Nokia Solutions and Networks T6BV1 GSM 1900 Base Transceiver Station User Manual 68P02902W12 A UK CI
Nokia Solutions and Networks GSM 1900 Base Transceiver Station 68P02902W12 A UK CI
Contents
- 1. Indoor Service Manual
- 2. Outdoor service manual
Outdoor service manual
For:cll
Printed on:Tue, Nov 6, 2001 09:51:08
From book:68P02902W12-A-UK-CI
Document:cat_tabs
Last saved on:Tue, Nov 6, 2001 09:50:56
Document:newcover
Last saved on:Tue, Nov 6, 2001 09:50:45
Document:cover (back)
Last saved on:Tue, Nov 6, 2001 09:50:44
Document:newspine1
Last saved on:Tue, Nov 6, 2001 09:50:45
Document:spine1 (back)
Last saved on:Tue, Nov 6, 2001 09:50:46
Document:insidecover-legal
Last saved on:Tue, Nov 6, 2001 09:50:56
Document:toc
Last saved on:Tue, Nov 6, 2001 09:50:56
Document:Introduction
Last saved on:Tue, Nov 6, 2001 09:50:56
Document:Warnings and Cautions
Last saved on:Tue, Nov 6, 2001 09:50:56
Document:Manual information
Last saved on:Tue, Nov 6, 2001 09:50:56
Document:tabs 1 to 5
Last saved on:Tue, Nov 6, 2001 09:50:50
( ...)

CATEGORY 423
INSTALLATION AND
CONFIGURATION
CATEGORY 523
MAINTENANCE
INFORMATION
CATEGORY 623
PARTS INFORMATION INDEXCATEGORY 323
TECHNICAL DESCRIPTION
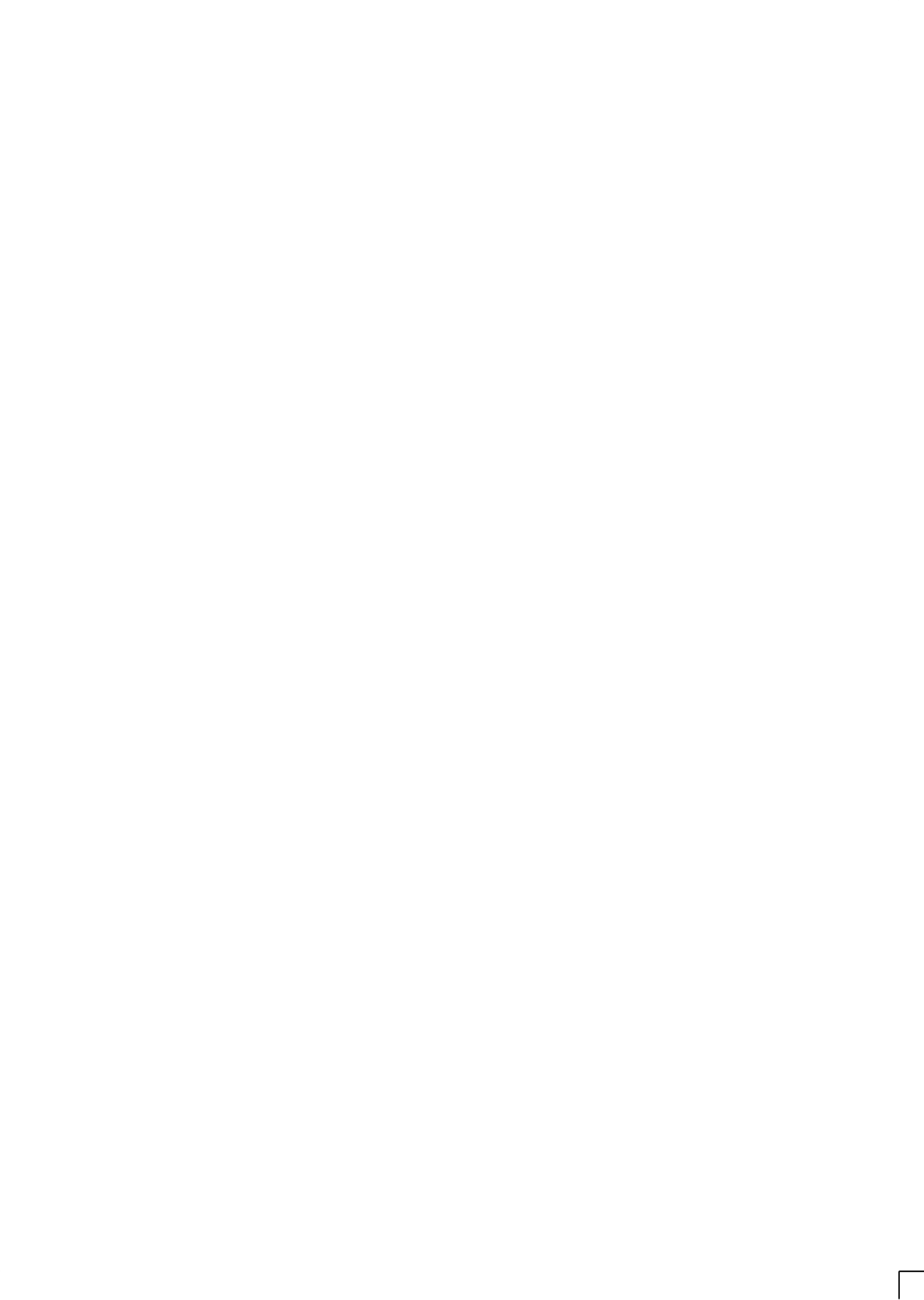
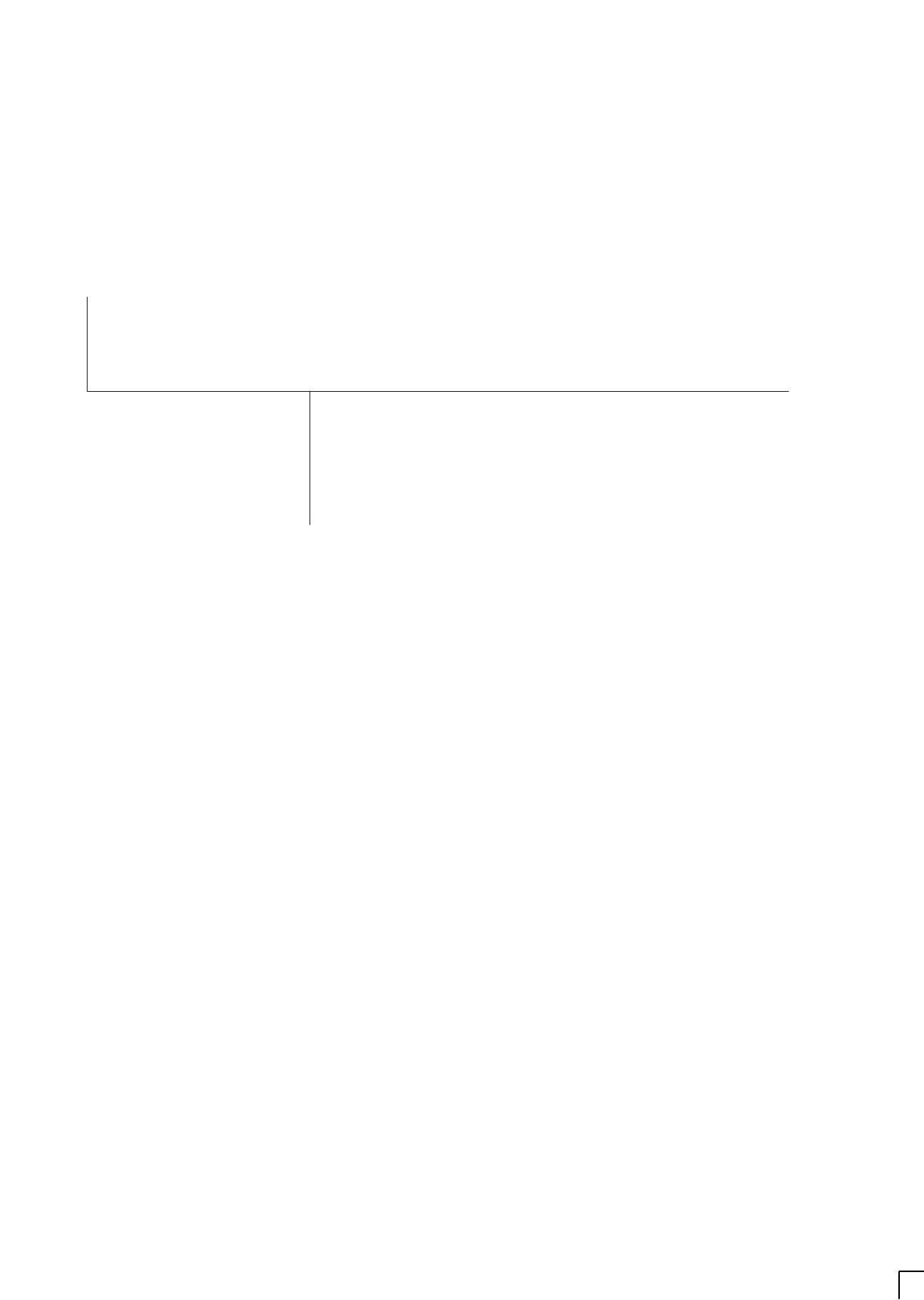
Including:
68P02902W02-A
68P02902W03-A
68P02902W04-A
68P02902W05-A
Horizon
macro
outdoor
CONTROLLED INTRODUCTION
Service Manual
GSM-204-020
68P02902W12-A
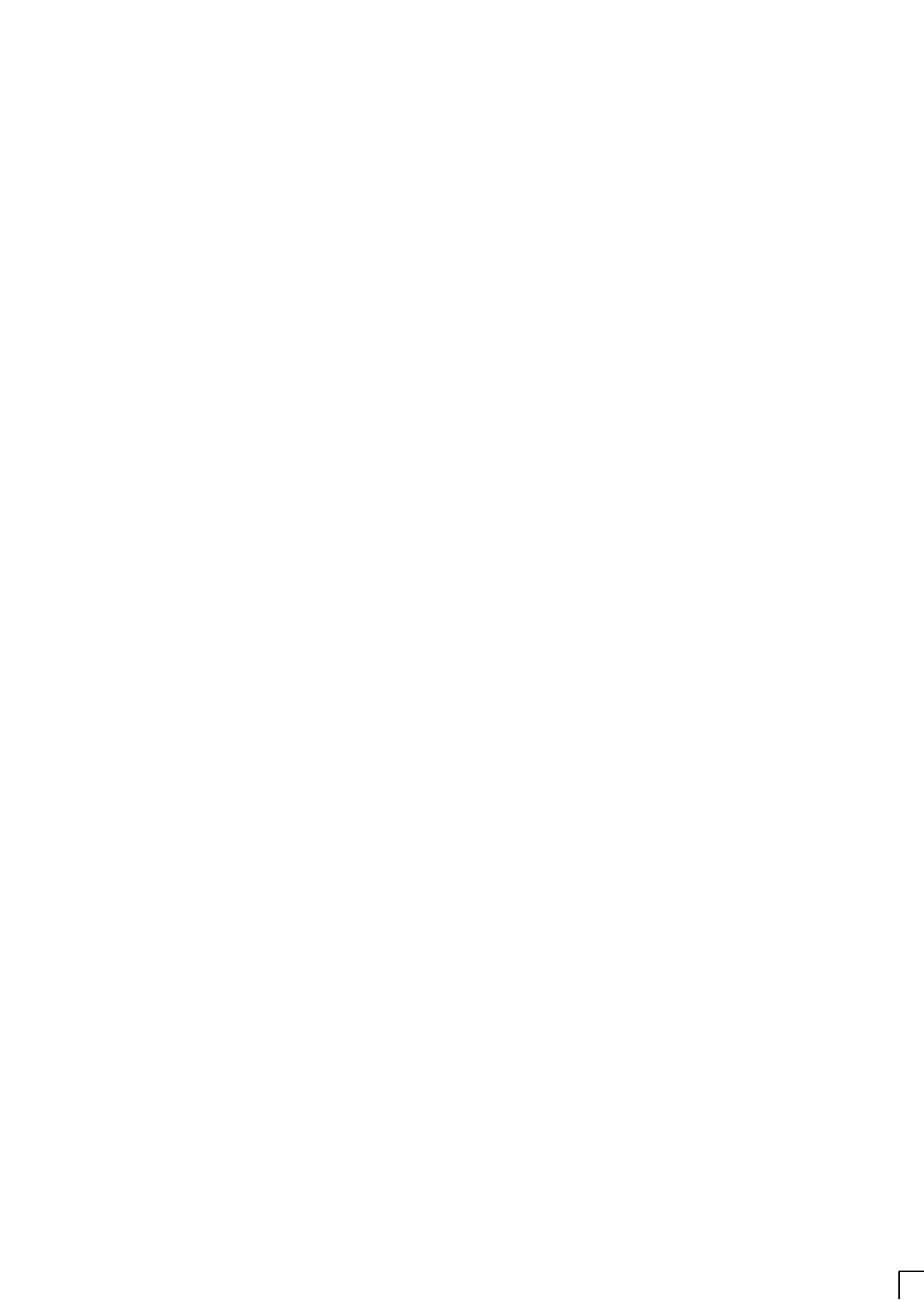
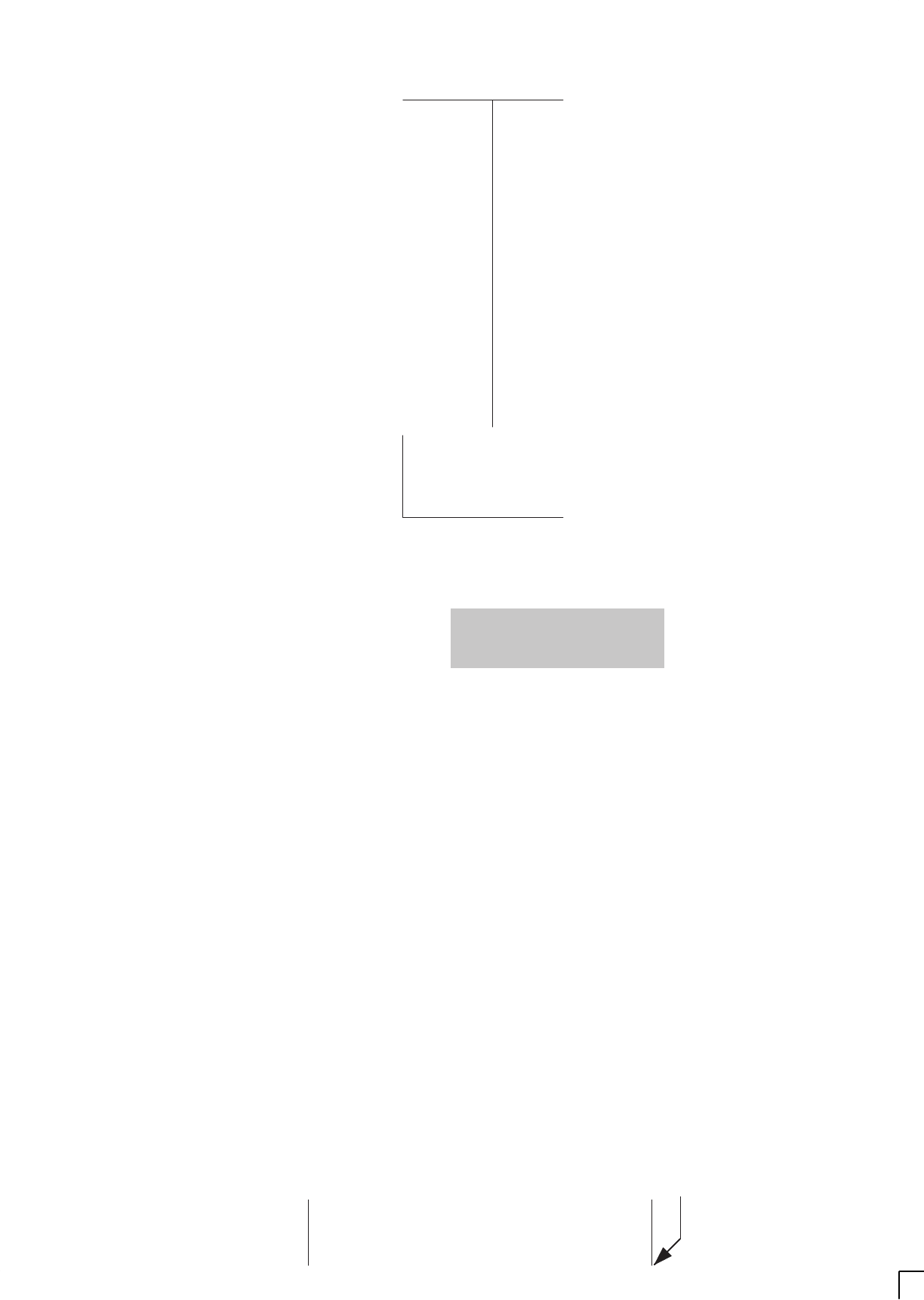
CONTROLLED
INTRODUCTION
68P02902W02-A
68P02902W03-A
68P02902W04-A
68P02902W05-A
68P02902W12-A
Service Manual
Horizon
macro
outdoor
GSM-204-020
CONTROLLED INTRODUCTION
Horizon
macro
outdoor
Including:
Positin mark for TED spine
Service
Manual
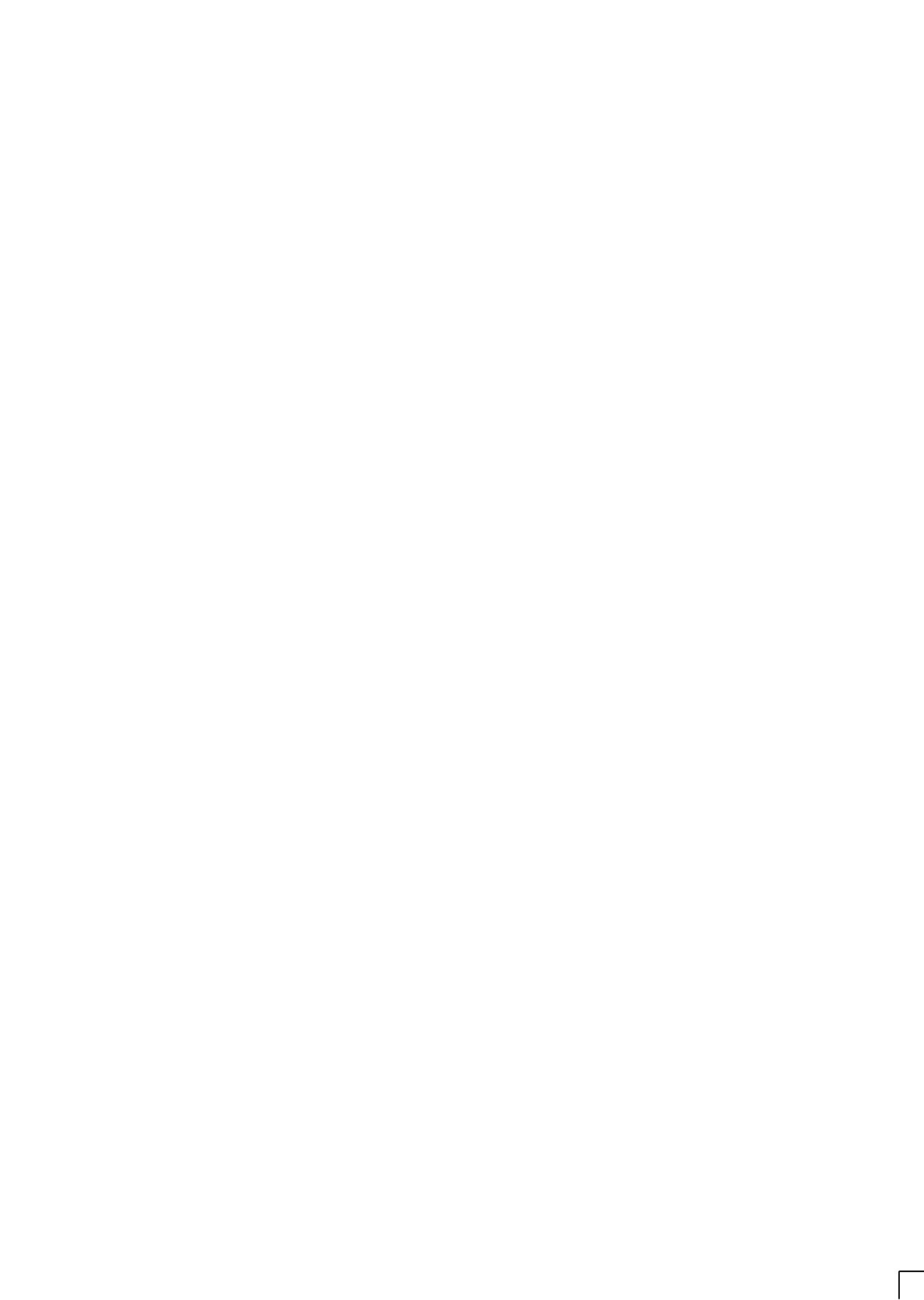
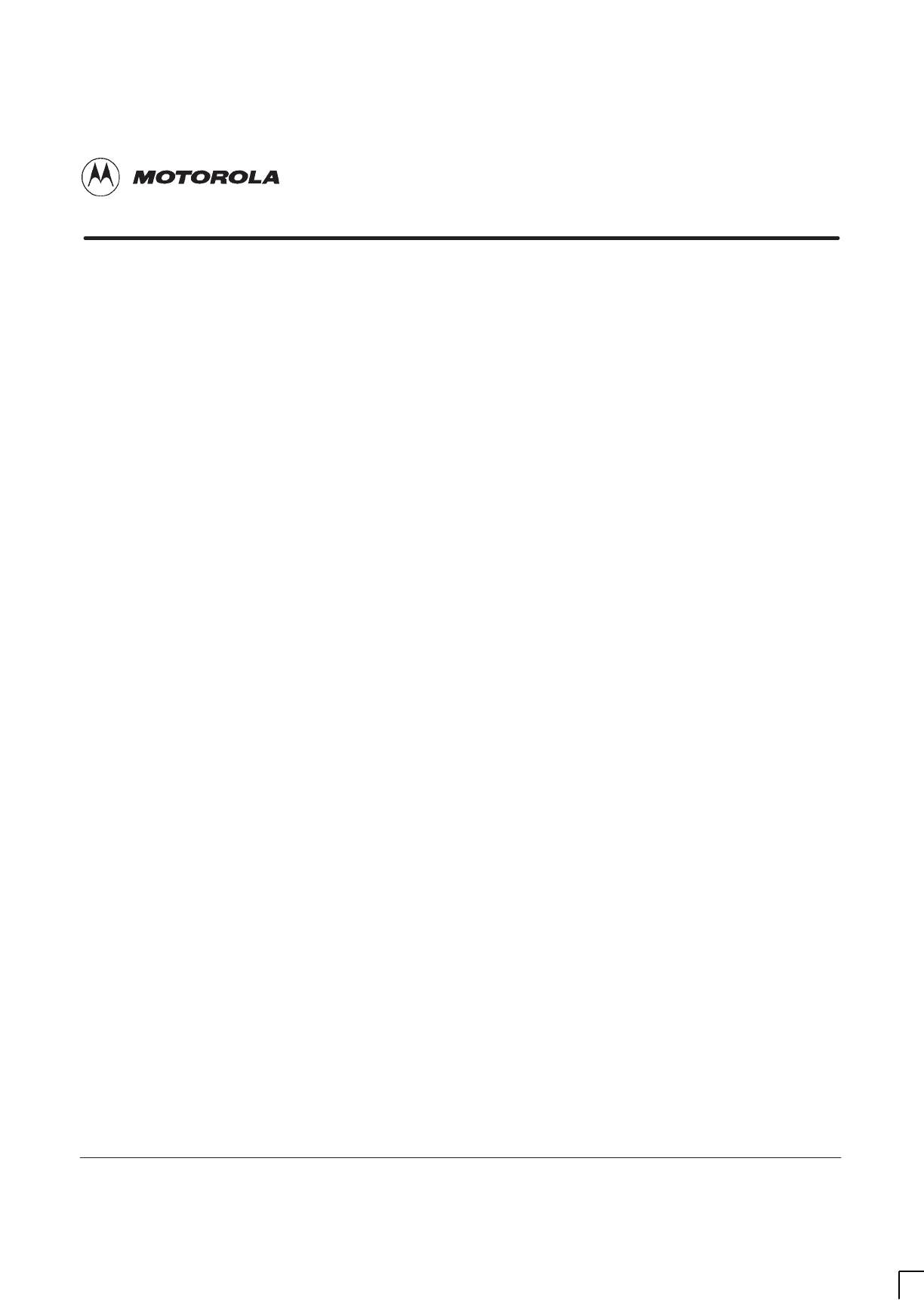
31st Oct 01
Service Manual: Horizon
macro
outdoor
68P02902W12-A
CONTROLLED INTRODUCTION
i
GSM-204-020
Service Manual
Horizon
macro
outdoor
Motorola 1999-2001
All Rights Reserved
Printed in the U.K.
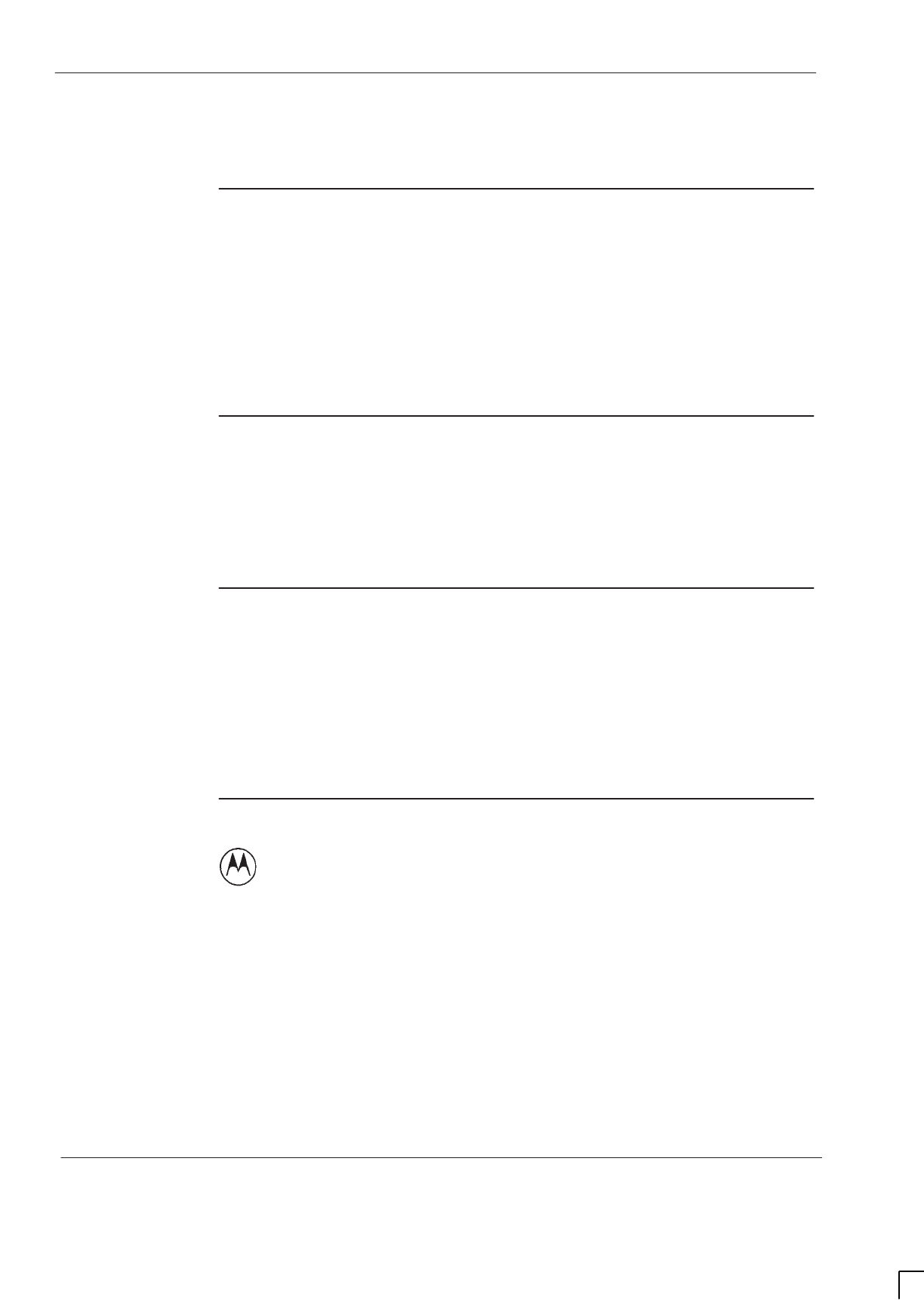
GSM-204-020
31st Oct 01
ii
Service Manual: Horizon
macro
outdoor
CONTROLLED INTRODUCTION
68P02902W12-A
Copyrights, notices and trademarks
Copyrights
The Motorola products described in this document may include copyrighted Motorola computer
programs stored in semiconductor memories or other media. Laws in the United States and other
countries preserve for Motorola certain exclusive rights for copyright computer programs, including the
exclusive right to copy or reproduce in any form the copyright computer program. Accordingly, any
copyright Motorola computer programs contained in the Motorola products described in this document
may not be copied or reproduced in any manner without the express written permission of Motorola.
Furthermore, the purchase of Motorola products shall not be deemed to grant either directly or by
implication, estoppel or otherwise, any license under the copyrights, patents or patent applications of
Motorola, except for the rights that arise by operation of law in the sale of a product.
Restrictions
The software described in this document is the property of Motorola. It is furnished under a license
agreement and may be used and/or disclosed only in accordance with the terms of the agreement.
Software and documentation are copyright materials. Making unauthorized copies is prohibited by
law. No part of the software or documentation may be reproduced, transmitted, transcribed, stored
in a retrieval system, or translated into any language or computer language, in any form or by any
means, without prior written permission of Motorola.
Accuracy
While reasonable efforts have been made to assure the accuracy of this document, Motorola
assumes no liability resulting from any inaccuracies or omissions in this document, or from the use
of the information obtained herein. Motorola reserves the right to make changes to any products
described herein to improve reliability, function, or design, and reserves the right to revise this
document and to make changes from time to time in content hereof with no obligation to notify any
person of revisions or changes. Motorola does not assume any liability arising out of the application
or use of any product or circuit described herein; neither does it convey license under its patent
rights of others.
Trademarks
and
MOTOROLA
are registered trademarks of Motorola Inc.
Aspira, Intelligence Everywhere, M-Cell and Taskfinder are trademarks of Motorola Inc.
All other brands and corporate names are trademarks of their respective owners.
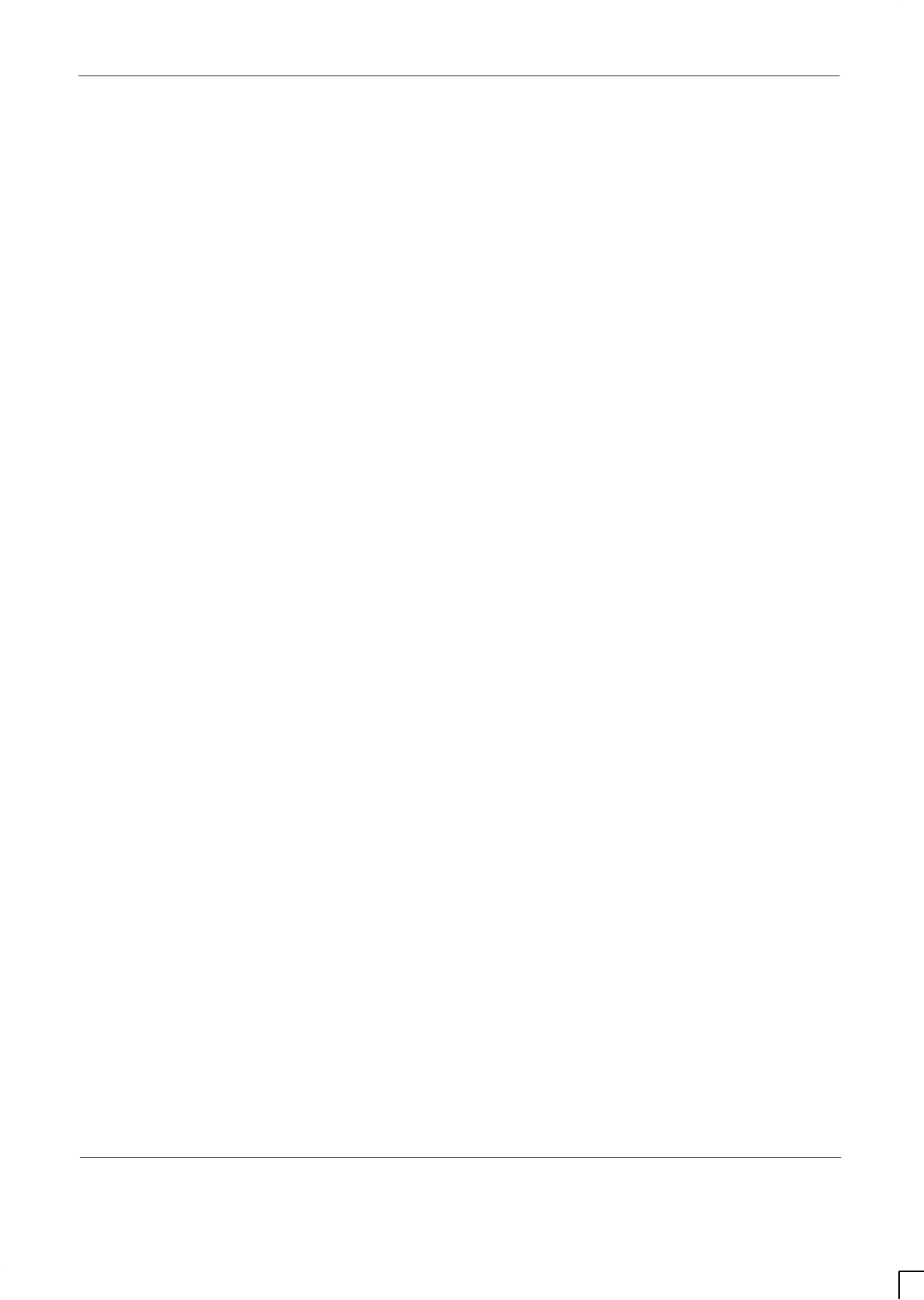
GSM-204-020
31st Oct 01
Service Manual: Horizon
macro
outdoor
68P02902W12-A
CONTROLLED INTRODUCTION
iii
Issue status of this manual 1. . . . . . . . . . . . . . . . . . . . . . . . . . . . . . . . . . . . . . . . . . . .
General information 2. . . . . . . . . . . . . . . . . . . . . . . . . . . . . . . . . . . . . . . . . . . . . . . . . .
First aid in case of electric shock 4. . . . . . . . . . . . . . . . . . . . . . . . . . . . . . . . . . . . . . .
Reporting safety issues 5. . . . . . . . . . . . . . . . . . . . . . . . . . . . . . . . . . . . . . . . . . . . . . .
Warnings and cautions 6. . . . . . . . . . . . . . . . . . . . . . . . . . . . . . . . . . . . . . . . . . . . . . .
General warnings 7. . . . . . . . . . . . . . . . . . . . . . . . . . . . . . . . . . . . . . . . . . . . . . . . . . . .
General cautions 9. . . . . . . . . . . . . . . . . . . . . . . . . . . . . . . . . . . . . . . . . . . . . . . . . . . . .
Devices sensitive to static 10. . . . . . . . . . . . . . . . . . . . . . . . . . . . . . . . . . . . . . . . . . . . .
Motorola GSM manual set 11. . . . . . . . . . . . . . . . . . . . . . . . . . . . . . . . . . . . . . . . . . . .
GMR amendment 14. . . . . . . . . . . . . . . . . . . . . . . . . . . . . . . . . . . . . . . . . . . . . . . . . . . .
GMR amendment record 15. . . . . . . . . . . . . . . . . . . . . . . . . . . . . . . . . . . . . . . . . . . . . .
Category 323
Technical Description (Tech.) i. . . . . . . . . . . . . . . . . . . . . . . . . . . . . . . . . . . . . . .
Chapter 1
Overview and specifications i. . . . . . . . . . . . . . . . . . . . . . . . . . . . . . . . . . .
Equipment introduction and manual definition Tech. 1–1. . . . . . . . . . . . . . . . . . . . . . . . . . .
Overview of Horizonmacro outdoor Tech. 1–1. . . . . . . . . . . . . . . . . . . . . . . . . . . . . . . .
Names and acronyms for main cabinet equipment Tech. 1–2. . . . . . . . . . . . . . . . . .
Configuration information Tech. 1–3. . . . . . . . . . . . . . . . . . . . . . . . . . . . . . . . . . . . . . . .
Finding information in this manual Tech. 1–4. . . . . . . . . . . . . . . . . . . . . . . . . . . . . . . . .
Cabinet view Tech. 1–5. . . . . . . . . . . . . . . . . . . . . . . . . . . . . . . . . . . . . . . . . . . . . . . . . . .
Functional diagram of Horizonmacro outdoor Tech. 1–6. . . . . . . . . . . . . . . . . . . . . . .
M-Cell6 comparison with Horizonmacro outdoor Tech. 1–7. . . . . . . . . . . . . . . . . . . . . . . . .
Comparison overview Tech. 1–7. . . . . . . . . . . . . . . . . . . . . . . . . . . . . . . . . . . . . . . . . . .
Horizonmacro and M-Cell6 compatibility Tech. 1–7. . . . . . . . . . . . . . . . . . . . . . . . . . .
Comparison of Horizonmacro and M-Cell6 connections and modules Tech. 1–8. .
Specifications Tech. 1–9. . . . . . . . . . . . . . . . . . . . . . . . . . . . . . . . . . . . . . . . . . . . . . . . . . . . . . .
Introduction to specifications Tech. 1–9. . . . . . . . . . . . . . . . . . . . . . . . . . . . . . . . . . . . .
Software requirements Tech. 1–9. . . . . . . . . . . . . . . . . . . . . . . . . . . . . . . . . . . . . . . . . .
Approval and safety Tech. 1–9. . . . . . . . . . . . . . . . . . . . . . . . . . . . . . . . . . . . . . . . . . . .
Environmental limits Tech. 1–9. . . . . . . . . . . . . . . . . . . . . . . . . . . . . . . . . . . . . . . . . . . . .
Power requirements Tech. 1–10. . . . . . . . . . . . . . . . . . . . . . . . . . . . . . . . . . . . . . . . . . . . .
RF power output Tech. 1–11. . . . . . . . . . . . . . . . . . . . . . . . . . . . . . . . . . . . . . . . . . . . . . . .
Sensitivity Tech. 1–12. . . . . . . . . . . . . . . . . . . . . . . . . . . . . . . . . . . . . . . . . . . . . . . . . . . . . .
Battery backup Tech. 1–12. . . . . . . . . . . . . . . . . . . . . . . . . . . . . . . . . . . . . . . . . . . . . . . . .
BSC connectivity options Tech. 1–12. . . . . . . . . . . . . . . . . . . . . . . . . . . . . . . . . . . . . . . .
Outdoor cabinet dimensions Tech. 1–12. . . . . . . . . . . . . . . . . . . . . . . . . . . . . . . . . . . . . .
Weights Tech. 1–13. . . . . . . . . . . . . . . . . . . . . . . . . . . . . . . . . . . . . . . . . . . . . . . . . . . . . . . .
Torque values Tech. 1–13. . . . . . . . . . . . . . . . . . . . . . . . . . . . . . . . . . . . . . . . . . . . . . . . . .
Cabinets enhancements Tech. 1–13. . . . . . . . . . . . . . . . . . . . . . . . . . . . . . . . . . . . . . . . .
Frequency capability Tech. 1–14. . . . . . . . . . . . . . . . . . . . . . . . . . . . . . . . . . . . . . . . . . . .
Structural considerations Tech. 1–16. . . . . . . . . . . . . . . . . . . . . . . . . . . . . . . . . . . . . . . . .
Outdoor site dimensions Tech. 1–17. . . . . . . . . . . . . . . . . . . . . . . . . . . . . . . . . . . . . . . . .
View of maximum site template layout Tech. 1–18. . . . . . . . . . . . . . . . . . . . . . . . . . . . .
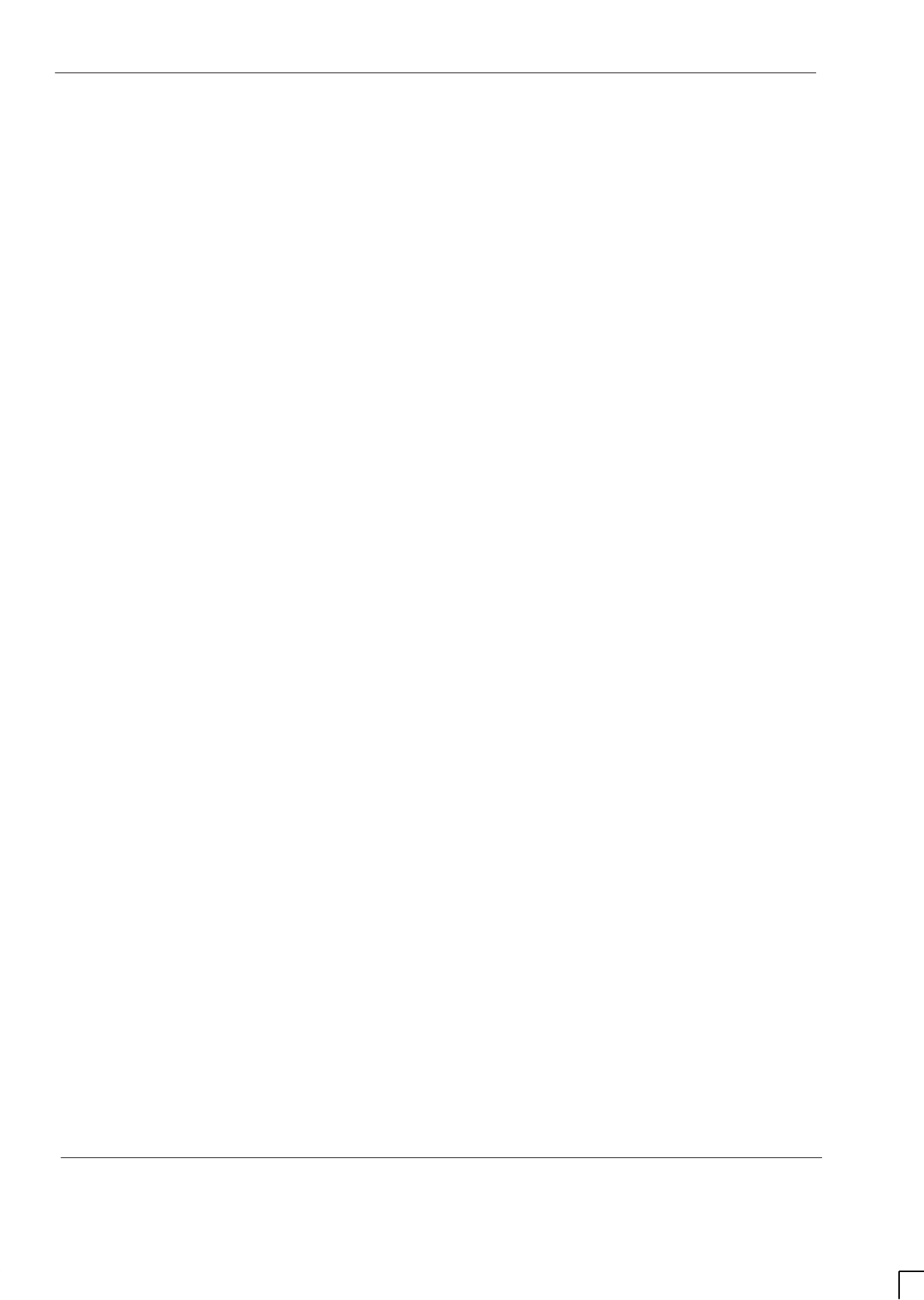
GSM-204-020
31st Oct 01
iv
Service Manual: Horizon
macro
outdoor
CONTROLLED INTRODUCTION
68P02902W12-A
Chapter 2
Cabinet structure i. . . . . . . . . . . . . . . . . . . . . . . . . . . . . . . . . . . . . . . . . . . . . .
Outdoor cabinet structure Tech. 2–1. . . . . . . . . . . . . . . . . . . . . . . . . . . . . . . . . . . . . . . . . . . . .
External cabinet view Tech. 2–1. . . . . . . . . . . . . . . . . . . . . . . . . . . . . . . . . . . . . . . . . . . .
Overview of structure description Tech. 2–2. . . . . . . . . . . . . . . . . . . . . . . . . . . . . . . . .
Space required around cabinet Tech. 2–2. . . . . . . . . . . . . . . . . . . . . . . . . . . . . . . . . . .
Filled cabinet view Tech. 2–3. . . . . . . . . . . . . . . . . . . . . . . . . . . . . . . . . . . . . . . . . . . . . .
SURF harness Tech. 2–4. . . . . . . . . . . . . . . . . . . . . . . . . . . . . . . . . . . . . . . . . . . . . . . . . . . . . . .
SURF harness detail Tech. 2–4. . . . . . . . . . . . . . . . . . . . . . . . . . . . . . . . . . . . . . . . . . . .
Cabinet view with installed SURF harness Tech. 2–4. . . . . . . . . . . . . . . . . . . . . . . . .
SURF harness view Tech. 2–5. . . . . . . . . . . . . . . . . . . . . . . . . . . . . . . . . . . . . . . . . . . . .
Top section Tech. 2–6. . . . . . . . . . . . . . . . . . . . . . . . . . . . . . . . . . . . . . . . . . . . . . . . . . . . . . . . . .
Top section description Tech. 2–6. . . . . . . . . . . . . . . . . . . . . . . . . . . . . . . . . . . . . . . . . .
Top section diagram Tech. 2–7. . . . . . . . . . . . . . . . . . . . . . . . . . . . . . . . . . . . . . . . . . . . .
Krone blocks Tech. 2–7. . . . . . . . . . . . . . . . . . . . . . . . . . . . . . . . . . . . . . . . . . . . . . . . . . .
AC outlet socket Tech. 2–7. . . . . . . . . . . . . . . . . . . . . . . . . . . . . . . . . . . . . . . . . . . . . . . .
Earth plates Tech. 2–8. . . . . . . . . . . . . . . . . . . . . . . . . . . . . . . . . . . . . . . . . . . . . . . . . . . .
Blank and expansion plates Tech. 2–9. . . . . . . . . . . . . . . . . . . . . . . . . . . . . . . . . . . . . .
Cage backplane interface panel harness assembly (CBIA) Tech. 2–10. . . . . . . . . . . . . . . .
CBIA overview Tech. 2–10. . . . . . . . . . . . . . . . . . . . . . . . . . . . . . . . . . . . . . . . . . . . . . . . . .
CBIA and interface panel schematic view Tech. 2–10. . . . . . . . . . . . . . . . . . . . . . . . . .
Backplane and harness view Tech. 2–11. . . . . . . . . . . . . . . . . . . . . . . . . . . . . . . . . . . . .
CBIA cage function and diagram Tech. 2–12. . . . . . . . . . . . . . . . . . . . . . . . . . . . . . . . . .
CBIA harness function Tech. 2–12. . . . . . . . . . . . . . . . . . . . . . . . . . . . . . . . . . . . . . . . . . .
CBIA backplane function Tech. 2–13. . . . . . . . . . . . . . . . . . . . . . . . . . . . . . . . . . . . . . . . .
Attachment of cage to cabinet Tech. 2–13. . . . . . . . . . . . . . . . . . . . . . . . . . . . . . . . . . . .
CBIA interface panel Tech. 2–14. . . . . . . . . . . . . . . . . . . . . . . . . . . . . . . . . . . . . . . . . . . . . . . . .
Interface panel function Tech. 2–14. . . . . . . . . . . . . . . . . . . . . . . . . . . . . . . . . . . . . . . . . .
Interface panel diagram Tech. 2–14. . . . . . . . . . . . . . . . . . . . . . . . . . . . . . . . . . . . . . . . . .
Interface panel pinouts Tech. 2–14. . . . . . . . . . . . . . . . . . . . . . . . . . . . . . . . . . . . . . . . . .
Power supply enclosure Tech. 2–15. . . . . . . . . . . . . . . . . . . . . . . . . . . . . . . . . . . . . . . . . . . . . .
Power supply enclosure overview Tech. 2–15. . . . . . . . . . . . . . . . . . . . . . . . . . . . . . . . .
View of power supply enclosure Tech. 2–15. . . . . . . . . . . . . . . . . . . . . . . . . . . . . . . . . .
Power supply unit Tech. 2–16. . . . . . . . . . . . . . . . . . . . . . . . . . . . . . . . . . . . . . . . . . . . . . .
Alarms interface board Tech. 2–16. . . . . . . . . . . . . . . . . . . . . . . . . . . . . . . . . . . . . . . . . .
Alarms interface board connectors Tech. 2–17. . . . . . . . . . . . . . . . . . . . . . . . . . . . . . . .
TMS test switches Tech. 2–18. . . . . . . . . . . . . . . . . . . . . . . . . . . . . . . . . . . . . . . . . . . . . .
Customer equipment racking Tech. 2–18. . . . . . . . . . . . . . . . . . . . . . . . . . . . . . . . . . . . .
Outdoor cabinet doors and lid Tech. 2–19. . . . . . . . . . . . . . . . . . . . . . . . . . . . . . . . . . . . . . . . .
Door function Tech. 2–19. . . . . . . . . . . . . . . . . . . . . . . . . . . . . . . . . . . . . . . . . . . . . . . . . . .
Door views Tech. 2–19. . . . . . . . . . . . . . . . . . . . . . . . . . . . . . . . . . . . . . . . . . . . . . . . . . . . .
Lid function Tech. 2–20. . . . . . . . . . . . . . . . . . . . . . . . . . . . . . . . . . . . . . . . . . . . . . . . . . . .
Lid view Tech. 2–20. . . . . . . . . . . . . . . . . . . . . . . . . . . . . . . . . . . . . . . . . . . . . . . . . . . . . . .
Chapter 3
Thermal management system i. . . . . . . . . . . . . . . . . . . . . . . . . . . . . . . . . .
Horizonmacro outdoor temperature control Tech. 3–1. . . . . . . . . . . . . . . . . . . . . . . . . . . . . .
Temperature control overview Tech. 3–1. . . . . . . . . . . . . . . . . . . . . . . . . . . . . . . . . . . .
Cabinet over temperature control Tech. 3–1. . . . . . . . . . . . . . . . . . . . . . . . . . . . . . . . .
Temperature sensors Tech. 3–1. . . . . . . . . . . . . . . . . . . . . . . . . . . . . . . . . . . . . . . . . . . .
Cabinet restart after shutdown Tech. 3–2. . . . . . . . . . . . . . . . . . . . . . . . . . . . . . . . . . . .
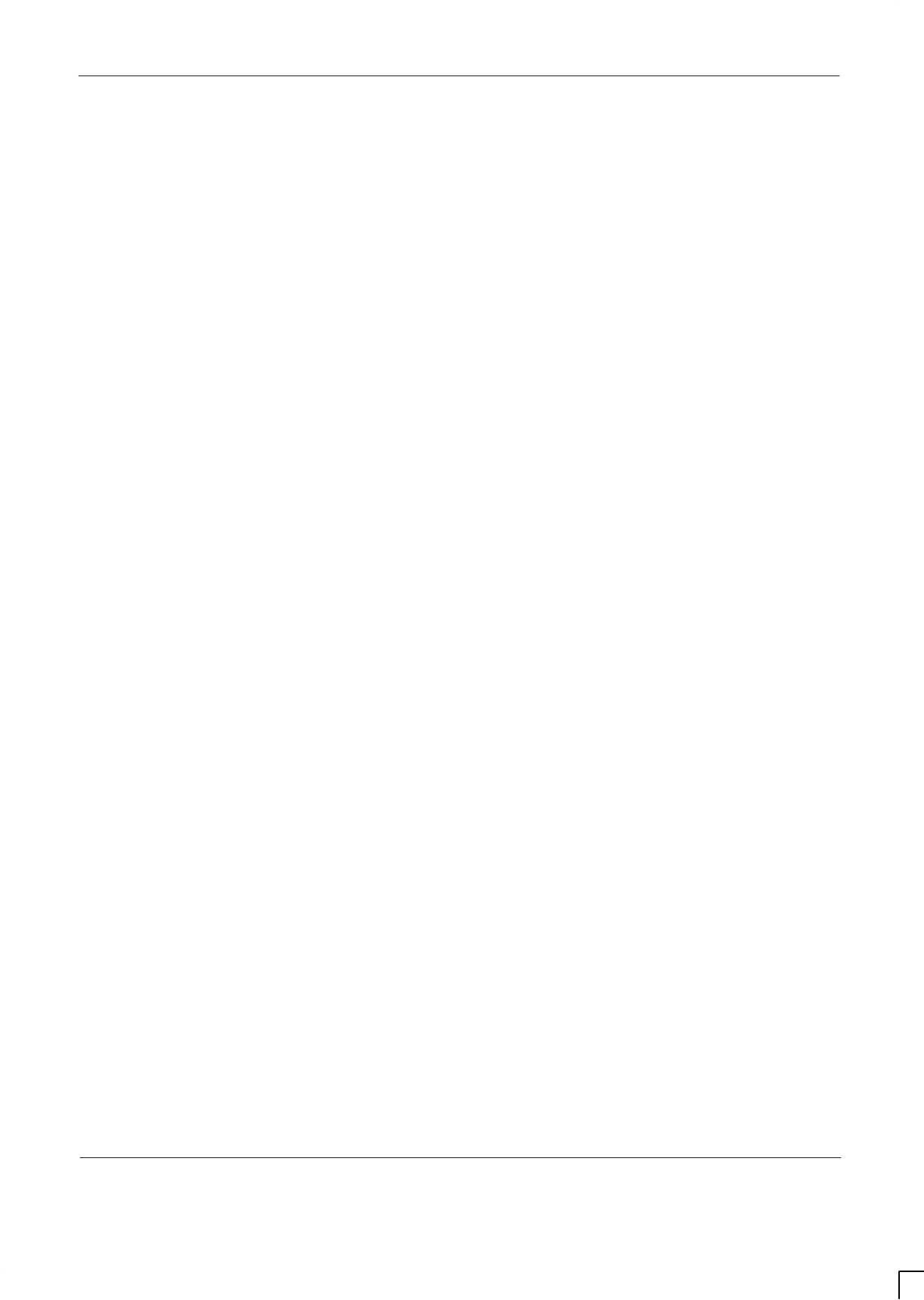
GSM-204-020
31st Oct 01
Service Manual: Horizon
macro
outdoor
68P02902W12-A
CONTROLLED INTRODUCTION
v
Thermal management system (TMS) Tech. 3–3. . . . . . . . . . . . . . . . . . . . . . . . . . . . . . . . . . .
TMS overview Tech. 3–3. . . . . . . . . . . . . . . . . . . . . . . . . . . . . . . . . . . . . . . . . . . . . . . . . .
View of TMS unit Tech. 3–3. . . . . . . . . . . . . . . . . . . . . . . . . . . . . . . . . . . . . . . . . . . . . . . .
Heat exchanger components Tech. 3–4. . . . . . . . . . . . . . . . . . . . . . . . . . . . . . . . . . . . .
TMS functional description Tech. 3–5. . . . . . . . . . . . . . . . . . . . . . . . . . . . . . . . . . . . . . .
Heat exchanger functional diagram Tech. 3–6. . . . . . . . . . . . . . . . . . . . . . . . . . . . . . .
Chapter 4
Cabinet power supplies i. . . . . . . . . . . . . . . . . . . . . . . . . . . . . . . . . . . . . . . .
Horizonmacro outdoor power supplies Tech. 4–1. . . . . . . . . . . . . . . . . . . . . . . . . . . . . . . . . .
Power supply overview Tech. 4–1. . . . . . . . . . . . . . . . . . . . . . . . . . . . . . . . . . . . . . . . . .
Power supply unit view Tech. 4–2. . . . . . . . . . . . . . . . . . . . . . . . . . . . . . . . . . . . . . . . . .
View of main cage power modules Tech. 4–3. . . . . . . . . . . . . . . . . . . . . . . . . . . . . . . .
Introduction to power distribution Tech. 4–4. . . . . . . . . . . . . . . . . . . . . . . . . . . . . . . . . . . . . . .
Power distribution overview Tech. 4–4. . . . . . . . . . . . . . . . . . . . . . . . . . . . . . . . . . . . . .
View of power supply unit cage Tech. 4–4. . . . . . . . . . . . . . . . . . . . . . . . . . . . . . . . . . .
AC power distribution Tech. 4–5. . . . . . . . . . . . . . . . . . . . . . . . . . . . . . . . . . . . . . . . . . . . . . . . .
View of ac power components Tech. 4–5. . . . . . . . . . . . . . . . . . . . . . . . . . . . . . . . . . .
AC distribution description Tech. 4–6. . . . . . . . . . . . . . . . . . . . . . . . . . . . . . . . . . . . . . .
AC outlet socket Tech. 4–7. . . . . . . . . . . . . . . . . . . . . . . . . . . . . . . . . . . . . . . . . . . . . . . .
View of the ac outlet socket Tech. 4–8. . . . . . . . . . . . . . . . . . . . . . . . . . . . . . . . . . . . . .
AC distribution diagram Tech. 4–8. . . . . . . . . . . . . . . . . . . . . . . . . . . . . . . . . . . . . . . . . .
DC power distribution Tech. 4–9. . . . . . . . . . . . . . . . . . . . . . . . . . . . . . . . . . . . . . . . . . . . . . . . .
DC distribution overview Tech. 4–9. . . . . . . . . . . . . . . . . . . . . . . . . . . . . . . . . . . . . . . . .
View of dc power components Tech. 4–9. . . . . . . . . . . . . . . . . . . . . . . . . . . . . . . . . . .
DC distribution diagram Tech. 4–10. . . . . . . . . . . . . . . . . . . . . . . . . . . . . . . . . . . . . . . . . .
DC distribution description Tech. 4–10. . . . . . . . . . . . . . . . . . . . . . . . . . . . . . . . . . . . . . .
View of the dc circuit breaker panel Tech. 4–11. . . . . . . . . . . . . . . . . . . . . . . . . . . . . . .
Customer equipment power supplies Tech. 4–11. . . . . . . . . . . . . . . . . . . . . . . . . . . . . .
Internal battery backup Tech. 4–11. . . . . . . . . . . . . . . . . . . . . . . . . . . . . . . . . . . . . . . . . .
Internal battery arrangement Tech. 4–12. . . . . . . . . . . . . . . . . . . . . . . . . . . . . . . . . . . . .
View of battery sense lead Tech. 4–12. . . . . . . . . . . . . . . . . . . . . . . . . . . . . . . . . . . . . . .
External battery backup connection Tech. 4–13. . . . . . . . . . . . . . . . . . . . . . . . . . . . . . .
View of the dc interface panel Tech. 4–13. . . . . . . . . . . . . . . . . . . . . . . . . . . . . . . . . . . .
Control and alarm board (CAB) Tech. 4–14. . . . . . . . . . . . . . . . . . . . . . . . . . . . . . . . . . . . . . . .
Introduction to the CAB Tech. 4–14. . . . . . . . . . . . . . . . . . . . . . . . . . . . . . . . . . . . . . . . . .
CAB views Tech. 4–15. . . . . . . . . . . . . . . . . . . . . . . . . . . . . . . . . . . . . . . . . . . . . . . . . . . . .
CAB indicators and controls Tech. 4–16. . . . . . . . . . . . . . . . . . . . . . . . . . . . . . . . . . . . . .
CAB front panel fuses Tech. 4–17. . . . . . . . . . . . . . . . . . . . . . . . . . . . . . . . . . . . . . . . . . .
CAB control functions Tech. 4–18. . . . . . . . . . . . . . . . . . . . . . . . . . . . . . . . . . . . . . . . . . .
CAB alarm functions Tech. 4–20. . . . . . . . . . . . . . . . . . . . . . . . . . . . . . . . . . . . . . . . . . . .
CAB additional functions Tech. 4–22. . . . . . . . . . . . . . . . . . . . . . . . . . . . . . . . . . . . . . . . .
DIP switches Tech. 4–25. . . . . . . . . . . . . . . . . . . . . . . . . . . . . . . . . . . . . . . . . . . . . . . . . . .
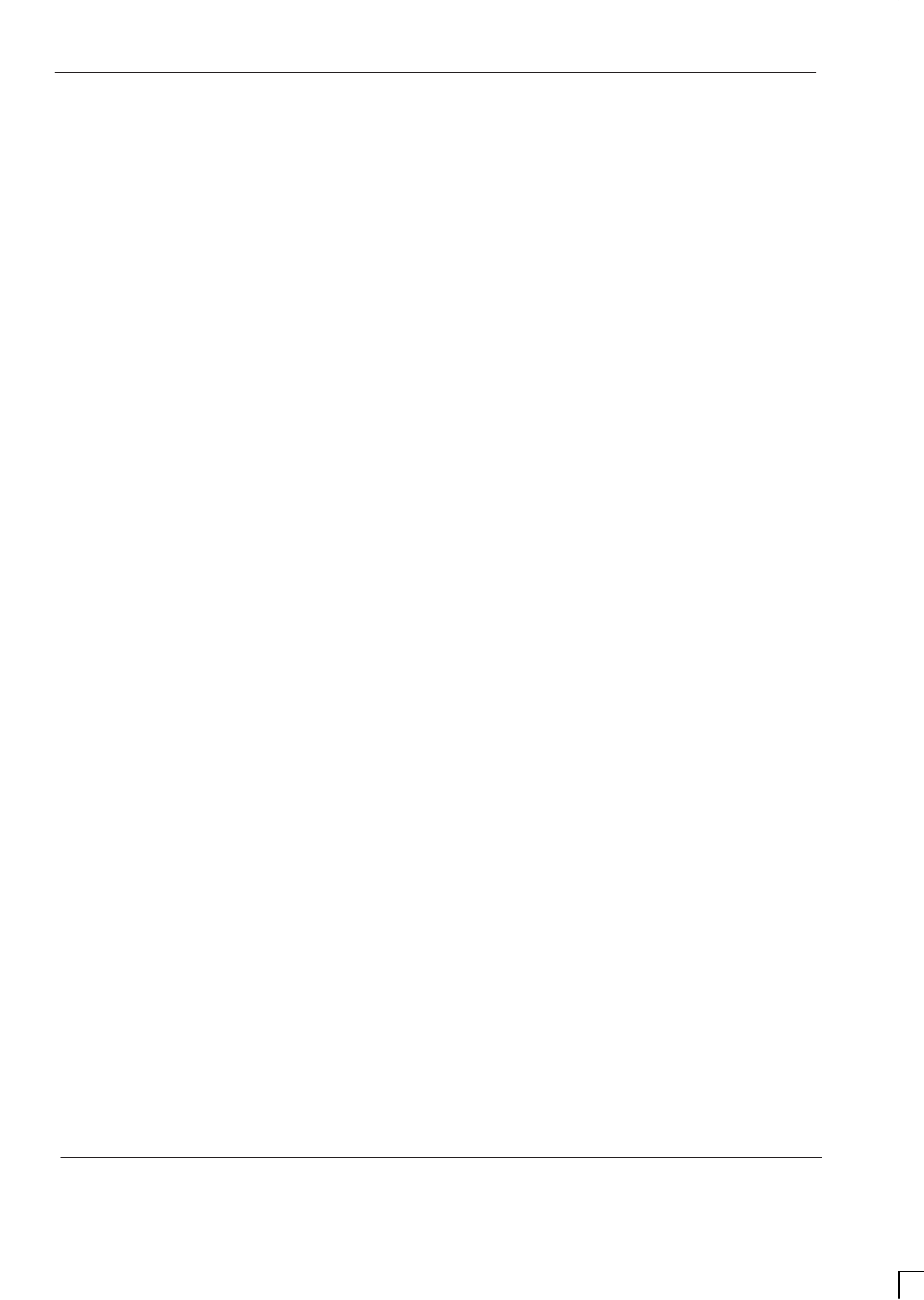
GSM-204-020
31st Oct 01
vi
Service Manual: Horizon
macro
outdoor
CONTROLLED INTRODUCTION
68P02902W12-A
The outdoor power supply module (TOPSM) Tech. 4–26. . . . . . . . . . . . . . . . . . . . . . . . . . . .
TOPSM overview Tech. 4–26. . . . . . . . . . . . . . . . . . . . . . . . . . . . . . . . . . . . . . . . . . . . . . .
View of TOPSM Tech. 4–26. . . . . . . . . . . . . . . . . . . . . . . . . . . . . . . . . . . . . . . . . . . . . . . . .
TOPSM functional description Tech. 4–26. . . . . . . . . . . . . . . . . . . . . . . . . . . . . . . . . . . .
LED display Tech. 4–27. . . . . . . . . . . . . . . . . . . . . . . . . . . . . . . . . . . . . . . . . . . . . . . . . . . .
Functional diagram Tech. 4–27. . . . . . . . . . . . . . . . . . . . . . . . . . . . . . . . . . . . . . . . . . . . . .
Monitoring Tech. 4–28. . . . . . . . . . . . . . . . . . . . . . . . . . . . . . . . . . . . . . . . . . . . . . . . . . . . .
Protection circuits Tech. 4–28. . . . . . . . . . . . . . . . . . . . . . . . . . . . . . . . . . . . . . . . . . . . . . .
Thermal protection Tech. 4–28. . . . . . . . . . . . . . . . . . . . . . . . . . . . . . . . . . . . . . . . . . . . . .
Control and alarm signals Tech. 4–29. . . . . . . . . . . . . . . . . . . . . . . . . . . . . . . . . . . . . . . .
TOPSM pinouts Tech. 4–30. . . . . . . . . . . . . . . . . . . . . . . . . . . . . . . . . . . . . . . . . . . . . . . . .
Power supply module (PSM) Tech. 4–31. . . . . . . . . . . . . . . . . . . . . . . . . . . . . . . . . . . . . . . . . .
PSM overview Tech. 4–31. . . . . . . . . . . . . . . . . . . . . . . . . . . . . . . . . . . . . . . . . . . . . . . . . .
PSM location and redundancy Tech. 4–31. . . . . . . . . . . . . . . . . . . . . . . . . . . . . . . . . . . .
PSM module view Tech. 4–32. . . . . . . . . . . . . . . . . . . . . . . . . . . . . . . . . . . . . . . . . . . . . . .
PSM alarms Tech. 4–32. . . . . . . . . . . . . . . . . . . . . . . . . . . . . . . . . . . . . . . . . . . . . . . . . . . .
PSM LEDs Tech. 4–32. . . . . . . . . . . . . . . . . . . . . . . . . . . . . . . . . . . . . . . . . . . . . . . . . . . . .
PSM backplane protection Tech. 4–33. . . . . . . . . . . . . . . . . . . . . . . . . . . . . . . . . . . . . . .
Circuit breaker module (CBM) Tech. 4–34. . . . . . . . . . . . . . . . . . . . . . . . . . . . . . . . . . . . . . . . .
CBM overview Tech. 4–34. . . . . . . . . . . . . . . . . . . . . . . . . . . . . . . . . . . . . . . . . . . . . . . . . .
View of the CBM Tech. 4–34. . . . . . . . . . . . . . . . . . . . . . . . . . . . . . . . . . . . . . . . . . . . . . . .
Operation of the CBM Tech. 4–35. . . . . . . . . . . . . . . . . . . . . . . . . . . . . . . . . . . . . . . . . . .
MicroBCU power supply module (BPSM) Tech. 4–36. . . . . . . . . . . . . . . . . . . . . . . . . . . . . . . .
Introduction to the BPSM Tech. 4–36. . . . . . . . . . . . . . . . . . . . . . . . . . . . . . . . . . . . . . . .
BPSM diagram Tech. 4–36. . . . . . . . . . . . . . . . . . . . . . . . . . . . . . . . . . . . . . . . . . . . . . . . .
Functional description Tech. 4–37. . . . . . . . . . . . . . . . . . . . . . . . . . . . . . . . . . . . . . . . . . .
Chapter 5
RF modules i. . . . . . . . . . . . . . . . . . . . . . . . . . . . . . . . . . . . . . . . . . . . . . . . . . .
RF equipment detail Tech. 5–1. . . . . . . . . . . . . . . . . . . . . . . . . . . . . . . . . . . . . . . . . . . . . . . . . .
Overview of RF equipment Tech. 5–1. . . . . . . . . . . . . . . . . . . . . . . . . . . . . . . . . . . . . . .
RF specifications Tech. 5–1. . . . . . . . . . . . . . . . . . . . . . . . . . . . . . . . . . . . . . . . . . . . . . .
Receive (Rx) RF hardware Tech. 5–2. . . . . . . . . . . . . . . . . . . . . . . . . . . . . . . . . . . . . .
Transmit (Tx) RF hardware Tech. 5–3. . . . . . . . . . . . . . . . . . . . . . . . . . . . . . . . . . . . . . .
Rx/Tx single antenna duplexing Tech. 5–3. . . . . . . . . . . . . . . . . . . . . . . . . . . . . . . . . . .
RF overview and RF test function Tech. 5–4. . . . . . . . . . . . . . . . . . . . . . . . . . . . . . . . . . . . . .
RF overview Tech. 5–4. . . . . . . . . . . . . . . . . . . . . . . . . . . . . . . . . . . . . . . . . . . . . . . . . . . .
RF main component explanation Tech. 5–4. . . . . . . . . . . . . . . . . . . . . . . . . . . . . . . . . .
RF loopback test function Tech. 5–5. . . . . . . . . . . . . . . . . . . . . . . . . . . . . . . . . . . . . . . .
RF loopback hardware Tech. 5–5. . . . . . . . . . . . . . . . . . . . . . . . . . . . . . . . . . . . . . . . . .
RF loopback software operation Tech. 5–5. . . . . . . . . . . . . . . . . . . . . . . . . . . . . . . . . .
Functional diagram of RF Tech. 5–6. . . . . . . . . . . . . . . . . . . . . . . . . . . . . . . . . . . . . . . .
Description of RF test modes Tech. 5–7. . . . . . . . . . . . . . . . . . . . . . . . . . . . . . . . . . . . .
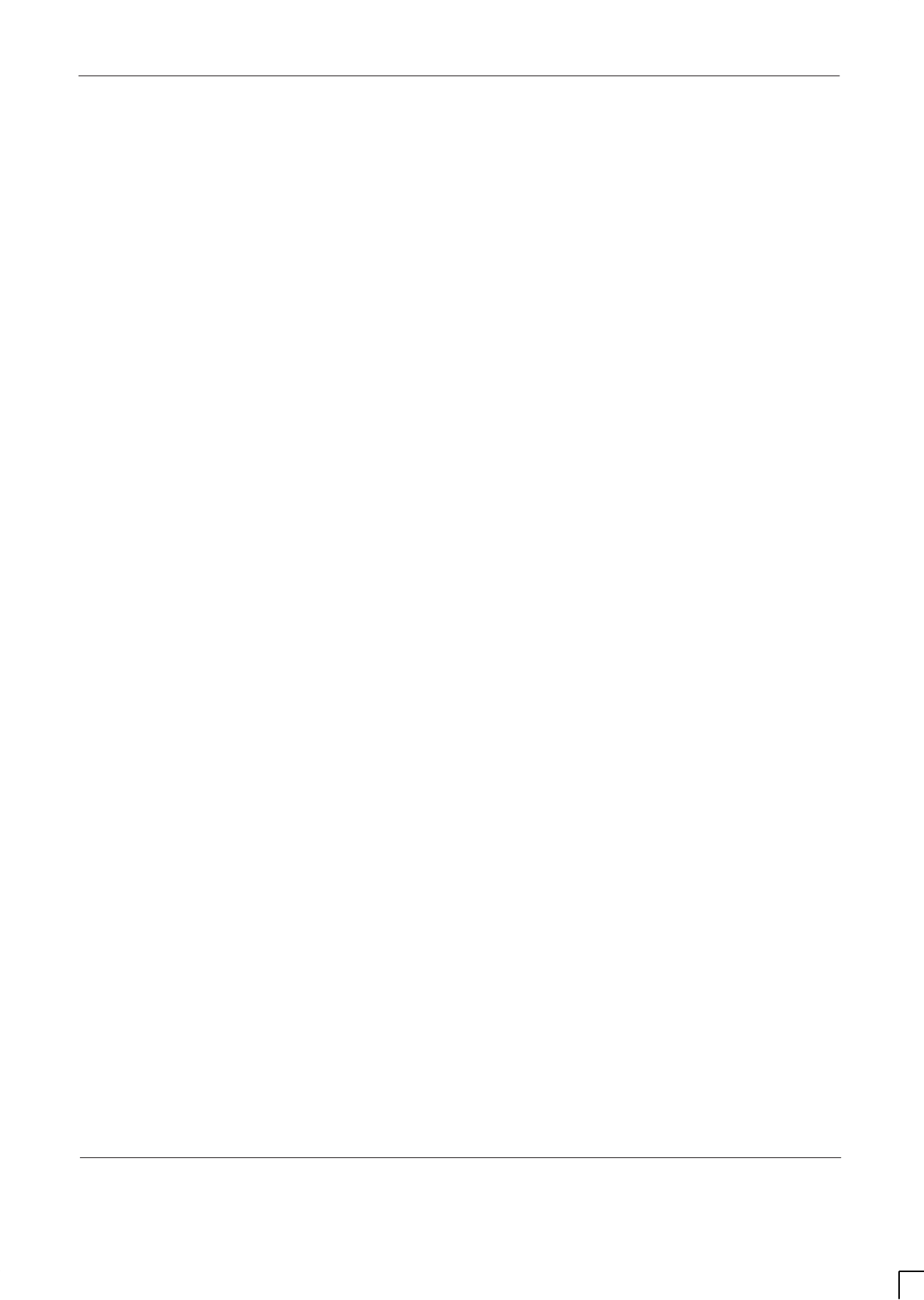
GSM-204-020
31st Oct 01
Service Manual: Horizon
macro
outdoor
68P02902W12-A
CONTROLLED INTRODUCTION
vii
Compact transceiver unit (CTU) Tech. 5–8. . . . . . . . . . . . . . . . . . . . . . . . . . . . . . . . . . . . . . . .
Overview of the CTU Tech. 5–8. . . . . . . . . . . . . . . . . . . . . . . . . . . . . . . . . . . . . . . . . . . .
CTU internal boards Tech. 5–8. . . . . . . . . . . . . . . . . . . . . . . . . . . . . . . . . . . . . . . . . . . . .
Alarm reporting Tech. 5–9. . . . . . . . . . . . . . . . . . . . . . . . . . . . . . . . . . . . . . . . . . . . . . . . .
View of CTU Tech. 5–10. . . . . . . . . . . . . . . . . . . . . . . . . . . . . . . . . . . . . . . . . . . . . . . . . . . .
CTU connectors and reset Tech. 5–11. . . . . . . . . . . . . . . . . . . . . . . . . . . . . . . . . . . . . . .
CTU input/output diagram Tech. 5–12. . . . . . . . . . . . . . . . . . . . . . . . . . . . . . . . . . . . . . . .
CTU Tx connector Tech. 5–13. . . . . . . . . . . . . . . . . . . . . . . . . . . . . . . . . . . . . . . . . . . . . .
CTU Rx function Tech. 5–13. . . . . . . . . . . . . . . . . . . . . . . . . . . . . . . . . . . . . . . . . . . . . . . .
CTU Tx function Tech. 5–14. . . . . . . . . . . . . . . . . . . . . . . . . . . . . . . . . . . . . . . . . . . . . . . .
CTU digital processing and control functions Tech. 5–16. . . . . . . . . . . . . . . . . . . . . . .
CTU uplink/downlink Tech. 5–19. . . . . . . . . . . . . . . . . . . . . . . . . . . . . . . . . . . . . . . . . . . .
CTU frequency hopping Tech. 5–20. . . . . . . . . . . . . . . . . . . . . . . . . . . . . . . . . . . . . . . . . . . . . . .
Overview of CTU frequency hopping Tech. 5–20. . . . . . . . . . . . . . . . . . . . . . . . . . . . . .
Synthesizer frequency hopping (SFH) Tech. 5–20. . . . . . . . . . . . . . . . . . . . . . . . . . . . .
SFH example not through BCCH Tech. 5–21. . . . . . . . . . . . . . . . . . . . . . . . . . . . . . . . . .
SFH example hopping through BCCH carrier Tech. 5–21. . . . . . . . . . . . . . . . . . . . . . .
Baseband frequency hopping (BBH) Tech. 5–22. . . . . . . . . . . . . . . . . . . . . . . . . . . . . .
BBH example Tech. 5–22. . . . . . . . . . . . . . . . . . . . . . . . . . . . . . . . . . . . . . . . . . . . . . . . . .
SURF module Tech. 5–24. . . . . . . . . . . . . . . . . . . . . . . . . . . . . . . . . . . . . . . . . . . . . . . . . . . . . . .
SURF module overview Tech. 5–24. . . . . . . . . . . . . . . . . . . . . . . . . . . . . . . . . . . . . . . . . .
Single band SURF module view Tech. 5–25. . . . . . . . . . . . . . . . . . . . . . . . . . . . . . . . . .
Functional description of the single band SURF Tech. 5–26. . . . . . . . . . . . . . . . . . . .
Single band SURF functional diagram Tech. 5–27. . . . . . . . . . . . . . . . . . . . . . . . . . . . .
Dual band SURF module view Tech. 5–28. . . . . . . . . . . . . . . . . . . . . . . . . . . . . . . . . . . .
Functional description of dual band SURF modules Tech. 5–29. . . . . . . . . . . . . . . . .
Dual band SURF functional diagram Tech. 5–30. . . . . . . . . . . . . . . . . . . . . . . . . . . . . .
Transmit blocks overview Tech. 5–31. . . . . . . . . . . . . . . . . . . . . . . . . . . . . . . . . . . . . . . . . . . . .
Introduction to transmit blocks Tech. 5–31. . . . . . . . . . . . . . . . . . . . . . . . . . . . . . . . . . . .
Screw retention in Tx block locations Tech. 5–31. . . . . . . . . . . . . . . . . . . . . . . . . . . . . .
View of basket for Tx blocks Tech. 5–32. . . . . . . . . . . . . . . . . . . . . . . . . . . . . . . . . . . . . .
Transmit block connectors Tech. 5–32. . . . . . . . . . . . . . . . . . . . . . . . . . . . . . . . . . . . . . .
View of Tx block connectors Tech. 5–33. . . . . . . . . . . . . . . . . . . . . . . . . . . . . . . . . . . . . .
Tx block blanking plate Tech. 5–34. . . . . . . . . . . . . . . . . . . . . . . . . . . . . . . . . . . . . . . . . . . . . . .
Purpose of Tx block blanking plate Tech. 5–34. . . . . . . . . . . . . . . . . . . . . . . . . . . . . . . .
View of Tx block blanking plate Tech. 5–34. . . . . . . . . . . . . . . . . . . . . . . . . . . . . . . . . . .
Feedthrough plate Tech. 5–35. . . . . . . . . . . . . . . . . . . . . . . . . . . . . . . . . . . . . . . . . . . . . . . . . . .
Purpose of feedthrough plate Tech. 5–35. . . . . . . . . . . . . . . . . . . . . . . . . . . . . . . . . . . . .
View of feedthrough plate Tech. 5–35. . . . . . . . . . . . . . . . . . . . . . . . . . . . . . . . . . . . . . . .
Feedthrough plate connectors Tech. 5–35. . . . . . . . . . . . . . . . . . . . . . . . . . . . . . . . . . . .
HCU plate Tech. 5–36. . . . . . . . . . . . . . . . . . . . . . . . . . . . . . . . . . . . . . . . . . . . . . . . . . . . . . . . . . .
HCU overview Tech. 5–36. . . . . . . . . . . . . . . . . . . . . . . . . . . . . . . . . . . . . . . . . . . . . . . . . .
HCU view Tech. 5–36. . . . . . . . . . . . . . . . . . . . . . . . . . . . . . . . . . . . . . . . . . . . . . . . . . . . . .
HCU functional diagram Tech. 5–36. . . . . . . . . . . . . . . . . . . . . . . . . . . . . . . . . . . . . . . . .
HCU connectors Tech. 5–37. . . . . . . . . . . . . . . . . . . . . . . . . . . . . . . . . . . . . . . . . . . . . . . .
TDF Tech. 5–38. . . . . . . . . . . . . . . . . . . . . . . . . . . . . . . . . . . . . . . . . . . . . . . . . . . . . . . . . . . . . . . .
Overview of TDF Tech. 5–38. . . . . . . . . . . . . . . . . . . . . . . . . . . . . . . . . . . . . . . . . . . . . . . .
TDF view Tech. 5–38. . . . . . . . . . . . . . . . . . . . . . . . . . . . . . . . . . . . . . . . . . . . . . . . . . . . . .
TDF functional diagram Tech. 5–39. . . . . . . . . . . . . . . . . . . . . . . . . . . . . . . . . . . . . . . . . .
TDF connectors Tech. 5–39. . . . . . . . . . . . . . . . . . . . . . . . . . . . . . . . . . . . . . . . . . . . . . . .
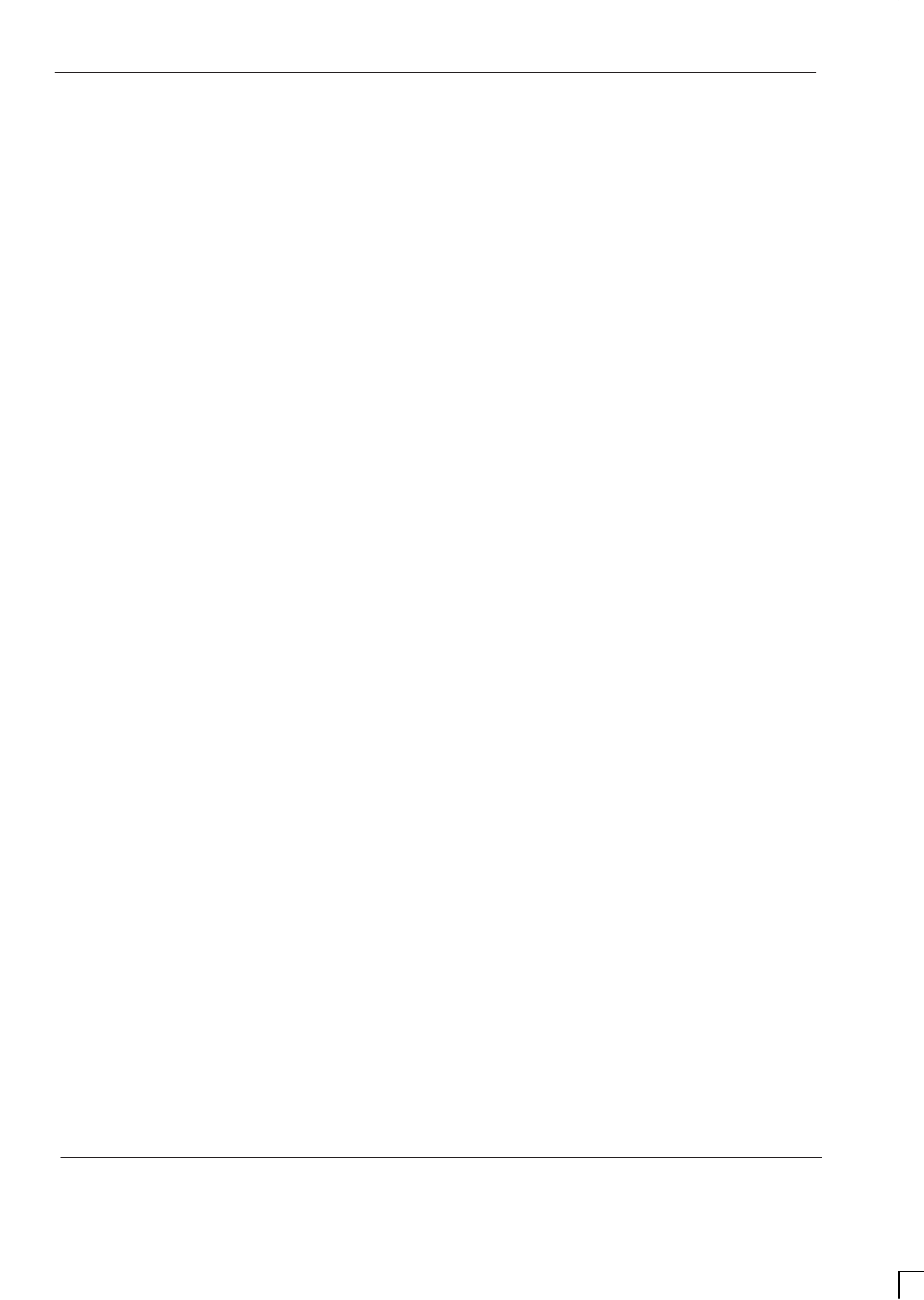
GSM-204-020
31st Oct 01
viii
Service Manual: Horizon
macro
outdoor
CONTROLLED INTRODUCTION
68P02902W12-A
Dual band TDF Tech. 5–40. . . . . . . . . . . . . . . . . . . . . . . . . . . . . . . . . . . . . . . . . . . . . . . . . . . . . .
Overview of Dual band TDF Tech. 5–40. . . . . . . . . . . . . . . . . . . . . . . . . . . . . . . . . . . . . .
Dual band TDF view Tech. 5–40. . . . . . . . . . . . . . . . . . . . . . . . . . . . . . . . . . . . . . . . . . . . .
Dual band TDF functional diagram Tech. 5–41. . . . . . . . . . . . . . . . . . . . . . . . . . . . . . . .
Dual band TDF connectors Tech. 5–41. . . . . . . . . . . . . . . . . . . . . . . . . . . . . . . . . . . . . . .
DCF Tech. 5–42. . . . . . . . . . . . . . . . . . . . . . . . . . . . . . . . . . . . . . . . . . . . . . . . . . . . . . . . . . . . . . . .
DCF overview Tech. 5–42. . . . . . . . . . . . . . . . . . . . . . . . . . . . . . . . . . . . . . . . . . . . . . . . . .
DCF view Tech. 5–42. . . . . . . . . . . . . . . . . . . . . . . . . . . . . . . . . . . . . . . . . . . . . . . . . . . . . .
DCF functional diagram Tech. 5–43. . . . . . . . . . . . . . . . . . . . . . . . . . . . . . . . . . . . . . . . . .
DCF connectors Tech. 5–43. . . . . . . . . . . . . . . . . . . . . . . . . . . . . . . . . . . . . . . . . . . . . . . .
DDF Tech. 5–44. . . . . . . . . . . . . . . . . . . . . . . . . . . . . . . . . . . . . . . . . . . . . . . . . . . . . . . . . . . . . . . .
Overview of DDF Tech. 5–44. . . . . . . . . . . . . . . . . . . . . . . . . . . . . . . . . . . . . . . . . . . . . . .
DDF view Tech. 5–44. . . . . . . . . . . . . . . . . . . . . . . . . . . . . . . . . . . . . . . . . . . . . . . . . . . . . .
DDF functional diagram Tech. 5–45. . . . . . . . . . . . . . . . . . . . . . . . . . . . . . . . . . . . . . . . . .
DDF connectors Tech. 5–45. . . . . . . . . . . . . . . . . . . . . . . . . . . . . . . . . . . . . . . . . . . . . . . .
Chapter 6
Digital modules i. . . . . . . . . . . . . . . . . . . . . . . . . . . . . . . . . . . . . . . . . . . . . . .
Overview of digital modules Tech. 6–1. . . . . . . . . . . . . . . . . . . . . . . . . . . . . . . . . . . . . . . . . . .
Overview and redundancy Tech. 6–1. . . . . . . . . . . . . . . . . . . . . . . . . . . . . . . . . . . . . . .
Digital module and BPSM locations Tech. 6–2. . . . . . . . . . . . . . . . . . . . . . . . . . . . . . .
MCUF and NIU redundancy Tech. 6–3. . . . . . . . . . . . . . . . . . . . . . . . . . . . . . . . . . . . .
Full size and half size modules Tech. 6–3. . . . . . . . . . . . . . . . . . . . . . . . . . . . . . . . . . .
Digital module and CTU connections Tech. 6–4. . . . . . . . . . . . . . . . . . . . . . . . . . . . . .
Diagram of digital module and CTU connections Tech. 6–4. . . . . . . . . . . . . . . . . . . .
MCUF Tech. 6–5. . . . . . . . . . . . . . . . . . . . . . . . . . . . . . . . . . . . . . . . . . . . . . . . . . . . . . . . . . . . . .
MCUF overview Tech. 6–5. . . . . . . . . . . . . . . . . . . . . . . . . . . . . . . . . . . . . . . . . . . . . . . . .
Capability to replace MCU of M-Cell6 and M-Cell2 Tech. 6–5. . . . . . . . . . . . . . . . . .
GPROC TSW and GLCK functions Tech. 6–6. . . . . . . . . . . . . . . . . . . . . . . . . . . . . . . .
MCUF module view Tech. 6–6. . . . . . . . . . . . . . . . . . . . . . . . . . . . . . . . . . . . . . . . . . . . .
MCUF functional diagram Tech. 6–7. . . . . . . . . . . . . . . . . . . . . . . . . . . . . . . . . . . . . . . .
Link to redundant MCUF Tech. 6–8. . . . . . . . . . . . . . . . . . . . . . . . . . . . . . . . . . . . . . . . .
Front panel interfaces Tech. 6–8. . . . . . . . . . . . . . . . . . . . . . . . . . . . . . . . . . . . . . . . . . .
Front panel switches and indicators Tech. 6–9. . . . . . . . . . . . . . . . . . . . . . . . . . . . . . .
PIX interfaces Tech. 6–10. . . . . . . . . . . . . . . . . . . . . . . . . . . . . . . . . . . . . . . . . . . . . . . . . .
DRAM, flash EPROM and code loading functions Tech. 6–10. . . . . . . . . . . . . . . . . . .
ASIC functionality Tech. 6–11. . . . . . . . . . . . . . . . . . . . . . . . . . . . . . . . . . . . . . . . . . . . . . .
Sync block functionality Tech. 6–12. . . . . . . . . . . . . . . . . . . . . . . . . . . . . . . . . . . . . . . . . .
Integral MCUF FMUX functionality Tech. 6–14. . . . . . . . . . . . . . . . . . . . . . . . . . . . . . . .
NIU Tech. 6–15. . . . . . . . . . . . . . . . . . . . . . . . . . . . . . . . . . . . . . . . . . . . . . . . . . . . . . . . . . . . . . . .
Overview of NIU Tech. 6–15. . . . . . . . . . . . . . . . . . . . . . . . . . . . . . . . . . . . . . . . . . . . . . . .
NIU locations Tech. 6–15. . . . . . . . . . . . . . . . . . . . . . . . . . . . . . . . . . . . . . . . . . . . . . . . . . .
NIU command identity number Tech. 6–15. . . . . . . . . . . . . . . . . . . . . . . . . . . . . . . . . . . .
NIU view and LEDs Tech. 6–16. . . . . . . . . . . . . . . . . . . . . . . . . . . . . . . . . . . . . . . . . . . . .
NIU functionality Tech. 6–17. . . . . . . . . . . . . . . . . . . . . . . . . . . . . . . . . . . . . . . . . . . . . . . .
NIU diagram Tech. 6–18. . . . . . . . . . . . . . . . . . . . . . . . . . . . . . . . . . . . . . . . . . . . . . . . . . .
Control processor Tech. 6–19. . . . . . . . . . . . . . . . . . . . . . . . . . . . . . . . . . . . . . . . . . . . . . .
NIU/MCUF framing and clocks Tech. 6–19. . . . . . . . . . . . . . . . . . . . . . . . . . . . . . . . . . . .
Distance measurement Tech. 6–20. . . . . . . . . . . . . . . . . . . . . . . . . . . . . . . . . . . . . . . . . .
Radio signalling links (RSLs) Tech. 6–20. . . . . . . . . . . . . . . . . . . . . . . . . . . . . . . . . . . . .
T1 NIU need to set link type Tech. 6–20. . . . . . . . . . . . . . . . . . . . . . . . . . . . . . . . . . . . . .
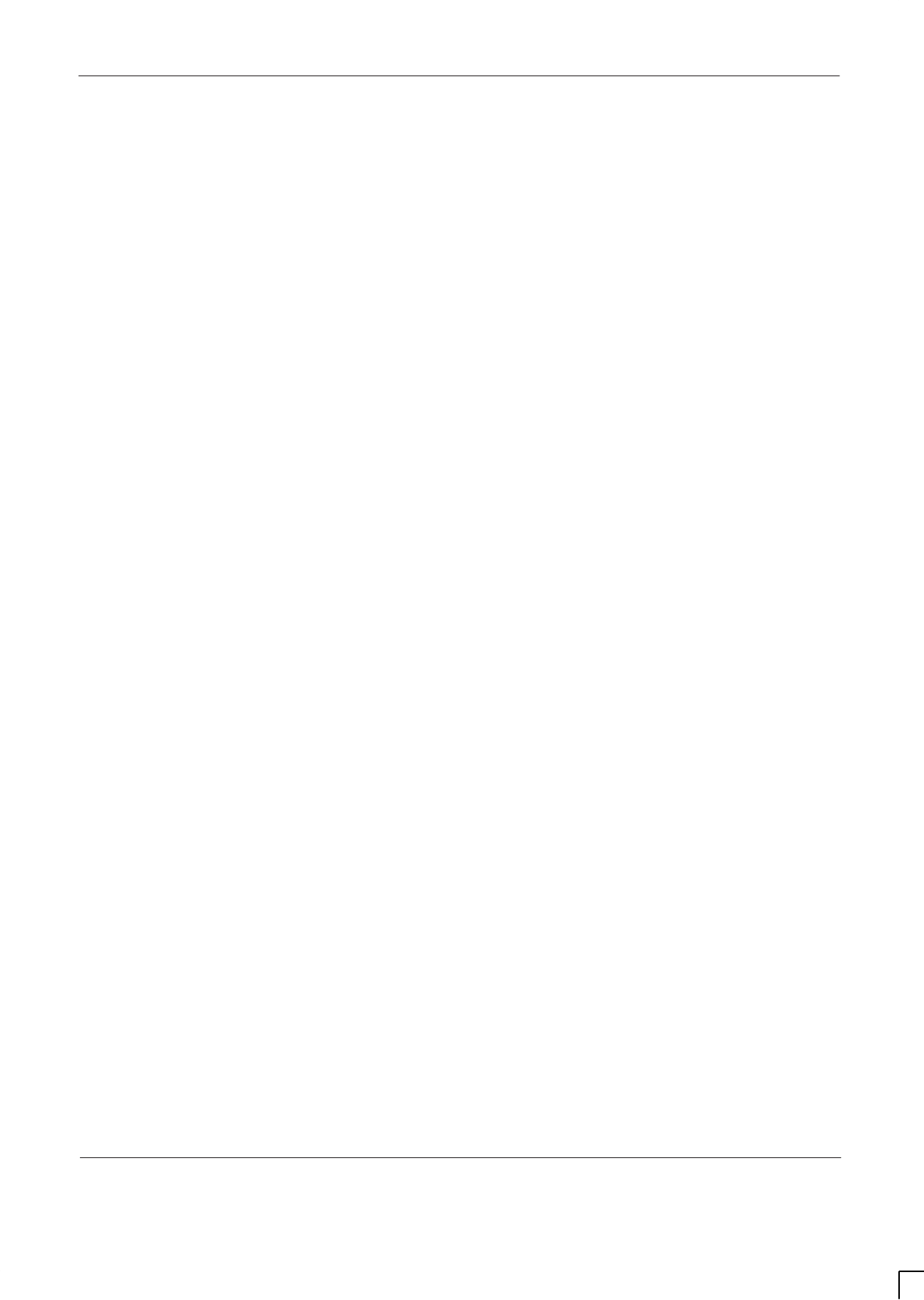
GSM-204-020
31st Oct 01
Service Manual: Horizon
macro
outdoor
68P02902W12-A
CONTROLLED INTRODUCTION
ix
T43/BIB-NIU - E1/T1 mapping Tech. 6–21. . . . . . . . . . . . . . . . . . . . . . . . . . . . . . . . . . . . . . . . .
Overview of T43/BIB-NIU connection Tech. 6–21. . . . . . . . . . . . . . . . . . . . . . . . . . . . . .
NIU to T43/BIB mapping and command ID Tech. 6–21. . . . . . . . . . . . . . . . . . . . . . . . .
Diagram of T43 connection to NIUs Tech. 6–22. . . . . . . . . . . . . . . . . . . . . . . . . . . . . . .
FMUX module and FMUX function Tech. 6–23. . . . . . . . . . . . . . . . . . . . . . . . . . . . . . . . . . . . .
Overview of FMUX module Tech. 6–23. . . . . . . . . . . . . . . . . . . . . . . . . . . . . . . . . . . . . . .
FMUX module view Tech. 6–23. . . . . . . . . . . . . . . . . . . . . . . . . . . . . . . . . . . . . . . . . . . . .
FMUX functional diagram Tech. 6–24. . . . . . . . . . . . . . . . . . . . . . . . . . . . . . . . . . . . . . . .
FMUX functional explanation Tech. 6–24. . . . . . . . . . . . . . . . . . . . . . . . . . . . . . . . . . . . .
Alarm module Tech. 6–25. . . . . . . . . . . . . . . . . . . . . . . . . . . . . . . . . . . . . . . . . . . . . . . . . . . . . . .
Alarm module overview Tech. 6–25. . . . . . . . . . . . . . . . . . . . . . . . . . . . . . . . . . . . . . . . . .
Alarm module view Tech. 6–25. . . . . . . . . . . . . . . . . . . . . . . . . . . . . . . . . . . . . . . . . . . . . .
Alarm module functionality Tech. 6–26. . . . . . . . . . . . . . . . . . . . . . . . . . . . . . . . . . . . . . .
Alarm module replacement – effect on alarms Tech. 6–26. . . . . . . . . . . . . . . . . . . . . .
Alarm collection from extension cabinets Tech. 6–26. . . . . . . . . . . . . . . . . . . . . . . . . . .
Alarm module display presentation Tech. 6–27. . . . . . . . . . . . . . . . . . . . . . . . . . . . . . . .
Chapter 7
Auxiliary equipment housing i. . . . . . . . . . . . . . . . . . . . . . . . . . . . . . . . . . .
Auxiliary equipment housing overview Tech. 7–1. . . . . . . . . . . . . . . . . . . . . . . . . . . . . . . . . .
Introduction to the auxiliary equipment housing Tech. 7–1. . . . . . . . . . . . . . . . . . . . .
Auxiliary equipment housing mechanical design Tech. 7–1. . . . . . . . . . . . . . . . . . . .
View of auxiliary equipment housing Tech. 7–2. . . . . . . . . . . . . . . . . . . . . . . . . . . . . . .
Temperature control within the auxiliary equipment housing Tech. 7–3. . . . . . . . . . . . . . .
Temperature control equipment Tech. 7–3. . . . . . . . . . . . . . . . . . . . . . . . . . . . . . . . . . .
Operation of the temperature control equipment Tech. 7–3. . . . . . . . . . . . . . . . . . . .
External alarms interface board Tech. 7–4. . . . . . . . . . . . . . . . . . . . . . . . . . . . . . . . . . . . . . . .
Function of the external alarms interface board Tech. 7–4. . . . . . . . . . . . . . . . . . . . .
External alarms interface board connections Tech. 7–4. . . . . . . . . . . . . . . . . . . . . . .
Common applications for the auxiliary equipment housing Tech. 7–5. . . . . . . . . . . . . . . . .
Auxiliary equipment housing as a battery box Tech. 7–5. . . . . . . . . . . . . . . . . . . . . . .
View of auxiliary equipment housing as battery box Tech. 7–6. . . . . . . . . . . . . . . . .
Chapter 8
Cable shroud i. . . . . . . . . . . . . . . . . . . . . . . . . . . . . . . . . . . . . . . . . . . . . . . . .
Introduction to the cable shroud Tech. 8–1. . . . . . . . . . . . . . . . . . . . . . . . . . . . . . . . . . . . . . . .
Overview of the cable shroud Tech. 8–1. . . . . . . . . . . . . . . . . . . . . . . . . . . . . . . . . . . . .
Cable shroud configurations Tech. 8–1. . . . . . . . . . . . . . . . . . . . . . . . . . . . . . . . . . . . . .
The cable shroud assembly Tech. 8–2. . . . . . . . . . . . . . . . . . . . . . . . . . . . . . . . . . . . . . . . . . .
Description of the cable shroud assembly Tech. 8–2. . . . . . . . . . . . . . . . . . . . . . . . . .
View of the cable shroud Tech. 8–2. . . . . . . . . . . . . . . . . . . . . . . . . . . . . . . . . . . . . . . . .
Category 423
Installation & Configuration (Inst.) i. . . . . . . . . . . . . . . . . . . . . . . . . . . . . . . . . .
Chapter 1
Introduction to installation i. . . . . . . . . . . . . . . . . . . . . . . . . . . . . . . . . . . . .
Introduction to installation and configuration Inst. 1–1. . . . . . . . . . . . . . . . . . . . . . . . . . . . .
Manual scope Inst. 1–1. . . . . . . . . . . . . . . . . . . . . . . . . . . . . . . . . . . . . . . . . . . . . . . . . .
Safety instructions Inst. 1–2. . . . . . . . . . . . . . . . . . . . . . . . . . . . . . . . . . . . . . . . . . . . . .
Software requirements Inst. 1–2. . . . . . . . . . . . . . . . . . . . . . . . . . . . . . . . . . . . . . . . . .
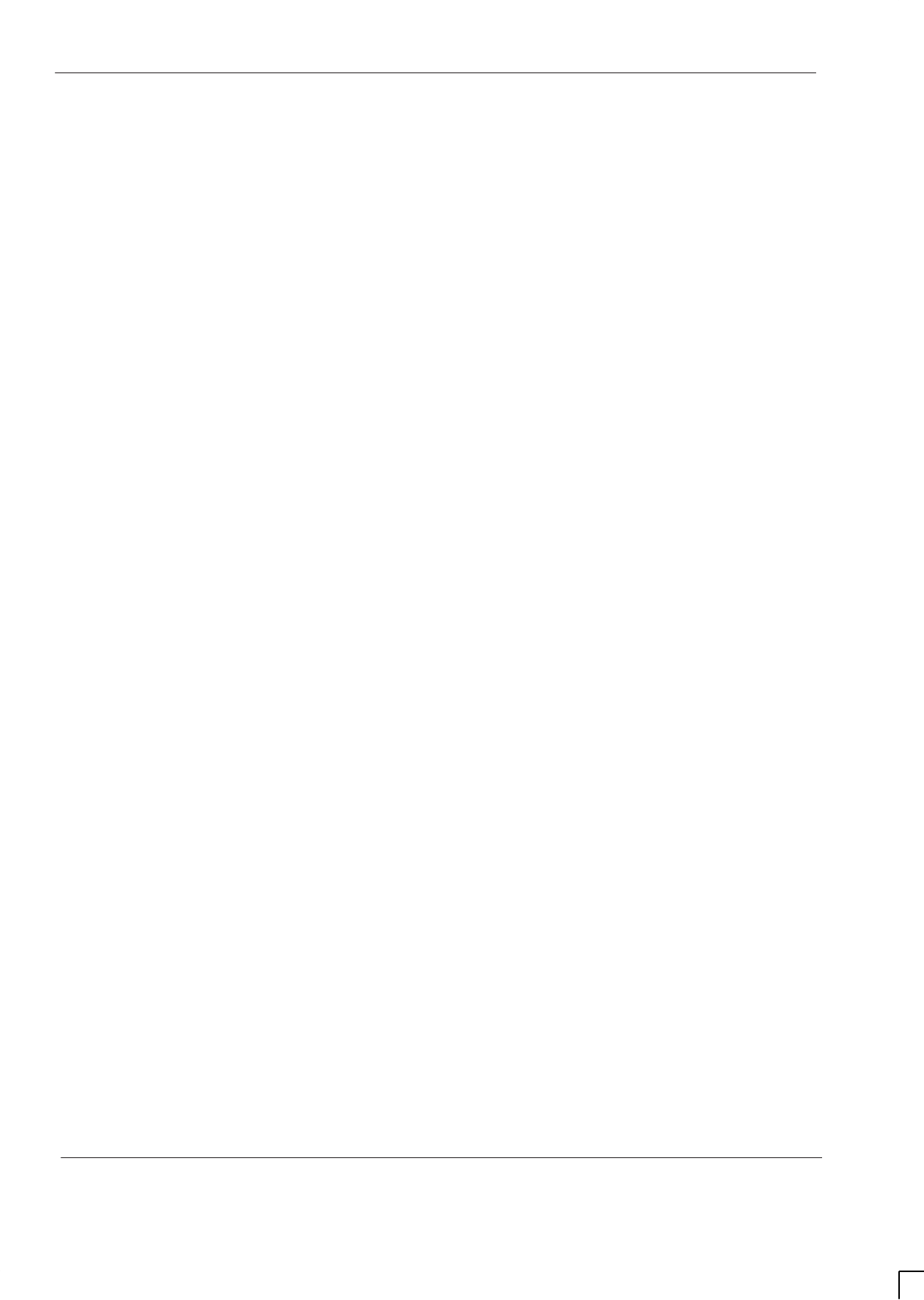
GSM-204-020
31st Oct 01
x
Service Manual: Horizon
macro
outdoor
CONTROLLED INTRODUCTION
68P02902W12-A
Horizonmacro outdoor tool list Inst. 1–3. . . . . . . . . . . . . . . . . . . . . . . . . . . . . . . . . . . . . . . . .
Overview of tool list Inst. 1–3. . . . . . . . . . . . . . . . . . . . . . . . . . . . . . . . . . . . . . . . . . . . .
Tool list Inst. 1–3. . . . . . . . . . . . . . . . . . . . . . . . . . . . . . . . . . . . . . . . . . . . . . . . . . . . . . . .
Chapter 2
Site preparation i. . . . . . . . . . . . . . . . . . . . . . . . . . . . . . . . . . . . . . . . . . . . . . .
Preparation overview Inst. 2–1. . . . . . . . . . . . . . . . . . . . . . . . . . . . . . . . . . . . . . . . . . . . . . . . .
Overview to site preparation Inst. 2–1. . . . . . . . . . . . . . . . . . . . . . . . . . . . . . . . . . . . . .
Pre-installation procedures Inst. 2–1. . . . . . . . . . . . . . . . . . . . . . . . . . . . . . . . . . . . . . .
Site requirements and considerations Inst. 2–2. . . . . . . . . . . . . . . . . . . . . . . . . . . . . . . . . . .
Overview of requirements Inst. 2–2. . . . . . . . . . . . . . . . . . . . . . . . . . . . . . . . . . . . . . . .
Outdoor cabinet dimensions Inst. 2–2. . . . . . . . . . . . . . . . . . . . . . . . . . . . . . . . . . . . . .
Cabinet weights Inst. 2–2. . . . . . . . . . . . . . . . . . . . . . . . . . . . . . . . . . . . . . . . . . . . . . . .
Torque values Inst. 2–2. . . . . . . . . . . . . . . . . . . . . . . . . . . . . . . . . . . . . . . . . . . . . . . . . .
Power requirements Inst. 2–3. . . . . . . . . . . . . . . . . . . . . . . . . . . . . . . . . . . . . . . . . . . . .
Environmental requirements Inst. 2–4. . . . . . . . . . . . . . . . . . . . . . . . . . . . . . . . . . . . . .
Structural requirements Inst. 2–5. . . . . . . . . . . . . . . . . . . . . . . . . . . . . . . . . . . . . . . . . .
Outdoor site dimensions Inst. 2–6. . . . . . . . . . . . . . . . . . . . . . . . . . . . . . . . . . . . . . . . .
View of maximum site template layout Inst. 2–7. . . . . . . . . . . . . . . . . . . . . . . . . . . . .
Visiting the site Inst. 2–9. . . . . . . . . . . . . . . . . . . . . . . . . . . . . . . . . . . . . . . . . . . . . . . . . . . . . .
Overview of visiting the site Inst. 2–9. . . . . . . . . . . . . . . . . . . . . . . . . . . . . . . . . . . . . .
Before departure to site Inst. 2–9. . . . . . . . . . . . . . . . . . . . . . . . . . . . . . . . . . . . . . . . . .
Arrival at all sites Inst. 2–9. . . . . . . . . . . . . . . . . . . . . . . . . . . . . . . . . . . . . . . . . . . . . . . .
Arriving at occupied sites Inst. 2–9. . . . . . . . . . . . . . . . . . . . . . . . . . . . . . . . . . . . . . . .
Arriving at unoccupied sites Inst. 2–10. . . . . . . . . . . . . . . . . . . . . . . . . . . . . . . . . . . . . .
Leaving site during installation and optimization Inst. 2–10. . . . . . . . . . . . . . . . . . . .
Rubbish removal Inst. 2–10. . . . . . . . . . . . . . . . . . . . . . . . . . . . . . . . . . . . . . . . . . . . . . . .
Rural sites Inst. 2–11. . . . . . . . . . . . . . . . . . . . . . . . . . . . . . . . . . . . . . . . . . . . . . . . . . . . .
On site safety Inst. 2–11. . . . . . . . . . . . . . . . . . . . . . . . . . . . . . . . . . . . . . . . . . . . . . . . . .
Preparing the site Inst. 2–12. . . . . . . . . . . . . . . . . . . . . . . . . . . . . . . . . . . . . . . . . . . . . . . . . . . .
Introduction to site preparation Inst. 2–12. . . . . . . . . . . . . . . . . . . . . . . . . . . . . . . . . . .
Base site structure Inst. 2–12. . . . . . . . . . . . . . . . . . . . . . . . . . . . . . . . . . . . . . . . . . . . . .
Site requirements Inst. 2–12. . . . . . . . . . . . . . . . . . . . . . . . . . . . . . . . . . . . . . . . . . . . . . .
Site access Inst. 2–12. . . . . . . . . . . . . . . . . . . . . . . . . . . . . . . . . . . . . . . . . . . . . . . . . . . .
Site layout Inst. 2–12. . . . . . . . . . . . . . . . . . . . . . . . . . . . . . . . . . . . . . . . . . . . . . . . . . . . .
Earthing the site Inst. 2–13. . . . . . . . . . . . . . . . . . . . . . . . . . . . . . . . . . . . . . . . . . . . . . . . . . . . .
Overview Inst. 2–13. . . . . . . . . . . . . . . . . . . . . . . . . . . . . . . . . . . . . . . . . . . . . . . . . . . . . .
Earthing requirements Inst. 2–13. . . . . . . . . . . . . . . . . . . . . . . . . . . . . . . . . . . . . . . . . . .
Earth electrode system Inst. 2–13. . . . . . . . . . . . . . . . . . . . . . . . . . . . . . . . . . . . . . . . . .
Cross bonding Inst. 2–14. . . . . . . . . . . . . . . . . . . . . . . . . . . . . . . . . . . . . . . . . . . . . . . . . .
Earthing procedure Inst. 2–14. . . . . . . . . . . . . . . . . . . . . . . . . . . . . . . . . . . . . . . . . . . . . .
Earth electrode testing Inst. 2–14. . . . . . . . . . . . . . . . . . . . . . . . . . . . . . . . . . . . . . . . . . .
Preparing the foundation Inst. 2–16. . . . . . . . . . . . . . . . . . . . . . . . . . . . . . . . . . . . . . . . . . . . . .
Overview of foundation preparation Inst. 2–16. . . . . . . . . . . . . . . . . . . . . . . . . . . . . . .
Horizonmacro foundation Inst. 2–16. . . . . . . . . . . . . . . . . . . . . . . . . . . . . . . . . . . . . . . .
Preparing the foundation Inst. 2–17. . . . . . . . . . . . . . . . . . . . . . . . . . . . . . . . . . . . . . . . .
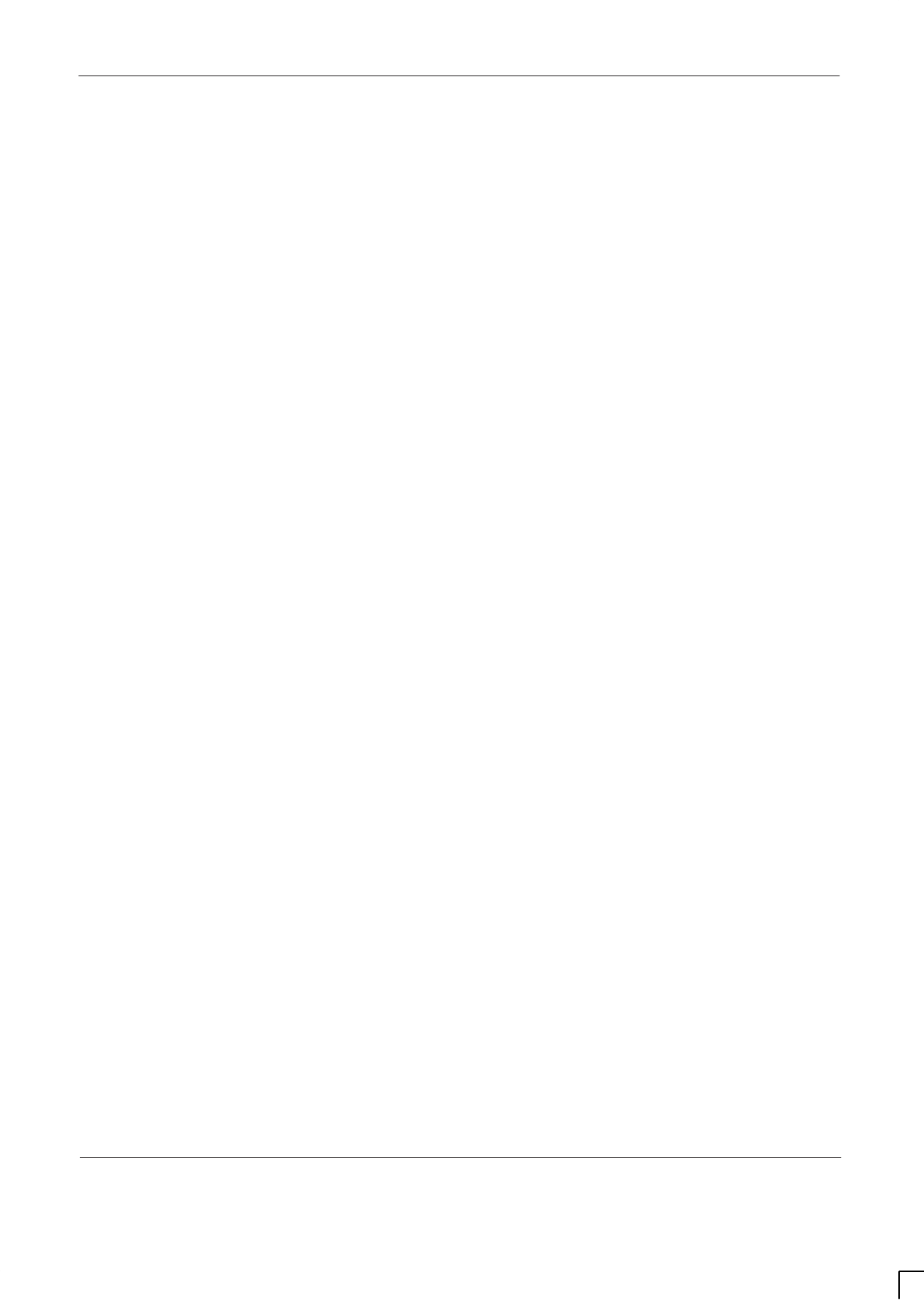
GSM-204-020
31st Oct 01
Service Manual: Horizon
macro
outdoor
68P02902W12-A
CONTROLLED INTRODUCTION
xi
Chapter 3
Installing the BTS cabinet i. . . . . . . . . . . . . . . . . . . . . . . . . . . . . . . . . . . . . .
Installation overview Inst. 3–1. . . . . . . . . . . . . . . . . . . . . . . . . . . . . . . . . . . . . . . . . . . . . . . . . .
Introduction to installation Inst. 3–1. . . . . . . . . . . . . . . . . . . . . . . . . . . . . . . . . . . . . . . .
Installation sections Inst. 3–1. . . . . . . . . . . . . . . . . . . . . . . . . . . . . . . . . . . . . . . . . . . . .
E1/T1 line testing Inst. 3–1. . . . . . . . . . . . . . . . . . . . . . . . . . . . . . . . . . . . . . . . . . . . . . .
Cabinet view Inst. 3–2. . . . . . . . . . . . . . . . . . . . . . . . . . . . . . . . . . . . . . . . . . . . . . . . . . .
Equipment package units Inst. 3–3. . . . . . . . . . . . . . . . . . . . . . . . . . . . . . . . . . . . . . . .
Equipment delivery and packaging Inst. 3–4. . . . . . . . . . . . . . . . . . . . . . . . . . . . . . . . . . . . .
Delivery and packaging overview Inst. 3–4. . . . . . . . . . . . . . . . . . . . . . . . . . . . . . . . .
Packaging Inst. 3–4. . . . . . . . . . . . . . . . . . . . . . . . . . . . . . . . . . . . . . . . . . . . . . . . . . . . .
Weather conditions affecting unpacking/installation Inst. 3–5. . . . . . . . . . . . . . . . . . . . . . .
Overview of weather considerations Inst. 3–5. . . . . . . . . . . . . . . . . . . . . . . . . . . . . . .
Weather conditions Inst. 3–5. . . . . . . . . . . . . . . . . . . . . . . . . . . . . . . . . . . . . . . . . . . . . .
Maintenance cover Inst. 3–5. . . . . . . . . . . . . . . . . . . . . . . . . . . . . . . . . . . . . . . . . . . . . .
Unpacking and preparing the cabinet Inst. 3–7. . . . . . . . . . . . . . . . . . . . . . . . . . . . . . . . . . .
Tools Inst. 3–7. . . . . . . . . . . . . . . . . . . . . . . . . . . . . . . . . . . . . . . . . . . . . . . . . . . . . . . . . .
Safety considerations Inst. 3–7. . . . . . . . . . . . . . . . . . . . . . . . . . . . . . . . . . . . . . . . . . .
Cabinet access procedures Inst. 3–8. . . . . . . . . . . . . . . . . . . . . . . . . . . . . . . . . . . . . .
Procedures for unpacking and preparing the cabinet Inst. 3–9. . . . . . . . . . . . . . . .
Visual inspection Inst. 3–11. . . . . . . . . . . . . . . . . . . . . . . . . . . . . . . . . . . . . . . . . . . . . . . .
Safe disposal of packing material Inst. 3–11. . . . . . . . . . . . . . . . . . . . . . . . . . . . . . . . .
CTU module allotted slot retention Inst. 3–11. . . . . . . . . . . . . . . . . . . . . . . . . . . . . . . .
Installing the template and mounting bolt anchors Inst. 3–12. . . . . . . . . . . . . . . . . . . . . . . .
Introduction to template and mounting bolt anchor installation Inst. 3–12. . . . . . . .
View of template Inst. 3–12. . . . . . . . . . . . . . . . . . . . . . . . . . . . . . . . . . . . . . . . . . . . . . . .
Procedure for installing template Inst. 3–13. . . . . . . . . . . . . . . . . . . . . . . . . . . . . . . . . .
Recommended bolt length for concrete base Inst. 3–13. . . . . . . . . . . . . . . . . . . . . . .
Procedure for installing cabinet bolt anchors Inst. 3–14. . . . . . . . . . . . . . . . . . . . . . .
Fitting the outdoor cabinet onto its base Inst. 3–15. . . . . . . . . . . . . . . . . . . . . . . . . . . . . . . .
Procedure for fitting a BTS cabinet Inst. 3–15. . . . . . . . . . . . . . . . . . . . . . . . . . . . . . . .
Mounting additional cabinets Inst. 3–15. . . . . . . . . . . . . . . . . . . . . . . . . . . . . . . . . . . . .
Earthing and transient protection Inst. 3–16. . . . . . . . . . . . . . . . . . . . . . . . . . . . . . . . . . . . . . .
Site earthing Inst. 3–16. . . . . . . . . . . . . . . . . . . . . . . . . . . . . . . . . . . . . . . . . . . . . . . . . . .
Secondary transient and lightning protection Inst. 3–16. . . . . . . . . . . . . . . . . . . . . . .
Connecting the internal batteries Inst. 3–17. . . . . . . . . . . . . . . . . . . . . . . . . . . . . . . . . . . . . . .
Introduction to connecting the internal batteries Inst. 3–17. . . . . . . . . . . . . . . . . . . . .
Internal battery connection procedure Inst. 3–17. . . . . . . . . . . . . . . . . . . . . . . . . . . . .
View of internal battery tray Inst. 3–18. . . . . . . . . . . . . . . . . . . . . . . . . . . . . . . . . . . . . .
Installing and connecting power and earth cabling Inst. 3–19. . . . . . . . . . . . . . . . . . . . . . .
Overview of power and earth cabling Inst. 3–19. . . . . . . . . . . . . . . . . . . . . . . . . . . . . .
Cable routeing Inst. 3–19. . . . . . . . . . . . . . . . . . . . . . . . . . . . . . . . . . . . . . . . . . . . . . . . . .
Cabinet earthing points Inst. 3–20. . . . . . . . . . . . . . . . . . . . . . . . . . . . . . . . . . . . . . . . . .
Power supply cable colour coding Inst. 3–20. . . . . . . . . . . . . . . . . . . . . . . . . . . . . . . . .
Preparing for connection Inst. 3–21. . . . . . . . . . . . . . . . . . . . . . . . . . . . . . . . . . . . . . . . .
Connecting 230 V single phase ac power cables Inst. 3–22. . . . . . . . . . . . . . . . . . . . . . . . .
Configuring the number 1 ac distribution box Inst. 3–22. . . . . . . . . . . . . . . . . . . . . . .
Connecting 230 V ac single phase mains input cables Inst. 3–22. . . . . . . . . . . . . . .
230 V ac single phase wiring diagram Inst. 3–23. . . . . . . . . . . . . . . . . . . . . . . . . . . . .
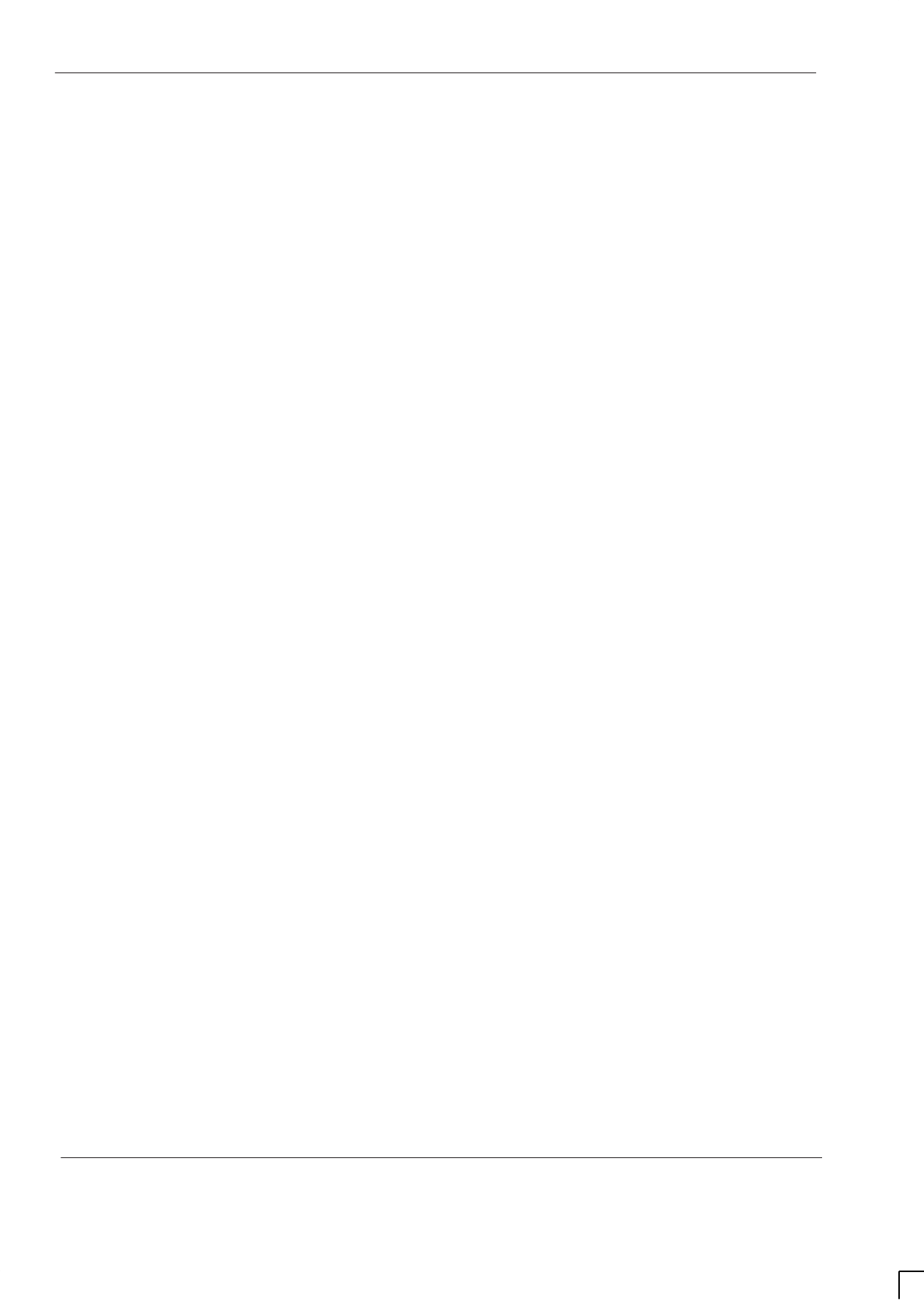
GSM-204-020
31st Oct 01
xii
Service Manual: Horizon
macro
outdoor
CONTROLLED INTRODUCTION
68P02902W12-A
Connecting 110 V single phase ac power cables Inst. 3–24. . . . . . . . . . . . . . . . . . . . . . . . .
Configuring the number 1 ac distribution box Inst. 3–24. . . . . . . . . . . . . . . . . . . . . . .
Connecting 110 V ac single phase mains input cables Inst. 3–24. . . . . . . . . . . . . . .
110 V ac single phase wiring diagram Inst. 3–25. . . . . . . . . . . . . . . . . . . . . . . . . . . . .
Connecting 230 V 3-phase (star) ac power cables Inst. 3–26. . . . . . . . . . . . . . . . . . . . . . . .
Configuring the number 1 ac distribution box Inst. 3–26. . . . . . . . . . . . . . . . . . . . . . .
Connecting 230 V ac 3-phase (star) mains input cables Inst. 3–26. . . . . . . . . . . . . .
230 V ac 3-phase (star) wiring diagram Inst. 3–27. . . . . . . . . . . . . . . . . . . . . . . . . . . .
Connecting 230 V 3-phase (delta) ac power cables Inst. 3–28. . . . . . . . . . . . . . . . . . . . . . .
Configuring the number 1 ac distribution box Inst. 3–28. . . . . . . . . . . . . . . . . . . . . . .
Connecting 230 V ac 3-phase (delta) mains input cables Inst. 3–29. . . . . . . . . . . . .
230 V ac 3-phase (delta) wiring diagram Inst. 3–30. . . . . . . . . . . . . . . . . . . . . . . . . . .
Connecting antennas Inst. 3–31. . . . . . . . . . . . . . . . . . . . . . . . . . . . . . . . . . . . . . . . . . . . . . . . .
Overview of antenna connections Inst. 3–31. . . . . . . . . . . . . . . . . . . . . . . . . . . . . . . . .
Cable entry earth plates Inst. 3–32. . . . . . . . . . . . . . . . . . . . . . . . . . . . . . . . . . . . . . . . .
Fitting inter-cabinet RF cables to earth plates Inst. 3–32. . . . . . . . . . . . . . . . . . . . . . .
Routeing RF cables between cabinets. Inst. 3–33. . . . . . . . . . . . . . . . . . . . . . . . . . . .
Types of RF connector Inst. 3–33. . . . . . . . . . . . . . . . . . . . . . . . . . . . . . . . . . . . . . . . . .
Torque of RF connectors Inst. 3–33. . . . . . . . . . . . . . . . . . . . . . . . . . . . . . . . . . . . . . . . .
Fitting left side (cable entry) earth plate Inst. 3–34. . . . . . . . . . . . . . . . . . . . . . . . . . . .
Fitting expansion plates Inst. 3–35. . . . . . . . . . . . . . . . . . . . . . . . . . . . . . . . . . . . . . . . . .
RF connection principles Inst. 3–36. . . . . . . . . . . . . . . . . . . . . . . . . . . . . . . . . . . . . . . . .
Rx/Tx single antenna duplexing Inst. 3–36. . . . . . . . . . . . . . . . . . . . . . . . . . . . . . . . . . .
Suggested RF configurations Inst. 3–37. . . . . . . . . . . . . . . . . . . . . . . . . . . . . . . . . . . . . . . . . .
Overview of configuration diagrams Inst. 3–37. . . . . . . . . . . . . . . . . . . . . . . . . . . . . . .
Single cabinet connection kits and cables Inst. 3–38. . . . . . . . . . . . . . . . . . . . . . . . . .
Multiple cabinet connection kits and cables Inst. 3–39. . . . . . . . . . . . . . . . . . . . . . . .
Configuration for omni 1 Inst. 3–40. . . . . . . . . . . . . . . . . . . . . . . . . . . . . . . . . . . . . . . . .
Configuration for omni 1 or 2 (with/without diversity) Inst. 3–41. . . . . . . . . . . . . . . . .
Configuration for omni 3 or 4 Inst. 3–42. . . . . . . . . . . . . . . . . . . . . . . . . . . . . . . . . . . . .
Configuration for omni 3 Inst. 3–42. . . . . . . . . . . . . . . . . . . . . . . . . . . . . . . . . . . . . . . . .
Configuration for omni 4 Inst. 3–43. . . . . . . . . . . . . . . . . . . . . . . . . . . . . . . . . . . . . . . . .
Configuration for omni 5 or 6 Inst. 3–43. . . . . . . . . . . . . . . . . . . . . . . . . . . . . . . . . . . . .
Configuration for sector 1/1 or 2/2 Inst. 3–44. . . . . . . . . . . . . . . . . . . . . . . . . . . . . . . . .
Configuration for sector 1/1 Inst. 3–44. . . . . . . . . . . . . . . . . . . . . . . . . . . . . . . . . . . . . .
Configuration for single cabinet sector 3/3 Inst. 3–45. . . . . . . . . . . . . . . . . . . . . . . . .
Configuration for 2 cabinet sector 3/3 Inst. 3–46. . . . . . . . . . . . . . . . . . . . . . . . . . . . . .
Configuration for 2 cabinet sector 4/4 Inst. 3–46. . . . . . . . . . . . . . . . . . . . . . . . . . . . . .
Configuration for 2 cabinet sector 5/5 or 6/6 Inst. 3–47. . . . . . . . . . . . . . . . . . . . . . . .
Configuration for single cabinet sector 1/1/1, 1/1/2, 1/2/2 or 2/2/2 Inst. 3–48. . . . .
Configuration for 2 cabinet sector 2/2/2 Inst. 3–49. . . . . . . . . . . . . . . . . . . . . . . . . . . .
Configuration for 2 cabinet sector 3/3/3 or 4/4/4 Inst. 3–50. . . . . . . . . . . . . . . . . . . .
Configuration for 3 cabinet sector 3/3/3 Inst. 3–51. . . . . . . . . . . . . . . . . . . . . . . . . . . .
Configuration for 2 cabinet sector 4/4/4 Inst. 3–52. . . . . . . . . . . . . . . . . . . . . . . . . . . .
Configuration for 3 cabinet sector 4/4/4 Inst. 3–53. . . . . . . . . . . . . . . . . . . . . . . . . . . .
Configuration for sector 5/5/5 or 6/6/6 Inst. 3–54. . . . . . . . . . . . . . . . . . . . . . . . . . . . .
Configuration for sector 8/8/8 Inst. 3–55. . . . . . . . . . . . . . . . . . . . . . . . . . . . . . . . . . . . .
Configuration for dual band 1/1/1-3/3/3 Inst. 3–56. . . . . . . . . . . . . . . . . . . . . . . . . . . .
Configuration for dual band 3/3/3-1/1/1 Inst. 3–56. . . . . . . . . . . . . . . . . . . . . . . . . . . .
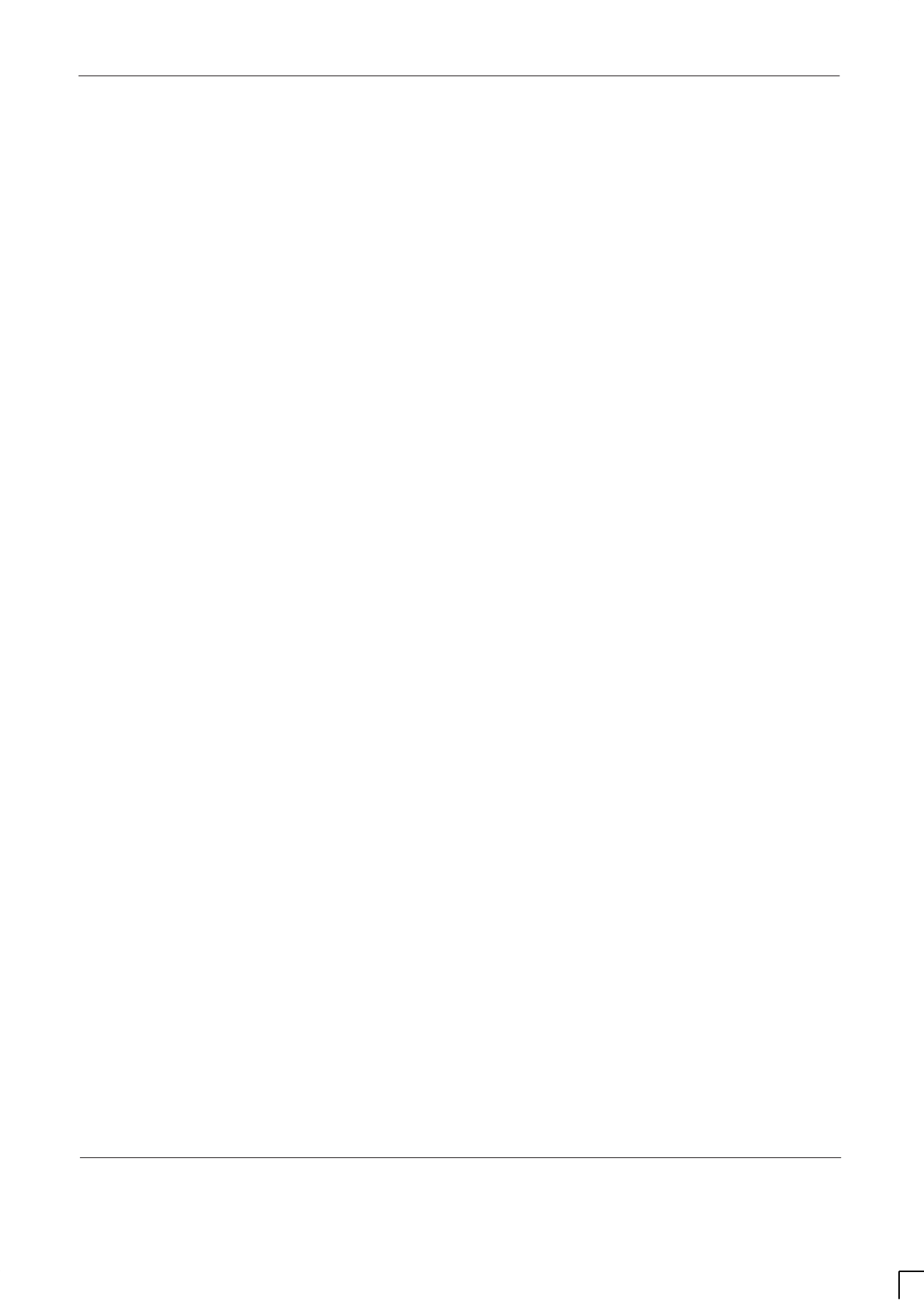
GSM-204-020
31st Oct 01
Service Manual: Horizon
macro
outdoor
68P02902W12-A
CONTROLLED INTRODUCTION
xiii
Connecting fibre optic cables Inst. 3–57. . . . . . . . . . . . . . . . . . . . . . . . . . . . . . . . . . . . . . . . . .
Location of fibre optic connections Inst. 3–57. . . . . . . . . . . . . . . . . . . . . . . . . . . . . . . .
Care of fibres Inst. 3–57. . . . . . . . . . . . . . . . . . . . . . . . . . . . . . . . . . . . . . . . . . . . . . . . . . .
Connecting fibre optic cables between cabinets Inst. 3–60. . . . . . . . . . . . . . . . . . . . .
Interface panel cabling Inst. 3–61. . . . . . . . . . . . . . . . . . . . . . . . . . . . . . . . . . . . . . . . . . . . . . . .
Interface panel diagram and pinout overview Inst. 3–61. . . . . . . . . . . . . . . . . . . . . .
Interface panel connector pinout tables Inst. 3–62. . . . . . . . . . . . . . . . . . . . . . . . . . . .
GPS connector Inst. 3–62. . . . . . . . . . . . . . . . . . . . . . . . . . . . . . . . . . . . . . . . . . . . . . . . .
RTC connector (not used) Inst. 3–63. . . . . . . . . . . . . . . . . . . . . . . . . . . . . . . . . . . . . . . .
BIB (BIM) interconnection Inst. 3–64. . . . . . . . . . . . . . . . . . . . . . . . . . . . . . . . . . . . . . . .
T43 (CIM) interconnection Inst. 3–65. . . . . . . . . . . . . . . . . . . . . . . . . . . . . . . . . . . . . . .
PIX inputs and outputs Inst. 3–66. . . . . . . . . . . . . . . . . . . . . . . . . . . . . . . . . . . . . . . . . .
ICS connector Inst. 3–67. . . . . . . . . . . . . . . . . . . . . . . . . . . . . . . . . . . . . . . . . . . . . . . . . .
External alarm connector Inst. 3–68. . . . . . . . . . . . . . . . . . . . . . . . . . . . . . . . . . . . . . . .
Chapter 4
Installing the cable shroud i. . . . . . . . . . . . . . . . . . . . . . . . . . . . . . . . . . . . .
Introduction to cable shroud installation Inst. 4–1. . . . . . . . . . . . . . . . . . . . . . . . . . . . . . . . .
Preparing to install the cable shroud Inst. 4–1. . . . . . . . . . . . . . . . . . . . . . . . . . . . . . .
Considerations when installing the cable shroud Inst. 4–1. . . . . . . . . . . . . . . . . . . .
Cable shroud installation procedures Inst. 4–2. . . . . . . . . . . . . . . . . . . . . . . . . . . . . . . . . . .
Attaching the cable shroud frame to the BTS cabinet Inst. 4–2. . . . . . . . . . . . . . . .
Adapting the shroud for cable entry from below ground Inst. 4–4. . . . . . . . . . . . . .
Adapting the shroud for cable entry from ground level Inst. 4–5. . . . . . . . . . . . . . .
Adapting the shroud for high level cable entry Inst. 4–6. . . . . . . . . . . . . . . . . . . . . .
Installation between cabinets (or the AEH) Inst. 4–7. . . . . . . . . . . . . . . . . . . . . . . . .
Cable routeing for multiple cabinet sites Inst. 4–10. . . . . . . . . . . . . . . . . . . . . . . . . . .
Chapter 5
Installing the auxiliary equipment housing i. . . . . . . . . . . . . . . . . . . . . .
Procedures for installing the auxiliary equipment housing Inst. 5–1. . . . . . . . . . . . . . . . .
Assumptions regarding site preparation Inst. 5–1. . . . . . . . . . . . . . . . . . . . . . . . . . . .
Layout of the auxiliary equipment housing Inst. 5–1. . . . . . . . . . . . . . . . . . . . . . . . .
Auxiliary equipment housing packaging Inst. 5–2. . . . . . . . . . . . . . . . . . . . . . . . . . . .
Introduction to installing the auxiliary equipment housing Inst. 5–2. . . . . . . . . . . . .
Installing the auxiliary equipment housing template Inst. 5–3. . . . . . . . . . . . . . . . . .
Installing auxiliary equipment housing bolt anchors Inst. 5–4. . . . . . . . . . . . . . . . . .
Bolting the auxiliary equipment housing to the floor Inst. 5–5. . . . . . . . . . . . . . . . .
Installing batteries in the auxiliary equipment housing Inst. 5–6. . . . . . . . . . . . . . . . . . . . .
Introduction to battery installation Inst. 5–6. . . . . . . . . . . . . . . . . . . . . . . . . . . . . . . . .
Installing batteries Inst. 5–7. . . . . . . . . . . . . . . . . . . . . . . . . . . . . . . . . . . . . . . . . . . . . .
Auxiliary equipment housing (AEH) connections Inst. 5–10. . . . . . . . . . . . . . . . . . . . . . . . .
Earthing the AEH Inst. 5–10. . . . . . . . . . . . . . . . . . . . . . . . . . . . . . . . . . . . . . . . . . . . . . .
Connecting dc cables to the AEH Inst. 5–10. . . . . . . . . . . . . . . . . . . . . . . . . . . . . . . . .
Connecting the alarm signal cables Inst. 5–11. . . . . . . . . . . . . . . . . . . . . . . . . . . . . . .
Internal connections in the AEH Inst. 5–11. . . . . . . . . . . . . . . . . . . . . . . . . . . . . . . . . .
Configuring battery backup to supply two BTS cabinets Inst. 5–12. . . . . . . . . . . . . . . . . . .
Introduction to configuring battery backup Inst. 5–12. . . . . . . . . . . . . . . . . . . . . . . . . .
Removing the power distribution box Inst. 5–12. . . . . . . . . . . . . . . . . . . . . . . . . . . . . .
Interior view of power distribution box Inst. 5–13. . . . . . . . . . . . . . . . . . . . . . . . . . . . .
Removing the parallelling links Inst. 5–14. . . . . . . . . . . . . . . . . . . . . . . . . . . . . . . . . . . .
Refitting the power distribution box Inst. 5–15. . . . . . . . . . . . . . . . . . . . . . . . . . . . . . . .
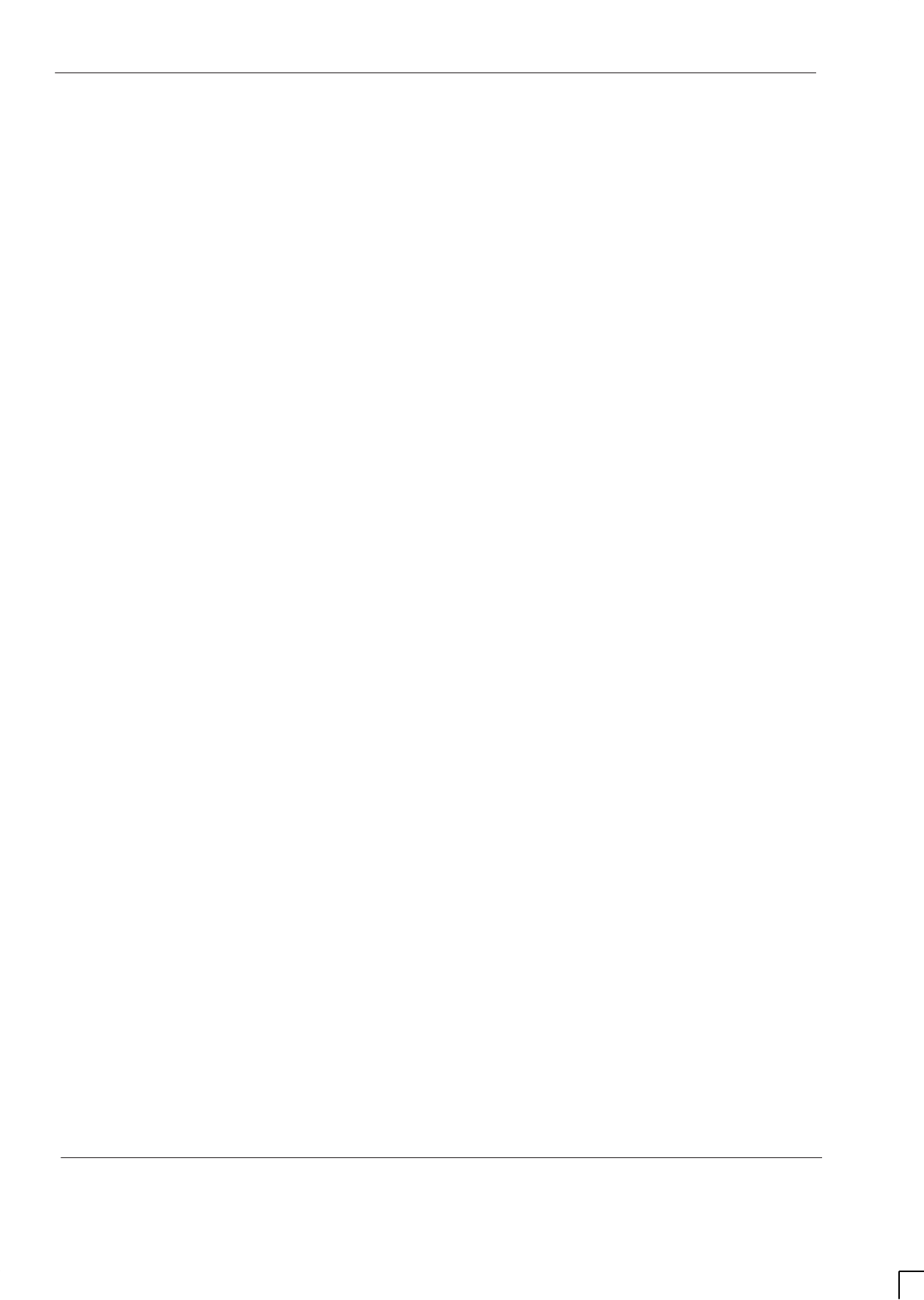
GSM-204-020
31st Oct 01
xiv
Service Manual: Horizon
macro
outdoor
CONTROLLED INTRODUCTION
68P02902W12-A
Chapter 6
Interoperability between different Motorola BTSs i. . . . . . . . . . . . . . . .
Introduction to interoperability Inst. 6–1. . . . . . . . . . . . . . . . . . . . . . . . . . . . . . . . . . . . . . . . .
Mixed product sites Inst. 6–1. . . . . . . . . . . . . . . . . . . . . . . . . . . . . . . . . . . . . . . . . . . . .
Architectural constraints Inst. 6–1. . . . . . . . . . . . . . . . . . . . . . . . . . . . . . . . . . . . . . . . .
BTS architectures and interoperability Inst. 6–2. . . . . . . . . . . . . . . . . . . . . . . . . . . . . . . . . .
M-Cell6 and Horizonmacro architectures Inst. 6–2. . . . . . . . . . . . . . . . . . . . . . . . . . .
Example mixed site Inst. 6–3. . . . . . . . . . . . . . . . . . . . . . . . . . . . . . . . . . . . . . . . . . . . .
Technical issues Inst. 6–4. . . . . . . . . . . . . . . . . . . . . . . . . . . . . . . . . . . . . . . . . . . . . . . .
Receive path Inst. 6–4. . . . . . . . . . . . . . . . . . . . . . . . . . . . . . . . . . . . . . . . . . . . . . . . . . .
Transmit path Inst. 6–7. . . . . . . . . . . . . . . . . . . . . . . . . . . . . . . . . . . . . . . . . . . . . . . . . .
M-Cell6 and Horizonmacro hardware equivalents Inst. 6–10. . . . . . . . . . . . . . . . . . .
Further configuration information Inst. 6–10. . . . . . . . . . . . . . . . . . . . . . . . . . . . . . . . . .
Example configurations Inst. 6–11. . . . . . . . . . . . . . . . . . . . . . . . . . . . . . . . . . . . . . . . . .
Special hardware Inst. 6–14. . . . . . . . . . . . . . . . . . . . . . . . . . . . . . . . . . . . . . . . . . . . . . .
Chapter 7
Commissioning of outdoor cabinet i. . . . . . . . . . . . . . . . . . . . . . . . . . . . .
Commissioning overview Inst. 7–1. . . . . . . . . . . . . . . . . . . . . . . . . . . . . . . . . . . . . . . . . . . . . .
Overview of commissioning Inst. 7–1. . . . . . . . . . . . . . . . . . . . . . . . . . . . . . . . . . . . . .
PC to MCUF cable pin connections Inst. 7–1. . . . . . . . . . . . . . . . . . . . . . . . . . . . . . .
Test equipment Inst. 7–2. . . . . . . . . . . . . . . . . . . . . . . . . . . . . . . . . . . . . . . . . . . . . . . . .
Pre-power up checks Inst. 7–3. . . . . . . . . . . . . . . . . . . . . . . . . . . . . . . . . . . . . . . . . . . . . . . . .
Overview of pre-power up checks Inst. 7–3. . . . . . . . . . . . . . . . . . . . . . . . . . . . . . . . .
Visual inspection Inst. 7–4. . . . . . . . . . . . . . . . . . . . . . . . . . . . . . . . . . . . . . . . . . . . . . . .
Request for connection Inst. 7–4. . . . . . . . . . . . . . . . . . . . . . . . . . . . . . . . . . . . . . . . . .
Earth continuity check Inst. 7–5. . . . . . . . . . . . . . . . . . . . . . . . . . . . . . . . . . . . . . . . . . .
AC power system insulation check Inst. 7–5. . . . . . . . . . . . . . . . . . . . . . . . . . . . . . . .
Connecting input power Inst. 7–6. . . . . . . . . . . . . . . . . . . . . . . . . . . . . . . . . . . . . . . . . . . . . . .
Pre-connection checks Inst. 7–6. . . . . . . . . . . . . . . . . . . . . . . . . . . . . . . . . . . . . . . . . .
Connecting ac power Inst. 7–6. . . . . . . . . . . . . . . . . . . . . . . . . . . . . . . . . . . . . . . . . . . .
Connecting to a single phase ac power supply Inst. 7–6. . . . . . . . . . . . . . . . . . . . . .
Connecting to a three phase (star) ac power supply Inst. 7–7. . . . . . . . . . . . . . . . .
Connecting to a three phase (delta) ac power supply Inst. 7–7. . . . . . . . . . . . . . . .
Powering up the cabinet Inst. 7–8. . . . . . . . . . . . . . . . . . . . . . . . . . . . . . . . . . . . . . . . . . . . . .
Power-up overview Inst. 7–8. . . . . . . . . . . . . . . . . . . . . . . . . . . . . . . . . . . . . . . . . . . . . .
Power up procedure without code load Inst. 7–8. . . . . . . . . . . . . . . . . . . . . . . . . . . .
Power down of the cabinet Inst. 7–10. . . . . . . . . . . . . . . . . . . . . . . . . . . . . . . . . . . . . . .
Power up procedure with code load Inst. 7–11. . . . . . . . . . . . . . . . . . . . . . . . . . . . . . .
Installation and configuration Inst. 7–14. . . . . . . . . . . . . . . . . . . . . . . . . . . . . . . . . . . . .
Components involved in power up procedures Inst. 7–15. . . . . . . . . . . . . . . . . . . . . .
Testing the thermal management system (TMS) Inst. 7–16. . . . . . . . . . . . . . . . . . . . . . . . .
Overview of TMS test Inst. 7–16. . . . . . . . . . . . . . . . . . . . . . . . . . . . . . . . . . . . . . . . . . . .
Test facilities Inst. 7–16. . . . . . . . . . . . . . . . . . . . . . . . . . . . . . . . . . . . . . . . . . . . . . . . . . .
Diagram of TMS airflow Inst. 7–17. . . . . . . . . . . . . . . . . . . . . . . . . . . . . . . . . . . . . . . . . .
Test procedure Inst. 7–18. . . . . . . . . . . . . . . . . . . . . . . . . . . . . . . . . . . . . . . . . . . . . . . . .
Testing the battery backup Inst. 7–19. . . . . . . . . . . . . . . . . . . . . . . . . . . . . . . . . . . . . . . . . . . .
Overview of battery backup test Inst. 7–19. . . . . . . . . . . . . . . . . . . . . . . . . . . . . . . . . .
Battery backup test procedures Inst. 7–19. . . . . . . . . . . . . . . . . . . . . . . . . . . . . . . . . . .
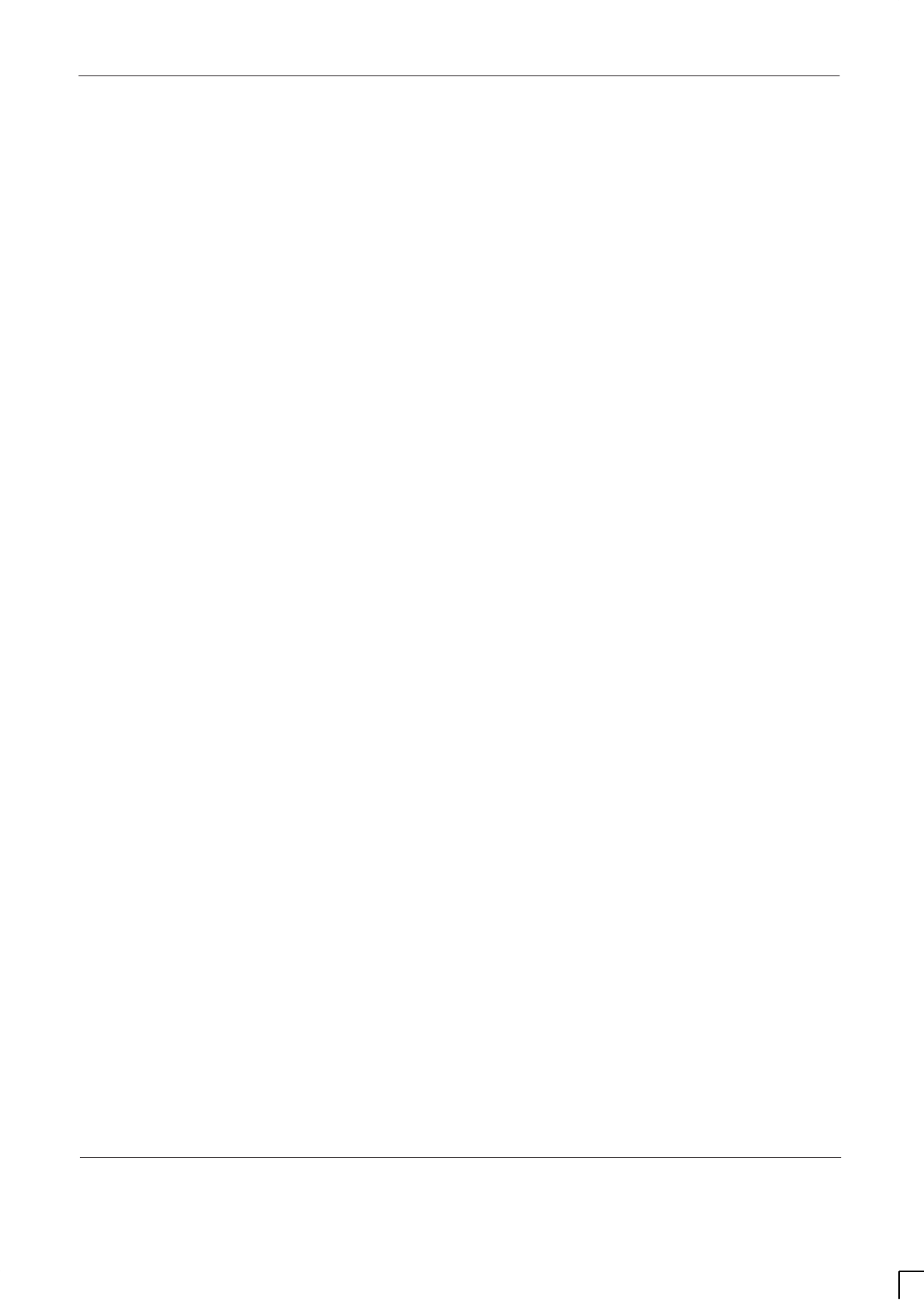
GSM-204-020
31st Oct 01
Service Manual: Horizon
macro
outdoor
68P02902W12-A
CONTROLLED INTRODUCTION
xv
Sample form 1: Request for connection Inst. 7–21. . . . . . . . . . . . . . . . . . . . . . . . . . . . . . . . .
Sample form 2: Completion and inspection form Inst. 7–23. . . . . . . . . . . . . . . . . . . . . . . . .
Chapter 8
Decommissioning the equipment i. . . . . . . . . . . . . . . . . . . . . . . . . . . . . . .
Introduction to decommissioning the Horizonmacro outdoor cabinet Inst. 8–1. . . . . . . .
Overview Inst. 8–1. . . . . . . . . . . . . . . . . . . . . . . . . . . . . . . . . . . . . . . . . . . . . . . . . . . . . .
Prerequisite Inst. 8–1. . . . . . . . . . . . . . . . . . . . . . . . . . . . . . . . . . . . . . . . . . . . . . . . . . . .
Lifting cabinets Inst. 8–1. . . . . . . . . . . . . . . . . . . . . . . . . . . . . . . . . . . . . . . . . . . . . . . . .
Decommissioning the Horizonmacro outdoor cabinet Inst. 8–2. . . . . . . . . . . . . . . . . . . . .
Introduction Inst. 8–2. . . . . . . . . . . . . . . . . . . . . . . . . . . . . . . . . . . . . . . . . . . . . . . . . . . .
To decommission using checklist Inst. 8–2. . . . . . . . . . . . . . . . . . . . . . . . . . . . . . . . . .
Before starting Inst. 8–2. . . . . . . . . . . . . . . . . . . . . . . . . . . . . . . . . . . . . . . . . . . . . . . . . .
Power down of the cabinet Inst. 8–2. . . . . . . . . . . . . . . . . . . . . . . . . . . . . . . . . . . . . . .
Procedure Inst. 8–3. . . . . . . . . . . . . . . . . . . . . . . . . . . . . . . . . . . . . . . . . . . . . . . . . . . . .
BTS checklist Inst. 8–4. . . . . . . . . . . . . . . . . . . . . . . . . . . . . . . . . . . . . . . . . . . . . . . . . . .
Category 523
Maintenance Information (Maint.) i. . . . . . . . . . . . . . . . . . . . . . . . . . . . . . . . . . .
Chapter 1
Introduction to maintenance i. . . . . . . . . . . . . . . . . . . . . . . . . . . . . . . . . . .
Maintenance information introduction Maint. 1–1. . . . . . . . . . . . . . . . . . . . . . . . . . . . . . . . . . .
Safety Maint. 1–1. . . . . . . . . . . . . . . . . . . . . . . . . . . . . . . . . . . . . . . . . . . . . . . . . . . . . . . . .
Tools Maint. 1–1. . . . . . . . . . . . . . . . . . . . . . . . . . . . . . . . . . . . . . . . . . . . . . . . . . . . . . . . . .
Weather conditions affecting access Maint. 1–2. . . . . . . . . . . . . . . . . . . . . . . . . . . . . . . . . . . .
Overview of weather considerations Maint. 1–2. . . . . . . . . . . . . . . . . . . . . . . . . . . . . . .
Weather conditions Maint. 1–2. . . . . . . . . . . . . . . . . . . . . . . . . . . . . . . . . . . . . . . . . . . . . .
Maintenance cover Maint. 1–2. . . . . . . . . . . . . . . . . . . . . . . . . . . . . . . . . . . . . . . . . . . . . .
Chapter 2
General maintenance i. . . . . . . . . . . . . . . . . . . . . . . . . . . . . . . . . . . . . . . . . .
General maintenance overview Maint. 2–1. . . . . . . . . . . . . . . . . . . . . . . . . . . . . . . . . . . . . . . .
In this chapter Maint. 2–1. . . . . . . . . . . . . . . . . . . . . . . . . . . . . . . . . . . . . . . . . . . . . . . . . .
Reporting faulty devices Maint. 2–1. . . . . . . . . . . . . . . . . . . . . . . . . . . . . . . . . . . . . . . . .
Cleaning agents Maint. 2–2. . . . . . . . . . . . . . . . . . . . . . . . . . . . . . . . . . . . . . . . . . . . . . . .
Torque values Maint. 2–2. . . . . . . . . . . . . . . . . . . . . . . . . . . . . . . . . . . . . . . . . . . . . . . . . .
Maintenance support procedures Maint. 2–3. . . . . . . . . . . . . . . . . . . . . . . . . . . . . . . . . . . . . .
Door opening and closing Maint. 2–3. . . . . . . . . . . . . . . . . . . . . . . . . . . . . . . . . . . . . . . .
Lid opening and closing Maint. 2–3. . . . . . . . . . . . . . . . . . . . . . . . . . . . . . . . . . . . . . . . .
TMS front cover removal and refitting Maint. 2–4. . . . . . . . . . . . . . . . . . . . . . . . . . . . . .
General maintenance procedures Maint. 2–5. . . . . . . . . . . . . . . . . . . . . . . . . . . . . . . . . . . . . .
Type of procedures Maint. 2–5. . . . . . . . . . . . . . . . . . . . . . . . . . . . . . . . . . . . . . . . . . . . .
Assumptions - door, lid and TMS front cover Maint. 2–5. . . . . . . . . . . . . . . . . . . . . . . .
Cleaning inlet and outlet grilles Maint. 2–5. . . . . . . . . . . . . . . . . . . . . . . . . . . . . . . . . . .
Checking normal operation Maint. 2–6. . . . . . . . . . . . . . . . . . . . . . . . . . . . . . . . . . . . . . .
Inspection of cabinet, locks and hinges Maint. 2–7. . . . . . . . . . . . . . . . . . . . . . . . . . . .
Periodic check of the installation Maint. 2–8. . . . . . . . . . . . . . . . . . . . . . . . . . . . . . . . . .
TMS testing Maint. 2–8. . . . . . . . . . . . . . . . . . . . . . . . . . . . . . . . . . . . . . . . . . . . . . . . . . . .
Battery backup test procedures Maint. 2–10. . . . . . . . . . . . . . . . . . . . . . . . . . . . . . . . . . .
Return to service Maint. 2–11. . . . . . . . . . . . . . . . . . . . . . . . . . . . . . . . . . . . . . . . . . . . . . . .
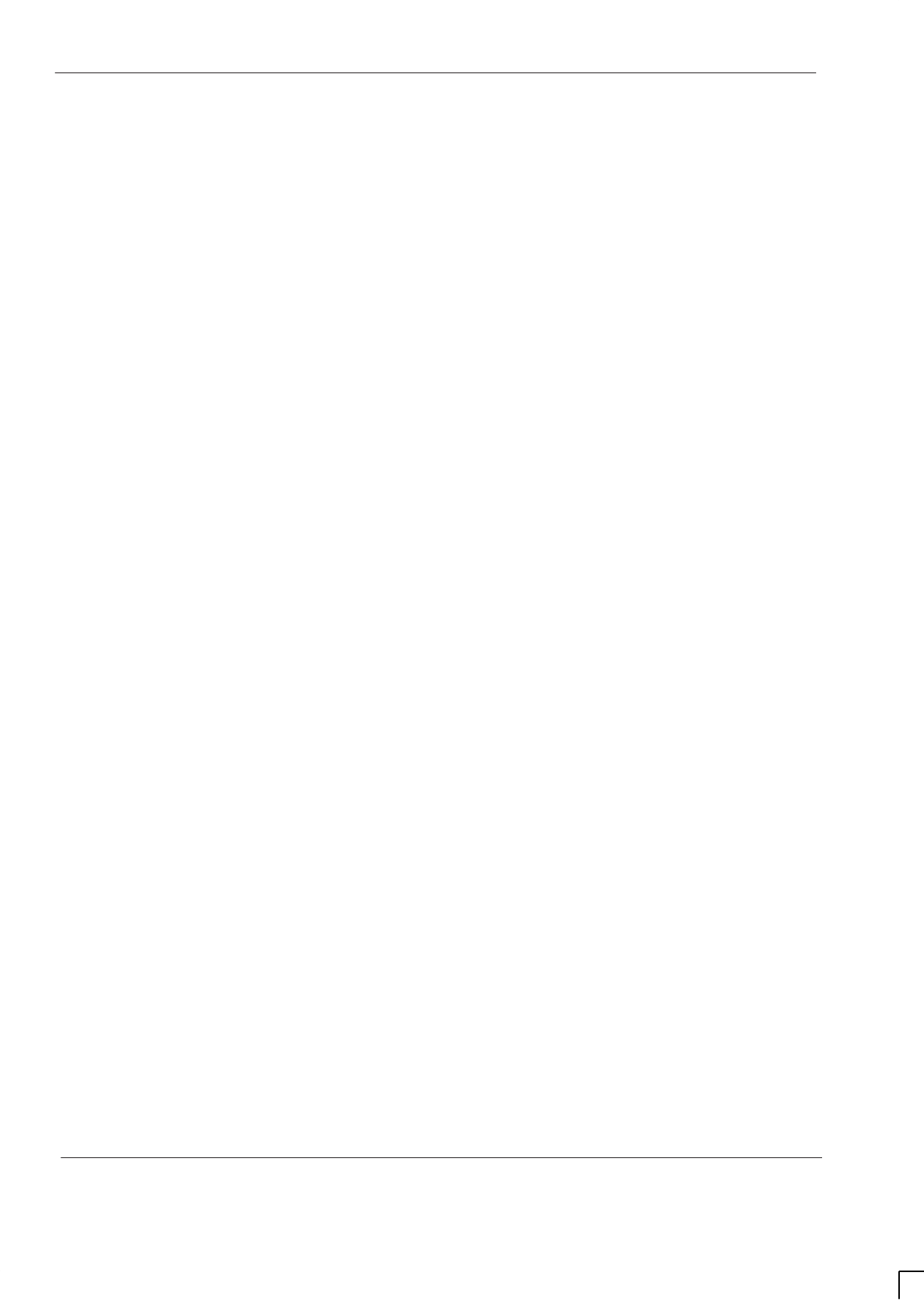
GSM-204-020
31st Oct 01
xvi
Service Manual: Horizon
macro
outdoor
CONTROLLED INTRODUCTION
68P02902W12-A
Chapter 3
FRU replacement procedures i. . . . . . . . . . . . . . . . . . . . . . . . . . . . . . . . . .
Overview of FRU replacement procedures Maint. 3–1. . . . . . . . . . . . . . . . . . . . . . . . . . . . . .
Field replaceable units (FRUs) Maint. 3–1. . . . . . . . . . . . . . . . . . . . . . . . . . . . . . . . . . . .
FRU list Maint. 3–1. . . . . . . . . . . . . . . . . . . . . . . . . . . . . . . . . . . . . . . . . . . . . . . . . . . . . . . .
Torque values Maint. 3–2. . . . . . . . . . . . . . . . . . . . . . . . . . . . . . . . . . . . . . . . . . . . . . . . . .
FRU view of cabinet Maint. 3–2. . . . . . . . . . . . . . . . . . . . . . . . . . . . . . . . . . . . . . . . . . . . .
Replacing a door Maint. 3–3. . . . . . . . . . . . . . . . . . . . . . . . . . . . . . . . . . . . . . . . . . . . . . . . . . . . .
Introduction to door replacement Maint. 3–3. . . . . . . . . . . . . . . . . . . . . . . . . . . . . . . . . .
Views of the cabinet doors Maint. 3–3. . . . . . . . . . . . . . . . . . . . . . . . . . . . . . . . . . . . . . .
Door replacement procedure Maint. 3–4. . . . . . . . . . . . . . . . . . . . . . . . . . . . . . . . . . . . .
Replacing the lid Maint. 3–5. . . . . . . . . . . . . . . . . . . . . . . . . . . . . . . . . . . . . . . . . . . . . . . . . . . . .
Introduction to lid replacement Maint. 3–5. . . . . . . . . . . . . . . . . . . . . . . . . . . . . . . . . . . .
View of the cabinet lid Maint. 3–5. . . . . . . . . . . . . . . . . . . . . . . . . . . . . . . . . . . . . . . . . . .
Replacing a lid Maint. 3–6. . . . . . . . . . . . . . . . . . . . . . . . . . . . . . . . . . . . . . . . . . . . . . . . . .
Replacing environmental seals Maint. 3–7. . . . . . . . . . . . . . . . . . . . . . . . . . . . . . . . . . . . . . . .
Introduction to environmental seal replacement Maint. 3–7. . . . . . . . . . . . . . . . . . . . .
Replacing an environmental seal for the lid Maint. 3–7. . . . . . . . . . . . . . . . . . . . . . . . .
Replacing an environmental seal on a door Maint. 3–7. . . . . . . . . . . . . . . . . . . . . . . .
Replacing a thermal management system (TMS) unit Maint. 3–8. . . . . . . . . . . . . . . . . . . . .
Introduction to TMS replacement Maint. 3–8. . . . . . . . . . . . . . . . . . . . . . . . . . . . . . . . . .
View of the TMS unit Maint. 3–8. . . . . . . . . . . . . . . . . . . . . . . . . . . . . . . . . . . . . . . . . . . .
Removing the TMS unit Maint. 3–9. . . . . . . . . . . . . . . . . . . . . . . . . . . . . . . . . . . . . . . . . .
Refitting the TMS unit Maint. 3–10. . . . . . . . . . . . . . . . . . . . . . . . . . . . . . . . . . . . . . . . . . .
Replacing TMS unit components Maint. 3–11. . . . . . . . . . . . . . . . . . . . . . . . . . . . . . . . . . . . . . .
Introduction to TMS unit component replacement Maint. 3–11. . . . . . . . . . . . . . . . . . .
Replacing a TMS fan Maint. 3–11. . . . . . . . . . . . . . . . . . . . . . . . . . . . . . . . . . . . . . . . . . . .
Replacing the TMS control board Maint. 3–12. . . . . . . . . . . . . . . . . . . . . . . . . . . . . . . . .
Replacing the TMS gasket Maint. 3–12. . . . . . . . . . . . . . . . . . . . . . . . . . . . . . . . . . . . . . .
Replacing a cabinet temperature sensor Maint. 3–13. . . . . . . . . . . . . . . . . . . . . . . . . . . . . . . .
Overview of main cage temperature sensor FRUs Maint. 3–13. . . . . . . . . . . . . . . . . . .
Replaceing a main cage temperature sensor Maint. 3–13. . . . . . . . . . . . . . . . . . . . . . .
Replacing a dc circuit breaker Maint. 3–14. . . . . . . . . . . . . . . . . . . . . . . . . . . . . . . . . . . . . . . . .
Introduction to dc circuit breaker replacement Maint. 3–14. . . . . . . . . . . . . . . . . . . . . .
View of the dc circuit breaker panel Maint. 3–14. . . . . . . . . . . . . . . . . . . . . . . . . . . . . . .
Replacing a dc circuit breaker Maint. 3–14. . . . . . . . . . . . . . . . . . . . . . . . . . . . . . . . . . . .
Replacing the control and alarm board (CAB) Maint. 3–15. . . . . . . . . . . . . . . . . . . . . . . . . . . .
Introduction to CAB replacement Maint. 3–15. . . . . . . . . . . . . . . . . . . . . . . . . . . . . . . . . .
View of CAB Maint. 3–15. . . . . . . . . . . . . . . . . . . . . . . . . . . . . . . . . . . . . . . . . . . . . . . . . . .
Replacing a CAB Maint. 3–16. . . . . . . . . . . . . . . . . . . . . . . . . . . . . . . . . . . . . . . . . . . . . . .
Replacing the outdoor power supply module (TOPSM) Maint. 3–17. . . . . . . . . . . . . . . . . . . .
TOPSM replacement Maint. 3–17. . . . . . . . . . . . . . . . . . . . . . . . . . . . . . . . . . . . . . . . . . . .
View of TOPSM Maint. 3–17. . . . . . . . . . . . . . . . . . . . . . . . . . . . . . . . . . . . . . . . . . . . . . . . .
Replacing a TOPSM Maint. 3–18. . . . . . . . . . . . . . . . . . . . . . . . . . . . . . . . . . . . . . . . . . . .
Replacing a power supply module (PSM) Maint. 3–19. . . . . . . . . . . . . . . . . . . . . . . . . . . . . . .
Introduction to PSM replacement Maint. 3–19. . . . . . . . . . . . . . . . . . . . . . . . . . . . . . . . .
View of PSM Maint. 3–19. . . . . . . . . . . . . . . . . . . . . . . . . . . . . . . . . . . . . . . . . . . . . . . . . . .
Replacing a non-redundant PSM Maint. 3–20. . . . . . . . . . . . . . . . . . . . . . . . . . . . . . . . .
Replacing a redundant PSM Maint. 3–21. . . . . . . . . . . . . . . . . . . . . . . . . . . . . . . . . . . . .
BPSM replacement Maint. 3–21. . . . . . . . . . . . . . . . . . . . . . . . . . . . . . . . . . . . . . . . . . . . .
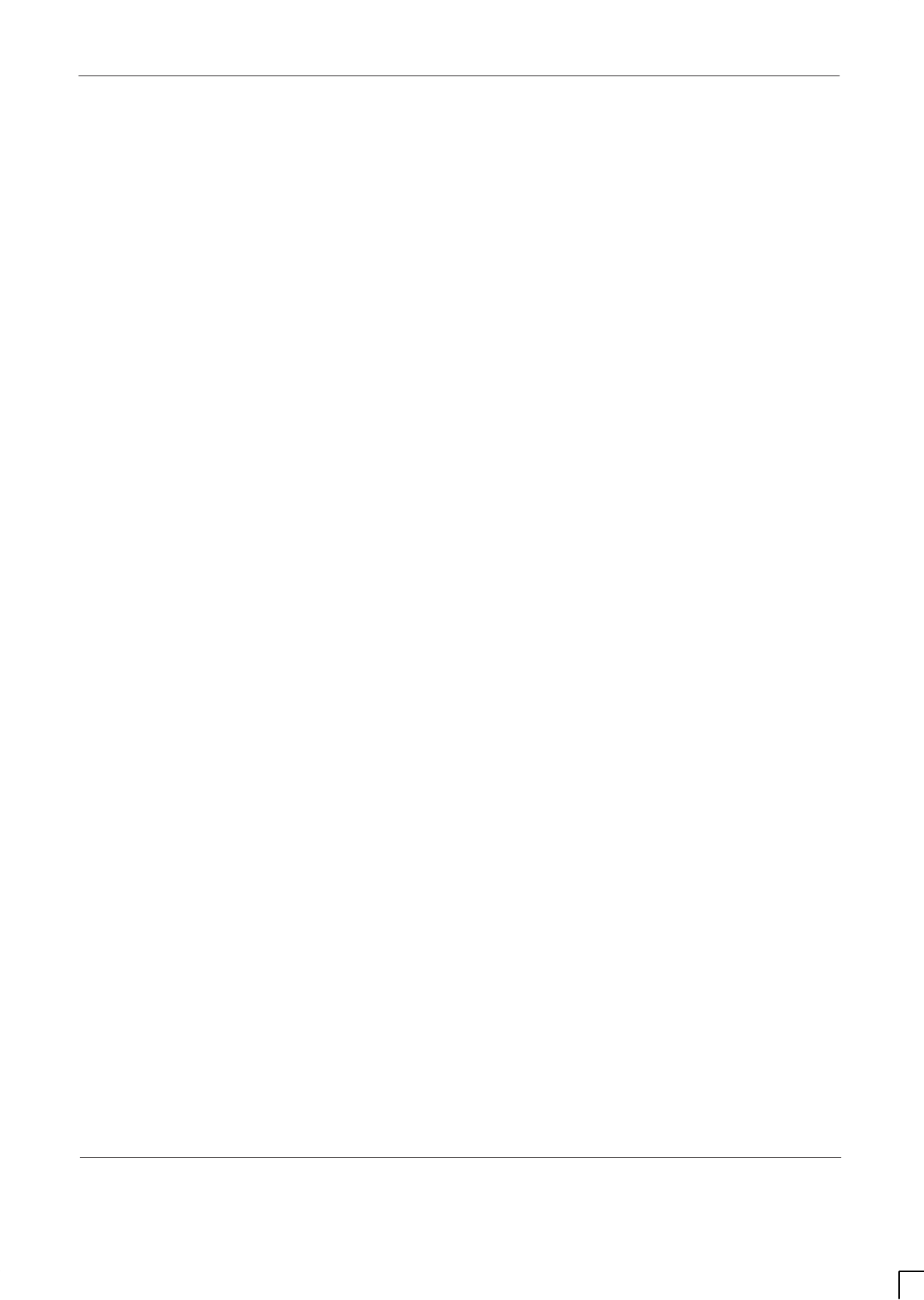
GSM-204-020
31st Oct 01
Service Manual: Horizon
macro
outdoor
68P02902W12-A
CONTROLLED INTRODUCTION
xvii
Replacing a circuit breaker module (CBM) Maint. 3–22. . . . . . . . . . . . . . . . . . . . . . . . . . . . . . .
Preconditions for CBM replacement Maint. 3–22. . . . . . . . . . . . . . . . . . . . . . . . . . . . . . .
Views of CBM Maint. 3–22. . . . . . . . . . . . . . . . . . . . . . . . . . . . . . . . . . . . . . . . . . . . . . . . . .
Replacing a CBM Maint. 3–23. . . . . . . . . . . . . . . . . . . . . . . . . . . . . . . . . . . . . . . . . . . . . . .
Replacing the internal batteries Maint. 3–24. . . . . . . . . . . . . . . . . . . . . . . . . . . . . . . . . . . . . . . .
Introduction to internal battery replacement Maint. 3–24. . . . . . . . . . . . . . . . . . . . . . . .
Battery arrangement Maint. 3–25. . . . . . . . . . . . . . . . . . . . . . . . . . . . . . . . . . . . . . . . . . . .
Removing the battery tray Maint. 3–25. . . . . . . . . . . . . . . . . . . . . . . . . . . . . . . . . . . . . . . .
Removing and replacing the batteries Maint. 3–26. . . . . . . . . . . . . . . . . . . . . . . . . . . . .
View showing battery replacement components Maint. 3–27. . . . . . . . . . . . . . . . . . . . .
Replacing a CTU Maint. 3–28. . . . . . . . . . . . . . . . . . . . . . . . . . . . . . . . . . . . . . . . . . . . . . . . . . . . .
Preconditions to CTU replacement Maint. 3–28. . . . . . . . . . . . . . . . . . . . . . . . . . . . . . . .
View of CTU Maint. 3–28. . . . . . . . . . . . . . . . . . . . . . . . . . . . . . . . . . . . . . . . . . . . . . . . . . . .
Replacement procedure for CTU Maint. 3–29. . . . . . . . . . . . . . . . . . . . . . . . . . . . . . . . . .
Replacing a SURF module Maint. 3–31. . . . . . . . . . . . . . . . . . . . . . . . . . . . . . . . . . . . . . . . . . . .
Preconditions for SURF replacement Maint. 3–31. . . . . . . . . . . . . . . . . . . . . . . . . . . . . .
View of the SURF Maint. 3–31. . . . . . . . . . . . . . . . . . . . . . . . . . . . . . . . . . . . . . . . . . . . . . .
Replacing a SURF module Maint. 3–32. . . . . . . . . . . . . . . . . . . . . . . . . . . . . . . . . . . . . . .
Replacing a Tx block Maint. 3–34. . . . . . . . . . . . . . . . . . . . . . . . . . . . . . . . . . . . . . . . . . . . . . . . .
Preconditions to Tx block replacement Maint. 3–34. . . . . . . . . . . . . . . . . . . . . . . . . . . . .
Views of typical Tx block Maint. 3–35. . . . . . . . . . . . . . . . . . . . . . . . . . . . . . . . . . . . . . . . .
Replacing a Tx block Maint. 3–36. . . . . . . . . . . . . . . . . . . . . . . . . . . . . . . . . . . . . . . . . . . .
Tx block blanking plate, feedthrough plate or HCU replacement Maint. 3–37. . . . . .
Krone block replacement Maint. 3–38. . . . . . . . . . . . . . . . . . . . . . . . . . . . . . . . . . . . . . . . . . . . . .
Introduction to Krone block replacement Maint. 3–38. . . . . . . . . . . . . . . . . . . . . . . . . . .
Krone block location diagram Maint. 3–38. . . . . . . . . . . . . . . . . . . . . . . . . . . . . . . . . . . . .
Replacing a Krone block Maint. 3–39. . . . . . . . . . . . . . . . . . . . . . . . . . . . . . . . . . . . . . . . .
Digital module and BPSM replacement Maint. 3–40. . . . . . . . . . . . . . . . . . . . . . . . . . . . . . . . .
Preconditions for digital module replacement Maint. 3–40. . . . . . . . . . . . . . . . . . . . . . .
Digital module location diagram Maint. 3–40. . . . . . . . . . . . . . . . . . . . . . . . . . . . . . . . . . .
Replacing a digital module Maint. 3–41. . . . . . . . . . . . . . . . . . . . . . . . . . . . . . . . . . . . . . .
Redundant MCUF firmware compatibility Maint. 3–43. . . . . . . . . . . . . . . . . . . . . . . . . . . . . . . .
Overview of MCUF firmware compatibility Maint. 3–43. . . . . . . . . . . . . . . . . . . . . . . . . .
Checking MCUF firmware compatibility Maint. 3–43. . . . . . . . . . . . . . . . . . . . . . . . . . . .
Updating redundant MCUF firmware Maint. 3–43. . . . . . . . . . . . . . . . . . . . . . . . . . . . . .
Testing MCUF redundancy Maint. 3–46. . . . . . . . . . . . . . . . . . . . . . . . . . . . . . . . . . . . . . .
Additional replacement parts Maint. 3–47. . . . . . . . . . . . . . . . . . . . . . . . . . . . . . . . . . . . . . . . . .
Policy on non-FRU parts Maint. 3–47. . . . . . . . . . . . . . . . . . . . . . . . . . . . . . . . . . . . . . . . .
List of non-FRU parts Maint. 3–47. . . . . . . . . . . . . . . . . . . . . . . . . . . . . . . . . . . . . . . . . . . .
Procedure for replacing non-FRU parts Maint. 3–47. . . . . . . . . . . . . . . . . . . . . . . . . . . .
CBIA attachment screws Maint. 3–47. . . . . . . . . . . . . . . . . . . . . . . . . . . . . . . . . . . . . . . . .
Chapter 4
Auxiliary equipment housing maintenance i. . . . . . . . . . . . . . . . . . . . . .
Introduction to auxiliary equipment housing maintenance Maint. 4–1. . . . . . . . . . . . . . . . .
Auxiliary equipment housing FRUs Maint. 4–1. . . . . . . . . . . . . . . . . . . . . . . . . . . . . . . .
Auxiliary equipment housing FRU view Maint. 4–2. . . . . . . . . . . . . . . . . . . . . . . . . . . .
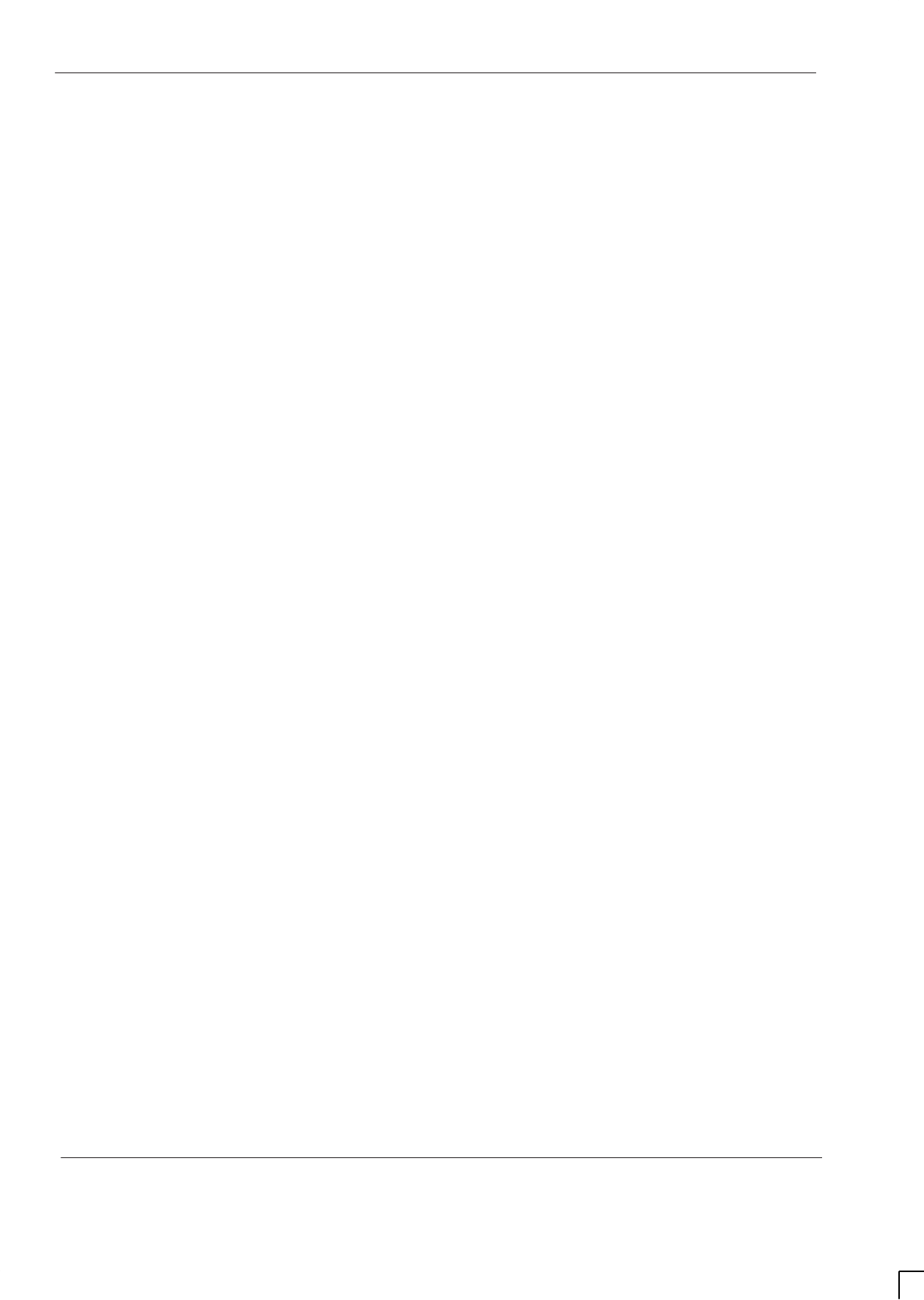
GSM-204-020
31st Oct 01
xviii
Service Manual: Horizon
macro
outdoor
CONTROLLED INTRODUCTION
68P02902W12-A
Replacing the power distribution box Maint. 4–3. . . . . . . . . . . . . . . . . . . . . . . . . . . . . . . . . . .
Introduction to power distribution box replacement Maint. 4–3. . . . . . . . . . . . . . . . . .
Removing the power distribution box Maint. 4–3. . . . . . . . . . . . . . . . . . . . . . . . . . . . . .
Fitting a replacement power distribution box Maint. 4–4. . . . . . . . . . . . . . . . . . . . . . . .
Replacing the lid on the auxiliary equipment housing Maint. 4–5. . . . . . . . . . . . . . . . . . . . .
Detailed view of the cabinet lid Maint. 4–5. . . . . . . . . . . . . . . . . . . . . . . . . . . . . . . . . . .
Removing the lid Maint. 4–6. . . . . . . . . . . . . . . . . . . . . . . . . . . . . . . . . . . . . . . . . . . . . . . .
Fitting a new lid Maint. 4–7. . . . . . . . . . . . . . . . . . . . . . . . . . . . . . . . . . . . . . . . . . . . . . . . .
Replacing the door on the auxiliary equipment housing Maint. 4–8. . . . . . . . . . . . . . . . . . .
Removing the cabinet door Maint. 4–8. . . . . . . . . . . . . . . . . . . . . . . . . . . . . . . . . . . . . . .
Fitting a replacement door Maint. 4–8. . . . . . . . . . . . . . . . . . . . . . . . . . . . . . . . . . . . . . .
Replacing the front panel or fan Maint. 4–9. . . . . . . . . . . . . . . . . . . . . . . . . . . . . . . . . . . . . . . .
Replacing the front panel Maint. 4–9. . . . . . . . . . . . . . . . . . . . . . . . . . . . . . . . . . . . . . . .
Replacing the fan Maint. 4–10. . . . . . . . . . . . . . . . . . . . . . . . . . . . . . . . . . . . . . . . . . . . . . .
Replacing a heater mat Maint. 4–11. . . . . . . . . . . . . . . . . . . . . . . . . . . . . . . . . . . . . . . . . . . . . . .
Introduction to heater mat replacement Maint. 4–11. . . . . . . . . . . . . . . . . . . . . . . . . . . .
Heater mat replacement procedure Maint. 4–11. . . . . . . . . . . . . . . . . . . . . . . . . . . . . . .
Replacing an environmental seal on the housing Maint. 4–12. . . . . . . . . . . . . . . . . . . . . . . . .
Introduction to replacing a seal Maint. 4–12. . . . . . . . . . . . . . . . . . . . . . . . . . . . . . . . . . .
Replacing the lid environmental seal Maint. 4–12. . . . . . . . . . . . . . . . . . . . . . . . . . . . . .
Replacing the door environmental seal Maint. 4–12. . . . . . . . . . . . . . . . . . . . . . . . . . . .
Category 623
Parts Information (Parts) i. . . . . . . . . . . . . . . . . . . . . . . . . . . . . . . . . . . . . . . . . . .
Chapter 1
Parts list i. . . . . . . . . . . . . . . . . . . . . . . . . . . . . . . . . . . . . . . . . . . . . . . . . . . . . .
Parts information introduction Parts 1–1. . . . . . . . . . . . . . . . . . . . . . . . . . . . . . . . . . . . . . . . . .
Horizonmacro outdoor parts lists Parts 1–1. . . . . . . . . . . . . . . . . . . . . . . . . . . . . . . . . .
FRU items Parts 1–1. . . . . . . . . . . . . . . . . . . . . . . . . . . . . . . . . . . . . . . . . . . . . . . . . . . . .
Ordering method Parts 1–1. . . . . . . . . . . . . . . . . . . . . . . . . . . . . . . . . . . . . . . . . . . . . . . .
Diagram of Horizonmacro outdoor FRU modules Parts 1–2. . . . . . . . . . . . . . . . . . . .
Diagram of auxiliary equipment housing FRU modules Parts 1–3. . . . . . . . . . . . . . .
Parts for Horizonmacro outdoor Parts 1–4. . . . . . . . . . . . . . . . . . . . . . . . . . . . . . . . . . . . . . . .
Spares Table Parts 1–4. . . . . . . . . . . . . . . . . . . . . . . . . . . . . . . . . . . . . . . . . . . . . . . . . . .
Parts for optional equipment Parts 1–7. . . . . . . . . . . . . . . . . . . . . . . . . . . . . . . . . . . . . . . . . . .
Introduction to optional equipment parts lists Parts 1–7. . . . . . . . . . . . . . . . . . . . . . .
Spares table for the cable shroud Parts 1–7. . . . . . . . . . . . . . . . . . . . . . . . . . . . . . . . .
Spares table for the auxiliary equipment housing Parts 1–7. . . . . . . . . . . . . . . . . . . .
Glossary of terms unique to this equipment Parts 1–8. . . . . . . . . . . . . . . . . . . . . . . . . . . . . .
Overview of the glossary Parts 1–8. . . . . . . . . . . . . . . . . . . . . . . . . . . . . . . . . . . . . . . . .
Glossary of terms Parts 1–8. . . . . . . . . . . . . . . . . . . . . . . . . . . . . . . . . . . . . . . . . . . . . . .
Index I–1. . . . . . . . . . . . . . . . . . . . . . . . . . . . . . . . . . . . . . . . . . . . . . . . . . . . . . . . .
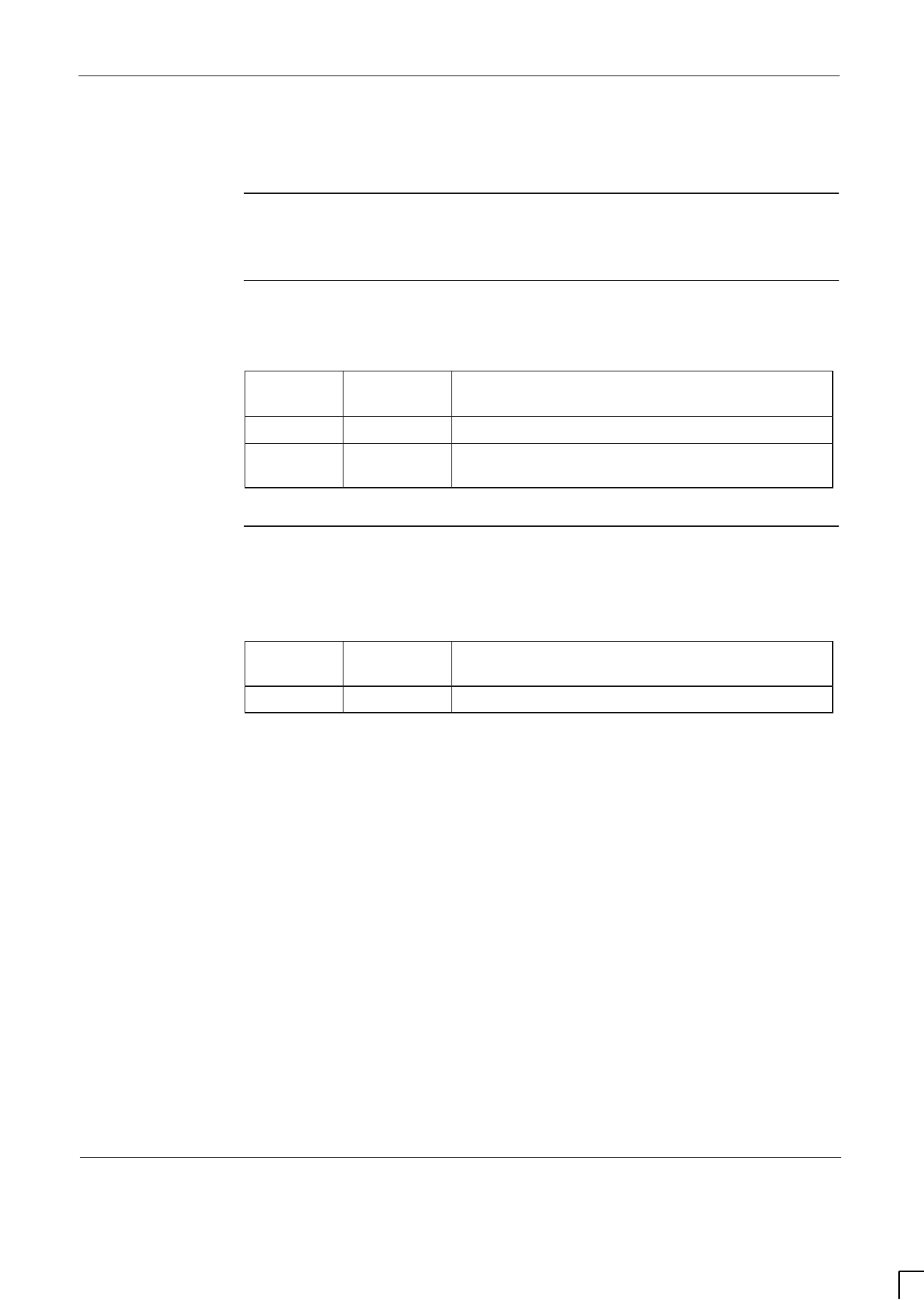
GSM-204-020 Issue status of this manual
31st Oct 01
Service Manual: Horizon
macro
outdoor
68P02902W12-A
CONTROLLED INTRODUCTION
1
Issue status of this manual
Introduction
The following shows the issue status of this manual since it was first released.
Version
information
The following lists the versions of this manual in order of manual issue:
Manual
issue Date of
issue Remarks
O12th Jan 00 Original issue.
A31st Oct 01 Updated to include details for GSM850 and
PCS1900.
Resolution of
Service
Requests
The following Service Requests are now resolved in this manual:
Service
Request GMR
Number Remarks
N/A N/A
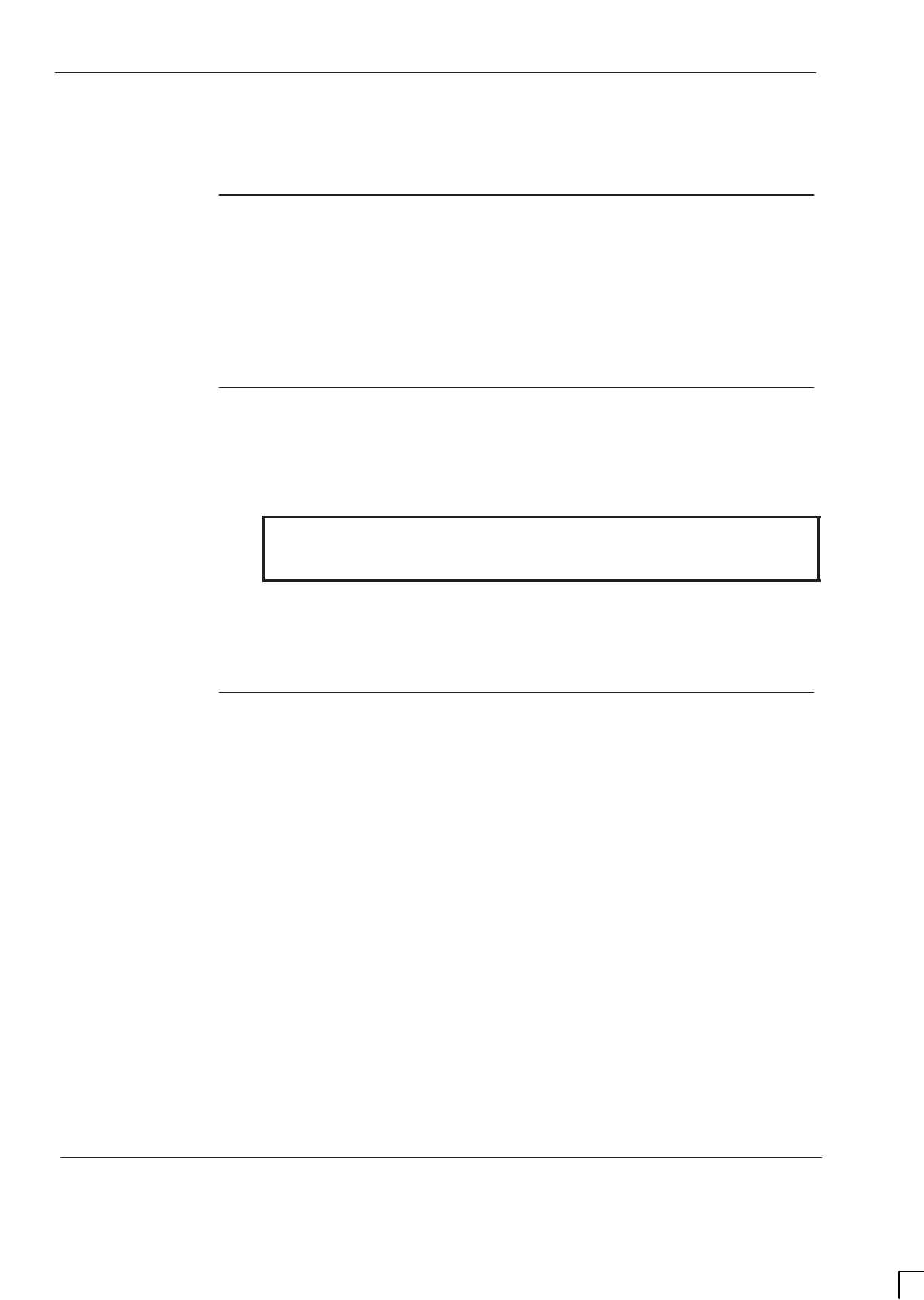
GSM-204-020
General information
31st Oct 01
2
Service Manual: Horizon
macro
outdoor
CONTROLLED INTRODUCTION
68P02902W12-A
General information
Important
notice
If this manual was obtained when attending a Motorola training course, it will not
be updated or amended by Motorola. It is intended for TRAINING PURPOSES
ONLY. If it was supplied under normal operational circumstances, to support a
major software release, then corrections will be supplied automatically by
Motorola in the form of General Manual Revisions (GMRs).
Purpose
Motorola cellular communications manuals are intended to instruct and assist
personnel in the operation, installation and maintenance of the Motorola cellular
infrastructure equipment and ancillary devices. It is recommended that all
personnel engaged in such activities be properly trained by Motorola.
WARNING Failure to comply with Motorola’s operation, installation
and maintenance instructions may, in exceptional
circumstances, lead to serious injury or death.
These manuals are not intended to replace the system and equipment training
offered by Motorola, although they can be used to supplement and enhance the
knowledge gained through such training.
About this
manual
The manual contains: technical description of the hardware elements,
installation and configuration information, repair procedures and parts lists for
the Horizon
macro
outdoor equipment in Motorola GSM850, GSM/EGSM900,
DCS1800 and PCS1900 systems.
The objectives are to help the reader:
Gain an overview of the equipment and interconnection of components.
Understand the function and operation of all components.
Recognize configurations, and equivalent module functions to M-Cell
6
(a
previous BTS type, interchangeable with Horizon
macro
).
Be aware of the warnings (potential for harm to people) and cautions
(potential for harm to equipment) to be observed when working on the
equipment.
Understand how to install and commission the equipment.
Understand how to inspect, maintain, and repair the equipment.
Have a clear ready reference for all dedicated information in one manual.
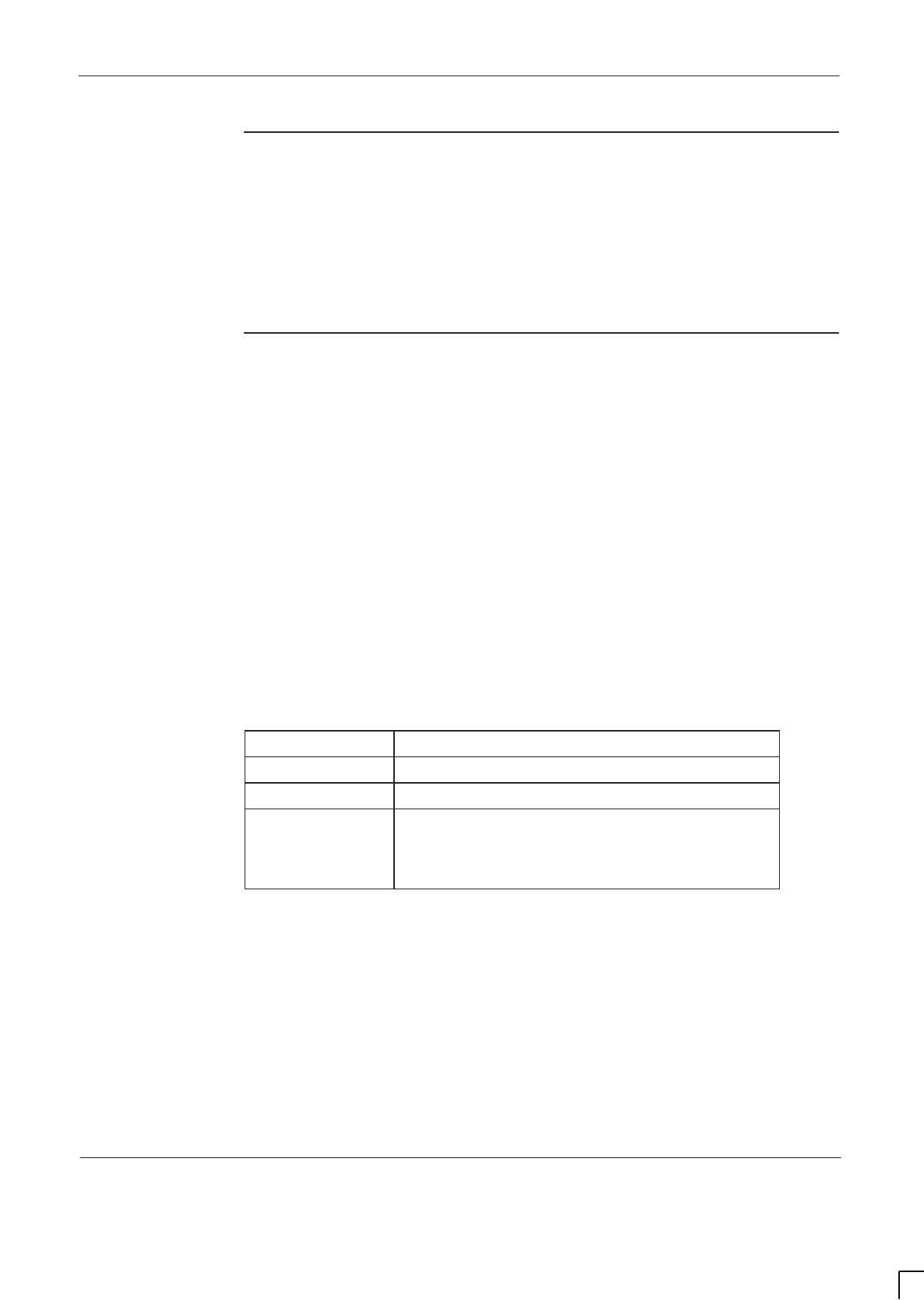
GSM-204-020 General information
31st Oct 01
Service Manual: Horizon
macro
outdoor
68P02902W12-A
CONTROLLED INTRODUCTION
3
Cross
references
Throughout this manual, cross references are made to the chapter numbers and
section names. The section name cross references are printed bold in text.
This manual is divided into uniquely identified and numbered chapters that, in
turn, are divided into sections. Sections are not numbered, but are individually
named at the top of each page, and are listed in the table of contents.
Text
conventions
The following conventions are used in the Motorola cellular infrastructure
manuals to represent keyboard input text, screen output text and special key
sequences.
Input
Characters typed in at the keyboard are shown like
this.
Output
Messages, prompts, file listings, directories, utilities, and
environmental variables that appear on the screen are shown like
this.
Special key sequences
Special key sequences are represented as follows:
CTRL–c Press the Control and c keys at the same time.
ALT–f Press the Alt and f keys at the same time.
|Press the pipe symbol key.
CR or RETURN Press the Return (Enter) key. The Return key is
identified with the ↵ symbol on both the PC and
the Sun keyboards. The keyboard Return key
may also be identified with the word Return.
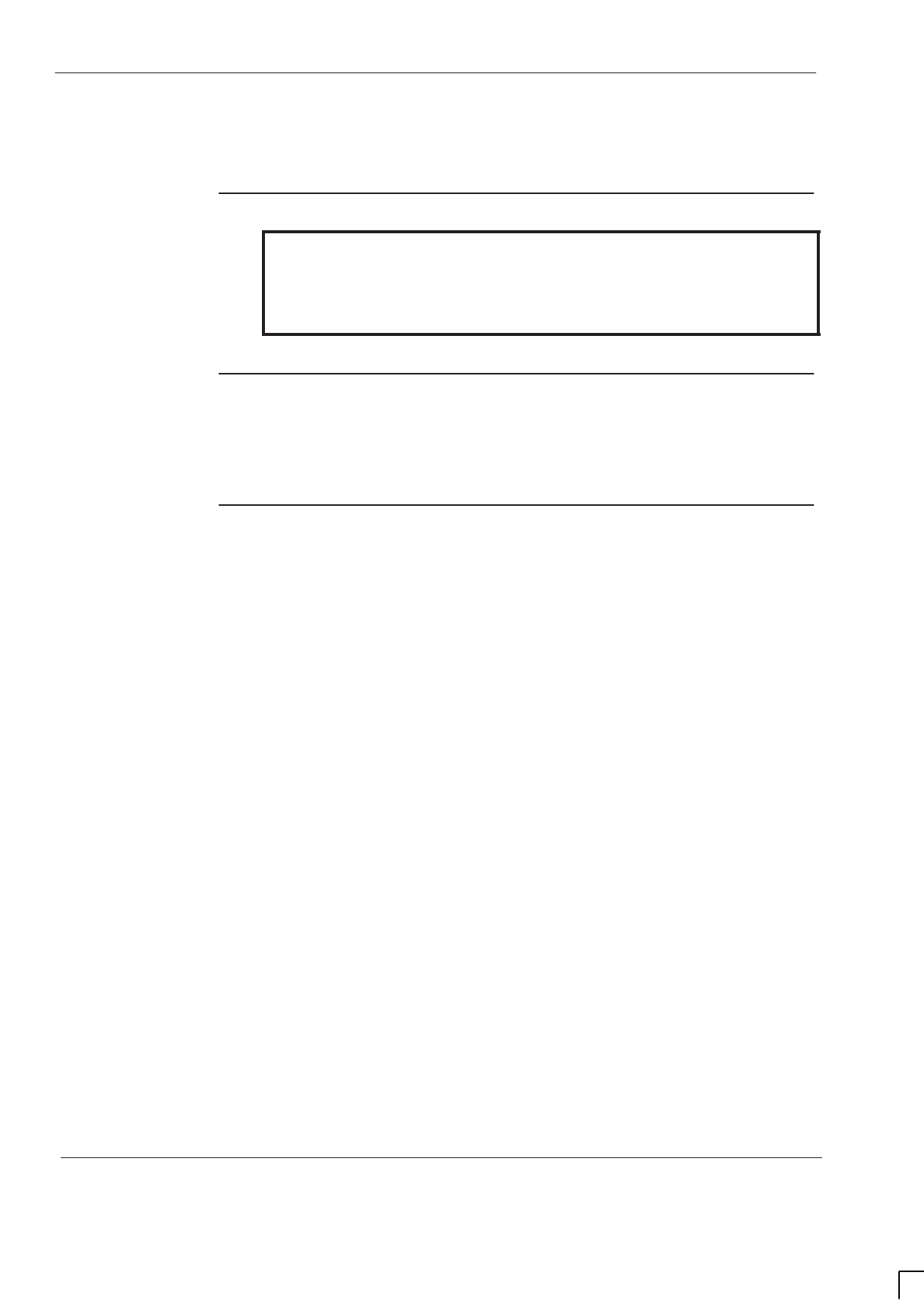
GSM-204-020
First aid in case of electric shock
31st Oct 01
4
Service Manual: Horizon
macro
outdoor
CONTROLLED INTRODUCTION
68P02902W12-A
First aid in case of electric shock
Warning
WARNING Do not touch the victim with your bare hands until the
electric circuit is broken.
Switch off. If this is not possible, protect yourself with
dry insulating material and pull or push the victim clear of
the conductor.
Artificial
respiration
In the event of an electric shock it may be necessary to carry out artificial
respiration. Send for medical assistance immediately.
Burns treatment
If the patient is also suffering from burns, then, without hindrance to artificial
respiration, carry out the following:
1. Do not attempt to remove clothing adhering to the burn.
2. If help is available, or as soon as artificial respiration is no longer required,
cover the wound with a dry dressing.
3. Do not apply oil or grease in any form.
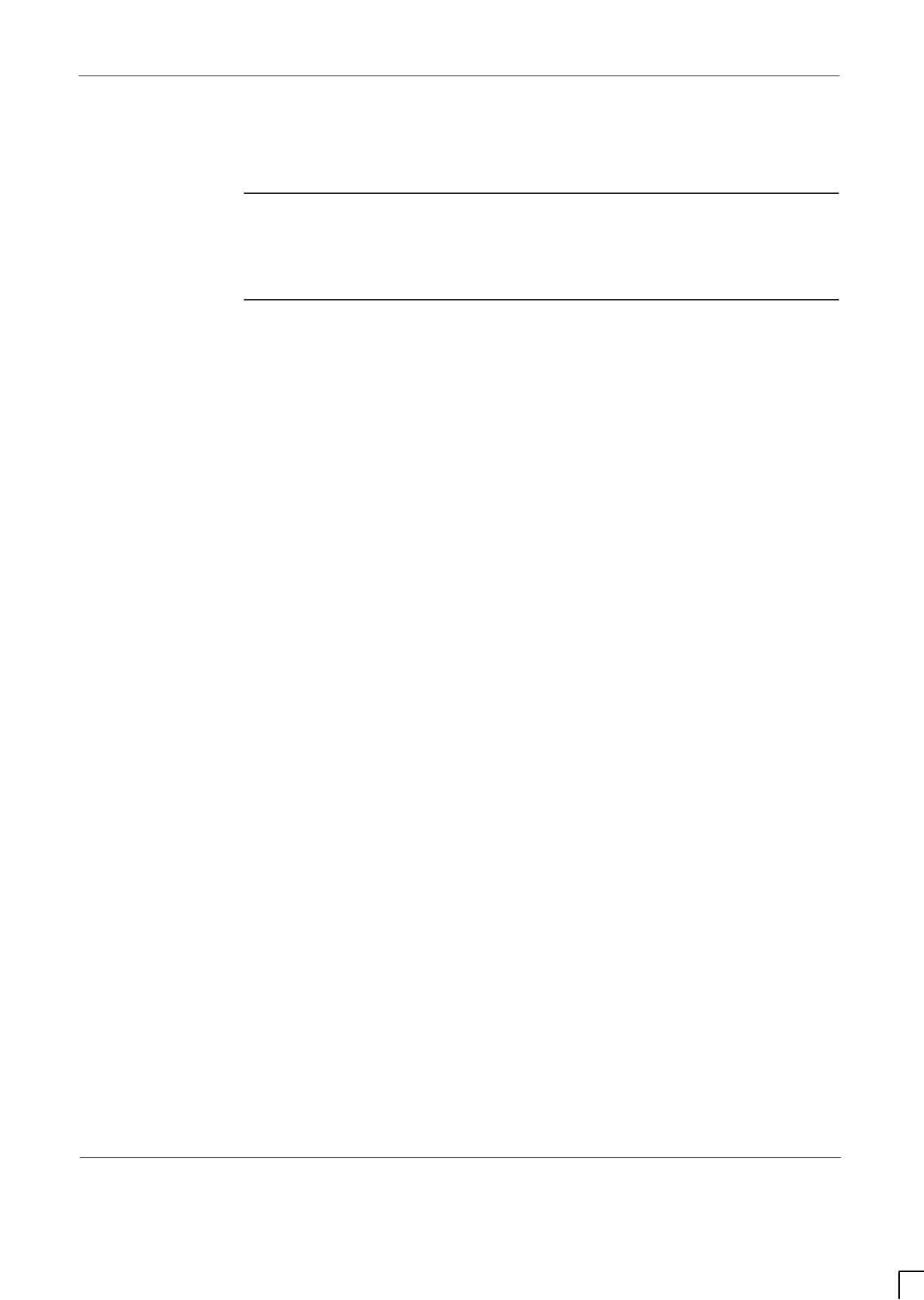
GSM-204-020 Reporting safety issues
31st Oct 01
Service Manual: Horizon
macro
outdoor
68P02902W12-A
CONTROLLED INTRODUCTION
5
Reporting safety issues
Introduction
Whenever a safety issue arises, carry out the following procedure in all
instances. Ensure that all site personnel are familiar with this procedure.
Procedure
Whenever a safety issue arises:
1. Make the equipment concerned safe, for example, by removing power.
2. Make no further attempt to tamper with the equipment.
3. Report the problem directly to the Customer Network Resolution Centre,
Swindon +44 (0)1793 565444 or China +86 10 68437733 (telephone) and
follow up with a written report by fax, Swindon +44 (0)1793 430987 or
China +86 10 68423633 (fax).
4. Collect evidence from the equipment under the guidance of the Customer
Network Resolution Centre.
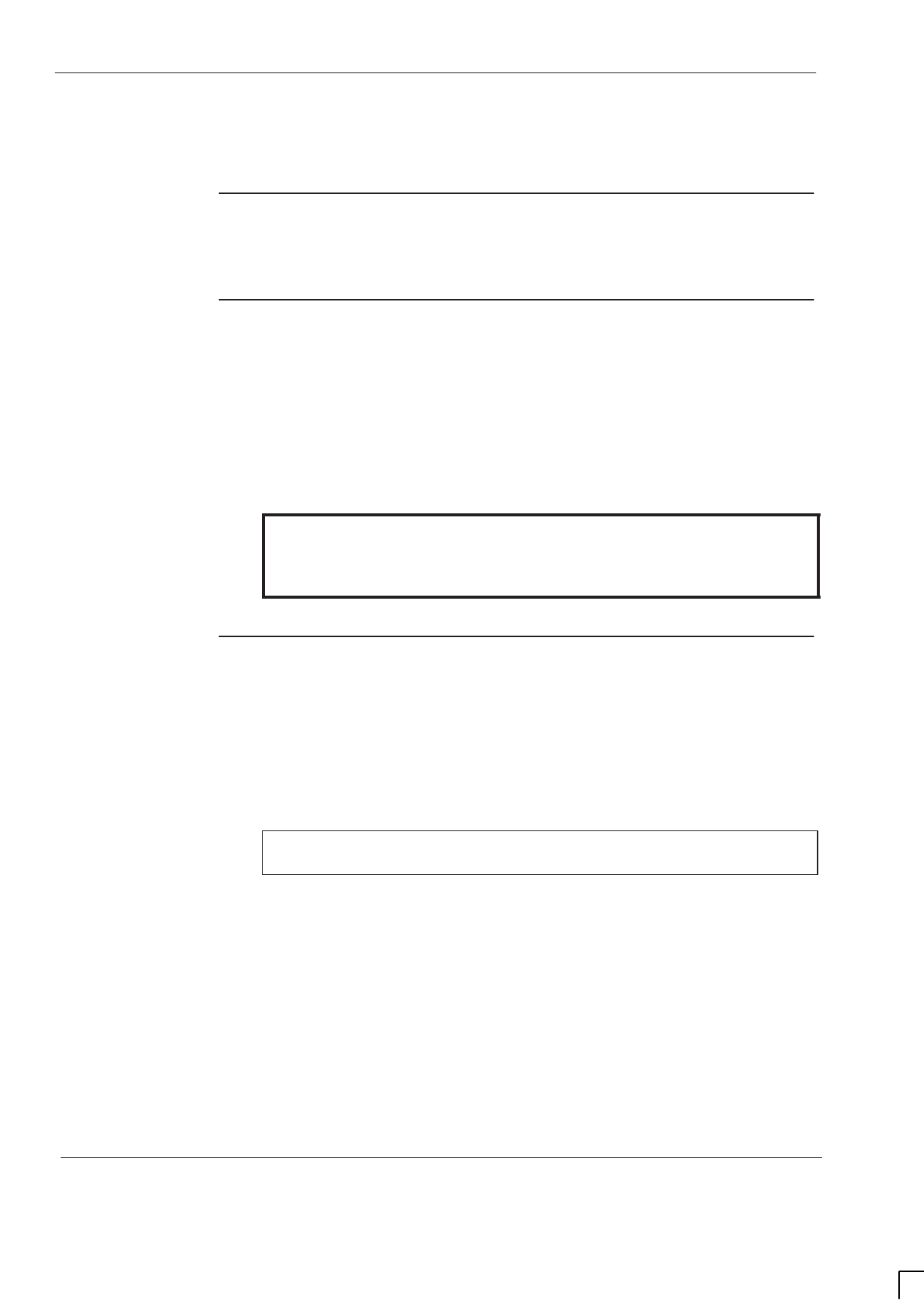
GSM-204-020
Warnings and cautions
31st Oct 01
6
Service Manual: Horizon
macro
outdoor
CONTROLLED INTRODUCTION
68P02902W12-A
Warnings and cautions
Introduction
The following describes how warnings and cautions are used in this manual and
in all manuals of this Motorola manual set.
Warnings
Definition of Warning
A warning is used to alert the reader to possible hazards that could cause loss
of life, physical injury, or ill health. This includes hazards introduced during
maintenance, for example, the use of adhesives and solvents, as well as those
inherent in the equipment.
Example and format
WARNING Do not look directly into fibre optic cables or data in/out
connectors. Laser radiation can come from either the data
in/out connectors or unterminated fibre optic cables
connected to data in/out connectors.
Cautions
Definition of Warning
A caution means that there is a possibility of damage to systems, software or
individual items of equipment within a system. However, this presents no danger
to personnel.
Example and format
CAUTION Do not use test equipment that is beyond its calibration
due date when testing Motorola base stations.
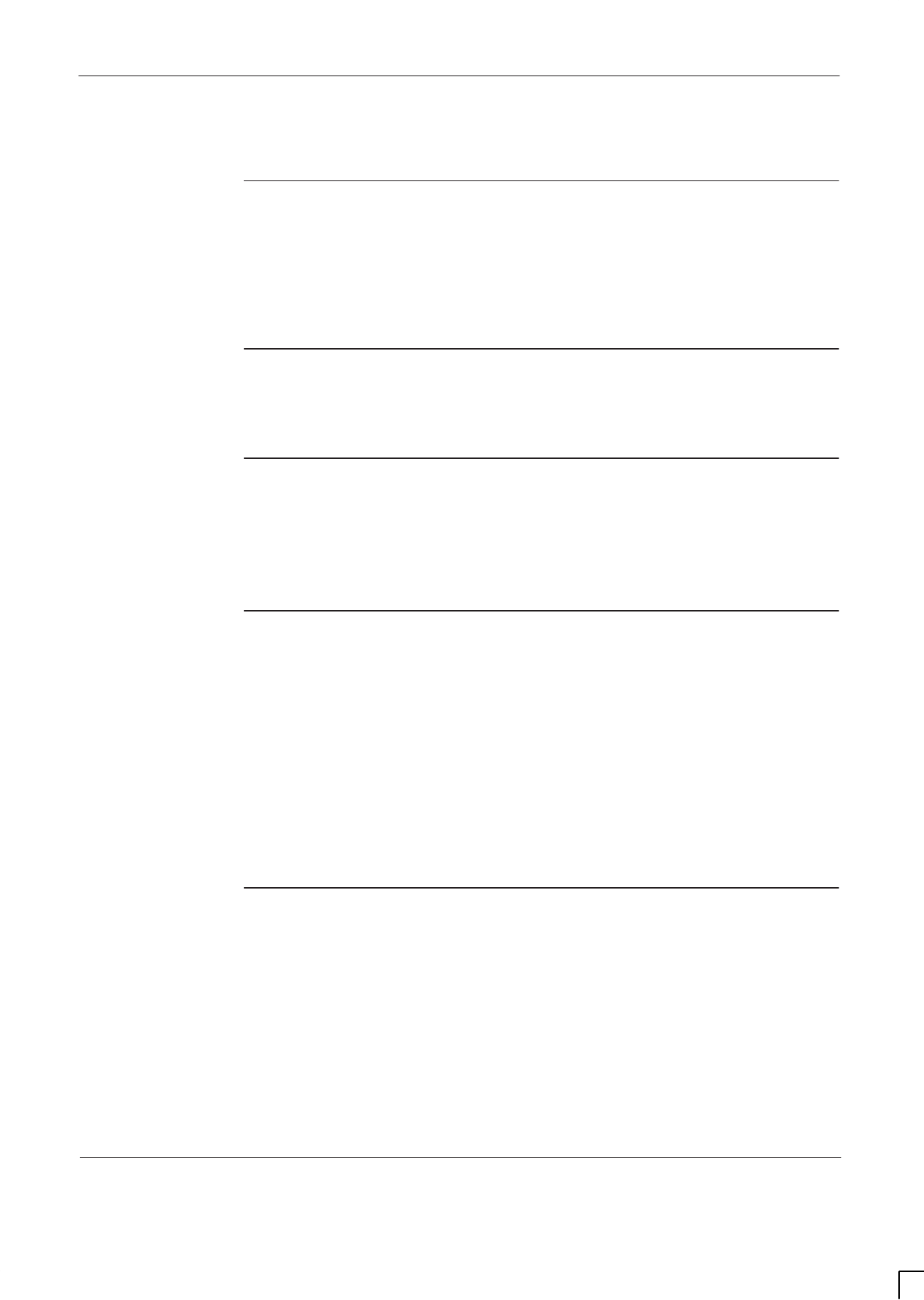
GSM-204-020 General warnings
31st Oct 01
Service Manual: Horizon
macro
outdoor
68P02902W12-A
CONTROLLED INTRODUCTION
7
General warnings
Introduction
Observe the following warnings during all phases of operation, installation and
maintenance of the equipment described in the Motorola manuals. Failure to
comply with these warnings, or with specific warnings elsewhere in the Motorola
manuals, violates safety standards of design, manufacture and intended use of
the equipment. Motorola assumes no liability for the customer’s failure to comply
with these requirements.
Warning labels
Personnel working with or operating Motorola equipment must comply with any
warning labels fitted to the equipment. Warning labels must not be removed,
painted over or obscured in any way.
Specific
warnings
Warnings particularly applicable to the equipment are positioned on the
equipment and within the text of this manual. These must be observed by all
personnel at all times when working with the equipment, as must any other
warnings given in text, on the illustrations and on the equipment.
High voltage
Certain Motorola equipment operates from a dangerous high voltage of 230 V
ac single phase or 415 V ac three phase supply which is potentially lethal.
Therefore, the areas where the ac supply power is present must not be
approached until the warnings and cautions in the text and on the equipment
have been complied with.
To achieve isolation of the equipment from the ac supply, the ac input isolator
must be set to off and locked.
Within the United Kingdom (UK) regard must be paid to the requirements of the
Electricity at Work Regulations 1989. There may also be specific country
legislation which need to be complied with, depending on where the equipment
is used.
RF radiation
High RF potentials and electromagnetic fields are present in the base station
equipment when in operation. Ensure that all transmitters are switched off when
any antenna connections have to be changed. Do not key transmitters
connected to unterminated cavities or feeders.
Refer to the following standards:
ANSI IEEE C95.1-1991,
IEEE Standard for Safety Levels with Respect to
Human Exposure to Radio Frequency Electromagnetic Fields, 3 kHz to
300 GHz
.
CENELEC 95 ENV 50166-2,
Human Exposure to Electromagnetic Fields
High Frequency (10 kHz to 300 GHz)
.
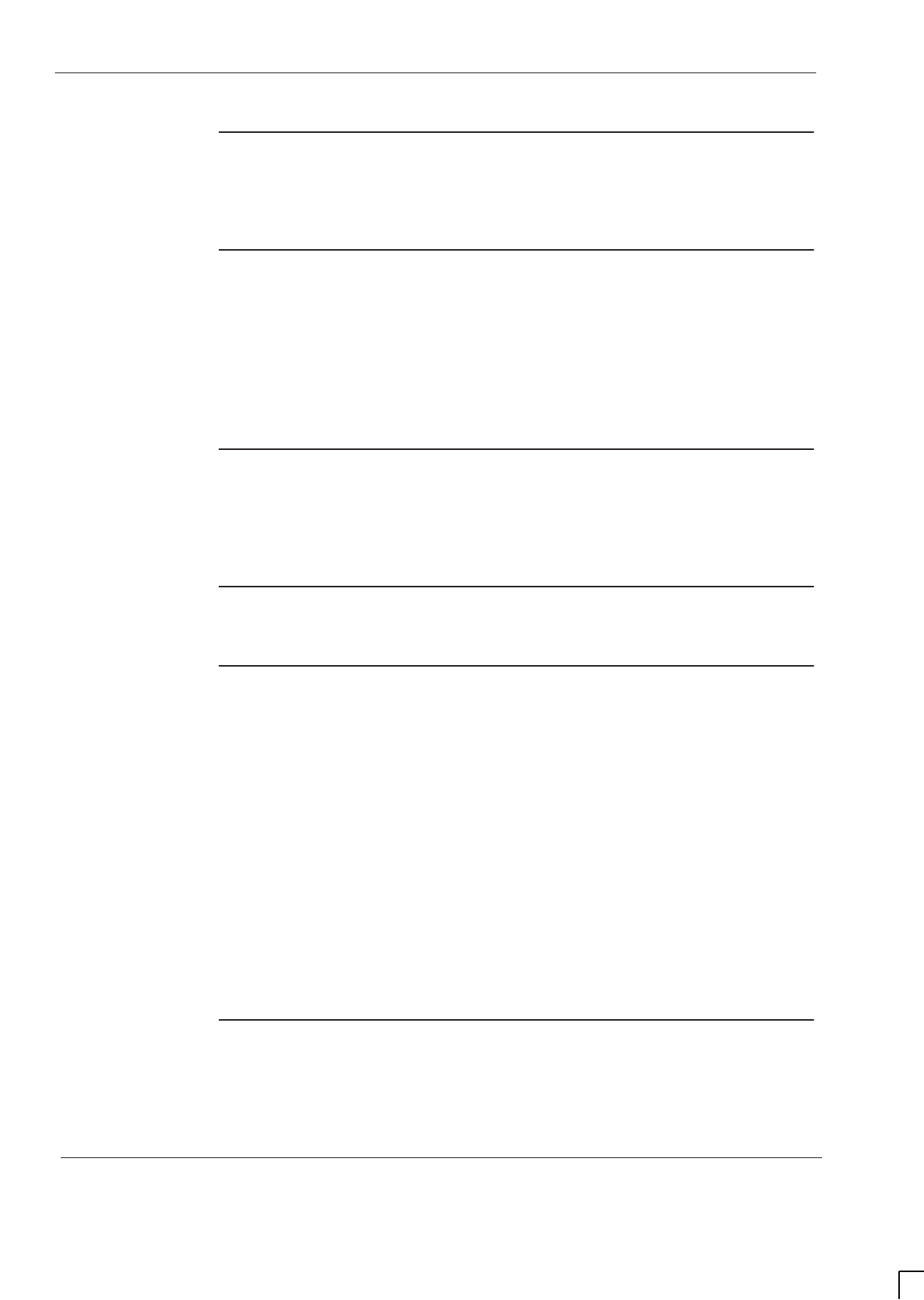
GSM-204-020
General warnings
31st Oct 01
8
Service Manual: Horizon
macro
outdoor
CONTROLLED INTRODUCTION
68P02902W12-A
Laser radiation
Do not look directly into fibre optic cables or optical data in/out connectors.
Laser radiation can come from either the data in/out connectors or unterminated
fibre optic cables connected to data in/out connectors.
Lifting
equipment
When dismantling heavy assemblies, or removing or replacing equipment, the
competent responsible person must ensure that adequate lifting facilities are
available. Where provided, lifting frames must be used for these operations.
When equipments have to be manhandled, reference must be made to the
Manual Handling of Loads Regulations 1992 (UK) or to the relevant manual
handling of loads legislation for the country in which the equipment is used.
Do not ... ... substitute parts or modify equipment.
Because of the danger of introducing additional hazards, do not install substitute
parts or perform any unauthorized modification of equipment. Contact Motorola
if in doubt to ensure that safety features are maintained.
Battery supplies
Do not wear earth straps when working with standby battery supplies.
Toxic material
Certain equipment may incorporate components containing the highly toxic
material Beryllium or its oxide Beryllia or both. These materials are especially
hazardous if:
Beryllium materials are absorbed into the body tissues through the skin,
mouth, or a wound.
The dust created by breakage of Beryllia is inhaled.
Toxic fumes are inhaled from Beryllium or Beryllia involved in a fire.
Beryllium warning labels are fitted to equipment incorporating Beryllium or
Beryllium Oxide. Observe all safety instructions given on warning labels.
Beryllium Oxide is used within some components as an electrical insulator.
Captive within the component it presents no health risk whatsoever. However, if
the component should be broken open or burnt, the Beryllium Oxide, in the form
of dust or fumes, could be released, with the potential for harm.
Lithium
batteries
Lithium batteries, if subjected to mistreatment, may burst and ignite. Defective
lithium batteries must not be removed or replaced. Any boards containing
defective lithium batteries must be returned to Motorola for repair.
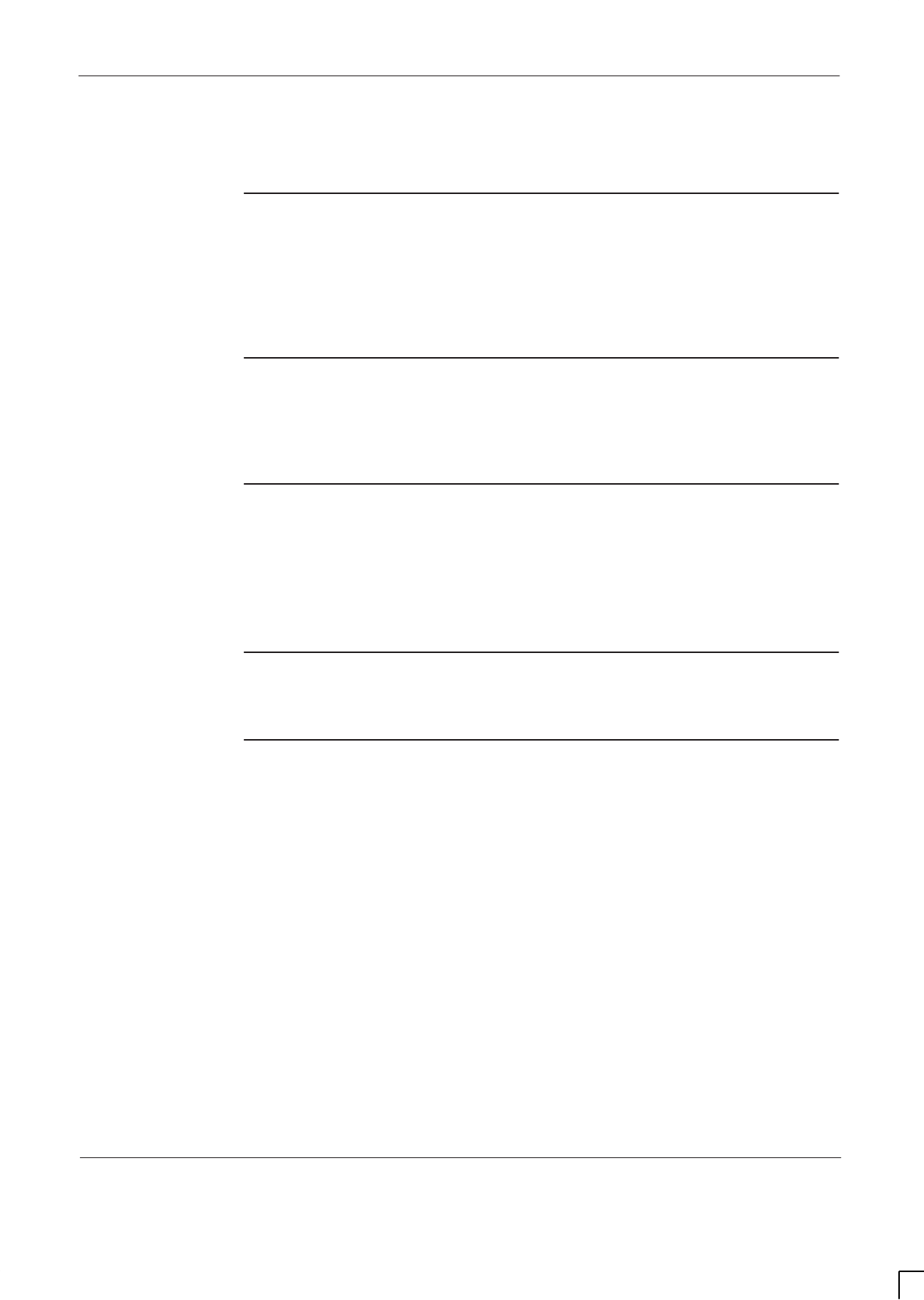
GSM-204-020 General cautions
31st Oct 01
Service Manual: Horizon
macro
outdoor
68P02902W12-A
CONTROLLED INTRODUCTION
9
General cautions
Introduction
Observe the following cautions during operation, installation and maintenance of
the equipment described in the Motorola manuals. Failure to comply with these
cautions or with specific cautions elsewhere in the Motorola manuals may result
in damage to the equipment. Motorola assumes no liability for the customer’s
failure to comply with these requirements.
Caution labels
Personnel working with or operating Motorola equipment must comply with any
caution labels fitted to the equipment. Caution labels must not be removed,
painted over or obscured in any way.
Specific
cautions
Cautions particularly applicable to the equipment are positioned within the text
of this manual. These must be observed by all personnel at all times when
working with the equipment, as must any other cautions given in text, on the
illustrations and on the equipment.
Fibre optics
The bending radius of all fibre optic cables must not be less than 30 mm.
Static discharge
Motorola equipment contains CMOS devices that are vulnerable to static
discharge. Although the damage caused by static discharge may not be
immediately apparent, CMOS devices may be damaged in the long term due to
static discharge caused by mishandling. Wear an approved earth strap when
adjusting or handling digital boards.
See Devices sensitive to static for further information.
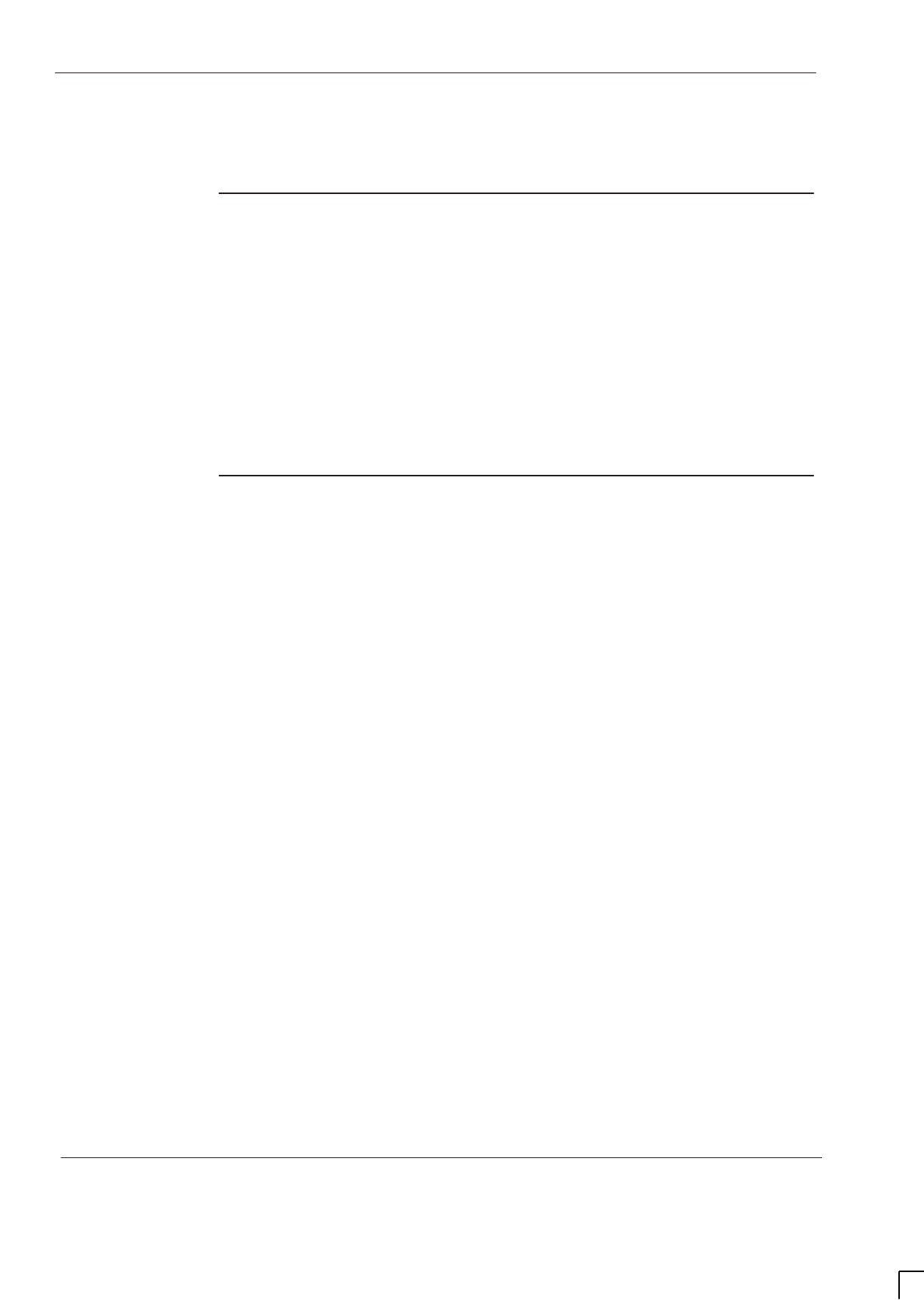
GSM-204-020
Devices sensitive to static
31st Oct 01
10
Service Manual: Horizon
macro
outdoor
CONTROLLED INTRODUCTION
68P02902W12-A
Devices sensitive to static
Introduction
Certain metal oxide semiconductor (MOS) devices embody in their design a thin
layer of insulation that is susceptible to damage from electrostatic charge. Such
a charge applied to the leads of the device could cause irreparable damage.
These charges can be built up on nylon overalls, by friction, by pushing the
hands into high insulation packing material or by use of unearthed soldering
irons.
MOS devices are normally despatched from the manufacturers with the leads
shorted together, for example, by metal foil eyelets, wire strapping, or by
inserting the leads into conductive plastic foam. Provided the leads are shorted
it is safe to handle the device.
Special
handling
techniques
In the event of one of these devices having to be replaced, observe the
following precautions when handling the replacement:
Always wear an earth strap which must be connected to the electrostatic
point (ESP) on the equipment.
Leave the short circuit on the leads until the last moment. It may be
necessary to replace the conductive foam by a piece of wire to enable the
device to be fitted.
Do not wear outer clothing made of nylon or similar man made material. A
cotton overall is preferable.
If possible work on an earthed metal surface. Wipe insulated plastic work
surfaces with an anti-static cloth before starting the operation.
All metal tools should be used and when not in use they should be placed
on an earthed surface.
Take care when removing components connected to electrostatic sensitive
devices. These components may be providing protection to the device.
When mounted onto printed circuit boards (PCBs), MOS devices are normally
less susceptible to electrostatic damage. However PCBs should be handled with
care, preferably by their edges and not by their tracks and pins, they should be
transferred directly from their packing to the equipment (or the other way
around) and never left exposed on the workbench.
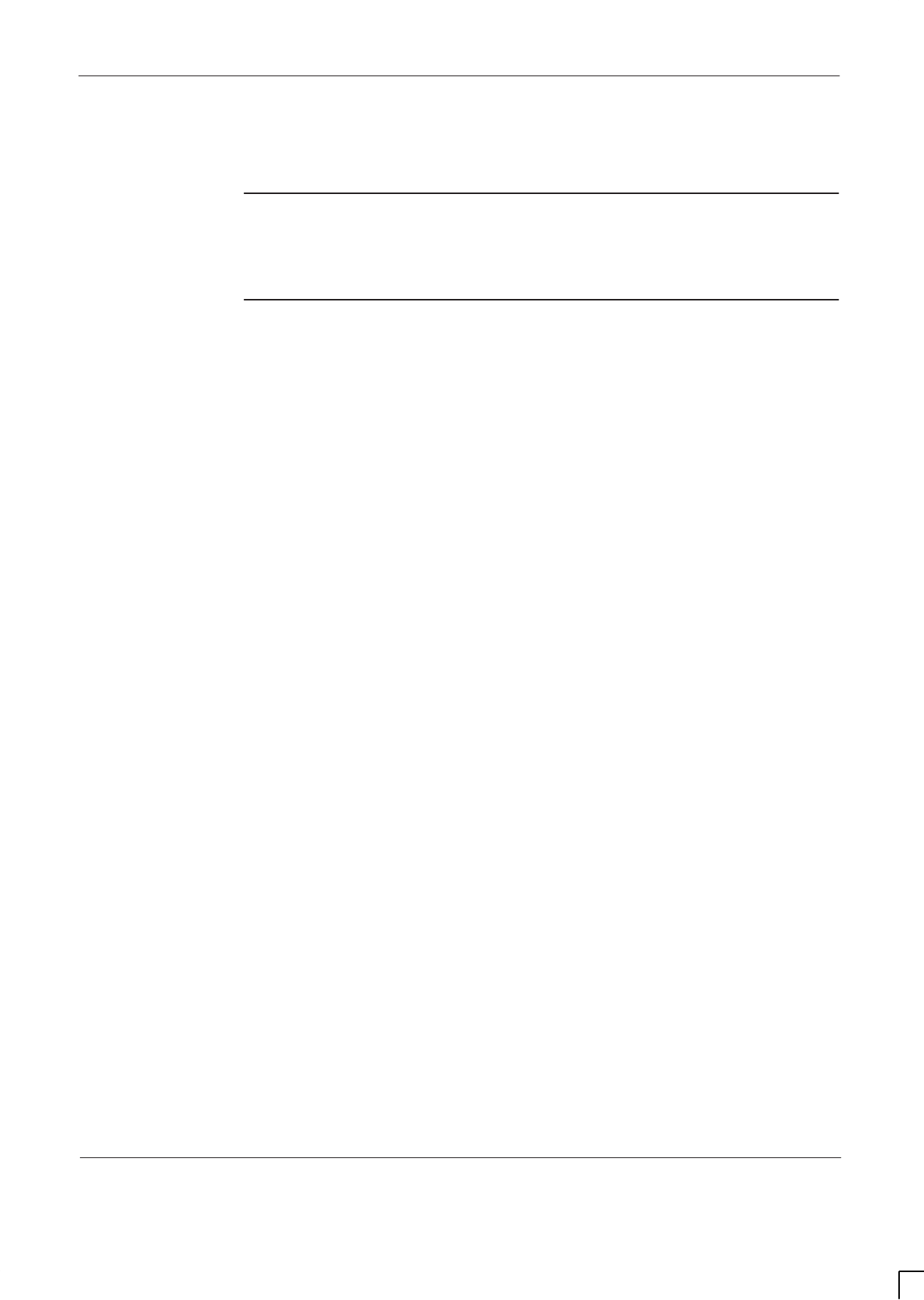
GSM-204-020 Motorola GSM manual set
31st Oct 01
Service Manual: Horizon
macro
outdoor
68P02902W12-A
CONTROLLED INTRODUCTION
11
Motorola GSM manual set
Introduction
The following manuals provide the information needed to operate, install and
maintain the Motorola equipment.
Generic GSM
manuals
The following are the generic manuals in the GSM manual set, these manuals
are release dependent:
Classification
number Name Order number
GSM-100-101 System Information: General 68P02901W01. . . . . . . . . . . . . . . . . . .
GSM-100-201 Operating Information: GSM System Operation 68P02901W14. . .
GSM-100-202 Operating Information: OMC-R System
Administration 68P02901W19. . . . . . . . . . . . . . . . . . . . . . . . . . . . . . .
GSM-100-313 Technical Description: OMC-R Database Schema 68P02901W34.
GSM-100-320 Technical Description: BSS Implementation 68P02901W36. . . . . . .
GSM-100-321 Technical Description: BSS Command Reference 68P02901W23.
GSM-100-403 Installation & Configuration: GSM System
Configuration 68P02901W17. . . . . . . . . . . . . . . . . . . . . . . . . . . . . . . .
GSM-100-423 Installation & Configuration: BSS Optimization 68P02901W43. . . .
GSM-100-413 Installation & Configuration: OMC-R Clean Install 68P02901W47. .
GSM-100-501 Maintenance Information: Alarm Handling at
the OMC-R 68P02901W26. . . . . . . . . . . . . . . . . . . . . . . . . . . . . . . . . .
GSM-100-520 Maintenance Information: BSS Timers 68P02901W58. . . . . . . . . . .
GSM-100-521 Maintenance Information: Device State Transitions 68P02901W57
GSM-100-523 Maintenance Information: BSS Field
Troubleshooting 68P02901W51. . . . . . . . . . . . . . . . . . . . . . . . . . . . . .
GSM-100-503 Maintenance Information: GSM Statistics
Application 68P02901W56. . . . . . . . . . . . . . . . . . . . . . . . . . . . . . . . . .
GSM-100-721 Software Release Notes: BSS/RXCDR 68P02901W72. . . . . . . . . .
GSM-100-712 Software Release Notes: OMC-R System 68P02901W74. . . . . . . .
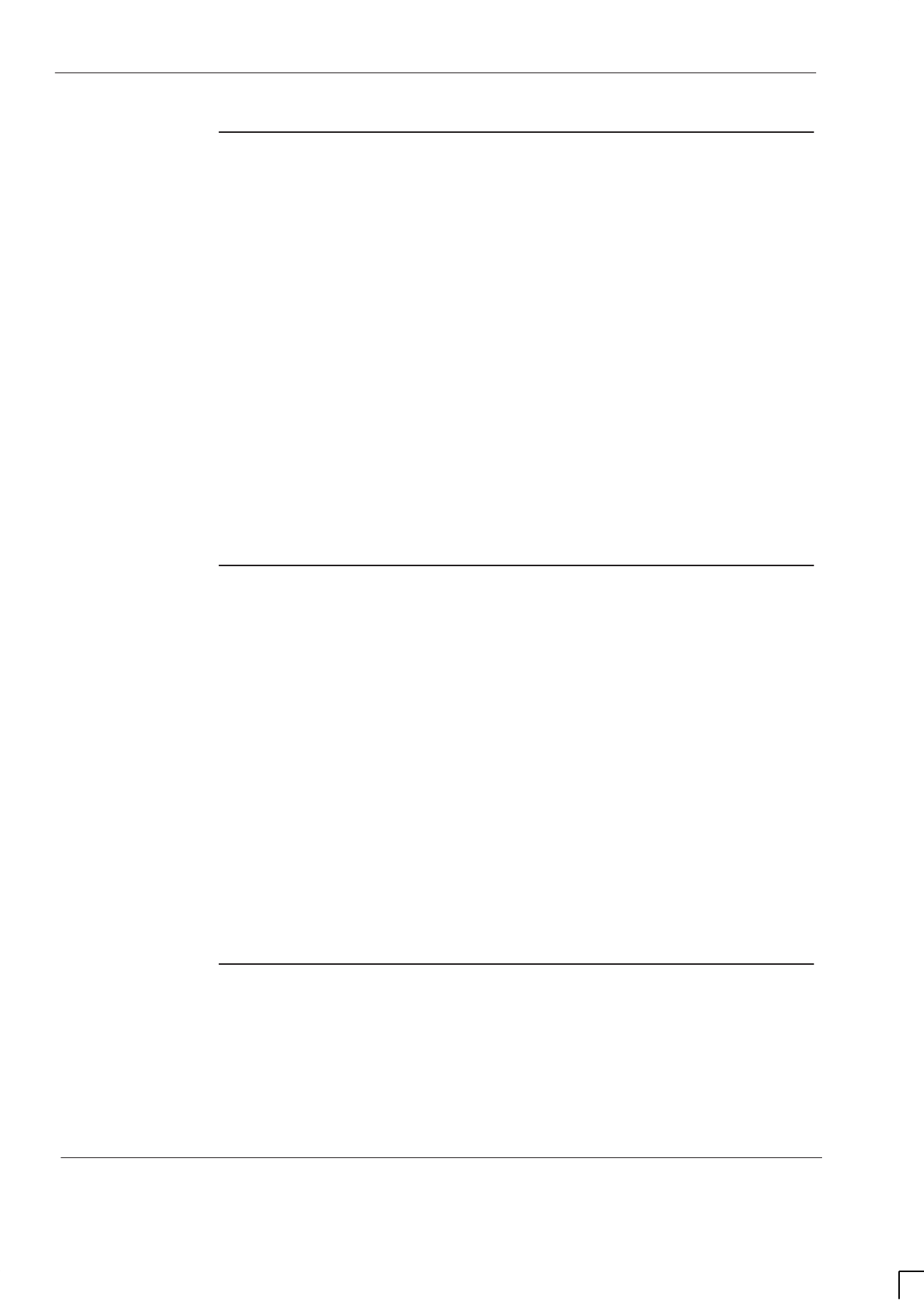
GSM-204-020
Motorola GSM manual set
31st Oct 01
12
Service Manual: Horizon
macro
outdoor
CONTROLLED INTRODUCTION
68P02902W12-A
Related GSM
manuals
The following are related Motorola GSM manuals:
Classification
number Name Order number
GSM-001-103 System Information: BSS Equipment Planning 68P02900W21. . . .
GSM-002-103 System Information: DataGen 68P02900W22. . . . . . . . . . . . . . . . . .
GSM-002-703 Software Release Notes: DataGen 68P02900W76. . . . . . . . . . . . . .
GSM-005-103 System Information: GSM Advance Operational
Impact 68P02900W25. . . . . . . . . . . . . . . . . . . . . . . . . . . . . . . . . . . . . .
GSM-008-103 System Information: Network Health Analyst 68P02900W36. . . . . .
GSM-008-703 Software Release Notes: Network Health Analyst 68P02900W77.
GSM-TOOLS-001 System Information: Cell Optimization (COP) 68P02900W90. . . . .
GSM-TOOLS-002 System Information: Motorola Analysis and
Reporting System (MARS) 68P02900W94. . . . . . . . . . . . . . . . . . . . .
GSM-TOOLS-701 Software Release Notes: Cell Optimization (COP) 68P02900W69.
GSM-TOOLS-702 Software Release Notes: Motorola Analysis and
Reporting System (MARS) 68P02900W68. . . . . . . . . . . . . . . . . . . . .
GSM-006-202 Operating Information: OMC-R System
Administration (OSI) 68P02901W10. . . . . . . . . . . . . . . . . . . . . . . . . .
GSM-006-413 Installation & Configuration: OSI Clean Install 68P02901W39. . . . .
GSM-006-712 Software Release Notes: OMC-R OSI System 68P02901W70. . . .
Generic GPRS
manuals
The following are the generic manuals in the GPRS manual set, these manuals
are release dependent:
Classification
number Name Order number
GPRS-300-101 System Information: GPRS Overview 68P02903W01. . . . . . . . . . . .
GPRS-300-202 Operating Information: OMC-G System
Administration 68P02903W03. . . . . . . . . . . . . . . . . . . . . . . . . . . . . . .
GPRS-300-222 Operating Information: GSN System Administration 68P02903W37
GPRS-300-313 Technical Description: OMC-G Database Schema 68P02903W46.
GPRS-300-321 Technical Description: GSN Command Reference 68P02903W18.
GPRS-300-423 Installation & Configuration: GSN Clean Install 68P02903W47. . . .
GPRS-300-413 Installation & Configuration: OMC-G Clean Install 68P02903W04.
GPRS-300-501 Maintenance Information: Alarm Handling at
the OMC-G 68P02903W19. . . . . . . . . . . . . . . . . . . . . . . . . . . . . . . . . .
GPRS-300-503 Maintenance Information: GSN Statistics
Application 68P02903W20. . . . . . . . . . . . . . . . . . . . . . . . . . . . . . . . . .
GPRS-300-722 Software Release Notes: GSN System 68P02903W76. . . . . . . . . .
GPRS-300-712 Software Release Notes: OMC-G System 68P02903W70. . . . . . . .
Related GPRS
manuals
The following are related Motorola GPRS manuals:
Classification
number Name Order number
GPRS-001-103 System Information: GPRS Equipment Planning 68P02903W02. .
GPRS-005-103 System Information: GSN Advance Operational
Impact 68P02903W38. . . . . . . . . . . . . . . . . . . . . . . . . . . . . . . . . . . . . .
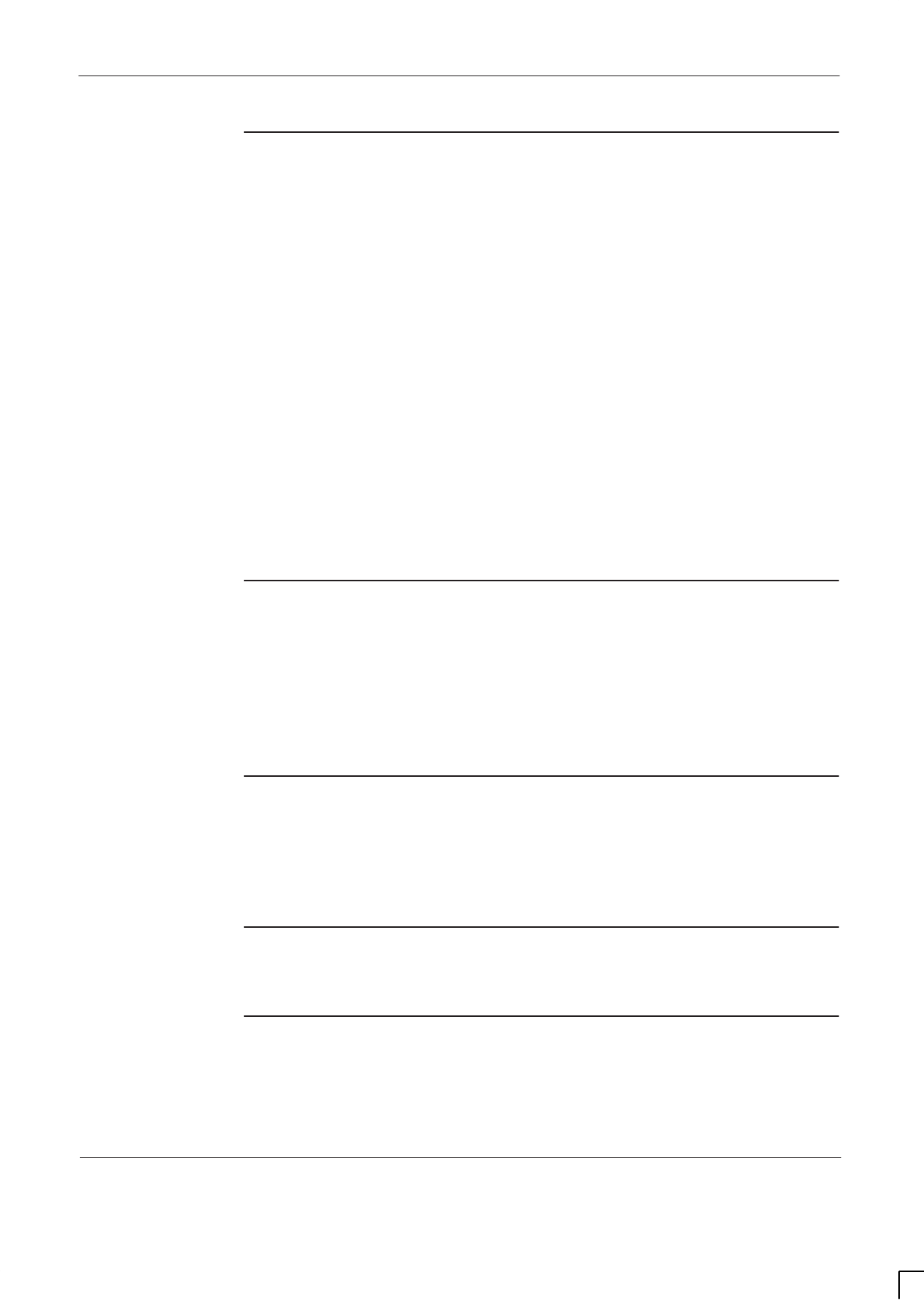
GSM-204-020 Motorola GSM manual set
31st Oct 01
Service Manual: Horizon
macro
outdoor
68P02902W12-A
CONTROLLED INTRODUCTION
13
BSS service
manuals
The following are the Motorola Base Station service manuals, these manuals
are not release dependent. The internal organization and makeup of service
manual sets may vary, they may consist of from one to four separate manuals,
but they can all be ordered using the overall catalogue number shown below:
Classification
number Name Order number
GSM-100-020 Service Manual: BTS 68P02901W37. . . . . . . . . . . . . . . . . . . . . . . . . .
GSM-100-030 Service Manual: BSC/RXCDR 68P02901W38. . . . . . . . . . . . . . . . . .
GSM-105-020 Service Manual: M-Cell
2
68P02901W75. . . . . . . . . . . . . . . . . . . . . . .
GSM-106-020 Service Manual: M-Cell
6
68P02901W85. . . . . . . . . . . . . . . . . . . . . . .
GSM-201-020 Service Manual: M-Cell
city
and M-Cell
city+
68P02901W95. . . . . . .
GSM-202-020 Service Manual: M-Cell
access
68P02901W65. . . . . . . . . . . . . . . . . .
GSM-203-020 Service Manual: Horizon
micro
68P02902W36. . . . . . . . . . . . . . . . . .
GSM-206-020 Service Manual: Horizon
compact
68P02902W15. . . . . . . . . . . . . . .
GSM-205-020 Service Manual: Horizon
macro
Indoor 68P02902W06. . . . . . . . . . .
GSM-204-020 Service Manual: Horizon
macro
Outdoor 68P02902W12. . . . . . . . . .
GSM-207-020 Service Manual: Horizon
office
68P02902W46. . . . . . . . . . . . . . . . . .
GSM-209-020 Service Manual: Horizon
micro2
Horizon
compact2
68P02902W61.
GSM-208-020 Service Manual: Horizon
macro
12 Carrier Outdoor 68P02902W66
GPRS service
manuals
The following are the Motorola GPRS service manuals, these manuals include
the Packet Control Unit (PCU) service manual which becomes part of the BSS
for GPRS:
GPRS-301-020 Service Manual:GPRS Support Nodes (GSN) 68P02903W05. . . . .
GPRS-302-020 Service Manual: Packet Control Unit (PCU) 68P02903W10. . . . . . .
Classification
number
The classification number is used to identify the type and level of a manual. For
example, manuals with the classification number GSM-100-2xx contain
operating information.
Order number
The Motorola 68P order (catalogue) number is used to order manuals.
Ordering
manuals
All orders for Motorola manuals must be placed with your Motorola Local Office
or Representative. Manuals are ordered using the order (catalogue) number.
Motorola manual sets may also be ordered on CD-ROM.
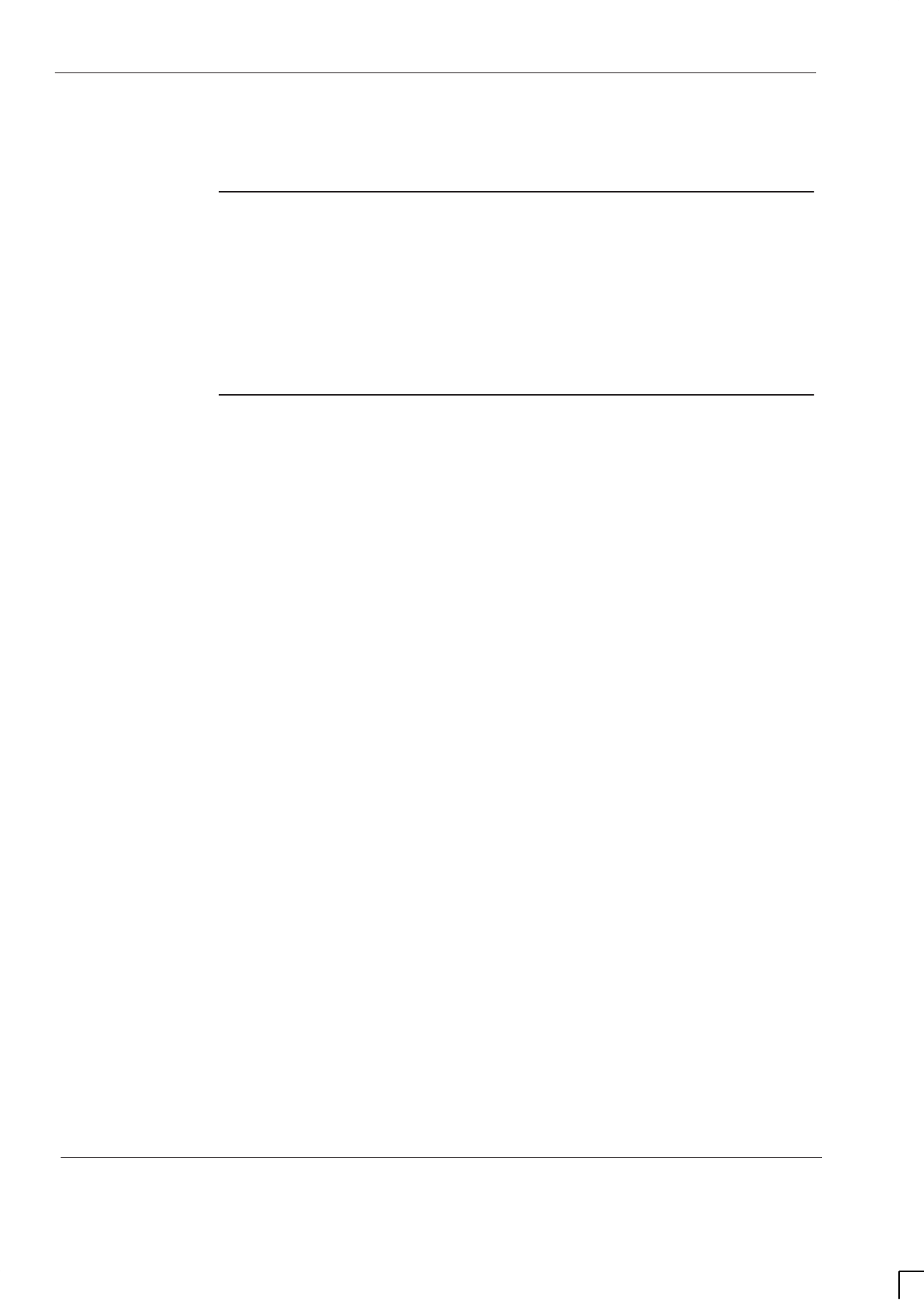
GSM-204-020
GMR amendment
31st Oct 01
14
Service Manual: Horizon
macro
outdoor
CONTROLLED INTRODUCTION
68P02902W12-A
GMR amendment
Introduction to
GMRs
Changes to a manual that occur after the printing date are incorporated into the
manual using General Manual Revisions (GMRs). GMRs are issued to correct
Motorola manuals as and when required. A GMR has the same identity as the
target manual. Each GMR is identified by a number in a sequence that starts at
01 for each manual at each issue. GMRs are issued in the form of loose leaf
pages, with a pink instruction sheet on the front.
GMR procedure
When a GMR is received, remove and replace pages in this manual, as detailed
on the GMR pink instruction sheet.
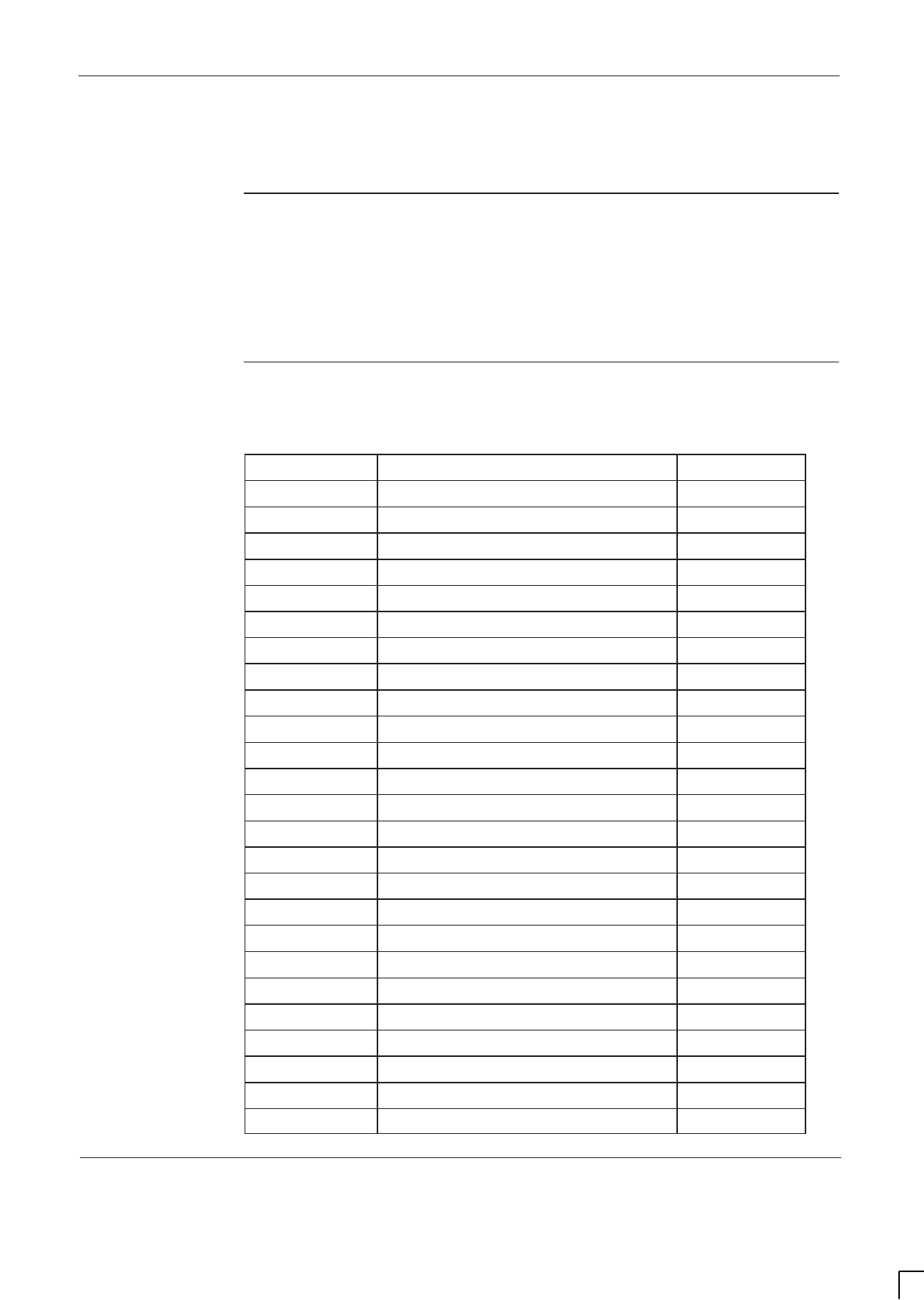
GSM-204-020 GMR amendment record
31st Oct 01
Service Manual: Horizon
macro
outdoor
68P02902W12-A
CONTROLLED INTRODUCTION
15
GMR amendment record
GMR
instructions
When a GMR is inserted in this manual, the amendment record below is
completed to record the GMR. Retain the pink instruction sheet that
accompanies each GMR and insert it in a suitable place in this manual for future
reference.
Amendment
record
Record the insertion of GMRs in this manual in the following table:
GMR number Incorporated by (signature) Date
01
02
03
04
05
06
07
08
09
10
11
12
13
14
15
16
17
18
19
20
21
22
23
24
25
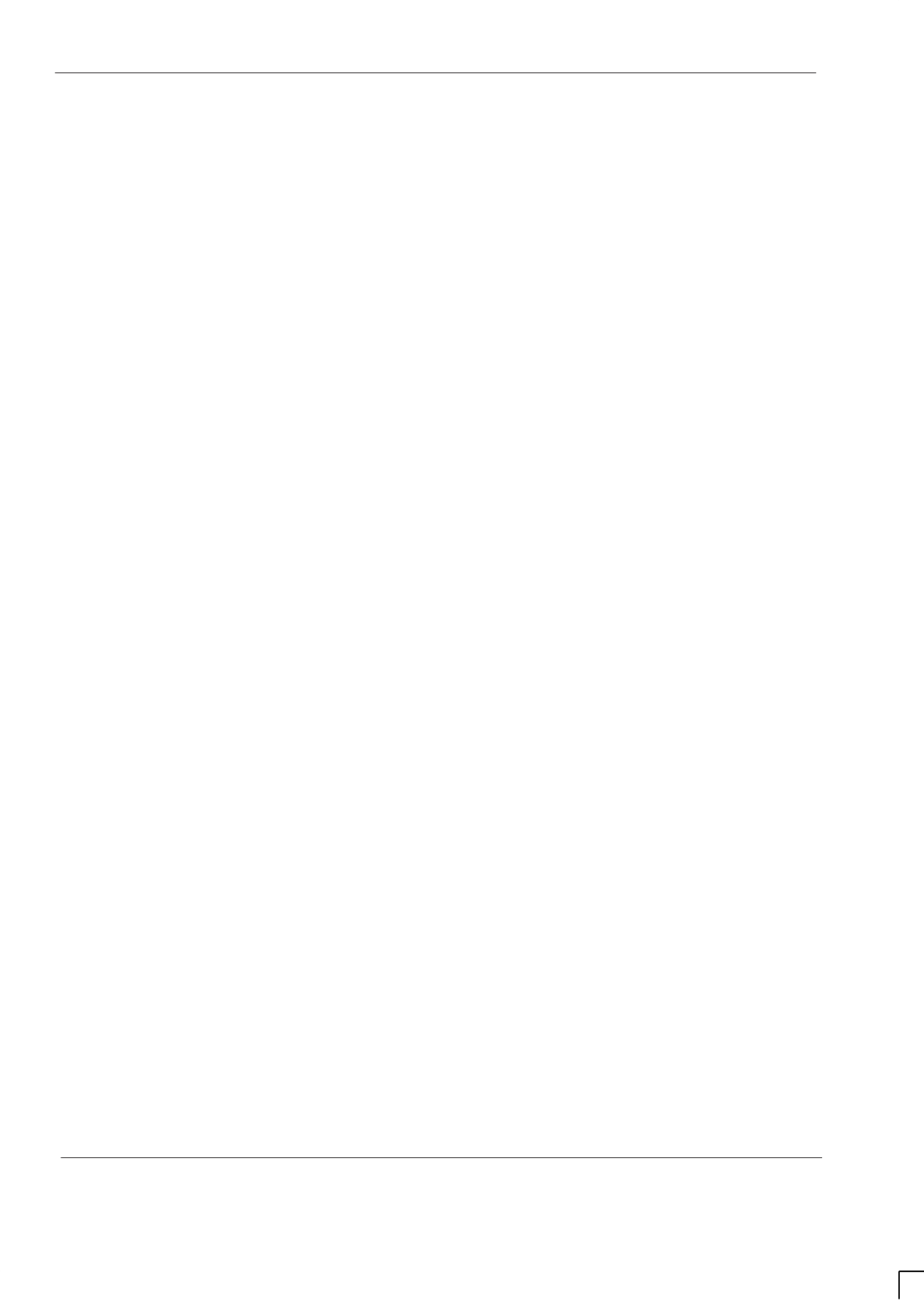
GSM-204-020
GMR amendment record
31st Oct 01
16
Service Manual: Horizon
macro
outdoor
CONTROLLED INTRODUCTION
68P02902W12-A

CHAPTER 2
CABINET STRUCTURE CHAPTER 3
THERMAL MANAGEMENT
SYSTEM
CHAPTER 4
CABINET POWER SUPPLIES CHAPTER 5
RF MODULES
CHAPTER 1
OVERVIEW AND
SPECIFICATIONS
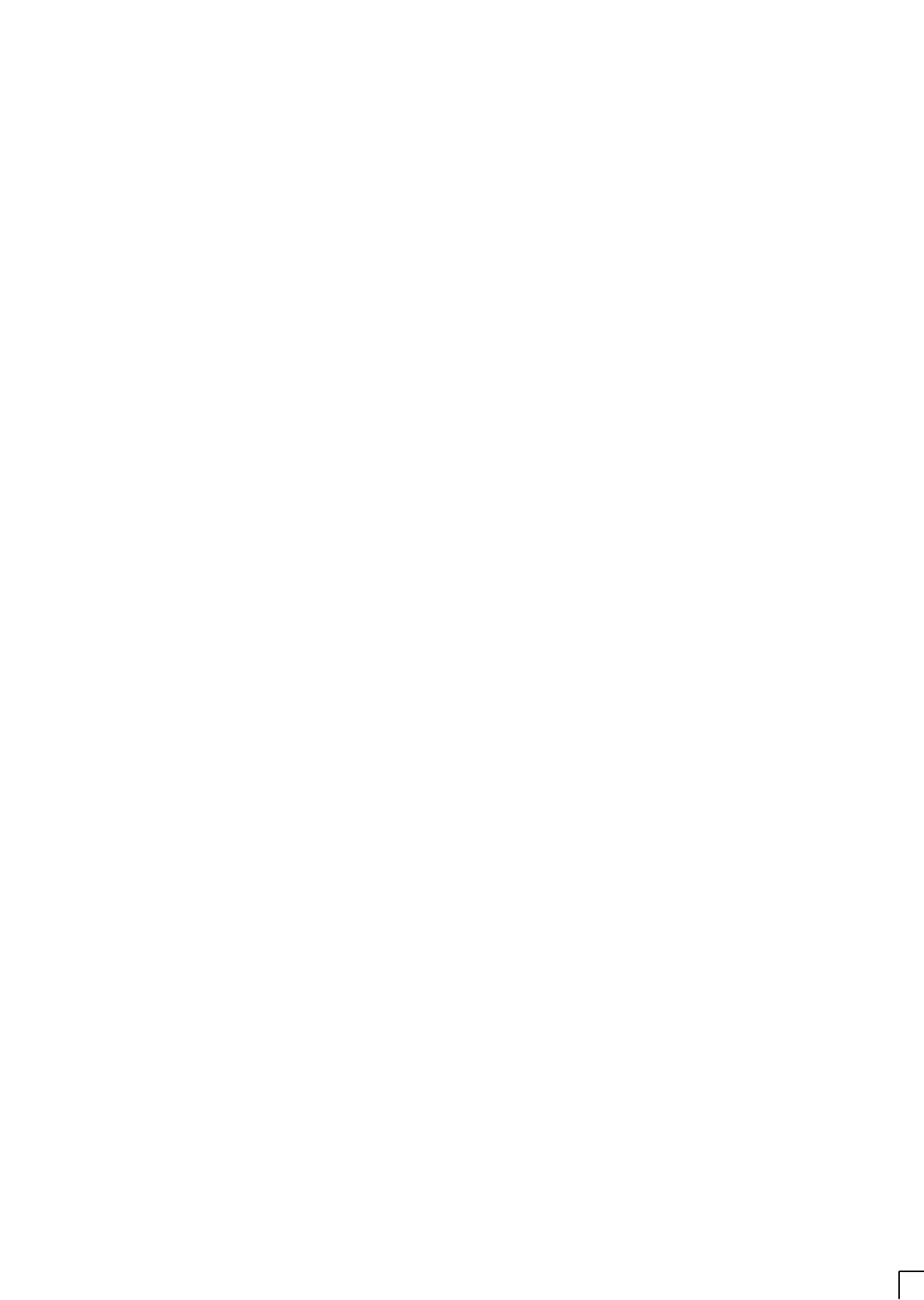

