LENNOX Air Handler (indoor Blower&evap) Manual L0805330
User Manual: LENNOX LENNOX Air Handler (indoor blower&evap) Manual LENNOX Air Handler (indoor blower&evap) Owner's Manual, LENNOX Air Handler (indoor blower&evap) installation guides
Open the PDF directly: View PDF .
Page Count: 20

®
,1,_2008Lennox Industries Inc,
Dallas, Texas, USA
X_ WARNING
CAUTION
IMPORTANT
_, IMPORTANT
RETAIN THESE INSTRUCTIONS
INSTALLATION
INSTRUCTIONS
Dave Lennox Signature ®
Collection CB31MV Units
MULTI-POSITION AIR HANDLER
505,341M
04/08
Supersedes 07/07
TeCh nical
bNcations
Litho U.S.A.
CB31MV Up-flow/Down-flow Unit Dimensions .... 2
CB31MV Horizontal LH/RH Unit Dimensions ...... 3
General Information ........................... 4
Shipping and Packing List ...................... 4
Requirements ................................. 4
Installing the Unit .............................. 4
Brazing Connections ........................... 8
Installing the Condensate Drain ................. 9
Inspecting and Replacing Filters ................. 9
Sealing the Unit ............................... 9
Adjusting the BDC3 Blower Control Board ........ 9
Adjusting the Blower Speed .................... 9
Making Electrical Connections .................. 11
Repairing or Replacing Cabinet Insulation ......... 20
FOR FUTURE REFERENCE
CHECK FOR AND REMOVE THE FOLLOWING ITEMS BEFORE OPERATING UNIT.
MOTOR SHIPPING BOLT
TOP CAP SHIPPING BRACKET (REPLACE
SCREWS IN TOP CAP AFTER REMOVAL)
C
HOUSING SUPPORT PAD
MOTOR SHIPPING BRACKET
REFRIGERANT LINE CAPS [SEE
BRAZING CONNECTION ON PAGE 8]
F
B
HORIZONTAL DRAIN PAN (SEE UP-FLOW
APPLICATIONS ON PAGE 4 AND
DOWN-FLOWAPPLICATIONS ON PAGE 6 )
E
DG
CONFIGURATION JUMPERS (IF NECESSARY) (SEE
ADJUSTING THE BDC3 BLOWER CONTROL BOARD
ON PAGE 11.
04/08
IIIlllllllllllllllllllll Page 1 505,341M
IIIHIIIIIIIIIIIIIIIIIIIIIIIIIIIIIIIIIIIIIIIIIII

DIMENSION A B CD E
CB31MV-041 inches (ram) 51 (1295) 21-1/4 (540) 22-5/8 (502) 19-3/4 (575) 21 (533)
CB31MV-051, -065 inches (ram) 58-1/2 (1486) 21-1/4 (540) 24-5/8 (625) 19-3/4 (502) 23 (584)
F G H
20 (508) 26-3/8 (670) 24-5/8 (625)
20 (508) 27-7/8 (708) 30-5/8 (778)
SUPPLY AIR
3/4
(19) OPENING
3/4 3/4
(1_
LINE VOLTAGE LOW VOLTAGE
INLETS INLETS
(TOP ANDLEFT (TOP AND
SIDE) RIGHT SIDE)
t8 8
-(18)
GOPTIONAL
ELECTRIC
HEAT
(FIELD
INSTALLED)
PIPING
................. DETAILPLATE(SEE
/BELOW)
SUCT,ON
LINE X
! LIQUILIN ED..,....,.._€C
FILTER
5/8 5/8
(18) (18)
FRONT VIEW
UP-FLOW POSITION
1
(25)
RETURN AIR
5/8
(18)
SIDE VIEW
5/8
(18)
(215)
TOP VIEW
PIPING _ B
PLATE
(SEE
DETAIL
BELOW
LEFT)
FILTER
ACCESS FILTER
\
SUCTION
LINE
,i-
/=
LIQUID
LINE
5/8
SUPPLY (16) _SUPPLy A l.-
5/8 5/8 LOWVOLTAGE /tz°U (1/''_'_ 5/8)
(16) (16) (RIGHT SIDE)
LINE VOLTAGE
FRONT VIEW (LEFT SIDE) // SIDE VIEW
t
OPTIONAL ELECTRIC
HEAT (FIELD INSTALLED)
DOWN-FLOW POSITION
DETAIL OF PIPING PLATE
505341M 04/08
Page 2

DIMENSION A B CD E
CB31MV-041 inches (ram) 51 (1295) 21-1/4 (540) 22-5/8 (502) 19-3/4 (575) 21 (533)
CB31MV-051, -065 inches (ram) 58-1/2 (1486) 21-1/4 (540) 24-5/8 (625) 19-3/4 (502) 23 (584)
F G H
20 (508) 26-3/8 (670) 24-5/8 (625)
20 (508) 27-7/8 (708) 30-5/8 (778)
CONDENSATE
DRAINS (2)
5/8(15)
LIQUID
LINE FILTER
DETAIL OF PIPING PLATE \
5/8(16)
1 (25)
/
I!! i
I! i i
I!::!::::::::::::
uu
J\
\ SUCTION LINE
LIQUID
LINE TOP VIEW
t
C
/
OPTIONAL ELECTRIC
HEAT
(FIELD INSTALLED) LINE VOLTAGE INLETS
(TOP AND RIGHT SIDE)
3/4
11-1/16 (19)
FILTER
ACCESS LOW VOLTAGE INLETS
5/8 (16) (BOTTOM AND RIGHT SIDE)
END VIEW FRONT VIEW END VIEW
HORIZONTAL POSITION (RIGHT-HAND AIR DISCHARGE)
3/4
(19)
3/4
(19)
FILTER
SUCTION
LINE
3/4
(19) 11q/16
3/4 t
(19) I ...........
DAIR :
3/4
(19) -'_
OPTIONAL ELECTRIC HEAT SUCTION LINE jU I1_LIQUID
(FIELD INSTALLED) LINE
TOP VIEW
5/8(16)
LOW VOLTAGE INLETS
(TOP AND LEFT SIDE)
/
LINE VOLTAGE INLETS 1-3/4
(BOTTOM AND LEFT SIDE) (44)
END VIEW FRONT VIEW
LIQUID /
LINE
FILTER
ACCESS
DETAIL OF PIPING PLATE
1 (25)
CONDENSATE
DRAINS (2)
1-1/2
(38)
HORIZONTAL POSITION (LEFT-HAND AIR DISCHARGE)
5/8(16)
5/8(16)
END VIEW
Page 3
CB31MV SERIES

A, WARNING IThis unit is approved for installation clearance to
combustible material as stated on the unit rating plate,
Accessibility and service clearances must take
precedence over combustible material clearances.
WARNING
The CB31MV air handler units are designed for installation
with optional field-installed electric heat and a matched
remote outdoor unit, These units are for indoor installation
only, The units are designed for multi-positional
installations and are shipped (completely assembled) from
the factory for installation in up-flow or horizontal
right-hand air discharge applications,
These instructions are intended as a general guide and do
not supersede local or national codes in any way. Consult
authorities having jurisdiction before installation. Check
equipment for shipping damage; if found, immediately
report damage to the last carrier.
Package 1 of 1 contains the following:
1--Assembled air handler unit
2--Drip shields (for down-flow application only)
In addition to conforming to manufacturer's installation
instructions and local municipal building codes, installation
of Lennox air handler units (with or without optional electric
heat), MUST conform with the following National Fire
Protection Association (NFPA) standards:
•NFPA No. 90A - Standard for Installation of Air
Conditioning and Ventilation Systems
• NFPA No. 90B - Standard for Installation of Residence
Type Warm Air Heating and Air Conditioning Systems
CB31MV units are factory-configured for installation in
up-flow or horizontal right-hand air discharge applications.
The units must be field-modified for installation in either
down-flow or horizontal left-hand air discharge
applications,
DISASSEMBLE AND REASSEMBLE AIR HANDLER
UNIT
The CB31MV air handler unit consists of two sections
which are shipped assembled from the factory, If
necessary, the unit may be disassembled to facilitate
setting the unit, Follow the steps below:
To disassemble:
Step 1. Remove access panels.
Step 2. Remove both blower and coil assemblies. This
will lighten the cabinet for lifting,
Step 3. Remove one screw from the left and right posts
inside the unit. Remove one screw from each
side on the back of the unit, Unit sections will
now separate,
To reassemble:
Step 1. Align cabinet sections together,
Step 2, Reinstall screws,
Step 3, Replace blower and coil assemblies.
Step 4. Replace access panel,
UP-FLOW AIR DISCHARGE APPLICATION
Use the following procedures to configure the unit for
up-flow operations:
Step 1. Remove access panels.
Step 2. Remove corrugated padding from the space
between the blower and coil assemblies,
Step 3. Discard drip shields which are shipped inside
corner post packaging. The shields are used in
down-flow applications only.
Step 4. The horizontal drain pan must be removed when
the coil blower is installed in the up-flow position,
Removing horizontal drain pain will allow proper
airflow and increase efficiency.
505341M 04/08
Page 4

