Launch Tech DS601 Automotive Diagnosis Terminal User Manual Maximus 3 0 English R indd
Launch Tech Co., Ltd. Automotive Diagnosis Terminal Maximus 3 0 English R indd
Users Manual
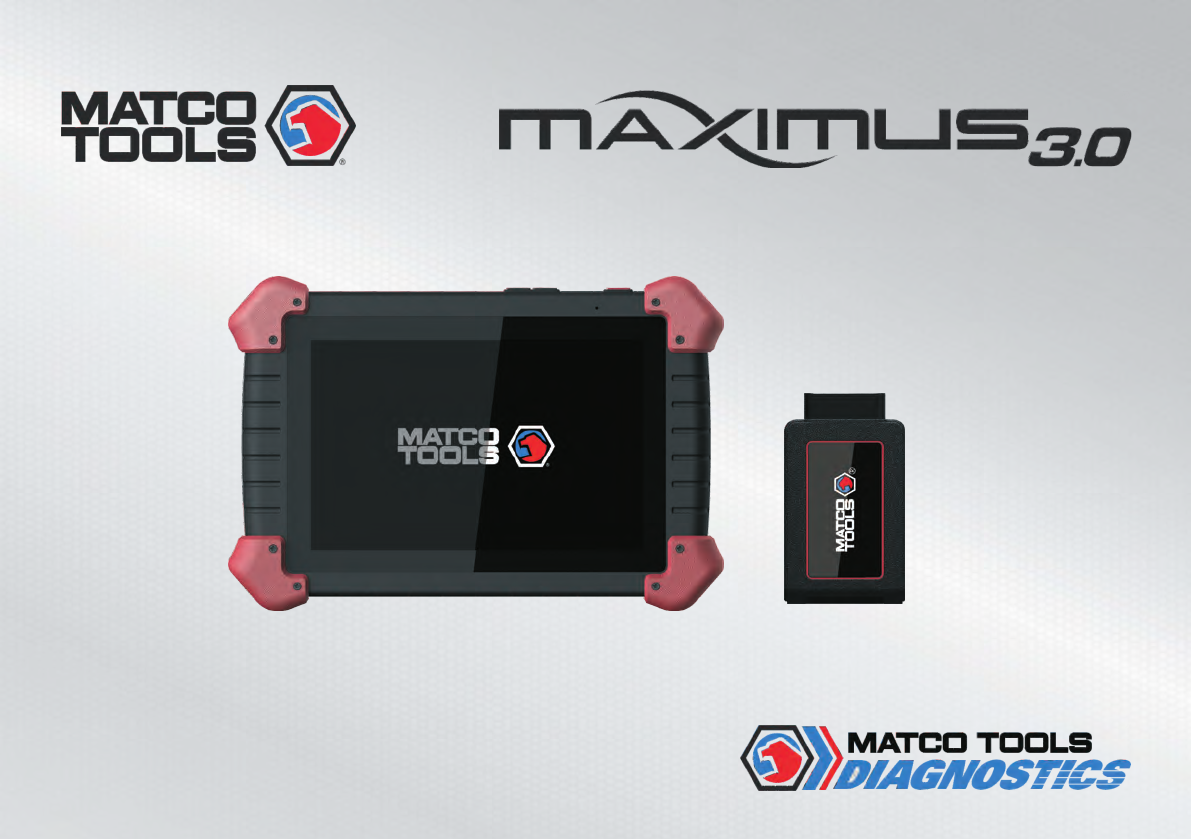
www.matcotools.com
www.maximus3.com
User Manual
(V1.0)
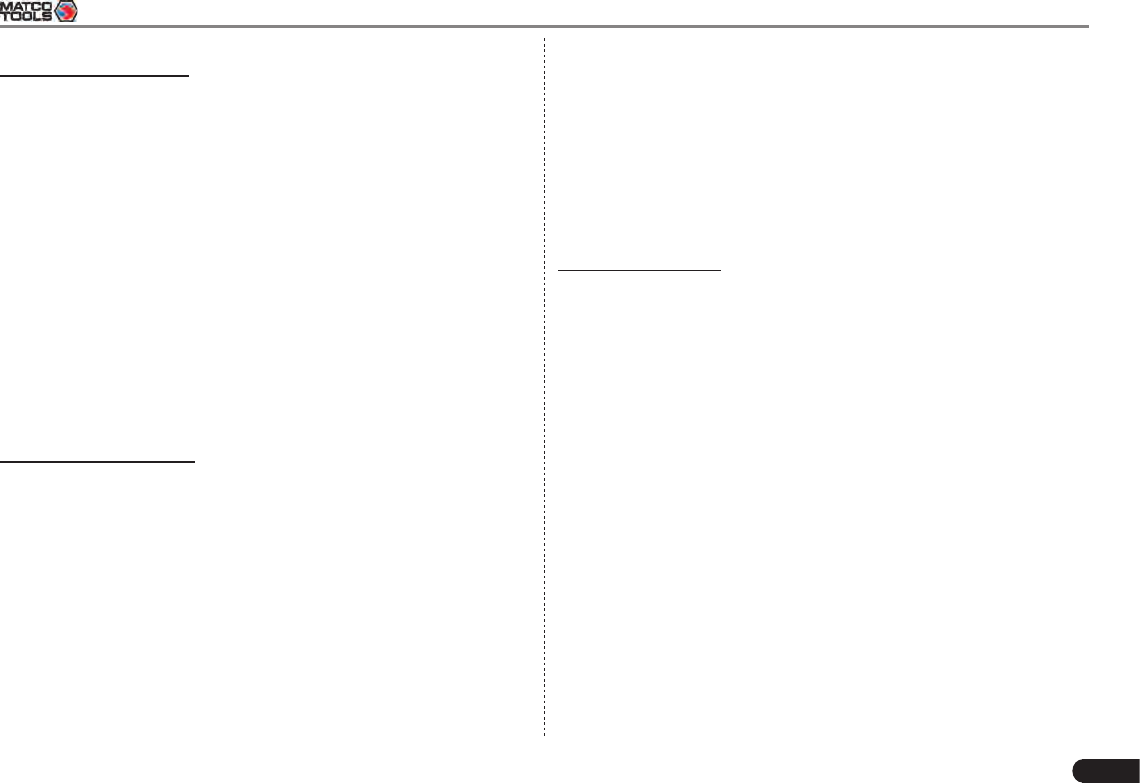
Maximus 3.0 User's Manual
I
Copyright Information
Copyright © 2018 by LAUNCH TECH. CO., LTD. All rights reserved.
No part of this publication may be reproduced, stored in a retrieval
system, or transmitted in any form or by any means, electronic,
mechanical, photocopying, recording or otherwise, without the prior
written permission of LAUNCH. The information contained herein is
designed only for the use of this unit. LAUNCH is not responsible for
any use of this information as applied to other units.
Neither LAUNCH nor its affiliates shall be liable to the purchaser
of this unit or third parties for damages, losses, costs, or expenses
incurred by purchaser or third parties as a result of: Accident,
misuse, or abuse of this unit, or unauthorized modications, repairs,
or alterations to this unit, or failure to strictly comply with LAUNCH
operating and maintenance instructions. LAUNCH shall not be liable
for any damages or problems arising from the use of any options or
any consumable products other than those designated as Original
LAUNCH Products or LAUNCH Approved Products by LAUNCH.
Trademark Information
LAUNCH is a registered trademark of LAUNCH TECH CO., LTD.
(also called LAUNCH for short) in China and other countries.
All other LAUNCH trademarks, service marks, domain names,
logos, and company names referred to in this manual are either
trademarks, registered trademarks, service marks, domain names,
logos, company names of or are otherwise the property of LAUNCH
or its affiliates. In countries where any of the LAUNCH trademarks,
service marks, domain names, logos and company names are not
registered, LAUNCH claims other rights associated with unregistered
trademarks, service marks, domain names, logos, and company
names. Other products or company names referred to in this manual
may be trademarks of their respective owners. You may not use any
trademark, service mark, domain name, logo, or company name
of LAUNCH or any third party without permission from the owner
of the applicable trademark, service mark, domain name, logo, or
company name. You may contact LAUNCH by visiting the website
at www.cnlaunch.com, or writing to LAUNCH TECH. CO., LTD.,
Launch Industrial Park, North of Wuhe Avenue, Banxuegang, Bantian,
Longgang, Shenzhen, Guangdong, P.R.China, to request written
permission to use Materials on this manual for purposes or for all other
questions relating to this manual.
Safety Precautions
Before using Maximus 3.0, please read the following safety information
carefully.
• Never collide, throw, or punch Maximus 3.0, and avoid falling,
extruding and blending it.
• Do not use Maximus 3.0 in exceptionally cold or hot, dusty, damp
or dry environments.
• In places where Maximus 3.0 is forbidden or using Maximus 3.0
may cause interference or generate a potential risk, please turn it
off.
• To ensure a safe driving, please do not use Maximus 3.0 while
driving.
• Turn off Maximus 3.0 before boarding any airplane.
• Do not dismantle Maximus 3.0 by yourself. If there is any inquiry,
please contact the dealer.
• Never place Maximus 3.0 into apparatus with strong
electromagnetic eld.
• Keep Maximus 3.0 far away from magnetic devices because its
radiations may erase the data stored on Maximus 3.0.
• Store Maximus 3.0 out of reach of children and do not allow
children to use it unsupervised.
• Please use the included battery and charger. Otherwise, explosion
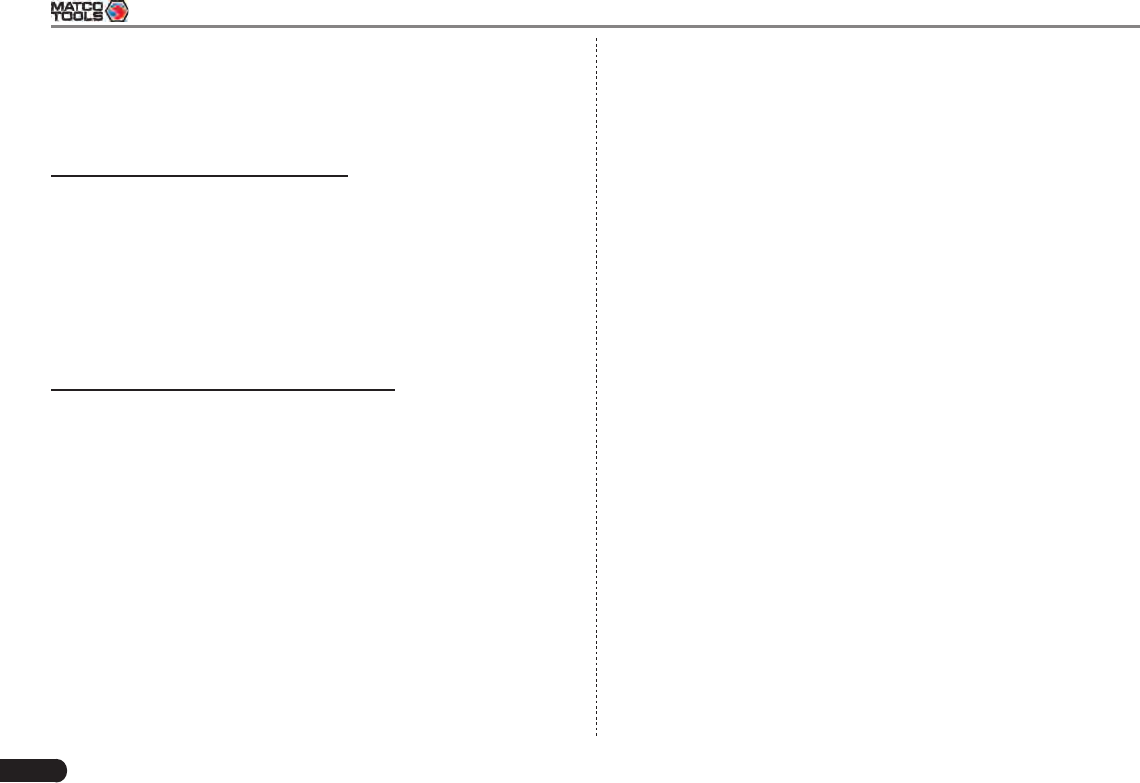
II
Maximus 3.0 User's Manual
may happen.
• Do not disconnect power abruptly when Maximus 3.0 is being
formatted or in process of uploading or downloading. Or else it may
result in program error.
Precautions on Using Maximus 3.0
• The ignition switch should be OFF while plugging or unplugging the
VCI device.
• If your vehicle keeps unattended for a week or a long period, it is
suggested to unplug the dongle from vehicle’s DLC to save battery
power.
• While diagnosing a vehicle, you are not advised to use phone
or messaging, because it may cause a data communication
interruption. If it happens, it is abnormal and just try to re-do it.
Precautions on Operating Vehicle’s ECU
• Do not disconnect the vehicle inner consumer when the ignition
switch is ON. High voltage transients may encounter at the moment
of disconnecting, which may damage the sensors and the ECU.
• Protect the computer from magnetic object.
• Do cut off the power supply of ECU system before welding on the
vehicle.
• Pay more attention to the ECU and the sensors when the operation
is next to them.
• Ground yourself when you disassemble PROM, otherwise ECU
and sensors will be damaged by static electricity.
• Do connect ECU harness connector firmly, otherwise electronic
elements, such as IC inside ECU, will be damaged.
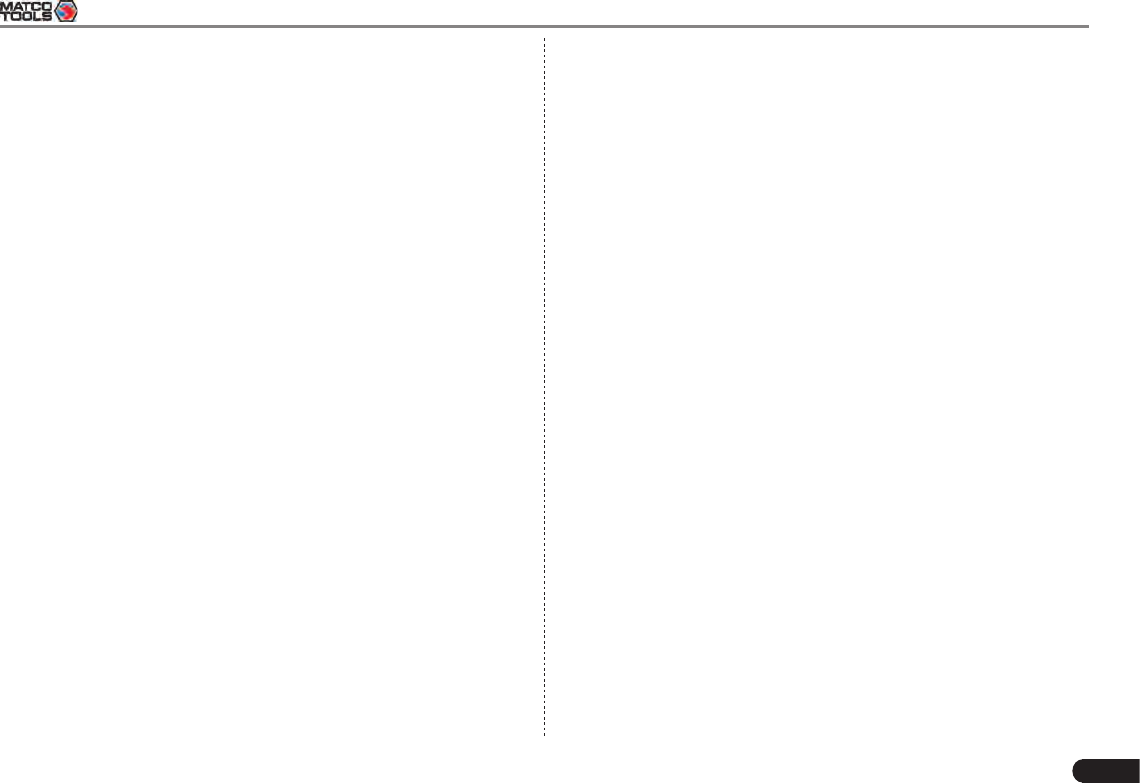
Maximus 3.0 User's Manual
III
Table of Contents
1 Introduction ...............................................................................1
1.1 Product Prole ............................................................................... 1
1.2 Features ........................................................................................ 1
1.3 Technical Specications ................................................................ 2
1.3.1 Maximus 3.0 Tablet ............................................................... 2
1.3.2 VCI Dongle (Only for Passenger Vehicle Conguration) ...... 2
2 Knowledge of Maximus 3.0......................................................3
2.1 Maximus 3.0 Tablet ........................................................................ 4
2.2 Maximus 3.0 Docking Station ........................................................ 5
2.3 VCI Dongle (Only for Passenger Vehicle Conguration) ............... 6
2.4 Accessory Checklist....................................................................... 7
3 Preparations..............................................................................9
3.1 Charging Maximus 3.0................................................................... 9
3.2 On Using Your Battery ................................................................... 9
3.3 Power On / Power Off Maximus 3.0 ............................................. 9
3.3.1 Power on .............................................................................. 9
3.3.2 Power off .............................................................................. 9
3.4 Tips On Finger Operations .......................................................... 10
3.5 Lock & unlock the screen ............................................................ 10
3.5.1 Lock the screen .................................................................. 10
3.5.2 Unlock the screen ............................................................... 10
3.6 Locator & Navigation Buttons ...................................................... 10
3.7 Status Bar .....................................................................................11
3.8 Adjust brightness ..........................................................................11
3.9 Set standby time ...........................................................................11
3.10 Adjust the volume .......................................................................11
3.11 Changing Language ...................................................................11
3.12 WLAN Setting .............................................................................11
4 Initial Use.................................................................................13
4.1 User Registration ......................................................................... 13
4.2 Basic Operations on Diagnostic App ........................................... 15
4.2.1 Switch between different function modules ........................ 15
4.2.2 How to arrange diagnostic vehicle software icons?............ 15
4.2.3 How to distinguish if the software is locked or not? ............ 15
4.3 Function Modules ........................................................................ 15
4.3.1 Diagnostics ......................................................................... 15
4.3.2 Toolbox ............................................................................... 16
4.4 Diagnostics toolbar ...................................................................... 16
5 Start Diagnostics ....................................................................18
5.1 Connections................................................................................. 18
5.1.1 Preparation ......................................................................... 18
5.1.2 DLC Location ...................................................................... 18
5.1.3 Vehicle Connection (For Passenger Vehicle Version) ........ 18
5.2 Communication Setting ............................................................... 19
5.2.1 Pairing up via Wireless (BT) communication ...................... 19
5.2.2 USB cable connection ........................................................ 19
5.3 Start Diagnostics ......................................................................... 20
5.3.1 AutoDetect (VIN SCAN)...................................................... 20
5.3.2 Manual Diagnosis ............................................................... 23
5.4 Maintenance Reset...................................................................... 32
5.4.1 Oil Reset Service ................................................................ 32
5.4.2 Electronic Parking Brake Reset .......................................... 33
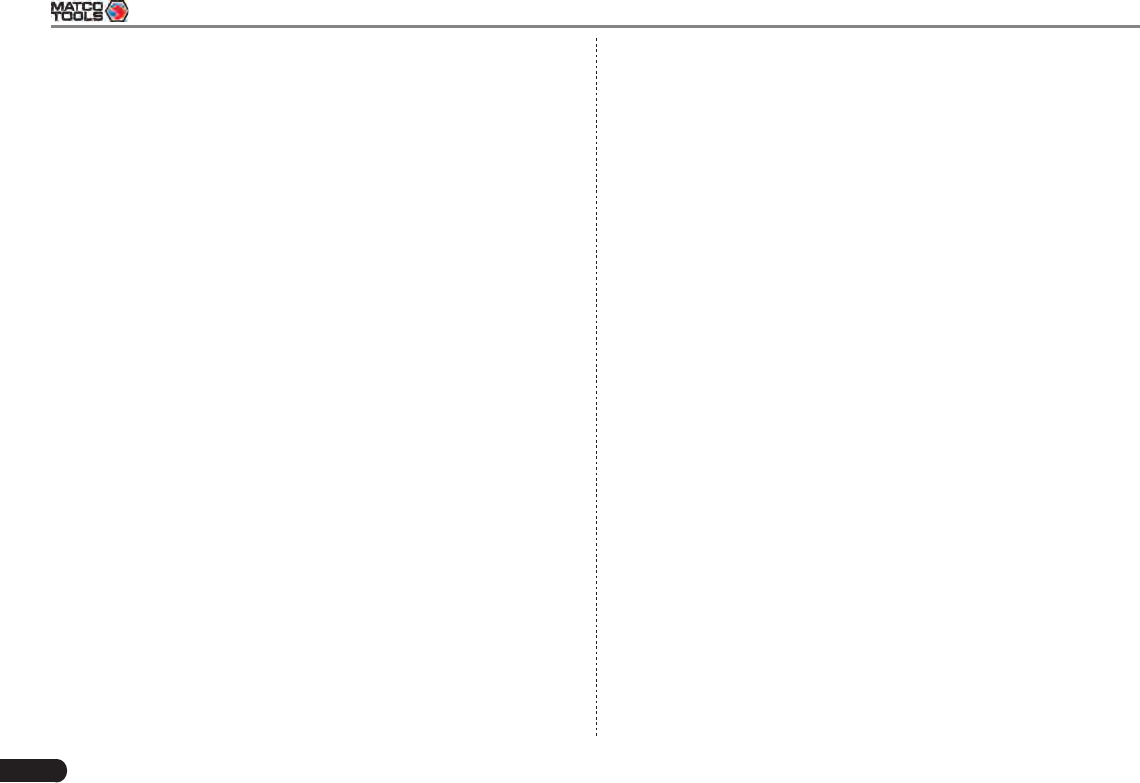
IV
Maximus 3.0 User's Manual
5.4.3 Steering Angle Calibration .................................................. 33
5.4.4 ABS Bleeding...................................................................... 33
5.4.5 Tire Pressure Monitor System Reset .................................. 33
5.4.6 Gear Learning..................................................................... 33
5.4.7 IMMO Service ..................................................................... 33
5.4.8 Injector Coding ................................................................... 34
5.4.9 Battery Maintenance System Reset ................................... 34
5.4.10 Diesel Particulate Filter (DPF) Regeneration ................... 34
5.4.11 Electronic Throttle Position Reset .................................... 35
5.4.12 Gearbox Matching ............................................................ 35
5.4.13 AFS (Adaptive Front-lighting System) Reset ................... 35
5.4.14 Sunroof Initialization ......................................................... 35
5.4.15 Suspension Calibration .................................................... 35
5.5 Diagnostic History (Previous Session) ....................................... 35
5.6 I/M Readiness ............................................................................. 36
6 Toolbox ....................................................................................37
6.1 Saved Reports ............................................................................. 37
6.1.1 Health Report ..................................................................... 37
6.1.2 Remote Report ................................................................... 37
6.1.3 Playback ............................................................................. 37
6.2 Tech-To-Tech ............................................................................... 38
6.2.1 Interface Layout .................................................................. 38
6.2.2 Add Friends ........................................................................ 39
6.2.3 Start Instant Messaging ...................................................... 39
6.2.4 Launch Remote Diagnosis (Device-To-Device) .................. 40
6.2.5 Launch Remote Diagnosis (Device-To-PC) ........................ 42
6.3 Feedback ..................................................................................... 44
6.4 Update ......................................................................................... 44
6.4.1 Update Diagnostic Software & APP .................................... 44
6.4.2 Download software ............................................................. 45
6.4.3 Renew software subscription.............................................. 45
6.5 Settings........................................................................................ 45
6.5.1 General ............................................................................... 45
6.5.2 VCI...................................................................................... 45
6.5.3 VCI Management................................................................ 46
6.5.4 Activate VCI ........................................................................ 46
6.5.5 Firmware Fix ....................................................................... 46
6.5.6 Icon Size ............................................................................. 46
6.5.7 Color Theme ....................................................................... 46
6.5.8 MD Printer Connection ....................................................... 46
6.5.9 Print Information ................................................................. 47
6.5.10 Data Stream Sample ........................................................ 48
6.5.11 Vehicle Voltage ................................................................. 48
6.5.12 Favorites ........................................................................... 48
6.5.13 Diagnostic Software Clear ................................................ 48
6.5.14 Backup/Restore ................................................................ 49
6.5.15 Login/Exit from current account ........................................ 49
6.6 Help ............................................................................................. 49
7 Applications ............................................................................ 50
7.1 Sensorbox & Multimeter (Optional) ............................................. 50
7.1.1 Product summary ............................................................... 50
7.1.2 Structure and Accessories .................................................. 51
7.1.3 Sensor Simulation .............................................................. 52
7.1.4 Multimeter ........................................................................... 55
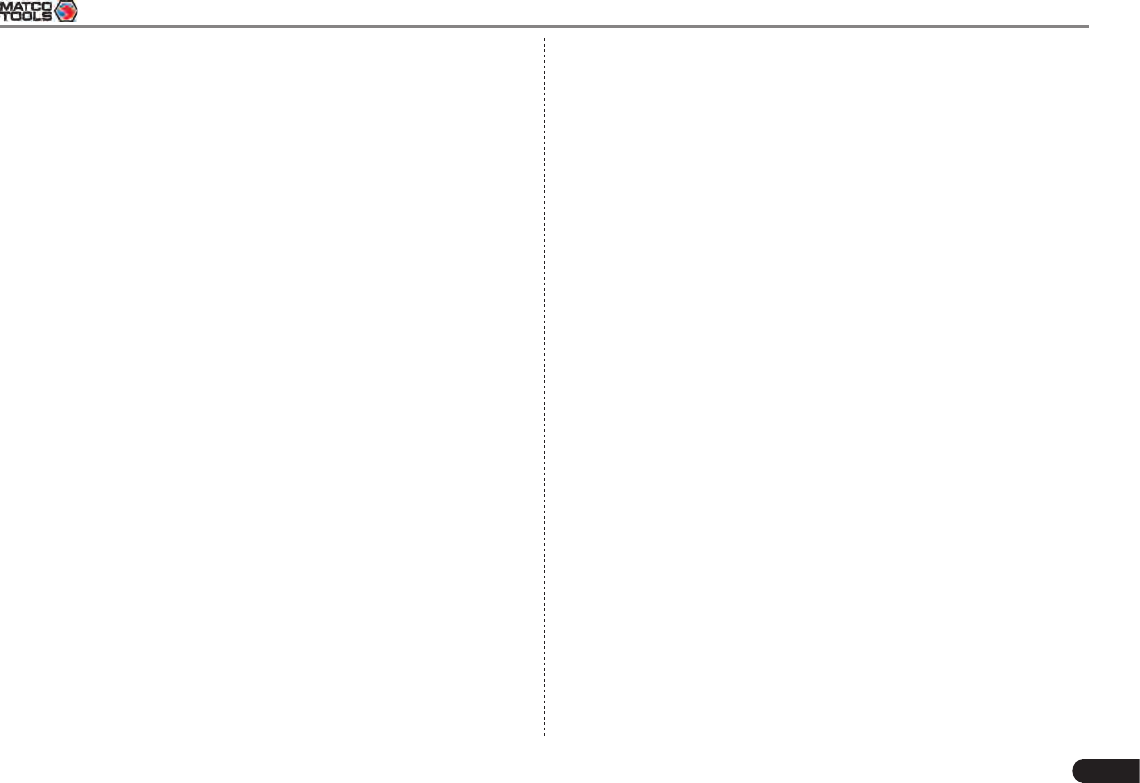
Maximus 3.0 User's Manual
V
7.2 Batterybox (Optional)................................................................... 57
7.2.1 Product Summary ............................................................... 57
7.2.2 Test Environment ................................................................ 58
7.2.3 Batterybox Structure and Test Accessories ........................ 58
7.2.4 Connections & Operations.................................................. 59
7.2.5 Precautions on battery test ................................................ 61
7.3 Oscilloscope (Optional) ............................................................... 62
7.3.1 Introduction ......................................................................... 62
7.3.2 Structure & Accessories ..................................................... 63
7.3.3 Connection & Initial Use ..................................................... 64
7.3.4 Operations .......................................................................... 65
7.4 Ignition (Optional) ........................................................................ 71
7.4.1 Secondary-distributor ignition analysis ............................... 71
7.4.2 Secondary-simultaneous ignition analysis.......................... 73
7.4.3 Secondary-direct ignition analysis ...................................... 73
7.4.4 Waveform analysis mode ................................................... 74
7.5 Videoscope (Optional) ................................................................. 77
7.5.1 Introduction ......................................................................... 77
7.5.2 About Videoscope ............................................................... 77
7.5.3 Technical Parameters ......................................................... 78
7.5.4 Connections & Operations.................................................. 79
Appendix - FAQ .......................................................................... 80
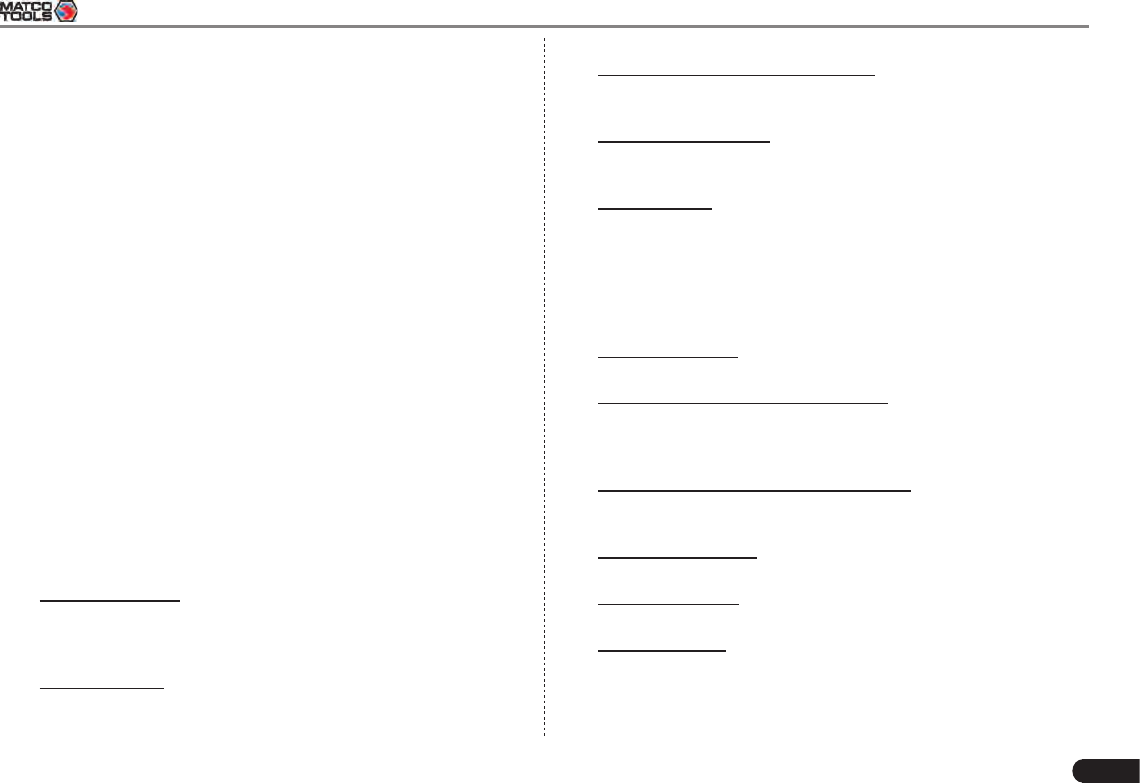
Maximus 3.0 User's Manual
1
• Tech-To-Tech (Remote Diagnosis): This option aims to help
repair shops or technicians launch instant messaging and remote
diagnosis, making the repair job getting xed faster.
• Maintenance & Reset: All kinds of common maintenance and
reset items, such as Oil lamp reset, DPF regeneration, ABS
bleeding etc can be done.
• I/M Readiness: I/M refers to Inspection and Maintenance that
is legislated by the Government to meet federal clean-air
standards. I/M Readiness indicates whether or not the various
emissions-related systems on the vehicle are operating properly
and are ready for Inspection and Maintenance testing. Moreover,
this module also has a direct access to generic OBD, saving time
to enter into the system.
• One-click Update: Lets you update your diagnostic software
online.
• Diagnostic History (Previous Session): Provides a quick access
to the tested vehicles and users can choose to view the test
report or resume from previous diagnostic session, without the
necessity of starting from scratch.
• Pre- and Post- Repair Result Comparison: By comparing the pre-
repair and post-repair report, you can clearly determine which
vehicle issues have been xed and which remained unsolved.
• Diagnostic Feedback: Enables you to submit the vehicle issue to
us for analysis and troubleshooting.
• Vehicle Coverage: Quick dial to view the vehicle models that
Maximus 3.0 covers.
• Backup/Restore: This feature lets you back up the recorded
files to external storage device/restore the recorded data from
external storage device.
2. WLAN connection is supported.
1 Introduction
1.1 Product Prole
Maximus 3.0 is an evolutionary smart solution for specialized
automotive diagnosis and maintenance. It inherits from LAUNCH’s
advanced diagnosing technology and is characterized by covering a
wide range of vehicles, featuring powerful functions, and providing
precise test result.
Through the wireless communication between VCI dongle and
Maximus 3.0 handset, it achieves full car model and full system
vehicle trouble diagnosis, which include Reading DTCs, Clearing
DTCs, Reading Data Stream, Actuation Test and Special Functions.
Moreover, taking advantage of the mobile Internet, it also integrates
One-click Update, Tech-To-Tech (Remote Diagnosis) and Repair Data,
which helps to diagnose vehicle issues more efficiently, and greatly
increase customer’s retention and boost shop revenue.
Maximus 3.0 adopts a higher performance-price ratio display tablet,
which comes loaded with the powerful 8-core 2GHz processor, 4G
RAM, and a 10.1” sunlight readable capacitive touch screen with a
resolution of 1920 x 1200 pixels.
1.2 Features
1. Diagnose:
• Smart Diagnosis: This module allows you to use the VIN
information of the currently identied vehicle to access its data
(including vehicle information, historical diagnostic records) from
the cloud server to perform quick test.
• Local Diagnosis: To perform diagnosis by executing on-screen
commands step by step. Diagnosis functions include: Read
DTCs, Clear DTCs, Read Data Stream, Special Functions etc.
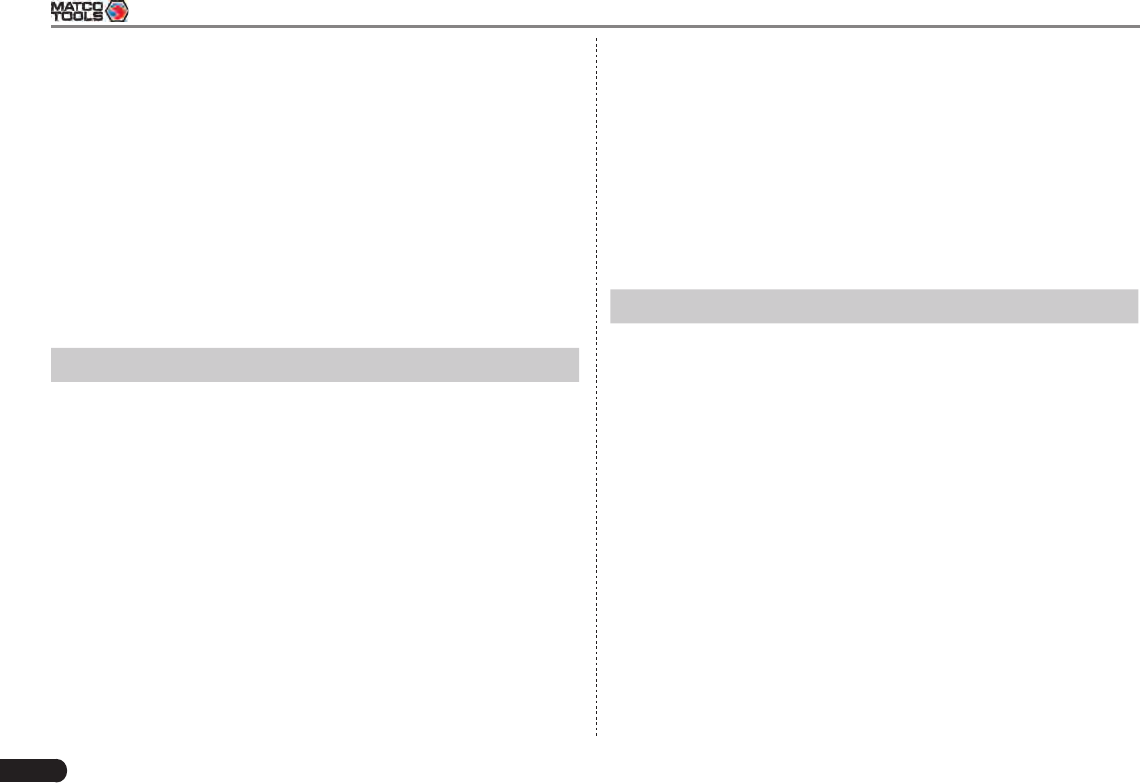
2
Maximus 3.0 User's Manual
Sensor Gravity Accelerometer
3-Axis Acceleration Sensor
Power and Battery 9000mAh lithium-polymer battery
Charging via 5V DC power supply
Operating Temperature -10℃ ~ 50℃(14 ~122℉)
Storage Temperature -20℃ ~ 70℃(-4 ~158℉)
1.3.2 VCI Dongle (Only for Passenger Vehicle Conguration)
Item Description
Working temperature -10℃ ~ 50℃(14 ~122℉)
Storage temperature -20℃ ~ 70℃(-4 ~158℉)
Relative humidity 20% ~ 90%
3. Web browser: Users can make online search and visit any website.
4. Equipped with multiple universal serial BUS ports for connecting
PC, and other add-on modules such as Scopebox, Sensorbox and
Batterybox.
5. Other Android-based applications can be customized to install or
uninstall.
6. File Manager: Lets you manage les or downloaded les stored in
memory card efciently.
7. Settings: To congure your personalized Maximus 3.0.
1.3 Technical Specications
1.3.1 Maximus 3.0 Tablet
Item Description
Operating system Android 7.1
CPU 8-core processor, 2GHz
Display 10.1 inch capacitive touch screen with
1920 x 1200 resolution
Memory 4GB
Hard disk 64GB
Connectivity • WLAN (802.11 b/g/n/ac)
• Universal serial BUS Ports (1 x Type-C
+ 1 x Type-A)
• BT 2.1 & 2.4
Cameras 8MP front-facing camera + 13MP rear-
facing camera
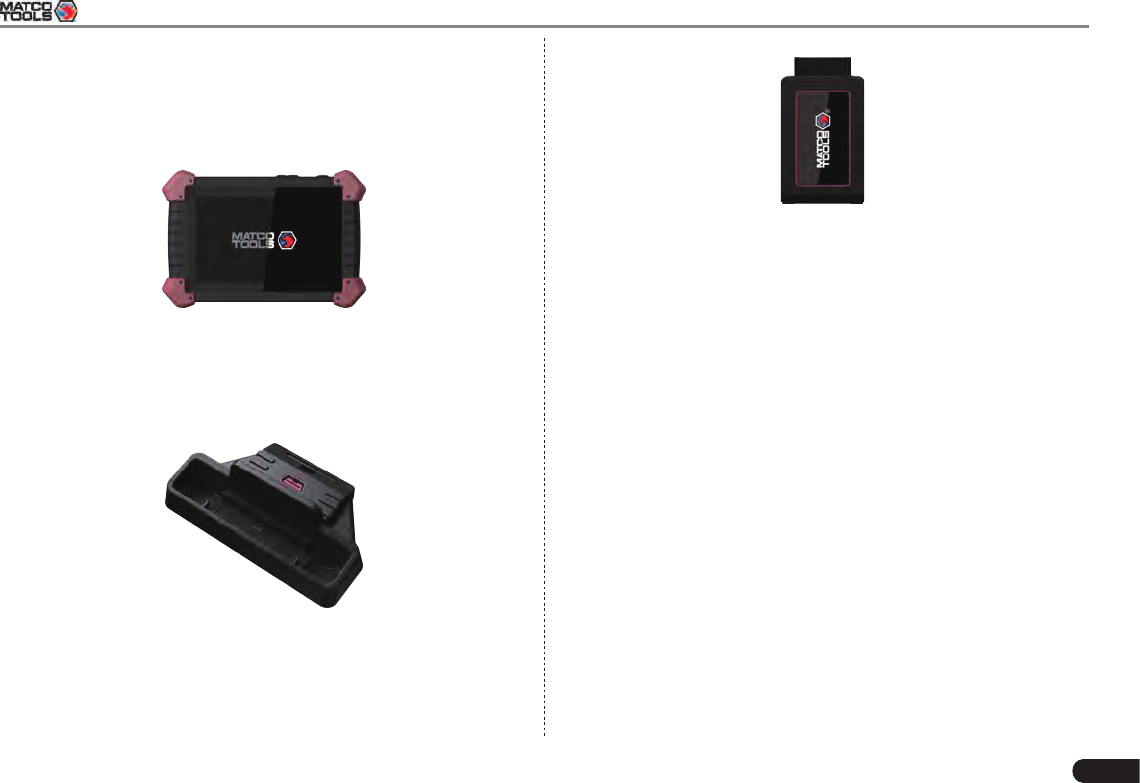
Maximus 3.0 User's Manual
3
2 Knowledge of Maximus 3.0
There are three main components to the Maximus 3.0 system:
• Maximus 3.0 Tablet -- the central processor and monitor for the
system (For details, please refer to Chapter 2.1.)
Fig. 2-1
• Maximus 3.0 Docking Station -- the platform for charging Maximus
3.0 tablet and extending functions (For details, please refer to
Chapter 2.2.)
Fig. 2-2
• VCI Device -- the device for accessing vehicle data (For details,
please refer to Chapter 2.3.)
