LENNOX Air Handler Auxiliary Heater Kit Manual L0805584
User Manual: LENNOX LENNOX Air Handler Auxiliary Heater Kit Manual LENNOX Air Handler Auxiliary Heater Kit Owner's Manual, LENNOX Air Handler Auxiliary Heater Kit installation guides
Open the PDF directly: View PDF .
Page Count: 12

zEA,tcOx .
_;_,1997 Lennox Industries {nc,
Dallas, Texas, USA
/
I
I
The EvenHeater'" ECB29EH electric heat sections pro-
vide field installed staged electric heat for Lennox Elite 10"
CB29M, Elite 12" CB30M, Elite 12" CB30U, and Power-
Mate" CB31MV blower coil units.
In heat pump applications, the electric heat is staged to
provide supplemental heat to meet desired comfort levels.
When the electric heat section is used in applications that
do not have a heat pump, the elements are staged to limit
heat so that it meets heating demands only.
Adjust element staging by changing the location of the
supply air temperature-selection jumper on the ECH1
control board.
ECB29EH heat sections are available in single-phase
9kW, 12.5 kW, 15 kW, and 20kW sizes. Heaters are
equipped with circuit breakers. Refer to the engineering
handbook for specific heat section applications.
INSTALLATION
INSTRUCTIONS
EVENHEATER TM ELECTRIC
HEAT SECTIONS
ELECTRIC HEAT SECTIONS F_-_ Technical
503,675M _'LLL. Publications
5/99
Supersedes 7/97 Lithe U.S.A.
ECB29EH Electric Heat Sections ................. 1
Shipping & Packing List ......................... 1
General Information ............................ 1
Heat Section Installation ........................ 2
Circuit Breaker Installation ....................... 2
Thermistor Installation .......................... 4
EHCl Control Board Installation .................. 4
Electrical Connections .......................... 5
Blower Speed Connections ...................... 6
Discharge Air Temperature Adjustment ............ 6
Unit Start-Up .................................. 6
Troubleshooting ................................ 6
Wiring Diagrams ............................... 7
RETAIN THESE INSTRUCTIONS
FOR FUTURE REFERENCE
These instructions are intended as a general guide and do
not supersede local codes in any way. Consult authorities
having jurisdiction before installation. Read these instruc-
tions thoroughly before installing the heater section.
The electric heat section and all other equipment used in
HVAC systems must only be installed by qualified installers
or technicians. You must follow federal, state, and local
codes while installing this or any other HVAC equipment.
,& WARNING
Package 1 of 1 contains:
1 - Assembled electric heat section
1 - Bag assembly containing the following:
10-Screws; 1-Wiring diagram; 2-Wire nuts
1 - EHC1 control board assembly
1 - Supply air plenum thermistor
2 - Adhesive-backed foam seals
1 - Control bracket
Inspect the heater section for shipping damage. If you find
any damage, immediately contact the last carrier.
Be sure to disconnect all power to unit while installing and
servicing the equipment. Use proper tools and protective
equipment during installation and service.
Installation of Lennox blower sections with or without op-
tional electric heat must conform with standards in the Na-
tional Fire Protection Association (NFPA) "Standard for
Installation of Air Conditioning and Ventilation Systems
NFPA No. 90A," and "Standard for Installation of Resident
Type Warm Air Heating and Air Conditioning System, No.
90B," manufacturer's installation instructions, and local
municipal building codes.
Page 1

Before installing the unit, check information on unit rat-
ing plate to ensure unit meets job specification, proper
electrical power is available and that proper duct clear-
ances are maintained.
WARNING
NOTE-It is easier to install the ECB29EH heat section in
the blower coil unit before the unff is set and the plenum is
attached.
1 - Shut off all power to blower coil unit, More than
one disconnect may be required.
2 - Remove blower section access panel.
3 - Remove electric heat knockout in blower coil vesti-
bule panel for the appropriate size of heater used.
Remove extended width knockout to allow for
installation of 20kW heater. See figure 1.
BLOWER COIL KNOCKOUTS
KNOCKOUT FOR:
(_ CB29M-21/26,-31 _)
1_ CB30M-21/26 _)
""\ Holes In knockout allow
•room for dtagonal cutters
used to cut through
sheet metal.
JJ CB29M-41, -46, -51, -55
CB31MV-41, -51, -65
II II
a 20kW el_rlC heater.
FIGURE 1
4- Slide electric heat section into blower section. Be
careful that heating elements do not rub against
sheet metal opening when sliding into blower sec-
tion. Hole(s) on each side of the heater line up with
holes in the blower coil control box. Secure elec-
tric heater into place with screws provided in bag
assembly.
1 - Install circuit breaker on blower deck flange. Use
provided screws to secure. See figure 2.
ELECTRIC HEAT SECTION
WITH CIRCUIT BREAKERS
In downflow applications, circuit breakers
must be rotated 180 °to the UP position.
BLOWER DECK
\/ CIRCUIT -\ •
AvBREAKERS
CIRCUIT ._-"__._-_
BRE_KE__R,,,_- .--_._J I
BRACKET _r CIRCUIT BREAKER
MOUNTING SCREW
(Remove screw and slide breakers off
mounting rail. Rotate breakers 180 °and
slide bark on rail. Secure with screw.)
NOTE -When applied in the downflow position, the cir.
cuit breakers must be rotated to the UP position. See
figure 2 and follow the procedure below.
a - Disconnect power to the unit if present.
b - Remove screw and slide breakers off mount-
ing rail.
NOTE- Wire tie closest to the circuit breaker may
need to be removed to allow for rotation.
c - Rotate circuit breaker 180 °.
d - Slide circuit breaker back on rail and secure in
place with previously removed screw.
2- Blower coil access panels are factory supplied
with a patch plate over the circuit breaker open-
ing. Remove the circuit breaker patch plate from
the blower access panel. See figure 3
3 - Replace the unit blower access door.
4 - Choose the appropriately sized adhesive-backed
circuit breaker seal and remove any perforated
sections (if needed). Apply the seal to the outside
of the blower access panel so that the seal is snug
around the circuit breakers.
5 - Break the patch plate for the specific size of elec-
tric heat unit/blower coil unit being installed. Dis-
card unused piece of patch plate. Refer to figure
4 for CB29M-21/26, CB29M-31, CB30M-21/26,
CB30U-21/26 units; refer to figure 5 for all other
blower coil units.
6 - Secure the patch plate on the blower access door.
Page 2