CHAPTER 7
AUXILIARY EQUIPMENT
HOUSING
CHAPTER 8
CABLE SHROUD
CHAPTER 6
DIGITAL MODULES
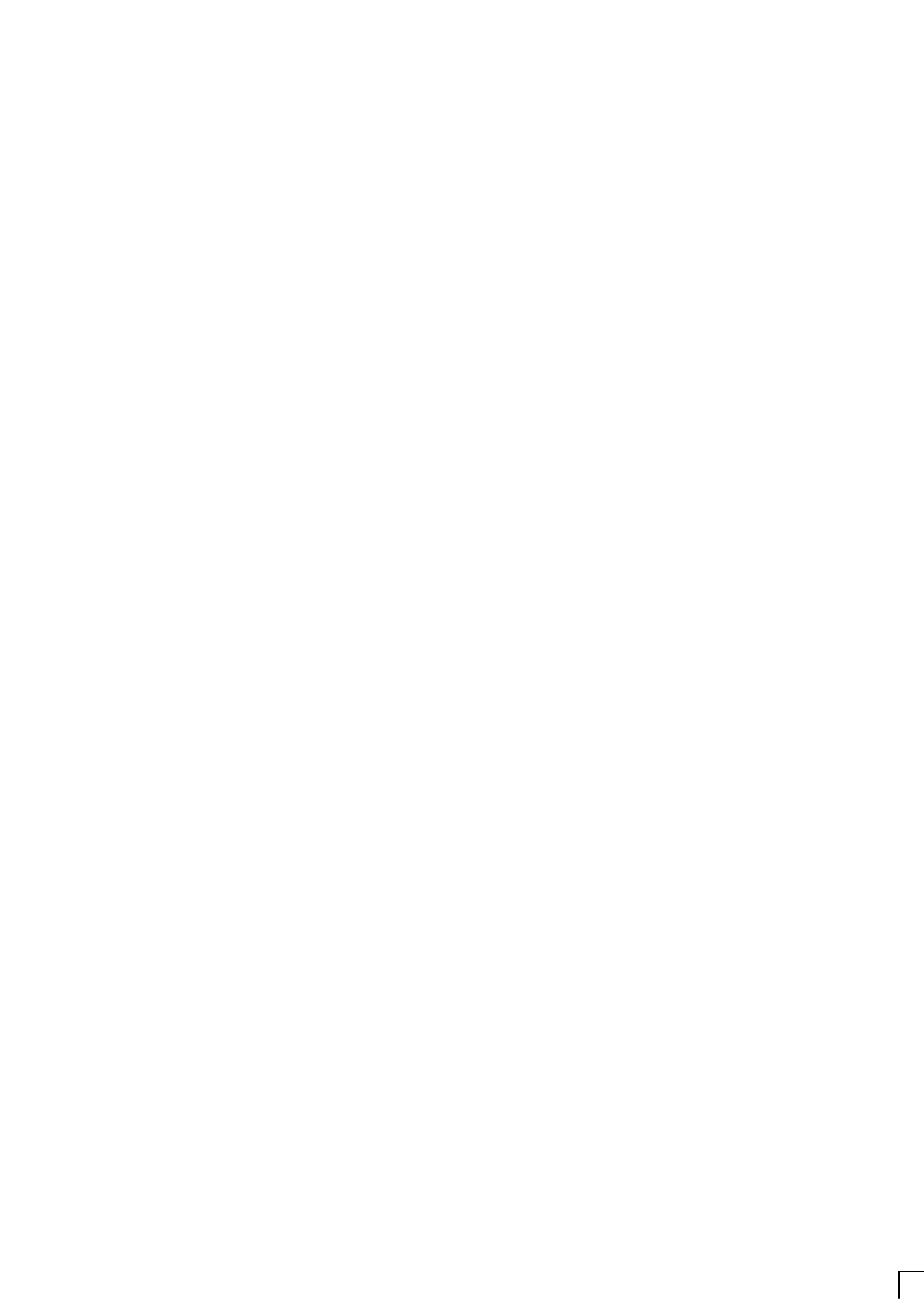
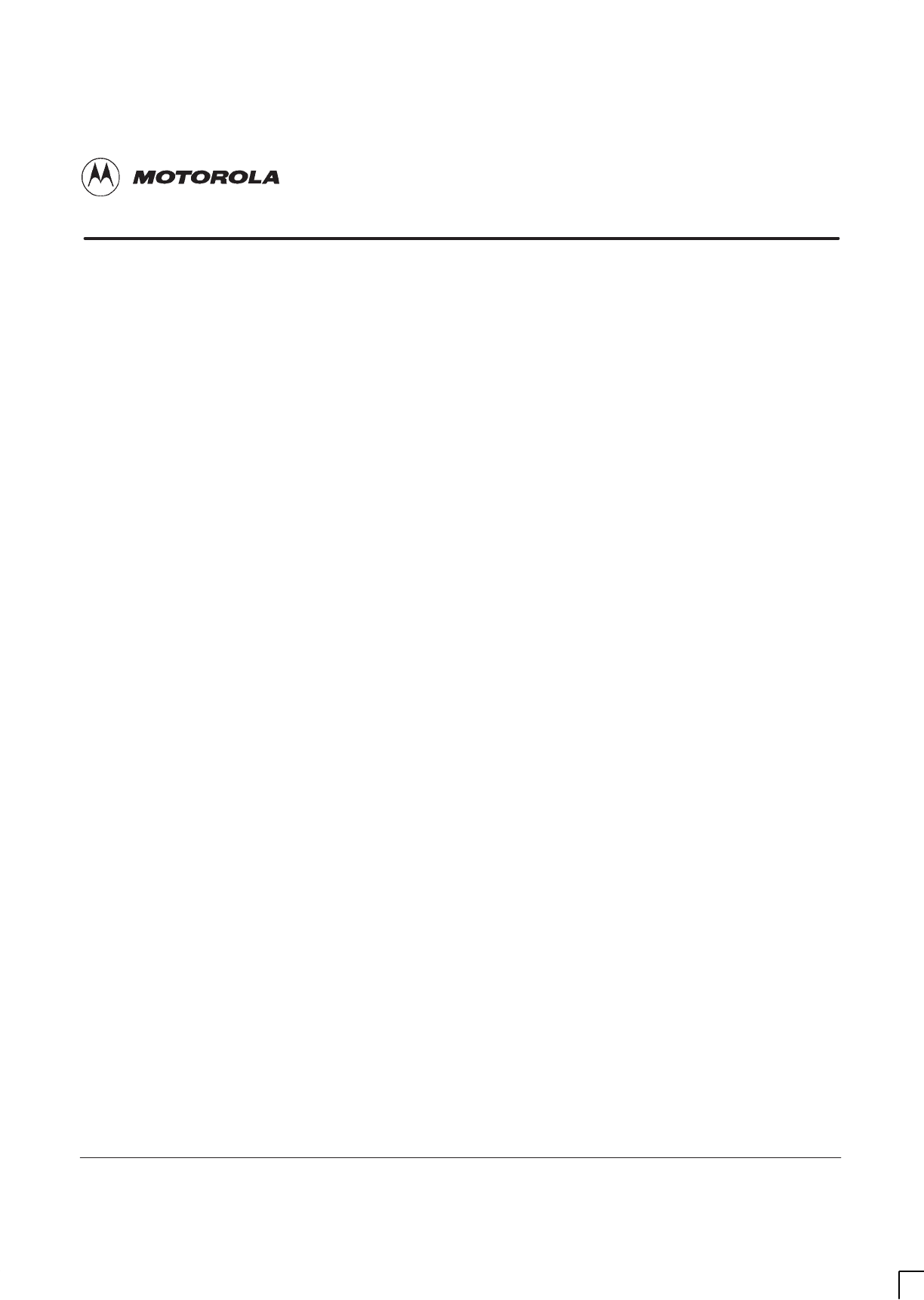
31st Oct 01
Technical Description: Horizon
macro
outdoor
68P02902W02-A
CONTROLLED INTRODUCTION
i
Category 323
Technical Description (Tech.)
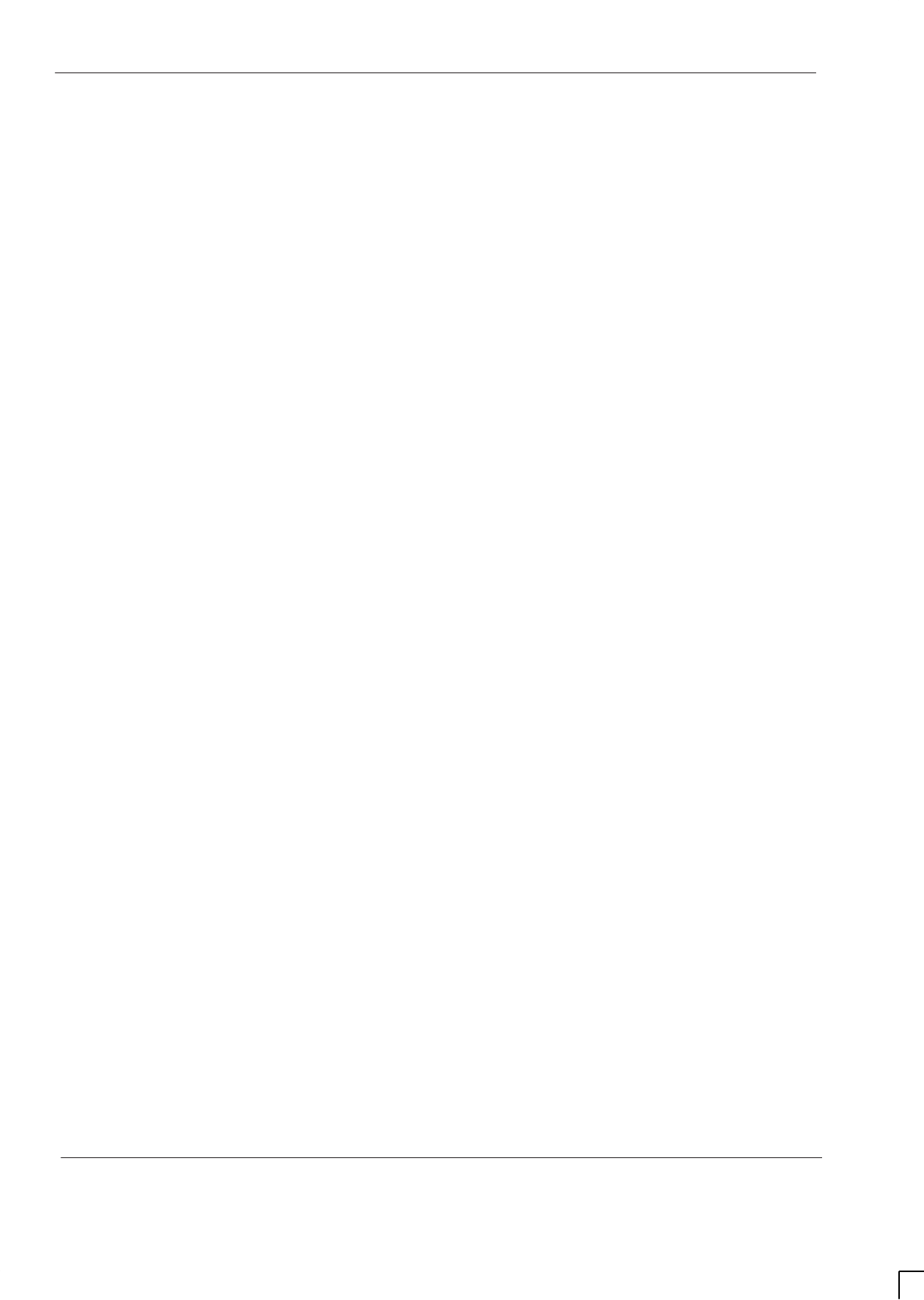
GSM-204-323
31st Oct 01
ii
Technical Description: Horizon
macro
outdoor
CONTROLLED INTRODUCTION
68P02902W02-A
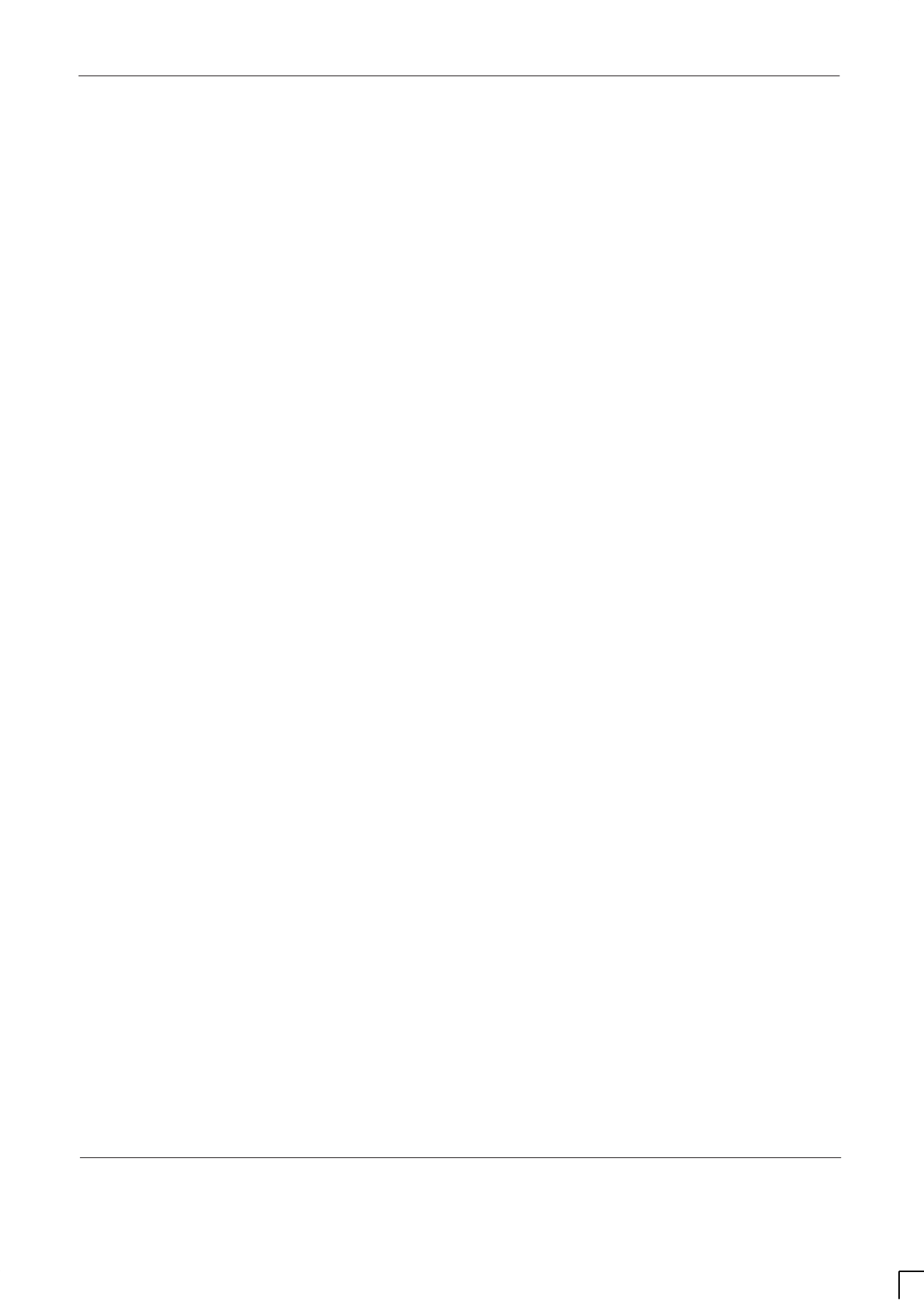
GSM-204-323
31st Oct 01
Technical Description: Horizon
macro
outdoor
68P02902W02-A
CONTROLLED INTRODUCTION
iii
Category 323
Technical Description (Tech.) i. . . . . . . . . . . . . . . . . . . . . . . . . . . . . . . . . . . . . . .
Chapter 1
Overview and specifications i. . . . . . . . . . . . . . . . . . . . . . . . . . . . . . . . . . .
Equipment introduction and manual definition Tech. 1–1. . . . . . . . . . . . . . . . . . . . . . . . . . .
Overview of Horizonmacro outdoor Tech. 1–1. . . . . . . . . . . . . . . . . . . . . . . . . . . . . . . .
Names and acronyms for main cabinet equipment Tech. 1–2. . . . . . . . . . . . . . . . . .
Configuration information Tech. 1–3. . . . . . . . . . . . . . . . . . . . . . . . . . . . . . . . . . . . . . . .
Finding information in this manual Tech. 1–4. . . . . . . . . . . . . . . . . . . . . . . . . . . . . . . . .
Cabinet view Tech. 1–5. . . . . . . . . . . . . . . . . . . . . . . . . . . . . . . . . . . . . . . . . . . . . . . . . . .
Functional diagram of Horizonmacro outdoor Tech. 1–6. . . . . . . . . . . . . . . . . . . . . . .
M-Cell6 comparison with Horizonmacro outdoor Tech. 1–7. . . . . . . . . . . . . . . . . . . . . . . . .
Comparison overview Tech. 1–7. . . . . . . . . . . . . . . . . . . . . . . . . . . . . . . . . . . . . . . . . . .
Horizonmacro and M-Cell6 compatibility Tech. 1–7. . . . . . . . . . . . . . . . . . . . . . . . . . .
Comparison of Horizonmacro and M-Cell6 connections and modules Tech. 1–8. .
Specifications Tech. 1–9. . . . . . . . . . . . . . . . . . . . . . . . . . . . . . . . . . . . . . . . . . . . . . . . . . . . . . .
Introduction to specifications Tech. 1–9. . . . . . . . . . . . . . . . . . . . . . . . . . . . . . . . . . . . .
Software requirements Tech. 1–9. . . . . . . . . . . . . . . . . . . . . . . . . . . . . . . . . . . . . . . . . .
Approval and safety Tech. 1–9. . . . . . . . . . . . . . . . . . . . . . . . . . . . . . . . . . . . . . . . . . . .
Environmental limits Tech. 1–9. . . . . . . . . . . . . . . . . . . . . . . . . . . . . . . . . . . . . . . . . . . . .
Power requirements Tech. 1–10. . . . . . . . . . . . . . . . . . . . . . . . . . . . . . . . . . . . . . . . . . . . .
RF power output Tech. 1–11. . . . . . . . . . . . . . . . . . . . . . . . . . . . . . . . . . . . . . . . . . . . . . . .
Sensitivity Tech. 1–12. . . . . . . . . . . . . . . . . . . . . . . . . . . . . . . . . . . . . . . . . . . . . . . . . . . . . .
Battery backup Tech. 1–12. . . . . . . . . . . . . . . . . . . . . . . . . . . . . . . . . . . . . . . . . . . . . . . . .
BSC connectivity options Tech. 1–12. . . . . . . . . . . . . . . . . . . . . . . . . . . . . . . . . . . . . . . .
Outdoor cabinet dimensions Tech. 1–12. . . . . . . . . . . . . . . . . . . . . . . . . . . . . . . . . . . . . .
Weights Tech. 1–13. . . . . . . . . . . . . . . . . . . . . . . . . . . . . . . . . . . . . . . . . . . . . . . . . . . . . . . .
Torque values Tech. 1–13. . . . . . . . . . . . . . . . . . . . . . . . . . . . . . . . . . . . . . . . . . . . . . . . . .
Cabinets enhancements Tech. 1–13. . . . . . . . . . . . . . . . . . . . . . . . . . . . . . . . . . . . . . . . .
Frequency capability Tech. 1–14. . . . . . . . . . . . . . . . . . . . . . . . . . . . . . . . . . . . . . . . . . . .
Structural considerations Tech. 1–16. . . . . . . . . . . . . . . . . . . . . . . . . . . . . . . . . . . . . . . . .
Outdoor site dimensions Tech. 1–17. . . . . . . . . . . . . . . . . . . . . . . . . . . . . . . . . . . . . . . . .
View of maximum site template layout Tech. 1–18. . . . . . . . . . . . . . . . . . . . . . . . . . . . .
Chapter 2
Cabinet structure i. . . . . . . . . . . . . . . . . . . . . . . . . . . . . . . . . . . . . . . . . . . . . .
Outdoor cabinet structure Tech. 2–1. . . . . . . . . . . . . . . . . . . . . . . . . . . . . . . . . . . . . . . . . . . . .
External cabinet view Tech. 2–1. . . . . . . . . . . . . . . . . . . . . . . . . . . . . . . . . . . . . . . . . . . .
Overview of structure description Tech. 2–2. . . . . . . . . . . . . . . . . . . . . . . . . . . . . . . . .
Space required around cabinet Tech. 2–2. . . . . . . . . . . . . . . . . . . . . . . . . . . . . . . . . . .
Filled cabinet view Tech. 2–3. . . . . . . . . . . . . . . . . . . . . . . . . . . . . . . . . . . . . . . . . . . . . .
SURF harness Tech. 2–4. . . . . . . . . . . . . . . . . . . . . . . . . . . . . . . . . . . . . . . . . . . . . . . . . . . . . . .
SURF harness detail Tech. 2–4. . . . . . . . . . . . . . . . . . . . . . . . . . . . . . . . . . . . . . . . . . . .
Cabinet view with installed SURF harness Tech. 2–4. . . . . . . . . . . . . . . . . . . . . . . . .
SURF harness view Tech. 2–5. . . . . . . . . . . . . . . . . . . . . . . . . . . . . . . . . . . . . . . . . . . . .
Top section Tech. 2–6. . . . . . . . . . . . . . . . . . . . . . . . . . . . . . . . . . . . . . . . . . . . . . . . . . . . . . . . . .
Top section description Tech. 2–6. . . . . . . . . . . . . . . . . . . . . . . . . . . . . . . . . . . . . . . . . .
Top section diagram Tech. 2–7. . . . . . . . . . . . . . . . . . . . . . . . . . . . . . . . . . . . . . . . . . . . .
Krone blocks Tech. 2–7. . . . . . . . . . . . . . . . . . . . . . . . . . . . . . . . . . . . . . . . . . . . . . . . . . .
AC outlet socket Tech. 2–7. . . . . . . . . . . . . . . . . . . . . . . . . . . . . . . . . . . . . . . . . . . . . . . .
Earth plates Tech. 2–8. . . . . . . . . . . . . . . . . . . . . . . . . . . . . . . . . . . . . . . . . . . . . . . . . . . .
Blank and expansion plates Tech. 2–9. . . . . . . . . . . . . . . . . . . . . . . . . . . . . . . . . . . . . .
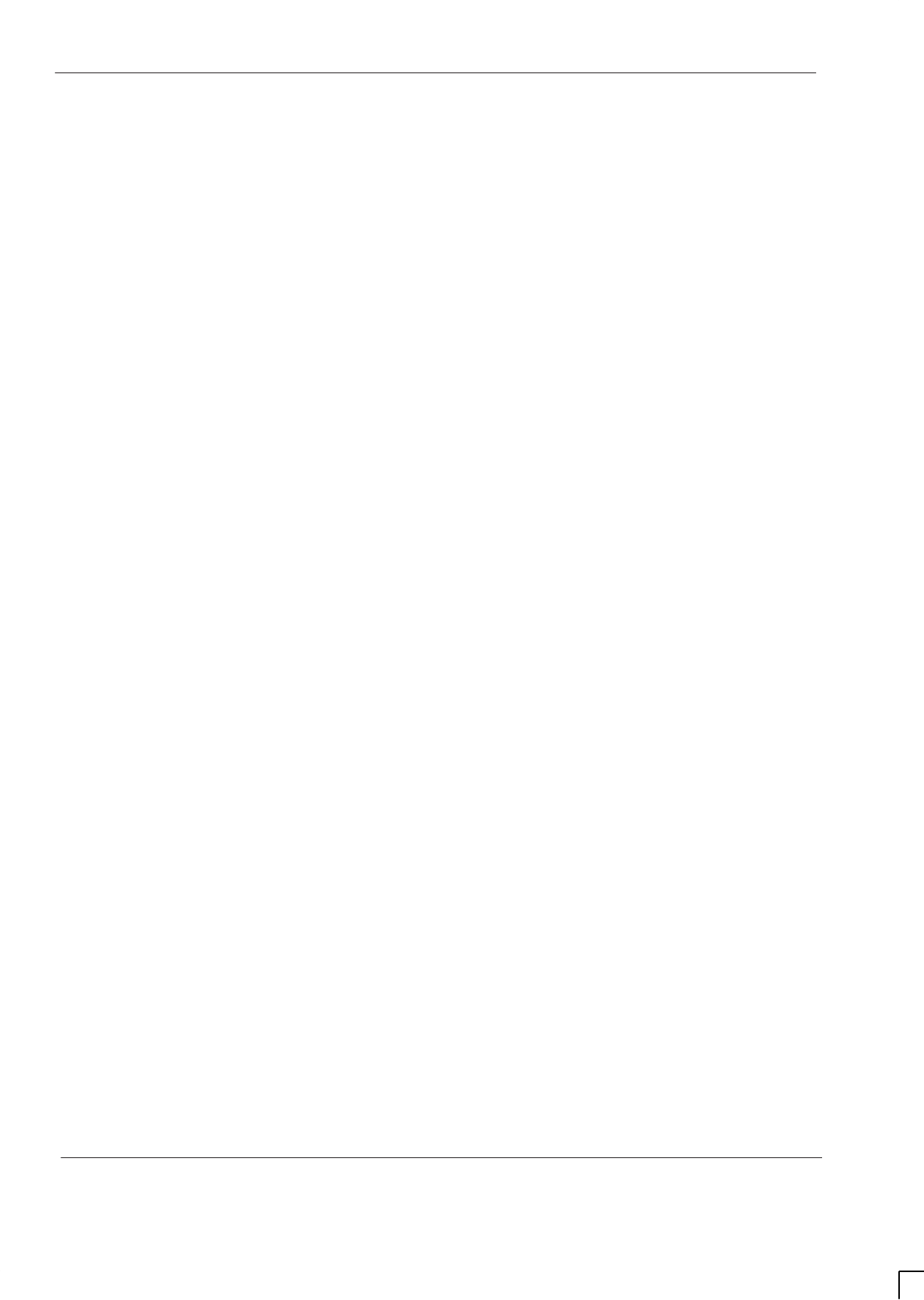
GSM-204-323
31st Oct 01
iv
Technical Description: Horizon
macro
outdoor
CONTROLLED INTRODUCTION
68P02902W02-A
Cage backplane interface panel harness assembly (CBIA) Tech. 2–10. . . . . . . . . . . . . . . .
CBIA overview Tech. 2–10. . . . . . . . . . . . . . . . . . . . . . . . . . . . . . . . . . . . . . . . . . . . . . . . . .
CBIA and interface panel schematic view Tech. 2–10. . . . . . . . . . . . . . . . . . . . . . . . . .
Backplane and harness view Tech. 2–11. . . . . . . . . . . . . . . . . . . . . . . . . . . . . . . . . . . . .
CBIA cage function and diagram Tech. 2–12. . . . . . . . . . . . . . . . . . . . . . . . . . . . . . . . . .
CBIA harness function Tech. 2–12. . . . . . . . . . . . . . . . . . . . . . . . . . . . . . . . . . . . . . . . . . .
CBIA backplane function Tech. 2–13. . . . . . . . . . . . . . . . . . . . . . . . . . . . . . . . . . . . . . . . .
Attachment of cage to cabinet Tech. 2–13. . . . . . . . . . . . . . . . . . . . . . . . . . . . . . . . . . . .
CBIA interface panel Tech. 2–14. . . . . . . . . . . . . . . . . . . . . . . . . . . . . . . . . . . . . . . . . . . . . . . . .
Interface panel function Tech. 2–14. . . . . . . . . . . . . . . . . . . . . . . . . . . . . . . . . . . . . . . . . .
Interface panel diagram Tech. 2–14. . . . . . . . . . . . . . . . . . . . . . . . . . . . . . . . . . . . . . . . . .
Interface panel pinouts Tech. 2–14. . . . . . . . . . . . . . . . . . . . . . . . . . . . . . . . . . . . . . . . . .
Power supply enclosure Tech. 2–15. . . . . . . . . . . . . . . . . . . . . . . . . . . . . . . . . . . . . . . . . . . . . .
Power supply enclosure overview Tech. 2–15. . . . . . . . . . . . . . . . . . . . . . . . . . . . . . . . .
View of power supply enclosure Tech. 2–15. . . . . . . . . . . . . . . . . . . . . . . . . . . . . . . . . .
Power supply unit Tech. 2–16. . . . . . . . . . . . . . . . . . . . . . . . . . . . . . . . . . . . . . . . . . . . . . .
Alarms interface board Tech. 2–16. . . . . . . . . . . . . . . . . . . . . . . . . . . . . . . . . . . . . . . . . .
Alarms interface board connectors Tech. 2–17. . . . . . . . . . . . . . . . . . . . . . . . . . . . . . . .
TMS test switches Tech. 2–18. . . . . . . . . . . . . . . . . . . . . . . . . . . . . . . . . . . . . . . . . . . . . .
Customer equipment racking Tech. 2–18. . . . . . . . . . . . . . . . . . . . . . . . . . . . . . . . . . . . .
Outdoor cabinet doors and lid Tech. 2–19. . . . . . . . . . . . . . . . . . . . . . . . . . . . . . . . . . . . . . . . .
Door function Tech. 2–19. . . . . . . . . . . . . . . . . . . . . . . . . . . . . . . . . . . . . . . . . . . . . . . . . . .
Door views Tech. 2–19. . . . . . . . . . . . . . . . . . . . . . . . . . . . . . . . . . . . . . . . . . . . . . . . . . . . .
Lid function Tech. 2–20. . . . . . . . . . . . . . . . . . . . . . . . . . . . . . . . . . . . . . . . . . . . . . . . . . . .
Lid view Tech. 2–20. . . . . . . . . . . . . . . . . . . . . . . . . . . . . . . . . . . . . . . . . . . . . . . . . . . . . . .
Chapter 3
Thermal management system i. . . . . . . . . . . . . . . . . . . . . . . . . . . . . . . . . .
Horizonmacro outdoor temperature control Tech. 3–1. . . . . . . . . . . . . . . . . . . . . . . . . . . . . .
Temperature control overview Tech. 3–1. . . . . . . . . . . . . . . . . . . . . . . . . . . . . . . . . . . .
Cabinet over temperature control Tech. 3–1. . . . . . . . . . . . . . . . . . . . . . . . . . . . . . . . .
Temperature sensors Tech. 3–1. . . . . . . . . . . . . . . . . . . . . . . . . . . . . . . . . . . . . . . . . . . .
Cabinet restart after shutdown Tech. 3–2. . . . . . . . . . . . . . . . . . . . . . . . . . . . . . . . . . . .
Thermal management system (TMS) Tech. 3–3. . . . . . . . . . . . . . . . . . . . . . . . . . . . . . . . . . .
TMS overview Tech. 3–3. . . . . . . . . . . . . . . . . . . . . . . . . . . . . . . . . . . . . . . . . . . . . . . . . .
View of TMS unit Tech. 3–3. . . . . . . . . . . . . . . . . . . . . . . . . . . . . . . . . . . . . . . . . . . . . . . .
Heat exchanger components Tech. 3–4. . . . . . . . . . . . . . . . . . . . . . . . . . . . . . . . . . . . .
TMS functional description Tech. 3–5. . . . . . . . . . . . . . . . . . . . . . . . . . . . . . . . . . . . . . .
Heat exchanger functional diagram Tech. 3–6. . . . . . . . . . . . . . . . . . . . . . . . . . . . . . .
Chapter 4
Cabinet power supplies i. . . . . . . . . . . . . . . . . . . . . . . . . . . . . . . . . . . . . . . .
Horizonmacro outdoor power supplies Tech. 4–1. . . . . . . . . . . . . . . . . . . . . . . . . . . . . . . . . .
Power supply overview Tech. 4–1. . . . . . . . . . . . . . . . . . . . . . . . . . . . . . . . . . . . . . . . . .
Power supply unit view Tech. 4–2. . . . . . . . . . . . . . . . . . . . . . . . . . . . . . . . . . . . . . . . . .
View of main cage power modules Tech. 4–3. . . . . . . . . . . . . . . . . . . . . . . . . . . . . . . .
Introduction to power distribution Tech. 4–4. . . . . . . . . . . . . . . . . . . . . . . . . . . . . . . . . . . . . . .
Power distribution overview Tech. 4–4. . . . . . . . . . . . . . . . . . . . . . . . . . . . . . . . . . . . . .
View of power supply unit cage Tech. 4–4. . . . . . . . . . . . . . . . . . . . . . . . . . . . . . . . . . .
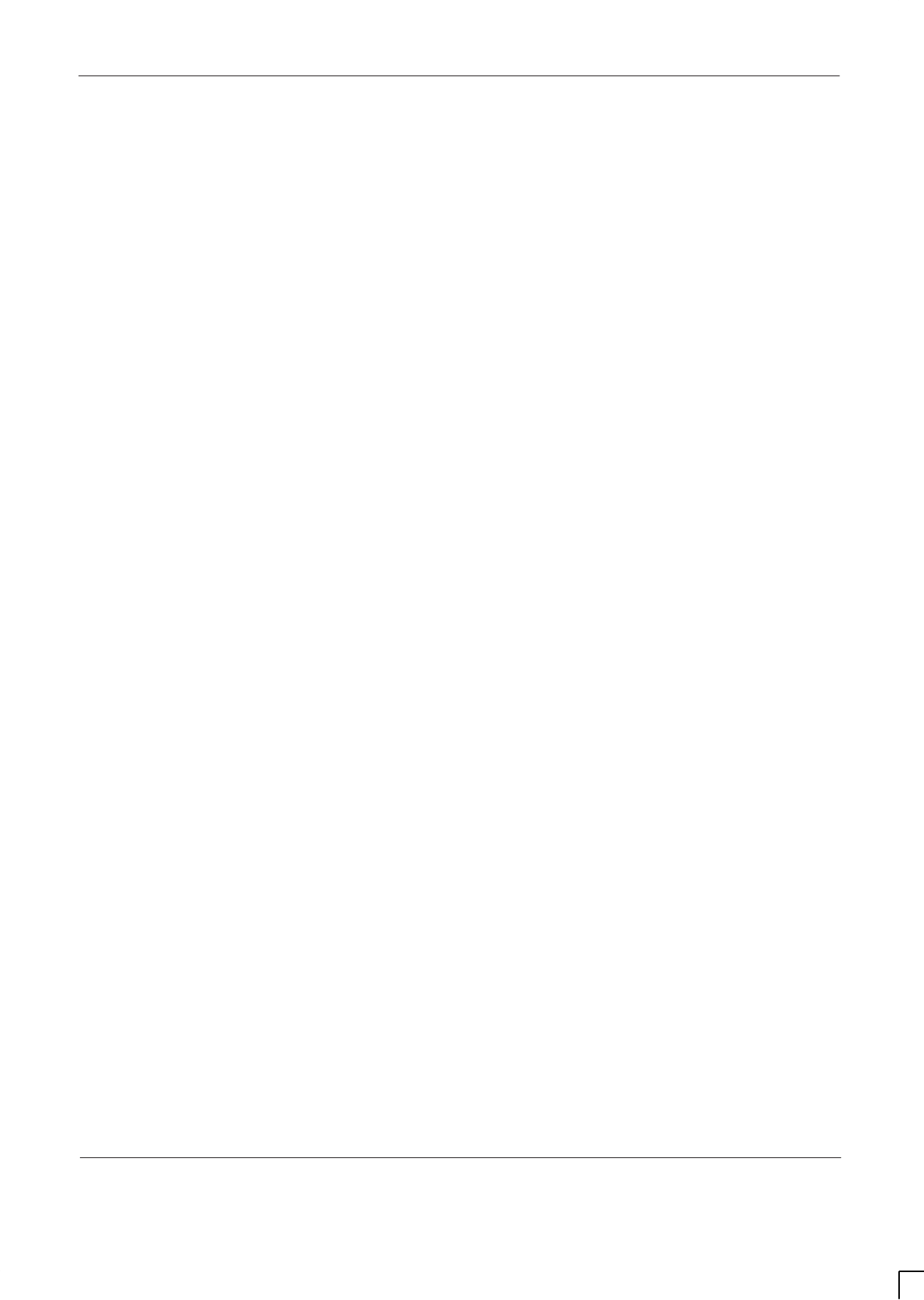
GSM-204-323
31st Oct 01
Technical Description: Horizon
macro
outdoor
68P02902W02-A
CONTROLLED INTRODUCTION
v
AC power distribution Tech. 4–5. . . . . . . . . . . . . . . . . . . . . . . . . . . . . . . . . . . . . . . . . . . . . . . . .
View of ac power components Tech. 4–5. . . . . . . . . . . . . . . . . . . . . . . . . . . . . . . . . . .
AC distribution description Tech. 4–6. . . . . . . . . . . . . . . . . . . . . . . . . . . . . . . . . . . . . . .
AC outlet socket Tech. 4–7. . . . . . . . . . . . . . . . . . . . . . . . . . . . . . . . . . . . . . . . . . . . . . . .
View of the ac outlet socket Tech. 4–8. . . . . . . . . . . . . . . . . . . . . . . . . . . . . . . . . . . . . .
AC distribution diagram Tech. 4–8. . . . . . . . . . . . . . . . . . . . . . . . . . . . . . . . . . . . . . . . . .
DC power distribution Tech. 4–9. . . . . . . . . . . . . . . . . . . . . . . . . . . . . . . . . . . . . . . . . . . . . . . . .
DC distribution overview Tech. 4–9. . . . . . . . . . . . . . . . . . . . . . . . . . . . . . . . . . . . . . . . .
View of dc power components Tech. 4–9. . . . . . . . . . . . . . . . . . . . . . . . . . . . . . . . . . .
DC distribution diagram Tech. 4–10. . . . . . . . . . . . . . . . . . . . . . . . . . . . . . . . . . . . . . . . . .
DC distribution description Tech. 4–10. . . . . . . . . . . . . . . . . . . . . . . . . . . . . . . . . . . . . . .
View of the dc circuit breaker panel Tech. 4–11. . . . . . . . . . . . . . . . . . . . . . . . . . . . . . .
Customer equipment power supplies Tech. 4–11. . . . . . . . . . . . . . . . . . . . . . . . . . . . . .
Internal battery backup Tech. 4–11. . . . . . . . . . . . . . . . . . . . . . . . . . . . . . . . . . . . . . . . . .
Internal battery arrangement Tech. 4–12. . . . . . . . . . . . . . . . . . . . . . . . . . . . . . . . . . . . .
View of battery sense lead Tech. 4–12. . . . . . . . . . . . . . . . . . . . . . . . . . . . . . . . . . . . . . .
External battery backup connection Tech. 4–13. . . . . . . . . . . . . . . . . . . . . . . . . . . . . . .
View of the dc interface panel Tech. 4–13. . . . . . . . . . . . . . . . . . . . . . . . . . . . . . . . . . . .
Control and alarm board (CAB) Tech. 4–14. . . . . . . . . . . . . . . . . . . . . . . . . . . . . . . . . . . . . . . .
Introduction to the CAB Tech. 4–14. . . . . . . . . . . . . . . . . . . . . . . . . . . . . . . . . . . . . . . . . .
CAB views Tech. 4–15. . . . . . . . . . . . . . . . . . . . . . . . . . . . . . . . . . . . . . . . . . . . . . . . . . . . .
CAB indicators and controls Tech. 4–16. . . . . . . . . . . . . . . . . . . . . . . . . . . . . . . . . . . . . .
CAB front panel fuses Tech. 4–17. . . . . . . . . . . . . . . . . . . . . . . . . . . . . . . . . . . . . . . . . . .
CAB control functions Tech. 4–18. . . . . . . . . . . . . . . . . . . . . . . . . . . . . . . . . . . . . . . . . . .
CAB alarm functions Tech. 4–20. . . . . . . . . . . . . . . . . . . . . . . . . . . . . . . . . . . . . . . . . . . .
CAB additional functions Tech. 4–22. . . . . . . . . . . . . . . . . . . . . . . . . . . . . . . . . . . . . . . . .
DIP switches Tech. 4–25. . . . . . . . . . . . . . . . . . . . . . . . . . . . . . . . . . . . . . . . . . . . . . . . . . .
The outdoor power supply module (TOPSM) Tech. 4–26. . . . . . . . . . . . . . . . . . . . . . . . . . . .
TOPSM overview Tech. 4–26. . . . . . . . . . . . . . . . . . . . . . . . . . . . . . . . . . . . . . . . . . . . . . .
View of TOPSM Tech. 4–26. . . . . . . . . . . . . . . . . . . . . . . . . . . . . . . . . . . . . . . . . . . . . . . . .
TOPSM functional description Tech. 4–26. . . . . . . . . . . . . . . . . . . . . . . . . . . . . . . . . . . .
LED display Tech. 4–27. . . . . . . . . . . . . . . . . . . . . . . . . . . . . . . . . . . . . . . . . . . . . . . . . . . .
Functional diagram Tech. 4–27. . . . . . . . . . . . . . . . . . . . . . . . . . . . . . . . . . . . . . . . . . . . . .
Monitoring Tech. 4–28. . . . . . . . . . . . . . . . . . . . . . . . . . . . . . . . . . . . . . . . . . . . . . . . . . . . .
Protection circuits Tech. 4–28. . . . . . . . . . . . . . . . . . . . . . . . . . . . . . . . . . . . . . . . . . . . . . .
Thermal protection Tech. 4–28. . . . . . . . . . . . . . . . . . . . . . . . . . . . . . . . . . . . . . . . . . . . . .
Control and alarm signals Tech. 4–29. . . . . . . . . . . . . . . . . . . . . . . . . . . . . . . . . . . . . . . .
TOPSM pinouts Tech. 4–30. . . . . . . . . . . . . . . . . . . . . . . . . . . . . . . . . . . . . . . . . . . . . . . . .
Power supply module (PSM) Tech. 4–31. . . . . . . . . . . . . . . . . . . . . . . . . . . . . . . . . . . . . . . . . .
PSM overview Tech. 4–31. . . . . . . . . . . . . . . . . . . . . . . . . . . . . . . . . . . . . . . . . . . . . . . . . .
PSM location and redundancy Tech. 4–31. . . . . . . . . . . . . . . . . . . . . . . . . . . . . . . . . . . .
PSM module view Tech. 4–32. . . . . . . . . . . . . . . . . . . . . . . . . . . . . . . . . . . . . . . . . . . . . . .
PSM alarms Tech. 4–32. . . . . . . . . . . . . . . . . . . . . . . . . . . . . . . . . . . . . . . . . . . . . . . . . . . .
PSM LEDs Tech. 4–32. . . . . . . . . . . . . . . . . . . . . . . . . . . . . . . . . . . . . . . . . . . . . . . . . . . . .
PSM backplane protection Tech. 4–33. . . . . . . . . . . . . . . . . . . . . . . . . . . . . . . . . . . . . . .
Circuit breaker module (CBM) Tech. 4–34. . . . . . . . . . . . . . . . . . . . . . . . . . . . . . . . . . . . . . . . .
CBM overview Tech. 4–34. . . . . . . . . . . . . . . . . . . . . . . . . . . . . . . . . . . . . . . . . . . . . . . . . .
View of the CBM Tech. 4–34. . . . . . . . . . . . . . . . . . . . . . . . . . . . . . . . . . . . . . . . . . . . . . . .
Operation of the CBM Tech. 4–35. . . . . . . . . . . . . . . . . . . . . . . . . . . . . . . . . . . . . . . . . . .
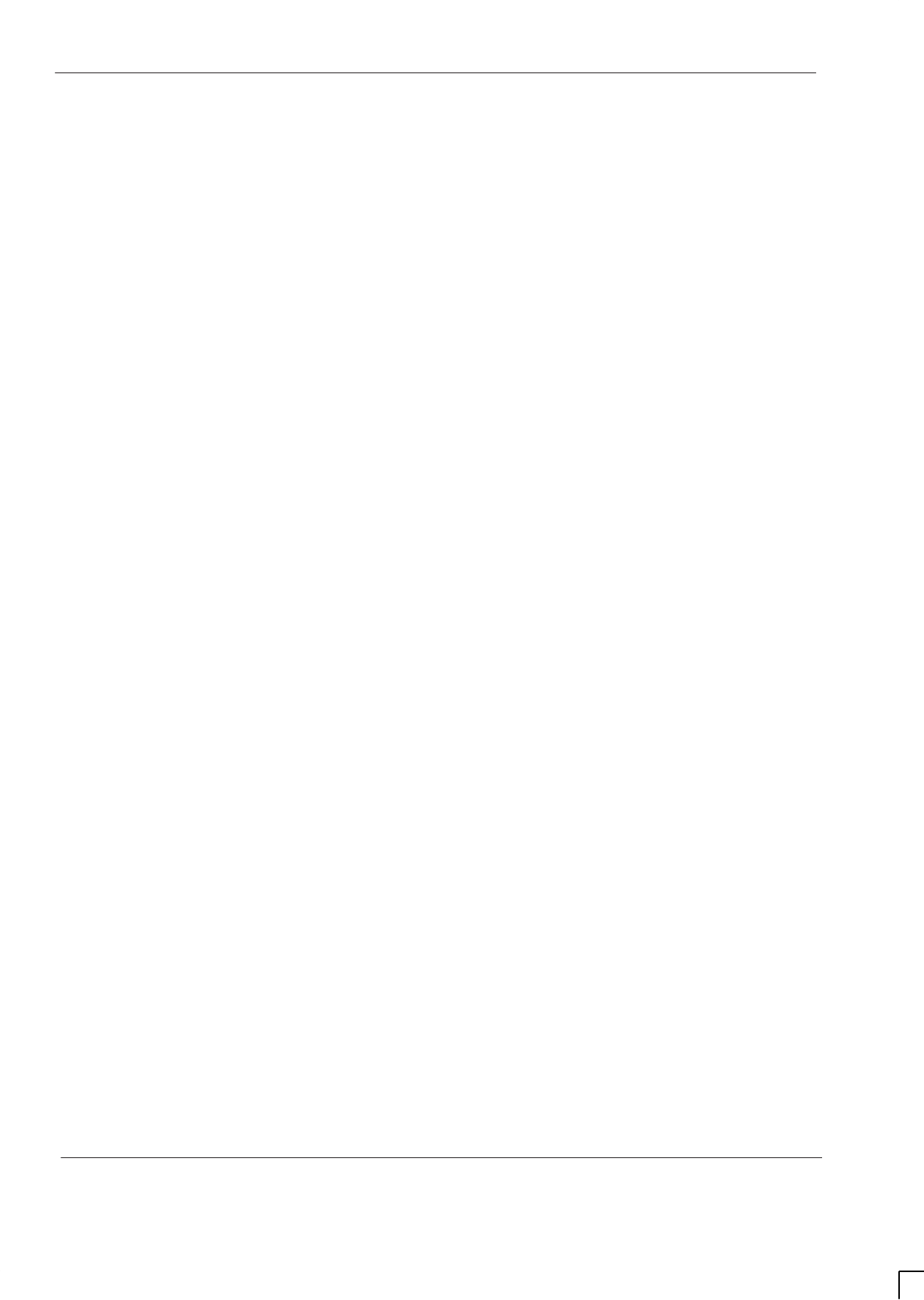
GSM-204-323
31st Oct 01
vi
Technical Description: Horizon
macro
outdoor
CONTROLLED INTRODUCTION
68P02902W02-A
MicroBCU power supply module (BPSM) Tech. 4–36. . . . . . . . . . . . . . . . . . . . . . . . . . . . . . . .
Introduction to the BPSM Tech. 4–36. . . . . . . . . . . . . . . . . . . . . . . . . . . . . . . . . . . . . . . .
BPSM diagram Tech. 4–36. . . . . . . . . . . . . . . . . . . . . . . . . . . . . . . . . . . . . . . . . . . . . . . . .
Functional description Tech. 4–37. . . . . . . . . . . . . . . . . . . . . . . . . . . . . . . . . . . . . . . . . . .
Chapter 5
RF modules i. . . . . . . . . . . . . . . . . . . . . . . . . . . . . . . . . . . . . . . . . . . . . . . . . . .
RF equipment detail Tech. 5–1. . . . . . . . . . . . . . . . . . . . . . . . . . . . . . . . . . . . . . . . . . . . . . . . . .
Overview of RF equipment Tech. 5–1. . . . . . . . . . . . . . . . . . . . . . . . . . . . . . . . . . . . . . .
RF specifications Tech. 5–1. . . . . . . . . . . . . . . . . . . . . . . . . . . . . . . . . . . . . . . . . . . . . . .
Receive (Rx) RF hardware Tech. 5–2. . . . . . . . . . . . . . . . . . . . . . . . . . . . . . . . . . . . . .
Transmit (Tx) RF hardware Tech. 5–3. . . . . . . . . . . . . . . . . . . . . . . . . . . . . . . . . . . . . . .
Rx/Tx single antenna duplexing Tech. 5–3. . . . . . . . . . . . . . . . . . . . . . . . . . . . . . . . . . .
RF overview and RF test function Tech. 5–4. . . . . . . . . . . . . . . . . . . . . . . . . . . . . . . . . . . . . .
RF overview Tech. 5–4. . . . . . . . . . . . . . . . . . . . . . . . . . . . . . . . . . . . . . . . . . . . . . . . . . . .
RF main component explanation Tech. 5–4. . . . . . . . . . . . . . . . . . . . . . . . . . . . . . . . . .
RF loopback test function Tech. 5–5. . . . . . . . . . . . . . . . . . . . . . . . . . . . . . . . . . . . . . . .
RF loopback hardware Tech. 5–5. . . . . . . . . . . . . . . . . . . . . . . . . . . . . . . . . . . . . . . . . .
RF loopback software operation Tech. 5–5. . . . . . . . . . . . . . . . . . . . . . . . . . . . . . . . . .
Functional diagram of RF Tech. 5–6. . . . . . . . . . . . . . . . . . . . . . . . . . . . . . . . . . . . . . . .
Description of RF test modes Tech. 5–7. . . . . . . . . . . . . . . . . . . . . . . . . . . . . . . . . . . . .
Compact transceiver unit (CTU) Tech. 5–8. . . . . . . . . . . . . . . . . . . . . . . . . . . . . . . . . . . . . . . .
Overview of the CTU Tech. 5–8. . . . . . . . . . . . . . . . . . . . . . . . . . . . . . . . . . . . . . . . . . . .
CTU internal boards Tech. 5–8. . . . . . . . . . . . . . . . . . . . . . . . . . . . . . . . . . . . . . . . . . . . .
Alarm reporting Tech. 5–9. . . . . . . . . . . . . . . . . . . . . . . . . . . . . . . . . . . . . . . . . . . . . . . . .
View of CTU Tech. 5–10. . . . . . . . . . . . . . . . . . . . . . . . . . . . . . . . . . . . . . . . . . . . . . . . . . . .
CTU connectors and reset Tech. 5–11. . . . . . . . . . . . . . . . . . . . . . . . . . . . . . . . . . . . . . .
CTU input/output diagram Tech. 5–12. . . . . . . . . . . . . . . . . . . . . . . . . . . . . . . . . . . . . . . .
CTU Tx connector Tech. 5–13. . . . . . . . . . . . . . . . . . . . . . . . . . . . . . . . . . . . . . . . . . . . . .
CTU Rx function Tech. 5–13. . . . . . . . . . . . . . . . . . . . . . . . . . . . . . . . . . . . . . . . . . . . . . . .
CTU Tx function Tech. 5–14. . . . . . . . . . . . . . . . . . . . . . . . . . . . . . . . . . . . . . . . . . . . . . . .
CTU digital processing and control functions Tech. 5–16. . . . . . . . . . . . . . . . . . . . . . .
CTU uplink/downlink Tech. 5–19. . . . . . . . . . . . . . . . . . . . . . . . . . . . . . . . . . . . . . . . . . . .
CTU frequency hopping Tech. 5–20. . . . . . . . . . . . . . . . . . . . . . . . . . . . . . . . . . . . . . . . . . . . . . .
Overview of CTU frequency hopping Tech. 5–20. . . . . . . . . . . . . . . . . . . . . . . . . . . . . .
Synthesizer frequency hopping (SFH) Tech. 5–20. . . . . . . . . . . . . . . . . . . . . . . . . . . . .
SFH example not through BCCH Tech. 5–21. . . . . . . . . . . . . . . . . . . . . . . . . . . . . . . . . .
SFH example hopping through BCCH carrier Tech. 5–21. . . . . . . . . . . . . . . . . . . . . . .
Baseband frequency hopping (BBH) Tech. 5–22. . . . . . . . . . . . . . . . . . . . . . . . . . . . . .
BBH example Tech. 5–22. . . . . . . . . . . . . . . . . . . . . . . . . . . . . . . . . . . . . . . . . . . . . . . . . .
SURF module Tech. 5–24. . . . . . . . . . . . . . . . . . . . . . . . . . . . . . . . . . . . . . . . . . . . . . . . . . . . . . .
SURF module overview Tech. 5–24. . . . . . . . . . . . . . . . . . . . . . . . . . . . . . . . . . . . . . . . . .
Single band SURF module view Tech. 5–25. . . . . . . . . . . . . . . . . . . . . . . . . . . . . . . . . .
Functional description of the single band SURF Tech. 5–26. . . . . . . . . . . . . . . . . . . .
Single band SURF functional diagram Tech. 5–27. . . . . . . . . . . . . . . . . . . . . . . . . . . . .
Dual band SURF module view Tech. 5–28. . . . . . . . . . . . . . . . . . . . . . . . . . . . . . . . . . . .
Functional description of dual band SURF modules Tech. 5–29. . . . . . . . . . . . . . . . .
Dual band SURF functional diagram Tech. 5–30. . . . . . . . . . . . . . . . . . . . . . . . . . . . . .
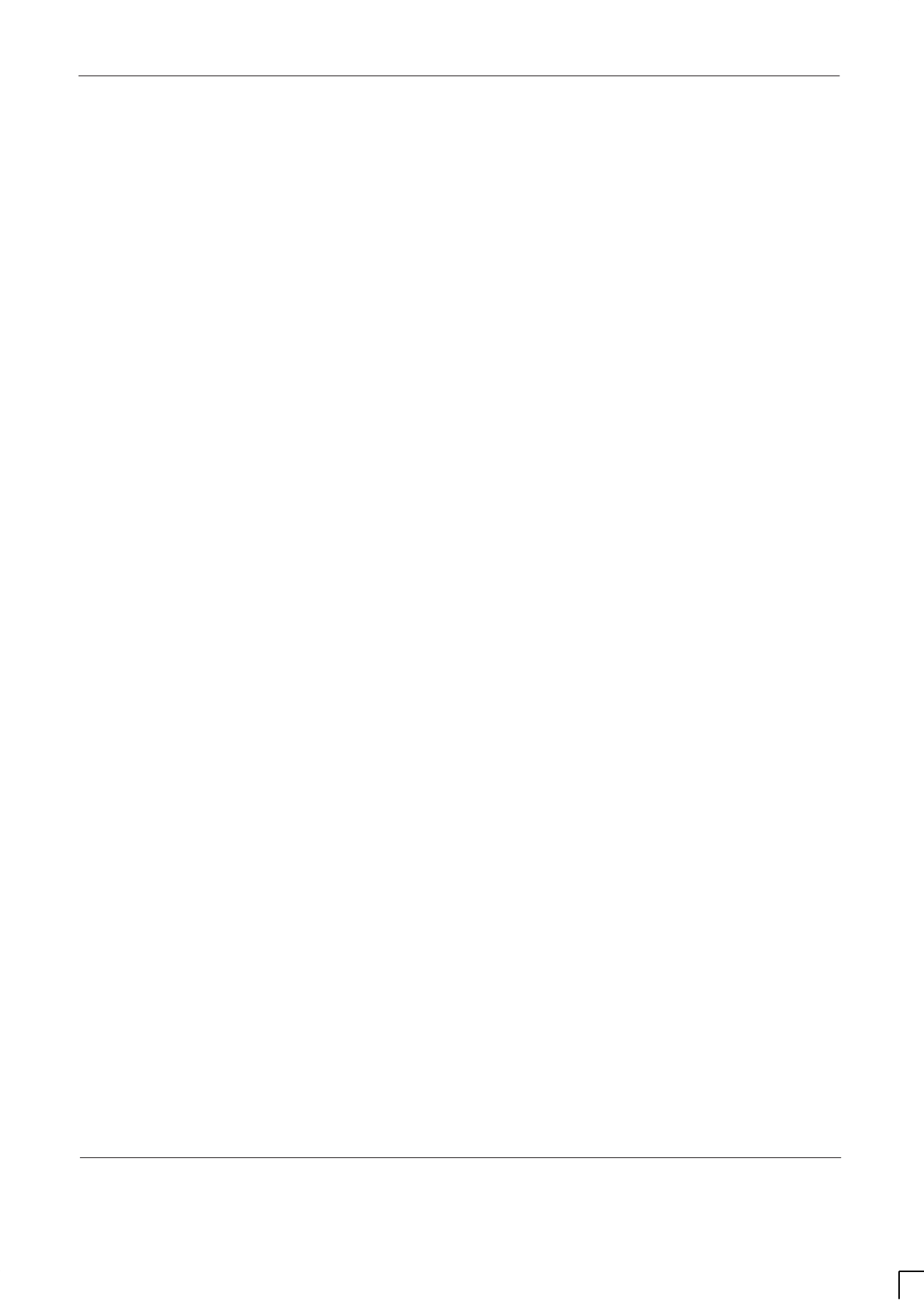
GSM-204-323
31st Oct 01
Technical Description: Horizon
macro
outdoor
68P02902W02-A
CONTROLLED INTRODUCTION
vii
Transmit blocks overview Tech. 5–31. . . . . . . . . . . . . . . . . . . . . . . . . . . . . . . . . . . . . . . . . . . . .
Introduction to transmit blocks Tech. 5–31. . . . . . . . . . . . . . . . . . . . . . . . . . . . . . . . . . . .
Screw retention in Tx block locations Tech. 5–31. . . . . . . . . . . . . . . . . . . . . . . . . . . . . .
View of basket for Tx blocks Tech. 5–32. . . . . . . . . . . . . . . . . . . . . . . . . . . . . . . . . . . . . .
Transmit block connectors Tech. 5–32. . . . . . . . . . . . . . . . . . . . . . . . . . . . . . . . . . . . . . .
View of Tx block connectors Tech. 5–33. . . . . . . . . . . . . . . . . . . . . . . . . . . . . . . . . . . . . .
Tx block blanking plate Tech. 5–34. . . . . . . . . . . . . . . . . . . . . . . . . . . . . . . . . . . . . . . . . . . . . . .
Purpose of Tx block blanking plate Tech. 5–34. . . . . . . . . . . . . . . . . . . . . . . . . . . . . . . .
View of Tx block blanking plate Tech. 5–34. . . . . . . . . . . . . . . . . . . . . . . . . . . . . . . . . . .
Feedthrough plate Tech. 5–35. . . . . . . . . . . . . . . . . . . . . . . . . . . . . . . . . . . . . . . . . . . . . . . . . . .
Purpose of feedthrough plate Tech. 5–35. . . . . . . . . . . . . . . . . . . . . . . . . . . . . . . . . . . . .
View of feedthrough plate Tech. 5–35. . . . . . . . . . . . . . . . . . . . . . . . . . . . . . . . . . . . . . . .
Feedthrough plate connectors Tech. 5–35. . . . . . . . . . . . . . . . . . . . . . . . . . . . . . . . . . . .
HCU plate Tech. 5–36. . . . . . . . . . . . . . . . . . . . . . . . . . . . . . . . . . . . . . . . . . . . . . . . . . . . . . . . . . .
HCU overview Tech. 5–36. . . . . . . . . . . . . . . . . . . . . . . . . . . . . . . . . . . . . . . . . . . . . . . . . .
HCU view Tech. 5–36. . . . . . . . . . . . . . . . . . . . . . . . . . . . . . . . . . . . . . . . . . . . . . . . . . . . . .
HCU functional diagram Tech. 5–36. . . . . . . . . . . . . . . . . . . . . . . . . . . . . . . . . . . . . . . . .
HCU connectors Tech. 5–37. . . . . . . . . . . . . . . . . . . . . . . . . . . . . . . . . . . . . . . . . . . . . . . .
TDF Tech. 5–38. . . . . . . . . . . . . . . . . . . . . . . . . . . . . . . . . . . . . . . . . . . . . . . . . . . . . . . . . . . . . . . .
Overview of TDF Tech. 5–38. . . . . . . . . . . . . . . . . . . . . . . . . . . . . . . . . . . . . . . . . . . . . . . .
TDF view Tech. 5–38. . . . . . . . . . . . . . . . . . . . . . . . . . . . . . . . . . . . . . . . . . . . . . . . . . . . . .
TDF functional diagram Tech. 5–39. . . . . . . . . . . . . . . . . . . . . . . . . . . . . . . . . . . . . . . . . .
TDF connectors Tech. 5–39. . . . . . . . . . . . . . . . . . . . . . . . . . . . . . . . . . . . . . . . . . . . . . . .
Dual band TDF Tech. 5–40. . . . . . . . . . . . . . . . . . . . . . . . . . . . . . . . . . . . . . . . . . . . . . . . . . . . . .
Overview of Dual band TDF Tech. 5–40. . . . . . . . . . . . . . . . . . . . . . . . . . . . . . . . . . . . . .
Dual band TDF view Tech. 5–40. . . . . . . . . . . . . . . . . . . . . . . . . . . . . . . . . . . . . . . . . . . . .
Dual band TDF functional diagram Tech. 5–41. . . . . . . . . . . . . . . . . . . . . . . . . . . . . . . .
Dual band TDF connectors Tech. 5–41. . . . . . . . . . . . . . . . . . . . . . . . . . . . . . . . . . . . . . .
DCF Tech. 5–42. . . . . . . . . . . . . . . . . . . . . . . . . . . . . . . . . . . . . . . . . . . . . . . . . . . . . . . . . . . . . . . .
DCF overview Tech. 5–42. . . . . . . . . . . . . . . . . . . . . . . . . . . . . . . . . . . . . . . . . . . . . . . . . .
DCF view Tech. 5–42. . . . . . . . . . . . . . . . . . . . . . . . . . . . . . . . . . . . . . . . . . . . . . . . . . . . . .
DCF functional diagram Tech. 5–43. . . . . . . . . . . . . . . . . . . . . . . . . . . . . . . . . . . . . . . . . .
DCF connectors Tech. 5–43. . . . . . . . . . . . . . . . . . . . . . . . . . . . . . . . . . . . . . . . . . . . . . . .
DDF Tech. 5–44. . . . . . . . . . . . . . . . . . . . . . . . . . . . . . . . . . . . . . . . . . . . . . . . . . . . . . . . . . . . . . . .
Overview of DDF Tech. 5–44. . . . . . . . . . . . . . . . . . . . . . . . . . . . . . . . . . . . . . . . . . . . . . .
DDF view Tech. 5–44. . . . . . . . . . . . . . . . . . . . . . . . . . . . . . . . . . . . . . . . . . . . . . . . . . . . . .
DDF functional diagram Tech. 5–45. . . . . . . . . . . . . . . . . . . . . . . . . . . . . . . . . . . . . . . . . .
DDF connectors Tech. 5–45. . . . . . . . . . . . . . . . . . . . . . . . . . . . . . . . . . . . . . . . . . . . . . . .
Chapter 6
Digital modules i. . . . . . . . . . . . . . . . . . . . . . . . . . . . . . . . . . . . . . . . . . . . . . .
Overview of digital modules Tech. 6–1. . . . . . . . . . . . . . . . . . . . . . . . . . . . . . . . . . . . . . . . . . .
Overview and redundancy Tech. 6–1. . . . . . . . . . . . . . . . . . . . . . . . . . . . . . . . . . . . . . .
Digital module and BPSM locations Tech. 6–2. . . . . . . . . . . . . . . . . . . . . . . . . . . . . . .
MCUF and NIU redundancy Tech. 6–3. . . . . . . . . . . . . . . . . . . . . . . . . . . . . . . . . . . . .
Full size and half size modules Tech. 6–3. . . . . . . . . . . . . . . . . . . . . . . . . . . . . . . . . . .
Digital module and CTU connections Tech. 6–4. . . . . . . . . . . . . . . . . . . . . . . . . . . . . .
Diagram of digital module and CTU connections Tech. 6–4. . . . . . . . . . . . . . . . . . . .
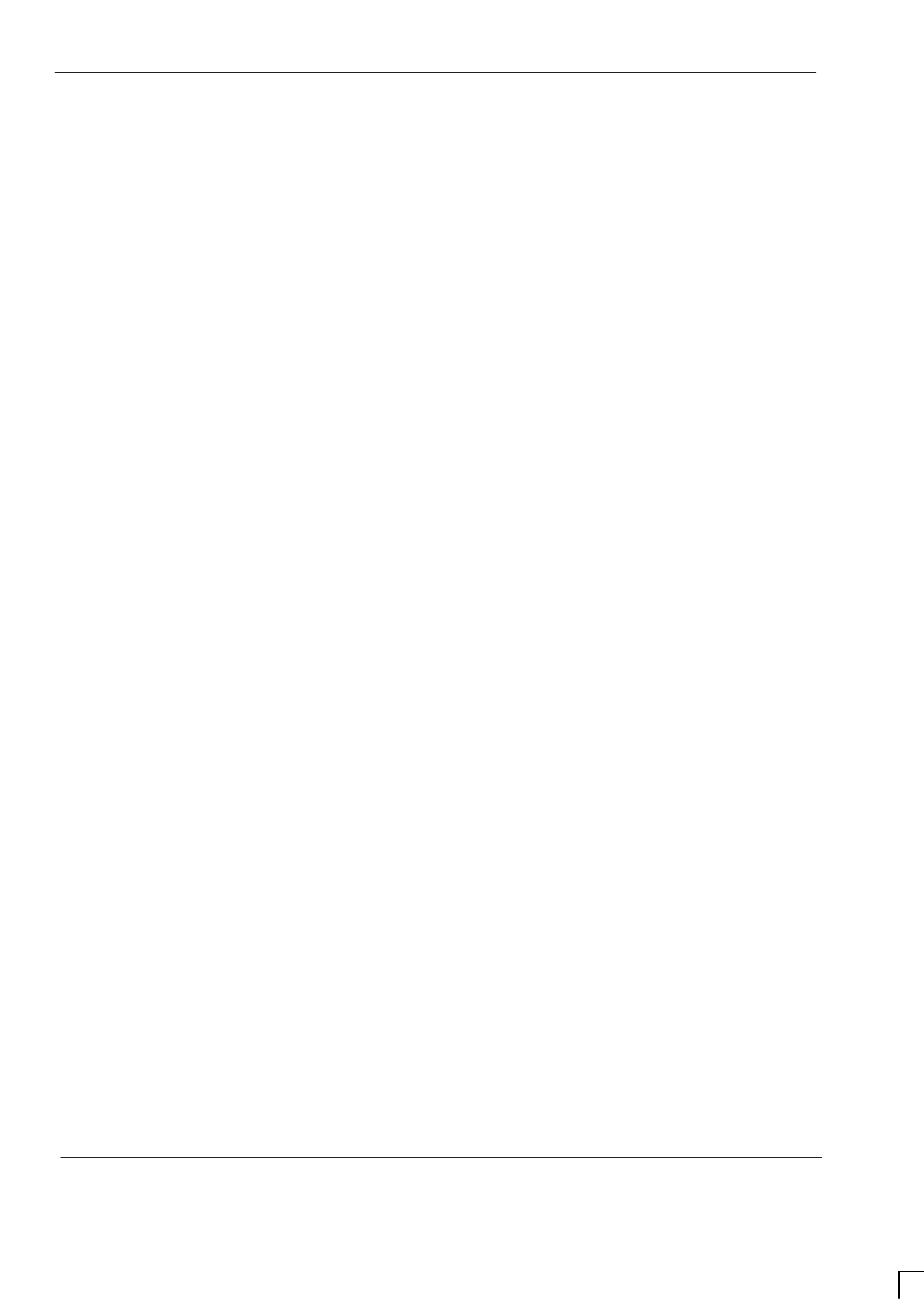
GSM-204-323
31st Oct 01
viii
Technical Description: Horizon
macro
outdoor
CONTROLLED INTRODUCTION
68P02902W02-A
MCUF Tech. 6–5. . . . . . . . . . . . . . . . . . . . . . . . . . . . . . . . . . . . . . . . . . . . . . . . . . . . . . . . . . . . . .
MCUF overview Tech. 6–5. . . . . . . . . . . . . . . . . . . . . . . . . . . . . . . . . . . . . . . . . . . . . . . . .
Capability to replace MCU of M-Cell6 and M-Cell2 Tech. 6–5. . . . . . . . . . . . . . . . . .
GPROC TSW and GLCK functions Tech. 6–6. . . . . . . . . . . . . . . . . . . . . . . . . . . . . . . .
MCUF module view Tech. 6–6. . . . . . . . . . . . . . . . . . . . . . . . . . . . . . . . . . . . . . . . . . . . .
MCUF functional diagram Tech. 6–7. . . . . . . . . . . . . . . . . . . . . . . . . . . . . . . . . . . . . . . .
Link to redundant MCUF Tech. 6–8. . . . . . . . . . . . . . . . . . . . . . . . . . . . . . . . . . . . . . . . .
Front panel interfaces Tech. 6–8. . . . . . . . . . . . . . . . . . . . . . . . . . . . . . . . . . . . . . . . . . .
Front panel switches and indicators Tech. 6–9. . . . . . . . . . . . . . . . . . . . . . . . . . . . . . .
PIX interfaces Tech. 6–10. . . . . . . . . . . . . . . . . . . . . . . . . . . . . . . . . . . . . . . . . . . . . . . . . .
DRAM, flash EPROM and code loading functions Tech. 6–10. . . . . . . . . . . . . . . . . . .
ASIC functionality Tech. 6–11. . . . . . . . . . . . . . . . . . . . . . . . . . . . . . . . . . . . . . . . . . . . . . .
Sync block functionality Tech. 6–12. . . . . . . . . . . . . . . . . . . . . . . . . . . . . . . . . . . . . . . . . .
Integral MCUF FMUX functionality Tech. 6–14. . . . . . . . . . . . . . . . . . . . . . . . . . . . . . . .
NIU Tech. 6–15. . . . . . . . . . . . . . . . . . . . . . . . . . . . . . . . . . . . . . . . . . . . . . . . . . . . . . . . . . . . . . . .
Overview of NIU Tech. 6–15. . . . . . . . . . . . . . . . . . . . . . . . . . . . . . . . . . . . . . . . . . . . . . . .
NIU locations Tech. 6–15. . . . . . . . . . . . . . . . . . . . . . . . . . . . . . . . . . . . . . . . . . . . . . . . . . .
NIU command identity number Tech. 6–15. . . . . . . . . . . . . . . . . . . . . . . . . . . . . . . . . . . .
NIU view and LEDs Tech. 6–16. . . . . . . . . . . . . . . . . . . . . . . . . . . . . . . . . . . . . . . . . . . . .
NIU functionality Tech. 6–17. . . . . . . . . . . . . . . . . . . . . . . . . . . . . . . . . . . . . . . . . . . . . . . .
NIU diagram Tech. 6–18. . . . . . . . . . . . . . . . . . . . . . . . . . . . . . . . . . . . . . . . . . . . . . . . . . .
Control processor Tech. 6–19. . . . . . . . . . . . . . . . . . . . . . . . . . . . . . . . . . . . . . . . . . . . . . .
NIU/MCUF framing and clocks Tech. 6–19. . . . . . . . . . . . . . . . . . . . . . . . . . . . . . . . . . . .
Distance measurement Tech. 6–20. . . . . . . . . . . . . . . . . . . . . . . . . . . . . . . . . . . . . . . . . .
Radio signalling links (RSLs) Tech. 6–20. . . . . . . . . . . . . . . . . . . . . . . . . . . . . . . . . . . . .
T1 NIU need to set link type Tech. 6–20. . . . . . . . . . . . . . . . . . . . . . . . . . . . . . . . . . . . . .
T43/BIB-NIU - E1/T1 mapping Tech. 6–21. . . . . . . . . . . . . . . . . . . . . . . . . . . . . . . . . . . . . . . . .
Overview of T43/BIB-NIU connection Tech. 6–21. . . . . . . . . . . . . . . . . . . . . . . . . . . . . .
NIU to T43/BIB mapping and command ID Tech. 6–21. . . . . . . . . . . . . . . . . . . . . . . . .
Diagram of T43 connection to NIUs Tech. 6–22. . . . . . . . . . . . . . . . . . . . . . . . . . . . . . .
FMUX module and FMUX function Tech. 6–23. . . . . . . . . . . . . . . . . . . . . . . . . . . . . . . . . . . . .
Overview of FMUX module Tech. 6–23. . . . . . . . . . . . . . . . . . . . . . . . . . . . . . . . . . . . . . .
FMUX module view Tech. 6–23. . . . . . . . . . . . . . . . . . . . . . . . . . . . . . . . . . . . . . . . . . . . .
FMUX functional diagram Tech. 6–24. . . . . . . . . . . . . . . . . . . . . . . . . . . . . . . . . . . . . . . .
FMUX functional explanation Tech. 6–24. . . . . . . . . . . . . . . . . . . . . . . . . . . . . . . . . . . . .
Alarm module Tech. 6–25. . . . . . . . . . . . . . . . . . . . . . . . . . . . . . . . . . . . . . . . . . . . . . . . . . . . . . .
Alarm module overview Tech. 6–25. . . . . . . . . . . . . . . . . . . . . . . . . . . . . . . . . . . . . . . . . .
Alarm module view Tech. 6–25. . . . . . . . . . . . . . . . . . . . . . . . . . . . . . . . . . . . . . . . . . . . . .
Alarm module functionality Tech. 6–26. . . . . . . . . . . . . . . . . . . . . . . . . . . . . . . . . . . . . . .
Alarm module replacement – effect on alarms Tech. 6–26. . . . . . . . . . . . . . . . . . . . . .
Alarm collection from extension cabinets Tech. 6–26. . . . . . . . . . . . . . . . . . . . . . . . . . .
Alarm module display presentation Tech. 6–27. . . . . . . . . . . . . . . . . . . . . . . . . . . . . . . .
Chapter 7
Auxiliary equipment housing i. . . . . . . . . . . . . . . . . . . . . . . . . . . . . . . . . . .
Auxiliary equipment housing overview Tech. 7–1. . . . . . . . . . . . . . . . . . . . . . . . . . . . . . . . . .
Introduction to the auxiliary equipment housing Tech. 7–1. . . . . . . . . . . . . . . . . . . . .
Auxiliary equipment housing mechanical design Tech. 7–1. . . . . . . . . . . . . . . . . . . .
View of auxiliary equipment housing Tech. 7–2. . . . . . . . . . . . . . . . . . . . . . . . . . . . . . .
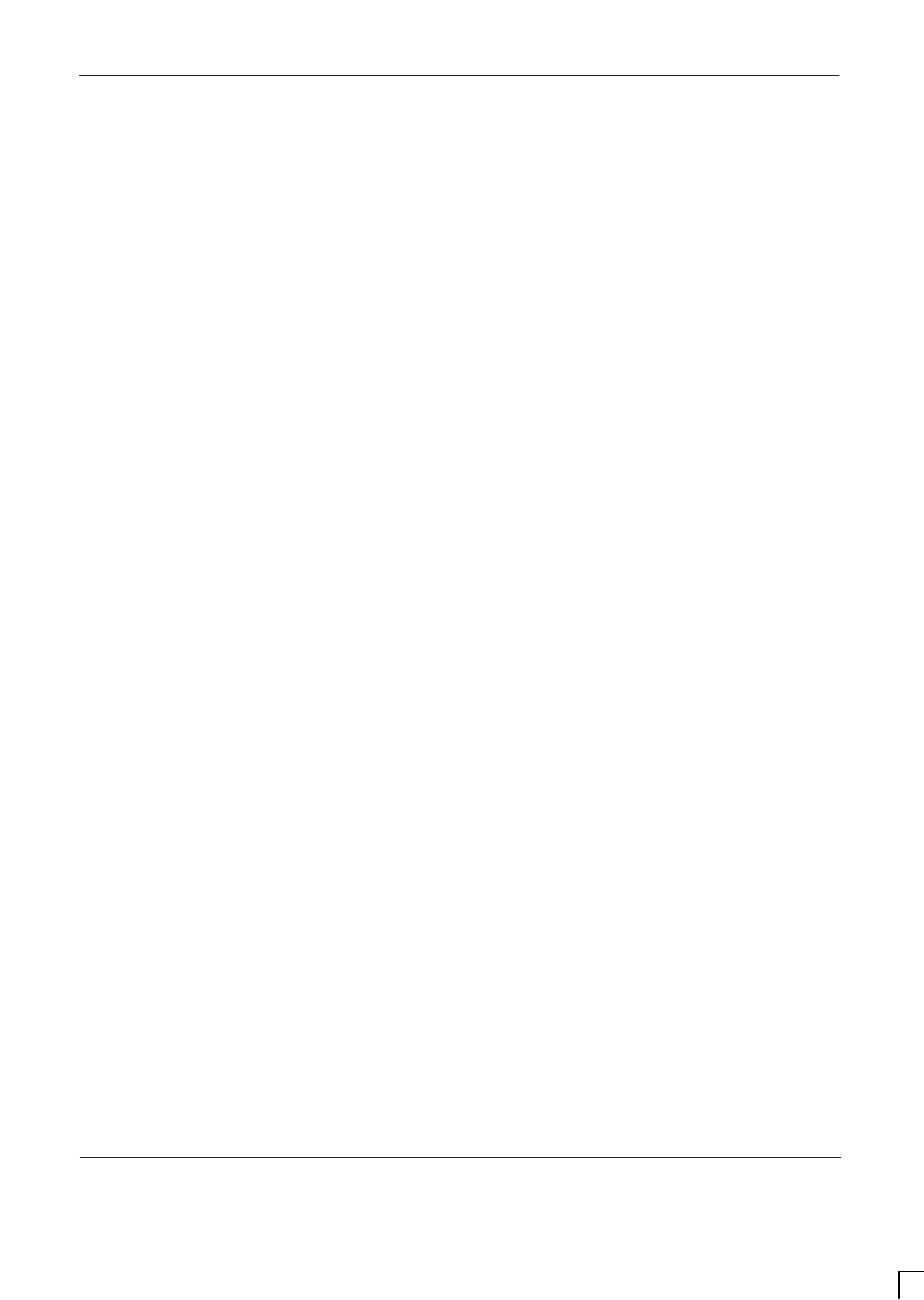
GSM-204-323
31st Oct 01
Technical Description: Horizon
macro
outdoor
68P02902W02-A
CONTROLLED INTRODUCTION
ix
Temperature control within the auxiliary equipment housing Tech. 7–3. . . . . . . . . . . . . . .
Temperature control equipment Tech. 7–3. . . . . . . . . . . . . . . . . . . . . . . . . . . . . . . . . . .
Operation of the temperature control equipment Tech. 7–3. . . . . . . . . . . . . . . . . . . .
External alarms interface board Tech. 7–4. . . . . . . . . . . . . . . . . . . . . . . . . . . . . . . . . . . . . . . .
Function of the external alarms interface board Tech. 7–4. . . . . . . . . . . . . . . . . . . . .
External alarms interface board connections Tech. 7–4. . . . . . . . . . . . . . . . . . . . . . .
Common applications for the auxiliary equipment housing Tech. 7–5. . . . . . . . . . . . . . . . .
Auxiliary equipment housing as a battery box Tech. 7–5. . . . . . . . . . . . . . . . . . . . . . .
View of auxiliary equipment housing as battery box Tech. 7–6. . . . . . . . . . . . . . . . .
Chapter 8
Cable shroud i. . . . . . . . . . . . . . . . . . . . . . . . . . . . . . . . . . . . . . . . . . . . . . . . .
Introduction to the cable shroud Tech. 8–1. . . . . . . . . . . . . . . . . . . . . . . . . . . . . . . . . . . . . . . .
Overview of the cable shroud Tech. 8–1. . . . . . . . . . . . . . . . . . . . . . . . . . . . . . . . . . . . .
Cable shroud configurations Tech. 8–1. . . . . . . . . . . . . . . . . . . . . . . . . . . . . . . . . . . . . .
The cable shroud assembly Tech. 8–2. . . . . . . . . . . . . . . . . . . . . . . . . . . . . . . . . . . . . . . . . . .
Description of the cable shroud assembly Tech. 8–2. . . . . . . . . . . . . . . . . . . . . . . . . .
View of the cable shroud Tech. 8–2. . . . . . . . . . . . . . . . . . . . . . . . . . . . . . . . . . . . . . . . .
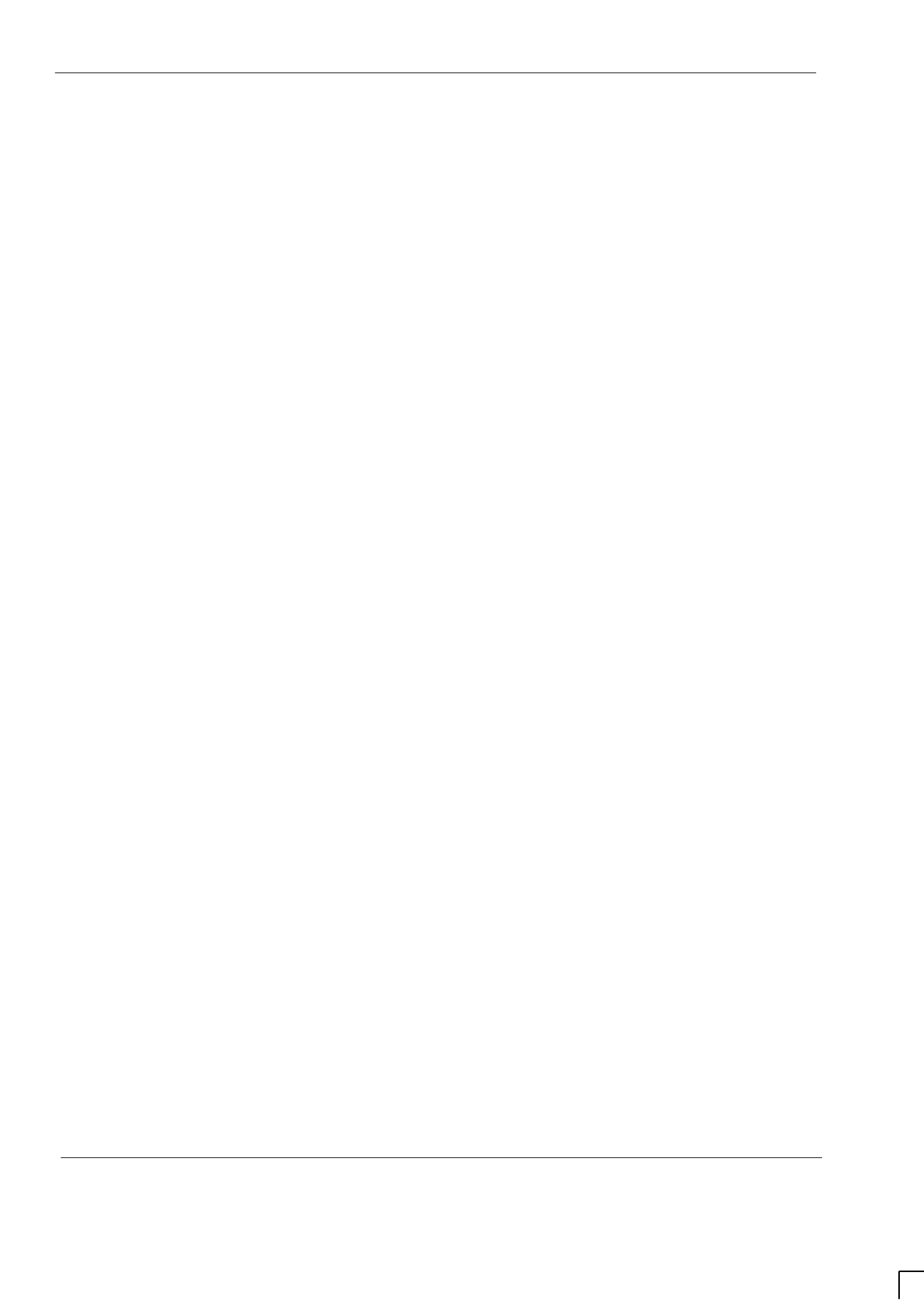
GSM-204-323
31st Oct 01
x
Technical Description: Horizon
macro
outdoor
CONTROLLED INTRODUCTION
68P02902W02-A
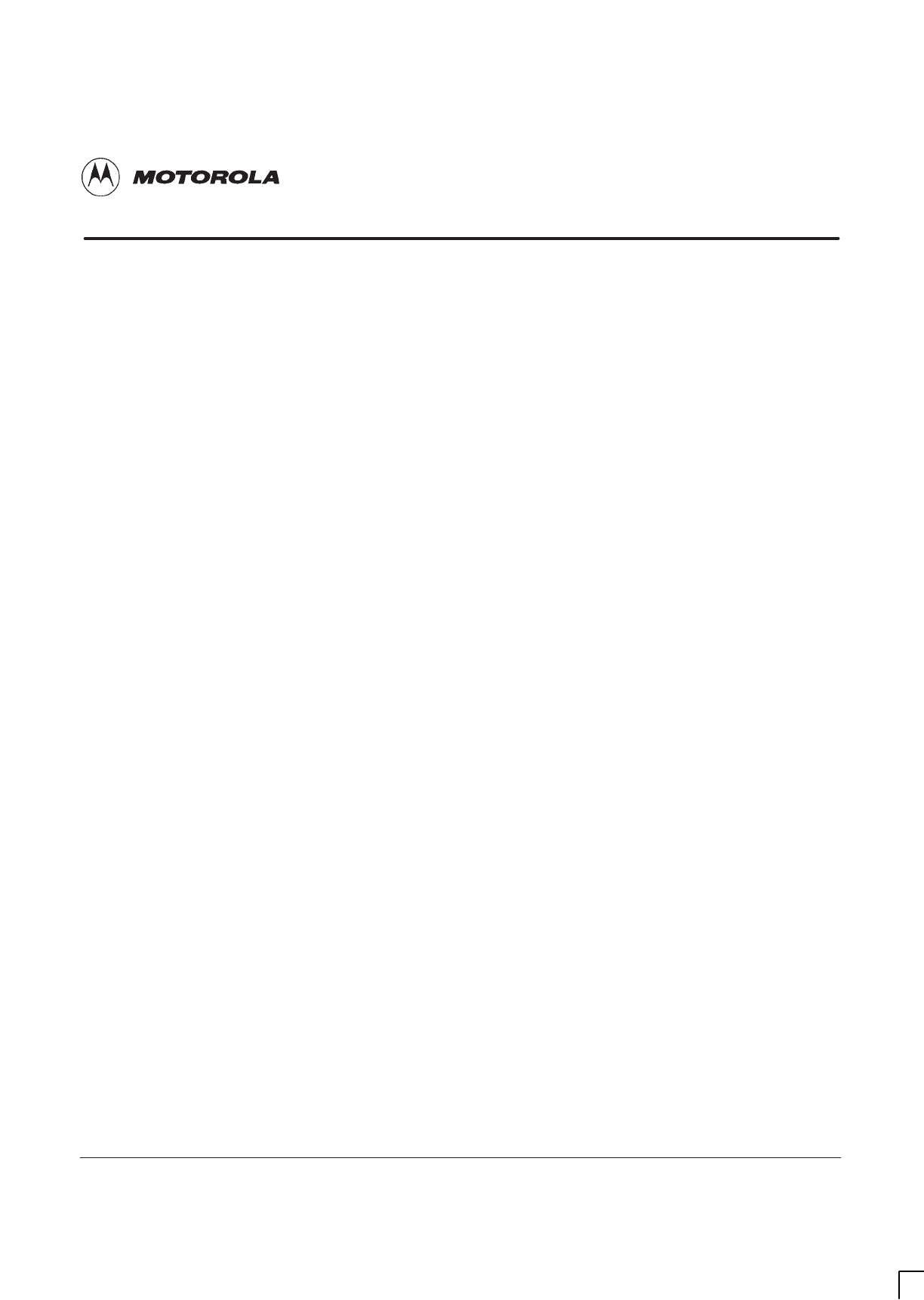
31st Oct 01
Technical Description: Horizon
macro
outdoor
68P02902W02-A
CONTROLLED INTRODUCTION
i
Chapter 1
Overview and specifications
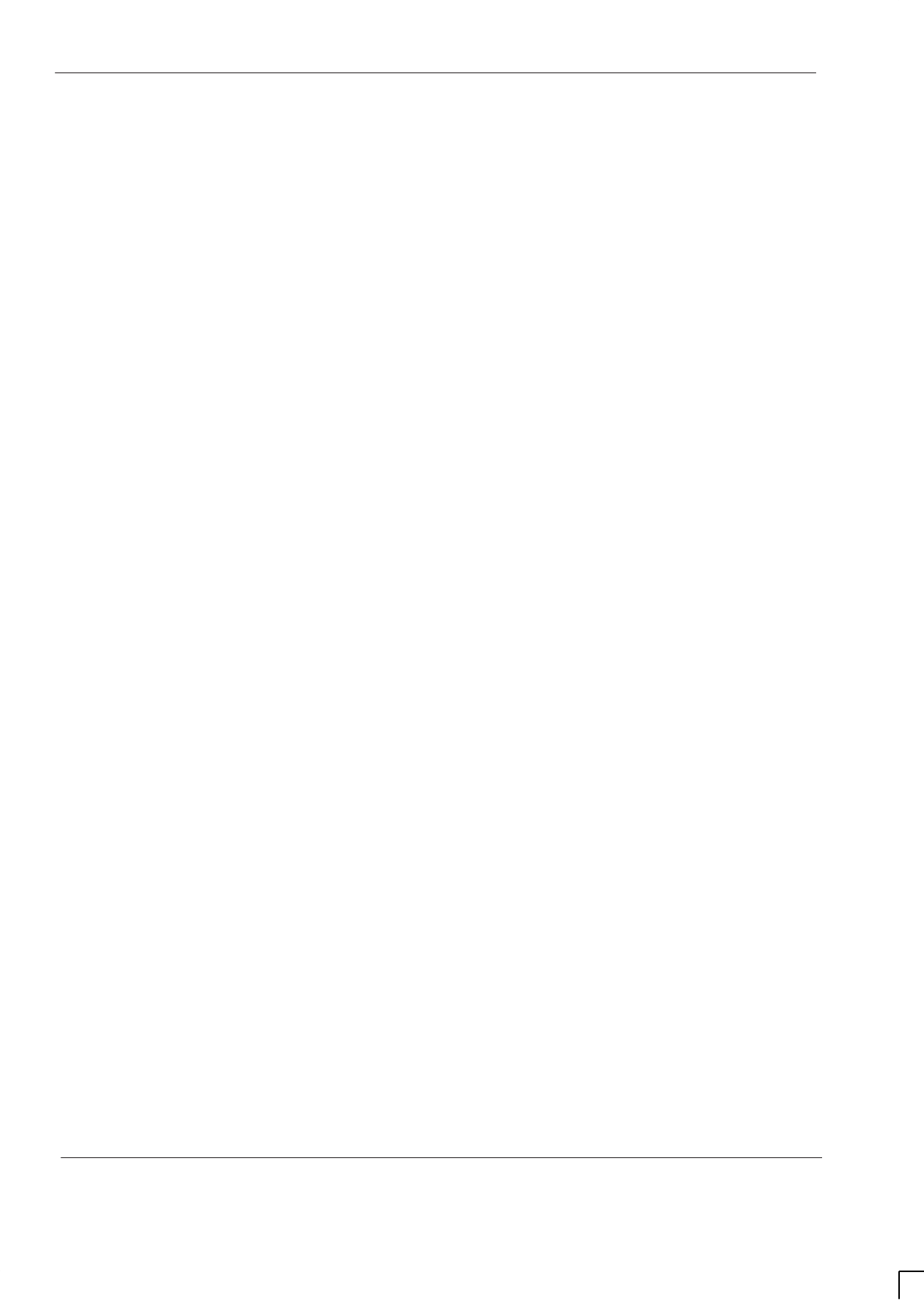
GSM-204-323
31st Oct 01
ii
Technical Description: Horizon
macro
outdoor
CONTROLLED INTRODUCTION
68P02902W02-A
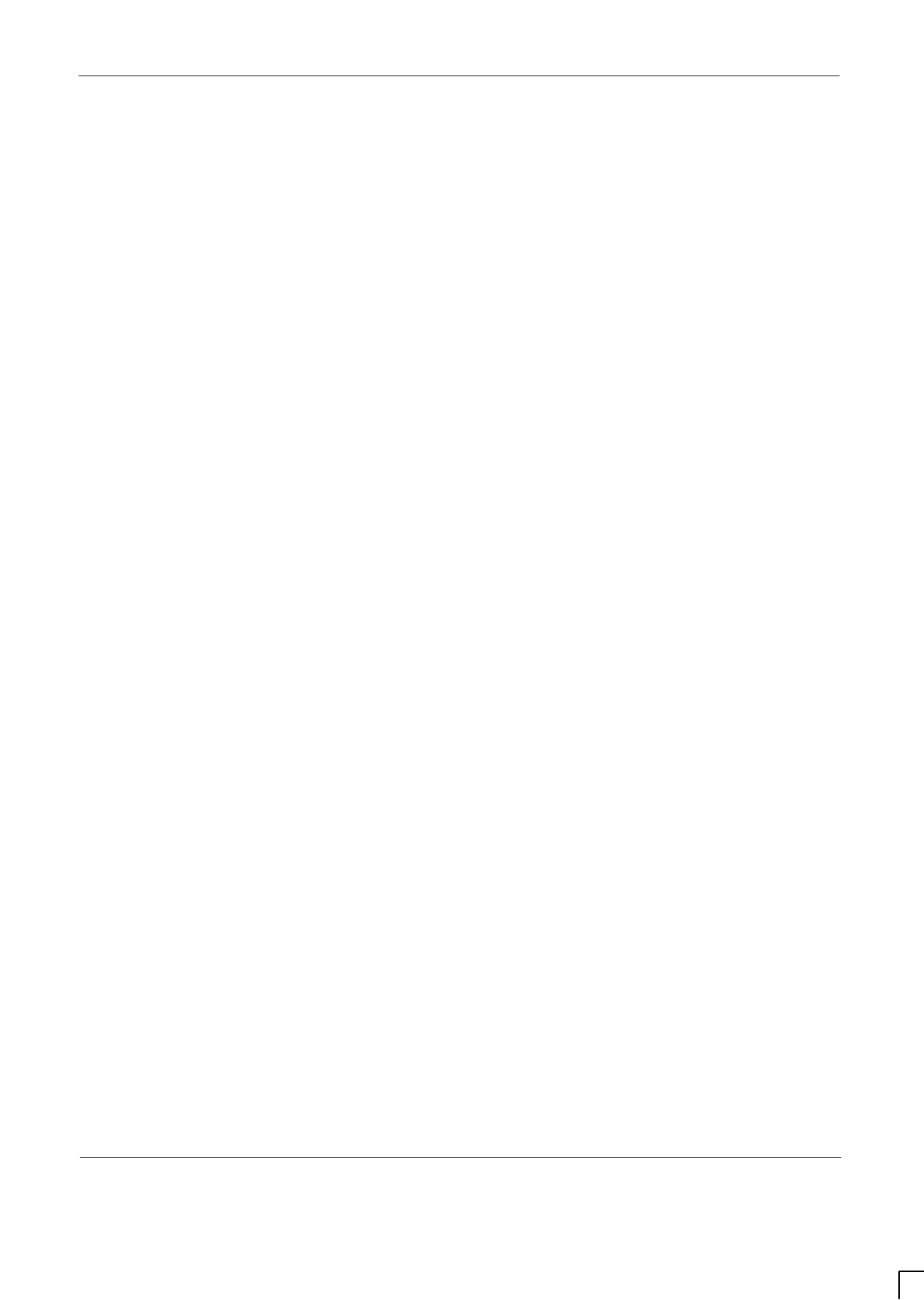
GSM-204-323
31st Oct 01
Technical Description: Horizon
macro
outdoor
68P02902W02-A
CONTROLLED INTRODUCTION
iii
Chapter 1
Overview and specifications i. . . . . . . . . . . . . . . . . . . . . . . . . . . . . . . . . . .
Equipment introduction and manual definition Tech. 1–1. . . . . . . . . . . . . . . . . . . . . . . . . . .
Overview of Horizonmacro outdoor Tech. 1–1. . . . . . . . . . . . . . . . . . . . . . . . . . . . . . . .
Names and acronyms for main cabinet equipment Tech. 1–2. . . . . . . . . . . . . . . . . .
Configuration information Tech. 1–3. . . . . . . . . . . . . . . . . . . . . . . . . . . . . . . . . . . . . . . .
Finding information in this manual Tech. 1–4. . . . . . . . . . . . . . . . . . . . . . . . . . . . . . . . .
Cabinet view Tech. 1–5. . . . . . . . . . . . . . . . . . . . . . . . . . . . . . . . . . . . . . . . . . . . . . . . . . .
Functional diagram of Horizonmacro outdoor Tech. 1–6. . . . . . . . . . . . . . . . . . . . . . .
M-Cell6 comparison with Horizonmacro outdoor Tech. 1–7. . . . . . . . . . . . . . . . . . . . . . . . .
Comparison overview Tech. 1–7. . . . . . . . . . . . . . . . . . . . . . . . . . . . . . . . . . . . . . . . . . .
Horizonmacro and M-Cell6 compatibility Tech. 1–7. . . . . . . . . . . . . . . . . . . . . . . . . . .
Comparison of Horizonmacro and M-Cell6 connections and modules Tech. 1–8. .
Specifications Tech. 1–9. . . . . . . . . . . . . . . . . . . . . . . . . . . . . . . . . . . . . . . . . . . . . . . . . . . . . . .
Introduction to specifications Tech. 1–9. . . . . . . . . . . . . . . . . . . . . . . . . . . . . . . . . . . . .
Software requirements Tech. 1–9. . . . . . . . . . . . . . . . . . . . . . . . . . . . . . . . . . . . . . . . . .
Approval and safety Tech. 1–9. . . . . . . . . . . . . . . . . . . . . . . . . . . . . . . . . . . . . . . . . . . .
Environmental limits Tech. 1–9. . . . . . . . . . . . . . . . . . . . . . . . . . . . . . . . . . . . . . . . . . . . .
Power requirements Tech. 1–10. . . . . . . . . . . . . . . . . . . . . . . . . . . . . . . . . . . . . . . . . . . . .
RF power output Tech. 1–11. . . . . . . . . . . . . . . . . . . . . . . . . . . . . . . . . . . . . . . . . . . . . . . .
Sensitivity Tech. 1–12. . . . . . . . . . . . . . . . . . . . . . . . . . . . . . . . . . . . . . . . . . . . . . . . . . . . . .
Battery backup Tech. 1–12. . . . . . . . . . . . . . . . . . . . . . . . . . . . . . . . . . . . . . . . . . . . . . . . .
BSC connectivity options Tech. 1–12. . . . . . . . . . . . . . . . . . . . . . . . . . . . . . . . . . . . . . . .
Outdoor cabinet dimensions Tech. 1–12. . . . . . . . . . . . . . . . . . . . . . . . . . . . . . . . . . . . . .
Weights Tech. 1–13. . . . . . . . . . . . . . . . . . . . . . . . . . . . . . . . . . . . . . . . . . . . . . . . . . . . . . . .
Torque values Tech. 1–13. . . . . . . . . . . . . . . . . . . . . . . . . . . . . . . . . . . . . . . . . . . . . . . . . .
Cabinets enhancements Tech. 1–13. . . . . . . . . . . . . . . . . . . . . . . . . . . . . . . . . . . . . . . . .
Frequency capability Tech. 1–14. . . . . . . . . . . . . . . . . . . . . . . . . . . . . . . . . . . . . . . . . . . .
Structural considerations Tech. 1–16. . . . . . . . . . . . . . . . . . . . . . . . . . . . . . . . . . . . . . . . .
Outdoor site dimensions Tech. 1–17. . . . . . . . . . . . . . . . . . . . . . . . . . . . . . . . . . . . . . . . .
View of maximum site template layout Tech. 1–18. . . . . . . . . . . . . . . . . . . . . . . . . . . . .
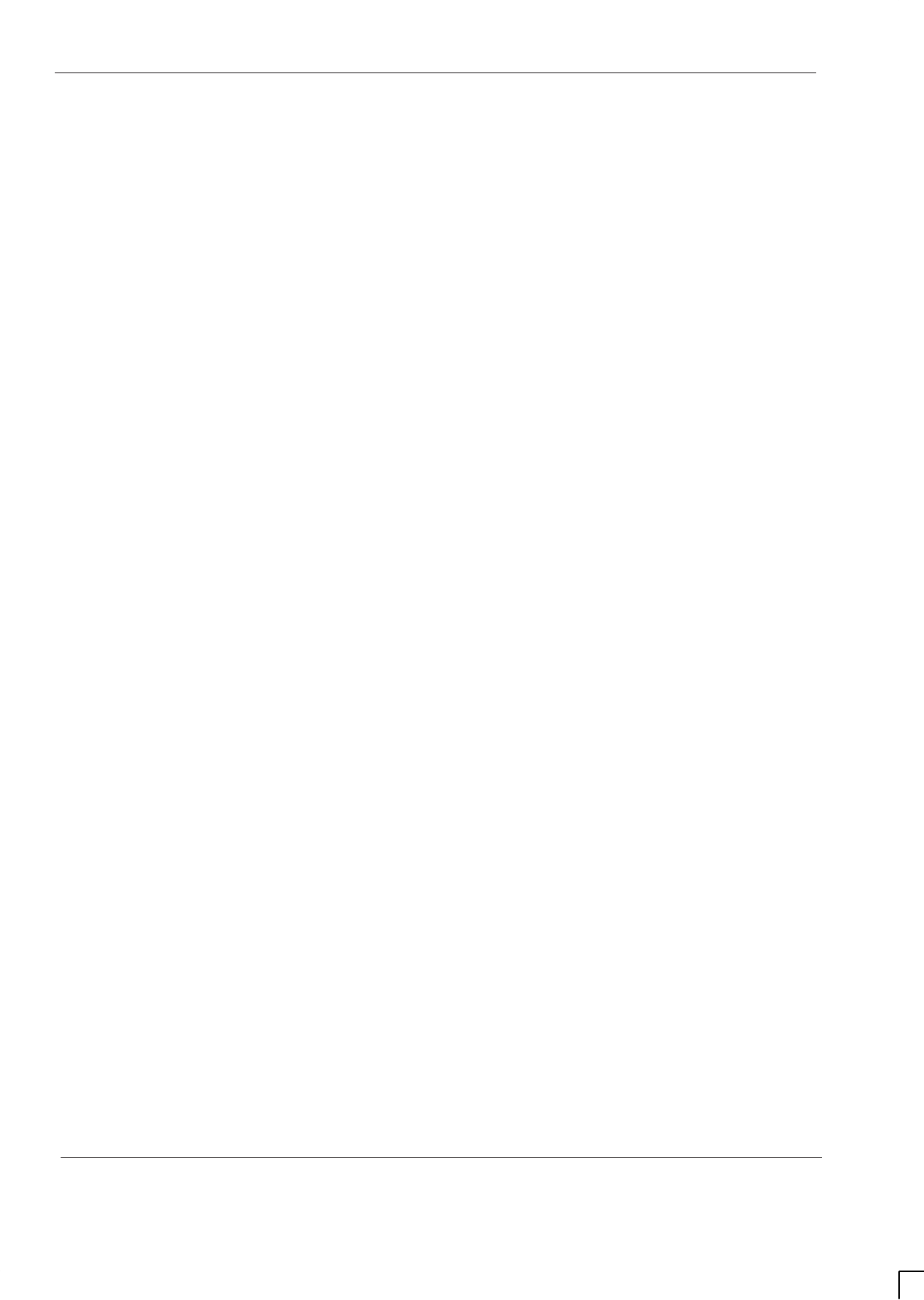
GSM-204-323
31st Oct 01
iv
Technical Description: Horizon
macro
outdoor
CONTROLLED INTRODUCTION
68P02902W02-A
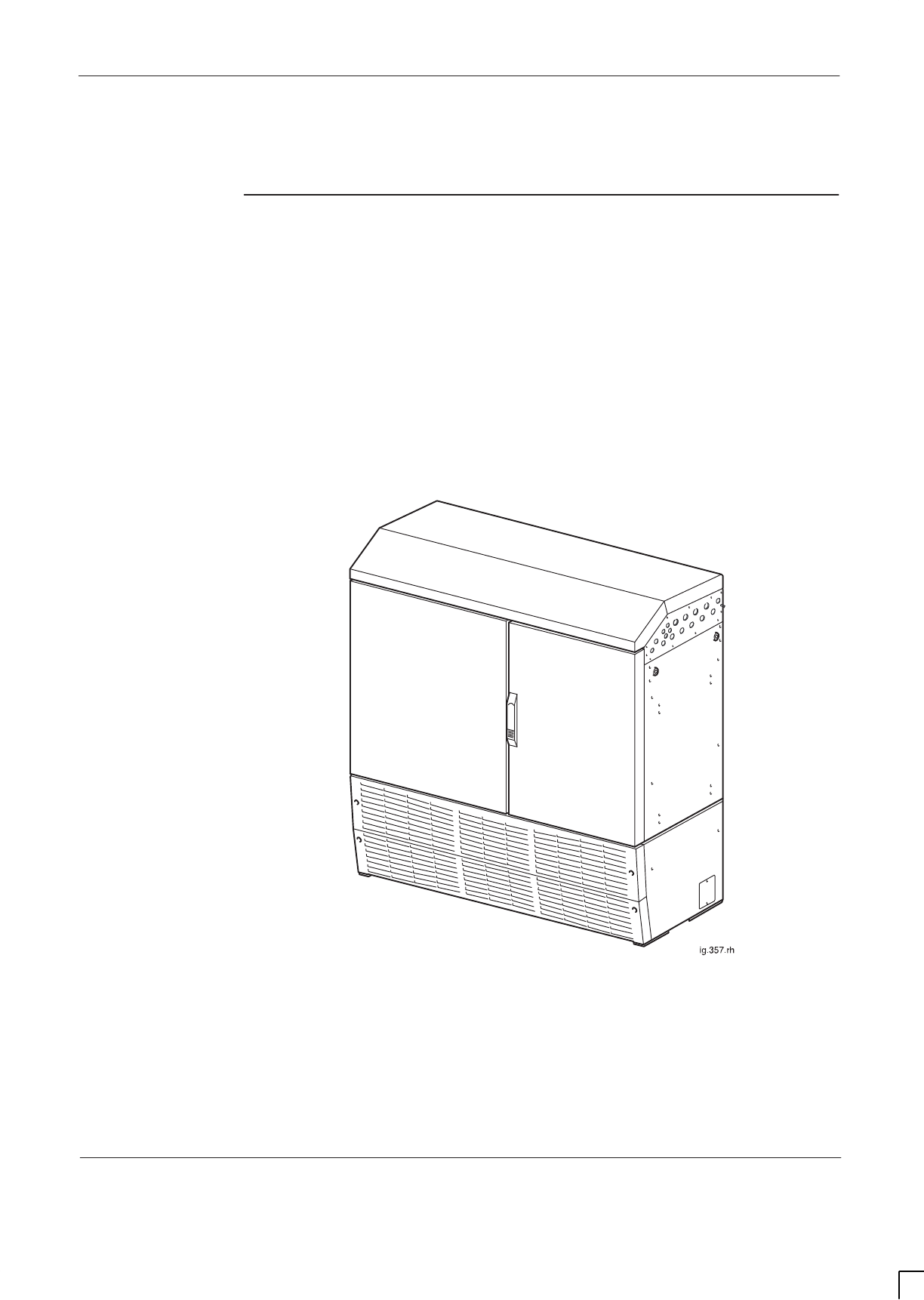
GSM-204-323 Equipment introduction and manual definition
31st Oct 01
Technical Description: Horizon
macro
outdoor
68P02902W02-A
CONTROLLED INTRODUCTION
Tech. 1–1
Equipment introduction and manual definition
Overview of
Horizon
macro
outdoor
The Horizon
macro
outdoor
is a six carrier Base Transceiver Station (BTS)
cabinet, with variants that operate in the following frequency bands: GSM850,
GSM/EGSM900, DCS1800 and PCS1900.
Outdoor cabinets operate from nominal 110 V single phase or nominal 230 V,
single or three phase, ac supply. Cabinet temperature control is provided by a
thermal management system (TMS) located in the bottom of the unit.
This section provides the reader with a introduction to the equipment, and
describes the structure of the manual.
Figure 1-1 shows an external view of a standard Horizon
macro
outdoor cabinet.
Figure 1-1 External view of the Horizon
macro
outdoor cabinet
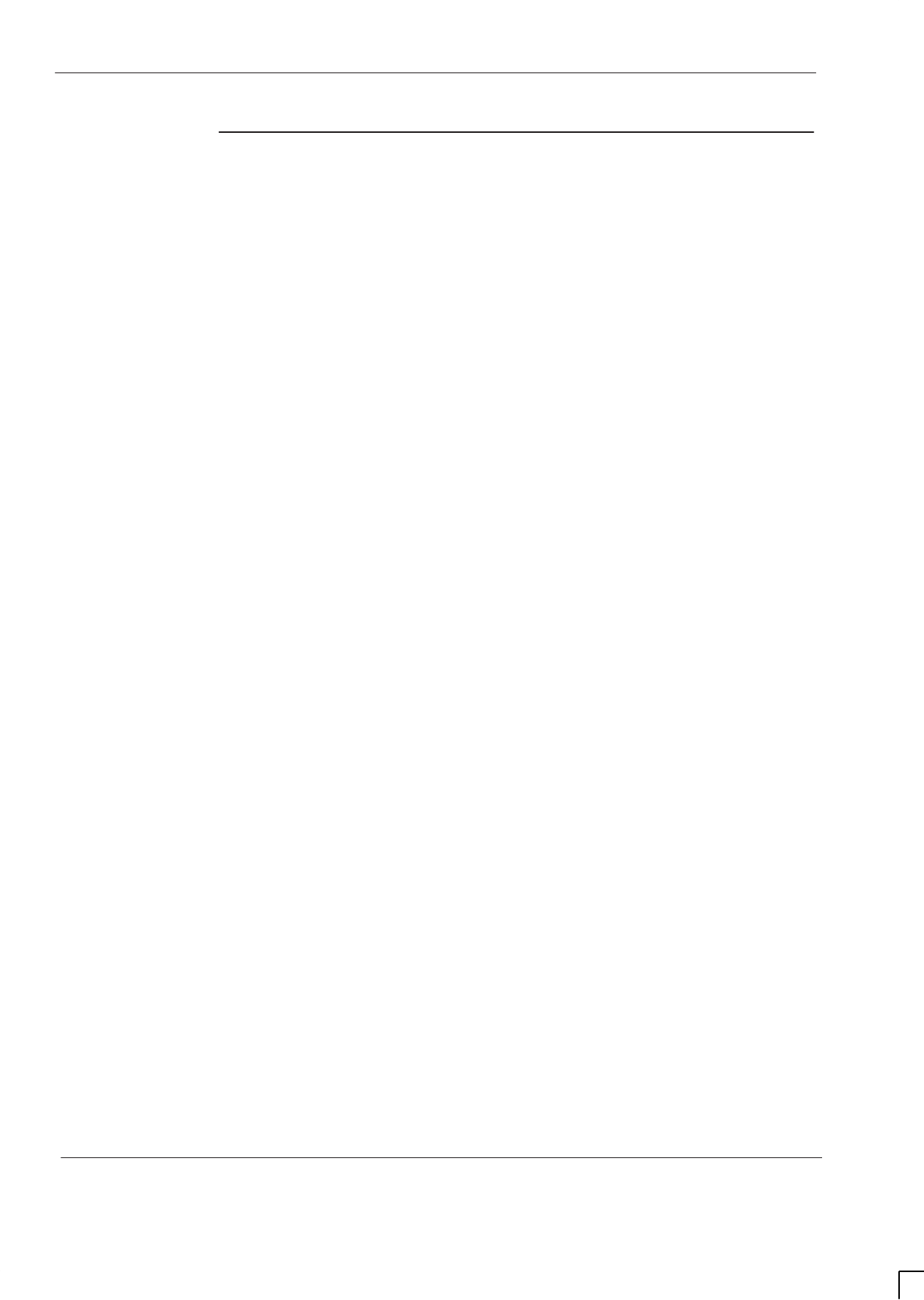
GSM-204-323
Equipment introduction and manual definition
31st Oct 01
Tech. 1–2
Technical Description: Horizon
macro
outdoor
CONTROLLED INTRODUCTION
68P02902W02-A
Names and
acronyms for
main cabinet
equipment
This section is intended to give the reader a basic understanding of how
components interconnect.
The outdoor BTS cabinet consists of a top section, a centre section (containing
the radio enclosure and the power supply enclosure), and a bottom section.
On the left side of the centre section is the radio enclosure, and this contains
the CIBA main cage.
The main cage contains the following equipment (see Figure 1-2):
A digital module shelf, located in the lower right side of the cabinet. This
contains master and optional redundant digital modules:
Fibre optic multiplexer (FMUX), 1 + 1 redundant (if required).
Main Control Unit with dual FMUX (MCUF), 1 + 1 redundant (if required).
Network Interface Units (NIUs).
An alarm board (no redundancy option).
One or two (for redundancy) BCU Power Supply Modules (BPSMs).
Up to three Power Supply Modules (PSMs) and one Circuit Breaker
Module (CBM) in the upper right part of the cage. The PSMs are load
sharing, with the third PSM providing optional redundancy.
Up to six Compact Transceiver Units (CTUs), located in the left side of the
cage.
The right side of the centre section is the power supply enclosure. It contains
the Power Supply Unit (PSU), an alarms interface board and 6 U of standard
rack space for customer specific equipment.
The PSU includes the following equipment (see Figure 1-2):
The number 2 ac distribution box, located in the upper right side of the
unit.
A dc circuit breaker panel, located in the upper left side of the unit.
An internal battery tray, located in the lower right side of the unit.
Up to three of The Outdoor Power Supply Modules (TOPSMs), in the
lower left side of the unit. The TOPSMs are load sharing, with the third
TOPSM providing optional redundancy.
A Control and Alarm Board (CAB).
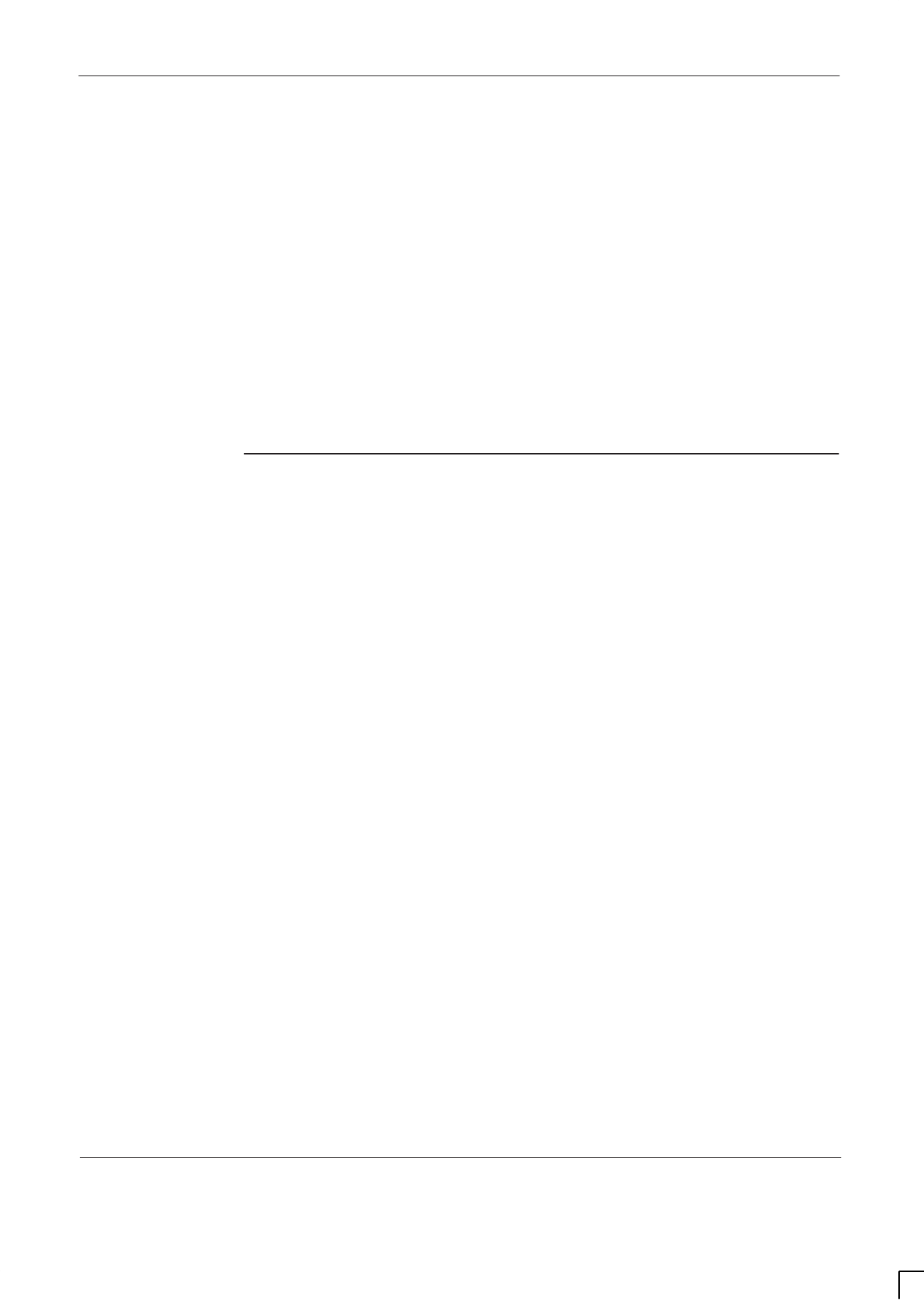
GSM-204-323 Equipment introduction and manual definition
31st Oct 01
Technical Description: Horizon
macro
outdoor
68P02902W02-A
CONTROLLED INTRODUCTION
Tech. 1–3
The top section contains the following equipment (see Figure 1-2):
RF modules, comprising transmit (Tx) blocks and a receive (Rx) module,
the Sectorized Universal Receiver Front end (SURF). The various Tx
blocks are listed in Specifications in this chapter.
The interface panel for internal, power and alarm connectors and
customer communications connectors.
The number 1 ac distribution box.
Krone blocks for customer defined alarms and customer communications.
An ac outlet socket for installation and maintenance use.
The bottom section contains:
The Thermal Management System (TMS).
Configuration
information
Configuration information can be found in
Installation and Configuration:
(GSM-204-423)
in this manual.
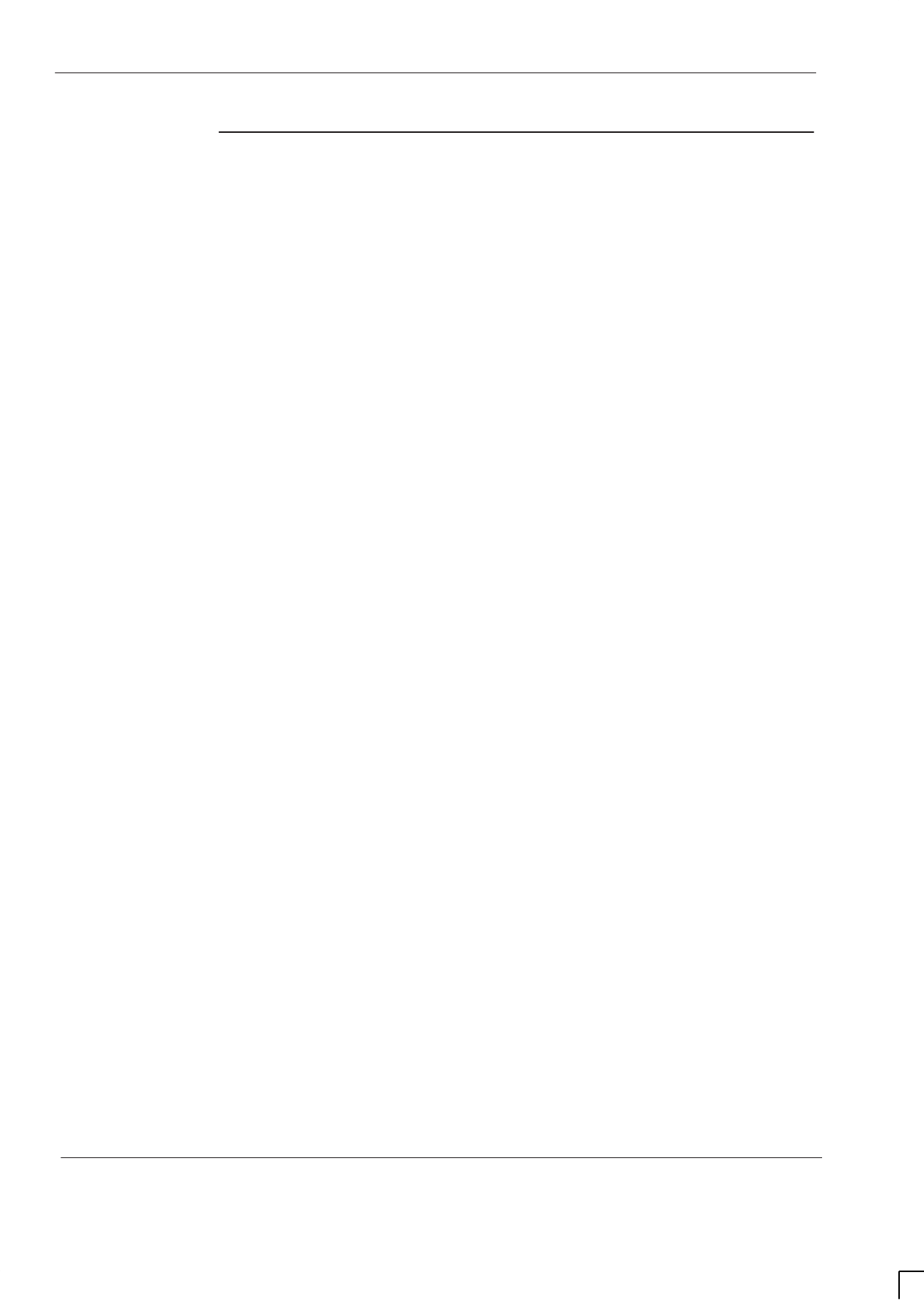
GSM-204-323
Equipment introduction and manual definition
31st Oct 01
Tech. 1–4
Technical Description: Horizon
macro
outdoor
CONTROLLED INTRODUCTION
68P02902W02-A
Finding
information in
this manual
This service manual comprises the four categories below:
Category 323
Provides an introduction, specification, and technical description.
Category 423
Provides information for installation and commissioning.
Category 523
Provides information on maintenance and repair, with procedures to
change Field Replaceable Units (FRUs).
Category 623
Provides the range of options and spares, with diagrams to illustrate
FRUs.
The Category 323 technical description is divided into chapters based on
functionality, as shown in Figure 1-2:
Overview and specifications
This chapter provides a summary of the equipment to enable the reader to
understand terminology, and thus locate information via the TOCs and
index.
Cabinet structure, including:
Interface panel, main cage,power supply enclosure, doors and lid.
Thermal management system (TMS), describing:
TMS units.
Cabinet power supply, including:
Power distribution, TOPSM, PSM, BPSM and circuit breaker module.
RF modules, including:
CTU, SURF and Tx Blocks.
Digital modules, including:
MCUF, NIU, T43/BIB connections, FMUX and alarm module.
Information regarding optional equipment is also provided:
Auxiliary equipment housing.
Cable shroud.
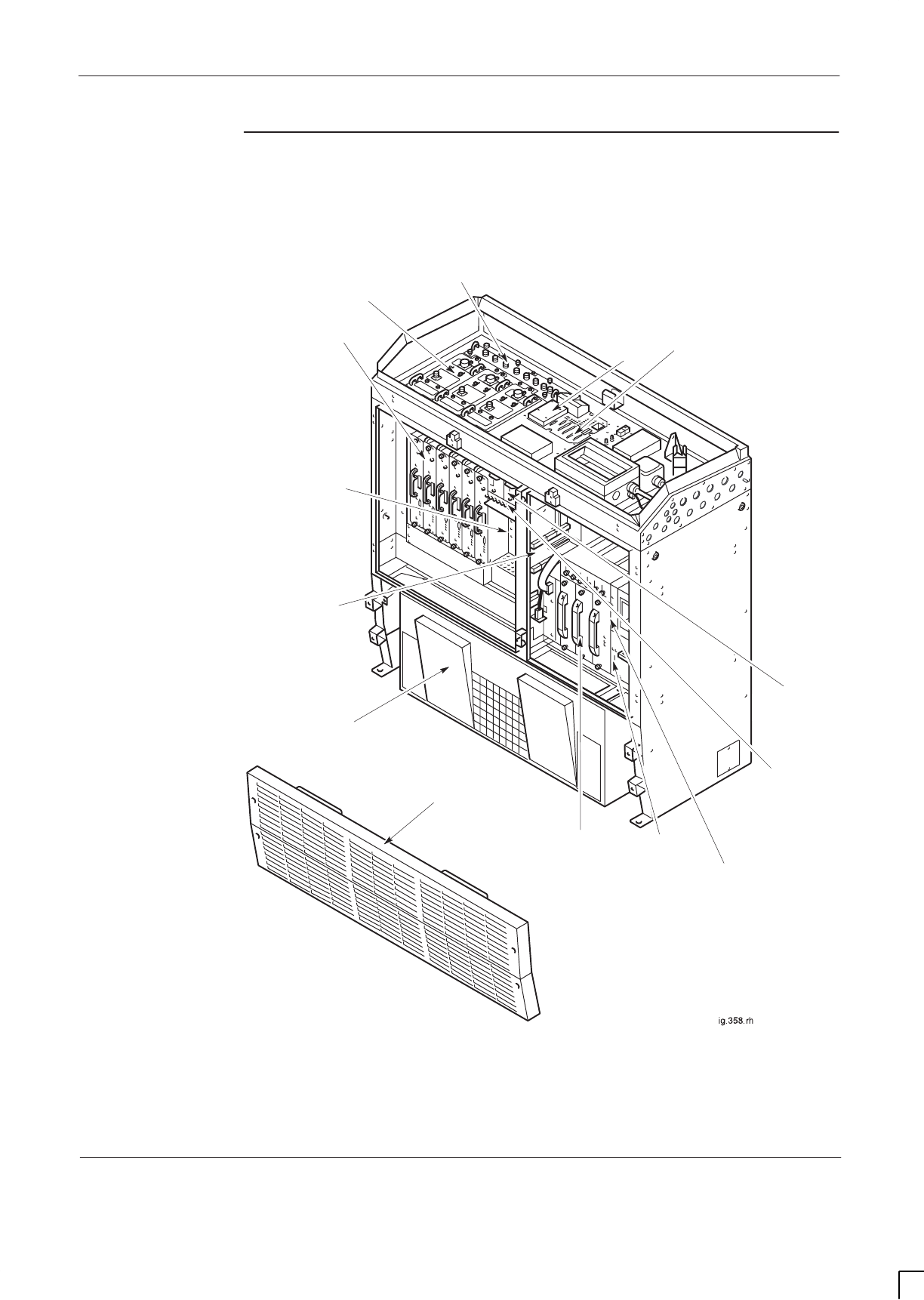
GSM-204-323 Equipment introduction and manual definition
31st Oct 01
Technical Description: Horizon
macro
outdoor
68P02902W02-A
CONTROLLED INTRODUCTION
Tech. 1–5
Cabinet view
Figure 1-2 shows the location of components and main headings for detailed
information in this technical description category of the manual.
THREE PSMs
THREE Tx BLOCKS
(DCFs SHOWN AS
EXAMPLE)
ONE SURF
(Rx)
SIX CTUs
ALARM BOARD
MCUF
FMUX/NIU/BPSM
INTERFACE PANEL
CONNECTORS
CIRCUIT
BREAKER
MODULE (CBM)
T43/BIB
THREE
TOPSMs
ALARMS
INTERFACE
BOARD
CONTROL AND
ALARM BOARD
INTERNAL
BATTERY
TRAY
TMS UNIT
TMS FRONT
COVER
RF MODULES
THERMAL
MANAGEMENT SYSTEM
DIGITAL
MODULES
POWER SUPPLIES AND
DISTRIBUTION
CABINET
STRUCTURE
Figure 1-2 Cabinet with components identified (doors and lid removed)
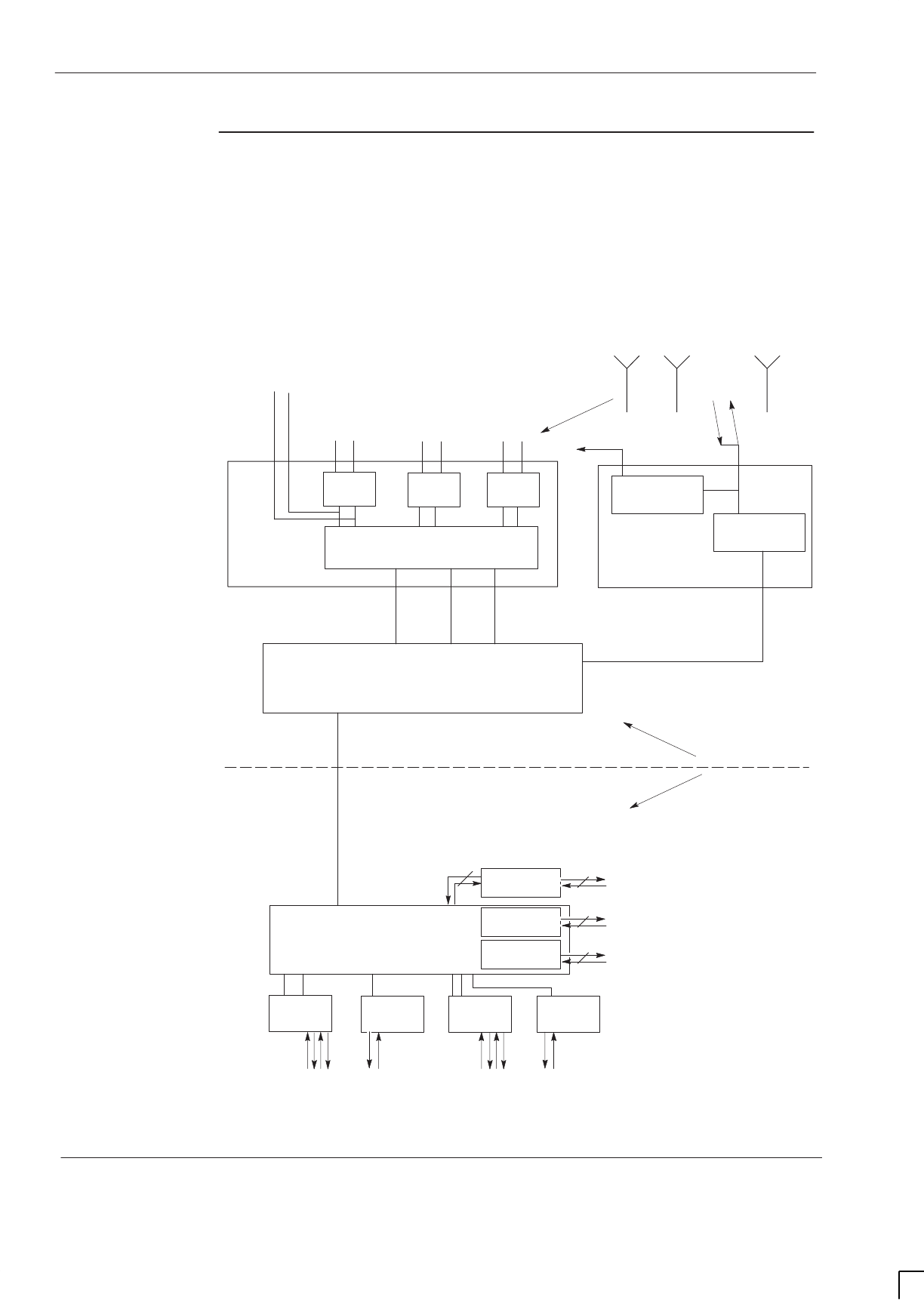
GSM-204-323
Equipment introduction and manual definition
31st Oct 01
Tech. 1–6
Technical Description: Horizon
macro
outdoor
CONTROLLED INTRODUCTION
68P02902W02-A
Functional
diagram of
Horizon
macro
outdoor
Figure 1-3 shows the functional modules of a Horizon
macro
. Only one
transceiver and one Tx block have been shown, and the thermal management
system and power supplies are also omitted, for clarity.
SWITCH (CONTROLLED BY CTU)
MCUF FMUX
FMUX
TO FMUX OF
EXTENSION CABINET
6
1
NIU
TO NETWORK
NIU NIU NIU
RF
MODULES
DIGITAL
MODULES
UP TO SIX TRANSCEIVERS
(CTUs)
UP TO THREE
Tx BLOCKS
ANTENNAS (Tx and Rx
SEPARATE OR COMBINED)
SURF
Rx0 Rx2Rx1
Rx A Rx B
Tx
TO SURF or
MCell6 Rx OF
EXTENSION
CABINET
Tx FILTER
Rx FILTER
RF LOOPBACK
EXT
FMUX
1
1
TO FMUX OF
EXTENSION CABINET
TO FMUX OF
EXTENSION CABINET
0B 1B1A 2A 2B0A
Figure 1-3 Functional diagram of cabinet components
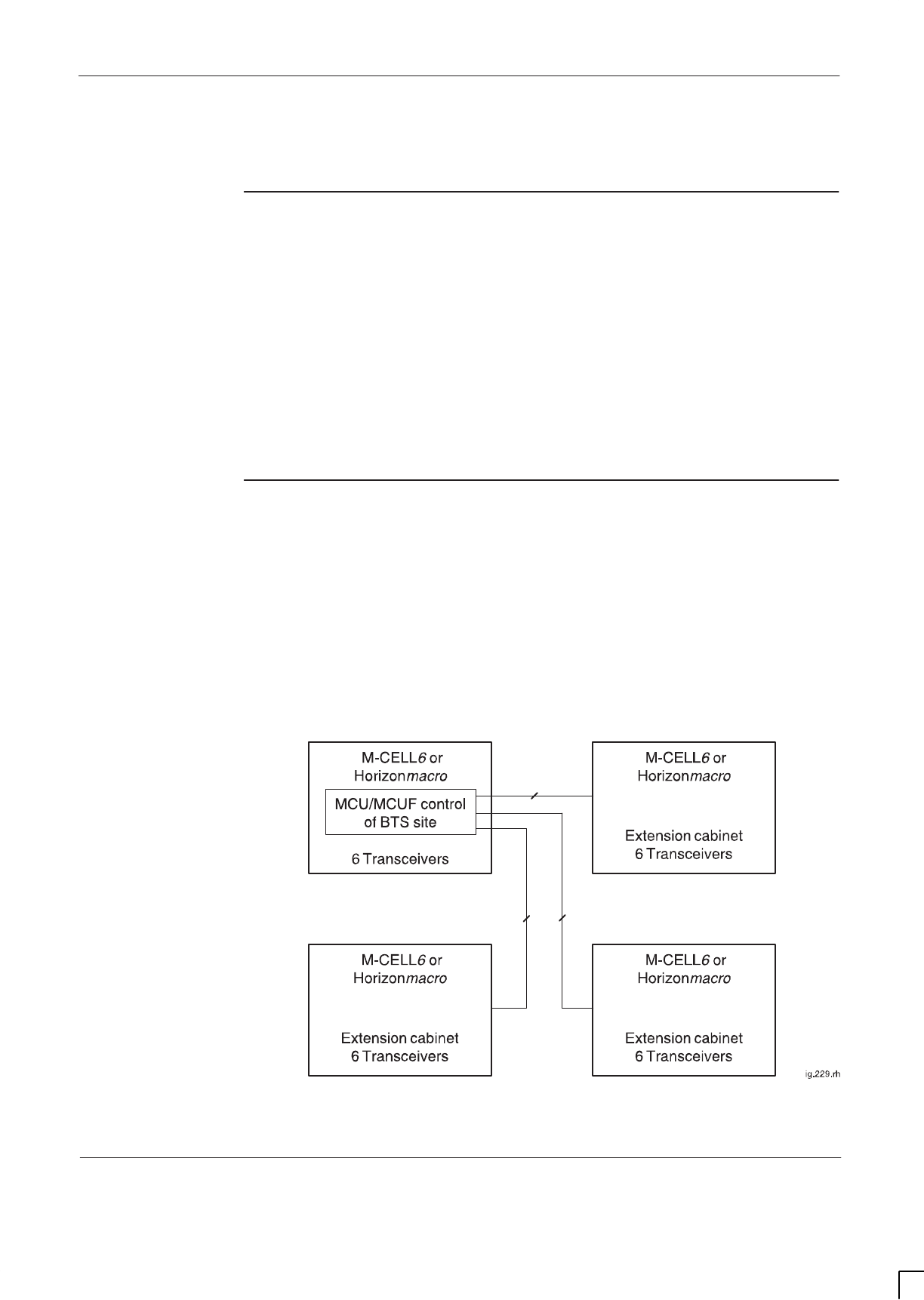
GSM-204-323 M-Cell
6
comparison with Horizon
macro
outdoor
31st Oct 01
Technical Description: Horizon
macro
outdoor
68P02902W02-A
CONTROLLED INTRODUCTION
Tech. 1–7
M-Cell
6
comparison with Horizon
macro
outdoor
Comparison
overview
The Horizon
macro
is a replacement for M-Cell
2/6
base stations, and the
GSM/EGSM900 and DCS1800 Horizon
macro
outdoor variants are directly
compatible with M-Cell
6
. For example, a combination of up to four Horizon
macro
and M-Cell
6
BTSs can be combined to form a single site, with either a
Horizon
macro
or an M-Cell
6
being in control of the other units. Since many
customers are familiar with M-Cell
6
and will use Horizon
macro
with M-Cell
6
,
equivalent components are described in this section to assist understanding.
The Horizon
macro
outdoor BTS cabinet uses reduced size and higher reliability
components. Horizon
macro
outdoor sites can also have auxiliary equipment
housings installed to enable extended battery backup equipment to be fitted.
Horizon
macro
and M-Cell
6
compatibility
A 24-carrier BTS site (in an 8/8/8 configuration) can be achieved by combining
four units as shown in Figure 1-4. This is the maximum BTS size. Each unit can
be either a Horizon
macro
or an M-Cell
6
. Either a Horizon
macro
or an M-Cell
6
can control the other three units; the MCU of M-Cell
6
and the MCUF of
Horizon
macro
having identical control functions.
An MCUF can be fitted into an M-Cell
6
and will then function as an MCU.
However, an MCU cannot be fitted into a Horizon
macro
. Figure 1-4 shows a
schematic diagram of the digital connectons in a four cabinet BTS site.
22
2
Figure 1-4 Digital connections in maximum BTS site
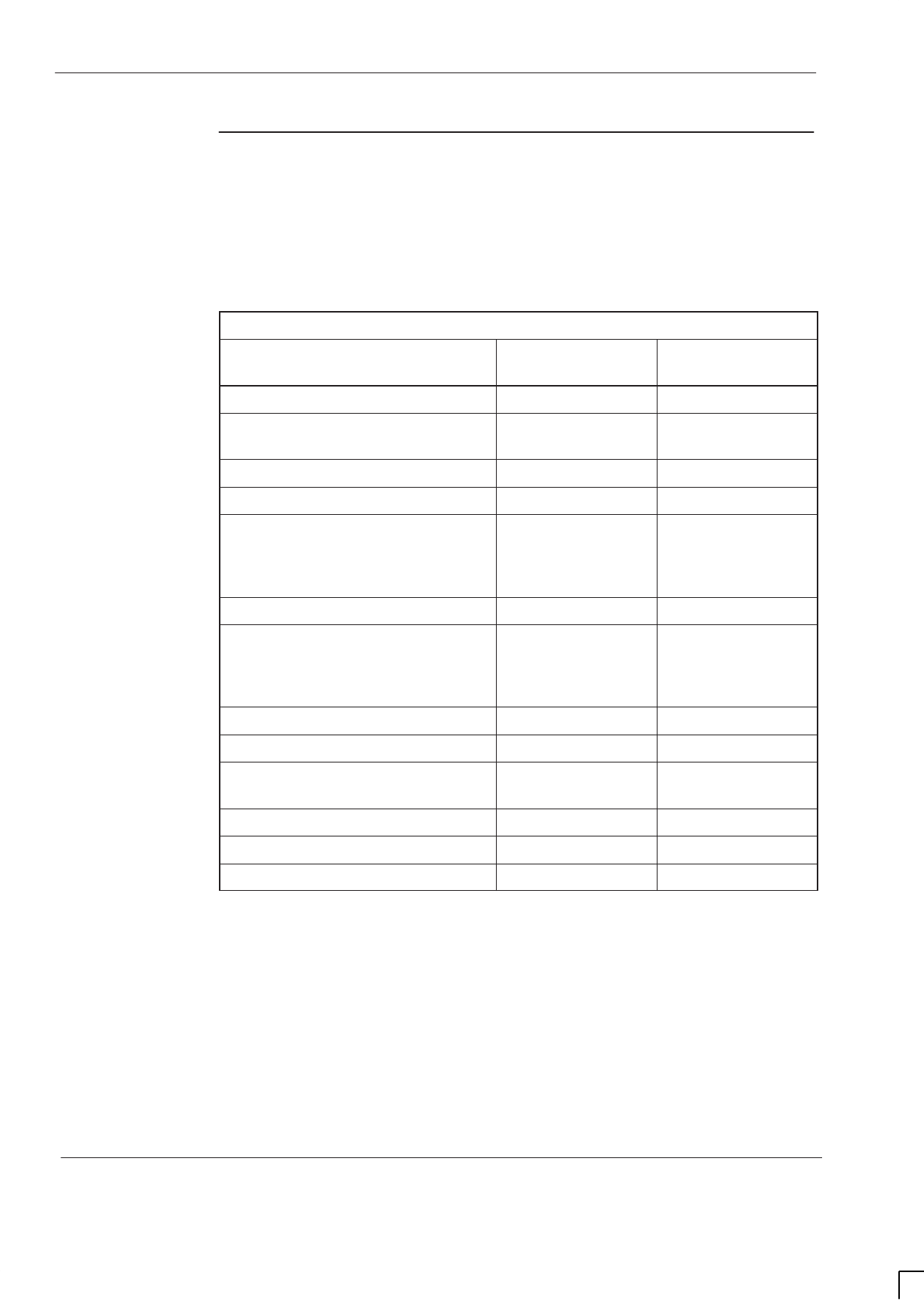
GSM-204-323
M-Cell
6
comparison with Horizon
macro
outdoor
31st Oct 01
Tech. 1–8
Technical Description: Horizon
macro
outdoor
CONTROLLED INTRODUCTION
68P02902W02-A
Comparison of
Horizon
macro
and M-Cell
6
connections
and modules
Table 1-1 compares the main components of the Horizon
macro
outdoor with
equivalent components of M-Cell
6
(the previous generation of equipment).
Table 1-1 Main components of Horizon
macro
compared with M-Cell
6
Function Horizon
macro
component M-Cell
6
equivalent
Power supply modules (ac to dc) TOPSM APSM
Input power conversion units (dc to
dc) PSM PSM (different)
Power to radios and BPSM Backplane Cables
Transceiver CTU TCU/TCU-B
Main processor board (formerly
GPROC, KSW and GCLK boards
in BTS4/5/6 (pre–M-Cell)
equipment)
MCUF MCU
Connection radio to MCU Backplane FOX
Connection MCU to transceivers in
another cabinet MCUF internal
FMUX (two) or
external FMUX
(one)
FMUX
Rx components and distribution SURF DNLB and IADU
Radio to Rx components SURF Harness Cables
Tx components DCF, TDF, DDF,
and HCU CBF, MPDM,
HPDM and HC
Links to terrestrial network NIU NIU
E1/T1 links T43/BIB T43/BIB
Power for digital boards BPSM BPSM
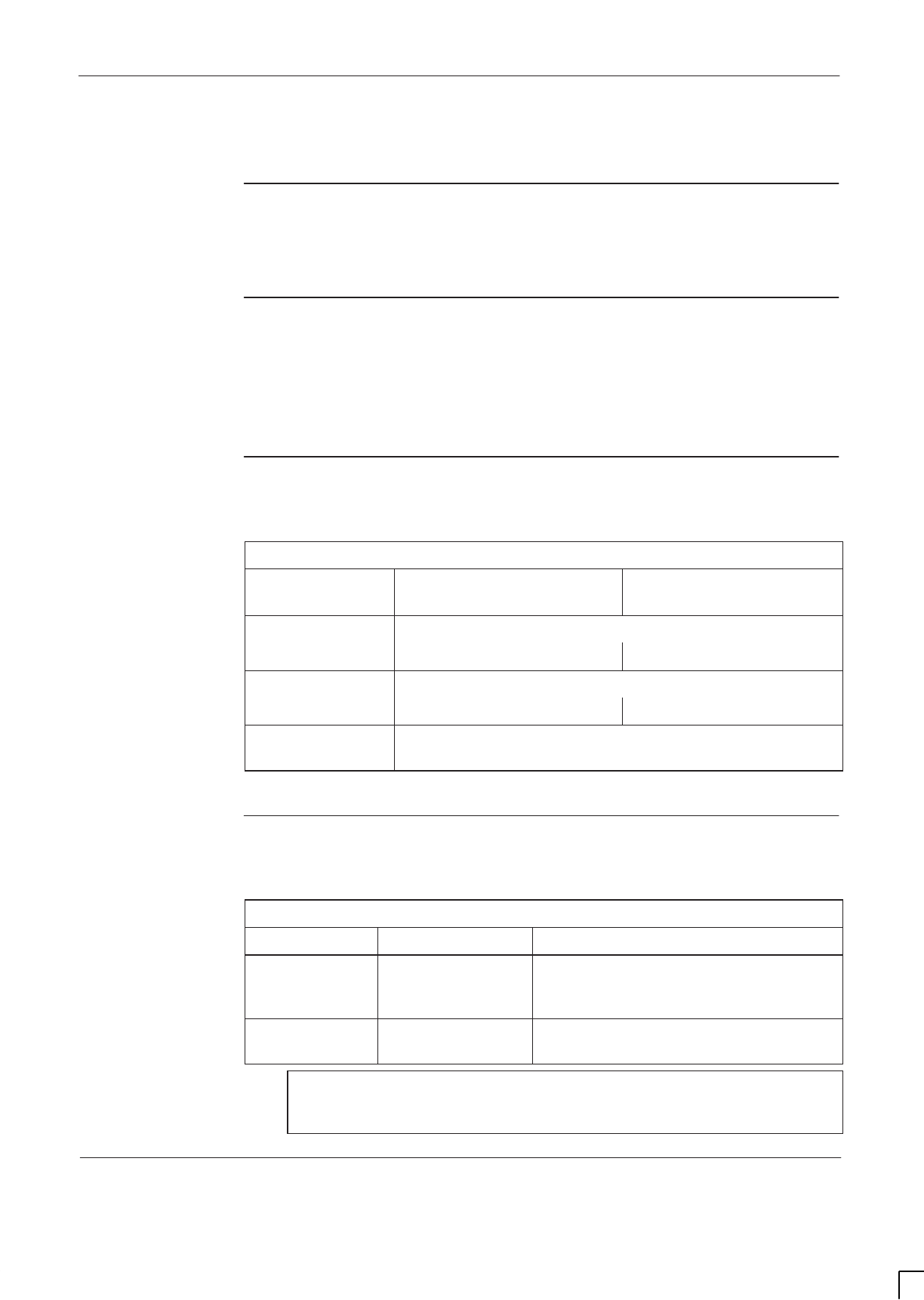
GSM-204-323 Specifications
31st Oct 01
Technical Description: Horizon
macro
outdoor
68P02902W02-A
CONTROLLED INTRODUCTION
Tech. 1–9
Specifications
Introduction to
specifications
All Horizon
macro
outdoor specifications, including frequency band
characteristics, are included in this section.
Software
requirements
The GSM/EGSM900 and DCS1800 BTSs require software release GSR4 (or
later) in the network.
The GSM850 and PCS1900 BTSs require software release GSR5.1 (or later) in
the network.
Approval and
safety
Table 1-2 lists the specifications with which the Horizon
macro
outdoor complies.
Table 1-2 Specification compliance
GSM/EGSM900 &
DCS1800 GSM850 & PCS1900
Type approval EN 301 502
CFR47 Parts 2, 22 and 24
EMC EN 301 489–8
CFR Parts 2, 15, 22 and 24
Safety EN 60950, IEC 950, EN 60215, IEC 215,
CSA 22.2 No. 950, UL1950
The Horizon
macro
outdoor is designed to comply with BS7671 (16th edition).
Environmental
limits
Table 1-3 lists the operating and storage environmental limits.
Table 1-3 Environmental limits
Environment Temperature Relative Humidity
Operating –40 C to +50 C
plus a solar gain
of 1.2 kW/m2
5% to 100% relative humidity, not to
exceed 30 g water / m3 air.
Storage –45 C to +70 C8% to 100% relative humidity, not to
exceed 30 g water / m3 air.
NOTE This specification is valid up to 3 km altitude,
corresponding to an atmospheric pressure range of 648 to
1048 millibars.
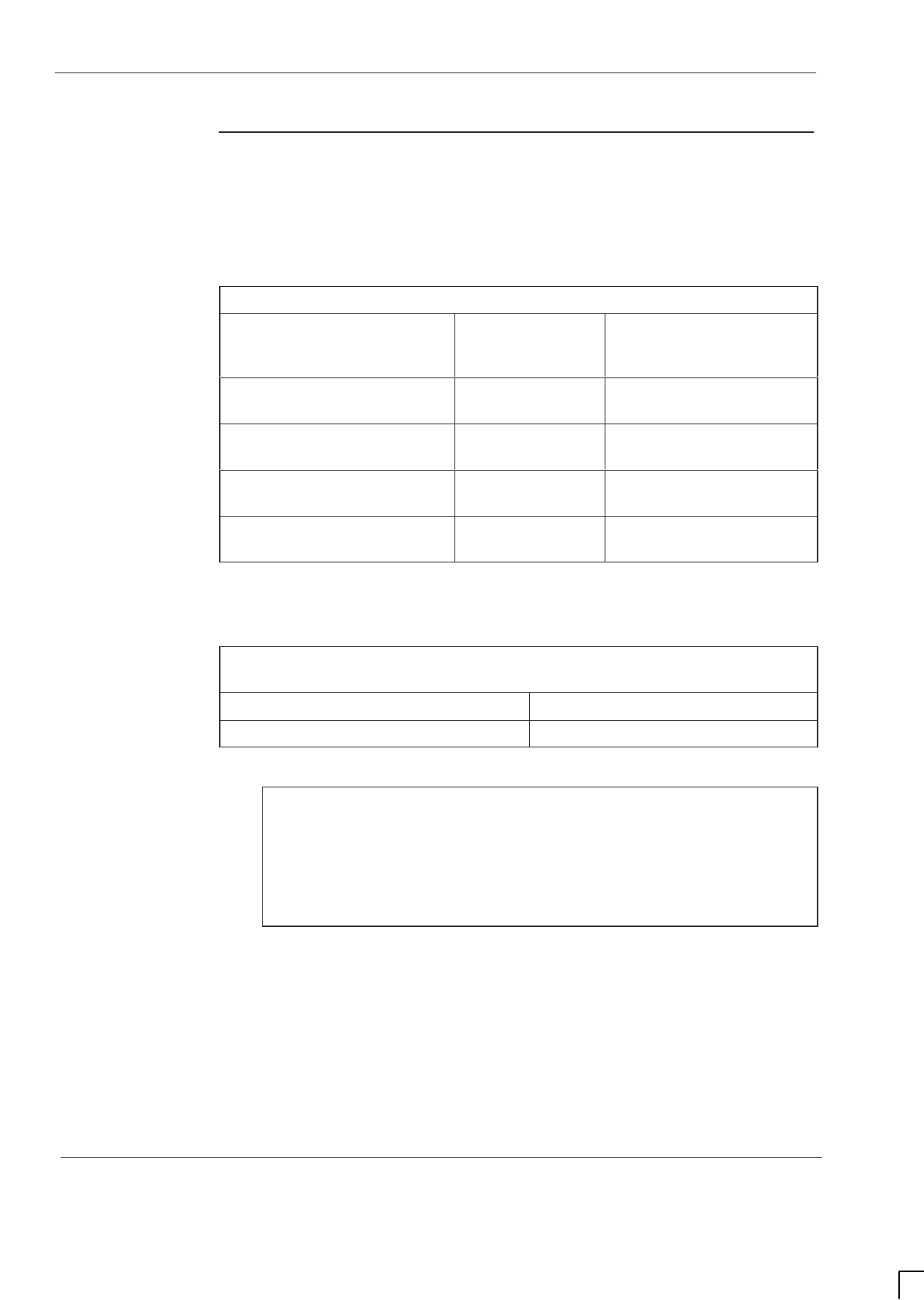
GSM-204-323
Specifications
31st Oct 01
Tech. 1–10
Technical Description: Horizon
macro
outdoor
CONTROLLED INTRODUCTION
68P02902W02-A
Power
requirements
Cabinet input power supply requirements
Table 1-4 lists the power supply requirements for the different power supply
options.
Table 1-4 Main outdoor cabinet power requirements
Nominal voltage Supply voltage
and frequency
range
Current supply
maximum
110 V ac single phase 88 to 134 V ac
at 45 to 66 Hz 54.4 A
(at nominal voltage)
230 V ac single phase 176 to 265 V ac
at 45 to 66 Hz 26.1 A
(at nominal voltage)
230 V ac three phase
and neutral (star) 176 to 265 V ac
at 45 to 66 Hz 26.1 A
(at nominal voltage)
230 V ac three phase
without neutral (delta) 176 to 265 V ac
at 45 to 66 Hz 26.1 A
(at nominal voltage)
Power consumption (dc and ac)
Table 1-5 lists typical and maximum power consuption values.
Table 1-5 Power consumption of full cabinet, including digital redundancy
and external battery charging
Typical measured consumption Maximum power consumption
2200 W 5600 W
NOTE Maximum power consumption figures are theoretical
values derived under extreme conditions and are affected
by variables such as temperature, component tolerances,
transmission power and supply voltage.
Although these figures must be considered when planning
site power requirements, typical measured consumption
values will be lower.
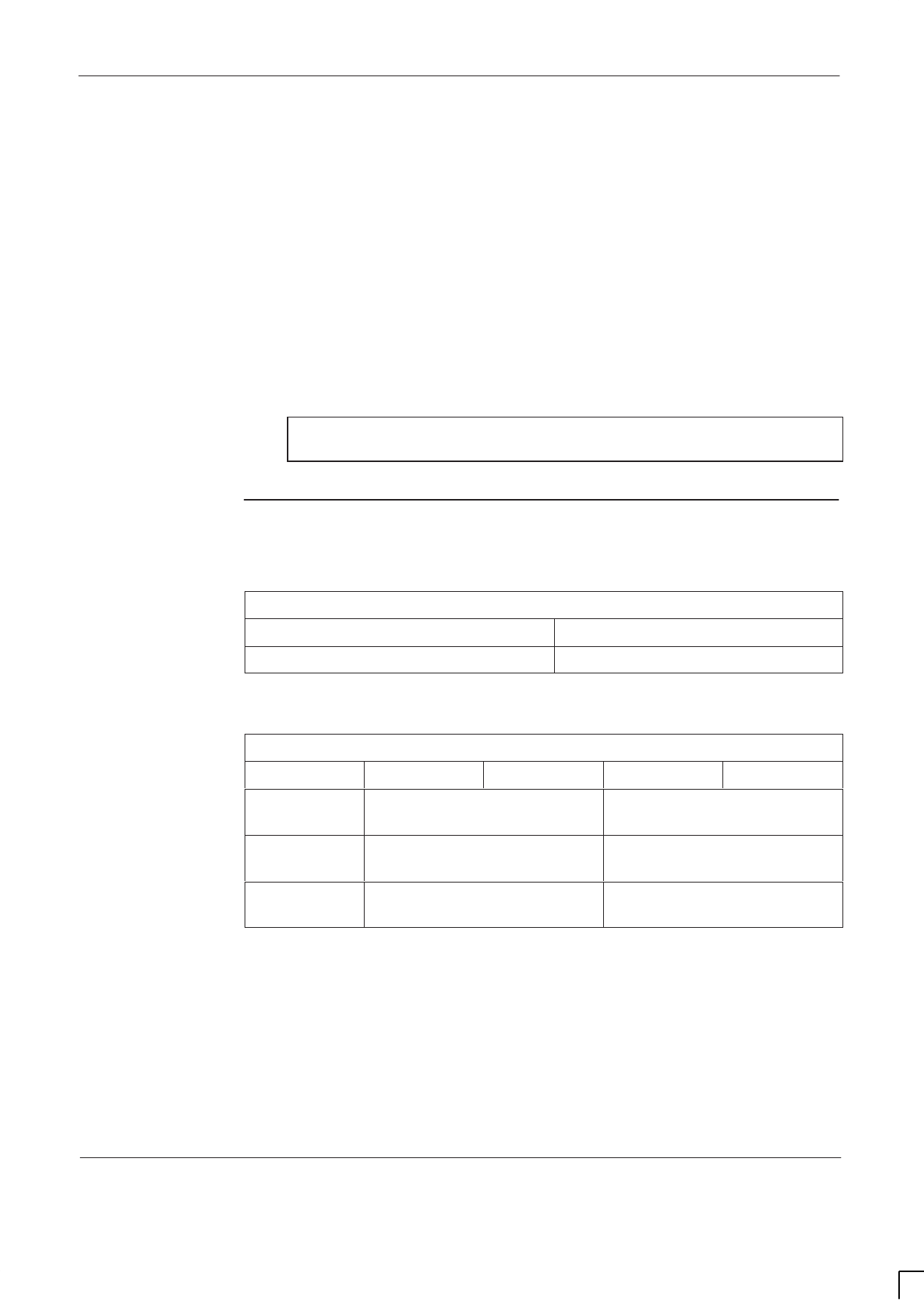
GSM-204-323 Specifications
31st Oct 01
Technical Description: Horizon
macro
outdoor
68P02902W02-A
CONTROLLED INTRODUCTION
Tech. 1–11
Maximum thermal dissipation
Thermal dissipation has to remove the energy of maximum power consumption,
less RF power output of the six transceivers.
Maximum power consumption: 5600 W.
Six CTUs at full power at DCF Tx blocks:
1800 MHz: (6 x 16 = 96) approx. 100 W.
900 MHz: (6 x 20 = 120) 120 W.
Maximum thermal dissipation 1800 MHz: 5600 – 100 = 5500 W.
Maximum thermal dissipation 900 MHz: 5600 – 120 = 5480 W.
NOTE Thermal dissipation figures are not currently available for
when 850 MHz or 1900 MHz CTUs are used.
RF power
output
Table 1-6 lists the RF power output of the CTU types.
Table 1-6 RF power output at CTU Tx connector
GSM850 and EGSM900 DCS1800 and PCS 1900
60 W (47.8 dBm) +/–1.0 dBm 50 W (47.0 dBm) +/– 1.0 dBm
Table 1-7 lists the expected power output from the various Tx blocks for both
types of CTU.
Table 1-7 RF power output at cabinet after Tx blocks
Tx block GSM850 EGSM900 DCS1800 PCS1900
TDF 40 W
(46.0 dBm) 32 W
(45.1 dBm)
DCF 20 W
(43.0 dBm) 16 W
(42.1 dBm)
DDF 8.5 W
(39.3 dBm) 7 W
(38.5 dBm)
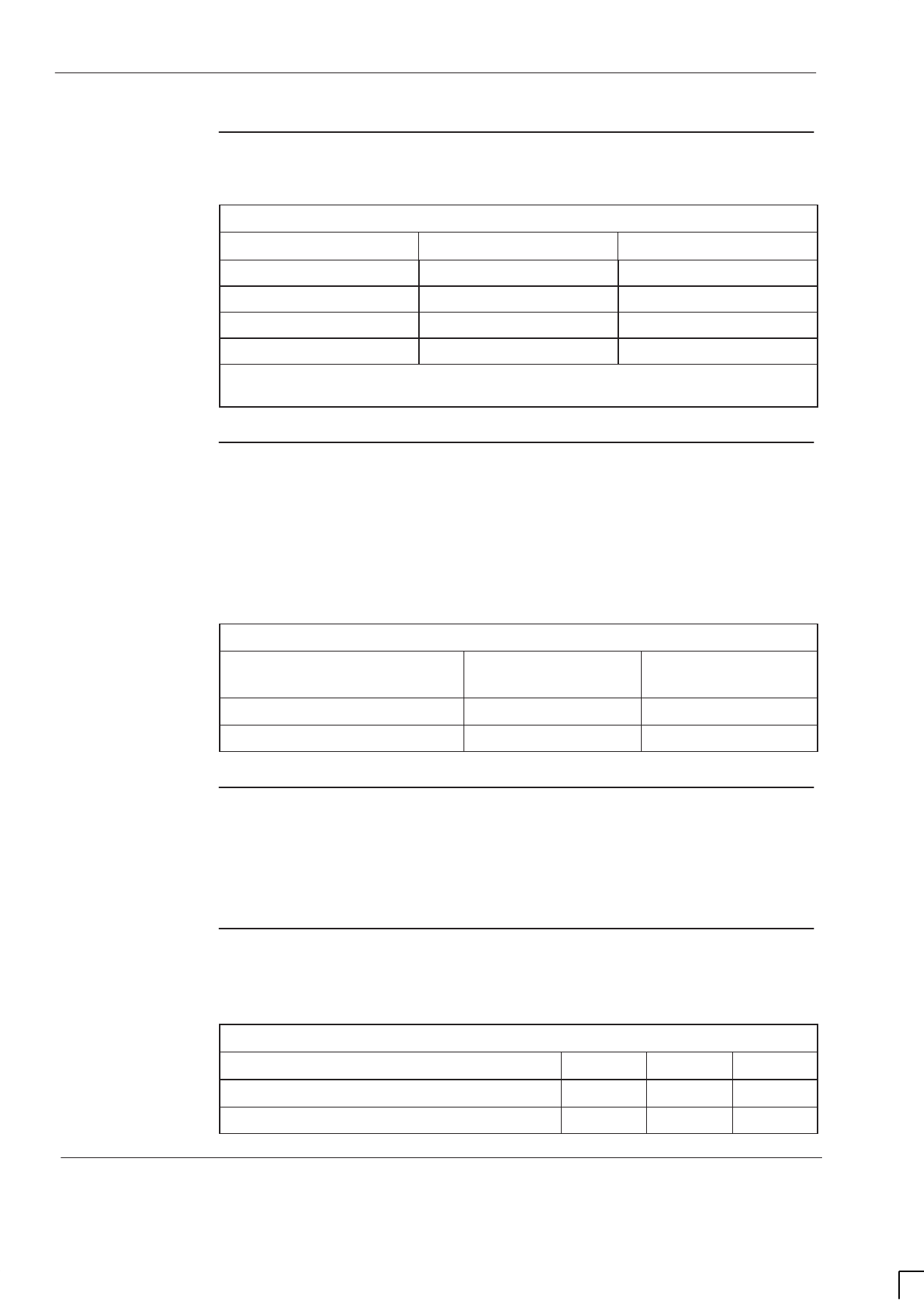
GSM-204-323
Specifications
31st Oct 01
Tech. 1–12
Technical Description: Horizon
macro
outdoor
CONTROLLED INTRODUCTION
68P02902W02-A
Sensitivity
The receive sensitivity of the equipment is shown in Table 1-8.
Table 1-8 Rx sensitivity *
Frequency Band Without Duplexer With Duplexer
850 MHz –107 dBm –106 dBm
900 MHz –107 dBm –106 dBm
1800 MHz –108.5 dBm –107.5 dBm
1900 MHz –107 dBm –106 dBm
* Guaranteed over all channel types, fading profiles, RF frequencies
and operating conditions.
Battery backup
The Horizon
macro
outdoor cabinet is fitted with minimal battery backup
(sufficient to send a low voltage disconnect imminent alarm). Optional additional
battery backup capacity is provided by installation of an optional auxiliary
equipment housing.
Table 1-9 lists the capacity and the typical duration of the various battery backup
options.
Table 1-9 Backup power specifications
Location Capacity Typical power
duration
Internal batteries 15 Ah 5 to 15 minutes
External batteries 200 Ah Up to 8 hours
BSC
connectivity
options
Options exist for E1, T1 and HDSL (star and daisy chain) connection.
Outdoor cabinet
dimensions
The dimensions of the outdoor cabinets are shown in Table 1-10.
Table 1-10 Cabinet dimensions
Cabinet type Height Width Depth
Horizon
macro
outdoor cabinet 1364 mm 1300 mm 594 mm
Auxiliary equipment housing (AEH) 1364 mm 604 mm 594 mm
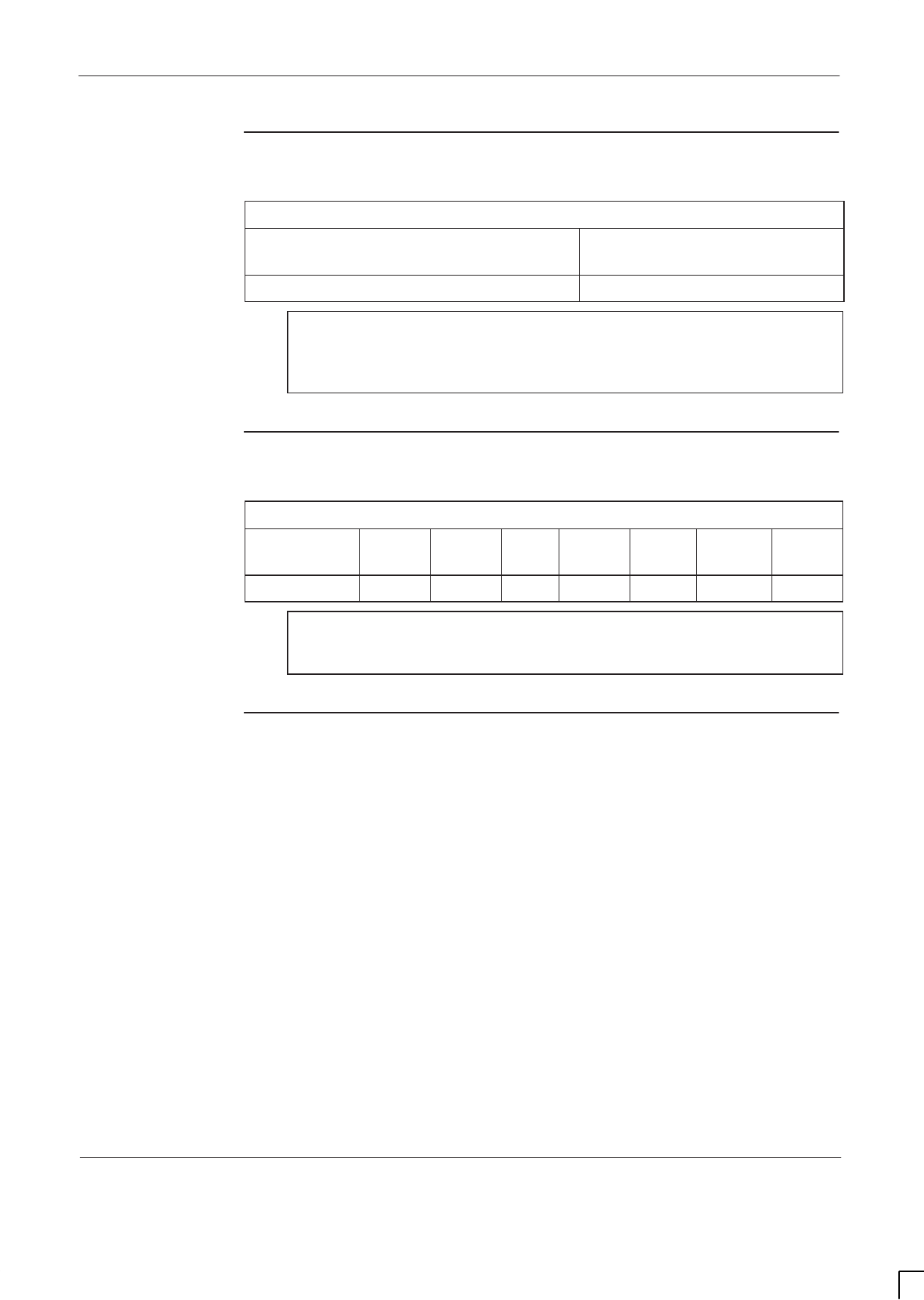
GSM-204-323 Specifications
31st Oct 01
Technical Description: Horizon
macro
outdoor
68P02902W02-A
CONTROLLED INTRODUCTION
Tech. 1–13
Weights
The weights of cabinets are shown in Table 1-11.
Table 1-11 Outdoor cabinet weights
BTS cabinet with six transceivers Auxiliary equipment housing
empty / 16 batteries fitted
360 kg 110 kg / 500 kg
NOTE Consider future expansion. The foundation or structure on
which the BTS cabinet is mounted must be of sufficient
strength to support a maximum gross weight of 360 kg for
each BTS cabinet and 500 kg for each AEH.
Torque values
The torque values for Horizon
macro
outdoor are listed in Table 1-12.
Table 1-12 Torque values for all cabinet screws/bolts and RF connectors
Size of
screw/bolt M4 M6 M8 M10 SMA N-type 7/16
Torque value 2.2 Nm 3.4 Nm 5 Nm 10 Nm 1 Nm 3.4 Nm 25 Nm
NOTE Torque values used with M12 anchor bolts will depend on
the anchor bolt manufacturer. Check manufacturer’s data
for correct values.
Cabinets
enhancements
External cabinet colours
The external cabinets are finished in one of the following colours:
Standard dark grey.
M-Cell match.
Dark brown.
Green.
Brick red.
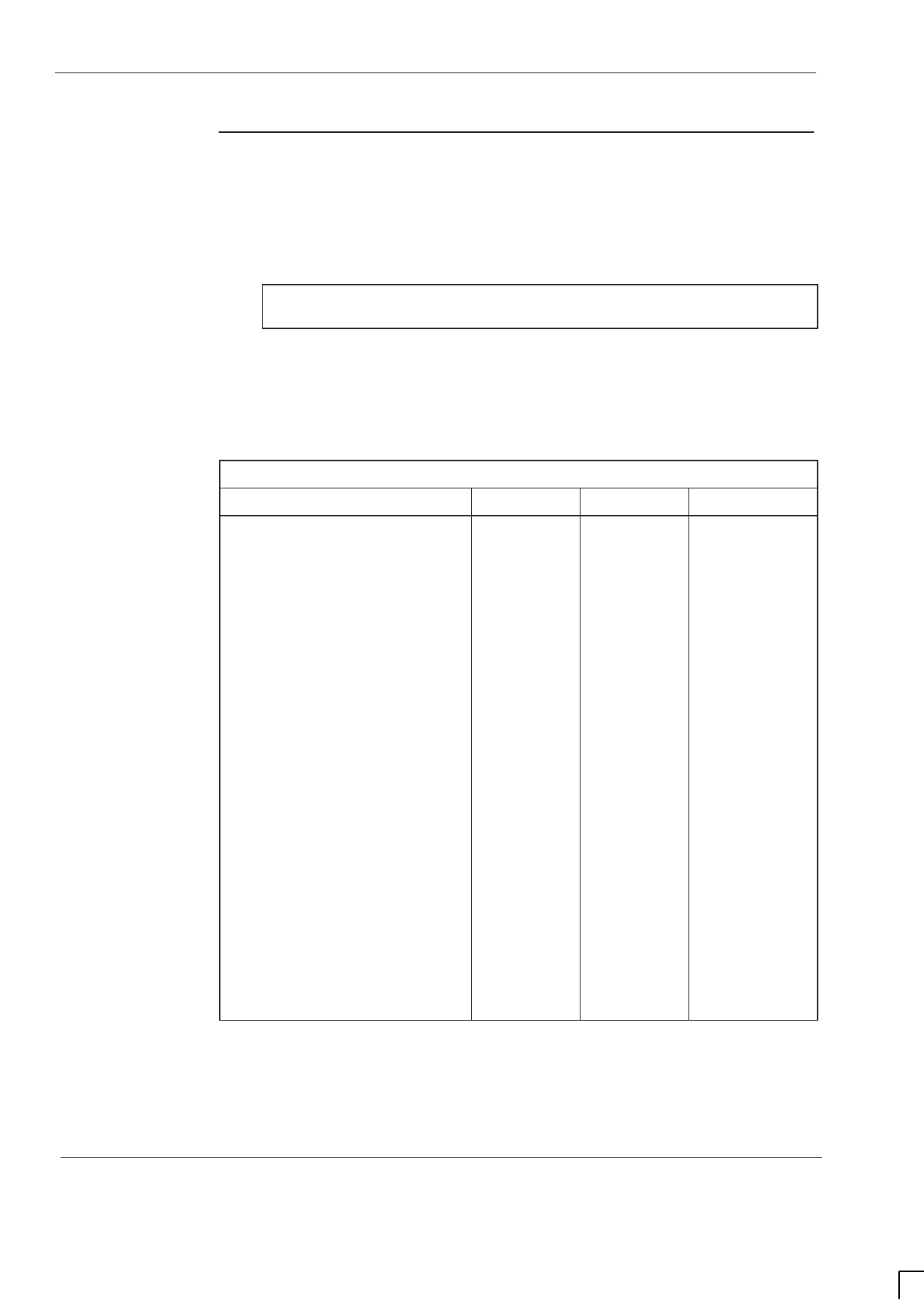
GSM-204-323
Specifications
31st Oct 01
Tech. 1–14
Technical Description: Horizon
macro
outdoor
CONTROLLED INTRODUCTION
68P02902W02-A
Frequency
capability
Frequency hopping
The Horizon
macro
outdoor supports baseband frequency hopping (BBH) and
synthesizer frequency hopping (SFH).
NOTE Baseband frequency hopping is not supported in the
GSM850 and PCS1900 Horizon
macro
outdoor variants.
Frequency band characteristics
BTS radio channels (RF carriers) are full duplex (transmit and receive) with the
characteristics listed in Table 1-13 for GSM/EGSM900 and DCS1800 BTSs and
in Table 1-14 for GSM850 and PCS1900 BTSs.
Table 1-13 Frequency band characteristics – GSM/EGSM900 and DCS1800
GSM900 EGSM DCS1800
Transmit frequency band
(MHz) 935 to 960 925 to 960 1805 to 1880
Receive frequency band (MHz) 890 to 915 880 to 915 1710 to 1785
Transmit/receive duplex
separation (MHz) 45 45 95
Channel width (kHz) 200 200 200
Number of channels 124 174 374
Transmit frequency guard
bands (MHz) 935.0 to
935.1
959.9 to
960.0
925.0 to
925.1
959.9 to
960.0
1805.0 to
1805.1
1879.9 to
1880.0
Receive frequency guard
bands (MHz) 890.0 to
890.1
914.9 to
915.0
880.0 to
880.1
914.9 to
915.0
1710.0 to
1710.1
1784.9 to
1785.0
Transmit channel centre
frequency (MHz) Even 10ths
of a MHz
from 935.2
to 959.8
Even 10ths
of a MHz
from 925.2
to 959.8
Even 10ths of
a MHz from
1805.2 to
1879.8
Receive channel centre
frequency (MHz) Even 10ths
of a MHz
from 890.2
to 914.8
Even 10ths
of a MHz
from 880.2
to 914.8
Even 10ths of
a MHz from
1710.2 to
1784.8
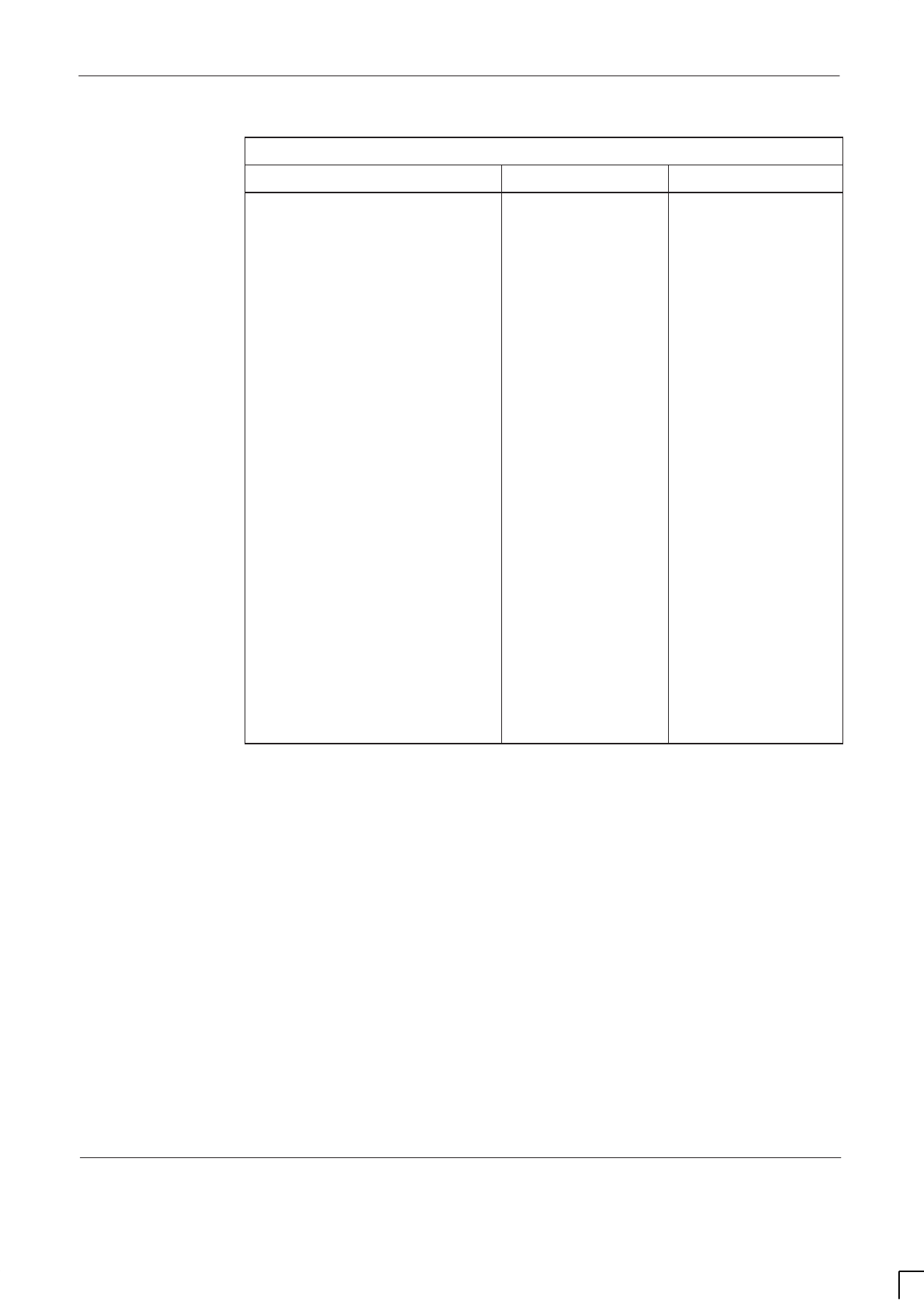
GSM-204-323 Specifications
31st Oct 01
Technical Description: Horizon
macro
outdoor
68P02902W02-A
CONTROLLED INTRODUCTION
Tech. 1–15
Table 1-14 Frequency band characteristics – GSM850 and PCS1900
GSM850 PCS1900
Transmit frequency band (MHz) 869 to 894 1930 to 1990
Receive frequency band (MHz) 824 to 849 1850 to 1910
Transmit/receive duplex
separation (MHz) 45 80
Channel width (kHz) 200 200
Number of channels 124 299
Transmit frequency guard
bands (MHz) 869.0 to 869.1
893.9 to 894.0 1930.0 to 1930.1
1989.9 to 1990.0
Receive frequency guard bands
(MHz) 824.0 to 824.1
848.9 to 849.0 1850.0 to 1850.1
1909.9 to 1910.0
Transmit channel centre
frequency (MHz) Even 10ths of a
MHz from
869.2 to 893.8
Even 10ths of a
MHz from
1930.2 to 1989.8
Receive channel centre
frequency (MHz) Even 10ths of a
MHz from
824.2 to 848.8
Even 10ths of a
MHz from
1850.2 to 1909.8
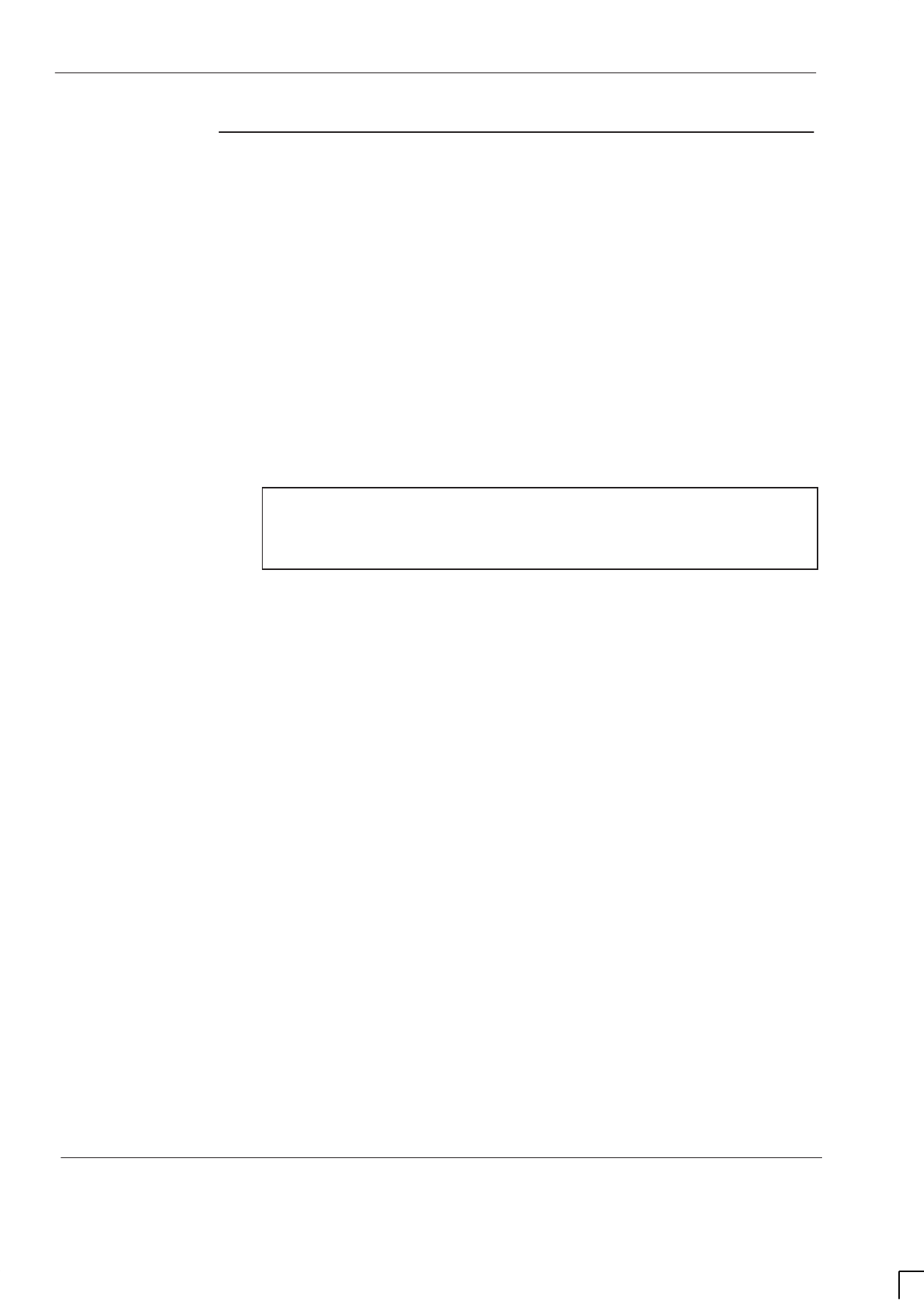
GSM-204-323
Specifications
31st Oct 01
Tech. 1–16
Technical Description: Horizon
macro
outdoor
CONTROLLED INTRODUCTION
68P02902W02-A
Structural
considerations
There must be adequate clearance at the front of (648 mm), and above
(1900 mm), the equipment for operation and maintenance purposes. It is also
recommended that there is adequate side clearance to open the doors to 120°
(see Figure 1-5), and to fit the optional shroud on the cable entry side.
The foundation or structure on which the BTS cabinet is mounted must be of
sufficient strength to withstand 105 knot (120 mph) winds on the cabinet front or
rear and a maximum gross weight of 360 kgs.
The cabinet ventilation entry and exhaust is solely from the bottom front of the
cabinet, allowing a cabinet to be placed against a wall. However, a minimum
clearance of 240 mm is required on the cable entry side, between the cabinet
and obstructions, such as a wall or another cabinet.
Allow 1000 mm clearance at front and side where possible, to facilitate
installation and maintenance.
NOTE In seismically active areas, Motorola suggest using a
qualified structural engineer to assess frame mounting
requirements, such as floor construction, mounting
anchors and cell site construction.
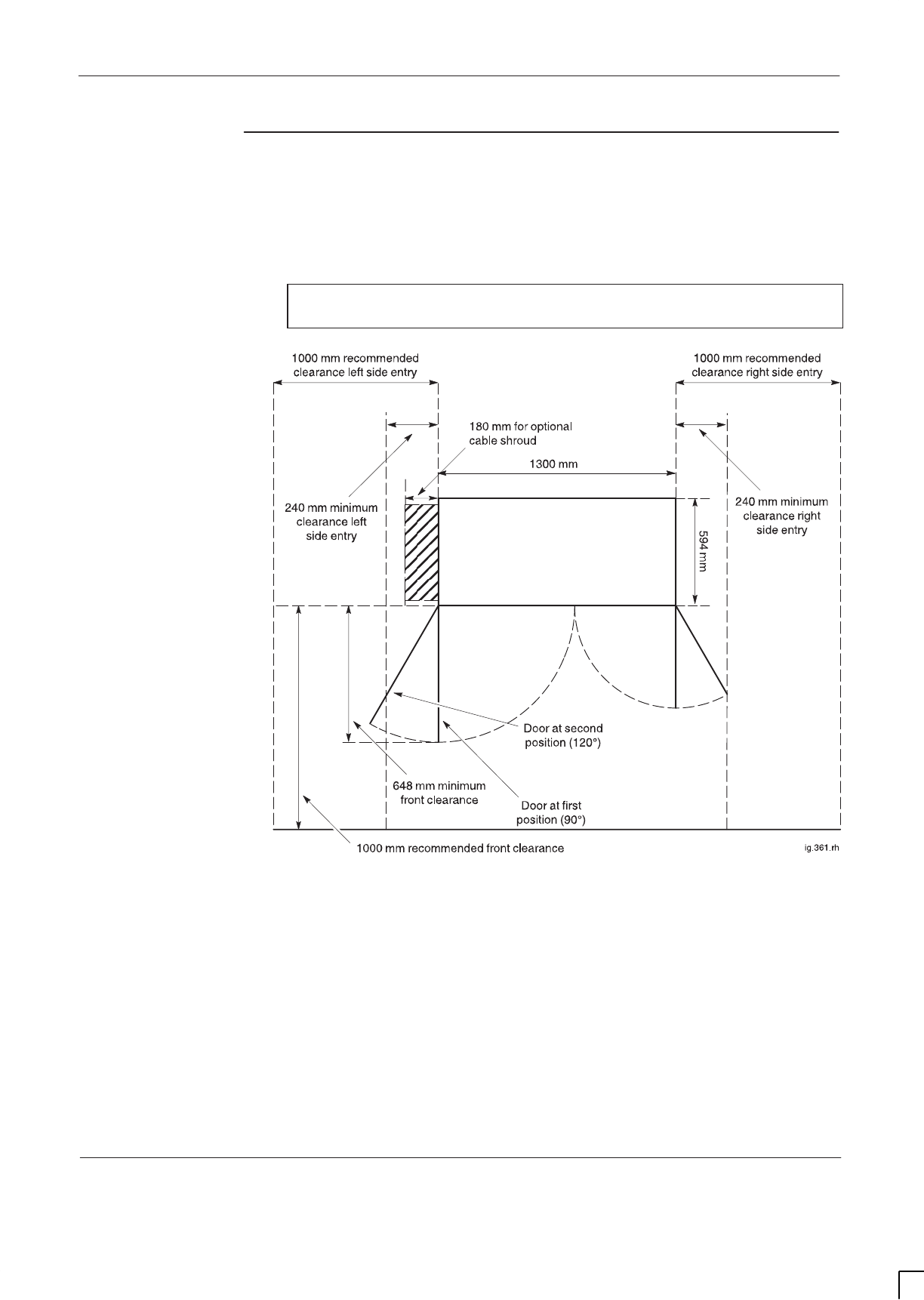
GSM-204-323 Specifications
31st Oct 01
Technical Description: Horizon
macro
outdoor
68P02902W02-A
CONTROLLED INTRODUCTION
Tech. 1–17
Outdoor site
dimensions
Basic outdoor site
Figure 1-5 shows the site layout plan for a single cabinet with dimensions and
required clearances (optional auxiliary equipment housing not shown).
NOTE Allow 180 mm additional side clearance if a cable shroud
is to be fitted.
OUTDOOR CABINET
Figure 1-5 Outdoor cabinet site layout plan view (cable entry on left side)
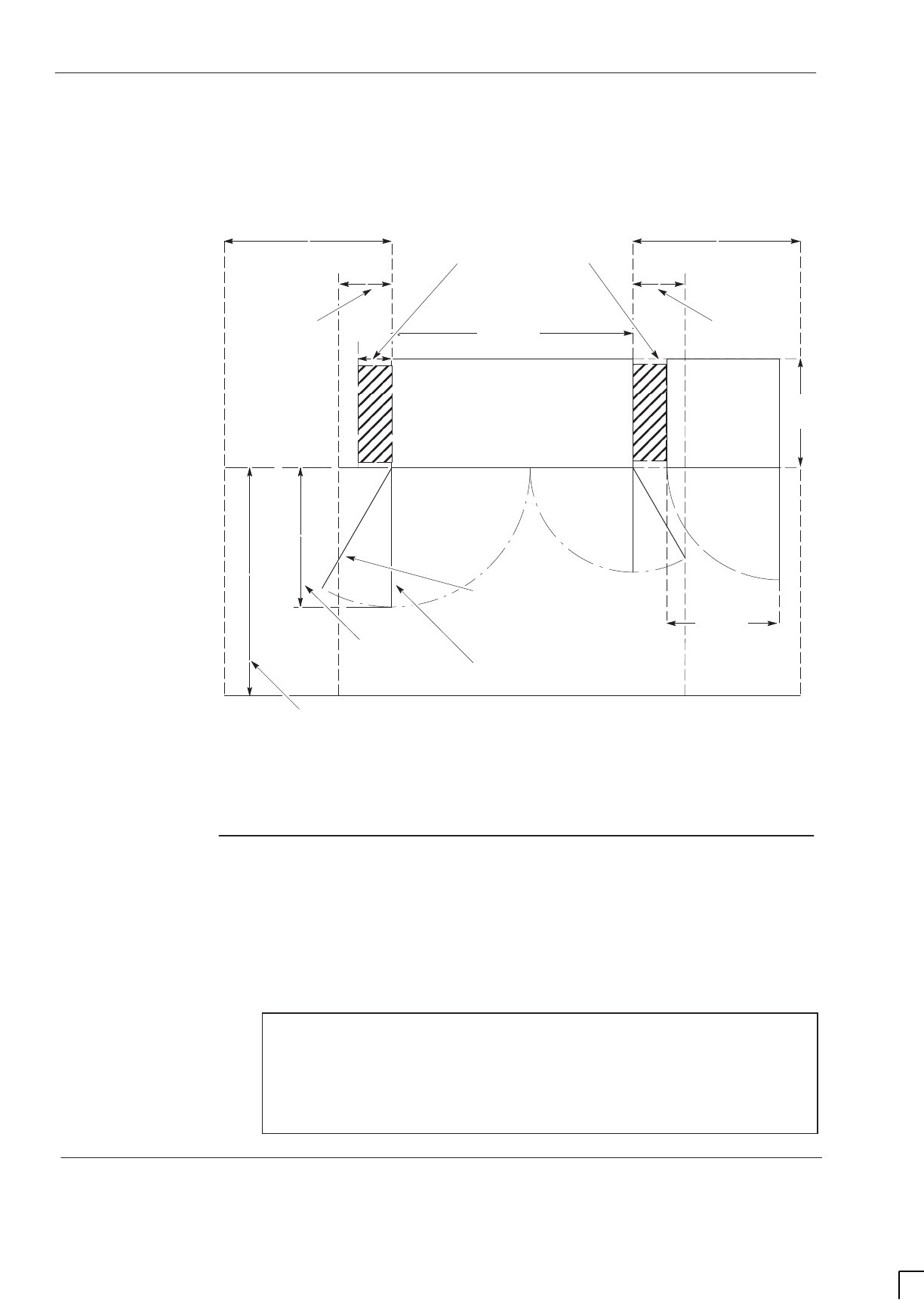
GSM-204-323
Specifications
31st Oct 01
Tech. 1–18
Technical Description: Horizon
macro
outdoor
CONTROLLED INTRODUCTION
68P02902W02-A
Outdoor site with auxiliary equipment housing
Figure 1-6 shows the site layout plan for a single cabinet and optional auxiliary
equipment housing with dimensions and required clearances.
Door at second position
(120°)
Door at first position
(90°)
1000 mm recommended
clearance left side entry 1000 mm recommended
clearance right side entry
240 mm
minimum
clearance left
side entry
1000 mm recommended front clearance
648 mm
minimum front
clearance
240 mm
minimum
clearance right
side entry
OUTDOOR CABINET
1300 mm
594
mm
180 mm for optional cable
shroud
AEH
604 mm
for optional AEH
Figure 1-6 Outdoor cabinet site layout plan view (including optional equipment)
View of
maximum site
template layout
Figure 1-7 shows a plan view of the template layout for the maximum site
configuration. Using the dimensions and clearances shown, the site layout for
any combination of BTS cabinets and auxiliary equipment housings can be
calculated.
NOTE If a steel structure is to be used instead of a concrete
base, the dimensions shown in Figure 2-3 can be used to
determine the location of the mounting bolt holes.
Figure 1-7 only shows template and mounting hole
dimensions and clearances, cabinet dimensions are
slightly larger.
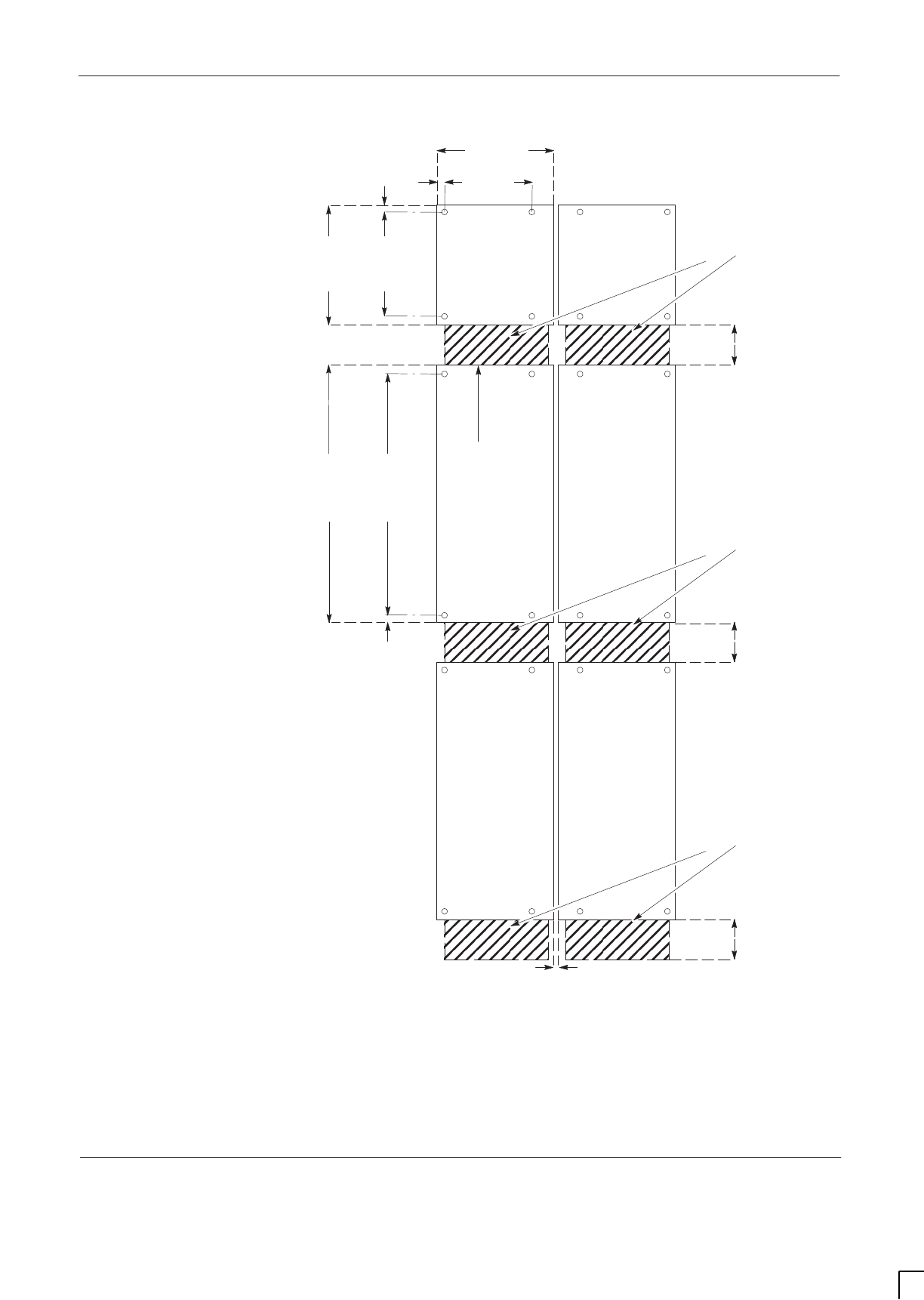
GSM-204-323 Specifications
31st Oct 01
Technical Description: Horizon
macro
outdoor
68P02902W02-A
CONTROLLED INTRODUCTION
Tech. 1–19
10
mm
18 mm
AEH
template
AEH
template
BTS
CABINET
template
BTS
CABINET
template
BTS
CABINET
template
BTS
CABINET
template
POSITION OF
SHROUDS
(if used)
POSITION OF
SHROUDS
(if used)
POSITION OF
SHROUDS
(if used) 180 mm180 mm180 mm
597 mm
544 mm
26.5 mm
21.5 mm
1293 mm
1250 mm
531.5 mm
405 mm
Figure 1-7 Plan view of template layout for maximum site configuration
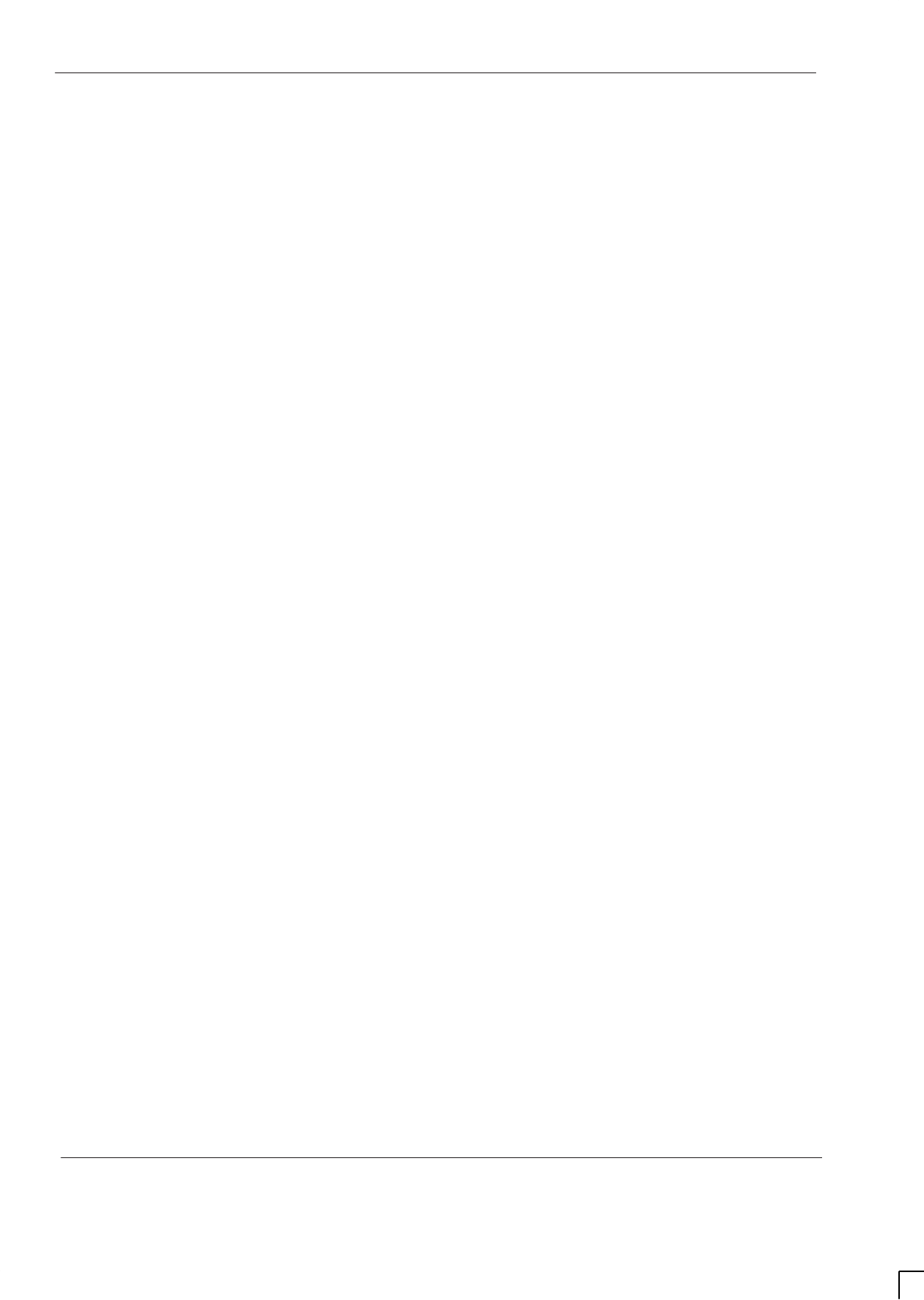
GSM-204-323
Specifications
31st Oct 01
Tech. 1–20
Technical Description: Horizon
macro
outdoor
CONTROLLED INTRODUCTION
68P02902W02-A
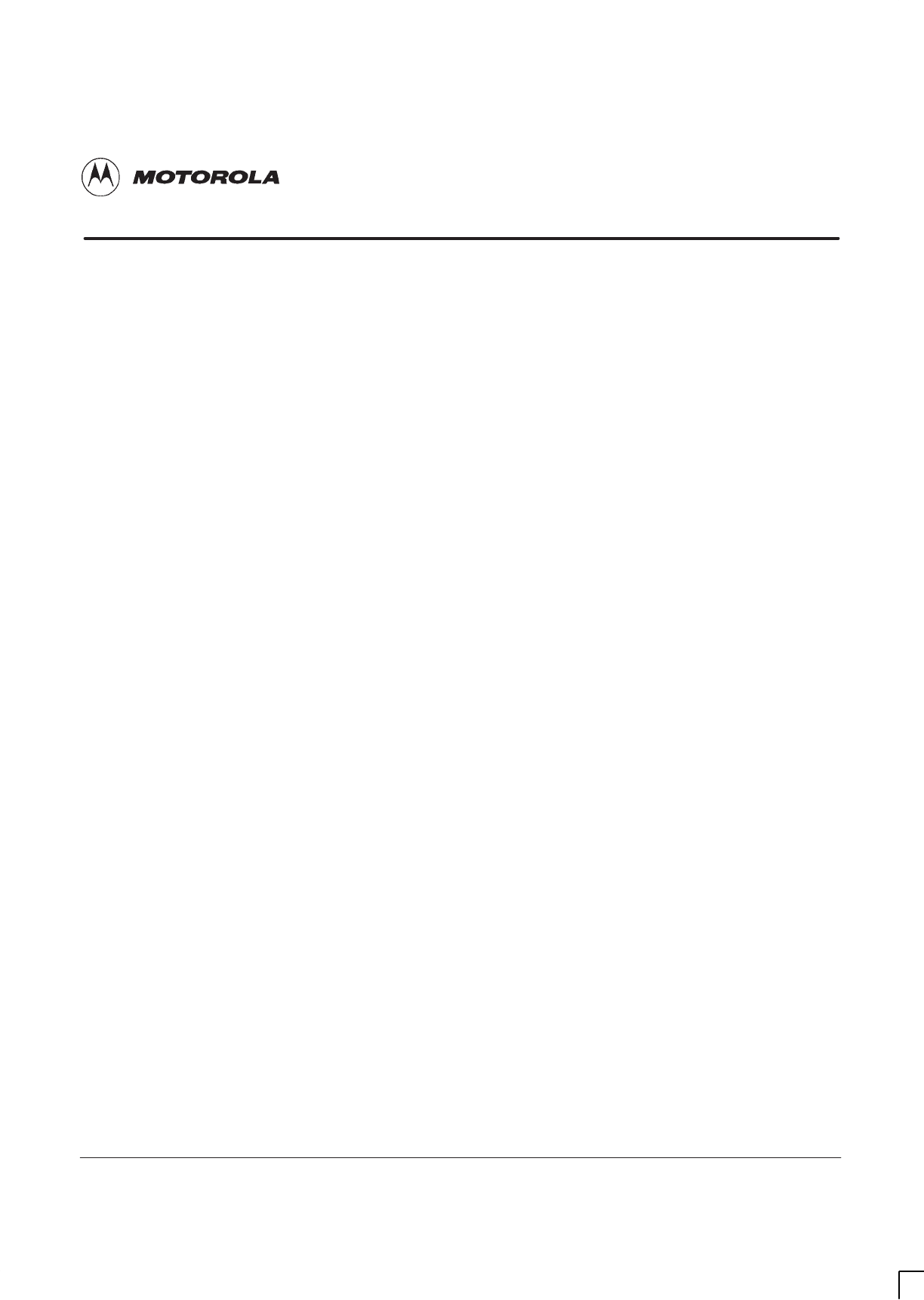
31st Oct 01
Technical Description: Horizon
macro
outdoor
68P02902W02-A
CONTROLLED INTRODUCTION
i
Chapter 2
Cabinet structure
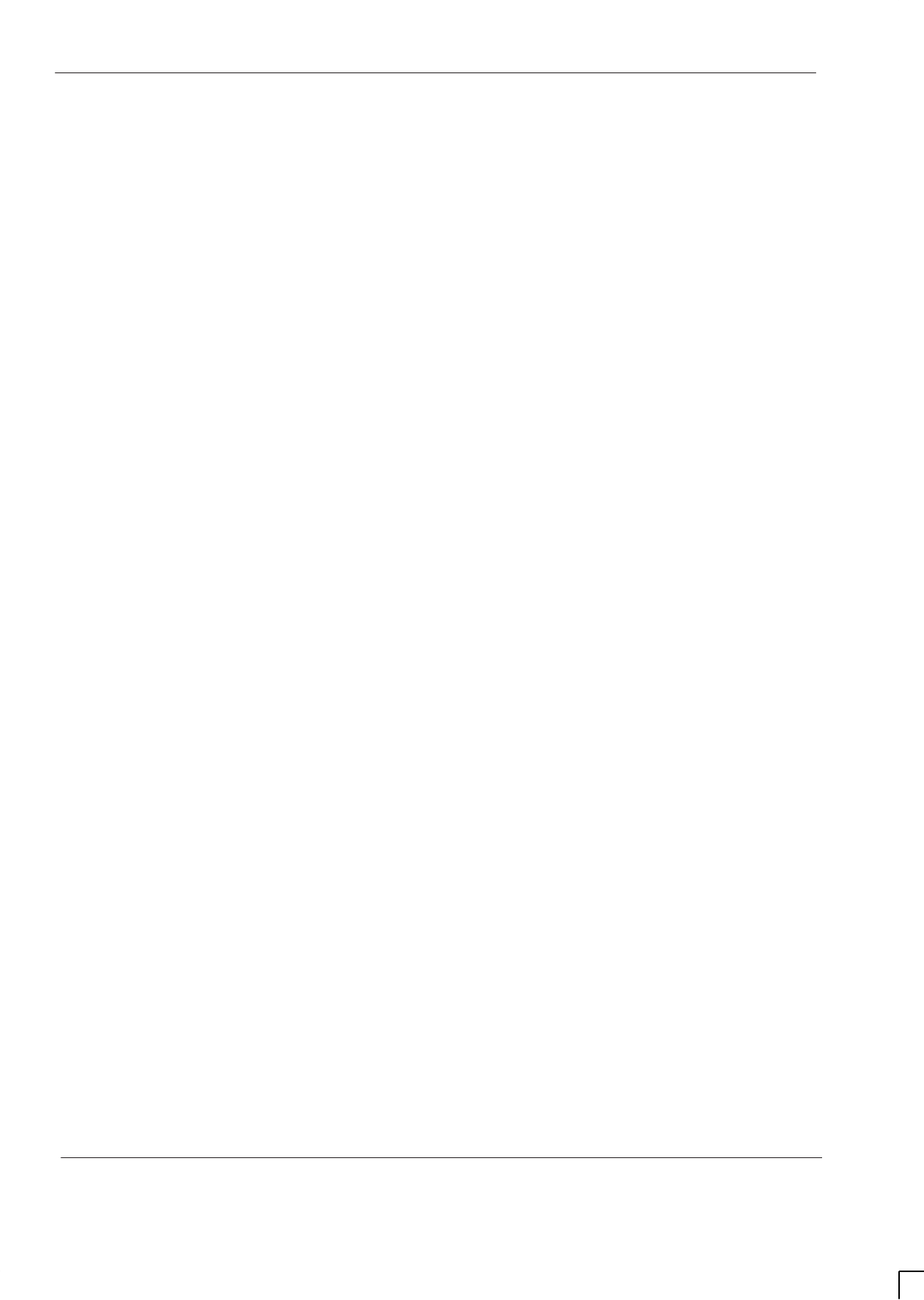
GSM-204-323
31st Oct 01
ii
Technical Description: Horizon
macro
outdoor
CONTROLLED INTRODUCTION
68P02902W02-A
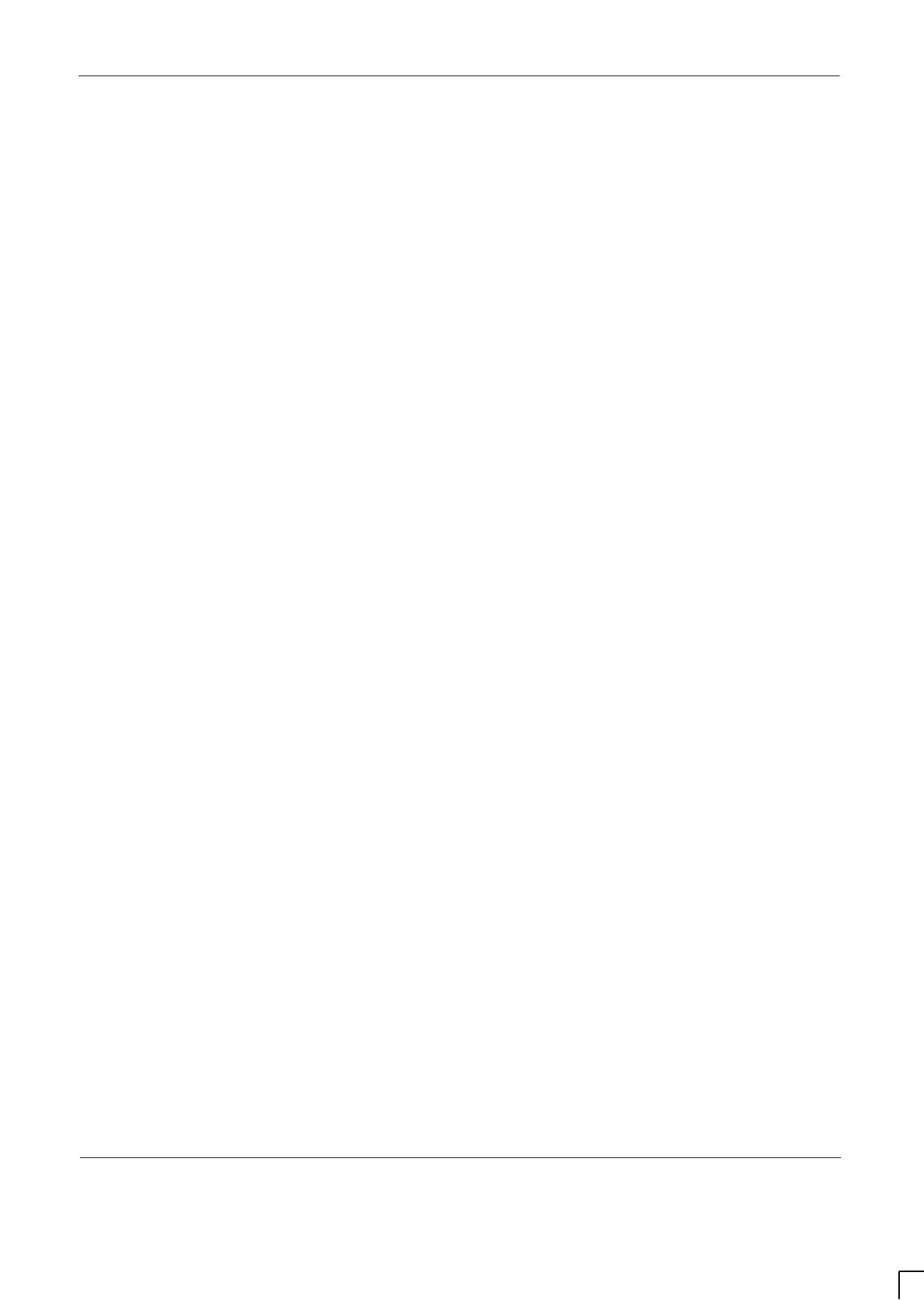
GSM-204-323
31st Oct 01
Technical Description: Horizon
macro
outdoor
68P02902W02-A
CONTROLLED INTRODUCTION
iii
Chapter 2
Cabinet structure i. . . . . . . . . . . . . . . . . . . . . . . . . . . . . . . . . . . . . . . . . . . . . .
Outdoor cabinet structure Tech. 2–1. . . . . . . . . . . . . . . . . . . . . . . . . . . . . . . . . . . . . . . . . . . . .
External cabinet view Tech. 2–1. . . . . . . . . . . . . . . . . . . . . . . . . . . . . . . . . . . . . . . . . . . .
Overview of structure description Tech. 2–2. . . . . . . . . . . . . . . . . . . . . . . . . . . . . . . . .
Space required around cabinet Tech. 2–2. . . . . . . . . . . . . . . . . . . . . . . . . . . . . . . . . . .
Filled cabinet view Tech. 2–3. . . . . . . . . . . . . . . . . . . . . . . . . . . . . . . . . . . . . . . . . . . . . .
SURF harness Tech. 2–4. . . . . . . . . . . . . . . . . . . . . . . . . . . . . . . . . . . . . . . . . . . . . . . . . . . . . . .
SURF harness detail Tech. 2–4. . . . . . . . . . . . . . . . . . . . . . . . . . . . . . . . . . . . . . . . . . . .
Cabinet view with installed SURF harness Tech. 2–4. . . . . . . . . . . . . . . . . . . . . . . . .
SURF harness view Tech. 2–5. . . . . . . . . . . . . . . . . . . . . . . . . . . . . . . . . . . . . . . . . . . . .
Top section Tech. 2–6. . . . . . . . . . . . . . . . . . . . . . . . . . . . . . . . . . . . . . . . . . . . . . . . . . . . . . . . . .
Top section description Tech. 2–6. . . . . . . . . . . . . . . . . . . . . . . . . . . . . . . . . . . . . . . . . .
Top section diagram Tech. 2–7. . . . . . . . . . . . . . . . . . . . . . . . . . . . . . . . . . . . . . . . . . . . .
Krone blocks Tech. 2–7. . . . . . . . . . . . . . . . . . . . . . . . . . . . . . . . . . . . . . . . . . . . . . . . . . .
AC outlet socket Tech. 2–7. . . . . . . . . . . . . . . . . . . . . . . . . . . . . . . . . . . . . . . . . . . . . . . .
Earth plates Tech. 2–8. . . . . . . . . . . . . . . . . . . . . . . . . . . . . . . . . . . . . . . . . . . . . . . . . . . .
Blank and expansion plates Tech. 2–9. . . . . . . . . . . . . . . . . . . . . . . . . . . . . . . . . . . . . .
Cage backplane interface panel harness assembly (CBIA) Tech. 2–10. . . . . . . . . . . . . . . .
CBIA overview Tech. 2–10. . . . . . . . . . . . . . . . . . . . . . . . . . . . . . . . . . . . . . . . . . . . . . . . . .
CBIA and interface panel schematic view Tech. 2–10. . . . . . . . . . . . . . . . . . . . . . . . . .
Backplane and harness view Tech. 2–11. . . . . . . . . . . . . . . . . . . . . . . . . . . . . . . . . . . . .
CBIA cage function and diagram Tech. 2–12. . . . . . . . . . . . . . . . . . . . . . . . . . . . . . . . . .
CBIA harness function Tech. 2–12. . . . . . . . . . . . . . . . . . . . . . . . . . . . . . . . . . . . . . . . . . .
CBIA backplane function Tech. 2–13. . . . . . . . . . . . . . . . . . . . . . . . . . . . . . . . . . . . . . . . .
Attachment of cage to cabinet Tech. 2–13. . . . . . . . . . . . . . . . . . . . . . . . . . . . . . . . . . . .
CBIA interface panel Tech. 2–14. . . . . . . . . . . . . . . . . . . . . . . . . . . . . . . . . . . . . . . . . . . . . . . . .
Interface panel function Tech. 2–14. . . . . . . . . . . . . . . . . . . . . . . . . . . . . . . . . . . . . . . . . .
Interface panel diagram Tech. 2–14. . . . . . . . . . . . . . . . . . . . . . . . . . . . . . . . . . . . . . . . . .
Interface panel pinouts Tech. 2–14. . . . . . . . . . . . . . . . . . . . . . . . . . . . . . . . . . . . . . . . . .
Power supply enclosure Tech. 2–15. . . . . . . . . . . . . . . . . . . . . . . . . . . . . . . . . . . . . . . . . . . . . .
Power supply enclosure overview Tech. 2–15. . . . . . . . . . . . . . . . . . . . . . . . . . . . . . . . .
View of power supply enclosure Tech. 2–15. . . . . . . . . . . . . . . . . . . . . . . . . . . . . . . . . .
Power supply unit Tech. 2–16. . . . . . . . . . . . . . . . . . . . . . . . . . . . . . . . . . . . . . . . . . . . . . .
Alarms interface board Tech. 2–16. . . . . . . . . . . . . . . . . . . . . . . . . . . . . . . . . . . . . . . . . .
Alarms interface board connectors Tech. 2–17. . . . . . . . . . . . . . . . . . . . . . . . . . . . . . . .
TMS test switches Tech. 2–18. . . . . . . . . . . . . . . . . . . . . . . . . . . . . . . . . . . . . . . . . . . . . .
Customer equipment racking Tech. 2–18. . . . . . . . . . . . . . . . . . . . . . . . . . . . . . . . . . . . .
Outdoor cabinet doors and lid Tech. 2–19. . . . . . . . . . . . . . . . . . . . . . . . . . . . . . . . . . . . . . . . .
Door function Tech. 2–19. . . . . . . . . . . . . . . . . . . . . . . . . . . . . . . . . . . . . . . . . . . . . . . . . . .
Door views Tech. 2–19. . . . . . . . . . . . . . . . . . . . . . . . . . . . . . . . . . . . . . . . . . . . . . . . . . . . .
Lid function Tech. 2–20. . . . . . . . . . . . . . . . . . . . . . . . . . . . . . . . . . . . . . . . . . . . . . . . . . . .
Lid view Tech. 2–20. . . . . . . . . . . . . . . . . . . . . . . . . . . . . . . . . . . . . . . . . . . . . . . . . . . . . . .
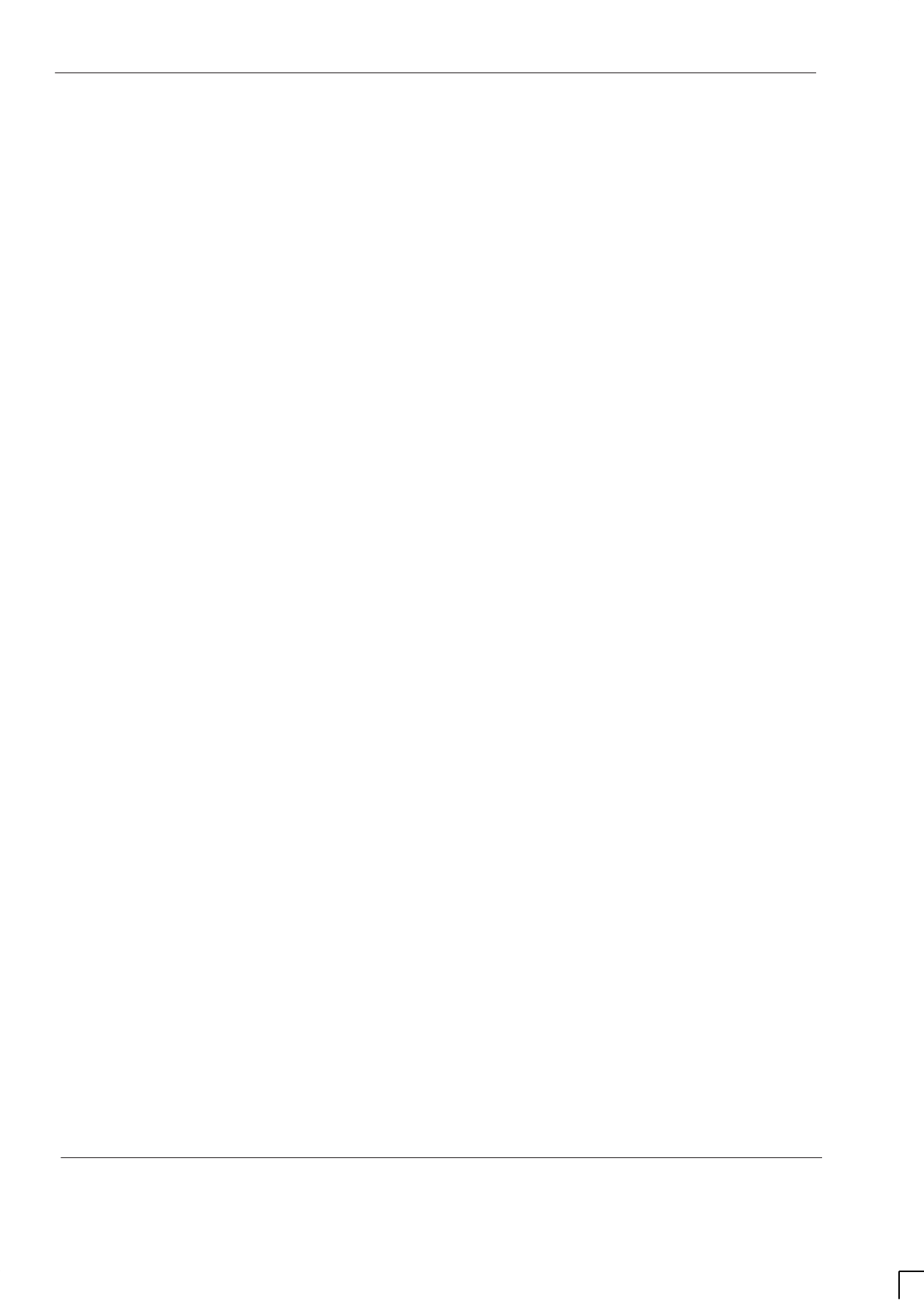
GSM-204-323
31st Oct 01
iv
Technical Description: Horizon
macro
outdoor
CONTROLLED INTRODUCTION
68P02902W02-A
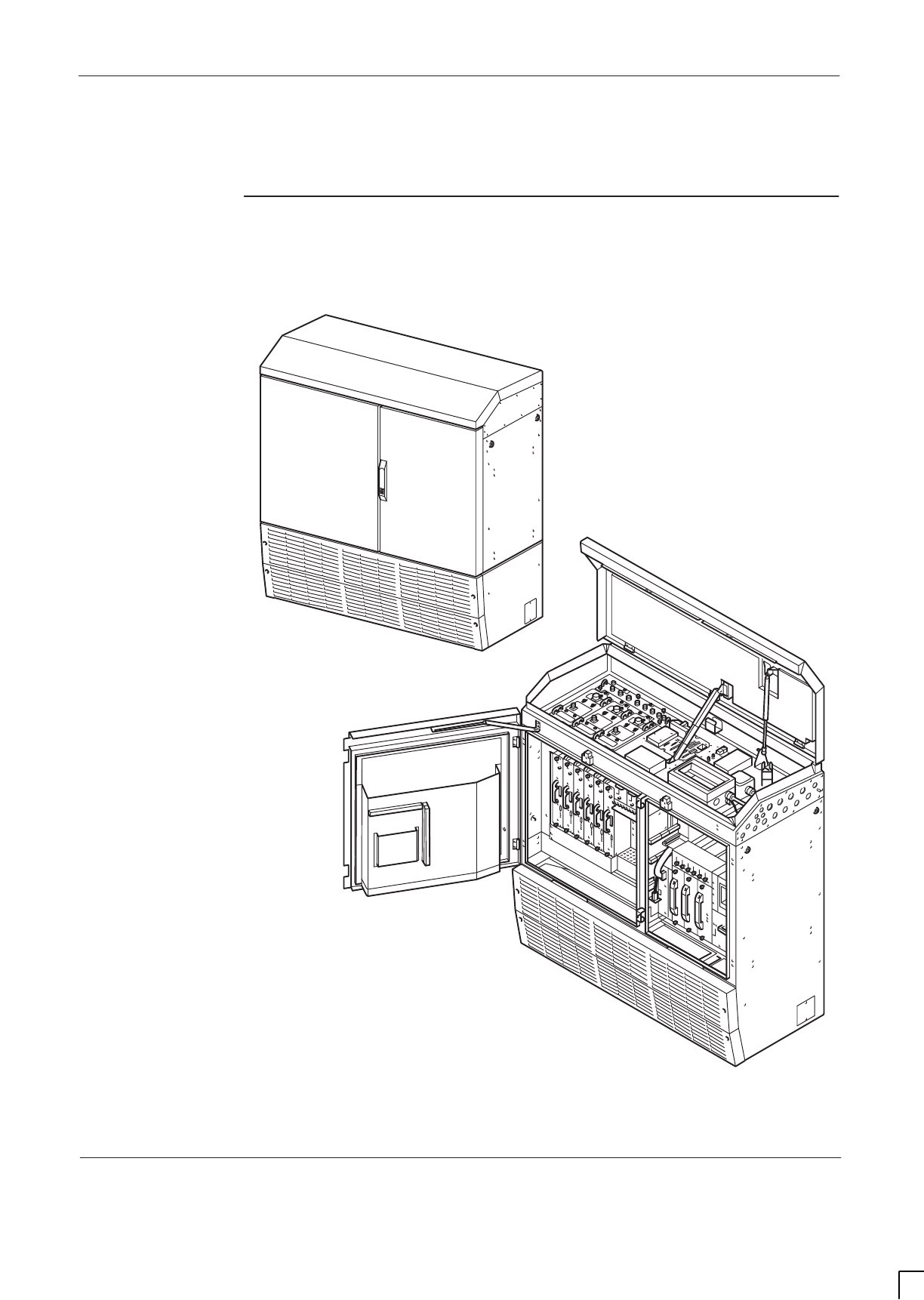
GSM-204-323 Outdoor cabinet structure
31st Oct 01
Technical Description: Horizon
macro
outdoor
68P02902W02-A
CONTROLLED INTRODUCTION
Tech. 2–1
Outdoor cabinet structure
External cabinet
view
Figure 2-1 shows an external view of a closed outdoor cabinet, and the cabinet
with doors and lid open, (right door omitted for clarity).
Figure 2-1 Closed cabinet and cabinet with lid and doors open
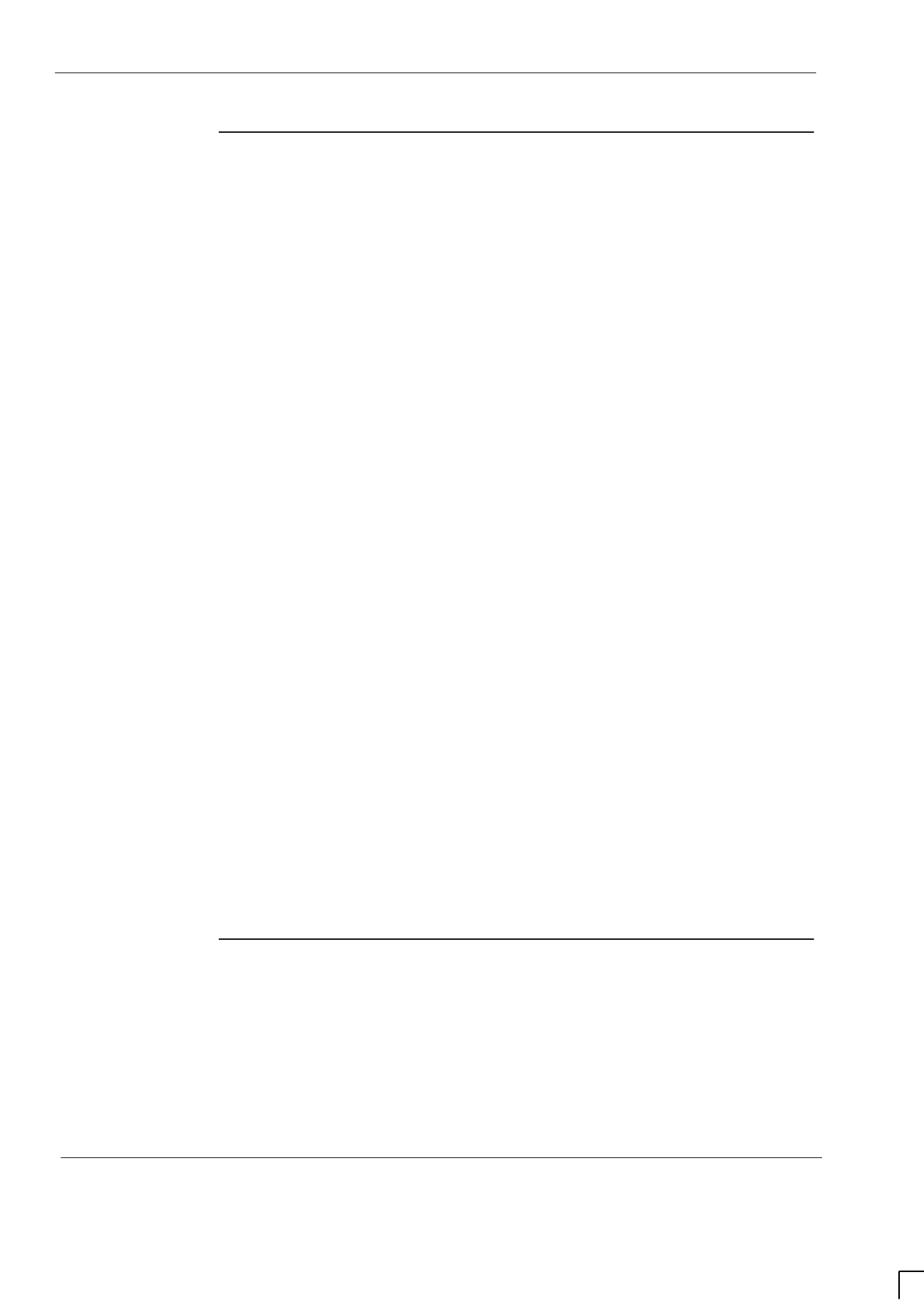
GSM-204-323
Outdoor cabinet structure
31st Oct 01
Tech. 2–2
Technical Description: Horizon
macro
outdoor
CONTROLLED INTRODUCTION
68P02902W02-A
Overview of
structure
description
The outdoor cabinet is shown in Figure 2-2. The cabinet is itended for minimum
maintenance and maximum ease of module replacement and has access only
from the front and top.
This chapter describes the cabinet structure and the inner connections to assist
understanding the cabinet functions. There should be no need to dismantle the
cabinet beyond Field Replaceable Unit (FRU) level.
The cabinet structure components are explained in the following sections:
SURF harness
This section describes the SURF harness connections between the SURF
and the backplane and transceivers. These are not normally visible in a
fully equipped cabinet.
Top section
This section describes the top section holding the Tx blocks, the interface
panel, the SURF module, the number 1 ac distribution box and an ac
outlet socket.
Cage backplane interface panel harness assembly (CBIA)
This section describes the CBIA. It also describes the backplane
connections between all modules, and the harness from the backplane to
the interface top panel connectors. These are not normally accessible in a
fully equipped cabinet.
Power supply enclosure
This section shows the location of the Power Supply Unit (PSU) and the
racking for customer equipment.
Doors, lid and cable shrouds
This section describes the structure and function of the doors, lid and
cable shrouds.
Space required
around cabinet
See Specifications in Chapter 1.
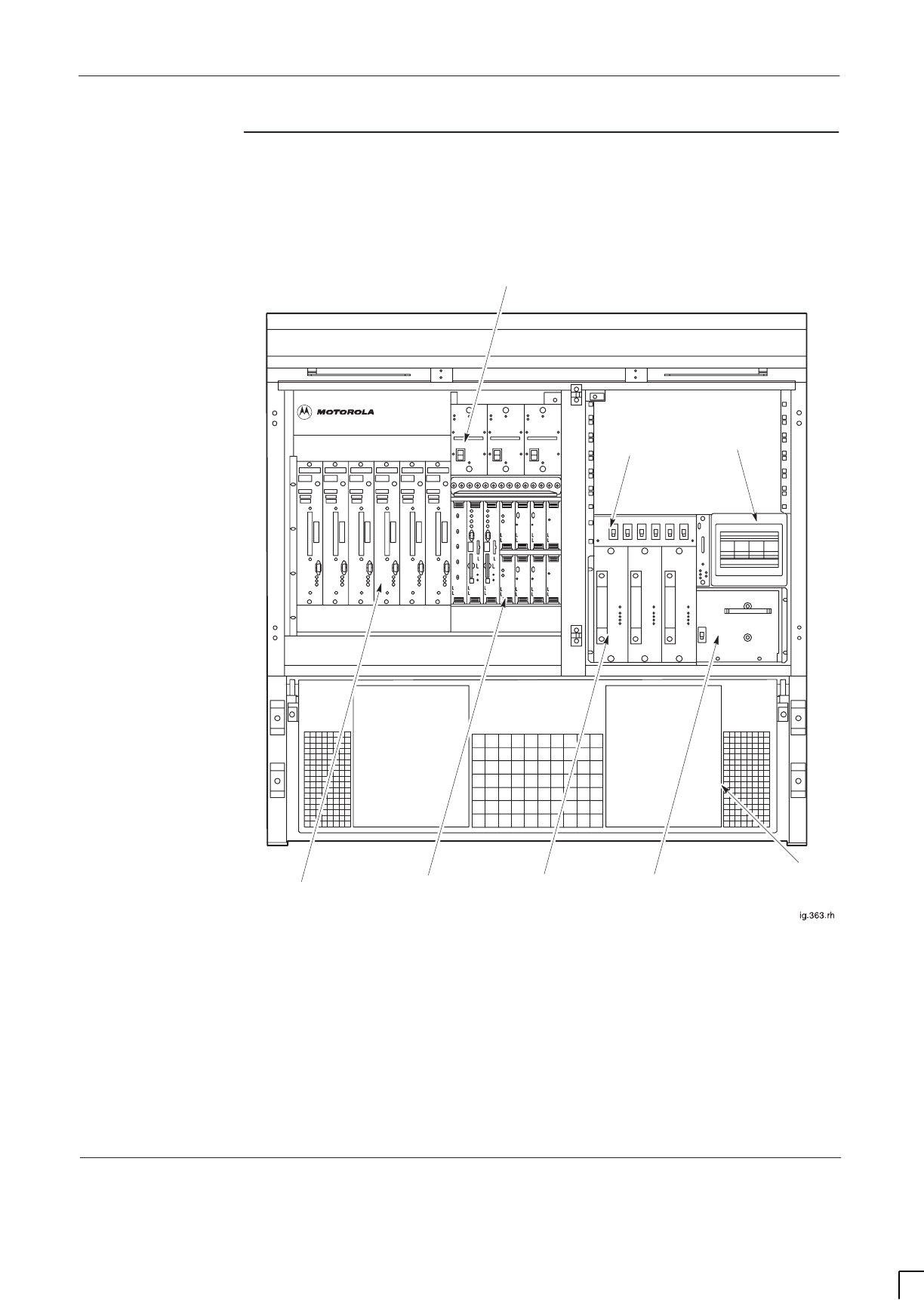
GSM-204-323 Outdoor cabinet structure
31st Oct 01
Technical Description: Horizon
macro
outdoor
68P02902W02-A
CONTROLLED INTRODUCTION
Tech. 2–3
Filled cabinet
view
Figure 2-2 shows a front view of the outdoor cabinet with the maximum number
of modules installed, The main components visible from the front are identified.
The doors and TMS front cover have been omitted for clarity.
No2 AC
DISTRIBUTION
BOX
CTUs DIGITAL
MODULES TOPSMs
TMS
INTERNAL
BATTERY
TRAY
PSMs
DC CIRCUIT
BREAKERS
Figure 2-2 Horizon
macro
outdoor cabinet showing main components
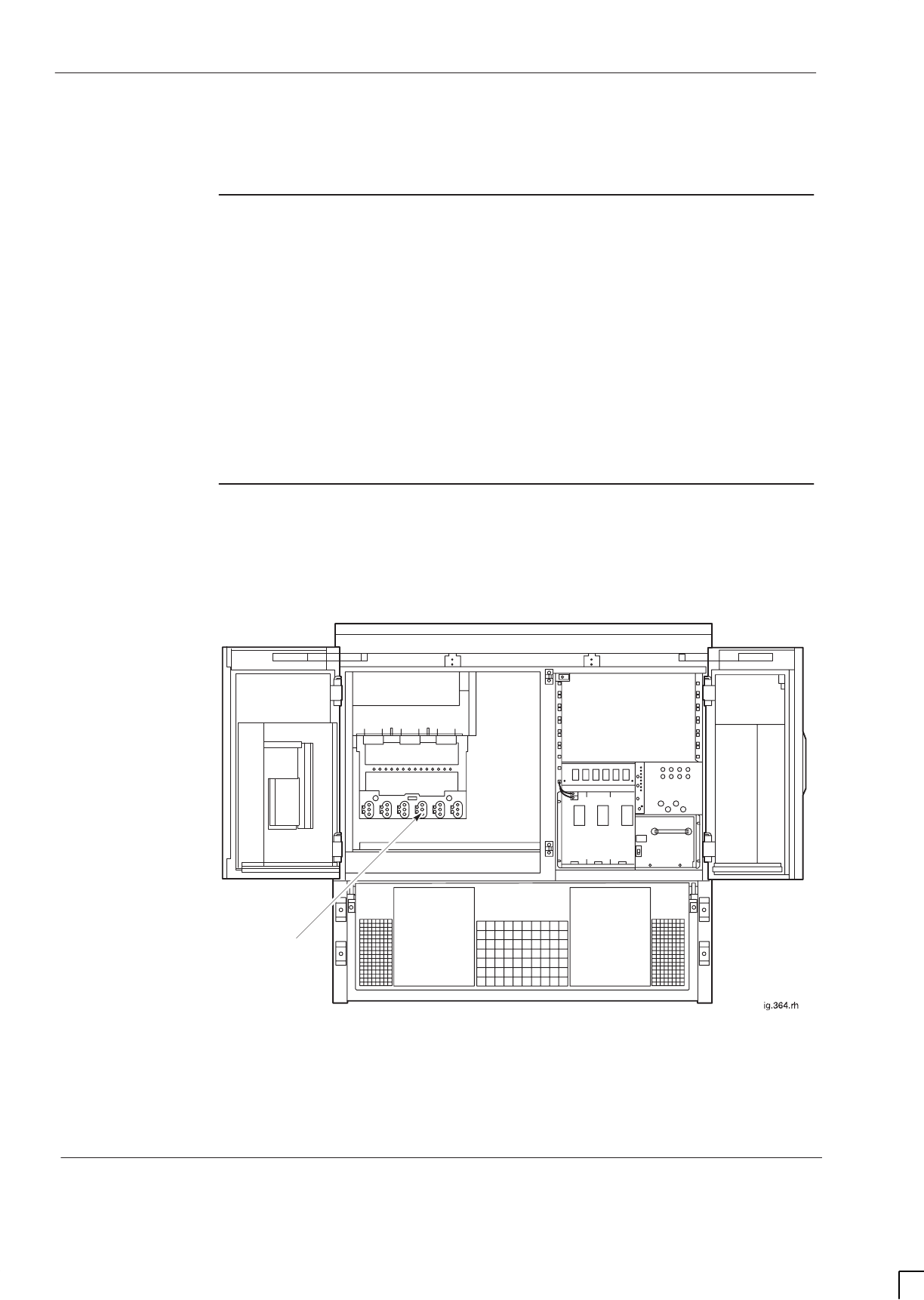
GSM-204-323
SURF harness
31st Oct 01
Tech. 2–4
Technical Description: Horizon
macro
outdoor
CONTROLLED INTRODUCTION
68P02902W02-A
SURF harness
SURF harness
detail
The SURF harness is fitted on the back wall of the cabinet. The chassis of the
harness supports the SURF module.
The SURF harness provides:
Three connectors to the SURF, for RF and power.
One RF connector to each CTU, consisting of three inputs, one each for
RxA, RxB and RF loopback test, as shown in Figure 2-4. The RF
connectors are free floating to ensure fitting of CTU modules.
One connector to the backplane, for power from the PSMs.
Cabinet view
with installed
SURF harness
Figure 2-3 shows the SURF harness installed in an empty cabinet. The SURF
harness cables have been omitted for clarity.
SURF HARNESS
(see Figure 2-4 for a
detailed view)
Figure 2-3 Location of the SURF harness in the cabinet
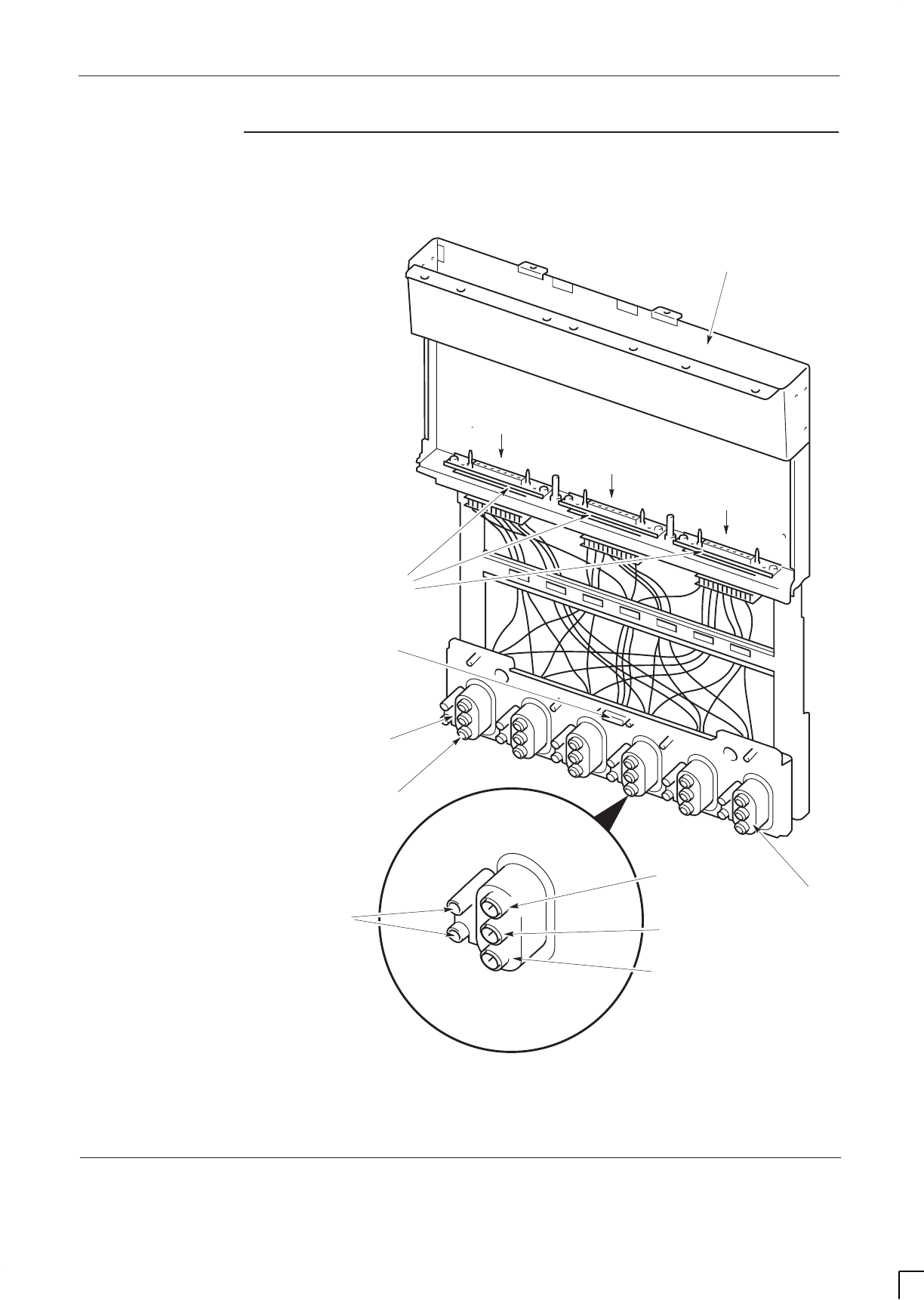
GSM-204-323 SURF harness
31st Oct 01
Technical Description: Horizon
macro
outdoor
68P02902W02-A
CONTROLLED INTRODUCTION
Tech. 2–5
SURF harness
view
Figure 2-4 shows the SURF harness with connectors indicated.
CONNECTOR FOR
EACH CTU
POWER CONNECTOR TO
BACKPLANE
SLOT FOR SURF
MODULE
RxA X 6
RxB X 6
RF LOOPBACK X 6
CTU 0
CTU 5
THREE CONNECTORS
TO SURF
LOCATING PINS
RxA
RF LOOPBACK
TEST PORT (L)
RxB
Figure 2-4 SURF harness with connectors indicated
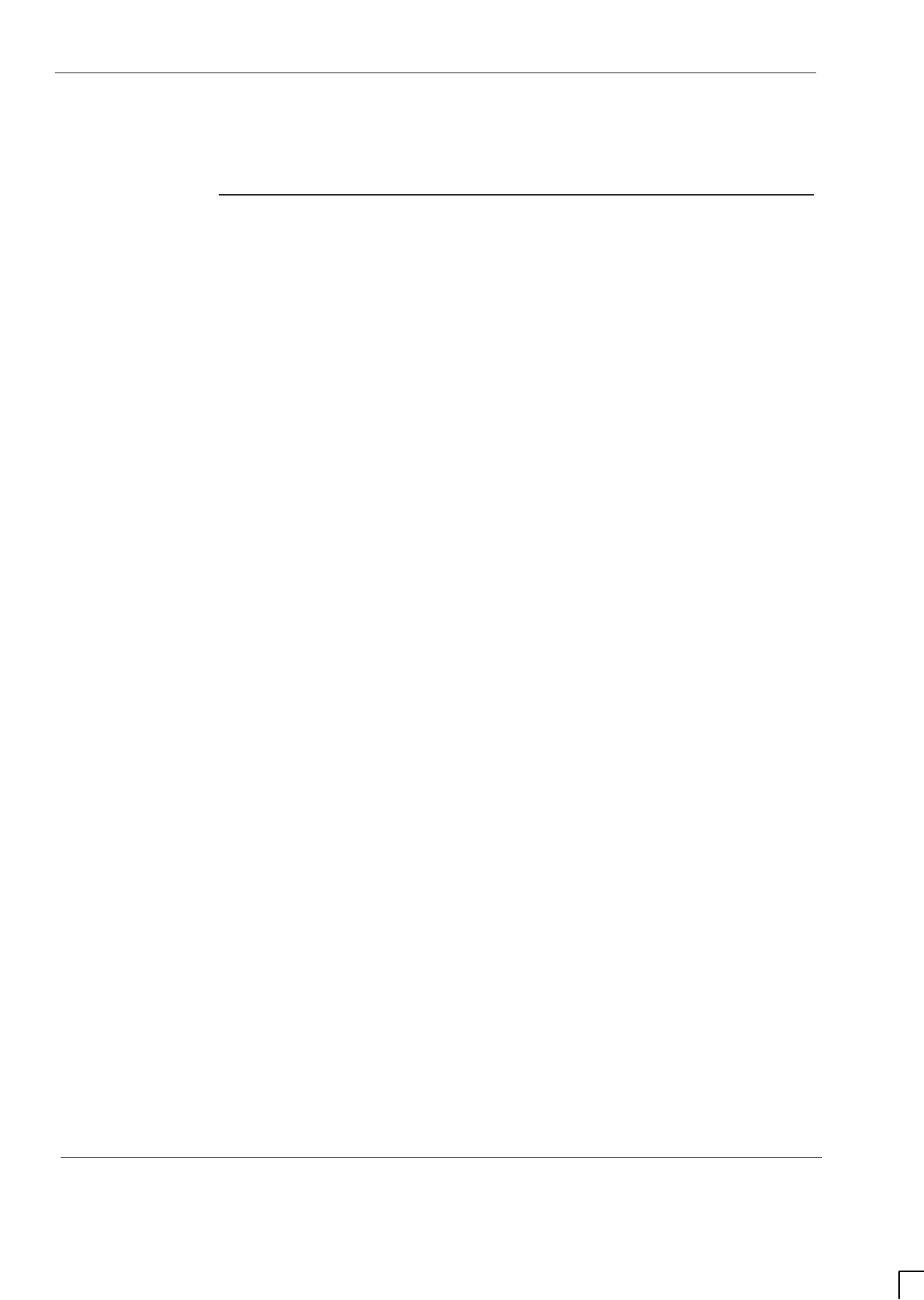
GSM-204-323
Top section
31st Oct 01
Tech. 2–6
Technical Description: Horizon
macro
outdoor
CONTROLLED INTRODUCTION
68P02902W02-A
Top section
Top section
description
The top section provides:
A basket to hold up to three Tx blocks. This includes three holes to enable
connection of CTU Tx cables to the underside of each Tx block. The holes
also allow cooling of the Tx blocks from underneath.
A slot for insertion of the SURF module.
A location hole for the interface panel. The interface panel is positioned
into the top section from underneath and fixed from the top.
Cable holes for fibre optic extension cables (from the MCUF FMUX to an
FMUX of another cabinet), and alarm cables.
Earth plates fitted to the ends of the top wrap. The earth plate contains the
RF cabling, which allows the connection of external antennas to internal
RF cabling, at the cable entry side. A blank plate or expansion plate is
fitted at the opposite end of the top wrap.
A panel for the power supply unit dc output and external battery cables.
A location hole for the number 1 ac distribution box (the power supply
input connection and switching). The number 1 ac distribution box slots
into the top section from underneath.
The top section also houses krone blocks and an ac outlet socket.
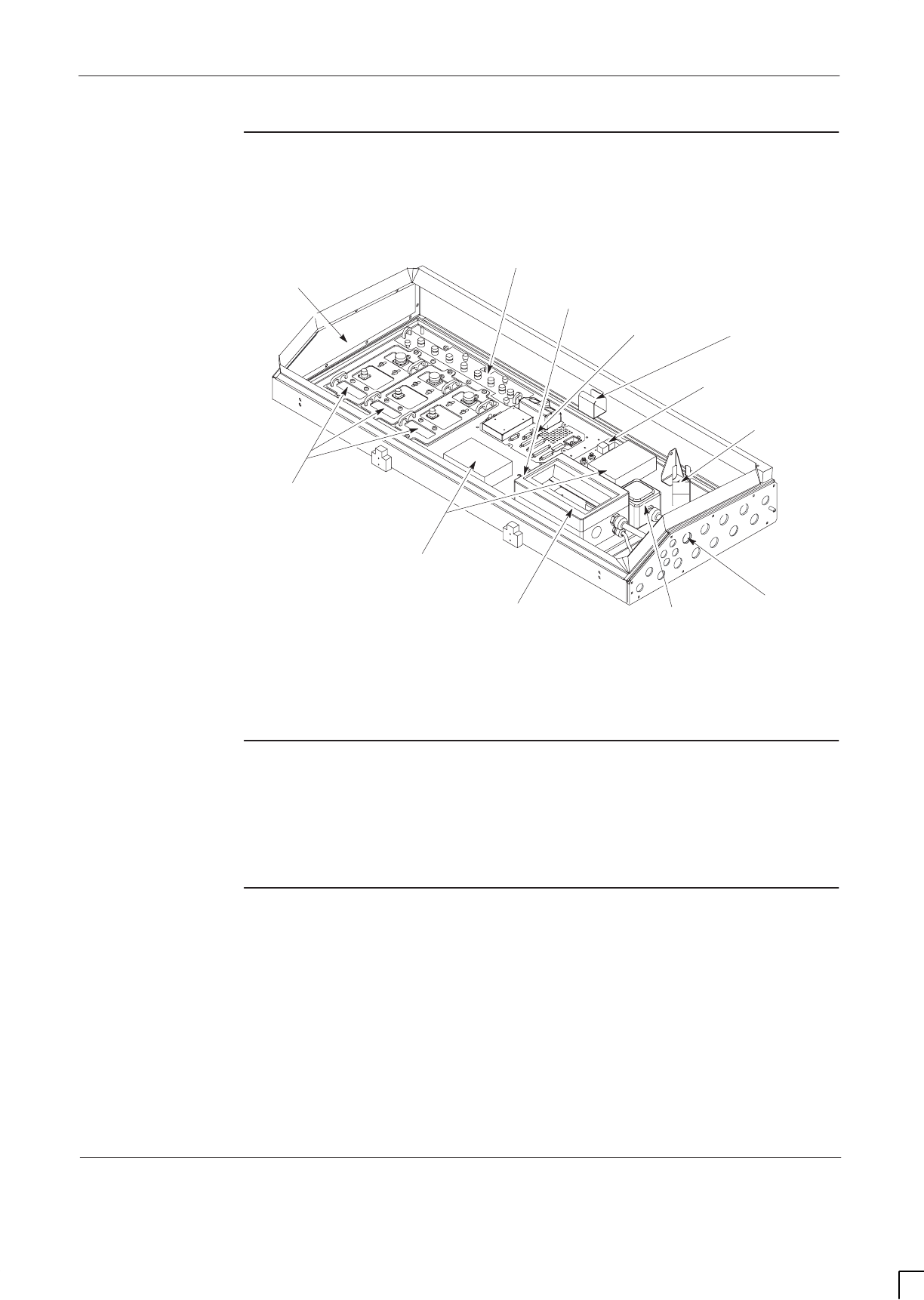
GSM-204-323 Top section
31st Oct 01
Technical Description: Horizon
macro
outdoor
68P02902W02-A
CONTROLLED INTRODUCTION
Tech. 2–7
Top section
diagram
Figure 2-5 shows the top section with the major features labelled.
BLANK PLATE (LEFT
EARTH PLATE OR
EXPANSION
PLATE OPTIONAL)
THREE Tx
BLOCKS
INTERFACE PANEL
KRONE BLOCKS
PANEL FOR DC OUTPUT
AND EXTERNAL
BATTERY CABLES
RIGHT EARTH PLATE
(RF CABLE OMITTED
FOR CLARITY)
SURF MODULE
AC OUTLET
SOCKET
NUMBER 1 AC
DISTRIBUTION BOX
CABLE GUIDE
CABLE GUIDE
CABLE HOLE FOR FIBRE
OPTIC EXTENSION CABLES
Figure 2-5 Top section with major features labelled
Krone blocks
Two krone blocks are mounted on the top panel as an interface for:
Customer alarms.
Customer communications.
AC outlet
socket
The ac outlet socket is described in Power distribution in Chapter 4 of this
category
Technical Description: (GSM-204-323)
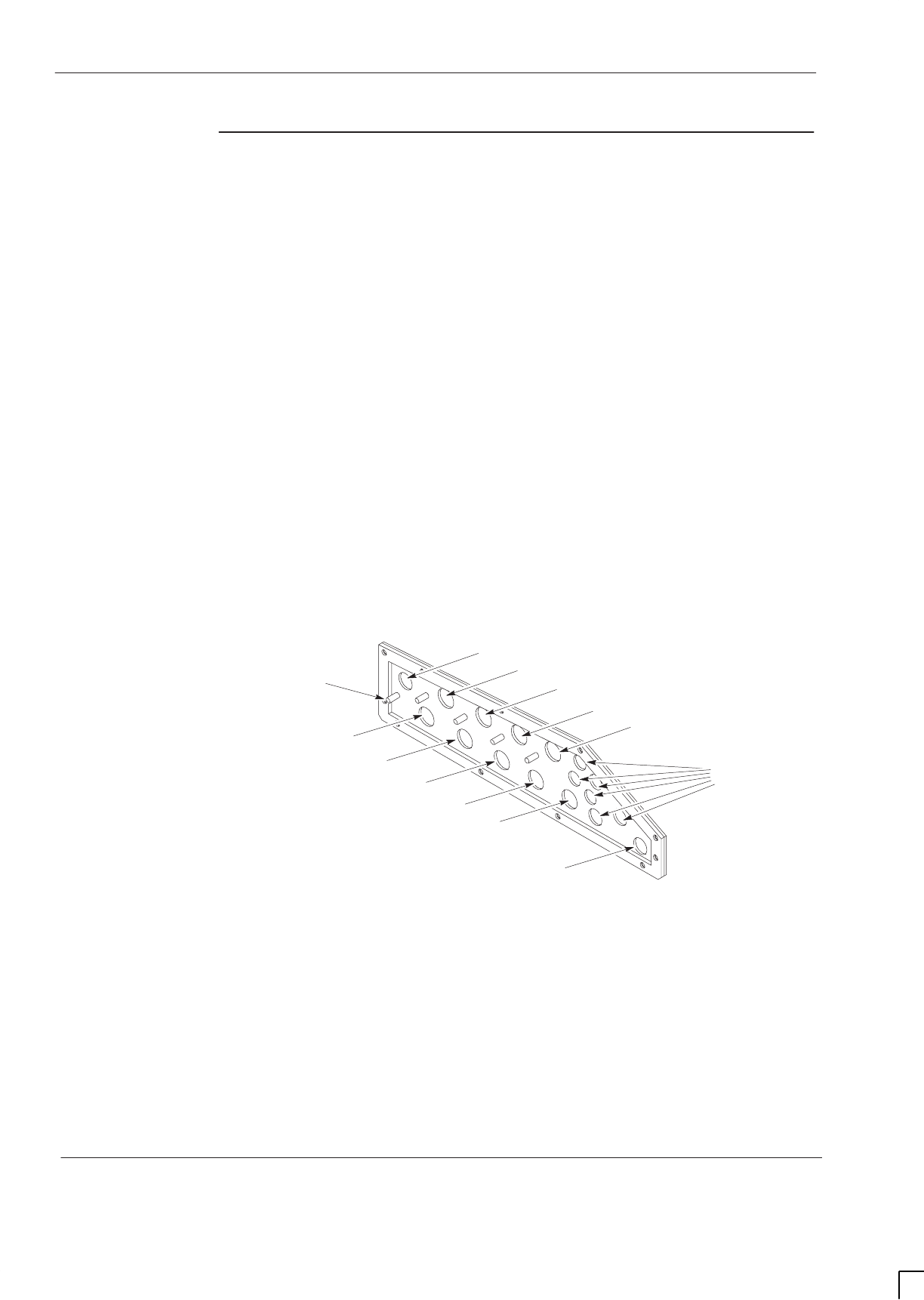
GSM-204-323
Top section
31st Oct 01
Tech. 2–8
Technical Description: Horizon
macro
outdoor
CONTROLLED INTRODUCTION
68P02902W02-A
Earth plates
An earth/connector plate is fitted to the cable entry side of the cabinet. The
earth plate is supplied with:
Three N-type to 7/16 bulkhead cables, (for connection between earth plate
and SURF module).
Three 7/16 to 7/16 bulkhead cables, (for connection between earth plate
and Tx block ANT connector).
Provision to fit up to three extra long RF cables, (for connection between
cabinets in multiple cabinet site configurations).
– Rx0B, Rx1B and Rx2B on the right side plate.
– Rx0A, Rx 1A and Rx2A on the left side plate.
The cabinet earth plate has the following functions:
Provision of the main cabinet earth connection.
Provision of a connection point for customer antennas.
Weatherproof pass-through for: ac power, external battery and customer
communications cables.
Figure 2-6 shows the layout of the right earth/connector plate viewed from inside
the top section (the layout for the left plate is a mirror image of this). The six
permanently connected RF cables are omitted for clarity.
TX 0
AC IN
DC INRX 1B
RX 0B
RX 2ARX 1A
RX 0A
TX 1
TX 2
RX 2B
EARTH STUD
COMMS
Figure 2-6 Cable entry side earth plate
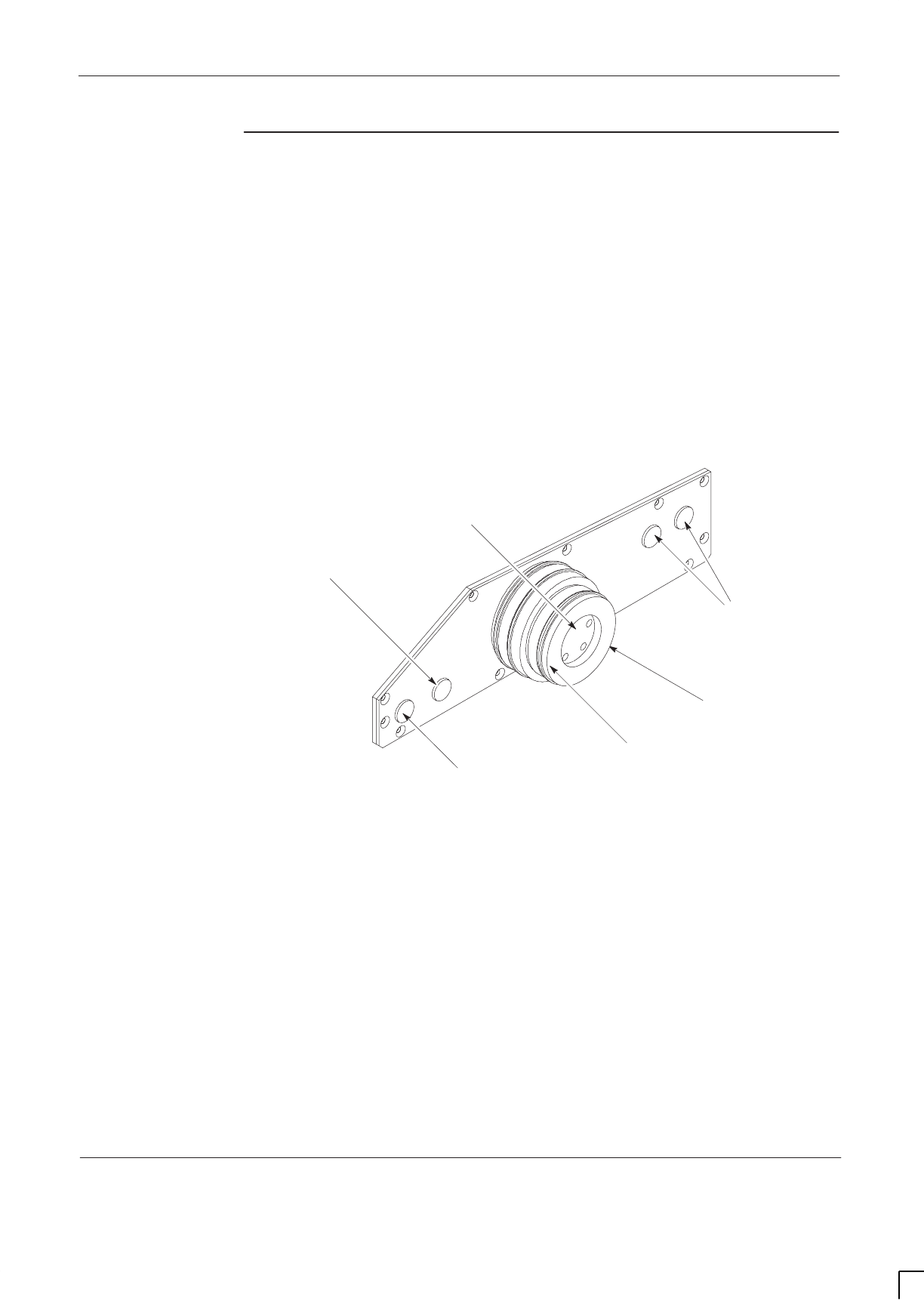
GSM-204-323 Top section
31st Oct 01
Technical Description: Horizon
macro
outdoor
68P02902W02-A
CONTROLLED INTRODUCTION
Tech. 2–9
Blank and
expansion
plates
A blank or expansion plate is fitted to the opposite end of the cabinet. The
expansion plate provides:
Weatherproof pass-through for: ac power, external battery and customer
communications cables.
RF cable pass-through for multiple cabinet sites.
The expansion plate is supplied with the cable pass-throughs sealed by
blanking plugs. The plug must be removed from each pass-through before the it
can be used.
Figure 2-7 shows a right side expansion plate, (left side expansion plate is a
mirror image of right side plate).
RF PASS-THROUGH
FIVE CABLE GLAND
BATTERY BACKUP CABLE
PASS-THROUGH
EARTH CABLE
PASS-THROUGH
AC CABLE
PASS-THROUGH
FIBRE OPTIC
EXTENSION CABLE
PASS-THROUGH
(not visible)
RUBBER
GLAND HOUSING
Figure 2-7 Expansion plate (right side)
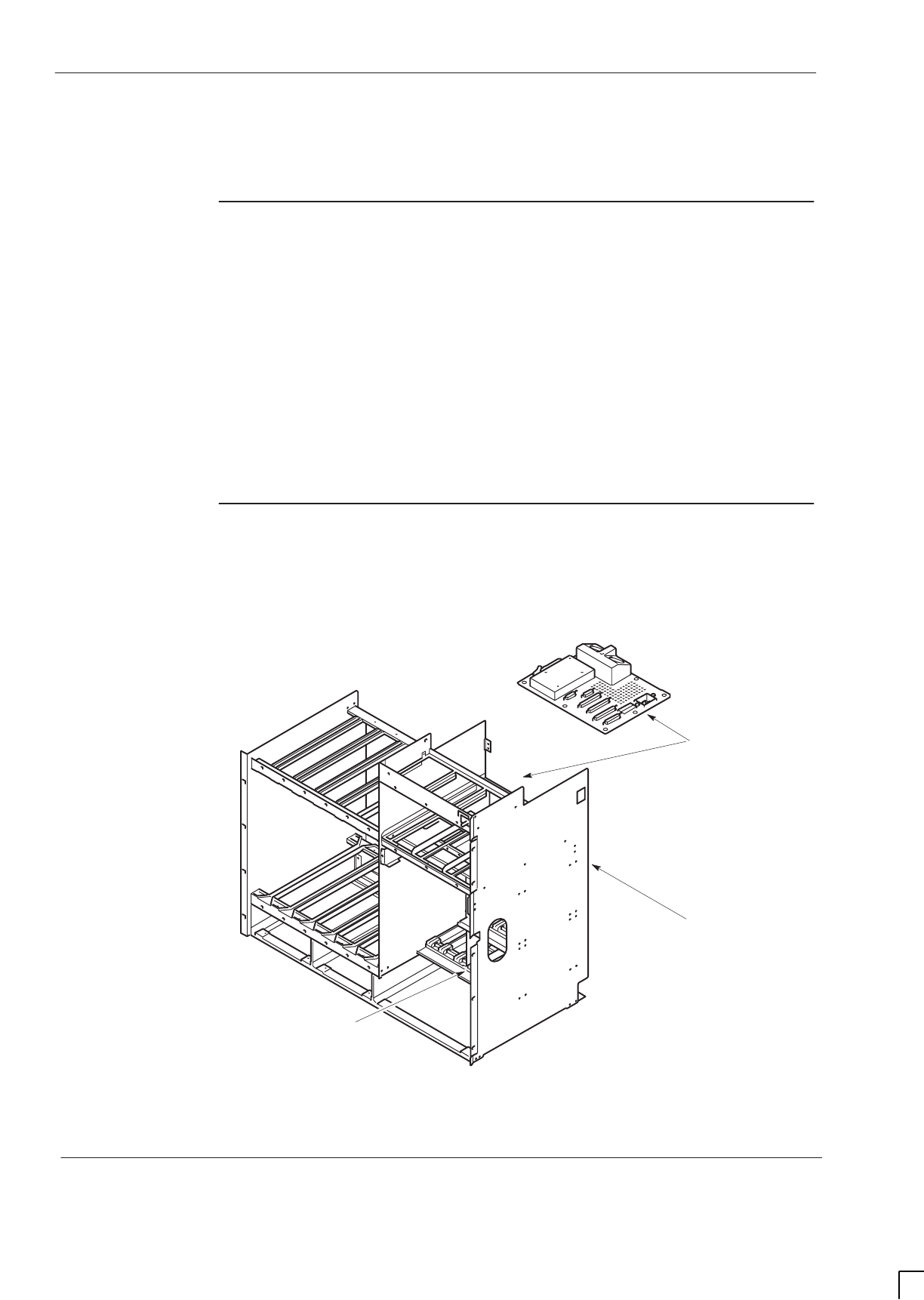
GSM-204-323
Cage backplane interface panel harness assembly (CBIA)
31st Oct 01
Tech. 2–10
Technical Description: Horizon
macro
outdoor
CONTROLLED INTRODUCTION
68P02902W02-A
Cage backplane interface panel harness assembly (CBIA)
CBIA overview
The CBIA provides a platform for module installation, and power and digital
signal interconnection to cabinet modules. The CBIA consists of:
The main cage – provides compartments for fans, CTUs, digital modules,
BPSMs, PSMs and CBM.
The backplane – routes power and signals for all cage modules and power
to the SURF.
The harness – links the backplane to the interface panel.
The interface panel – carries the T43/BIB, the internal dc power and
communications connectors.
CBIA and
interface panel
schematic view
Figure 2-8 shows the CBIA main cage and interface panel.
ig.236.rh
DIGITAL MODULE
SECTION OF CAGE
INTERFACE
PANEL
MAIN
CAGE
BACKPLANE
ATTACHED TO
ENTIRE BACK
OF CAGE
HARNESS LINKS
BACKPLANE
CONNECTORS TO
UNDERSIDE OF
INTERFACE PANEL
Figure 2-8 View of CBIA cage and interface panel
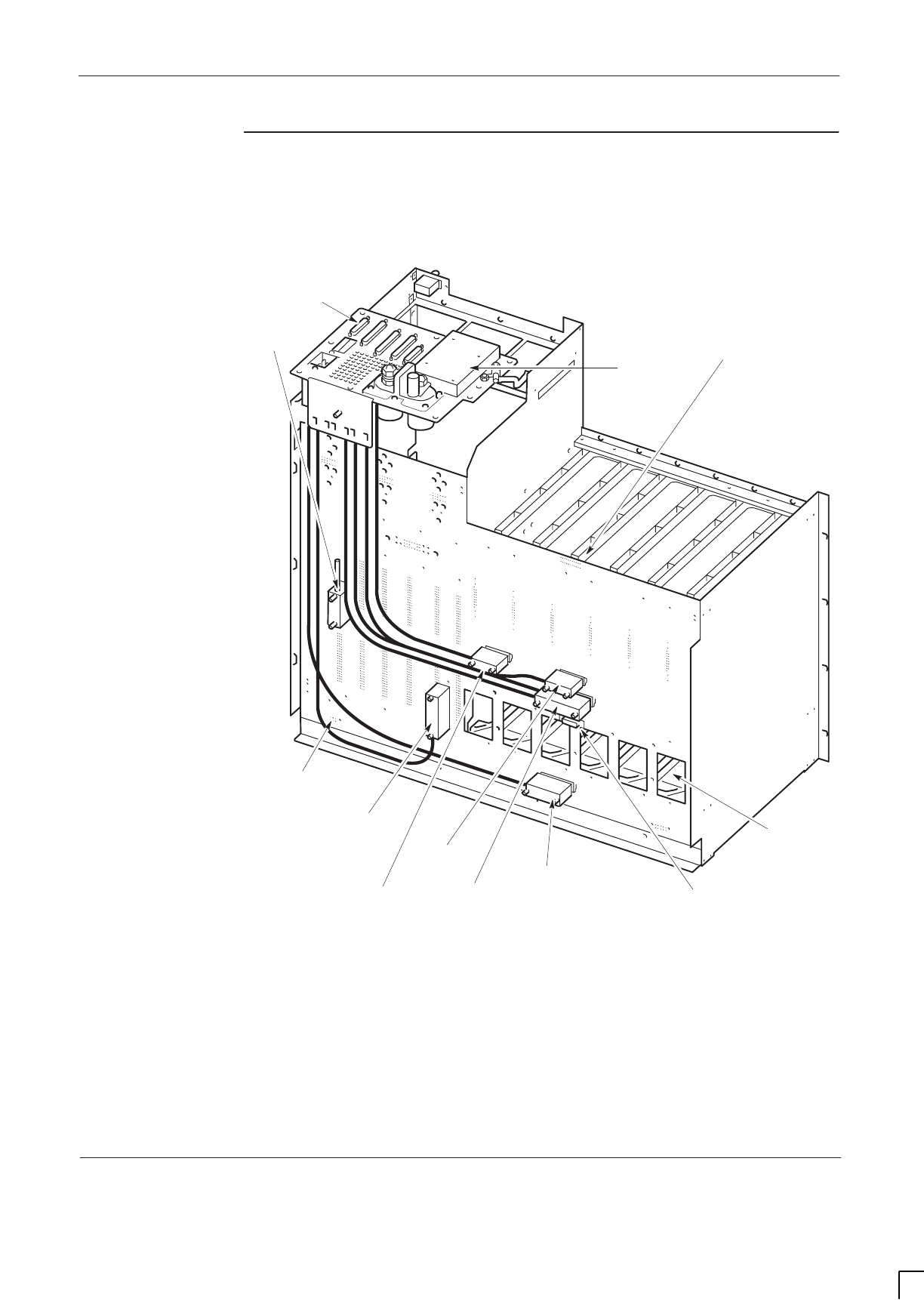
GSM-204-323 Cage backplane interface panel harness assembly (CBIA)
31st Oct 01
Technical Description: Horizon
macro
outdoor
68P02902W02-A
CONTROLLED INTRODUCTION
Tech. 2–11
Backplane and
harness view
Figure 2-9 shows the CBIA harness linking the interface panel and the
backplane at the rear of the main cage, including the temperature sensors.
Each backplane harness connector is identified.
ig.237.rh
ICS J26
THREE
TEMPERATURE
SENSORS
DOOR SWITCH
CONNECTOR J55
(not used)
SIX CTU
CONNECTOR
HOLES FOR
SURF
HARNESS
POWER
CONNECTOR
FOR SURF
HARNESS
NIU to T43/BIB
J21
INTERFACE
PANEL
EXTERNAL
ALARMS J23
GPS J22
(if fitted)
RTC J32
PIX J25
T43/BIB
Figure 2-9 Rear view of cage showing backplane and harness
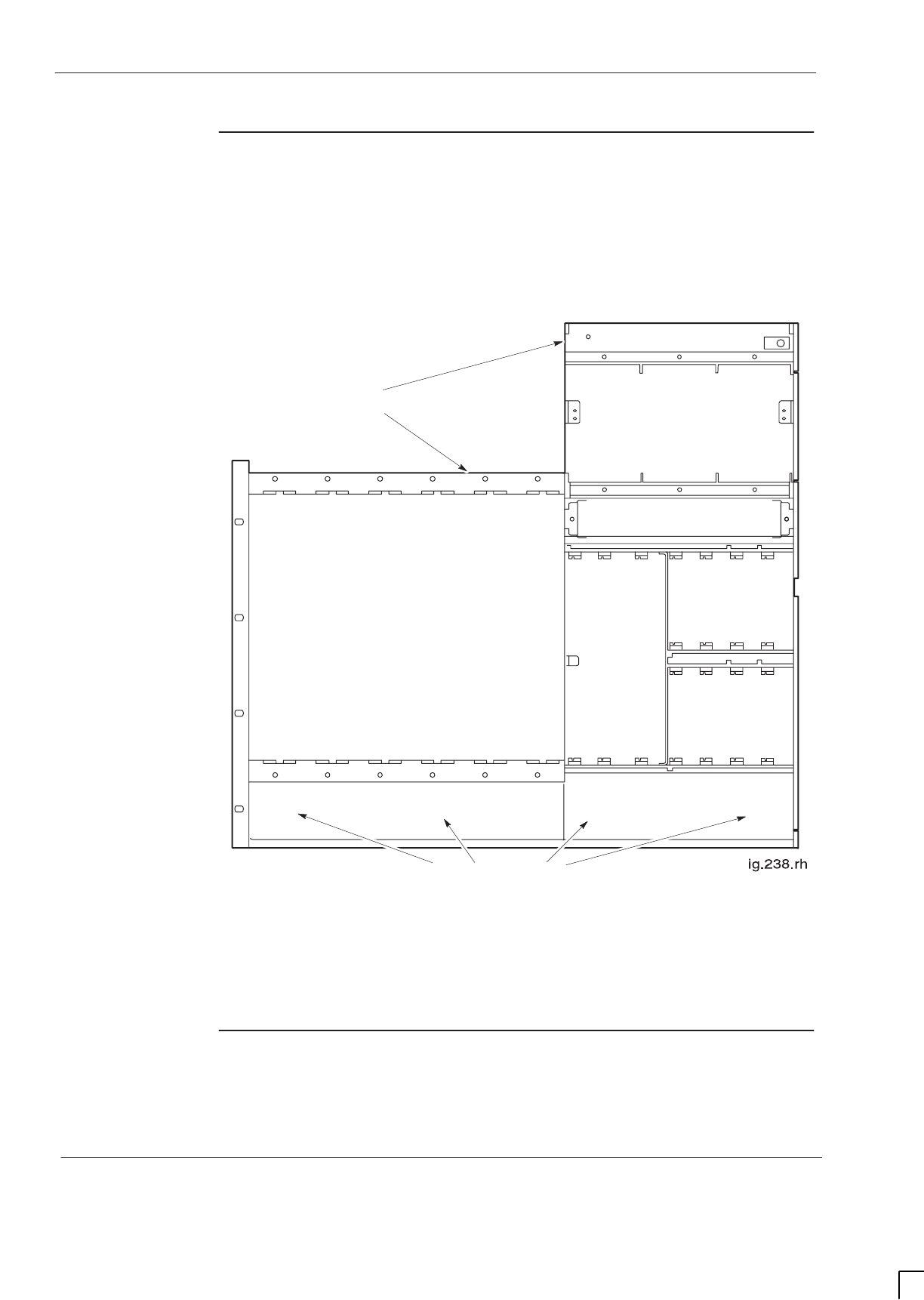
GSM-204-323
Cage backplane interface panel harness assembly (CBIA)
31st Oct 01
Tech. 2–12
Technical Description: Horizon
macro
outdoor
CONTROLLED INTRODUCTION
68P02902W02-A
CBIA cage
function and
diagram
The main cage holds modules and supports the backplane. Each compartment
has appropriate sliders for insertion of the modules. Figure 2-10 shows the
module compartments of the cage.
CIRCUIT BREAKER MODULE
CAGE
TRANSCEIVERS
BLANKING PLATE
FULL SIZE
DIGITAL
MODULES
(MCUFs
AND
ALARM)
HALF SIZE DIGITAL
MODULES (FMUX,
NIUs AND BPSM)
POWER SUPPLY MODULES
(PSMs)
HALF SIZE DIGITAL
MODULES (FMUX,
NIUs AND BPSM)
Figure 2-10 Front view of cage showing where modules fit
CBIA harness
function
The harness provides cables to link connectors on the backplane with
connectors on the underside of the interface panel.
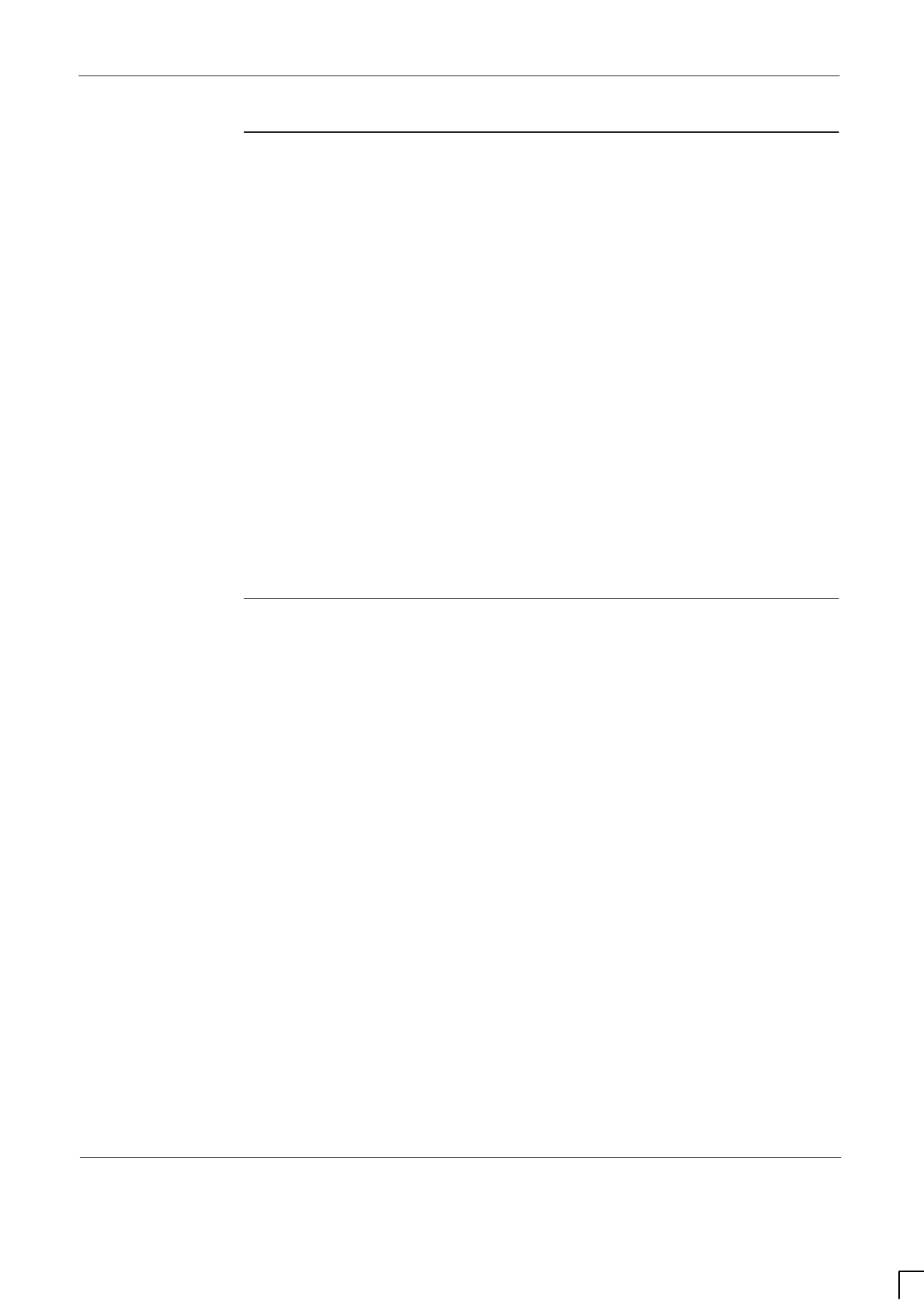
GSM-204-323 Cage backplane interface panel harness assembly (CBIA)
31st Oct 01
Technical Description: Horizon
macro
outdoor
68P02902W02-A
CONTROLLED INTRODUCTION
Tech. 2–13
CBIA backplane
function
The cabinet design enables all possible RF and digital module combinations to
be served by the same backplane. The only module-to-module cabling required
within the radio enclosure are the Tx cables from the transceivers to the Tx
blocks.
The backplane is a multilayered printed circuit board with attached connectors
on front and back. The backplane:
Routes power and digital signals throughout the cabinet.
Provides connectors for the harness cables linking to the interface panel.
Provides connectors for plug in modules.
Provides power to the SURF harness, when the main cage is inserted into
the cabinet.
Provides a connector for the door switch cable.
Provides connectors for three heat sensors in the main cage above the
CTUs.
Provides a connection (Fan 0) for the TMS fan fail alarm cable.
Attachment of
cage to cabinet
The CBIA is fitted to the cabinet at the factory and is not intended to be
removed in the course of normal maintenance or FRU replacement procedures.
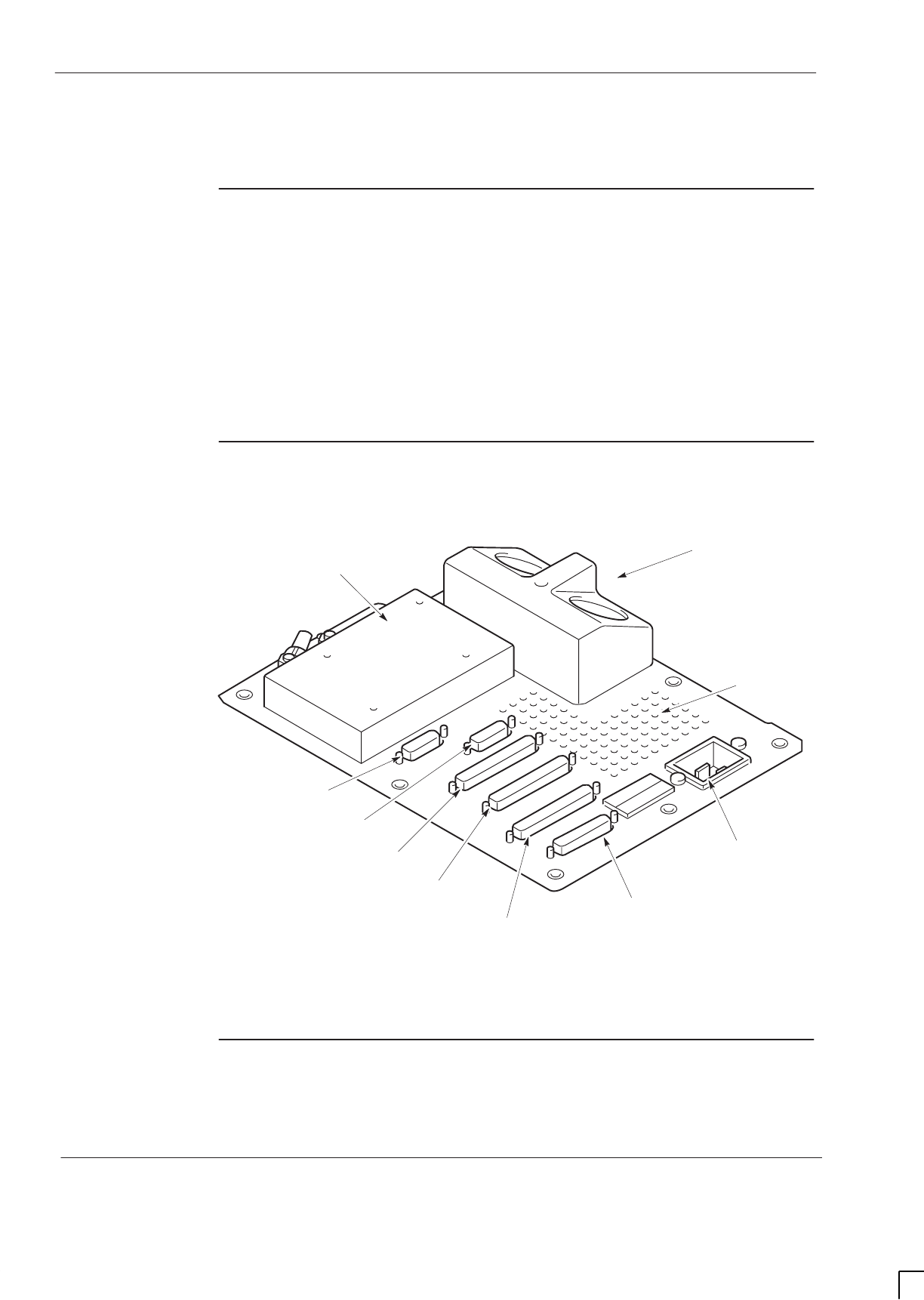
GSM-204-323
CBIA interface panel
31st Oct 01
Tech. 2–14
Technical Description: Horizon
macro
outdoor
CONTROLLED INTRODUCTION
68P02902W02-A
CBIA interface panel
Interface panel
function
The interface panel provides internal connection points to:
The power supply unit dc output.
PSU and TMS alarms.
Connection points to all telecommunications links.
All connectors are linked to the backplane through the CBIA harness. Plastic
connector covers (supplied by Motorola) protect unused connectors from
damage by static electricity or foreign matter.
Interface panel
diagram
Figure 2-11 shows the functions of the interface panel connectors.
ig.239.rh
T43/BIB
AC POWER
SOCKET INPUT
(not used)
DC POWER
INPUT
GPS
(if fitted)
not used
PIX 0
EXTERNAL ALARMS
(PSU and TMS ALARMS)
PIX 1
ICS
VENTILATION
GRILLE
Figure 2-11 Layout of the interface panel
Interface panel
pinouts
Interface panel pinouts are detailed in
Installation and Configuration:
(GSM-204-423)
Interface panel cabling
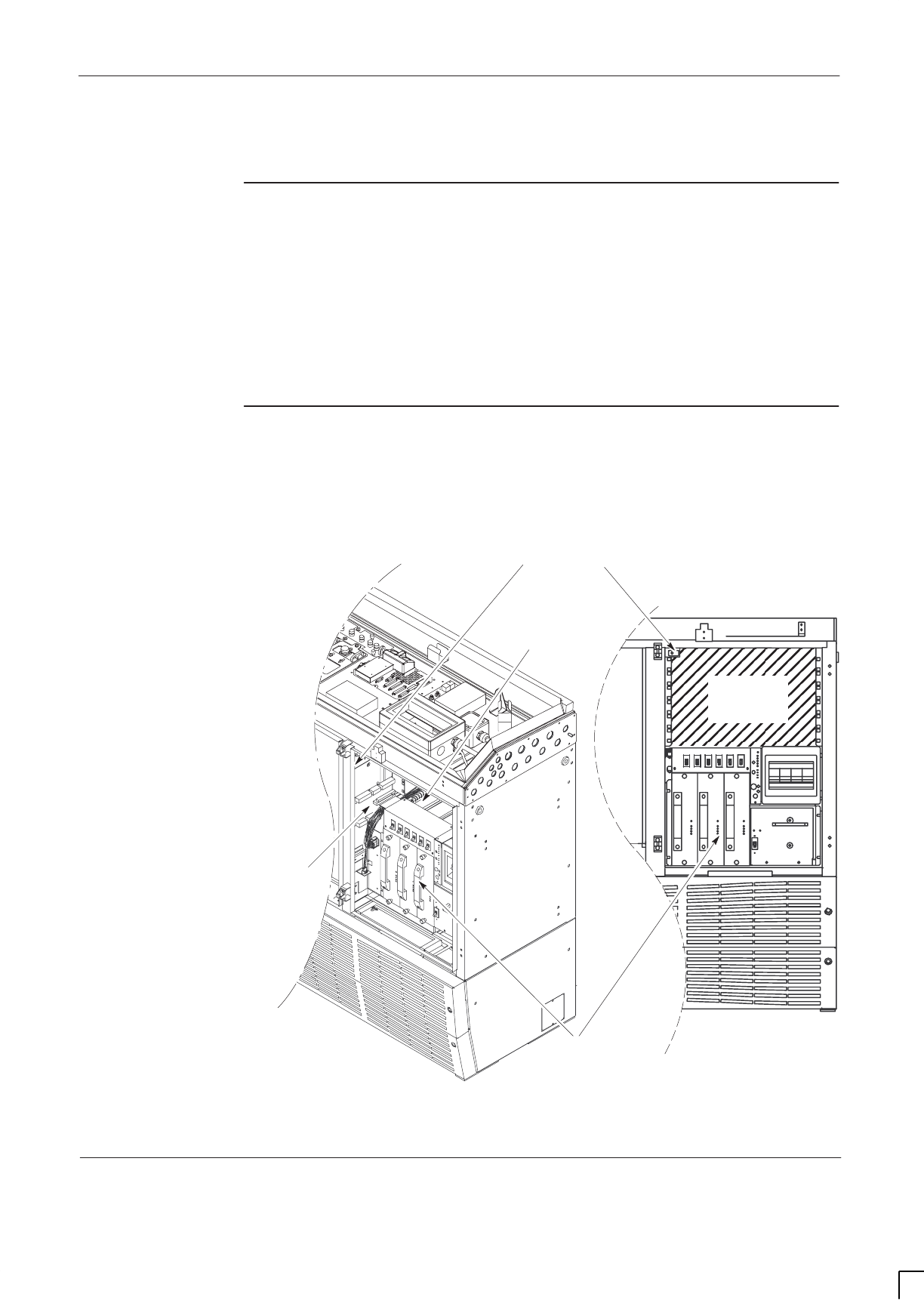
GSM-204-323 Power supply enclosure
31st Oct 01
Technical Description: Horizon
macro
outdoor
68P02902W02-A
CONTROLLED INTRODUCTION
Tech. 2–15
Power supply enclosure
Power supply
enclosure
overview
The power supply enclosure contains:
The Power Supply Unit (PSU), complete with up to three TOPSMs.
An alarm interface board to connect PSU and TMS alarms.
The door open alarm microswitch, located in the upper left corner.
Six U height of standard 19 inch rack space for customer equipment.
View of power
supply
enclosure
Figure 2-12 shows an isometric and a front view of the power supply enclosure
of the cabinet.
ALARMS
INTERFACE
BOARD
DOOR OPEN ALARM
MICROSWITCH
CUSTOMER
EQUIPMENT
RACKING
TOPSMs IN
PSU
SPACE FOR
CUSTOMER
EQUIPMENT
Figure 2-12 The power supply enclosure
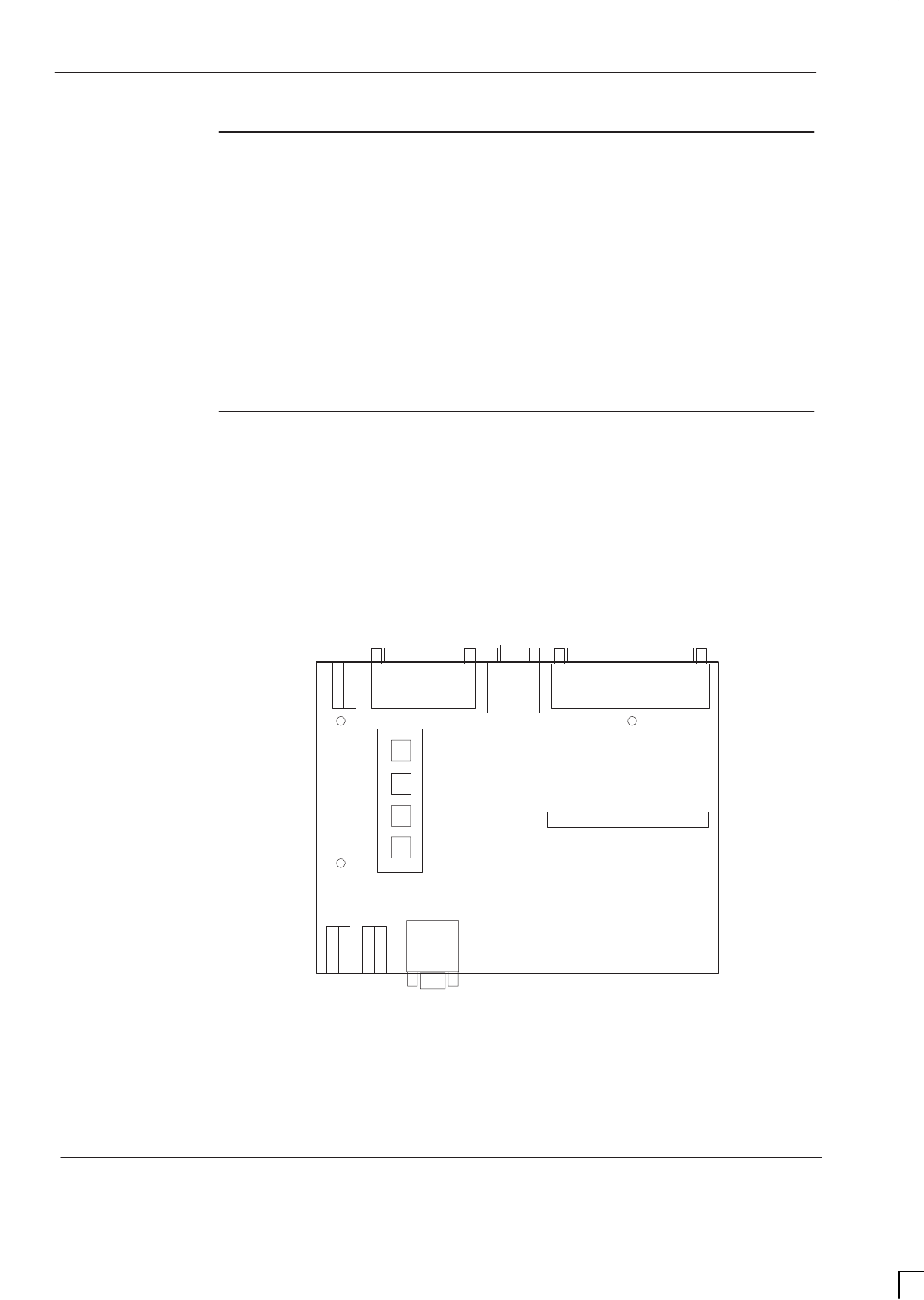
GSM-204-323
Power supply enclosure
31st Oct 01
Tech. 2–16
Technical Description: Horizon
macro
outdoor
CONTROLLED INTRODUCTION
68P02902W02-A
Power supply
unit
The PSU contains:
Up to three TOPSMs for input power conversion.
Minimal battery backup.
Circuit isolation and protection devices.
A control and alarm board.
The PSU is described in detail in Chapter 4 of this category (Cabinet power
supplies, Power distribution).
Alarms
interface board
The alarms interface board provides a connection point for alarms generated by
the auxiliary equipment housing, PSU and TMS. The alarms are then routed to
the external alarm connector of the interface panel, with the exception of the
TMS fan fail, which is routed through the main cage backplane (Fan 0
connector) to the alarm module.
The alarms interface board also houses the TMS test switches.
Figure 2-13 Shows the layout of the alarms interface board.
PL1 PL3
INTERNAL FANS
(SW3)
TEST OVERRIDE
(SW1)
HEATER ON
(SW2)
EXTERNAL FANS
(SW4) PL4
PL5
PL2
PL8
PL6PL7
Figure 2-13 Layout of the alarms interface board
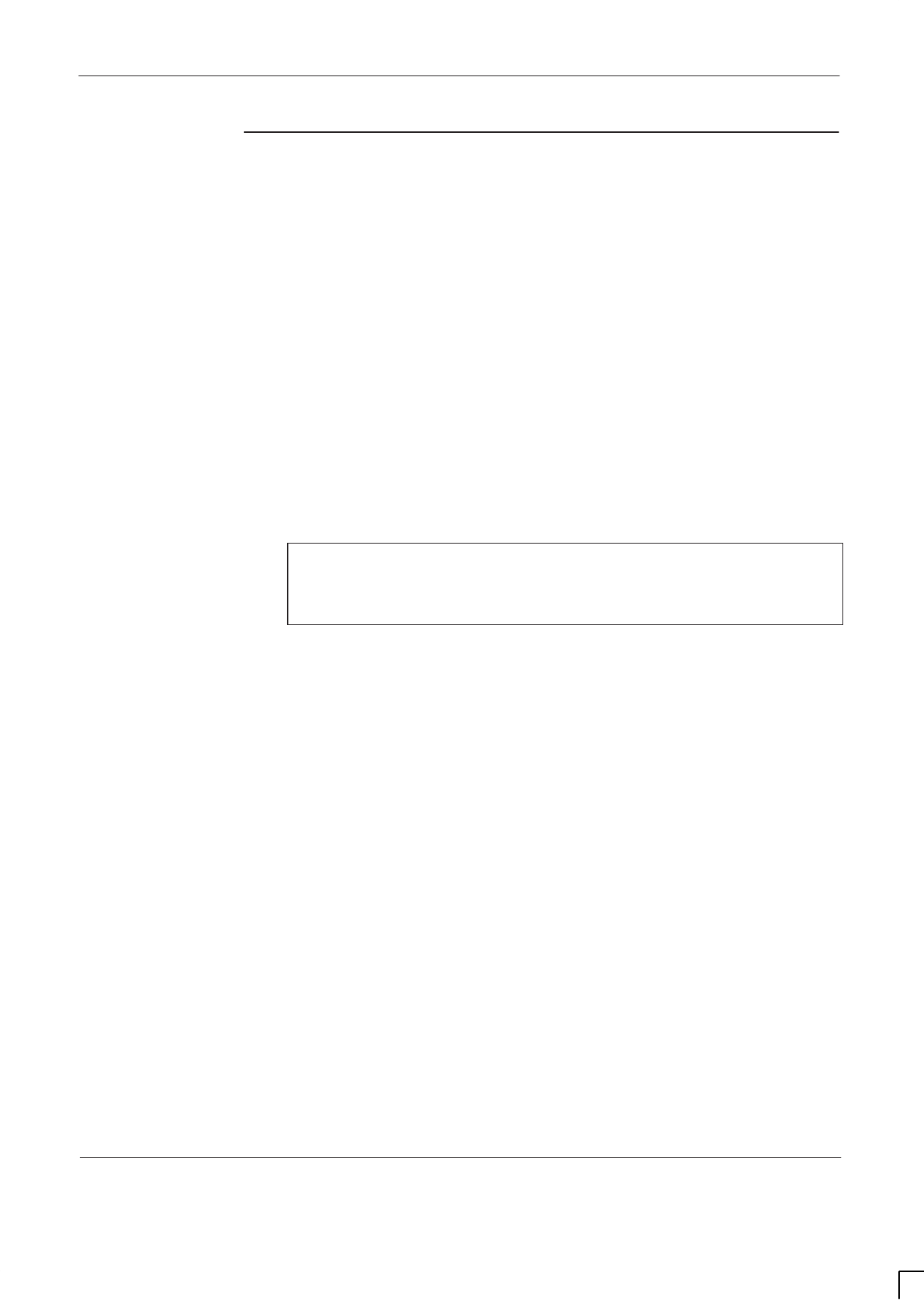
GSM-204-323 Power supply enclosure
31st Oct 01
Technical Description: Horizon
macro
outdoor
68P02902W02-A
CONTROLLED INTRODUCTION
Tech. 2–17
Alarms
interface board
connectors
The function of each alarms interface board connector is described below:
PL1 Connects to the auxiliary equipment housing alarm output
signal cable.
PL2 Connects to the interface panel PIX0 connector, to enable
remote initiation of battery tests.
PL3 Connects to the interface panel external alarms connector.
PL4 Connects to the PSU control interface board.
PL5 Connects TMS test inputs and alarm outputs.
PL6 Connects TMS fan alarm outputs to main cage backplane.
PL7 Connector for smoke alarms (not in use).
PL8 Connector for door microswitches.
NOTE PIX0 connector PL2 is normally disconnected and stowed.
If remote initiation/reporting functionality of internal battery
capacity test is to be used, PL2 must be connected to
alarms interface board.
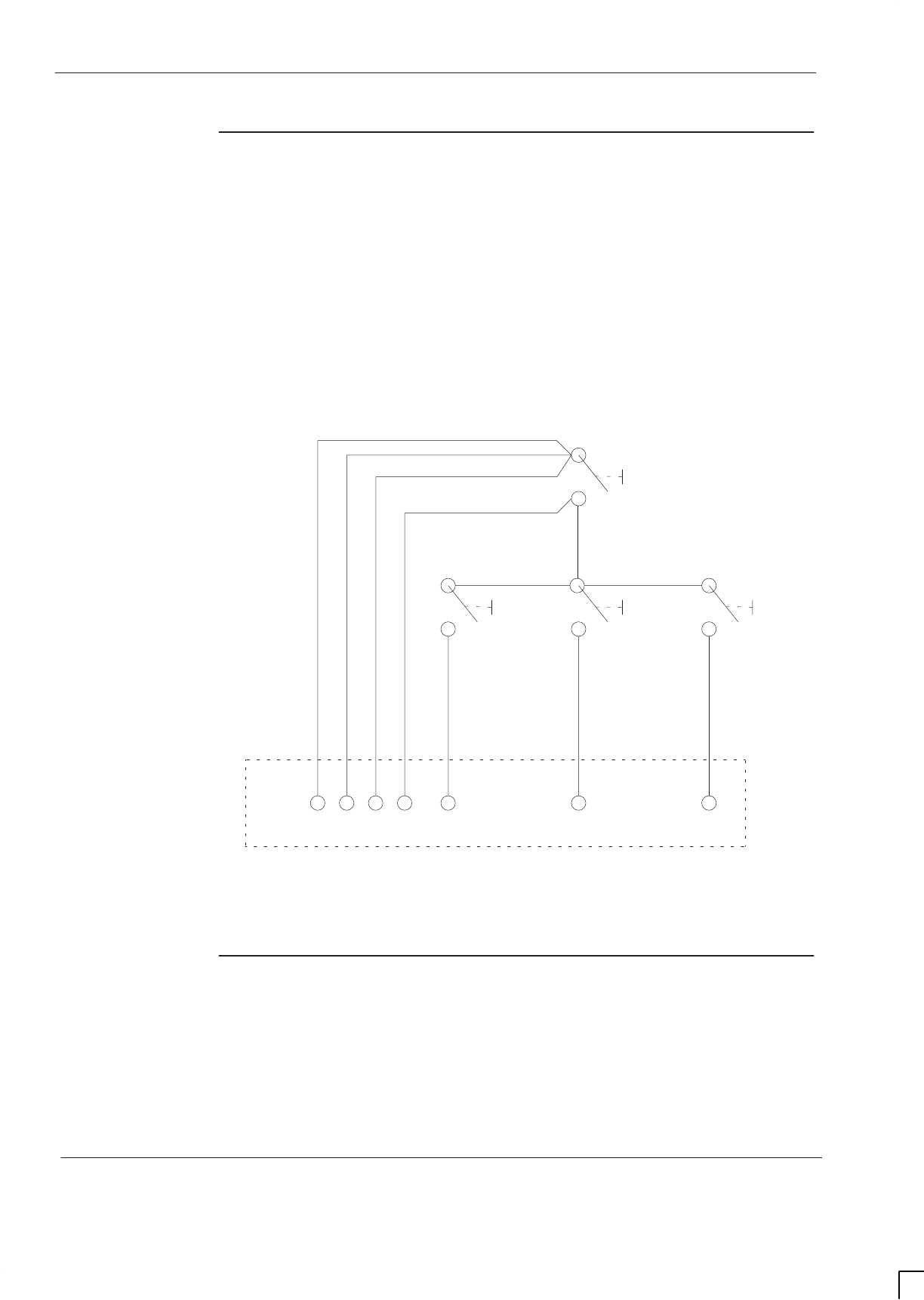
GSM-204-323
Power supply enclosure
31st Oct 01
Tech. 2–18
Technical Description: Horizon
macro
outdoor
CONTROLLED INTRODUCTION
68P02902W02-A
TMS test
switches
Four TMS test switches are mounted on the alarms interface board. Operation
of the override switch causes the TMS control board to set the fans to minimum
speed and the heaters to off, regardless of environmental conditions. The
override switch must be held to enable further test steps. Subsequent operation
of the individual fan switches will set the corresponding fans to maximum speed.
Operation of the heater switch sets the heaters to on, indicated by the
illumination of an LED in the recirculation air return aperture of the power supply
enclosure.
Figure 2-14 shows the interconnection diagram of the TMS push button test
switches.
HEATER
ON
N/O
N/O
N/O
N/O
TEST
OVERRIDE
Pole
SW4SW3
SW2
Pole PolePole
SW1
11 13 15 10 12 14
PL5
9
INTERNAL
FANS EXTERNAL
FANS
Figure 2-14 Interconnection diagram of the TMS test switches
Customer
equipment
racking
Provision is made within the power supply enclosure for the fitting of customer
specific equipment, in 6 U of standard 19 inch equipment racking. Adjacent to
the racking are four 125 W power outlets (– 55 V dc and earth), labelled
COMMS 1 to COMMS 4. These are supplied from individual 5 A dc circuit
breakers on the outdoor PSU.
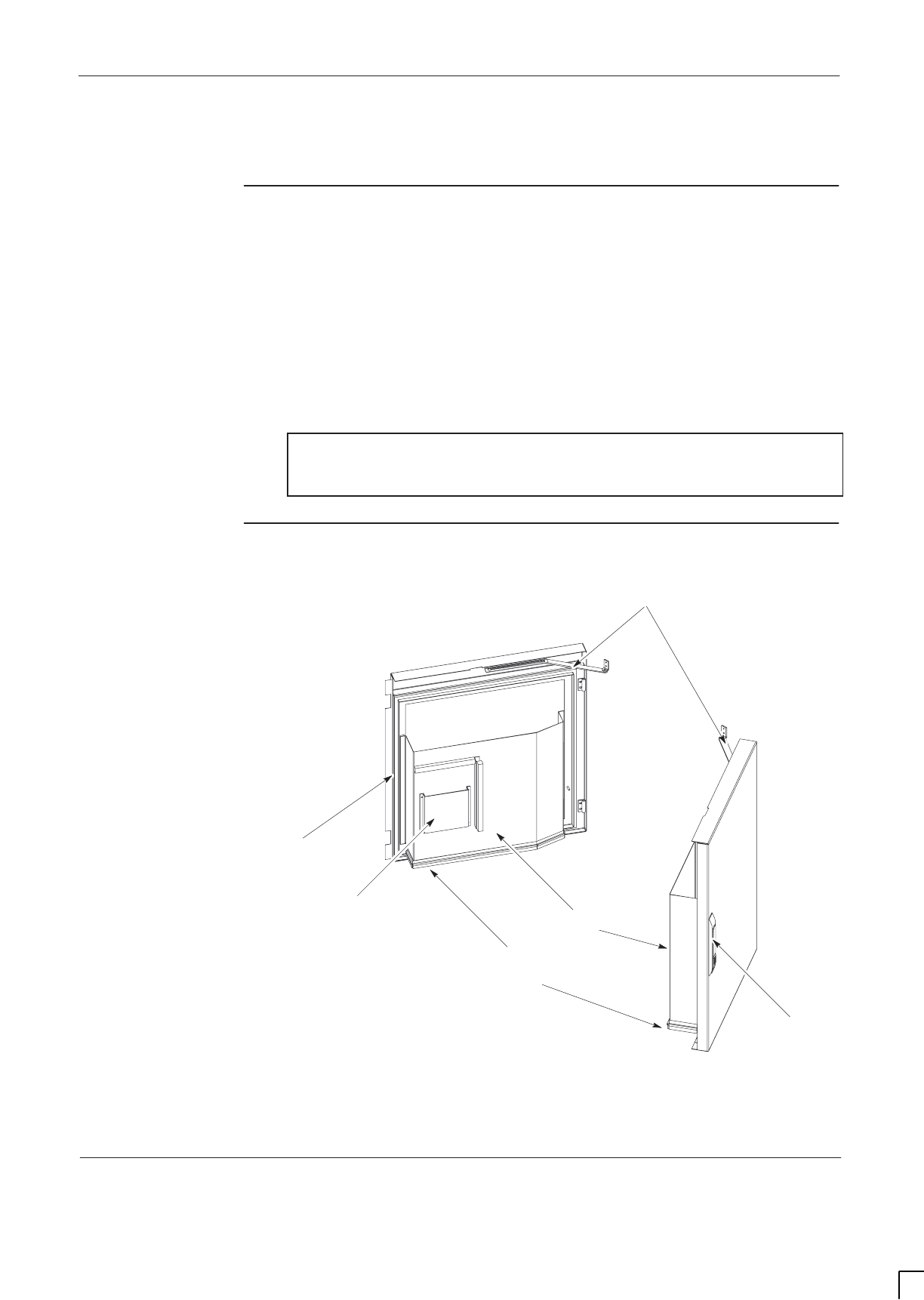
GSM-204-323 Outdoor cabinet doors and lid
31st Oct 01
Technical Description: Horizon
macro
outdoor
68P02902W02-A
CONTROLLED INTRODUCTION
Tech. 2–19
Outdoor cabinet doors and lid
Door function
The doors have the following functions:
Provide physical security and environmental protection.
Assist in correct thermal management by ducting return airflow.
Provide EMC shielding.
The door wind stops enable the doors to to be latched open at the 90° or 120°
position. The power supply enclosure door, when closed, overlaps the radio
enclosure door. The doors also overlap the TMS front cover and the latches of
the lid. The power supply enclosure door therefore provides the single locking
point for the cabinet and has the striker for the door open alarm microswitch.
NOTE When the Horizon
macro
outdoor is delivered, the keys for
the door are contained in a plastic bag, fastened to the
front grille of the TMS.
Door views
Figure 2-15 shows the cabinet doors with major features labelled.
LOCKING LATCH
HANDLE
RADIO ENCLOSURE
DOOR
POWER SUPPLY
ENCLOSURE DOOR
WIND STOPS
AIR DUCT
BRUSH SEALS
A5 DOCUMENT
POCKET
ENVIRONMENTAL
SEAL
AIR DUCTS
Figure 2-15 View of cabinet doors
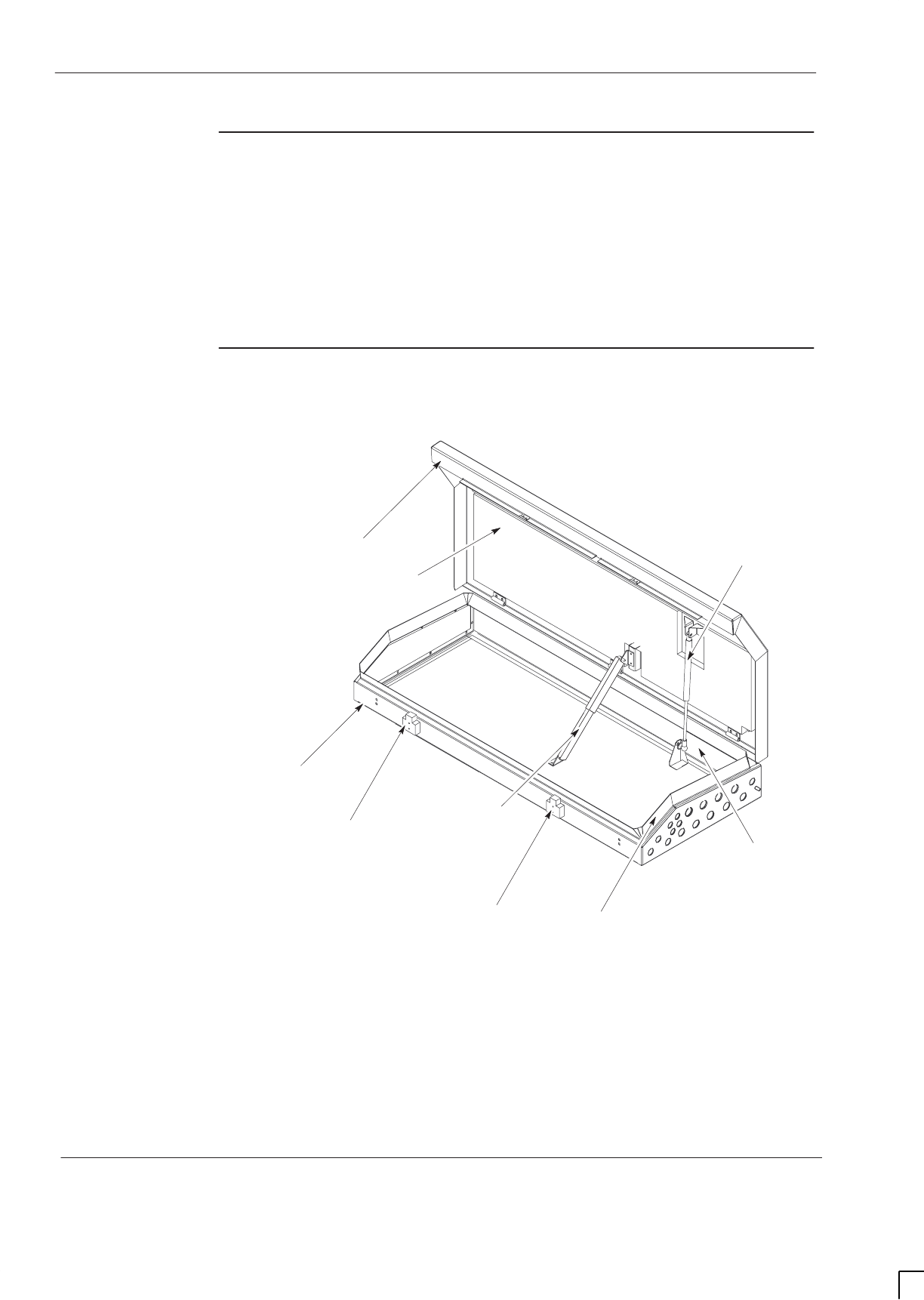
GSM-204-323
Outdoor cabinet doors and lid
31st Oct 01
Tech. 2–20
Technical Description: Horizon
macro
outdoor
CONTROLLED INTRODUCTION
68P02902W02-A
Lid function
The lid has the following functions:
Provides physical security.
Provides environmental protection.
The lid has a gas strut to assist in opening and a mechanical stay to limit
movement when open in windy conditions. The securing latches can only be
accessed when the cabinet doors are open.
Lid view
Figure 2-16 shows the lid and the cabinet top wrap with the main features
labelled.
ENVIRONMENTAL
SEAL
TOP SECTION
MECHANICAL
STAY
LID GAS STRUT
INSULATION
FOAM
SECURING
LATCH
SECURING
LATCH
CABINET
TOP WRAP
Figure 2-16 View of the cabinet lid
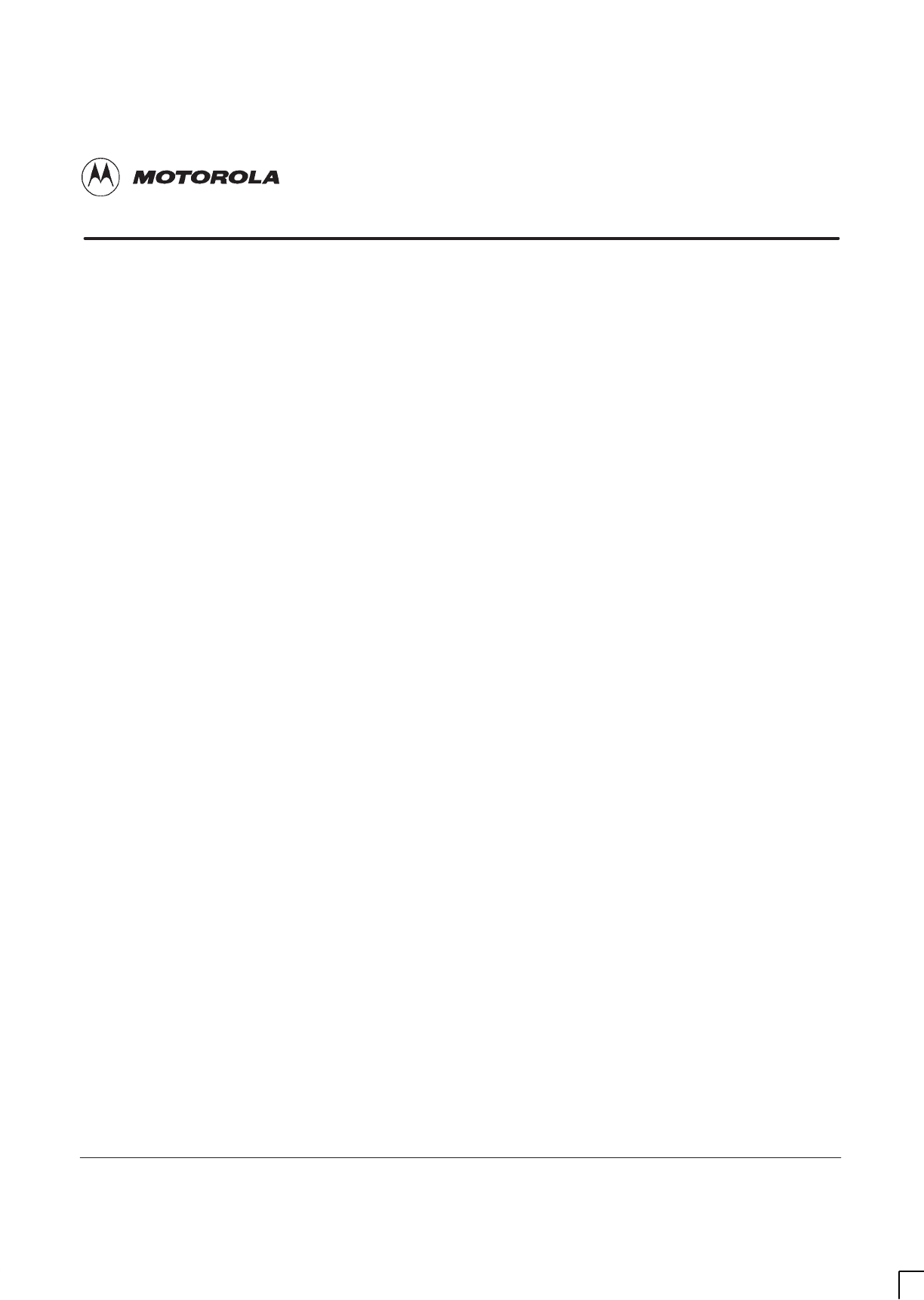
31st Oct 01
Technical Description: Horizon
macro
outdoor
68P02902W02-A
CONTROLLED INTRODUCTION
i
Chapter 3
Thermal management system
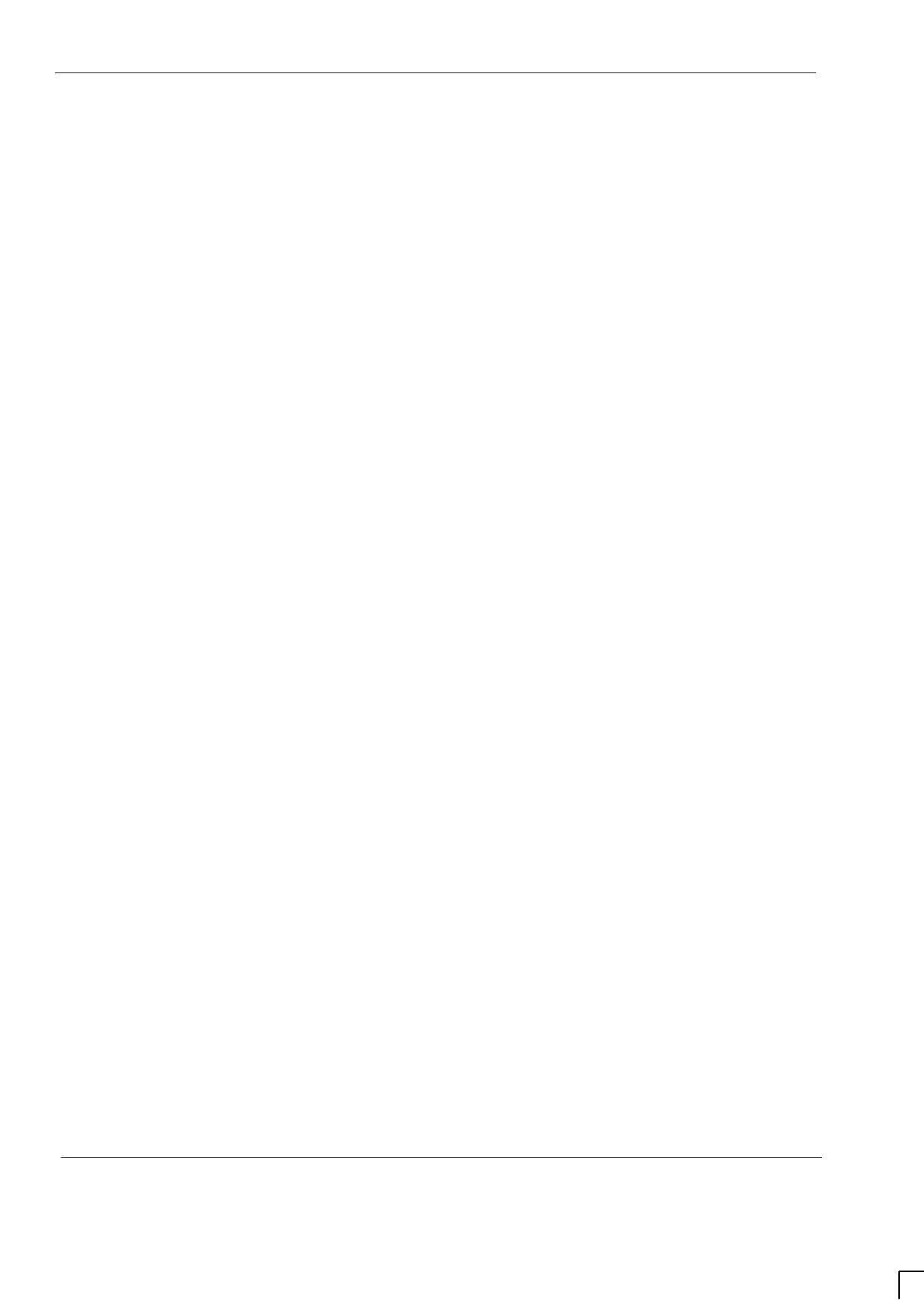
GSM-204-323
31st Oct 01
ii
Technical Description: Horizon
macro
outdoor
CONTROLLED INTRODUCTION
68P02902W02-A
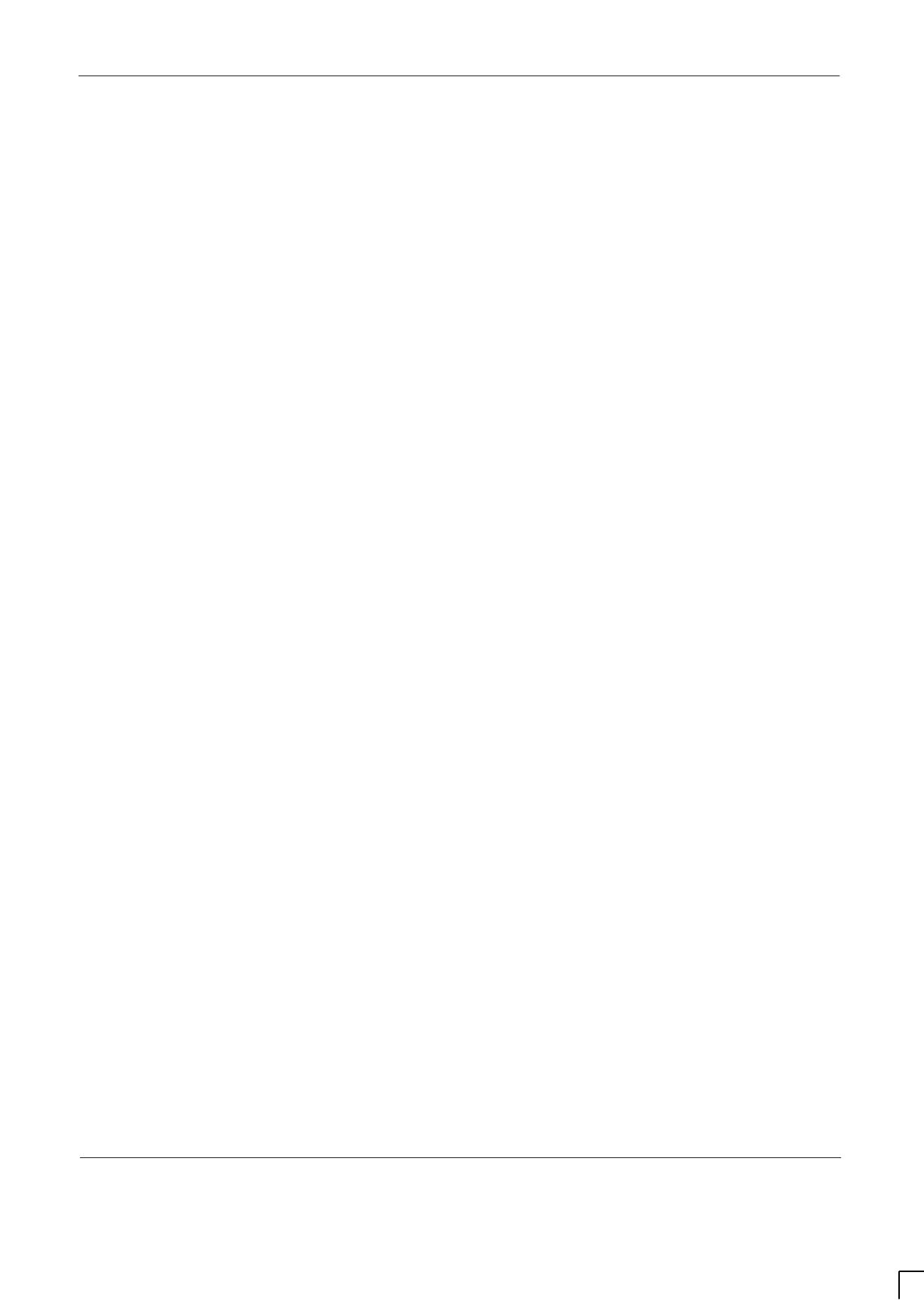
GSM-204-323
31st Oct 01
Technical Description: Horizon
macro
outdoor
68P02902W02-A
CONTROLLED INTRODUCTION
iii
Chapter 3
Thermal management system i. . . . . . . . . . . . . . . . . . . . . . . . . . . . . . . . . .
Horizonmacro outdoor temperature control Tech. 3–1. . . . . . . . . . . . . . . . . . . . . . . . . . . . . .
Temperature control overview Tech. 3–1. . . . . . . . . . . . . . . . . . . . . . . . . . . . . . . . . . . .
Cabinet over temperature control Tech. 3–1. . . . . . . . . . . . . . . . . . . . . . . . . . . . . . . . .
Temperature sensors Tech. 3–1. . . . . . . . . . . . . . . . . . . . . . . . . . . . . . . . . . . . . . . . . . . .
Cabinet restart after shutdown Tech. 3–2. . . . . . . . . . . . . . . . . . . . . . . . . . . . . . . . . . . .
Thermal management system (TMS) Tech. 3–3. . . . . . . . . . . . . . . . . . . . . . . . . . . . . . . . . . .
TMS overview Tech. 3–3. . . . . . . . . . . . . . . . . . . . . . . . . . . . . . . . . . . . . . . . . . . . . . . . . .
View of TMS unit Tech. 3–3. . . . . . . . . . . . . . . . . . . . . . . . . . . . . . . . . . . . . . . . . . . . . . . .
Heat exchanger components Tech. 3–4. . . . . . . . . . . . . . . . . . . . . . . . . . . . . . . . . . . . .
TMS functional description Tech. 3–5. . . . . . . . . . . . . . . . . . . . . . . . . . . . . . . . . . . . . . .
Heat exchanger functional diagram Tech. 3–6. . . . . . . . . . . . . . . . . . . . . . . . . . . . . . .
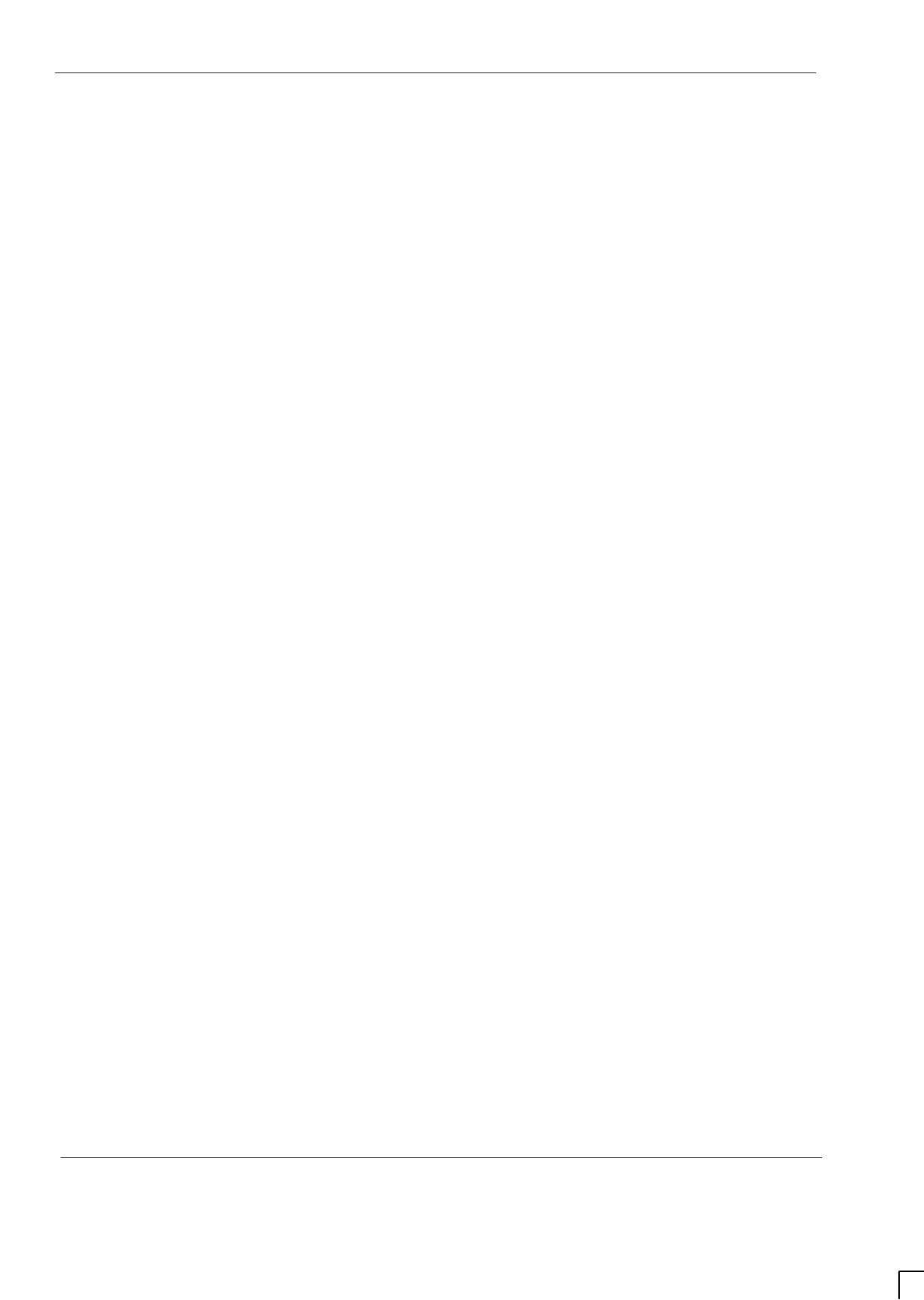
GSM-204-323
31st Oct 01
iv
Technical Description: Horizon
macro
outdoor
CONTROLLED INTRODUCTION
68P02902W02-A
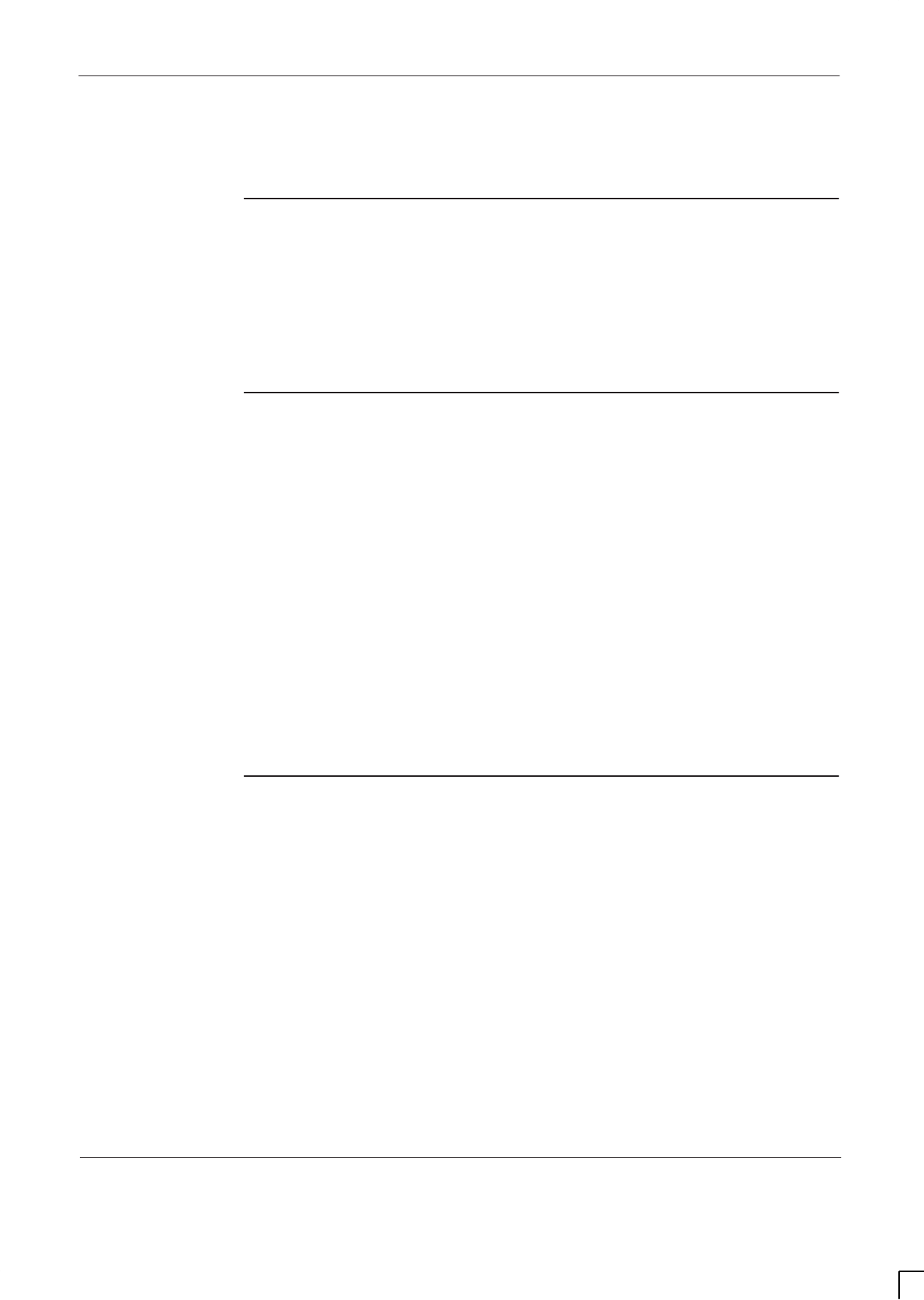
GSM-204-323 Horizonmacro outdoor temperature control
31st Oct 01
Technical Description: Horizon
macro
outdoor
68P02902W02-A
CONTROLLED INTRODUCTION
Tech. 3–1
Horizon
macro
outdoor temperature control
Temperature
control
overview
The Horizon
macro
outdoor cabinet contains equipment that has to be
maintained within the operational temperature range to ensure correct operation
of the equipment, and to guard against premature failure of the individual
components.
Cabinet over
temperature
control
Under overheat conditions, as the temperature rises above preset levels,
temperature sensors located in various areas within the cabinet provide alarms.
A further increase in temperature causes sensors, set at higher temperature
thresholds, to initiate PSM or cabinet shutdown. The cabinet is restarted when
the sensors are reset by a substantial fall in temperature.
TOPSMs and CTUs have their own internal total shutdown responses to
overheating. The CTUs shutdown at 92 C.
850/900 MHz CTUs also have an internal 4 dB power reduction shutdown
response to overheating, at 85 C. 1800/1900 MHz CTUs have a 0.6 dB cut
back at 70 C in addition to the 4 dB power reduction at 85 C.
Both the CTU and TOPSM shutdowns provide a second level of cabinet
protection, independent of the cabinet heat sensors.
Temperature
sensors
Radio enclosure temperature sensors
Temperature sensors are located above the transceiver compartment (see Cage
backplane interface panel harness assembly Figure 2-9) and consist of the
following:
One 70 C sensor, providing sensing for a cabinet overtemperature alarm
when the EMC enclosure temperature exceeds the preset level. The alarm
is processed by the alarm module and the MCUF, and sent on to the
OMC-R, via the BSC.
Two 85 C sensors initiate shutdown of the PSMs to protect the cabinet
equipment from heat damage. Both sensors must detect excess
temperature for the shutdown to take place; this reduces the risk of an
unnecessary shutdown due to sensor failure. If a shutdown occurs, there
is no prior notification to the OMC-R.
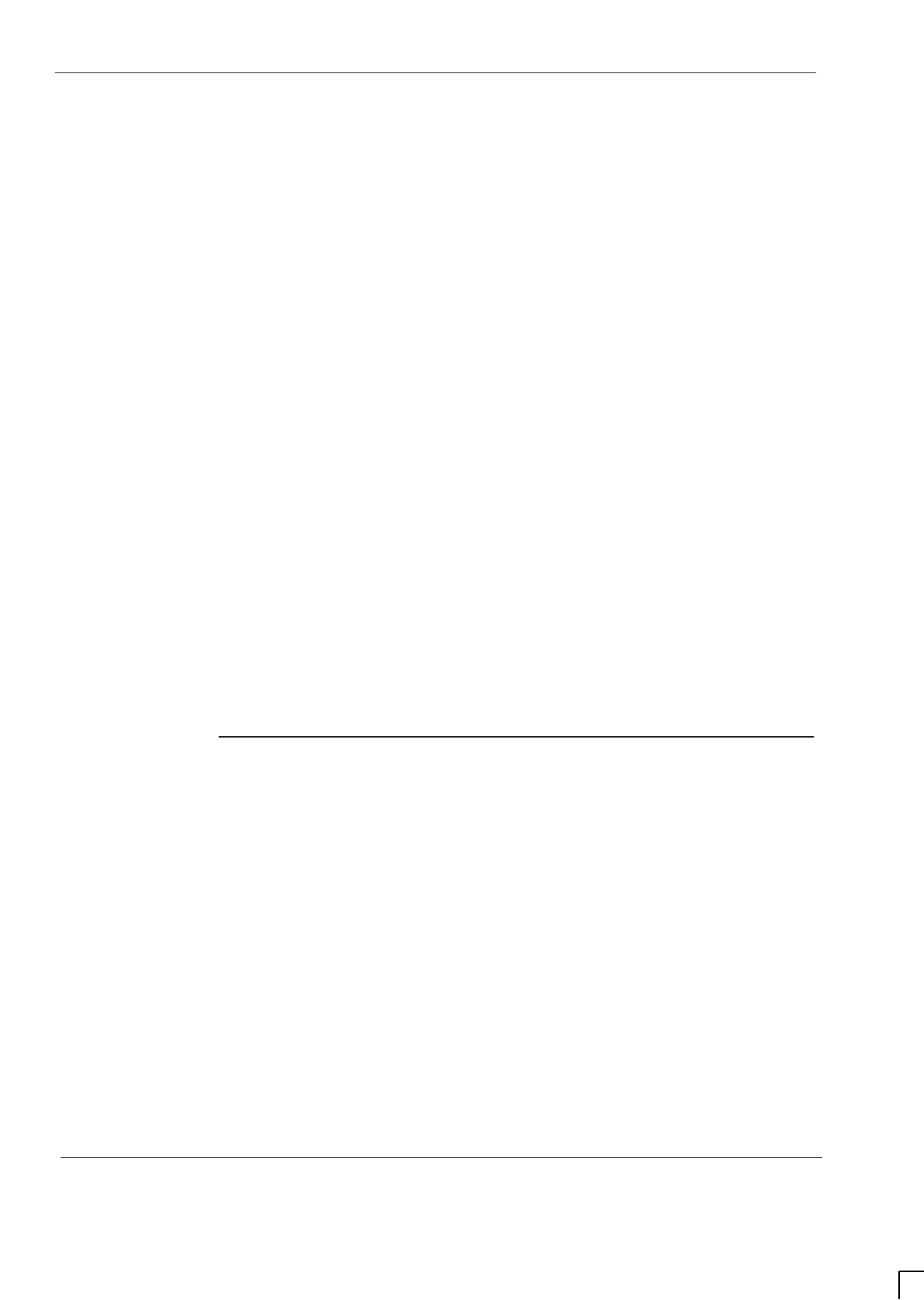
GSM-204-323
Horizonmacro outdoor temperature control
31st Oct 01
Tech. 3–2
Technical Description: Horizon
macro
outdoor
CONTROLLED INTRODUCTION
68P02902W02-A
Power supply enclosure temperature sensors
The power supply enclosure temperature sensors are located on the control and
alarm board (see Outdoor PSU control and alarm board (CAB)) and consist
of the following:
One 70 C sensor, providing sensing for a cabinet overtemperature alarm
when the non EMC enclosure temperature exceeds the planned level. The
alarm is generated by the control and alarm board, and passed as an
external alarm to the alarm module, where it is sent on to the OMC-R via
the BSC. Operation of this sensor will also reduce the TOPSM output
voltage as described in Outdoor PSU control and alarm board (CAB).
One 78 C sensor, which initiates disconnection of the battery contactor,
the comms contactor and shutdown of the TOPSMs. This will shut down
the BTS. If a shutdown occurs, there is no prior notification to the OMC-R.
TMS temperature sensors
The two TMS temperature sensors are located within the TMS unit (see
Thermal management system (TMS) Figure 3-2), in the returned recirculation
airflow from the EMC and non EMC enclosures. They have the following
functions:
Either sensor provides sensing for the TMS overtemperature alarm when
the TMS returned recirculation air temperature exceeds 68C. The alarm
is generated by the TMS control board, processed by the control and
alarm board, and passed as an external alarm to the alarm module, where
it is sent on to the OMC-R via the BSC.
The TMS temperature sensors also provide the TMS control board with
thermal data used in controlling fan speed and heater operation.
Cabinet restart
after shutdown
The cabinet is restarted when the overtemperature condition initiating shutdown
has reset.
The CAB re-enables the TOPSMs when the 78 C temperature sensor
has reset at 60 C.
The two 85 C temperature sensors reset at 55 C. This re-establishes an
earth point for the PSM internal detectors connected to the cabinet heat
sensors, which then reactivate the PSM outputs.
The cabinet then restarts as a normal power up.
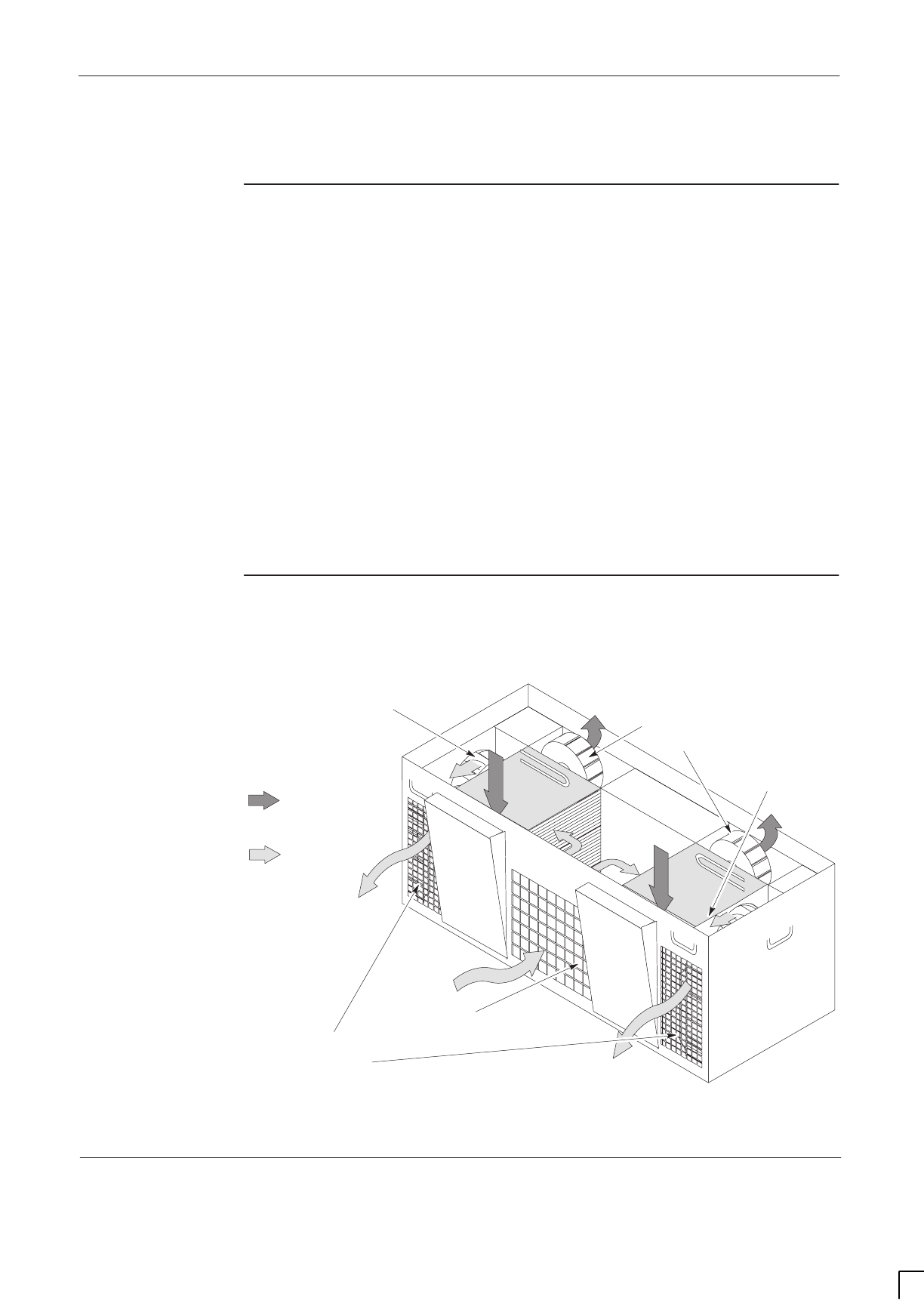
GSM-204-323 Thermal management system (TMS)
31st Oct 01
Technical Description: Horizon
macro
outdoor
68P02902W02-A
CONTROLLED INTRODUCTION
Tech. 3–3
Thermal management system (TMS)
TMS overview
The equipment installed in the cabinet emits heat, which must be removed in
order to maintain the correct working temperature.
The thermal management system (TMS) unit maintains the cabinet internal
temperature within the operational range of the installed equipment, provided
the external ambient temperature is within the range of –40 °C to +50 °C.
An alarm is generated if the return air temperature from the BTS enclosures
exceeds 68 °C.
The TMS unit contains:
Two recuperators.
Two ambient air fans (external fans).
Two recirculation air fans (internal fans).
Two ac electric heater elements.
One TMS control board.
Two temperature sensors.
View of TMS
unit
Figure 3-1 shows a view of the TMS unit with airflows indicated and access
panels and air ducts omitted for clarity.
RECIRCULATION
AIR FANS
AMBIENT
AIR INLET
AMBIENT
AIR OUTLETS
AMBIENT
AIR FAN
RECIRCULATION
AIRFLOW
AMBIENT
AIRFLOW
KEY LOCATION OF
THE TMS
CONTROL BOARD
Figure 3-1 View of the TMS unit
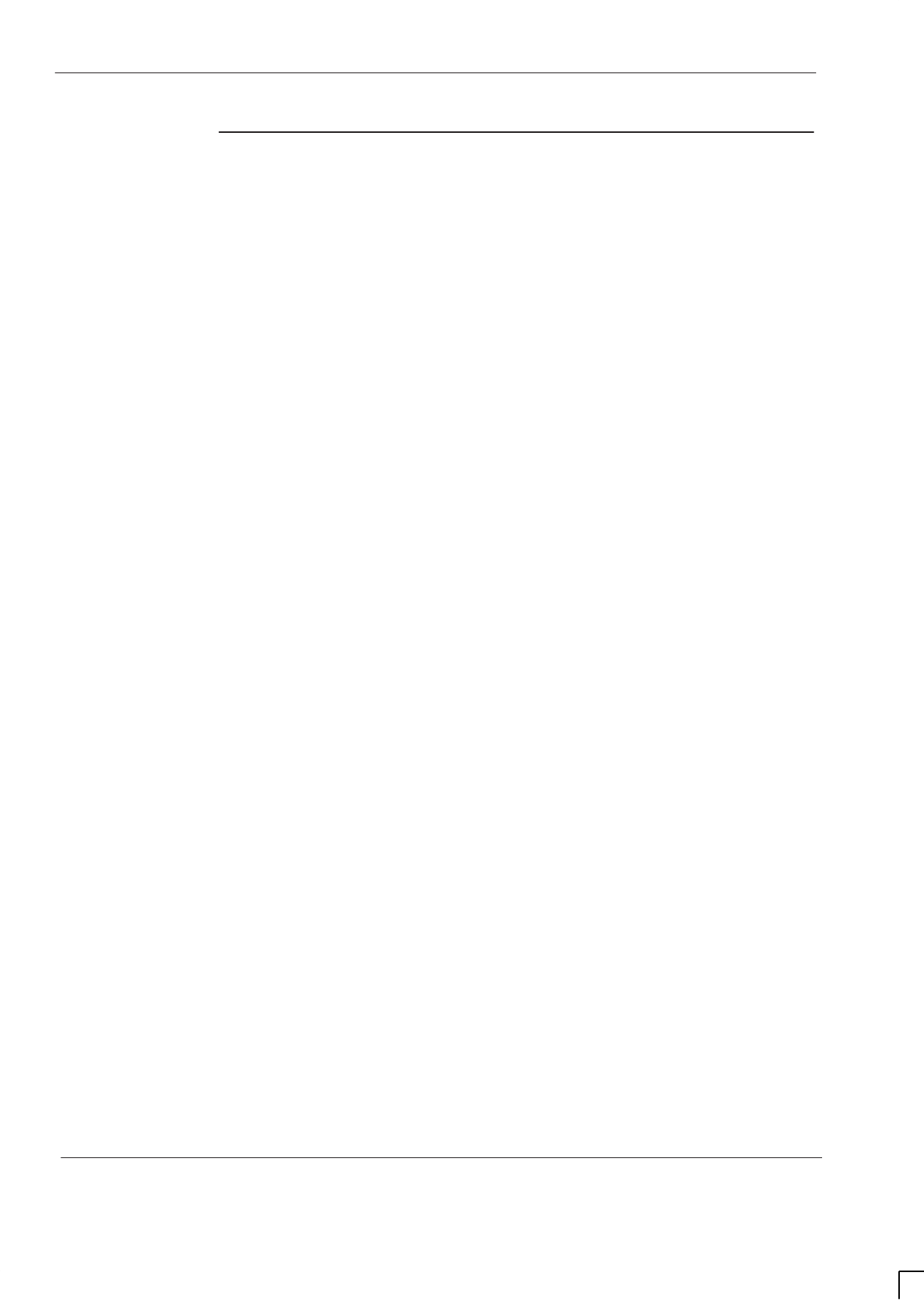
GSM-204-323
Thermal management system (TMS)
31st Oct 01
Tech. 3–4
Technical Description: Horizon
macro
outdoor
CONTROLLED INTRODUCTION
68P02902W02-A
Heat exchanger
components
The heat exchanger consists of the following items:
Recuperators
The recuperators are manufactured from a series of epoxy resin coated
aluminium sheets, sealed at alternate edges to form two sets of narrow air
passages, one set for the ambient air and one set for the recirculated air, but the
air streams do not mix.
Ambient air fans (external fans)
The two ambient air fans are located one on each side of the unit. The fans are
of the radial type with backward curved blades for maximum efficiency. The fan
impeller is direct driven by a –48 V dc motor with a solid state commutator. The
fan contains its own pulse width modulation (PWM) speed control circuitry.
Recirculation air fans (internal fans)
The recirculation air fans are located at the rear of the unit. The fans are of the
same type and operate the same way as the ambient air fans.
AC heater elements
The ac heater elements are located in the recirculation air inlet to the cabinet
enclosures, at the top of the unit. There are two individual heaters, each with its
own high limit thermostat attached.
TMS control board
The control board is located in the top right side of the TMS unit behind the
cable well. The control board has the following functions:
Interpretation of thermal data from the TMS temperature sensors.
Control of the speed of ambient and recirculation fans.
Control of the operation of ac heater elements.
Generation of TMS alarm signals.
Configuration of heater elements for 230 V ac or 110 V ac input voltages.
Temperature sensors
The temperature sensors are located at the top of the TMS unit in the
recirculation air return aperture. The functions of the TMS temperature sensors
are described in Horizon
macro
outdoor temperature control in this chapter.