Fig. 2-3 (Only for Passenger Vehicle Conguration)
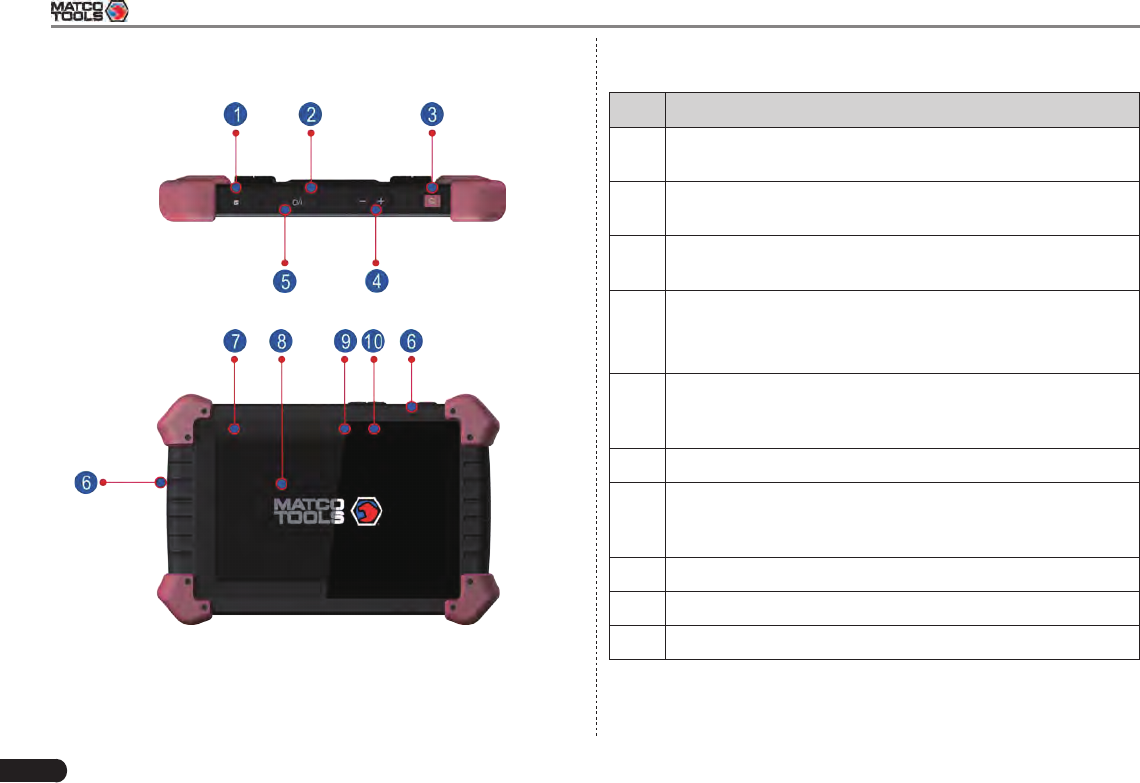
4
Maximus 3.0 User's Manual
2.1 Maximus 3.0 Tablet
Fig. 2-4 Maximus 3.0 Tablet (front & side view)
Table 2-1 formulates ports and indicators of Maximus 3.0 tablet:
No. Name & Descriptions
1Memory Card Slot -- To store the memory card for storage
expansion.
2Type C Charging Port -- Reserved for charging the Maximus
3.0 tablet.
3Power/Screen Lock Button -- To turn the tablet on/off with
long press, or lock the screen with short press.
4
Volume Buttons -- To adjust the volume.
*Note: Press and hold [POWER] and [VOL -] key to capture the
current screenshot.
5Data Transmission Port -- Reserved for add-on modules
(such as Batterybox, Scopebox, Sensorbox and Videoscope),
and other devices with similar port.
6Microphone
7Charging indicator -- It illuminates red while Maximus 3.0
tablet is charging. Once charging is nished, it will illuminate
solid green.
810.1" Capacitive Touch Screen
9Ambient Light Sensor
10 Front Camera
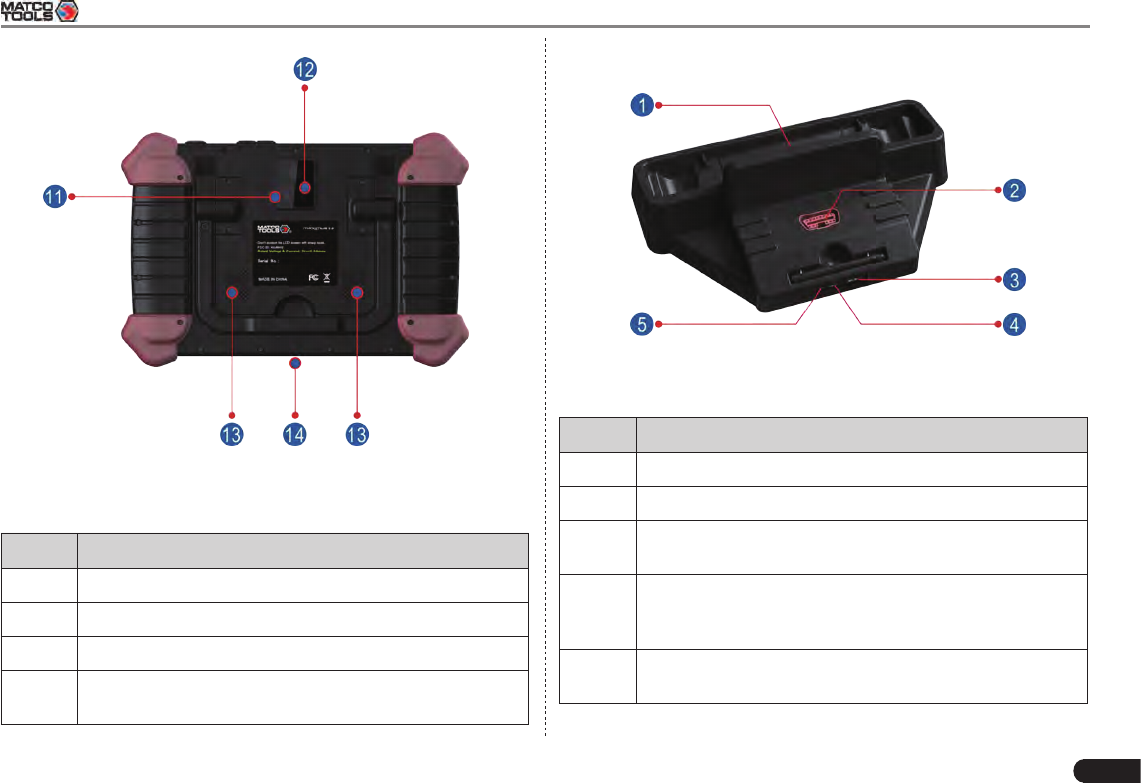
Maximus 3.0 User's Manual
5
2.2 Maximus 3.0 Docking Station
Fig. 2-6 Maximus 3.0 Docking Station
Table 2-3 formulates ports of Maximus 3.0 docking station
No. Name & Descriptions
1Charging Slot -- To charge the tablet.
2OBD16 Socket -- To store the VCI dongle to avoid loss.
3Data Transmission Port -- Reserved for add-on modules,
and other devices with similar port.
4Type C Charging Port -- Use the power adaptor to supply
power to the docking station through connection to AC
outlet.
5Power LED -- Illuminates solid green when it is powered
up.
Fig. 2-5 Maximus 3.0 Tablet (rear view)
Table 2-2 formulates parts of Maximus 3.0 tablet (rear):
No. Name & Descriptions
11 Rear Camera
12 Camera Flash
13 Audio Speaker
14 Adjustable Kickstand - Flip out it to any angle and work
comfortable at your desk, or hang it on the steering wheel.
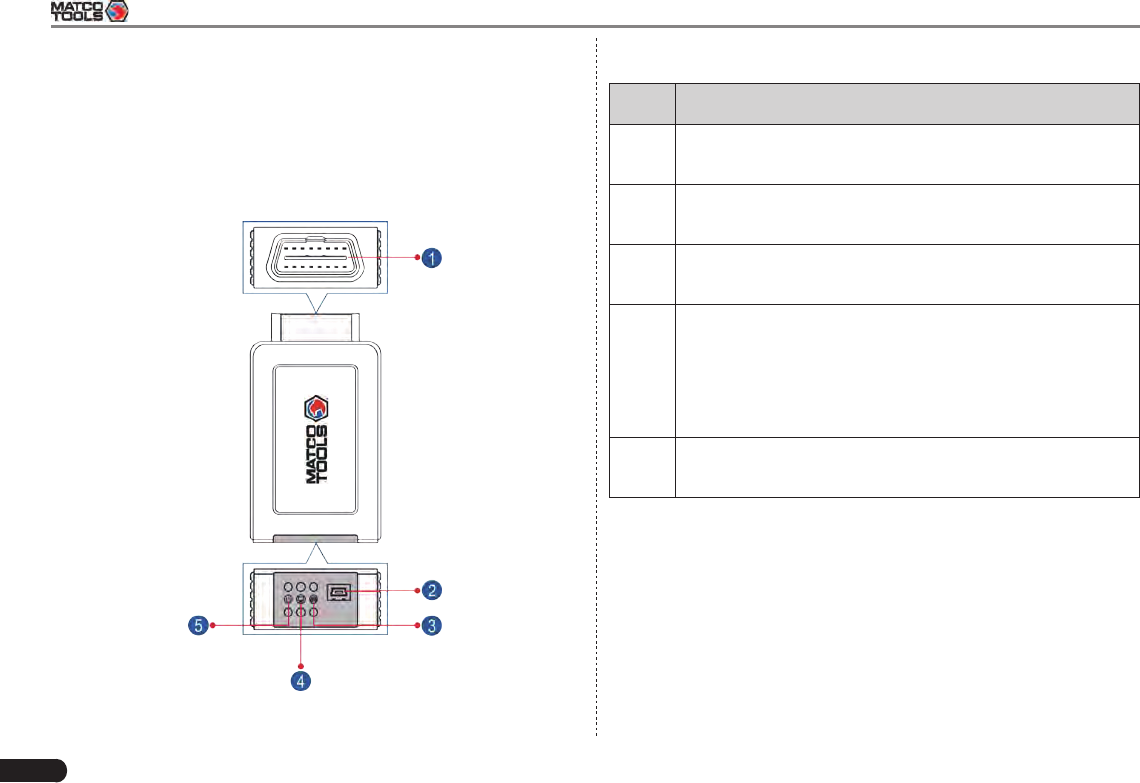
6
Maximus 3.0 User's Manual
2.3 VCI Dongle (Only for Passenger Vehicle
Conguration)
The VCI dongle works as a vehicle communication interface device,
which is used to connect to the vehicle’s DLC (Data Link Connector)
directly or via OBD II extension cable to read the vehicle data and
then send it to the Maximus 3.0 handset via wireless communication.
Fig. 2-7 VCI dongle
Table 2-4 formulates ports and indicators of VCI dongle:
No. Name & Descriptions
1OBD II-16 Diagnostic Connector -- To connect on
vehicle’s OBDII DLC.
2Data Transmission Port -- To connect to the Maximus 3.0
tablet to perform vehicle diagnosis via data cable.
3ECU Communication Indicator -- It ashes when the
dongle is communicating with the vehicle.
4
BT/USB Communication Indicator
• BLUE indicates that the dongle is working in wireless
communication (BT) mode (default mode).
• It illuminates red when the dongle is connected to the
handset via data cable.
5Power LED -- It lights up while the dongle is plugged into
the vehicle’s DLC.
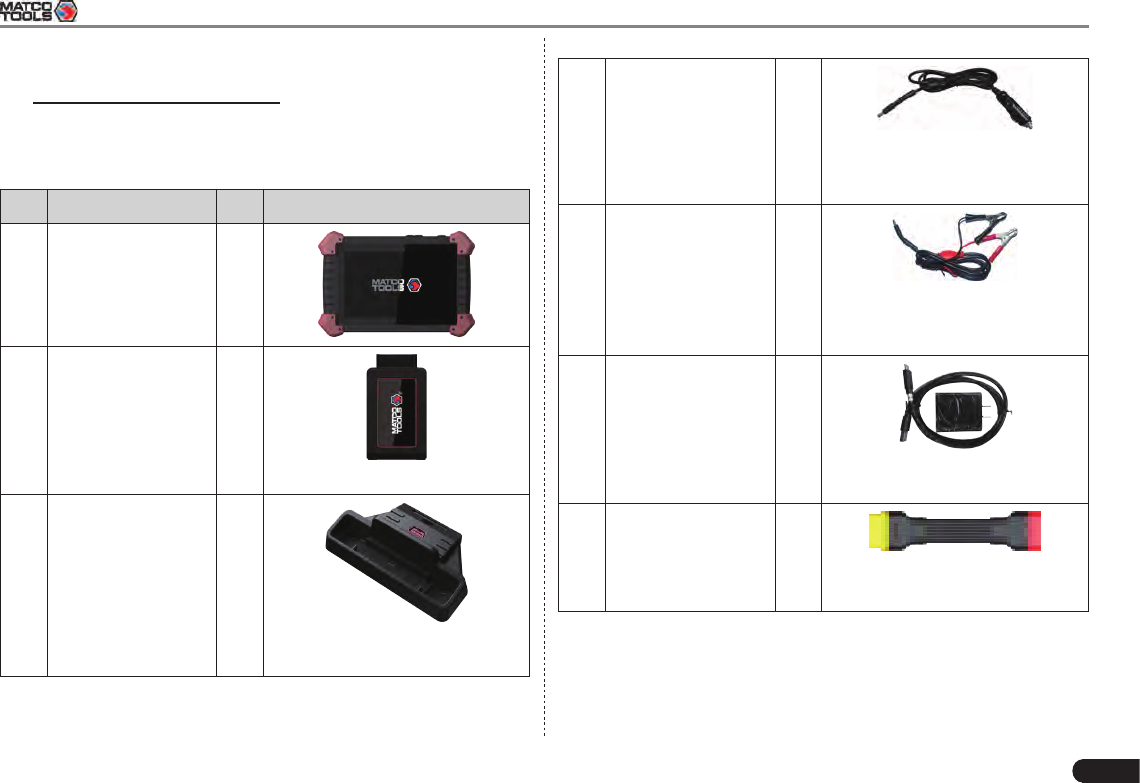
Maximus 3.0 User's Manual
7
2.4 Accessory Checklist
For different product configurations, the included accessories may
vary. For detailed items, please consult from the local agency or check
the package list supplied with Maximus 3.0 together.
Table 2-5 -- Maximus 3.0 common accessories and descriptions
No. Name Qt. Picture
1Maximus 3.0 Tablet 1
2VCI Dongle 1
(To connect to vehicle’s DLC.)
3Docking Station 1
(To charge the Maximus 3.0
tablet.)
4Cigarette Lighter
Cable 1(To supply power to non-16pin
dongle via vehicle’s cigarette
lighter receptacle.)
5Battery Clamps
Cable 1(To provide power to the non-16
pin dongle through connection to
the vehicle's battery.)
6Power Adaptor 1
(To supply power to the tablet
through connection to AC outlet.)
7OBD II extension
cable 1(To connect the VCI device for
extension purpose.)

8
Maximus 3.0 User's Manual
8OBDI Adaptor 1
(A adaptor cable for connecting
non-16 pin dongle.)
9Password
Envelope 1
(A piece of paper bearing
Product S/N and Activation
Code, which is required for your
registration.)
10 Non-16pin Dongle
Kit
(Optional. For detailed non-
16pin dongles, please check the
package box.)
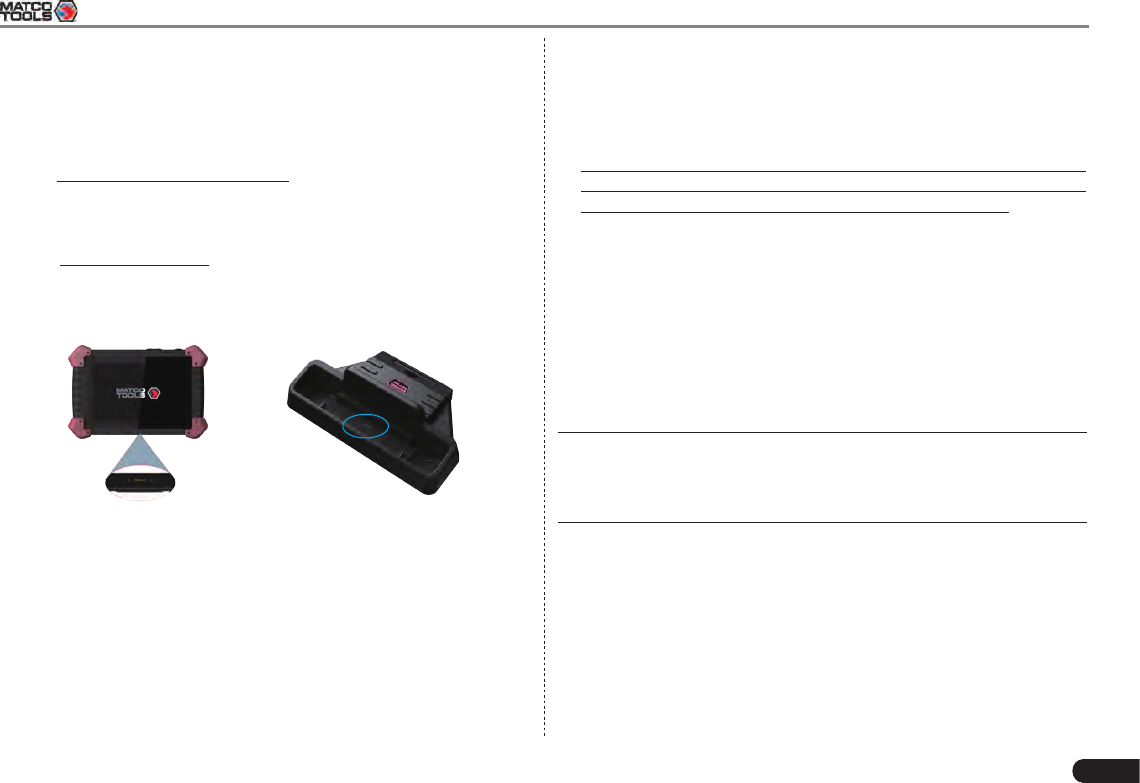
Maximus 3.0 User's Manual
9
3 Preparations
3.1 Charging Maximus 3.0
Choose any of the followings to charge your Maximus 3.0:
A. Use the included 5V power adaptor: Connect one end of the power
adaptor to Type C charging port of the Maximus 3.0 handset, and
the other end to the AC outlet. Never use other similar adaptors to
charge Maximus 3.0.
B. Use the docking station: Follow the steps described as below to
charge your Maximus 3.0:
1. Locate the charging slot on the bottom of Maximus 3.0 tablet and
the docking station. See Fig. 3-1 & Fig. 3-2.
Fig. 3-1 Fig. 3-2
2. Align the charging slots, and then dock the tablet into the station to
ensure that it is rmly seated on the docking station.
3. Insert one end of the included power cord to the charging port
of the docking station, then the other end into the AC outlet. The
charging LED illuminates solid red while charging.
4. Once it illuminates solid green, it indicates that the battery is fully
charged. Disconnect the docking station from the AC outlet.
3.2 On Using Your Battery
• If the battery keeps unused for a long time or battery is completely
discharged, it is normal that it can not be turned on while being
charged. Please charge it for a period and then turn it on.
• Please use the included power adaptor to recharge your Maximus
3.0. We assume no responsibility for damage or loss resulting from
using other similar adaptors other than the specied one.
• The charging time of battery varies with temperature condition and
battery consumption status.
• While Maximus 3.0 has low battery, a beep will sound. If it is very
low, Maximus 3.0 will be switched off automatically.
3.3 Power On / Power Off Maximus 3.0
3.3.1 Power on
Press the POWER key until it is slightly vibrated to turn on Maximus
3.0.
*Note: If it is the rst me you use Maximus 3.0 or Maximus 3.0 keeps idle
for a long me, Maximus 3.0 could fail to be turned on. It results from low
baery. In this case, please recharge your Maximus 3.0 for a while and try
to turn it on.
3.3.2 Power off
1. Press the POWER key for about 3 seconds, an option menu will
pop up on the screen.
2. Tap “Power off” to turn off Maximus 3.0.
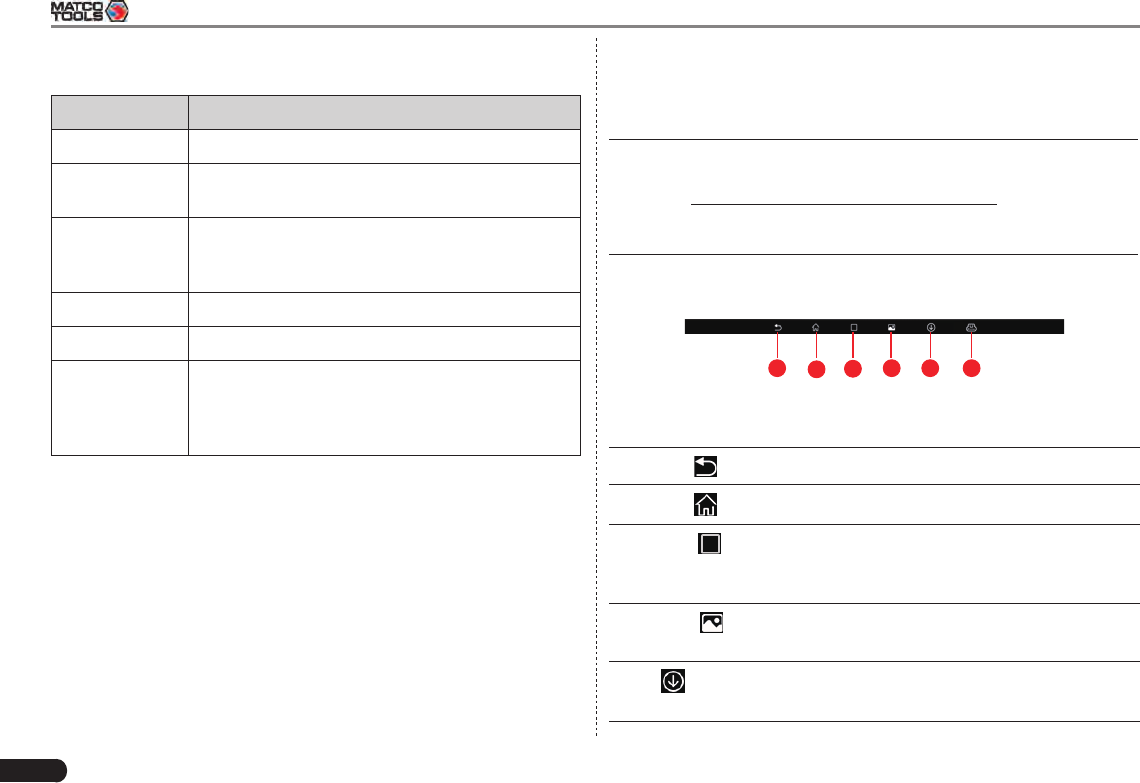
10
Maximus 3.0 User's Manual
3.4 Tips On Finger Operations
Actions Results
Single-tap To select a item or launch a program.
Double-tap To zoom in so that the text on a webpage appears
in a column that ts your device’s screen.
Long press Press and hold on the current interface or area
until a contextual menu pops up on the screen,
and then release it.
Slide To jump to different pages.
Drag Tap the desktop icon and drop it to other location.
Spread apart /
Pinch together
To zoom in manually, place two fingers on the
screen and then spread them apart. To zoom out,
place two fingers apart on the screen and then
pinch them together.
3.5 Lock & unlock the screen
Many screen lock modes are available on Maximus 3.0. Take the
preset screen-lock mode as example for demonstration.
3.5.1 Lock the screen
• When Maximus 3.0 is ON, press [POWER] key once to lock the
screen;
• The system will lock the screen automatically after Maximus 3.0
remains idle over the preset standby time.
3.5.2 Unlock the screen
Press [POWER] key to activate the screen, and then drag the lock to
“Unlock” position.
*Notes:
1. In case you forgot the screen lock, please refer to Appendix - FAQ for
details. You are not suggested to use the screen lock.
2. If you use “unlock the pattern”, you have to draw the right target
paern to unlock it.
3.6 Locator & Navigation Buttons
1234 5 6
Fig. 3-3
On-screen keys and status bar are as follows:
1Tap
to return to the previous screen or exit the application.
2 Tap
to navigate to the Android System’s home screen.
3
Tap
to display a list of applications that are currently
running or recently used. To open an application, tap it. To
remove an application, swipe it upwards.
4Tap
to capture the current screen and all captured
screenshots are stored in the Screenshots folder.
5: Once some upgradable diagnostic software are detected,
the icon will turn highlighted.

Maximus 3.0 User's Manual
11
6: Shows whether the VCI device is properly connected or
not.
3.7 Status Bar
For some common indicators, please see the following table.
Icons Denitions Icons Denitions
Airplane mode BT is on
Positioning GPS Charging
Battery is fully charged Low battery
New mail Preparing memory
card
Uploading Downloading
*Note: When the icon appears on the status bar, please charge it
immediately.
3.8 Adjust brightness
Maximus 3.0 is equipped with a built-in light intensity sensor. It can
adjust the screen brightness according to the ambient light intensity
automatically. Alternatively, you can also adjust it manually.
Tips: Reducing the brightness of the screen is helpful to save the power
of Maximus 3.0.
1. On the main menu screen, tap Settings > Display > Brightness.
2. Drag the slider to adjust it as desired.
3.9 Set standby time
If no activities are made within the dened standby period, the screen
will be locked automatically and the system enters sleep mode to save
power.
1. On the main menu screen, tap Settings > Display > Sleep.
2. Choose the desired sleep time.
3.10 Adjust the volume
This option enables you to adjust the volume of the ringtones, media
player, alarm and notice.
1. On the main menu screen, tap Settings > Sound > Volume.
2. Drag the slider to adjust it.
*Note: Alternatively, you can also press the volume keys to control the
volume of the current applicaon.
3.11 Changing Language
Maximus 3.0 supports multiple languages. To change the language of
the tool, please do the following:
1. On the home screen, tap on Settings -> Language & Input ->
Languages.
2. Tap on “Add a language”, and then choose the desired language
from the list.
3. Tap and hold the desired language and drag it to the top of the
screen and then release it, the system will change into the target
language.
3.12 WLAN Setting
*Note: Once WLAN is set as ON, Maximus 3.0 will consume more
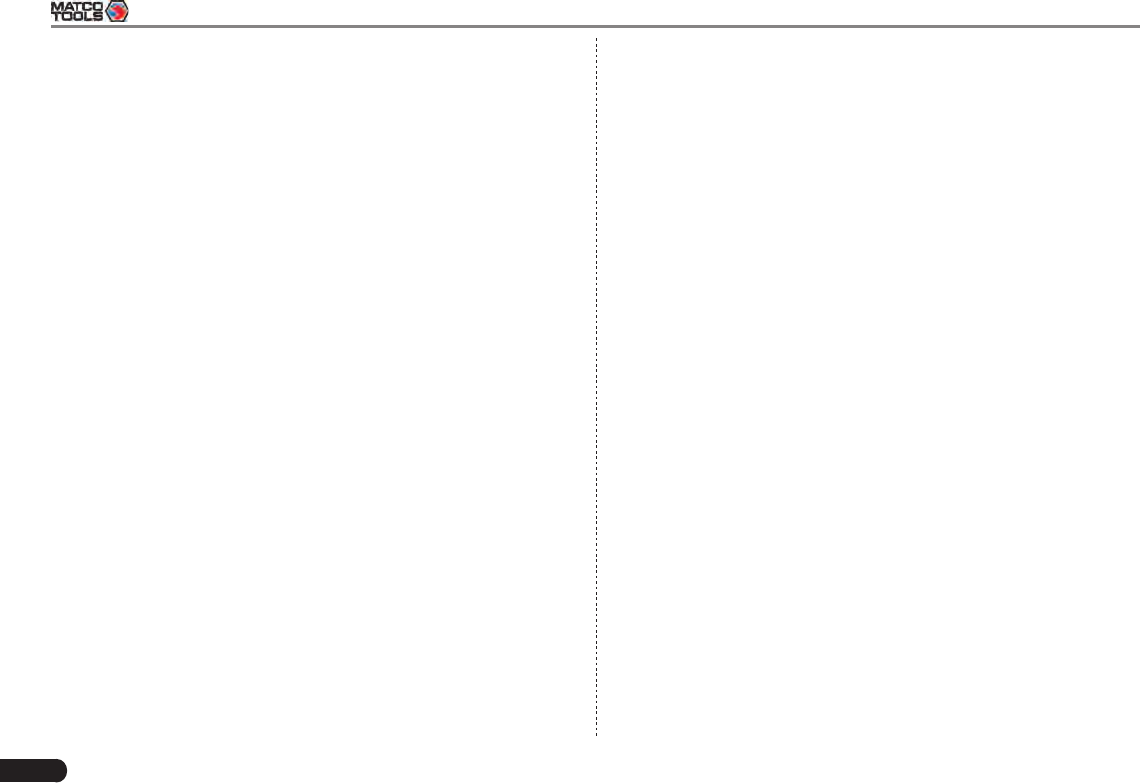
12
Maximus 3.0 User's Manual
power. While it keeps unused, please set it off to save power. While
WLAN keeps unused, please turn it off to conserve battery power.
Maximus 3.0 has built-in Wi-Fi that can be used to get online. Once
you’re online, you can register your tool, update diagnostic software &
APK, browse the Internet, get apps and send email on your network.
1. On the main menu screen, tap Settings > WLAN.
2. Tap or slide the switch to ON, Maximus 3.0 starts searching for all
available wireless LANs.
3. Choose the desired network,
• If the network you chose is open, you can connect on it directly;
• If the selected network is encrypted and secured with WPA, you
have to input the right access password to connect.
When Maximus 3.0 is in range of the WLAN, it will connect to the
previously linked network automatically.
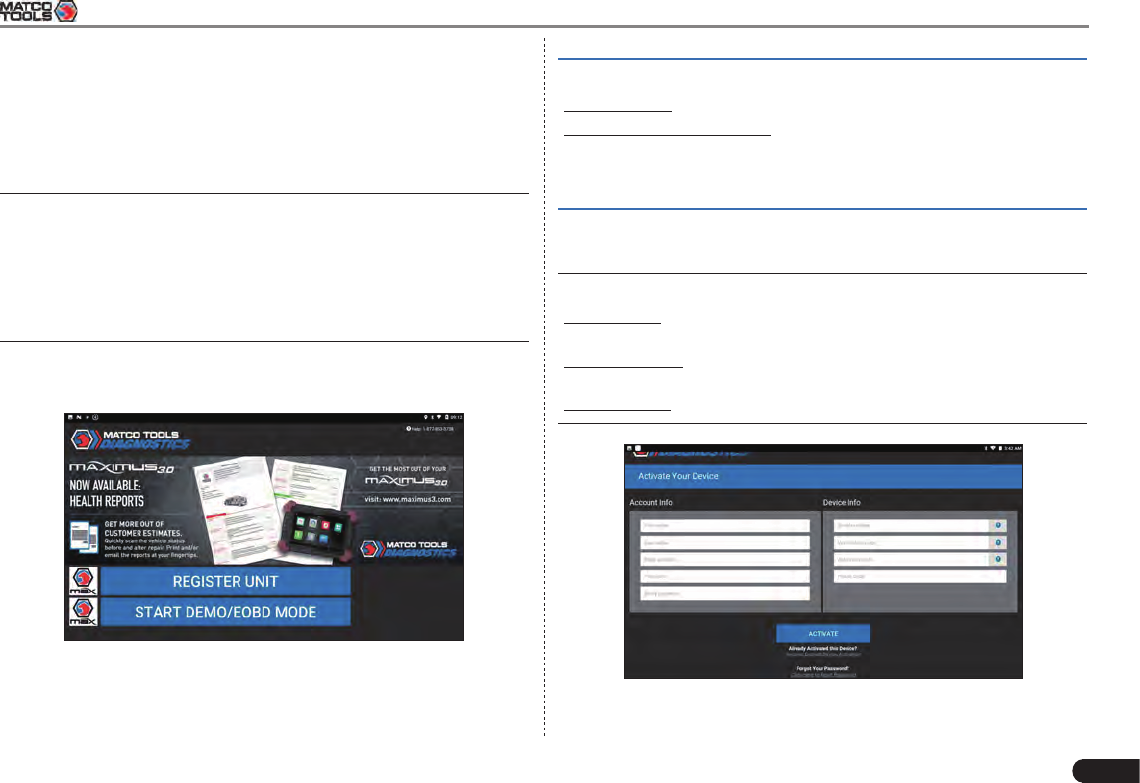
Maximus 3.0 User's Manual
13
4 Initial Use
4.1 User Registration
Users need to experience an sign-up process before using Maximus
3.0.
*Notes:
• Before registering, please make sure that your handset has a strong and
stable Wi-Fi signal.
• While acvang device, the Serial number and Vericaon code can be
found in the included password envelope. To obtain Activation code,
please contact with your dealer.
Follow the steps below to proceed:
1. Tap “Maximus 3.0” on the home screen to Fig. 4-1.
Fig. 4-1
On-screen Buons:
REGISTER UNIT: For new user, tap it to go to step 2.
START DEMO/EOBD MODE: Two free programs (DEMO & EOBD) are
preset in this App. This option enables you to experience the diagnostic
procedures even if you have not acvated your device or VCI dongle is not
used.
2. Fill in your account information and device information and then tap
on “ACTIVATE” to enter Fig. 4-3.
*Note:
Serial number is a 12-digit number starng with 98 -- you can nd it on the
back of your tool.
Vericaon code is a 8-digit number stored in the Private & Condenal
sheet.
Acvaon code is printed on the receipt, or consult your dealer for it.
Fig. 4-2
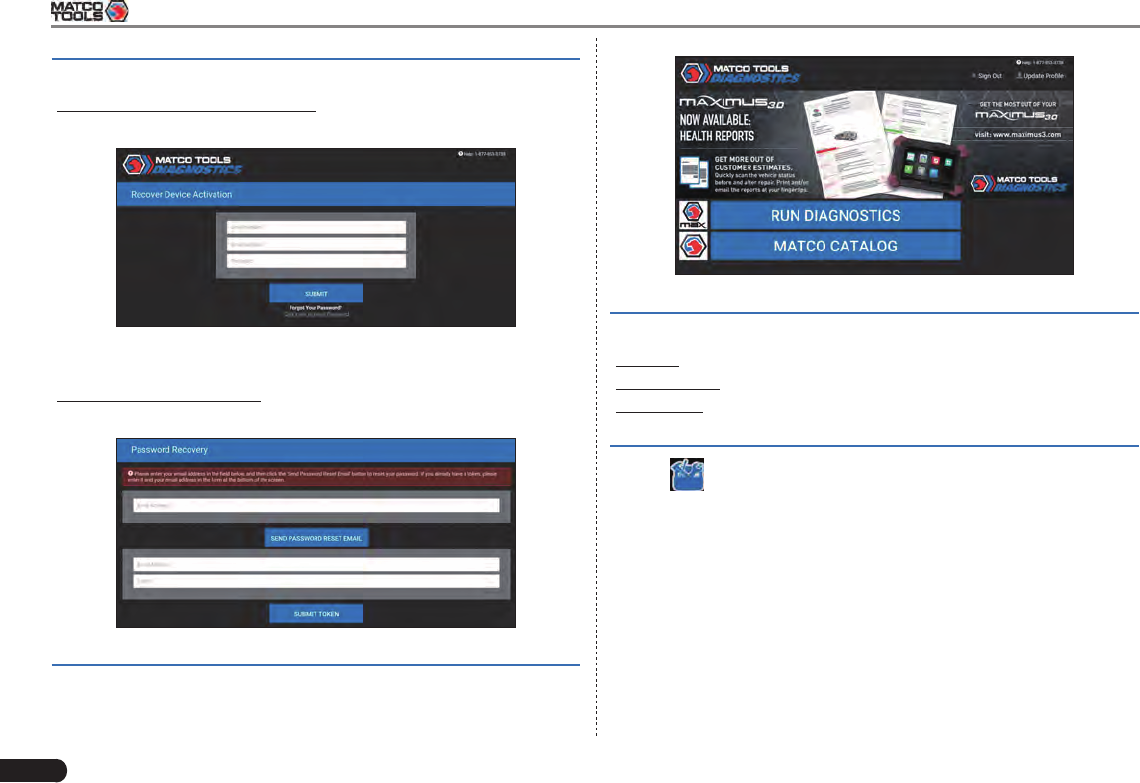
14
Maximus 3.0 User's Manual
Fig. 4-3
On-screen Buons:
Sign Out: Tap it to log out the system.
Update Prole: Tap it to modify personal informaon.
Update App: If a newer App version is detected, this buon will appear on
the screen. Tap it to keep synchronized with the latest version.
4. Tap “ ” on the top left-hand corner of the screen (Fig. 4-4) to
switch to the Toolbox module. See Fig. 4-5.
On-screen Buons:
Recover Current Device Activation: If you have already activated your
Maximus 3.0, tap it to navigate to the following screen.
Input Serial number, Email address and Password, and then tap “SUBMIT”
to sign in and go to Fig. 4-3.
Click Here to Reset Password: If you forgot the password, tap it to go to the
following screen.
Follow the on-screen instrucons to reset a new password.
3. Tap “RUN DIAGNOSTICS” to launch diagnostics. See Fig. 4-4.
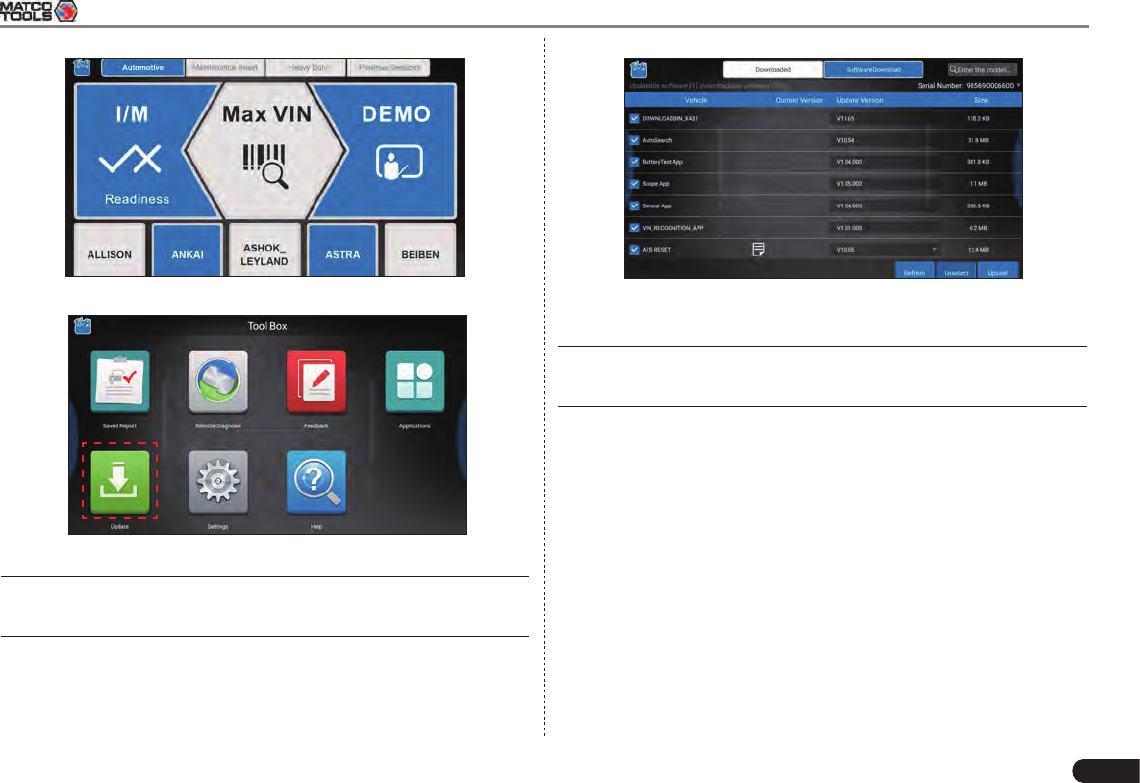
Maximus 3.0 User's Manual
15
Fig. 4-4
Fig. 4-5
*Note: If a red dot appears on upper right corner of the Update logo, it
indicates newer soware is available.
5. Tap “Update” to enter the update center.
Fig. 4-6
Make sure all brands are selected, tap “Update” to start updating.
*Note: Download and installaon will take approximately 10 minutes
depending on the internet connecon.
Once downloading is complete, the software package will be installed
automatically.
Tap the “OK” button on the pop-up message box when update is
complete.
4.2 Basic Operations on Diagnostic App
4.2.1 Switch between different function modules
There are 2 function modules available on the Maximus 3.0:
Diagnostics and Toolbox.
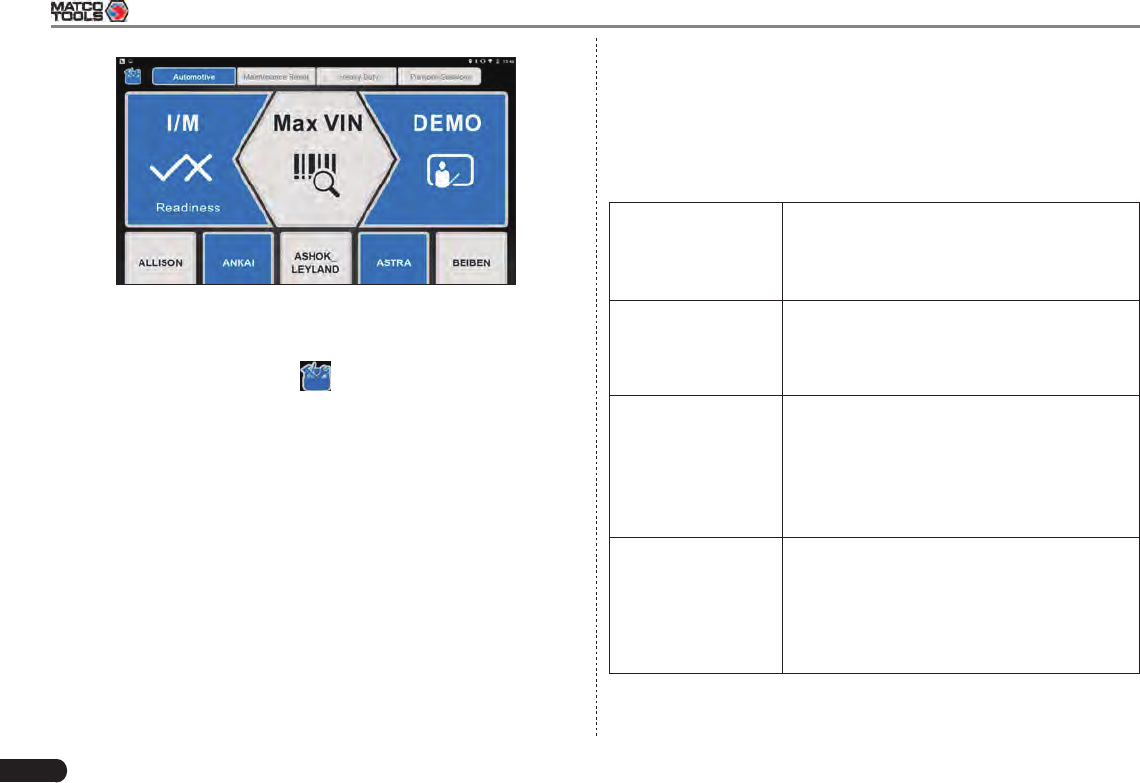
16
Maximus 3.0 User's Manual
Fig. 4-7
Swipe in from the left/right edge of the screen to switch between
function modules.
Alternatively, you can also tap on the upper left corner of the
screen to toggle between Diagnostics and Toolbox.
4.2.2 How to arrange diagnostic vehicle software icons?
All software icons, by default are organized by the system. Many
display rules are available to meet your preference.
To re-organize it, press and hold certain software icon, an option menu
pops up on the screen. Choose the display rule and the system will
arrange the icon as desired.
If you choose “Pin to the top”, the icon will be displayed on the top of
the screen and marked with an orange solid dot.
4.2.3 How to distinguish if the software is locked or not?
If the software is locked, tap it to display the latest software summary.
In this case, you need to purchase the software to unlock its content.
Once it is unlocked, the software icon will turn into orange.
4.3 Function Modules
There are 2 function modules available on the Maximus 3.0:
Diagnostics and Toolbox.
4.3.1 Diagnostics
It mainly includes the following items:
Automotive
Configures Maximus 3.0 to operate as a
diagnostic tool exclusively for passenger cars.
