Makita 2703 User Manual 10 TABLE SAW Manuals And Guides L0522870
MAKITA Saw Table Manual L0522870 MAKITA Saw Table Owner's Manual, MAKITA Saw Table installation guides
User Manual: Makita 2703 2703 MAKITA 10 TABLE SAW - Manuals and Guides View the owners manual for your MAKITA 10 TABLE SAW #2703. Home:Tool Parts:Makita Parts:Makita 10 TABLE SAW Manual
Open the PDF directly: View PDF .
Page Count: 28

Table Saw
With Electric BraKe
210 mm (8-1/4")
MODEL 2702Xl
MODEL 2702
255 mm (10")
MODEL 2703X1
MODEL 2703
iiiiiiiiiiiiiiiiiiiiiiiiiiiiiiiiiiiiiiiiiiiiiiiiiiii
iiiiiiiiiiiiiiiiiiiiiiiiiiiiiiiiiiiiiiiiiiiiiiiiiiii
r_ DOUBLE
INSULATION
INSTRUCTION MANUAL
WARNING: For your personal safety, READ and UNDERSTAND before using.
SAVE THESE INSTRUCTIONS FOR FUTURE REFERENCE.
www.makita.com
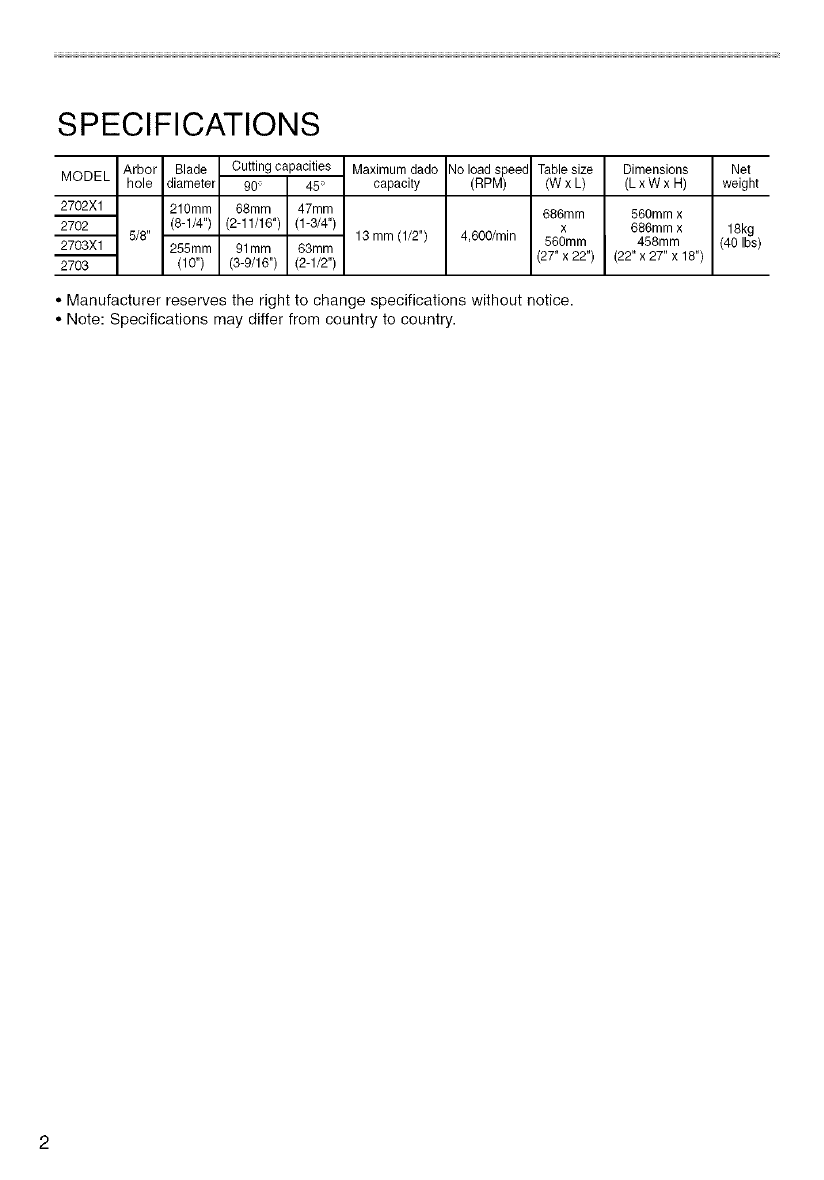
SPECIFICATIONS
MODEL Arbor
hole
2702X1
2702 _8"
2703X1
2703
Blade Cutting capacities Maximum dado
diameter 90 450 capacity
210rnrn 68rnm 47mm
(8-1/4") (2-11/16") (1-3/4") 13 mm (1/2")
255rnrn 91rnm 63mm
(10") (3-9/16") (2-1/2")
Noloadspeed Tablesize Dimensions
(RPM) (Wx L) (Lx W x H)
686mrn 560mrn x
x 686mrn x
4,600/min 560mrn 458rnm
(27" x 22") (22" x 27" x 18")
Net
weight
18kg
(40 Ibs)
• Manufacturer reserves the right to change specifications without notice.
• Note: Specifications may differ from country to country.
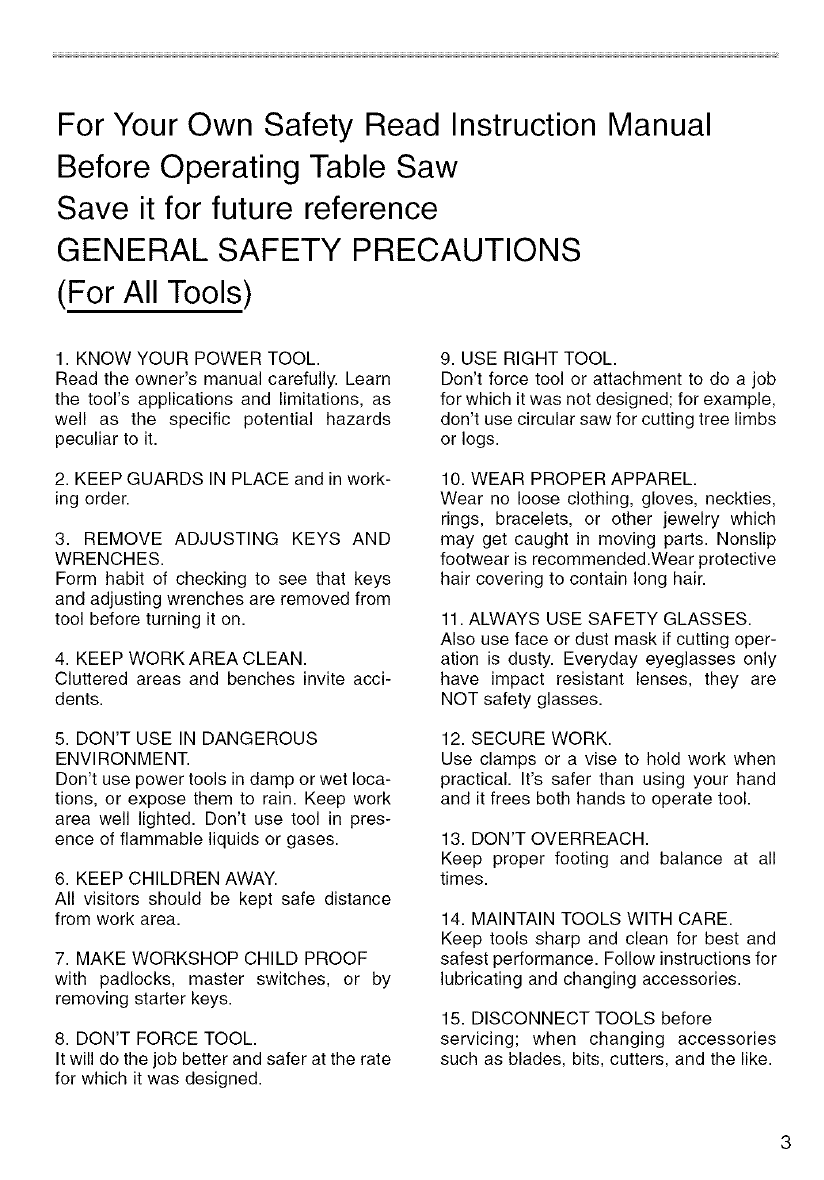
For Your Own Safety Read Instruction Manual
Before Operating Table Saw
Save it for future reference
GENERAL SAFETY PRECAUTIONS
(For All Tools)
1. KNOW YOUR POWER TOOL.
Read the owner's manual carefully. Learn
the tool's applications and limitations, as
well as the specific potential hazards
peculiar to it.
2. KEEP GUARDS IN PLACE and in work-
ing order.
3. REMOVE ADJUSTING KEYS AND
WRENCHES.
Form habit of checking to see that keys
and adjusting wrenches are removed from
tool before turning it on.
4. KEEP WORK AREA CLEAN.
Cluttered areas and benches invite acci-
dents.
5. DON'T USE IN DANGEROUS
ENVIRONMENT.
Don't use power tools in damp or wet loca-
tions, or expose them to rain. Keep work
area well lighted. Don't use tool in pres-
ence of flammable liquids or gases.
6. KEEP CHILDREN AWAY.
All visitors should be kept safe distance
from work area.
7. MAKE WORKSHOP CHILD PROOF
with padlocks, master switches, or by
removing starter keys.
8. DON'T FORCE TOOL.
It will do the job better and safer at the rate
for which it was designed.
9. USE RIGHT TOOL.
Don't force tool or attachment to do a job
for which it was not designed; for example,
don't use circular saw for cutting tree limbs
or logs.
10. WEAR PROPER APPAREL.
Wear no loose clothing, gloves, neckties,
rings, bracelets, or other jewelry which
may get caught in moving parts. Nonslip
footwear is recommended.Wear protective
hair covering to contain long hair.
11. ALWAYS USE SAFETY GLASSES.
Also use face or dust mask if cutting oper-
ation is dusty. Everyday eyeglasses only
have impact resistant lenses, they are
NOT safety glasses.
12. SECURE WORK.
Use clamps or a vise to hold work when
practical. It's safer than using your hand
and it frees both hands to operate tool.
13. DON'T OVERREACH.
Keep proper footing and balance at all
times.
14. MAINTAIN TOOLS WITH CARE.
Keep tools sharp and clean for best and
safest performance. Follow instructions for
lubricating and changing accessories.
15. DISCONNECT TOOLS before
servicing; when changing accessories
such as blades, bits, cutters, and the like.

