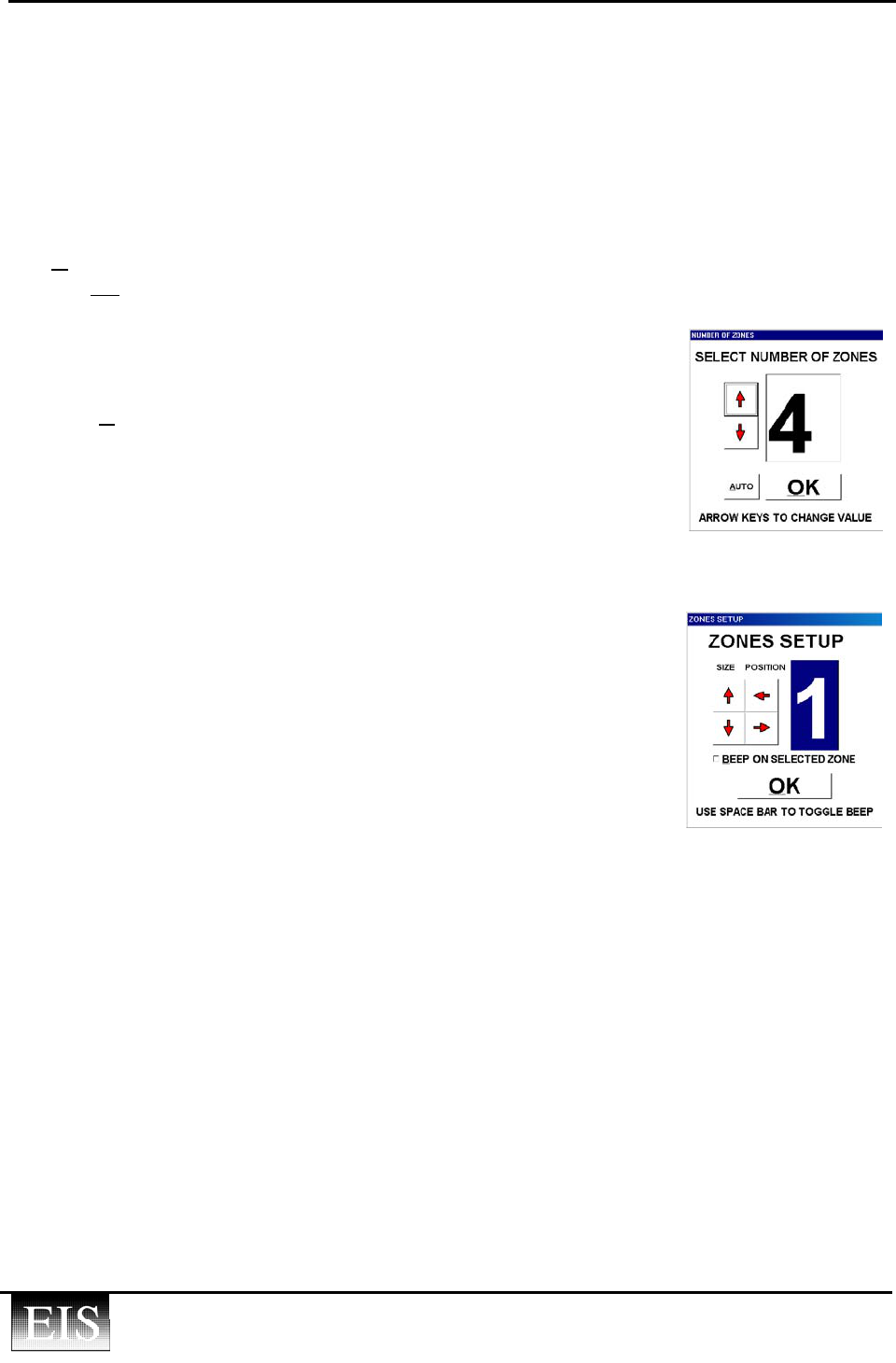
RTMS User Manual Issue 3.2 15
EIS Electronic Integrated Systems Inc.
Zone Setup – Sidefired Modes
Vehicle target “blips” are displayed along the range scale in real time. The objective of zone setup
is to use these blips to identify the correct range slices as detection zones. Only detection of
vehicles inside the configured zones will close contacts (zone numbers correspond to contact
numbers) and generate traffic data. Targets blips outside of configured zones are ignored.
Automatic Zone Setup
The AUTO button (RTMS X3/K3 Rev. 6.1 and up only) initiates automatic setup of detection
zones to all detected traffic lanes (up to 8). The automated process requires sufficient traffic levels
and is aborted if it is too low to determine position of lanes.
⇒ Select ZONES button. The NUMBER OF ZONES window will be
displayed.
⇒ Click AUTO for automated zone setup (number and position of
zones). This will be done with a fine tune of zero only.
When the process is completed, Zone numbers will be in ascending
order as the distance increases. Make zone and fine tune changes
using the Manual procedure.
Manual Zone Setup – Side-fired Mode
⇒ Use the UP/DOWN keys (or click the arrows) to change the number
of zones. In a side-fired mode, the number of zones is set to the
number of lanes to be monitored by the RTMS.
⇒ Press ENTER, click OK or type O to progress to the next stage,
zone positioning and sizing.
⇒ Select any zone by typing its number, e.g. type “1” to select Zone 1.
The zone icon starts flashing and can be moved. The setup utility
allows full flexibility in assigning a number to the detection zone,
e.g. Zone #1 may correspond to the lane closest to the sensor or
farthest away from the sensor. Zone numbers do not have to be in sequence.
⇒ Glance at the screen when vehicles cross the RTMS beam in the lane intended as the detection
zone. Use LEFT/RIGHT arrows (in the ZONES SETUP window or on keyboard) to move
the zone icon to its desired position along the range scale, to surround the vehicle blips.
Repeat the process for each of the lanes to be monitored.
Press the Space-bar to toggle a “presence indication” beep, which sounds when a blip is
detected in the selected zone. The beep allows detection confirmation in a zone without
looking at the screen.
In most cases, each lane requires a single range-slice zone. Multiple range-slice zones can be
employed in intersection applications, e.g. to combine through-lanes into a single detection zone.
A contact corresponding to the zone number is closed as long as presence is detected in any lane
inside the zone.
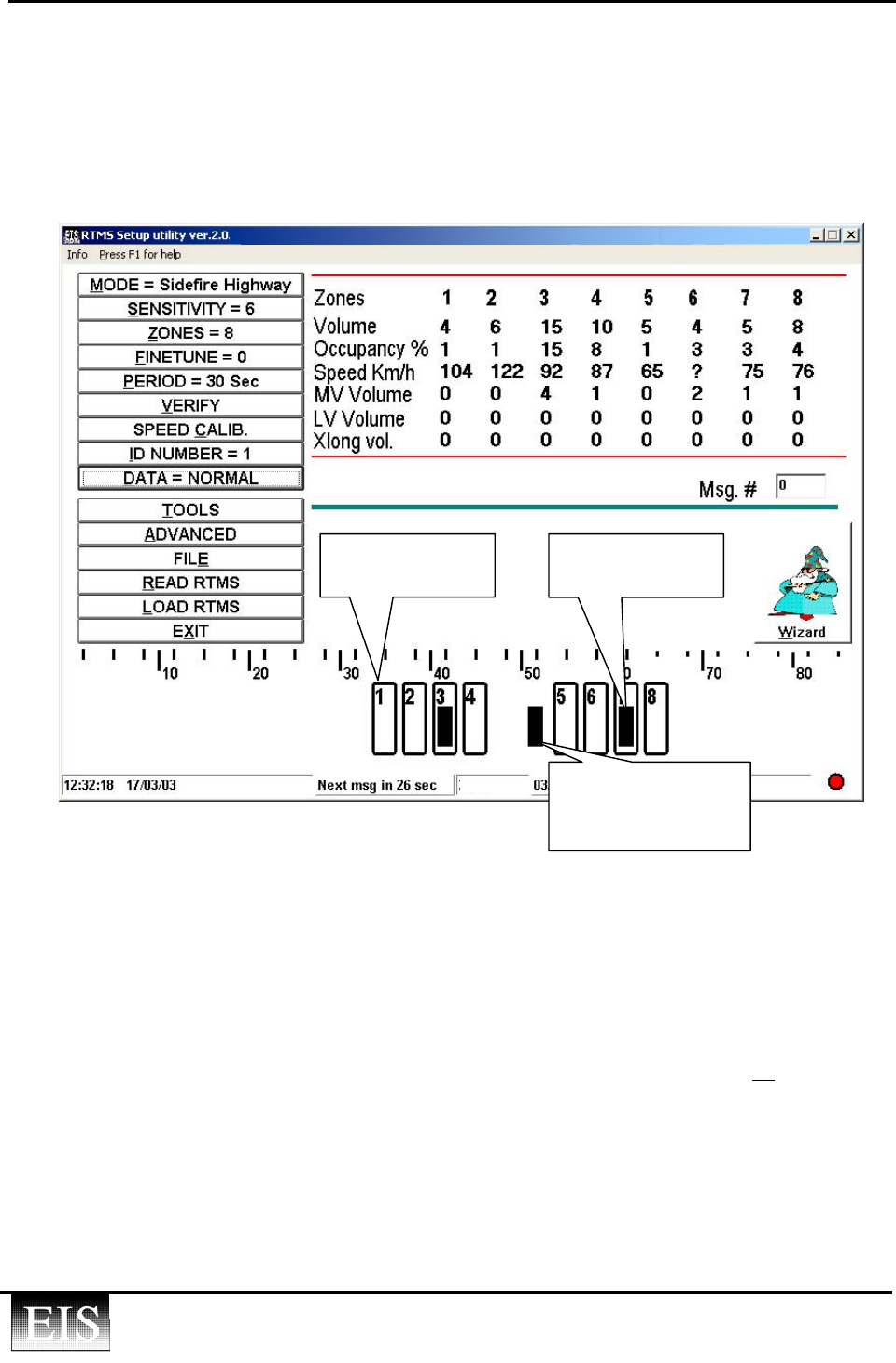
RTMS User Manual Issue 3.2 16
EIS Electronic Integrated Systems Inc.
If two blips show simultaneously in a wide zone, they will be counted as one. Thus in highway
and counting applications multiple slice zones are useful in rare cases where it is necessary to
cover a wide lane.
⇒ Use UP/DOWN keys (or click SIZE arrows) to increase or decrease the size of the zone (to
multiple range slices).
⇒ After all zones are positioned, Press ENTER, click OK or type O to close the window.
Fig 13. Zone icons and target blips
Fine Tune
“Splashing” is defined as a single vehicle (mainly trucks) causing two blips in adjacent detection
zones. A vehicle straddling two lanes or the detection zone straddling two lanes may be the cause.
It results in over-counting and is undesirable.
Fine Tuning minimizes splashing, by making small adjustments to the size of all range slices
(about 2% of the range per step for a maximum of ±10%). Farther range slices are affected more
than closer ones. When the Fine Tune setting is changed to correct a splash, some vehicle blips
may shift out of the defined zones. It may be necessary to re-enter ZONE SETUP to redefine
zone positions, particularly further zones. Fine Tune is also used to reduce the effects of barriers
on detection in nearby lanes. Adjust Fine Tune to confine barrier signals to a single range slice.
Note: The effect of Fine Tune is only shown on the screen by the behavior of vehicle blips.
Zone icon
(Number shown)
Target blip in
configured zone
Target blip not in a
configured zone
e.g. barrier (ignored)
12.5V
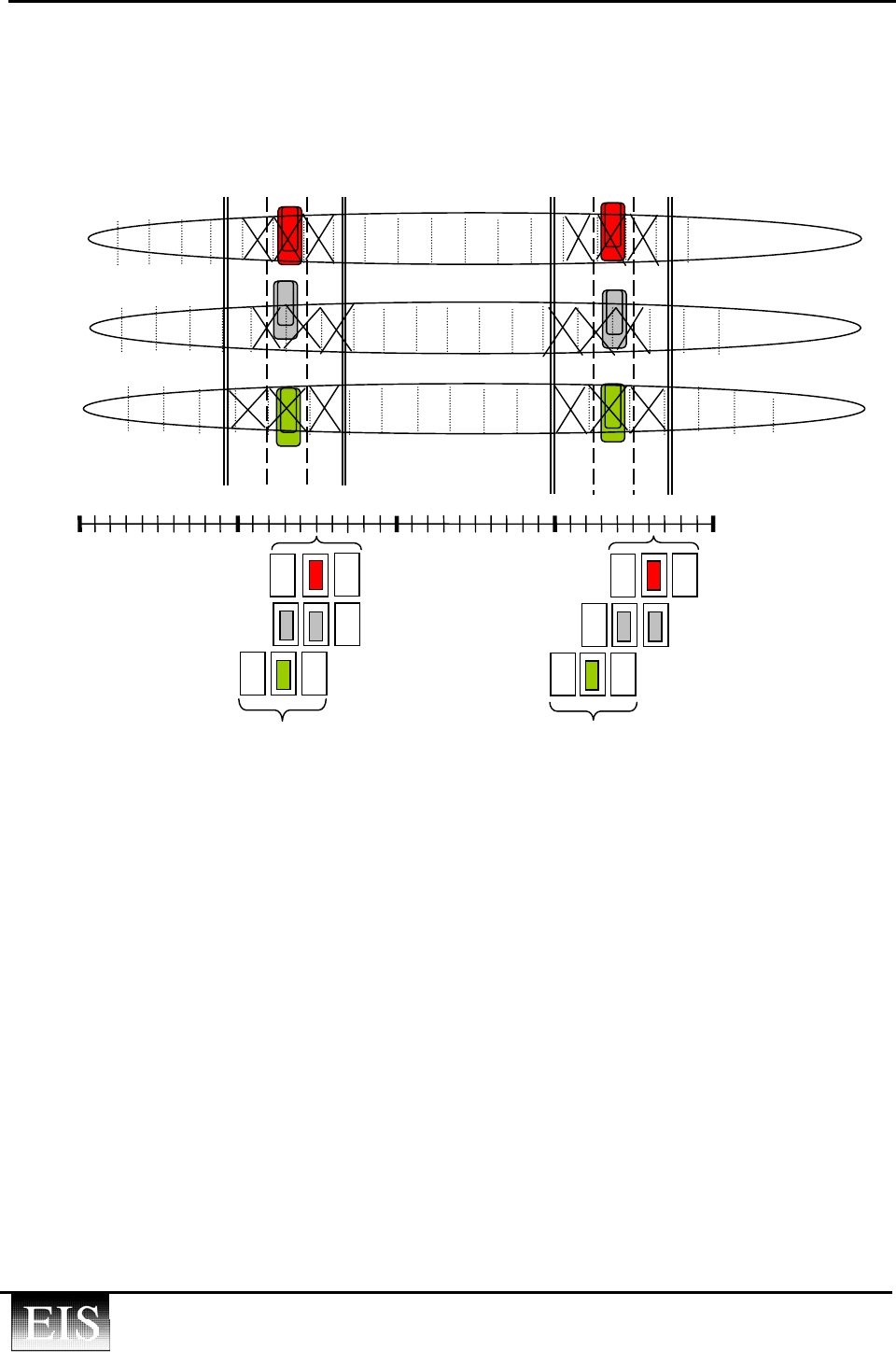
RTMS User Manual Issue 3.2 17
EIS Electronic Integrated Systems Inc.
Typically, a “splash” into a lower range slice (closer to the sensor), is corrected by increasing the
Fine Tune number (blips are pushed up-range – into the correct slice). Conversely, a “splash” into
a higher range slice can be pulled down, by reducing the Fine Tune number.
The diagram below illustrates how Fine Tune setting affects the position of range slices and
detection zones. In this example, at FT=0 the range-slices straddle two lanes and produce
splashing. Both FT= +5 and FT= -4 yield acceptable results.
Fig 14. The effect of Fine Tune Control on vehicle blips
When dealing with a few detection zones, it is easier to find a correct fine tune setting to satisfy
all traffic lanes. Attempting to monitor many lanes with a single sensor may require a
compromise on the counting accuracy in some lanes due to splashing.
Whenever Fine Tune changes are made, the RTMS “captures” the new background and requires
about 30 seconds to “settle”.
4 5 6
7
3 4 5 6
6
1
2
3
4
5
6
1
2
3
4
5
6
7
7
1
2
3
4
5
6
7
8
8
8
9
9
9
16 17
18
16
15 16 17
14
17 18 19
15
13
19
FT= +5
FT= 0
FT= -4
1 2
Lane #
14
5 815 16 17 18
Range Slice numbers
Acceptable Zone setup
at FT= -4
6
4
Acceptable Zone set-up
at FT= +5
1 2 3 4 5 6
Zone Setup
dis
p
la
y
3 Splashing at FT=0
1 2 3
1 2 3 5 6
7
15
Distance scale
0 10 20 30 40
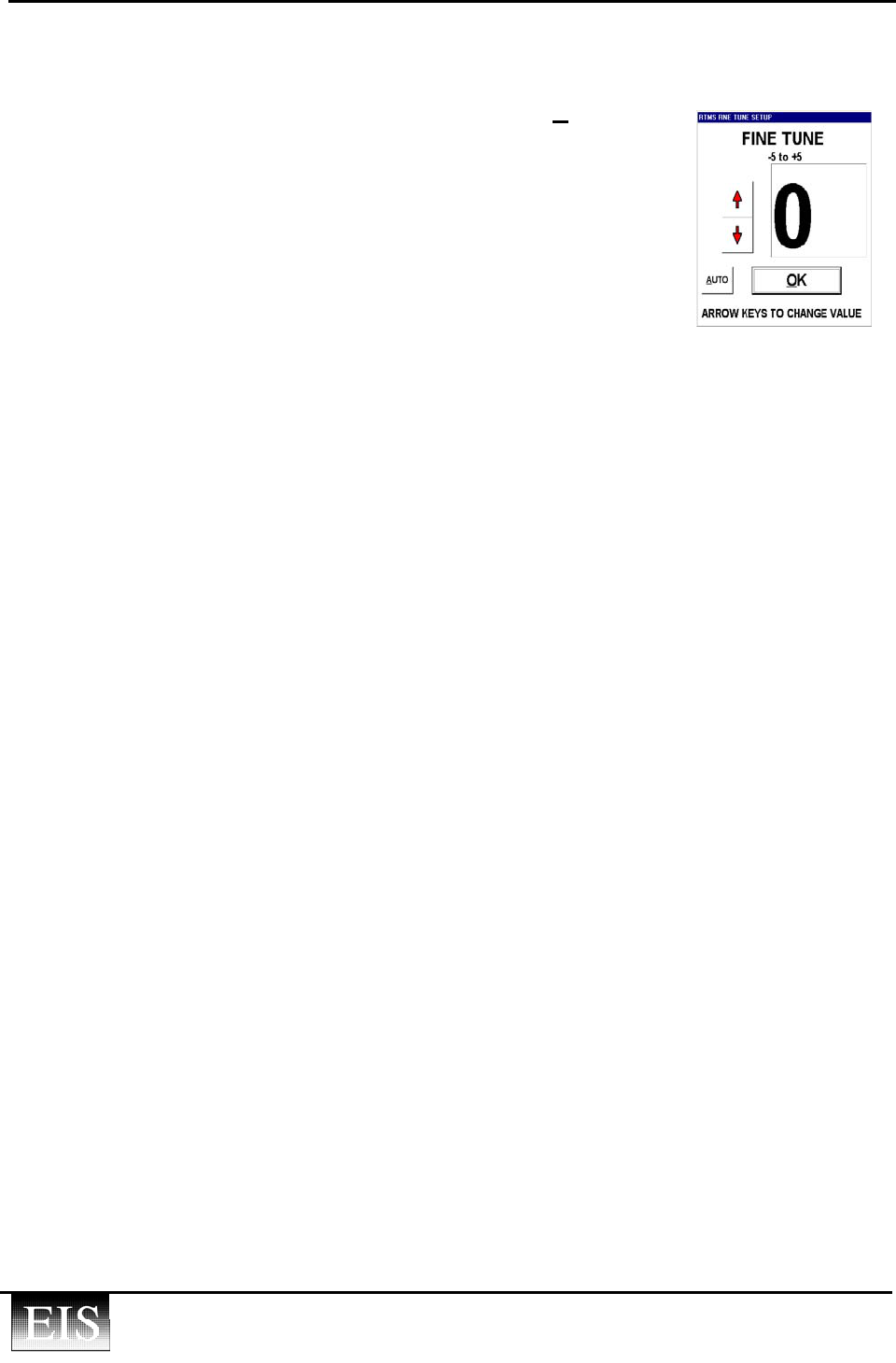
RTMS User Manual Issue 3.2 18
EIS Electronic Integrated Systems Inc.
Fine Tune Setup
Automated or manual setup procedure can be selected
⇒ If the first and last zones are well defined, you can click AUTO
(RTMS X3/K3 Rev. 6.1 and up ) to initiate automatic Fine Tune
(Zone setup included). When the process is completed, further
changes can be made using manual procedure.
⇒ For manual Fine tune setup start with setting of “0”. Observe the
incidence of splashes and determine whether the Fine Tune number
should be increased or decreased. Use the arrows in the window or the
Up/Down keyboard keys. To ensure the best Fine Tune value was
found and protect the performance against small drifts,find the Fine
Tune “sweet spot” by modifying FT +/-1 and visually verify that the changes have very little
effect.
⇒ Click OK when satisfied with the setting to save it in the RTMS
Zone Setup – Forward-looking Mode
Use of Wizard for Forward-Looking mode zone setup.
Initiate the automated zone setup either by clicking the Wizard icon or AUTO button on the
Zone Setup window.
⇒ Enter the Height and Offset parameters when prompted.
⇒ The Wizard will determine, based upon traffic, the best location for the 3-zone speed-trap. If
it cannot find a good speed trap due to incorrect RTMS aiming, low volume or other causes, it
will display Warnings.
Manual Zone Setup – Forward-looking Mode
⇒ Set Number of Zones to 8 and position all zones in sequence with the first zone at
approximately at 8m (8 yards) from the sensor (farther if the sensor is higher than 5M)
Observe approaching (or receding) vehicles in the lane as "waves" of blips and adjust the tilt
and sway angles so that blip waves from small vehicles go through at least 5 of the 8 zones
and so that vehicles in adjacent lanes do not show blips in the zones. Detection of vehicles
from an adjacent lane indicates that the sensor is angled in that direction.
⇒ Fine Tune control affects the size of the zones and may be used to improve smooth passage
through all three detection zones. Set it to +5.
⇒ Perform count vefication over 50 vehicles or more. Find three consecutive zones, with vehicle
counts in close agreement with each other and with the manual count.
The location of these three zones will form the speed-trap. Note their position on the range
scale and using ZONES, move zones No. 1, 2 and 3 over these three consecutive zone
positions (ie. zones 5, 6 and 7), then reduce the number of zones to 3.
Only Zone #1 is used for Volume and Occupancy data. Zone #2 and #3 complete the speed trap
and help monitor the direction of travel.
The per vehicle speed measurement (it has a distinctive beep), is made only if the vehicle is
detected in all three zones. It is displayed if the Per Vehicle Speed box is check-marked.
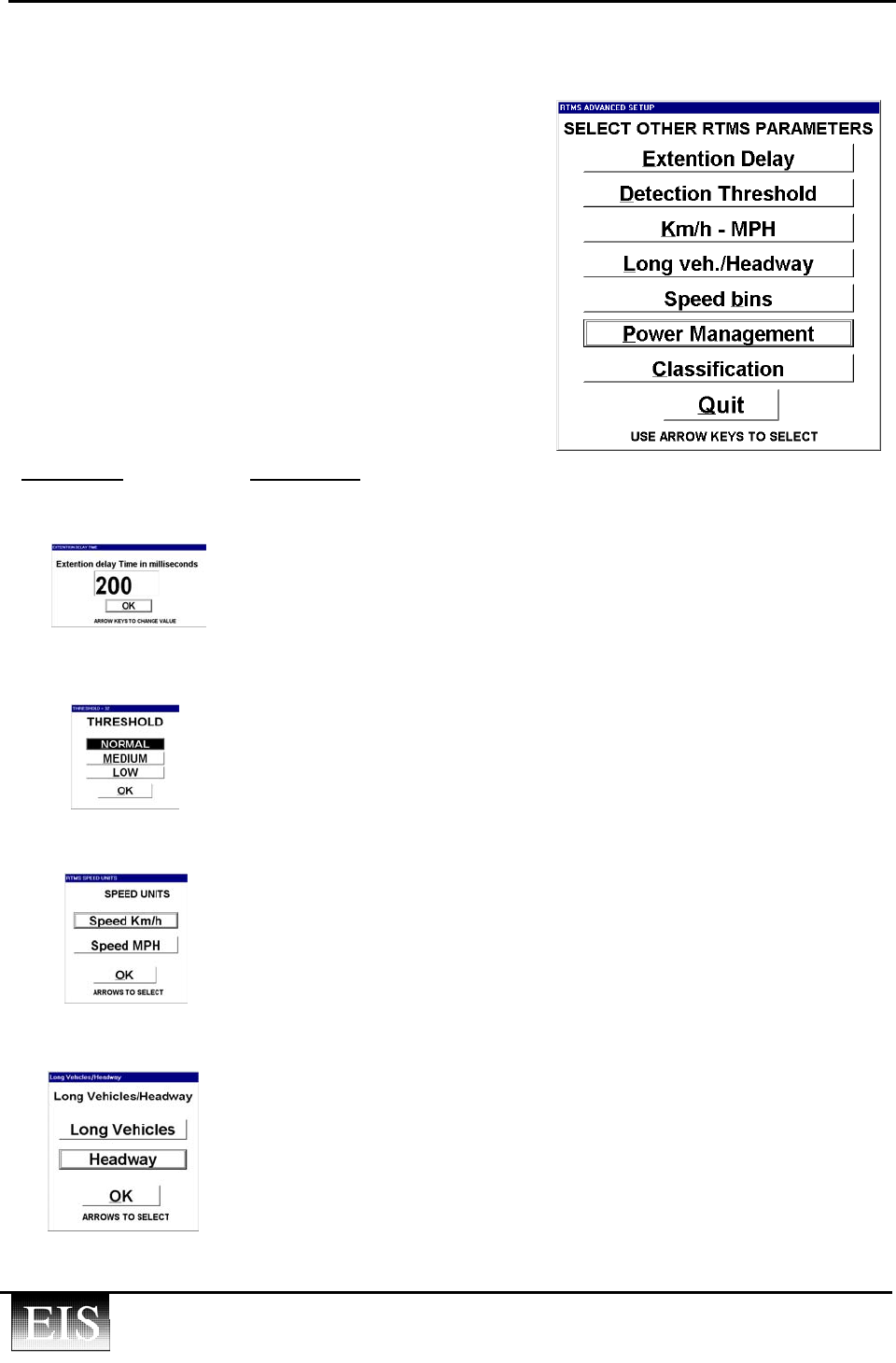
RTMS User Manual Issue 3.2 19
EIS Electronic Integrated Systems Inc.
Advanced Parameters.
⇒ Select the ADVANCED button to display RTMS ADVANCED SETUP window to change
default parameters or set other features.
The number of displayed functions depends on the
version of RTMS. Shown here is a maximum set
(RTMS X3/Ks Rev 6.1 and up).
⇒ Select the desired parameter (click the button or
highlight it using any of the arrow keys then press
ENTER).
⇒ Make changes to the parameters and save them by
clicking OK
⇒ Select Quit to exit this window without changing any
parameters
Parameter Description
Extension Delay Allows setting of Extension Delay Time to other than Mode default.
⇒ Use UP/DOWN keys to change it in steps of 10 ms and 100 ms up
to 3 seconds. Larger delay times can combine vehicles.
⇒ Press ENTER (or click OK ) to accept the displayed value.
Detection Threshold Allows setting of the Detection threshold to other than the Mode
default. Lower thresholds effectively increase the sensitivity.
Note: Setting not shown elsewhere on screen.
⇒ Select Normal, Medium or Low (mouse click or use UP/DOWN
keys followed by ENTER). The window will close automatically.
⇒ Select OK to exit without change to this parameter
Km/h – MPH The speed data generated by the RTMS is always in km/h. The PC
uses this setting to display speed data in the desired units on the screen
or in saved text files. Current selection is highlighted
⇒ Select required units. Observe the change in screen display in the
traffic statistics area.