Max VIN (VIN Decoding) and Manual
Diagnosis are supported.
Maintenance Reset
To perform all kinds of common repair &
maintenance items, including electronic
throttle position reset, ABS bleeding, oil lamp
reset and DPF regeneration etc.
Heavy Duty
Configures Maximus 3.0 to operate as a
diagnostic tool exclusively for commercial
vehicles.
*Note: This function requires an extra VCI
module and only applies to the Maximus 3.0 of
Commercial Passenger Edition.
Previous Session
When a vehicle diagnosis is performed,
Maximus 3.0 records the detailed diagnostic
information. This function provides a quick
access to the previously tested vehicles.
Testing can be resumed from the previous
operation without starting from scratch.
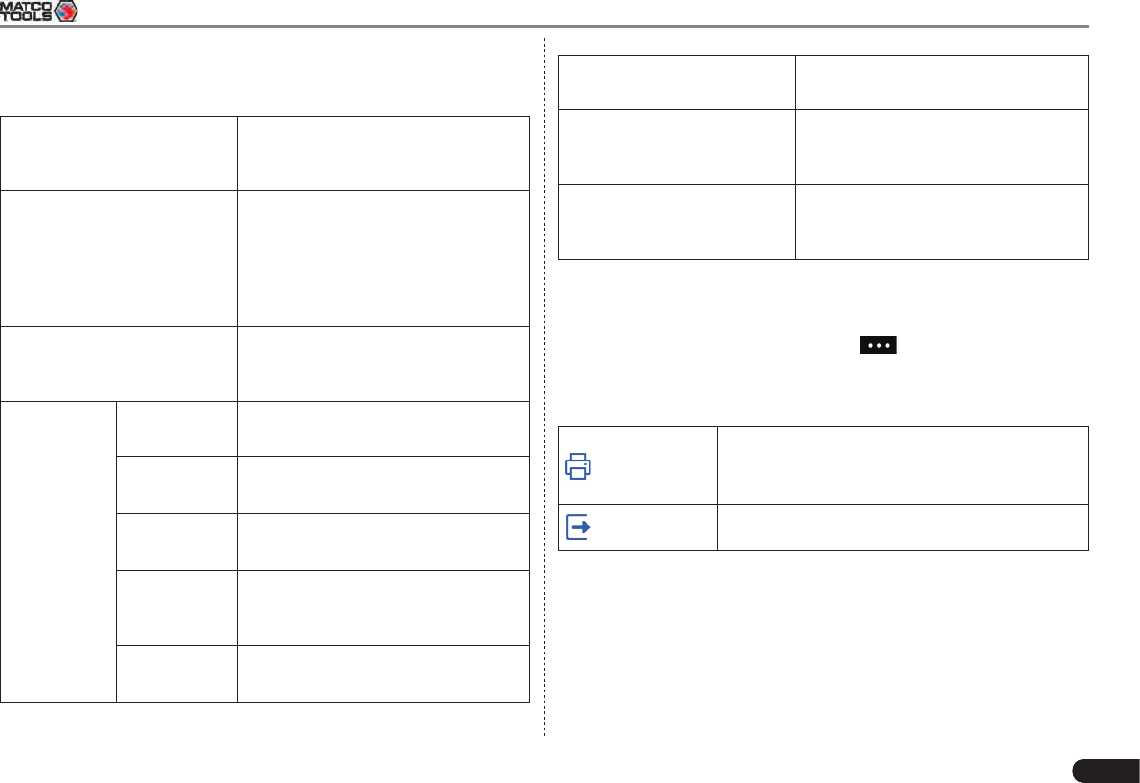
Maximus 3.0 User's Manual
17
4.3.2 Toolbox
It mainly includes the following items:
Saved Report Includes Health report, Diagnostic
feedback, Waveform Playback and
Remote report.
Tech-To-Tech
This option aims to help repair
shops or technicians launch instant
messaging and remote diagnosis,
making the repair job getting fixed
faster even from thousands of miles
away.
Feedback This item allows you to feedback
your diagnostic problems to us for
analysis and troubleshooting.
Applications
Videoscope
(Optional) To check unseen or unreachable
parts or components.
Oscilloscope
(Optional)
To determine vehicle electrical
equipment and circuit trouble.
Sensor
(Optional)
To diagnose/simulate vehicle ECU
sensor trouble.
Multimeter
(Optional)
To measure physical parameters
such as voltage, resistance,
frequency etc.
Battery
(Optional)
To test whether vehicle's battery is
good or not.
Update To update vehicle diagnostic software
and APK.
Settings To make some system settings,
including Printer connection, Icon
size, Color theme and Logout etc.
Help Includes FAQ, Vehicle Coverage,
Quick Start Guide, User Manual and
Function Notes.
4.4 Diagnostics toolbar
The diagnostics toolbar contains a number of buttons that enables
various procedures. It is hidden under at the top of the vehicle
diagnostic screens throughout the diagnostic session. Refer to the
table below for a brief description of the functions of the diagnostics
toolbar buttons.
Print Tap to print the current screen.
To perform printing, you need to purchase an
extra Wi-Fi printer separately.
Exit Session Tap to exit the current diagnostic session.
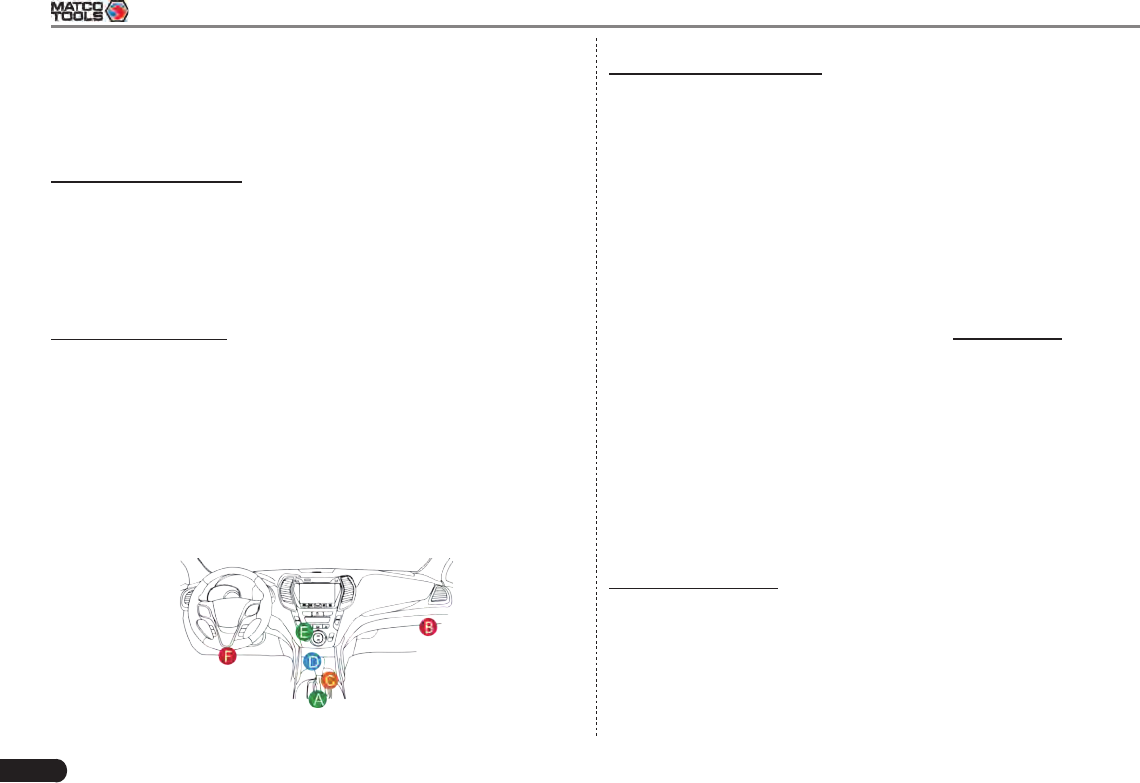
18
Maximus 3.0 User's Manual
5 Start Diagnostics
5.1 Connections
5.1.1 Preparation
Normal testing conditions
• Turn on the vehicle power supply.
• Vehicle battery voltage range should be 9-14V and working voltage
of Maximus 3.0 is 5V.
• Throttle should be closed at its close position.
5.1.2 DLC Location
1. For Passenger Cars,
The DLC (Data Link Connector or Diagnostic Link Connector) is the
standardized 16-cavity connector where diagnostic code readers
interface with the vehicle’s on-board computer. The DLC is usually
located 12 inches from the center of the instrument panel (dash),
under or around the driver’s side for most vehicles. If Data Link
Connector is not located under dashboard, a label should be there
telling location. For some Asian and European vehicles, the DLC
is located behind the ashtray and the ashtray must be removed
to access the connector. If the DLC cannot be found, refer to the
vehicle’s service manual for the location.
Fig. 5-1
2. For Commercial Vehicles,
The DLC is generally located in driver’s cab.
5.1.3 Vehicle Connection (For Passenger Vehicle Version)
The method used to connect the VCI device to a vehicle’s DLC
depends on the vehicle’s conguration as follows:
• A vehicle equipped with an OBD II management system supplies
both communication and 12V power through a standardized DLC.
• A vehicle not equipped with an OBD II management system
supplies communication through a DLC connection, and in some
cases supplies 12V power through the cigarette lighter receptacle
or a connection to the vehicle battery.
Follow the steps mentioned below to connect OBD II vehicle:
1. Locate vehicle’s DLC socket.
2. Plug the VCI device into the vehicle’s DLC socket (It is suggested
to use the OBD II extension cable to connect the VCI device and
DLC socket.).
3. Choose one of the two ways to obtain power from:
A. Power adaptor: Connect one end of the included power adaptor
to Power interface of Maximus 3.0 tablet, and the other end to
AC outlet.
B. Internal battery pack: For details on how to recharge Maximus
3.0, see “Chapter 3.1 Charging Maximus 3.0”.
For non-OBDII vehicle, proceed as follows:
1. Locate vehicle’s DLC socket.
2. Select the corresponding non-16pin dongle.
3. Plug the non-16pin end of the dongle into the DLC socket, then
connect the other end to the OBD I adaptor, and then tighten the
captive screws.
4. Connect the other end of the adaptor to the included VCI device.

Maximus 3.0 User's Manual
19
5. To supply power to OBD I adaptor from:
A. Cigaretter Lighter Cable: Connect one end of the cigarette lighter
cable to vehicle’s cigarette lighter receptacle, and the other end to
the power jack of OBDI adaptor.
Fig. 5-2
B. Battery Clamps Cable: Connect one end of the battery clamps
cable to vehicle’s battery, and the other end to the power jack of
OBDI adaptor.
Fig. 5-3
5.2 Communication Setting
There are 2 ways available for Maximus 3.0 to communicate
with the VCI device: BT(wireless) communication and USB cable
connection. User can choose either of the following ways to establish
communication.
5.2.1 Pairing up via Wireless (BT) communication
Refer to Chapter 5.1.3 Vehicle Connection to connect the Maximus 3.0
and VCI device.
1. Enter Bluetooth setting screen (“Settings” -> “BLUETOOTH”),
slide the switch to ON and Maximus 3.0 will start searching for all
available devices.
2. Tap the desired one from the result list to pair and match. By
default, the Bluetooth ID of the VCI dongle starts with 98********00
(where ******** stands for 8 digits).
3. If the pair request pops up on the screen, enter the request pin
code (default code: 0000 or 1234).
4. Once pairing is successfully done, the VCI dongle will be shown on
the top of the “Paired devices” list and the VCI icon on the lower
right corner of the screen will light up.
*Notes:
• If you logged in the account on another diagnostic tool and the VCI
dongle has ever been paired up with that tool, you need to cancel
pairing first before using a different tool to proceed new diagnostic
session. Tap “Seng” -> “Bluetooth” -> the icon next to the device
name, and then tap “FORGET” on the pop-up dialog box to unpair it.
• In case no Bluetooth setting is done before diagnostic software is
launched, you can also configure it while using the App. For details,
please refer to “Chapter 5.3 Start diagnoscs”.
5.2.2 USB cable connection
1. Connect one end of the USB cable (optional) to the Data I/O port of
the VCI device.
2. Connect the other end to the USB port of the Maximus 3.0 handset.
The power indicator of the VCI device lights up.
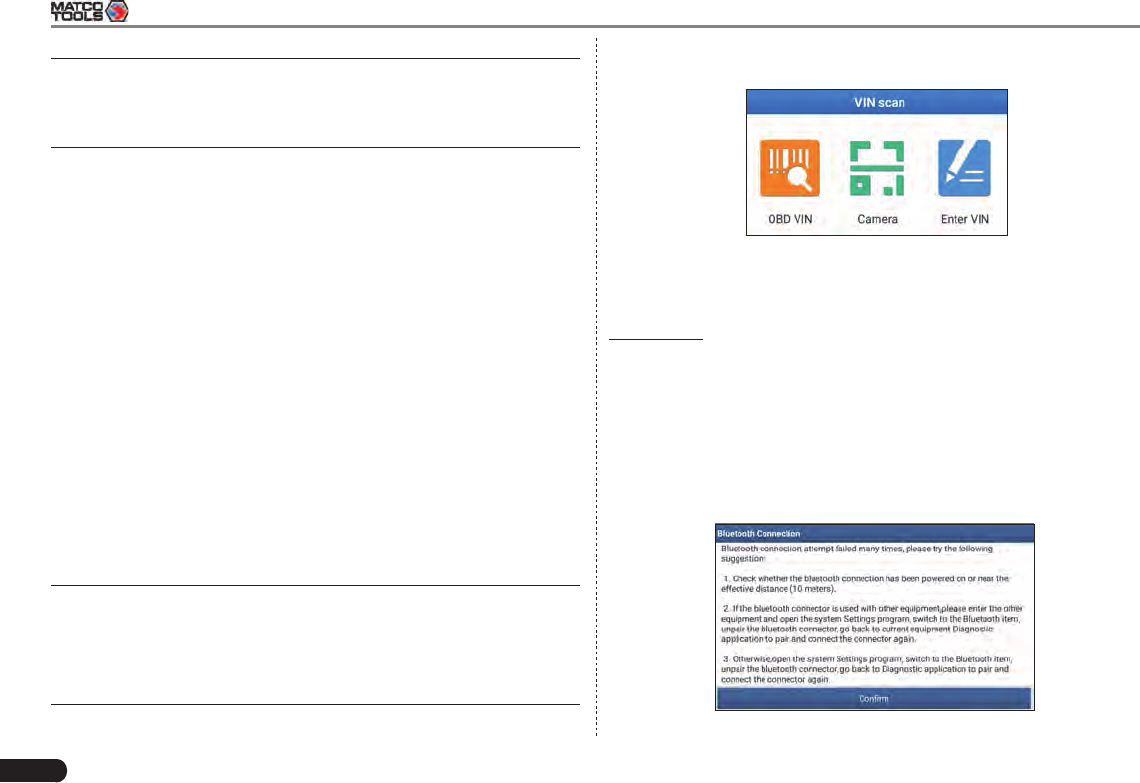
20
Maximus 3.0 User's Manual
*Note: The USB connection provides the most stable and fastest
communicaon. When all the communicaon methods are applied at the
same me, the Maximus 3.0 system will use the USB communicaon as the
default priority.
5.3 Start Diagnostics
On the Diagnostics page, tap “Automotive/Heavy Duty” to enter the
vehicle selection page.
2 approaches are provided for you to access the vehicle diagnostic
software.
5.3.1 Max VIN (VIN Decoding)
Through simple wireless (BT) communication between the Maximus
3.0 handset and VCI, you can easily get the VIN (Vehicle Identication
Number) information of the currently identied vehicle. Once the VIN
is successfully identified, the system will retrieve it from the remote
server and then guide you to vehicle information page without the
necessity of step-by-step manual menu selection (Early model may
need manual selection).
The vehicle information page lists all historical diagnostic records of
the vehicle, which lets the technician have a total command of the
vehicle faults. In addition, a quick dial to local diagnosis and diagnostic
function are also available on this page for reducing the roundabout
time and increasing productivity.
*Notes:
• Before using this function, please make sure the VCI is properly
connected to the vehicle’s DLC. For detailed connection, see Chapter
5.1.3 “Vehicle Connecon”.
• A stable network connecon is required for this funcon.
Follow the steps below to proceed.
1. Tap “Max VIN” to enter Fig. 5-4.
Fig. 5-4
In this case, automatic scan (OBD VIN), camera and manual input
(INPUT VIN) are available.
a). OBD VIN: In this mode, the VCI device should be plugged into the
vehicle’s DLC rst, and then a wireless (BT) communication should
be established between Maximus 3.0 and the VCI dongle.
Tap “OBD VIN”, the system starts decoding the VIN to enter general
information about the vehicle (year, make, model etc.). When the
process is complete, Fig. 5-10 appears.
* Note: If the VCI is not paired up with the Maximus 3.0 handset before
doing this step, an advisory message prompng Bluetooth connecon failure
appears on the screen.
Fig. 5-5
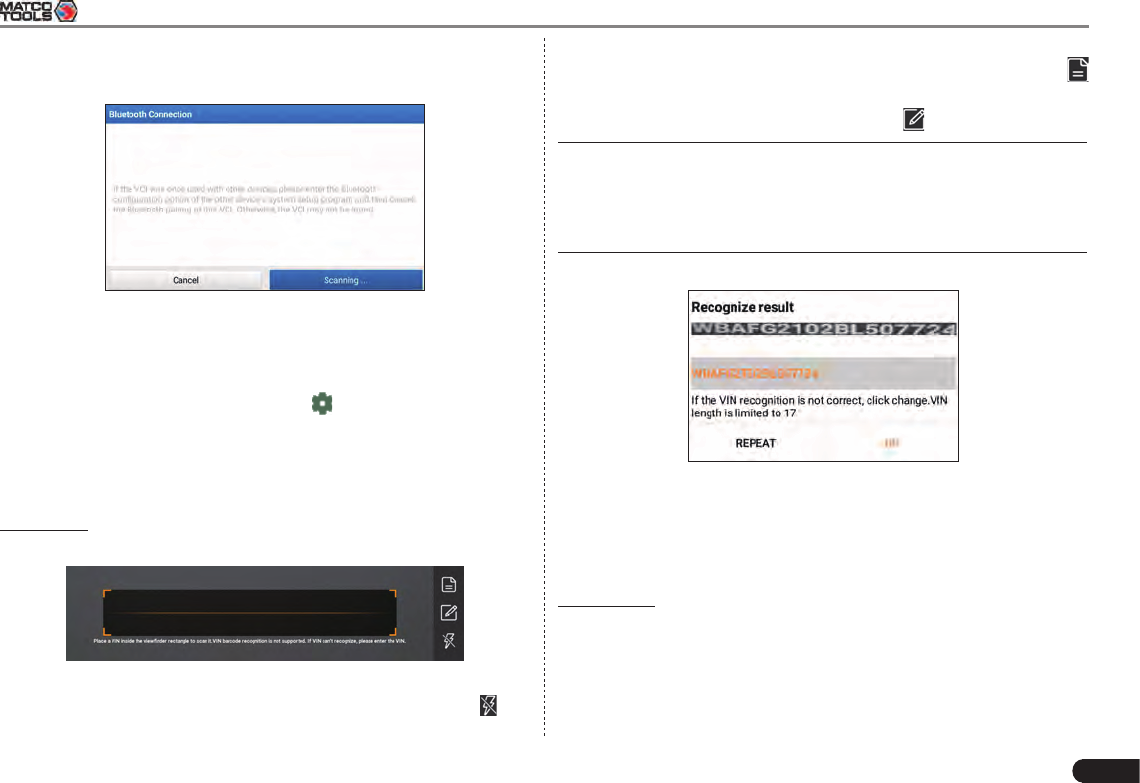
Maximus 3.0 User's Manual
21
• If you have scanned the VIN of the vehicle, tap VIN record icon
to select it from the record list.
• In case the handset failed to identify it, tap to enter it manually.
*Note: In general, vehicle identification numbers are standardized - all
contain 17 characters. VIN characters may be capital letters A through Z
and numbers 1 through 0; however, the leers I, O and Q are never used
in order to avoid mistakes of misreading. No signs or spaces are allowed in
the VIN.
After scanning, the screen automatically displays the result.
Fig. 5-8
• If the VIN scanned is incorrect, tap the result eld to modify it and
then tap “OK”. If the VIN exists on the remote server, the system
will enter the vehicle information screen. See Fig. 5-10.
• To scan it again, tap “REPEAT”.
c). Enter VIN: In this mode, you need to input the VIN manually.
The most recognizable location for this number is in the top left corner
on the vehicle’s dashboard. Other locations include the driver’s door
or post, and the rewall under the hood.
Tap “Enter VIN” and a screen similar to Fig. 5-9 will appear:
Check all the possible reasons carefully, and then tap “Conrm” to enter the
following screen.
Fig. 5-6
If the VCI was once used with other devices, you need to cancel the pairing
of the VCI rst via either one of the following ways:
• On the Android’s home screen, tap “Sengs” -> “Bluetooth” -> Choose
the desired VCI from the Paired list. Tap “ ”, and then tap “FORGET” to
unpair it.
• Go to “Toolbox“, tap “Settings” -> “VCI Management” -> “Deactivate
matching”.
In Fig. 5-6, tap “Scan” to start searching for the VCI and pairing up with it.
b).Camera: In this mode, you need to place the VIN inside the
viewnder rectangle to scan it.
Fig. 5-7
• If the ambient light is too weak, please turn the camera ash on.

22
Maximus 3.0 User's Manual
Fig. 5-9
Input the VIN, and tap “OK” to start decoding the vehicle VIN.
1. If the VIN can be found from the server database, a screen similar
to Fig. 5-10 displays:
Fig. 5-10
• Tap “Diagnostic” to start a new diagnostic session.
• Tap “Maintenance record” to view its historical repair record. If there
are records available, it will be listed on the screen in sequence of
date. If no records exist, the screen will show “No Record”.
Fig. 5-11
• Tap “View record” to view the details of the current diagnostic
report.
• To perform other functions, tap “Quick access” to directly go to the
function selection screen. Choose the desired one to start a new
diagnostic session.
2. If the handset failed to access the VIN information, the screen will
display as below:
Fig. 5-12
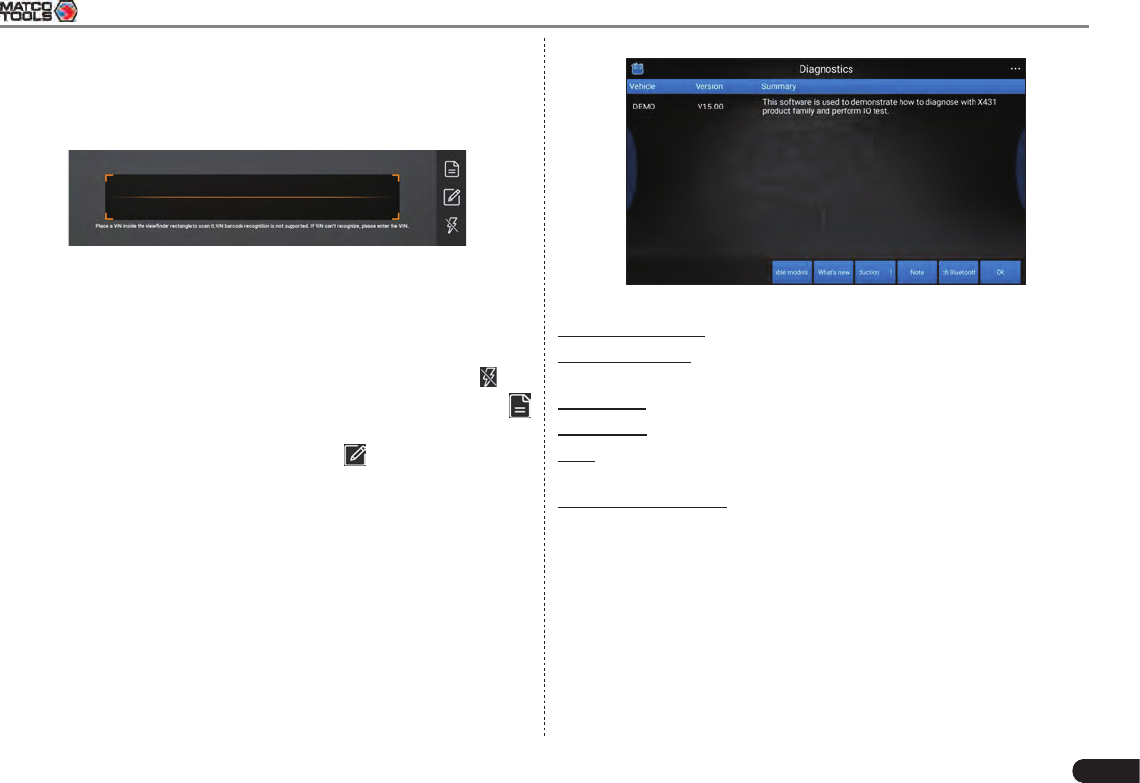
Maximus 3.0 User's Manual
23
• Tap “Diagnostic” to launch the Local Diagnosis module and start
a new diagnostic session. Refer to Chapter 5.3.2 for detailed
diagnostic operations.
• Tap “Scan VIN”, a screen similar to the following appears:
Fig. 5-13
Place the VIN inside the viewfinder rectangle to scan it. The most
recognizable location for this number is in the top left corner on the
vehicle’s dashboard. Other locations include the driver’s door or post,
and the rewall under the hood.
• If the ambient light is too weak, please turn the camera ash on.
• If you have scanned the VIN of the vehicle, tap VIN record icon
to select it from the record list.
• In case the handset failed to identify it, tap to enter it manually.
After scanning, the screen automatically displays the result.
• If the VIN scanned is incorrect, tap the result eld to modify it and
then tap “OK”. If the VIN exists on the remote server, the system
will enter the vehicle information screen.
• To scan it again, tap “REPEAT”.
5.3.2 Manual Diagnosis
Take Demo as an example to demonstrate how to diagnose a vehicle.
1). Select diagnostic software version: Tap the “DEMO” to go to Step
2. (*Note: If more than one version is available on this handset, it will be
listed on the screen.)
Fig. 5-14
On-screen Buttons:
Testable models: Tap to view the vehicle models that the current
diagnostic software covers.
What’s new: Tap to view the optimized items and enhancements.
Introduction: Tap to check the software function list.
Note: Tap to read some precautions on using the current diagnostic
software.
Search Bluetooth (BT): Tap to search for the available VCI dongle.
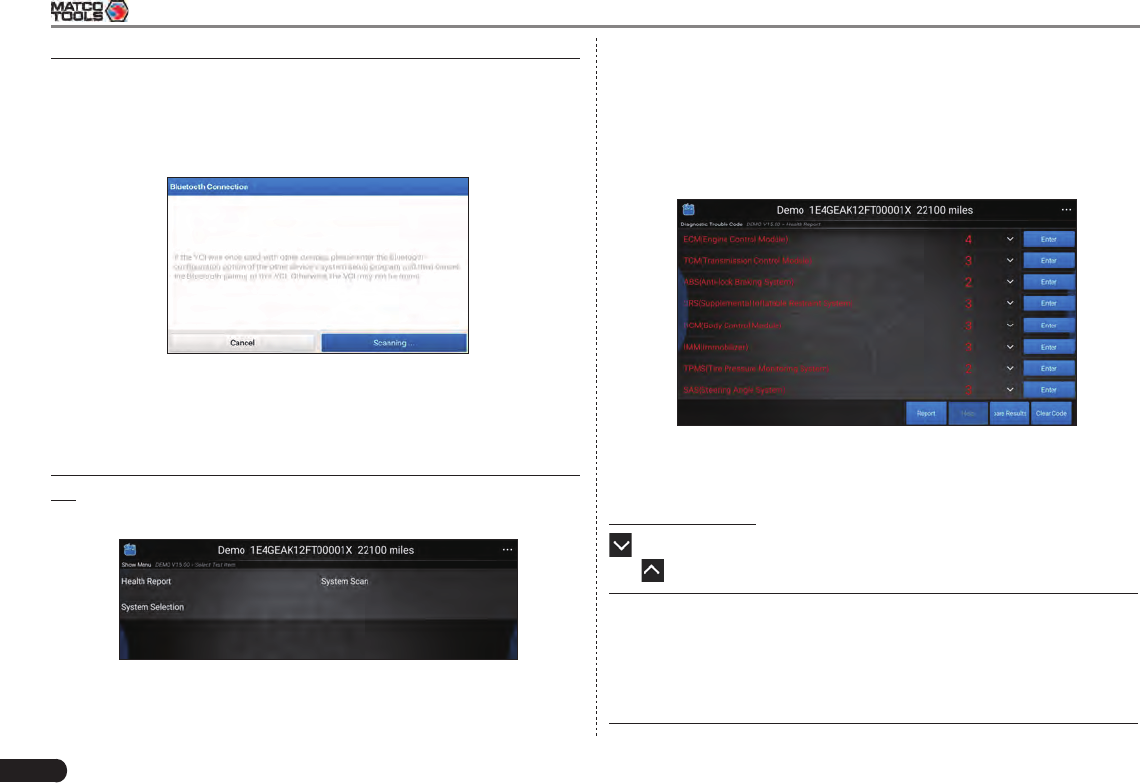
24
Maximus 3.0 User's Manual
*Notes:
• Bluetooth connecon is not required to run the DEMO program.
• If a vehicle is tested and no Bluetooth connection is made before
diagnosis, tap “Search Bluetooth”, a dialog box similar to the following
appears:
Fig. 5-15
Tap “Scan” to start searching for the VCI. Once it is found, tap it to start
pairing.
If the Maximus 3.0 handset has paired with the VCI, it will enter Step 2
directly.
OK: Tap it to go to next step.
2). Select test item: Select the desired test item to proceed.
Fig. 5-16
5.3.2.1 Health Report (Quick Test)
This function varies from vehicle to vehicle. It enables you to quickly
access all the electronic control units of the vehicle and generate a
detailed report about vehicle health.
Tap “Health Report” to scan the vehicle control modules. When
scanning is complete, the following screen appears.
Fig. 5-17
In Fig. 5-17, systems with fault code are displayed in red and systems
functioning normally are displayed in white.
On-screen Buttons:
: Tap to view detailed Diagnostic Trouble Codes (DTCs) information.
Tap to hide it.
*Note: Diagnostic Trouble Codes or Fault Codes can be used to identify
which engine systems or components that are malfunctioning. Never
replace a part based only on the DTC definition. Retrieving and using
DTCs for troubleshoong vehicle operaon is only one part of an overall
diagnosc strategy. Follow tesng procedures (in vehicle’s service manual),
instrucons and owcharts to conrm the locaons of the problem.
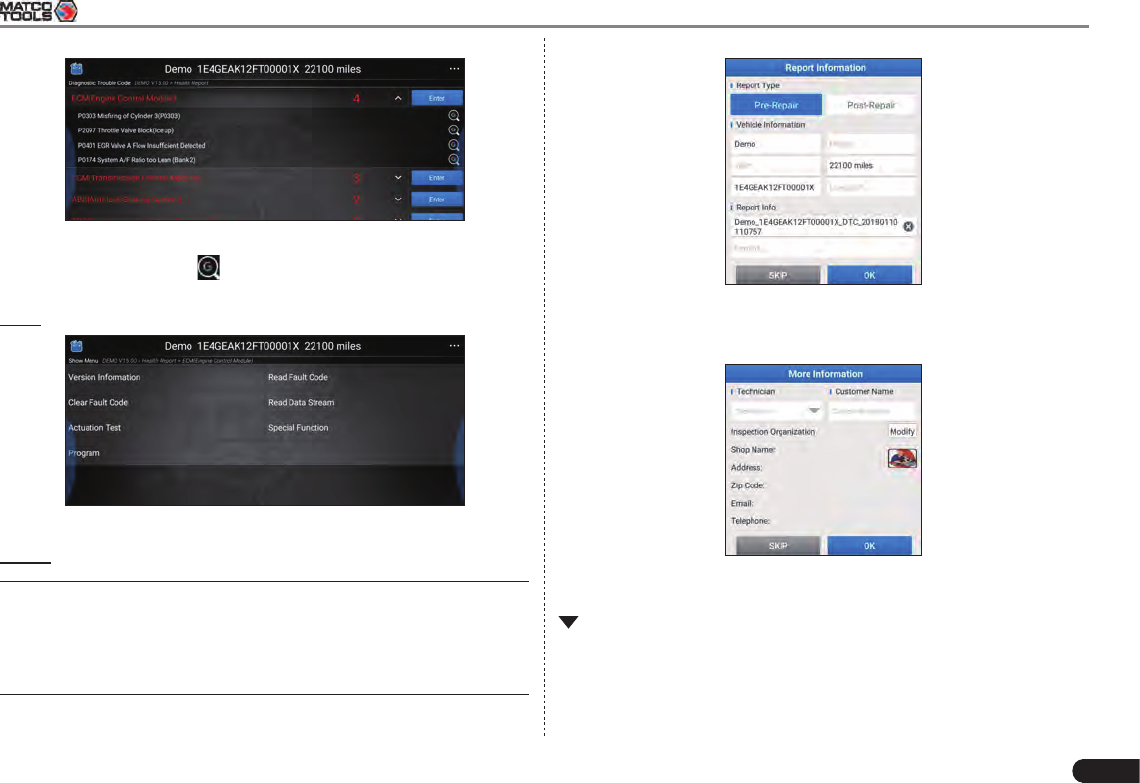
Maximus 3.0 User's Manual
25
Fig. 5-18
Highlight a DTC, and tap to search online for detailed information
about the selected DTC.
Enter: Tap to select other test functions.
Fig. 5-19
Report: Tap to save it as a report of the current data in text format.
*Note: Diagnosc report is classied into two categories: Pre-Repair report
and Post-Repair report.
To facilitate the comparison of the pre-repair and post-repair reports and
get accurate test result, please make sure you saved the right type of the
diagnosc report.
Fig. 5-20
Choose the report type and input the required information, and then
tap “OK”.
Fig. 5-21
Input the technician (*If you have entered the technician name before, tap
directly to select it from the pull-down list) and customer name and
then tap “OK” to conrm and navigate to the report details page.
For workshop information, tap “Modify” to revise it, then tap “Save”.
To skip the workshop information, tap “Skip” to go to the report details
page.
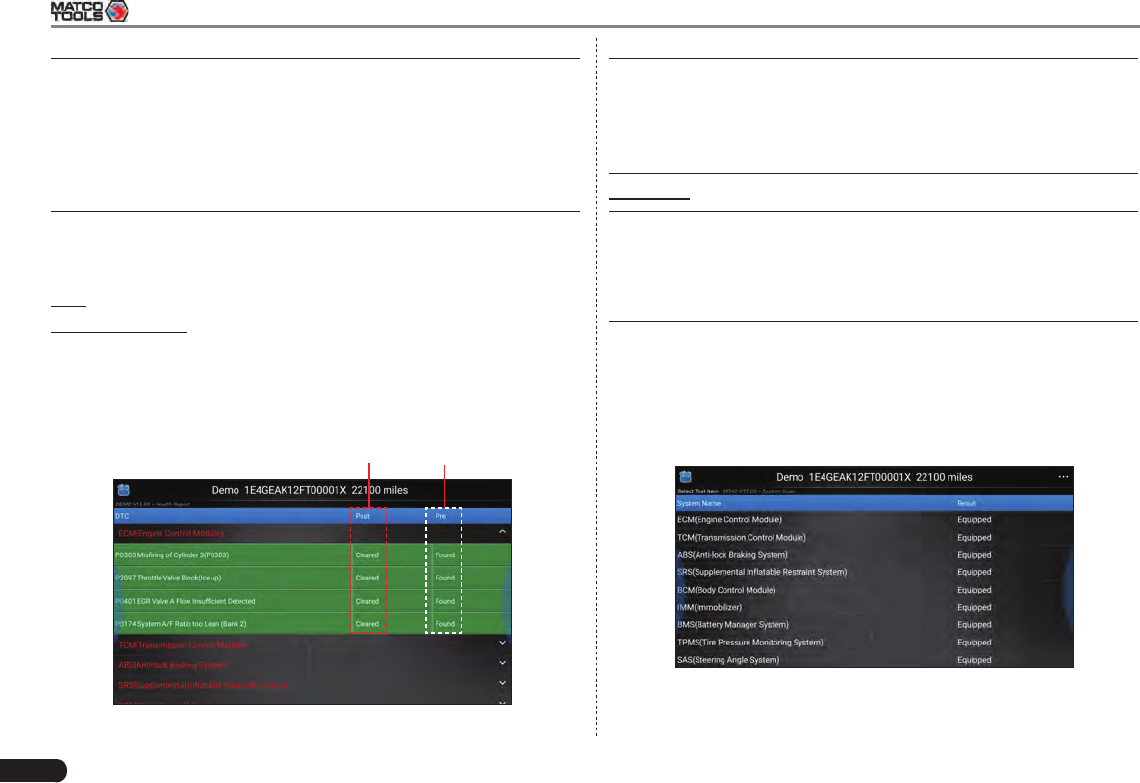
26
Maximus 3.0 User's Manual
*Note: Workshop information can also be revised from the “Print
Informaon” in “Toolbox” -> “Sengs”.
Once you configured the information, it will be automatically generated
every time the diagnostic report is saved. All vehicle and workshop
information will be appended as tags on the diagnostic report, which
allows you to easily retrieve the desired report while performing “Filter”
funcon of Diagnosc Report.
On the report details page, tap “Save” to save it. All diagnostic reports
can be accessed from “Toolbox” -> “Saved Reports” -> “Health
Report”.
Help: Tap to view the help information of the selected DTC item.
Compare Results: After you have made some repairs based on the
pre-repair diagnostic report and re-diagnose the vehicle, tap “Compare
Result” to select the pre-repair report to compare. By comparison of
the pre- and post- repair reports, you can easily identify which DTCs
are cleared and which remain unxed.
The DTC status
of post-repair
The DTC status
of pre-repair
Fig. 5-22
*Note: Before performing this funcon, please make sure that:
• You have saved a pre-repair report of the currently tested vehicle, and
• You have already made some repairs and service and cleared the DTCs
after the pre-repair reported is generated. Otherwise, no differences
exist between the pre- and post- repair reports.
Clear DTC: Tap to clear the existing diagnostic trouble codes.
*Note: Clearing DTCs does not x the problem(s) that caused the code(s)
to be set. If proper repairs to correct the problem that caused the code(s)
to be set are not made, the code(s) will appear again and the check engine
light will illuminate as soon as the problem that cause the DTC to set
manifests itself.
5.3.2.2 System Scan
Use this option to quickly scan and identify which systems are installed
on the vehicle.
In Fig. 5-16, tap “System Scan” to scan the vehicle control modules.
When scanning is complete, the following screen appears.
Fig. 5-23
Tap the desired system to navigate to the test function selection
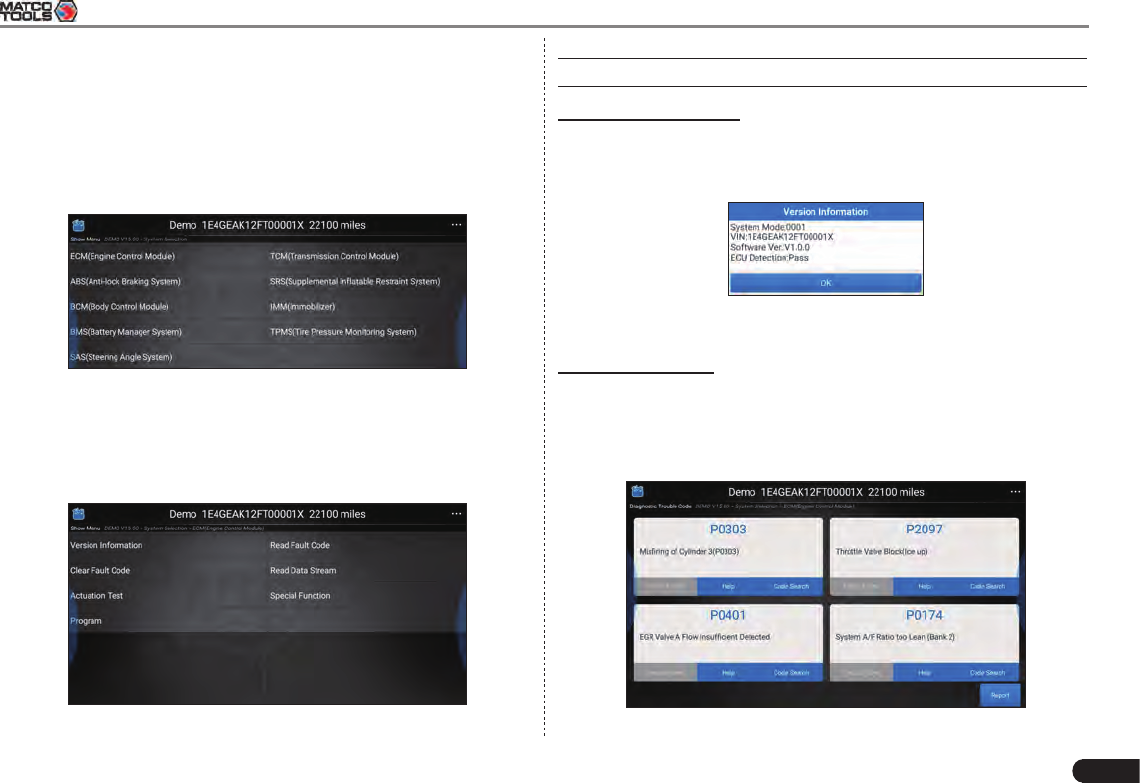
Maximus 3.0 User's Manual
27
screen. For detailed operations on test function, please refer to
Chapter 5.3.2.3.
5.3.2.3 System Selection
This option allows you manually select the test system and function
step by step.
In Fig. 5-16, tap “System Selection”, the screen displays as follows:
Fig. 5-24
Swipe the screen from the bottom to view the vehicle system on the
next page.
Tap the desired system (take “ECM” for example) to jump to the test
function page.
Fig. 5-25
*Note: Dierent vehicle has dierent diagnosc menus.
A. Version Information
This function is used to read the version information of system mode,
vehicle VIN, software and ECU.
In Fig. 5-25, tap “Version Information”, the screen displays as follows:
Fig. 5-26
Tap “OK” to conrm and exit.
B. Read Fault Code
This function displays the detailed information of DTC records
retrieved from the vehicle’s control system.
In Fig. 5-25, tap “Read Fault Code”, the screen will display the
diagnostic result.