16.REDUCETHERISKOF
UNINTENTIONALSTARTING.
Makesureswitchisinoffpositionbefore
pluggingin.
17. USE RECOMMENDEDACCES-
SORIES.
Consulttheowner'smanualfor recom-
mendedaccessories.Theuseofimproper
accessoriesmaycauseriskof injuryto
persons.
18.NEVERSTANDONTOOL.
Seriousinjurycouldoccurif thetoolis
tippedorif thecuttingtoolisaccidentally
contacted.
19.CHECKDAMAGEDPARTS.
Beforefurtheruseofthetool,aguardor
otherpartthatisdamagedshouldbecare-
fullycheckedtodeterminethatitwilloper-
ateproperlyandperformitsintendedfunc-
tion-checkforalignmentofmovingparts,
bindingof movingparts,breakageof
parts,mounting,andanyotherconditions
thatmayaffectitsoperation.Aguardor
otherpartthatisdamagedshouldbeprop-
erlyrepairedorreplaced.
20.DIRECTIONOFFEED.
Feedworkintoa bladeorcutteragainst
thedirectionofrotationofthebladeorcut-
teronly.
21. NEVERLEAVETOOLRUNNING
UNATTENDED.TURNPOWEROFF.
Don'tleavetooluntilit comesto acom-
pletestop.
22. Whenservicinguseonlyidentical
replacementparts.
23.POLARIZEDPLUGS.
Toreducetheriskof electricshock,this
equipmenthasapolarizedplug(oneblade
iswiderthantheother).Thisplugwillfitin
apolarizedoutletonlyoneway.Iftheplug
doesnotfitfullyintheoutlet,reversethe
plug.Ifit stilldoesnotfit,contacta quali-
fiedelectriciantoinstalltheproperoutlet.
Donotchangethepluginanyway.
VOLTAGEWARNING:
Beforeconnectingthetoolto a power
source(receptacle,outlet,etc.)besure
thevoltagesuppliedisthesameasthat
specifiedonthenameplateofthetool.A
powersourcewithvoltagegreaterthan
thatspecifiedfor thetoolcanresultin
SERIOUSINJURYtotheuser- aswellas
damageto thetool.Ifindoubt,DONOT
PLUGIN THETOOL.Usinga power
sourcewithvoltagelessthanthename-
plateratingisharmfultothemotor.
EXTENSIONCORDS.
Makesureyourextensioncordisingoodcondition.Whenusinganextensioncord,be
suretouseoneheawenoughtocarrythecurrentyourproductwilldraw.Anundersized
cordwillcauseadropinlinevoltageresultinginlossofpowerandoverheating.Table1
showsthecorrectsizetousedependingoncordlengthandnameplateampererating.If
indoubt,usethenextheaviergage.Thesmallerthegagenumber,theheavierthecord.
Ampere Rating
More than Not more than
0 6
6 10
10 12
12 16
Table 1. Minimum gage for cord
Volts Total length of cord in feet
12ov 2_ft I _oft. I loo.. I _o..
AWG
16 16
16 14
16 14
18 14
18 12
16 12
14 12 Not Recommended

ADDITIONAL SAFETY RULES
DO NOT let comfort or familiarity with product (gained from repeated use) replace strict
adherence to table saw safety rules. If you use this tool unsafely or incorrectly, you can
suffer serious personal injury.
1. Wear eye protection. 10. NEVER wear gloves during operation.
2. Don't use the tool in presence of flam-
mable liquids or gases.
11. Keep hands out of the line of the saw
blade.
3. NEVER use the tool with an abrasive
cut-off wheel installed.
4. Check the blade carefully for cracks or
damage before operation. Replace cracked
or damaged blade immediately.
5. Clean the spindle, flanges (especially
the installing surface) and hex nut before
installing the blade. Poor installation may
cause vibration/wobbling or slippage of
the blade.
12. NEVER stand or permit anyone else to
stand in line with the path of the saw
blade.
13. Make sure the blade is not contacting
the spreader or workpiece before the
switch is turned on.
14. Before cutting an actual workpiece, let
the tool run for a while. Watch for vibration
or wobbling that could indicate poor instal-
lation or a poorly balanced blade.
6. Use saw-blade guard and spreader for
every operation for which it can be used,
including all through sawing operations.
Always assemble and install the blade guard
following the step by step instructions out-
lined in this manual. Through sawing opera-
tions are those in which the blade cuts
completely through the workpiece as in
ripping or cross cutting. NEVER use the
tool with a faulty blade guard or secure the
blade guard with a rope, string, etc. Any
irregular operation of the blade guard
should be corrected immediately.
7. Immediately reattach the guard and
spreader after completing an operation which
requires removal of the guard.
8. Do not cut metals such as nails and
screws.Inspect for and remove all nails,
screws and other foreign matter from the
workpiece before operation.
9. Remove wrenches, cut-off pieces, etc.
from the table before the switch is tumed on.
15. NEVER make any adjustments while
tool is running. Disconnect tool before
making any adjustments.
16. Use a push stick when required. Push
sticks MUST be used for ripping narrow
workpieces to keep your hands and fingers
well away from the blade.
17. Pay particular attention to instructions for
reducing riskof KICKBACK.KICKBACKis a sud-
den reaction to a pinched, bound or misaligned
saw blade. KICKBACK causes the ejection of
the workpiece from the tool back towards the
operator. KICKBACKS CAN LEAD TO SERI-
OUS PERSONAL INJURY.Avoid KICKBACKS
by keeping the blade sharp, by keeping the rip
fence parallel to the blade, by keeping the
spreader, antikickback pawls and blade guard
in place and operating properly, by not releas-
ing the workpiece until you have pushed it all
the way past the blade, and by not ripping a
workpiecethat is twisted or warped or does not
have a straight edge to guide along the
fence.