Step5.
Step6.
Placeunitindesiredlocation.Unitmustbelevel.
Connectreturnand supplyair plenumsas
requiredusingsheetmetalscrews.
If the applicationwill not includea returnair
plenum,installtheunitonaraisedstandatleast
14"fromthefloorto ensureproperair return.
Lennoxoffersanoptionalup-flowunitstandas
listedintable1.
UP-FLOW/
Fq
I;
II
II
DOWN-FLOW oo_J
DRAIN PAN i
i
HORIZONTAL DRAIN PAN
1(MUST BE REMOVED)
Figure 1. Up-flow Configuration
Table 1. Optional Unit Side Stand (Up-Flow Only)
Model Kit Number
-21,-26, and -31 45K31
-41 through -65. 45K32
HORIZONTAL RIGHT-HAND AIR DISCHARGE
APPLICATION
Use the following procedures to configure the unit for
horizontal right-hand discharge operations:
NOTE -For horizontal applications, a secondary drain pan
is recommended. Refer to local codes.
Step 1.
Step 2.
Step 3.
Remove access panels and the horizontal drip
shield (-068 model) and the corrugated padding
between the blower and coil assembly. Discard
the corrugated padding and the down-flow drip
shields from the foam pads on top of the unit.
Install the horizontal shield on the front edge of
the horizontal drain pan as illustrated in figure 2.
No further adjustment is necessary. Set unit so
that it is sloped 1/4 inch towards the drain pan end
of the unit.
Step 4. If suspending the unit, it must be supported
along the entire length of the cabinet. If using
chain or strap, use a piece of angle iron or sheet
metal attached to the unit (either above or below)
so that the full length of the cabinet is supported.
Use securing screws no longer than 1/2 inch to
avoid damage to coil or filter as illustrated in
figure 3. Connect return and supply air plenums
as required using sheet metal screws.
HORIZONTAL DRIP SHIELD (-068
MODELS)
UP-LOAD /DOWN-FLOW
DRAIN PAN
Page 5
DOWN-FLOW RAILHORIZONTAL DRAIN
PAN
NO ADJUSTMENT IS NECESSARY
Figure 2. Right-hand Discharge Configuration
HORIZONTAL RIGHT-HAND DISCHARGE
APPLICATION IN HIGH HUMIDITY AREAS
For horizontal applications in high humidity areas remove
the down-flow rail closest to the drain pan.
To remove rail:
Step 1. Remove the screws from the rail at the back of
unit and at the cabinet support rail.
Step 2. Remove the down-flow rail then replace screws.
Step 3. Seal around the exiting drain pipe, liquid line,
and suction line to prevent humid air from
infiltrating into the unit.
1/2 IN. SCREWS MAXIMUM
ANGLE IRON OR
SHEET METAL
ELECTRICAL INLET
CLEARANCE 4 IN. (102 MM)
FRONT VIEW END VIEW
Figure 3. Suspending Horizontal Unit
AIMPORTANT
HORIZONTAL LEFT-HAND AIR DISCHARGE
APPLICATION
SECURING TAB ON HORIZONTAL
CABINET SUPPORT RAIL DRIP SHIELD
DOWNFLOW 7'_ HORIZONTAL
RAIL DRAIN PAN
Figure 4. Left-hand Air Discharge Configuration
CB31MV SERIES