GSM-204-323 Thermal management system (TMS)
31st Oct 01
Technical Description: Horizon
macro
outdoor
68P02902W02-A
CONTROLLED INTRODUCTION
Tech. 3–5
TMS functional
description
The TMS unit provides either cooling or heating to maintain the internal
temperature of the Horizon
macro
outdoor BTS cabinet within the operational
range of the installed equipment. The TMS temperature sensors measure the
temperature of the returned recirculation air from the cabinet equipment
enclosures.
Cooling
The TMS employs an indirect cooling system to protect the radio equipment
against atmospheric contaminants. Cooling is provided by recirculating air
through two air to air heat exchangers. Two separate airflow paths are driven
through the two recuperators by fans; the warmer air stream gives off heat to
the colder air stream.
The TMS control board manages the speed of both sets of fans. The control
board initiates an increase in fan speed when either TMS temperature sensor
detects an increase in temperature, above a control threshold. A reduction in
fan speed is only achieved when both sensors detect a decrease in temperature
below the control threshold.
The recirculation air fans run continuously. As the temperature rises, the
ambient air fans start. A further temperature rise causes both fans ramp up to
full speed.
The recirculation air fans run at 60% of full speed at all temperatures, up to
55 °C. Fan speed increases linearly as the temperature rises, until it reaches full
speed at 60 °C.
The ambient air fans are inhibited at temperatures below 40 °C and run at 60%
of full speed between 40 °C and 55 °C. Fan speed then increases linearly as the
temperature rises, until it reaches full speed at 60 °C.
Heating
At low temperatures and in cold start conditions, ac electric heaters are used to
maintain the cabinet internal temperature at operational levels. Only the
recirculation air fans operate when the TMS is heating the cabinet.
Heater element operation is managed by the TMS control board. The control
board switches the heaters on when either TMS temperature sensor detects a
decrease in temperature to below 10 °C, but only switches the heaters off when
both TMS temperature sensors detect a corresponding rise in temperature to
above 20 °C.
Heater function is indicated by the illumination of an LED, mounted on the rear
verical wall at the top right of the recirculation air outlet aperture, below and in
front of the power supply enclosure.
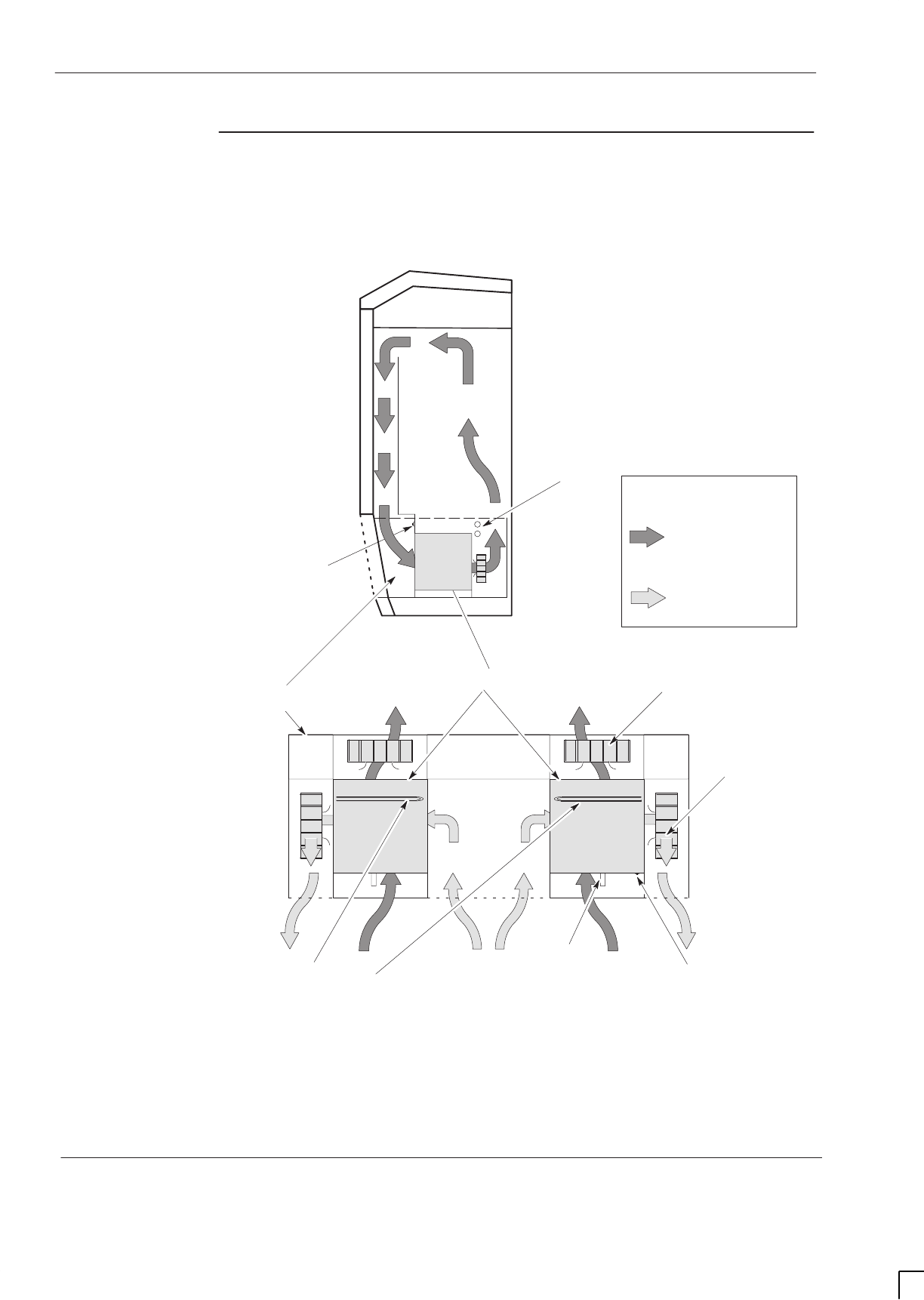
GSM-204-323
Thermal management system (TMS)
31st Oct 01
Tech. 3–6
Technical Description: Horizon
macro
outdoor
CONTROLLED INTRODUCTION
68P02902W02-A
Heat exchanger
functional
diagram
Figure 3-2 shows a representation of the airflow paths through the
Horizon
macro
outdoor cabinet.
RECUPERATORS
Horizon
macro
outdoor
BTS CABINET CABINET
EQUIPMENT
TMS UNIT
RECIRCULATION
AIRFLOW
AMBIENT
AIRFLOW
RECIRCULATION
FAN
AMBIENT FAN
HEATER
ELEMENT
HEATER
ELEMENTS
SIDE ELEVATION VIEW OF
RECIRCULATION AIRFLOW
THROUGH CABINET
PLAN VIEW OF AIRFLOW
THROUGH TMS UNIT
KEY
HEATER
FUNCTION LED
TMS
TEMPERATURE
SENSOR
HEATER
FUNCTION LED
Figure 3-2 Functional diagram of TMS airflow
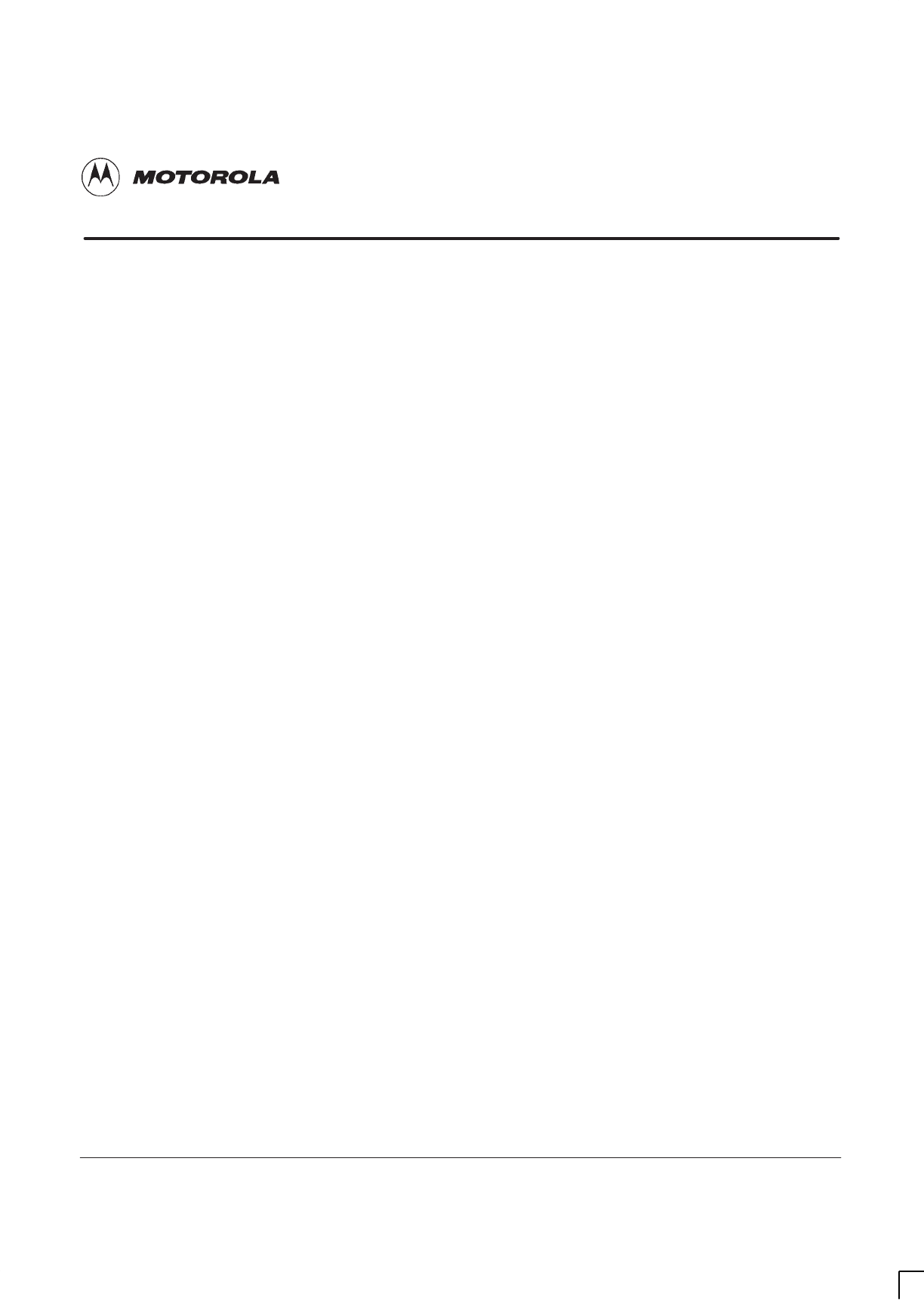
31st Oct 01
Technical Description: Horizon
macro
outdoor
68P02902W02-A
CONTROLLED INTRODUCTION
i
Chapter 4
Cabinet power supplies
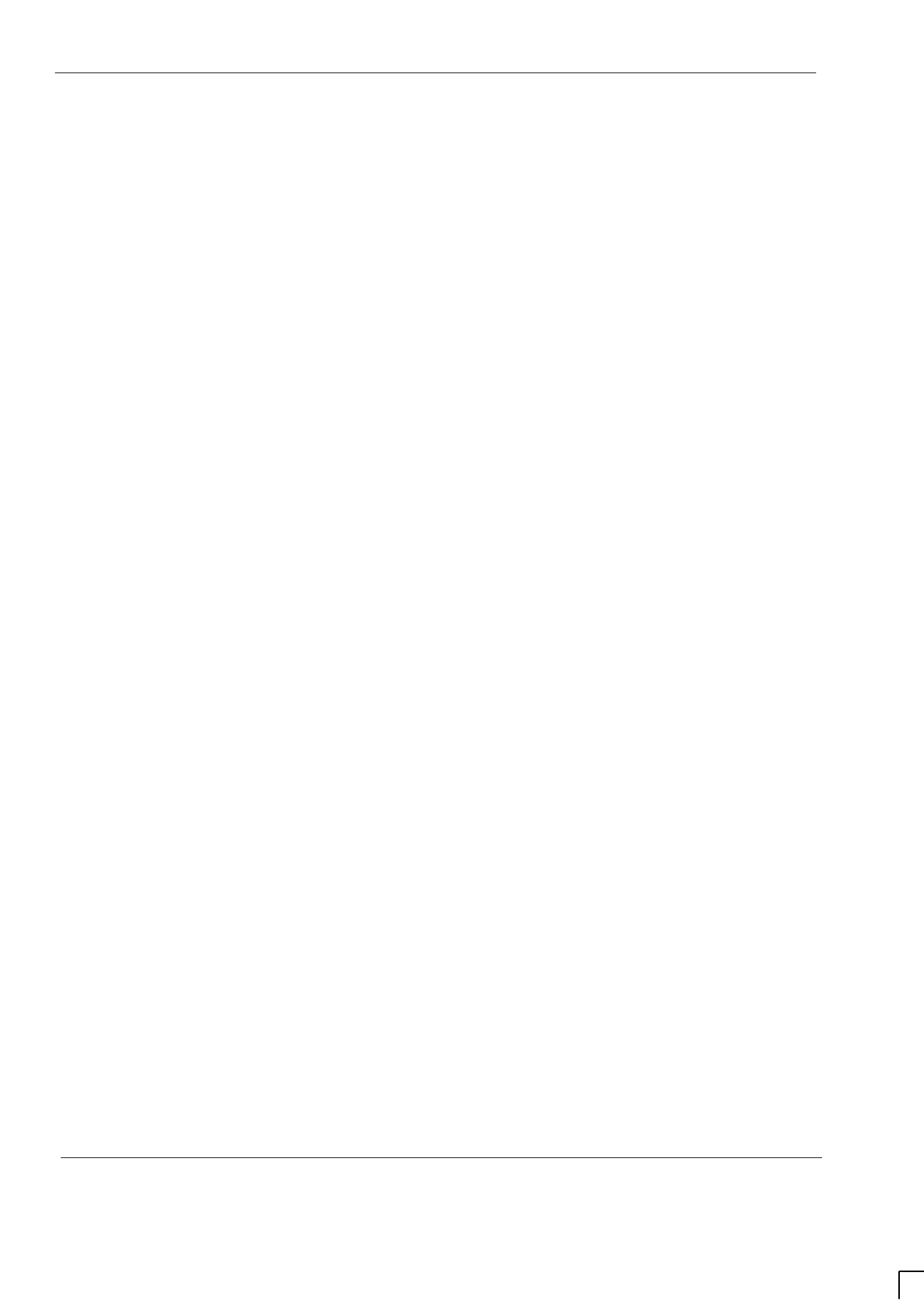
GSM-204-323
31st Oct 01
ii
Technical Description: Horizon
macro
outdoor
CONTROLLED INTRODUCTION
68P02902W02-A
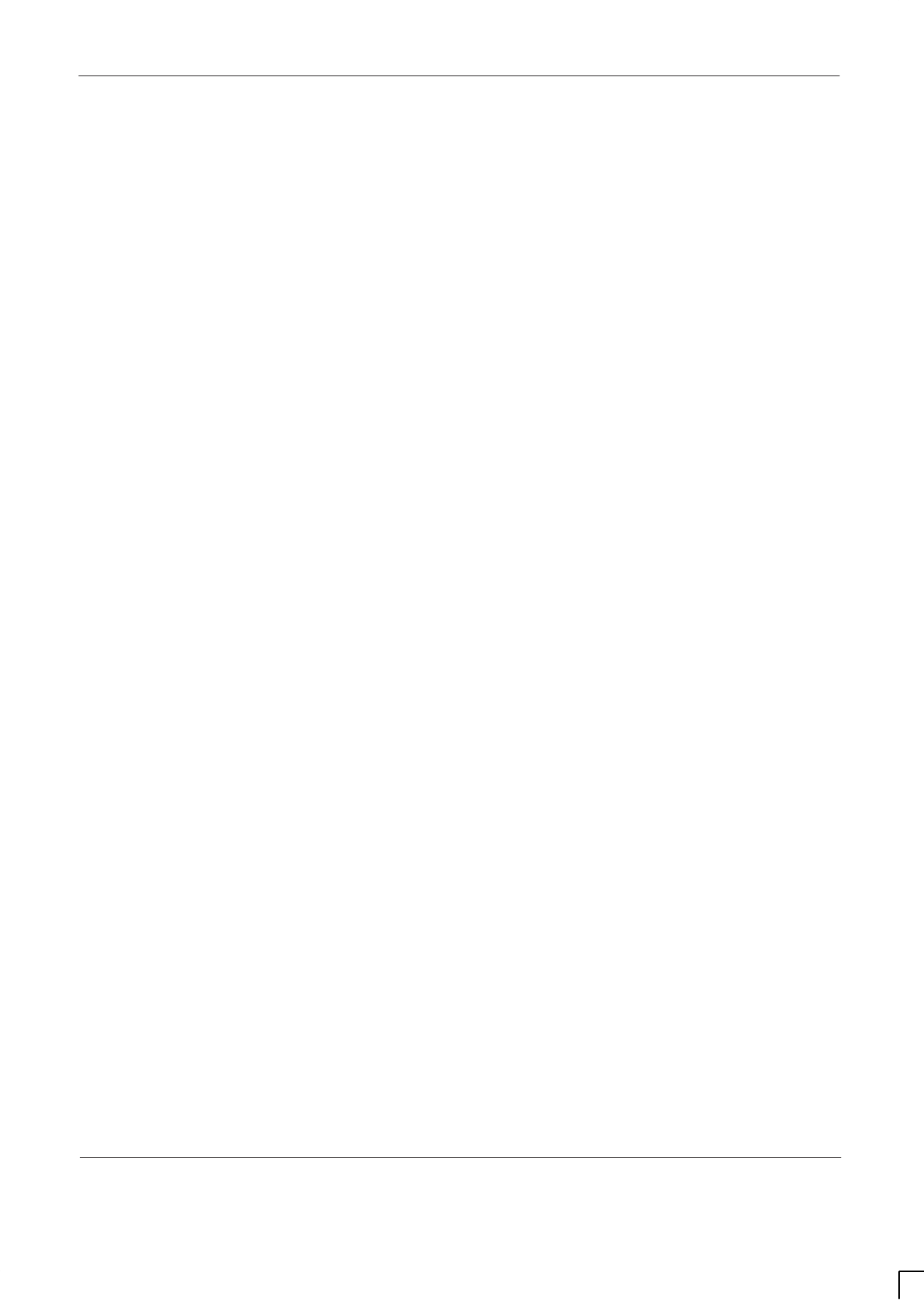
GSM-204-323
31st Oct 01
Technical Description: Horizon
macro
outdoor
68P02902W02-A
CONTROLLED INTRODUCTION
iii
Chapter 4
Cabinet power supplies i. . . . . . . . . . . . . . . . . . . . . . . . . . . . . . . . . . . . . . . .
Horizonmacro outdoor power supplies Tech. 4–1. . . . . . . . . . . . . . . . . . . . . . . . . . . . . . . . . .
Power supply overview Tech. 4–1. . . . . . . . . . . . . . . . . . . . . . . . . . . . . . . . . . . . . . . . . .
Power supply unit view Tech. 4–2. . . . . . . . . . . . . . . . . . . . . . . . . . . . . . . . . . . . . . . . . .
View of main cage power modules Tech. 4–3. . . . . . . . . . . . . . . . . . . . . . . . . . . . . . . .
Introduction to power distribution Tech. 4–4. . . . . . . . . . . . . . . . . . . . . . . . . . . . . . . . . . . . . . .
Power distribution overview Tech. 4–4. . . . . . . . . . . . . . . . . . . . . . . . . . . . . . . . . . . . . .
View of power supply unit cage Tech. 4–4. . . . . . . . . . . . . . . . . . . . . . . . . . . . . . . . . . .
AC power distribution Tech. 4–5. . . . . . . . . . . . . . . . . . . . . . . . . . . . . . . . . . . . . . . . . . . . . . . . .
View of ac power components Tech. 4–5. . . . . . . . . . . . . . . . . . . . . . . . . . . . . . . . . . .
AC distribution description Tech. 4–6. . . . . . . . . . . . . . . . . . . . . . . . . . . . . . . . . . . . . . .
AC outlet socket Tech. 4–7. . . . . . . . . . . . . . . . . . . . . . . . . . . . . . . . . . . . . . . . . . . . . . . .
View of the ac outlet socket Tech. 4–8. . . . . . . . . . . . . . . . . . . . . . . . . . . . . . . . . . . . . .
AC distribution diagram Tech. 4–8. . . . . . . . . . . . . . . . . . . . . . . . . . . . . . . . . . . . . . . . . .
DC power distribution Tech. 4–9. . . . . . . . . . . . . . . . . . . . . . . . . . . . . . . . . . . . . . . . . . . . . . . . .
DC distribution overview Tech. 4–9. . . . . . . . . . . . . . . . . . . . . . . . . . . . . . . . . . . . . . . . .
View of dc power components Tech. 4–9. . . . . . . . . . . . . . . . . . . . . . . . . . . . . . . . . . .
DC distribution diagram Tech. 4–10. . . . . . . . . . . . . . . . . . . . . . . . . . . . . . . . . . . . . . . . . .
DC distribution description Tech. 4–10. . . . . . . . . . . . . . . . . . . . . . . . . . . . . . . . . . . . . . .
View of the dc circuit breaker panel Tech. 4–11. . . . . . . . . . . . . . . . . . . . . . . . . . . . . . .
Customer equipment power supplies Tech. 4–11. . . . . . . . . . . . . . . . . . . . . . . . . . . . . .
Internal battery backup Tech. 4–11. . . . . . . . . . . . . . . . . . . . . . . . . . . . . . . . . . . . . . . . . .
Internal battery arrangement Tech. 4–12. . . . . . . . . . . . . . . . . . . . . . . . . . . . . . . . . . . . .
View of battery sense lead Tech. 4–12. . . . . . . . . . . . . . . . . . . . . . . . . . . . . . . . . . . . . . .
External battery backup connection Tech. 4–13. . . . . . . . . . . . . . . . . . . . . . . . . . . . . . .
View of the dc interface panel Tech. 4–13. . . . . . . . . . . . . . . . . . . . . . . . . . . . . . . . . . . .
Control and alarm board (CAB) Tech. 4–14. . . . . . . . . . . . . . . . . . . . . . . . . . . . . . . . . . . . . . . .
Introduction to the CAB Tech. 4–14. . . . . . . . . . . . . . . . . . . . . . . . . . . . . . . . . . . . . . . . . .
CAB views Tech. 4–15. . . . . . . . . . . . . . . . . . . . . . . . . . . . . . . . . . . . . . . . . . . . . . . . . . . . .
CAB indicators and controls Tech. 4–16. . . . . . . . . . . . . . . . . . . . . . . . . . . . . . . . . . . . . .
CAB front panel fuses Tech. 4–17. . . . . . . . . . . . . . . . . . . . . . . . . . . . . . . . . . . . . . . . . . .
CAB control functions Tech. 4–18. . . . . . . . . . . . . . . . . . . . . . . . . . . . . . . . . . . . . . . . . . .
CAB alarm functions Tech. 4–20. . . . . . . . . . . . . . . . . . . . . . . . . . . . . . . . . . . . . . . . . . . .
CAB additional functions Tech. 4–22. . . . . . . . . . . . . . . . . . . . . . . . . . . . . . . . . . . . . . . . .
DIP switches Tech. 4–25. . . . . . . . . . . . . . . . . . . . . . . . . . . . . . . . . . . . . . . . . . . . . . . . . . .
The outdoor power supply module (TOPSM) Tech. 4–26. . . . . . . . . . . . . . . . . . . . . . . . . . . .
TOPSM overview Tech. 4–26. . . . . . . . . . . . . . . . . . . . . . . . . . . . . . . . . . . . . . . . . . . . . . .
View of TOPSM Tech. 4–26. . . . . . . . . . . . . . . . . . . . . . . . . . . . . . . . . . . . . . . . . . . . . . . . .
TOPSM functional description Tech. 4–26. . . . . . . . . . . . . . . . . . . . . . . . . . . . . . . . . . . .
LED display Tech. 4–27. . . . . . . . . . . . . . . . . . . . . . . . . . . . . . . . . . . . . . . . . . . . . . . . . . . .
Functional diagram Tech. 4–27. . . . . . . . . . . . . . . . . . . . . . . . . . . . . . . . . . . . . . . . . . . . . .
Monitoring Tech. 4–28. . . . . . . . . . . . . . . . . . . . . . . . . . . . . . . . . . . . . . . . . . . . . . . . . . . . .
Protection circuits Tech. 4–28. . . . . . . . . . . . . . . . . . . . . . . . . . . . . . . . . . . . . . . . . . . . . . .
Thermal protection Tech. 4–28. . . . . . . . . . . . . . . . . . . . . . . . . . . . . . . . . . . . . . . . . . . . . .
Control and alarm signals Tech. 4–29. . . . . . . . . . . . . . . . . . . . . . . . . . . . . . . . . . . . . . . .
TOPSM pinouts Tech. 4–30. . . . . . . . . . . . . . . . . . . . . . . . . . . . . . . . . . . . . . . . . . . . . . . . .
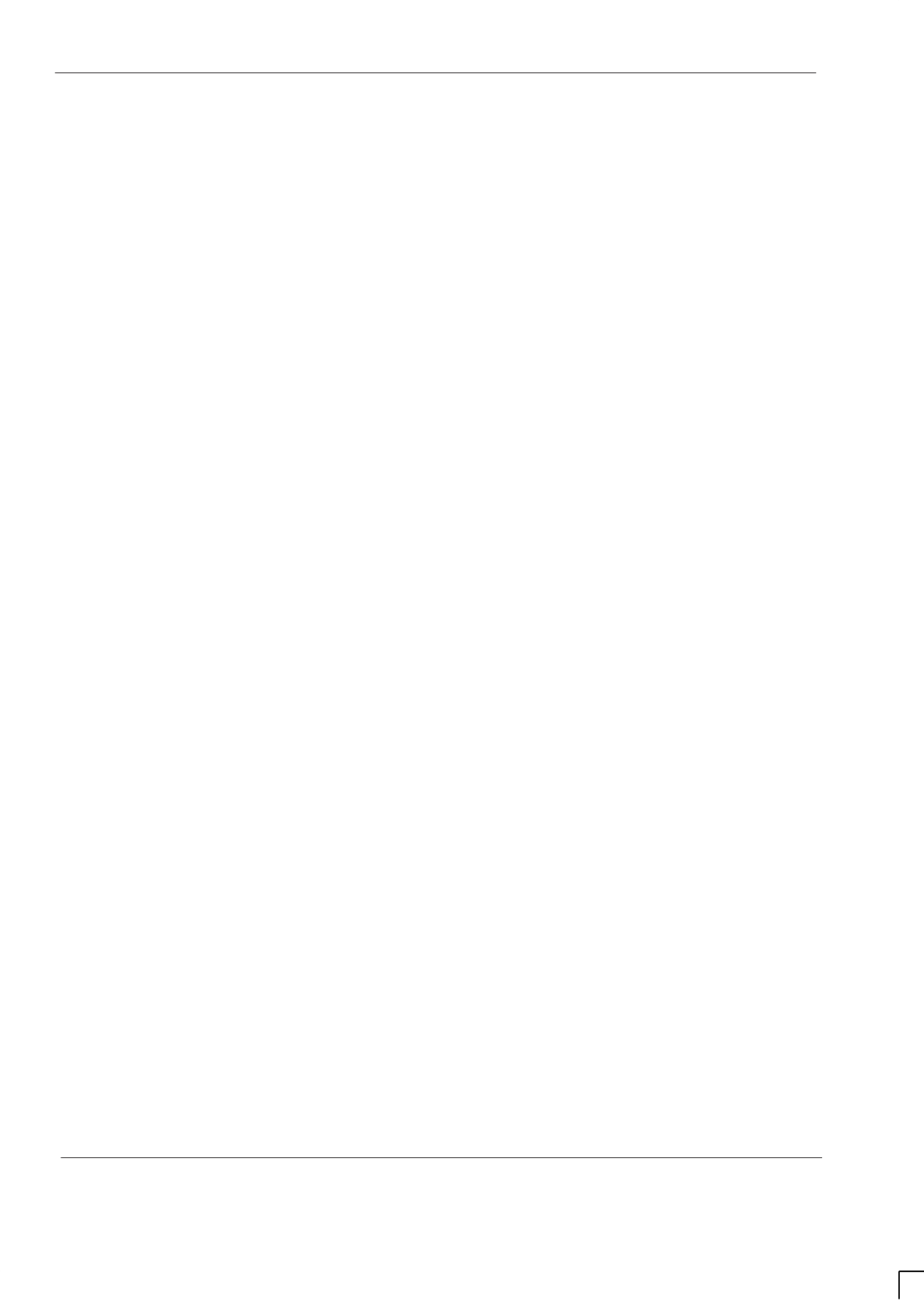
GSM-204-323
31st Oct 01
iv
Technical Description: Horizon
macro
outdoor
CONTROLLED INTRODUCTION
68P02902W02-A
Power supply module (PSM) Tech. 4–31. . . . . . . . . . . . . . . . . . . . . . . . . . . . . . . . . . . . . . . . . .
PSM overview Tech. 4–31. . . . . . . . . . . . . . . . . . . . . . . . . . . . . . . . . . . . . . . . . . . . . . . . . .
PSM location and redundancy Tech. 4–31. . . . . . . . . . . . . . . . . . . . . . . . . . . . . . . . . . . .
PSM module view Tech. 4–32. . . . . . . . . . . . . . . . . . . . . . . . . . . . . . . . . . . . . . . . . . . . . . .
PSM alarms Tech. 4–32. . . . . . . . . . . . . . . . . . . . . . . . . . . . . . . . . . . . . . . . . . . . . . . . . . . .
PSM LEDs Tech. 4–32. . . . . . . . . . . . . . . . . . . . . . . . . . . . . . . . . . . . . . . . . . . . . . . . . . . . .
PSM backplane protection Tech. 4–33. . . . . . . . . . . . . . . . . . . . . . . . . . . . . . . . . . . . . . .
Circuit breaker module (CBM) Tech. 4–34. . . . . . . . . . . . . . . . . . . . . . . . . . . . . . . . . . . . . . . . .
CBM overview Tech. 4–34. . . . . . . . . . . . . . . . . . . . . . . . . . . . . . . . . . . . . . . . . . . . . . . . . .
View of the CBM Tech. 4–34. . . . . . . . . . . . . . . . . . . . . . . . . . . . . . . . . . . . . . . . . . . . . . . .
Operation of the CBM Tech. 4–35. . . . . . . . . . . . . . . . . . . . . . . . . . . . . . . . . . . . . . . . . . .
MicroBCU power supply module (BPSM) Tech. 4–36. . . . . . . . . . . . . . . . . . . . . . . . . . . . . . . .
Introduction to the BPSM Tech. 4–36. . . . . . . . . . . . . . . . . . . . . . . . . . . . . . . . . . . . . . . .
BPSM diagram Tech. 4–36. . . . . . . . . . . . . . . . . . . . . . . . . . . . . . . . . . . . . . . . . . . . . . . . .
Functional description Tech. 4–37. . . . . . . . . . . . . . . . . . . . . . . . . . . . . . . . . . . . . . . . . . .
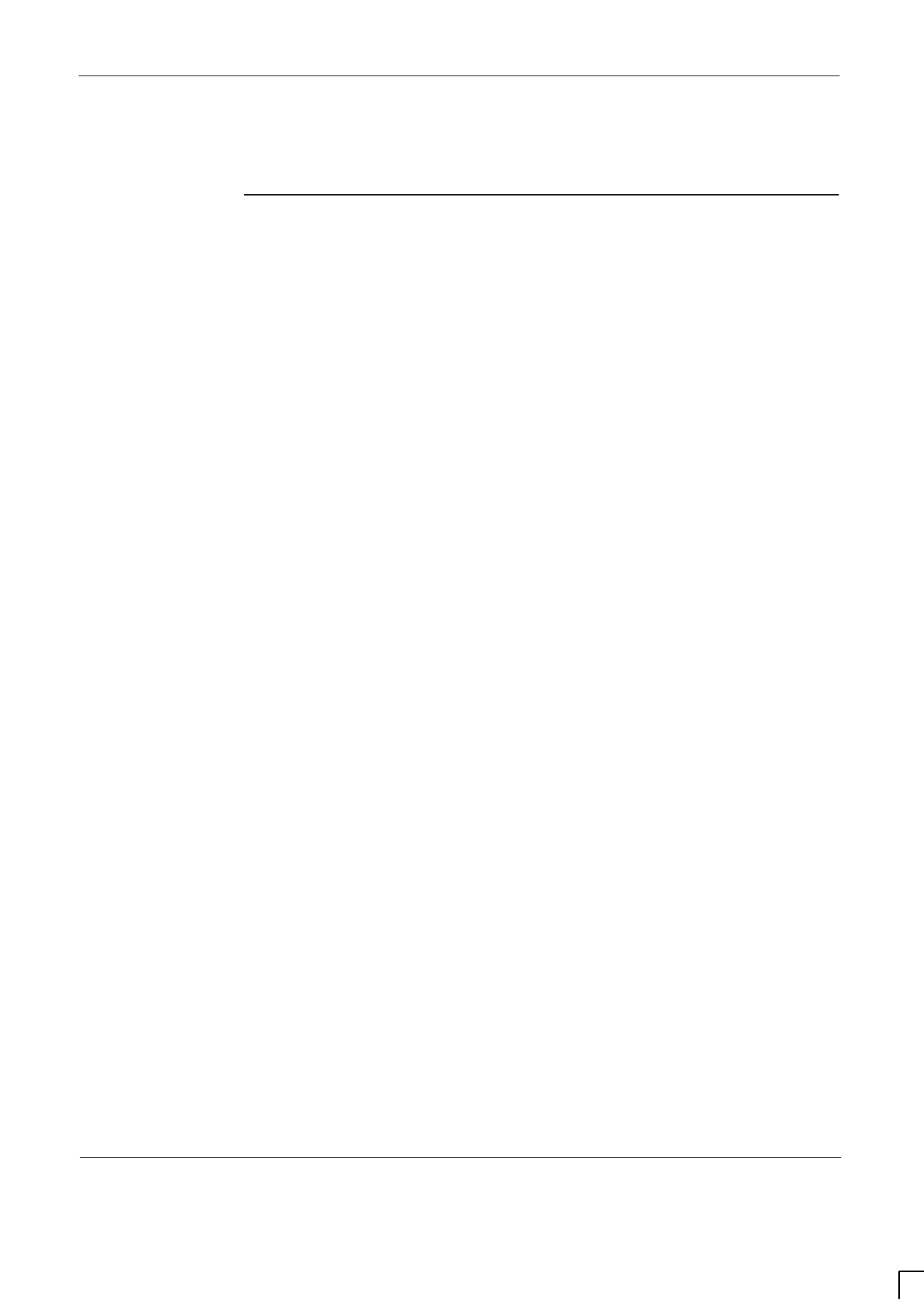
GSM-204-323 Horizonmacro outdoor power supplies
31st Oct 01
Technical Description: Horizon
macro
outdoor
68P02902W02-A
CONTROLLED INTRODUCTION
Tech. 4–1
Horizon
macro
outdoor power supplies
Power supply
overview
The Horizon
macro
outdoor power supplies consist of the following elements:
The power supply unit (PSU) containing:
– AC distribution and input ac supply connection.
– DC distribution and internal battery back-up.
– The PSU Control and Alarm Board (CAB).
– The Outdoor Power Supply Modules (TOPSMs).
The main cage Power Supply Modules (PSMs).
The Circuit Breaker Module (CBM).
The BCU Power Supply Module (BPSM).
Optional external battery back-up can also be fitted, housed in the AEH.
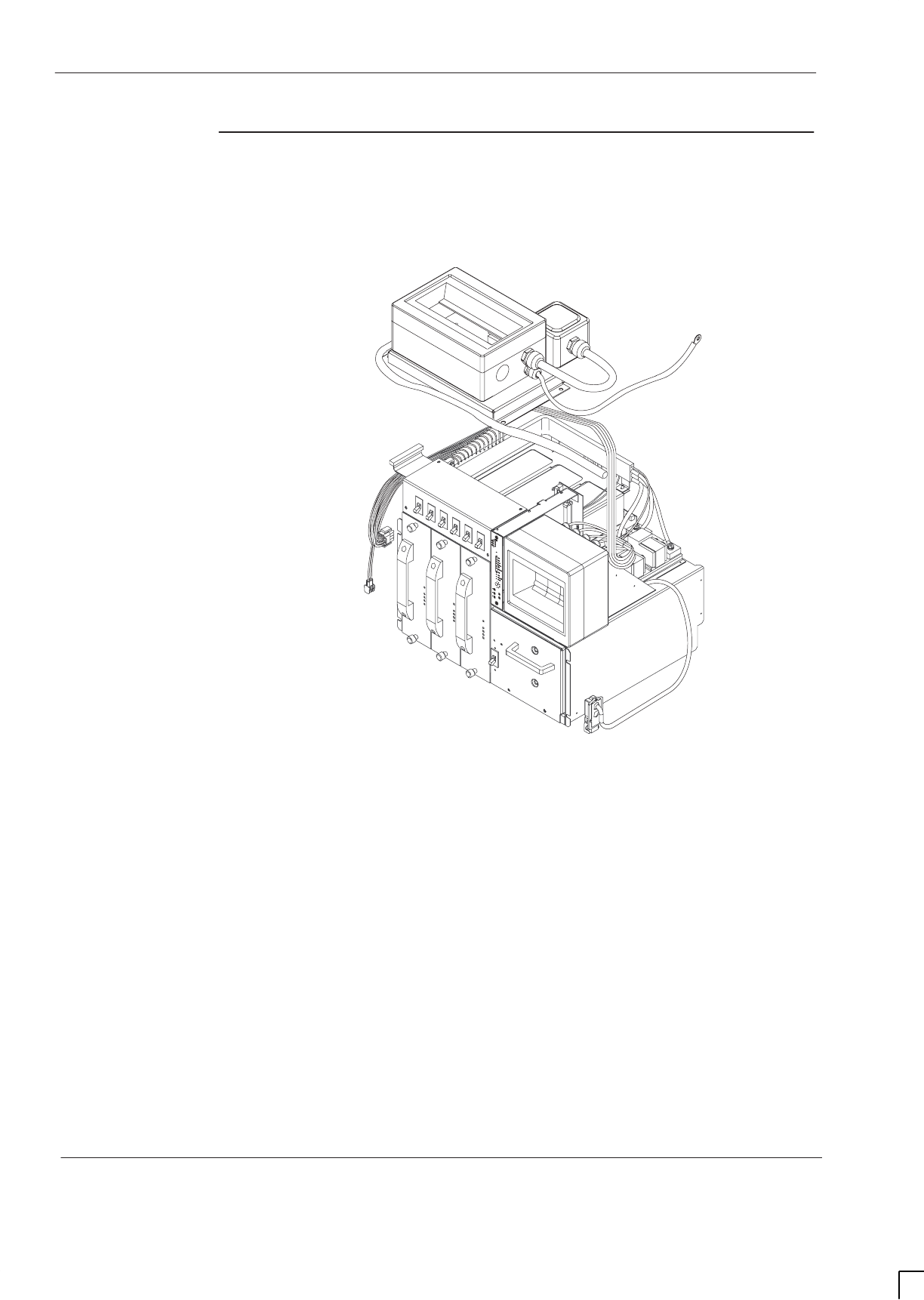
GSM-204-323
Horizonmacro outdoor power supplies
31st Oct 01
Tech. 4–2
Technical Description: Horizon
macro
outdoor
CONTROLLED INTRODUCTION
68P02902W02-A
Power supply
unit view
Figure 4-1 shows the power supply unit (with its associated distribution boxes
and the CAB), and the TOPSMs. The cabinet structure has been omitted for
clarity.
Figure 4-1 Horizon
macro
outdoor PSU
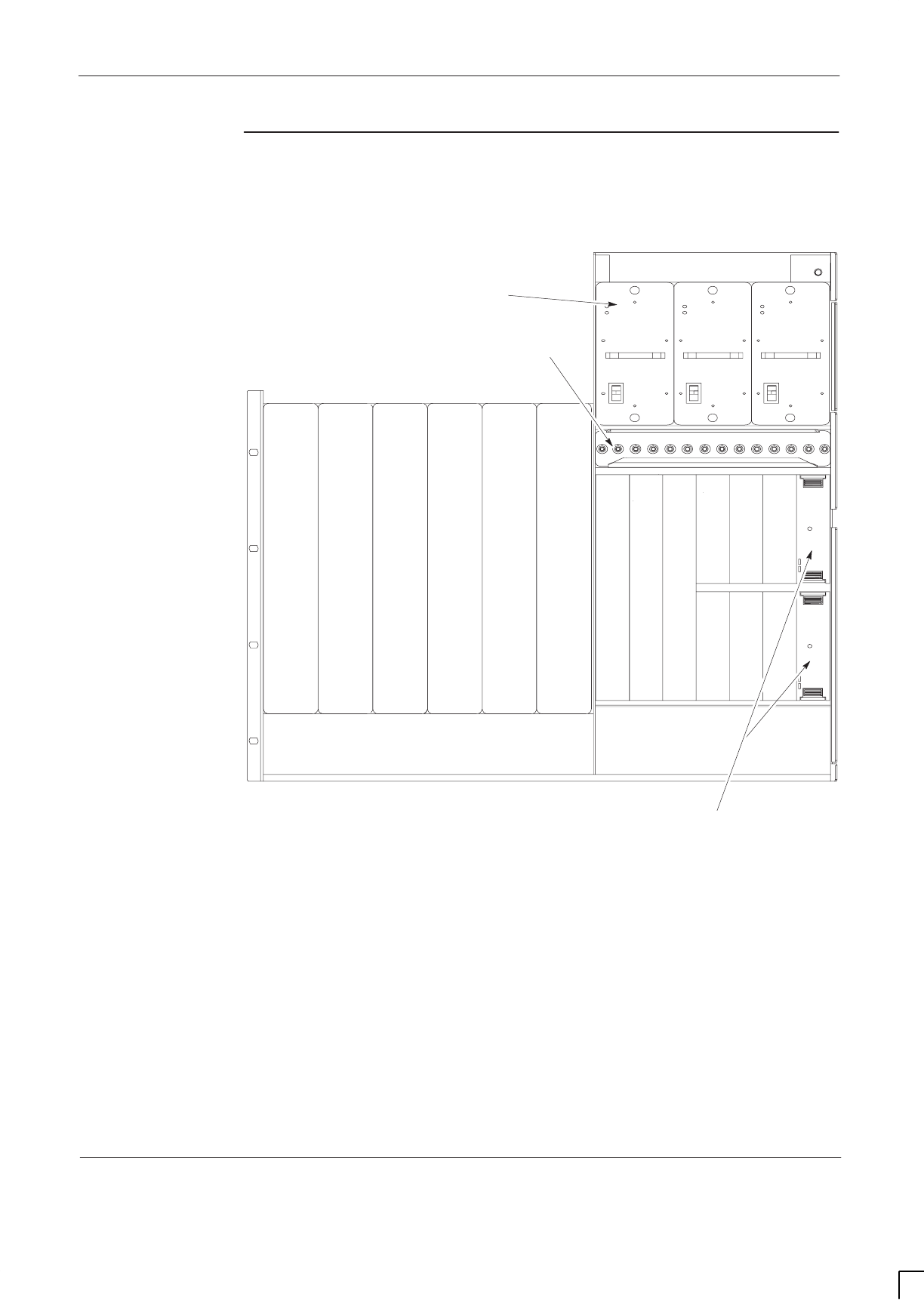
GSM-204-323 Horizonmacro outdoor power supplies
31st Oct 01
Technical Description: Horizon
macro
outdoor
68P02902W02-A
CONTROLLED INTRODUCTION
Tech. 4–3
View of main
cage power
modules
Figure 4-2 shows the main cage with its power modules indicated.
BPSMs
PSMs
CBM
Figure 4-2 Main cage power modules
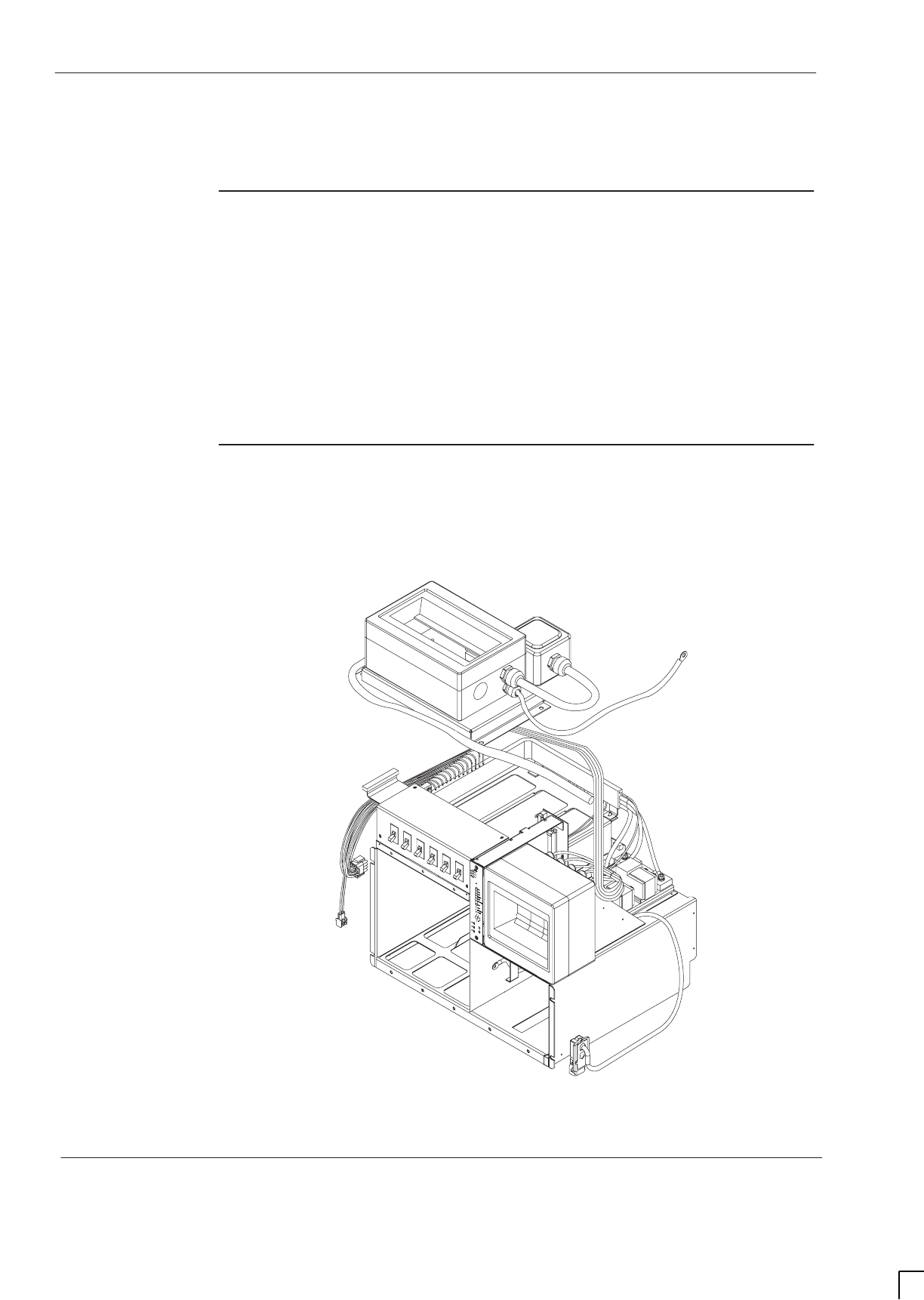
GSM-204-323
Introduction to power distribution
31st Oct 01
Tech. 4–4
Technical Description: Horizon
macro
outdoor
CONTROLLED INTRODUCTION
68P02902W02-A
Introduction to power distribution
Power
distribution
overview
The power supply unit cage is the main power distribution assembly within the
Horizon
macro
outdoor BTS cabinet.
The power distribution system consists of two main functional elements:
Two ac distribution boxes and their associated cables.
Six dc circuit breakers, two contactors, the multilayer busbar and dc
cables.
View of power
supply unit
cage
Figure 4-3 shows the power supply unit cage, its associated distribution boxes
and cables, with the cabinet structure omitted for clarity.
Figure 4-3 AC power supply unit cage
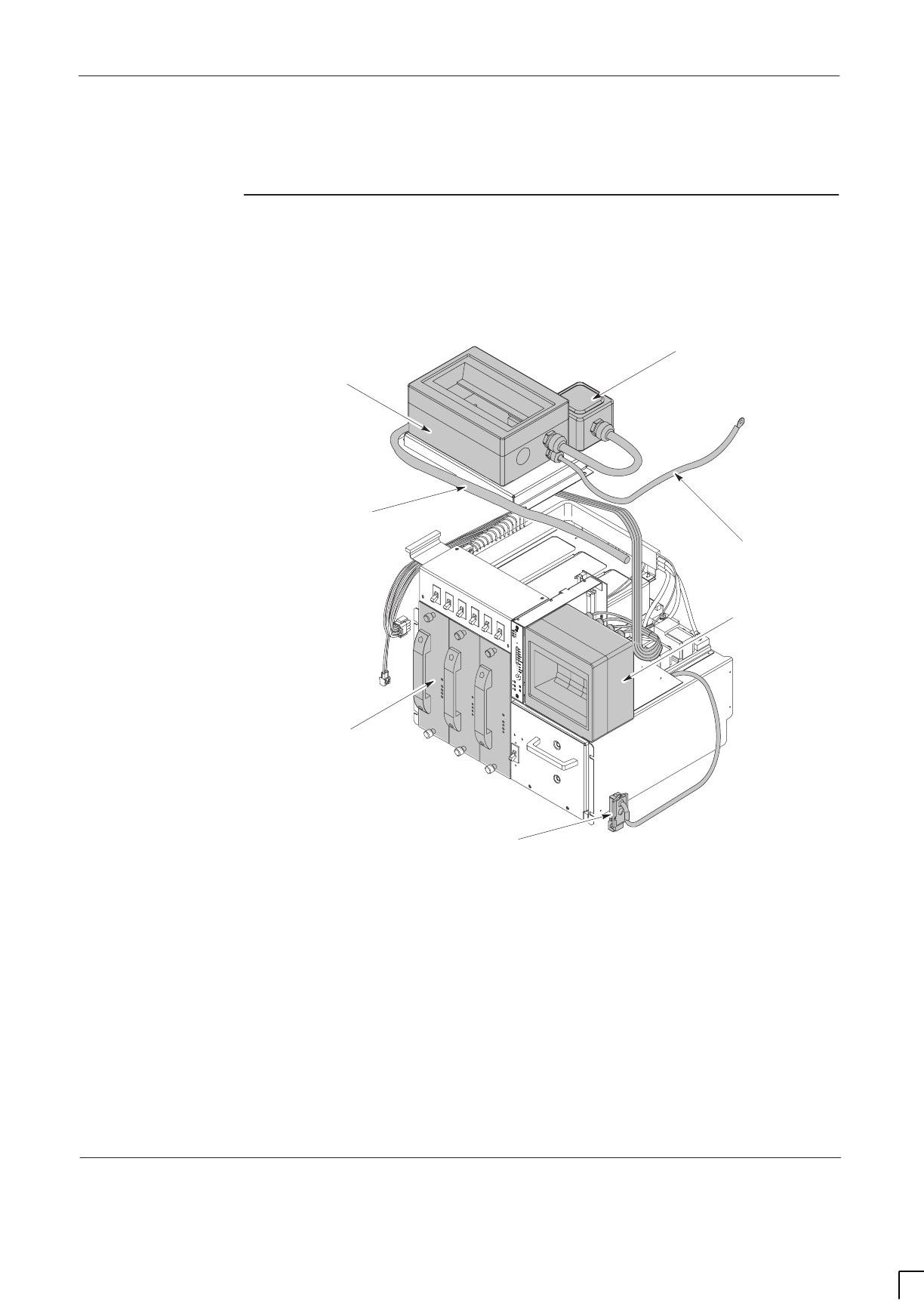
GSM-204-323 AC power distribution
31st Oct 01
Technical Description: Horizon
macro
outdoor
68P02902W02-A
CONTROLLED INTRODUCTION
Tech. 4–5
AC power distribution
View of
ac power
components
Figure 4-4 shows the ac power distribution components and the associated
cables (shaded), with the cabinet structure omitted for clarity.
NUMBER 1 AC
DISTRIBUTION BOX
AC OUTLET SOCKET
PSU EARTH CABLE
NUMBER 2 AC
DISTRIBUTION BOX
INCOMING
MAINS SUPPLY
TOPSM
TMS HEATER SUPPLY
Figure 4-4 AC power distribution components
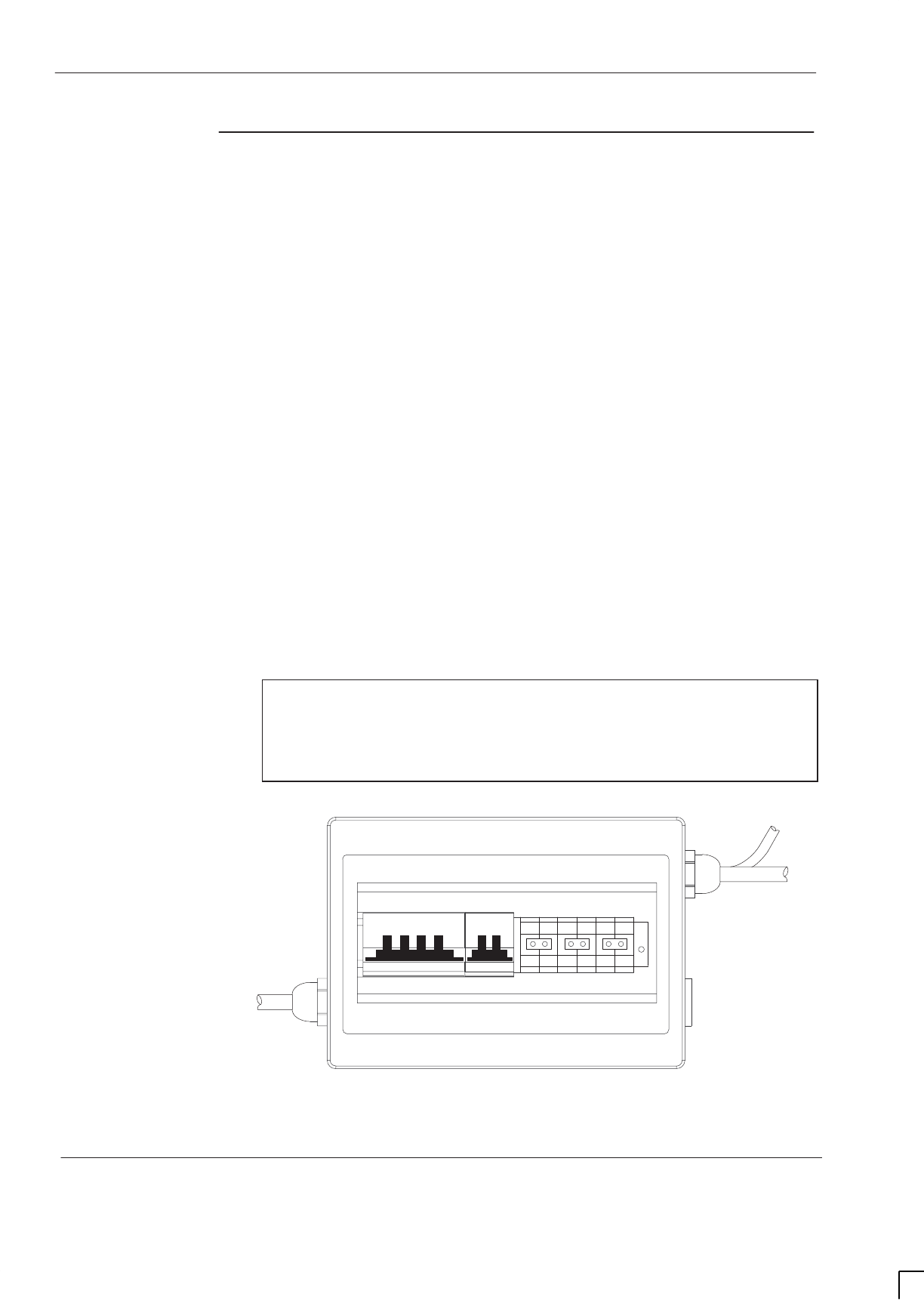
GSM-204-323
AC power distribution
31st Oct 01
Tech. 4–6
Technical Description: Horizon
macro
outdoor
CONTROLLED INTRODUCTION
68P02902W02-A
AC distribution
description
There are two ac distribution boxes and an ac power outlet socket associated
with the Horizon
macro
outdoor PSU.
Number 1 ac distribution box
The number 1 ac distribution box (see Figure 4-5) is located in the top panel of
the cabinet. It contains circuit protective devices and a terminal block, and
provides:
The termination point for the incoming mains supply.
A four pole 32 A main circuit breaker (also used as a switched disconnect
for external ac power supplies).
A double pole 6 amp (30 mA) residual current breaker with overcurrent
protection (RCBO) to supply the ac power outlet socket.
The means of configuring the BTS to accept the following incoming mains
supply voltages:
– 230 V ac 50 Hz single phase and neutral.
– 230 V ac 50 Hz three phase and neutral (star configuration).
– 230 V ac 50 Hz three phase (delta configuration).
– 110 V ac 60 Hz single phase and neutral.
NOTE When the Horizon
macro
is supplied by 110 V single
phase, the 4 pole main circuit breaker is configured as two
parallel pairs – one pair breaking the live phase and one
pair breaking the neutral. This provides circuit protection at
a total of 64 amps.
MAINS DISCONNECT
4 POLE 32 A TYPE C AC SOCKET
6 A 30mA
1 3 5 7 9 11
2 4 6 8 10 12
Figure 4-5 The number 1 ac distribution box
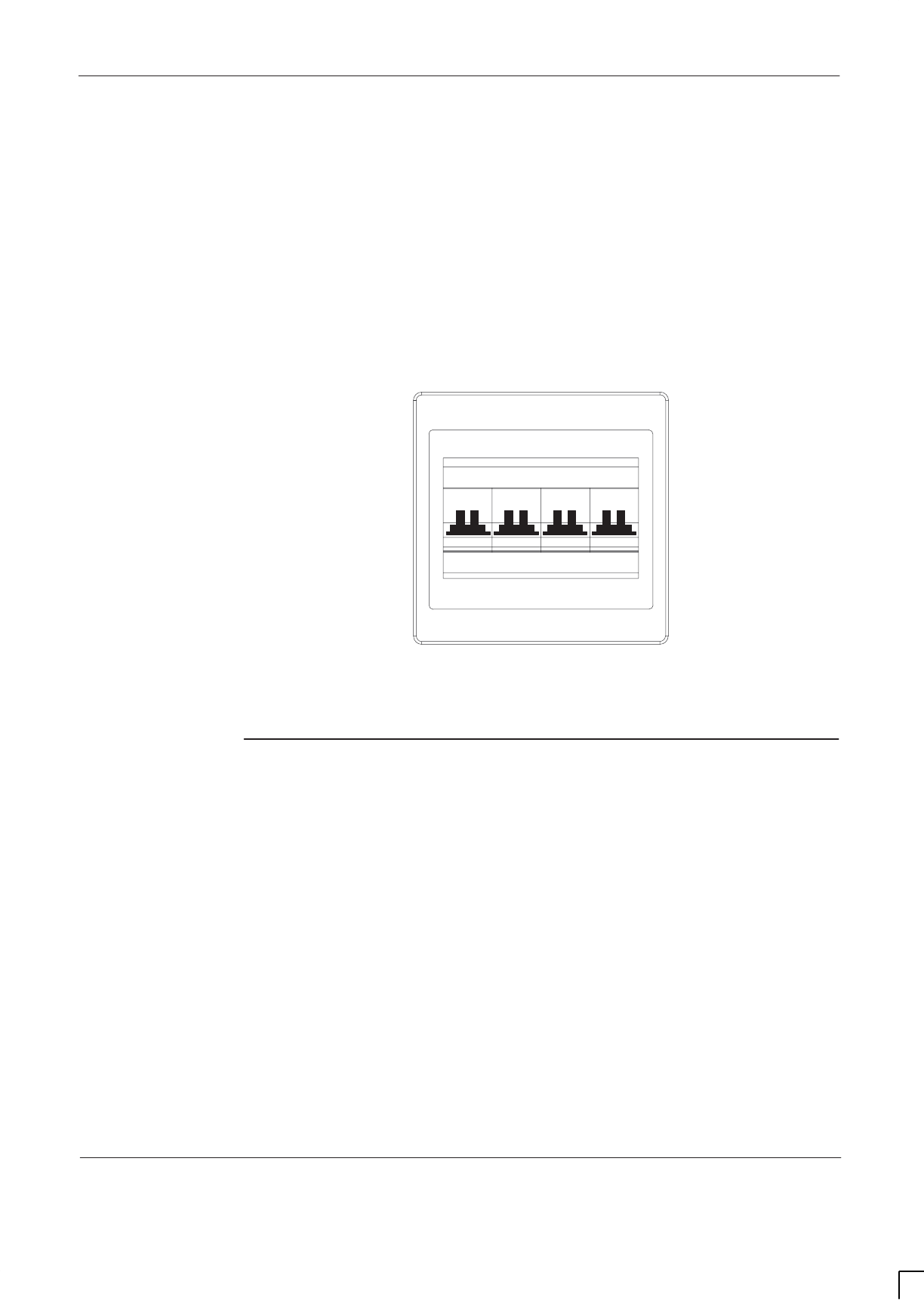
GSM-204-323 AC power distribution
31st Oct 01
Technical Description: Horizon
macro
outdoor
68P02902W02-A
CONTROLLED INTRODUCTION
Tech. 4–7
Number 2 ac distribution box
The number 2 ac distribution box (see Figure 4-6) is located in the upper right of
the PSU and contains circuit protective devices as follows:
Three 20 amp double pole circuit breakers to supply the outdoor power
supply modules (TOPSMs).
One 10 amp double pole circuit breaker to supply the thermal
management system (TMS) heaters.
Each double pole circuit breaker also acts as a switched disconnect for its
respective circuit, breaking both feed and return lines. The output of each circuit
breaker is fed to its load by discrete cables.
TMS
10 A TYPE B
PSU 1
20 A TYPE B
PSU 0
20 A TYPE B
PSU 2
20 A TYPE B
Figure 4-6 The number 2 ac distribution box
AC outlet
socket
The socket (see Figure 4-7) is a European domestic type and is housed in a
weatherproof enclosure which has an IP56 protection rating. It is nominally rated
at 230 V, 5 A max and is supplied from a 30 mA RCBO in the number 1 ac
distribution box.
The purpose of the socket is to allow site engineers to use standard 230 V
portable test and diagnostic equipment when installing, commissioning or
servicing the Horizon
macro
outdoor BTS.

GSM-204-323
AC power distribution
31st Oct 01
Tech. 4–8
Technical Description: Horizon
macro
outdoor
CONTROLLED INTRODUCTION
68P02902W02-A
View of the ac
outlet socket
Figure 4-7 shows a view of the ac outlet socket.
NUMBER 1 AC
DISTRIBUTION BOX
AC OUTLET SOCKET
Figure 4-7 AC outlet socket
AC distribution
diagram
Figure 4-8 shows a block diagram of the ac distribution within the Horizon
macro
BTS cabinet.
T
O
P
S
M
1
T
O
P
S
M
0
T
O
P
S
M
2
HORIZON
MACRO
MAIN CAGE
INCOMING
AC SUPPLY
NUMBER 1 DISTRIBUTION
BOX OUTLET SOCKET (ac)
NUMBER 2
DISTRIBUTION
BOX
TMS TMS HEATERS
PLUG/SOCKET
Figure 4-8 AC distribution block diagram
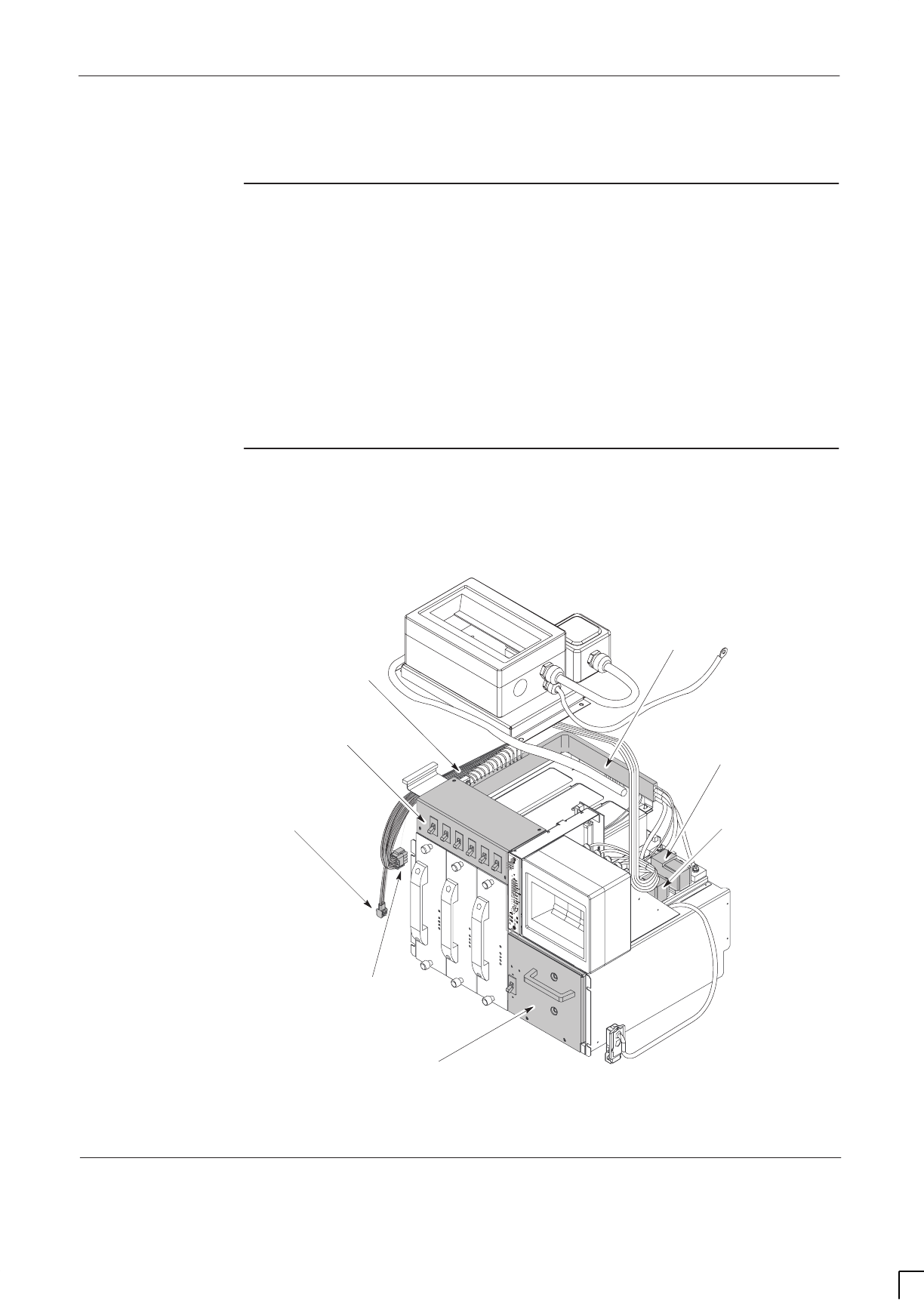
GSM-204-323 DC power distribution
31st Oct 01
Technical Description: Horizon
macro
outdoor
68P02902W02-A
CONTROLLED INTRODUCTION
Tech. 4–9
DC power distribution
DC distribution
overview
The regulated dc output of the TOPSM is distributed through the multilayer
busbar to:
The main cage PSMs.
TMS fans.
Customer specific equipment racking power outlets (COMMS 1 to 4).
Internal battery backup.
The connectors for optional external battery backup, (located on the dc
interface panel, within the top panel enclosure).
View of
dc power
components
Figure 4-9 shows the dc power distribution components and the associated
cables (shaded), with the cabinet structure omitted for clarity.
TMS FANS AND
CUSTOMER COMMS
SUPPLY CABLES
MULTILAYER
BUSBAR
BATTERY CONTACTOR
DC CIRCUIT BREAKER
PANEL
INTERNAL BATTERY TRAY
COMMS CONTACTOR
TMS FANS
CONNECTOR
CUSTOMER COMMS
SUPPLY CONNECTOR
Figure 4-9 DC power distribution components
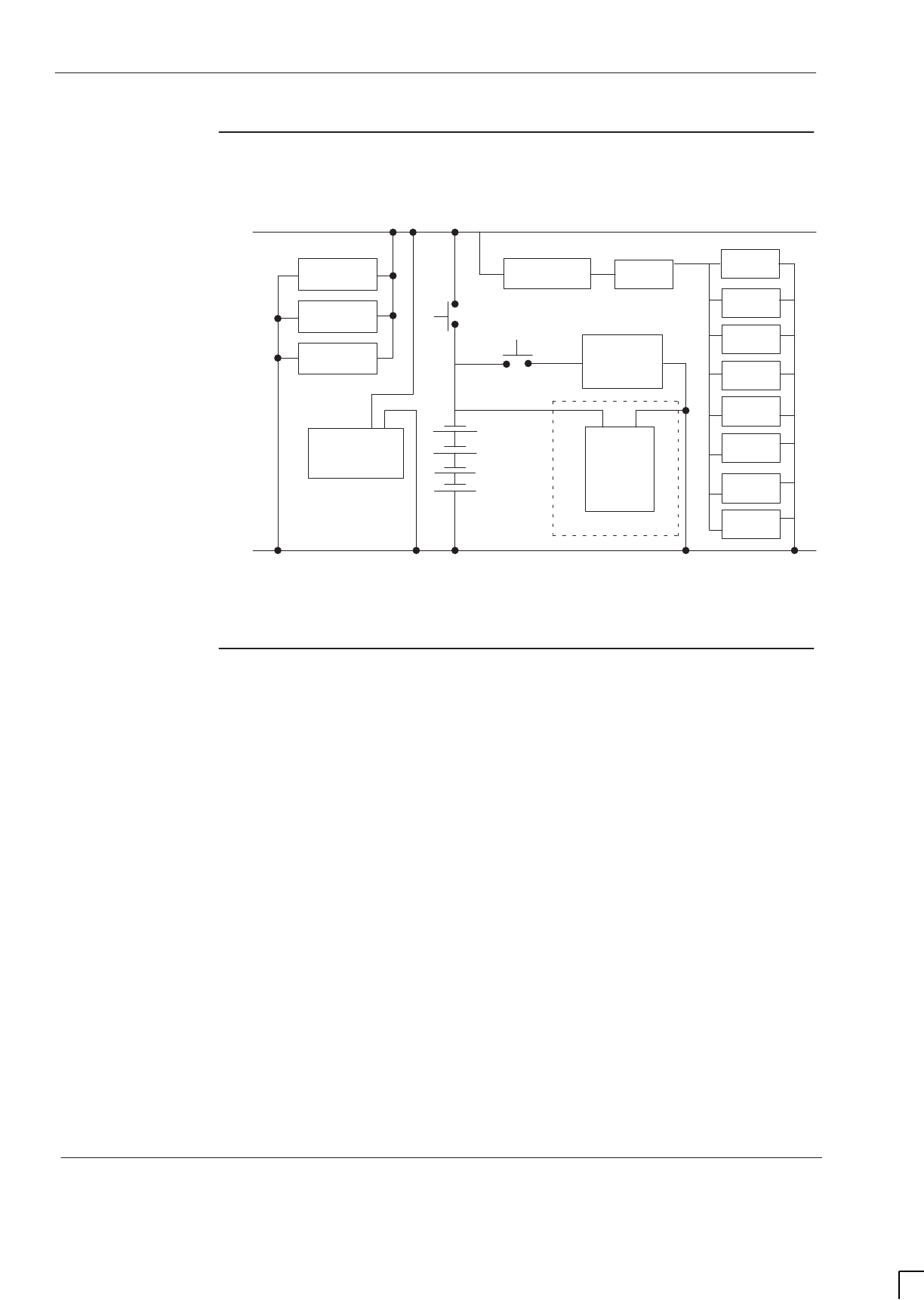
GSM-204-323
DC power distribution
31st Oct 01
Tech. 4–10
Technical Description: Horizon
macro
outdoor
CONTROLLED INTRODUCTION
68P02902W02-A
DC distribution
diagram
Figure 4-10 shows the –55 V dc distribution as a block diagram.
SURF
BPSMS
CBM
TMS FANS CTU
CTU
CTU
CTU
CTU
CTU
COMMS
EQUIPMENT
EXTERNAL
BATTERY
CABINET
COMMS
CONTACTOR
PSM
(DC/DC conv)
TOPSM
INTERNAL
BATTERIES
TOPSM
TOPSM
BATT
CONTACTOR
0 V dc
–55 V dc
Figure 4-10 DC distribution block diagram
DC distribution
description
The main cage dc supply is routed from the left side of the multilayer busbar
through the dc interface panel (see Figure 4-14) to the main cage interface
panel. Circuit protection for the main cage is provided by the CBM and internal
fusing in the PSMs.
The other circuits supplied from the multilayer busbar are protected by individual
circuit breakers. Six of the circuit breakers are mounted on the dc circuit breaker
panel of the outdoor PSU, as shown in Figure 4-11. The internal batteries have
a separate 80 A circuit breaker, housed within the battery mounting tray. The
circuit breakers also function as switched disconnects for their respective loads.
The PSU cage has two contactors as part of the dc distribution system. During
periods of battery back-up, the contactors will progressively disconnect battery
loads as battery voltage decreases, to prevent deep discharge of backup
batteries. The operation of these contactors is controlled by the control and
alarm board and is described in detail in Outdoor PSU control and alarm
board (CAB)
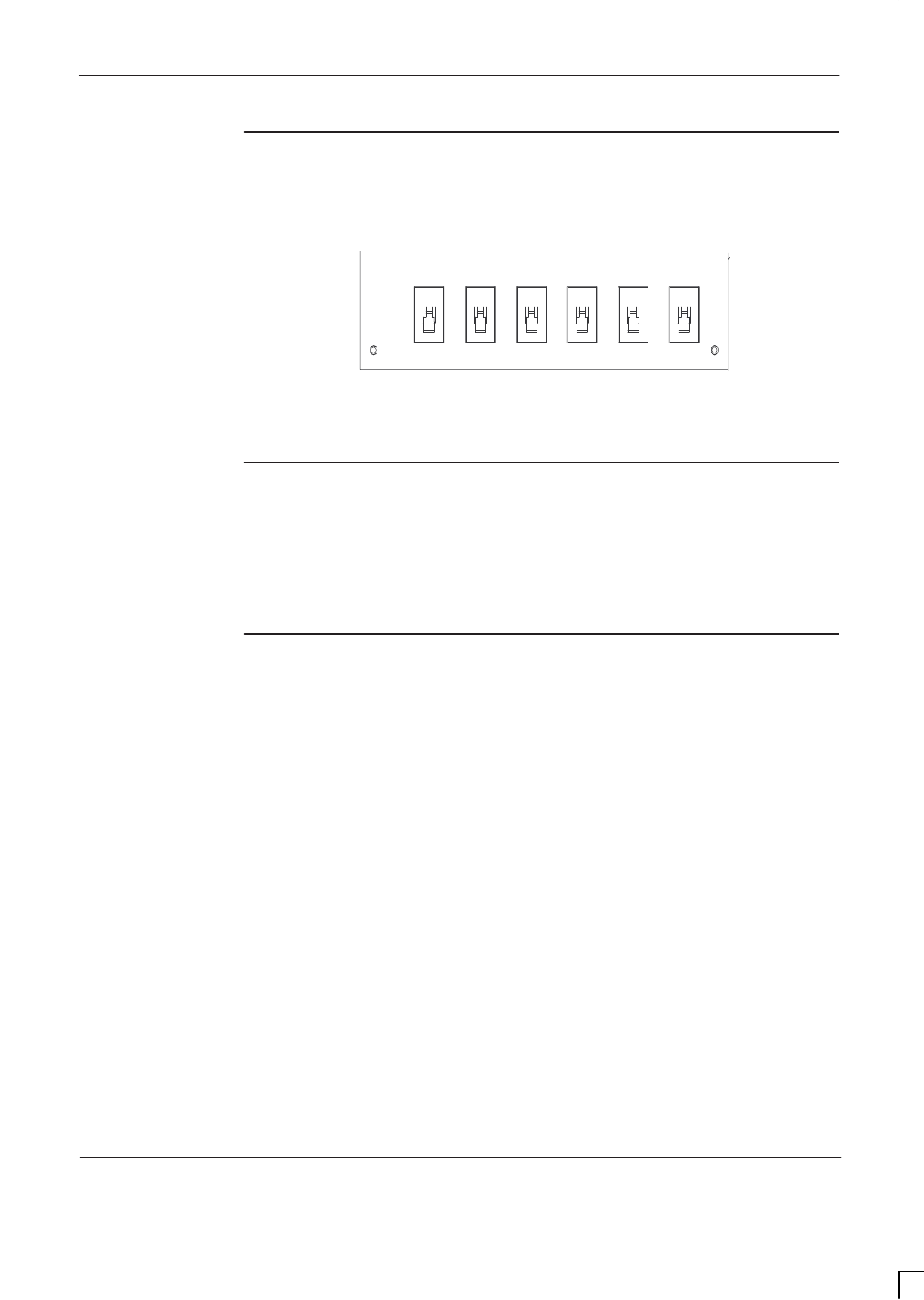
GSM-204-323 DC power distribution
31st Oct 01
Technical Description: Horizon
macro
outdoor
68P02902W02-A
CONTROLLED INTRODUCTION
Tech. 4–11
View of the dc
circuit breaker
panel
Figure 4-11 shows a front view of the dc circuit breaker panel.
EXT
BATT TMS
FANS COMMS
1
80 A10 A5 A5 A5 A5 A
COMMS
2COMMS
3COMMS
4
Figure 4-11 The dc circuit breaker panel
Customer
equipment
power supplies
The four power outlets mounted adjacent to the customer equipment racks are
supplied from the multilayer busbar by individual 5 A circuit breakers,
(see Figure 4-11).
Internal battery
backup
The internal battery tray, located at the lower right side of the PSU, holds four
12 V batteries connected in series to provide a total output of 48 V dc, with a
capacity of 15 Ah.
The internal batteries are protected by an 80 A circuit breaker, mounted on the
battery tray front panel. The circuit breaker also functions as a disconnect switch
for the internal batteries.
Battery voltage sensing leads are fed from the negative terminal of each battery
to a four way connector on the battery tray. This is connected to the control and
alarm board (CAB). The sensed voltages are used by the battery capacity test
and battery selector switch functions of the CAB.
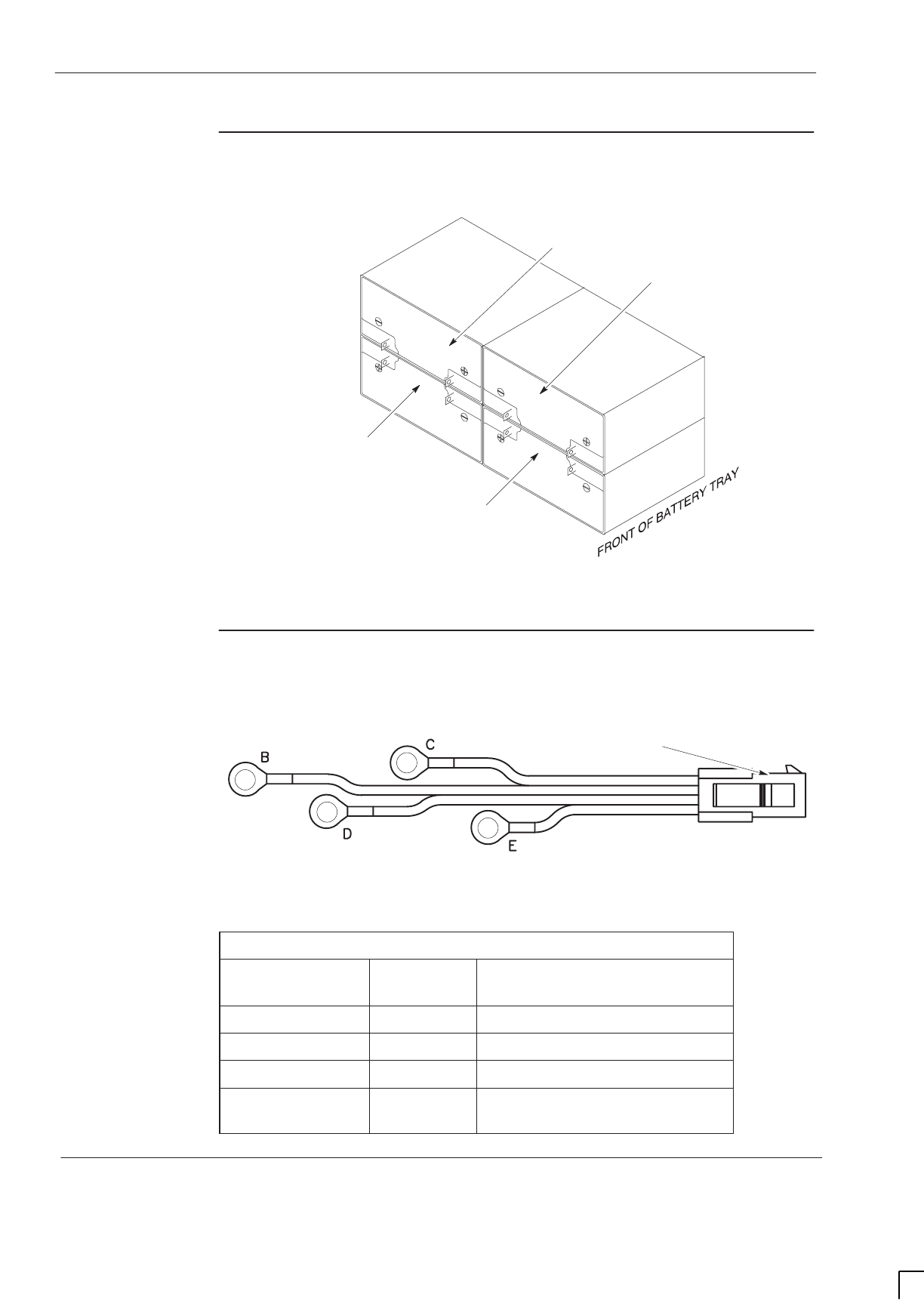
GSM-204-323
DC power distribution
31st Oct 01
Tech. 4–12
Technical Description: Horizon
macro
outdoor
CONTROLLED INTRODUCTION
68P02902W02-A
Internal battery
arrangement
Figure 4-12 shows how the batteries are arranged in the battery tray.
BATTERY 1
BATTERY 2
BATTERY 3
BATTERY 4
Figure 4-12 Internal battery arrangement in the battery tray
View of battery
sense lead
Figure 4-13 show the internal battery sense lead.
M6 INSULATED
RING TERMINALS MOLEX 4 WAY CONNECTOR
Figure 4-13 Battery sense lead assembly
Table 4-1 details the wiring schedule of the battery sense lead.
Table 4-1 Battery sense lead to Molex connector
Molex
connector pin Terminal
ident Location
1 C Battery 1 –ve terminal
2 B Battery 2 –ve terminal
3 D Battery 3 –ve terminal
4 E Battery 4 –ve terminal at
circuit breaker top terminal
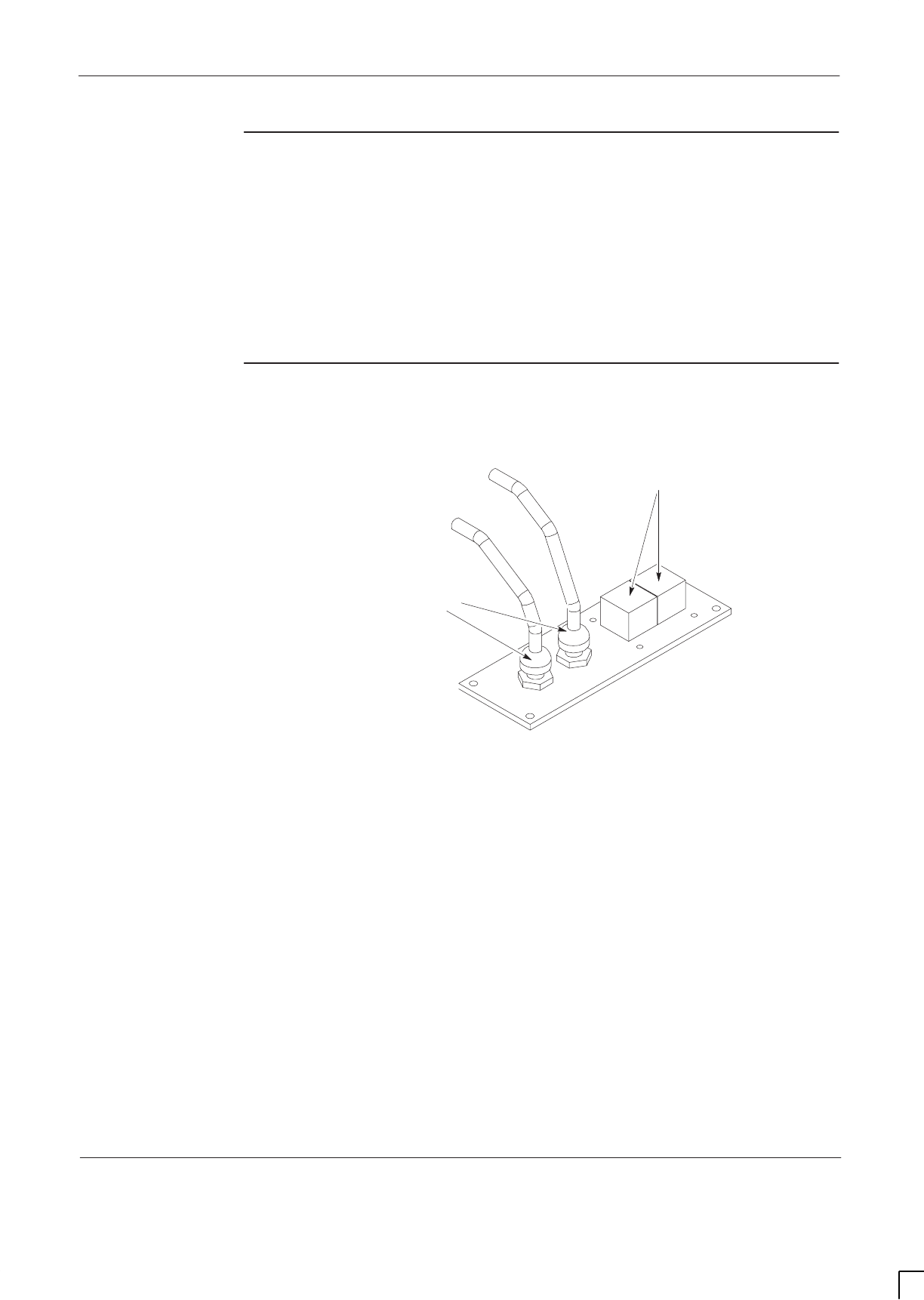
GSM-204-323 DC power distribution
31st Oct 01
Technical Description: Horizon
macro
outdoor
68P02902W02-A
CONTROLLED INTRODUCTION
Tech. 4–13
External battery
backup
connection
The external battery connection cables are routed from the left side of the
multilayer busbar to connectors on the dc interface panel (see Figure 4-14).
Circuit protection and disconnect switching are provided by an 80 A circuit
breaker mounted on the dc circuit breaker panel. External battery backup is
further described in Common applications for the auxiliary equipment
housing in Chapter 7.
View of the dc
interface panel
Figure 4-14 shows a view of the dc interface panel.
DC OUTPUT CABLES
EXTERNAL BATTERY
CONNECTORS
Figure 4-14 The dc interface panel
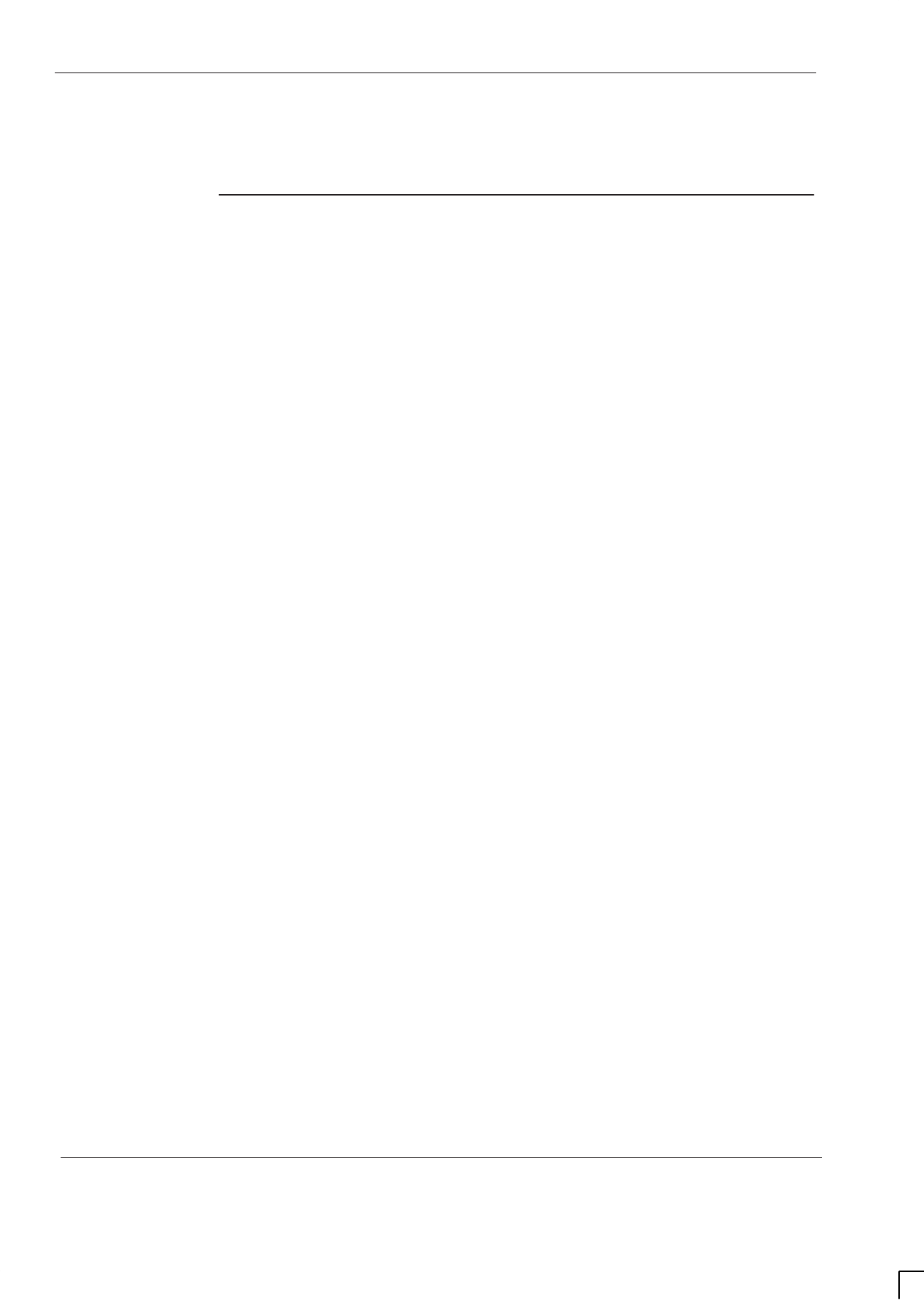
GSM-204-323
Control and alarm board (CAB)
31st Oct 01
Tech. 4–14
Technical Description: Horizon
macro
outdoor
CONTROLLED INTRODUCTION
68P02902W02-A
Control and alarm board (CAB)
Introduction to
the CAB
The CAB is located in the outdoor PSU between the dc circuit breaker panel
and the number 2 ac distribution box. It provides the following functions:
Control of TOPSM output voltage (voltage trim).
TOPSM disable relay control.
Control of battery and communications contactors:
– During cabinet power up.
– During low voltage disconnect (LVD).
Monitoring of battery voltage and temperature.
Monitoring of TOPSM input and output failure signals.
Monitoring of non EMC enclosure temperature.
Monitoring of alarms from the cabinet, the TMS, and the auxiliary
equipment housing.
Performing a battery charge capacity test on the internal batteries.
The CAB sources dc power from all of the following:
The distributed dc regulated output of the TOPSMs.
The TOPSM auxiliary output.
The communications equipment side of the outdoor PSU communications
contactor.
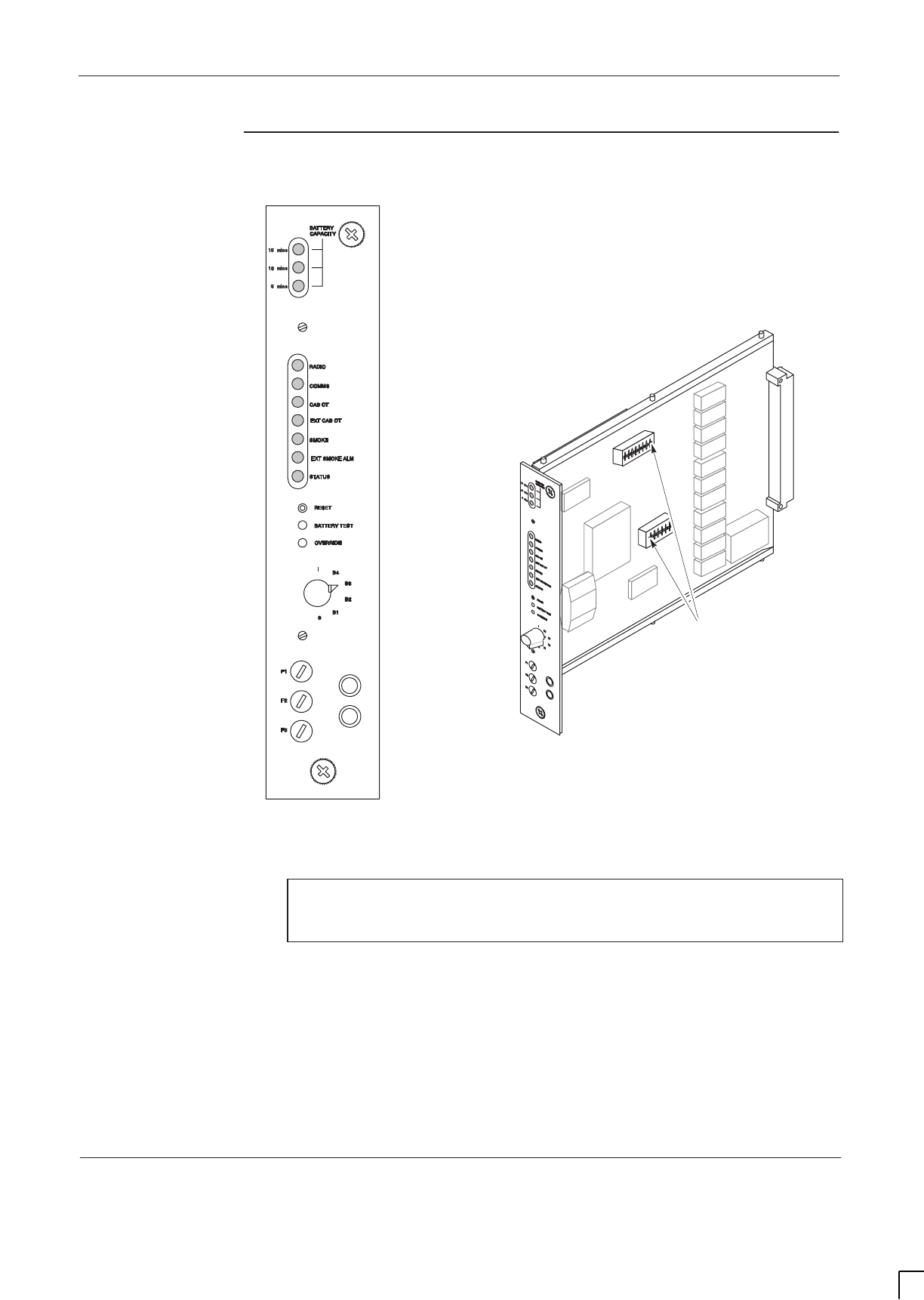
GSM-204-323 Control and alarm board (CAB)
31st Oct 01
Technical Description: Horizon
macro
outdoor
68P02902W02-A
CONTROLLED INTRODUCTION
Tech. 4–15
CAB views
Figure 4-15 shows views of the CAB and its front panel.
DIP SWITCHES
SW2 AND SW4
(see Note below)
Figure 4-15 Control and alarm board
NOTE There are two manufacturers of the CAB. Each is fully
compatible with the PSU, although circuit board layout
may differ.
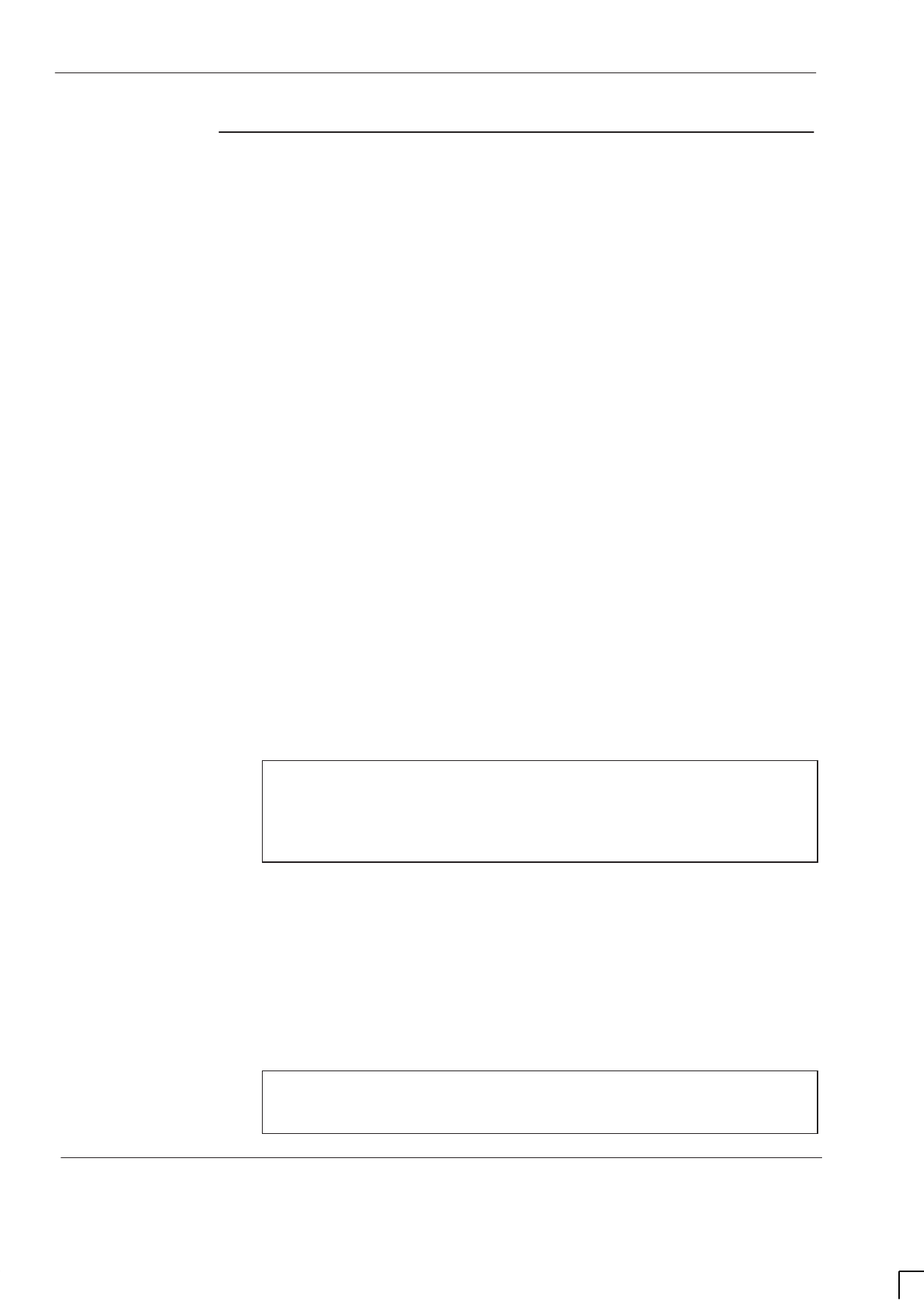
GSM-204-323
Control and alarm board (CAB)
31st Oct 01
Tech. 4–16
Technical Description: Horizon
macro
outdoor
CONTROLLED INTRODUCTION
68P02902W02-A
CAB indicators
and controls
Front panel indicators
BATTERY CAPACITY (green).
– >15 mins.
– >10 mins.
– >5 mins.
One LED is lit, displaying result of last battery capacity test. The three
LEDs flash during the test and one remains lit to indicate test result.
RADIO (green).
Normally lit, this LED indicates that the battery contactor is closed and that
radio loads are connected to the backup batteries, (where fitted).
COMMS (green).
Normally lit, this LED indicates that the communications contactor is
closed and that customer communications loads are being supplied.
CAB OT (red).
Normally unlit, this LED indicates a cabinet over temperature alarm state.
EXT CAB OT (red).
Normally unlit, this LED indicates an auxiliary equipment housing over
temperature alarm state.
SMOKE (red).
Normally unlit, this LED indicates a cabinet (optional) smoke detector
alarm state.
NOTE The smoke detector alarm functions are only activated by
optional customer supplied smoke detectors.
No provision has been made for the fixing of a smoke
detector within the main cabinet or the auxiliary equipment
housing.
EXT SMOKE ALM (red).
Normally unlit, this LED indicates an auxiliary equipment housing
(optional) smoke detector alarm state.
STATUS (green).
Normally lit, this LED indicates that the cabinet is within normal operating
conditions, and will flash on and off when any alarm signal is present. The
status indicator will flash if either the battery or communications contactor
is open.
NOTE Opening the door triggers the door open alarm, causing
the status LED to flash. To check the true status, press the
door microswitch to simulate closing the door.
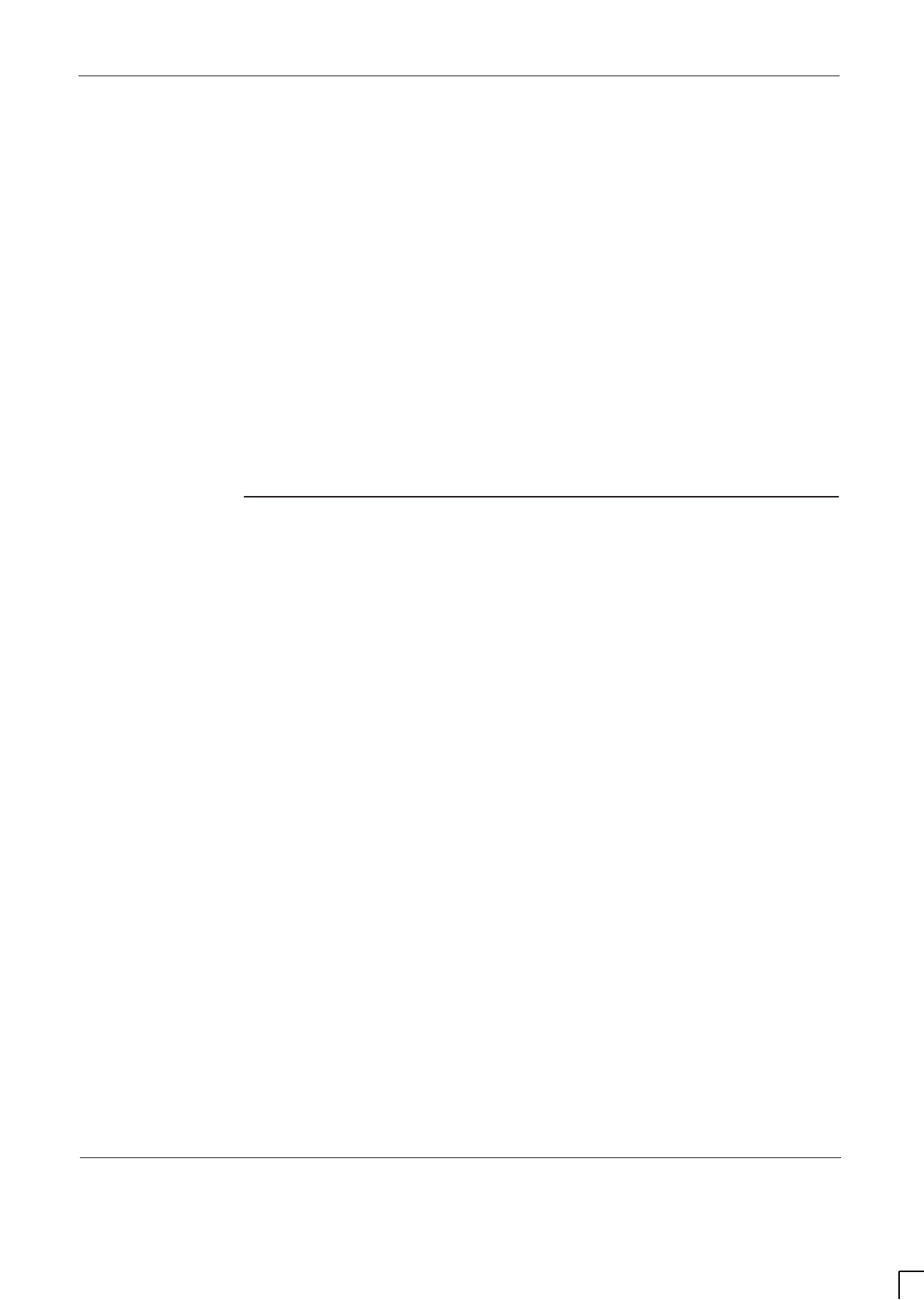
GSM-204-323 Control and alarm board (CAB)
31st Oct 01
Technical Description: Horizon
macro
outdoor
68P02902W02-A
CONTROLLED INTRODUCTION
Tech. 4–17
Front panel switches and buttons
Front panel switches and buttons are provided for the following:
BATTERY TEST.
Initiates battery charge capacity test of internal batteries.
Battery selector switch.
Connects two 4 mm sockets on front panel to internal batteries to allow
monitoring of battery condition.
OVERRIDE.
Overrides disconnected enable signals to the TOPSMs for fault diagnosis.
RESET.
Resets the CAB after an auxiliary equipment housing over temperature
trip.
CAB front panel
fuses
The CAB front panel has three cartridge fuses, providing circuit protection for:
Battery contactor (F1).
Communications contactor (F2).
Control and alarm board (F3).
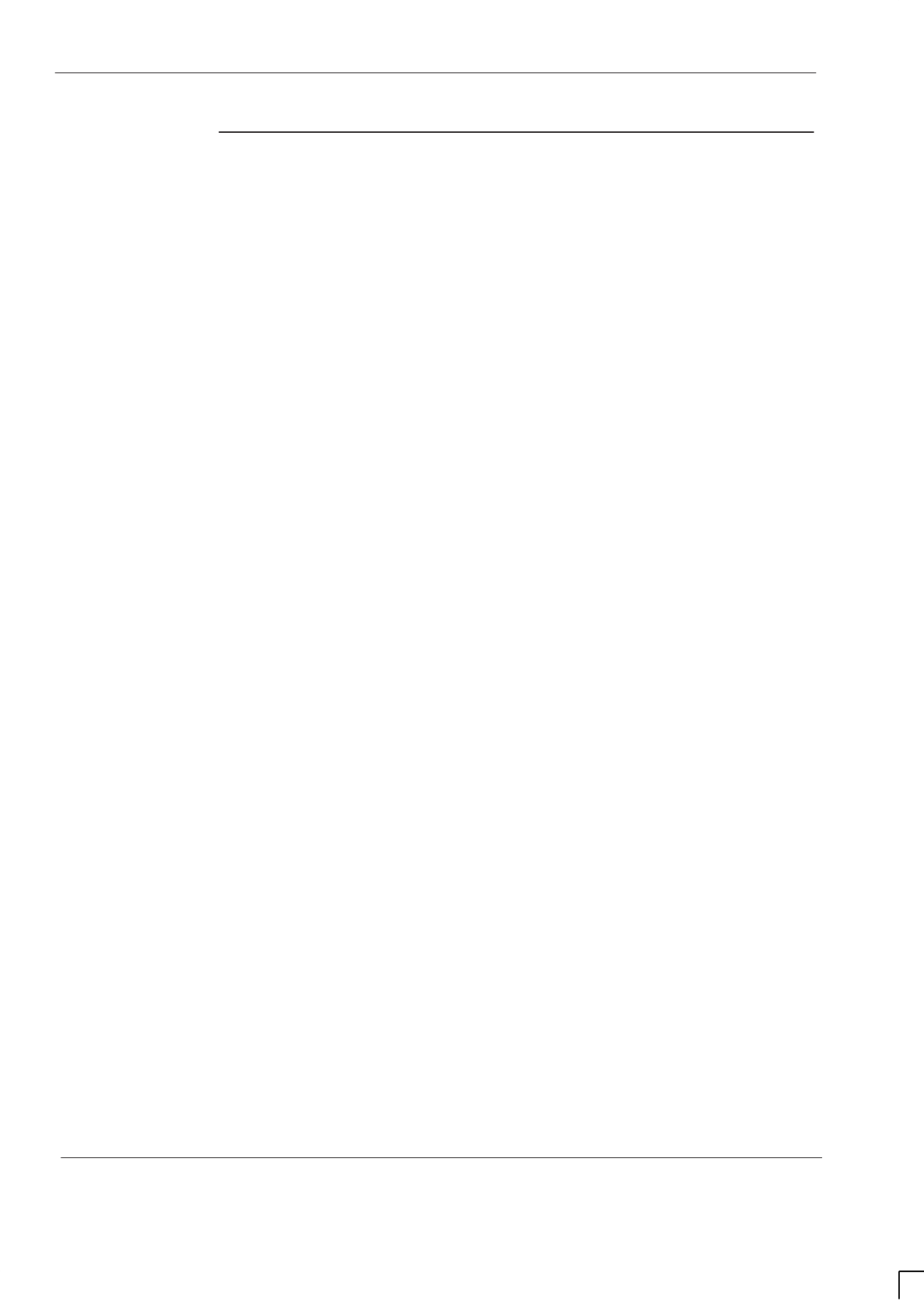
GSM-204-323
Control and alarm board (CAB)
31st Oct 01
Tech. 4–18
Technical Description: Horizon
macro
outdoor
CONTROLLED INTRODUCTION
68P02902W02-A
CAB control
functions
The CAB has the following control functions:
Voltage trim.
TOPSM disable relay control.
Control of contactors during power up.
Low voltage disconnect (LVD).
Over temperature trip.
Smoke trip.
Voltage trim
The CAB generates the control signal voltage (V trim) used to regulate TOPSM
output to produce a temperature-compensated battery charging voltage. The
temperature sensor is mounted on the CAB for internal batteries, and mounted
in the auxiliary equipment housing for external batteries. A dip switch on the
CAB (SW2–8) is used to select either internal or external battery temperature
sensing.
TOPSM disable relay control
On detection of an over temperature trip alarm or a smoke alarm from the BTS
cabinet, the CAB energises the coil of the TOPSM disable relay, interrupting the
enable in signal and shutting down the TOPSM –55 V outputs. The TOPSM
disable relay will remain energized until the alarm condition has cleared and, in
the case of a smoke alarm longer than 30 seconds, the cabinet ac supply has
been cycled or the CAB front panel reset switch has been operated. Operation
of the CAB front panel override switch will interrupt this function, for a 30 second
period, to allow fault diagnosis to be performed.
Control of contactors during power up
The CAB monitors the following signals during power up of the Horizon
macro
cabinet:
TOPSM auxiliary voltage within 9 to 15 V dc range
Cabinet over temperature alarm.
Cabinet smoke alarm.
If the alarm signals are inactive, the CAB will close the battery and
communications contactors, to supply customer communications equipment and
charge the backup batteries.
If the CAB detects a cabinet over temperature or cabinet smoke alarm during
power up, then the TOPSM disable relay operates, as described in TOPSM
disable relay control in this section.
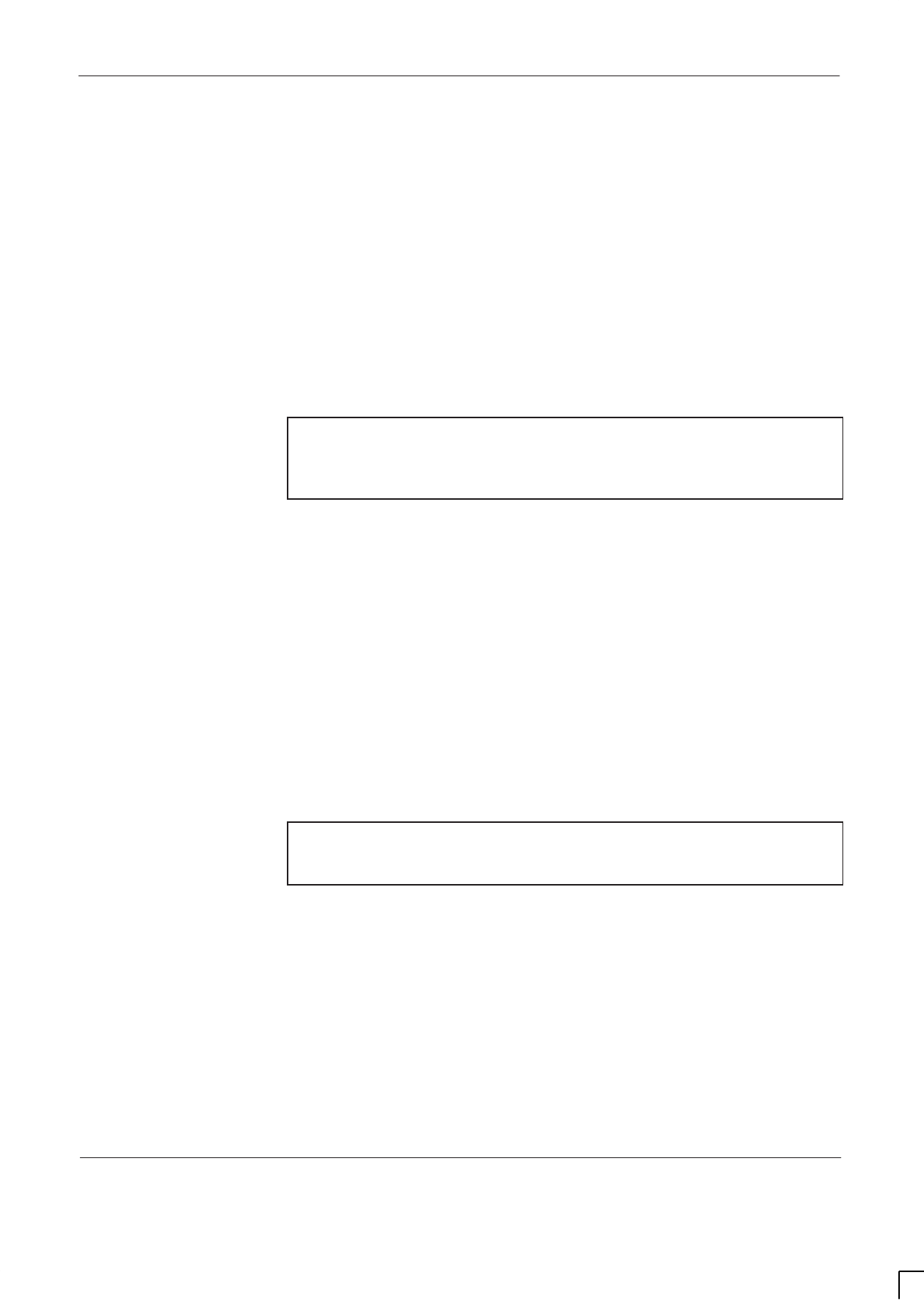
GSM-204-323 Control and alarm board (CAB)
31st Oct 01
Technical Description: Horizon
macro
outdoor
68P02902W02-A
CONTROLLED INTRODUCTION
Tech. 4–19
Low voltage disconnect (LVD)
The CAB constantly monitors battery voltage. During periods of back-up battery
operation, the CAB will progressively reduce the load to prevent deep discharge
of the batteries.
The CAB generates a low voltage disconnect imminent alarm when the battery
terminal voltage reaches –44 V. As the battery voltage level drops further, the
CAB de-energizes the battery contactor at –41V, disconnecting the radios from
the battery power. At 39.5V, the communications contactor is de-energized to
prevent extreme deep discharge of the back up batteries.
The LVD threshold for the communications contactor is lower than that of the
battery contactor, to ensure customer communications equipment remains
powered for as long as possible after radio power has been lost.
NOTE Once the communications contactor has opened the CAB
will lose all power input connections. CAB functions are
only re-established when the ac supply is restored to the
cabinet. The cabinet then restarts as a normal power up.
Over temperature trip
The CAB generates a cabinet over temperature trip signal when both the 78 C
sensor and the 70 C sensor are active (see Horizon
macro
outdoor
temperature control).
The cabinet over temperature trip signal disconnects the battery contactor, the
communications contactor, and disables the TOPSMs. This will shut down the
BTS, and if a shutdown occurs, there is no prior notification to the OMC-R other
than the over temperature alarm.
The CAB re-enables the TOPSMs when both temperature sensors have reset at
60 C. The cabinet then restarts as a normal power up.
Smoke trip
NOTE The following smoke trip functions have not been
implemented in the main cabinet or the auxiliary
equipment housing.
The CAB generates smoke trip control signals after it has been in receipt of a
smoke alarm for 30 seconds.
The Horizon
macro
outdoor cabinet smoke trip signal disconnects the
battery contactor, the communications contactor and disables of the
TOPSMs. The BTS will shut down without prior notification to the OMC-R,
other than the smoke alarm.
A smoke trip signal from the auxiliary equipment housing initiates a remote
disconnection of the external batteries.
Once generated, the smoke trip control signals remain active until the input
mains ac is cycled, or the CAB front panel reset button is operated.
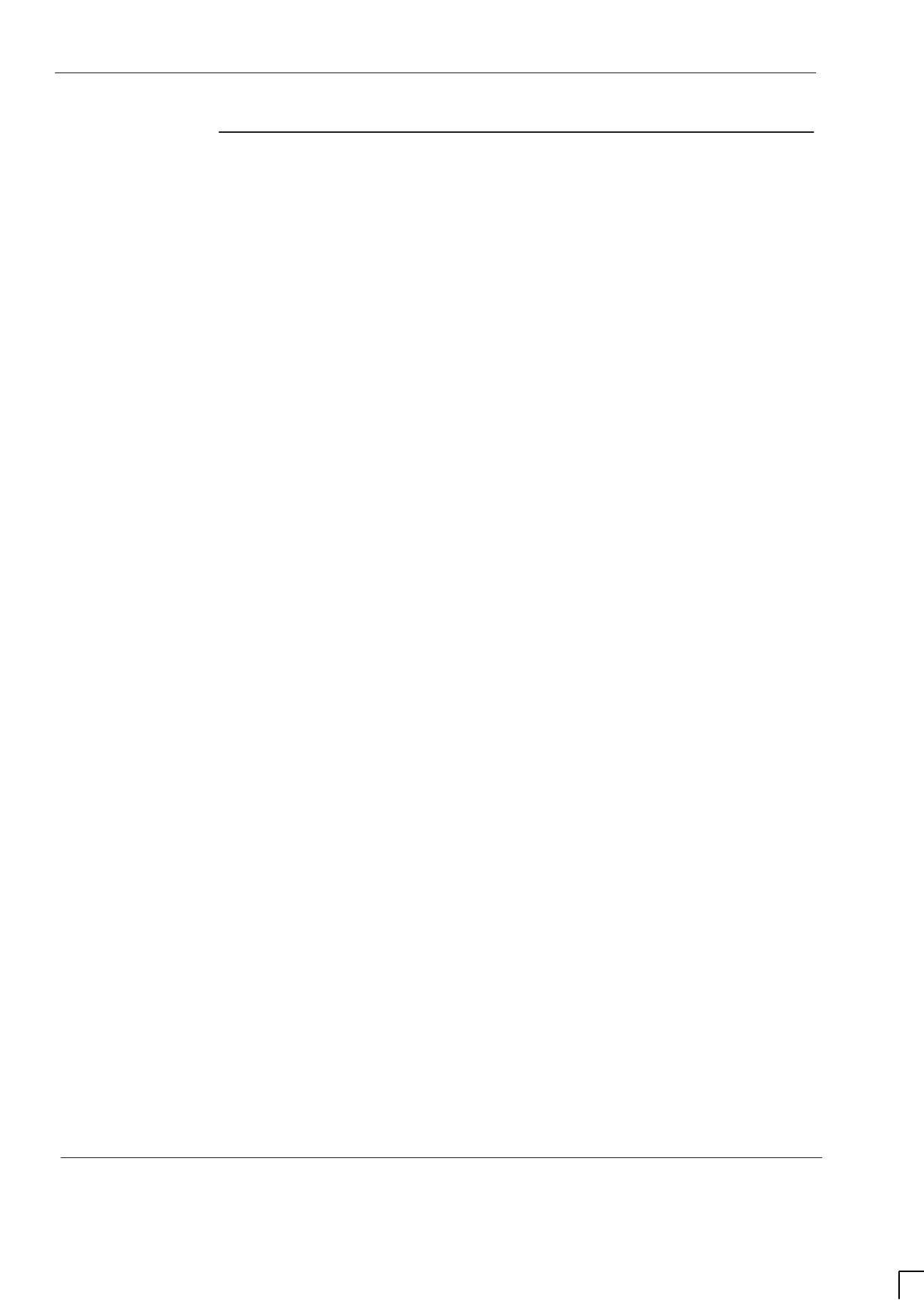
GSM-204-323
Control and alarm board (CAB)
31st Oct 01
Tech. 4–20
Technical Description: Horizon
macro
outdoor
CONTROLLED INTRODUCTION
68P02902W02-A
CAB alarm
functions
The CAB generates or processes the following alarms:
Over temperature alarms:
– Power supply enclosure over temperature.
– TMS over temperature.
– TMS 2 over temperature (not used).
– Auxiliary equipment housing over temperature.
Power supply alarms:
– TOPSM dc output fail.
– Mains input fail.
– Low voltage disconnect imminent.
TMS fail alarms:
– TMS fail.
– TMS 2 fail (not used).
Smoke alarms:
– Optional smoke detector.
– Optional auxiliary equipment housing smoke detector.
Door open alarms:
– BTS cabinet door open.
– Auxiliary equipment housing door open.
Except for TOPSM dc output fail, the alarms originate at sensors which use
voltage-free contacts to indicate an alarm by going open contact.
The CAB sends the alarms through the alarms interface board and the interface
panel as external alarms to the digital alarm module. All alarms to this module
indicate an alarm by going open-circuit. The alarms are processed by the alarm
module and MCUF, and sent on to the OMC-R via the BSC.
Auxiliary equipment housing alarms can be inhibited using the SW2 DIP
switches mounted on the CAB pcb.
Over temperature alarms
The operation of the over temperature alarms associated with the CAB is
described in Horizon
macro
outdoor temperature control.
Power supply alarms
The TOPSM dc output fail and mains input fail alarm signals are generated by a
single changeover relay within each TOPSM.
A single TOPSM alarm signal is interpreted by the CAB as a TOPSM dc
output fail.
A fail signal from all installed TOPSMs is interpreted by the CAB as an ac
supply input fail.
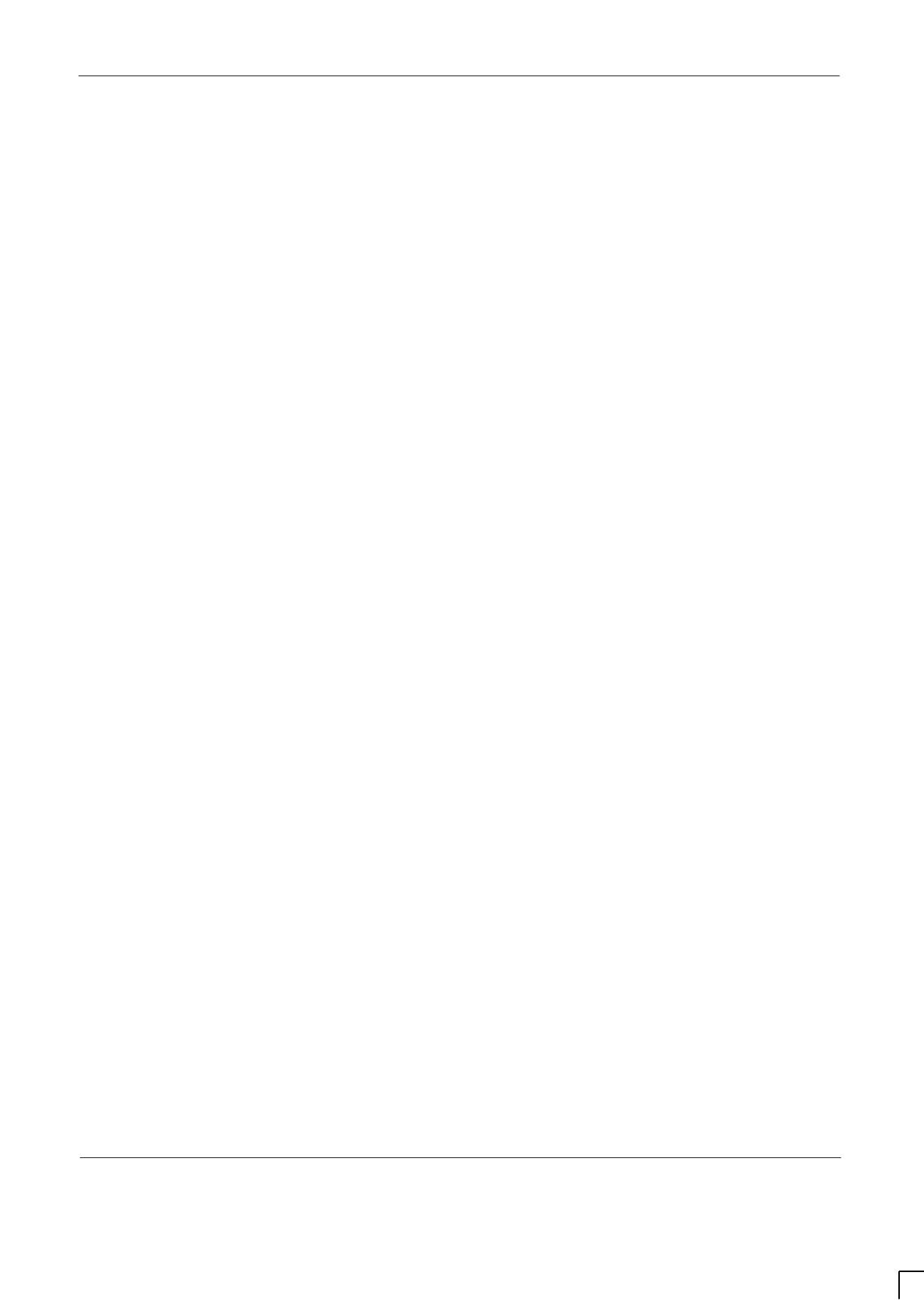
GSM-204-323 Control and alarm board (CAB)
31st Oct 01
Technical Description: Horizon
macro
outdoor
68P02902W02-A
CONTROLLED INTRODUCTION
Tech. 4–21
TMS fail alarm
A TMS fail alarm is generated by the TMS control board when any fan or heater
fails. The alarm signal is routed to the CAB through the alarms interface panel. It
is then processed by the CAB and sent to the digital alarm module.
A separate fan fail signal, generated by the TMS control board, is fed to the
digital alarm module without processing by the CAB.
Smoke alarms
Smoke alarms originate at optional (customer supplied and fitted) smoke
detectors. The alarm is then processed by the CAB and sent to the digital alarm
module. Dip switches mounted on the CAB printed circuit board are used to
inhibit the alarm signals when smoke detectors are not fitted.
Door open alarms
The BTS cabinet door open alarm is generated by the CAB when the
microswitch mounted in the top left corner of the power supply enclosure is
open-circuit.
The auxiliary equipment housing door open alarm signal originates at a door
mounted microswitch, and is generated by the CAB when the microswitch
mounted in the auxiliary equipment housing is open-circuit.
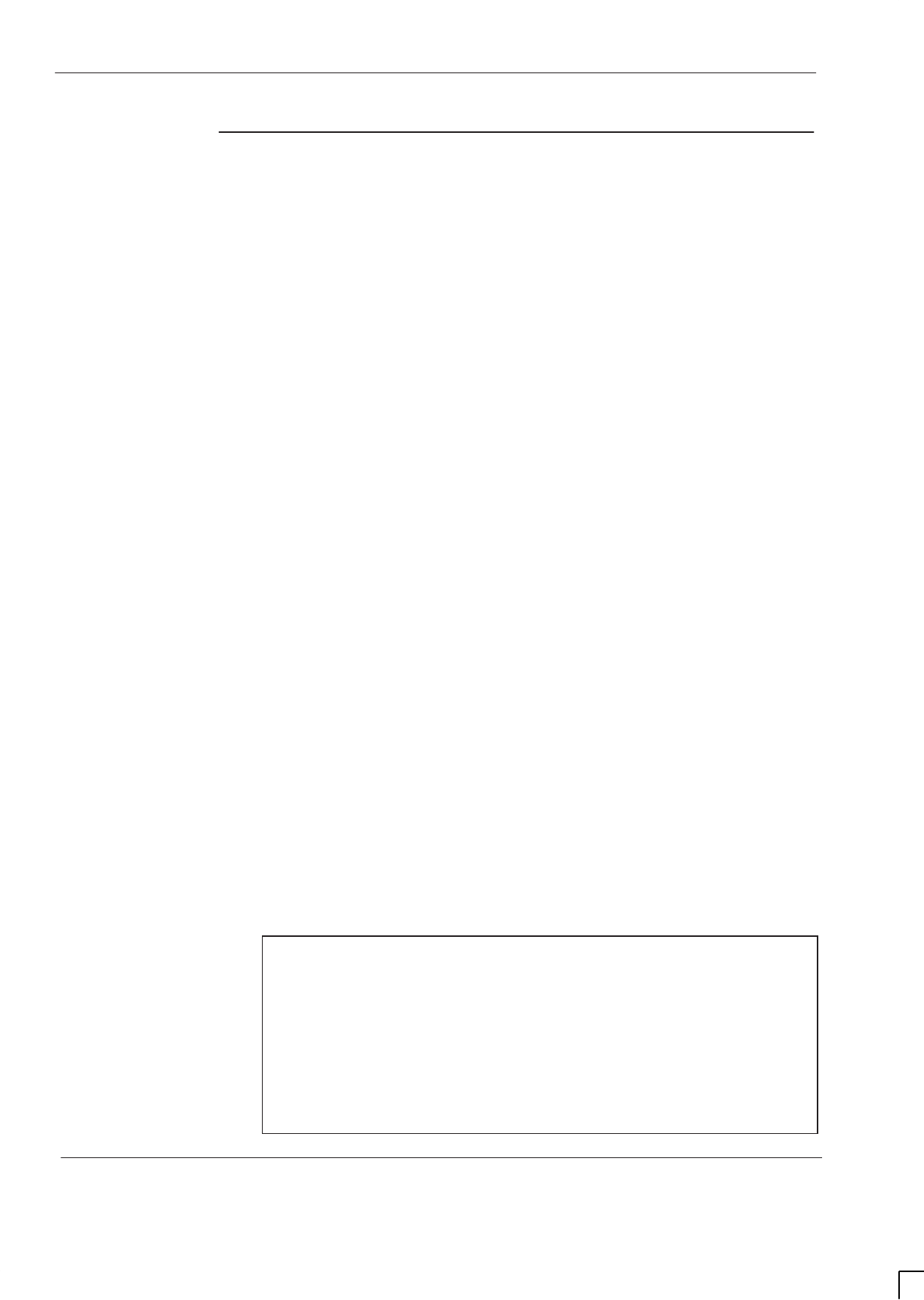
GSM-204-323
Control and alarm board (CAB)
31st Oct 01
Tech. 4–22
Technical Description: Horizon
macro
outdoor
CONTROLLED INTRODUCTION
68P02902W02-A
CAB additional
functions
The CAB also provides the following functions:
Internal battery capacity test.
Battery selector.
Debug.
Internal battery capacity test
The CAB performs an internal battery capacity test when:
CAB front panel BATTERY TEST push button switch is operated.
Automated self-test carried out periodically.
Initiated remotely from the OMC-R.
During the battery capacity test, the CAB sets the TOPSM outputs to –43 V by
adjusting the voltage trim signal so that the internal batteries supply the cabinet
loads. The CAB then monitors the time taken for the battery terminal voltage to
drop to –44 V or times out after 15 minutes. The CAB front panel battery
capacity LEDs indicate the discharge time, and a relay-generated signal is sent
to the OMC-R. The LEDs and relays remain active displaying the result of the
last test conducted.
The internal battery capacity test is remotely initiated by short circuiting the site
output relay 1 common and normally open contacts (C and NO) of PIX0. The
results of the test are reported by site alarm inputs 1 to 3 to the OMC-R.
> 5 mins PIX0 site alarm input 3 short circuit.
>10 mins PIX0 site alarm inputs 2 and 3 short circuit.
>15 mins PIX0 site alarm inputs 1, 2 and 3 short circuit.
Internal battery capacity test cannot be initiated if there are system alarms
active, the door microswitch must be pressed to override the door open alarm.
If an alarm occurs during the test, the TOPSM is reset to its normal temperature
compensated operating voltage and the battery discharge test is interrupted.
The CAB then responds to the alarm signal as normal.
The dip switches SW 4 inhibit or set periodicity (between 1 and 30 days) of
automated internal battery capacity test, (default setting is inhibited).
NOTE PIX0 site alarms are connected to the CAB through PL2 of
the alarms interface board. PL2 is disconnected and tied
back when supplied, if this functionality is required PL2
must be connected to the alarms interface board.
The battery capacity test discharges the internal batteries
to –44 V dc. If an external power supply failure occurs
immediately after the test, the battery back up duration is
reduced to approximately 3 minutes. The internal batteries
recharge to approximately 80% capacity in less than one
hour.
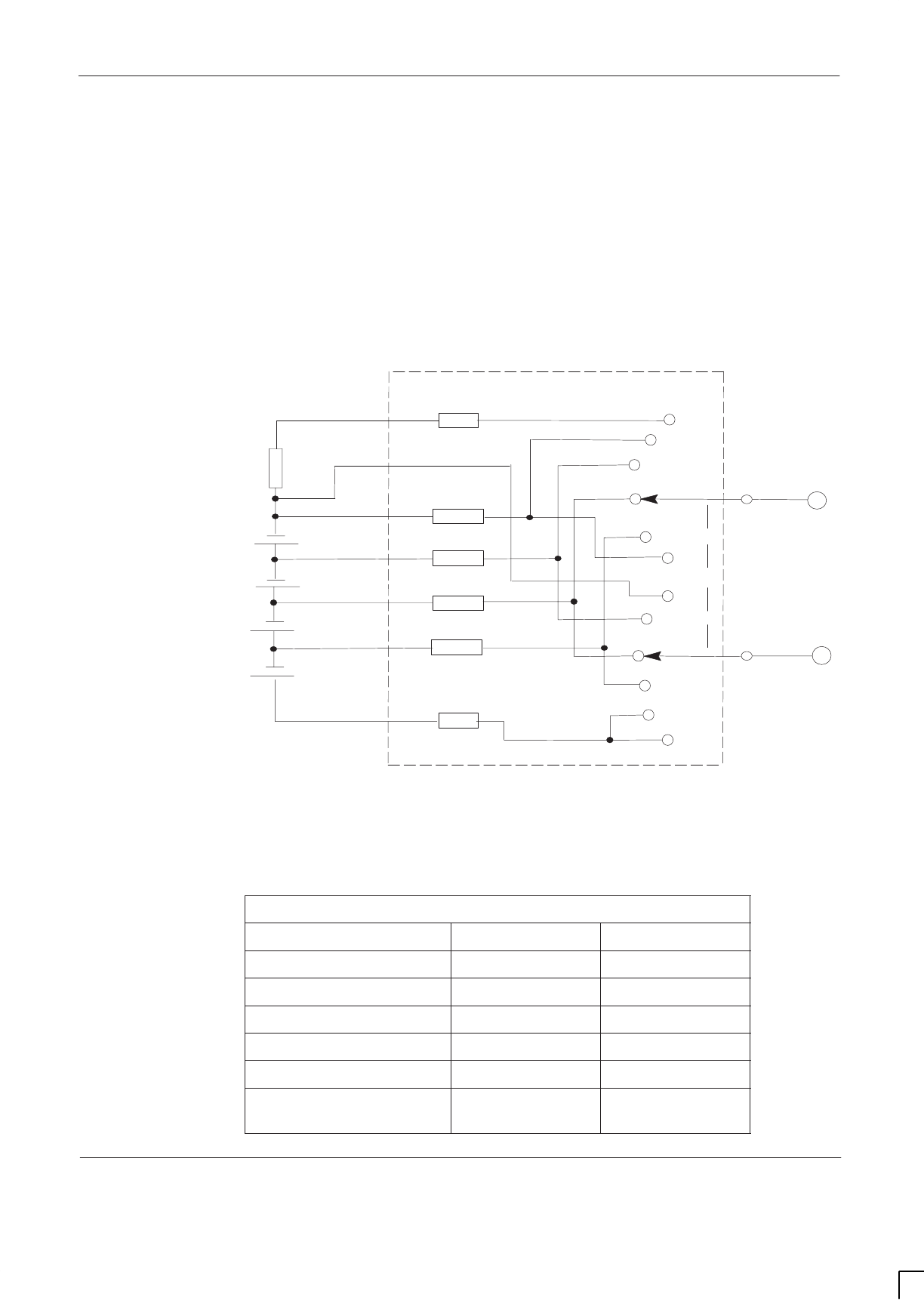
GSM-204-323 Control and alarm board (CAB)
31st Oct 01
Technical Description: Horizon
macro
outdoor
68P02902W02-A
CONTROLLED INTRODUCTION
Tech. 4–23
Battery selector
The battery selector switch connects two 4 mm DM sockets on the CAB front
panel to the internal batteries, to allow measurement of:
Total battery voltage.
Individual battery voltage.
Battery current, measured by millivolt equivalent (0.75 mV equals 1 A).
Figure 4-16 shows the battery selector test circuit.
5K1
5K1
5K1
5K1
5K1
5K1
1
+I
–I
C28
B28
f
a
a
b
c
d
e
b
c
d
e
DM
SOCKETS
BLUE
BLACK
0 V
–12 V
–24 V
–36 V
–48 V
f
CONTROL BOARD
2
A32
B31
A31
A23,24,25
B32
Figure 4-16 Diagram of the battery selector test circuit
Table 4-2 shows the expected DMM values for each position of the test switch.
Table 4-2 Battery selector switch test values
Test switch setting Reading Cell under test
a– 48 V dc All
b–12 V dc Cell 1
c–12 V dc Cell 2
d–12 V dc Cell 3
e–12 V dc Cell 4
fBattery charge
current All
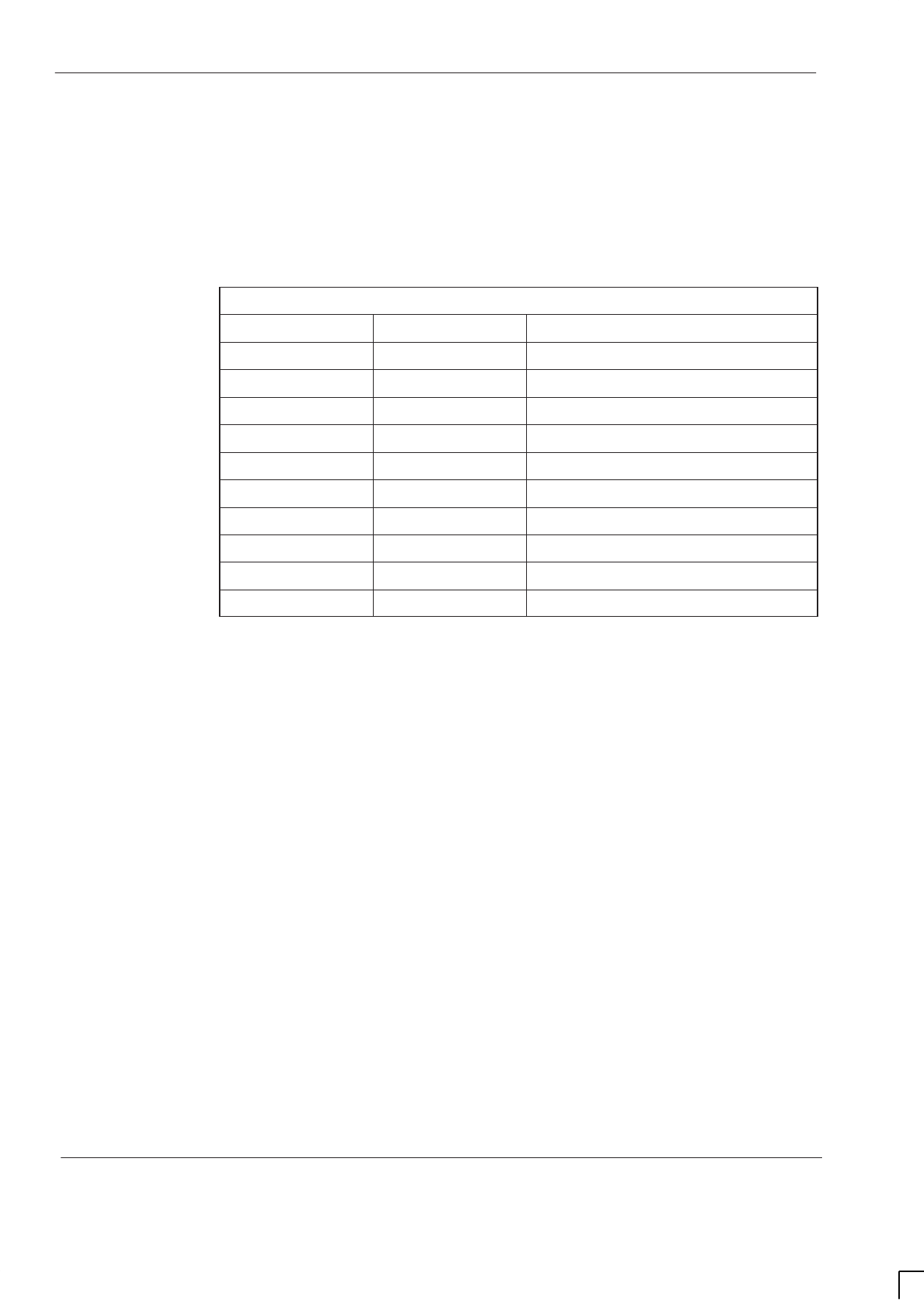
GSM-204-323
Control and alarm board (CAB)
31st Oct 01
Tech. 4–24
Technical Description: Horizon
macro
outdoor
CONTROLLED INTRODUCTION
68P02902W02-A
Debug
The CAB front panel LEDs can be remapped to indicate alarm status to assist in
fault finding, particularly before connection of the Horizon
macro
site to the
network. Operation of a dip switch (SW 4–5) and resetting the CAB causes the
front panel LEDs to illuminate when the alarm is clear.
The CAB front panel LEDs are remapped as shown in Table 4-3
Table 4-3 Remapping of CAB front panel LEDs
Front panel LED Colour Debug function
15 mins Green Mains fail
10 mins Green TOPSM output
5 mins Green TOPSM auxiliary voltage
RADIO Green Not used
COMMS Green Not used
CAB OT Red Cabinet over temperature
EXT CAB OT Red External cabinet over temperature
SMOKE Red Smoke alarm
EXT SMOKE ALM Red External smoke alarm
STATUS Green Status
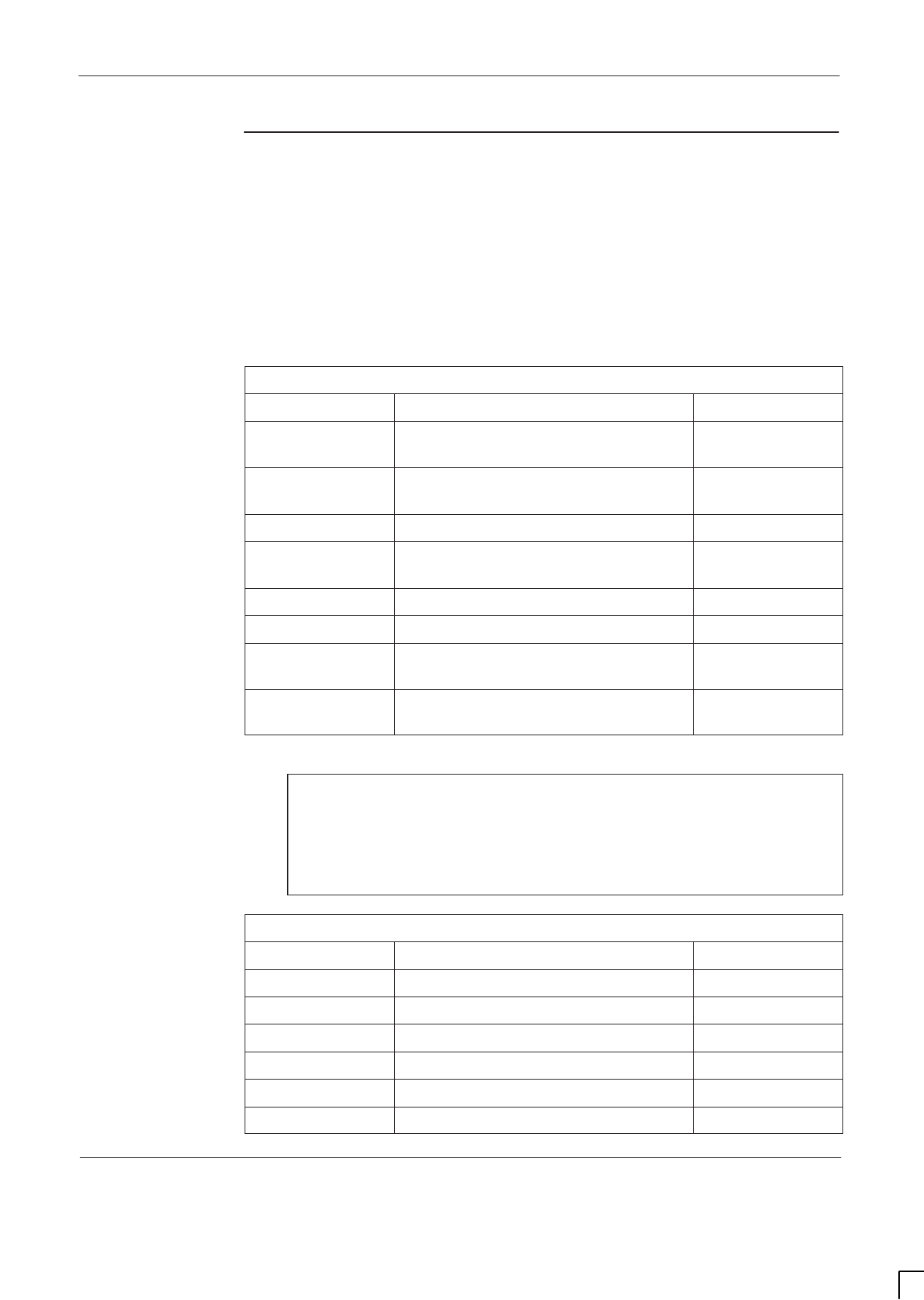
GSM-204-323 Control and alarm board (CAB)
31st Oct 01
Technical Description: Horizon
macro
outdoor
68P02902W02-A
CONTROLLED INTRODUCTION
Tech. 4–25
DIP switches
Two of the banks of DIP switches mounted on the CAB circuit board are used to
configure alarm board functions (SW2 and SW4). The location on the board and
exact appearance varies with manufacturer.
SW2 used to inhibit auxiliary equipment housing and optional smoke alarm
signals.
SW4 used to inhibit or set periodicity of automated internal battery
capacity test and to set the CAB into debug mode.
Table 4-4 shows the function of SW2 individual dip switches.
Table 4-4 SW2 DIP switch settings
Switch No Function Position
1Auxiliary equipment housing over
temperature alarm ON to inhibit
2Auxiliary equipment housing over
temperature trip input ON to inhibit
3TMS 2 over temperature alarm ON to inhibit
4Auxiliary equipment housing door
alarm ON to inhibit
5TMS 2 fail alarm ON to inhibit
6BTS cabinet smoke alarm ON to inhibit
7Auxiliary equipment housing smoke
alarm ON to inhibit
8Internal/external battery temperature
sensing ON for internal
Table 4-5 shows the function of SW4 individual dip switches.
NOTE If more than one switch is selected, delay timing is
cumulative up to a maximum of 30 days. If no switches are
set, the delay period is 1 day.
By default, the CAB is configured with automated battery
capacity test inhibited and the delay DIP switches set to
30 days.
Table 4-5 SW4 DIP switch settings
Switch No Function Position
12 day delay setting OFF to select
24 day delay setting OFF to select
38 day delay setting OFF to select
416 day delay setting OFF to select
5 Debug OFF to select
6Automated battery capacity test inhibit ON to select
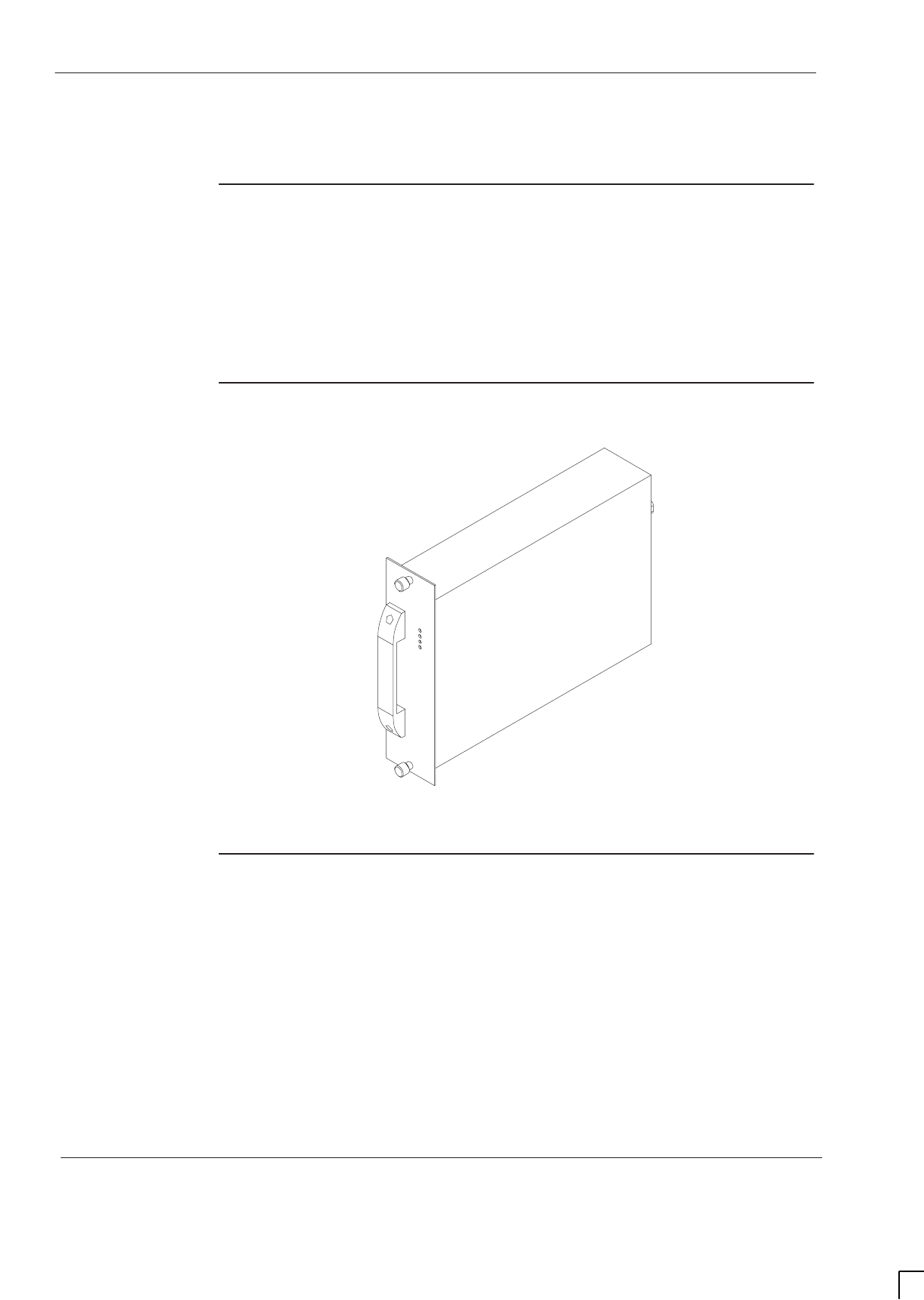
GSM-204-323
The outdoor power supply module (TOPSM)
31st Oct 01
Tech. 4–26
Technical Description: Horizon
macro
outdoor
CONTROLLED INTRODUCTION
68P02902W02-A
The outdoor power supply module (TOPSM)
TOPSM
overview
This section describes the TOPSM used in the Horizon
macro
outdoor cabinets.
Three TOPSMs provide adequate operating power for all the modules within the
base station and full battery charging (including external extended battery
backup). Under normal operating conditions, two TOPSMs provide sufficient
power to operate all BTS modules and trickle charge the batteries and the third
TOPSM then provides redundancy.
View of TOPSM
Figure 4-17 shows a view of the TOPSM.
Figure 4-17 The outdoor power supply module (TOPSM)
TOPSM
functional
description
The TOPSM system is a power factor-corrected, wide input, ac power supply
module. Each TOPSM is a switching type ac/dc power converter with the
following regulated dc output:
–55 V at 23.5 A (maximum output current).
1200 W (nominal).
The outputs of each TOPSM are connected in parallel by the power supply
cage. The TOPSMs in the system actively share the load.
The regulated dc output is fed through the multilayer busbar to the interface
panel and the dc circuit breaker panel to power the base station.
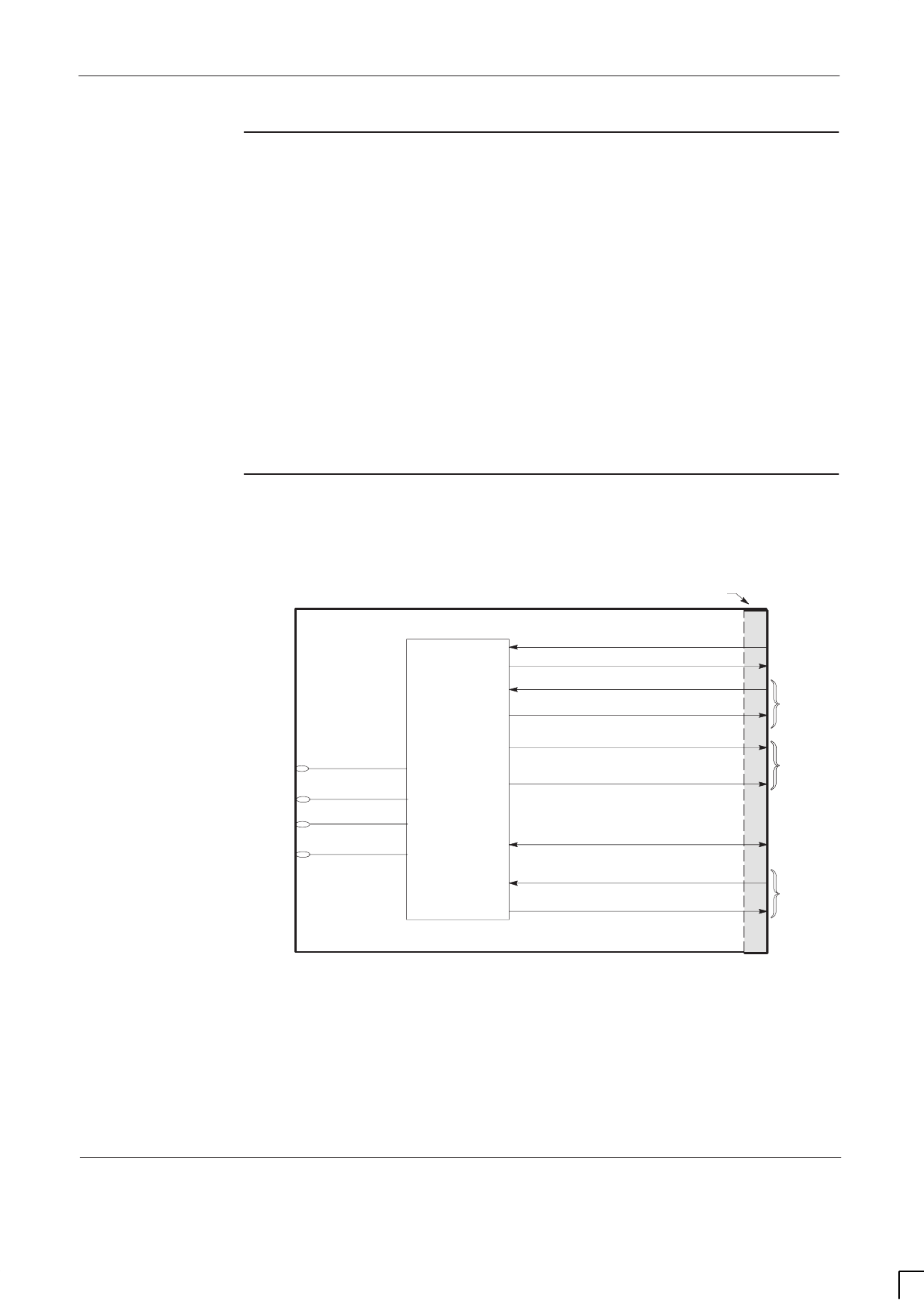
GSM-204-323 The outdoor power supply module (TOPSM)
31st Oct 01
Technical Description: Horizon
macro
outdoor
68P02902W02-A
CONTROLLED INTRODUCTION
Tech. 4–27
LED display
There are four LEDs mounted on the front of the TOPSM, which indicate the
following:
I/P HEALTHY (yellow) - lit when the input voltage is present and within
specified limits (88 to 264 V ac).
OVERVOLTAGE (red) - lit when the TOPSM has shut down due to an
output voltage in excess of –59.9 V dc.
OVERCURRENT (red) - lit when the TOPSM is in current limit and
delivering a current in the range 22 A to 24 A. The LED is normally unlit,
but when lit does not necessarily indicate the existence of a fault as this
may be due to recharging of the batteries after an ac supply interruption.
O/P HEALTHY (green) - lit when output voltage is present and within
specified limits (–39 to –59.9 V dc).
Functional
diagram
Figure 4-18 shows a functional representation of the outdoor power supply
module (TOPSM).
I/P HEALTHY
OUTPUT FAIL
INPUT FAIL
BACKPLANE CONNECTOR
RED
LED
YELLOW
LED
VIN (88 V to 264 V)
POWER
CONVERTER
AND
SYSTEM
MONITOR
VOLTAGE TRIM
VOUT (–55 V)
ENABLE IN
O/P HEALTHY
OVERVOLTAGE
I/LIMIT
RED
LED
GREEN
LED
CONTROL
AND
ALARM
CURRENT SHARE OTHER
TOPSMs
AUXILIARY SUPPLY (12V)
CONTROL
AND
ALARM
ENABLE OUT
RELAY 1 ON
RECTIFIER
PCB
Figure 4-18 Functional diagram of TOPSM
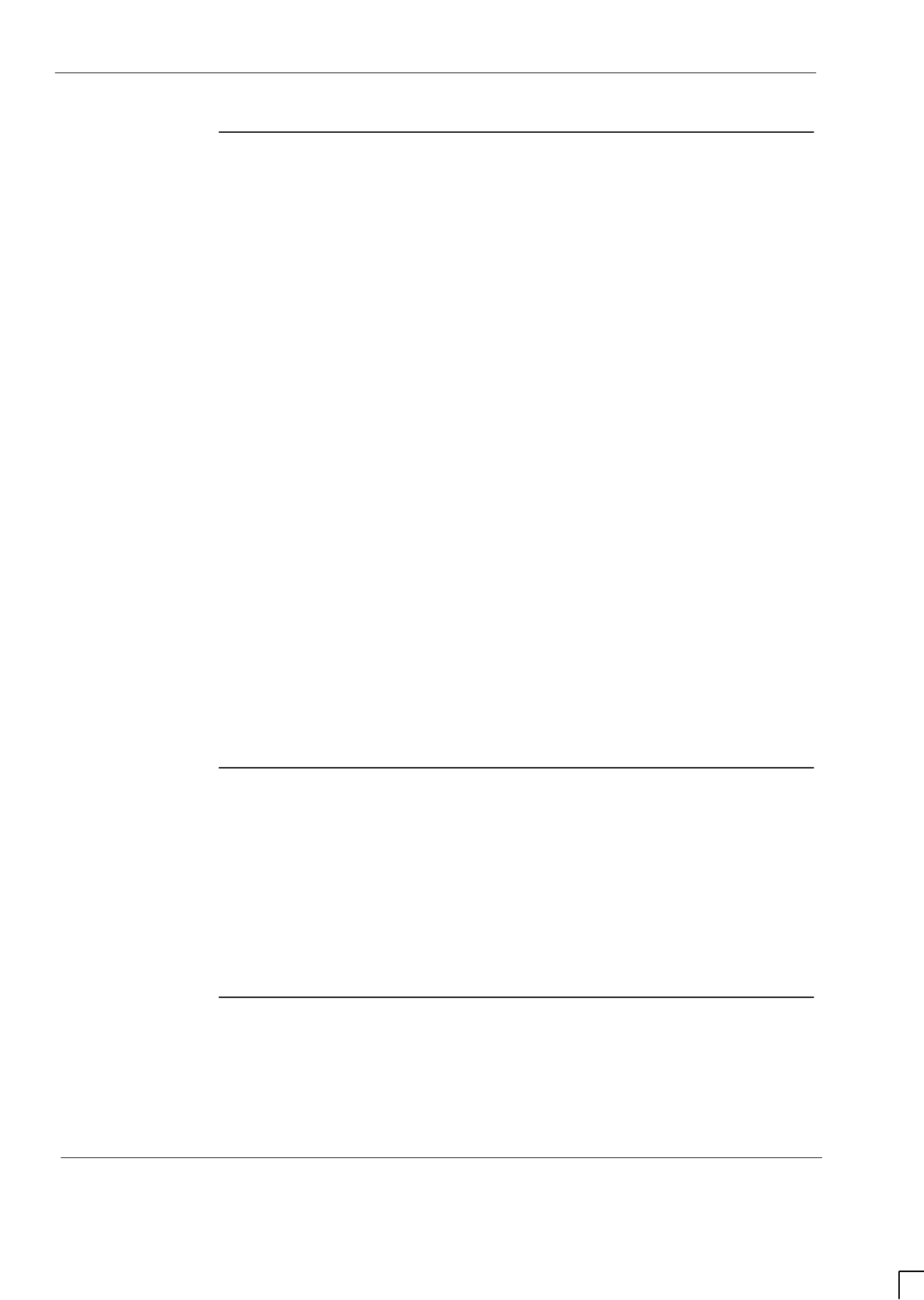
GSM-204-323
The outdoor power supply module (TOPSM)
31st Oct 01
Tech. 4–28
Technical Description: Horizon
macro
outdoor
CONTROLLED INTRODUCTION
68P02902W02-A
Monitoring
Internal
Internal TOPSM circuits monitor for the following:
–55 V output voltage regulation.
The –55 V output is also regulated to provide temperature compensation
for the float charging of the internal batteries (battery backup) in the range
–52.88 V at 40 C to –56.72 V at 0 C.
Overvoltage protection – provides shutdown if the output voltage exceeds
–59.9 V.
Overcurrent protection – provides constant current limiting at 22 to 24 A,
unless output voltage drops below 39.6 V, when the output current will fold
back to between 3 and 8 A.
Enable control of TOPSM from the control and alarm board.
External
The control and alarm board monitors common alarm signals generated by the
changeover relays fitted within the TOPSMs. The possible alarms are:
Mains input fail - This alarm is active if all the fitted TOPSMs lose their
input supply or the input drops below their operating minimum value.
DC output fail - This alarm is active if the output from one or more fitted
TOPSMs fails, or goes outside the preset tolerance level.
Alarm conditions generated by the TOPSM may be detected by one of the red
LEDs being lit, or by the dc output fail and mains input healthy LEDs being unlit.
Protection
circuits
Activation of the protection circuits causes the TOPSM to shut down. During a
shutdown, the output circuits of the malfunctioning TOPSM are isolated and its
output healthy LED is switched off. The malfunctioning TOPSM informs the
control and alarm board of the shutdown condition. An alarm signal is also
activated and sent to the control and alarm board if all TOPSMs detect loss of
ac input voltage. After an alarm condition has ceased, normal TOPSM operation
is automatically restored.
Thermal
protection
The TOPSM is provided with additional internal thermal protection. If the
ambient temperature of the TOPSM exceeds a safe level then it shuts down,
causing an alarm message to be sent to the control and alarm board. Normal
TOPSM operation resumes after the temperature returns to a safe level.
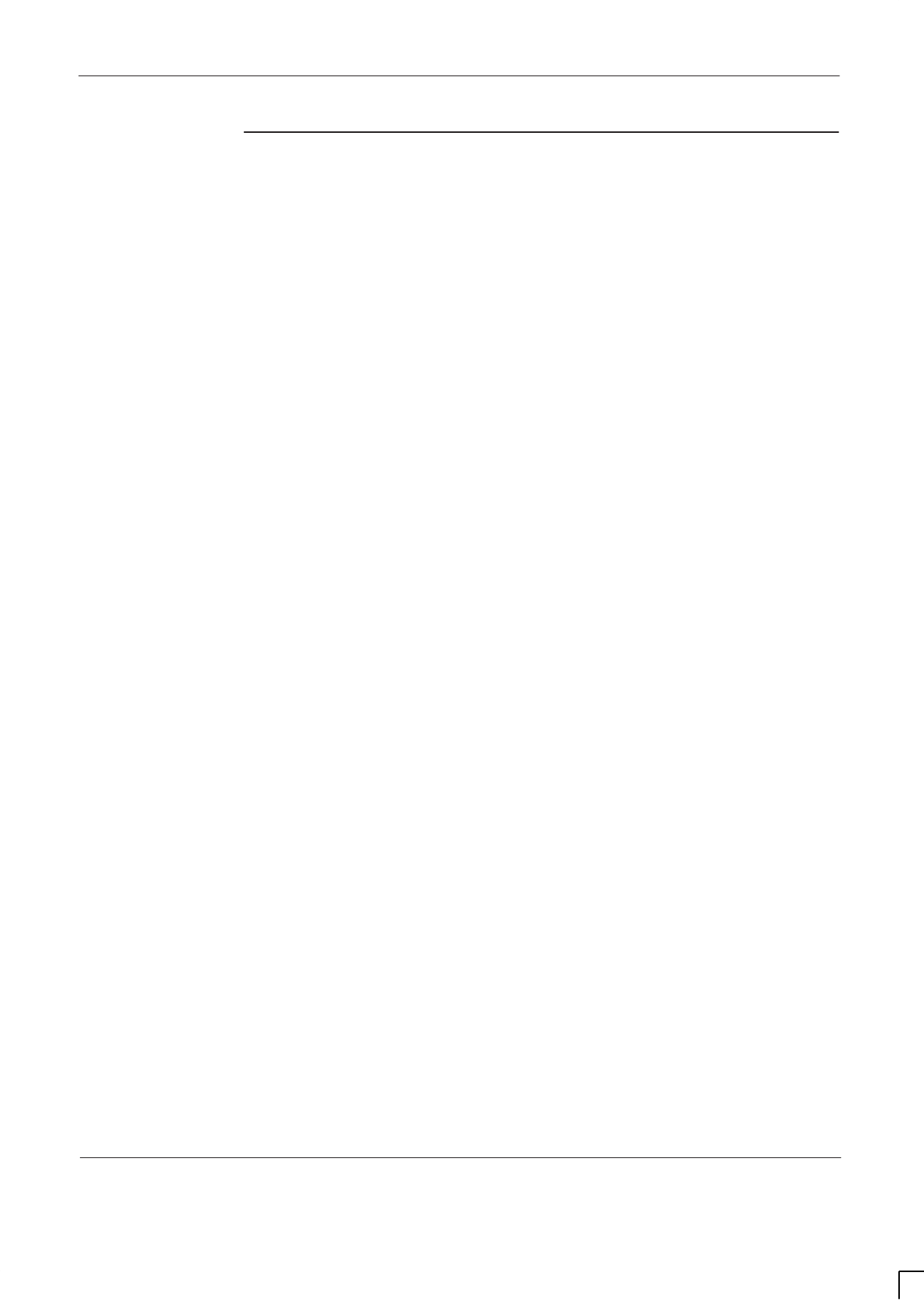
GSM-204-323 The outdoor power supply module (TOPSM)
31st Oct 01
Technical Description: Horizon
macro
outdoor
68P02902W02-A
CONTROLLED INTRODUCTION
Tech. 4–29
Control and
alarm signals
The following signals are associated with TOPSM control and alarms:
Enable out
An independent –55 V output from each TOPSM commoned together and
connected to the normally closed contacts of the disable relay (relay 1), on
the backplane of the power supply unit cage.
Enable in
This signal, fed from the normally closed contacts of the disable relay
(relay 1) on the backplane of the power supply unit cage, enables the
TOPSM output (the relay is operated by the the control and alarm board
under fault conditions).
Voltage trim
A variable voltage signal, generated by the control and alarm board, used
to regulate the TOPSM output in order to produce a temperature
compensated battery charging voltage, to ensure that the internal or
external batteries are not overcharged.
Current share
A signal representing the average current for the total system. Each
TOPSM compares its output current with the average current and adjusts
its output voltage so as to equalize its output current with the average
system current.
Auxiliary supply
A 12 V supply independent of the TOPSM output, but referenced to it,
used to power the control and alarm board circuitry when the TOPSM
output is inhibited.
Input healthy
The normally open contact of the isolated changeover relay used to
indicate that the input is within specification.
Output healthy
The normally closed contact of the isolated changeover relay used to
indicate that the output is within specification.
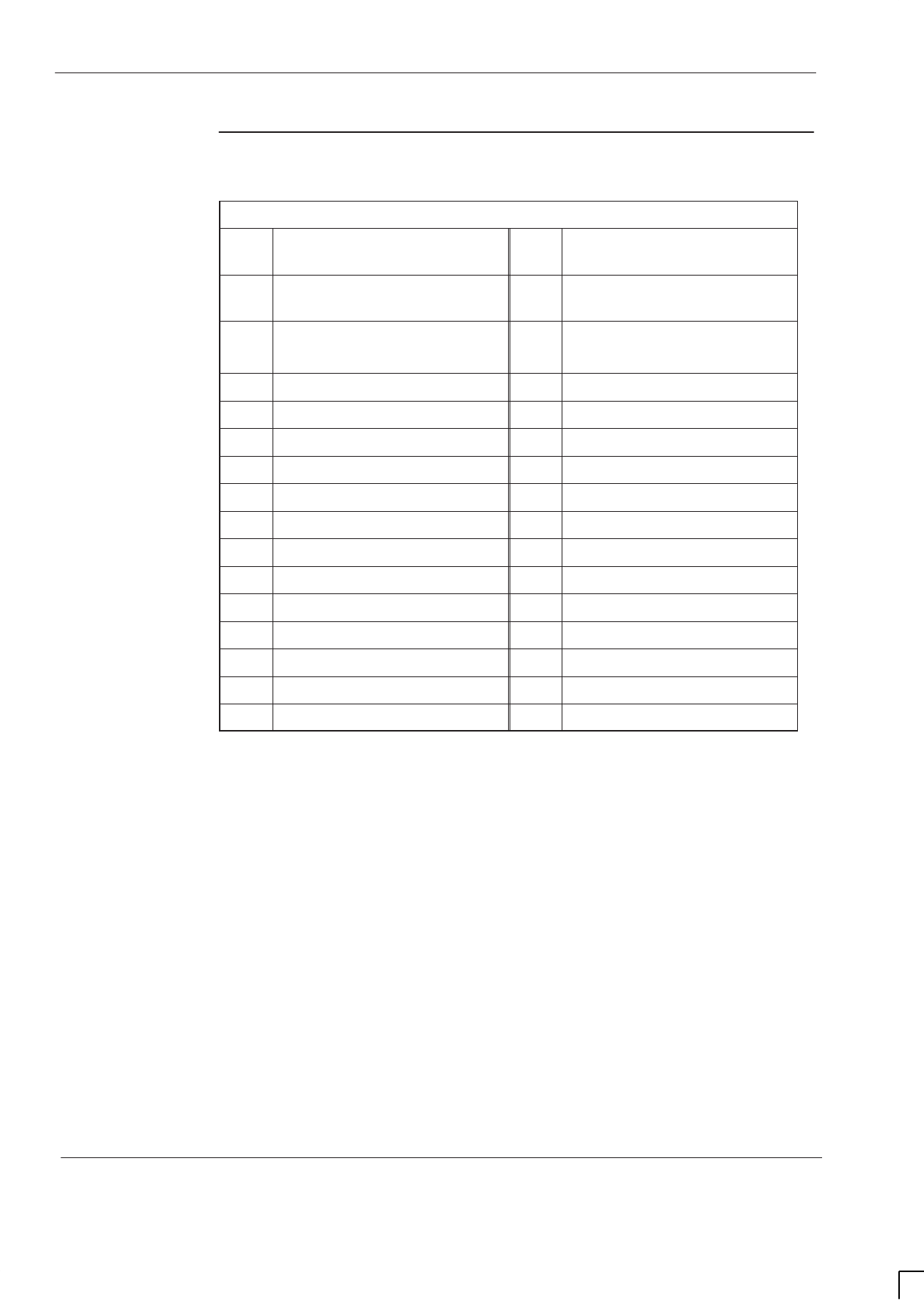
GSM-204-323
The outdoor power supply module (TOPSM)
31st Oct 01
Tech. 4–30
Technical Description: Horizon
macro
outdoor
CONTROLLED INTRODUCTION
68P02902W02-A
TOPSM pinouts
Table 4-6 lists the TOPSM pinout connections.
Table 4-6 TOPSM pin connections (29-way Elcon)
Pin
No Signal/Description Pin
No Signal/Description
1+0 V output 16 Relay N/C
(TOPSM output healthy)
2–55 V output 17 Relay N/O
(TOPSM mains input healthy)
3Not connected 18 Not connected
4Not connected 19 Not connected
5Voltage trim 20 Not connected
6Link enable input 21 Opto input
7Not connected 22 Forced current share
8Not connected 23 Not connected
9Link enable output 24 Not connected
10 Not connected 25 Opto common
11 Not connected 26 Earth
12 Not connected 27 Not connected
13 +12 V auxiliary supply 28 AC input (neutral)
14 Not connected 29 AC input (live)
15 Relay common
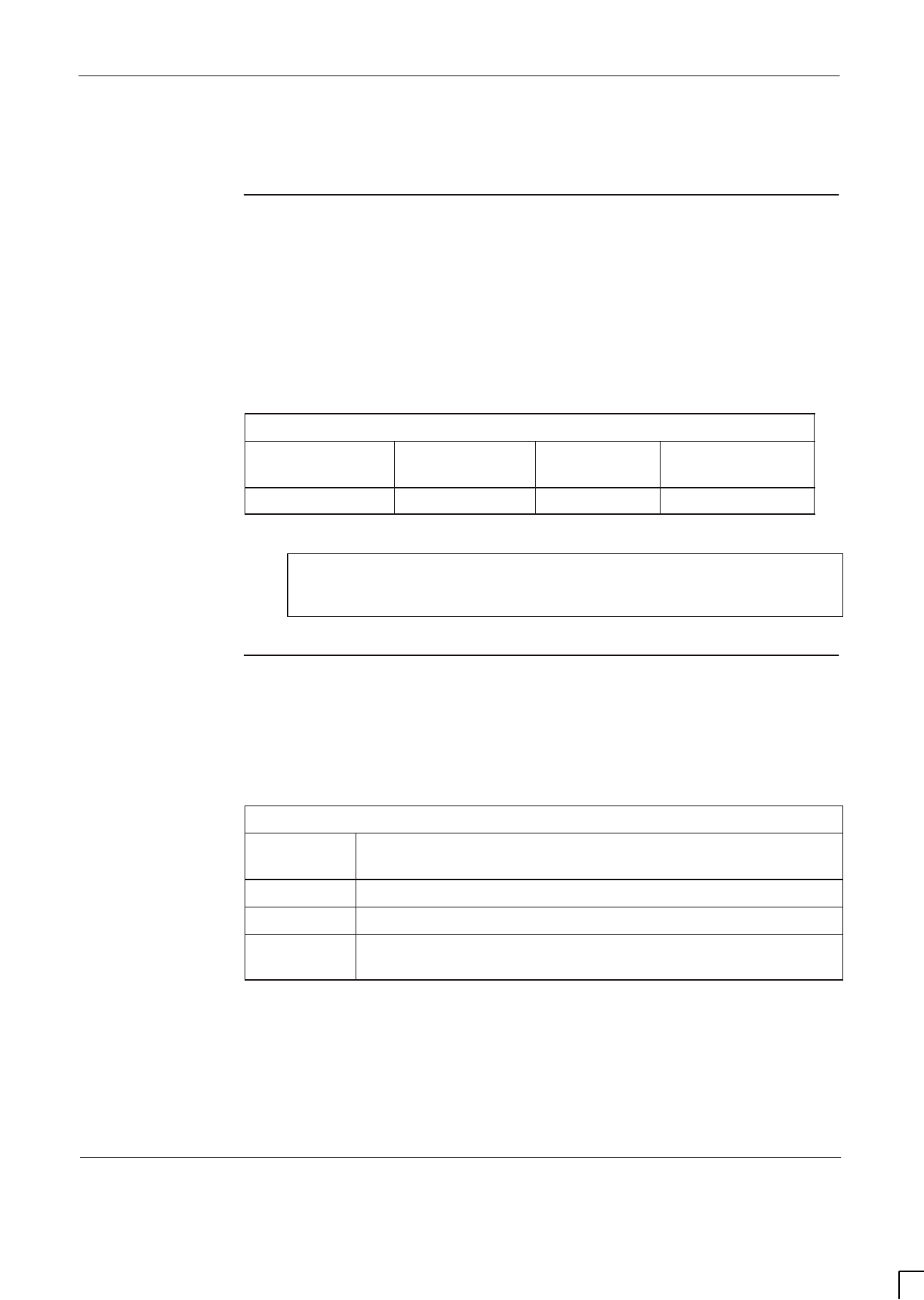
GSM-204-323 Power supply module (PSM)
31st Oct 01
Technical Description: Horizon
macro
outdoor
68P02902W02-A
CONTROLLED INTRODUCTION
Tech. 4–31
Power supply module (PSM)
PSM overview
The PSM is a dc to dc converter, providing a stabilized +27 V output to power all
the main cage equipment.
Only one type of PSM is used in the Horizon
macro
outdoor:
Nominal –48 V (positive earth).
The PSMs are fed from a backplane connector, and use pulse width modulation
to generate output supply. A front panel switch (shown in Figure 4-19) disables
the output, reducing the input current as shown in Table 4-7.
Table 4-7 Input currents for power supply module
Type of PSM Output voltage
full load Input current
full load Input load when
output switch off
–48 V nominal dc +27 V 18 A 0.5 A
NOTE There are several manufacturers of the PSMs. Each is
fully compatible with the same type of PSM of a different
manufacturer.
PSM location
and redundancy
The PSMs are located above the digital cage and circuit breaker module. There
are three slots, two for maximum main cage configuration and one for
redundancy. Table 4-8 shows the recommended number of PSMs for different
operational configurations.
Table 4-8 PSM operational configurations
Number of
PSMs fitted Maximum load capability
1Complete operation of cabinet for up to three CTUs.
2Complete operation of cabinet for up to six CTUs.
3Redundancy and power load sharing (further enhancing
reliability by reducing temperature of operation).
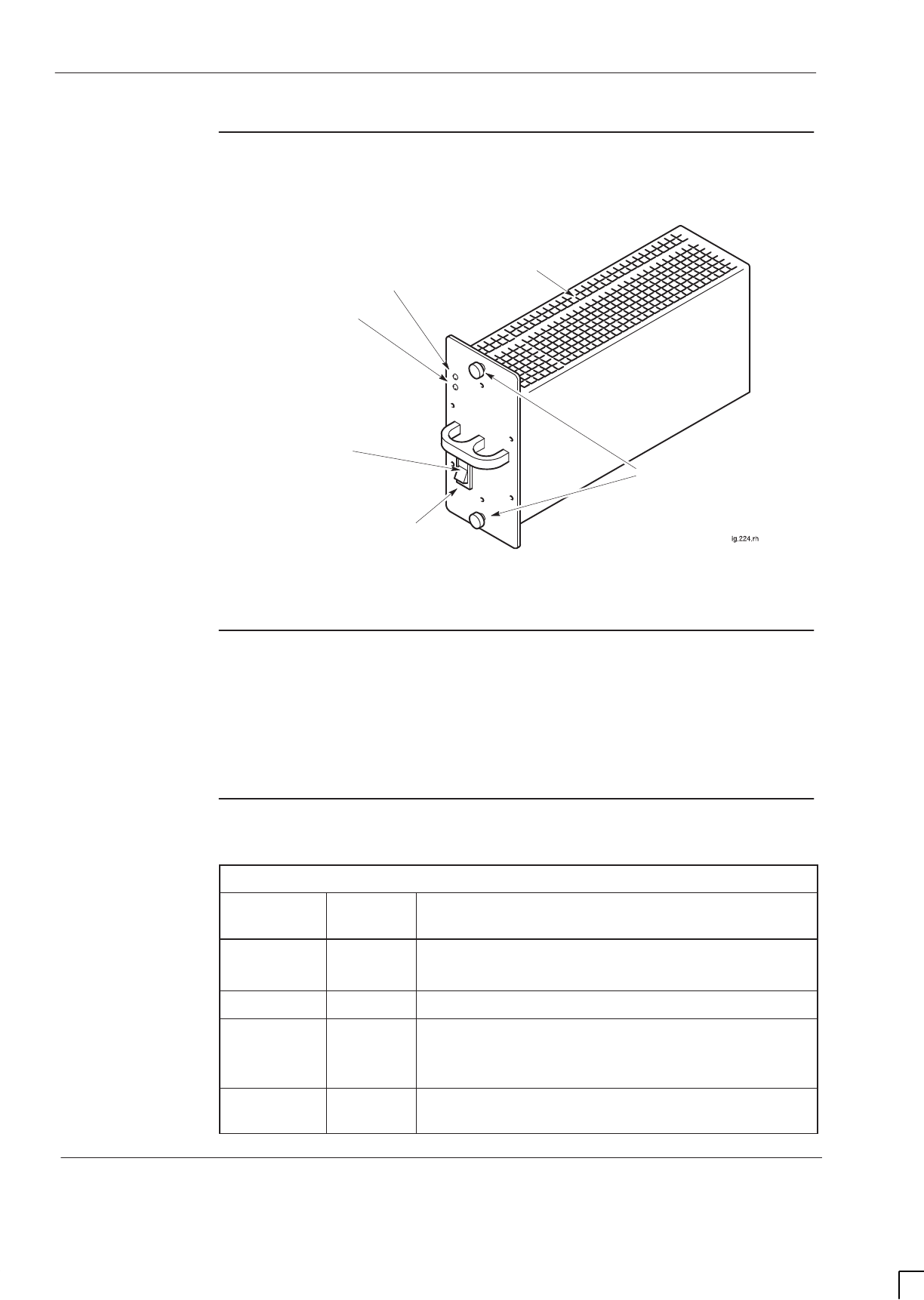
GSM-204-323
Power supply module (PSM)
31st Oct 01
Tech. 4–32
Technical Description: Horizon
macro
outdoor
CONTROLLED INTRODUCTION
68P02902W02-A
PSM module
view
Figure 4-19 shows a view of the PSM with LEDs identified.
PSM FRONT PANEL
AIR VENTS ON
ENTIRE TOP AND
BOTTOM PANELS
GREEN LED
ACTIVE
RED LED
ALARM
OUTPUT DISABLE
SWITCH
M4 MODULE ATTACHMENT
SCREWS
Figure 4-19 View of PSM
PSM alarms
There are three alarms for each PSM, indicated by LEDs (see Table 4-9):
Output fail.
Input fail.
Over temperature.
PSM LEDs
The PSM LEDs function with the properties shown in Table 4-9.
Table 4-9 Power supply module LEDs function
Green LED
ACTIVE Red LED
ALARM Indication
OFF OFF 1. Cabinet power supply off, or
2. Module not connected.
ON OFF Normal operation.
OFF ON 1. Output disable switch off, or
2. Alarm condition with module unable to supply
power.
ON ON Internal problem (such as over temperature), but
still able to maintain supply.
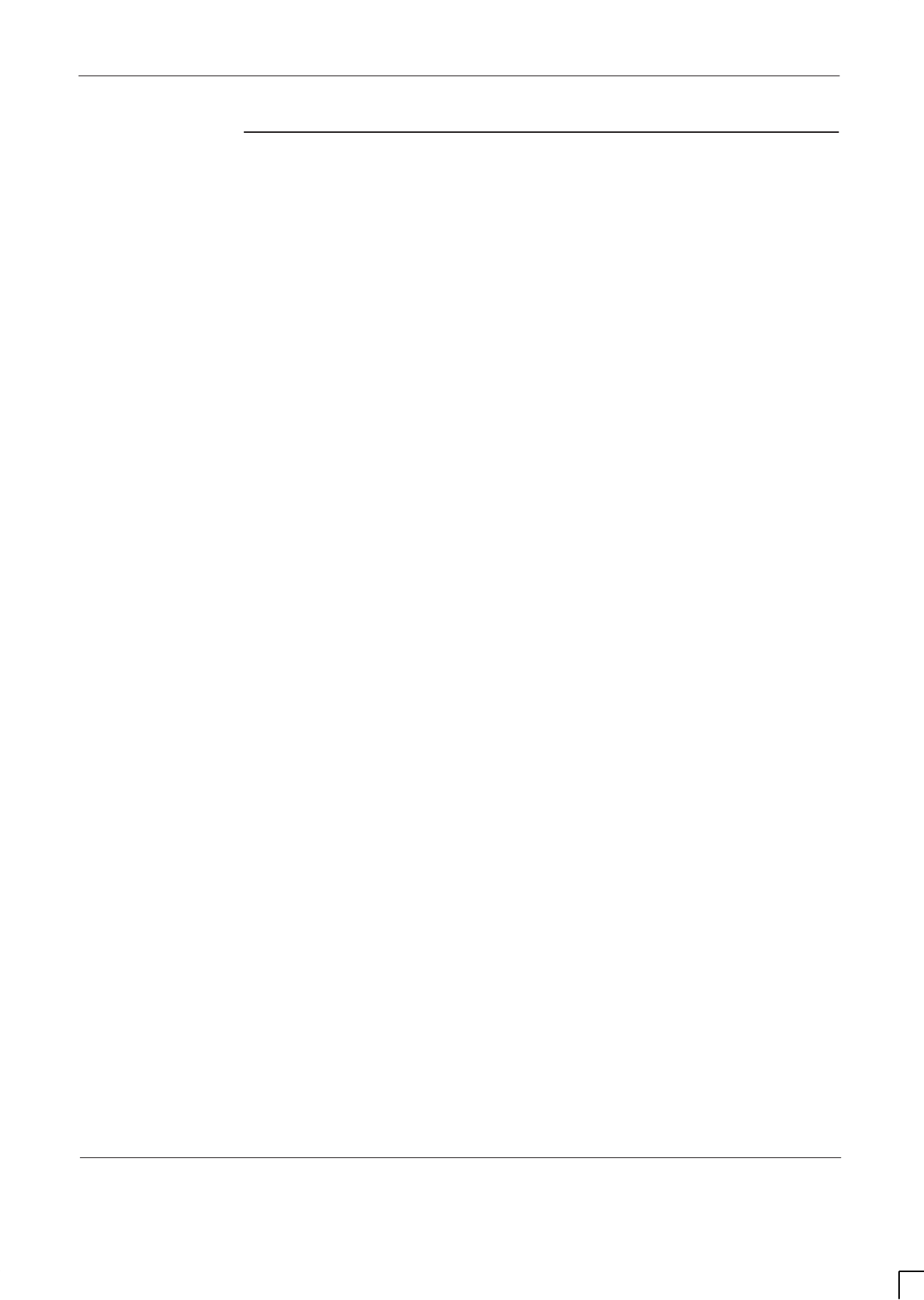
GSM-204-323 Power supply module (PSM)
31st Oct 01
Technical Description: Horizon
macro
outdoor
68P02902W02-A
CONTROLLED INTRODUCTION
Tech. 4–33
PSM backplane
protection
If a power track on the backplane is broken or short-circuited, the PSM detects
the fault and shuts down to prevent further damage.
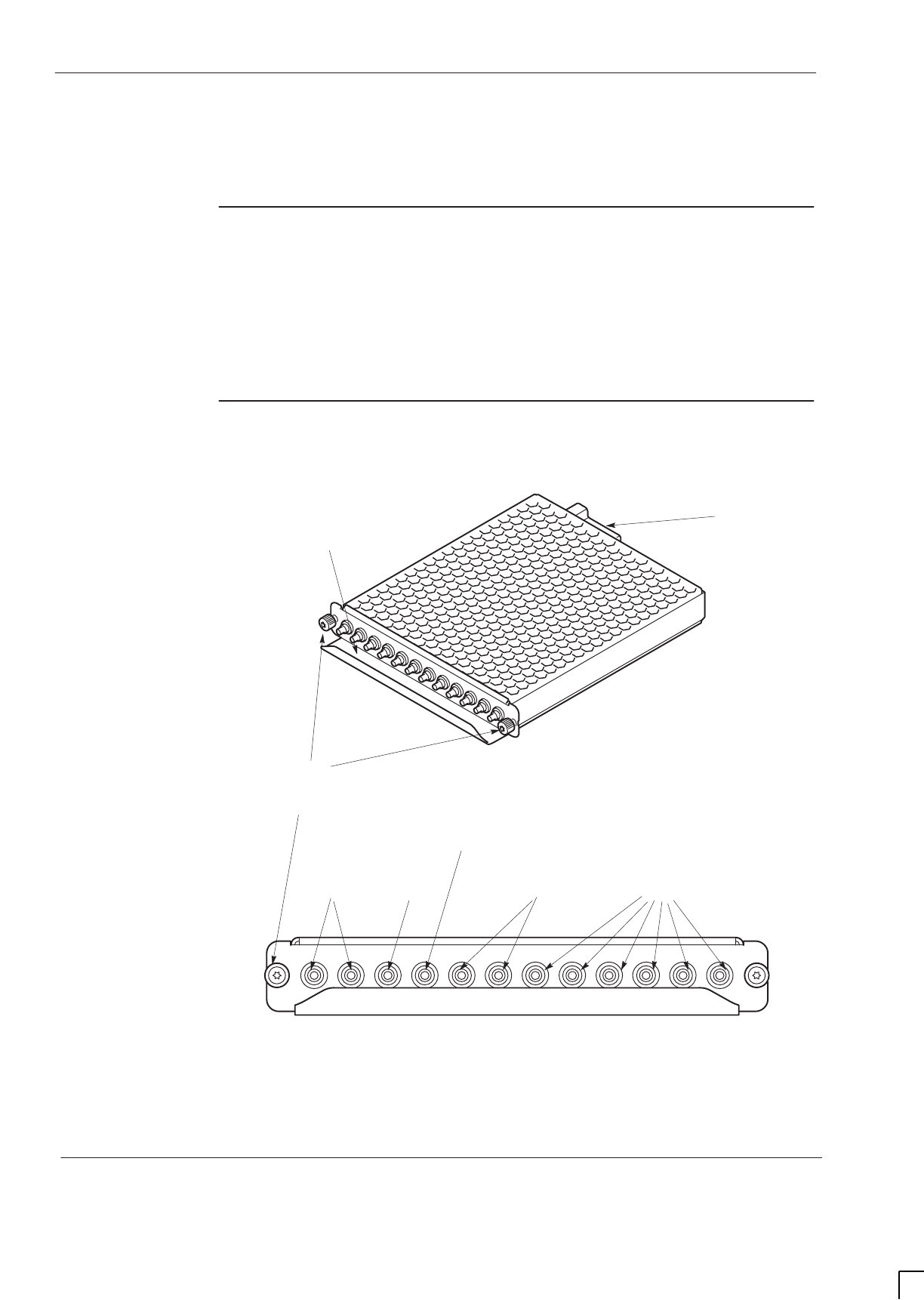
GSM-204-323
Circuit breaker module (CBM)
31st Oct 01
Tech. 4–34
Technical Description: Horizon
macro
outdoor
CONTROLLED INTRODUCTION
68P02902W02-A
Circuit breaker module (CBM)
CBM overview
The CBM provides circuit protection and manual isolation for the CTUs, SURF
and BPSMs. The CBM is located above the digital module shelf and below the
PSMs. The honeycomb casing permits cabinet ventilation through the module.
The CBM is connected to the backplane, providing isolator switches and
overload protection for equipment indicated on its front panel (see Figure 4-20).
View of the CBM
Figure 4-20 shows views of the CBM with circuit breaker buttons identified.
FRONT VIEW
BACKPLANE CONNECTOR
M4 MODULE ATTACHMENT
SCREWS
HANDLE-BAFFLE
ig.281.rh
6 CTUs (0 TO 5)
15 A2 A4 A
7 A
NOT USED SURF
NOT USED
BPSMs (A AND B)
7 A
Figure 4-20 Views of CBM with circuit breaker buttons identified
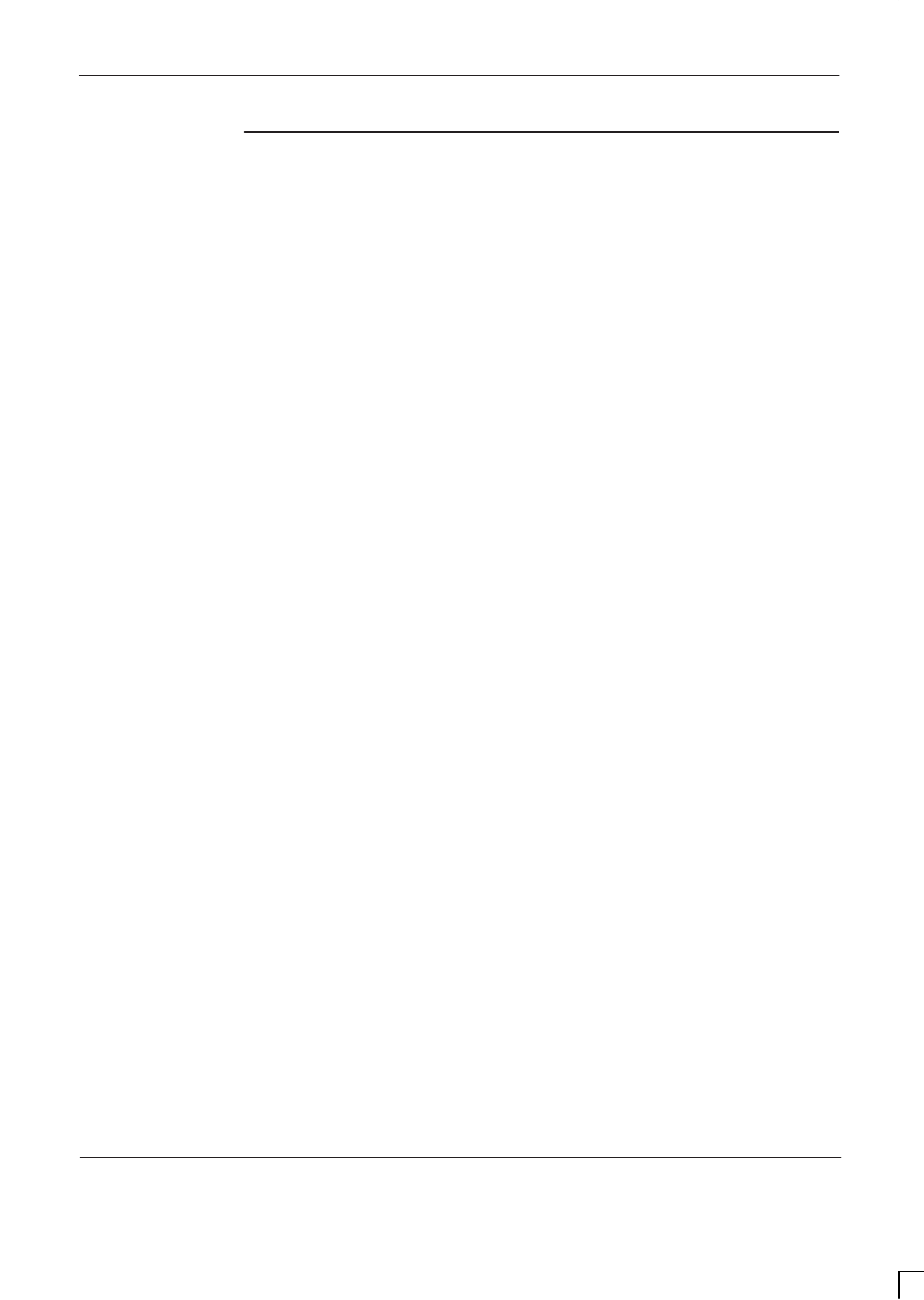
GSM-204-323 Circuit breaker module (CBM)
31st Oct 01
Technical Description: Horizon
macro
outdoor
68P02902W02-A
CONTROLLED INTRODUCTION
Tech. 4–35
Operation of the
CBM
Power for each module is supplied via the appropriate circuit breaker switch.
Overload of any circuit results in appropriate front panel circuit breaker button
tripping to the off (out) position. The button can be pressed to the on (in)
position when the overload problem has been corrected.
CTUs, BPSMs, and the SURF can be isolated by pressing and releasing the
appropriate button to the off (out) position. Power is restored by pushing the
appropriate button to the on (in) position.
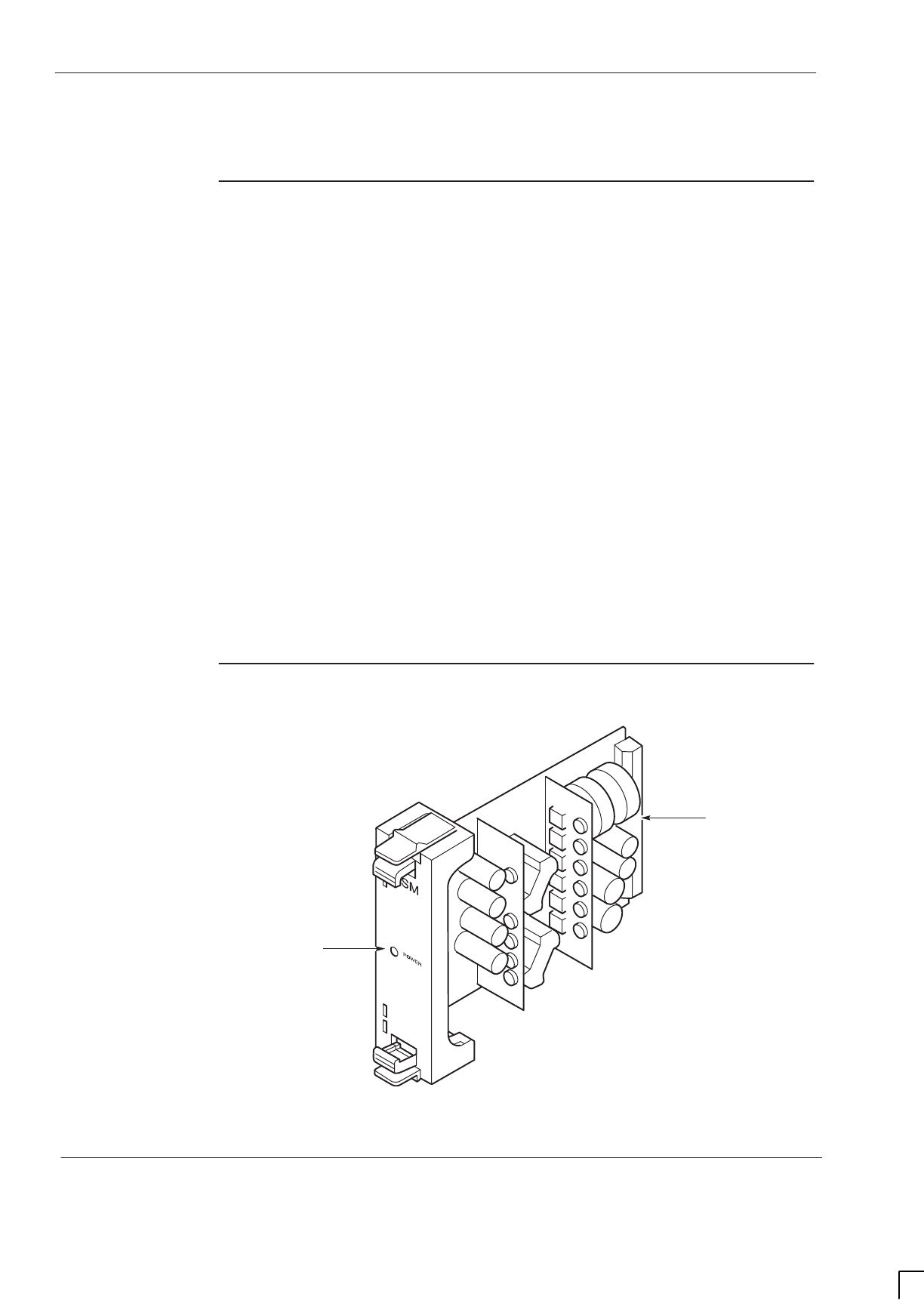
GSM-204-323
MicroBCU power supply module (BPSM)
31st Oct 01
Tech. 4–36
Technical Description: Horizon
macro
outdoor
CONTROLLED INTRODUCTION
68P02902W02-A
MicroBCU power supply module (BPSM)
Introduction to
the BPSM
This section describes the BCU power supply module (BPSM). The BPSM,
located in the digital module shelf of the main cage, supplies regulated dc power
to the digital modules.
A single master BPSM mounted in the lower half of the digital module shelf can
provide sufficient power for:
One MCUF.
One FMUX.
Two NIUs.
The alarm module.
An optional second BPSM can be fitted in the upper half of the digital module
shelf to supply any or all of the following:
Backup power to the alarm module, which is the only digital module
supplied by both BPSMs (for redundancy).
Optional redundant MCUF and associated FMUX.
Power for up to two additional NIUs.
During normal operation, with all the outputs within their regulation limits, a
green LED located on the front panel is illuminated. No alarms are generated
by the BPSM.
BPSM diagram
Figure 4-21 shows a BPSM.
ig.274.rh
BACKPLANE
CONNECTOR
GREEN LED
Figure 4-21 BPSM view
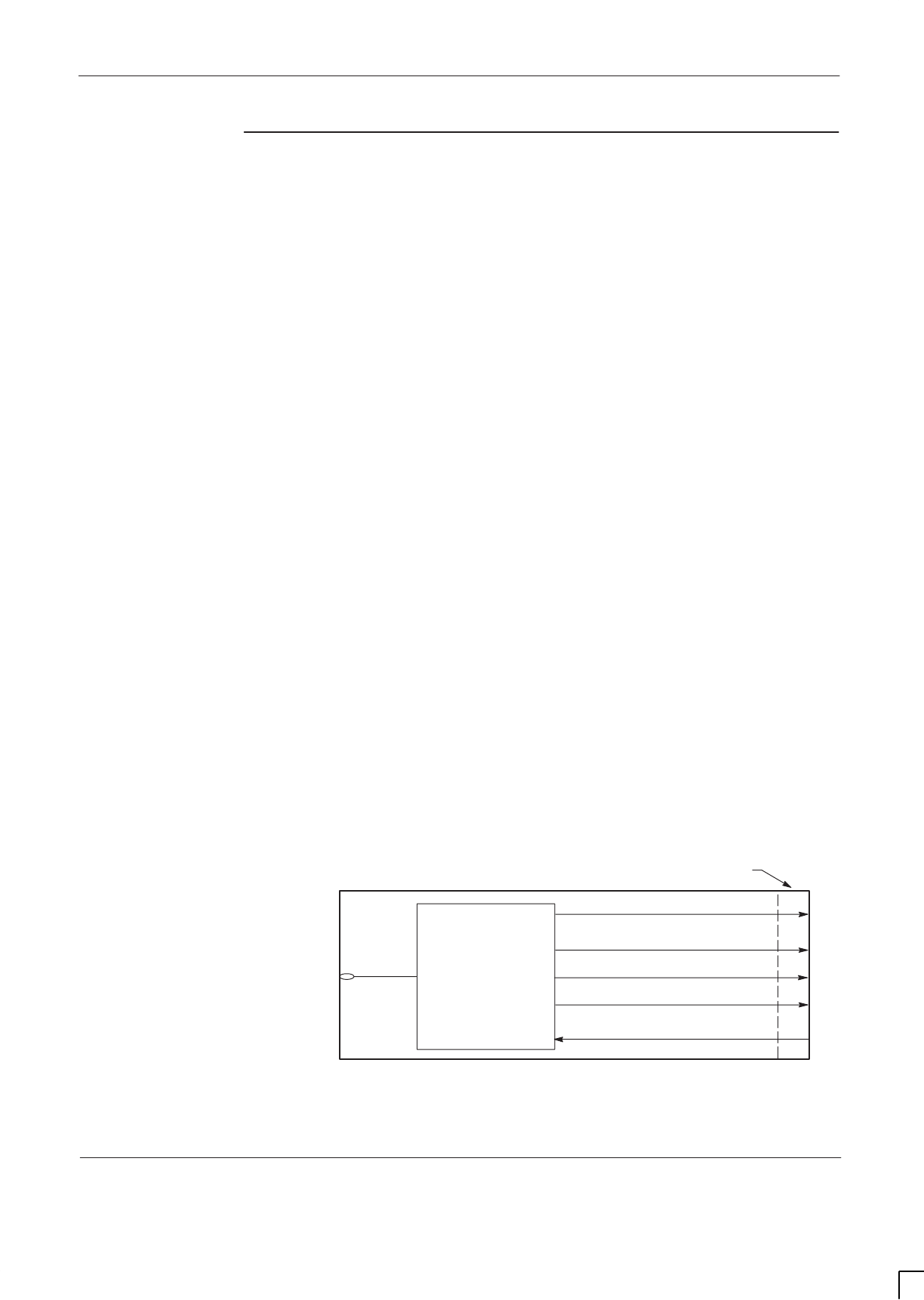
GSM-204-323 MicroBCU power supply module (BPSM)
31st Oct 01
Technical Description: Horizon
macro
outdoor
68P02902W02-A
CONTROLLED INTRODUCTION
Tech. 4–37
The BPSM is a switching type dc/dc power converter that converts the cabinet
+27 V dc power to the following regulated dc outputs:
+3.3 V ±% at 10 A (full load current)
+5 V ±2 % at 10 A (full load current).
+12 V ±5 % at 4 A (full load current).
–12 V ±5 % at 2 A (full load current).
Internal BPSM circuits monitor the +3.3 V, +5 V, +12 V and –12 V outputs for the
following purposes:
Output voltage regulation.
Overvoltage protection - provides shutdown if the output voltage exceeds
1.1 to 1.2 times the rated output.
Overcurrent protection - maximum output current has the following limits:
– 1.1 to 1.8 times full load rating of +3.3 V output.
– 1.1 to 1.8 times full load rating of +5 V output.
– 1.25 to 2 times full load rating of +12 V and –12 V outputs.
Circuit protection
Additional internal circuitry protects the BPSM:
Input dc reverse polarity protection, achieved by an input series diode.
Thermal protection by automatic BPSM shutdown. Normal BPSM
operation resumes after BPSM temperature returns to a safe level.
A 10 A fuse is located near the backplane connector.
LED display
An active (green) LED mounted on the front of the BPSM is lit when all output
voltages are present and within specified limits. A functional diagram is shown in
Figure 4-22.
ig.275.rh
Green
LED
Power converter and
system monitor
VOUT (+5 V)
VIN (+27 V)
VOUT (+3.3 V)
BACKPLANE CONNECTOR
VOUT (+12 V)
VOUT (–12 V)
Figure 4-22 Functional diagram of BPSM
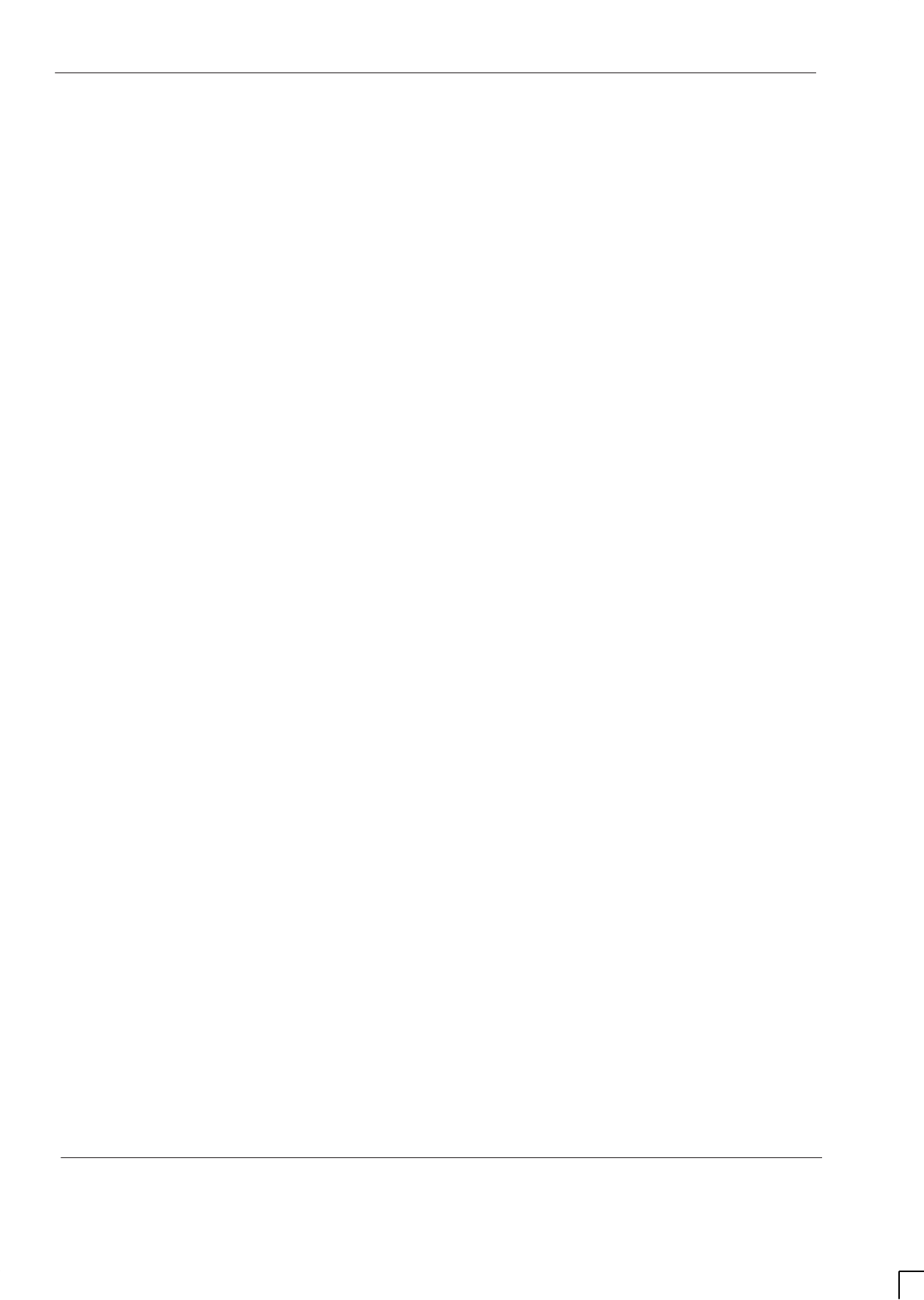
GSM-204-323
MicroBCU power supply module (BPSM)
31st Oct 01
Tech. 4–38
Technical Description: Horizon
macro
outdoor
CONTROLLED INTRODUCTION
68P02902W02-A
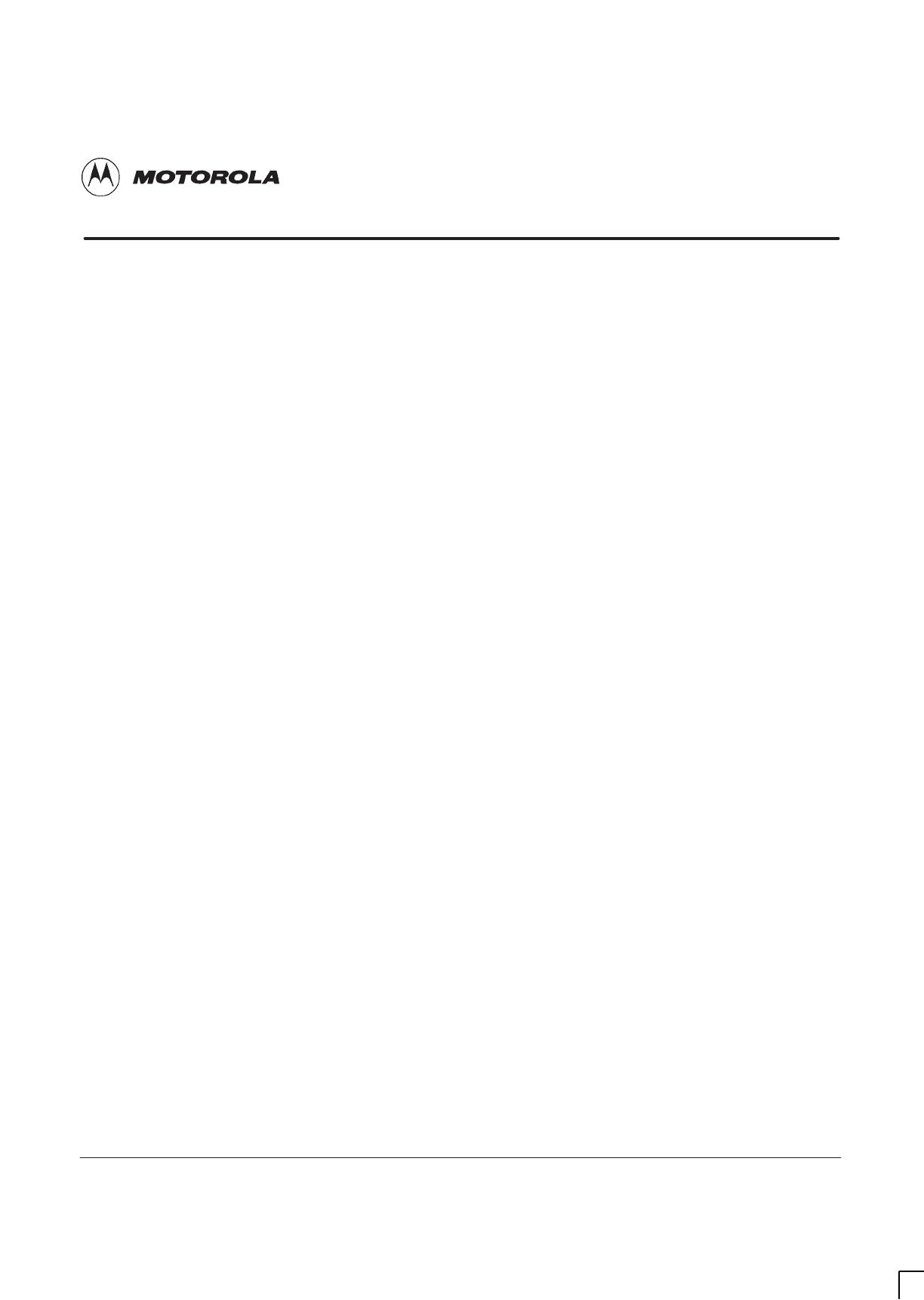
31st Oct 01
Technical Description: Horizon
macro
outdoor
68P02902W02-A
CONTROLLED INTRODUCTION
i
Chapter 5
RF modules
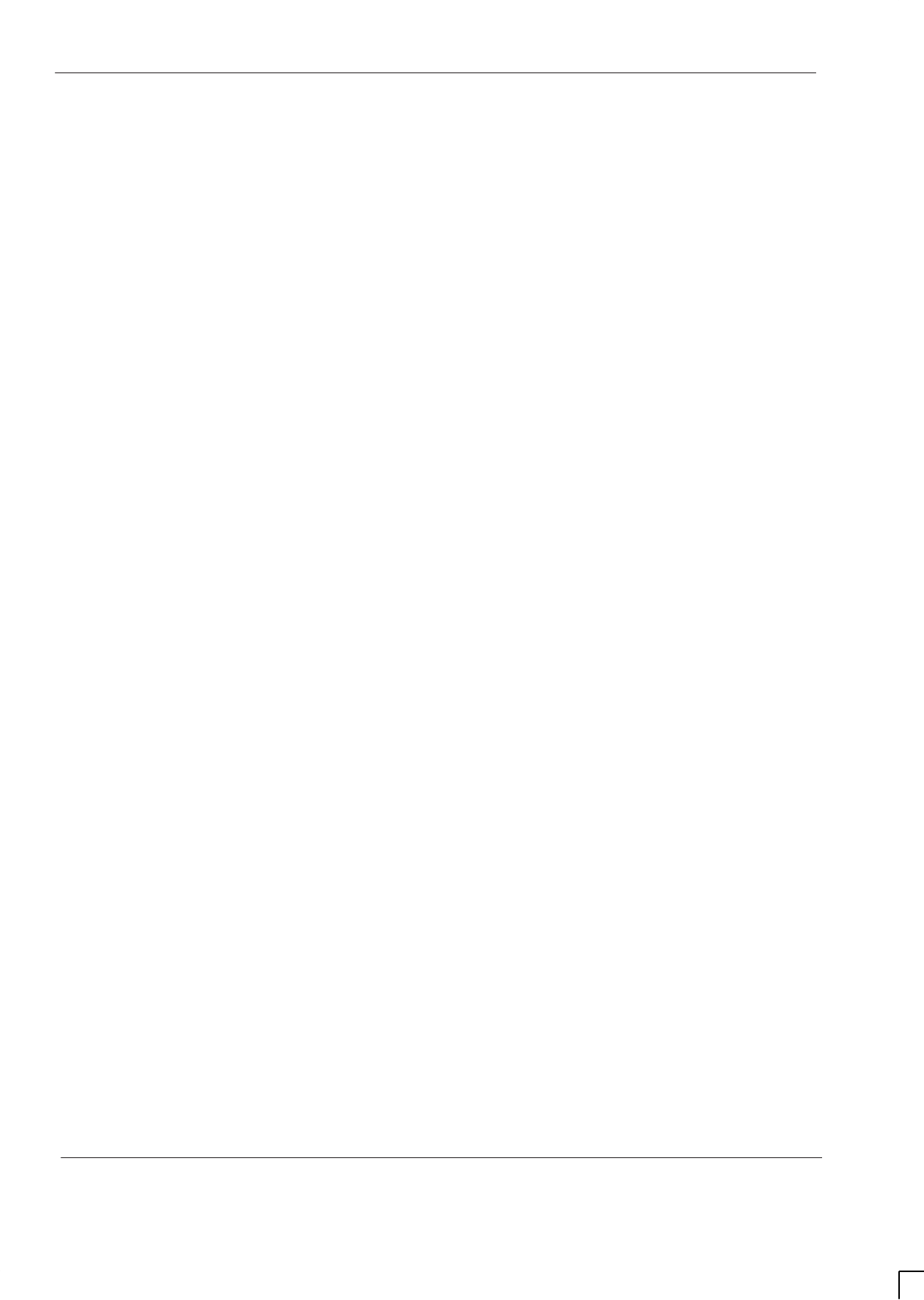
GSM-204-323
31st Oct 01
ii
Technical Description: Horizon
macro
outdoor
CONTROLLED INTRODUCTION
68P02902W02-A
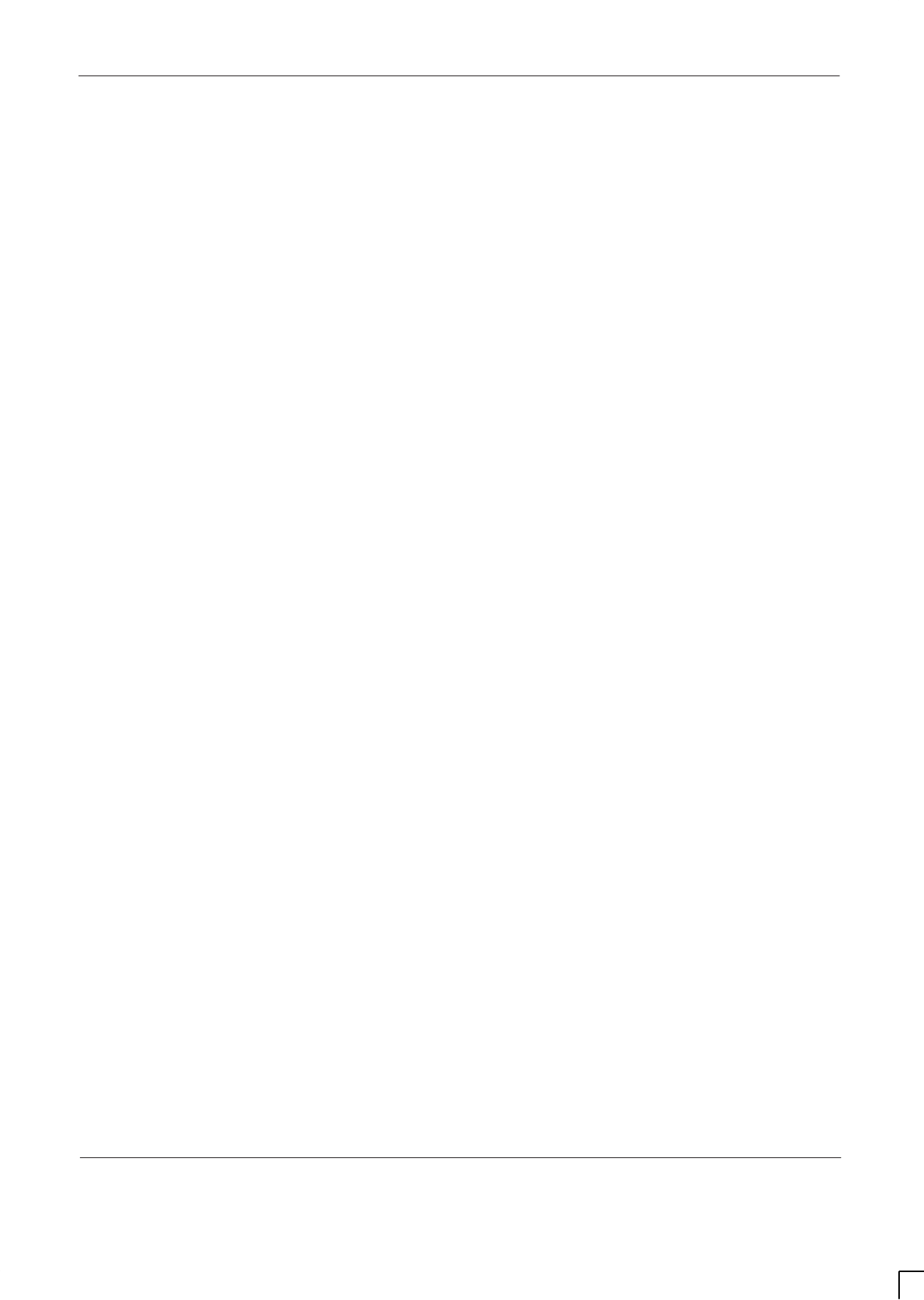
GSM-204-323
31st Oct 01
Technical Description: Horizon
macro
outdoor
68P02902W02-A
CONTROLLED INTRODUCTION
iii
Chapter 5
RF modules i. . . . . . . . . . . . . . . . . . . . . . . . . . . . . . . . . . . . . . . . . . . . . . . . . . .
RF equipment detail Tech. 5–1. . . . . . . . . . . . . . . . . . . . . . . . . . . . . . . . . . . . . . . . . . . . . . . . . .
Overview of RF equipment Tech. 5–1. . . . . . . . . . . . . . . . . . . . . . . . . . . . . . . . . . . . . . .
RF specifications Tech. 5–1. . . . . . . . . . . . . . . . . . . . . . . . . . . . . . . . . . . . . . . . . . . . . . .
Receive (Rx) RF hardware Tech. 5–2. . . . . . . . . . . . . . . . . . . . . . . . . . . . . . . . . . . . . .
Transmit (Tx) RF hardware Tech. 5–3. . . . . . . . . . . . . . . . . . . . . . . . . . . . . . . . . . . . . . .
Rx/Tx single antenna duplexing Tech. 5–3. . . . . . . . . . . . . . . . . . . . . . . . . . . . . . . . . . .
RF overview and RF test function Tech. 5–4. . . . . . . . . . . . . . . . . . . . . . . . . . . . . . . . . . . . . .
RF overview Tech. 5–4. . . . . . . . . . . . . . . . . . . . . . . . . . . . . . . . . . . . . . . . . . . . . . . . . . . .
RF main component explanation Tech. 5–4. . . . . . . . . . . . . . . . . . . . . . . . . . . . . . . . . .
RF loopback test function Tech. 5–5. . . . . . . . . . . . . . . . . . . . . . . . . . . . . . . . . . . . . . . .
RF loopback hardware Tech. 5–5. . . . . . . . . . . . . . . . . . . . . . . . . . . . . . . . . . . . . . . . . .
RF loopback software operation Tech. 5–5. . . . . . . . . . . . . . . . . . . . . . . . . . . . . . . . . .
Functional diagram of RF Tech. 5–6. . . . . . . . . . . . . . . . . . . . . . . . . . . . . . . . . . . . . . . .
Description of RF test modes Tech. 5–7. . . . . . . . . . . . . . . . . . . . . . . . . . . . . . . . . . . . .
Compact transceiver unit (CTU) Tech. 5–8. . . . . . . . . . . . . . . . . . . . . . . . . . . . . . . . . . . . . . . .
Overview of the CTU Tech. 5–8. . . . . . . . . . . . . . . . . . . . . . . . . . . . . . . . . . . . . . . . . . . .
CTU internal boards Tech. 5–8. . . . . . . . . . . . . . . . . . . . . . . . . . . . . . . . . . . . . . . . . . . . .
Alarm reporting Tech. 5–9. . . . . . . . . . . . . . . . . . . . . . . . . . . . . . . . . . . . . . . . . . . . . . . . .
View of CTU Tech. 5–10. . . . . . . . . . . . . . . . . . . . . . . . . . . . . . . . . . . . . . . . . . . . . . . . . . . .
CTU connectors and reset Tech. 5–11. . . . . . . . . . . . . . . . . . . . . . . . . . . . . . . . . . . . . . .
CTU input/output diagram Tech. 5–12. . . . . . . . . . . . . . . . . . . . . . . . . . . . . . . . . . . . . . . .
CTU Tx connector Tech. 5–13. . . . . . . . . . . . . . . . . . . . . . . . . . . . . . . . . . . . . . . . . . . . . .
CTU Rx function Tech. 5–13. . . . . . . . . . . . . . . . . . . . . . . . . . . . . . . . . . . . . . . . . . . . . . . .
CTU Tx function Tech. 5–14. . . . . . . . . . . . . . . . . . . . . . . . . . . . . . . . . . . . . . . . . . . . . . . .
CTU digital processing and control functions Tech. 5–16. . . . . . . . . . . . . . . . . . . . . . .
CTU uplink/downlink Tech. 5–19. . . . . . . . . . . . . . . . . . . . . . . . . . . . . . . . . . . . . . . . . . . .
CTU frequency hopping Tech. 5–20. . . . . . . . . . . . . . . . . . . . . . . . . . . . . . . . . . . . . . . . . . . . . . .
Overview of CTU frequency hopping Tech. 5–20. . . . . . . . . . . . . . . . . . . . . . . . . . . . . .
Synthesizer frequency hopping (SFH) Tech. 5–20. . . . . . . . . . . . . . . . . . . . . . . . . . . . .
SFH example not through BCCH Tech. 5–21. . . . . . . . . . . . . . . . . . . . . . . . . . . . . . . . . .
SFH example hopping through BCCH carrier Tech. 5–21. . . . . . . . . . . . . . . . . . . . . . .
Baseband frequency hopping (BBH) Tech. 5–22. . . . . . . . . . . . . . . . . . . . . . . . . . . . . .
BBH example Tech. 5–22. . . . . . . . . . . . . . . . . . . . . . . . . . . . . . . . . . . . . . . . . . . . . . . . . .
SURF module Tech. 5–24. . . . . . . . . . . . . . . . . . . . . . . . . . . . . . . . . . . . . . . . . . . . . . . . . . . . . . .
SURF module overview Tech. 5–24. . . . . . . . . . . . . . . . . . . . . . . . . . . . . . . . . . . . . . . . . .
Single band SURF module view Tech. 5–25. . . . . . . . . . . . . . . . . . . . . . . . . . . . . . . . . .
Functional description of the single band SURF Tech. 5–26. . . . . . . . . . . . . . . . . . . .
Single band SURF functional diagram Tech. 5–27. . . . . . . . . . . . . . . . . . . . . . . . . . . . .
Dual band SURF module view Tech. 5–28. . . . . . . . . . . . . . . . . . . . . . . . . . . . . . . . . . . .
Functional description of dual band SURF modules Tech. 5–29. . . . . . . . . . . . . . . . .
Dual band SURF functional diagram Tech. 5–30. . . . . . . . . . . . . . . . . . . . . . . . . . . . . .
Transmit blocks overview Tech. 5–31. . . . . . . . . . . . . . . . . . . . . . . . . . . . . . . . . . . . . . . . . . . . .
Introduction to transmit blocks Tech. 5–31. . . . . . . . . . . . . . . . . . . . . . . . . . . . . . . . . . . .
Screw retention in Tx block locations Tech. 5–31. . . . . . . . . . . . . . . . . . . . . . . . . . . . . .
View of basket for Tx blocks Tech. 5–32. . . . . . . . . . . . . . . . . . . . . . . . . . . . . . . . . . . . . .
Transmit block connectors Tech. 5–32. . . . . . . . . . . . . . . . . . . . . . . . . . . . . . . . . . . . . . .
View of Tx block connectors Tech. 5–33. . . . . . . . . . . . . . . . . . . . . . . . . . . . . . . . . . . . . .
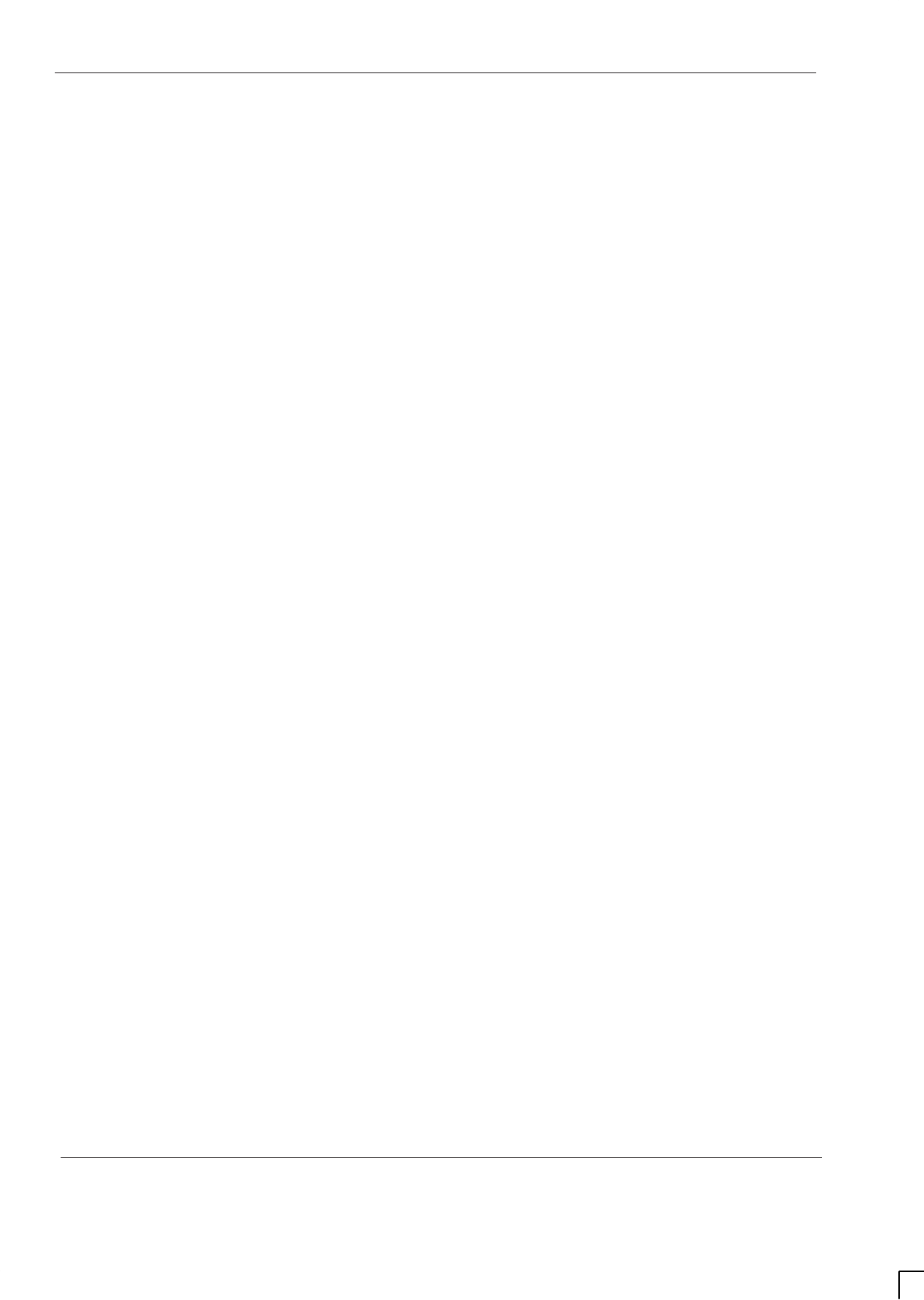
GSM-204-323
31st Oct 01
iv
Technical Description: Horizon
macro
outdoor
CONTROLLED INTRODUCTION
68P02902W02-A
Tx block blanking plate Tech. 5–34. . . . . . . . . . . . . . . . . . . . . . . . . . . . . . . . . . . . . . . . . . . . . . .
Purpose of Tx block blanking plate Tech. 5–34. . . . . . . . . . . . . . . . . . . . . . . . . . . . . . . .
View of Tx block blanking plate Tech. 5–34. . . . . . . . . . . . . . . . . . . . . . . . . . . . . . . . . . .
Feedthrough plate Tech. 5–35. . . . . . . . . . . . . . . . . . . . . . . . . . . . . . . . . . . . . . . . . . . . . . . . . . .
Purpose of feedthrough plate Tech. 5–35. . . . . . . . . . . . . . . . . . . . . . . . . . . . . . . . . . . . .
View of feedthrough plate Tech. 5–35. . . . . . . . . . . . . . . . . . . . . . . . . . . . . . . . . . . . . . . .
Feedthrough plate connectors Tech. 5–35. . . . . . . . . . . . . . . . . . . . . . . . . . . . . . . . . . . .
HCU plate Tech. 5–36. . . . . . . . . . . . . . . . . . . . . . . . . . . . . . . . . . . . . . . . . . . . . . . . . . . . . . . . . . .
HCU overview Tech. 5–36. . . . . . . . . . . . . . . . . . . . . . . . . . . . . . . . . . . . . . . . . . . . . . . . . .
HCU view Tech. 5–36. . . . . . . . . . . . . . . . . . . . . . . . . . . . . . . . . . . . . . . . . . . . . . . . . . . . . .
HCU functional diagram Tech. 5–36. . . . . . . . . . . . . . . . . . . . . . . . . . . . . . . . . . . . . . . . .
HCU connectors Tech. 5–37. . . . . . . . . . . . . . . . . . . . . . . . . . . . . . . . . . . . . . . . . . . . . . . .
TDF Tech. 5–38. . . . . . . . . . . . . . . . . . . . . . . . . . . . . . . . . . . . . . . . . . . . . . . . . . . . . . . . . . . . . . . .
Overview of TDF Tech. 5–38. . . . . . . . . . . . . . . . . . . . . . . . . . . . . . . . . . . . . . . . . . . . . . . .
TDF view Tech. 5–38. . . . . . . . . . . . . . . . . . . . . . . . . . . . . . . . . . . . . . . . . . . . . . . . . . . . . .
TDF functional diagram Tech. 5–39. . . . . . . . . . . . . . . . . . . . . . . . . . . . . . . . . . . . . . . . . .
TDF connectors Tech. 5–39. . . . . . . . . . . . . . . . . . . . . . . . . . . . . . . . . . . . . . . . . . . . . . . .
Dual band TDF Tech. 5–40. . . . . . . . . . . . . . . . . . . . . . . . . . . . . . . . . . . . . . . . . . . . . . . . . . . . . .
Overview of Dual band TDF Tech. 5–40. . . . . . . . . . . . . . . . . . . . . . . . . . . . . . . . . . . . . .
Dual band TDF view Tech. 5–40. . . . . . . . . . . . . . . . . . . . . . . . . . . . . . . . . . . . . . . . . . . . .
Dual band TDF functional diagram Tech. 5–41. . . . . . . . . . . . . . . . . . . . . . . . . . . . . . . .
Dual band TDF connectors Tech. 5–41. . . . . . . . . . . . . . . . . . . . . . . . . . . . . . . . . . . . . . .
DCF Tech. 5–42. . . . . . . . . . . . . . . . . . . . . . . . . . . . . . . . . . . . . . . . . . . . . . . . . . . . . . . . . . . . . . . .
DCF overview Tech. 5–42. . . . . . . . . . . . . . . . . . . . . . . . . . . . . . . . . . . . . . . . . . . . . . . . . .
DCF view Tech. 5–42. . . . . . . . . . . . . . . . . . . . . . . . . . . . . . . . . . . . . . . . . . . . . . . . . . . . . .
DCF functional diagram Tech. 5–43. . . . . . . . . . . . . . . . . . . . . . . . . . . . . . . . . . . . . . . . . .
DCF connectors Tech. 5–43. . . . . . . . . . . . . . . . . . . . . . . . . . . . . . . . . . . . . . . . . . . . . . . .
DDF Tech. 5–44. . . . . . . . . . . . . . . . . . . . . . . . . . . . . . . . . . . . . . . . . . . . . . . . . . . . . . . . . . . . . . . .
Overview of DDF Tech. 5–44. . . . . . . . . . . . . . . . . . . . . . . . . . . . . . . . . . . . . . . . . . . . . . .
DDF view Tech. 5–44. . . . . . . . . . . . . . . . . . . . . . . . . . . . . . . . . . . . . . . . . . . . . . . . . . . . . .
DDF functional diagram Tech. 5–45. . . . . . . . . . . . . . . . . . . . . . . . . . . . . . . . . . . . . . . . . .
DDF connectors Tech. 5–45. . . . . . . . . . . . . . . . . . . . . . . . . . . . . . . . . . . . . . . . . . . . . . . .
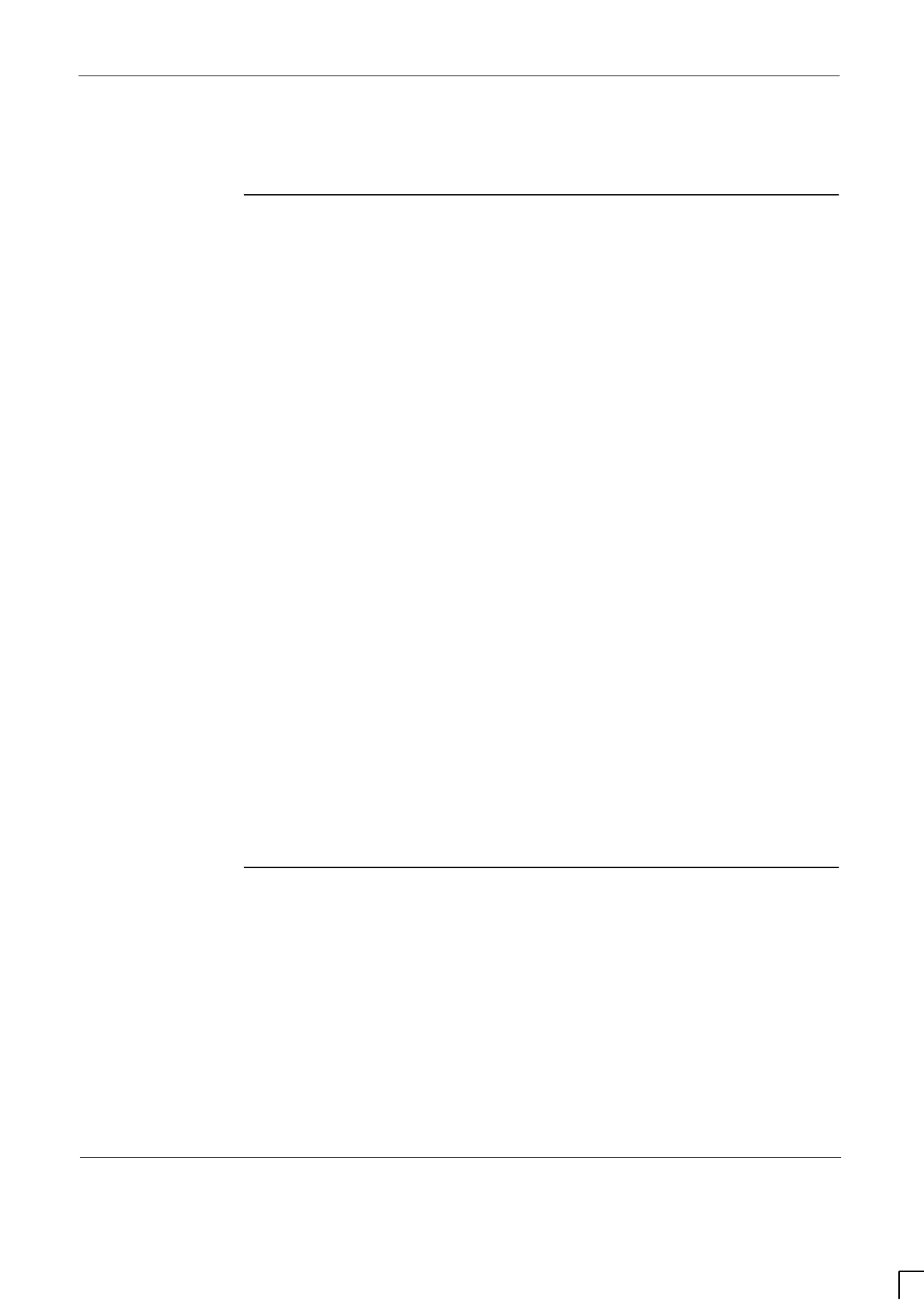
GSM-204-323 RF equipment detail
31st Oct 01
Technical Description: Horizon
macro
outdoor
68P02902W02-A
CONTROLLED INTRODUCTION
Tech. 5–1
RF equipment detail
Overview of RF
equipment
This chapter describes the functional operation of the Radio Frequency (RF)
modules used in the cabinet.
The RF equipment provides a transmit and receive path between the Mobile
Station (MS) and the cabinet transceiver. All descriptions are presented at a
block diagram level.
RF modules
The following RF modules are described in this chapter:
Compact Transceiver Unit (CTU).
Sectorized Universal Receiver Front-end (SURF) module (for receive
path), both single and dual band variants.
Several types of transmit block, with the generic name of Tx block. Tx
blocks are used for various configurations of the transmit path, depending
on the number of antennas, transceivers and functionality.
RF general information and loopback test function
The following additional information is presented in this chapter:
General definition of transmit and receive functions in this RF equipment
detail section.
An RF overview and RF test function description in the next section.
An explanation of CTU frequency hopping in a section immediately after
the CTU section.
These sections are intended to assist the reader in understanding the
information on the RF modules.
RF
specifications
All equipment meets or exceeds ETSI regulations. Frequency information is
listed in the Specifications part of this manual.
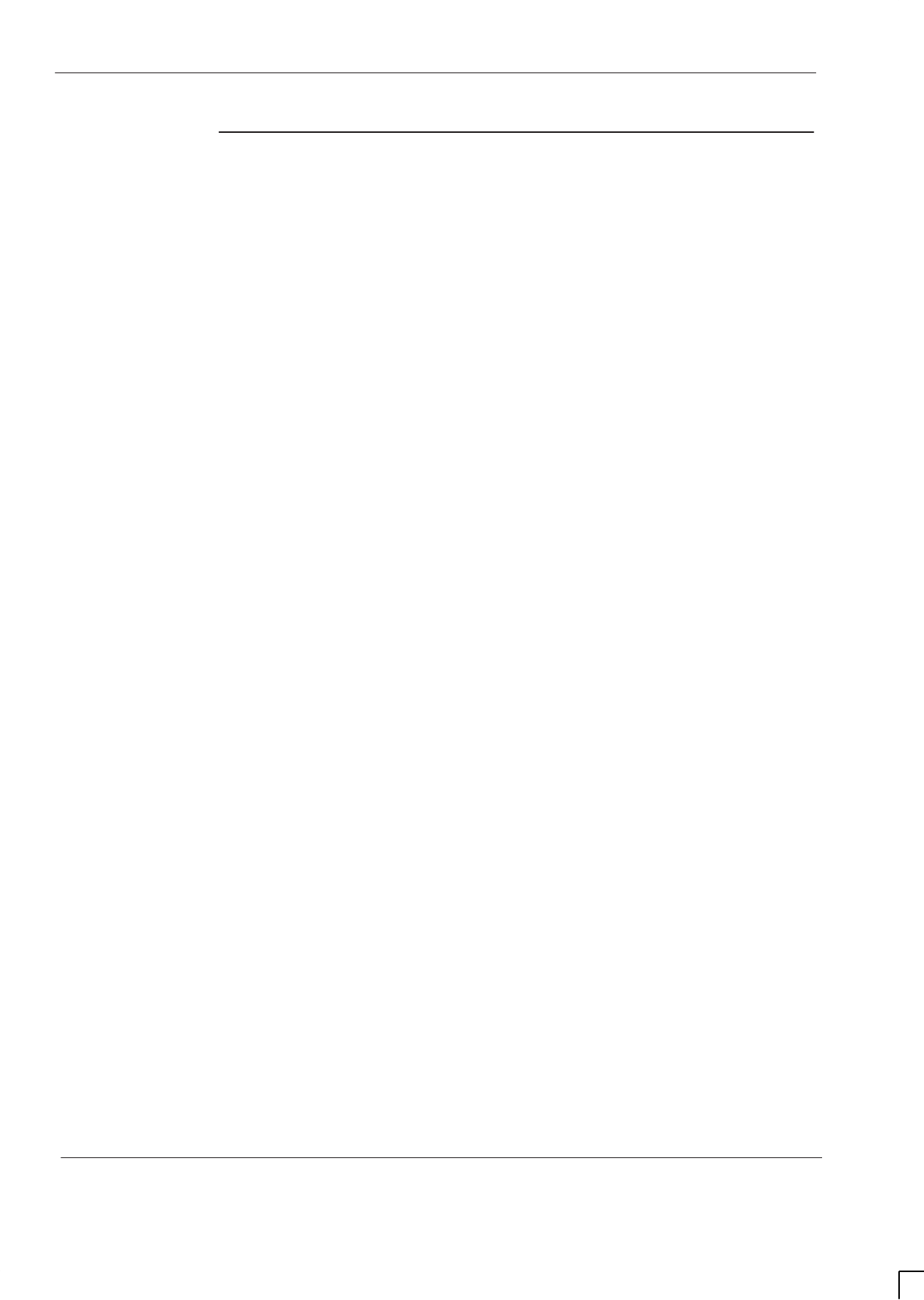
GSM-204-323
RF equipment detail
31st Oct 01
Tech. 5–2
Technical Description: Horizon
macro
outdoor
CONTROLLED INTRODUCTION
68P02902W02-A
Receive (Rx)
RF hardware
Receiver RF hardware consists of the SURF module and optional Tx block
receive path, and the receive section of the CTU.
The SURF module provides bandpass filtering and low-noise amplification for up
to three sectors, with diversity receive antenna signals, together with switching
to CTUs.
CTU Rx role
The CTU provides the following receive functions:
Receiver tuning (on a timeslot basis) to any receive channel frequency.
Demodulation and equalization of the receive channel signal.
Measurement of the Received Signal Strength Indication (RSSI) and
signal quality.
Recovery of received data from the demodulated radio channel.
Channel decoding of the received data and processing of the recovered
signal. Traffic data is passed on to the MCUF for routeing to the MSC.
Digital interface to the SURF module, which controls selection by the
SURF switch of the receive signals from the appropriate antenna.
Comparison and processing of an additional receive path from a second
diversity antenna input to compensate for multipath fading and
interference.
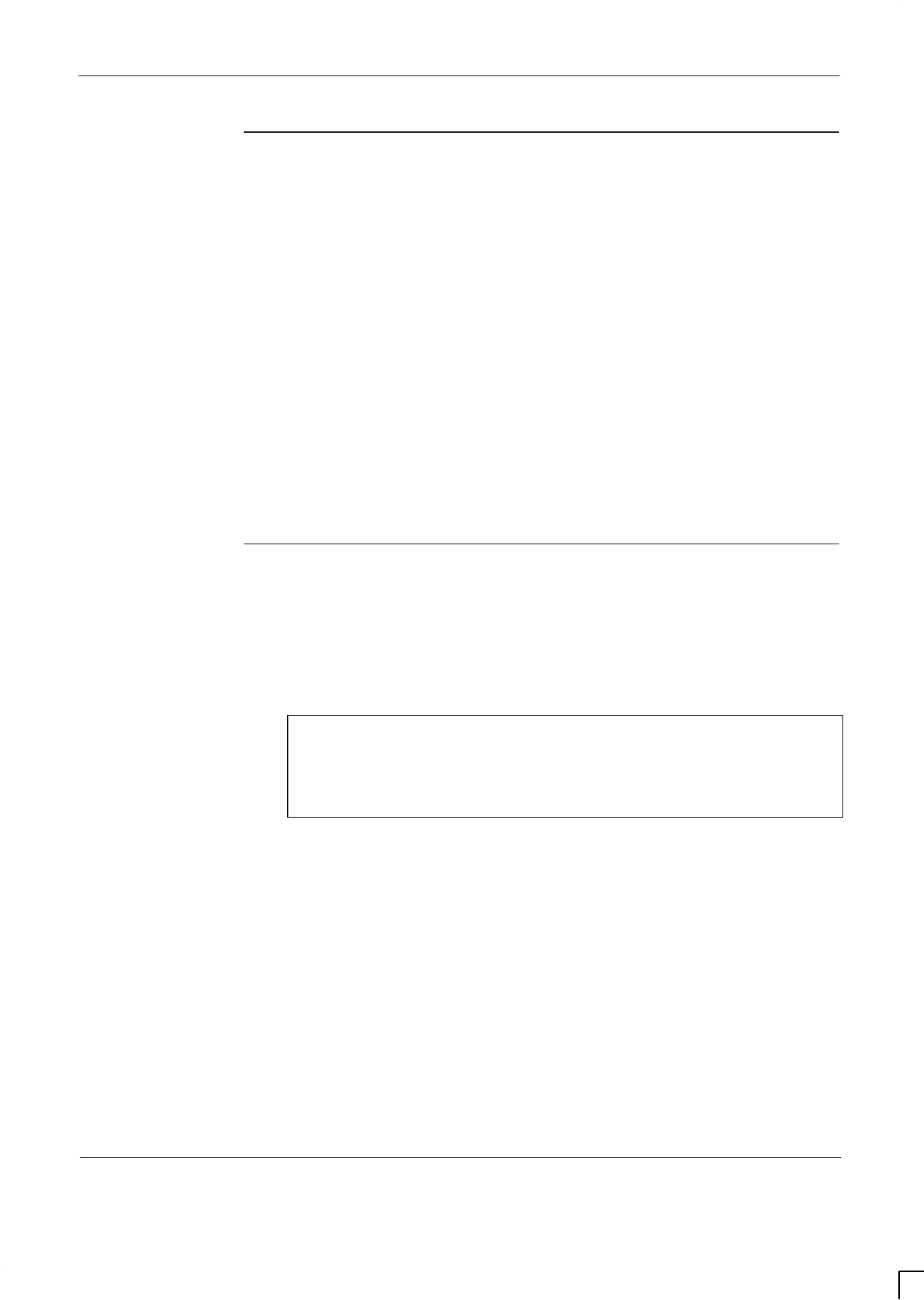
GSM-204-323 RF equipment detail
31st Oct 01
Technical Description: Horizon
macro
outdoor
68P02902W02-A
CONTROLLED INTRODUCTION
Tech. 5–3
Transmit (Tx)
RF hardware
Transmit RF hardware consists of Tx blocks in appropriate combinations to meet
requirements of antenna sharing for the transceivers.
CTU Tx role
The CTU provides the following transmit functions:
Transmit tuning (on a timeslot basis) for generation of any transmit
channel RF frequency.
Encoding transmit data output.
Digital modulation of transmit data onto the transmit radio channel signal.
Final RF power amplification and output power level control of the transmit
radio channel RF signal.
Channel encoding of the data to be transmitted, interleaving signal and
traffic channel data, as defined by ETSI.
Rx/Tx single
antenna
duplexing
Duplexers allow a single antenna to be used for both transmit and receive
operations. Duplexers exist within several of the transmit blocks. Normally
duplexed RF signals are used through one antenna, with a second receive
antenna to provide diversity.
CAUTION If a single antenna (non–diversity) is required, the duplex
antenna RF receive cable from the transmit block must be
connected to the RxA path at the SURF. Simply switching
off diversity at the OMC-R without the correct SURF
configuration will cause a loss of reception.
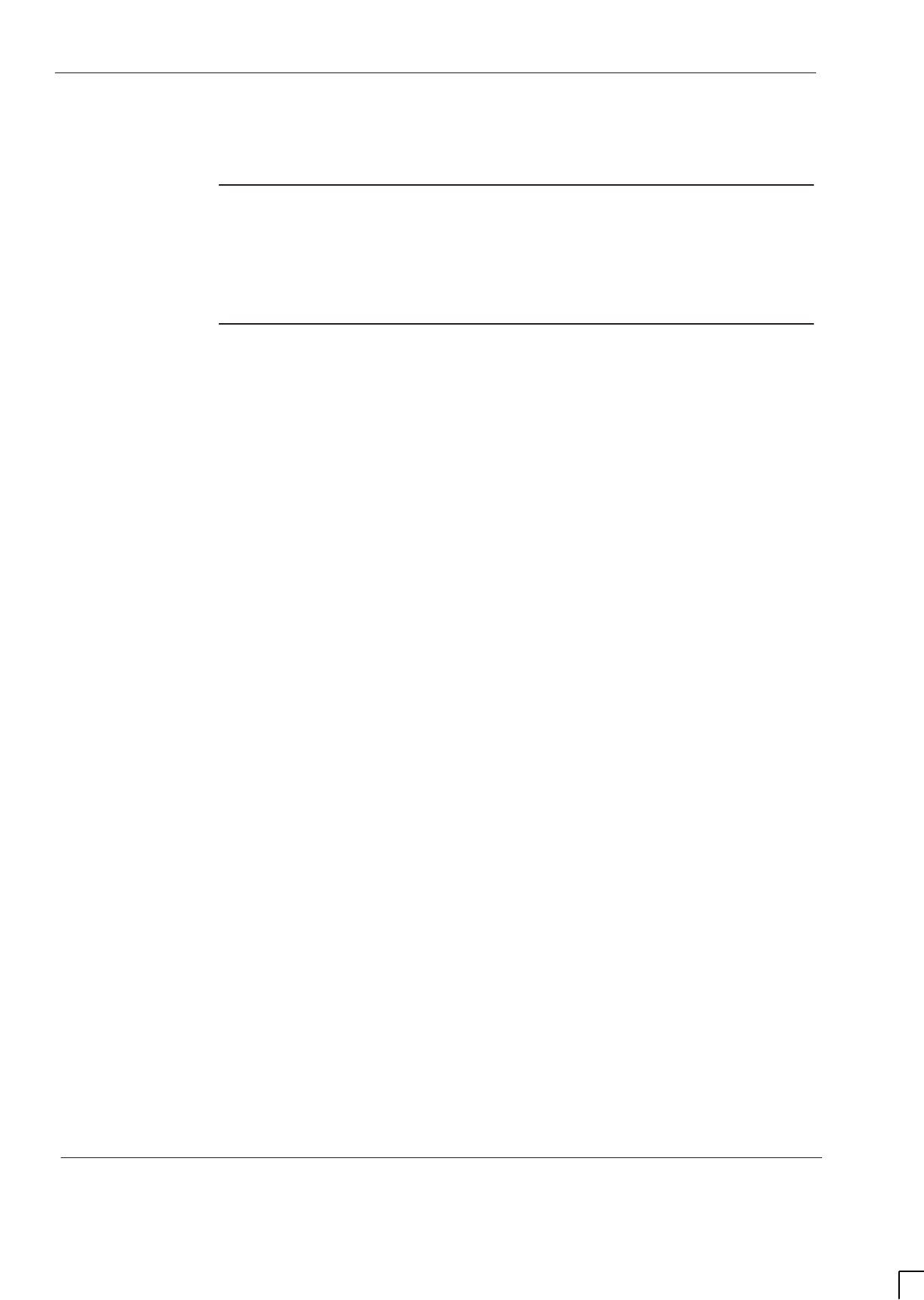
GSM-204-323
RF overview and RF test function
31st Oct 01
Tech. 5–4
Technical Description: Horizon
macro
outdoor
CONTROLLED INTRODUCTION
68P02902W02-A
RF overview and RF test function
RF overview
This section explains the RF functional blocks and additional RF loopback test
capability.
The terminology, functionality and optional capabilities are set out, as a basis for
understanding more detailed descriptions in RF module sections of this chapter.
RF main
component
explanation
The following description should be read in conjunction with Figure 5-1.
The RF equipment consists of three main blocks:
The CTU.
The SURF module.
The Tx block.
CTU
The CTU can operate at 850 MHz, 900 MHz, 1800 MHz or 1900 MHz,
depending on the BTS variant ordered. It can receive two inputs, RxA and RxB,
from the SURF. These inputs are converted into digital voice/data. The two Rx
signals provide diversity of the Rx function from the MS (uplink).
The CTU also generates a Tx data signal, translated from digital voice/data,
which is transmitted by cable to the Tx block for antenna transmission to the MS
(downlink).
The third (middle) port provides an RF loopback test signal capability, for
automatic transmission of RF test signals to the SURF.
SURF modules
One of six variants of the SURF module can be installed in the Horizon
macro
outdoor:
Single band 850 MHz SURF.
Single band 900 MHz SURF.
Dual band 900 MHz SURF.
Single band 1800 MHz SURF
Dual band 1800 MHz SURF.
Single band 1900 MHz SURF.
The single band SURF modules accept up to three pairs of antenna inputs, and
the dual band SURF modules accept up to four pairs of antenna inputs. The
SURF switches the inputs to the appropriate CTUs under the control of the
database via the MCUF. There are two inputs to each CTU for Rx diversity.
The SURF also contains loopback test circuitry, connecting with a test signal
from each CTU.
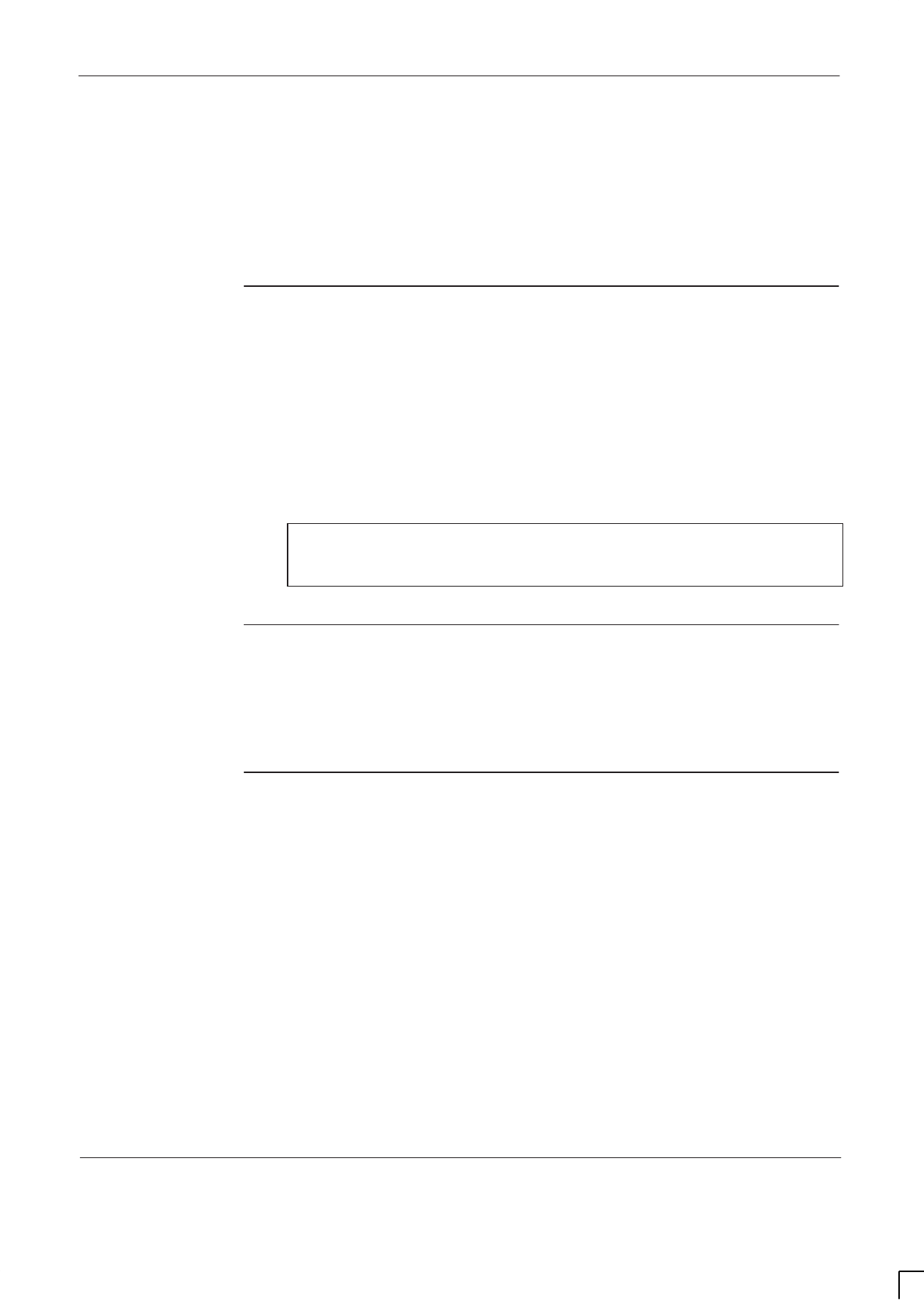
GSM-204-323 RF overview and RF test function
31st Oct 01
Technical Description: Horizon
macro
outdoor
68P02902W02-A
CONTROLLED INTRODUCTION
Tech. 5–5
Tx block
There are up to three Tx blocks, each block serving two CTUs.
Tx blocks filter the transmit signal for the required Tx band. Tx blocks also use
filters to enable the Rx frequency signal to be passed to the SURF, if one
antenna is used for both Tx and Rx signals.
RF loopback
test function
The loopback test function is primarily used to identify faults when the RF
system has failed. The loopback test function enables a diagnostic capability at
the OMC-R, by creating a test signal to identify if the fault is either:
Software (that the OMC-R can correct).
Particular hardware (CTU or SURF).
The result is a reduction in site assessment visits, and avoidance of
unnecessary visits when hardware is functioning correctly.
NOTE The RF loopback test feature available on the
Horizon
macro
is not available on previous generations of
equipment.
RF loopback
hardware
The RF loopback test function is essentially a hardware capability built into the
CTU and the SURF. Software instructions activate the test hardware, to route
test signals through the RF system.
RF loopback
software
operation
When installed with suitable software, GSR5 or later, the OMC-R can operate
the loopback test functions, and receive the results of the tests.
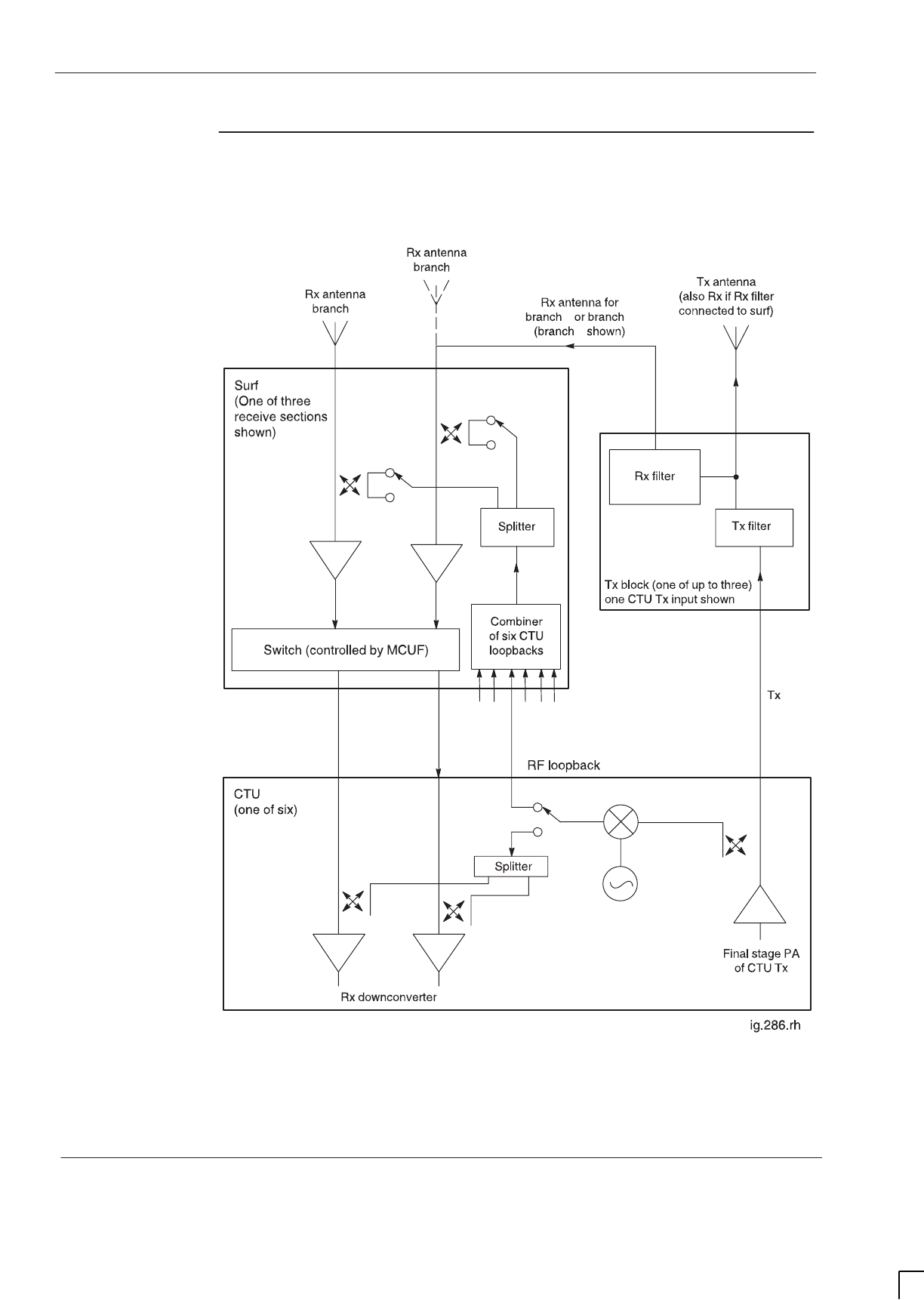
GSM-204-323
RF overview and RF test function
31st Oct 01
Tech. 5–6
Technical Description: Horizon
macro
outdoor
CONTROLLED INTRODUCTION
68P02902W02-A
Functional
diagram of RF
Figure 5-1 shows the basic RF and loopback/VSWR test functions. For clarity,
only one CTU and one Tx block is shown, together with part of the SURF.
RxA RxB
B
AAB
B
Figure 5-1 RF functional diagram
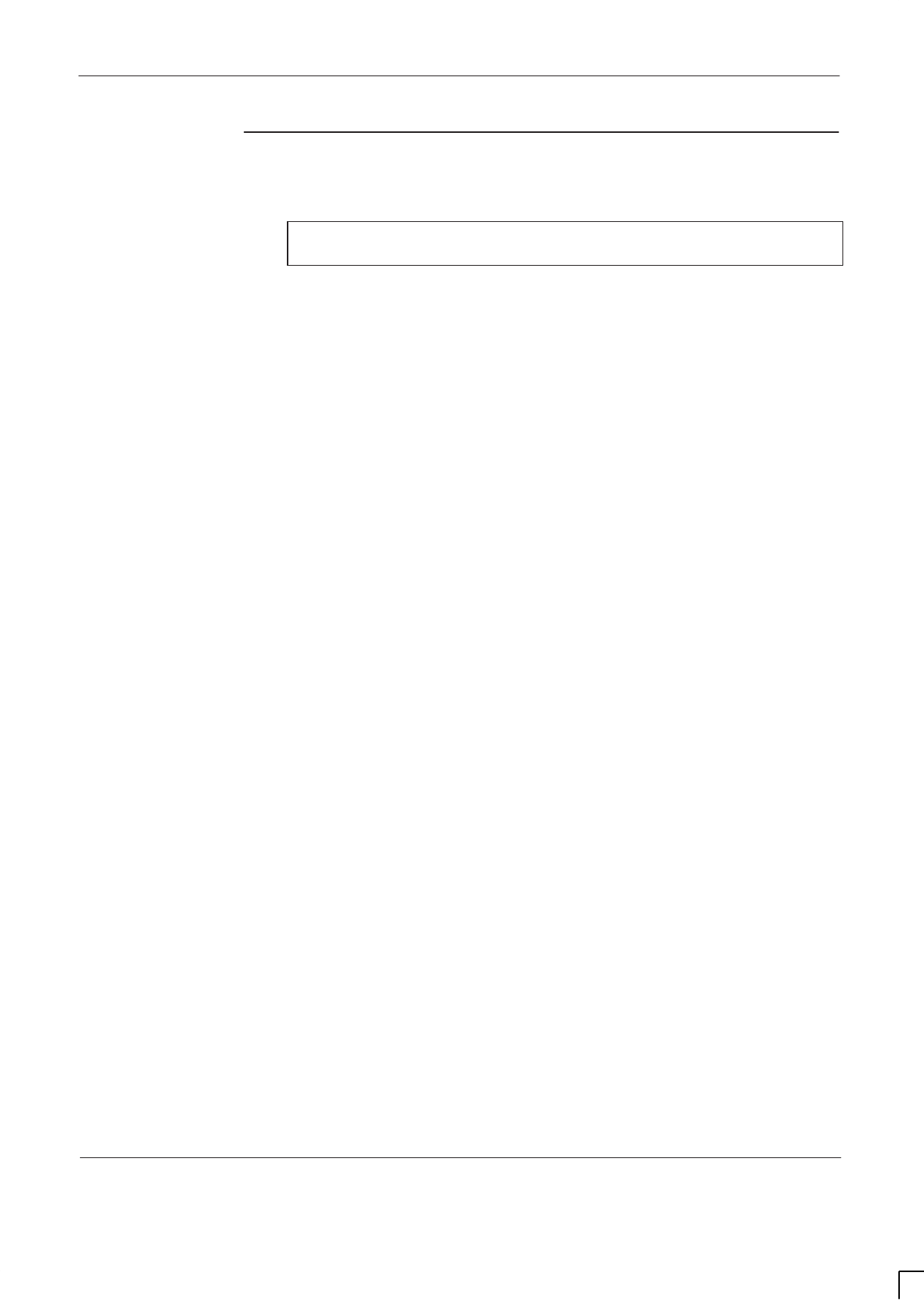
GSM-204-323 RF overview and RF test function
31st Oct 01
Technical Description: Horizon
macro
outdoor
68P02902W02-A
CONTROLLED INTRODUCTION
Tech. 5–7
Description of
RF test modes
The following description should be read in conjunction with Figure 5-1.
NOTE The RF test capability described requires software load
GSR5 or later.
The loopback test hardware picks up an attenuated signal by coupled link from
the normal CTU transmit signal.
The signal is mixed down to the receive band for testing the Rx functionality of
the SURF and CTU. Power to the loopback circuitry is automatically turned off
when the radio is in normal operation.
SURF test mode
The loopback signal is injected into the antenna receive path of the SURF by
coupled link. This tests the complete SURF and CTU Rx system path.
Test of CTU Rx circuitry
The loopback signal is injected directly into the Rx input of the CTU. This tests
the receive circuitry of the CTU.
VSWR test mode
The test signal, at Rx frequency, is injected into the antenna port through a
coupled link on the SURF. Reflected power is monitored by the receive system
to calculate VSWR. Detection of a high VSWR may indicate the presence of a
cable or antenna fault.
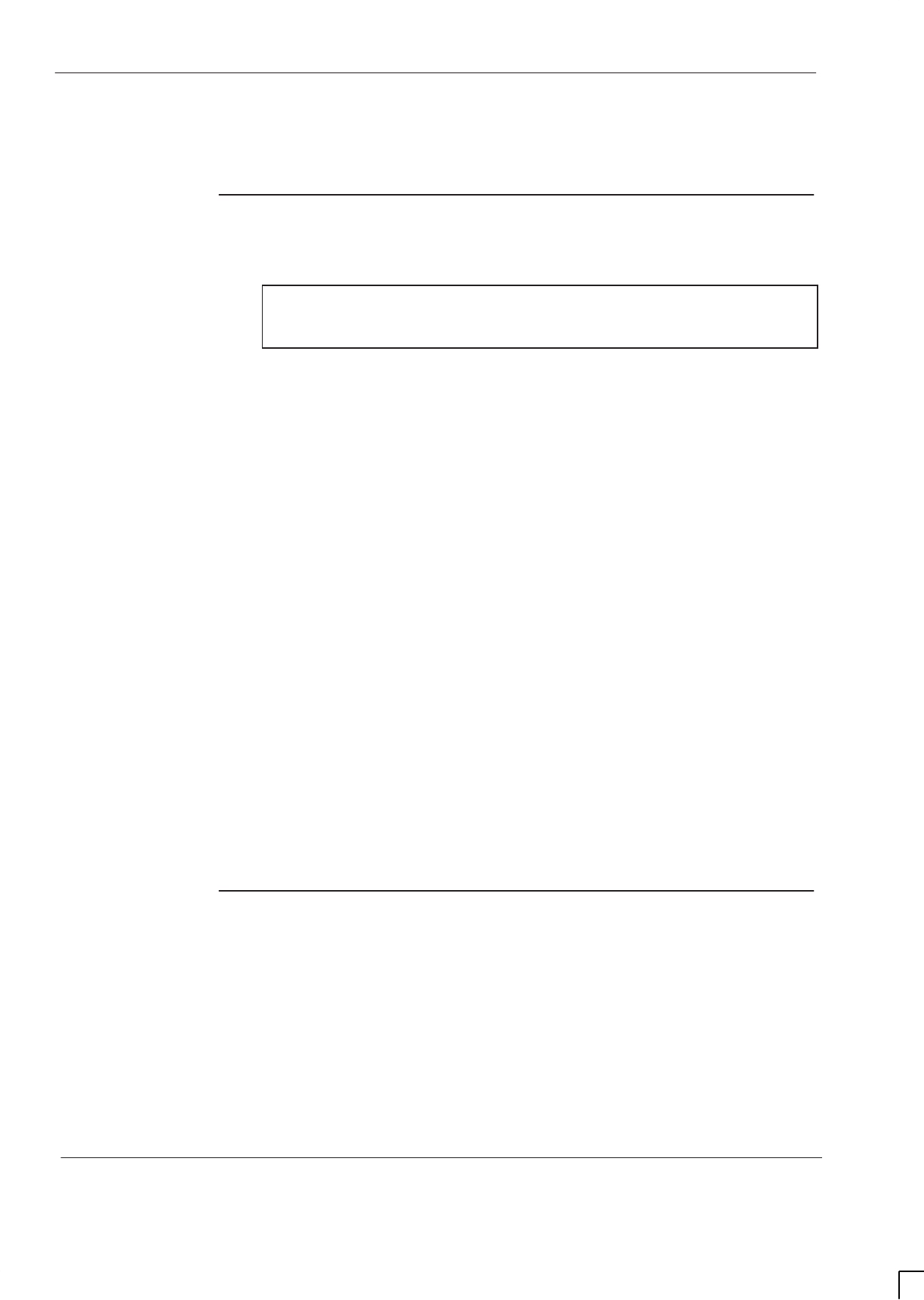
GSM-204-323
Compact transceiver unit (CTU)
31st Oct 01
Tech. 5–8
Technical Description: Horizon
macro
outdoor
CONTROLLED INTRODUCTION
68P02902W02-A
Compact transceiver unit (CTU)
Overview of the
CTU
This section provides the technical description of the CTU.
NOTE The CTU may be an 850 MHz, 900 MHz, 1800 MHz or a
1900 MHz transceiver, depending on requirements. The
functionality of the CTU is the same for all variants.
The CTU:
Generates the RF frequencies required to perform the transmit and
receive functions.
Contains the digital circuitry required for eight timeslots of channel
equalization, encoding and decoding, and transceiver control logic.
The CTU provides the air interface between a BSS and MSs, with the following
features:
Diversity reception capability (input from two antennas). This improves the
reception quality in the presence of multipath fading and interference.
Frequency change on a timeslot basis for frequency hopping and
equipment sharing.
Transmit power control.
CTU Tx RF output specification
For Tx RF output, see
Technical Description: GSM-205-323
Specifications.
Location and requirements
The CTU shelf is adjacent to the digital module shelf in the base of the cabinet.
The cabinet can contain six CTUs. A minimum of one CTU must be fitted in
each cabinet.
CTU internal
boards
The CTU is a single Field Replaceable Unit (FRU), which contains:
CTU transceiver (XCVR) board.
Power amplifier (PA) board.
Power supply unit.
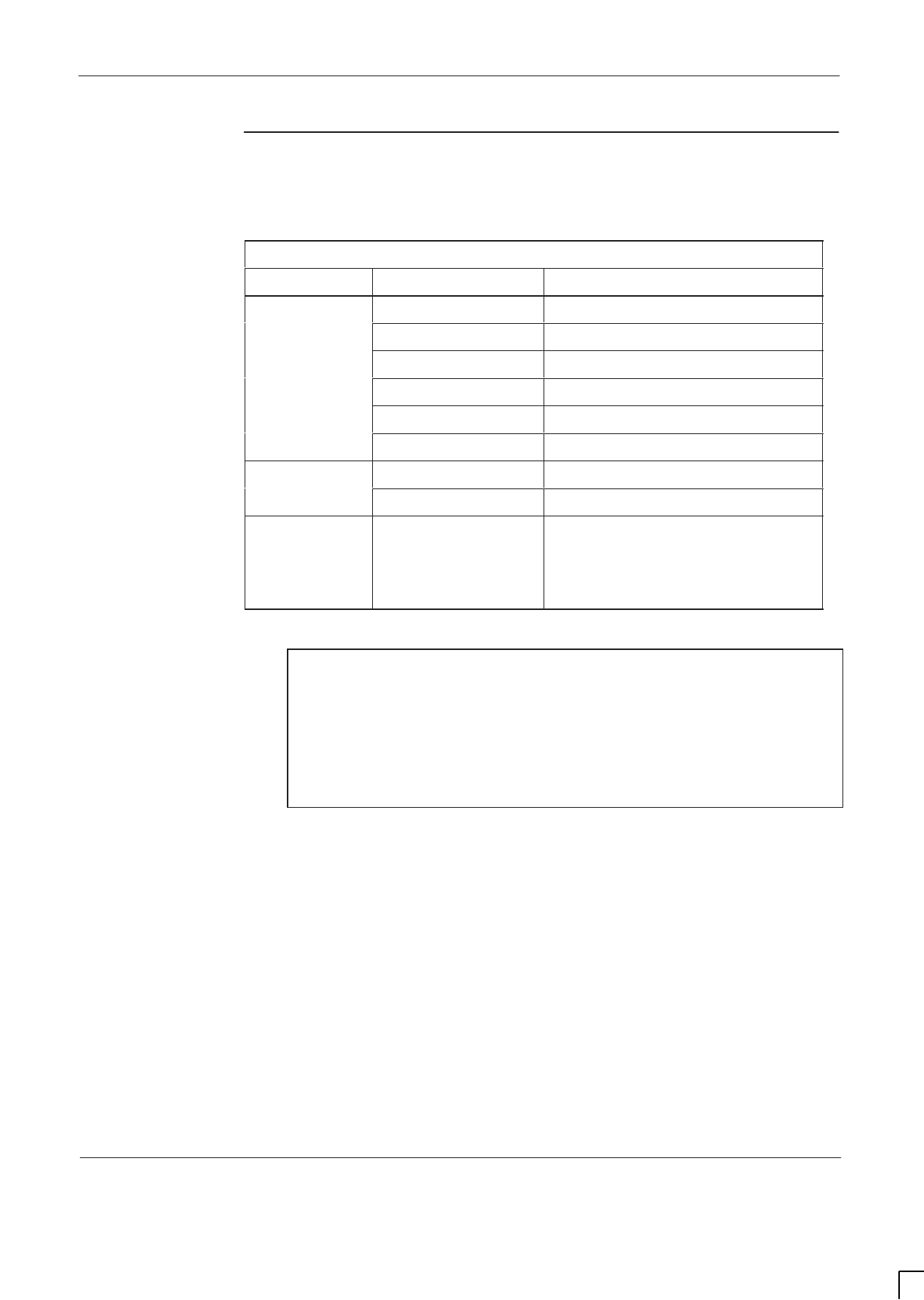
GSM-204-323 Compact transceiver unit (CTU)
31st Oct 01
Technical Description: Horizon
macro
outdoor
68P02902W02-A
CONTROLLED INTRODUCTION
Tech. 5–9
Alarm reporting
The CTU status is displayed by LED indicators on the front panel, as shown in
Figure 5-2, and detailed in Table 5-1. Major sub-systems, such as synthesizers
and RF amplifiers, are monitored with alarm signals as necessary.
Table 5-1 CTU front panel status indicators
Indicator LED When the LED is Then CTU
RADIO
STATUS
OFF Module off
STATUS Flashing green Code required or being loaded
Green Normal operational mode
Flashing yellow Test mode
Yellow Radio inhibited
Red Alarm condition
Transmit (Tx)
STATUS
OFF Transmitter is off
STATUS Yellow Transmitter is keyed on
RADIO
STATUS AND
TRANSMIT
(Tx) STATUS
Both LEDs flashing
rapidly Non-volatile memory boot code
upgrade
(Do not remove power nor reset)
(see CAUTION)
CAUTION When both LEDs are flashing, the boot code is
downloading into non-volatile memory for software
upgrade. Power should not be removed, nor the cabinet
reset, until downloading has been completed, as this will
corrupt the non-volatile memory. If the boot code is
corrupted, contact Motorola Customer Network Resolution
Centre requesting the boot code restoration procedure
and the appropriate boot code file.
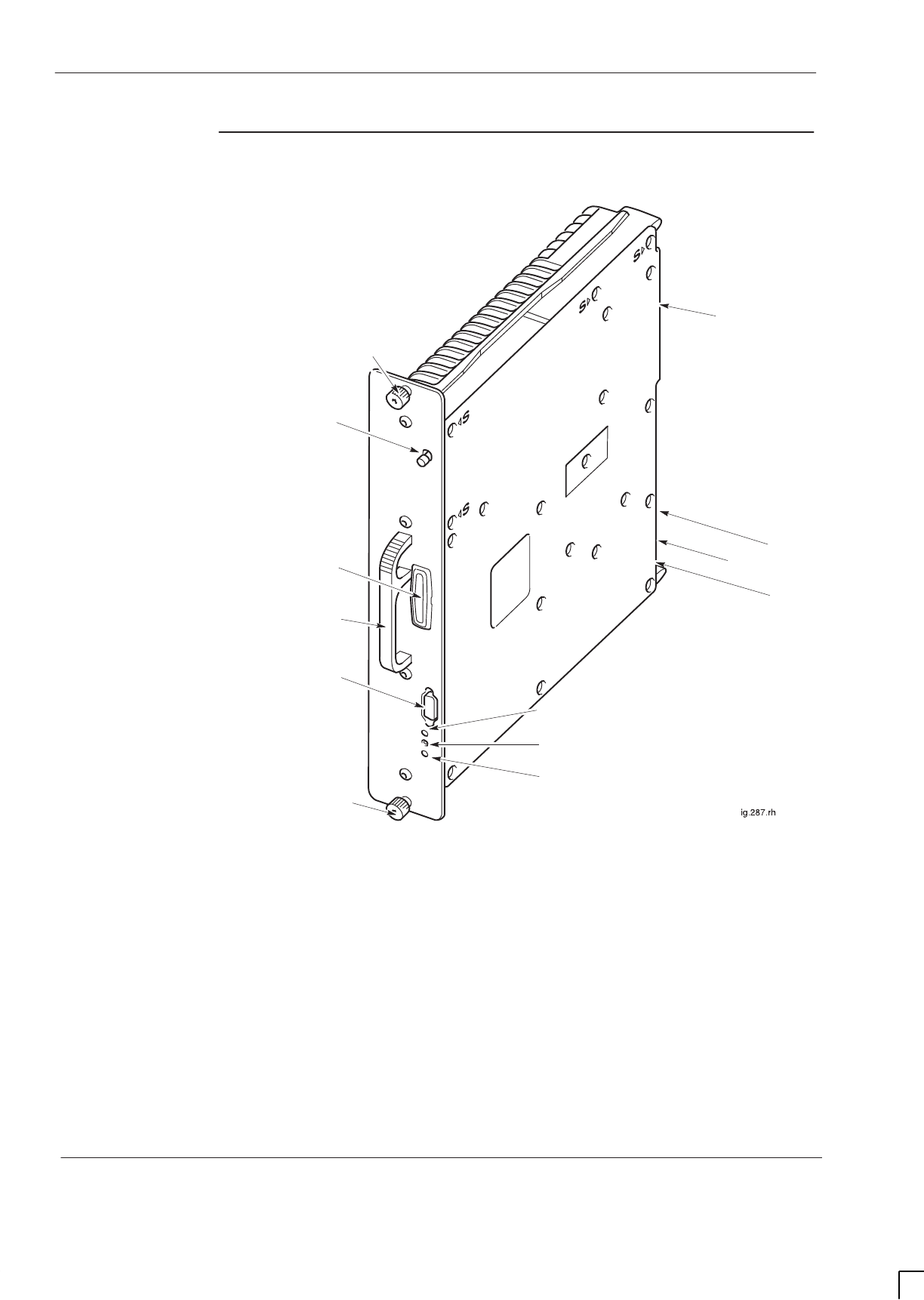
GSM-204-323
Compact transceiver unit (CTU)
31st Oct 01
Tech. 5–10
Technical Description: Horizon
macro
outdoor
CONTROLLED INTRODUCTION
68P02902W02-A
View of CTU
Figure 5-2 shows a CTU with its main features identified.
Tx OUT
CONNECTOR
Tx STATUS LED
HANDLE
M4 MODULE ATTACHMENT
SCREW
M4 MODULE
ATTACHMENT SCREW
TTY INTERFACE
CONTROL
PROCESSOR
TEST INTERFACE
RADIO STATUS LED
RECESSED MANUAL
RESET BUTTON (if fitted)
RxA
RxB
LOOPBACK
TEST PORT (L)
BACKPLANE POWE
R
AND SIGNAL
CONNECTOR
Figure 5-2 View of CTU showing main external features
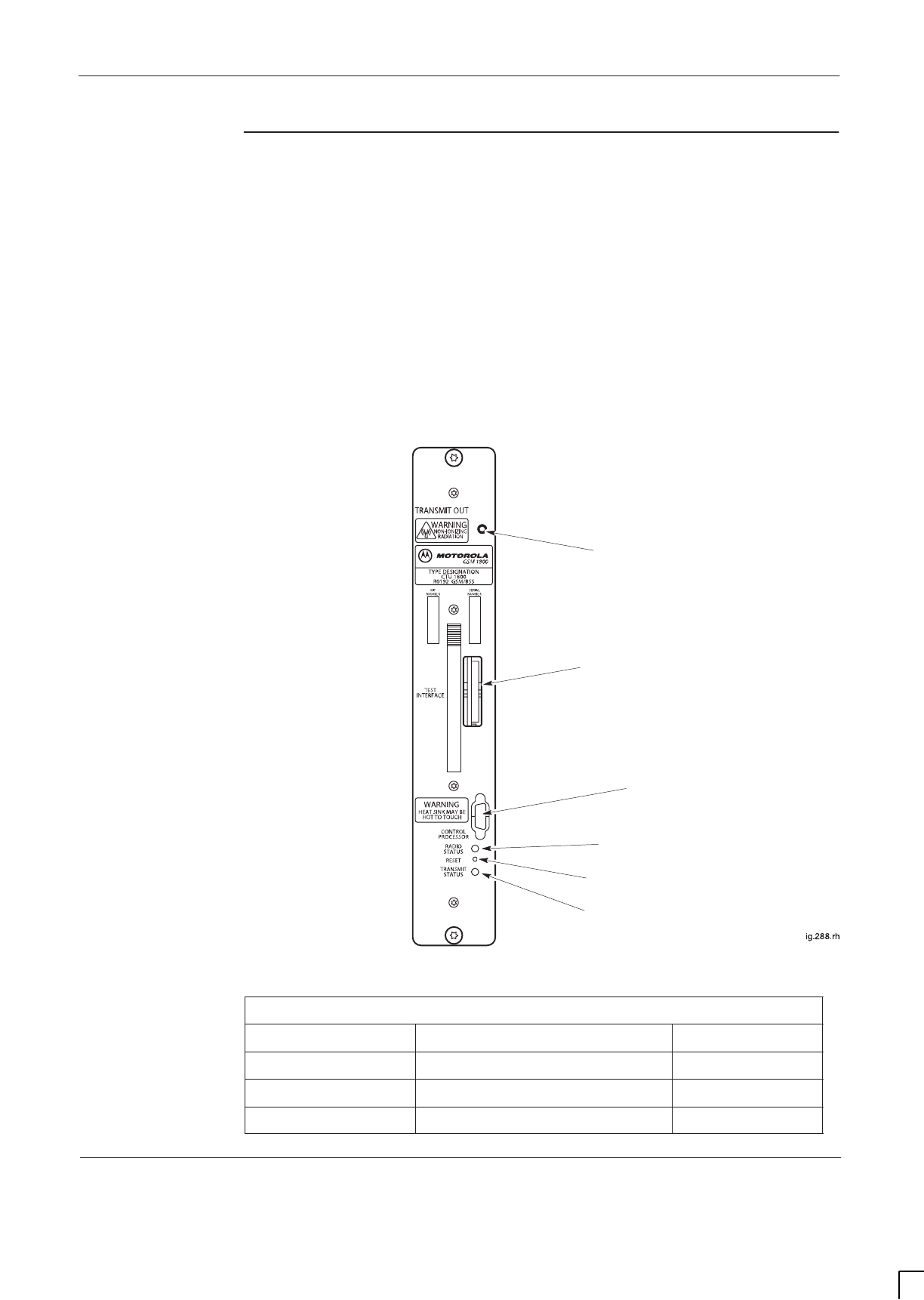
GSM-204-323 Compact transceiver unit (CTU)
31st Oct 01
Technical Description: Horizon
macro
outdoor
68P02902W02-A
CONTROLLED INTRODUCTION
Tech. 5–11
CTU connectors
and reset
The TTY RS-232 serial port has three serial links onto the 9-way connector:
Radio subsystem (RSS).
Equalizer and control processor (EQCP).
Channel coder control processor (CCCP).
A test interface port on the CTU front panel provides access to critical test
points for factory alignment and maintenance.
Pressing the reset push button generates a hard reset of the processor,
initiating a normal power-up. Later versions of the CTU (mid 2001 onward), have
no reset button, reset is acheived by operation of the appproriate CTU circuit
breaker on the CBM.
Figure 5-3 shows the front panel and Table 5-2 shows connector functions.
.
Tx OUT CONNECTOR
TTY INTERFACE
TEST INTERFACE
Tx STATUS LED
RADIO STATUS LED
RECESSED MANUAL
RESET BUTTON (if fitted)
Figure 5-3 CTU front panel showing connectors and reset button
Table 5-2 CTU front panel connectors
Front panel legend Function Connection to
TRANSMIT OUT Transmitter RF output Tx Block
TTY INTERFACE Test access to processor Three RS-232s
TEST INTERFACE Factory use Test equipment
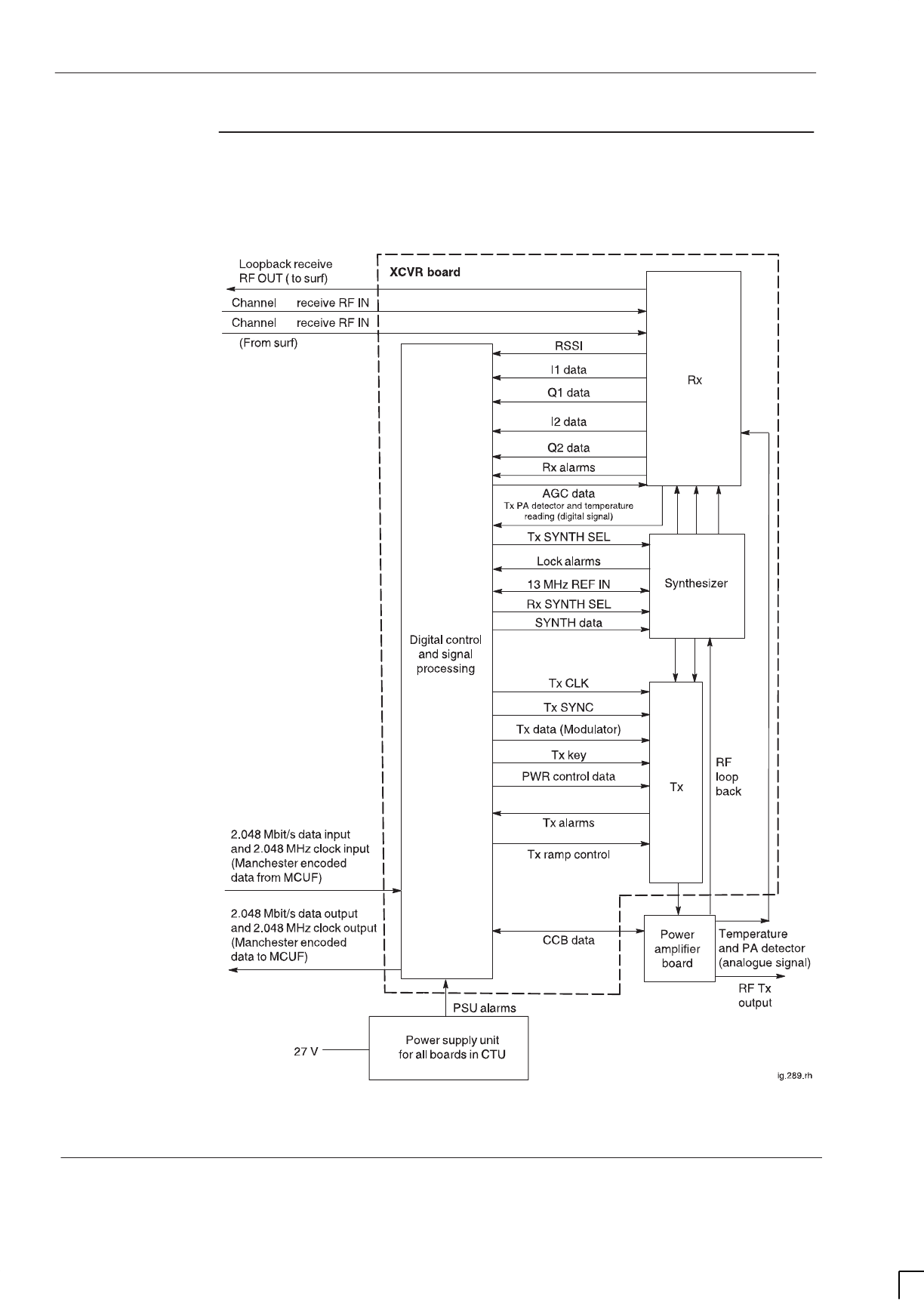
GSM-204-323
Compact transceiver unit (CTU)
31st Oct 01
Tech. 5–12
Technical Description: Horizon
macro
outdoor
CONTROLLED INTRODUCTION
68P02902W02-A
CTU
input/output
diagram
Figure 5-4 shows a block diagram of the CTU with the inputs/outputs annotated.
A
B
Figure 5-4 CTU block diagram
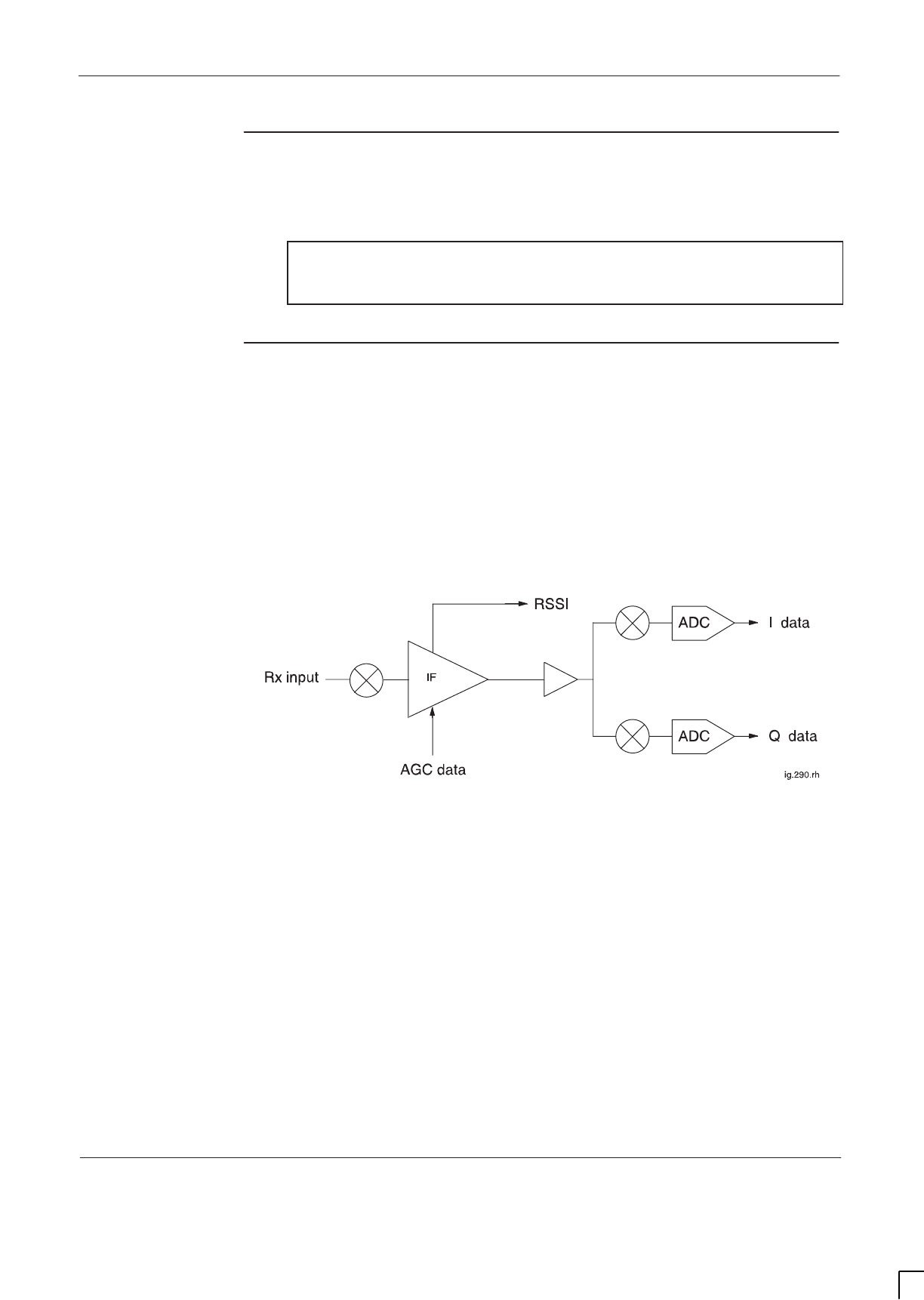
GSM-204-323 Compact transceiver unit (CTU)
31st Oct 01
Technical Description: Horizon
macro
outdoor
68P02902W02-A
CONTROLLED INTRODUCTION
Tech. 5–13
CTU Tx
connector
The CTU Tx connector is a short SMA to SMA link to the base of the
appropriate Tx block or feed through plate.
NOTE The Tx cable has a 90° SMA connector at one end, and a
straight SMA connector at the other end. The 90° end is
designed for connection to the Tx port of a CTU.
CTU Rx
function
The receiver part of the CTU accepts two amplified and filtered receive antenna
signals from the SURF module. These two signals are applied to inputs (branch
A and branch B) of the CTU transceiver board. Figure 5-5 shows a CTU receiver
functional diagram for one branch.
The input from the SURF module is filtered to ensure the signal level and
frequency range are correct for the next stage.
RSSI data is used for Automatic Gain Control (AGC) to ensure signal strength is
correct for the Intermediate Frequency (IF) stage.
Figure 5-5 CTU receiver functional diagram for one branch
The primary signal flow of the IF is to support traffic and control data.
The path is demodulated into quadrature signals and filtered by baseband
analogue filters. These signals are then digitized (I1/I2 data and Q1/Q2 data)
and made available to the equalizer for the purposes of receive synchronization
and data recovery.
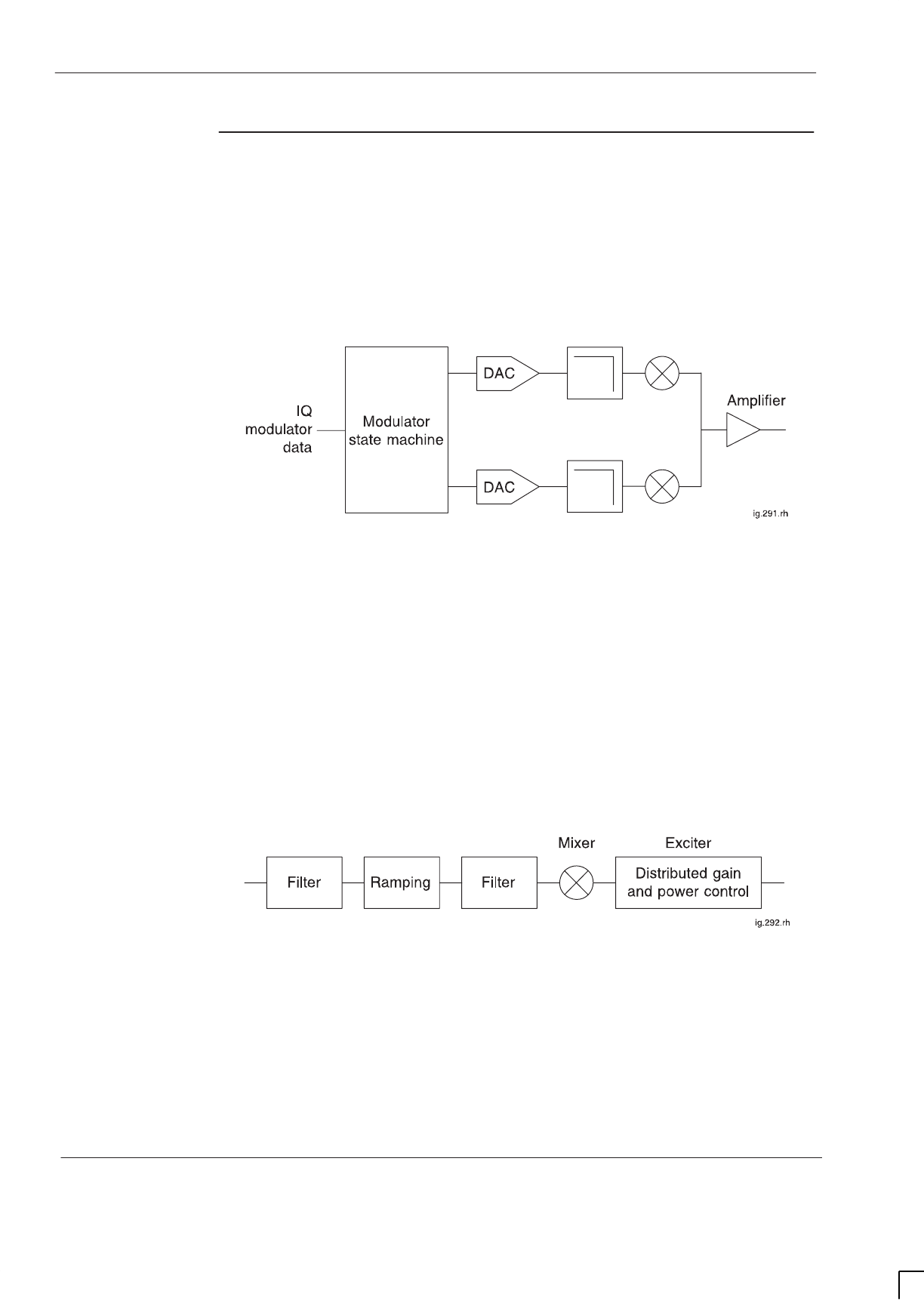
GSM-204-323
Compact transceiver unit (CTU)
31st Oct 01
Tech. 5–14
Technical Description: Horizon
macro
outdoor
CONTROLLED INTRODUCTION
68P02902W02-A
CTU Tx function
IQ modulator
Figure 5-6 shows a functional diagram of the IQ modulator. IQ modulator data
for eight timeslot channels is applied to the modulator state machine. This data
is encoded, serial-to-parallel converted, Gaussian filtered and split into
quadrature components. The quadrature components are D/A converted and
applied to a quadrature modulator to create a Gaussian Minimum Shift Keyed
(GMSK) carrier at an intermediate frequency.
Figure 5-6 IQ modulator functional diagram
IF and exciter stages
Figure 5-7 shows a functional diagram of the IF and exciter stages. The low
level modulated carrier is applied to a combination of analogue and digital
attenuators for RF power control. The power control data comes from the digital
sections of the XCVR. The output of the power control elements is further
amplified by an exciter chain to drive the power amplifier.
The GMSK modulated IF is filtered and applied to the input of a controlled gain
amplifier for transmitter pulse sloping (ramped). The ramped signal is filtered
and then mixed with the main transmitter injection and is up converted to the
final transmit channel frequency.
Figure 5-7 IF and exciter functional diagram
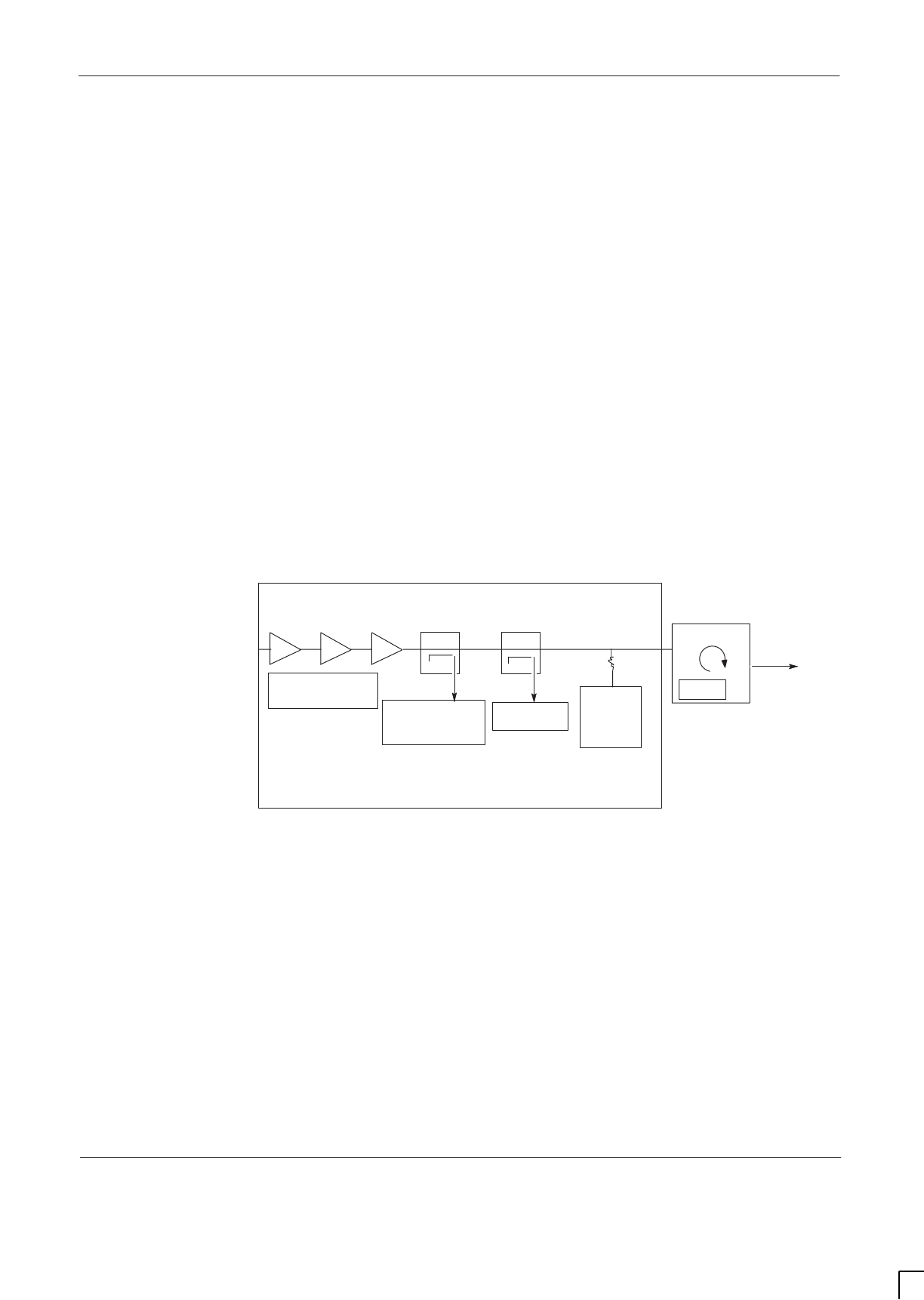
GSM-204-323 Compact transceiver unit (CTU)
31st Oct 01
Technical Description: Horizon
macro
outdoor
68P02902W02-A
CONTROLLED INTRODUCTION
Tech. 5–15
Power amplifier board
Figure 5-8 shows a functional diagram of the power amplifier (PA). The PA
board provides amplification and a forward power detector. The isolator protects
the PA board amplifiers. The detected output is used to adjust the final CTU RF
power output level by the digital sections of the XCVR.
The PA board consists of six functional blocks:
RF power amplifier.
RF forward power directional coupler.
RF forward power detector.
Temperature sensor.
CCB control.
RF loopback circuit.
The isolator performs two functions:
Isolates multiple transmitters to reduce intermodulation distortion.
Protects the RF power amplifier from possible damage resulting from load
mismatches.
RF FORWARD
POWER
DETECTOR
LOAD
RF OUTPUT
ISOLATOR
RF POWER
AMPLIFIERS
TEMPERATURE
SENSOR CCB
DATA
INJECT
LOOPBACK
DIRECTIONAL
COUPLER
RF LOOPBACK
DIRECTIONAL
COUPLER
PA BOARD
Figure 5-8 Power amplifier board functional diagram
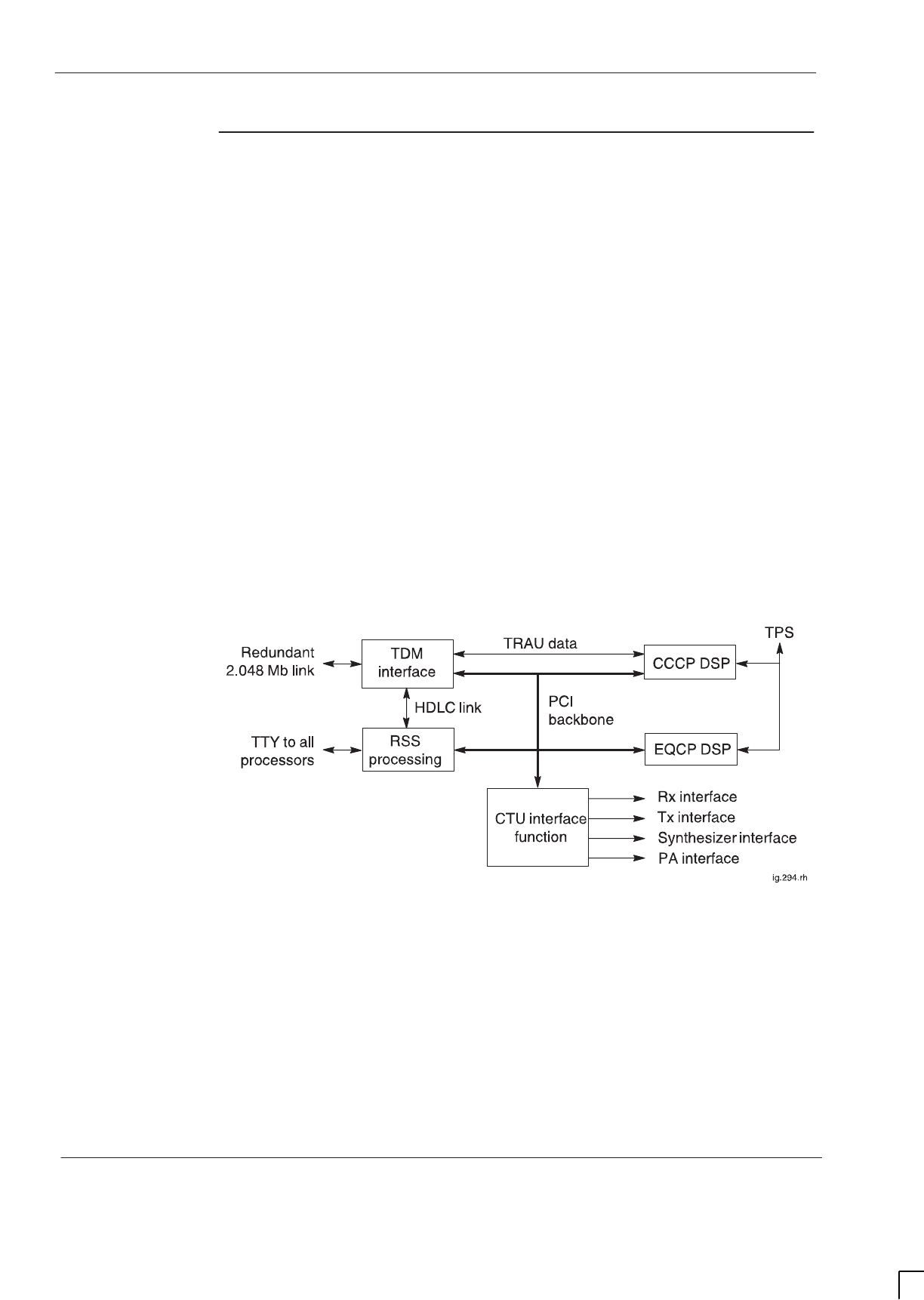
GSM-204-323
Compact transceiver unit (CTU)
31st Oct 01
Tech. 5–16
Technical Description: Horizon
macro
outdoor
CONTROLLED INTRODUCTION
68P02902W02-A
CTU digital
processing and
control
functions
The CTU digital processing and control function provides control and RF
processing for that CTU. These functions include:
2.048 Mbit/s links which interface with up to two MCUFs for redundancy.
A software processing platform for the Radio Sub System (RSS)
Digital Signal Processors (DSPs) for radio control and channel
equalization (EQCP).
DSPs for channel coding, data routeing, and baseband hopping (CCCP).
Control of RF systems: diversity receiver, transmitter, and power amplifier.
Alarm monitoring of internal devices and external cabinet elements.
Control of external modules, including CCBs (not used in the
Horizon
macro
outdoor) and the SURF.
Maintenance ports for processor TTY, test point sub system, and CTU
test connections.
Figure 5-9 shows a CTU digital functional diagram.
Figure 5-9 CTU digital functional diagram
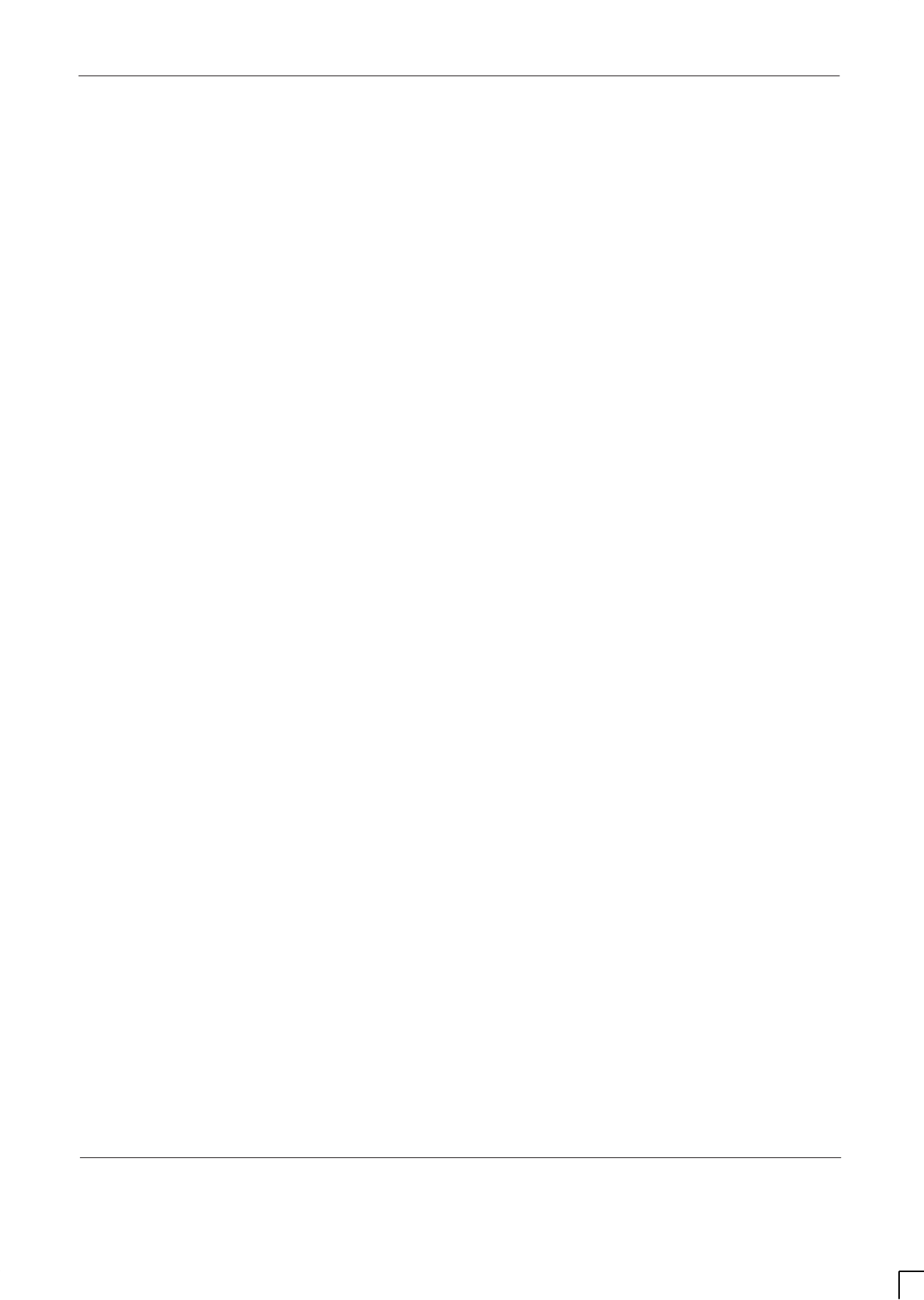
GSM-204-323 Compact transceiver unit (CTU)
31st Oct 01
Technical Description: Horizon
macro
outdoor
68P02902W02-A
CONTROLLED INTRODUCTION
Tech. 5–17
2 Mbit/s TDM Links
The CTU interfaces to the redundant MCUF are by 2.048 Mbit/s links on the
backplane (or FMUX modules in extension cabinets). These links are
Manchester encoded, thus providing both clock and data in a single connection.
The recovered clock provides a frequency reference for the CTU. The Rx and
Tx circuitry supports FMUX fibre optic lengths of up to 1 km.
The TDM links are formatted into 32 x 64 kbit/s timeslots to provide:
Downlink and uplink TRAU speech data.
Downlink baseband hopping data to be routed to/from other CTUs.
Cell site air interface synchronization.
HDLC channel for control information between RSS and MCUF.
Baseband routeing information to indicate source of downlink baseband
hopping data.
RSS processor
The RSS processor function communicates with:
The MCUF via dedicated 64 kbit/s timeslots in the TDM link.
The rest of the digital control functions by the peripheral communications
interface (PCI) bus.
A dual port interface for communication with the CCCP.
A TTY interface is also provided for user support.
The RSS processor memory includes flash EPROM and 8 Mbytes of DRAM.
Flash EPROM is used for code storage.
EQCP processor
The EQCP processor handles all radio control functions and the channel
equalizer function. The EQCP controls the Rx and Tx function via the CTU
control function on a per timeslot basis. These EQCP functions include:
Alarm management.
Downlink burst building and modulator control.
Transmitter power control.
Synthesizer channel control.
RF frequency hopping.
Receiver front end and remote tune combiner control.
Uplink synchronization and equalization.
Diversity receiver control.
Receiver Automatic Gain Control (AGC).
Receive signal strength (RXLEV) calculation.
Timing advance calculation.
Support of front panel indicators.
The EQCP communicates with the rest of the digital control functions via the
common PCI bus interface. A TTY interface is provided for radio level
calibration, system monitoring, and CTU level test.
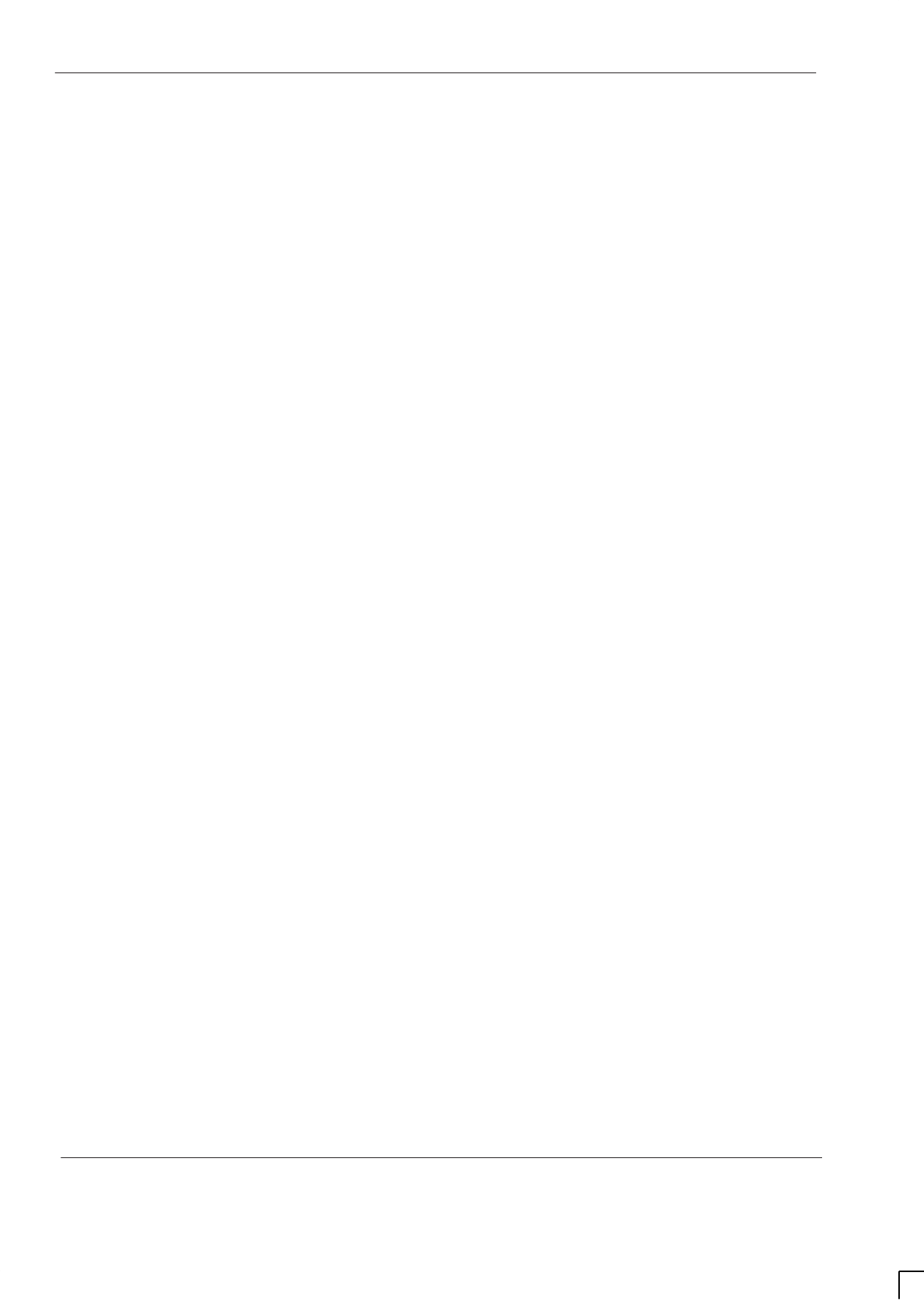
GSM-204-323
Compact transceiver unit (CTU)
31st Oct 01
Tech. 5–18
Technical Description: Horizon
macro
outdoor
CONTROLLED INTRODUCTION
68P02902W02-A
CCCP processor
The CCCP processor handles all the GSM specified layer 1 channel encoding
and decoding functions for speech and control data associated with the air
interface. In addition, it manages the routeing of TRAU frames and baseband
hopping (BBH) data, via the TDM interface, to and from the MCUF. The CCCP
functions include:
Uplink channel decoding.
Downlink channel encoding.
GSM specified encryption algorithms.
Baseband frequency hopping (not supported in GSM850 or PCS1900
BTS variants).
TRAU frame collection and synchronization.
Alarms management.
The CCCP communicates with the rest of the digital control functions via the
common PCI bus interface. A dual port RAM (DPR) is also used in the downlink
direction for communications from RSS. In addition to the TDM function, a serial
link is provided to support uplink and downlink TRAU data.
CTU interface function
The CTU interface function provides the air interface timing and radio control
circuitry required for Rx (uplink) and Tx (downlink) control functions. A common
PCI bus allows all the processing elements, including the RSS processor,
EQCP, and CCCP, to communicate with the various CTU functions. The CTU
interface includes:
Master GSM air interface timing function.
Independent Rx gain control interface for each diversity receiver branch.
Baseband Rx data interface for each diversity receiver branch.
Receiver front end and remote tune combiner control.
Tx data interface, including GMSK modulator which provides baseband
data to the transmitter.
Tx and power amplifier power control interface.
Rx and Tx frequency synthesizer control, which supports RF frequency
hopping.
CTU and cabinet alarm data collection.
Alarms sampling and multiplexing.
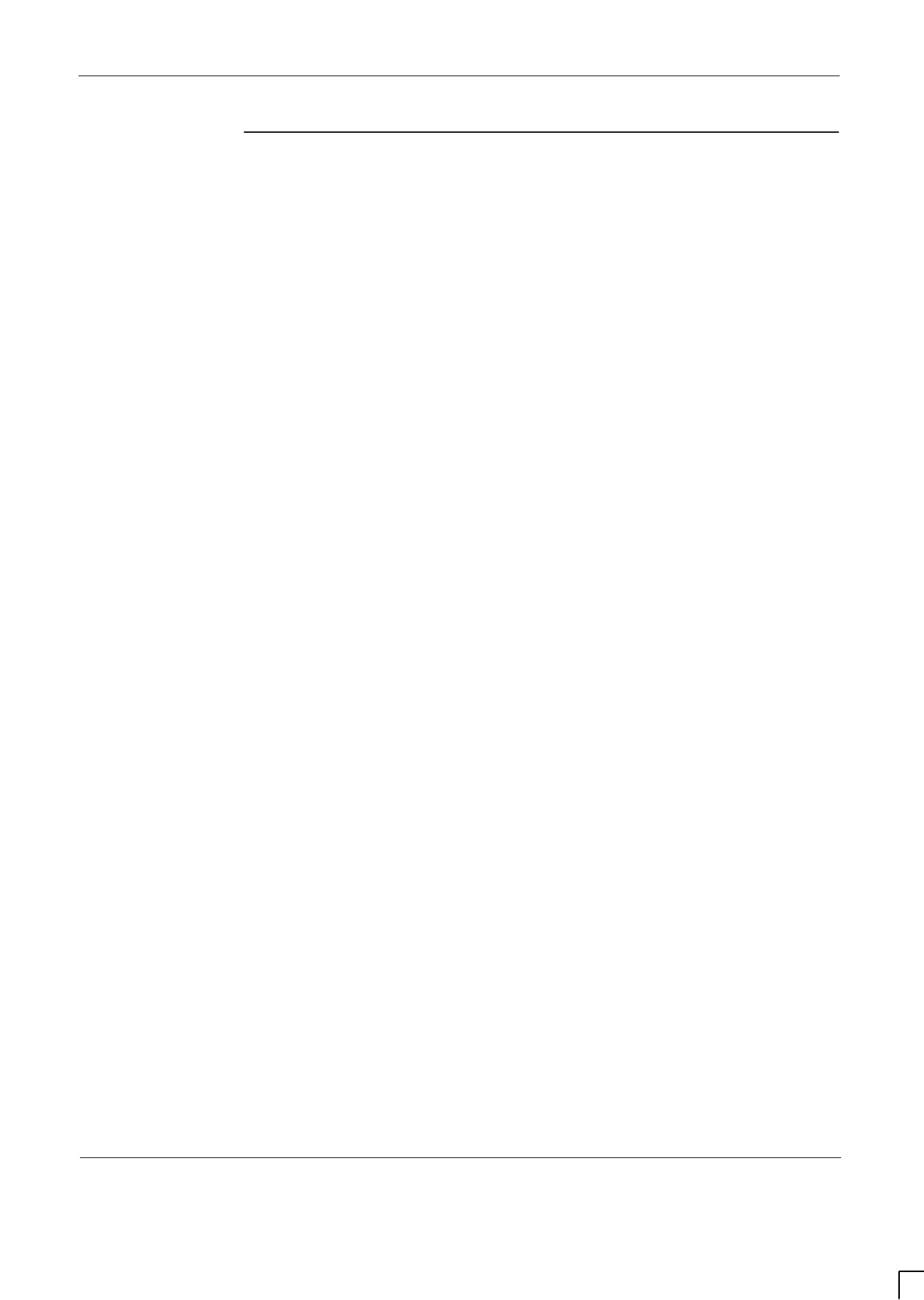
GSM-204-323 Compact transceiver unit (CTU)
31st Oct 01
Technical Description: Horizon
macro
outdoor
68P02902W02-A
CONTROLLED INTRODUCTION
Tech. 5–19
CTU
uplink/downlink
Downlink traffic data flow
Downlink TRAU data is received by the TDM function from the MCUF. This data
is then routed to the CCCP function, where it is encoded (cyclic, block, and
convolutional), interleaved, and encrypted to GSM recommendations.
Signalling messages are also received from the RSS processor and encoded.
These traffic and control messages are built into air interface frames and then
routed back to the MCUF via the TDM function for baseband hopping. The
CCCP calculates a BBH routeing word, which informs the MCUF as to which
fibre link it would like to be the source of its post-hopped data. The post-hopped
data is then once again sent back down to the appropriate CTU where it is
received by the TDM function and passed to the EQCP function. The EQCP
inserts training sequence and guard bits to the data bits and forwards the data
on to the modulator for transmission. The EQCP also programs the CTU for the
correct RF channel and transmit power level for this transmitted burst.
Uplink traffic data flow
Baseband uplink traffic and control data messages are received by the CTU
interface function and sent to the EQCP where they are equalized. The EQCP
also calculates timing advance and RXLEV information, which is forwarded to
the RSS process. The recovered data bits are forwarded into the CCCP
process, where it is de-interleaved, decoded, and decrypted into TRAU frames.
Control messages are passed to the RSS function, while TRAU frames are sent
to the MCUF via the TDM interface.
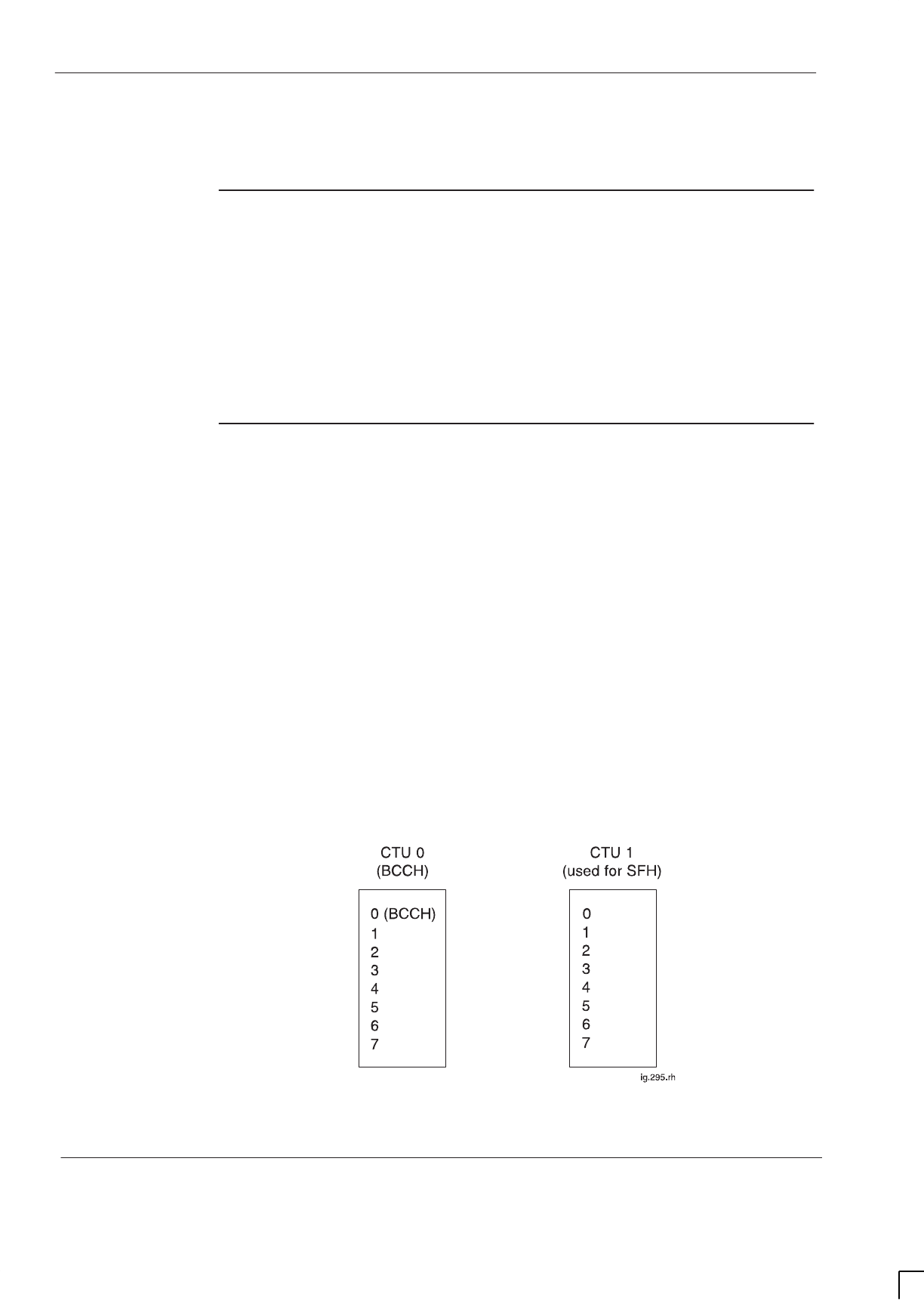
GSM-204-323
CTU frequency hopping
31st Oct 01
Tech. 5–20
Technical Description: Horizon
macro
outdoor
CONTROLLED INTRODUCTION
68P02902W02-A
CTU frequency hopping
Overview of
CTU frequency
hopping
The CTU supports two types of frequency hopping, Synthesizer Frequency
Hopping (SFH) and BaseBand frequency Hopping (BBH). This section provides
an explanation of both types.
In both cases, the MS switches channels after every transmit/receive (Tx/Rx)
burst pair. The difference between SFH and BBH is in the method by which
channel switching is achieved at the BTS.
Synthesizer
frequency
hopping (SFH)
SFH uses the frequency agility of the CTU to change Tx/Rx frequency on any
timeslot (TS), without affecting other timeslots.
Only wideband (CBF/Hybrid) combining can be used with SFH.
With SFH, each TS is allocated a number of frequencies (max 64) over which to
perform the hopping. When determining the hardware requirement for CTUs
using SFH, the following rules apply:
A minimum of two CTUs are required per cell due to BCCH requirements.
Timeslot 0 of CTU 0 is used for the BCCH carrier as shown in Figure 5-10.
CTU 0 cannot use SFH. Only CTU 1 and additional CTUs can use SFH.
Hopping through the BCCH carrier (using the BCCH carrier frequency as
one of the SFH frequencies) is permitted except for timeslot 0. However,
the corresponding timeslot for the BCCH CTU will be switched off for this
period.
Figure 5-10 shows the minimum SFH requirement.
Figure 5-10 Minimum SFH requirement
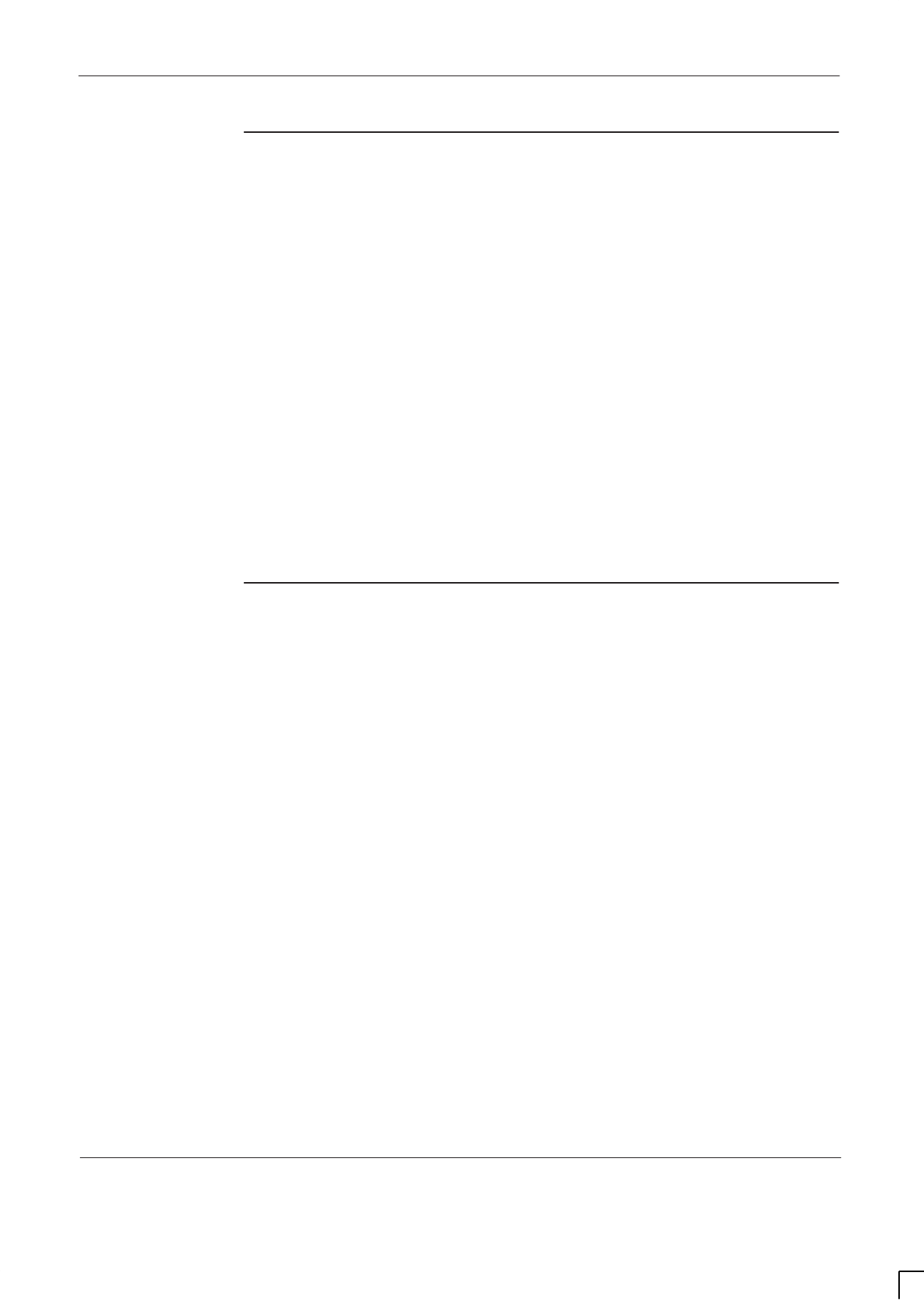
GSM-204-323 CTU frequency hopping
31st Oct 01
Technical Description: Horizon
macro
outdoor
68P02902W02-A
CONTROLLED INTRODUCTION
Tech. 5–21
SFH example
not through
BCCH
CTU 0
In this example of SFH, CTU 0 provides the BCCH and cannot frequency hop.
CTU 0 has to transmit at maximum cell site power to meet the BCCH
requirement. Timeslots are used as shown below:
TS 0 = Combined BCCH TS (BCCH/CCCH/DCCH). Transmitted at
maximum cell site power.
TS 1-7 = Traffic channels, all non-hopping. All traffic channels transmit at
maximum cell site power.
CTU 1 and additional CTUs
CTU 1 and any additional CTUs provide SFH traffic channels as shown below:
TS 0-7 = Frequency hopping traffic channels. The frequency allocated to
the BCCH of CTU 0 cannot be used for frequency hopping purposes.
SFH example
hopping
through BCCH
carrier
CTU 0
In this example of SFH, CTU 0 provides the BCCH and cannot frequency hop.
CTU 0 has to transmit at maximum cell site power to meet the BCCH
requirement. Timeslots are used as shown below:
TS 0 = Combined BCCH timeslot (BCCH/CCCH/DCCH). Transmitted at
maximum cell site power.
TS 1-7 = Unused timeslots transmitting dummy bursts for BCCH. All
channels transmit at maximum cell site power.
CTU 1 and additional CTUs
CTU 1 and any additional CTUs provide SFH traffic channels as shown below:
TS 0 = Frequency hopping traffic channel, but prevented from using
BCCH frequency.
TS 1-7 =Frequency hopping traffic channels, using all available
frequencies, including BCCH.
When the SFH selects the BCCH frequency, the CTU transmits at maximum cell
site power and the corresponding TS on CTU 0 is switched off for this period.
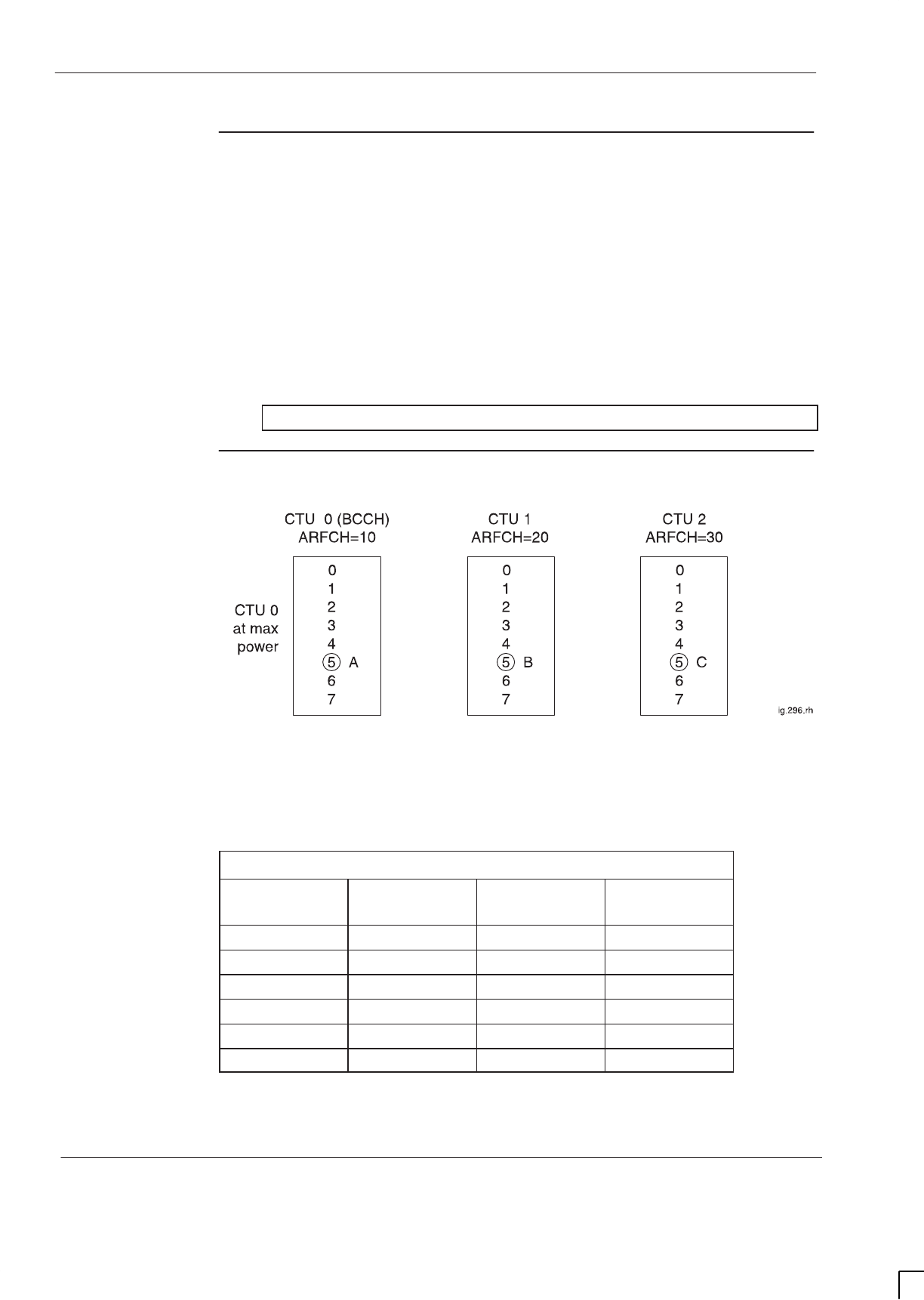
GSM-204-323
CTU frequency hopping
31st Oct 01
Tech. 5–22
Technical Description: Horizon
macro
outdoor
CONTROLLED INTRODUCTION
68P02902W02-A
Baseband
frequency
hopping (BBH)
BBH requires all eight timeslots of the CTU Tx (downlink) at the same frequency.
In the Rx (uplink) direction, the frequency agility of the CTU is used to change
timeslot frequencies on a timeslot basis. The BCCH frequency is always
transmitted at maximum cell site power.
BBH can use either Tx blocks or CCB Tx combining equipment. The main
reason for using BBH instead of SFH is to enable frequency hopping when
using CCBs, because the mechanical tuning of CCBs is too slow for SFH.
The number of CTUs required to support BBH is equal to the number of
frequencies used.
NOTE BBH is not supported on GSM850 or PCS1900 BTSs.
BBH example
In Figure 5-11 MSs A, B and C are using TS 5 of CTUs 0, 1 and 2 respectively.
Figure 5-11 Diagram of BBH example using three CTUs
If the MSs are using cyclic hopping across ARFCNs 10, 20, 30 (an example
using EGSM900), each MS must transmit a burst of information each TDMA
frame (4.615 ms) on a different frequency. The data for the burst is received by
each CTU in turn (ARFCN 10, 20, 30), as shown in Table 5-3:
Table 5-3 BBH sequence example (EGSM900)
Burst Sequence
Steps CTU 0
Tx Rx
CTU 1
Tx Rx
CTU 2
Tx Rx
1 A10 A10 B20 B20 C30 C30
2 C10 A20 A20 B30 B30 C10
3 B10 A30 C20 B10 A30 C20
4 (same as 1) A10 A10 B20 B20 C30 C30
5 (same as 2) C10 A20 A20 B30 B30 C10
6 (same as 3) B10 A30 C20 B10 A30 C20
In the uplink direction, the controlling CTU (for example CTU 0 for MS A in
Figure 5-11) tunes TS 5 in accordance with the frequency expected from the MS
for that particular burst.
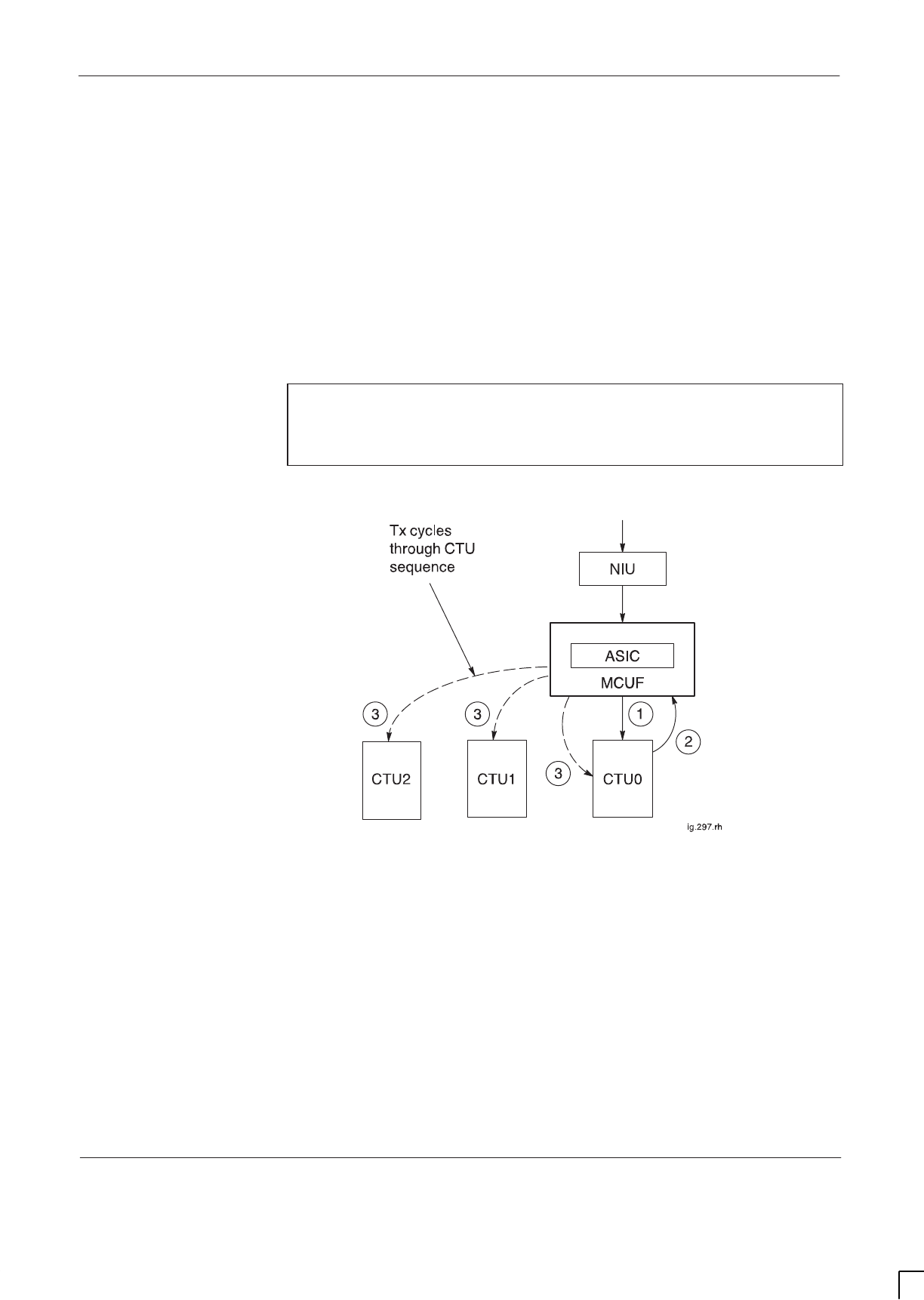
GSM-204-323 CTU frequency hopping
31st Oct 01
Technical Description: Horizon
macro
outdoor
68P02902W02-A
CONTROLLED INTRODUCTION
Tech. 5–23
Transmit
The transmit is described by the following, as shown in Figure 5-12:
1. Traffic data from the network is passed through the NIU to the MCUF.
Within the MCUF an ASIC switches the data to CTU 0 (the dedicated CTU
for this particular MS call example).
2. The CTU, having processed the data (channel coding, interleaving,
encryption and routeing information) then passes the data back to the
ASIC.
3. The ASIC follows the BBH routeing information to direct the data to the
next Tx CTU in the sequence of Table 5-3.
NOTE BBH differs from normal and SFH CTU Tx procedures, in
that the data is directed to CTUs in a cyclic sequence at
stage 3. Without BBH, stage 3 always routes data to the
original CTU.
Figure 5-12 shows a schematic diagram of an example of baseband hopping.
Figure 5-12 Schematic of baseband hopping (BBH) example
Receive
Data from the MS is received by one CTU allocated to that MS (in this case
CTU 0). The CTU will synthesize hop to the Rx signal. This ensures that the
handover and equalizers within only one CTU will be connected to a particular
MS.
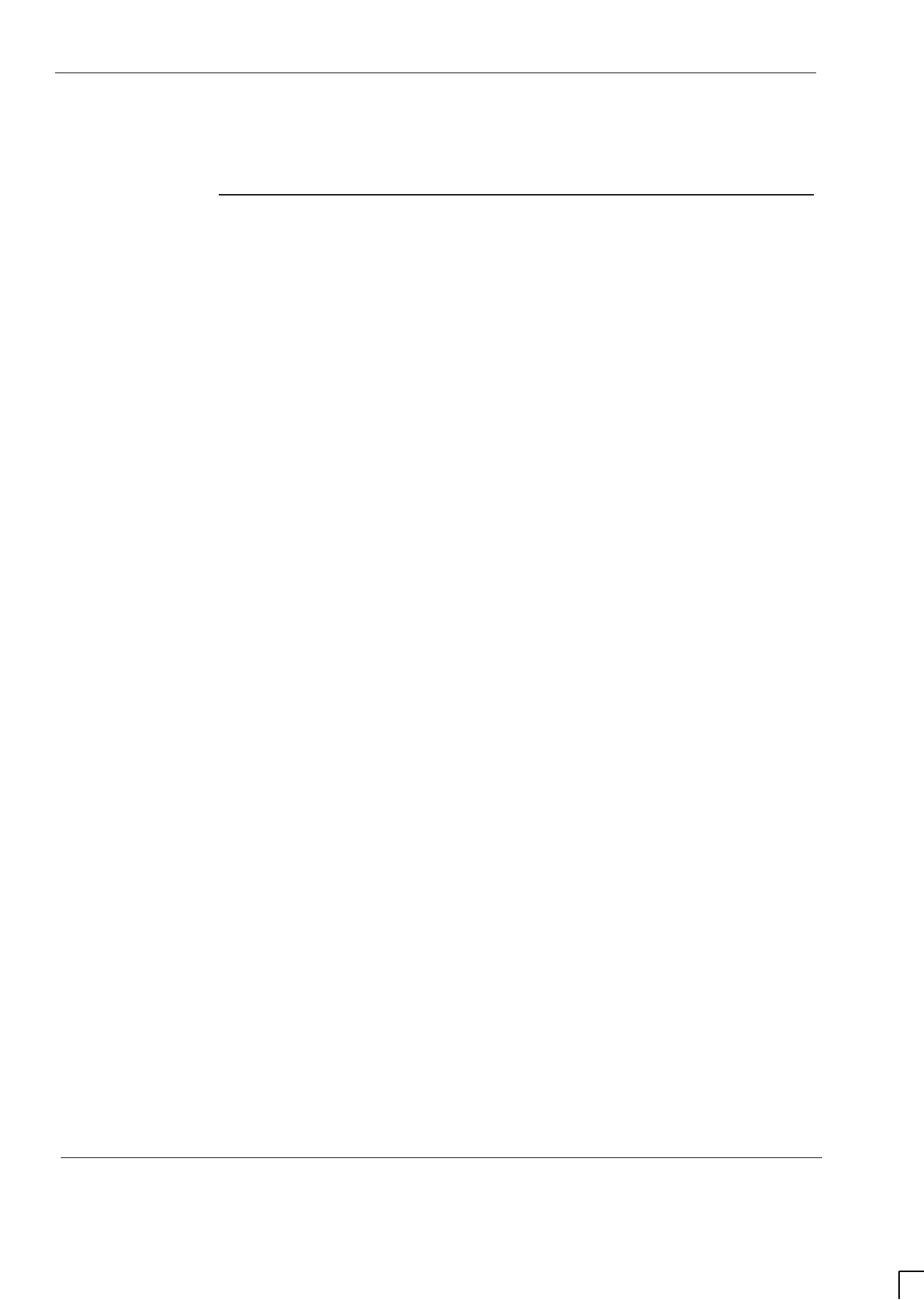
GSM-204-323
SURF module
31st Oct 01
Tech. 5–24
Technical Description: Horizon
macro
outdoor
CONTROLLED INTRODUCTION
68P02902W02-A
SURF module
SURF module
overview
The sectorized universal receiver front end (SURF) module is located in a slot at
the rear of the cabinet top panel. Three connectors on the underside of the
module connect to the SURF harness which provides connectivity to up to six
compact transceiver units (CTUs). Antenna connections are located on the top
of the unit.
There are six types of SURF module available for the Horizon
macro
outdoor
BTS, depending on the frequency variant:
850 (MHz) single band SURF.
900 (MHz) single band SURF.
900 (MHz) dual band SURF.
1800 (MHz) single band SURF.
1800 (MHz) dual band SURF.
1900 (MHz) single band SURF.
The single band SURFs contains three amplifier sections for connection to three
pairs of receive antenna inputs providing reception at the appropriate frequency.
The 900 dual band SURF contains three amplifier sections for connection to
three pairs of antennas providing 900 MHz reception and, being dual band, a
further amplifier section for connection to a pair of 1800 MHz receive antennas.
The 1800 dual band SURF similarly contains three amplifier sections for
connection to three pairs of antennas providing 1800 MHz reception and a
further amplifier section for connection to a pair of 900 MHz receive antennas.
Each amplifier section provides two receive outputs which may be directed to
any of the six CTUs, by the switch section. There are three connections to each
CTU; RxA, RxB and loopback test (L).
The two receive outputs from amplifier 0 are split and may be used as
extensions to other cabinets if required. These act as extended antenna
connections from antenna 0. The extension cables are connected to the
receive antenna connection ports on the SURF of the extension cabinet (which
is able to respond to each amplified signal as if it were a normal antenna input).
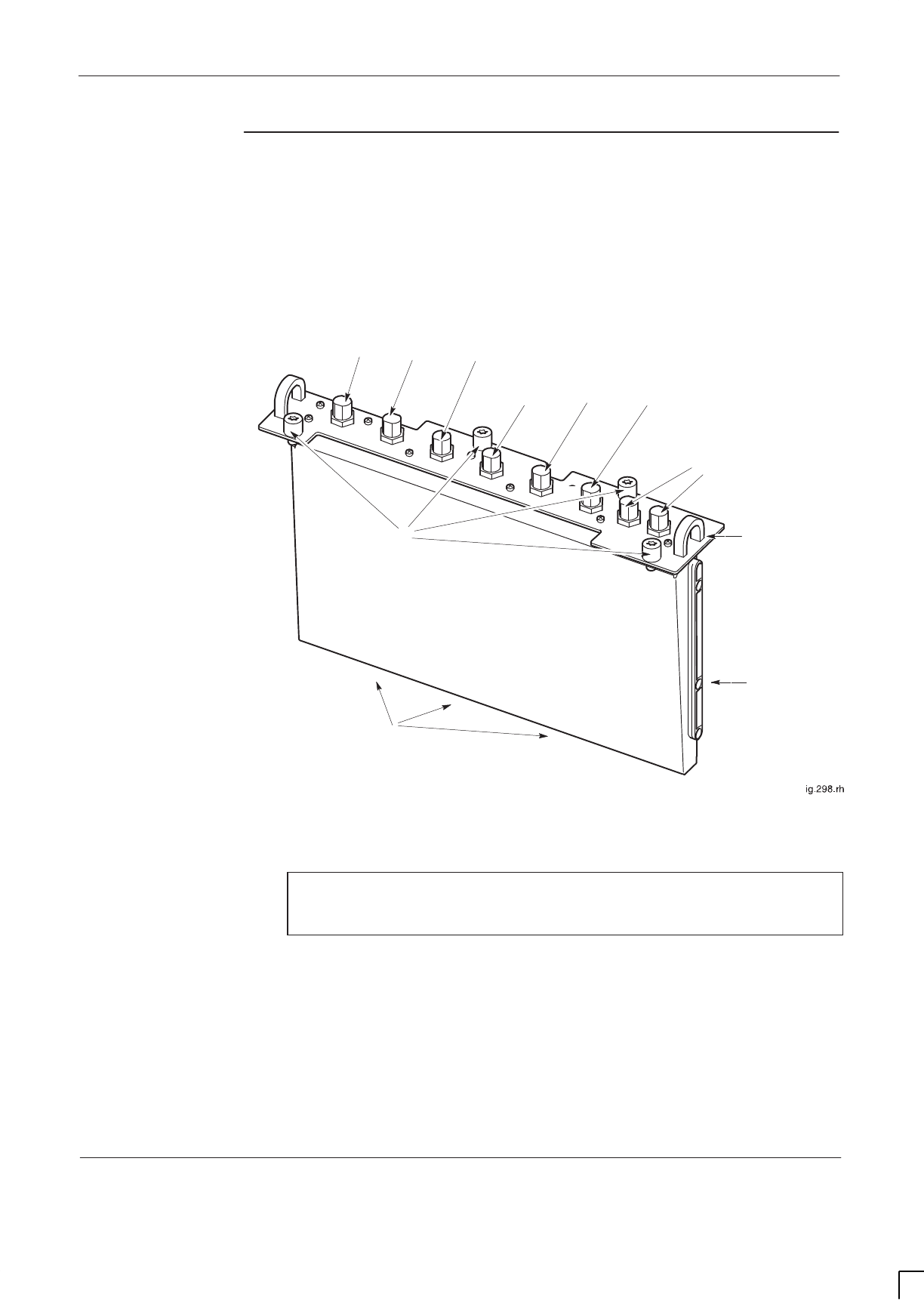
GSM-204-323 SURF module
31st Oct 01
Technical Description: Horizon
macro
outdoor
68P02902W02-A
CONTROLLED INTRODUCTION
Tech. 5–25
Single band
SURF module
view
Figure 5-13 shows a view of a single band SURF module, with features
identified.
RXn
1B
RXn
2B
GUIDE RAIL FOR
INSERTION
SIX N-TYPE RECEIVE ANTENNA CONNECTIONS
(2 PER DLNB EQUIVALENT)
EXTENSION PORTS TO
OTHER CABINETS
3 CONNECTORS ON UNDERSIDE
TO SURF HARNESS
HANDLE FOR
MODULE
REMOVAL
M6 MODULE
ATTACHMENT
SCREWS
RXn
0A
RXn
1A
RXn
2A
RXn
0B
SURF
MODULE
Figure 5-13 View of single band SURF module
NOTE Where RXn appears in Figure 5-13, the n may be 850,
900, 1800 or 1900, depending on the frequency of the
SURF module.
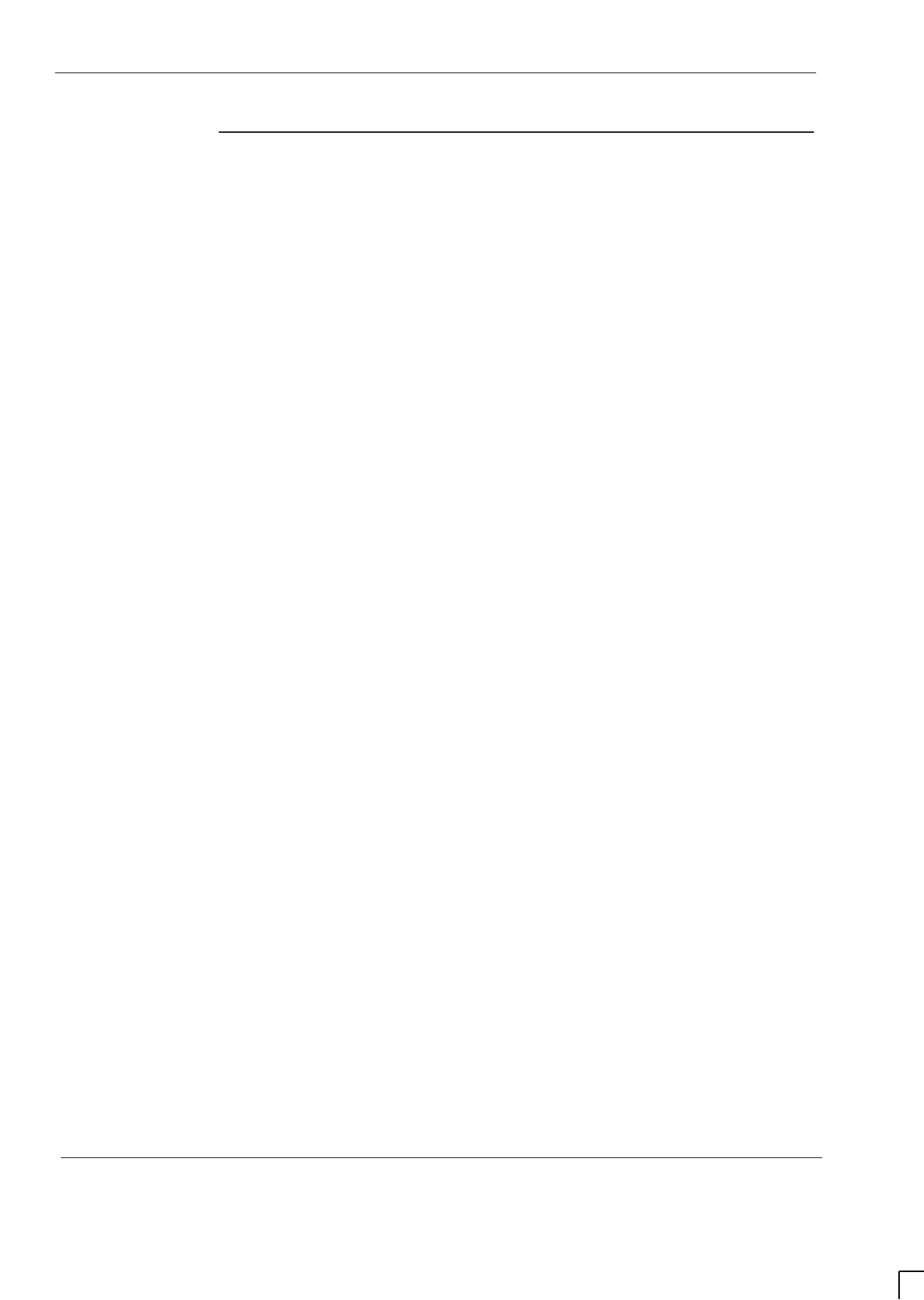
GSM-204-323
SURF module
31st Oct 01
Tech. 5–26
Technical Description: Horizon
macro
outdoor
CONTROLLED INTRODUCTION
68P02902W02-A
Functional
description of
the single band
SURF
The single band SURF provides front end filtering, amplification, and matrix
control of the RF receive signal between the antenna and the CTU
The single band SURF functional sections (Figure 5-14) consist of loopback,
filtering, amplification, splitting, digital processing and power selection.
Each section is duplicated for the second diversity path except for the digital
and dc power section which is shared by the two diversity paths. There are
three antenna pair inputs (ANT 0, ANT 1 and ANT 2) for each of the two
diversity branches (Branch A and Branch B). There are six outputs to the CTU
for each of the two diversity branches as well as one input from the CTU for the
loopback (LPBK) signal. There is also an output for an expansion cabinet for
ANT 0 on each branch.
The software database must be configured at the OMC-R to accept CTUs of the
same frequency in the appropriate cabinet locations.
The digital section switch, under the control of the database (signalled through
the MCUF and CTUs), routes the six amplifier outputs to the appropriate CTUs.
The digital and power supply section is also responsible for loopback switch
control, manual overrides, alarms and dc voltages.
The RF loopback test function is described in RF overview and RF test
function in this chapter.
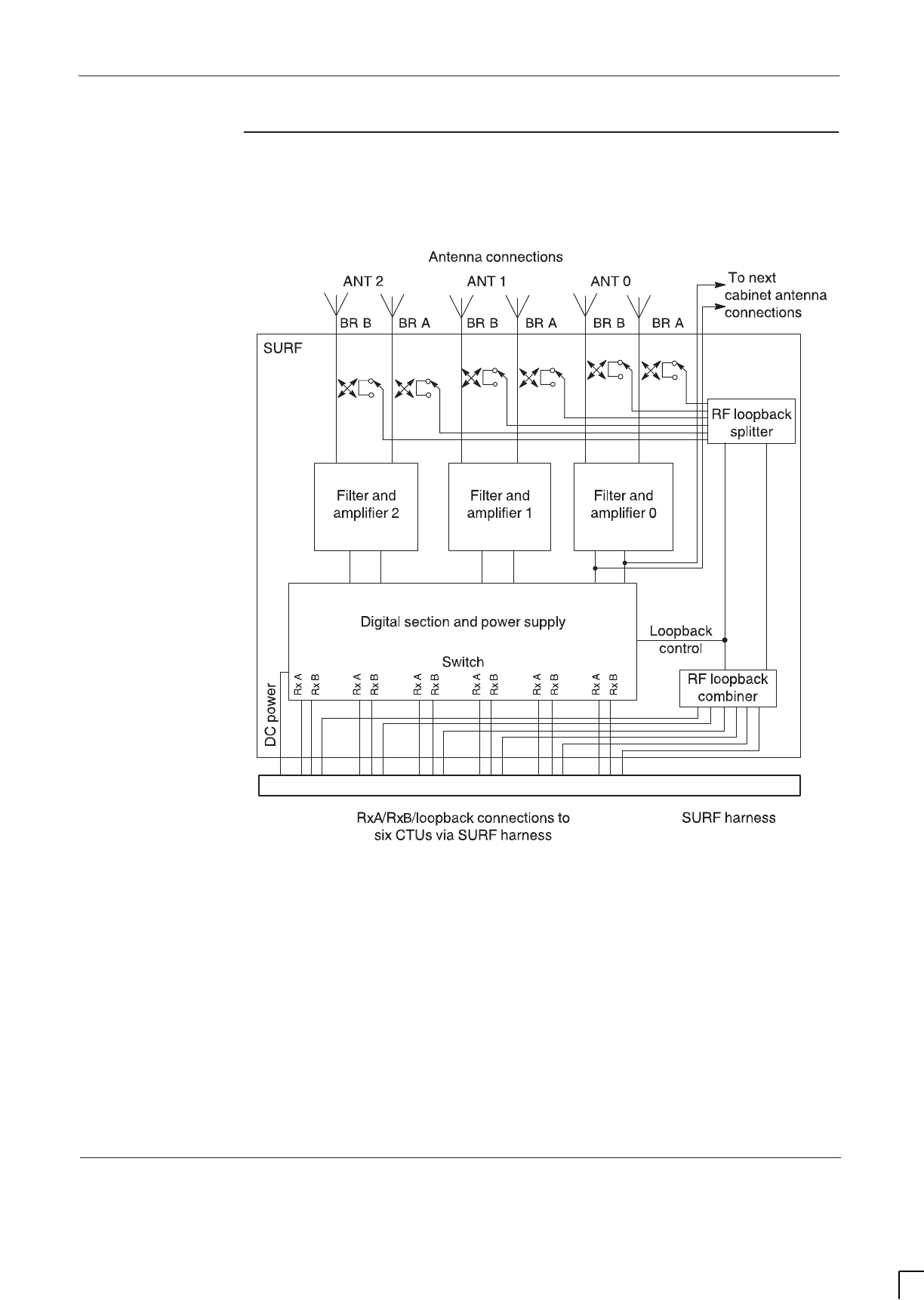
GSM-204-323 SURF module
31st Oct 01
Technical Description: Horizon
macro
outdoor
68P02902W02-A
CONTROLLED INTRODUCTION
Tech. 5–27
Single band
SURF functional
diagram
Figure 5-14 shows a functional diagram of the single band SURF module.
Figure 5-14 Functional diagram of the single band SURF module
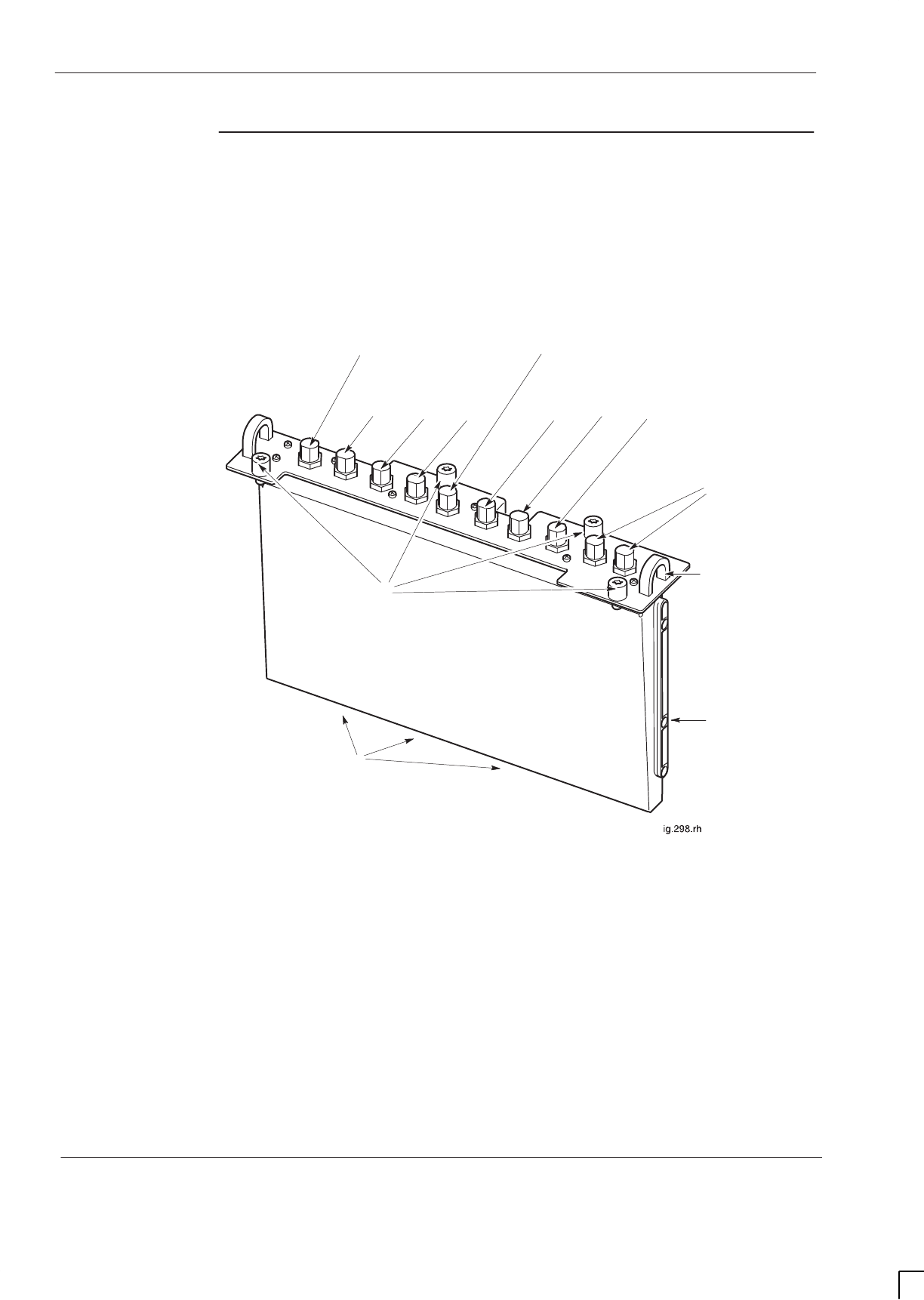
GSM-204-323
SURF module
31st Oct 01
Tech. 5–28
Technical Description: Horizon
macro
outdoor
CONTROLLED INTRODUCTION
68P02902W02-A
Dual band
SURF module
view
Figure 5-15 shows a view of a dual band SURF module with features identified,
both the 900 and 1800 variants are similar in appearance.
GUIDE RAIL
FOR INSERTION
EXTENSION PORTS
TO OTHER CABINETS
3 CONNECTORS ON
UNDERSIDE TO SURF
HARNESS
HANDLE FOR
MODULE
REMOVAL
M6 MODULE
ATTACHMENT SCREWS
DUAL BAND
SURF
EIGHT N-TYPE RECEIVE ANTENNA CONNECTIONS
(2 PER DLNB EQUIVALENT)
SECOND
FREQUENCY Rx 0B
MAIN FREQUENCY
Rx 1BRx 2B Rx 0B
SECOND
FREQUENCY Rx 0A
Rx 0ARx 1ARx 2A
MAIN FREQUENCY
Figure 5-15 View of dual band SURF module with features identified
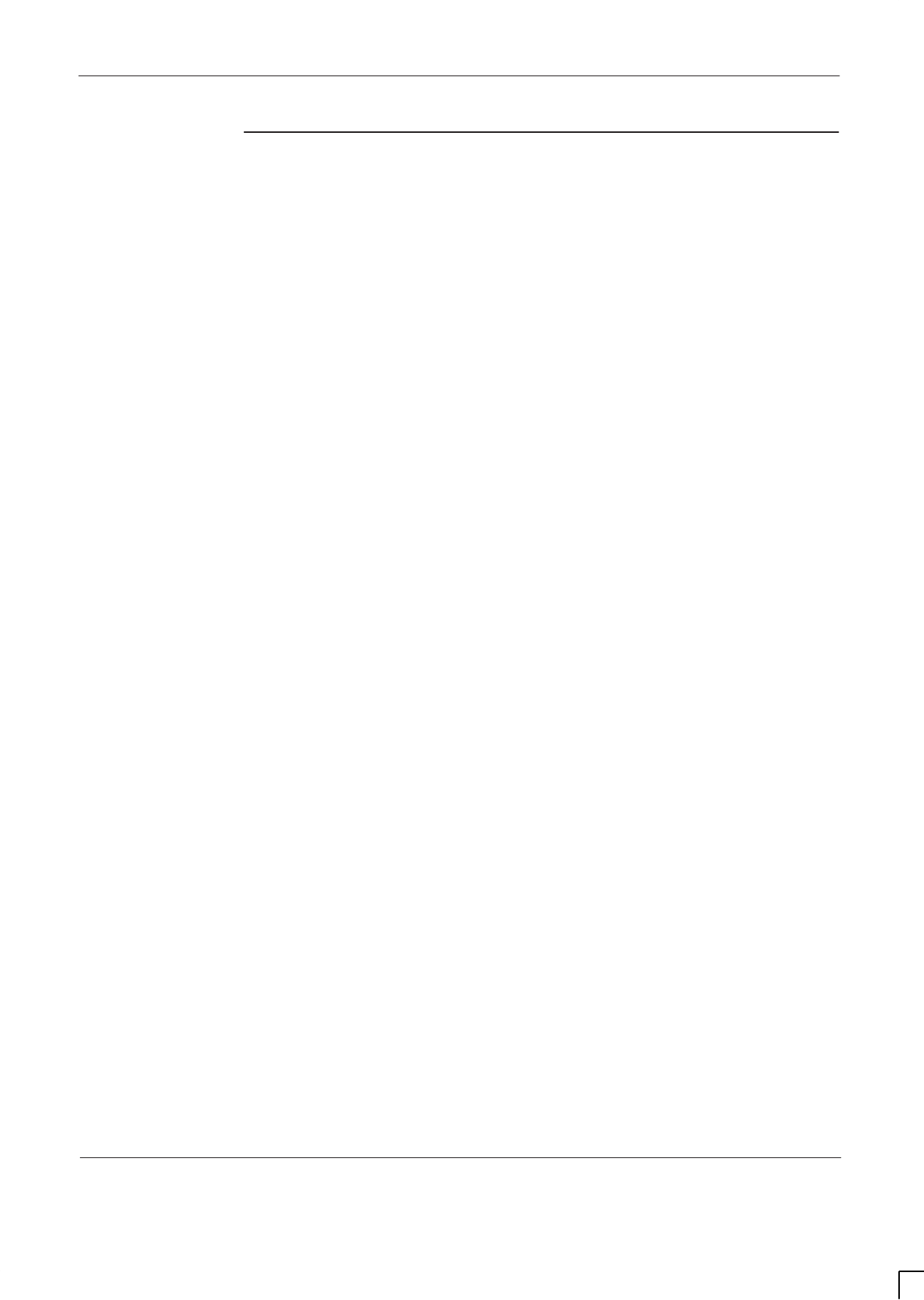
GSM-204-323 SURF module
31st Oct 01
Technical Description: Horizon
macro
outdoor
68P02902W02-A
CONTROLLED INTRODUCTION
Tech. 5–29
Functional
description of
dual band SURF
modules
The dual band SURF modules provide front end filtering, amplification, and
matrix control of the RF receive signal between the antenna and the CTU. The
dual band SURFs each have three antenna pair connections providing main
frequency reception, and one antenna pair providing reception on a second
frequency. The two types of dual band (DB) SURF enable 900 CTUs to be
mixed with 1800 CTUs in any combination, up to the maximum total of six CTUs
per cabinet.
The dual band SURF functional sections (see Figure 5-16) consist of loopback,
filtering, amplification, splitting, digital processing and power selection.
Each section is duplicated for the second diversity path, except for the digital
and dc power section, which is shared by the two diversity paths. There are four
antenna pair inputs (ANT 0, ANT 1, ANT 2 and ANT DB) for each of the two
diversity branches (branch A and branch B). There are six outputs to the CTU
for each of the two diversity branches, as well as one input from the CTU for the
loopback (LPBK) signal. There is also an output for an expansion cabinet for
ANT 0 on each branch.
The software database has to be configured at the OMC-R to accept 1800
CTUs and 900 CTUs in the appropriate cabinet locations.
Digital codes are transmitted from the 900 CTUs and 1800 CTUs to the digital
section. The digital codes are different, so that 900 or 1800 CTUs can be
recognized and appropriate switching can be made to the required antenna for
transmission and reception.
The digital and power supply section is also responsible for loopback switch
control, manual overrides, alarms and dc voltages.
The RF loopback test function is described in RF overview and RF test
function in this chapter.
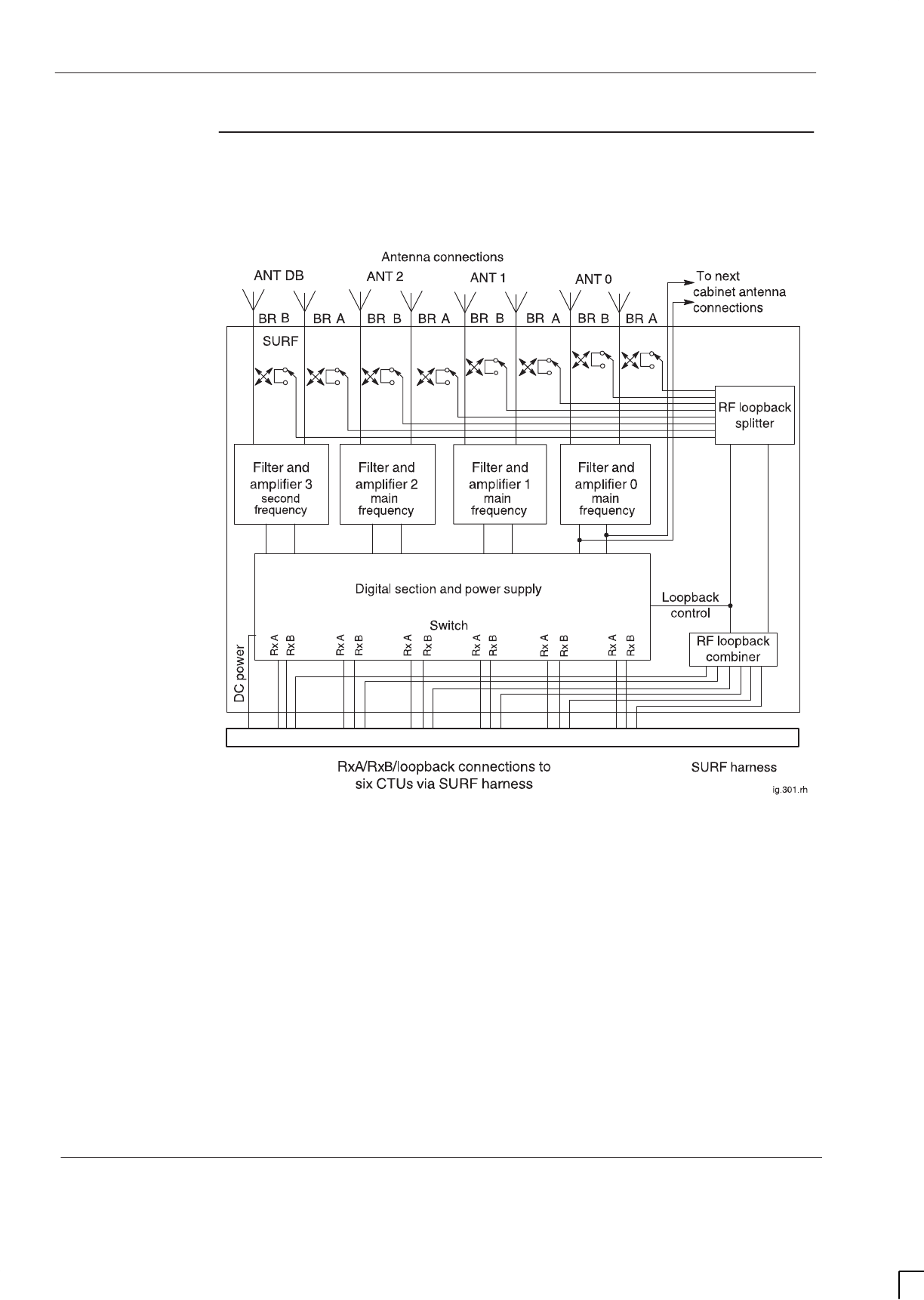
GSM-204-323
SURF module
31st Oct 01
Tech. 5–30
Technical Description: Horizon
macro
outdoor
CONTROLLED INTRODUCTION
68P02902W02-A
Dual band
SURF functional
diagram
Figure 5-16 shows a functional diagram of the dual band SURF module.
Figure 5-16 Functional diagram of the dual band SURF module
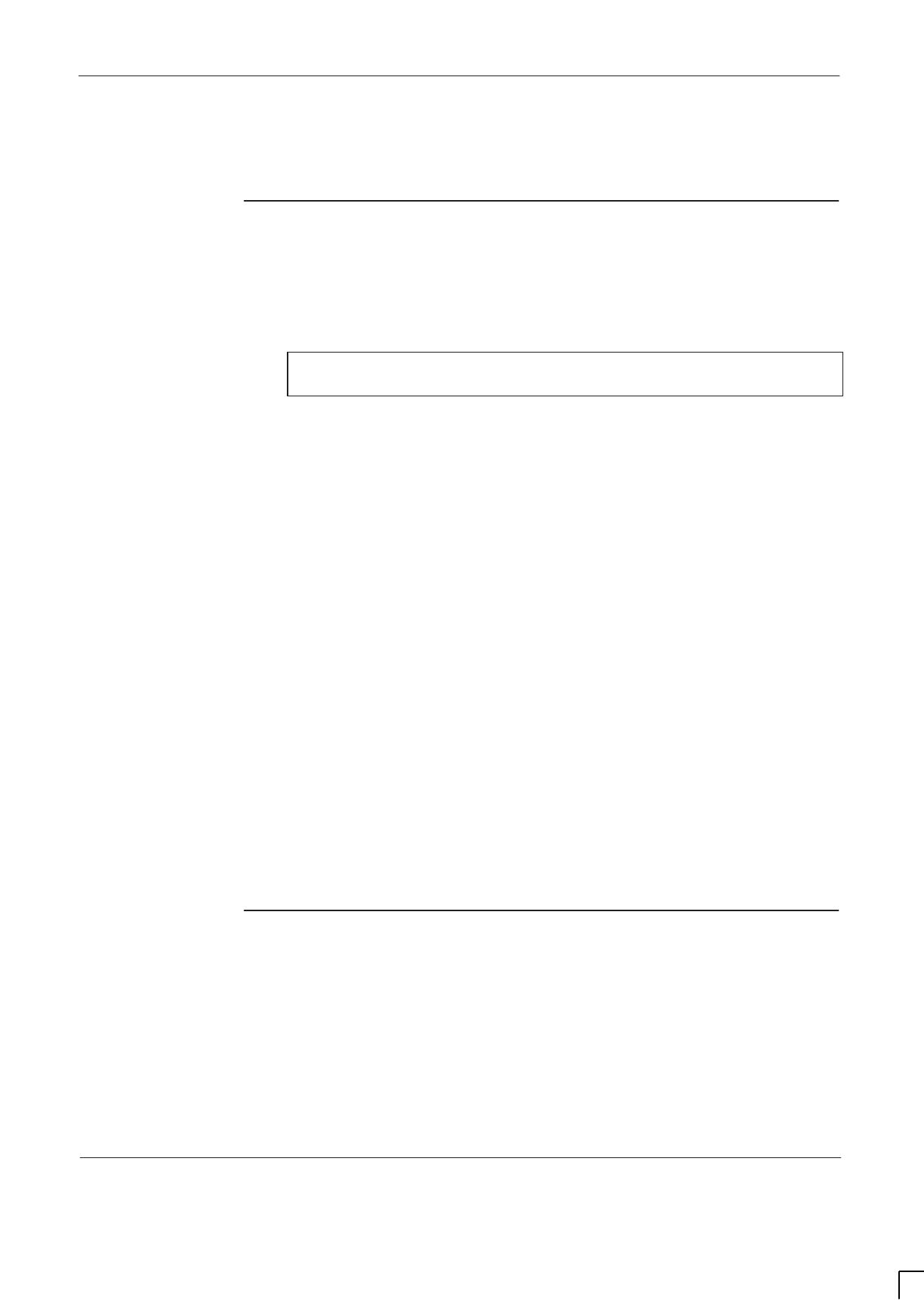
GSM-204-323 Transmit blocks overview
31st Oct 01
Technical Description: Horizon
macro
outdoor
68P02902W02-A
CONTROLLED INTRODUCTION
Tech. 5–31
Transmit blocks overview
Introduction to
transmit blocks
Transmit (Tx) blocks are located in three positions in the basket above the
CTUs. There are four types of transmit (Tx) blocks, three of which are available
as 850, 900, 1800 or 1900 variants, and one dual band variant (for use with
900 MHz or 1800 MHz BTSs only).
CAUTION Unused Tx block locations must be covered with a
blanking plate for correct air flow and EMC shielding.
TDF (850, 900, 1800 or 1900) = Twin Duplexed Filter.
Dual band TDF (900/1800) = Dual band twin duplexed filter.
DCF (850, 900, 1800 or 1900) = Duplexed Combining bandpass Filter.
DDF (850, 900, 1800 or 1900) = Dual-stage Duplexed combining Filter.
These Tx blocks are cooled by airflow from underneath. The DDF has fins,
whereas the TDF, dual band TDF and DCF do not.
Tx blocks are attached to the top surface of the top panel using two M6 screws.
Three types of plate can be located in the basket, one as blanking plate and two
to interface CTU Tx cables:
Blanking plate. This ensures proper airflow and EMC shielding for an
unused basket Tx Block location.
Feedthrough plate. This converts two SMA connectors to two N-type
connectors, used for connecting Tx cables to DDFs.
Hybrid Combining Unit (HCU). This combines two SMA connectors to
one N-type, enabling two additional CTUs to be connected to a DDF.
The plates are attached to the base of the top panel basket using six M4
screws.
Screw retention
in Tx block
locations
The plates are attached to the base of the top panel basket using six M4
screws.
Tx blocks are attached to the top surface of the top panel using two M6 screws.
To ensure correct EMC shielding and general containment, it is important to
ensure that all Tx block/plate screw locations have a screw in place and
tightened to correct torque.
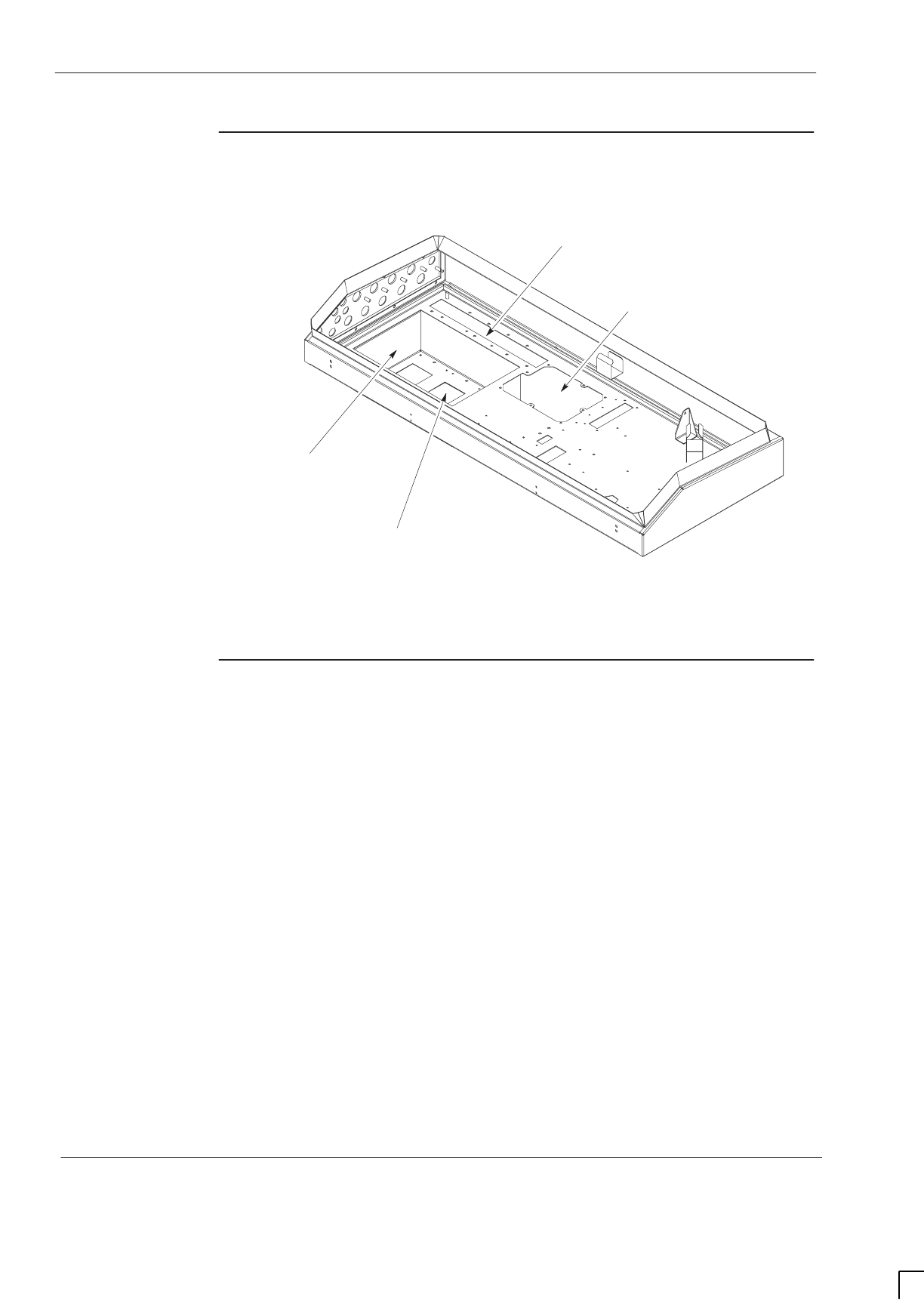
GSM-204-323
Transmit blocks overview
31st Oct 01
Tech. 5–32
Technical Description: Horizon
macro
outdoor
CONTROLLED INTRODUCTION
68P02902W02-A
View of basket
for Tx blocks
Figure 5-17 shows the top section basket which holds the Tx blocks.
SLOT FOR SURF MODULE
LOCATION HOLE
FOR INTERFACE
PANEL
BASKET TO HOLD
THREE Tx BLOCKS
HOLE FOR ONE Tx BLOCK
CTU CONNECTIONS
Figure 5-17 View of top section showing Tx block basket
Transmit block
connectors
The transmit block connectors are of the following types:
SMA connectors for cables to transceivers.
7/16 connectors to antennas.
N-type duplex receive connectors; also used by HCU inputs and the
feedthrough plate.
The SMA connectors are underneath the unit (for ease of connection to the
CTUs), and the other connectors are on top, as shown in Figure 5-18.
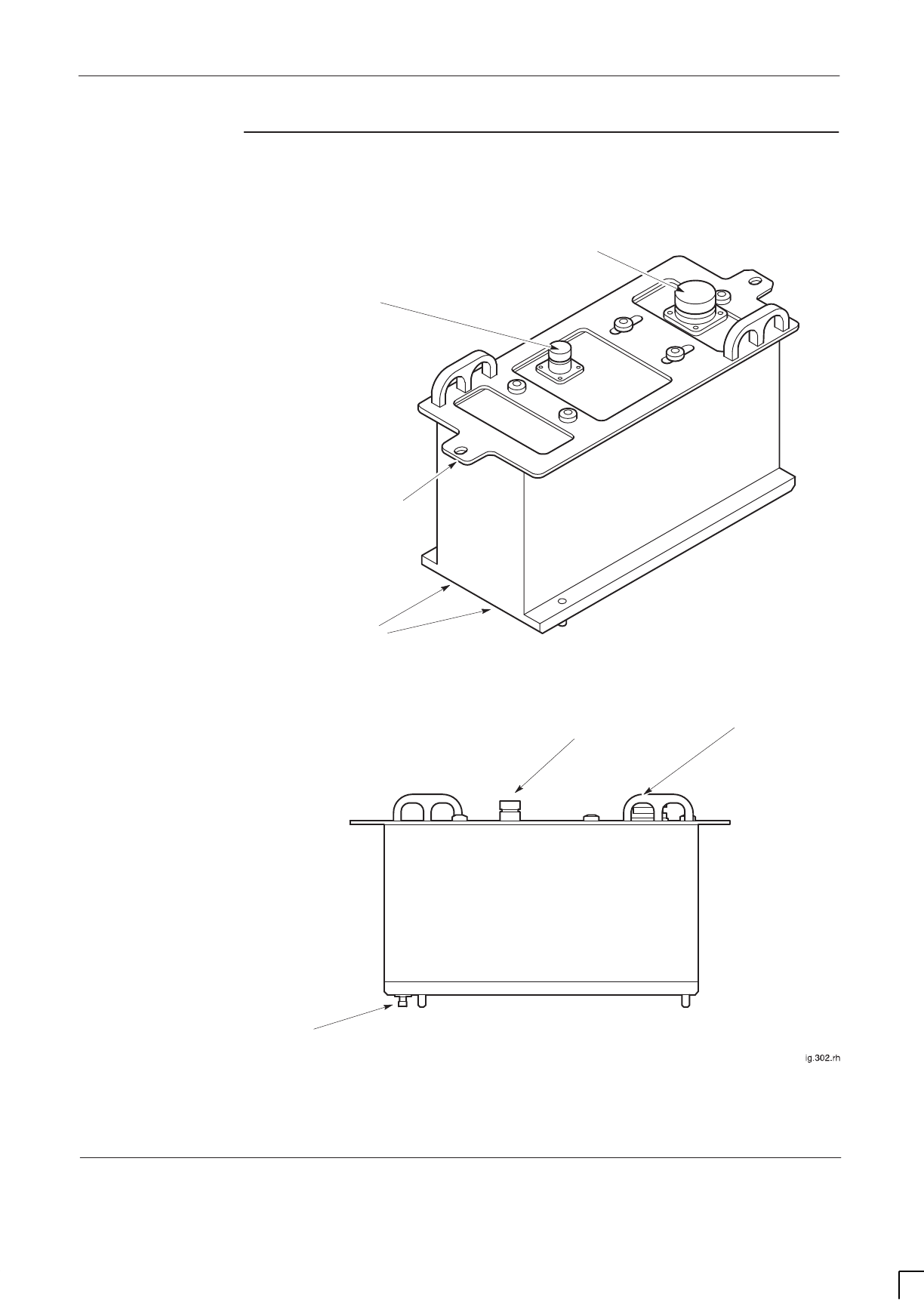
GSM-204-323 Transmit blocks overview
31st Oct 01
Technical Description: Horizon
macro
outdoor
68P02902W02-A
CONTROLLED INTRODUCTION
Tech. 5–33
View of Tx block
connectors
Figure 5-18 shows a typical Tx block with connector locations.
SMA Tx CONNECTORS
FROM CTUs
SIDE VIEW
ISOMETRIC VIEW
7/16 CONNECTOR TO
ANTENNA
N-TYPE CONNECTOR
TO SURF
HOLE FOR TOP
PANEL BASKET
ATTACHMENT
7/16 CONNECTOR TO
ANTENNA
N-TYPE CONNECTOR
TO SURF
SMA Tx CONNECTORS
FROM CTUs
Figure 5-18 Typical Tx block
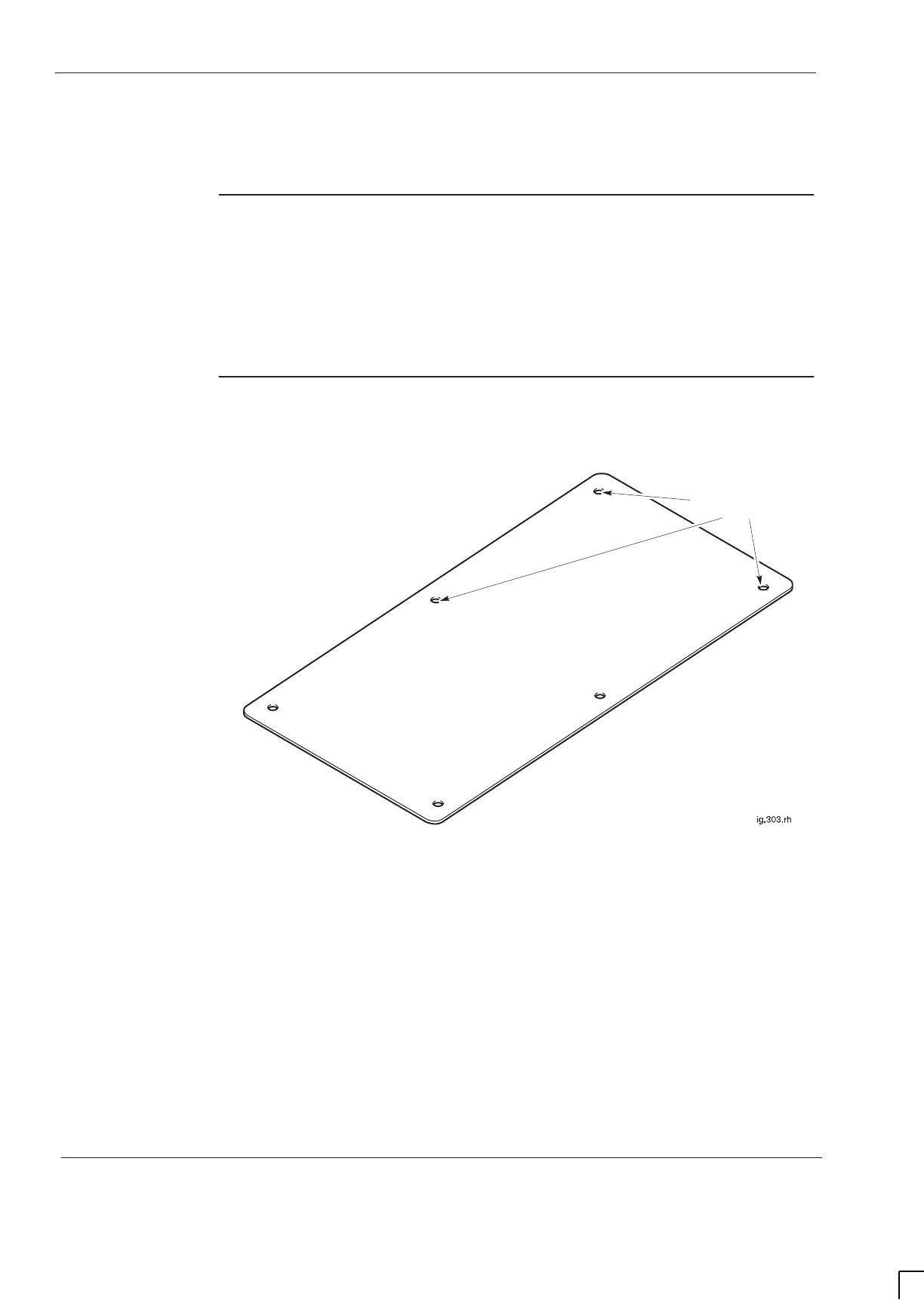
GSM-204-323
Tx block blanking plate
31st Oct 01
Tech. 5–34
Technical Description: Horizon
macro
outdoor
CONTROLLED INTRODUCTION
68P02902W02-A
Tx block blanking plate
Purpose of Tx
block blanking
plate
A blanking plate is fitted in locations where a Tx block is not required. The
blanking plate ensures correct airflow through the cabinet.
The plate is attached to the base of the top panel basket using six M4 screws.
View of Tx block
blanking plate
Figure 5-19 shows a view of the Tx block blanking plate.
M4 HOLES FOR
ATTACHMENT
Figure 5-19 View of Tx block blanking plate
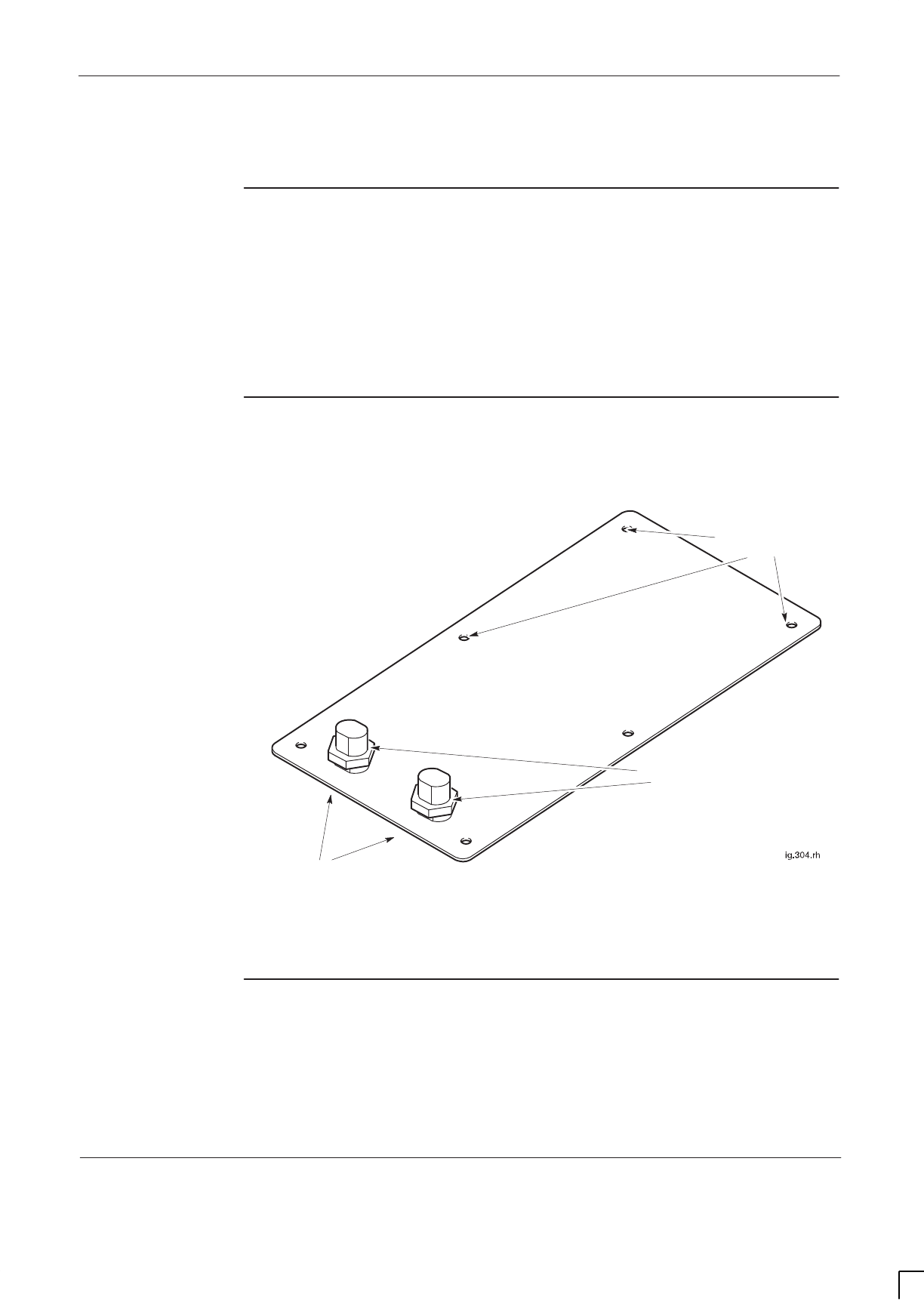
GSM-204-323 Feedthrough plate
31st Oct 01
Technical Description: Horizon
macro
outdoor
68P02902W02-A
CONTROLLED INTRODUCTION
Tech. 5–35
Feedthrough plate
Purpose of
feedthrough
plate
The feedthrough plate converts the normal SMA connector from the CTU to an
N-type connector. Each feedthrough plate has a pair of these converters, one
for each of two CTUs. The top N-type connectors are used to connect with the
(optional) third Tx port on the top of a DDF Tx block.
The plate is attached to the base of the top panel basket using six M4 screws.
View of
feedthrough
plate
Figure 5-20 shows a top view of a feedthrough plate.
N-TYPE
CONNECTORS FOR
CCBs OR DDFs
SMA CONNECTORS BENEATH
FROM CTUs
M4 HOLES FOR
ATTACHMENT
Figure 5-20 View of feedthrough plate
Feedthrough
plate
connectors
Each feedthrough plate connects to:
The Tx outputs of two CTUs, using SMA connectors.
Tx inputs of DDFs, using N-type connectors.
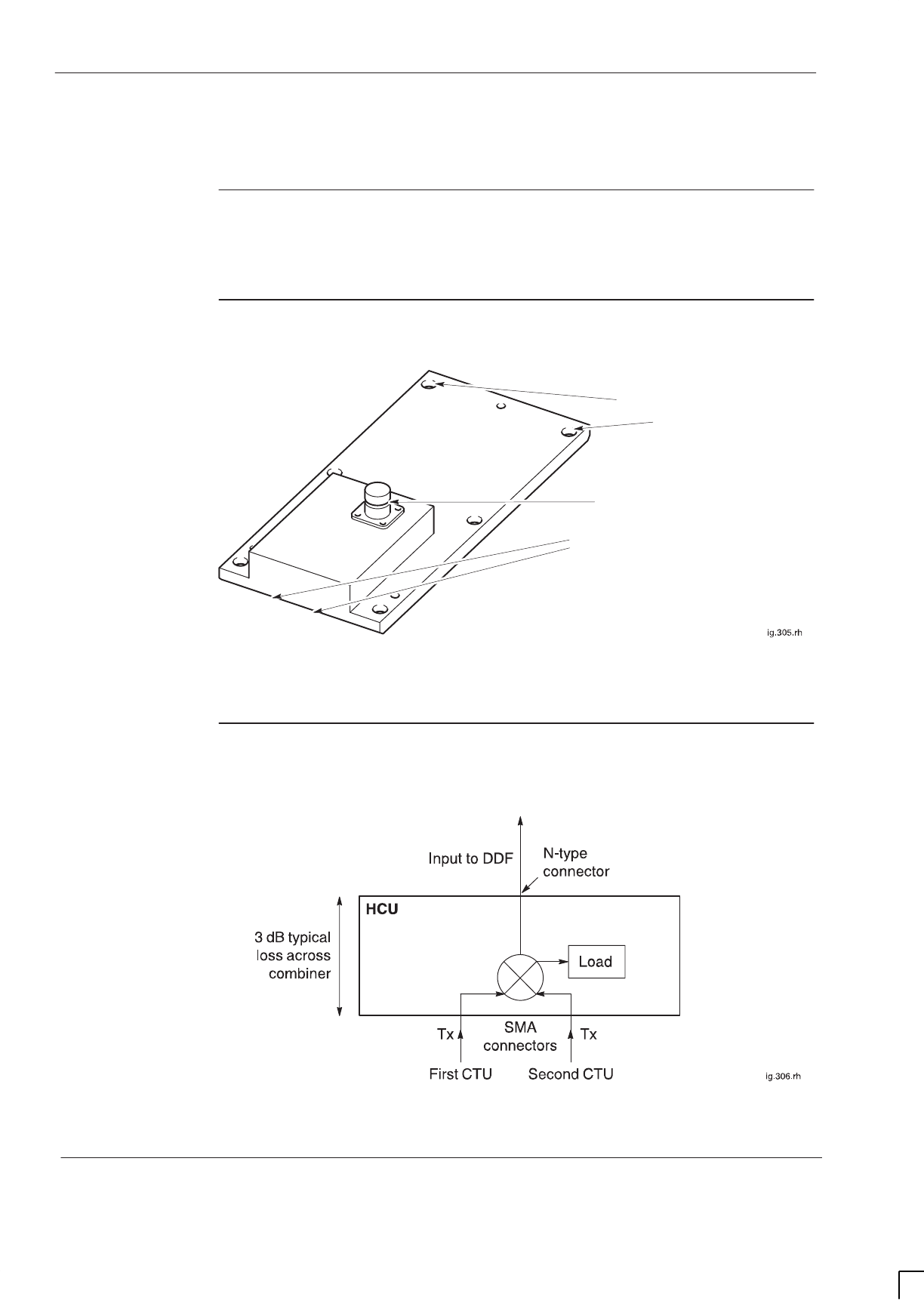
GSM-204-323
HCU plate
31st Oct 01
Tech. 5–36
Technical Description: Horizon
macro
outdoor
CONTROLLED INTRODUCTION
68P02902W02-A
HCU plate
HCU overview
The hybrid combining unit (HCU) combines two CTU Tx outputs.
There are six holes for attachment into the bottom of the Tx block basket.
HCU view
Figure 5-21 shows the HCU plate with connectors identified.
N-TYPE CONNECTOR TO DDF
SMA TRANSMIT CONNECTORS
BENEATH HCU MODULE FROM CTUs
M4 HOLES FOR
ATTACHMENT
Figure 5-21 HCU plate view showing connectors
HCU functional
diagram
Figure 5-22 shows a functional diagram of the HCU.
Figure 5-22 HCU functional diagram
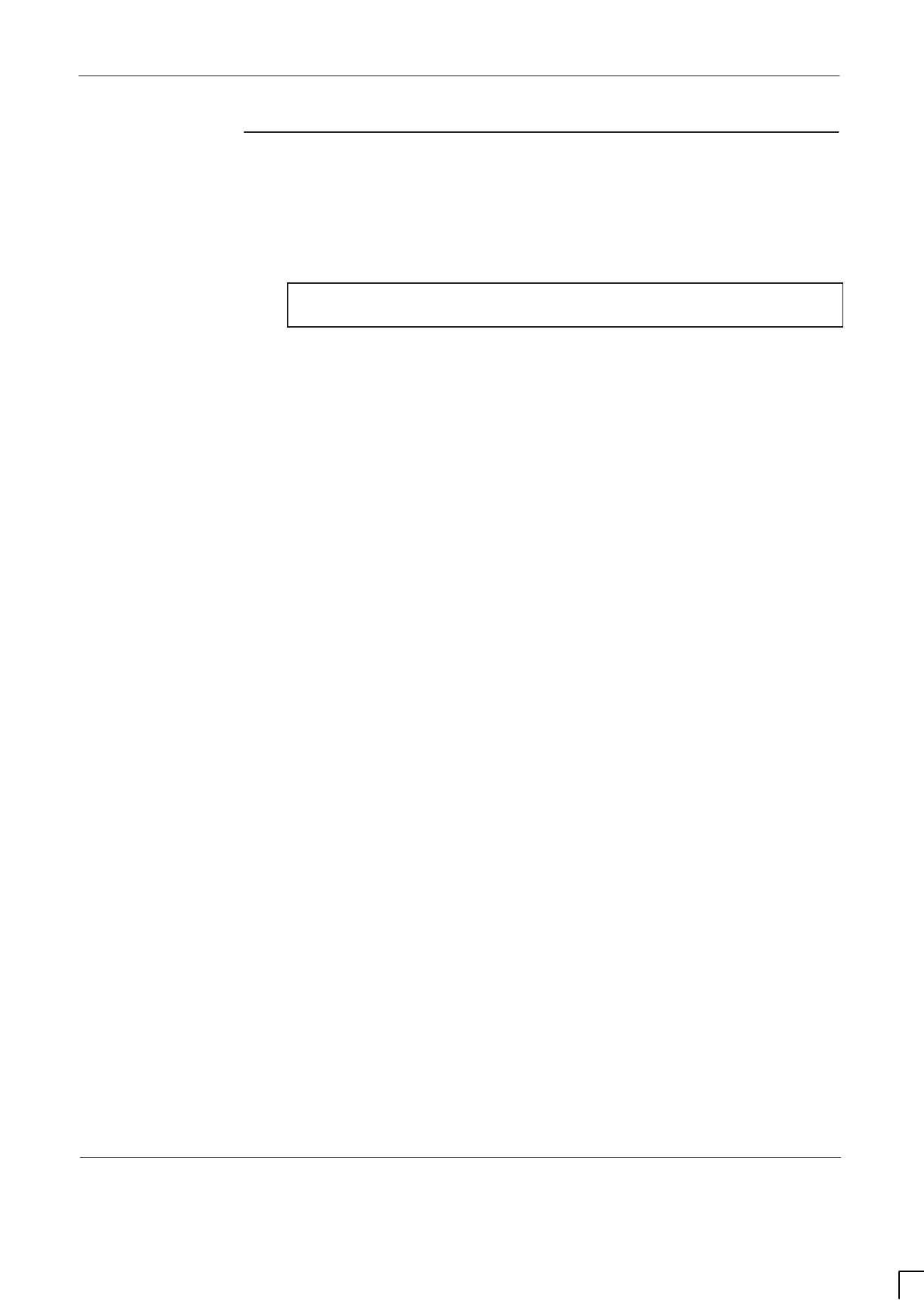
GSM-204-323 HCU plate
31st Oct 01
Technical Description: Horizon
macro
outdoor
68P02902W02-A
CONTROLLED INTRODUCTION
Tech. 5–37
HCU
connectors
Each HCU connects to:
The Tx outputs of two CTUs, using SMA connectors.
A Tx input of a DDF, using an N-type connector.
NOTE All unused SMA inputs to HCU modules must be fitted
with 50 ohm load terminations.
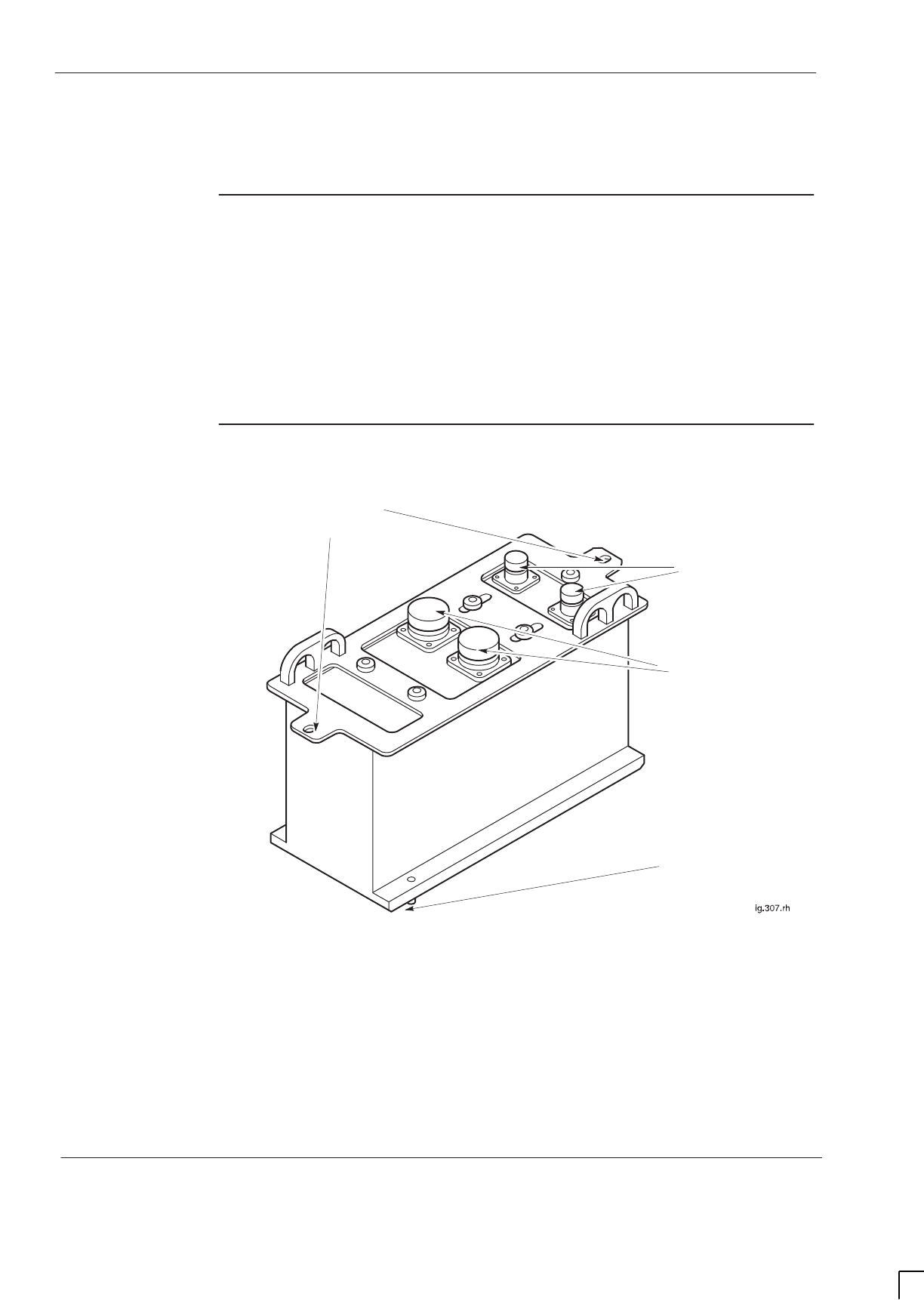
GSM-204-323
TDF
31st Oct 01
Tech. 5–38
Technical Description: Horizon
macro
outdoor
CONTROLLED INTRODUCTION
68P02902W02-A
TDF
Overview of
TDF
The purpose of the twin duplexed filter (TDF) Tx block is to enable each
antenna to serve one CTU for both Tx and Rx.
The TDF has two identical sections, each providing a single path from a CTU to
a separate antenna. There is no combining in the TDF.
The TDF is located in the basket above the CTUs and is attached to the top
surface of the top panel using two M6 screws.
TDF view
Figure 5-23 shows the TDF Tx block with connectors identified.
HOLES FOR TOP PANEL
BASKET ATTACHMENT
7/16 CONNECTORS
TO ANTENNAS
TWO SMA Tx
CONNECTORS BENEATH
TDF (FROM CTU)
N-TYPE
CONNECTORS
TO SURF
Figure 5-23 View of TDF Tx block with connectors identified
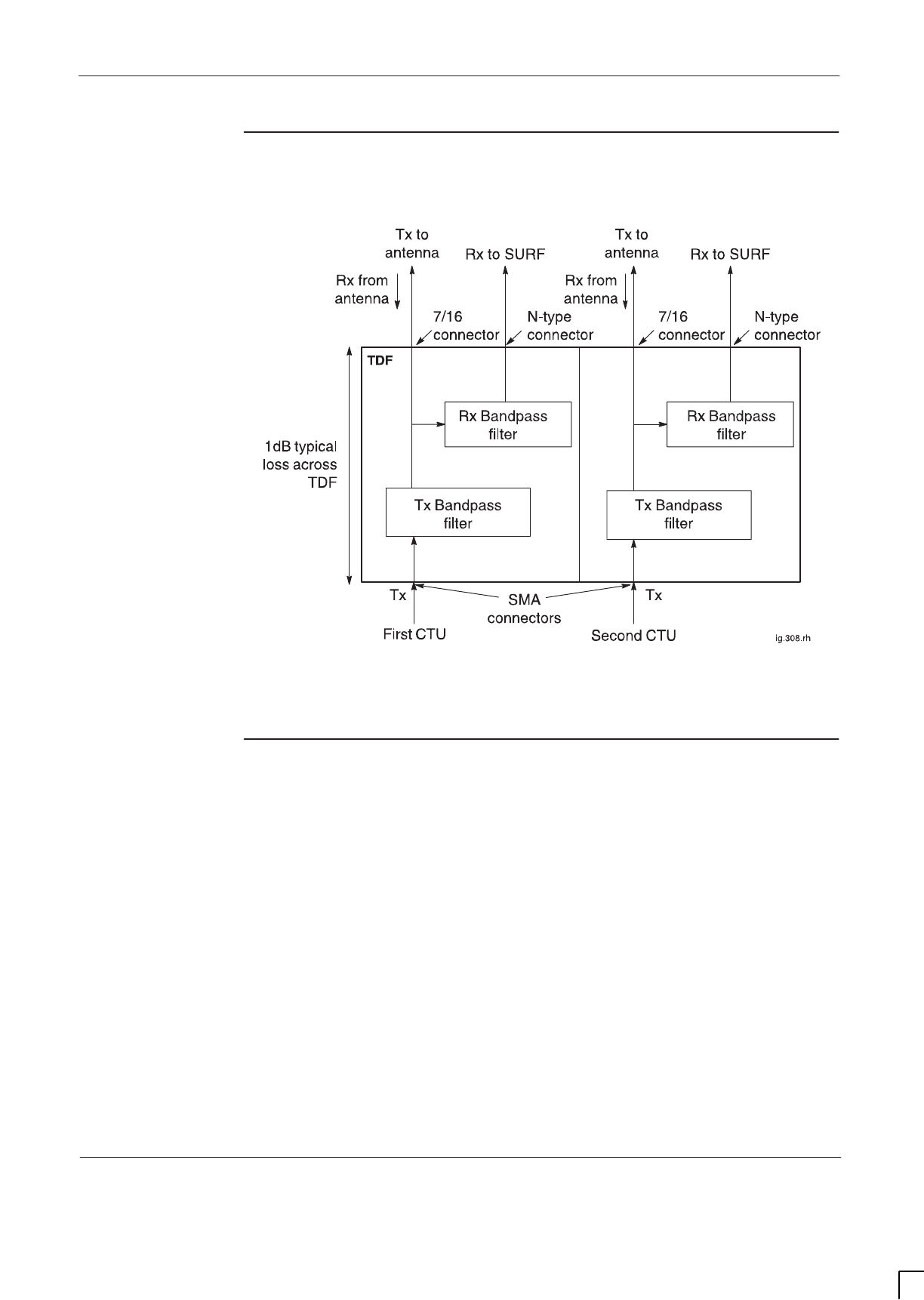
GSM-204-323 TDF
31st Oct 01
Technical Description: Horizon
macro
outdoor
68P02902W02-A
CONTROLLED INTRODUCTION
Tech. 5–39
TDF functional
diagram
Figure 5-24 shows a functional diagram of the TDF.
Figure 5-24 TDF functional diagram
TDF connectors
Each TDF connects to:
The Tx outputs of two CTUs, using SMA connectors. The two connectors
are underneath the TDF.
Two antennas, each for both Rx and Tx, using 7/16 connectors. These
connectors are on top of the TDF.
The SURF, using two N-type connectors. These connectors are on top of
the TDF.
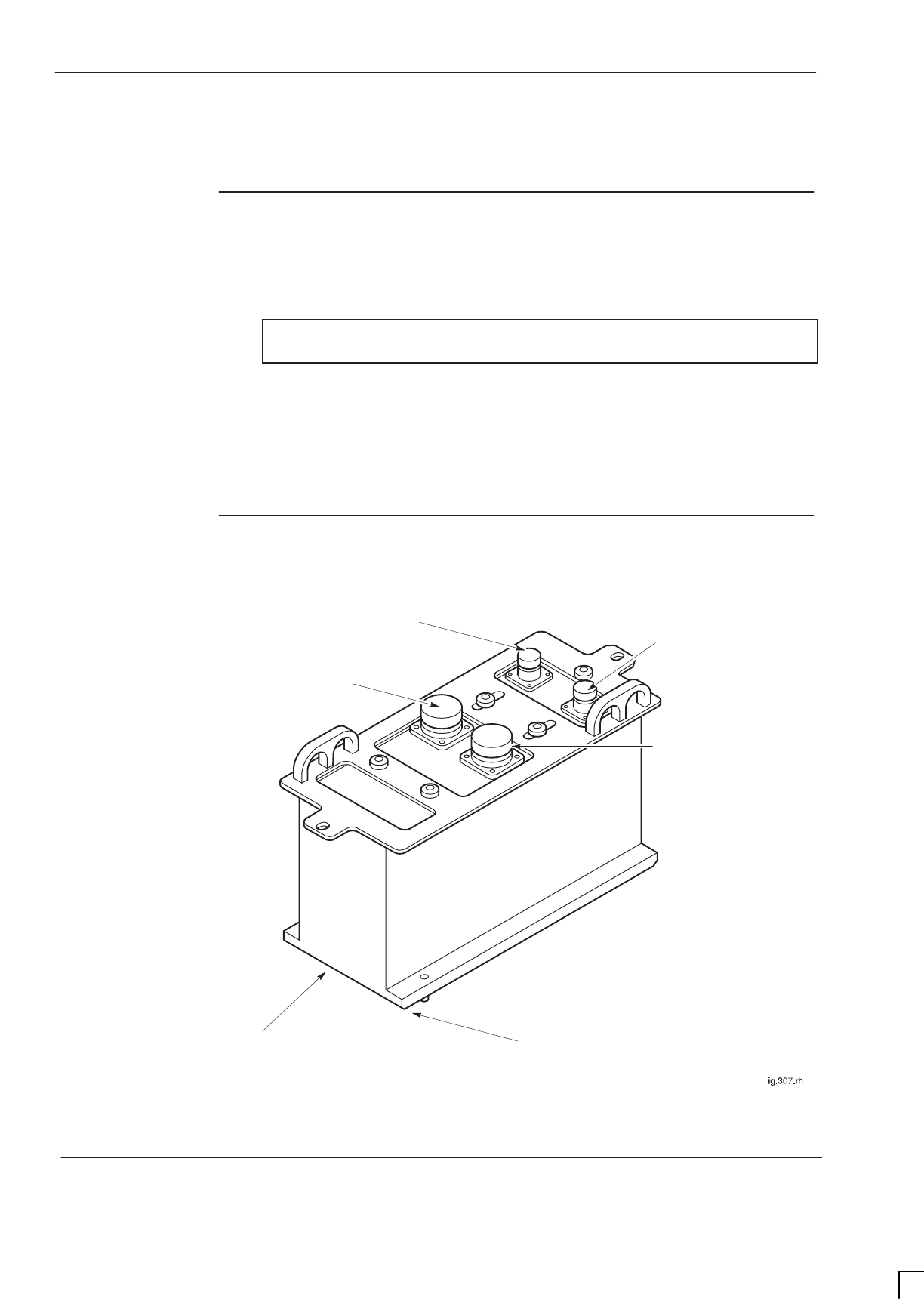
GSM-204-323
Dual band TDF
31st Oct 01
Tech. 5–40
Technical Description: Horizon
macro
outdoor
CONTROLLED INTRODUCTION
68P02902W02-A
Dual band TDF
Overview of
Dual band TDF
The purpose of the dual band twin duplexed filter (dual band TDF) Tx block is to
enable one 900 MHz antenna to serve one EGSM900 CTU for both Tx and Rx,
and an 1800 MHz antenna to serve one DCS1800 CTU for both Tx and Rx.
NOTE A dual band TDF is not currently available for use with the
GSM850 or PCS1900 BTS variants.
The dual band TDF is essentially a TDF with one section providing a path for
900 MHz signals and another section providing a path for 1800 MHz signals.
There is no combining in the dual band TDF.
The dual band TDF is located in the basket above the CTUs, and attached to
the top surface of the top panel using two M6 screws.
Dual band TDF
view
Figure 5-25 shows the dual band TDF Tx block with connectors identified:
7/16 CONNECTOR TO
1800 MHz ANTENNA
(ANT. DCS 1800)
SMA Tx CONNECTOR
BENEATH DUAL BAND TDF
(FROM 1800 CTU)
N-TYPE CONNECTOR TO
1800 MHz SURF CONNECTION
N-TYPE CONNECTOR TO
900 MHz SURF CONNECTION
7/16 CONNECTOR TO
900 MHz ANTENNA
(ANT. EGSM 900)
SMA Tx CONNECTOR
BENEATH DUAL BAND TDF
(FROM 900 CTU)
Figure 5-25 View of dual band TDF Tx block with connectors identified
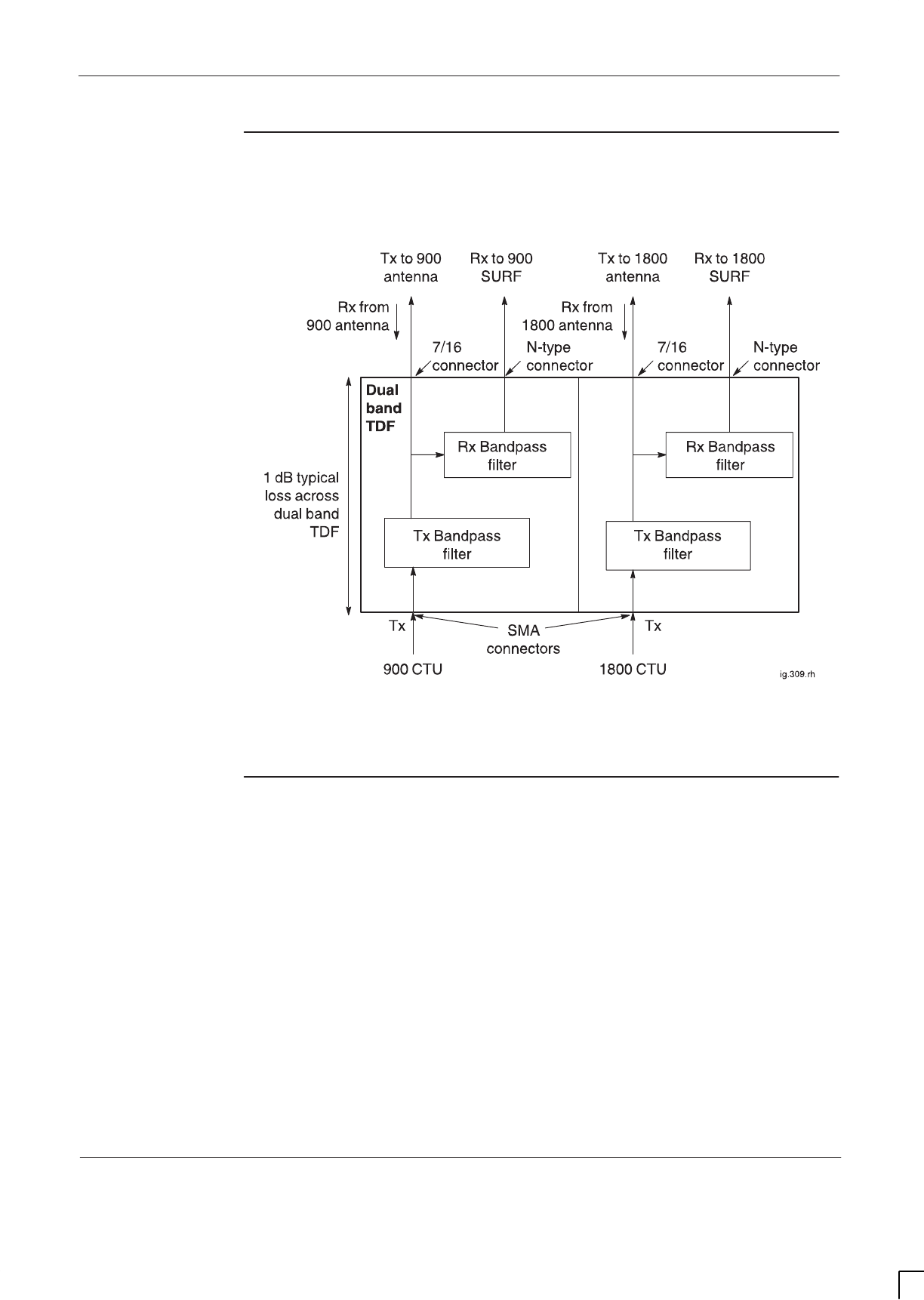
GSM-204-323 Dual band TDF
31st Oct 01
Technical Description: Horizon
macro
outdoor
68P02902W02-A
CONTROLLED INTRODUCTION
Tech. 5–41
Dual band TDF
functional
diagram
Figure 5-26 shows a functional diagram of the dual band TDF.
Figure 5-26 Dual band TDF functional diagram
Dual band TDF
connectors
Each dual band TDF connects to:
The Tx output of one 900 CTU and one 1800 CTU, using SMA
connectors. The two connectors are underneath the dual band TDF.
One 900 MHz antenna and one 1800 MHz antenna. Each antenna is used
for both Rx and Tx, and each is connected to the dual band TDF using
7/16 connectors. These connectors are on top of the dual band TDF.
A SURF module with dual band capability. Two N-type connectors, located
on top of the dual band TDF, connect one receive path to the SURF’s
900 MHz input and one receive path to the SURF’s 1800 MHz input.
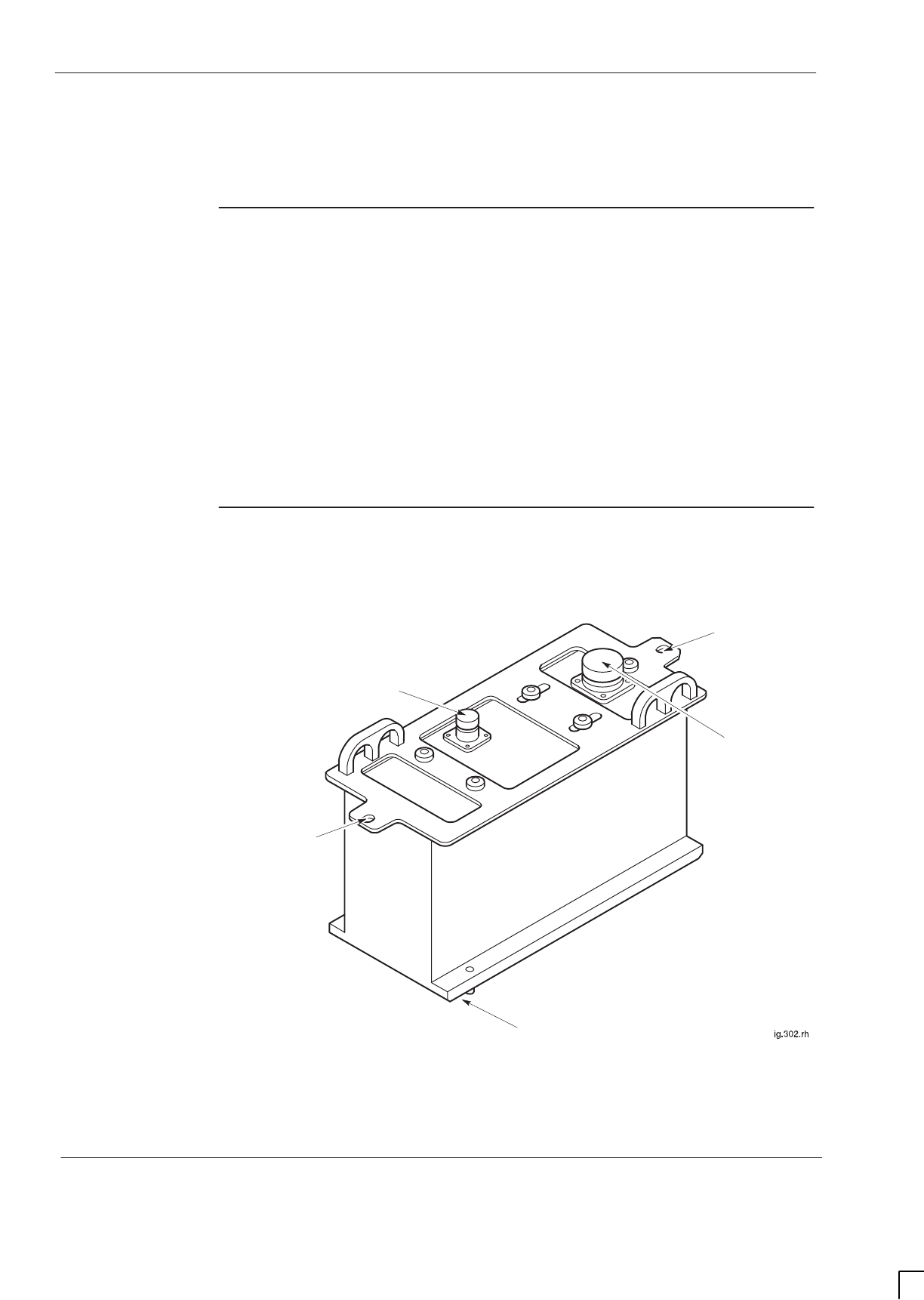
GSM-204-323
DCF
31st Oct 01
Tech. 5–42
Technical Description: Horizon
macro
outdoor
CONTROLLED INTRODUCTION
68P02902W02-A
DCF
DCF overview
The purpose of the duplexed combining bandpass filter (DCF) Tx block is to
enable each antenna to serve two CTUs for both Tx and Rx.
The DCF combines two Tx inputs, dissipating half the power within an internal
load.
The signal then passes through a bandpass filter and out to the antenna.
A receive bandpass filter passes only the Rx signal to the SURF module.
The DCF is located in the basket above the CTUs and is attached to the top
surface of the top panel using two M6 screws.
DCF view
Figure 5-27 shows a DCF with connectors identified.
HOLE FOR TOP
PANEL BASKET
ATTACHMENT
N-TYPE CONNECTOR TO
SURF
7/16 CONNECTOR
TO ANTENNA
TWO SMA Tx CONNECTORS
BENEATH DCF (FROM CTU)
HOLE FOR TOP
PANEL BASKET
ATTACHMENT
Figure 5-27 DCF Tx block view with connectors identified
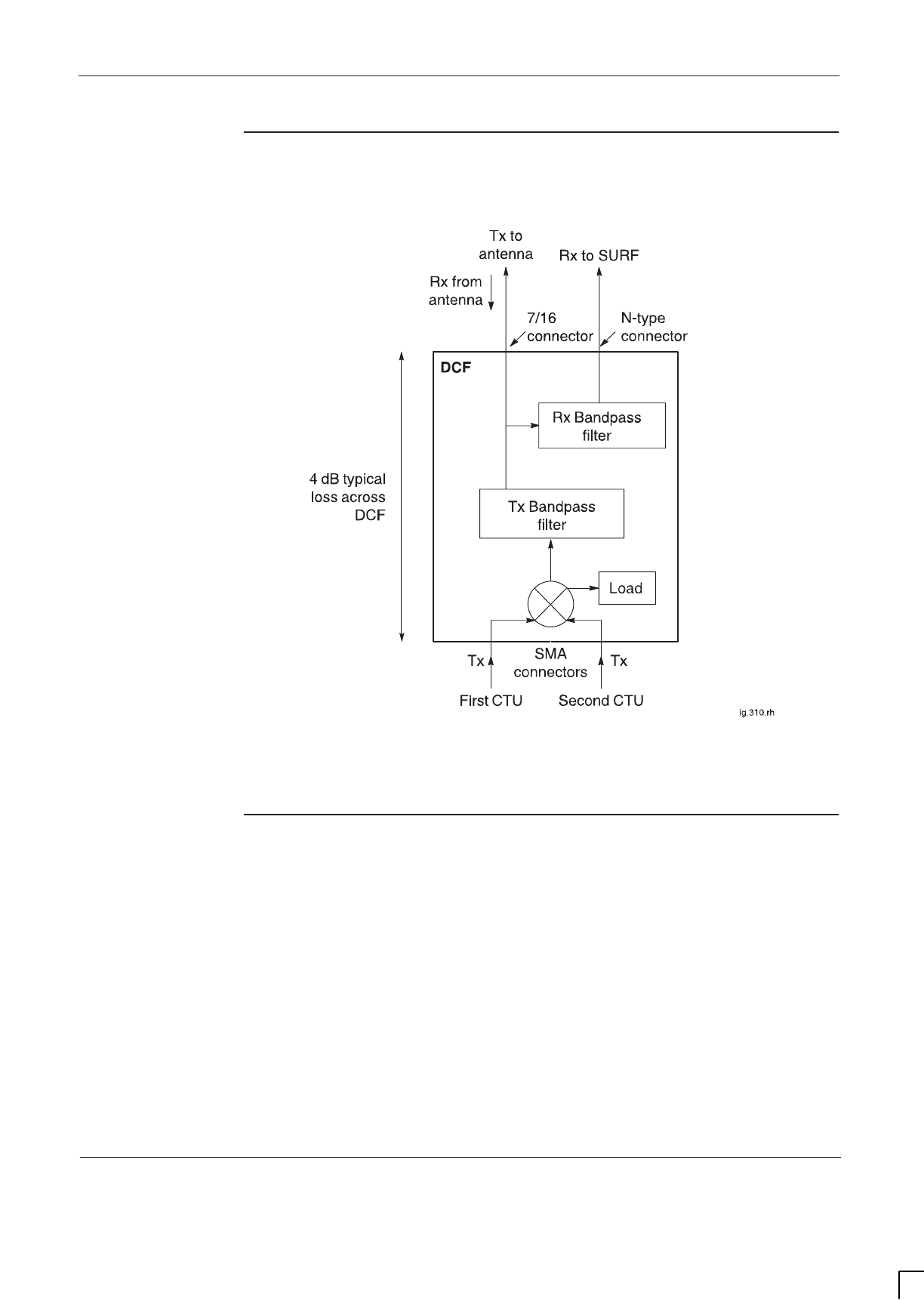
GSM-204-323 DCF
31st Oct 01
Technical Description: Horizon
macro
outdoor
68P02902W02-A
CONTROLLED INTRODUCTION
Tech. 5–43
DCF functional
diagram
Figure 5-28 shows a functional diagram of the DCF.
Figure 5-28 Functional diagram of DCF
DCF connectors
Each DCF connects to:
The Tx outputs of two CTUs, using SMA connectors. The two connectors
are underneath the DCF.
A single antenna for both Rx and Tx, using a 7/16 connector. This
connector is on top of the DCF.
The SURF, using an N-type connector. This connector is on top of the
DCF.
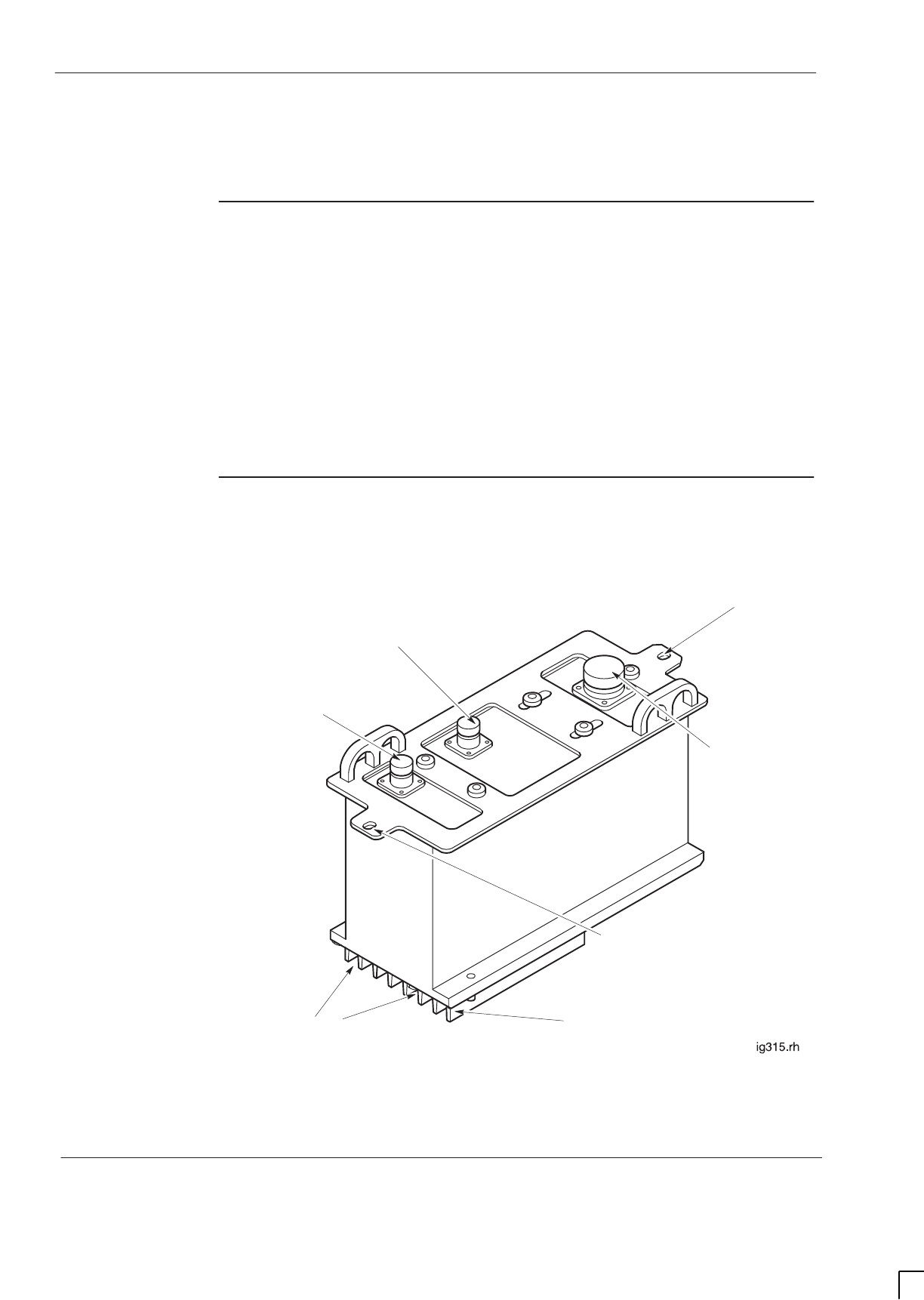
GSM-204-323
DDF
31st Oct 01
Tech. 5–44
Technical Description: Horizon
macro
outdoor
CONTROLLED INTRODUCTION
68P02902W02-A
DDF
Overview of
DDF
The dual-stage duplexed combining filter (DDF) differs from the DCF in having a
second stage of combining to allow a third CTU Tx input. This third CTU Tx
input is connected to either:
A feedthrough plate connector for a single additional CTU or
An HCU plate connector for combining two additional CTUs.
The DDF is located in the basket above the CTUs and is attached to the top
surface of the top panel using two M6 screws.
DDF view
Figure 5-29 shows a view of the DDF Tx block with connectors identified.
HOLE FOR TOP
PANEL BASKET
ATTACHMENT
N-TYPE CONNECTOR TO
SURF
TWO SMA Tx CONNECTORS
BENEATH DDF (FROM CTU)
7/16 CONNECTOR
TO ANTENNA
N-TYPE CONNECTOR
FROM CTU BY
FEEDTHROUGH PLATE
OR HCU
HOLE FOR TOP
PANEL BASKET
ATTACHMENT
COOLING FINS
Figure 5-29 DDF Tx block view with connectors identified
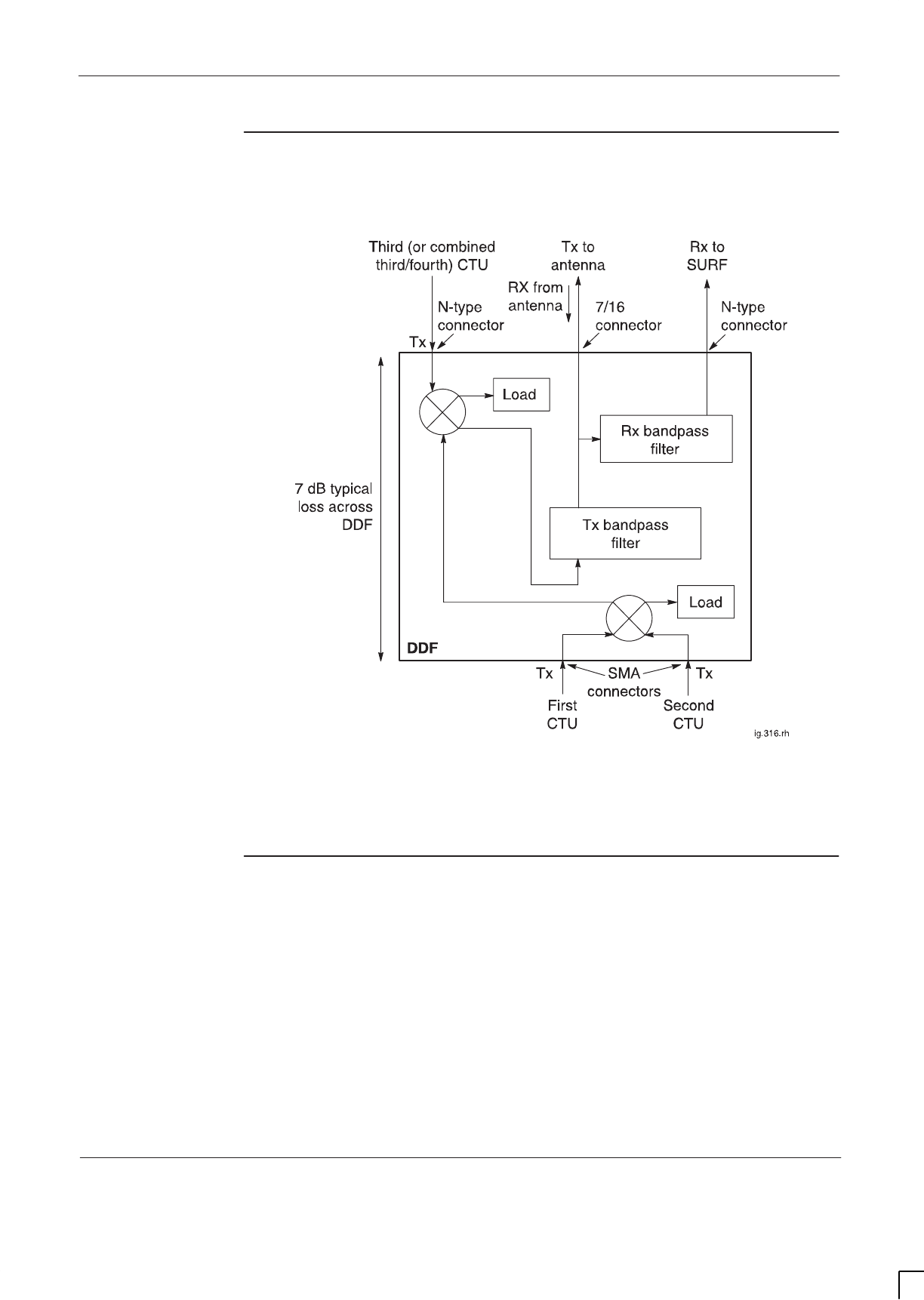
GSM-204-323 DDF
31st Oct 01
Technical Description: Horizon
macro
outdoor
68P02902W02-A
CONTROLLED INTRODUCTION
Tech. 5–45
DDF functional
diagram
Figure 5-30 shows a functional diagram of the DDF.
Figure 5-30 Functional diagram of the DDF
DDF connectors
Each DDF connects to:
The Tx outputs of three or four CTUs, using:
Two SMA connectors underneath the DDF.
An N-type connector on top of the DDF for connection to a feedthrough
plate (for a third CTU) or HCU plate (for combined third/fourth CTUs).
A single antenna for both Rx and Tx, using a 7/16 connector. This
connector is on top of the DDF.
The SURF, using an N-type connector. This connector is on top of the
DDF.
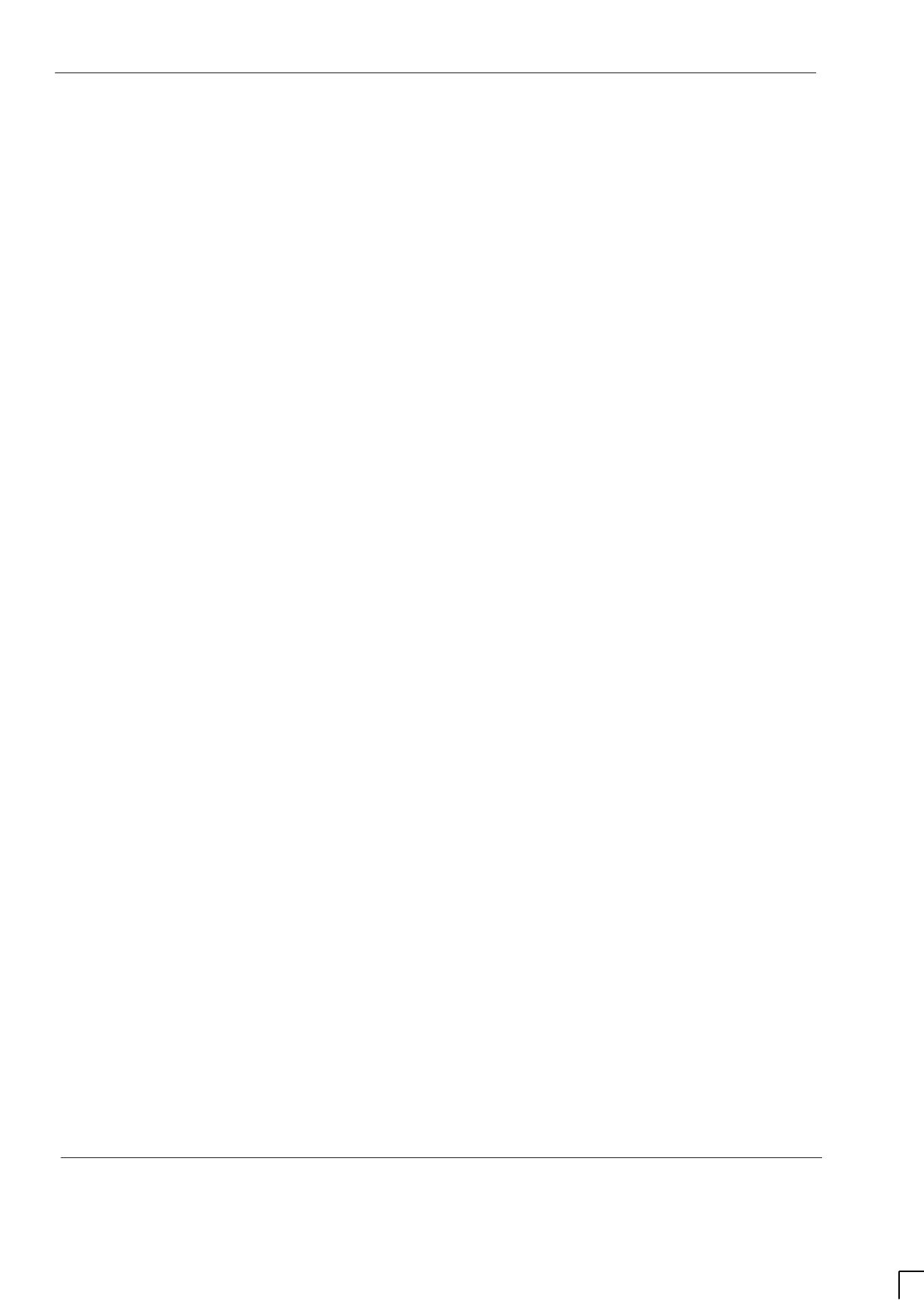
GSM-204-323
DDF
31st Oct 01
Tech. 5–46
Technical Description: Horizon
macro
outdoor
CONTROLLED INTRODUCTION
68P02902W02-A
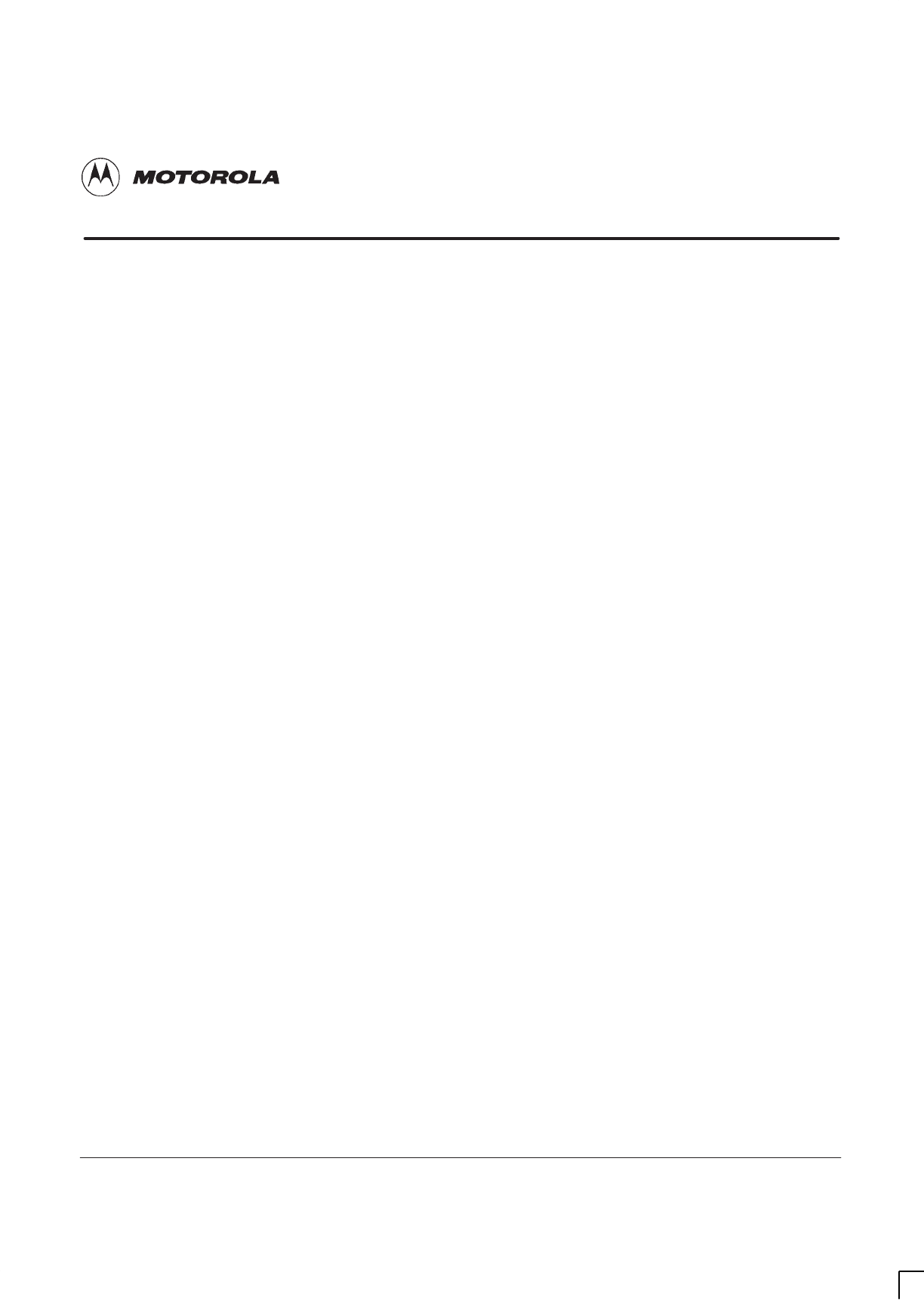
31st Oct 01
Technical Description: Horizon
macro
outdoor
68P02902W02-A
CONTROLLED INTRODUCTION
i
Chapter 6
Digital modules
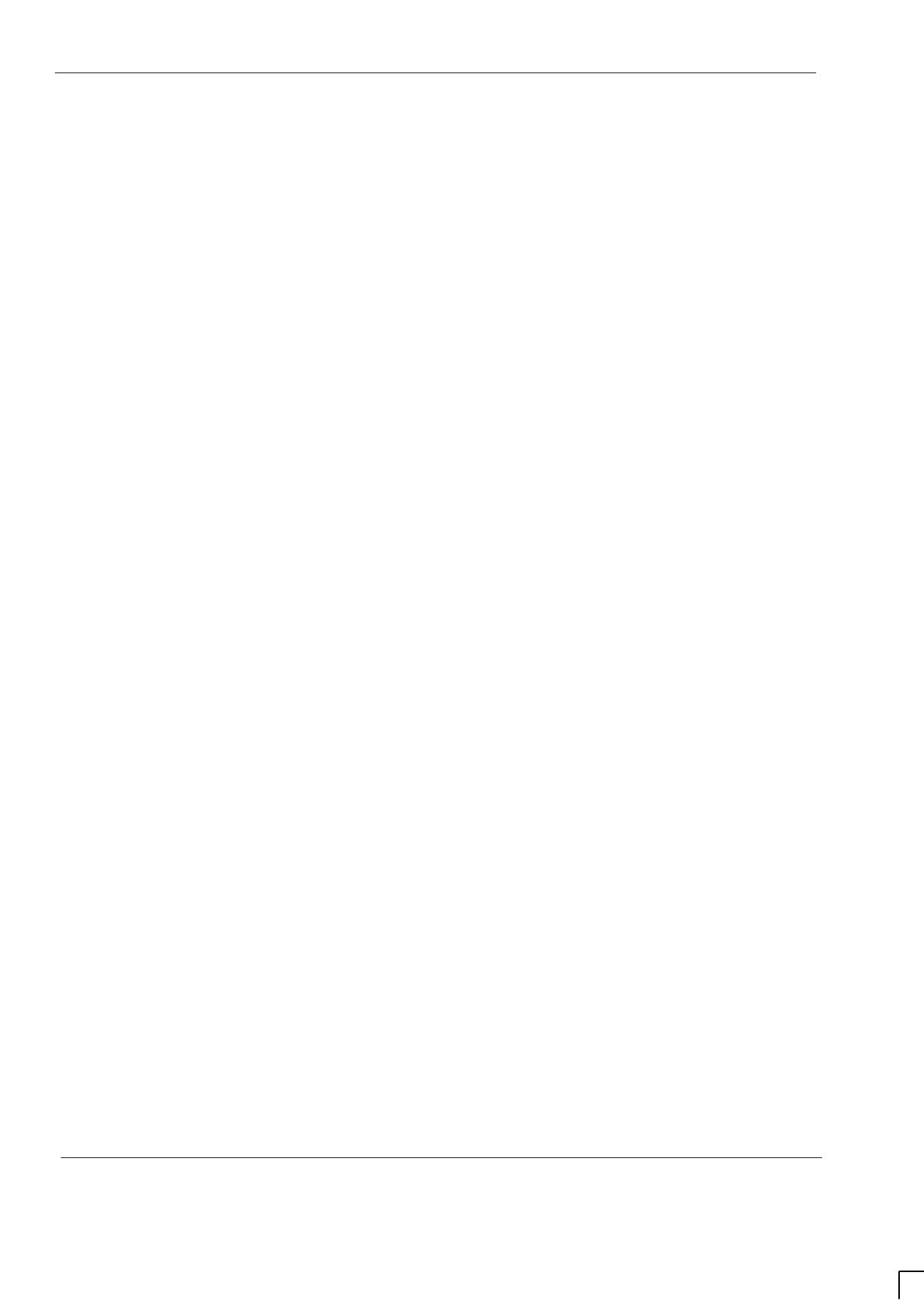
GSM-204-323
31st Oct 01
ii
Technical Description: Horizon
macro
outdoor
CONTROLLED INTRODUCTION
68P02902W02-A
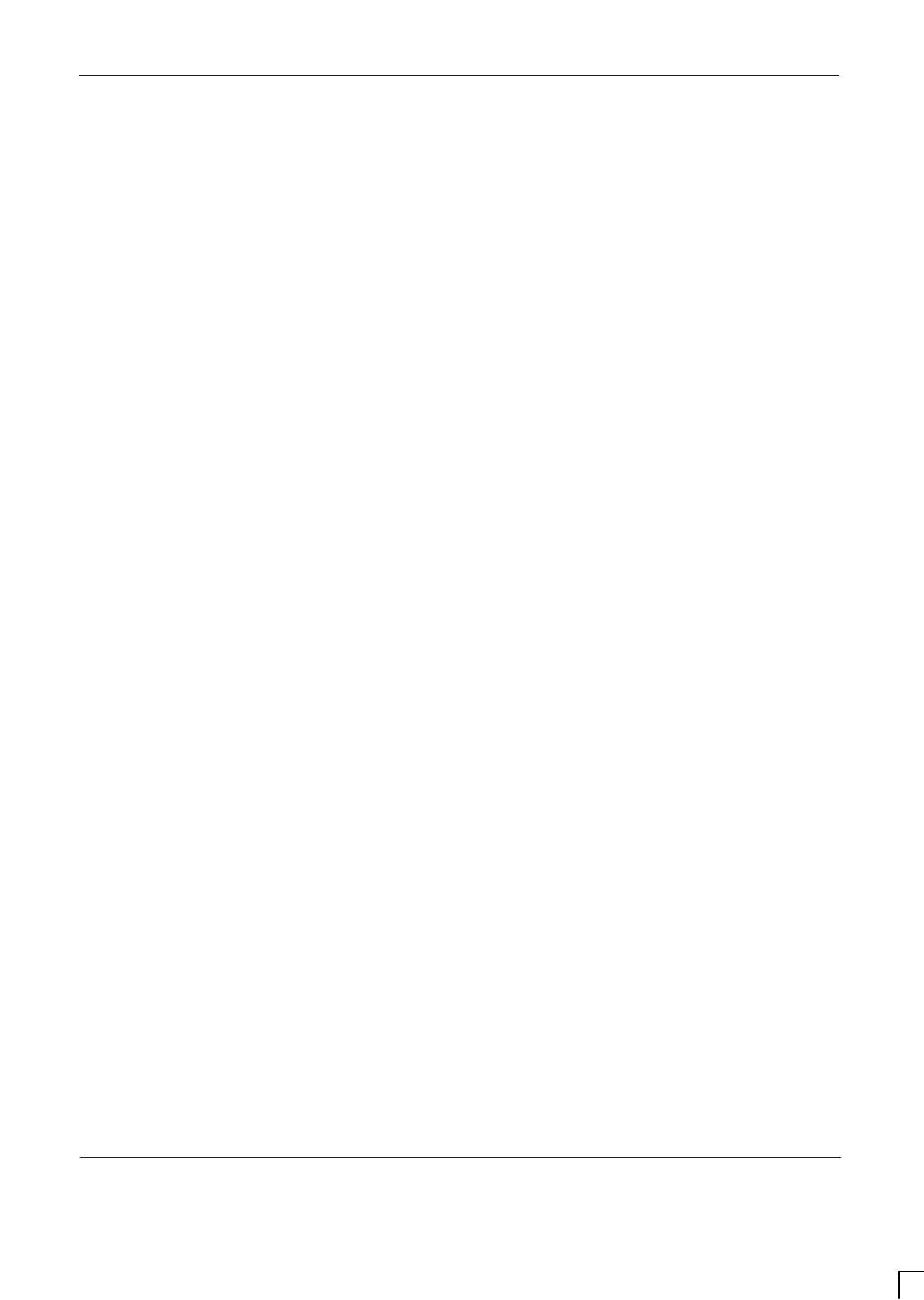
GSM-204-323
31st Oct 01
Technical Description: Horizon
macro
outdoor
68P02902W02-A
CONTROLLED INTRODUCTION
iii
Chapter 6
Digital modules i. . . . . . . . . . . . . . . . . . . . . . . . . . . . . . . . . . . . . . . . . . . . . . .
Overview of digital modules Tech. 6–1. . . . . . . . . . . . . . . . . . . . . . . . . . . . . . . . . . . . . . . . . . .
Overview and redundancy Tech. 6–1. . . . . . . . . . . . . . . . . . . . . . . . . . . . . . . . . . . . . . .
Digital module and BPSM locations Tech. 6–2. . . . . . . . . . . . . . . . . . . . . . . . . . . . . . .
MCUF and NIU redundancy Tech. 6–3. . . . . . . . . . . . . . . . . . . . . . . . . . . . . . . . . . . . .
Full size and half size modules Tech. 6–3. . . . . . . . . . . . . . . . . . . . . . . . . . . . . . . . . . .
Digital module and CTU connections Tech. 6–4. . . . . . . . . . . . . . . . . . . . . . . . . . . . . .
Diagram of digital module and CTU connections Tech. 6–4. . . . . . . . . . . . . . . . . . . .
MCUF Tech. 6–5. . . . . . . . . . . . . . . . . . . . . . . . . . . . . . . . . . . . . . . . . . . . . . . . . . . . . . . . . . . . . .
MCUF overview Tech. 6–5. . . . . . . . . . . . . . . . . . . . . . . . . . . . . . . . . . . . . . . . . . . . . . . . .
Capability to replace MCU of M-Cell6 and M-Cell2 Tech. 6–5. . . . . . . . . . . . . . . . . .
GPROC TSW and GLCK functions Tech. 6–6. . . . . . . . . . . . . . . . . . . . . . . . . . . . . . . .
MCUF module view Tech. 6–6. . . . . . . . . . . . . . . . . . . . . . . . . . . . . . . . . . . . . . . . . . . . .
MCUF functional diagram Tech. 6–7. . . . . . . . . . . . . . . . . . . . . . . . . . . . . . . . . . . . . . . .
Link to redundant MCUF Tech. 6–8. . . . . . . . . . . . . . . . . . . . . . . . . . . . . . . . . . . . . . . . .
Front panel interfaces Tech. 6–8. . . . . . . . . . . . . . . . . . . . . . . . . . . . . . . . . . . . . . . . . . .
Front panel switches and indicators Tech. 6–9. . . . . . . . . . . . . . . . . . . . . . . . . . . . . . .
PIX interfaces Tech. 6–10. . . . . . . . . . . . . . . . . . . . . . . . . . . . . . . . . . . . . . . . . . . . . . . . . .
DRAM, flash EPROM and code loading functions Tech. 6–10. . . . . . . . . . . . . . . . . . .
ASIC functionality Tech. 6–11. . . . . . . . . . . . . . . . . . . . . . . . . . . . . . . . . . . . . . . . . . . . . . .
Sync block functionality Tech. 6–12. . . . . . . . . . . . . . . . . . . . . . . . . . . . . . . . . . . . . . . . . .
Integral MCUF FMUX functionality Tech. 6–14. . . . . . . . . . . . . . . . . . . . . . . . . . . . . . . .
NIU Tech. 6–15. . . . . . . . . . . . . . . . . . . . . . . . . . . . . . . . . . . . . . . . . . . . . . . . . . . . . . . . . . . . . . . .
Overview of NIU Tech. 6–15. . . . . . . . . . . . . . . . . . . . . . . . . . . . . . . . . . . . . . . . . . . . . . . .
NIU locations Tech. 6–15. . . . . . . . . . . . . . . . . . . . . . . . . . . . . . . . . . . . . . . . . . . . . . . . . . .
NIU command identity number Tech. 6–15. . . . . . . . . . . . . . . . . . . . . . . . . . . . . . . . . . . .
NIU view and LEDs Tech. 6–16. . . . . . . . . . . . . . . . . . . . . . . . . . . . . . . . . . . . . . . . . . . . .
NIU functionality Tech. 6–17. . . . . . . . . . . . . . . . . . . . . . . . . . . . . . . . . . . . . . . . . . . . . . . .
NIU diagram Tech. 6–18. . . . . . . . . . . . . . . . . . . . . . . . . . . . . . . . . . . . . . . . . . . . . . . . . . .
Control processor Tech. 6–19. . . . . . . . . . . . . . . . . . . . . . . . . . . . . . . . . . . . . . . . . . . . . . .
NIU/MCUF framing and clocks Tech. 6–19. . . . . . . . . . . . . . . . . . . . . . . . . . . . . . . . . . . .
Distance measurement Tech. 6–20. . . . . . . . . . . . . . . . . . . . . . . . . . . . . . . . . . . . . . . . . .
Radio signalling links (RSLs) Tech. 6–20. . . . . . . . . . . . . . . . . . . . . . . . . . . . . . . . . . . . .
T1 NIU need to set link type Tech. 6–20. . . . . . . . . . . . . . . . . . . . . . . . . . . . . . . . . . . . . .
T43/BIB-NIU - E1/T1 mapping Tech. 6–21. . . . . . . . . . . . . . . . . . . . . . . . . . . . . . . . . . . . . . . . .
Overview of T43/BIB-NIU connection Tech. 6–21. . . . . . . . . . . . . . . . . . . . . . . . . . . . . .
NIU to T43/BIB mapping and command ID Tech. 6–21. . . . . . . . . . . . . . . . . . . . . . . . .
Diagram of T43 connection to NIUs Tech. 6–22. . . . . . . . . . . . . . . . . . . . . . . . . . . . . . .
FMUX module and FMUX function Tech. 6–23. . . . . . . . . . . . . . . . . . . . . . . . . . . . . . . . . . . . .
Overview of FMUX module Tech. 6–23. . . . . . . . . . . . . . . . . . . . . . . . . . . . . . . . . . . . . . .
FMUX module view Tech. 6–23. . . . . . . . . . . . . . . . . . . . . . . . . . . . . . . . . . . . . . . . . . . . .
FMUX functional diagram Tech. 6–24. . . . . . . . . . . . . . . . . . . . . . . . . . . . . . . . . . . . . . . .
FMUX functional explanation Tech. 6–24. . . . . . . . . . . . . . . . . . . . . . . . . . . . . . . . . . . . .
Alarm module Tech. 6–25. . . . . . . . . . . . . . . . . . . . . . . . . . . . . . . . . . . . . . . . . . . . . . . . . . . . . . .
Alarm module overview Tech. 6–25. . . . . . . . . . . . . . . . . . . . . . . . . . . . . . . . . . . . . . . . . .
Alarm module view Tech. 6–25. . . . . . . . . . . . . . . . . . . . . . . . . . . . . . . . . . . . . . . . . . . . . .
Alarm module functionality Tech. 6–26. . . . . . . . . . . . . . . . . . . . . . . . . . . . . . . . . . . . . . .
Alarm module replacement – effect on alarms Tech. 6–26. . . . . . . . . . . . . . . . . . . . . .
Alarm collection from extension cabinets Tech. 6–26. . . . . . . . . . . . . . . . . . . . . . . . . . .
Alarm module display presentation Tech. 6–27. . . . . . . . . . . . . . . . . . . . . . . . . . . . . . . .
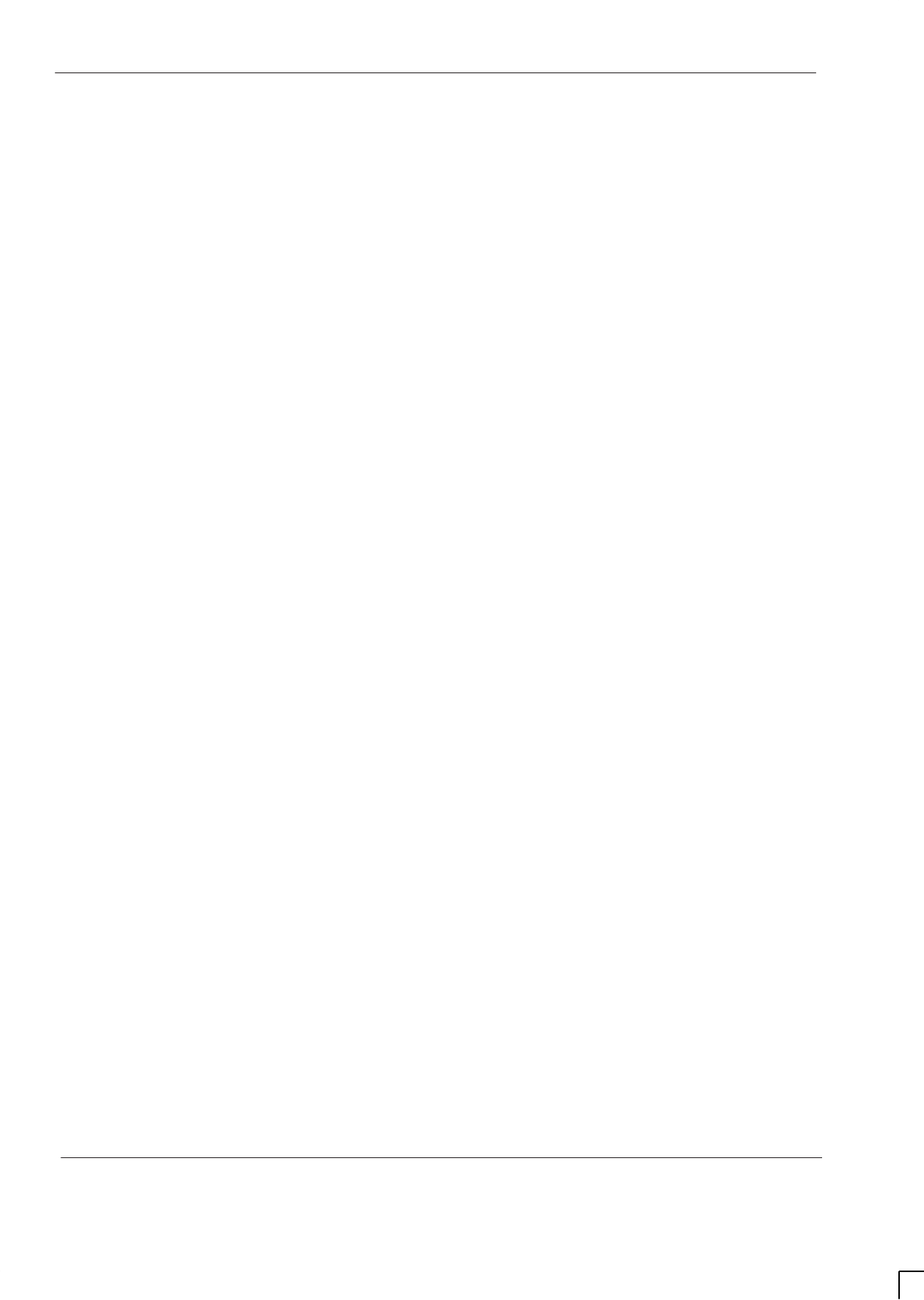
GSM-204-323
31st Oct 01
iv
Technical Description: Horizon
macro
outdoor
CONTROLLED INTRODUCTION
68P02902W02-A
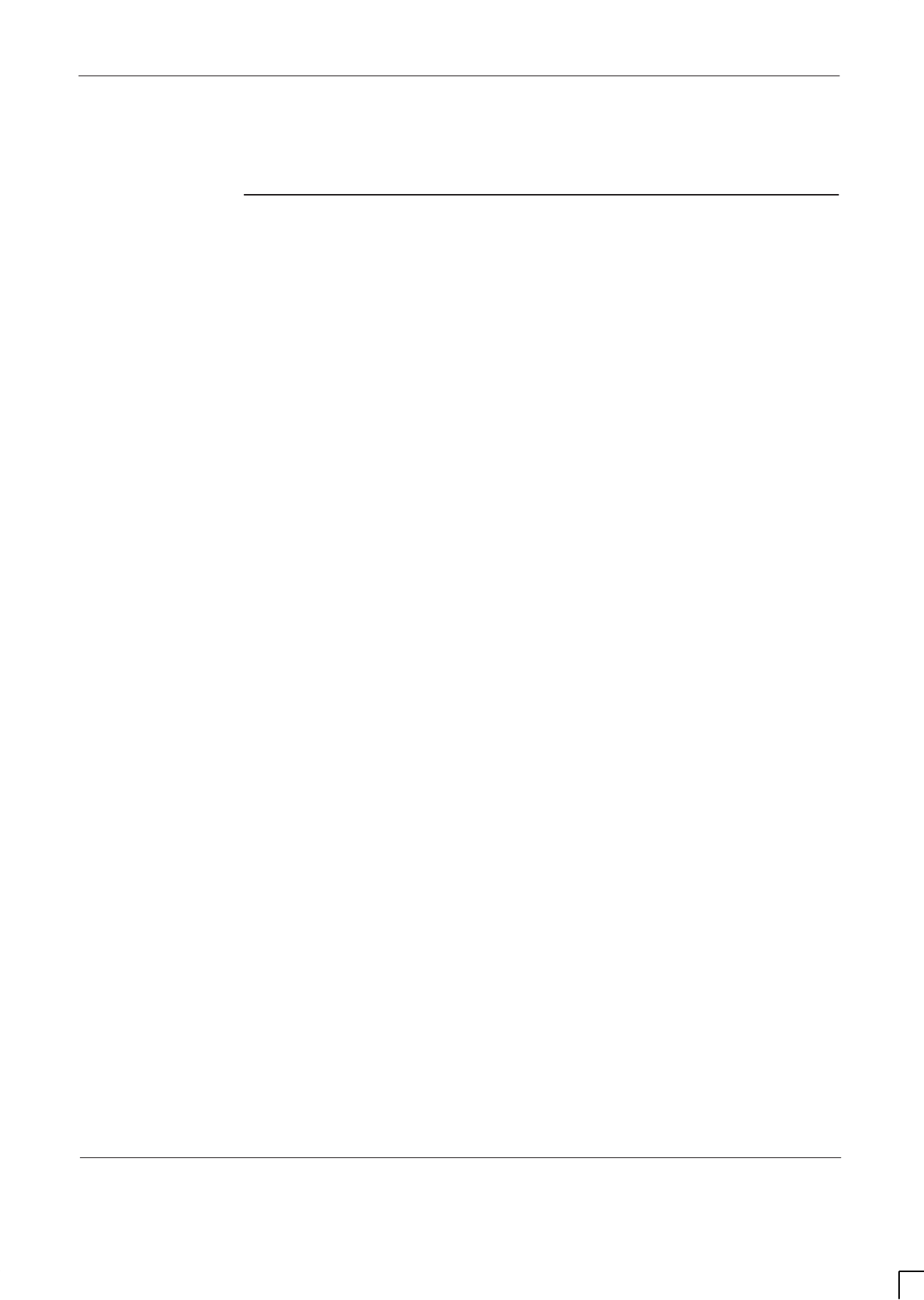
GSM-204-323 Overview of digital modules
31st Oct 01
Technical Description: Horizon
macro
outdoor
68P02902W02-A
CONTROLLED INTRODUCTION
Tech. 6–1
Overview of digital modules
Overview and
redundancy
Digital modules provide the equivalent of M-Cell
6
micro base control unit
(µBCU) functionality for the Horizon
macro.
They are located in the bottom right
side of the main cage, and are electronically interconnected through the
backplane. Fibre optic connections are at the front of the appropriate modules.
Each digital module is assigned A or B, with one BPSM for A and one BPSM for
B. The alarm module is not assigned to A or B, as it is supplied by both BPSMs
for redundancy.
The master MCUF is assigned to A, and the redundant MCUF to B, each with
an associated FMUX.
The four NIUs are used by the operational MCUF, but two NIUs are powered by
BPSM A and two NIUs by BPSM B.
All slots are annotated with the legend of the appropriate module and located as
shown in Figure 6-1.
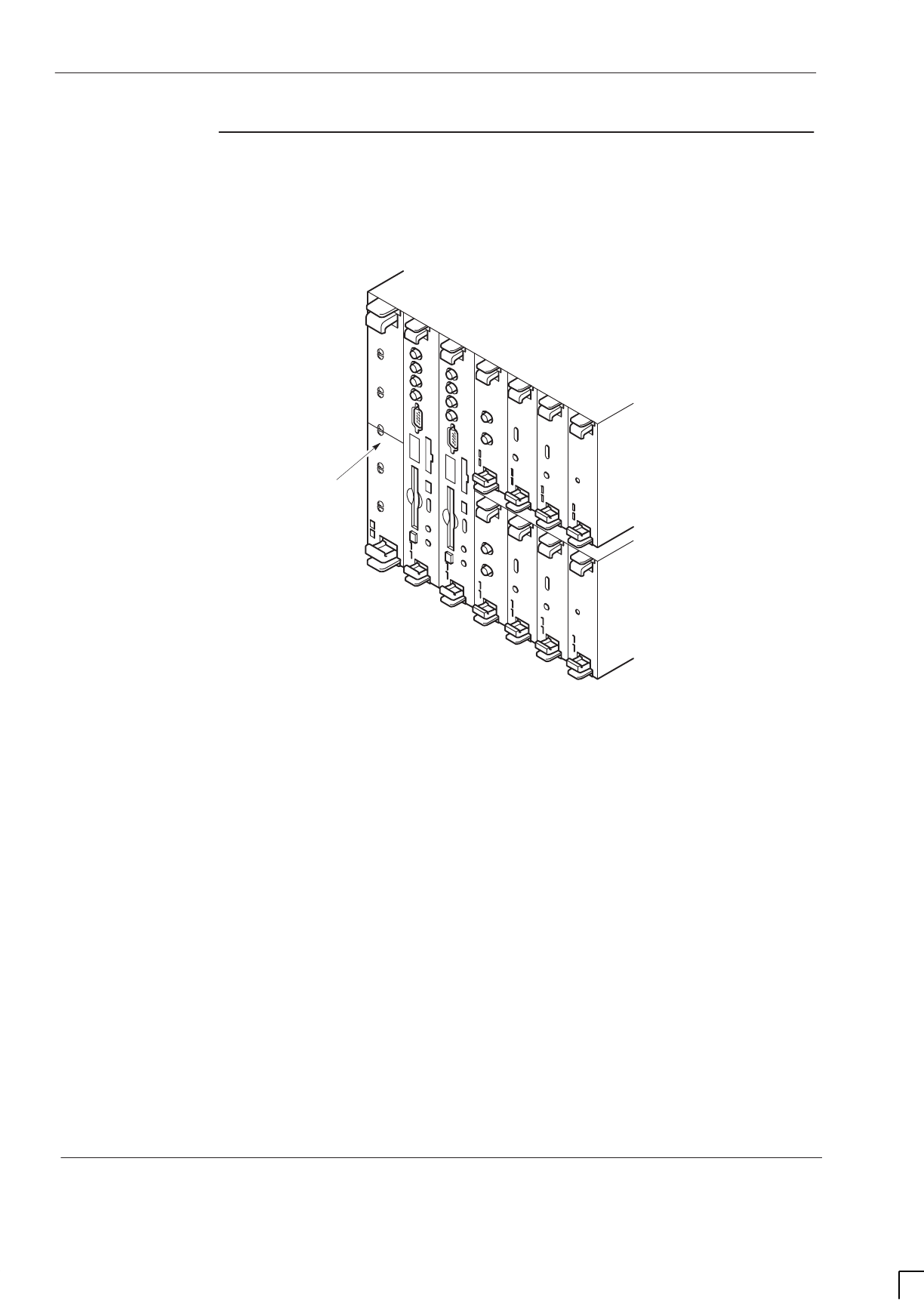
GSM-204-323
Overview of digital modules
31st Oct 01
Tech. 6–2
Technical Description: Horizon
macro
outdoor
CONTROLLED INTRODUCTION
68P02902W02-A
Digital module
and BPSM
locations
Figure 6-1 shows the position of modules within the digital module section of the
main cage
ig.322.rh
ALARM
MODULE
NIU B0
NIU B1
BPSM
BPSM
FMUX
FMUX
MCUF A
MCUF B
NIU A0
NIU A1
REDUNDANT (B)
MASTER (A)
DIGITAL
MODULE SHELF
Figure 6-1 Digital and BPSM module locations, including optional redundancy
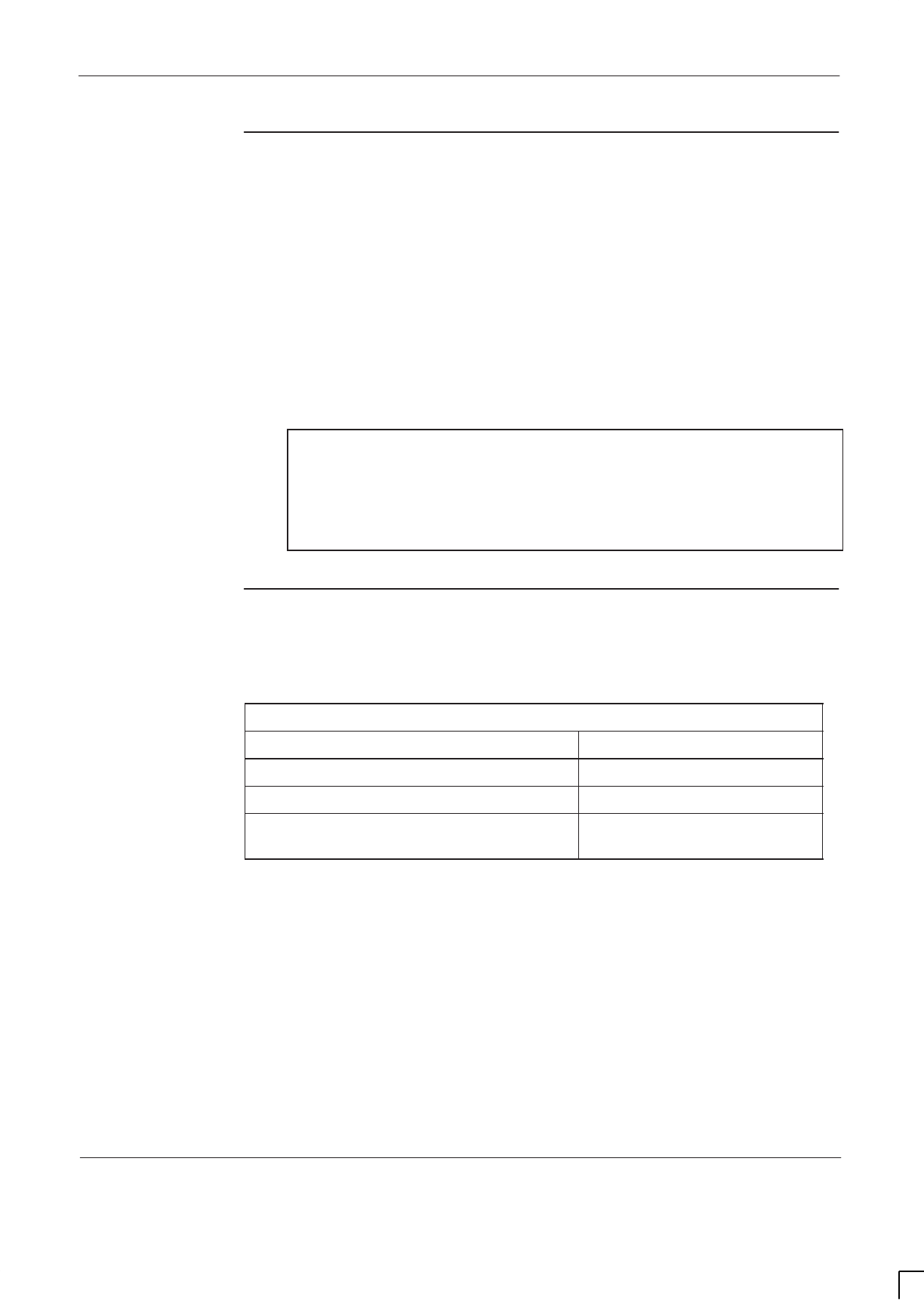
GSM-204-323 Overview of digital modules
31st Oct 01
Technical Description: Horizon
macro
outdoor
68P02902W02-A
CONTROLLED INTRODUCTION
Tech. 6–3
MCUF and NIU
redundancy
The digital module shelf can:
Support two MCUFs at a BTS site, one master, one slave (for
redundancy).
Enable master MCUF failure to result in slave MCUF becoming master
after reset.
Enable OMC-R operator to initiate master/slave MCUF swap.
Configure CTUs by the master MCUF.
All four NIUs operate from the master MCUF, but each pair of NIUs depend on a
BPSM for power. All NIUs configure to the master MCUF clock.
NOTE When fitting a replacement redundant MCUF, care must
be taken to ensure firmware compatibility with the master
MCUF. Firmware incompatibility may result in a loss of
communication between the two MCUFs so that the
redundant MCUF is not in a position to take control in the
event of a failure of the master MCUF.
Full size and
half size
modules
Modules are full size and half size as shown in Table 6-1.
Table 6-1 Full size and half size digital modules
Full size modules Half size modules
Main Control Unit with dual FMUX (MCUF) Network Interface Unit (NIU)
Alarm module Fibre optic Multiplexer (FMUX)
BPSM (µBCU Power Supply
Module)
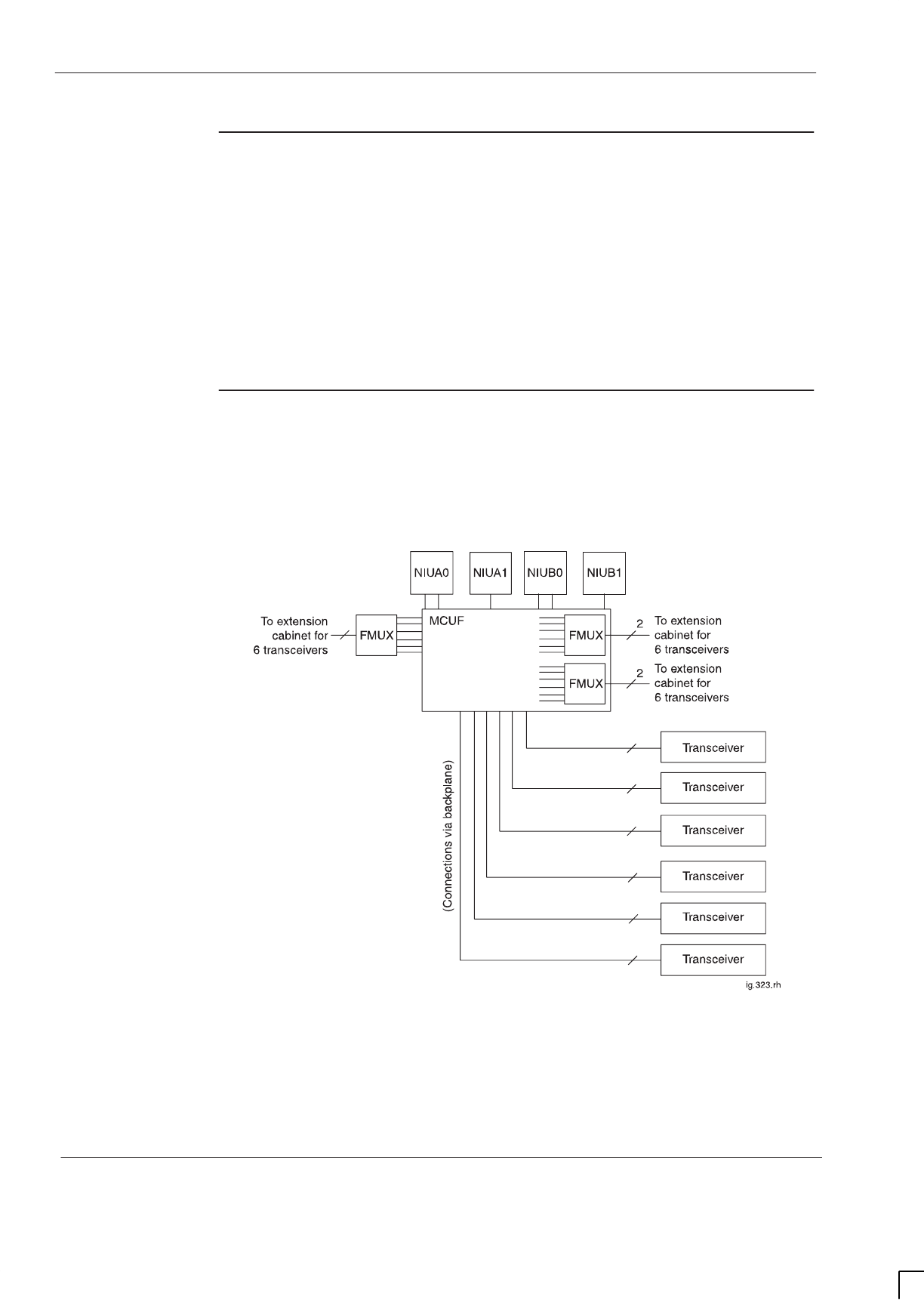
GSM-204-323
Overview of digital modules
31st Oct 01
Tech. 6–4
Technical Description: Horizon
macro
outdoor
CONTROLLED INTRODUCTION
68P02902W02-A
Digital module
and CTU
connections
The MCUF is connected to the CTUs in the same cabinet through the
backplane. Optional connection to CTUs in up to three additional cabinets (six
CTUs per cabinet) is by fibre optic links. FMUXs, two internal to the MCUF and
one half size module, convert the electronic data stream into a fibre optic signal.
An FMUX module in each extension cabinet converts the fibre optic signal back
to electronic data stream, for transmission to CTUs via the backplane.
The NIU modules convert signals for terrestrial E1 or T1 lines.
Diagram of
digital module
and CTU
connections
Figure 6-2 shows a block diagram of digital module and CTU connections,
without redundancy.
Figure 6-2 Digital module and CTU connections
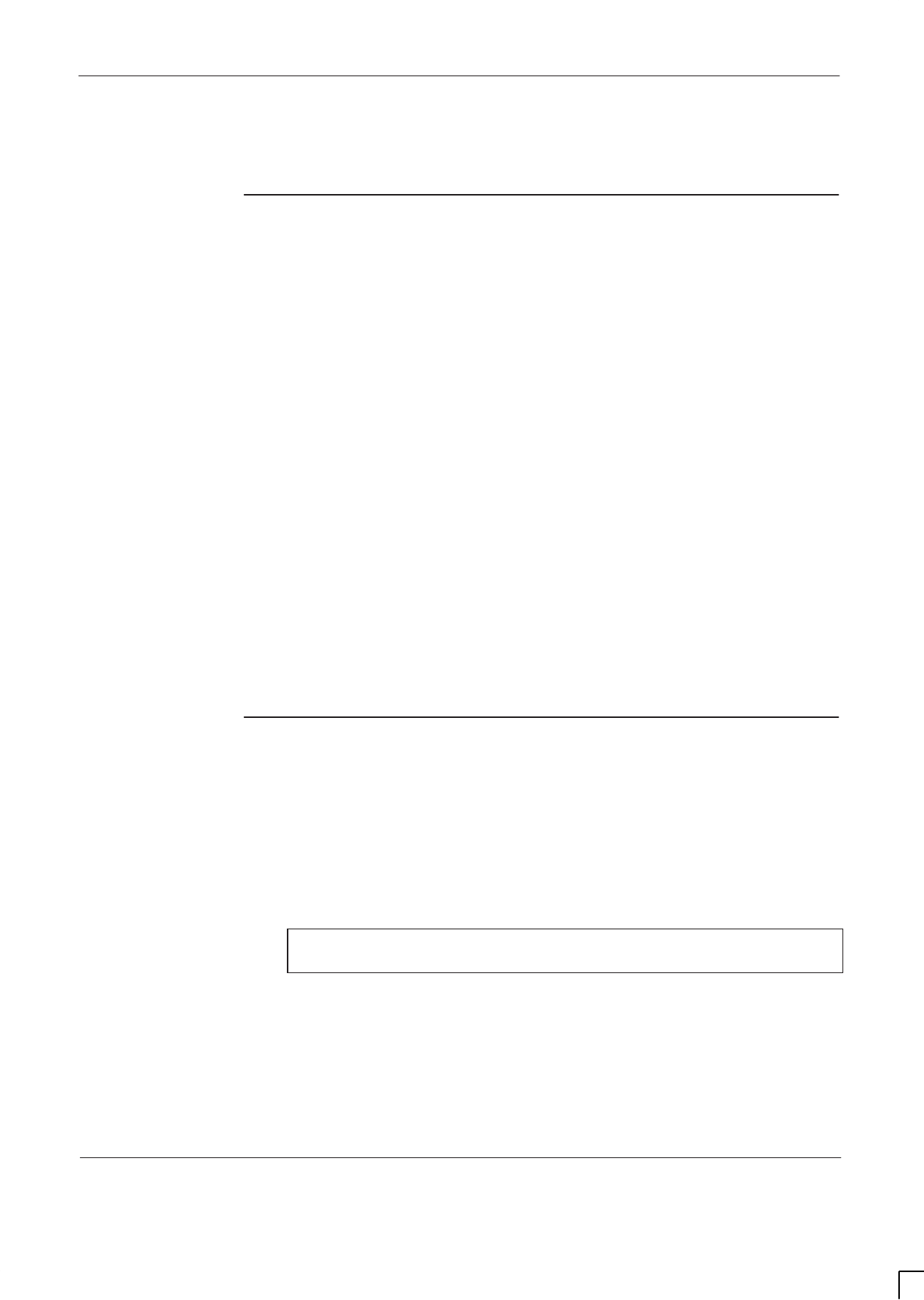
GSM-204-323 MCUF
31st Oct 01
Technical Description: Horizon
macro
outdoor
68P02902W02-A
CONTROLLED INTRODUCTION
Tech. 6–5
MCUF
MCUF overview
The main control unit with dual FMUX(MCUF) provides the site processing
functions, apart from RF functions of the transceiver. The MCUF also provides
switching for up to six network interfaces (via four NIUs) and up to 24
transceivers.
The cabinet may contain up to two MCUF modules, (one master and one for
redundancy). Each site and module has an electronic ID for remote
identification.
The MCUF provides the following functions:
Maintenance and operational/control processing.
Call processing (for example resource management and switching of
baseband hopping data).
Switching of traffic and control information.
Timing reference and network/BTS master clock synchronization.
The functionality of two FMUX.
Support of up to six transceivers via backplane in first cabinet and up to an
additional 18 transceivers via FMUX connections to other cabinets.
Support of up to six E1 or T1 circuits, via NIU modules.
Support of the CSFP function via the PCMCIA flash memory card.
Capability to
replace MCU of
M-Cell
6
and
M-Cell
2
The MCUF combines the MCU function of M-Cell
6
with two FMUX modules. If
the MCUF is installed in an M-Cell
6
or M-Cell
2
, it automatically reverts to the
functionality of an MCU and the integral FMUX devices no longer operate. In
M-Cell
2
, reverting to MCU mode includes the ability to directly connect to two
transceivers by modified use of the front panel FMUX fibre optic connections.
NOTE This capability to use MCUF in M-Cell
6
and M-Cell
2
is only
possible with GSR4 software release or later.
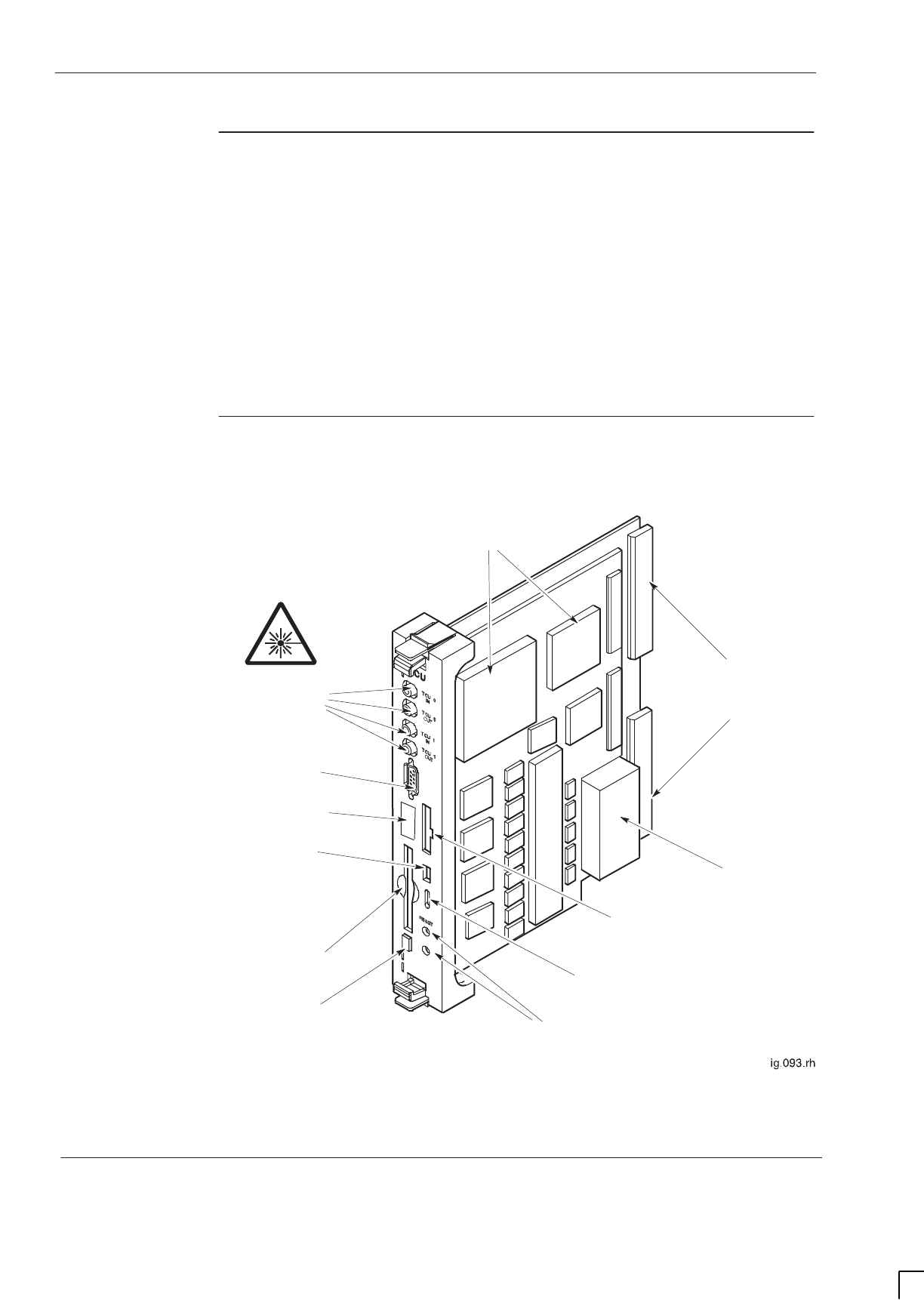
GSM-204-323
MCUF
31st Oct 01
Tech. 6–6
Technical Description: Horizon
macro
outdoor
CONTROLLED INTRODUCTION
68P02902W02-A
GPROC TSW
and GLCK
functions
The MCU section of the MCUF module combines functions of older generation
equipment:
The BTP (Base Transceiver Processor) functions and CSFP (Code
Storage Facility Processor) functions (provided PCMCIA card fitted),
formerly achieved by generic processor boards (GPROCs).
The timeslot switch (TSW).
The generic clock (GCLK).
MCUF module
view
Figure 6-3 shows an MCUF module.
(FULL - REMOVES SOFTWARE FROM MEMORY
CPU – RESETS MCUF CPU)
PCMCIA
CARD SLOT STATUS LEDS (RED &
GREEN)
CAL PORT
TTY MMI
PROCESSORS
OSCILLATOR
DEBUG PORT
BDM PORT
RESET BUTTONS
PCMCIA EJECT
BUTTON
INTERNAL FMUX
FIBRE OPTIC
CONNECTIONS
BACKPLANE
CONNECTORS
Figure 6-3 View of the MCUF
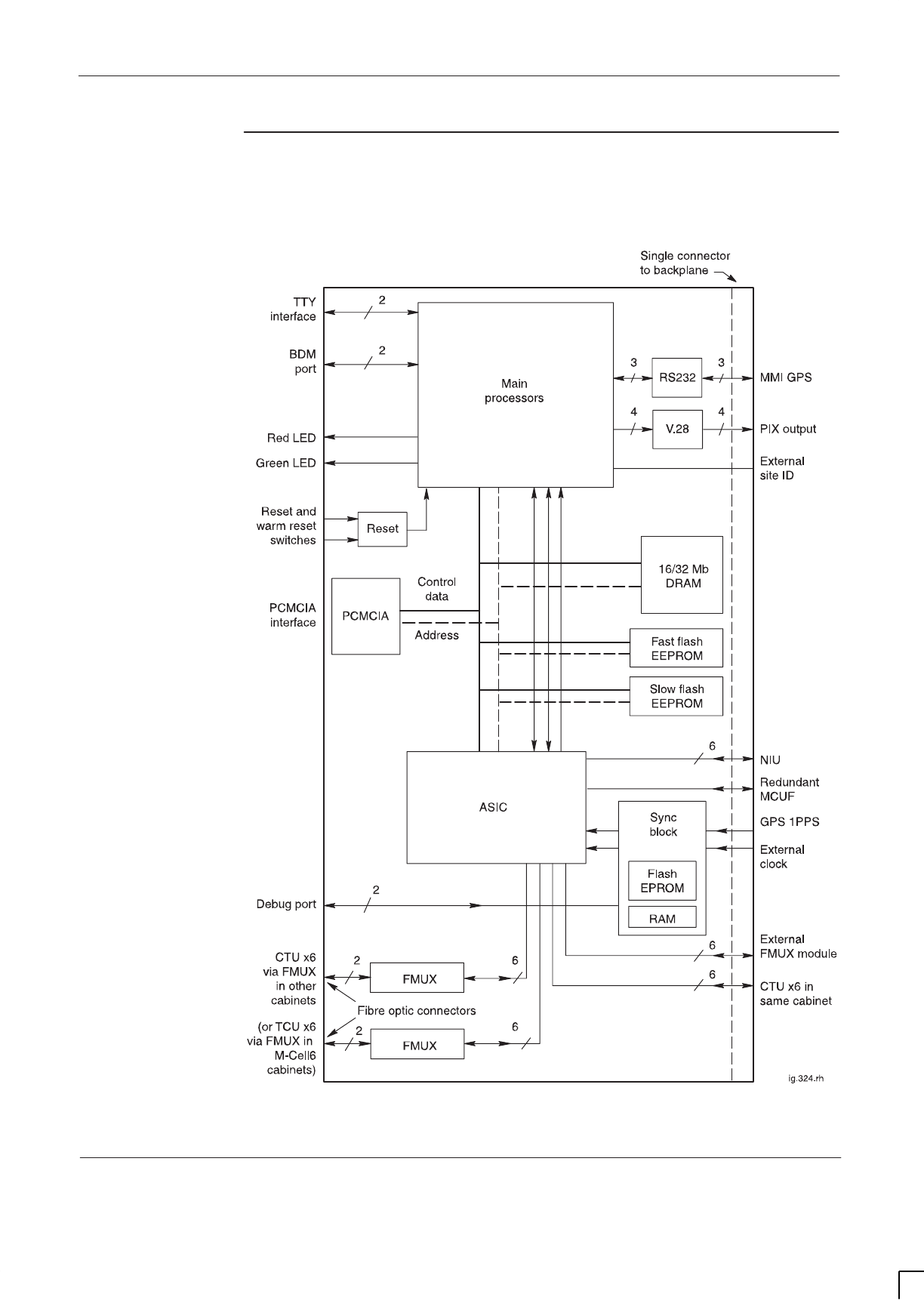
GSM-204-323 MCUF
31st Oct 01
Technical Description: Horizon
macro
outdoor
68P02902W02-A
CONTROLLED INTRODUCTION
Tech. 6–7
MCUF
functional
diagram
Figure 6-4 shows a functional diagram of the MCUF.
(IF USED)
(IF USED)
Figure 6-4 Functional diagram of MCUF in MCUF mode
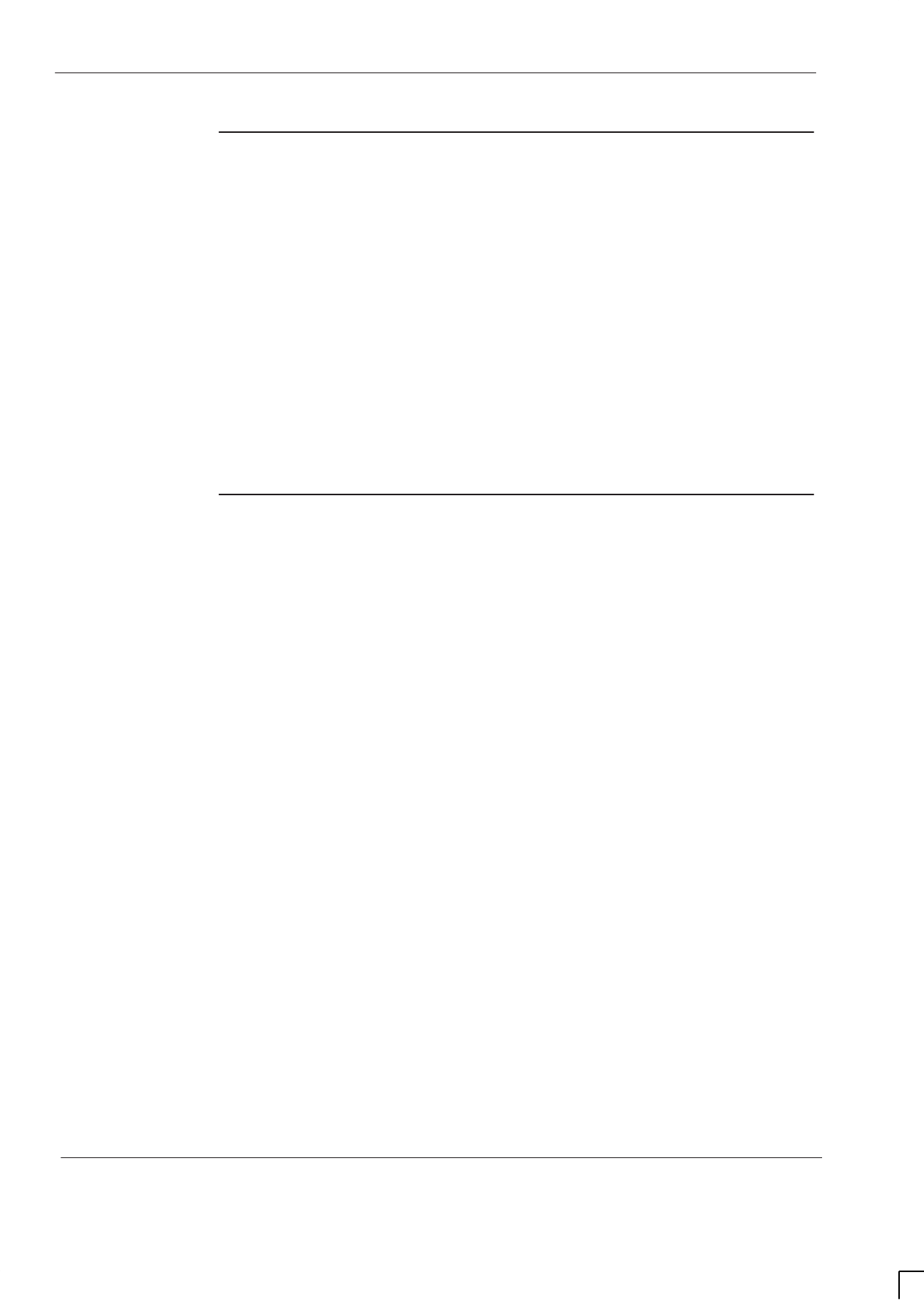
GSM-204-323
MCUF
31st Oct 01
Tech. 6–8
Technical Description: Horizon
macro
outdoor
CONTROLLED INTRODUCTION
68P02902W02-A
Link to
redundant
MCUF
The link to the redundant MCUF is similar to a transceiver link, but does not
have the BBH capability or the link delay measurement and compensation
facility. The 6.12 s, and 60 ms signals, are inserted into timeslots 8 and 16.
When the MCUF is in slave mode, timeslot and E1/T1 clock information is
extracted from the MCUF link and passed to the sync block.
The main processor HDLC link to the redundant MCUF can be routed in any
unused timeslot(s) of this link.
The ASIC can switch any timeslot on the redundancy link to any timeslot on any
of the other links connected to it such as the transceiver links, network links,
redundancy link or processor links.
Front panel
interfaces
TTY interface
A standard TTY interface is provided on the front panel, of 9.6 kbit/s (8 bits, No
parity, 1 stop bit (8 N 1)). A local maintenance terminal can be attached to this
port to use the Man Machine Interface (MMI) of the MCUF.
Debug and BDM ports
Two front panel ports are for Motorola factory and development use only:
The debug port, consists of a TTY connection to the sync processor to
access sync firmware, together with other connections to the ASIC and
main processors.
The Background Debug Mode (BDM) port is used for low level debugging
of the main processors.
FMUX fibre optic connections
There are fibre optic connections from the integral FMUX functionality of the
MCUF. The fibre optic connectors enable connection to MCUF or FMUX
modules in other cabinets for additional transceivers.
CAL port
The CAL port on the front panel of the MCUF can be used to calibrate the sync
block clock via MMI commands. The 8 kHz reference output is used in GCLK
calibration procedure (see
Installation & Configuration BSS Optimization
(GSM-100-423)
).
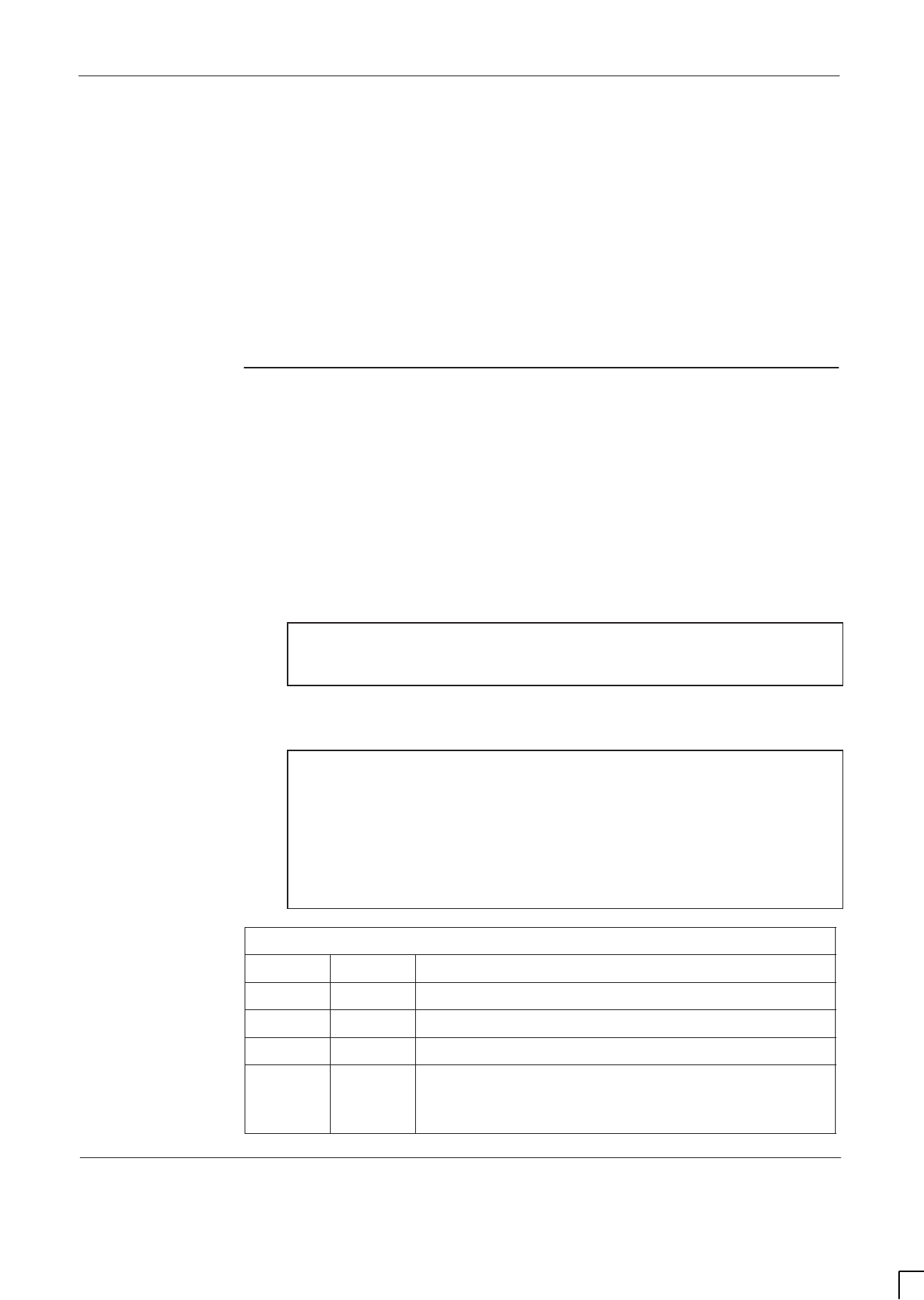
GSM-204-323 MCUF
31st Oct 01
Technical Description: Horizon
macro
outdoor
68P02902W02-A
CONTROLLED INTRODUCTION
Tech. 6–9
PCMCIA interface
The PCMCIA card is located on the front panel of the MCUF, and is used for:
Code Storage Facility Processor (CSFP) memory.
Rapid site initialization.
The PCMCIA socket is an industrial standard 68 pin single socket, fitted with an
ejector. The PCMCIA interface supports rev 2.1 type I and II cards.
The 20 Mbyte card can be write enabled, for upgrade of site information, or
disabled to protect card use for other sites or secure the site code.
Front panel
switches and
indicators
The front panel of the MCUF module has two reset switches as shown in
Figure 6-3:
FULL is a hard reset (power up - removes software from the memory).
CPU is a soft reset (this resets the MCUF main processors, but the
software remains in RAM).
A hard reset results in the software being reloaded to the DRAM, in the same
way as normal power up.
NOTE During the CPU (soft) reset, pressing CPU reset again will
perform a hard reset. Double pressing of the CPU reset
thus has the same effect as a hard reset.
The MCUF has two front panel LEDs (one green and one red) as shown in
Figure 6-3, with indications as shown in Table 6-2.
CAUTION When red and green LEDs are flashing, the boot code is
downloading into non-volatile memory for software
upgrade. Power should not be removed, nor the cabinet
reset, until downloading has been completed, as this will
corrupt the non-volatile memory. If the boot code is
corrupted, contact Motorola Customer Network Resolution
Centre requesting the boot code restoration procedure
and the appropriate boot code file.
Table 6-2 MCUF front panel LED indications
Red Green Status
Off Off Board not powered up or in rest cycle
Off On Normal operation
On Off Fault condition
Flashing Flashing Non-volatile memory boot code upgrade
(Do not remove power or reset – see above
CAUTION)
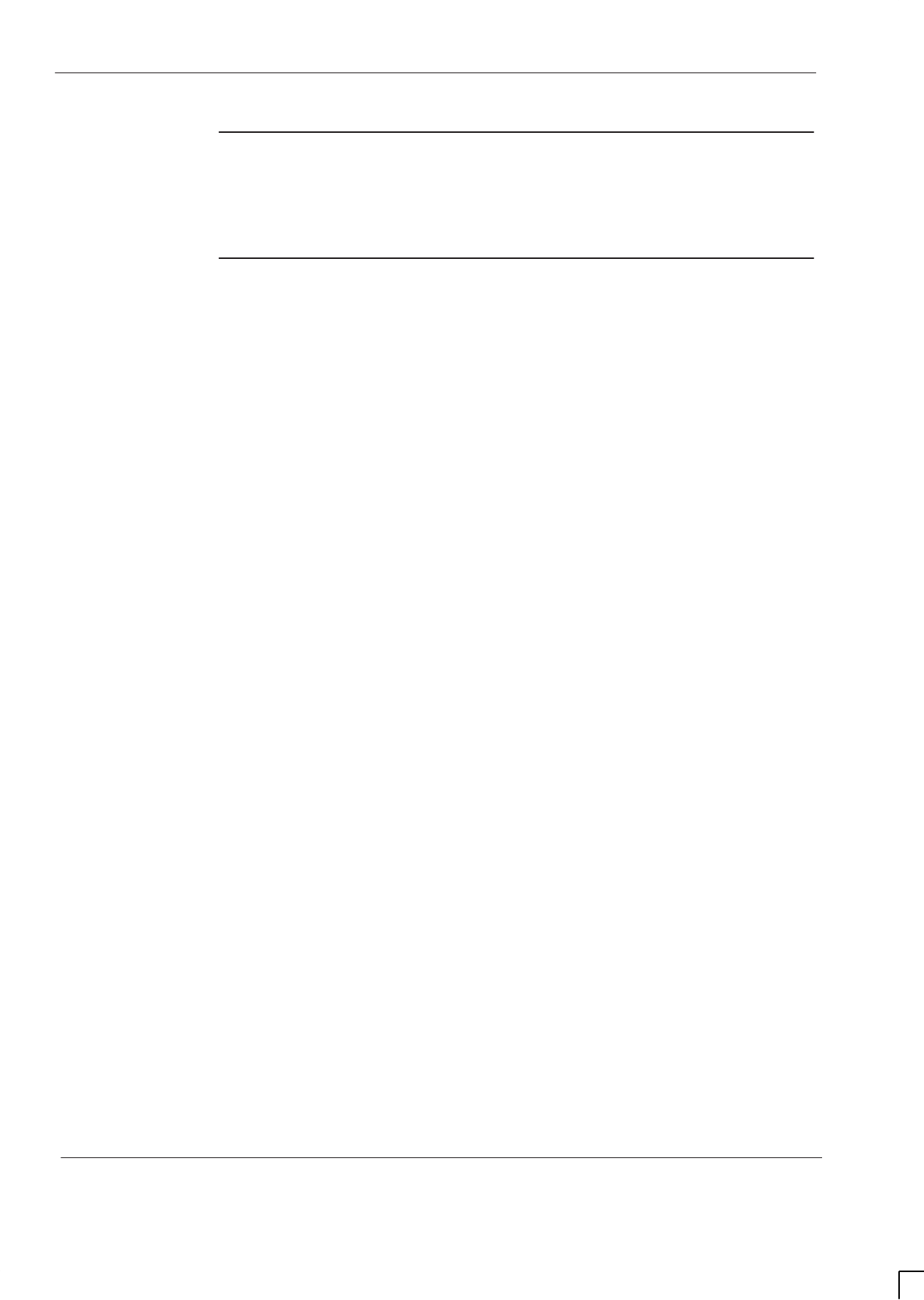
GSM-204-323
MCUF
31st Oct 01
Tech. 6–10
Technical Description: Horizon
macro
outdoor
CONTROLLED INTRODUCTION
68P02902W02-A
PIX interfaces
The MCUF provides four PIX outputs on the backplane, driven at V. 28 levels.
The four PIX outputs, routed to the cabinet alarm board, enable relay contact
control of external customer equipment.
DRAM, flash
EPROM and
code loading
functions
DRAM
The 16 Mbyte DRAM provides operational code and data storage for the main
processors. There is also a SIMM socket in the circuit board, enabling the
addition of a further 16 Mbytes if required. After software initialization, the DRAM
uses ECC protection. Memory protection is provided by the main processors.
Fast flash EPROM
The fast flash 1 Mbyte bank is used for boot code and executive process code.
It has a fast access time (<75 ns) , enabling direct execution. The boot code is
factory set, and reprogrammed only in major software upgrades.
Slow flash EPROM
The slow flash 0.5 Mbyte bank is used for non-volatile data storage of diagnostic
data and module ID information.
Code loading
The boot and executive code, held in the fast flash EPROM, initiates the MCUF
on power up or reset. If a PCMCIA memory card is fitted, operational code may
be obtained and copied to the DRAM for execution. If no card or code is
available, the operational code is obtained from the BSC.
Before execution, the operational code held in DRAM is checked with code held
at the BSC. The BSC downloads any changed code objects to the DRAM.
After successful checking of the DRAM operational code, the code is executed,
and the PCMCIA memory card updated with any changed objects.
CSFP code loading
If a PCMCIA memory card is available, then a code storage facility processor
(CSFP) function can be supported. A new software load can be downloaded in
the background, without any reduction in service, and stored on the PCMCIA
card.
Once the complete load has been transferred to the PCMCIA card, a code swap
can be initiated. The site is reset and the new software brought into service (<10
minutes). As a precaution, the old version is held on the PCMCIA card to
support a roll back to the original version if required.
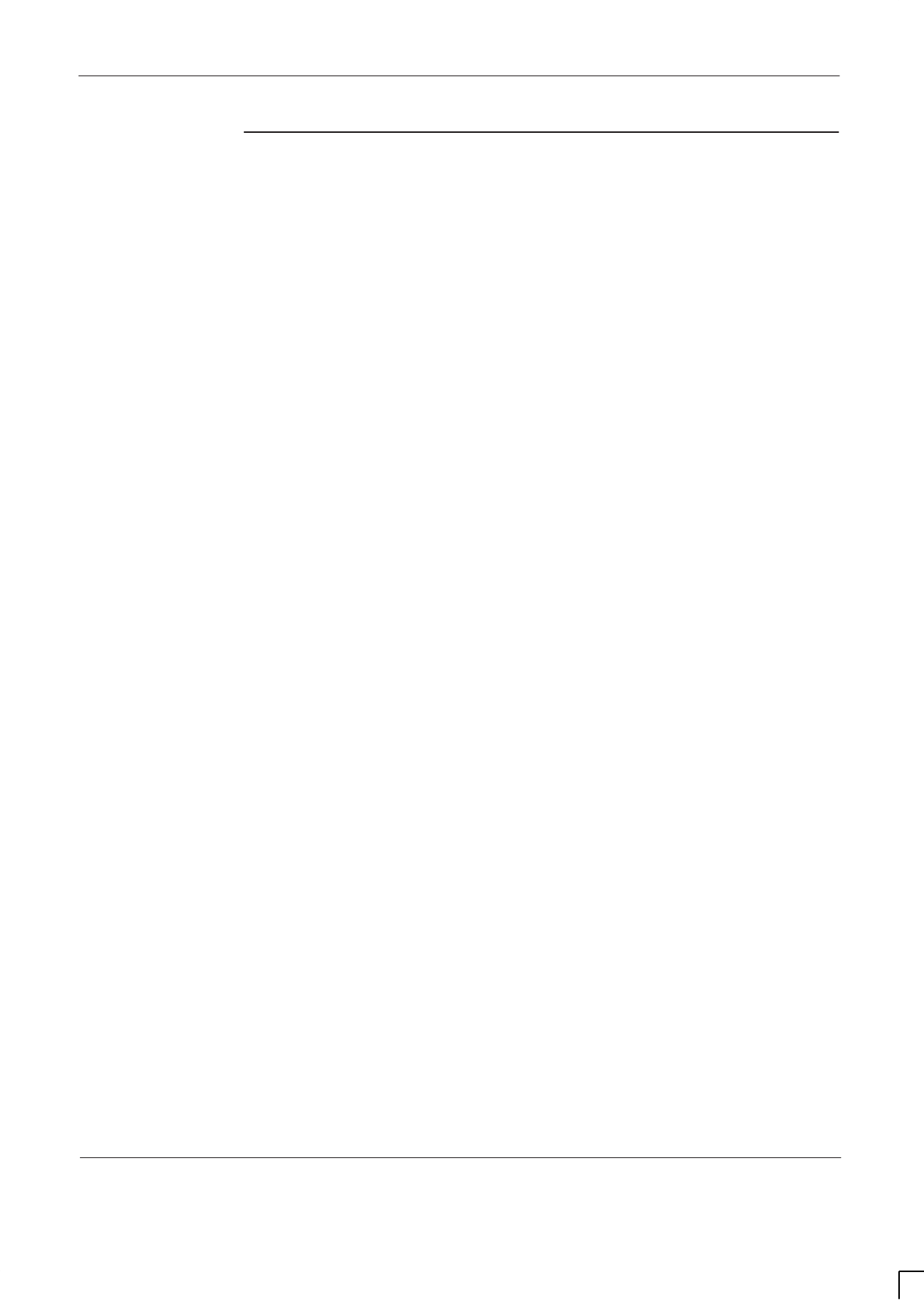
GSM-204-323 MCUF
31st Oct 01
Technical Description: Horizon
macro
outdoor
68P02902W02-A
CONTROLLED INTRODUCTION
Tech. 6–11
ASIC
functionality
The Application Specific Integrated Circuit (ASIC) provides central switching
capabilities for the MCUF. It is capable of supporting up to 24 transceivers,
together with up to six network interfaces and two links to the on-board
processors, one link to the sync processor and a link to the redundant MCUF.
The link to the sync processor is used for code loading purposes only. The ASIC
supports baseband hopping across the 24 transceiver links.
The ASIC provides interface features associated with the transceiver links,
these include synchronization features to allow for delay in the link to the
transceivers, and the necessary framing and encoding to support the link.
All of the serial links into the ASIC are internal lines (I lines), 125 s framed,
with 32 eight bit timeslots per frame.
ASIC transceiver link features
The ASIC interfaces to a maximum of 24 transceiver links. The ASIC can switch
any timeslot on any of the transceiver links to any timeslot on other links
connected to the ASIC; transceiver links, network links, MCUF redundancy link
or processor links.
The ASIC provides the following features associated with the transceiver links:
Link advance/delay compensation
The ASIC will continually measure the round trip delay on each transceiver
link to calculate a timing advance for each link. The link advance is
applied, and can be adjusted, by the main processor via the processor
parallel interface.
BBH data switching
BBH switching is performed automatically on any timeslot configured as
BBH data. A single timeslot from the transceiver is selected for BBH
routeing information, and defines which transceiver link (0-23) should be
used for downlink.
Timing reference insertion
The ASIC receives timing pulses from the sync block and inserts the
appropriate bits into the transceiver downlink synchronization and framing
timeslots. The sync block will provide a version of the 6.12 s and 60 ms
signals that is advanced by 125 s for this purpose.
Manchester coding/decoding
The transceiver links are all Manchester coded/decoded by the ASIC. This
function can be switched on or off (default on) on a per link basis. The
disable feature is for applications outside of the MCUF module.
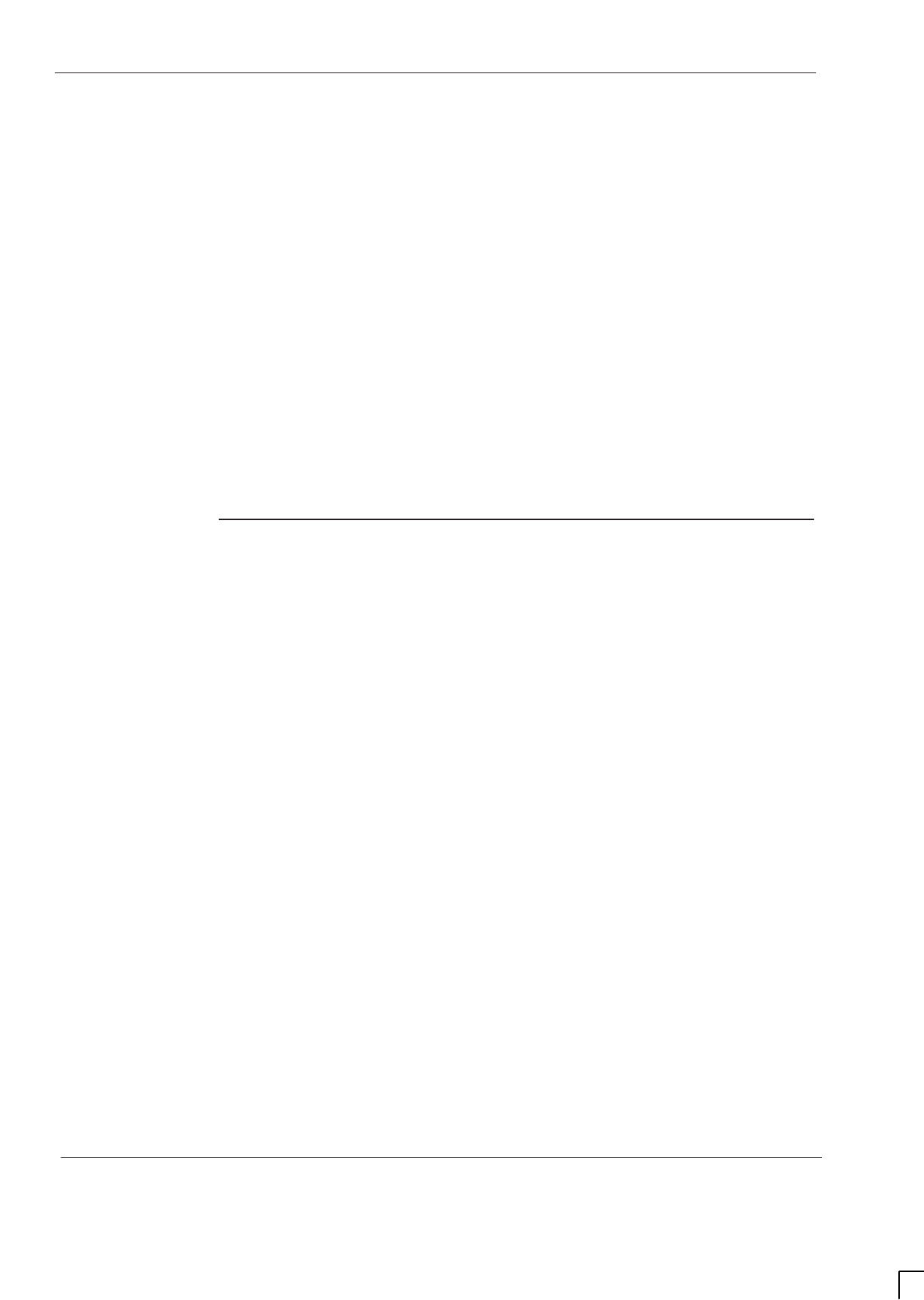
GSM-204-323
MCUF
31st Oct 01
Tech. 6–12
Technical Description: Horizon
macro
outdoor
CONTROLLED INTRODUCTION
68P02902W02-A
ASIC/network and processor link switching
The ASIC supports a maximum of six network links and two main processor
links. The data to/from these links can be switched to/from any timeslot on other
links connected to the ASIC.
The two links to the main processor allow it to route HDLC and other links to the
appropriate place:
24 HDLC timeslots for the BCF RSS channel to each transceiver.
Four timeslots for NIU control channels (two local, two redundant).
Sync processor code load channel.
Two channels for RSL links.
One HDLC channel occupying up to three timeslots to the redundant
MCUF.
Sync block
functionality
The sync block is controlled via the parallel interface of the main processors and
is responsible for site synchronization functions. It generates all required local
references from a high stability local clock source. This clock source may also
be locked to the incoming network clocks.
The sync clock source is in the form of a crystal oscillator (OCXO) which warms
up for phase locking in 4 minutes, and achieves frequency stabilization in 15
minutes.
Site frame reference generation and re-timing includes:
2.048 MHz - For serial communications.
16.384 MHz - For FMUX communications.
125 s - For NIU framing and transceiver framing.
60 ms- For transceiver GSM timing.
6.12 s - For GSM superframe.
The reference clocks available to the sync block are:
Six network extracted clocks (E1/T1 source via NIUs). Any of the NIU
modules under control of the MCUF can extract a reference clock from an
E1/T1 link and pass to the Sync block.
CAL port. The CAL port can be used to calibrate the sync block clock via
MMI commands. The reference output provides a monitoring point.
Redundant MCUF link.
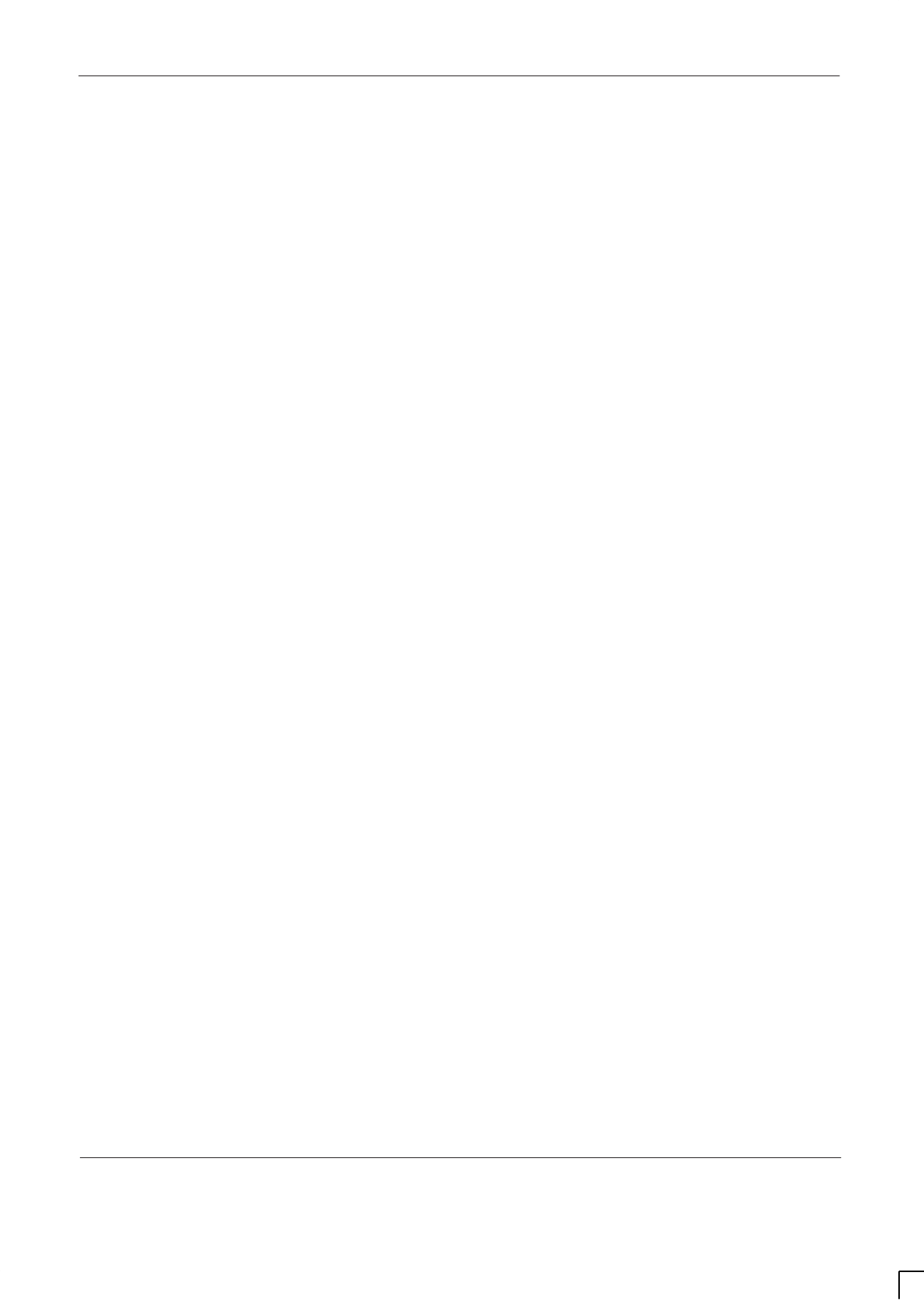
GSM-204-323 MCUF
31st Oct 01
Technical Description: Horizon
macro
outdoor
68P02902W02-A
CONTROLLED INTRODUCTION
Tech. 6–13
Phase lock loop (PLL) operating modes
The PLL uses the selected reference signal as the loop reference clock. It
includes an OCXO accurate to 0.05 ppm, a phase comparator and a loop filter.
The PLL has the following operating modes:
Warm-up
The PLL is open loop and using the calibration frequency, but the OCXO
is not yet warmed up.
Set frequency
The PLL is open loop and using the calibration frequency, and the OCXO
is warmed up.
Fast tune
Closed loop with wide filter for coarse locking to the reference (extracted
from network clock).
Fine tune
Closed loop with narrow filter for accurate locking to the reference
(extracted from network clock).
When in fine tune closed loop mode, the accuracy is 0.01 ppm.
Sync block code load
The sync block controller has a dedicated 2.048 Mbit/s serial link into the ASIC
enabling a 64 kbit/s HDLC channel to the main processors for code loading.
The sync block includes 256 kbytes of flash EPROM, which is used to store:
Boot code.
Operational code.
The boot code, which cannot be altered, queries the main processors on the
current version of the sync operational code.
If the stored operational code is the correct version, the boot code will move the
operational code to RAM and execute the code.
If the query results in the need for new operational code, the sync processor will
download the operational code from the main processors via the ASIC to the
RAM in the sync block.
After a successful download, the boot code programmes the flash EPROM with
the new operational code and runs the operational code in RAM.
GSM counters
The following counters are provided:
GSM frame incremented every 4.615 ms; range 0 - 1325.
GSM superframe incremented every 6.12 s; range 0 - 2047.
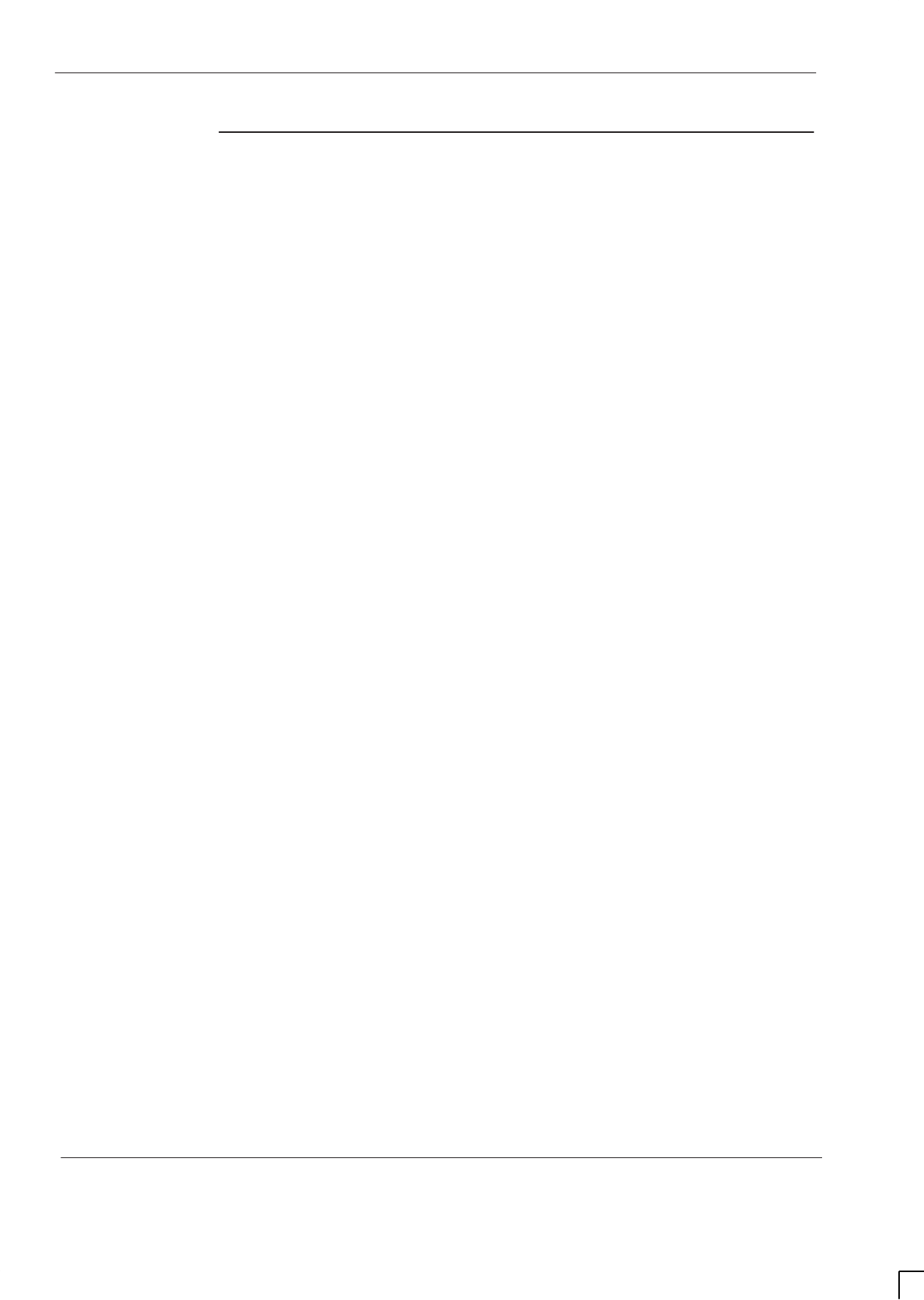
GSM-204-323
MCUF
31st Oct 01
Tech. 6–14
Technical Description: Horizon
macro
outdoor
CONTROLLED INTRODUCTION
68P02902W02-A
Integral MCUF
FMUX
functionality
The equivalent function of two FMUX modules exists integral to the MCUF,
enabling two extension cabinets to be connected. To enable total of four
cabinets to be joined together as one BTS site, an FMUX module is also
required in the master cabinet to connect the third extension cabinet. A single
cabinet site has no need for the FMUX functionality, because the MCUF
connects with the cabinet CTUs through the backplane.
Each fibre optic multiplexer (FMUX) function multiplexes and demultiplexes six,
full duplex, transceiver links to one (TX/Rx) pair of fibre optic cables. This
enables up to six transceivers in a single extension cabinet (either
Horizon
macro
or M-Cell
6
) to be linked to the master cabinet.
Each FMUX fibre optic link is full duplex 16.384 Mbit/s. The FMUX optical link is
capable of driving up to 1 km.
For functional description of FMUX see FMUX module and FMUX function in
this chapter.