18.Donotperformanyoperationfreehand.
Freehandmeansusingyourhandstosup-
portorguidetheworkpiece,inlieuofarip
fenceormitergauge.
19.NEVERreacharoundor oversaw
blade.NEVERreachforaworkpieceuntil
thesawbladehascompletelystopped.
20.Avoidabrupt,fastfeeding.Feedas
slowlyaspossiblewhencuttinghardwork-
pieces.Donotbendortwistworkpiecewhile
feeding.Ifyoustallorjamthebladeinthe
workpiece,turnthetooloffimmediately.
Unplugthetool.Thenclearthejam.
21.NEVERremovecut-offpiecesnearthe
bladeortouchthebladeguardwhilethe
bladeisrunning.
22.Knockoutanylooseknotsfromwork-
pieceBEFOREbeginningtocut.
23.Don'tabusecord.Neveryankcordto
disconnectfromreceptacle.Keepcord
awayfromheat,oil, waterandsharp
edges.
24. Somematerialcontainschemicals
whichmaybetoxic.Takecautionto pre-
ventworkingdustinhalationandskincon-
tact.Followmaterialsuppliersafetydata.
25.Theguardcanbeliftedduringwork-
piecesetupandfor easeof cleaning.
Alwaysmakesurethatguardhoodis
downandflat againstsawtablebefore
plugginginthetool.
WARNING:
MISUSEorfailuretofollowthesafetyrulesstatedinthisinstructionmanualmaycause
seriouspersonalinjury.
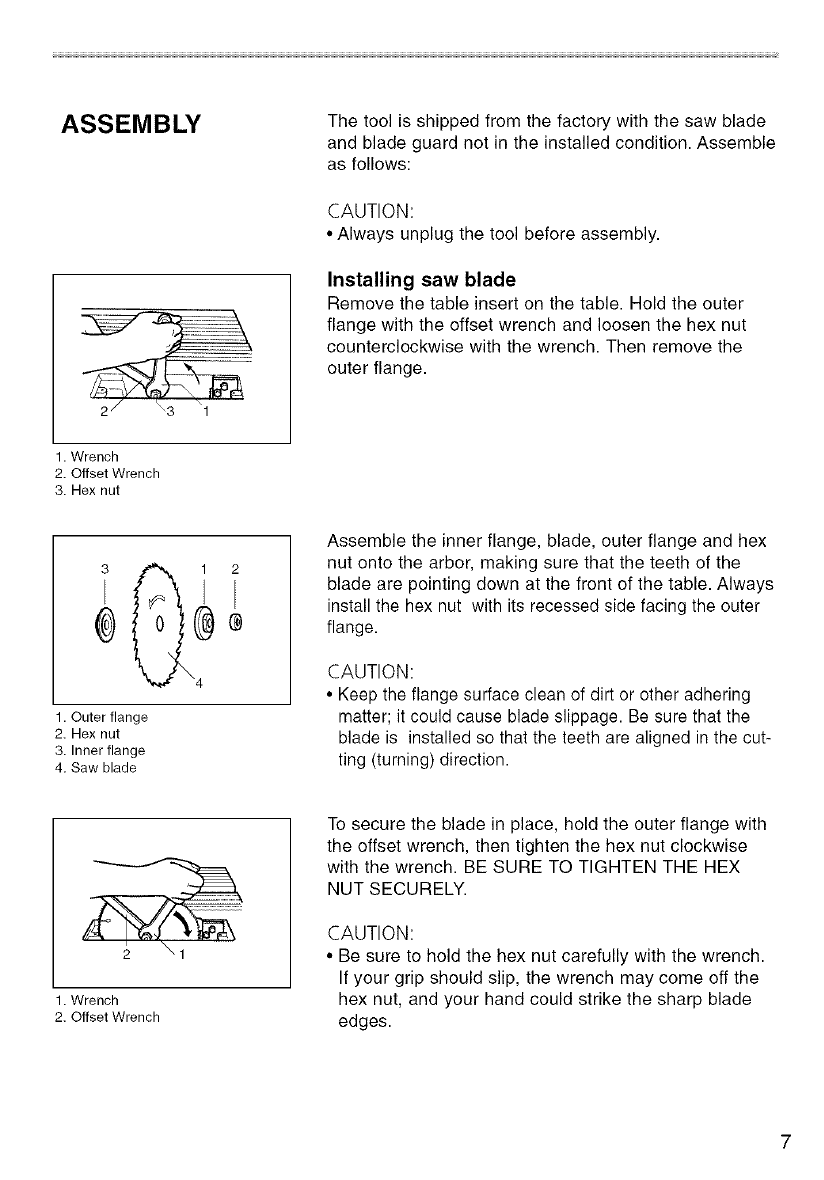
ASSEMBLY The tool is shipped from the factory with the saw blade
and blade guard not in the installed condition. Assemble
as follows:
CAUTION:
• Always unplug the tool before assembly.
Installing saw blade
Remove the table insert on the table. Hold the outer
flange with the offset wrench and loosen the hex nut
counterclockwise with the wrench. Then remove the
outer flange.
1. Wrench
2. Offset Wrench
3. Hex nut
¢
1. Outer flange
2. Hex nut
3. Inner flange
4. Saw blade
Assemble the inner flange, blade, outer flange and hex
nut onto the arbor, making sure that the teeth of the
blade are pointing down at the front of the table. Always
install the hex nut with its recessed side facing the outer
flange.
CAUTION:
• Keep the flange surface clean of dirt or other adhering
matter; it could cause blade slippage. Be sure that the
blade is installed so that the teeth are aligned in the cut-
ting (turning) direction.
1. Wrench
2. Offset Wrench
To secure the blade in place, hold the outer flange with
the offset wrench, then tighten the hex nut clockwise
with the wrench. BE SURE TO TIGHTEN THE HEX
NUT SECURELY.
CAUTION:
• Be sure to hold the hex nut carefully with the wrench.
If your grip should slip, the wrench may come off the
hex nut, and your hand could strike the sharp blade
edges.
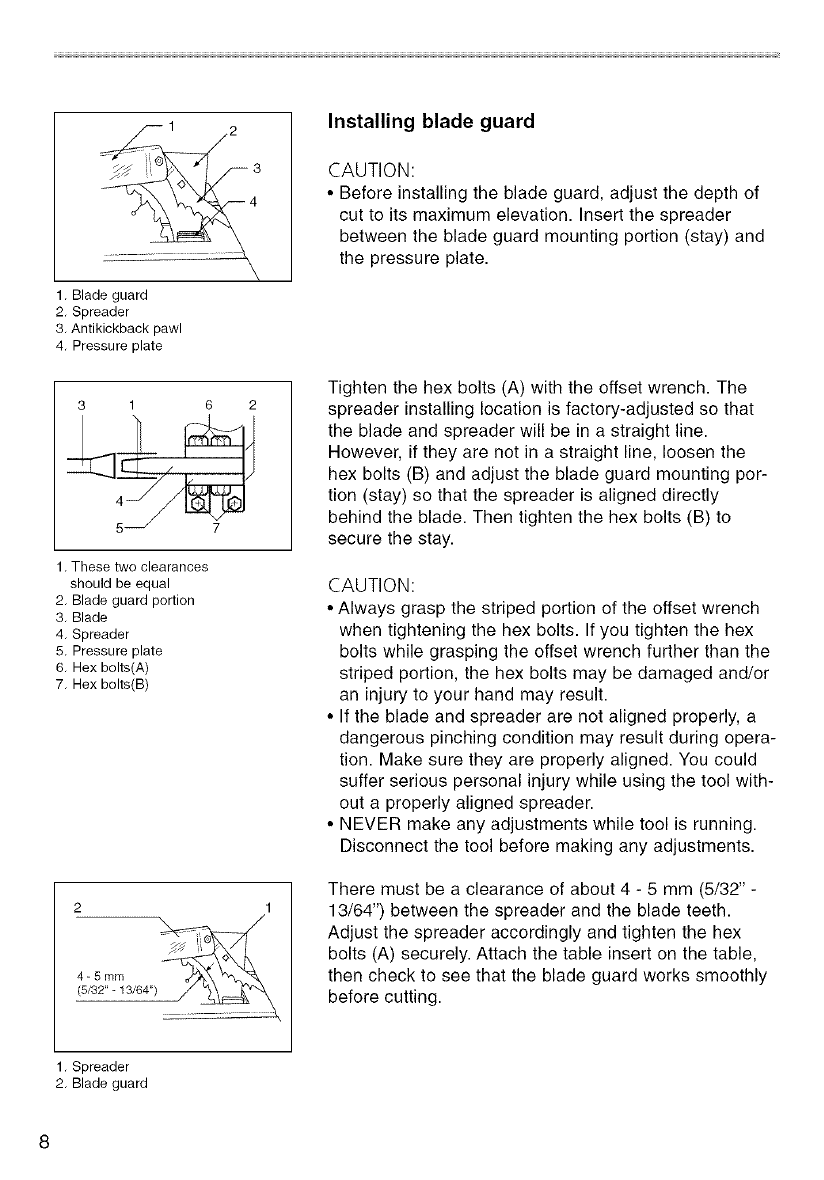
3
1. Blade guard
2. Spreader
3. Antikickback pawl
4. Pressure plate
3 1 6 2
1. These two clearances
should be equal
2. Blade guard portion
3. Blade
4. Spreader
5. Pressure plate
6. Hex bolts(A)
7. Hex bolts(B)
2 1
?./ i'.
4-5ram(5/32" -13/64")
Installing blade guard
CAUTION:
• Before installing the blade guard, adjust the depth of
cut to its maximum elevation. Insert the spreader
between the blade guard mounting portion (stay) and
the pressure plate.
Tighten the hex bolts (A) with the offset wrench. The
spreader installing location is factory-adjusted so that
the blade and spreader will be in a straight line.
However, if they are not in a straight line, loosen the
hex bolts (B) and adjust the blade guard mounting por-
tion (stay) so that the spreader is aligned directly
behind the blade. Then tighten the hex bolts (B) to
secure the stay.
CAUTION:
• Always grasp the striped portion of the offset wrench
when tightening the hex bolts. If you tighten the hex
bolts while grasping the offset wrench further than the
striped portion, the hex bolts may be damaged and/or
an injury to your hand may result.
• If the blade and spreader are not aligned properly, a
dangerous pinching condition may result during opera-
tion. Make sure they are properly aligned. You could
suffer serious personal injury while using the tool with-
out a properly aligned spreader.
• NEVER make any adjustments while tool is running.
Disconnect the tool before making any adjustments.
There must be a clearance of about 4 - 5 mm (5/32" -
13/64") between the spreader and the blade teeth.
Adjust the spreader accordingly and tighten the hex
bolts (A) securely. Attach the table insert on the table,
then check to see that the blade guard works smoothly
before cutting.
1. Spreader
2. Blade guard
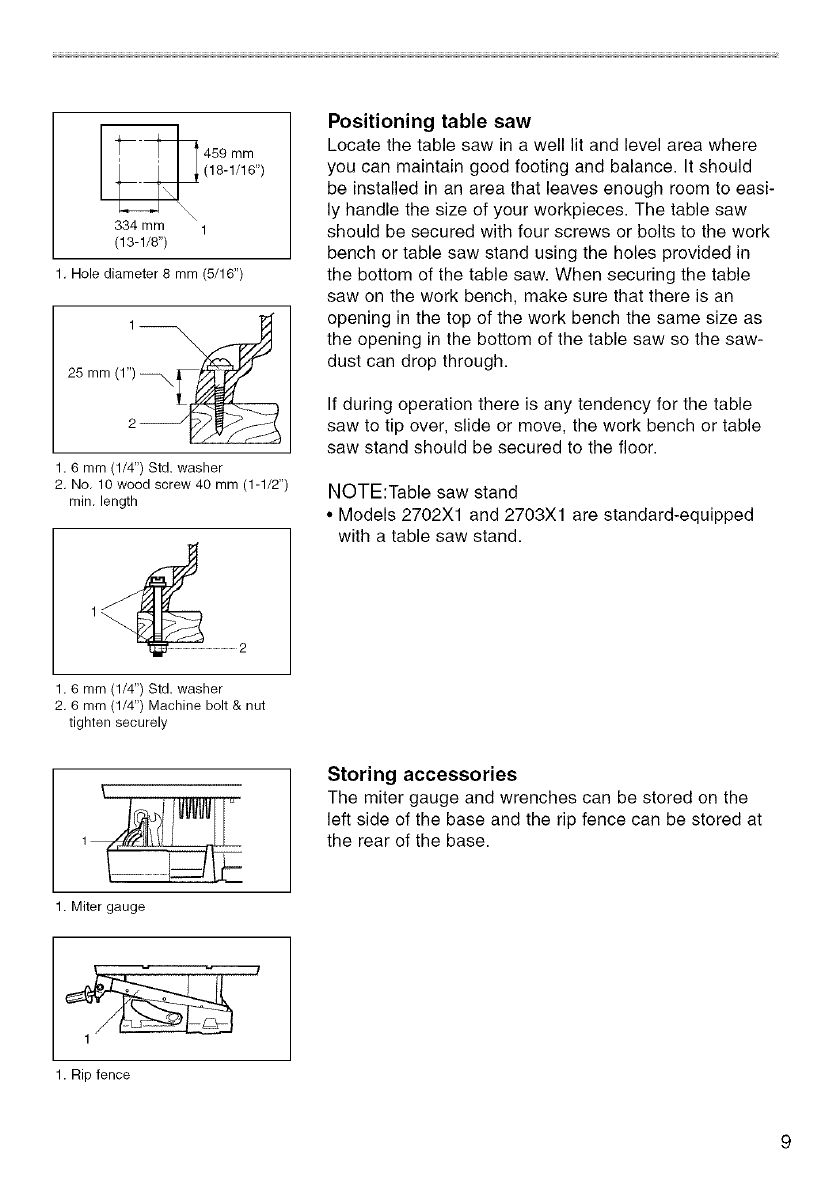
459mm
(18-1/16")
334mm 1
(13-1/8")
1.Holediameter8mm(5/16")
25mm(1"
1.6mm(1/4")Std.washer
2.No.10woodscrew40mm(1-1/2")
rain.length
Positioning table saw
Locate the table saw in a well lit and level area where
you can maintain good footing and balance. It should
be installed in an area that leaves enough room to easi-
ly handle the size of your workpieces. The table saw
should be secured with four screws or bolts to the work
bench or table saw stand using the holes provided in
the bottom of the table saw. When securing the table
saw on the work bench, make sure that there is an
opening in the top of the work bench the same size as
the opening in the bottom of the table saw so the saw-
dust can drop through.
If during operation there is any tendency for the table
saw to tip over, slide or move, the work bench or table
saw stand should be secured to the floor.
NOTE:Table saw stand
• Models 2702Xl and 2703Xl are standard-equipped
with a table saw stand.
1.6 mm (1/4") Std. washer
2.6 mm (1/4") Machine bolt & nut
tighten securely
\
1. Miter gauge
Storing accessories
The miter gauge and wrenches can be stored on the
left side of the base and the rip fence can be stored at
the rear of the base.
1. Rip fence
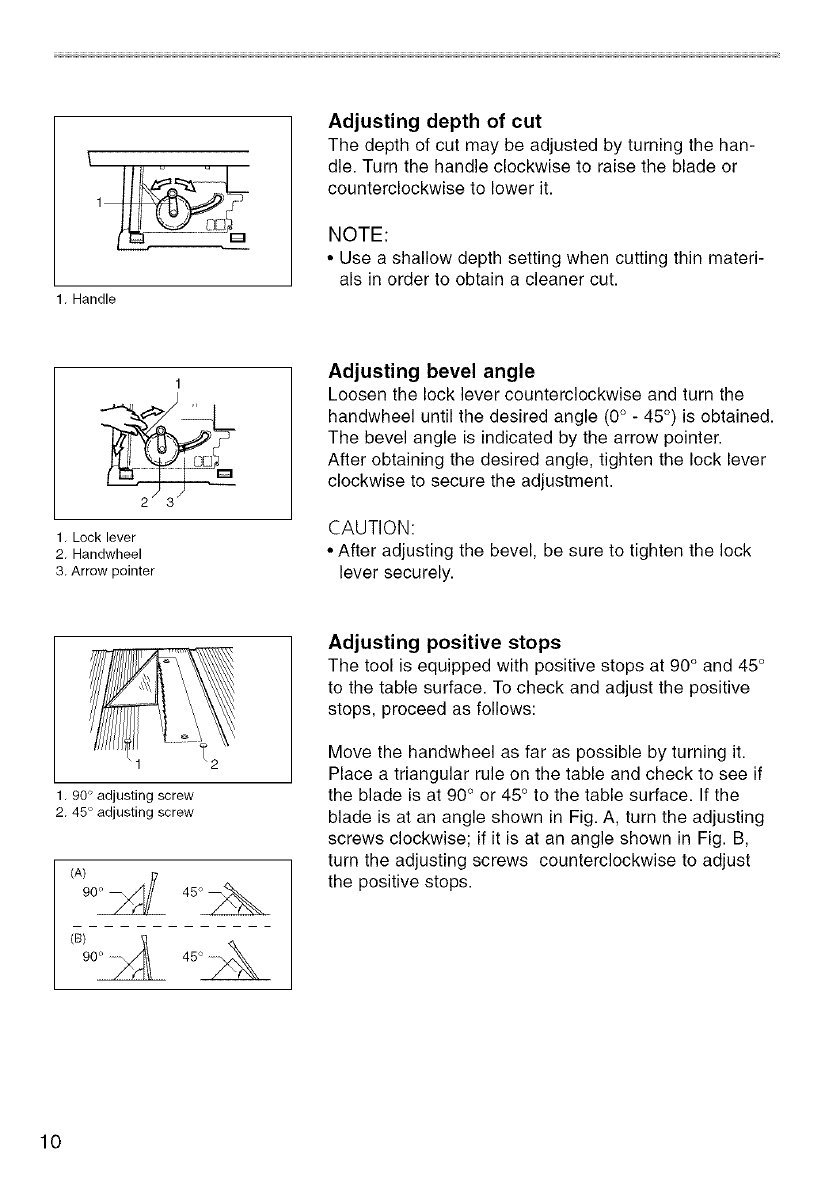
1.Handle
Adjusting depth of cut
The depth of cut may be adjusted by turning the han-
dle. Turn the handle clockwise to raise the blade or
counterclockwise to lower it.
NOTE:
• Use a shallow depth setting when cutting thin materi-
als in order to obtain a cleaner cut.
1
1. Lock lever
2. Handwheel
3. Arrow pointer
Adjusting bevel angle
Loosen the lock lever counterclockwise and turn the
handwheel until the desired angle (0° - 45 °) is obtained.
The bevel angle is indicated by the arrow pointer.
After obtaining the desired angle, tighten the lock lever
clockwise to secure the adjustment.
CAUTION:
• After adjusting the bevel, be sure to tighten the lock
lever securely.
1.90" adjusting screw
2.45 ° adjusting screw
(B)
Adjusting positive stops
The tool is equipped with positive stops at 90° and 45 °
to the table surface. To check and adjust the positive
stops, proceed as follows:
Move the handwheel as far as possible by turning it.
Place a triangular rule on the table and check to see if
the blade is at 90° or 45 ° to the table surface. If the
blade is at an angle shown in Fig. A, turn the adjusting
screws clockwise; if it is at an angle shown in Fig. B,
turn the adjusting screws counterclockwise to adjust
the positive stops.
10