NOTE -For horizontal applications, a secondary drain pan
is recommended. Refer to local codes.
Use the following procedures to configure the unit for
horizontal left-hand discharge operations:
Step 1, Remove access panels. Remove corrugated
padding from space between the blower and coil
assemblies. Discard drip shields which are
shipped inside corner post packaging. The
shields are used in down-flow applications only,
Step 2, Slide coil assembly from unit, Remove the
horizontal drain pan,
Step 3, Remove drain plugs from back drain holes on
horizontal drain pan, Reinstall plugs on front
holes,
Step 4, Rotate drain pan 180° front to back and install it
on the opposite side of coil,
Step 5, Remove screws from top cap. Remove
horizontal drip shield screw located in the center
of the back coil end seal as illustrated in figure 5
on page 6,
Step 6. Rotate horizontal drip shield 180° front to back.
Step 7, Remove plastic plug from left hole on coil front
end seal and re-install plug in back hole,
Step 8, Reinstall horizontal drip shield screw in front coil
end seal, Drip shield should drain downward into
horizontal drain pan inside coil,
DRIP TOP CAP ROTATED TO
SHIELD CORRECT POSITION
\
CABINET \ TOP CAP SCREWS
\
/
DRAIN PAN DRAIN PAN
REINSTALLED SHIPPING
HERE LOCATION
t
-- DRAIN PLUGS --
REINSTALLED HERE REMOVED FROM HERE
COIL SHOWN IN UPLOAD POSITION FOR EASY CONVERSION
ALIGN HOLES
WITH HOLES
IN COIL END
PLATE,
TOP
CAP _
90 o BACK COIL
BEND END SEAL
Figure 5. Field Modification (left-hand air discharge)
Step 9, Rotate top cap 180° front to back and align with
unused screw holes, Holes must align with front
and back coil end plates. Note that top cap has
a 45° bend on one side and 90° bend on the
other. The 90° bend must be on the same side
as the horizontal drain pan as illustrated in figure
figure 5,
NOTE -Use extreme care when reinstalling screws into
coil end plate engaging holes. Coil damage could result by
misatignment.
Step 10, From the up-flow position, flip cabinet 90° to the
left and set into place. Replace coil assembly.
Secure coil in place by bending down tab on
cabinet support rail as illustrated in figures 4 and
5,
NOTE -For horizontal applications in high humidity
areas, remove the down-flow rail closest to the drain pan.
To remove rail, remove screw from rail at back of unit and
at cabinet support rail. Remove down-flow rail then replace
screws. Also, seal around the exiting drain pipe, liquid and
suction tines to prevent infiltration of humid air.
Step 11, Knock out drain seal plate from access door.
Secure plate to cabinet front flange using the
provided screw,
Step 12. Flip access door and replace it on the unit,
Step 13, Set unit so that it is sloped 1/4 inch towards the
drain pan end of the unit as illustrated in figure
6. Connect return and supply air plenums as
required using sheet metal screws.
Step 14, If suspending the unit, it must be supported
along the entire length of the cabinet, tf using
chain or strap, use a piece of angle iron or sheet
metal attached to the unit (either above or below)
so that the full length dthe cabinet is supported,
Use securing screws no longer than 1/2 inch to
avoid damage to coil or filter as illustrated in
figure 3 on page 5, Connect return and supply
air plenums as required using sheet metal
screws,
THIS CORNER
SHOULD BE
1/4" HIGHER
THAN DRAIN
CORNER THIS CORNER
SHOULD BE
1/4" HIGHER
THAN DRAIN
CORNER
Figure 6. Sloping for Proper Drainage
DOWN-FLOW AIR DISCHARGE APPLICATIONS
Use the following procedures to configure the unit for
down-flow operations:
505341M 04/08
Page 6
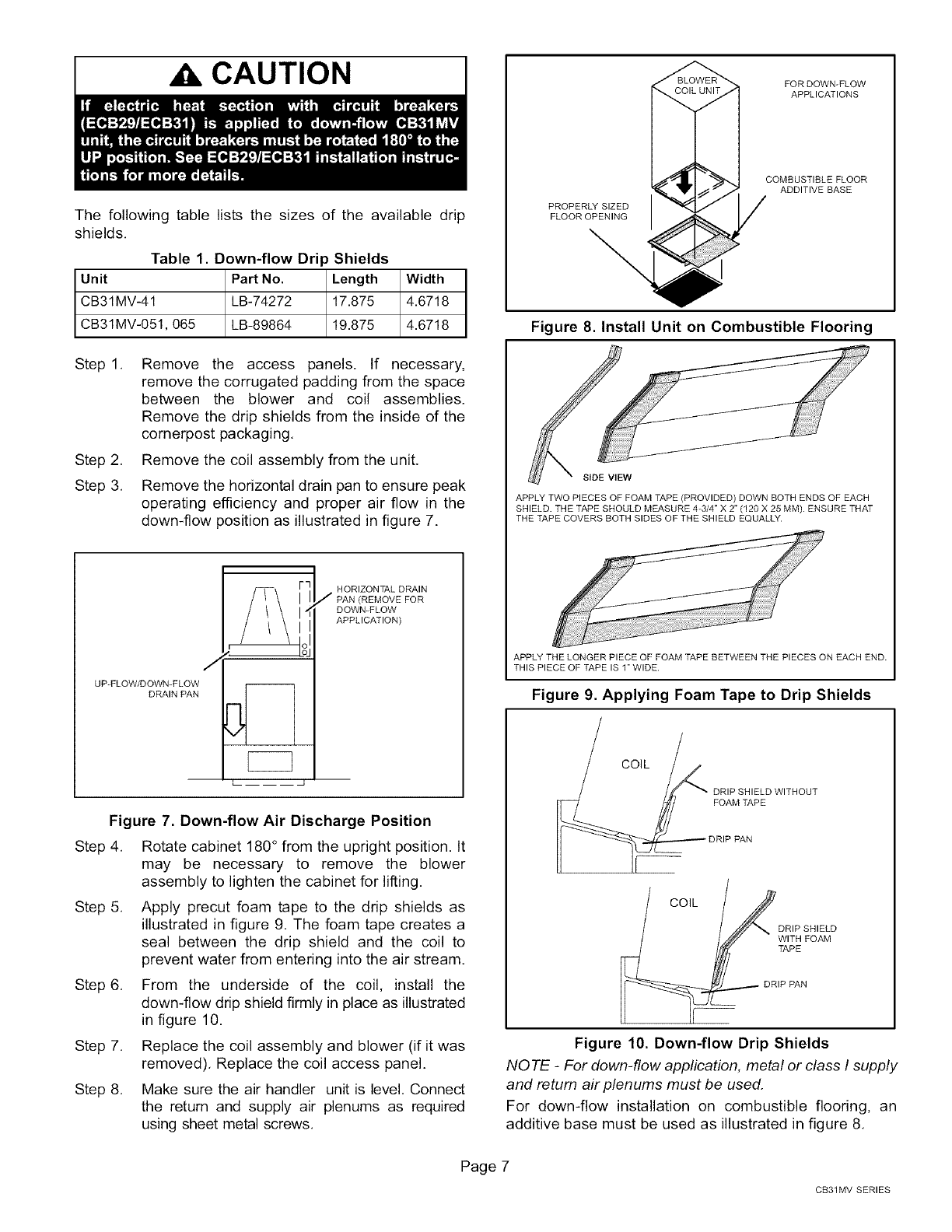
CAUTION
The following table lists the sizes of the available drip
shields,
Table 1. Down-flow Drip Shields
Unit Part No. Length Width
CB31MV-41 LB-74272 17.875 4.6718
CB31MV-051,065 LB-89864 19.875 4.6718
Step 1,
Step 2,
Step 3,
Remove the access panels. If necessary,
remove the corrugated padding from the space
between the blower and coil assemblies.
Remove the drip shields from the inside of the
cornerpost packaging,
Remove the coil assembly from the unit.
Remove the horizontal drain pan to ensure peak
operating efficiency and proper air flow in the
down-flow position as illustrated in figure 7.
J
UP-FLOW/DOWN-FLOW
DRAIN PAN
F_ HORIZONTAL DRAIN
J PAN (REMOVE FOR
14 DOWN-FLOW
ij_oOjAPPLICATION)
Figure 7. Down-flow Air Discharge Position
Step 4. Rotate cabinet 180° from the upright position. It
may be necessary to remove the blower
assembly to lighten the cabinet for lifting.
Step 5, Apply precut foam tape to the drip shields as
illustrated in figure 9, The foam tape creates a
seal between the drip shield and the coil to
prevent water from entering into the air stream,
Step 6, From the underside of the coil, install the
down-flow drip shield firmly in place as illustrated
in figure 10.
Step 7, Replace the coil assembly and blower (if it was
removed), Replace the coil access panel.
Step 8, Make sure the air handler unit is level. Connect
the return and supply air plenums as required
using sheet metal screws,
PROPERLY SIZED
FLOOR OPENING
FOR DOWN-FLOW
APPLICATIONS
COMBUSTIBLE FLOOR
ADDITIVE BASE
Figure 8. Install Unit on Combustible Flooring
SIDE VIEW
APPLY TWO PIECES OF FOAM TAPE (PROVIDED) DOWN BOTH ENDS OF EACH
SHIELD. THE TAPE SHOULD MEASURE 4-3/4" X 2" (120 X 25 MM). ENSURE THAT
THE TAPE COVERS BOTH SIDES OF THE SHIELD EQUALLY.
APPLY THE LONGER PIECE OF FOAM TAPE BETWEEN THE PIECES ON EACH END.
THIS PIECE OF TAPE IS 1" WIDE.
Figure 9. Applying Foam Tape to Drip Shields
COIL _
_ FDoRIAPMSHT/ELDWITHOUT
DRIP PAN
COIL /
DR,PPAN
Figure 10. Down-flow Drip Shields
NOTE -For down-flow application, metal or class I supply
and return air plenums must be used.
For down-flow installation on combustible flooring, an
additive base must be used as illustrated in figure 8.
Page 7
CB31MV SERIES
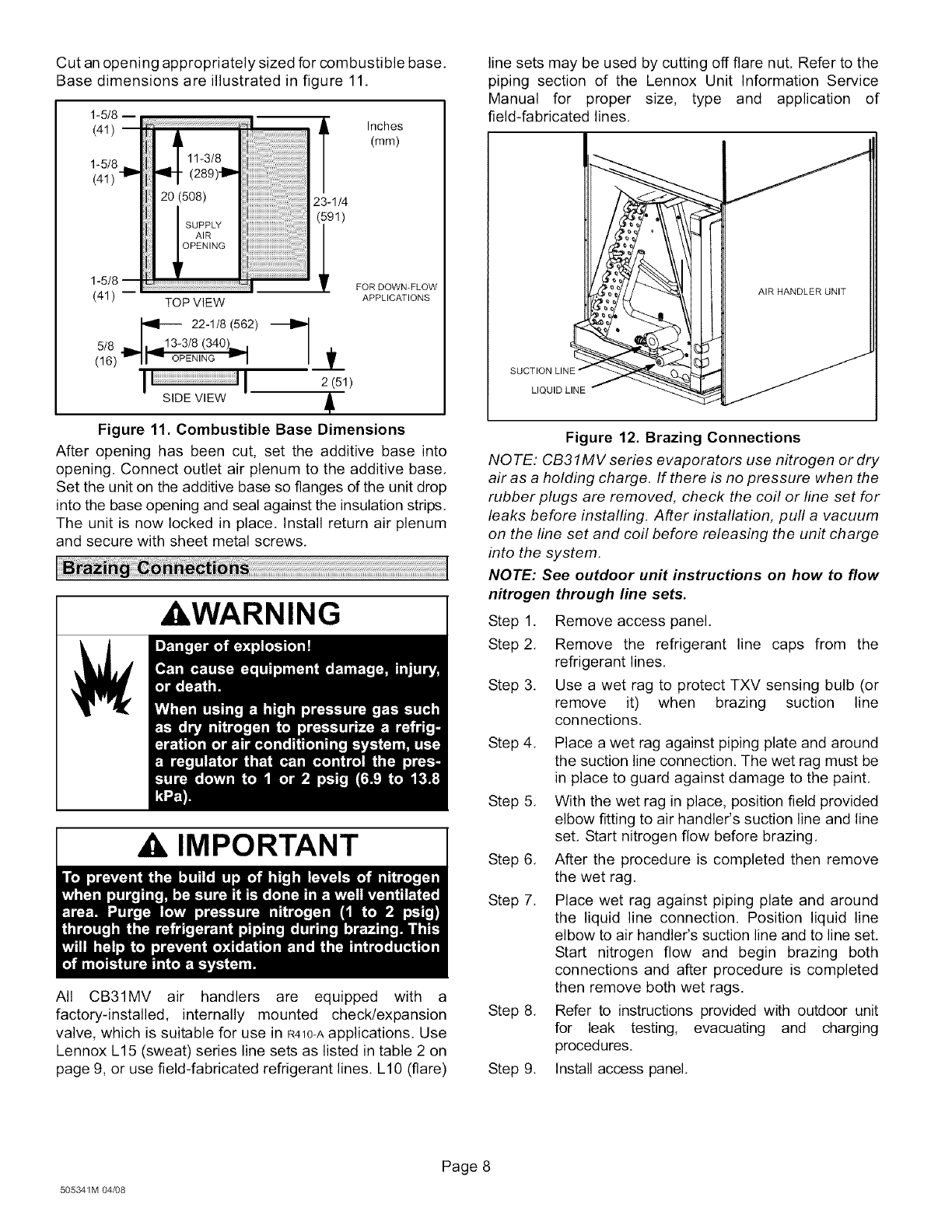
Cut an opening appropriately sized for combustible base.
Base dimensions are illustrated in figure 11+
1-5/8 --
(41)
1-5/8
(41)
Inches
(mm)
23-1/4
(i 91)
I_.1L 11-3/8
(289)-IP'
2o(5o8)
IO UPPLY
AIR
PENING
1-5/8 ................................................................. FORDOWN-FLOW
(41) -- TOP VIEW APPLICATIONS
22-1/8 (562)
5/8 I. 13-3/8 (340)
(16) "1_ _'_ _ V
ILIIsioEViEW 51)
Figure 11. Combustible Base Dimensions
After opening has been cut, set the additive base into
opening. Connect outlet air plenum to the additive base.
Set the unit on the additive base so flanges of the unit drop
into the base opening and seal against the insulation strips.
The unit is now locked in place. Install return air plenum
and secure with sheet metal screws.
WARNÁNG
IMPORTANT
All CB31MV air handlers are equipped with a
factory-installed, internally mounted check/expansion
valve, which is suitable for use in R410-Aapplications. Use
Lennox L15 (sweat) series line sets as listed in table 2 on
page 9, or use field-fabricated refrigerant lines. L10 (flare)
line sets may be used by cutting off flare nut. Refer to the
piping section of the Lennox Unit Information Service
Manual for proper size, type and application of
field-fabricated lines.
SUC
LIQUID LINE
AIR HANDLER UNIT
Figure 12. Brazing Connections
NOTE: CB31MV series evaporators use nitrogen or dry
air as a holding charge. If there is no pressure when the
rubber plugs are removed, check the coil or line set for
leaks before installing. After installation, puff a vacuum
on the line set and coil before releasing the unit charge
into the system.
NOTE: See outdoor unit instructions on how to flow
nitrogen through line sets.
Step 1. Remove access panel.
Step 2+ Remove the refrigerant line caps from the
refrigerant lines.
Step 3. Use a wet rag to protect TXV sensing bulb (or
remove it) when brazing suction line
connections.
Step 4+ Place a wet rag against piping plate and around
the suction line connection. The wet rag must be
in place to guard against damage to the paint.
Step 5+ With the wet rag in place, position field provided
elbow fitting to air handler's suction line and line
set. Start nitrogen flow before brazing.
Step 6+ After the procedure is completed then remove
the wet rag.
Step 7. Place wet rag against piping plate and around
the liquid line connection. Position liquid line
elbow to air handler's suction line and to line set.
Start nitrogen flow and begin brazing both
connections and after procedure is completed
then remove both wet rags.
Step 8+ Refer to instructions provided with outdoor unit
for leak testing, evacuating and charging
procedures.
Step 9. Install access panel.
505341M 04/08
Page 8