GSM-204-323 NIU
31st Oct 01
Technical Description: Horizon
macro
outdoor
68P02902W02-A
CONTROLLED INTRODUCTION
Tech. 6–15
NIU
Overview of NIU
The network interface unit (NIU) module provides two E1 or two T1 termination
links to the terrestrial network. The NIU E1/T1 outputs are connected to a T43 or
BIB board, depending on the impedance matching requirement of the customer
terrestrial circuits.
There are two types of NIU board, one for E1, one for T1. The NIU layout is
common to both E1 and T1, the only differences being in the associated crystal
oscillators and line matching resistor values.
An on-board NIU control processor provides network interface configuration and
supervision, controlled by the MCUF.
NIU locations
The cabinet may contain up to four NIU modules in the digital module shelf, as
shown in Figure 6-1. Two NIUs are located in the master (lower) part of the
cage. Two NIUs are in the redundant (upper) part of the cage, though these
upper NIUs are also used for non-redundant purposes.
An NIU in slot A0 supports two E1/T1 links.
An NIU in slot A1 supports one E1/T1 link.
An NIU in slot B0 supports two E1/T1 links.
An NIU in slot B1 supports one E1/T1 link.
NIU command
identity number
Each NIU is identified in the database by an identity number, from 0 to 3.
Table 6-3 shows the NIU slots and equivalent identity number.
Table 6-3 NIU slot and equivalent command identity
NIU (MSI) identity number
used in commands NIU slot
0 A0
1 B0
2 A1
3 B1
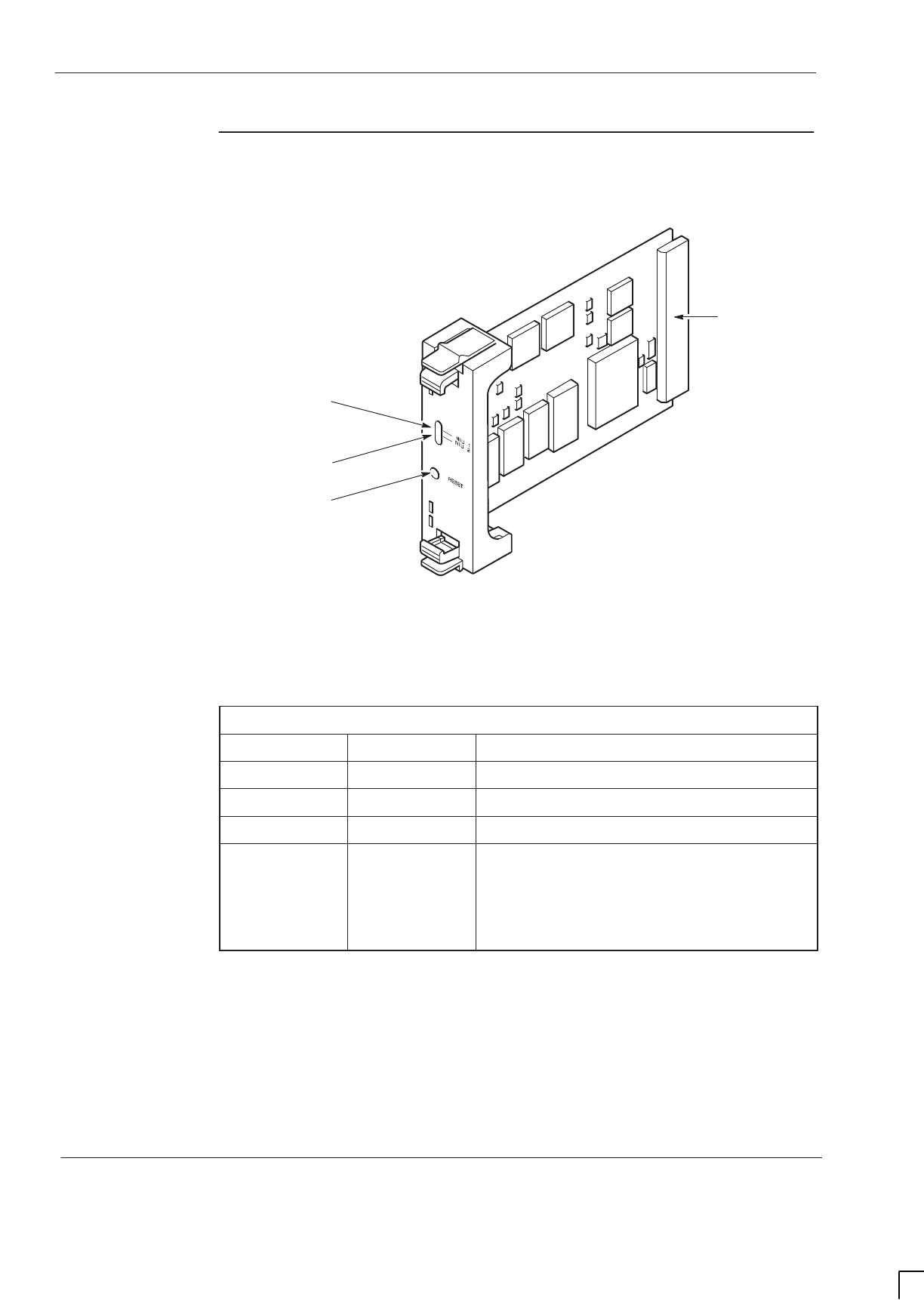
GSM-204-323
NIU
31st Oct 01
Tech. 6–16
Technical Description: Horizon
macro
outdoor
CONTROLLED INTRODUCTION
68P02902W02-A
NIU view and
LEDs
Figure 6-5 shows an NIU module.
ig.325.rh
RESET/DISABLE
SWITCH
NIU GREEN LED
BACKPLANE
CONNECTOR
NIU RED LED
Figure 6-5 View of NIU module
The NIU status is indicated by the two front panel LEDs, one green and one red,
controlled by the on-board processor, as shown in Table 6-4.
Table 6-4 NIU LED Display
Red LED Green LED Status of NIU board
Off Off NIU not powered up or in reset cycle.
Off On Normal operation.
Flashing Flashing NIU undergoing system code download.
On On NIU self testing following switch on or
reboot.
Red LED extinguishes after 20 seconds, or
after 50 seconds following a reboot due to
code download.
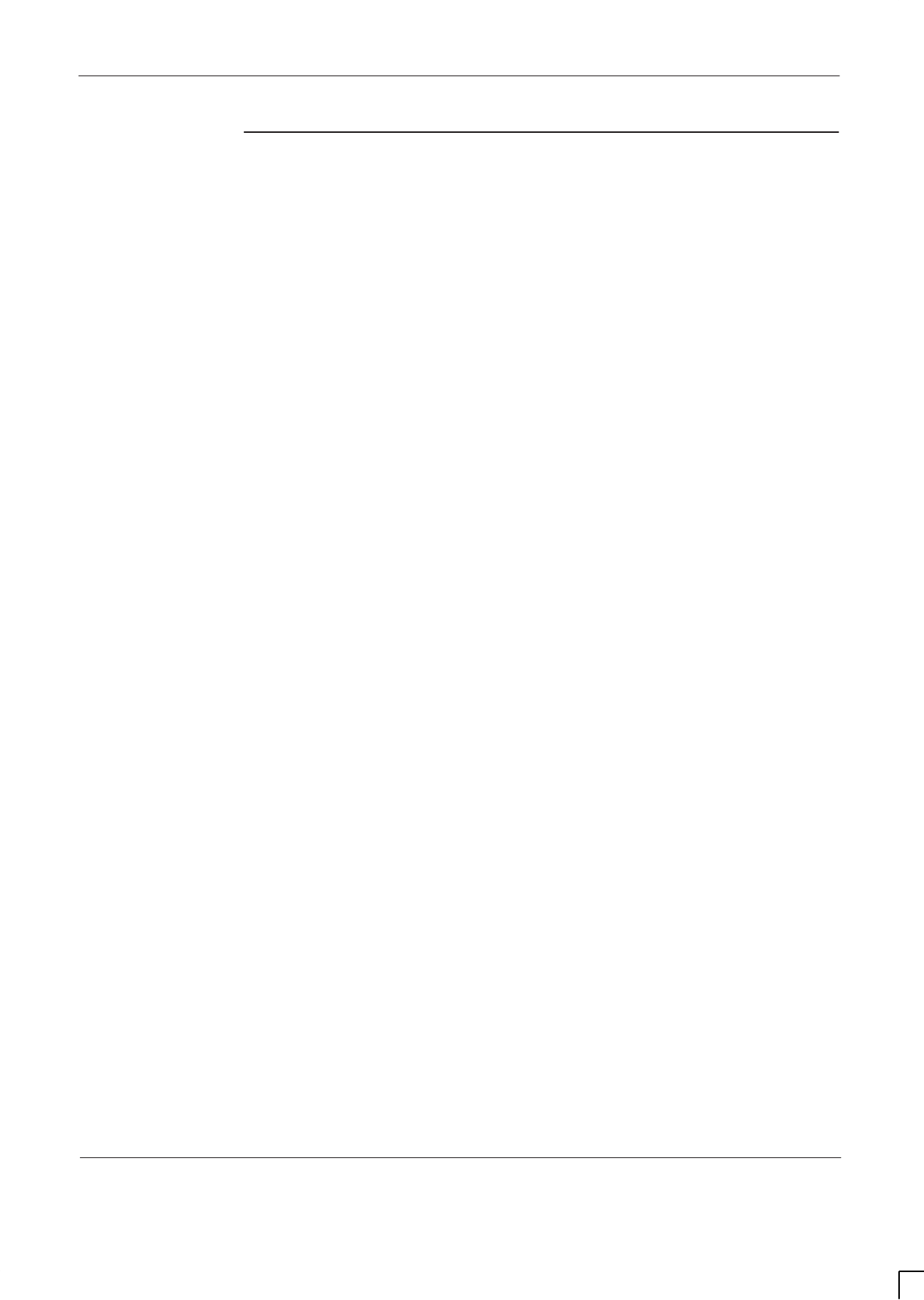
GSM-204-323 NIU
31st Oct 01
Technical Description: Horizon
macro
outdoor
68P02902W02-A
CONTROLLED INTRODUCTION
Tech. 6–17
NIU
functionality
The NIU provides two E1/T1 interfaces into the network (link 0 and link 1) as
well as LAPD encoding/decoding and clock recovery from a selected E1/T1 link.
The second E1/T1 interface (link 1) is not used for NIUs placed in positions at
A1 and B1, as shown in Figure 6-1.
An NIU control processor provides network interface configuration and
supervision, controlled by the MCUF. The NIU control processor maintains two
independent control links in the redundant configuration (one to each MCUF),
each using timeslot 0 of MCUF link 0.
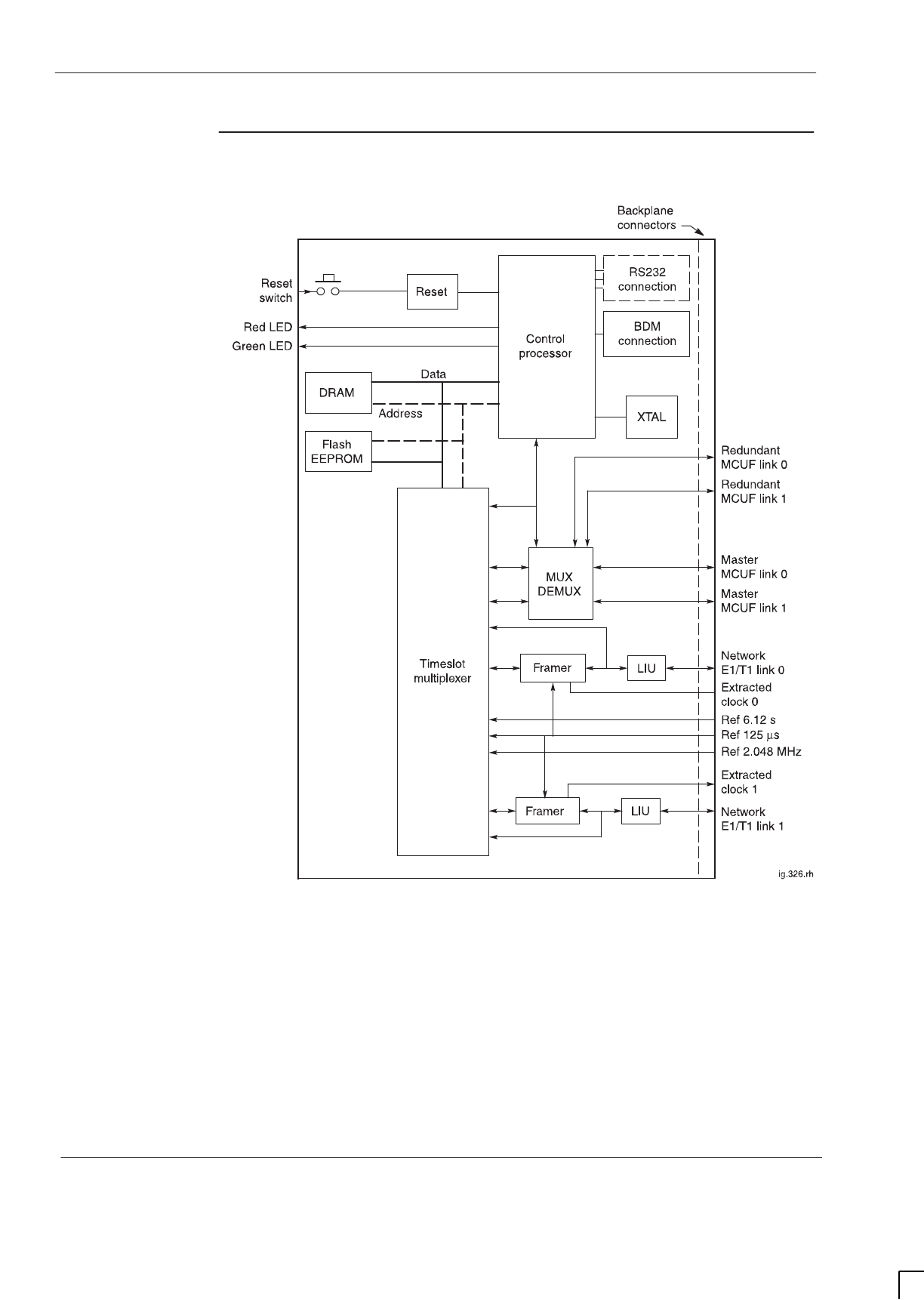
GSM-204-323
NIU
31st Oct 01
Tech. 6–18
Technical Description: Horizon
macro
outdoor
CONTROLLED INTRODUCTION
68P02902W02-A
NIU diagram
Figure 6-6 identifies the functional blocks in the NIU.
Figure 6-6 Functional diagram of NIU module
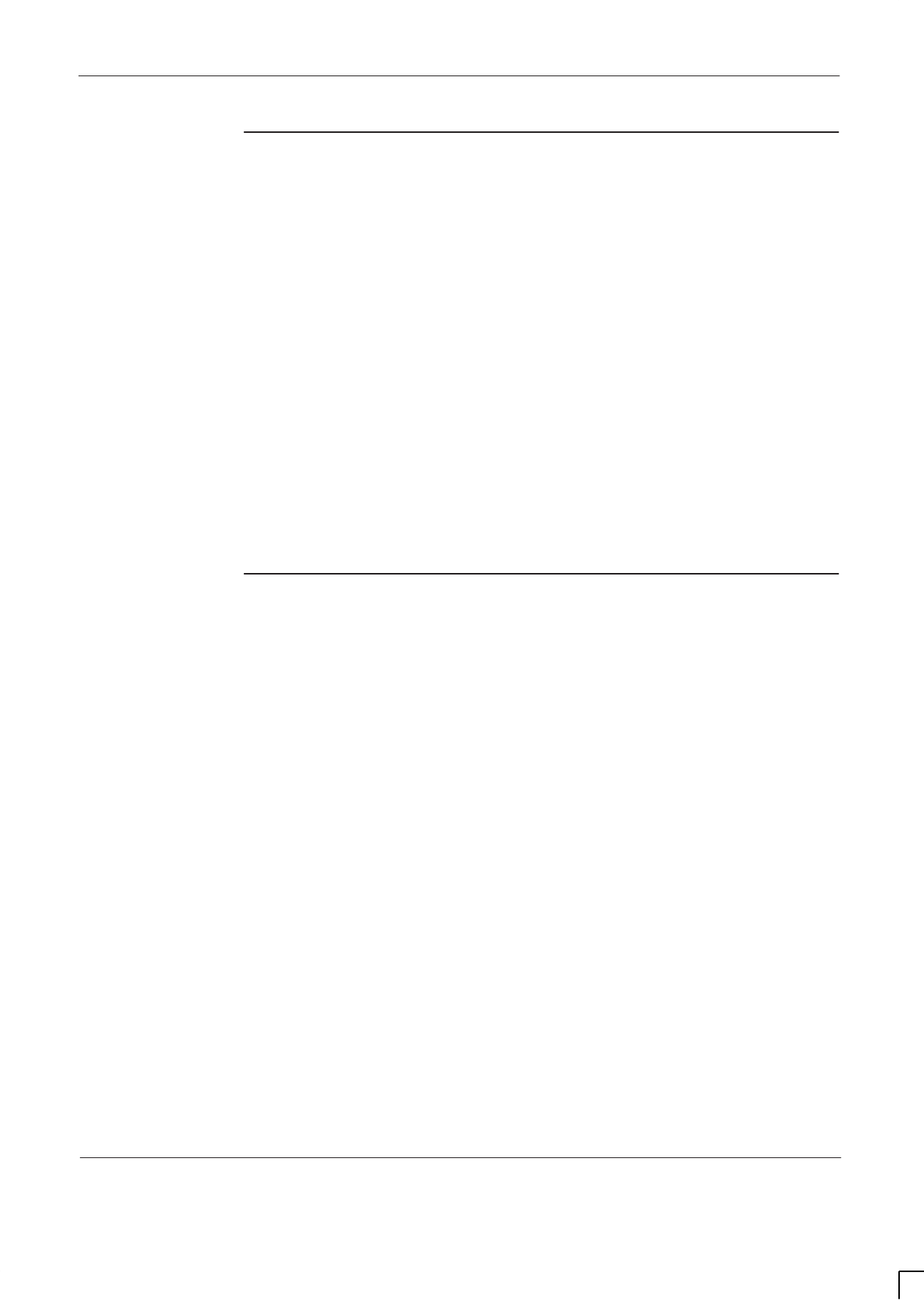
GSM-204-323 NIU
31st Oct 01
Technical Description: Horizon
macro
outdoor
68P02902W02-A
CONTROLLED INTRODUCTION
Tech. 6–19
Control
processor
The control processor interfaces to timeslot 0 of link 0 from each connected
MCUF.
The processor uses 512 kbytes of flash EPROM for boot code, operational code
storage and module ID. Code is executed directly from the flash EPROM. The
boot code can be overwritten under control of the MCUF, if required.
The processor also has an on-chip 1 Mbyte of DRAM.
TTY Ports
The processing section provides two TTY ports for Motorola debugging
purposes only.
Resets
The processor is capable of soft resetting itself. The front panel reset causes a
hard reset of the entire board. Power-on also resets the processor.
The MCUF is able to reset the NIU via a message on the HDLC link.
NIU/MCUF
framing and
clocks
The control processor is supplied with a clock from an on-board crystal
oscillator, which has an output enable pad for test purposes. The framer
devices also have their own crystal oscillators on-board.
The framer devices provide the decoded and jitter attenuated receive data, for
passing to the MCUF.
The framer devices also extract a clock signal from an E1/T1 link, which is then
passed to the MCUF synchronization circuit. At the MCUF, this signal is used to
phase lock a local 16.384 MHz clock signal. Once phase locked, three reference
clock signals are provided for NIU use:
REF 2.048 MHz clock signal.
REF 6.12 s clock signal.
REF 125 s clock signal.
The NIU transmit and receive framing is controlled by this 125 s reference
pulse received from the MCUF.
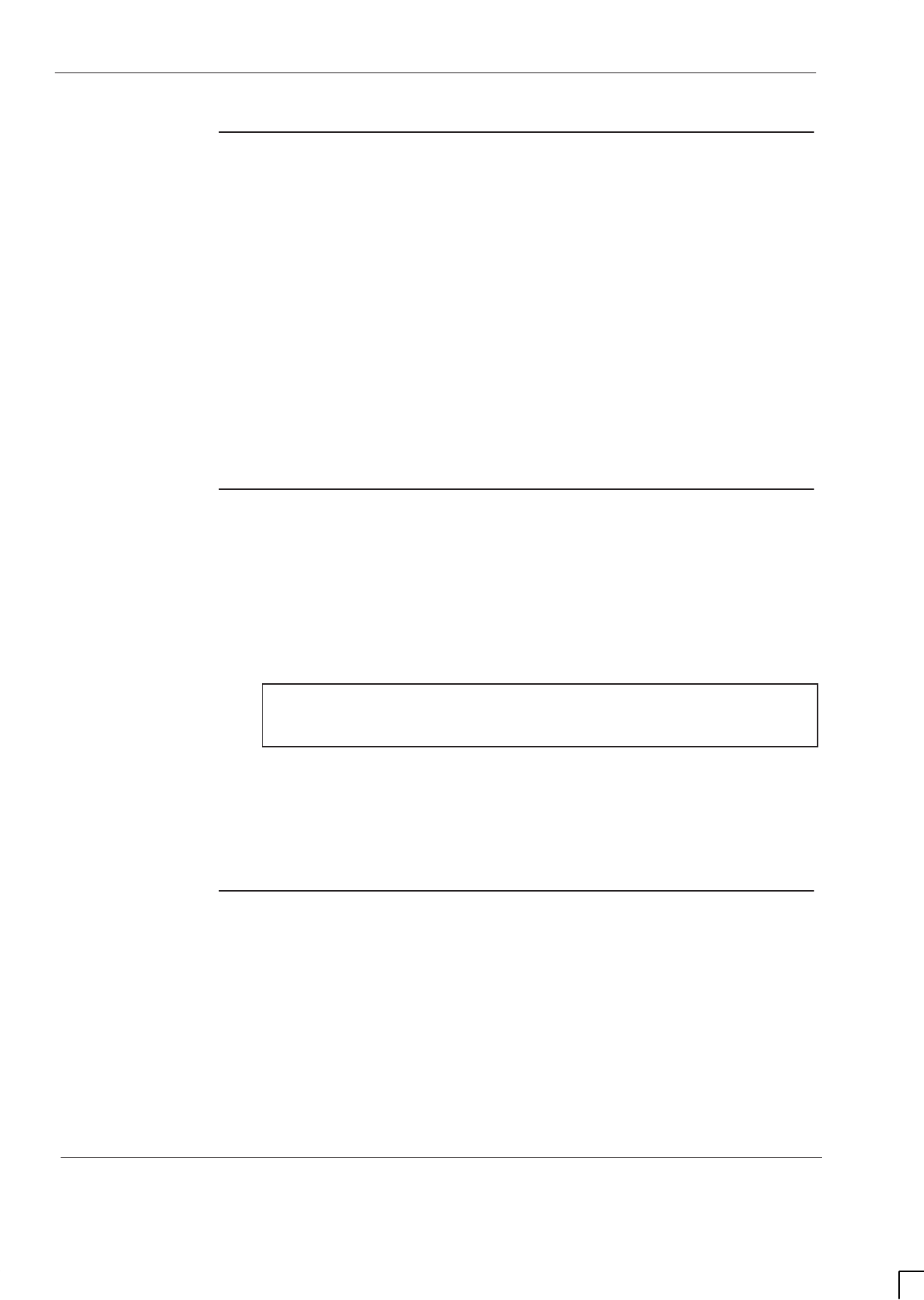
GSM-204-323
NIU
31st Oct 01
Tech. 6–20
Technical Description: Horizon
macro
outdoor
CONTROLLED INTRODUCTION
68P02902W02-A
Distance
measurement
The NIU provides the ability to perform network distance delay measurement on
either of the two network links. Measurement can only be performed on one link
at a time.
Three modes of operation are possible:
Mode 1. A pattern is transmitted in a selected network timeslot and the
corresponding receive timeslot is monitored for its return. The delay is
measured to an accuracy of ± 488 ns. The pattern is transmitted on the
6.12 second reference signal.
Mode 2. The receive link is monitored for the pattern. When received, the
pattern is transmitted back in the next frame. The time between receipt
and transmission of the pattern is measured to an accuracy of +/–488 ns.
Mode 3. The receive link is monitored for the pattern. When it is detected,
a strobe is generated for the MCUF sync block.
Radio signalling
links (RSLs)
The radio signalling links (RSL) to the BSC from the main processor on the
MCUF are 64 kbit/s LAPD links. The LAPD encoding of this RSL data is
performed on the NIU by the NIU control processor.
The RSL links between the MCUF and NIU must be sent as follows:
RSL link 1 is embedded in the NIU control link; that is, it will be in timeslot
0 of link 0 to the NIU. This link is important for initialization.
NOTE When the NIU is on a network link to a BSC or another
BTS, the RSL can be placed on either link on any default
timeslot other than zero.
RSL link 2 is on a different timeslot from that used for the network
connection
The NIU will support a maximum of two RSL links. The RSL links may both be
on a single network link or shared between the two network links.
The NIU hardware supports switching for 64 k and 16 k LAPD channels.
T1 NIU need to
set link type
T1 NIUs and E1 NIUs cannot be interchanged. A T1 link line consists of 24
timeslots, as opposed to 32 timeslots for an E1 link line. A T1 link generates
specific T1 alarms, referred to as Red alarms. A T1 NIU supports the same MSI
type of device transitions as an E1 NIU.
The OMC-R operator should set the link type, or it will default the site to an E1
system. In ROM, it is set by a ROM-only MMI command. In RAM, it is a
database parameter set by a chg_element command.
The RSL default timeslots are the same for a T1 NIU and an E1 NIU. The basic
mechanism for communicating and configuring is also the same.
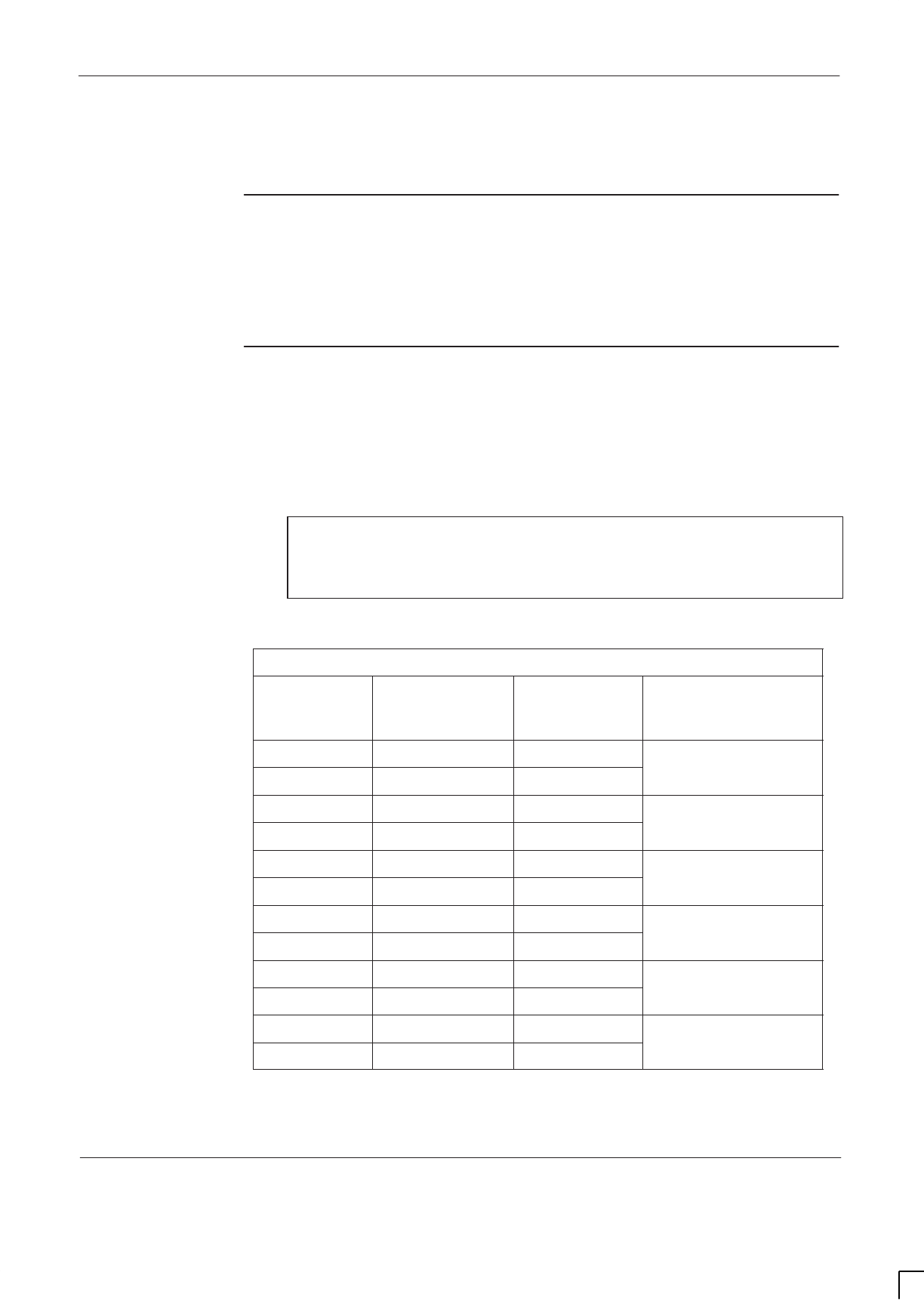
GSM-204-323 T43/BIB-NIU - E1/T1 mapping
31st Oct 01
Technical Description: Horizon
macro
outdoor
68P02902W02-A
CONTROLLED INTRODUCTION
Tech. 6–21
T43/BIB-NIU - E1/T1 mapping
Overview of
T43/BIB-NIU
connection
The NIU network interface (E1/T1) links connect to a single T43 (CIM) or BIB
(BIM) board on top of the cabinet by a single backplane connector and cable.
NIU to T43/BIB
mapping and
command ID
One T43 or BIB board is connected to the BCU. Only six network interfaces
are used, three pairs to the master NIU modules, and three pairs to the
redundant NIU modules. Each NIU is identified in the database by an identity
number, from 0 to 3, as shown in the final column of Table 6-5.
NOTE The redundant NIU modules are only redundant in the
sense of being supplied by a different BPSM, and can
thus continue to operate if the Master BPSM fails. All NIUs
are available for separate use.
Table 6-5 defines the mapping from the T43/BIB connector to NIU boards.
Table 6-5 T43/BIB connector to NIU boards
T43 network
side
connector
37-way D-type
connections
(BIB)
NIU location NIU identity
(MSI)
used in commands
J1 1,20 NIU A0 - Tx1 MSI(NIU) 0
J2 2,21 NIU A0 - Rx1
J7 7,26 NIU A0 - Tx2 MSI(NIU) 0
J8 8,27 NIU A0 - Rx2
J13 13,32 NIU A1 - Tx1 MSI(NIU) 2
J14 14,33 NIU A1 - Rx1
J4 4,23 NIU B0 - Tx1 MSI(NIU) 1
J5 5,24 NIU B0 - Rx1
J10 10,29 NIU B0 - Tx2 MSI(NIU) 1
J11 11,30 NIU B0 - Rx2
J16 16,35 NIU B1 - Tx1 MSI(NIU) 3
J17 17,36 NIU B1 - Rx1

GSM-204-323
T43/BIB-NIU - E1/T1 mapping
31st Oct 01
Tech. 6–22
Technical Description: Horizon
macro
outdoor
CONTROLLED INTRODUCTION
68P02902W02-A
Diagram of T43
connection to
NIUs
Figure 6-7 shows a diagram of T43 connection to NIUs.
NIU A0
J0
T43
NIU A1
NIU B0
NIU B1
J1
J2
J7
J8
J13
J14
J4
J5
J10
J11
J17
J16
Figure 6-7 Diagram of T43 connection to NIUs
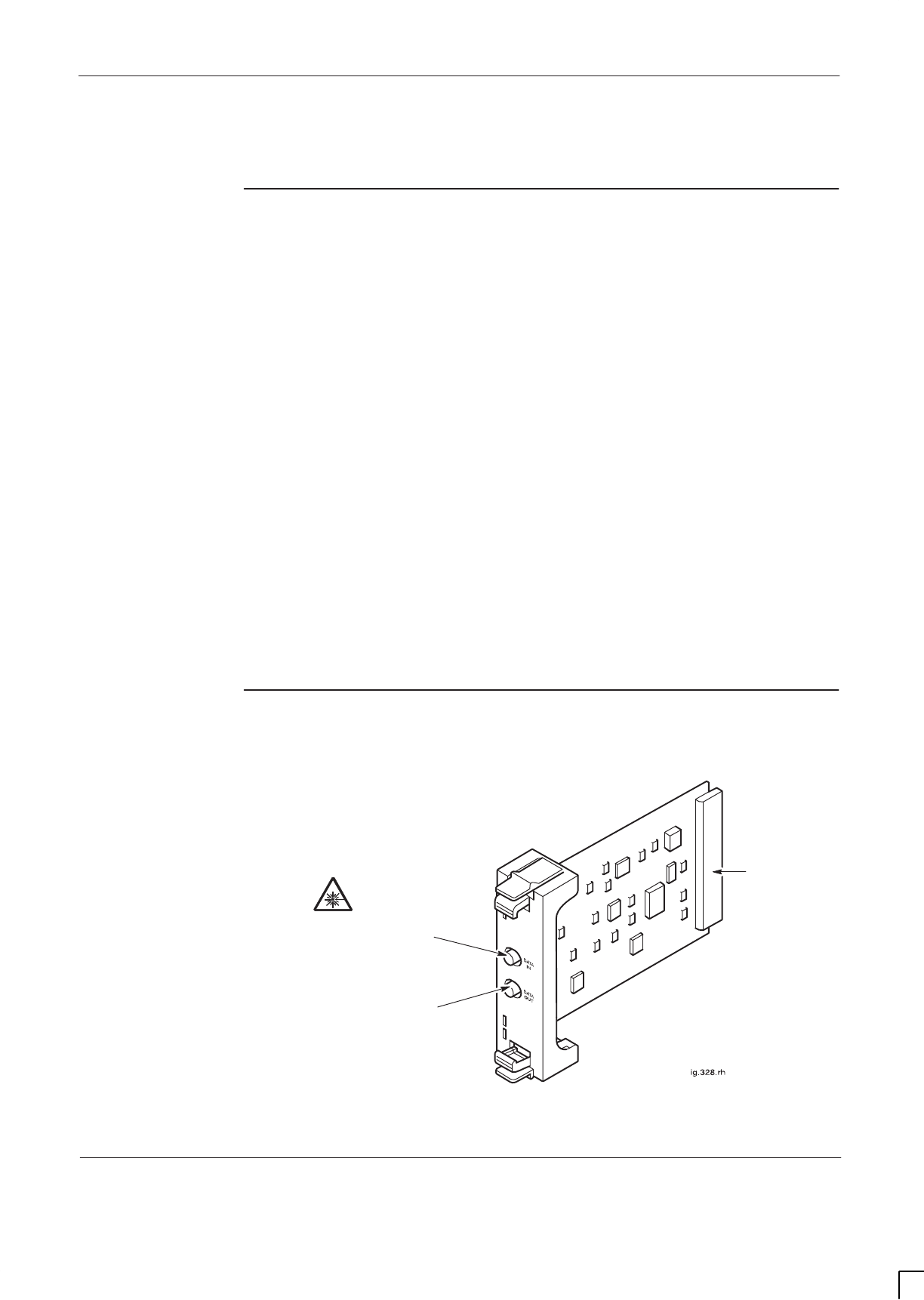
GSM-204-323 FMUX module and FMUX function
31st Oct 01
Technical Description: Horizon
macro
outdoor
68P02902W02-A
CONTROLLED INTRODUCTION
Tech. 6–23
FMUX module and FMUX function
Overview of
FMUX module
The fibre optic multiplexer (FMUX) module multiplexes and demultiplexes six,
full duplex, transceiver links to one (TX/Rx) pair of fibre optic cables. This
enables up to six transceivers in a single extension cabinet (either
Horizon
macro
or M-Cell
6
) to be linked to the master cabinet.
The FMUX module has two modes of operation:
Working in conjunction with the MCUF to multiplex/demultiplex transceiver
links to/from a third extension cabinet.
Operating in the extension cabinet to supply the transceivers in that
cabinet.
To enable a total of four cabinets to be joined together as one BTS site, an
FMUX module is required in the master cabinet to connect the third extension
cabinet. A single cabinet site has no need for an FMUX module, because the
MCUF connects with the cabinet CTUs through the backplane.
Two FMUX modules may be fitted in the digital module shelf, one for the master
MCUF, and one for the slave. An extension cabinet only requires one FMUX to
connect to six transceivers within the cabinet, (plus one for redundancy if
required).
Each FMUX fibre optic link is full duplex 16.384 Mbit/s. The FMUX optical link is
capable of driving up to 1 km.
FMUX module
view
Figure 6-8 shows an FMUX module.
BACKPLANE
CONNECTOR
FIBRE OPTIC INPUT FROM
ANOTHER MCUF/FMUX IN
ANOTHER CABINET AT THE SITE
FIBRE OPTIC OUTPUT TO
ANOTHER MCUF/FMUX IN
ANOTHER CABINET AT THE SITE
Figure 6-8 View of FMUX module
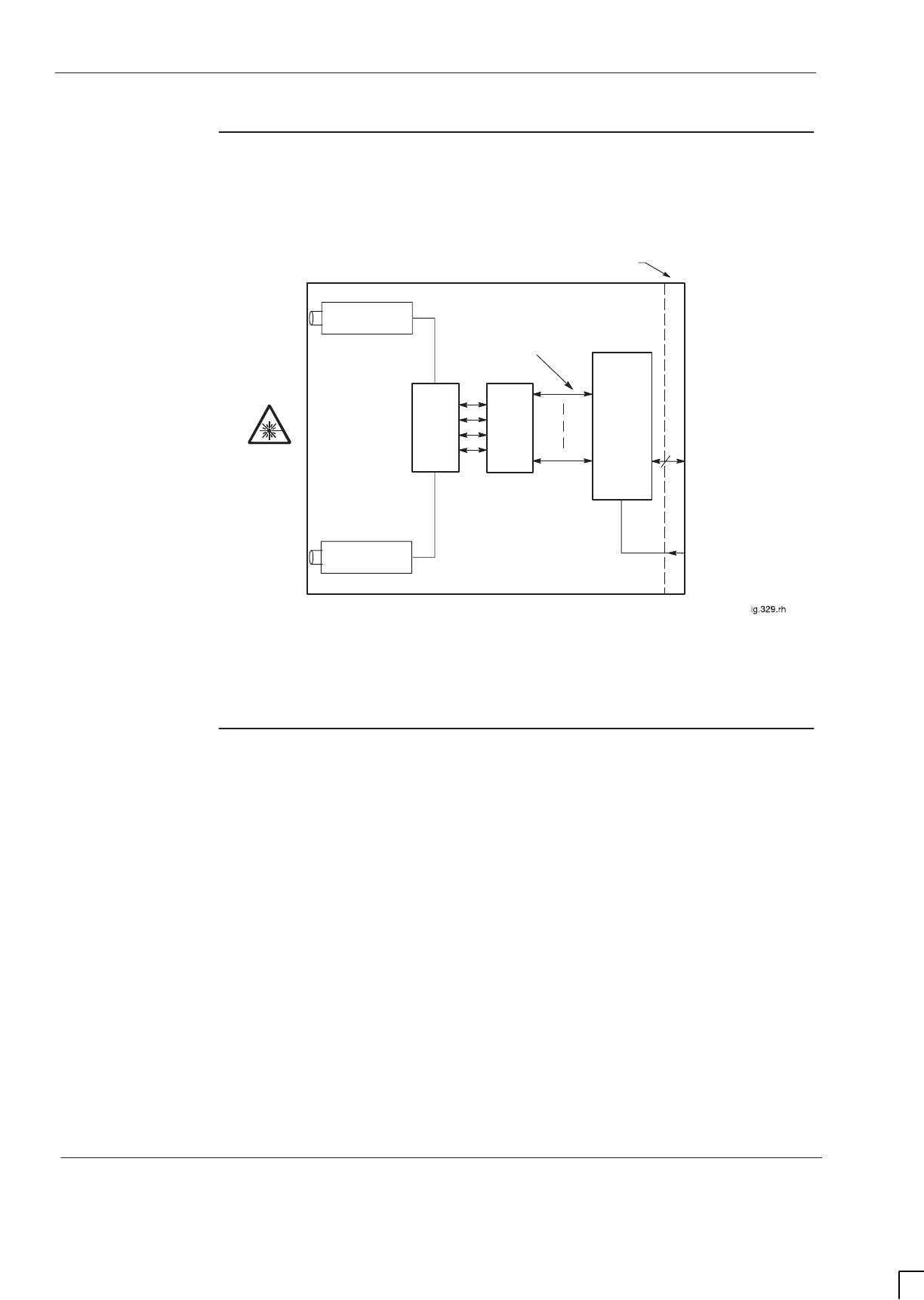
GSM-204-323
FMUX module and FMUX function
31st Oct 01
Tech. 6–24
Technical Description: Horizon
macro
outdoor
CONTROLLED INTRODUCTION
68P02902W02-A
FMUX
functional
diagram
Figure 6-9 shows a block diagram of the FMUX module.
FIBRE OPTIC
RECEIVER
FIBRE OPTIC
TRANSMITTER
BACKPLANE CONNECTOR
Rx
DATA
Tx
DATA
SELECT
CONTROL
(FROM
MCUF)
6
MUX/
DEMUX 2:1
SELECT TO MCUF (IF
MASTER
CABINET)
MANCHESTER
ENCODED
Tx/Rx
6
TO FMUX IN
ANOTHER
CABINET
TO FMUX IN
ANOTHER
CABINET
TO CTUs OR
TCUs (IF
EXTENSION
CABINET)
Figure 6-9 Functional diagram of FMUX module
FMUX
functional
explanation
The MCUF transmits and receives a 2.048 Mbit/s data stream link to each
operational transceiver. In the master cabinet this is achieved by the backplane,
without using an FMUX.
If the transceiver is in an extension cabinet, the master cabinet FMUX combines
the data stream with up to five others (see Figure 6-9), and then converts the
electronic signal to fibre optic, for onward transmission to the extension cabinet.
At the extension cabinet, another FMUX converts the fibre optic signal back to
electronic form, for transmission to the transceivers.
The data stream return from the extension cabinet is a reverse of the above.
The multiplexer/demultiplexer can support up to six transceiver links. It uses a
16.384 Mbit/s Manchester encoded serial data link organized as 256 x eight bit
timeslots in a 125s frame. Manchester coding is used to detect errors,
indicated at timeslot zero for each transceiver, enabling error correction at the
other FMUX.
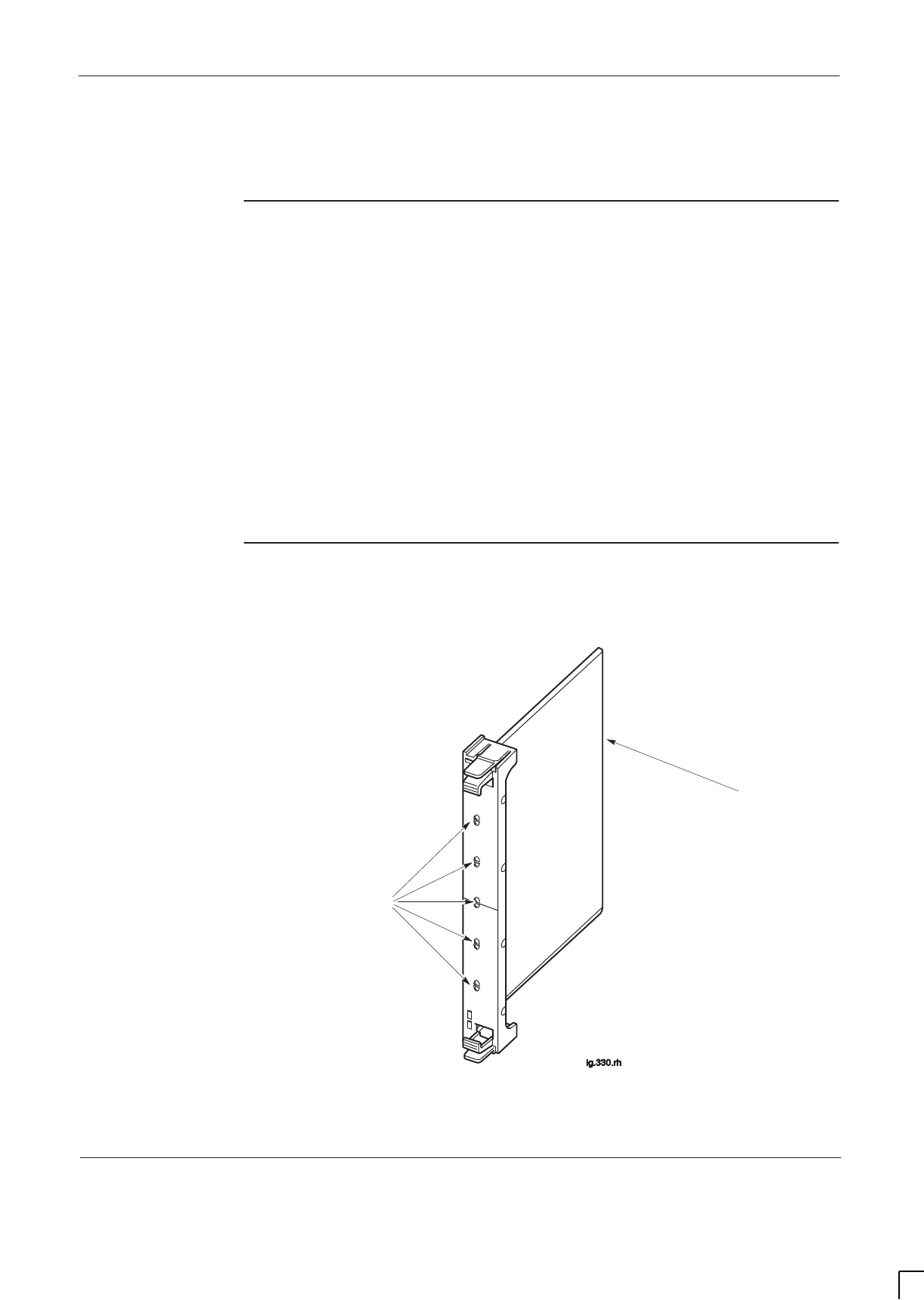
GSM-204-323 Alarm module
31st Oct 01
Technical Description: Horizon
macro
outdoor
68P02902W02-A
CONTROLLED INTRODUCTION
Tech. 6–25
Alarm module
Alarm module
overview
The alarm module is located in the digital module shelf, adjacent to the MCUFs.
It provides the cabinet equipment with an external alarm system to report
operational status. The alarm module:
Collects all cabinet alarms (received from the backplane).
Provides current sensing for 16 customer inputs, referred to as site
alarms. These inputs are provided by the PIX connectors PIX0 and PIX1.
Controls up to four relay driven outputs linked to customer equipment
(changeover contacts 30 V, 1 A maximum). These outputs are provided by
the PIX0 connector.
Transmits alarm information to all CTUs in the same cabinet.
Alarm module
view
Figure 6-10 shows an alarm module.
BACKPLANE
CONNECTOR
5 LED PAIRS
Figure 6-10 Alarm module view
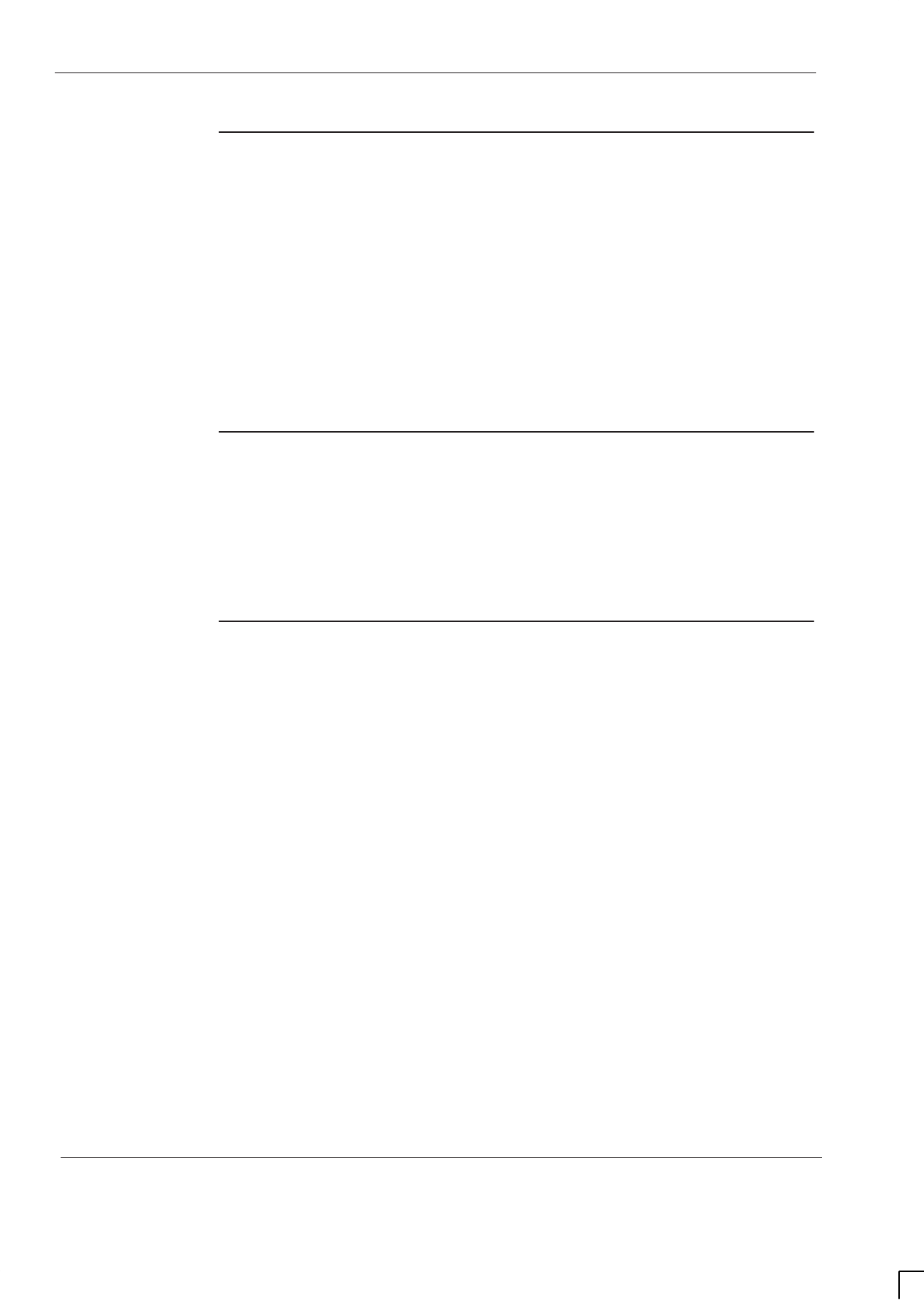
GSM-204-323
Alarm module
31st Oct 01
Tech. 6–26
Technical Description: Horizon
macro
outdoor
CONTROLLED INTRODUCTION
68P02902W02-A
Alarm module
functionality
The alarm module receives inputs from:
The external alarm connector on the interface panel, (from the CAB and
the alarms interface board).
Cabinet PSMs (identifying type, manufacturer and slot number).
Environmental control devices.
Customer defined alarms.
The alarm board receives these inputs, encodes them, and then passes the
code word to all CTUs in the cabinet via the backplane.
Alarm module
replacement –
effect on alarms
The alarm module can be replaced while the cabinet system is running (hot
replacement). This will temporarily interrupt alarms, with the OMC-R receiving
an additional alarm module out of service alarm, which automatically clears
upon correct insertion of the replacement module.
Alarm collection
from extension
cabinets
Extension cabinet alarms are sent from the extension cabinet alarm module to
the extension cabinet CTUs. The CTUs transmit the alarms to the main cabinet,
by using the normal FMUX connection, for transmission to the MCUF.
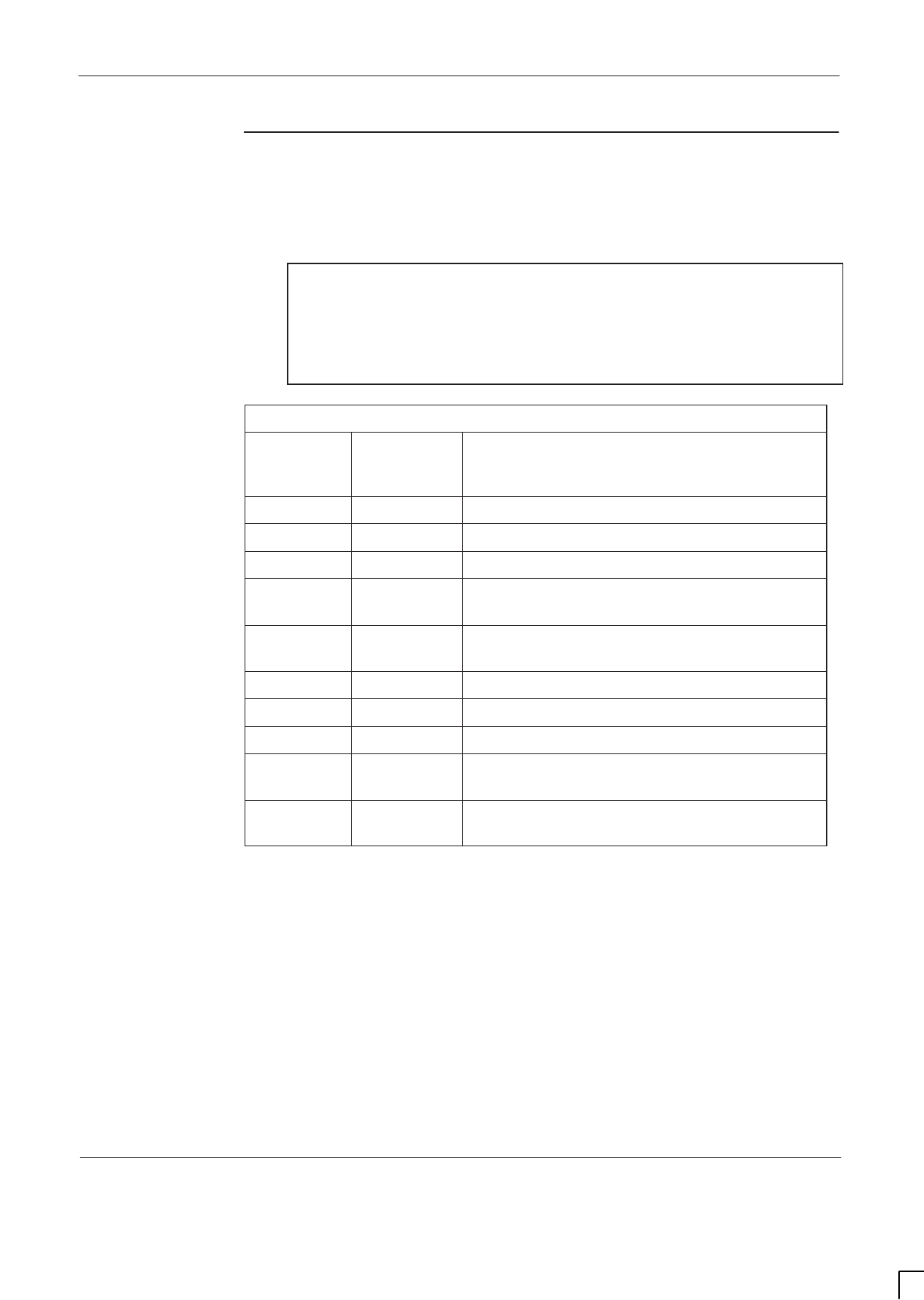
GSM-204-323 Alarm module
31st Oct 01
Technical Description: Horizon
macro
outdoor
68P02902W02-A
CONTROLLED INTRODUCTION
Tech. 6–27
Alarm module
display
presentation
All alarms indicators are green when equipment is functioning correctly, and red
when equipment is faulty. The locations are shown in Table 6-6.
NOTE Seven of the LEDs are used in the Horizon
macro
outdoor.
LEDs marked red in Table 6-6 are on in alarm state, and
off in normal operation.
LEDs marked bicolour in Table 6-6 (fans) are green when
all fans are operating correctly, and red if one or more
fans are faulty.
Table 6-6 Alarm module LEDs
LED
location Light
colour
states
Equipment monitored by light
(Green = OK, Red = FAULT)
1 (top) red AC supply to ac input failed.
2 red Rectifier output failed.
3 red Not used (LED permanently off).
4 red Cabinet door or auxiliary equipment housing
door open alarm.
5 red Low voltage disconnect (LVD) alarm (battery
backup option).
6 bicolour TMS fans fully operational.
7 bicolour Not used (LED permanently green).
8 bicolour Not used (LED permanently green).
9 red TMS 1 failed
(thermal management system).
10 (bottom) red TMS 2 failed
(auxiliary equipment housing).
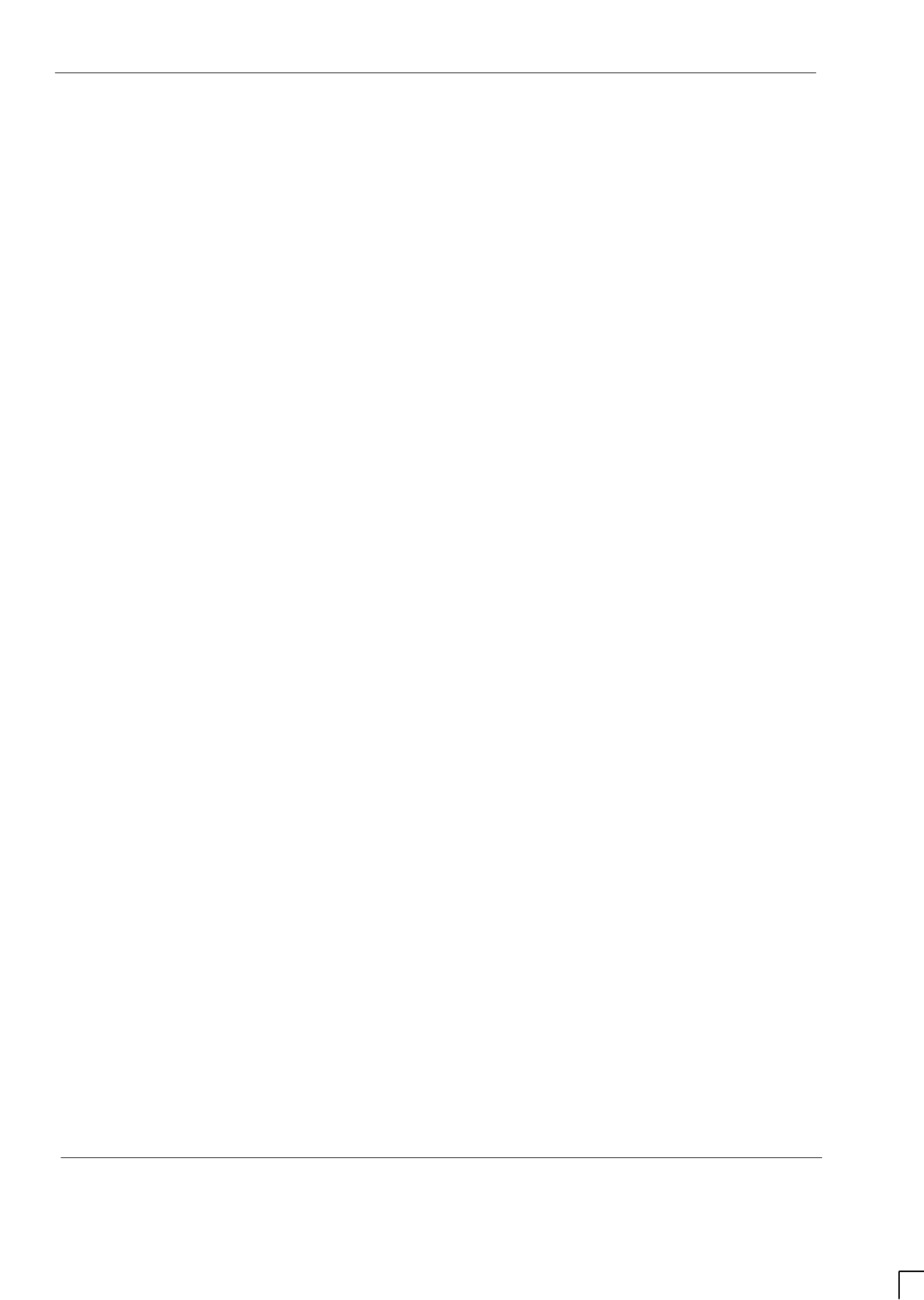
GSM-204-323
Alarm module
31st Oct 01
Tech. 6–28
Technical Description: Horizon
macro
outdoor
CONTROLLED INTRODUCTION
68P02902W02-A
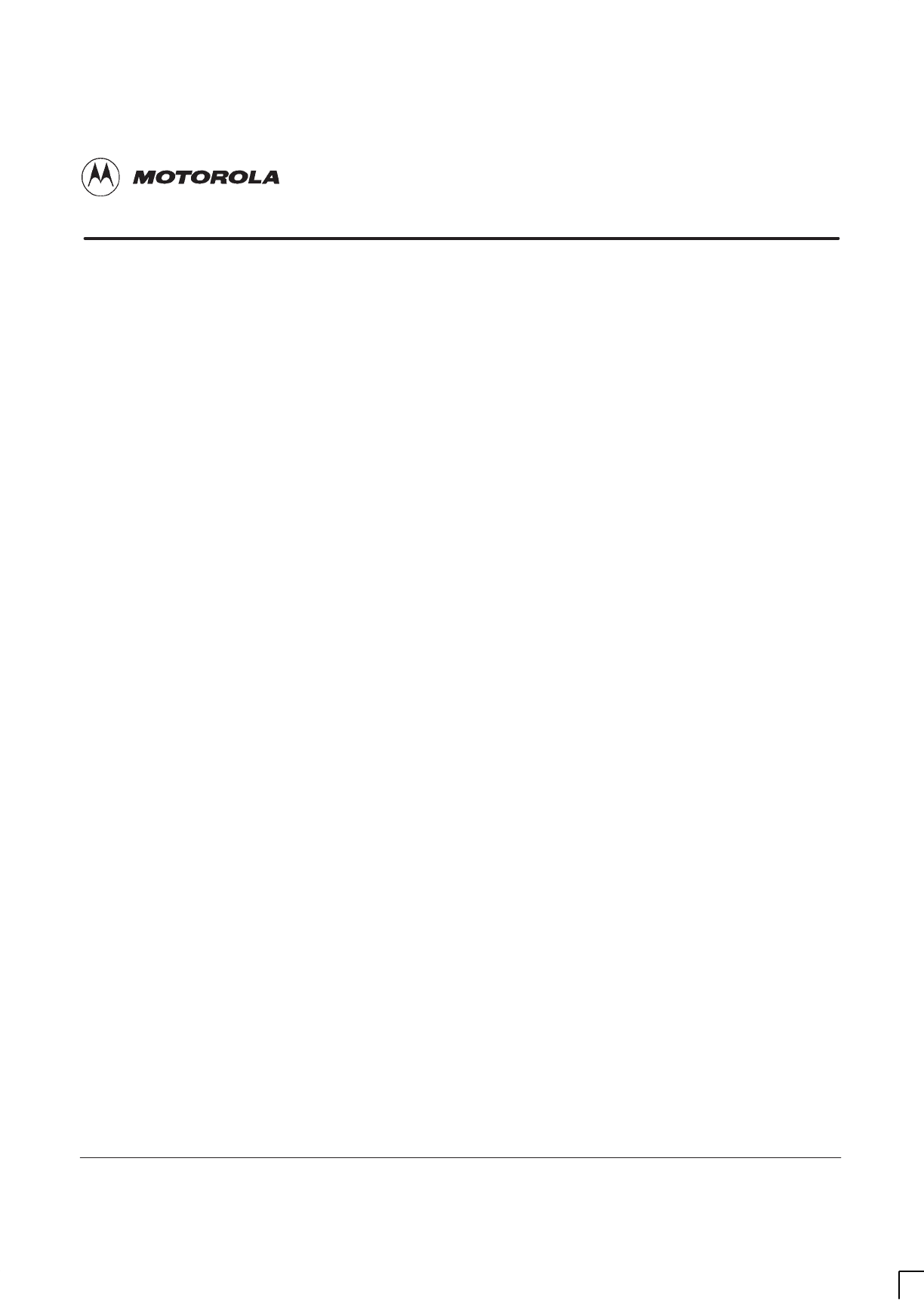
31st Oct 01
Technical Description: Horizon
macro
outdoor
68P02902W02-A
CONTROLLED INTRODUCTION
i
Chapter 7
Auxiliary equipment housing
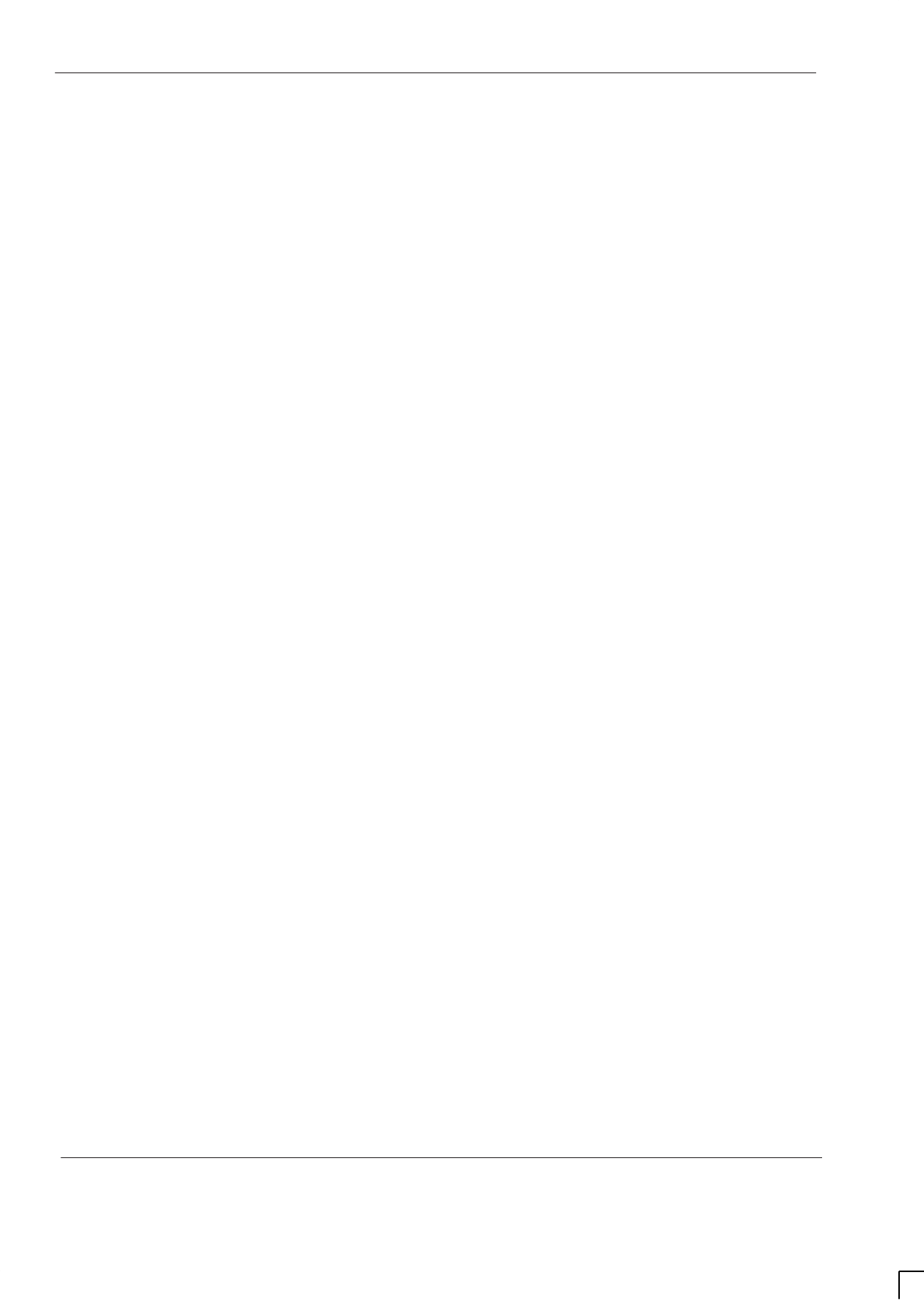
GSM-204-323
31st Oct 01
ii
Technical Description: Horizon
macro
outdoor
CONTROLLED INTRODUCTION
68P02902W02-A
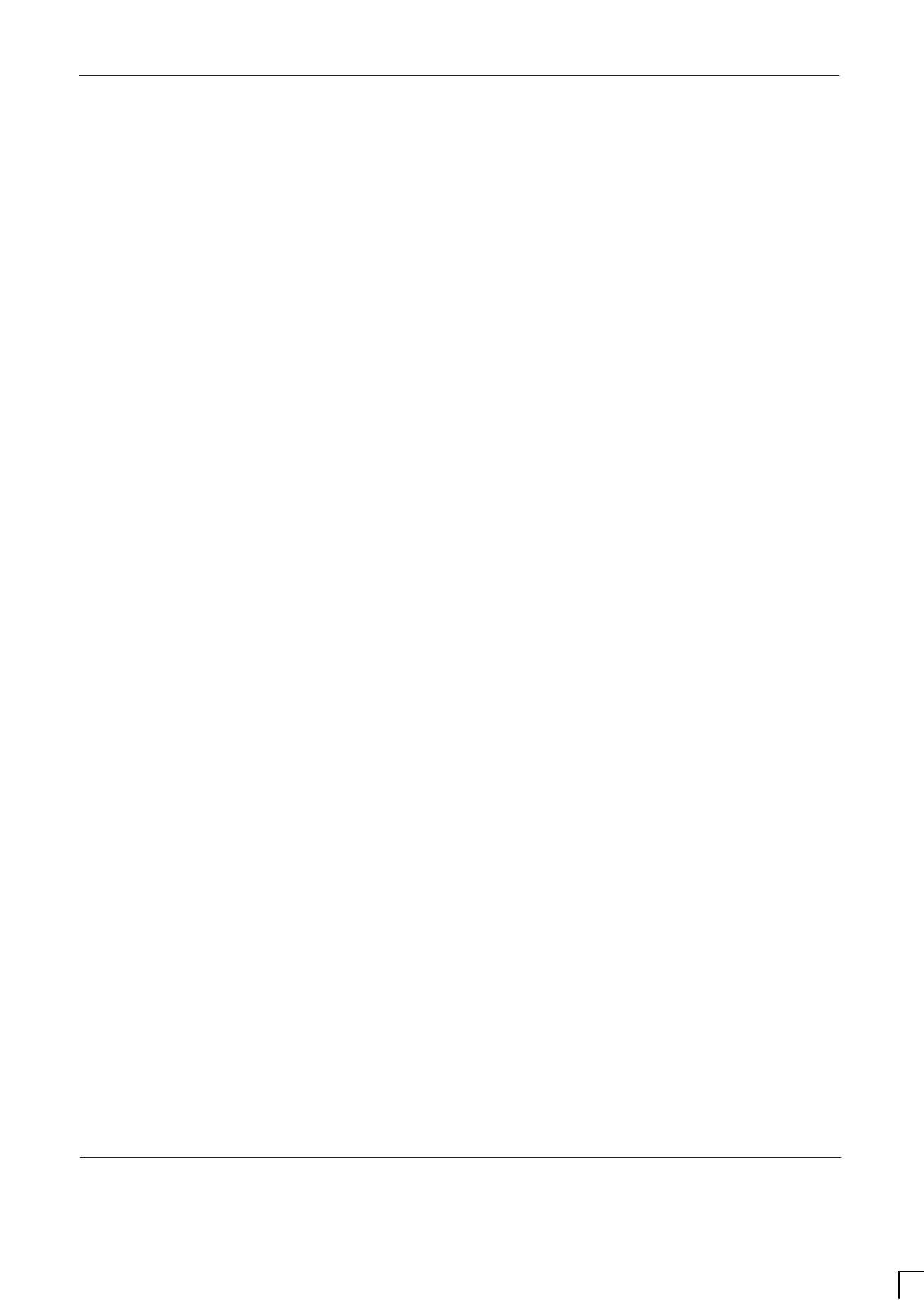
GSM-204-323
31st Oct 01
Technical Description: Horizon
macro
outdoor
68P02902W02-A
CONTROLLED INTRODUCTION
iii
Chapter 7
Auxiliary equipment housing i. . . . . . . . . . . . . . . . . . . . . . . . . . . . . . . . . . .
Auxiliary equipment housing overview Tech. 7–1. . . . . . . . . . . . . . . . . . . . . . . . . . . . . . . . . .
Introduction to the auxiliary equipment housing Tech. 7–1. . . . . . . . . . . . . . . . . . . . .
Auxiliary equipment housing mechanical design Tech. 7–1. . . . . . . . . . . . . . . . . . . .
View of auxiliary equipment housing Tech. 7–2. . . . . . . . . . . . . . . . . . . . . . . . . . . . . . .
Temperature control within the auxiliary equipment housing Tech. 7–3. . . . . . . . . . . . . . .
Temperature control equipment Tech. 7–3. . . . . . . . . . . . . . . . . . . . . . . . . . . . . . . . . . .
Operation of the temperature control equipment Tech. 7–3. . . . . . . . . . . . . . . . . . . .
External alarms interface board Tech. 7–4. . . . . . . . . . . . . . . . . . . . . . . . . . . . . . . . . . . . . . . .
Function of the external alarms interface board Tech. 7–4. . . . . . . . . . . . . . . . . . . . .
External alarms interface board connections Tech. 7–4. . . . . . . . . . . . . . . . . . . . . . .
Common applications for the auxiliary equipment housing Tech. 7–5. . . . . . . . . . . . . . . . .
Auxiliary equipment housing as a battery box Tech. 7–5. . . . . . . . . . . . . . . . . . . . . . .
View of auxiliary equipment housing as battery box Tech. 7–6. . . . . . . . . . . . . . . . .
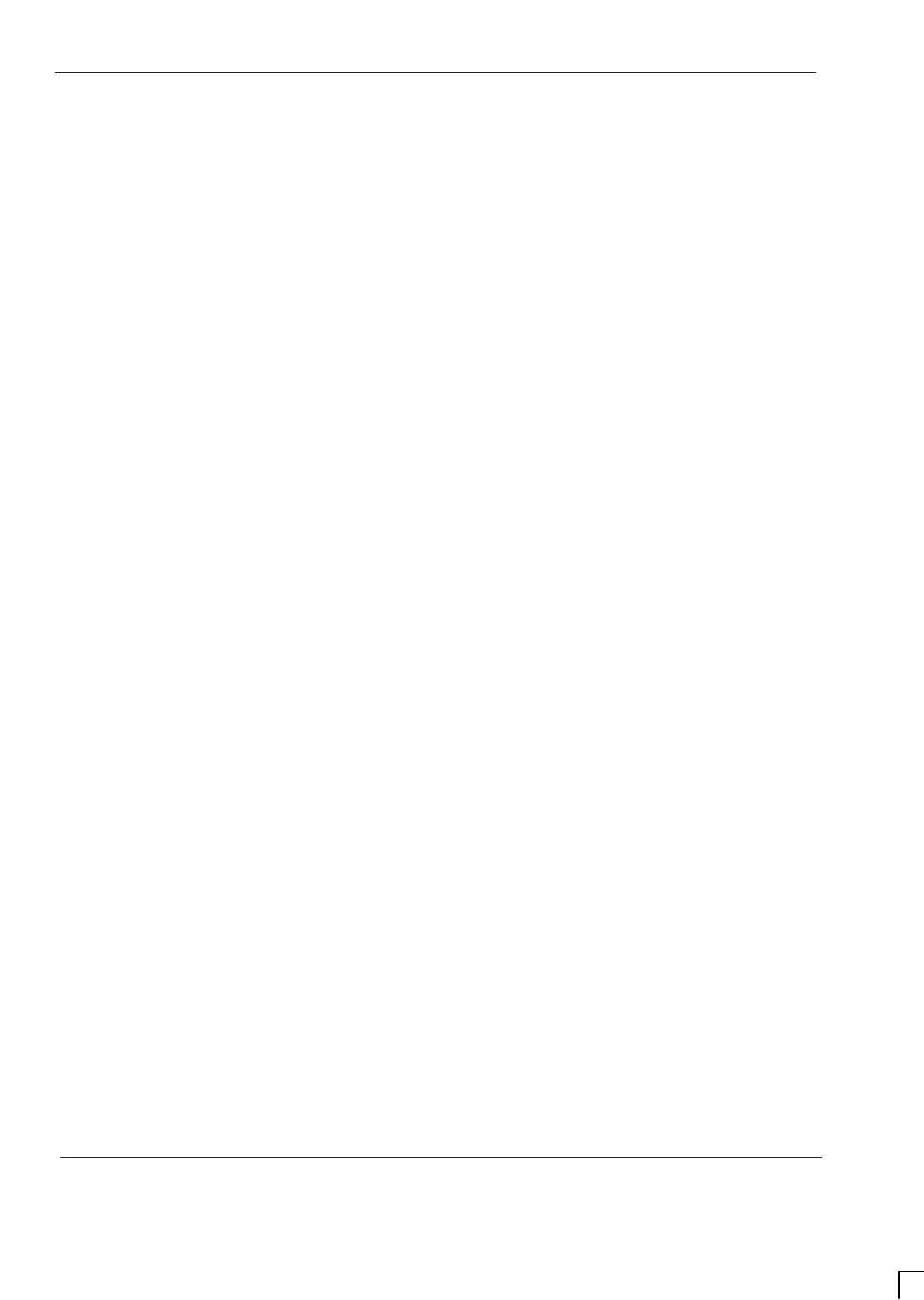
GSM-204-323
31st Oct 01
iv
Technical Description: Horizon
macro
outdoor
CONTROLLED INTRODUCTION
68P02902W02-A
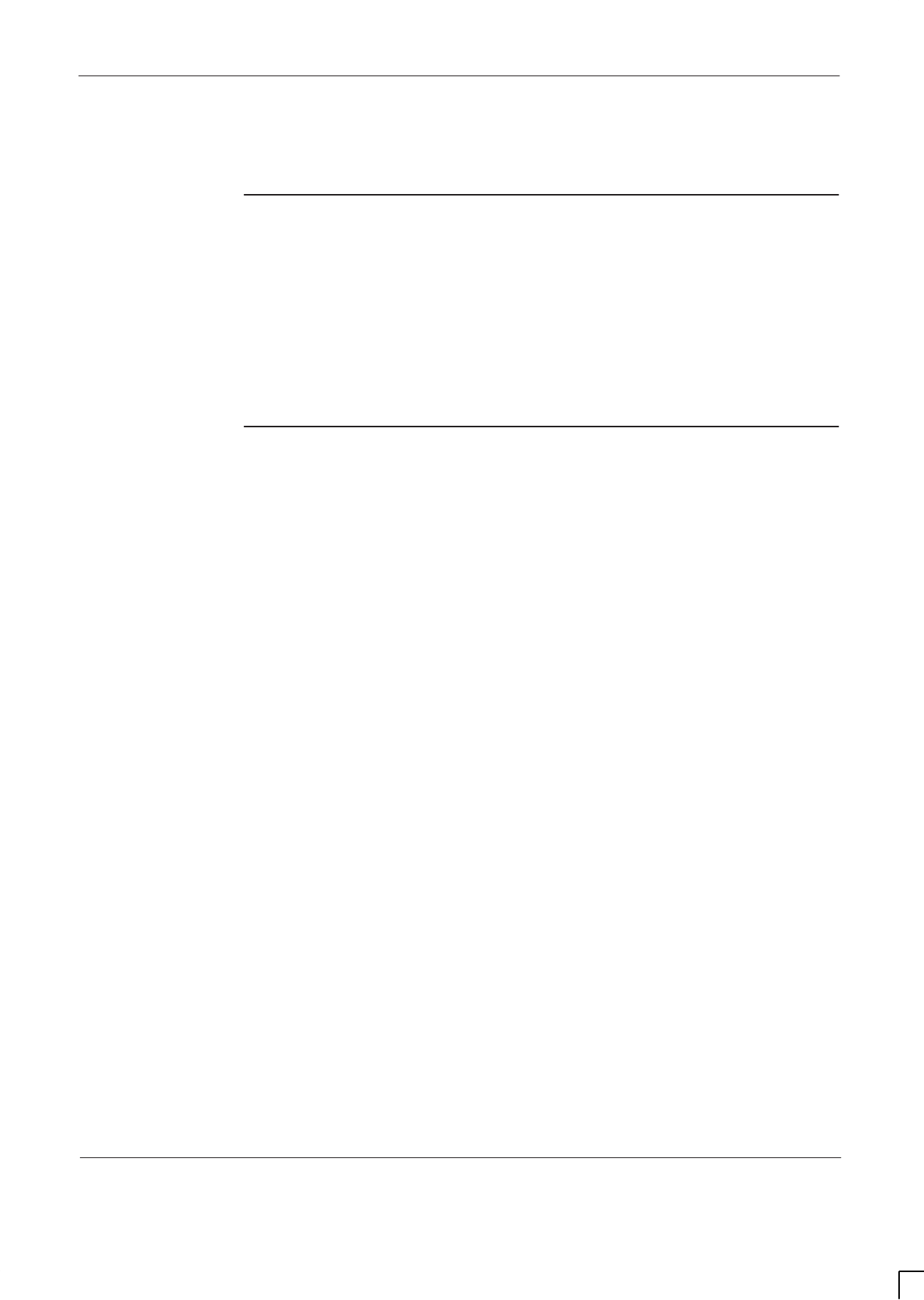
GSM-204-323 Auxiliary equipment housing overview
31st Oct 01
Technical Description: Horizon
macro
outdoor
68P02902W02-A
CONTROLLED INTRODUCTION
Tech. 7–1
Auxiliary equipment housing overview
Introduction to
the auxiliary
equipment
housing
The auxiliary equipment housing is an optional multi-purpose secure enclosure
for use with the Horizon
macro
outdoor cabinet. It can be installed on either side
of the BTS cabinet and provides space for the installation of additional
equipment at the site. Additional auxiliary equipment housings may be installed
adjacent to one another.
Auxiliary
equipment
housing
mechanical
design
The external design of the auxiliary equipment housing is based on that of the
Horizon
macro
outdoor cabinet – the procedure for opening/closing the door and
lid are identical (except that there is only one lid catch on the auxiliary
equipment housing).
The auxiliary equipment housing contains 23 U of standard equipment racking,
with shelving fitted as standard.
Additional equipment can include:
External battery backup system.
Customer supplied equipment.
Cable entry to the auxiliary equipment housing is through either side, dependant
on site configuration. The cables pass through the earth plates, fitted on both
sides of the housing. Internal connections are made through a power
distribution box containing circuit breakers, mounted on the inside of the lid.
This box also contains an external alarms interface board, which sends alarm
signals to the main cabinet.
Two pairs of Anderson connectors are fitted to the underside of the power
distribution box. The rear pair is for the dc power connection to the main
cabinet. The front pair is for an extension connection, either to another main
cabinet, or to an additional auxiliary equipment housing.
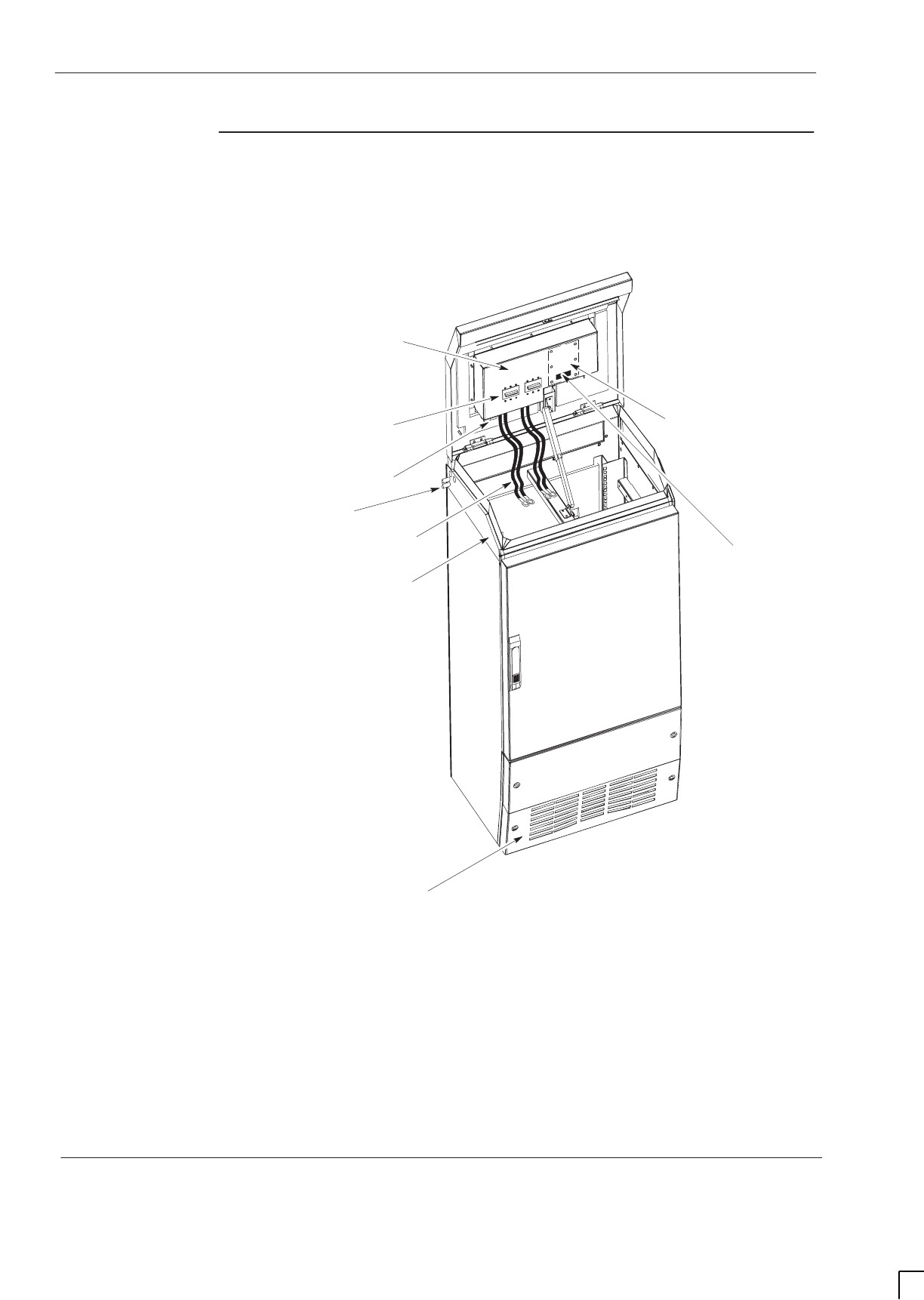
GSM-204-323
Auxiliary equipment housing overview
31st Oct 01
Tech. 7–2
Technical Description: Horizon
macro
outdoor
CONTROLLED INTRODUCTION
68P02902W02-A
View of auxiliary
equipment
housing
Figure 7-1 shows an external view of an unequipped auxiliary equipment
housing with the lid open.
EARTH STUDS
ACCESS TO PL1,
PL2 AND PL3
POWER DISTRIBUTION
BOX
FRONT PANEL, CONTAINING
FAN ASSEMBLY
CIRCUIT BREAKERS EXTERNAL ALARMS
INTERFACE BOARD
(MOUNTED INSIDE POWER
DISTRIBUTION BOX)
DC POWER CONNECTORS
BATTERY CABLES
EARTH PLATE
Figure 7-1 Auxiliary equipment housing, showing major components
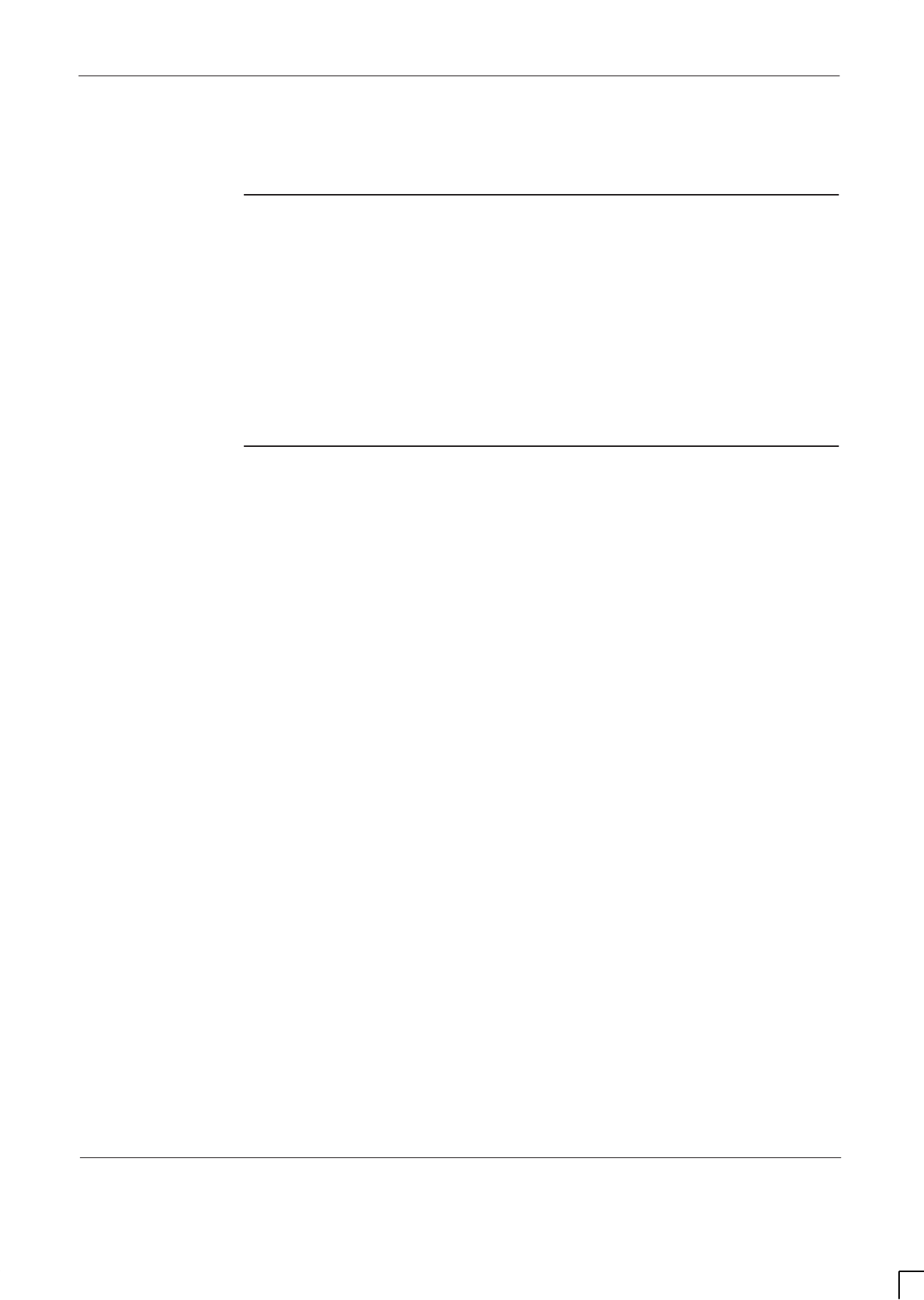
GSM-204-323 Temperature control within the auxiliary equipment housing
31st Oct 01
Technical Description: Horizon
macro
outdoor
68P02902W02-A
CONTROLLED INTRODUCTION
Tech. 7–3
Temperature control within the auxiliary equipment housing
Temperature
control
equipment
The temperature within the auxiliary equipment housing is regulated by the
following equipment:
A fan, mounted in the lower front panel, to provide cooling and warm air
circulation.
Heater mats, bonded to a metal plate and fitted to the battery trays below
each battery monoblock, to provide heating.
Operation of the
temperature
control
equipment
The fan operates from a –48 V dc supply, connected through PL7 on the
external alarms interface board and protected by a 500 mA anti-surge fuse. The
heater mats each require –48 V dc, connected through PL8, PL9, PL10 and
PL11 for heater mats 1 to 4 respectively on the external alarms interface board.
The supply voltage to each mat is protected by a 5 A fuse.
The 8 W fan operates continually regardless of ambient temperature. The
heater mats operate the ambient temperature is less than 12 °C (+/–3 °C).
The auxiliary equipment housing contains two temperature sensors, providing
sensing for an over temperature alarm and an over temperature trip control
signal.
If the over temperature alarm sensor is triggered (cabinet temperature reaches
55 to 60 °C), this causes an alarm signal to be sent to the OMC-R via the CAB
in the main cabinet. If the over temperature trip sensor is triggered (cabinet
temperature reaches 65 °C, +/–3 °C), the external alarms interface board
disconnects the remote operation circuit breakers, thus removing the supply to
the main cabinet. When the temperature drops to 5 °C below the trip level, the
external alarms interface board causes the circuit breakers to close, thus
restoring the supply to the main cabinet.
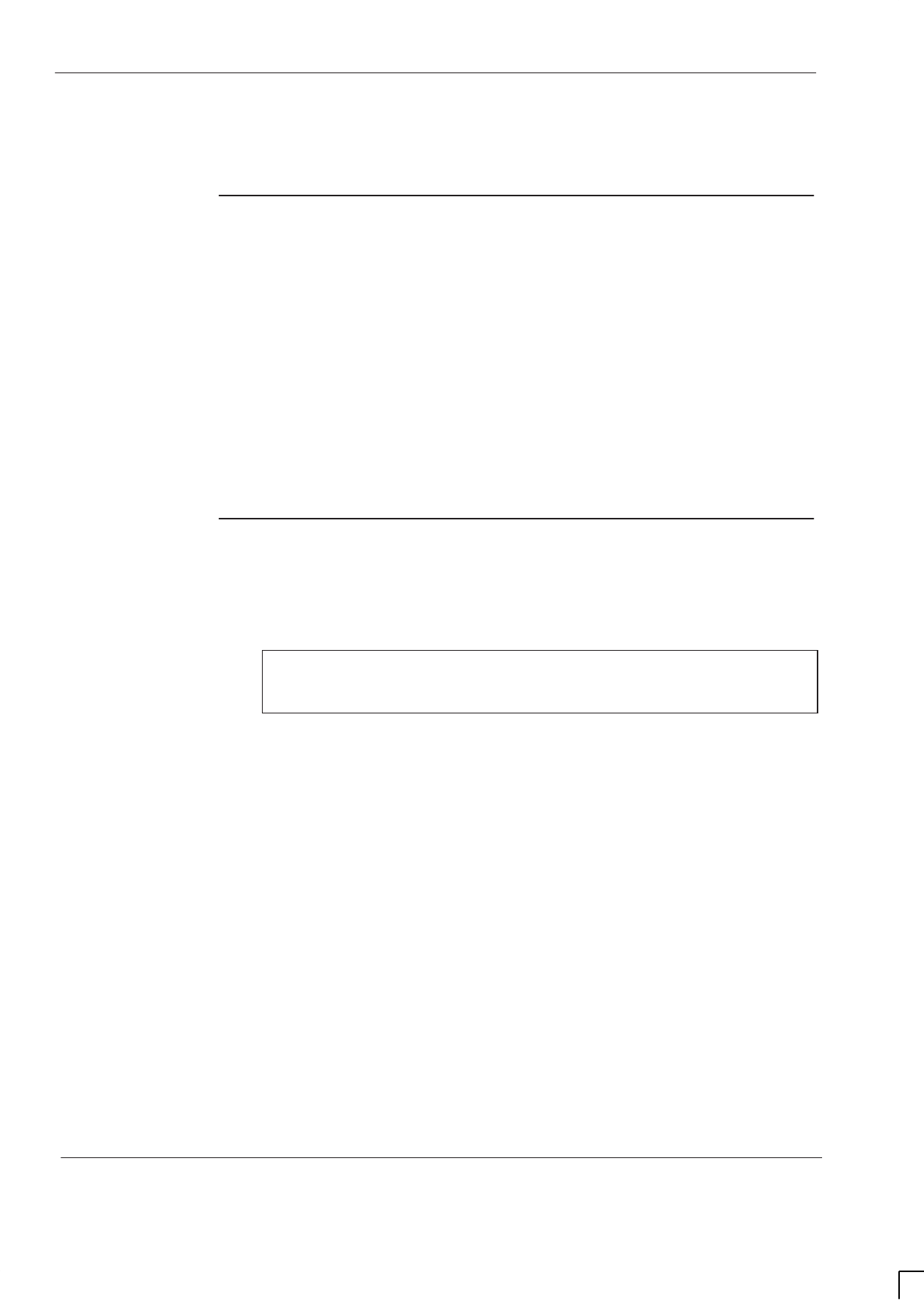
GSM-204-323
External alarms interface board
31st Oct 01
Tech. 7–4
Technical Description: Horizon
macro
outdoor
CONTROLLED INTRODUCTION
68P02902W02-A
External alarms interface board
Function of the
external alarms
interface board
The external alarms interface board is mounted in the power distribution box, in
the lid of the auxiliary equipment housing. It has the following functions:
Provides power to the temperature control equipment in the auxiliary
equipment housing.
Relays alarm signals from the auxiliary equipment housing through the
alarms interface board in the Horizon
macro
outdoor BTS cabinet to the
CAB.
Provides facilities to extend control and alarm functions to a second BTS
cabinet or auxiliary equipment housing.
External alarms
interface board
connections
Power, control and alarm signals are relayed through the external alarms
interface board as described below.
NOTE Cables for connecting the heater mats, fan and
control/alarm signals are extended to the outside of the
power distribution box.
Power connections
External power (–48 V dc) is connected to PL12, pins 1 and 2 on the interface
board via the rear pair of Anderson connectors on the bottom left side of the
power distribution box. If a second BTS cabinet is connected, the supply voltage
is connected to PL12 pins 3 and 4 via the front pair of Anderson connectors.
The fan is powered from PL7. The four heater mats are individually connected
to PL8, PL9, PL10 and PL11.
Control connections
Control signals to trip the circuit breakers in the event of an overtemperature
alarm signal (temperature reaches 65 °C, +/–3 °C) or a low voltage supply
signal (supply voltage drops below 38 V dc).
Alarm connections
The following alarm signals are routed through the interface board to the CAB:
Overtemperature alarm signal (PL1, pins 5 and 6).
Door open signal (PL4).
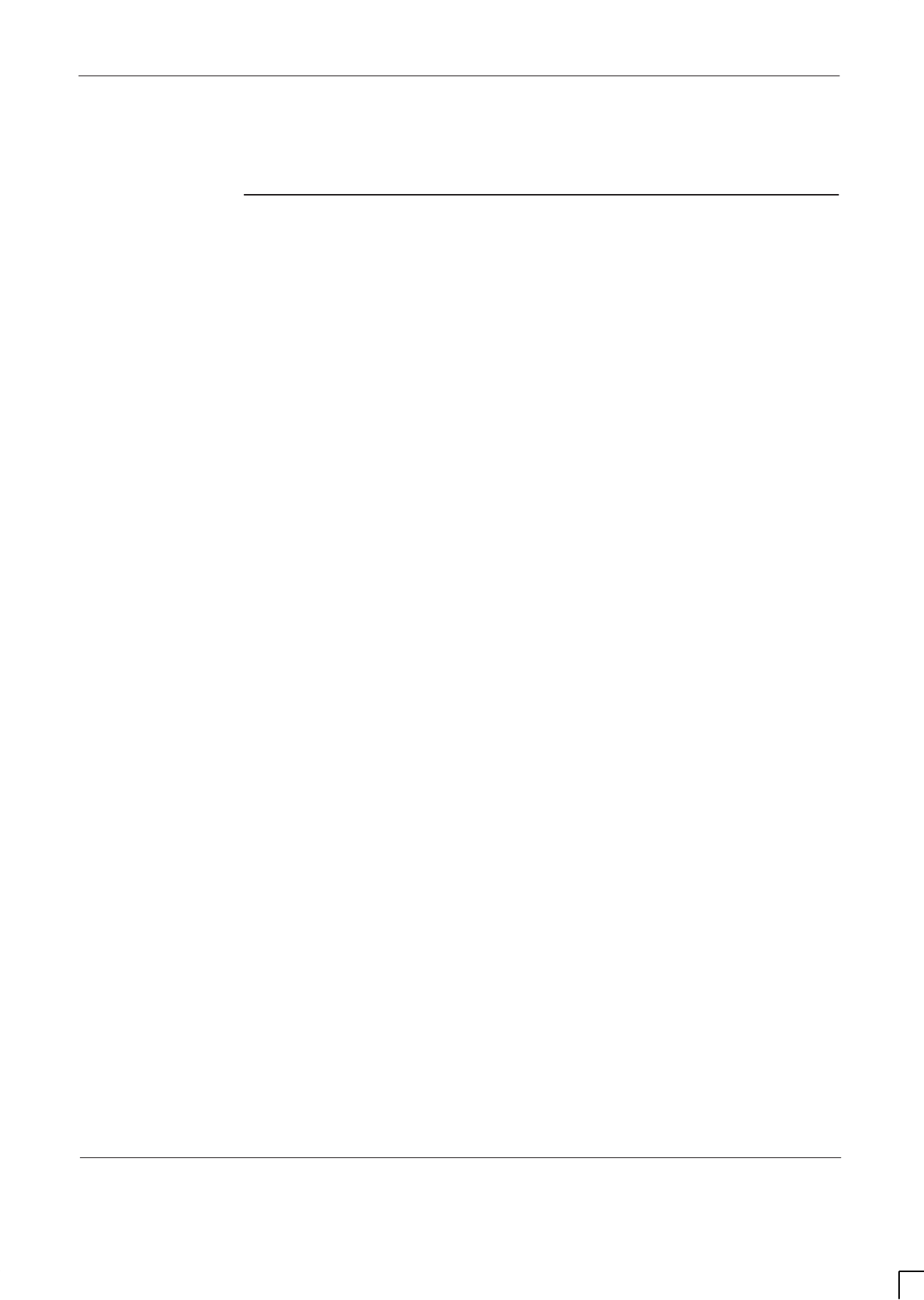
GSM-204-323 Common applications for the auxiliary equipment housing
31st Oct 01
Technical Description: Horizon
macro
outdoor
68P02902W02-A
CONTROLLED INTRODUCTION
Tech. 7–5
Common applications for the auxiliary equipment housing
Auxiliary
equipment
housing as a
battery box
The most common application for the auxiliary equipment housing is to use it for
battery backup for the Horizon
macro
outdoor cabinet, by fitting optional batteries
(see Figure 7-2).
Up to 16 x 6 V batteries can be mounted on four shelves. Each bank of eight
batteries must be wired in series to provide –48 V dc, and the two banks are
normally wired in parallel to provide increased backup duration.
Alternatively, each of the two banks of batteries can be independently
connected to separate BTS cabinets.
Additional auxiliary equipment housings may be installed with the batteries
connected in parallel to provide extra battery capacity, further increasing backup
duration.
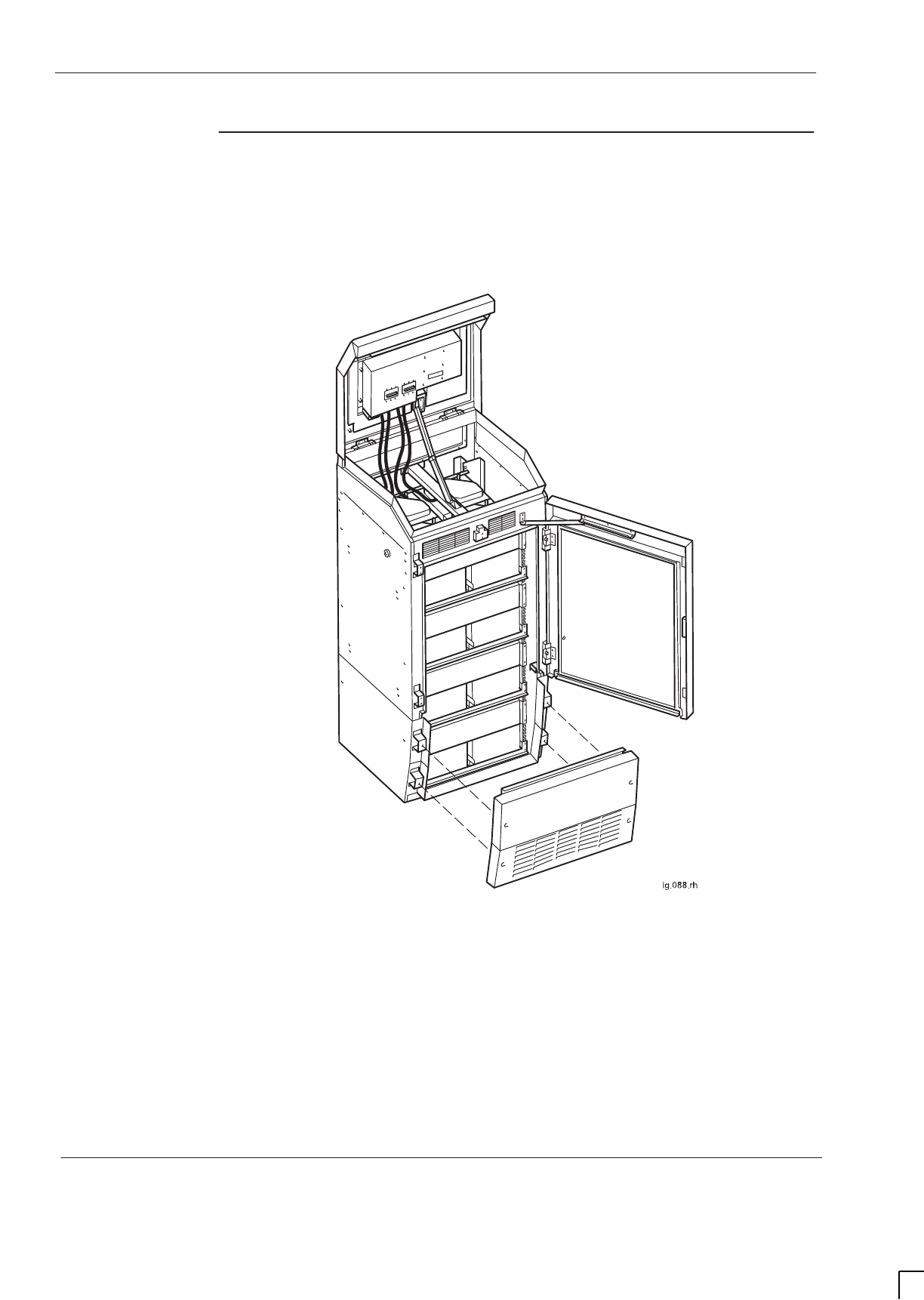
GSM-204-323
Common applications for the auxiliary equipment housing
31st Oct 01
Tech. 7–6
Technical Description: Horizon
macro
outdoor
CONTROLLED INTRODUCTION
68P02902W02-A
View of auxiliary
equipment
housing as
battery box
Figure 7-2 shows an auxiliary equipment housing with the door and lid open and
batteries installed.
Figure 7-2 Auxiliary equipment housing with batteries installed
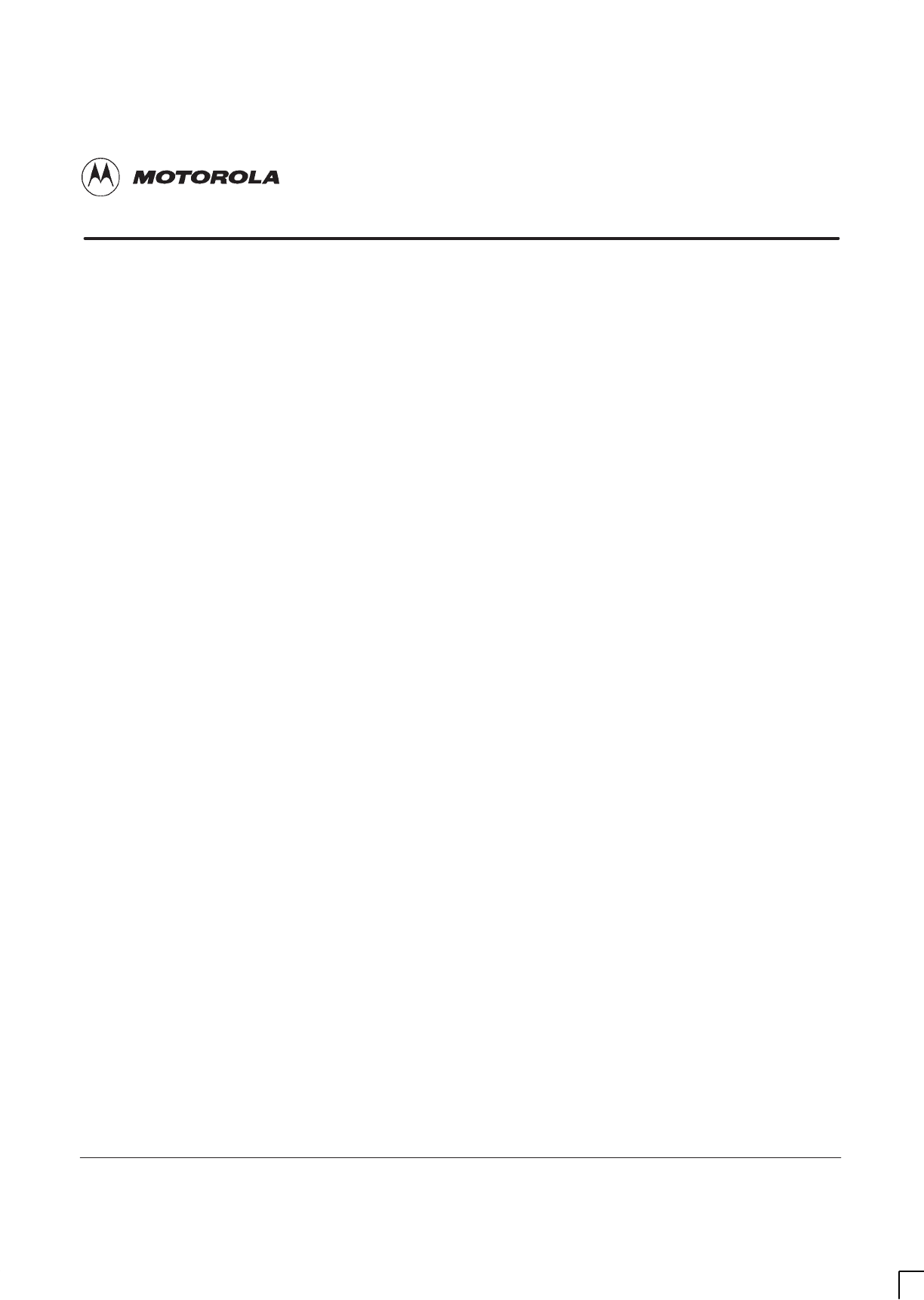
31st Oct 01
Technical Description: Horizon
macro
outdoor
68P02902W02-A
CONTROLLED INTRODUCTION
i
Chapter 8
Cable shroud
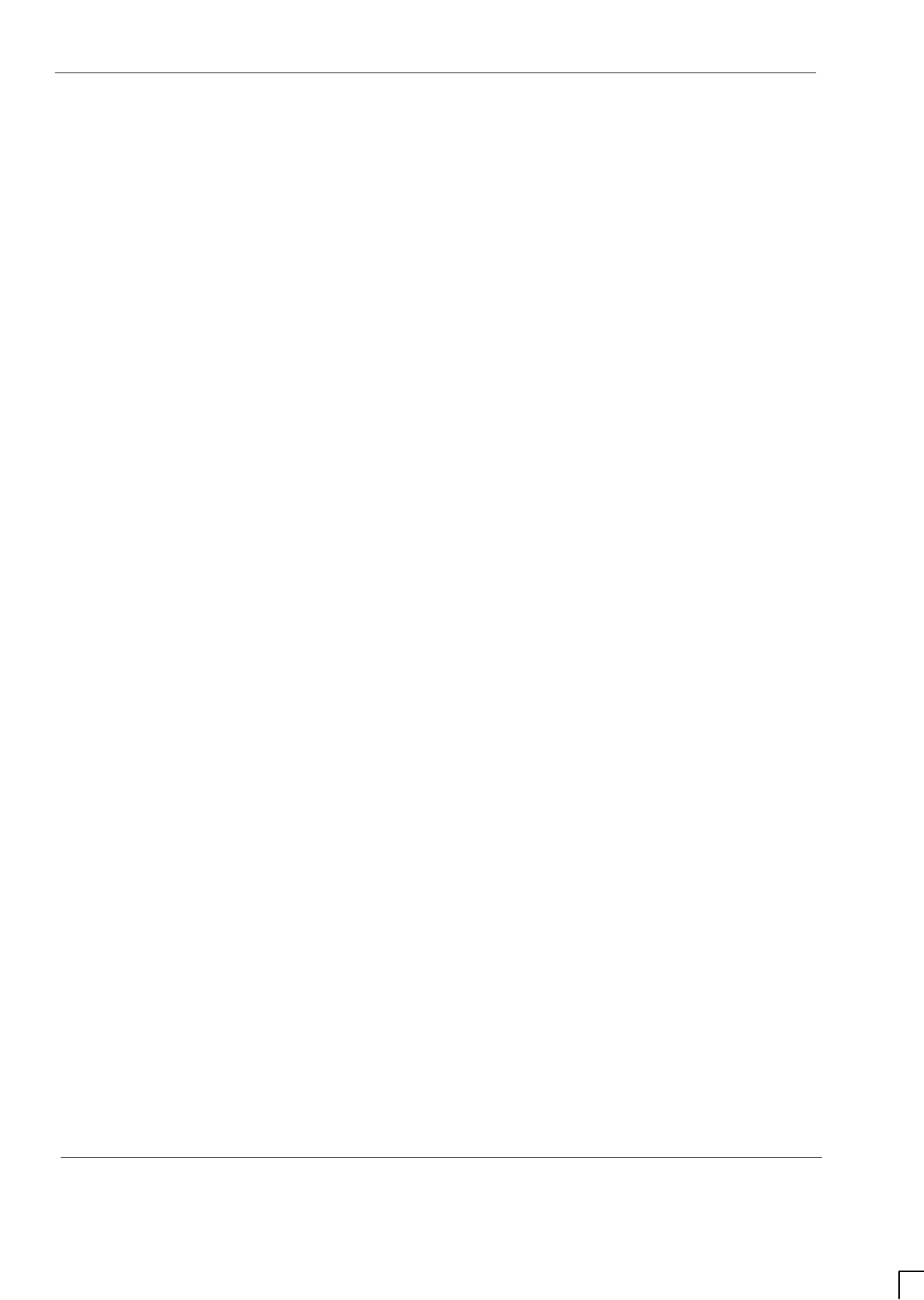
GSM-204-323
31st Oct 01
ii
Technical Description: Horizon
macro
outdoor
CONTROLLED INTRODUCTION
68P02902W02-A
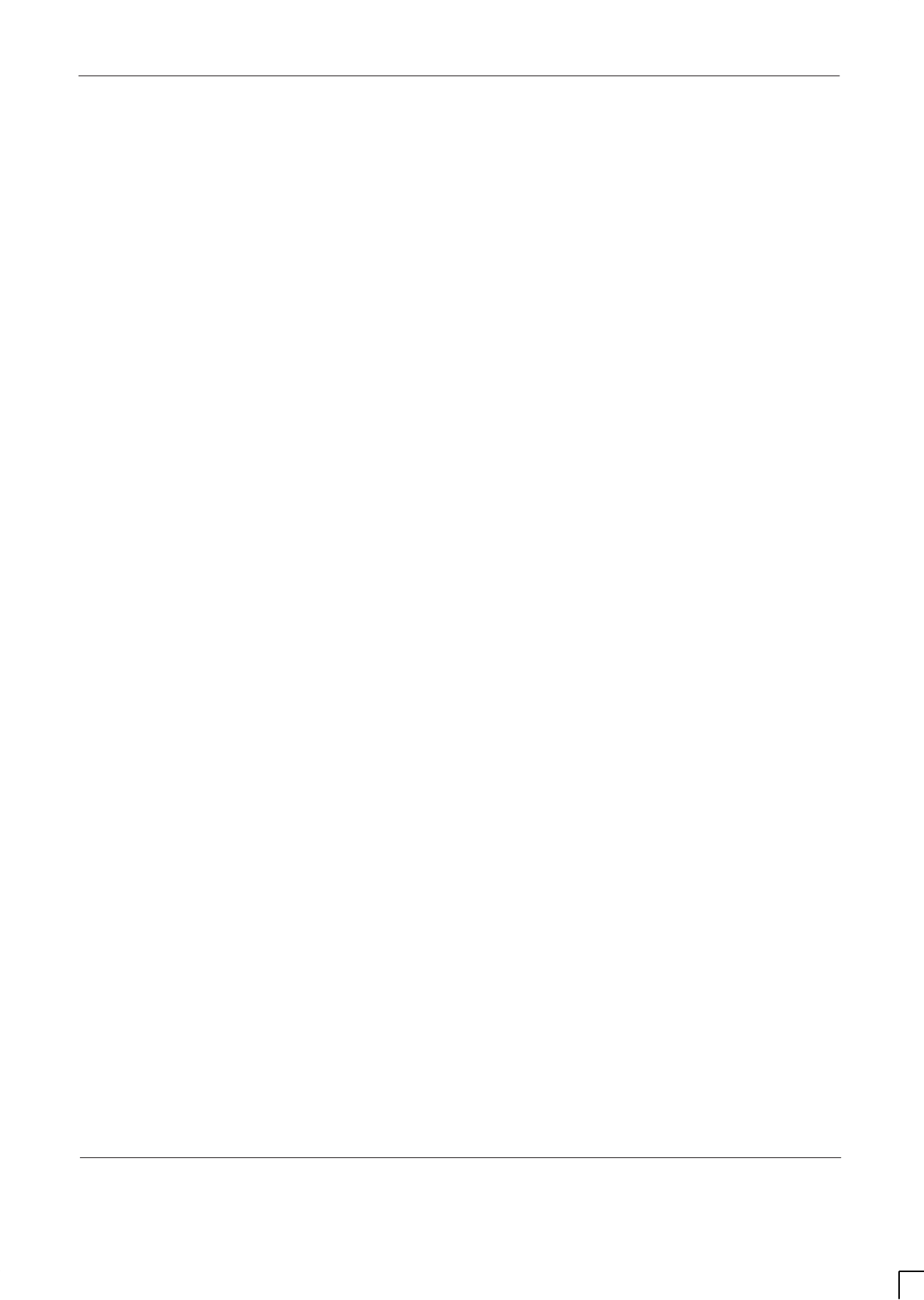
GSM-204-323
31st Oct 01
Technical Description: Horizon
macro
outdoor
68P02902W02-A
CONTROLLED INTRODUCTION
iii
Chapter 8
Cable shroud i. . . . . . . . . . . . . . . . . . . . . . . . . . . . . . . . . . . . . . . . . . . . . . . . .
Introduction to the cable shroud Tech. 8–1. . . . . . . . . . . . . . . . . . . . . . . . . . . . . . . . . . . . . . . .
Overview of the cable shroud Tech. 8–1. . . . . . . . . . . . . . . . . . . . . . . . . . . . . . . . . . . . .
Cable shroud configurations Tech. 8–1. . . . . . . . . . . . . . . . . . . . . . . . . . . . . . . . . . . . . .
The cable shroud assembly Tech. 8–2. . . . . . . . . . . . . . . . . . . . . . . . . . . . . . . . . . . . . . . . . . .
Description of the cable shroud assembly Tech. 8–2. . . . . . . . . . . . . . . . . . . . . . . . . .
View of the cable shroud Tech. 8–2. . . . . . . . . . . . . . . . . . . . . . . . . . . . . . . . . . . . . . . . .
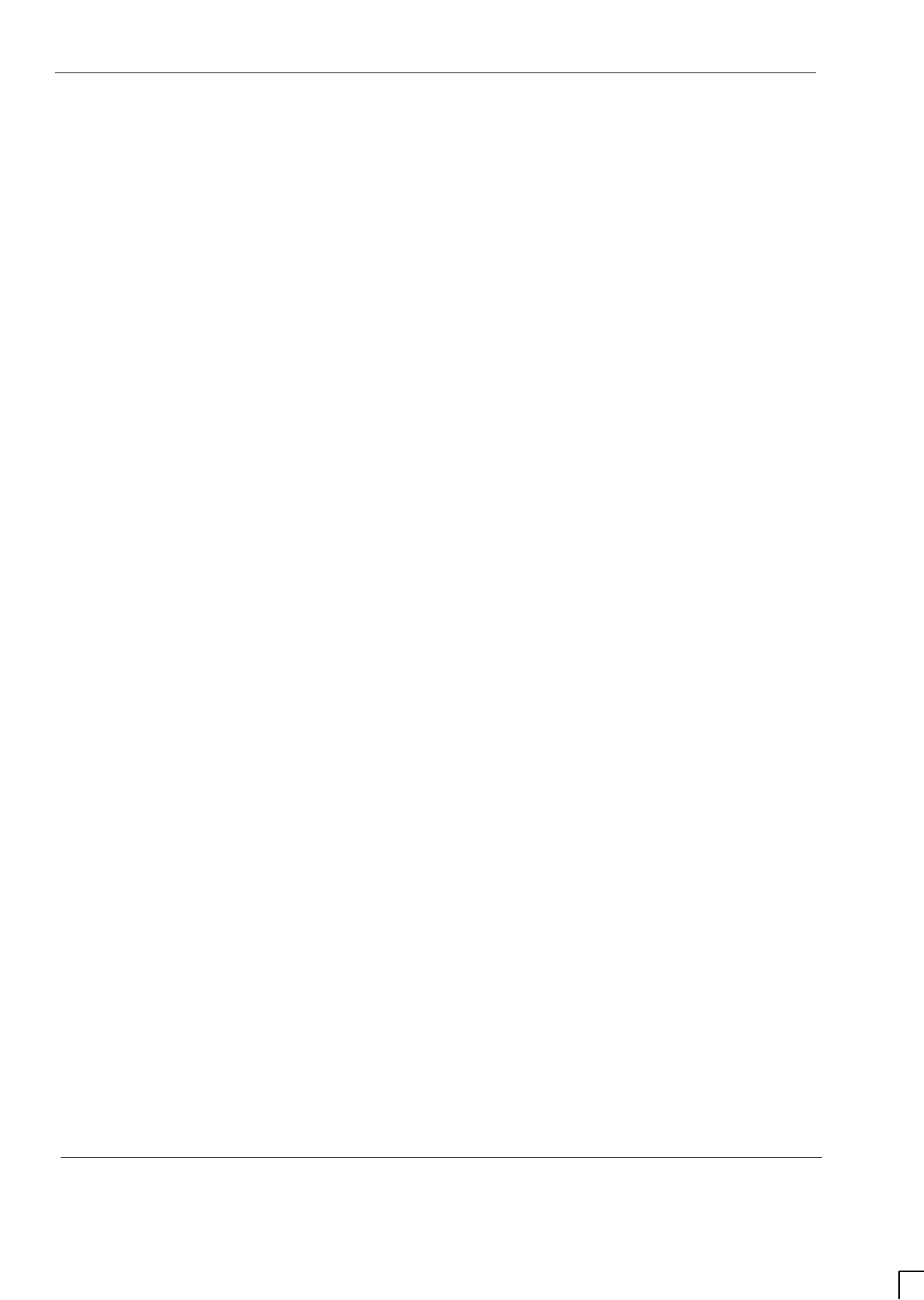
GSM-204-323
31st Oct 01
iv
Technical Description: Horizon
macro
outdoor
CONTROLLED INTRODUCTION
68P02902W02-A
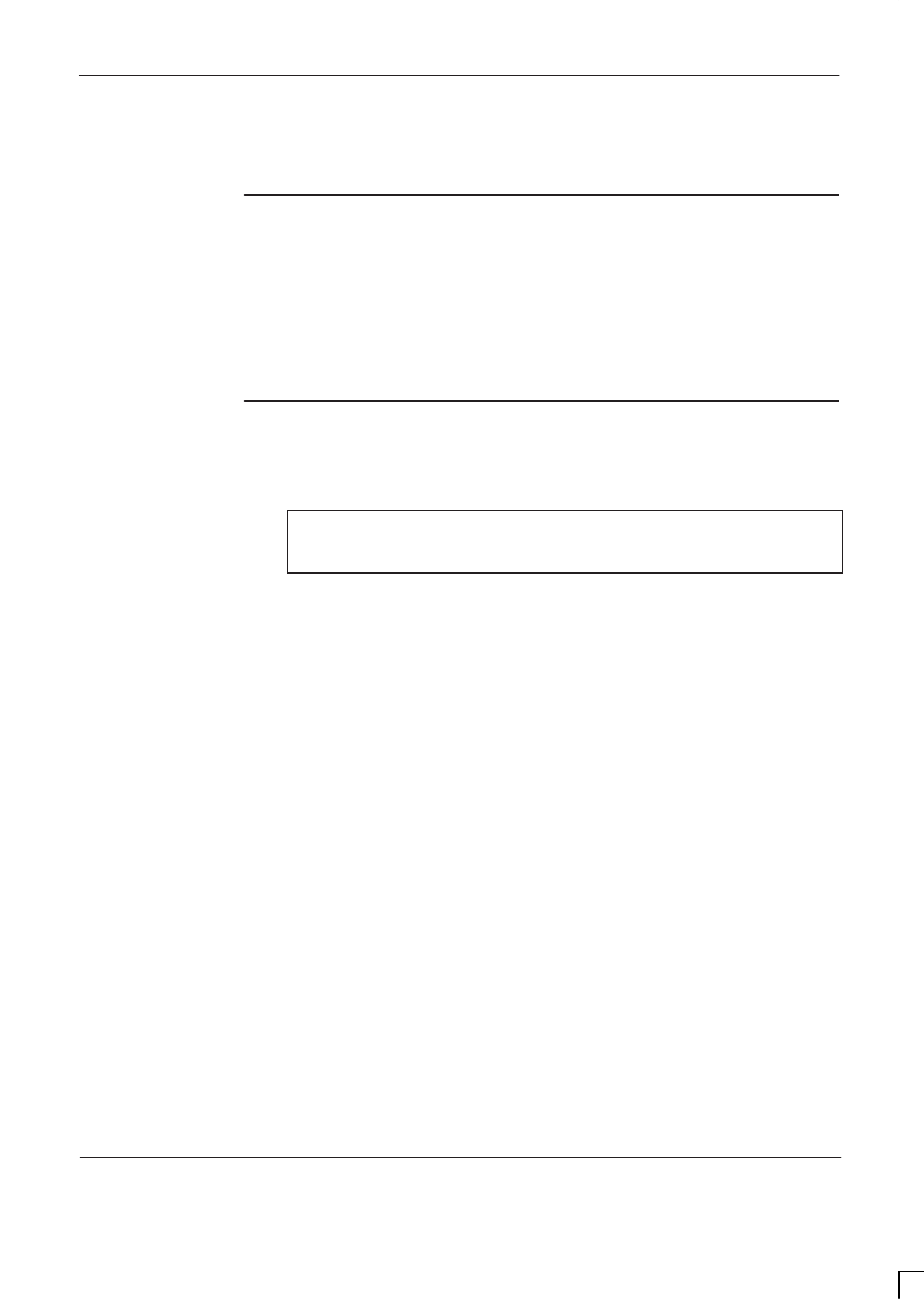
GSM-204-323 Introduction to the cable shroud
31st Oct 01
Technical Description: Horizon
macro
outdoor
68P02902W02-A
CONTROLLED INTRODUCTION
Tech. 8–1
Introduction to the cable shroud
Overview of the
cable shroud
The cable shroud is an optional kit which is designed specifically for use with
Horizon
macro
outdoor cabinets and the auxiliary equipment housing. It provides
concealment for the power supply input to the main cabinet and the antenna
feed cables, connections between the main cabinet and the auxiliary equipment
housing, connections between two main cabinets, or connections between two
auxiliary equipment housings.
Cable shroud
configurations
Although only one cable shroud kit is available, it can be used for each of the
following configurations:
NOTE Chapter 5 of the installation part of this manual provides
illustrations of how some of these configurations can be
implemented.
Below ground cable entry concealment for the Horizon
macro
outdoor
cabinet.
Ground level cable entry concealment for the Horizon
macro
outdoor
cabinet.
High level cable entry concealment for the Horizon
macro
outdoor cabinet.
Cable entry concealment between two Horizon
macro
outdoor cabinets.
Cable entry concealment between an Horizon
macro
outdoor cabinet and
an auxiliary equipment housing.
Cable entry concealment between two auxiliary equipment housings.
In addition to the above configurations, the shroud can be fitted on either the left
side or the right side of a cabinet.
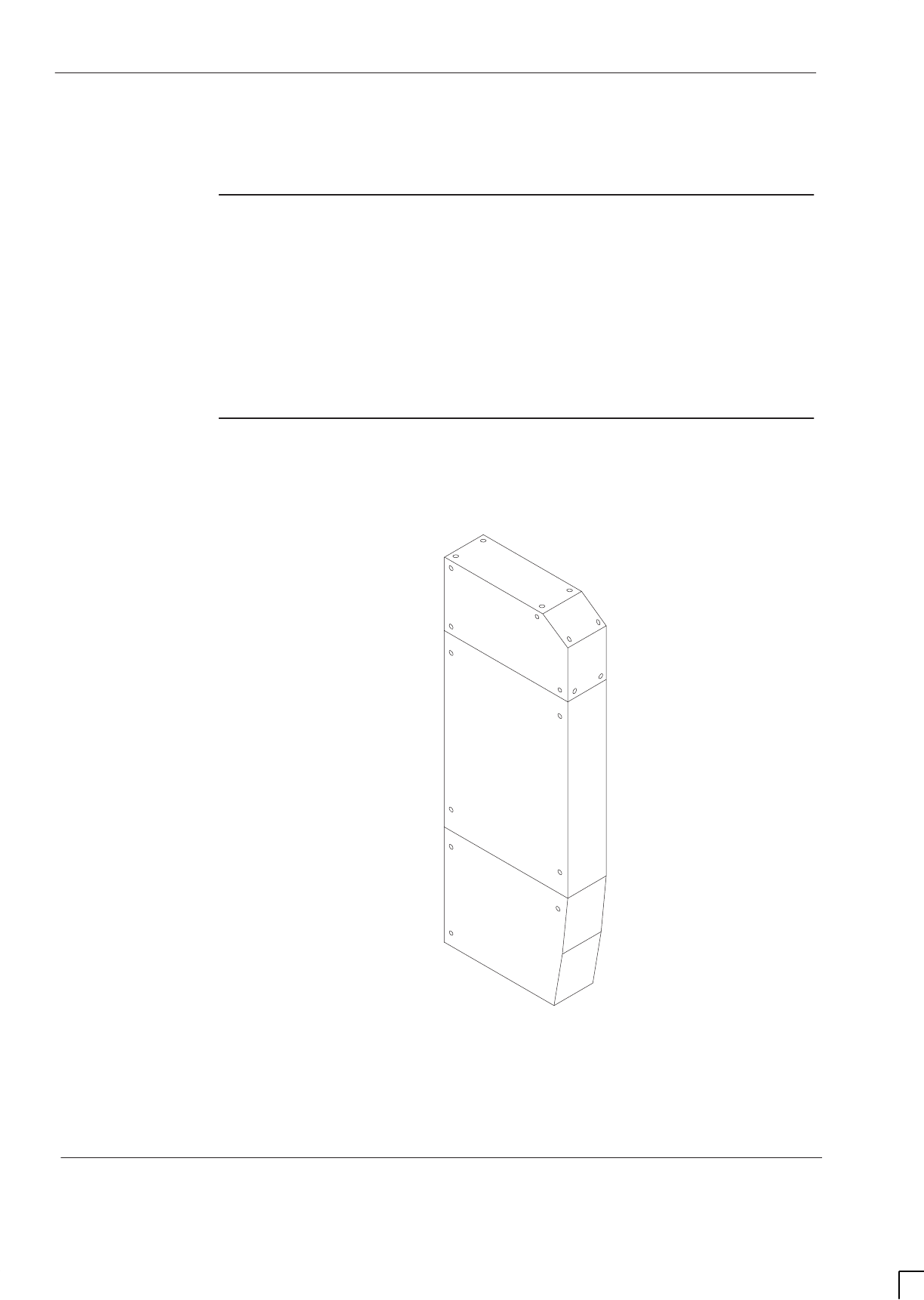
GSM-204-323
The cable shroud assembly
31st Oct 01
Tech. 8–2
Technical Description: Horizon
macro
outdoor
CONTROLLED INTRODUCTION
68P02902W02-A
The cable shroud assembly
Description of
the cable
shroud
assembly
The cable shroud comprises a metal frame fitted with several metal panels,
which are attached to the frame with anti-tamper screws. Panels can be
removed from or attached to the frame, depending on how the shroud is used.
The frame of the shroud is secured to the side of a cabinet using screws.
View of the
cable shroud
The cable shroud is delivered fully assembled, with all the metal plates attached
to the frame, as shown in Figure 8-1.
Figure 8-1 Cable shroud assembly