Fig. 5-27
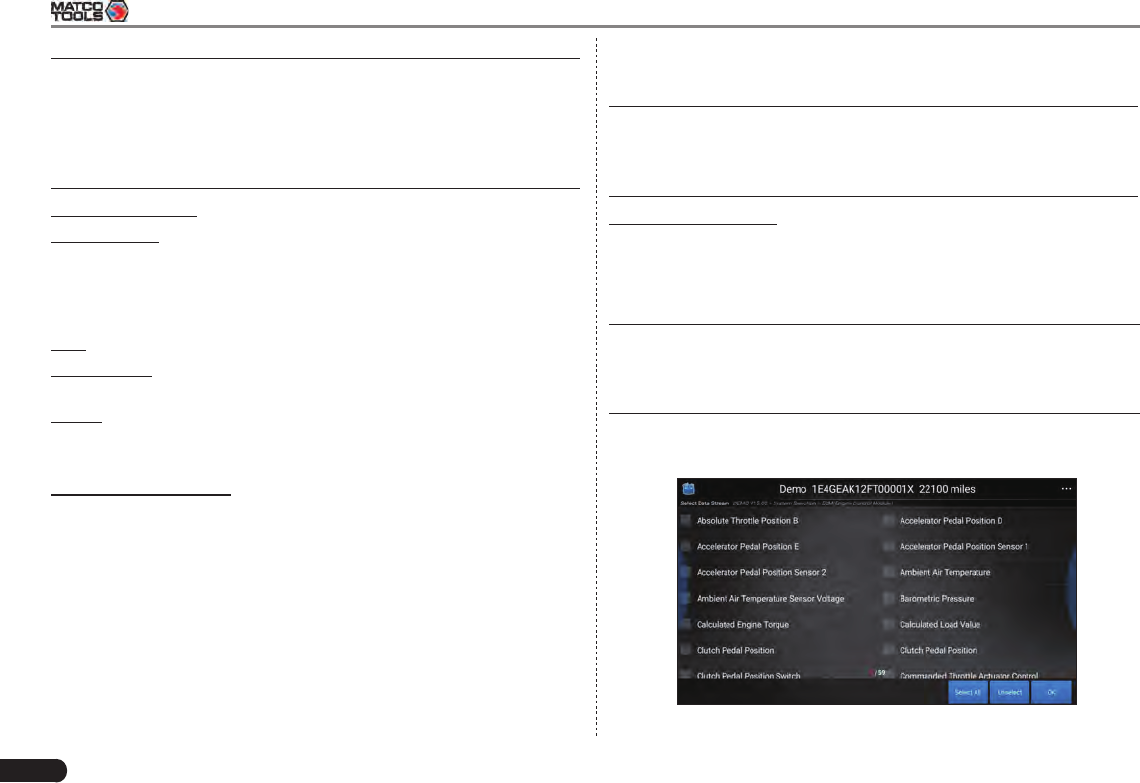
28
Maximus 3.0 User's Manual
*Note: Retrieving and using DTCs for troubleshooting vehicle operation
is only one part of an overall diagnostic strategy. Never replace a part
based only on the DTC denion. Each DTC has a set of tesng procedures,
instrucons and ow charts that must be followed to conrm the locaon
of the problem. This information can be found in the vehicle’s service
manual.
On-screen Buttons:
Freeze Frame: When an emission-related fault occurs, certain vehicle
conditions are recorded by the on-board computer. This information
is referred to as freeze frame data. Freeze frame data includes a
snapshot of critical parameter values at the time the DTC is set. If it is
illuminated, tap it to view the freeze frame data.
Help: Tap to view the help information.
Code Search: Tap it to search for more information about the current
DTC online.
Report: To save the current data in text format. All diagnostic reports
can be accessed from “Toolbox” -> “Saved Reports” -> “Health
Report”.
C. Clear Fault Memory
After reading the retrieved codes from the vehicle and certain repairs
have been carried out, you can use this function to erase the codes
from the vehicle. Before performing this function, please be sure the
vehicle’s ignition key is in the ON position with the engine off.
Clearing DTCs does not x the problem(s) that caused the code(s) to
be set. If proper repairs to correct the problem that caused the code(s)
to be set are not made, the code(s) will appear again and the check
engine light will illuminate as soon as the problem that cause the DTC
to set manifests itself.
In Fig. 5-25, tap “Clear Fault Memory”, a conrmation dialog box pops
up on the screen. Tap “Yes” and the system will automatically delete
the currently existing trouble code.
*Note: Aer clearing, you should retrieve trouble codes once more or turn
ignion on and retrieve codes again. If there are sll some trouble codes in
the system, please troubleshoot the code using a factory diagnosis guide,
then clear the code and recheck.
D. Read Data Stream
This option lets you view and capture (record) real-time Live Data.
This data including current operating status for parameters and/or
sensor information can provide insight on overall vehicle performance.
It can also be used to guide vehicle repair.
*Note: If you must drive the vehicle in order to perform a troubleshoong
procedure, ALWAYS have a second person help you. Trying to drive and
operate the diagnosc tool at the same me is dangerous, and could cause
a serious trac accident.
In Fig. 5-25, tap “Read Data Stream”, the system will display data
stream items.
Fig. 5-28
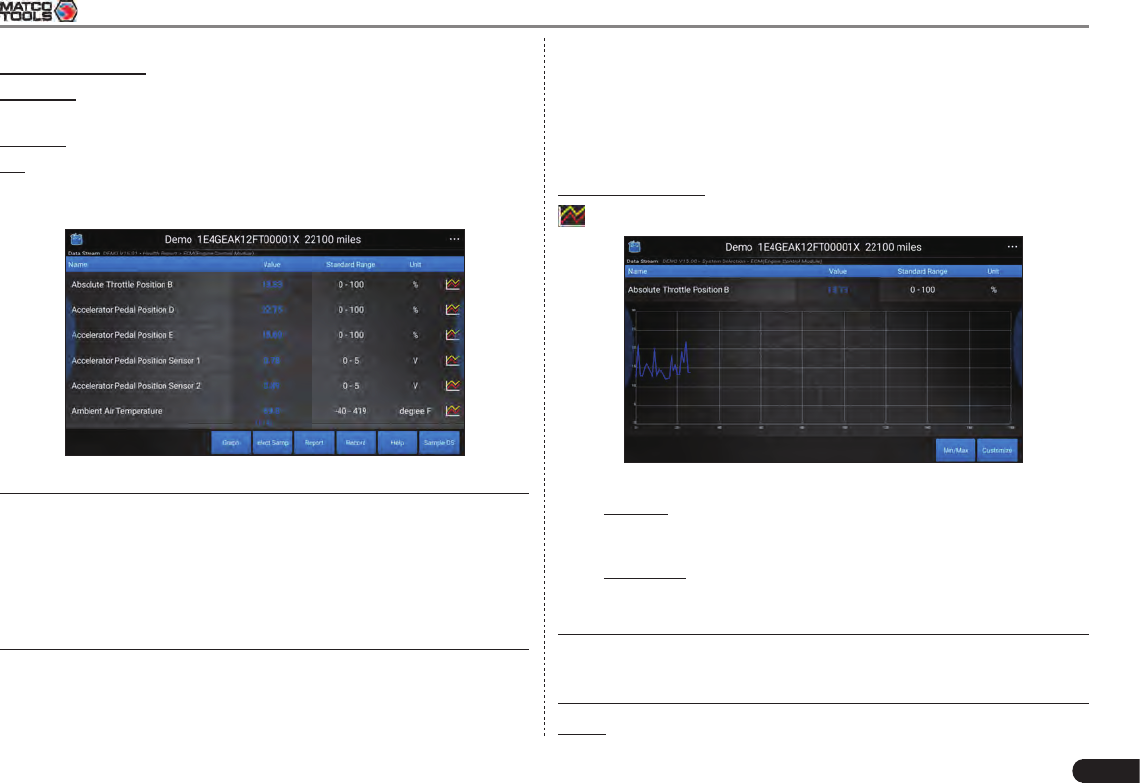
Maximus 3.0 User's Manual
29
On-screen Buttons:
Select All: Tap it to select all items of the current page. To select
certain data stream item, just check the box before the item name.
Unselect: Tap it to deselect all data stream items.
OK: Tap it to conrm and jump to the next step.
After selecting the desired items, tap “OK” to enter the data stream
reading page.
Fig. 5-29
*Notes:
1. If the value of the data stream item is out of the range of the standard
(reference) value, the whole line will display in red. If it complies with
the reference value, it displays in blue (normal mode).
2. The indicator 1/X shown on the bottom of the screen stands for the
current page/total page number. Swipe the screen from the right/le to
advance/return to the next/previous page.
There are 3 types of display modes available for data viewing, allowing
you to view various types of parameters in the most suitable way.
• Value – this is the default mode which displays the parameters in
texts and shows in list format.
• Graph – displays the parameters in waveform graphs.
• Combine – this option is mostly used in graph merge status for data
comparison. In this case, different items are marked in different
colors.
On-screen Buttons:
: Tap it to view the waveform graph of the current data stream item.
Fig. 5-30
• Min/Max: Tap “Min/Max” to dene the maximum/minimum value.
Once the value goes beyond the specied value, the system will
alarm.
• Customize: If desired, you can customize to show only those
PIDs you are interested in viewing. Tap “Customize” to add/
change other data stream items.
*Note: The real time (Live Data) vehicle operating information (values/
status) that the on-board computer supplies to the tool for each sensor,
actuator, switch, etc. is called Parameter Idencaon Data (IPD).
Graph: Tap it to view the waveform.
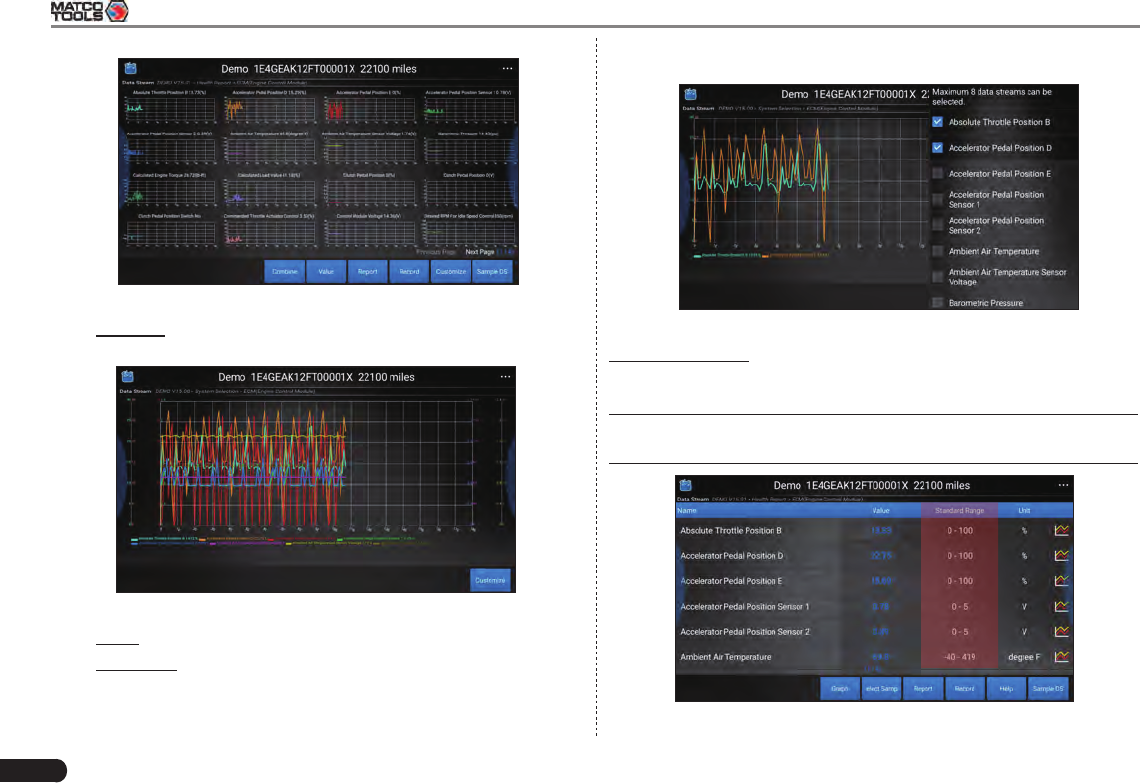
30
Maximus 3.0 User's Manual
Fig. 5-31
• Combine: This option is mostly used in graph merge status for
data comparison.
Fig. 5-32
• Value: Tap to display the parameters in texts.
• Customize: This option allows you to select only the PIDs that
you wish to display. Tap it, a pull-down list of the data stream
items appears on the screen. Select (Up to 8 data stream items
can be selected)/deselect the desired items and then screen will
display/remove the corresponding waveforms immediately.
Fig. 5-33
Select Sample DS: Tap it to select the sample DS le, the values you
customized and saved in process of DS sampling will be imported into
the “Standard Range”(See below) column for your comparison.
*Note: Before executing this function, you have to sample the values of
data stream items and save it as an sample DS le.
Fig. 5-34
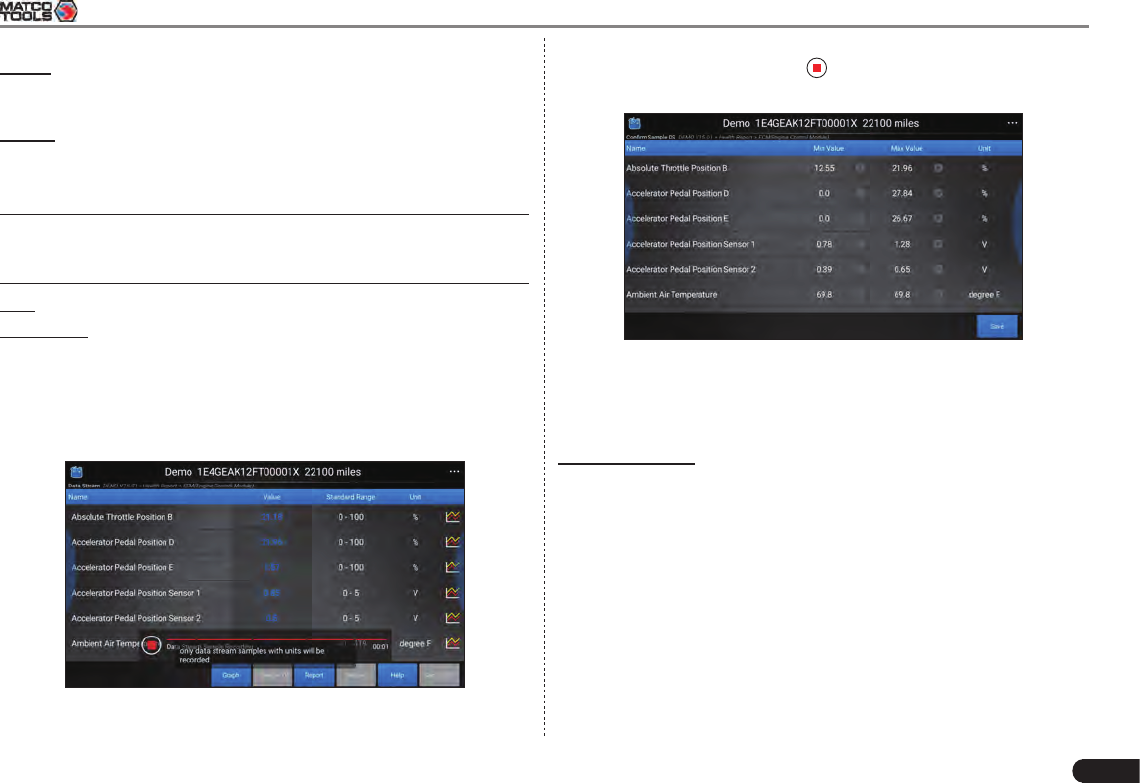
Maximus 3.0 User's Manual
31
Report: To save the current data as a diagnostic report. All diagnostic
reports can be accessed from “Toolbox” -> “Saved Reports” -> “Health
Report”.
Record: Tap to start recording diagnostic data. Recorded live data can
serve as valuable information to help you in troubleshooting of vehicle
problems. All diagnostic records can be replayed from “Toolbox” ->
“Saved reports” -> “Playback”.
*Note: The saved le follows the naming rule: It begins with vehicle type,
and then the record starting time and ends with .x431 (To differentiate
between les, please congure the accurate system me).
Help: Tap to view the help information.
Sample DS: This item enables you to customize the standard range
of live data stream items and save it as DS sample le. Each time you
run the data stream items, you can call out the corresponding sample
data to overwrite the current standard range.
Tap it to start recording the sample data (*Only data stream items with
units will be recorded), and the screen displays as below:
Fig. 5-35
Once recording is complete, tap to stop it and navigate to the data
revision screen.
Fig. 5-36
Tap the Min./Max. value to change it. After modifying all desired items,
tap “Save” to save it as an sample DS le. All DS les are stored under
the “Data Stream Sample” le of “Settings” in “Toolbox”.
E. Actuation Test
This option is used to access vehicle-specific subsystem and
component tests. Available test vary by vehicle manufacturer, year,
and model. During the actuation test, the Maximus 3.0 handset
outputs commands to the ECU in order to drive the actuators, and
then determines the integrity of the system or parts by reading the
ECU data, or by monitoring the operation of the actuators, such as
switching a injector between two operating states.
In Fig. 5-25, tap “Actuation Test”, the system will display as follows:
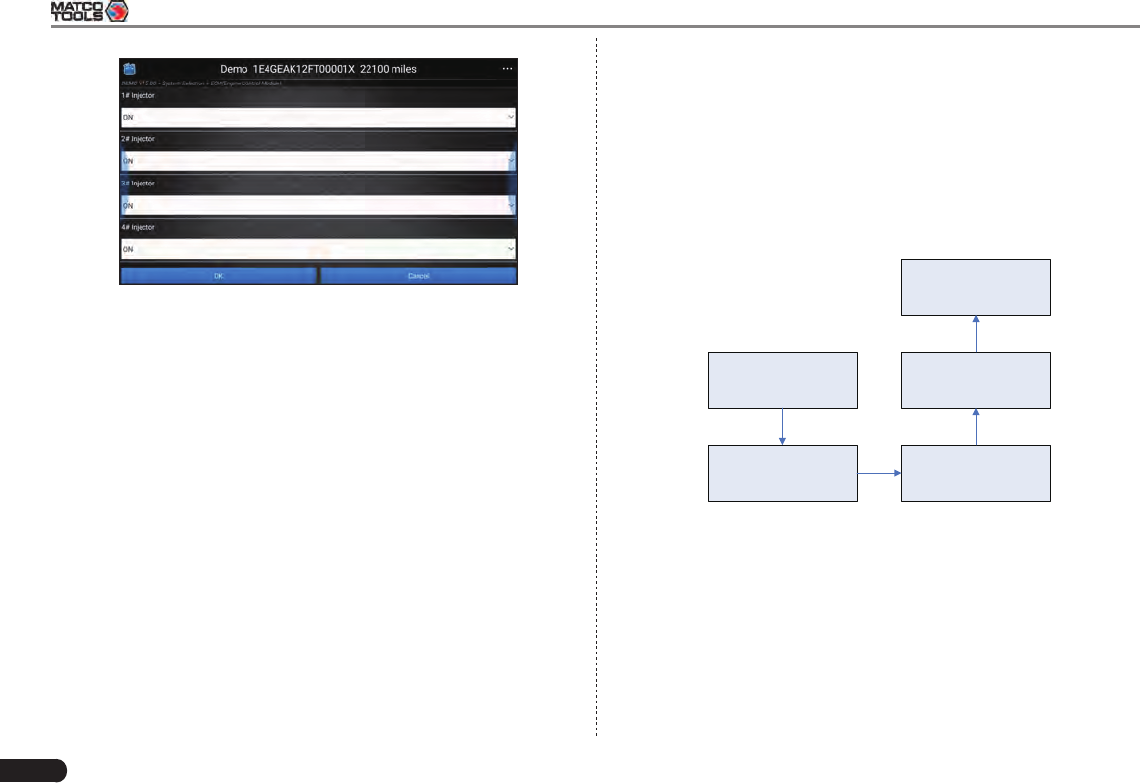
32
Maximus 3.0 User's Manual
Fig. 5-37
Simply follow the on-screen instructions and make appropriate
selections to complete the test. Each time when an operation is
successfully executed, “Completed” displays.
5.4 Maintenance Reset
In addition to amazing & powerful diagnostic function, Maximus 3.0
also features various service functions. The most commonly performed
service functions contain:
• Oil Reset Service
• Electronic Parking Brake Reset
• Steering Angle Calibration
• ABS Bleeding
• TPMS (Tire Pressure Monitor System) Reset
• Gear Learning
• IMMO Service
• Injector Coding
• Battery Maintenance System
• Diesel Particulate Filter (DPF) Regeneration
• Electronic Throttle Position Reset
There are two methods to reset service lamp: Manual reset or Auto
reset. Auto reset follows the principle of sending command from the
tool to vehicle’s ECU to do resetting. While using manual reset, users
just follow the on-screen instructions to select appropriate execution
options, enter correct data or values, and perform necessary actions,
the system will guide you through the complete performance for
various service operations.
Select “Reset”
Select the desired reset
item (e.g. oil lamp reset
etc.) Select the car brand
Select the service mode
(The available mode varies
from vehicle to vehicle)
Follow the instructions
on the screen to operate
Figure 5-38
5.4.1 Oil Reset Service
This function allows you to perform reset for the engine oil life system,
which calculates an optimal oil life change interval depending on the
vehicle driving conditions and climate.
This function can be performed in the following cases:
1. If the service lamp is on, you must provide service for the car. After
service, you need to reset the driving mileage or driving time so that
the service lamp turns off and the system enables the new service
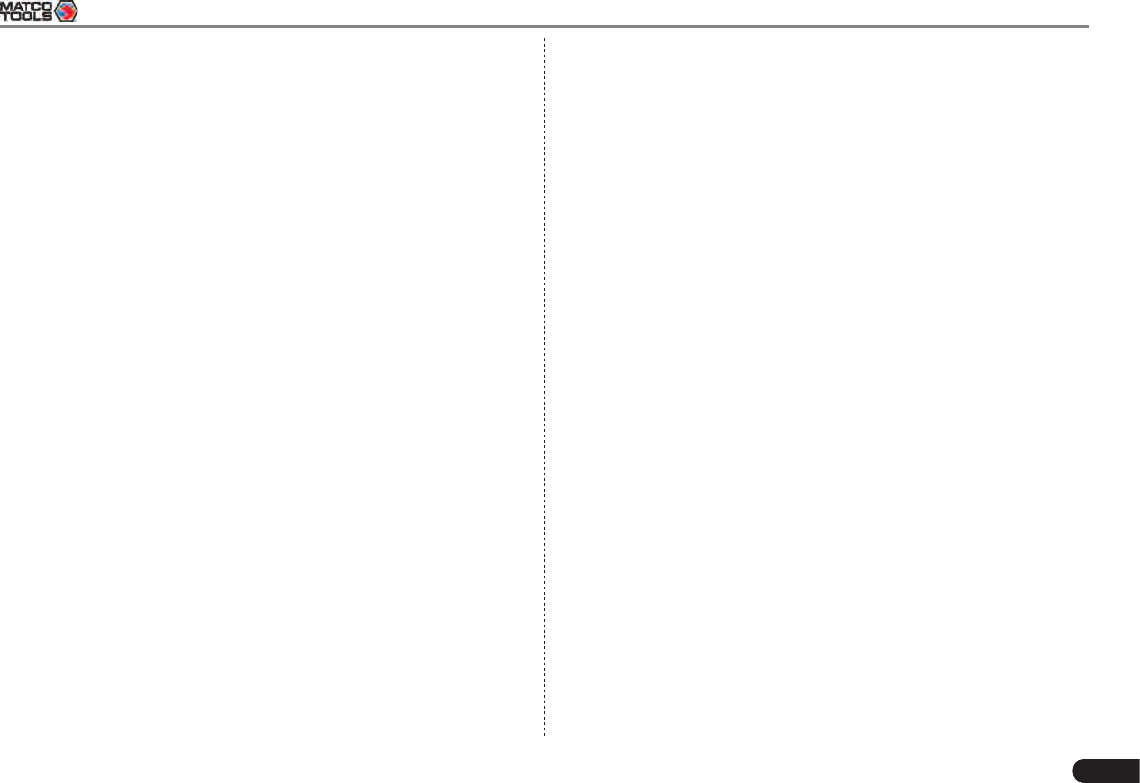
Maximus 3.0 User's Manual
33
cycle.
2. After changing engine oil or electric appliances that monitor oil life,
you need to reset the service lamp.
5.4.2 Electronic Parking Brake Reset
1. If the brake pad wears the brake pad sense line, the brake pad
sense line sends a signal sense line to the on-board computer to
replace the brake pad. After replacing the brake pad, you must
reset the brake pad. Otherwise, the car alarms.
2. Reset must be performed in the following cases:
a) The brake pad and brake pad wear sensor are replaced.
b) The brake pad indicator lamp is on.
c) The brake pad sensor circuit is short, which is recovered.
d) The servo motor is replaced.
5.4.3 Steering Angle Calibration
To reset the steering angle, rst nd the relative zero point position for
the car to drive in straight line. Taking this position as reference, the
ECU can calculate the accurate angle for left and right steering.
After replacing the steering angle position sensor, replacing steering
mechanical parts (such as steering gearbox, steering column, end tie
rod, steering knuckle), performing four-wheel alignment, or recovering
car body, you must reset the steering angle.
5.4.4 ABS Bleeding
This function allows you to perform various bi-directional tests to check
the operating conditions of Anti-lock Braking System (ABS).
1. When the ABS contains air, the ABS bleeding function must
be performed to bleed the brake system to restore ABS brake
sensitivity.
2. If the ABS computer, ABS pump, brake master cylinder, brake
cylinder, brake line, or brake fluid is replaced, the ABS bleeding
function must be performed to bleed the ABS.
5.4.5 Tire Pressure Monitor System Reset
This function allows you to quickly look up the tire sensor IDs from the
vehicle’s ECU, as well as to perform TPMS replacement and sensor
test.
1. After the tire pressure MIL turns on and maintenance is performed,
the tire pressure resetting function must be performed to reset tire
pressure and turn off the tire pressure MIL.
2. Tire pressure resetting must be performed after maintenance is
performed in the following cases: tire pressure is too low, tire leaks,
tire pressure monitoring device is replaced or installed, tire is
replaced, tire pressure sensor is damaged, and tire is replaced for
the car with tire pressure monitoring function.
5.4.6 Gear Learning
The crankshaft position sensor learns crankshaft tooth machining
tolerance and saves to the computer to more accurately diagnose
engine misres. If tooth learning is not performed for a car equipped
with Delphi engine, the MIL turns on after the engine is started. The
diagnostic device detects the DTC P1336 ‘tooth not learned’. In this
case, you must use the diagnostic device to perform tooth learning for
the car. After tooth learning is successful, the MIL turns off.
After the engine ECU, crankshaft position sensor, or crankshaft
ywheel is replaced, or the DTC ‘tooth not learned’ is present, tooth
learning must be performed.
5.4.7 IMMO Service
An immobilizer is an anti-theft mechanism that prevents a vehicle’s
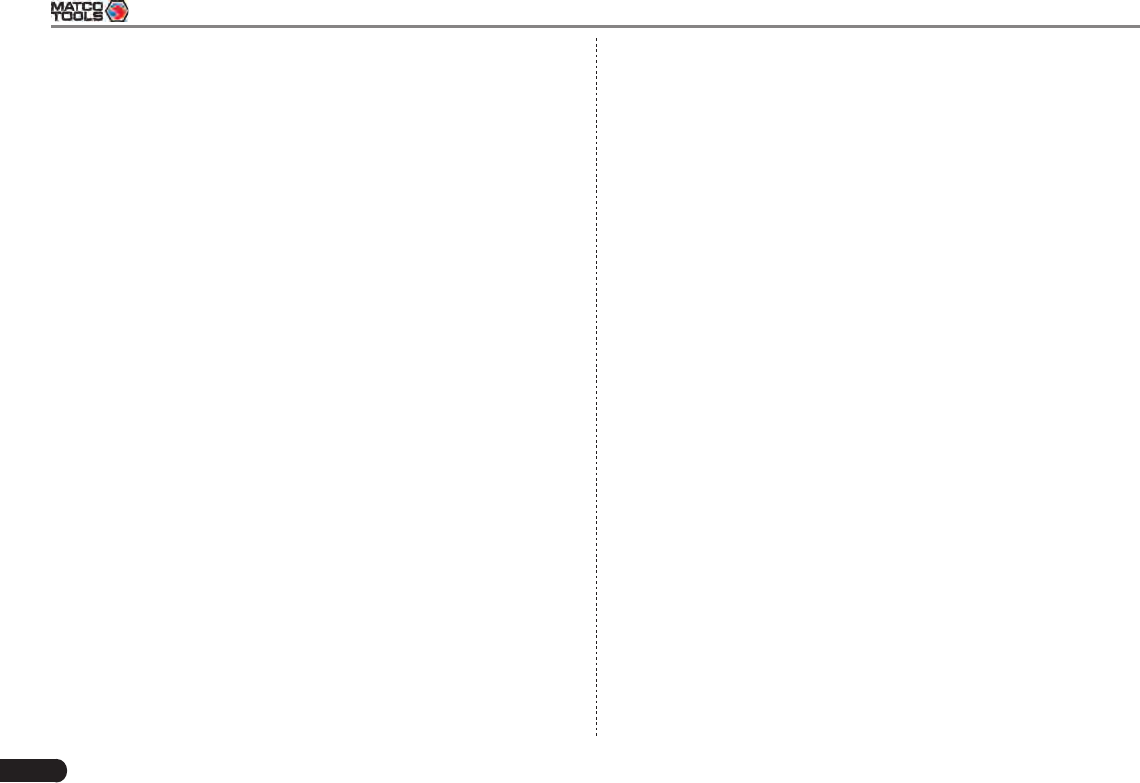
34
Maximus 3.0 User's Manual
engine from starting unless the correct ignition key or other device
is present. Most new vehicles have an immobilizer as standard
equipment. An important advantage of this system is that it doesn’t
require the car owner to activate it since it operates automatically. An
immobilizer is considered as providing much more effective anti-theft
protection than an audible alarm alone.
As an anti-theft device, an immobilizer disables one of the systems
needed to start a car’s engine, usually the ignition or the fuel supply.
This is accomplished by radio frequency identification between a
transponder in the ignition key and a device called a radio frequency
reader in the steering column. When the key is placed in the ignition,
the transponder sends a signal with a unique identication code to the
reader, which relays it to a receiver in the vehicle’s computer control
module. If the code is correct, the computer allows the fuel supply and
ignition systems to operate and start the car. If the code is incorrect or
absent, the computer disables the system, and the car will be unable
to start until the correct key is placed in the ignition.
To prevent the car being used by unauthorized keys, the anti-theft key
matching function must be performed so that the immobilizer control
system on the car identifies and authorizes remote control keys to
normally use the car.
When the ignition switch key, ignition switch, combined instrument
panel, ECU, BCM, or remote control battery is replaced, anti-theft key
matching must be performed.
5.4.8 Injector Coding
Write injector actual code or rewrite code in the ECU to the injector
code of the corresponding cylinder so as to more accurately control or
correct cylinder injection quantity.
After the ECU or injector is replaced, injector code of each cylinder
must be conrmed or re-coded so that the cylinder can better identify
injectors to accurately control fuel injection.
5.4.9 Battery Maintenance System Reset
This function enables you to perform a resetting operation on the
monitoring unit of vehicle battery, in which the original low battery fault
information will be cleared and battery matching will be done.
Battery matching must be performed in the following cases:
a) Main battery is replaced. Battery matching must be performed to
clear original low battery information and prevent the related control
module from detecting false information. If the related control
module detects false information, it will invalidate some electric
auxiliary functions, such as automatic start & stop function, sunroof
without one-key trigger function, power window without automatic
function.
b) Battery monitoring sensor. Battery matching is performed to re-
match the control module and motoring sensor to detect battery
power usage more accurately, which can avoid an error message
displaying on the instrument panel.
5.4.10 Diesel Particulate Filter (DPF) Regeneration
DPF regeneration is used to clear PM (Particulate Matter) from the
DPF filter through continuous combustion oxidation mode (such as
high temperature heating combustion, fuel additive or catalyst reduce
PM ignition combustion) to stabilize the lter performance.
DPF regeneration may be performed in the following cases:
a) The exhaust back pressure sensor is replaced.
b) The PM trap is removed or replaced.
c) The fuel additive nozzle is removed or replaced.
d) The catalytic oxidizer is removed or replaced.
e) The DPF regeneration MIL is on and maintenance is performed.
f) The DPF regeneration control module is replaced.
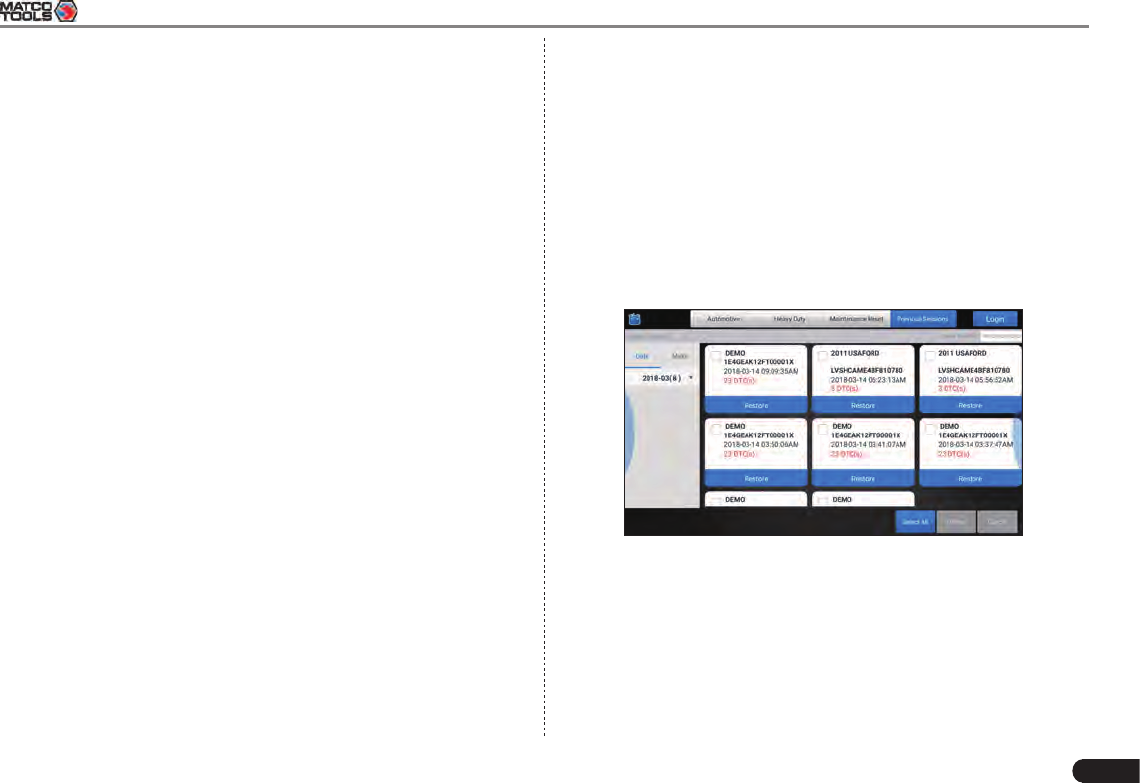
Maximus 3.0 User's Manual
35
5.4.11 Electronic Throttle Position Reset
This function enables you to make initial settings to throttle actuators
and returns the “learned” values stored on ECU to the default state.
Doing so can accurately control the actions of regulating throttle (or
idle engine) to adjust the amount of air intake.
5.4.12 Gearbox Matching
1. This function can complete the gearbox self-learning to improve
gear shifting quality.
2. When the gearbox is disassembled or repaired (after some of
the car battery is powered off), it will lead to shift delay or impact
problem. In this case, this function needs to be done so that the
gearbox can automatically compensate according to the driving
conditions so as to achieve more comfortable and better shift
quality.
5.4.13 AFS (Adaptive Front-lighting System) Reset
This feature is used to initialize the adaptive headlamp system.
According to the ambient light intensity, the adaptive headlamp system
may decide whether to automatically turn on the headlamps, and
timely adjust the headlamp lighting angle while monitoring the vehicle
speed and body posture.
5.4.14 Sunroof Initialization
This function can set the sunroof lock off, closed when it rains, sliding /
tilting sunroof memory function, temperature threshold outside the car
etc.
5.4.15 Suspension Calibration
1. This function can adjust the height of the body.
2. When replacing the body height sensor in the air suspension
system, or control module or when the vehicle level is incorrect,
you need to perform this function to adjust the body height sensor
for level calibration.
5.5 Diagnostic History (Previous Session)
Generally once a vehicle diagnosis is performed, Maximus 3.0 will
record the every details of diagnostic process. The History function
provides a quick access to the tested vehicles and users can resume
from the last operation, without the necessity of starting from scratch.
Tap “Previous Session”, all diagnostic records will be listed on the
screen in date sequence.
Fig. 5-39
• Tap certain vehicle model to view the details of the last diagnostic
report.
• To delete certain diagnostic history, select it and then tap “Delete”.
To delete all historical records, tap “Select All” and then tap “Delete”.
• Tap “Restore” to directly navigate to the function selection page of
last diagnostic operation. Choose the desired option to proceed.
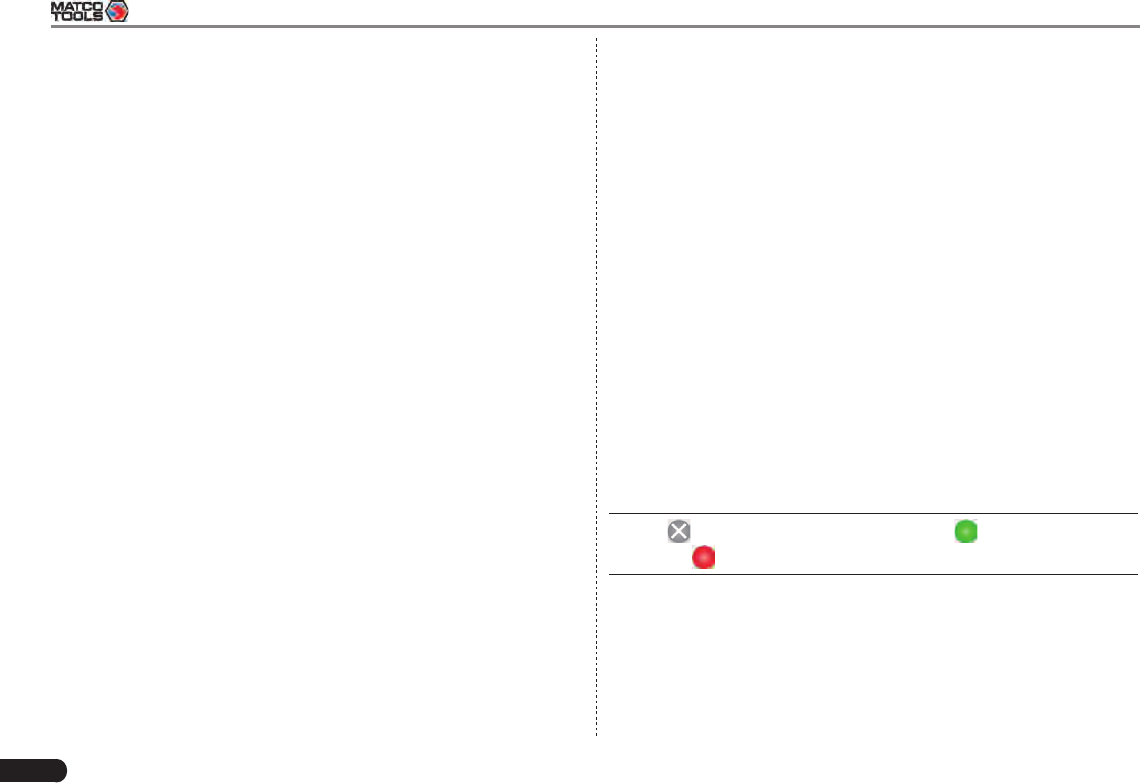
36
Maximus 3.0 User's Manual
5.6 I/M Readiness
An important part of a vehicle’s OBD II system is the Readiness
Monitors, which are indicators used to nd out if all of the emissions
components have been evaluated by the OBD II system. They are
running periodic tests on specic systems and components to ensure
that they are performing within allowable limits.
Currently, there are eleven OBD II Readiness Monitors (or I/M
Monitors) defined by the U.S. Environmental Protection Agency
(EPA). Not all monitors are supported in every vehicles and the exact
number of monitors in any vehicle depends on the motor vehicle
manufacturer’s emissions control strategy.
Continuous Monitors -- Some of the vehicle components or systems
are continuously tested by the vehicle’s OBD II system, while others
are tested only under specific vehicle operating conditions. The
continuously monitored components listed below are always ready:
1. Misre
2. Fuel System
3. Comprehensive Components (CCM)
Once the vehicle is running, the OBD II system is continuously
checking the above components, monitoring key engine sensors,
watching for engine misre, and monitoring fuel demands.
Non-Continuous Monitors -- Unlike the continuous monitors, many
emissions and engine system components require the vehicle to be
operated under specic conditions before the monitor is ready. These
monitors are termed non-continuous monitors and are listed below:
1) EGR System
2) O2 Sensors
3) Catalyst
4) Evaporative System
5) O2 Sensor Heater
6) Secondary air Injection
7) Heated Catalyst
8) A/C system
I/M refers to Inspection and Maintenance that is legislated by the
Government to meet federal clean-air standards. I/M Readiness
indicates whether or not the various emissions-related systems on
the vehicle are operating properly and are ready for Inspection and
Maintenance testing.
The purpose of the I/M Readiness Monitor Status is to indicate which
of the vehicle’s Monitors have run and completed their diagnosis
and testing, and which ones have not yet run and completed testing
and diagnosis of their designated sections of the vehicle’s emissions
system.
The I/M Readiness Monitor Status function also can be used (after
repair of a fault has been performed) to confirm that the repair has
been performed correctly, and/or to check for Monitor Run Status.
Tap [I/M Readiness] on the Diagnostics main menu screen to start
checking. After checking all I/M readiness status, the screen will output
the result.
*Note: means not available on this vehicle, means incomplete or
not ready, means Completed or Monitor Ok.
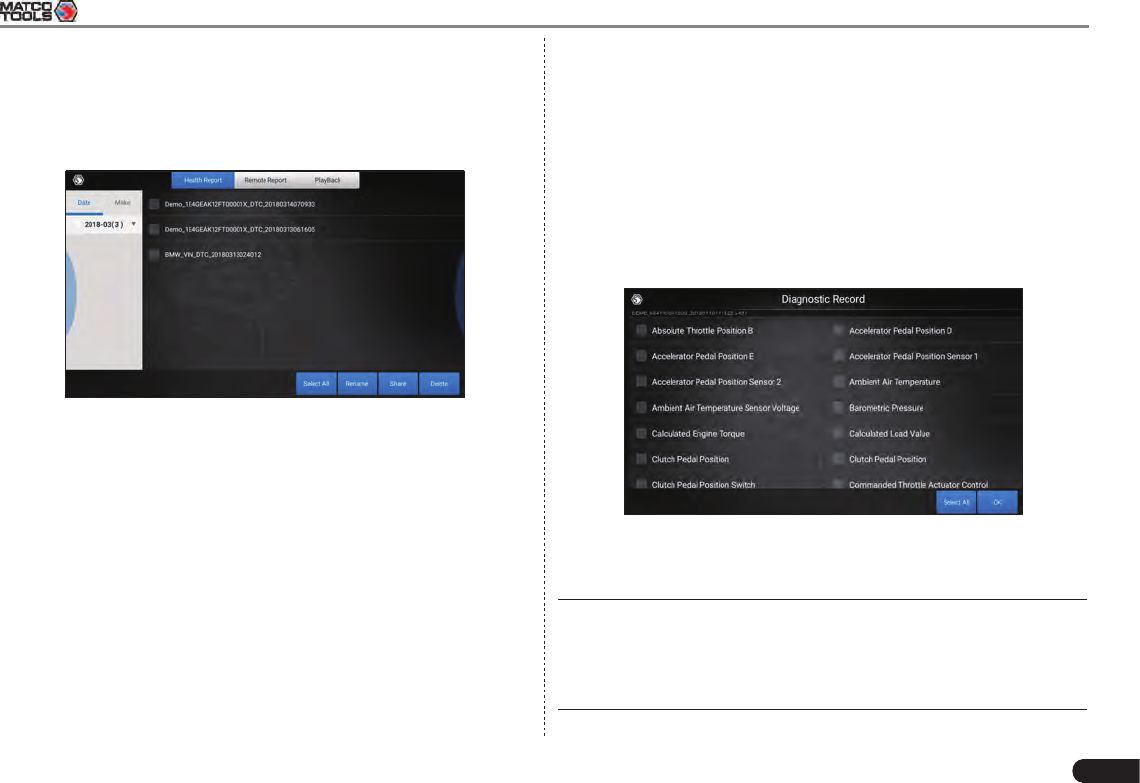
Maximus 3.0 User's Manual
37
6 Toolbox
6.1 Saved Reports
Tap “Saved Reports”, a screen similar to the following appears.