Table 2. Refrigerant Line Kits
Vapor/ L10 L15
CB31MV Liquid Suction
Units Line Line Sets Line Sets
Line
L10-41 L15-41
3/8 in 3/4 in.
-41 20 ff. - 50 ft. 20ff.-50ff.
(10 ram) (19 mm) (6m-15m) (6m-15m)
L10-65 L15-65
3/8 in 7/8 in.
-51 30 fl, - 50 ft. 30 ft, - 50 ft,
(10 mm) (22 mm) (9m-15m) (9m-15m)
3/8 in 1-1/8 in. Field Field
-65 (10 mm) (29 mm) Fabricated Fabricated
• Slope horizontal runs 1 inch per 10 feet of drain line to
offset friction.
• Leave an open vent in the drain line, as shown in figure
13 to overcome line length, friction and static pressure.
• Construct drains in a manner which will facilitate future
cleaning. Drains must not interfere with filter access as
illustrated in figure 13 on page 9.
• Route auxiliary drain to an area where homeowner will
notice it draining. The auxiliary drain line does not
required venting or a trap. Refer to local codes.
Connect main condensate drain and route downward to an
open drain or sump. Do not connect drain to a closed waste
system. Refer to figure 13 for typical condensate trap
configuration.
VENT MUST EXTEND ABOVE THE HEIGHT OF THE COIL"
DRAIN PAN BY 2 INCHES (51 MM). VENT
DRAIN PAN
TRAP MUST BE DEEP ENOUGH TO OFFSET
MAXIMUM STATIC DIFFERENCE (GENERAL
2 INCHES [51MM]).
TRAP (49P66)
DRAIN LINE SHOULD SLOPE A MINIMUM 1 INCH PER
10 FEET (25 MM PER 3 M) TO APPROVED DRAIN
Figure 13. Condensate Drain Connection
It is recommended that the auxiliary drain be connected to
a drain line for all units. If auxiliary drain is not connected, it
must be plugged with provided cap. For down-flow units,
the auxiliary drain MUST be connected and routed to a
drain. See figure 14 on page 9 for main and auxiliary
drain locations.
LEFT-HAND UP-FLOW OR RIGHT-HAND
DISCHARGE DOWN-FLOW DISCHARGE
AUXILIARY DRAIN ON LEFT
[ oo ]
MAIN DRAIN ON RIGHT
Figure 14. Main and Auxiliary Drain Locations
The following practices are recommended to ensure
condensate removal:
• Drain piping should not be smaller than the drain
connections at drain pan.
• Install a trap in the main drain line. The trap must be
deep enough to offset the difference in static pressure
between drain pan and atmosphere. Generally, two
inches is satisfactory for medium static applications.
AIMPORTANT
Filters may be duct-mounted or installed in cabinet. A filter
is factory-installed. Note that filter access door fits over
access panel. Air leakage will occur if access panel is
placed over filter door.
Filters should be inspected monthly and must be cleaned
or replaced when dirty to assure proper furnace operation.
Units are equipped with standard throw-away type filters
which should be replaced when dirty.
To replace filter:
Step 1. Loosen the thumbscrews holding the filter panel
in place.
Step 2. Slide the filter out of the guides on either side of
cabinet.
Step 3. Insert new filter.
Step 4. Replace panel.
See table 3 for replacement filter sizes.
Table 3. Filter Dimensions
Unit Model No. Filter Size inches (mm)
CB31MV-41 20x 22(508 x 559)
CB31MV-51, -65 20x 24(508 x 610)
Seal the unit so that warm air is not allowed into the
cabinet. Warm air introduces moisture, which results in
water blow-off problems. This is especially important when
the unit is installed in an unconditioned area.
Make sure the liquid line and suction line entry points are
sealed with either the provided flexible elastomeric thermal
insulation, or field provided material (e.g. Armaflex,
Permagum or equivalent). Any of the previously mention
materials may be used to seal around the main and
auxiliary drains, and around open areas of electrical inlets.
CB31MV units are equipped with a variable speed motor
that is capable of maintaining a specified CFM throughout
the external static range. A particular CFM can be obtained
by positioning jumpers (COOL, HEAT, and ADJUST) on
Page 9
CB31MV SERIES