CHAPTER 2
SITE PREPARATION CHAPTER 3
INSTALLING THE BTS
CABINET
CHAPTER 4
INSTALLING THE CABLE
SHROUD
CHAPTER 5
INSTALLING THE AUXILIARY
EQUIPMENT HOUSING
CHAPTER 1
INTRODUCTION TO
INSTALLATION
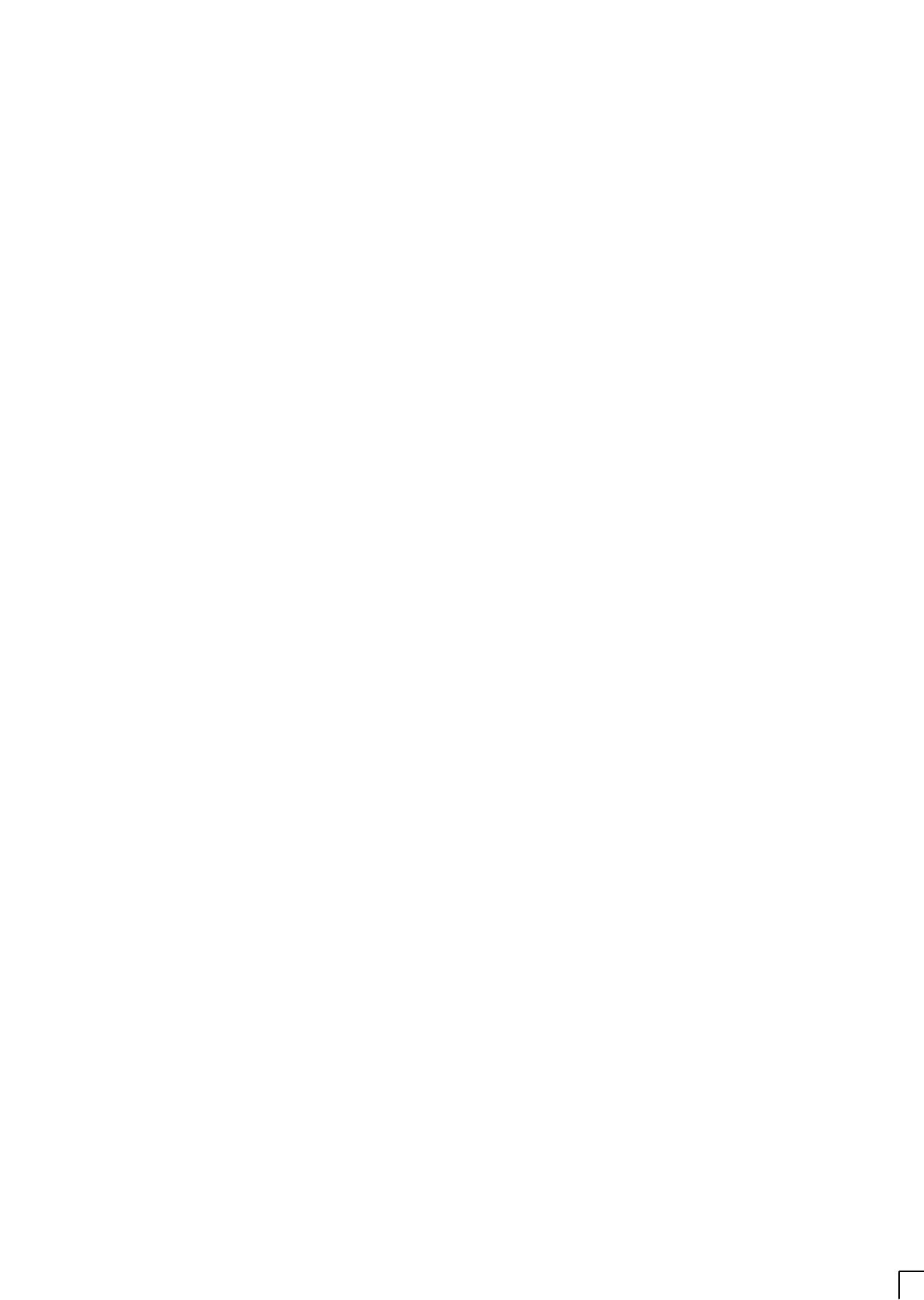

CHAPTER 7
COMMISSIONING THE
OUTDOOR CABINET
CHAPTER 8
DECOMMISSIONING THE
EQUIPMENT
CHAPTER 6
INTEROPERABILITY
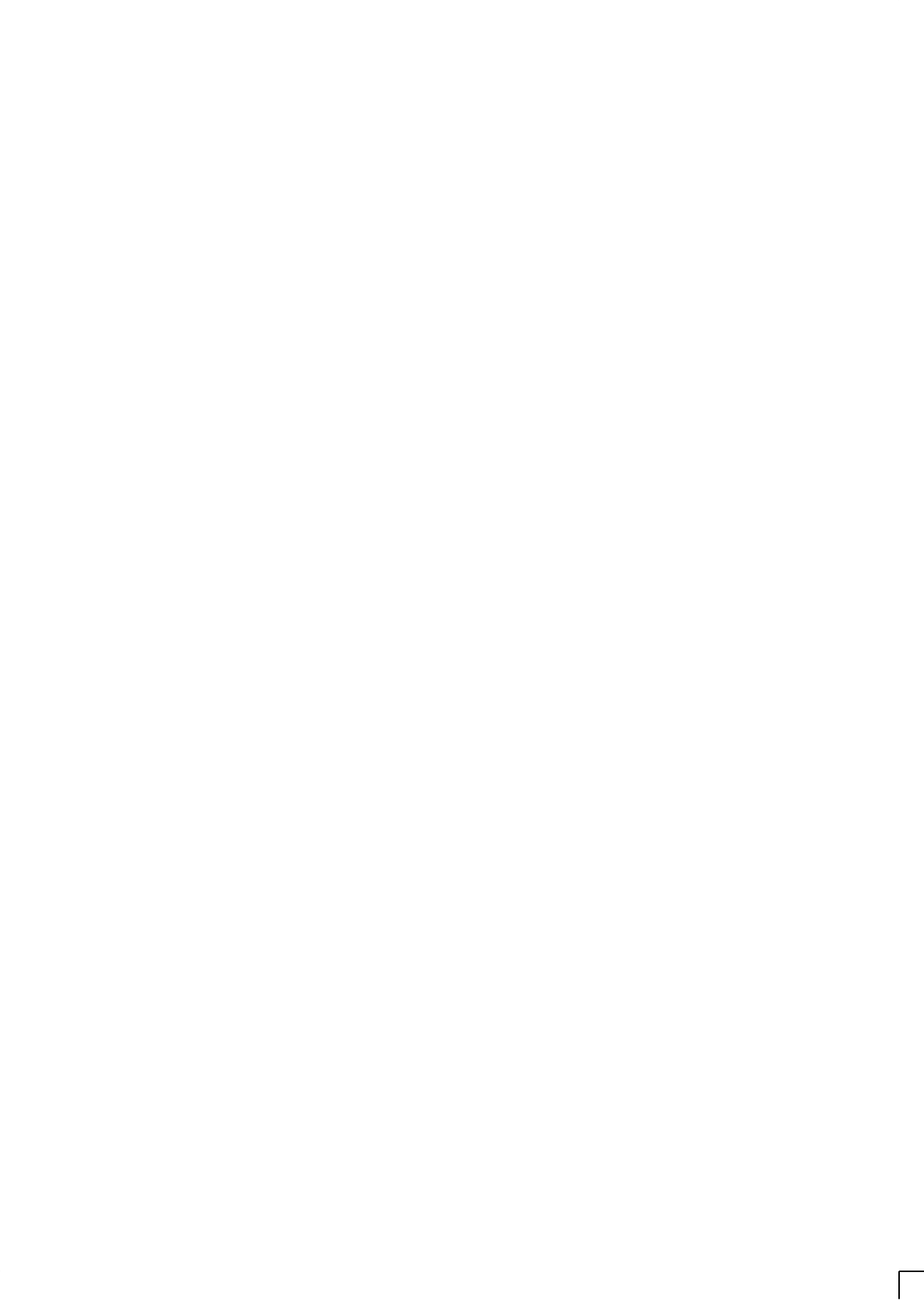
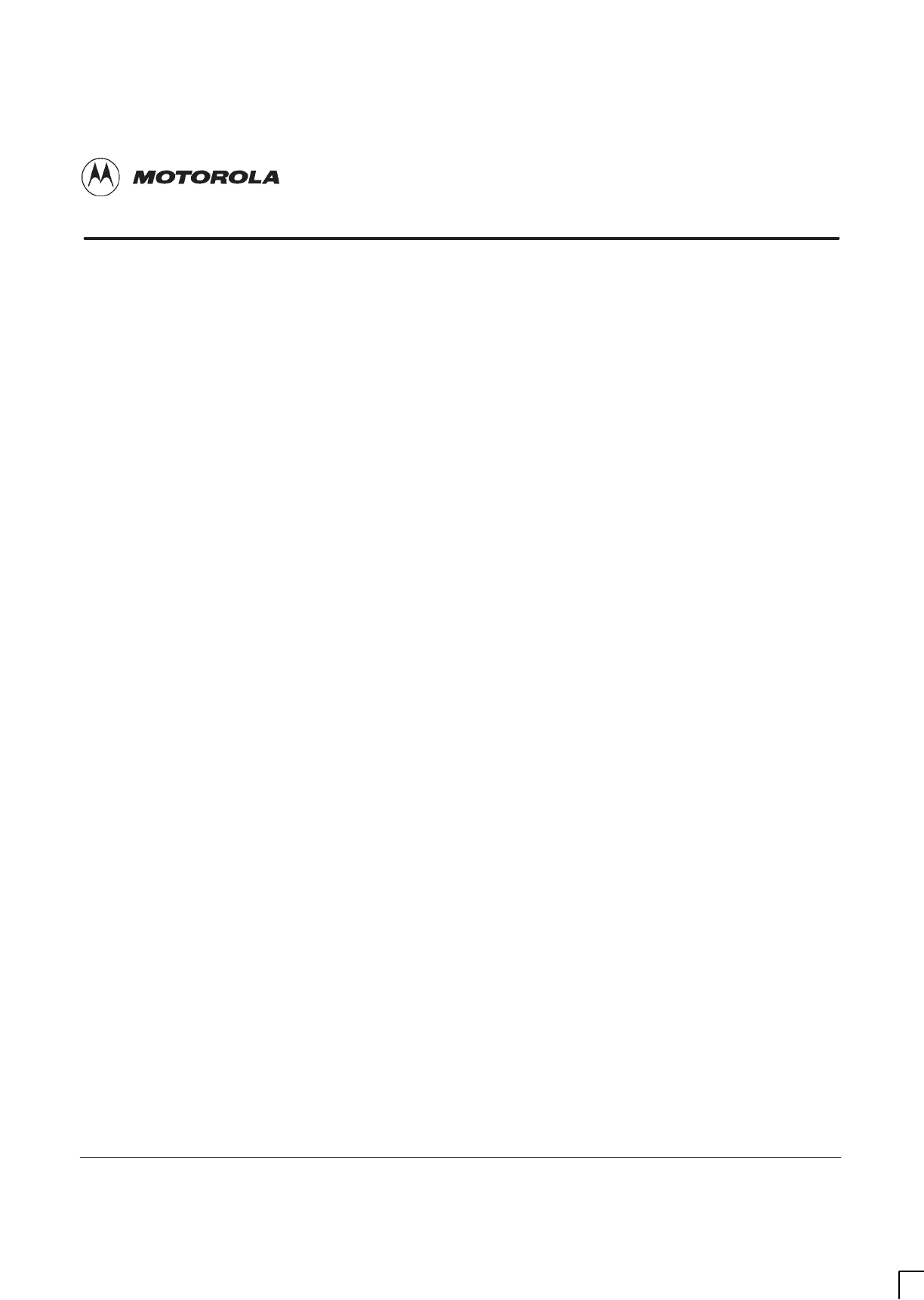
31st Oct 01
Installation & Configuration: Horizon
macro
outdoor
68P02902W03-A
CONTROLLED INTRODUCTION
i
Category 423
Installation & Configuration (Inst.)
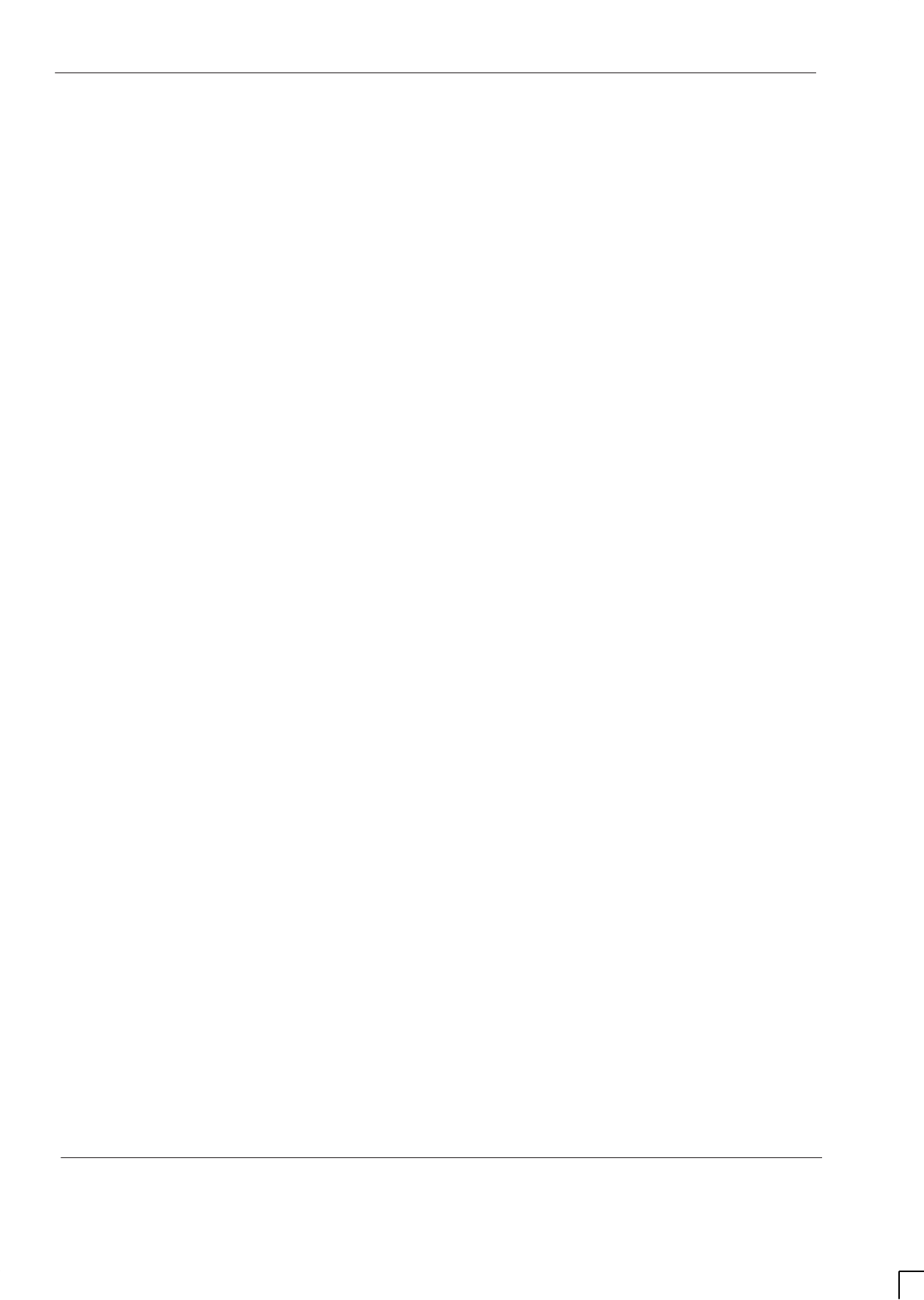
GSM-204-423
31st Oct 01
ii
Installation & Configuration: Horizon
macro
outdoor
CONTROLLED INTRODUCTION
68P02902W03-A
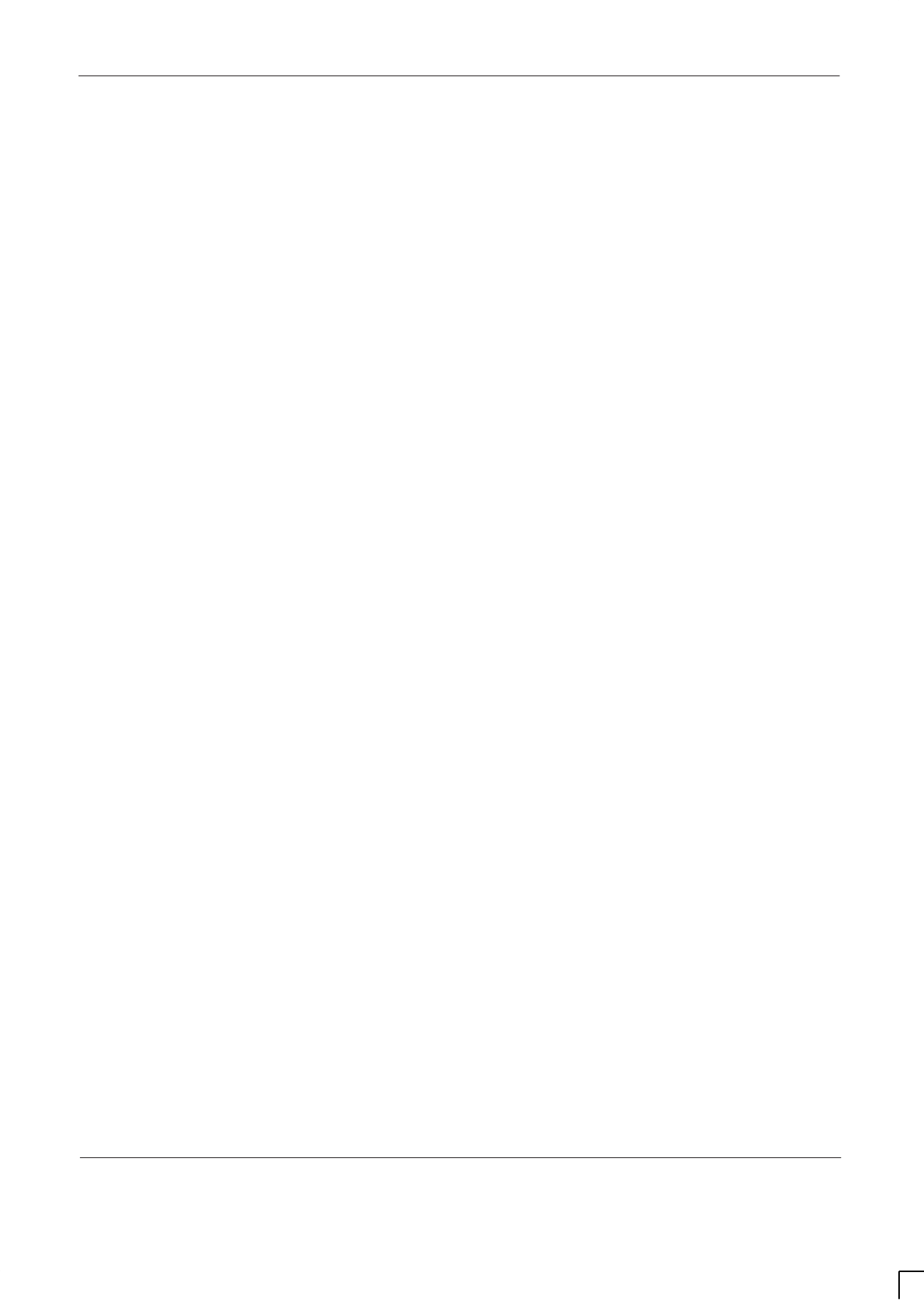
GSM-204-423
31st Oct 01
Installation & Configuration: Horizon
macro
outdoor
68P02902W03-A
CONTROLLED INTRODUCTION
iii
Category 423
Installation & Configuration (Inst.) i. . . . . . . . . . . . . . . . . . . . . . . . . . . . . . . . . .
Chapter 1
Introduction to installation i. . . . . . . . . . . . . . . . . . . . . . . . . . . . . . . . . . . . .
Introduction to installation and configuration Inst. 1–1. . . . . . . . . . . . . . . . . . . . . . . . . . . . .
Manual scope Inst. 1–1. . . . . . . . . . . . . . . . . . . . . . . . . . . . . . . . . . . . . . . . . . . . . . . . . .
Safety instructions Inst. 1–2. . . . . . . . . . . . . . . . . . . . . . . . . . . . . . . . . . . . . . . . . . . . . .
Software requirements Inst. 1–2. . . . . . . . . . . . . . . . . . . . . . . . . . . . . . . . . . . . . . . . . .
Horizonmacro outdoor tool list Inst. 1–3. . . . . . . . . . . . . . . . . . . . . . . . . . . . . . . . . . . . . . . . .
Overview of tool list Inst. 1–3. . . . . . . . . . . . . . . . . . . . . . . . . . . . . . . . . . . . . . . . . . . . .
Tool list Inst. 1–3. . . . . . . . . . . . . . . . . . . . . . . . . . . . . . . . . . . . . . . . . . . . . . . . . . . . . . . .
Chapter 2
Site preparation i. . . . . . . . . . . . . . . . . . . . . . . . . . . . . . . . . . . . . . . . . . . . . . .
Preparation overview Inst. 2–1. . . . . . . . . . . . . . . . . . . . . . . . . . . . . . . . . . . . . . . . . . . . . . . . .
Overview to site preparation Inst. 2–1. . . . . . . . . . . . . . . . . . . . . . . . . . . . . . . . . . . . . .
Pre-installation procedures Inst. 2–1. . . . . . . . . . . . . . . . . . . . . . . . . . . . . . . . . . . . . . .
Site requirements and considerations Inst. 2–2. . . . . . . . . . . . . . . . . . . . . . . . . . . . . . . . . . .
Overview of requirements Inst. 2–2. . . . . . . . . . . . . . . . . . . . . . . . . . . . . . . . . . . . . . . .
Outdoor cabinet dimensions Inst. 2–2. . . . . . . . . . . . . . . . . . . . . . . . . . . . . . . . . . . . . .
Cabinet weights Inst. 2–2. . . . . . . . . . . . . . . . . . . . . . . . . . . . . . . . . . . . . . . . . . . . . . . .
Torque values Inst. 2–2. . . . . . . . . . . . . . . . . . . . . . . . . . . . . . . . . . . . . . . . . . . . . . . . . .
Power requirements Inst. 2–3. . . . . . . . . . . . . . . . . . . . . . . . . . . . . . . . . . . . . . . . . . . . .
Environmental requirements Inst. 2–4. . . . . . . . . . . . . . . . . . . . . . . . . . . . . . . . . . . . . .
Structural requirements Inst. 2–5. . . . . . . . . . . . . . . . . . . . . . . . . . . . . . . . . . . . . . . . . .
Outdoor site dimensions Inst. 2–6. . . . . . . . . . . . . . . . . . . . . . . . . . . . . . . . . . . . . . . . .
View of maximum site template layout Inst. 2–7. . . . . . . . . . . . . . . . . . . . . . . . . . . . .
Visiting the site Inst. 2–9. . . . . . . . . . . . . . . . . . . . . . . . . . . . . . . . . . . . . . . . . . . . . . . . . . . . . .
Overview of visiting the site Inst. 2–9. . . . . . . . . . . . . . . . . . . . . . . . . . . . . . . . . . . . . .
Before departure to site Inst. 2–9. . . . . . . . . . . . . . . . . . . . . . . . . . . . . . . . . . . . . . . . . .
Arrival at all sites Inst. 2–9. . . . . . . . . . . . . . . . . . . . . . . . . . . . . . . . . . . . . . . . . . . . . . . .
Arriving at occupied sites Inst. 2–9. . . . . . . . . . . . . . . . . . . . . . . . . . . . . . . . . . . . . . . .
Arriving at unoccupied sites Inst. 2–10. . . . . . . . . . . . . . . . . . . . . . . . . . . . . . . . . . . . . .
Leaving site during installation and optimization Inst. 2–10. . . . . . . . . . . . . . . . . . . .
Rubbish removal Inst. 2–10. . . . . . . . . . . . . . . . . . . . . . . . . . . . . . . . . . . . . . . . . . . . . . . .
Rural sites Inst. 2–11. . . . . . . . . . . . . . . . . . . . . . . . . . . . . . . . . . . . . . . . . . . . . . . . . . . . .
On site safety Inst. 2–11. . . . . . . . . . . . . . . . . . . . . . . . . . . . . . . . . . . . . . . . . . . . . . . . . .
Preparing the site Inst. 2–12. . . . . . . . . . . . . . . . . . . . . . . . . . . . . . . . . . . . . . . . . . . . . . . . . . . .
Introduction to site preparation Inst. 2–12. . . . . . . . . . . . . . . . . . . . . . . . . . . . . . . . . . .
Base site structure Inst. 2–12. . . . . . . . . . . . . . . . . . . . . . . . . . . . . . . . . . . . . . . . . . . . . .
Site requirements Inst. 2–12. . . . . . . . . . . . . . . . . . . . . . . . . . . . . . . . . . . . . . . . . . . . . . .
Site access Inst. 2–12. . . . . . . . . . . . . . . . . . . . . . . . . . . . . . . . . . . . . . . . . . . . . . . . . . . .
Site layout Inst. 2–12. . . . . . . . . . . . . . . . . . . . . . . . . . . . . . . . . . . . . . . . . . . . . . . . . . . . .
Earthing the site Inst. 2–13. . . . . . . . . . . . . . . . . . . . . . . . . . . . . . . . . . . . . . . . . . . . . . . . . . . . .
Overview Inst. 2–13. . . . . . . . . . . . . . . . . . . . . . . . . . . . . . . . . . . . . . . . . . . . . . . . . . . . . .
Earthing requirements Inst. 2–13. . . . . . . . . . . . . . . . . . . . . . . . . . . . . . . . . . . . . . . . . . .
Earth electrode system Inst. 2–13. . . . . . . . . . . . . . . . . . . . . . . . . . . . . . . . . . . . . . . . . .
Cross bonding Inst. 2–14. . . . . . . . . . . . . . . . . . . . . . . . . . . . . . . . . . . . . . . . . . . . . . . . . .
Earthing procedure Inst. 2–14. . . . . . . . . . . . . . . . . . . . . . . . . . . . . . . . . . . . . . . . . . . . . .
Earth electrode testing Inst. 2–14. . . . . . . . . . . . . . . . . . . . . . . . . . . . . . . . . . . . . . . . . . .
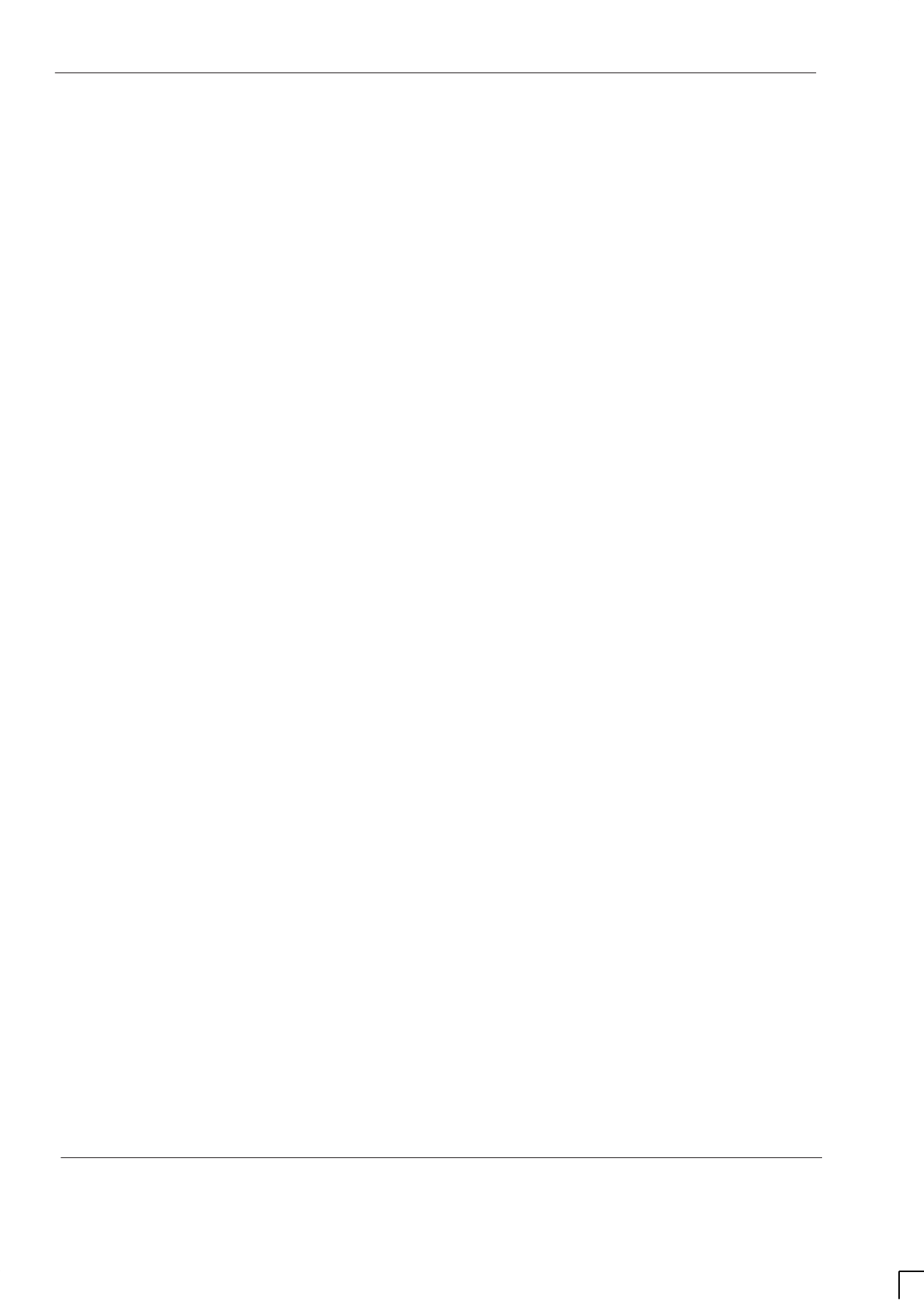
GSM-204-423
31st Oct 01
iv
Installation & Configuration: Horizon
macro
outdoor
CONTROLLED INTRODUCTION
68P02902W03-A
Preparing the foundation Inst. 2–16. . . . . . . . . . . . . . . . . . . . . . . . . . . . . . . . . . . . . . . . . . . . . .
Overview of foundation preparation Inst. 2–16. . . . . . . . . . . . . . . . . . . . . . . . . . . . . . .
Horizonmacro foundation Inst. 2–16. . . . . . . . . . . . . . . . . . . . . . . . . . . . . . . . . . . . . . . .
Preparing the foundation Inst. 2–17. . . . . . . . . . . . . . . . . . . . . . . . . . . . . . . . . . . . . . . . .
Chapter 3
Installing the BTS cabinet i. . . . . . . . . . . . . . . . . . . . . . . . . . . . . . . . . . . . . .
Installation overview Inst. 3–1. . . . . . . . . . . . . . . . . . . . . . . . . . . . . . . . . . . . . . . . . . . . . . . . . .
Introduction to installation Inst. 3–1. . . . . . . . . . . . . . . . . . . . . . . . . . . . . . . . . . . . . . . .
Installation sections Inst. 3–1. . . . . . . . . . . . . . . . . . . . . . . . . . . . . . . . . . . . . . . . . . . . .
E1/T1 line testing Inst. 3–1. . . . . . . . . . . . . . . . . . . . . . . . . . . . . . . . . . . . . . . . . . . . . . .
Cabinet view Inst. 3–2. . . . . . . . . . . . . . . . . . . . . . . . . . . . . . . . . . . . . . . . . . . . . . . . . . .
Equipment package units Inst. 3–3. . . . . . . . . . . . . . . . . . . . . . . . . . . . . . . . . . . . . . . .
Equipment delivery and packaging Inst. 3–4. . . . . . . . . . . . . . . . . . . . . . . . . . . . . . . . . . . . .
Delivery and packaging overview Inst. 3–4. . . . . . . . . . . . . . . . . . . . . . . . . . . . . . . . .
Packaging Inst. 3–4. . . . . . . . . . . . . . . . . . . . . . . . . . . . . . . . . . . . . . . . . . . . . . . . . . . . .
Weather conditions affecting unpacking/installation Inst. 3–5. . . . . . . . . . . . . . . . . . . . . . .
Overview of weather considerations Inst. 3–5. . . . . . . . . . . . . . . . . . . . . . . . . . . . . . .
Weather conditions Inst. 3–5. . . . . . . . . . . . . . . . . . . . . . . . . . . . . . . . . . . . . . . . . . . . . .
Maintenance cover Inst. 3–5. . . . . . . . . . . . . . . . . . . . . . . . . . . . . . . . . . . . . . . . . . . . . .
Unpacking and preparing the cabinet Inst. 3–7. . . . . . . . . . . . . . . . . . . . . . . . . . . . . . . . . . .
Tools Inst. 3–7. . . . . . . . . . . . . . . . . . . . . . . . . . . . . . . . . . . . . . . . . . . . . . . . . . . . . . . . . .
Safety considerations Inst. 3–7. . . . . . . . . . . . . . . . . . . . . . . . . . . . . . . . . . . . . . . . . . .
Cabinet access procedures Inst. 3–8. . . . . . . . . . . . . . . . . . . . . . . . . . . . . . . . . . . . . .
Procedures for unpacking and preparing the cabinet Inst. 3–9. . . . . . . . . . . . . . . .
Visual inspection Inst. 3–11. . . . . . . . . . . . . . . . . . . . . . . . . . . . . . . . . . . . . . . . . . . . . . . .
Safe disposal of packing material Inst. 3–11. . . . . . . . . . . . . . . . . . . . . . . . . . . . . . . . .
CTU module allotted slot retention Inst. 3–11. . . . . . . . . . . . . . . . . . . . . . . . . . . . . . . .
Installing the template and mounting bolt anchors Inst. 3–12. . . . . . . . . . . . . . . . . . . . . . . .
Introduction to template and mounting bolt anchor installation Inst. 3–12. . . . . . . .
View of template Inst. 3–12. . . . . . . . . . . . . . . . . . . . . . . . . . . . . . . . . . . . . . . . . . . . . . . .
Procedure for installing template Inst. 3–13. . . . . . . . . . . . . . . . . . . . . . . . . . . . . . . . . .
Recommended bolt length for concrete base Inst. 3–13. . . . . . . . . . . . . . . . . . . . . . .
Procedure for installing cabinet bolt anchors Inst. 3–14. . . . . . . . . . . . . . . . . . . . . . .
Fitting the outdoor cabinet onto its base Inst. 3–15. . . . . . . . . . . . . . . . . . . . . . . . . . . . . . . .
Procedure for fitting a BTS cabinet Inst. 3–15. . . . . . . . . . . . . . . . . . . . . . . . . . . . . . . .
Mounting additional cabinets Inst. 3–15. . . . . . . . . . . . . . . . . . . . . . . . . . . . . . . . . . . . .
Earthing and transient protection Inst. 3–16. . . . . . . . . . . . . . . . . . . . . . . . . . . . . . . . . . . . . . .
Site earthing Inst. 3–16. . . . . . . . . . . . . . . . . . . . . . . . . . . . . . . . . . . . . . . . . . . . . . . . . . .
Secondary transient and lightning protection Inst. 3–16. . . . . . . . . . . . . . . . . . . . . . .
Connecting the internal batteries Inst. 3–17. . . . . . . . . . . . . . . . . . . . . . . . . . . . . . . . . . . . . . .
Introduction to connecting the internal batteries Inst. 3–17. . . . . . . . . . . . . . . . . . . . .
Internal battery connection procedure Inst. 3–17. . . . . . . . . . . . . . . . . . . . . . . . . . . . .
View of internal battery tray Inst. 3–18. . . . . . . . . . . . . . . . . . . . . . . . . . . . . . . . . . . . . .
Installing and connecting power and earth cabling Inst. 3–19. . . . . . . . . . . . . . . . . . . . . . .
Overview of power and earth cabling Inst. 3–19. . . . . . . . . . . . . . . . . . . . . . . . . . . . . .
Cable routeing Inst. 3–19. . . . . . . . . . . . . . . . . . . . . . . . . . . . . . . . . . . . . . . . . . . . . . . . . .
Cabinet earthing points Inst. 3–20. . . . . . . . . . . . . . . . . . . . . . . . . . . . . . . . . . . . . . . . . .
Power supply cable colour coding Inst. 3–20. . . . . . . . . . . . . . . . . . . . . . . . . . . . . . . . .
Preparing for connection Inst. 3–21. . . . . . . . . . . . . . . . . . . . . . . . . . . . . . . . . . . . . . . . .
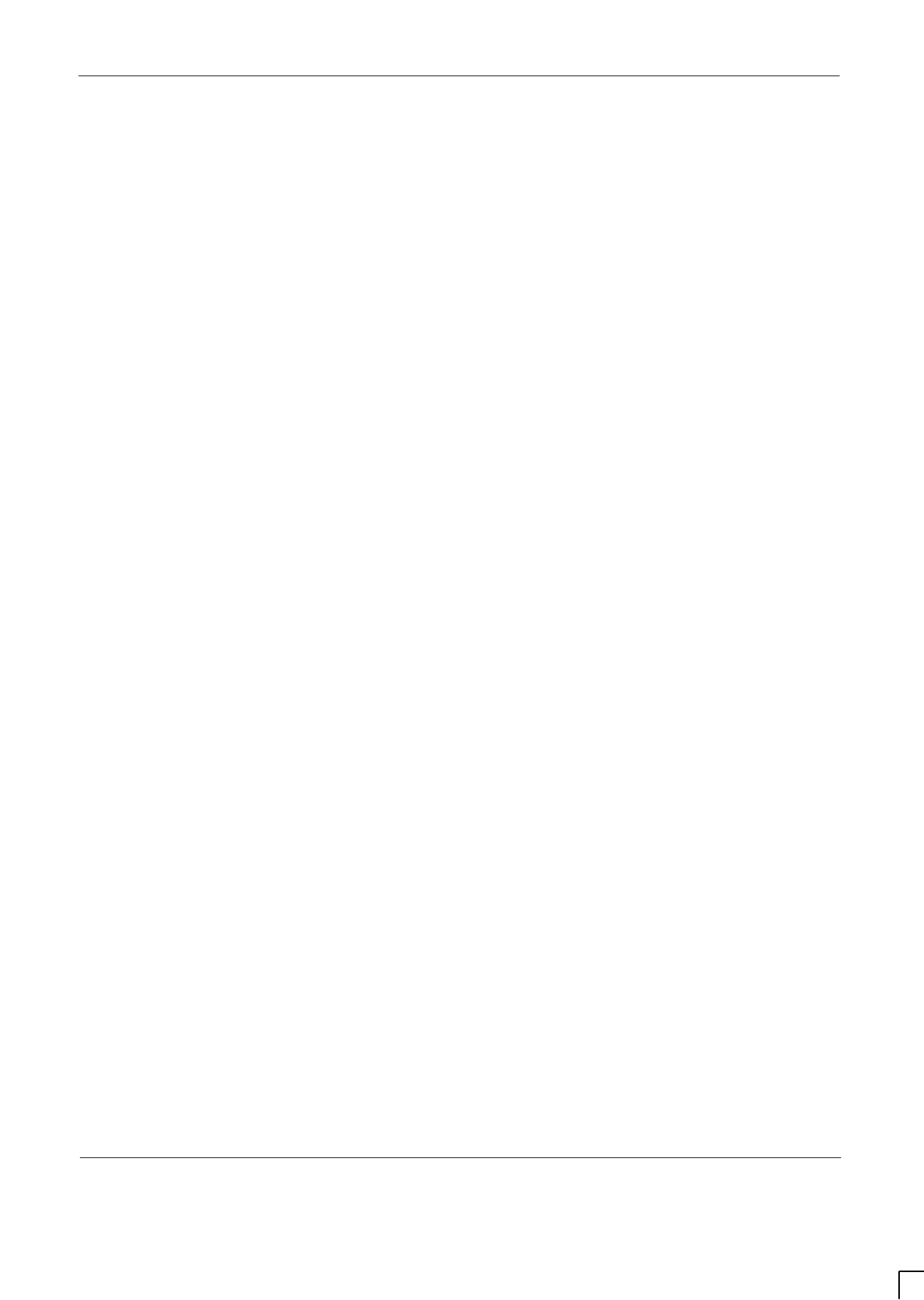
GSM-204-423
31st Oct 01
Installation & Configuration: Horizon
macro
outdoor
68P02902W03-A
CONTROLLED INTRODUCTION
v
Connecting 230 V single phase ac power cables Inst. 3–22. . . . . . . . . . . . . . . . . . . . . . . . .
Configuring the number 1 ac distribution box Inst. 3–22. . . . . . . . . . . . . . . . . . . . . . .
Connecting 230 V ac single phase mains input cables Inst. 3–22. . . . . . . . . . . . . . .
230 V ac single phase wiring diagram Inst. 3–23. . . . . . . . . . . . . . . . . . . . . . . . . . . . .
Connecting 110 V single phase ac power cables Inst. 3–24. . . . . . . . . . . . . . . . . . . . . . . . .
Configuring the number 1 ac distribution box Inst. 3–24. . . . . . . . . . . . . . . . . . . . . . .
Connecting 110 V ac single phase mains input cables Inst. 3–24. . . . . . . . . . . . . . .
110 V ac single phase wiring diagram Inst. 3–25. . . . . . . . . . . . . . . . . . . . . . . . . . . . .
Connecting 230 V 3-phase (star) ac power cables Inst. 3–26. . . . . . . . . . . . . . . . . . . . . . . .
Configuring the number 1 ac distribution box Inst. 3–26. . . . . . . . . . . . . . . . . . . . . . .
Connecting 230 V ac 3-phase (star) mains input cables Inst. 3–26. . . . . . . . . . . . . .
230 V ac 3-phase (star) wiring diagram Inst. 3–27. . . . . . . . . . . . . . . . . . . . . . . . . . . .
Connecting 230 V 3-phase (delta) ac power cables Inst. 3–28. . . . . . . . . . . . . . . . . . . . . . .
Configuring the number 1 ac distribution box Inst. 3–28. . . . . . . . . . . . . . . . . . . . . . .
Connecting 230 V ac 3-phase (delta) mains input cables Inst. 3–29. . . . . . . . . . . . .
230 V ac 3-phase (delta) wiring diagram Inst. 3–30. . . . . . . . . . . . . . . . . . . . . . . . . . .
Connecting antennas Inst. 3–31. . . . . . . . . . . . . . . . . . . . . . . . . . . . . . . . . . . . . . . . . . . . . . . . .
Overview of antenna connections Inst. 3–31. . . . . . . . . . . . . . . . . . . . . . . . . . . . . . . . .
Cable entry earth plates Inst. 3–32. . . . . . . . . . . . . . . . . . . . . . . . . . . . . . . . . . . . . . . . .
Fitting inter-cabinet RF cables to earth plates Inst. 3–32. . . . . . . . . . . . . . . . . . . . . . .
Routeing RF cables between cabinets. Inst. 3–33. . . . . . . . . . . . . . . . . . . . . . . . . . . .
Types of RF connector Inst. 3–33. . . . . . . . . . . . . . . . . . . . . . . . . . . . . . . . . . . . . . . . . .
Torque of RF connectors Inst. 3–33. . . . . . . . . . . . . . . . . . . . . . . . . . . . . . . . . . . . . . . . .
Fitting left side (cable entry) earth plate Inst. 3–34. . . . . . . . . . . . . . . . . . . . . . . . . . . .
Fitting expansion plates Inst. 3–35. . . . . . . . . . . . . . . . . . . . . . . . . . . . . . . . . . . . . . . . . .
RF connection principles Inst. 3–36. . . . . . . . . . . . . . . . . . . . . . . . . . . . . . . . . . . . . . . . .
Rx/Tx single antenna duplexing Inst. 3–36. . . . . . . . . . . . . . . . . . . . . . . . . . . . . . . . . . .
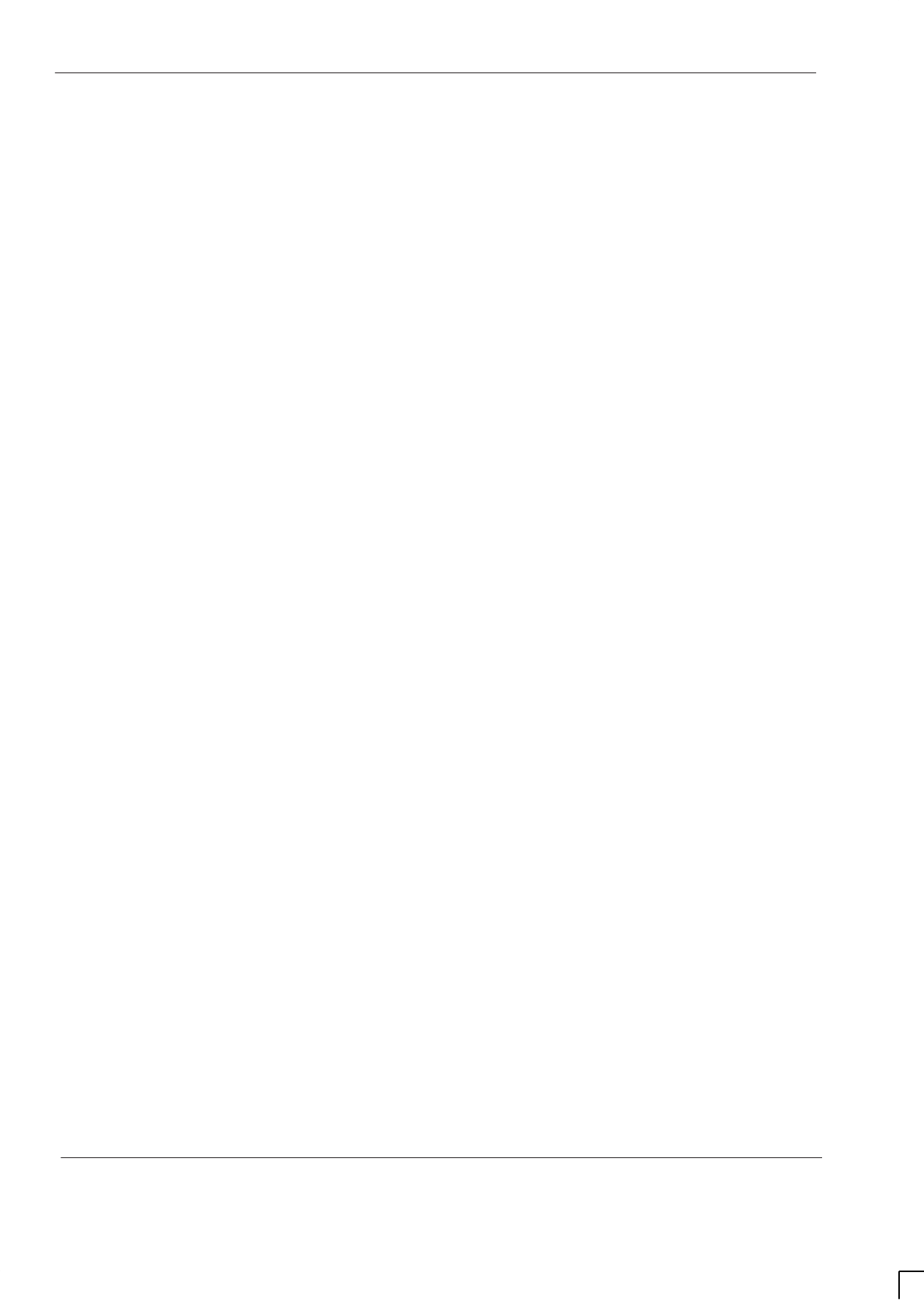
GSM-204-423
31st Oct 01
vi
Installation & Configuration: Horizon
macro
outdoor
CONTROLLED INTRODUCTION
68P02902W03-A
Suggested RF configurations Inst. 3–37. . . . . . . . . . . . . . . . . . . . . . . . . . . . . . . . . . . . . . . . . .
Overview of configuration diagrams Inst. 3–37. . . . . . . . . . . . . . . . . . . . . . . . . . . . . . .
Single cabinet connection kits and cables Inst. 3–38. . . . . . . . . . . . . . . . . . . . . . . . . .
Multiple cabinet connection kits and cables Inst. 3–39. . . . . . . . . . . . . . . . . . . . . . . .
Configuration for omni 1 Inst. 3–40. . . . . . . . . . . . . . . . . . . . . . . . . . . . . . . . . . . . . . . . .
Configuration for omni 1 or 2 (with/without diversity) Inst. 3–41. . . . . . . . . . . . . . . . .
Configuration for omni 3 or 4 Inst. 3–42. . . . . . . . . . . . . . . . . . . . . . . . . . . . . . . . . . . . .
Configuration for omni 3 Inst. 3–42. . . . . . . . . . . . . . . . . . . . . . . . . . . . . . . . . . . . . . . . .
Configuration for omni 4 Inst. 3–43. . . . . . . . . . . . . . . . . . . . . . . . . . . . . . . . . . . . . . . . .
Configuration for omni 5 or 6 Inst. 3–43. . . . . . . . . . . . . . . . . . . . . . . . . . . . . . . . . . . . .
Configuration for sector 1/1 or 2/2 Inst. 3–44. . . . . . . . . . . . . . . . . . . . . . . . . . . . . . . . .
Configuration for sector 1/1 Inst. 3–44. . . . . . . . . . . . . . . . . . . . . . . . . . . . . . . . . . . . . .
Configuration for single cabinet sector 3/3 Inst. 3–45. . . . . . . . . . . . . . . . . . . . . . . . .
Configuration for 2 cabinet sector 3/3 Inst. 3–46. . . . . . . . . . . . . . . . . . . . . . . . . . . . . .
Configuration for 2 cabinet sector 4/4 Inst. 3–46. . . . . . . . . . . . . . . . . . . . . . . . . . . . . .
Configuration for 2 cabinet sector 5/5 or 6/6 Inst. 3–47. . . . . . . . . . . . . . . . . . . . . . . .
Configuration for single cabinet sector 1/1/1, 1/1/2, 1/2/2 or 2/2/2 Inst. 3–48. . . . .
Configuration for 2 cabinet sector 2/2/2 Inst. 3–49. . . . . . . . . . . . . . . . . . . . . . . . . . . .
Configuration for 2 cabinet sector 3/3/3 or 4/4/4 Inst. 3–50. . . . . . . . . . . . . . . . . . . .
Configuration for 3 cabinet sector 3/3/3 Inst. 3–51. . . . . . . . . . . . . . . . . . . . . . . . . . . .
Configuration for 2 cabinet sector 4/4/4 Inst. 3–52. . . . . . . . . . . . . . . . . . . . . . . . . . . .
Configuration for 3 cabinet sector 4/4/4 Inst. 3–53. . . . . . . . . . . . . . . . . . . . . . . . . . . .
Configuration for sector 5/5/5 or 6/6/6 Inst. 3–54. . . . . . . . . . . . . . . . . . . . . . . . . . . . .
Configuration for sector 8/8/8 Inst. 3–55. . . . . . . . . . . . . . . . . . . . . . . . . . . . . . . . . . . . .
Configuration for dual band 1/1/1-3/3/3 Inst. 3–56. . . . . . . . . . . . . . . . . . . . . . . . . . . .
Configuration for dual band 3/3/3-1/1/1 Inst. 3–56. . . . . . . . . . . . . . . . . . . . . . . . . . . .
Connecting fibre optic cables Inst. 3–57. . . . . . . . . . . . . . . . . . . . . . . . . . . . . . . . . . . . . . . . . .
Location of fibre optic connections Inst. 3–57. . . . . . . . . . . . . . . . . . . . . . . . . . . . . . . .
Care of fibres Inst. 3–57. . . . . . . . . . . . . . . . . . . . . . . . . . . . . . . . . . . . . . . . . . . . . . . . . . .
Connecting fibre optic cables between cabinets Inst. 3–60. . . . . . . . . . . . . . . . . . . . .
Interface panel cabling Inst. 3–61. . . . . . . . . . . . . . . . . . . . . . . . . . . . . . . . . . . . . . . . . . . . . . . .
Interface panel diagram and pinout overview Inst. 3–61. . . . . . . . . . . . . . . . . . . . . .
Interface panel connector pinout tables Inst. 3–62. . . . . . . . . . . . . . . . . . . . . . . . . . . .
GPS connector Inst. 3–62. . . . . . . . . . . . . . . . . . . . . . . . . . . . . . . . . . . . . . . . . . . . . . . . .
RTC connector (not used) Inst. 3–63. . . . . . . . . . . . . . . . . . . . . . . . . . . . . . . . . . . . . . . .
BIB (BIM) interconnection Inst. 3–64. . . . . . . . . . . . . . . . . . . . . . . . . . . . . . . . . . . . . . . .
T43 (CIM) interconnection Inst. 3–65. . . . . . . . . . . . . . . . . . . . . . . . . . . . . . . . . . . . . . .
PIX inputs and outputs Inst. 3–66. . . . . . . . . . . . . . . . . . . . . . . . . . . . . . . . . . . . . . . . . .
ICS connector Inst. 3–67. . . . . . . . . . . . . . . . . . . . . . . . . . . . . . . . . . . . . . . . . . . . . . . . . .
External alarm connector Inst. 3–68. . . . . . . . . . . . . . . . . . . . . . . . . . . . . . . . . . . . . . . .
Chapter 4
Installing the cable shroud i. . . . . . . . . . . . . . . . . . . . . . . . . . . . . . . . . . . . .
Introduction to cable shroud installation Inst. 4–1. . . . . . . . . . . . . . . . . . . . . . . . . . . . . . . . .
Preparing to install the cable shroud Inst. 4–1. . . . . . . . . . . . . . . . . . . . . . . . . . . . . . .
Considerations when installing the cable shroud Inst. 4–1. . . . . . . . . . . . . . . . . . . .
Cable shroud installation procedures Inst. 4–2. . . . . . . . . . . . . . . . . . . . . . . . . . . . . . . . . . .
Attaching the cable shroud frame to the BTS cabinet Inst. 4–2. . . . . . . . . . . . . . . .
Adapting the shroud for cable entry from below ground Inst. 4–4. . . . . . . . . . . . . .
Adapting the shroud for cable entry from ground level Inst. 4–5. . . . . . . . . . . . . . .
Adapting the shroud for high level cable entry Inst. 4–6. . . . . . . . . . . . . . . . . . . . . .
Installation between cabinets (or the AEH) Inst. 4–7. . . . . . . . . . . . . . . . . . . . . . . . .
Cable routeing for multiple cabinet sites Inst. 4–10. . . . . . . . . . . . . . . . . . . . . . . . . . .
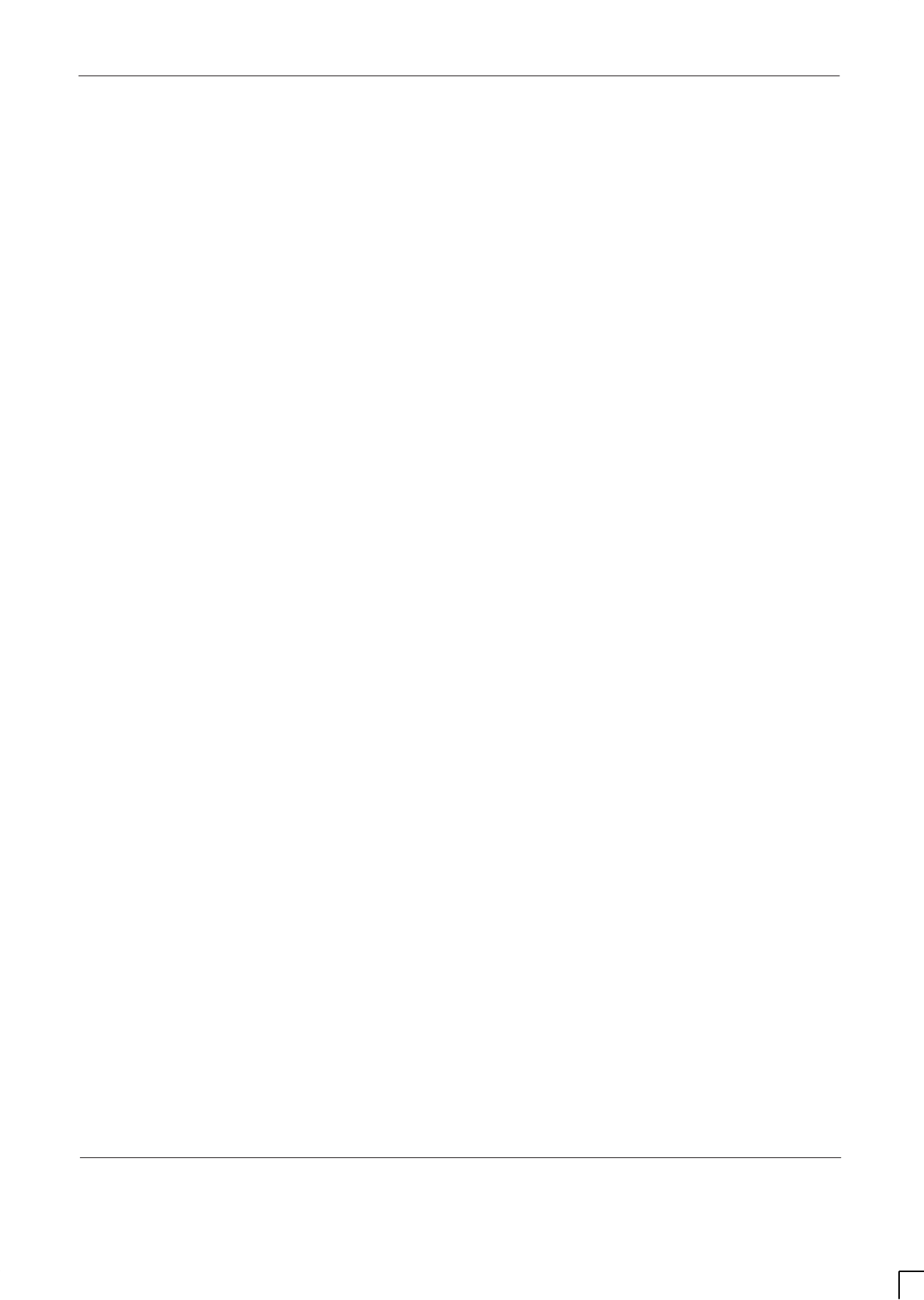
GSM-204-423
31st Oct 01
Installation & Configuration: Horizon
macro
outdoor
68P02902W03-A
CONTROLLED INTRODUCTION
vii
Chapter 5
Installing the auxiliary equipment housing i. . . . . . . . . . . . . . . . . . . . . .
Procedures for installing the auxiliary equipment housing Inst. 5–1. . . . . . . . . . . . . . . . .
Assumptions regarding site preparation Inst. 5–1. . . . . . . . . . . . . . . . . . . . . . . . . . . .
Layout of the auxiliary equipment housing Inst. 5–1. . . . . . . . . . . . . . . . . . . . . . . . .
Auxiliary equipment housing packaging Inst. 5–2. . . . . . . . . . . . . . . . . . . . . . . . . . . .
Introduction to installing the auxiliary equipment housing Inst. 5–2. . . . . . . . . . . . .
Installing the auxiliary equipment housing template Inst. 5–3. . . . . . . . . . . . . . . . . .
Installing auxiliary equipment housing bolt anchors Inst. 5–4. . . . . . . . . . . . . . . . . .
Bolting the auxiliary equipment housing to the floor Inst. 5–5. . . . . . . . . . . . . . . . .
Installing batteries in the auxiliary equipment housing Inst. 5–6. . . . . . . . . . . . . . . . . . . . .
Introduction to battery installation Inst. 5–6. . . . . . . . . . . . . . . . . . . . . . . . . . . . . . . . .
Installing batteries Inst. 5–7. . . . . . . . . . . . . . . . . . . . . . . . . . . . . . . . . . . . . . . . . . . . . .
Auxiliary equipment housing (AEH) connections Inst. 5–10. . . . . . . . . . . . . . . . . . . . . . . . .
Earthing the AEH Inst. 5–10. . . . . . . . . . . . . . . . . . . . . . . . . . . . . . . . . . . . . . . . . . . . . . .
Connecting dc cables to the AEH Inst. 5–10. . . . . . . . . . . . . . . . . . . . . . . . . . . . . . . . .
Connecting the alarm signal cables Inst. 5–11. . . . . . . . . . . . . . . . . . . . . . . . . . . . . . .
Internal connections in the AEH Inst. 5–11. . . . . . . . . . . . . . . . . . . . . . . . . . . . . . . . . .
Configuring battery backup to supply two BTS cabinets Inst. 5–12. . . . . . . . . . . . . . . . . . .
Introduction to configuring battery backup Inst. 5–12. . . . . . . . . . . . . . . . . . . . . . . . . .
Removing the power distribution box Inst. 5–12. . . . . . . . . . . . . . . . . . . . . . . . . . . . . .
Interior view of power distribution box Inst. 5–13. . . . . . . . . . . . . . . . . . . . . . . . . . . . .
Removing the parallelling links Inst. 5–14. . . . . . . . . . . . . . . . . . . . . . . . . . . . . . . . . . . .
Refitting the power distribution box Inst. 5–15. . . . . . . . . . . . . . . . . . . . . . . . . . . . . . . .
Chapter 6
Interoperability between different Motorola BTSs i. . . . . . . . . . . . . . . .
Introduction to interoperability Inst. 6–1. . . . . . . . . . . . . . . . . . . . . . . . . . . . . . . . . . . . . . . . .
Mixed product sites Inst. 6–1. . . . . . . . . . . . . . . . . . . . . . . . . . . . . . . . . . . . . . . . . . . . .
Architectural constraints Inst. 6–1. . . . . . . . . . . . . . . . . . . . . . . . . . . . . . . . . . . . . . . . .
BTS architectures and interoperability Inst. 6–2. . . . . . . . . . . . . . . . . . . . . . . . . . . . . . . . . .
M-Cell6 and Horizonmacro architectures Inst. 6–2. . . . . . . . . . . . . . . . . . . . . . . . . . .
Example mixed site Inst. 6–3. . . . . . . . . . . . . . . . . . . . . . . . . . . . . . . . . . . . . . . . . . . . .
Technical issues Inst. 6–4. . . . . . . . . . . . . . . . . . . . . . . . . . . . . . . . . . . . . . . . . . . . . . . .
Receive path Inst. 6–4. . . . . . . . . . . . . . . . . . . . . . . . . . . . . . . . . . . . . . . . . . . . . . . . . . .
Transmit path Inst. 6–7. . . . . . . . . . . . . . . . . . . . . . . . . . . . . . . . . . . . . . . . . . . . . . . . . .
M-Cell6 and Horizonmacro hardware equivalents Inst. 6–10. . . . . . . . . . . . . . . . . . .
Further configuration information Inst. 6–10. . . . . . . . . . . . . . . . . . . . . . . . . . . . . . . . . .
Example configurations Inst. 6–11. . . . . . . . . . . . . . . . . . . . . . . . . . . . . . . . . . . . . . . . . .
Special hardware Inst. 6–14. . . . . . . . . . . . . . . . . . . . . . . . . . . . . . . . . . . . . . . . . . . . . . .
Chapter 7
Commissioning of outdoor cabinet i. . . . . . . . . . . . . . . . . . . . . . . . . . . . .
Commissioning overview Inst. 7–1. . . . . . . . . . . . . . . . . . . . . . . . . . . . . . . . . . . . . . . . . . . . . .
Overview of commissioning Inst. 7–1. . . . . . . . . . . . . . . . . . . . . . . . . . . . . . . . . . . . . .
PC to MCUF cable pin connections Inst. 7–1. . . . . . . . . . . . . . . . . . . . . . . . . . . . . . .
Test equipment Inst. 7–2. . . . . . . . . . . . . . . . . . . . . . . . . . . . . . . . . . . . . . . . . . . . . . . . .
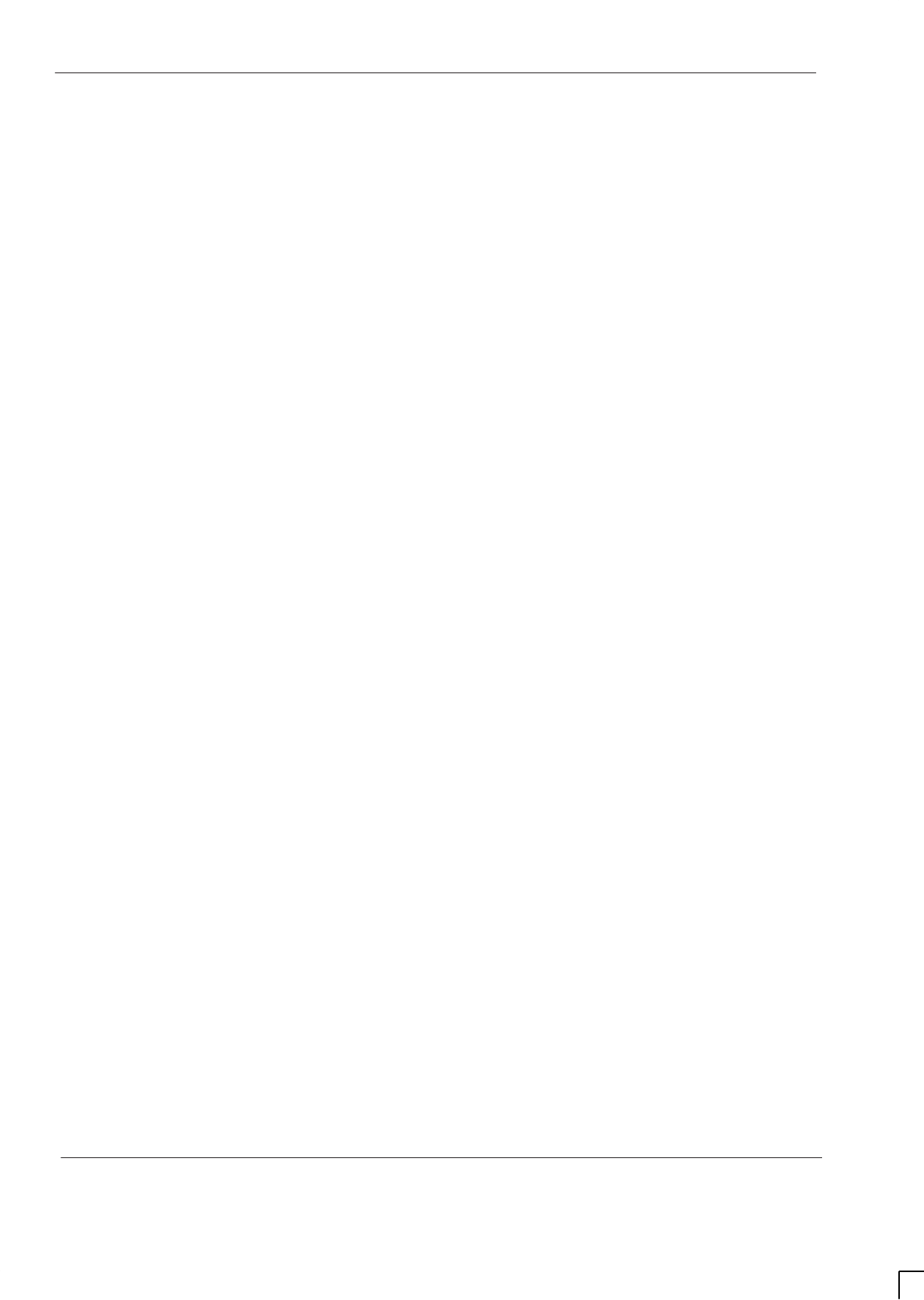
GSM-204-423
31st Oct 01
viii
Installation & Configuration: Horizon
macro
outdoor
CONTROLLED INTRODUCTION
68P02902W03-A
Pre-power up checks Inst. 7–3. . . . . . . . . . . . . . . . . . . . . . . . . . . . . . . . . . . . . . . . . . . . . . . . .
Overview of pre-power up checks Inst. 7–3. . . . . . . . . . . . . . . . . . . . . . . . . . . . . . . . .
Visual inspection Inst. 7–4. . . . . . . . . . . . . . . . . . . . . . . . . . . . . . . . . . . . . . . . . . . . . . . .
Request for connection Inst. 7–4. . . . . . . . . . . . . . . . . . . . . . . . . . . . . . . . . . . . . . . . . .
Earth continuity check Inst. 7–5. . . . . . . . . . . . . . . . . . . . . . . . . . . . . . . . . . . . . . . . . . .
AC power system insulation check Inst. 7–5. . . . . . . . . . . . . . . . . . . . . . . . . . . . . . . .
Connecting input power Inst. 7–6. . . . . . . . . . . . . . . . . . . . . . . . . . . . . . . . . . . . . . . . . . . . . . .
Pre-connection checks Inst. 7–6. . . . . . . . . . . . . . . . . . . . . . . . . . . . . . . . . . . . . . . . . .
Connecting ac power Inst. 7–6. . . . . . . . . . . . . . . . . . . . . . . . . . . . . . . . . . . . . . . . . . . .
Connecting to a single phase ac power supply Inst. 7–6. . . . . . . . . . . . . . . . . . . . . .
Connecting to a three phase (star) ac power supply Inst. 7–7. . . . . . . . . . . . . . . . .
Connecting to a three phase (delta) ac power supply Inst. 7–7. . . . . . . . . . . . . . . .
Powering up the cabinet Inst. 7–8. . . . . . . . . . . . . . . . . . . . . . . . . . . . . . . . . . . . . . . . . . . . . .
Power-up overview Inst. 7–8. . . . . . . . . . . . . . . . . . . . . . . . . . . . . . . . . . . . . . . . . . . . . .
Power up procedure without code load Inst. 7–8. . . . . . . . . . . . . . . . . . . . . . . . . . . .
Power down of the cabinet Inst. 7–10. . . . . . . . . . . . . . . . . . . . . . . . . . . . . . . . . . . . . . .
Power up procedure with code load Inst. 7–11. . . . . . . . . . . . . . . . . . . . . . . . . . . . . . .
Installation and configuration Inst. 7–14. . . . . . . . . . . . . . . . . . . . . . . . . . . . . . . . . . . . .
Components involved in power up procedures Inst. 7–15. . . . . . . . . . . . . . . . . . . . . .
Testing the thermal management system (TMS) Inst. 7–16. . . . . . . . . . . . . . . . . . . . . . . . .
Overview of TMS test Inst. 7–16. . . . . . . . . . . . . . . . . . . . . . . . . . . . . . . . . . . . . . . . . . . .
Test facilities Inst. 7–16. . . . . . . . . . . . . . . . . . . . . . . . . . . . . . . . . . . . . . . . . . . . . . . . . . .
Diagram of TMS airflow Inst. 7–17. . . . . . . . . . . . . . . . . . . . . . . . . . . . . . . . . . . . . . . . . .
Test procedure Inst. 7–18. . . . . . . . . . . . . . . . . . . . . . . . . . . . . . . . . . . . . . . . . . . . . . . . .
Testing the battery backup Inst. 7–19. . . . . . . . . . . . . . . . . . . . . . . . . . . . . . . . . . . . . . . . . . . .
Overview of battery backup test Inst. 7–19. . . . . . . . . . . . . . . . . . . . . . . . . . . . . . . . . .
Battery backup test procedures Inst. 7–19. . . . . . . . . . . . . . . . . . . . . . . . . . . . . . . . . . .
Sample form 1: Request for connection Inst. 7–21. . . . . . . . . . . . . . . . . . . . . . . . . . . . . . . . .
Sample form 2: Completion and inspection form Inst. 7–23. . . . . . . . . . . . . . . . . . . . . . . . .
Chapter 8
Decommissioning the equipment i. . . . . . . . . . . . . . . . . . . . . . . . . . . . . . .
Introduction to decommissioning the Horizonmacro outdoor cabinet Inst. 8–1. . . . . . . .
Overview Inst. 8–1. . . . . . . . . . . . . . . . . . . . . . . . . . . . . . . . . . . . . . . . . . . . . . . . . . . . . .
Prerequisite Inst. 8–1. . . . . . . . . . . . . . . . . . . . . . . . . . . . . . . . . . . . . . . . . . . . . . . . . . . .
Lifting cabinets Inst. 8–1. . . . . . . . . . . . . . . . . . . . . . . . . . . . . . . . . . . . . . . . . . . . . . . . .
Decommissioning the Horizonmacro outdoor cabinet Inst. 8–2. . . . . . . . . . . . . . . . . . . . .
Introduction Inst. 8–2. . . . . . . . . . . . . . . . . . . . . . . . . . . . . . . . . . . . . . . . . . . . . . . . . . . .
To decommission using checklist Inst. 8–2. . . . . . . . . . . . . . . . . . . . . . . . . . . . . . . . . .
Before starting Inst. 8–2. . . . . . . . . . . . . . . . . . . . . . . . . . . . . . . . . . . . . . . . . . . . . . . . . .
Power down of the cabinet Inst. 8–2. . . . . . . . . . . . . . . . . . . . . . . . . . . . . . . . . . . . . . .
Procedure Inst. 8–3. . . . . . . . . . . . . . . . . . . . . . . . . . . . . . . . . . . . . . . . . . . . . . . . . . . . .
BTS checklist Inst. 8–4. . . . . . . . . . . . . . . . . . . . . . . . . . . . . . . . . . . . . . . . . . . . . . . . . . .
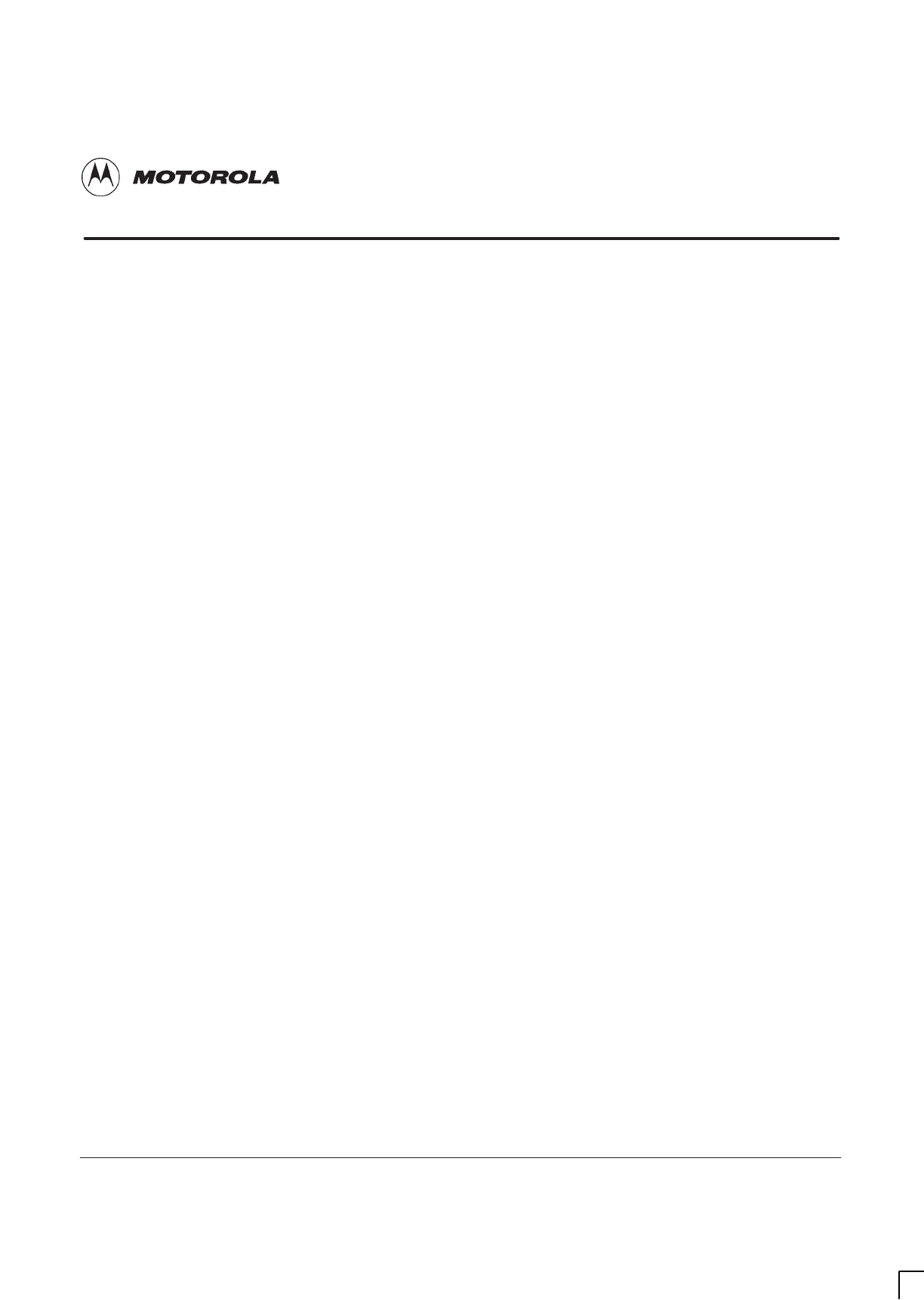
31st Oct 01
Installation & Configuration: Horizon
macro
outdoor
68P02902W03-A
CONTROLLED INTRODUCTION
i
Chapter 1
Introduction to installation
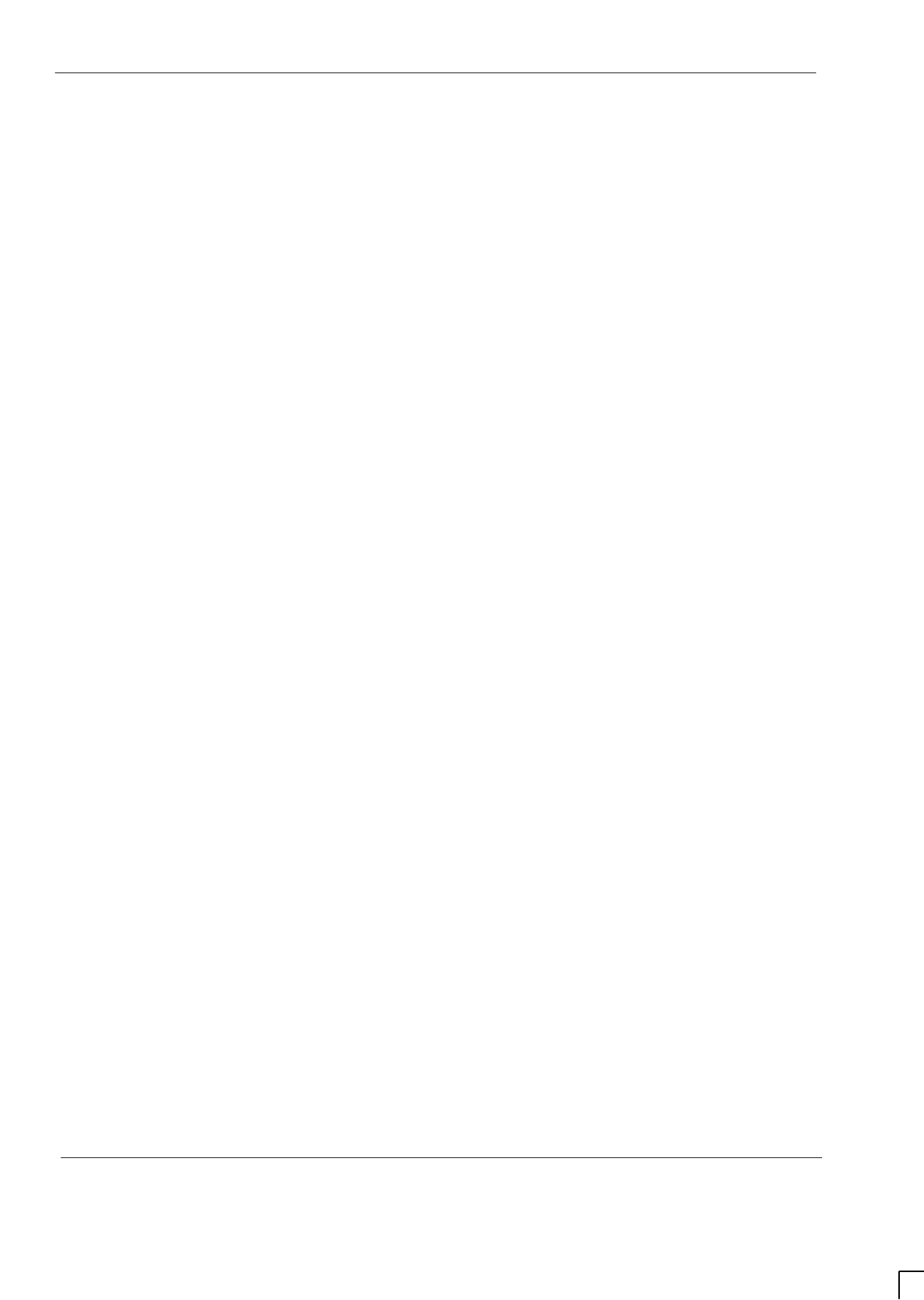
GSM-204-423
31st Oct 01
ii
Installation & Configuration: Horizon
macro
outdoor
CONTROLLED INTRODUCTION
68P02902W03-A
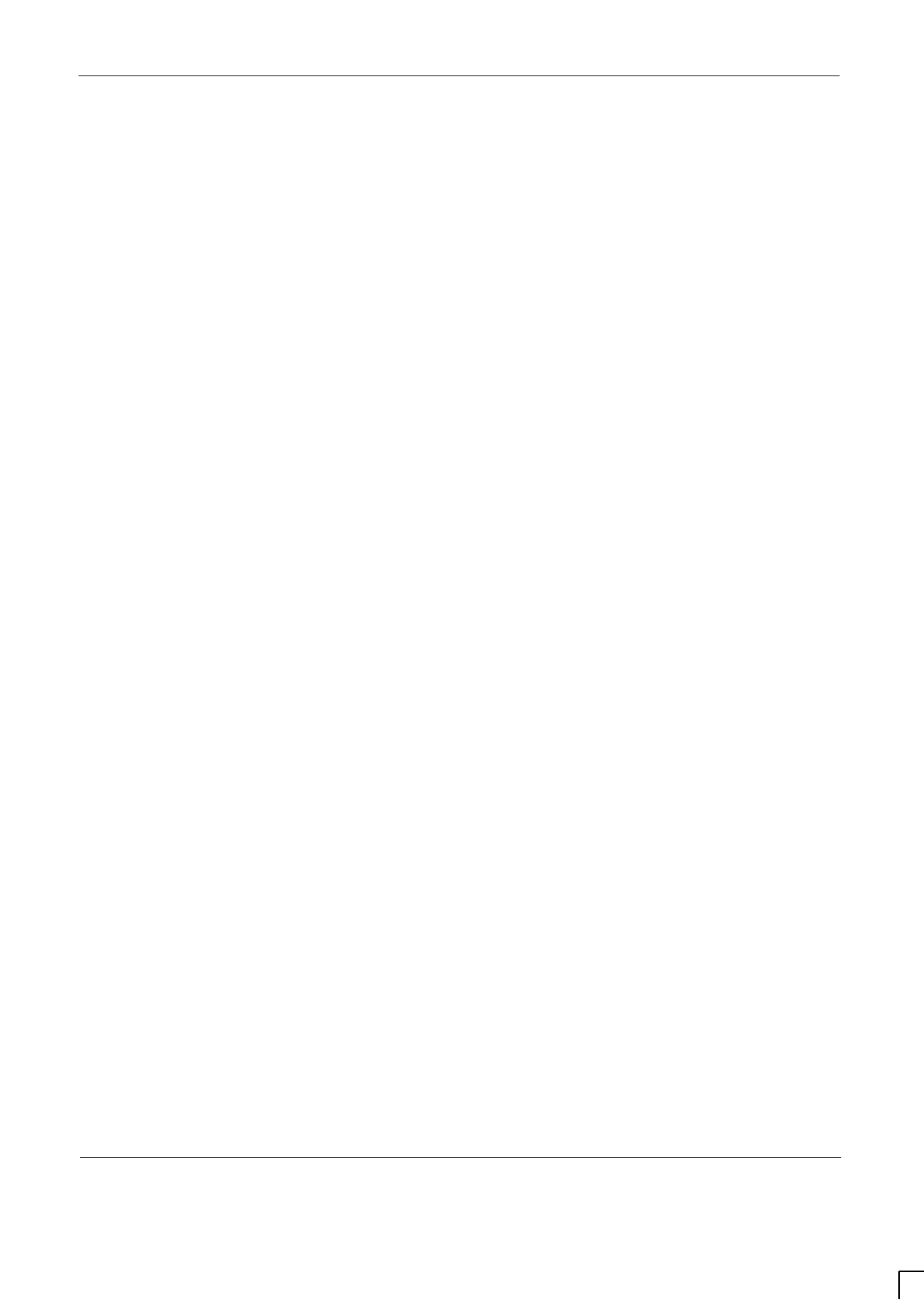
GSM-204-423
31st Oct 01
Installation & Configuration: Horizon
macro
outdoor
68P02902W03-A
CONTROLLED INTRODUCTION
iii
Chapter 1
Introduction to installation i. . . . . . . . . . . . . . . . . . . . . . . . . . . . . . . . . . . . .
Introduction to installation and configuration Inst. 1–1. . . . . . . . . . . . . . . . . . . . . . . . . . . . .
Manual scope Inst. 1–1. . . . . . . . . . . . . . . . . . . . . . . . . . . . . . . . . . . . . . . . . . . . . . . . . .
Safety instructions Inst. 1–2. . . . . . . . . . . . . . . . . . . . . . . . . . . . . . . . . . . . . . . . . . . . . .
Software requirements Inst. 1–2. . . . . . . . . . . . . . . . . . . . . . . . . . . . . . . . . . . . . . . . . .
Horizonmacro outdoor tool list Inst. 1–3. . . . . . . . . . . . . . . . . . . . . . . . . . . . . . . . . . . . . . . . .
Overview of tool list Inst. 1–3. . . . . . . . . . . . . . . . . . . . . . . . . . . . . . . . . . . . . . . . . . . . .
Tool list Inst. 1–3. . . . . . . . . . . . . . . . . . . . . . . . . . . . . . . . . . . . . . . . . . . . . . . . . . . . . . . .
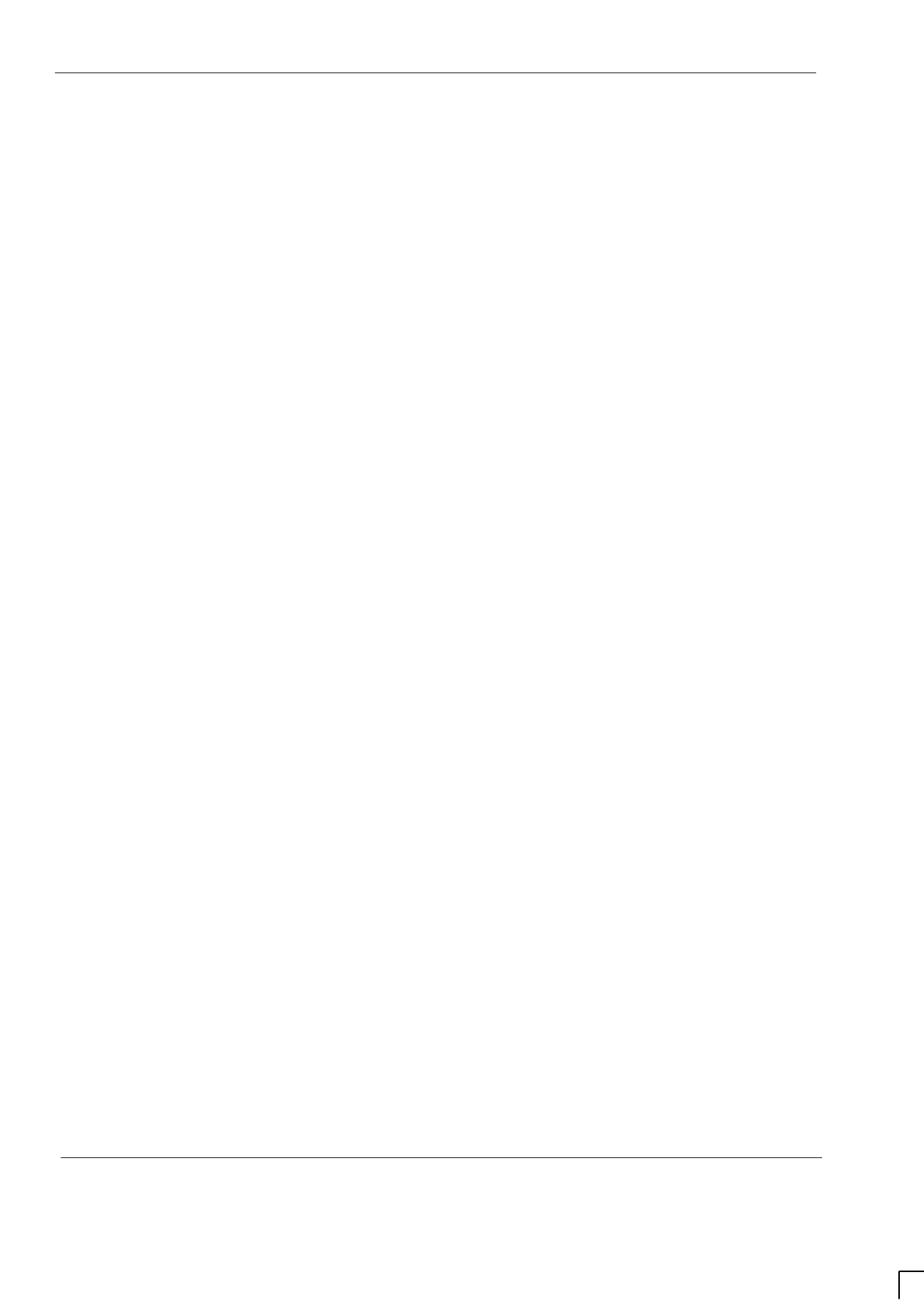
GSM-204-423
31st Oct 01
iv
Installation & Configuration: Horizon
macro
outdoor
CONTROLLED INTRODUCTION
68P02902W03-A
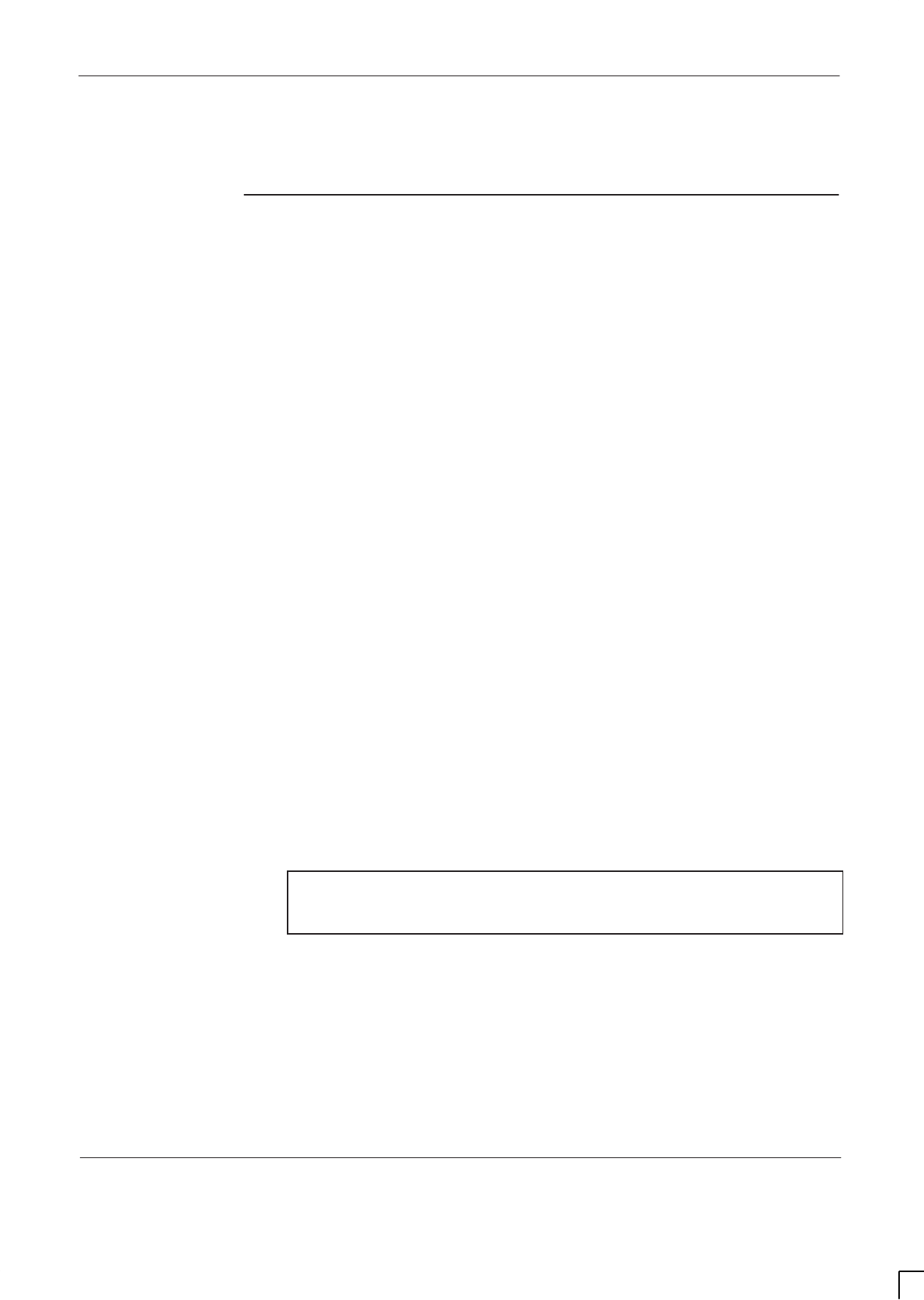
GSM-204-423 Introduction to installation and configuration
31st Oct 01
Installation & Configuration: Horizon
macro
outdoor
68P02902W03-A
CONTROLLED INTRODUCTION
Inst. 1–1
Introduction to installation and configuration
Manual scope
This category (GSM-204-423) covers installation and commissioning for the
cabinet, arranged in the following chapters:
Chapter 1 Introduction
General information, safety precautions, and information about tools needed to
install the equipment.
Chapter 2 Site preparation
Describes the procedures to be followed for initially preparing the site and
installing the necessary ducting and concrete base.
Chapter 3 Installation of outdoor cabinet
All procedures necessary to install the cabinet ready for operation, with an
overview of the different configurations available.
Chapter 4 Installing the cable shroud
Procedures for installing the optional cable shroud in various configurations.
Chapter 5 Installing the auxiliary equipment cabinet
All procedures necessary to install the optional auxiliary equipment cabinet,
ready for operation.
Chapter 6 Commissioning of outdoor cabinet
All procedures necessary to enable the cabinet to be fully operational.
Chapter 7 Decommissioning of outdoor cabinet
All procedures necessary to decommission the outdoor cabinet.
NOTE For hardware optimization and base site integration, refer
to
Installation and Configuration: BSS Optimization:
(GSM-100-423) 68P2901W43
.
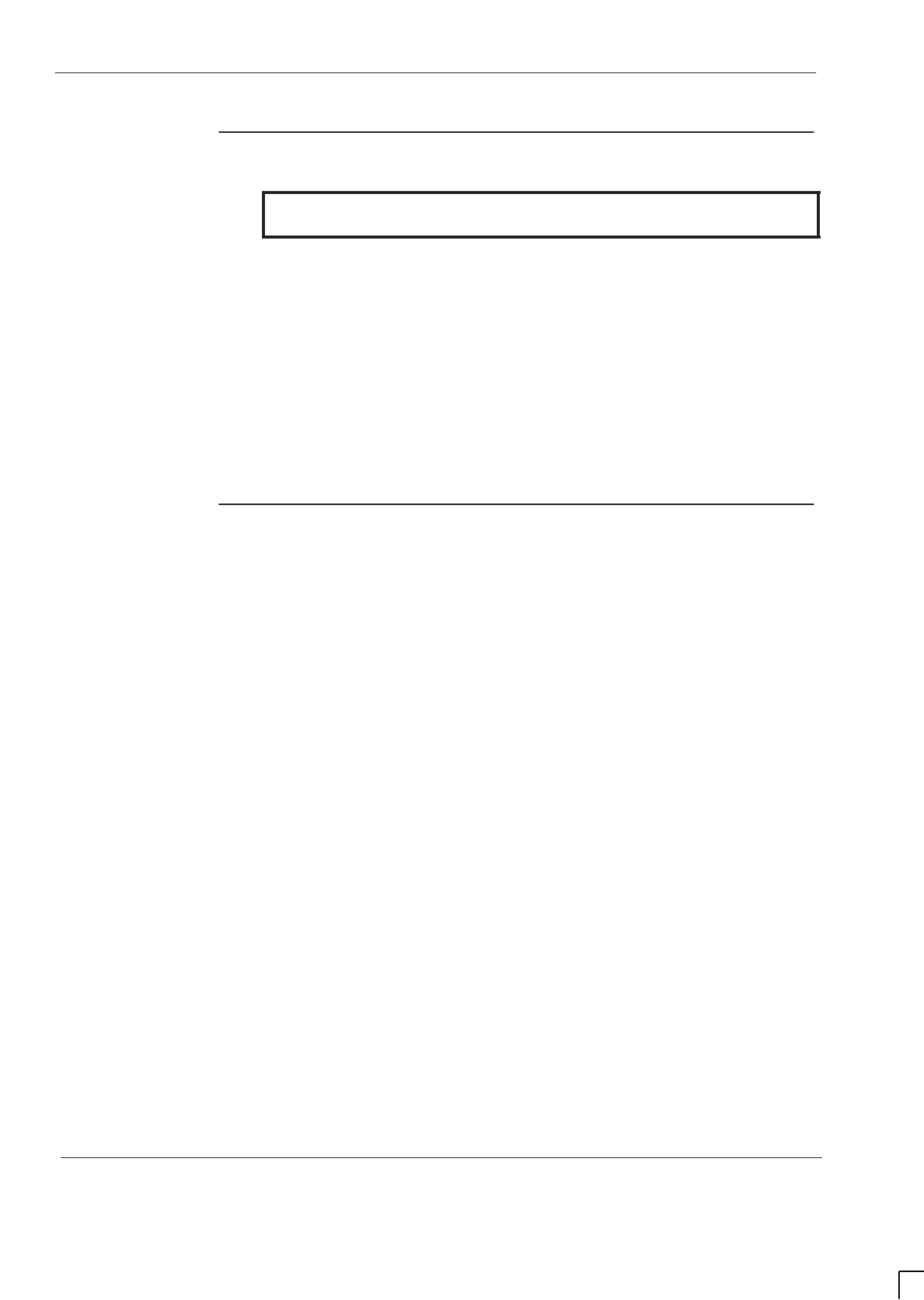
GSM-204-423
Introduction to installation and configuration
31st Oct 01
Inst. 1–2
Installation & Configuration: Horizon
macro
outdoor
CONTROLLED INTRODUCTION
68P02902W03-A
Safety
instructions
WARNING This equipment must only be installed by trained
personnel.
The following safety instructions must be observed when installing the
equipment described in this manual:
The installation and configuration procedures described in this manual
must only be carried out by suitably trained personnel.
Installation and commissioning must comply with all relevant national and
regional regulations.
The equipment must only be installed in a location to which unauthorized
access can be prevented.
Cabinets must be bolted down.
Software
requirements
The GSM/EGSM900 and DCS1800 BTSs require BSS and OMC-R software
release GSR4 (or later) in the network.
The GSM850 and PCS1900 BTSs require BSS and OMC-R software release
GSR5.1 (or later) in the network.
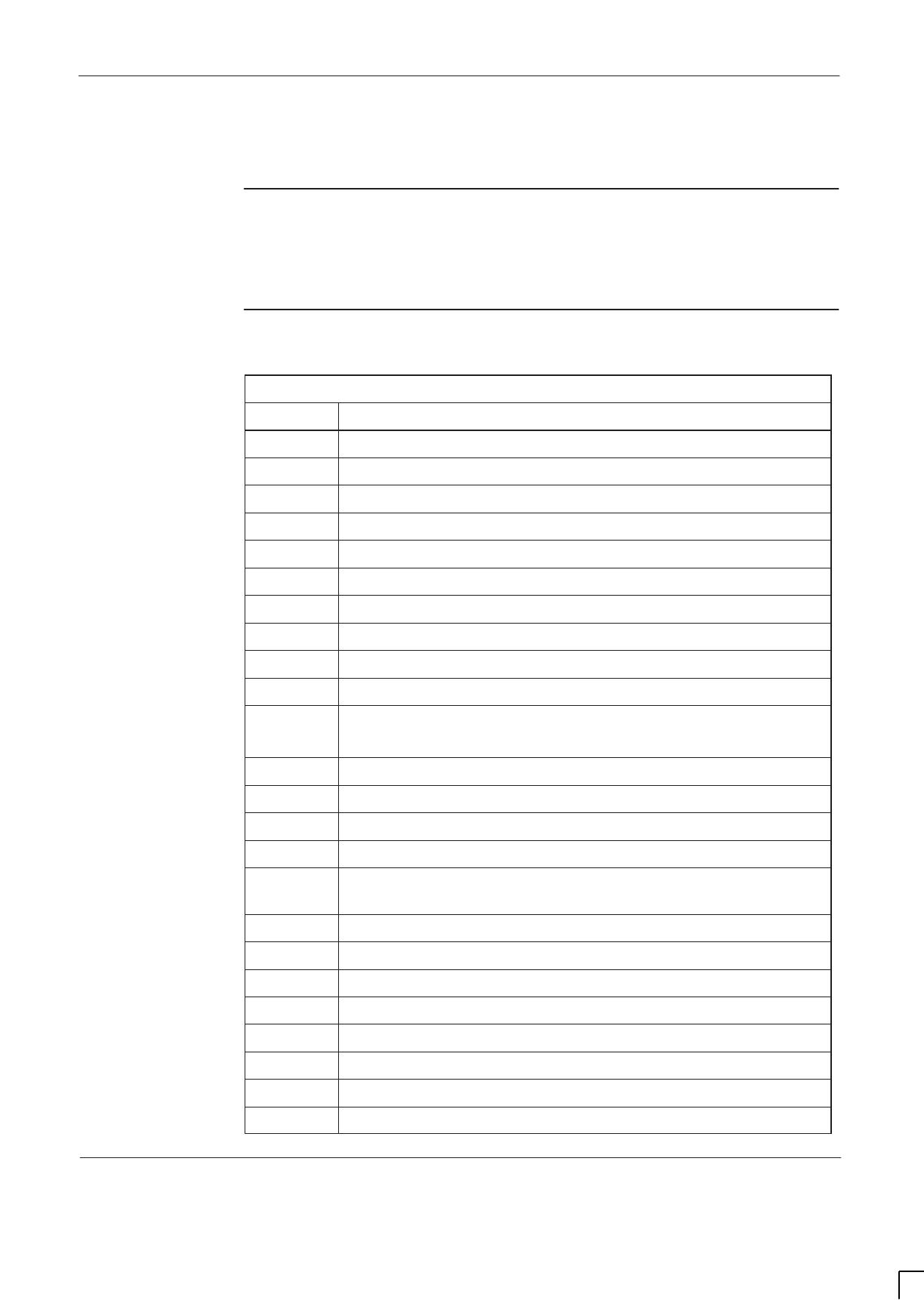
GSM-204-423 Horizonmacro outdoor tool list
31st Oct 01
Installation & Configuration: Horizon
macro
outdoor
68P02902W03-A
CONTROLLED INTRODUCTION
Inst. 1–3
Horizon
macro
outdoor tool list
Overview of tool
list
This section lists the recommended tools required for installing, commissioning
and maintaining the Horizon
macro
outdoor cabinet.
Tool list
Table 1-1 lists the recommended tools for Horizon
macro
outdoor.
Table 1-1 Horizon
macro
outdoor tool list
Quantity Description
1 pair Safety goggles
1Hard hat
1Dust mask
1 pair Ear defenders
1Antistatic wrist strap with coiled lead
1Antistatic mat
1Marker pen
1 Torch
1Socket set (A/F/Metric 13 mm or 1/2 sq drive)
1280 mm insulated adjustable spanner
1 each Combination spanners A/F:
1/4, 5/16, 3/8, 7/16, 1/2, 9/16, 5/8, 11/16, 7/8, 3/4, 1.
1 each Combination spanners metric: 8 mm to 25 mm
1Ratchet ring spanner (15 mm x 13 mm)
1Torque spanner (12 mm)
1Torque wrench (1–25 Nm)
1Torx driver set (T10 to T30) and Security Torx driver set (T10 to
T30)
16 mm torque spanner (for SMA Tx Block connectors)
1Security Allen key set
1Claw hammer
1Pipe cutter
1Junior hacksaw
1300 mm hacksaw
1 pair 150 mm side cutters
1 pair 150 mm heavy duty side cutters
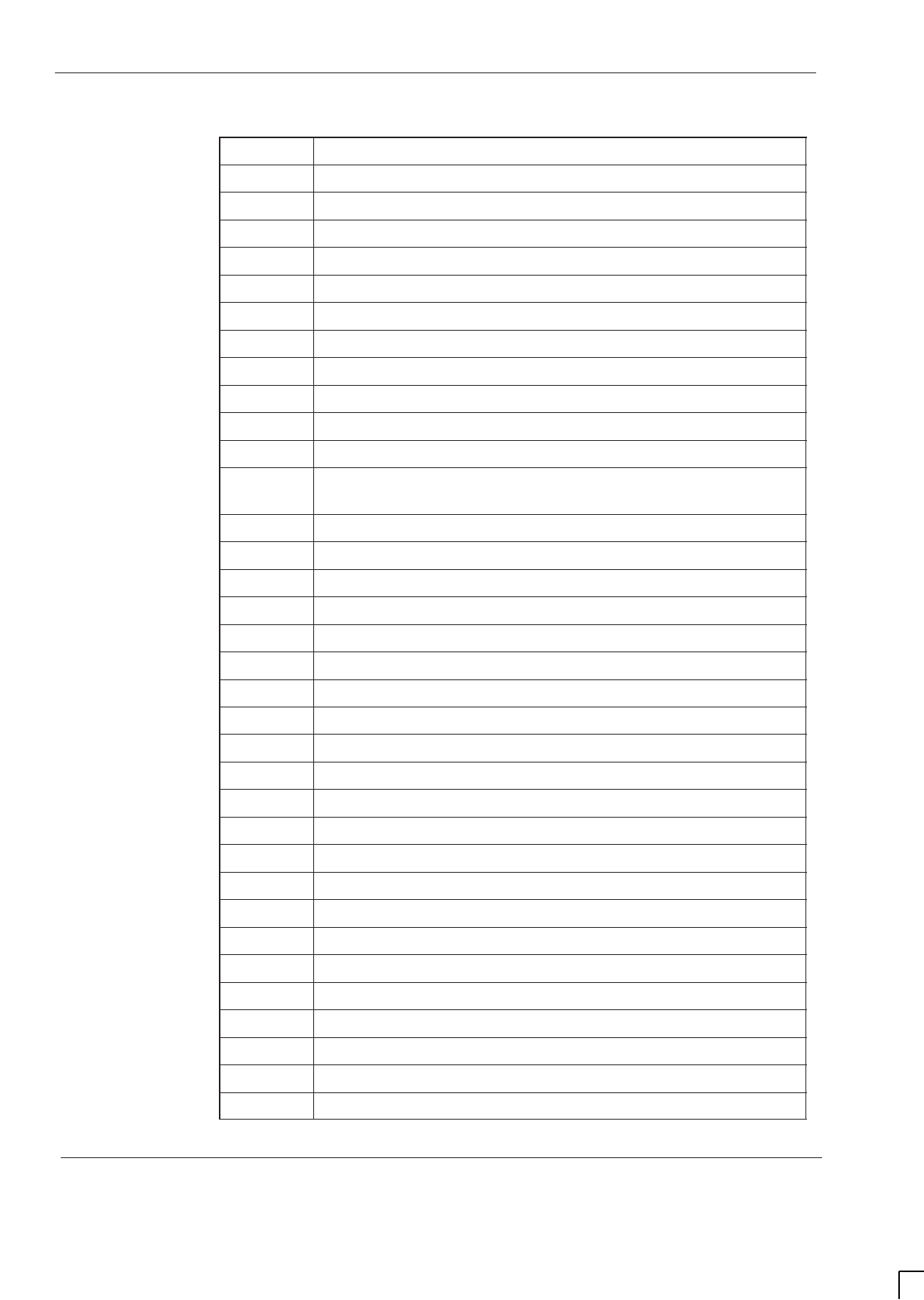
GSM-204-423
Horizonmacro outdoor tool list
31st Oct 01
Inst. 1–4
Installation & Configuration: Horizon
macro
outdoor
CONTROLLED INTRODUCTION
68P02902W03-A
Quantity Description
1 pair Flush cut wire cutters
1 pair Light duty cable cutters
1 pair Cable shears
1Knife with retractable blade
1 pair General purpose pliers
1 pair Snipe nose pliers
1 pair Industrial scissors
1 pair GP serrated jaw pliers
1Set of jeweller’s screwdrivers
1Screwdriver set (including flat and cross-head blades)
1Isolating transformer (suitable for site use)
1Piston drill (suitable for drilling concrete and capable of
accepting an M20 drill bit)
1M20 drill bit
1Drill bit set
16 m 240 V extension cable (twin outlet)
1Soldering iron (dual temperature) with holder
1Coax cable stripper for 2002 (75 ohm coaxial cable)
1Hand crimp tool
1Crimp tool for type 43 connectors
1BNC crimp tool with inserts
1Telephone plug crimp tool
150 mm crimp tool
1Cable tie gun
11.5 m wooden step ladder
1Table vice
1250 mm vice grips
17.5 m tape measure
1300 mm steel rule
1Spirit level (1 m)
1Centre punch
1Pocket scriber
1250 mm half round file
1 pair Straight point tweezers
1Null modem
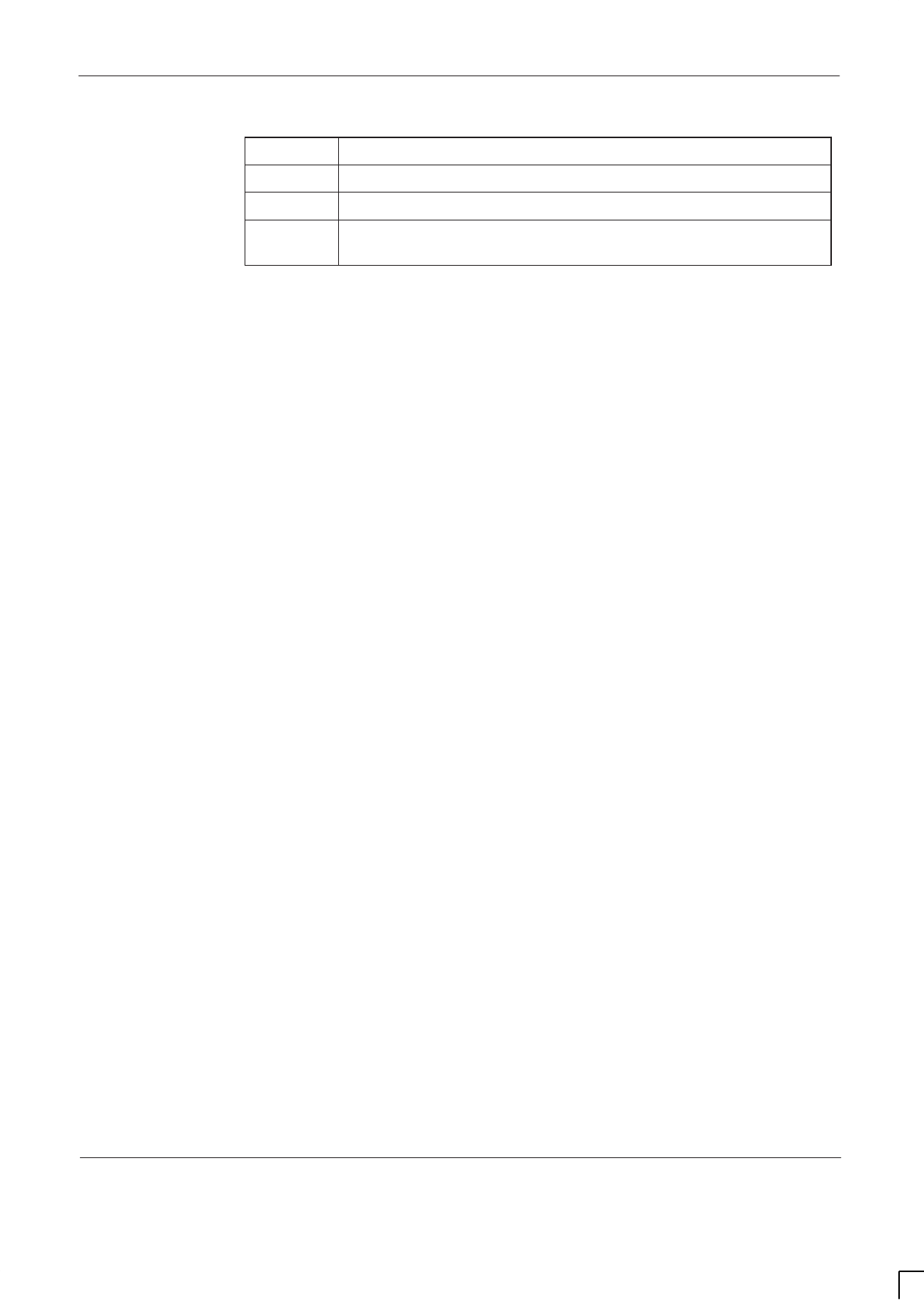
GSM-204-423 Horizonmacro outdoor tool list
31st Oct 01
Installation & Configuration: Horizon
macro
outdoor
68P02902W03-A
CONTROLLED INTRODUCTION
Inst. 1–5
Quantity Description
1RS232 mini tester
1M to M gender changer
4M16 collared eye bolts (min. rating 400 kg)
Bolts must be manufactured to CE conformity.
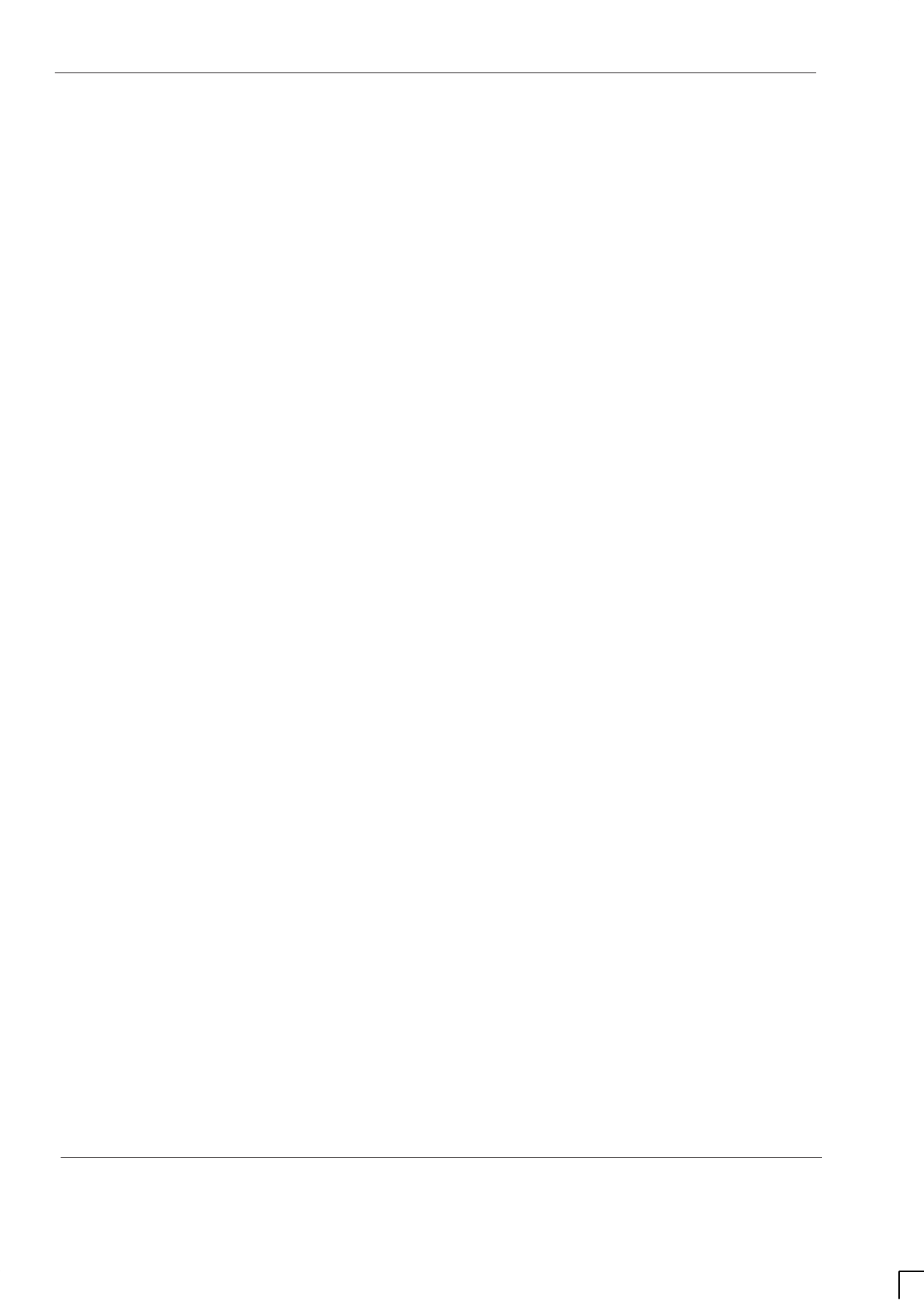
GSM-204-423
Horizonmacro outdoor tool list
31st Oct 01
Inst. 1–6
Installation & Configuration: Horizon
macro
outdoor
CONTROLLED INTRODUCTION
68P02902W03-A
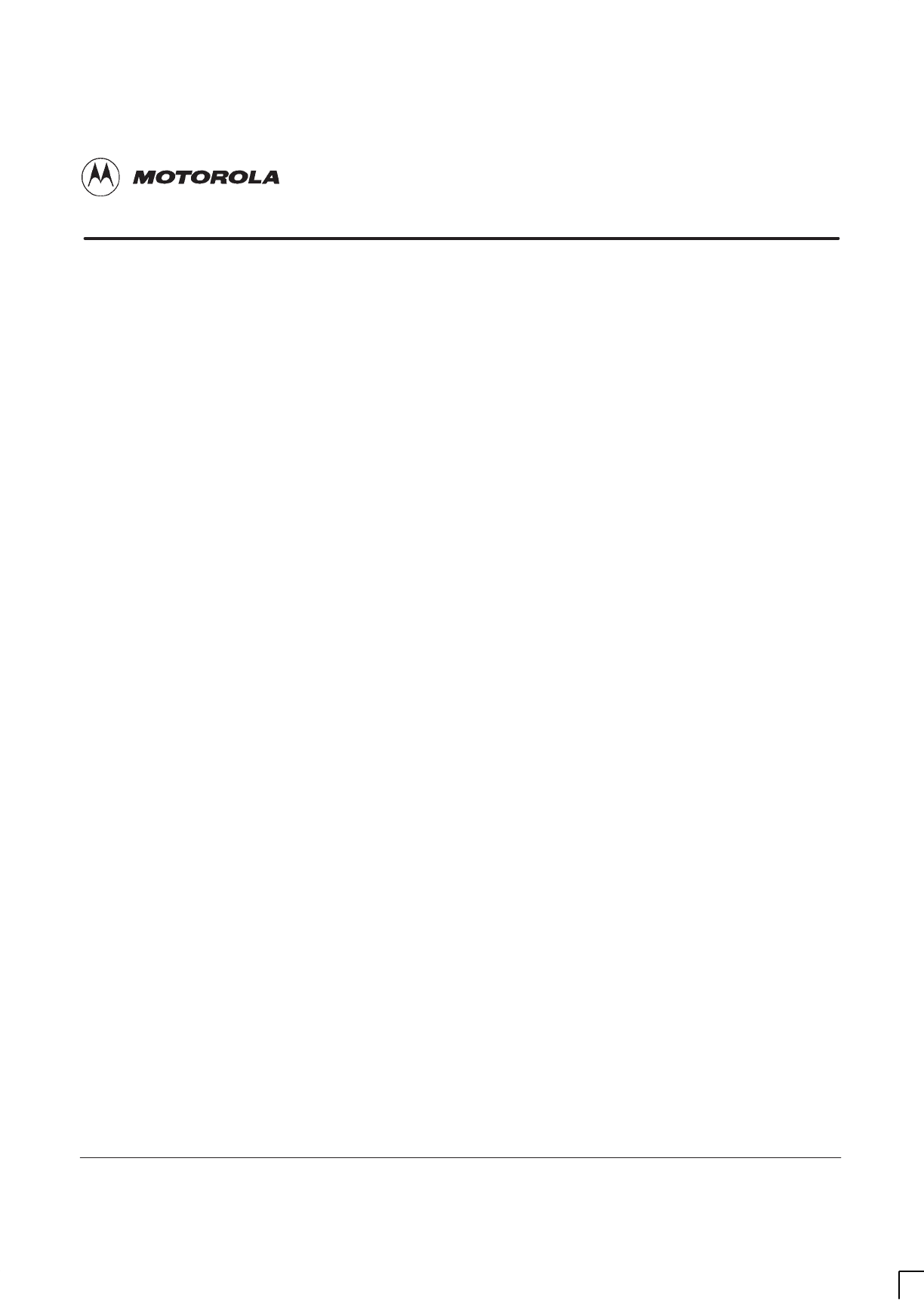
31st Oct 01
Installation & Configuration: Horizon
macro
outdoor
68P02902W03-A
CONTROLLED INTRODUCTION
i
Chapter 2
Site preparation
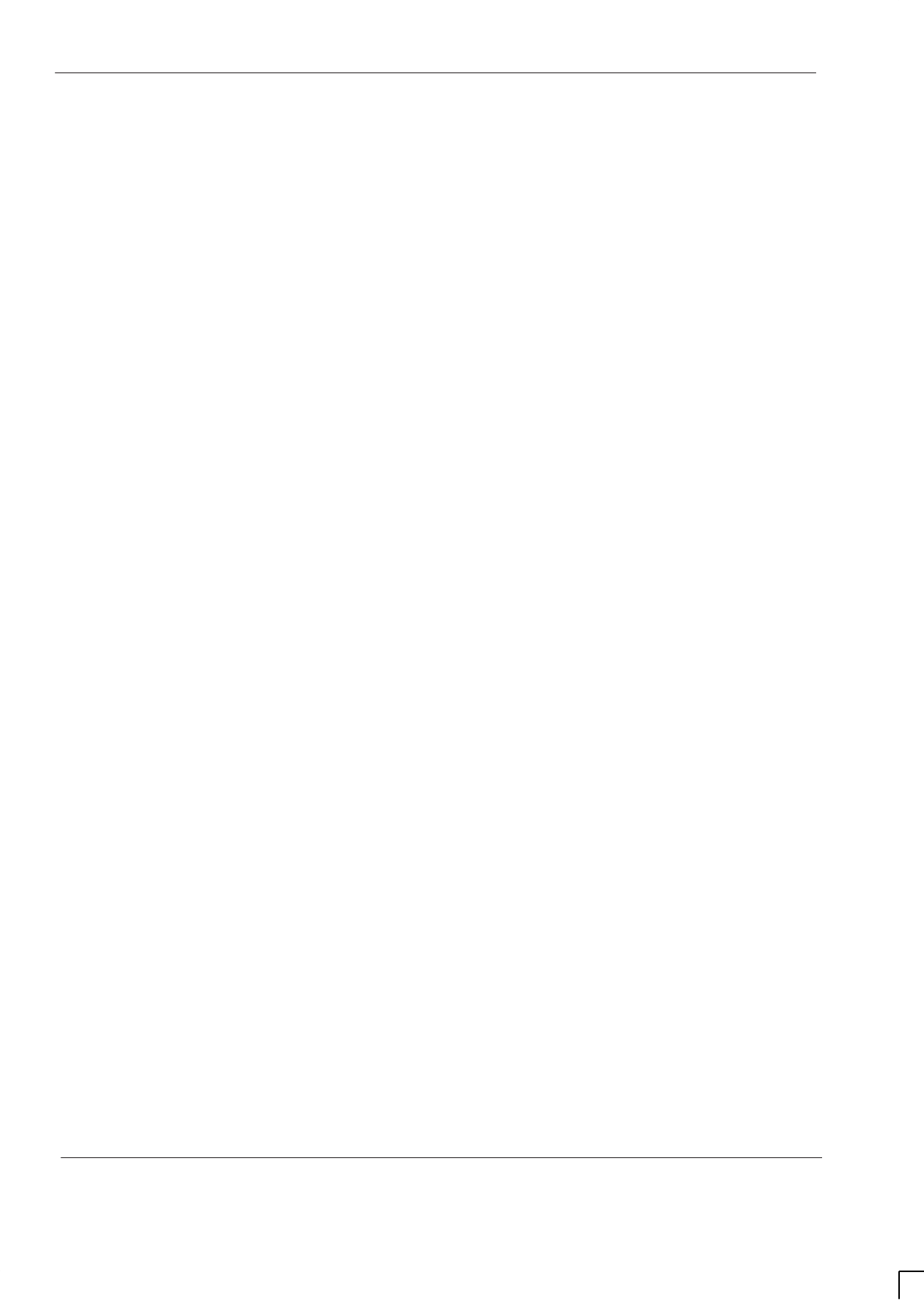
GSM-204-423
31st Oct 01
ii
Installation & Configuration: Horizon
macro
outdoor
CONTROLLED INTRODUCTION
68P02902W03-A
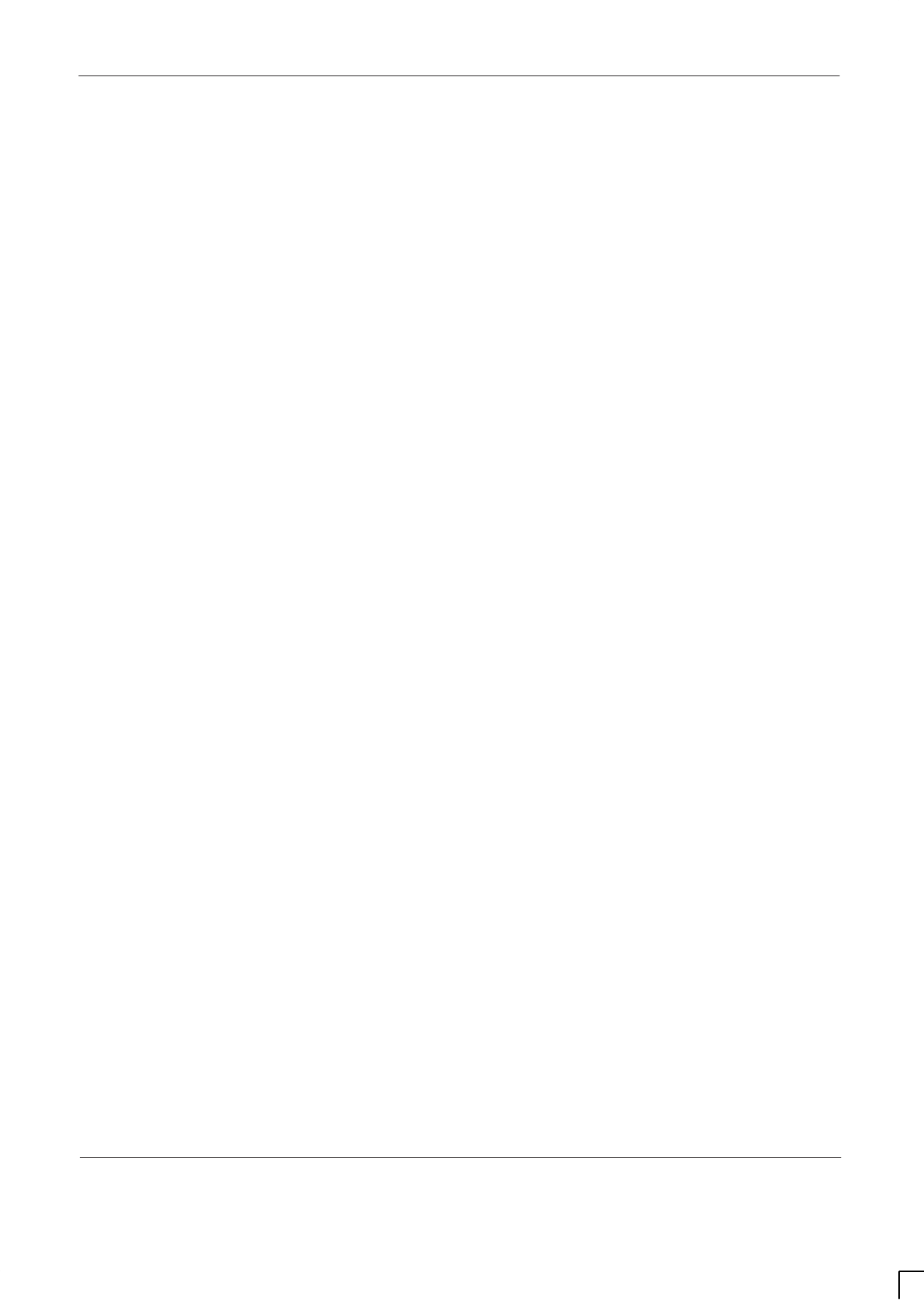
GSM-204-423
31st Oct 01
Installation & Configuration: Horizon
macro
outdoor
68P02902W03-A
CONTROLLED INTRODUCTION
iii
Chapter 2
Site preparation i. . . . . . . . . . . . . . . . . . . . . . . . . . . . . . . . . . . . . . . . . . . . . . .
Preparation overview Inst. 2–1. . . . . . . . . . . . . . . . . . . . . . . . . . . . . . . . . . . . . . . . . . . . . . . . .
Overview to site preparation Inst. 2–1. . . . . . . . . . . . . . . . . . . . . . . . . . . . . . . . . . . . . .
Pre-installation procedures Inst. 2–1. . . . . . . . . . . . . . . . . . . . . . . . . . . . . . . . . . . . . . .
Site requirements and considerations Inst. 2–2. . . . . . . . . . . . . . . . . . . . . . . . . . . . . . . . . . .
Overview of requirements Inst. 2–2. . . . . . . . . . . . . . . . . . . . . . . . . . . . . . . . . . . . . . . .
Outdoor cabinet dimensions Inst. 2–2. . . . . . . . . . . . . . . . . . . . . . . . . . . . . . . . . . . . . .
Cabinet weights Inst. 2–2. . . . . . . . . . . . . . . . . . . . . . . . . . . . . . . . . . . . . . . . . . . . . . . .
Torque values Inst. 2–2. . . . . . . . . . . . . . . . . . . . . . . . . . . . . . . . . . . . . . . . . . . . . . . . . .
Power requirements Inst. 2–3. . . . . . . . . . . . . . . . . . . . . . . . . . . . . . . . . . . . . . . . . . . . .
Environmental requirements Inst. 2–4. . . . . . . . . . . . . . . . . . . . . . . . . . . . . . . . . . . . . .
Structural requirements Inst. 2–5. . . . . . . . . . . . . . . . . . . . . . . . . . . . . . . . . . . . . . . . . .
Outdoor site dimensions Inst. 2–6. . . . . . . . . . . . . . . . . . . . . . . . . . . . . . . . . . . . . . . . .
View of maximum site template layout Inst. 2–7. . . . . . . . . . . . . . . . . . . . . . . . . . . . .
Visiting the site Inst. 2–9. . . . . . . . . . . . . . . . . . . . . . . . . . . . . . . . . . . . . . . . . . . . . . . . . . . . . .
Overview of visiting the site Inst. 2–9. . . . . . . . . . . . . . . . . . . . . . . . . . . . . . . . . . . . . .
Before departure to site Inst. 2–9. . . . . . . . . . . . . . . . . . . . . . . . . . . . . . . . . . . . . . . . . .
Arrival at all sites Inst. 2–9. . . . . . . . . . . . . . . . . . . . . . . . . . . . . . . . . . . . . . . . . . . . . . . .
Arriving at occupied sites Inst. 2–9. . . . . . . . . . . . . . . . . . . . . . . . . . . . . . . . . . . . . . . .
Arriving at unoccupied sites Inst. 2–10. . . . . . . . . . . . . . . . . . . . . . . . . . . . . . . . . . . . . .
Leaving site during installation and optimization Inst. 2–10. . . . . . . . . . . . . . . . . . . .
Rubbish removal Inst. 2–10. . . . . . . . . . . . . . . . . . . . . . . . . . . . . . . . . . . . . . . . . . . . . . . .
Rural sites Inst. 2–11. . . . . . . . . . . . . . . . . . . . . . . . . . . . . . . . . . . . . . . . . . . . . . . . . . . . .
On site safety Inst. 2–11. . . . . . . . . . . . . . . . . . . . . . . . . . . . . . . . . . . . . . . . . . . . . . . . . .
Preparing the site Inst. 2–12. . . . . . . . . . . . . . . . . . . . . . . . . . . . . . . . . . . . . . . . . . . . . . . . . . . .
Introduction to site preparation Inst. 2–12. . . . . . . . . . . . . . . . . . . . . . . . . . . . . . . . . . .
Base site structure Inst. 2–12. . . . . . . . . . . . . . . . . . . . . . . . . . . . . . . . . . . . . . . . . . . . . .
Site requirements Inst. 2–12. . . . . . . . . . . . . . . . . . . . . . . . . . . . . . . . . . . . . . . . . . . . . . .
Site access Inst. 2–12. . . . . . . . . . . . . . . . . . . . . . . . . . . . . . . . . . . . . . . . . . . . . . . . . . . .
Site layout Inst. 2–12. . . . . . . . . . . . . . . . . . . . . . . . . . . . . . . . . . . . . . . . . . . . . . . . . . . . .
Earthing the site Inst. 2–13. . . . . . . . . . . . . . . . . . . . . . . . . . . . . . . . . . . . . . . . . . . . . . . . . . . . .
Overview Inst. 2–13. . . . . . . . . . . . . . . . . . . . . . . . . . . . . . . . . . . . . . . . . . . . . . . . . . . . . .
Earthing requirements Inst. 2–13. . . . . . . . . . . . . . . . . . . . . . . . . . . . . . . . . . . . . . . . . . .
Earth electrode system Inst. 2–13. . . . . . . . . . . . . . . . . . . . . . . . . . . . . . . . . . . . . . . . . .
Cross bonding Inst. 2–14. . . . . . . . . . . . . . . . . . . . . . . . . . . . . . . . . . . . . . . . . . . . . . . . . .
Earthing procedure Inst. 2–14. . . . . . . . . . . . . . . . . . . . . . . . . . . . . . . . . . . . . . . . . . . . . .
Earth electrode testing Inst. 2–14. . . . . . . . . . . . . . . . . . . . . . . . . . . . . . . . . . . . . . . . . . .
Preparing the foundation Inst. 2–16. . . . . . . . . . . . . . . . . . . . . . . . . . . . . . . . . . . . . . . . . . . . . .
Overview of foundation preparation Inst. 2–16. . . . . . . . . . . . . . . . . . . . . . . . . . . . . . .
Horizonmacro foundation Inst. 2–16. . . . . . . . . . . . . . . . . . . . . . . . . . . . . . . . . . . . . . . .
Preparing the foundation Inst. 2–17. . . . . . . . . . . . . . . . . . . . . . . . . . . . . . . . . . . . . . . . .
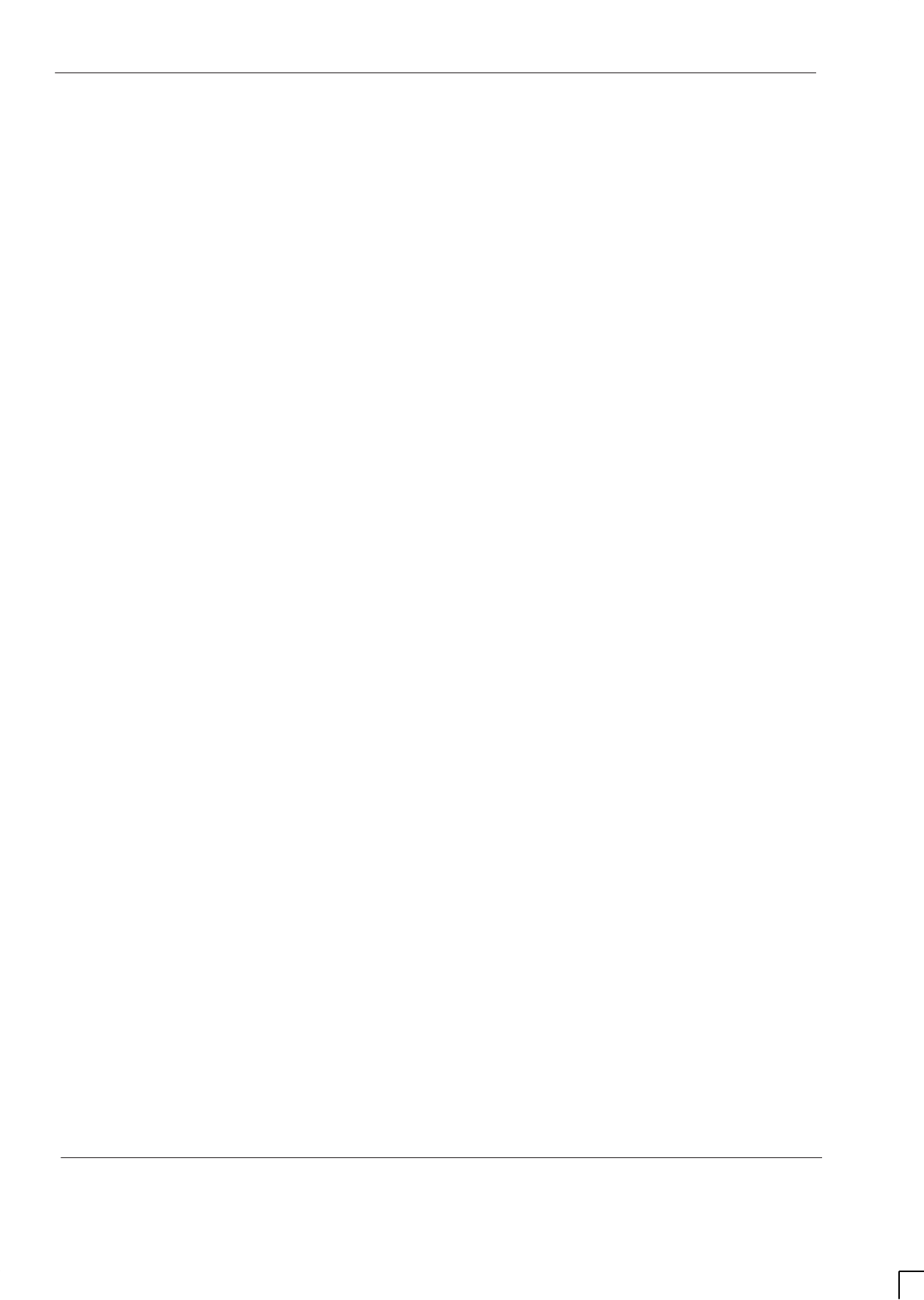
GSM-204-423
31st Oct 01
iv
Installation & Configuration: Horizon
macro
outdoor
CONTROLLED INTRODUCTION
68P02902W03-A
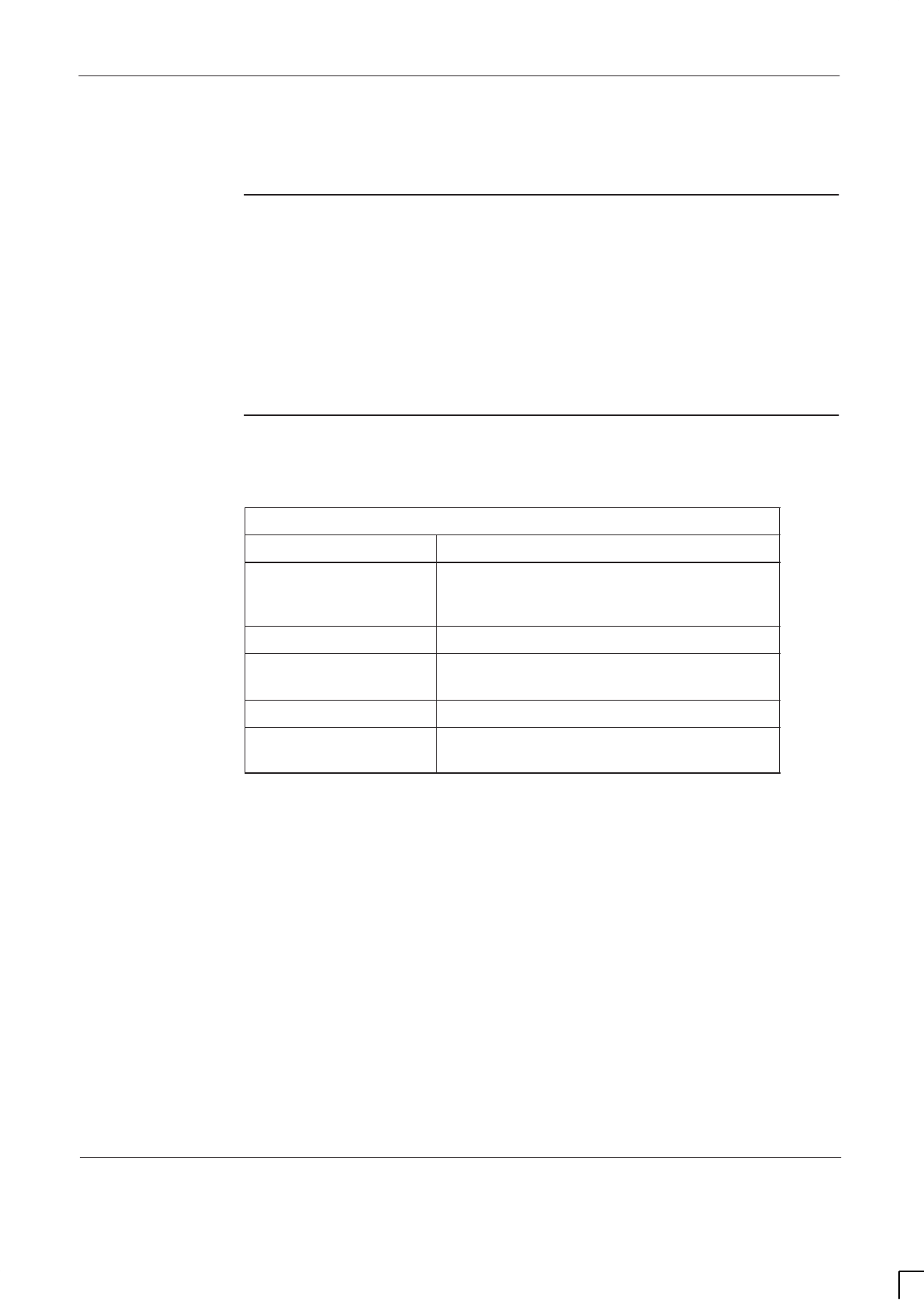
GSM-204-423 Preparation overview
31st Oct 01
Installation & Configuration: Horizon
macro
outdoor
68P02902W03-A
CONTROLLED INTRODUCTION
Inst. 2–1
Preparation overview
Overview to site
preparation
This chapter contains:
Information that should be read for initial planning.
Information that should be read for safe completion of procedures.
Pre-installation procedures to be followed to prepare the site before
beginning the installation.
Pre-installation
procedures
Pre-installation for the cabinet comprises the sections listed in Table 2-1.
Table 2-1 Pre-installation sections in this chapter
Section Description
Site requirements and
considerations Details mechanical, electrical and structural
parameters to be taken into account when
selecting a site.
Visiting the site Defines the site operating procedures.
Preparing the site Details general site construction
parameters.
Earthing the site Earthing techniques.
Preparing the
foundation Details the procedures for laying the cabinet
foundations and fitting the cabinet template.
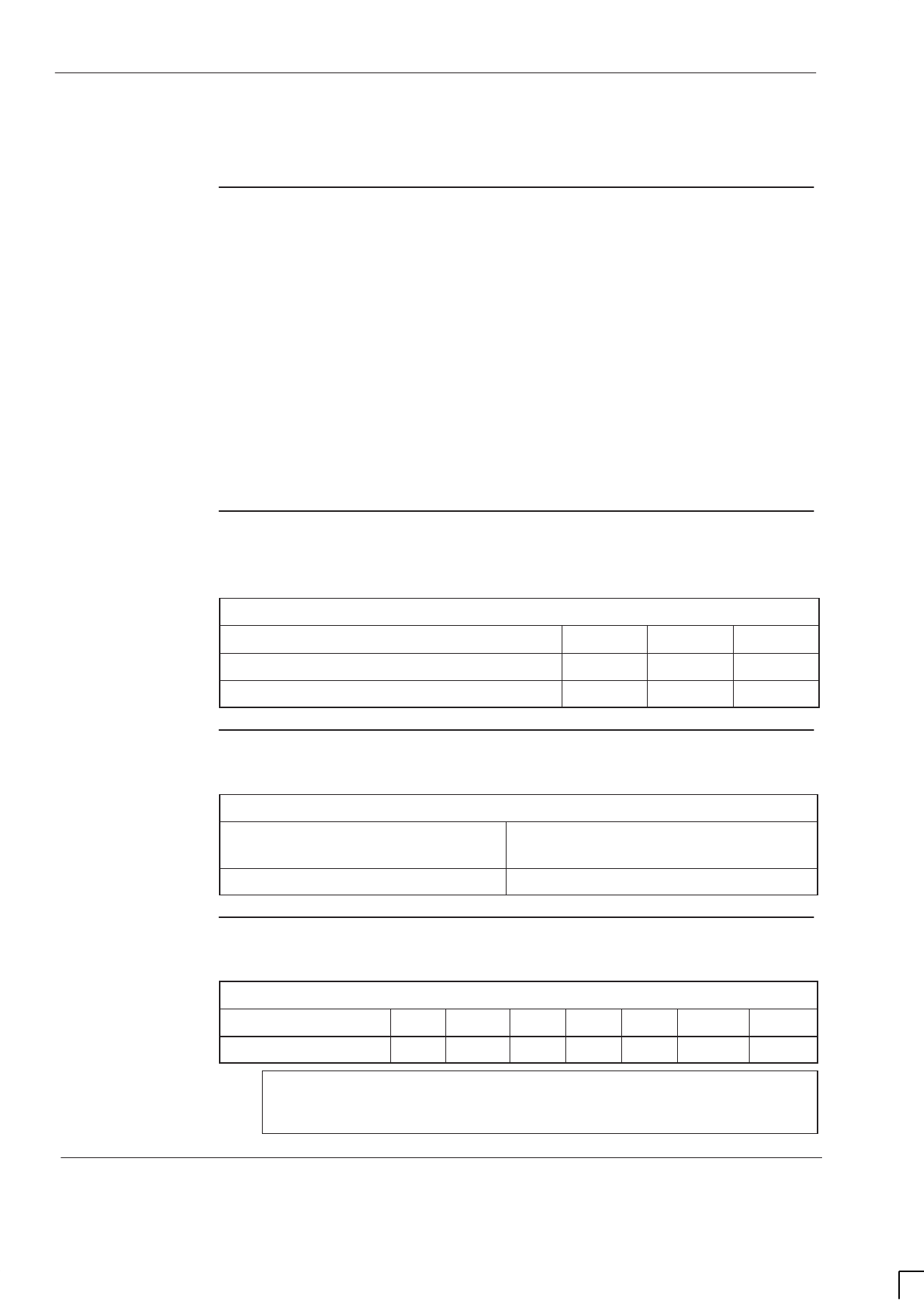
GSM-204-423
Site requirements and considerations
31st Oct 01
Inst. 2–2
Installation & Configuration: Horizon
macro
outdoor
CONTROLLED INTRODUCTION
68P02902W03-A
Site requirements and considerations
Overview of
requirements
The base site area, where the equipment is to be installed, must meet:
Structural requirements including:
– Space for all conditions, including maintenance, expansion and
associated cables.
– Allowance for cabinet height.
– Allowance for weight, including that for potential additions on
expansion.
– Additional space to allow doors to be fully opened to 120 degrees.
Environmental and power requirements, as defined in manual
specifications.
Outdoor cabinet
dimensions
The dimensions of cabinets are shown in Table 2-2.
Table 2-2 Cabinet dimensions
Cabinet type Height Width Depth
Horizon
macro
outdoor cabinet 1364 mm 1300 mm 594 mm
Horizon
macro
auxiliary equipment housing 1364 mm 604mm 594 mm
Cabinet weights
The cabinet weights are shown in Table 2-3.
Table 2-3 Outdoor cabinet weights
BTS cabinet with six transceivers Auxiliary equipment housing empty
/ 16 batteries fitted
360 kg 110 kg / 500 kg
Torque values
Use the torque values listed in Table 2-4 during installation (see NOTE for M12).
Table 2-4 Torque values for all cabinet screws/bolts or RF connectors
Screw/bolt size M4 M6 M8 M10 SMA N-type 7/16
Torque value (Nm) 2.2 3.4 5 10 1 3.4 25
NOTE The setting of torque value for M12 anchor screws/bolts
depends on local supplies. Refer to the manufacturer’s
data for correct values.
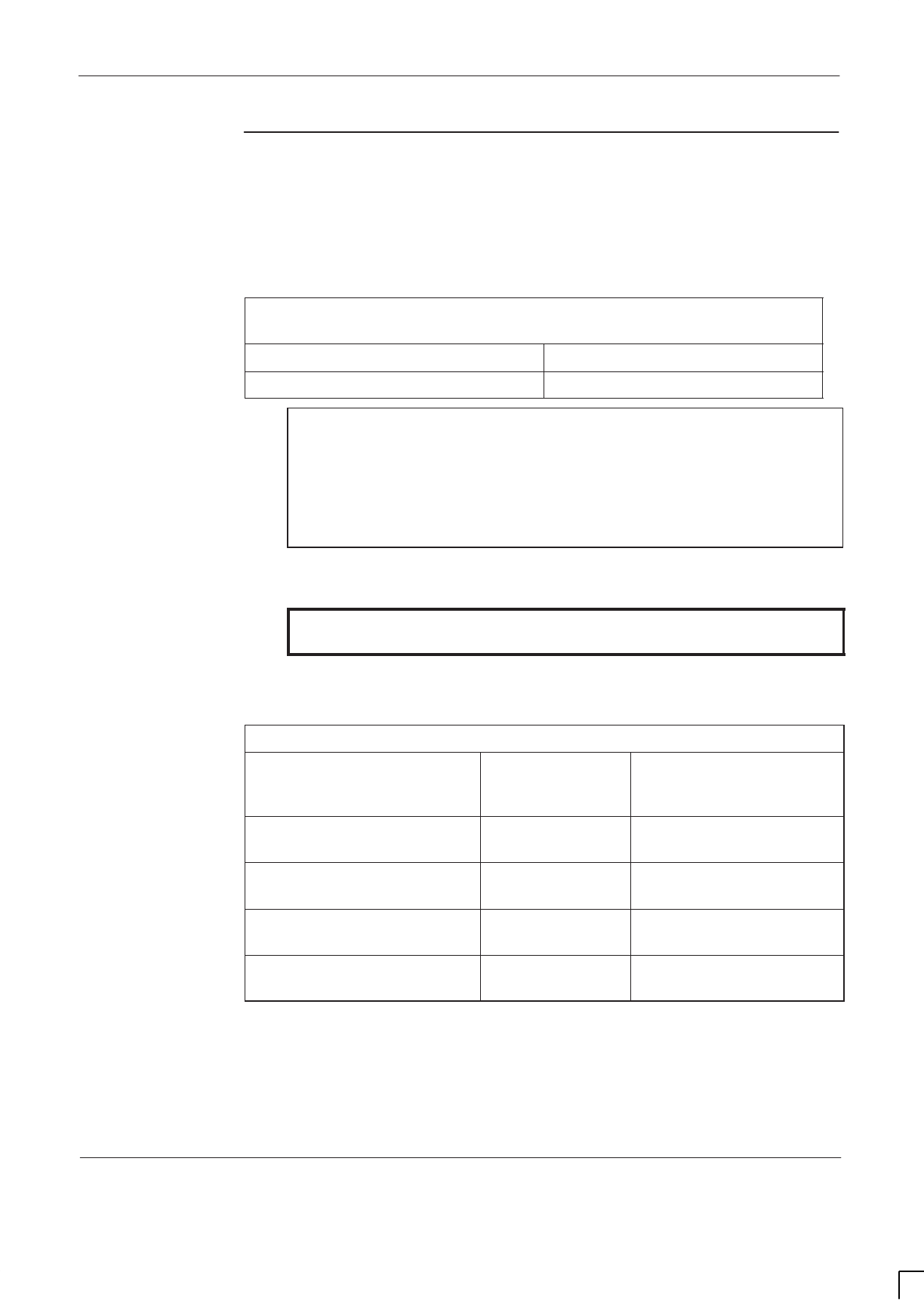
GSM-204-423 Site requirements and considerations
31st Oct 01
Installation & Configuration: Horizon
macro
outdoor
68P02902W03-A
CONTROLLED INTRODUCTION
Inst. 2–3
Power
requirements
The power requirements of cabinets depends on the configuration.
Power consumption (dc and ac)
Table 2-5 lists typical and maximum power consumption values.
Table 2-5 Power consumption of full cabinet, including digital redundancy
and external battery charging
Typical measured consumption Maximum power consumption
2200 W 5600 W
NOTE Maximum power consumption figures are theoretical
values derived under extreme conditions and are affected
by variables such as temperature, component tolerances,
transmission power and supply voltage. Although these
figures must be considered when planning site power
requirements, typical measured consumption values will
be lower.
Cabinet input power supply requirements
WARNING All cabinets and supply cables must be protected by an
upstream fuse or circuit breaker.
Table 2-6 lists the power supply requirements for the different power supply
options.
Table 2-6 Main outdoor cabinet power requirements
Nominal voltage Supply voltage
and frequency
range
Current supply
maximum
110 V ac single phase 88 to 134 V ac
at 45 to 66 Hz 54.4 A
(at nominal voltage)
230 V ac single phase 176 to 265 V ac
at 45 to 66 Hz 26.1 A
(at nominal voltage)
230 V ac three phase
and neutral (star) 176 to 265 V ac
at 45 to 66 Hz 26.1 A
(at nominal voltage)
230 V ac three phase
without neutral (delta) 176 to 265 V ac
at 45 to 66 Hz 26.1 A
(at nominal voltage)
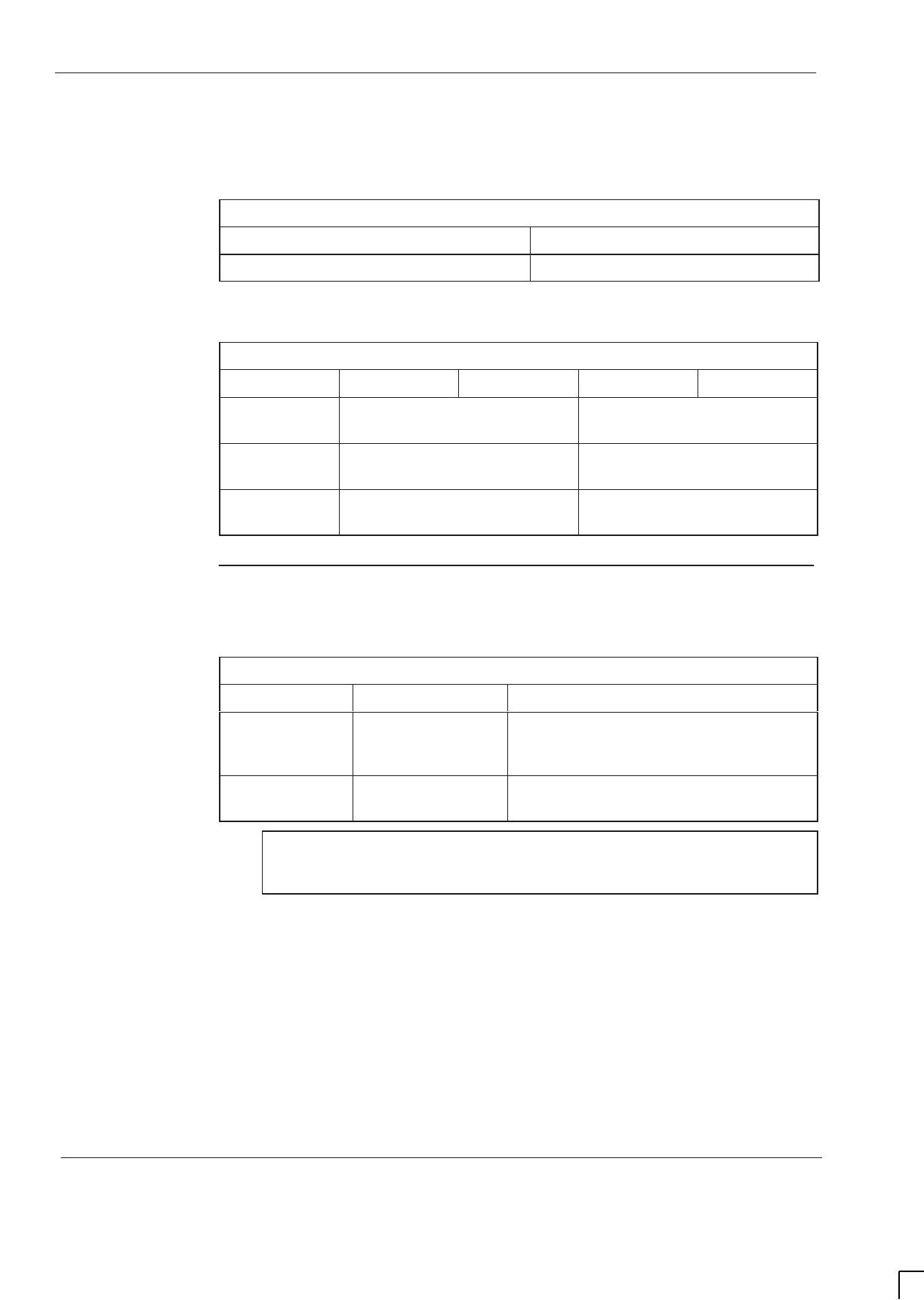
GSM-204-423
Site requirements and considerations
31st Oct 01
Inst. 2–4
Installation & Configuration: Horizon
macro
outdoor
CONTROLLED INTRODUCTION
68P02902W03-A
RF output power
Table 2-7 lists the RF power output of the CTU types.
Table 2-7 CTU RF power output at Tx connector
GSM850 and EGSM900 DCS1800 and PCS1900
60 W (47.8 dBm) +/–1.0 dBm 50 W (47.0 dBm) +/– 1.0 dBm
Table 2-8 lists the expected power output from the various Tx blocks for both
types of CTU.
Table 2-8 RF power output at cabinet after Tx blocks
Tx block GSM850 EGSM900 DCS1800 PCS1900
TDF 40 W
(46.0 dBm) 32 W
(45.1 dBm)
DCF 20 W
(43.0 dBm) 16 W
(42.1 dBm)
DDF 8.5 W
(39.3 dBm) 7 W
(38.5 dBm)
Environmental
requirements
Table 2-9 lists the operating environmental limits.
Table 2-9 Environmental limits
Environment Temperature Relative Humidity
Operating –40 C to +50 C
plus a solar gain
of 1.2 kW/m2
5% to 100% relative humidity, not to
exceed 30 g water / m3 air.
Storage –45 C to +70 C8% to 100% relative humidity, not to
exceed 30 g water / m3 air.
NOTE This specification is valid up to 3 km altitude,
corresponding to an atmospheric pressure range of 648 to
1048 millibars.
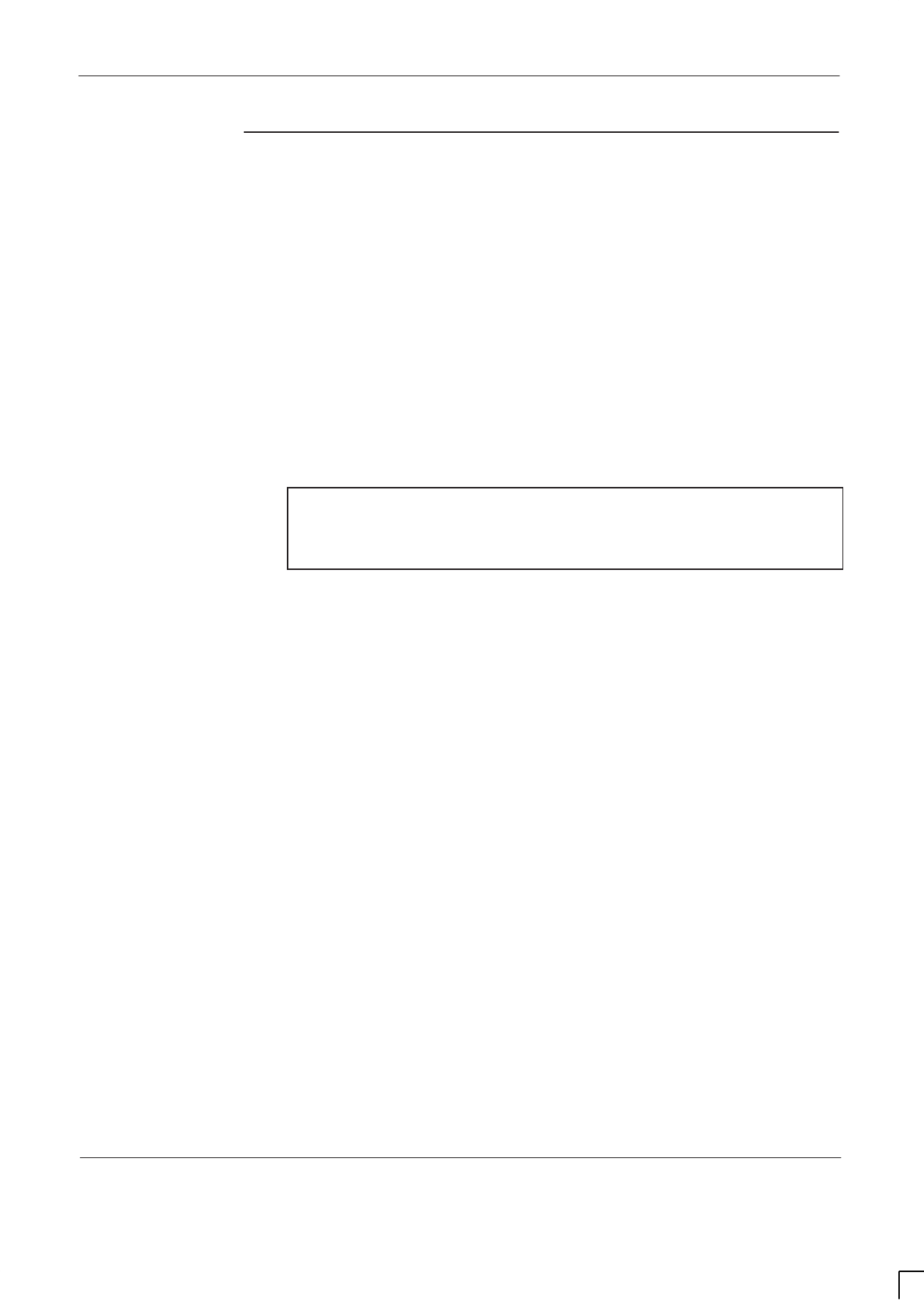
GSM-204-423 Site requirements and considerations
31st Oct 01
Installation & Configuration: Horizon
macro
outdoor
68P02902W03-A
CONTROLLED INTRODUCTION
Inst. 2–5
Structural
requirements
There must be adequate clearance at the front of (648 mm), and above
(1900 mm), the equipment for operation and maintenance purposes. It is also
recommended that there is adequate side clearance to open the doors to 120°
(see Figure 2-1), and to fit the optional shroud on the cable entry side.
The foundation or structure on which the BTS cabinet is mounted must be of
sufficient strength to withstand 105 knot (120 mph) winds on the cabinet front or
rear and a maximum gross weight of 360 kgs.
The cabinet ventilation entry and exhaust is solely from the bottom front of the
cabinet, allowing a cabinet to be placed against a wall. However, a minimum
clearance of 240 mm is required on the cable entry side, between the cabinet
and obstructions, such as a wall or another cabinet.
Allow 1000 mm clearance at front and side where possible, to facilitate
installation and maintenance.
NOTE In seismically active areas, Motorola suggest using a
qualified structural engineer to assess frame mounting
requirements, such as floor construction, mounting
anchors and cell site construction.
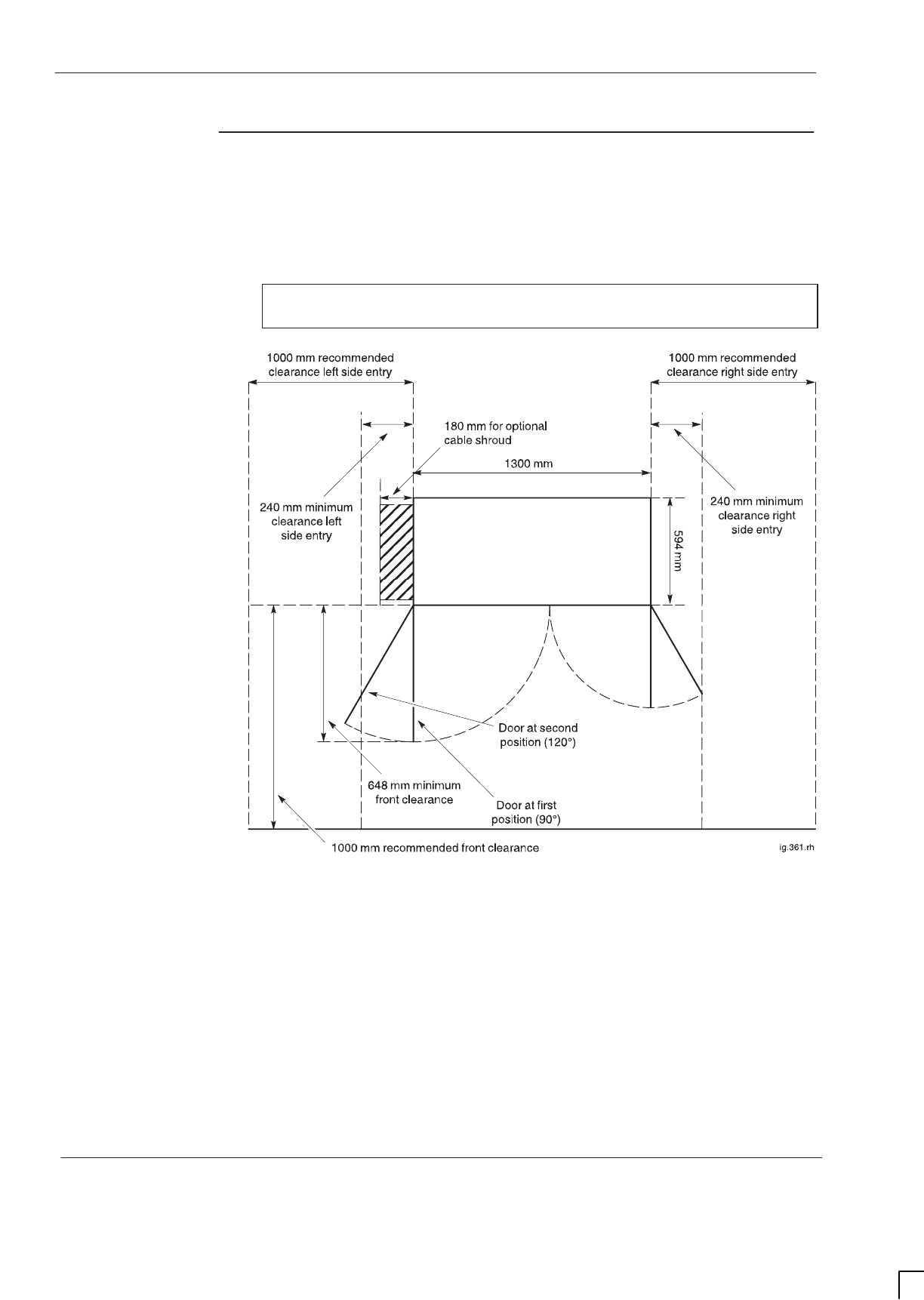
GSM-204-423
Site requirements and considerations
31st Oct 01
Inst. 2–6
Installation & Configuration: Horizon
macro
outdoor
CONTROLLED INTRODUCTION
68P02902W03-A
Outdoor site
dimensions
Basic outdoor site
Figure 2-1 shows the site layout plan for a single cabinet with dimensions and
required clearances (optional auxiliary equipment housing not shown).
NOTE Allow 180 mm additional side clearance if a cable shroud
is to be fitted.
OUTDOOR CABINET
Figure 2-1 Outdoor cabinet site layout plan view (cable entry on left side)
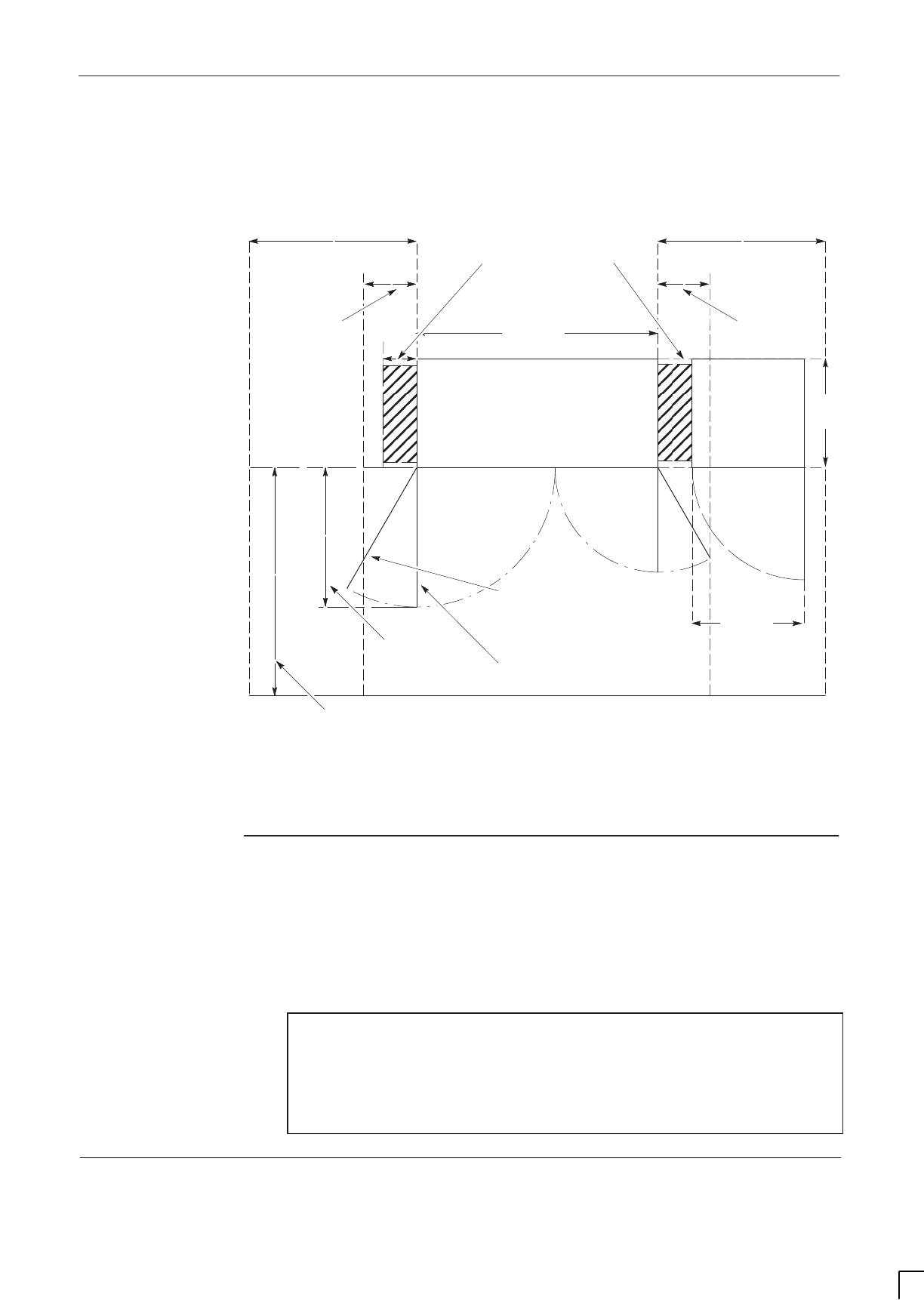
GSM-204-423 Site requirements and considerations
31st Oct 01
Installation & Configuration: Horizon
macro
outdoor
68P02902W03-A
CONTROLLED INTRODUCTION
Inst. 2–7
Outdoor site with auxiliary equipment housing
Figure 2-2 shows the site layout plan for a single cabinet and optional auxiliary
equipment housing with dimensions and required clearances.
Door at second position
(120°)
Door at first position
(90°)
1000 mm recommended
clearance left side entry 1000 mm recommended
clearance right side entry
240 mm
minimum
clearance left
side entry
1000 mm recommended front clearance
648 mm
minimum front
clearance
240 mm
minimum
clearance right
side entry
OUTDOOR CABINET
1300 mm
594
mm
180 mm for optional cable
shroud
AEH
604 mm
for optional AEH
Figure 2-2 Outdoor cabinet site layout plan view (including optional equipment)
View of
maximum site
template layout
Figure 2-3 shows a plan view of the template layout for the maximum site
configuration. Using the dimensions and clearances shown, the site layout for
any combination of BTS cabinets and auxiliary equipment housings can be
calculated.
NOTE If a steel structure is to be used instead of a concrete
base, the dimensions shown in Figure 2-3 can be used to
determine the location of the mounting bolt holes.
Figure 2-3 only shows template and mounting hole
dimensions and clearances, cabinet dimensions are
slightly larger.
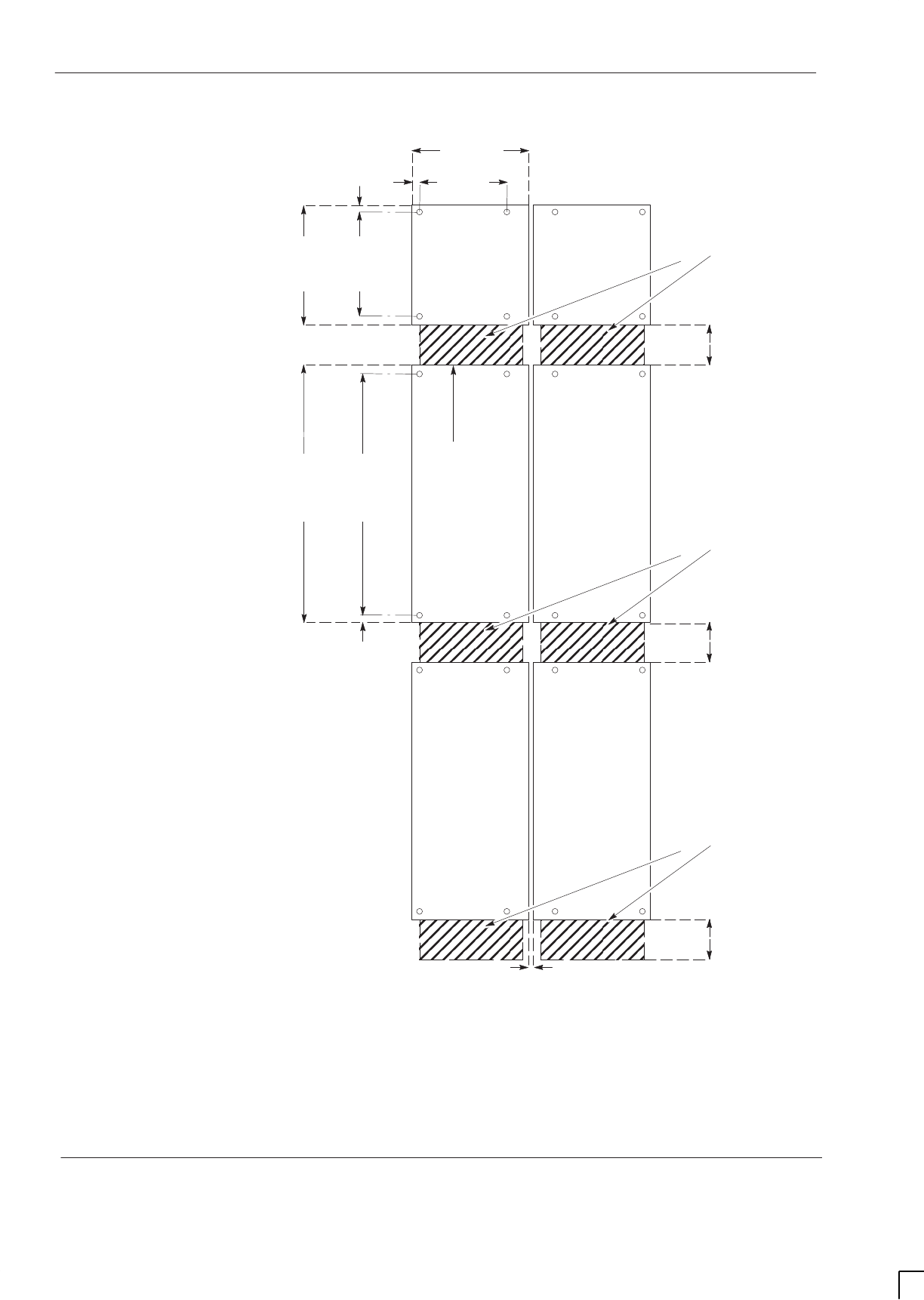
GSM-204-423
Site requirements and considerations
31st Oct 01
Inst. 2–8
Installation & Configuration: Horizon
macro
outdoor
CONTROLLED INTRODUCTION
68P02902W03-A
10
mm
18 mm
AEH
template
AEH
template
BTS
CABINET
template
BTS
CABINET
template
BTS
CABINET
template
BTS
CABINET
template
POSITION OF
SHROUDS
(if used)
POSITION OF
SHROUDS
(if used)
POSITION OF
SHROUDS
(if used) 180 mm180 mm180 mm
597 mm
544 mm
26.5 mm
21.5 mm
1293 mm
1250 mm
531.5 mm
405 mm
Figure 2-3 Plan view of template layout for maximum site configuration
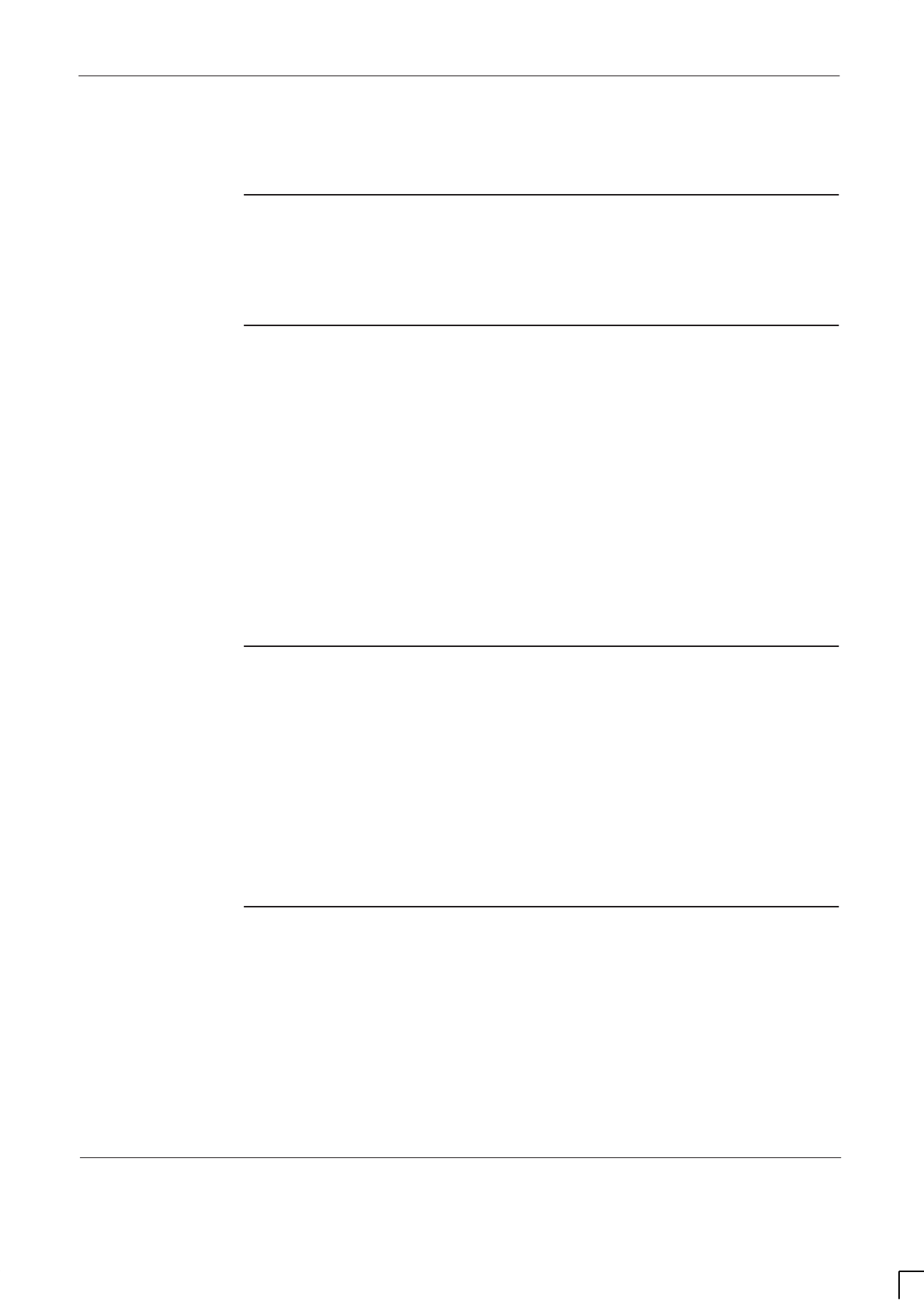
GSM-204-423 Visiting the site
31st Oct 01
Installation & Configuration: Horizon
macro
outdoor
68P02902W03-A
CONTROLLED INTRODUCTION
Inst. 2–9
Visiting the site
Overview of
visiting the site
When preparing to do work at a site and upon arrival, follow the instructions
provided in this section.
Before
departure to
site
Before departing to the site:
1. Ensure that team members have adequate test equipment, tools, and
hardware to carry out the task. Check for any special requirements.
2. Contact the person in charge of the site to advise of the team’s estimated
time of arrival and the expected duration of their stay on the site. This will
usually have been dealt with previously, but it is always advisable to make
sure that the information has been passed on.
3. Ensure that the team read the site access details on each visit to a site as
local regulations may change.
Arrival at all
sites
When entering any site:
1. Do not enter the site until contact has been made with the OMC-R or
MSC. Contact the local OMC-R and local MSC to announce the team’s
arrival before entering the site.
2. Enter the site and check for site alarms, for example intruder alarms, that
may have been activated by entry.
3. Read any local instructions.
Arriving at
occupied sites
In any exchange or occupied building, contact the person in charge or caretaker
of the site, who will explain local regulations. This person may also advise teams
on parking, rubbish removal, and canteen facilities.
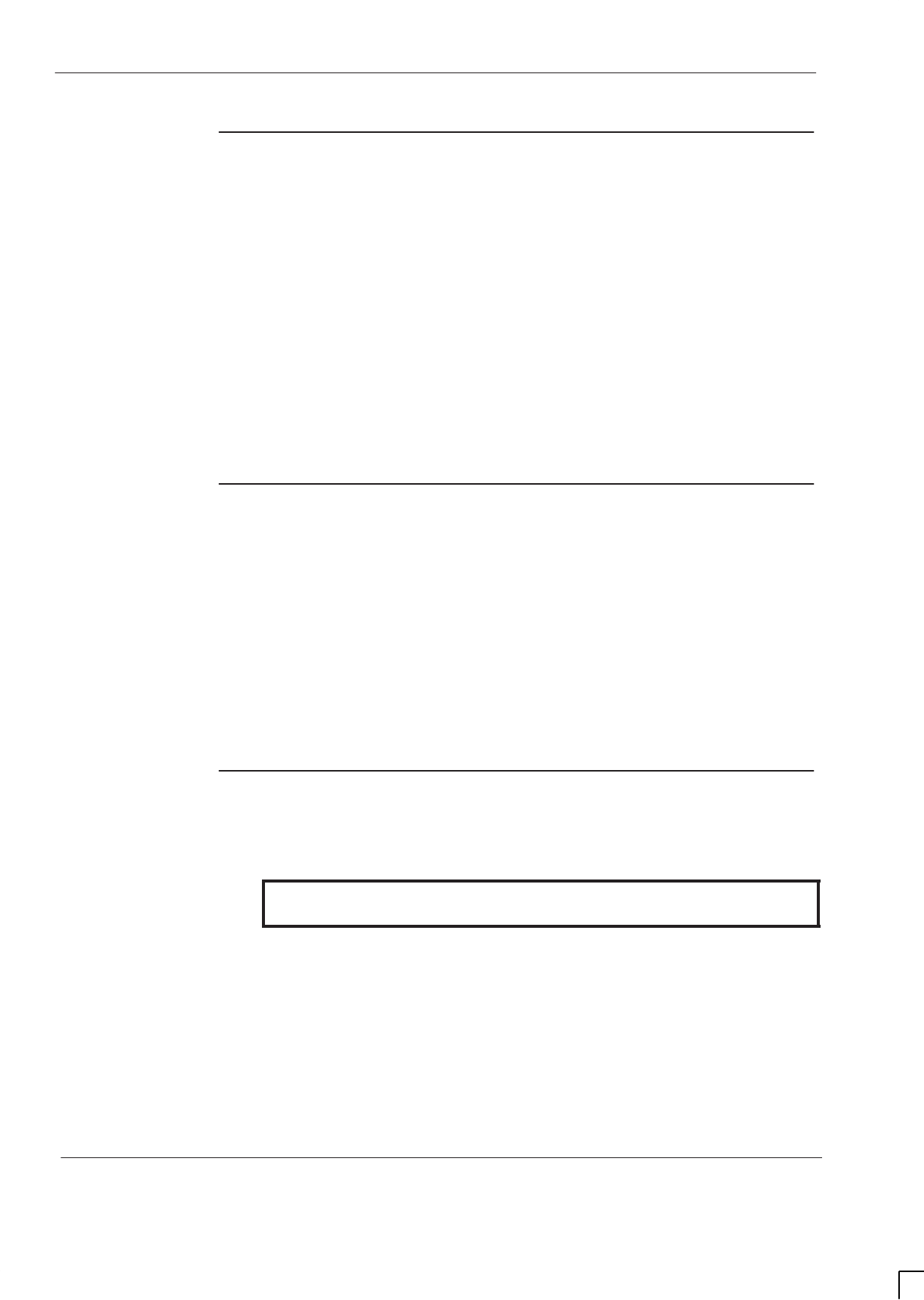
GSM-204-423
Visiting the site
31st Oct 01
Inst. 2–10
Installation & Configuration: Horizon
macro
outdoor
CONTROLLED INTRODUCTION
68P02902W03-A
Arriving at
unoccupied
sites
When entering an unoccupied site:
1. Do not enter the site until contact has been made with the OMC-R or
MSC. Contact the local OMC-R and local MSC to announce the team’s
arrival before entering the site.
2. Enter the site and check for site alarms, for example intruder alarms, that
may have been activated by entry.
3. Advise the local OMC-R or MSC that the team is on site and indicate the
expected duration of time on site.
4. Arrange with the OMC-R or MSC to check the E1/T1 links as soon as
possible.
Leaving site
during
installation and
optimization
When leaving a site:
1. Contact the local OMC-R or MSC to announce the team’s departure.
2. Out of hours, if an alarm is fitted and the local MSC staff have gone home,
contact the Network Control Centre or OMC-R and inform them of the
team’s departure.
3. Sign out of the site as necessary.
Rubbish
removal
Clear rubbish from the site on completion of the job, unless otherwise indicated
by the customer.
WARNING Do not burn rubbish, as packaging might give off toxic
gases.
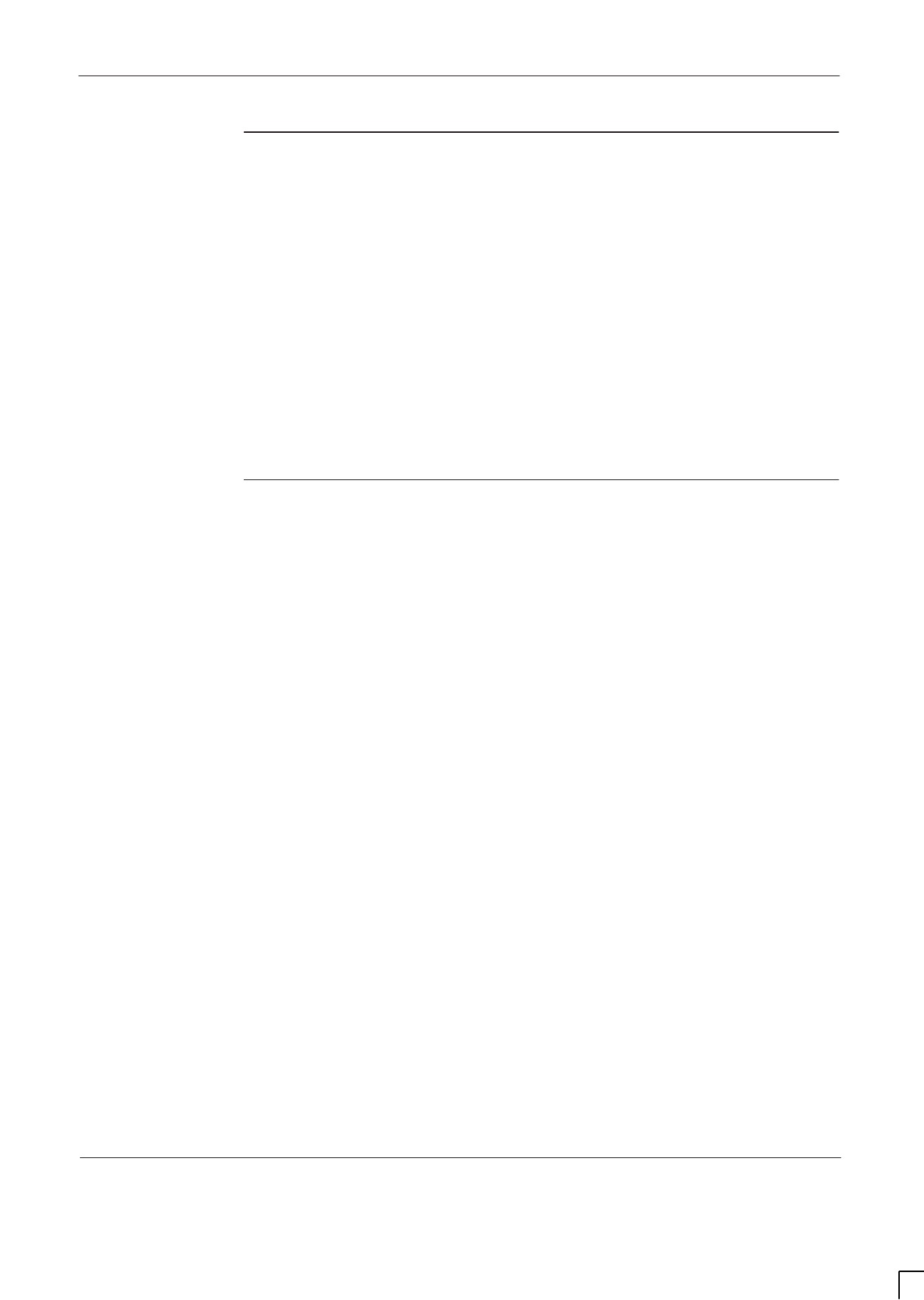
GSM-204-423 Visiting the site
31st Oct 01
Installation & Configuration: Horizon
macro
outdoor
68P02902W03-A
CONTROLLED INTRODUCTION
Inst. 2–11
Rural sites
It is the responsibility of the senior member of the team to ensure that all
personnel on site are aware of the country code and, especially with respect to
water authority sites, any relevant health regulations.
Adhere to these points of the Country Code:
Guard against all risk of fire.
Fasten all gates (remember site visits could be traced back if a complaint
is made).
Leave no litter.
Drive carefully on country roads and observe speed restrictions at all
times.
Keep to the paths/tracks across farm land.
On site safety
All personnel must:
Ensure that under no circumstances should anyone move cabinets without
assistance. Cabinets must be safely positioned at all times.
Wear supplied safety helmets when antenna or overhead work is in
progress, and when local regulations require them.
Wear supplied safety goggles and dust masks when drilling. This is
particularly important when drilling overhead ironwork.
Wear supplied ear protectors while drilling is in progress.
Wear approved safety footwear when moving heavy equipment.
Stop any work that you are supervising should any person in your team not be
properly protected, or be unaware of safety requirements.
When installing cable ties, even temporarily, cut the excess or tail properly. This
is to prevent sharp edges inflicting injury when not cut flush with the locking
edge.
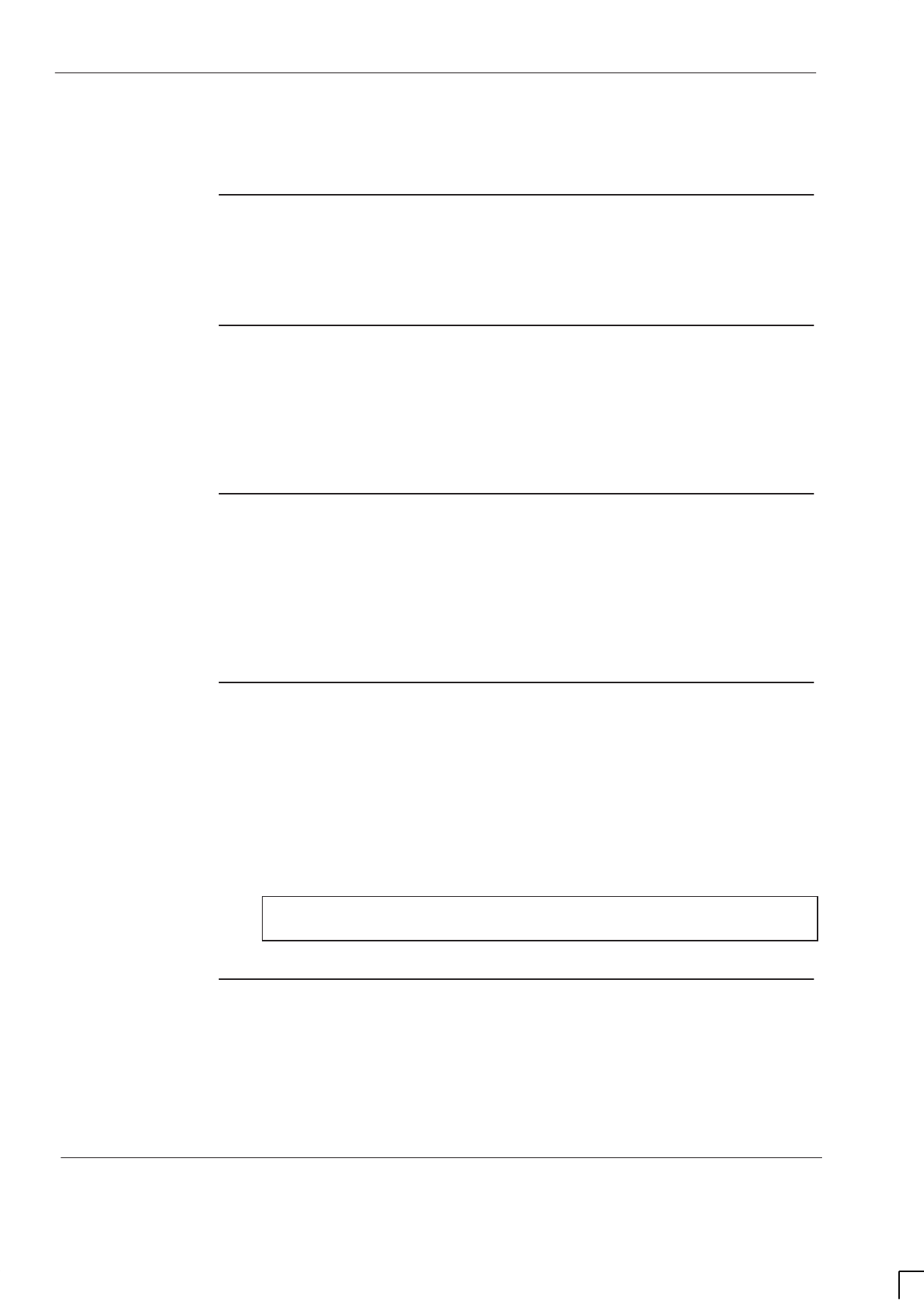
GSM-204-423
Preparing the site
31st Oct 01
Inst. 2–12
Installation & Configuration: Horizon
macro
outdoor
CONTROLLED INTRODUCTION
68P02902W03-A
Preparing the site
Introduction to
site preparation
This section provides a general overview on the preparation of a site, and site
requirements. For specific sites, refer to the site-specific documentation.
Base site
structure
The base site structure should be designed to meet accepted cellular system
specifications. Additionally, the site must meet the environmental and electrical
operating criteria. See Site requirements and considerations earlier in this
chapter.
Site
requirements
The customer should provide secure access, free from unauthorized personnel,
ample protection from fire, and adequate lighting and clearance at the front and
rear of the equipment for operation and maintenance. Additionally, four cable
ducts with sufficient space for communications cables, power cables, earth
cables, and antenna RF cables should be provided.
Site access
The site access road and equipment receiving area must be constructed of
asphalt, concrete, or other suitable load bearing aggregate, capable of
supporting the transportation vehicle and the cabinet. The area available and
overhead clearance must be sufficient to accommodate turning or reversing of
the transportation vehicle, and to allow the vehicle to depart after unloading.
Ensure there is a minimum overhead clearance of 6 m to enable the
Horizon
macro
cabinet to be lifted from the transport vehicle. Take special care if
the cabinet has to be lifted in the vicinity of overhead cables.
NOTE Ensure the areas, for unloading and installation are clear
of standing water, fallen leaves, mud, and building debris.
Site layout
The site layout plans are provided in the Site requirements and
considerations section. Figure 2-1, Figure 2-2 and Figure 2-3 show the site
layout plans with dimensions.
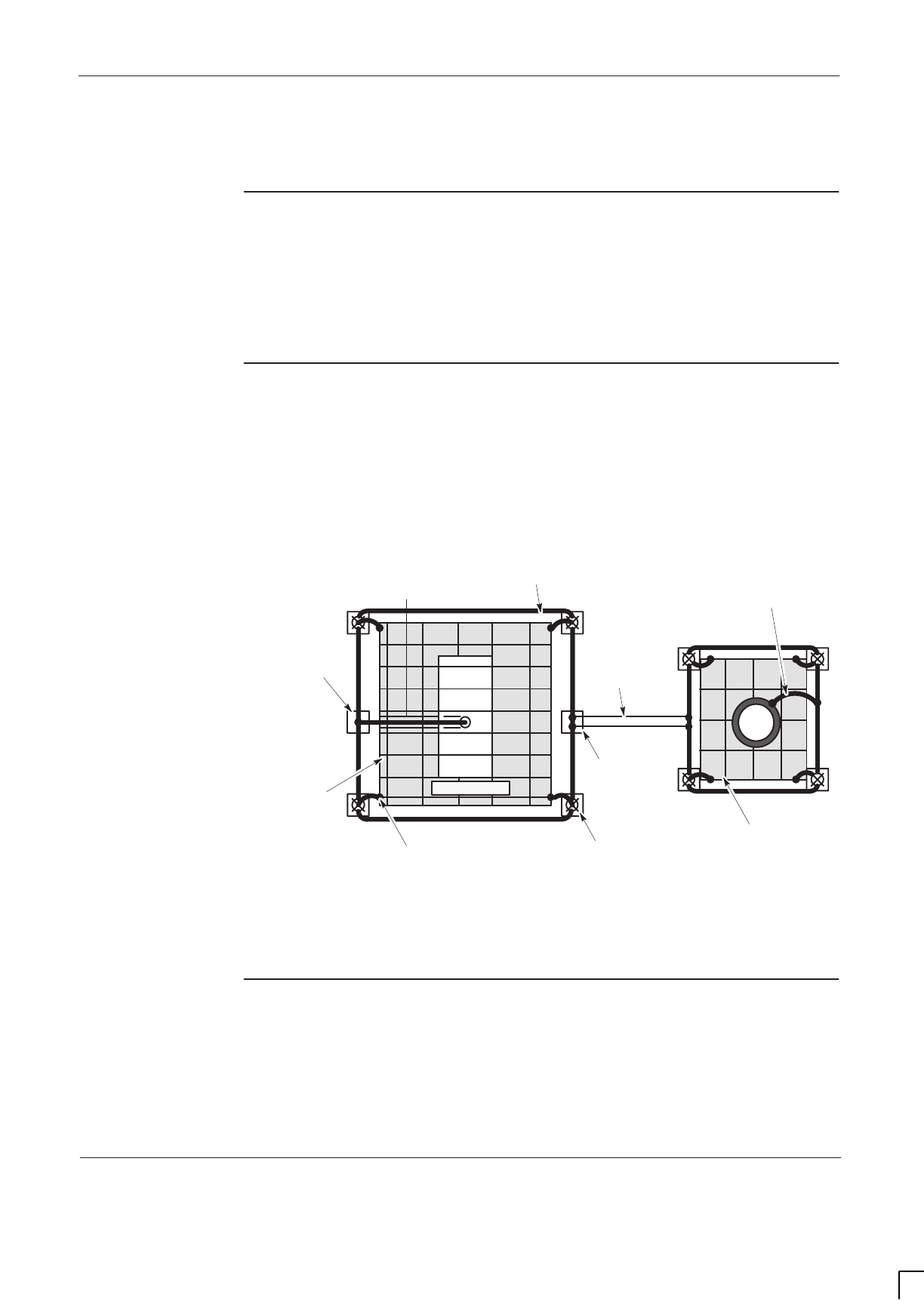
GSM-204-423 Earthing the site
31st Oct 01
Installation & Configuration: Horizon
macro
outdoor
68P02902W03-A
CONTROLLED INTRODUCTION
Inst. 2–13
Earthing the site
Overview
The following provides information on suggested earthing procedures for an
outdoor site.
The separate earth systems must be isolated from each other to facilitate
periodic testing of the earth systems. Earth inspection pits are provided for this
purpose.
Earthing
requirements
Each cabinet site external earth must be assessed on an individual site basis,
as conditions will vary considerably depending on local soil conditions and site
topography. It is essential that a site survey and soil resistance test be
performed before installation. The site architect defines the site and foundation
earthing requirements to ensure a resistance of less than 10 ohms. A typical site
earthing plan is shown in Figure 2-4.
FOUNDATION
CABINET(S)
COPPER
TAPE
EARTH CONDUCTOR
INTO CABINET VIA
PVC PIPE
CROSS BONDING
MAST BONDING (ONE
SHOWN FOR CLARITY)
FOUNDATION
METALWORK BONDING
FOUNDATION
METALWORK BONDING
FOUR PLACES MINIMUM
FOUNDATION
METALWORK
TEST
CONNECTION
INSPECTION
BOX
EARTH RODS WITH
INSPECTION BOXES FOR
SYSTEM TEST
CROSS
BONDING TEST
CONNECTION
INSPECTION
BOX
MAST
Figure 2-4 Typical site earthing plan for open field site
Earth electrode
system
The earth electrode system consists of a series of interconnected earth
electrodes (minimum of four) that are located outside the foundation reinforcing
metalwork. Refer to Figure 2-4 for details. The earth rods should be connected
together using TCO30 solid tape conductors, avoiding any sharp bends; a
minimum bend radius of 250 mm is recommended.
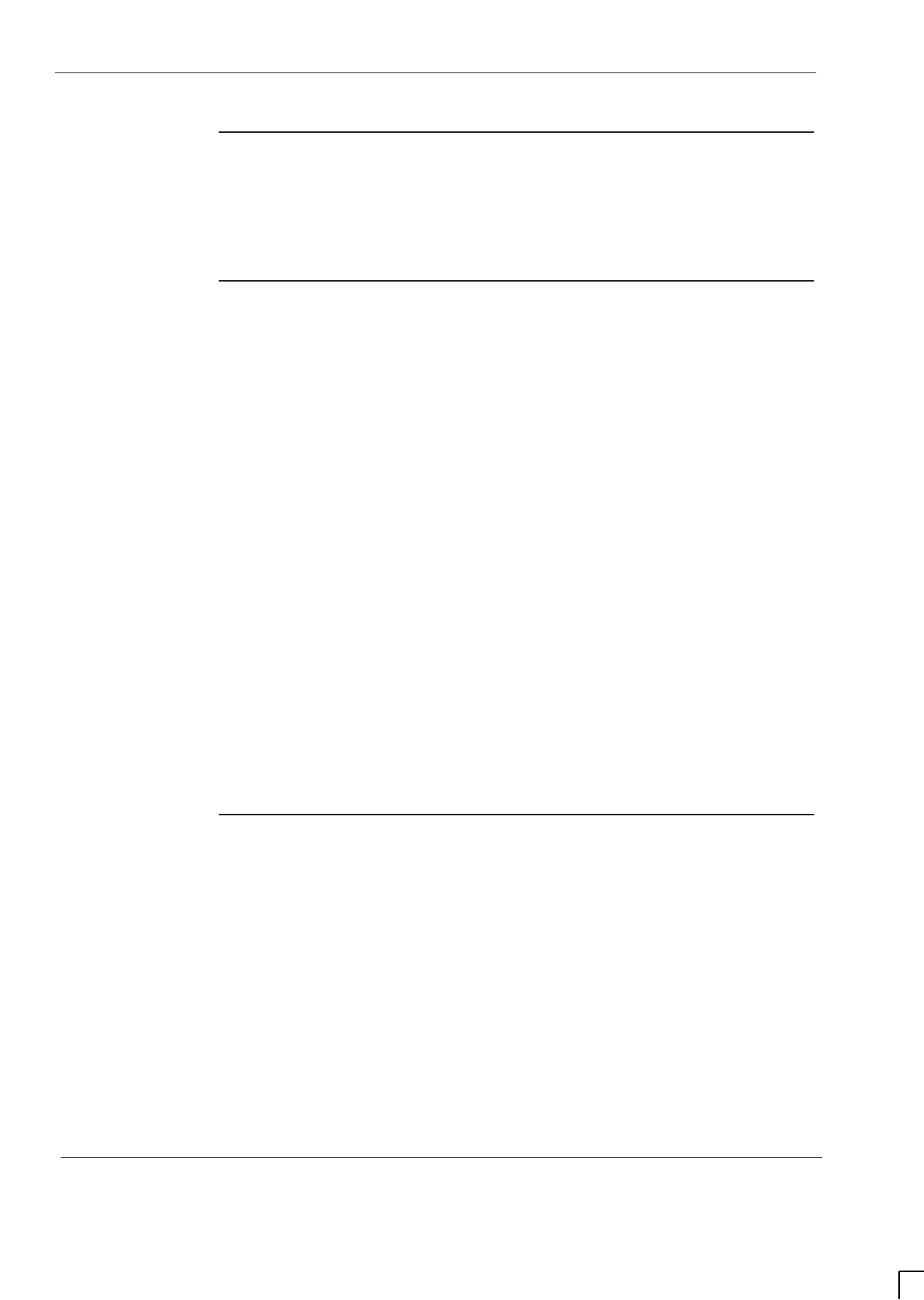
GSM-204-423
Earthing the site
31st Oct 01
Inst. 2–14
Installation & Configuration: Horizon
macro
outdoor
CONTROLLED INTRODUCTION
68P02902W03-A
Cross bonding
Foundation metalwork must be connected to the earth electrode network. The
earth system must also be cross-bonded to an adjacent antenna mast, with two
connections made between the two systems. All earth cable terminations must
be crimped, clamped or welded; soldered joints are not permitted.
Earthing
procedure
The cabinet equipment must be earthed as detailed in this procedure. Make
provision for routeing the earth cables into the site and to the cabinet before
beginning installation of the system racks.
Excavate the site to accommodate the foundation to a depth determined by the
site architect. For the earth components to be used, refer to Figure 2-4 and
proceed as follows:
1. Drive a minimum of four copper earth rods 2.4 m long below the surface,
and connect these rods together with 70 mm cross-sectional area (CSA)
solid conductor.
2. Connect the earth rods to the cabinet earth busbar via a 70 mm CSA solid
conductor.
3. Check that the earth electrode installation resistance is less than 10 ohms.
If the resistance is greater than 10 ohms, install more earth rods to bring
the resistance within specification.
4. Cross-bond the earth system to the adjacent antenna mast earth with
conductors of 70 mm CSA, buried at a depth of not less than 500 mm.
5. Bond equipment such as fences, fuel tanks, metal buildings, or steel
building skids associated with the site to the closest earthing rod or
bonding wire.
Earth electrode
testing
Earth electrodes should be tested as detailed in BS7671 16th Edition or
equivalent national and regional regulations. One of three methods of earth
electrode test (earth mat) is used:
Fall of potential.
61.8% rule.
Slope method.
The method of test to be used at a specific site is determined by the site
conditions, the extent of the earth system and the limitations of the site
boundaries. The method used at the site is to be determined from the earth
electrode compliancy certificate and repeated annually. Before proceeding with
the test, ensure that the resistance of the test leads is less than 0.05 ohms.
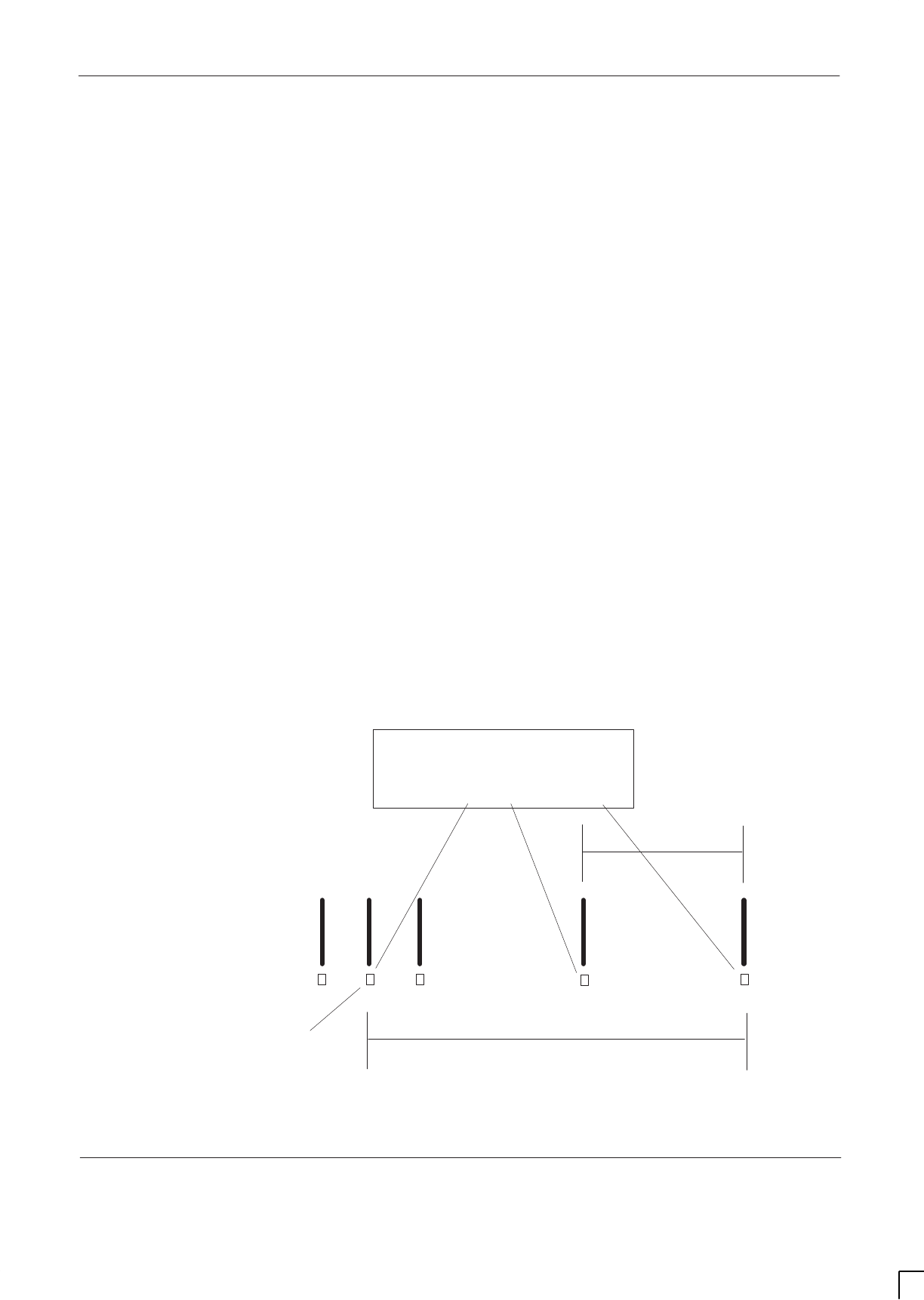
GSM-204-423 Earthing the site
31st Oct 01
Installation & Configuration: Horizon
macro
outdoor
68P02902W03-A
CONTROLLED INTRODUCTION
Inst. 2–15
Fall of potential
This method of testing is used for measuring resistance of earth electrodes but
is only practical on single earth electrode systems.
Drive the current test spike and potential spike into the ground as shown in
Figure 2-5. Perform the three resistance tests and check that the average of the
three tests is less than 10.0 ohms.
61.8% Rule
This method applies when the three electrodes (earth, potential and current) can
be positioned in a straight line, the soil is homogenous and also when single
electrode systems are being used.
Set up the test equipment as shown in Figure 2-5 with the potential spike placed
at a distance of 61.8% of the distance from the earth electrode to the current
test spike. A greater accuracy can be achieved by increasing the number of
readings.
Slope method
This method applies to large earth systems. Refer to Figure 2-5, but insert the
potential spike at a number of points between the earth system and the current
spike. A minimum of six readings must be taken to plot a graph and this graph
compared to published tables to calculate the resistance.
On completion of testing, complete and sign the earth electrode test
documentation (Forms of Completion and Inspection Certificate).
PAT Tester
C2 P2 C1/P1
(Test 2)
3 m
(Test 3)
25 m
Potential
spike Earth
electrode
50 m
(Test 1)
Current
test
spike
3 m
Figure 2-5 Earth electrode test setup
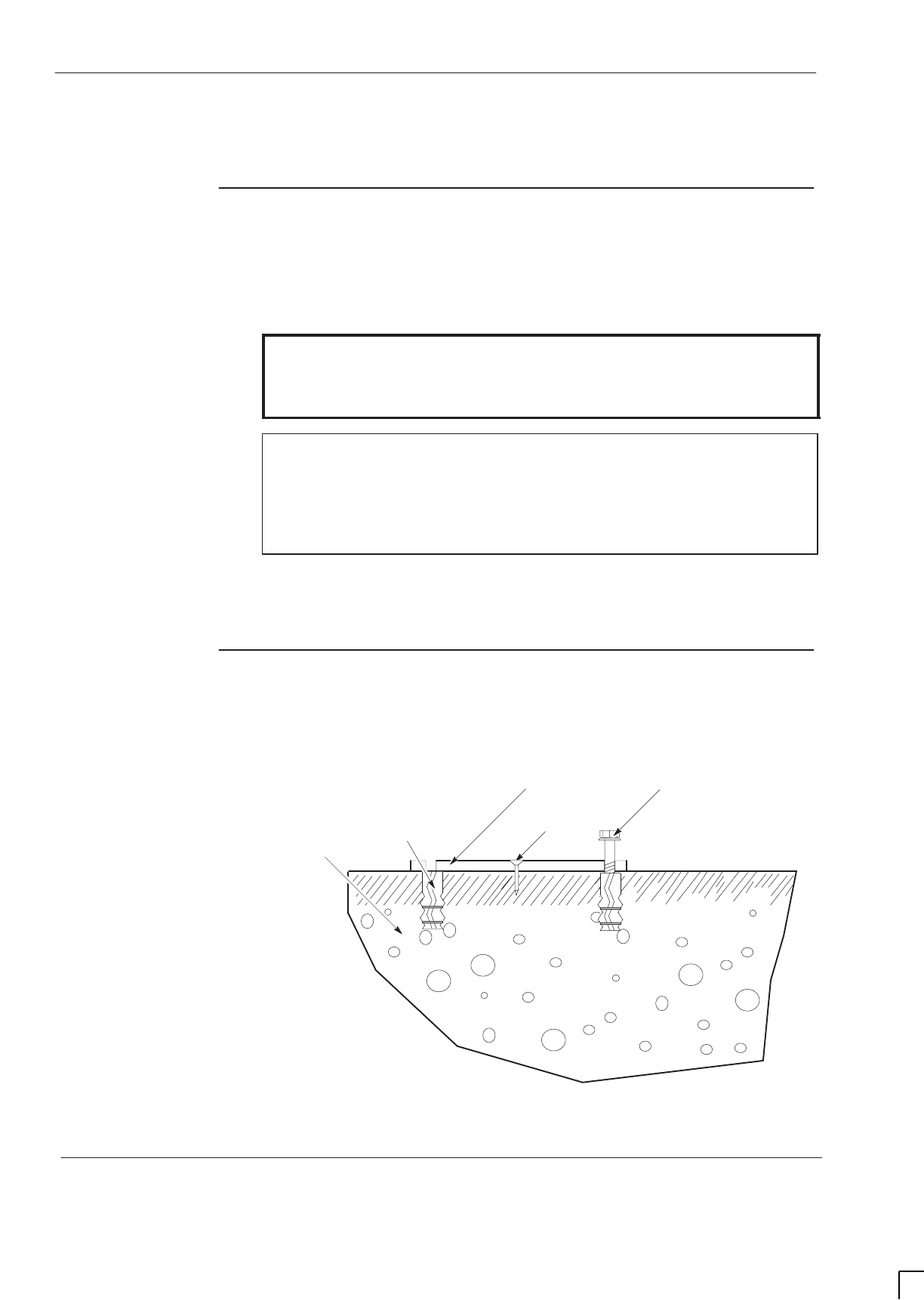
GSM-204-423
Preparing the foundation
31st Oct 01
Inst. 2–16
Installation & Configuration: Horizon
macro
outdoor
CONTROLLED INTRODUCTION
68P02902W03-A
Preparing the foundation
Overview of
foundation
preparation
Motorola recommend the cabinet be installed on a separate concrete base of
sufficient size and construction to accommodate the Horizon
macro
cabinet size
and weight, as determined by a structural engineer.
WARNING Excavations exceeding 1.2 m in depth must be adequately
shored to prevent land slip or trench collapse. Excavated
earth must not be placed within 1 m of the excavation
edge.
NOTE At the customers discretion a steel structure may also be
used, with size, construction and layout determined by a
structural engineer.
Reference should be made to Site requirements and
considerations in this chapter for details of equipment
weights and dimensions.
The foundation depth is determined by a soil survey performed by the site
architect, but must be of sufficient strength to withstand 105 knot (120 mph)
winds on the cabinet front or rear and a maximum gross weight of 360 kgs.
Horizon
macro
foundation
The following cross-sectional diagram in Figure 2-6 shows a typical foundation
for the Horizon
macro
(bolts and anchors not to scale).
CONCRETE
FOUNDATION
M 12 ANCHOR
TEMPLATE
No 10
SCREW
M 12 BOLTS USED TO SECURE
CABINETS
Figure 2-6 Typical Horizon
macro
foundation
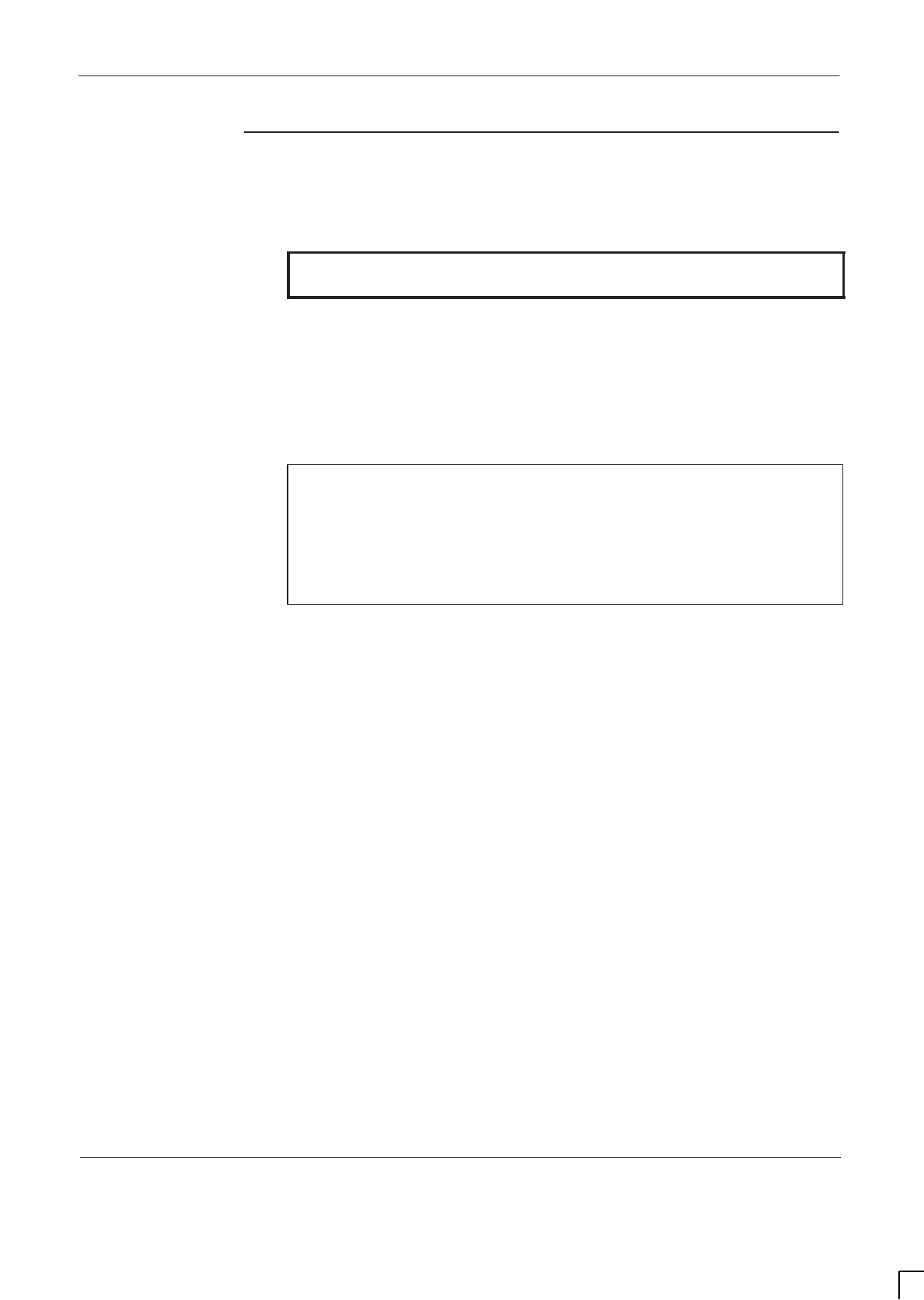
GSM-204-423 Preparing the foundation
31st Oct 01
Installation & Configuration: Horizon
macro
outdoor
68P02902W03-A
CONTROLLED INTRODUCTION
Inst. 2–17
Preparing the
foundation
To prepare the foundation:
1. Excavate the foundation (refer to Figure 2-6).
WARNING Do not place excavated earth within 1 m of the excavation
edge.
2. Erect the concrete shuttering to produce the required base.
3. Position the cable ducts (if low level cable entry method is in use). Ensure
that they are positioned so that they face towards the cabinet entry point.
4. Make the foundation from 20 mm mix concrete with the cable ducts (If
used) mounted in position. If required, locally thicken the areas around the
foundation bolts.
CAUTION Ensure the concrete is laid to give a water run off with
tapered edges. Where a field site, other than an already
permanent hard standing, is laid, the foundation must
have a bevelled finish.
To avoid over stressing the cabinet, use a spirit level or
theodolite to check that the concrete plinth surface is level
to 3 mm across diagonals.
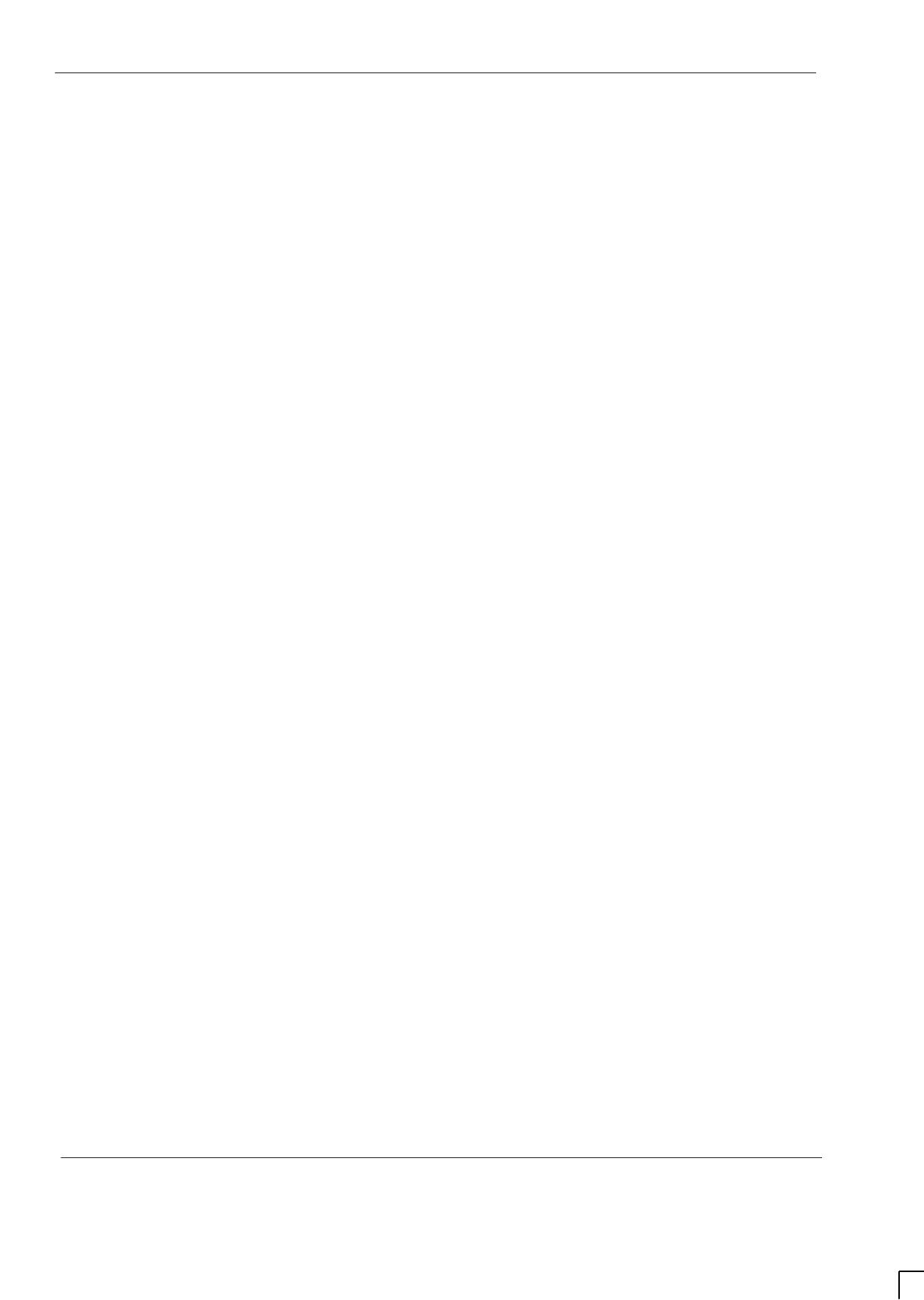
GSM-204-423
Preparing the foundation
31st Oct 01
Inst. 2–18
Installation & Configuration: Horizon
macro
outdoor
CONTROLLED INTRODUCTION
68P02902W03-A
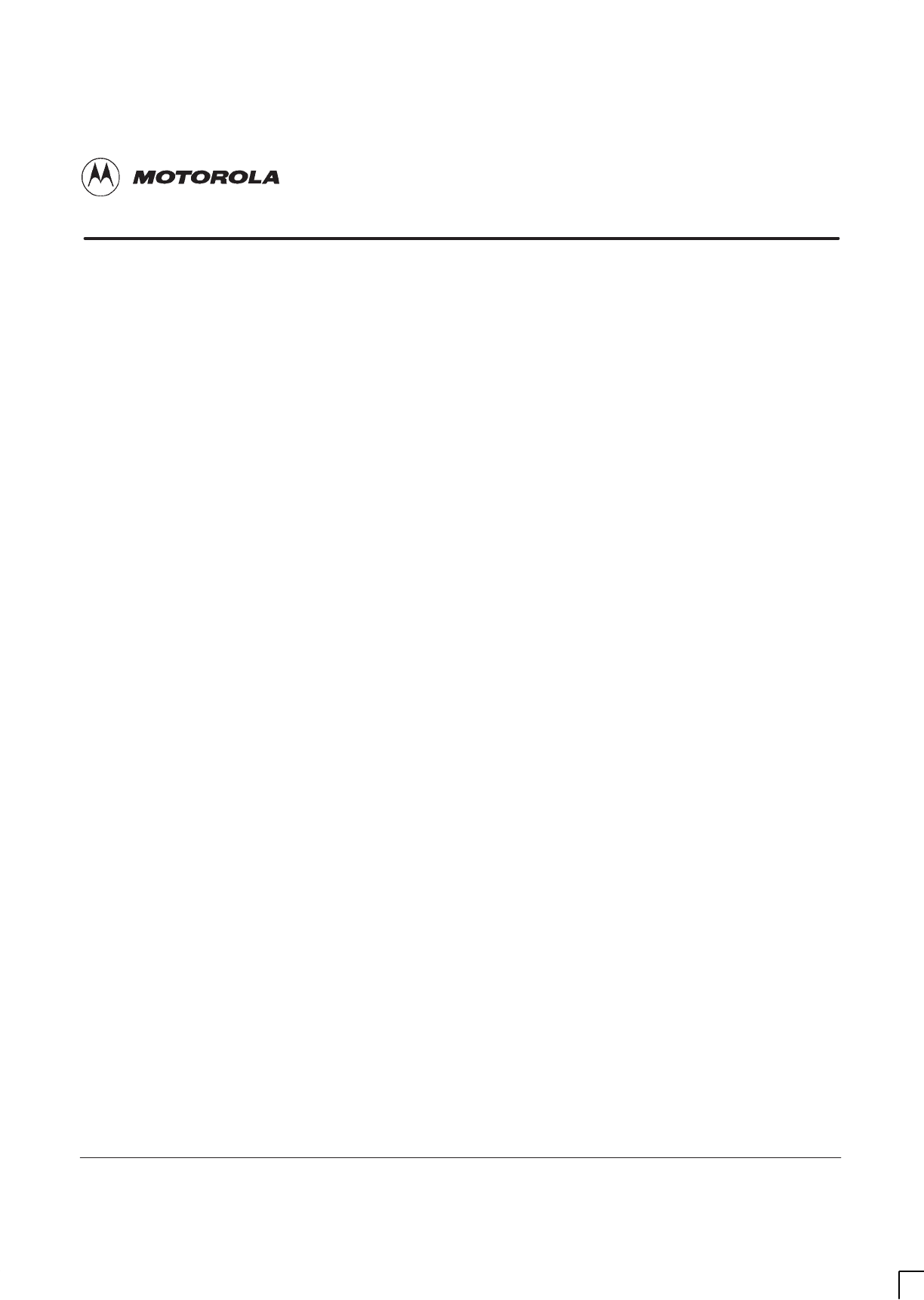
31st Oct 01
Installation & Configuration: Horizon
macro
outdoor
68P02902W03-A
CONTROLLED INTRODUCTION
i
Chapter 3
Installing the BTS cabinet
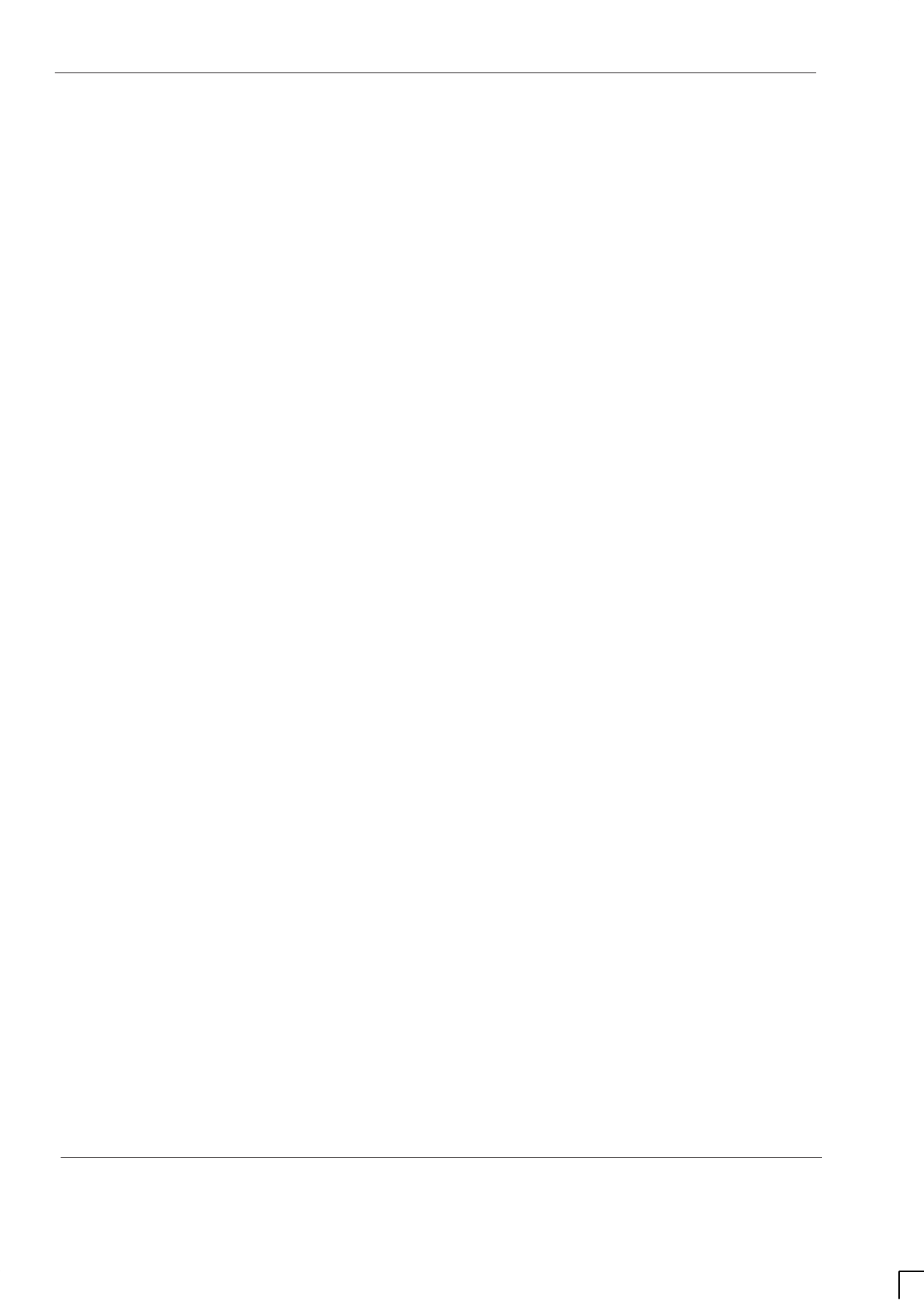
GSM-204-423
31st Oct 01
ii
Installation & Configuration: Horizon
macro
outdoor
CONTROLLED INTRODUCTION
68P02902W03-A
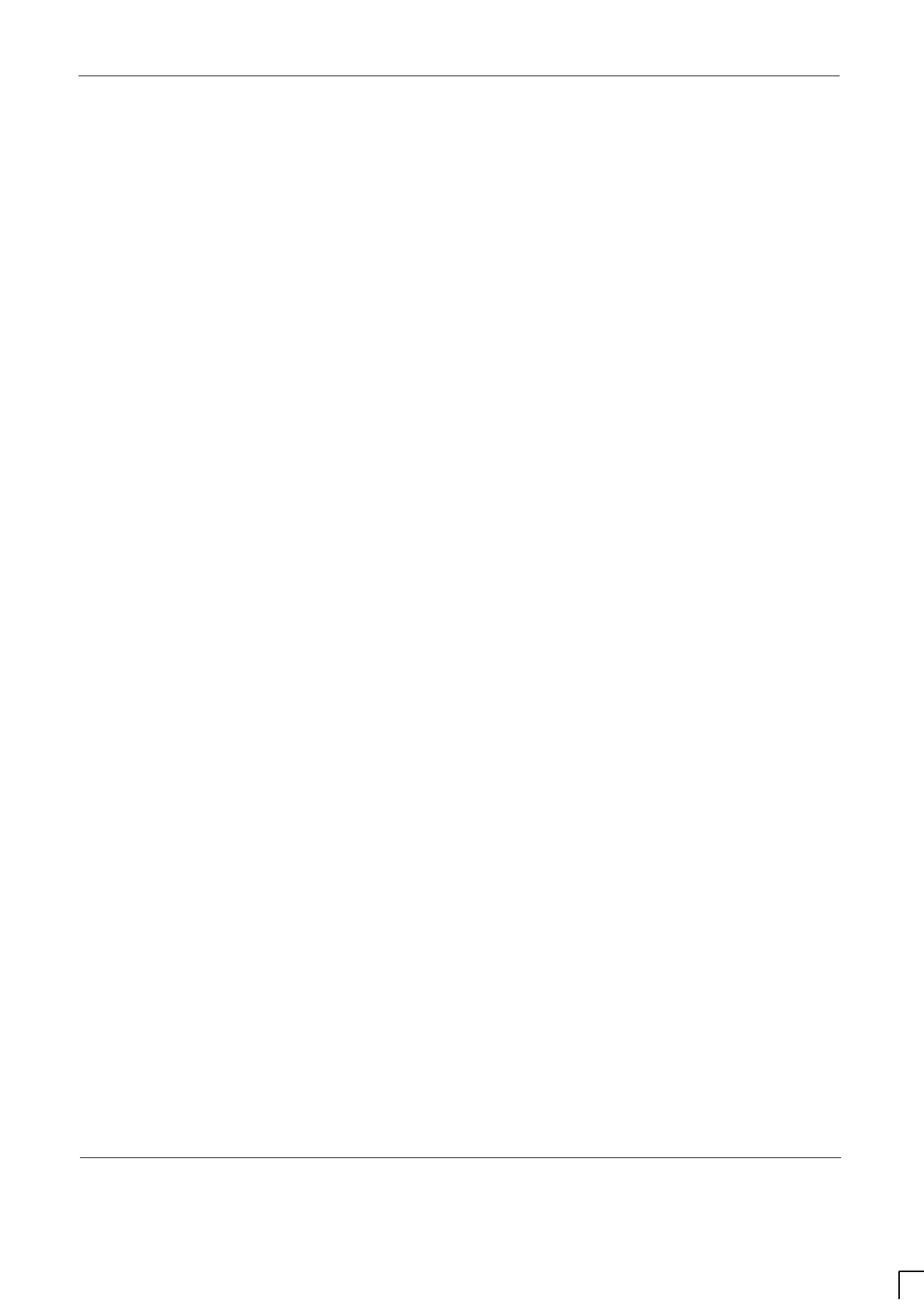
GSM-204-423
31st Oct 01
Installation & Configuration: Horizon
macro
outdoor
68P02902W03-A
CONTROLLED INTRODUCTION
iii
Chapter 3
Installing the BTS cabinet i. . . . . . . . . . . . . . . . . . . . . . . . . . . . . . . . . . . . . .
Installation overview Inst. 3–1. . . . . . . . . . . . . . . . . . . . . . . . . . . . . . . . . . . . . . . . . . . . . . . . . .
Introduction to installation Inst. 3–1. . . . . . . . . . . . . . . . . . . . . . . . . . . . . . . . . . . . . . . .
Installation sections Inst. 3–1. . . . . . . . . . . . . . . . . . . . . . . . . . . . . . . . . . . . . . . . . . . . .
E1/T1 line testing Inst. 3–1. . . . . . . . . . . . . . . . . . . . . . . . . . . . . . . . . . . . . . . . . . . . . . .
Cabinet view Inst. 3–2. . . . . . . . . . . . . . . . . . . . . . . . . . . . . . . . . . . . . . . . . . . . . . . . . . .
Equipment package units Inst. 3–3. . . . . . . . . . . . . . . . . . . . . . . . . . . . . . . . . . . . . . . .
Equipment delivery and packaging Inst. 3–4. . . . . . . . . . . . . . . . . . . . . . . . . . . . . . . . . . . . .
Delivery and packaging overview Inst. 3–4. . . . . . . . . . . . . . . . . . . . . . . . . . . . . . . . .
Packaging Inst. 3–4. . . . . . . . . . . . . . . . . . . . . . . . . . . . . . . . . . . . . . . . . . . . . . . . . . . . .
Weather conditions affecting unpacking/installation Inst. 3–5. . . . . . . . . . . . . . . . . . . . . . .
Overview of weather considerations Inst. 3–5. . . . . . . . . . . . . . . . . . . . . . . . . . . . . . .
Weather conditions Inst. 3–5. . . . . . . . . . . . . . . . . . . . . . . . . . . . . . . . . . . . . . . . . . . . . .
Maintenance cover Inst. 3–5. . . . . . . . . . . . . . . . . . . . . . . . . . . . . . . . . . . . . . . . . . . . . .
Unpacking and preparing the cabinet Inst. 3–7. . . . . . . . . . . . . . . . . . . . . . . . . . . . . . . . . . .
Tools Inst. 3–7. . . . . . . . . . . . . . . . . . . . . . . . . . . . . . . . . . . . . . . . . . . . . . . . . . . . . . . . . .
Safety considerations Inst. 3–7. . . . . . . . . . . . . . . . . . . . . . . . . . . . . . . . . . . . . . . . . . .
Cabinet access procedures Inst. 3–8. . . . . . . . . . . . . . . . . . . . . . . . . . . . . . . . . . . . . .
Procedures for unpacking and preparing the cabinet Inst. 3–9. . . . . . . . . . . . . . . .
Visual inspection Inst. 3–11. . . . . . . . . . . . . . . . . . . . . . . . . . . . . . . . . . . . . . . . . . . . . . . .
Safe disposal of packing material Inst. 3–11. . . . . . . . . . . . . . . . . . . . . . . . . . . . . . . . .
CTU module allotted slot retention Inst. 3–11. . . . . . . . . . . . . . . . . . . . . . . . . . . . . . . .
Installing the template and mounting bolt anchors Inst. 3–12. . . . . . . . . . . . . . . . . . . . . . . .
Introduction to template and mounting bolt anchor installation Inst. 3–12. . . . . . . .
View of template Inst. 3–12. . . . . . . . . . . . . . . . . . . . . . . . . . . . . . . . . . . . . . . . . . . . . . . .
Procedure for installing template Inst. 3–13. . . . . . . . . . . . . . . . . . . . . . . . . . . . . . . . . .
Recommended bolt length for concrete base Inst. 3–13. . . . . . . . . . . . . . . . . . . . . . .
Procedure for installing cabinet bolt anchors Inst. 3–14. . . . . . . . . . . . . . . . . . . . . . .
Fitting the outdoor cabinet onto its base Inst. 3–15. . . . . . . . . . . . . . . . . . . . . . . . . . . . . . . .
Procedure for fitting a BTS cabinet Inst. 3–15. . . . . . . . . . . . . . . . . . . . . . . . . . . . . . . .
Mounting additional cabinets Inst. 3–15. . . . . . . . . . . . . . . . . . . . . . . . . . . . . . . . . . . . .
Earthing and transient protection Inst. 3–16. . . . . . . . . . . . . . . . . . . . . . . . . . . . . . . . . . . . . . .
Site earthing Inst. 3–16. . . . . . . . . . . . . . . . . . . . . . . . . . . . . . . . . . . . . . . . . . . . . . . . . . .
Secondary transient and lightning protection Inst. 3–16. . . . . . . . . . . . . . . . . . . . . . .
Connecting the internal batteries Inst. 3–17. . . . . . . . . . . . . . . . . . . . . . . . . . . . . . . . . . . . . . .
Introduction to connecting the internal batteries Inst. 3–17. . . . . . . . . . . . . . . . . . . . .
Internal battery connection procedure Inst. 3–17. . . . . . . . . . . . . . . . . . . . . . . . . . . . .
View of internal battery tray Inst. 3–18. . . . . . . . . . . . . . . . . . . . . . . . . . . . . . . . . . . . . .
Installing and connecting power and earth cabling Inst. 3–19. . . . . . . . . . . . . . . . . . . . . . .
Overview of power and earth cabling Inst. 3–19. . . . . . . . . . . . . . . . . . . . . . . . . . . . . .
Cable routeing Inst. 3–19. . . . . . . . . . . . . . . . . . . . . . . . . . . . . . . . . . . . . . . . . . . . . . . . . .
Cabinet earthing points Inst. 3–20. . . . . . . . . . . . . . . . . . . . . . . . . . . . . . . . . . . . . . . . . .
Power supply cable colour coding Inst. 3–20. . . . . . . . . . . . . . . . . . . . . . . . . . . . . . . . .
Preparing for connection Inst. 3–21. . . . . . . . . . . . . . . . . . . . . . . . . . . . . . . . . . . . . . . . .
Connecting 230 V single phase ac power cables Inst. 3–22. . . . . . . . . . . . . . . . . . . . . . . . .
Configuring the number 1 ac distribution box Inst. 3–22. . . . . . . . . . . . . . . . . . . . . . .
Connecting 230 V ac single phase mains input cables Inst. 3–22. . . . . . . . . . . . . . .
230 V ac single phase wiring diagram Inst. 3–23. . . . . . . . . . . . . . . . . . . . . . . . . . . . .
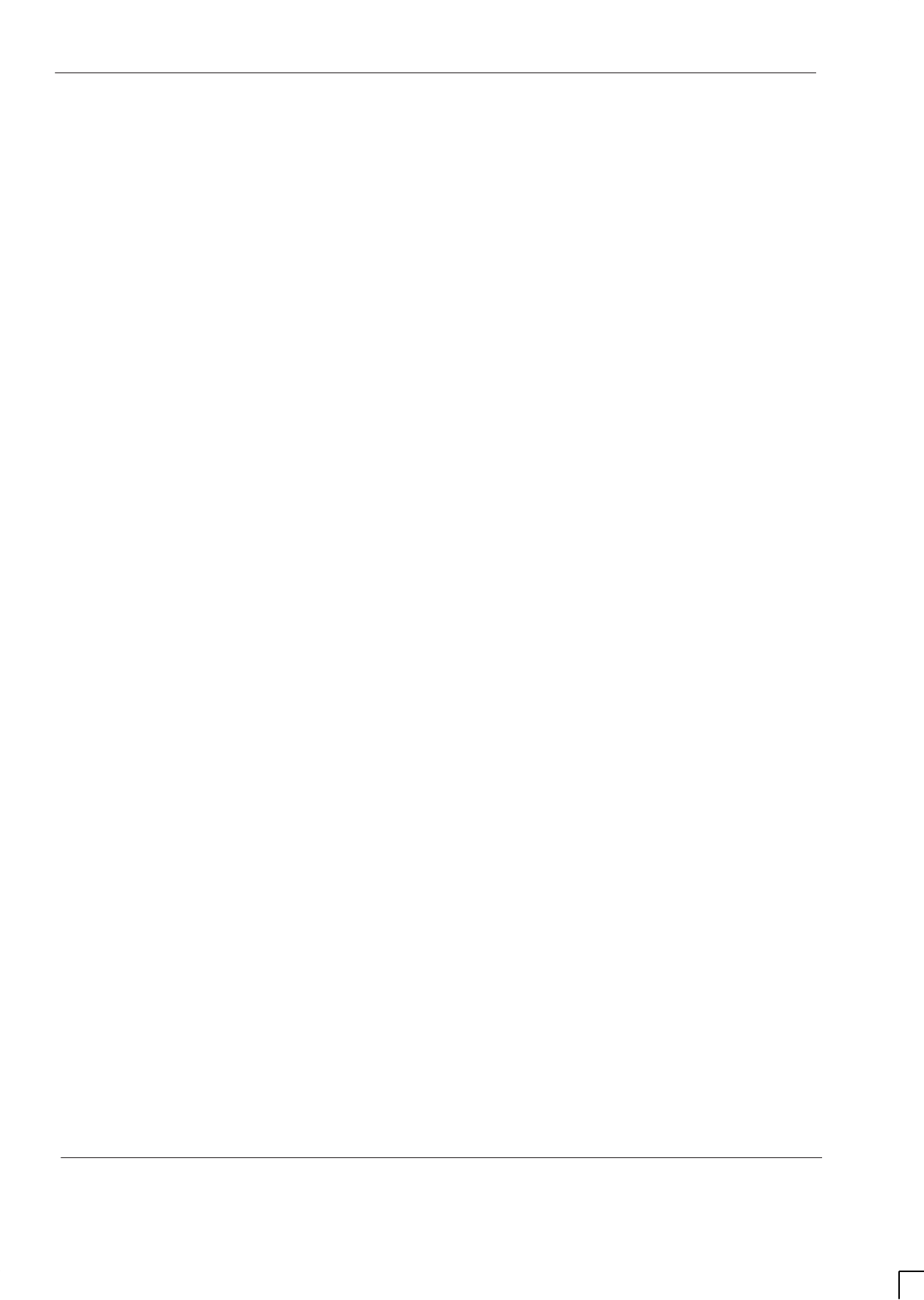
GSM-204-423
31st Oct 01
iv
Installation & Configuration: Horizon
macro
outdoor
CONTROLLED INTRODUCTION
68P02902W03-A
Connecting 110 V single phase ac power cables Inst. 3–24. . . . . . . . . . . . . . . . . . . . . . . . .
Configuring the number 1 ac distribution box Inst. 3–24. . . . . . . . . . . . . . . . . . . . . . .
Connecting 110 V ac single phase mains input cables Inst. 3–24. . . . . . . . . . . . . . .
110 V ac single phase wiring diagram Inst. 3–25. . . . . . . . . . . . . . . . . . . . . . . . . . . . .
Connecting 230 V 3-phase (star) ac power cables Inst. 3–26. . . . . . . . . . . . . . . . . . . . . . . .
Configuring the number 1 ac distribution box Inst. 3–26. . . . . . . . . . . . . . . . . . . . . . .
Connecting 230 V ac 3-phase (star) mains input cables Inst. 3–26. . . . . . . . . . . . . .
230 V ac 3-phase (star) wiring diagram Inst. 3–27. . . . . . . . . . . . . . . . . . . . . . . . . . . .
Connecting 230 V 3-phase (delta) ac power cables Inst. 3–28. . . . . . . . . . . . . . . . . . . . . . .
Configuring the number 1 ac distribution box Inst. 3–28. . . . . . . . . . . . . . . . . . . . . . .
Connecting 230 V ac 3-phase (delta) mains input cables Inst. 3–29. . . . . . . . . . . . .
230 V ac 3-phase (delta) wiring diagram Inst. 3–30. . . . . . . . . . . . . . . . . . . . . . . . . . .
Connecting antennas Inst. 3–31. . . . . . . . . . . . . . . . . . . . . . . . . . . . . . . . . . . . . . . . . . . . . . . . .
Overview of antenna connections Inst. 3–31. . . . . . . . . . . . . . . . . . . . . . . . . . . . . . . . .
Cable entry earth plates Inst. 3–32. . . . . . . . . . . . . . . . . . . . . . . . . . . . . . . . . . . . . . . . .
Fitting inter-cabinet RF cables to earth plates Inst. 3–32. . . . . . . . . . . . . . . . . . . . . . .
Routeing RF cables between cabinets. Inst. 3–33. . . . . . . . . . . . . . . . . . . . . . . . . . . .
Types of RF connector Inst. 3–33. . . . . . . . . . . . . . . . . . . . . . . . . . . . . . . . . . . . . . . . . .
Torque of RF connectors Inst. 3–33. . . . . . . . . . . . . . . . . . . . . . . . . . . . . . . . . . . . . . . . .
Fitting left side (cable entry) earth plate Inst. 3–34. . . . . . . . . . . . . . . . . . . . . . . . . . . .
Fitting expansion plates Inst. 3–35. . . . . . . . . . . . . . . . . . . . . . . . . . . . . . . . . . . . . . . . . .
RF connection principles Inst. 3–36. . . . . . . . . . . . . . . . . . . . . . . . . . . . . . . . . . . . . . . . .
Rx/Tx single antenna duplexing Inst. 3–36. . . . . . . . . . . . . . . . . . . . . . . . . . . . . . . . . . .
Suggested RF configurations Inst. 3–37. . . . . . . . . . . . . . . . . . . . . . . . . . . . . . . . . . . . . . . . . .
Overview of configuration diagrams Inst. 3–37. . . . . . . . . . . . . . . . . . . . . . . . . . . . . . .
Single cabinet connection kits and cables Inst. 3–38. . . . . . . . . . . . . . . . . . . . . . . . . .
Multiple cabinet connection kits and cables Inst. 3–39. . . . . . . . . . . . . . . . . . . . . . . .
Configuration for omni 1 Inst. 3–40. . . . . . . . . . . . . . . . . . . . . . . . . . . . . . . . . . . . . . . . .
Configuration for omni 1 or 2 (with/without diversity) Inst. 3–41. . . . . . . . . . . . . . . . .
Configuration for omni 3 or 4 Inst. 3–42. . . . . . . . . . . . . . . . . . . . . . . . . . . . . . . . . . . . .
Configuration for omni 3 Inst. 3–42. . . . . . . . . . . . . . . . . . . . . . . . . . . . . . . . . . . . . . . . .
Configuration for omni 4 Inst. 3–43. . . . . . . . . . . . . . . . . . . . . . . . . . . . . . . . . . . . . . . . .
Configuration for omni 5 or 6 Inst. 3–43. . . . . . . . . . . . . . . . . . . . . . . . . . . . . . . . . . . . .
Configuration for sector 1/1 or 2/2 Inst. 3–44. . . . . . . . . . . . . . . . . . . . . . . . . . . . . . . . .
Configuration for sector 1/1 Inst. 3–44. . . . . . . . . . . . . . . . . . . . . . . . . . . . . . . . . . . . . .
Configuration for single cabinet sector 3/3 Inst. 3–45. . . . . . . . . . . . . . . . . . . . . . . . .
Configuration for 2 cabinet sector 3/3 Inst. 3–46. . . . . . . . . . . . . . . . . . . . . . . . . . . . . .
Configuration for 2 cabinet sector 4/4 Inst. 3–46. . . . . . . . . . . . . . . . . . . . . . . . . . . . . .
Configuration for 2 cabinet sector 5/5 or 6/6 Inst. 3–47. . . . . . . . . . . . . . . . . . . . . . . .
Configuration for single cabinet sector 1/1/1, 1/1/2, 1/2/2 or 2/2/2 Inst. 3–48. . . . .
Configuration for 2 cabinet sector 2/2/2 Inst. 3–49. . . . . . . . . . . . . . . . . . . . . . . . . . . .
Configuration for 2 cabinet sector 3/3/3 or 4/4/4 Inst. 3–50. . . . . . . . . . . . . . . . . . . .
Configuration for 3 cabinet sector 3/3/3 Inst. 3–51. . . . . . . . . . . . . . . . . . . . . . . . . . . .
Configuration for 2 cabinet sector 4/4/4 Inst. 3–52. . . . . . . . . . . . . . . . . . . . . . . . . . . .
Configuration for 3 cabinet sector 4/4/4 Inst. 3–53. . . . . . . . . . . . . . . . . . . . . . . . . . . .
Configuration for sector 5/5/5 or 6/6/6 Inst. 3–54. . . . . . . . . . . . . . . . . . . . . . . . . . . . .
Configuration for sector 8/8/8 Inst. 3–55. . . . . . . . . . . . . . . . . . . . . . . . . . . . . . . . . . . . .
Configuration for dual band 1/1/1-3/3/3 Inst. 3–56. . . . . . . . . . . . . . . . . . . . . . . . . . . .
Configuration for dual band 3/3/3-1/1/1 Inst. 3–56. . . . . . . . . . . . . . . . . . . . . . . . . . . .
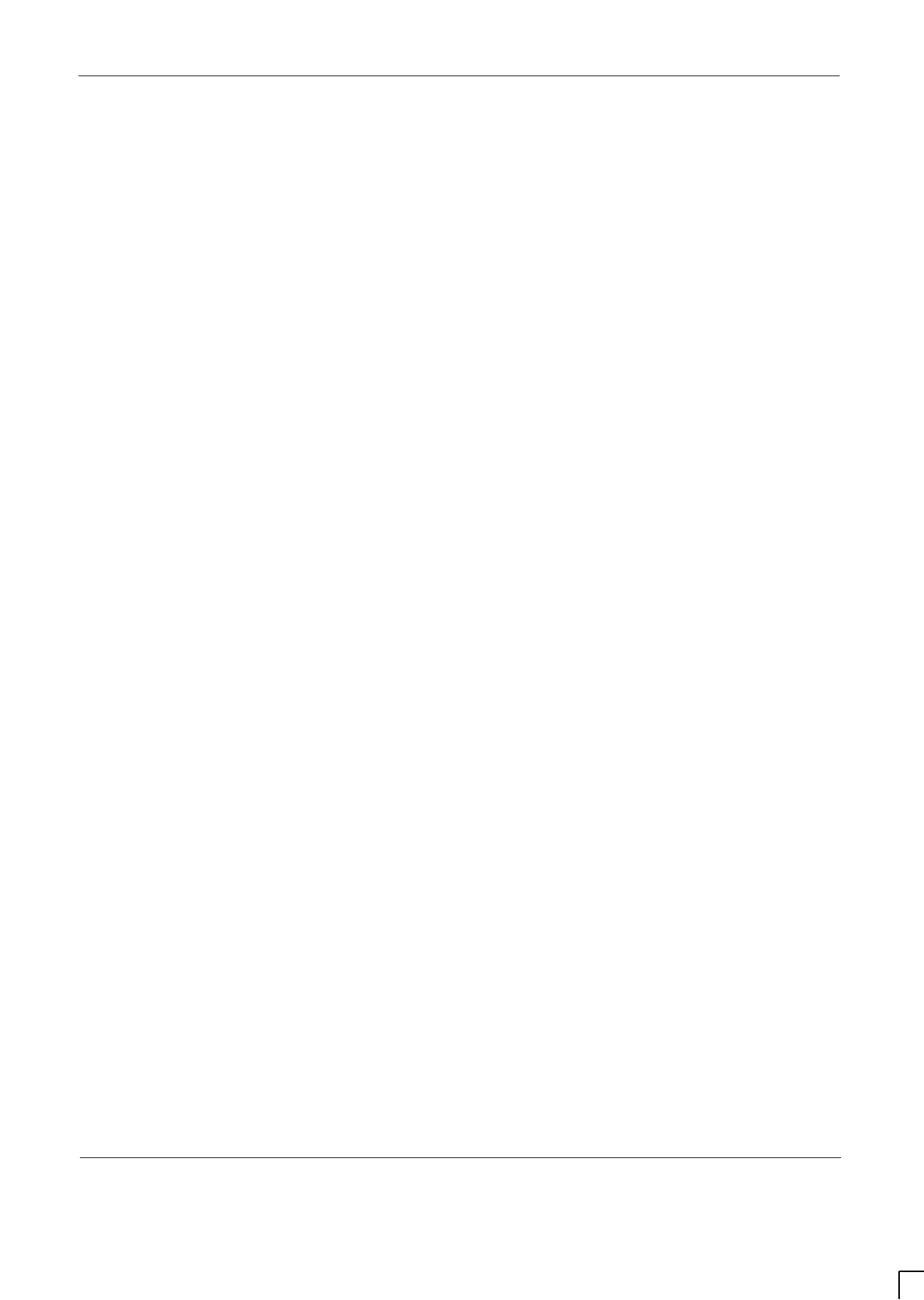
GSM-204-423
31st Oct 01
Installation & Configuration: Horizon
macro
outdoor
68P02902W03-A
CONTROLLED INTRODUCTION
v
Connecting fibre optic cables Inst. 3–57. . . . . . . . . . . . . . . . . . . . . . . . . . . . . . . . . . . . . . . . . .
Location of fibre optic connections Inst. 3–57. . . . . . . . . . . . . . . . . . . . . . . . . . . . . . . .
Care of fibres Inst. 3–57. . . . . . . . . . . . . . . . . . . . . . . . . . . . . . . . . . . . . . . . . . . . . . . . . . .
Connecting fibre optic cables between cabinets Inst. 3–60. . . . . . . . . . . . . . . . . . . . .
Interface panel cabling Inst. 3–61. . . . . . . . . . . . . . . . . . . . . . . . . . . . . . . . . . . . . . . . . . . . . . . .
Interface panel diagram and pinout overview Inst. 3–61. . . . . . . . . . . . . . . . . . . . . .
Interface panel connector pinout tables Inst. 3–62. . . . . . . . . . . . . . . . . . . . . . . . . . . .
GPS connector Inst. 3–62. . . . . . . . . . . . . . . . . . . . . . . . . . . . . . . . . . . . . . . . . . . . . . . . .
RTC connector (not used) Inst. 3–63. . . . . . . . . . . . . . . . . . . . . . . . . . . . . . . . . . . . . . . .
BIB (BIM) interconnection Inst. 3–64. . . . . . . . . . . . . . . . . . . . . . . . . . . . . . . . . . . . . . . .
T43 (CIM) interconnection Inst. 3–65. . . . . . . . . . . . . . . . . . . . . . . . . . . . . . . . . . . . . . .
PIX inputs and outputs Inst. 3–66. . . . . . . . . . . . . . . . . . . . . . . . . . . . . . . . . . . . . . . . . .
ICS connector Inst. 3–67. . . . . . . . . . . . . . . . . . . . . . . . . . . . . . . . . . . . . . . . . . . . . . . . . .
External alarm connector Inst. 3–68. . . . . . . . . . . . . . . . . . . . . . . . . . . . . . . . . . . . . . . .
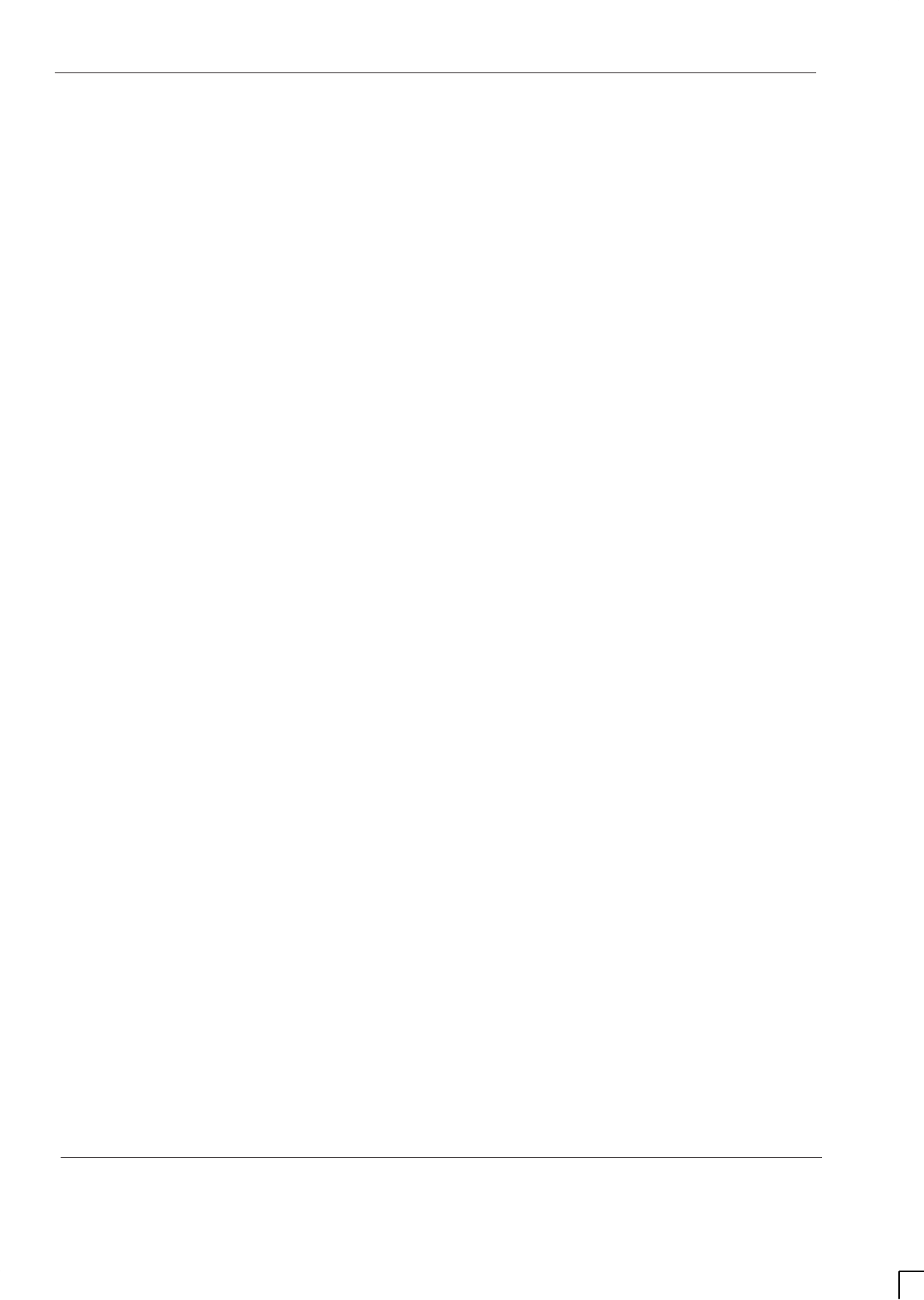
GSM-204-423
31st Oct 01
vi
Installation & Configuration: Horizon
macro
outdoor
CONTROLLED INTRODUCTION
68P02902W03-A
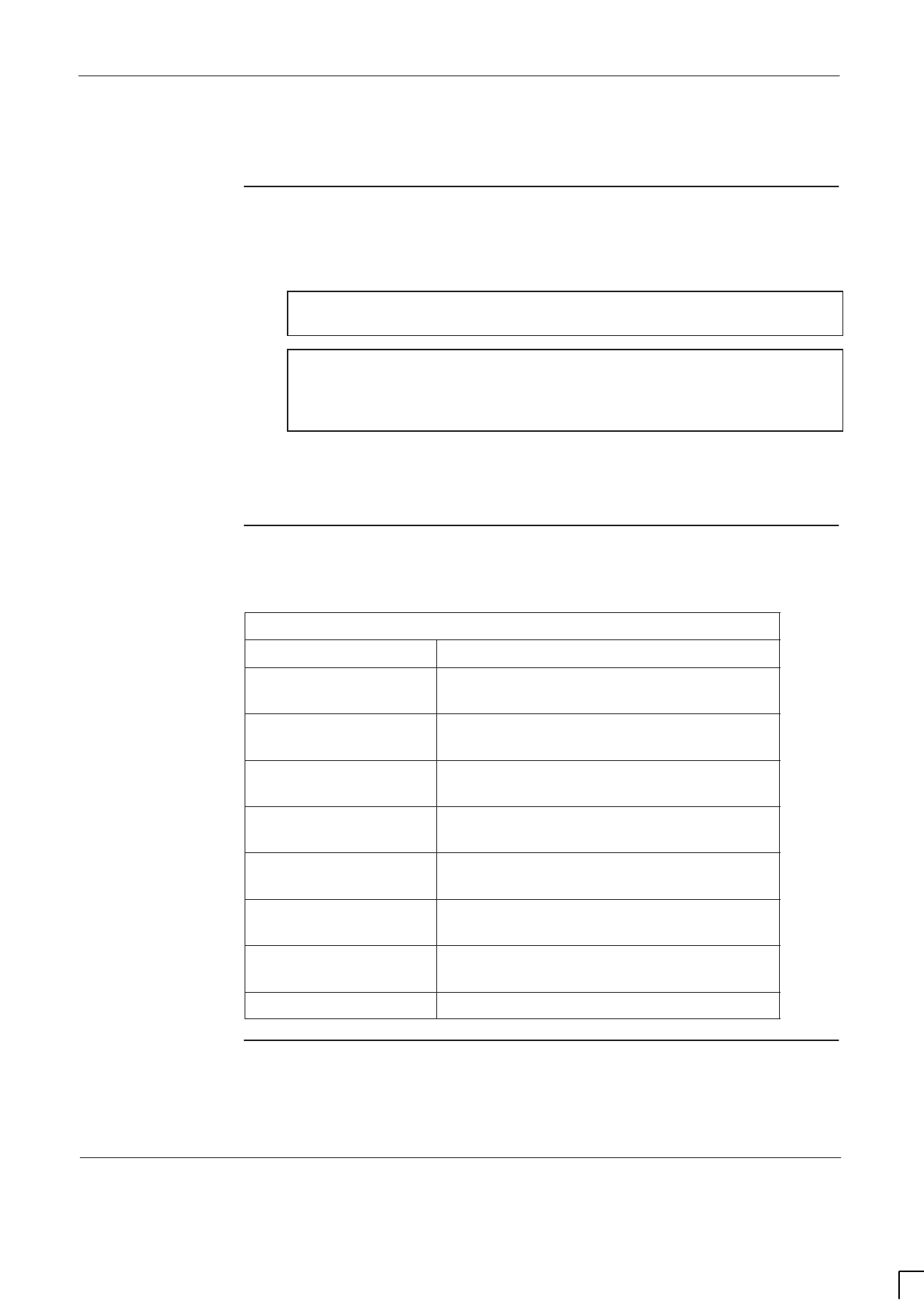
GSM-204-423 Installation overview
31st Oct 01
Installation & Configuration: Horizon
macro
outdoor
68P02902W03-A
CONTROLLED INTRODUCTION
Inst. 3–1
Installation overview
Introduction to
installation
This chapter provides the information required to install the Horizon
macro
outdoor cabinet and its internal and external interfaces.
CAUTION Ensure that all site associated equipment is completely
installed before commissioning the cabinet for operation.
NOTE Some site equipment may not be produced by Motorola,
including battery chargers, power supplies, and antennas.
Refer to site-specific documentation and non-Motorola
vendor instructions.
Before starting an installation, ensure the site has been prepared according to
the description summarised in Preparation overview in Chapter 2, and the
site-specific documentation.
Installation
sections
Installing cabinets comprises the sections shown in Table 3-1.
Table 3-1 Installation sections in this chapter
Section Description
Equipment delivery
and unpacking Information on delivery packaging, and how
to unpack the equipment.
Fitting outdoor
cabinet onto base Provides procedure for attaching cabinet to
prepared plinth.
Earthing and transient
protection Describes site earthing procedures and
cabinet internal earths.
Connecting the
internal batteries Describes the procedure for connecting up
the internal batteries.
Installing power and
earth cabling Describes the power supply earthing
requirements.
Connecting input
power Describes the correct sequence for power
connection.
Connecting antennas
and RF configurations Describes setting up antenna connections
and sample RF configurations.
Interface cabling Describes cabling to the interface panel.
E1/T1 line
testing
If an E1/T1 line has been provided, contact the local MSC and, at the earliest
opportunity, arrange to test the line back to the MSC.
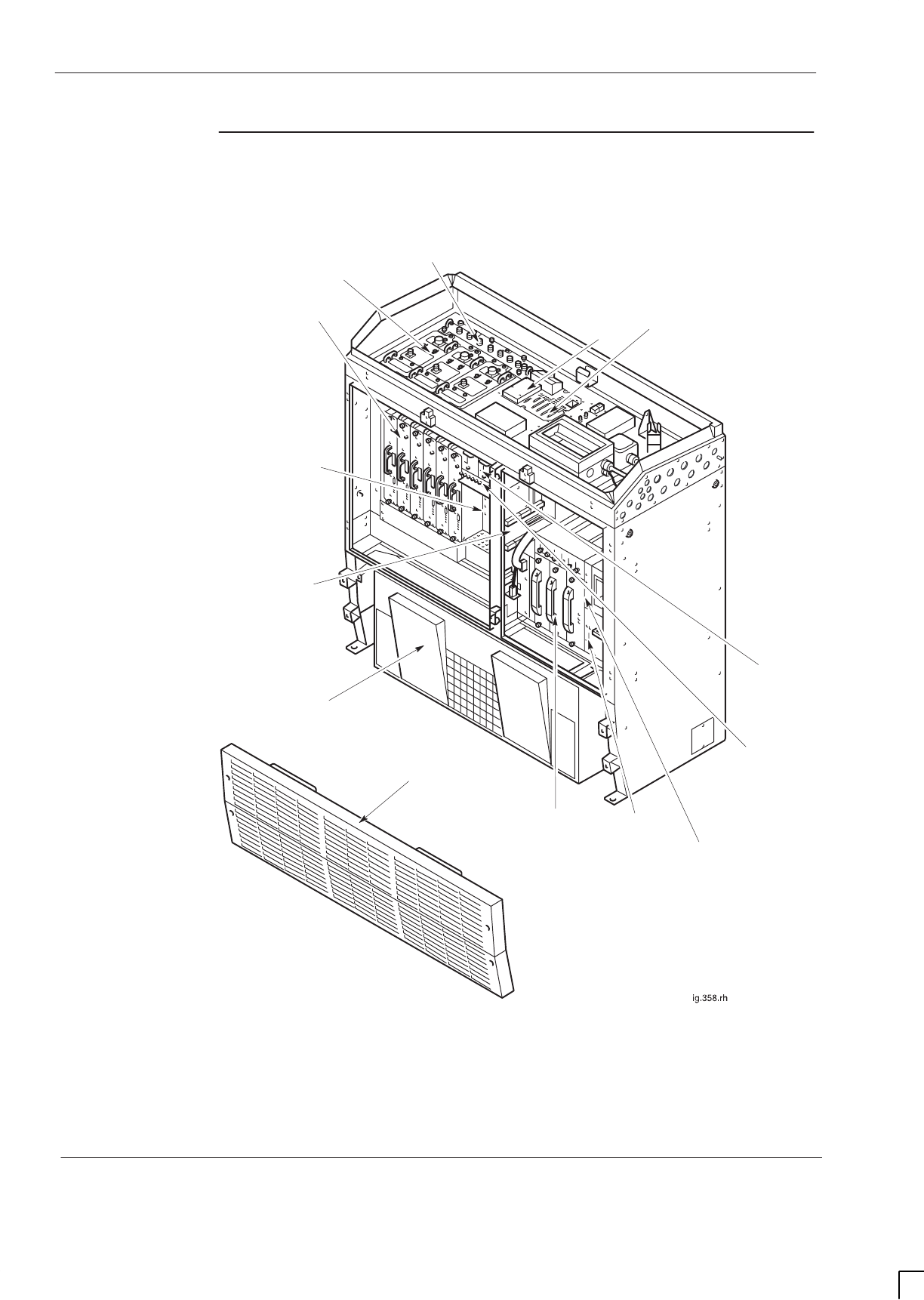
GSM-204-423
Installation overview
31st Oct 01
Inst. 3–2
Installation & Configuration: Horizon
macro
outdoor
CONTROLLED INTRODUCTION
68P02902W03-A
Cabinet view
Figure 3-1 shows a filled cabinet, with main components identified, doors and lid
omitted for clarity.
THREE PSMs
THREE Tx BLOCKS
(DCFs SHOWN AS
EXAMPLE)
ONE SURF
(Rx)
SIX CTUs
ALARM BOARD
MCUF
FMUX/NIU/BPSM
INTERFACE PANEL
CONNECTORS
CIRCUIT
BREAKER
MODULE (CBM)
T43/BIB
THREE
TOPSMs
ALARMS
INTERFACE
BOARD
CAB
INTERNAL
BATTERY
TRAY
TMS UNIT
TMS FRONT
COVER
Figure 3-1 Cabinet with components identified (door and hood removed)
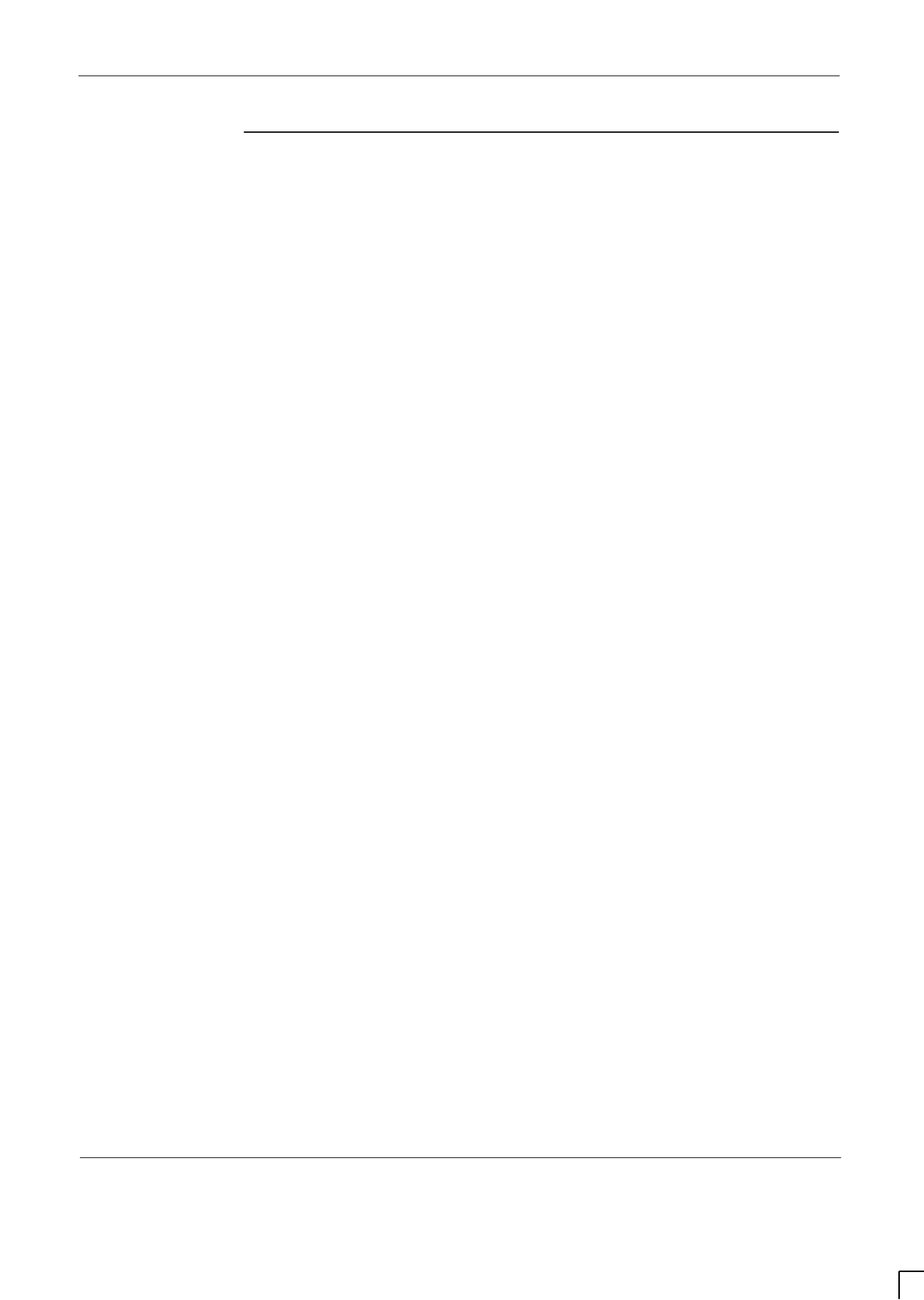
GSM-204-423 Installation overview
31st Oct 01
Installation & Configuration: Horizon
macro
outdoor
68P02902W03-A
CONTROLLED INTRODUCTION
Inst. 3–3
Equipment
package units
The cabinet equipment is supplied already fitted to the cabinet. The only
exceptions to this are:
Installation template, (supplied with cabinet).
Cable shroud (this is optional equipment).
Auxiliary equipment housing (this is optional equipment).
Equipment to be installed in the auxiliary equipment housing,
(this is optional equipment).
Installation anchor bolts, eye bolts and small fixing screws, (not supplied).
Cabinet equipment
Horizon
macro
cabinet equipment fitted and tested prior to shipping includes:
CTU modules.
Digital modules.
Power distribution and alarm interface equipment.
Internal batteries.
Thermal management system.
All intra-cabinet cabling, (RF and fibre optic).
Comms cables and power cable feed-through glands.
Cable assembly BIB to krone block.
Any additional blanks, (CTU, RF, digital module, TOPSM or PSM).
Items not supplied with Horizon
macro
The installer must supply the following equipment:
4 x M16 collared eye bolts (minimum rating 400 kg each).
Bolts must be manufactured to CE conformity.
Number 10 screws and expanding plastic plugs.
4 x M12 anchor bolts and expanding anchors.