1
1. Arrow pointer
After adjusting the positive stops, set the blade at 90° to
the table surface. Then adjust the arrow pointer so that
its right edge is aligned to the 0° graduation.
1. Fence holder
2. Guide rail
3. Grip
Installing and adjusting rip fence
Raise the grip of the rip fence. Install the rip fence on
the table so that the fence holder engages with the
guide rail. The rip fence can be secured by lowering the
grip.
A
1. Scale
1
3
1. Hex bolts
2. Adjusting nut
3. Grip
To check to be sure that the rip fence is parallel with the
blade, secure the rip fence 2 - 3 mm (5/64" - 1/8" ) from
the blade. Raise the blade up to maximum elevation.
Mark one of the blade teeth with a crayon. Measure the
distance (A) and (B) between the rip fence and blade.
Take both measurements using the tooth marked with
the crayon.These two measurements should be identi-
cal. If the rip fence is not parallel with the blade, pro-
ceed as follows:
1. Turn the adjusting nut counterclockwise a couple of
turns.
2. Loosen the two hex bolts on the rip fence with the
wrench provided.
3. Adjust the rip fence until it becomes parallel with the
blade.
4. Lower the grip to secure the rip fence.
5. Tighten the two hex bolts on the rip fence.
11

CAUTION:
• Always grasp the striped portion of the wrench when
tightening the hex bolts. If you tighten the hex bolts
while grasping the wrench further than the striped por-
tion, the hex bolts may be damaged and/or an injury
to your hand may result.
6. With the grip of the rip fence lowered, turn the adjust-
ing nut clockwise to secure the rear end of the rip
fence. Do not turn the adjusting nut clockwise exces-
sively. You may have some difficulty adjusting the rip
fence parallel with the saw blade when repositioning
the rip fence.
CAUTION:
Be sure to adjust the rip fence so that it is parallel with the
blade, or a dangerous kickback condition may occur.
3 4
1. Screw
2. Fence holder
3. Scale plate
4. Arrow mark
Bring the rip fence up flush against the side of the
blade. Make sure that the arrow pointer on the fence
holder points to the 0 graduation. If the arrow pointer
does not point to the 0 graduation, loosen the screw on
the scale plate and adjust the scale plate.
1
2
1. Switch lever
2. Key
Switch action
This tool is equipped with a special type of switch to
prevent unintentional starting. To start the tool, first
depress the switch lever.While keeping it depressed,
pull its lower portion toward you. To stop the tool, press
the lower portion of the switch lever.
12

When operating the switch lever, it is convenient to
view it through the window area in the table.
CAUTION:
• When not using the tool, remove the key and store it
in a secure place. This prevents unauthorized opera-
tion.
• Before plugging in the tool, always check to see that
the switch lever actuates properly and returns to the
"OFF" position.
• Do not pull the switch lever hard without the key. This
can cause breakage of the switch.
OPERATION CAUTION:
• Always use "work helpers" such as push sticks and
push blocks when there is a danger that your hands or
fingers will come close to the blade.
• Always hold the workpiece firmly with the table and
the rip fence or miter gauge. Do not bend or twist it
while feeding. If the workpiece is bent or twisted, dan-
gerous kickbacks may occur.
• NEVER withdraw the workpiece while the blade is run-
ning. If you must withdraw the workpiece before com-
pleting a cut, first switch the tool off while holding the
workpiece firmly. Wait until the blade has come to a
complete stop before withdrawing the workpiece.
Failure to do so may cause dangerous kickbacks.
• NEVER remove cut-off material while the blade is run-
ning.
• NEVER place your hands or fingers in the path of the
saw blade. Be especially careful with bevel cuts.
• Always secure the rip fence firmly, or dangerous kick-
backs may occur.
• Always use "work helpers" such as push sticks and
push blocks when cutting small or narrow workpieces,
or when the dado head is hidden from view while cut-
ting.
Work helpers
Push sticks, push blocks or auxiliary fence are types of
"work helpers". Use them to make safe, sure cuts with-
out the need for the operator to contact the blade with
any part of the body.
13