CIRCUIT BREAKER SEAL
AND PATCH PLATE INSTALLATION CIRCUIT
BREAKERS
CIRCUIT
BREAKER SEAL
\
PATCH PLATE BLOWER DECK
CIRCUIT
BREAKER
BRACKET
! DISCARD
PATCH L..._.__j
BREAK AT THIS POINT
FIGURE 3
PATCH PLATE
(Shipped installed on CB unit)
III /
S °;o n/
f I i /
Patch plate
shown with longest section on
right side, Patch plate may be
factory installed with long sec-
tion on left side.
CIRCUIT BREAKER SEAL
(Shipped with electrical heat
and Field installed)
Dotted lines'
are perforations
CIRCUIT BREAKER HEATER
AND PATCH PLATE CONFIGURATION
CB29M-21126, CB29M-31, CB30M-21/26
_26
ECB29EH-gCB
Side
Of
Unit
ECB29EH-12.5CB
ECB29EH-15CB
Side
Of
Unit
ROTATE 180 ° and
install over opening
I I
ILong
Section
Break at this point
FIGURE 4
ROTATE 180 °and
install over opening
r-.-3-_- _:_ ....
I I I
I I I Long
I { I Section
L _L_I_ _ ..........
Break at this point
Page 3

CIRCUIT BREAKER HEATER
AND PATCH PLATE CONFIGURATION
CB29M-41, CB29M-46, CB29M-51, CB29M-65 AND
CB30M-31, CB30M-41, CB30M-46, CB30M-51 CB30M-65 AND
CB31M-41, CB31M-51, CB31M-65 AND
C830U-31, CB30U-41/46, CB30U-51/65
PATCH PLATE
(Shipped installed on CB unit)
Patch plate
shown with longest section on right
side, Patch plate may be factory
installed with long section on Left side.
CIRCUIT BREAKER SEAL
(Shipped with electrical heat
and Field installed)
Dotted lines
are perforations
ECB29EH-gCB
Side
Of
ROTATE 180 °and
install over o
f-- -_-=q
I I
I [
I1
L c=/
Break at this point
ECB31EH-gCB, ECB29EH-12.SCB
ECB29EH-15CB, ECB29EH-20CB
Side
Of
install over opening
-1
II
I I i
L_,J _J
IDISCARD ]_
Break at this point
FIGURE 5
See figure 6 for thermistor installation.
1 - Drill a 5/8" hole in supply air plenum front. Locate
hole 10" (254mm) above blower coil cabinet top,
centered side to side.
2- Insert thermistor probe into the hole and secure
with two provided #8-18 self-drill self-tap screws.
3 - Adjust the probe depth as shown in figure 6.
4- Before installing the EHC1 control board assem-
bly, run the two thermistor leads through low volt-
age cabinet knockout opening and connect to
"DAT" terminals on control board.
Refer to figure 7 for control board assembly installation.
1- Assemble ECH1 control board with mounting
bracket. See figure 7 for orientation.
2 - On CB29M, CB3OM & CB3OU units -
Align EHC1 control board assembly bracket holes
with existing blower deck flange holes (located on
the right side of the flange) and secure control
board assembly with two provided screws.
3-On CB31MV units -
Use the two existing screws that secure the vari-
able speed motor control board bracket to blower
deck flange to install the EHC1 control board as-
sembly to blower deck flange.
THERMISTOR INSTALLATION
THERMISTOR
(center side to side) _
Probe* 5-9/16 L
1012541 depth 11411 p"
SUPPLY
AIR PLENUM
UNIT SUPPLY
AIR OPENING
OPTIONAL
ELECTRIC
HEAT
(Reid
Installed)
* Thermistor probe depth is measured from front
of blower coil unit supply air opening - not supply
air plenum front (unless they are identical).
RGURE 6
Page 4

EHC1CONTROLBOARDINSTALLATION
f f
I
I
I,Blower
Existing blower deckflange holes
I
_\ EHCl Control board assembly
_. _/ \ Thermostat terminal strip this side
FIGURE 7
EHCl CONTROL BOARD WITH WIRE HARNESS
Thermistor terminals Thermostat
.... .terminal strip
//nermostat
terminals _
DAT W1
;..........J°* 00.w
io,_G 2G eo
............./O 130oEG
100 DEG
85 DEG
Heater indicator Diagnostic
lights indicator
Temperature lights
selection jumper
Wire harness jack Wire harness p
FIGURE 8
AWARNING
NOTE-Refer to nameplate on blower coil unit for mini-
mum circuit ampacity and maximum overcurrent protec-
tion size.
The blower coil units are provided with openings for use
with 1-1/2 inch trade size (1-31/32 inch diameter) con-
duit. A conduit reducer washer has been provided for
use if installing smaller conduit.
Refer to figure 9 for typical condensing unit application
and figure 10 for typical heat pump application with a
blower coil unit and an electric heat section.
Refer to figure 11 and 12 for typical system diagram for
the CB29M/CB30M/CB30U unit with installed electric
heat sections and figure 13 and 14 for typical system
diagram for the CB31MV unit with installed electric
heat section,
Make wiring connections as follows -
Refer to figures 8 and 9 for condensing unit applica-
tion and to figures 8 and 10 for heat pump applica-
tion.
1 - Connect field power supply wiring to circuit break-
er(s).
2 - Connect heater section wire harness plug "P2" to
EHC1 control board left side wire harness jack
"J166."
3- Remove interface harness from blower coil sec-
tion. Connect blower coil section wire harness jack
"J2" to EHC1 control board right side wire harness
plug "P166."
4 - Use provided wire nut to connect stripped yel-
low wire from "Y" terminal of EHC1 control
board to wire from "Y1" terminal of indoor ther-
mostat inside blower coil cabinet.
5 - In heat pump applications only -
Use provided wire nut to connect stripped
orange wire from "O" terminal of EHC1 control
board to wire from "0" terminal of indoor ther-
mostat inside control box. Remove the factory
installed jumper between EHC1 control board
terminals "O" and "R."
6- Disconnect existing red wire from terminal "R" of
TB1 terminal block. Connect this wire to tab of tab/
receptacle combination of red wire from terminal
"R" of EHC1 control board. Then connect thiswire-
assembly to terminal "R" of TB1 terminal block.
7 - In applications where outdoor thermostat is used
only -
Remove jumper between "W2" and "R" of TB1 ter-
minal block and connect outdoor thermostat leads
to "W2" and "'R."
Page 5

When using the ECB29EH heat section with the CB29M,
CB30M, CB30U or CB31MV series blower coil units, the
blower speed must be adjusted according to the size of
electric heat and blower coil unit. The minimum blow-
er setting for each blower size, with any heat sections
in any application is HIGH. See specific blower coil
installation instructions for blower speed adjustment
procedure and location.
The EHC1 control board can be adjusted to provide
four different discharge air temperatures: 85°F
(29.5°C), 100°F (37.8°C), 115°F (46.1°C) and 130°F
(54.4°C). To adjust the factory setting of 85°F (29.5°C),
move the temperature selection jumper on the EHC1
control board to the desired setting (see figure 8).
The EHC1 control board uses the discharge air temper-
atu re value provided by the thermistor to maintain the
selected discharge air temperature by staging on the
required number of heating elements.
When higher discharge air temperatures are required
for comfort or to satisfy the heating load, change the
temperature selection jumper on the EHC1 control
board to a higher setting. In heat pump applications,
when the heat pump is on and a "Wl" demand is pres-
ent from the indoor thermostat, the control board tem-
perature setting will automatically increase to the next
higher setting. Once the "Wl" demand is satisfied or
removed, the control board temperature setting will
automatically return to the jumper setting.
1 - Replace blower compartment access cover.
2 - Restore power to unit.
3 - Set thermostat heat anticipator to 0.4 amps.
4 - Set thermostat above room temperature.
5 - Verify that element staging and supply air tempera-
tures are correct for the given application. If unex-
pected results are obtained, check heat pump and
heat section for normal operation. Atable show-
ing diagnostic codes for the EHC1 control board is
given in the troubleshooting section of these
instructions.
6 - Set thermostat to desired setting.
7-Affix wiring diagram sticker to blower scroll,
aligned with existing CB unit wiring diagram
sticker.
Refer to table 1 for EHC1 control board diagnostic
codes.
See figure 8 for location of diagnostic and operation
indicator LEDs.
Page 6