GSM-204-423
Equipment delivery and packaging
31st Oct 01
Inst. 3–4
Installation & Configuration: Horizon
macro
outdoor
CONTROLLED INTRODUCTION
68P02902W03-A
Equipment delivery and packaging
Delivery and
packaging
overview
Before the cabinet equipment arrives, installation personnel should designate
an area at the site where the equipment can be unloaded. This area should also
be suitable for unpacking the equipment, if necessary. Consult with the heavy
freight or moving company and the owners of the site to select this area.
CAUTION The cabinet equipment should be delivered to the site
while still contained in its packaging. This is to protect the
cabinet from damage and moisture whilst in transit.
The equipment should be carefully delivered to the site by the freight company,
along with the necessary moving dollies and padding. Use the dollies and
padding to move the equipment from the unloading area to the installation point.
NOTE Keep all paperwork, whether attached to the packaging or
found inside the cabinet.
Packaging
The equipment cabinets are shipped in crates of a similar construction to that
shown in Figure 3-2.
WOODEN
SPREADER
CARDBOARD
DELIVERY BOX
CABINET
WOODEN DELIVERY
BASE
SECURING BOLTS
WOODEN PACKING
PIECE
TEMPLATE
BOX LID
BLANKS AND
ACCESSORY TRAYS
Figure 3-2 Typical shipping crate
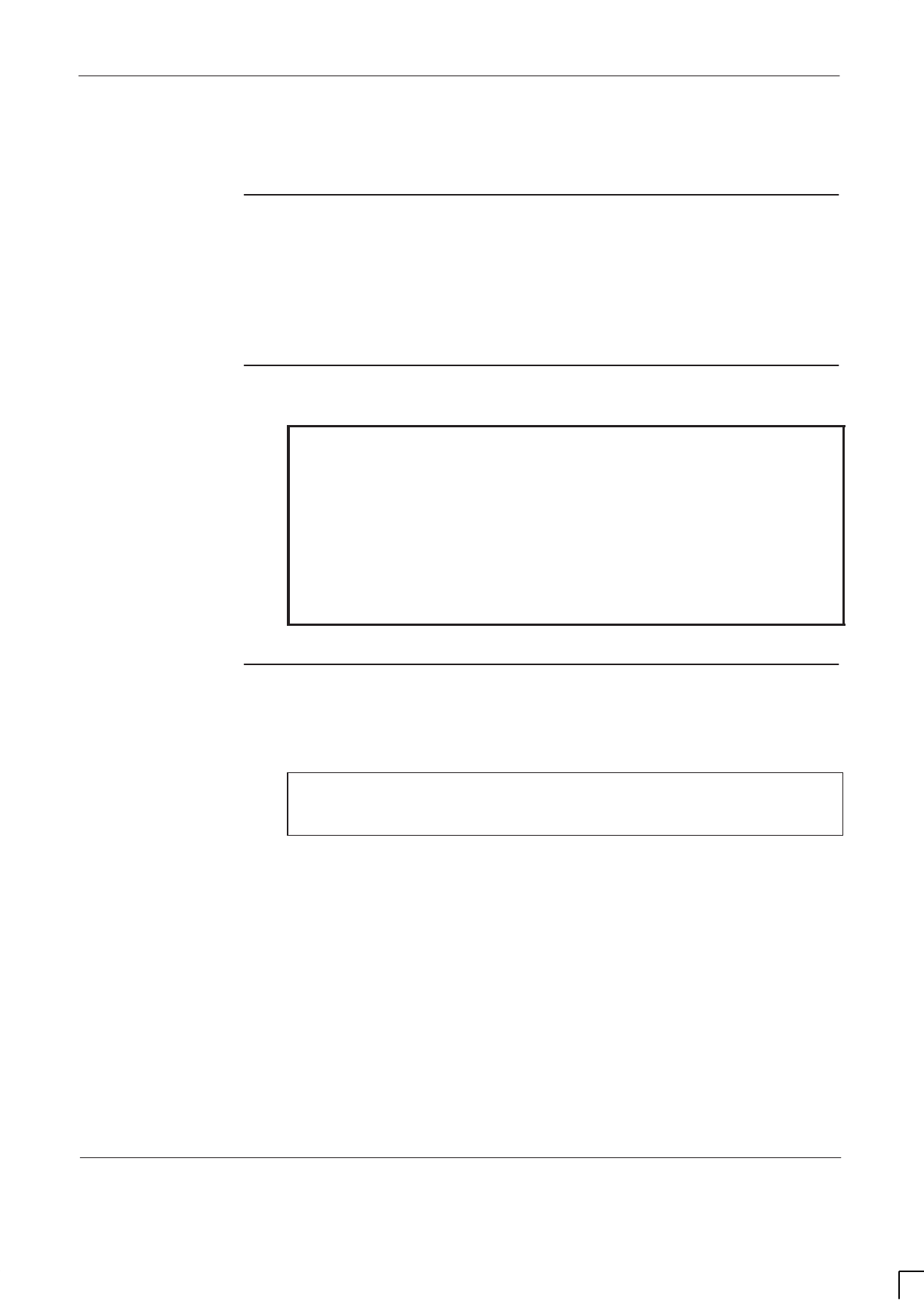
GSM-204-423 Weather conditions affecting unpacking/installation
31st Oct 01
Installation & Configuration: Horizon
macro
outdoor
68P02902W03-A
CONTROLLED INTRODUCTION
Inst. 3–5
Weather conditions affecting unpacking/installation
Overview of
weather
considerations
Before beginning the unpacking/installation process, it is important to read and
take into account the following information concerning the climatic conditions at
the intended site.
Weather
conditions
WARNING Due consideration should be given to the hazards of wind
and other inclement weather conditions when installing the
Horizon
macro
equipment. This is especially important
when using a ladder to gain access.
Use your discretion at all times. Do not climb a ladder,
scaffolding, or use some other similar method of
access, if you feel unsafe to do so under these
weather conditions.
Do not attempt to open the cabinet doors if the wind
speed exceeds 25 knots (30 mph).
Maintenance
cover
Motorola recommend the use of a maintenance cover for access to the
Horizon
macro
cabinets during inclement weather conditions.
NOTE The maintenance cover is not supplied with the
Horizon
macro
equipment and should be provided by the
customer, if required.
Installation and configuration procedures for the Horizon
macro
cabinets are
dependent on the weather conditions. There are three situations where the
recommended guidelines should be considered before commencing work:
No access.
Access with maintenance cover.
Access without maintenance cover.
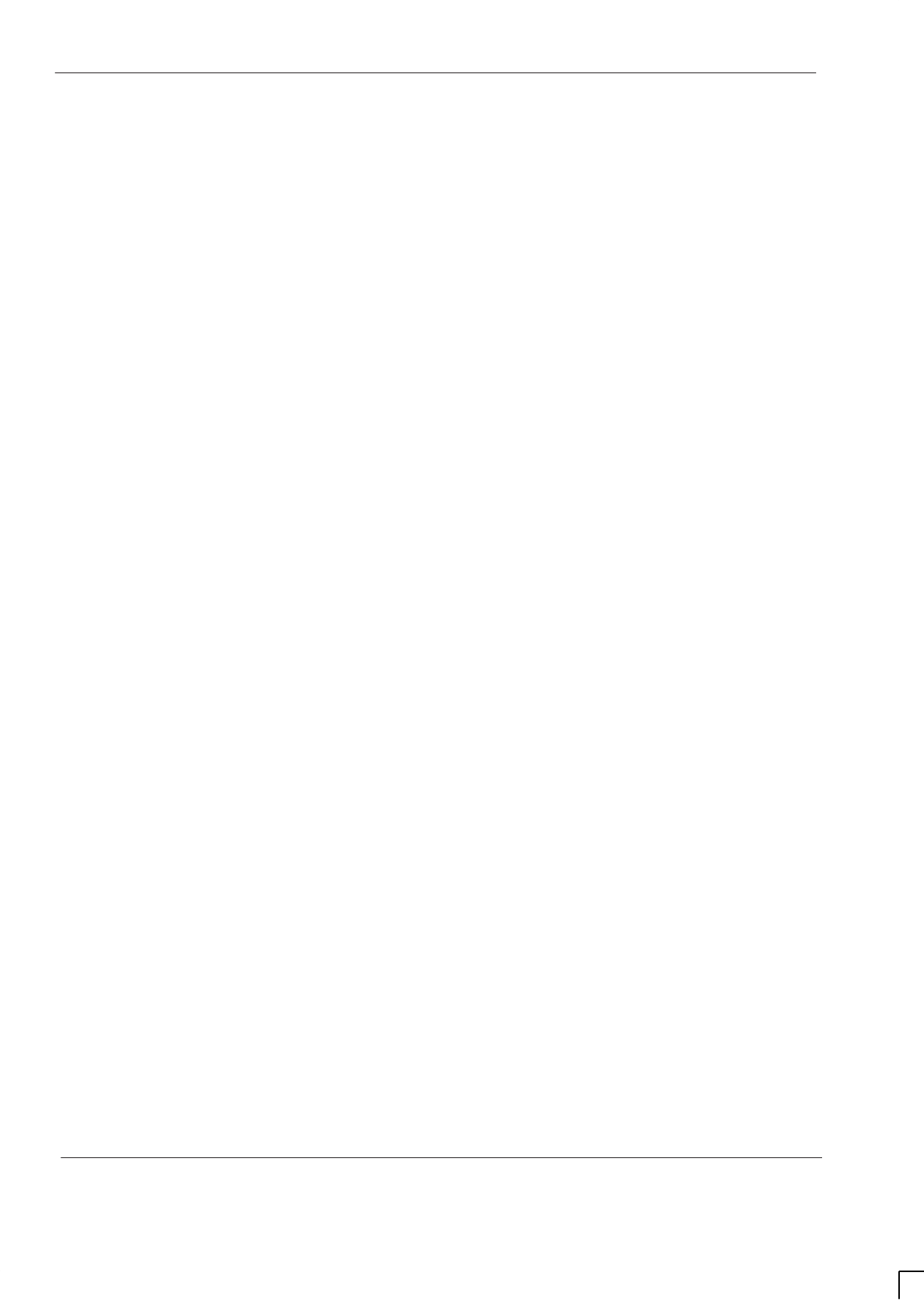
GSM-204-423
Weather conditions affecting unpacking/installation
31st Oct 01
Inst. 3–6
Installation & Configuration: Horizon
macro
outdoor
CONTROLLED INTRODUCTION
68P02902W03-A
No access
Access should not be attempted to the cabinets during the following actual or
imminent inclement weather conditions, with or without the maintenance cover:
Winds in excess of 25 knots (30 mph).
Heavy persistent rain, snow, hail or sleet.
During an electrical storm.
Access with maintenance cover
Access may be made to the cabinet under the following conditions with the use
of the maintenance cover:
Wind speeds of less than 25 knots (30 mph).
Persistent rain, snow, hail or sleet.
Where airborne substances (such as leaves or dust) may cause a
problem.
Access without maintenance cover
Access may be made under the following conditions without the use of the
maintenance cover:
Wind speeds of less than 25 knots (30 mph).
No precipitation occurring or likely to occur during the maintenance period.
When the temperature is between –30 C to 40 C.
Under these conditions the cover of the cabinet may be removed.
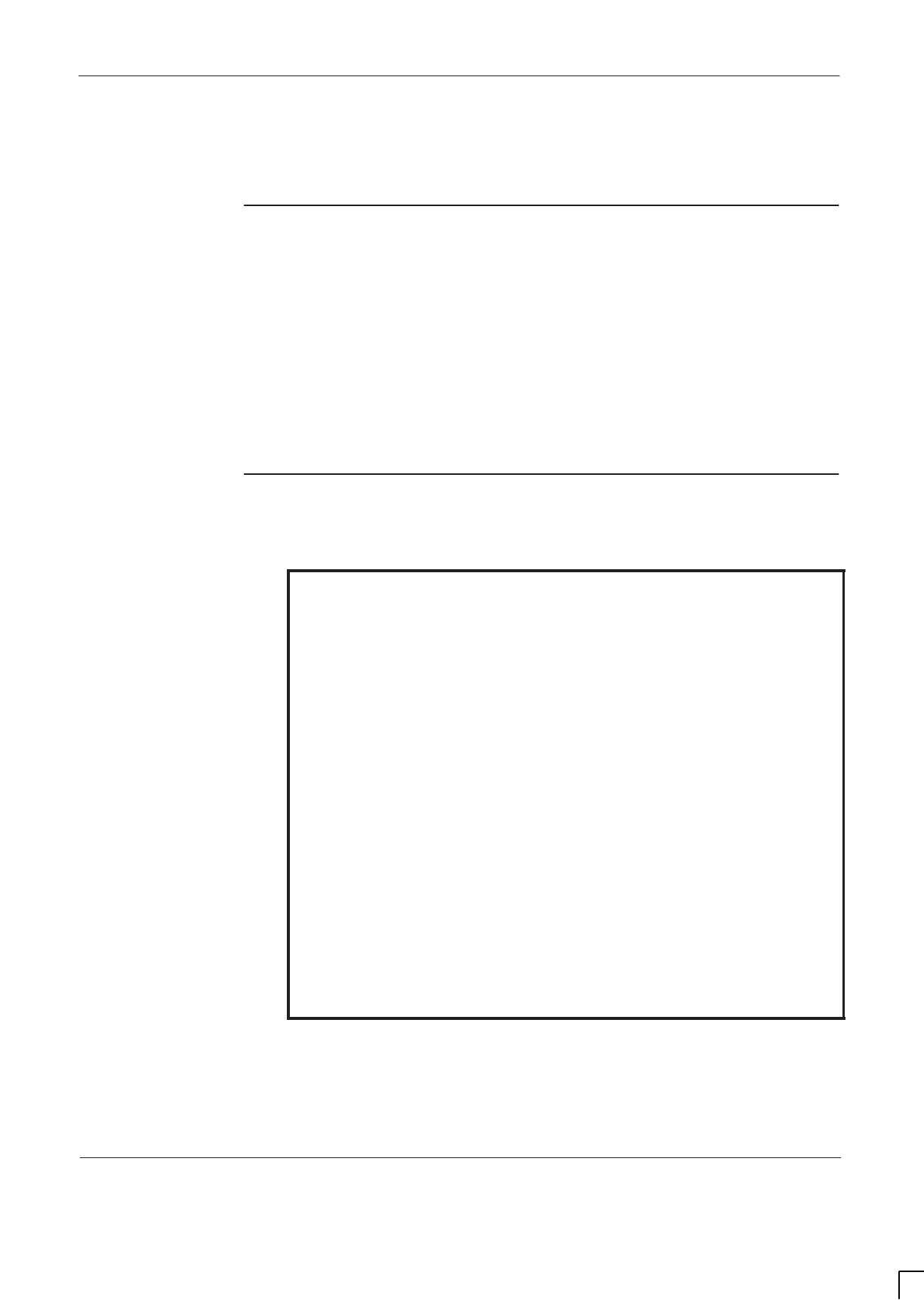
GSM-204-423 Unpacking and preparing the cabinet
31st Oct 01
Installation & Configuration: Horizon
macro
outdoor
68P02902W03-A
CONTROLLED INTRODUCTION
Inst. 3–7
Unpacking and preparing the cabinet
Tools
Use these tools to unpack, prepare and fit the cabinet:
Knife.
Screwdriver set.
Spirit level.
Socket set.
280 mm adjustable spanner.
Torque wrench.
Lifting straps and 4 x M16 collared eyebolts and suitable hydraulic lifting
gear.
Safety
considerations
For each of the cabinets to be installed, consider the following notes:
WARNING Fully equipped Horizon
macro
outdoor BTS cabinets can
weigh up to 360 kg. Handle cabinets with extreme caution,
and in accordance with any local health and safety
regulations.
Horizon
macro
cabinets are heavy and should not be
installed without the use of lifting equipment unless
sufficient personnel are available to ensure that Health
and Safety regulations are not breached.
Horizon
macro
outdoor cabinets are fitted with four lifting
points, designed to accommodate M16 eyebolts, built into
the cabinet sides. Eyebolts used to lift the cabinet must be
of the collared type, must be manufactured to CE
conformity, and must have a safe working load of 400 kg
each.
Eyebolts, must be visually checked for damage before
use. If any damage is apparent, DO NOT USE. The
eyebolts must not be overtightened; hand tight is
sufficient.
Motorola recommend the use of slings in conjunction with
hydraulic lifting apparatus for moving and positioning
Horizon
macro
cabinets.
In addition to these points, refer to and comply with any
local regulations that govern the use of lifting equipment.
For the subsequent use of eyebolts, there may be local regulations that govern
the use of lifting equipment and stipulate a test and/or examination regime. If
the eyebolts are to be used, ensure that all such regulations are met.
The installation support procedures are described in the following sections.
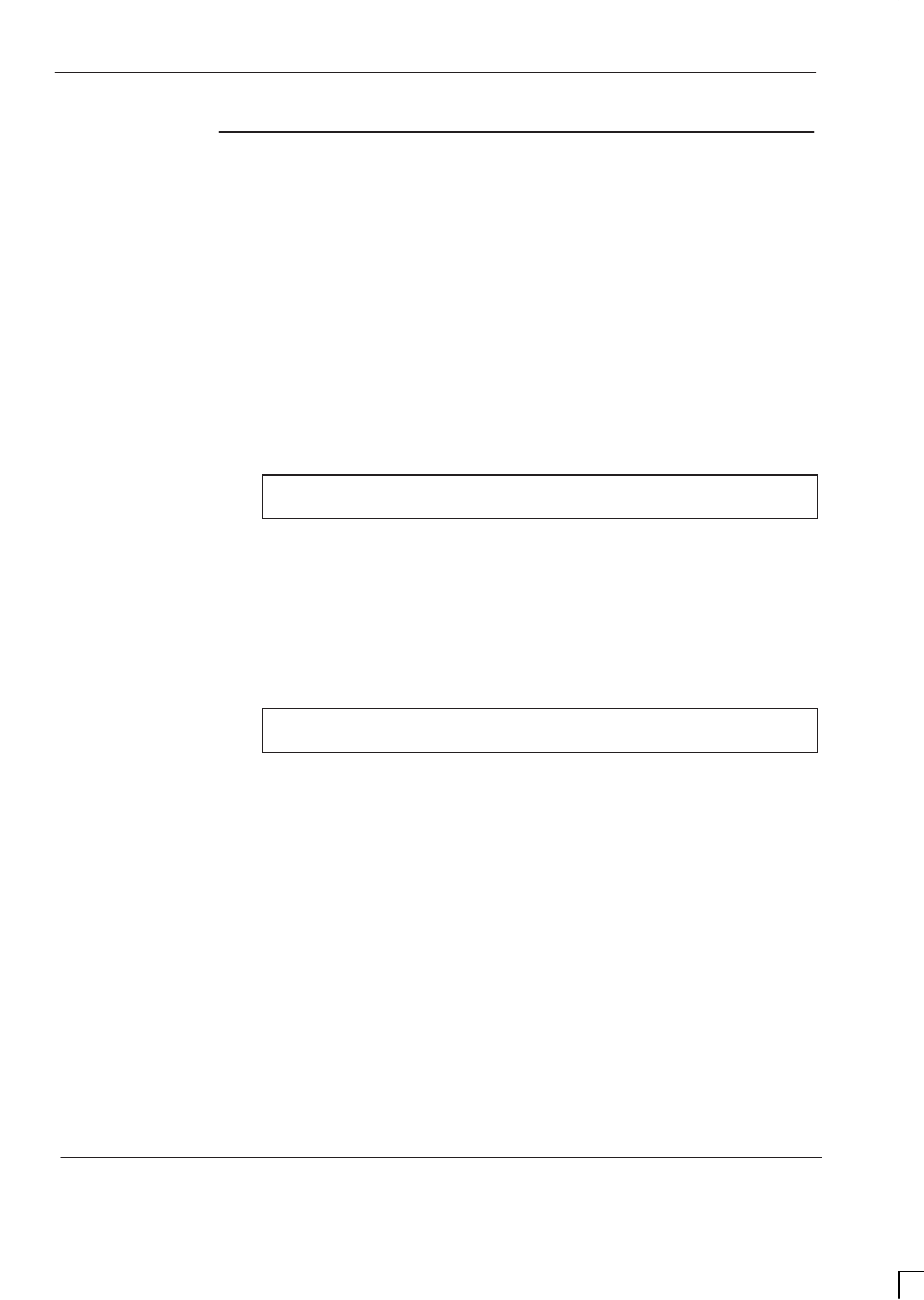
GSM-204-423
Unpacking and preparing the cabinet
31st Oct 01
Inst. 3–8
Installation & Configuration: Horizon
macro
outdoor
CONTROLLED INTRODUCTION
68P02902W03-A
Cabinet access
procedures
Cabinet access procedures include:
Door and lid opening and closing.
TMS front cover removal and refitting.
Door opening and closing
The door lock has a spring loaded handle. The door is operated as follows:
1. Insert key into lock and turn clockwise until spring loaded handle releases.
2. Turn handle a quarter turn anti-clockwise to open the lock.
3. Open power supply enclosure door to 90 locking position.
4. Open radio enclosure door to 90 locking position.
NOTE If the equipment is active, a door open alarm will be
generated.
5. To open doors to 120, lift up middle of appropriate wind stop.
6. To close, lift up middle of wind stop, close doors firmly, radio enclosure
door first.
7. Turn handle a quarter turn clockwise, push handle flush and remove key
to lock the door.
Lid opening and closing
NOTE The lid can only be opened and closed when both doors
are open.
The lid is opened as follows:
1. Ensure both cabinet doors are open to the 90 position.
2. Undo the two draw latches by turning anti-clockwise, and ensure the catch
hook is clear of lip on the lid.
3. Lift the lid until the mechanical stay audibly locks.
The lid is closed as follows:
1. Press the lock stud on the mechanical stay to release.
2. Lower the lid.
3. Hook the draw latches over the lip and turn clockwise to lock.
4. Ensure operating tab is stowed flat.
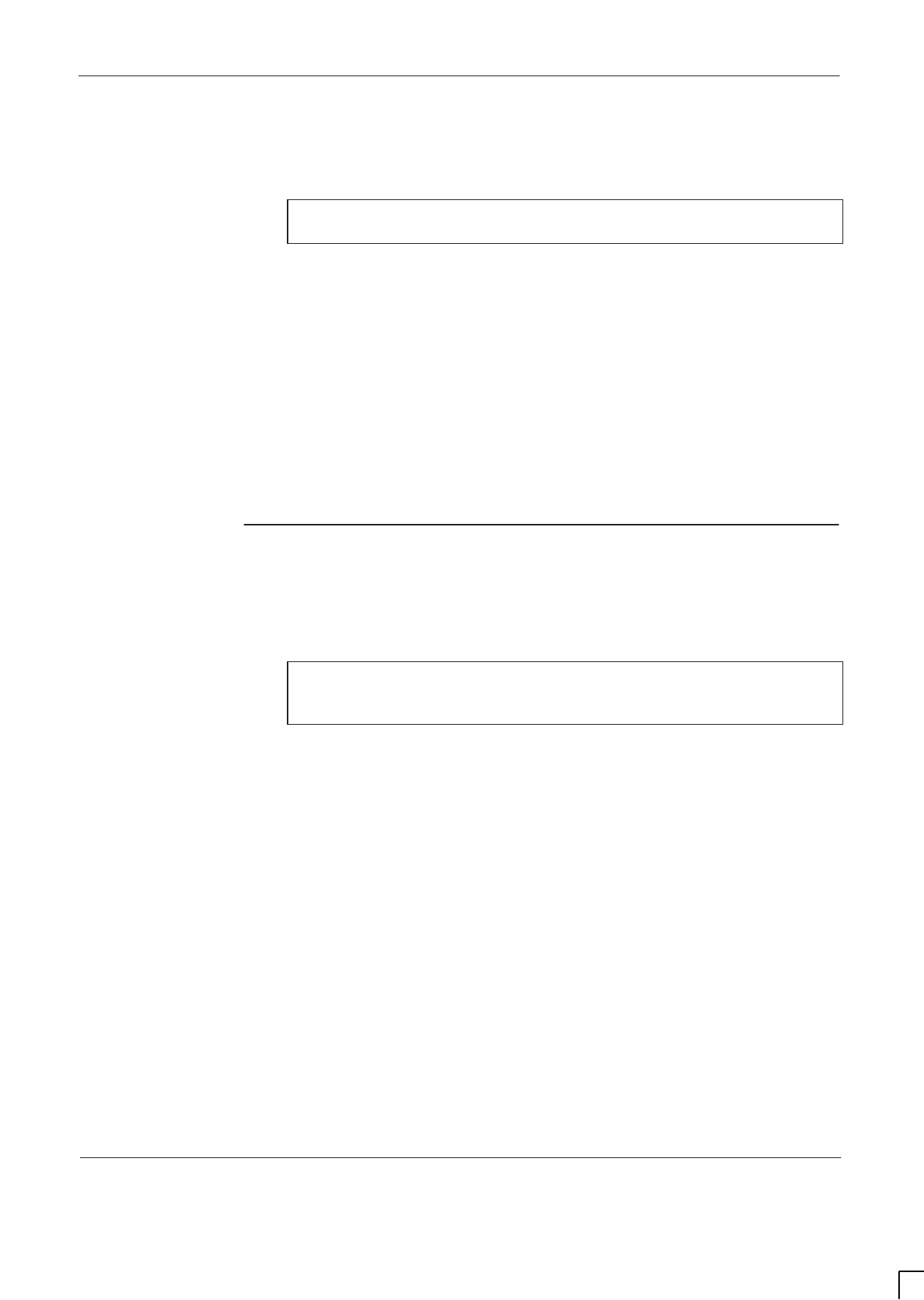
GSM-204-423 Unpacking and preparing the cabinet
31st Oct 01
Installation & Configuration: Horizon
macro
outdoor
68P02902W03-A
CONTROLLED INTRODUCTION
Inst. 3–9
TMS front cover removal and refitting
To remove the TMS front cover:
NOTE The TMS front cover can only be removed and refitted
when both doors are open.
1. Remove and retain the four push in plastic covers.
2. Using a cross point screwdriver, undo the four captive fasteners by turning
anticlockwise until they release.
3. Lift the TMS front cover away from the cabinet and store safely.
To refit the TMS front cover:
1. Refit the TMS front cover and line up the four fasteners.
2. Using a cross point screw driver, tighten the four captive fasteners.
3. Refit the four push in plastic covers.
Procedures for
unpacking and
preparing the
cabinet
The following describes the procedure for unpacking the equipment.
NOTE It is recommended that the installer reads through the
following procedure before starting to unpack and install
the equipment.
Dismantling the shipping packaging and obtaining template
To dismantle the shipping packaging and obtain template:
1. Cut the plastic banding that secures the packaging.
2. Lift the lid free of the box.
3. Remove separate template from the inside of the box lid, and deliver to
the site for site preparation.
4. Remove the wooden spreader and the blanks and accessory trays from
the box.
5. Undo the taped fastening on the box side.
6. Unwrap the box from around the cabinet, (the wrap-around box is secured
by velcro).
7. Unbolt the two wooden packing pieces from the lifting points in the cabinet
sides.
The cabinet is now ready to be prepared for lifting.
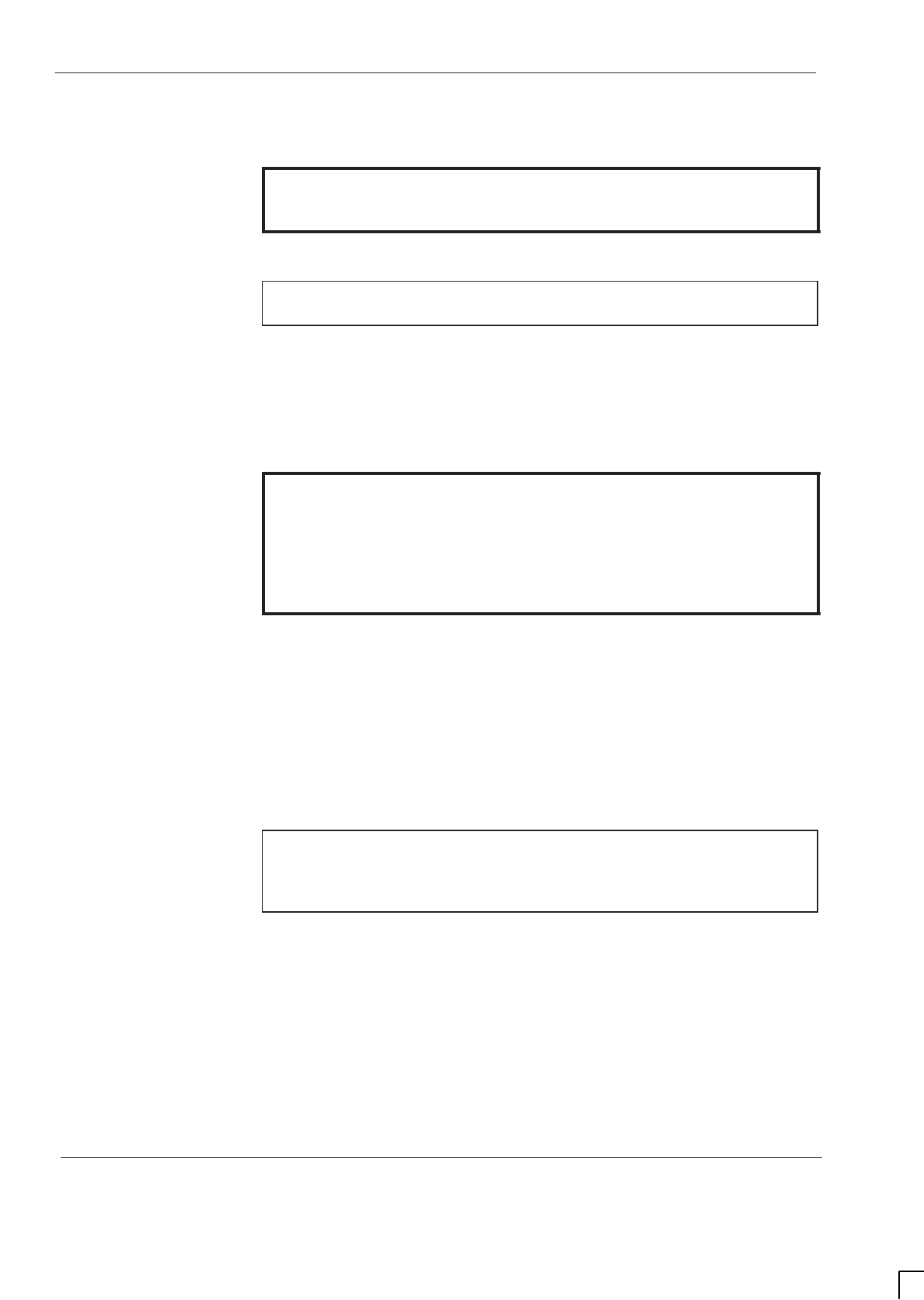
GSM-204-423
Unpacking and preparing the cabinet
31st Oct 01
Inst. 3–10
Installation & Configuration: Horizon
macro
outdoor
CONTROLLED INTRODUCTION
68P02902W03-A
Preparing the cabinet for lifting
WARNING The cabinet can weigh up to 360 kg. Handle with extreme
caution, and in accordance with local health and safety
regulations.
To prepare the cabinet for lifting and remove it from the wooden delivery base:
CAUTION Care must be taken to avoid damaging the cabinet in any
way, especially by scratching the outer surfaces.
1. Carefully remove the cling wrap surrounding the cabinet.
2. Inspect the equipment immediately for damage. Report the extent of any
damage to the transport company.
3. Insert the eyebolts into the threaded lifting points on the cabinet sides,
ensuring that no cross-threading occurs.
WARNING Before attempting to insert the eyebolts, visually check
each one for damage. If any damage is apparent, DO
NOT USE.
Do not overtighten the eyebolts; hand tight is sufficient. Do
not tighten eyebolts with a t-bar or spanner. Screw the
eyebolt fully into the lifting point so that no thread is left
exposed.
4. Attach lifting straps to the eyebolts and connect to lifting gear.
5. Open the cabinet doors and remove the TMS front cover (see Cabinet
access procedures this section) and the two rear mounting bolt cover
plates and store safely.
6. Refer to Figure 3-2 and remove the four nuts securing the cabinet to the
wooden delivery base.
7. Unscrew the securing bolts from underneath the wooden delivery base
until they are clear of the cabinet.
CAUTION The cabinet may be subject to bending and distortion
during installation. To minimize this the TMS front cover
must be fitted and the cabinet doors must be closed,
before lifting the cabinet.
8. Refit the TMS front cover and close the cabinet doors.
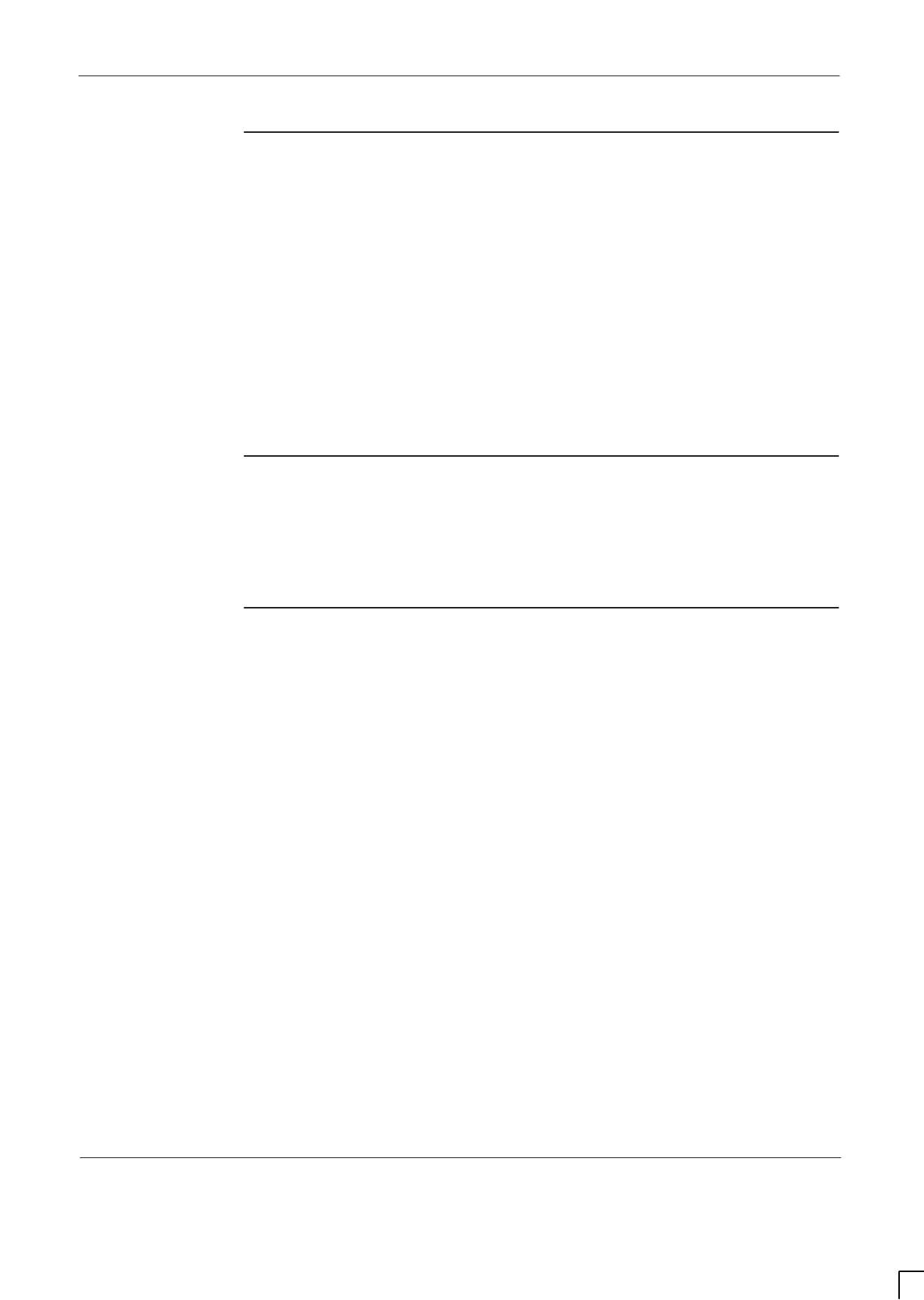
GSM-204-423 Unpacking and preparing the cabinet
31st Oct 01
Installation & Configuration: Horizon
macro
outdoor
68P02902W03-A
CONTROLLED INTRODUCTION
Inst. 3–11
Visual
inspection
After unpacking and preparation for lifting carry out a visual inspection on:
Cabinet exterior
Examine the exterior of the cabinets for structural, paint or mechanical damage
and report any damage to Motorola.
Cabinet interior
Examine the interior of the cabinet for structural, paint or mechanical damage
and report any damage to Motorola.
The cabinet can now be lifted gently and manoeuvred to the concrete base.
Safe disposal of
packing
material
The packing material used by Motorola is non-returnable, and should be
disposed of safely.
CTU module
allotted slot
retention
CTUs are supplied already fitted into the cabinet, with Tx cable correctly
attached at the factory. The CTUs must remain in the allotted slots for factory
calibrations to be valid.
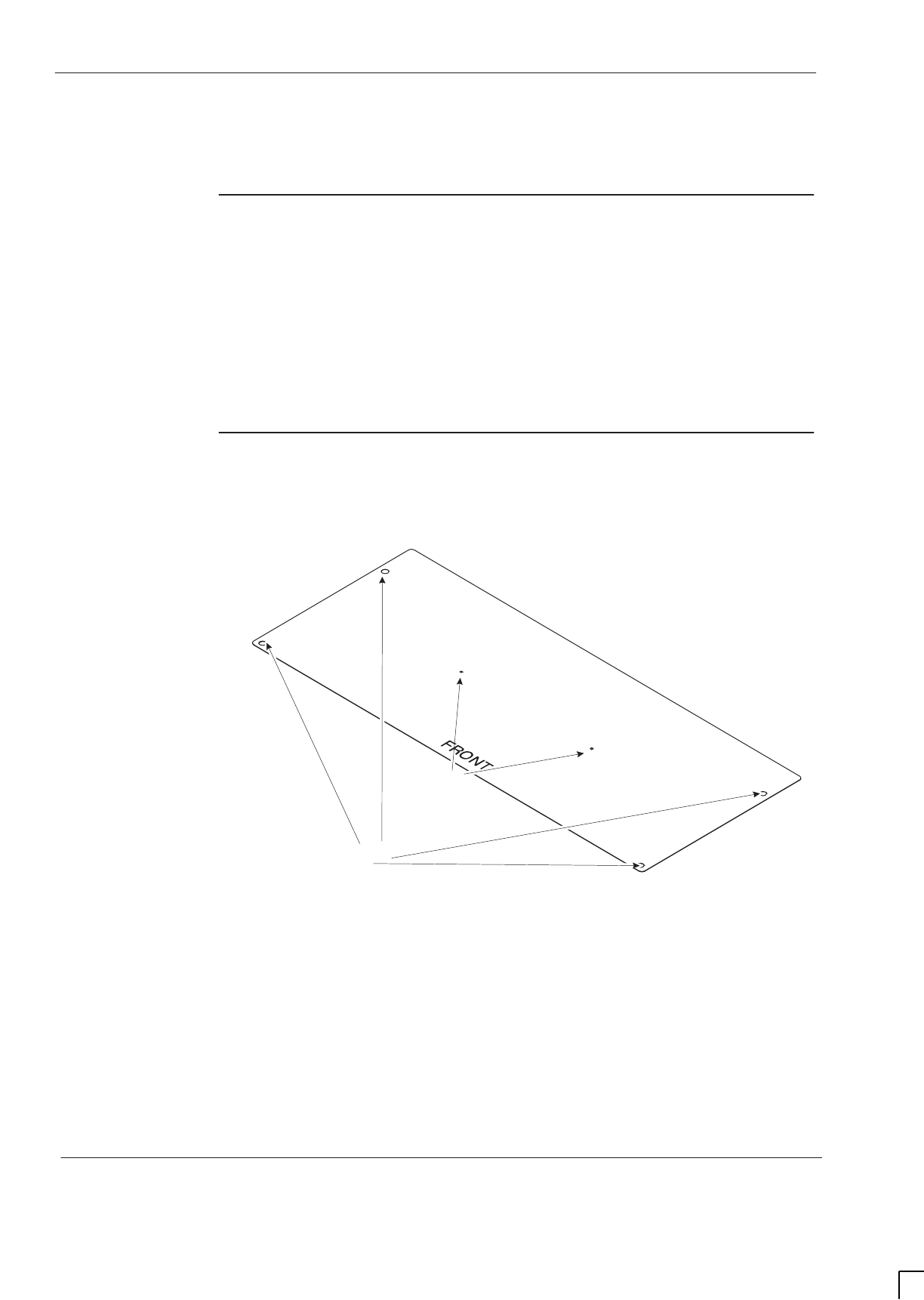
GSM-204-423
Installing the template and mounting bolt anchors
31st Oct 01
Inst. 3–12
Installation & Configuration: Horizon
macro
outdoor
CONTROLLED INTRODUCTION
68P02902W03-A
Installing the template and mounting bolt anchors
Introduction to
template and
mounting bolt
anchor
installation
The Horizon
macro
outdoor BTS cabinet is supplied with an alloy template. The
template is installed before the cabinet to show the locations of the cabinet
mounting bolt anchors. There is no need to remove the template after
installation of the expanding bolt anchors.
View of
template
Figure 3-3 shows the template used in installing the Horizon
macro
outdoor
cabinet.
CLEARANCE FOR CABINET
MOUNTING BOLTS
No. 10 TEMPLATE
MOUNTING SCREW
HOLES
Figure 3-3 Horizon
macro
outdoor template
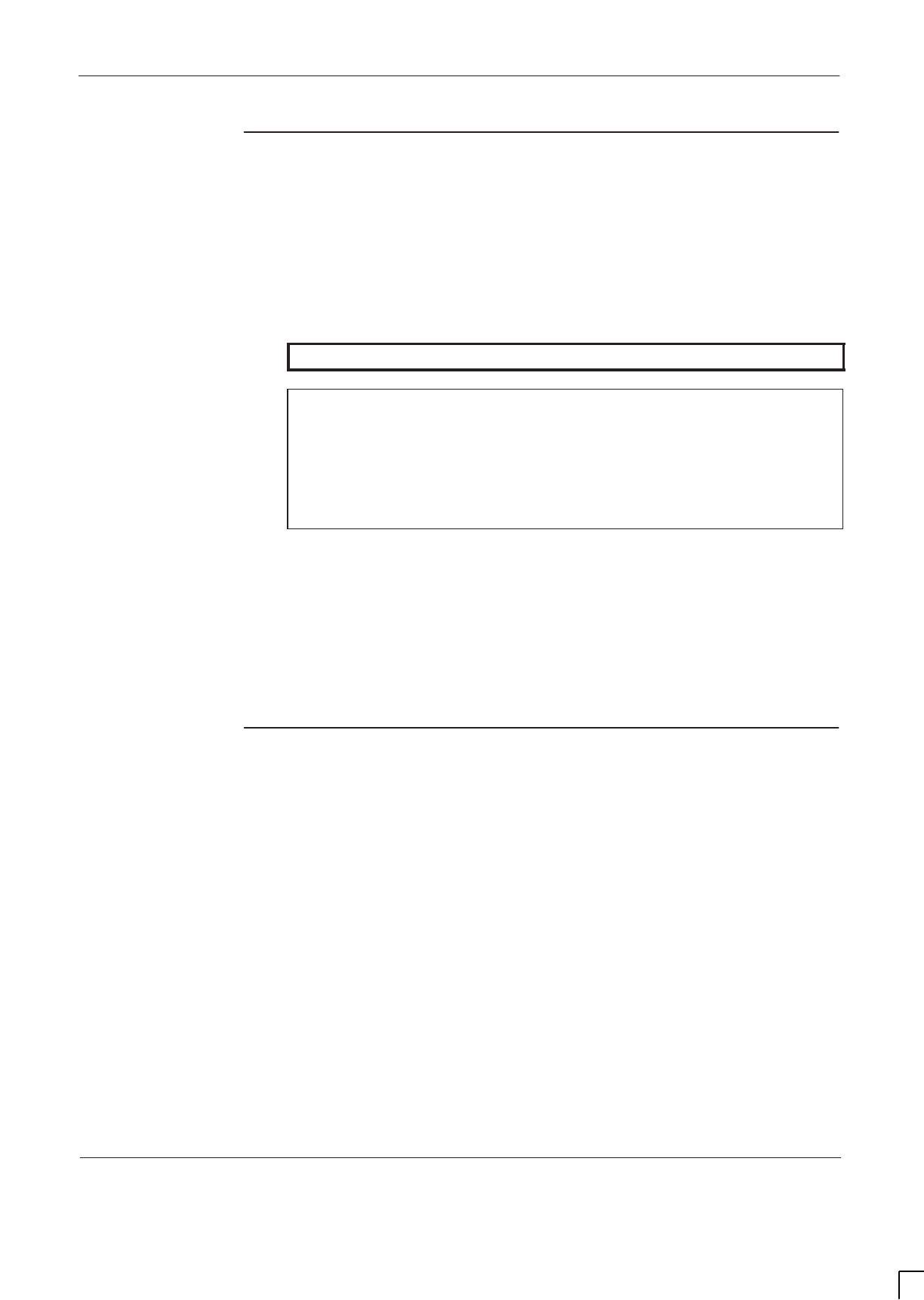
GSM-204-423 Installing the template and mounting bolt anchors
31st Oct 01
Installation & Configuration: Horizon
macro
outdoor
68P02902W03-A
CONTROLLED INTRODUCTION
Inst. 3–13
Procedure for
installing
template
The template must be secured to the concrete base before drilling the mounting
holes for the M12 anchor bolts.
1. Move the cabinet template to the selected mounting position.
2. Mark the positions of the two template mounting screw holes in the
template.
WARNING Wear safety glasses and a dust mask when drilling holes.
CAUTION Drilling concrete flooring produces cement dust, which is
harmful to equipment and wiring. Protect the cabinets and
any nearby equipment from dust. Use a tarpaulin, cloth, or
plastic sheeting to cover exposed equipment. Clean up
any accumulated debris from the anchor installation
carefully before exposing the equipment. Use drilling
equipment suitable for cutting steel reinforced concrete.
3. Drill out the two holes to a depth and clearance for No. 10 screws.
4. Fit plastic expanding plugs into the mounting holes.
5. Position the template over the mounting holes and secure using No. 10
screws.
6. When satisfied that the template is correctly installed, carry out procedure
for installing the cabinet anchor bolts.
Recommended
bolt length for
concrete base
The length of the M12 steel anchor bolts must be determined by a structural
engineer, but must be of sufficient strength to withstand 105 knot (120 mph)
winds on the cabinet front or rear for a maximum gross weight of 360 kg.
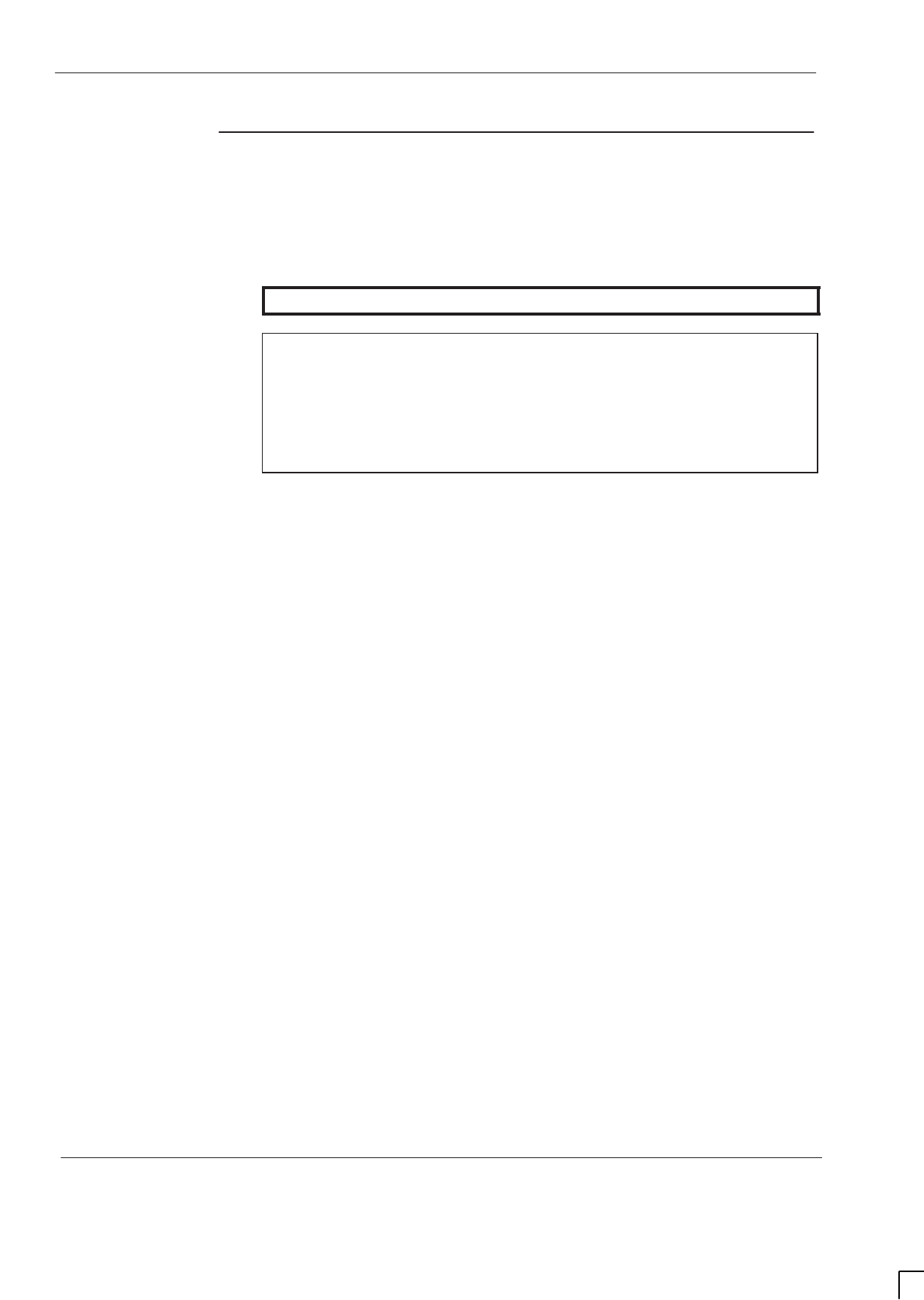
GSM-204-423
Installing the template and mounting bolt anchors
31st Oct 01
Inst. 3–14
Installation & Configuration: Horizon
macro
outdoor
CONTROLLED INTRODUCTION
68P02902W03-A
Procedure for
installing
cabinet bolt
anchors
The concrete base must be drilled to accept the M12 anchor bolts. Washers,
bushes and M12 steel bolts must be supplied by the customer.
WARNING Wear safety glasses and a dust mask when drilling holes.
CAUTION Drilling concrete flooring produces cement dust, which is
harmful to equipment and wiring. Protect the cabinets and
any nearby equipment from dust. Use a tarpaulin, cloth, or
plastic sheeting to cover exposed equipment. Clean up
any accumulated debris from the anchor installation
carefully before exposing the equipment. Use drilling
equipment suitable for cutting steel reinforced concrete.
1. Using the four holes in the template as a guide, drill the concrete base to a
depth and clearance for the M12 anchor bolts.
2. Fit the M12 mounting anchors to the holes in the base.
3. Fit the anchor bolts with the supplied bushes and washers, through the
template, to each anchor.
4. Tension up the anchor bolts to expand the anchors.
5. Remove and retain the M12 bolts and washers for later use.
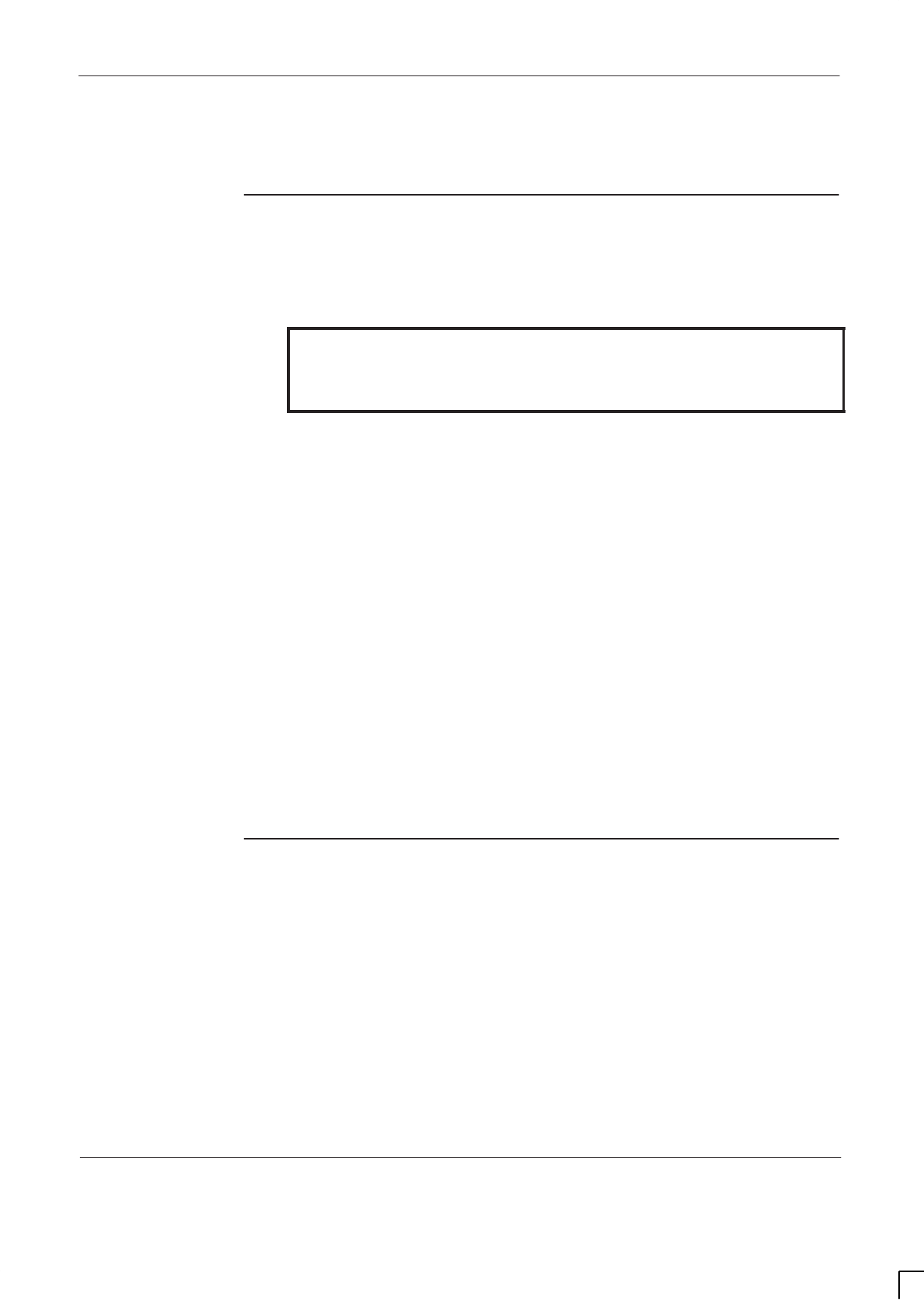
GSM-204-423 Fitting the outdoor cabinet onto its base
31st Oct 01
Installation & Configuration: Horizon
macro
outdoor
68P02902W03-A
CONTROLLED INTRODUCTION
Inst. 3–15
Fitting the outdoor cabinet onto its base
Procedure for
fitting a BTS
cabinet
To fit a Horizon
macro
outdoor BTS cabinet onto a prepared concrete base, (or
steel structure):
WARNING An equipped Horizon
macro
BTS cabinet can weigh up to
360 kg.
Observe proper lifting precautions and handle each
cabinet with extreme caution to avoid tipping.
1. Place the Horizon
macro
outdoor BTS cabinet onto the template, (or steel
structure).
2. Open the cabinet doors and remove the TMS front cover see Unpacking
and preparing the cabinet (cabinet access procedures).
3. Line up the fixing holes in the bottom of the cabinet with the previously
installed anchors, (or holes in steel structure).
4. Place a flat washer onto each M12 mounting bolt and fit the four mounting
bolts loosely. Do not tighten yet.
5. Use a spirit level to verify that the cabinet is level. If necessary, use shims
to level the cabinet. Tighten up the mounting bolts to the correct torque,
(the setting of torque value for M12 anchor screws/bolts depends on local
supplies. Refer to the manufacturer’s data for correct values).
6. Refit the bottom front panel and the two rear mounting bolt cover plates,
previously retained.
7. Remove each of the eyebolts from their threaded holes (located on the
sides of the cabinet), and return the eyebolts to the tool kit for future use.
Mounting
additional
cabinets
At this stage, additional Horizon
macro
outdoor BTS cabinets, optional cable
shrouds and/or optional auxiliary equipment housings may be installed,
depending on the site configuration (see Site requirements and
considerations). Refer to Chapters 2, 4 and 5 in this category for information
on installing, multiple cabinet layouts, cable shrouds and auxiliary equipment
housings.
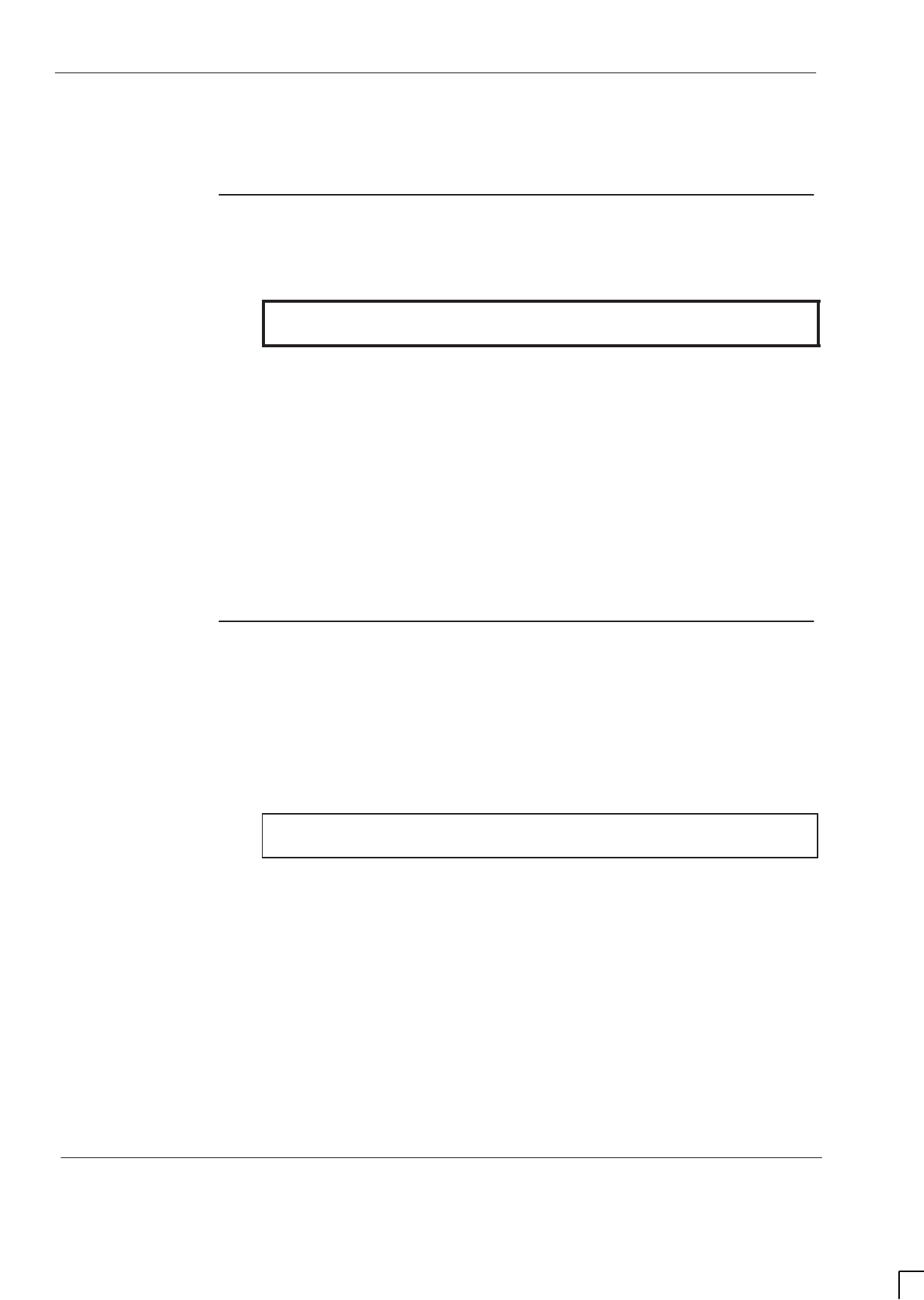
GSM-204-423
Earthing and transient protection
31st Oct 01
Inst. 3–16
Installation & Configuration: Horizon
macro
outdoor
CONTROLLED INTRODUCTION
68P02902W03-A
Earthing and transient protection
Site earthing
This part of the manual summarizes general procedures for earthing the site.
Refer to the
Grounding guidelines for cellular radio installations 68P81150E62
,
for detailed earthing information.
WARNING Each cabinet must be earthed separately. Cabinets must
not be daisy chained together.
The cell site equipment must be earthed (in the same common earth point
as its power source).
Provision should be made for earthing the site before beginning the
installation of the system cabinets. See Earthing the site in Chapter 2 of
this Category.
There is an earthing terminal (stud) located on the earth/connector plate
on the cable entry side of each BTS cabinet, and auxiliary equipment
housing.
Refer to the site-specific documentation for detailed site earthing
information.
Secondary
transient and
lightning
protection
All E1/T1 lines connected to Motorola equipment have secondary transient
protection as part of the BIB or T43 board. Ensure the receive and transmit
antenna connections to the cabinet are fed through coaxial electromagnetic
protection (EMP) devices.
CAUTION The end–user is responsible for transient protection of the
E1/T1 lines connected to Motorola equipment.
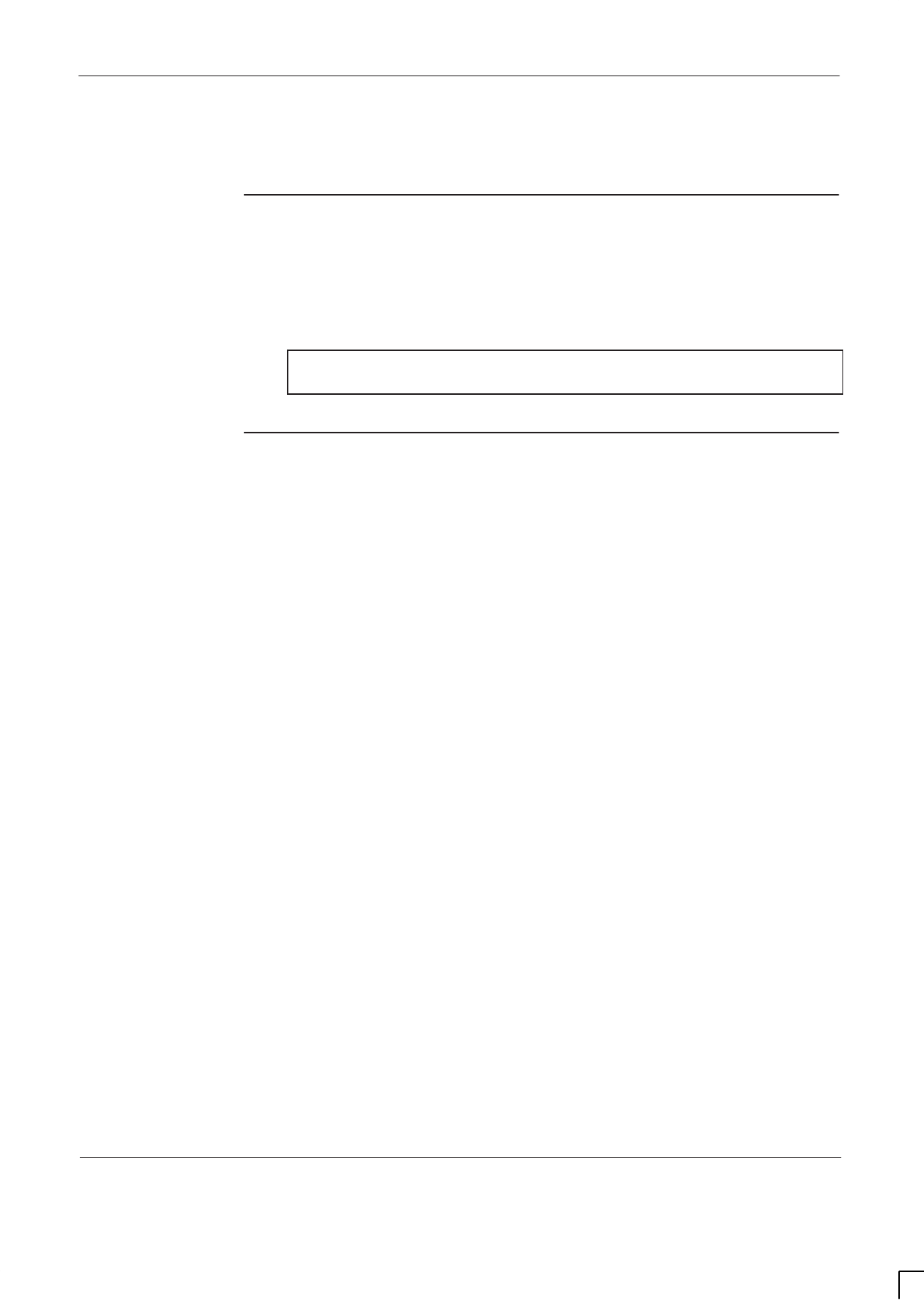
GSM-204-423 Connecting the internal batteries
31st Oct 01
Installation & Configuration: Horizon
macro
outdoor
68P02902W03-A
CONTROLLED INTRODUCTION
Inst. 3–17
Connecting the internal batteries
Introduction to
connecting the
internal
batteries
The Horizon
macro
outdoor cabinet is delivered with the internal batteries
disconnected (for safety reasons).
CAUTION The batteries must be reconnected before external ac
power is connected to the cabinet.
Internal battery
connection
procedure
To connect the internal batteries (refer to Figure 3-4):
1. Ensure battery circuit breaker is set to off.
2. Undo the two battery tray retaining screws and pull the tray forward until
the two battery cables and the battery sense lead (4-way Molex
connector) can be accessed.
3. Remove the heatshrink sleeves from the battery cable terminations.
Connect the blue cable to the bottom breaker terminal and the black cable
to the front (red) positive terminal.
4. Ensure the four battery sense leads are connected as shown in Figure 3-4
and plug the black Molex 4-way connector into its socket on the battery
retaining strap.
5. Push the tray back into the cage and tighten the retaining screws.
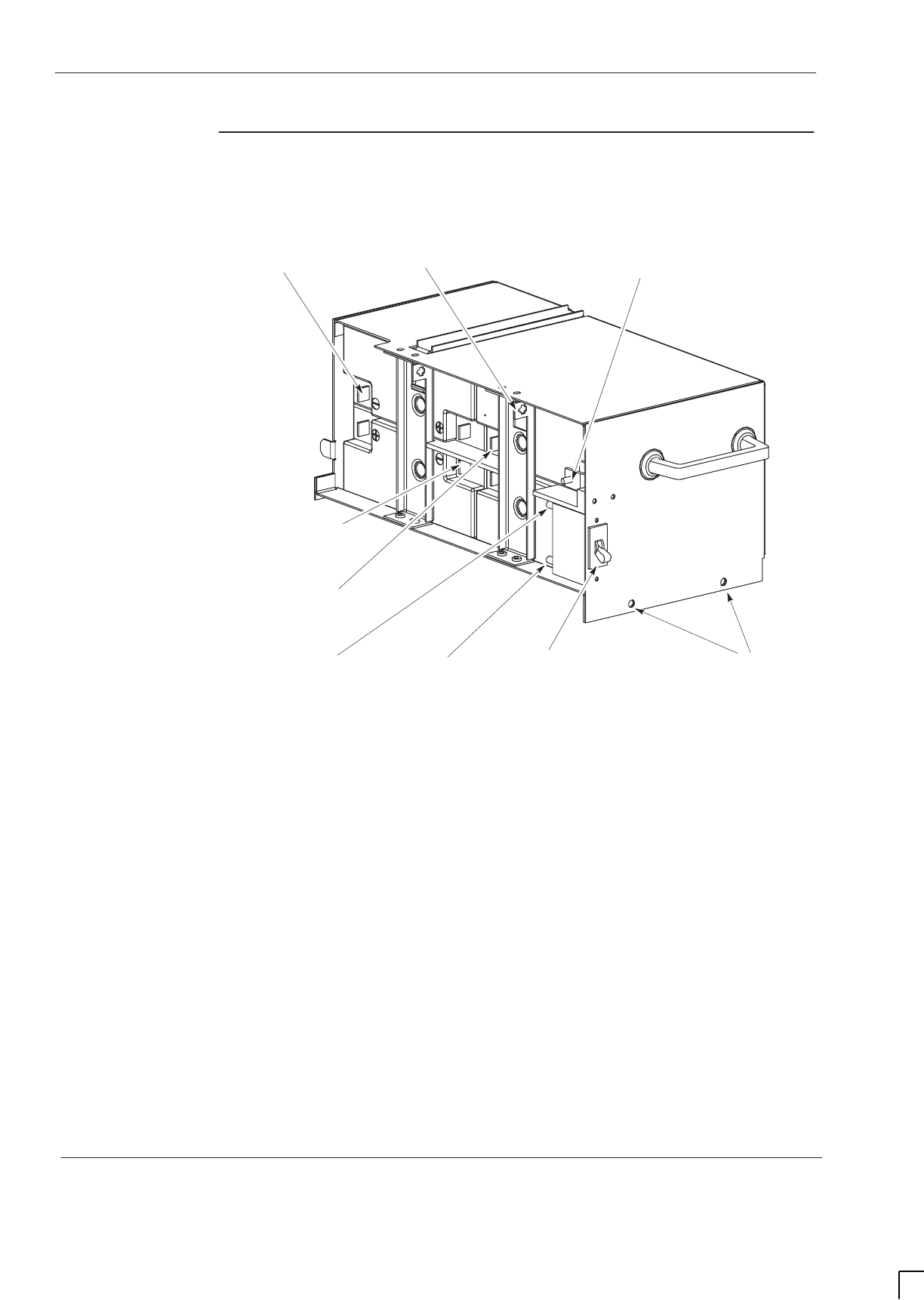
GSM-204-423
Connecting the internal batteries
31st Oct 01
Inst. 3–18
Installation & Configuration: Horizon
macro
outdoor
CONTROLLED INTRODUCTION
68P02902W03-A
View of internal
battery tray
Figure 3-4 shows a view of the internal battery tray.
SENSE LEAD
TERMINAL B
BATTERY TRAY
RETAINING SCREWS
FRONT +VE
BATTERY TERMINAL
(black cable)
4-WAY BATTERY SENSE
LEAD MOLEX CONNECTOR
BOTTOM BREAKER
TERMINAL
(blue cable)
CIRCUIT BREAKER
SWITCH
SENSE LEAD
TERMINAL D
SENSE LEAD
TERMINAL E
(top breaker
terminal)
SENSE LEAD
TERMINAL C
Figure 3-4 Making the connections on the internal battery tray
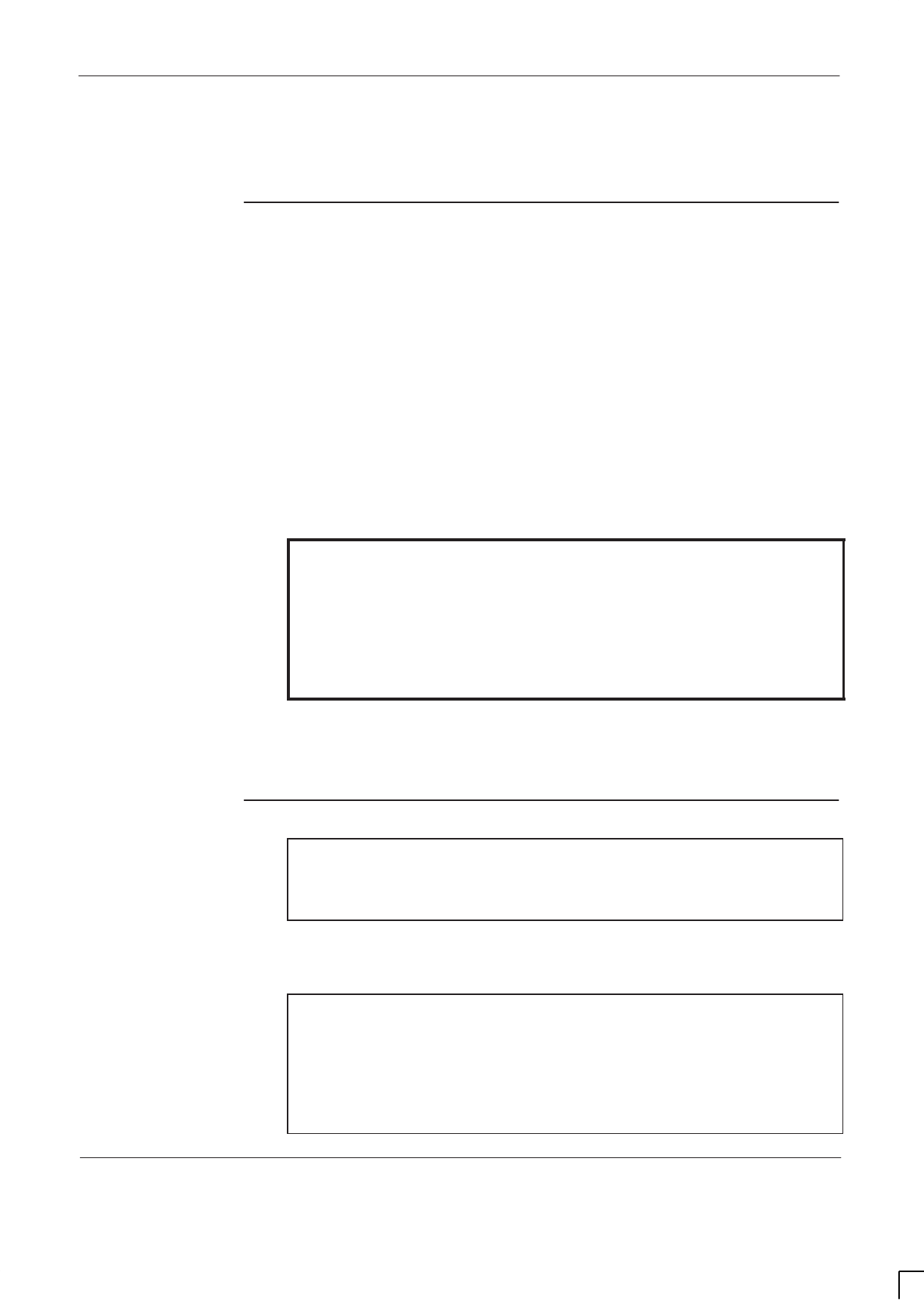
GSM-204-423 Installing and connecting power and earth cabling
31st Oct 01
Installation & Configuration: Horizon
macro
outdoor
68P02902W03-A
CONTROLLED INTRODUCTION
Inst. 3–19
Installing and connecting power and earth cabling
Overview of
power and earth
cabling
On delivery, the Horizon
macro
outdoor BTS cabinet is configured for a 230 V ac
single phase power supply. The possible configurations of ac power supplies
are:
Single phase (110 V).
Single phase (230 V) – default configuration.
Three phase star (230 V).
Three phase delta (230 V).
This section describes the procedures for connecting power and earth cabling to
the cabinet.
WARNING Do not daisy chain cabinet earths together.
Do not make ac input power connections at the main
power source at this time. Connecting input power is
the final installation procedure, carried out as part of
commissioning in Chapter 6 of this category.
Cabinets must be earthed with a conductor capable of
carrying the full fault current of the overcurrent protection
device.
Power specifications can be found in Chapter 2 Site requirements and
considerations.
Cable routeing
CAUTION Ensure that covers are fitted to any unused connectors on
the cabinet interconnect panel. The covers protect the
connectors from damage by static electricity or foreign
matter.
Adequate means should be provided for routeing cables from the main power
source to the equipment, such as a cable trough or conduit.
NOTE The current-carrying capacity of a cable for continuous
service is affected by all of the following factors
(references: IEC 364, BS7671):
– Ambient temperature.
– Grouping.
– Partial or total enclosure in thermal insulating material.
– Frequency (ac only).
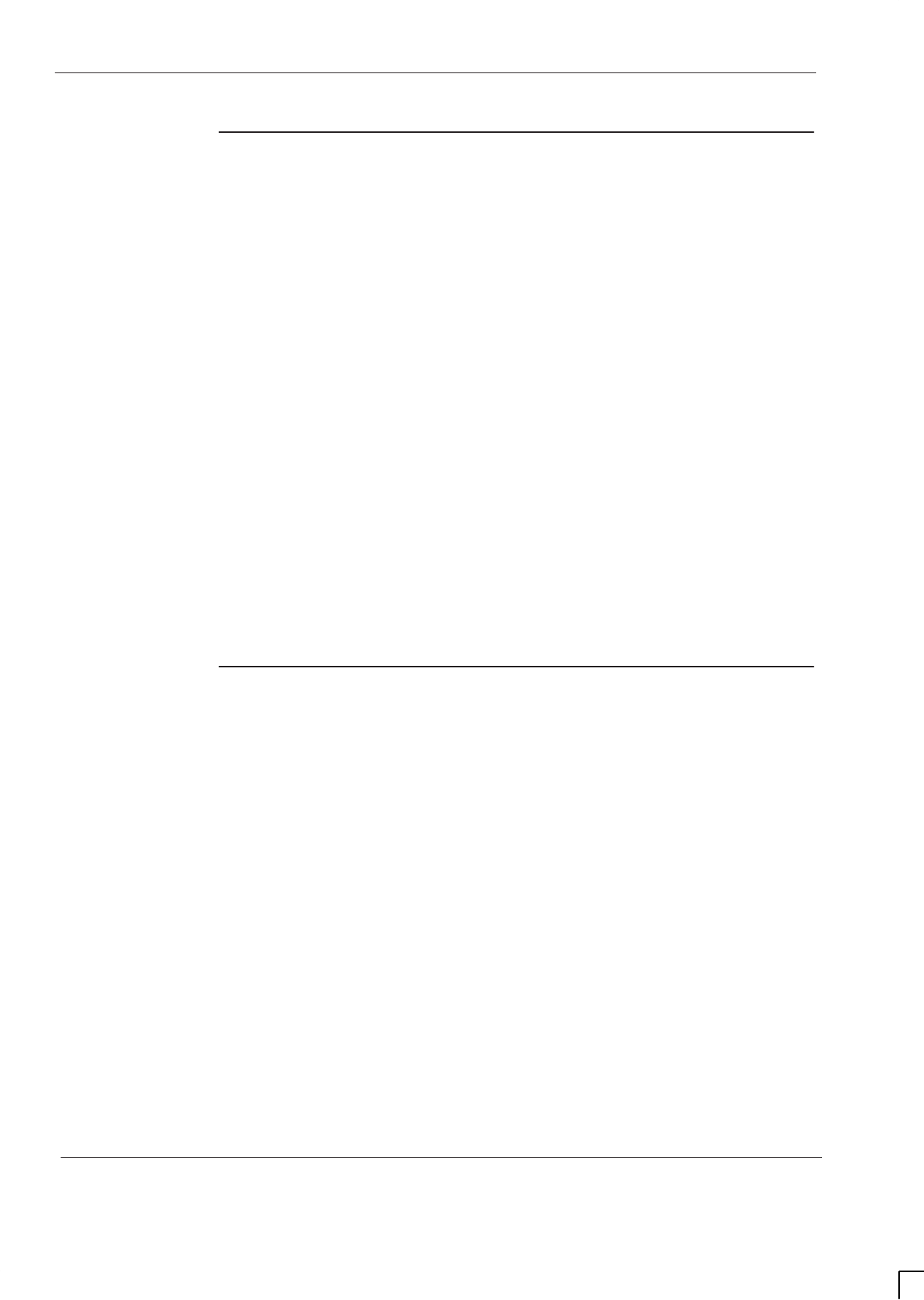
GSM-204-423
Installing and connecting power and earth cabling
31st Oct 01
Inst. 3–20
Installation & Configuration: Horizon
macro
outdoor
CONTROLLED INTRODUCTION
68P02902W03-A
Cabinet
earthing points
The main earth connection point is located on the earth/connector plate on the
cable entry side. This connection is for protective earthing, lightning protection
and functional earthing of the cabinet.
To earth the BTS cabinet:
1. Ensure the M8 chassis earth studs, located in rear corners of the top
section, are connected to the BTS cabinet earth plate.
2. Connect the earth plate stud to the site earth using a 35 mm2
cross-sectional area, green and yellow sheathed, stranded conductor.
Additional internal earths are:
Two M8 chassis earth studs, located in rear corners of the top section.
Number 1 ac distribution box in the top section.
Number 2 ac distribution box in the power supply unit (PSU).
PSU cage earth stud, located behind the number 2 ac distribution box.
An M6 threaded stud on the top interface panel, adjacent to the dc input.
Main cage to underside of interface panel above PSM.
AC socket to underside of interface panel at rear of panel.
Earth bonding from doors and lid to the cabinet chassis.
Earth bonding from the TMS heat exchanger to the cabinet chassis.
Power supply
cable colour
coding
To connect an outdoor cabinet to the EXTERNAL ac power source, observe the
following rules.
Single-phase supply
For single-phase ac connections:
The line power cable is brown or red.
The neutral cable is blue or black.
The earth cable is green and yellow.
Three-phase supply
For three-phase ac connections:
The phase A power cable is red.
The phase B power cable is blue.
The phase C power cable is yellow.
The neutral cable is black.
The earth cable is green and yellow.
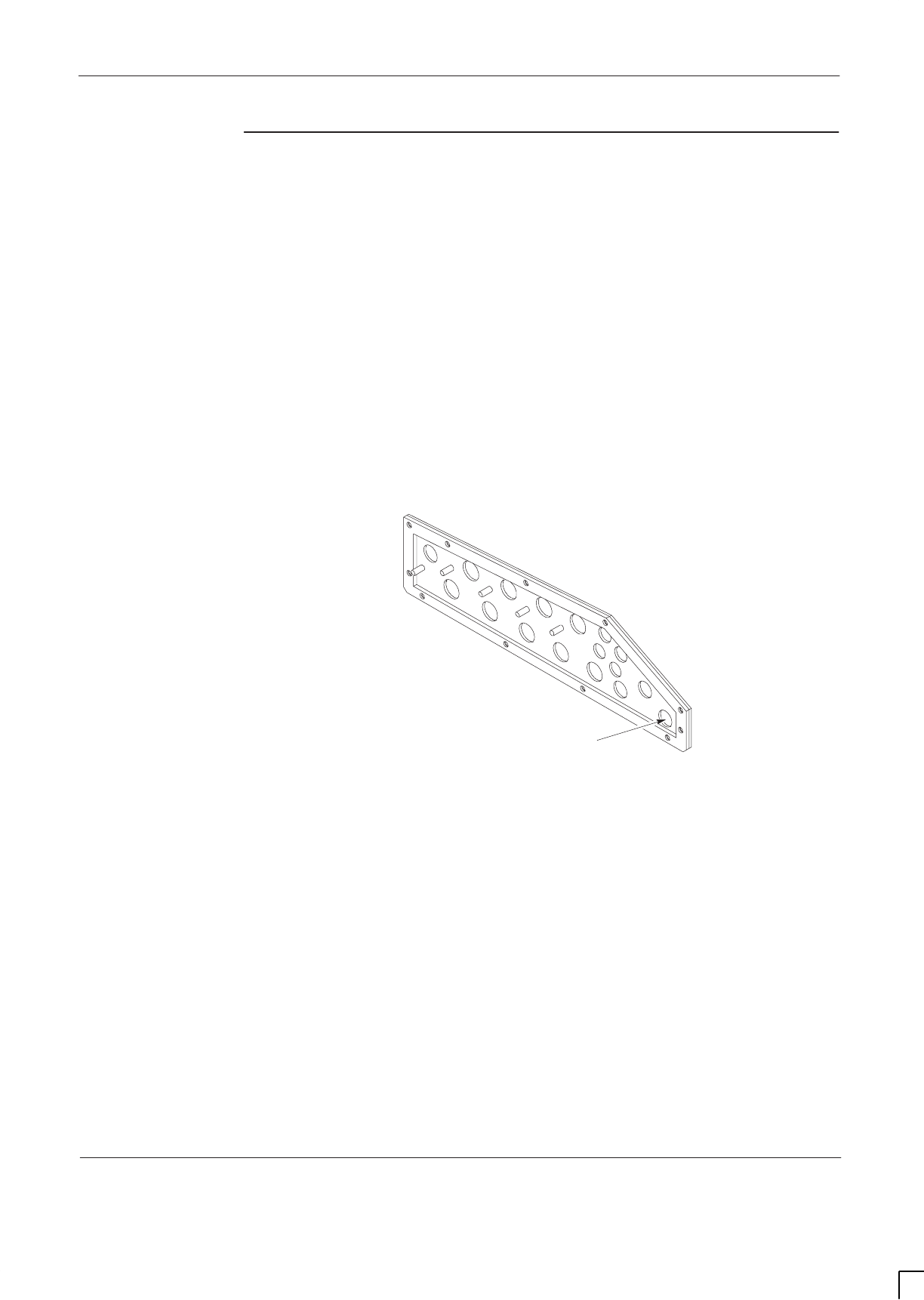
GSM-204-423 Installing and connecting power and earth cabling
31st Oct 01
Installation & Configuration: Horizon
macro
outdoor
68P02902W03-A
CONTROLLED INTRODUCTION
Inst. 3–21
Preparing for
connection
To prepare for connecting ac power cables to an Horizon
macro
outdoor cabinet:
1. Unscrew the four captive securing screws and remove and retain number
1 ac distribution box insulated cover.
2. Disconnect and remove the remains of the factory test cable from the
number 1 ac distribution box.
3. Tighten all screws disturbed in step 2.
4. Position the screened power cable, complete with earth, in a conduit.
Route the conduit to the ac power outlet point.
5. Feed the ac power cable into the Horizon
macro
cabinet through the AC IN
hole in the earth plate (see Figure 3-5) and through one of the supplied
cable glands. From the outside of the cabinet, push the cable gland (with
the sealing ring) into the AC IN hole, and from the inside, fit the earth tag
and secure with the locking nut.
AC IN
Figure 3-5 Earth plate, showing location of entry hole for ac supply cable
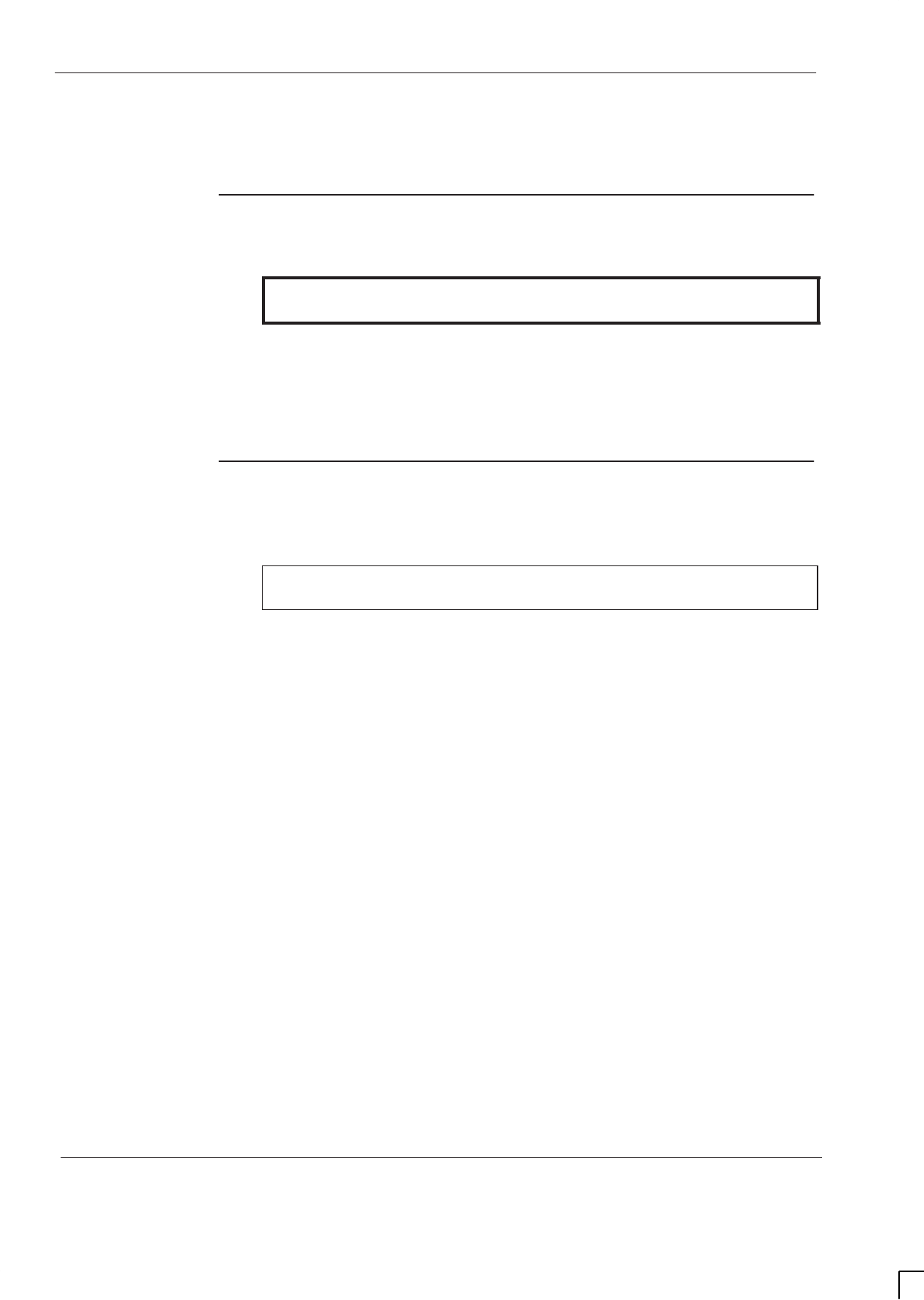
GSM-204-423
Connecting 230 V single phase ac power cables
31st Oct 01
Inst. 3–22
Installation & Configuration: Horizon
macro
outdoor
CONTROLLED INTRODUCTION
68P02902W03-A
Connecting 230 V single phase ac power cables
Configuring the
number 1 ac
distribution box
WARNING Ensure that the mains input isolator is set to position O
(off) and source is isolated before proceeding.
On delivery, the Horizon
macro
outdoor BTS cabinet is configured for a 230 V ac
single phase power supply.
If connecting to a single phase 230 V ac supply, no configuration of the number
1 ac distribution box is required.
Connecting
230 V ac single
phase mains
input cables
CAUTION 230 V single phase link is fitted to the four pole MCB and
must remain fitted for safety requirements.
To connect a 230 V earth, live, and neutral power cable to the number 1 ac
distribution box:
1. Connect the ac power input earth cable (green/yellow) to terminal 1 of the
earth terminal block in the number 1 ac distribution box, and check the
connection of the cabinet earth cable to terminal 2. Secure both cables.
2. Secure the screen at the cabinet entry gland.
3. Connect the live ac cable (brown or red) to linked terminals B2, C2, D2 of
the four pole MCB in the number 1 ac distribution box, and secure.
4. Connect the neutral ac cable (blue or black) to terminal A2 of the four pole
MCB in the number 1 ac distribution box, and secure.
5. Check the security of all connections within the number 1 ac distribution
box.
6. Refit the previously retained cover of the number 1 ac distribution box.
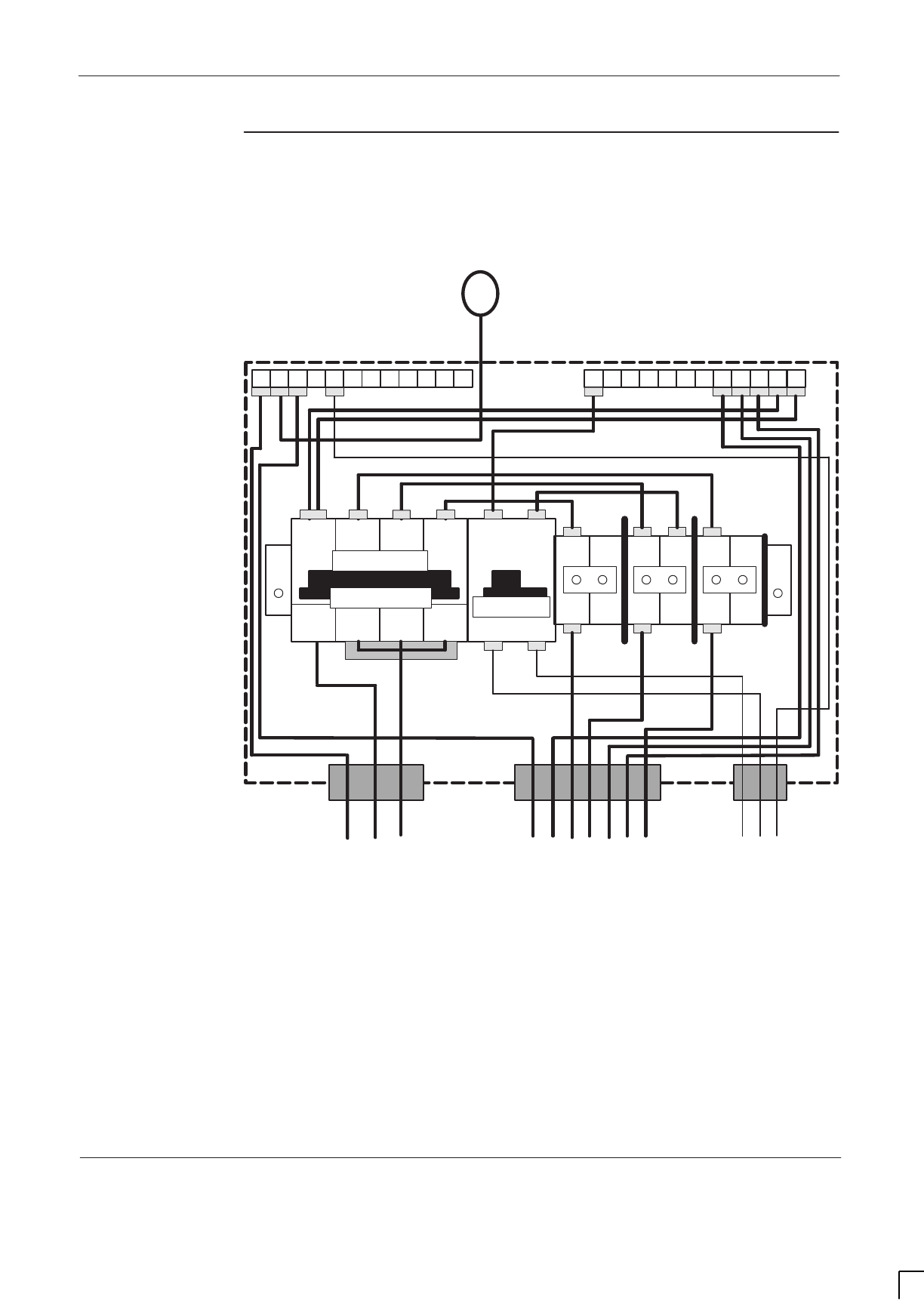
GSM-204-423 Connecting 230 V single phase ac power cables
31st Oct 01
Installation & Configuration: Horizon
macro
outdoor
68P02902W03-A
CONTROLLED INTRODUCTION
Inst. 3–23
230 V ac single
phase wiring
diagram
Figure 3-6 shows the wiring diagram for the number 1 ac distribution box when
configured for a 230 V ac single phase power supply.
7
RCBO
EARTH NEUTRAL
TO AC
OUTLET
SOCKET
INCOMING
AC
SUPPLY
1
12108642
119753
4 POLE MCB
A1 B1 C1 D1 E1 F1
A2 B2 C2 D2 E2 F2
1 2 3 4 5 8 9 10 1112 123456789101112
32 A Type C
MAIN CHASSIS
EARTH
TO AC
DISTRIBUTION BOX 2
6
NEL
6 A 30 mA
NEL
Figure 3-6 Wiring diagram (230 V ac single phase)

GSM-204-423
Connecting 110 V single phase ac power cables
31st Oct 01
Inst. 3–24
Installation & Configuration: Horizon
macro
outdoor
CONTROLLED INTRODUCTION
68P02902W03-A
Connecting 110 V single phase ac power cables
Configuring the
number 1 ac
distribution box
WARNING Ensure that the mains input isolator is set to position O
(off) and source is isolated before proceeding.
On delivery the Horizon
macro
outdoor BTS cabinet is configured for a 230 V ac
single phase power supply.
If connecting to a single phase 110 V ac supply configure the number 1 power
distribution box as follows (refer to Figure 3-7):
1. Retain the single phase link fitted across terminals B2, C2 and D2 on the
four pole MCB.
2. Disconnect the neutral cables from Terminal A1 of the four pole MCB.
3. Disconnect and remove the neutral cables from terminals 1 and 2 on the
neutral terminal block.
4. Tighten all screws disturbed in this procedure.
NOTE Pole A of the four pole MCB is not used in 110 V ac
configurations.
The procedure for configuring the number 1 distribution box for 110 V operation
is now complete.
Connecting
110 V ac single
phase mains
input cables
To connect a 110 V ac earth, live, and neutral power cable to the number 1 ac
distribution box:
1. Connect the mains input earth cable (green/yellow) to terminal 1 of the
earth terminal block in the number 1 ac distribution box, and check the
connection of the cabinet earth cable to terminal 2. Secure both cables.
2. Secure the screen at the cabinet entry gland.
3. Connect the neutral cable (blue or black) to terminal 1 of the neutral
terminal block in the number 1 ac distribution box, and secure.
4. Connect the live cable (brown or red) to linked terminals B2, C2 and D2 of
the four pole MCB in the number 1 ac distribution box, and secure.
5. Check the security of all connections within the distribution box and then
refit the previously retained cover.
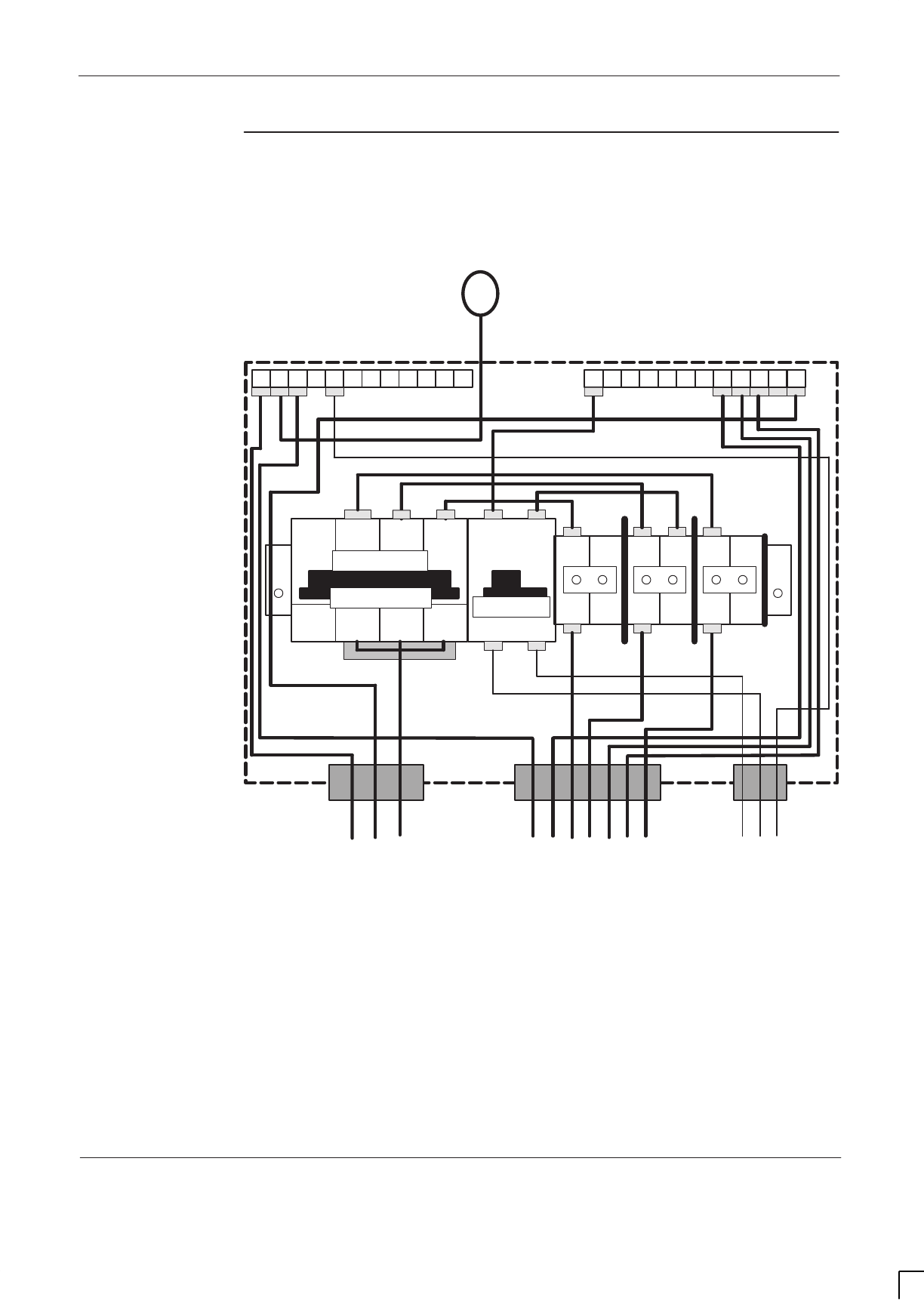
GSM-204-423 Connecting 110 V single phase ac power cables
31st Oct 01
Installation & Configuration: Horizon
macro
outdoor
68P02902W03-A
CONTROLLED INTRODUCTION
Inst. 3–25
110 V ac single
phase wiring
diagram
Figure 3-7 shows the wiring diagram for the number 1 ac distribution box when
configured for a 110 V ac single phase power supply.
7
RCBO
EARTH NEUTRAL
TO AC
OUTLET
SOCKET
INCOMING
AC
SUPPLY
1
12108642
119753
4 POLE MCB
A1 B1 C1 D1 E1 F1
A2 B2 C2 D2 E2 F2
1 2 3 4 5 8 9 10 1112 123456789101112
32 A Type C
MAIN CHASSIS
EARTH
TO AC
DISTRIBUTION BOX 2
6
NEL
6 A 30 mA
NEL
Figure 3-7 Wiring diagram (110 V ac single phase)
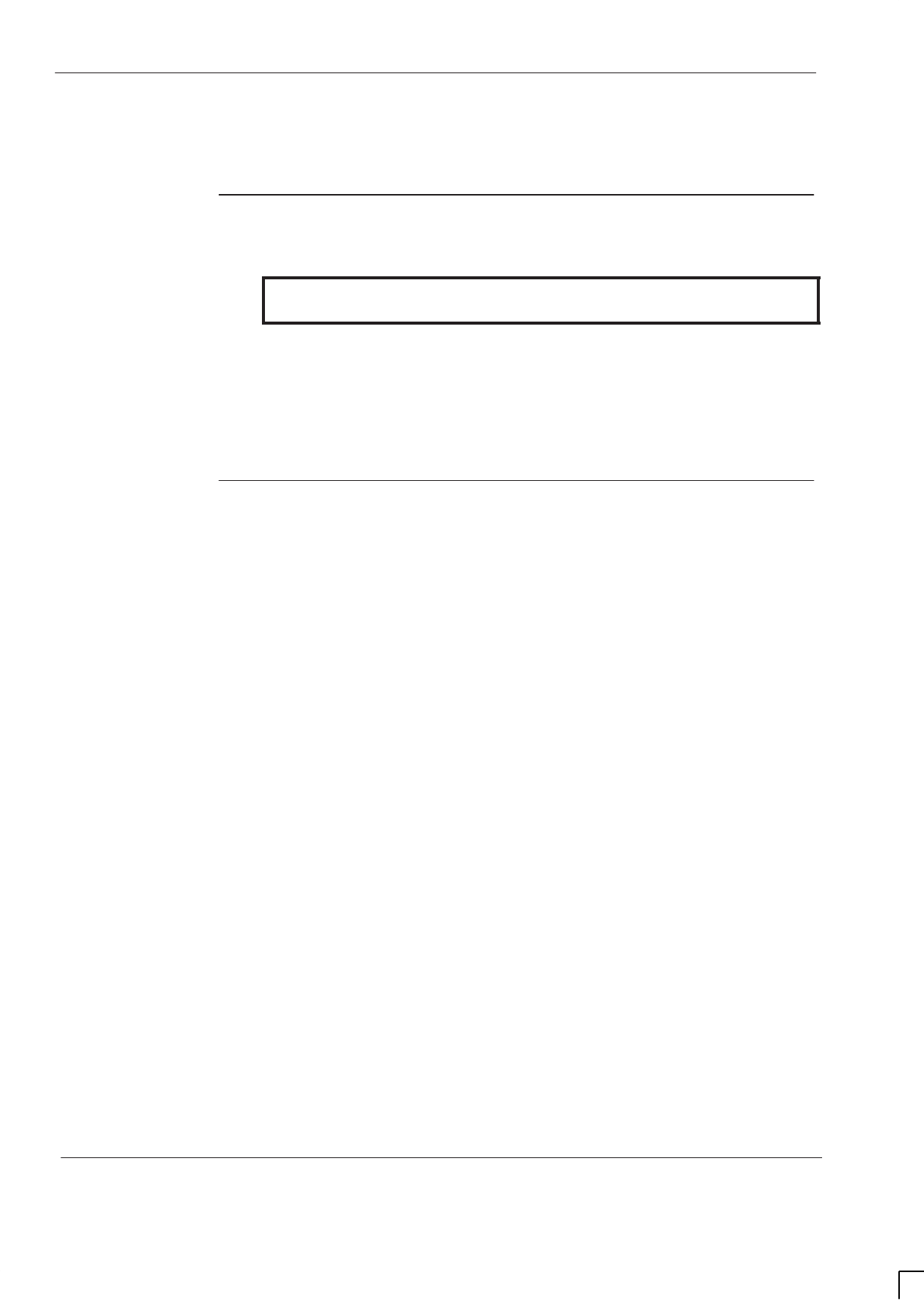
GSM-204-423
Connecting 230 V 3-phase (star) ac power cables
31st Oct 01
Inst. 3–26
Installation & Configuration: Horizon
macro
outdoor
CONTROLLED INTRODUCTION
68P02902W03-A
Connecting 230 V 3-phase (star) ac power cables
Configuring the
number 1 ac
distribution box
WARNING Ensure that the mains input isolator is set to position O
(off) and source is isolated before proceeding.
On delivery the Horizon
macro
outdoor BTS cabinet is configured for a 230 V ac
single phase power supply.
If connecting to a three phase and neutral (star) 230 V ac supply, remove the
230 V single phase link fitted to terminals B2, C2 and D2 on the four pole MCB
before proceeding further.
Connecting
230 V ac
3-phase (star)
mains input
cables
To connect the earth, 3-phase (star), and neutral power cables to the number 1
ac distribution box:
1. Connect the mains input earth cable (green/yellow) to terminal 1 of the
earth terminal block in the number 1 ac distribution box, and check the
connection of the cabinet earth cable to terminal 2. Secure both cables.
2. Secure the screen at the cabinet entry gland.
3. Connect the neutral cable (black), to terminal A2 of the four pole MCB in
the number 1 ac distribution box, and secure.
4. Connect the phase 1 cable (red), to terminal D2 of the four pole MCB in
the number 1 ac distribution box, and secure.
5. Connect the phase 2 cable (yellow), to terminal C2 of the four pole MCB in
the number 1 ac distribution box, and secure.
6. Connect the phase 3 cable (blue), to terminal B2 of the four pole MCB in
the number 1 ac distribution box, and secure.
7. Refit the previously retained cover of the number 1 ac distribution box.
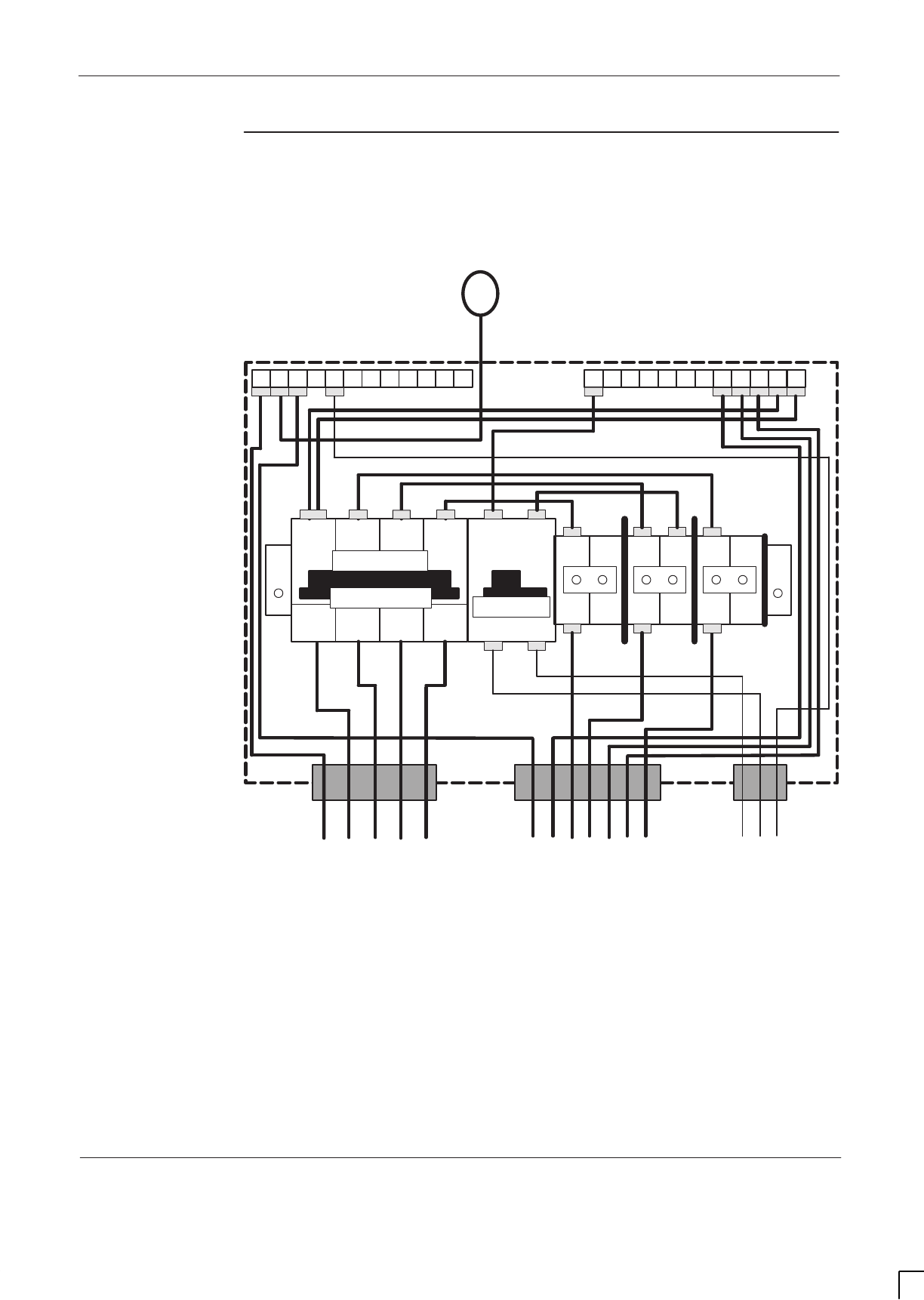
GSM-204-423 Connecting 230 V 3-phase (star) ac power cables
31st Oct 01
Installation & Configuration: Horizon
macro
outdoor
68P02902W03-A
CONTROLLED INTRODUCTION
Inst. 3–27
230 V ac
3-phase (star)
wiring diagram
Figure 3-8 shows the wiring diagram for the number 1 ac distribution box when
configured for a 230 V ac 3-phase and neutral (star) power supply.
7
RCBO
EARTH NEUTRAL
TO AC
OUTLET
SOCKET
INCOMING
AC
SUPPLY
1
12108642
119753
4 POLE MCB
A1 B1 C1 D1 E1 F1
A2 B2 C2 D2 E2 F2
1 2 3 4 5 8 9 10 1112 123456789101112
32 A Type C
MAIN CHASSIS
EARTH
TO AC
DISTRIBUTION BOX 2
6
NEL2
6 A 30 mA
NELL3 L1
Figure 3-8 Wiring diagram for 230 V ac 3-phase (star)
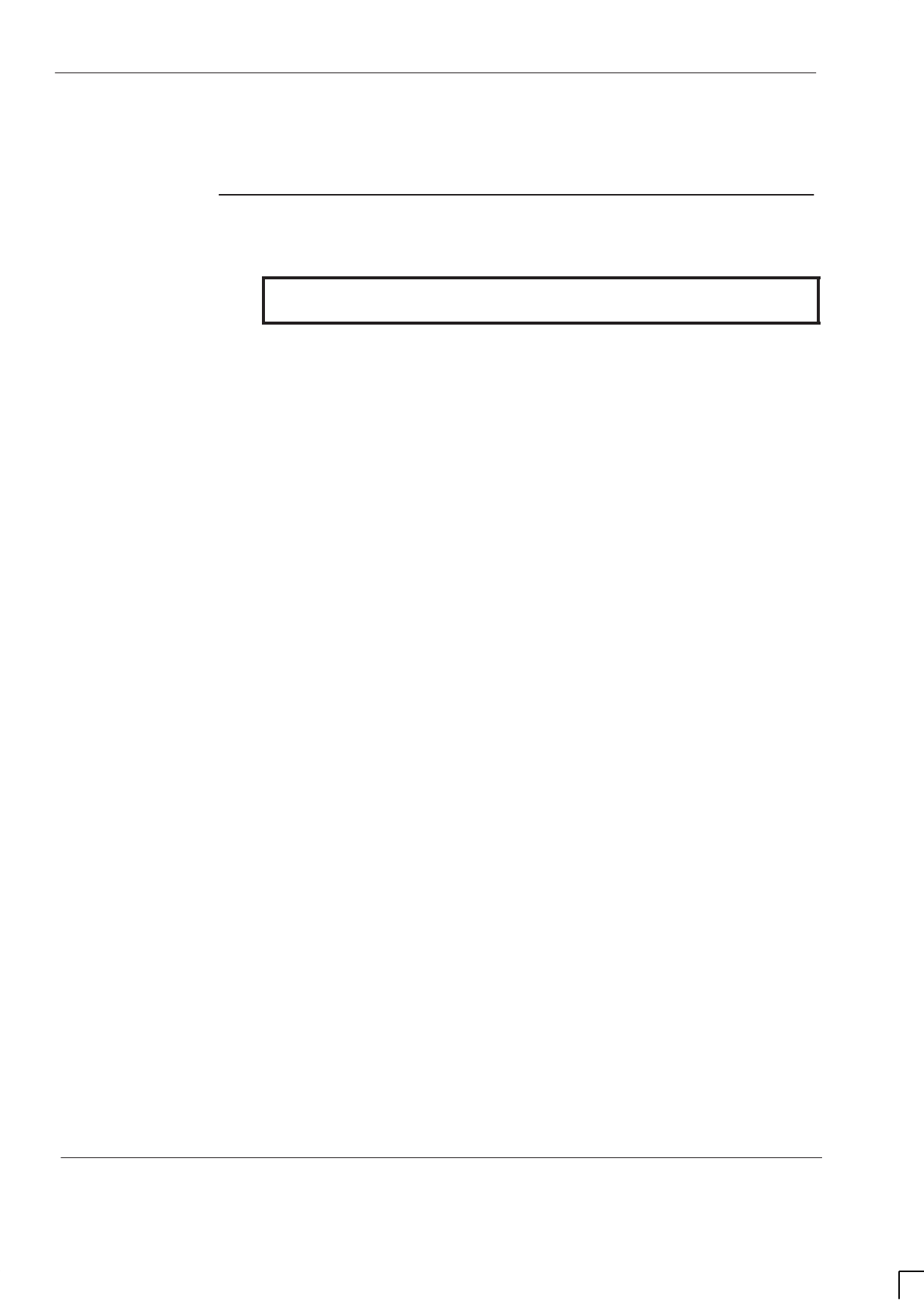
GSM-204-423
Connecting 230 V 3-phase (delta) ac power cables
31st Oct 01
Inst. 3–28
Installation & Configuration: Horizon
macro
outdoor
CONTROLLED INTRODUCTION
68P02902W03-A
Connecting 230 V 3-phase (delta) ac power cables
Configuring the
number 1 ac
distribution box
WARNING Ensure that the mains input isolator is set to position O
(off) and source is isolated before proceeding.
On delivery the Horizon
macro
outdoor BTS cabinet is configured for a 230 V ac
single phase power supply.
If connecting to a 230 V 3-phase (delta) ac supply, configure the number 1
power distribution box as follows (refer to Figure 3-9):
1. Remove the wire from terminal 12 on the neutral terminal block and
connect it to terminal 3 on the connector block.
2. Remove the wire from terminal 5 on the neutral terminal block and connect
it to terminal 8 on the connector block.
3. Remove the wire from terminal 4 on the neutral terminal block and connect
it to terminal 12 on the connector block.
4. Remove the wire from terminal 3 on the neutral terminal block and connect
it to terminal 4 on the connector block.
5. Remove the 230 V single phase link fitted to terminals B2, C2 and D2 on
the four pole MCB
The procedure for configuring the number 1 distribution box for 230 V 3-phase
(delta) operation is now complete.
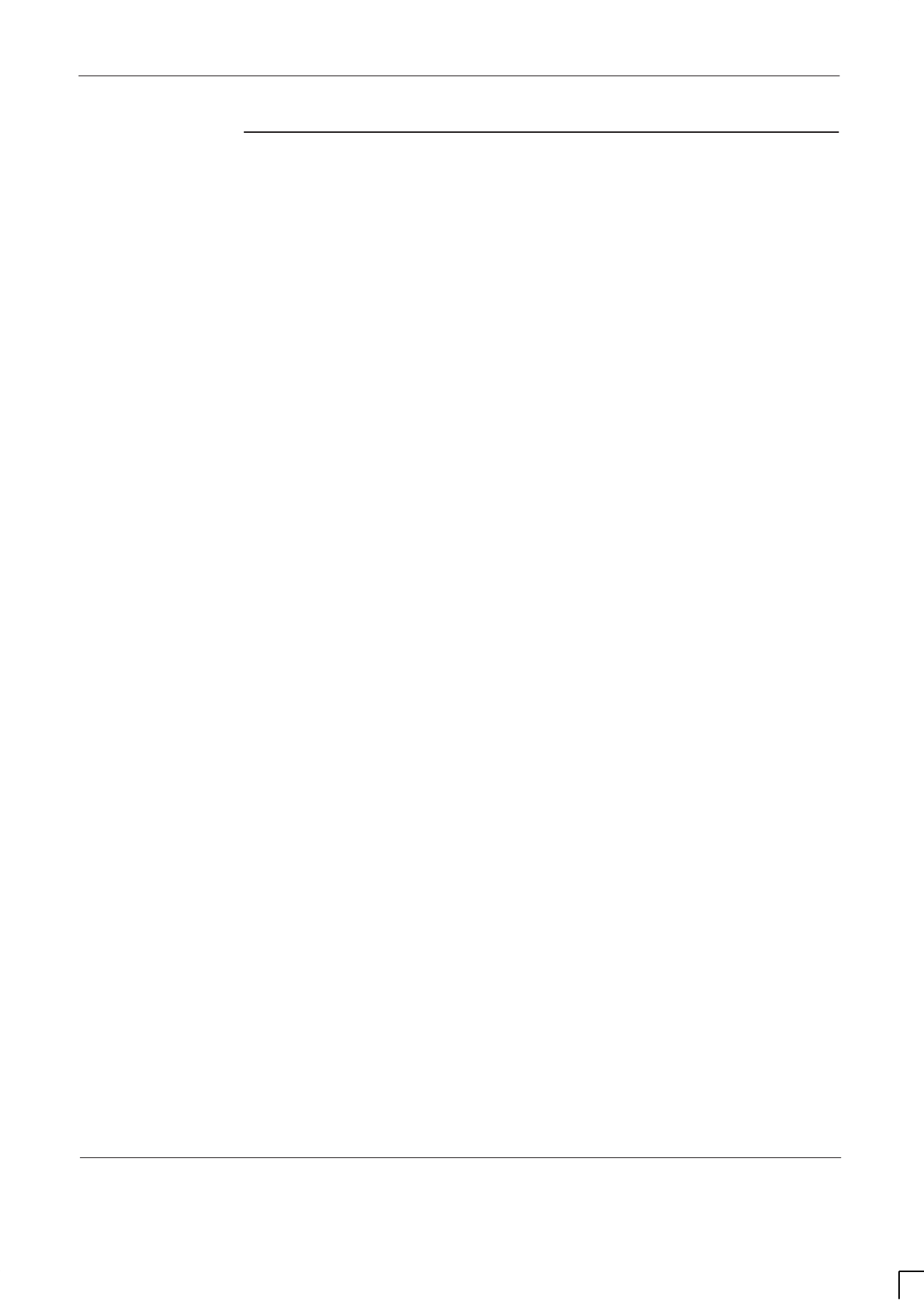
GSM-204-423 Connecting 230 V 3-phase (delta) ac power cables
31st Oct 01
Installation & Configuration: Horizon
macro
outdoor
68P02902W03-A
CONTROLLED INTRODUCTION
Inst. 3–29
Connecting
230 V ac
3-phase (delta)
mains input
cables
To connect the earth, 3-phase (delta) cables to the number 1 ac distribution box:
1. Connect the mains input earth cable (green/yellow) to terminal 1 of the
earth terminal block in the number 1 ac distribution box, and check the
connection of the main chassis earth cable to terminal 2. Secure both
cables.
2. Secure the screen at the cabinet entry gland.
3. Connect the phase 1 cable (red), to terminal D2 of the four pole MCB in
the number 1 ac distribution box, and secure.
4. Connect the phase 2 cable (yellow), to terminal C2 of the four pole MCB in
the number 1 ac distribution box, and secure.
5. Connect the phase 3 cable (blue), to terminal B2 of the four pole MCB in
the number 1 ac distribution box, and secure.
6. Refit the previously retained cover of the number 1 ac distribution box.
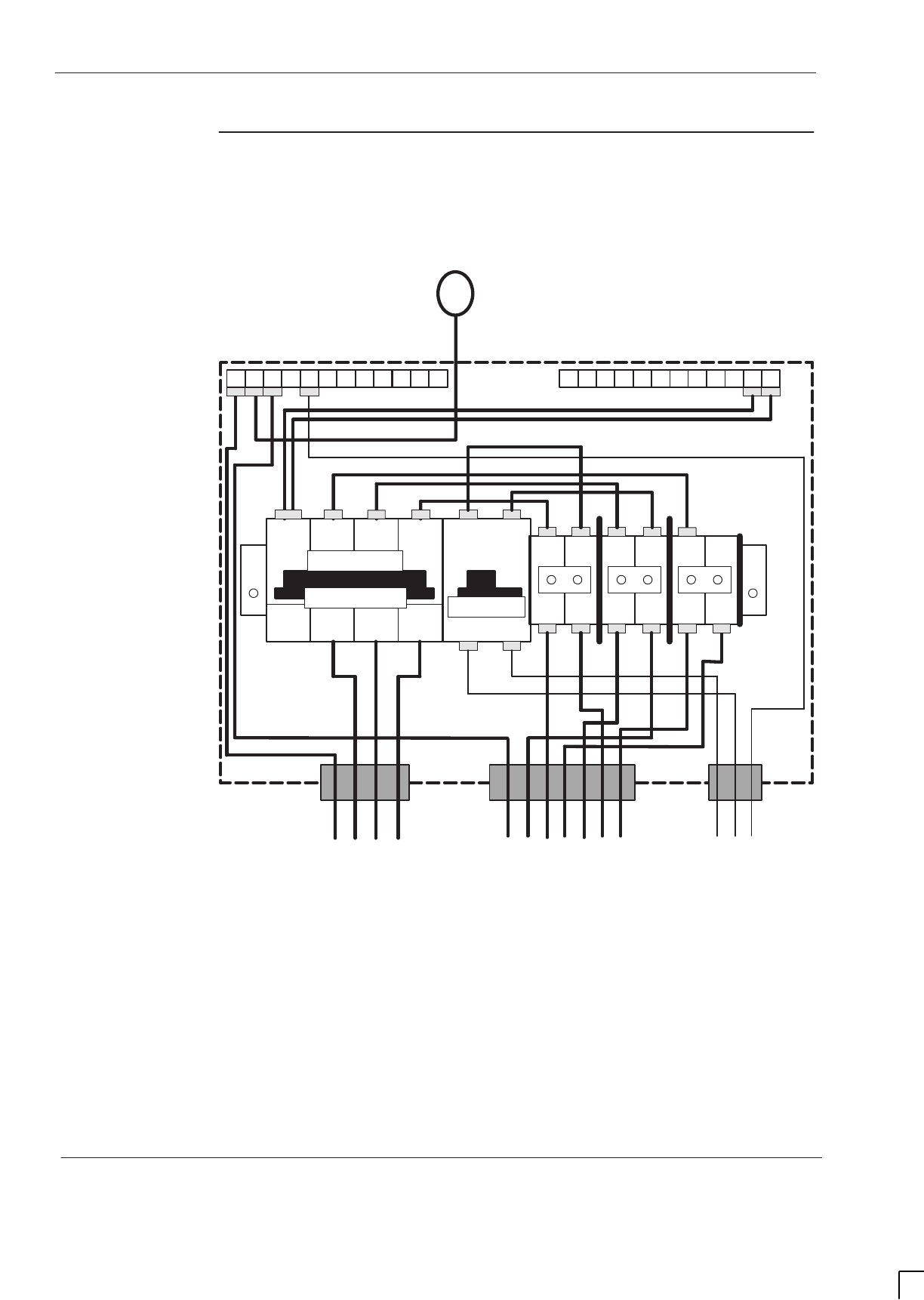
GSM-204-423
Connecting 230 V 3-phase (delta) ac power cables
31st Oct 01
Inst. 3–30
Installation & Configuration: Horizon
macro
outdoor
CONTROLLED INTRODUCTION
68P02902W03-A
230 V ac
3-phase (delta)
wiring diagram
Figure 3-9 shows the wiring diagram for the number 1 ac distribution box when
configured for a 230 V ac 3-phase (delta) power supply.
7
RCBO
EARTH NEUTRAL
TO AC
OUTLET
SOCKET
INCOMING
AC
SUPPLY
1
12108642
119753
4 POLE MCB
A1 B1 C1 D1 E1 F1
A2 B2 C2 D2 E2 F2
1 2 3 4 5 8 9 10 1112 123456789101112
32 A Type C
MAIN CHASSIS
EARTH
TO AC
DISTRIBUTION BOX 2
6
EL2
6 A 30 mA
NELL3 L1
Figure 3-9 Wiring diagram for 230 V ac 3-phase (delta)
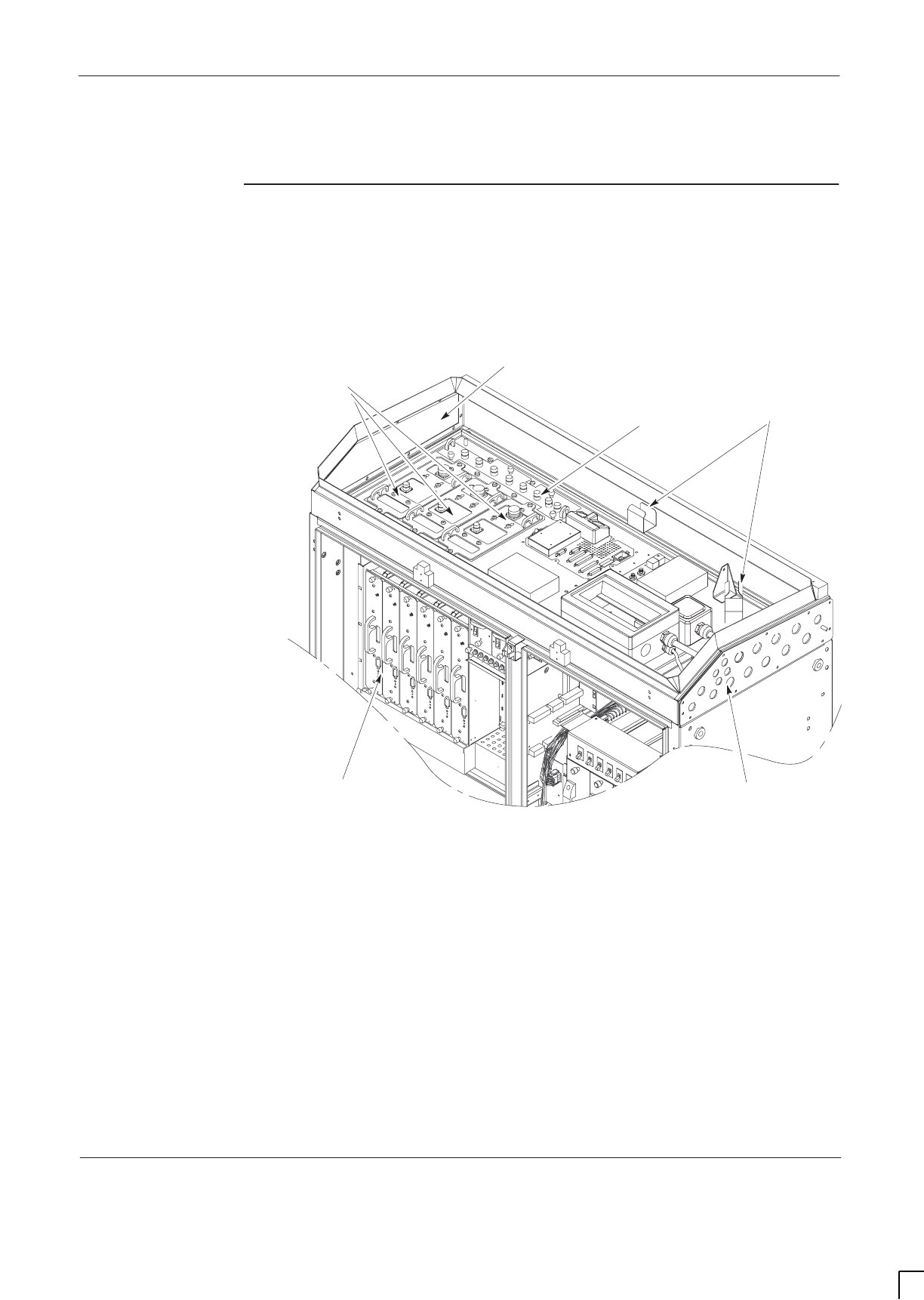
GSM-204-423 Connecting antennas
31st Oct 01
Installation & Configuration: Horizon
macro
outdoor
68P02902W03-A
CONTROLLED INTRODUCTION
Inst. 3–31
Connecting antennas
Overview of
antenna
connections
The components shown in Figure 3-10 provide all the RF connections to the
cabinet and internally within the cabinet. Up to four cabinets can be
interconnected to form a single BTS site.
THREE
TRANSMITTER/RECEIVERS
(Tx BLOCKS)
SURF (Rx)
SIX TRANSCEIVERS
(CTUs)
CABLE GUIDES
RIGHT EARTH PLATE
(RF CABLE OMITTED
FOR CLARITY)
BLANK PLATE (LEFT
EARTH PLATE OR
EXPANSION
PLATE OPTIONAL)
Figure 3-10 Location of RF components
Site configurations supplied by Motorola have appropriate earth, expansion or
blanking plates fitted and all internal RF cables supplied. Antennas need only be
connected to the earth/connector plate as all RF connections internal to the
cabinet, (those between CTUs, Tx blocks, SURF and earth/connector plates),
are cabled correctly for the cabinet configuration supplied.
Multiple cabinet configurations have additional RF cabling, stored, for shipping,
in the master cabinet. These cables will need to be routed to the expansion
cabinets and connected as shown in the Suggested RF configurations
Variations in site layout and RF configuration may require the fitting of left side
cable entry earth plates and/or expansion plates.
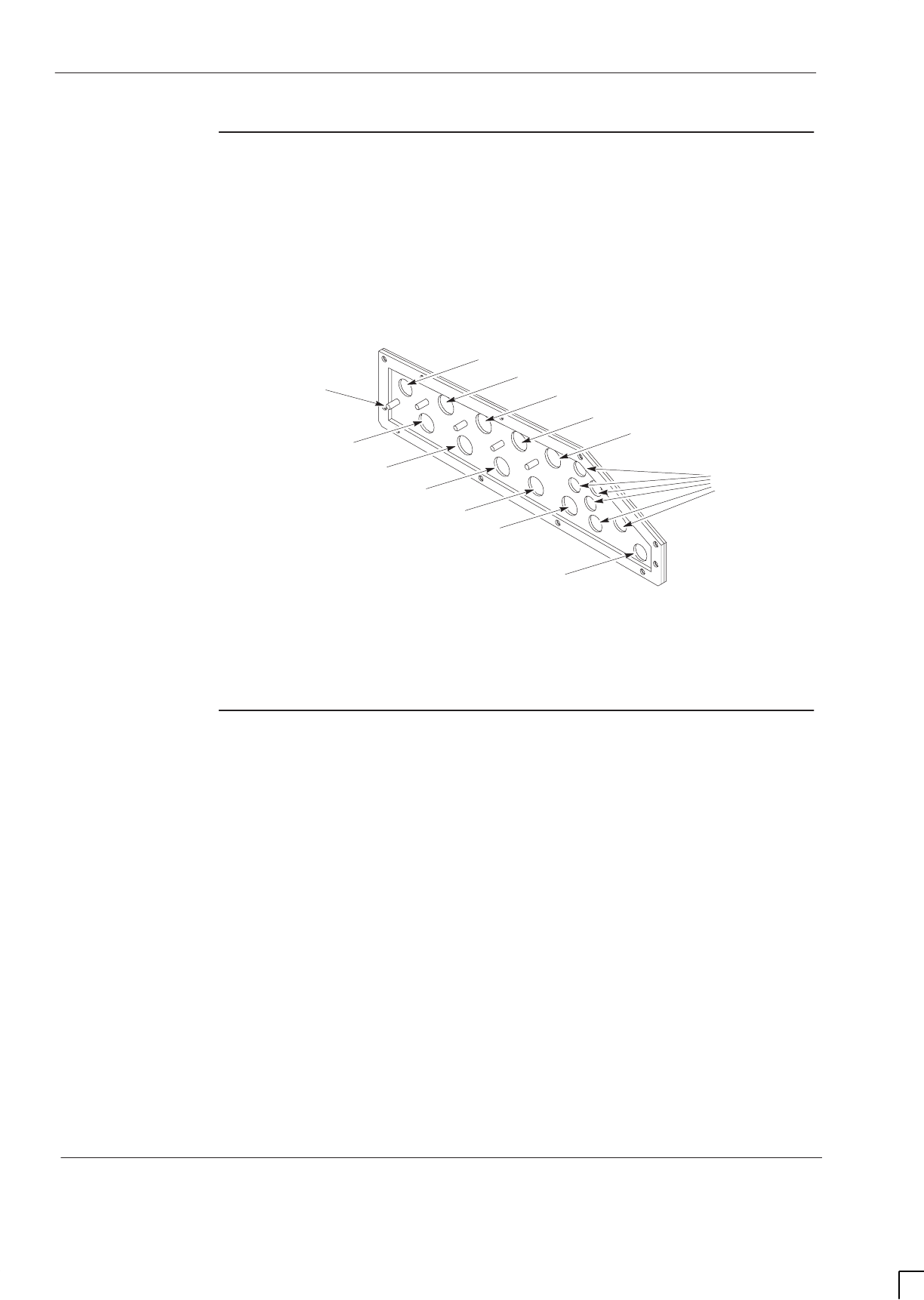
GSM-204-423
Connecting antennas
31st Oct 01
Inst. 3–32
Installation & Configuration: Horizon
macro
outdoor
CONTROLLED INTRODUCTION
68P02902W03-A
Cable entry
earth plates
The standard cabinet is supplied with the earth/connector plate, with attached
RF cables, located on the right side of the top section. If required, an optional
earth/connector plate can be fitted on the left side of the top section instead.
Figure 3-11 shows the layout of the right earth/connector plate viewed from
inside the top section (the layout for the left plate is a mirror image of this). The
six permanently connected RF cables are omitted for clarity.
TX 0
AC IN
DC INRX 1B
RX 0B
RX 2ARX 1A
RX 0A
TX 1
TX 2
RX 2B
EARTH STUD
COMMS
Figure 3-11 Diagram of left earth/connector plate connections
Fitting
inter-cabinet RF
cables to earth
plates
When installing a multiple cabinet configuration or expanding an existing site it
may be necessary to fit long RF cables to an existing earth plate. Extension RF
cables are listed in Table 3-4 in this chapter.
To fit extension RF cables to an earth plate:
1. Remove the grey weather seal from an unused RF position, on the earth
plate and discard.
2. Remove the nut and washer from the fixed bulkhead connector of the
extetsion RF cable.
3. Feed the threaded portion of the bulkhead connector through the earth
plate from the inside.
4. Refit the washer and nut to the bulkhead connector and tighten to the
correct torque, (see Site requirements and considerations in Chapter 2
of this category).
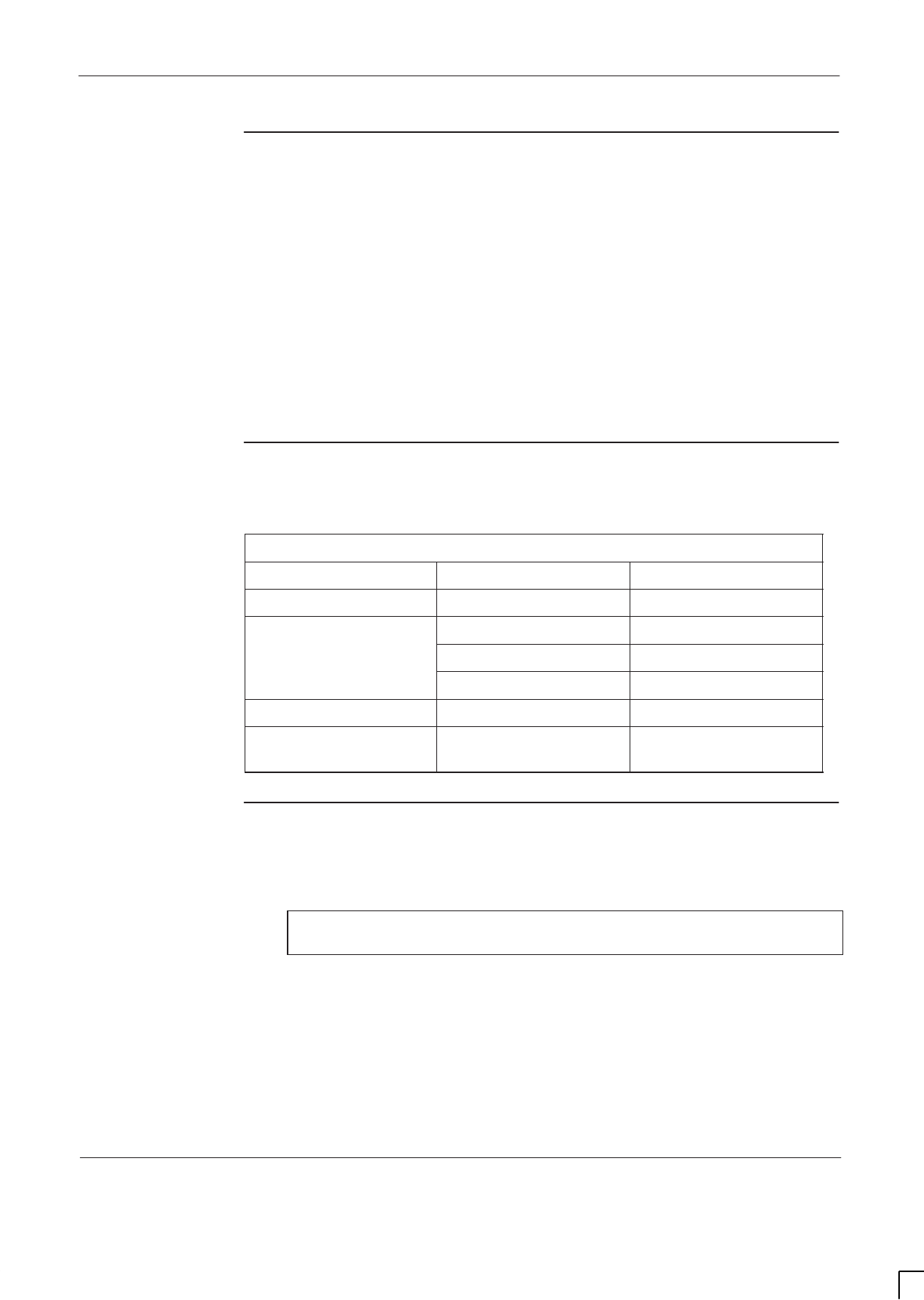
GSM-204-423 Connecting antennas
31st Oct 01
Installation & Configuration: Horizon
macro
outdoor
68P02902W03-A
CONTROLLED INTRODUCTION
Inst. 3–33
Routeing RF
cables between
cabinets.
When routeing RF cables between cabinets in Motorola supplied configurations:
1. Remove the expansion plate pass through blanks, as required.
2. Undo the two hose clips securing each RF cable gland housing and
remove gland assembly.
3. Feed any RF cables through the expansion plates.
Refer to Cable shroud installation procedures (Installation between cabinets
and Cable routeing for multiple cabinet sites) in Chapter 4 of this category for
full details of RF gland refitting and shroud installation.
Types of RF
connector
Table 3-2 list the RF module connectors with their destinations.
Table 3-2 RF module connectors and destinations
RF module Type of connector Destination
CTU transceiver SMA Tx block (underneath)
Tx block SMA CTU transceiver
N-type SURF
7/16 Earth/connector plate
SURF N-type Rx N-type of Tx Block
Earth/connector plate 7/16 Antenna or
additional cabinets
Torque of RF
connectors
For correct torque of connectors, see
Installation & Configuration: GSM-204-423
Chapter 2 Site requirements and considerations.
CAUTION Care should be taken when tightening SMA connectors to
avoid damage by excessive force.
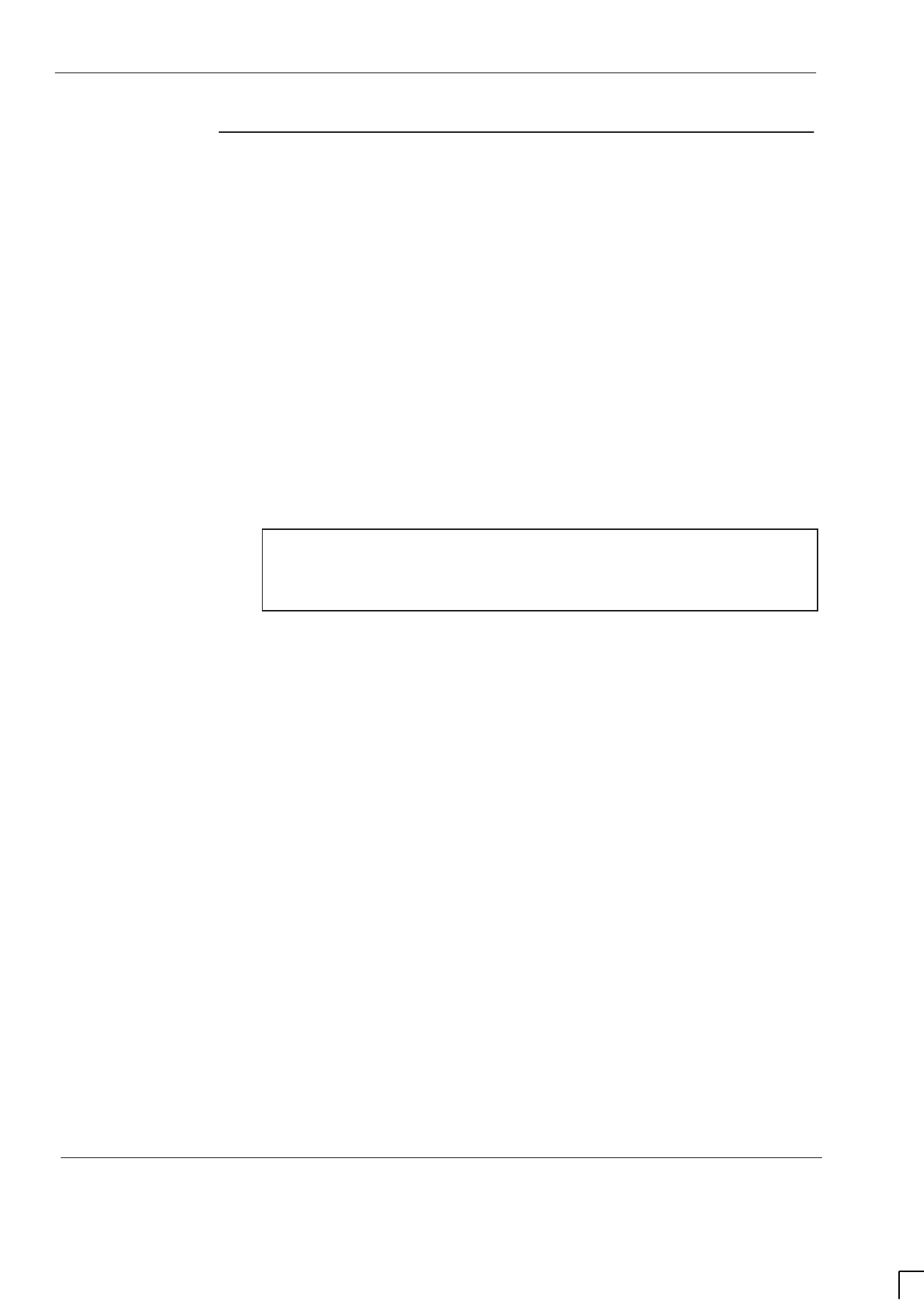
GSM-204-423
Connecting antennas
31st Oct 01
Inst. 3–34
Installation & Configuration: Horizon
macro
outdoor
CONTROLLED INTRODUCTION
68P02902W03-A
Fitting left side
(cable entry)
earth plate
To fit the left side (cable entry) earth plate:
1. Remove and retain the eleven M6 anti-tamper Torx screws securing the
left side blanking plate, (if fitted). Remove the blanking plate.
2. Fit left side (cable entry) earth plate and secure with previously retained
Torx screws. Tighten securing screws to the correct torque (see Site
requirements and considerations in Chapter 2 of this category).
3. Connect the short earth cable to the left side cabinet earth stud and
tighten to the correct torque.
4. Route RF cables and long earth cable from left side earth plate through
top section cable guides, indicated in Figure 3-10.
5. Remove the earth cable from the interface panel earth stud and fit long
earth cable from left side earth plate. Tighten to correct torque (see Site
requirements and considerations in Chapter 2 of this category).
CAUTION Incorrect connection of RF cables could result in network
planning and optimization difficulties, care must be taken
to ensure that the correct RF configuration for the site is
maintained.
6. Note the identification of the existing connections between the right earth
plate and RF components. Disconnect each cable from the SURF module
or Tx block, one at a time, and connect corresponding RF cable from left
side earth plate, until all RF cables, appropriate for the desired RF
configuration, are connected.
7. Disconnect the short earth cable from the right side cabinet earth stud.
8. Remove and retain the eleven M6 anti-tamper Torx screws securing the
right side earth plate. Remove the right side earth plate, complete with
cables.
9. Fit right side blanking plate and secure using with previously retained Torx
screws. Tighten securing screws to the correct torque (see Site
requirements and considerations in Chapter 2 of this category).
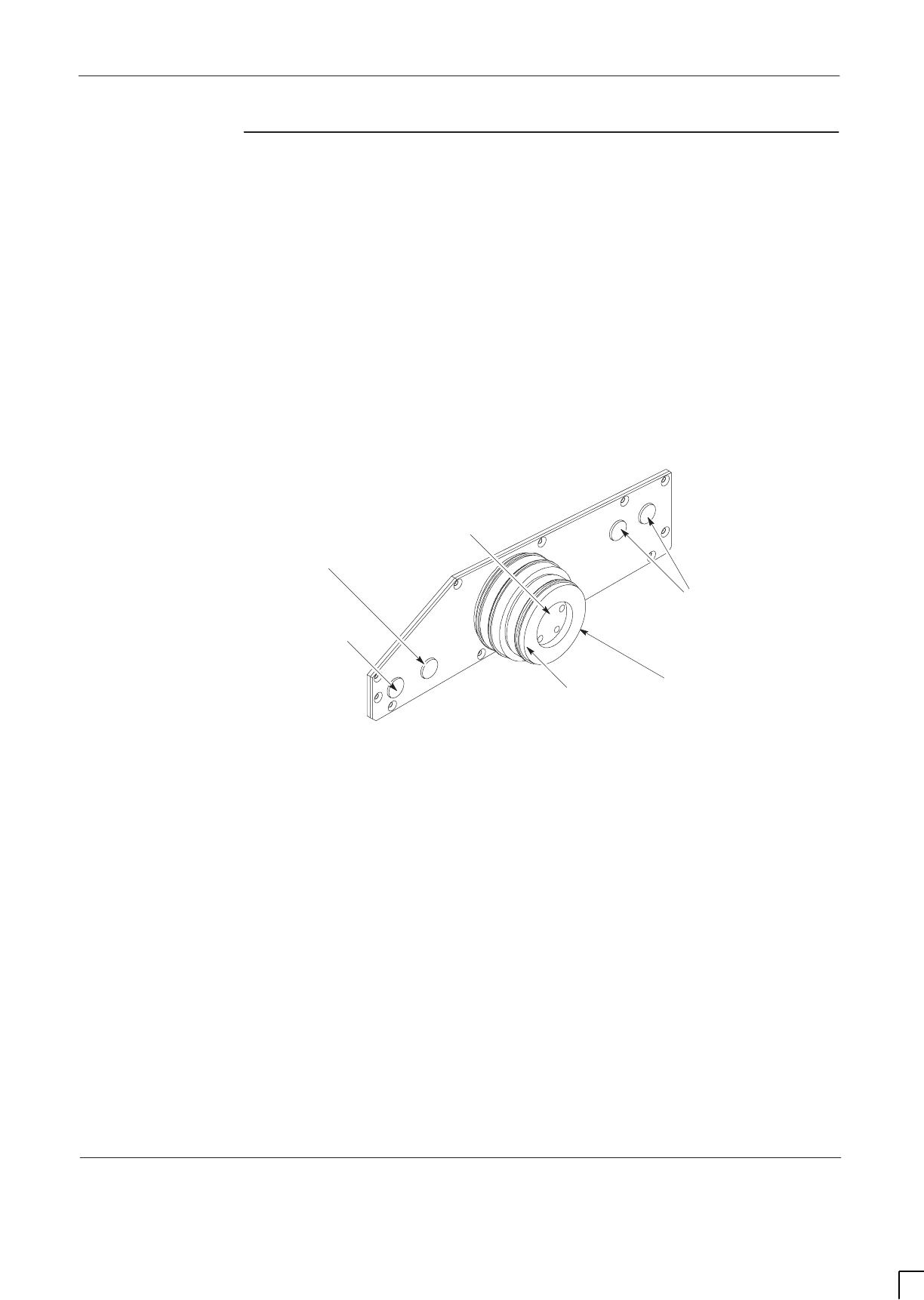
GSM-204-423 Connecting antennas
31st Oct 01
Installation & Configuration: Horizon
macro
outdoor
68P02902W03-A
CONTROLLED INTRODUCTION
Inst. 3–35
Fitting
expansion
plates
To fit an expansion plate:
1. Remove and retain the eleven M6 anti-tamper Torx screws securing the
earth plate or blanking plate, (if fitted), and remove.
2. Fit the expansion plate and secure with previously retained Torx screws.
Tighten securing screws to the correct torque (see Site requirements and
considerations in Chapter 2 of this category).
3. To make the RF, dc power, fibre optic and signal connections between
multiple cabinets, (see Cable shroud installation procedures in Chapter
4 of this category).
Figure 3-12 shows an expansion plate, with cable pass-through ports indicated.
RF PASS-THROUGH
FIVE CABLE GLAND
BATTERY BACKUP CABLE
PASS-THROUGH
EARTH CABLE
PASS-THROUGH
AC CABLE
PASS-THROUGH
FIBRE OPTIC
EXTENSION CABLE
PASS-THROUGH
(not visible)
RUBBER
GLAND HOUSING
Figure 3-12 Expansion plate
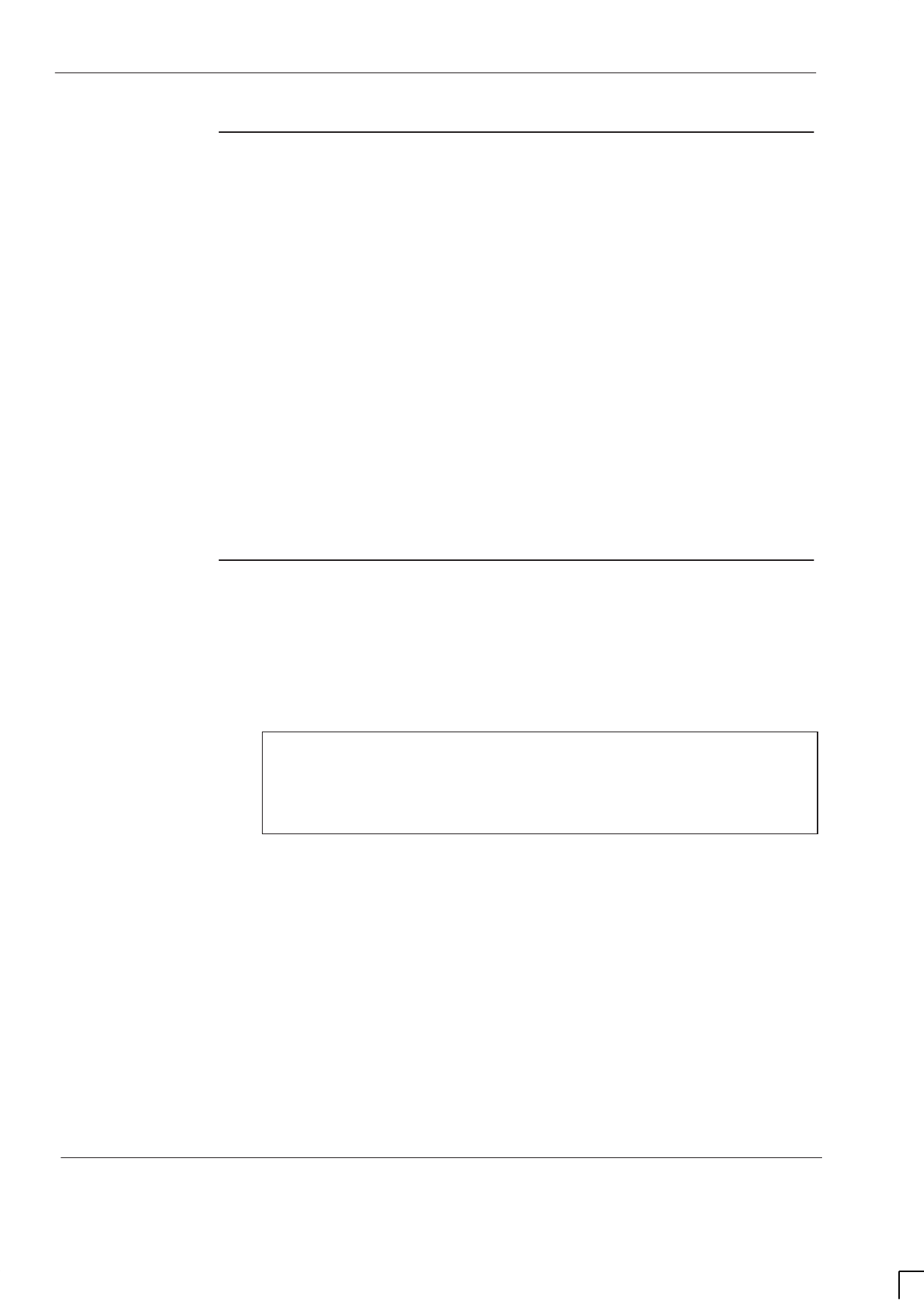
GSM-204-423
Connecting antennas
31st Oct 01
Inst. 3–36
Installation & Configuration: Horizon
macro
outdoor
CONTROLLED INTRODUCTION
68P02902W03-A
RF connection
principles
The primary receive path is connected to the A branch of the SURF module,
either directly or from the Rx connector on the Tx block in non-diversity
configurations. The diversity receive path is connected to the B path on the
SURF. This is normally duplexed with the transmit signal on a single antenna,
and fed to the SURF from the Rx connector on the Tx block. Within any single
cabinet the lowest numbered sector is normally connected to amplifier 0
connections, and higher numbered sectors to amplifiers 1 and 2 as appropriate.
For example, sector one is connected to SURF connectors 0A and 0B, sector
two to 1A and 1B, and sector three to 2A and 2B. However, if a sector is split
between two cabinets, the split sector antennas must be connected to amplifier
0, (this is the only path with connection to the extension ports). Extension ports
must be connected to the correct branch at the destination cabinet.
The transmit path feeds from the CTUs to the Tx block or feedthrough plate
immediately above. Two signals are combined in most Tx blocks, A third signal
can be combined using a feedthrough plate and the third input of a DDF. The Tx
blocks then duplex the Tx signal with the diversity Rx signal, before feeding to
the antenna.
Rx/Tx single
antenna
duplexing
Duplexers allow a single antenna to be used for both transmit and receive
operations. Duplexers exist within several of the transmit blocks. Normally
duplexed RF signals are used through one antenna, with a second receive
antenna to provide diversity.
NOTE If a single antenna (non-diversity) is required, the duplex
antenna RF receive cable from the transmit block must be
connected to the Rx A path at the SURF. Simply switching
off diversity at the OMC-R without the correct SURF
configuration will cause a loss of reception.
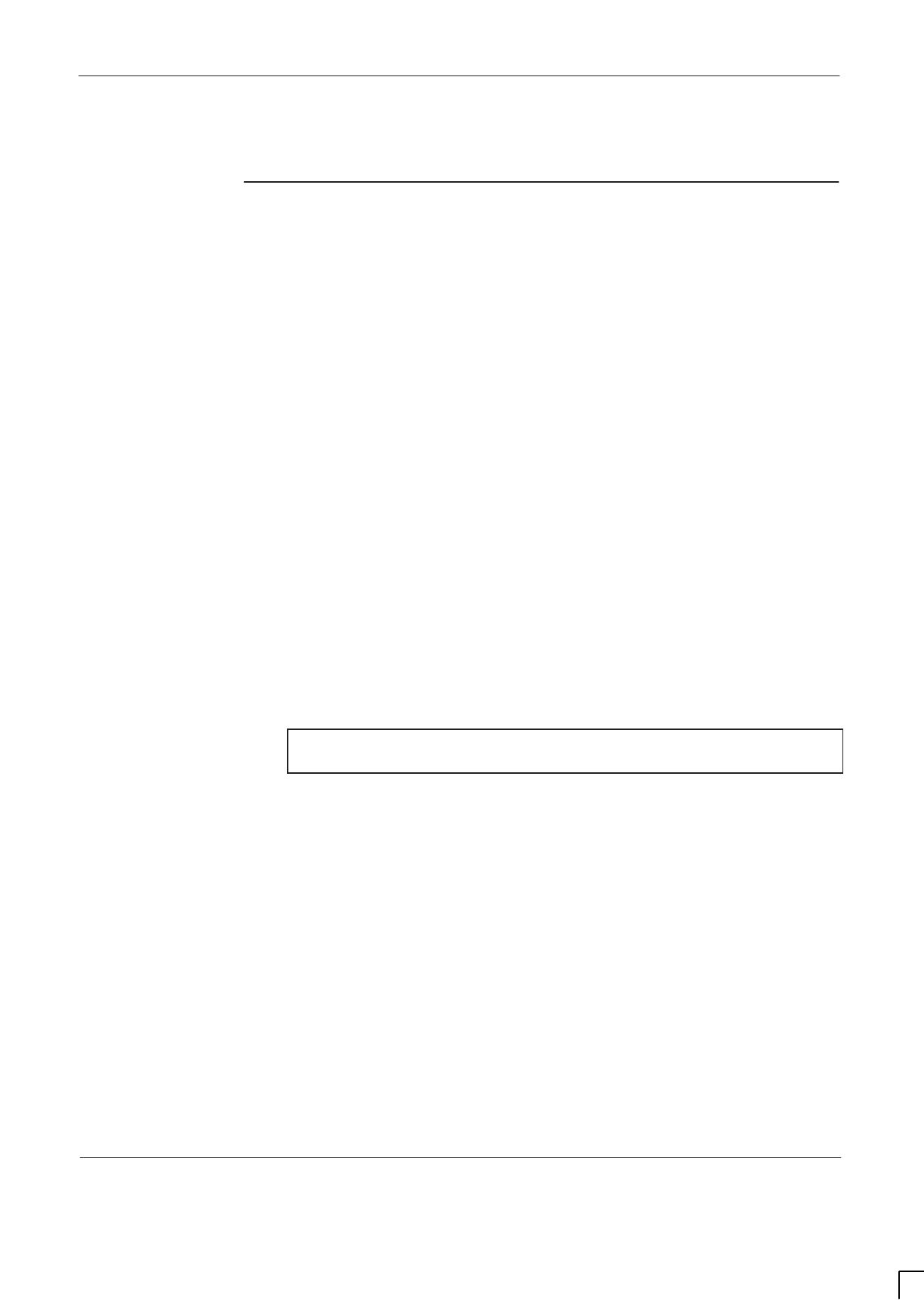
GSM-204-423 Suggested RF configurations
31st Oct 01
Installation & Configuration: Horizon
macro
outdoor
68P02902W03-A
CONTROLLED INTRODUCTION
Inst. 3–37
Suggested RF configurations
Overview of
configuration
diagrams
The following series of RF configuration diagrams show suggested ways of
connecting together Horizon
macro
SURF and Tx blocks to meet different
operational requirements. The series of diagrams is by no means exhaustive,
and numerous alternative configurations may be adopted to achieve the same
aim.
Each Horizon
macro
cabinet is represented by a SURF module, three Tx blocks
and an earth plate. In a standard cabinet the Tx blocks and SURF module are
supplied connected to a right side entry earth plate, (left side cable entry
requires fitting of optional earth plate kit). A blanking panel, or expansion plate
(for multiple cabinet configurations), is fitted on the opposite side of the cabinet
top section. Antenna connecting cables, not supplied as part of the
Horizon
macro
equipment, connect to the outside of the earth plate.
Interconnecting cables are not individually identified as different cables are
used, dependant on physical layout.
With the exception of Figure 3-33 and Figure 3-34 the diagrams are applicable
for single band operation at 850, 900, 1800 or 1900 MHz, although only the
1800 MHz SURF module is illustrated. Connections to the dual band 900 or
1800 SURF are identified in the same way as those to the single band SURF,
with the addition of two extra connectors provided for dual band use.
Figure 3-33 shows one way of achieving dual band operation using two
Horizon
macro
cabinets. A single band 1800 SURF is installed in one cabinet
and a dual band 900 SURF in the other. Figure 3-34 shows another, using one
of each type of dual band SURF.
NOTE Dual band SURFs are not available for GSM850 or
PCS1900 BTS variants.
Diversity is assumed in all the RF configuration diagrams shown here, except for
Figure 3-14. Other non-diversity configurations can be derived from this figure
by ensuring that the single receive path is always connected to branch A at the
SURF module.
Digital connections
Digital connections between cabinets are not shown in the following diagrams.
Fibre optic cables used to provide digital connections between cabinets are
described in Connecting fibre optic cables.
Depopulated site configurations
The purpose of a depopulated site configuration is to allow customers to provide
a future expansion capability, at the time of installation. The diagram showing
the final target configuration is to be used to connect TX blocks, SURF and
antennas. Depopulated site configurations are supplied with fully equipped RF
section to achieve the target configuration, with CTUs only fitted to alternate
slots. CTUs are fitted in slots 0, 2 and 4. Unused Tx block SMA connectors must
be fitted with 50 ohm terminating loads.
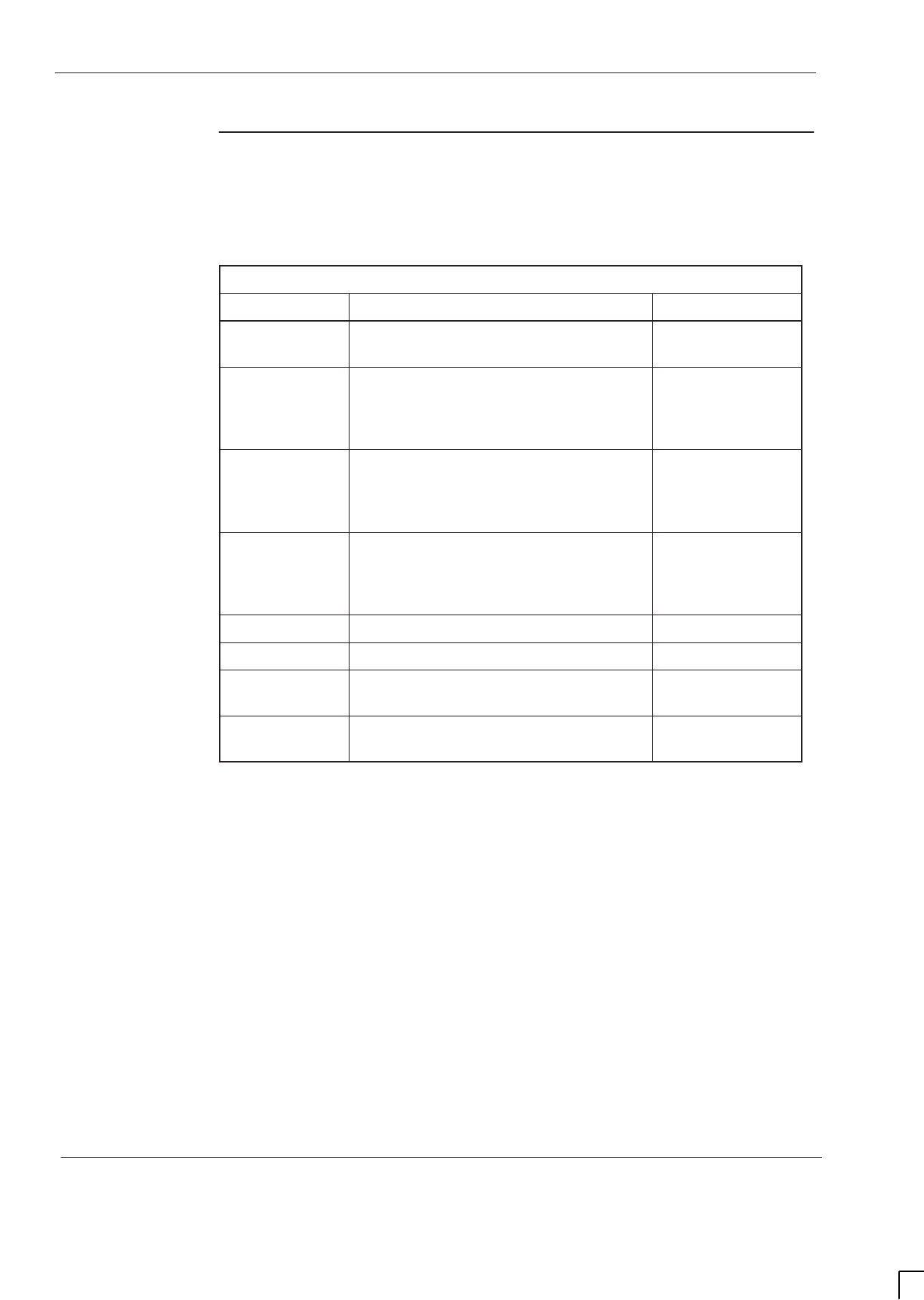
GSM-204-423
Suggested RF configurations
31st Oct 01
Inst. 3–38
Installation & Configuration: Horizon
macro
outdoor
CONTROLLED INTRODUCTION
68P02902W03-A
Single cabinet
connection kits
and cables
Table 3-3 lists cable types and kits used for SURF/Tx block and antenna
interconnections for a single cabinet.
Table 3-3 SURF/Tx block and antenna interconnecting kits and cables
Part number Description Use
3086225N01 34.5 cm coaxial cable terminated at
either end with straight N-type plugs. Tx block to SURF
(inside cabinet)
3086225N02 28 cm coaxial cable terminated at one
end with a straight N-type plug, and at
the other end with a right-angle N-type
plug.
Tx block to Tx
block
(inside cabinet)
SVLN1320 Left side entry earth plate kit contains
three each of:
– N-type to 7/16 bulkhead cables
– 7/16 to 7/16 bulkhead cables
Interface between
antenna cables
and Tx blocks
and/or SURF
SVLN1321 Right side entry earth plate kit contains
three each of:
– N-type to 7/16 bulkhead cables
– 7/16 to 7/16 bulkhead cables
Interface between
antenna cables
and Tx blocks
and/or SURF
SVLN1322 Left side blanking panel Blank plate
SVLN1323 Right side blanking panel Blank plate
SVLN1324 Left side expansion plate, with five
cable gland Multiple cabinet
configurations
SVLN1325 Right side expansion plate, with five
cable gland Multiple cabinet
configurations
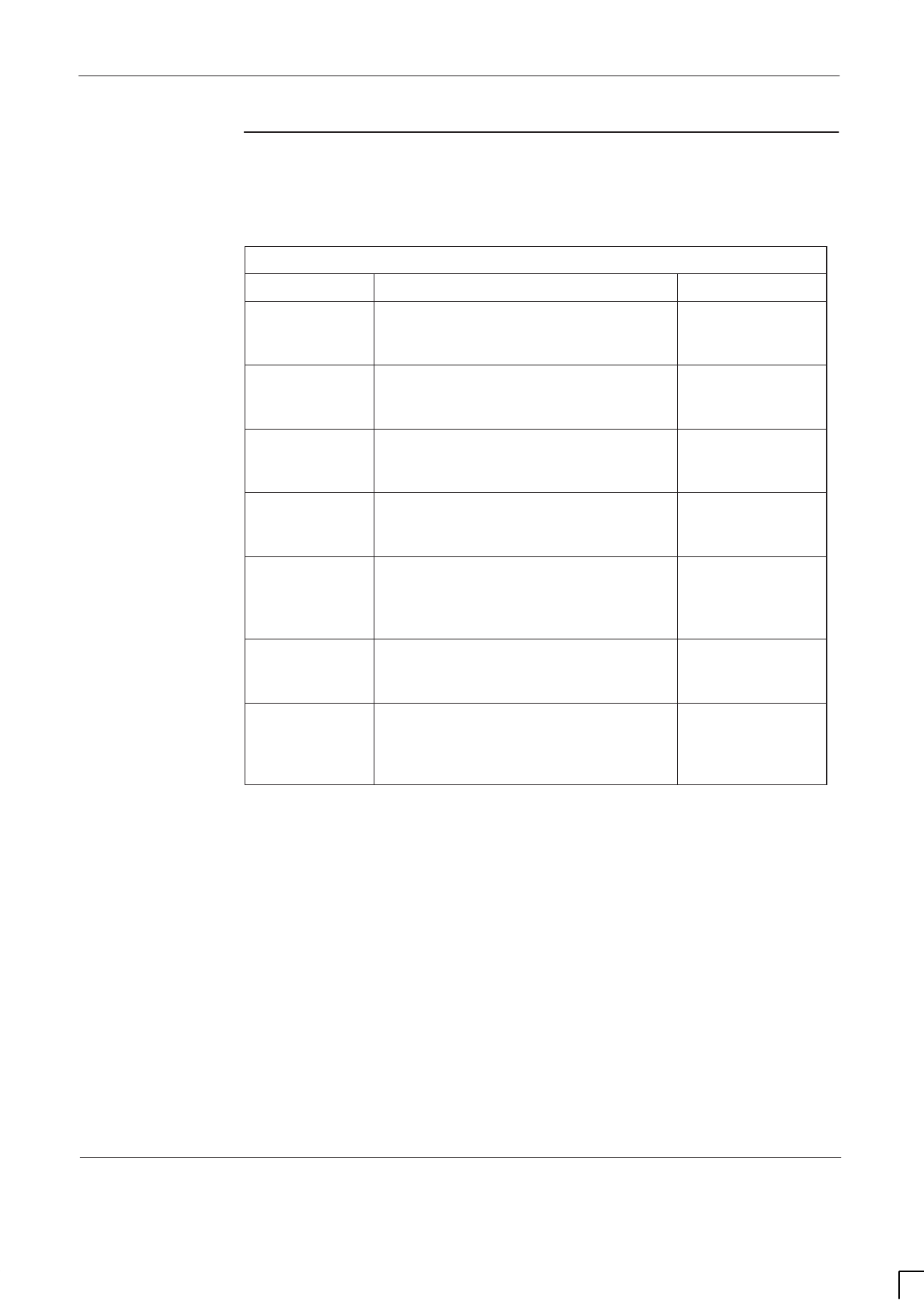
GSM-204-423 Suggested RF configurations
31st Oct 01
Installation & Configuration: Horizon
macro
outdoor
68P02902W03-A
CONTROLLED INTRODUCTION
Inst. 3–39
Multiple cabinet
connection kits
and cables
Table 3-4 lists interconnection cable kits used in multiple cabinet layouts.
Table 3-4 Multiple cabinet interconnection kits
Part number Description Use
SVKN1313 3 m coaxial cable terminated at each
end with N-type plugs. Intercabinet RF
cable.
SURF to SURF in
back to back
layouts
SVKN1314 2 m coaxial cable terminated at each
end with N-type plugs. Intercabinet RF
cable.
SURF to SURF in
side by side
layouts
SVKN1315 2.15 m coaxial cable terminated at
each end with N-type plugs.
Intercabinet RF cable.
DDF to HCU in
side by side
layouts
SVKN1316 2 m coaxial cable terminated with an
N-type plug at one end, and a 7/16 at
the other. Intercabinet RF cable.
SURF to earth
plate in left side of
adjacent cabinet
SVKN1317 2.85 m coaxial cable terminated with
an N-type plug at one end, and a 7/16
at the other. Intercabinet RF cable.
SURF to earth
plate in right side
of adjacent
cabinet
SVKN1318 2.15 m coaxial cable terminated at
each end with 7/16-type plugs.
Intercabinet RF cable
Tx block to earth
plate in left side of
adjacent cabinet
SVKN1319 3 m coaxial cable terminated at each
end with 7/16-type plugs. Intercabinet
RF cable
Tx block to earth
plate in right side
of adjacent
cabinet
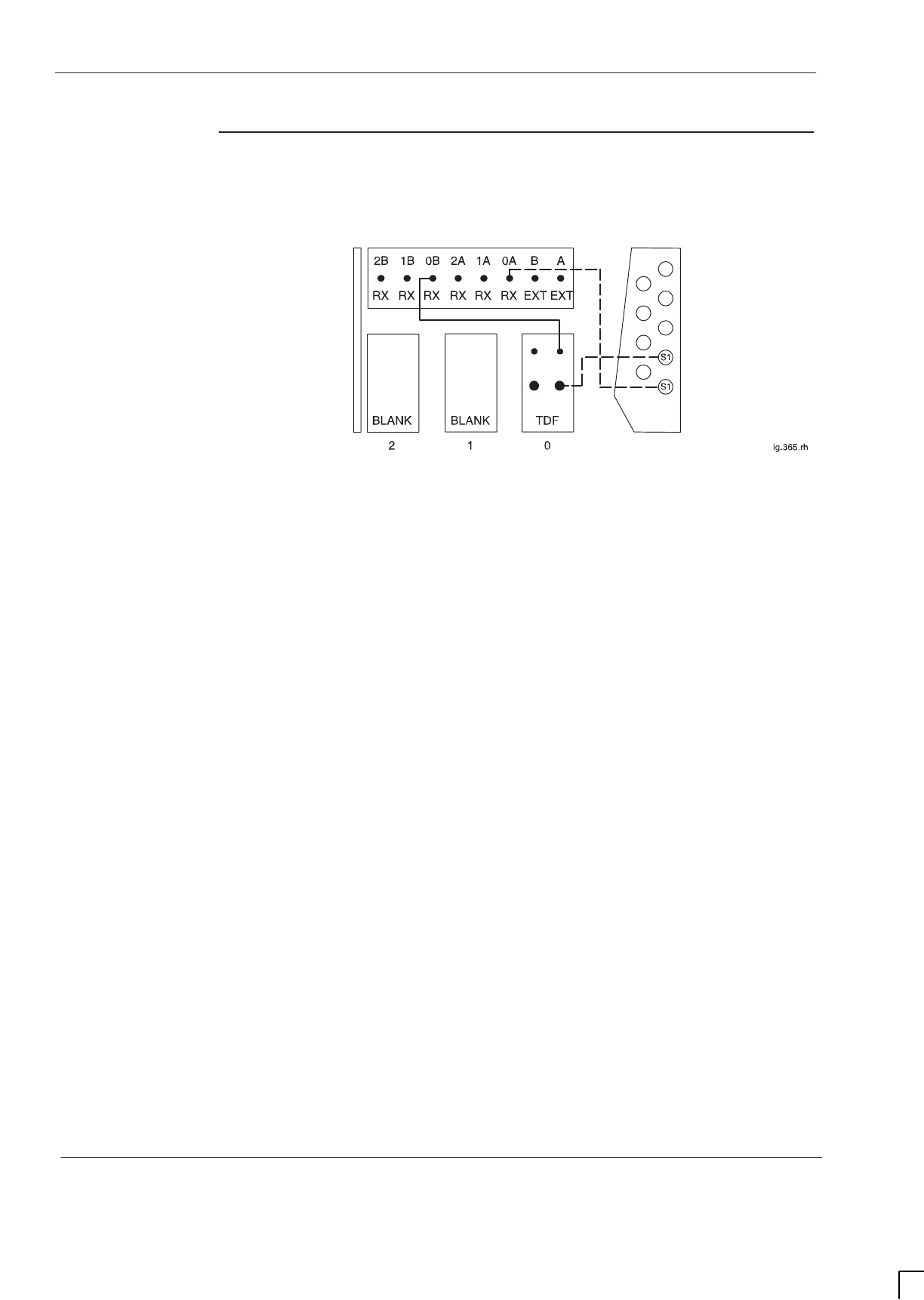
GSM-204-423
Suggested RF configurations
31st Oct 01
Inst. 3–40
Installation & Configuration: Horizon
macro
outdoor
CONTROLLED INTRODUCTION
68P02902W03-A
Configuration
for omni 1
Figure 3-13 shows a suggested configuration, using one Horizon
macro
cabinet,
for omni 1 with twin duplexed filter.
Figure 3-13 Single cabinet omni 1 with TDF
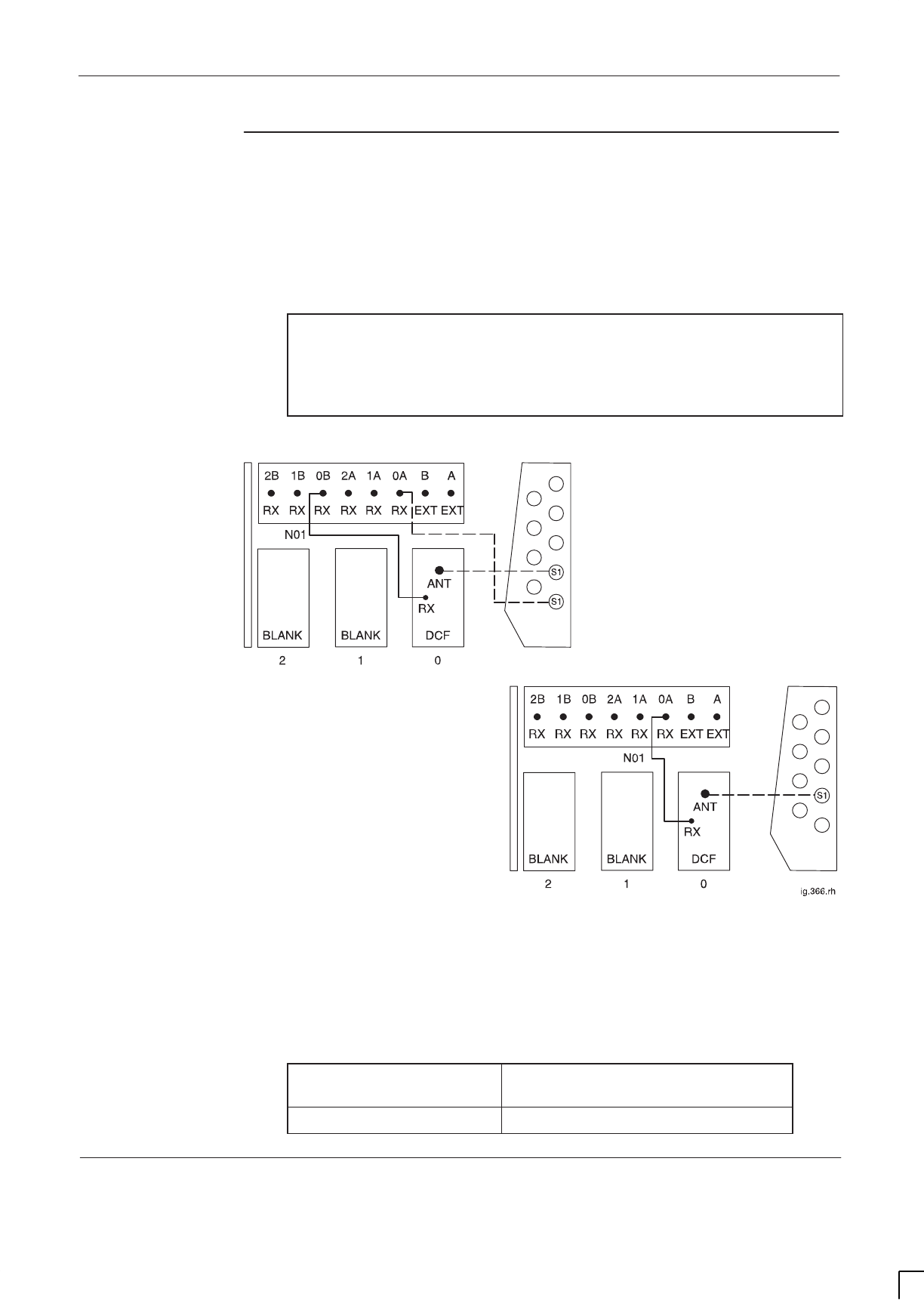
GSM-204-423 Suggested RF configurations
31st Oct 01
Installation & Configuration: Horizon
macro
outdoor
68P02902W03-A
CONTROLLED INTRODUCTION
Inst. 3–41
Configuration
for omni 1 or 2
(with/without
diversity)
Figure 3-14 shows suggested single Horizon
macro
cabinet configurations, with
and without diversity, for omni 1 or omni 2 with duplexed combining bandpass
filter.
CAUTION If a single antenna (non-diversity) is required, the duplex
antenna RF receive cable from the transmit block must be
connected to the RxA path at the SURF. Simply switching
off diversity at the OMC-R without the correct SURF
configuration will cause a loss of reception.
WITH DIVERSITY
WITHOUT DIVERSITY
Figure 3-14 Single cabinet omni 1 or 2 with DCF
Unused SMA connectors must be fitted with 50 ohm terminating loads as shown
below.
If configured for... Then 50 ohm load required on
unused SMA input to...
omni 1 DCF 0
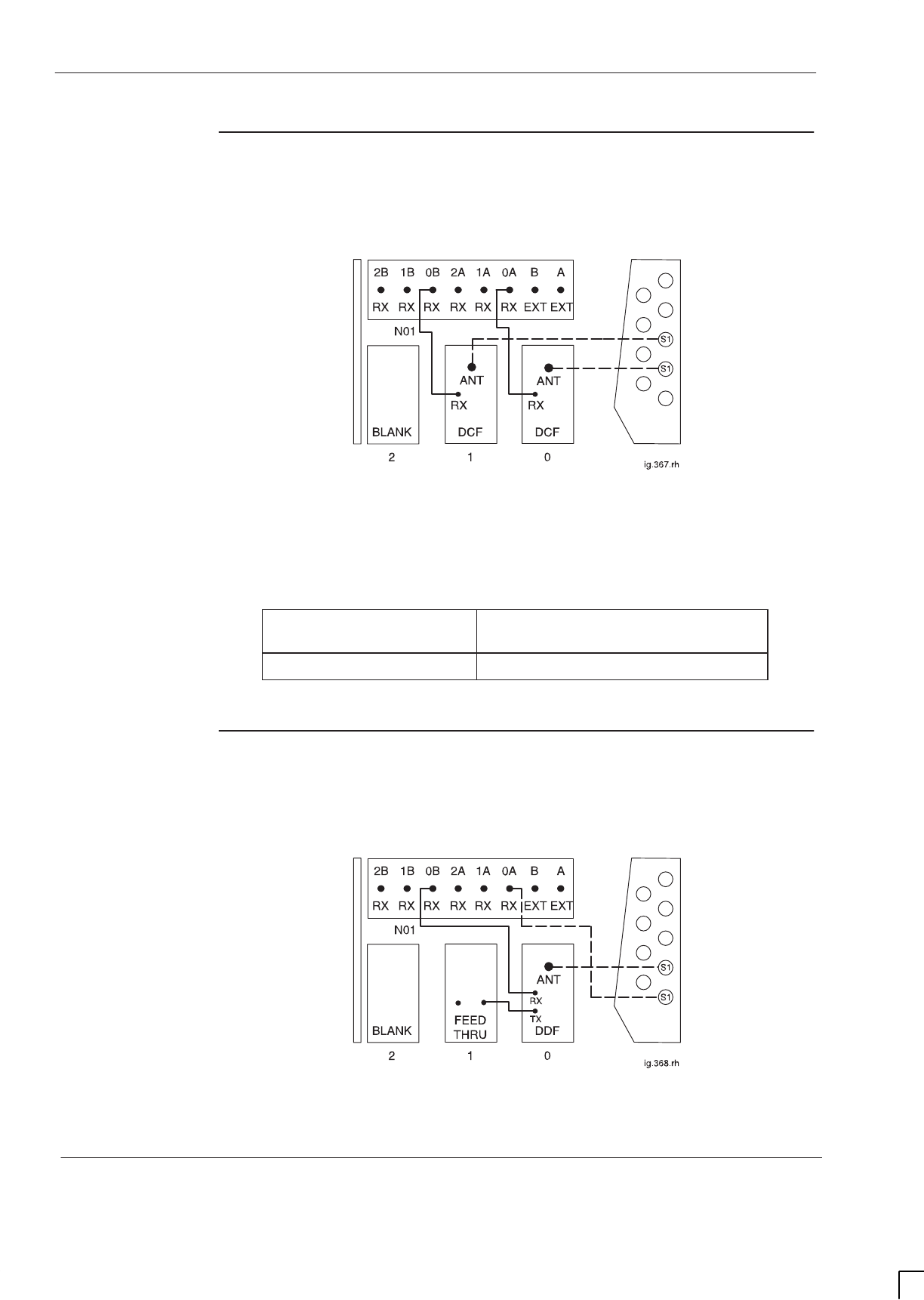
GSM-204-423
Suggested RF configurations
31st Oct 01
Inst. 3–42
Installation & Configuration: Horizon
macro
outdoor
CONTROLLED INTRODUCTION
68P02902W03-A
Configuration
for omni 3 or 4
Figure 3-15 shows a suggested configuration, using a single Horizon
macro
cabinet, for omni 3 or omni 4 with duplexed combining bandpass filter.
Figure 3-15 Single cabinet omni 3 or 4 with DCF
Unused SMA connectors must be fitted with 50 ohm terminating loads as shown
below.
If configured for... Then 50 ohm load required on
unused SMA input to...
omni 3 DCF 1
Configuration
for omni 3
Figure 3-16 shows a suggested configuration, using one Horizon
macro
cabinet,
for omni 3 with dual stage duplexed combining filter.
Figure 3-16 Single cabinet omni 3 with DDF
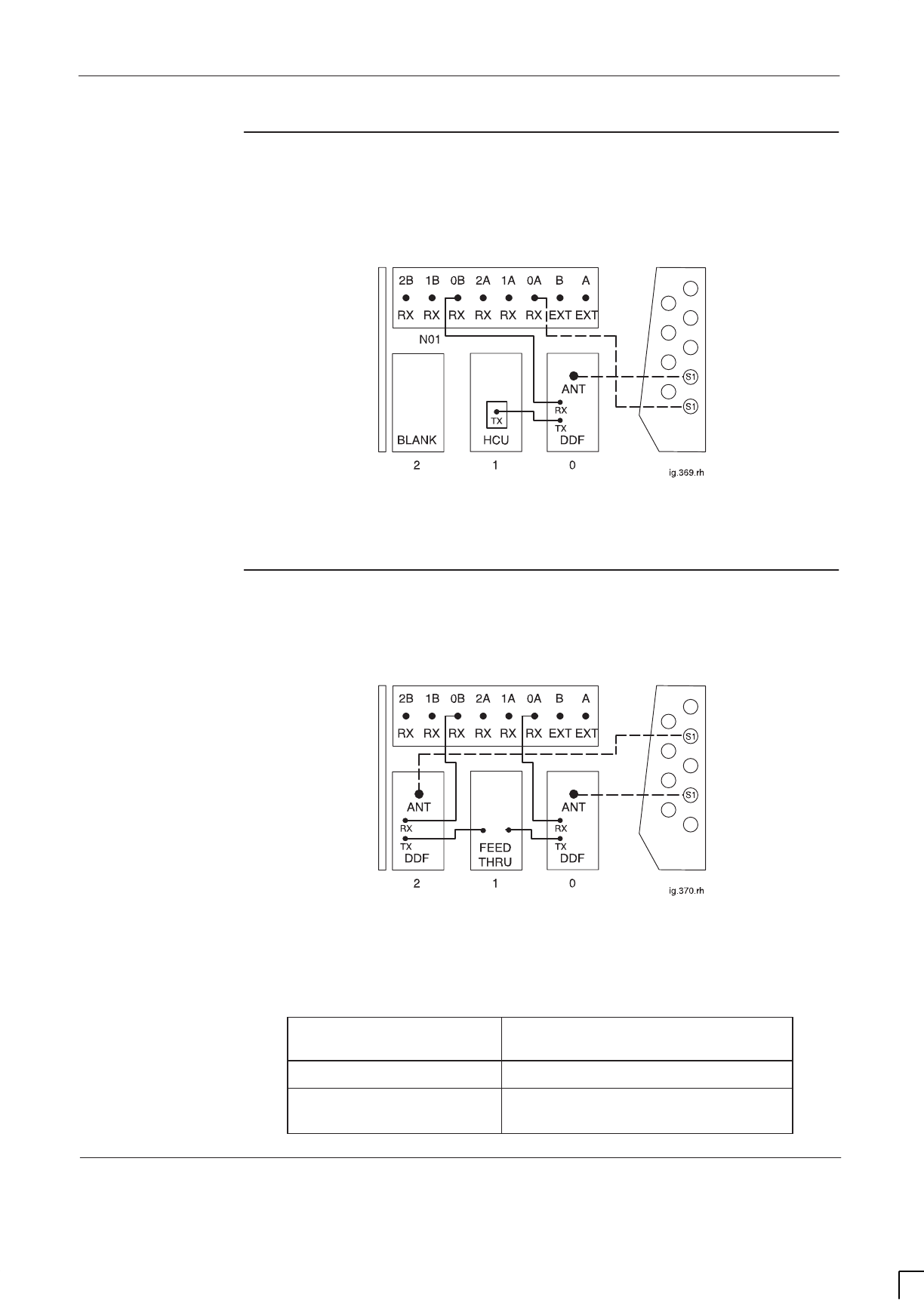
GSM-204-423 Suggested RF configurations
31st Oct 01
Installation & Configuration: Horizon
macro
outdoor
68P02902W03-A
CONTROLLED INTRODUCTION
Inst. 3–43
Configuration
for omni 4
Figure 3-17 shows a suggested configuration, using a single Horizon
macro
cabinet, for omni 4 with dual stage duplexed combining filter and hybrid
combining unit.
Figure 3-17 Single cabinet omni 4 with DDF and HCU
Configuration
for omni 5 or 6
Figure 3-18 shows a suggested configuration, using one Horizon
macro
cabinet,
for omni 5 or 6 with dual stage duplexed combining filter and air combining.
Figure 3-18 Single cabinet omni 5 or 6 with DDF and air combining
Unused SMA connectors must be fitted with 50 ohm terminating loads as shown
below.
If configured for... Then 50 ohm load required on
unused SMA input to...
omni 5 DDF 2
omni 3
(depopulated omni 6) all Tx modules from
radio slots 1, 3, and 5
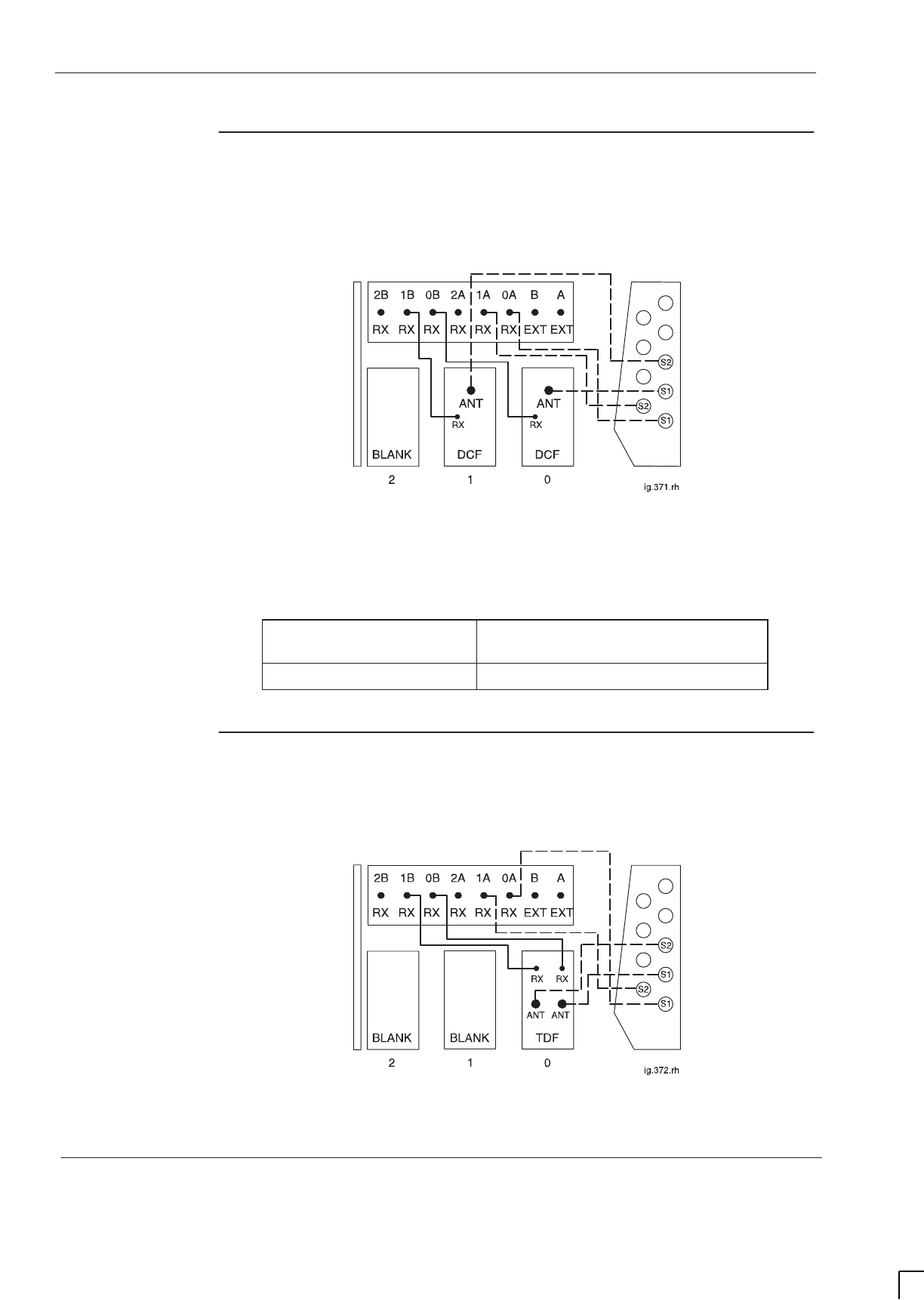
GSM-204-423
Suggested RF configurations
31st Oct 01
Inst. 3–44
Installation & Configuration: Horizon
macro
outdoor
CONTROLLED INTRODUCTION
68P02902W03-A
Configuration
for sector 1/1 or
2/2
Figure 3-19 shows a suggested configuration, using a single Horizon
macro
cabinet, for sector 1/1 or 2/2 with duplexed combining bandpass filter.
Figure 3-19 Single cabinet sector 1/1 or 2/2 with DCF
Unused SMA connectors must be fitted with 50 ohm terminating loads as shown
below.
If configured for... Then 50 ohm load required on
unused SMA input to...
sector 1/1 DCF 0 and DCF 2
Configuration
for sector 1/1
Figure 3-20 shows a suggested configuration, using one Horizon
macro
cabinet,
for sector 1/1 with twin duplexed filter.
Figure 3-20 Single cabinet sector 1/1 with TDF
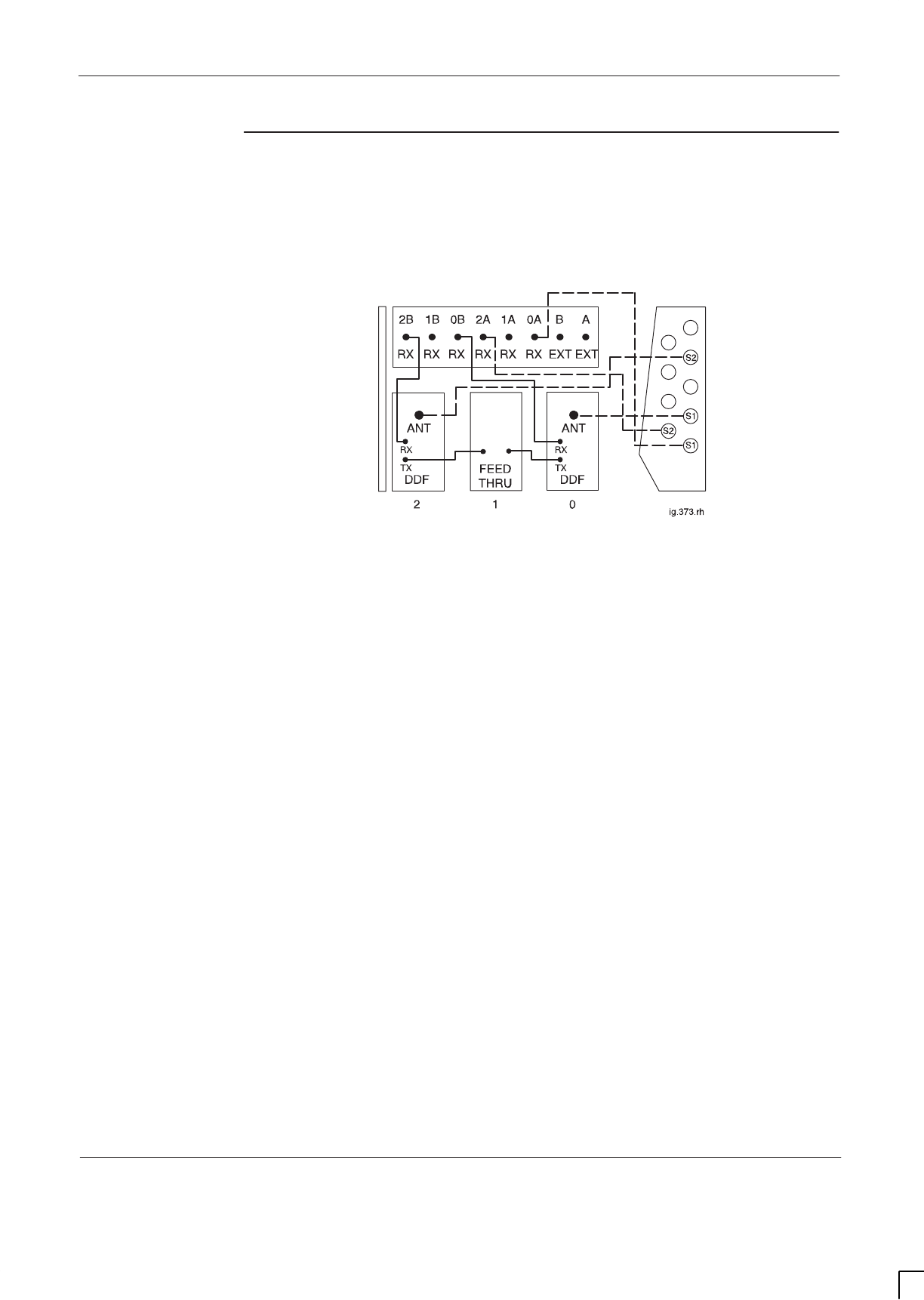
GSM-204-423 Suggested RF configurations
31st Oct 01
Installation & Configuration: Horizon
macro
outdoor
68P02902W03-A
CONTROLLED INTRODUCTION
Inst. 3–45
Configuration
for single
cabinet sector
3/3
Figure 3-21 shows a suggested configuration, using one Horizon
macro
cabinet,
for sector 3/3 with dual stage duplexed combining filter.
Figure 3-21 Single cabinet sector 3/3 with DDF
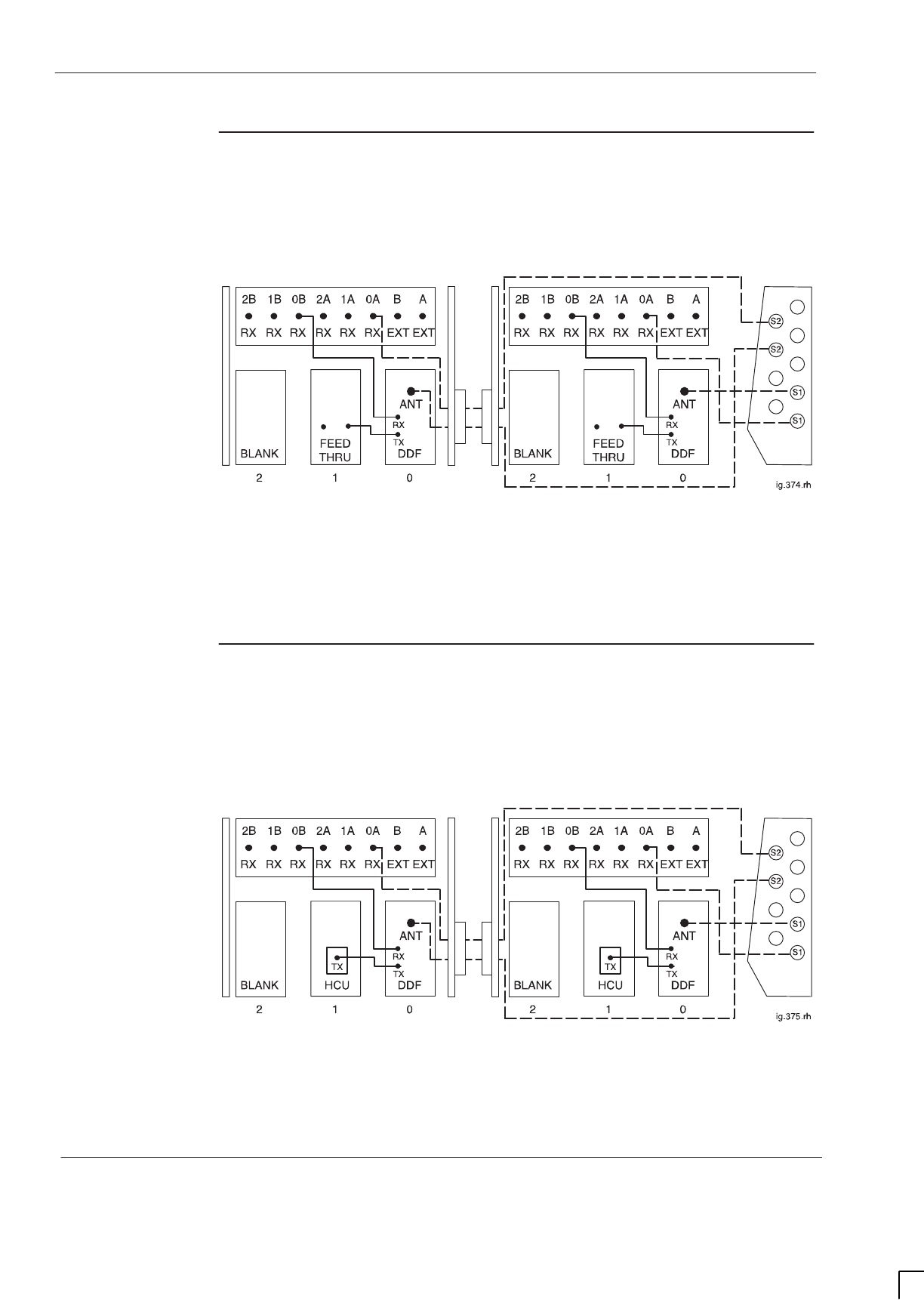
GSM-204-423
Suggested RF configurations
31st Oct 01
Inst. 3–46
Installation & Configuration: Horizon
macro
outdoor
CONTROLLED INTRODUCTION
68P02902W03-A
Configuration
for 2 cabinet
sector 3/3
Figure 3-22 shows a suggested configuration, using two Horizon
macro
cabinets,
for sector 3/3 with dual stage duplexed combining filter.
CABINET 2 CABINET 1
(master)
Figure 3-22 Two cabinet sector 3/3 with DDF
Configuration
for 2 cabinet
sector 4/4
Figure 3-23 shows a suggested configuration, using two Horizon
macro
cabinets,
for sector 4/4 with dual stage duplexed combining filter and hybrid combining
unit.
CABINET 2 CABINET 1
(master)
Figure 3-23 Two cabinet sector 4/4 with DDF and HCU
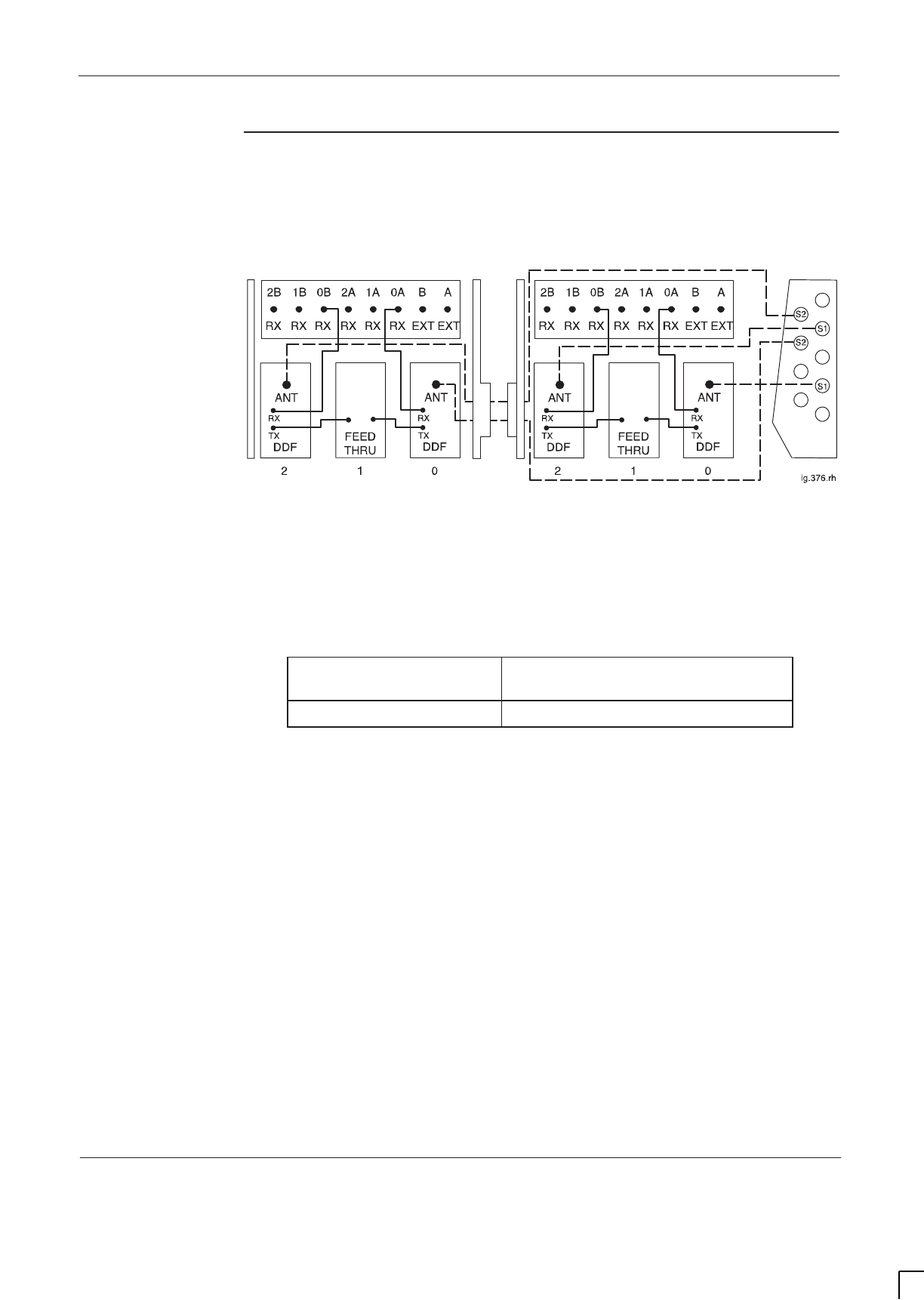
GSM-204-423 Suggested RF configurations
31st Oct 01
Installation & Configuration: Horizon
macro
outdoor
68P02902W03-A
CONTROLLED INTRODUCTION
Inst. 3–47
Configuration
for 2 cabinet
sector 5/5 or 6/6
Figure 3-24 shows a suggested configuration, using two Horizon
macro
cabinets,
for sector 5/5 or 6/6 with dual stage duplexed combining filter and air combining.
CABINET 2 CABINET 1
(master)
Figure 3-24 Two cabinet sector 5/5 or 6/6 with DDF and air combining
Unused SMA connectors must be fitted with 50 ohm terminating loads as shown
below.
If configured for... Then 50 ohm load required on
unused SMA input to...
sector 5/5 both DDF 2 modules
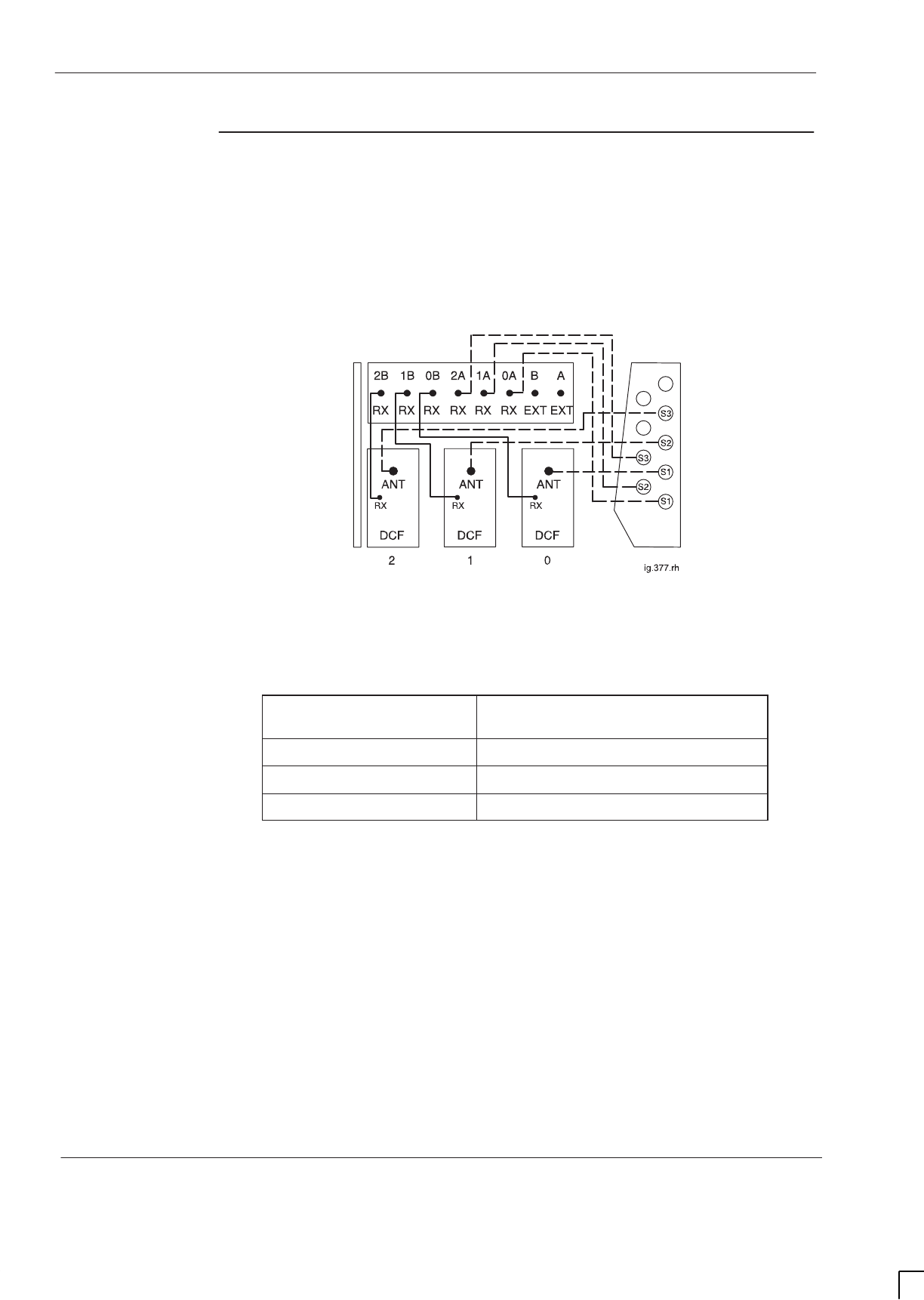
GSM-204-423
Suggested RF configurations
31st Oct 01
Inst. 3–48
Installation & Configuration: Horizon
macro
outdoor
CONTROLLED INTRODUCTION
68P02902W03-A
Configuration
for single
cabinet sector
1/1/1, 1/1/2, 1/2/2
or 2/2/2
Figure 3-25 shows a suggested configuration, using a single Horizon
macro
cabinet, for sector 1/1/1, 1/1/2, 1/2/2 or 2/2/2 with duplexed combining
bandpass filter.
Figure 3-25 Single cabinet sector 1/1/1, 1/1/2, 1/2/2 or 2/2/2 with DCF
Unused SMA connectors must be fitted with 50 ohm terminating loads as shown
below.
If configured for... Then 50 ohm load required on
unused SMA input to...
Sector 1/1/1 DCF 0, 1 and 2
Sector 1/1/2 DCF 1 and 2
Sector 1/2/2 DCF 2
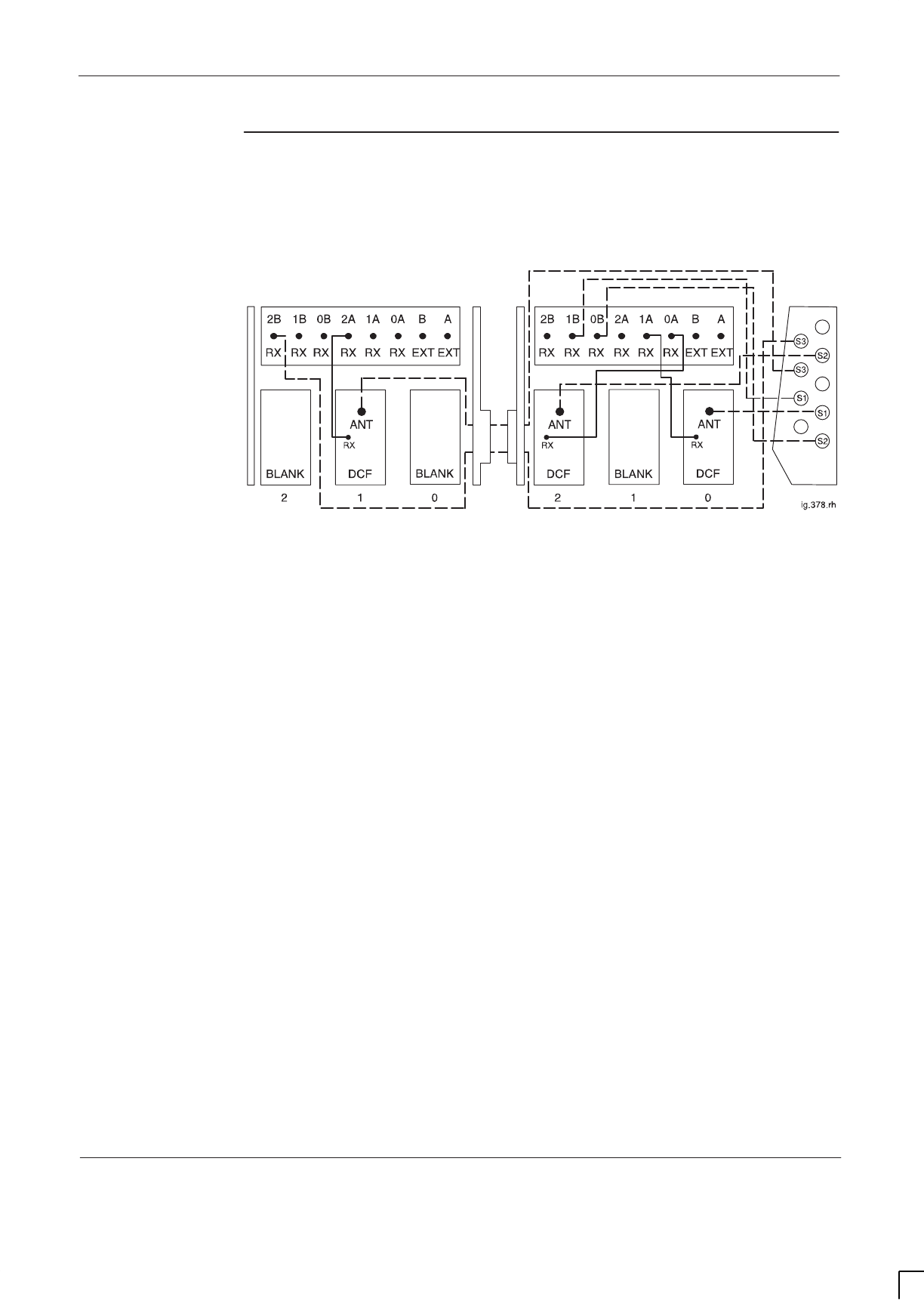
GSM-204-423 Suggested RF configurations
31st Oct 01
Installation & Configuration: Horizon
macro
outdoor
68P02902W03-A
CONTROLLED INTRODUCTION
Inst. 3–49
Configuration
for 2 cabinet
sector 2/2/2
Figure 3-26 shows a suggested configuration, using two Horizon
macro
cabinets,
for sector 2/2/2 with duplexed combining bandpass filter.
CABINET 2 CABINET 1
(master)
Figure 3-26 Two cabinet sector 2/2/2 with DCF
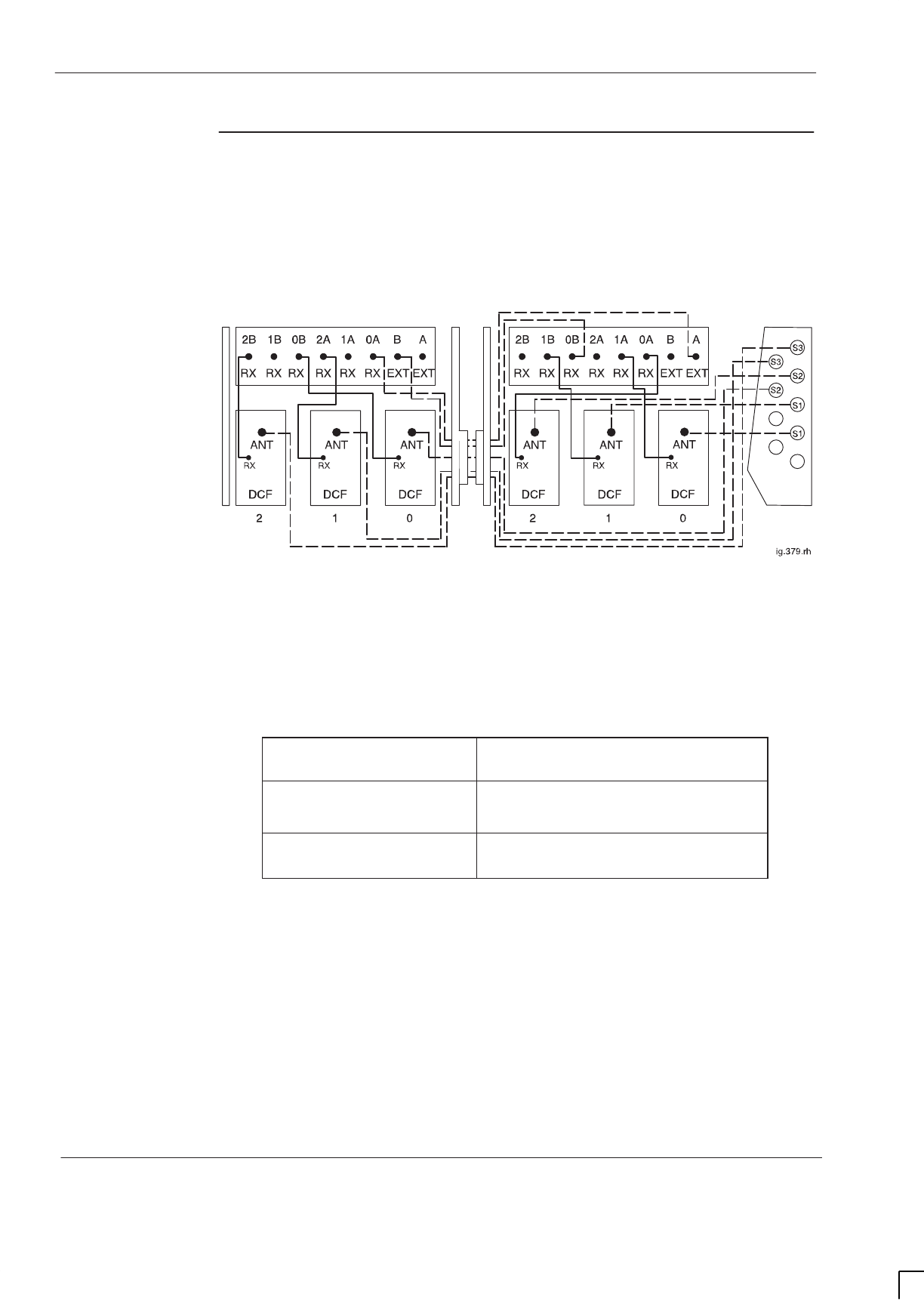
GSM-204-423
Suggested RF configurations
31st Oct 01
Inst. 3–50
Installation & Configuration: Horizon
macro
outdoor
CONTROLLED INTRODUCTION
68P02902W03-A
Configuration
for 2 cabinet
sector 3/3/3 or
4/4/4
Figure 3-27 shows a suggested configuration, using two Horizon
macro
cabinets,
for sector 3/3/3 or sector 4/4/4 with duplexed combining bandpass filter and air
combining.
CABINET 2 CABINET 1
(master)
Figure 3-27 Two cabinet sector 3/3/3 or sector 4/4/4 with DCF and air
combining
Unused SMA connectors must be fitted with 50 ohm terminating loads as shown
below.
If configured for... Then 50 ohm load required on
unused SMA input to...
sector 3/3/3 cabinet 1, DCF 1
cabinet 2, DCF 0 and DCF 2
2/2/2 (depopulated 4/4/4) all Tx modules from
radio slots 1, 3, and 5
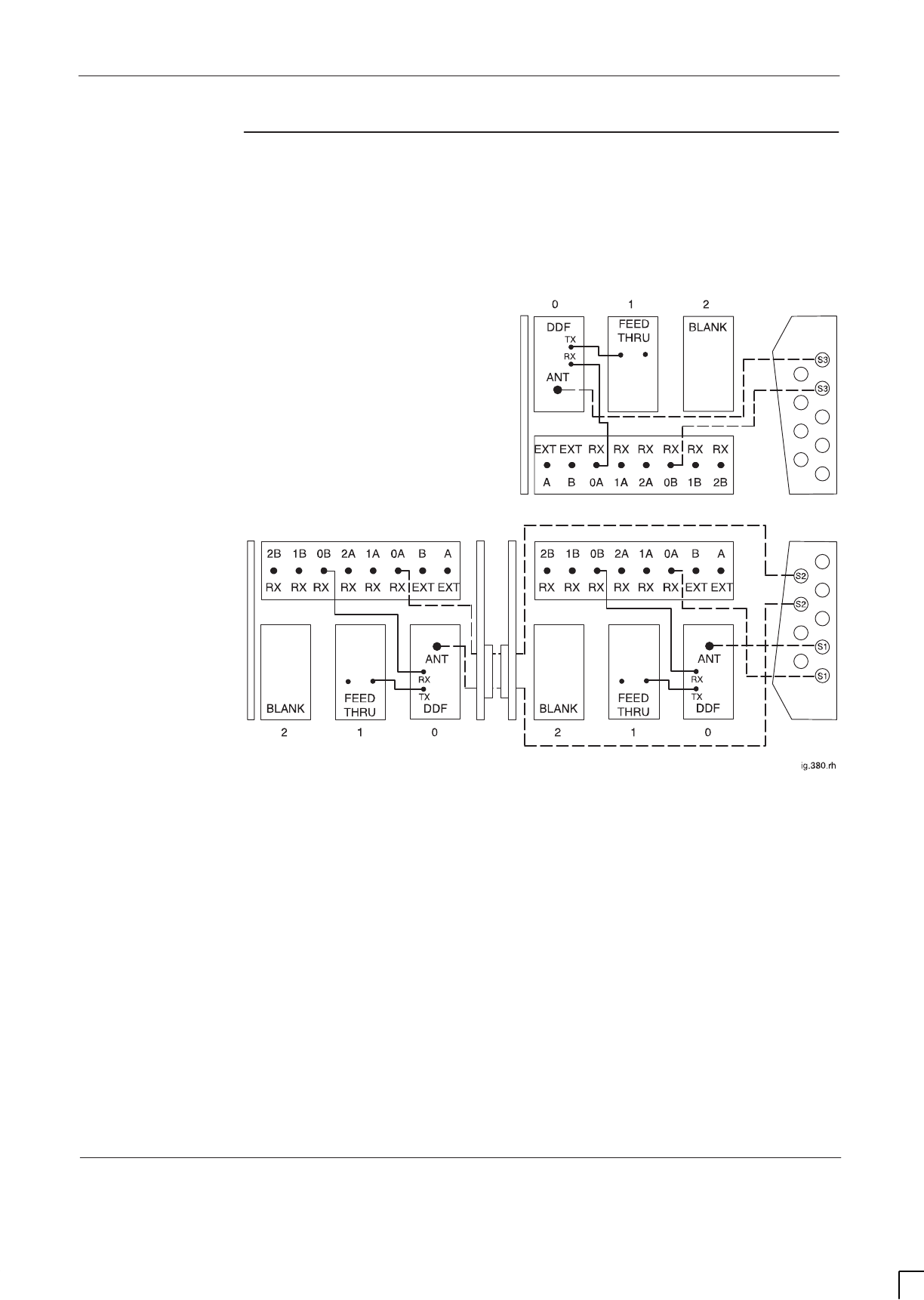
GSM-204-423 Suggested RF configurations
31st Oct 01
Installation & Configuration: Horizon
macro
outdoor
68P02902W03-A
CONTROLLED INTRODUCTION
Inst. 3–51
Configuration
for 3 cabinet
sector 3/3/3
Figure 3-28 shows a suggested configuration, using three Horizon
macro
cabinets, for sector 3/3/3 with dual stage duplexed combining filter.
CABINET 2
CABINET 3
CABINET 1
(master)
Figure 3-28 Three cabinet sector 3/3/3 with DDF
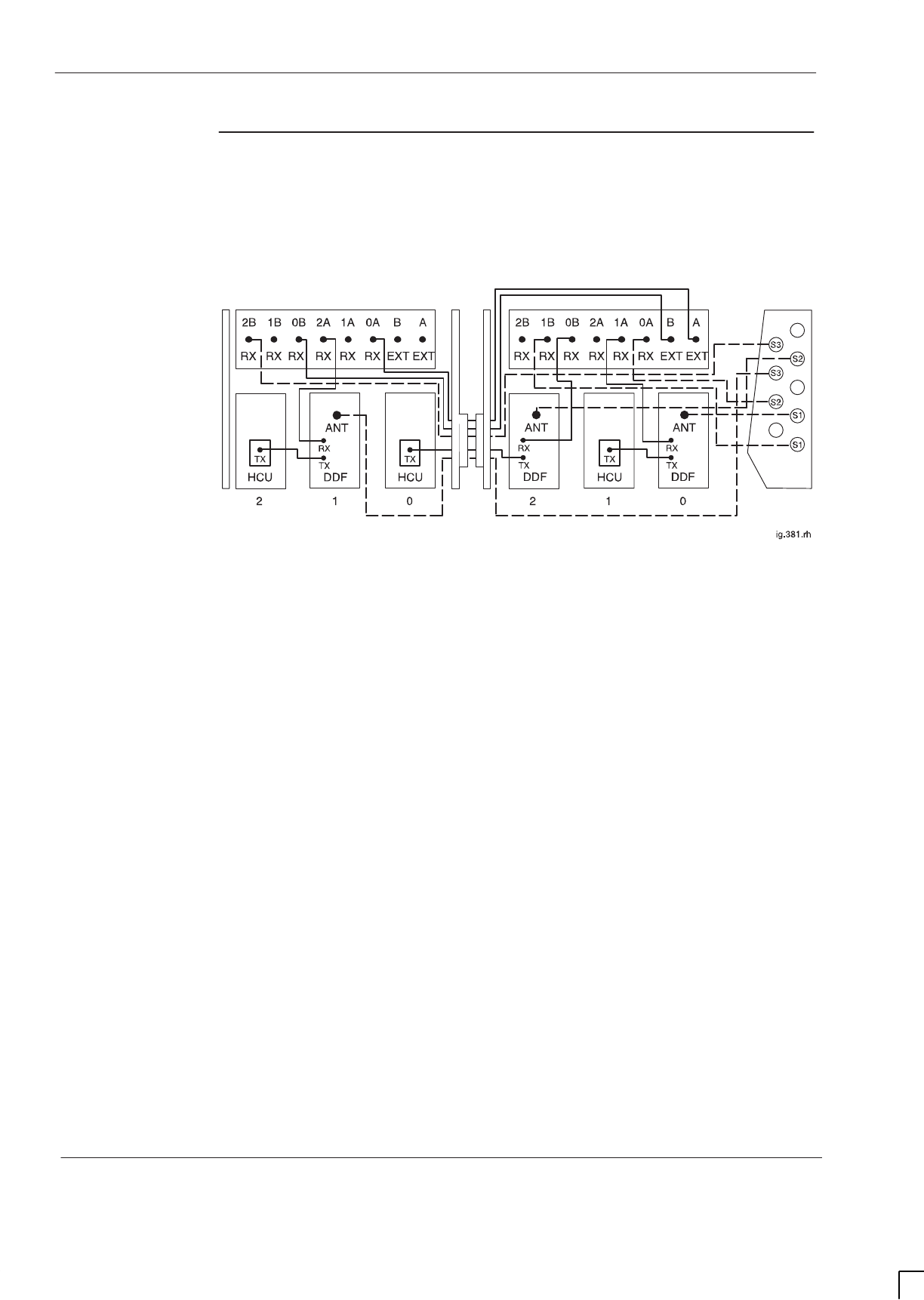
GSM-204-423
Suggested RF configurations
31st Oct 01
Inst. 3–52
Installation & Configuration: Horizon
macro
outdoor
CONTROLLED INTRODUCTION
68P02902W03-A
Configuration
for 2 cabinet
sector 4/4/4
Figure 3-29 shows a suggested configuration, using two Horizon
macro
cabinets,
for sector 4/4/4 with dual stage duplexed combining filter and hybrid combining
unit.
CABINET 2 CABINET 1
(master)
Figure 3-29 Two cabinet sector 4/4/4 with DDF and HCU
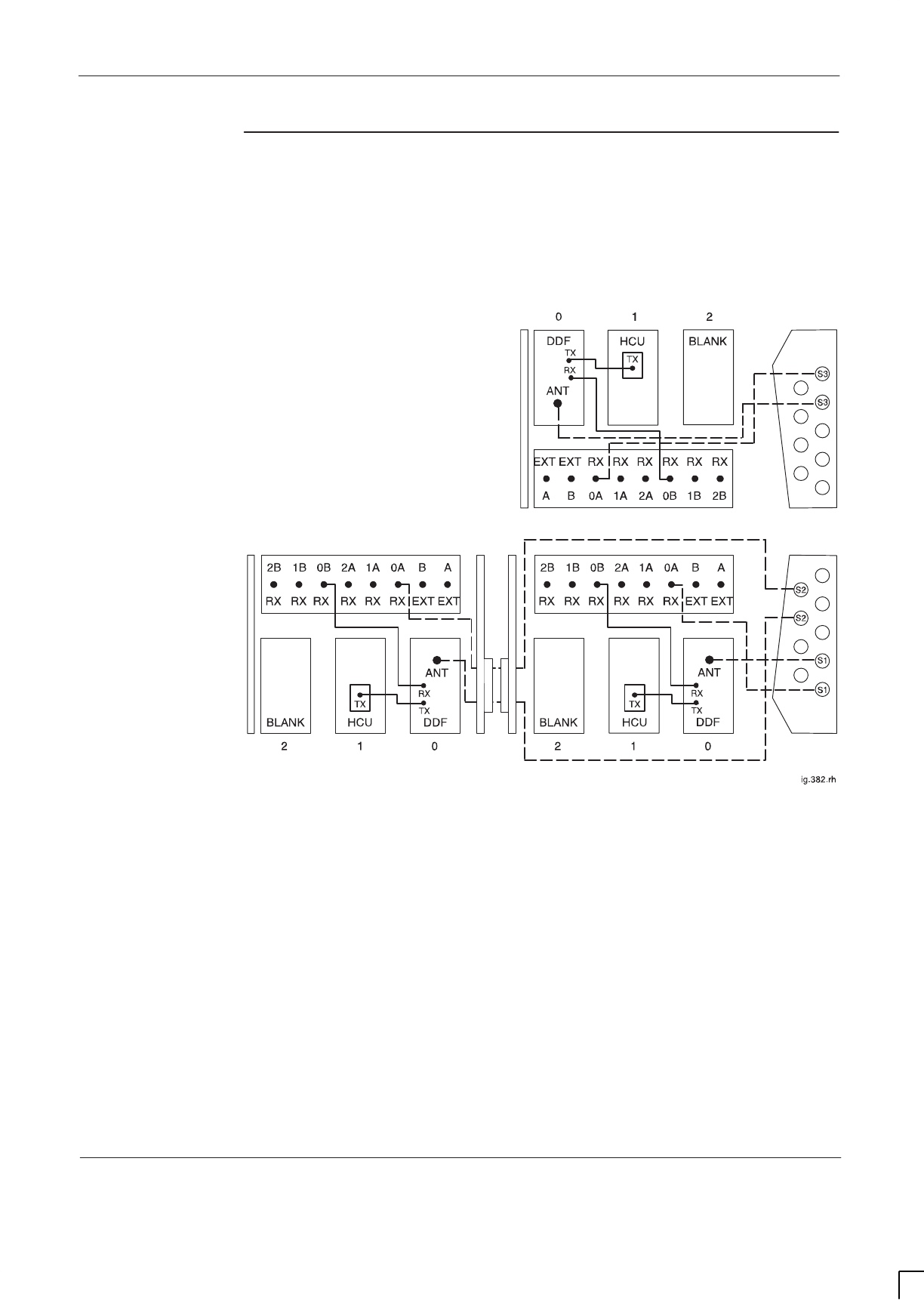
GSM-204-423 Suggested RF configurations
31st Oct 01
Installation & Configuration: Horizon
macro
outdoor
68P02902W03-A
CONTROLLED INTRODUCTION
Inst. 3–53
Configuration
for 3 cabinet
sector 4/4/4
Figure 3-30 shows a suggested configuration, using three Horizon
macro
cabinets, for sector 4/4/4 with dual stage duplexed combining filter and hybrid
combining unit.
CABINET 2
CABINET 3
CABINET 1
(master)
Figure 3-30 Three cabinet sector 4/4/4 with DDF and HCU
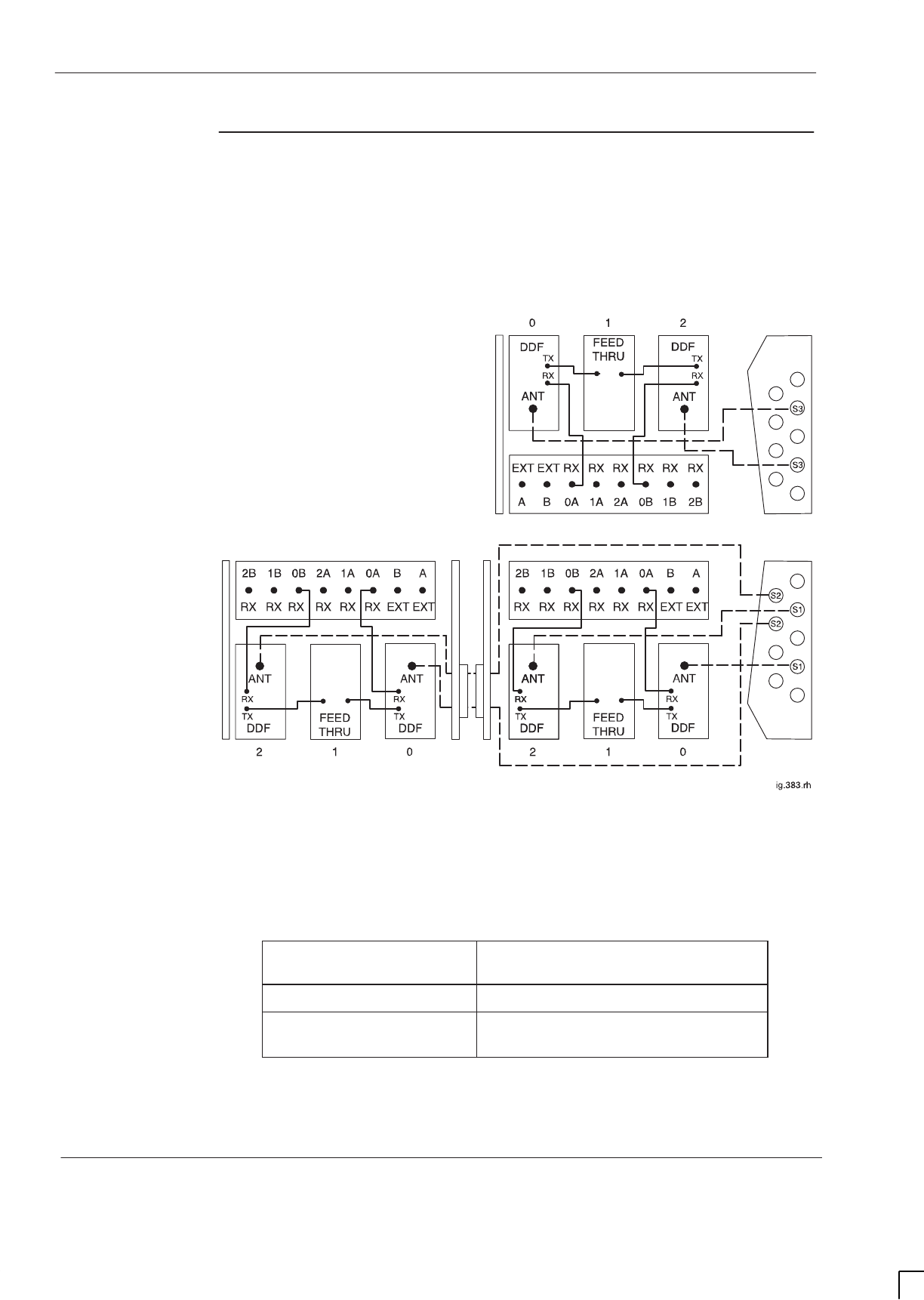
GSM-204-423
Suggested RF configurations
31st Oct 01
Inst. 3–54
Installation & Configuration: Horizon
macro
outdoor
CONTROLLED INTRODUCTION
68P02902W03-A
Configuration
for sector 5/5/5
or 6/6/6
Figure 3-31 shows a suggested configuration, using three Horizon
macro
cabinets, for sector 5/5/5 or sector 6/6/6 with dual stage duplexed combining
filter and air combining.
CABINET 2
CABINET 3
CABINET 1
(master)
Figure 3-31 Sector 5/5/5 or sector 6/6/6 with DDF and air combining
Unused SMA connectors must be fitted with 50 ohm terminating loads as shown
below.
If configured for... Then 50 ohm load required on
unused SMA input to...
sector 5/5/5 all DDF 2 modules
3/3/3 (depopulated 6/6/6) all Tx modules from
radio slots 1, 3, and 5
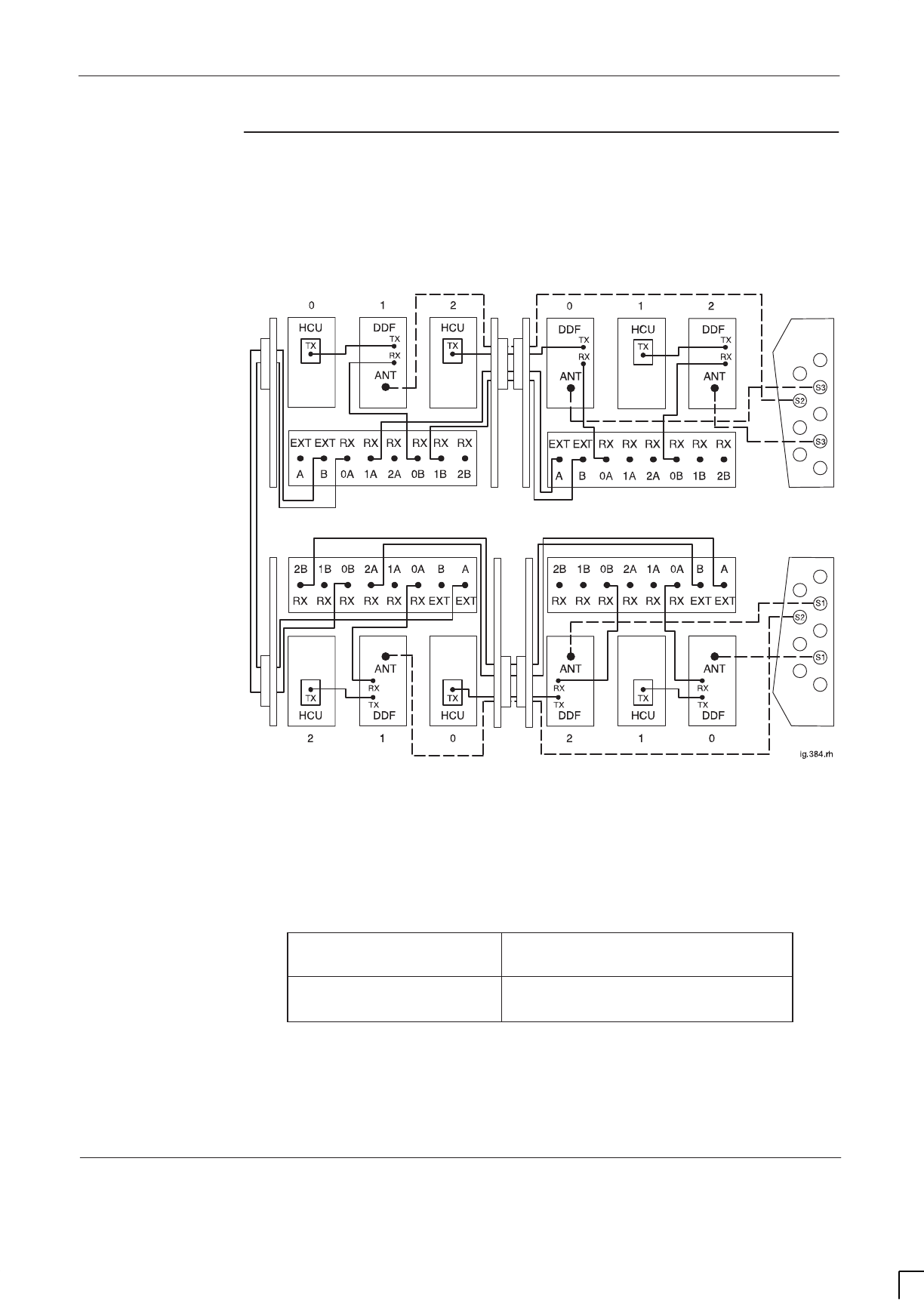
GSM-204-423 Suggested RF configurations
31st Oct 01
Installation & Configuration: Horizon
macro
outdoor
68P02902W03-A
CONTROLLED INTRODUCTION
Inst. 3–55
Configuration
for sector 8/8/8
Figure 3-32 shows a suggested configuration, using four Horizon
macro
cabinets, for sector 8/8/8 with dual stage duplexed combining filter, hybrid
combining unit and air combining.
CABINET 2
CABINET 4
CABINET 1
(master)
CABINET 3
Figure 3-32 Sector 8/8/8 with DDF, HCU and air combining
Unused SMA connectors must be fitted with 50 ohm terminating loads as shown
below.
If configured for... Then 50 ohm load required on
unused SMA input to...
4/4/4 (depopulated 8/8/8) all Tx modules from
radio slots 1, 3, and 5
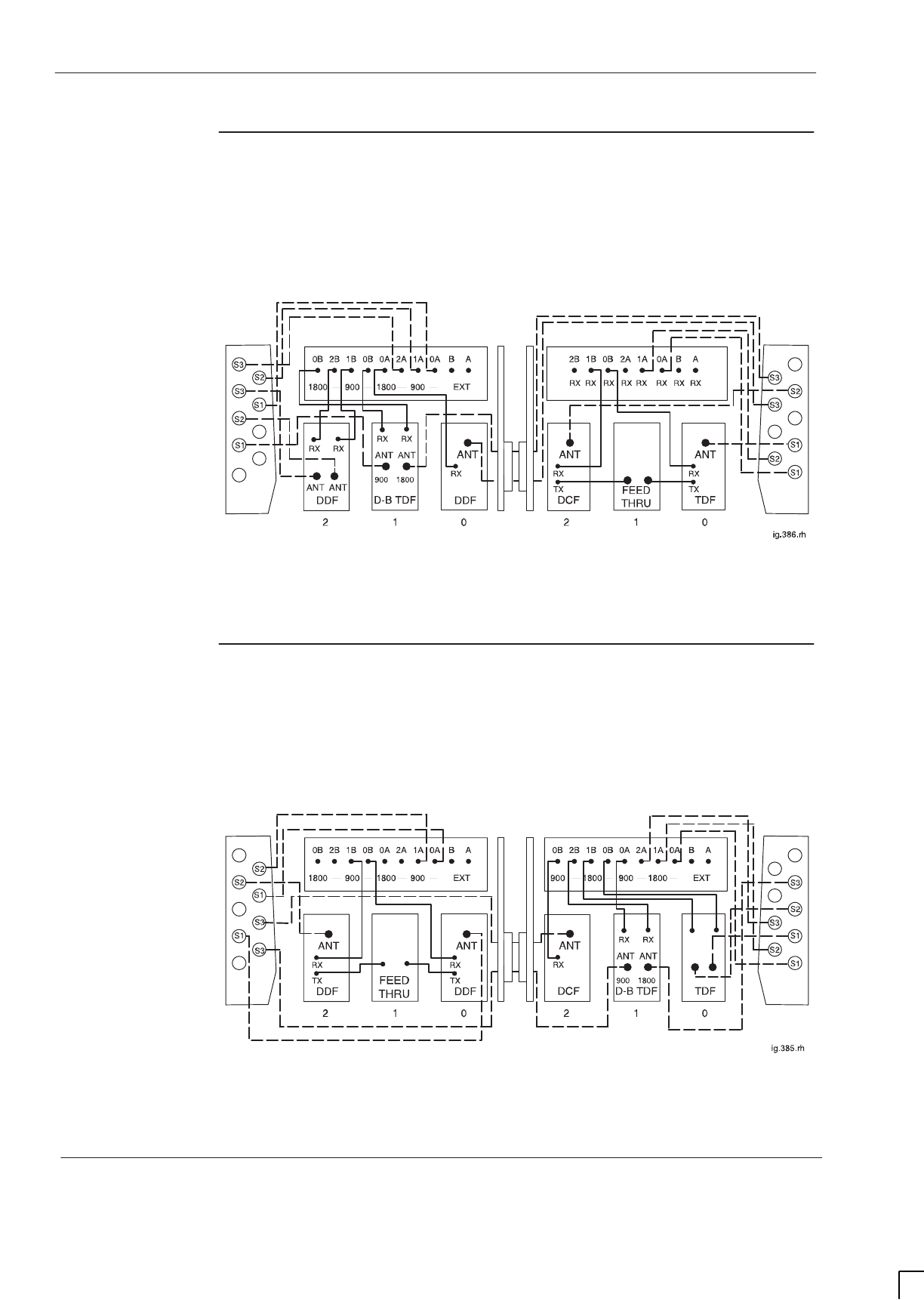
GSM-204-423
Suggested RF configurations
31st Oct 01
Inst. 3–56
Installation & Configuration: Horizon
macro
outdoor
CONTROLLED INTRODUCTION
68P02902W03-A
Configuration
for dual band
1/1/1-3/3/3
Figure 3-33 shows a suggested configuration, using two Horizon
macro
cabinets,
for dual band sector 1/1/1–3/3/3 operation, where sector 1/1/1 is EGSM900 and
sector 3/3/3 is DCS1800. This dual band configuration requires one single band
1800 SURF and one dual band 900 SURF.
Figure 3-33 Two cabinet dual band sector 1/1/1-3/3/3
Unused SMA connectors must be fitted with 50 ohm terminating loads.
Configuration
for dual band
3/3/3-1/1/1
Figure 3-34 shows a suggested configuration, using two Horizon
macro
cabinets,
for dual band sector 3/3/3–1/1/1 operation, where sector 3/3/3 is EGSM900 and
sector 1/1/1 is DCS1800. This dual band configuration requires one dual band
1800 SURF and one dual band 900 SURF.
Figure 3-34 Two cabinet dual band sector 3/3/3-1/1/1
Unused SMA connectors must be fitted with 50 ohm terminating loads.