120 mT1 300 Tim(2")
I I
6 ram (1/4") j _ 50ram (2")
2_ .___ /_ 300 mm (12")
130 mm _
(5") 5_Zr,_)m
,_ 100 mm (4")
9.5 mm (3/8")4
50 ram (2") _"_ 8 mm (5/16")
1. Face/edge parallel
2. Handle
3. Wood screw
4. Glue together
Push stick
(H) 9.5 mrn _ 130 rnm (5")
19 mm@_ 9.5 mm I (50')mm
(3/4) _'i;'_"_ g80 mm (15")
Y \
A push stick can be easily made from a piece of ply-
wood 19 mm (3/4") to 25 mm (1") thick.
Cut out the hatched area on the stick and smooth
edges with a file. (H) dimension should be less than
12.7 mm (1/2") so as to be thinner than the workpiece.
Push block
Use a 19 mm (3/4") piece of plywood.
Handle should be in center of plywood piece. Fasten
with glue and wood screws as shown. Small piece 9.5
mm x 8 mm x 50 mm (3/8" x 5/16" x 2") of wood must
always be glued to plywood to keep the blade from
dulling if the operator cuts into push block by mistake.
(Never use nails in push block.)
9.5mm 19mm 120ram
(3/8") (3/4") (4-3/4")
140 mm
460 mm (18" (5-1/2")
Fasten with glue and wood screws.
1. Face/edge parallel
Auxiliary fence
Make auxiliary fence from 9.5 mm (3/8") and 19 mm
(3/4") plywood pieces.
14
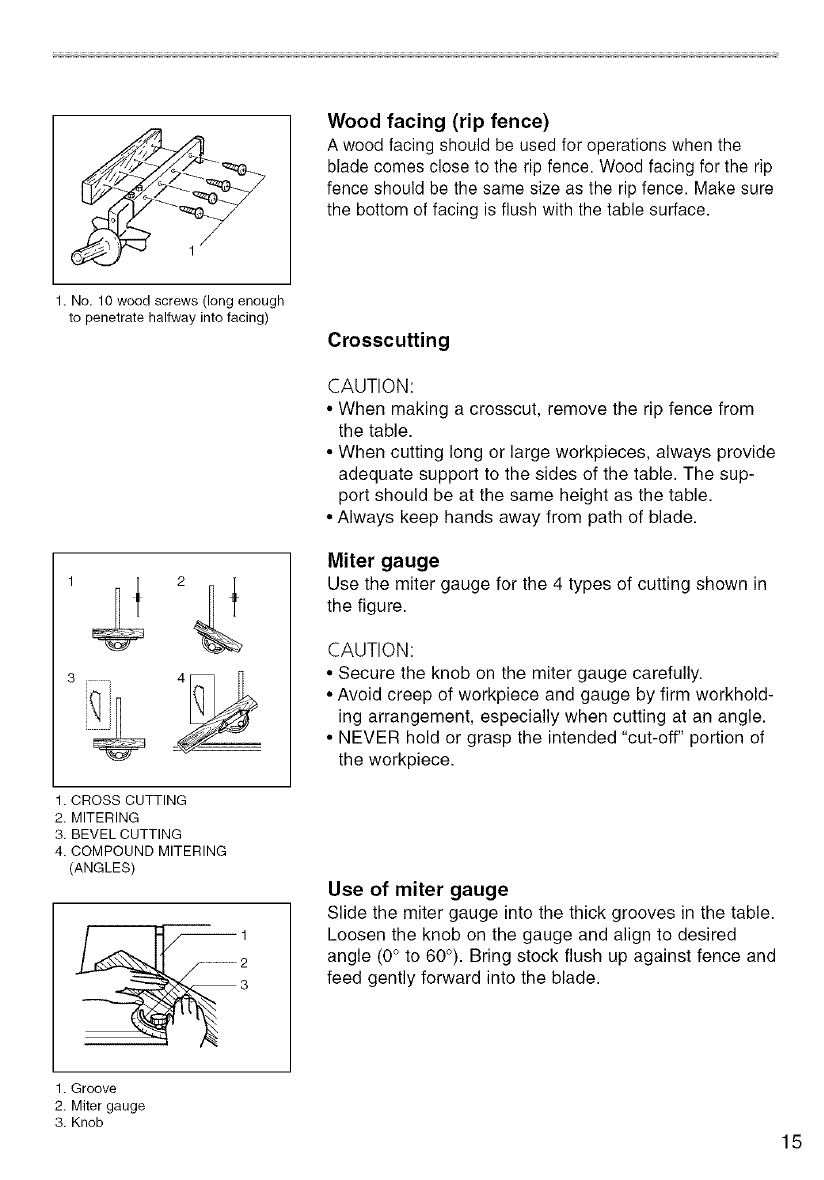
1
1. No. 10 wood screws (long enough
to penetrate halfway into facing)
1. CROSS CUTTING
2. MITERING
3. BEVEL CUTTING
4. COMPOUND MITERING
(ANGLES)
1. Groove
2. Miter gauge
3. Knob
Wood facing (rip fence)
A wood facing should be used for operations when the
blade comes close to the rip fence. Wood facing for the rip
fence should be the same size as the rip fence. Make sure
the bottom of facing is flush with the table surface.
Crosscutting
CAUTION:
• When making a crosscut, remove the rip fence from
the table.
• When cutting long or large workpieces, always provide
adequate support to the sides of the table. The sup-
port should be at the same height as the table.
• Always keep hands away from path of blade.
Miter gauge
Use the miter gauge for the 4 types of cutting shown in
the figure.
CAUTION:
• Secure the knob on the miter gauge carefully.
• Avoid creep of workpiece and gauge by firm workhold-
ing arrangement, especially when cutting at an angle.
• NEVER hold or grasp the intended "cut-off" portion of
the workpiece.
Use of miter gauge
Slide the miter gauge into the thick grooves in the table.
Loosen the knob on the gauge and align to desired
angle (0° to 60°). Bring stock flush up against fence and
feed gently forward into the blade.
15

Auxiliary wood facing (miter gauge)
To prevent a long board from wobbling, fit the miter
gauge with an auxiliary fence board. Fasten with
bolts/nuts after drilling holes, but fasteners must not
protrude from the face board.
Ripping
CAUTION:
• When ripping, remove the miter gauge from the table.
• When cutting long or large workpieces, always provide
adequate support behind the table. DO NOT allow a
long board to move or shift on the table. This will
cause the blade to bind and increase the possibility of
kickback and personal injury. The support should be at
the same height as the table.
Before operating the table saw, check to be sure that
the antikickback pawls operate properly. Turn the tool
off and unplug it. Feed the workpiece under the blade
guard and along both sides of the blade to simulate cut-
ting. Try to withdraw the workpiece on each side by
pulling it toward you. The antikickback pawls should
grab the workpiece and prevent it from moving back
toward the operator. Always keep the antikickback
pawls sharp so they will operate properly. Keep them
sharp by using a round-shaped file to maintain the origi-
nal shape of the pawls.
1. Adjust the depth of cut a bit higher than the thickness
of the workpiece.
2. Position the rip fence to the desired width of rip and
lock in place by lowering the grip. Before ripping,
make sure the rear end of the rip fence is secured
firmly. If it is not secured enough, follow the proce-
dures in "Installing and adjusting rip fence" described
on page 11 and 12.
16
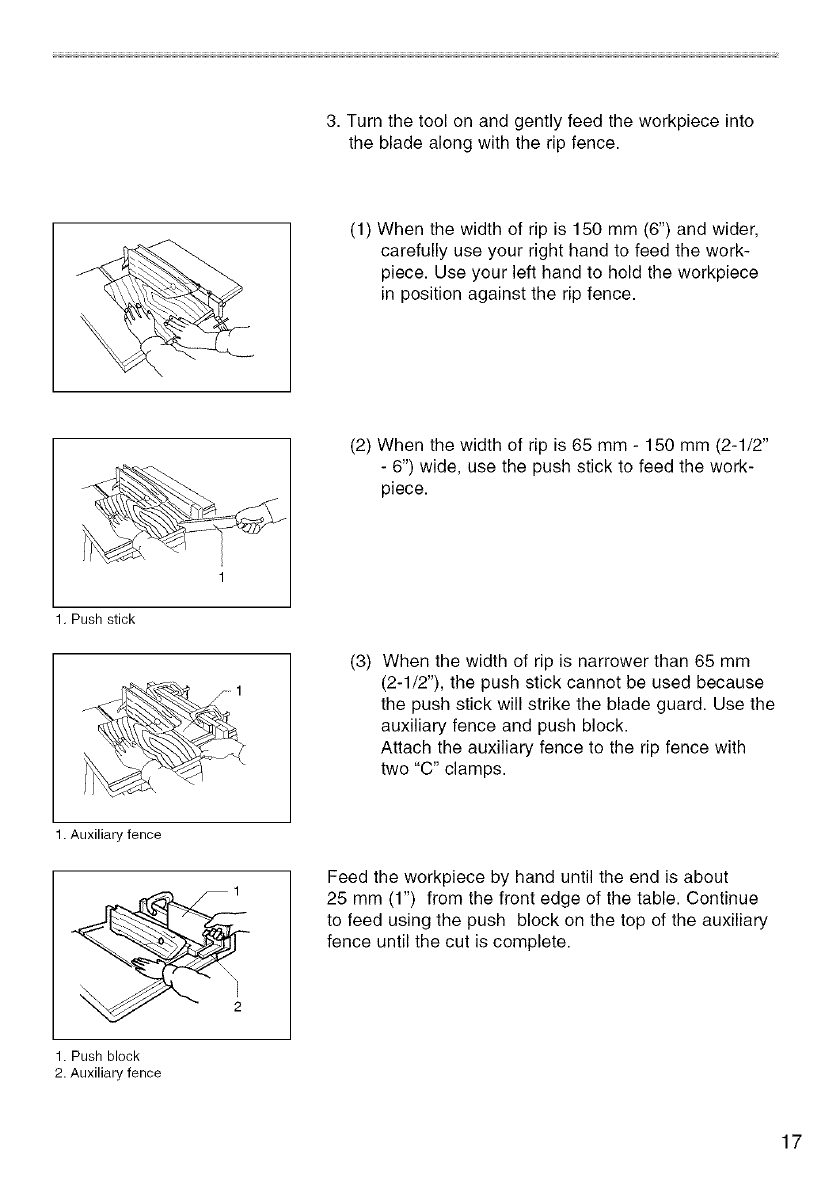
3. Turn the tool on and gently feed the workpiece into
the blade along with the rip fence.
(1) When the width of rip is 150 mm (6") and wider,
carefully use your right hand to feed the work-
piece. Use your left hand to hold the workpiece
in position against the rip fence.
(2) When the width of rip is 65 mm - 150 mm (2-1/2"
- 6") wide, use the push stick to feed the work-
piece.
1. Push stick
(3) When the width of rip is narrower than 65 mm
(2-1/2"), the push stick cannot be used because
the push stick will strike the blade guard. Use the
auxiliary fence and push block.
Attach the auxiliary fence to the rip fence with
two "C" clamps.
1. Auxiliary fence
1. Push block
2. Auxiliary fence
Feed the workpiece by hand until the end is about
25 mm (1") from the front edge of the table. Continue
to feed using the push block on the top of the auxiliary
fence until the cut is complete.
17
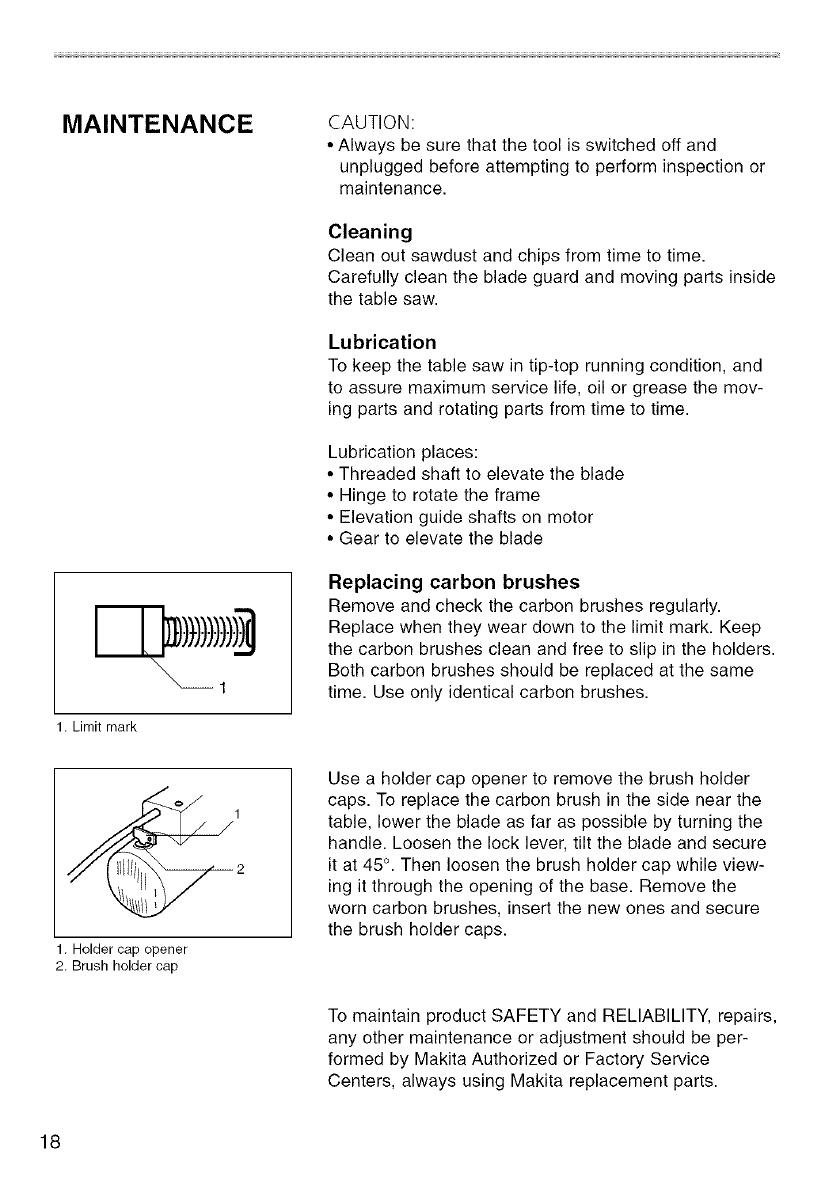
MAINTENANCE
1. Limit mark
1. Holder cap opener
2. Brush holder cap
CAUTION:
• Always be sure that the tool is switched off and
unplugged before attempting to perform inspection or
maintenance.
Cleaning
Clean out sawdust and chips from time to time.
Carefully clean the blade guard and moving parts inside
the table saw.
Lubrication
To keep the table saw in tip-top running condition, and
to assure maximum service life, oil or grease the mov-
ing parts and rotating parts from time to time.
Lubrication places:
• Threaded shaft to elevate the blade
• Hinge to rotate the frame
• Elevation guide shafts on motor
• Gear to elevate the blade
Replacing carbon brushes
Remove and check the carbon brushes regularly.
Replace when they wear down to the limit mark. Keep
the carbon brushes clean and free to slip in the holders.
Both carbon brushes should be replaced at the same
time. Use only identical carbon brushes.
Use a holder cap opener to remove the brush holder
caps. To replace the carbon brush in the side near the
table, lower the blade as far as possible by turning the
handle. Loosen the lock lever, tilt the blade and secure
it at 45 °. Then loosen the brush holder cap while view-
ing it through the opening of the base. Remove the
worn carbon brushes, insert the new ones and secure
the brush holder caps.
To maintain product SAFETY and RELIABILITY, repairs,
any other maintenance or adjustment should be per-
formed by Makita Authorized or Factory Service
Centers, always using Makita replacement parts.
18