TABLE1
EHC1 CONTROLBOARDDIAGNOSTICCODES
BOARD DIAGNOSTIC PATTERNS
DIAG 1 _Flashing Slow
DIAG 2 •On
DIAG 1 •On
DIAG 2 _Flashing Slow
DIAG 1 _1_ Fleshing Alternately fast
DIAG 2 -_ Flashing Alternately Slow
DIAG 1 1"_ Fleshing Alternately Slow
DIAG 2 1_ _ Fleshing Alternately Fast
DIAG 1 •Continuously On
DIAG 2 OContinuously Off
DIAG 1 O Continuously Off
DIAG 2 •Continuously On
DIAG 1 •Continuously On
DIAG 2 •Continuously On
MODE INDICATION
Normal Operation
Shorted Thermistor*
REMEDY
None. Slow fleshing LED signifies normsl operation.
General Failure
General Failure
General Failure
Check thermistor for short circuit
Open Thermistor* Check thermistor for open circuit.
Jumper Error Resistor fault on board, Board must be replaced.
No Jumper** No temperature-seloctlon jumper installed. Install jumper
Component fault on board. Board must be replaced.
Component fault on board. Board must be replaced.
Component fault on board. Board must be replaced,
Component fault on board. Board must be replaced.
DIAG 1 O Continuously Off General Failure
DIAG 2 O Continuously Off
* This mode of operation is indicated b_ elements staging on every 4 minutes until "WI" demand is satisfied.
** Last setting retained by board if jumper removed while unit operating; if no jumper present on
power-up,the default setting of 85°F is used by the board.
LI 208-240/60/I
K3 INDOOR
CIRCUIT BREAKERS BLOWER RELAY
HEATING ELEMENTS
| ((_Z'Z_x_.-._'x/'''''_z_HEATRELAYs []''lJ
i-- ............_-- "L__r
EHC1 CONTROL BOARD IO O O O O O
\LLI_J
FJ \ I _t j
I \................. t
d
Avl g
COOLING APPLICATION WITH ELECTRIC HEAT
NOTE-USE COPPER
C0_CTORS ONLY,
REFER TO UNIT RATING PLATE
FOR MINIMUM CIRCUIT AMPACITY
AND MAXIMUM OVERCURRENT
PROTECTION SIZE
LINE VOLTAGE FIELD INSTALLED
CLASS 2 VOLTAGE FIELD INSTALLED
NEC/CEC
L_ TO EXTERNAL LOAD 24VAC
AT .50 AMP MAXIMUM
,,t,,THERMOSTAT HEAT ANTICIPATION
SETTING .4 AMP (ELECTRIC HEAT)
FACTORY INSTALLED JUMPER
SEE UNIT FOR QUANTITY OF ELEMENTS
OR HEAT RELAYS
WHEN OUTDOOR THERMOSTAT IS USED,
CONNECT LEADS TO TERMINALS
"R" AND "W2 _AND REMOVE JUMPER BE-
TWEEN TERMINALS "R' AND "W2,"
FIGURE 9
Page 7

L2 LI
r1,o,,o,,o
I C,RC,.,,rB,'=.'.,,:ERS,_
L_ -- ,E,,,"r,N,_EW.,EN',',,
.EZ
,_k--
K3 INDOOR
BLOWER RELAY
EHCICONTROLBOARD
I
II I
I II
J I
J
K22
BI ItEAT
I
I
!
I
I
I
J
HEAT PUMP APPLICATION
WITH ELECTRIC HEAT
LINE VOLTAGE FIELD INSTALLED
CLASS 2 VOLTAGE FIELD INSTALLED
NEC/CEC
THERMOSTAT HEAT ANTICIPATION
SETTING 0.4 AMP ELECTRIC HEAT
FACTORY INSTALLED JUMPERS
WHEN OUTDOOR THERMOSTAT IS USED,
CONNECT LEADS TO TERMINALS
"R" AND "W2" AND REMOVE JUMPER BE-
TWEEN TERMINALS "R' AND "W2,"
EMERGENCY HEAT RELAY (USED ONLY IF OUT-
DOOR T'STAT IS USED) FIELD PROVIDED
AND INSTALLED NEAR INDOOR UNIT. 24VAC
5VA MAX NEC/CEC CLASS 2
=R
$23
m
USING SERVICE UGHT OPTION ($54) WITH SOME ELECTRONIC THERMOSTATS
MAY REQUIRE MOVING $54 COMMON WIRE TO Y1 IN HEAT PUMP UNIT.
,A
,_ COMMON USED ONLY ON SOME THERMOSTATS.
,_ Y2 USED ONLY WHEN TWO SPEED COMPRESSOR IS USED (HP21). _
,/_ AMBIENT COMPENSATING THERMISTOR CONNECTION USED ONLY ON SOME THERMOSTATS. _
SEE UNIT FOR QUANTITY OF ELEMENTS
OR HEAT RELAYS
_ REMOVE_ACTOR_JUMPER .._
Y
FIGURE 10
Page 8

CB29M/CB30M/CB30UBLOWERCOIL UNITWITHINSTALLEDECB29ELECTRICHEAT - P VOLTAGE- 9.0 & 20 KW
_REFER TO UNIT
NAMEPLATE FOR
MINIMUM CIRCUIT
AMPACITY AND
MAXIMUM OVERCURRENT
PROTECTION
REFER TO FACTORY
BLOWER SPEED TAP
SELECTION CHART ON
UNIT FOR BLOWER
SPEED INFORMATION.
_REMOVE FACTORY
INSTALLED JUMPER
FOR HEAT PUMP
APPLICATIONS,
LF.JWE JUMPER
IN CONDENSING UNIT
APPLICATIONS.
_WHEN OLKIX)OR
THERMOSTAT IS USED,
CONNECT ACROSS
TERMINALS =R* AND "W2"
AND REMOVE JUMPER
BEIWEEN "R" & "W2*
CIRCUIT 2 NOT USED
ON 9 KW ELEMENT
PI{,6 J2