GSM-204-423 Connecting fibre optic cables
31st Oct 01
Installation & Configuration: Horizon
macro
outdoor
68P02902W03-A
CONTROLLED INTRODUCTION
Inst. 3–57
Connecting fibre optic cables
Location of
fibre optic
connections
In an installation configuration with more than one Horizon
macro
outdoor
cabinet, fibre optic connections are used to link the MCUF in the master cabinet
to the extension cabinets. A maximum of three extension cabinets can be added
to the master cabinet.
Connections from the master cabinet are provided by three fibre optic
multiplexers (FMUXs). Two are located integral to the MCUF, and the third is a
separate module located in the slot next to the master MCUF. Additional
redundant modules may be installed for both MCUF and FMUX modules.
Extension cabinets have only a single FMUX, with optional redundancy, for fibre
optic connectivity to the master cabinet.
Tx and Rx data connections to the MCUF and FMUXs are located on the front
panel of each module.
Three different types of fibre optic cable, coloured orange and terminated with
ST fibre connectors, are available for use. These are described in Table 3-5.
Table 3-5 Extension cabinet fibre optic cables
Order
number Length Description
SVKN1244 5.6 m long connects master cabinet to first extension
SVKN1245 7.6 m long connects master cabinet to second extension
SVKN1246 7.6 m long connects master cabinet to third extension
WARNING Do not look directly into a fibre optic cable or the data
in/out connectors of the FMUX or MCUF, with or without
the use of optical aids. Laser radiation can come from
either the data in/out connectors or unterminated fibre
optic cables connected to data in/out connectors.
Care of fibres
Optical fibre cables contain an inner core, which is a strand of glass coated by a
cladding (sometimes in two layers), and an outer protective sheath which
provides mechanical protection.
The fibre acts as a light waveguide. In order for the link to work correctly light
must be propagated with minimal losses from end-to-end of the fibre. A number
of problems can prevent this from happening, resulting in a potentially faulty link.
Care must be taken to ensure that the conditions that follow are met.
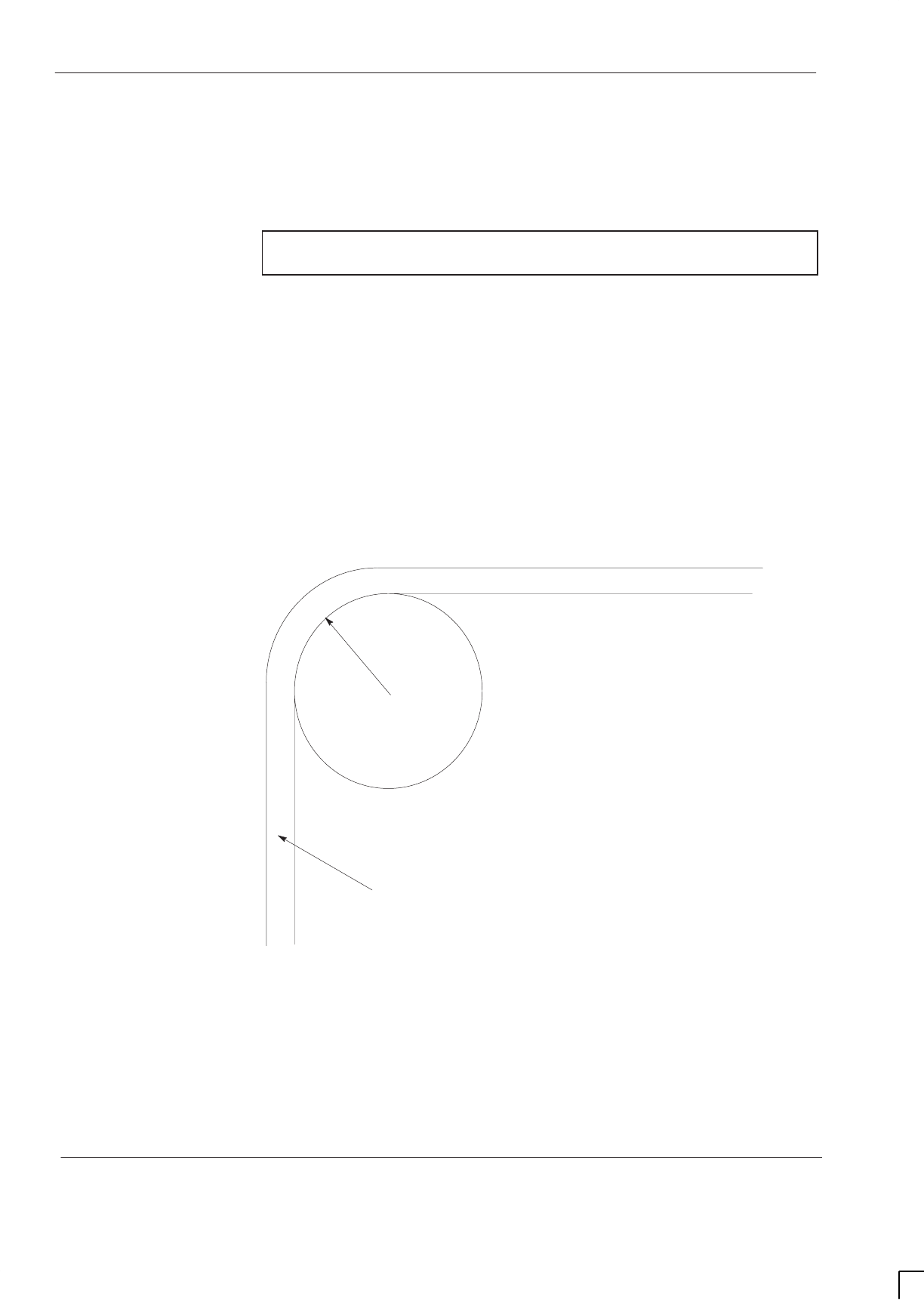
GSM-204-423
Connecting fibre optic cables
31st Oct 01
Inst. 3–58
Installation & Configuration: Horizon
macro
outdoor
CONTROLLED INTRODUCTION
68P02902W03-A
Minimum bend radius
All optical fibres have a minimum bend radius. This represents the smallest
circle that is allowed to be formed from a loop of fibre, that is how tight it can be
coiled, looped or bent.
CAUTION Under no circumstances should fibres be bent tighter than
the minimum bend radius.
If fibres are bent tighter than the minimum bend radius then two possible effects
can happen:
Excessive light loss can occur from the outside of the bend, resulting in a
loss of performance.
The fibre can fracture due to microscopic imperfections in the surface.
This type of break is invisible externally. If such a break occurs, excessive
light loss would be permanent and light would be scattered and reflected
from the break in the fibre. Returning the fibre to straight will not help and
the whole assembly will require replacement.
For glass fibres (orange or green outer sheath) the long term minimum bend
radius is approximately 30 mm.
Figure 3-35 illustrates the minimum bend radius for fibre optic cables.
30 mm
FIBRE OPTIC CABLE
Figure 3-35 Minimum bend radius of 30 mm
If the fibre is under tension (being stretched), the bend radius should be much
larger, at least doubled. This is because the tension in the fibre can increase
the possibilities of damage.
If in doubt about the radius, the fibre should be allowed to form its natural bend
radius by allowing it to bend under gravity only. This natural bend radius is
normally greater than 30 mm.
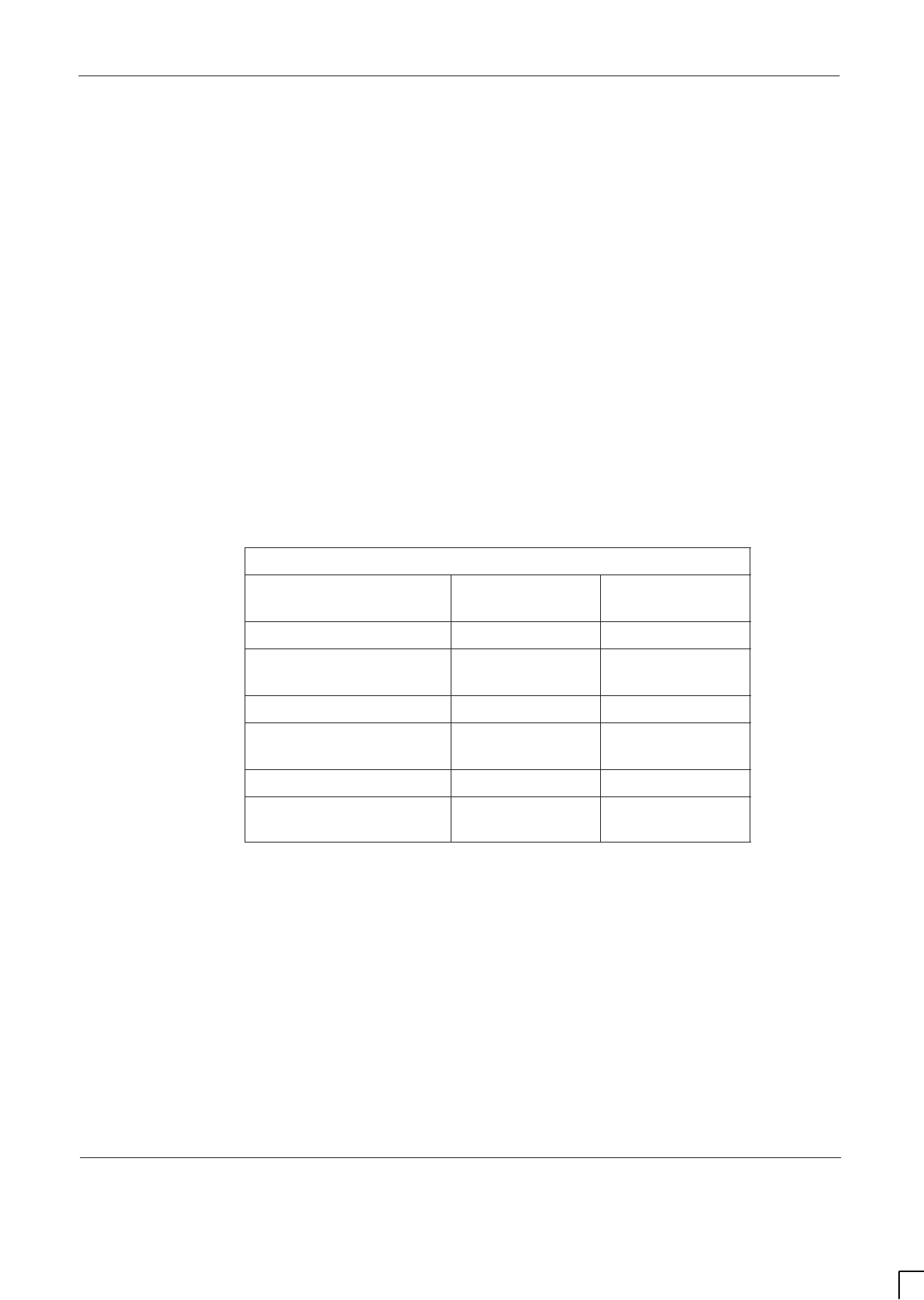
GSM-204-423 Connecting fibre optic cables
31st Oct 01
Installation & Configuration: Horizon
macro
outdoor
68P02902W03-A
CONTROLLED INTRODUCTION
Inst. 3–59
Protecting fibres and connectors
To maintain good light transmission through the fibre optic link it is essential to
maintain cleanliness of the connector end surfaces and/or bare fibre ends.
At all times when fibres are not connected into the system, the connector
protective caps (normally red) should be fitted and kept in place. This is
especially important when routeing fibres during installation.
Cleaning fibres and connectors
Cleanliness of fibre terminations and connectors is essential. If cleaning of
contaminated optical components is required, then all areas should be wiped
gently with a lint free cloth soaked in a suitable cleaning solution. Care should
be taken to ensure the ends of the fibres are not scratched in any way.
Connecting glass fibre cables
Fibre-ST connectors are used to terminate the fibre optic cables. These are
push fit and should not be tightened when connecting. Table 3-6 shows the fibre
optic interconnections between master and extension cabinets in multiple
cabinet sites.
Table 3-6 Fibre optic interconnections
Master cabinet
connection Extension
cabinet FMUX
connection
MCUF TCU0 FMUX0 IN 2nd cabinet DATA OUT
MCUF TCU0 FMUX0
OUT 2nd cabinet DATA IN
MCUF TCU1 FMUX1 IN 3rd cabinet DATA OUT
MCUF TCU1 FMUX1
OUT 3rd cabinet DATA IN
FMUX module DATA IN 4th cabinet DATA OUT
FMUX module DATA
OUT 4th cabinet DATA IN
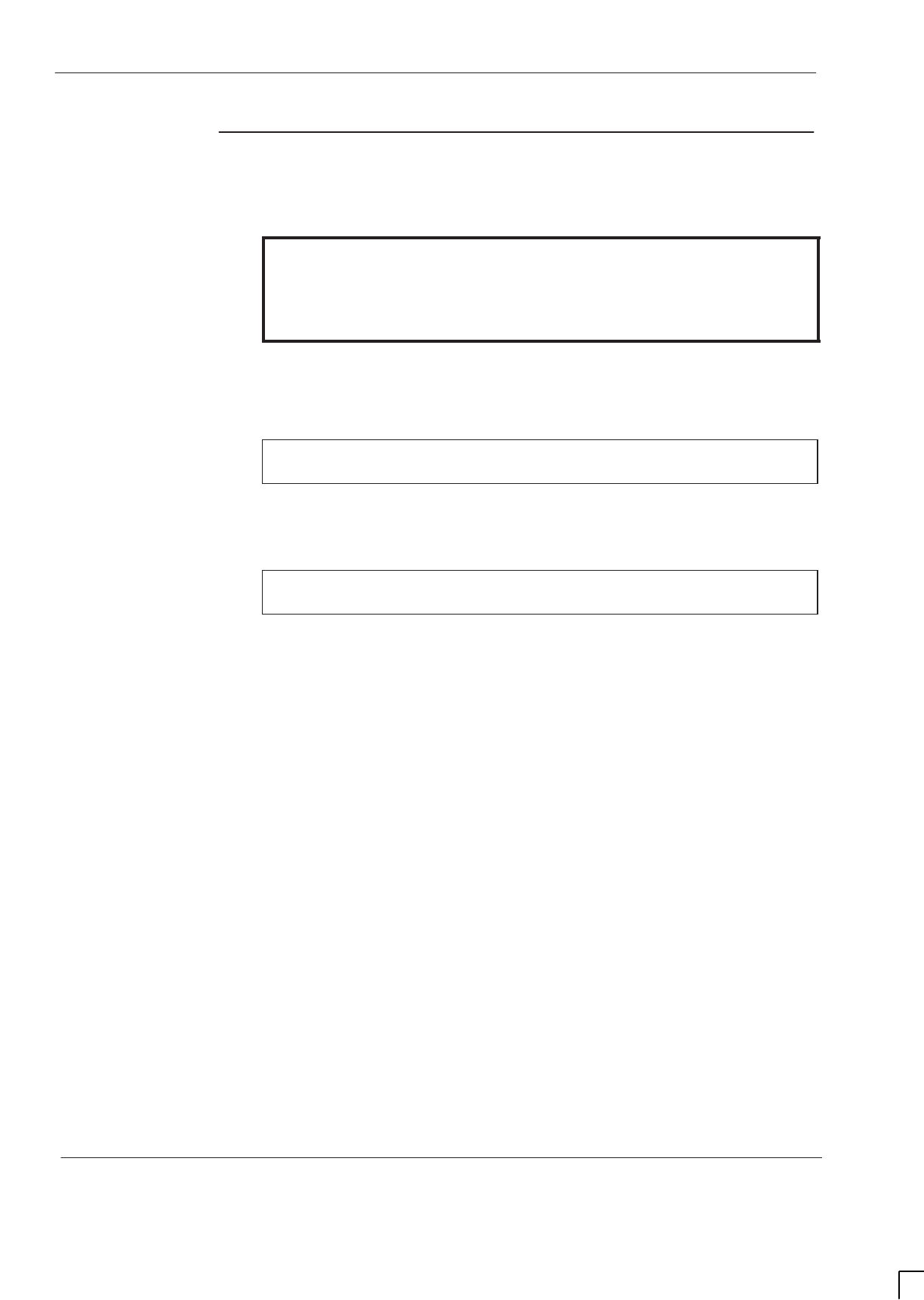
GSM-204-423
Connecting fibre optic cables
31st Oct 01
Inst. 3–60
Installation & Configuration: Horizon
macro
outdoor
CONTROLLED INTRODUCTION
68P02902W03-A
Connecting
fibre optic
cables between
cabinets
WARNING Do not look directly into a fibre optic cable or the data
in/out connectors of the FMUX or MCUF, with or without
the use of optical aids. Laser radiation can come from
either the data in/out connectors or unterminated fibre
optic cables connected to data in/out connectors.
To connect fibre optic cables between master and extension cabinets in multiple
cabinet sites.
1. Open master and extension cabinet doors and lids.
CAUTION Under no circumstances should fibres be bent tighter than
the minimum bend radius.
2. Route the appropriate length extension cabinet fibre optic cable from the
digital module compartment of the master cabinet, through the aperture in
the right side of the main cage, to the top section of the cabinet.
CAUTION Under no circumstances should any tools, such as pliers,
be used to connect ST fibre connectors.
3. Connect the push fit ST connector of the fibre optic cables to the
appropriate ports on the master MCUF, or master FMUX module, front
panel (see Table 3-6).
4. Lay the fibre optic cable into the cable guides and route through the
expansion panels to the extension cabinet.
5. Route the fibre optic cable, following existing cable layout as far as
possible, through the fibre optic cable hole in the cabinet top section to the
extension cabinet FMUX.
6. Connect the push fit ST connector of the fibre optic cables to the data
ports on the extension cabinet master FMUX front panel.
7. Repeat steps 2 to 6 for digital redundancy MCUF and FMUX, if fitted.
8. Repeat steps 2 to 7 for additional extension cabinets.
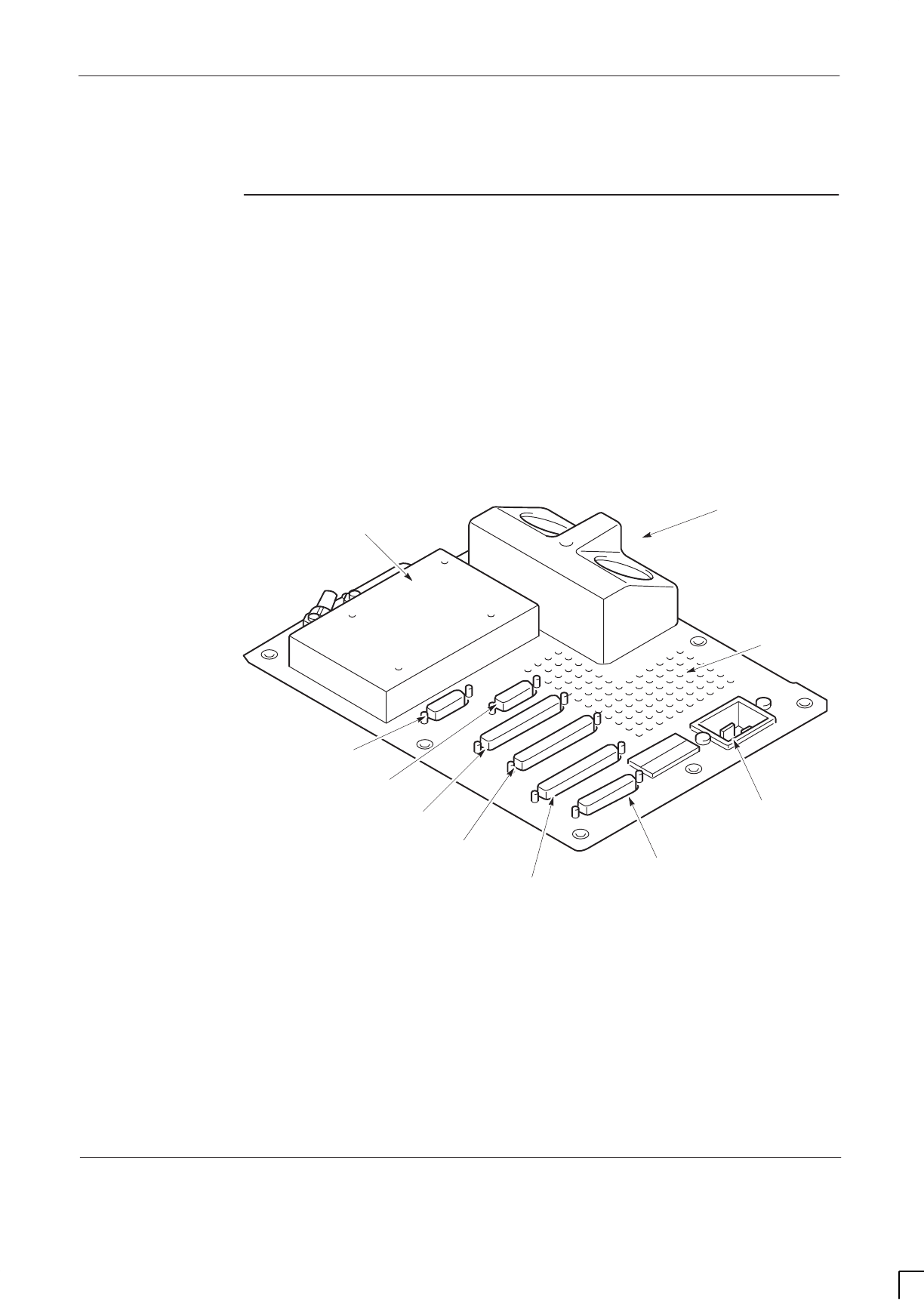
GSM-204-423 Interface panel cabling
31st Oct 01
Installation & Configuration: Horizon
macro
outdoor
68P02902W03-A
CONTROLLED INTRODUCTION
Inst. 3–61
Interface panel cabling
Interface panel
diagram and
pinout
overview
All maincage connectors are located on the interface panel. Each connector is
marked with the appropriate label. Power connectors are also located on the
interface panel.
An extension cabinet fibre optic cable is not connected to the interface panel,
but directly connected to the FMUX digital module in the main cage. The fibre
optic cable enters the cabinet through a hole on the top panel in front of the
interface panel.
Figure 3-36 shows the locations of all the interface panel connectors.
ig.239.rh
T43/BIB
AC POWER
SOCKET INPUT
(not used)
DC POWER
INPUT
GPS
(if fitted)
not used
PIX 0
EXTERNAL ALARMS
(PSU and TMS ALARMS)
PIX 1
ICS
VENTILATION
GRILLE
Figure 3-36 Interface panel connector locations
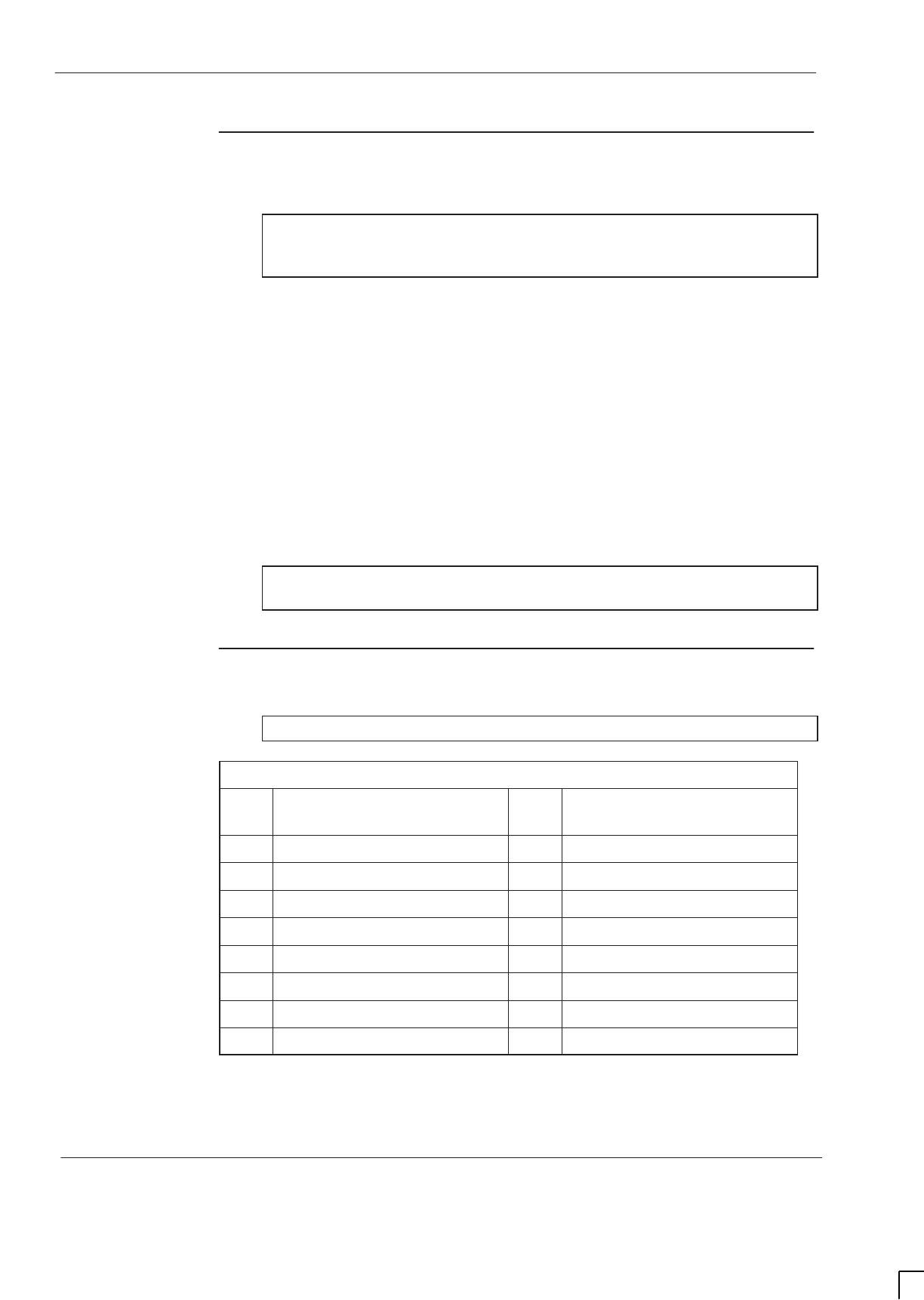
GSM-204-423
Interface panel cabling
31st Oct 01
Inst. 3–62
Installation & Configuration: Horizon
macro
outdoor
CONTROLLED INTRODUCTION
68P02902W03-A
Interface panel
connector
pinout tables
CAUTION Keep the plastic connector covers (supplied by Motorola)
on unused connectors to protect from damage by static or
foreign matter.
The following tables list the connector pinouts:
GPS, see Table 3-7.
RTC, see Table 3-8.
BIB, see Table 3-9.
T43, see Table 3-10.
PIX0, see Table 3-11.
PIX1, see Table 3-12.
ICS, see Table 3-13.
External alarms, see Table 3-14.
NOTE Some pin connections only refer to indoor or outdoor
cabinets.
GPS connector
Table 3-7 lists the GPS pin out connections.
NOTE The GPS connector is optional on later BTS cabinets.
Table 3-7 GPS pin connections (15-way D-type)
Pin
no. Signal/Description Pin
no. Signal/Description
1GPS power 1 9GPS return 1
2Rx negative 10 GPS power 2
3Rx positive 11 PPS positive
4Tx negative 12 PPS negative
5Tx positive 13 Not connected
6Spare (not connected) 14 Not connected
7VPP (not connected) 15 Not connected
8GPS return 2
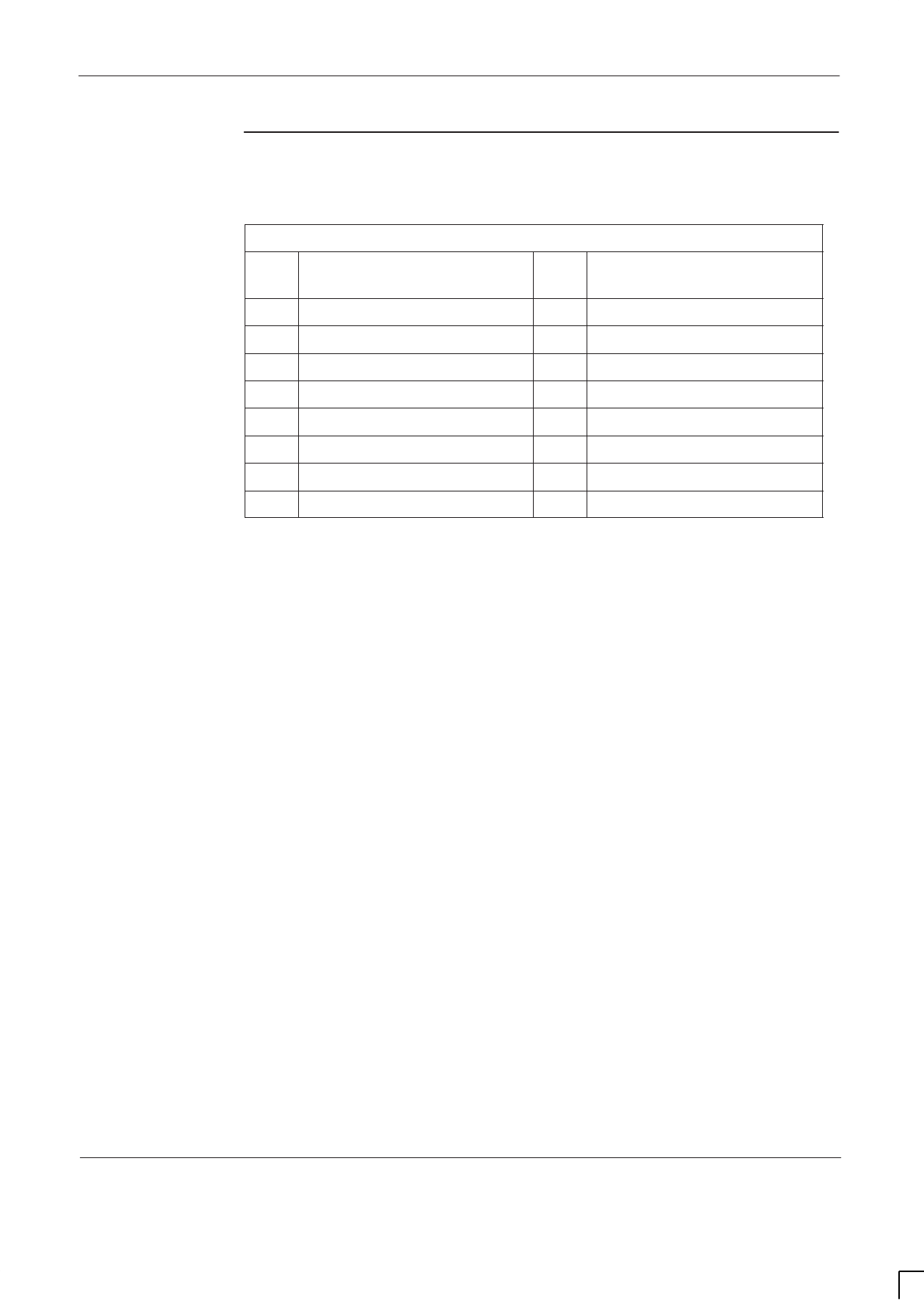
GSM-204-423 Interface panel cabling
31st Oct 01
Installation & Configuration: Horizon
macro
outdoor
68P02902W03-A
CONTROLLED INTRODUCTION
Inst. 3–63
RTC connector
(not used)
Table 3-8 lists the RTC connector pinouts:
Table 3-8 RTC pin connections (15-way D-type)
Pin
no. Signal/Description Pin
no. Signal/Description
1Not connected 9Not connected
2Not connected 10 Not connected
3RTC0 27 V 11 Earth
4RTC0 27 V 12 Earth
5Not connected 13 Not connected
6RTC1 27 V 14 Earth
7RTC1 27 V 15 Earth
8Not connected
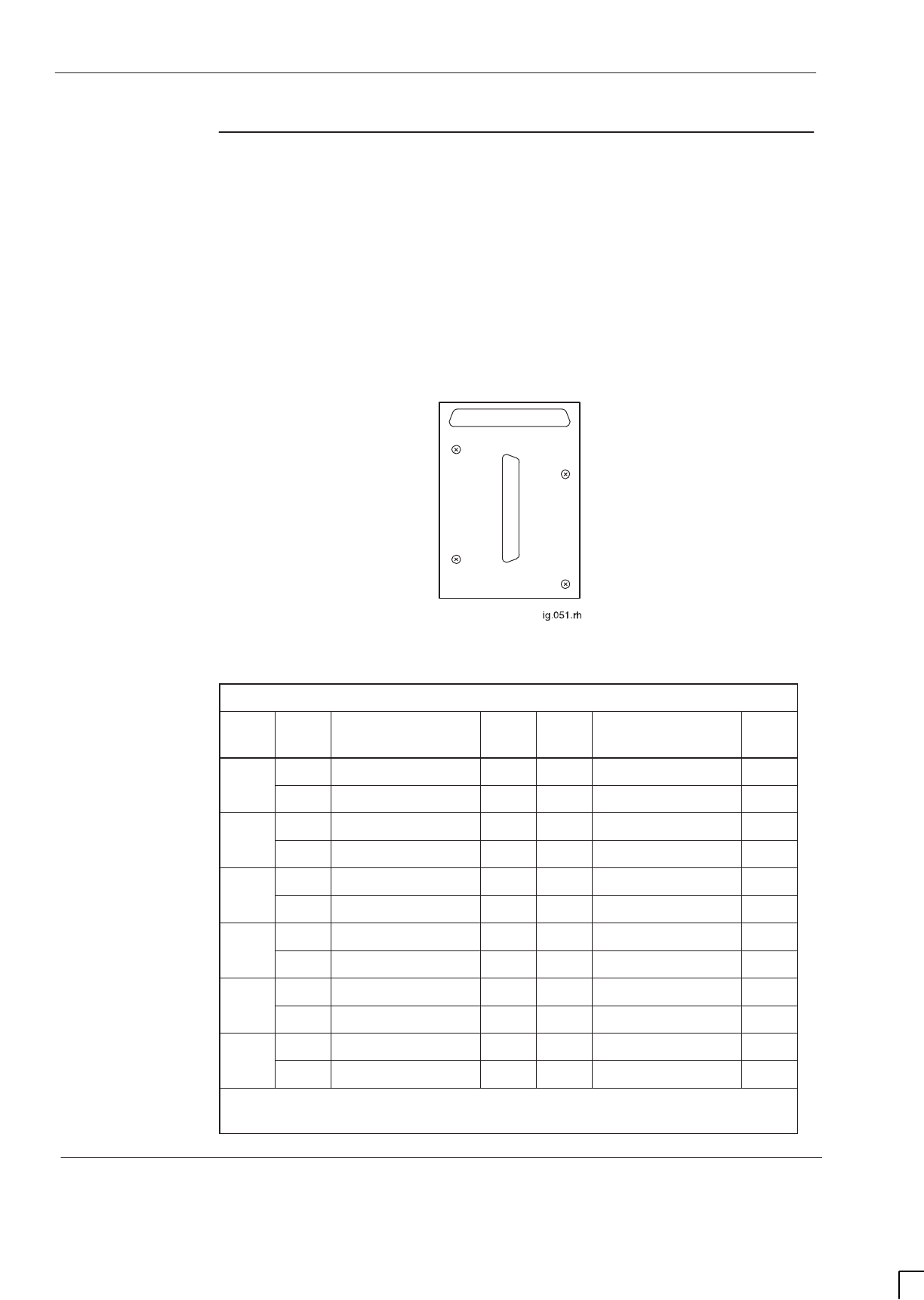
GSM-204-423
Interface panel cabling
31st Oct 01
Inst. 3–64
Installation & Configuration: Horizon
macro
outdoor
CONTROLLED INTRODUCTION
68P02902W03-A
BIB (BIM)
interconnection
The Balanced-line Interconnect Board (BIB), also known as BIM, provides the
line isolation between the E1/T1 circuit lines and the the CBIA backplane. The
board provides an interface for up to six input and six output balanced 120 ohm
lines. 12 transformers are used to provide line isolation while maintaining
impedance matching between the E1/T1 circuit lines and the NIU module. Each
transformer has a 1:1 turns ratio to match the external and backplane 120 ohm
connections.
Connection is made using a 37-pin D-type connector to both the BIB and the
external PCM twisted pair circuit lines. Figure 3-37 shows a typical BIB and
Table 3-9 lists the BIB interconnections.
J1
J0
Figure 3-37 Balanced-line interconnect board (BIB)
Table 3-9 BIB interconnections
NIU/
port Pin
no. Equipment/Ext Pin
no. Pin
no. Equipment/Ext Pin
no.
0/0 J0-1 Tx1+ J1-1 J0-20 Tx1– J1-20
J0-2 Rx1+ J1-2 J0-21 Rx1– J1-21
not
d
J0-4 Tx4+ J1-4 J0-23 Tx4– J1-23
used J0-5 Rx4+ J1-5 J0-24 Rx4– J1-24
0/1 J0-7 Tx2+ J1-7 J0-26 Tx2– J1-26
J0-8 Rx2+ J1-8 J0-27 Rx2– J1-27
not
d
J0-10 Tx5+ J1-10 J0-29 Tx5– J1-29
used J0-11 Rx5+ J1-11 J0-30 Rx5– J1-30
1/0 J0-13 Tx3+ J1-13 J0-32 Tx3– J1-32
J0-14 Rx3+ J1-14 J0-33 Rx3– J1-33
not
d
J0-16 Tx6+ J1-16 J0-35 Tx6– J1-35
used J0-17 Rx6+ J1-17 J0-36 Rx6– J1-36
Connector J0 and J1, pins 3,6,9,12,15,18,19, 22, 25, 28, 31, 34 and 37 are
connected to earth
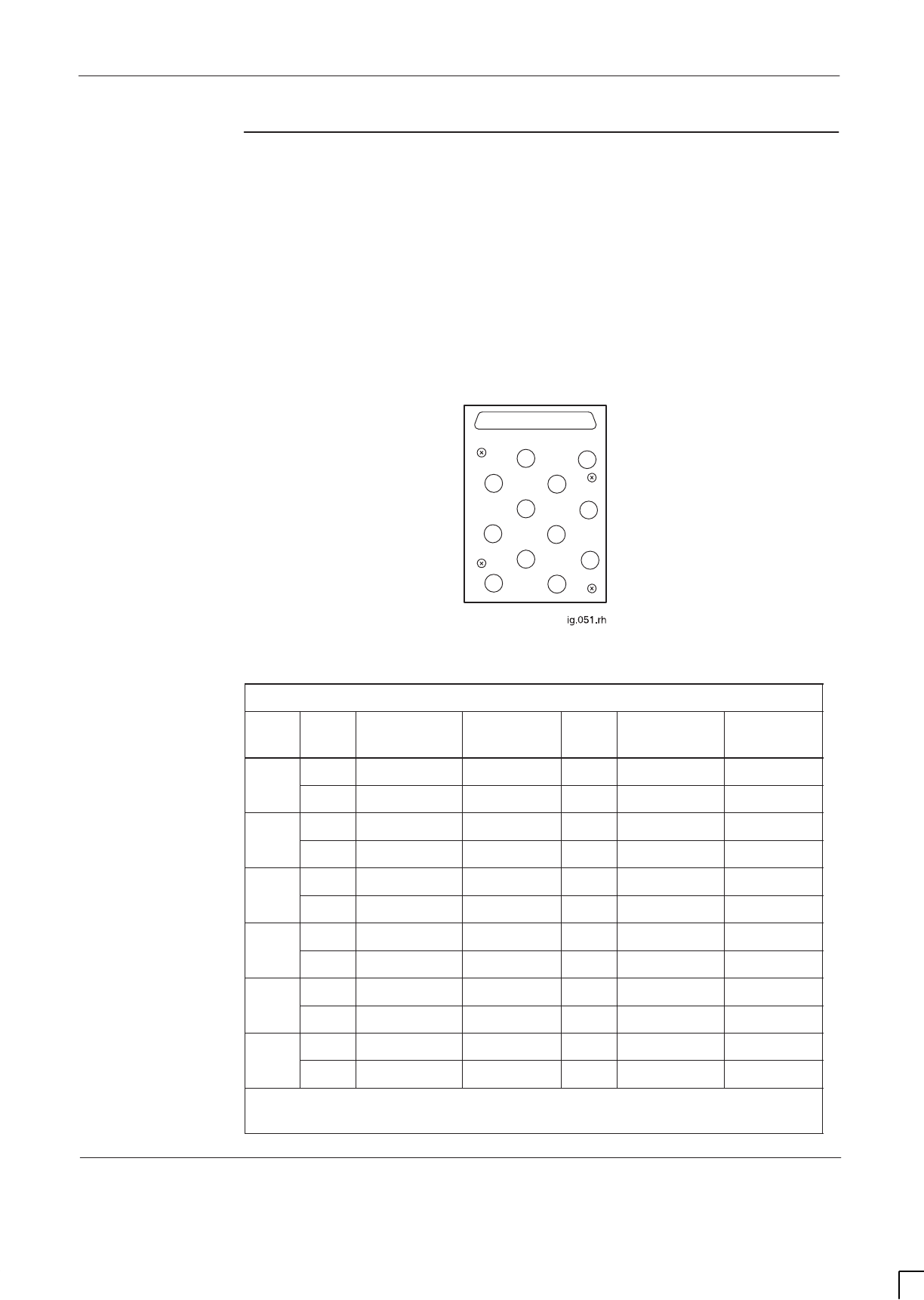
GSM-204-423 Interface panel cabling
31st Oct 01
Installation & Configuration: Horizon
macro
outdoor
68P02902W03-A
CONTROLLED INTRODUCTION
Inst. 3–65
T43 (CIM)
interconnection
The Type 43 Interconnect Board (T43), also known as CIM, provides the
impedance matching and line isolation between the E1/T1 circuit lines and the
CBIA backplane. The board provides an interface for up to six input and six
output unbalanced coaxial 75 ohm lines. 12 transformers are used to provide
impedance matching and line isolation between the E1/T1 circuit lines and the
NIU module. Each transformer has a 1:1.25 turns ratio to match the external 75
ohm and backplane 120 ohm connections.
Connection is made using a 37-pin D-type connector to the interconnect board
and twelve type 43 coaxial connectors to the external E1/T1 circuit lines.
Figure 3-38 shows a typical T43, and Table 3-10 lists the T43 interconnections.
J1
J2
J5
J4
J7
J8
J10
J13 J11
J14
J16
J17
J0
Figure 3-38 Type 43 interconnect board (T43)
Table 3-10 T43 interconnections
NIU/
port Pin
no. Equipment
/ Ext Pin no. Pin
no. Equipment
/ Ext Pin no.
0/0 J0-1 Tx1+ J1 centre J0-20 Tx1– J1 shield
J0-2 Rx1+ J2 centre J0-21 Rx1– J2 shield
not
d
J0-4 Tx4+ J4 centre J0-23 Tx4– J4 shield
used J0-5 Rx4+ J5 centre J0-24 Rx4– J5 shield
0/1 J0-7 Tx2+ J7 centre J0-26 Tx2– J7 shield
J0-8 Rx2+ J8 centre J0-27 Rx2– J8 shield
not
d
J0-10 Tx5+ J10 centre J0-29 Tx5– J10 shield
used J0-11 Rx5+ J11 centre J0-30 Rx5– J11 shield
1/0 J0-13 Tx3+ J13 centre J0-32 Tx3– J13 shield
J0-14 Rx3+ J14 centre J0-33 Rx3– J14 shield
not
d
J0-16 Tx6+ J16 centre J0-35 Tx6– J16 shield
used J0-17 Rx6+ J17 centre J0-36 Rx6– J17 shield
Connector J0, pins 3,6,9,12,15,18,19, 22, 25, 28, 31, 34 and 37 are not
used
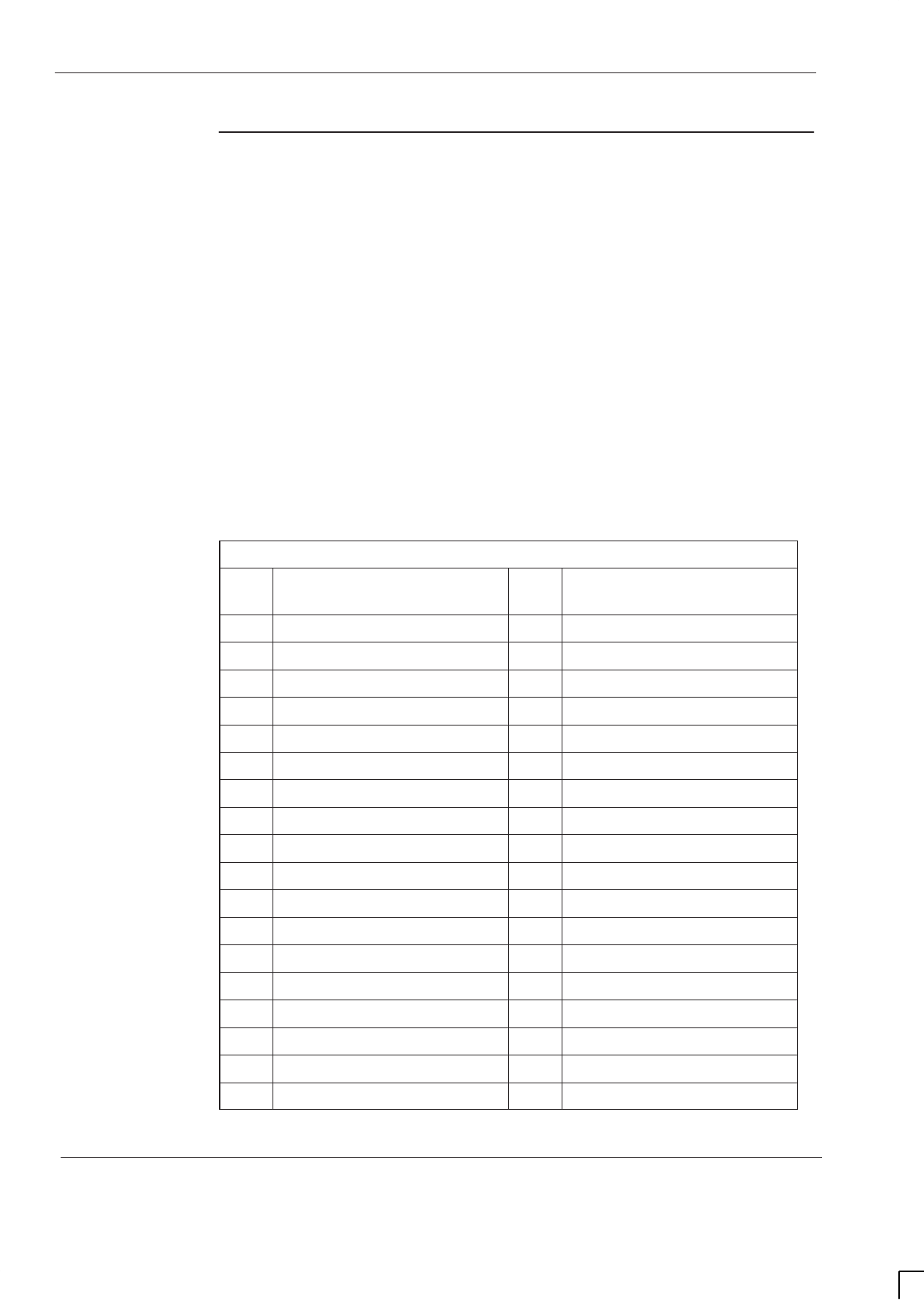
GSM-204-423
Interface panel cabling
31st Oct 01
Inst. 3–66
Installation & Configuration: Horizon
macro
outdoor
CONTROLLED INTRODUCTION
68P02902W03-A
PIX inputs and
outputs
PIX outputs
PIX outputs comprise four relay contacts controlled by the alarm board and
MCUF. The relays have multiple contacts, some normally open and some
normally closed. The contacts are rated for 1 A at 30 V. The contacts may be
used for control of external equipment such as fans or audible alarms.
PIX inputs
PIX inputs comprise 16 connections to external sensors. These inputs report
alarms to the BSC, via the alarm board and MCUF, which forwards the alarms to
the OMC-R. The end-user supplies the external sensors. Each sensor connects
across an opto-coupled pair of PIX inputs (eight per PIX connector).
All sensors must be dry-contact type with the following specification:
5 kohms or greater across sense inputs for logic 1 (PIX opto-coupler off).
500 ohms or less across sense inputs for logic 0 (PIX opto-coupler on).
Table 3-11 shows PIX0 connections and Table 3-12 shows PIX1 connections.
Table 3-11 PIX0 pin connections (37-way D-type)
Pin
no. Signal/Description Pin
no. Signal/Description
1Site input Ext 1–1 19 Not connected
2Site input Ext 2–1 20 Site input Ext 1–2
3Site input Ext 3–1 21 Site input Ext 2–2
4Site input Ext 4–1 22 Site input Ext 3–2
5Site input Ext 5–1 23 Site input Ext 4–2
6Site input Ext 6–1 24 Site input Ext 5–2
7Site input Ext 7–1 25 Site input Ext 6–2
8Site input Ext 8–1 26 Site input Ext 7–2
9Not connected 27 Site input Ext 8–2
10 Not connected 28 spare
11 Site output relay 1 – NO 29 Site output relay 1 – NC
12 Site output relay 2 – NO 30 Site output relay 1 – COM
13 Site output relay 2 – NC 31 Site output relay 2 – COM
14 Site output relay 3 – NO 32 Site output relay 3 – NC
15 Site output relay 4 – NO 33 Site output relay 3 – COM
16 Site output relay 4 – NC 34 Site output relay 4 – COM
17 Not connected 35 Not connected
18 Not connected 36 Not connected
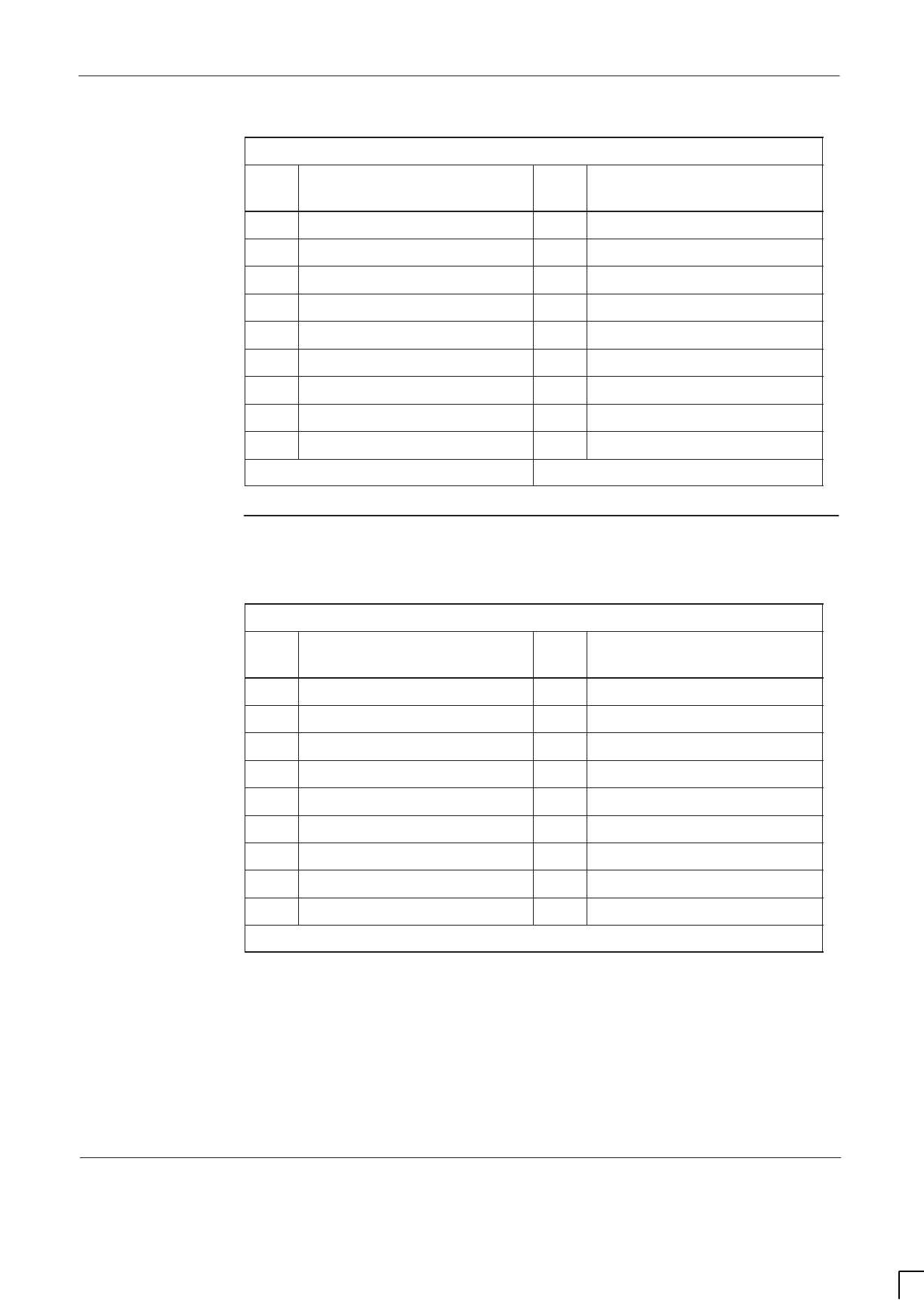
GSM-204-423 Interface panel cabling
31st Oct 01
Installation & Configuration: Horizon
macro
outdoor
68P02902W03-A
CONTROLLED INTRODUCTION
Inst. 3–67
Table 3-12 PIX1 pin connections (37-way D-type)
Pin
no. Signal/Description Pin
no. Signal/Description
1Site input Ext 9–1 19 Not connected
2Site input Ext 10–1 20 Site input Ext 9–2
3Site input Ext 11–1 21 Site input Ext 10–2
4Site input Ext 12–1 22 Site input Ext 11–2
5Site input Ext 13–1 23 Site input Ext 12–2
6Site input Ext 14–1 24 Site input Ext 13–2
7Site input Ext 15–1 25 Site input Ext 14–2
8Site input Ext 16–1 26 Site input Ext 15–2
9Not connected 27 Site input Ext 16–2
Pins 10 to 18 not connected Pins 28 to 37 not connected
ICS connector
Table 3-13 lists the Integrated Cell Site (ICS) connector pinouts. This is a future
feature.
Table 3-13 ICS pin connections (25-way D-type)
Pin
no. Signal/Description Pin
no. Signal/Description
1ICS0 TTY earth 10 ICS3 TTY earth
2ICS0 TTY Rx 11 ICS3 TTY Rx
3ICS0 TTY Tx 12 ICS3 TTY Tx
4ICS1 TTY earth 13 ICS4 TTY earth
5ICS1 TTY Rx 14 ICS4 TTY Rx
6ICS1 TTY Tx 15 ICS4 TTY Tx
7ICS2 TTY earth 16 ICS5 TTY earth
8ICS2 TTY Rx 17 ICS5 TTY Rx
9ICS2 TTY Tx 18 ICS5 TTY Tx
Pins 19 to 25 not connected
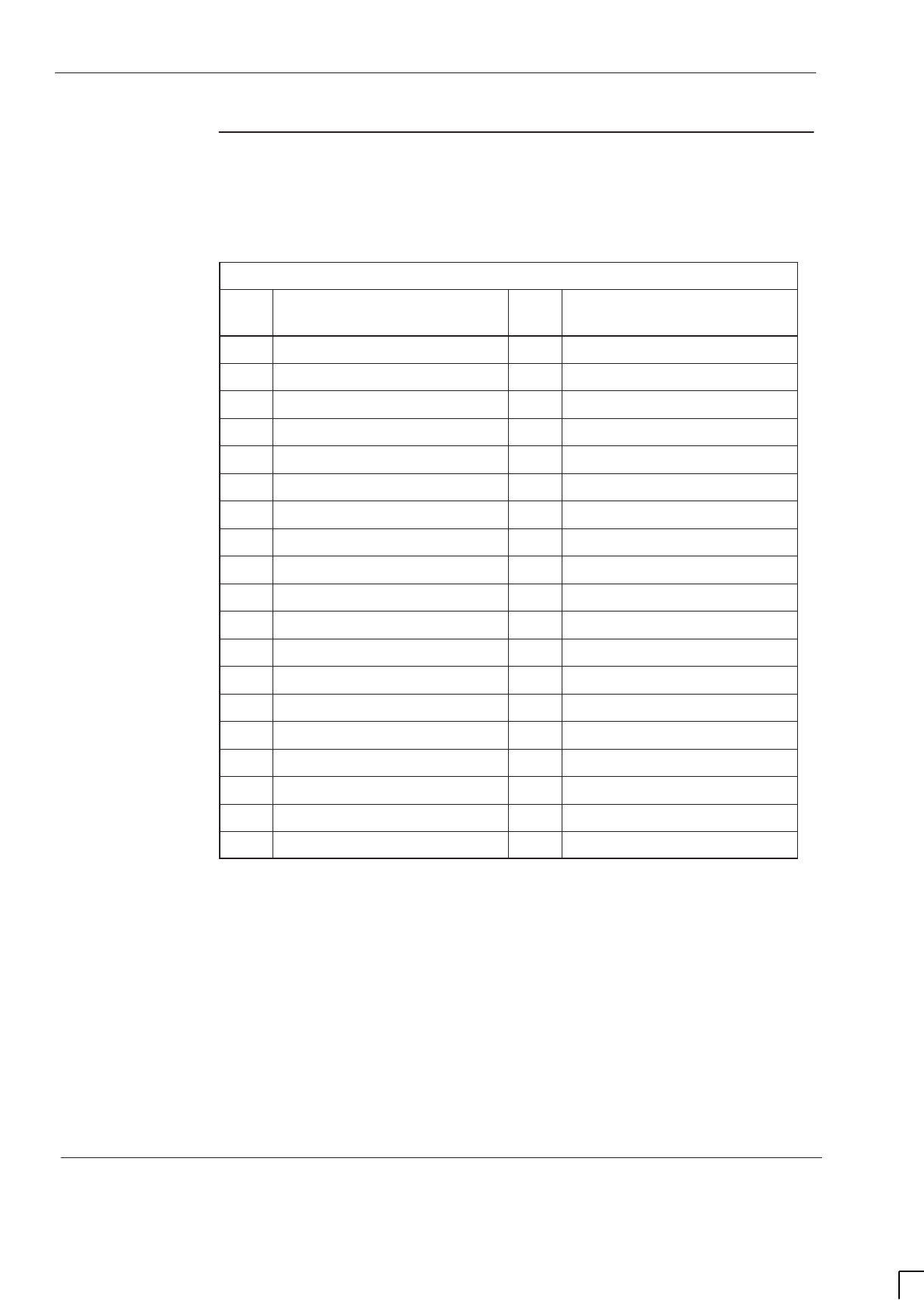
GSM-204-423
Interface panel cabling
31st Oct 01
Inst. 3–68
Installation & Configuration: Horizon
macro
outdoor
CONTROLLED INTRODUCTION
68P02902W03-A
External alarm
connector
This connector is connected to the alarms interface board PL3 by the factory.
Table 3-14 lists the external alarms connections. Ten alarms are also shown on
the alarm board front panel LEDs.
Table 3-14 External alarms pin connections (37-way D-type)
Pin
no. Signal/Description Pin
no. Signal/Description
1Mains AC fail 20 Rectifier return
2Mains AC return 21 Not connected
3Not connected 22 Not connected
4Not connected 23 AUX TMS overtemp
5TMS 1 failure 24 AUX TMS overtemp return
6TMS 1 return 25 Door 2 open
7TMS 2 failure 26 Door 2 return
8TMS 2 return 27 Optional smoke alarm
9Not connected 28 Optional smoke alarm return
10 Not connected 29 AUX EQUIP overtemp alarm
11 Not connected 30 AUX EQUIP overtemp return
12 Not connected 31 Not connected
13 Overtemp alarm 32 Not connected
14 Overtemp return 33 Not connected
15 Low voltage alarm 34 Not connected
16 Low voltage return 35 Not connected
17 Not connected 36 CAB overtemp
18 Not connected 37 CAB overtemp return
19 Rectifier fail
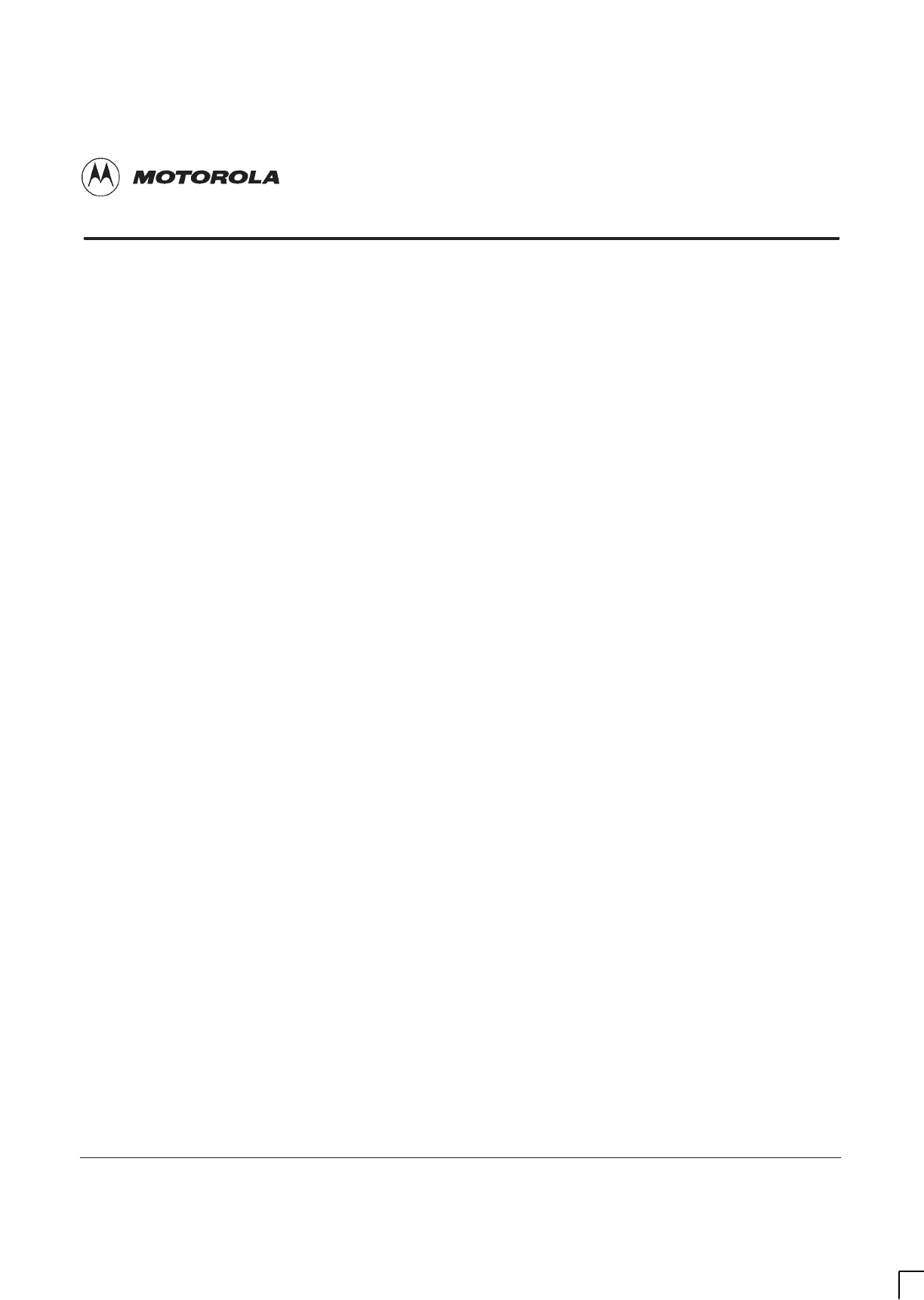
31st Oct 01
Installation & Configuration: Horizon
macro
outdoor
68P02902W03-A
CONTROLLED INTRODUCTION
i
Chapter 4
Installing the cable shroud
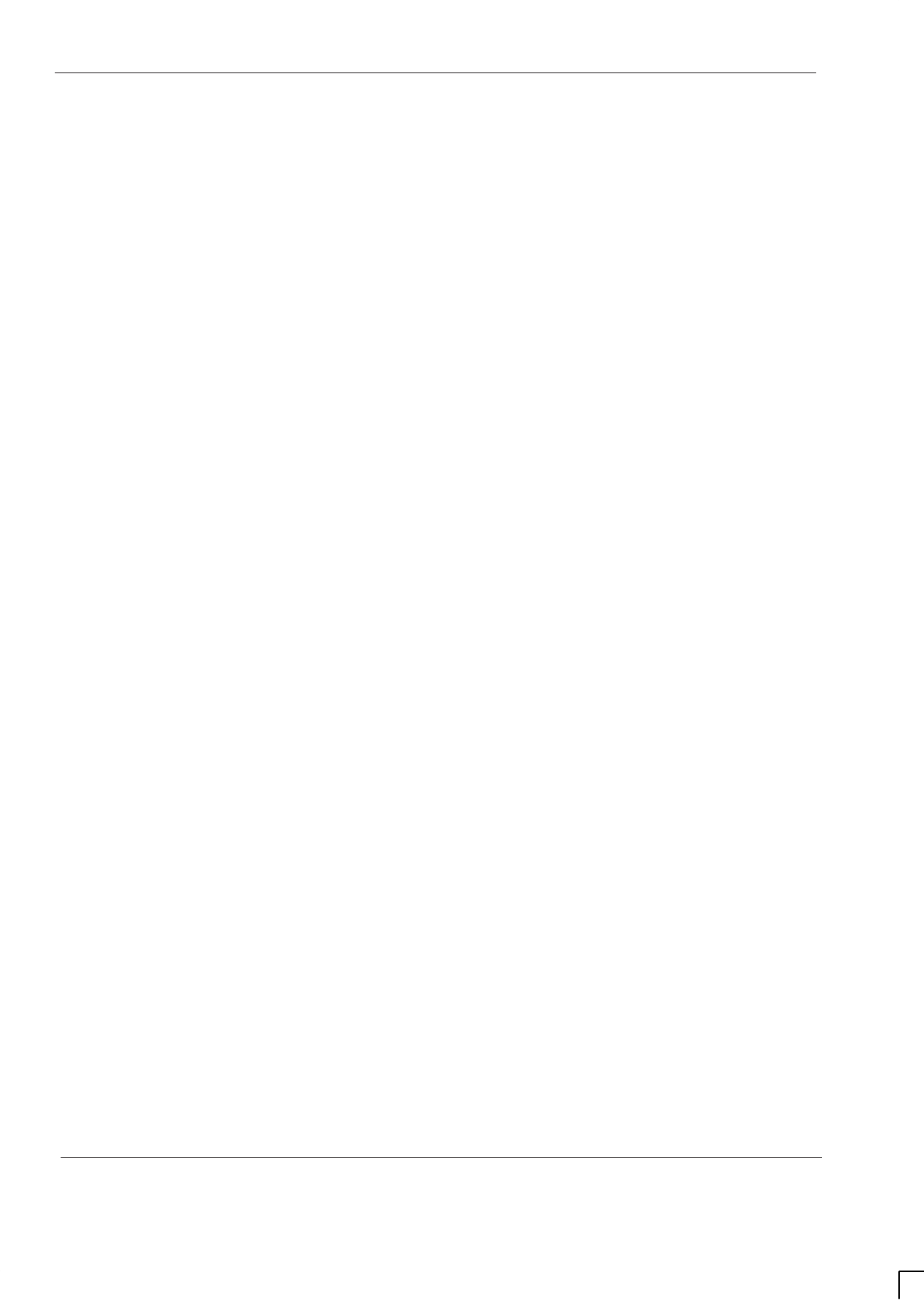
GSM-204-423
31st Oct 01
ii
Installation & Configuration: Horizon
macro
outdoor
CONTROLLED INTRODUCTION
68P02902W03-A
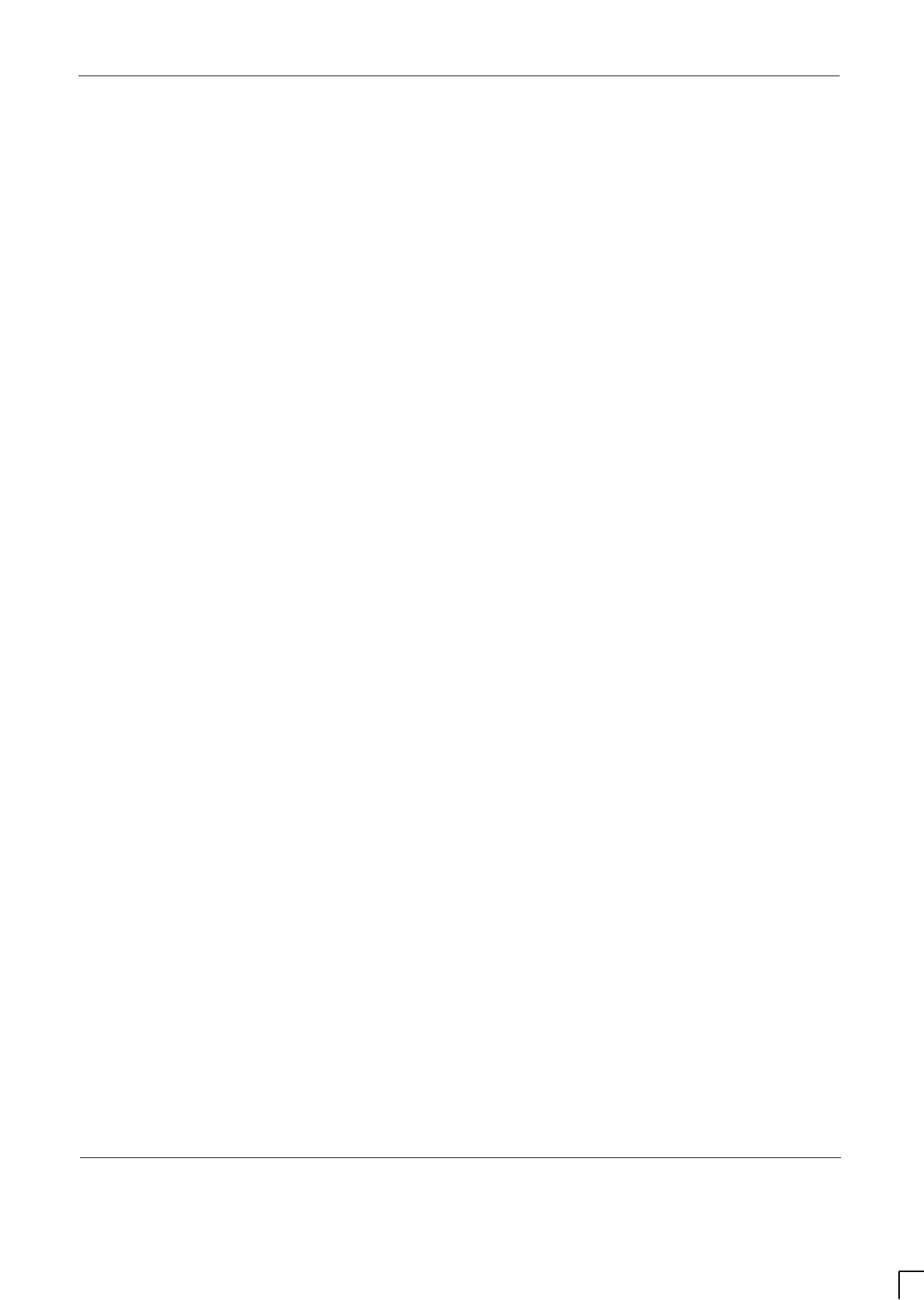
GSM-204-423
31st Oct 01
Installation & Configuration: Horizon
macro
outdoor
68P02902W03-A
CONTROLLED INTRODUCTION
iii
Chapter 4
Installing the cable shroud i. . . . . . . . . . . . . . . . . . . . . . . . . . . . . . . . . . . . .
Introduction to cable shroud installation Inst. 4–1. . . . . . . . . . . . . . . . . . . . . . . . . . . . . . . . .
Preparing to install the cable shroud Inst. 4–1. . . . . . . . . . . . . . . . . . . . . . . . . . . . . . .
Considerations when installing the cable shroud Inst. 4–1. . . . . . . . . . . . . . . . . . . .
Cable shroud installation procedures Inst. 4–2. . . . . . . . . . . . . . . . . . . . . . . . . . . . . . . . . . .
Attaching the cable shroud frame to the BTS cabinet Inst. 4–2. . . . . . . . . . . . . . . .
Adapting the shroud for cable entry from below ground Inst. 4–4. . . . . . . . . . . . . .
Adapting the shroud for cable entry from ground level Inst. 4–5. . . . . . . . . . . . . . .
Adapting the shroud for high level cable entry Inst. 4–6. . . . . . . . . . . . . . . . . . . . . .
Installation between cabinets (or the AEH) Inst. 4–7. . . . . . . . . . . . . . . . . . . . . . . . .
Cable routeing for multiple cabinet sites Inst. 4–10. . . . . . . . . . . . . . . . . . . . . . . . . . .
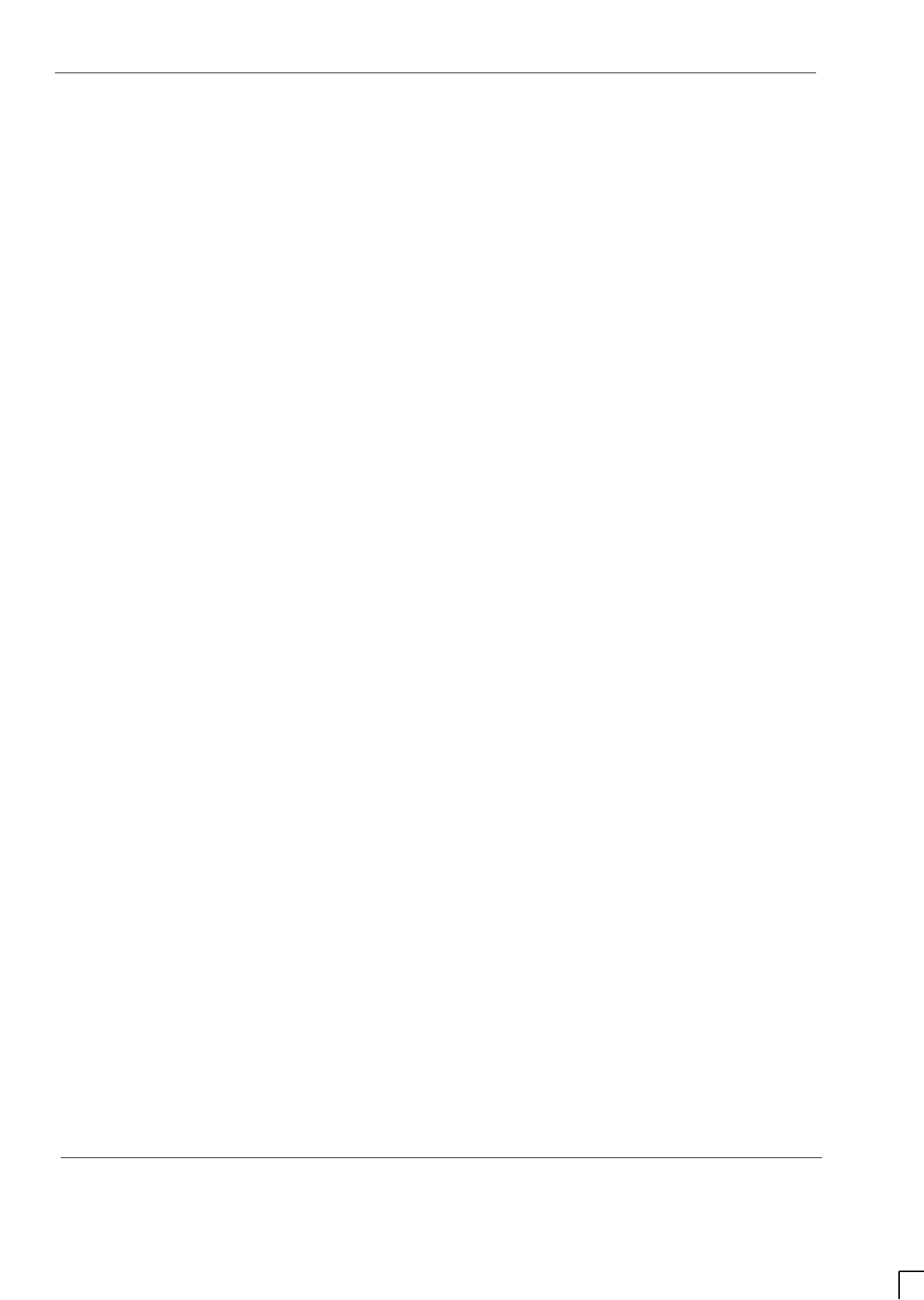
GSM-204-423
31st Oct 01
iv
Installation & Configuration: Horizon
macro
outdoor
CONTROLLED INTRODUCTION
68P02902W03-A
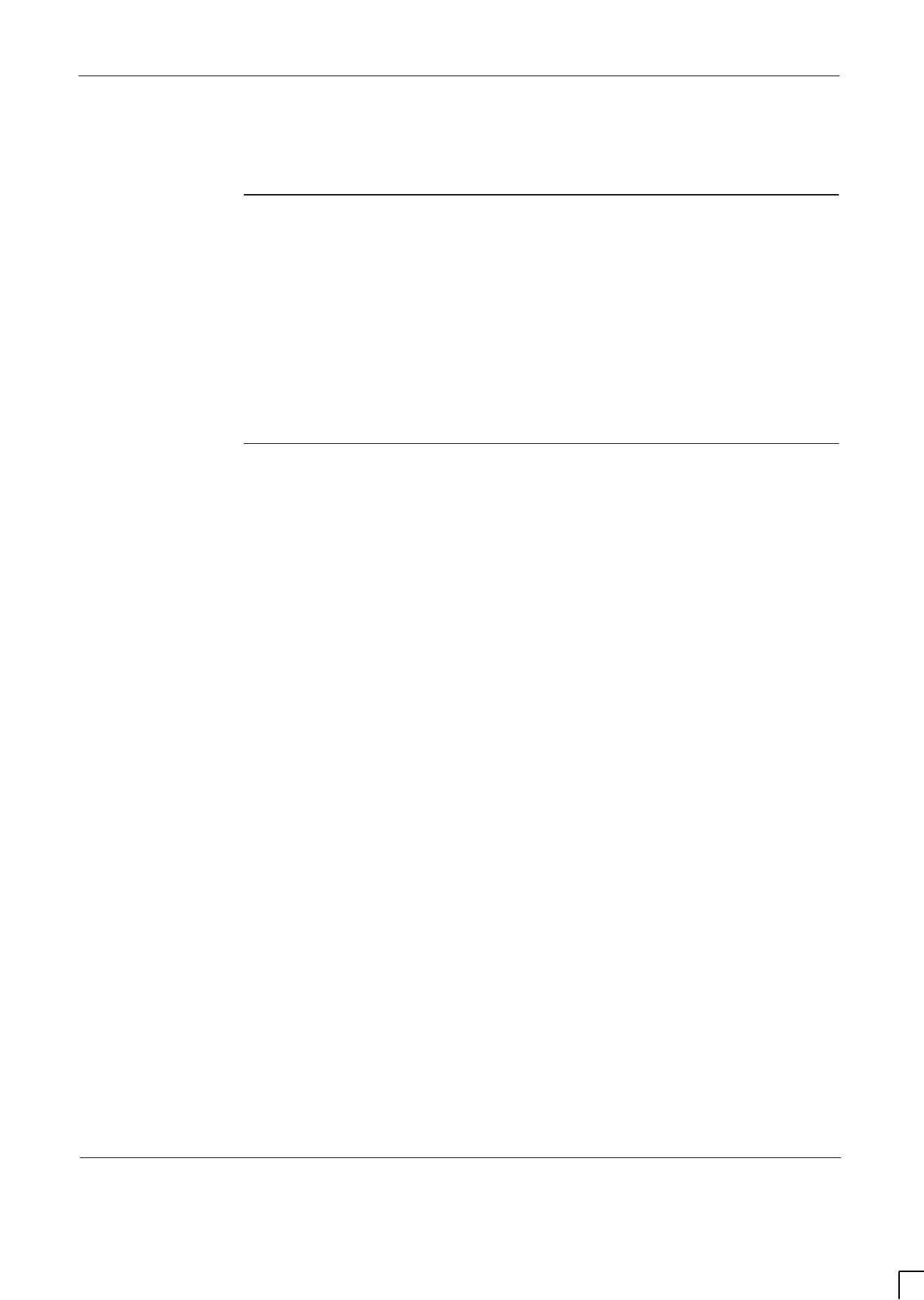
GSM-204-423 Introduction to cable shroud installation
31st Oct 01
Installation & Configuration: Horizon
macro
outdoor
68P02902W03-A
CONTROLLED INTRODUCTION
Inst. 4–1
Introduction to cable shroud installation
Preparing to
install the cable
shroud
The cable shroud is installed after the BTS cabinet is in position. If the shroud is
to be used for cable concealment between two BTS cabinets or a BTS cabinet
and an auxiliary equipment housing, 182 mm space must be allowed between
templates, (see Site requirements and considerations in Chapter 2 of this
category). This will ensure the correct spacing between the cabinets for the
shroud. A shroud template is provided, with the shroud, as an aid to determine
the space required.
Considerations
when installing
the cable
shroud
The cable shroud is normally installed on the right side of the BTS cabinet. It
can be installed on the left side of the cabinet, if the cabinet has been fitted with
the earth/connector plate mounted on the left side. The cable shroud can also
be installed between adjacent BTS cabinets or between a BTS cabinet and an
auxiliary equipment housing (AEH).
Only the procedures for attaching the cable shroud to the right side of the
cabinet, and between cabinets, are described in this chapter. The procedures
for attaching the cable shroud to the left side of the cabinet are the same, but
mirrored. The side panels of the shroud can be attached to either side of the
shroud frame to allow this.
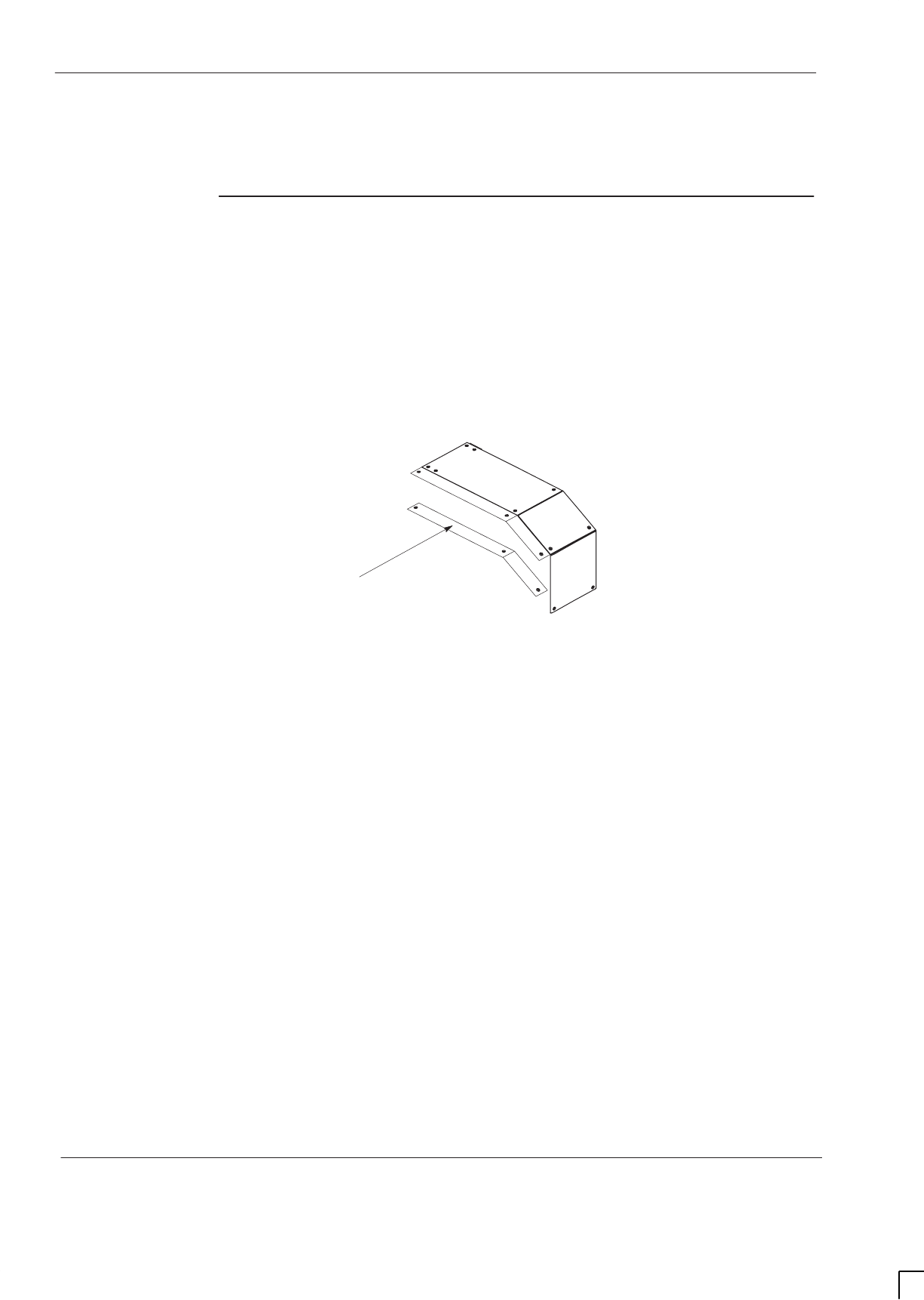
GSM-204-423
Cable shroud installation procedures
31st Oct 01
Inst. 4–2
Installation & Configuration: Horizon
macro
outdoor
CONTROLLED INTRODUCTION
68P02902W03-A
Cable shroud installation procedures
Attaching the
cable shroud
frame to the
BTS cabinet
The procedure for attaching the cable shroud frame to the right side of the BTS
cabinet is as follows (letters in parentheses refer to Figure 4-2):
1. Remove the side panels from the cable shroud frame.
2. Separate the two flanges from the left side of the shroud top panel (see
Figure 4-1) and remove one of them.
FLANGE
Figure 4-1 Shroud top panel detail showing the left hand flanges
3. Open the lid of the BTS cabinet.
4. Screw three M8 bolts loosely into the holes indicated by the arrows STEP
(4) in (A).
5. Slide the rear panel of the shroud onto the rear two bolts and then screw
two M8 bolts into the holes indicated by the arrows STEP (5) in (B).
Tighten all four bolts.
6. Slide the shroud front panel onto the previously installed bolt and then
screw two M8 bolts into the holes indicated by the arrows for STEP (6) in
(C). Tighten all four bolts.
7. Mount the shroud top cover (flanges already fitted) in place and secure to
the cabinet side by inserting an M8 bolt in the position indicated STEP (7)
in (C).
8. Secure the top cover to the shroud rear panel by tightening the two
anti-tamper screws indicated by the arrows STEP (8) in (D).
9. Secure the top cover to the shroud front panel by tightening the two
anti-tamper screws indicated by the arrows STEP (9) in (D).
The procedure for attaching the cable shroud frame is now complete. The
procedures for attaching the shroud side panels are described later in this
chapter and vary according to the method of cable entry required.
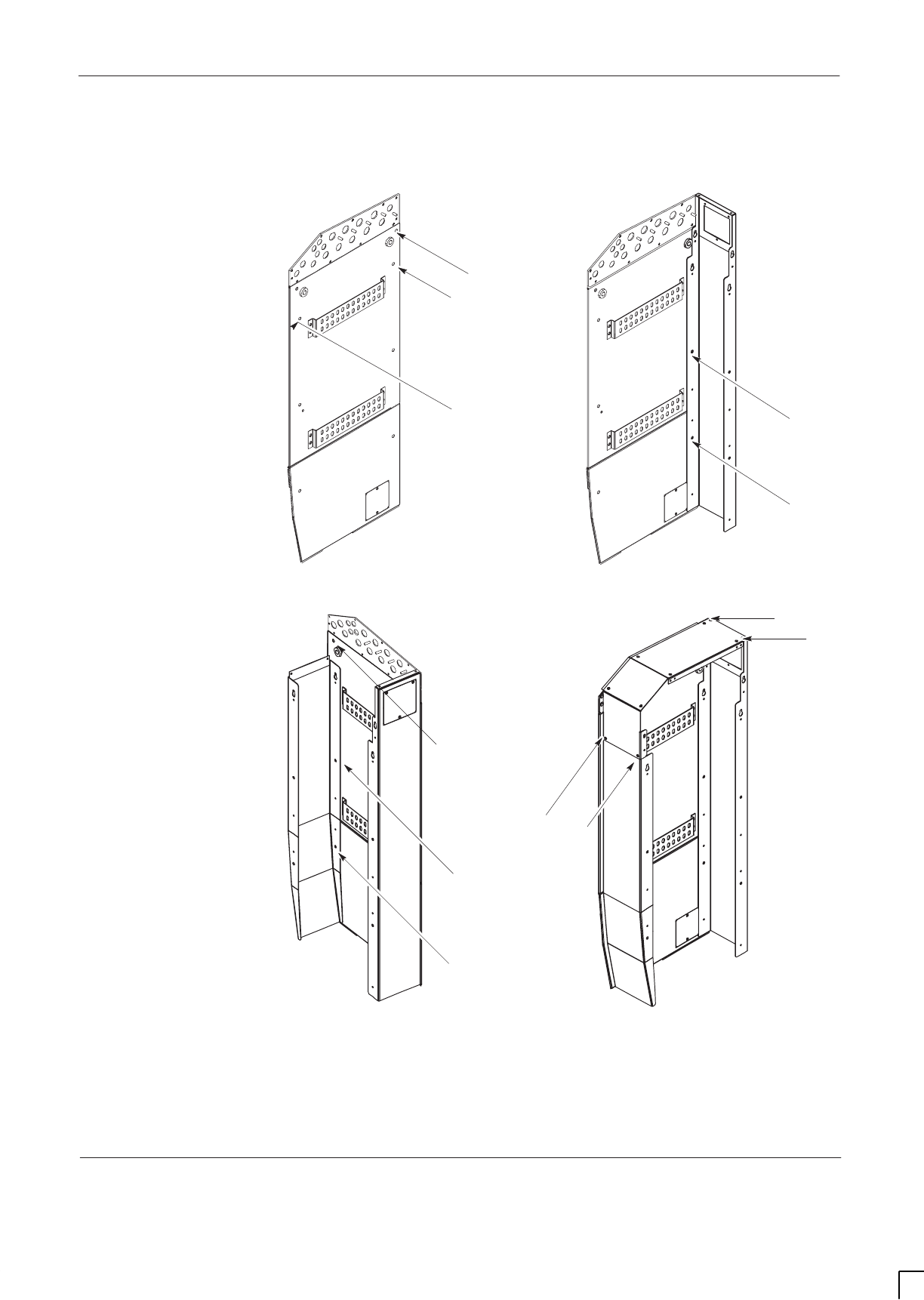
GSM-204-423 Cable shroud installation procedures
31st Oct 01
Installation & Configuration: Horizon
macro
outdoor
68P02902W03-A
CONTROLLED INTRODUCTION
Inst. 4–3
Figure 4-2 Shows the fitting of a cable shroud frame to a cabinet.
A B
CD
STEP (8)
STEP (9)
STEP (5)
STEP (5)
STEP (4)
STEP (4)
STEP (7)
STEP (6)
STEP (6)
Figure 4-2 Fixing the cable shroud frame to the left side of the cabinet
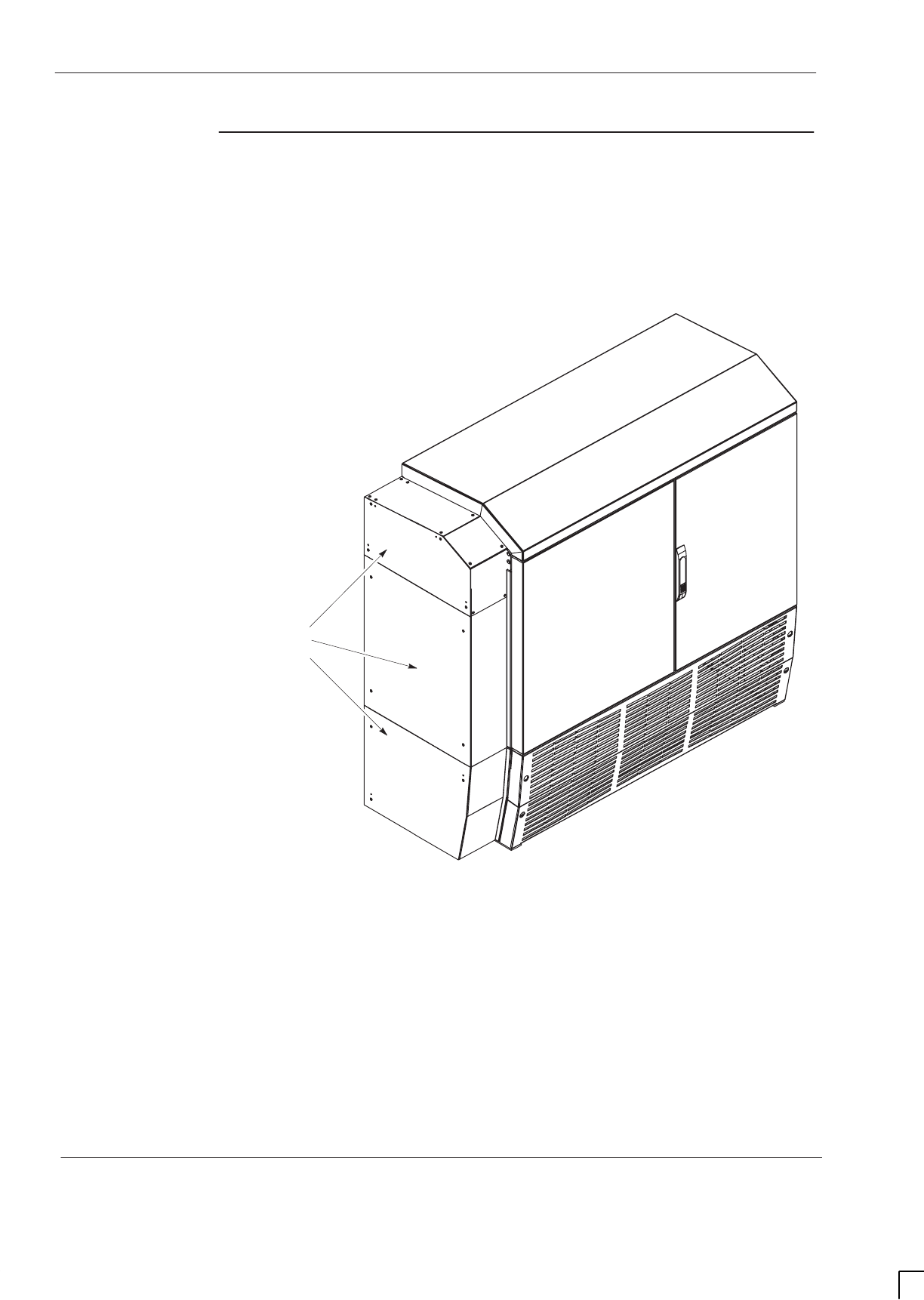
GSM-204-423
Cable shroud installation procedures
31st Oct 01
Inst. 4–4
Installation & Configuration: Horizon
macro
outdoor
CONTROLLED INTRODUCTION
68P02902W03-A
Adapting the
shroud for
cable entry from
below ground
If cable entry to the cabinet is from below ground, connect the cables to the
cabinet earthing plate and fit the three side panels to the shroud frame using
anti-tamper screws, as shown in Figure 4-3.
SIDE PANELS
Figure 4-3 Cable shroud adapted for cable entry from below ground
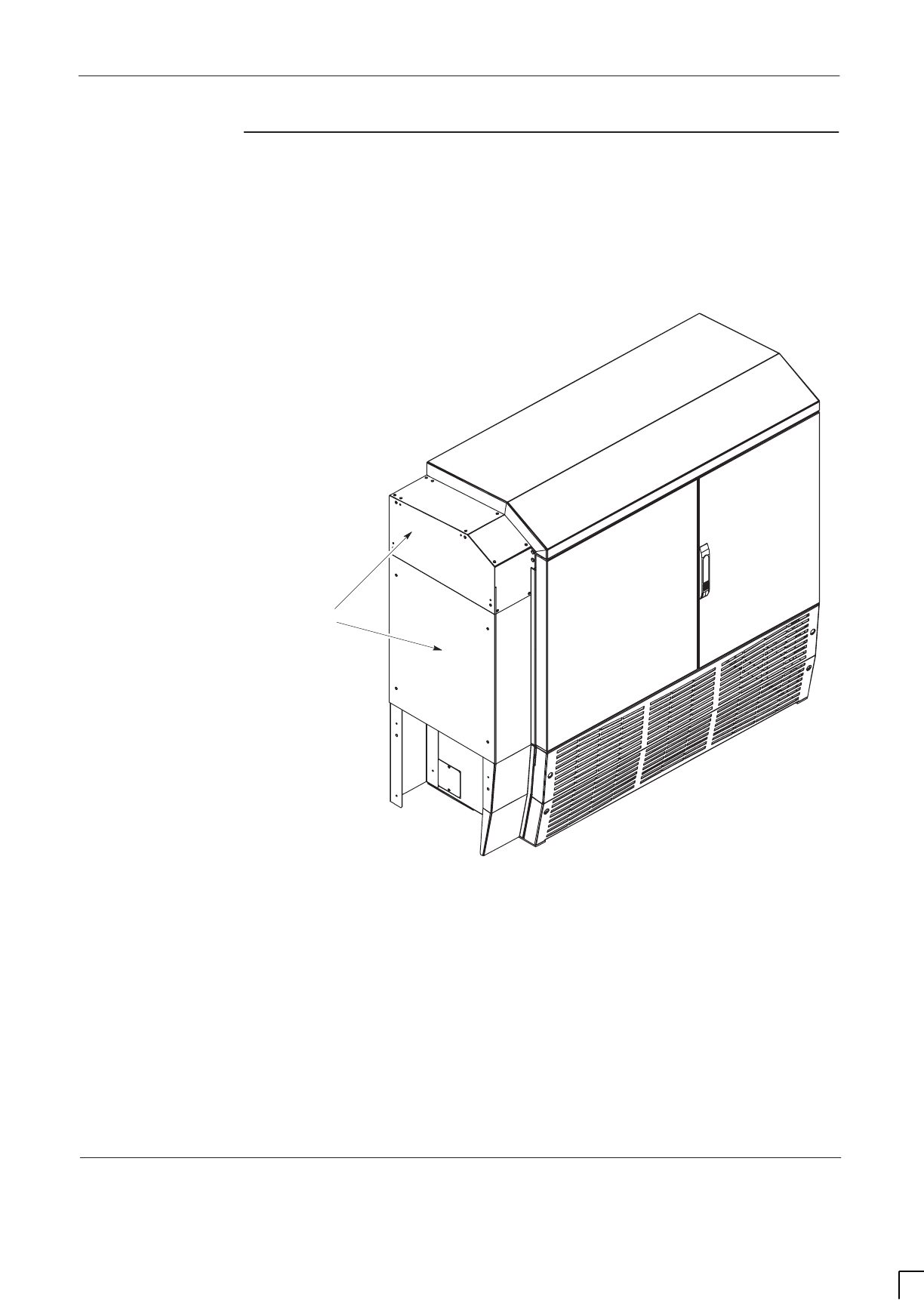
GSM-204-423 Cable shroud installation procedures
31st Oct 01
Installation & Configuration: Horizon
macro
outdoor
68P02902W03-A
CONTROLLED INTRODUCTION
Inst. 4–5
Adapting the
shroud for
cable entry from
ground level
If cable entry to the cabinet is from ground level, connect the cables to the
cabinet earthing plate and fit the two side panels to the shroud frame using
anti-tamper screws, as shown in Figure 4-4.
SIDE PANELS
Figure 4-4 Cable shroud adapted for cable entry from ground level
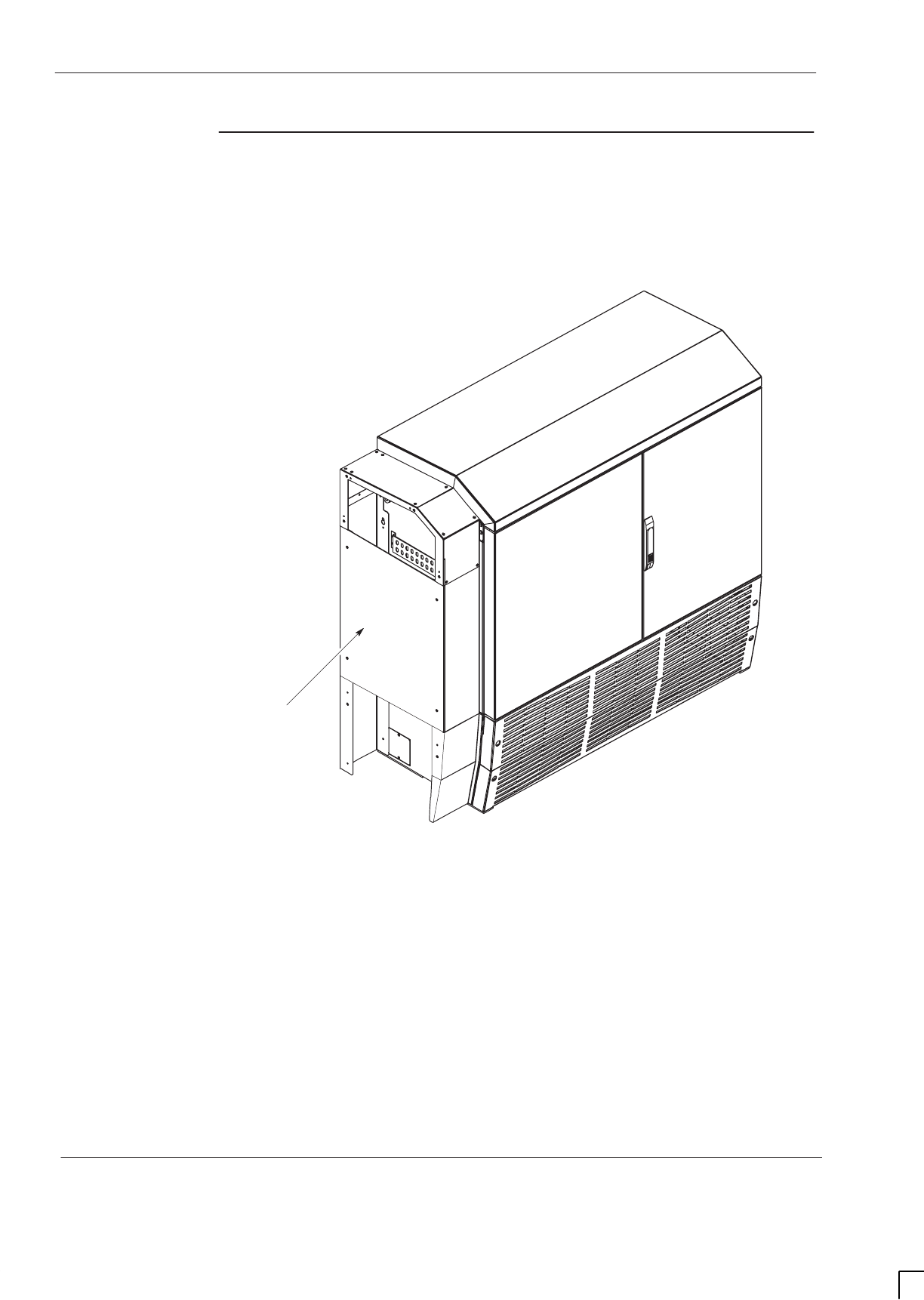
GSM-204-423
Cable shroud installation procedures
31st Oct 01
Inst. 4–6
Installation & Configuration: Horizon
macro
outdoor
CONTROLLED INTRODUCTION
68P02902W03-A
Adapting the
shroud for high
level cable entry
If high level cable entry to the cabinet is required, connect the cables to the
cabinet earthing plate and fit the side panel to the shroud frame using
anti-tamper screws, as shown in Figure 4-5.
SIDE PANEL
Figure 4-5 Cable shroud adapted for high level cable entry
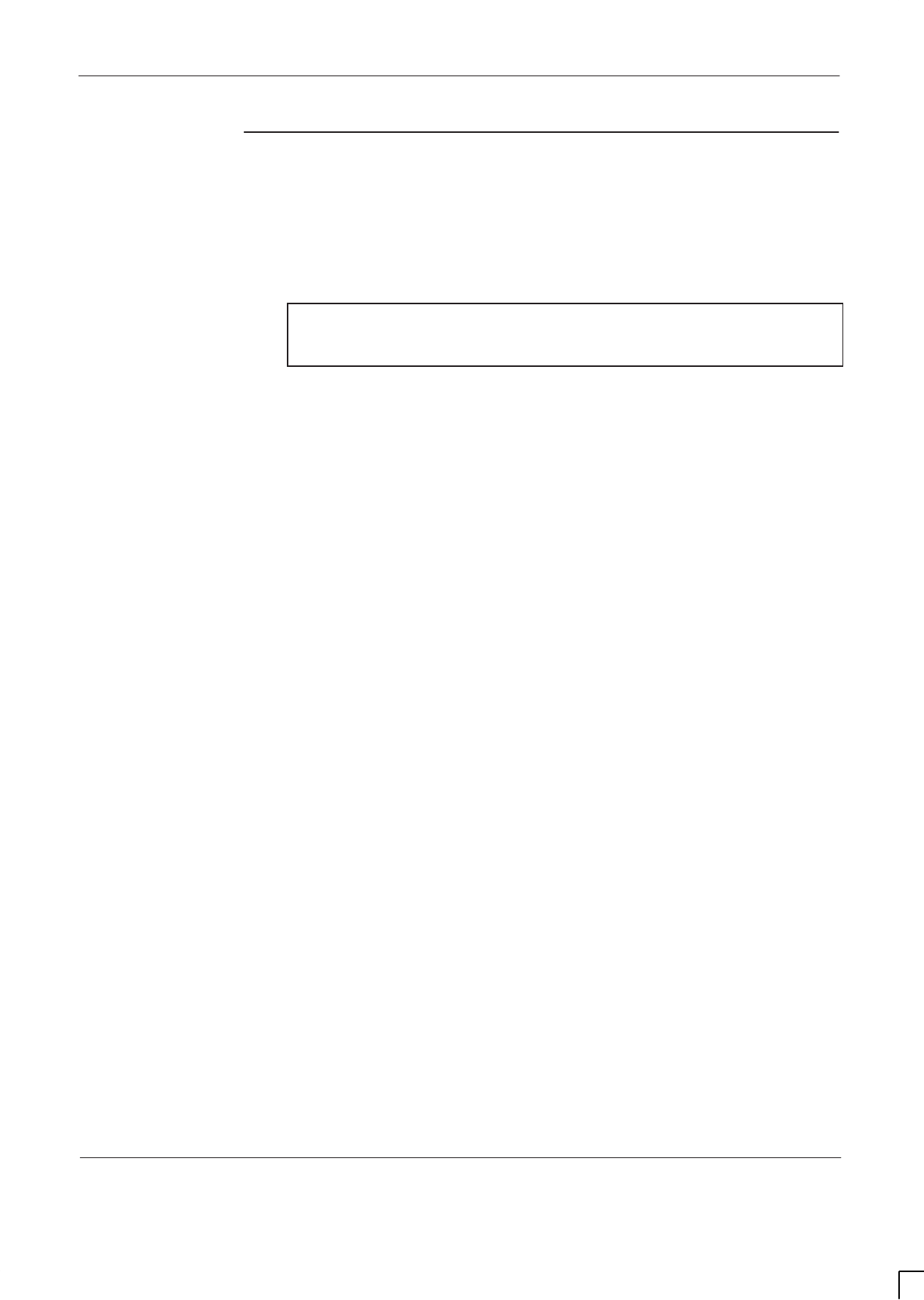
GSM-204-423 Cable shroud installation procedures
31st Oct 01
Installation & Configuration: Horizon
macro
outdoor
68P02902W03-A
CONTROLLED INTRODUCTION
Inst. 4–7
Installation
between
cabinets
(or the AEH)
This procedure must be carried out after the first cabinet has been bolted in
position and before any additional cabinet or auxiliary equipment housing (AEH)
is bolted down. Use the shroud template as an aid to determine spacing.
NOTE The procedure for installing the shroud between two BTS
cabinets or two auxiliary equipment housings is basically
the same and is described below.
To install the cable shroud between adjacent cabinets or between a cabinet and
the auxiliary equipment housing, proceed as follows:
1. Open the lids on both cabinets.
2. Remove the two cabinet end plates from the cabinet sides facing each
other and replace with expansion plates, (see Connecting antennas in
Chapter 3 of this category).
3. Attach the rear panel of the shroud to the first cabinet and then attach the
front panel, as described previously in Procedure for attaching the cable
shroud frame to the BTS cabinet.
4. Prior to manoeuvring a second BTS cabinet or AEH into final position:
– Remove the expansion plate pass through blanks, as required.
– Undo the two hose clips securing each RF cable gland housing and
remove gland assembly, (if RF connection required).
– Feed any dc power cables through the expansion plates.
5. Adjust the position of the second cabinet or AEH, if necessary, so that its
side is flush against the sides of the shroud and the bolt holes identified in
Figure 4-2 and Figure 4-6 are aligned. Bolt the rear and front panels of the
shroud to the side of the housing through these holes.
6. Make the dc power, fibre optic and signal connections between the two
cabinets, (see Figure 4-8 for routeing), and then bolt the cabinet or AEH to
the floor.
7. Make any RF connections, appropriate to the site configuration (see
Figure 4-8 for routeing and Suggested RF configurations), between the
cabinets. Remove the required number of blanking plugs and fit both
multi-cable glands over the RF cables.
8. Fit rubber housing around left cable gland and insert into left side
expansion plate, as shown in Figure 4-7 secure with two hose clips.
Repeat for right side gland.
9. Slide the shroud top cover in place and secure to the rear panel and front
panel by tightening the four anti-tamper screws, as described previously in
Procedure for attaching the cable shroud frame to the BTS cabinet.
The procedure for installing the cable shroud between cabinets and/or the
auxiliary equipment housing is now complete.
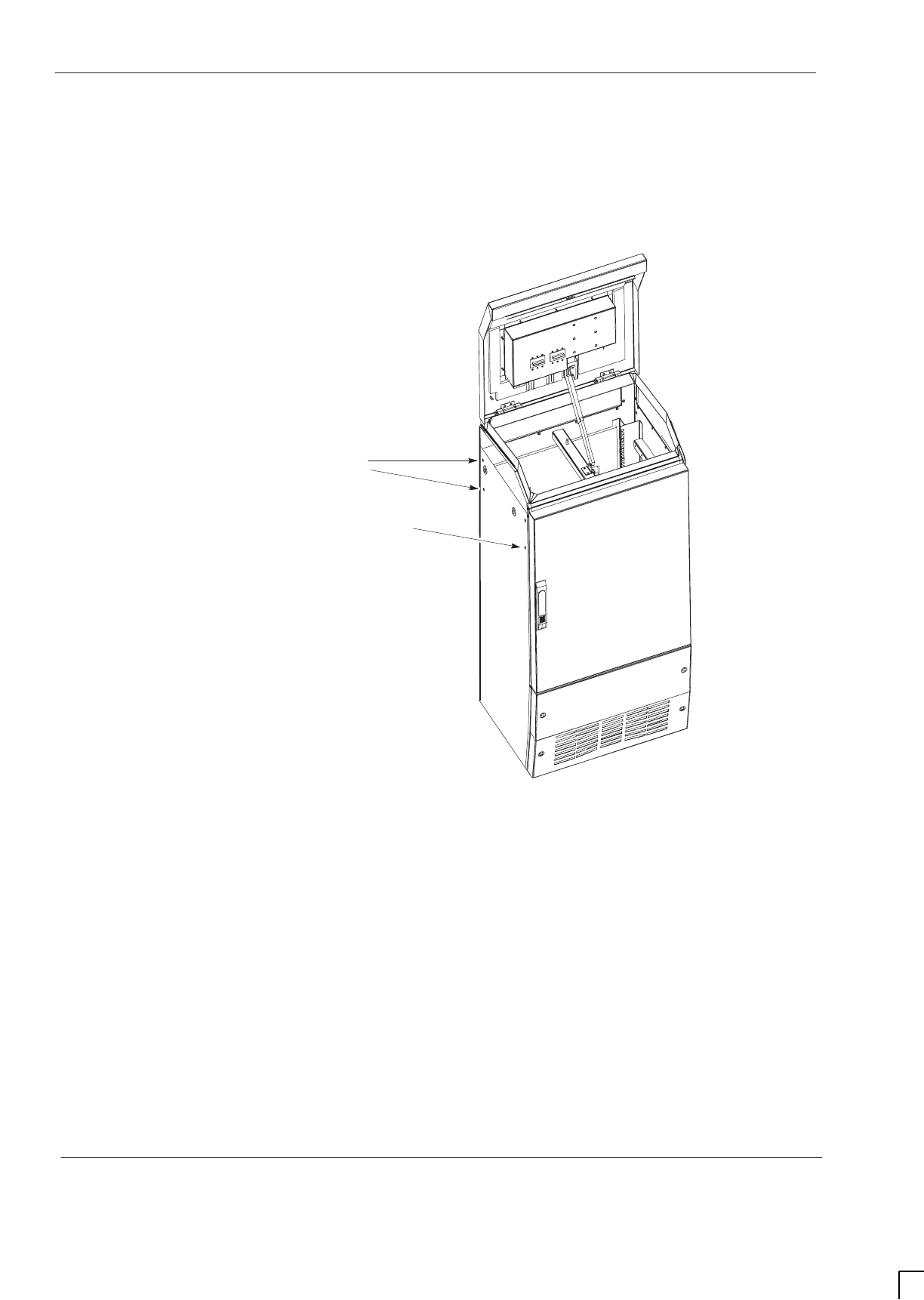
GSM-204-423
Cable shroud installation procedures
31st Oct 01
Inst. 4–8
Installation & Configuration: Horizon
macro
outdoor
CONTROLLED INTRODUCTION
68P02902W03-A
Shroud attachment points
Figure 4-6 shows the shroud attachment points on the auxiliary equipment
housing.
REAR PANEL
ATTACHMENT
POINTS
FRONT PANEL
ATTACHMENT
POINT
Figure 4-6 Shroud attachment points on the auxiliary equipment housing
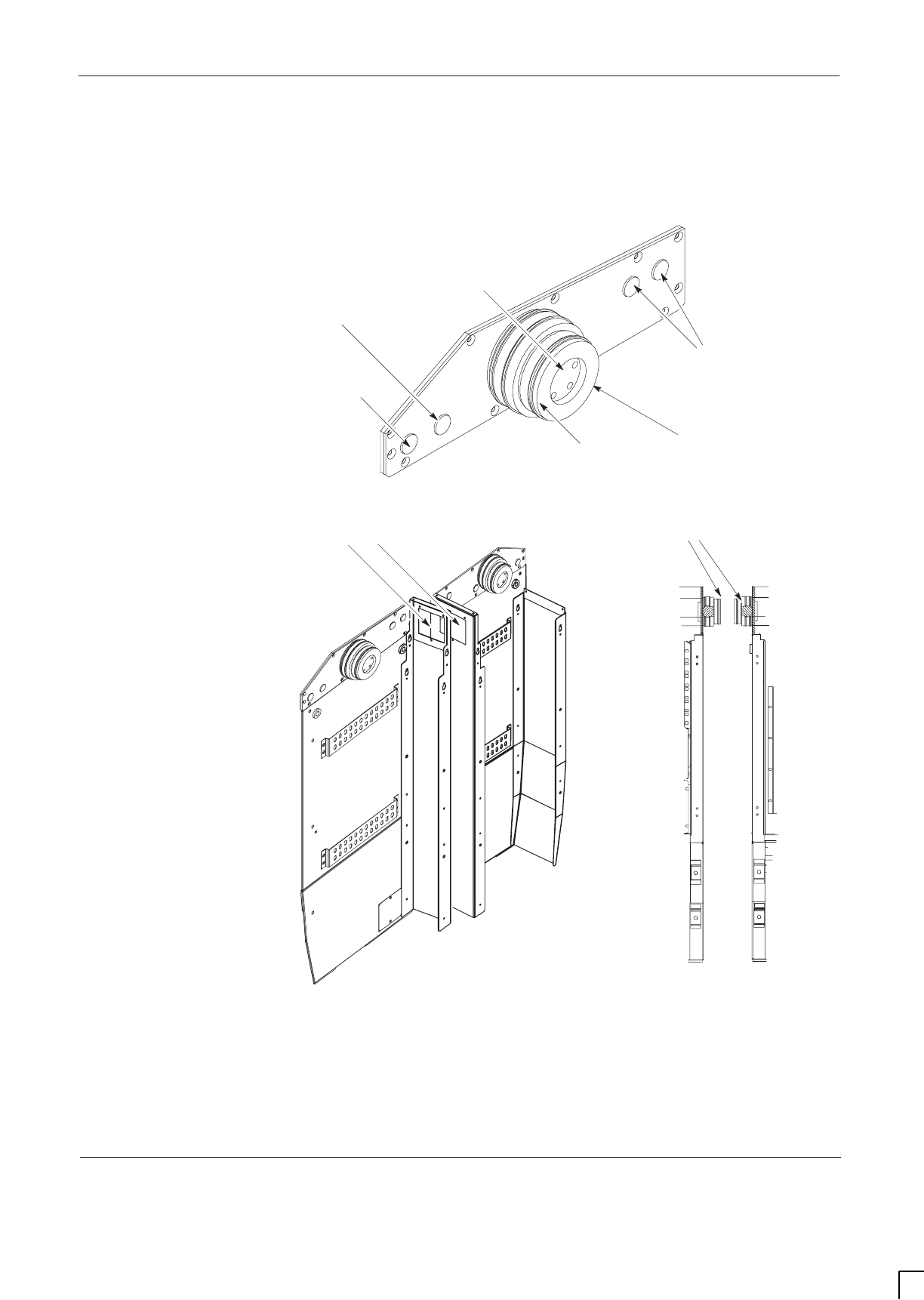
GSM-204-423 Cable shroud installation procedures
31st Oct 01
Installation & Configuration: Horizon
macro
outdoor
68P02902W03-A
CONTROLLED INTRODUCTION
Inst. 4–9
Cabinet expansion
Figure 4-7 shows the BTS cabinet expansion plate and two views showing the
recommended installation configurations.
PANELS REMOVED TO ALLOW
RF CONNECTION
VIEW SHOWING EXPANSION PLATES
WITH CABINETS INSTALLED
BACK TO BACK
VIEW SHOWING EXPANSION PLATES
WITH CABINETS INSTALLED
SIDE BY SIDE
(shroud omitted for clarity)
RF CABLE GLANDS
RF PASS-THROUGH
FIVE CABLE GLAND
BATTERY BACKUP CABLE
PASS-THROUGH
EARTH CABLE
PASS-THROUGH
AC CABLE
PASS-THROUGH
FIBRE OPTIC
EXTENSION CABLE
PASS-THROUGH
(not visible)
RUBBER
GLAND HOUSING
Figure 4-7 BTS cabinet expansion plate
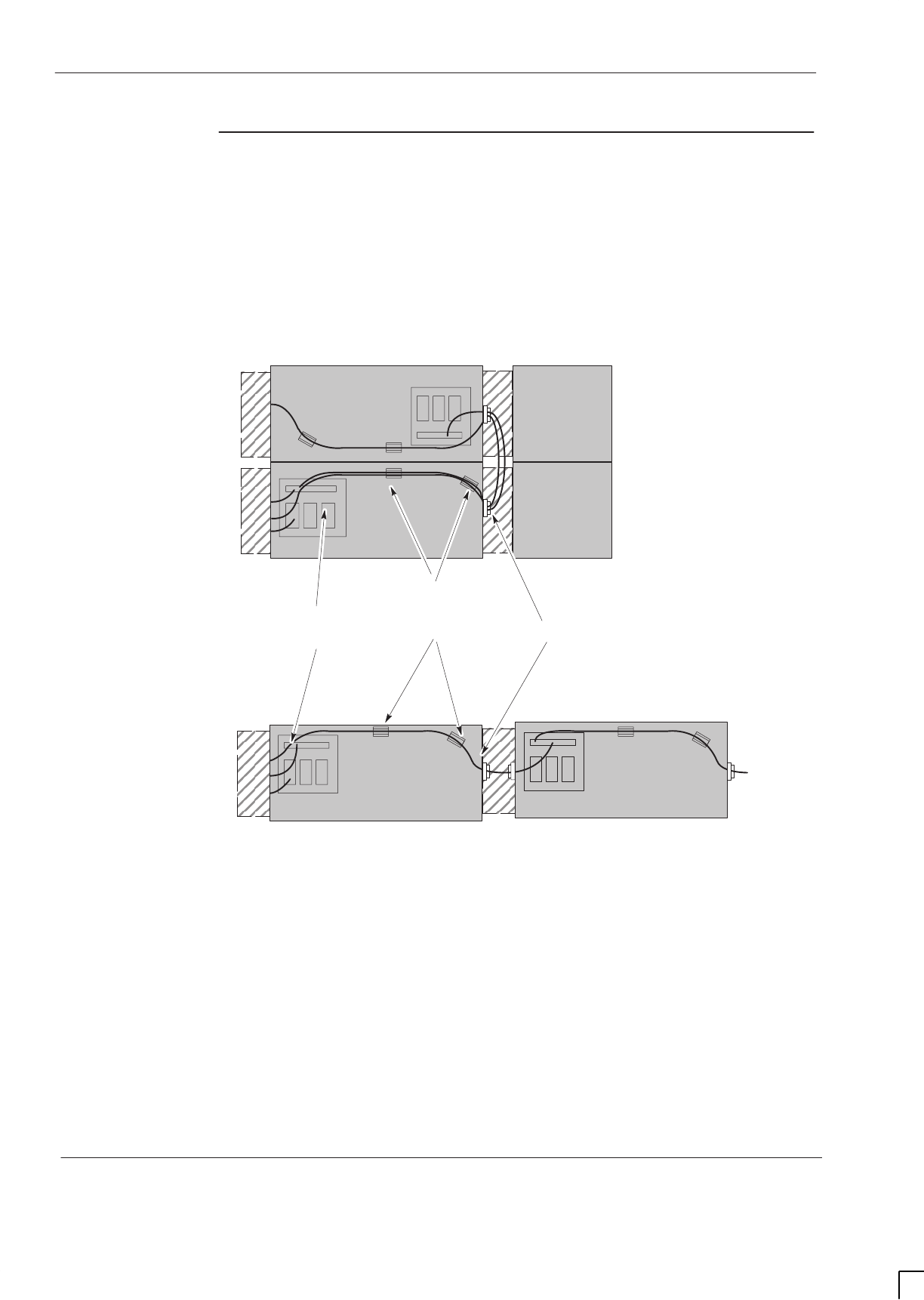
GSM-204-423
Cable shroud installation procedures
31st Oct 01
Inst. 4–10
Installation & Configuration: Horizon
macro
outdoor
CONTROLLED INTRODUCTION
68P02902W03-A
Cable routeing
for multiple
cabinet sites
Figure 4-8 shows a representation of the RF interconnection cable routeing
through the cabinets for multiple cabinet sites. FIbre optic interconnections
follow similar routeing. Cable routeing for more complex layouts may be derived
from these basic diagrams.
CABLE GUIDES
BACK TO BACK
LAYOUT
EXPANSION PLATE
GLAND
SIDE BY SIDE LAYOUT
(left side cable entry)
RF COMPONENTS
Figure 4-8 Guide to cable routeing through multiple cabinets
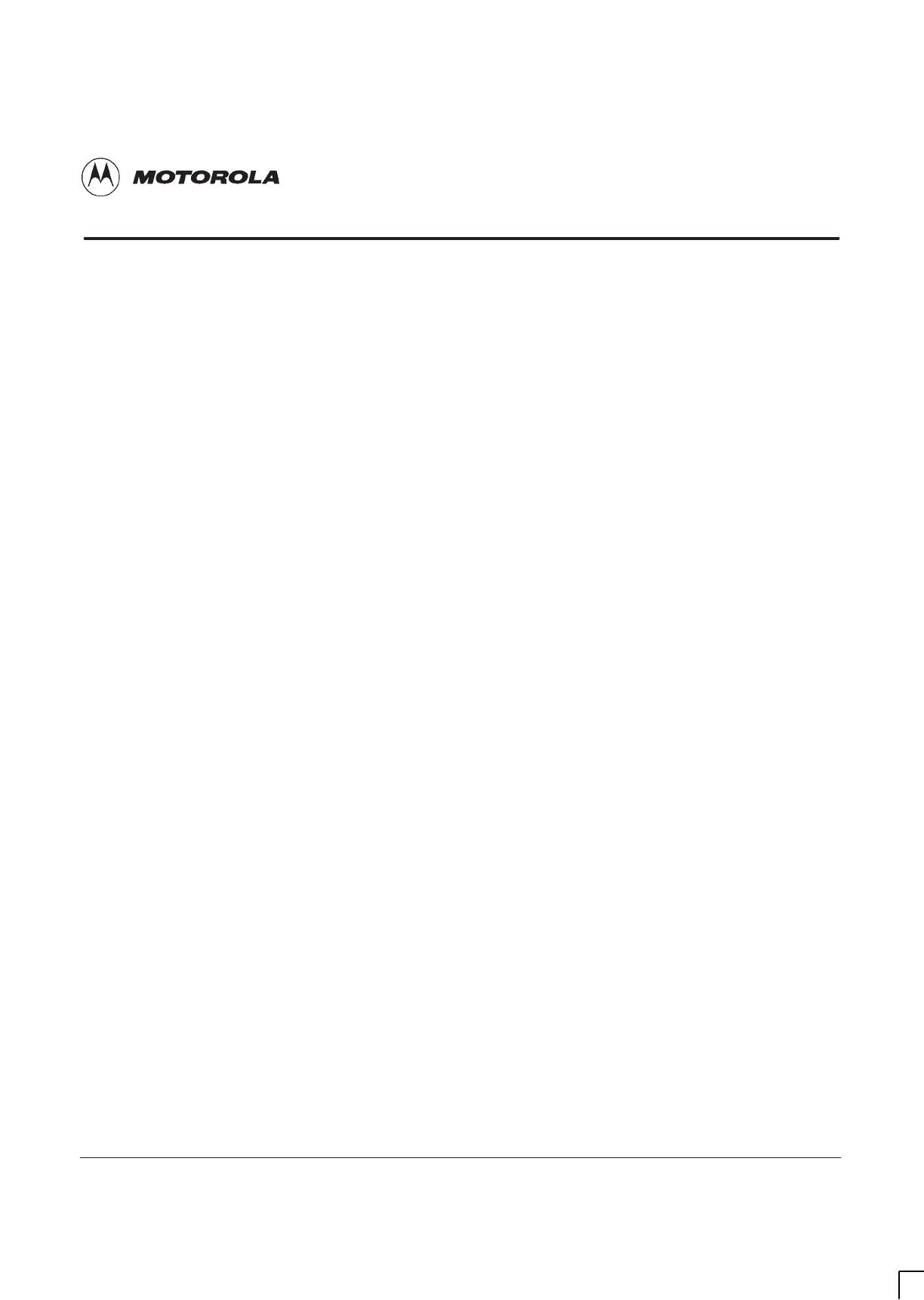
31st Oct 01
Installation & Configuration: Horizon
macro
outdoor
68P02902W03-A
CONTROLLED INTRODUCTION
i
Chapter 5
Installing the auxiliary equipment
housing
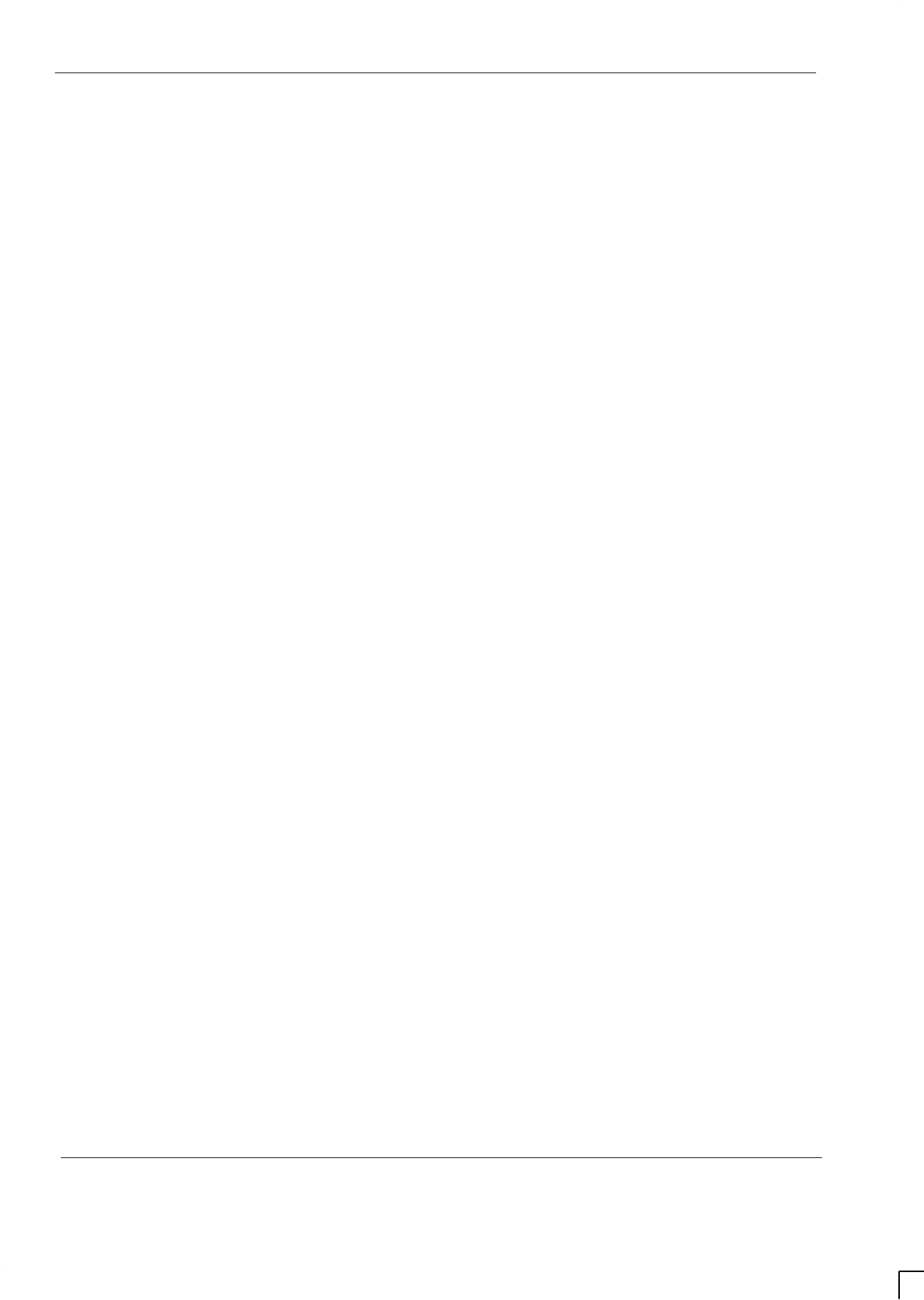
GSM-204-423
31st Oct 01
ii
Installation & Configuration: Horizon
macro
outdoor
CONTROLLED INTRODUCTION
68P02902W03-A
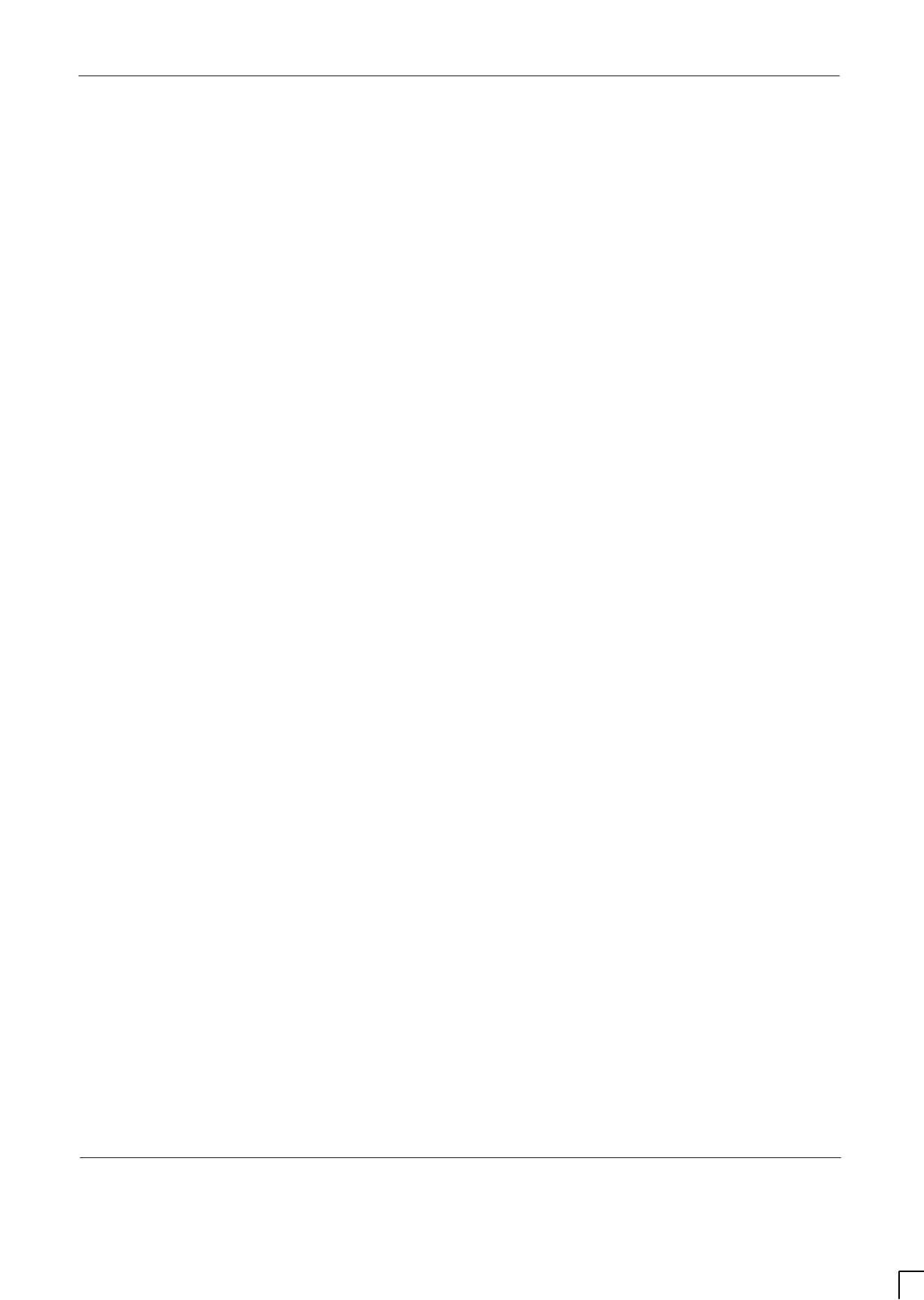
GSM-204-423
31st Oct 01
Installation & Configuration: Horizon
macro
outdoor
68P02902W03-A
CONTROLLED INTRODUCTION
iii
Chapter 5
Installing the auxiliary equipment housing i. . . . . . . . . . . . . . . . . . . . . .
Procedures for installing the auxiliary equipment housing Inst. 5–1. . . . . . . . . . . . . . . . .
Assumptions regarding site preparation Inst. 5–1. . . . . . . . . . . . . . . . . . . . . . . . . . . .
Layout of the auxiliary equipment housing Inst. 5–1. . . . . . . . . . . . . . . . . . . . . . . . .
Auxiliary equipment housing packaging Inst. 5–2. . . . . . . . . . . . . . . . . . . . . . . . . . . .
Introduction to installing the auxiliary equipment housing Inst. 5–2. . . . . . . . . . . . .
Installing the auxiliary equipment housing template Inst. 5–3. . . . . . . . . . . . . . . . . .
Installing auxiliary equipment housing bolt anchors Inst. 5–4. . . . . . . . . . . . . . . . . .
Bolting the auxiliary equipment housing to the floor Inst. 5–5. . . . . . . . . . . . . . . . .
Installing batteries in the auxiliary equipment housing Inst. 5–6. . . . . . . . . . . . . . . . . . . . .
Introduction to battery installation Inst. 5–6. . . . . . . . . . . . . . . . . . . . . . . . . . . . . . . . .
Installing batteries Inst. 5–7. . . . . . . . . . . . . . . . . . . . . . . . . . . . . . . . . . . . . . . . . . . . . .
Auxiliary equipment housing (AEH) connections Inst. 5–10. . . . . . . . . . . . . . . . . . . . . . . . .
Earthing the AEH Inst. 5–10. . . . . . . . . . . . . . . . . . . . . . . . . . . . . . . . . . . . . . . . . . . . . . .
Connecting dc cables to the AEH Inst. 5–10. . . . . . . . . . . . . . . . . . . . . . . . . . . . . . . . .
Connecting the alarm signal cables Inst. 5–11. . . . . . . . . . . . . . . . . . . . . . . . . . . . . . .
Internal connections in the AEH Inst. 5–11. . . . . . . . . . . . . . . . . . . . . . . . . . . . . . . . . .
Configuring battery backup to supply two BTS cabinets Inst. 5–12. . . . . . . . . . . . . . . . . . .
Introduction to configuring battery backup Inst. 5–12. . . . . . . . . . . . . . . . . . . . . . . . . .
Removing the power distribution box Inst. 5–12. . . . . . . . . . . . . . . . . . . . . . . . . . . . . .
Interior view of power distribution box Inst. 5–13. . . . . . . . . . . . . . . . . . . . . . . . . . . . .
Removing the parallelling links Inst. 5–14. . . . . . . . . . . . . . . . . . . . . . . . . . . . . . . . . . . .
Refitting the power distribution box Inst. 5–15. . . . . . . . . . . . . . . . . . . . . . . . . . . . . . . .
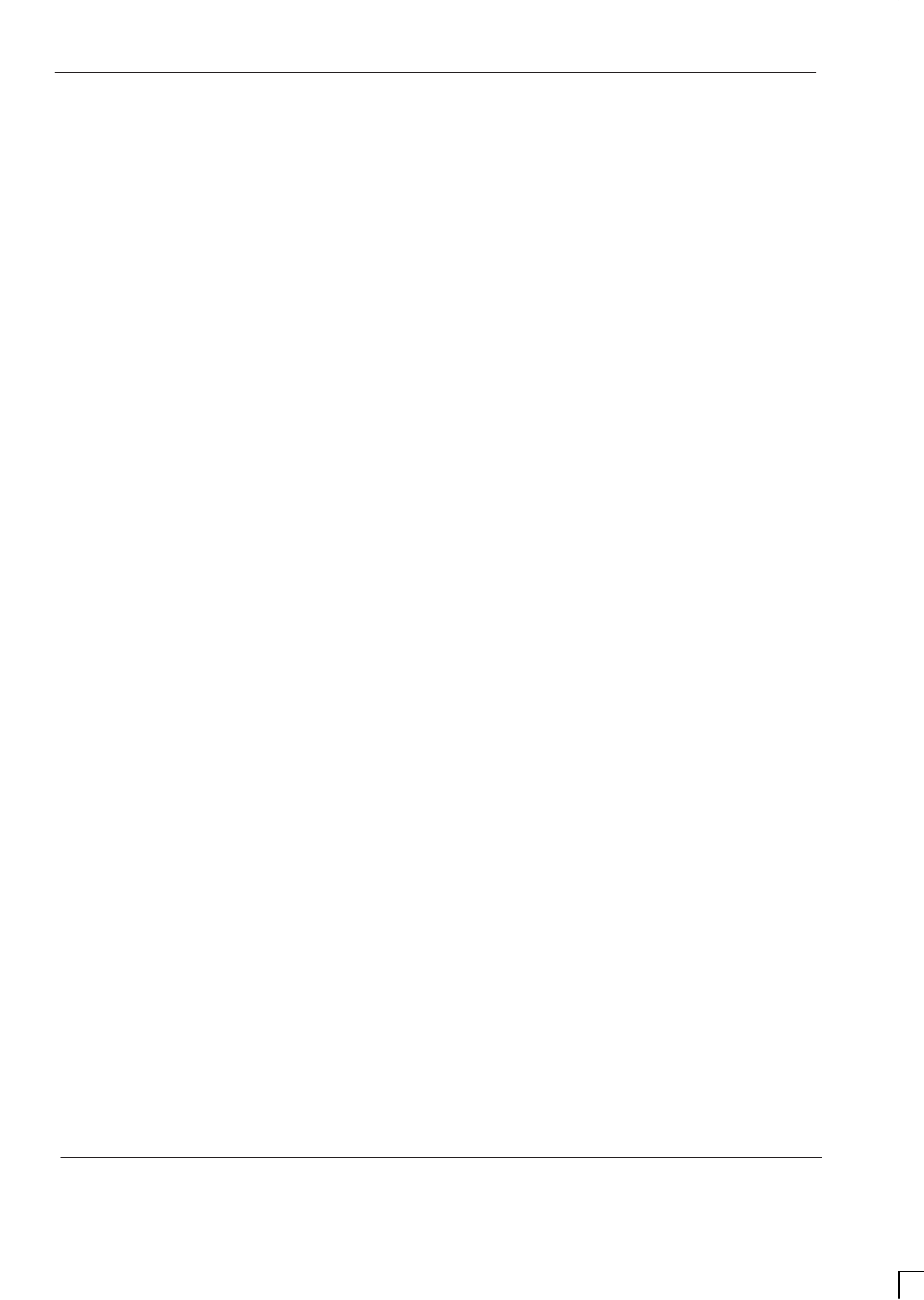
GSM-204-423
31st Oct 01
iv
Installation & Configuration: Horizon
macro
outdoor
CONTROLLED INTRODUCTION
68P02902W03-A
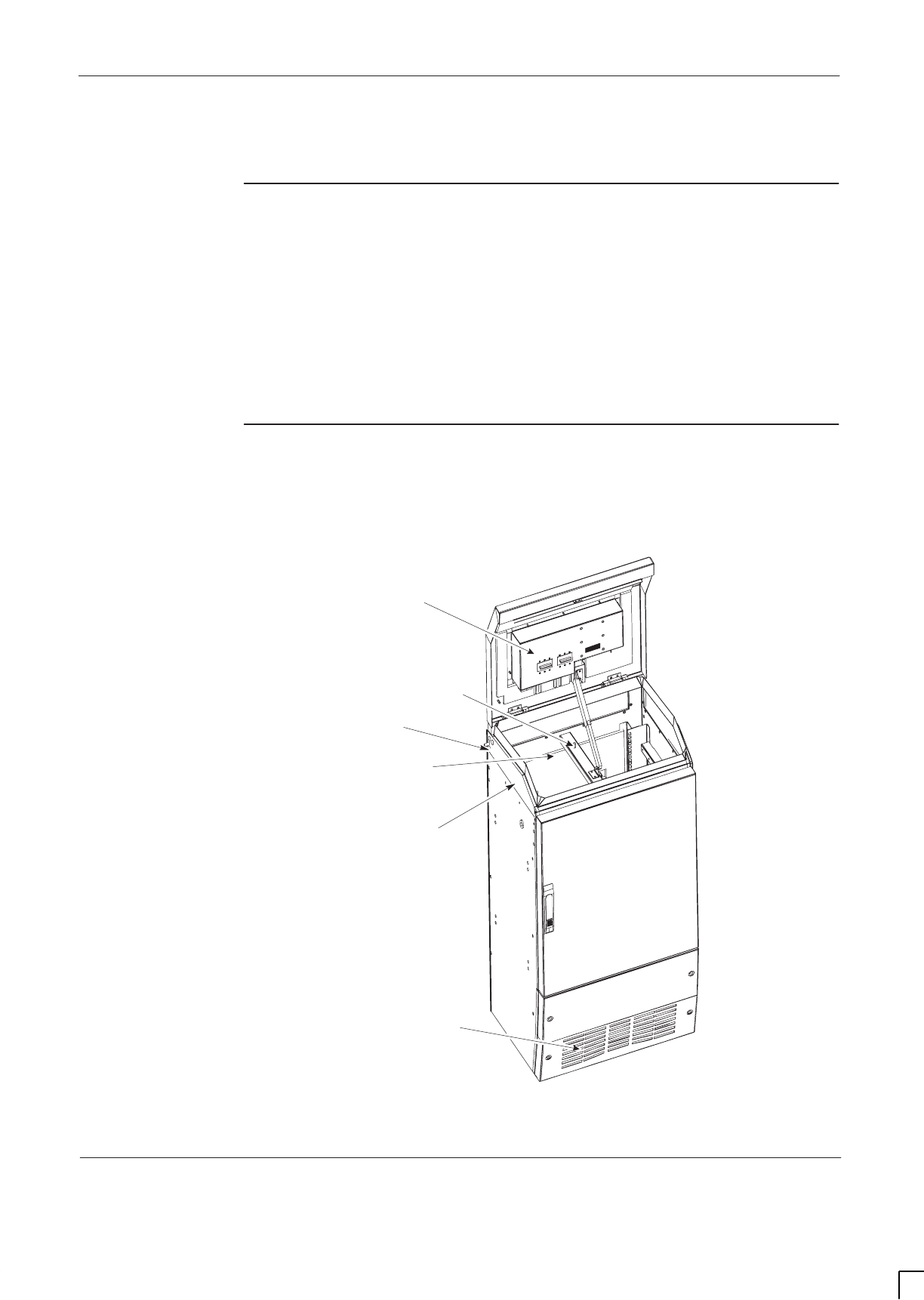
GSM-204-423 Procedures for installing the auxiliary equipment housing
31st Oct 01
Installation & Configuration: Horizon
macro
outdoor
68P02902W03-A
CONTROLLED INTRODUCTION
Inst. 5–1
Procedures for installing the auxiliary equipment housing
Assumptions
regarding site
preparation
The information contained in this chapter assumes that the site and the
foundation for the auxiliary equipment housing has been prepared in a similar
manner to that for the Horizon
macro
outdoor cabinet, as described in Chapter 2
of this category.
Most of the information contained in Chapter 3 regarding equipment delivery,
weather conditions affecting unpacking/installation and safety considerations is
also applicable to the auxiliary equipment housing.
Layout of the
auxiliary
equipment
housing
Figure 5-1 shows the layout of the auxiliary equipment housing.
POWER
DISTRIBUTION
BOX
FAN ASSEMBLY
(MOUNTED BEHIND GRILLE)
CABINET PROVIDING
23 U OF RACKING
SPACE
INTERNAL
CABINET EARTH
STUD
EARTH PLATE
EARTH
STUDS
Figure 5-1 The auxiliary equipment housing
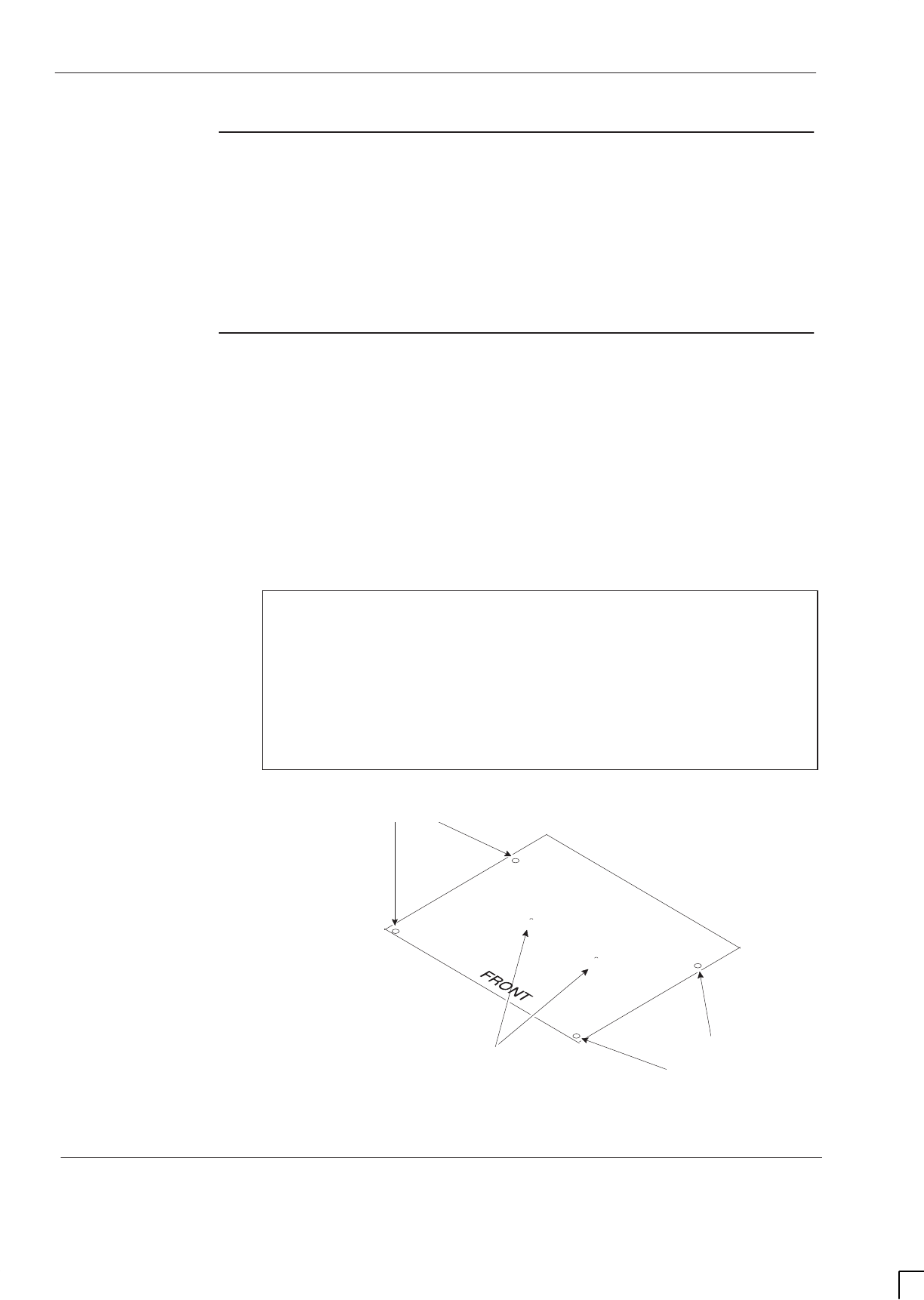
GSM-204-423
Procedures for installing the auxiliary equipment housing
31st Oct 01
Inst. 5–2
Installation & Configuration: Horizon
macro
outdoor
CONTROLLED INTRODUCTION
68P02902W03-A
Auxiliary
equipment
housing
packaging
The design of the packaging for the auxiliary equipment housing is similar to
that used for the BTS cabinet. The main difference is that the box is not
wrapped, but is of the “all in one” type and goes over the auxiliary equipment
housing.
Introduction to
installing the
auxiliary
equipment
housing
The auxiliary equipment housing can be installed on either side of the BTS
cabinet, normally on the opposite side to the antenna cable entry.
The auxiliary equipment cabinet is supplied with an alloy template (shown in
Figure 5-2), included in the packaging. The template is installed before the
cabinet to show the locations of the cabinet mounting bolt anchors. There is no
need to remove the template after installation of the expanding bolt anchors.
NOTE Ensure the template is installed on the correct side of the
BTS cabinet. If a cable shroud is to be fitted between the
BTS cabinet and the auxiliary equipment housing, its
mounting template must be placed on the ground between
the BTS cabinet and the auxiliary equipment housing
template to ensure that the spacing between the two
cabinets is correct. The shroud should be secured to the
BTS cabinet before the auxiliary equipment housing is
fixed in position.
No. 10 TEMPLATE
MOUNTING SCREW HOLES
CLEARANCE FOR
CABINET
MOUNTING BOLTS
CLEARANCE FOR CABINET
MOUNTING BOLTS
Figure 5-2 Auxiliary equipment housing template
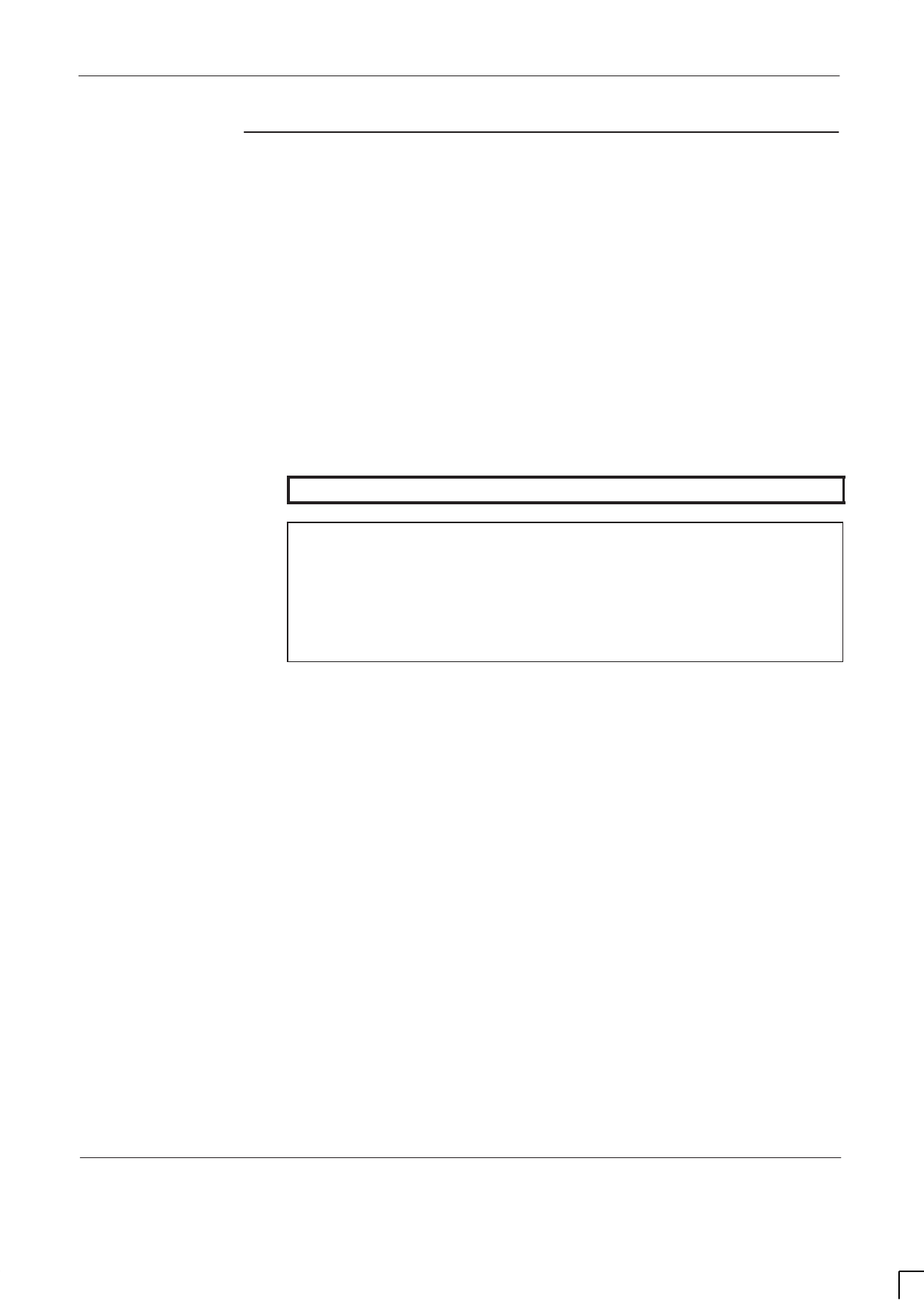
GSM-204-423 Procedures for installing the auxiliary equipment housing
31st Oct 01
Installation & Configuration: Horizon
macro
outdoor
68P02902W03-A
CONTROLLED INTRODUCTION
Inst. 5–3
Installing the
auxiliary
equipment
housing
template
The template (shown in Figure 5-2) must be secured to the concrete floor before
drilling the holes for the M12 anchor bolts.
1. If required, place the cable shroud template on the ground against the
appropriate side of the BTS cabinet, so it will act as a spacer between the
BTS cabinet and the auxiliary equipment housing.
2. Move the auxiliary equipment cabinet template to the selected mounting
position, flush against the cable shroud template.
3. Mark the positions of the two template mounting screw holes in the
template.
WARNING Wear safety glasses and a dust mask when drilling holes.
CAUTION Drilling concrete flooring produces cement dust, which is
harmful to equipment and wiring. Protect the cabinet and
any nearby equipment from dust. Use a tarpaulin, cloth, or
plastic sheeting to cover exposed equipment. Clean up
any accumulated debris from the anchor installation
carefully before uncovering the equipment. Use drilling
equipment suitable for cutting steel reinforced concrete.
4. Drill out the two holes to a depth and clearance for No. 10 screws.
5. Fit plastic expanding plugs into the mounting holes.
6. Position the template over the mounting holes and secure using No. 10
screws.
7. When satisfied that the template is correctly installed, carry out procedure
for installing the cabinet anchor bolts.
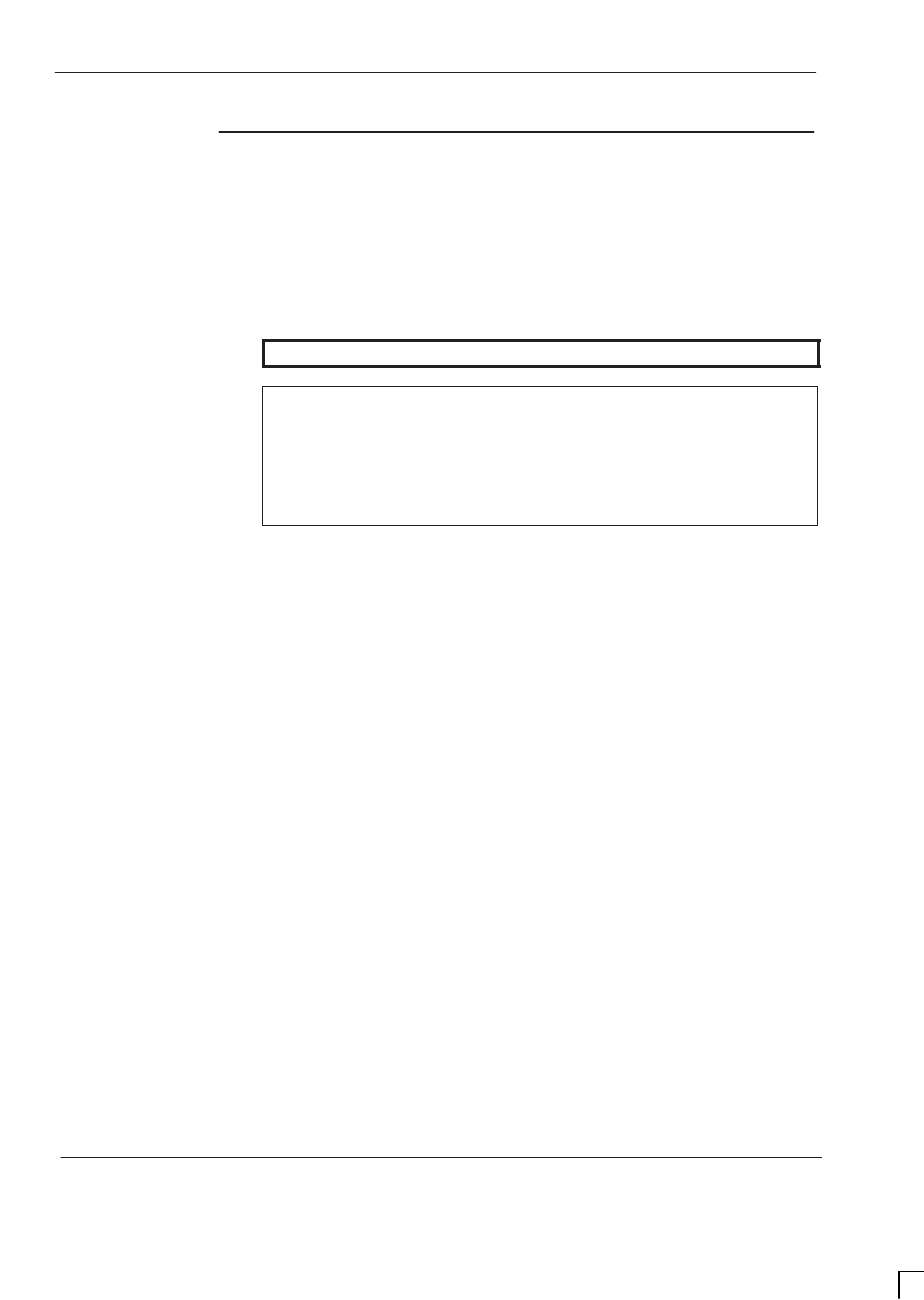
GSM-204-423
Procedures for installing the auxiliary equipment housing
31st Oct 01
Inst. 5–4
Installation & Configuration: Horizon
macro
outdoor
CONTROLLED INTRODUCTION
68P02902W03-A
Installing
auxiliary
equipment
housing bolt
anchors
The concrete floor must be drilled to accept the M12 anchor bolts. Washers,
bushes and M12 steel bolts must be supplied by the customer.
The recommended length of the M12 steel anchor bolts is 105 mm minimum.
WARNING Wear safety glasses and a dust mask when drilling holes.
CAUTION Drilling concrete flooring produces cement dust, which is
harmful to equipment and wiring. Protect the cabinets and
any nearby equipment from dust. Use a tarpaulin, cloth, or
plastic sheeting to cover exposed equipment. Clean up
any accumulated debris from the anchor installation
carefully before exposing the equipment. Use drilling
equipment suitable for cutting steel reinforced concrete.
1. Using the four holes in the template as a guide, drill the concrete floor to a
depth and clearance for the M12 anchor bolts.
2. Fit the M12 mounting anchors to the holes in the floor.
3. Fit the anchor bolts with the supplied bushes and washers, through the
template, to each anchor.
4. Tension up the anchor bolts to expand the anchors.
5. Remove and retain the M12 bolts and washers for later use.
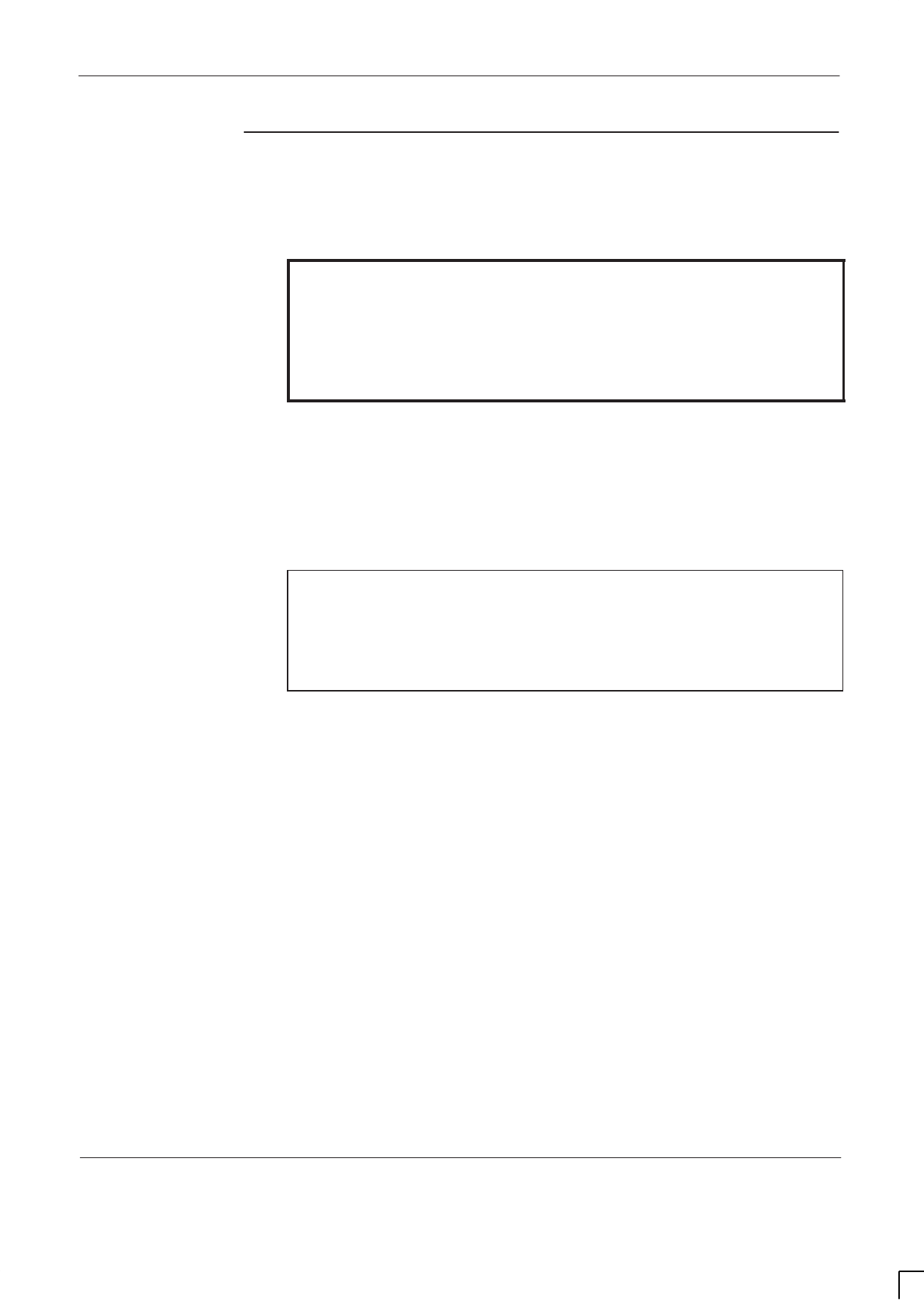
GSM-204-423 Procedures for installing the auxiliary equipment housing
31st Oct 01
Installation & Configuration: Horizon
macro
outdoor
68P02902W03-A
CONTROLLED INTRODUCTION
Inst. 5–5
Bolting the
auxiliary
equipment
housing to the
floor
WARNING An unequipped auxiliary equipment housing weighs 110
kg. Observe proper lifting precautions and handle the
cabinet with extreme caution to avoid tipping.
The auxiliary equipment housing must be lifted by fitting
eyebolts to the sides of the cabinet. Refer to Safety
considerations in Unpacking and preparing the
cabinet for information about eyebolt selection and use.
1. Manoeuvre the empty auxiliary equipment housing onto the template, but
do not bolt in position yet.
2. Remove each of the eyebolts from their threaded holes and return the
eyebolts to the tool kit for future use.
3. Open the housing lid and install the dc power and alarm signal cables
between the BTS cabinet and the auxiliary equipment housing.
NOTE The auxiliary equipment cabinet can be secured to the
cable shroud, if one is used. Refer to Chapter 4 of this
category for information regarding the installation of a
cable shroud between a BTS cabinet and the auxiliary
equipment housing. The cable shroud and dc power cable
must be installed before the housing is bolted to the floor.
4. Disconnect the power cable to the fan and remove the front panel
containing the fan assembly. Also remove all the battery trays.
5. Line up the fixing holes in the bottom of the housing with the previously
installed anchors.
6. Place a flat washer onto each M12 mounting bolt and fit the four mounting
bolts loosely. Do not tighten yet.
7. Using a spirit level, verify that the auxiliary equipment housing is level.
8. Tighten up the mounting bolts to the correct torque, (see Site
requirements and considerations in Chapter 2 of this category).
9. Refit the bottom front panel, previously retained.
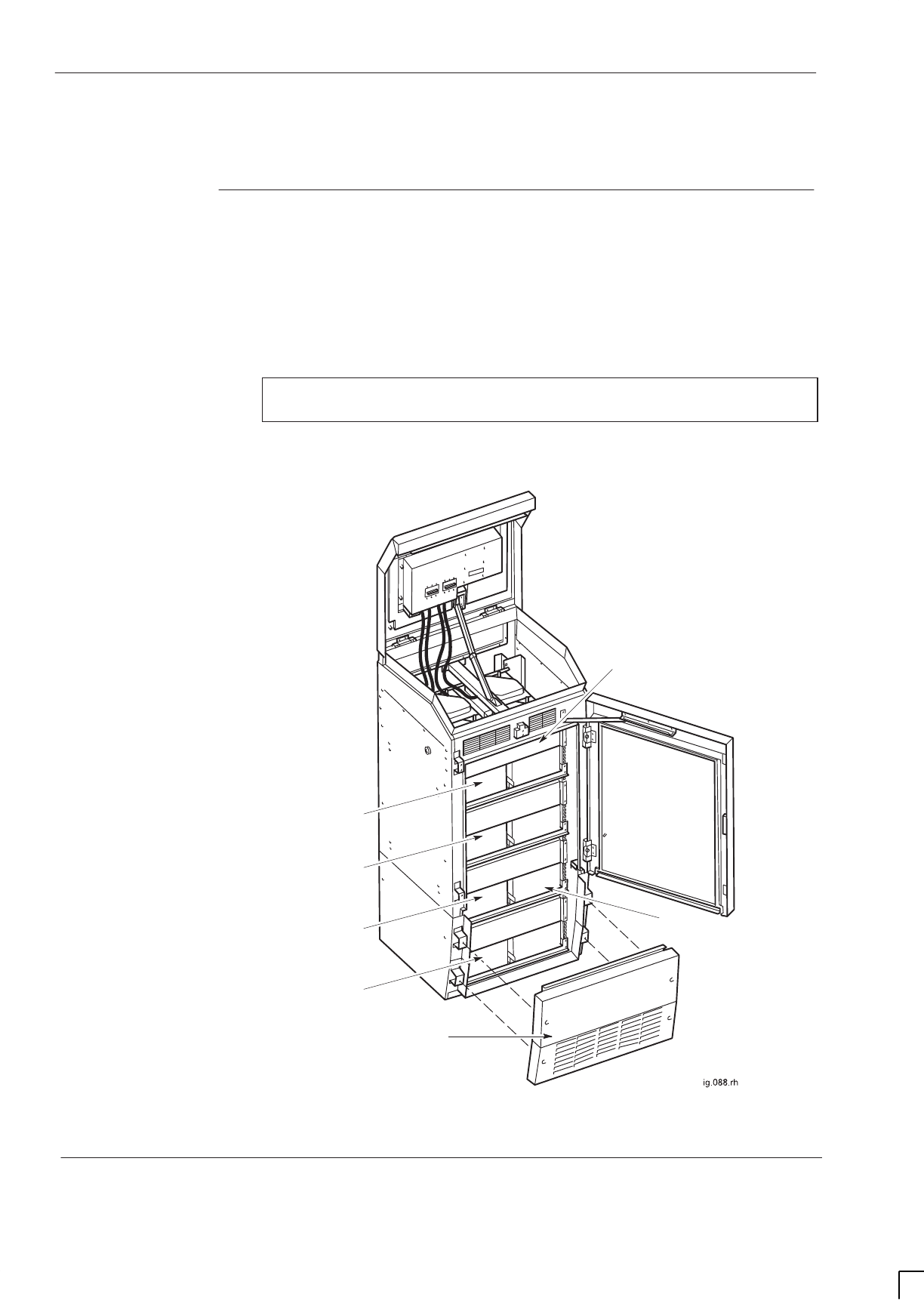
GSM-204-423
Installing batteries in the auxiliary equipment housing
31st Oct 01
Inst. 5–6
Installation & Configuration: Horizon
macro
outdoor
CONTROLLED INTRODUCTION
68P02902W03-A
Installing batteries in the auxiliary equipment housing
Introduction to
battery
installation
The auxiliary equipment housing can be fitted with two banks of eight 6 V
batteries, mounted on four battery trays. Each bank is wired together in series to
provide –48 V dc backup power for the Horizon
macro
outdoor cabinet. The two
banks can be wired in parallel, to provide increased backup duration for a single
BTS cabinet, or fed separately to two BTS cabinets.
NOTE Batteries must be fully charged and load tested before
installation.
Figure 5-3 shows a typical battery arrangement in the auxiliary equipment
housing when a full complement of 16 batteries is installed.
BANK 2, ROW 2
BANK 1, ROW 2
FRONT PANEL
(CONTAINING FAN
ASSEMBLY)
BANK 2, ROW 1
BANK 1, ROW 1
BATTERY TRAY
FRONT RETAINING PLATE
Figure 5-3 Battery arrangement in the auxiliary equipment housing
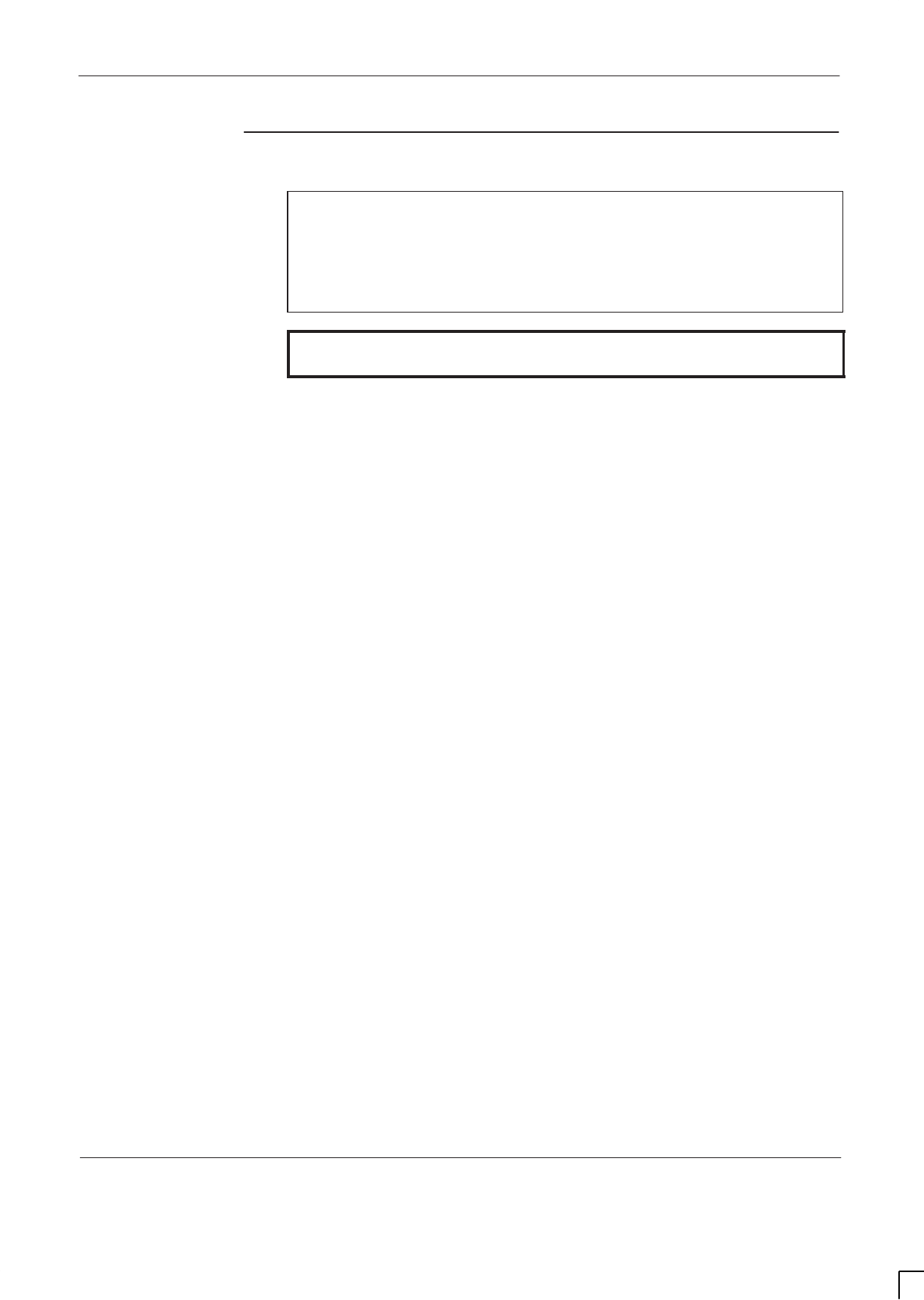
GSM-204-423 Installing batteries in the auxiliary equipment housing
31st Oct 01
Installation & Configuration: Horizon
macro
outdoor
68P02902W03-A
CONTROLLED INTRODUCTION
Inst. 5–7
Installing
batteries
NOTE Battery trays, retaining plates and leads are supplied with
the auxiliary equipment housing (AEH).
Batteries are not supplied with the AEH. They must be
obtained separately by the customer.
Motorola recommend the use of Yuasa or Hawker 6 V
batteries (kit number SVPN1216 contains eight batteries).
WARNING The batteries are capable of supplying high short circuit
currents and as such provides a high energy hazard.
To install batteries in the auxiliary equipment housing:
1. Ensure that batteries to be installed are fully charged and load tested in
accordance with battery manufacturers handbook.
2. Remove the front panel from the housing by undoing the six retaining
screws and disconnecting the cable to the fan assembly (contained within
the front panel).
3. Disconnect the heater mat power connectors at each tray and remove the
upper three battery trays in the auxiliary equipment housing (if not already
removed).
4. Install the four batteries onto the bottom tray in the cabinet so that the
positive and negative terminals match the arrangement shown in
Figure 5-4.
5. Connect the leads to the terminals as shown in Figure 5-5 and then fit the
front retaining plate.
6. Install the battery tray for row 2 in the auxiliary equipment housing,
reconnecting the heater mat power connector at the tray.
7. Install the four batteries onto the row 2 tray so that the positive and
negative terminals match the arrangement shown in Figure 5-6.
8. Connect the leads from the batteries in row 1 to the terminals of the
batteries in row 2 as shown in Figure 5-7. Fit the front retaining plate.
9. Connect the black cable from the power distribution box on the lid to the
positive terminal on the left rear battery in row 2.
10. Connect the blue cable from the power distribution box on the lid to the
negative terminal on the right rear battery in row 2.
Repeat steps 3 to 9 of the above procedure if a second bank of batteries is to
be installed in the housing above the first bank.
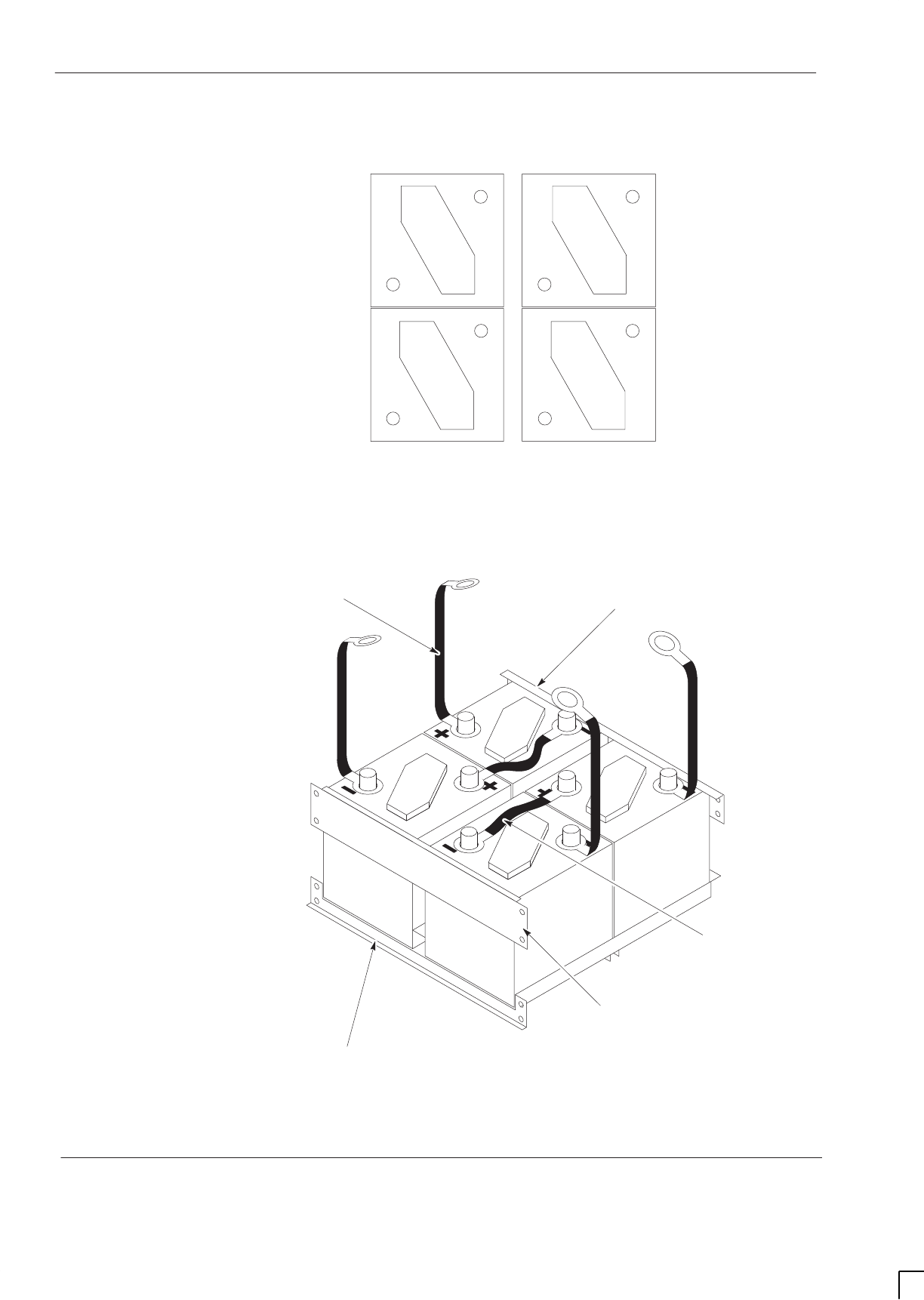
GSM-204-423
Installing batteries in the auxiliary equipment housing
31st Oct 01
Inst. 5–8
Installation & Configuration: Horizon
macro
outdoor
CONTROLLED INTRODUCTION
68P02902W03-A
Figure 5-4 show a plan view of the batteries in row 1.
FRONT
+
–
+
–
+
–
+
–
Figure 5-4 Layout for batteries in row 1
Figure 5-5 shows the battery and cable arrangement in row 1.
FRONT RETAINING PLATE
BATTERY TRAY
REAR RETAINING PLATE
PART No. 3086432N06
PART No. 3086432N07
Figure 5-5 Battery arrangement in row 1 with cables attached
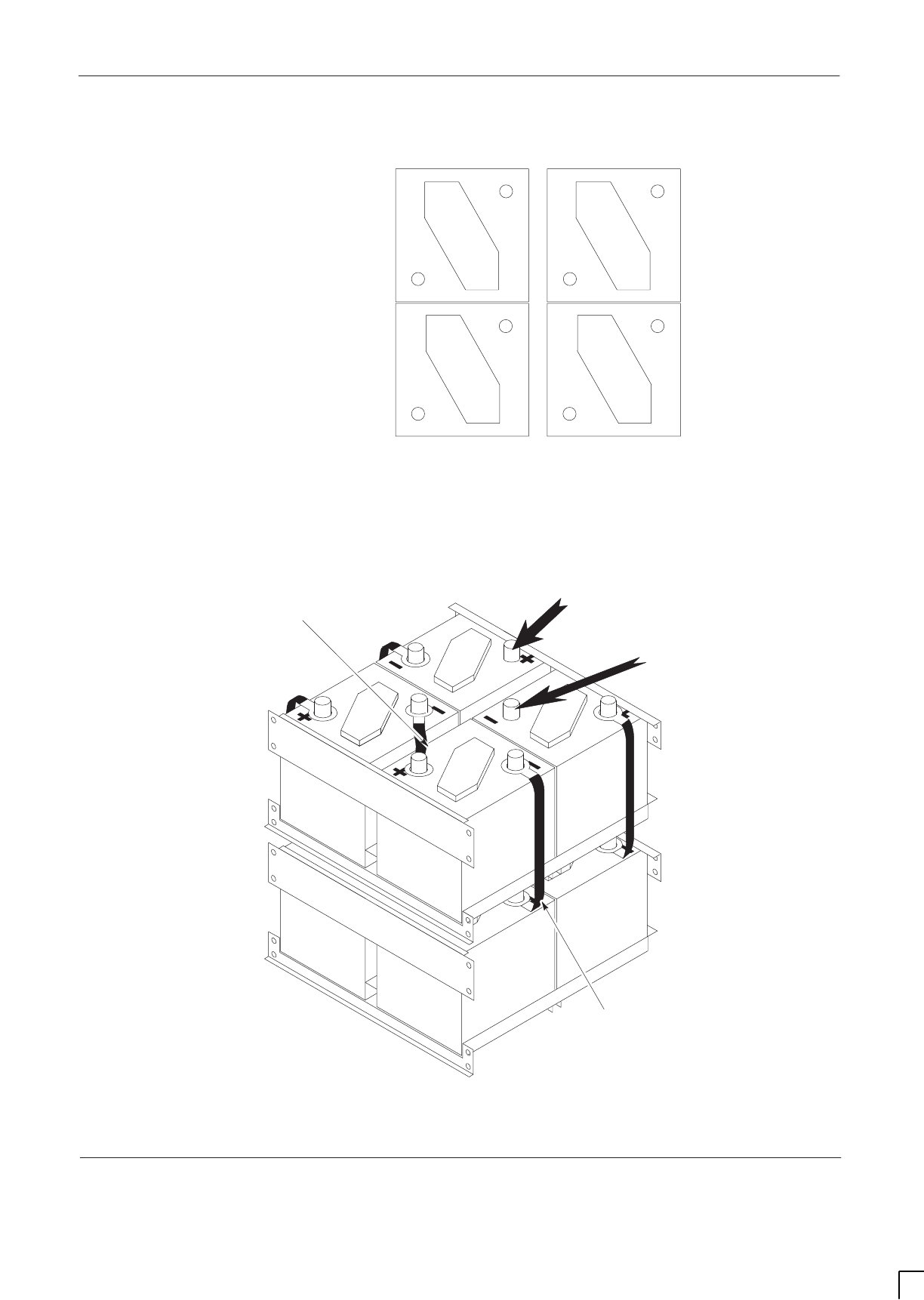
GSM-204-423 Installing batteries in the auxiliary equipment housing
31st Oct 01
Installation & Configuration: Horizon
macro
outdoor
68P02902W03-A
CONTROLLED INTRODUCTION
Inst. 5–9
Figure 5-6 show a plan view of the batteries in row 2.
FRONT
+
–
+
–
+
–
+
–
Figure 5-6 Layout for batteries in row 2
Figure 5-7 shows the battery and cable arrangement in row 1.
–VE CONNECTION (BLUE
CABLE) TO POWER
DISTRIBUTION BOX
PART No. 3086432N04 (BANK 1)
PART No. 3086432N02 (BANK 2)
+VE CONNECTION (BLACK CABLE) TO POWER
DISTRIBUTION BOX
PART No. 3086432N03 (BANK 1)
PART No. 3086432N01 (BANK 2)
PART No.
3086432N06
PART No.
3086432N07
Figure 5-7 Battery arrangement in row 2 with cables attached
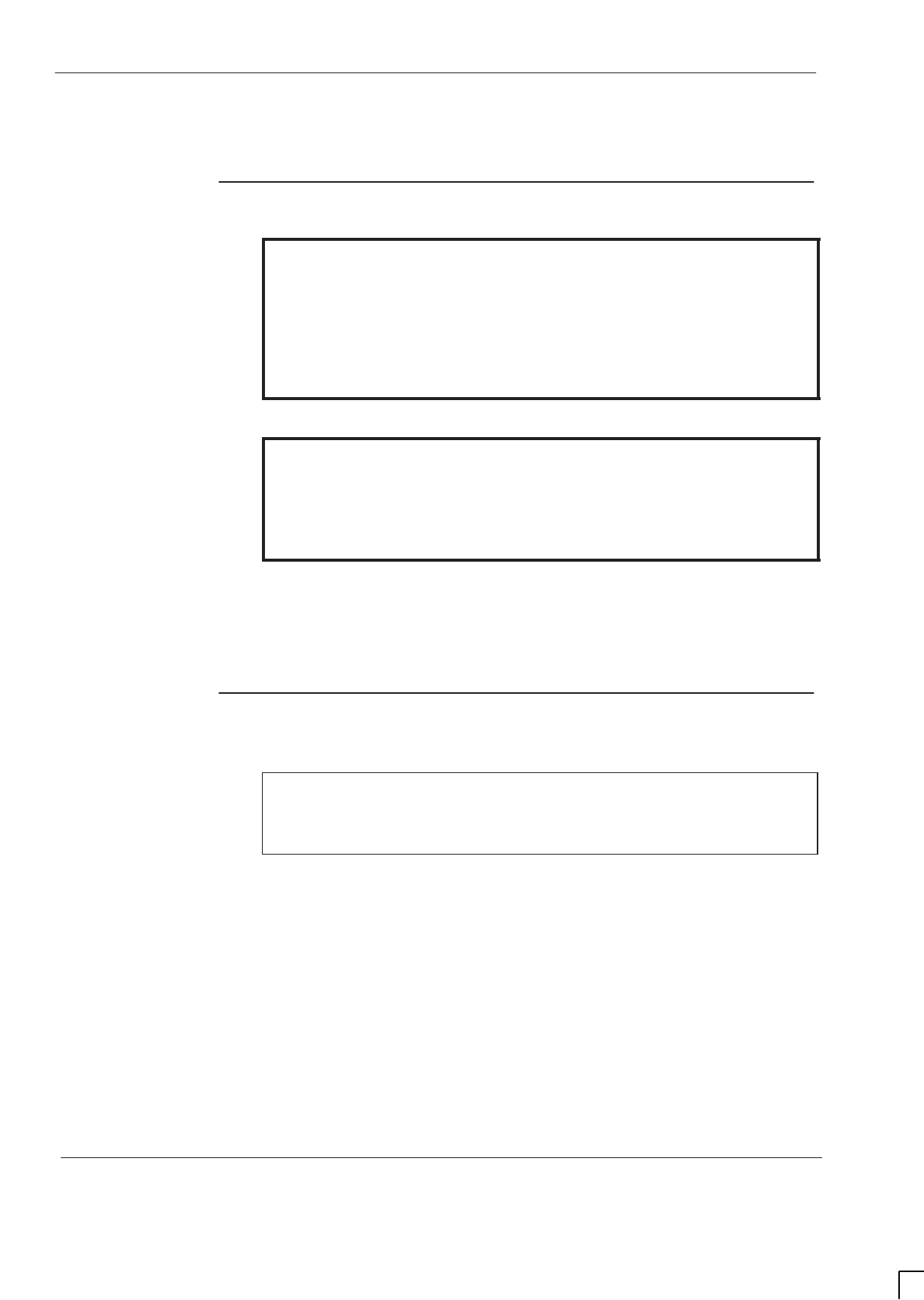
GSM-204-423
Auxiliary equipment housing (AEH) connections
31st Oct 01
Inst. 5–10
Installation & Configuration: Horizon
macro
outdoor
CONTROLLED INTRODUCTION
68P02902W03-A
Auxiliary equipment housing (AEH) connections
Earthing the
AEH
WARNING Do not daisy chain cabinet earths together.
Do not make ac input power connections at the main
power source at this time. Connecting input power is
the final installation procedure, carried out as part of
commissioning in Chapter 6 of this category.
Cabinets must be earthed with a conductor capable of
carrying the full fault current of the overcurrent protection
device.
To earth the AEH:
WARNING The AEH centre cross beam earth stud is connected to
the right side earth plate when supplied.
The AEH can be earthed at either side, however, if left
side AEH earth plate is to be connected to site earth,
centre cross beam earth stud must be disconnected from
right side and reconnected to left side AEH earth plate.
1. Connect the earth plate stud to the site earth using a 35 mm2
cross-sectional area, green and yellow sheathed, stranded conductor.
2. Ensure the earth stud on the cabinet centre cross beam is connected to
the AEH earth plate that is to be connected to the site earth, or to the BTS
cabinet earth plate, through the expansion plate.
Connecting dc
cables to the
AEH
CAUTION When using external batteries, the Horizon
macro
outdoor
BTS cabinet internal batteries must be switch isolated to
ensure correct operation of the temperature-compensated
battery charging system.
The auxiliary equipment cabinet requires –48 V dc connections to operate. The
dc cables come from the Anderson connectors on the dc interface panel in the
BTS cabinet. The dc cables from the BTS cabinet connect to the rear pair of
Anderson connectors at the base of the power distribution box.
The supply to the auxiliary equipment housing can be isolated using the EXT
BATT circuit breaker on the dc circuit breaker panel in the main cabinet.
Battery power from the auxiliary equipment housing to the main cabinet can be
isolated using the circuit breakers on the front of the power distribution box.
The front pair of Anderson connectors on the power distribution box can be
used to connect either a second BTS cabinet, (refer to Configuring battery
backup in this chapter), or an additional auxiliary equipment housing, thus
connecting the batteries in parallel to provide extra battery capacity, further
increasing backup duration..
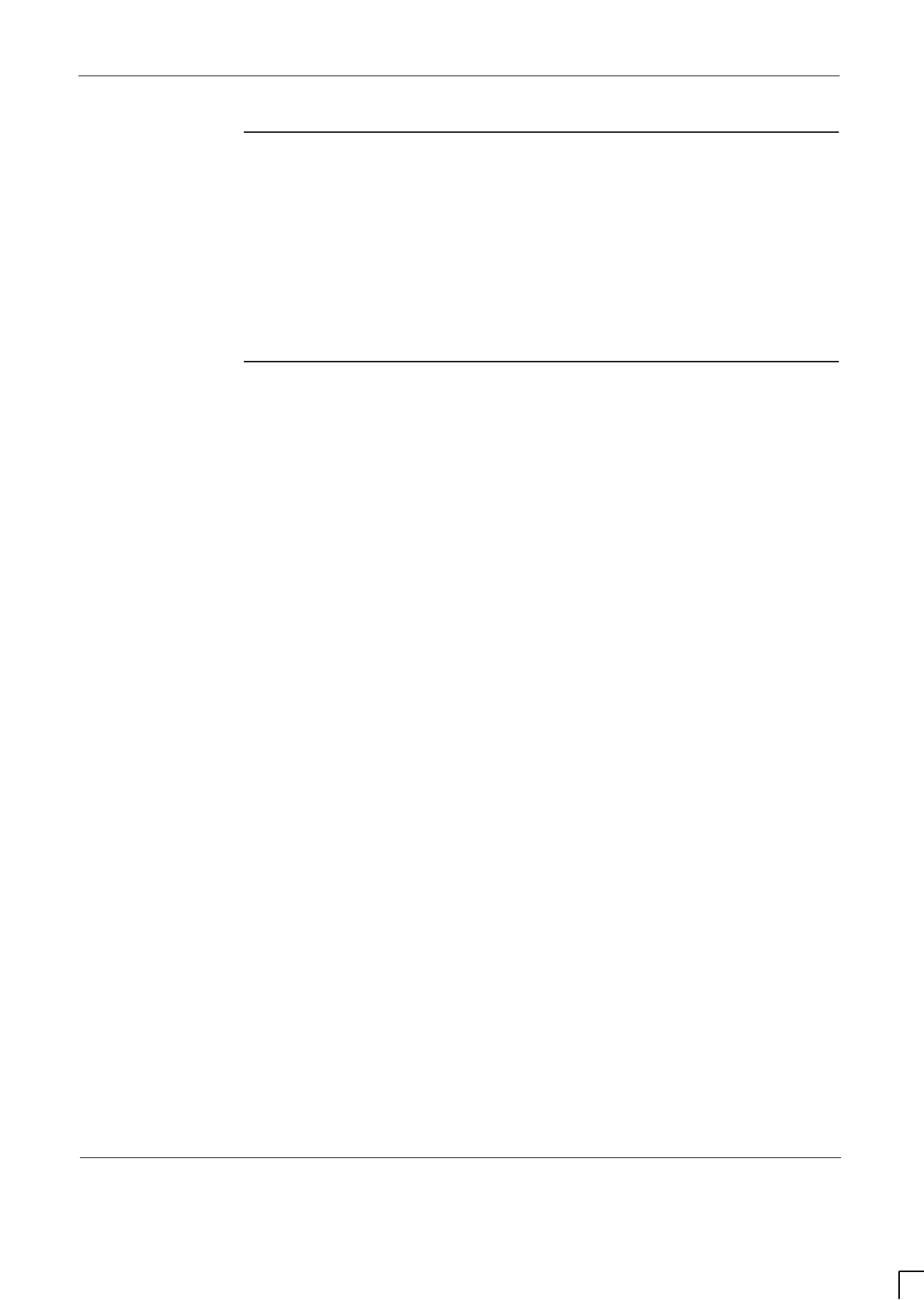
GSM-204-423 Auxiliary equipment housing (AEH) connections
31st Oct 01
Installation & Configuration: Horizon
macro
outdoor
68P02902W03-A
CONTROLLED INTRODUCTION
Inst. 5–11
Connecting the
alarm signal
cables
The alarm signal cable from the alarms interface board in the main BTS cabinet
plugs into the connector PL1 on the front right of the power distribution box. PL2
is for connection to the alarms interface board of a second BTS cabinet, and
PL3 is to allow connection of a second AEH The cables are labelled for
identification. PL1, PL2 and PL3 are accessed through an opening in the front
face of the power distribution box.
Internal
connections in
the AEH
Six additional flying leads are connected to the power distribution box:
One provides power to the fan.
Four provide power to the heater mats
One connects to the door microswitch.
All leads are labelled clearly for identification.
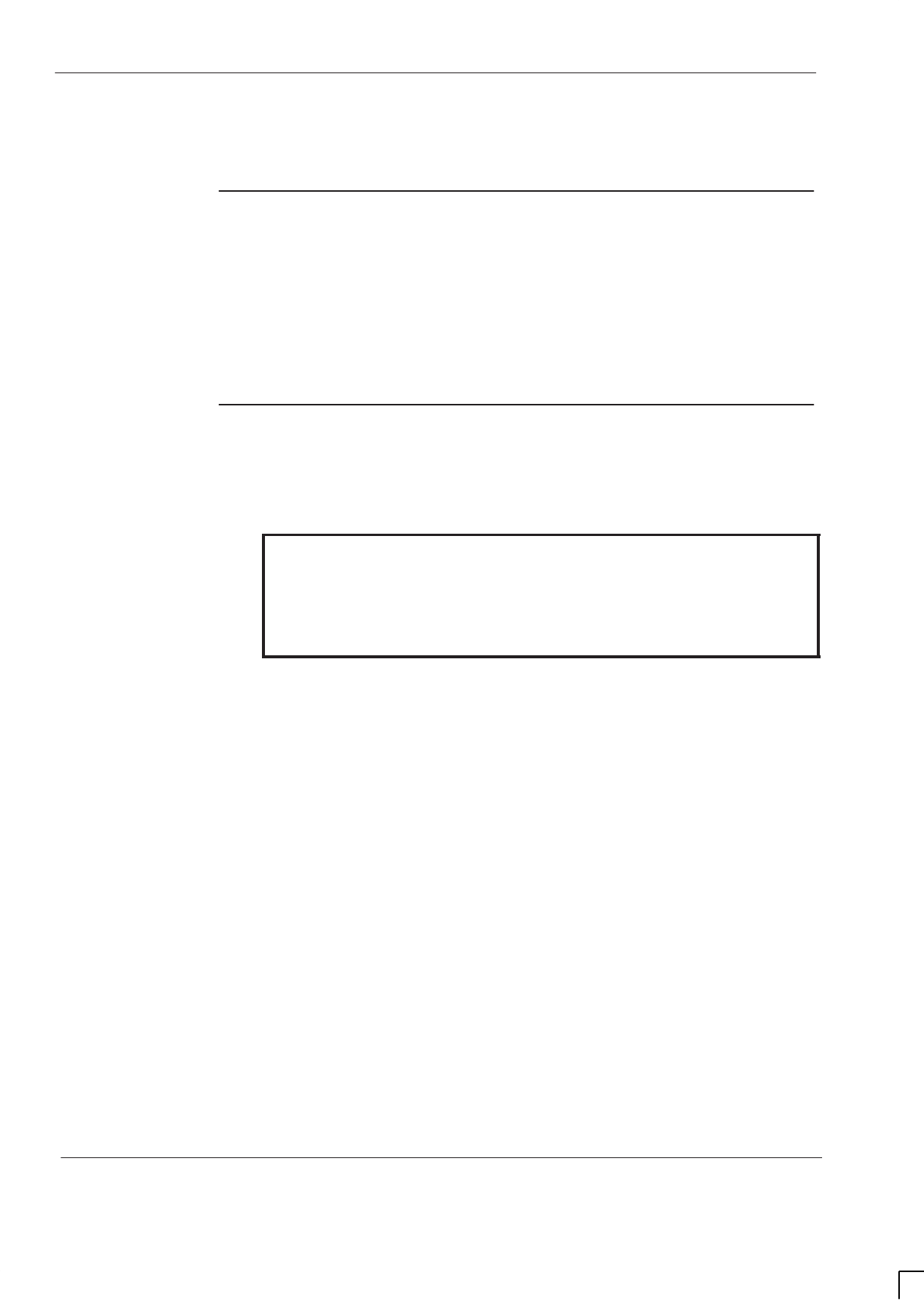
GSM-204-423
Configuring battery backup to supply two BTS cabinets
31st Oct 01
Inst. 5–12
Installation & Configuration: Horizon
macro
outdoor
CONTROLLED INTRODUCTION
68P02902W03-A
Configuring battery backup to supply two BTS cabinets
Introduction to
configuring
battery backup
The circuit breakers in the power distribution box are linked in parallel when
supplied. The links must be removed if two BTS cabinets are to be connected to
one auxiliary equipment housing.
The power distribution box must be removed to gain access to the parallelling
links and refitted after the links have been removed.
Removing the
power
distribution box
The procedure for removing the power distribution box from the auxiliary
equipment housing is as follows:
WARNING The batteries are capable of supplying high short circuit
currents and as such provides a high energy hazard.
Isolate the auxiliary equipment housing from the main
cabinet by switching off the EXT BATT circuit breaker on
the dc circuit breaker panel in the main cabinet before
commencing work.
1. Open the cabinet door, release the lid latch and raise the lid.
2. Switch off the circuit breakers on the front of the power distribution box
and then disconnect the dc input cables, (if fitted), from the Anderson
connectors on the left side of the power distribution box.
3. Unplug the alarm signal cables from PL1, PL2 and PL3 on the front of the
power distribution box.
4. Disconnect the two cables which connect the top bank of batteries (bank
2, row 2) to the power distribution box and tie the cables safely out of the
way. Undo the battery terminal connections between bank 2, row 2 and
bank 2, row 1 and then remove the row 2 battery tray, followed by the row
1 battery tray.
5. Disconnect the two cables which connect battery bank 1, row 2 to the
power distribution box and tie the cables safely out of the way.
6. Undo the eight M4 nuts which secure the power distribution box to the lid
and then remove the box.
7. Unplug the door microswitch alarm cable from the external alarm interface
board.
8. Unplug the power cables for the heater mats and the fan from the external
alarm interface board.
The parallelling links can now be removed.
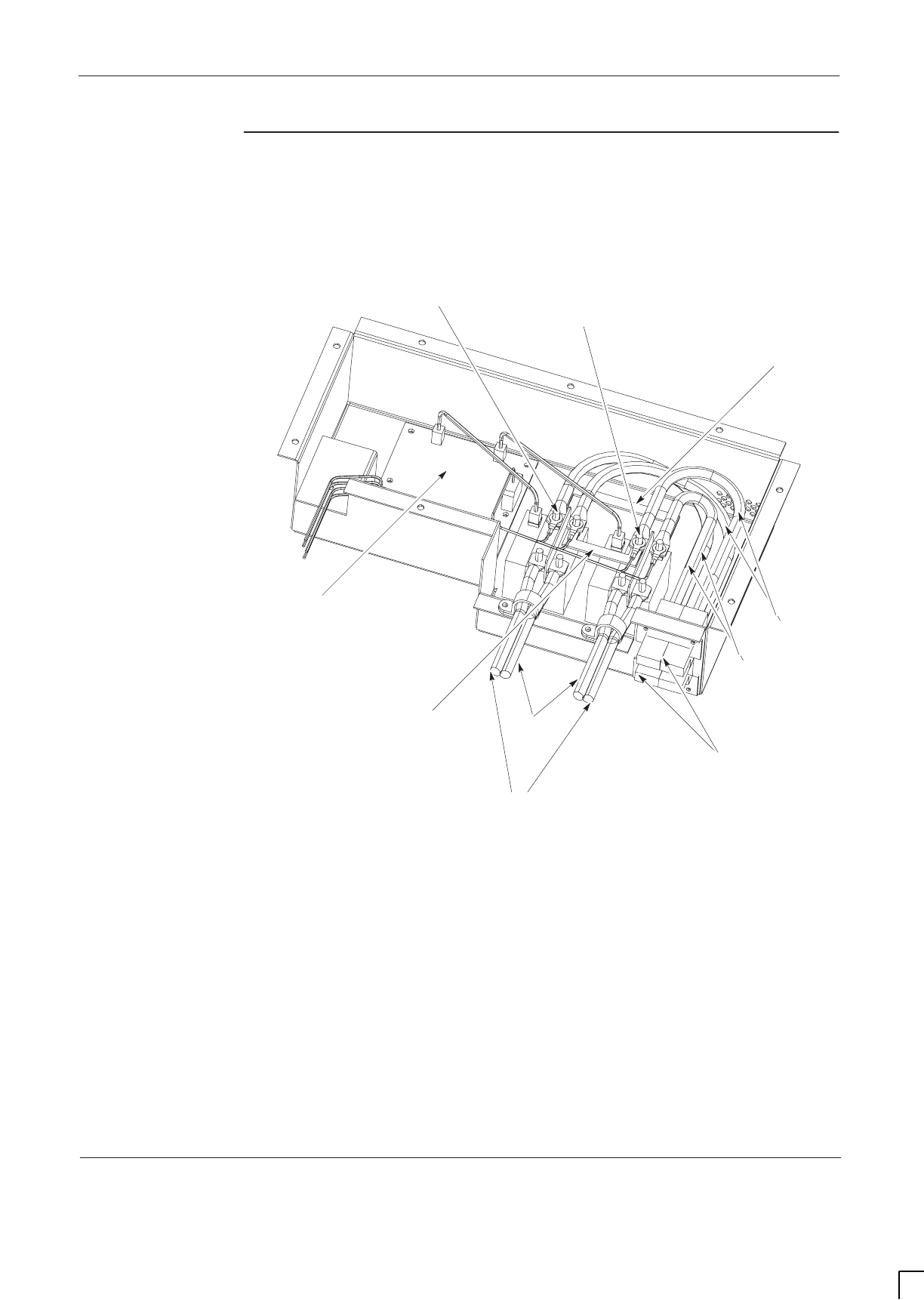
GSM-204-423 Configuring battery backup to supply two BTS cabinets
31st Oct 01
Installation & Configuration: Horizon
macro
outdoor
68P02902W03-A
CONTROLLED INTRODUCTION
Inst. 5–13
Interior view of
power
distribution box
Figure 5-8 shows the interior of the power distribution box, with the components
for battery backup configuration identified.
CIRCUIT BREAKER 2
CONNECTIONS
0 V LINK
–48 V LINK
ANDERSON CONNECTORS
CIRCUIT BREAKER 1
CONNECTIONS
EXTERNAL ALARM
INTERFACE BOARD –48 V
CABLES
(blue)
0 V
CABLES
(black)
–48 V
CABLES
(blue)
0 V
CABLES
(black)
Figure 5-8 Interior of power distribution box
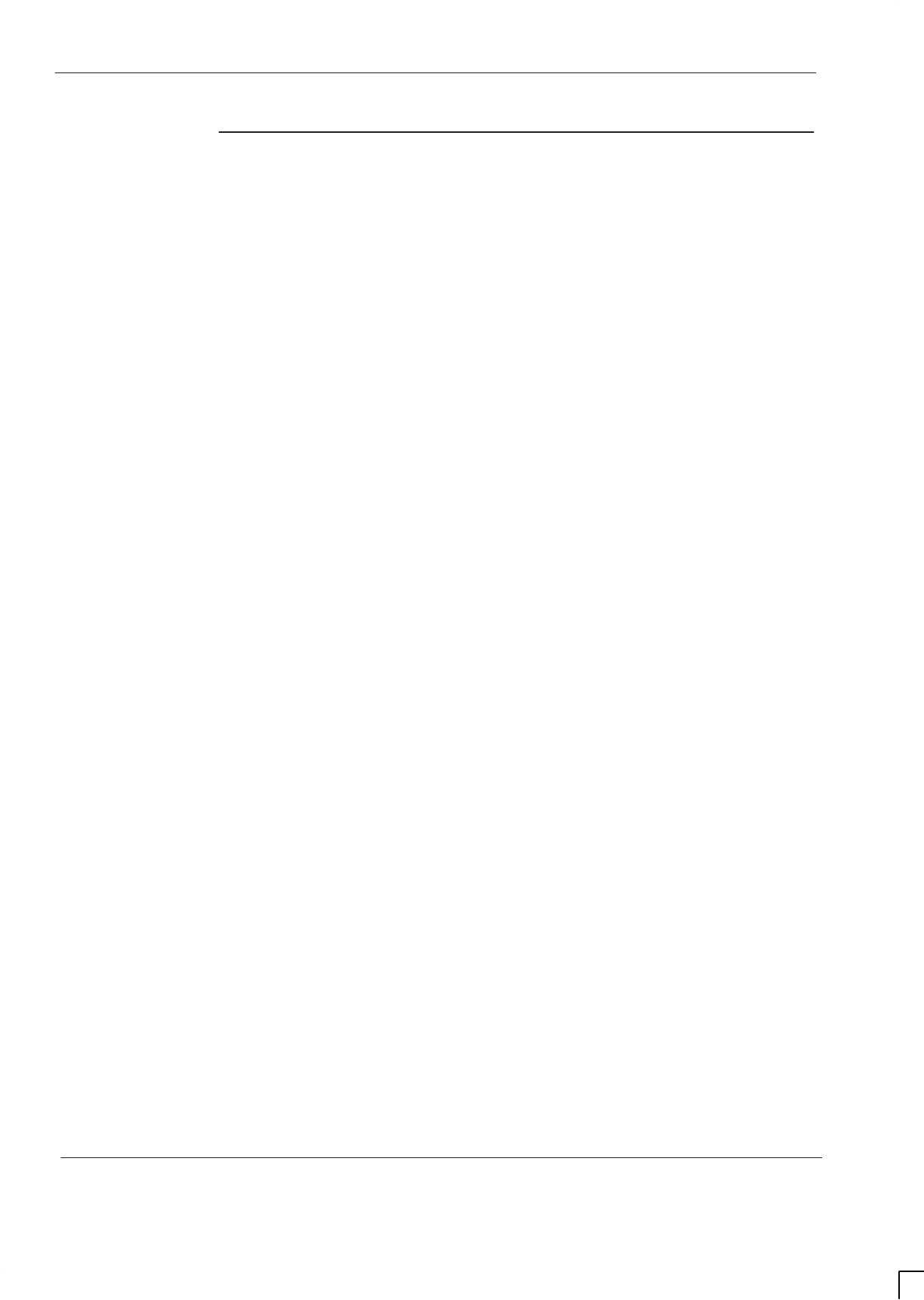
GSM-204-423
Configuring battery backup to supply two BTS cabinets
31st Oct 01
Inst. 5–14
Installation & Configuration: Horizon
macro
outdoor
CONTROLLED INTRODUCTION
68P02902W03-A
Removing the
parallelling
links
To remove the parallelling links refer to Figure 5-8 and:
1. Ensure the power distribution box is disconnected from the –48 V dc
supply and the batteries.
2. Remove the four M6 nuts, plain washers and star washers, securing the
cables from the Anderson connectors to the circuit breakers, and retain.
3. Note the location and insulation colour of the four ring terminals connected
to the external alarm interface board, and remove from the circuit breaker
studs.
4. Remove the four terminals connecting the Anderson connectors to the
circuit breakers, noting the position of each terminal.
5. Remove the 0 volt link and the –48 volt link from the circuit breakers.
6. Refit the black 0 volt and the blue –48 volt cable terminals to the outer
stud on each circuit breaker, in the position previously noted in step 4.
7. Refit the four ring terminals from the external alarms interface board to the
circuit breakers, in the locations noted in step 3.
8. Ensure that the insulation colour of all refitted cables is correctly matched.
9. Refit the four M6 star washers, plain washers and nuts, and tighten to the
correct torque, (see Site requirements and considerations in Chapter 2
of this category).
The power distribution box can now be refitted.
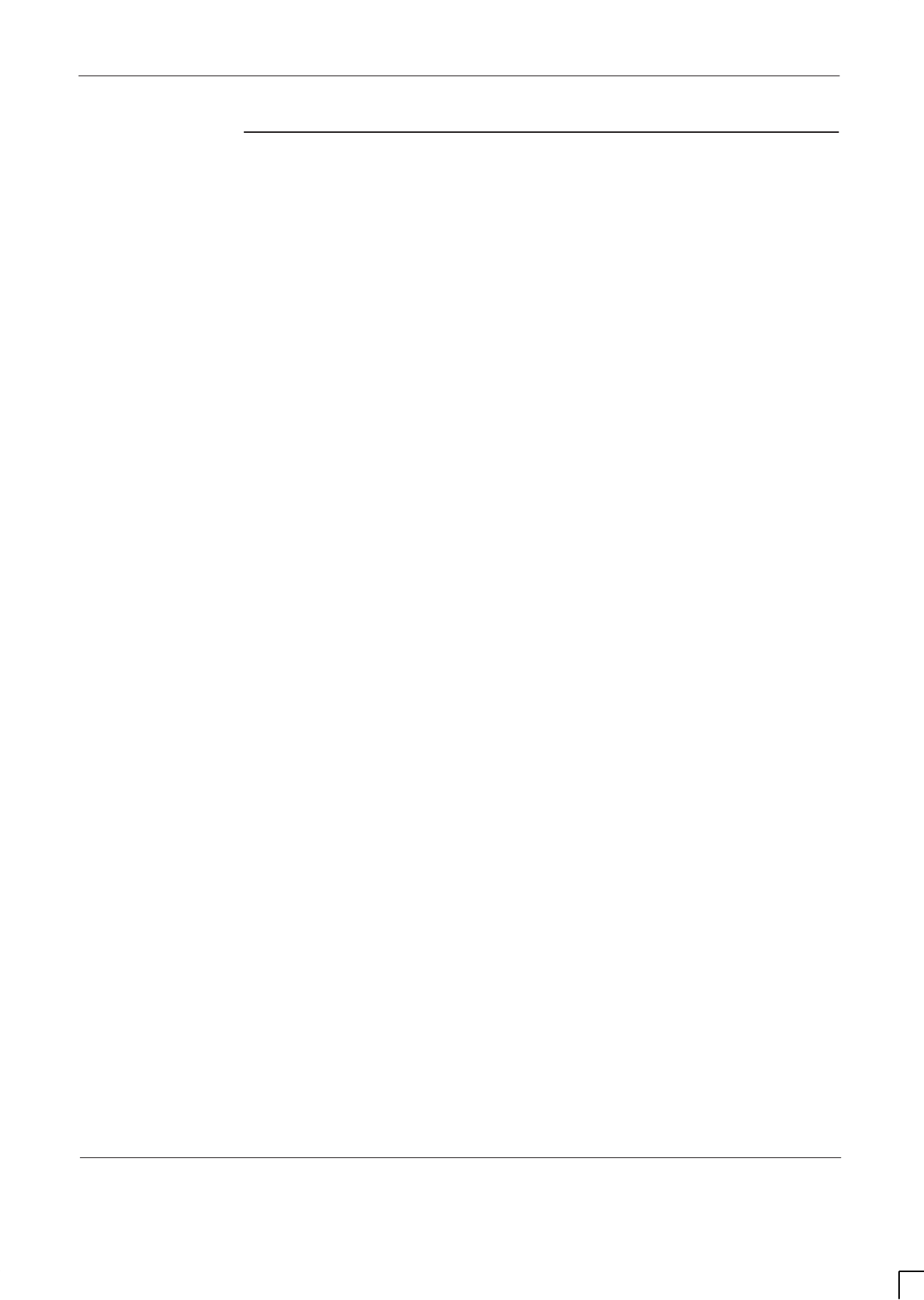
GSM-204-423 Configuring battery backup to supply two BTS cabinets
31st Oct 01
Installation & Configuration: Horizon
macro
outdoor
68P02902W03-A
CONTROLLED INTRODUCTION
Inst. 5–15
Refitting the
power
distribution box
The procedure for refitting the power distribution box is as follows:
1. Connect the power cables for the heater mats and the fan to the external
alarm interface board.
2. Connect the alarm cables for the door microswitch to the external alarm
interface board.
3. Mount the power distribution box onto the underside of the lid and secure
in position using the M4 nuts.
4. Connect the longer pair of battery cables from the power distribution box
to their terminals on battery bank 1, row 2. The blue cable connects to
negative and the black cable connects to positive.
5. Install the bank 2, row 1 battery tray, followed by the bank 2, row 2 battery
tray and then remake the terminal connections between the two rows
(refer to
Installation and Configuration: (GSM-204-423)
Installing
batteries in the auxiliary equipment housing if necessary. Connect the
remaining pair of battery cables to the positive and negative terminals on
the top bank of batteries.
6. Connect the alarm signal cables to PL1, PL2 and PL3 on the front of the
power distribution box.
7. Connect the dc power cables from one BTS cabinet to the rear pair of
Anderson connectors on the power distribution box. Connect the dc power
cables from the second BTS cabinet to the front pair of Anderson
connectors.
8. Switch on the circuit breakers on the front of the power distribution box
and then close the lid and the cabinet door.
9. Switch on the EXT BATT circuit breaker on the dc circuit breaker panel in
the main cabinet.
The procedures for configuring the battery backup to supply two BTS cabinets
are now complete.
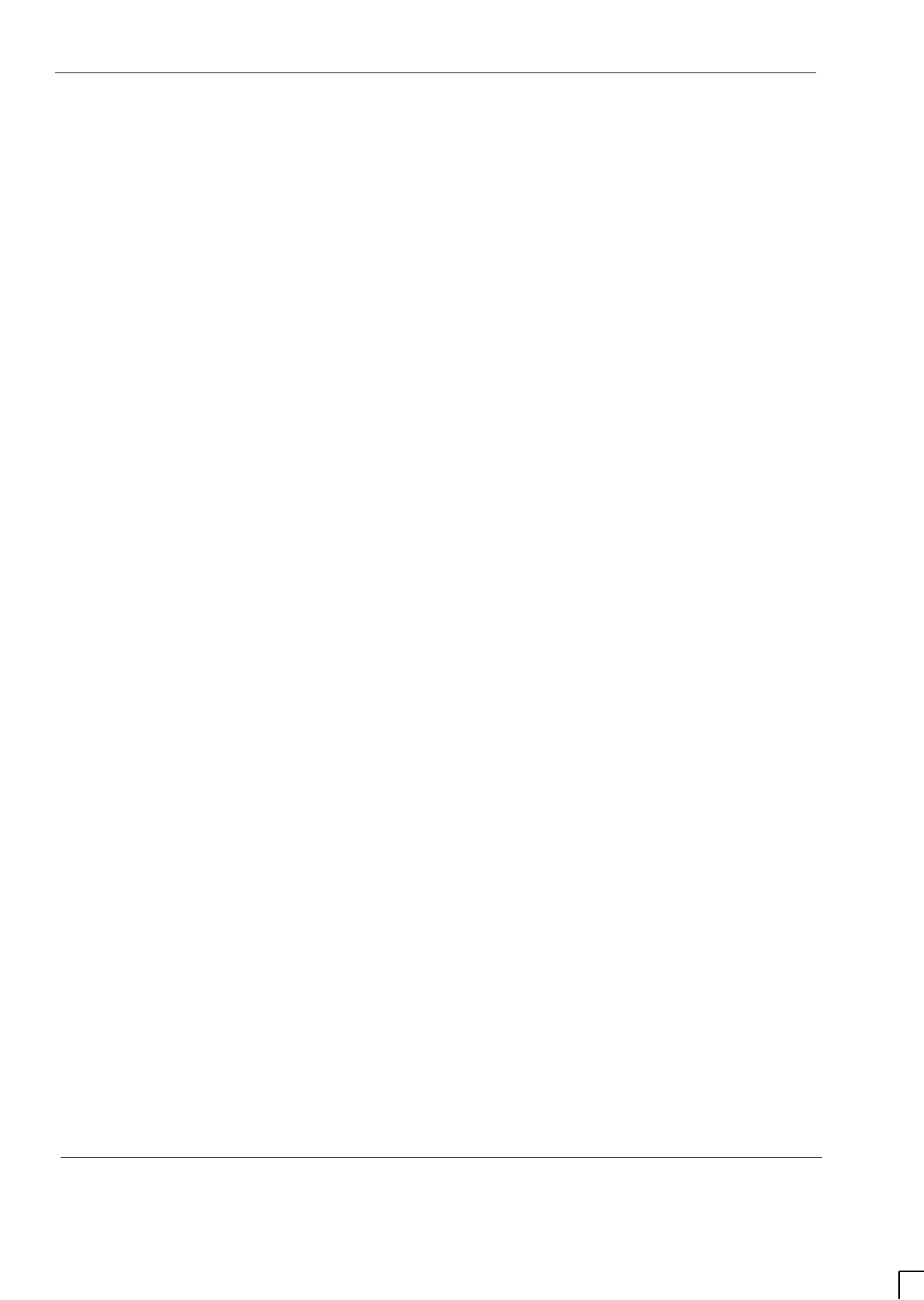
GSM-204-423
Configuring battery backup to supply two BTS cabinets
31st Oct 01
Inst. 5–16
Installation & Configuration: Horizon
macro
outdoor
CONTROLLED INTRODUCTION
68P02902W03-A
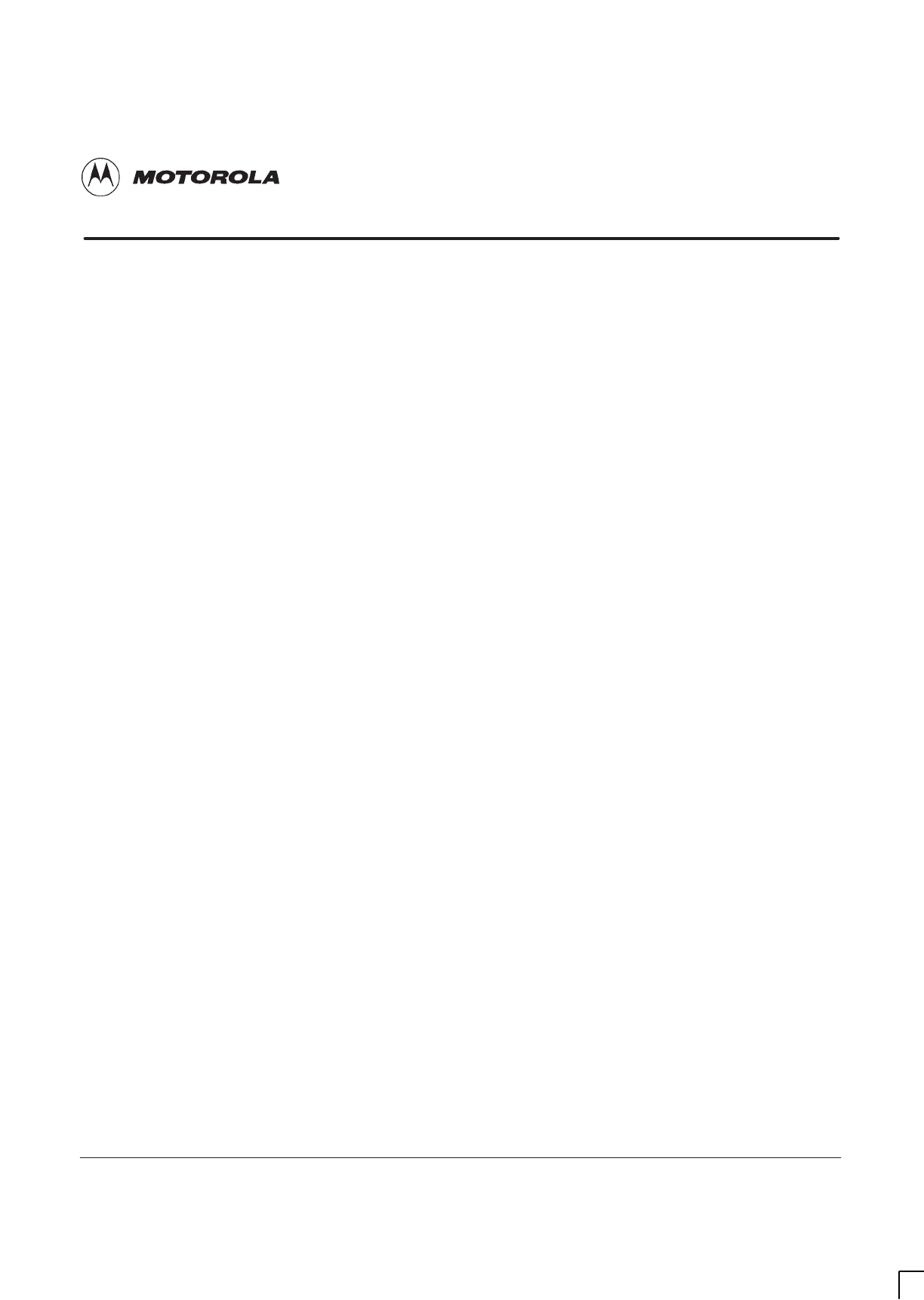
31st Oct 01
Installation & Configuration: Horizon
macro
outdoor
68P02902W03-A
CONTROLLED INTRODUCTION
i
Chapter 6
Interoperability between different
Motorola BTSs
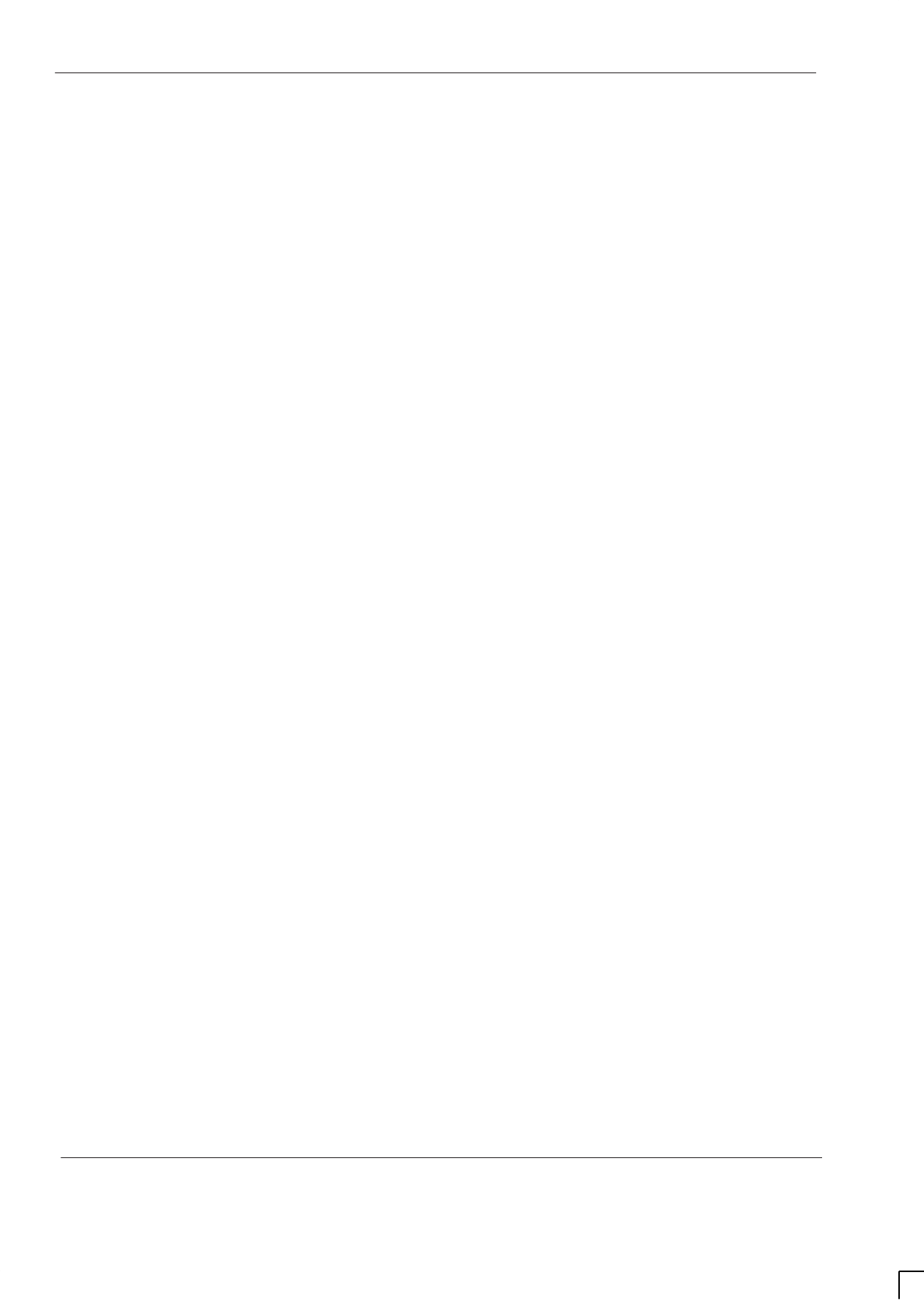
GSM-204-423
31st Oct 01
ii
Installation & Configuration: Horizon
macro
outdoor
CONTROLLED INTRODUCTION
68P02902W03-A
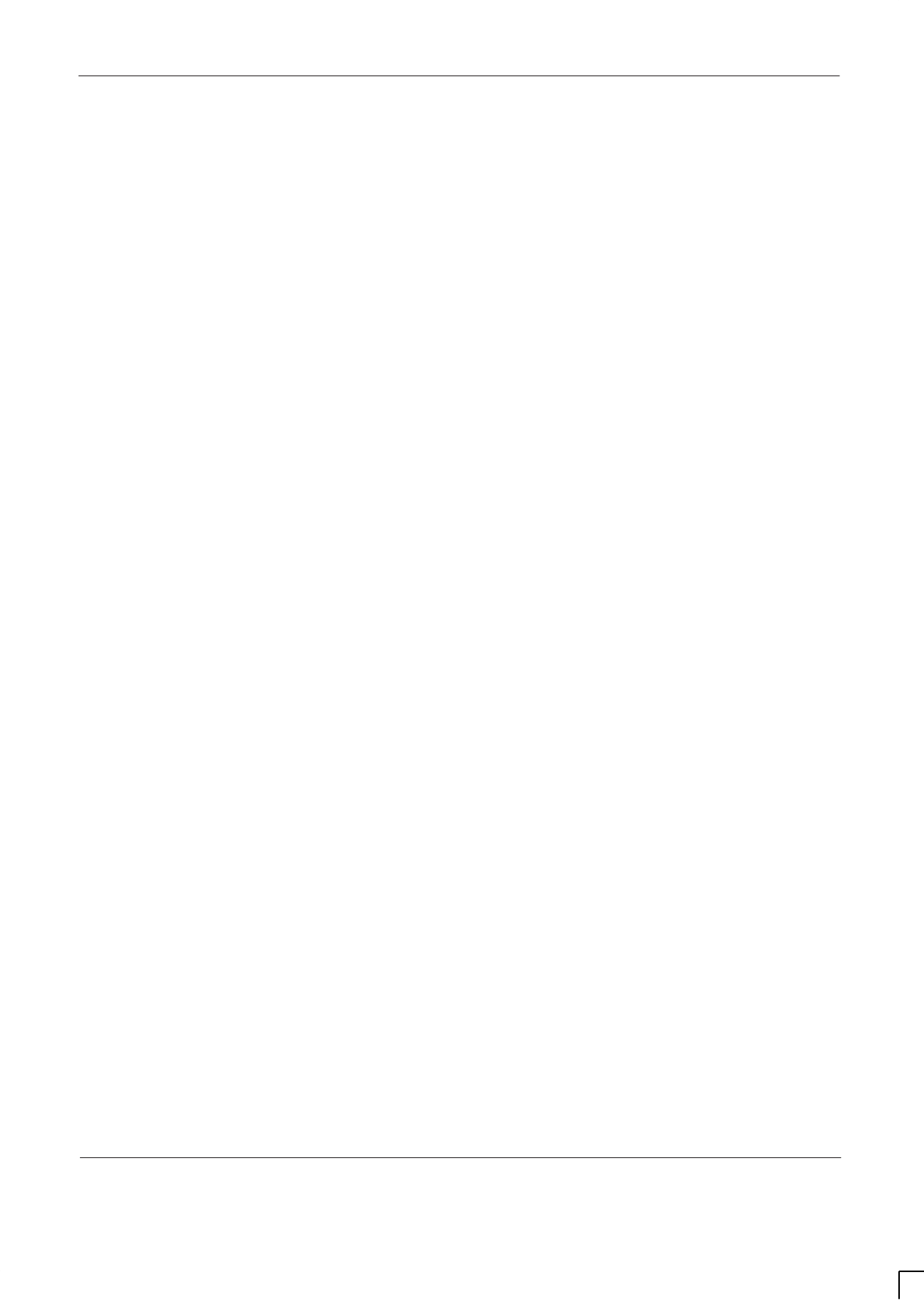
GSM-204-423
31st Oct 01
Installation & Configuration: Horizon
macro
outdoor
68P02902W03-A
CONTROLLED INTRODUCTION
iii
Chapter 6
Interoperability between different Motorola BTSs i. . . . . . . . . . . . . . . .
Introduction to interoperability Inst. 6–1. . . . . . . . . . . . . . . . . . . . . . . . . . . . . . . . . . . . . . . . .
Mixed product sites Inst. 6–1. . . . . . . . . . . . . . . . . . . . . . . . . . . . . . . . . . . . . . . . . . . . .
Architectural constraints Inst. 6–1. . . . . . . . . . . . . . . . . . . . . . . . . . . . . . . . . . . . . . . . .
BTS architectures and interoperability Inst. 6–2. . . . . . . . . . . . . . . . . . . . . . . . . . . . . . . . . .
M-Cell6 and Horizonmacro architectures Inst. 6–2. . . . . . . . . . . . . . . . . . . . . . . . . . .
Example mixed site Inst. 6–3. . . . . . . . . . . . . . . . . . . . . . . . . . . . . . . . . . . . . . . . . . . . .
Technical issues Inst. 6–4. . . . . . . . . . . . . . . . . . . . . . . . . . . . . . . . . . . . . . . . . . . . . . . .
Receive path Inst. 6–4. . . . . . . . . . . . . . . . . . . . . . . . . . . . . . . . . . . . . . . . . . . . . . . . . . .
Transmit path Inst. 6–7. . . . . . . . . . . . . . . . . . . . . . . . . . . . . . . . . . . . . . . . . . . . . . . . . .
M-Cell6 and Horizonmacro hardware equivalents Inst. 6–10. . . . . . . . . . . . . . . . . . .
Further configuration information Inst. 6–10. . . . . . . . . . . . . . . . . . . . . . . . . . . . . . . . . .
Example configurations Inst. 6–11. . . . . . . . . . . . . . . . . . . . . . . . . . . . . . . . . . . . . . . . . .
Special hardware Inst. 6–14. . . . . . . . . . . . . . . . . . . . . . . . . . . . . . . . . . . . . . . . . . . . . . .
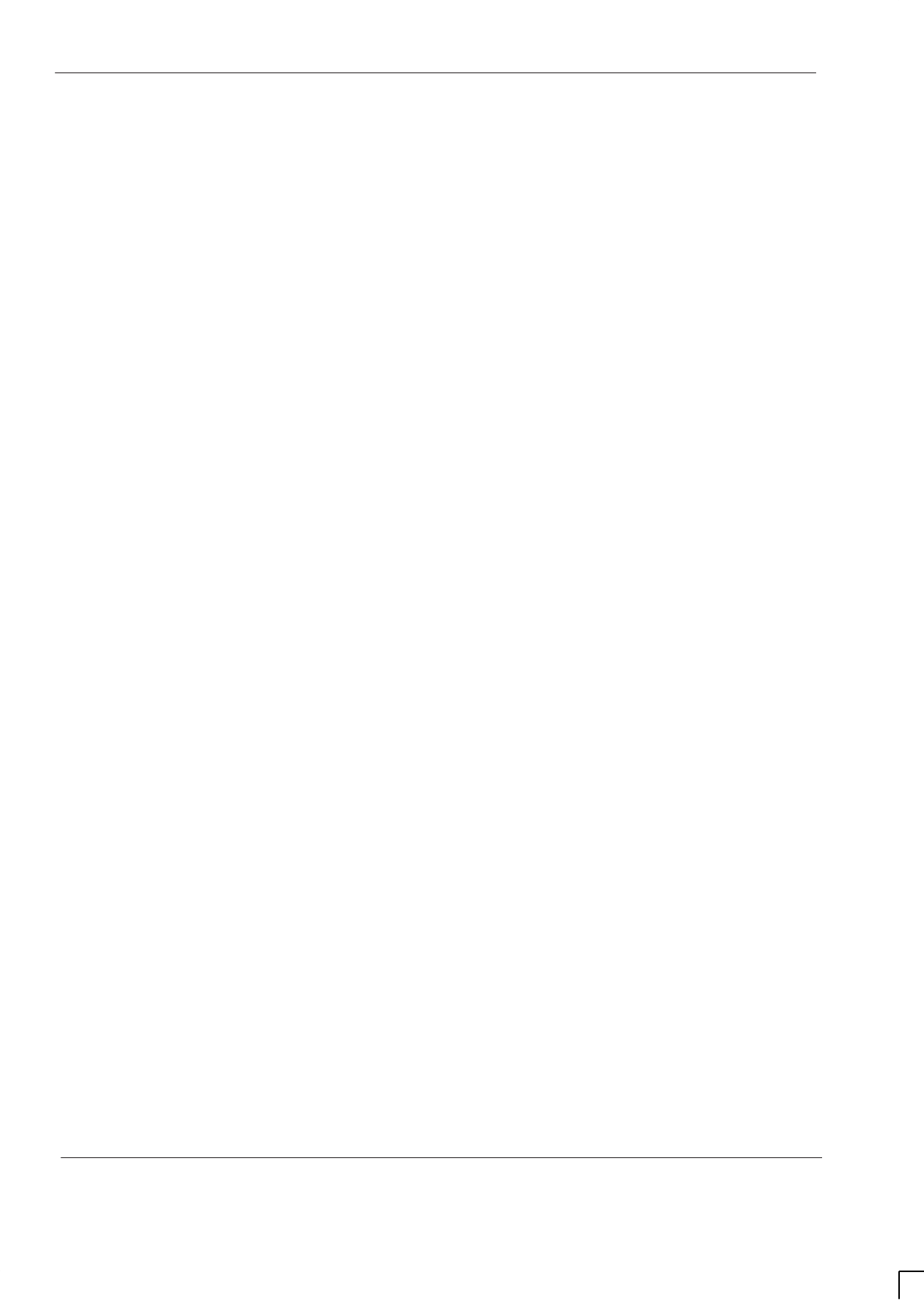
GSM-204-423
31st Oct 01
iv
Installation & Configuration: Horizon
macro
outdoor
CONTROLLED INTRODUCTION
68P02902W03-A
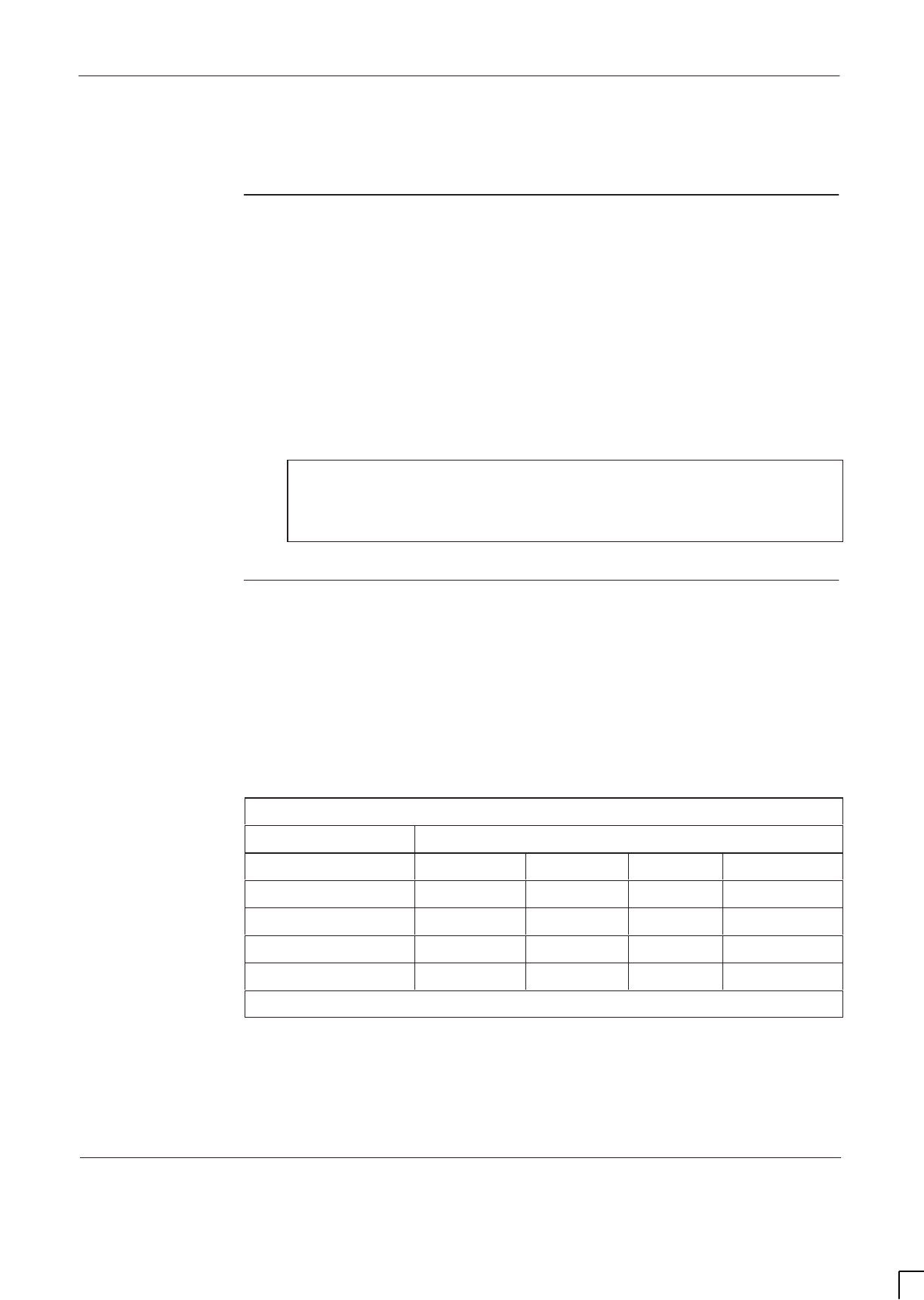
GSM-204-423 Introduction to interoperability
31st Oct 01
Installation & Configuration: Horizon
macro
outdoor
68P02902W03-A
CONTROLLED INTRODUCTION
Inst. 6–1
Introduction to interoperability
Mixed product
sites
This chapter describes how the Horizon
macro
6 carrier outdoor can be used in
conjunction with other Motorola BTS products.
Different Motorola product types can be collocated at the same physical site
without restriction, provided they are configured as logically separate
installations, and in accordance with the normal product engineering rules.
When mixed product types are installed at the same logical
site
,
a number of
technical issues arise that restrict the hardware that can be configured, and the
way it is interfaced. This chapter explains which product types can be mixed in
this way, and how they are interfaced.
NOTE This chapter only applies to the Horizon
macro
GSM/
EGSM900 and DCS1800 BTS variants.
GSM850 and PCS1900 Horizon
macro
BTS variants
cannot be mixed with other Motorola BTS types.
Architectural
constraints
To enable different product types to be used at the same logical site, one
product type is chosen as master
,
which is connected to the extender equipment
so that the two product types can function as a single, logical BTS. This
approach is viable when the product types to be interfaced have similar
architectures.
Motorola BTS product types that can be interfaced for collocation at a single
logical site are therefore restricted to those shown in Table 6-1 below.
Table 6-1 BTS compatibility for collocation at a single logical site
Master Extender
InCell M-Cell
2
M-Cell
6
Horizon
macro
InCell Discontinued No No No
M-Cell
2
No Yes* Yes* No
M-Cell
6
No No Yes* Yes
Horizon
macro
No No Yes* Yes
* Check for availability before ordering
Indoor and outdoor cabinets can be mixed, but different mechanical
arrangements may be required for routeing the inter-cabinet cabling.
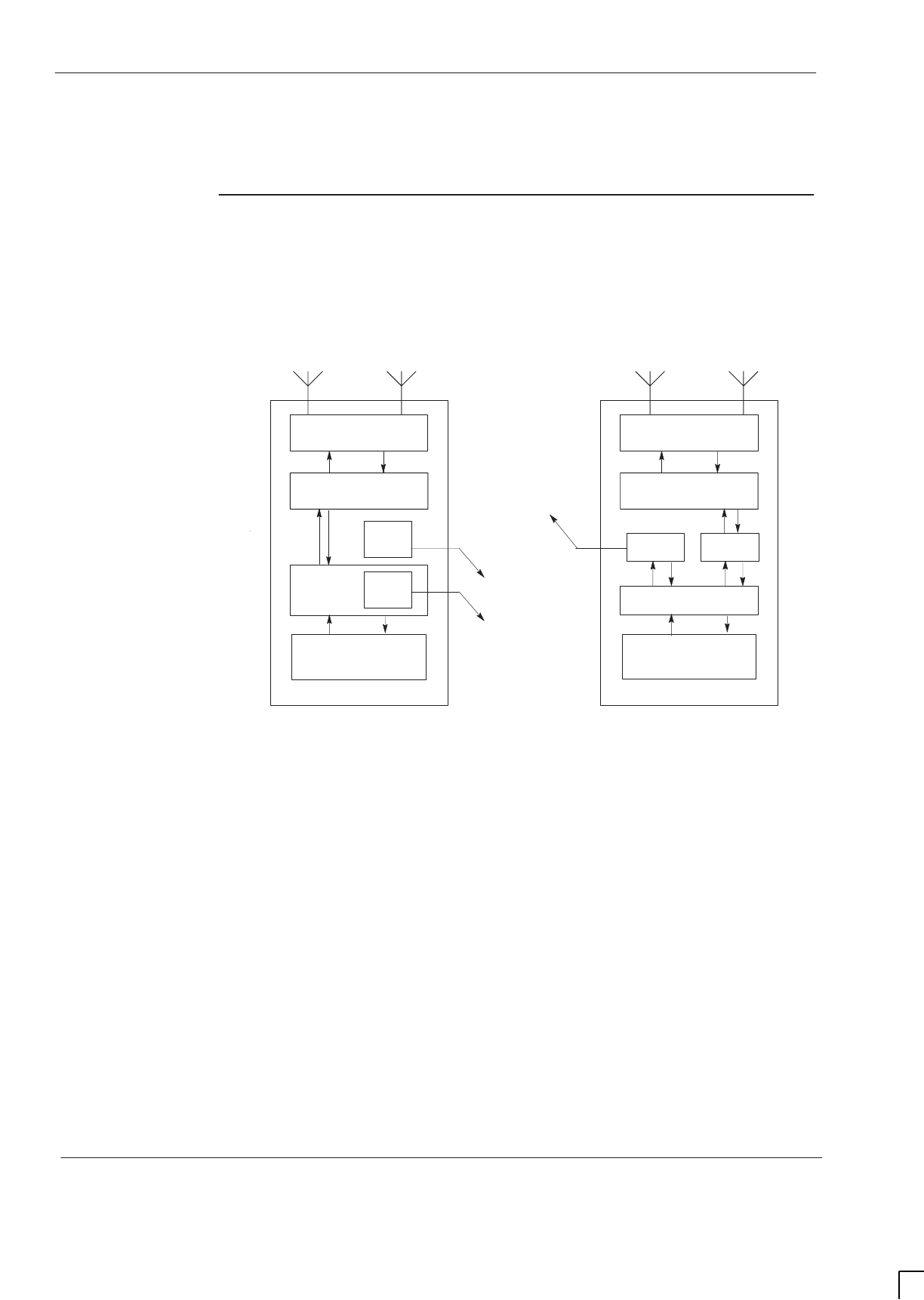
GSM-204-423
BTS architectures and interoperability
31st Oct 01
Inst. 6–2
Installation & Configuration: Horizon
macro
outdoor
CONTROLLED INTRODUCTION
68P02902W03-A
BTS architectures and interoperability
M-Cell
6
and
Horizon
macro
architectures
Figure 6-1 represents the high level architecture of the M-Cell
6
and
Horizon
macro
BTSs. Both systems provide an optical interface for connection to
remote transceivers, which in a normal installation would be used to connect to
transceivers of the same product type.
CTU
RF coupling
MCUF FMUX
Network termination
functions
FMUX
Horizon
macro
M-Cell
6
Fibre optic links
to remote radios
TCU
RF coupling
MCU
FMUX
Network termination
functions
FOX
Figure 6-1 High level architecture of M-Cell
6
and Horizon
macro
BTSs
However, since the optical interface is identical for both products, it can be used
to link an M-Cell
6
to Horizon
macro
transceivers, or a Horizon
macro
to M-Cell
6
transceivers. The principle is shown in Figure 6-2.
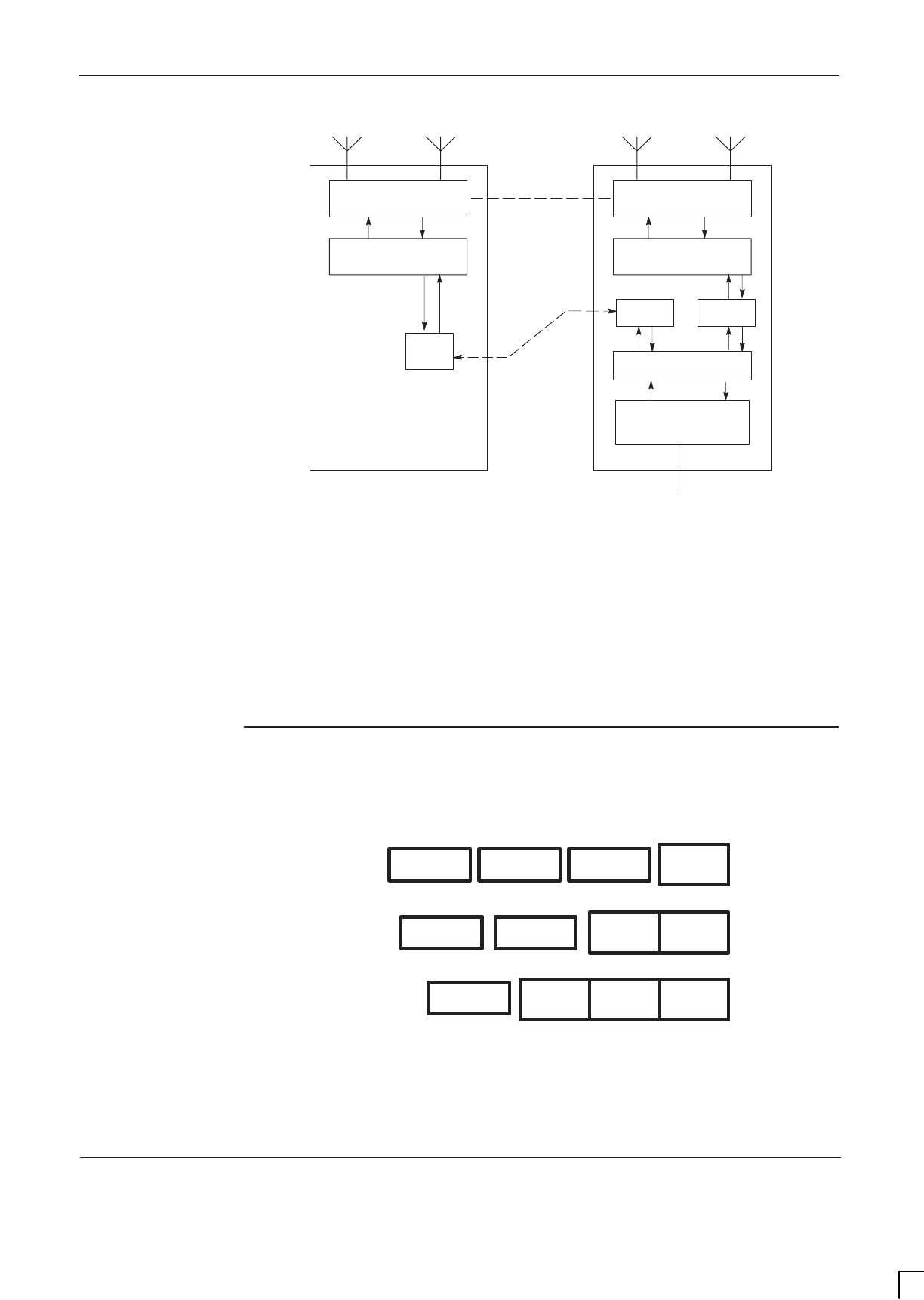
GSM-204-423 BTS architectures and interoperability
31st Oct 01
Installation & Configuration: Horizon
macro
outdoor
68P02902W03-A
CONTROLLED INTRODUCTION
Inst. 6–3
CTU
Horizon
macro
(Extender)
RF coupling
FMUX
Fibre optic link
TCU
RF coupling
MCU
FMUX
Network termination
functions
Cross connections
(see text)
Abis Interface
FOX
M-Cell
6
(Master)
Figure 6-2 Example of interfacing different products at a single logical site
When two product types are interfaced in this way, the control function for the
entire BTS is implemented by the master product. In Figure 6-2, this is the
M-Cell
6
. In practice, either BTS can be configured as master according to the
needs of the network concerned.
Example mixed
site
A multi-cabinet mixed site can typically be achieved in several ways. Figure 6-3
shows the alternatives layouts for a four cabinet mixed BTS site.
M-Cell
6
M-Cell
6
M-Cell
6
M-Cell
6
M-Cell
6
M-Cell
6
Layout1
Layout3
Layout2 Horizon
macro
Horizon
macro
Horizon
macro
Horizon
macro
Horizon
macro
Horizon
macro
Figure 6-3 Example of alternative layouts for a 4-cabinet mixed BTS site
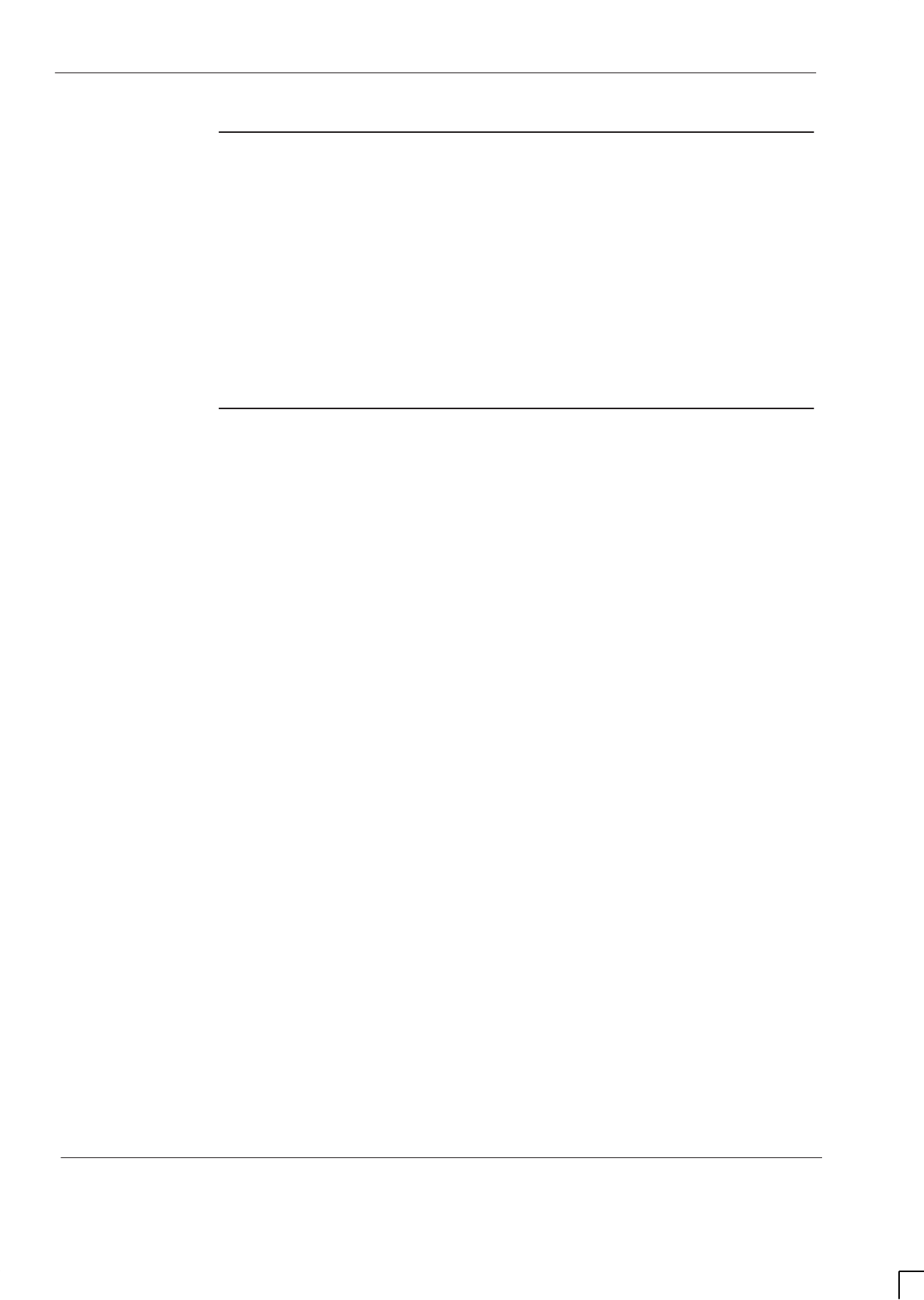
GSM-204-423
BTS architectures and interoperability
31st Oct 01
Inst. 6–4
Installation & Configuration: Horizon
macro
outdoor
CONTROLLED INTRODUCTION
68P02902W03-A
Technical
issues
When mixing different BTS types, the interface may be required to resolve
some or all of the following issues, depending on the site configuration:
The interface must deliver both Rx and Rxdiv (receive diversity) signals to
each transceiver.
The interface must not change the uplink (receive) signal level delivered to
any transceiver.
The interface must ensure that in the mixed BTS configuration, RF
combiners remain correctly loaded.
Receive path
When a cell is wholly configured within one cabinet, there is no requirement to
connect the uplink or downlink RF signals between the master and extender
cabinets. The only interface between the cabinets in this type of mixed BTS
configuration is therefore at digital level, between FMUXs via the fibre optic link.
When a cell is split between two cabinets, the uplink signals must be connected
between the cabinets since both Rx and Rxdiv signals are required at each
transceiver. In this situation the downlink signal may or may not require
connection between cabinets, depending on the site configuration. The uplink
connectivity requirements are shown in Figure 6-4 (DCS1800) and Figure 6-5
(GSM900).
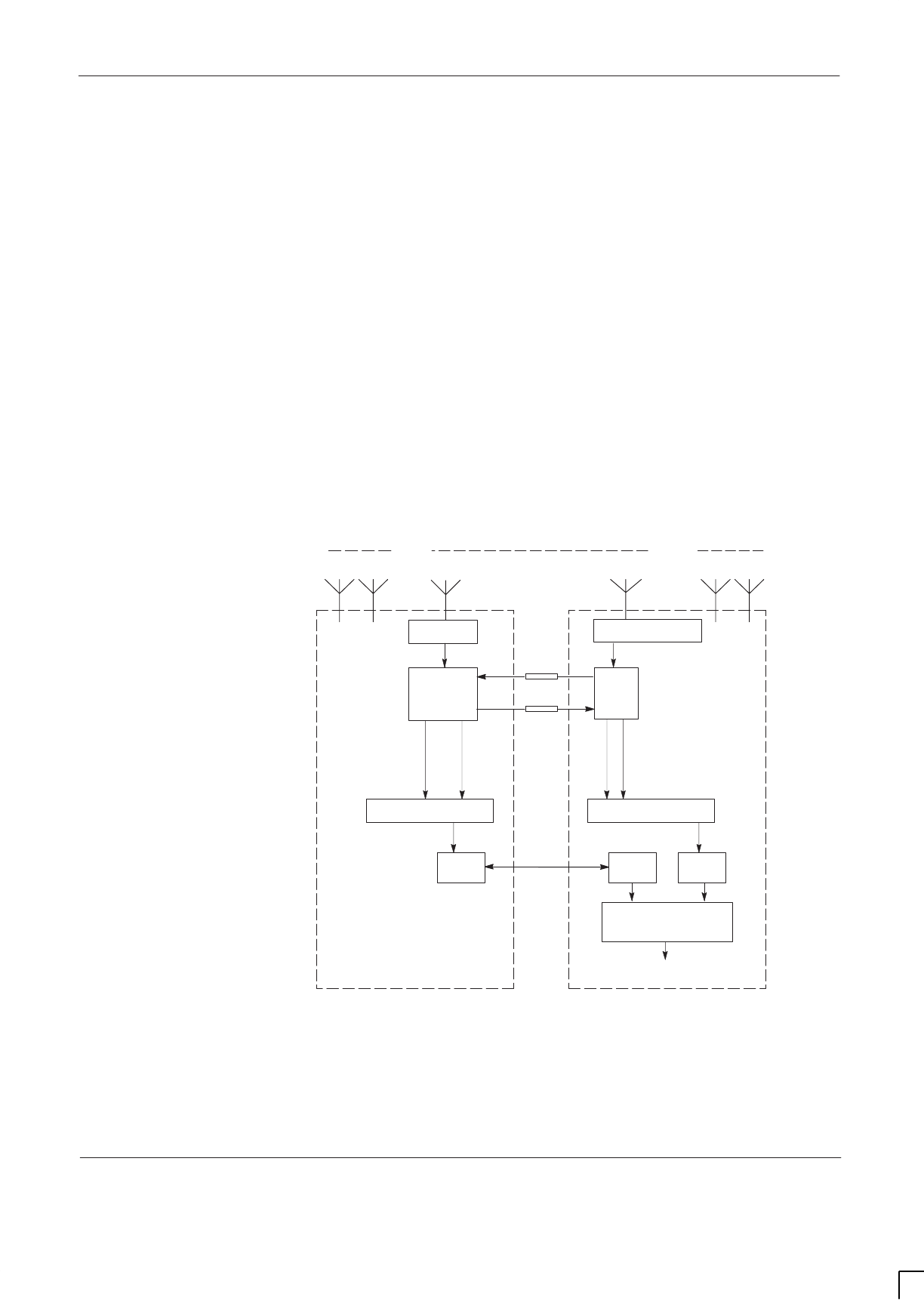
GSM-204-423 BTS architectures and interoperability
31st Oct 01
Installation & Configuration: Horizon
macro
outdoor
68P02902W03-A
CONTROLLED INTRODUCTION
Inst. 6–5
DCS1800
Refer to Figure 6-4. In the Horizon
macro
cabinet, low noise amplification in the
SURF module first boosts the Rx signal by +13 dB. Separate Rx outputs from
the SURF are then discretely routed to relevant transceivers in the master
cabinet, and to the LNA in the extender cabinet. Since the LNA boosts the Rx
signal by a further +13 dB, a 13 dB attenuator is placed in the signal path to
offset this additional signal gain, which would otherwise result in signal levels
outside the permitted range for the transceivers.
The Rxdiv signal is similarly given a +13 dB boost by the LNA in the extender
cabinet. Separate Rxdiv outputs from the LNA are then discretely routed to
relevant receivers in the extender cabinet, and to the SURF module in the
master cabinet. Since the SURF provides a further +13 dB boost, a 13 dB
attenuator is again placed in the signal path to offset this additional gain.
In this way, the arrangement shown in Figure 6-4 delivers Rx and Rxdiv signals
to the uplink path in both cabinets, at the required signal level.
To NIU and Abis
Interface
Rx
Rxdiv
M-Cell
6
(Master)
CTU
Cell A Cell B Cell C
Rxdiv
Rx Rx Rxdiv
Duplexer
SURF +13 dB
–13 dB
+13 dB
Rxdiv
Rx
LNA
Rx Rxdiv
–13 dB
TCU
Horizon
macro
(Extender)
Rxdiv
Rx
FMUX
MCU
FMUX
Fibre
optic
link
Duplexer
FOX
Figure 6-4 Functional overview of the receive path for a DCS1800 split cell
configuration
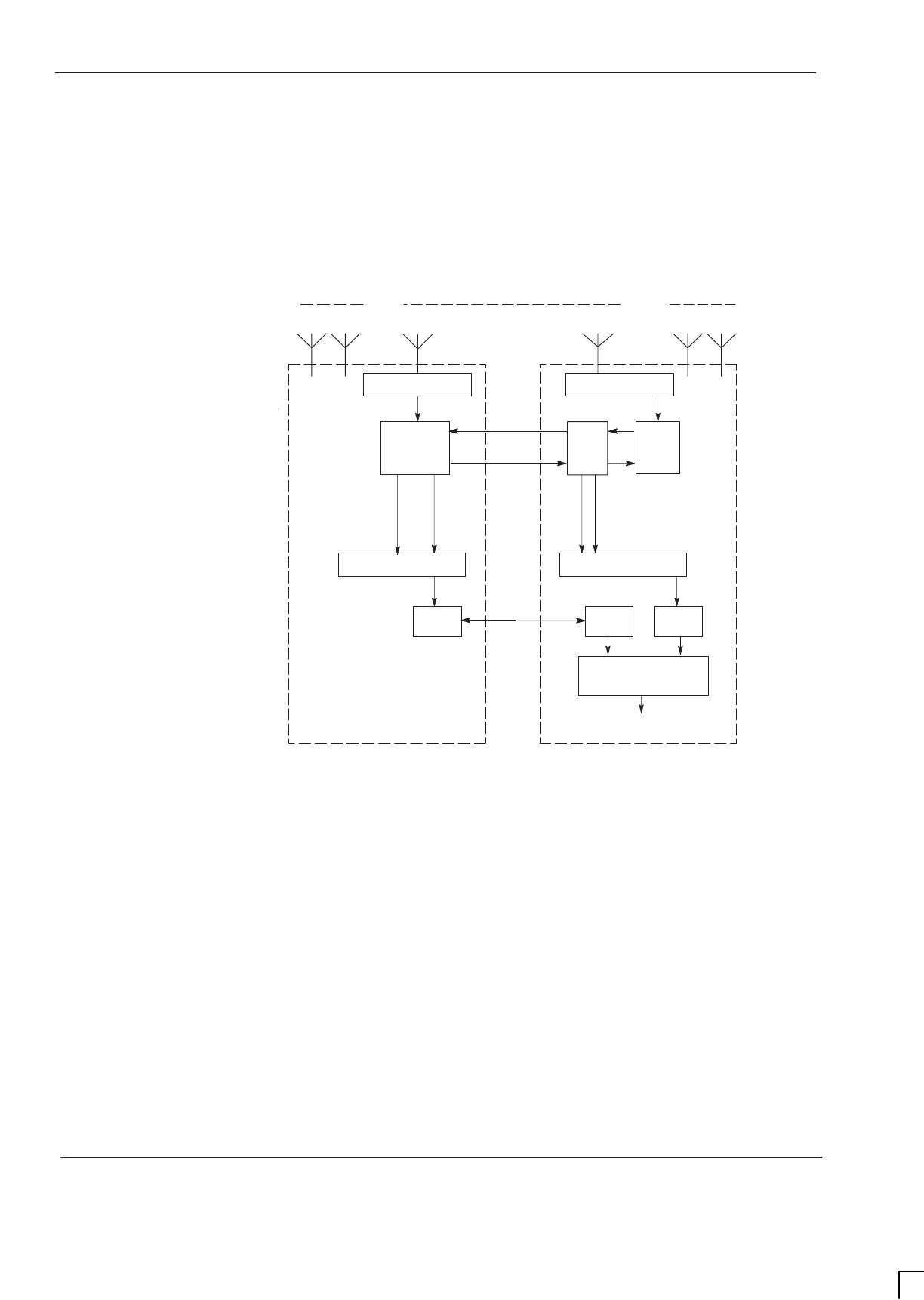
GSM-204-423
BTS architectures and interoperability
31st Oct 01
Inst. 6–6
Installation & Configuration: Horizon
macro
outdoor
CONTROLLED INTRODUCTION
68P02902W03-A
GSM900
Refer to Figure 6-5. In GSM900 products, RF gain for the IADU and SURF is
configurable. A split cell configuration is therefore dealt with in the same way as
that described for DCS1800, except that the 13 dB attennuators are not
required. Instead, the required signal level is maintained by using appropriate
gain settings for the IADU and SURF.
CTU
Cell A Cell B Cell C
Rxdiv
Rx Rx Rxdiv
Duplexer
IADU
*
SURF
*
Rxdiv
Rx
DLNB
Rx Rxdiv
TCU
Rx
Rxdiv
Rxdiv
Rx
* Configurable gain
Duplexer
To NIU and Abis
Interface
M-Cell
6
(Master)Horizon
macro
(Extender)
FMUX
MCU
FMUX
Fibre
optic
link
FOX
Figure 6-5 Functional overview of the receive path for a GSM900 split cell
configuration
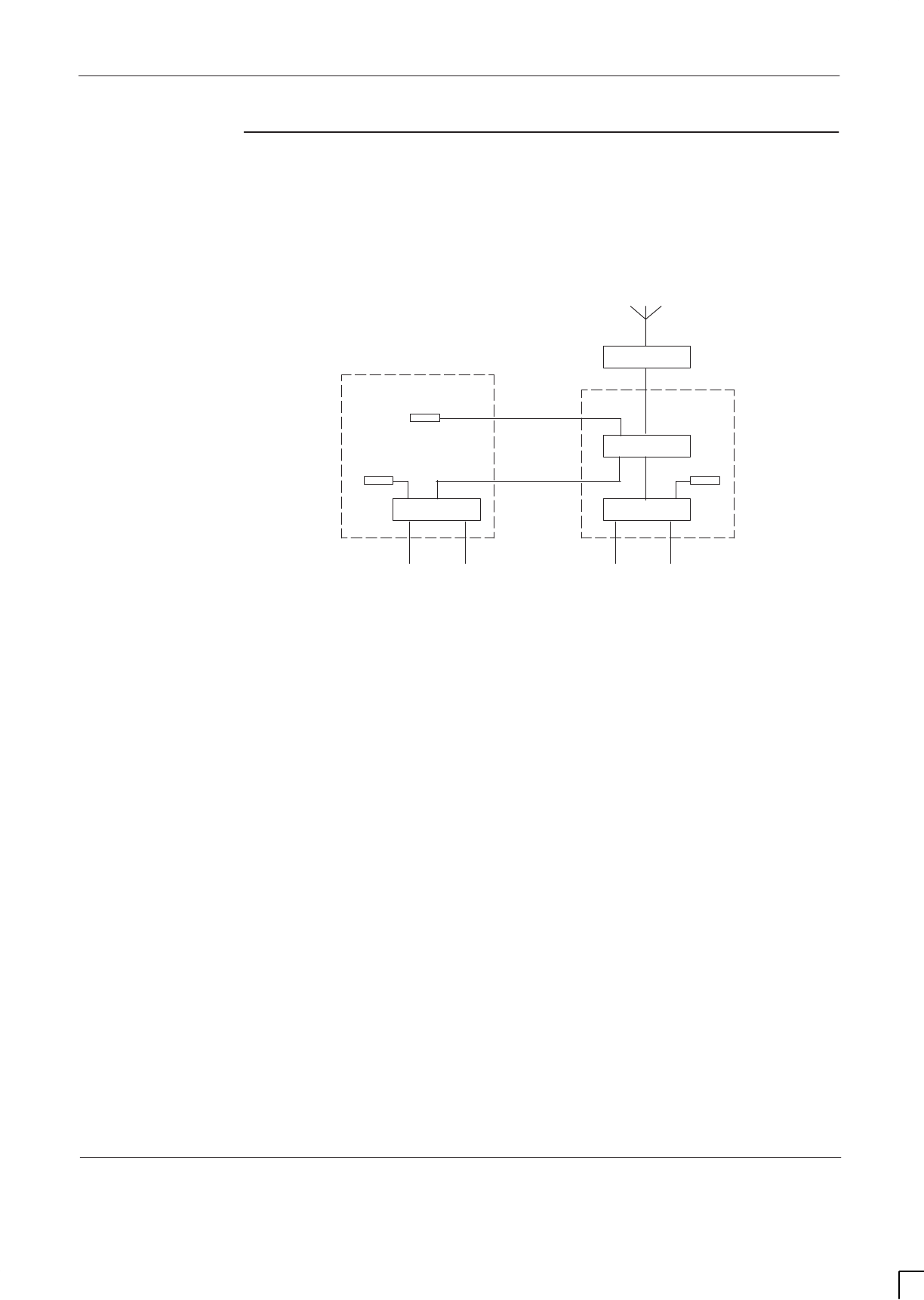
GSM-204-423 BTS architectures and interoperability
31st Oct 01
Installation & Configuration: Horizon
macro
outdoor
68P02902W03-A
CONTROLLED INTRODUCTION
Inst. 6–7
Transmit path
M-Cell
6
combining
When configuring the downlink paths for a cell using three carriers or more, it
may be necessary to provide additional external RF load(s) for the combiners.
This is illustrated by Figure 6-6, which shows a typical M-Cell
6
combining
arrangement for a 4-carrier cell.
Hybrid
HybridHybrid
Duplexer
Load
Load
3IP CBF
HCOMB
External
load
One carrier from each of four transceivers
Carrier 1 Carrier 2 Carrier 3 Carrier 4
Figure 6-6 Typical M-Cell
6
arrangement for combining four carriers
Carriers 1 and 2 are combined in a hybrid combiner (HCOMB) module. The
output from this module provides one of the three inputs to the 3IP CBF. The
HCOMB is equipped with an internal RF load, and is therefore self–contained.
The 3IP CBF requires one RF load for each of the two hybrids it contains, but is
equipped with only a single internal RF load. An additional load is therefore
provided for this purpose on the HCOMB casing.
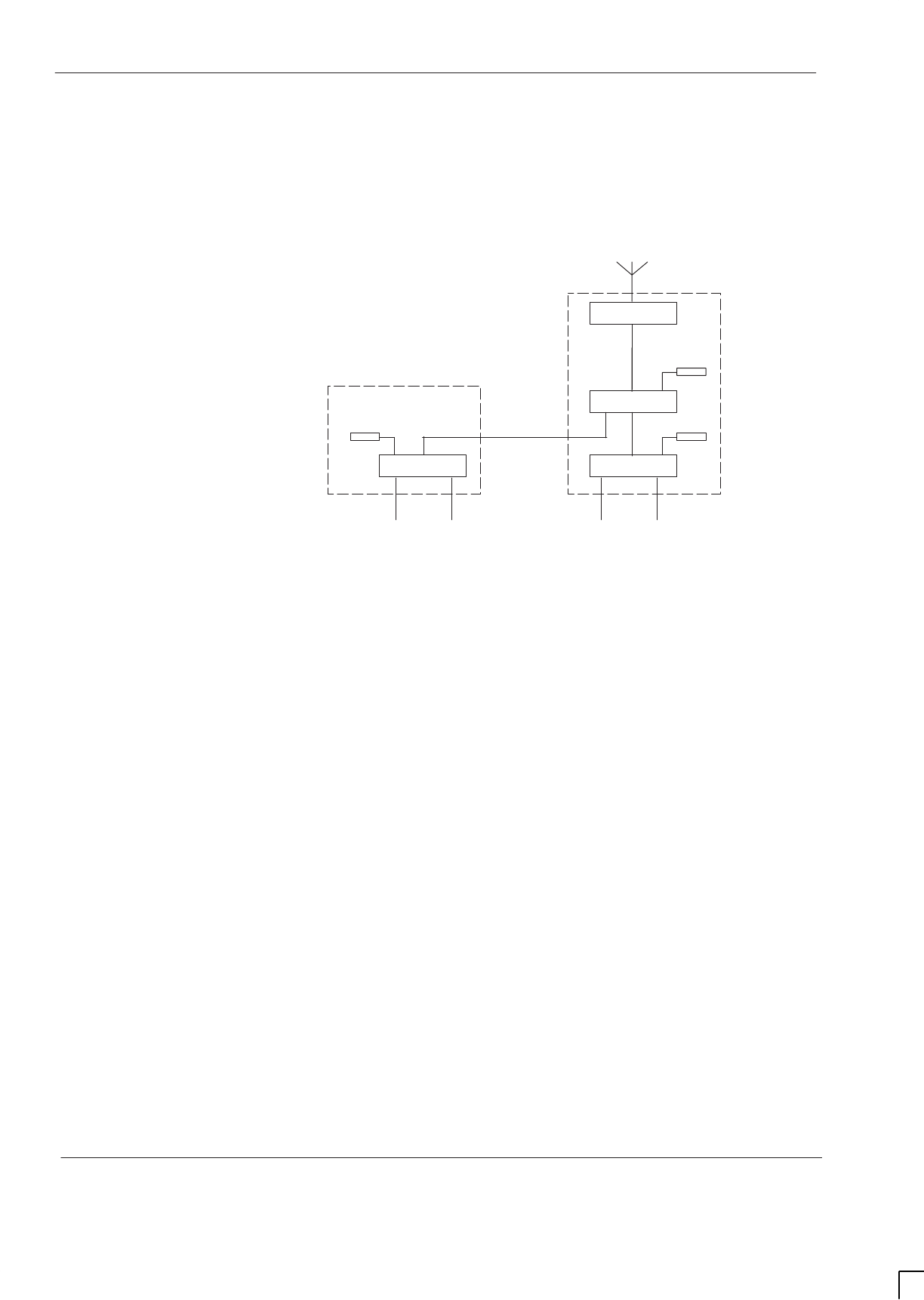
GSM-204-423
BTS architectures and interoperability
31st Oct 01
Inst. 6–8
Installation & Configuration: Horizon
macro
outdoor
CONTROLLED INTRODUCTION
68P02902W03-A
Horizon
macro
combining
A similar arrangement is used in the Horizon
macro
, which uses a Hybrid
Combiner Unit (HCU) and Dual stage Duplexed combining Filter (DDF), as
shown in Figure 6-7. The DDF has three input ports together with two internal
RF loads, and therefore does not require the addition of any external load.
Hybrid
HybridHybrid
Duplexer
Load
Load
DDF
HCU
One carrier from each of four transceivers
Carrier 1 Carrier 2 Carrier 3 Carrier 4
Load
Figure 6-7 Typical Horizon
macro
arrangement for combining four carriers
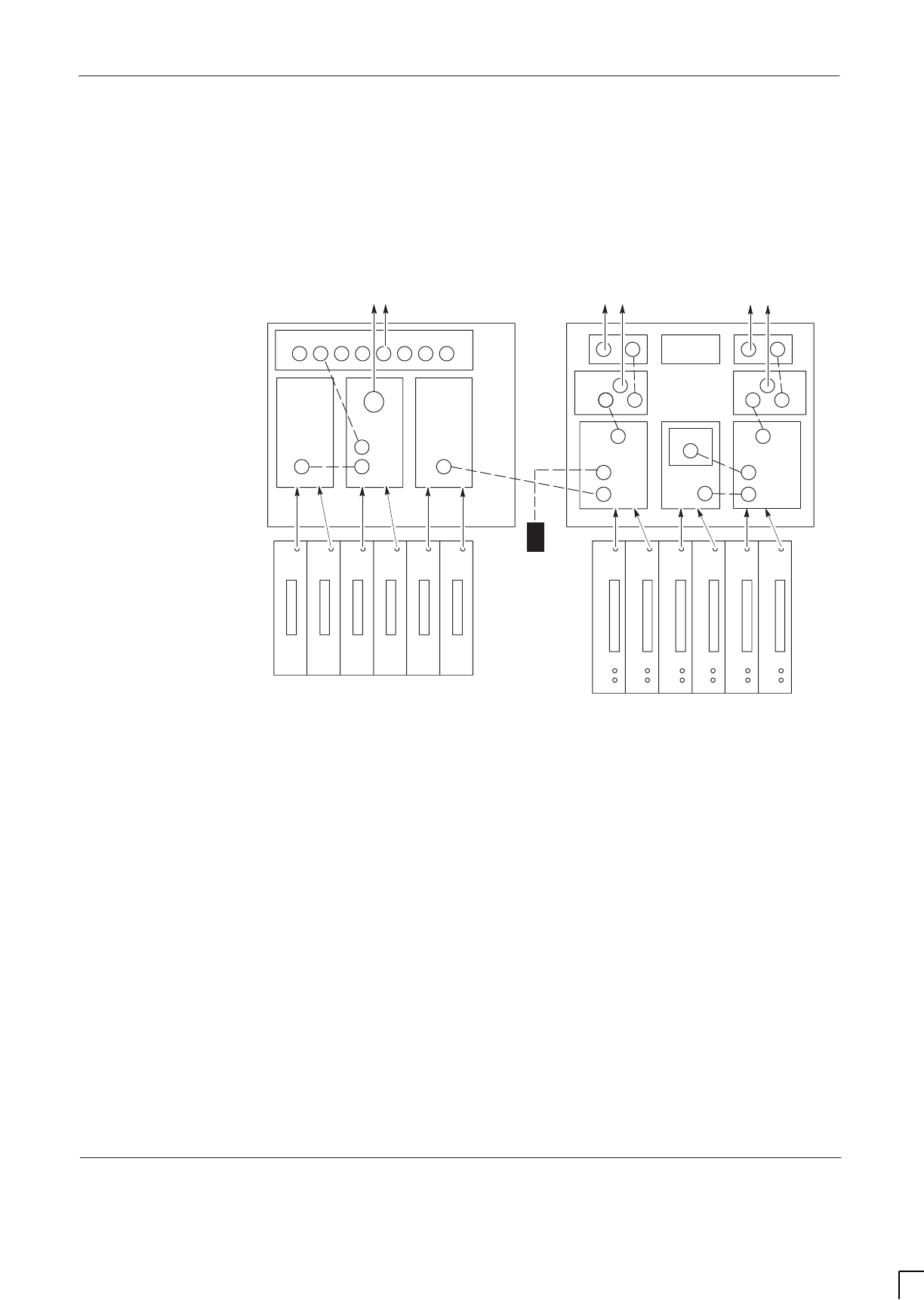
GSM-204-423 BTS architectures and interoperability
31st Oct 01
Installation & Configuration: Horizon
macro
outdoor
68P02902W03-A
CONTROLLED INTRODUCTION
Inst. 6–9
Mixed equipment combining
When the two different product types are interfaced, a situation can arise where
a 3IP CBF is connected to an HCU, as shown in Figure 6-8. In this configuration
it is therefore necessary to provide an additional external RF load for this 3IP
CBF. The example in Figure 6-8 shows downlink connections for a 4/4/4
configuration using mixed BTS types.
3IP CBF 2
Load
Load
HCOMB
HCU 2 DDF HCU 1
543 21011109876
2B 1B 0B 2A 1A 0A B A
Sector3 Sector2 Sector1
M-Cell
6
Horizon
macro
3IP CBF 1
Figure 6-8 Downlink configuration for a 4/4/4 mixed cabinet installation.
Inputs for the DDF are carriers 8 and 9, together with the output of HCU2. The
DDF contains two RF loads and is therefore self-contained. Inputs to 3IP CBF1
are carriers 0 and 1, together with the combined output of HCOMB. 3IP CBF1
contains a single load and is therefore connected to the external load mounted
on HCOMB. Inputs for 3IP CBF2 are carriers 4 and 5, together with the output
of HCU1, from the master cabinet. 3IP CBF2 contains a single load and
therefore requires the addition of an external 50 ohm load, as shown.
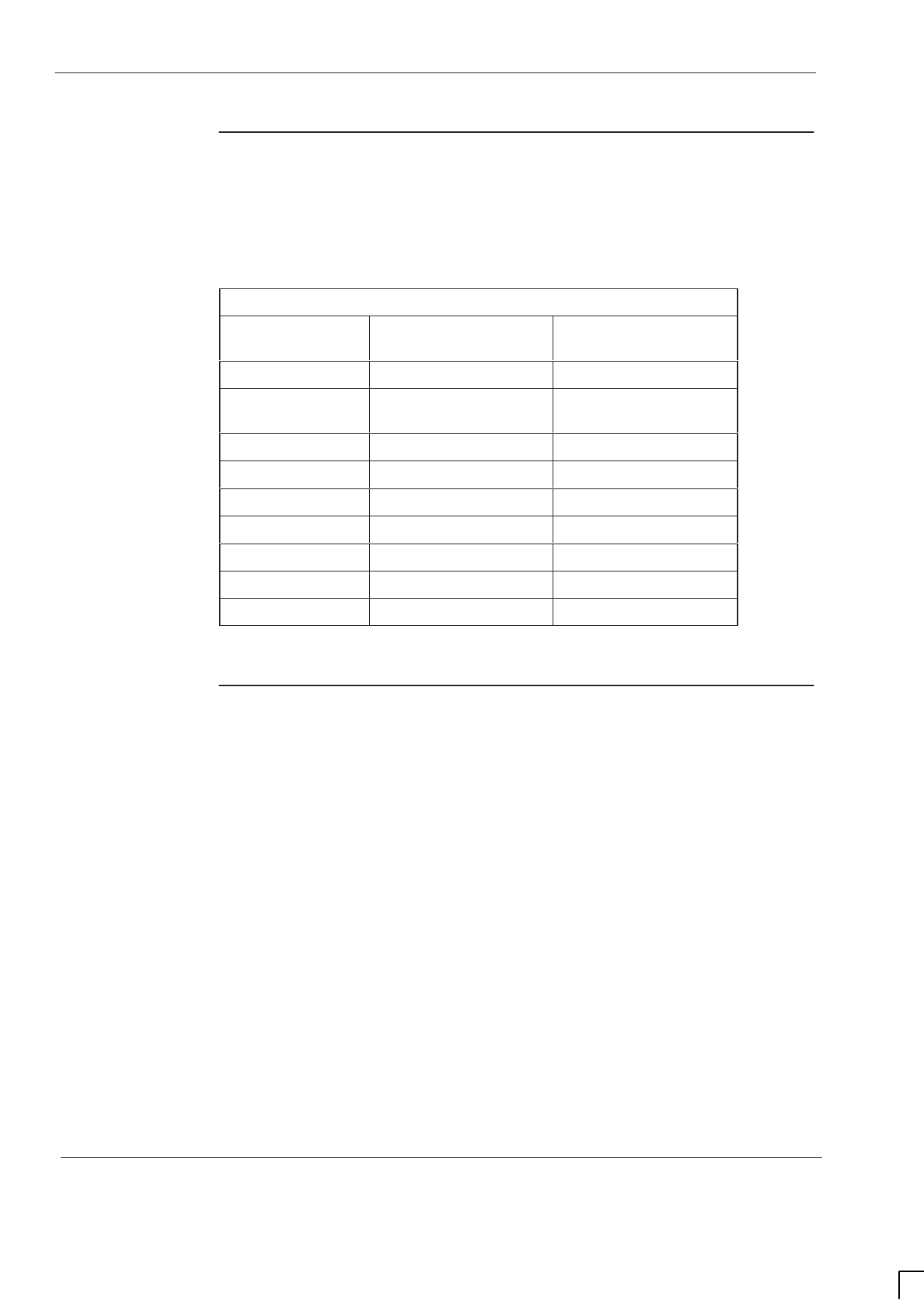
GSM-204-423
BTS architectures and interoperability
31st Oct 01
Inst. 6–10
Installation & Configuration: Horizon
macro
outdoor
CONTROLLED INTRODUCTION
68P02902W03-A
M-Cell
6
and
Horizon
macro
hardware
equivalents
Table 6-2 shows the RF hardware equivalents for the Horizon
macro
and M-Cell
6
BTSs.
Table 6-2 RF hardware equivalents for Horizon
macro
/M-Cell
6
Horizon
macro
900/1800 M-Cell 900 M-Cell 1800
DCF CBF + duplexer Hybrid + duplexer
DDF 3- input CBF* +
duplexer 2 x hybrid + dup/BPF
HCU Hybrid Hybrid
Feedthrough plate Non-hybrid (no equivalent)
TDF TBF + duplexer 2 x dup/BPF
CCB master CCB master CCB master
CCB extender CCB extender CCB extender
SURF 3 x DLNB + IADU 3 x LNA
Split Sector Cable Rx Extender (no equivalent)
* 3-input CBF contains only one internal 50 ohm load.
Further
configuration
information
Provided the functional guidelines described in this chapter are followed, the
steps involved in upgrading an existing site with mixed equipment are
essentially the same as with a conventional upgrade:
Determine the number of additional carriers required in the upgraded site.
Based on the required site configuration (for example, 4/4/4), use the
functional guidelines provided in this chapter to decide the most effective
hardware configuration for the additional cabinet(s).
Special upgrade kits are available for specified configurations.
Configuration diagrams and product ordering help are available from the
Motorola local office.
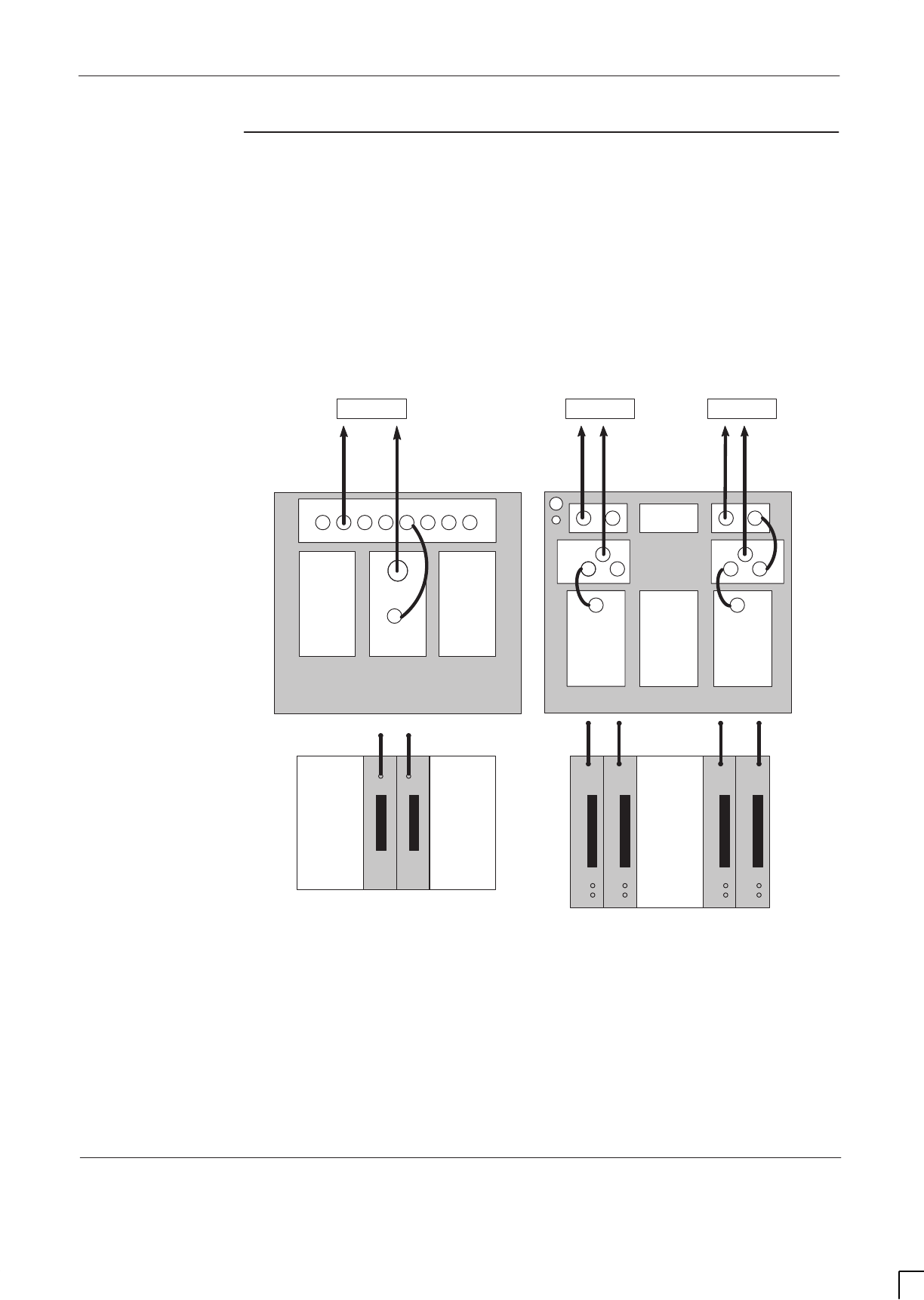
GSM-204-423 BTS architectures and interoperability
31st Oct 01
Installation & Configuration: Horizon
macro
outdoor
68P02902W03-A
CONTROLLED INTRODUCTION
Inst. 6–11
Example
configurations
Configuration diagrams provided by the Motorola local office show top of rack
cable and antenna connections for mixed product configurations, together with
details of external RF loads required. Figure 6-9, Figure 6-10 and Figure 6-11
are examples of the type of diagram that can be provided.
GSM900 2/2/2 configuration using two cabinets
In this configuration, there are no split cells, and therefore no uplink/downlink
connections between the cabinets. The CBFs are 2-input devices, consequently
no external RF loads are required.
Sector 2
2B 1B 0B 2A 1A 0A B A
BLANK BLANKDCF CBF BLANK CBF
EXT
Sector 3 Sector 1
Horizon
macro
M-Cell
6
Figure 6-9 GSM900 mixed Horizon
macro
/ M-Cell
6
2/2/2 configuration using
two cabinets
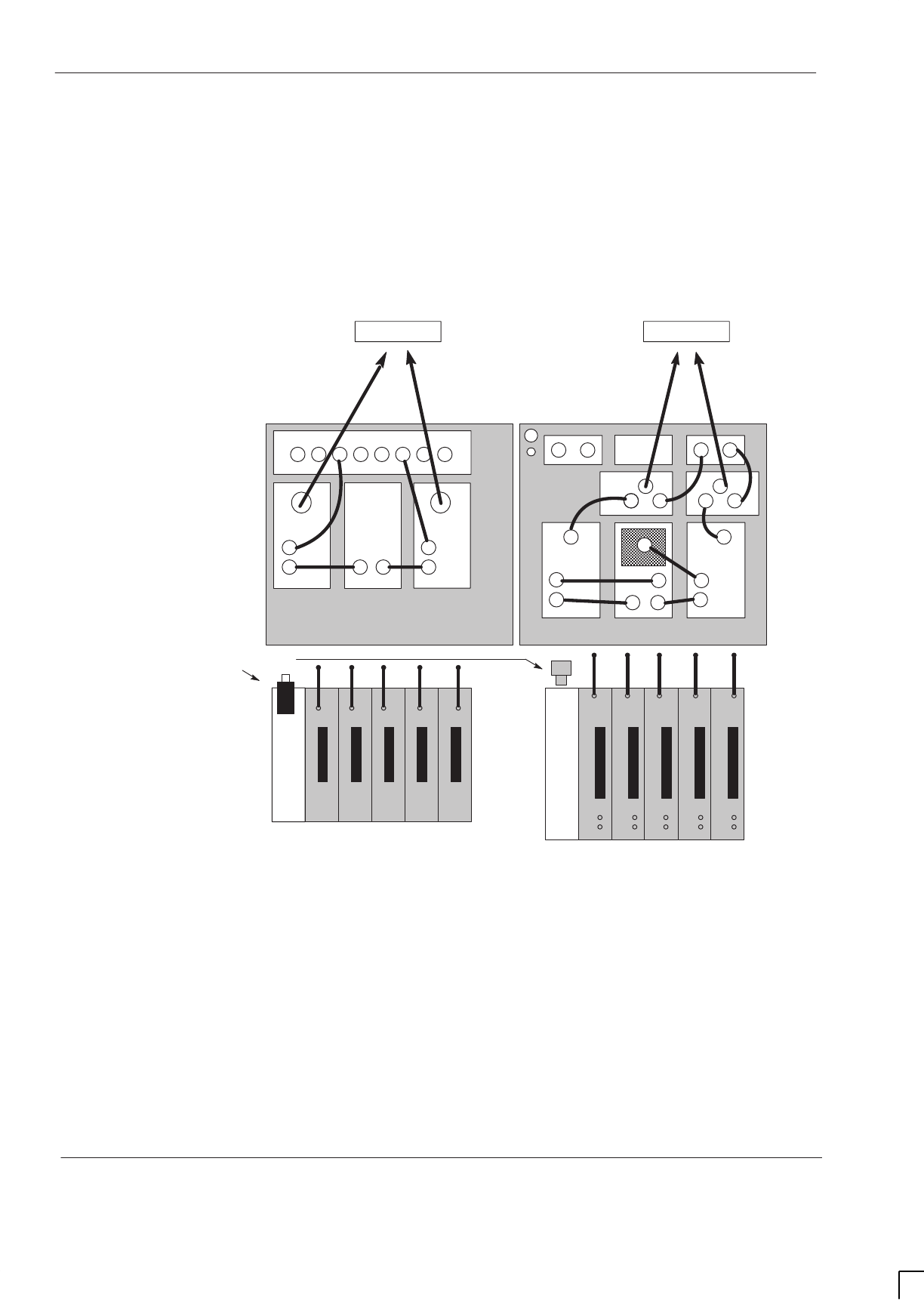
GSM-204-423
BTS architectures and interoperability
31st Oct 01
Inst. 6–12
Installation & Configuration: Horizon
macro
outdoor
CONTROLLED INTRODUCTION
68P02902W03-A
GSM900 5/5 configuration using two cabinets
In this configuration, there are no split cells, and therefore no uplink or downlink
connections between the cabinets. In the M-Cell
6
cabinet, both 3IP CBFs are
configured with external loads provided by the NON HYB. In the Horizon
macro,
one DDF has two direct RF inputs, plus a third input via the FEEDTHRU. The
second DDF has two RF inputs, one direct and one via the FEEDTHRU. This
arrangement facilitates using the transceivers in sequence. The two 50 ohm
loads are required to terminate the unused DDF/3IP CBF input ports.
2B 1B 0B 2A 1A 0A B A
DDF2 DDF1FEEDTHRU 3IP CBF2 NON-HYB 3IP CBF1
EXT
50 ohm loads
Sector 1Sector 2
Horizon
macro
M-Cell
6
Figure 6-10 GSM900 mixed Horizon
macro
/ M-Cell
6
5/5 configuration using
two cabinets
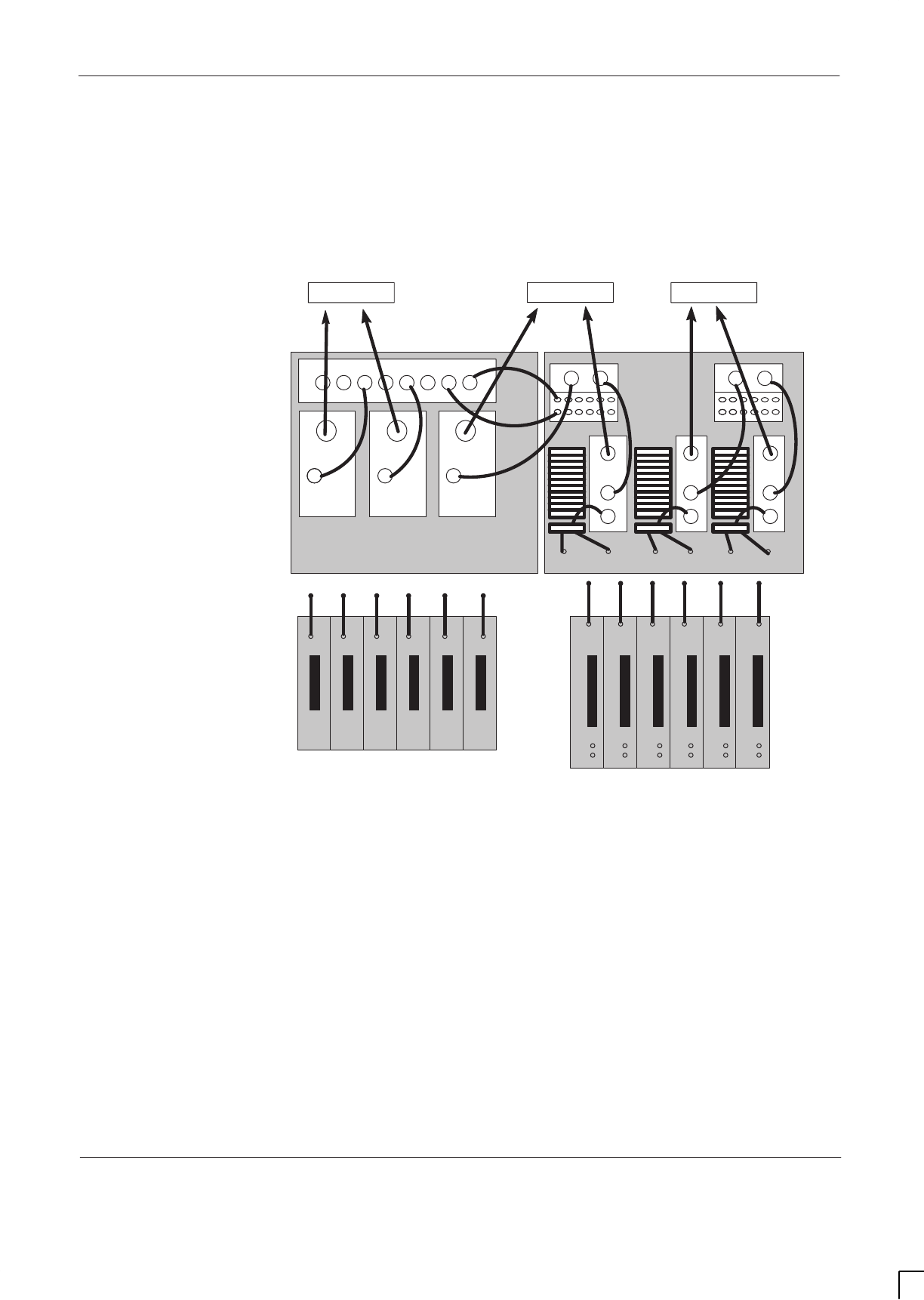
GSM-204-423 BTS architectures and interoperability
31st Oct 01
Installation & Configuration: Horizon
macro
outdoor
68P02902W03-A
CONTROLLED INTRODUCTION
Inst. 6–13
DCS1800 4/4/4 configuration using two cabinets
In this configuration, sector 2 is split between the cabinets. The uplink Rx and
Rxdiv signals for sector 2 are therefore connected between the BTS types to
ensure the availability of both signals in both cabinets. In the M-Cell
6
cabinet,
2-input hybrids are used for combining, each configured with a discrete external
load.
2B 1B 0B 2A 1A 0A B A
DCF HYB
EXT
DCF DCF DUP DUP DUPHYB HYB
Sector 2Sector 3 Sector 1
Horizon
macro
M-Cell
6
Figure 6-11 DCS1800 Mixed Horizon
macro
/ M-Cell
6
4/4/4 configuration using
two cabinets
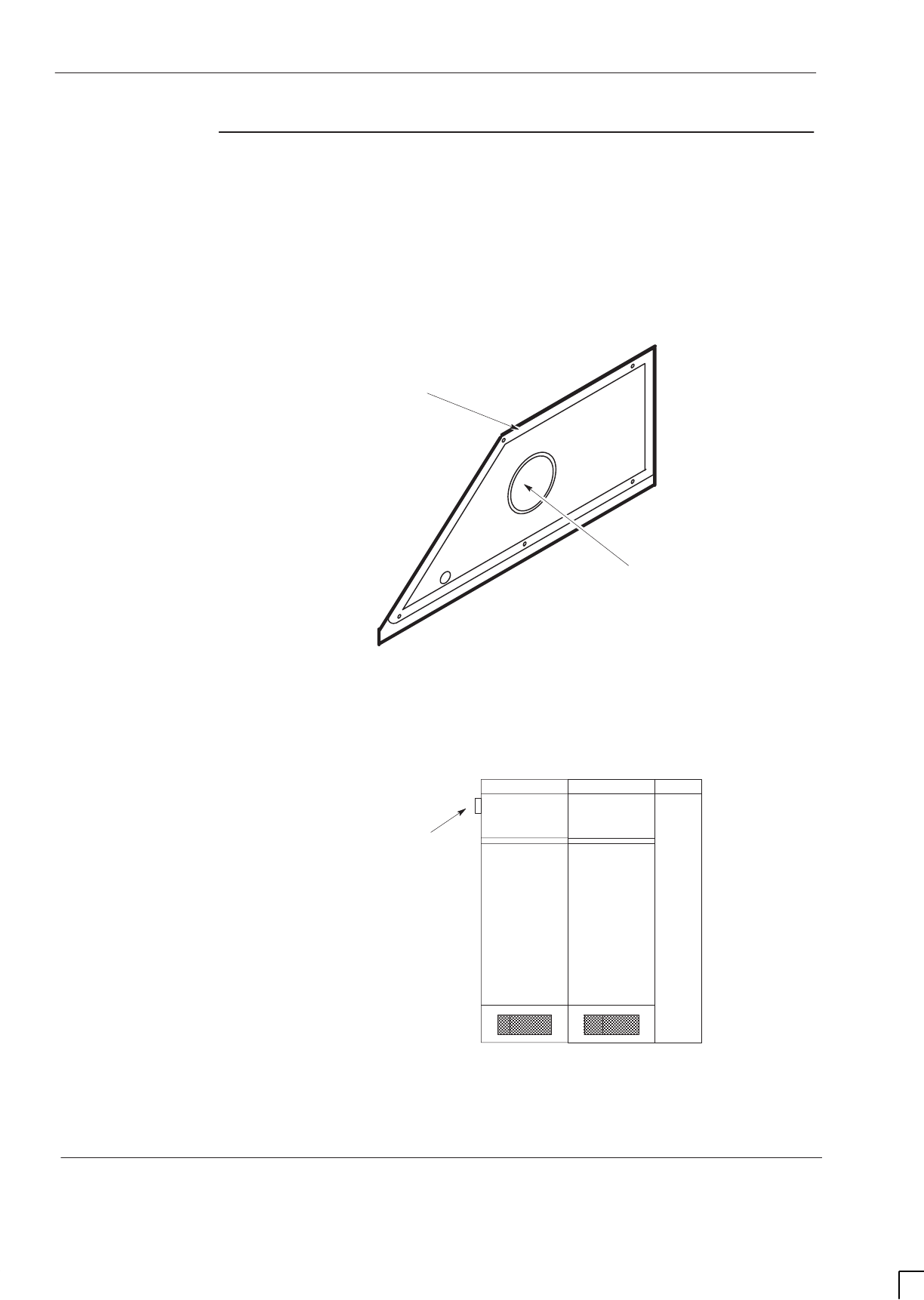
GSM-204-423
BTS architectures and interoperability
31st Oct 01
Inst. 6–14
Installation & Configuration: Horizon
macro
outdoor
CONTROLLED INTRODUCTION
68P02902W03-A
Special
hardware
A range of cables is available for uplink, downlink and fibre optic connections,
together with the uplink attennuators described earlier. Contact the Motorola
local office for further details.
In addition, the mounting plate and snap-in multi cable gland shown in
Figure 6-12 are required when expanding M-Cell
6
outdoor sites with
Horizonmacro cabinets. In this type of configuration, the Horizon
macro
equipment is located to the left of the M-Cell
6
cabinets.
CABLE GLAND ENTRY PORT ACCEPTS
SNAP-IN MULTI CABLE GLAND
ENVIRONMENTAL
GASKET
Figure 6-12 Special cable gland plate required for mixed M-Cell
6
and
Horizon
macro
installations
The mounting plate is located as shown in Figure 6-13 in place of the original
blanking plate fitted to the M-Cell
6
.
MULTI CABLE
GLAND
M-Cell
6
CABINETS
Figure 6-13 Location of the snap-in multi cable gland and mounting plate in the
M-Cell
6
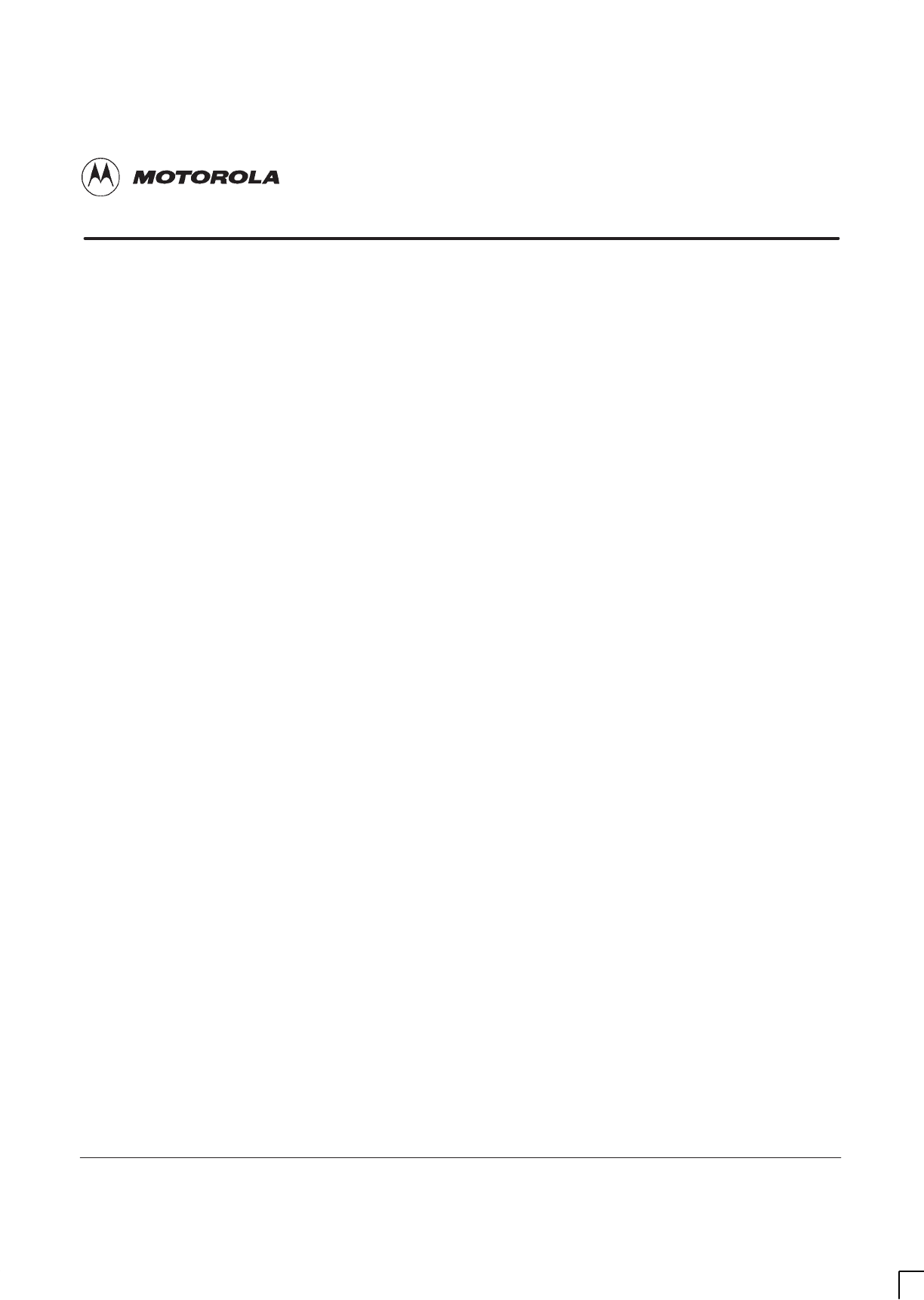
31st Oct 01
Installation & Configuration: Horizon
macro
outdoor
68P02902W03-A
CONTROLLED INTRODUCTION
i
Chapter 7
Commissioning of outdoor cabinet
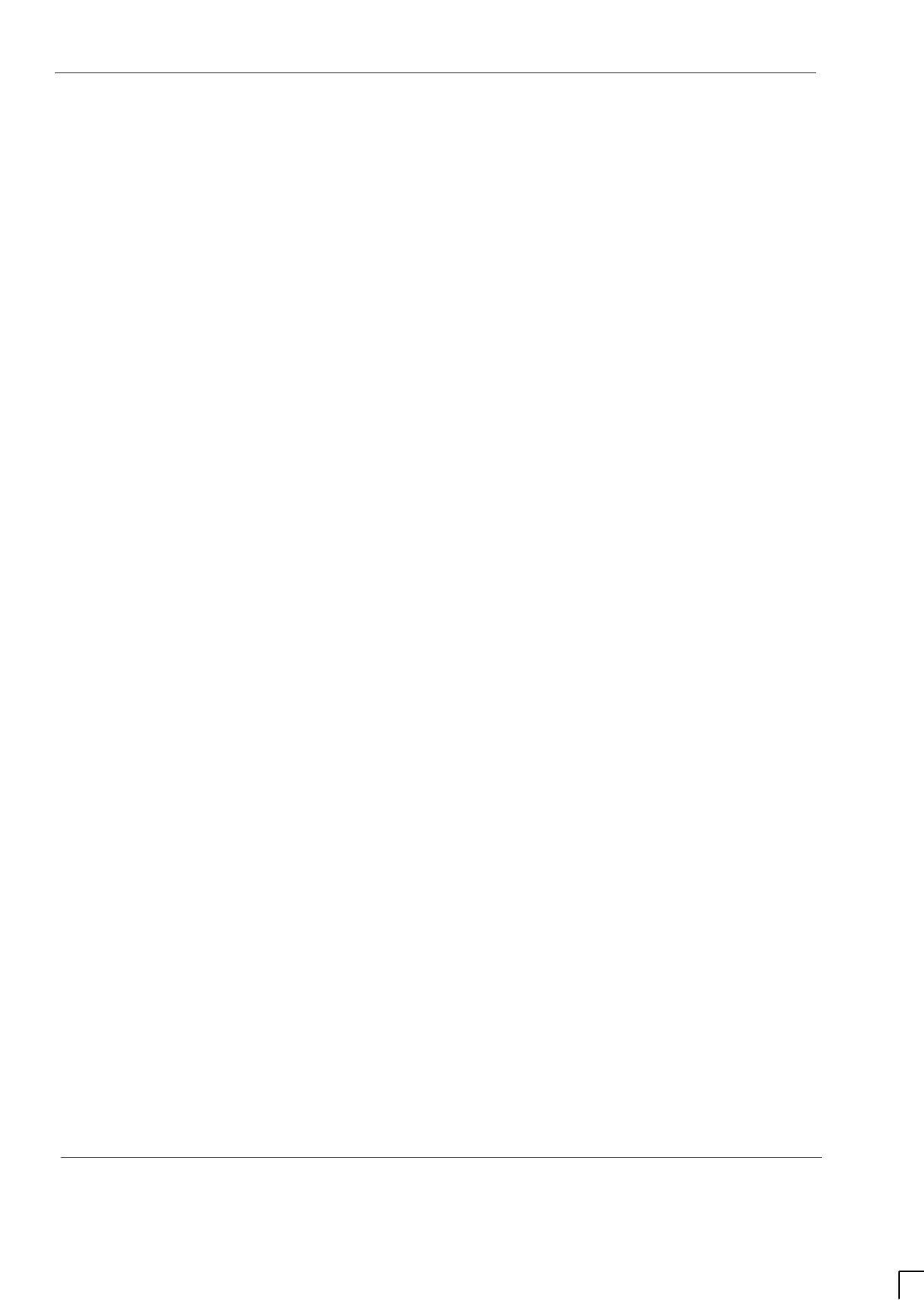
GSM-204-423
31st Oct 01
ii
Installation & Configuration: Horizon
macro
outdoor
CONTROLLED INTRODUCTION
68P02902W03-A
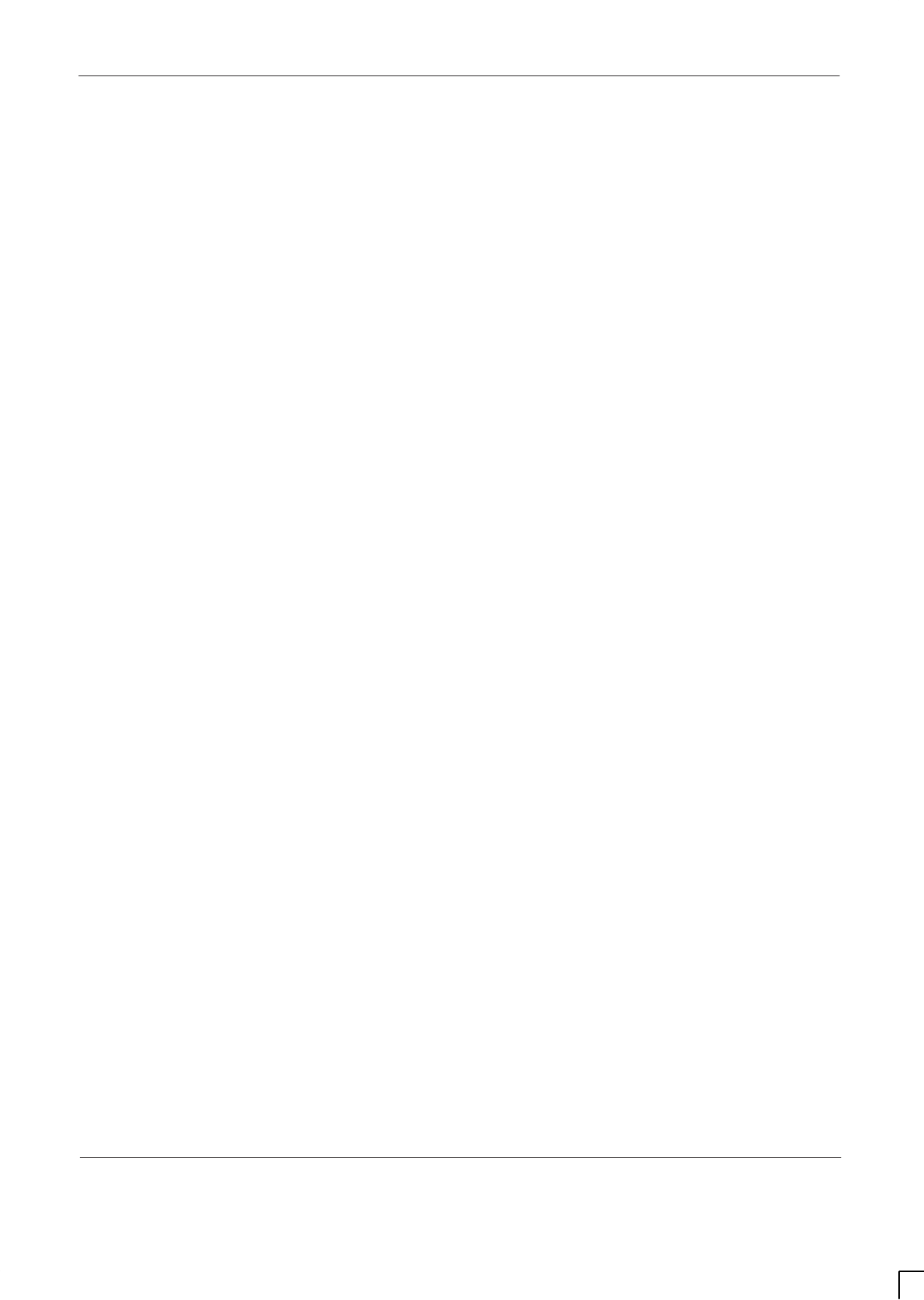
GSM-204-423
31st Oct 01
Installation & Configuration: Horizon
macro
outdoor
68P02902W03-A
CONTROLLED INTRODUCTION
iii
Chapter 7
Commissioning of outdoor cabinet i. . . . . . . . . . . . . . . . . . . . . . . . . . . . .
Commissioning overview Inst. 7–1. . . . . . . . . . . . . . . . . . . . . . . . . . . . . . . . . . . . . . . . . . . . . .
Overview of commissioning Inst. 7–1. . . . . . . . . . . . . . . . . . . . . . . . . . . . . . . . . . . . . .
PC to MCUF cable pin connections Inst. 7–1. . . . . . . . . . . . . . . . . . . . . . . . . . . . . . .
Test equipment Inst. 7–2. . . . . . . . . . . . . . . . . . . . . . . . . . . . . . . . . . . . . . . . . . . . . . . . .
Pre-power up checks Inst. 7–3. . . . . . . . . . . . . . . . . . . . . . . . . . . . . . . . . . . . . . . . . . . . . . . . .
Overview of pre-power up checks Inst. 7–3. . . . . . . . . . . . . . . . . . . . . . . . . . . . . . . . .
Visual inspection Inst. 7–4. . . . . . . . . . . . . . . . . . . . . . . . . . . . . . . . . . . . . . . . . . . . . . . .
Request for connection Inst. 7–4. . . . . . . . . . . . . . . . . . . . . . . . . . . . . . . . . . . . . . . . . .
Earth continuity check Inst. 7–5. . . . . . . . . . . . . . . . . . . . . . . . . . . . . . . . . . . . . . . . . . .
AC power system insulation check Inst. 7–5. . . . . . . . . . . . . . . . . . . . . . . . . . . . . . . .
Connecting input power Inst. 7–6. . . . . . . . . . . . . . . . . . . . . . . . . . . . . . . . . . . . . . . . . . . . . . .
Pre-connection checks Inst. 7–6. . . . . . . . . . . . . . . . . . . . . . . . . . . . . . . . . . . . . . . . . .
Connecting ac power Inst. 7–6. . . . . . . . . . . . . . . . . . . . . . . . . . . . . . . . . . . . . . . . . . . .
Connecting to a single phase ac power supply Inst. 7–6. . . . . . . . . . . . . . . . . . . . . .
Connecting to a three phase (star) ac power supply Inst. 7–7. . . . . . . . . . . . . . . . .
Connecting to a three phase (delta) ac power supply Inst. 7–7. . . . . . . . . . . . . . . .
Powering up the cabinet Inst. 7–8. . . . . . . . . . . . . . . . . . . . . . . . . . . . . . . . . . . . . . . . . . . . . .
Power-up overview Inst. 7–8. . . . . . . . . . . . . . . . . . . . . . . . . . . . . . . . . . . . . . . . . . . . . .
Power up procedure without code load Inst. 7–8. . . . . . . . . . . . . . . . . . . . . . . . . . . .
Power down of the cabinet Inst. 7–10. . . . . . . . . . . . . . . . . . . . . . . . . . . . . . . . . . . . . . .
Power up procedure with code load Inst. 7–11. . . . . . . . . . . . . . . . . . . . . . . . . . . . . . .
Installation and configuration Inst. 7–14. . . . . . . . . . . . . . . . . . . . . . . . . . . . . . . . . . . . .
Components involved in power up procedures Inst. 7–15. . . . . . . . . . . . . . . . . . . . . .
Testing the thermal management system (TMS) Inst. 7–16. . . . . . . . . . . . . . . . . . . . . . . . .
Overview of TMS test Inst. 7–16. . . . . . . . . . . . . . . . . . . . . . . . . . . . . . . . . . . . . . . . . . . .
Test facilities Inst. 7–16. . . . . . . . . . . . . . . . . . . . . . . . . . . . . . . . . . . . . . . . . . . . . . . . . . .
Diagram of TMS airflow Inst. 7–17. . . . . . . . . . . . . . . . . . . . . . . . . . . . . . . . . . . . . . . . . .
Test procedure Inst. 7–18. . . . . . . . . . . . . . . . . . . . . . . . . . . . . . . . . . . . . . . . . . . . . . . . .
Testing the battery backup Inst. 7–19. . . . . . . . . . . . . . . . . . . . . . . . . . . . . . . . . . . . . . . . . . . .
Overview of battery backup test Inst. 7–19. . . . . . . . . . . . . . . . . . . . . . . . . . . . . . . . . .
Battery backup test procedures Inst. 7–19. . . . . . . . . . . . . . . . . . . . . . . . . . . . . . . . . . .
Sample form 1: Request for connection Inst. 7–21. . . . . . . . . . . . . . . . . . . . . . . . . . . . . . . . .
Sample form 2: Completion and inspection form Inst. 7–23. . . . . . . . . . . . . . . . . . . . . . . . .
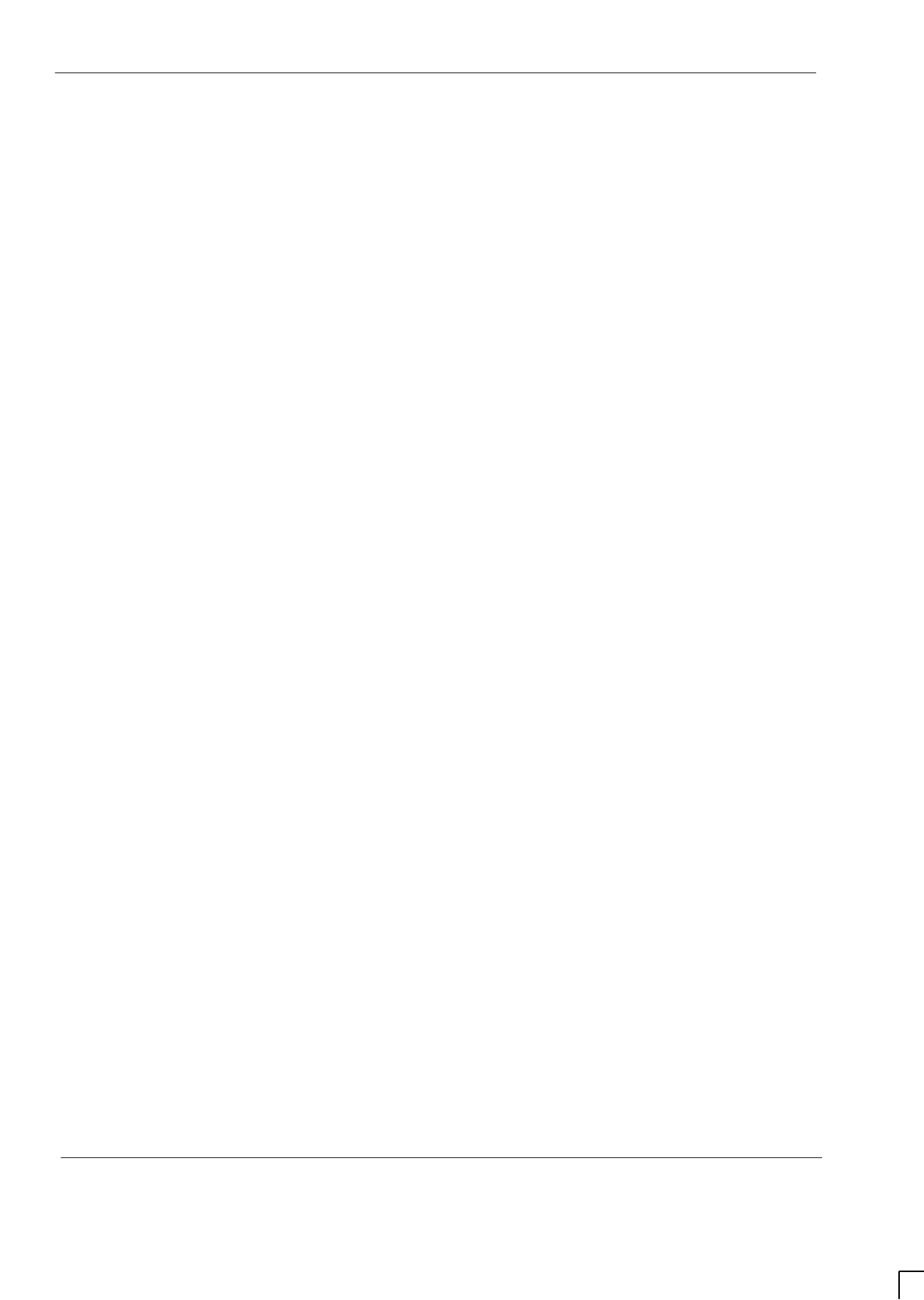
GSM-204-423
31st Oct 01
iv
Installation & Configuration: Horizon
macro
outdoor
CONTROLLED INTRODUCTION
68P02902W03-A
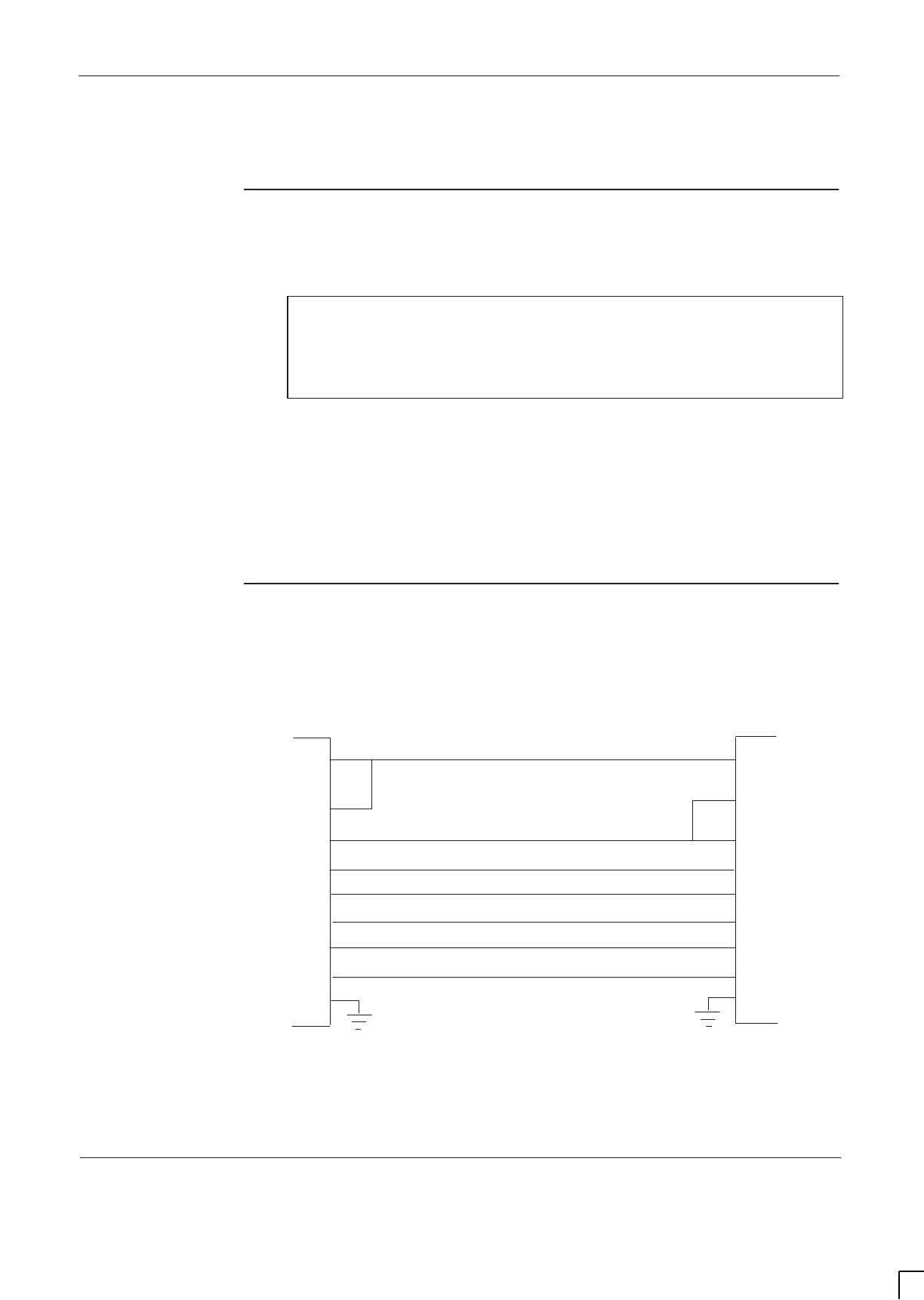
GSM-204-423 Commissioning overview
31st Oct 01
Installation & Configuration: Horizon
macro
outdoor
68P02902W03-A
CONTROLLED INTRODUCTION
Inst. 7–1
Commissioning overview
Overview of
commissioning
This chapter provides information required for the commissioning of cabinets
and their internal and external interfaces.
NOTE Some equipment at the site may not be produced by
Motorola, including power supplies, customer
communications equipment and antennas. Refer to site
specific documentation and the non-Motorola vendor
instructions.
All site preparation (Chapter 2) and equipment installation (Chapter 3) must be
completed before commissioning. Commissioning consists of the following:
Pre-power up checks.
Powering up the cabinet.
Optimization procedures as described in
Installation and Configuration:
BSS Optimization (GSM-100-423) 68P02901W43
, issue G or later.
PC to MCUF
cable pin
connections
Figure 7-1 shows the pin connections for the personal computer (PC) to MCUF
test cable. These are standard null modem pin connections.
TO PC COMMUNICATIONS PORT
9-WAY D-TYPE MALE TO MCUF TTY PORT
9-WAY D-TYPE FEMALE
PIN NUMBER
PIN NUMBER
4 m LONG SCREENED CABLE
1
6
4
1
4
6
2
32
3
55
7
8
8
7
99
Figure 7-1 9-way to 9-way PC to MCUF cable pin connections
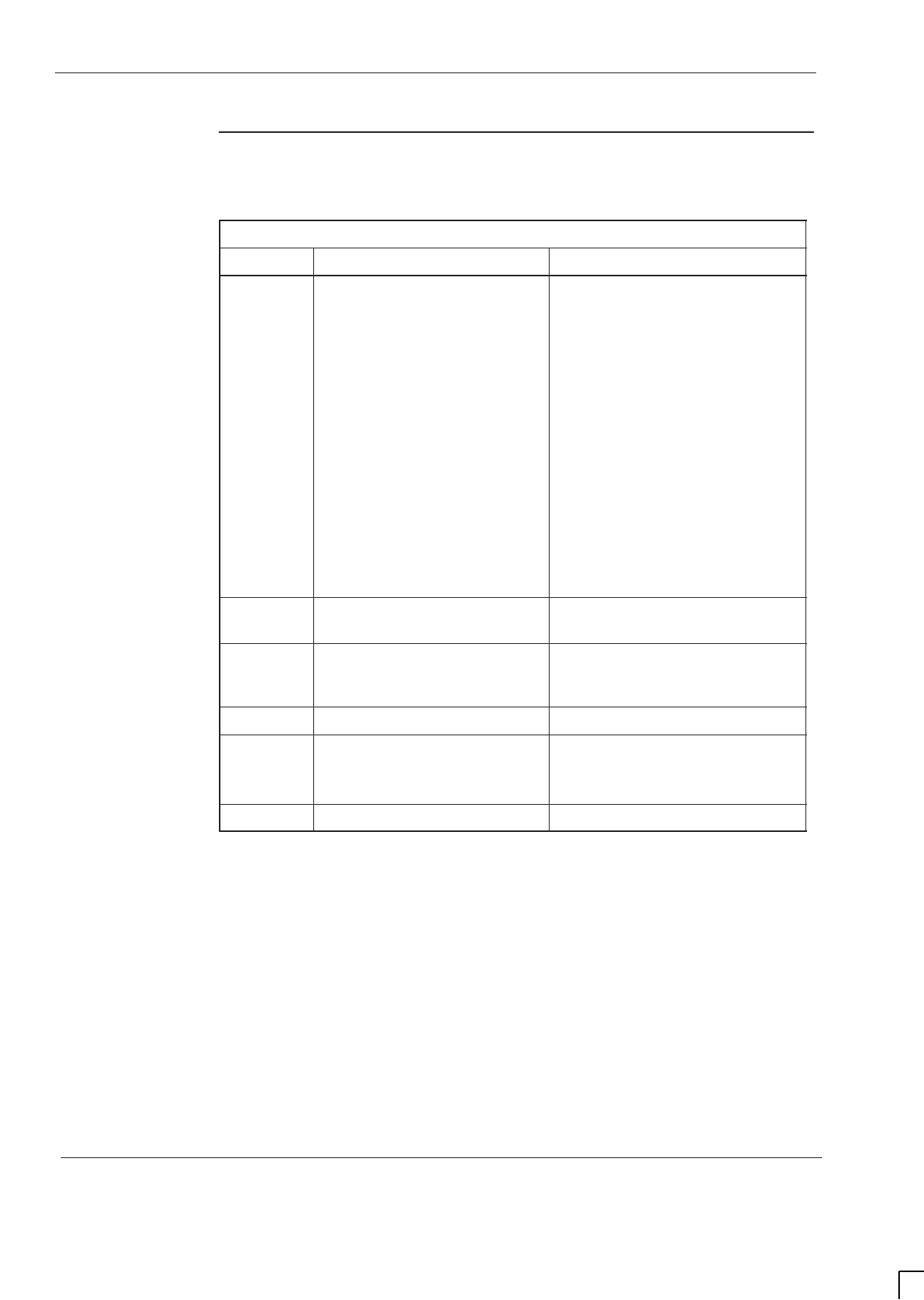
GSM-204-423
Commissioning overview
31st Oct 01
Inst. 7–2
Installation & Configuration: Horizon
macro
outdoor
CONTROLLED INTRODUCTION
68P02902W03-A
Test equipment
Table 7-1 provides details of the test equipment required to perform the
commissioning procedures in this chapter.
Table 7-1 Test equipment required for commissioning
Quantity Description Comments
1
IBM compatible portable
Personal Computer (PC) (486
DX2 or DX4 minimum)
The basic requirements are:
TFT colour screen.
170 Mbyte hard drive
(minimum).
Minimum 4 Mbyte RAM (8 Mbyte
recommended).
3.5 inch floppy drive.
Serial port.
CD-ROM drive (recommended)
PCMCIA (Type 2) compatible
slot.
Windows 3.1 loaded and
running in 386 enhanced mode.
Battery power.
1Commercial terminal emulator
software PC PLUS or similar software
(suitable for PC being used)
1Digital multimeter (must be
sensitive enough to measure
0.05 ohms)
Hewlett Packard E2378A or
equivalent.
1ESD protection kit
19-way male D-type to 9-way
female D-type For PC to MCUF.
Pin connections shown in
Figure 7-1.
1PAT tester Insulation and earth tester.
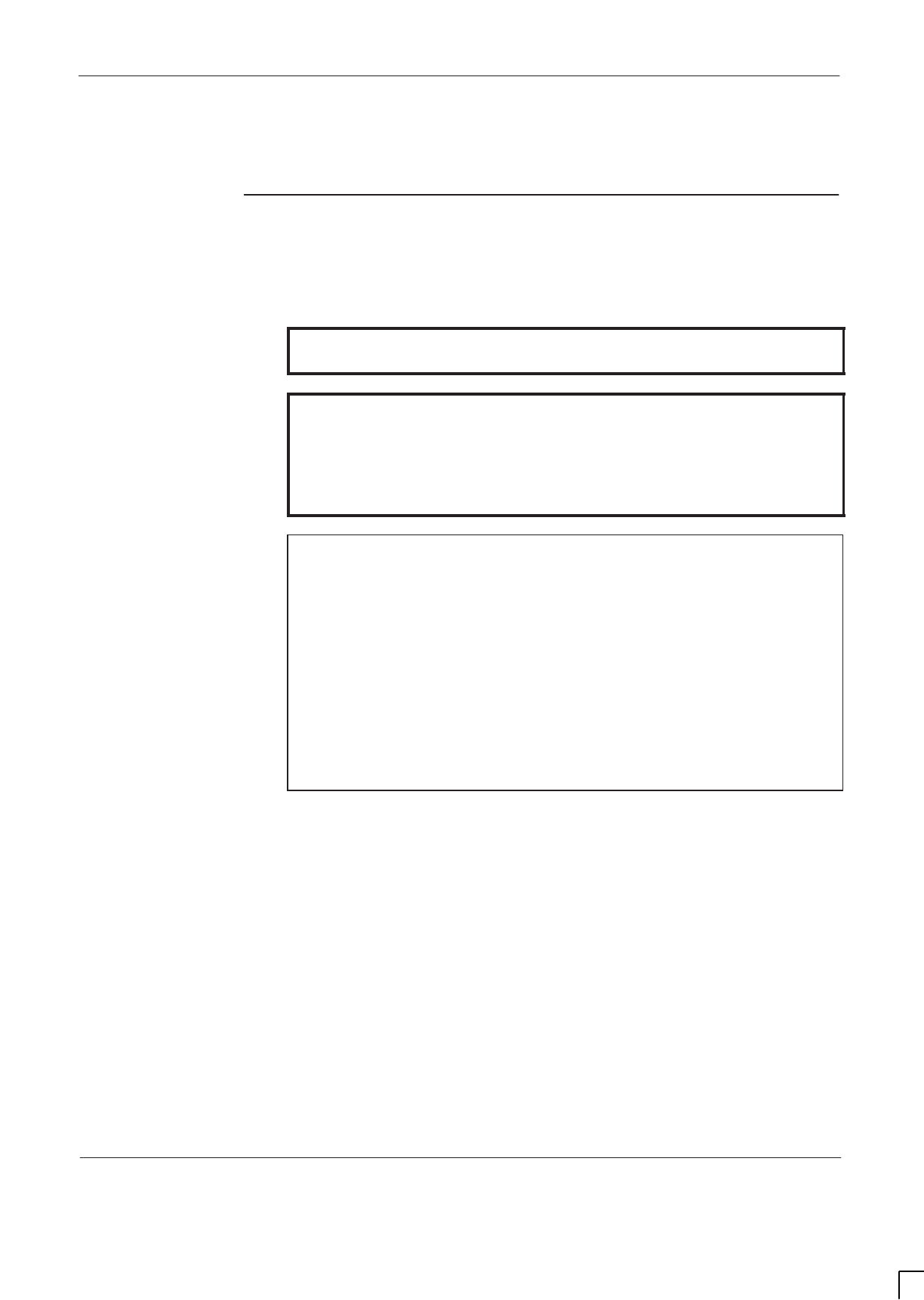
GSM-204-423 Pre-power up checks
31st Oct 01
Installation & Configuration: Horizon
macro
outdoor
68P02902W03-A
CONTROLLED INTRODUCTION
Inst. 7–3
Pre-power up checks
Overview of
pre-power up
checks
This section contains procedures for testing the power system prior to applying
power to the cabinet.
WARNING The power system checks provided in this section must be
performed before the equipment is powered up.
WARNING Up to 415 V ac is present within the cabinet when the
cabinet is directly connected to an ac supply.
Earth straps are not to be worn during the commissioning
of the ac and dc power system. Watches and other
jewellery should be removed.
Only insulated tools should be used.
CAUTION This equipment contains CMOS devices and is vulnerable
to static discharge. Although the damage may not be
immediately apparent, CMOS devices may be damaged in
the long term due to mishandling causing barrier
breakdown.
The approved earth strap (high impedance) must be worn
at all times when adjusting or handling the processor
cards (but see the warning above, regarding the use of
earth straps).
If the cabinet door is kept open for long periods of time
during commissioning, an alternative method of cooling
must be provided to avoid damage to the equipment
through overheating.
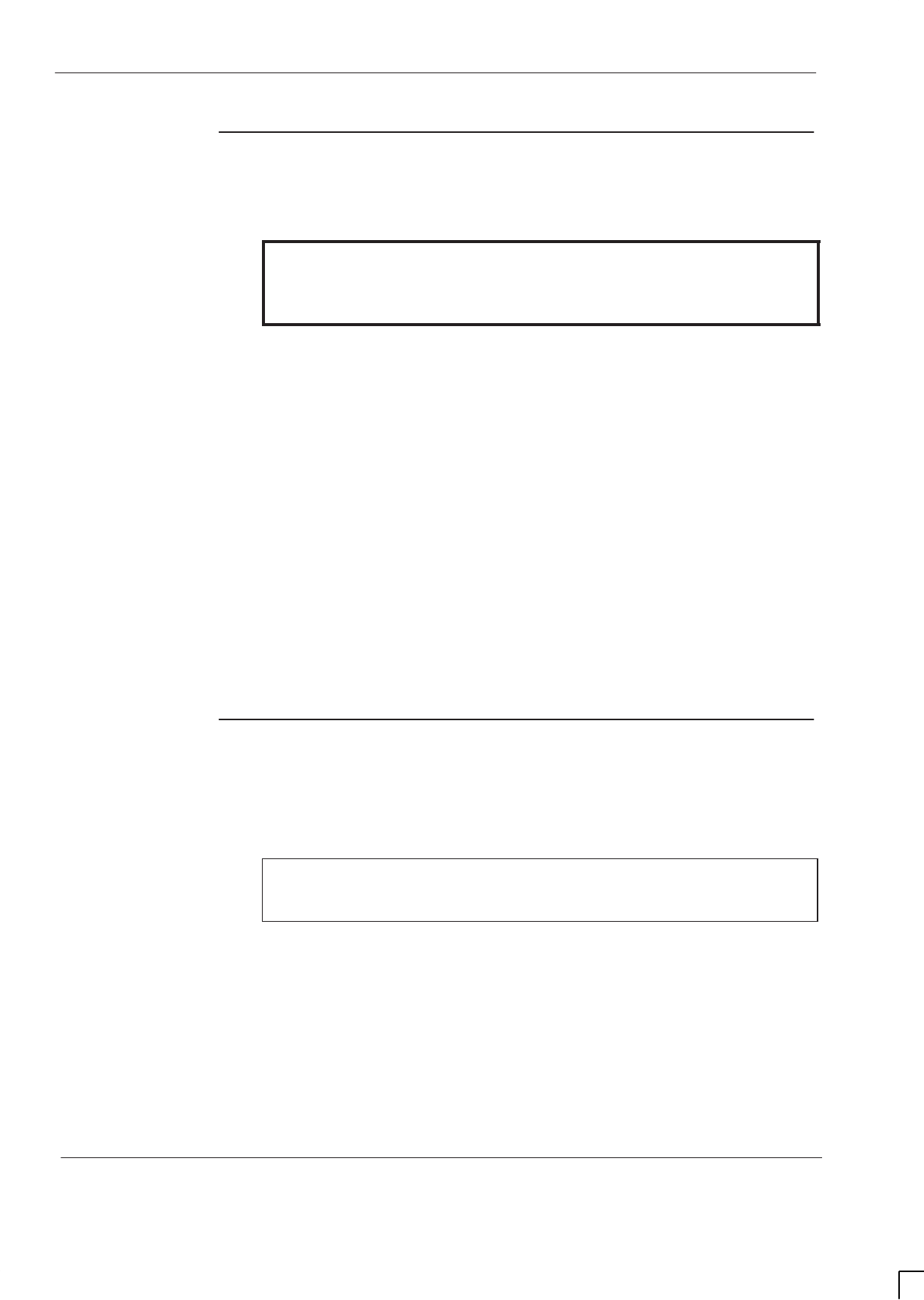
GSM-204-423
Pre-power up checks
31st Oct 01
Inst. 7–4
Installation & Configuration: Horizon
macro
outdoor
CONTROLLED INTRODUCTION
68P02902W03-A
Visual
inspection
Inspect the installation for damage in accordance with BS 7671, 16th Edition
(Section 712), or the IEC 364 or local equivalent.
WARNING If damage is discovered during the visual inspection, the
commissioning must not proceed further until the damage
has been inspected and rectified by the manufacturers or
their representatives.
Power equipment
Examine the power equipment for mechanical damage and report any damage
to Motorola.
Ensure all cabinet earth plates are connected to the site earth.
Cabinet structure
Examine the exterior and interior of the cabinets for structural, paint or
mechanical damage and report any damage to Motorola.
Weather protection
Check all environmental seals to ensure they are not damaged.
Check that all cables entering the cabinet have grommets fitted at the point of
entry to prevent the ingress of water. If any holes in the earth plates are not
used, these must have rubber bungs fitted to prevent water entering the cabinet.
Request for
connection
Ensure that all correct Request for connection and Completion and
inspection form certificates have been sent to the local electricity supply board.
NOTE Samples of a typical Request for connection and a
Completion and inspection form are shown in Sample
form 1 and Sample form 2 at the end of this chapter.
Apply conductive non-oxidizing grease to the earth mat connection on the earth
busbar if an earth mat connection is used.
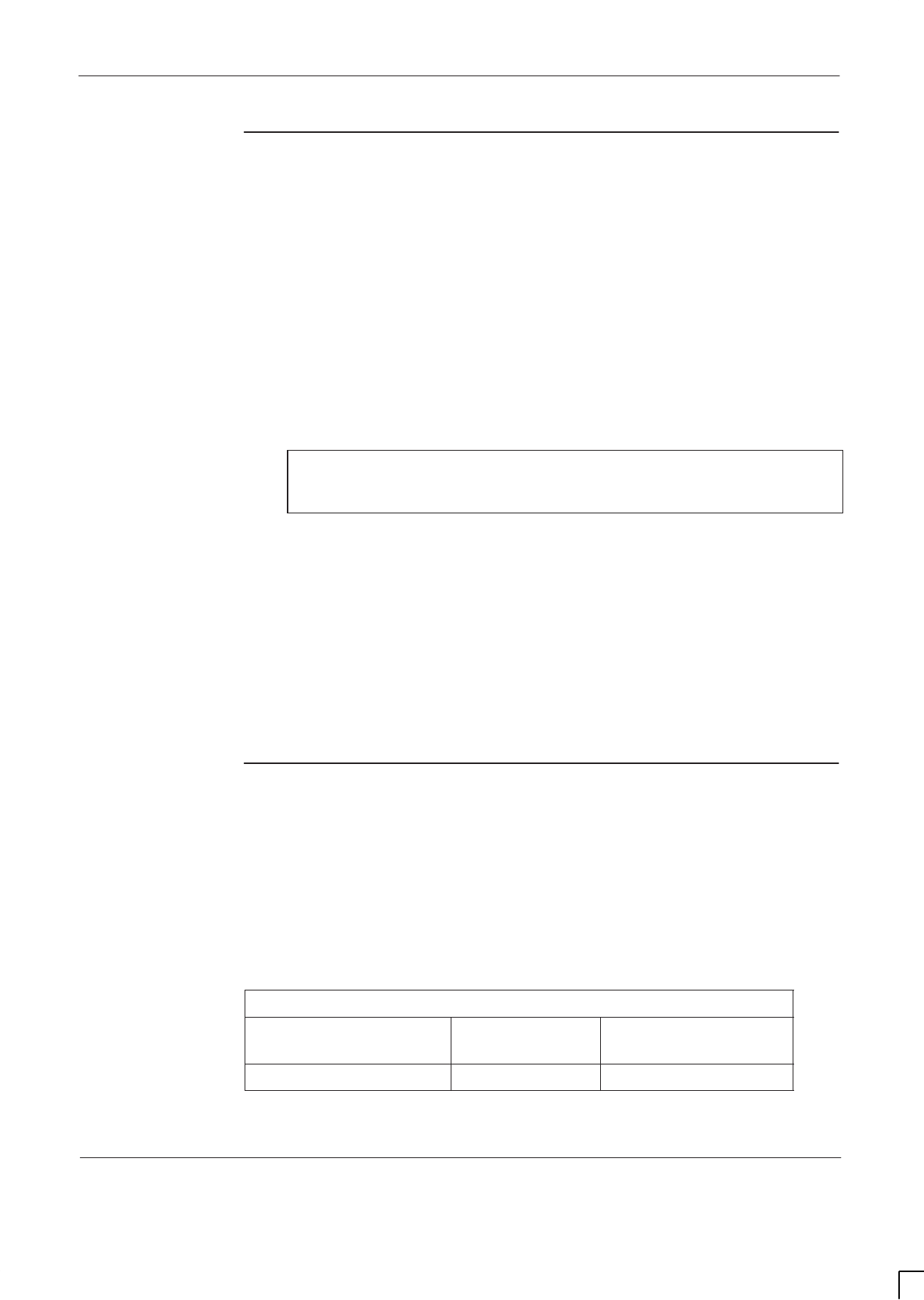
GSM-204-423 Pre-power up checks
31st Oct 01
Installation & Configuration: Horizon
macro
outdoor
68P02902W03-A
CONTROLLED INTRODUCTION
Inst. 7–5
Earth continuity
check
Ensure an earth continuity check has been performed on appropriate
equipment, if required. Use the digital multimeter to check that the resistance of
the test equipment leads is less than 0.05 ohms.
Main equipment earths
Connect the PAT tester to the earth terminal and to the following earth points:
Antenna feeders.
AC supply input earth.
– The local electricity company termination point.
– AC supply isolator.
– Number 1 ac distribution box earth terminal block.
NOTE The external switched isolator will not be connected to
earth if it is a double insulated device and will therefore
not need to be tested.
Cabinet earth/connector plates.
TMS unit chassis.
Cabinet chassis (rear right stud).
Power supply unit chassis.
Doors and lid.
Auxiliary equipment housing chassis.
Check that the measured resistance is less than 0.1 ohms with the tester
connected to a conductive surface (bare metal) at extreme ends of the earth
cables.
AC power
system
insulation
check
Ensure an insulation check has been performed on all ac power cables which
supply the site up to the ac input to the cabinet. Testing must be carried out in
accordance with the BS 7671, 16th Edition (section 713-04–01 to 713-04-06), or
IEC 364 equivalent, at the voltage levels shown in Table 7-2, using an approved
insulation tester. Check that the resistance at each point is as shown in
Table 7-2.
Table 7-2 BS7671 (16th edition) Table 71A (part of)
Parameter AC test voltage
(volts) Minimum insulation
(megaohms)
Up to and including 500 V 500 0.5
When the test has been completed, sign the completion and inspection
certificate, a sample of which may be found in Sample form 2.
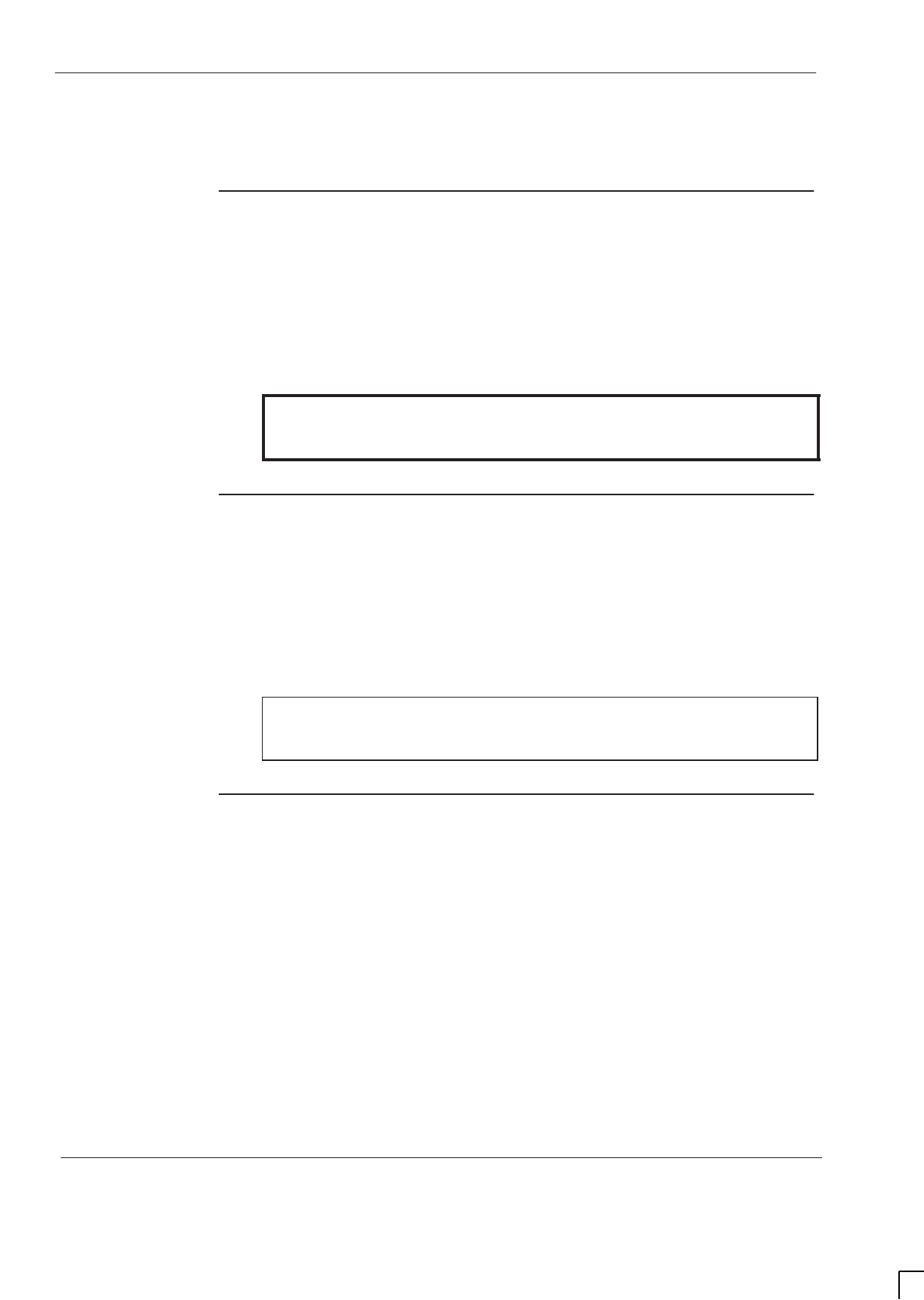
GSM-204-423
Connecting input power
31st Oct 01
Inst. 7–6
Installation & Configuration: Horizon
macro
outdoor
CONTROLLED INTRODUCTION
68P02902W03-A
Connecting input power
Pre-connection
checks
At this point in the installation, ensure that:
All cabinet earth plates are connected to the site earth.
The cabinets are not already connected to the external ac power source.
The cabinets are connected to the ac power cabling.
The ac power cabling is routed to the electricity supply company outlet.
WARNING Do not wear an anti static wrist strap while servicing the
power supplies or power distribution cabling, as serious
personal injury can result.
Connecting ac
power
The Request for connection should have been sent to the local electricity
supply board when the equipment left the manufacturer.
Ensure that the Request for connection and the Completion and
inspection certificate have been sent to the electricity supply company.
Ensure that the cabinet door is open when the electricity company
representative is in attendance.
NOTE If a cable shroud and/or an auxiliary equipment cabinet is
to be installed, the installation should be carried out before
connecting the ac supply to the main cabinet.
Connecting to a
single phase ac
power supply
To connect the single phase and earth power cable to the electricity supply
outlet:
1. Connect the earth ac cable (green/yellow) to the earth point in the power
supply outlet, and secure.
2. Connect the line ac cable (brown or red) to the line connection in the
power supply outlet, and secure.
3. Connect the neutral ac cable (blue or black), to the neutral connection in
the power supply outlet and secure.
4. Do not connect the screen, but cut it back level with the outer insulation.
5. Refit and secure the ac terminal block insulated cover, and refit the screws
and washers.
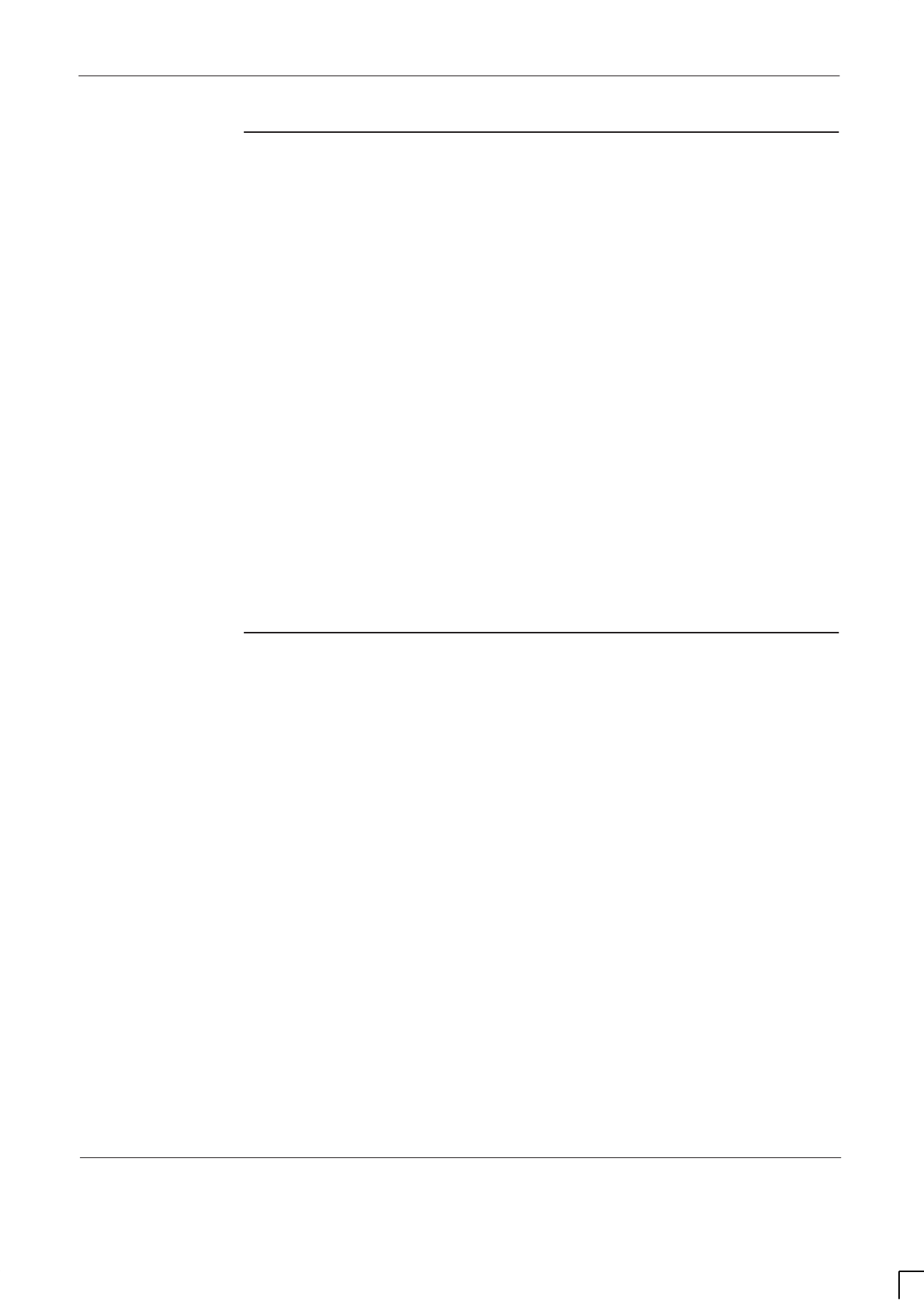
GSM-204-423 Connecting input power
31st Oct 01
Installation & Configuration: Horizon
macro
outdoor
68P02902W03-A
CONTROLLED INTRODUCTION
Inst. 7–7
Connecting to a
three phase
(star) ac power
supply
To connect the earth, 3-phase, and neutral power cables to the electricity supply
outlet:
1. Connect the earth ac cable (green/yellow), to the earth point in the power
supply outlet and secure.
2. Connect the phase A cable (red), to the red phase connection in the
power supply outlet and secure.
3. Connect the phase B cable (yellow), to the blue phase connection in the
power supply outlet and secure.
4. Connect the phase C cable (blue), to the yellow phase connection in the
power supply outlet and secure.
5. Connect the neutral ac cable (black), to the neutral connection in the
power supply outlet and secure.
6. Do not connect the screen, but cut it back level with the outer insulation.
7. Refit and secure the ac terminal block insulated cover, and refit the screws
and washers.
Connecting to a
three phase
(delta) ac power
supply
To connect the earth and 3-phase power cables to the electricity supply outlet:
1. Connect the earth ac cable (green/yellow), to the earth point in the power
supply outlet and secure.
2. Connect the phase A cable (red), to the red phase connection in the
power supply outlet and secure.
3. Connect the phase B cable (yellow), to the blue phase connection in the
power supply outlet and secure.
4. Connect the phase C cable (blue), to the yellow phase connection in the
power supply outlet and secure.
5. Do not connect the screen, but cut it back level with the outer insulation.
6. Refit and secure the ac terminal block insulated cover, and refit the screws
and washers.
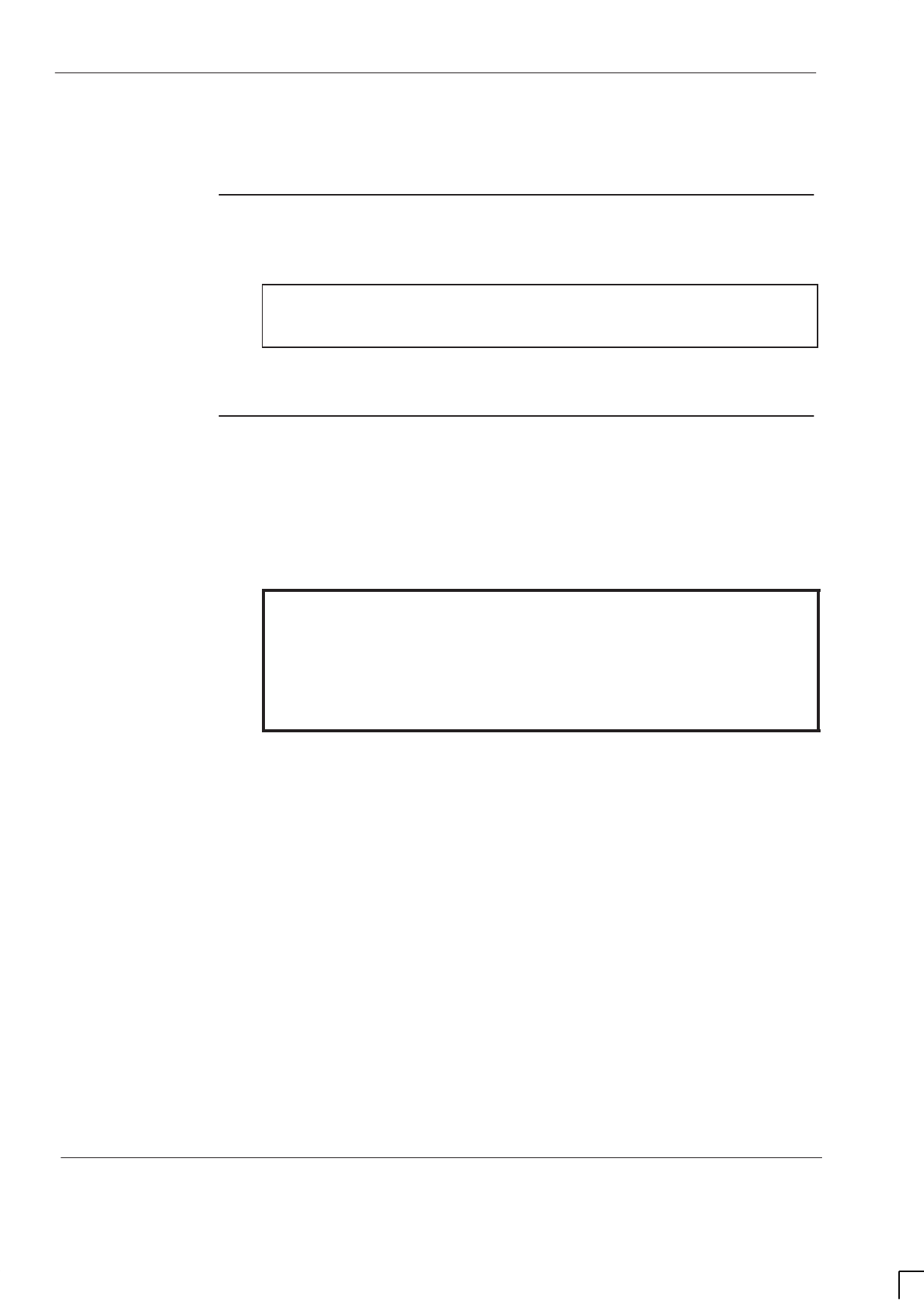
GSM-204-423
Powering up the cabinet
31st Oct 01
Inst. 7–8
Installation & Configuration: Horizon
macro
outdoor
CONTROLLED INTRODUCTION
68P02902W03-A
Powering up the cabinet
Power-up
overview
This procedure assumes all previous procedures have been completed.
CAUTION Ensure the correct –48/60 V dc PSMs are fitted.
Ensure that there is no blockage to ventilation at the base
of the cabinet.
Relevant components to power up procedures are shown in Figure 7-2.
Power up
procedure
without code
load
The following procedure should be carried out to power up the cabinet, with no
code load. This proves the cabinet hardware is capable of operation. The
procedure for cabinet code load is described in the next section.
WARNING Earth straps are not to be worn during the commissioning
of the power system, and watches and other jewellery
should be removed.
Only insulated tools should be used.
The power source must be supplied to the cabinet via a
suitable overcurrent protective device and be isolated from
the BTS cabinet.
Procedure to prepare the cabinet for power up without code load
Proceed as follows to prepare the cabinet prior to power up:
1. Verify that the power source isolator is set to off.
2. Disconnect all E1/T1 lines from the BTS.
3. If fitted, remove the optional PCMCIA card from the MCUF slot.
4. Set the switch of each PSM to the OUTPUT DISABLE position.
5. Set all circuit breakers in both ac distribution boxes to off.
6. Set all circuit breakers on the PSU dc circuit breaker panel to off.
7. Set the internal and external battery circuit breakers to off.
8. Press and release all push on/push off circuit breaker buttons on the CBM
to the out (off) position.