Fig. 6-1
6.1.1 Health Report
This module stores all diagnostic reports generated in process of
vehicle diagnosis.
All the diagnostic reports are sorted by Date and Make. Tap the
desired type to re-arrange and lter it.
• To select certain report, check the box before the report. To select
all reports, tap “Select All”. To deselect all, tap “Unselect”.
• To revise the lename of the report, select the desired one and tap
“Rename”.
• To share the report with others, select the desired one and then tap
“Share”.
• Select the desired report and then tap “Delete” to delete it.
6.1.2 Remote Report
This option lists all diagnostic reports generated in process of remote
diagnostics.
6.1.3 Playback
If user records the running parameters or waveform graphs while
reading data stream, it will be saved as diagnostic records and appear
under this tab. You can use this option to view recorded live data.
Frame playback and auto playback are supported.
Tap “Playback”, and select certain diagnostic record to enter:
Fig. 6-2
Select the desired data stream items and tap “OK” to jump to the
playback page:
*Note: While viewing recorded live data, carefully look for any irregularies
in any of the PID values/signal informaon (TEMP, RPM, etc). If any PIDs
go beyond the standard range value, or irregularies are detected, follow
the procedures in the vehicle’s service manual to perform additional
troubleshoong and repair.
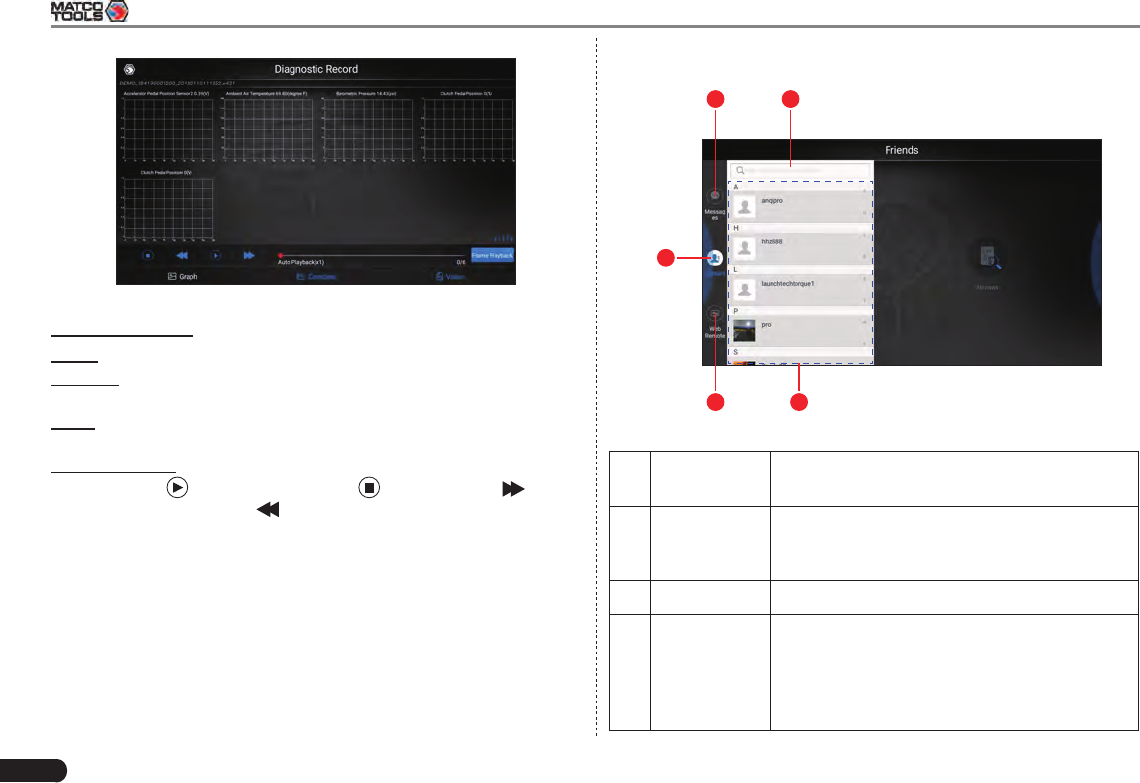
38
Maximus 3.0 User's Manual
Fig. 6-3
On-screen Buttons:
Graph – Displays the parameters in waveform graphs.
Combine – This option is mostly used in graph merge status for data
comparison. In this case, different items are marked in different colors.
Value – This is the default mode which displays the parameters in
texts and shows in list format.
Frame Playback – Plays back the recorded data stream items frame
by frame. Tap to start playing. Tap to stop it. Tap to fast
forward to next frame. Tap to reverse to previous frame. Once it is
in frame playback mode, this button changes into “Auto Playback”.
6.2 Tech-To-Tech
This option aims to help repair shops or technicians launch instant
messaging and remote diagnosis, making the vehicle (even thousands
of miles away) repair job getting xed faster.
6.2.1 Interface Layout
21
5
4 3
Fig. 6-4
1 Message tab Once an incoming message reaches, a red dot
will appear on the upper right corner of the tab.
2 Search bar Directly input the username of the Maximus 3.0
to start searching, and then tap the desired one
to add it into your friend list.
3 Friends List By default, the screen appears blank.
4WEB Remote
switch
Tap to slide the switch to ON, the Maximus 3.0
keeps online and becomes visible on the web
client. In this case, inform the technician of
your product S/N, and he/she will control your
Maximus 3.0 remotely.
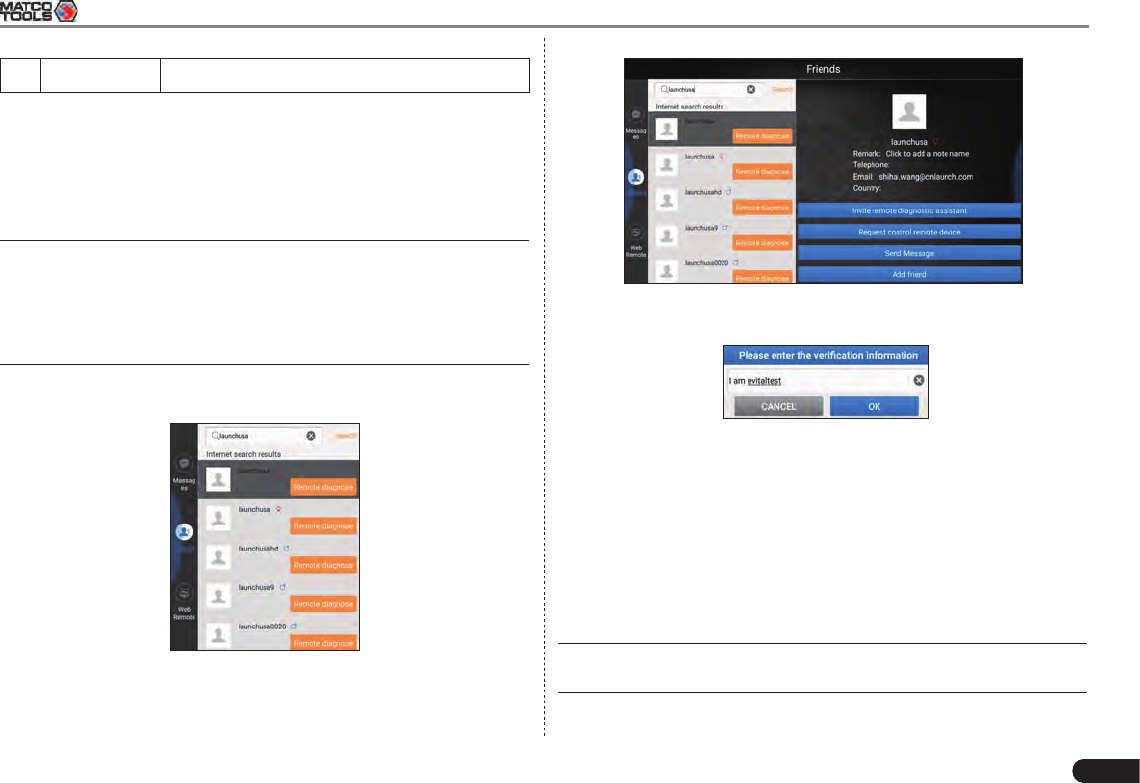
Maximus 3.0 User's Manual
39
5 Contact tab Tap to enter the friend list.
6.2.2 Add Friends
Tap “Contact” to enter the contact page. By default it appears blank.
In the search bar, input the partner’s username and tap “Search”
button next to the search bar to starts searching from Launch’s golo
business database.
*Note: The partner must be the users who have registered their Launch’s
diagnosc tools. They may be the following:
• Workshop
• Technician
• golo users
Once the result matches the keyword, a screen similar to the following
will appear:
Fig. 6-5
Tap “Remote Diagnose”, a dialog box pops up:
Fig. 6-6
Tap “Add friend” to send your request.
Fig. 6-7
Once the partner receives the request, a beep will sound. Tap the
“Message” tab:
• Once the partner agreed your request, he/she will automatically be
listed in the Contact tab.
• If a counterpart sent you a friend request, you can tap “Agree” to
conrm and his/her name will appear in the friend list (Contact). Or
tap “Ignore” to ignore this request.
6.2.3 Start Instant Messaging
*Note: The I/M (Instant Messaging) funcon is open to all users who had
Launch’s diagnosc tool equipped with this module.
After adding your friends, tap the desired fellow technician’s photo to
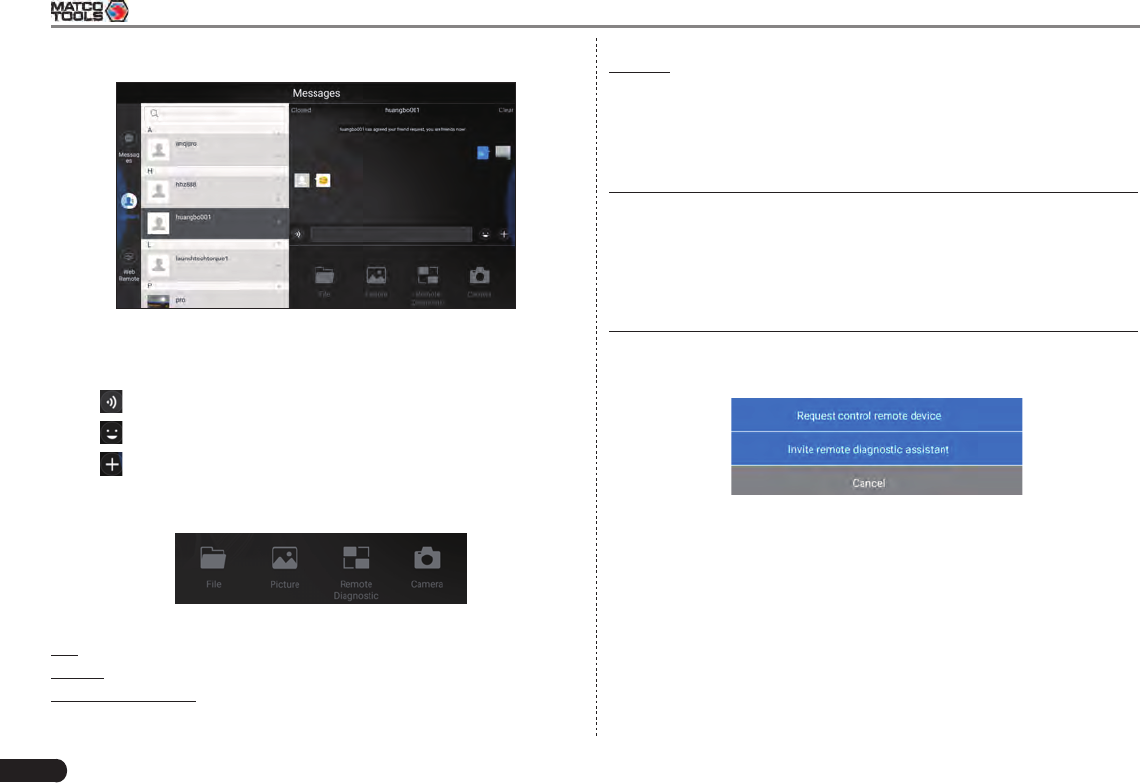
40
Maximus 3.0 User's Manual
enter a screen similar to the following:
Fig. 6-8
Tap the input eld and use the on-screen keyboard to enter the text
message, and then tap “Send” to send it.
• Tap to send the voice message.
• Tap to send the emoj.
• Tap to call out more function options.
• Tap “Clear” to delete all the partner’s dialog logs.
• Tap “Close” to close the current dialog.
Fig. 6-9
File: Choose diagnostic reports or local les to send.
Picture: Choose screenshots or pictures to send.
Remote Diagnostic: To start a remote diagnostic session. For details,
refer to Chapter 6.2.4.
Camera: Open camera to take pictures.
6.2.4 Launch Remote Diagnosis (Device-To-Device)
The Maximus 3.0 handset is allowed to initiate remote diagnosis with
other diagnostic tools (including but not limited to the Maximus 3.0) of
Launch family, which are equipped with this module.
* Notes: Before performing this operaon, please make sure the following
condions are met no maer which side sends the remote request:
• Turn on the vehicle power supply.
• Throle should be in a closed posion.
• The Maximus 3.0 should be properly connected to the vehicle’s DLC and
a successful communicaon is required.
In Fig. 6-9, tap “Remote Diagnostic”, a pull-down menu including the
following options appears:
Fig. 6-10
These options are dened as follows:

Maximus 3.0 User's Manual
41
Actions Results
Request control
remote device
Request to control the partner’s device
remotely to help him diagnose the vehicle.
*Notes:
• Remote diagnosis has the same diagnostic
steps as manual diagnosis.
• In process of remote diagnosis, tap the
buon to send a voice message.
• Once vehicle diagnosis is complete, a report
will be created. Input your comments on this
report, and then tap “Send Report” to send it
to the partner.
• If you have a local vehicle diagnosis in process,
please exit it first before starting remote
diagnosis.
Tap “Request control remote device”
Wait for partner’s confirmation
Start connecting after request confirmed
Start Diagnosis
Generate diagnostic report
Invite remote
diagnostic assistant
If you need support, just use this option
to invite a technician to perform a remote
control on your tool.
*Notes:
• Remote diagnosis has the same diagnosc
steps as manual diagnosis.
• In process of remote diagnosis, tap the
buon to send voice message.
• Once you received the report from the
partner, tap “View Report” to view details.
All diagnosc reports are saved “Toolbox” ->
“Saved Reports” -> “Remote Reports”.
Tap “Invite remote diagnostic assistant”
Choose the desired diagnostic software
Wait for partner’s confirmation
Start connecting after request confirmed
Start Diagnosis
Generate diagnostic report
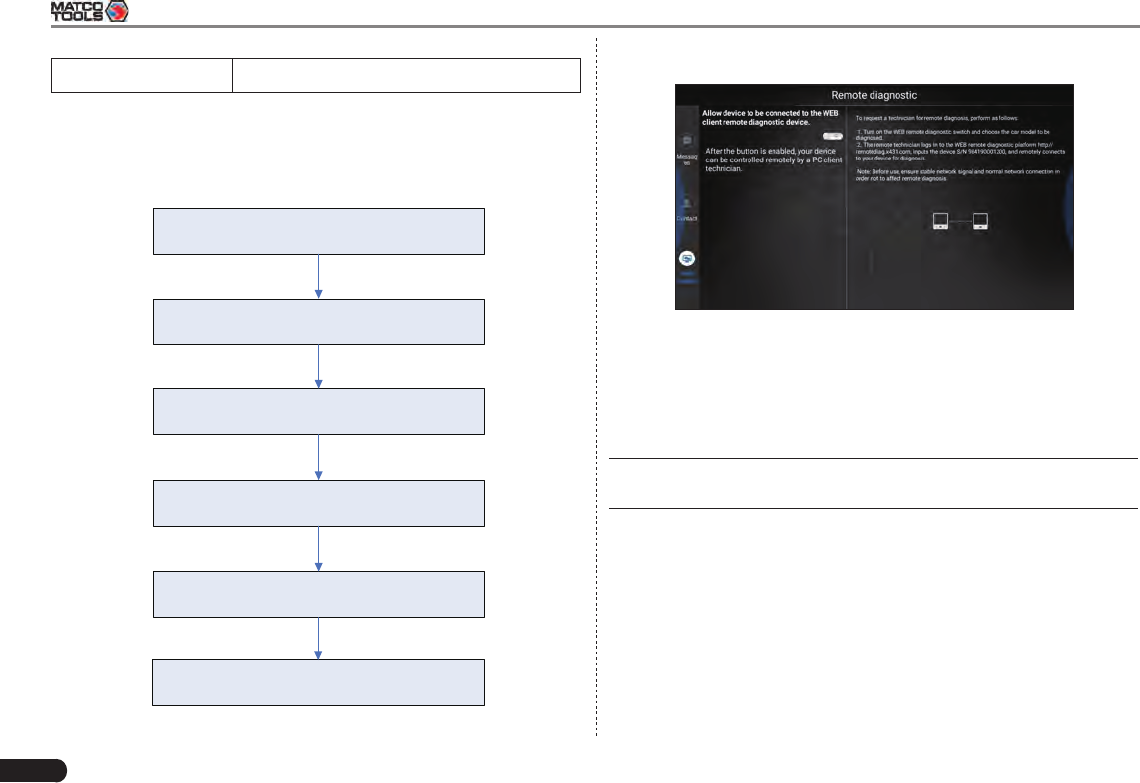
42
Maximus 3.0 User's Manual
Cancel To cancel this operation.
6.2.5 Launch Remote Diagnosis (Device-To-PC)
Except that the remote diagnosis can be done between different
diagnostic tools that come loaded with the module, user also can ask
for remote control from PC client technician.
Slide the switch to ON
Notify the partner of the remote diagnostic web link
Input the partner’s official account and password
Input the Serial Number of your handset
Start Diagnosis
Generate diagnostic report
Fig. 6-11
Tap the “Web Remote” tab, the screen displays as follows:
Fig. 6-12
1. Slide the switch “Allow device to be connected to the WEB client
remote diagnostic device” to ON so that the partner can nd and
connect to this device while using the PC.
2. Notify the partner of the PC client website http://remote.x431.com.
When the partner accesses the link, the PC displays as below:
*Note: Before processing remote diagnosis, please make sure the Maximus
3.0 handset is properly connected to the vehicle.
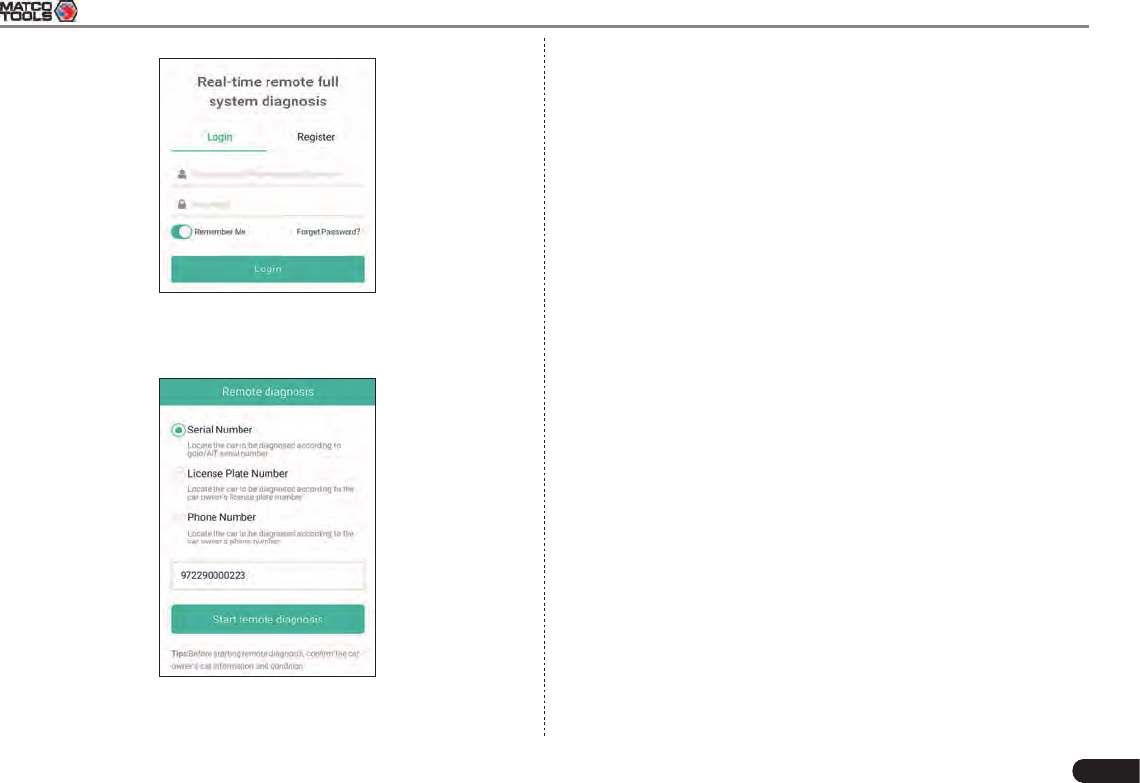
Maximus 3.0 User's Manual
43
Fig. 6-13
3. Tell the partner to input his own official technician account and
password, and then tap “Login” to navigate to the following gure.
Fig. 6-14
4. Tell the partner to check the box “Serial number” and enter the
Serial Number provided by you, and then tap “Start remote
diagnosis” to control your device remotely.
In process of remote diagnosis, please note the following things:
1) You are not suggested to execute any action.
2) The partner is not allowed to save any diagnostic reports or
records on your handset.
The operations in remote diagnosis are same as those in local
diagnosis. Once the session is complete, a remote diagnostic report
will be automatically generated.

44
Maximus 3.0 User's Manual
6.3 Feedback
This item allows you to feedback your diagnostic problems to us for
analysis and troubleshooting.
Tap “Feedback”, the following 3 options will be displayed on the left
column of the screen.
A. Feedback
Tap a tested vehicle model to enter the feedback screen.
1) Tap “Choose File” to open the target folder and choose the desired
diagnostic logs.
2) Choose the failure type and ll in the detailed failure description in
the blank text box and telephone or email address. After inputting,
tap “Submit Result” to send it to us.
B. History
Tap it to view all diagnostic feedback records. Different process states
are marked with different colors.
C. Ofine list
Tap it to display all diagnostic feedback logs which have not been
submitted successfully due to network failure. Once the handset
gets a stable network signal, it will be uploaded to the remote server
automatically.
6.4 Update
This module allows you to update the diagnostic software & App, and
renew the software subscription.
If you did not download the software in process of product registration
or a pop-up message prompting you that some new software can
be updated, you may use this option to download it or keep it
synchronized with the latest version.
Tap “Update” to enter the update center.
Fig. 6-15
This page includes two options: Downloaded and Software
Downloaded.
6.4.1 Update Diagnostic Software & APP
By default, the system enters the “Downloaded” page and all
diagnostic software to be updated is selected.
• To deselect certain software, tap “Unselect”, and then check the box
next to vehicle model.
• To refresh the downloaded list, tap “Refresh”.
• To free up more storage space or you have downloaded several
versions of diagnostic software, you can use “Delete” to clear the
old versions and only retain the latest versions.
Tap “Update” to start downloading. It may take several minutes to
nish it, please be patient to wait.
To pause downloading, tap “Stop”. To resume it, tap “Continue”. If
network connection failure occurs, tap “Retry” to try again.
Once download is finished, the software packages will be installed
automatically.
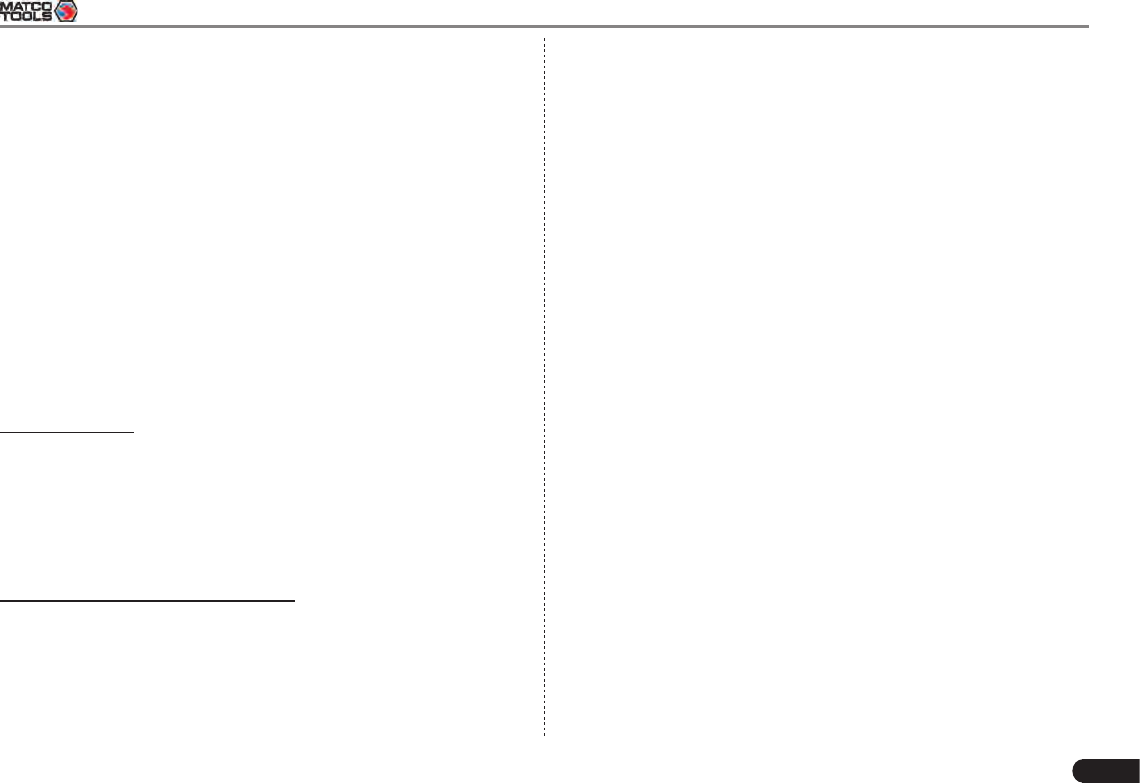
Maximus 3.0 User's Manual
45
6.4.2 Download software
If some software has not been downloaded yet or removed, you can
use the “Software Download” option to download it.
• To deselect certain software, tap “Unselect”, and then check the box
next to vehicle model.
• To refresh the downloaded list, tap “Refresh”.
• Tap “Update” to start downloading. It may take several minutes to
nish it, please be patient to wait.
6.4.3 Renew software subscription
If the software subscription is due or expires, the system will prompt
you to renew your subscription and a “Renewal” button will appear on
the bottom of the update page.
There are two ways available for you to make payment: PayPal and
Subscription Renewal Card (*need to buy it from the local dealer where
you purchased the Maximus 3.0).
A. Using PayPal
1. Tap “Renewal” on the update page to navigate to the renewal type
selection screen.
2. Select “PayPal”, and then follow the on-screen instructions to nish
the transaction.
3. After payment, go to update center to update the diagnostic
software.
B. Using Subscription Renewal Card
1. Tap “Renewal” to navigate to the renewal type selection screen.
2. Select “Subscription Renewal Card”.
3. Input the 24-digit pin code of Subscription Renewal Card and then
tap “Submit” to nish the renewal.
4. Go to update center to update the diagnostic software.
6.5 Settings
This module allows you to manage diagnostic reports, VCI devices,
configure wireless printer and print information and add favorite
website etc.
6.5.1 General
6.5.1.1 Units of Measurement
It is designed to set the measurement unit. Metric System and English
System are available.
6.5.1.2 Expiration Reminder
All pre-installed diagnostic software is free to use for 30 days. Once it
expires, it will be locked automatically and the system will prompt you
to activate your VCI if the expiration reminder is ON.
6.5.1.3 Identix Settings
This option is used to set whether the free 30-day trial Identix shows
or not.
6.5.1.4 Auto Update
This option is used to set whether automatic update function is ON.
6.5.2 VCI
This option allows you to manage all activated VCI dongles.
If several VCI dongles are activated on this tool, a list of VCI dongles
will be displayed on the screen. If your tool extends to support heavy-
duty trucks, you need to switch to the corresponding VCI dongle
before diagnosing it.
Once you choose the dongle that belongs to other account, you have
to log out, and then input the right account to continue.
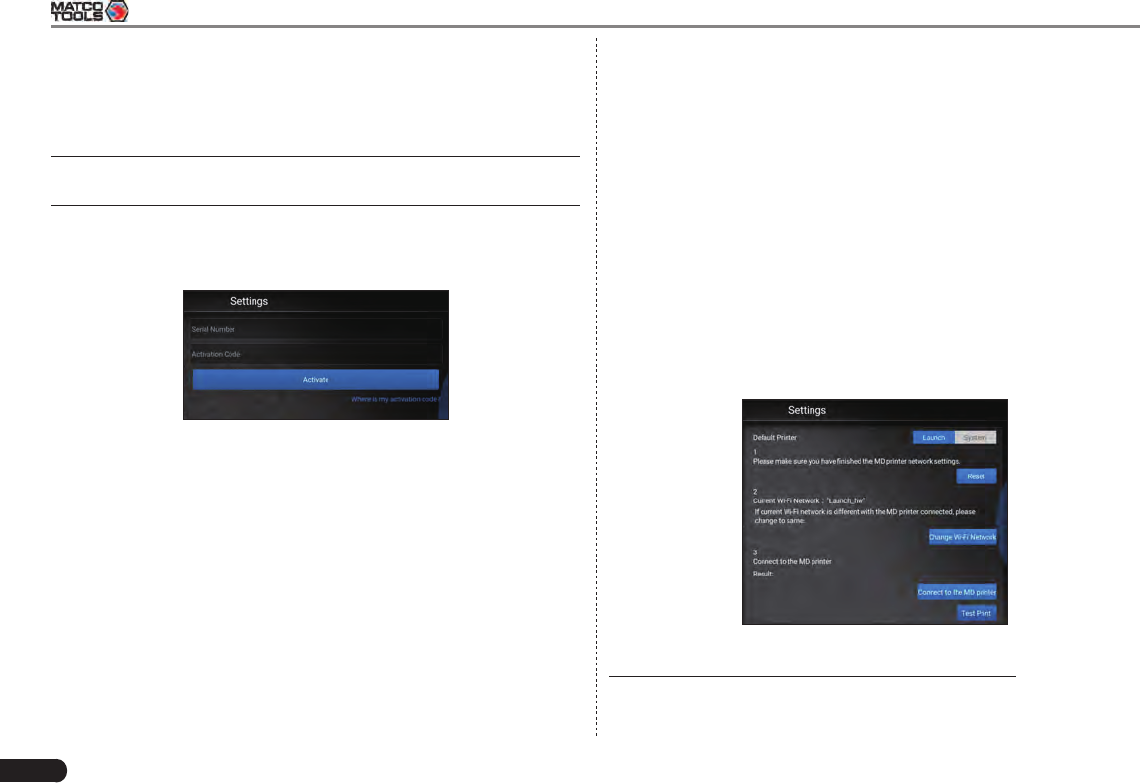
46
Maximus 3.0 User's Manual
6.5.3 VCI Management
If you use the current account to test a vehicle with another Maximus
3.0, please use this item to unpair the VCI device with the previously
paired Maximus 3.0.
* Note: please be sure to keep the VCI device powered on while performing
the operaon.
6.5.4 Activate VCI
This item lets you to activate a new VCI device.
Fig. 6-16
Input the Serial Number and Activation Code, and then tap “Activate”
to activate it.
6.5.5 Firmware Fix
Use this item to upgrade and fix diagnostic firmware. During fixing,
please do not cut power or switch to other interfaces.
6.5.6 Icon Size
This feature allows you to set the size of the diagnostic software icon
according to your preference.
Drag the slider to different size and the system will display the
corresponding effect.
6.5.7 Color Theme
This item enables you to set the color theme of the App.
Once you changed it, you have to reboot the system for the change to
take effect.
6.5.8 MD Printer Connection
This option is used to establish a wireless connection between
Maximus 3.0 and the printer (sold separately) while performing printing
operations.
The App is compatible with the “Wi-Fi Printer” (sold separately) and
“System” (external printer).
Follow the steps below to connect the Wi-Fi printer.
1. Tap “MD Printer Connection”.
Below describes how to congure the Wi-Fi Printer.
Fig. 6-17
A. If it is the rst time you have operated this printer, please proceed
the following:
2. For initial use, you are suggested to reset the printer: Press and
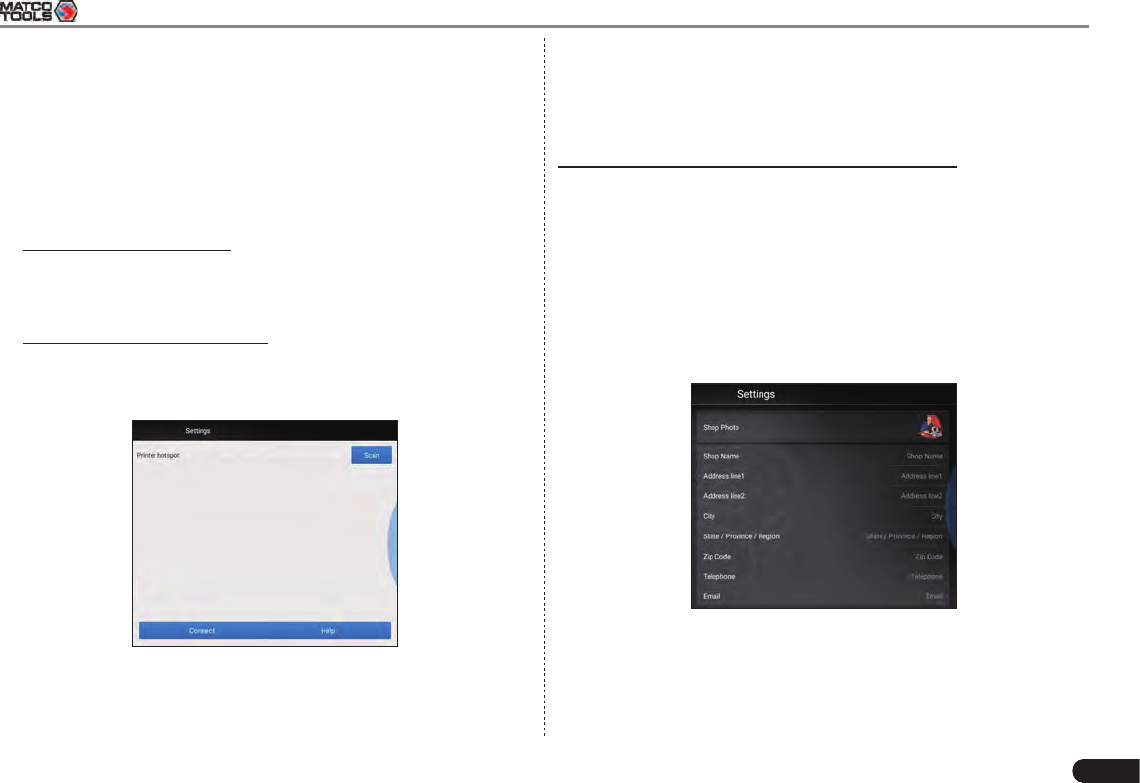
Maximus 3.0 User's Manual
47
hold [MODE] & [FEED] for 8 seconds, the following resetting
command will be printed out:
at + default = 1
ok
at + reboot = 1
rebooting...
3. Tap “Reset” to congure Wi-Fi printer.
Step 1: Connect the printer:
Tap “Scan” to select the desired printer hotspot named with
X-431PRINTER-XXXX (XXXX stands for 4 characters), and then
tap “Connect” to enter Step 2.
Step 2: Join the printer into LAN:
Tap “Scan” to select the desired local Wi-Fi network from the
list, and type in the security password (If it is an open network,
password is not required), and then tap “Conrm”.
Fig. 6-18
4. Once the Wi-Fi network of the printer is connected and the printer
is found, tap “Test Print” to test the printing.
Now you can use the Wi-Fi printer to print!
If the printer is not found, please reset the printer to default factory
settings (refer to Step 2 for details) and check whether the current
device and the printer are on the same LAN.
B. If you have congured the Wi-Fi printer to the LAN:
2. Tap “Connect to Printer”:
a). If the local network remains as it is, tap “Test Print” directly to
test the printing.
b). If the local network changes, you have to reboot and recongure
the Wi-Fi printer.
6.5.9 Print Information
This option lets you define your print information. It mainly includes
Workshop, Address, Zip Code, Telephone, Email etc.
Fig. 6-19
After inputting, tap “Save”.
Once you saved the print information, it will be loaded automatically in
the “More Information” box every time you save the diagnostic report.
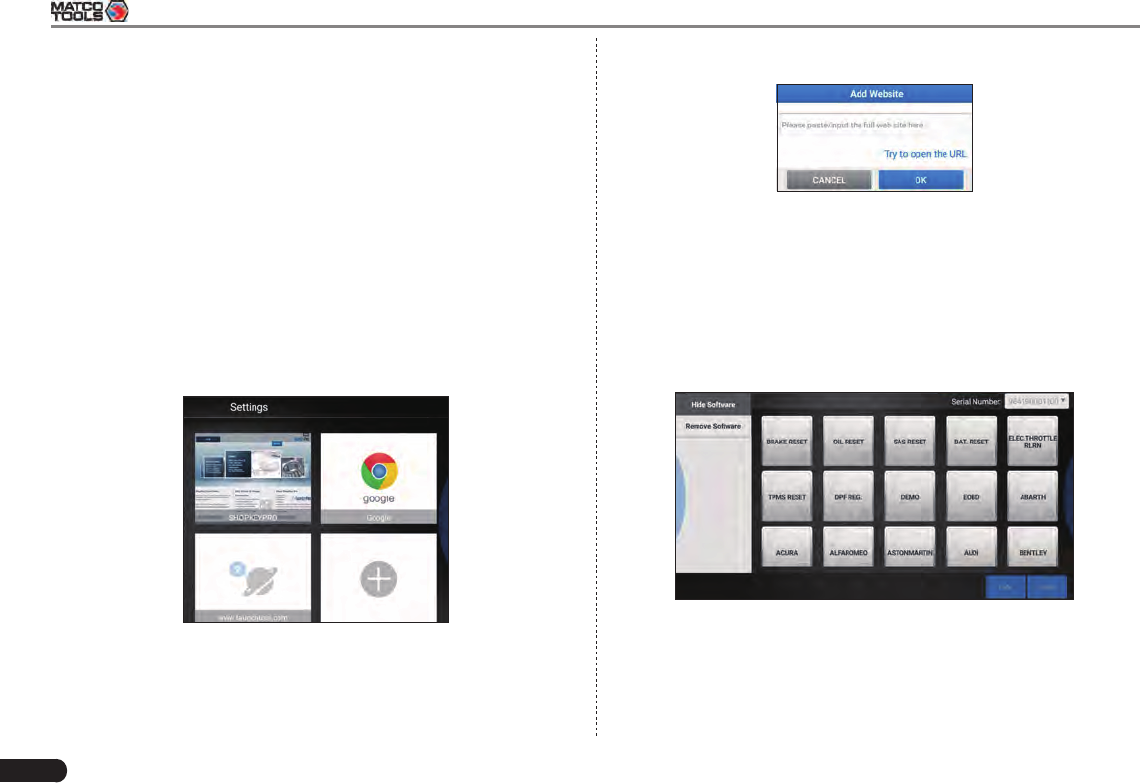
48
Maximus 3.0 User's Manual
6.5.10 Data Stream Sample
This feature allows you to manage the recorded data stream sample
les.
6.5.11 Vehicle Voltage
This item is used to detect the voltage of the currently tested vehicle
when the VCI is plugged into the vehicle’s DLC.
6.5.12 Favorites
This feature provides you quick accesses to some renowned and
popular repair and maintenance website links. These may include
general information about a component or system, diagnostic and
troubleshooting procedures and/or repair instructions. Moreover you
can also add more repair websites into Favorites so that you can
quickly open them in future.
Fig. 6-20
Tap the desired website to visit it.
To add certain website into favorites, scroll the screen to until it
reaches to the bottom, tap “+”, a dialog box similar to the following
appears.
Fig. 6-21
Type in the full web site in the blank, and tap “OK”, it will be listed in
the Favorites.
6.5.13 Diagnostic Software Clear
This item allows you to hide/clear the diagnostic software that is not
frequently used.
Tap “Software Clear”, the screen displays as follows:
Fig. 6-22
Under the “Hide Software” tab, select the desired software logo (a
“Checkmark” will show in the checkbox located at the lower right
corner) and tap “Hide”, it will become invisible. Tap “Unhide” to undo
the hide operation.