K:I
CB29M/CB30M/CB30U BLOWER COIL UNIT WITH INSTALLED ECB29 ELECTRIC HEAT - P VOLTAGE - 12.5 & 15 KW
_REFER TO UNIT
NAMEPLATE FOR
MiNiMUM CIRCUIT
AMPACITY AND
MAXIMUM OVERCURRENT
PROTECTION
/_ REFER TO FACTORY
BLOWER SPEED TAP
SELECTION CHART ON
UNIT FOR BLOWER
SPEED INFORMATION,
/_ REMOVE FACTORY
INSTALLED JUMPER
FOIl HEAT PUMP
APPUCATIONS.
LEAVE JUMPER
IN CONDENSING UNiT
APPLICATIONS.
_WHEN OUTDOOR
THERMOSTAT IS USED,
CONNECT ACROSS
TERMINALS "R" AND =W2"
AND REMOVE JUMPER
BETWEEN "R" & "W2"
-- --CLASS II VOLTAGE FIELD INSTALLED
_LI_ V_lkSE EIEtOINSTALLED
NOTE - USE COPPER CONDUCTORS ONLY
ILB#IBI,_,,,.,..liFE16
HEATINGUNITS-ELECTRIC
ECB29EH- 12.5CB- 1 - P i
iECB29EH -15CB - t - P
532,582W
2€V pGli_R R
P*3
p
IdOTOR5H(3'lf_
[
_TOR SPEED "rAP CHART
-_ ZCV CBVt_0N C
LIN_ VOLTAGE FIEIO WIRING
CLA_S IT VOLTAGE FIELD WIRINB
H s/gs
LI_IN_X_*._,.x. IIRI 6 DIAGRAH (o/9s)
COILS-BLOYIER COIL UNITS i
CB29M-21/26,31,41/46,51/65-1 -P
CB30M-21/2_,31,41/46,51/65-1 -P
CB3OU -21/26,31,41/46,51/65-1 -P
iCOIL _CTION-
s.,,,.,., r...., (531,613W='"r.. N.. (
*_9 >f
"-- ..... "-'
CB 4. I_,_pi,_TI_R-I_L_R I_ITOR
K3 _,12 MAC_-ELECTRICHAT
/" i_ >;Z4v _ I.L^Y*E(mNOulzER HE*T I
ii_['_ ECB S_L_IED
/_ ! _T82 ITER_IIiN_LSTRIP-LINIT j

m

K_
CB31MV BLOWER COIL UNIT WITH INSTALLED ECB29 ELECTRIC HEAT -P-VOLTAGE -12.5 & 15 KW
=to
DB_ _ K_
ARE_RTOU.ITI_!_l
_TE,O_ )iOOi_ _ OI
MINIMUM CIRCUIT _ --
MAXIMUM OVERCURRENT
PROTECTION K34 t:_
Z_ REFER TO F/_-_TORY _i(_i
BLOWER SPEED TAP _T_IPTION i
SELECTION CHART ON _EY i C_h_Nl
bk45 _IROL_LE --'_)
UNIT FOR BLOVIrF_R , _ _
REMOVE FACTORY
iNSTALLED JUMPER
FOR HEAT PUMP
APPUCAllONS,
LEAVE JUMPER
IN CONDENSING UNff
APPUC_T1ONS,
/_ WHEN OLITIX)OR
THERMOSTAT IS USED,
CONNECT ACR06S
TERMINALS "R" AND =W2"
AND REMOVE JUMPER
BETWEEN "R" & "W2*
'b_ m-_ ,,_
iooii
I STATU'£
P2 Jle_ LEO'S [
! ,,_ ^)v,._e
( ,oooo
( _,io o ) (
iTE_PIR)- _-- --
_LECT --
iL
i OAT i
_ . 0,,0r,le,o!
)LEJ_'X,,_=.......|IR]XG
i_'ING UNITSELECTRIC
IECB29EH -12.5CB- I - P
ECB29EH- 15CB- I -P
IIIH{NI'&IiIOITYCONTROL (k2'O) 15 NOT _ INCOWBINATIDN TilTH TlmilOSPF.F.O_5011,
CLW'iECT JUk_ER BE_€ "Y2" AND "(_3"
i/_ _'_N HUMIDITY CONTROL (kZO IS NOt Ur_ IN
COk_BIN_TIO_ WITH SINOLE ISLED CO_RE&_.
CD_WECT JUI_=ER _Tt_EN "YI" ANO "OS =
_,,..,,, _or,,,.) 532,582W_'r., ,,.
_LASS IIVOLTAGE FIELD INSTALLED
mLIN_ VOLT_E FIELD INSTALLED
_NOIES OPTI(}_kLCO_NIS
NOTE - USE COPPER CONDUCTORS ONLY
)