the BDC3 control board. The jumpers are labeled 1,2, 3,
and 4. Each of the numbers corresponds with an air
volume (CFM) setting. The ADJUST jumper is labeled
Test, -, +, and Norm. The + and - pin settings are used to
add or subtract a percentage of the CFM selected. The
Test jumper is used to operate the motor in the test mode.
The delay jumper controls the timing for the fan delay.
Table 4. Blower Speed Tap Selection
RECOMMENDED SPEED TAP SELECTION
COOL HEAT
CB31MV Condensing Unit With
Air Handler Condensing Unit Heat Pump Electric Heat Only Heat Pump With Electric Heat
-041 COOL PIN #3 COOL PIN #3 HEAT PIN #4 HEAT PIN #4
-051 COOL PIN #2 COOL PIN #2 HEAT PIN #1 HEAT PIN #1
-065 COOL PIN #3 COOL PIN #3 HEAT PIN #1 HEAT PIN #1
* Minimum setting for heat,
Figure 15 on page 10 provides an illustration of the BDC3
control board. Use tables 5 and 6 on page 12 to determine
the correct air volume for heat and cool speed taps.
ACCESSORY RELAY CONTACTS (DRIVES JP1 15 PIN PLUG
OPTIONAL ACCESSORY RELAY) f (BOARD TO MOTOR)
j_
O
ADJUS
HEATING SPEED COOLING SPEED FAN DELAY
SELECTOR PINS SELECTOR PINS SELECTOR PINS
OPERATIONAL SELECTOR PINS (AFFECTS
BOTH HEATING AND COOLING MODES)
Figure 15. BDC3 Variable Speed Control Board
Selections
Diagnostic LEDs located on the BDC3 control board are
provided to aid in identifying the unit's mode of operation.
Certain scenarios will arise depending on the jumper
positions. Read through the jumper settings sections
before adjusting Blower speed. Refer to figure 15 for
identification.
DIAGNOSTIC LEDS
Step 1. RUN LED indicates there is a demand for the
Blower motor to run,
Step 2. CFM LED indicates the CFM at which the unit is
operating. The light flashes once for
approximately every 100 CFM For example, if
the unit is operating at 1000 CFM, CFM LED will
flash 10 times. If the CFM is 1150, CFM LED will
flash 11 full times plus one fast or half fiash,
At times the light may appear to flicker or glow. This takes
place when the control is communicating with the motor
between cycles. This is normal operation.
The appropriate speed according to application and CFM
need is selected by moving jumper pins.
IMPORTANT
Table 4 lists the recommended factory Blower speed tap
selections for CB31MV series units. These settings are for
nominal tonnage match-ups with the CB31MV. When
matched with other sizes, it is recommended that the CFM
be adjusted to approximately 400 CFM per ton.
To change jumper positions, gently pull the jumper off the
pins and place it on the desired set of pins. The following
section outlines the different jumper selections available
and conditions associated with each one as illustrated in
figure 15.
After the CFM for each application has been determined,
the jumper settings must be adjusted to reflect those given
in tables 5 and 6. From the tables, determine which row of
CFM volumes most closely matches the desired CFM
Once a specific row has been chosen (+, NORMAL, or -),
CFM volumes from other rows cannot be used. Below are
descriptions of the jumper selections.
ADJUST JUMPERS
The ADJUST pins allow the motor to run at normal speed,
approximately 10% higher, or approximately 10% lower than
normal speed, Table 5 gives three rows (+, NORMAL, and -)
with their respective CFM volumes. Notice that the normal
adjustment setting for heat speed position #3 is 1315 CFM
The + adjustment setting for that position is 1445 CFM and
for the - adjustment setting is 1185 CFM After the
adjustment setting has been determined, chose the
remainder speed jumper settings from those offered in the
table in that row,
The TEST pin is available to bypass the BDC3 control and
run the motor at approximately 70% to test that the motor is
operational, This is beneficial primarily in troubleshooting,
G must be energized for motor to run.
505341M 04/08
Page 10

COOLJUMPERS
TheCOOLjumperisusedtodeterminetheCFMduring
either1)coolingor2)heatpumpoperationwithouta callfor
electricheat.Thesejumperselectionsareactivatedfor
coolingwhenY2and DSterminalsin the CB31MVare
energizedandforheatingwhenY2isenergized,
ApplicationswithouttheSignatureStat'"humiditycontrol
willprovideeither70%oftheCOOLCFMduringfirst-stage
coolingfortwo-speedoutdoorunits.100%ofCOOLCFM
isprovidedforsystemswitha single-speedoutdoorunit,
Applicationswith the SignatureStat'"humiditycontrol
createdifferentCFMvolumes,For example,duringa
first-stagecoolingcall (two-speedoutdoorunit) with
demandfrom the SignatureStat'"thermostat,the air
volumeis40%oftheCOOLjumperselection.Foranormal
COOL(Pin#2settingforCB31MV-41),theCFMis1125;
thereducedspeedis450CFM(1125x 40%=450).This
arrangementprovidesfor additionaldehumidification
duringstandardfirststagecooling.Seetables7 and8for
variousscenariosconcerninguseoftheSignatureStat'"
humiditycontrolandtheCB31MVseriesunit,
ForapplicationswithHarmonyII(_zonecontrol,theBlower
CFMvolumeis determinedby the HarmonyII control
center.Theminimumairhandlerspeedis predetermined
at650CFMfor-41seriesunitsand850CFMfor-51and
-65 series units.This speedis not adjustable,See
footnotesintables5and6,
Withthethermostatsetfor"ContinuousFan"andwithouta
callforheatingorcooling,theCB31MVwillprovided50%
oftheCOOLCFMselected,
NOTE -For two-speed heat pumps, air handler will operate
at 70% of the COOL selection until supplemental electric
heat is demanded. At that time, the air handler will operate
at the HEAT speed selected, This arrangement provides
for warmer supply air during second-stage heating.
HEAT" JUMPERS
The HEAT jumper is used to determine CFM during
electric heat operation only, These jumper selections are
activated only when W1 is energized,
DELAY JUMPERS
The DELAY jumper is used to set the specific motor fan
operation during cooling mode. Depending on the
application, one of four options may be chosen by moving
the jumper to the appropriate set of pins,
B Once demand is met, motor runs at 100% for 45
seconds, Then,
C ramps down to stop.
NOTE -Blower OFF DELAY also applies during heat
pump operation
#3 Pins Jumpered --
A Motor runs at 82% for approximately 7-1/2
minutes. If demand has not been satisfied after
7-1/2 minutes,
B motor runs at 100% until demand is satisfied,
A BI C
C Once demand is met, motor ramps down to stop.
#4 Pins Jumpered --
A Motor runs at 50% for 30 seconds,
B Motor then runs at 82% for approximately 7-1/2
minutes. If demand has not been satisfied after
7-1/2 minutes,
C Motor runs at 100% until demand is satisfied.
D Once demand is met, motor runs at 50% for 30
seconds. Then,
B C/ D
A._/
E ramps down to stop.
Wiring must conform to the current National Electric Code
ANSI/NFPA No, 70, or Canadian Electric Code Part I, CSA
Standard C22.1, and local building codes. Refer to
following wiring diagrams, See unit nameplate for
minimum circuit ampacity and maximum overcurrent
protection size,
Select the proper supply circuit conductors in
accordance with tables 310-16 and 310-17 in the
National Electric Code, ANSI/NFPA No. 70 or tables 1
through 4 in the Canadian Electric Code, Part I, CSA
Standard C22,1,
Xk WARNING
I[,,_ [_o]_i_ii_l_o]_l_l[o]i[o]_,,_ [o]_Ik'14
#1 Pins Jumpered --
A Motor runs at 100% until demand is satisfied,
A B
oFF___/
B Once demand is met, motor ramps down to stop.
#2 Pins Jumpered --
A Motor runs at 100% until demand is satisfied,
This unit is provided with knockouts for conduit, Refer to
figure 16 for unit schematic wiring diagram. Refer to
figures 17, 19, 20 and 21 for typical field wiring.
Separate openings have been provided for 24V low
voltage and line voltage, Refer to the dimension illustration
of specific location,
WARNING
A c
Page 11
CB31MV SERIES