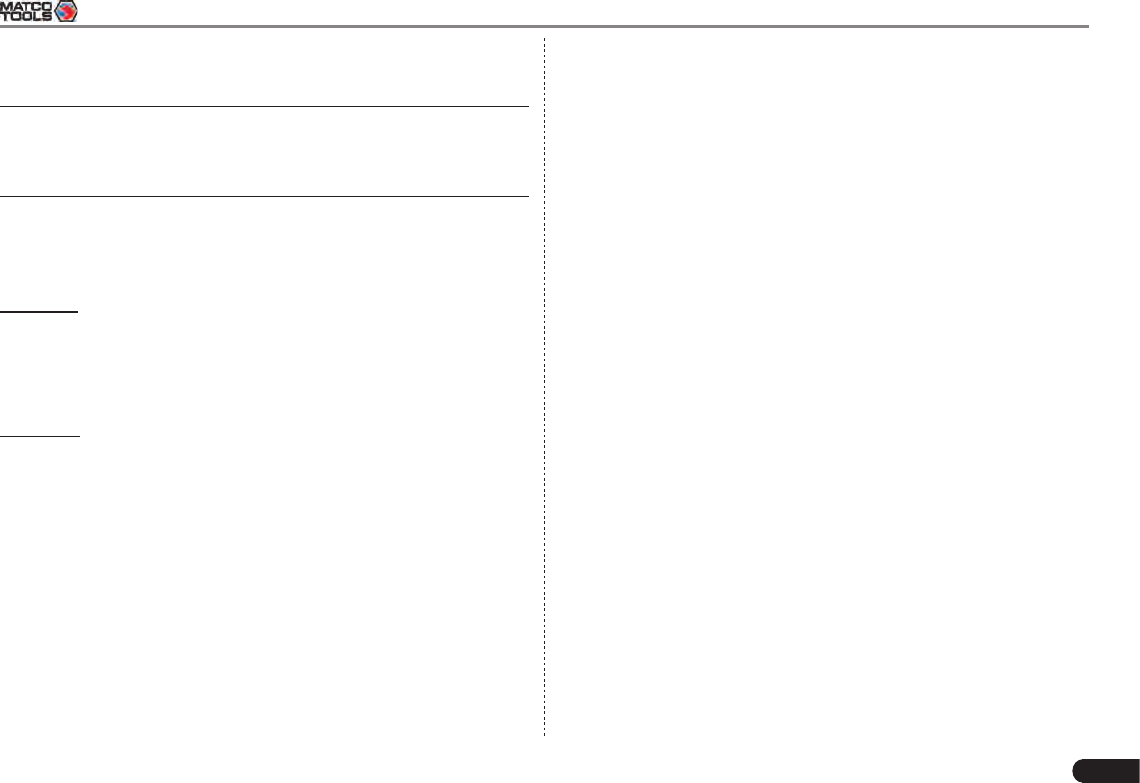
Maximus 3.0 User's Manual
49
Under the “Remove Software” tab, select the desired software logo
and tap “Delete”, it will disappear from the screen.
*Note: Removing soware may completely delete the soware from the
handset. If some software keeps unattended and the handset runs out
of space, you can use this feature to remove it. To re-download it, go to
“Update” -> “Soware Download”.
6.5.14 Backup/Restore
This option lets you backup/restore the important data to/from external
storage device.
A. Backup
1). Insert the U disk into the Data Transmission Port of the handset.
2). Tap “Backup” to select the data folder to be backed up.
3). Tap “Backup” on the bottom of the screen to copy it to the U disk.
4). Unplug the U disk from the handset.
B. Restore
1). Insert the U disk into the Data Transmission Port of the handset.
2). Tap “Restore” to select the data folder to be restored.
3). Tap “Restore” on the bottom of the screen to copy it to the handset.
4). Unplug the U disk from the handset.
6.5.15 Login/Exit from current account
To logout the current user ID, tap “Exit from current account”.
To login the system again, tap “Login”.
6.6 Help
FAQ, Vehicle Coverage, Quick Start Guide and User Manual are
included.

50
Maximus 3.0 User's Manual
7 Applications
7.1 Sensorbox & Multimeter (Optional)
7.1.1 Product summary
Maximus 3.0 provides an optional function of automotive sensor
simulation test. “Sensor” function is specially designed to diagnose
and simulate vehicle sensor faults quickly and conveniently, including
“DC voltage simulation”, “Fixed frequency simulation”, “Predefined
waveform simulation” and “Hand-painted waveform simulation”.
Vehicle sensors are the signal input devices for electrical control
systems, which can transform all kinds of running parameters, such
as vehicle speed, coolant temperature, engine RPM, air ow, throttle
opening, etc., into the electronic signal for the vehicle computer who
can optimize the engine running status per the above-mentioned
parameters to keep the engine working in a prime status.
Meanwhile, it integrates the functions of automobile multimeter, which
enables users to perform voltage, resistance and frequency test. (The
function utilizes the same hardware device as the sensor module)
It features automotive sensor simulation test and multimeter test
function.
Sensorbox
Parameters Scope
Precision ±5%
Voltage range -5V~+5V
Max output current 70mA
Predened frequency range 0~150Hz
Square-wave signal pulse frequency 0~15KHz
Square-wave signal duty ratio 10%~90%
Multimeter
Parameters Scope
Precision ±5%
Voltage test Testing range DC-400V~+400V
Input impedance 10Mohm
Resistance test Testing range 0~40Mohm
Frequency test
Testing range 0~25KHz
Input impedance 1000Gohm
Input voltage 1~12V
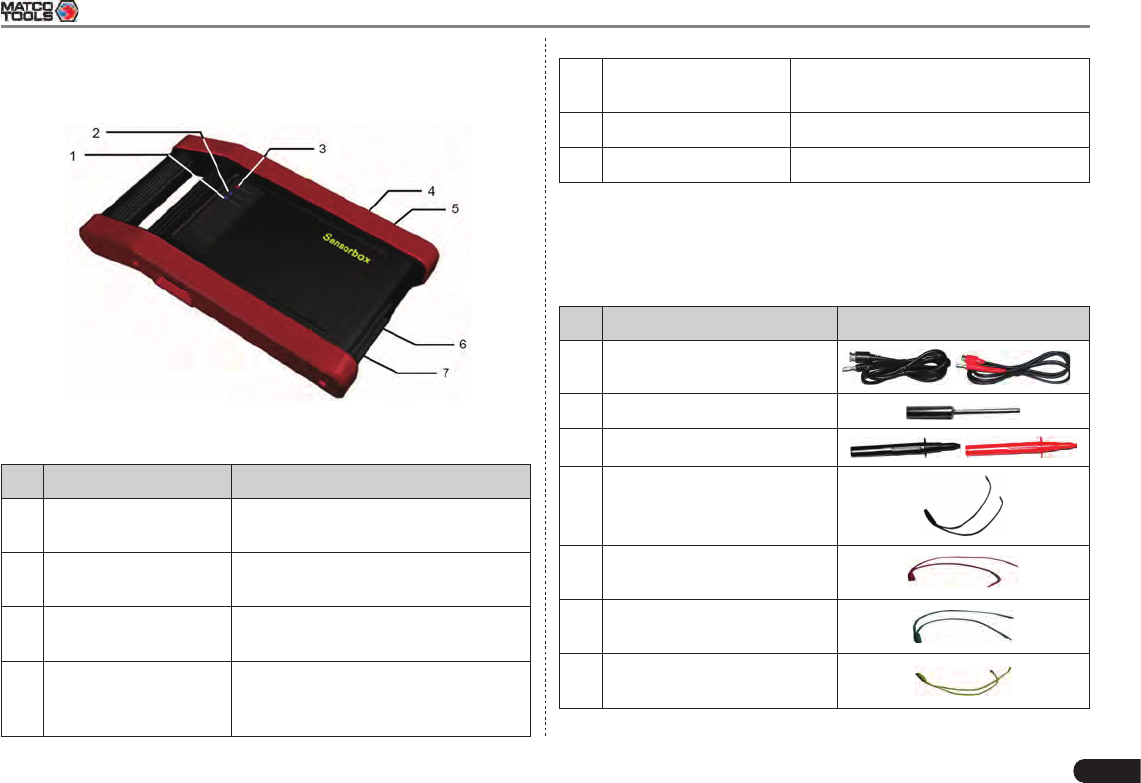
Maximus 3.0 User's Manual
51
7.1.2 Structure and Accessories
7.1.2.1 Sensorbox structure
Fig. 7-1 Structural diagram of Sensorbox
Below shows the ports and indicators for Maximus 3.0 sensorbox
No. Name Description
1Data receiving indicator Indicator (green) for receiving data
from main unit.
2Data sending indicator Indicator (green) for sending data to
main unit.
3Power indicator It keeps steady on (red) after
Sensorbox is powered on.
4B-shaped data port Connect to main unit with USB cable
when it is applied as separated USB
device.
5Power connector Connect to power supply through the
power adaptor.
6COM Common terminal of multimeter
7VΩHz Testing terminal of multimeter
7.1.2.2 Sensorbox accessories
Maximus 3.0 sensorbox accessories include sensor test cable, probe
etc. For detailed items, please see the packing list.
Below formulates the accessories of Maximus 3.0 sensorbox
No. Name Picture
1Sensor test cable
2Sensor probe
3 Multimeter probe
4Electronic control converting
cable 1
5Electronic control converting
cable 2
6Electronic control converting
cable 3
7Electronic control converting
cable 4
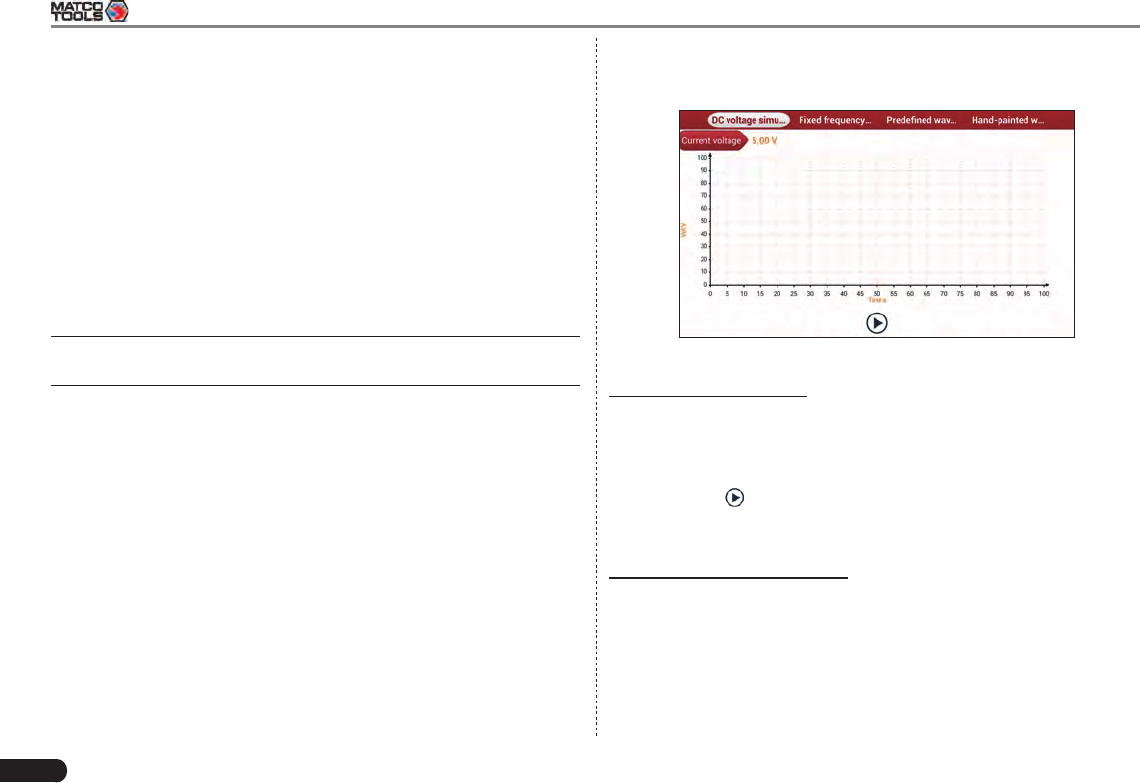
52
Maximus 3.0 User's Manual
7.1.3 Sensor Simulation
7.1.3.1 Connections
1. Firstly, power on the Maximus 3.0 handset.
1. Connect the B-shaped terminal of data cable to the B-shaped port
of the Sensorbox, and the other end to the Data transmission port
of the Maximus 3.0 handset.
2. Plug one end of the sensor test cable (black) into the “COM”
interface of the sensorbox, then connect the other end to the test
probe or electronic control converting cable.
3. Connect one end of the sensor test cable (red) into the “VΩHz”
interface of the sensorbox, and then connect the other end to the
test probe or electronic control converting cable.
*Note: Choose corresponding cables and test probes according to dierent
terminals.
7.1.3.2 Simulation test
Simulation test enables users to exactly judge if the sensor is good or
not to avoid replacing components blindly. For example, the trouble
code indicates the fault is in water temperature sensor itself. But we
need to confirm whether the fault results from water temperature
sensor or the connections between ECU and sensors, or ECU itself.
In this case, we can make full use of simulation test to input the signal
of simulating water temperature sensor, instead of water temperature
sensor, to the microcomputer. If the engine works better and the fault
vanishes, the fault is in the water temperature sensor. If the fault
still occurs, input the signal to the corresponding terminals of ECU.
Consequently, if the fault disappears, the fault lies in the connection
between water temperature sensor and ECU, otherwise, the fault
exists in ECU.
After all connections are properly made, power on your Maximus 3.0,
launch Maximus 3.0 application and enter the function menu interface,
then tap “Sensor” to enter the test selection screen.
Fig. 7-2
1. DC voltage simulation
In Fig. 7-2, tap [Current voltage], then tap “+” or “-” to adjust the output
voltage value. Alternatively, user can also tap edit box, then use the
on-screen keyboard to input the desired value directly. After selecting
or inputting the desired voltage based on the working characteristics of
sensor, tap the button, then the Maximus 3.0 will begin to output the
simulation voltages. Please note the red probe is the output terminal
of simulation voltage.
2. Fixed frequency simulation
This option enables you to simulate the square wave signal of pulse
frequency of 0.1 ~ 15 kHz, amplitude range of -5V ~ +5 V and duty
cycle 10% ~ 90%.
In Fig. 7-2, tap “Fixed frequency simulation” to enter a screen similar
to the following gure.
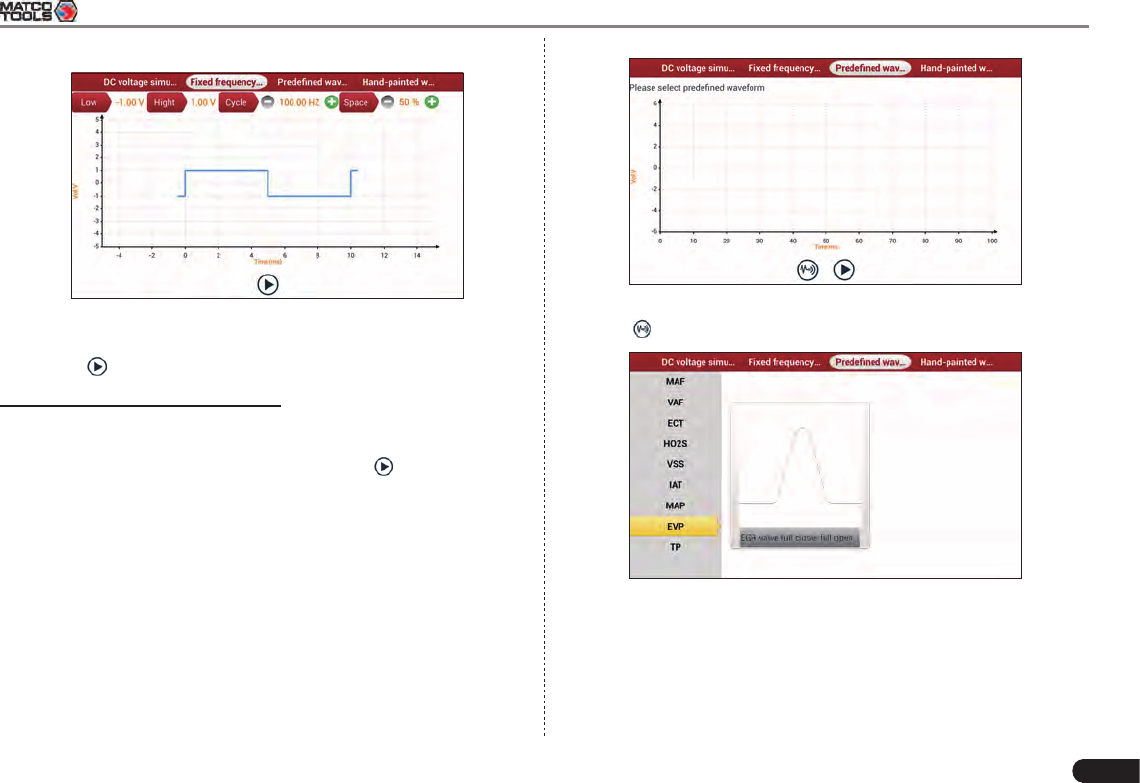
Maximus 3.0 User's Manual
53
Fig. 7-3
Tap the setting option tab, then tap “+” or “-” to adjust the output,After
setting, tap to perform the test.
3. Predened waveform simulation
Maximus 3.0 provides some common sensor waveforms which have
been predened to facilitate users to simulate sensor signals. As long
as you call out the predened waveform, then tap to start simulating
output of corresponding sensor waveform and no more parameter
settings of simulation waveform are required.
In Fig. 7-2, tap “Predened waveform simulation” to enter the following
screen.
Fig. 7-4
Here, tap button, a screen similar to the following gure will appear.
Fig. 7-5
In above figure, the left setting column stands for sensor types and
the right area displays waveform. The sensor types are explained as
below:
ECT: Coolant Temperature Sensor
EVP: EGR Valve Position Sensor

54
Maximus 3.0 User's Manual
HO2S: Heated Oxygen Sensor
IAT: Intake Air Temperature Sensor
MAF: Mass Air Flow Sensor
MAP: Manifold Absolute Pressure Sensor
TP: Throttle Position Sensor
VAF: Volume Air Flow Sensor
VSS: Vehicle Speed Sensor
For example, tap “ECT” – “Warm (NTC Thermistor)”, the right screen
will display the waveform of the sensor.
Fig. 7-6
Tap the waveform, then the pre-dened waveform has been set.
Fig. 7-7
Tap button to perform simulation test.
4. Hand-painted waveform simulation
This option offers great convenience for users to simulate special
waveform or fault wave. Users only draw the shape of waveform which
needs to be simulated in central drawing area, and then configure
some parameters on the top, namely high level, low level, and cycle
of waveform, then tap , Maximus 3.0 will output a waveform as
desired.
Warning: Just draw a complete periodic waveform (when it is outpued,
the system will regard the waveform in the drawing area as a periodic one).
Users should draw as large as wave in drawing zone so that the system can
sample more points to reduce tolerance. While drawing, just pay aenon
to the shape of waveform, high level, low level and period can be ignored,
which can be set in the Congure opon.
In Fig. 7-2, tap “Hand-painted waveform simulation”, a screen similar
to the following gure will appear.
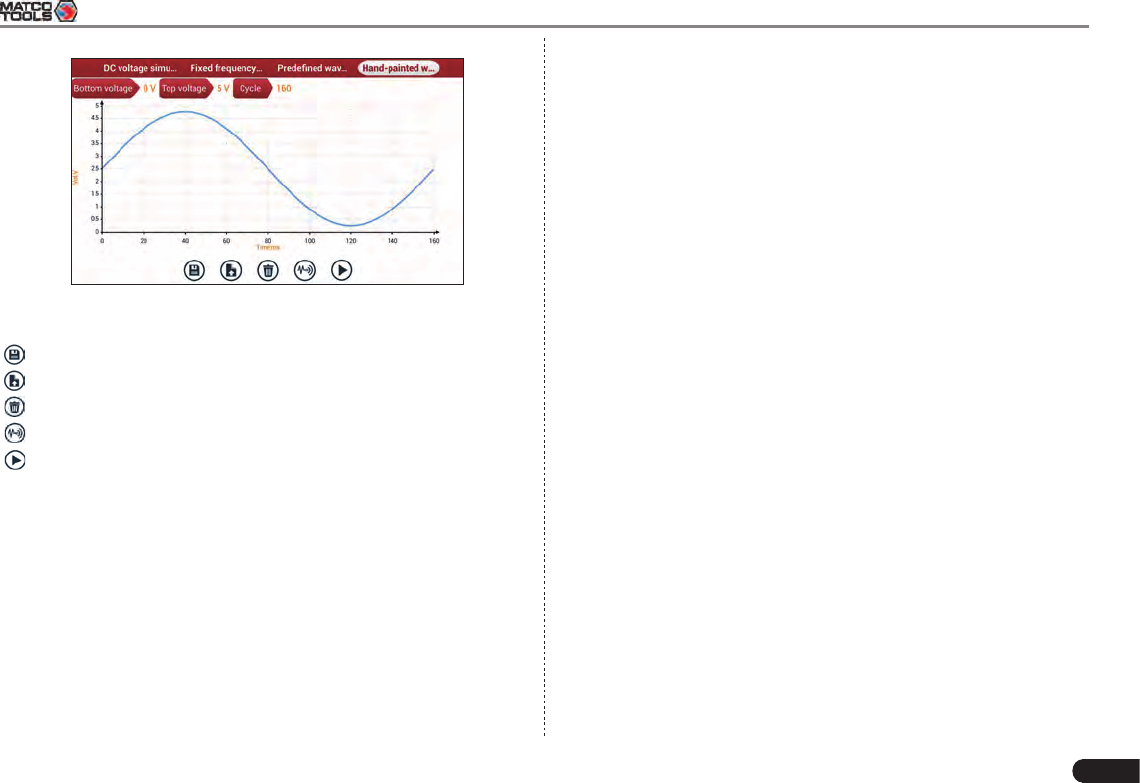
Maximus 3.0 User's Manual
55
Fig. 7-8
Button descriptions:
[]: Save the current waveform.
[]: Loads the previously saved hand-drawn waveform.
[]: Clear all hand-drawn waveform.
[]: Tap to call out the predened waveform for reference.
[]: Continues the following operation.
7.1.3.3 Precautions on checking vehicle sensor
• Hold the connector when plugging or unplugging it. Do not pull the
cable for unplugging.
• At rst check the fuse, fusible line and terminals. Then check others
after eliminating these faults.
• When measuring voltage, the ignition switch should be on and the
battery voltage should not be less than 11V.
• When measuring voltage, please shake the lead lightly in the
vertical and horizontal direction for more precision.
• When checking whether there is open in the line, disconnect the
CEU and the relevant sensor at rst, then measure the resistance
among the ports of sensor in order to determine whether open-
circuit / contact fault exists or not.
• When checking if there is a short in the line, please disconnect the
CEU and the relevant sensor, then measure the resistance value of
the ports between the connected port and the vehicle body. If the
resistance value is more than 1MΩ, no fault occurs.
• Before disassembling the engine electrical control system cable,
cut off the power supply, that is, turn the ignition switch OFF and
disconnect the cables on the battery poles.
• Contact the test probe and the two terminals/ the two leads to be
measured when measuring the voltage between the two terminals
or the two leads.
• Contact the red test probe to the terminal/ the cable to be
measured, and the black probe to the ground when measuring
voltage of one terminal/ one cable.
• When checking the continuity of the terminals, contacts and leads,
the method for measuring their resistances can be used.
• Check the faults in the terminals of the CEU to sensors, relays, etc.
• There are two test probes in the testing wire. The black one is the
common signal terminal (signal GND); the red one is the input
terminal for voltage, resistance, and frequency test and output
terminal for simulation voltage, simulation frequency and oxygen
sensor. Please choose the correct probes to match the different
terminals.
7.1.4 Multimeter
7.1.4.1 Operations
Make sure Maximus 3.0 main unit and the sensorbox are properly
connected, power on Maximus 3.0 and enter the Applications menu
interface, tap “Multimeter” to display the test menu.
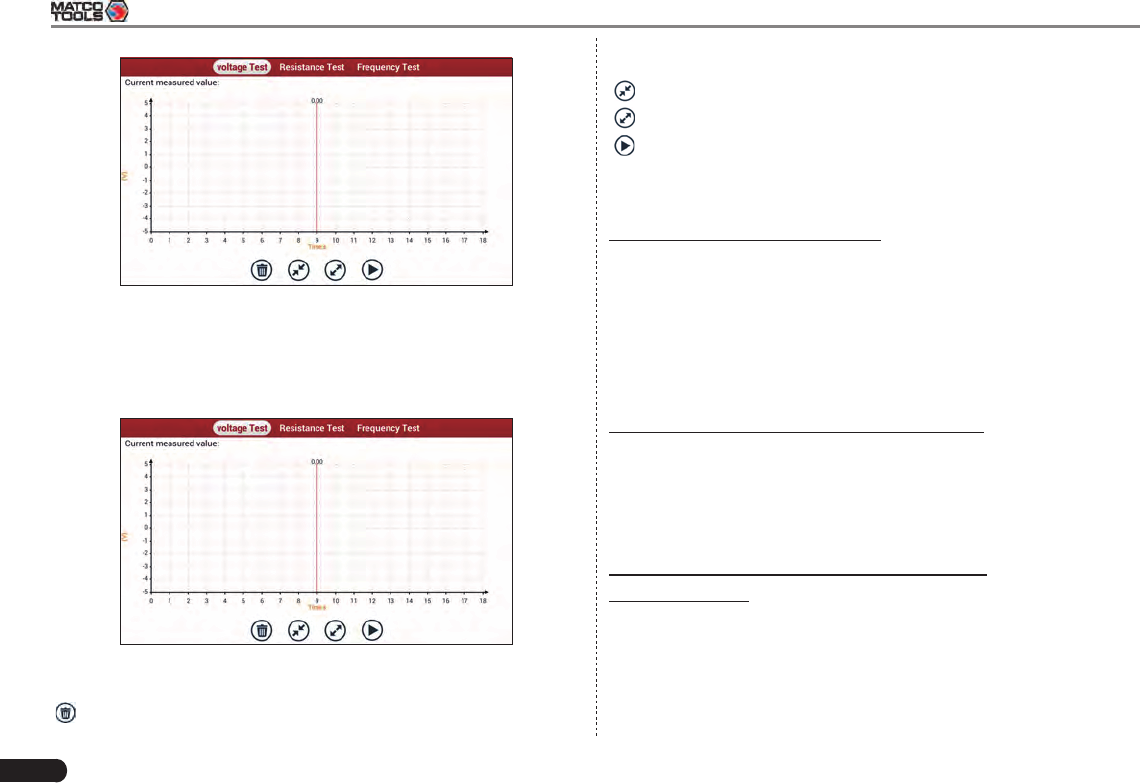
56
Maximus 3.0 User's Manual
Fig. 7-9
Click the desired test as shown above to perform related test.
The operation method on Resistance test and Frequency test is
identical to that of Voltage test. Here just take Voltage test as an
example for demonstration.
Fig. 7-10
The following operations can be done:
[]: Erases the currently displayed waveform and display it starting
from the left.
[]: Reduces the range and zoom in the waveform.
[]: Increase the range and zoom out the waveform.
[]: Starts or stops the testing process.
7.1.4.2 Test sample
Knock sensor testing
(1) Resistance test for knock sensor
Switch ignition “OFF”, unplug the wire connector of knock sensor, test
the resistance between the wire terminal and the case of knock sensor
with “Resistance test” function, it shall be ∞(disconnected), and if it
is 0Ω(conductive), which means the knock sensor shall be replaced.
For the magnetostriction knock sensor, it can also test the resistance
by the “Resistance measurement” function; the resistance shall be
compliant with the specied value (see specic service manual for the
detailed data), otherwise, the knock sensor shall be replaced.
(2) Checking for the output signal of knock sensor
Unplug the wire connector of knock sensor, check voltage between
knock sensor connector terminal and ground wire of knock, it should
be output pulse voltage; otherwise, the knock sensor shall be
replaced.
Coolant temperature sensor testing
(1) Resistance test for coolant temperature sensor
On vehicle testing:
Switch ignition “OFF” and unplug the wire connector of coolant
temperature sensor, then use the “Resistance measurement” to test
the Resistance between two terminals of sensor. The relationship
between the resistance and the temperature is in inversely proportion
(negative temperature coefcient), which shall be less than 1kΩ during
warming up.
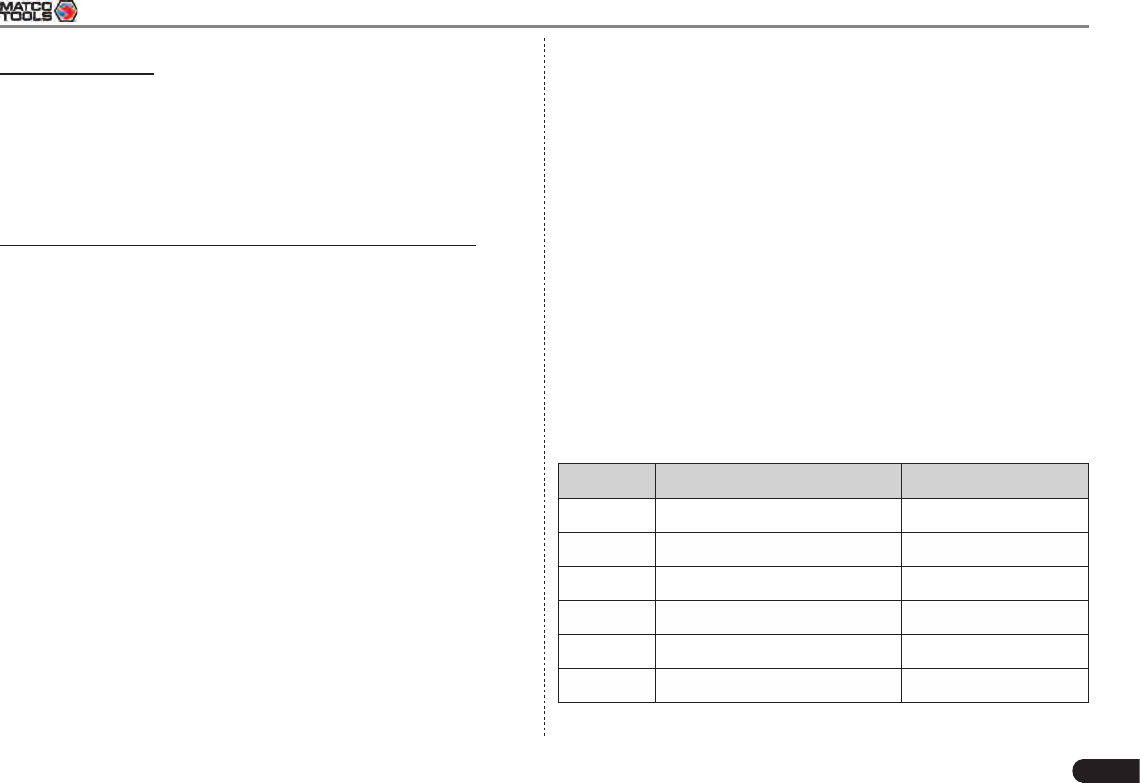
Maximus 3.0 User's Manual
57
Independent testing:
Unplug the wire connector of coolant temperature sensor, then remove
the sensor from the engine; place the sensor into a breaker with water
and heat the water, then use the “Resistance measurement” to test
the Resistance between two terminals of coolant temperature sensor
at different water temperature. Compared the measured value with the
standard value, if the Resistance is not compliant with the standard,
then the coolant temperature sensor shall be replaced.
(2) Output signal voltage testing for coolant temperature sensor
After installing the coolant temperature sensor, plug the wire connector
of sensor, and then switch ignition ON, test the output signal voltage
between the two terminals of wire connector. The tested voltage shall
be in inverse proportional with the coolant temperature. When the
harness of coolant temperature sensor is disconnected, the voltage
shall be about 5V if the ignition switch is ON.
7.2 Batterybox (Optional)
7.2.1 Product Summary
Maximus 3.0 provides an optional function of automotive battery
test, which adopts the latest state-of-the-art conductance testing
technology in the world and can test vehicle’s battery status. Two
testing environments (Inside the Vehicle and Outside the Vehicle)
are available and applicable to battery test. In addition to battery test,
charging system and actuation system test can be done while Inside
the Vehicle is selected.
It supports various battery standards and specifications, including
CCA, DIN, IEC, EN, JIS, SAE and GB etc. It is specically designed
to help car owner, repair workshop, battery factory use battery test
instrument properly and determine whether the battery is normal or
not.
Battery test aims to check starting plumbic acid storage batteries for
vehicles, ship, boats and aviations, etc. It can test all kinds of batteries
complying with CCA, DIN, JIS, EN, GB and SA standards. For detailed
test standards, see the following table.
Standards Standard (Full name) Test capacity range
CCA Battery Council International 100~1700
DIN Deutsche Industry Normen 100~1200
JIS Japanese Industry Standard 26A17~245H52
EN Europe Norm 100~1700
IEC National Electrical Commission 100~1200
GB Chinese National Standard 100~1200
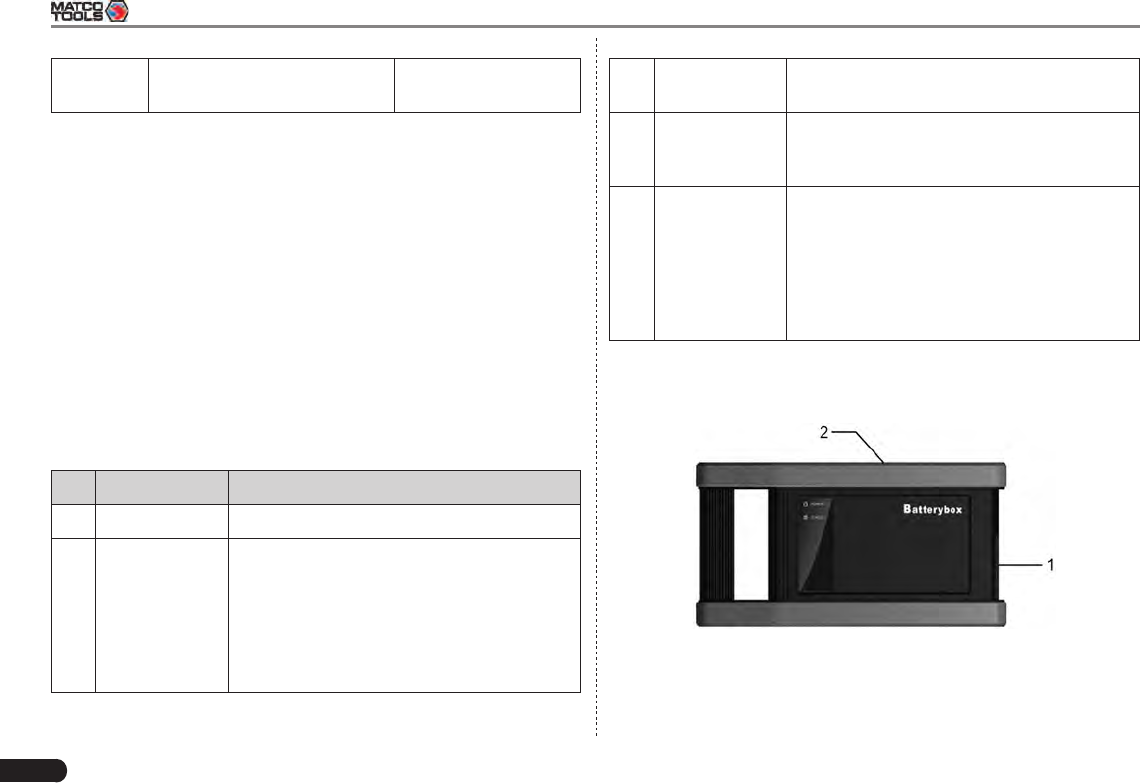
58
Maximus 3.0 User's Manual
SAE Society of Automotive
Engineers 100~1700
7.2.2 Test Environment
7.2.2.1 Test environment
Inside the vehicle test indicates that the battery connects to loading
devices, such as engine, etc. After doing battery test, it can perform
charging system and actuation system test, which is proceeded as a
whole simultaneously. Charging system and actuation system test is
not required but must not be performed before battery test. Because it
is difcult for vehicle technicians to judge where is faulty exactly if they
have the faintest idea of battery’s status itself.
Outside the vehicle test indicates that the battery is disconnected
from all loading devices on vehicles. Therefore, only battery test is
supported in this condition.
7.2.2.2 Battery status and description
There are mainly 5 states as follows:
No. States Descriptions
1 Good battery Indicates battery is normal.
2 Replace battery
Indicates that battery is aged or becomes
rejected, or battery life cycle approaches to
be exhausted. In this case, battery voltage
appears to be normal, but battery itself is
not well, i.e. battery polarity board has been
completely vulcanized or aged. Please
replace battery immediately.
3 Good-recharge Stands for low battery. The battery is good
itself.
4 Charge-retest It is better for a few batteries to be fully
charged before testing in order to avoid
judging in error under special conditions.
5 Bad cell
Indicates one of the battery cells is bad and
can not work normally, but for which one is
bad, it can’t be veried. In this case, battery
voltage is generally lower than 11V, mainly
resulting from internal circuitry damage, such
as short circuit, open circuit, dummy weld
etc.
7.2.3 Batterybox Structure and Test Accessories
7.2.3.1 Batterybox structure
Fig.7-11 Batterybox structure diagram
1. Battery connector: Connect to battery for battery test.
2. Type B terminal: Connect to the Maximus 3.0 tablet with data cable.
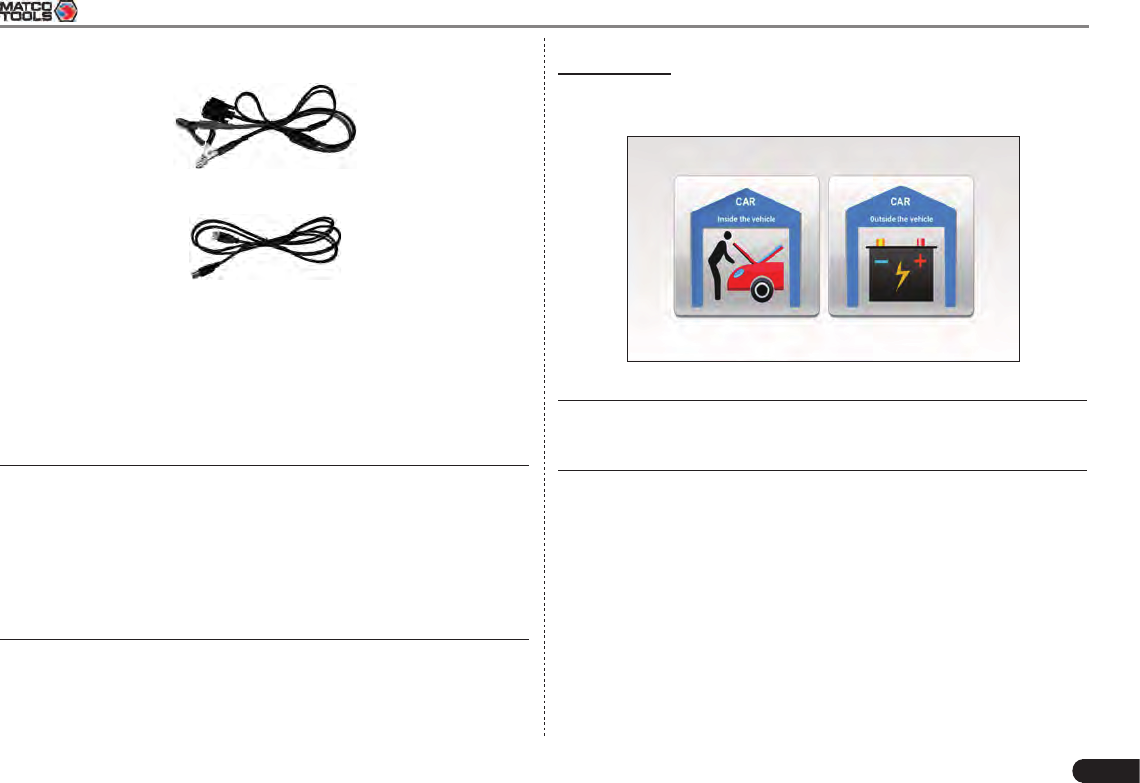
Maximus 3.0 User's Manual
59
7.2.3.2 Test accessories
Fig. 7-12 Kelvin clip
Fig. 7-13 A/B cable
7.2.4 Connections & Operations
7.2.4.1 Connection
Connect one end of the A/B cable to the Type B terminal of the
batterybox, and then connect the other end to the Data transmission
port of Maximus 3.0 tablet. This connection applies to outside the
vehicle test and inside the vehicle.
*Notes:
1. Wait about 10s and begin to communicate since the baerybox needs to
inialize aer connecon is complete, otherwise, communicaon may
fail.
2. Red lamp on the batterybox means it has been successfully powered
up. If the green light is always on, it indicates the clip is well connected;
while the green light blinks, it indicates that the clip has poor contact. Do
not perform any test unl the clip and A/B cable are properly connected.
7.2.4.2 Inside the vehicle test
Battery test and charging system & actuation system test can be done
in this mode.
1. Battery test
Enter the battery test main menu screen, and select a desired test
environment.
Fig. 7-14
*Note: The sequences of inside the vehicle and outside the vehicle test
are almost the same, but under inside the vehicle condion, all loads in
vehicles must be powered o for geng an exact test value.
1. Firstly, the system detects whether oating electricity exists or not
before testing. If yes, turn on the headlamp to remove it. Otherwise,
the system starts test program directly.
2. Tap [Inside the vehicle], the system starts detecting floating
electricity automatically. If floating electricity is detected, it will
prompt you to turn on the headlamp.
3. Follow the on-screen instructions to turn on headlamp, the system
starts removing oating electricity.
4. Once the oating electricity is removed, a prompt message box “The
oating electricity has been removed, please turn off the headlamp
to continue the testing” will appear on the screen.
5. Follow the on-screen instructions to turn off the headlamp and
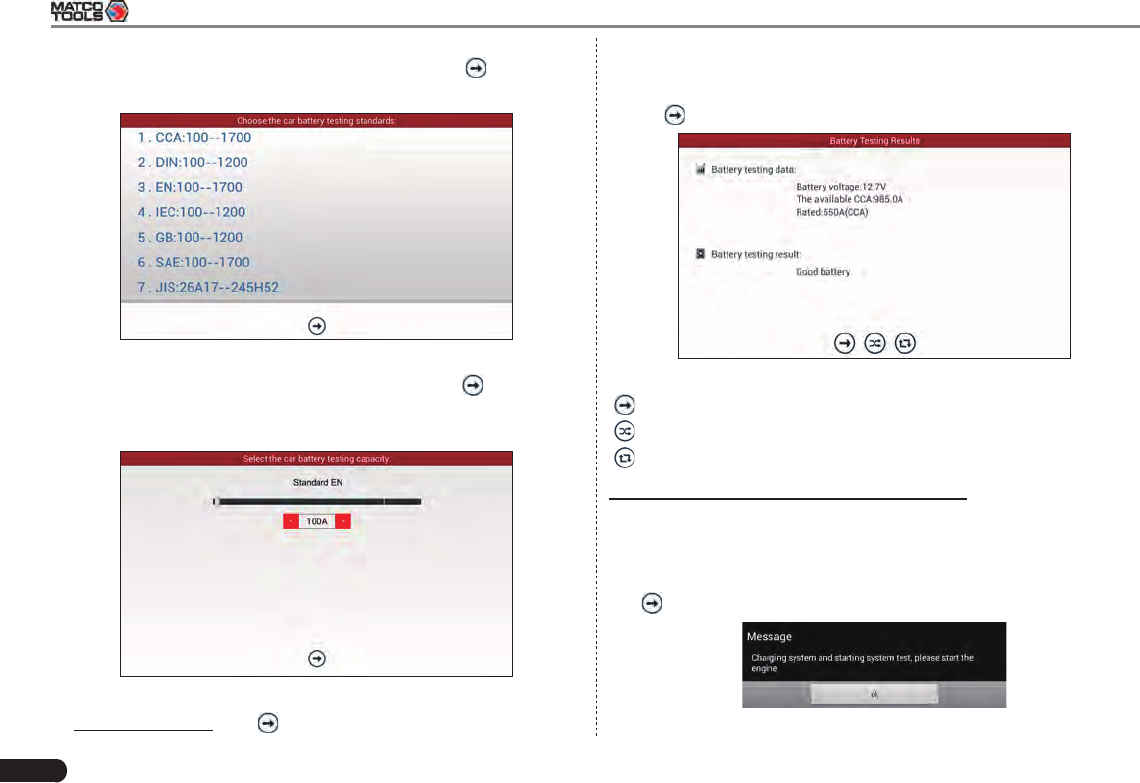
60
Maximus 3.0 User's Manual
tap [OK], the system will continue the testing. Tap , it will enter
testing standard selection screen.