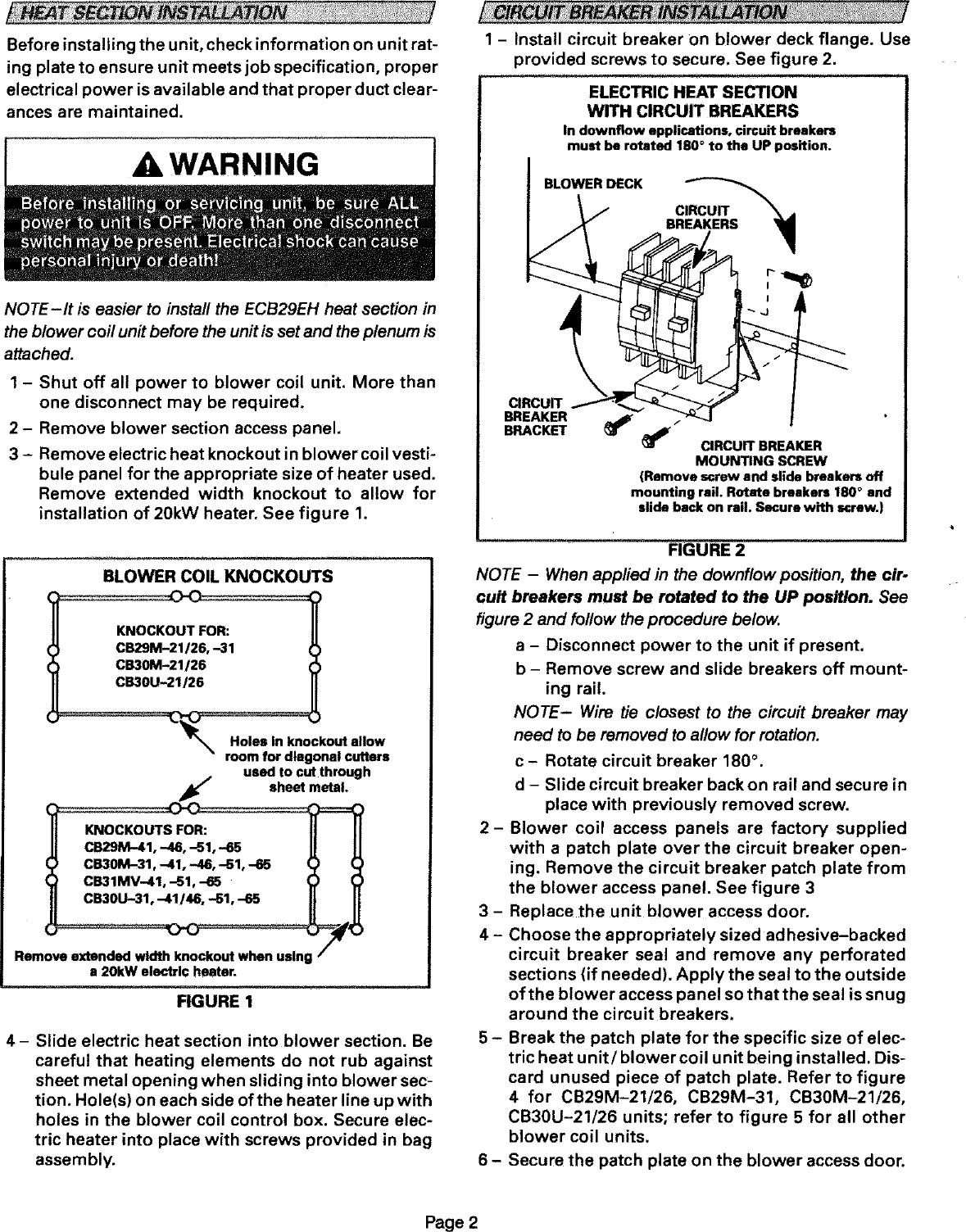
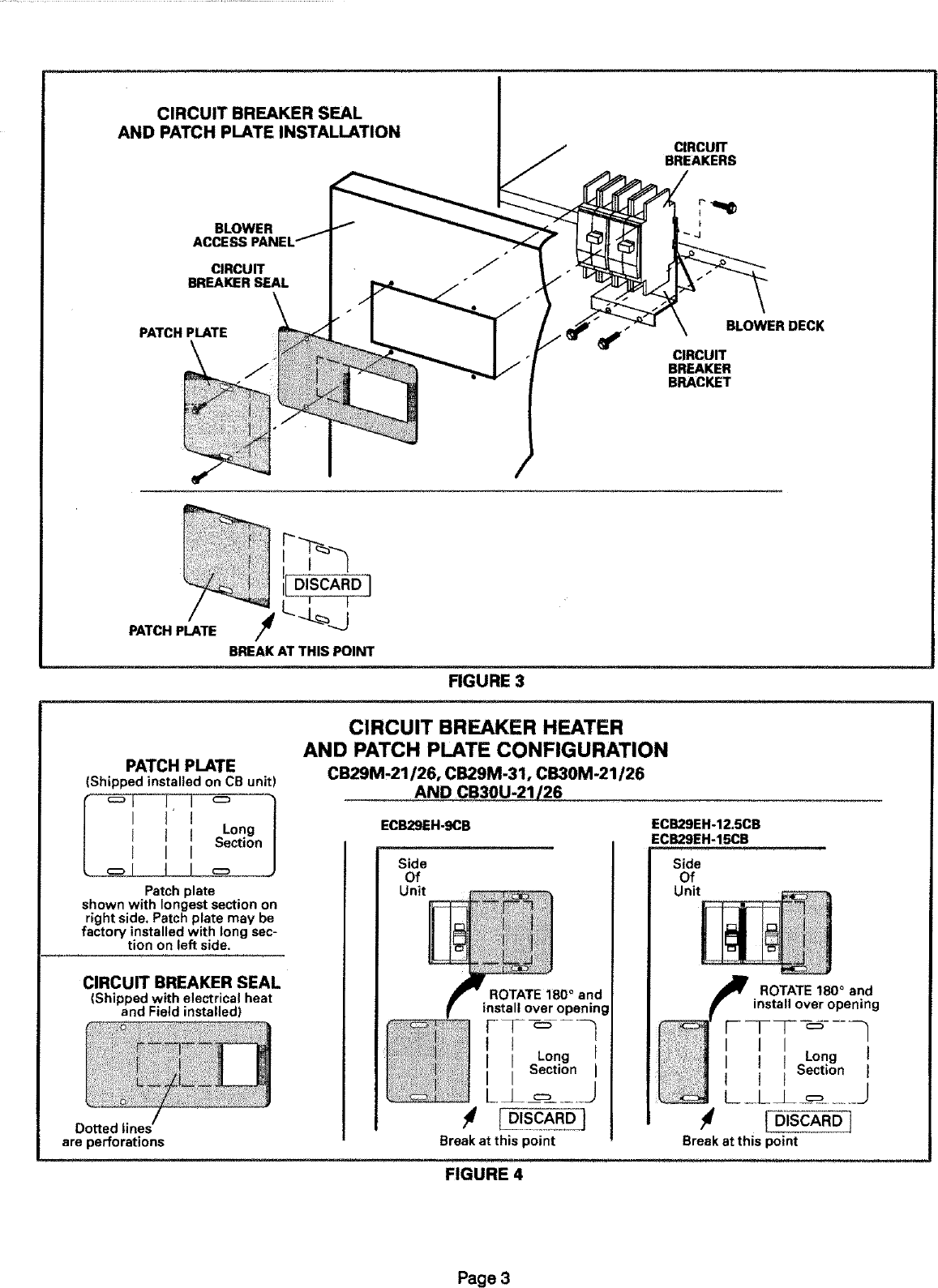