ACCESSORIES
1/8" 1/8" 1/16" 1/8" 1/8"
CAUTION:
•These accessories or attachments are recommended
for use with your Makita tool specified in this manual.
The use of any other accessories or attachments
might present a risk of injury to persons.
Only use accessory or attachment for its stated pur-
pose.
Dado head set (Part No. 191543-4)
A dado is cutting a rabbet or a wide groove into the
workpiece. The dado head set consists of two outside
cutters, three inside cutters and paper washers.
Outside cutters: 6"diameter 1/8" thick, 5/8"arbor hole, 2 pcs.
Inside cutters: 6"diameter 1/8"thick, 5/8"arbor hole, 2 pcs.
Inside cutter: 6"diameter 1/16"thick,5/8"arbor hole, 1 pc.
Paper washers: 8/8"arbor hole, 6 pcs.
Various combinations of these cutters are used to cut
grooves from 1/8" to 1/2" for use in making joints,
tenoning, grooving, etc.
/2
// s
X_
Dado flange set (Part No. 192693-8)
1. Dado outer flange
When cutting groove 1/4", 5/16", 3/8", 7/16" or 1/2",
use this dado outer flange.
2. Dado hex nut
When cutting groove 1/4", 5/16", 3/8", 7/16" or 1/2",
use this dado hex nut.
3. Ring
When cutting groove 1/4", 5/16", 3/8", 7/16" or 1/2",
use this ring.
4. Washer
When cutting groove 1/4", 5/16" or 3/8", use this
washer.
19

Table insert
(Part No. 317061-6)
When cutting grooves 5/16% 3/8",7/16" or 1/2" use this
table insert instead of the standard table insert.
To install the dado head set, proceed as follows:
1. Turn the tool off and unplug it before installing.
2. Remove the blade guard with the spreader.
3. Install the dado head set with the teeth pointing down
at the front of the table.
4. Use the chart below to select the proper cutters to
obtain the various cutting widths.
Spindle
1/8" 1/16" Dado Dad{
Inner Ring Outside Inside Inside Outside Outer Washer Outer Hex Hex
:lange Cutter cutter cutter cutter flange flange nut nut
CUT
WIDTH @
f'-\ f_,\
1/8" • • • • •
1/4" • • • • • • •
5/16" • • • • • • • •
3/8" • • • • • • • •
7/16" • • • • • • • •
1/2" • • •Ox2 • • •
CAUTION:
• For a 1/8" cut width, the outside cutter is assembled to
the spindle in the same manner as the saw blade.
• The outer flange or the dado outer flange must be
used for each cut width.
• The hex nut alone must not be used to secure the
dado on to the spindle.
20

123
NOTE:
• When widths slightly greater than the above are
required, fit the paper washers in between the inside
and outside cutters to adjust the width.
5. Arrange the cutters so that the tips of the inside cut-
ters are positioned at the gullets of the outside cutter.
When more than one inside cutter is used, space
the tips of the inside cutters equidistantly in relation
to one another. Poorly spaced cutters may cause
vibration and noise.
1, Inside cutter
2, Outside cutter
3. Gullet
When installing two outside cutters without any inside
cutter, be sure that the cutter tips do not face each
other.
6. While tightening the hex nut, be careful to maintain the
even spacing between the tips of the inside cutters.
7. Rotate the dado head one turn by hand to make sure
that it does not contact anything before operation.
19ram 115mm
(3/4") (4-1/2")
1. Kerf should be about 6 rnrn
(1/4") apart
When dadoing, use featherboards. The diagram shown
illustrates dimensions for making a typical featherboard.
It should be made from a straight piece of wood that is
free of knots or cracks.
21

22
1
i -2
• _ /#
3
1. "C"Clarnps
2, Facing board
3, Featherboard
4, Push stick
Featherboards are used to keep the workpiece in con-
tact with the rip fence and table as shown, and to stop
kickbacks.
To install featherboards, proceed as follows:
1. Turn the tool off and unplug it.
2. Add 8" high flat facing board to the rip fence, the full
length of the rip fence.
3. Mount featherboards to the rip fence and table as
shown, so that the leading edges of the feather-
boards will support the workpiece until the cut is
completed, and the workpiece has been pushed
completely past the cutter with a push stick.
4. Make sure featherboards are securely attached.
CAUTION:
• Only the Makita dado head set (Part No. 191543-4)
should be used with Makita table saw Model
2702/Model 2703. Do not use dado combinations
wider than 13 mm (1/2").
• After dadoing, ALWAYS replace the blade guard with
the spreader back in its original position on the table
saw.
• NEVER attempt bevel cuts when dadoing.
• NEVER dado if there is vibration (flutter) or a strange
noise.
• NEVER attempt dados in other than wood.
• Do not use the dado set for cut-offs.
• Feed work slowly, especially when cutting deep or wide
grooves or dados. If a deep cut is needed, make several
passes through the workpiece rather than one deep,
wide cut. Fast or abrupt feeds can be dangerous.
• Use a push stick. When the dado head is hidden from
view while cutting, your hands should never be on top
of the stock.
• A very dangerous throwback can result if the wood
becomes stuck and you try to remove it by pulling
toward you. Always stop the tool and wait for dado
head to come to a complete stop. Then simply with-
draw the wood.
WARNING:
• Use extra caution when the guard assembly is
removed for any non-through sawing operation such
as dadoing, rabbeting or resawing. Replace guard
immediately after non4hrough sawing is completed.