Fig. 7-15
6. Select a testing standard except for JIS and tap to enter the
following gure. Users can adjust capacity size by tapping on < or >
or by dragging the slider on the bar.
Fig. 7-16
If JIS is selected, tap , the system will enter Select testing
capacity screen. Users can select corresponding standard capacity
value according to battery model marked on battery.
7. Tap and the testing result will appear on the following screen.
Fig. 7-17
[ ]: Tap it to perform the charging system and starting system test.
[]: Tap to test it again.
[]: Tap it to reset the test.
2. Charging system and starting system test
While performing this test, the battery’s charging voltage value
and starting voltage can be obtained in case of engine starting and
accelerating. Based on the data, the system will judge whether
battery’s charging and actuation status is normal or not.
Tap in Fig. 7-17, a dialog box will pop up.
Fig. 7-18
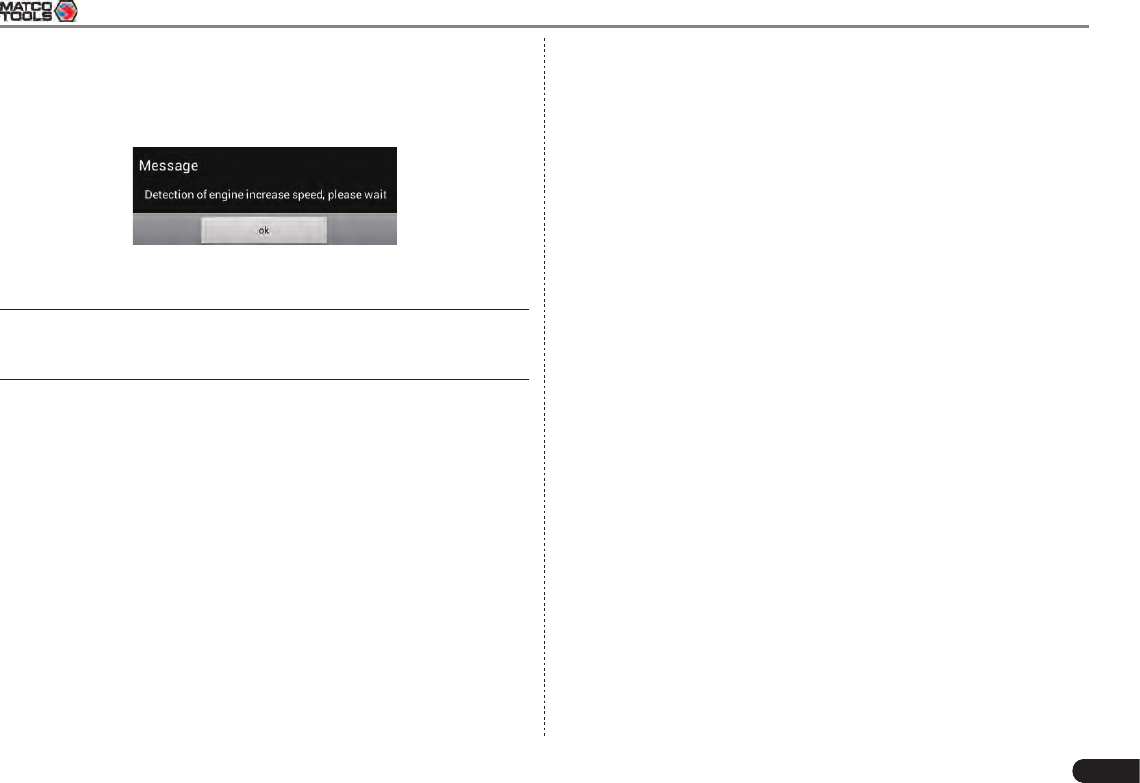
Maximus 3.0 User's Manual
61
After detecting engine starting, follow the instructions on the screen to
increase the speed.
The system begins to receive test data information after acceleration
was detected.
Fig. 7-19
Tap [OK], test data will be shown on the screen.
*Note: It is unnecessary to perform charging system and start system
test after finishing battery test, but battery test must be done before
undergoing charging system and starng system test.
7.2.4.3 Outside the vehicle test
It only applies to battery test and detecting oating electricity will be
ignored while performing battery test.
In Fig. 7-14, tap [Outside the vehicle] to select battery test standard.
The following operation steps are identical to Steps 6 ~ 7 in Chapter
7.2.4.2 Battery test. Please refer to it for details.
7.2.5 Precautions on battery test
For the purpose of getting accurate test results, unless otherwise
special required, all loads need to be power off such as headlamp,
engine etc. before testing battery.
The operating time required for charging system and actuation system
test varies from person to person. If the engine does not start or
accelerate within 30 seconds, the system will prompt you “receiving
timeout” and return to the initial status.
Whether Engine is off or not has no influence on charging and
actuation test result after increased speed is detected, but other loads
need to be powered off.
The accuracy of battery voltage, charging voltage, start voltage is
0.01V in test results; CCA (Cold Cranking Amps) precision is 5CCA.
Generally, charging voltage value is greater than starting voltage.
Charging voltage range is as follows: 13.8--14.5V for domestic vehicle;
13.3--15.5V for imported vehicles. The voltage varies with different
car models, so you have to judge based on related vehicle models.
In general, the DC voltage is stable, but it also varies with different
revolution speed.
Starting voltage range: The value higher than 9.6V is regular,
otherwise it is too low. Due to different situations, whether the starting
voltage is higher or not does not mean the vehicles or batteries are
faulty. For detailed faults, other special equipments are needed.
To validate the accuracy of the value, the best method is to collect
the signals of starting and charging voltage and observe it on an
oscillometer.
Generally, the voltage is lower than 11V for the bad cell battery, but it
is possible that the battery is completely exhausted or has a serious
low capacity. In this case, just recharge your battery. Bad cell always
happens when the loads on a stopping vehicle are turned on for a long
time.
Please note that it is normal for quick detecting of “Increase speed”
because it follows the theory of detecting “Increase speed”: If the
detected voltage is higher than the previous battery test voltage, the
system will prompt you a message of “Engine has been speeded”
It has no influence on test result in the event that engine’s output
voltage or engine revolution is not very stable. No matter whether
the vehicle is accelerated or not, the output voltage only differs within
0.2V.
While doing inside the vehicle test, Kelvin clip is always found to be
in poor contact. To remain it in good contact, please shake it several
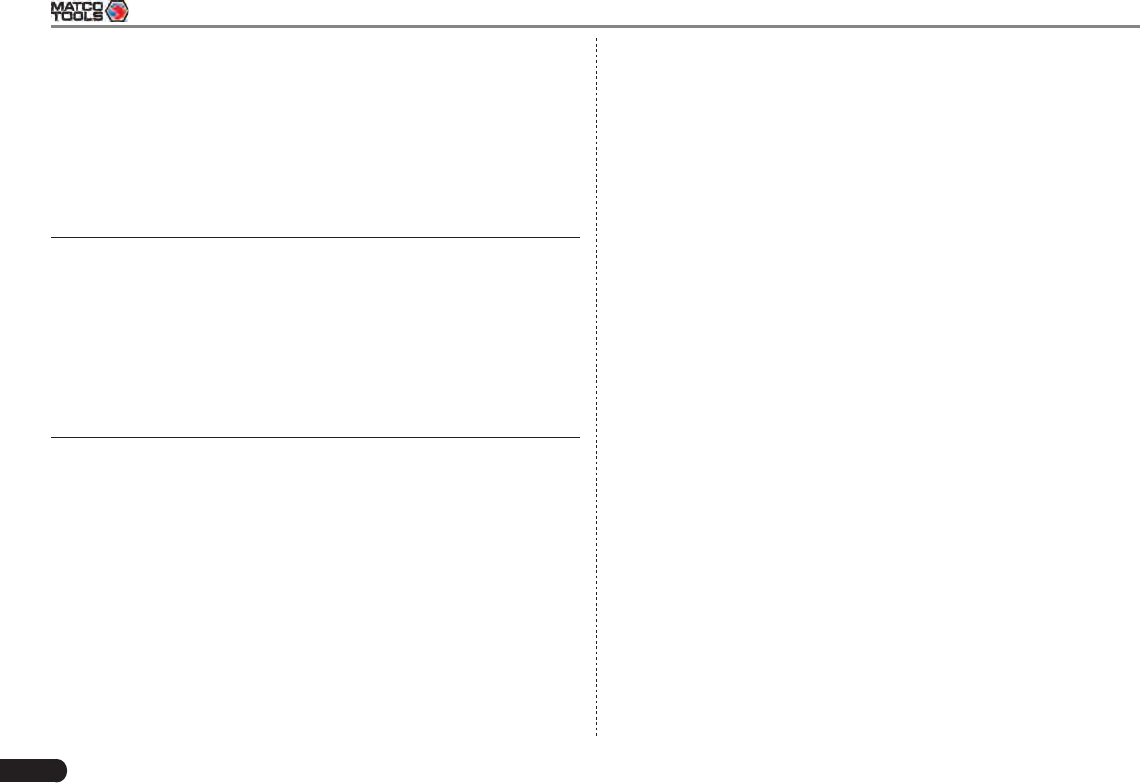
62
Maximus 3.0 User's Manual
times before testing. Take down the battery connector, and test it
again, the value probably varies. The deviation may arise from battery
connector.
Pay more attention to connect the clip. The battery poles connect
with conductor, which makes the clip has a poor connection when
testing battery. A tolerance of dozens of CCA occurs if the clip is out of
position, or oil, dust attaches on the pole. The gear and main body of
clip should be fully matched with battery poles.
*Notes:
1. Battery poles inside the vehicle are enveloped by connectors, which
may produce some errors for test results. The tolerance results from the
resistance of connectors. The greater the resistance value is, the greater
the tolerance becomes. But generally, the tolerance does not aect the
test conclusion.
2. Tesng the baery separately generates an exact test result. The baery
box is a very useful auxiliary tool for quick test. If any problems were
found, test it separately for geng an exact test result.
7.3 Oscilloscope (Optional)
7.3.1 Introduction
The Scopebox is an optional add-on module of Maximus 3.0, including
automotive oscilloscope and automotive ignition waveform.
Automotive oscilloscope can make the auto repair technician quickly
judge the faults on automotive electronic equipment and wiring, and
the oscilloscope sweep speed is far greater than the signal frequency
of such vehicles, usually 5-10 times of the measured signal. The
automotive oscilloscope not only can quickly acquire the circuit signal,
but also can slowly display the waveform to observe and analyze.
It can also record and store the tested signal waveform which can
be recalled to observe for the fast signal, having great convenience
to failure analysis. Either high-speed signal (e.g.: Injection nozzle,
intermittent fault signal) or the slow-speed signal (e.g. the throttle
position change and the oxygen sensor signal) can be observed
through automotive oscilloscope in an appropriate waveform.
The electronic signal can be compared and judged via measuring
ve parameters indexes. The ve parameters are the amplitude (the
maximum voltage of signal), the frequency (the cycle time of signal),
the shape (the appearance of signal), the pulse width (the duty cycle
or the time range of signal), and the array (the repetition characteristic
of signal), which can be tested, displayed, saved by the automotive
oscilloscope. Via the waveform analysis can further detect the circuit
fault on sensors, actuators, circuits, and electronic control units, etc.
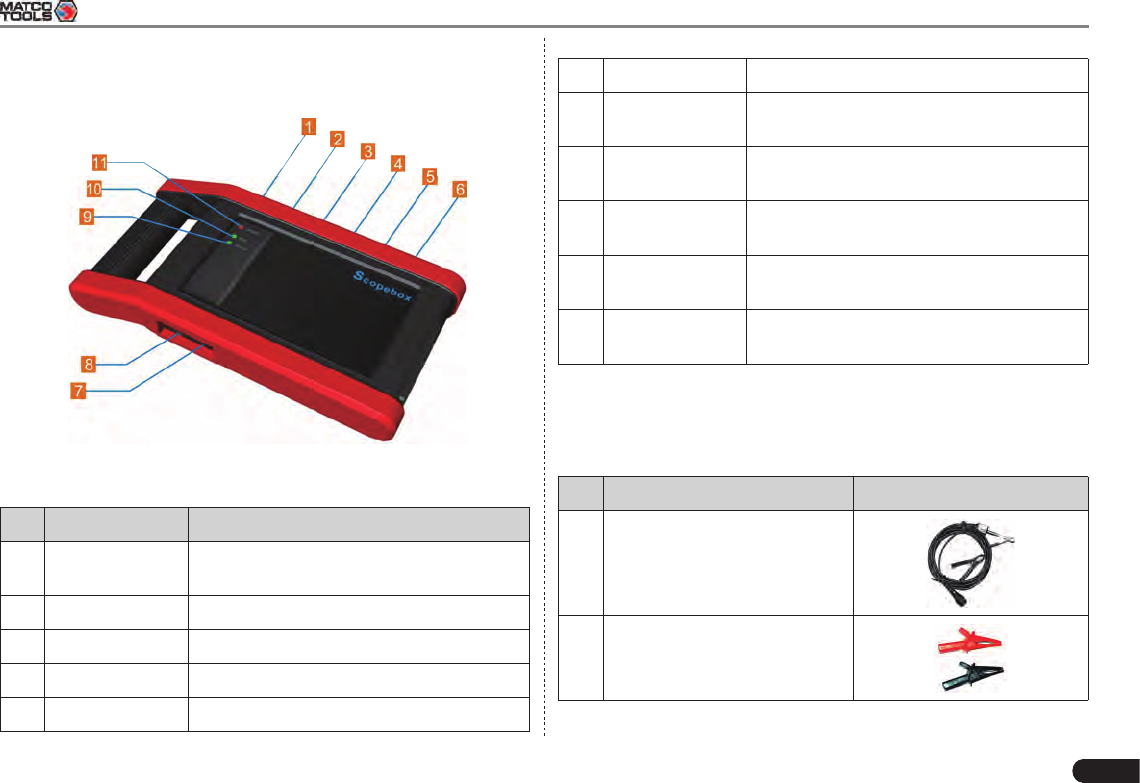
Maximus 3.0 User's Manual
63
7.3.2 Structure & Accessories
7.3.2.1 Scopebox structure
Fig. 7-20 Scopebox Structure Diagram
Below describes the ports and indicators for the Scopebox.
No. Name Descriptions
1Fixed signal
generator
Generate a square signal with xed 1K
frequency.
2 CH1 Channel 1
3 CH3 Channel 2
4 CH3 Channel 3
5 CH4 Channel 4
6 External trigger External trigger signal
7B-shaped USB
interface Connect main unit via USB cable as a
separate individual USB devices.
8 Power interface Connect to power supply via the power
adapter.
9Communication
indicator It blinks in process of data communication.
10 Running indicator It remains steady green after the Scopebox
is running.
11 Power indicator It keeps steady red after the Scopebox is
powered on.
7.3.2.2 Scopebox accessories
The Scopebox includes the secondary pickup cable for 4-channel
oscilloscope, crocodile clips for 4-channel oscilloscope, etc. See the
packing list attached to the product for the detailed accessories.
No. Name Picture
1Secondary ignition pickup for
4-channel oscilloscope
2Crocodile clips for 4-channel
oscilloscope
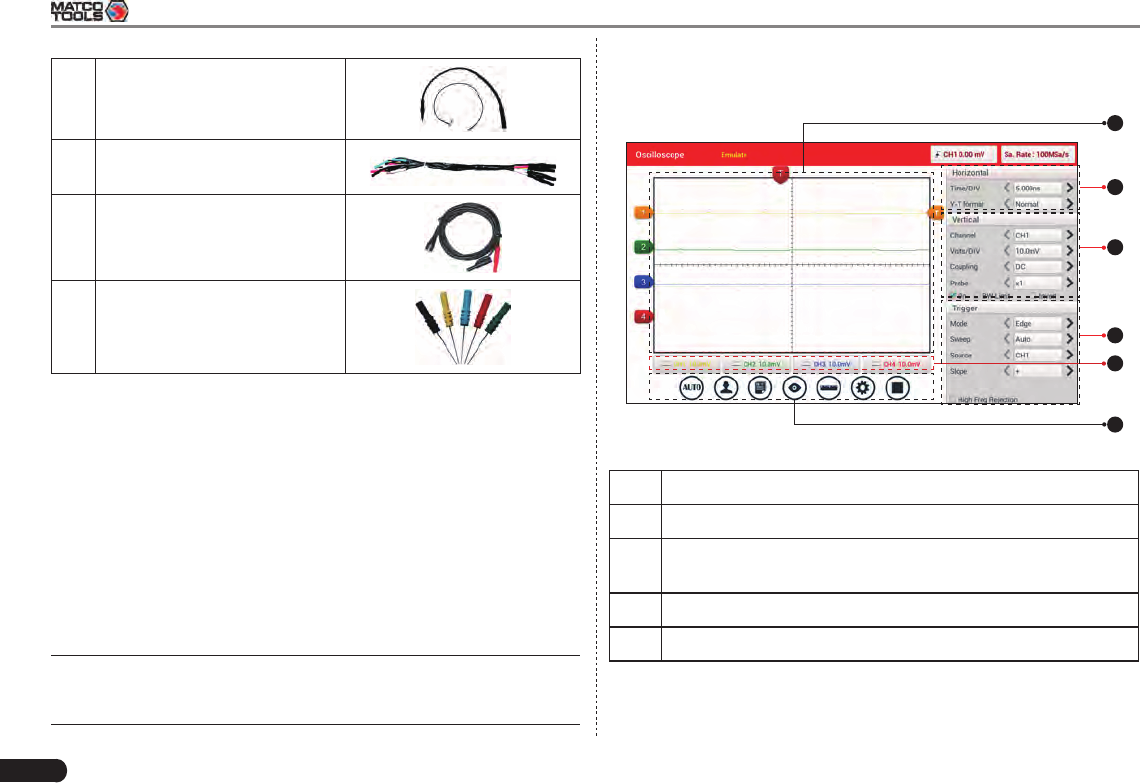
64
Maximus 3.0 User's Manual
3 Direct ignition extension cable
46-way universal guide line for
4-channel oscilloscope
5BNC to 4mm connector test
cable
6Pin connector suite for
4-channel oscilloscope
7.3.3 Connection & Initial Use
7.3.3.1 Connection
The Scopebox should work with the Maximus 3.0 tablet.
1. Firstly, power on the Maximus 3.0 handset.
2. Connect one end of the data cable to the B-shaped terminal of the
Scopebox, and then connect the other end to the Data transmission
port of Maximus 3.0 handset.
3. Then plug one end of ground cable of the Scopebox into external
trigger channel (GND), and the other end should be grounded.
4. Connect one end of probe cable to the CH1, CH2, CH3, or CH4 on
the Scopebox, and the other end to related signal terminal.
Warning: Please use the specic capacitance probe when diagnosing the
ignition high voltage line. Never connect the Scopebox to the ignition
secondary circuit directly.
7.3.3.2 Initial interface introduction
Below displays the initial interface of the Scopebox.
1
2
3
4
5
6
Fig. 7-21
1 Signal display area
2 Horizontal Settings: Controls the time base.
3Vertical Settings: Controls the amplitude of the displayed
signal.
4 Trigger Settings: Controls the start event of the sweep.
5 Channel Selection Button
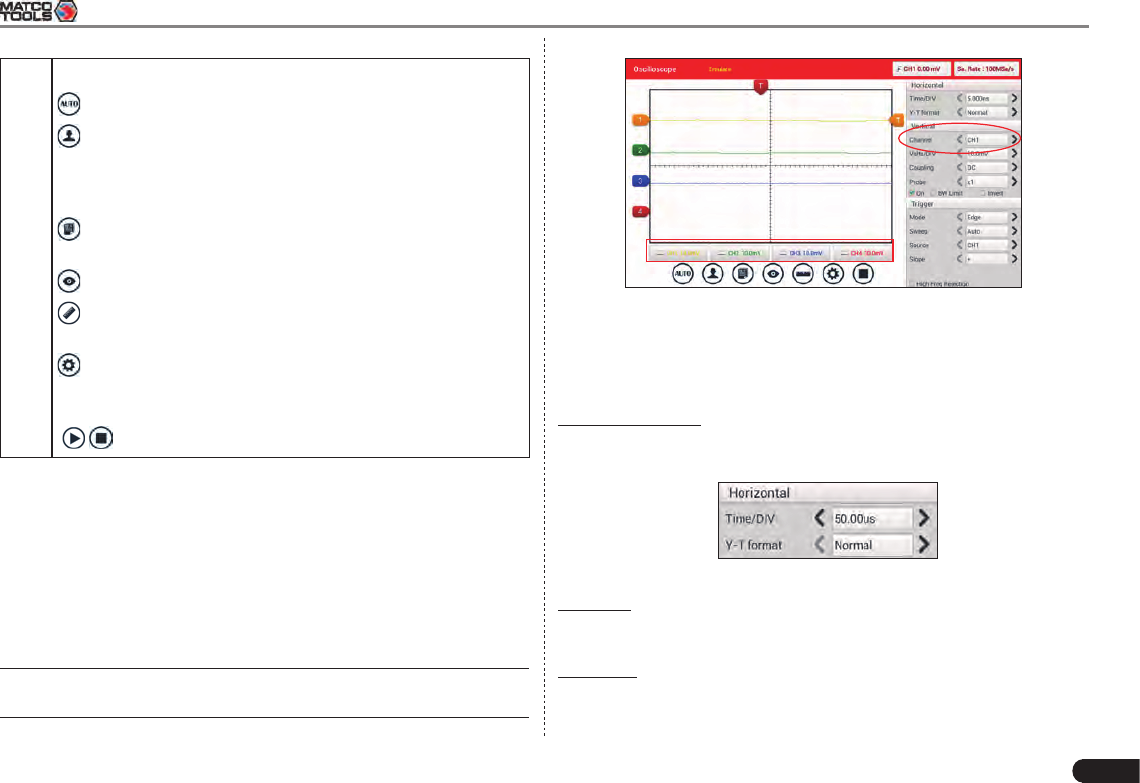
Maximus 3.0 User's Manual
65
6 Function Menu
[Auto]: It indicates auto trigger setting.
[Ref]: There are expert reference and base reference
available. Expert reference enables you to recall your
customized expert database, whereas base reference
provides automatic pre-setting function of specialized sensors.
[File]: Provides save snapshot, snapshot manager,
waveform record and waveform replay.
[View]: Calibration and display settings are available.
[Measure]: Includes signal source measurement, horizontal
measurement, vertical measurement and clear measurement.
[Settings]: Shows/hides the parameter settings area
including horizontal settings, vertical settings and trigger
settings.
/ [Start/Stop]: Starts/stops collecting waveforms.
7.3.4 Operations
7.3.4.1 Channel selection and attributes setting
<1> Channel selection
There are two ways available for channel selection:
A. Select from the channel tab shown at the bottom of the waveform
display area
B. Select from Vertical settings
*Note: For better comparison and identification, each channel and
waveform are marked in dierent colors.
Fig. 7-22
<2> Channel attributes & trigger setting
Channel attributes can be set via horizontal settings and vertical
settings.
Horizontal Settings
User can make some settings directly by tapping < or > next to
options.
Fig. 7-23
Time/DIV: Horizontal scale. If the waveform acquisition is stopped
(using the / button), the Time/DIV selector expands or compresses
the waveform.
Y-T format: The conventional oscilloscope display format. It shows the
voltage of a waveform record (on the vertical axis) as it varies over
time (on the horizontal axis).
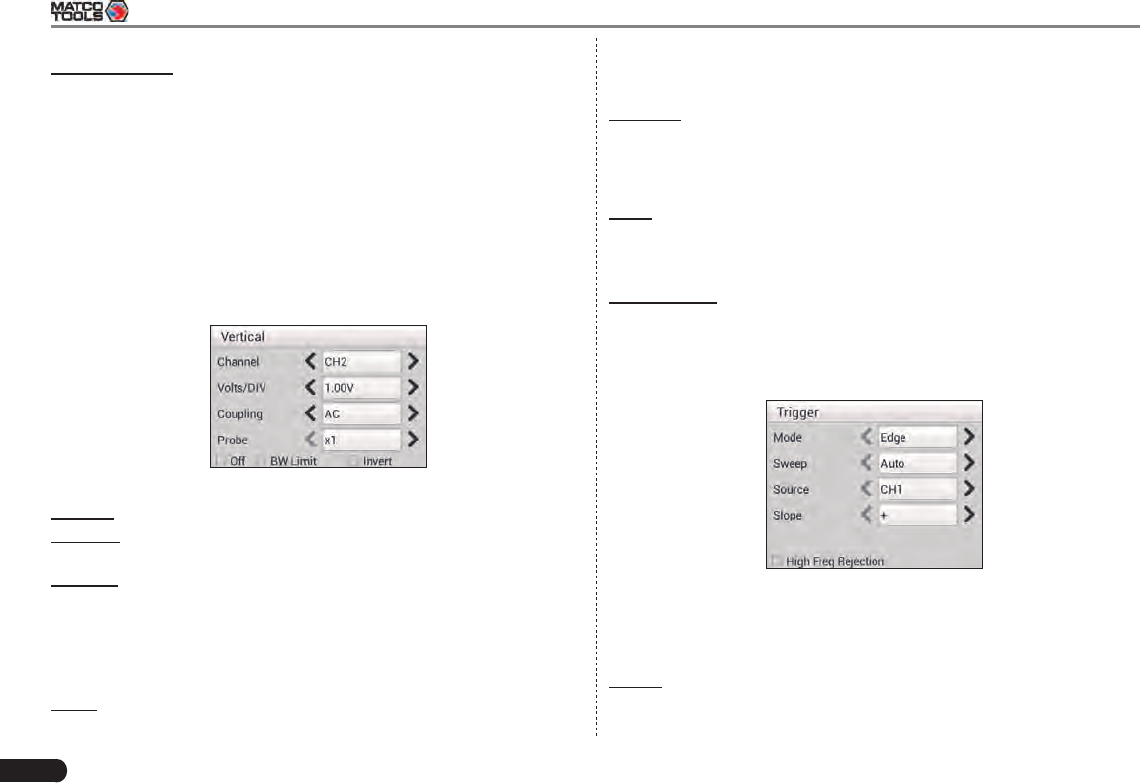
66
Maximus 3.0 User's Manual
Vertical Settings
The trigger determines when the Scopebox starts to acquire data and
display a waveform. When a trigger is set up properly, it can convert
unstable displays or blank screens into meaningful waveforms.
When the Scopebox starts to acquire a waveform, it collects enough
data so that it can draw the waveform to the left of the trigger point.
The Scopebox continues to acquire data while waiting for the trigger
condition to occur. After it detects a trigger, the Scopebox continues to
acquire enough data so that it can draw the waveform to the right of
the trigger point.
User can make some settings directly by tapping < or > next to
options.
Fig. 7-24
Channel: To select the channel source.
Volts/DIV: It is dened as “Volts/Division” and mainly used to change
the resolution.
Coupling: Trigger coupling determines what part of the signal passes
to the trigger circuit. AC, DC and Ground are included:
• AC: Blocks the DC component of the input signal.
• DC: Passes both AC and DC components of the input signal.
• Ground: Disconnects the input signal.
Probe: When using a probe, the Scopebox allows you to select the
attenuation factor for the probe. The attenuation factor changes the
vertical scaling of the Scopebox so that the measurement results
reect the actual voltage levels at the probe tip.
BW Limit
• ON: Limits the channel bandwidth to 20MHz to reduce display
noise.
• OFF: Get full bandwidth.
Invert
• ON: Turn on the invert function.
• OFF: Restore to the original display of the waveform.
Trigger setting
Trigger indicates that when certain waveform meets the conditions that
are predened according to the requirements, the Scopebox acquires
the waveform and its adjacent section, and then presents it on the
screen.
Fig. 7-25
1) If Edge trigger is selected (An edge trigger determines whether the
Scopebox nds the trigger point on the rising or the falling edge of
a signal.):
Sweep: The sweep mode determines how the Scopebox behaves in
the absence of a trigger event. The Scopebox provides three trigger
modes: Auto, Normal, and Single.
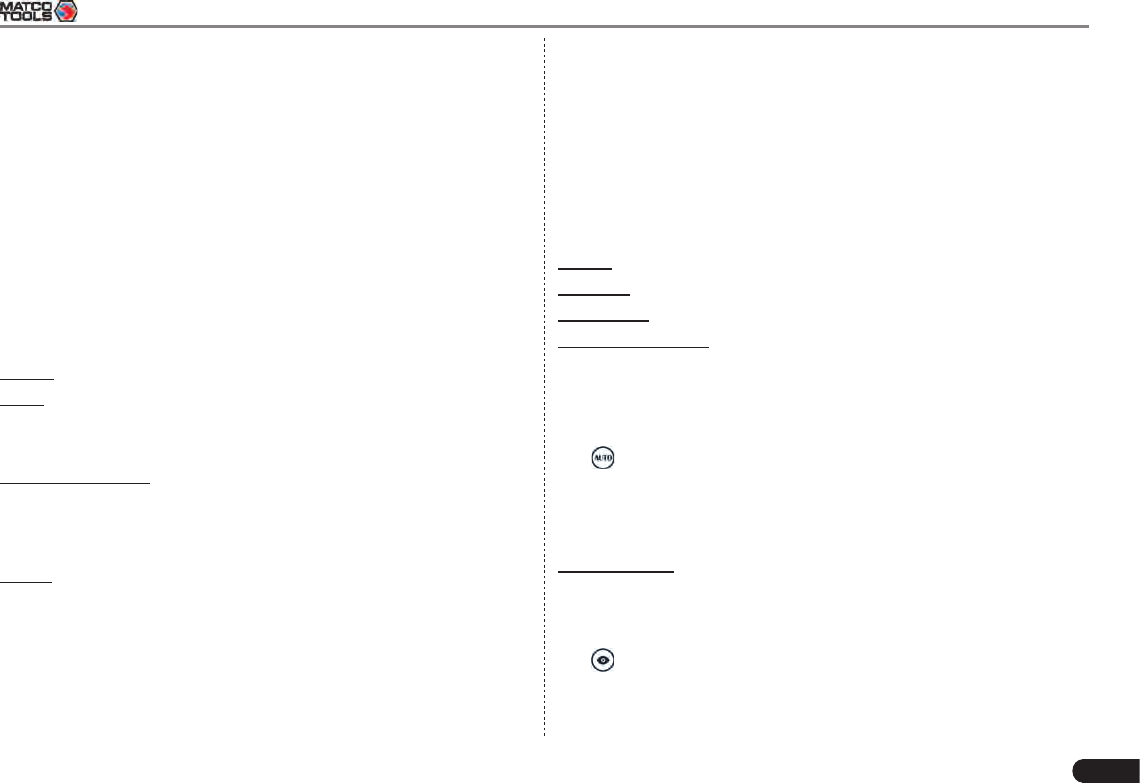
Maximus 3.0 User's Manual
67
• Auto: It allows the Scopebox to acquire waveforms even when it
does not detect a trigger condition. If no trigger condition occurs
while the Scopebox is waiting for a specic period, it will force itself
to trigger.
When forcing invalid triggers, the Scopebox can not synchronize
the waveform, and then waveform seems to roll across the display.
If valid triggers occur, the display becomes stable on the screen.
• Normal: This mode allows the Scopebox to acquire a waveform
only when it is triggered. If no trigger occurs, the Scopebox keeps
waiting, and the previous waveform, if any, will remain on the
display.
• Single: In this mode, it only acquires the waveform that generates
for the rst time the trigger conditions are met, and then stops after
nishing capture.
Source: Select which channel as trigger signal.
Slope:
• + : Trigger on rising edge
• - : Trigger on falling edge
High Freq Rejection: Reject high frequency signals when selected.
2) If Pulse Width trigger is selected (Pulse trigger occurs according to
the width of pulse. The abnormal signals can be detected through
setting up the pulse width condition):
Sweep: The sweep mode determines how the Scopebox behaves in
the absence of a trigger event. The Scopebox provides three trigger
modes: Auto, Normal, and Single.
• Auto: It allows the Scopebox to acquire waveforms even when it
does not detect a trigger condition. If no trigger condition occurs
while the Scopebox is waiting for a specic period, it will force itself
to trigger.
When forcing invalid triggers, the Scopebox can not synchronize
the waveform, and then waveform seems to roll across the display.
If valid triggers occur, the display becomes stable on the screen.
• Normal: This mode allows the Scopebox to acquire a waveform
only when it is triggered. If no trigger occurs, the Scopebox keeps
waiting, and the previous waveform, if any, will remain on the
display.
• Single: In this mode, it only acquires the waveform that generates
for the rst time the trigger conditions are met, and then stops after
nishing capture.
Source: Select which channel as trigger signal.
Condition: To select pulse condition.
Pulse Width: Set required pulse width.
High Freq Rejection: Reject high frequency signals when selected.
7.3.4.2 Auto
The Scopebox has an Auto feature that sets up the Scopebox
automatically to display the input signal in a best t.
Tap , the Scopebox may change the current settings to display the
signal. It automatically adjusts the vertical and horizontal scaling, as
well as the trigger coupling, position, slope, level and mode settings.
7.3.4.3 View Settings
<1> Calibration
This option adjusts the Scopebox’s internal circuitry to get the best
accuracy. Use this function to calibrate the Scopebox’s vertical and
horizontal systems.
Tap and then tap [Calibration], a dialog box similar to Fig. 7-26 will
appear.
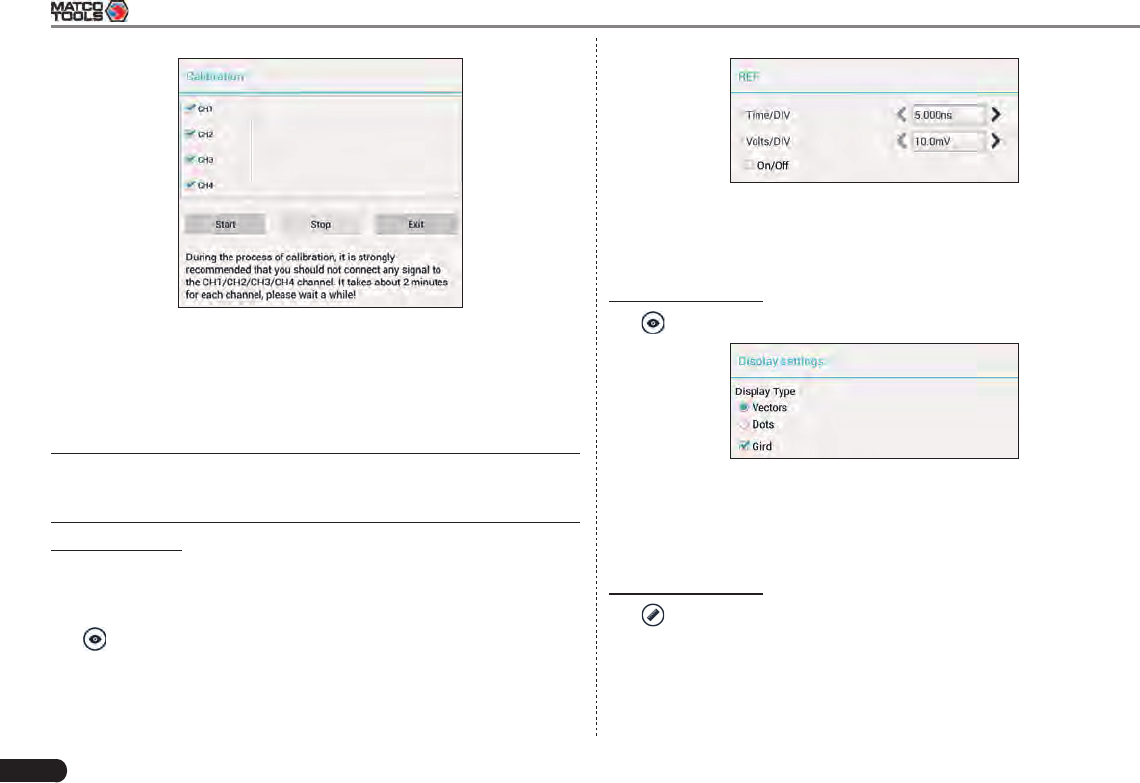
68
Maximus 3.0 User's Manual
Fig. 7-26
Check the box before the channel to select it. To deselect it, just
uncheck it. After choosing the desired channel(s), tap [Start] to
start calibration and [Start] button will be temporarily invalid during
calibrating. Tap [Stop] to stop calibrating. Once it becomes active, it
indicates calibration has completed.
*Note: In process of calibration, make sure CH1/CH2/CH3/CH4 has no
signal input. Moreover, calibraon may take several minutes and please be
paent to wait.
<2> REF settings
Reference waveforms are saved waveforms to be selected for display.
The reference function will be available after saving the selected
waveform to non-volatile memory.
Tap and then [REF] to enter the REF setting screen.
Fig. 7-27
Tap < or > to select the desired reference value for time/DIV and volts/
DIV. To show or hide the REF, just check/uncheck the box before On/
Off.
<3> Display settings
Tap and then [Display settings] to enter the setting screen.
Fig. 7-28
Select “Vectors” or “Dots” to display waveforms as vectors or dots.
Check / uncheck the box before Grid to turn on/off grid display.
7.3.4.4 Measure
<1> Channel source
Tap and then [Source], a screen similar to the following will appear.
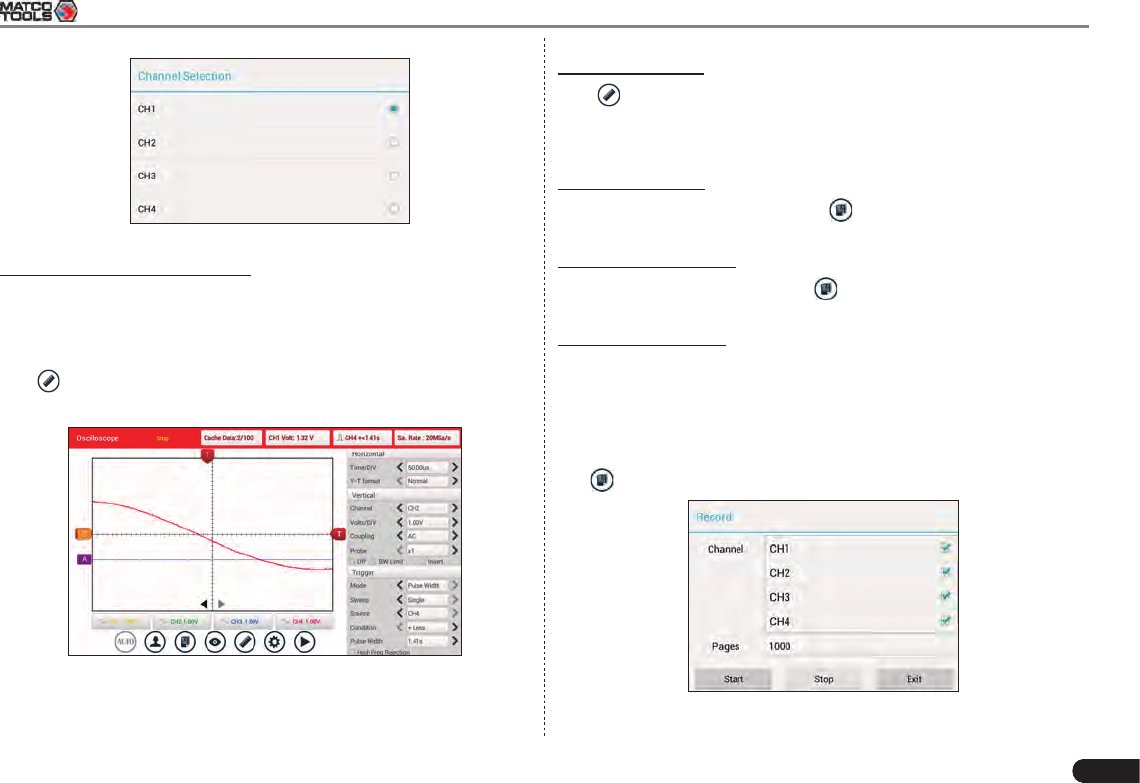
Maximus 3.0 User's Manual
69
Fig. 7-29
<2> Horizontal / Vertical measure
Horizontal Measure / Vertical Measure are used to measure voltage
parameter and time parameter respectively. Drag A line upwards or
downwards to control voltage. Move A line left or right to fine-tune
timebase. A line is a solid line and B line is a dotted line.
Tap and then [Horizontal Measure], a screen similar to the
following will appear.
Fig. 7-30
* Note: If no desired channel is selected, the system will take the current
source as the default channel.
<3> Clear measure
Tap and then [Clear Measure], the system will clear the
measurement result on screen.
7.3.4.5 File management
<1> Save snapshot
While viewing sampling data, tap and then [Save Snapshot] to
store the current screen.
<2> Snapshot manager
While viewing sampling data, tap and then [Snapshot Manager] to
enter. View, delete and edit operations are supported.
<3> Record waveform
This function is used to record input waveforms that are acquired by
the Scopebox at a specic period, and save it as waveform le which
can be recalled in future.
It can be performed only when the Scopebox is collecting data in
Normal mode.
Tap , then select [Record] from the pop-up menu to start recording.