ADJUST
Jumper
Setting
+
NORM
Table 5. CB31MV-041 Air Handler Performance
0through 0.80 in. w.g. (0 Through 200 Pa) External Static Pressure Range
BDC3 Jumper Speed Position
HEAT Speed
1234
cfm L/s cfm L/s cfm L/s cfm L/s
1230 580 1335 630 1445 680 1545 730
1120 530 1215 575 1315 620 1400 660
1010 475 1200 565 1185 560 1265 595
COOL Speed*
1 2 3 4
cfm L/s cfm L/s cfm L/s cfm L/s
1090 515 1225 580 1380 650 1545 730
975 460 1125 530 1275 600 1400 660
900 425 1000 470 1135 535 1265 595
* First-stage (two-stage units only) cooling is approximately 70% of the COOL speed rating,
Continuous fan speed is approximately 50% of COOL speed rating.
Lennox Harmony II Zone Control Applications - Minimum air handler speed is approximately 380 cfm (180 L/s).
NOTE - The effect of static pressure, filter and electric heater resistance is included in the air volumes listed.
ADJUST
Jumper
Setting
+
NORM
Table 6. CB31MV-051, -065 Air Handler Performance
0through 0.80 in. w.g. (0 Through 200 Pa) External Static Pressure Range
BDC3 Jumper Speed Position
HEAT Speed
1234
cfm L/s cfm L/s cfm L/s cfm L/s
1850 875 1960 925 2090 985 2150 1015
1705 805 1800 850 1900 895 2005 945
1560 735 1625 765 1720 810 1770 835
COOL Speed*
1 2 3 4
cfm L/s cfm L/s cfm L/s cfm L/s
1625 765 1820 860 2055 970 2145 1010
1425 670 1625 765 1805 850 2005 945
1205 570 1375 650 1555 735 1725 815
* First-stage (two-stage units only) cooling is approximately 70% of the COOL speed rating,
Continuous fan speed is approximately 50% of COOL speed rating.
Lennox Harmony II E Zone Control Applications - Minimum air handler speed is approximately 400 cfm (190 Lls).
NOTE - The effect of static pressure, filter and electric heater resistance is included in the air volumes listed.
Table 7. CB31MV SignatureStat'" and Single Stage Outdoor Unit
OperatingSequence system Demand ISystem Resp°nseAir
IThermostat Demand Relative Humidity IHandlerCFM
System
Condition Step Y1 O G W l Status D Compressor (COOL) Comments
NO CALL FOR DEHUMIDIFICATION
Normal 24 Compressor and indoor air
Operation 1 On On On Acceptable VAC High 100% handler follow thermostat de-
mand
BASIC MODE (only active on a Y! thermostat demand)
Normal 24 High 100% SignatureStat ' energizes Y1
Operation 1 On Acceptable VAC
oand de-energizes D on a call
Dehumidification
Call 2 On Demand VAC High 60%/65%* for dehumidification
PRECISION MODE (operates independent of a Y! thermostat demand)
Normal 24
Operation 1 On Acceptable VAC High 100% Dehumidification mode begins
Dehumidification O when humidity is greater than
call 2 On Demand VAC High 60%/65%* set point
o
Dehumidification
call ONLY 1 On Demand VAC High 60%/65%*
Jumpers at indoor unit with a single stage outdoor unit
With Condensing unit - Y1 to Y2 and R to O
With Heat Pump - Y1 to Y2
SignatureSr[at " will try to
maintain room humidity set-
point by allowing the room
space to maintain a cooler
room thermostat setpoint**
Lennox SignatureStat _' used for these applications are 51 M26 - 1 heat /1 cool or 51 M28 - 2 heat /2 cool heat pump
* During dehumidification, cooling air handler speed is as follows: 65% of COOL cfm for -41units, 60% COOL cfm for -51 and -61 units
** In Precision mode, SignatureStat _ thermostat built BEFORE October 2003 will maintain room temperature up to 3°F (1.8°C) cooler than room
thermostat setting. Precision thermostat built AFTER October 2003 will maintain room temperature up to 2°F (1.2°C) cooler than the room thermo-
stat setting.
505341M 04/08
Page 12

Table 8. CB31MV, SignatureStat" and Two-Stage Outdoor Unit
Thermostat Demand
System
Condition Step Y1 Y2 O G W1 W2
NO CALL FOR DEHUMIDIFICATION
Relative Humidity
Status D Compressor
Air Handler
CFM
(COOL) Comments
Normal
Operation - Y1 1 On On On Acceptable 24 VAC Low
Normal
Operation - Y2 2 On On On On Acceptable 24 VAC High
ROOM THERMOSTAT CALLS FOR FIRST STAGE COOLING
BASIC MODE (only active on a Y! thermostat demand)
Normal
Operation 1 On On On Acceptable 24 VAC Low
Dehumidificatio
n Call 2 On On On On Demand 24 VAC High
70%
100%
70%
60%/65%*
Compressor and in-
door air handler fol-
low thermostat de-
mand
SignatureStat ener-
gizes Y2 and de-en-
ergizes D on a call
for dehumidification
PRECISION MODE "operates independent of a Y1 thermostat demand)
Normal 1 On On On Acceptable 24 VAC Low
Operation
Dehumidificatio
n call 2 On On On On Demand 0 VAC High
Dehumidificatio
n call ONLY 1 On On On On Demand 0 VAC High
ROOM THERMOSTAT CALLS FOR FIRST AND SECOND STAGE COOLING
70%
60%/65%*
60%/65%*
Dehumidification
mode begins when
humidity is greater
than set point
**SignatureStat _'
will try to maintain
room humidity set-
point by allowing the
room space to
maintain a cooler
room thermostat
setpoint
BASIC MODE (only active on a Y1 thermostat demand)
Normal
Operation 1 On On On On Acceptable 24 VAC High
Dehumidificatio
n Call 2 On On On On Demand 0 VAC High
100%
60%/65%*
SignatureStat ener-
gizes Y2 and de-en-
ergizes D on a call
for dehumidification
Normal
Operation
Dehumidificatio
n call
Dehumidificatio
n call ONLY
1 On
2 On On On On
1 On On On On
PRECISION MODE
On On On
'operates independent of a Y! thermostat demand)
Acceptable
Demand
Demand
24 VAC High
0 VAC High
0 VAC High
Jumpers at indoor unit with a two stage outdoor unit
With Condensing unit - R to O
100%
60%/65%*
60%/65%*
Dehumidification
mode begins when
humidity is greater
than set point
**SignatureStat"
will try to maintain
room humidity set-
point by allowing the
room space to
maintain a cooler
With Heat Pump - none room thermostat
setpoint
Lennox SignatureStat" used for these applications are 51 M27 - 2 heat /2 cool or 51 M28 - 2 heat /2 cool heat pump.
* During dehumidification, cooling air handler speed is as follows: 65% of COOL cfm for -41 units, 60% COOL cfm for -51 and -61 units
** In Precision mode, SignatureStat _'thermostat built BEFORE October 2003 will maintain the room temperature up to 3°F (1.8°C) cooler than room
thermostat setting. Precision thermostat built AFTER October 2003 will maintain the room temperature up to 2°F (1.2°C) cooler than the room ther-
mostat setting.
Page13
CB31MV SERIES