⇒ Select OK to exit window without changes
Long Veh./Headway This parameter applies to the Sidefired Mode only. Headway is the
average time-gap between vehicles in units of 100ms.
⇒ Select either Long Vehicles, or Headway as required.
⇒ Select OK to exit the window without changes
For further details on definition of Long Vehicles, see Classification
below.
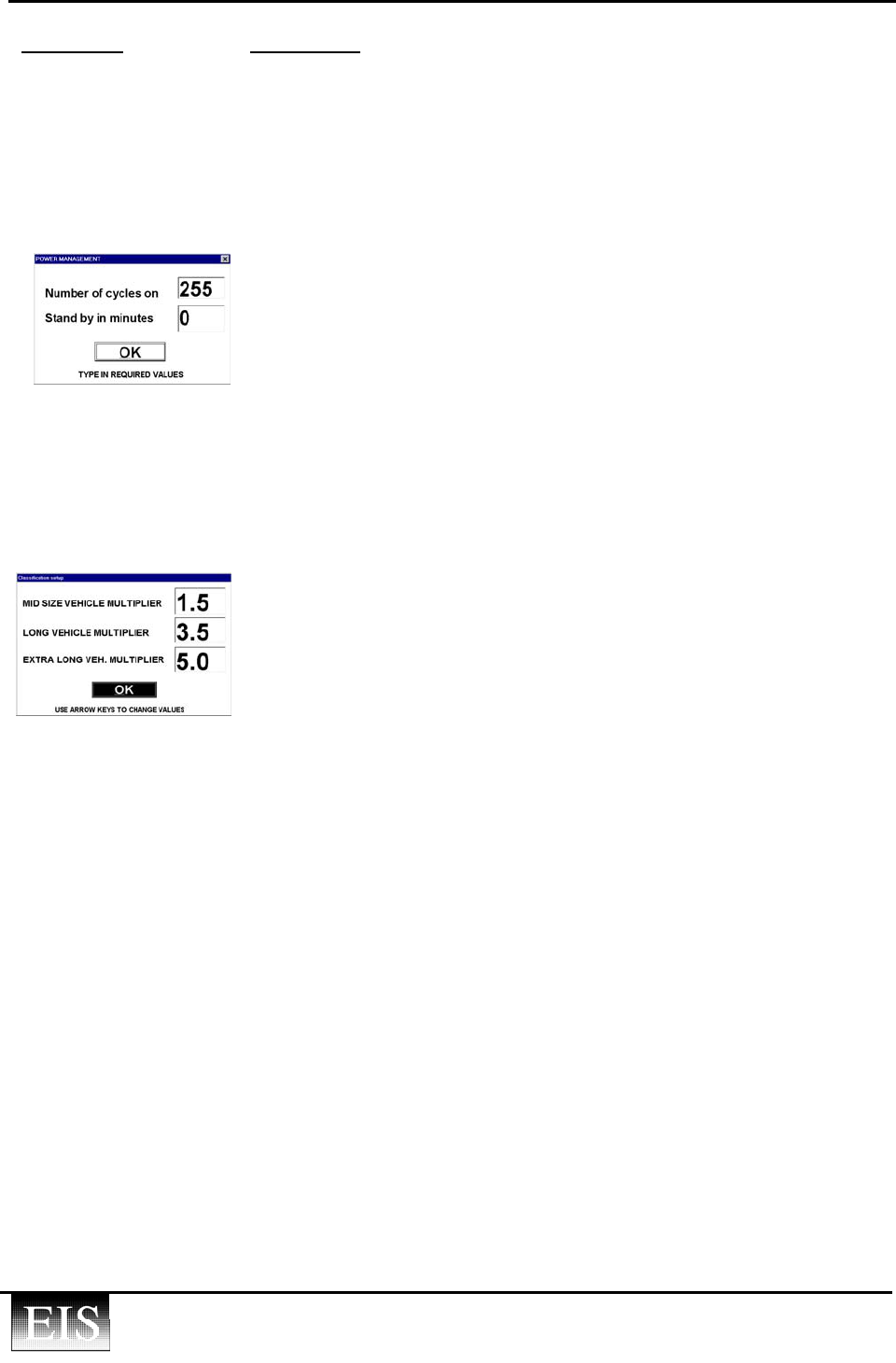
RTMS User Manual Issue 3.2 20
EIS Electronic Integrated Systems Inc.
Parameter Description
Speed Bins Opens a window used only in Forward-Looking mode. See section on
Additional Forward-Look Parameters below
Power Management
(Model X3/K3 only)
Power Management allows conservation of battery power in battery or
solar-powered applications by operating the RTMS in programmable
cycles. The RTMS must be factory-ordered with this option.
Two parameters are defined:
• Number of Message Periods (min of 3 suggested) the sensor
operates (0-254). It will go into standby 1-second after the last
period.
• Number of minutes the sensor is in standby and draws minimal
power (0 to 254).
⇒ Set the above as desired or set Number of cycles and Standby
time to 0 or 255 to turn Power Management off.
Classification
RTMS X2/K2 to X3/K3 Rev. 6.0 define only two vehicle classes, with
Long Vehicles being at least three times longer than average small
vehicles.
RTMS X3/K3 Rev. 6.1 and up add length classes: Mid-size and Extra
Long vehicles. All length classes are now user definable by specifying
a multiplier based on average small vehicle.
⇒ Click to open a window displaying multipliers
⇒ Use LEFT/RIGHT keys to highlight a selection
⇒ Use UP/DOWN keys to adjust multiplier in steps of 0.1
Note: Vehicle class counters are incremented when vehicles passing
the detection zone fall between class limits, e.g. if Long Vehicle
multiplier is 3.5 and Extra Long Vehicle multiplier is 5.0, only
vehicles with length between these multipliers will be reported as
Long Vehicles.
All classes are included in the volume count. Deduct the three classes
and the remainder are average vehicles (fourth class).
Note: Long Vehicle volumes will not be reported if Headway is
selected or if Message Period is higher than 300 seconds.
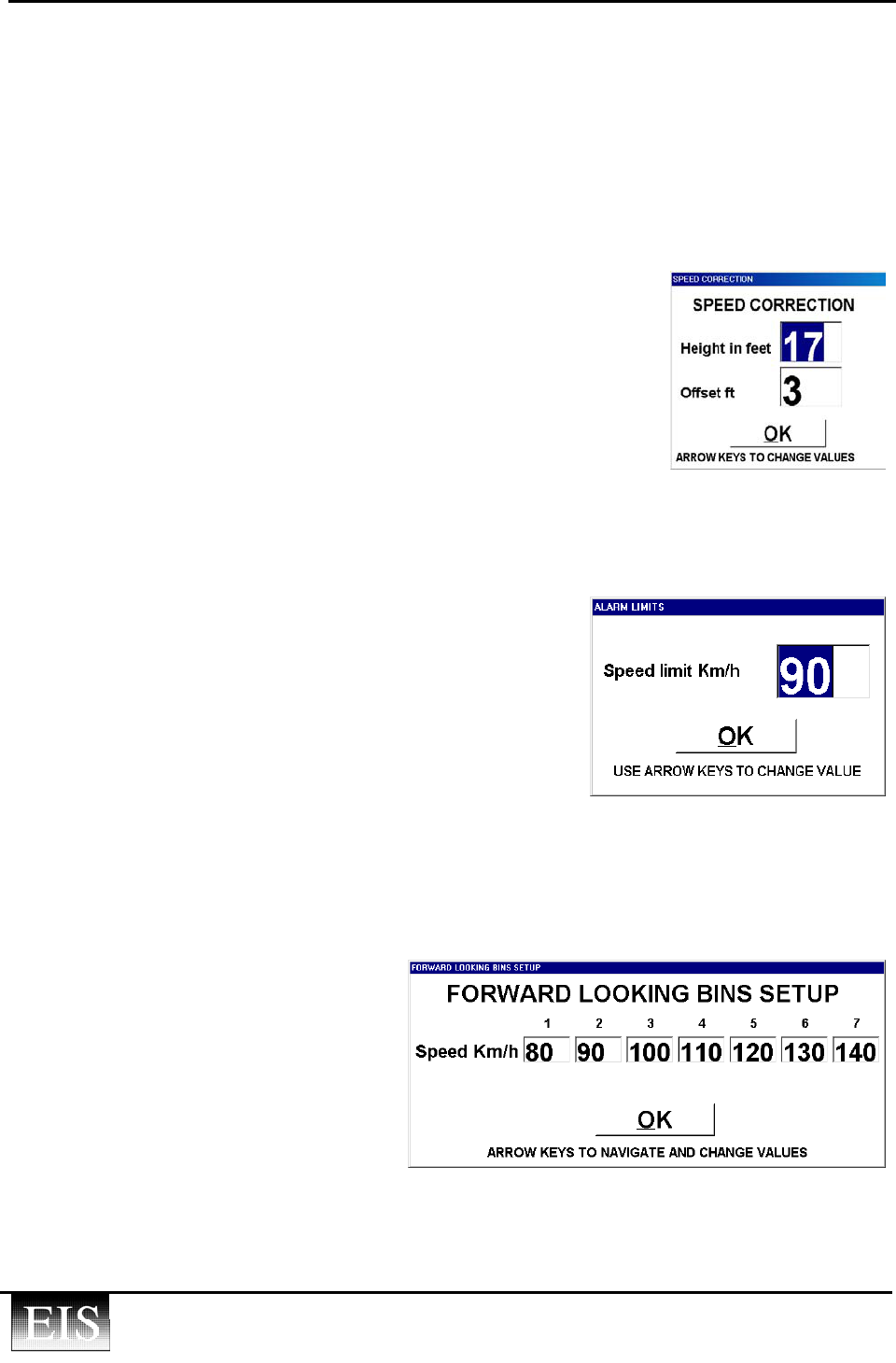
RTMS User Manual Issue 3.2 21
EIS Electronic Integrated Systems Inc.
Additional Forward-Looking Parameters
Setting of additional parameters is required when any Forward-Looking mode is selected.
Height and Offset
The SPEED CORRECTION window showing Height and Offset parameters is opened
automatically when these modes are selected. These parameters provide data for correction to the
Doppler speed measurements due to the angle of the beam:
Height Mounting height of the sensor above the road surface (e.g. 50 dcm or 17 feet).
Note: Doppler not active if set to “0”
Offset Distance from the sensor to the centerline of the monitored
lane
⇒ Use LEFT/RIGHT keys to highlight a parameter
⇒ Use UP/DOWN keys to change the value
⇒ key ENTER (or click OK) to exit the screen when desired values
are displayed.
Alarm Speed Limit
When Alarm Forward-Looking mode is selected, an additional ALARM LIMITS window opens
automatically:
⇒ Use UP/DOWN keys to set the alarm speed limit
⇒ Key ENTER or click OK when desired limit is displayed.
Speed bins
The user can specify up to 7 speed-bins for data collection.
Bin counters will be incremented by vehicles traveling
between the specified speed limits. The count of vehicles for which the sensor was unable to
determine speed is placed in the 8th bin.
⇒ Make sure the English/metric selection is as required before proceeding
⇒ Use LEFT/RIGHT keys or mouse click to highlight a bin.
⇒ Use UP/DOWN keys to set the bin’s
upper speed limit. The upper limit
setting of a bin automatically defines
the lower limit of the next bin. To
reset previous settings, reduce each
bin to minimum and set to desired
level.
⇒ Key ENTER or click OK to confirm
when all required values are displayed
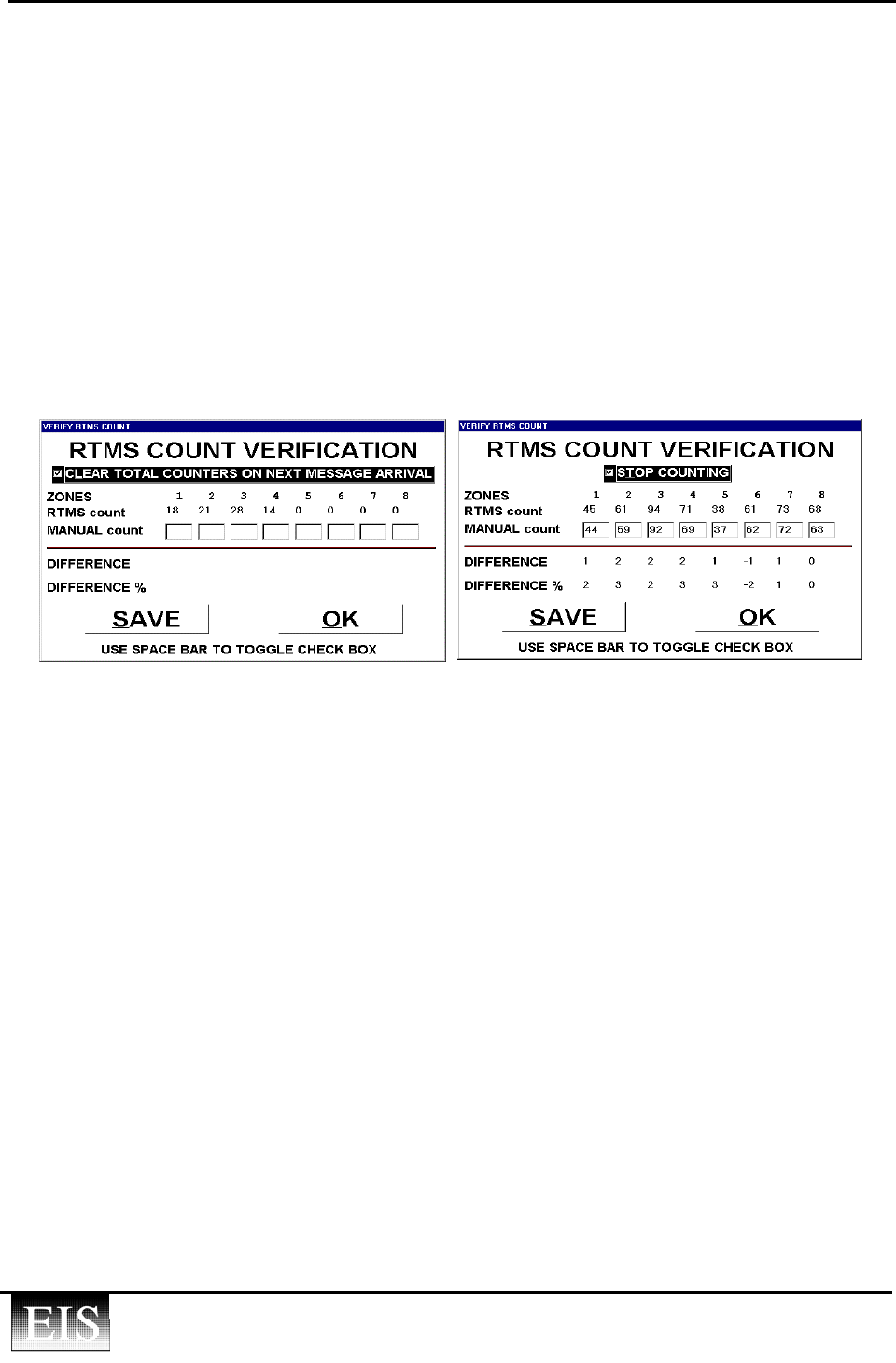
RTMS User Manual Issue 3.2 22
EIS Electronic Integrated Systems Inc.
Count Verification
To verify the setup correctness, one must compare RTMS detection to the presence of vehicles in
each lane. In Intersection mode applications, this is done visually over a period of time.
In highway modes (Sidefired or Forward-Looking) the Count Verification procedure compares
RTMS volumes in each detection zone to manual counts performed over the exact same interval.
Use of a hand-held tally counter for manual counting is recommended.
Perform the following steps:
⇒ Select PERIOD and set the Message Period to 30 seconds
⇒ Select VERIFY button
⇒ When the left-side window opens, tap the Space bar to checkmark the box in the CLEAR
TOTAL COUNTERS ON NEXT MESSAGE ARRIVAL field and get ready to start
counting.
⇒ At the end of the current Message Period the window background blinks, the PC beeps and
the RTMS count line is cleared, signaling the precise time to start the manual count.
⇒ Start counting vehicles in the selected lane as they cross the RTMS beam. Several people may
be involved, each counting traffic in an assigned lane.
⇒ At the end of each Message Period, signaled by a background blink and a beep, the RTMS
count in each zone is incremented by this period’s volume
⇒ Keep counting through several periods, until reaching at least 50 vehicles in that lane, then
stop counting precisely at the end of the Period.
⇒ Tap the space bar to checkmark the STOP COUNTING box, freezing the RTMS Count.
⇒ Enter the manual-count data in the corresponding detection zone boxes.
⇒ The PC displays the difference between the RTMS and the manual count reference in absolute
and % deviation. Deviation in beyond approx. +/-5% may require setup correction (e.g. zones,
Fine Tune or Sensitivity) to improve accuracy. The verification process should then be
repeated.
⇒ Successive Space bar tap recycles to the left hand window to repeat the process, if necessary.
⇒ In Forward-Looking modes, only Zone 1 (representing the RTMS count) needs verification.
⇒ Select SAVE to save the results of verification in a text file.
⇒ Select OK to exit to the main screen
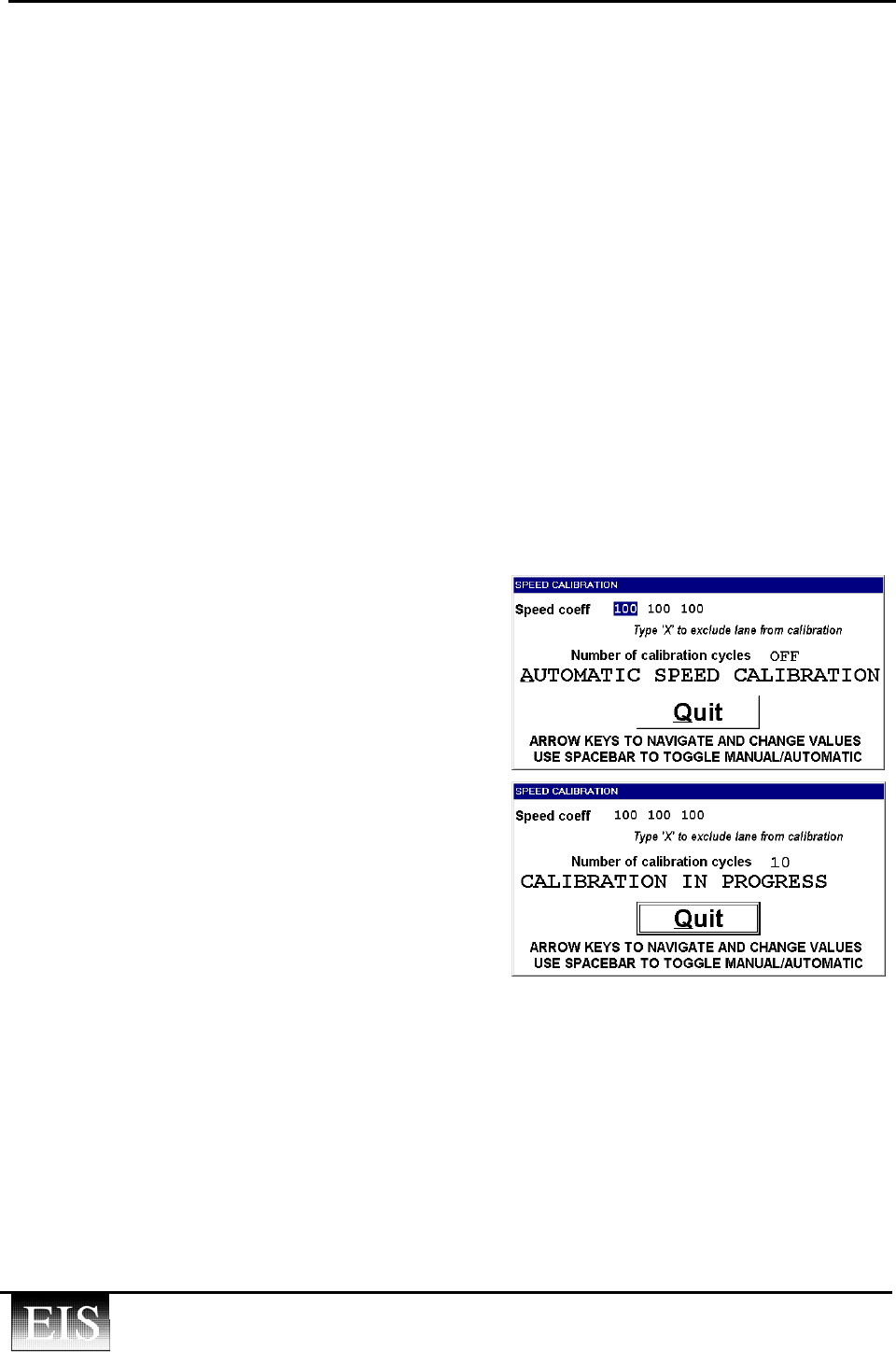
RTMS User Manual Issue 3.2 23
EIS Electronic Integrated Systems Inc.
Speed Calibration
This process adjusts internal coefficients used by the sensor to calculate the average speed of
traffic in each lane. It can be accomplished in two ways:
• Automatic Speed Calibration is intended for high-volume traffic, flowing at stable speed. It
requires entering per-lane reference speeds, which may be estimated or measured (e.g. by a
police radar) and setting the procedure duration as a number of Message Period cycles. 5
minutes (10 cycles of 30 seconds) is recommended.
• Manual Speed Calibration is intended for low-volume traffic (e.g. volume less than 5) or
when there are a high number of trucks. Here the coefficients are directly changed to bring the
calculated speed closer to the reference (estimated) speed.
Sidefired Speed Calibration
In Sidefired Highway mode, the RTMS uses the dwell-time of vehicles in their detection zones
for speed calculation. The zone’s “speed coefficient” is proportional to the zone length plus the
average car length.
Vehicles with dwell-time exceeding twice that of an average car are excluded from speed
averaging calculations. Good speed calibration is necessary for accurate average speed calculation
and truck classification.
Sidefired Automatic Speed Calibration
⇒ Select the SPEED CALIB. button to open the
window to define a Speed Reference for each
configured detection zone.
⇒ Use the LEFT/RIGHT keys to highlight the zone
references,calibration cycles or the Quit button.
⇒ Use UP/DOWN keys (or keyboard entry) to set
the desired reference speed in the highlighted
zone box lane. Reference speed is your estimate
of the current average speed in this lane. Type an
“X” to exclude that lane.
⇒ Select Number of calibration cycles and use UP
key to increase it in multiples of 5.
CALIBRATION IN PROGRESS will flash.
⇒ At the end of each Message Period, the Setup Utility adjusts the values of all active zone
coefficients to converge to the reference speeds. The number of cycles is counted down.
⇒ To block further changes in a zone coefficient, highlight the zone and type “X”.
⇒ When all speed measurements are reasonable or if traffic flow changes during calibration,
terminate the Calibration by clearing the number of calibration cycles to OFF (use DOWN
key). Continue when traffic flow resumes.
⇒ Select Quit (click or highlight and press ENTER). This will terminate speed calibration.
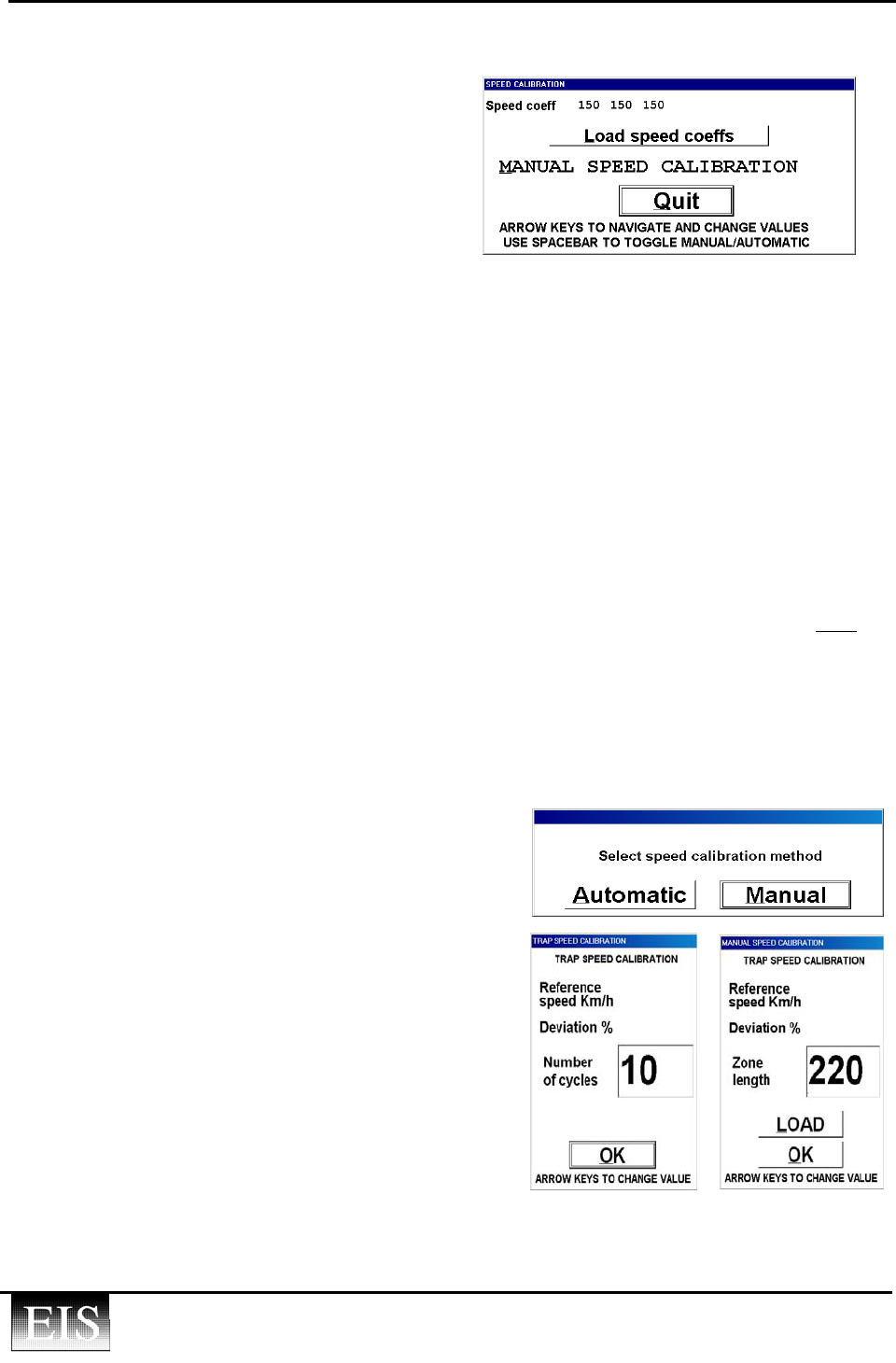
RTMS User Manual Issue 3.2 24
EIS Electronic Integrated Systems Inc.
Sidefired Manual Speed Calibration
⇒ Select SPEED CALIB button and tap the
space bar. The displayed Manual Speed
Calibration window will show the current
coefficients for each zone.
⇒ Compare the displayed speed measurement to
your estimated average speed in each lane.
⇒ Use LEFT/RIGHT keys to select zone and
UP/DOWN keys to adjust coefficients (in 150 to 640 range) proportionately to the required
change (e.g. if speed readings are 10% too low, increase that lane coefficient value by 10%).
⇒ Select Load speed coeffs or press L and key ENTER to update all RTMS coefficients.
⇒ Observe the effect on average speed measurements displayed on the screen at the end of the
next message period.
⇒ Click Quit to exit
Forward-Looking Speed calibration
Per Vehicle Speed
Per vehicle speed measurements is required for Forward-Looking mode speed calibration. Ensure
that the main screen box Per Vehicle Speed is check-marked while performing forward-looking
speed calibration. Click this box to suppress transmission of per vehicle data, if desired, after
completion of speed calibration.
The Forward-Looking Highway mode uses the averaged, per vehicle Doppler speed, as the
reference speed to calibrate the length of the speed trap to assure accuracy of “trap” speed
measurements at low speeds (below 15 Km/h).
Automatic speed calibration is included in the Wizard automated zone setup for the Forward-
Looking mode. It may also be independently initiated.