Fig. 7-31
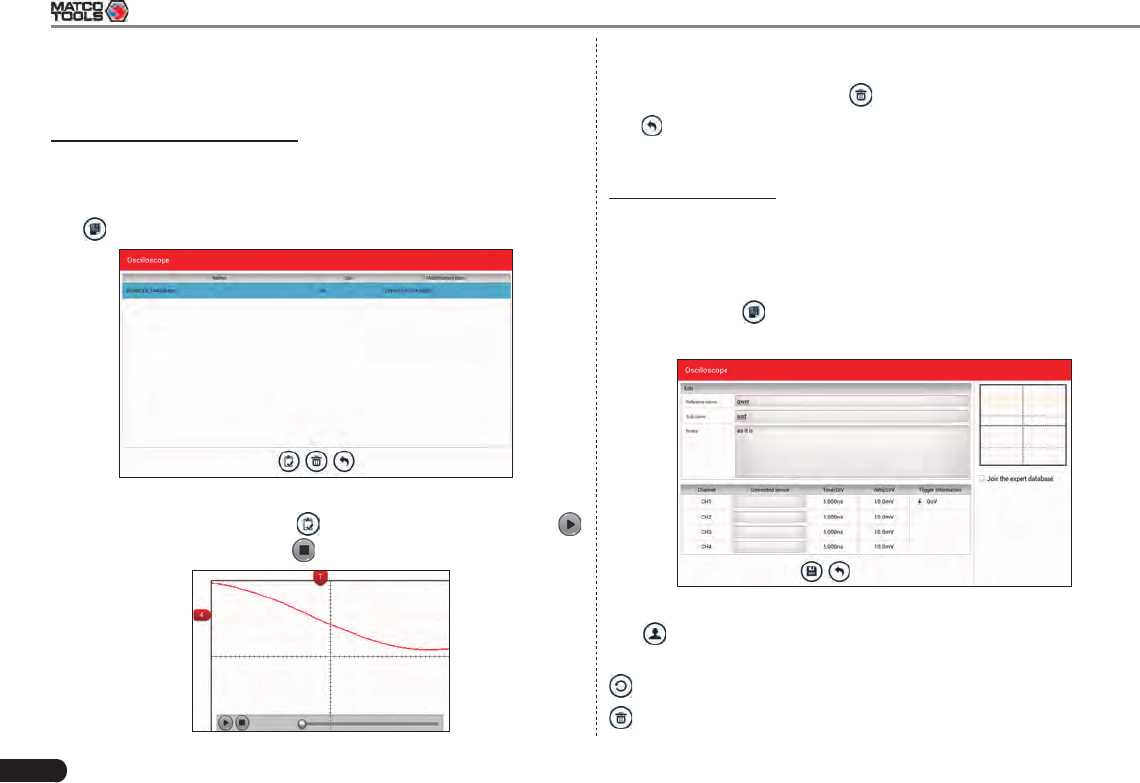
70
Maximus 3.0 User's Manual
Tap [Start] to start recording with a minimum record length of 10
frames, and [Stop] to stop recording. While recording, the recorded
pages will be shown on the screen.
<4> Load waveform for playback
The Import function enables you to import the stored waveform le for
playback and review. During replaying, the Scopebox stops collecting
data automatically.
Tap , then select [Waveform replay] from the pop-up menu to enter:
Fig. 7-32
Select the le rst, and then tap to open the waveform le. Tap
to starting the playback and tap to stop it.
Fig. 7-33
To delete the waveform le, tap .
Tap to return to the previous screen.
7.3.4.6 Expert reference
<1> Expert Reference
By default, it appears blank. As a matter of fact, Expert reference
database is generated by doing the following:
1. Open and edit a snapshot;
2. Select “Joint the expert database” (refer to the following illustration),
and then tap to save the waveform being displayed on the
screen as REF.
Fig. 7-34
Tap and then [Expert Reference] to enter, the following operation
can be done:
: To load and recall the selected le.
: To delete the selected le.

Maximus 3.0 User's Manual
71
: To edit the selected le.
<2> Base Reference
Preset waveforms of some sensors are available for your reference.
Fig. 7-35
7.4 Ignition (Optional)
The ignition system is the system which has greatest impact on
the performances of gasoline engine, as the statistical data shows
that nearly half of the failures are caused by poor work of electrical
system. And the performance tests of engine often start from the
ignition system. Nowadays ignition system includes distributor and
distributorless. Distributorless includes independent ignition and
simultaneous ignition.
1. Distributor ignition system i.e. contact breaker with contact-
controlled ignition system (commonly known as the platinum)
and contact breaker with noncontact-controlled ignition system
combined with magnet, hall components or infrared.
2. Independent ignition system: crankshaft sensor send out the
ignition timing signal and cylinder identification signal so that the
ignition system can send out ignition signal to specied cylinder in
specied time, each cylinder has its independent ignition coil.
3. Simultaneous ignition system: two cylinders share one ignition
coil, when two cylinder pistons reach top dead center at the same
time (one is compression, another is the exhaust), two spark plugs
will be ignited at the same time, at this time, the ignition for the
former cylinder is in high-pressure low temperature gas mixture,
the ignition is valid, while for the latter one is in low-pressure high
temperature exhaust gas, the ignition is invalid.
Maximus 3.0 can test and analyze the secondary signal for various
engine ignition systems.
The Ignition module utilizes the same hardware device as the Scope
module.
7.4.1 Secondary-distributor ignition analysis
Connections: Plug the BNC end of secondary ignition pickup into CH1/
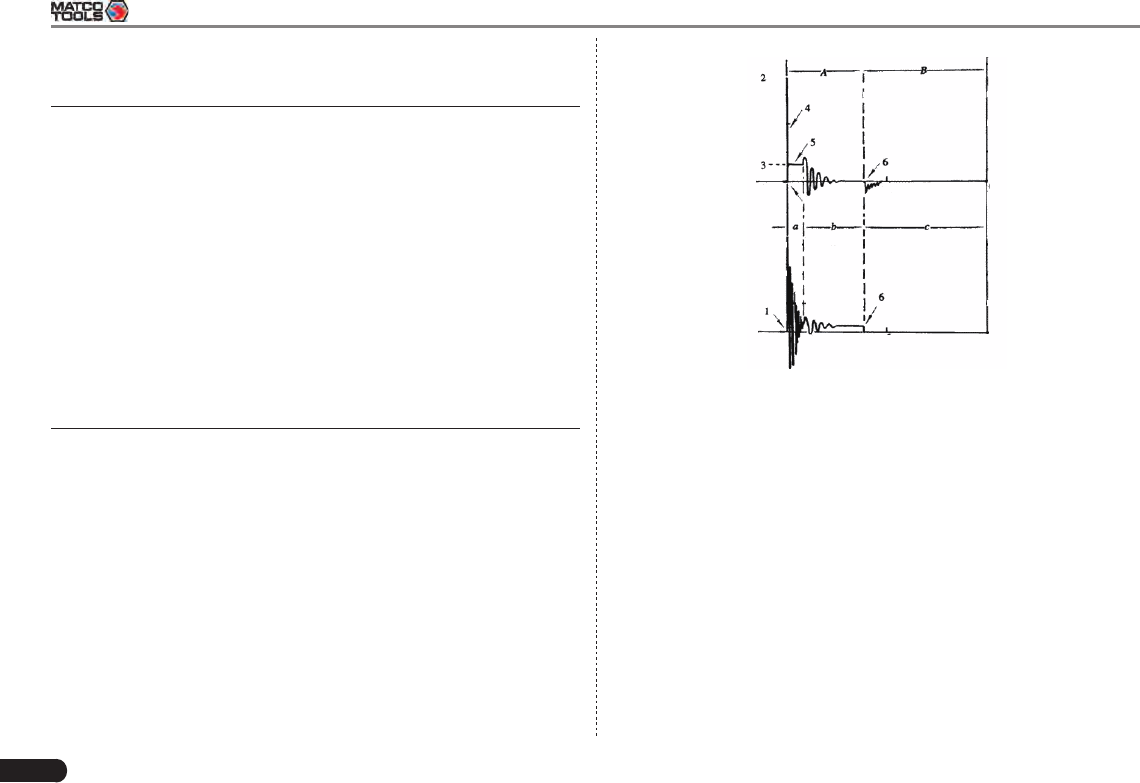
72
Maximus 3.0 User's Manual
CH2/CH3/CH4 channel of Scopebox, then connect the high-voltage
clip to high-voltage line, and crocodile clips to ground.
*Tips: Common ignion sequence (the specic sequence is subject to the
actual engine ignion sequence)
Four-stroke in-line four-cylinder: 1-2-4-3, or 1-3-4-2
Four-stroke in-line six-cylinder: 1-5-3-6-2-4, or 1-4-2-6-3-5
Four-stroke in-line eight-cylinder: 1-8-4-3-6-5-7-2
Five-cylinder: 1-2-4-5-3
V 6 engine: generally speaking, based on the person sing on the driver
cab, if the right side cylinder numbers on the right side, from the front
to the back are as follows: 1, 3, 5; and the cylinder numbers on the left
side, from the front to the back are as follows: 2, 4, 6; then the ignion
sequence is: 1-4-5-2-3-6. If the cylinder numbers on the right side, from
the front to the back are as follows: 2, 4, 6; and cylinder numbers on the
le side, from the front to the back are as follows: 1, 3, 5; then the ignion
sequence is: 1-6-5-4-3-2.
Figure 7-36 below shows the normal ignition waveform of distributor
ignition system, the upper one is the secondary waveform, and the
lower one is the primary waveform.
The secondary waveform
A section is contact open period; B section is make contact period,
which is the magnetizing eld of ignition coil.
Fig. 7-36
1) Contact break point: the primary circuit of ignition coil cut off, the
secondary voltage was sensed and increased sharply
2) Ignition voltage: secondary coil voltage overcome the damper of
high voltage line, the contact breaker gap and the spark plug gap to
release magnetizing energy, 1-2 section is the breakdown voltage
3) Spark voltage: For the capacitor discharge voltage
4) Ignition voltage pulse: For the charge and discharge sections
5) Spark line: The inductance discharge process, i.e. the mutual
inductance voltage of ignition coil maintains the conduction of
secondary circuit.
6) Contact point close the current ow into primary coil, the primary
coil oscillates due to the mutual inductance.
Primary ignition waveform
Section a shows the voltage oscillation on the primary circuit due to
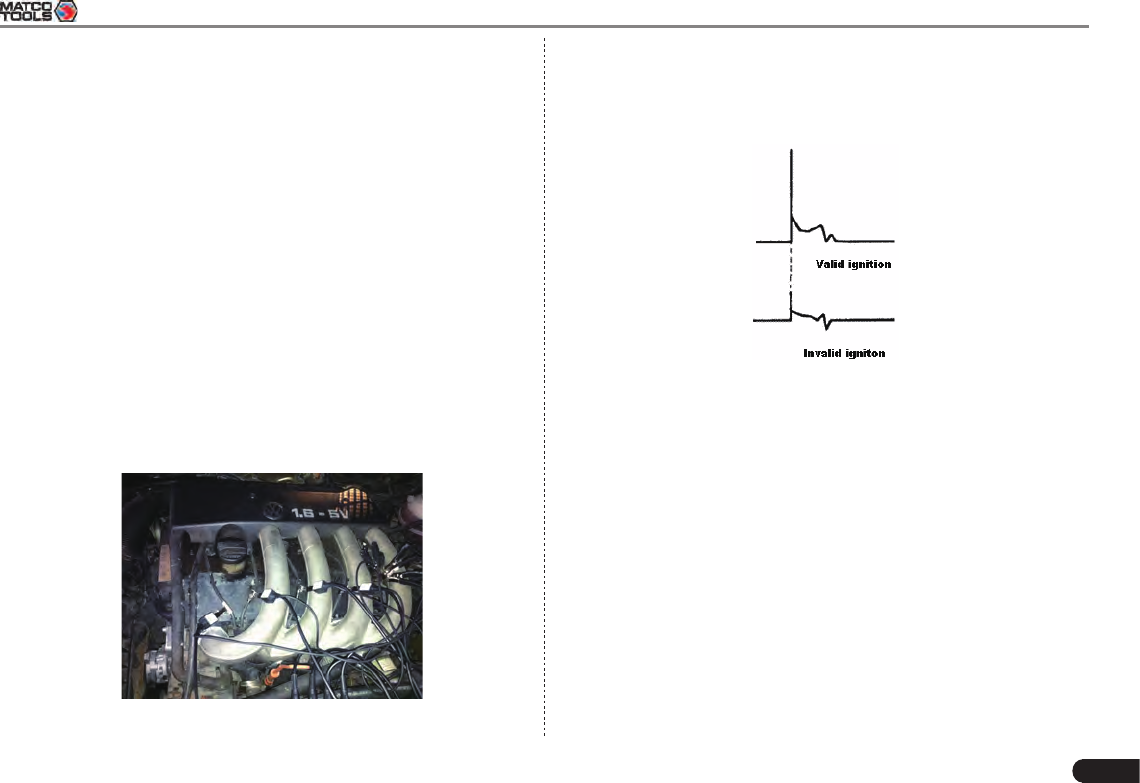
Maximus 3.0 User's Manual
73
the magnetic induction of spark in the duration;
Section b shows the damped oscillation generated by remaining
magnetic eld energy after the spark;
Section c shows the make contact magneting period of primary coil.
Seen from the waveform, the amplitudes of breaker contact closed
angle, break angle and breakdown voltage and spark voltage are very
clear, besides, the spark delay period and two oscillations can also
be tested. For the ignition system without faults, compared with the
whole cycle, the contact closed angle just 45%-50% (four-cylinder),
63%-70% (six-cylinder), or 64%-71% (eight-cyliner); the breakdown
voltage is over 15kv; the spark voltage is about 9kV, the spark period
is greater than 0.8ms. If these values or waveform are abnormal, it
means there is fault or the system needs to be adjusted.
7.4.2 Secondary-simultaneous ignition analysis
Connections: Plug the BNC end of secondary ignition pickup into CH1/
CH2/CH3/CH4 channel of Scopebox, then connect the high-voltage
clip to high-voltage line, and crocodile clips to ground.
Connection as shown in gure 7-37:
Fig. 7-37
Fig. 7-38 below shows the valid and invalid ignition waveforms. Under
the working status of valid ignition, the breakdown voltage and spark
voltage are higher because the cylinder is lled with fresh combustible
mixture gas, which has a lower ionization level and vice versa.
Fig. 7-38
7.4.3 Secondary-direct ignition analysis
Connection:
1) When the high-voltage wire is exposed, plug the BNC end of
secondary ignition pickup into CH1/CH2/CH3/CH4 channel of
Scopebox, then connect the high-voltage clip to high-voltage line,
and crocodile clips to ground.
2) If no high-voltage wire exposes, dismantle ignition coil of tested
cylinder and use direct ignition extension cord. Connect one end to
ignition coil which should be grounded via direct ignition grounding
wire, and insert the other end into cylinder to joint with spark plug.
Then plug the BNC end of secondary ignition pickup into CH1/CH2/
CH3/CH4 channel of Scopebox, then connect the high-voltage clip
to high-voltage line, and crocodile clips to ground.
Connections are shown in Fig. 7-39:
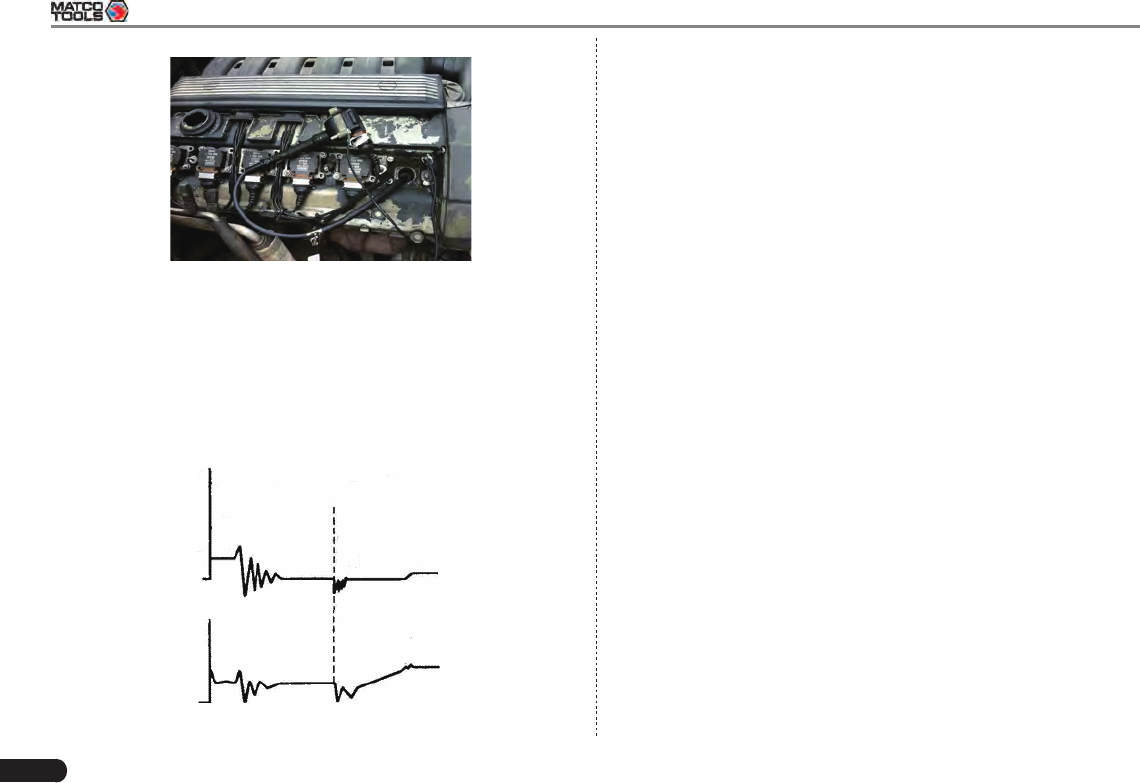
74
Maximus 3.0 User's Manual
Fig. 7-39
Fig. 7-40 shows the normal secondary (the upper one) and (the lower
one) primary ignition waveform of direct ignition system. Beause the
on/off of primary circuit is not opening/closing of mechanical contact,
but the conduction of transistor. The primary voltage has no obvious
oscillations within the duration, but the voltage increases during the
magnetization process due to current limiting, and this change can
cause corresponding uctuations of secondary voltage line as a result
of induction of ignition coil.
Fig. 7-40
7.4.4 Waveform analysis mode
The ignition secondary single-cylinder waveform test is mainly used to:
a. Analyze the ignition dwell angle of single cylinder.(ignition coil
charging time)
b. Analyze the capability of ignition coil and secondary high tension
circuit (from ignition line to ignition voltage line).
c. Find the improper mixture A/F ratio of single cylinder (from
combustion line).
d. Analyze the capability of capacitance (platinum or ignition system).
e. Find the spark plug that causes misfire of the cylinder (from
combustion line).
This test can provide very meaningful information about the
combustion quality for each cylinder. If necessary, this test can also
be performed during driving. Since the secondary ignition waveform
is signicantly affected by different engines, fuel systems and ignition
conditions, it is useful for detecting the faults of engine mechanical
parts, fuel system components, and ignition system components.
Different parts of the waveform can specify that some components and
systems on the specic cylinder have faults. Refer to the instructions
for various parts of waveform for the related component working status
of specic waveform section.
Test methods and conditions:
Start the engine or drive the vehicle accroding to the driving
performance fault or poor ignition, etc. Confirm the consistence of
judgement standard (the amplitude, frequency, shape and pulse
width, etc., for each cylinder), check the fault of the waveform for
corresponding components.
Waveform results: observe the ignition coil at the beginning of
charging, the relative consistent falling edge represents the dwell
angle and ignition timing of each cylinder are precise.
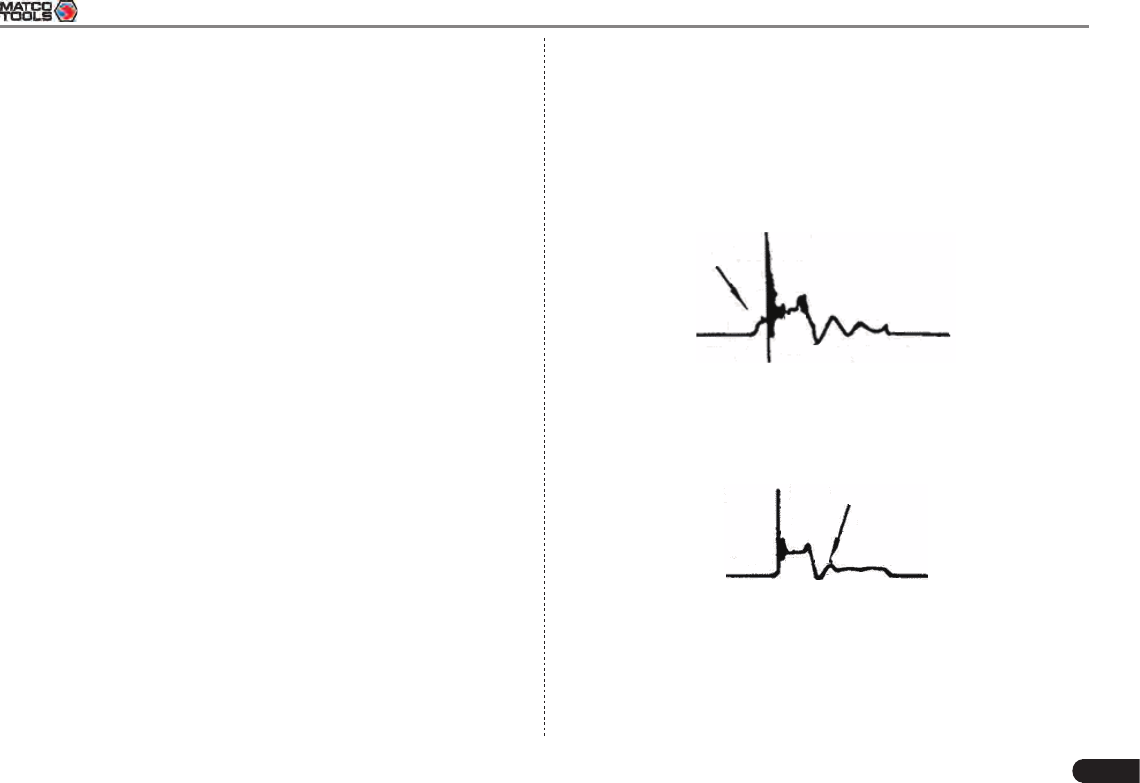
Maximus 3.0 User's Manual
75
Ignition line:
Observe the height consistence of flashover voltage. Too high
ashover voltage (even out of the oscilloscope screen) represents a
high resistance existed in the ignition secondary circuit (for example,
open circuit, or damaged spark plug or high voltage line, or too
large time gap on spark plug), while the too short sparking voltage
represents the resistance of ignition secondary circuit is lower than
normal value (due to pollutant and broken spark plug or the high
voltage line of spark plug has electrical leakage, etc.).
Spark or combustion voltage:
Observe the consistence of spark or combustion voltage, as it
represents the consistence of spark plug and the air-fuel ratio of each
cylinder. In case that the mixing ratio is too lean, the combustion
voltage will be lower than normal value.
Combustion line:
Observe the spark or the combustion line which shall be clean with
few clutter, as lots of clutter indicates the cylinder has poor ignition
due to ignite too early, damaged nozzle, pollutant spark plug, or other
reasons. The duration of combustion line indicates the mixing ratio of
the cylinder is abnormal lean or rich. Too long combustion line (usually
greater than 2ms) represents the mixing ratio is rich, whereas too
short of combustion line (usually less than 0.75ms) represents the
mixing ratio is lean.
Ignition coil oscillation:
Observe at least two oscillation waveforms after the combustion
line, which will be better if more than three oscillation waveforms, as
it represents the ignition coil and capacitor (on Platinum or ignition
system) are normal.
Primary voltage analysis
According to the faulty primary voltage waveform collected by the
ignition analysis, the related components and mechanical equipment
status of ignition system electrical circuit can be analyzed, which
provides a reliable basis for the adjustment and maintenance of power
circuit to avoid the blind demolition.
The waveform shown on Fig. 7-41, appears a lot of clutter on the
contact break point, which is obviously caused by the serious erosion
on contact break point. It can be veried via burnishing the contact or
changing the circuit breaker.
Fig. 7-41
For the primary voltage waveform shown on Fig. 7-42, the damped
attenuation cycles obviously reduced on the spark period, the
amplitude became lower, which is evidently caused by capacitor
leakage.
Fig. 7-42
The waveform on Fig. 7-43 shows the accidental pumping during
contact closing period. The irregular beating is caused by insufcient
spring force.

76
Maximus 3.0 User's Manual
Fig. 7-43
The curve on Fig. 7-44 shows the contact angle is too small during the
magnetizing period, which is caused by too large contact gap.
Fig. 7-44
A lot of clutter will be displayed on the horizontal section of primary
waveform if contact has poor grounding, as shown below gure 7-45.
Fig. 7-45
Fig. 7-46 shows the fault of low-voltage waveform in electronic ignition
system. The voltage does not rise during magnetizing, which indicates
that the effect of limitation of the circuit failed and no components on
distributorless ignition system can be adjusted. When this waveform is
abnormal, you can only replace the ignition coils, igniter, ignition signal
generator and cam position sensor, etc., one by one, to nd out the
faulty component or module.
Fig. 7-46
The secondary waveform is also affected by the spark plug, the
combustion process, mixture gas composition, the engine thermal
state of the ignition coil, etc., which is more complicated. The following
lists a large number of measured secondary faulty waveform for
reference. Since various factors lead to the failures, Fig. 7-47 just
shows the major possible factors for the failures.
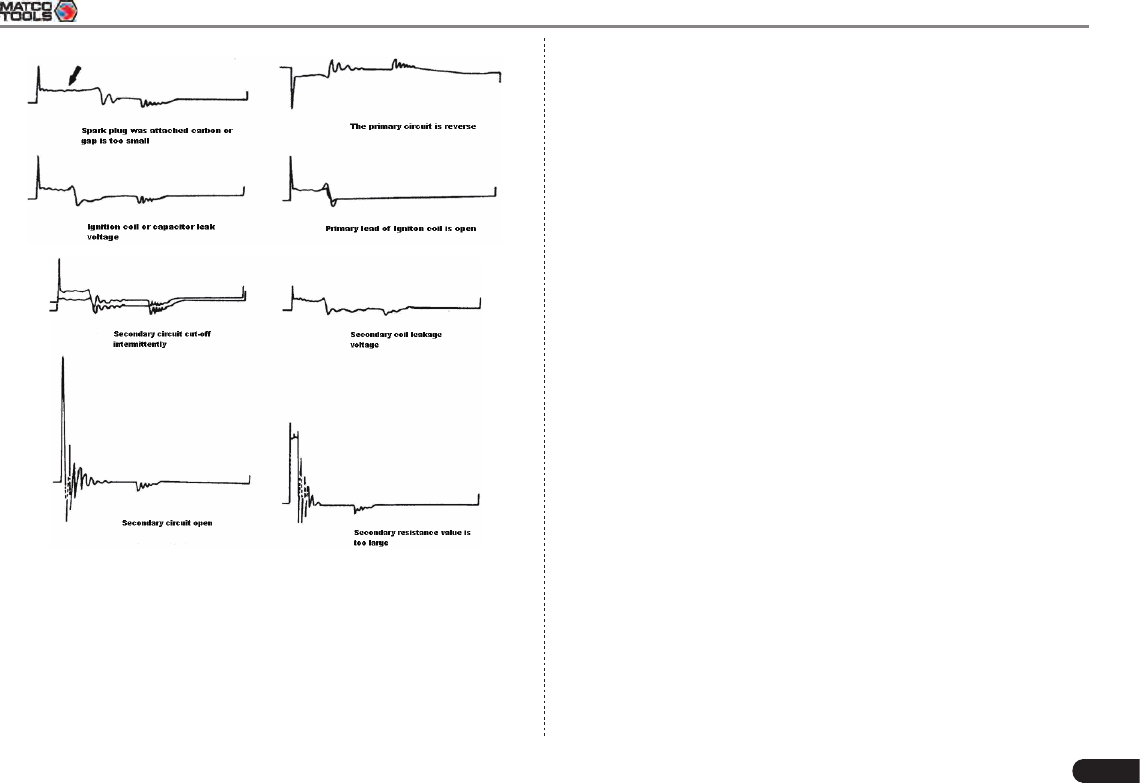
Maximus 3.0 User's Manual
77
Fig 7-47
7.5 Videoscope (Optional)
7.5.1 Introduction
Automotive videoscope is mainly applied to those unseen parts of
engine, fuel tank, braking system.
While testing a vehicle system, engine is one of the main parts to
be checked. To check if the internal of a engine is qualied or not or
whether internal carbon deposit and damage exists in the engine or
not, we can make full use of a videoscope to solve these quesitons.
Maximus 3.0 provides an optional function of videoscope.
The videoscope is mainly composed of an inspection camera, exible
tube and USB cable. The water-resistant camera lens with adjustable
LED lights enables you to observe the parts that can not be seen in
wet, dark, uid soaked places. The included exible tube is convenient
for easy inspection and allows for access to hard-to-reach areas.
In addition, the captured pictures and videos also provide you intuitive
data for easy analysis.
7.5.2 About Videoscope
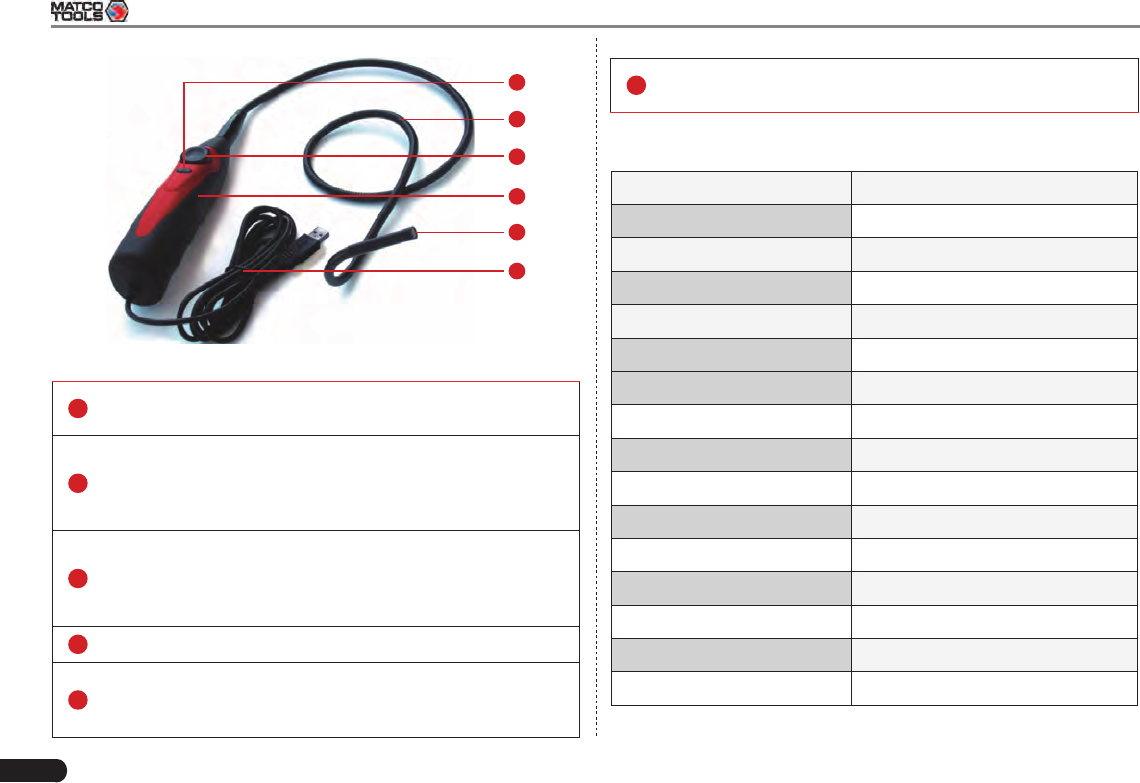
78
Maximus 3.0 User's Manual
1
3
4
2
6
5
Fig. 7-48
1Snapshot button: To take a snapshot of the current view and
save it to your LAUNCH diagnostic tool as an image.
2
Flexible tube: You can bend the neck to get in to hard-to-
reach places and even if it is not straight, it can still give you
pictures of what the camera is looking at. (*Note: Do NOT force
it too hard while bending the neck into strange shapes.)
3
Dial for LED light brightness: There are 4 LED lights in the
lens that act like a torch to illuminate dark spots where the
camera can not see well. This dial allows you to adjust the
light brightness.
4Handle
5Camera with 4 adjustable LED lights: The camera head
is water-resistant and is where you can attach the useful
optional accessories (magnet, mirror, hook) add-on.
6Data cable: Connect it to the diagnostic tool for viewing what
the camera captures.
7.5.3 Technical Parameters
Resolution 640 x 800 pixel (VGA)
Frame Rate 30fps (pictures/sec)
Image Sensor 1/12" CMOS
White Balance Automatic
Exposure Automatic
Light Source 4 adjustable LEDs
Power Supply 5V
Ambient temperature 0 to +65oC
Data Cable Length Approx. 2000mm
Probe & Camera Length 1030mm
Probe Cable Length 830mm
Min. Bending Radius 50mm
Lens Diameter 7.0mm
Probe Tube Diameter 6.0mm
Viewable Angle 60o
Lens Focal Length More than 50mm

Maximus 3.0 User's Manual
79
Net Weight Approx. 270g
7.5.4 Connections & Operations
1. Locate the data transmission port of the Maximus 3.0 handset.
2. Insert the data cable into the data transmission port of port of the
Maximus 3.0 handset.
3. Bend the neck of the flexible tube as desired and extend the
camera with adjustable LED lights to some unseen or unreachable
parts of engine, hydraulic system, nozzles etc.
4. After connections are properly made, press the [POWER] button on
the Maximus 3.0 handset to turn it on. Wait until the system enters
Job menu. Switch to the "Toolbox" module, tap "Applications"
-> "Videoscope" to run it, then the screen will display the scene
captured from the videoscope camera.
5. Adjust it until the lens stops in the desired place, then use the dial
for LED light brightness to adjust the brightness.
6. Press the Snapshot button on the videoscope to take a photo.
Alternatively, you can also press the Snapshot button on the
Maximus 3.0 handset to take photos.
To record a video, switch from Camera mode to Video mode and
tap Record button on the screen to start recording.
Images are captured in .jpg format and videos are recorded in .avi or
.mp4 format. All photographings and videos are saved in DCIM folder
where users can browse and replay it.
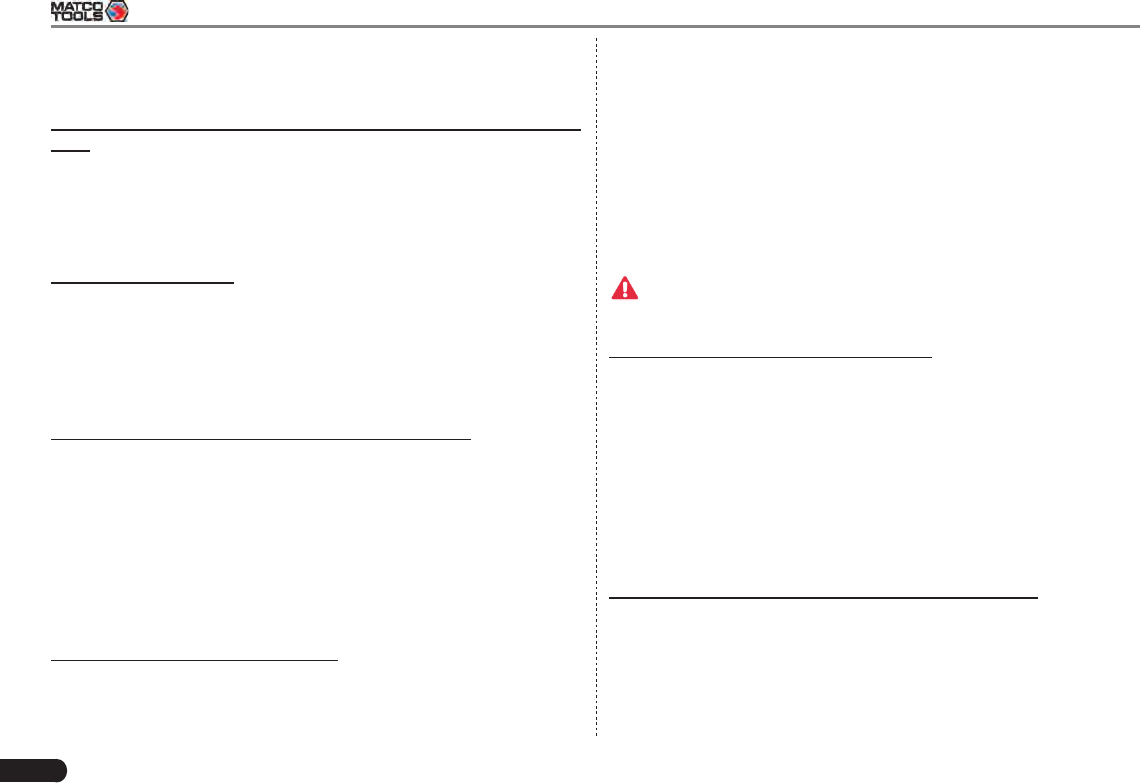
80
Maximus 3.0 User's Manual
Appendix - FAQ
1. Whether can I use other similar adaptors to charge Maximus
3.0?.
No. Please use the included 5V power adaptor to recharge your
Maximus 3.0. We assume no responsibility for damage or loss
resulting from using other similar adaptors other than the specified
one.
2. How to save power?
• Please turn off the screen while Maximus 3.0 keeps idle.
• Set a shorter standby time.
• Decrease the brightness of the screen.
• If Wi-Fi connection is not required, please turn it off.
• Disable GPS function if GPS service is not in use.
3. What should I do in case I forgot the screen lock?
You can set screen lock as pattern or password. If you forgot the
password, please consult your device provider or reset your device.
In light that you often use Maximus 3.0 to diagnose vehicles and it may
take you several minutes to do resetting, you are not recommended to
dene screen lock.
For detailed information on how to restore Maximus 3.0 to factory
settings, please refer to Item 4 “How to reset Maximus 3.0 tablet?”
described as below.
4. How to reset Maximus 3.0 tablet?
Do the followings to reset Maximus 3.0:
1. Ensure Maximus 3.0 is in OFF mode;
2. Hold and press VOLUME - key and POWER key until Maximus 3.0
enters system recovery mode;
3. Use the VOLUME + / VOLUME - key to move the highlight bar on
“wipe data / factory reset” and press POWER key to conrm;
4. Press VOLUME + / VOLUME - to select “yes” and press POWER
key to conrm;
5. Select “reboot system now” and press POWER key to restart the
system;
6. After resetting is complete, follow the on-screen instructions to
nish the system settings.
Warning: Reseng may cause data loss. Before doing so, please make
sure important data has been backed up.
5. How to do if the system runs slowly?
In this case, please do the followings:
> Check all running applications (“Settings” > “Apps” > Swipe the
screen from right to left until “RUNNING” tab appears) and stop
the unused applications (Tap the desired application, and then tap
“Stop”).
> Check all installed applications and remove the unnecessary
applications.
If all steps mentioned above are nished and the system still works
slowly. Please try to close the system and reboot your Maximus 3.0.
6. How to arrange diagnostic vehicle software icons?
All software icons, by default are organized by the system. Many
display rules are available to meet your preference.
To re-organize it, press and hold certain software icon, a option menu
pops up on the screen. Choose the display rule and the system will
arrange the icon as desired.
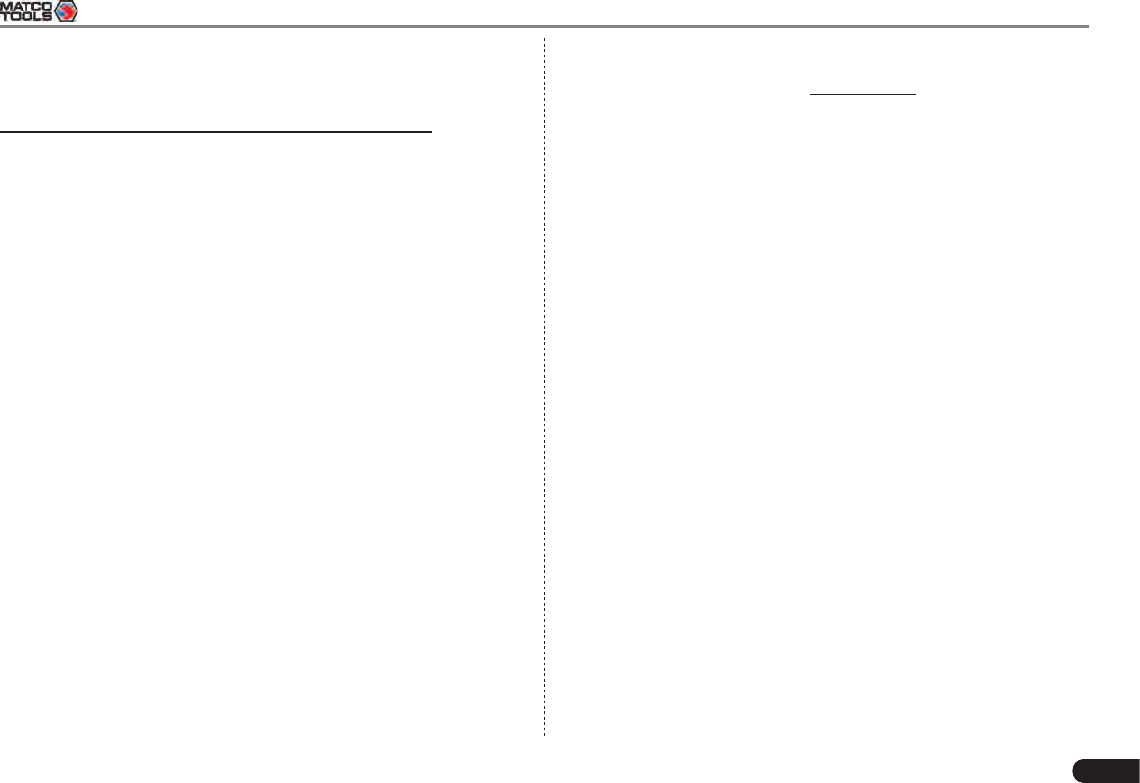
Maximus 3.0 User's Manual
81
If you choose “Pin to the top”, the icon will be displayed on the top of
the screen and marked with an orange solid dot.
7. How to distinguish if the software is locked or not?
If the software is locked, tap it to display the latest software summary.
In this case, you need to purchase the software to unlock its content.
Once it is unlocked, the software icon will turn into orange. In this
case, you need to renew your software subscription.
If you have any questions on the operation of the unit, please contact
Matco customer service number: 877-853-3738
Statement:
LAUNCH reserves the rights to make any change to product designs
and specications without notice. The actual object may differ a little
from the descriptions in the manual in physical appearance, color
and configuration. We have tried our best to make the descriptions
and illustrations in the manual as accurate as possible, and defects
are inevitable, if you have any question, please contact local dealer
or after-sale service center of LAUNCH, LAUNCH does not bear any
responsibility arising from misunderstandings.
FCC Statement
15.19
1. This device complies with Part 15 of the FCC Rules. Operation is subject to the following two
conditions:
(1) This device may not cause harmful interference.
(2) This device must accept any interference received, including interference that may cause
undesired operation.
15.21
Note: The grantee is not responsible for any changes or modifications not expressly approved by
the party responsible for compliance. Such modifications could void the user’s authority to operate
the equipment.
15.105(b)
NOTE: This equipment has been tested and found to comply with the limits for a Class B digital
device, pursuant to part 15 of the FCC Rules. These limits are designed to provide reasonable
protection against harmful interference in a residential installation.
This equipment generates uses and can radiate radio frequency energy and, if not installed and
used in accordance with the instructions, may cause harmful interference to radio communications.
However, there is no guarantee that interference will not occur in a particular installation. If this
equipment does cause harmful interference to radio or television reception, which can be
determined by turning the equipment off and on, the user is encouraged to try to correct the
interference by one or more of the following measures:
- Reorient or relocate the receiving antenna.
- Increase the separation between the equipment and receiver.
-Connect the equipment into an outlet on a circuit different from that to which the receiver is
connected.
-Consult the dealer or an experienced radio/TV technician for help
RF Exposure Statement
This equipment complies with FCC radiation exposure limits set forth for an uncontrolled
environment. This equipment should be installed and operated with minimum distance of 20 cm
between the radiator and your body.