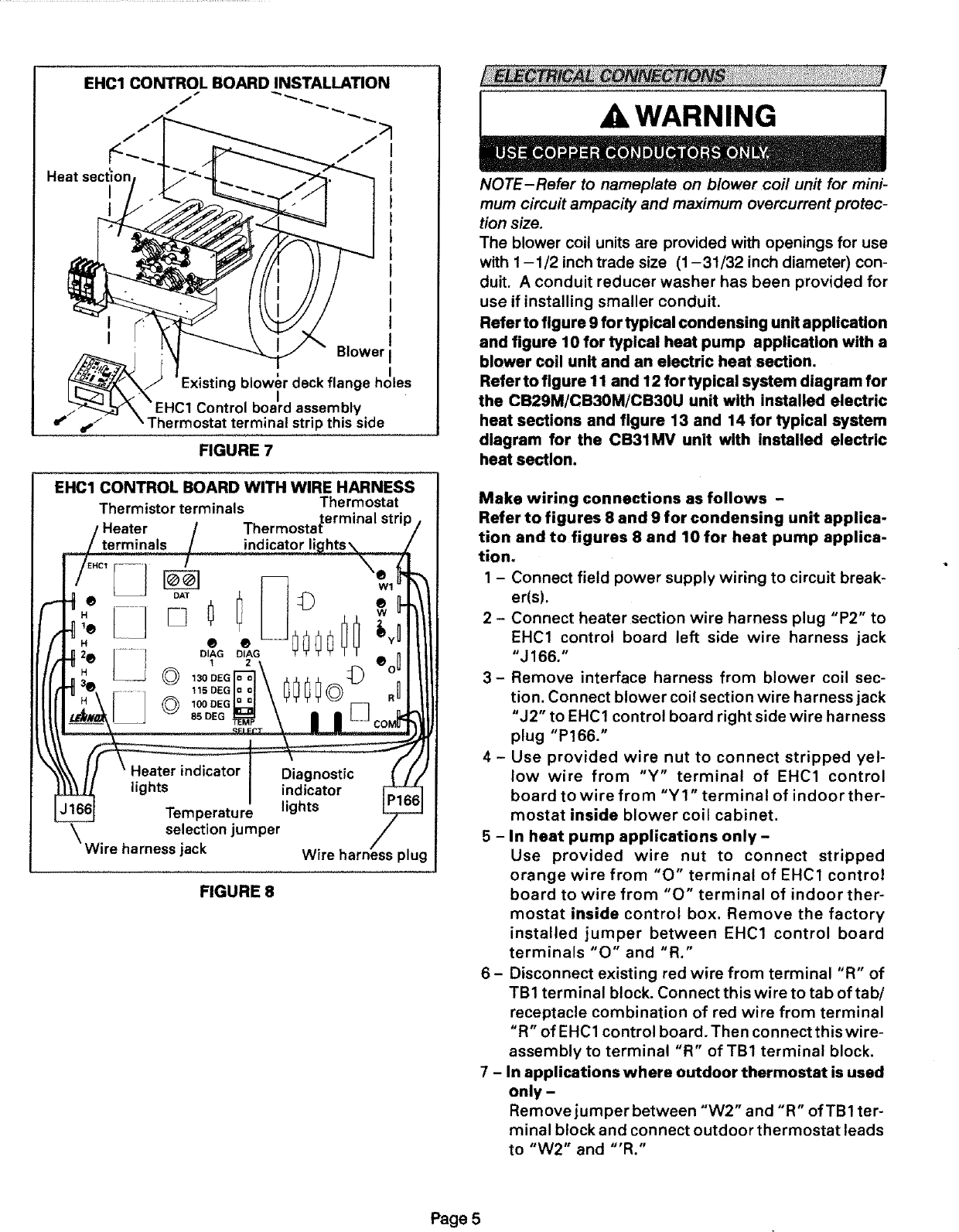
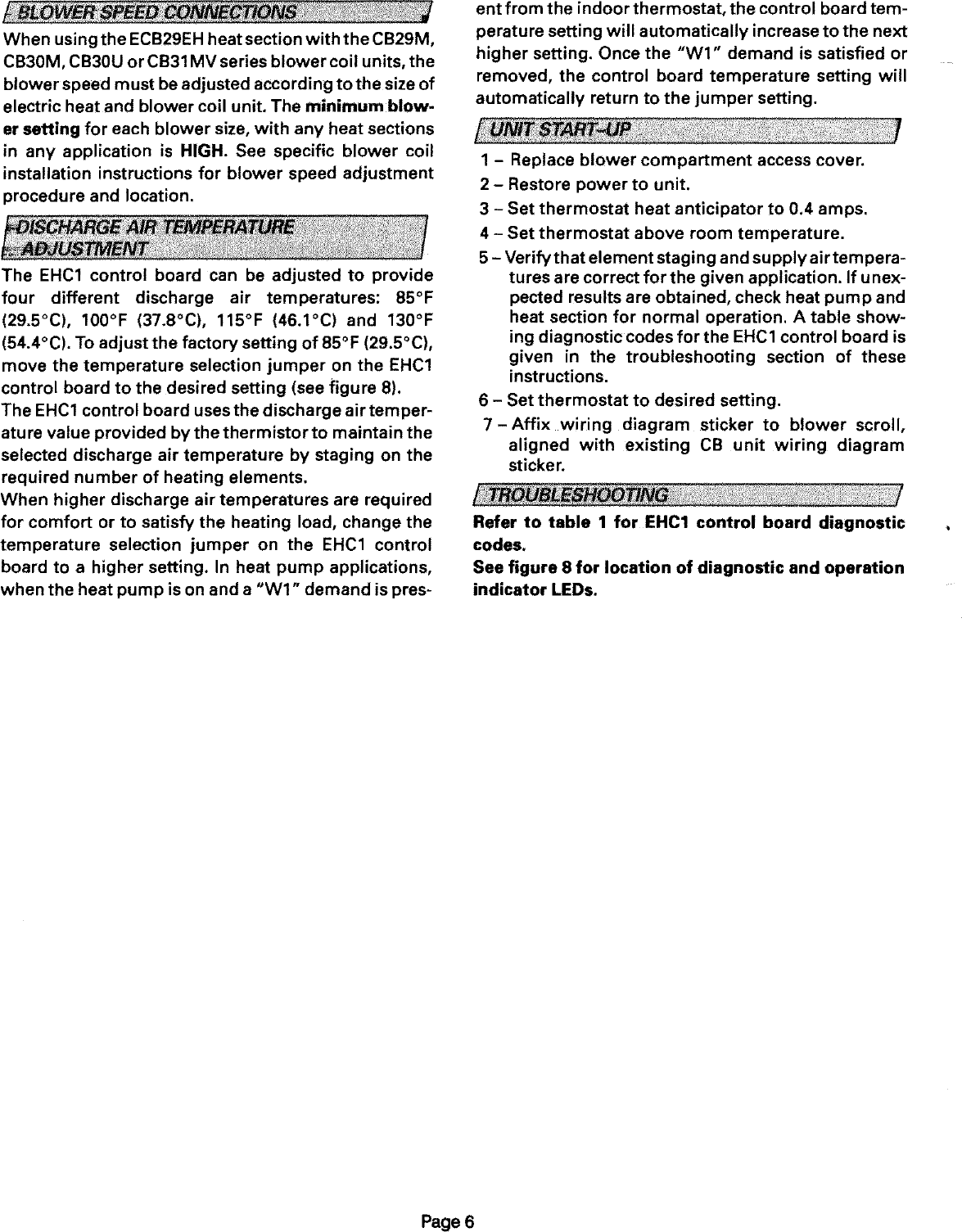
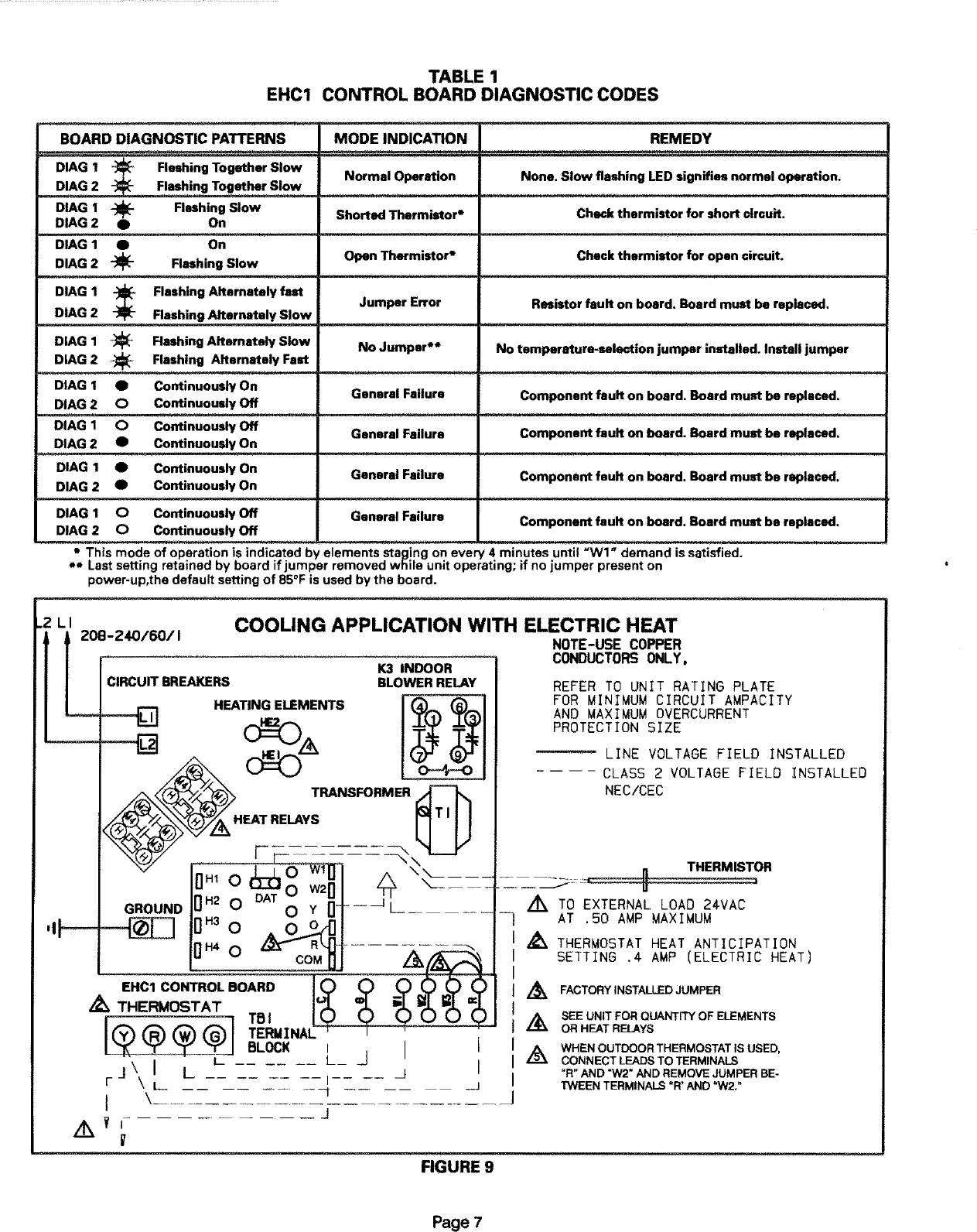