When SPEED CALIB is selected, a choice of
Automatic or Manual calibration is presented:
⇒ Select the required mode of calibration
In Automatic calibration, the recommended number of
cycles is 10 (at 30 sec. Period). The Doppler reference
speed and % deviation of the average speed from the
reference are updated at the end of each Message
Period. When deviation is less than 10%, exit the
program.
In Manual calibration the zone length coefficient must
be adjusted up or down (range 150 to 500)
⇒ Click LOAD and wait to get acceptable deviation
from the Reference speed .
⇒ Click OK to exit
100 96
-3 +3
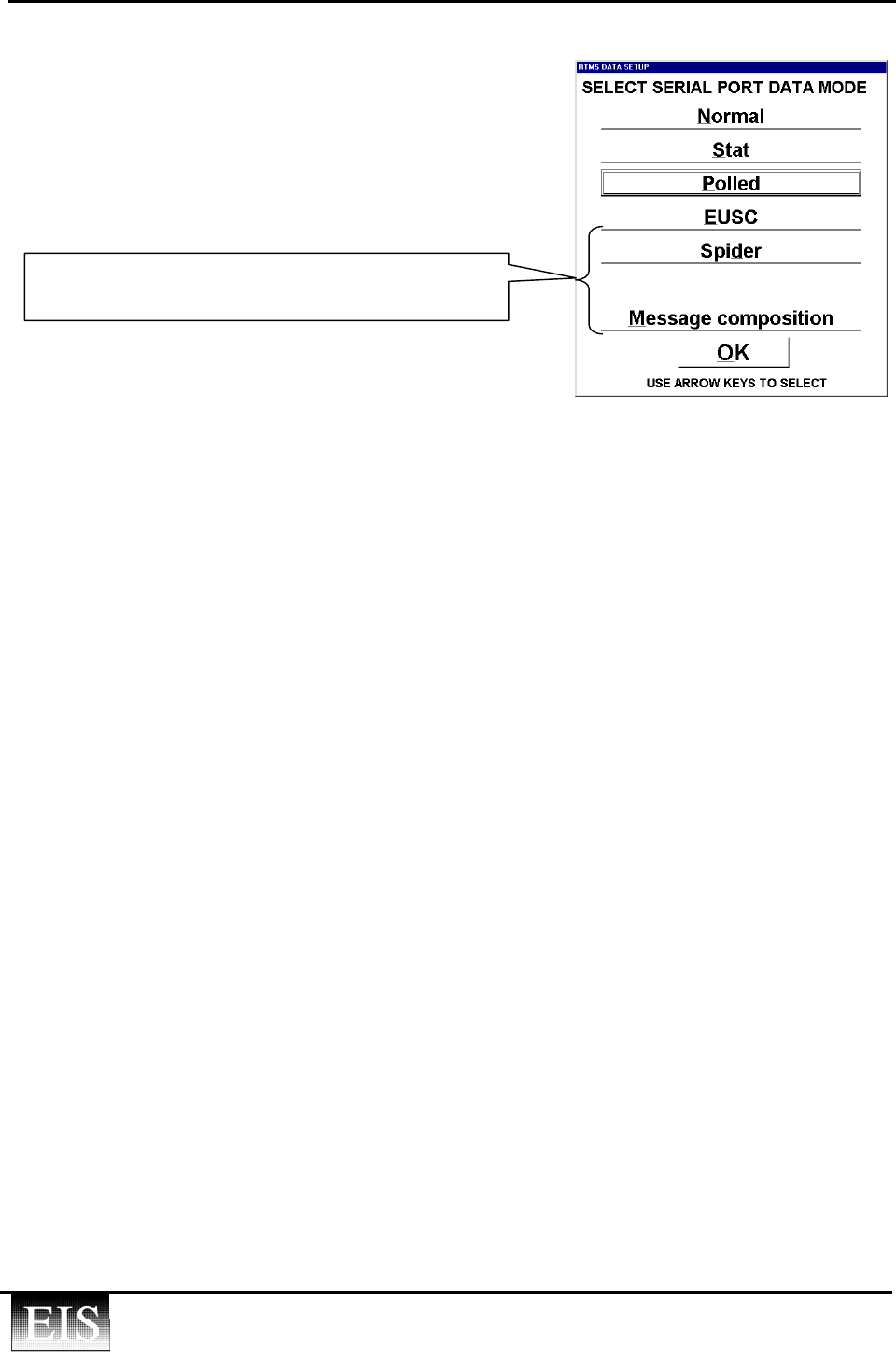
RTMS User Manual Issue 3.2 25
EIS Electronic Integrated Systems Inc.
Data Mode
Selecting the DATA button displays the RTMS DATA
SETUP window, which allows setting of the Data Port
Modes, described below:
Normal This mode is required for setup. Another mode may be selected, as required after
completion of setup.
In this mode the sensor is in constant two-way communication with the PC. Data
transmitted consists of target blips every 100 msec, per vehicle speed data in
Forward-looking mode, and the traffic data at the end of each Message Period.
Stat For use in non-polling applications where reduced number of messages is desired.
Sensor transmits statistic traffic data only, at the end of each Message Period.
Lamp at the lower right corner is flashing only during transmission.
Zones and blips are not displayed on the screen in this mode (“target” blip
messages are not received ). Sensor setup can be read with WinRtms.
Polled Sensor transmits statistic traffic data for the last Message Period stored in its
buffer only on receipt of a polling message with its ID Number.
The RTMS Setup Utility, set to the Multi-Drop communication mode, can poll,
display and record traffic data. See Communication Setup for further details
EUSC Presence event information is transmitted in this “polled-type” mode.
Zones and blips are not displayed on the screen in this mode.
Spider This mode operates in conjunction with the internal DSS modem. Detection event
information is transmitted at 0.5 sec intervals to a SPIDER controller
Zones and blips are not displayed on the screen in this mode.
Message
Composition
WinRtms utility allows you to expand the data generated by RTMS X3 Rev 6.1
and up. The minimum default data will match earlier revisions of RTMS.
Shown only with RTMS X3/K3 Rev 6.1 an
d
hi
g
h
er
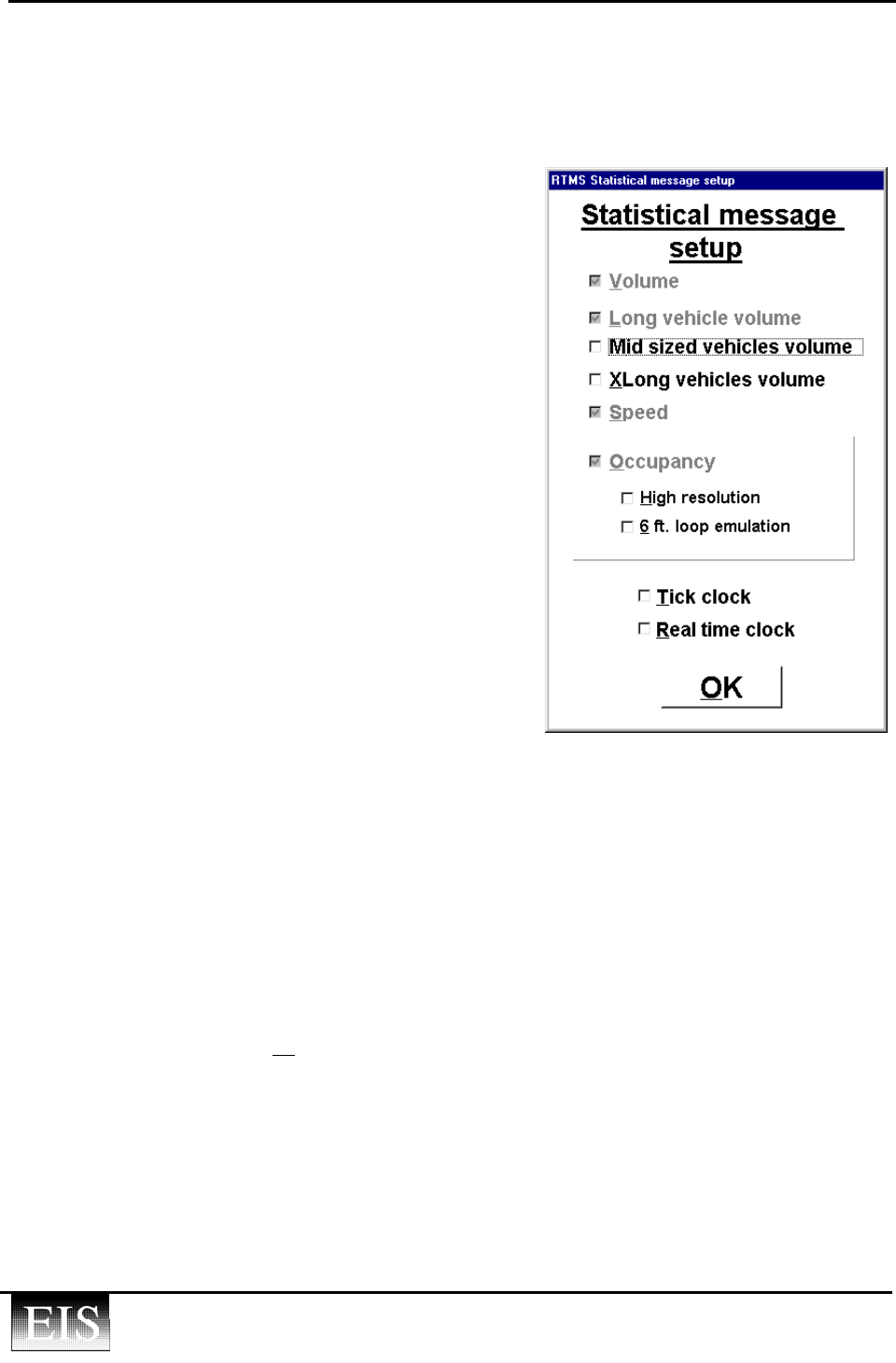
RTMS User Manual Issue 3.2 26
EIS Electronic Integrated Systems Inc.
Customization of traffic data (RTMS X3/K3 Rev 6.1 and up)
⇒ Click MESSAGE COMPOSITION button of the DATA MODE window to open the
STATISTICAL MESSAGE SETUP window, checkmark all the data types you wish to
receive and press OK to set them
New Data available with Rev 6.1 and up are:
• Two New Classes
Mid-size and XLong Vehicle volumes
• High Resolution Occupancy
Occupancy measurements with 0.1% resolution, . If
not selected, 1% resolution is used as with RTMS
X2/K2 and X3/K3 Rev 6.0 (which can be upgraded).
• 6 ft Loop Emulation
Corrects occupancy measurements to be equivalent to
the 6-foot loop data. If not selected, Occupancy
measurements are compatible with RTMS Model
X2/K2 data.
• Tick clock
Adds a 4-byte time-mark message based on 10ms
time-ticks, counted from the last sensor power-up.
• Real time clock
Adds a message with time and date stamp, from the
internal RTMS real-time clock.
Fig 15. Customization of Traffic Data
Note: The RTMS real-time clock is set by the PC during setup. If real-time clock messages are
requested, it is essential that the PC clock is correct.
The Traffic Statistics Display Area
The Statistics area displays zone-by-zone traffic data accumulated during the last Message Period.
Screen displays depend on the modes of operation. The definition of some traffic data is common
to all modes:
Volume Number of all vehicles that passed through the detection zone during the last
Message Period.
Occupancy % of time vehicles dwelled in the detection zone during the last Message Period.
It is rounded down to a whole number unless high resolution is specified
(RTMS X3/K3 Rev 6.1 or higher only)
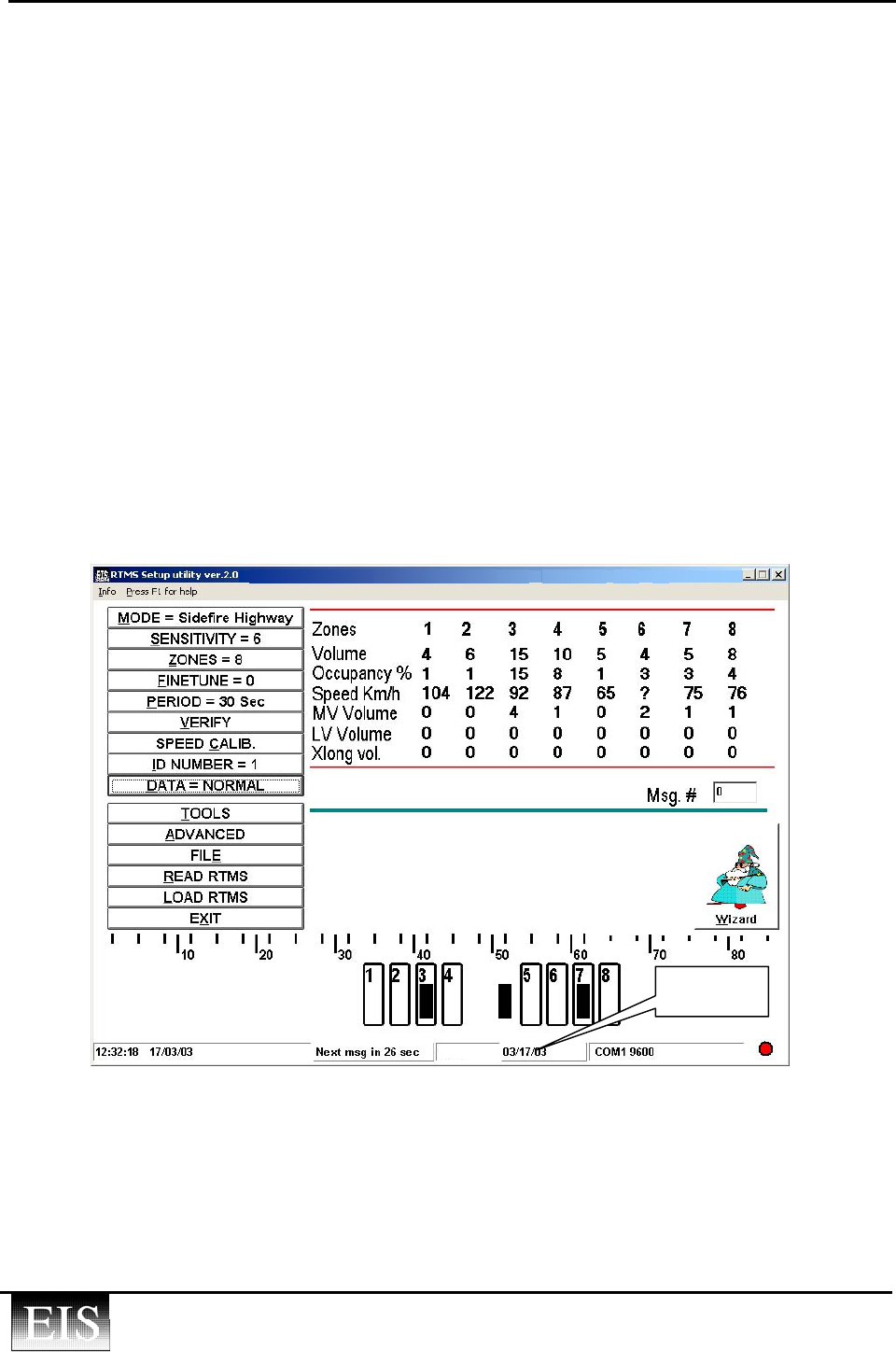
RTMS User Manual Issue 3.2 27
EIS Electronic Integrated Systems Inc.
Sidefired Data Definitions
Speed Average Speed of vehicles in the detection zone during the last Message Period. The
measurement does not include speed of larger vehicles (Medium, Long, Extra long)
The speed measurement may display “?” (unknown) when no vehicles were detected
during the Message Period (e.g. Volume = 0)
The last recorded speed will be displayed if no legitimate speed was received, or if only
trucks were detected for the period.
LV
Volume
Count of Long Vehicles. In RTMS X2/K2 & X3/K3 Rev 6.0, Long vehicles are defined
as 3 times the average length. In revision 6.1 and higher LV length is user-defined.
When Message Period is higher than 300 seconds, the LV Volume data byte is used as
overflow for total volume. Actual volume is equal to Volume plus 256*value of LV
Volume
MV and
Xlong
RTMS X3/K3 Rev 6.1 and up gives volumes for user-defined Mid-size and Extra-long
vehicles.
Fig 16. Side-fired mode setup and traffic data (F/W Rev 6.1)
Fig 16. Sidefired Statistical Traffic Data
Date of
setu
p
12.5V
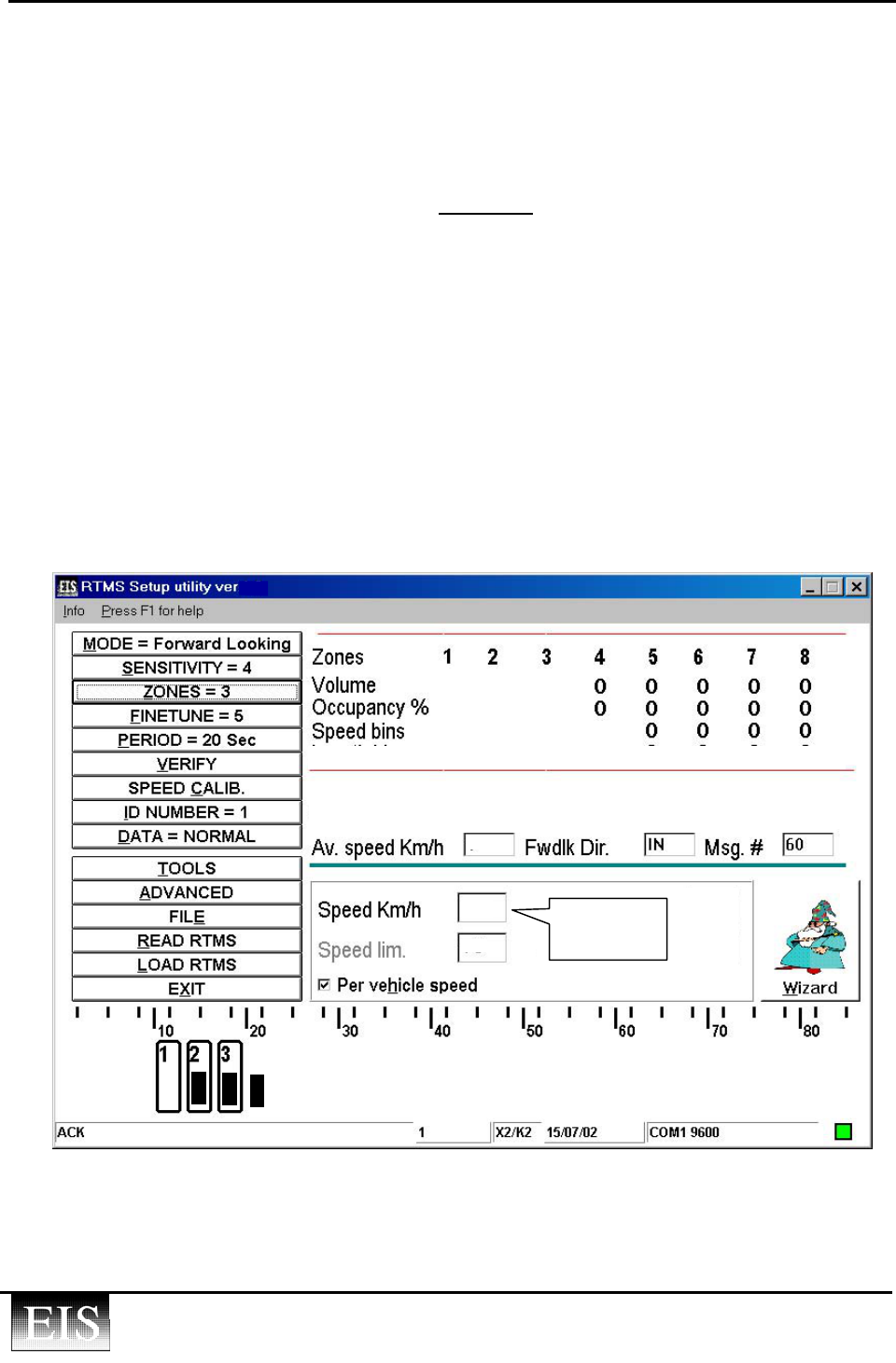
RTMS User Manual Issue 3.2 28
EIS Electronic Integrated Systems Inc.
Forward-looking Data Definitions
Volume,
Occupancy
Although Volume and Occupancy data are available for each of the three zones
of the speed trap. Zone 1 Volume and Occupancy shall be used as valid
measurements
Speed Bins Vehicle Volume in each of the speed bins, defined under Additional Forward-
Looking Mode Parameters (shown 4 bins defined). Bin 8 shows the number
of vehicles for which per vehicle speed could not be determined (Presence not
detected in all 3 zones of the speed trap).
Av. Speed Average of Forward-looking speed for all vehicles
Direction Direction of travel relative to the sequence of speed trap zones. IN= Vehicle
traverses the zone in the order of 3-2-1; OUT= in order of 1-2-3
Per vehicle
Speed/
Per vehicle speed measurement for vehicles traversing all three zones at speeds
above 10 mph, 15 Km/h.
Per vehicle speed must be checkmarked for this measurement to be displayed
Alarm mode speed limit is shown if Alarm mode is selected
Fig 17. Forward-Looking Mode traffic data
9 9 9
10 10 10
1 6 1
3
41
96 45
3.0
100
1
1
100
Per Vehicle
Speed
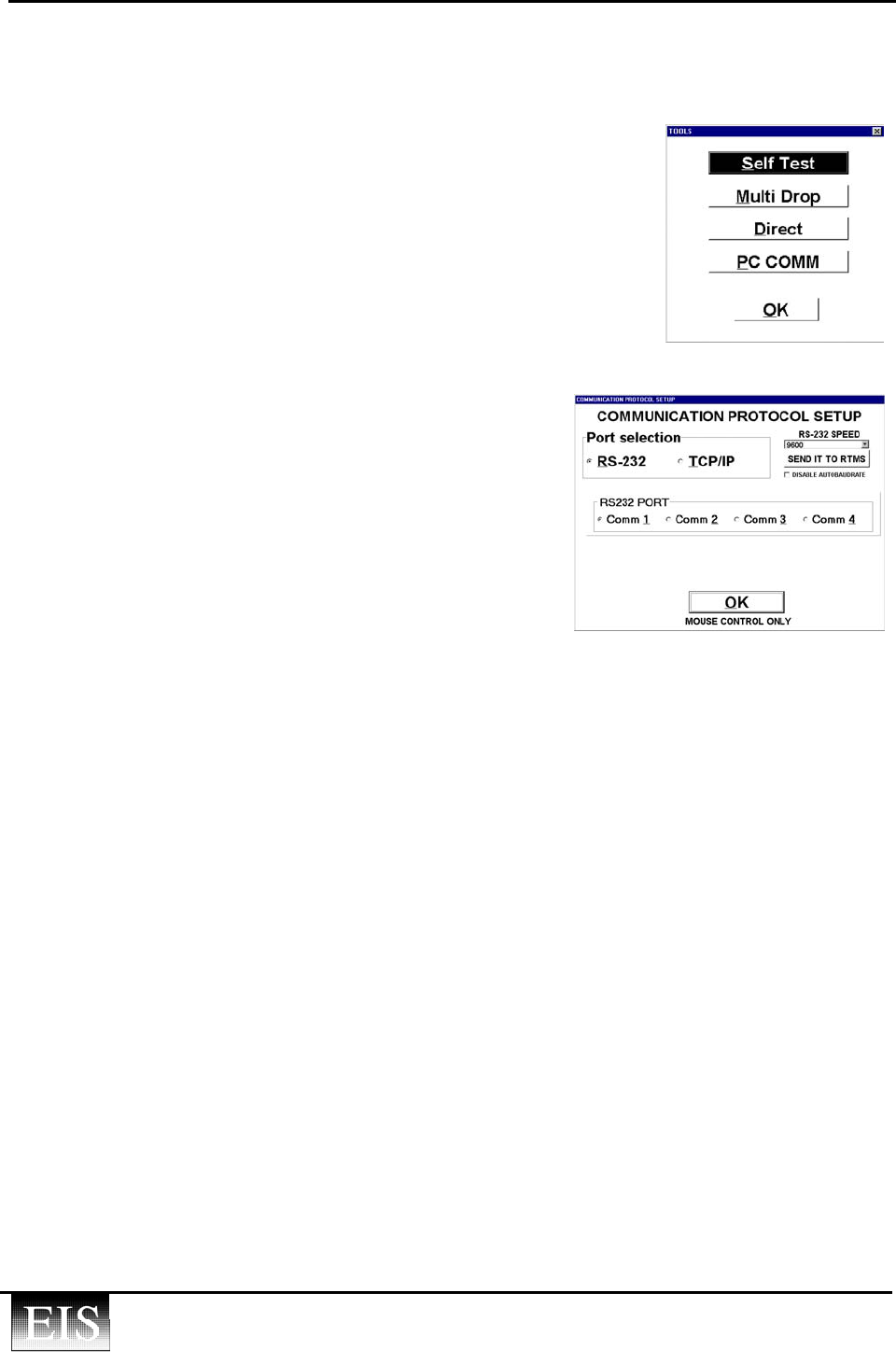
RTMS User Manual Issue 3.2 29
EIS Electronic Integrated Systems Inc.
5 NON-SETUP FUNCTIONS OF THE RTMS SETUP UTILITY
Setting the RTMS Setup Utility Communication Mode
Note: The RTMS Setup Utility starts in the last mode selected. To
change mode, an RTMS need not be connected. Do the following
⇒ Respond with NO to any messages presented on start-up
⇒ Open TOOLS window (highlight button and key Enter)
⇒ Select Direct mode when PC is connected to a single RTMS
⇒ Select Multi Drop mode to communicate with several sensors.
See Section on Communicating with Multiple RTMS units on
the next page.
Setting the PC Communication
⇒ Select PC COMM from the TOOLS window
COMMUNICATION PROTOCOL SETUP window
opens.
The default RS-232 setting applies if the RTMS is equipped
with RS-232 or RS-485 interface (identified by a label on
the underside of the sensor).
If RTMS is equipped with Ethernet interface as identified by
RJ45 connector and label on the underside of the sensor, see TCP/IP below
Serial Port only
⇒ Ensure correct COM port is selected
To communicate, the PC and RTMS serial ports must be set to the same speed. RTMS models
up to X2/K2 support only 9600 bits/sec. Model X3/K3 supports additional speeds up to
115200 bps. The RTMS Setup Utility attempts to adjust the PC COM speed to that of the
RTMS unless disabled by clicking the DISABLE AUTOBAUDRATE box.
Speeds lower than 9600 are useful where high quality transmission lines are not available.
They are, however, unsuitable for setup and must be set after completion of setup. If lower
speeds must be used, the RTMS data mode must be set to STAT to reduce the amount of data
and prevent communication problems.
⇒ Select the desired speed, suitable for the application from the drop-down menu and click the
SEND IT TO RTMS button to change both PC port and RTMS port speeds.
⇒ If the RTMS Model X3/K3 is equipped with the DSS modem a DSS MODEM SETUP
button will be on the window. Click it to display the setup window, shown in next section.
The DSS modem option forces the RTMS serial port to a speed of 115200 bps .
TCP/IP only
⇒ Click box if the RTMS is equipped with an Ethernet interface Set the displayed fields
(protocol (TCP or UDP), Local and Remote Port and Remote Host network address). Consult
Appendix 2 for instructions on re-programming the default IP address of the RTMS.
⇒ Click OK to save settings as displayed and to close the window.