1 3
1. Rabbet
2. First cut
3. Second cut
1. Rubber cap
2. Nut
3. Leg
4. Under stay
5. Stay
1. Bolt
2. Stand
How to perform rabbeting
1. Remove blade guard.
2. Attach auxiliary fence to rip fence for cuts that run the
length of the stock. Facing should be as high as the
workpiece is wide. Adjust fence and blade to desired
dimensions.
3. First cut: Hold board flat on table as in ordinary rip-
ping.
4. Second cut: Set workpiece on its edge. (Use feather-
boards, push stick, push block and so on, using pre-
cautions, safety rules and guidelines for ripping or
related work.)
5. For end-type rabbeting, if the workpiece is less than
10-1/2" wide, rest the wood flat on the table against
the miter gauge (with wood facing). The rip fence
should not be used.
6. After rabbeting is completed, immediately re-install
the blade guard as before.
Table saw stand (Part No. 192680-7)
Place the stays on a level location and assemble the
legs inside. Secure with the bolts and nuts, then attach
the rubber caps to the ends of the legs.
Now set the table saw on top of the assembled stand
and secure with four bolts, washers and nuts.
NOTE:
• Models 2702Xl and 2703Xl are standard-equipped
with a table saw stand.
23
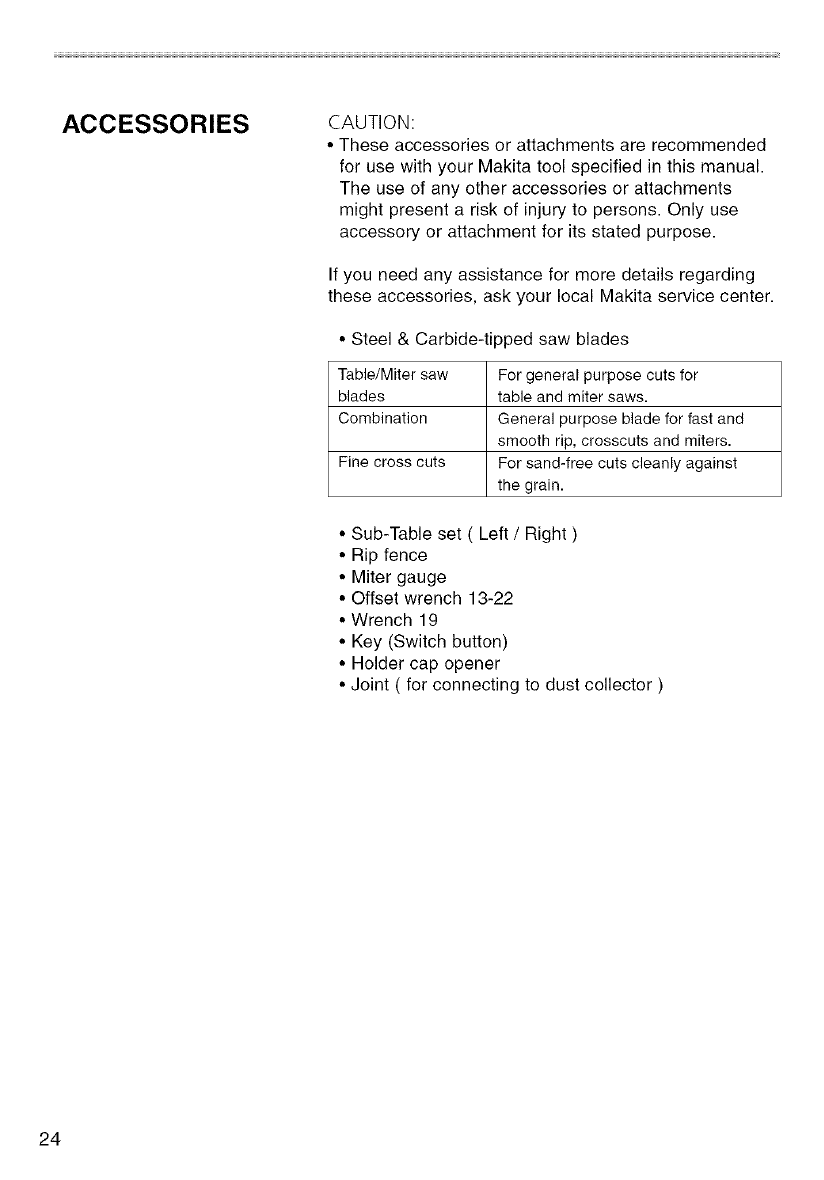
ACCESSORIES CAUTION:
•These accessories or attachments are recommended
for use with your Makita tool specified in this manual.
The use of any other accessories or attachments
might present a risk of injury to persons. Only use
accessory or attachment for its stated purpose.
If you need any assistance for more details regarding
these accessories, ask your local Makita service center.
• Steel & Carbide-tipped saw blades
Table/Miter saw For general purpose cuts for
blades table and miter saws.
Combination General purpose blade for fast and
smooth rip, crosscuts and miters.
Fine cross cuts For sand-free cuts cleanly against
the grain.
• Sub-Table set ( Left /Right )
• Rip fence
• Miter gauge
• Offset wrench 13-22
• Wrench 19
• Key (Switch button)
• Holder cap opener
• Joint ( for connecting to dust collector )
24
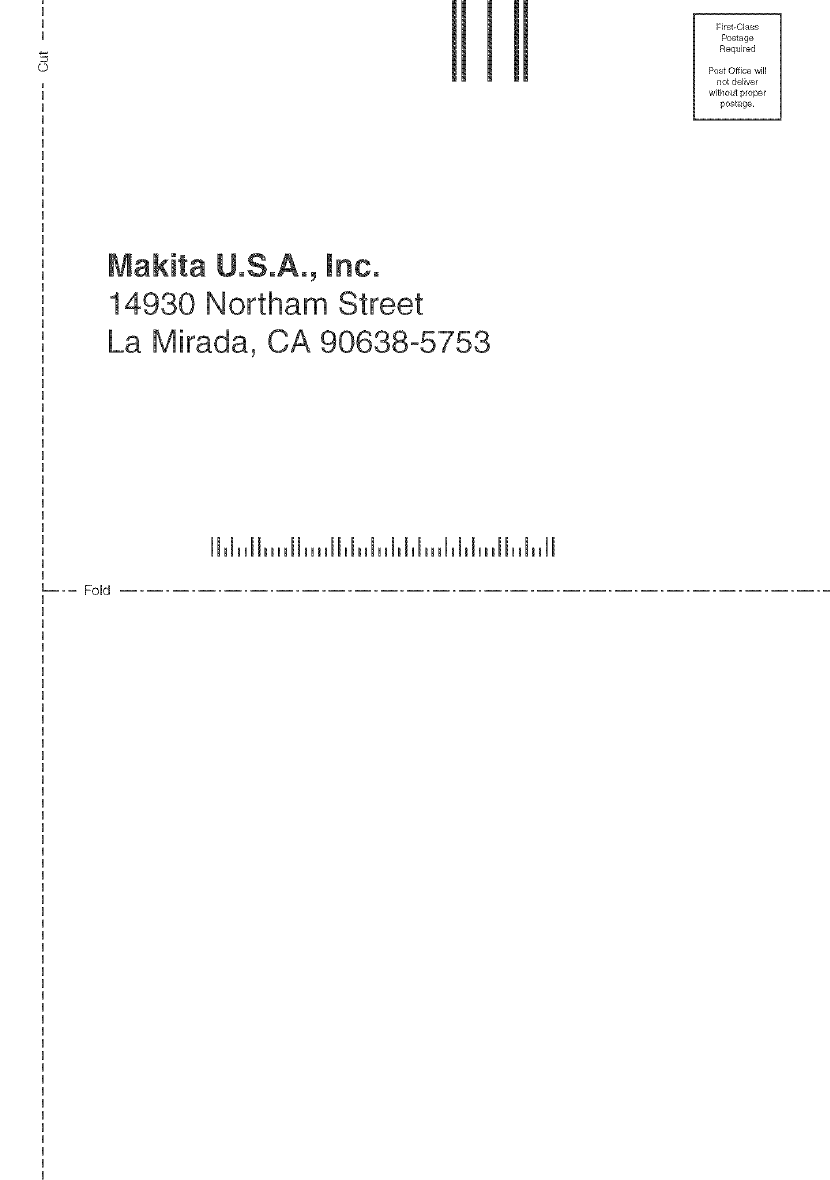
I
I
o
First-Class
Postage
Required
Post Office will
not deliver
without p_oper
postage
Makita U.S.A., inc.
14930 Northam Street
La Mirada, CA 90638-5753
Ul,l,ulh,u,ll,u,,llul,,lu,hlul,,,U,hlu,,llu,h,Ul
---- Fold
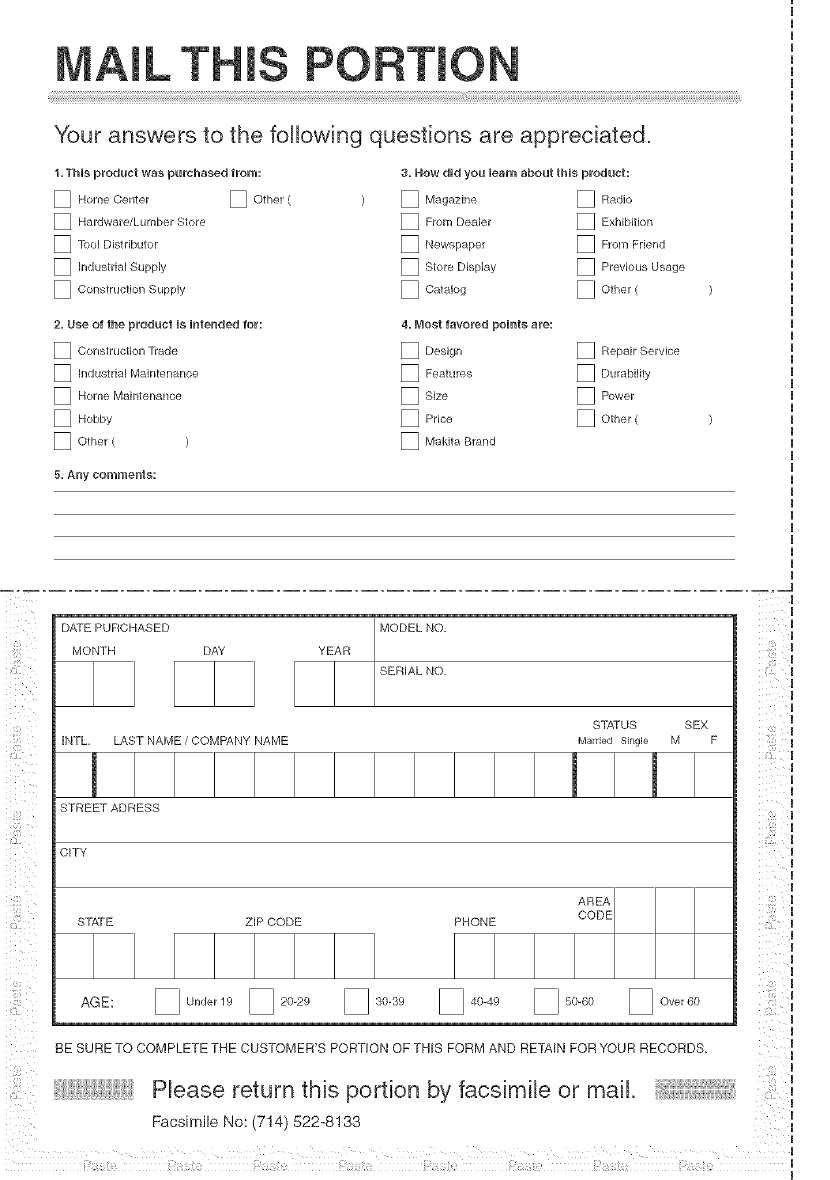
Your answers to the following questions are appreciated.
1, Th_ product was, purchased 1tom:
[] Home Center [] Other (
]Hardware/Lumber Store
[]hdustrial Supply
3, How d_d you _earn about th_ product:
[] Magazine [] Radii)
[] From DeaJer [] Exhibition
[] Newspaper [] From Friend
[] Store Display [] Previous Usage
[] Catalog [] Other(
2, Use ol the product _ _ntended 1or:
]Industrial Maintenance
] Home Maintenance
[] Hobby
[] Other ( )
4, Most _avored points are:
[] Design [] Repair Service
[] Features [] Durability
[]Size []Power
[] Price [] Other(
] Makita Brand
5=Any comment_:
DATE PURCHASED
MONTH DAY
MODEL NO.
YEAR
SERIAL NO.
STATUS
INTL. LAST NAME /COMPANY NAME Married Single
1 ! !
STREET ADFtESS
CITY
STA-[ E ZIP CODE PHONE
AREA
CODE
SEX
M F
AGE: _J UI,der 19 _J 20-29 _J 30-39 _J 40-49 _J 50-60 _J Over 60
BE SURE TO COMPLETE THE CUSTOMERS PORTION OF THIS FORM AND RETAIN FOR YOUR RECORDS,
Please return this portion by facsimile or mail.
I
I
I
I
I
I
I
I
I
I
I
I
I
I
I
I
II
I
I
I
I
I
Facsimile No: (714) 522_8!33 i
I