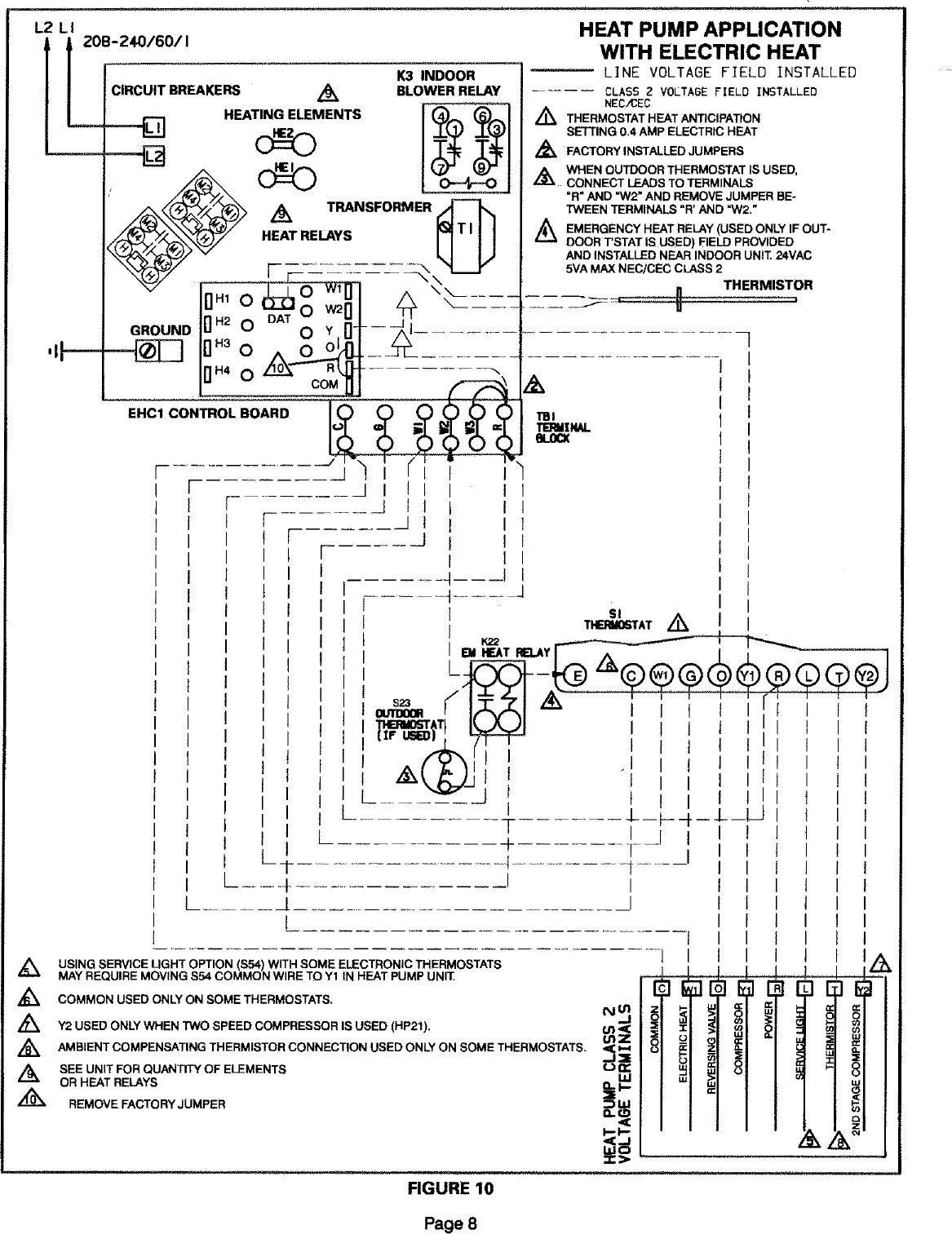
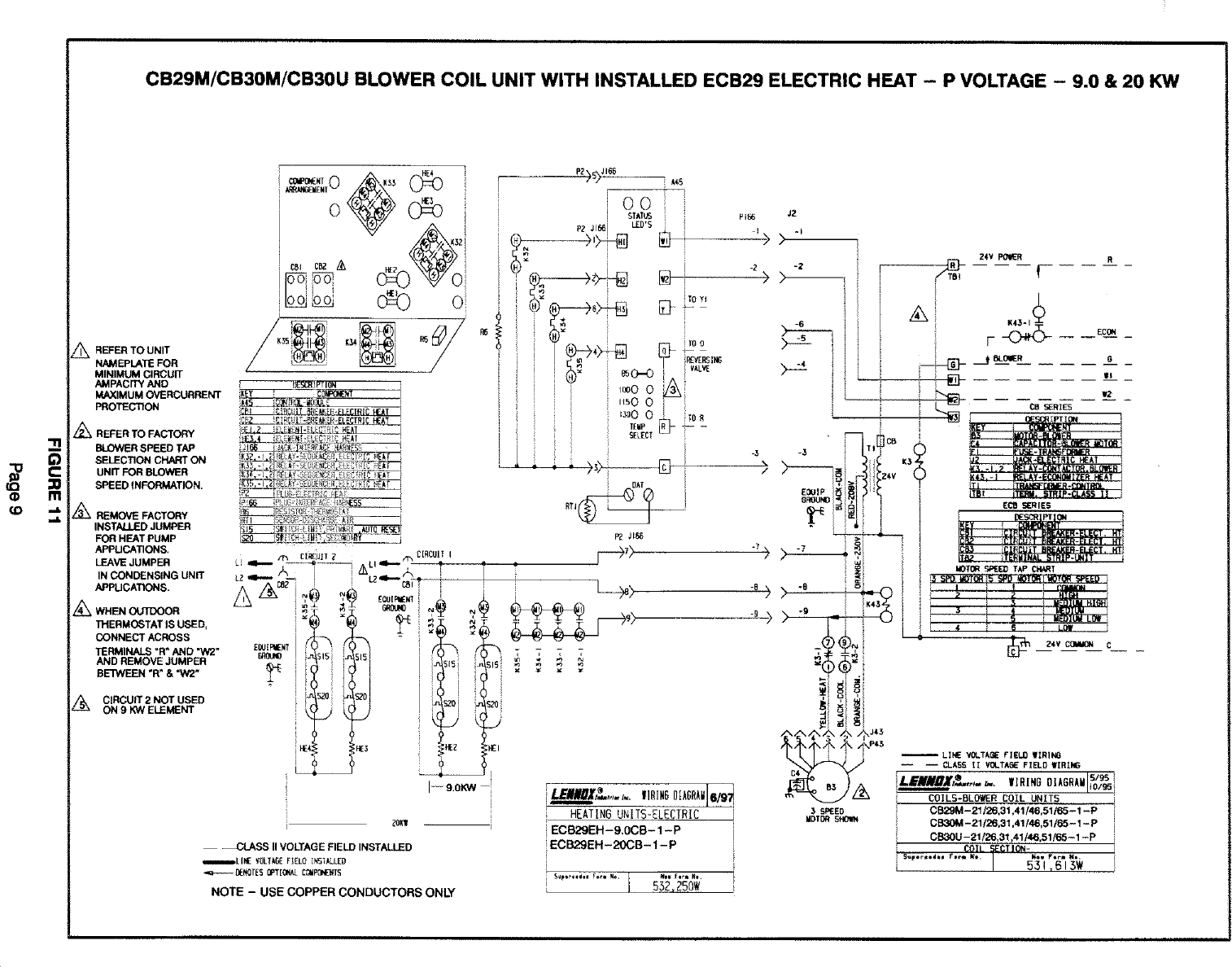