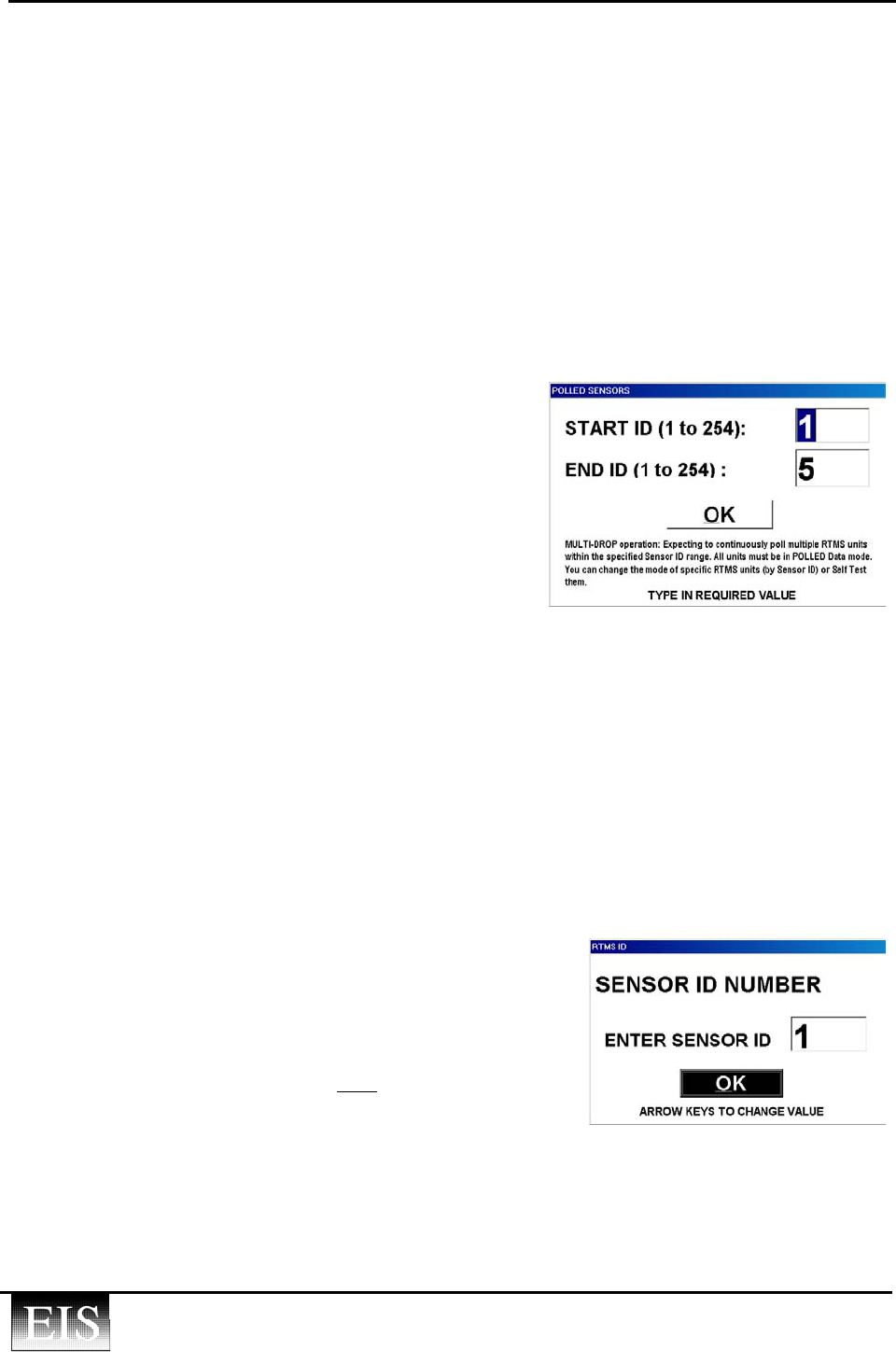
RTMS User Manual Issue 3.2 30
EIS Electronic Integrated Systems Inc.
Setup of Integral Digital Spread Spectrum Modem
A green rectangle displayed next to the data activity flashing “lamp” in the screen’s lower right
corner indicates that the RTMS is equipped with a DSS modem and that the modem is
communicating (synchronized) to a master. If the rectangle is red, there is no synchronization.
Internal DSS modems are setup at the factory according to the requirements of the installation and
should not require further setup. If changes are required refer to Appendix 3.
Communicating with multiple RTMS units in Multi-Drop Mode
The RTMS Setup Utility, when set into the Multi-drop mode, communicates with several RTMS
units connected to the COM port. The sensors will be in Polled Data mode. (Not applicable to
sensors with Ethernet (TCP/IP) interface).
The RTMS Setup Utility Multi-drop mode, selected via
the TOOLS menu (see Setting the RTMS Setup Utility
Communication Mode), will present the POLLED
SENSORS window shown:
⇒ Edit the required ID range limits of the com. line.
⇒ Select OK to activate
On restart, the RTMS setup Utility will present the POLLED SENSORS window with last
entered range of sensor IDs for acceptance or changes and force all RTMS units on the
communication link into the Polled mode.
Next it will generate sequential polling commands for all IDs in that range. The received data is
displayed in the Traffic Statistics area and the polled sensor ID in the lower left corner of the
screen. The received data can be stored as indicated in Data Recording.
Accessing a specific sensor in Multi-Drop Mode
To access a specific sensor, it is necessary to disable polling and change its data mode to Normal:
⇒ Confirm that RTMS Setup Utility is polling (Polled
Sensor IDs are displayed at the lower left corner)
⇒ Select the DATA button on the main screen and select the
NORMAL mode.
⇒ Specify the SENSOR ID Number in the presented
window using UP/DOWN keys only
⇒ Select OK (click it or use LEFT/RIGHT keys to
highlight followed by Enter)
The specified sensor’s Data mode is changed to Normal and polling of other sensors stops. The
RTMS Setup Utility communicates with that unit, automatically reading its setup and displaying
its parameters, blips and statistical data. Setup can be changed, as required.
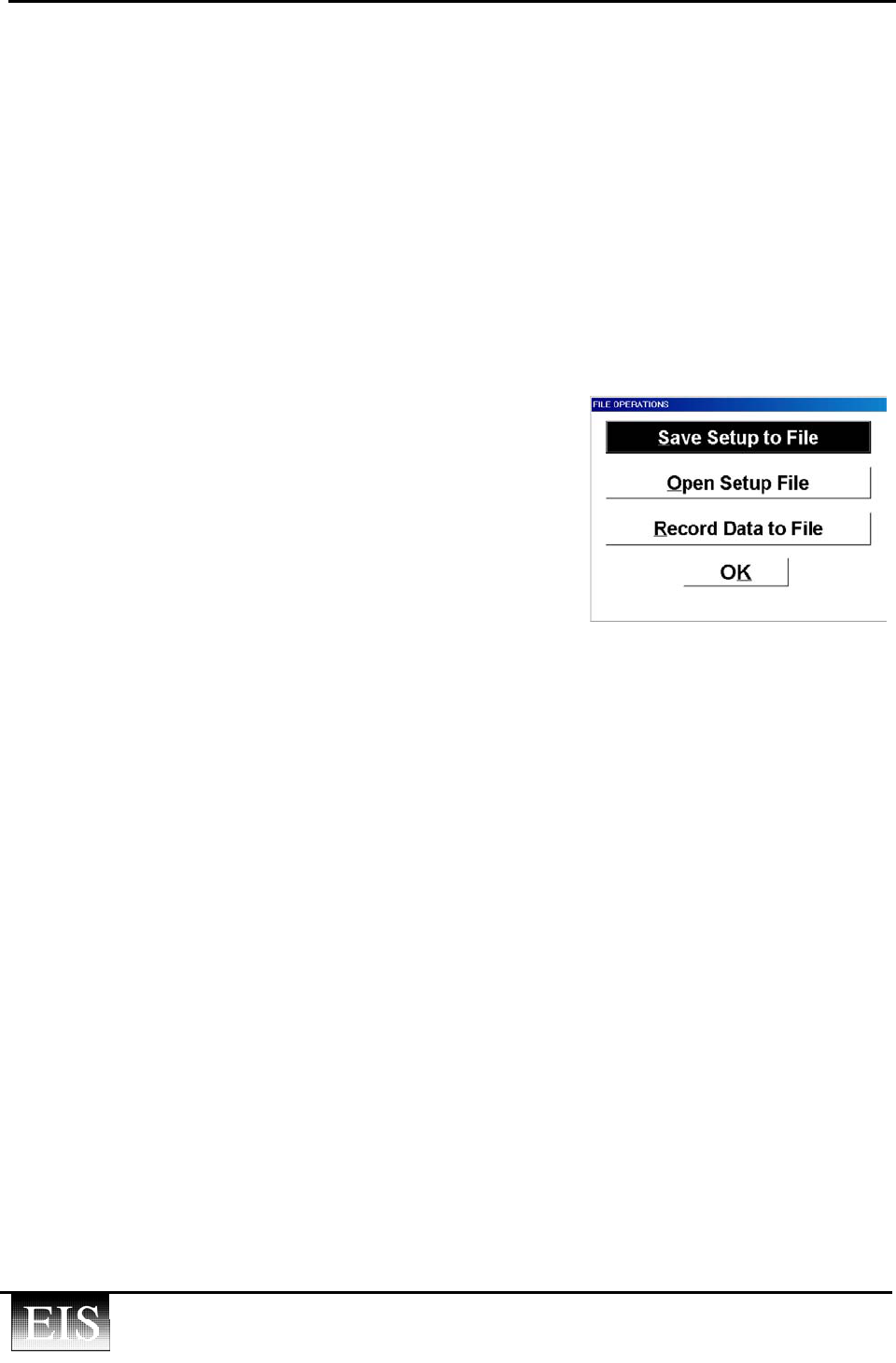
RTMS User Manual Issue 3.2 31
EIS Electronic Integrated Systems Inc.
⇒ To select another sensor for access, repeat the above steps. Only one sensor is allowed to be in
Normal mode to avoid message collisions. The previous sensor is forced into Polled.
⇒ To resume polling, change the last sensor’s data mode to Polled or exit the RTMS Setup
Utility. It will automatically open in Multi-drop mode and display the POLLED SENSORS
window.
⇒ To change the Setup Utility communications mode from Multi-drop, select TOOLS, then
Direct. The utility will now assume that the PC is connected to a single sensor in Normal
Data mode and will attempt to read its setup.
Saving and Retrieving Setup files
An RTMS setup can be saved on the PC as a disk-file.
⇒ Select FILE button opens the FILE OPERATIONS
window (shown)
⇒ Select Save Setup to File.
A Windows Save As dialog box, opens to allow folder
selection and file naming. The file will be saved with a
“.dat” extension.
To retrieve a saved file from a PC directory
⇒ Select Open Setup File Retrieved parameters are displayed on main screen buttons. At
this point they are not yet loaded into the RTMS.
Caution: The “dat” file loaded into an RTMS must be generated by a sensor with the same
Model and Revision to be compatible. Ensure that the RTMS ID is changed to the
correct one if loading another sensors setup.
⇒ Click YES to load displayed settings into RTMS. LOAD RTMS button on the main screen
can also do it.
⇒ Click NO or READ RTMS button to cancel retrieved screen and view current RTMS setup.
Data Recording
The RTMS Setup utility can record RTMS data onto a PC text file.
⇒ Select Record Data to File.
A Windows Save As dialog box will open for folder selection and file naming. The displayed
RECORDING DATA window indicates that recording is in progress
The generated file will have extension “.asc”. The sample file format below shows data generated
by RTMS with Rev 6.1 with maximum information selected. Speed units and Occupancy
definition are identified in the header .
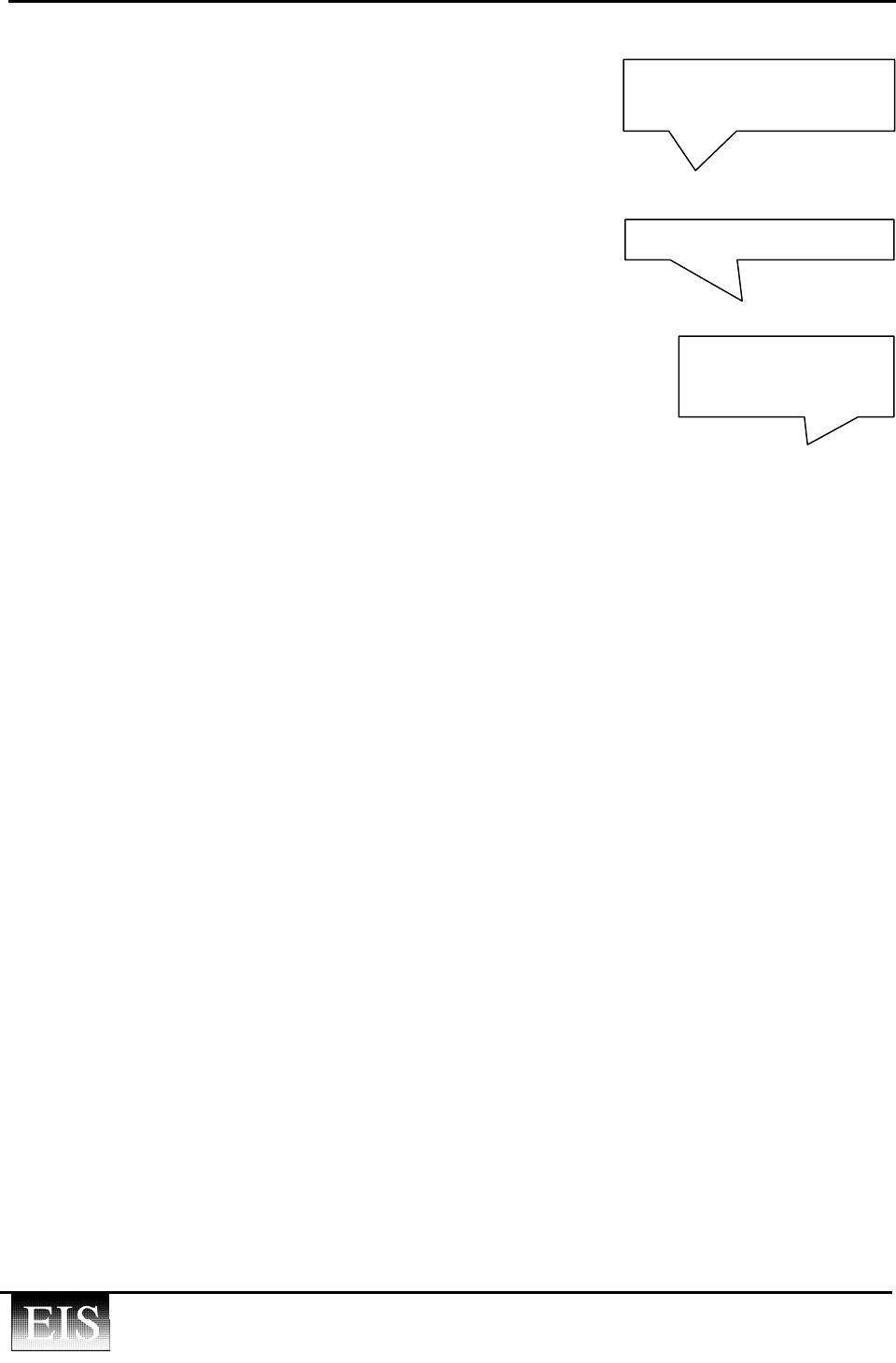
RTMS User Manual Issue 3.2 32
EIS Electronic Integrated Systems Inc.
RTMS STAT. MESSAGES ZONE: 1 2 3 4 5 6 7 8
SPEED IN Km/h. Occupancy 6 ft loop normalized.
11 03 2003 19:32:02
MESSAGE NO. 6 VOLUME: 5 8 19 17 6 9 11 16
LONG VEH: 0 0 0 0 1 2 2 0
STATION ID. 8 OCCUPANCY: 5 7 18 13 8 14 15 13
MID SIZE: 1 0 1 0 0 0 1 1
XLONG VEH: 0 0 0 0 1 0 0 0
FWDLK SPEED ? SIDEFRD SPD: 81 102 124 112 77 103 128 125 Dir. 128 V. 125 H. 80
11 03 2003 19:32:32
MESSAGE NO. 7 VOLUME: 6 8 10 11 11 12 14 17
LONG VEH: 0 0 0 0 0 3 2 0
STATION ID. 8 OCCUPANCY: 4 7 8 8 9 19 20 11
MID SIZE: 0 0 0 0 0 1 0 0
XLONG VEH: 0 0 0 0 0 0 1 0
FWDLK SPEED ? SIDEFRD SPD: 94 102 126 120 80 102 119 118 Dir. 128 V. 125 H. 80
11 03 2003 19:33:02
MESSAGE NO. 8 VOLUME: 6 7 16 12 6 11 11 13
LONG VEH: 0 0 0 0 0 0 0 0
STATION ID. 8 OCCUPANCY: 4 5 14 9 5 11 9 7
MID SIZE: 0 0 0 0 1 0 0 0
XLONG VEH: 0 0 0 0 0 0 0 0
FWDLK SPEED ? SIDEFRD SPD: 89 111 118 109 79 100 124 125 Dir. 128 V. 125 H. 80
Fig 18. Sample Recorded File Format
Self-Test diagnostic
The RTMS sensor can be tested any time to confirm that it is in working order. Select Self Test
from the TOOLS window. The PC sends a Self-test command to the sensor. During the 20
seconds required by the RTMS to complete the test, a progress bar is displayed, ending with a
display of the diagnostic results, including the RTMS firmware revision when the test is
completed. Self-Test should be performed with the sensor monitoring real traffic.
Support for Other Languages
The RTMS Setup Utility program allows replacement of the default English button legends and
menu labels to other languages.
A Notepad file “Rtmslng.txt” (partially shown below), is included in the same folder with the
“WinRtms.exe” program. Its default labels may be altered. To adapt the operation to your
language, edit this text file, replacing English legends by text in your language, after “=” using a
character set provided by your PC. Use character “&” to identify the next character as keyboard
shortcut.
[MainForm]
FormTitle=RTMS Setup utility ver.
MenuInfo=&Info
MenuHelp=Press F1 for help
ButtonMode=&MODE
ButtonSensitivity=&SENSITIVITY
ButtonZones=&ZONES
ButtonFineTune=&FINETUNE
ButtonPeriod=&PERIOD
ButtonVerify=&VERIFY
ButtonSpeedCalibration=SPEED &CALIB
ButtonIDnumber=&ID NUMBER
ButtonData=&DATA
ButtonTools=&TOOLS
ButtonAdvanced=&ADVANCED
ButtonFile=FIL&E
Power voltage (x 10), i.e. 12.5V
Direction (Applicable to FwdLk
mode, 0 =In, 128= Out )
Diagnostic byte.
Consult EIS if second
digit is not equal to “0”
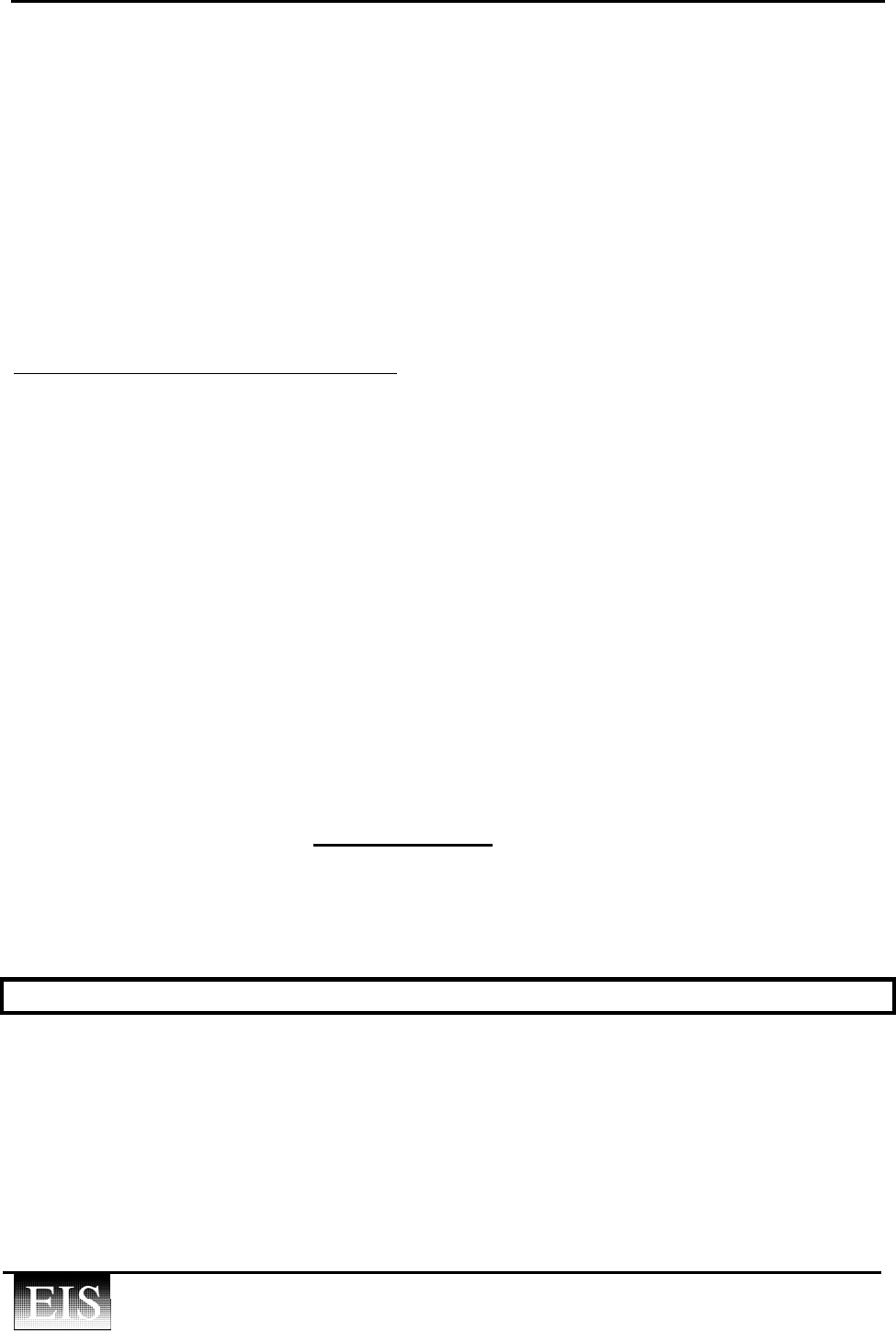
RTMS User Manual Issue 3.2 33
EIS Electronic Integrated Systems Inc.
6 CABLES
The RTMS cable
RTMS uses a single 32-pin MS connector for power and all outputs.
The RTMS is shipped with all required connectors, crimp pins and back-shells. Cables may
require on site preparation if their length is unknown or to pass them through conduits. The
installer must assemble the connector back-shell, crimp pins to cable wires and insert them into
the connector shells.
The RTMS cable should be UV protected where exposed. It should be overall shielded and
furnish sufficient number of stranded gauge #20 or #22 twisted pairs (e.g. Belden 95xx) to
provide the following:
Description # of pairs
Power 1 pair
Communication Port (one of 3 choices below)
RS-232 (standard) 2 pairs, 3 pairs when DSS option is provided
RS-485 (option) 3 pairs
TCP/IP (option) 2 pairs, max 10m (30’)- Use CAT5 for cable up to 100m (300’)
Zone Contacts 1 pair per zone.
Fail safe 1 pair
Auxiliary 12V DC power out 1 pair
For more details on wiring of the Communication port see the section on RTMS Serial
Communication and Cabling.
Fail safe is provided in conjunction with the use of the RTMS Interface Card (RIC) by contact
#9, which is closed when RTMS is powered, operational and in Normal data mode.
In preparing a cable:
⇒ Use the Daniels Manufacturing Corporation crimping tool M225200/1-01 AF8 with head no.
M22520/1-02) or equivalent. Do not solder pins!
⇒ Thread cable through the backshell before insertion of wires into shell is started.
⇒ Use the Insertion tool (red) to insert wires with crimped pin into shell.
⇒ Use the Extraction tool (white) to remove a crimped wire to correct an error
WARNING: DO NOT connect the cable shield or ground wire to the MS Connector’s shell
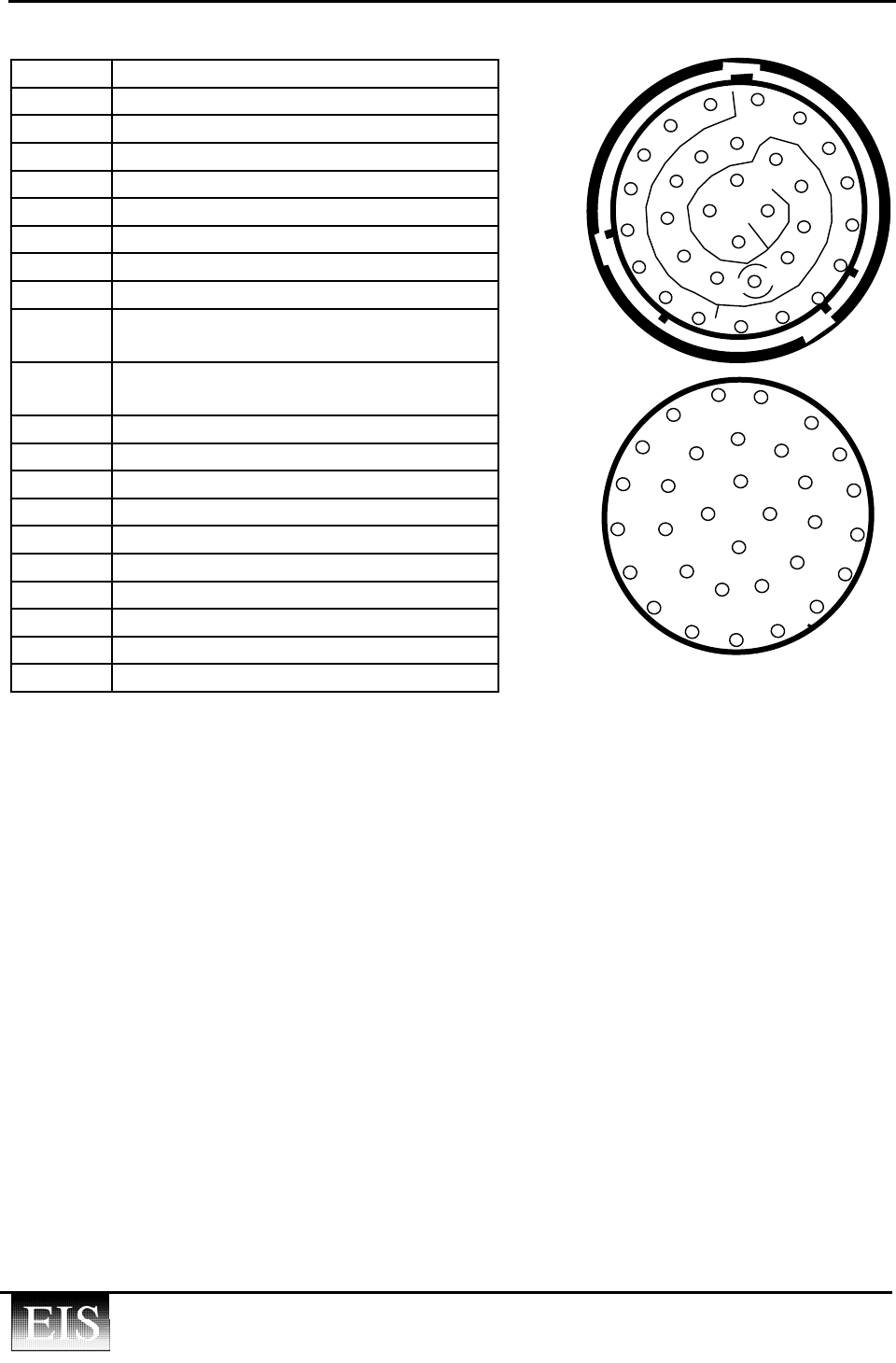
RTMS User Manual Issue 3.2 34
EIS Electronic Integrated Systems Inc.
RTMS MS Connector pin out
Pin No. Function
A,B Zone #1 contact
C,D Zone #2 contact
E,F Zone #3 contact
G,H Zone #4 contact
J,K Zone #5 contact
L,M Zone #6 contact
N,P Zone #7 contact
R,S Zone #8 contact
T Serial Port Input to RTMS
RS-232 Rx or RS-485 Rx -
V Serial Port Output from RTMS
RS-232 Tx or RS-485 Tx -
U,W Serial Port Signal Ground
X RS-485 Tx + or Ethernet Rx +
Y RS-485 Rx + or Ethernet Rx -
a DTR (DSS option only)
b +12V DC accessory power out
c Accessory power ground
d Contact #9 or Ethernet Tx +
e Contact #9 or Ethernet Tx -
f, g Low Voltage power 12-24V AC or DC
Fig 19. MS Connector Views
Power Cabling notes
• Standard low voltage 12-24V AC or DC
Low voltage power can be derived from:
• Controller cabinet 24VDC, if available
• Transformer in Controller or pole-mounted cabinet, 16-20V AC 10W recommended
• 12V Battery - Recharged by a solar panel or from lighting supply
The range of standard low voltage RTMS power at the input is 10.5V to 34V. Voltage outside this
range will cause the sensor to shut down. Cable resistance must not reduce available voltage
below the lower limit.