I LINE VOLTAGE FIELD WIRING
-- -- CLASS ]I VOLTAGE FIELD WIRING
A REFER TO FACTORY BLOWER SPEED TAP SELECTION
LLI CHART BELOW FOR GLOWER SPEED INFORMATION
A USE COPPER CONDUCTORS ONLY. REFER TO UNIT
Z_ NAMEPLATE FOR MINIMUM CIRCUIT AMPACITY
AND MAXIMUM OVERCURRENT PROTECTION SIZE
A NOTE-FOR NON-HEAT PUMP APPLICATION ONLY--
WHEN TWO STAGE THERMOSTAT IS USED, CONNECT
SECOND STAGE HEAT BULB TO TERMINAL "W2" AND
REMOVE JUMPER BETWEEN TERMINALS "R" &"WB"
/X JUMPER "R" TO "0" IS USED WITH CONDENSING
A_ UNIT. REMOVE "R" TO "O" JUMPER WHEN HEAT
PUMP IS USED.
AREMOVE JUMPER BETWEEN
"DO" AND "YI" WHEN
HUMIDITY CONTROL
(SIGNATURESTA_ IS USED,
A JUMPER "YI" TO "YB" IS
Lg& FOR SINGLE STAGE COOLING,
REMOVE JUMPER "YI _ TO _Y2"
FOR TWO STAGE COOLING.
A CO8 USED ON 51 AND 65 UNITS
LL& ONLY
z_ EOUIPMENT GROUND
LOCATED IN INDOORUNIT
A LB IS NOT PRESENT ON
(P) ELECTRIC HEATERS
A THE NUM6ER OF CIRCUITS VARY
ACCORDING TO HEATER MODEL,
REFER TO FAN COIL NAMEPLATE
FOR ACTUAL NUMBER EMPLOYED
A CONNECT POWER WIRES FROM
HEATER LABELED LI,L2 ON
"P* VOLTAGE UNITS ANO
LI,LG,L5 ON "Y" VOLTAGE
UNITS TO TB2 TERMINAL
J2
-Z
\ -8
/
FIELD WIRING FOR UNITS
WITHOUT CIRCUIT BREAKERS
CIRCUITLI _
A _ EOUIPMENTGROUND
DESCRIPTION
KEY COMPONENT
AI5 iCONTROL=BLOWER DRIVE
B3 AOTOR_BLOWER
CB8 iCIRCUIT BREAKER-TRANS Ti
Fi iFUSE-TRANSFORMER
J2 iJACK-ELECT. NEAT
J4G iJACH-OUTPUT
J48 iJACK=MOTOR.VAR SPD
J49 iJACK-MGTOR.VAR SPR
K20.-IUiRELAY-BLOWER
PAR iPLUG-OUTPUT
PAR iP_UG-MDTQR,VAR 5P#
PA9 iPIUG-MGTGR.VAR RPR
T_ iTRANSFDRWPR-CGNTRDJ
TRI iTFRM STRIPED ASS II
STRIP IN INDOOR UNIT,
CIRCUIT I
K20 z_ _ L_>
L_ \ BLACK _
ORANGE
RECOMMENENED BLOWER SPEED TAP SELECTION /
/
SPEED TAP SELECTION
"COOL" "HEAT"
CBBIMV *CONDENSING UNIT
BLOWER CONDEN5- HEAT WITH ELECTRIC HEAT PUMP WITH
COIL ING UNIT PUMP HEAT ONLY ELECTRIC HEAT
-41 COOL COOL HEAT HEAT
PIN _3 PIN #3 PIN _A PIN _A
-Sl COOL COOL HEAT HEAT
PIN _2 PIN _G PIN #1 PIN _I
_65 COOL COOL HEAT HEAT
PIN 13 PIN #3 PIN #I PIN #I
*MINIMUM SETTING FOR HEAT
FIELD WIRING FOR
UNITS WITH CIRCUIT BREAKERS
CIRCUIT CCIRCUIT 3 CIRCUIT Z
CR3 CB2 CBI A
A A A_A A_
AL3 _ AL3 "_ AL3"II"" --
EOOIPMENTEOOIRMENTGRGUNO
GROUND _ GROUND EQUIPMENT
BLACK
ORANGE
R 2AV POWER
_ DS
W_
WG
Y2
o
Yl
EV
R PoD o o _oo° R ° R R _°p
IL4"5.4_00000o O000 o ooo 0 o j
G4V
COMMON
Figure 16. CB31MV Blower Coil Unit Typical Wiring Diagram
505341M 04/08
Page 14

L2 LI 208-250/60/I
CIRCUIT
_LI BLACK
'_'_LZ ORANGE
FIELD-
SUPPLIED
WIRE NUTS
GROUND
o
o
o
LU
o 0
-J 0
0co
_ o
u_oz o
---JO 0
0
0
0
Al--7-_r-_
K20 INDOOR
BLOWER RELAY
TRANSFORMER
FUSE
?
s, A
THERMOSTAT ,- -,
I EL_.
J______
I
r
DS+ 0(_)Y _ YZ(_
I ILL x--
L-I----I-_ .-
I
I
,'
l (i I
FF:
"q-I-"
' Fi1@_
........
J
s-l_
REFER TO UNIT RATING
PLATE FOR MINIMUM
CIRCUIT AMPACITY AND
MAXIMUM OVERCURRENT
PROTECTION SIZE
iA
]]
I
H
I
i--- I....
!rJ [r'
rk! l
r_m ITERMINALA
°LI_TI_ iBLOCK /ZX
LINE VOLTAGE - FIELD-INSTALLED
CLASS 2 VOLTAGE - FIELD-INSTALLED NEC/CEC
NOTE -ALL REMAINING WIRES FACTORY-INSTALLED
TO EXTERNAL LOAD 24VAC AT .5 AMP MAXIMUM
Z_ NEC/CEC CLASS 2, 3 VA
Z_ FACTORY INSTALLED JUMPERS. -"R" to "0" USED ONLY IN CONDENSING UNIT APPLICATIONS. REMOVE IN HEAT
PUMP APPLICATIONS. REMOVE 'DS" TO "YI" JUMPER WHEN HUMIDITY CONTROL THERMOSTAT (SIGNATURES-
TAT_'>IS USED. REMOVE "Y1" TO "Y2" JUMPER IN TWO-STAGE COOLING APPLICATIONS.
Z_ FACTORY INSTALLED JUMPER
NOTE - USE COPPER CONDUCTORS ONLY
Figure 17. Cooling Application
Page 15
CB31MV SERIES

L2 LI 20B-2,f>O/60/I
CIRCUIT I
HEAT ELEMENT _1
c_ K32
HEAT RELAY *I
---_---L,BLAOK/_
_---L_0RAN0_
FIELD-
SUPPLIED
WIRE NUTS
GROUND
s,AA
THERMOSTAT ,- ....,
( i ; (L('
l_ I! I__.U.T]
11 IL---I,--4
II 1--t
Ir ' l
i FzE........
o
o
o
LU
_,. 0
o 0
0
(z:o
_ o
LnOZ 0
--JO 0
o
o
o
o__A
L.... F----F-
I
I
I
I
I
K20 INDOOR
BLOWER RELAY
TRANSFORMER
i]_
"7--r""
REFER TO UNIT RATING
PLATE FOR MINIMUM
CIRCUIT AMPACITY AND
MAXIMUM OVERCURRENT
PROTECTION SIZE
B
sq
#
I
F--- I....
!r# ....r'
;j-_2-_-+-,
r_r_ ITERMINAL _
LINE VOLTAGE - FIELD-INSTALLED
CLASS 2 VOLTAGE - FIELD-INSTALLED NEC/CEC
NOTE -ALL REMAINING WIRES FACTORY-INSTALLED
/'_ TO EXTERNAL LOAD 24VAC AT .5 AMP MAXIMUM
/'_ NEC/CEC CLASS 2, 3 VA
Z_ FACTORY INSTALLED JUMPERS. - 'R" to "0" USED ONLY IN CONDENSING UNIT APPLICATIONS. REMOVE IN HEAT
PUMP APPLICATIONS. REMOVE "DS" TO "YI" JUMPER WHEN HUMIDITY CONTROL THERMOSTAT (SIGNATURES-
TAT°'° IS USED. REMOVE "YI" TO "Y2" JUMPER IN TWO-STAGE COOLING APPLICATIONS.
,_ FACTORY INSTALLED JUMPER
//_ NOTE - USE COPPER CONDUCTORS ONLY
WHEN TWO-STAGE THERMOSTAT IS USED, CONNECT SECOND-STAGE HEAT BULB TO TERMINAL 'W2," REMOVE
JUMPER BETWEEN TERMINALS "R" AND "W2"
THERMOSTAT HEAT ANTICIPATION SETTING .4 AMP (ELECTRIC HEAT)
Figure 18. Cooling Application with Electric Heat
505341M 04/08
Page 16