CE
1-800-4-MAK]TA
RETAIN THIS PORTION FOR YOUR RECORDS
ALABAMA COLORADO LOUISIANA II EW 'CORK _OEP,'fO RiCO
2365 Pelham Rat kway 1183c_ E 51st Ave 5626 Jefferson H_y 4c_17 Ge41essee Street 200 Guayama St
Pelham AL 35124 DenJe_ CO 80239 2709 H_rahal/ LA 70123 ( heektowaga NY 14225 Hato Rey PR 00917
(205) 620 1791 (303) 371 2850 (504) 733 4138 (716/685 9503 (787/2:30 8776
t31 35 3tst Ave
,&RIZON,¢ FLORIDA MARYLANB Flusl/mg N¥ 11354 S'EF4NESSEE
3707 E Broadway Rd Ste 6 620 Douglas Ave Suite t 302 7541 4:SR4tchieHighway _718_886 0971 4655 Nolel/_ville Rd
_'hoenix AZ 85O4O AJtamol/teSprings FL 32714 Glen Bu_nie f,4D21061 Nashville TN 37211
_502_437 2350 _407_774 6OOO _410_:Sg00150 (615_3_1 9922
NORTH CAROL_N,&
75OEast Sample Road 3501 G S _yon St
ARKANS,¢S _'ompa_oBeach FL 33O64 ,_AS_,CCHUSETTS Charlotte NO23217 TEXAS
S11ackletold Shopl_ng Center _9:34) 781 633_ 232 Prov_denr__4W,/ _704_527 0611 12B01Stemmolls Fv,'ySte B09
240Soutl/ Sha_kleto_dRd Westwood MA O209O F_rmers _ranch TX 75234
St÷ C Thompson Oente_Waters _617_461 g754 (_72_243 1iS0
Utt_eao_k AR 72211 5501 W Waters Ave¸¸Ste 405 O'a_O
_50t_224:373_ Tampa FL33634 6253 E Ma_nS_ 12701 Director_ Dr
_t3_ 886 8292 _NNESO'r,_ Oolumbus OH 43213 Stattor_ TX 77477 3701
6427 Penn Ave South _614_86O 0222 (28t_ 5558665
CALIFORNIA Iqichfield MN 55423
4185O OhristySt _612_86_ 5199_EORGI,¢ 6379 Pearl Road 3453 _H3_ No_t_/St÷ 101
_remol/t O,€ _4:S3_ 5107 468ORive_ Green Pa_kv,_y _'a_maHeights OH 4413O Sal/A ntollio, TX 7_21
_5t0_557 9t_81 Dulut_/GA 3OO962556 _440_843 7555 (210_228 0675
_770_476 8_11 ,_SSOUP4
t421 N Clovis Ave ._te t12 _876 Watson Road t617 E Kempe_Rd
_resno OA _3727 St Lo_s blO 63126 2221 Sharowille OH 45246
_5:Sg_ 252 5156 _314_90_ gB89 _513_771 07_8
UTAH
t45 E 1300S S_e t01
Salt Lake City,UT 8411:S
ILLINO_S
t450 Fee_/an'_i_le_)r
Mt _ros_ect IL 60055 5011 (_0t_ 359 3410t4930 Northam St
La_irada CA 9063_ _753
_714_522 808_
_47_ 297 3100 NEBRASKA O KL,_HOMA
4129 S _4_hSt :%2 E t,4emoria_Road
Oma_ NE6_t27 Oklahoma City O_<73114 WAShiNGTON
_402_597 2_25 _405_752 2655 2222O84th Ave So _ld_ At970 Fultol/Avenue _ND_ANA
Sa,_mento CA 95525 _40_ bl_c_/igan Road¸ Unit 1 }<e41tWA _ts032
_916_482 5197 _ndianapoli_ IN 4625_ (253_395 8055
_317_334 9_80 NEV,CB_ OREGON
t440 SouthE _Stleet 3375 S Decatur _vd _28 t_t_/,¢venue NW
San_e_l/ardil/o CAg2408 Suites 22 24 _'olt_al/d ORg7209 W_SCONSlN
_909_885 t289 KANSAS Las Vegas¸ NV89t02 _503_222 t823 Un_o_n_]aza Shopping Ctr
_19 W 95t_/St _702_36_4277 2245 S 108th ._tWest AIlis W[
7574Cla_rernol/t Mesa _lvd Overland Pa_k KS 56212 53227
San Diego¸CA 92111 _913_542 t111 pENNSYLWNIA (414_ 5414775
_58_ 278 4471 NEW JERSEY Springwate_ r'laza
251 Her_odt_lvd 364 Wilmlngtol/W Cheste_
tSS_W4n,_hester_ KENTOCK¥ D_yton NJ08_I0 153_ _'lke
Campbell CA95O08 0501 t21_ S H_lstbourne Parkway _609_555 t212 Glen blill_ PA t9342
_408_379 0377 Louisville _4¥4O222 _610_4:S_ 4122
_502_326 374O
t6735 Satlcoy St, Ste 105 62OOBabcock Bird
Van Nuys CA _14O6 _qtl_balgh, PA 15237
_818_782 2440 _412_366 5363
CUSTOMER'S RECORD
When you need service: Send Date P_Jrchased
complele tool (prepaid)to oi/e
of the Makita FactoryService Dea]er's Name & Address
CentersHsted,otto anAuthorized
blakitaService Centel.Be sure
to attacha letterto the outside of Model No.
the carton detailingthe prob]em
with you_tool Serial No
27

Some dust created by power sanding, sawing, grinding, drilling, and other
construction activities contains chemicals known to the State of California
to cause cancer, birth defects or other reproductive harm, Some examples
of these chemicals are:
lead from bad=based paints,
ocrystalline silica from bricks and cement and other masonry products, and
oarsenic and chromium from chemically=treated lumber,
Your risk from these exposures varies, depending on how often you do this
type of work, To reduce your exposure to these chemicals: work in a wen
ventilated area, and work with approved safety equipment, such as those
dust masks that are specially designed to filter out microscopic particles,
MAKITA LIMITED ONE YEAR WARRANTY
Warranty Policy
Every Makita tool is thoroughly inspected and tested before leaving the factory. It is warranted to be free of
defects from workmanship and materials for the period of ONE YEAR from the date of original purchase,
Should any trouble develop during this one year period, return the COMPLETE tool, freight prepaid, to one of
Makita's Factory or Authorized Service Centers. If inspection shows the trouble is caused by defective
workmanship or material, Makita will repair (or at our option, replace) without charge.
This Warranty does not apply where:
* repairs have been made or attempted by others:
repairs are required because of normal wear and tear:
the tool has been abused misused or improperly maintained:
alterations have been made to the tool,
IN NO EVENT SHALL MAKITA BE LIABLE FOR ANY INDIRECT, INCIDENTAL OR CONSEQUENTIAL
DAMAGES FROM THE SALE OR USE OFTHE PRODUCT. THIS DISCLAIMER APPLIES BOTH DURING
AND AFTER THE TERM OF THIS WARRANTY.
MAKITA DISCLAIMS LIABILITY FOR ANY IMPLIED WARRANTIES, INCLUDING IMPLIED WARRANTIES OF
"MERCHANTABILITY" AND "FITNESS FOR A SPECIFIC PURPOSE," AFTER THE ONE YEAR TERM OF THIS
WARRANTY
This Warranty gives you specific legal rights, and you may also have other rights which vary from state to state.
Some states do not allow the exclusion or limitation of incidental or consequential damages, so the above
limitation or exclusion may not apply to you, Some states do not allow Nmitation on how long an implied
warranty lasts, so the above limitation may not apply to you.
Makita Corporation of America
2650 Buford Hwy., Buford, GA 30518
884129C060