Peak voltage at 24VAC is approximately 34V i.e. at upper cutoff. The use of 24V AC should be
avoided where cable runs are short.
Model X3/K3 includes internal cutoff switch at 11.5 V to prevent battery damage due to deep
discharge.
Rear view
Front view
C
D
E
F
G
L
M
N
P
R
S
U
h
j
H
J
K
T
V
W
X
Y
Z
a
b
c
d
e
f
g
B
A
B
C
D
E
F
G
L
M
N
P
R
S
U
j
H J
K
W
V
f
g
e
d
T
X
Y
Z b
c
A
h
a
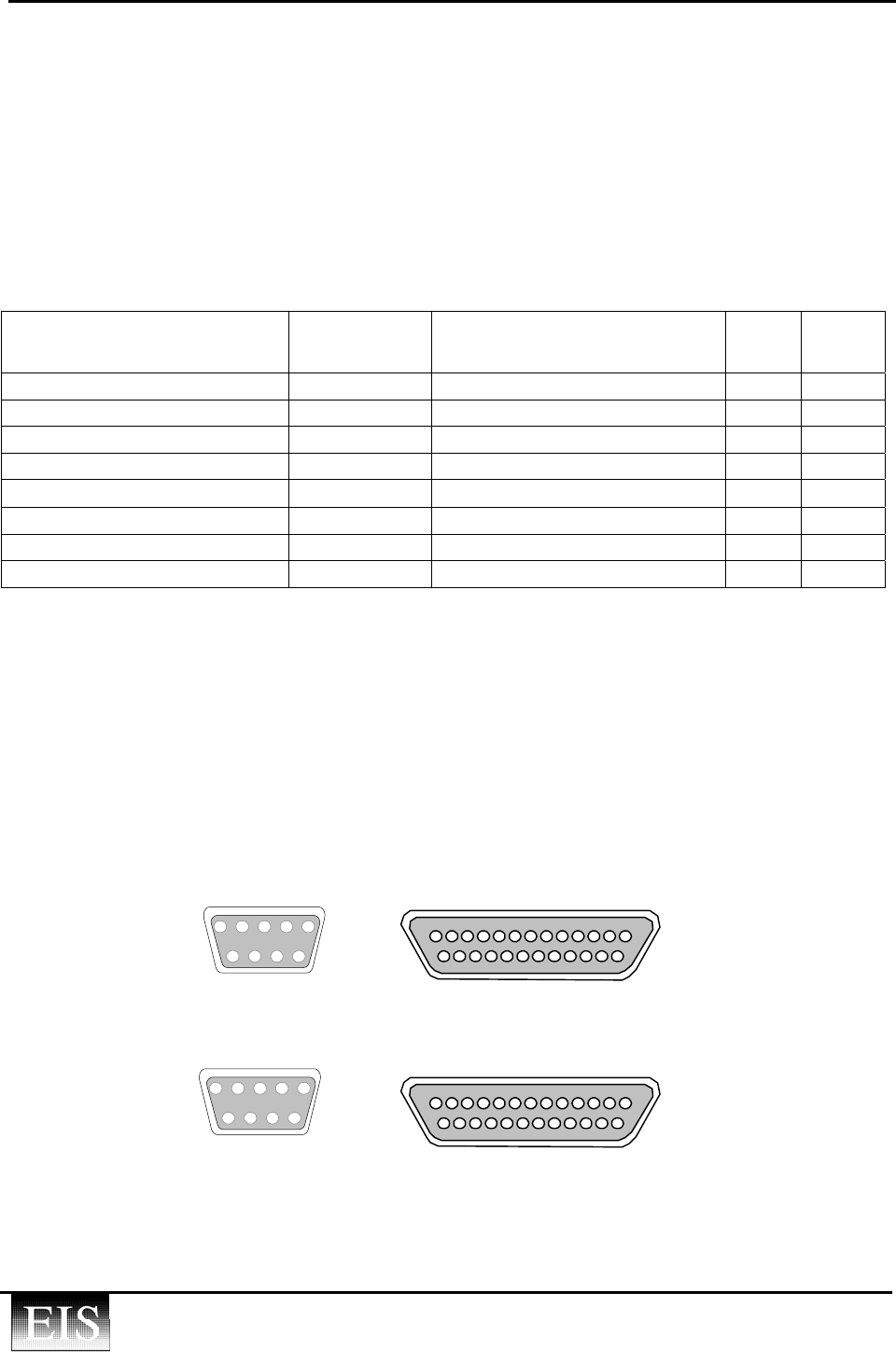
RTMS User Manual Issue 3.2 35
EIS Electronic Integrated Systems Inc.
RTMS Serial Communications and Cabling
Standards and Nomenclature
Data communication equipment is classified as Data Terminal Equipment (DTE), which
generates and stores data (e.g. PC) or Data Communication Equipment (DCE), e.g. modems.
RS-232 Serial ports use two types of RS-232 connectors, the 25-pin DB25 and the 9-pin DB9.
DTEs employ male connectors and DCEs employ female connectors. 8 essential functions and
their corresponding pin assignments are shown below.
A
bbreviation & Full Name Direction Function DB9
pin #
DB25
pin #
DCD Data Carrier Detect DCE to DTE Carrier received 1 8
Rx Receive data DCE to DTE Receive Data (by DTE) 2 3
Tx Transmit data DTE to DCE Transmit Data (by DTE) 3 2
DTR Data Terminal Ready DTE to DCE DTE ready to receive data 4 20
DSR Data Set Ready DCE to DTE DCE in communication mode 6 6
RTS Request To Send DTE to DCE DTE has data to send 7 4
CTS Clear To Send DCE to DTE DCE ready to receive data 8 5
Gnd Signal Ground Return path for Tx and Rx 5 7
Note that while a DTE transmits on Tx and receives on Rx, a DCE does the reverse, i.e. receives
on Tx and transmits on Rx. Control signals may be ON (Positive Voltage level in 5-15V range)
or OFF (negative voltage level in 5-15V range). To transmit, RTS, CTS, DSR, and DTR are
required to be in the ON state, where implemented (Note: not all signals are implemented by
DTEs and DCEs).
For convenience of cable preparation, rear views of pin layout of 9 and 25 pin connectors are
shown below.
Fig 20. Pin numbering of D-type connectors
DB9 Male
Rear View
5
DB9 Female
Rear View
1
9 6
5 1
9 6
DB25 Female
Rear View
1 13
14 25
1
13
1425
DB25 Male
Rear View
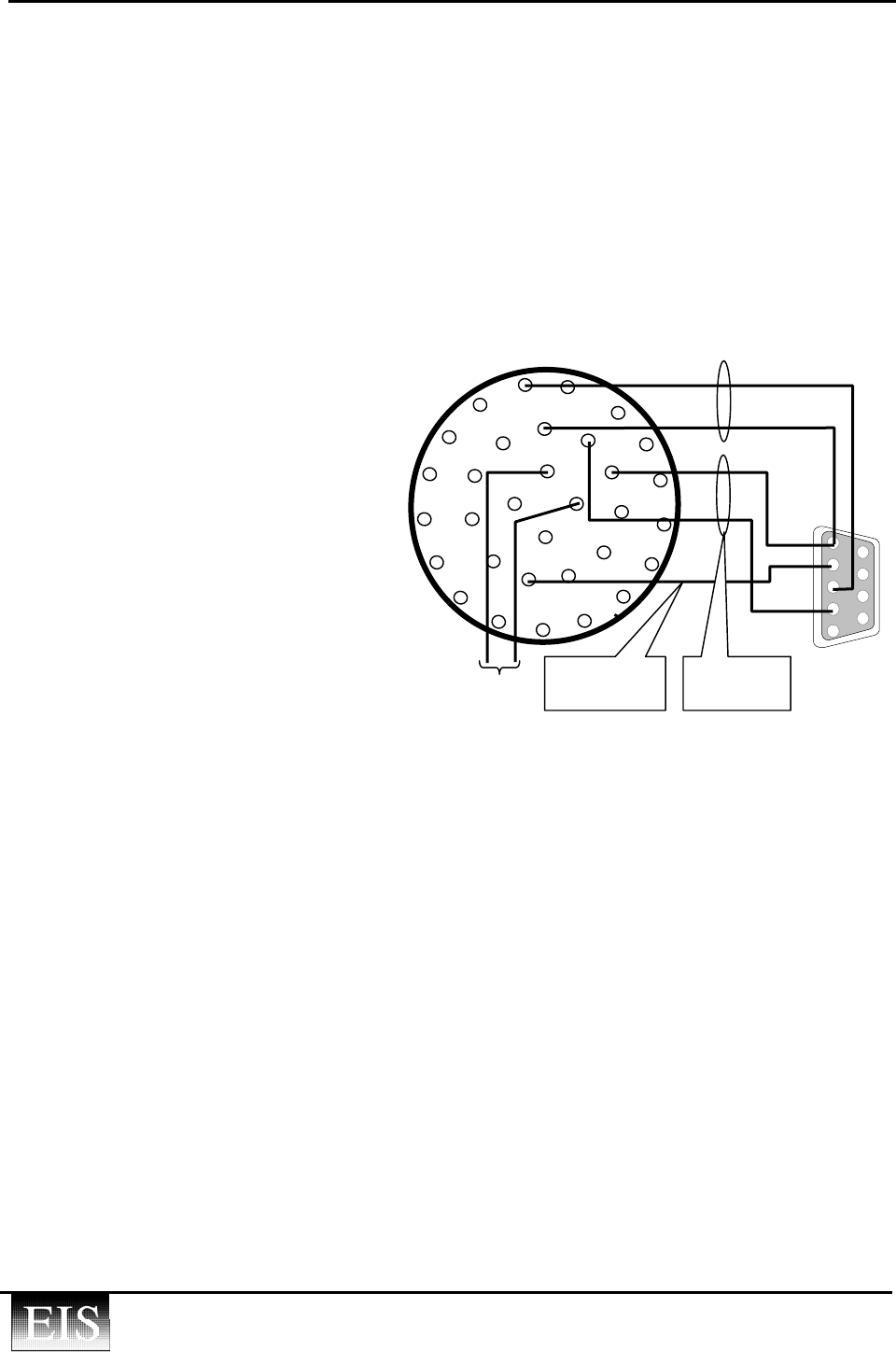
RTMS User Manual Issue 3.2 36
EIS Electronic Integrated Systems Inc.
RTMS Serial Port Wiring
RTMS Models X2/K2 have an isolated RS-232 port with a range up to 250m (800 feet) at a speed
of 9600 bits/sec. Modems are required if this range is exceeded.
RTMS models X3/K3 have a variable speed Serial port with speeds up to 115.2 kbits/sec selected
by the user during the setup. The serial port can also be configured as RS-485 (optional) for an
extended range up to 4000 ft. with multi-drop capabilities without the use of modems.
RS-232 Port wiring
The RTMS cable wiring is configured to provide a null modem function for direct connection of
the sensor to a PC for setup purposes using a standard extension cable.
To do this the RS-232 port is wired as a DCE, i.e. transposes transmit and receive lines and uses
a female 9-pin connector.
⇒ Connect as follows:
Twisted Pair 1
• MS pin V (red) to DB-9 pin 2 (Rx)
• MS pin U (black) to DB9 pin 5 (Gnd)
Twisted Pair 2
• MS pin T (red) to DB-9 pin 3 (Tx)
• MS pin W (black) to DB-9 Pin 5
Fig 21. RTMS RS-232 Port Wiring
RS-232 Port wiring – for RTMS with DSS Option
When the internal DSS Modem option is included, the RS-232 port wiring requires another wire.
⇒ Connect MS connector pin “a” to DB9F pin 4 (DTR).
During normal operation the RS-232 port feeds the DSS modem. On direct connection to a PC,
RTMS detects the positive voltage on pin “a” from the COM Port (DTR ON) and switches its RS-
232 Rx line to the PC. Upon disconnecting from the PC COM port, the RTMS will re-connect it
back to the DSS modem.
Without the above modification, the receive line will be connected to DSS, the RTMS Setup
Utility will be unable to send any commands to the RTMS and setup will not be possible.
DSS Modem
Option only
C
D
E
F
G
L
M
N
P
R
S
U
h
j
H
J
K
T
V
W
X
Y
Z
a
b
c
d
e
f
g
B
A
DB9 Female
Rear View
5
1
9
6
Twisted
pairs
2
3
4
•
•
•
•
•
•
•
•
•
•
•
Power
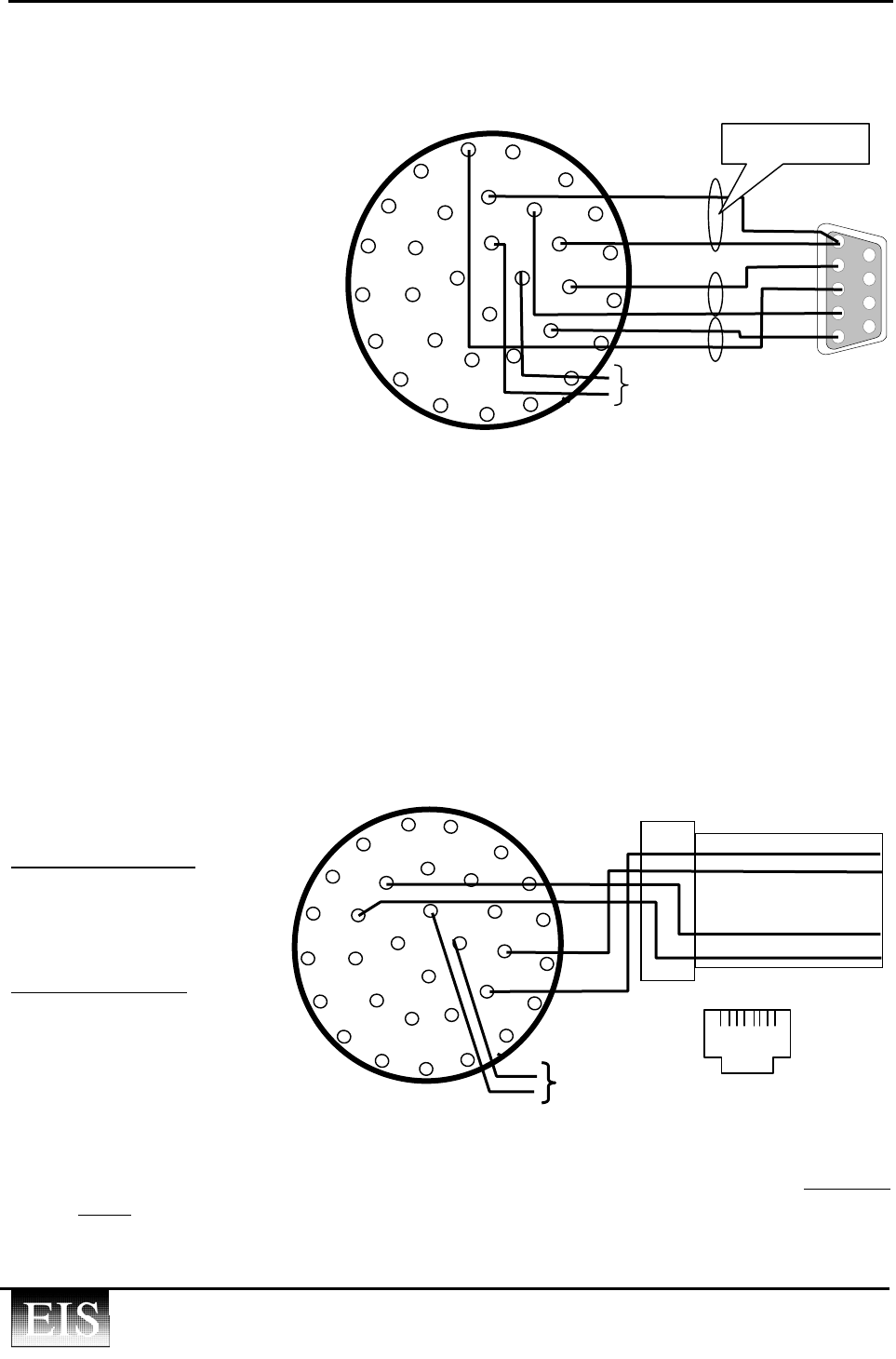
RTMS User Manual Issue 3.2 37
EIS Electronic Integrated Systems Inc.
RS-485 Serial Port Wiring ( Models X3/K3 only)
MS connector pins V, X, T, Y, U and W are assigned as RS-485 Tx-/ Tx+, Rx-/ Rx+ and ground
respectively.
⇒ Cable as three twisted pairs
with Rx- and Tx- connected to
red wires
⇒ Connect MS pins to DB9F as
follows:
Pin V (Tx-) to pin 2
Pin T (Rx-) to pin 3
Pin U/W (Gnd) to pin 5
Pin X (Tx+) to pin 4
Pin Y (Rx+) to pin 1
Fig 22. RTMS RS-485 Port Wiring
Note: This pin-out allows the cable to be compatible with RS-232 for a direct connection
( max. 30 feet) to a laptop for setup.
See Appendix 1 for further details on multi-drop configuration wiring.
TCP/IP (Ethernet) Port Wiring
MS Connector pins X, Y, d and e are assigned as the TCP/IP port Rx+/ Rx-, Tx+/ Tx- leads
respectively. Two twisted pair ethernet wiring standards employing RJ-45 connectors are in
common use, T568A and B. These differ by interchanging transmit and receive pairs. CAT5
stranded-wire cable must be used for lengths exceeding 10m (30 feet) to a max. of 100m (300 ft).
The shown MS connector to RJ-45 wiring conforms to T568B standard.
Twisted pair 1 (Tx)
Pin d to pin 1 (White/orange)
Pin e to pin 2 (Orange/white)
Twisted pair 2 (Rx)
Pin X to pin 3(White/green)
Pin Y to pin 6 (Green/white)
Fig 23. RTMS Ethernet Port Wiring
Note: Ethernet devices connect to hubs of the same standard using a straight networking patch
cable. Two ethernet devices of the same standard may be connected using a crossover
cable. RTMS connection to a PC or to an Ethernet bridge requires crossover cable if both
employ the same standarad. Carrying both types of cables is recommended when setting
up an RTMS equipped with TCP/IP interface.
C
D
E
F
GL
M
N
P
R
S
U
h
j
H
J
K
T
V
W
X
Y
Z
a
b
c
d
e
f
g
B
A
Pin 2 (Orange)
Pin 1 (White/Orange)
Pin 3 (White/Green)
Pin 6 (Green)
RJ-45
T568B
Tx +
Tx -
Rx +
Rx -
•
•
•
•
1 8
RS-45
Jack
•
•
Power
5
1
2
3
4
DB9 Female
Rear View
C
D
E
F
G
L
M
N
P
R
S
U
h
j
H
J
K
T
V
W
X
Y
Z
a
b
c
d
e
f
g
B
A
Sig Gnd
Sig Gnd
Tx + (B)
Tx - (A)
Rx + (B)
Rx - (A)
•
•
•
•
•
•
•
•
Power
•
•
•
Twisted pairs
•
•
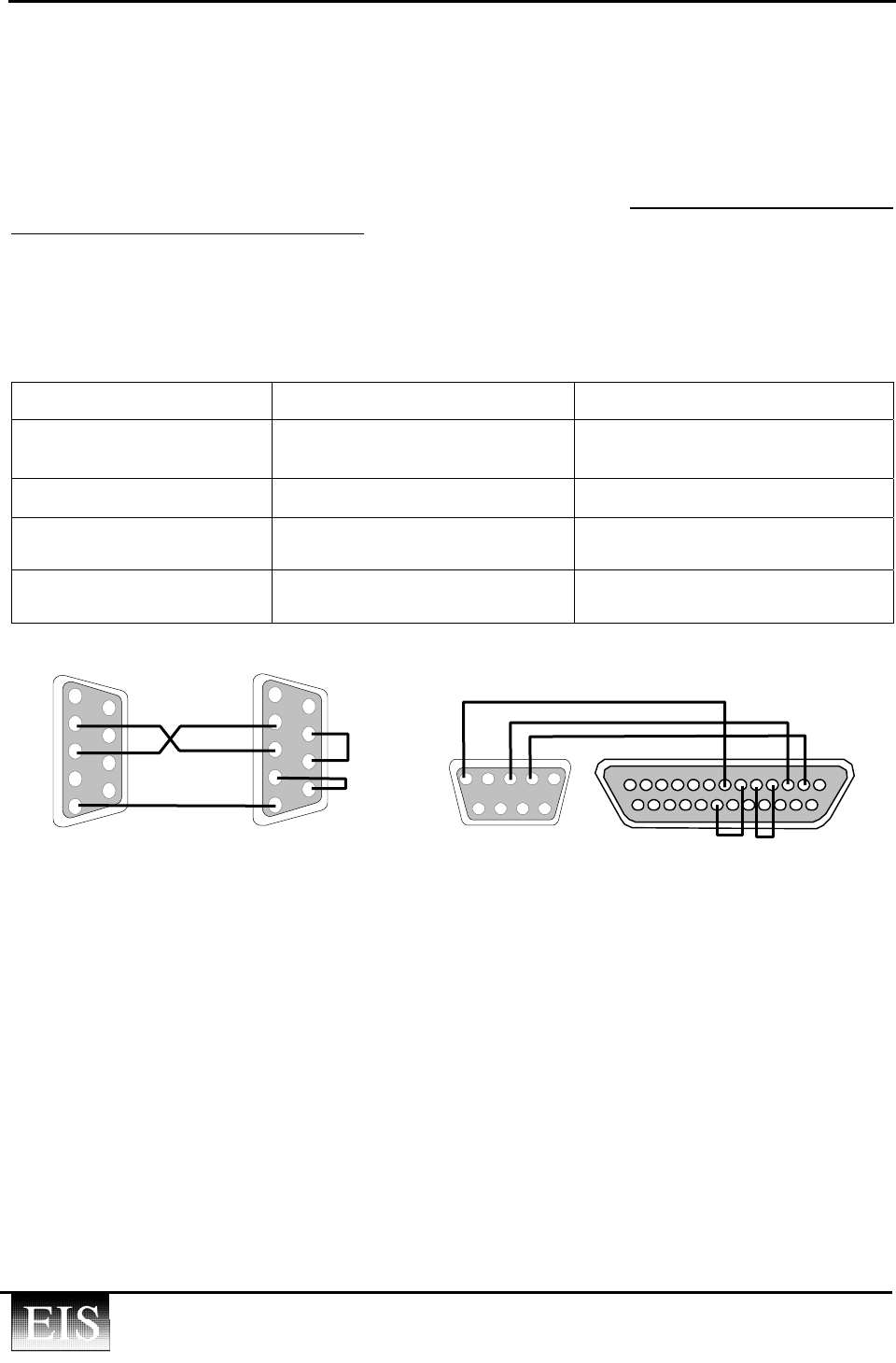
RTMS User Manual Issue 3.2 38
EIS Electronic Integrated Systems Inc.
Modem cabling
Modems may be wireless (CDPD, CDMA, Spread Spectrum) or wire-line (fiber or telephone
line). Most wireless modems use 9 pin connectors. Most line modems use 25 pin connectors.
Their connectors are female.
A cable connecting the RTMS Serial port to a modem must employ male connectors at both ends
and must transpose the Rx and Tx lines.
Since the RTMS serial port does not include any control lines, some modems may also require
looping of their own control lines (RTS, CTS, DTR, DSR) to always receive data.
The modem cable instructions below, show maximum requirements designed to meet the needs of
all modems. Connect pins of the male connectors as shown by the table and diagram below:
Connection function DB9 to DB9 (modem side) DB9 to DB25 (modem side)
⇒ Transpose Tx and Rx Pin 2 to Pin 3
Pin 3 to Pin 2
Pin 2 to Pin 2
Pin 3 to Pin 3
⇒ Connect Ground Pin 5 to Pin 5 Pin 5 to Pin 7
⇒ Connect RTS to CTS Pin 7 to Pin 8 on
modem side DB9
Pin 4 to Pin 5 on
modem side DB25
⇒ Connect DTR to DSR Pin 4 to Pin 6 on
modem side DB9
Pin 6 to Pin 20 on
modem side DB25
Fig 24. RTMS to Modem cables
5 1
9 6
•
•
•
1 13
1425
•
•
•
•
• •
Rear views of male connectors
5
1 9
6
5
1 9
6 •
•
•
• •
• •
•
•
•
RTMS side RTMS side Modem side Modem side
•
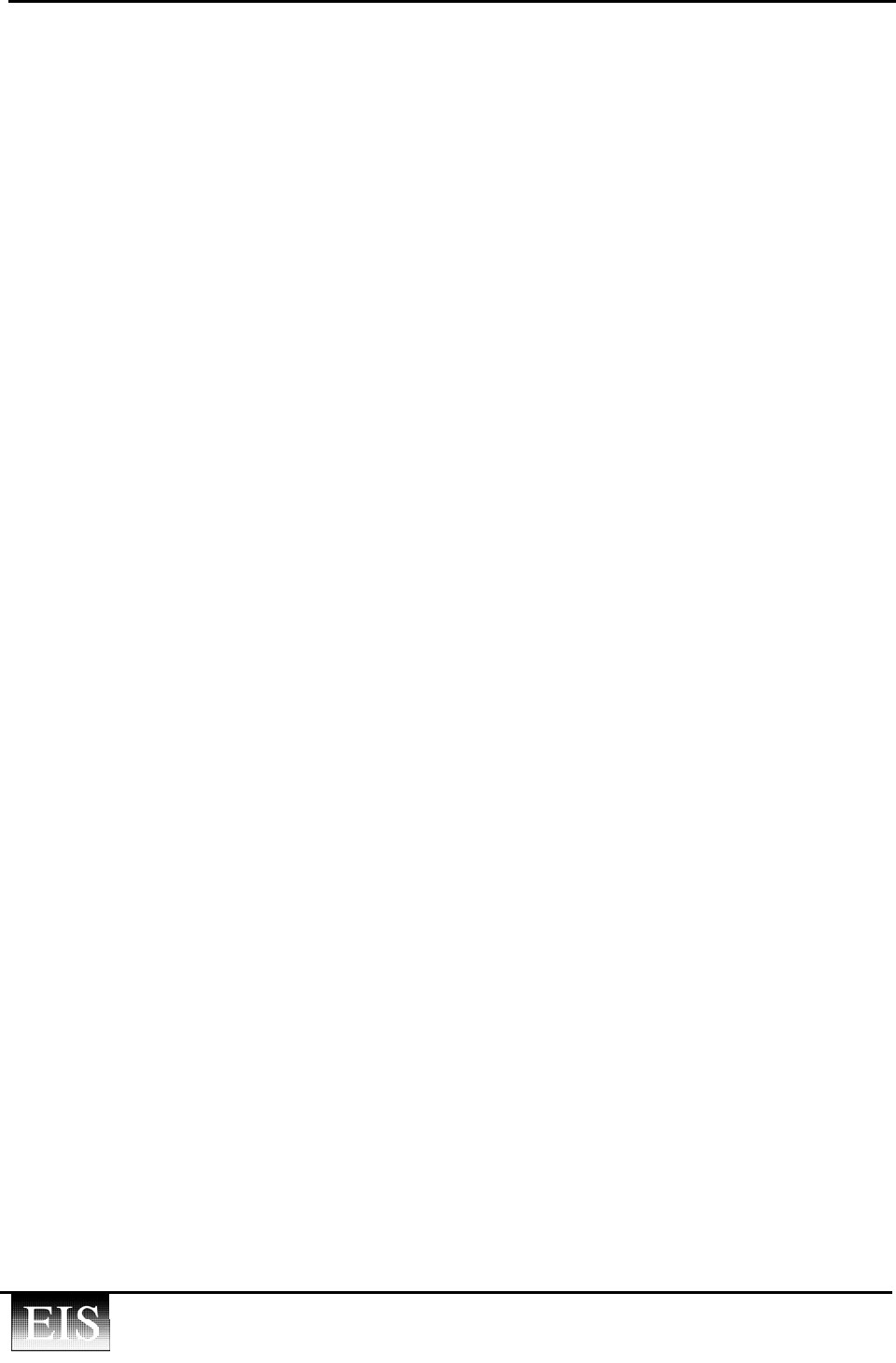
RTMS User Manual Issue 3.2 39
EIS Electronic Integrated Systems Inc.