L2 LI 208-230/60/I
CIRCUIT
,II
HEAT ELEMENT _I
FIELD-SUPPLIED O_)WIRE NUTS
(Orange)
GROUND
s,AA
THERMOSTAT ,- -,
I
I
L
K32
HEAT RELAY w l
+
0
0
0
W
>0
_: o
o 0
d 0
cl::o
wn-- 0
I.gl 0 Z
--_Jo 0
_: rn t_) 0
0
0
IL
i L --]----_
F7
.I
0
0
ii I i
_in 1 1
H--_- I-
I I I
II Ii
I I
,LI_
I---I---
L-I-.
K20 INDOOR
BLOWER RELAY
??
LINE VOLTA6E FIELD INSTALLED
CLASS 2 VOLTA6E FIELD INSTALLED
NEC/CEC
NOTE-ALL REMAINING WIRES FACTORY INSTALLED
Z_TO EXTERNAL LOAD 24VAC
AT .50AMP MAXIMUM
z_NEC/CEC CLASS 2 3VA
A ..... " ,.
FACTORY INSTALLED JUMPERS - "R" to "0" used only in con-
densmg unit apphcatlons, Remove in heat pump apphcatlons.
Remove "DS" to "YI" jumper when humidity control (SignatureStatt) is
used.
Remove "YI" to "Y2" jumper in two-stage cooling applications.
TRANSFORMER
FUSE
II
iI
II
!I
@@E
REFER TO UNIT RATING
PLATE FOR MINIMUM
CIRCUIT AMPACITY AND
MAXIMUM OVERCURRENT
PROTECTION SIZE
_e-:--n
° 7i
II
.I1
I
r [-"
It ___l__. I. _
.¢---4-".....
I
I
FI--,,I1
_@N%D A
TERMZNAL BLOCK
A FACTORY INSTALLED JUMPER
A NOTE-USE COPPERCONDUCTORSONLY
A WHEN TWO STAGE THERMOSTATIS USED,
CONI_CT SECONDSTAGE I_AT BULB
TO TERMINAL"W2," REMOVEJUMPER
BETWEEN TERMINALS"R" AND "W2"
ATHERMOSTAT HEAT ANTICIPATION
SETTIN6.4 AMP (ELECTRIC HEAT)
Figure 19. Cooling Application with Electric Heat
Page 17
CB31MV SERIES

Remove "R" to "0" factory-installed jumper
in heat pump applications.
\
A
"' i "f,/ I
r fl'l fi ]/r
I i IS i
II i ' I ll -- -l. "
I I l i t _[!___[ T
II,IIII i I'---I "q "-----I" T
'-it- I- _r
I' !! 'I I I
I! _--H---[ t
II '-I----I-- _.7----- 7 1
I1 I I I t I
i t--T--__--_ .
-- J----I.------, I ! i
-- L 1--- "-_-'
---- --i I I _/ I
S I THERMOSTAT
)I
)/.......
CCB I - 1
TERMINAL BLOCK
A
CLASS 2 VOLTAGE FIELD INSTALLED NEC/CEC
NOTE-ALL REMAINING WIRES FACTORY INSTALLED
L_ NEC/CEC CLASS 2 3VA
A FACTORY INSTALLED JUMPERS -'R" to '0" used only in condensing
unit applications. Remove in heat pump applications.
Remove 'DS" to 'YI" jumper when CCB1 humidity control (A20) is used,
L_ Remove 'YI" to 'Y2" jumper in two-stage cooling applications.
FACTORY INSTALLED JUMPER
,>9®
I
I
I
I
1
7_-!F-m-
I
I
HEAT PUMP CLASS 2
VOLTAGE TERMINALS
Figure 20. Heat Pump
505341M 04/08
Page 18

/_K EM HT RELAY
___ K22
_-- -i
_I I f I
Remove 'R"to'0" factory- /_ r,_ ('%) i
installedjumper inheat
pump applications.
$23 OUTOOORz_ /x
THERMOST.AT S I THERMOSTAT
[I F USED) -- r_
_ _ o _ ii i i i i _ i''
,,
I'" r",,'i r,nL/'n 1.r.__-,-:--- ,, ,,
I i I I I I IIII .... -I- T.__ __--'_..__ I I I
I I I II I ,'!'-I:_ ......... I I
, 11 ,._: __.._1--.... ._7..... __._
, ,",',,lli, 1111,____L_-_.:--I__. , _ , ,!, ,,
I I I i I II............ -.1- _ .--,-I-- J I
I I i-- I
I I L_ __T_. ............ ]
I I I -H- t I
I I LL.... L__D ............ i I
, ,IiL+--_,,Z--t---d ........ ,Z ----k- / I
' -_- --I J- 4I
I I .__--__'t_--_-- ----i- ............. I
I I--I --I ----jd_----T ----_l- ....... --,_ ---['_-_ - "T-"
IT-T-T---F,_---._J--------_------------- L-__-__T L- --i-_ ..--[
I I I I ,---J L _ I I I I
I I I "--J-q-_ I I I I I
I L-F---I------- I | ', I I I ' _
.... t--t--_ ', ,I I I ccB- DIB E'] E I_° ]
_ DDD__ _l-I]['R]r_ TERMINAL BLOCK _ E E -
I I,_ _o o _. ; <_
o_ _ r !
,_ CLASS 2 VOLTAGEFIELD INSTALLED NEC/CEC _ a: _: J
NOTE-ALL REMAINING WIRES FACTORY INSTALLED C_ _ _ _-
oo lil
Z_ THERMOSTAT HEAT.ANTICIPATION .n" (j (._) 3 ;
SETTING .€ AMP (ELECTRIC HEAT} _ _ _ i
,,,_ - ;(_
Z_ FACTORY INSTALLED JUMPER _ _ _ L
"-' LU __
z_WHEN OUTDOOR THERMOSTAT IS USED, "W"Z? >" _w
CONNECT LEADS TO TERMINALS "R" AND
AND RBAOVE JUMPER BETWEEN "R" AND "W2" _ _.
L_EMERGENCY HEAT RELAY (USED ONLY IF
OUTDOOR THERMOSTAT IS USED) FIELD
PROVIDED AND INSTALLED NEAR INDOOR
UNIT 2#VAC 5VA MAX NEC CLASS 2
!_NEC/CEC CLASS 2 3VA
W
HEAT PUMP CLASS 2
VOLTA6E TERMINALS
Z_ FACTORY INSTALLED JUMPERS, - "R" TO "0" USED ONLY IN CONDENSING UNIT
APPLICATIONS. REMOVE IN HEAT PUMP APPLICATIONS.
REMOVE "DS" TO "YI" JUMPER WHEN CCB1 HUMIDITY CONTROL (A20) IS USED.
REMOVE "YI" TO "Y2" JUMPER IN TWO-STAGE COOLING APPLICATIONS.
Figure 21. Heat Pump with Electric Heat
Page19
CB31MV SERIES

IMPORTANT
Matt- or foil-faced insulation is installed in indoor
equipment to provide a barrier between outside air
conditions (surrounding ambient temperature and
humidity) and the varying conditions inside the unit. If the
insulation barrier is damaged (wet, ripped, torn or
separated from the cabinet walls), the surrounding
ambient air will affect the inside surface temperature of the
cabinet. The temperature/humidity difference between the
inside and outside of the cabinet can cause condensation
on the inside or outside of the cabinet which leads to sheet
metal corrosion and subsequently, component failure.
REPAIRING DAMAGED INSULATION
Areas of condensation on the cabinet surface are an
indication that the insulation is in need of repair.
If the insulation in need of repair is otherwise in good
condition, the insulation should be cut in an X pattern,
peeled open, glued with an appropriate all-purpose glue
and placed back against the cabinet surface, being careful
to not overly compress the insulation so the insulation can
retain its original thickness. If such repair is not possible,
replace the insulation. If using foil-faced insulation, any
cut, tear, or separations in the insulation surface must be
taped with a similar foil-faced tape.
Figure 22. Repairing Insulation
WARNÁNG
505341M 04/08
Page 20