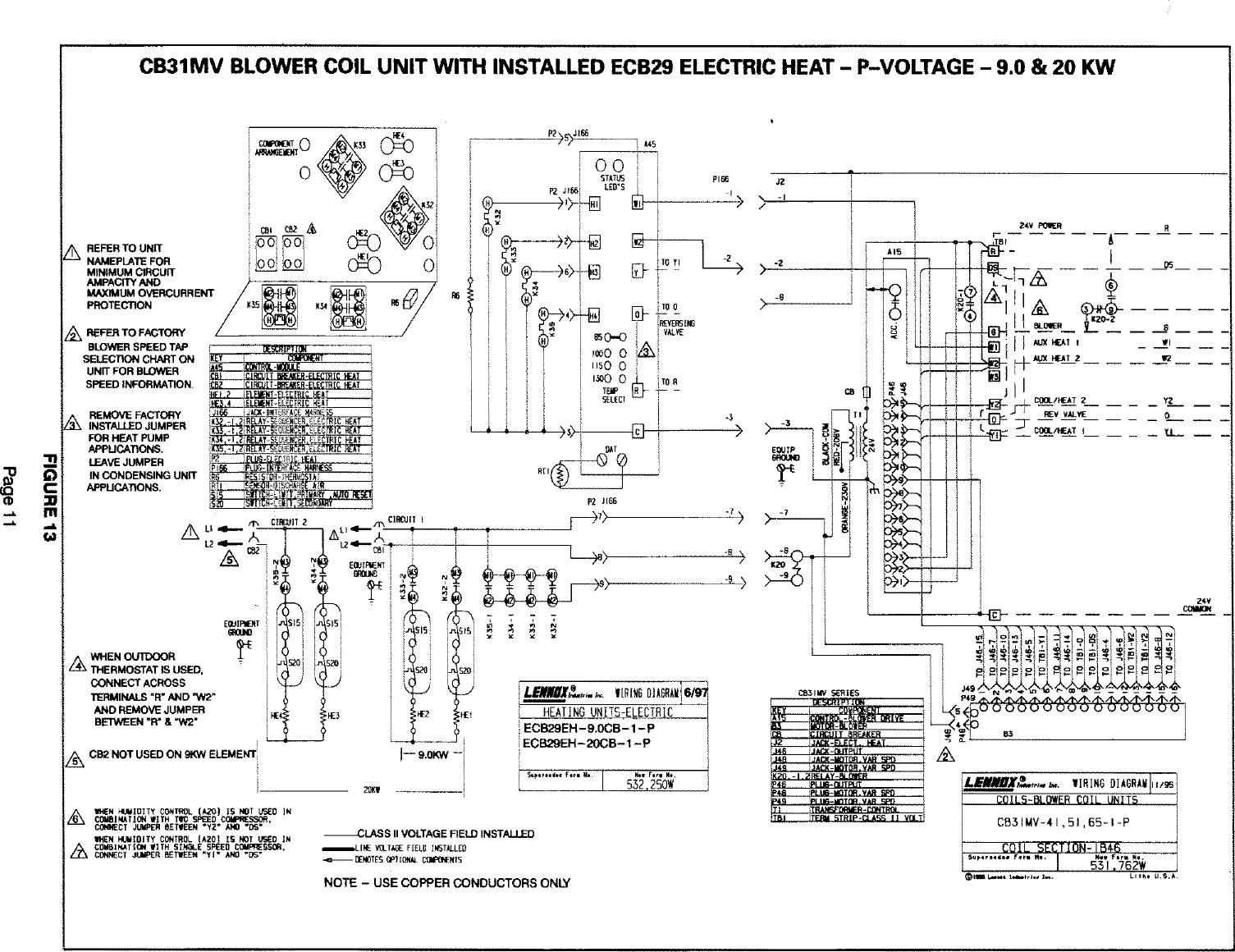