7 SERVICE AND WARRANTY
Service Information
The RTMS does not require routine maintenance. It is recommended that the Self-Test is
included in the installation procedure. Self-Test should be invoked with the unit installed and
aimed at a road. If the unit fails to operate, please refer to the troubleshooting guide or call EIS
technical support.
EIS Warranty
EIS Electronic Integrated Systems Inc. warrants this product to be free from defects in material
and workmanship for a period of two years from date of delivery. Damage due to accident, abuse
by the buyer, or unauthorized modification or operation outside the specifications is not covered
by the warranty.
CAUTION
Do not attempt to open, repair or disassemble the RTMS unit.
Such action (breaking the seal) will void their warranty.
Contact EIS if the unit requires servicing
EIS warrants that its software and firmware designated for use with the instrument will execute its
programming instructions when properly installed. EIS does not warrant that operation of
software or firmware will be uninterrupted or error free.
EIS Inc. will repair or replace at its option, any components, which prove to be defective during
the warranty period. Buyer shall pay for shipping charges to EIS. EIS will pay shipping charges
and insurance for warranty repaired product. Buyer will be invoiced for repair and shipping of
product repaired outside of warranty or when no fault found.
Units returned to EIS for service should include the following information with the shipment
Name and address of owner
Model number, serial number and software revision number
A complete description of the problem. e.g. under what conditions did the problem occur? What
equipment was attached? The Self Test indication.
Name and telephone number of someone familiar with the problem who may be contacted by EIS
personnel for further information if necessary.
Shipping address for the return.
The unit should be shipped in the original container. If it is unavailable, there should be
approximately one inch of packing material between the unit and inner carton e.g. plastic bubble-
wrap. The carton should be sealed with strong tape or strapping.
Note: Shipping papers, i.e. Commercial Invoices and Way Bills, should include the
statement "Shipped to Manufacturer for Repair" to avoid repayment of duties and taxes.
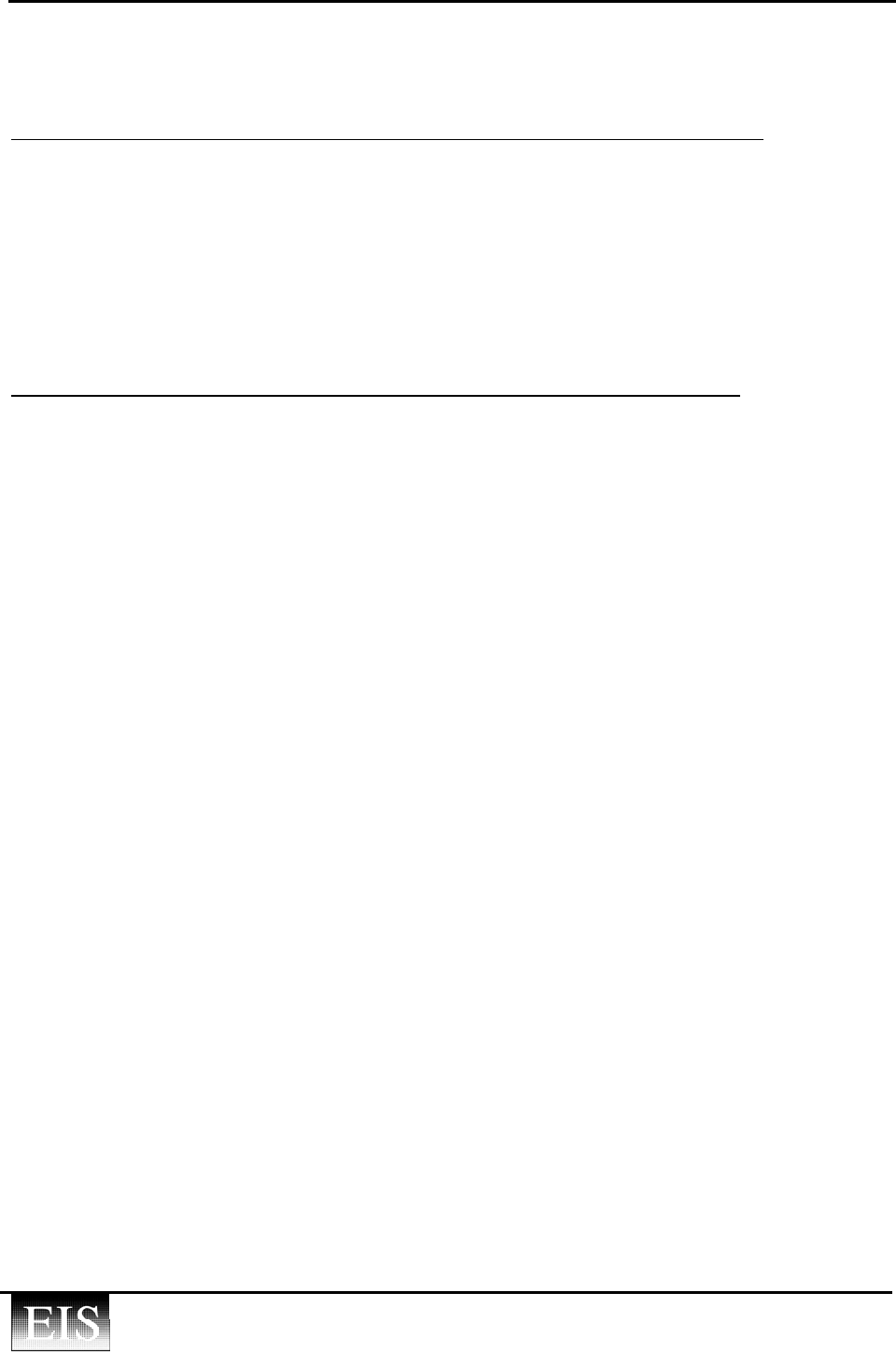
RTMS User Manual Issue 3.2 40
EIS Electronic Integrated Systems Inc.
8 TECHNICAL SPECIFICATIONS
Microwave Signal and Coverage area
Model X Model K
Center Frequency 10.525 GHz 24.125 GHz
Bandwidth 45MHz 45MHz
Power Output 10mW 10mW
Beam width – horizontal (azimuth) 15° 12°
Beam width – vertical (elevation) 40° 40°
Range 3-60m (10-200feet) 3-45m (10-150feet)
Number of detection zones 8 8
Measurements, their Accuracies and Ranges
Measurement % Error * Range
Per lane Volume (Sidefired) 5% 0-255
Per lane Occupancy (Sidefired) 5% 0-100 %
Per lane Classification by length (Sidefired) ±10% 0-255
Per lane Average Speed (Sidefired) ±10% X-band 0-160 km/h (0-100mph)
K-band 0-250 km/h (0-150mph)
Volume and Occupancy (Forward-looking) 2% Same as Sidefired
Average speed (Forward-looking) 2% X-band 0-160 km/h (0-100mph)
K-band 0-250 km/h (0-150mph)
Range Resolution 2-m (7 Ft.)
Time events resolution 10 msec.
* See Accuracy Performance Conditions
Mechanical
Enclosure dimensions 16x24x12 cm (6 x 9.5x 4.5 in.)
Overall dimensions 16x27x18 cm (6 x 10.5 x 7 in.)
Weight 2.2 Kg (5 Lbs.)
Enclosure Polycarbonate
Weatherproofing NEMA-4X and IP-65
Mounting Zinc plated steel universal ball-joint bracket. Vertical or Horizontal brackets
available. Lynch pin locking allows quick sensor replacement without disturbing
the aiming.
Allowable pole flexing less than 5 degrees.
Interfaces
Contacts
RTMS has 8 Opto-isolated contacts for presence indication and a 9th contact used for RS-232
RTS or Power-On indication.
Peak contact ratings are 100mA, 400V, 300mW.
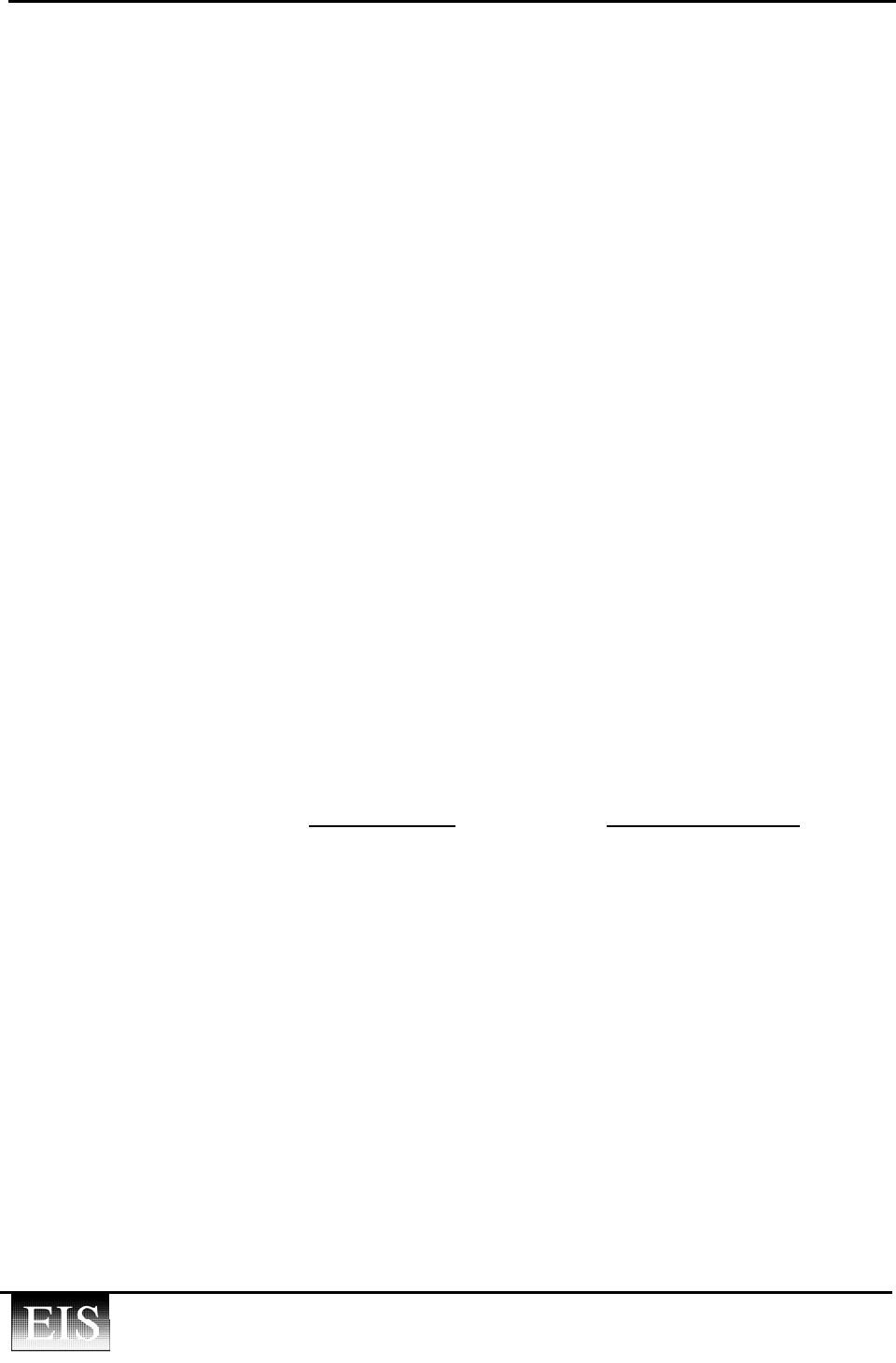
RTMS User Manual Issue 3.2 41
EIS Electronic Integrated Systems Inc.
Data Ports
• RTMS optically isolated serial port operates at No parity, 8 bit, 1 stop bit:
• Models X2 and K2 RS-232 interface operates at fixed 9600 bits/sec rate with a range up
to 250m (800 feet).
• Model X3/K3 (Rev. 6.1 and up) offer adjustable speed in 2400 to 115200 bits/sec range.
Operating distance depends on selected speed.
• Model X3/K3 RS-485 option extends range up to 1200m (4000 feet).
• Models X3 and K3 offer an optional ethernet port.
Maximum distance to hub or bridge - 100m (300 feet) when using CAT5 cable
Power requirements and consumption
RTMS Standard power requirement 12-24V AC or DC
Maximum voltage (Overvoltage shutdown limit) 34VDC or 24VAC
Not compatible with Ethernet or DSS options
Power consumption (Standard Power) Model X2 - 6 Watts Model K2 – 8 Watts
Model X3 –5 Watts Model K3 – 4 Watts
Additional Power consumption of options DSS 1.5 W
TCP/IP 1.2 W
Automatic recovery from power failure Within 5 seconds with DSS – 20 seconds
Surge immunity
The RTMS withstands ± 1kV surge (rise time = 1.2 µsec, hold = 50µsec) applied in differential
mode to all lines, power and output, as defined by IEC 1000-4-5 and EN 61000-4-5 standards
Environmental Conditions
Operating limits Shipping and Storage
Temperature range -37 to +74°C (-35 to 165°F) -40° to 80°C (-40° to 171°F)
Humidity Up to 95% Relative Humidity Up to 95% Relative Humidity
Vibration 2g up to 200Hz sinusoidal
Shock 5g 10ms half sine wave
Wind Winds up to 160 km/h (100mph) will not degrade performance
Precipitation (rain or snow) Up to 100mm/h
Electromagnetic Interference
The RTMS meets US FCC Rule part 15 Class A and Canadian CSA C108.8 M1983 Class A.
Reliability
Mean time between failures (MTBF) of the RTMS in its operating environment is 90000 hours
(10 years)
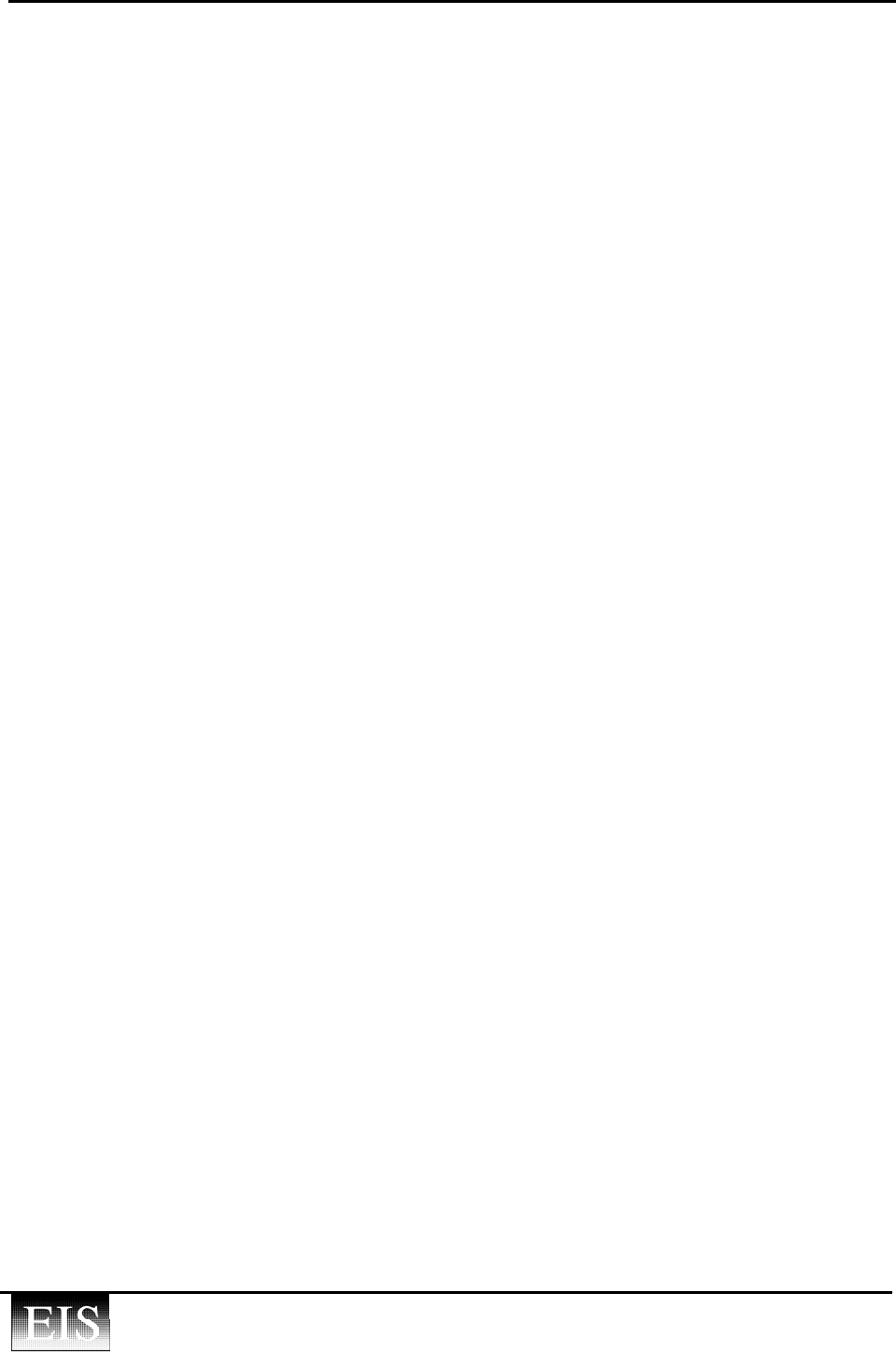
RTMS User Manual Issue 3.2 42
EIS Electronic Integrated Systems Inc.
Accuracy Performance Conditions!
Error performance parameters outlined above are achieved under normal, high-flow traffic
conditions and are subject to proper installation and setup. Reduced accuracy (higher errors) will
be experienced under the following conditions:
• Low speed, high congestion conditions: The RTMS tends to over-count under low speed
conditions (below 1mph) as the setting of the EDT parameter may not bridge nulls in the
reflected signals adequately resulting in multiple counts.
• Low vehicle volumes in Sidefired configuration (as experienced during night time) may
result in higher speed data fluctuations due to the small statistical sample.
• Improper selection of installation site: insufficient set-back, height beyond the
recommendation, obstruction by barriers or high fences before monitored lanes.
• Improper Fine Tune setting for the road geometry (lane width, barriers, etc.) will result in
“splashing” and, therefore, over-counting. In some cases, attempts to cover too many
traffic lanes with a single RTMS may result in inability to find correct Fine Tune setting
and compromised performance.
• In Forward-Looking Hwy configuration, high variance between the volumes in the speed-
trap zones due to improper aiming or obstructions within the trap range or incorrect
Height or Offset parameters may result in higher speed and length measurement errors.
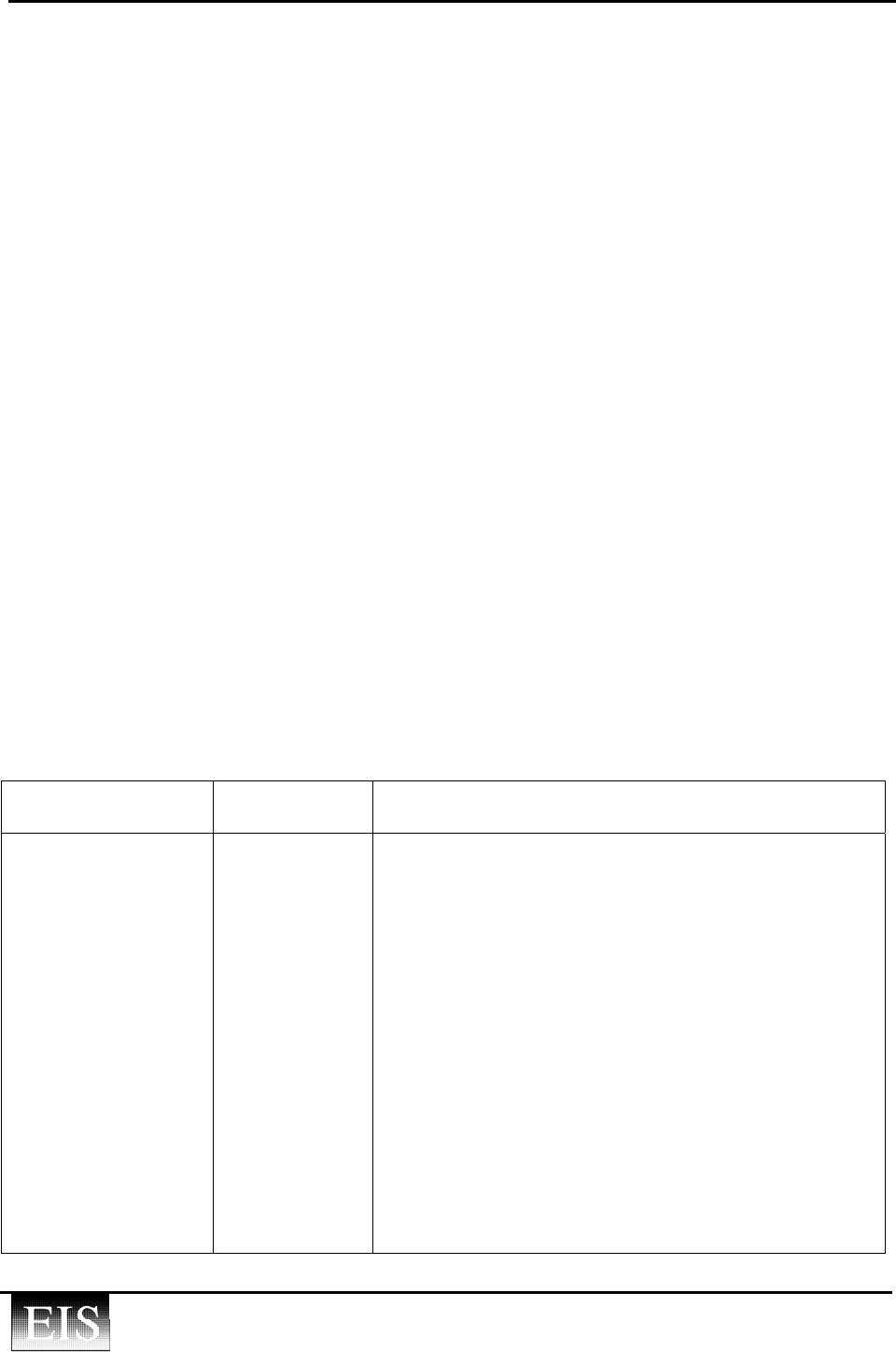
RTMS User Manual Issue 3.2 43
EIS Electronic Integrated Systems Inc.
9 RTMS TROUBLESHOOTING GUIDE
Field troubleshooting of the RTMS consists mostly of ensuring that the unit is powered and
communicating and running the Self-Test (two-way communication is required to run Self-Test).
Communication from a sensor in Normal mode is indicated by flickering of the “lamp” in the
lower right corner of the screen, denoting target data transmission activity.
The Self-Test is invoked using the RTMS Setup Utility by selecting TOOLS and Self-Test. The
test checks internal functions and locates hardware faults. The "All tests complete System OK!"
message is displayed on the screen if no faults are found. The following is a list of Self-Test
messages describing a fault and corrective action.
"Power supply fault!" Send back
"Modulator signal fault!" Send back
"Microwave module fault!" Call EIS
"Temperature calibrator fault!" Send back
"Modulator memory fault!" Send back
"Program memory fault!" Send back
"DSP fault!" Send back
"Gain too low or ADC fault!" Call EIS
"Logic failure" Call EIS
"No signal" Call EIS
"Saturation signal level" Call EIS
The Self-Test cannot test the Opto-pairs. It will, however, close the zone contacts for one second
in sequence. Operation of opto-isolated contacts can then be verified using the controller display,
ohm-meter or any other suitable device showing continuity.
The table below outlines symptoms and suggested action in troubleshooting power and
communication problems:
Symptom Possible
causes
Suggested action
“RTMS is not
responding…”
message continues to
be displayed after
attempts to set the
sensor to Normal
mode
Power failure
Cable problem
Hardware
• Check that the supply voltage is within limits at
source and at the MS connector as defined in
Section 6. Voltage outside the limits (too low or
too high) will cause power supply shut down.
• With power applied to the RTMS and DB9F
disconnected from PC, check the RTMS serial
Port by measuring approx –10V between pins 2
and 5 of the DB9F RS-232 connector. If the
voltage is not present there could be a hardware
fault in the RTMS serial port or power supply. If
neg voltage is there.
• Check cable pin-out and continuity particularly
between MS connector pin T and COM port’s
pin 3 (Tx line)
• Alternate serial option (see cabling sections)
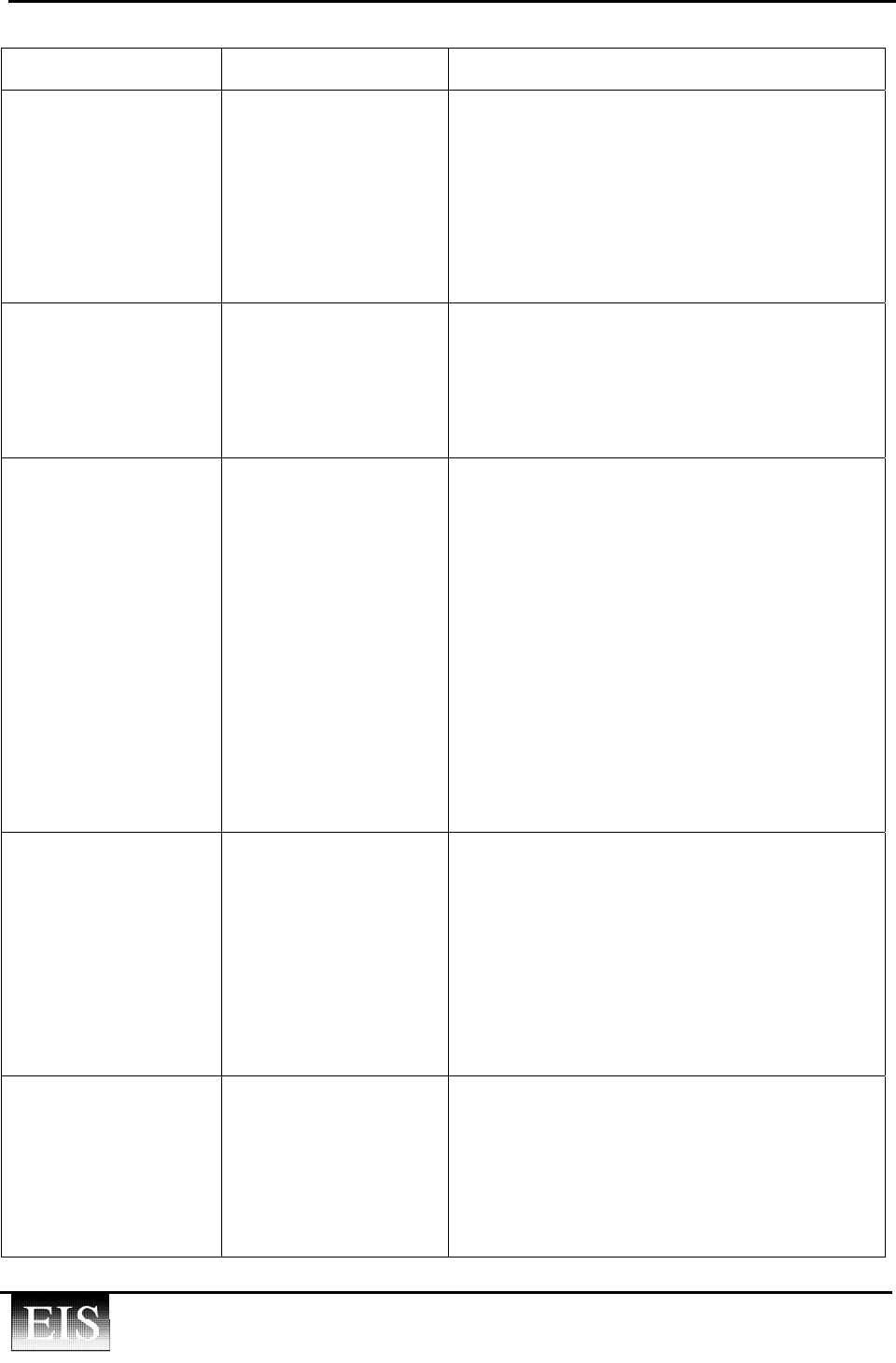
RTMS User Manual Issue 3.2 44
EIS Electronic Integrated Systems Inc.
Symptom Possible causes Suggested action
“RTMS is not
responding…”
message continues to
be displayed after
attempts to set the
sensor to Normal
mode
PC unable to
communicate with the
RTMS due to Serial
port setup or H/W
problems
• Check that the PC COM1 port is selected
via the default screen.
• Check that COM1 port is available and
not used by another application (e.g. serial
mouse)
• Check that PCs serial port is operational
(-5V present between pins 3 and 5)
Polling range window
is displayed on start of
RTMS Setup Utility
RTMS Setup Utility is
in Multi-drop Mode
• Click OK on the polling range window;
RTMS Setup default screen will be
displayed.
• Select TOOLS, Change to Direct mode,
if direct access to one RTMS is desired
Target “blips “ are
not shown on the
main screen displayed
on program initiation
(PC and sensor are
communicating)
RTMS is not in
NORMAL mode
Unit is not aimed
properly
Low Sensitivity
Internal parameters
corrupted
• Ensure the unit is in the Normal mode
• Generate a target by waving a hand in
front of the unit. If a blip does not appear
a hardware fault may be present.
• Check sensitivity setting. See if targets
appear when sensitivity is increased
• Recycle power to unit. Load a prepared
file on supplied software disks (e.g.
FWDLK) and then edit parameters (mode,
sensitivity, zone setup, etc)
• Run Self-Test if above not successful.
Report findings to EIS
Main screen shows
target blips but no
zone icons,
parameters on buttons
and all zero statistics.
Self-Test initiated but
results are not
displayed on PC
screen
PC receives but does
not send any
commands and has not
received the RTMS
setup.
• Check cable to ensure continuity between
MS connector pin T and COM port’s pin
3 (Tx line)
•
The setup program is
unable to read an
RTMS with DSS
modem (Messages
displayed; sensor
settings are not
displayed)
Pin “a” is not cabled.
PC cannot send any
commands and has not
received setup data
• Examine cable and correct to include pin
“a” cabling to DB9F pin 4 (DTR) if
omitted
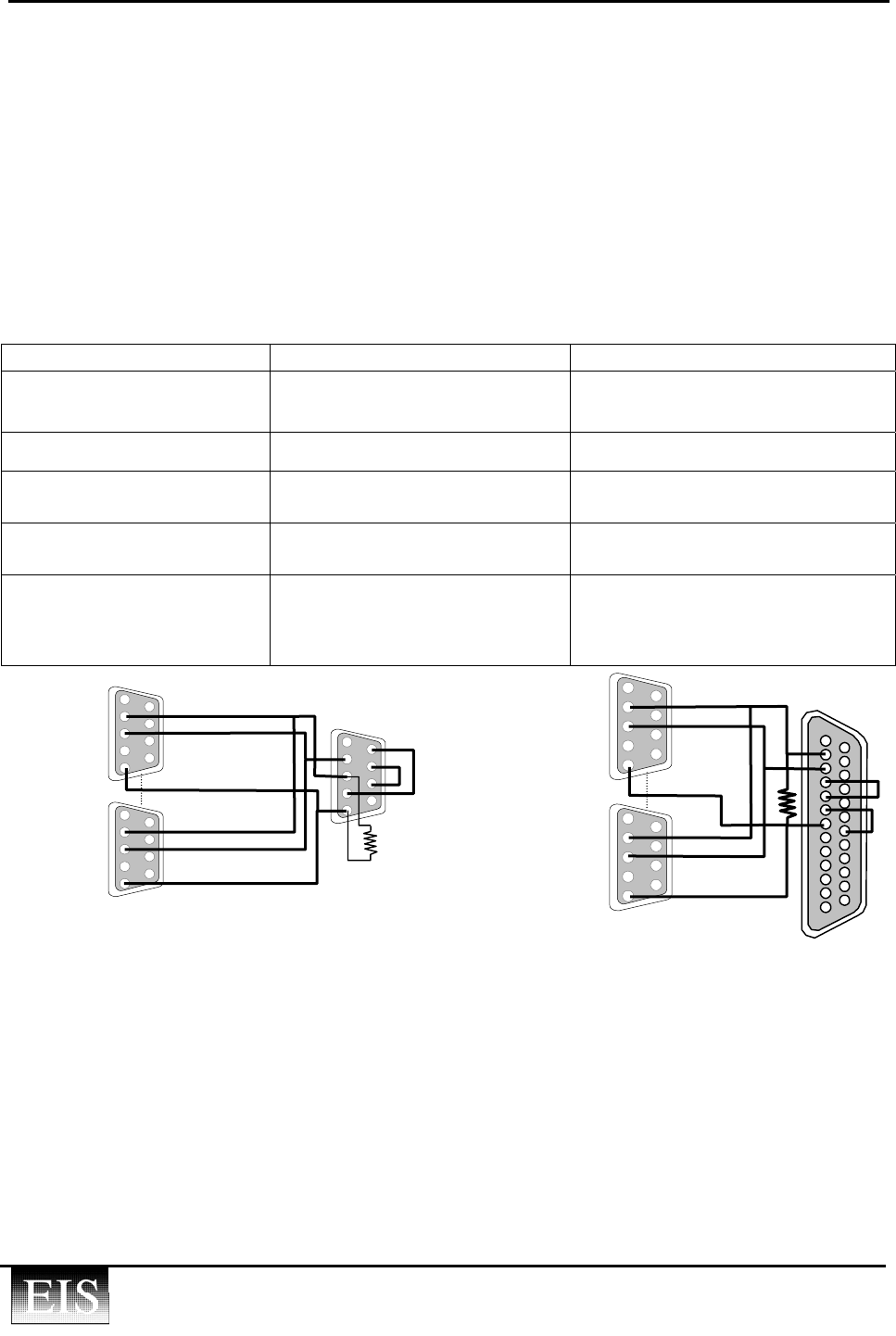
RTMS User Manual Issue 3.2 45
EIS Electronic Integrated Systems Inc.
5
1
9
6
5
1
9
6 5
1
9
6
h
h
h
h
h
h
h
h
h
h
h
h
h
h
h
h
100k
Ω
RTM
S
1
RTMS n
13
1 14
25
5
1
9
6
5
1
9
6
h
h
h
h
h
h
h
h
h
h
h
h
h
h
100kΩ
h
h
h
RTMS 1
RTMS n
APPENDIX 1 WIRING CONFIGURATIONS FOR MULTIPLE RTMS
Modem Sharing
A limited number of RTMS units in polled mode, located within a short distance, may share a
single modem. While models X2/K2 require use of contact #9 (see RTMS Cable modification
below) , models X3/K3 Serial port design allows two or more transmit lines to be connected
directly without interference.
A cable for modem sharing will have Y-cable construction and will consist of one DB-9M
connector per RTMS and one DB-9M or DB-25M connector at the modem, as shown below:
Modem-sharing Cable Construction
Connection type DB9 to DB9 (modem side) DB9 to DB25 (modem side)
⇒ Transpose Tx and Rx Pins 2 to Pin 3
Pins 3 to Pin2
Pins 2 to Pin 2
Pins 3 to Pin 3
⇒ Connect Signal Ground Pins 5 to Pin 5 Pins 5 to Pin 7
⇒ Strap RTS to CTS Pin 7 to Pin 8 on
modem side DB9
Pin 4 to Pin 5 on
modem DB25
⇒ Strap DTR to DSR Pin 4 to Pin 6 on
modem side DB9
Pin 6 to Pin 20 on
modem side DB25
⇒ Connect a 100kΩ
resistor from Tx to
ground to prevent noise
Pin 3 to Pin 5 on
modem side DB9
Pin 2 to Pin 7 on
modem side DB25
Fig 25. Modem sharing Y-cables
RTMS Model X2 Cable Modification
The design of the RTMS Serial port of the Model X2/K2 requires that only one transmit line is
connected to the modem at a time. This is achieved by using the Opto-isolator contact #9. The
RTMS closes this contact on receipt of its ID number in the polling message. The RTMS cable
must be modified to insert this contact in the transmit path, as outlined below:
⇒ Ensure pins d and e are present in the MS connector of each RTMS
⇒ Loop the RTMS transmit line (pin V) to pin “e” inside the MS connector back-shell
⇒ Connect pin “d” to pin 2 of RTMS DB9F connector. Note: pins “d” and “e” are
interchangeable. Looping pin V to pin “d” and cabling pin “e” to DB9 pin 2 is also correct
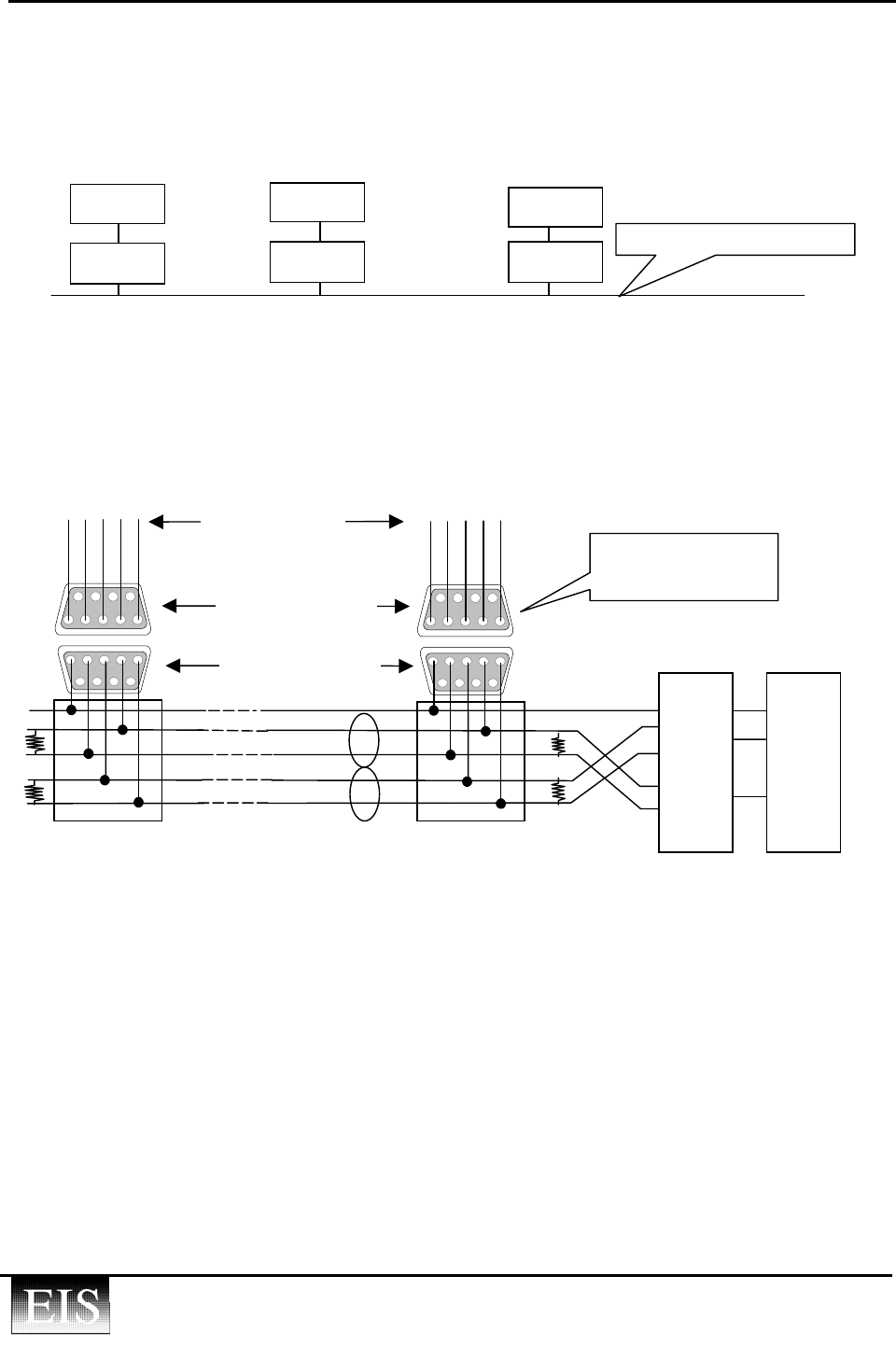
RTMS User Manual Issue 3.2 46
EIS Electronic Integrated Systems Inc.
Multi-drop Wiring
Multiple RTMS stations operating in Polled mode may be connected to a single communication
line or channel for transmission of data. Each must have its own modem when separated by more
than the limits of the serial port. Each RTMS receives the poll commands but transmits data only
on receipt of its own ID. See RTMS RS-232 port to Modem cables per Fig. 24
Fig 26. Multi-drop wiring configuration
For distances up to 4000 feet multi-drop configuration may employ the RS-485 Serial Port option.
Maximum number of units is 32. The communication line can be configured as 4-Wire (shown in
Fig. 27) or 2-Wire half-duplex (RTMS cannot transmit while its receiving) suitable for data
collection operation only. Consult RS-485/422 Application Guides for details on 2-Wire
configuration
Fig 27. RS-485 Port Multi-drop Wiring
Notes:
1. The use of DB9F connectors, as shown, allows direct connection to the laptops COM port for
setup. Wiring must allow for unplugging the RTMS from the transmission line. Use of
terminal blocks to connect the DB9M connectors to the transmission line is recommended.
2. Terminating resistors (100-120 ohms) are required at the extreme ends of the Receive and
Transmit transmission pairs.
3. Transmit and receive pairs must be transposed when connecting to a RS-485/232 converter
for direct interface with a DTE (Data processing System).
4. RS-485/232 converter pin assignment varies between models as it is not standardized.
4 Wire Transmission line
RTMS
Modem
RTMS
Modem
RTMS
Modem
See Fig 22 for pin
assignment
Last
RTMS
First
RTMS
Max. 4000 feet
5 1 2 3 4
Tx+
Rx+
Tx
-
Rx
-
Gnd
U /W X T V Y
5 1
9 6
• • • • •
• • • • •
DB9F connectors
DB9M connectors
5 1 2 3 4
Tx+
Rx+
Tx
-
Rx
-
Gnd
U /W X T V Y
5 1
9 6
•
•
•
•
•
•
•
•
•
•
Tx
Rx +
Sig. Gnd.
RS-485 to RS-232
Converter
Tx
Rx
Data
Processor
+
-
-
Connector
Block
Connector
Block
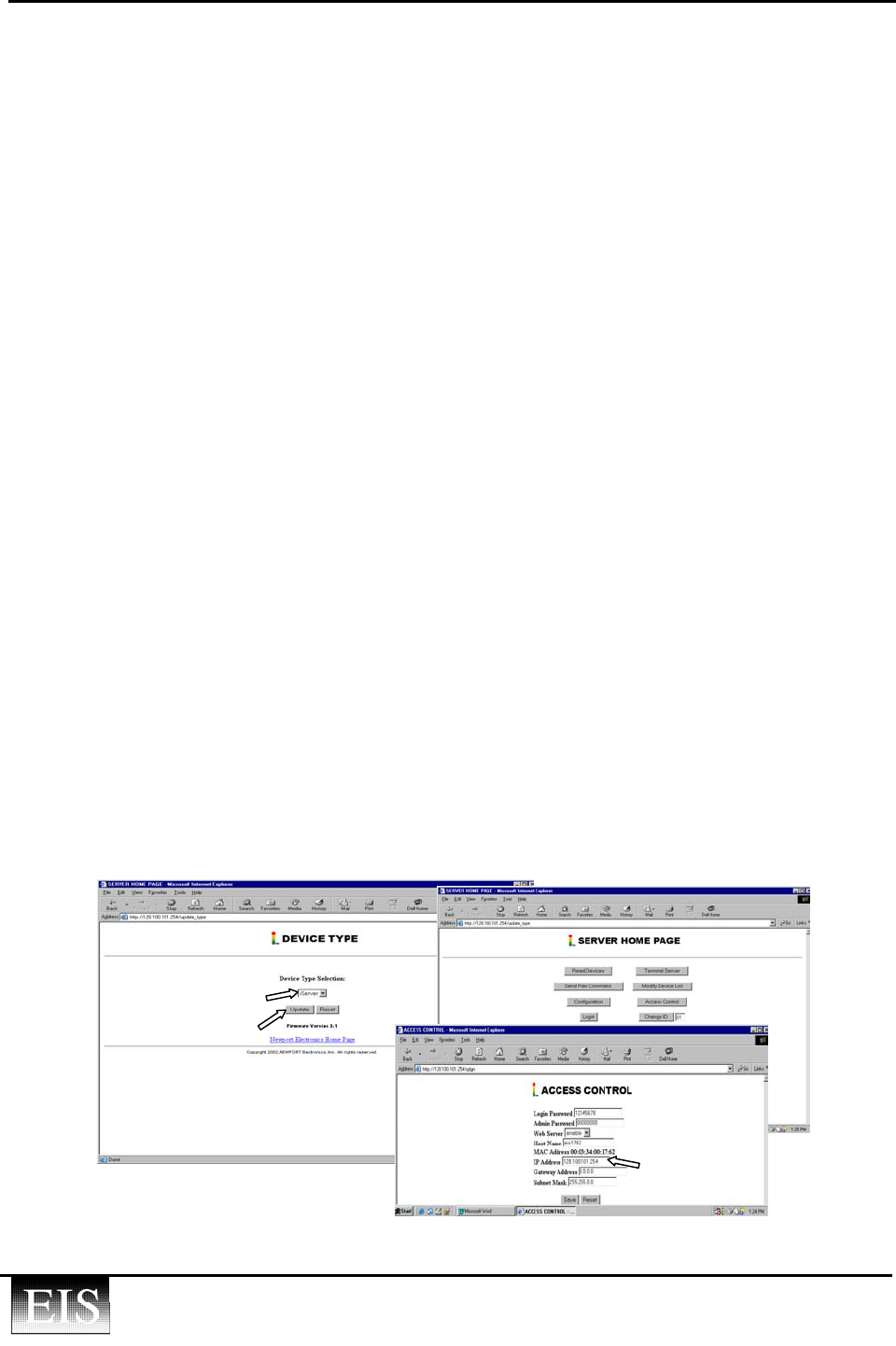
RTMS User Manual Issue 3.2 47
EIS Electronic Integrated Systems Inc.
APPENDIX 2 SETTING RTMS IP ADDRESS
Programming an IP address
The RTMS Micro-Server is programmed with a default IP address 128.100.101.254. This address
may be changed using a directly connected PC, as follows (note slight differences between
versions of Windows):
⇒ Set PC network address in the range 128.100.x.x in the following steps
• Access the Control Panel as applicable to your operating system
• Open “Network” (win 98) or Network Connections and Local Area
Connections/properties (Win XP)
• From the list of installed network components select and open “TCP/IP → xxx “ (Win
98) or “Internet Protocol (TCP/IP” (Win XP) that is installed on this PC. Check
System/Device Manager/Network Adapters under Control Panel to identify the correct
device
• Click Properties and “Specify an IP address” (Win 98) or Use Following IP Address
(WinXP)
• Enter 128.100.101.1, and Subnet = 255.255.0.0 . Click OK and Close
⇒ Power the RTMS and connect it to the PC network port using a network cable. Verify that a
correct cable is used by observing the PCs Network port Link and Activity indicator lights,
which should light
⇒ Open MS DOS prompt (under Programs) to ping the RTMS
Type C: \>ping 128.100.101.254 and observe response
⇒ If ping is successful, access the RTMS via a web browser (using the above network address)
On successful connection the Device Type page will be displayed. Select iServer from the
drop down menu and click Update to go to the home page, shown below.
⇒ Click Access Control
⇒ Enter Login password = 12345678 and Admin password = 00000000 when prompted (ensure
cursor is in the field before typing)
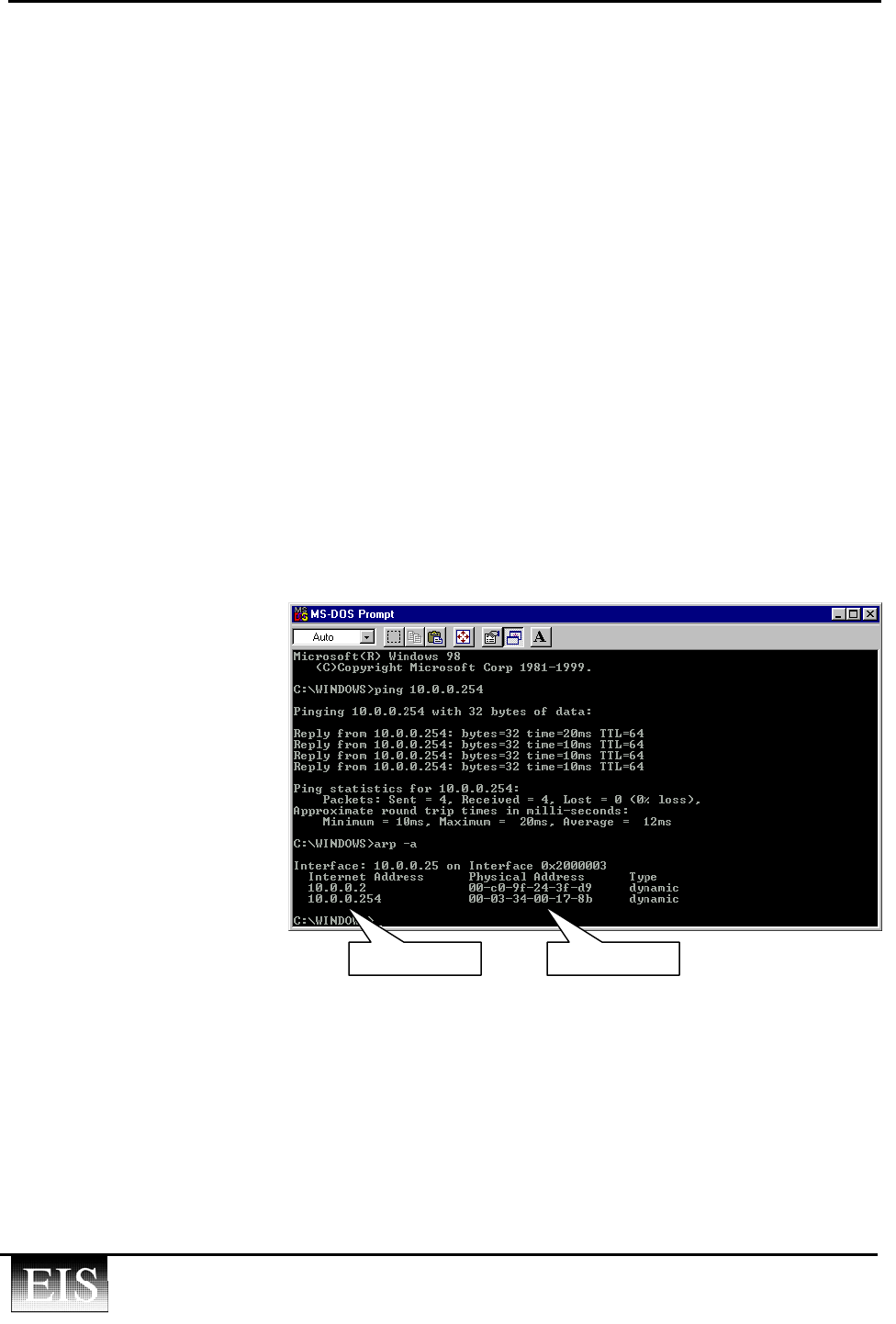
RTMS User Manual Issue 3.2 48
EIS Electronic Integrated Systems Inc.
⇒ Overwrite the IP Address and the Subnet Mask with the desired settings and click Save.
Do not open and make changes in any other settings accessible from the Server Home page
⇒ De-power the RTMS to allow the microserver to reset itself
⇒ Connect RTMS to a network hub (or Ethernet bridge)
⇒ Repeat ping routine over the network using the new IP address to verify ( use an opposite
cable type to connect to a hub)
Recovery Procedures
The MAC (Media Access Control) is a unique hardware number associated with each ethernet
interface. This 6 byte number (12 hexadecimal characters) is furnished with RTMS shipping
documents.
Lost MAC or IP address can be recovered from the RTMS if one of them is known. If both are
lost, the sensor must be returned to EIS for recovery.
Recovery of MAC address
The MAC address can be obtained using a similar procedure to changing the default IP address.
Note that MAC address is included in the Access Control page.
An alternate method uses the ARP (Address Resolution Protocol) protocol supported by the
microserver. The ARP Internet layer protocol, which uses MS DOS Prompt, is responsible for
determining the MAC (hardware) address that corresponds to a particular IP address.
The “arp –a” command
allows the user to view the
current contents of the ARP
cache of the local computer
(residing on the same
network) or remote
computer (residing on the
different network) through
a router.
A device should be
”pinged” using IP address
before using “arp –a”
command as shown by the
sample session
Recovery of IP address (MAC address known)
DNS (Domain Name System) enables individual devices to be recognized over a network based
on a Host name instead of an IP address. The default Host name for the microserver is "eis"
followed by the last four characters of the MAC address, e.g. eis178b.
Mac addressIP address
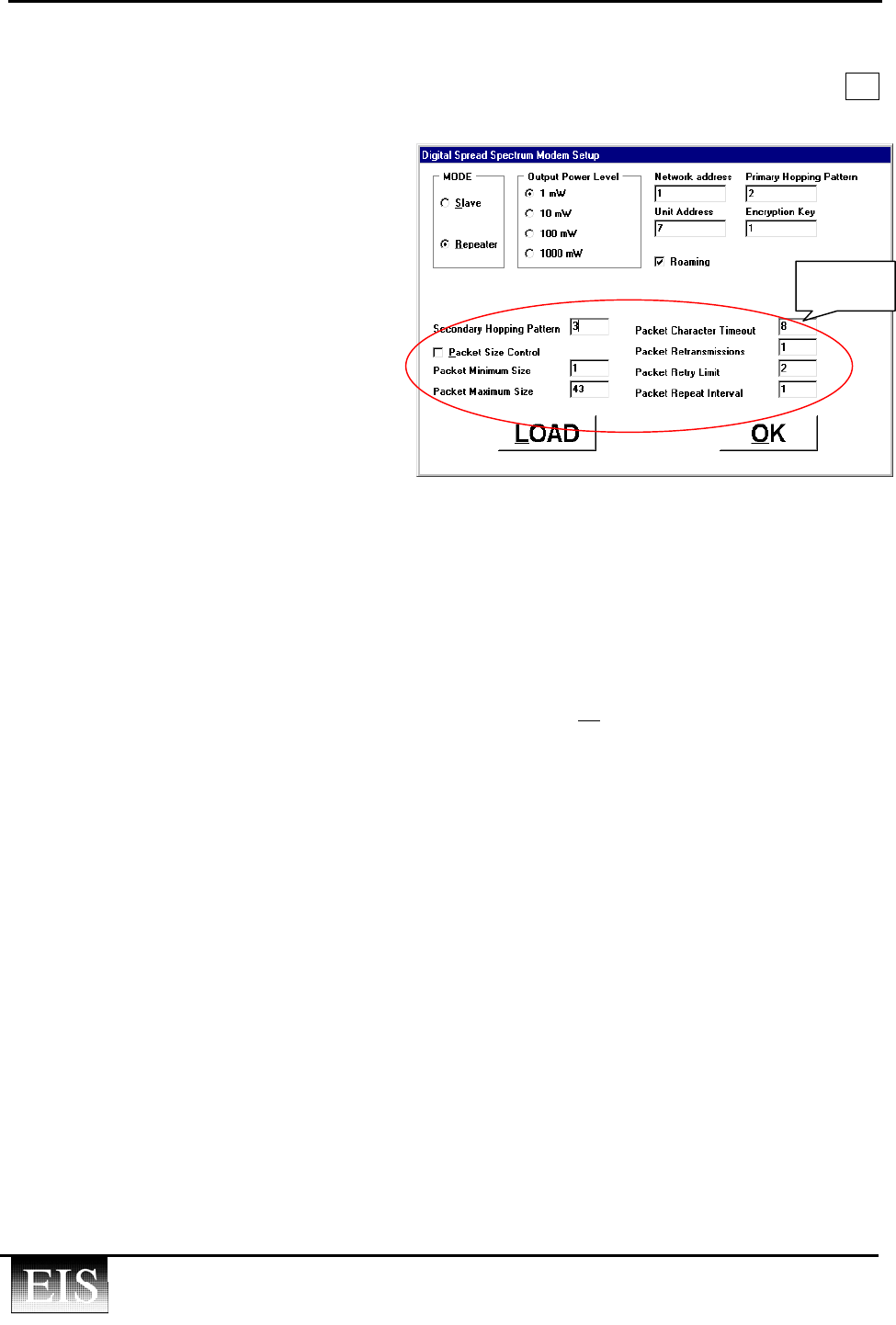
RTMS User Manual Issue 3.2 49
EIS Electronic Integrated Systems Inc.
APPENDIX 3 INTERNAL DSS MODEM SETUP
If the internal DSS modem fails to communicate with the master, as indicated by the red DSS
rectangle it may be necessary to view and make changes in the DSS setup. To view setup
⇒ Click TOOLS button and PC COMM
⇒ Click DSS Modem button on the
Communication Protocol Setup
window
⇒ Ensure settings are:
Slave mode for a simple line of sight
communication to the master.
Repeater if this modem relays data
from another DSS modem, which is not
in line of sight with the master.
Additional fields will be displayed
(shown)
Roaming is on. This feature of the transceiver allows Slaves and repeaters to locate a master
by the network address and encryption key and adopt its primary hopping pattern
The DSS parameters and their ranges should be as follows:
Advanced Par. Description
Network
Address
This address must be same for all RTMS units and the Master in a specific
system. Range 1-65535
Encryption
Key
This field must be set to the same value for all modems in a specific system,
including Master. Range 1-65535
Hopping
Patterns
The Primary Hopping Pattern field must be filled with a hopping sequence
(Range 1-63) for communication between the slave (or repeater) and the
system master. The Secondary Hopping Pattern, displayed when Repeater
is clicked, applies to communication between a repeater and its slave(s). It
must be different than the Primary Hopping Pattern
Unit Address Each modem must be set to a unique ID number within the system.
Output Power
Level
Output power should be kept at the lowest setting, which provides reliable
operation. 100 mW meets requirements of most applications. 1 mW or 10
mW may be sufficient in SPIDER applications at short ranges.
Packet Size
control
Allows packets generated by slaves and repeaters to be of different size than
masters.
Packet fields Effective only if Packet Control is clicked.
Min/Max
Packet size
Applicable to slaves and repeaters only if Packet size control is clicked.
Otherwise Master settings take precedence.
Click LOAD to save displayed settings, Click OK to exit without changes to settings
Additional
Fields
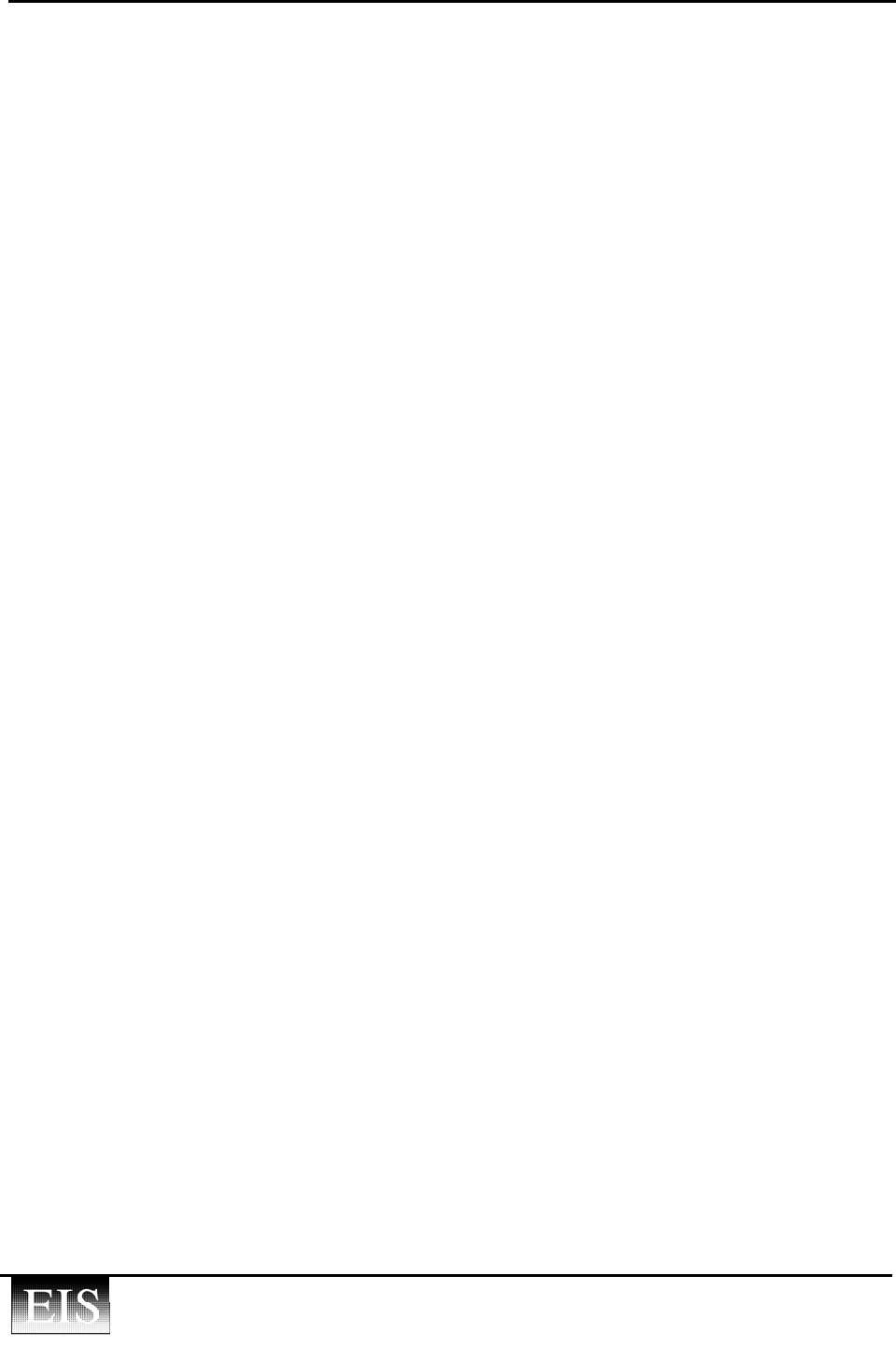
RTMS User Manual Issue 3.2 50
EIS Electronic Integrated Systems Inc.
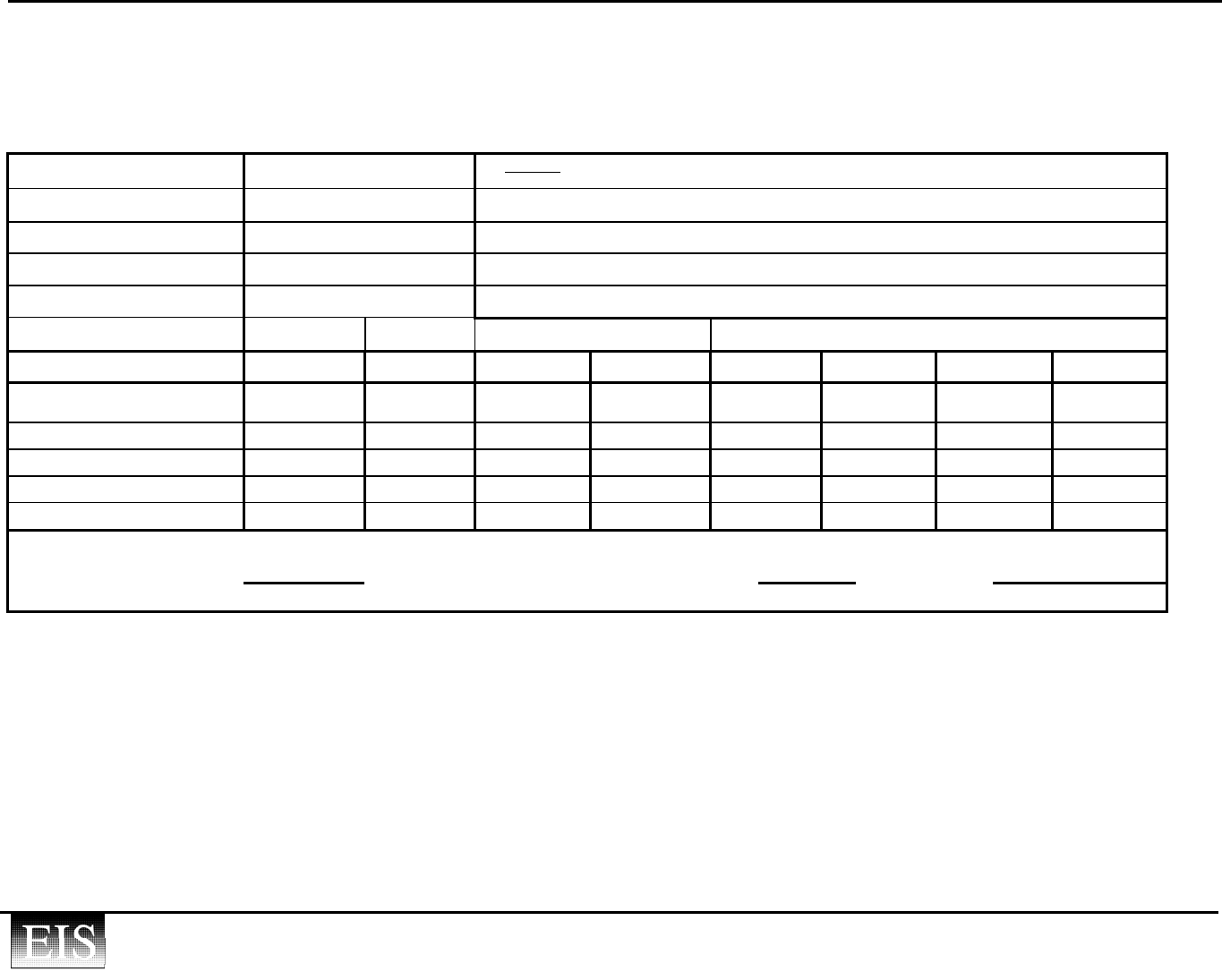
RTMS User Manual Issue 3.2 1
EIS Electronic Integrated Systems Inc.
APPENDIX 4 RECOMMENDED RTMS SETUP SHEETS
RTMS SET UP SHEET – HIGHWAY - Completed sample
RTMS ID # 1 NOTES 20 foot Median between Fast N and Fast S
LOCATION Mile 15 Trucks in Slow N
FINE TUNE -1
SENSITIVITY 5
SAVED FILE NAME May2002Mile15 When verifying counts a minimum of 50 vehicles must be counted
BARRIER/TYPE YES / NO yes BETWEEN WHICH LANES Jersey barrier between 2 and 3. 7 foot shoulders
ZONE 1 2 3 4 5 6 7 8
DIRECTION N N S S
LANE (FAST MID SLOW) Slow Fast Fast Slow
MANUAL COUNT 50 50 50 50
RTMS COUNT 51 48 49 51
% ERROR +2 -4 -2 +2
MESSAGE PERIOD 30 [SECS] POLL MODE (Y/N) Y TECH. INITIALS
APPROVED
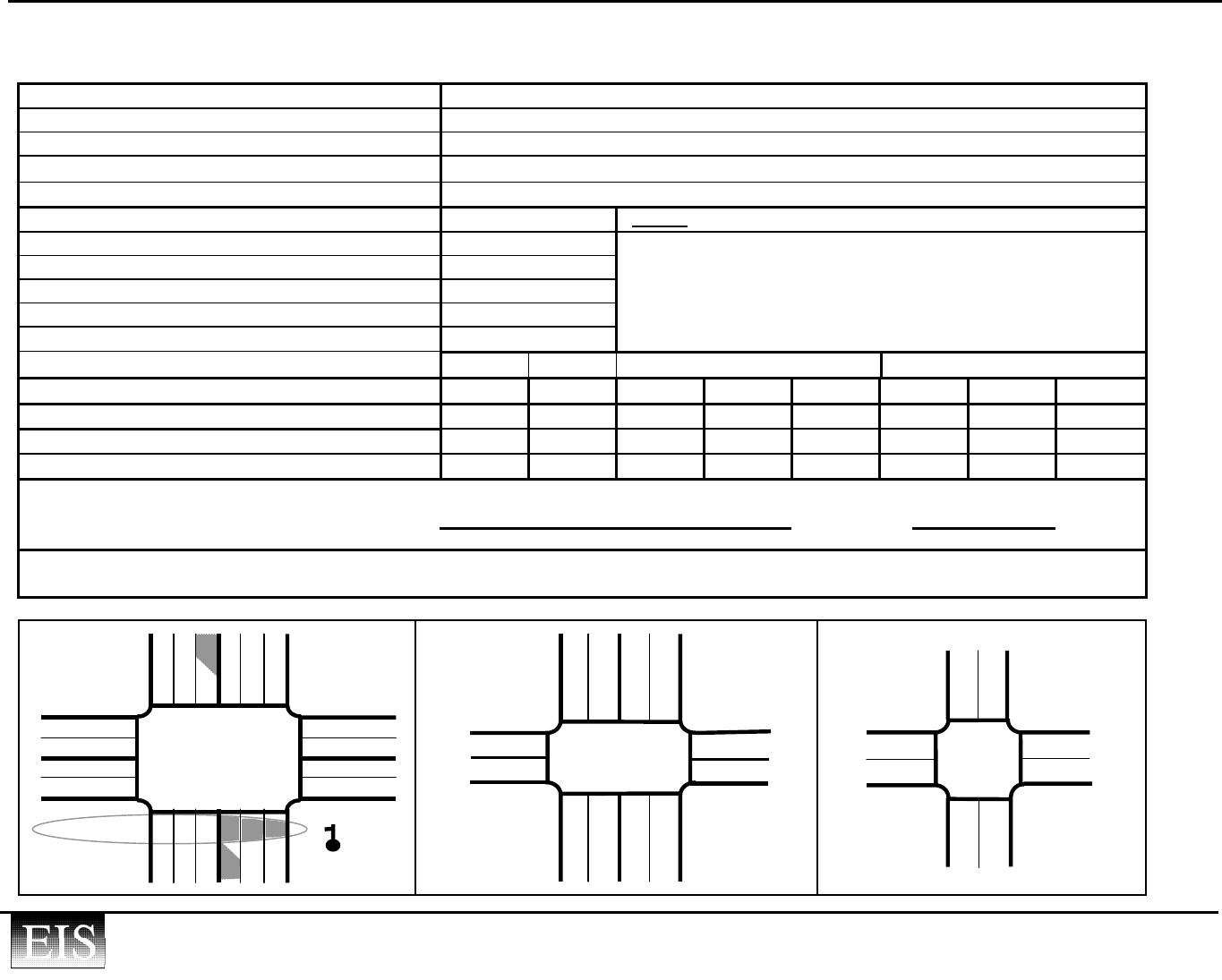
RTMS User Manual Issue 3.2 2
EIS Electronic Integrated Systems Inc.
RTMS SET UP SHEET – INTERSECTION - Completed sample
CITY / JURISTRICTION City of ABC
LOCATION / INTERSECTION Main & 1st Ave.
RTMS ACTIVE CORNER Main – Northbound
RTMS MOUNTED ON Existing pole 15 feet forward of stop bar. Extension arm used
RTMS ANGLE TO SIDE OF VEHICLES (Max 10 degrees) Less than 5 degrees
FINE TUNE -3 NOTES
SENSITIVITY 11 6 foot extension arm mounted on the pole to correct the position
RTMS EXTENSION DELAY TIME (A) 2 sec of the RTMS
DESIRED DELAY (B)
3 sec
CONTROLLER DELAY (A + B) 5 sec
SAVED FILE NAME Sep22 (main-1st)
OBSTRUCTIONS YES / NO No NAME OBSTRUCTIONS Clear line of sight
ZONE 1 2 3 4 5 6 7 8
DIRECTION N N N
LANE (LEFT TURN THROUGH RIGHT TURN) Thru/right Thru Left
VEHICLES DETECTED AND HELD
INSTALLATION COMPANY XYZ Electric TECH INITIALS
APPROVED
Show RTMS locations, Control Cabinet and specific lanes being detected.
For more info refer to RTMS User Manual
2 3 1
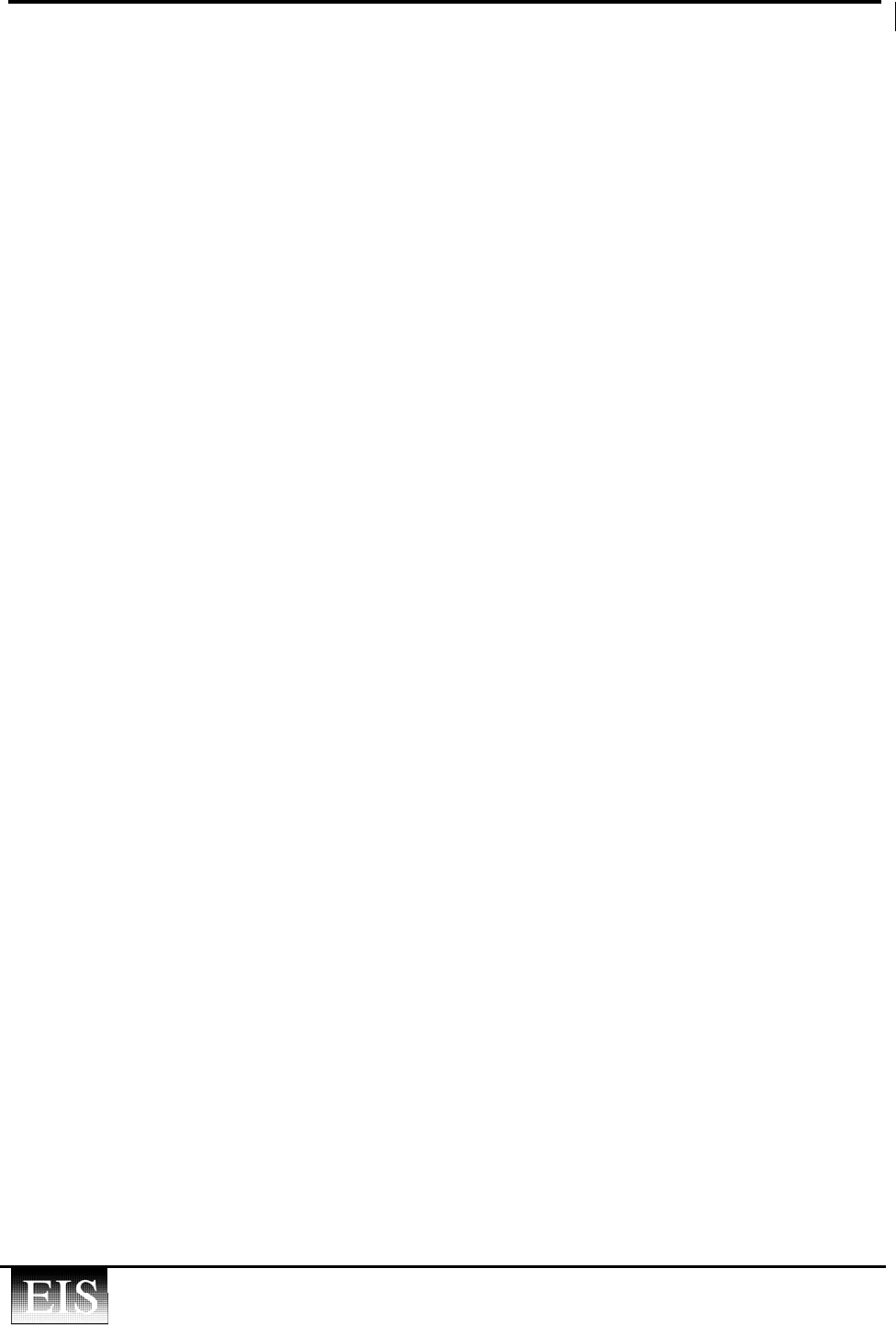
RTMS User Manual Issue 3.2 1
EIS Electronic Integrated Systems Inc.
INDEX
A
Advanced RTMS Parameters ............................ 12, 19
Aiming....................................................................... 5
Alarm Forward Look Mode..................................... 14
Alarm Speed Limit .................................................. 21
Automatic Speed Calibration................................... 23
B
Background.................................................... 2, 17, 22
Ball-joint.............................................................. 3, 40
Barrier........................................................................ 2
Beep............................................................. 15, 18, 22
C
Classification by length ........................... 2, 14, 20, 27
Count Verification ............................................. 12, 22
Crimping tool........................................................... 33
CTS.................................................................... 35, 38
D
Data Mode ....................................... 10, 12, 25, 31, 44
DCD......................................................................... 35
DCE ......................................................................... 35
Direct Mode......................................................... 9, 29
Doppler.............................................................. 14, 24
DSR ................................................................... 35, 38
DSS.................... 2, 3, 4, 25, 29, 30, 33, 34, 36, 41, 44
DSS modem Setup................................................... 49
DTE ......................................................................... 35
DTR ................................................................... 35, 38
E
EDT ......................................................... 2, 14, 19, 42
Ethernet ........................................................... 2, 3, 37
F
Fail-Safe .................................................................... 2
FCC ......................................................................... 41
Fine Tune......................................... 12, 16, 17, 18, 42
Firmware Revision .................................................. 32
Footprint .................................................................... 8
Forward-looking Mode.................. 1, 8, 12, 14, 21, 40
H
Headway.................................................................. 19
Height .............................................................. 1, 5, 21
High Resolution Occupancy.................................... 26
I
Incoming Inspection .................................................. 3
Installation ............................................................. 3, 4
Intersection .................................................... 7, 14, 22
IP address................................................. 9, 29, 47, 48
K
Km/h ............................................................ 12, 19, 41
L
Long vehicle (LV) ................................................... 20
Loop emulation (6ft)................................................ 26
Lynch pin................................................................... 4
M
Manual Speed Calibration ....................................... 23
Message Period................................ 12, 22, 23, 24, 25
Mid. Intersection...................................................... 14
Mid-size (MV)............................................. 20, 26, 27
Modem cabling ........................................................ 38
Modem sharing ........................................................ 45
Mounting ................................................................... 5
Mph.......................................................................... 12
MS Connector........................................ 33, 36, 43, 44
MTBF ...................................................................... 41
Multi Drop ..................................................... 9, 29, 30
N
NORMAL Data mode.............................................. 30
Nulls .................................................................... 2, 42
O
Offset ................................................................... 8, 21
Operating Mode................................................. 12, 14
Overpass ................................................................ 6, 8
P
Per Vehicle Speed.................................................... 24
Period....................................................................... 12
Power Management ................................................. 20
Power requirements ................................................. 41
R
Range slice........................................... 1, 2, 15, 16, 17
Real time clock ........................................................ 26
Reliability ................................................................ 41
Rev 6.1............................................. 11, 14, 25, 26, 27
RS-232................................. 10, 33, 35, 36, 40, 41, 43
RS-485......................................................... 33, 37, 41
Rtms.ini file ............................................................... 9
Rtmslng.txt file .......................................................... 9
RTS.............................................................. 35, 38, 40
Rx ...................................................................... 35, 38
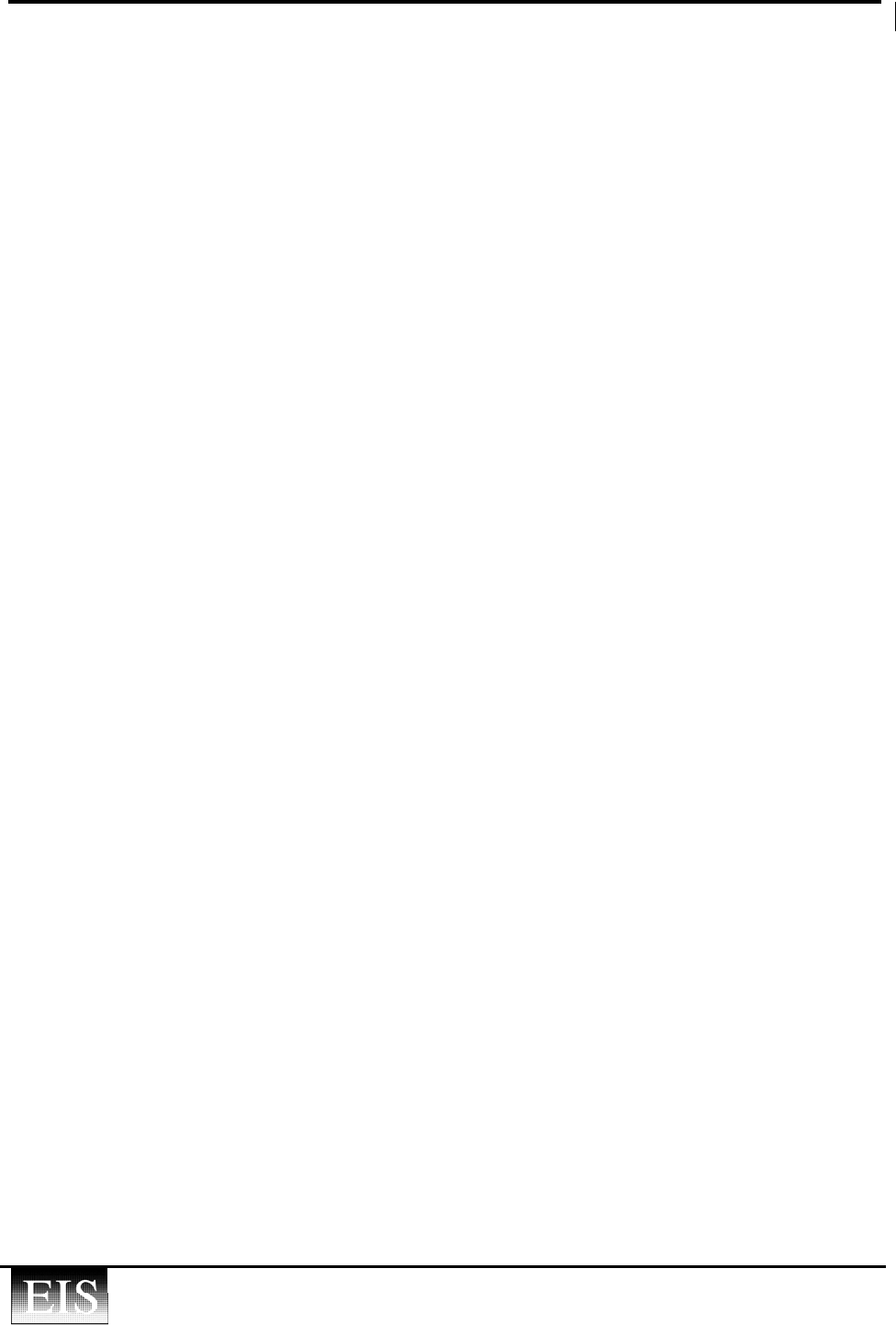
RTMS User Manual Issue 3.2 2
EIS Electronic Integrated Systems Inc.
S
Self Test................................................. 32, 39, 43, 44
Sensitivity.................................................... 12, 13, 44
Serial Port ............................................................ 3, 36
Serial Port speed...................................................... 29
Set-back ..................................................................... 5
Setup Files ............................................................... 31
Setup Sequence........................................................ 12
Side-fired Highway.................................... 1, 5, 14, 23
Sign-bridge ................................................................ 6
Speed bins................................................................ 21
Speed Calibration ........................................ 12, 23, 24
Speed trap ................................................................ 14
SPIDER ................................................................... 25
Station ID........................................................... 12, 25
Stop Bar Detection..................................................... 7
T
TCP/IP ..................................................................... 37
Threshold....................................................... 2, 14, 19
Tick clock ................................................................ 26
TOOLS ........................................................ 31, 32, 43
Tx .......................................................... 35, 38, 43, 44
U
USB ........................................................................... 9
V
Vehicle Detection ...................................................... 2
Verify................................................................. 12, 22
W
Wizard ..................................................... 9, 12, 13, 24
X
XLong................................................................ 20, 26
Z
Zone icon ..................................................... 10, 15, 44
Zone setup.......................................................... 12, 15