GSM-204-423 Powering up the cabinet
31st Oct 01
Installation & Configuration: Horizon
macro
outdoor
68P02902W03-A
CONTROLLED INTRODUCTION
Inst. 7–9
Initial power up
To apply initial power to the cabinet:
1. Switch on the external power supply to the cabinet.
2. Set the four pole MCB and the 6 A RCBO in the number 1 ac distribution
box to on.
3. Set the TMS fans circuit breaker on the PSU dc circuit breaker panel to
on.
4. Set the TMS heater and TOPSM circuit breakers, in the number 2 ac
distribution box to on. Check that input healthy (yellow) and output healthy
(green) LEDs of each TOPSM illuminate as it is switched on. Check that
the radio and comms contactor LEDs on the CAB are illuminated.
5. Carry out a test of the TMS as described in Testing the thermal
management system (TMS).
Radio and digital Power up without code load
To apply power radios and digital modules:
1. Turn each PSM switch to the OUTPUT ENABLE position. Check that each
PSM has the active (green) LED on and the alarm (red) LED off.
2. Press the CBM circuit breaker button marked SURF.
3. Press the CBM circuit breaker button marked BPSM A and (if redundant
BPSM fitted) BPSM B. Check all associated digital module LEDs operate
correctly; green LEDs lit on BPSM, NIU and MCUF, and red LEDs off on
NIU and MCUF.
NOTE Both red and green LEDs are initially lit on the NIU while
the unit performs a self-test. The red LED will extinguish
after approximately 20 seconds, indicating a normal
condition.
4. Press the CBM circuit breaker buttons appropriate for the CTUs fitted, and
check that the RADIO STATUS LED for each CTU flashes green.
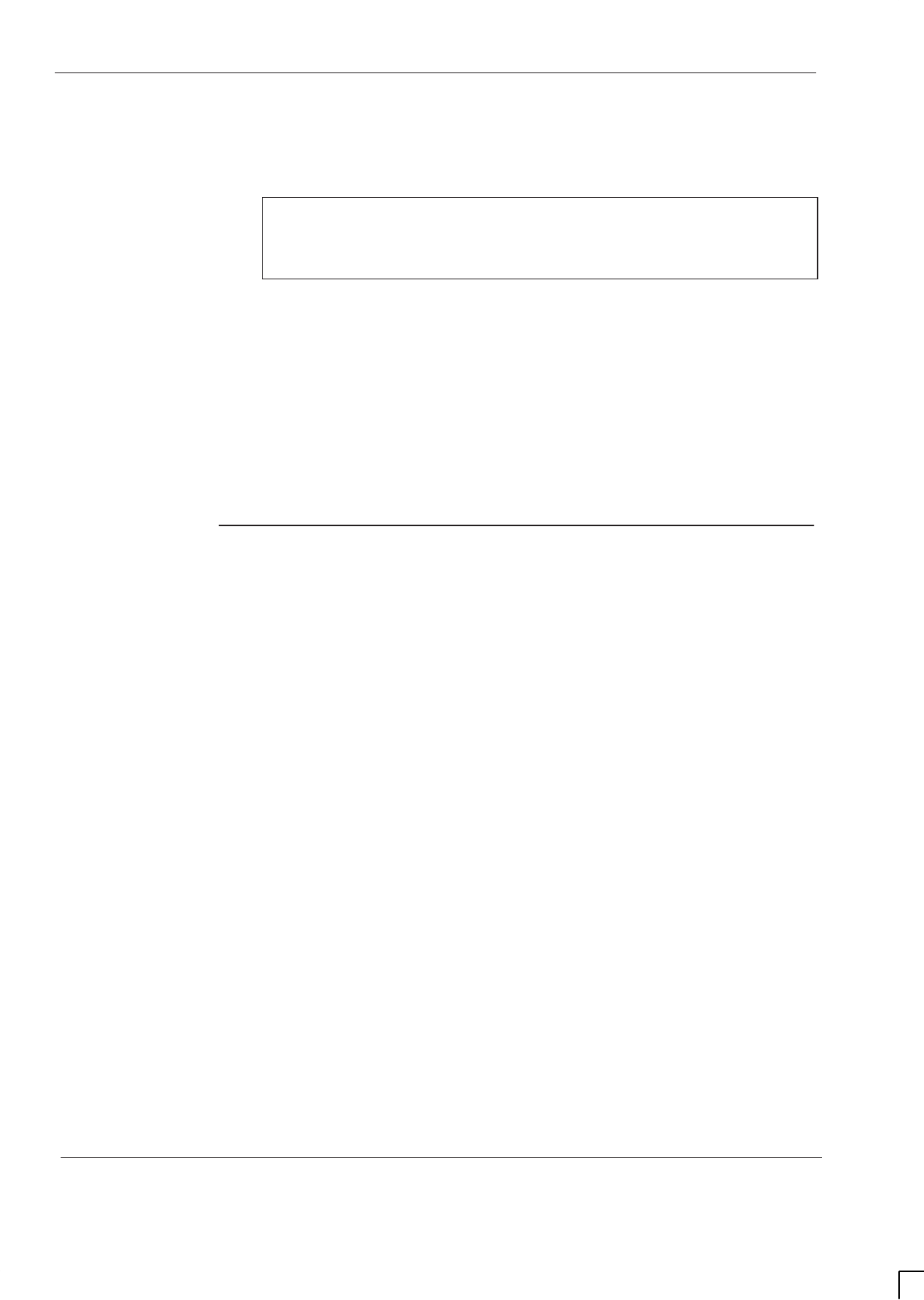
GSM-204-423
Powering up the cabinet
31st Oct 01
Inst. 7–10
Installation & Configuration: Horizon
macro
outdoor
CONTROLLED INTRODUCTION
68P02902W03-A
Battery backup and comms power up
To apply power to the backup batteries and communications equipment:
CAUTION When using external batteries, the Horizon
macro
outdoor
BTS cabinet internal batteries must be switch isolated to
ensure correct operation of the temperature-compensated
battery charging system.
1. Set the external battery or internal battery circuit breaker, depending on
backup battery configuration, to on.
2. Test operation of battery backup as described in Testing the batteruy
backup.
3. Set any comms circuit breakers, appropriate for the customer
communications equipment fitted, to on.
4. Close the doors and lid to ensure correct thermal management.
This completes the power up of the cabinet.
Power down of
the cabinet
If the cabinet is not required to remain powered up, power down the cabinet as
follows:
1. Press all CBM circuit breaker buttons to the out (off) position.
2. Switch each PSM to the OUTPUT DISABLE position.
3. Set the internal and external battery circuit breakers to off.
4. Set all circuit breakers on the PSU dc circuit breaker panel to off.
5. Set the number 2 ac distribution box circuit breakers to off.
6. Switch the four pole MCB and 6 A RCBO circuit breakers in the number 1
ac distribution box to off.
7. Switch off the external power supply to the cabinet.
This completes the power down of the cabinet.
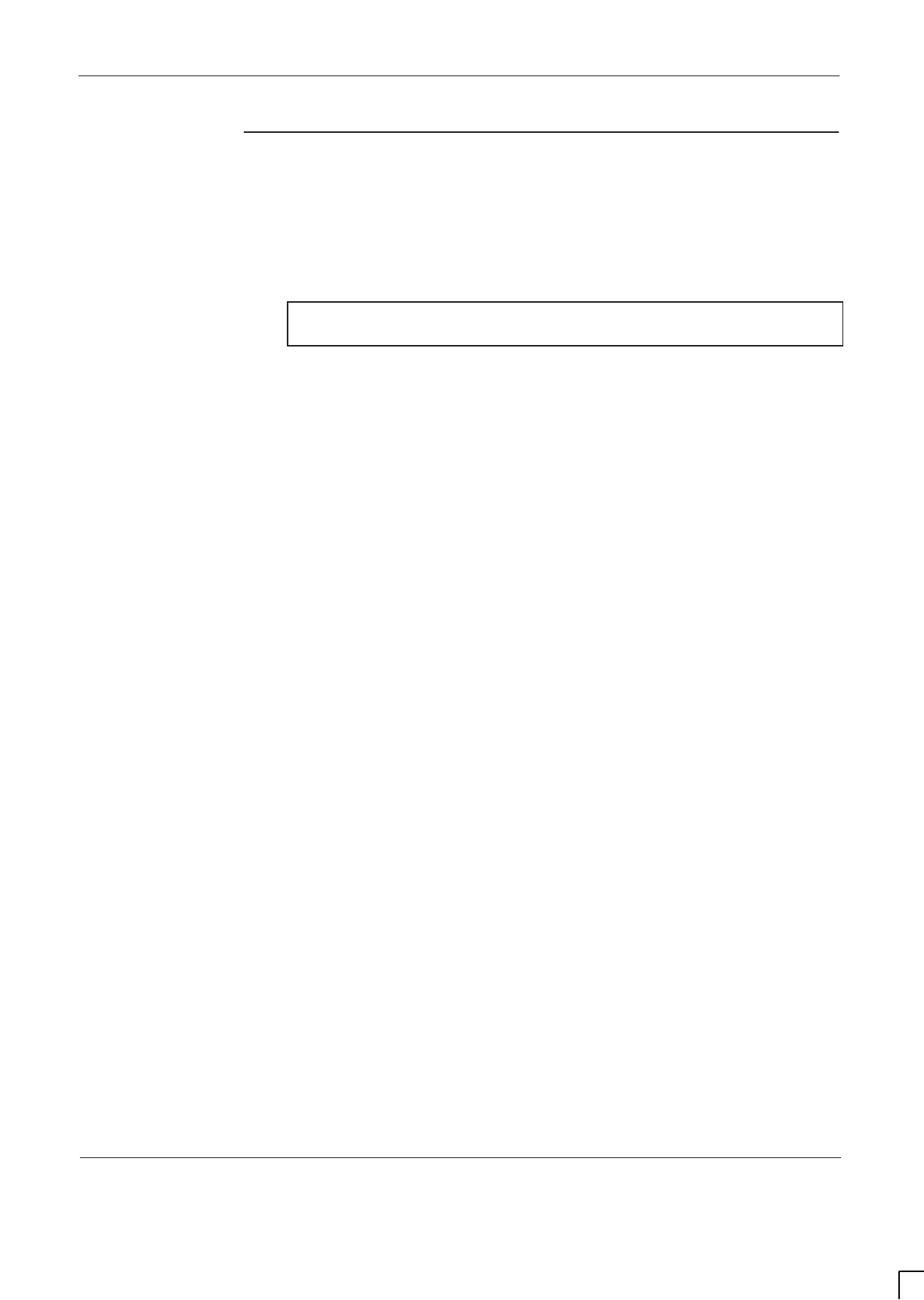
GSM-204-423 Powering up the cabinet
31st Oct 01
Installation & Configuration: Horizon
macro
outdoor
68P02902W03-A
CONTROLLED INTRODUCTION
Inst. 7–11
Power up
procedure with
code load
The following procedure should be carried out to power up the cabinet, with
code load. The code will be provided either direct from the BSC from the E1/T1
line, or from a PCMCIA card installed in the PCMCIA socket of the master
MCUF.
CAUTION This procedure should only be carried out by experienced
field personnel.
Preparing the cabinet for power up with code load
Proceed as follows to prepare the cabinet prior to power up:
1. Make the E1/T1 connection to BSC.
2. Insert (optional) PCMCIA card in MCUF PCMCIA socket.
3. Connect the 9 to 9-way cable from the PC serial A port to MCUF TTY port.
4. Start the terminal emulator program at the PC.
5. Change to Level 3, and at the MMI-RAM> prompt type: CTRL N
6. Set all circuit breakers in both ac distribution boxes and the PSU dc circuit
breaker panel to off.
7. Set the internal and external battery circuit breakers to off.
8. Set the switch of each PSM to the OUTPUT DISABLE position.
9. Press and release all push on/push off circuit breaker buttons to the out
(off) position.
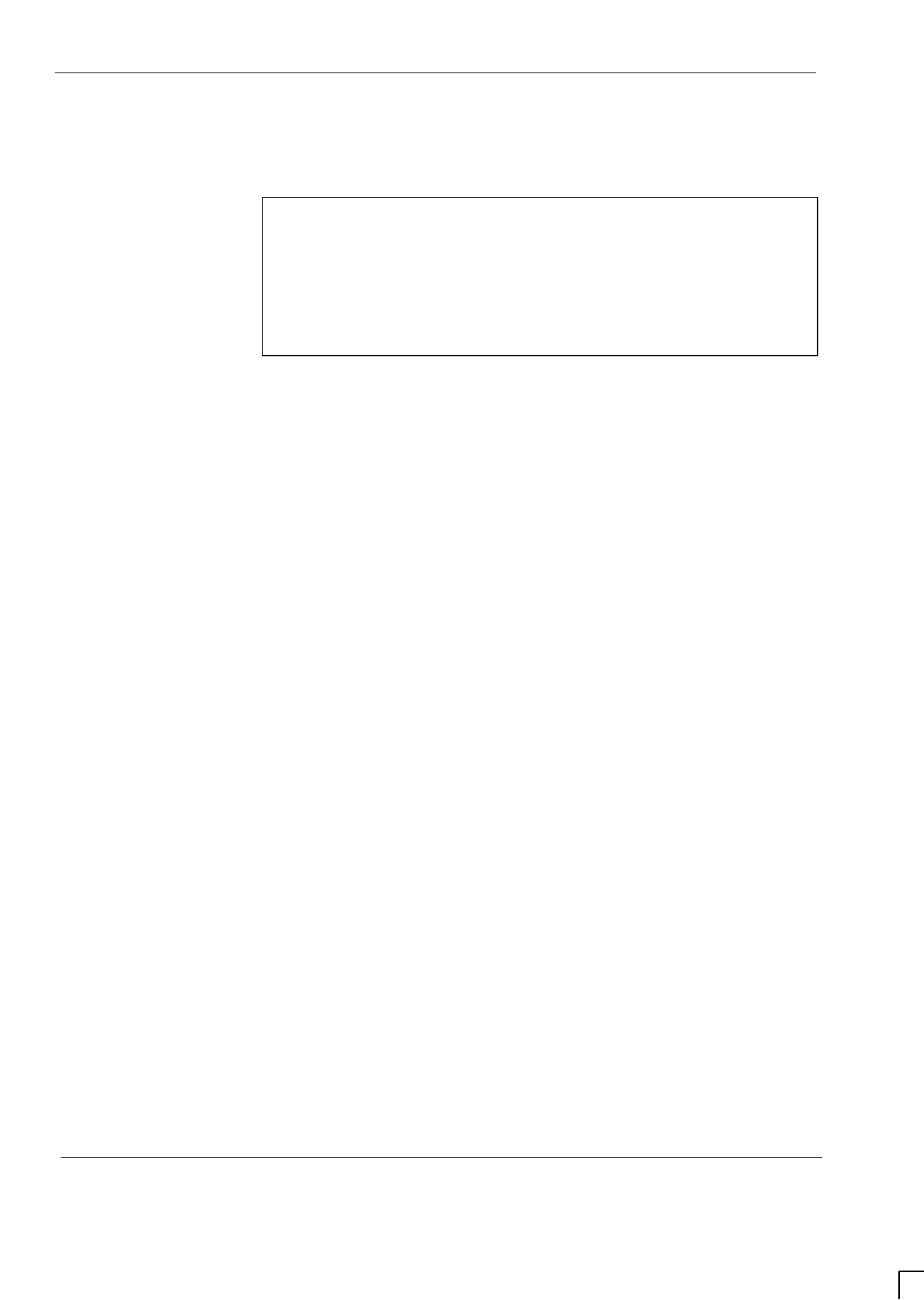
GSM-204-423
Powering up the cabinet
31st Oct 01
Inst. 7–12
Installation & Configuration: Horizon
macro
outdoor
CONTROLLED INTRODUCTION
68P02902W03-A
Initial power up
To apply initial power to the cabinet:
CAUTION When the two LEDs of the CTU, or the MCUF are flashing,
the boot code is downloading into non-volatile memory for
software upgrade. Do not remove power or reset the
cabinet until downloading has been completed, as this will
corrupt the non-volatile memory. If the boot code is
corrupted, contact Motorola Customer Network Resolution
Centre and request the boot code restoration procedure
and the appropriate boot code file.
1. Switch on the external power supply to the cabinet.
2. Set the four pole MCB and the 6 A RCBO, in number 1 ac distribution box,
to on.
3. Set the TMS fans circuit breaker on the PSU dc circuit breaker panel to
on.
4. Set the TMS heater and TOPSM circuit breakers, in the number 2 ac
distribution box to on. Check that input healthy (yellow) and output healthy
(green) LEDs of each TOPSM illuminate as it is switched on. Check that
the radio and comms contactor LEDs on the CAB are illuminated.
5. Carry out a test of the TMS as described in Testing the thermal
management system (TMS).
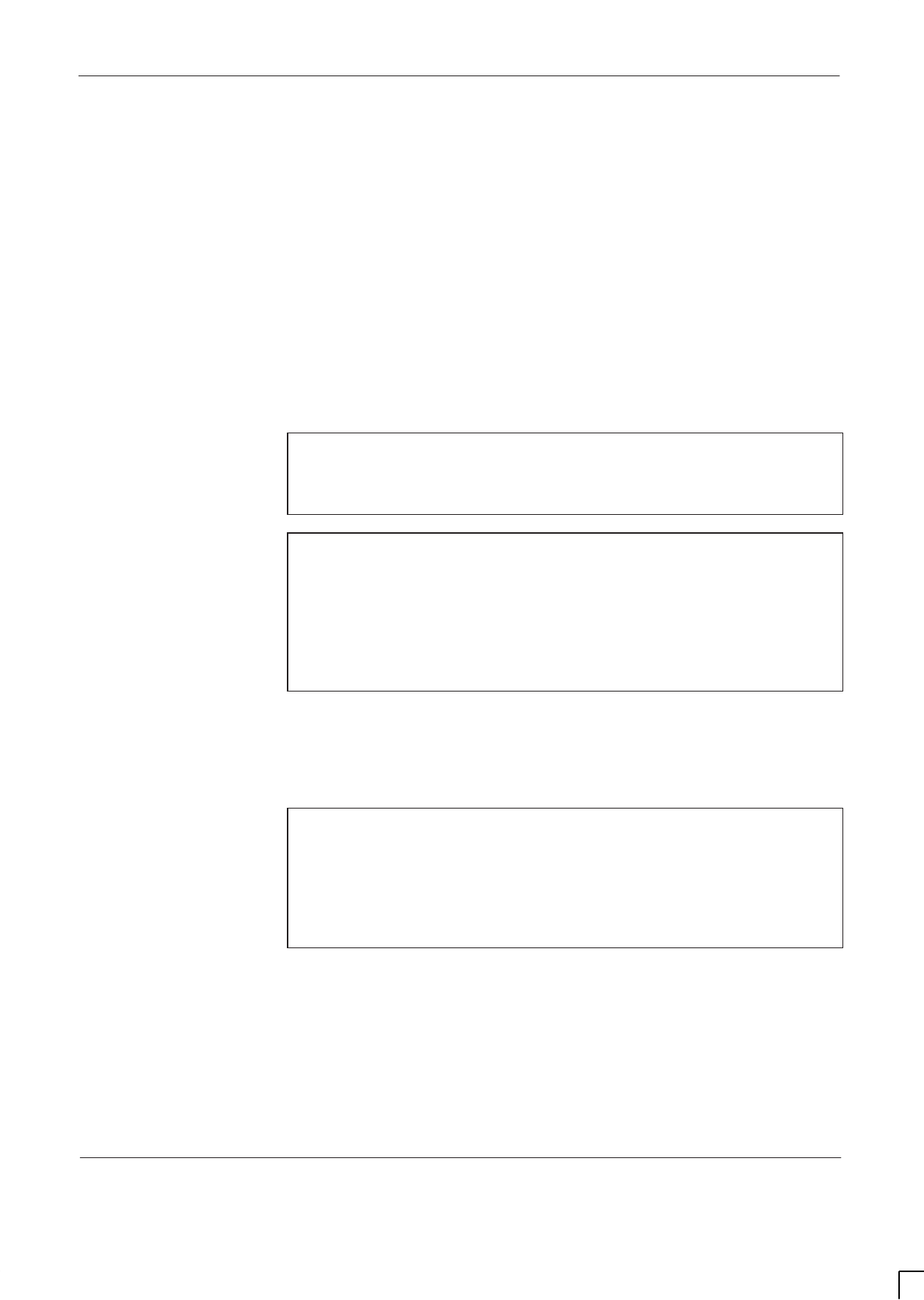
GSM-204-423 Powering up the cabinet
31st Oct 01
Installation & Configuration: Horizon
macro
outdoor
68P02902W03-A
CONTROLLED INTRODUCTION
Inst. 7–13
Radio and digital Power up with code load
To apply power radios and digital modules:
1. Turn each PSM switch to the OUTPUT ENABLE position. Check that each
PSM has the active (green) LED on and the alarm (red) LED off.
2. Press the CBM circuit breaker button marked SURF.
3. Press the CBM circuit breaker button marked BPSM A and (if a redundant
BPSM is fitted) BPSM B. Check all associated digital module LEDs
operate correctly; green LEDs lit on BPSM, NIU and MCUF, and red LEDs
off on NIU and MCUF.
MCUF initialization will commence at power up. A connection to the BSC
will be established and code download will take place. After completion of
the download, the site will be initialized.
NOTE Both red and green LEDs are initially lit on the NIU while
the unit performs a self-test. The red LED will extinguish
after approximately 50 seconds when rebooting after a
code download.
CAUTION If the code is a different version, the non-volatile memory
will be upgraded at this point. Both LEDs will be flashing,
and a warning message will appear on the PC terminal.
Do not power down or reset the cabinet as this will corrupt
the non-volatile memory. If this happens, contact Motorola
Customer Network Resolution Centre and request the
boot code restoration procedure and the appropriate boot
code file.
4. Press the CBM circuit breaker buttons for the appropriate CTUs fitted, and
check that the RADIO STATUS LED for each CTU flashes green.
At this point, after the MCUF has initialized, the CTUs will download code
from the MCUF.
CAUTION If the code is a different version, the non-volatile memory
will be upgraded at this point. Both LEDs will be flashing.
Do not power down or reset the cabinet as this will corrupt
the non-volatile memory. If this happens, contact Motorola
Customer Network Resolution Centre and request the
boot code restoration procedure and the appropriate boot
code file.
5. Once fully initialized, the RADIO STATUS LED on the front of each CTU
should be green, and each TRANSMIT STATUS LED should be either off
or yellow.
6. Disconnect the 9 to 9-way cable from the MCUF TTY port.
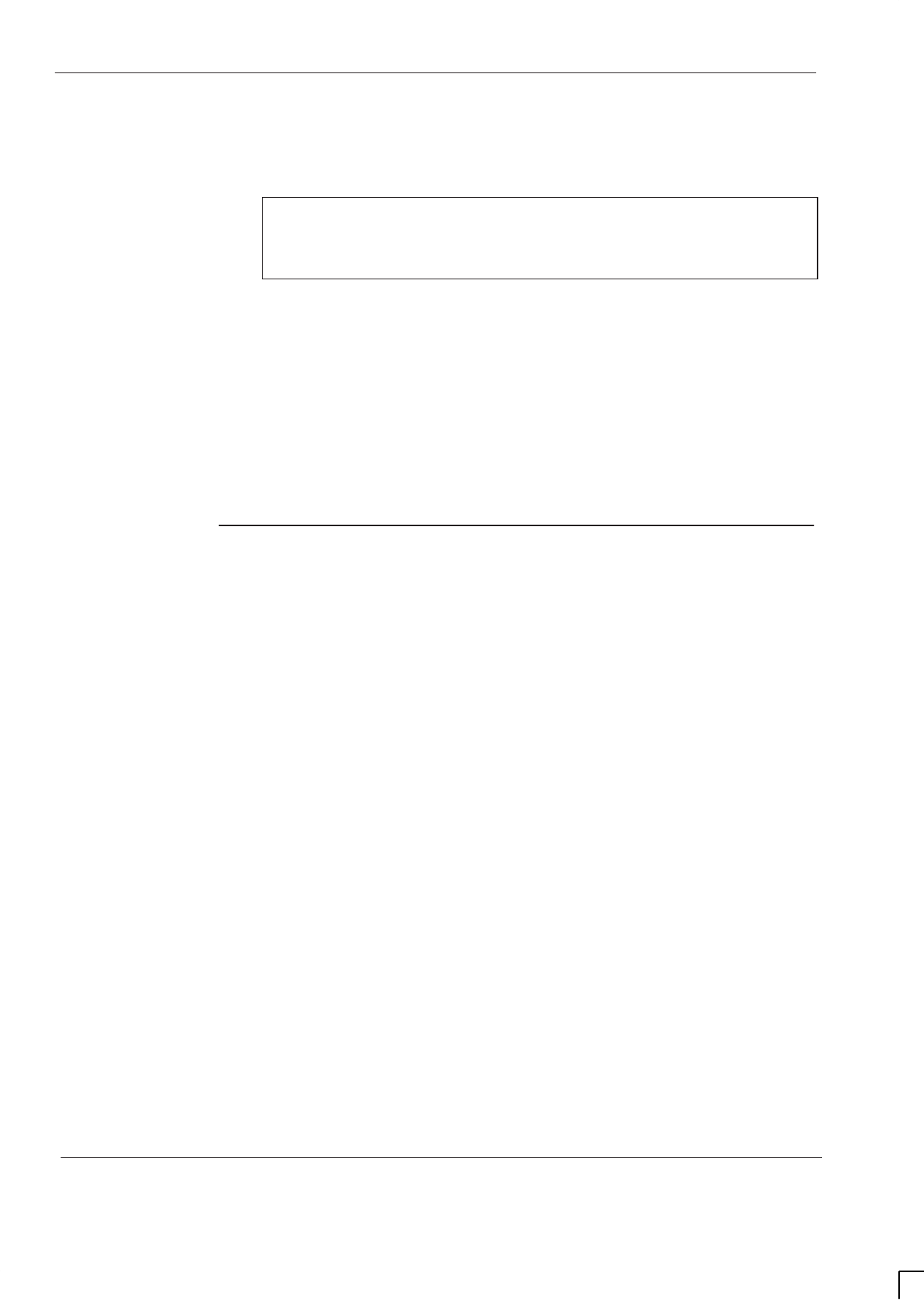
GSM-204-423
Powering up the cabinet
31st Oct 01
Inst. 7–14
Installation & Configuration: Horizon
macro
outdoor
CONTROLLED INTRODUCTION
68P02902W03-A
Battery backup and comms power up
To apply power to the backup batteries and communications equipment.
CAUTION When using external batteries, the Horizon
macro
outdoor
BTS cabinet internal batteries must be switch isolated to
ensure correct operation of the temperature-compensated
battery charging system.
1. Set the external battery or internal battery circuit breaker, depending on
the backup battery configuration, to on.
2. Test operation of battery backup as described in Testing the batteruy
backup.
3. Set any comms circuit breakers, appropriate for the customer
communications equipment fitted, to on.
4. Close the doors and lid to ensure correct thermal management.
This completes the power up of the cabinet.
Installation and
configuration
Consult
Installation and Configuration: BSS Optimization (GSM-100-423
68P02901W43)
for further procedures associated with ensuring a new site is
fully operational and optimized.
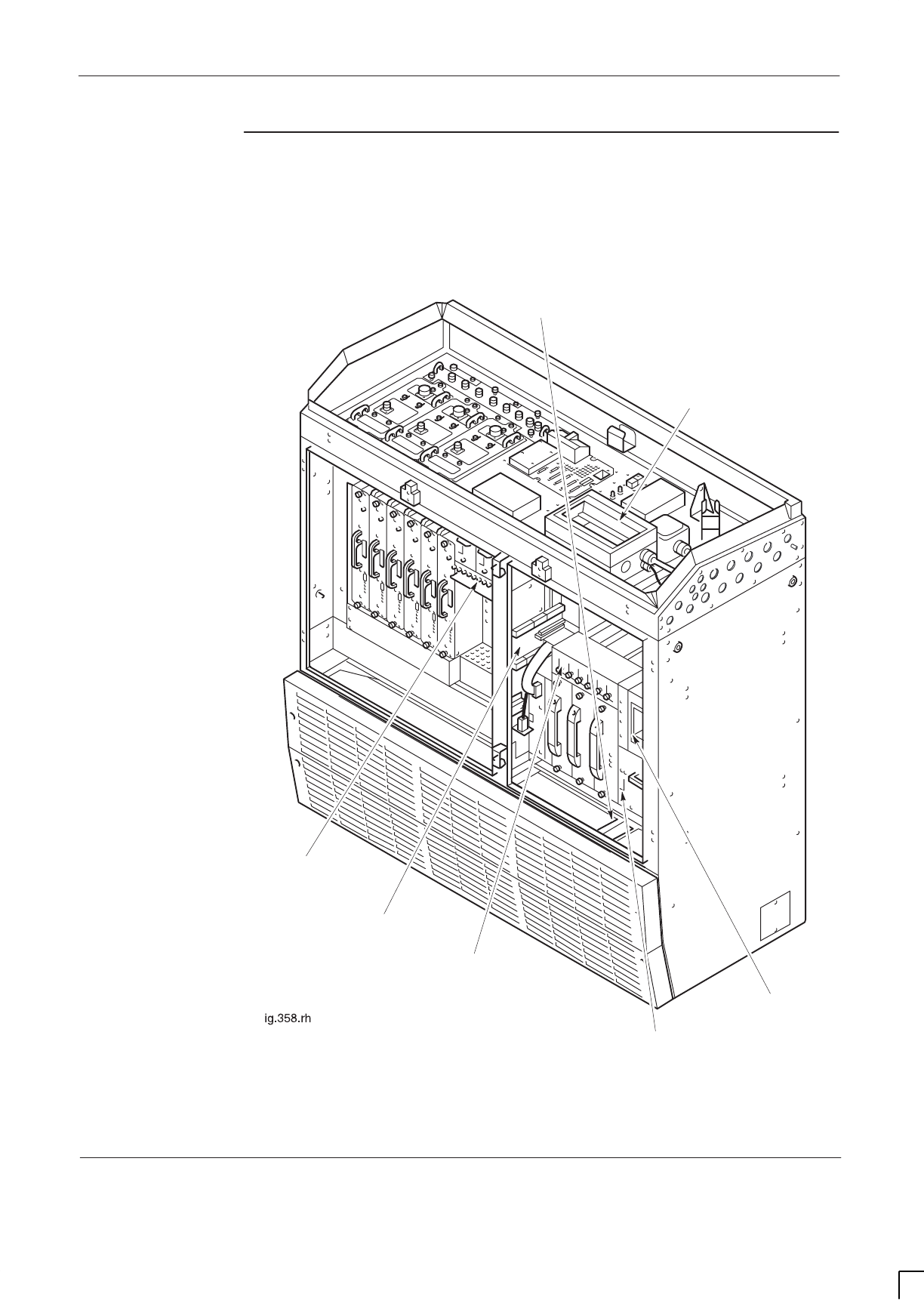
GSM-204-423 Powering up the cabinet
31st Oct 01
Installation & Configuration: Horizon
macro
outdoor
68P02902W03-A
CONTROLLED INTRODUCTION
Inst. 7–15
Components
involved in
power up
procedures
Figure 7-2 shows the cabinet components involved in power up procedures.
CIRCUIT
BREAKER
MODULE
NUMBER 1 AC
DISTRIBUTION
BOX
PSU DC CIRCUIT
BREAKER PANEL
INTERNAL BATTERY
CIRCUIT BREAKER
ALARMS INTERFACE
BOARD
TMS HEATER
FUNCTION
LED
NUMBER 2 AC
DISTRIBUTION
BOX
Figure 7-2 Location of components involved in power up procedures
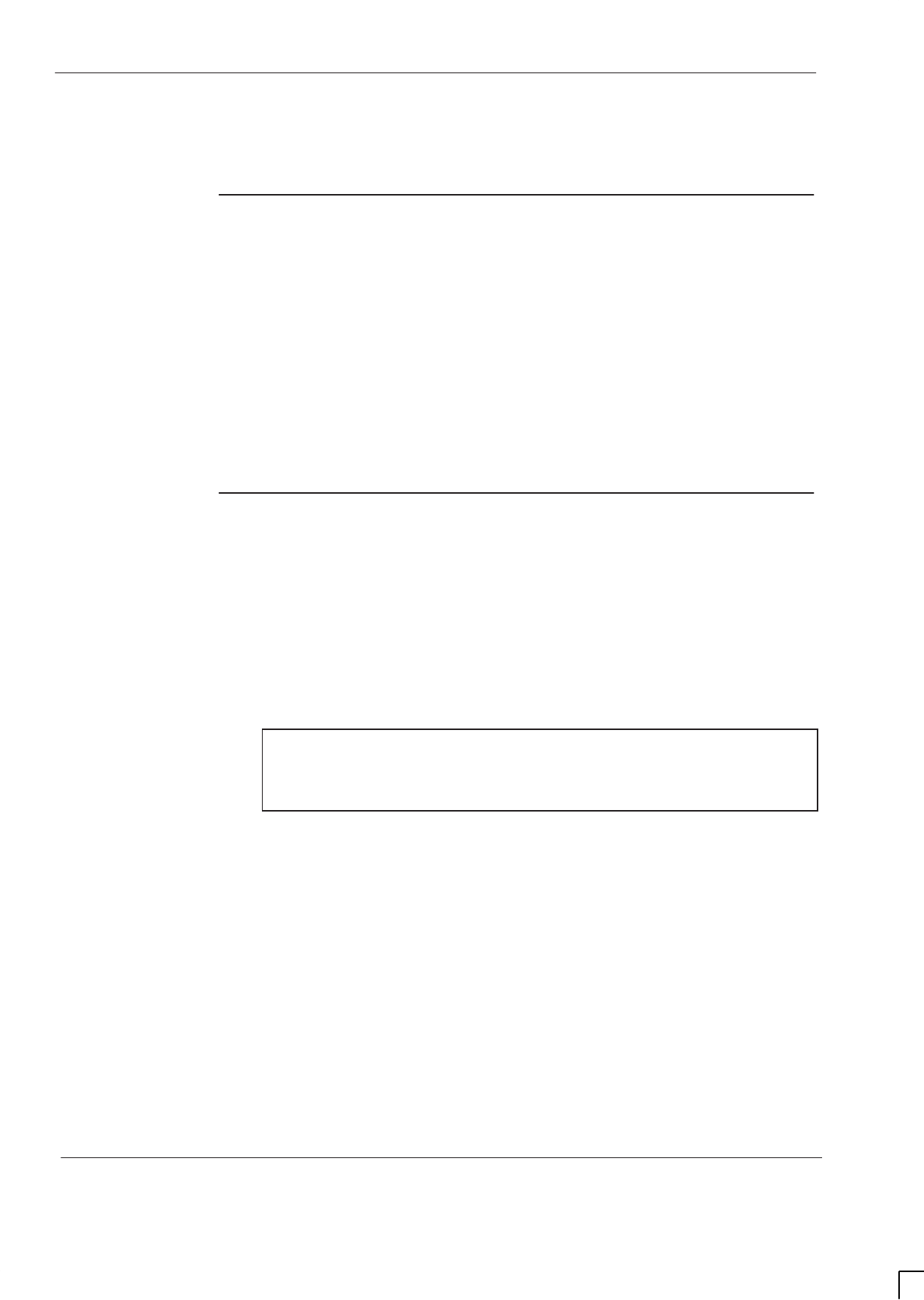
GSM-204-423
Testing the thermal management system (TMS)
31st Oct 01
Inst. 7–16
Installation & Configuration: Horizon
macro
outdoor
CONTROLLED INTRODUCTION
68P02902W03-A
Testing the thermal management system (TMS)
Overview of
TMS test
Objective
The TMS test verifies whether or not the TMS is operating correctly.
Test equipment
The TMS test does not require any test equipment.
Commands
The TMS test does not require any software commands.
Test facilities
A four button test switch is mounted on the alarms interface board next to the
power supply unit (PSU).
Provision is made to perform the following tests:
Operate the fans (minimum speed).
Change the recirculation air (internal) fan speed.
Change the ambient air (external) speed.
Operate the heater.
NOTE Heater function is indicated by the illumination of an LED,
mounted on the rear vertical wall at the top right of the
recirculation air outlet aperture, below and in front of the
power supply enclosure.
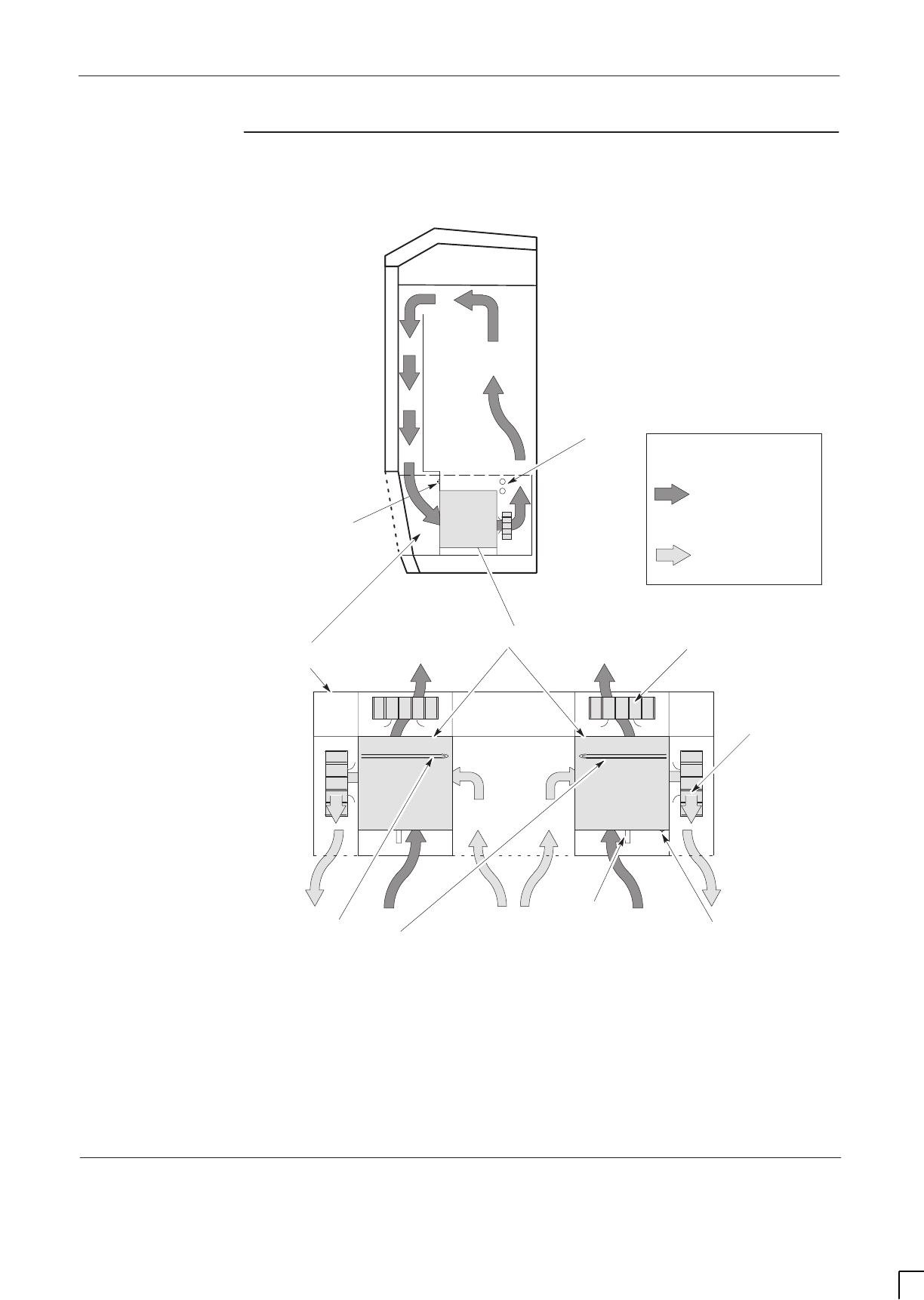
GSM-204-423 Testing the thermal management system (TMS)
31st Oct 01
Installation & Configuration: Horizon
macro
outdoor
68P02902W03-A
CONTROLLED INTRODUCTION
Inst. 7–17
Diagram of TMS
airflow
Figure 7-3 shows the airflow paths through the cabinet and TMS unit.
RECUPERATORS
Horizon
macro
outdoor
BTS CABINET CABINET
EQUIPMENT
TMS UNIT
RECIRCULATION
AIRFLOW
AMBIENT
AIRFLOW
RECIRCULATION
FAN
AMBIENT FAN
HEATER
ELEMENT
HEATER
ELEMENTS
SIDE ELEVATION VIEW OF
RECIRCULATION AIRFLOW
THROUGH CABINET
PLAN VIEW OF AIRFLOW
THROUGH TMS UNIT
KEY
HEATER
FUNCTION LED
TMS
TEMPERATURE
SENSOR
HEATER
FUNCTION LED
Figure 7-3 TMS airflow paths
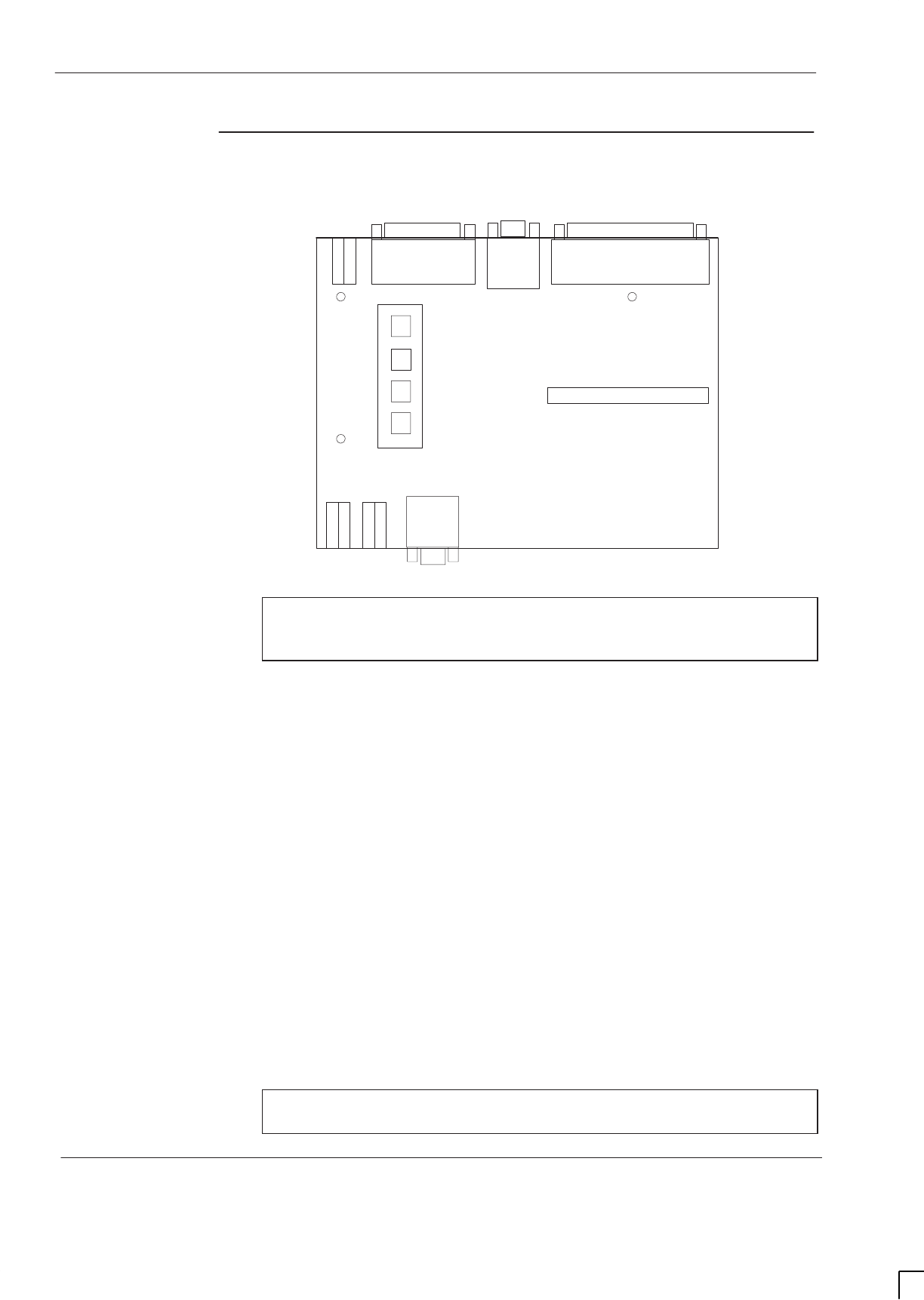
GSM-204-423
Testing the thermal management system (TMS)
31st Oct 01
Inst. 7–18
Installation & Configuration: Horizon
macro
outdoor
CONTROLLED INTRODUCTION
68P02902W03-A
Test procedure
Figure 7-4 shows the layout of the alarms interface board and shows the
location of the TMS test switches.
PL1 PL3
INTERNAL FANS
(SW3)
TEST OVERRIDE
(SW1)
HEATER ON
(SW2)
EXTERNAL FANS
(SW4) PL4
PL5
PL2
PL8
PL6PL7
CAUTION Do not operate the unit in test mode for more than 4
minutes, otherwise damage to the electronic equipment
may occur.
Figure 7-4 Layout of alarms interface board and TMS test switches
1. Open the power supply enclosure (right) cabinet door.
2. Press and hold the test override switch and check that the four fans are
rotating at minimum speed and the heater LED is off.
3. Press the internal fans switch and check that both recirculation fans
increase speed.
4. Release the internal fans switch and check that both recirculation fans
return to minimum speed.
5. Press the external fans switch and check that both ambient air fans
increase speed.
6. Release the external fans switch and check that both ambient air fans
return to minimum speed.
7. Press the heater switch and check that the heater LED is lit.
8. Release the heater and test override switches.
9. Close the cabinet doors and verify (by listening) that the TMS recirculation
fans are operating.
NOTE In step 9 ambient air fans may also run, depending on site
conditions.
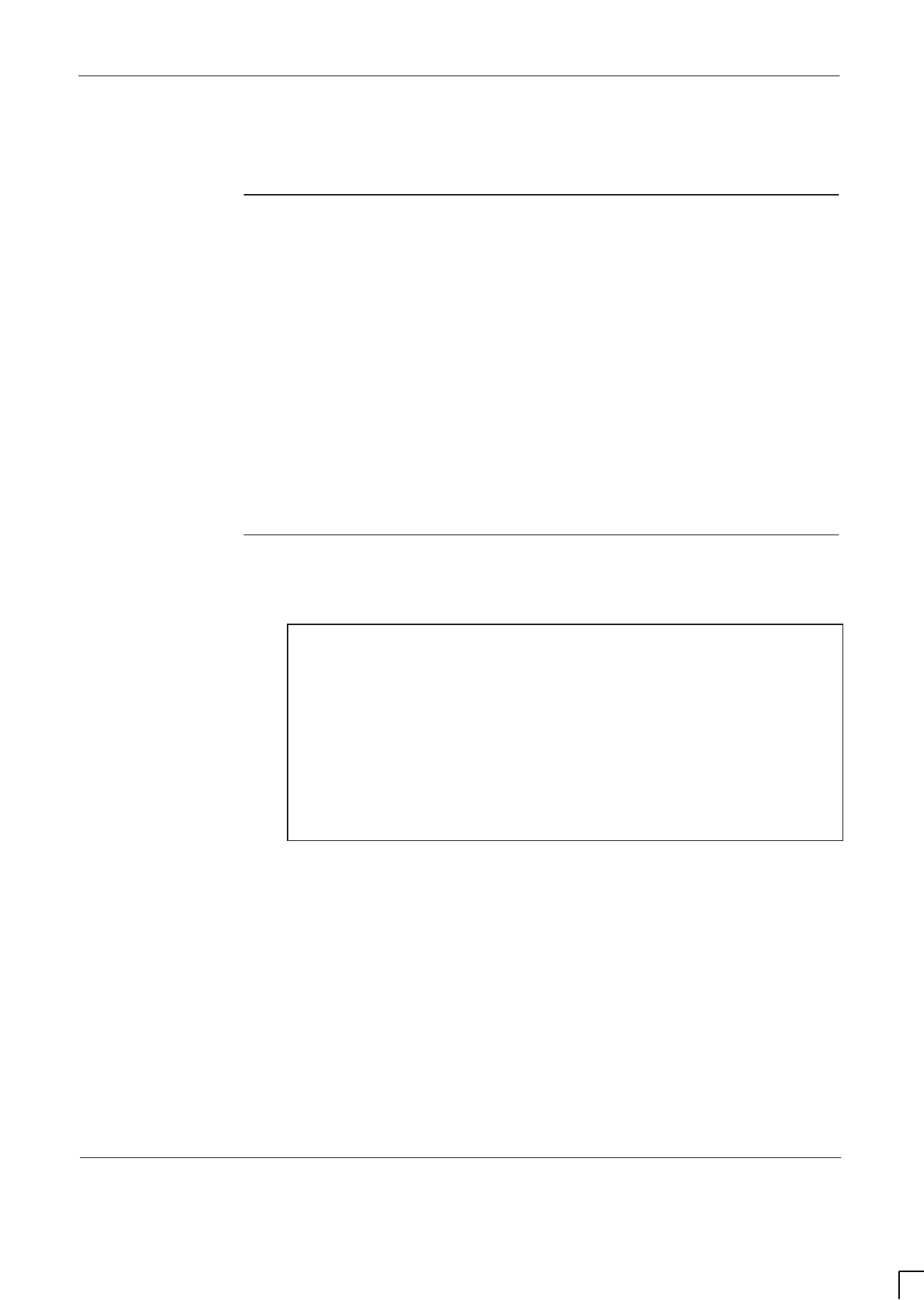
GSM-204-423 Testing the battery backup
31st Oct 01
Installation & Configuration: Horizon
macro
outdoor
68P02902W03-A
CONTROLLED INTRODUCTION
Inst. 7–19
Testing the battery backup
Overview of
battery backup
test
Objective
The battery backup test verifies whether or not the battery backup is operating
correctly.
Test equipment
The battery backup test does not require any test equipment.
Commands
The battery backup test does not require any software commands.
Battery backup
test procedures
The test procedure carried out will depend on battery backup configuration.
NOTE If the BTS cabinet is operational or otherwise visible to the
OMC-R, alarms will be generated. Notify the OMC-R
before carrying out these test procedures.
The internal or external batteries must be fully charged
before carrying out these test procedures.
The battery capacity test discharges the internal batteries
to –44 V dc. If an external power supply failure occurs
immediately after the test, the battery back up duration is
reduced to approximately 3 minutes. The internal batteries
recharge to approximately 80 % capacity in less than one
hour.
Internal battery backup
To test operation of internal battery backup:
1. Operate the CAB front panel BATTERY TEST button to initiate internal
battery capacity test.
2. Check that the BATTERY CAPACITY LEDs flash during the test.
3. Check the 15 mins battery capacity LED is illuminated at the end of the
test.
The test of internal battery backup operation is now complete.
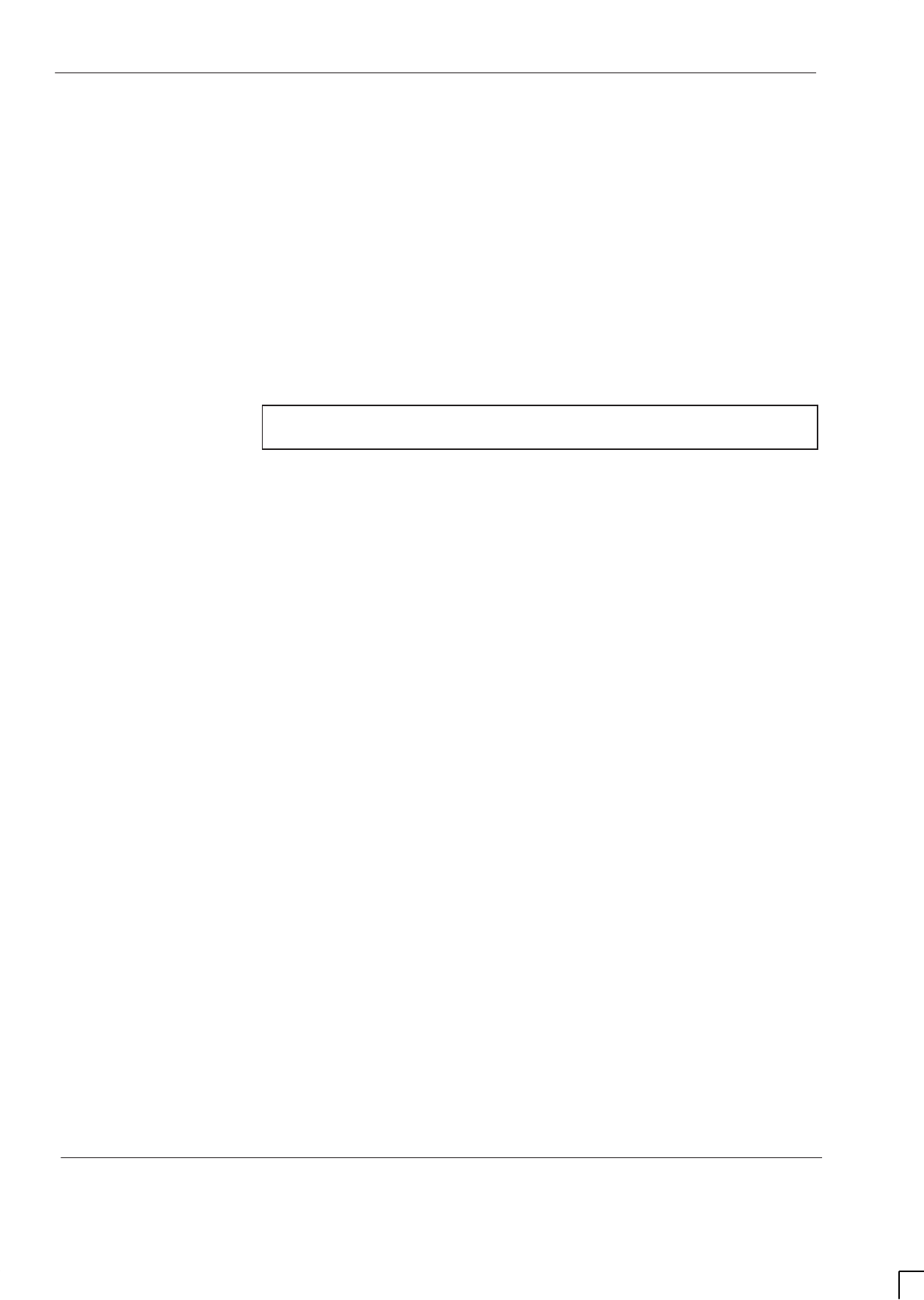
GSM-204-423
Testing the battery backup
31st Oct 01
Inst. 7–20
Installation & Configuration: Horizon
macro
outdoor
CONTROLLED INTRODUCTION
68P02902W03-A
External battery backup (AEH)
To test operation of external battery backup:
1. Switch the main 32 A circuit breaker to off to disconnect the external ac
supply.
2. Check that the yellow I/P HEALTHY and green O/P HEALTHY LEDs on
the three TOPSMs are extinguished.
3. Check that the green RADIO LED on the CAB remains illuminated.
4. Check that the RADIO STATUS LED for each CTU continues to flash
green.
5. Verify (by listening) that the TMS recirculation fans are operating.
NOTE In step 5 ambient air fans may also run, depending on site
conditions.
6. Switch the main 32 A circuit breaker to on to reconnect the external ac
supply.
7. Check that the yellow I/P HEALTHY and green O/P HEALTHY LEDs on
the three TOPSMs illuminate, and that the indications checked in steps 3
to 5 remain unchanged.
The test of external battery backup operation is now complete.
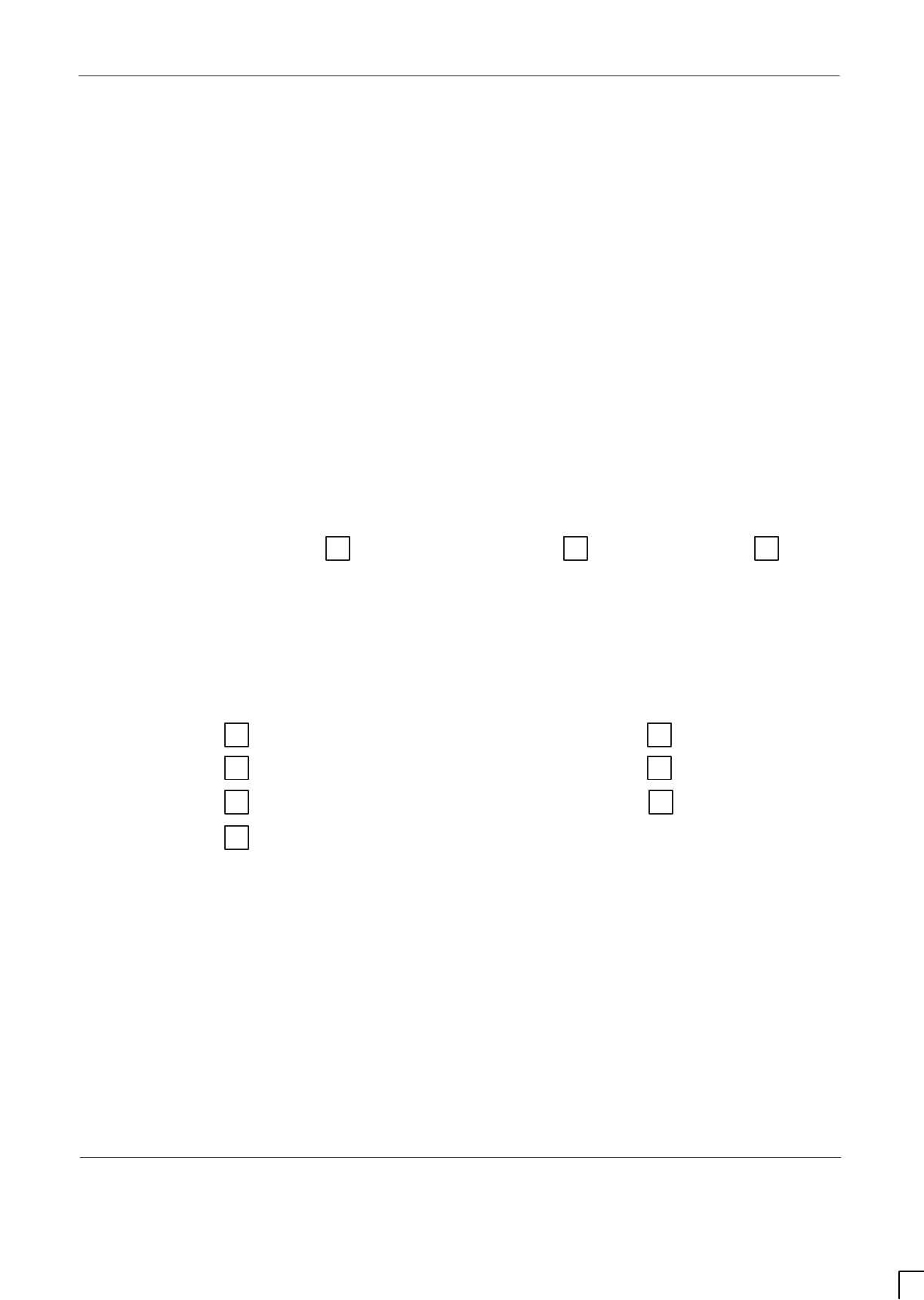
GSM-204-423 Sample form 1: Request for connection
31st Oct 01
Installation & Configuration: Horizon
macro
outdoor
68P02902W03-A
CONTROLLED INTRODUCTION
Inst. 7–21
Sample form 1: Request for connection
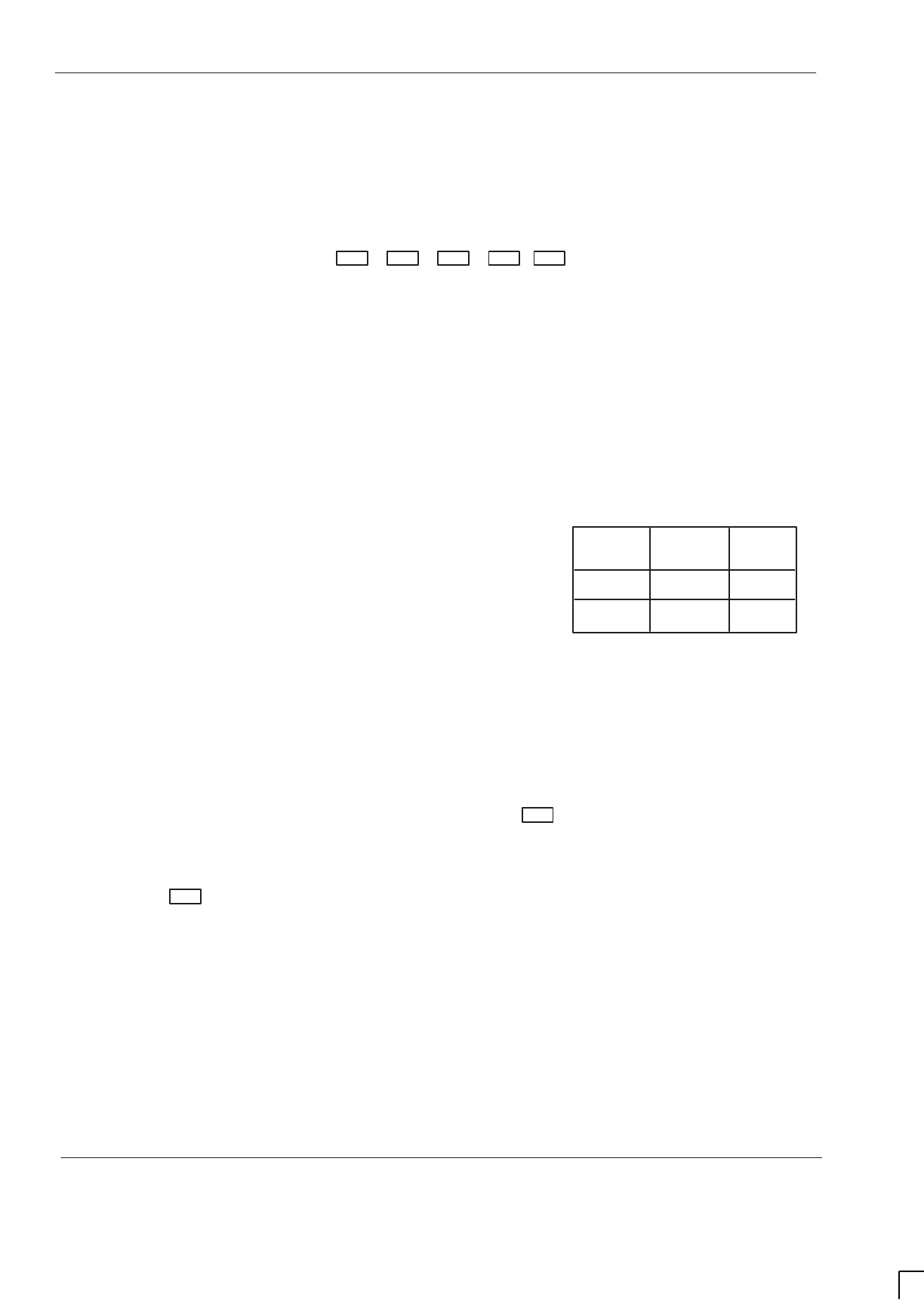
GSM-204-423
Sample form 1: Request for connection
31st Oct 01
Inst. 7–22
Installation & Configuration: Horizon
macro
outdoor
CONTROLLED INTRODUCTION
68P02902W03-A
PARTICULARS OF THE INSTALLATION
(Delete or complete items as appropriate)
Type of Installation New/alteration/addition/to existing installation
Type of earthing (312–03): TN–C TN–S TN–C–S TT IT
(Indicate in the box)
Earth Electrode Resistance . . . . . . . . . . . . . . . ohms
Method of Measurement . . . . . . . . . . . . . . . . . . . . . . . . . . . . . . . . . . . . . . . . . . . . .
Type (542–02–01) and Location . . . . . . . . . . . . . . . . . . . . . . . . . . . . . . . . . . . . . . . .
Characteristics of the supply at the origin of the installation ( 313–01 ):
Nominal voltage volts. . . . . . . . . . . . . . . . .
Frequency Hz Number of phases. . . . . . . . . . . . . . . . . . . . . . . . . . . . . . . . . . . . . . . . . . . . . .
Prospective short–circuit current kA. . . . . . . . . . . . . . . . . . . . . . .
Earth fault loop impedance (Ze) ohms. . . . . . . . . . . . . . . . . . . . . . . .
Maximum demand A per phase. . . . . . . . . .
Overcurrent protective device – Type BS Rating A. . . . . . . . . . . . . . . . . . . . . . . . . . . . . . . .
Main switch or circuit–breaker (460–01–02): Type BS Rating A No of poles . . . . .. . . . . . . . . . . . . . . . . . . . . . . . . . . . . . . . . . . .
(if an r.c.d., rated residual operating current I mA.). . . . . . . . . . . . . . . . . . . . . . . . . . . . . . . . . . . .
Method of protection against indirect contact:
1. Earthed equipotential bonding and automatic disconnection of supply
or
2. Other (Describe) . . . . . . . . . . . . . . . . . . . . . . . . . . . . . . . . . . . . . . . . . . . . . . . . . . . . . . . . . . . . . . . . . . . . . . . . . . . . . . . . . . . .
Main equipotential bonding conductors (413–02–01/02, 547–02–01): Size mm2
. . . . . . . . . . . . . . . . . . . . . . . . . . . .
schedule of Test Results: Continuation pages. . . . . . . . . . . . . . . . . . . . . . . . . . . . . . . . . . . . . . . . . . . . . . . . . . . . . . . . .
Details of departures (if any) from the Wiring Regulations (120–04, 120–05) . . . . . . . . . . . . . . . . . . . . . . . . . . . . . . . . . . . .
Comments on existing installation, where applicable (743–01–01): . . . . . . . . . . . . . . . . . . . . . . . . . . . . . . . . . . . . . . . . . . . .
ascertained
by
enquiry
determined
by
calculation
measured
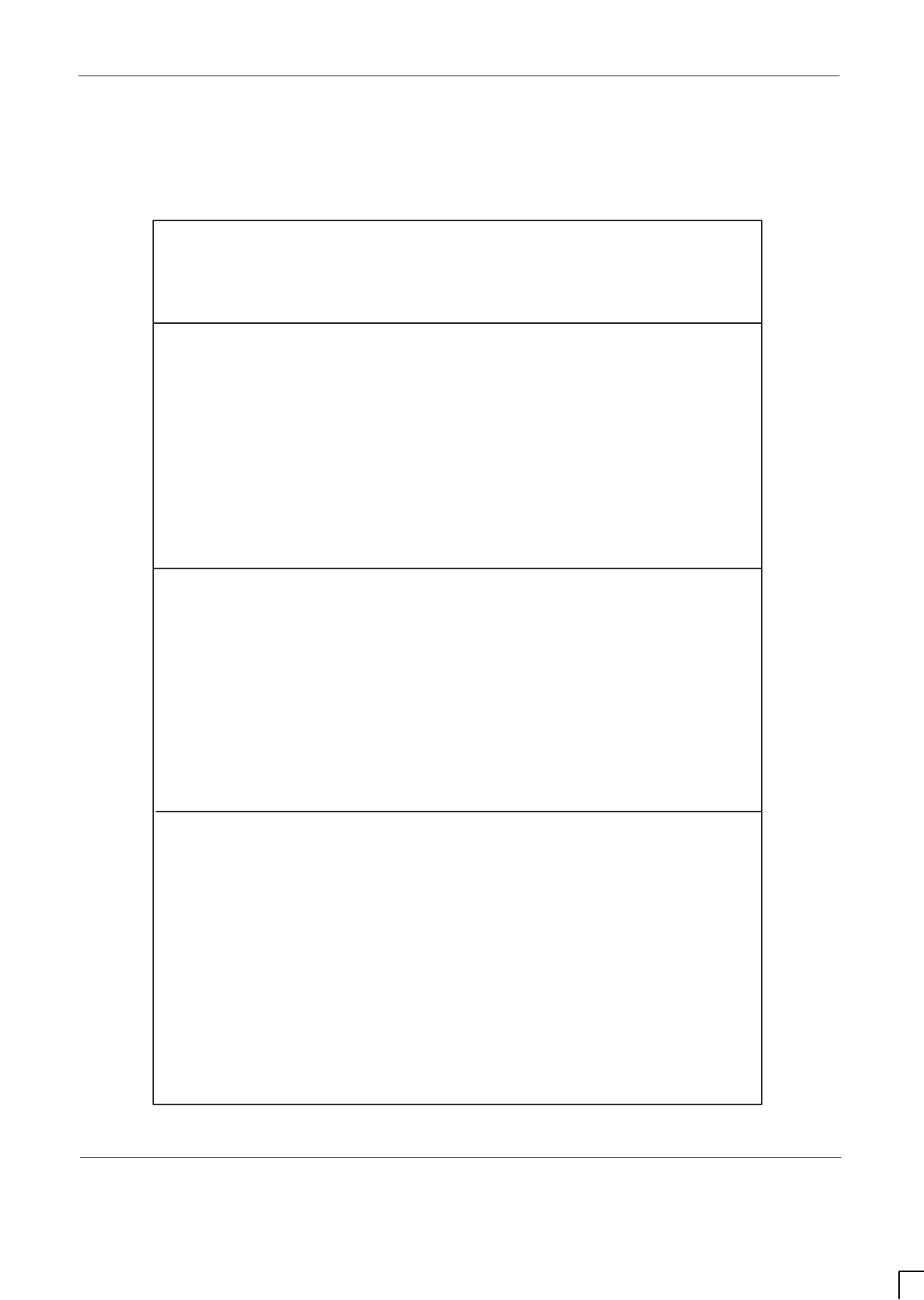
GSM-204-423 Sample form 2: Completion and inspection form
31st Oct 01
Installation & Configuration: Horizon
macro
outdoor
68P02902W03-A
CONTROLLED INTRODUCTION
Inst. 7–23
Sample form 2: Completion and inspection form
DETAILS OF THE INSTALLATION
Client:
Address:
DESIGN
I/We being the person(s) responsible (as indicated by my/our signatures below) for the Design of the electrical installation, particulars of which
are described on Page 3 of this form CERTIFY that the said work for which I/we have been responsible is to the best of my/our knowledge and
belief in accordance with the Regulations for Electrical Installations published by the Institution of Electrical Engineers, 16th Edition, amended
to (3.) (date . . . . . . . . .) except for the departures, if any, stated in this Certificate.
The extent of liability of the signatory is limited to the work described above as the subject of this Certificate.
For the DESIGN of the installation:
Name (In block Letters): Position:
for and on behalf of:
Address:
(2.) Signature: (3.) Date
CONSTRUCTION
I / We being the person(s) responsible ( as indicated by my/our signatures below ) for the Construction of the electrical installation, particulars of
which are described on Page 3 of this form CERTIFY that the said work for which I/we have been responsible is to the best of my/our knowledge
and belief in accordance with the Regulations for Electrical Installations published by the Institution of Electrical Engineers, 16th Edition,
amended to (3.) (date . . . . . . . . .) except for the departures, if any, stated in this Certificate.
The extent of liability of the signatory is limited to the work described above as the subject of this Certificate.
For the CONSTRUCTION of the installation:
Name (In block Letters): Position:
for and on behalf of:
Address:
(2.) Signature: (3.) Date
INSPECTION AND TEST
I / We being the person(s) responsible ( as indicated by my / our signatures below ) for the Inspection and Test of the electrical installation,
particulars of which are described on Page 3 of this form CERTIFY that the said work for which I/we have been responsible is to the best of my/
our knowledge and belief in accordance with the Regulations for Electrical Installations published by the Institution of Electrical Engineers, 16th
Edition, amended to (3.) (date . . . . . . . . .) except for the departures, if any, stated in this Certificate.
The extent of liability of the signatory is limited to the work described above as the subject of this Certificate.
For the INSPECTION AND TEST of the installation:
Name (In block Letters): Position:
for and on behalf of:
Address:
I RECOMMEND that this installation be further inspected and tested after an interval of not more than . . . . years (5.)
(2.) Signature: (3.) Date
(6) page 1 of . . . . pages
FORMS OF COMPLETION AND INSPECTION CERTIFICATE
(as prescribed in the IEE Regulations for Electrical Installations)
(1.) (see Notes overleaf)
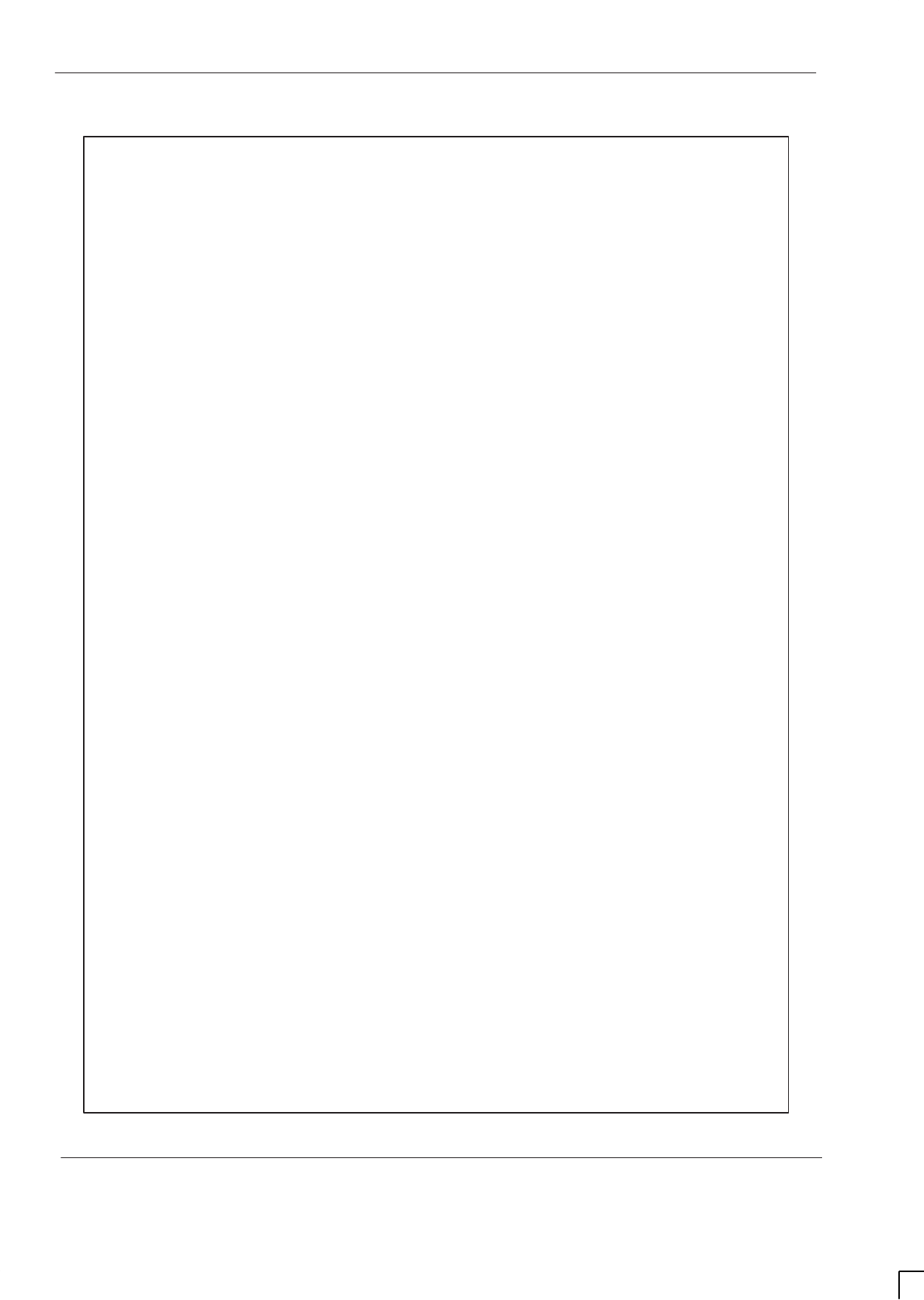
GSM-204-423
Sample form 2: Completion and inspection form
31st Oct 01
Inst. 7–24
Installation & Configuration: Horizon
macro
outdoor
CONTROLLED INTRODUCTION
68P02902W03-A
This document is intended for the initial certification of a new installation or of an alteration or addition to
an existing installation and of an inspection.
The signatures appended are those of the persons authorised by the companies executing the work of
design, construction and inspection and testing respectively. A signatory authorised to certify more than
one category of work shall sign in each of the appropriate places.
Dates to be inserted.
Where particulars of the installation recorded herein constitute a sufficient schedule for the purpose of
Regulation 514–09–01 further drawings / schedules need not be provided. For other installations the
additional drawings/schedules listed below apply.
Insert here the time interval recommended between periodic inspections. Regard should be paid to
relevant National or Local legislation and reference should be made to chapter 13.
The page numbers of each sheet should be indicated together with the total number of sheets involved.
(4) Schedule of additional records.
1.
2.
3.
4.
5.
6.
(6) page 2 of . . . . pages
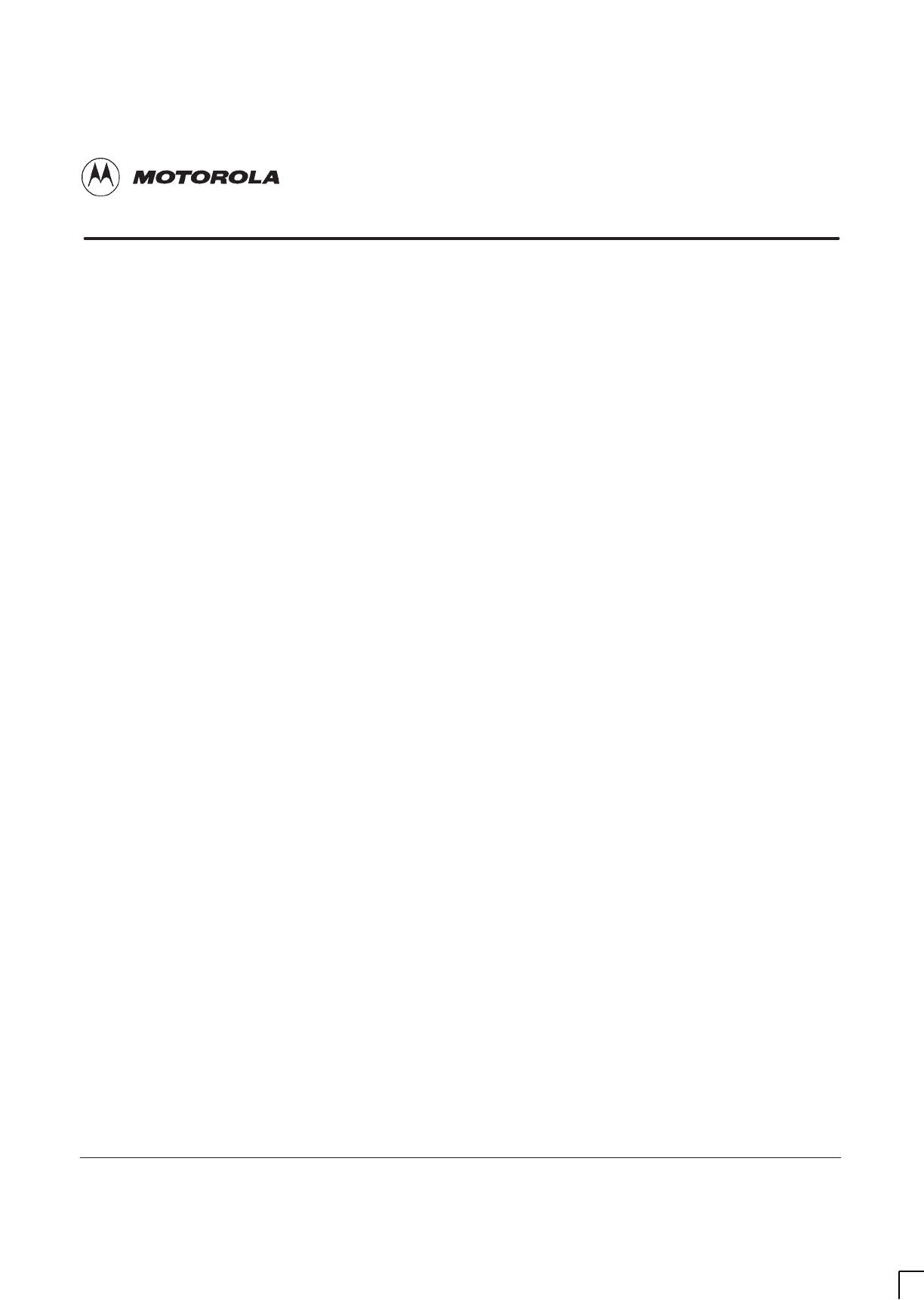
31st Oct 01
Installation & Configuration: Horizon
macro
outdoor
68P02902W03-A
CONTROLLED INTRODUCTION
i
Chapter 8
Decommissioning the equipment
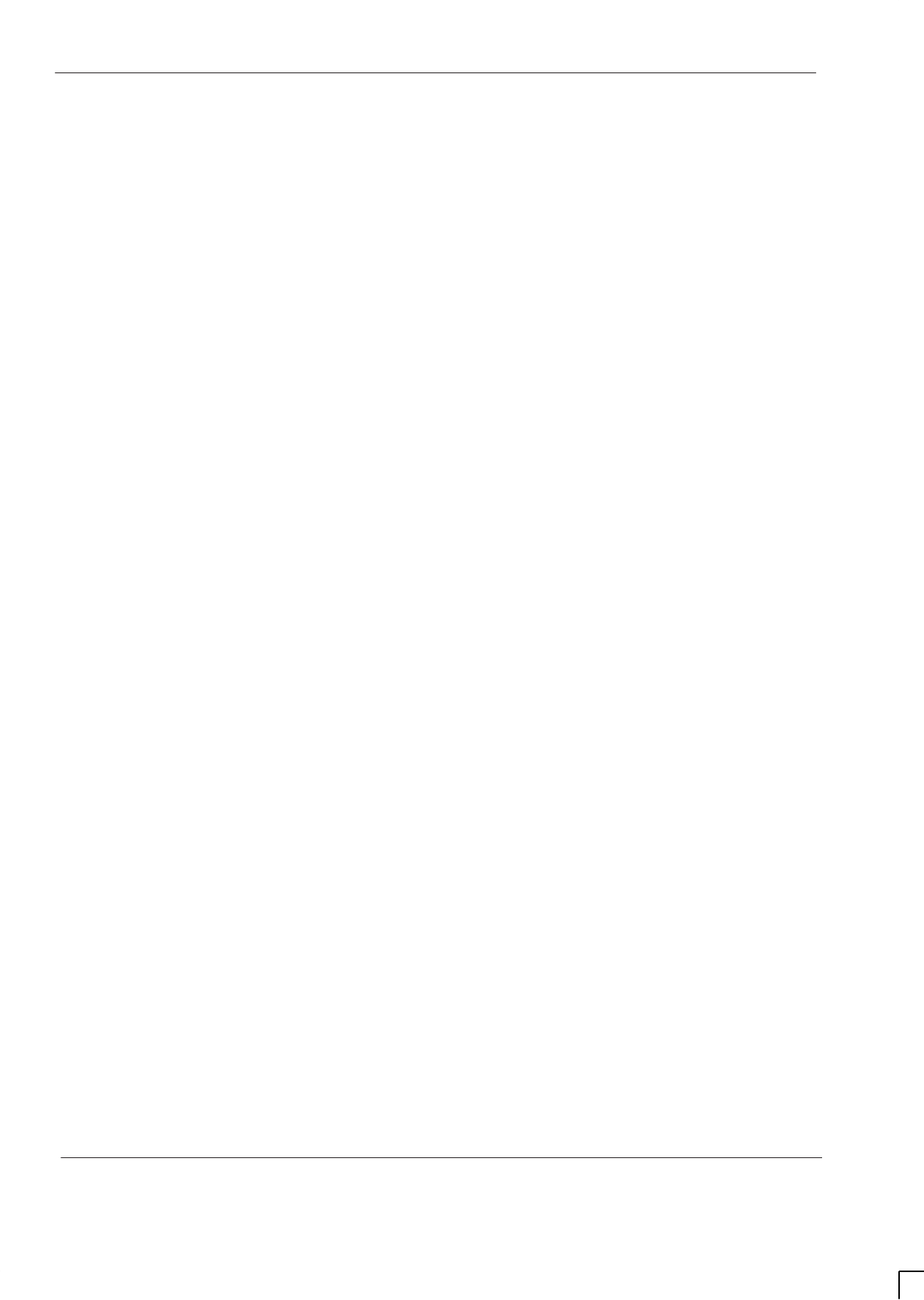
GSM-204-423
31st Oct 01
ii
Installation & Configuration: Horizon
macro
outdoor
CONTROLLED INTRODUCTION
68P02902W03-A
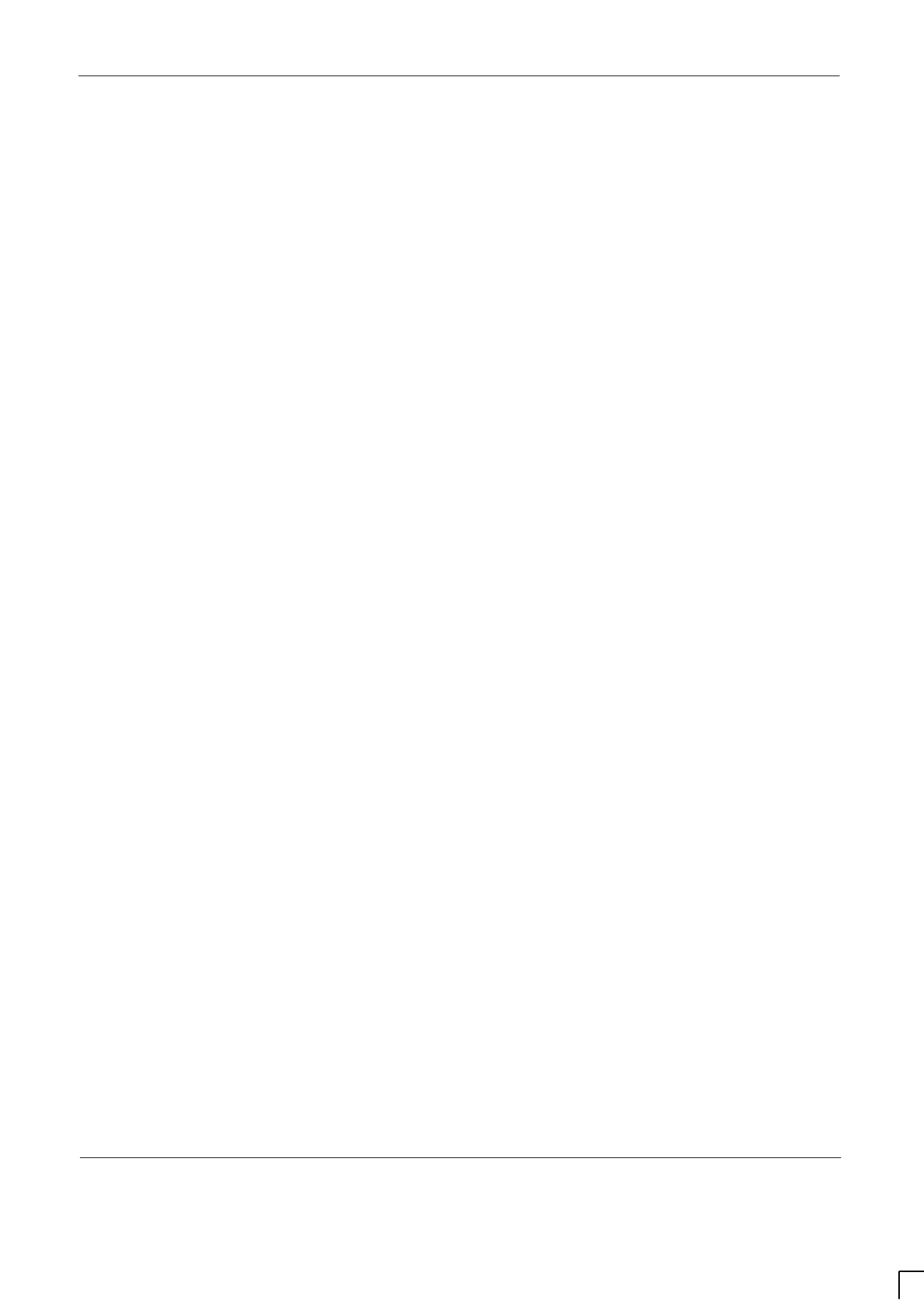
GSM-204-423
31st Oct 01
Installation & Configuration: Horizon
macro
outdoor
68P02902W03-A
CONTROLLED INTRODUCTION
iii
Chapter 8
Decommissioning the equipment i. . . . . . . . . . . . . . . . . . . . . . . . . . . . . . .
Introduction to decommissioning the Horizonmacro outdoor cabinet Inst. 8–1. . . . . . . .
Overview Inst. 8–1. . . . . . . . . . . . . . . . . . . . . . . . . . . . . . . . . . . . . . . . . . . . . . . . . . . . . .
Prerequisite Inst. 8–1. . . . . . . . . . . . . . . . . . . . . . . . . . . . . . . . . . . . . . . . . . . . . . . . . . . .
Lifting cabinets Inst. 8–1. . . . . . . . . . . . . . . . . . . . . . . . . . . . . . . . . . . . . . . . . . . . . . . . .
Decommissioning the Horizonmacro outdoor cabinet Inst. 8–2. . . . . . . . . . . . . . . . . . . . .
Introduction Inst. 8–2. . . . . . . . . . . . . . . . . . . . . . . . . . . . . . . . . . . . . . . . . . . . . . . . . . . .
To decommission using checklist Inst. 8–2. . . . . . . . . . . . . . . . . . . . . . . . . . . . . . . . . .
Before starting Inst. 8–2. . . . . . . . . . . . . . . . . . . . . . . . . . . . . . . . . . . . . . . . . . . . . . . . . .
Power down of the cabinet Inst. 8–2. . . . . . . . . . . . . . . . . . . . . . . . . . . . . . . . . . . . . . .
Procedure Inst. 8–3. . . . . . . . . . . . . . . . . . . . . . . . . . . . . . . . . . . . . . . . . . . . . . . . . . . . .
BTS checklist Inst. 8–4. . . . . . . . . . . . . . . . . . . . . . . . . . . . . . . . . . . . . . . . . . . . . . . . . . .
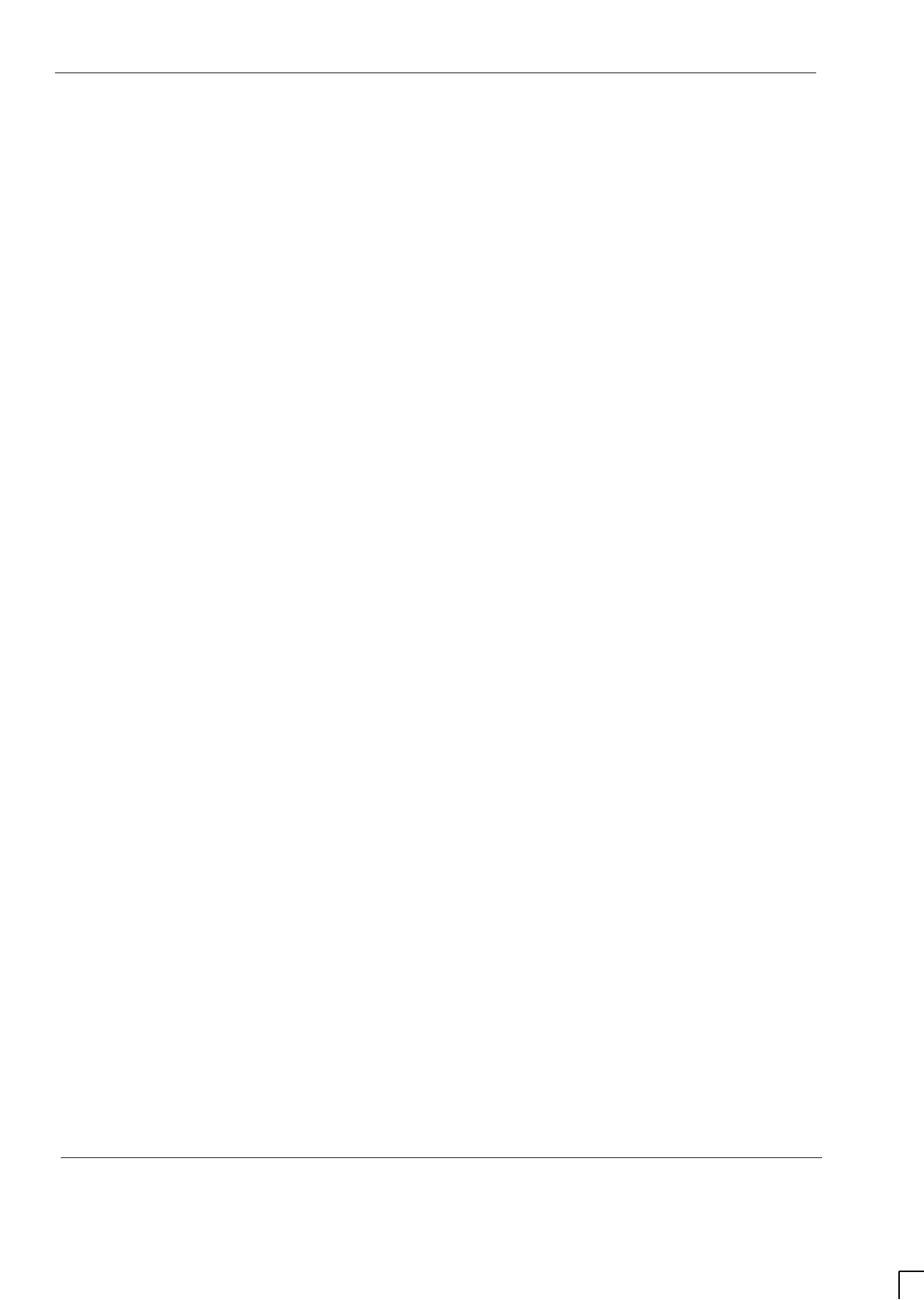
GSM-204-423
31st Oct 01
iv
Installation & Configuration: Horizon
macro
outdoor
CONTROLLED INTRODUCTION
68P02902W03-A
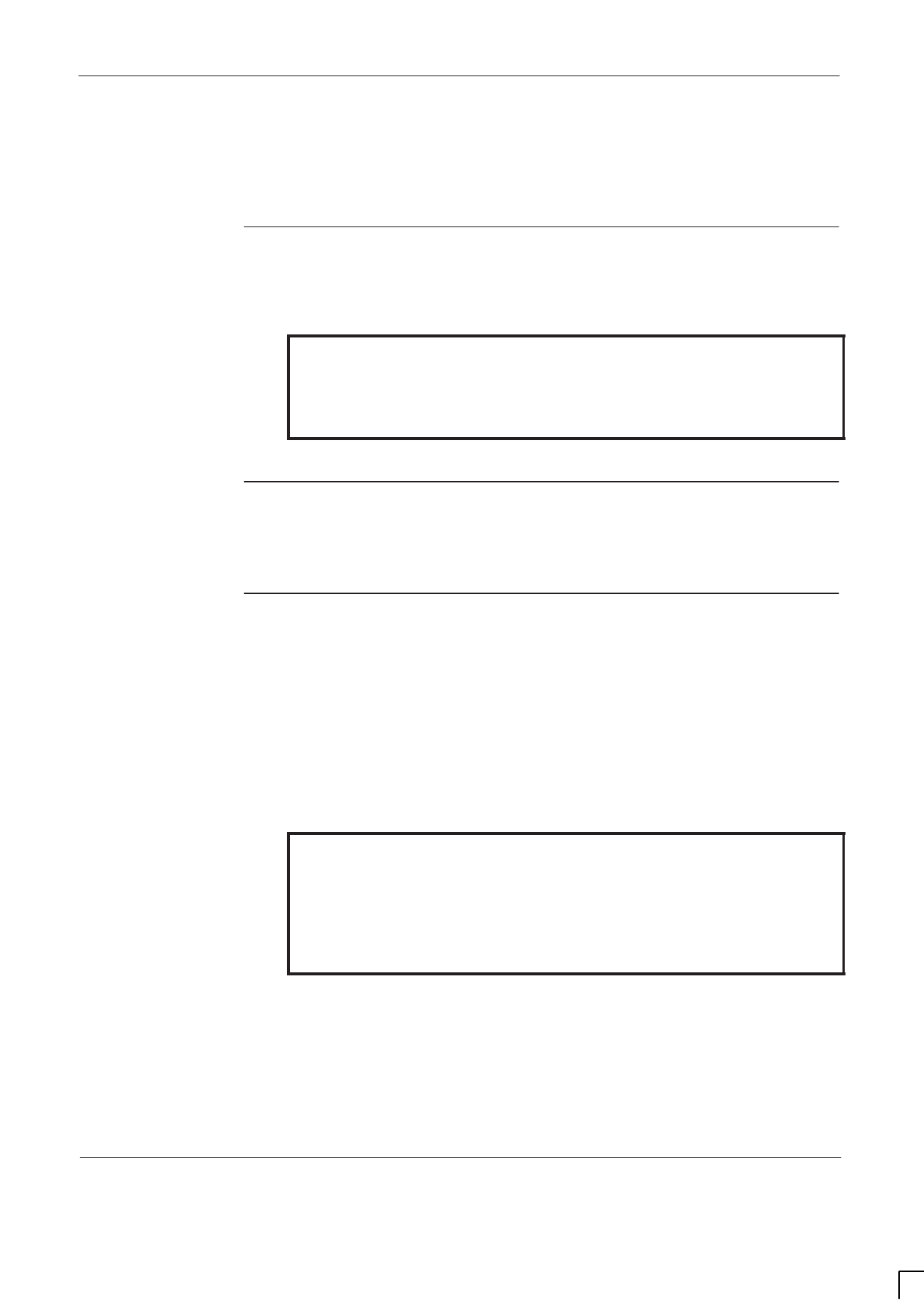
GSM-204-423 Introduction to decommissioning the Horizonmacro outdoor cabinet
31st Oct 01
Installation & Configuration: Horizon
macro
outdoor
68P02902W03-A
CONTROLLED INTRODUCTION
Inst. 8–1
Introduction to decommissioning the Horizon
macro
outdoor
cabinet
Overview
This chapter describes how to decommission the Horizon
macro
outdoor cabinet.
To decommission equipment not supplied by Motorola, for example E1/T1 links,
power supplies and antennas, refer to the vendor’s instructions.
WARNING Hazardous voltages exist inside the Horizon
macro
outdoor
cabinet.
Use extreme caution when working on a cabinet with
power applied. Remove all rings, watches and other
jewellery.
Prerequisite
Read all the earlier chapters of this installation section, before attempting to
decommission a Horizon
macro
outdoor cabinet.
Lifting cabinets
Horizon
macro
outdoor cabinets are fitted with four lifting points, designed to
accommodate M16 swivel head eyebolts, built into the cabinet sides. If swivel
head eyebolts are used to lift the cabinet, they must be manufactured to CE
conformity, and must have a safe weight load of 400 kg each.
Refer to Safety considerations from Unpacking and preparing the cabinet in
Chapter 3 of this category before lifting cabinets.
1. Carefully remove the plastic insert from the M16 threaded lifting point.
2. Insert the eyebolt into the thread, ensuring that no cross-threading occurs.
WARNING Before attempting to insert the eyebolts, visually check
each one for damage. If any damage is apparent, DO
NOT USE.
Do not overtighten the eyebolts; hand tight is sufficient. Do
not tighten eyebolts with a t-bar or spanner. Screw the
eyebolt fully into the lifting point so that no thread is left
exposed.
3. Repeat the procedure until all four eyebolts have been correctly fitted.
For continued use of eyebolts, there may be local regulations that govern the
use of lifting equipment and stipulate a test and/or examination regime. If the
eyebolts are to be used, ensure that all such regulations are met.
Remember to remove the eyebolts and refit the plastic inserts when the lifting
operation is complete.
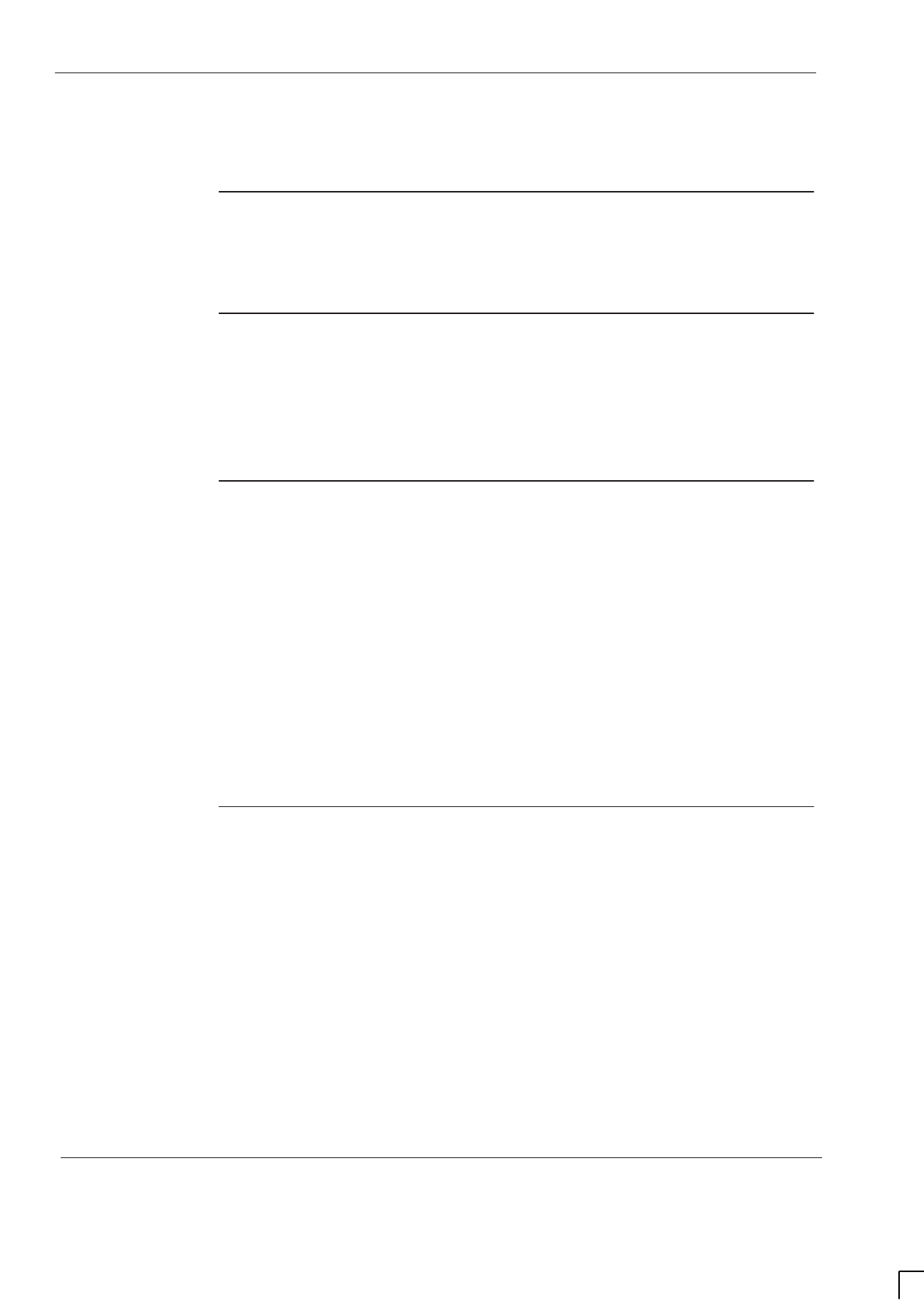
GSM-204-423
Decommissioning the Horizonmacro outdoor cabinet
31st Oct 01
Inst. 8–2
Installation & Configuration: Horizon
macro
outdoor
CONTROLLED INTRODUCTION
68P02902W03-A
Decommissioning the Horizon
macro
outdoor cabinet
Introduction
Use the following procedure to decommission the Horizon
macro
outdoor
cabinet, and use the checklist to check off each action as it is completed.
Photocopy the checklist as often as required. Do not write on the original.
To
decommission
using checklist
The following procedure should be recorded by use of the checklist, to check
that each action has been completed. Photocopy the checklist as often as
required; do not write on the original manual copy.
Before starting
Before starting to decommission the cabinet, ensure that:
The main power source is switched off and that no power is connected to
the cabinet. If an auxiliary equipment housing is connected to provide
battery backup, ensure that the dc power is isolated from the
Horizon
macro
outdoor cabinet.
Suitable packing crates and cartons are available to pack the
decommissioned equipment.
The OMC-R has taken the cabinet out of service.
The cabinet has been powered down, as described in Powering down
the cabinet in this section.
Any unused items have been retrieved from storage elsewhere.
Power down of
the cabinet
If the cabinet is not to remain powered up, power down as follows:
1. Press all CBM circuit breaker buttons to the out (off) position.
2. Switch each PSM to the OUTPUT DISABLE position.
3. Set the internal and external battery circuit breakers to off.
4. Set all circuit breakers on the PSU dc circuit breaker panel to off.
5. Set the number 2 ac distribution box circuit breakers to off.
6. Switch the four pole MCB and 6 amp RCBO circuit breakers in the number
1 ac distribution box to off.
7. Switch off the external power supply to the cabinet.
This completes the power down procedure for the cabinet.
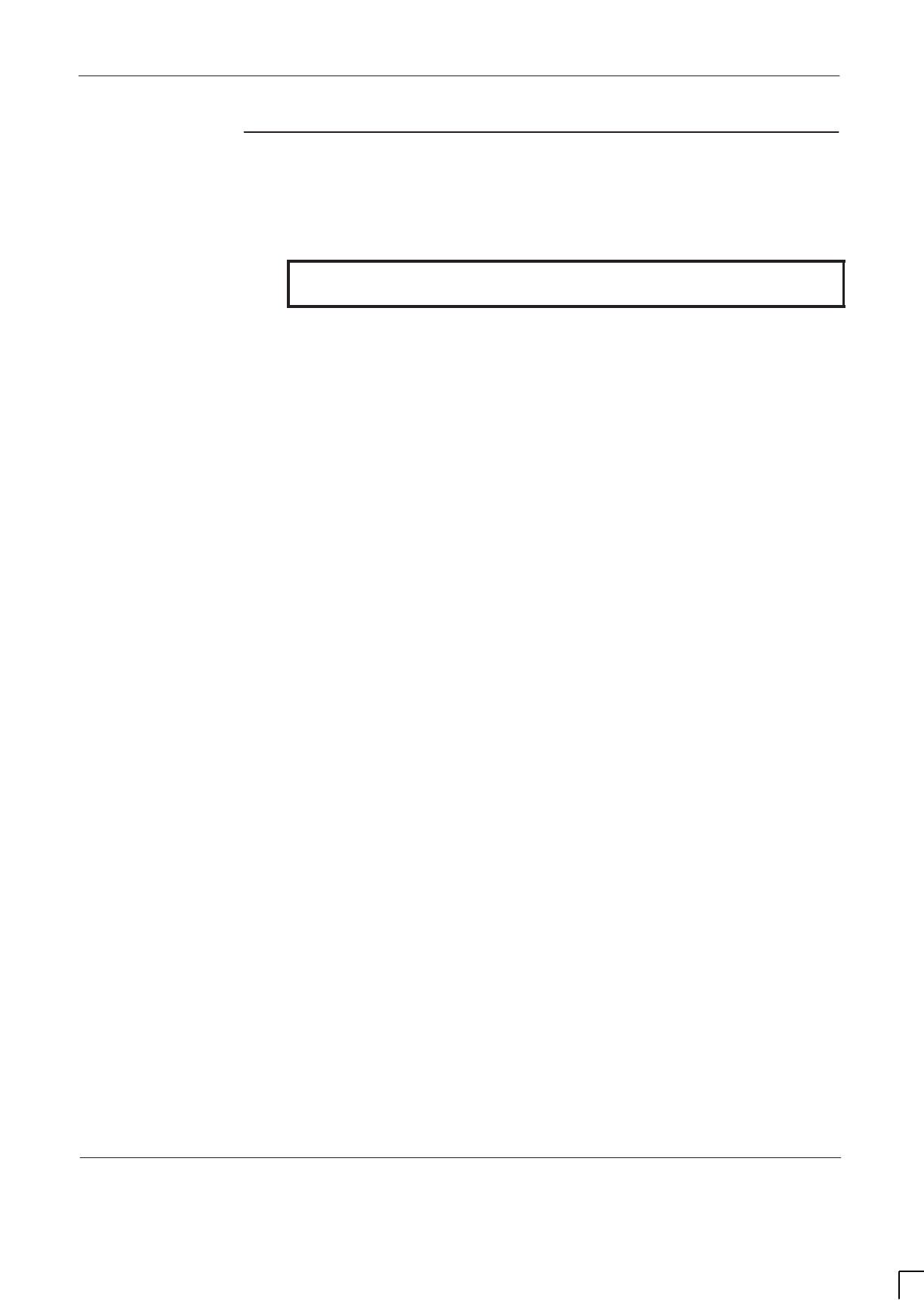
GSM-204-423 Decommissioning the Horizonmacro outdoor cabinet
31st Oct 01
Installation & Configuration: Horizon
macro
outdoor
68P02902W03-A
CONTROLLED INTRODUCTION
Inst. 8–3
Procedure
To decommission the cabinet:
1. Check the cabinet and its contents for signs of damage.
2. Use a digital voltmeter to ensure that power is not present in the cabinet.
WARNING Untidy disconnected cables can create a trip hazard to
personnel using the site.
3. Disconnect the cabinet input ac power cable from the power source and
the main input terminals. Withdraw the cable through the earthing plate
and store it in suitable packaging. Do not remove the cabinet earth lead
until all other cables have been disconnected.
4. Disconnect all antenna cables from their connections on the earthing
plate, and any transmit and receive RF cables from other cabinets.
5. Disconnect fibre optic cables between master cabinet and any extension
cabinets.
6. Disconnect the following cables (if fitted) from their connectors on the top
panel of the cabinet and withdraw the cables through the earthing plate:
– E1/T1 cables.
– Alarm cables.
– DC power cables (from auxiliary equipment housing, if fitted).
Refit the protective covers to all exposed terminals on the top panel.
7. Disconnect the cabinet earth cable and stow disconnected cables so that
they do not constitute a hazard to personnel using the site.
8. Unbolt the cabinet from the floor and move it to a location where it can be
safely packed into a wooden transit case.
9. Unbolt the alloy template and repack it with the cabinet.
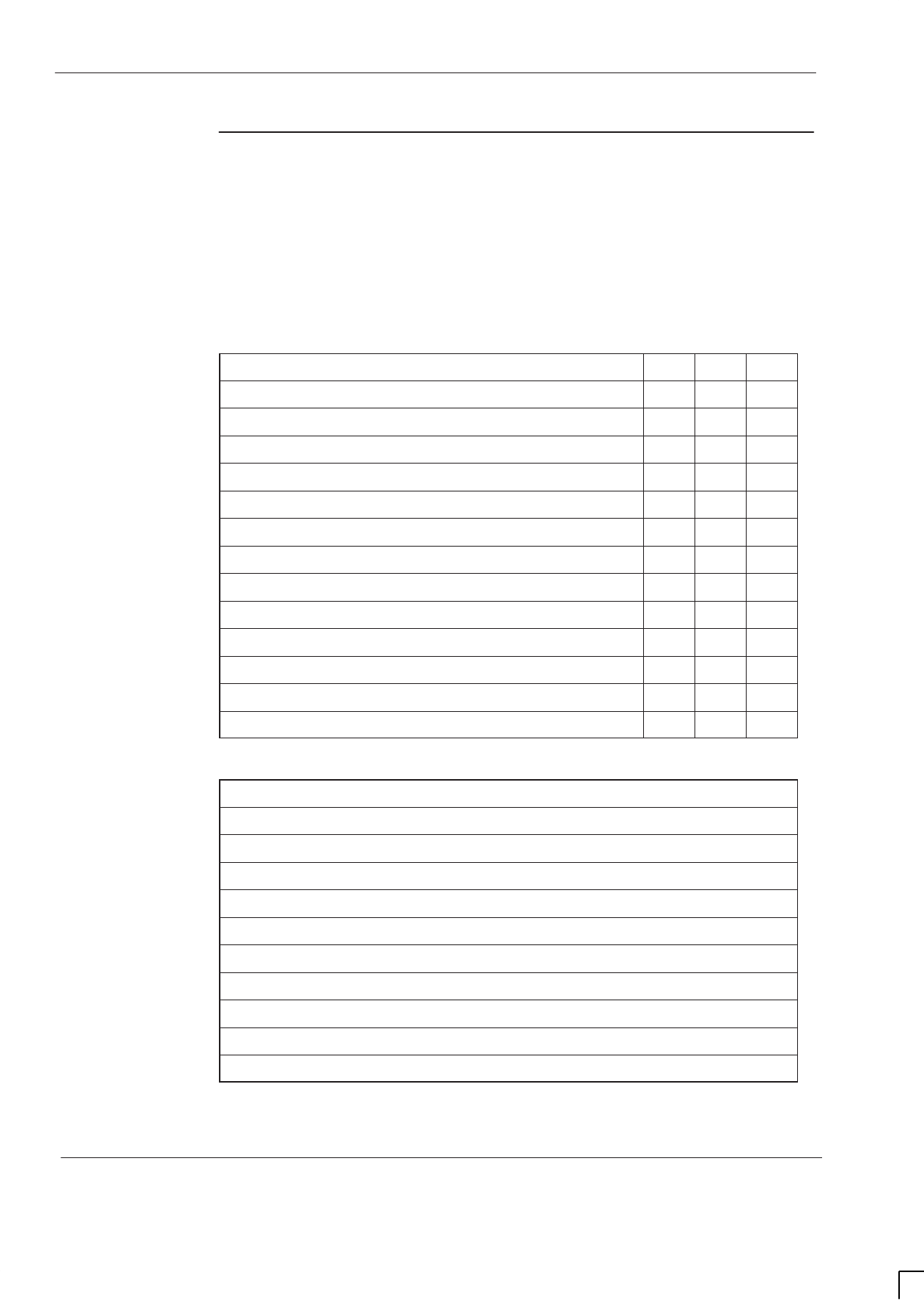
GSM-204-423
Decommissioning the Horizonmacro outdoor cabinet
31st Oct 01
Inst. 8–4
Installation & Configuration: Horizon
macro
outdoor
CONTROLLED INTRODUCTION
68P02902W03-A
BTS checklist
NAME _________________________________________DATE ___________
SIGNATURE ___________________________________
SITE NAME ____________________________________
EQUIPMENT TYPE ______________________________
NAT ID ________________________________________
ACTION Yes No N/A
Outdoor cabinet taken out of service by the OMC-R.
Packing material (including polythene bag) on site.
Is cabinet damaged? If yes, detail in comments box.
Power cable disconnected.
RF cables disconnected from earthing plate.
Interface panel cables disconnected.
DC power cables disconnected (if used).
Protective covers refitted to top panel connectors.
Earth cable disconnected from the cabinet.
Doors and lid closed and locked. Key stored safely.
Cabinet packed in transit case.
Cabinet base fixings removed and packed.
Cabinet template removed and packed.
COMMENTS

CHAPTER 2
GENERAL MAINTENANCE CHAPTER 3
FRU REPLACEMENT
PROCEDURES
CHAPTER 4
AUXILIARY EQUIPMENT
HOUSING MAINTENANCE
CHAPTER 1
INTRODUCTION TO
MAINTENANCE
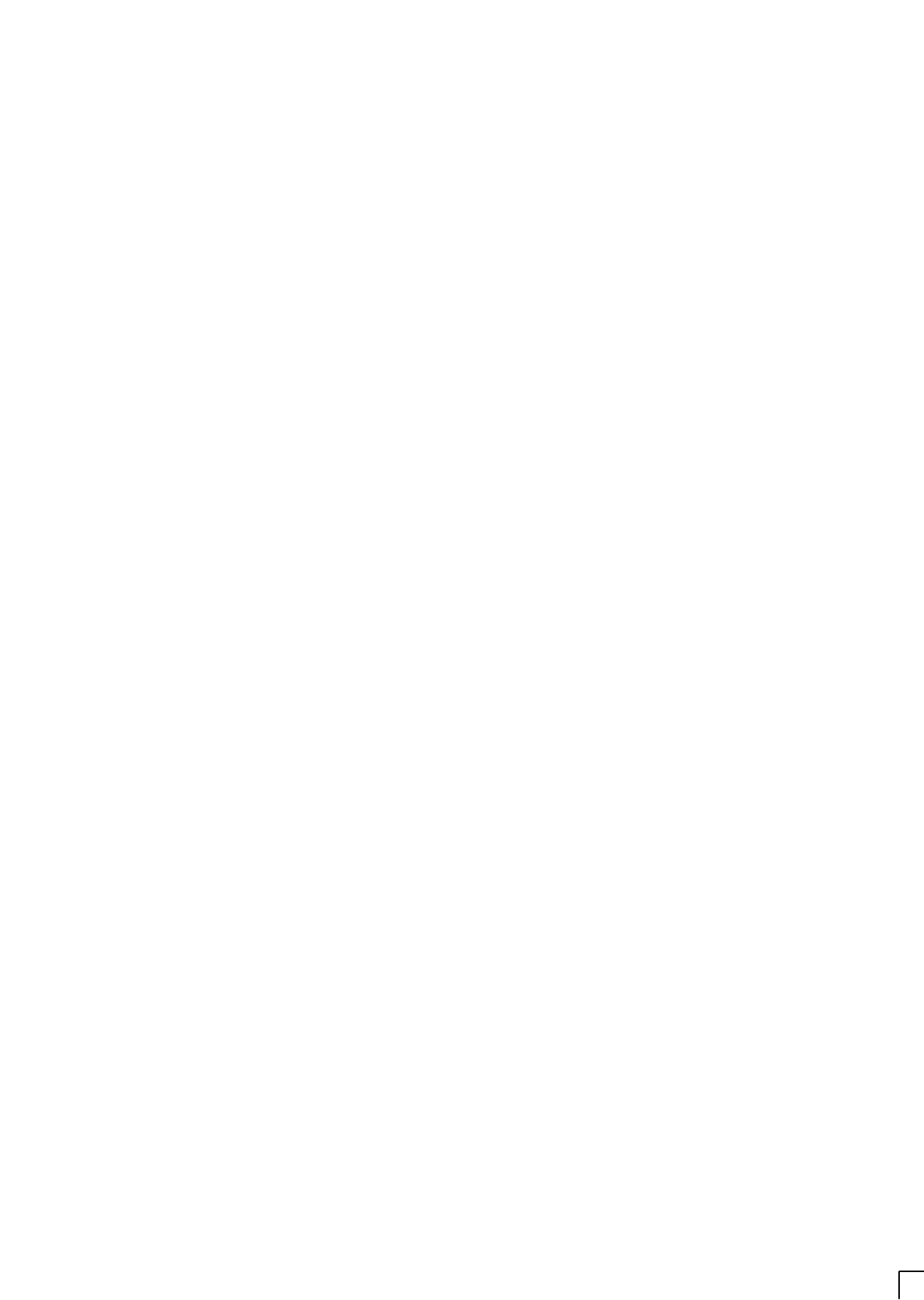
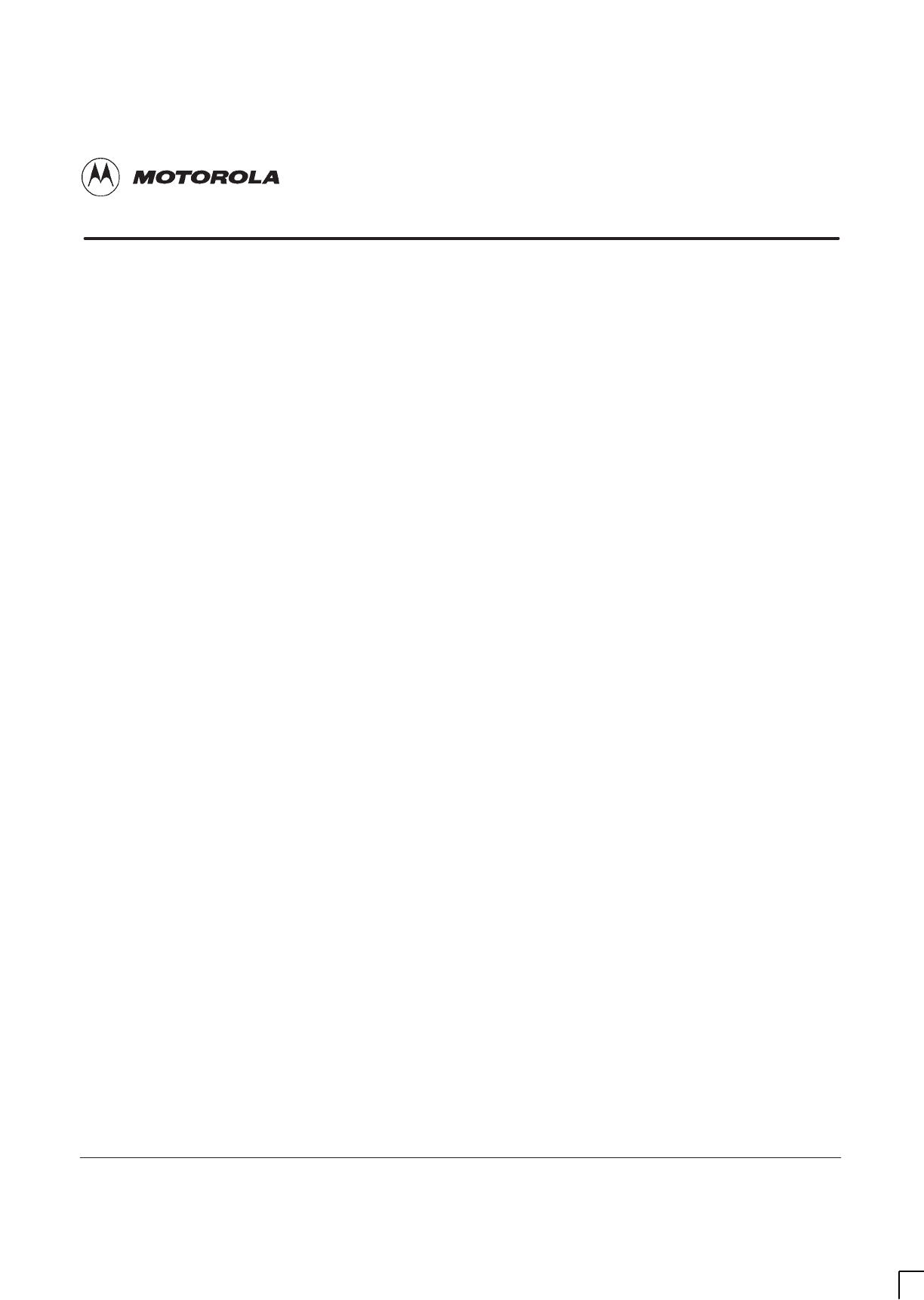
31st Oct 01
Maintenance Information: Horizon
macro
outdoor
68P02902W04-A
CONTROLLED INTRODUCTION
i
Category 523
Maintenance Information (Maint.)
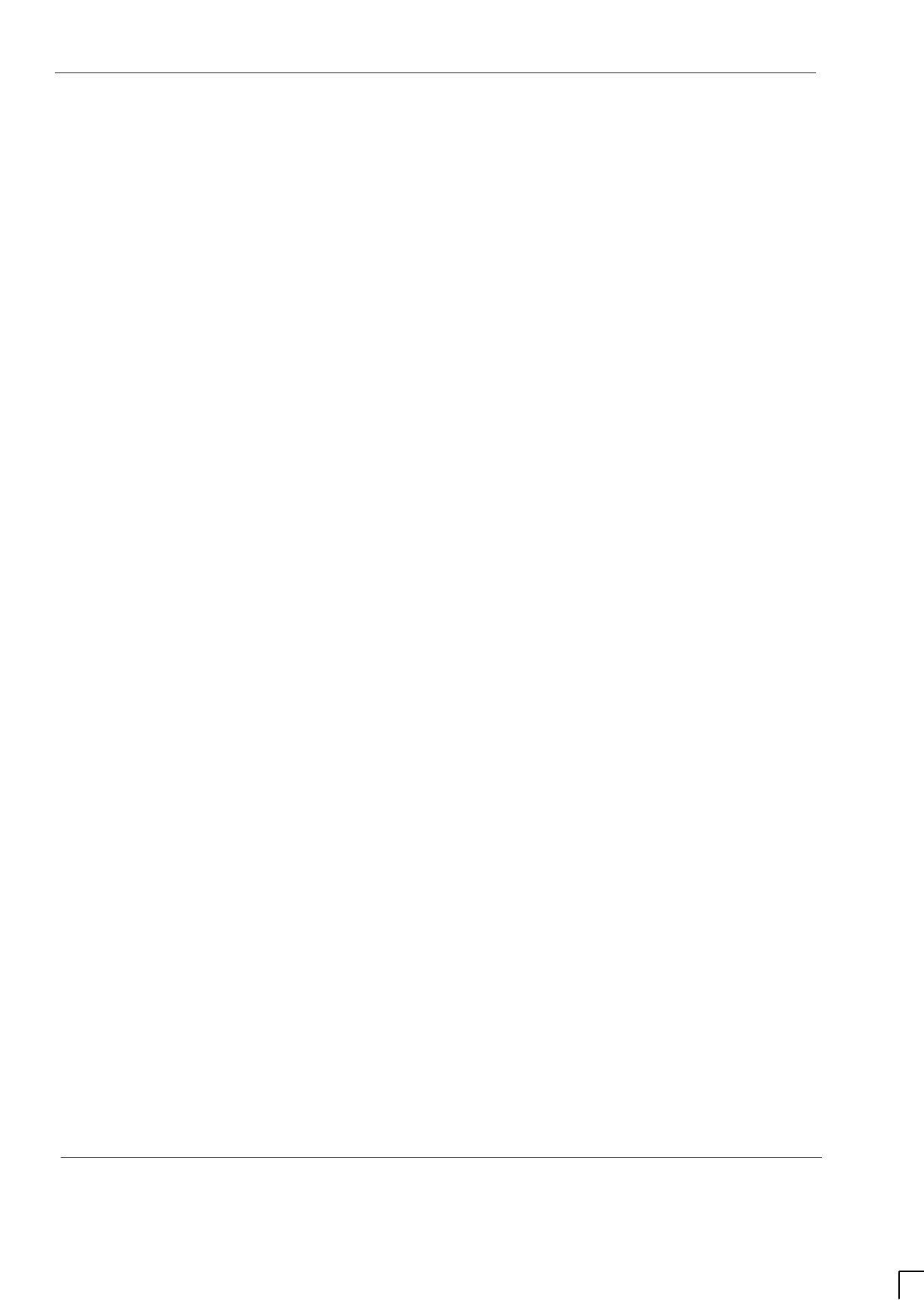
GSM-204-523
31st Oct 01
ii
Maintenance Information: Horizon
macro
outdoor
CONTROLLED INTRODUCTION
68P02902W04-A
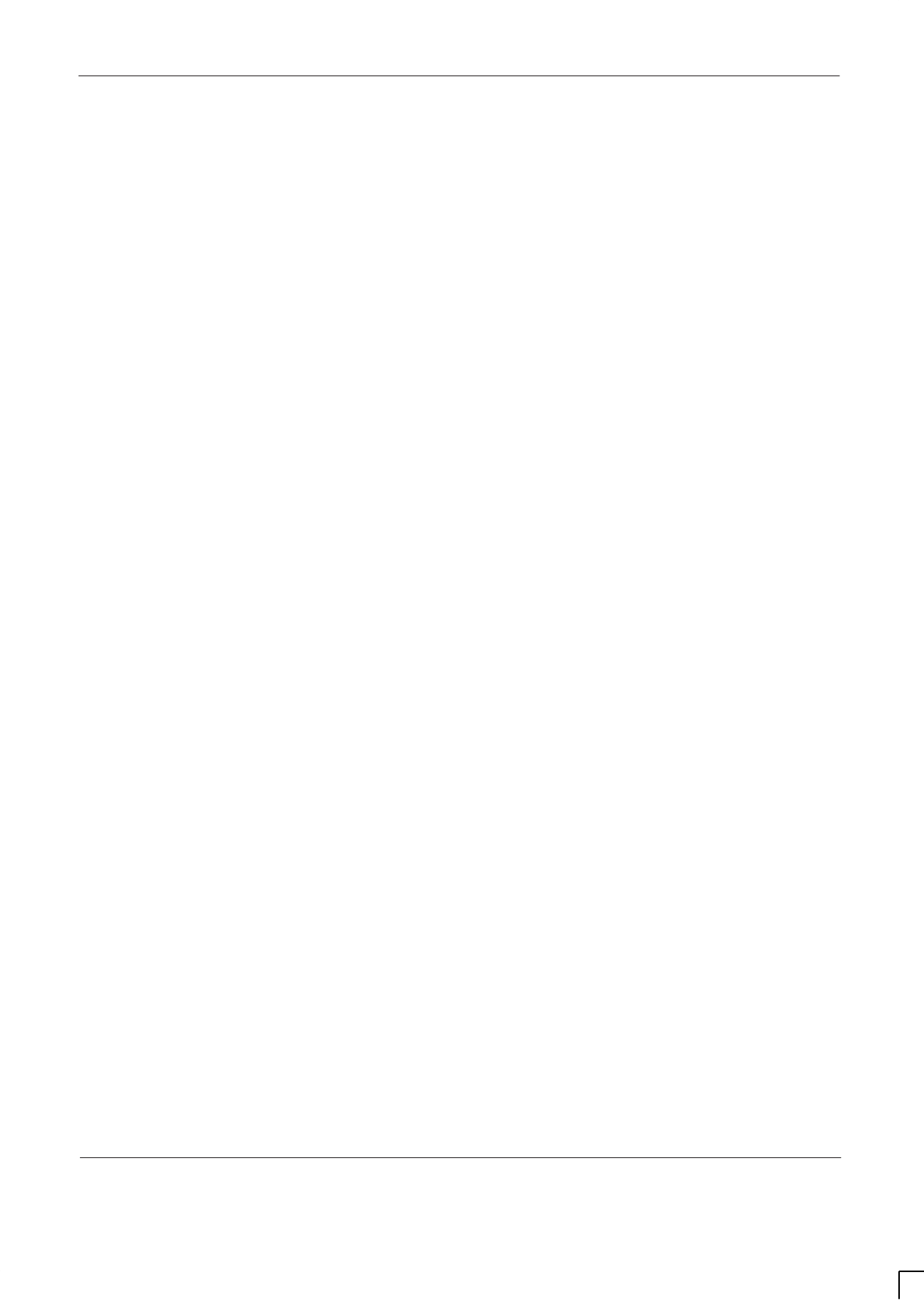
GSM-204-523
31st Oct 01
Maintenance Information: Horizon
macro
outdoor
68P02902W04-A
CONTROLLED INTRODUCTION
iii
Category 523
Maintenance Information (Maint.) i. . . . . . . . . . . . . . . . . . . . . . . . . . . . . . . . . . .
Chapter 1
Introduction to maintenance i. . . . . . . . . . . . . . . . . . . . . . . . . . . . . . . . . . .
Maintenance information introduction Maint. 1–1. . . . . . . . . . . . . . . . . . . . . . . . . . . . . . . . . . .
Safety Maint. 1–1. . . . . . . . . . . . . . . . . . . . . . . . . . . . . . . . . . . . . . . . . . . . . . . . . . . . . . . . .
Tools Maint. 1–1. . . . . . . . . . . . . . . . . . . . . . . . . . . . . . . . . . . . . . . . . . . . . . . . . . . . . . . . . .
Weather conditions affecting access Maint. 1–2. . . . . . . . . . . . . . . . . . . . . . . . . . . . . . . . . . . .
Overview of weather considerations Maint. 1–2. . . . . . . . . . . . . . . . . . . . . . . . . . . . . . .
Weather conditions Maint. 1–2. . . . . . . . . . . . . . . . . . . . . . . . . . . . . . . . . . . . . . . . . . . . . .
Maintenance cover Maint. 1–2. . . . . . . . . . . . . . . . . . . . . . . . . . . . . . . . . . . . . . . . . . . . . .
Chapter 2
General maintenance i. . . . . . . . . . . . . . . . . . . . . . . . . . . . . . . . . . . . . . . . . .
General maintenance overview Maint. 2–1. . . . . . . . . . . . . . . . . . . . . . . . . . . . . . . . . . . . . . . .
In this chapter Maint. 2–1. . . . . . . . . . . . . . . . . . . . . . . . . . . . . . . . . . . . . . . . . . . . . . . . . .
Reporting faulty devices Maint. 2–1. . . . . . . . . . . . . . . . . . . . . . . . . . . . . . . . . . . . . . . . .
Cleaning agents Maint. 2–2. . . . . . . . . . . . . . . . . . . . . . . . . . . . . . . . . . . . . . . . . . . . . . . .
Torque values Maint. 2–2. . . . . . . . . . . . . . . . . . . . . . . . . . . . . . . . . . . . . . . . . . . . . . . . . .
Maintenance support procedures Maint. 2–3. . . . . . . . . . . . . . . . . . . . . . . . . . . . . . . . . . . . . .
Door opening and closing Maint. 2–3. . . . . . . . . . . . . . . . . . . . . . . . . . . . . . . . . . . . . . . .
Lid opening and closing Maint. 2–3. . . . . . . . . . . . . . . . . . . . . . . . . . . . . . . . . . . . . . . . .
TMS front cover removal and refitting Maint. 2–4. . . . . . . . . . . . . . . . . . . . . . . . . . . . . .
General maintenance procedures Maint. 2–5. . . . . . . . . . . . . . . . . . . . . . . . . . . . . . . . . . . . . .
Type of procedures Maint. 2–5. . . . . . . . . . . . . . . . . . . . . . . . . . . . . . . . . . . . . . . . . . . . .
Assumptions - door, lid and TMS front cover Maint. 2–5. . . . . . . . . . . . . . . . . . . . . . . .
Cleaning inlet and outlet grilles Maint. 2–5. . . . . . . . . . . . . . . . . . . . . . . . . . . . . . . . . . .
Checking normal operation Maint. 2–6. . . . . . . . . . . . . . . . . . . . . . . . . . . . . . . . . . . . . . .
Inspection of cabinet, locks and hinges Maint. 2–7. . . . . . . . . . . . . . . . . . . . . . . . . . . .
Periodic check of the installation Maint. 2–8. . . . . . . . . . . . . . . . . . . . . . . . . . . . . . . . . .
TMS testing Maint. 2–8. . . . . . . . . . . . . . . . . . . . . . . . . . . . . . . . . . . . . . . . . . . . . . . . . . . .
Battery backup test procedures Maint. 2–10. . . . . . . . . . . . . . . . . . . . . . . . . . . . . . . . . . .
Return to service Maint. 2–11. . . . . . . . . . . . . . . . . . . . . . . . . . . . . . . . . . . . . . . . . . . . . . . .
Chapter 3
FRU replacement procedures i. . . . . . . . . . . . . . . . . . . . . . . . . . . . . . . . . .
Overview of FRU replacement procedures Maint. 3–1. . . . . . . . . . . . . . . . . . . . . . . . . . . . . .
Field replaceable units (FRUs) Maint. 3–1. . . . . . . . . . . . . . . . . . . . . . . . . . . . . . . . . . . .
FRU list Maint. 3–1. . . . . . . . . . . . . . . . . . . . . . . . . . . . . . . . . . . . . . . . . . . . . . . . . . . . . . . .
Torque values Maint. 3–2. . . . . . . . . . . . . . . . . . . . . . . . . . . . . . . . . . . . . . . . . . . . . . . . . .
FRU view of cabinet Maint. 3–2. . . . . . . . . . . . . . . . . . . . . . . . . . . . . . . . . . . . . . . . . . . . .
Replacing a door Maint. 3–3. . . . . . . . . . . . . . . . . . . . . . . . . . . . . . . . . . . . . . . . . . . . . . . . . . . . .
Introduction to door replacement Maint. 3–3. . . . . . . . . . . . . . . . . . . . . . . . . . . . . . . . . .
Views of the cabinet doors Maint. 3–3. . . . . . . . . . . . . . . . . . . . . . . . . . . . . . . . . . . . . . .
Door replacement procedure Maint. 3–4. . . . . . . . . . . . . . . . . . . . . . . . . . . . . . . . . . . . .
Replacing the lid Maint. 3–5. . . . . . . . . . . . . . . . . . . . . . . . . . . . . . . . . . . . . . . . . . . . . . . . . . . . .
Introduction to lid replacement Maint. 3–5. . . . . . . . . . . . . . . . . . . . . . . . . . . . . . . . . . . .
View of the cabinet lid Maint. 3–5. . . . . . . . . . . . . . . . . . . . . . . . . . . . . . . . . . . . . . . . . . .
Replacing a lid Maint. 3–6. . . . . . . . . . . . . . . . . . . . . . . . . . . . . . . . . . . . . . . . . . . . . . . . . .
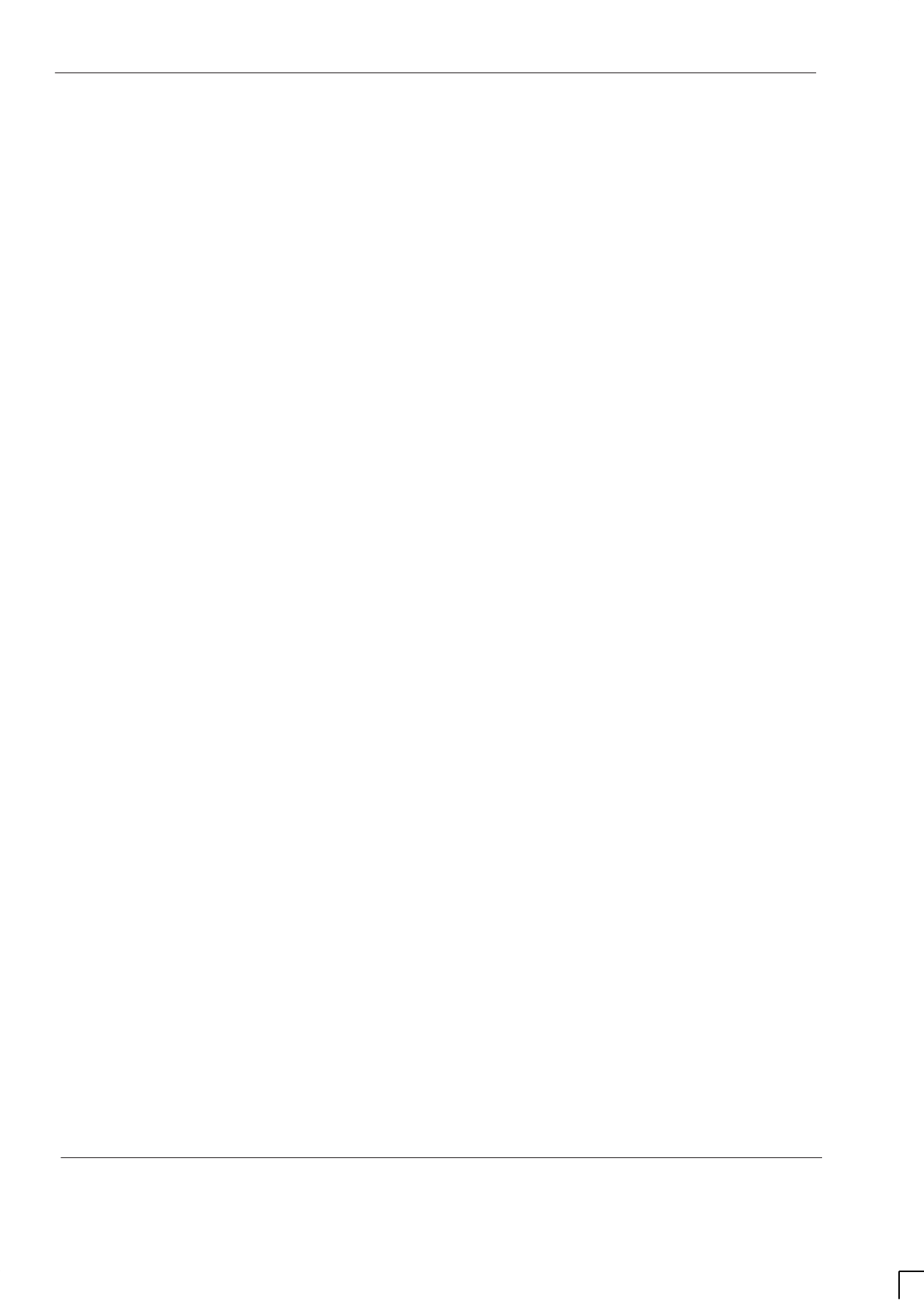
GSM-204-523
31st Oct 01
iv
Maintenance Information: Horizon
macro
outdoor
CONTROLLED INTRODUCTION
68P02902W04-A
Replacing environmental seals Maint. 3–7. . . . . . . . . . . . . . . . . . . . . . . . . . . . . . . . . . . . . . . .
Introduction to environmental seal replacement Maint. 3–7. . . . . . . . . . . . . . . . . . . . .
Replacing an environmental seal for the lid Maint. 3–7. . . . . . . . . . . . . . . . . . . . . . . . .
Replacing an environmental seal on a door Maint. 3–7. . . . . . . . . . . . . . . . . . . . . . . .
Replacing a thermal management system (TMS) unit Maint. 3–8. . . . . . . . . . . . . . . . . . . . .
Introduction to TMS replacement Maint. 3–8. . . . . . . . . . . . . . . . . . . . . . . . . . . . . . . . . .
View of the TMS unit Maint. 3–8. . . . . . . . . . . . . . . . . . . . . . . . . . . . . . . . . . . . . . . . . . . .
Removing the TMS unit Maint. 3–9. . . . . . . . . . . . . . . . . . . . . . . . . . . . . . . . . . . . . . . . . .
Refitting the TMS unit Maint. 3–10. . . . . . . . . . . . . . . . . . . . . . . . . . . . . . . . . . . . . . . . . . .
Replacing TMS unit components Maint. 3–11. . . . . . . . . . . . . . . . . . . . . . . . . . . . . . . . . . . . . . .
Introduction to TMS unit component replacement Maint. 3–11. . . . . . . . . . . . . . . . . . .
Replacing a TMS fan Maint. 3–11. . . . . . . . . . . . . . . . . . . . . . . . . . . . . . . . . . . . . . . . . . . .
Replacing the TMS control board Maint. 3–12. . . . . . . . . . . . . . . . . . . . . . . . . . . . . . . . .
Replacing the TMS gasket Maint. 3–12. . . . . . . . . . . . . . . . . . . . . . . . . . . . . . . . . . . . . . .
Replacing a cabinet temperature sensor Maint. 3–13. . . . . . . . . . . . . . . . . . . . . . . . . . . . . . . .
Overview of main cage temperature sensor FRUs Maint. 3–13. . . . . . . . . . . . . . . . . . .
Replaceing a main cage temperature sensor Maint. 3–13. . . . . . . . . . . . . . . . . . . . . . .
Replacing a dc circuit breaker Maint. 3–14. . . . . . . . . . . . . . . . . . . . . . . . . . . . . . . . . . . . . . . . .
Introduction to dc circuit breaker replacement Maint. 3–14. . . . . . . . . . . . . . . . . . . . . .
View of the dc circuit breaker panel Maint. 3–14. . . . . . . . . . . . . . . . . . . . . . . . . . . . . . .
Replacing a dc circuit breaker Maint. 3–14. . . . . . . . . . . . . . . . . . . . . . . . . . . . . . . . . . . .
Replacing the control and alarm board (CAB) Maint. 3–15. . . . . . . . . . . . . . . . . . . . . . . . . . . .
Introduction to CAB replacement Maint. 3–15. . . . . . . . . . . . . . . . . . . . . . . . . . . . . . . . . .
View of CAB Maint. 3–15. . . . . . . . . . . . . . . . . . . . . . . . . . . . . . . . . . . . . . . . . . . . . . . . . . .
Replacing a CAB Maint. 3–16. . . . . . . . . . . . . . . . . . . . . . . . . . . . . . . . . . . . . . . . . . . . . . .
Replacing the outdoor power supply module (TOPSM) Maint. 3–17. . . . . . . . . . . . . . . . . . . .
TOPSM replacement Maint. 3–17. . . . . . . . . . . . . . . . . . . . . . . . . . . . . . . . . . . . . . . . . . . .
View of TOPSM Maint. 3–17. . . . . . . . . . . . . . . . . . . . . . . . . . . . . . . . . . . . . . . . . . . . . . . . .
Replacing a TOPSM Maint. 3–18. . . . . . . . . . . . . . . . . . . . . . . . . . . . . . . . . . . . . . . . . . . .
Replacing a power supply module (PSM) Maint. 3–19. . . . . . . . . . . . . . . . . . . . . . . . . . . . . . .
Introduction to PSM replacement Maint. 3–19. . . . . . . . . . . . . . . . . . . . . . . . . . . . . . . . .
View of PSM Maint. 3–19. . . . . . . . . . . . . . . . . . . . . . . . . . . . . . . . . . . . . . . . . . . . . . . . . . .
Replacing a non-redundant PSM Maint. 3–20. . . . . . . . . . . . . . . . . . . . . . . . . . . . . . . . .
Replacing a redundant PSM Maint. 3–21. . . . . . . . . . . . . . . . . . . . . . . . . . . . . . . . . . . . .
BPSM replacement Maint. 3–21. . . . . . . . . . . . . . . . . . . . . . . . . . . . . . . . . . . . . . . . . . . . .
Replacing a circuit breaker module (CBM) Maint. 3–22. . . . . . . . . . . . . . . . . . . . . . . . . . . . . . .
Preconditions for CBM replacement Maint. 3–22. . . . . . . . . . . . . . . . . . . . . . . . . . . . . . .
Views of CBM Maint. 3–22. . . . . . . . . . . . . . . . . . . . . . . . . . . . . . . . . . . . . . . . . . . . . . . . . .
Replacing a CBM Maint. 3–23. . . . . . . . . . . . . . . . . . . . . . . . . . . . . . . . . . . . . . . . . . . . . . .
Replacing the internal batteries Maint. 3–24. . . . . . . . . . . . . . . . . . . . . . . . . . . . . . . . . . . . . . . .
Introduction to internal battery replacement Maint. 3–24. . . . . . . . . . . . . . . . . . . . . . . .
Battery arrangement Maint. 3–25. . . . . . . . . . . . . . . . . . . . . . . . . . . . . . . . . . . . . . . . . . . .
Removing the battery tray Maint. 3–25. . . . . . . . . . . . . . . . . . . . . . . . . . . . . . . . . . . . . . . .
Removing and replacing the batteries Maint. 3–26. . . . . . . . . . . . . . . . . . . . . . . . . . . . .
View showing battery replacement components Maint. 3–27. . . . . . . . . . . . . . . . . . . . .
Replacing a CTU Maint. 3–28. . . . . . . . . . . . . . . . . . . . . . . . . . . . . . . . . . . . . . . . . . . . . . . . . . . . .
Preconditions to CTU replacement Maint. 3–28. . . . . . . . . . . . . . . . . . . . . . . . . . . . . . . .
View of CTU Maint. 3–28. . . . . . . . . . . . . . . . . . . . . . . . . . . . . . . . . . . . . . . . . . . . . . . . . . . .
Replacement procedure for CTU Maint. 3–29. . . . . . . . . . . . . . . . . . . . . . . . . . . . . . . . . .
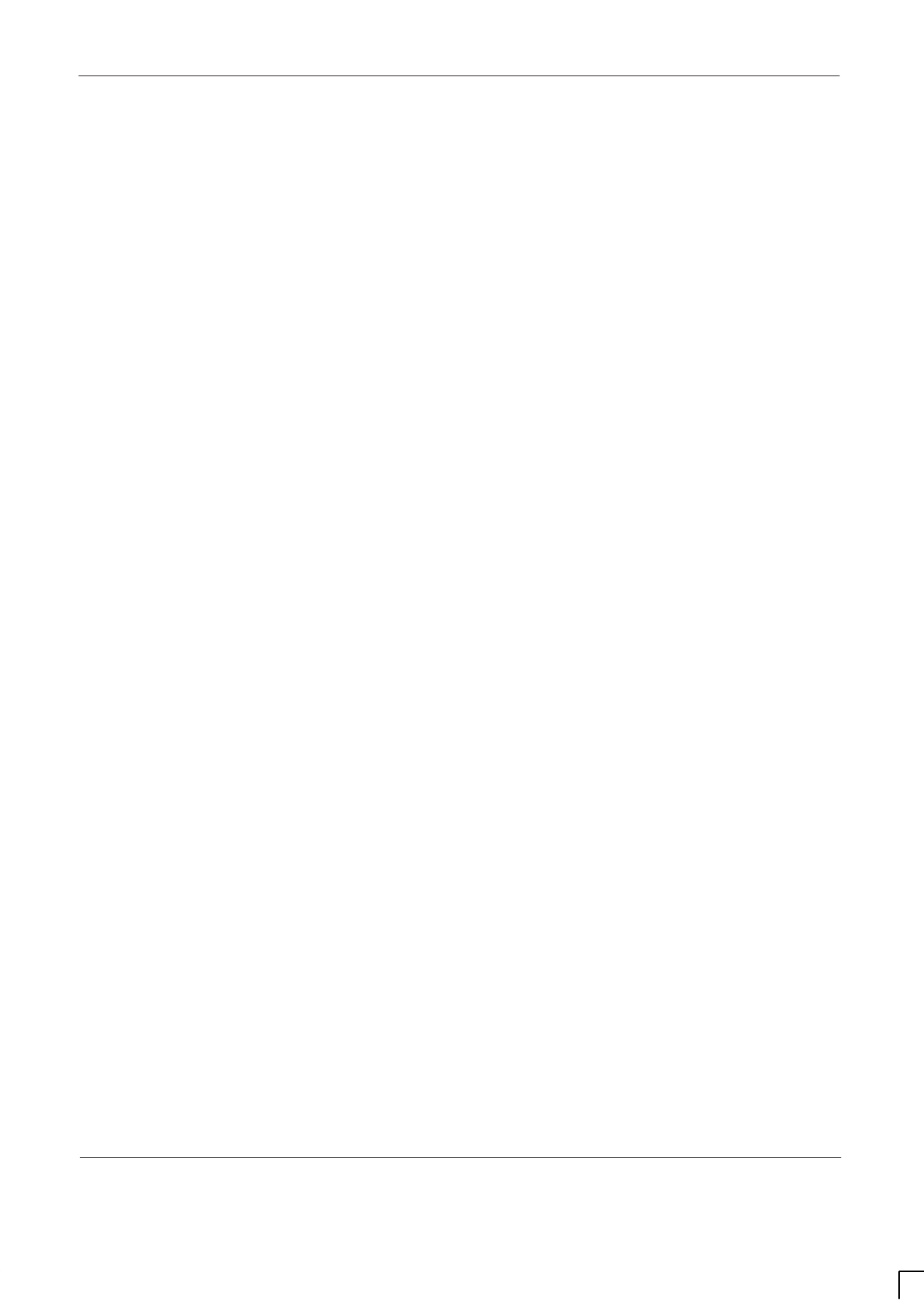
GSM-204-523
31st Oct 01
Maintenance Information: Horizon
macro
outdoor
68P02902W04-A
CONTROLLED INTRODUCTION
v
Replacing a SURF module Maint. 3–31. . . . . . . . . . . . . . . . . . . . . . . . . . . . . . . . . . . . . . . . . . . .
Preconditions for SURF replacement Maint. 3–31. . . . . . . . . . . . . . . . . . . . . . . . . . . . . .
View of the SURF Maint. 3–31. . . . . . . . . . . . . . . . . . . . . . . . . . . . . . . . . . . . . . . . . . . . . . .
Replacing a SURF module Maint. 3–32. . . . . . . . . . . . . . . . . . . . . . . . . . . . . . . . . . . . . . .
Replacing a Tx block Maint. 3–34. . . . . . . . . . . . . . . . . . . . . . . . . . . . . . . . . . . . . . . . . . . . . . . . .
Preconditions to Tx block replacement Maint. 3–34. . . . . . . . . . . . . . . . . . . . . . . . . . . . .
Views of typical Tx block Maint. 3–35. . . . . . . . . . . . . . . . . . . . . . . . . . . . . . . . . . . . . . . . .
Replacing a Tx block Maint. 3–36. . . . . . . . . . . . . . . . . . . . . . . . . . . . . . . . . . . . . . . . . . . .
Tx block blanking plate, feedthrough plate or HCU replacement Maint. 3–37. . . . . .
Krone block replacement Maint. 3–38. . . . . . . . . . . . . . . . . . . . . . . . . . . . . . . . . . . . . . . . . . . . . .
Introduction to Krone block replacement Maint. 3–38. . . . . . . . . . . . . . . . . . . . . . . . . . .
Krone block location diagram Maint. 3–38. . . . . . . . . . . . . . . . . . . . . . . . . . . . . . . . . . . . .
Replacing a Krone block Maint. 3–39. . . . . . . . . . . . . . . . . . . . . . . . . . . . . . . . . . . . . . . . .
Digital module and BPSM replacement Maint. 3–40. . . . . . . . . . . . . . . . . . . . . . . . . . . . . . . . .
Preconditions for digital module replacement Maint. 3–40. . . . . . . . . . . . . . . . . . . . . . .
Digital module location diagram Maint. 3–40. . . . . . . . . . . . . . . . . . . . . . . . . . . . . . . . . . .
Replacing a digital module Maint. 3–41. . . . . . . . . . . . . . . . . . . . . . . . . . . . . . . . . . . . . . .
Redundant MCUF firmware compatibility Maint. 3–43. . . . . . . . . . . . . . . . . . . . . . . . . . . . . . . .
Overview of MCUF firmware compatibility Maint. 3–43. . . . . . . . . . . . . . . . . . . . . . . . . .
Checking MCUF firmware compatibility Maint. 3–43. . . . . . . . . . . . . . . . . . . . . . . . . . . .
Updating redundant MCUF firmware Maint. 3–43. . . . . . . . . . . . . . . . . . . . . . . . . . . . . .
Testing MCUF redundancy Maint. 3–46. . . . . . . . . . . . . . . . . . . . . . . . . . . . . . . . . . . . . . .
Additional replacement parts Maint. 3–47. . . . . . . . . . . . . . . . . . . . . . . . . . . . . . . . . . . . . . . . . .
Policy on non-FRU parts Maint. 3–47. . . . . . . . . . . . . . . . . . . . . . . . . . . . . . . . . . . . . . . . .
List of non-FRU parts Maint. 3–47. . . . . . . . . . . . . . . . . . . . . . . . . . . . . . . . . . . . . . . . . . . .
Procedure for replacing non-FRU parts Maint. 3–47. . . . . . . . . . . . . . . . . . . . . . . . . . . .
CBIA attachment screws Maint. 3–47. . . . . . . . . . . . . . . . . . . . . . . . . . . . . . . . . . . . . . . . .
Chapter 4
Auxiliary equipment housing maintenance i. . . . . . . . . . . . . . . . . . . . . .
Introduction to auxiliary equipment housing maintenance Maint. 4–1. . . . . . . . . . . . . . . . .
Auxiliary equipment housing FRUs Maint. 4–1. . . . . . . . . . . . . . . . . . . . . . . . . . . . . . . .
Auxiliary equipment housing FRU view Maint. 4–2. . . . . . . . . . . . . . . . . . . . . . . . . . . .
Replacing the power distribution box Maint. 4–3. . . . . . . . . . . . . . . . . . . . . . . . . . . . . . . . . . .
Introduction to power distribution box replacement Maint. 4–3. . . . . . . . . . . . . . . . . .
Removing the power distribution box Maint. 4–3. . . . . . . . . . . . . . . . . . . . . . . . . . . . . .
Fitting a replacement power distribution box Maint. 4–4. . . . . . . . . . . . . . . . . . . . . . . .
Replacing the lid on the auxiliary equipment housing Maint. 4–5. . . . . . . . . . . . . . . . . . . . .
Detailed view of the cabinet lid Maint. 4–5. . . . . . . . . . . . . . . . . . . . . . . . . . . . . . . . . . .
Removing the lid Maint. 4–6. . . . . . . . . . . . . . . . . . . . . . . . . . . . . . . . . . . . . . . . . . . . . . . .
Fitting a new lid Maint. 4–7. . . . . . . . . . . . . . . . . . . . . . . . . . . . . . . . . . . . . . . . . . . . . . . . .
Replacing the door on the auxiliary equipment housing Maint. 4–8. . . . . . . . . . . . . . . . . . .
Removing the cabinet door Maint. 4–8. . . . . . . . . . . . . . . . . . . . . . . . . . . . . . . . . . . . . . .
Fitting a replacement door Maint. 4–8. . . . . . . . . . . . . . . . . . . . . . . . . . . . . . . . . . . . . . .
Replacing the front panel or fan Maint. 4–9. . . . . . . . . . . . . . . . . . . . . . . . . . . . . . . . . . . . . . . .
Replacing the front panel Maint. 4–9. . . . . . . . . . . . . . . . . . . . . . . . . . . . . . . . . . . . . . . .
Replacing the fan Maint. 4–10. . . . . . . . . . . . . . . . . . . . . . . . . . . . . . . . . . . . . . . . . . . . . . .
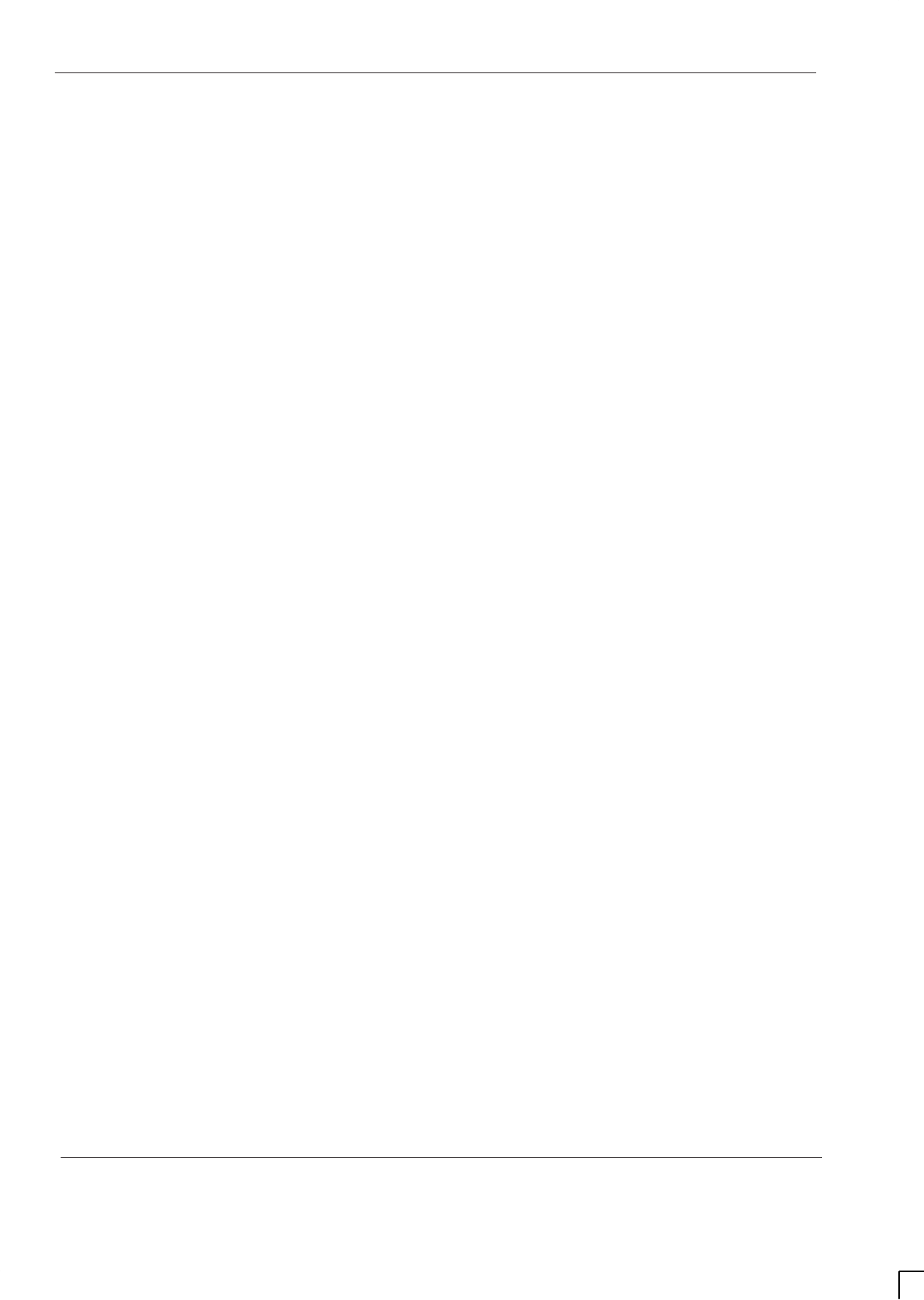
GSM-204-523
31st Oct 01
vi
Maintenance Information: Horizon
macro
outdoor
CONTROLLED INTRODUCTION
68P02902W04-A
Replacing a heater mat Maint. 4–11. . . . . . . . . . . . . . . . . . . . . . . . . . . . . . . . . . . . . . . . . . . . . . .
Introduction to heater mat replacement Maint. 4–11. . . . . . . . . . . . . . . . . . . . . . . . . . . .
Heater mat replacement procedure Maint. 4–11. . . . . . . . . . . . . . . . . . . . . . . . . . . . . . .
Replacing an environmental seal on the housing Maint. 4–12. . . . . . . . . . . . . . . . . . . . . . . . .
Introduction to replacing a seal Maint. 4–12. . . . . . . . . . . . . . . . . . . . . . . . . . . . . . . . . . .
Replacing the lid environmental seal Maint. 4–12. . . . . . . . . . . . . . . . . . . . . . . . . . . . . .
Replacing the door environmental seal Maint. 4–12. . . . . . . . . . . . . . . . . . . . . . . . . . . .
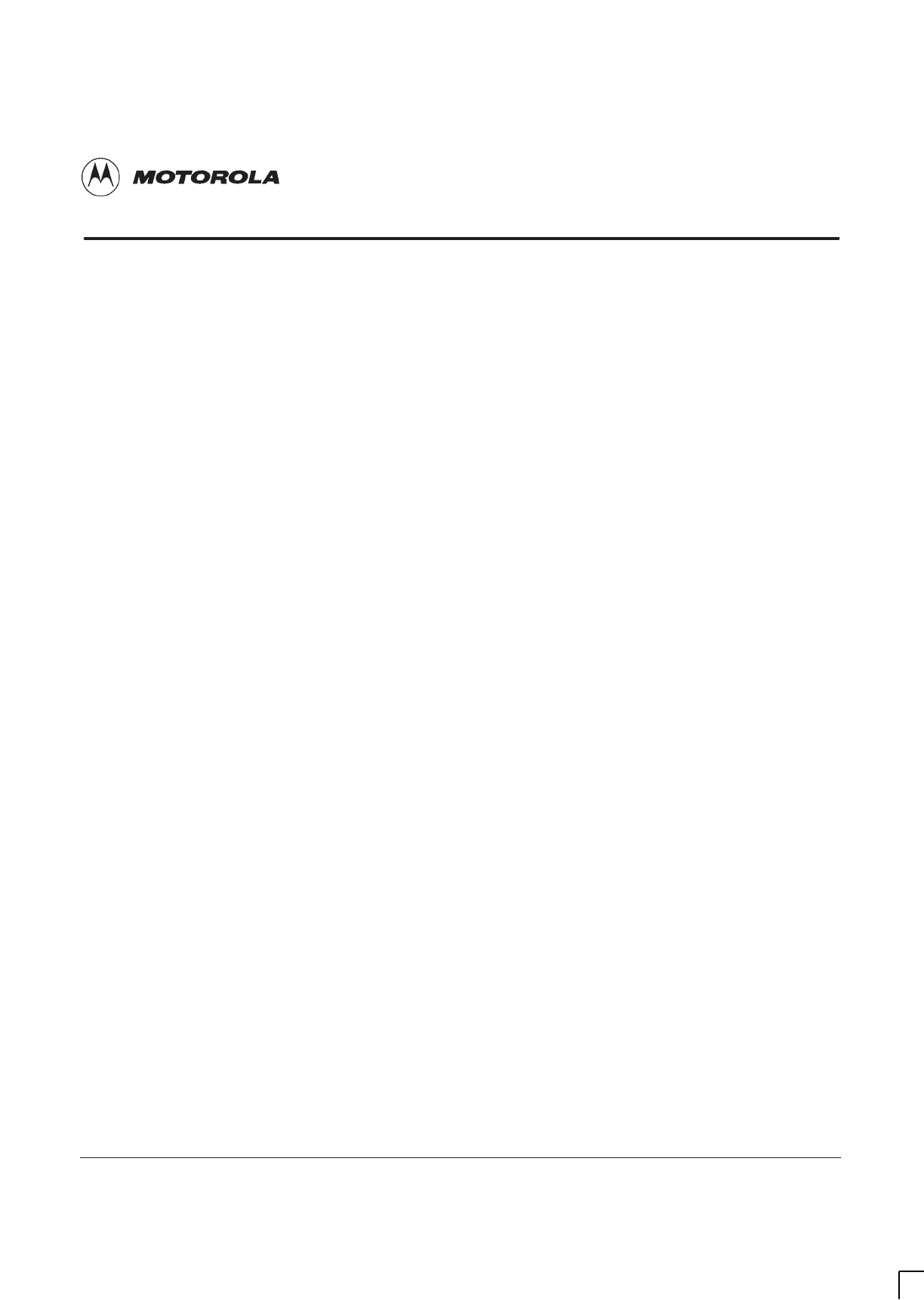
31st Oct 01
Maintenance Information: Horizon
macro
outdoor
68P02902W04-A
CONTROLLED INTRODUCTION
i
Chapter 1
Introduction to maintenance
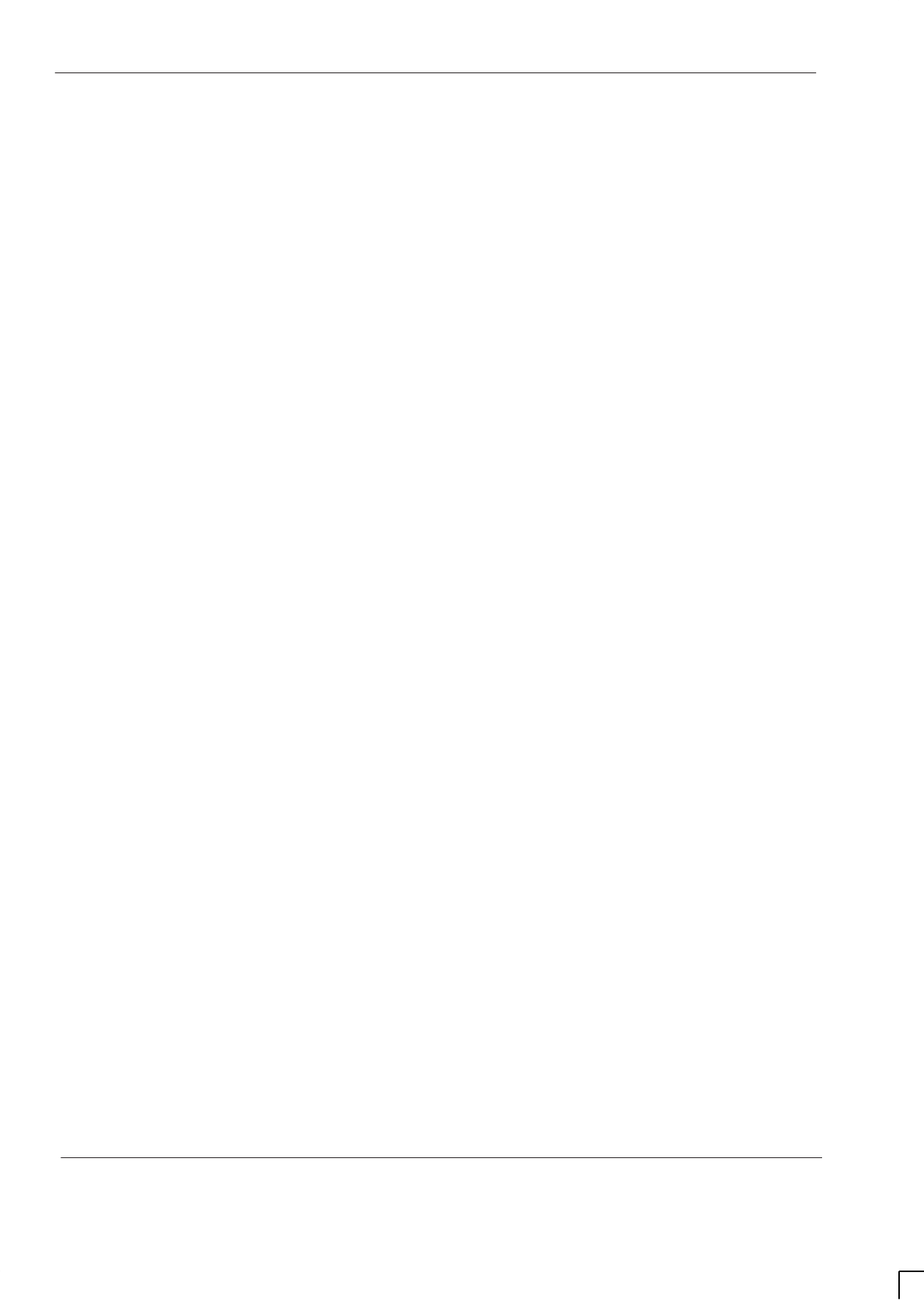
GSM-204-523
31st Oct 01
ii
Maintenance Information: Horizon
macro
outdoor
CONTROLLED INTRODUCTION
68P02902W04-A
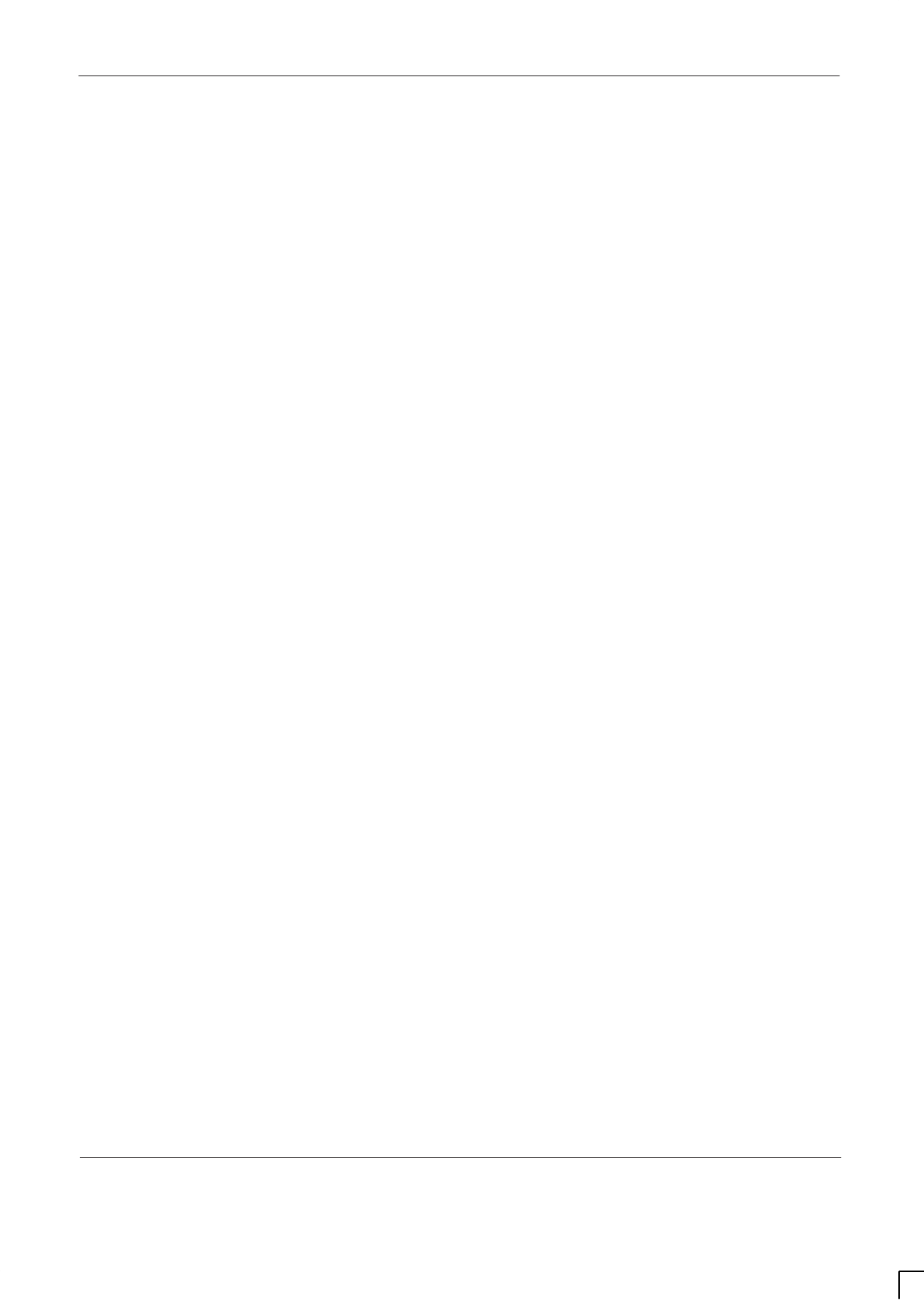
GSM-204-523
31st Oct 01
Maintenance Information: Horizon
macro
outdoor
68P02902W04-A
CONTROLLED INTRODUCTION
iii
Chapter 1
Introduction to maintenance i. . . . . . . . . . . . . . . . . . . . . . . . . . . . . . . . . . .
Maintenance information introduction Maint. 1–1. . . . . . . . . . . . . . . . . . . . . . . . . . . . . . . . . . .
Safety Maint. 1–1. . . . . . . . . . . . . . . . . . . . . . . . . . . . . . . . . . . . . . . . . . . . . . . . . . . . . . . . .
Tools Maint. 1–1. . . . . . . . . . . . . . . . . . . . . . . . . . . . . . . . . . . . . . . . . . . . . . . . . . . . . . . . . .
Weather conditions affecting access Maint. 1–2. . . . . . . . . . . . . . . . . . . . . . . . . . . . . . . . . . . .
Overview of weather considerations Maint. 1–2. . . . . . . . . . . . . . . . . . . . . . . . . . . . . . .
Weather conditions Maint. 1–2. . . . . . . . . . . . . . . . . . . . . . . . . . . . . . . . . . . . . . . . . . . . . .
Maintenance cover Maint. 1–2. . . . . . . . . . . . . . . . . . . . . . . . . . . . . . . . . . . . . . . . . . . . . .
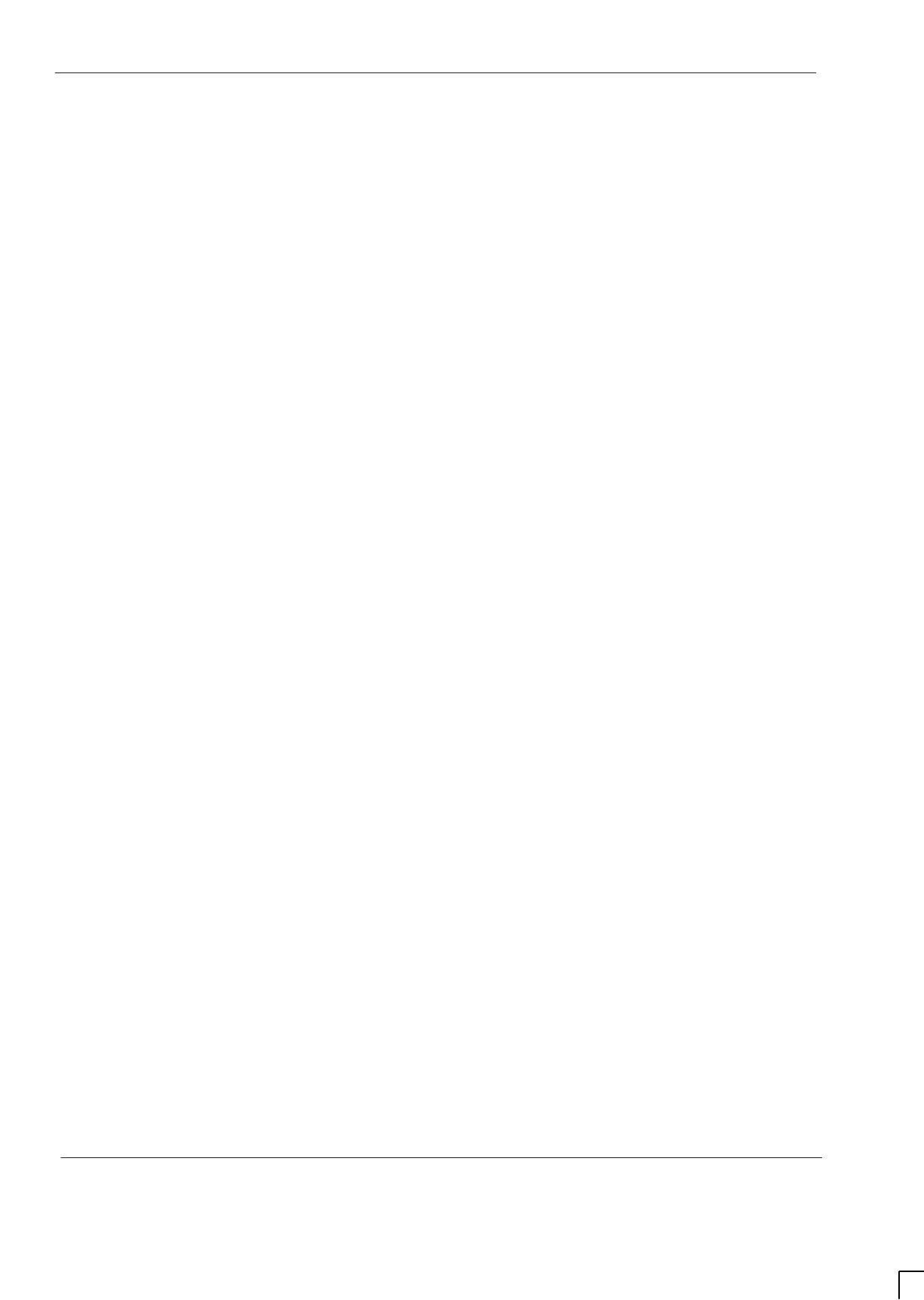
GSM-204-523
31st Oct 01
iv
Maintenance Information: Horizon
macro
outdoor
CONTROLLED INTRODUCTION
68P02902W04-A
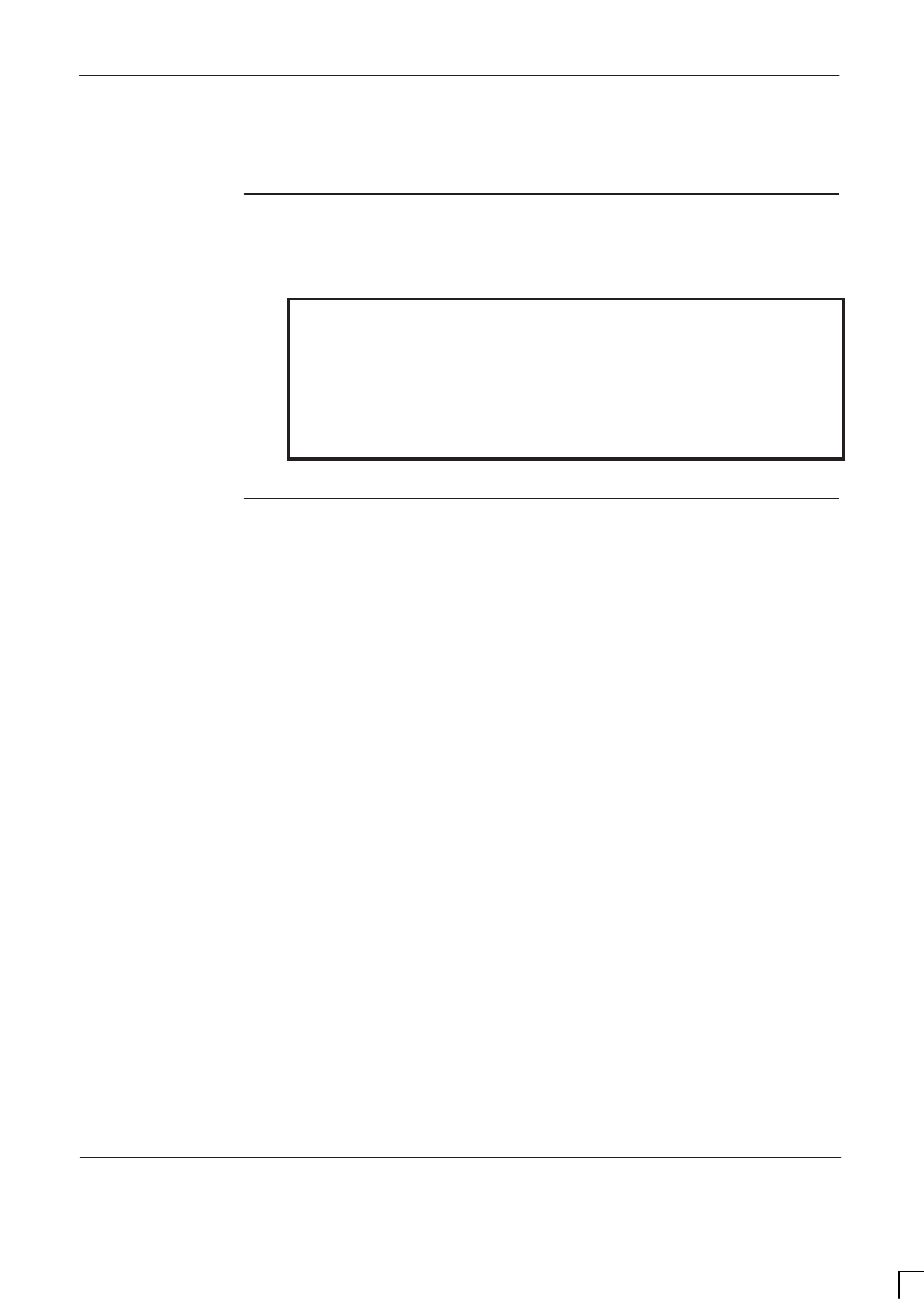
GSM-204-523 Maintenance information introduction
31st Oct 01
Maintenance Information: Horizon
macro
outdoor
68P02902W04-A
CONTROLLED INTRODUCTION
Maint. 1–1
Maintenance information introduction
Safety
Safety features are built into the equipment to protect against the potentially
lethal hazards that exist. All statements regarding safety within these routine
maintenance procedures must be adhered to when working on the equipment.
WARNING Potentially lethal voltages and high energy sources are
present in the cabinet when the external ac mains isolator
switch is set to the on position and/or batteries are
connected. Remove rings, watches and jewellery before
starting these procedures, and exercise extreme caution
when working on the equipment.
Maintenance procedures on this equipment must only be
carried out by suitably qualified personnel.
Tools
The tools required are those listed in
Installation and Configuration:
GSM-204-423
Chapter 1 Horizon
macro
outdoor tool kit.
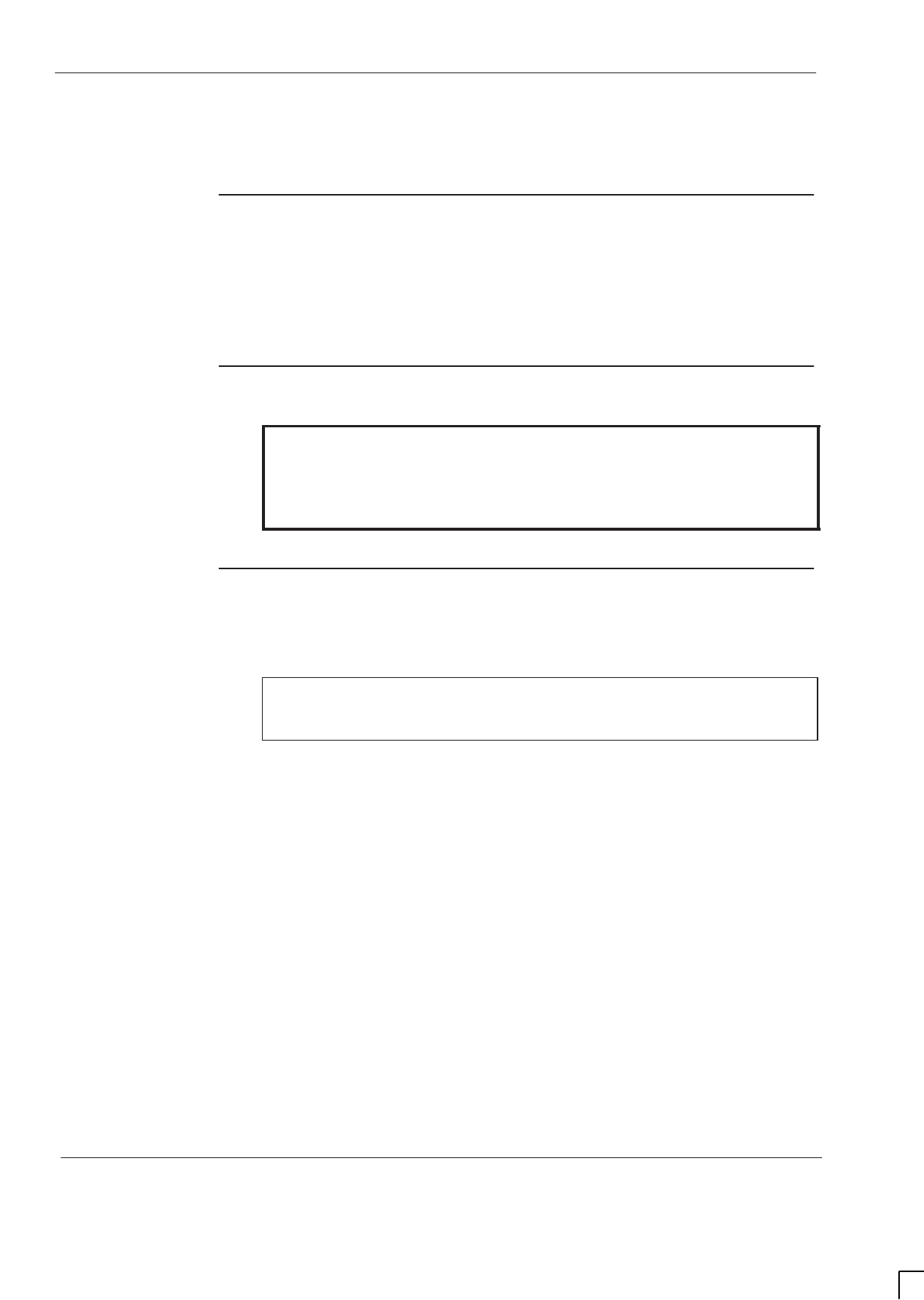
GSM-204-523
Weather conditions affecting access
31st Oct 01
Maint. 1–2
Maintenance Information: Horizon
macro
outdoor
CONTROLLED INTRODUCTION
68P02902W04-A
Weather conditions affecting access
Overview of
weather
considerations
Before beginning any maintenance procedure, it is important to read and take
into account the following information concerning the climatic conditions at the
intended site.
Weather
conditions
WARNING Due consideration should be given to the hazards of wind
and other inclement weather conditions.
Use your discretion at all times. Do not climb a ladder,
scaffolding or use a similar method of access if you
feel unsafe to do so under such weather conditions.
Maintenance
cover
Motorola recommend the use of a maintenance cover for access to the
Horizon
macro
cabinets during inclement weather conditions.
NOTE The maintenance cover is not supplied with the
Horizon
macro
equipment and should be provided by the
customer if required.
Installation and configuration procedures for the Horizon
macro
cabinets are
dependent on the weather conditions. There are three situations where the
recommended guidelines should be considered before commencing work:
No access.
Access with maintenance cover.
Access without maintenance cover.
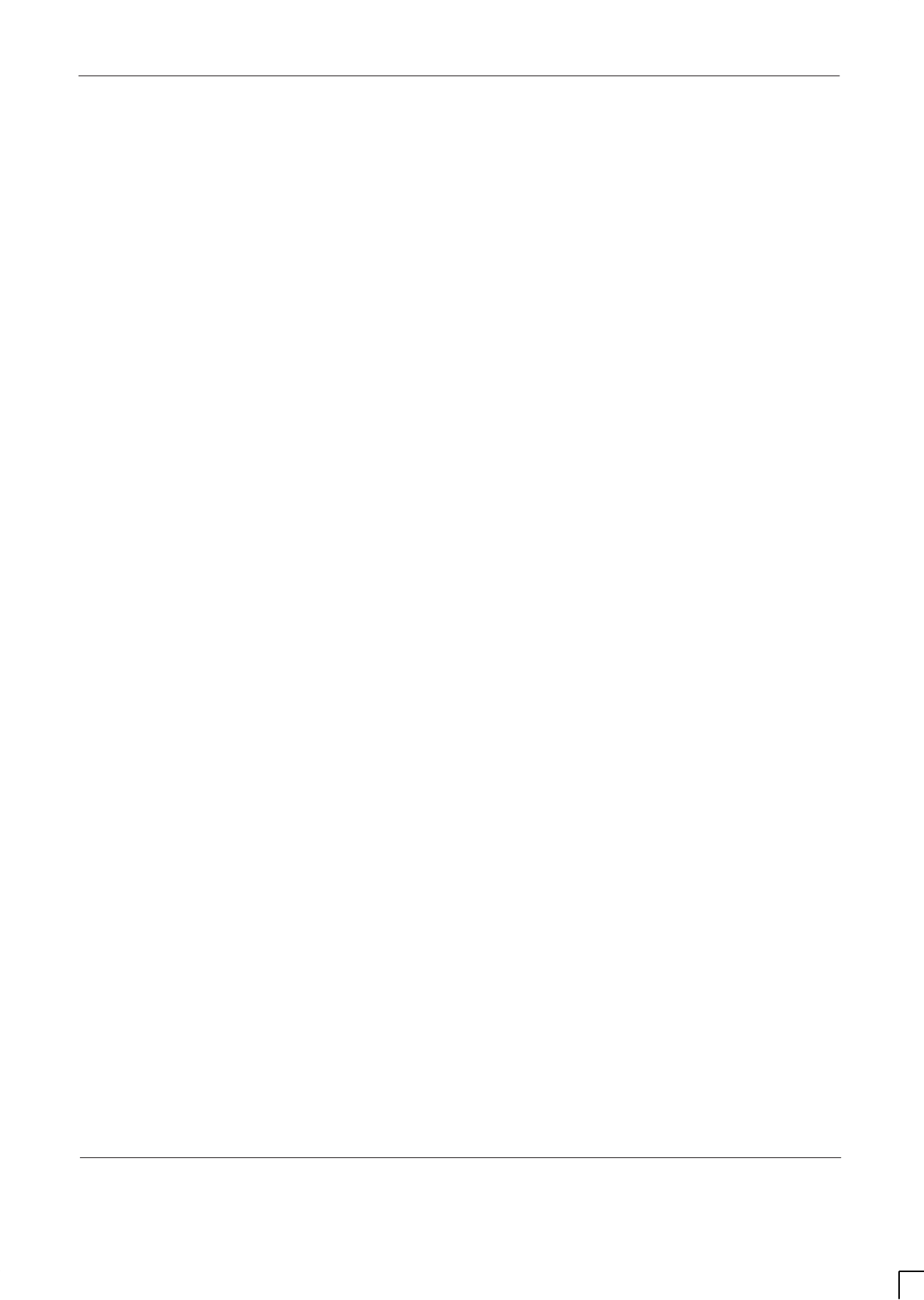
GSM-204-523 Weather conditions affecting access
31st Oct 01
Maintenance Information: Horizon
macro
outdoor
68P02902W04-A
CONTROLLED INTRODUCTION
Maint. 1–3
No access
Access to the cabinet should not be attempted during the following actual or
imminent inclement weather conditions, with or without the maintenance cover:
Winds in excess of 25 knots (30 mph).
Heavy persistent rain, snow, hail or sleet.
During an electrical storm.
Access with maintenance cover
Access to the cabinet may be made under the following conditions with the use
of the maintenance cover:
Wind speeds of less than 25 knots (30 mph).
Persistent rain, snow, hail or sleet.
Where airborne substances (such as leaves or dust) may cause a
problem.
Access without maintenance cover
Access may be made under the following conditions without the use of the
maintenance cover:
Wind speeds of less than 25 knots (30 mph).
No precipitation occurring or likely to occur during the maintenance period.
When the temperature is between –30 C to +40 C (–22 F to +104 F).
Under these conditions the cover of the cabinet may be removed.
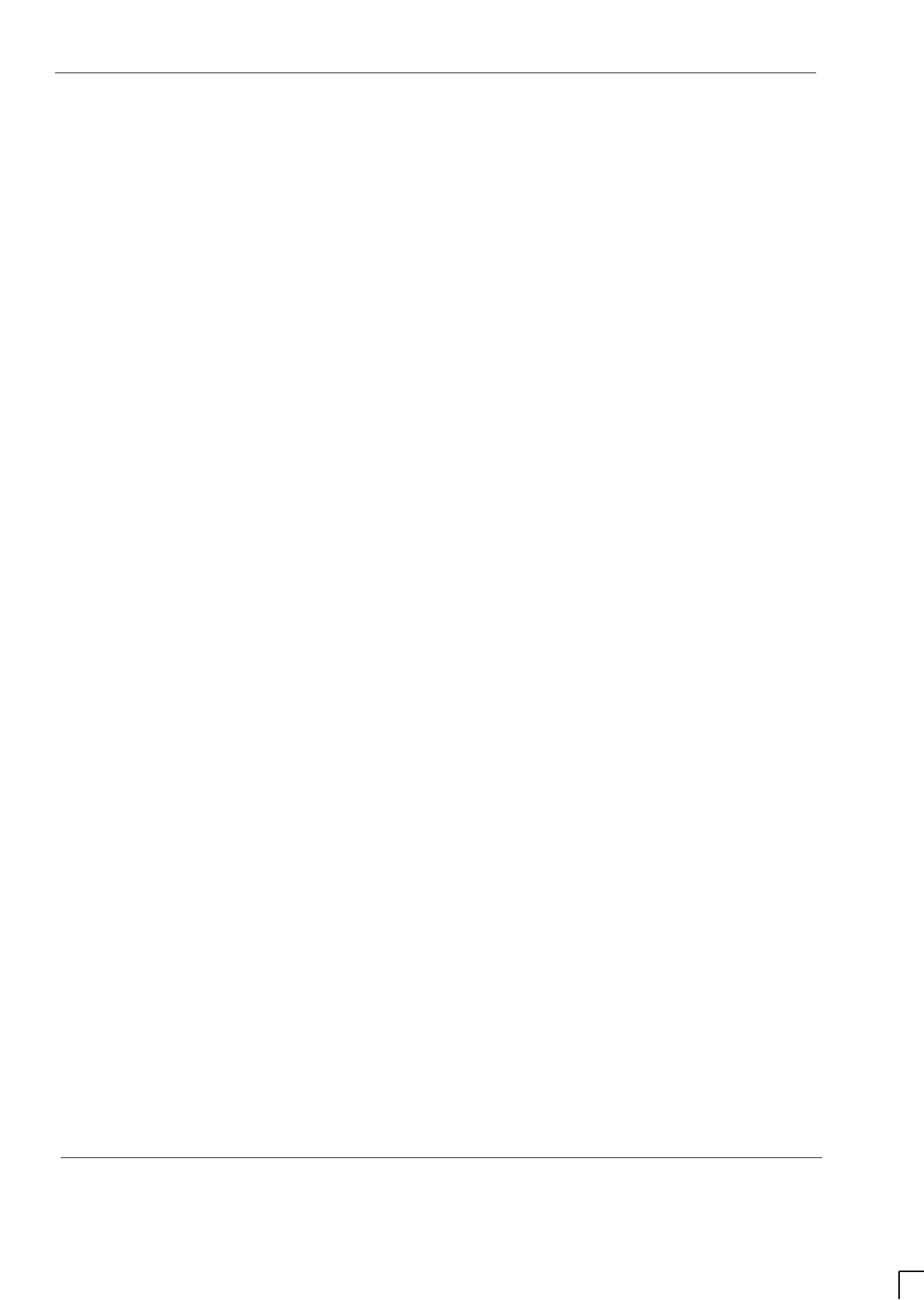
GSM-204-523
Weather conditions affecting access
31st Oct 01
Maint. 1–4
Maintenance Information: Horizon
macro
outdoor
CONTROLLED INTRODUCTION
68P02902W04-A
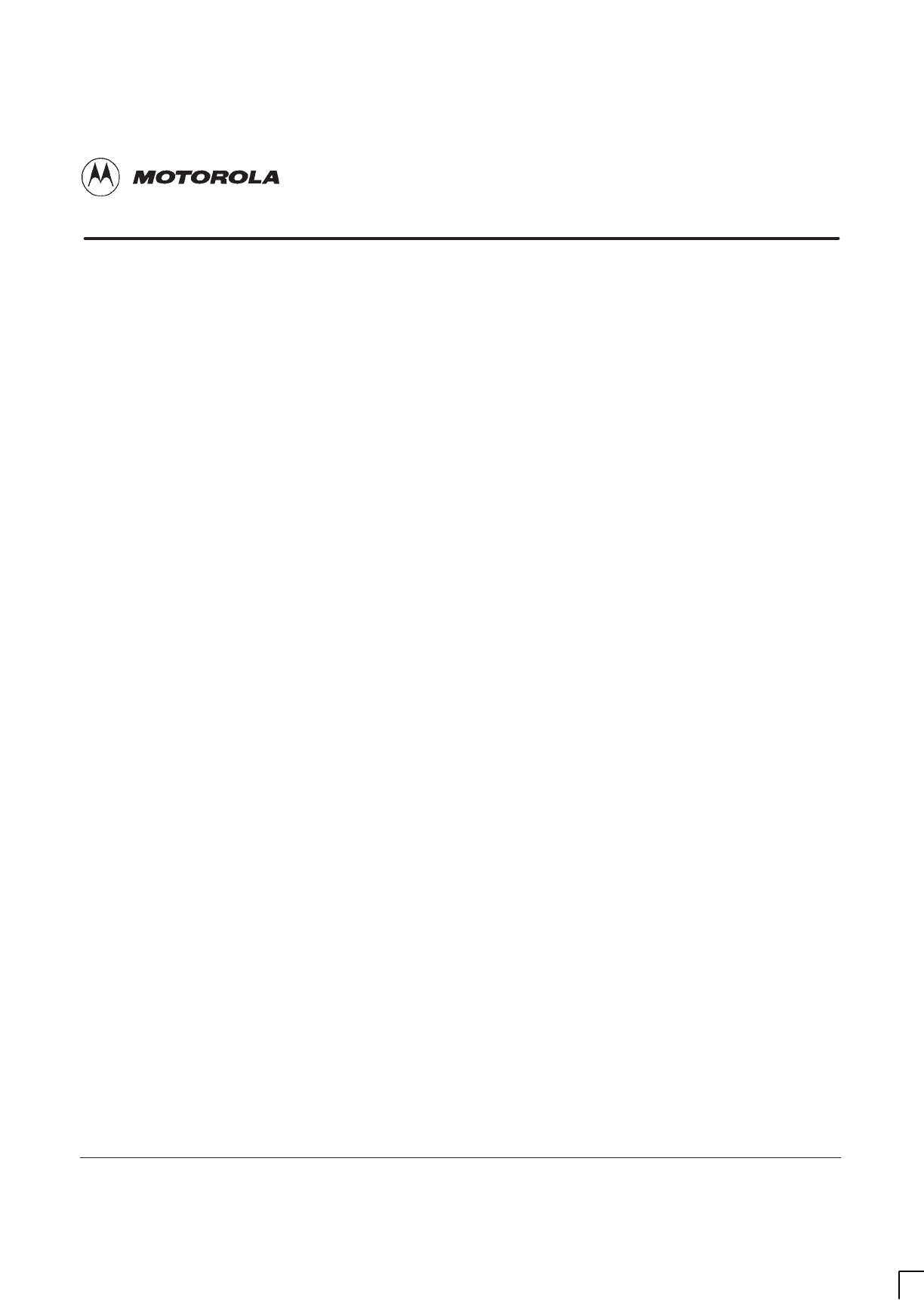
31st Oct 01
Maintenance Information: Horizon
macro
outdoor
68P02902W04-A
CONTROLLED INTRODUCTION
i
Chapter 2
General maintenance
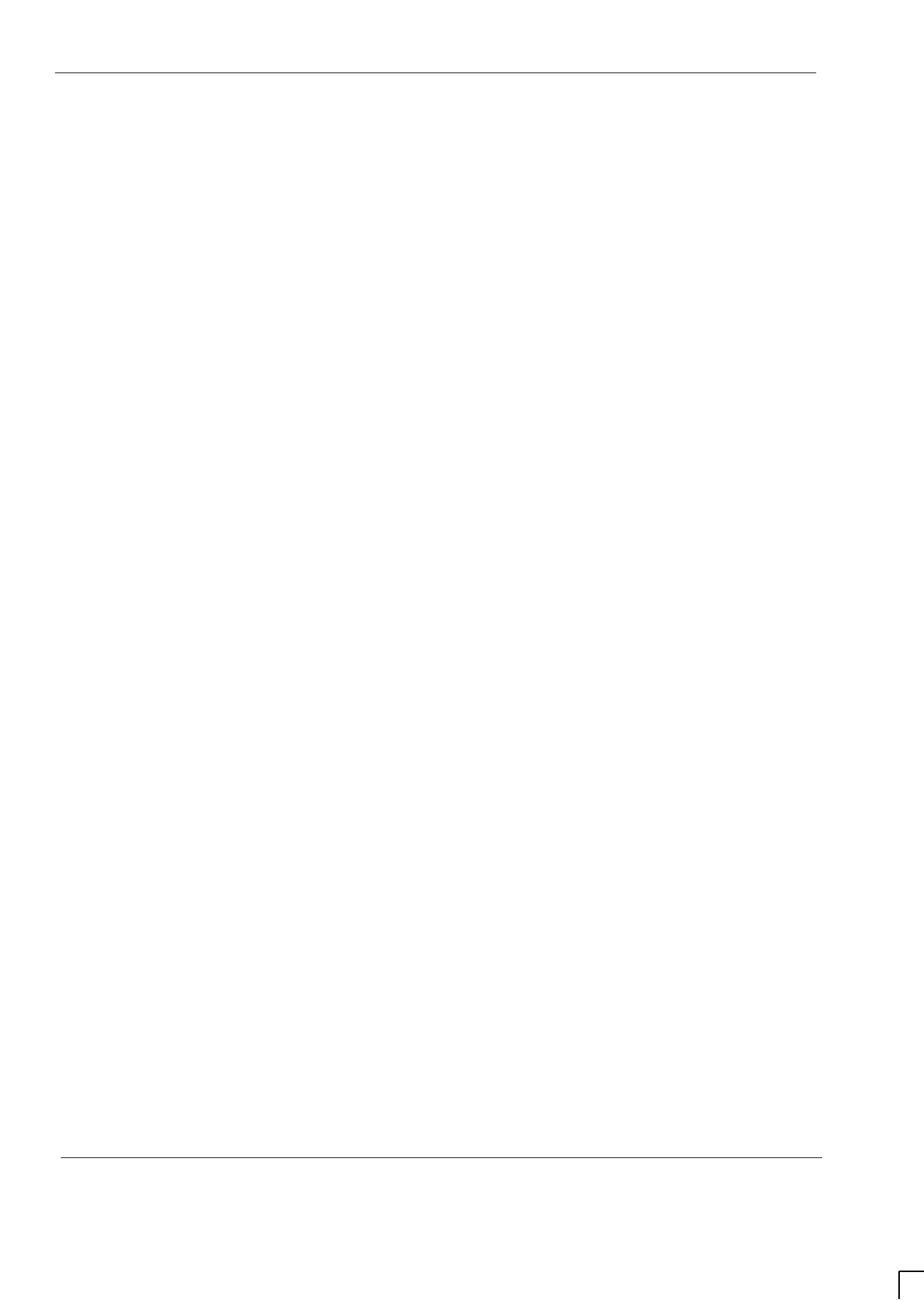
GSM-204-523
31st Oct 01
ii
Maintenance Information: Horizon
macro
outdoor
CONTROLLED INTRODUCTION
68P02902W04-A
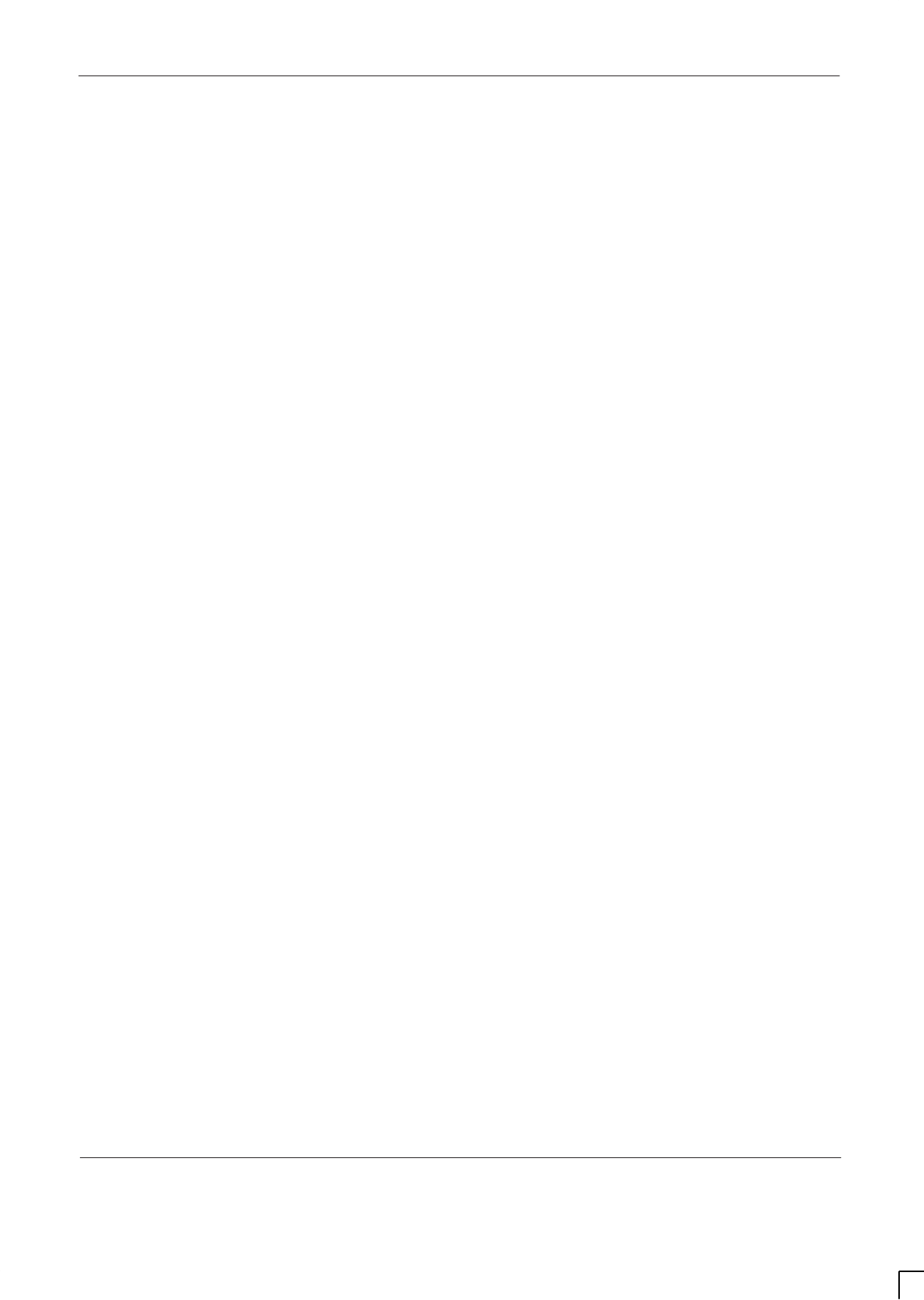
GSM-204-523
31st Oct 01
Maintenance Information: Horizon
macro
outdoor
68P02902W04-A
CONTROLLED INTRODUCTION
iii
Chapter 2
General maintenance i. . . . . . . . . . . . . . . . . . . . . . . . . . . . . . . . . . . . . . . . . .
General maintenance overview Maint. 2–1. . . . . . . . . . . . . . . . . . . . . . . . . . . . . . . . . . . . . . . .
In this chapter Maint. 2–1. . . . . . . . . . . . . . . . . . . . . . . . . . . . . . . . . . . . . . . . . . . . . . . . . .
Reporting faulty devices Maint. 2–1. . . . . . . . . . . . . . . . . . . . . . . . . . . . . . . . . . . . . . . . .
Cleaning agents Maint. 2–2. . . . . . . . . . . . . . . . . . . . . . . . . . . . . . . . . . . . . . . . . . . . . . . .
Torque values Maint. 2–2. . . . . . . . . . . . . . . . . . . . . . . . . . . . . . . . . . . . . . . . . . . . . . . . . .
Maintenance support procedures Maint. 2–3. . . . . . . . . . . . . . . . . . . . . . . . . . . . . . . . . . . . . .
Door opening and closing Maint. 2–3. . . . . . . . . . . . . . . . . . . . . . . . . . . . . . . . . . . . . . . .
Lid opening and closing Maint. 2–3. . . . . . . . . . . . . . . . . . . . . . . . . . . . . . . . . . . . . . . . .
TMS front cover removal and refitting Maint. 2–4. . . . . . . . . . . . . . . . . . . . . . . . . . . . . .
General maintenance procedures Maint. 2–5. . . . . . . . . . . . . . . . . . . . . . . . . . . . . . . . . . . . . .
Type of procedures Maint. 2–5. . . . . . . . . . . . . . . . . . . . . . . . . . . . . . . . . . . . . . . . . . . . .
Assumptions - door, lid and TMS front cover Maint. 2–5. . . . . . . . . . . . . . . . . . . . . . . .
Cleaning inlet and outlet grilles Maint. 2–5. . . . . . . . . . . . . . . . . . . . . . . . . . . . . . . . . . .
Checking normal operation Maint. 2–6. . . . . . . . . . . . . . . . . . . . . . . . . . . . . . . . . . . . . . .
Inspection of cabinet, locks and hinges Maint. 2–7. . . . . . . . . . . . . . . . . . . . . . . . . . . .
Periodic check of the installation Maint. 2–8. . . . . . . . . . . . . . . . . . . . . . . . . . . . . . . . . .
TMS testing Maint. 2–8. . . . . . . . . . . . . . . . . . . . . . . . . . . . . . . . . . . . . . . . . . . . . . . . . . . .
Battery backup test procedures Maint. 2–10. . . . . . . . . . . . . . . . . . . . . . . . . . . . . . . . . . .
Return to service Maint. 2–11. . . . . . . . . . . . . . . . . . . . . . . . . . . . . . . . . . . . . . . . . . . . . . . .
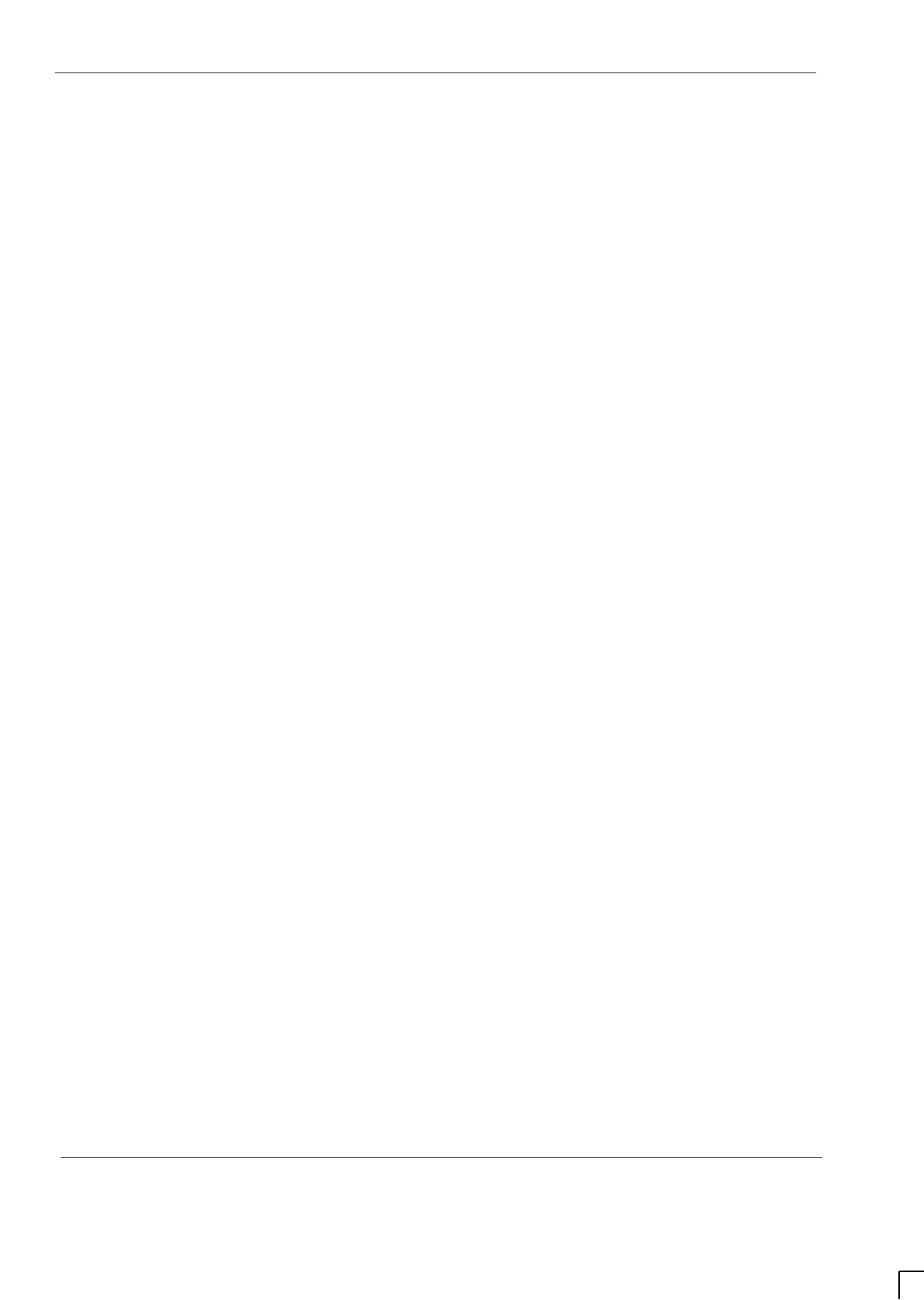
GSM-204-523
31st Oct 01
iv
Maintenance Information: Horizon
macro
outdoor
CONTROLLED INTRODUCTION
68P02902W04-A
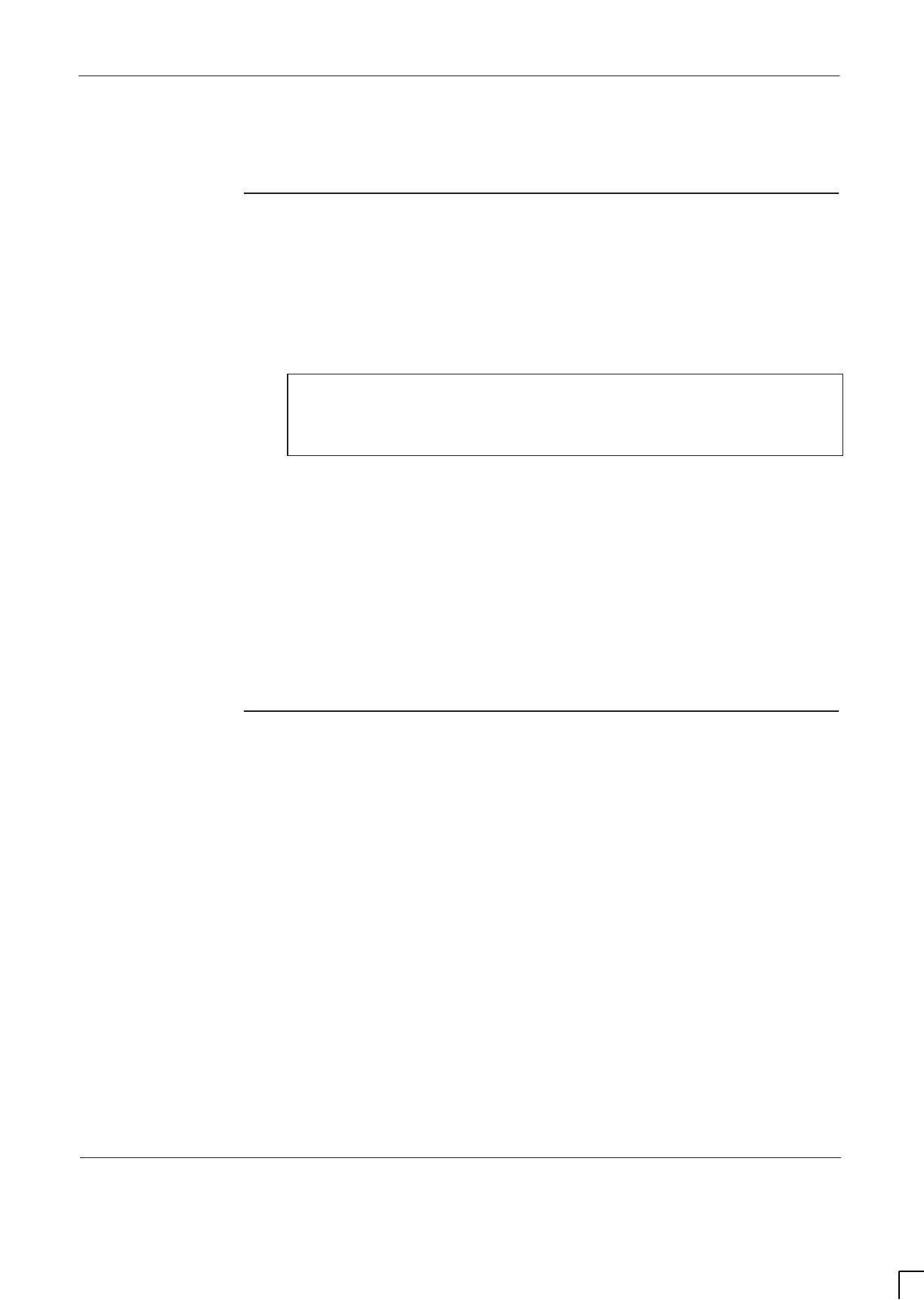
GSM-204-523 General maintenance overview
31st Oct 01
Maintenance Information: Horizon
macro
outdoor
68P02902W04-A
CONTROLLED INTRODUCTION
Maint. 2–1
General maintenance overview
In this chapter
This chapter contains the procedures for the general maintenance of a
Horizon
macro
outdoor BTS. There is no schedule for routine maintenance on
Horizon
macro
outdoor equipment. General maintenance procedures are to be
carried out during site visits in response to alarms (as required), or at intervals
deemed appropriate by the customer, (determined by the type of installation, its
use and operation, the frequency of maintenance and the external influences to
which it is subjected).
NOTE Since a Horizon
macro
BTS operates as part of a network,
the procedures in this chapter must be performed in
conjunction with the relevant network procedures in the
associated OMC-R manuals.
It is recommended that the following general maintenance procedures are
carried out for Horizon
macro
outdoor installations:
Ensure that cabinet air inlets and exhaust grilles are not blocked.
Check normal operation, including TMS fans. Also check cable integrity
and the condition of all connections.
Check battery backup operation and battery capacity.
Inspect general mechanical condition and finish of the cabinets.
Inspect locks, handles and hinges and door seals. Lubricate if required.
Reporting
faulty devices
During general maintenance and FRU replacement procedures, it may be
possible to identify signs of damage that might indicate a problem that could
repeat, cause additional damage, or be a symptom of a failure elsewhere.
Analysis of the problem may identify common faults and make corrective action
possible.
Whenever a safety issue arises:
Inform the OMC-R that an equipment safety problem has been identified.
Make the equipment concerned safe, for example, by removing power.
Make no further attempt to tamper with the equipment.
Report the problem directly to GSM Customer Network Resolution Centre
+44 (0)1793 565444 (telephone) and follow up with a written report by fax
+44 (0)1793 430987 (fax).
Collect evidence from the equipment under the guidance of the Customer
Network Resolution Centre.
Seek local office advice.
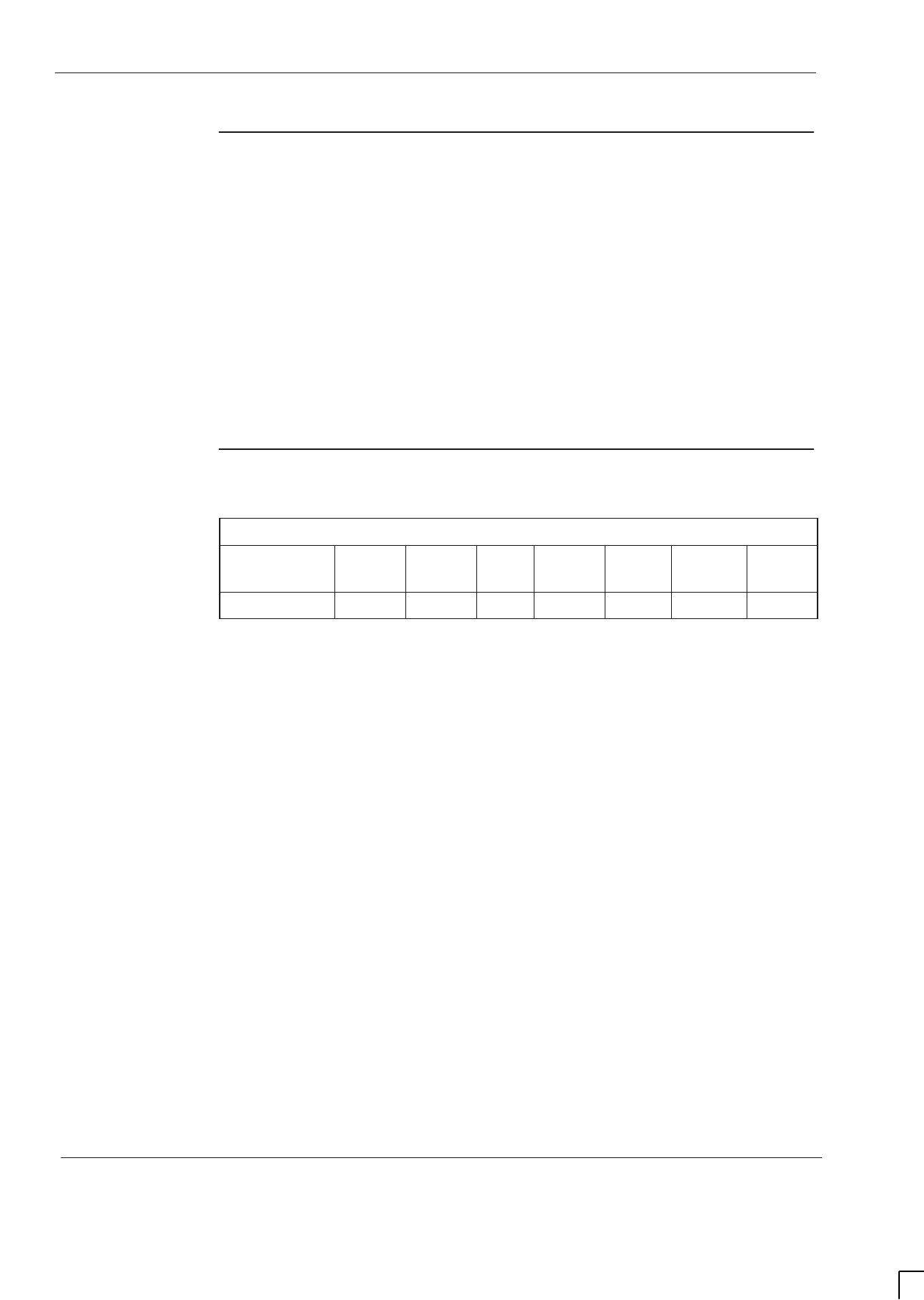
GSM-204-523
General maintenance overview
31st Oct 01
Maint. 2–2
Maintenance Information: Horizon
macro
outdoor
CONTROLLED INTRODUCTION
68P02902W04-A
Cleaning agents
The following is a list of cleaning agents and lubricant materials required for
general maintenance:
Dustpan
Soft brush
Mild detergent
De-ionized water.
Soft cloth.
Lubricant (WD40 or equivalent).
Light grease (TBI or equivalent).
Torque values
Table 2-1 details torque values used during FRU replacement procedures.
Table 2-1 Torque values for all cabinet screws/bolts and RF connectors
Size of
screw/bolt M4 M6 M8 M10 SMA N-type 7/16
Torque value 2.2 Nm 3.4 Nm 5 Nm 10 Nm 1 Nm 3.4 Nm 25 Nm
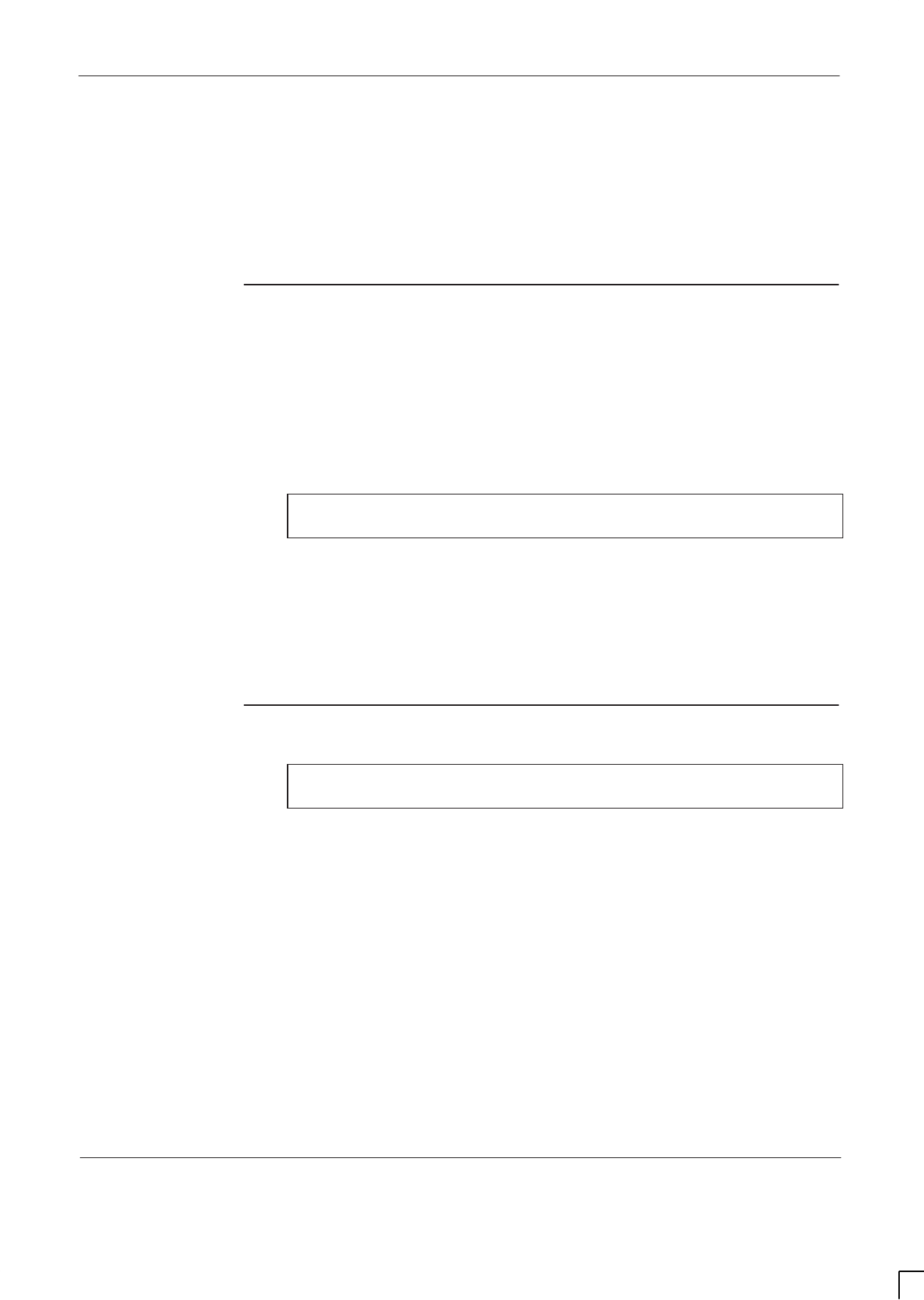
GSM-204-523 Maintenance support procedures
31st Oct 01
Maintenance Information: Horizon
macro
outdoor
68P02902W04-A
CONTROLLED INTRODUCTION
Maint. 2–3
Maintenance support procedures
The maintenance support procedures include the following:
Door and lid opening and closing.
TMS front cover removal and refitting.
Door opening
and closing
The door lock has a spring loaded handle. The door is operated as follows:
1. Insert key into lock and turn clockwise until spring loaded handle releases.
2. Turn handle a quarter turn anticlockwise to open the lock.
3. Open power supply enclosure door to 90 locking position.
4. Open radio enclosure door to 90 locking position.
NOTE If the equipment is active, a door open alarm will be
generated.
5. To open doors to 120, lift up middle of appropriate wind stop.
6. To close, lift up middle of wind stop, close doors firmly, radio enclosure
door first.
7. Turn handle a quarter turn clockwise, push handle flush and remove key
to lock.
Lid opening and
closing
NOTE The lid can only be opened and closed when both doors
are open.
The lid is opened as follows:
1. Ensure both cabinet doors are open to the 90 position.
2. Undo the two draw latches by turning anti clockwise, and ensure the catch
hook is clear of lip on the lid.
3. Lift the lid until the mechanical stay audibly locks.
The lid is closed as follows:
1. Press the lock stud on the mechanical stay to release.
2. Lower the lid.
3. Hook the draw latches over the lip and turn clockwise to lock.
4. Ensure operating tab is stowed flat.
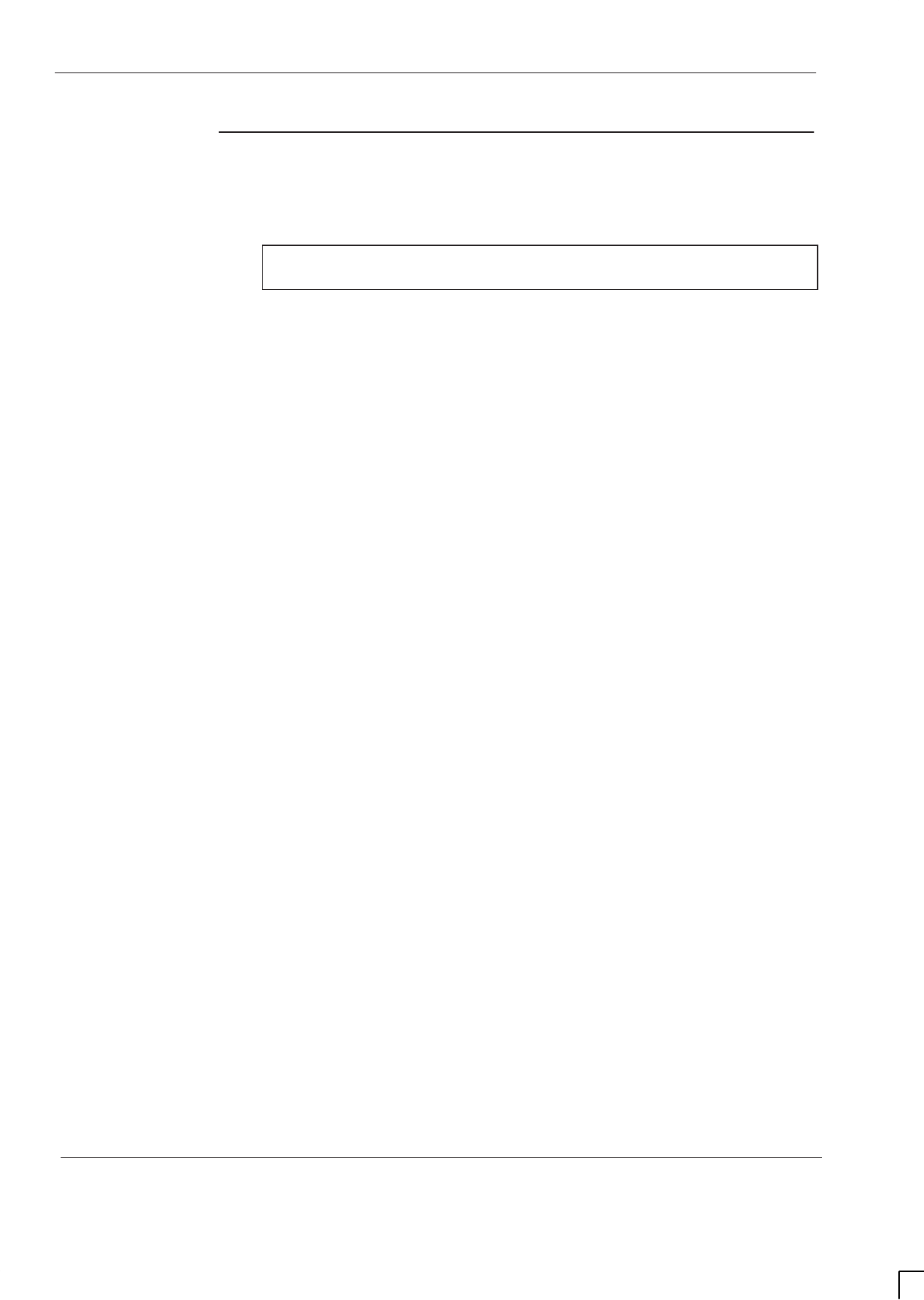
GSM-204-523
Maintenance support procedures
31st Oct 01
Maint. 2–4
Maintenance Information: Horizon
macro
outdoor
CONTROLLED INTRODUCTION
68P02902W04-A
TMS front cover
removal and
refitting
To remove the TMS front cover:
NOTE The TMS front cover can only be removed and refitted
when both doors are open.
1. Remove and retain the four push in plastic covers.
2. Using a crosspoint screwdriver, undo the four captive fasteners by turning
anticlockwise until they release.
3. Lift the TMS front cover away from the cabinet and store safely.
To refit the TMS front cover:
1. Refit the TMS front cover and line up the four fasteners.
2. Using a crosspoint screw driver, tighten the four captive fasteners.
3. Refit the four push in plastic covers.
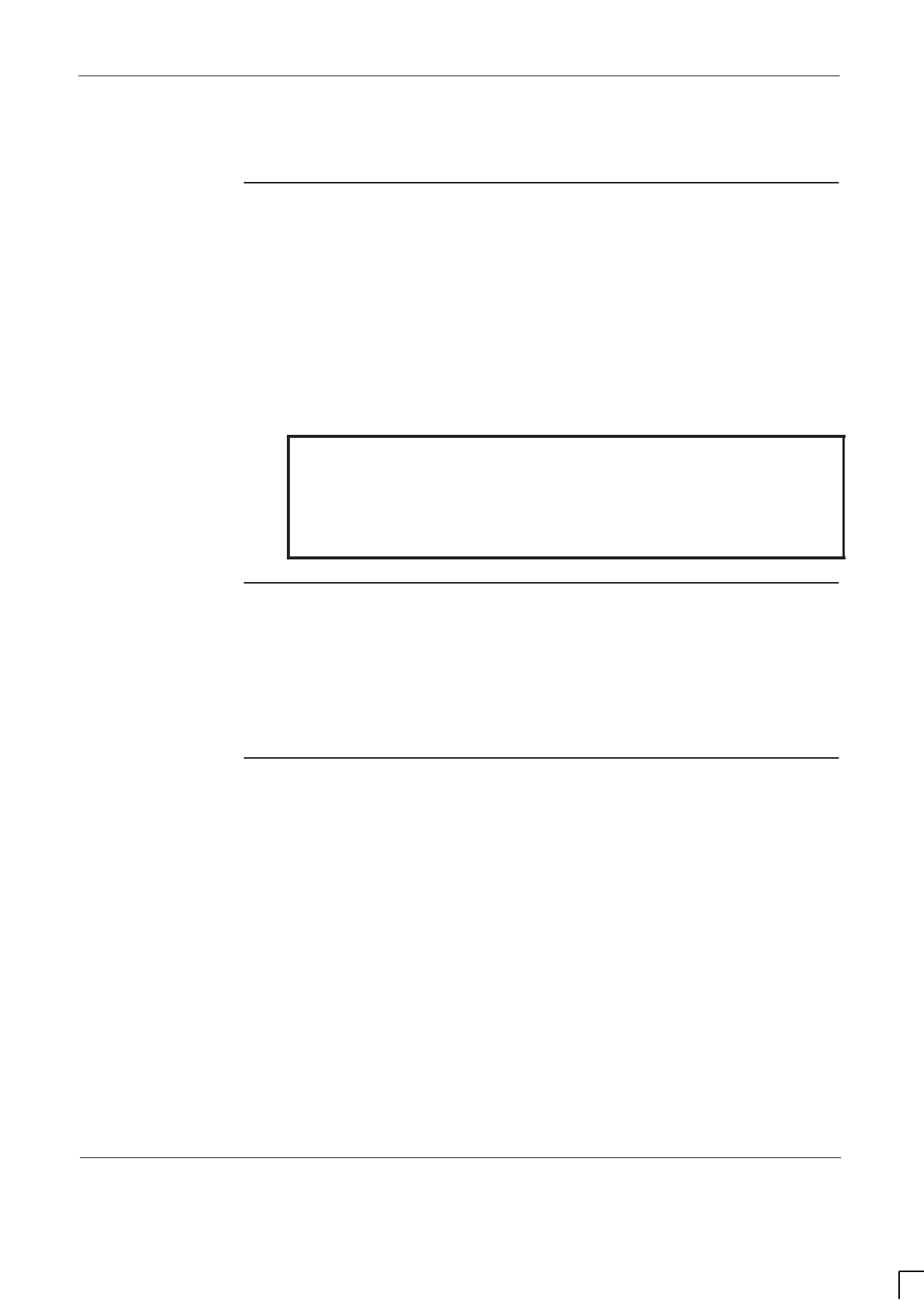
GSM-204-523 General maintenance procedures
31st Oct 01
Maintenance Information: Horizon
macro
outdoor
68P02902W04-A
CONTROLLED INTRODUCTION
Maint. 2–5
General maintenance procedures
Type of
procedures
The general maintenance procedures involve the following:
Cleaning air inlet and outlet grilles.
Checking and cleaning fans (only necessary if an overtemperature alarm
has occurred).
Checking normal operation.
Mechanical inspection of the cabinet, including inspection and lubrication
of locks and hinges.
Periodic check of the installation.
WARNING Potentially lethal voltages and high energy sources are
present in the cabinet when the external ac mains isolator
switch is set to the on position and/or batteries are
connected. Remove rings, watches and jewellery before
starting these procedures, and exercise extreme caution
when working on the equipment.
Assumptions -
door, lid and
TMS front cover
Any requirement to open or close a door, a lid, or remove/refit a TMS front cover
is assumed in the following procedures. Shutting the door or the lid is assumed
at the end of any procedure. Detailed descriptions of cabinet access procedures
are given in Maintenance support procedures.
Cleaning inlet
and outlet
grilles
Air is drawn in and expelled through the TMS front cover grille, at the base of
the front of the cabinet.
The following procedure should be followed to clean inlets, ducts and outlet
grilles:
Open the cabinet doors and examine door ducts and recirculation air
apertures. Clean as necessary, taking care to avoid damage.
Remove the TMS front cover and clean the grilles as necessary.
Examine the TMS unit ambient air inlet and outlet grilles. Clean as
necessary, taking care to avoid damage.
Use a brush to ensure the area under and around the TMS is clear of
debris.
Refit the TMS front cover.
Close the doors.
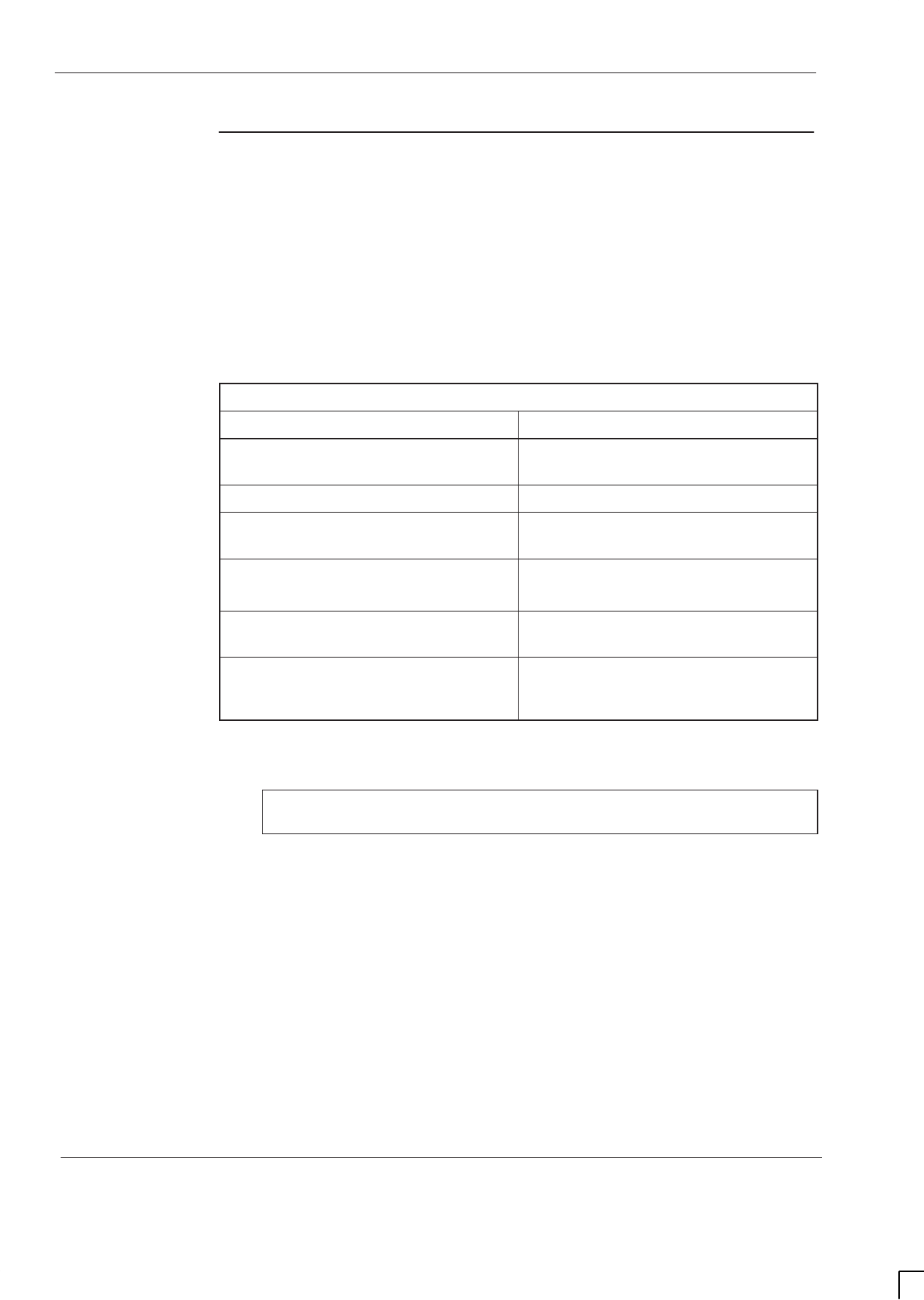
GSM-204-523
General maintenance procedures
31st Oct 01
Maint. 2–6
Maintenance Information: Horizon
macro
outdoor
CONTROLLED INTRODUCTION
68P02902W04-A
Checking
normal
operation
Check normal operation by visual inspection in the following procedure:
1. Inspect the inside of the cabinet and note any signs of physical damage,
overheating, loose connections, or badly fitting components. Take
appropriate action to correct the damage, and inform the OMC-R.
2. Note the LEDs lit on modules shown in Table 2-2 to ensure correct
functioning of the cabinet. If any red LEDs are lit, other than the door
alarm (alarm 3 on the alarm module), inform the OMC-R.
Table 2-2 Normal LED indication of cabinet modules
Equipment with LEDs Colour of LEDs lit
CTUs in locations 0 to 5 Tx status ORANGE or
Operational status GREEN
PSMs in locations 0 to 2 Top LED GREEN
Digital modules (NIU, MCUF, FMUX,
BPSM) GREEN
Alarm module 6, 7, 8 GREEN (fans)
3 RED (as door is open)
TOPSM Input healthy YELLOW
Output healthy GREEN
CAB Radio GREEN
Comms GREEN
Status FLASHING (as door is open)
3. Verify (by listening) that the TMS recirculation fans are operating.
NOTE In step 3 ambient air fans may also run, depending on site
conditions.

GSM-204-523 General maintenance procedures
31st Oct 01
Maintenance Information: Horizon
macro
outdoor
68P02902W04-A
CONTROLLED INTRODUCTION
Maint. 2–7
Inspection of
cabinet, locks
and hinges
Inspecting the cabinet exterior
Inspect the cabinet exterior using the following procedure:
Check exterior panels for dents and structural damage.
Check cabinet top connections for signs of overheating and security of
attachment.
Check cabinet exterior finish for signs of damage or deterioration. Restore
exterior finish as necessary.
Inspecting the doors and hood
Inspect the doors and hood using the following procedure:
Check cabinet doors and hood for distortion, security and correct
operation.
Check hinges for damage, security and correct operation. Carefully
lubricate the hinges. Ensure that all door seals are wiped clean of the
lubricant.
Check the hood mechanical stay and gas strut for damage, security and
correct operation. Carefully lubricate the moving parts of the mechanical
stay and gas strut and ensure that lubricated surfaces are dirt-free.
Check earth connection for damage and security.
Check door lock mechanism and inspect for ease of operation. Lubricate
the mechanism with light grease. Ensure that lubricated surfaces are
dirt-free.
Inspecting the cabinet interior
Inspect the cabinet interior using the following procedure:
Check all rack equipment for security of attachment, especially the
TOPSM PSM, CBM and CTU module attachment screws using a Torx
driver. Tighten to correct torque(see torque values in General
maintenance overview in this chapter).
Carry out a visual check of all wiring for signs of overheating and security
of attachment.
WARNING Do not over stress the earth connections, as this may
damage the connector and reduce the protective function.
Check the earth connections for corrosion and tightness using a torque
wrench. Tighten to the correct torque (see torque values in General
maintenance overview in this chapter).
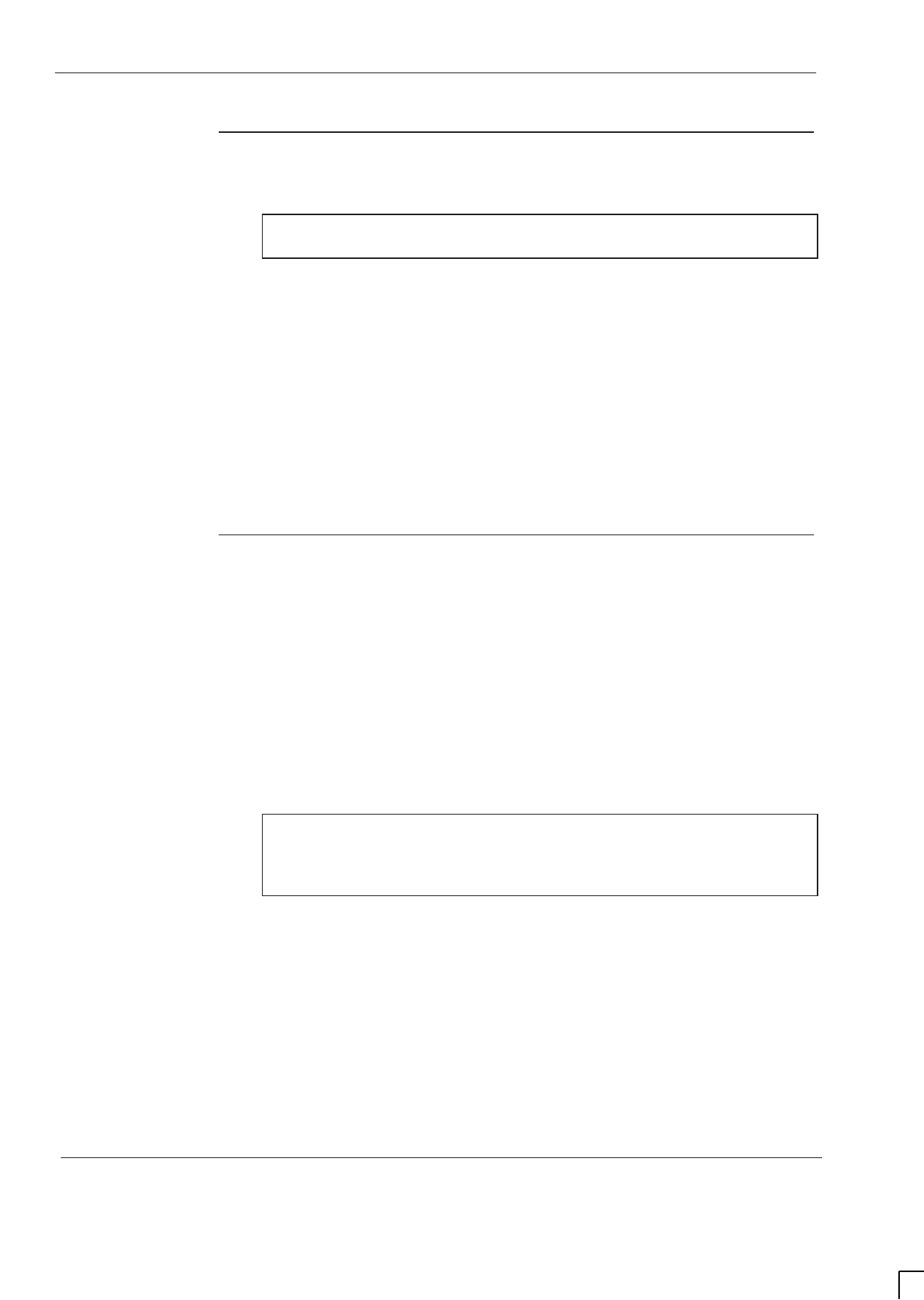
GSM-204-523
General maintenance procedures
31st Oct 01
Maint. 2–8
Maintenance Information: Horizon
macro
outdoor
CONTROLLED INTRODUCTION
68P02902W04-A
Periodic check
of the
installation
NOTE Refer to
Installation and Configuration: (GSM-204-423)
to
carry out the following procedures.
It is recommended that the following be performed periodically:
Inspection and testing in accordance with BS7671 (16th Edition Chapter
73), the IEC 364 equivalent or in accordance with local regulations.
Earth electrode test.
TMS testing.
Test backup battery capacity and operation.
The frequency of such periodic inspection and testing to be determined by the
type of installation, its use and operation, the frequency of maintenance and the
external influences to which it is subjected.
TMS testing
Test facilities
A four button test switch is mounted on the alarms interface board next to the
power supply unit (PSU).
Provision is made to perform the following tests:
Operate the fans (minimum speed).
Change the recirculation air (internal) fan speed.
Change the ambient air (external) speed.
Operate the heater.
NOTE Heater function is indicated by the illumination of an LED,
mounted on the rear vertical wall at the top right of the
recirculation air outlet aperture, below and in front of the
power supply enclosure.
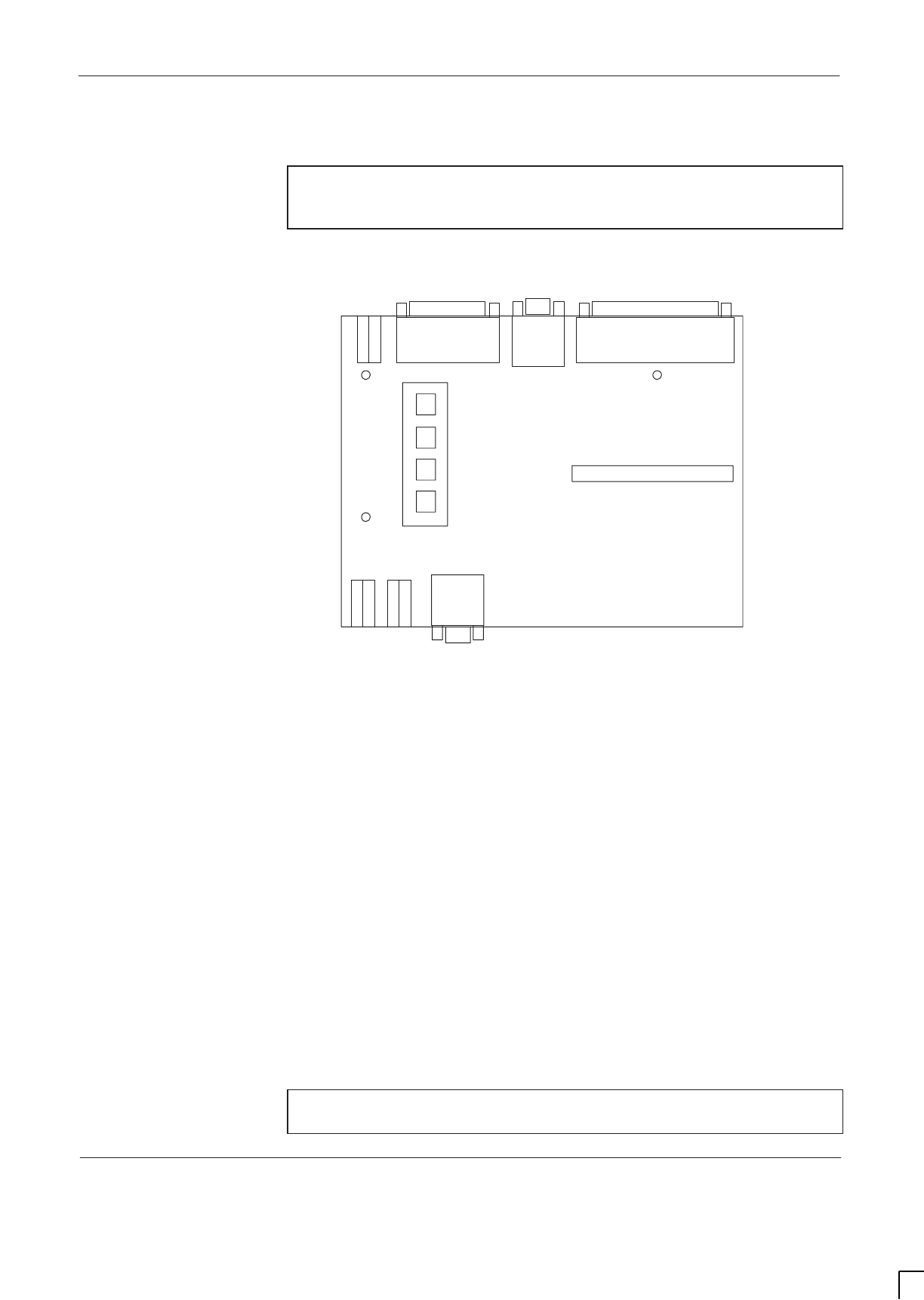
GSM-204-523 General maintenance procedures
31st Oct 01
Maintenance Information: Horizon
macro
outdoor
68P02902W04-A
CONTROLLED INTRODUCTION
Maint. 2–9
TMS Test procedure
CAUTION Do not operate the unit in this position for more than 4
minutes, otherwise damage to the electronic equipment
may occur.
Figure 2-1 shows the layout of the alarms interface board and shows the
position of the TMS test switches.
PL1 PL3
INTERNAL FANS
(SW3)
TEST OVERRIDE
(SW1)
HEATER ON
(SW2)
EXTERNAL FANS
(SW4) PL4
PL5
PL2
PL8
PL6PL7
Figure 2-1 Layout of alarms interface board and TMS test switches
1. Open the power supply enclosure (right) cabinet door.
2. Press and hold the test override switch and check that the four fans are
rotating at minimum speed and the heater LED is off.
3. Press the internal fans switch and check that both recirculation fans
increase speed.
4. Release the internal fans switch and check that both recirculation fans
return to minimum speed.
5. Press the external fans switch and check that both ambient air fans
increase speed.
6. Release the external fans switch and check that both ambient air fans
return to minimum speed.
7. Press the heater switch and check that the heater LED is lit.
8. Release the heater and test override switches.
9. Close the cabinet doors and verify (by listening) that the TMS recirculation
fans are operating.
NOTE In step 9 ambient air fans may also run, depending on site
conditions.
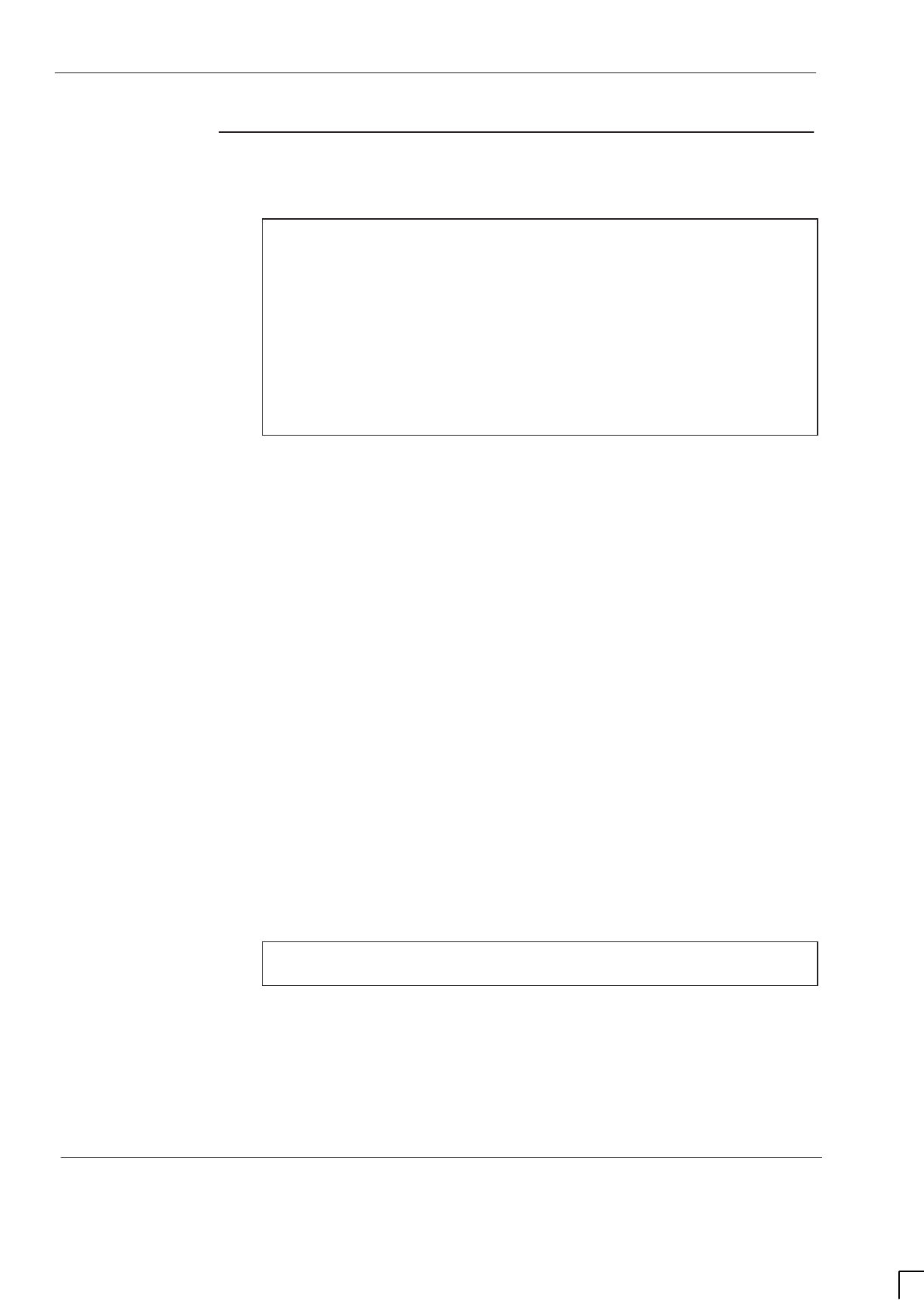
GSM-204-523
General maintenance procedures
31st Oct 01
Maint. 2–10
Maintenance Information: Horizon
macro
outdoor
CONTROLLED INTRODUCTION
68P02902W04-A
Battery backup
test procedures
The test procedure carried out will depend on battery backup configuration.
NOTE If the BTS cabinet is operational or otherwise visible to the
OMC-R, alarms will be generated. Notify the OMC-R
before carrying out these test procedures.
The internal or external batteries must be fully charged
before carrying out these test procedures.
The battery capacity test discharges the internal batteries
to –44 V dc. If an external power supply failure occurs
immediately after the test, the battery back up duration is
reduced to approximately 3 minutes. The internal batteries
recharge to approximately 80% capacity in less than one
hour.
Internal battery backup
To test operation of internal battery backup:
1. Operate the CAB front panel BATTERY TEST button to initiate internal
battery capacity test.
2. Check that the BATTERY CAPACITY LEDs flash during the test.
3. Check the 15 mins battery capacity LED is illuminated at the end of the
test.
The test of internal battery backup operation is now complete.
External battery backup (AEH)
To test operation of external battery backup:
1. Switch the main 32 A circuit breaker to off to disconnect the external ac
supply.
2. Check that the yellow I/P HEALTHY and green O/P HEALTHY LEDs on
the three TOPSMs are extinguished.
3. Check that the green RADIO LED on the CAB remains illuminated.
4. Check that the RADIO STATUS LED for each CTU continues to flash
green.
5. Verify (by listening) that the TMS recirculation fans are operating.
NOTE In step 5 ambient air fans may also run, depending on site
conditions.
6. Switch the main 32 A circuit breaker to on to reconnect the external ac
supply.
7. Check that the yellow I/P HEALTHY and green O/P HEALTHY LEDs on
the three TOPSMs illuminate, and that the indications checked in steps 3
to 5 remain unchanged.
The test of external battery backup operation is now complete.
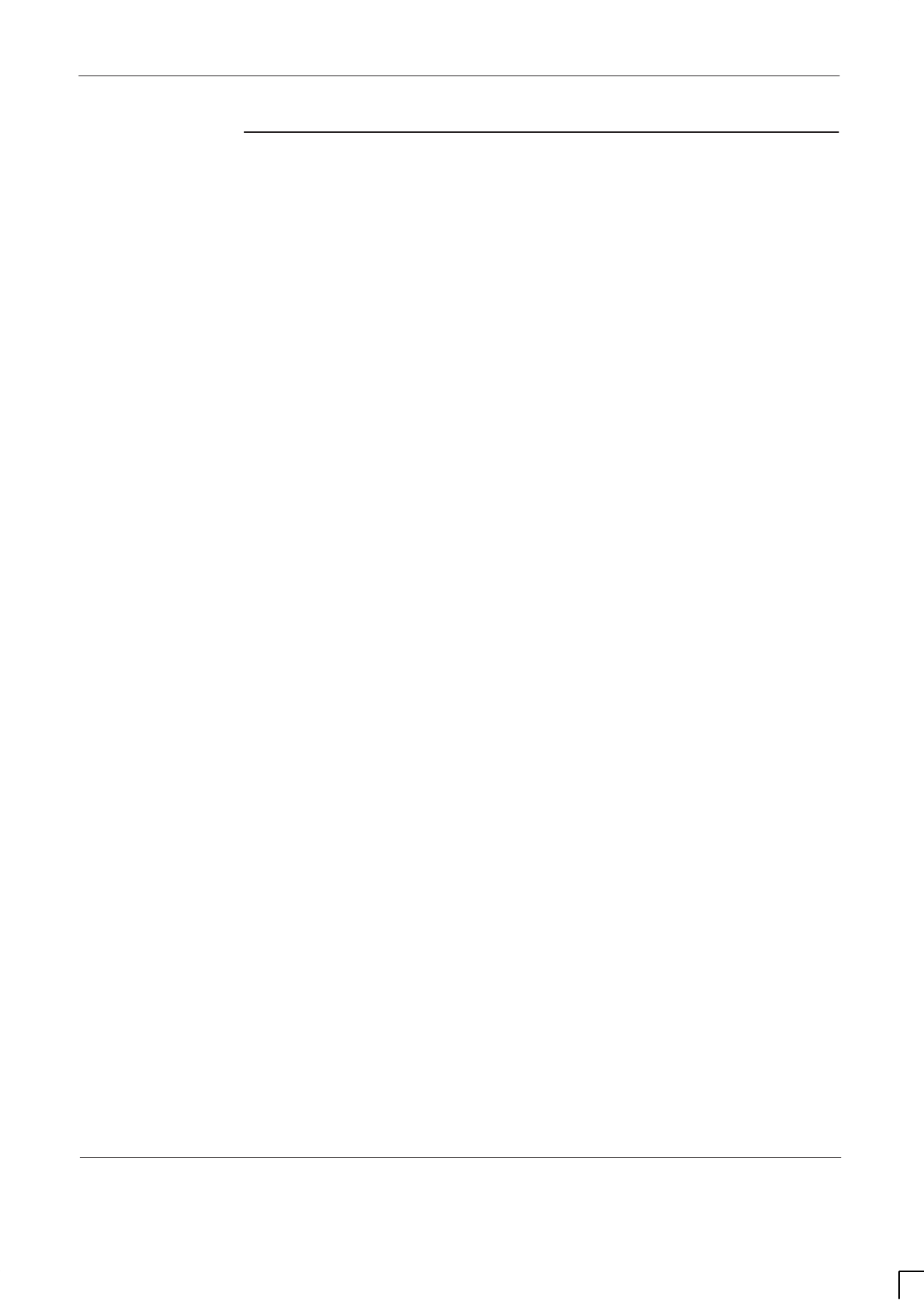
GSM-204-523 General maintenance procedures
31st Oct 01
Maintenance Information: Horizon
macro
outdoor
68P02902W04-A
CONTROLLED INTRODUCTION
Maint. 2–11
Return to
service
After procedures have been completed, restore the cabinet to its operational
state, if necessary, and notify the OMC-R of base station availability.
Log the maintenance activity.
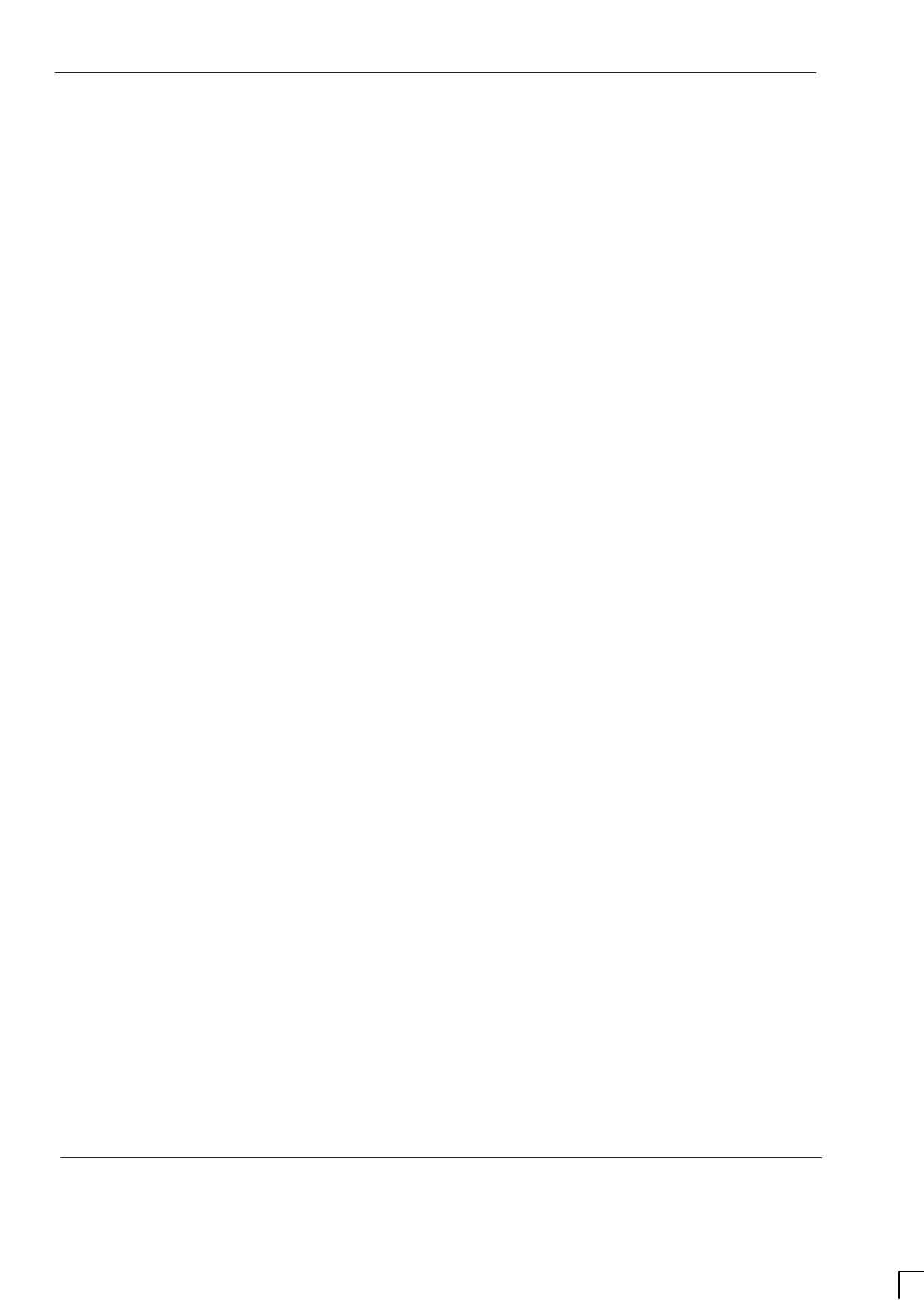
GSM-204-523
General maintenance procedures
31st Oct 01
Maint. 2–12
Maintenance Information: Horizon
macro
outdoor
CONTROLLED INTRODUCTION
68P02902W04-A
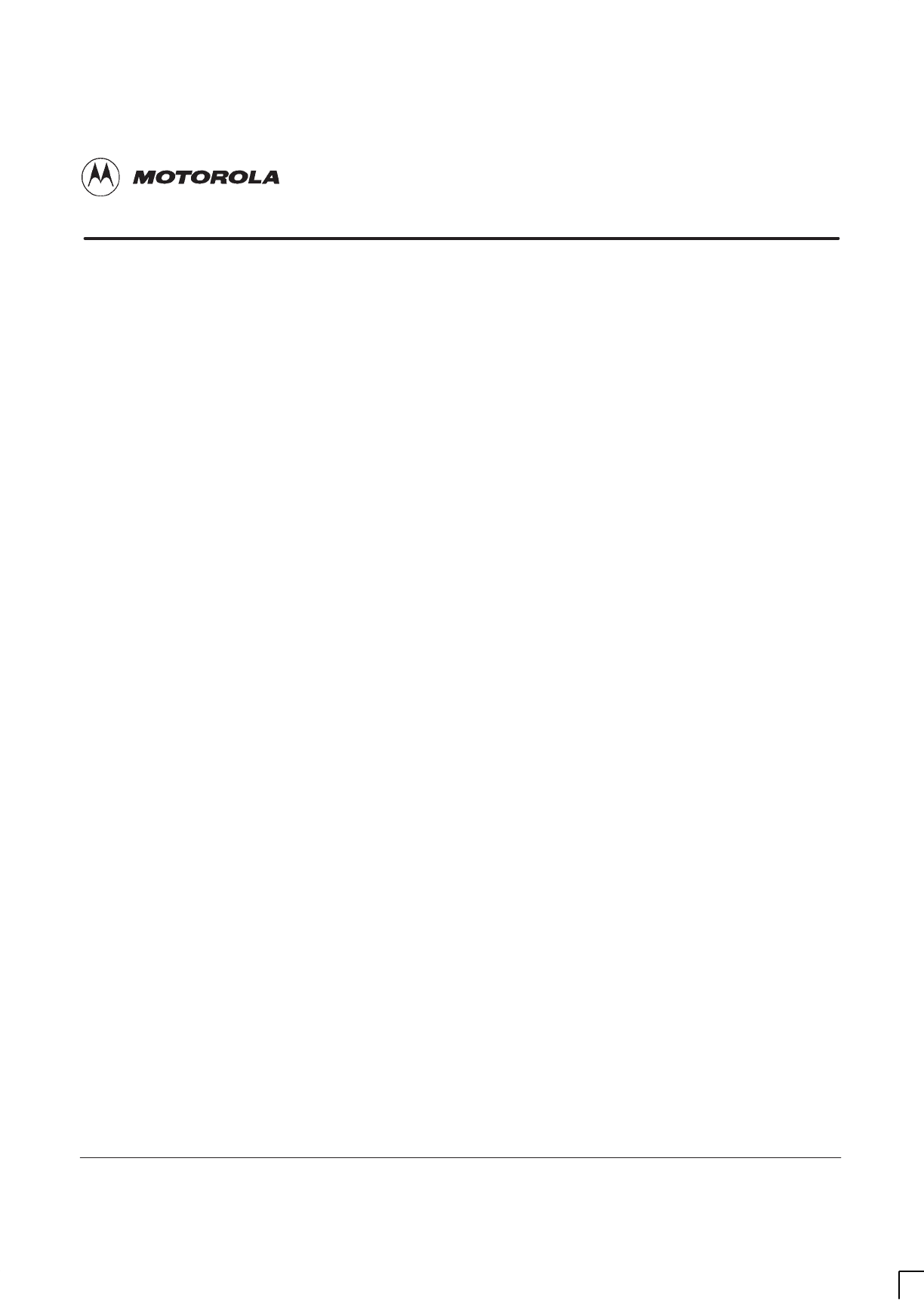
31st Oct 01
Maintenance Information: Horizon
macro
outdoor
68P02902W04-A
CONTROLLED INTRODUCTION
i
Chapter 3
FRU replacement procedures
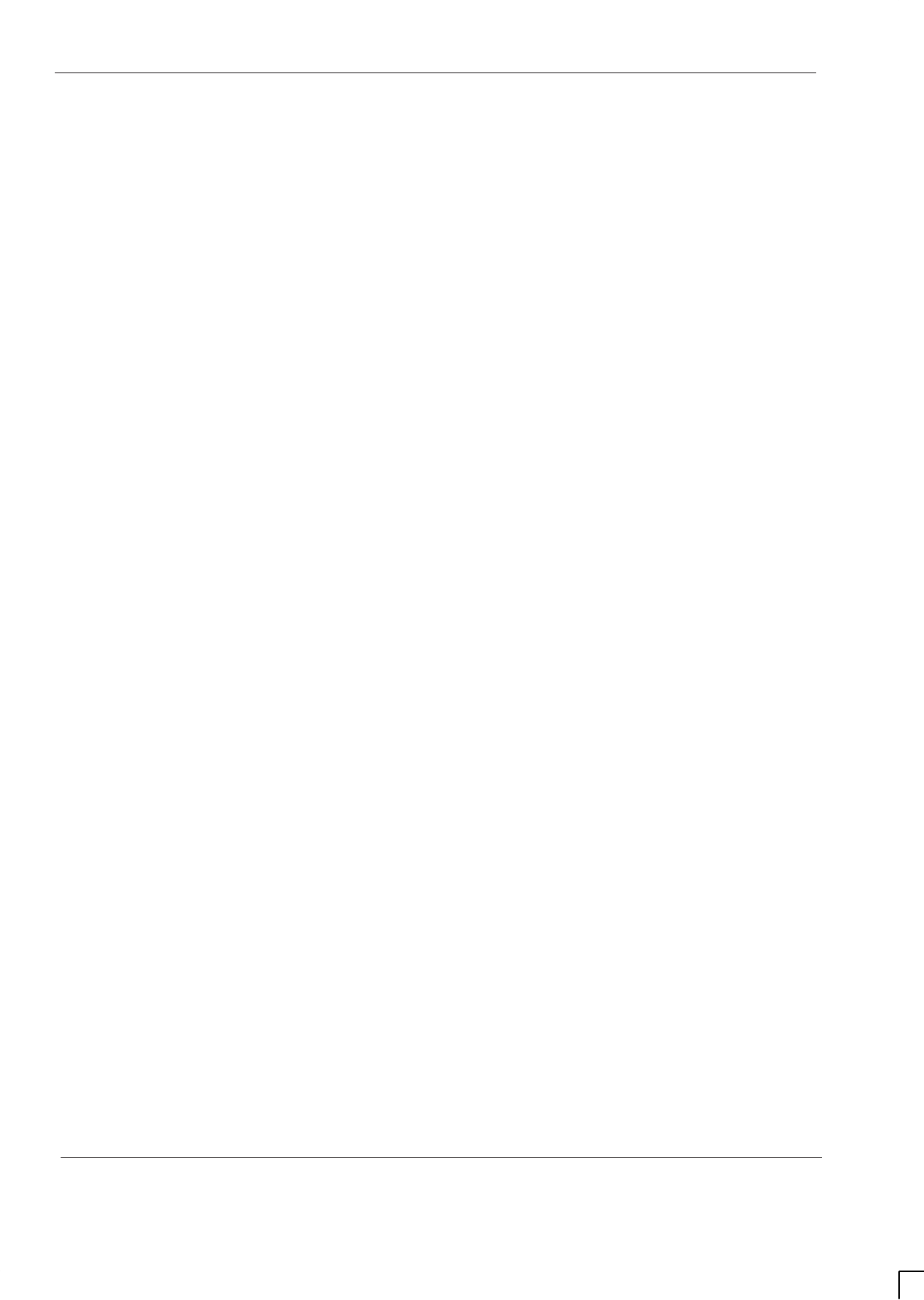
GSM-204-523
31st Oct 01
ii
Maintenance Information: Horizon
macro
outdoor
CONTROLLED INTRODUCTION
68P02902W04-A
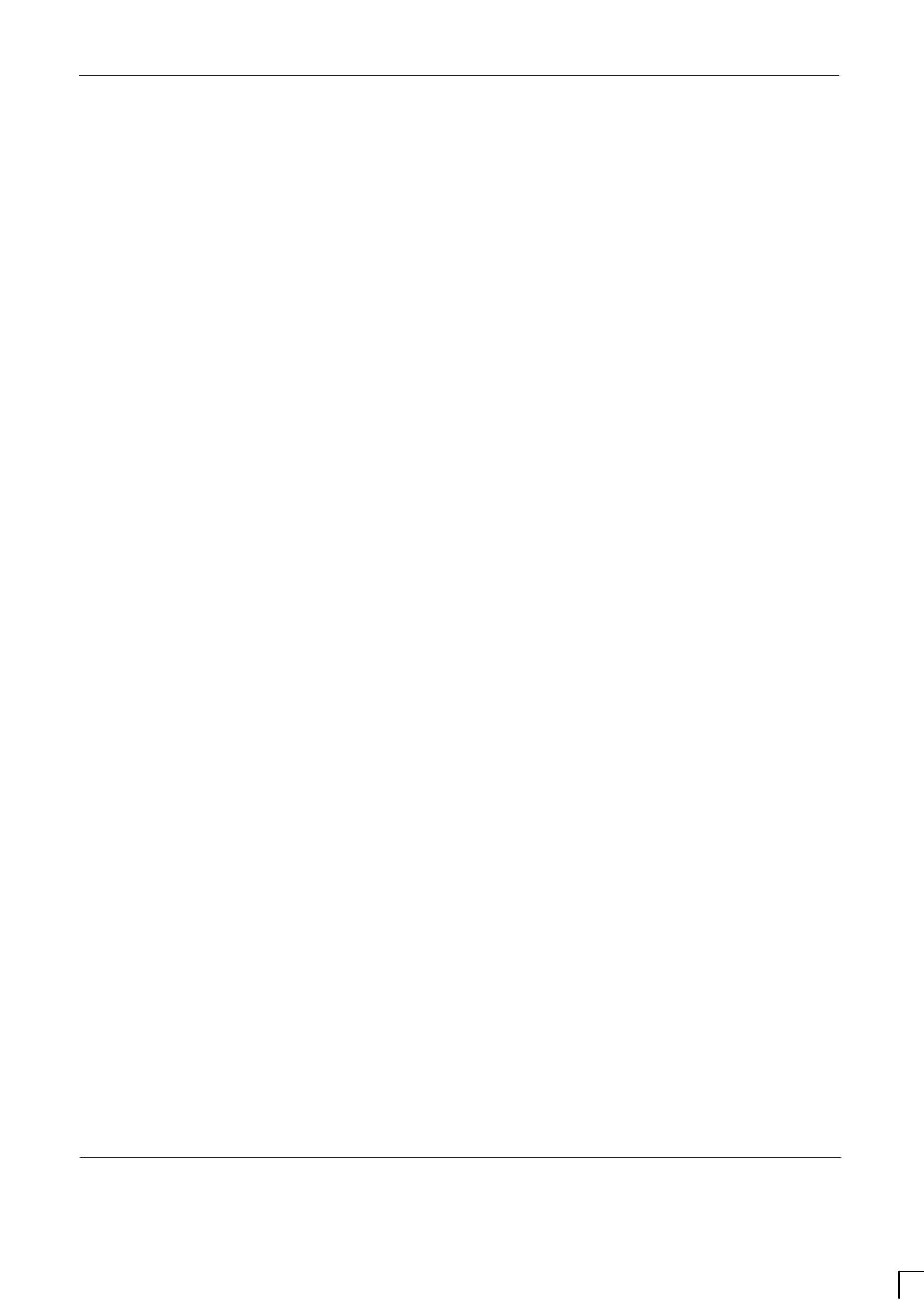
GSM-204-523
31st Oct 01
Maintenance Information: Horizon
macro
outdoor
68P02902W04-A
CONTROLLED INTRODUCTION
iii
Chapter 3
FRU replacement procedures i. . . . . . . . . . . . . . . . . . . . . . . . . . . . . . . . . .
Overview of FRU replacement procedures Maint. 3–1. . . . . . . . . . . . . . . . . . . . . . . . . . . . . .
Field replaceable units (FRUs) Maint. 3–1. . . . . . . . . . . . . . . . . . . . . . . . . . . . . . . . . . . .
FRU list Maint. 3–1. . . . . . . . . . . . . . . . . . . . . . . . . . . . . . . . . . . . . . . . . . . . . . . . . . . . . . . .
Torque values Maint. 3–2. . . . . . . . . . . . . . . . . . . . . . . . . . . . . . . . . . . . . . . . . . . . . . . . . .
FRU view of cabinet Maint. 3–2. . . . . . . . . . . . . . . . . . . . . . . . . . . . . . . . . . . . . . . . . . . . .
Replacing a door Maint. 3–3. . . . . . . . . . . . . . . . . . . . . . . . . . . . . . . . . . . . . . . . . . . . . . . . . . . . .
Introduction to door replacement Maint. 3–3. . . . . . . . . . . . . . . . . . . . . . . . . . . . . . . . . .
Views of the cabinet doors Maint. 3–3. . . . . . . . . . . . . . . . . . . . . . . . . . . . . . . . . . . . . . .
Door replacement procedure Maint. 3–4. . . . . . . . . . . . . . . . . . . . . . . . . . . . . . . . . . . . .
Replacing the lid Maint. 3–5. . . . . . . . . . . . . . . . . . . . . . . . . . . . . . . . . . . . . . . . . . . . . . . . . . . . .
Introduction to lid replacement Maint. 3–5. . . . . . . . . . . . . . . . . . . . . . . . . . . . . . . . . . . .
View of the cabinet lid Maint. 3–5. . . . . . . . . . . . . . . . . . . . . . . . . . . . . . . . . . . . . . . . . . .
Replacing a lid Maint. 3–6. . . . . . . . . . . . . . . . . . . . . . . . . . . . . . . . . . . . . . . . . . . . . . . . . .
Replacing environmental seals Maint. 3–7. . . . . . . . . . . . . . . . . . . . . . . . . . . . . . . . . . . . . . . .
Introduction to environmental seal replacement Maint. 3–7. . . . . . . . . . . . . . . . . . . . .
Replacing an environmental seal for the lid Maint. 3–7. . . . . . . . . . . . . . . . . . . . . . . . .
Replacing an environmental seal on a door Maint. 3–7. . . . . . . . . . . . . . . . . . . . . . . .
Replacing a thermal management system (TMS) unit Maint. 3–8. . . . . . . . . . . . . . . . . . . . .
Introduction to TMS replacement Maint. 3–8. . . . . . . . . . . . . . . . . . . . . . . . . . . . . . . . . .
View of the TMS unit Maint. 3–8. . . . . . . . . . . . . . . . . . . . . . . . . . . . . . . . . . . . . . . . . . . .
Removing the TMS unit Maint. 3–9. . . . . . . . . . . . . . . . . . . . . . . . . . . . . . . . . . . . . . . . . .
Refitting the TMS unit Maint. 3–10. . . . . . . . . . . . . . . . . . . . . . . . . . . . . . . . . . . . . . . . . . .
Replacing TMS unit components Maint. 3–11. . . . . . . . . . . . . . . . . . . . . . . . . . . . . . . . . . . . . . .
Introduction to TMS unit component replacement Maint. 3–11. . . . . . . . . . . . . . . . . . .
Replacing a TMS fan Maint. 3–11. . . . . . . . . . . . . . . . . . . . . . . . . . . . . . . . . . . . . . . . . . . .
Replacing the TMS control board Maint. 3–12. . . . . . . . . . . . . . . . . . . . . . . . . . . . . . . . .
Replacing the TMS gasket Maint. 3–12. . . . . . . . . . . . . . . . . . . . . . . . . . . . . . . . . . . . . . .
Replacing a cabinet temperature sensor Maint. 3–13. . . . . . . . . . . . . . . . . . . . . . . . . . . . . . . .
Overview of main cage temperature sensor FRUs Maint. 3–13. . . . . . . . . . . . . . . . . . .
Replaceing a main cage temperature sensor Maint. 3–13. . . . . . . . . . . . . . . . . . . . . . .
Replacing a dc circuit breaker Maint. 3–14. . . . . . . . . . . . . . . . . . . . . . . . . . . . . . . . . . . . . . . . .
Introduction to dc circuit breaker replacement Maint. 3–14. . . . . . . . . . . . . . . . . . . . . .
View of the dc circuit breaker panel Maint. 3–14. . . . . . . . . . . . . . . . . . . . . . . . . . . . . . .
Replacing a dc circuit breaker Maint. 3–14. . . . . . . . . . . . . . . . . . . . . . . . . . . . . . . . . . . .
Replacing the control and alarm board (CAB) Maint. 3–15. . . . . . . . . . . . . . . . . . . . . . . . . . . .
Introduction to CAB replacement Maint. 3–15. . . . . . . . . . . . . . . . . . . . . . . . . . . . . . . . . .
View of CAB Maint. 3–15. . . . . . . . . . . . . . . . . . . . . . . . . . . . . . . . . . . . . . . . . . . . . . . . . . .
Replacing a CAB Maint. 3–16. . . . . . . . . . . . . . . . . . . . . . . . . . . . . . . . . . . . . . . . . . . . . . .
Replacing the outdoor power supply module (TOPSM) Maint. 3–17. . . . . . . . . . . . . . . . . . . .
TOPSM replacement Maint. 3–17. . . . . . . . . . . . . . . . . . . . . . . . . . . . . . . . . . . . . . . . . . . .
View of TOPSM Maint. 3–17. . . . . . . . . . . . . . . . . . . . . . . . . . . . . . . . . . . . . . . . . . . . . . . . .
Replacing a TOPSM Maint. 3–18. . . . . . . . . . . . . . . . . . . . . . . . . . . . . . . . . . . . . . . . . . . .
Replacing a power supply module (PSM) Maint. 3–19. . . . . . . . . . . . . . . . . . . . . . . . . . . . . . .
Introduction to PSM replacement Maint. 3–19. . . . . . . . . . . . . . . . . . . . . . . . . . . . . . . . .
View of PSM Maint. 3–19. . . . . . . . . . . . . . . . . . . . . . . . . . . . . . . . . . . . . . . . . . . . . . . . . . .
Replacing a non-redundant PSM Maint. 3–20. . . . . . . . . . . . . . . . . . . . . . . . . . . . . . . . .
Replacing a redundant PSM Maint. 3–21. . . . . . . . . . . . . . . . . . . . . . . . . . . . . . . . . . . . .
BPSM replacement Maint. 3–21. . . . . . . . . . . . . . . . . . . . . . . . . . . . . . . . . . . . . . . . . . . . .
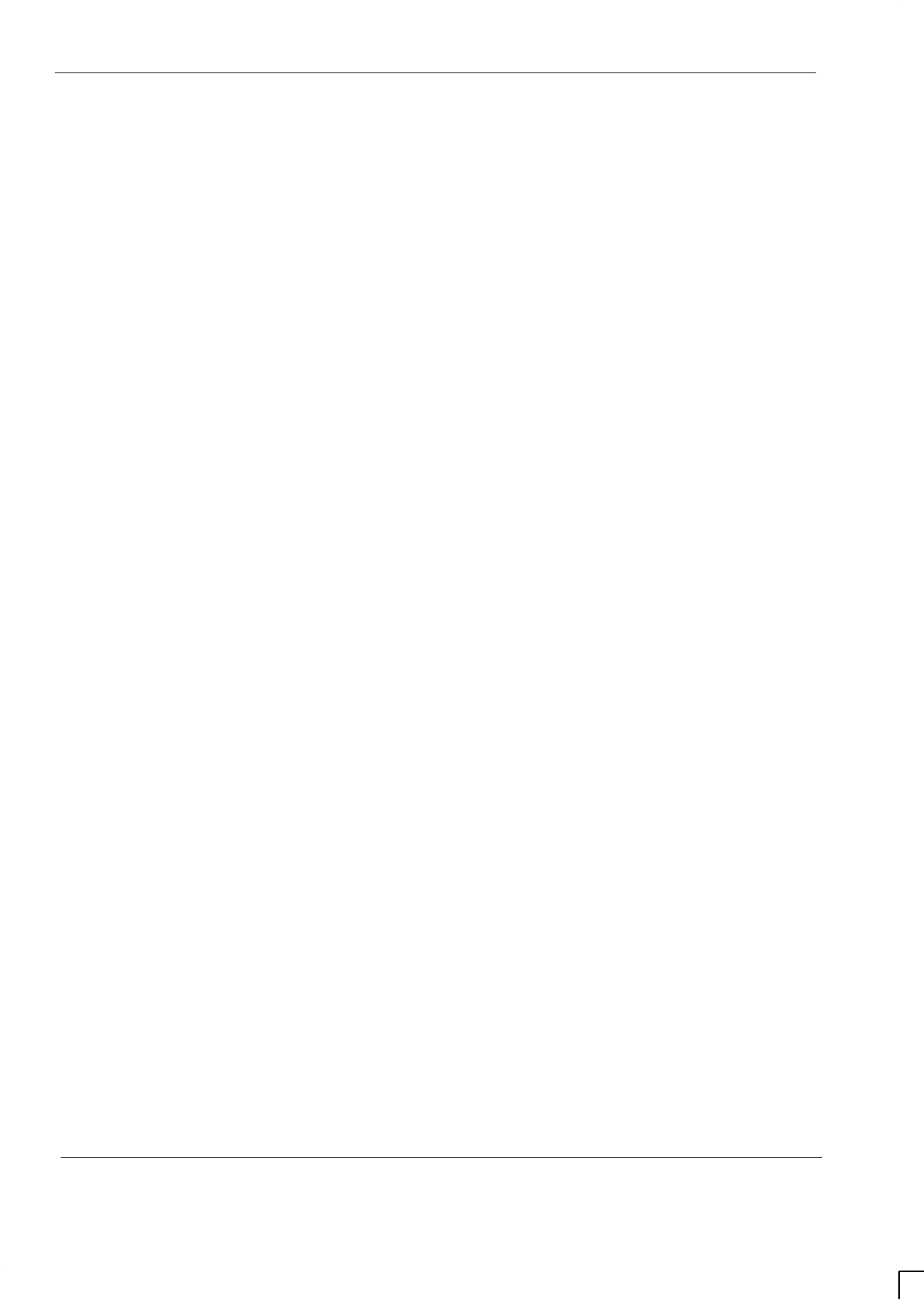
GSM-204-523
31st Oct 01
iv
Maintenance Information: Horizon
macro
outdoor
CONTROLLED INTRODUCTION
68P02902W04-A
Replacing a circuit breaker module (CBM) Maint. 3–22. . . . . . . . . . . . . . . . . . . . . . . . . . . . . . .
Preconditions for CBM replacement Maint. 3–22. . . . . . . . . . . . . . . . . . . . . . . . . . . . . . .
Views of CBM Maint. 3–22. . . . . . . . . . . . . . . . . . . . . . . . . . . . . . . . . . . . . . . . . . . . . . . . . .
Replacing a CBM Maint. 3–23. . . . . . . . . . . . . . . . . . . . . . . . . . . . . . . . . . . . . . . . . . . . . . .
Replacing the internal batteries Maint. 3–24. . . . . . . . . . . . . . . . . . . . . . . . . . . . . . . . . . . . . . . .
Introduction to internal battery replacement Maint. 3–24. . . . . . . . . . . . . . . . . . . . . . . .
Battery arrangement Maint. 3–25. . . . . . . . . . . . . . . . . . . . . . . . . . . . . . . . . . . . . . . . . . . .
Removing the battery tray Maint. 3–25. . . . . . . . . . . . . . . . . . . . . . . . . . . . . . . . . . . . . . . .
Removing and replacing the batteries Maint. 3–26. . . . . . . . . . . . . . . . . . . . . . . . . . . . .
View showing battery replacement components Maint. 3–27. . . . . . . . . . . . . . . . . . . . .
Replacing a CTU Maint. 3–28. . . . . . . . . . . . . . . . . . . . . . . . . . . . . . . . . . . . . . . . . . . . . . . . . . . . .
Preconditions to CTU replacement Maint. 3–28. . . . . . . . . . . . . . . . . . . . . . . . . . . . . . . .
View of CTU Maint. 3–28. . . . . . . . . . . . . . . . . . . . . . . . . . . . . . . . . . . . . . . . . . . . . . . . . . . .
Replacement procedure for CTU Maint. 3–29. . . . . . . . . . . . . . . . . . . . . . . . . . . . . . . . . .
Replacing a SURF module Maint. 3–31. . . . . . . . . . . . . . . . . . . . . . . . . . . . . . . . . . . . . . . . . . . .
Preconditions for SURF replacement Maint. 3–31. . . . . . . . . . . . . . . . . . . . . . . . . . . . . .
View of the SURF Maint. 3–31. . . . . . . . . . . . . . . . . . . . . . . . . . . . . . . . . . . . . . . . . . . . . . .
Replacing a SURF module Maint. 3–32. . . . . . . . . . . . . . . . . . . . . . . . . . . . . . . . . . . . . . .
Replacing a Tx block Maint. 3–34. . . . . . . . . . . . . . . . . . . . . . . . . . . . . . . . . . . . . . . . . . . . . . . . .
Preconditions to Tx block replacement Maint. 3–34. . . . . . . . . . . . . . . . . . . . . . . . . . . . .
Views of typical Tx block Maint. 3–35. . . . . . . . . . . . . . . . . . . . . . . . . . . . . . . . . . . . . . . . .
Replacing a Tx block Maint. 3–36. . . . . . . . . . . . . . . . . . . . . . . . . . . . . . . . . . . . . . . . . . . .
Tx block blanking plate, feedthrough plate or HCU replacement Maint. 3–37. . . . . .
Krone block replacement Maint. 3–38. . . . . . . . . . . . . . . . . . . . . . . . . . . . . . . . . . . . . . . . . . . . . .
Introduction to Krone block replacement Maint. 3–38. . . . . . . . . . . . . . . . . . . . . . . . . . .
Krone block location diagram Maint. 3–38. . . . . . . . . . . . . . . . . . . . . . . . . . . . . . . . . . . . .
Replacing a Krone block Maint. 3–39. . . . . . . . . . . . . . . . . . . . . . . . . . . . . . . . . . . . . . . . .
Digital module and BPSM replacement Maint. 3–40. . . . . . . . . . . . . . . . . . . . . . . . . . . . . . . . .
Preconditions for digital module replacement Maint. 3–40. . . . . . . . . . . . . . . . . . . . . . .
Digital module location diagram Maint. 3–40. . . . . . . . . . . . . . . . . . . . . . . . . . . . . . . . . . .
Replacing a digital module Maint. 3–41. . . . . . . . . . . . . . . . . . . . . . . . . . . . . . . . . . . . . . .
Redundant MCUF firmware compatibility Maint. 3–43. . . . . . . . . . . . . . . . . . . . . . . . . . . . . . . .
Overview of MCUF firmware compatibility Maint. 3–43. . . . . . . . . . . . . . . . . . . . . . . . . .
Checking MCUF firmware compatibility Maint. 3–43. . . . . . . . . . . . . . . . . . . . . . . . . . . .
Updating redundant MCUF firmware Maint. 3–43. . . . . . . . . . . . . . . . . . . . . . . . . . . . . .
Testing MCUF redundancy Maint. 3–46. . . . . . . . . . . . . . . . . . . . . . . . . . . . . . . . . . . . . . .
Additional replacement parts Maint. 3–47. . . . . . . . . . . . . . . . . . . . . . . . . . . . . . . . . . . . . . . . . .
Policy on non-FRU parts Maint. 3–47. . . . . . . . . . . . . . . . . . . . . . . . . . . . . . . . . . . . . . . . .
List of non-FRU parts Maint. 3–47. . . . . . . . . . . . . . . . . . . . . . . . . . . . . . . . . . . . . . . . . . . .
Procedure for replacing non-FRU parts Maint. 3–47. . . . . . . . . . . . . . . . . . . . . . . . . . . .
CBIA attachment screws Maint. 3–47. . . . . . . . . . . . . . . . . . . . . . . . . . . . . . . . . . . . . . . . .
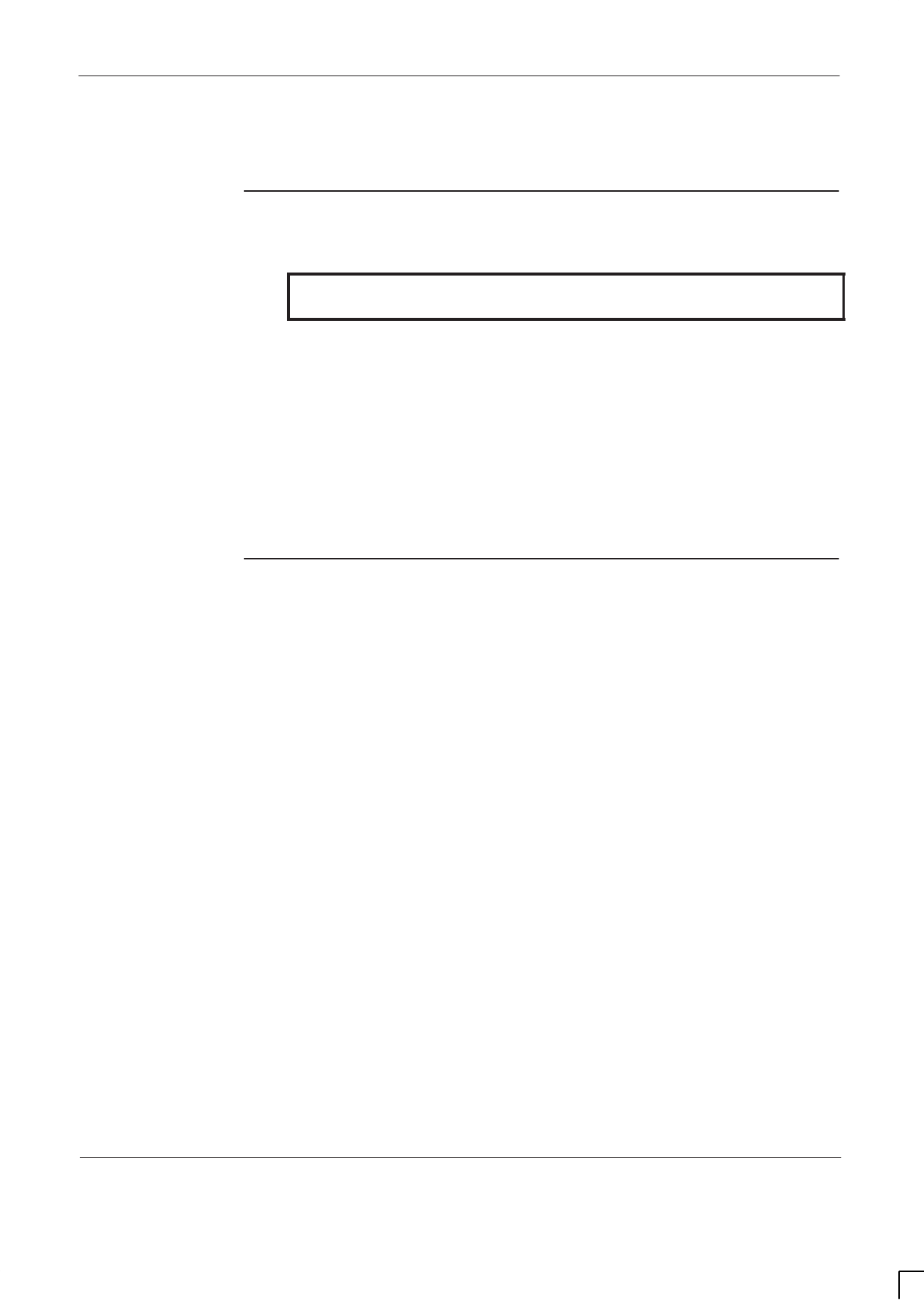
GSM-204-523 Overview of FRU replacement procedures
31st Oct 01
Maintenance Information: Horizon
macro
outdoor
68P02902W04-A
CONTROLLED INTRODUCTION
Maint. 3–1
Overview of FRU replacement procedures
Field
replaceable
units (FRUs)
WARNING Maintenance procedures on this equipment must only be
carried out by suitably qualified personnel.
This chapter provides information on replacement of Field Replaceable Units
(FRUs). Only components classed as FRUs are described in this chapter.
Any requirement to open or close a door, a lid, or remove/refit a TMS front cover
is assumed in procedures. Shutting the door, or the lid is assumed at the end of
any procedure. Detailed descriptions of cabinet access procedures are given in
Maintenance support procedures.
Where customers wish to perform a minor repair on an FRU, in order to save the
cost of full replacement, they should consult Motorola for more detailed
procedures or replacement components (see Additional replacement parts).
FRU list
The following is a list of FRUs used in this equipment:
Door.
Lid.
Environmental seals.
TMS unit.
TMS fans.
TMS control board.
Main cage temperature sensors.
DC circuit breaker panel.
Control and alarm board (CAB).
The outdoor power supply modules (TOPSMs).
Power supply module (PSM).
Circuit breaker module (CBM).
Internal battery tray.
CTUs.
SURF module.
Tx blocks including feedthrough plate.
Krone blocks.
Digital modules (MCUFs, NIUs, FMUXs, alarm board and also BPSMs).
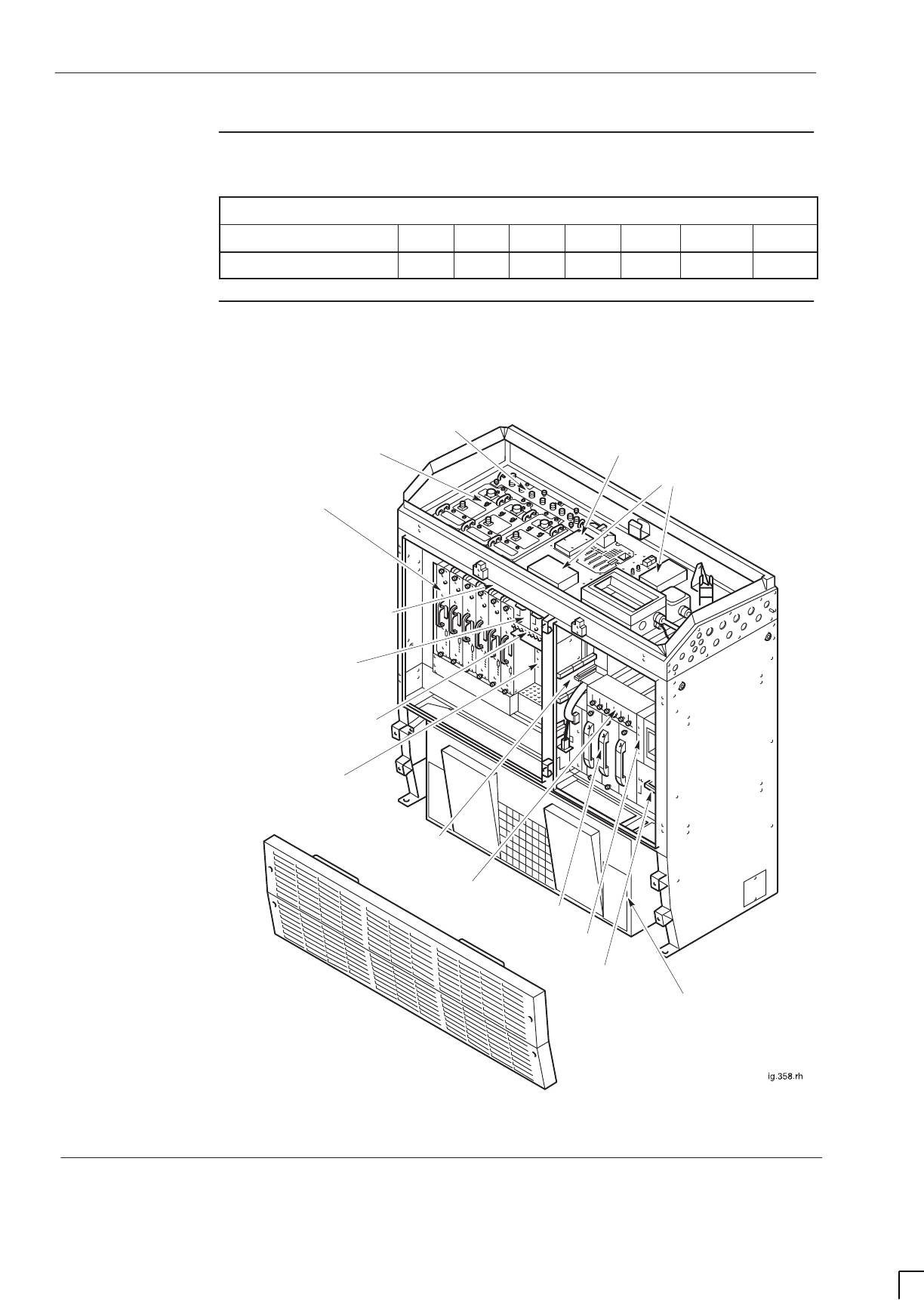
GSM-204-523
Overview of FRU replacement procedures
31st Oct 01
Maint. 3–2
Maintenance Information: Horizon
macro
outdoor
CONTROLLED INTRODUCTION
68P02902W04-A
Torque values
Table 3-1 details torque values used during FRU replacement procedures.
Table 3-1 Torque values for all cabinet screws/bolts and RF connectors
Size of screw/bolt M4 M6 M8 M10 SMA N-type 7/16
Torque value (Nm) 2.2 3.4 5 10 1 3.4 25
FRU view of
cabinet
Figure 3-1 shows a cabinet with FRUs identified. Doors and lid are shown in
relevant FRU sections.
PSMs (x3)
Tx BLOCKS x3
(DCFs SHOWN AS
EXAMPLE)
SURF (Rx)
CTUs (x6)
MAIN CAGE
TEMPERATURE
SENSORS (LOCATED
ON BACKPLANE)
DIGITAL
MODULES
ALARM BOARD, MCUF,
FMUX/NIU/BPSM
CIRCUIT BREAKER
MODULE (CBM)
T43/BIB
TOPSMs
(x3)
ALARMS
INTERFACE
BOARD
CAB
INTERNAL
BATTERIES TMS UNIT
KRONE BLOCKS
DC CIRCUIT
BREAKER PANEL
Figure 3-1 Cabinet, without doors or lid, showing FRU components
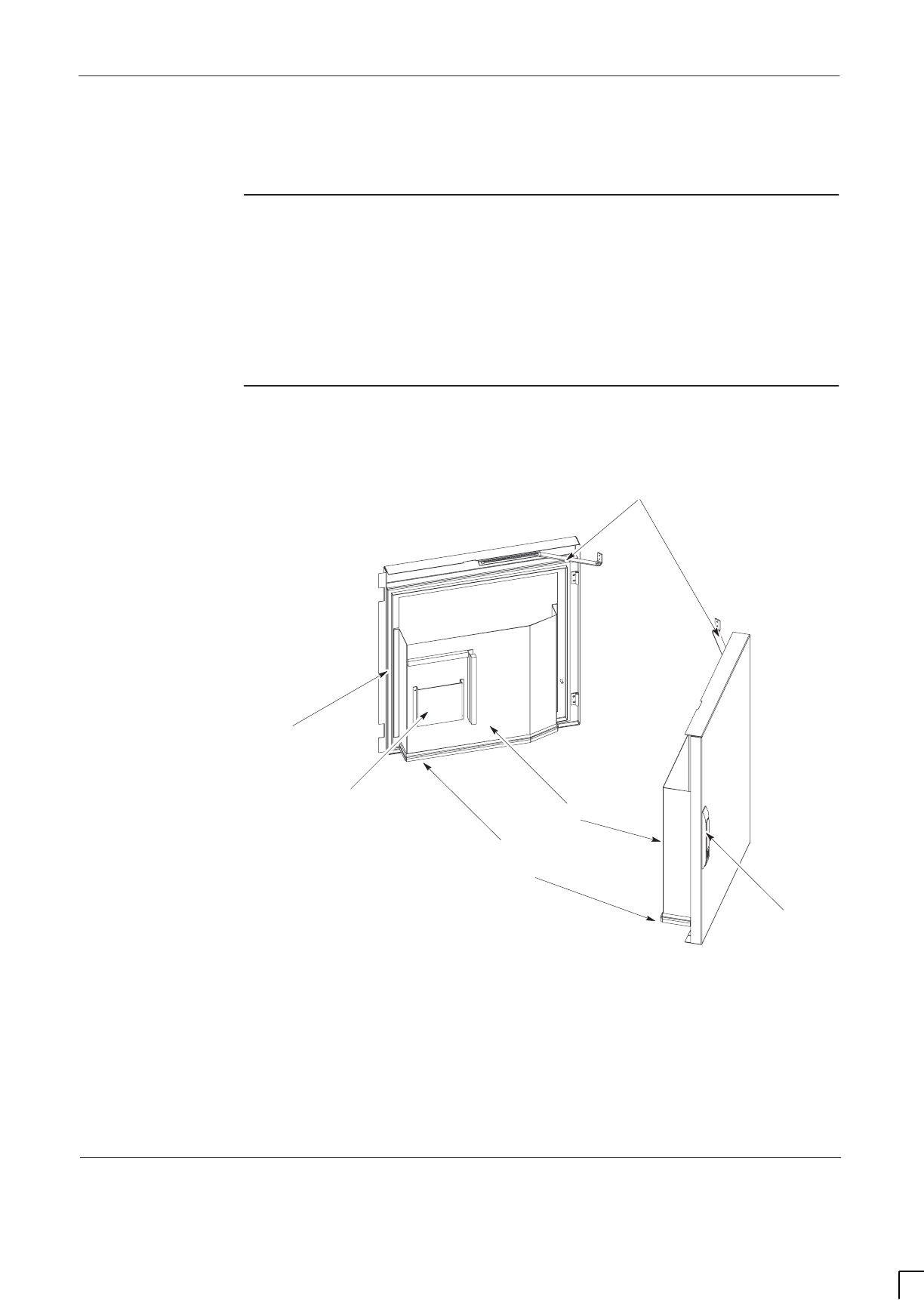
GSM-204-523 Replacing a door
31st Oct 01
Maintenance Information: Horizon
macro
outdoor
68P02902W04-A
CONTROLLED INTRODUCTION
Maint. 3–3
Replacing a door
Introduction to
door
replacement
The door is essential to the correct operation of the ventilation system. The door
also provides protection to equipment inside. For these reasons, the
replacement procedure should be completed in one session, and the cabinet
then closed.
Views of the
cabinet doors
Figure 3-2 shows the cabinet doors with major features labelled.
LOCKING LATCH
HANDLE
RADIO ENCLOSURE
DOOR
POWER SUPPLY
ENCLOSURE DOOR
WIND STOPS
AIR DUCT
BRUSH SEALS
AIR DUCTS
A5 DOCUMENT
POCKET
ENVIRONMENTAL
SEAL
Figure 3-2 View of cabinet doors
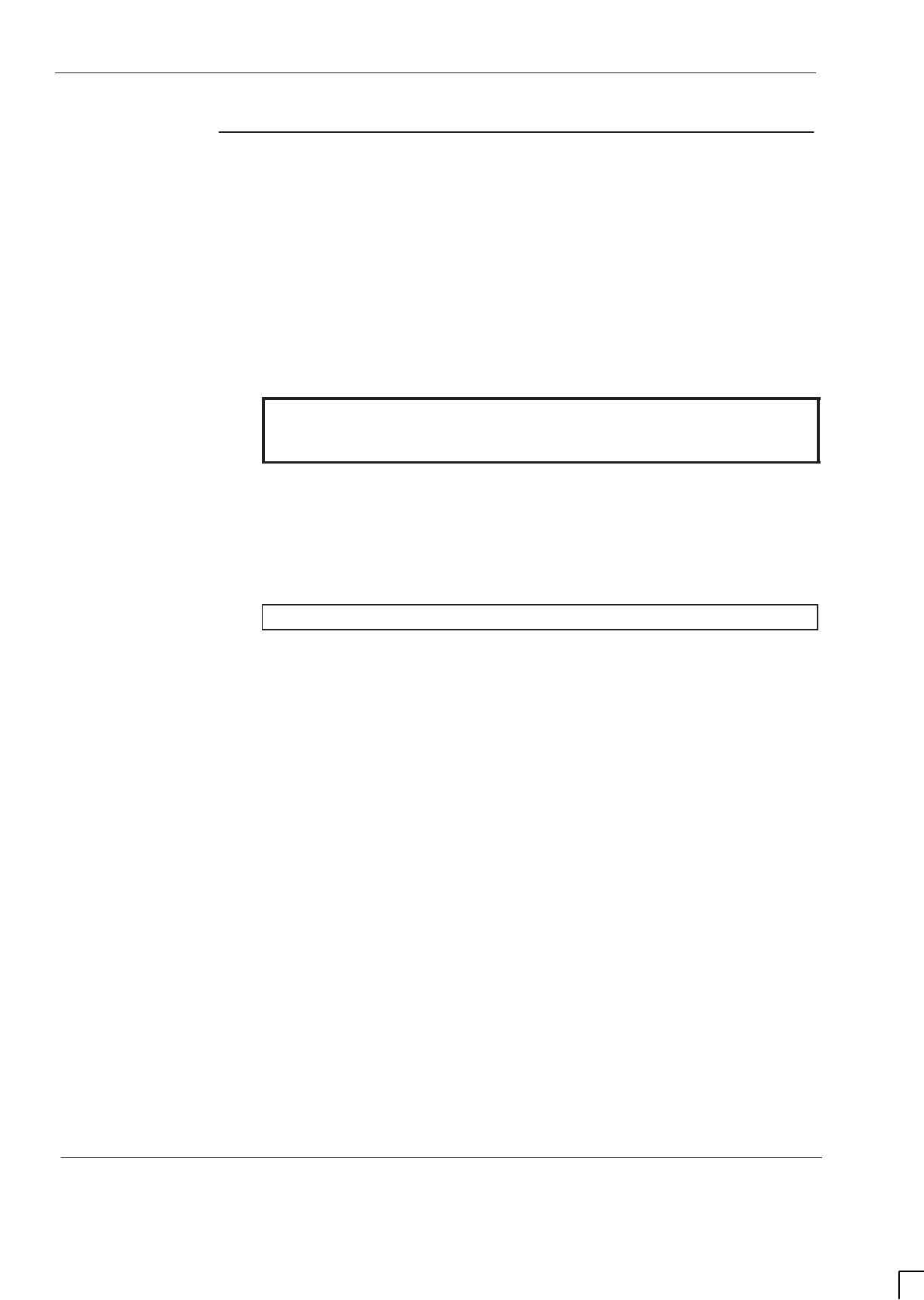
GSM-204-523
Replacing a door
31st Oct 01
Maint. 3–4
Maintenance Information: Horizon
macro
outdoor
CONTROLLED INTRODUCTION
68P02902W04-A
Door
replacement
procedure
Removing a faulty door
To remove a door proceed as follows:
1. Unscrew the M6 nut and star washer which secures the door earth cable
to the cabinet body.
2. Unscrew the wind stop from the cabinet.
3. Remove the circlips from the bottom of the hinge pins.
WARNING The radio enclosure door weighs 20 kg and the power
supply enclosure door weighs 15 kg. Handle with care
and observe proper lifting precautions.
4. Support the door and remove the two hinge pins by pulling their lugs in the
required direction, using long nose pliers.
5. Remove the door and place safely to one side.
Fitting a replacement door
CAUTION Take care to avoid damaging the door air duct seals.
To fit a replacement door proceed as follows:
1. Support the door, in position, so that the hinges line up.
2. Insert the two hinge pins fully into the hinges.
3. Fit the circlips into the recesses in the bottom of the hinges.
4. Screw the wind stop to the cabinet.
5. Attach the door earth cable to the cabinet using the M6 nut and star
washer. Tighten to the correct torque (see Overview of FRU replacement
procedures in this chapter).
6. Check door operation and that door locking mechanism functions
correctly.
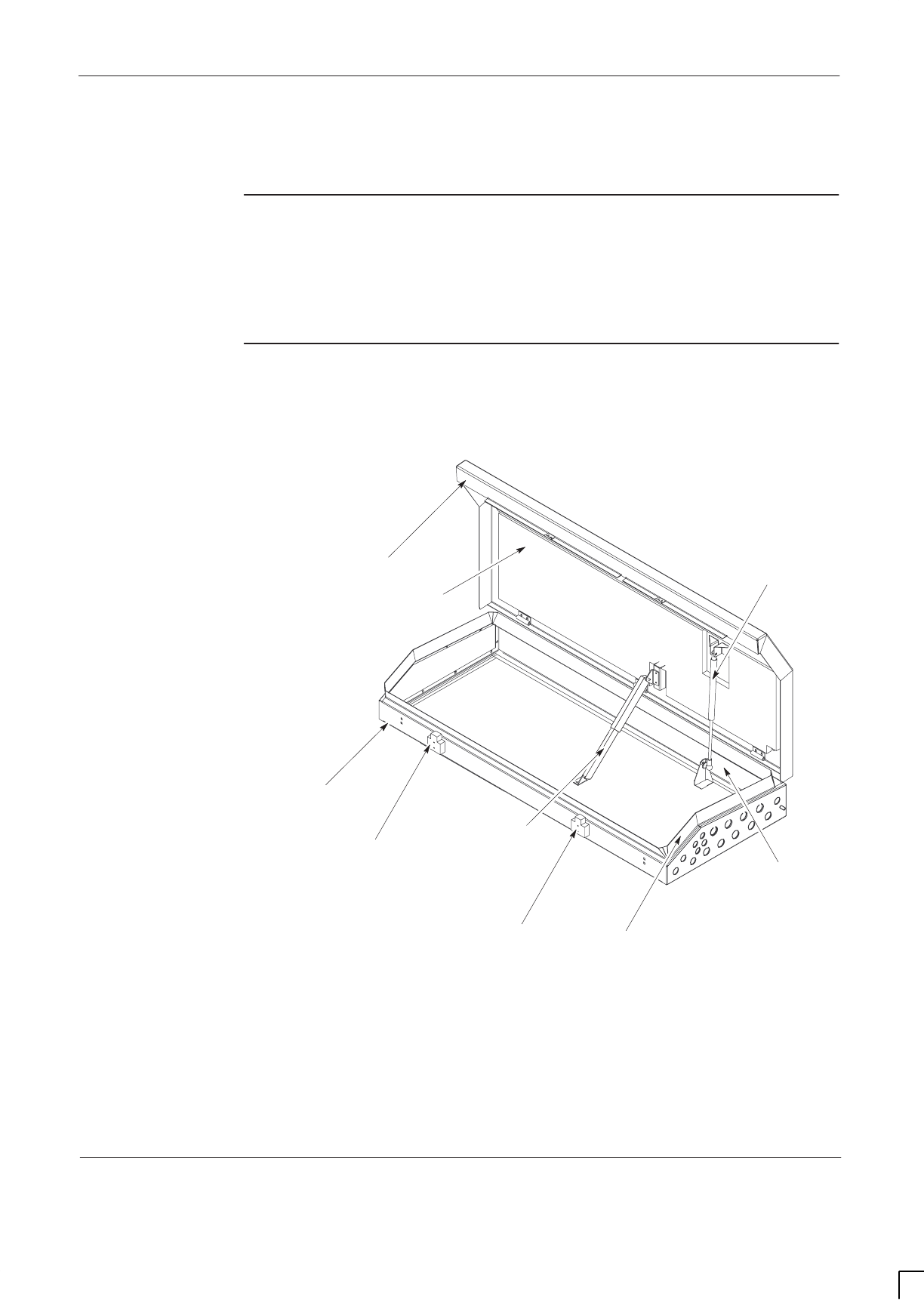
GSM-204-523 Replacing the lid
31st Oct 01
Maintenance Information: Horizon
macro
outdoor
68P02902W04-A
CONTROLLED INTRODUCTION
Maint. 3–5
Replacing the lid
Introduction to
lid replacement
The lid provides environmental protection to equipment inside. For this reason,
the replacement procedure should be completed in one session, and the
cabinet then closed.
View of the
cabinet lid
Figure 3-3 shows the lid and the cabinet top wrap with the main features
labelled.
ENVIRONMENTAL
SEAL
TOP SECTION
MECHANICAL
STAY
LID GAS STRUT
INSULATION
FOAM
SECURING
LATCH
SECURING
LATCH
CABINET
TOP WRAP
Figure 3-3 Inside view of the lid
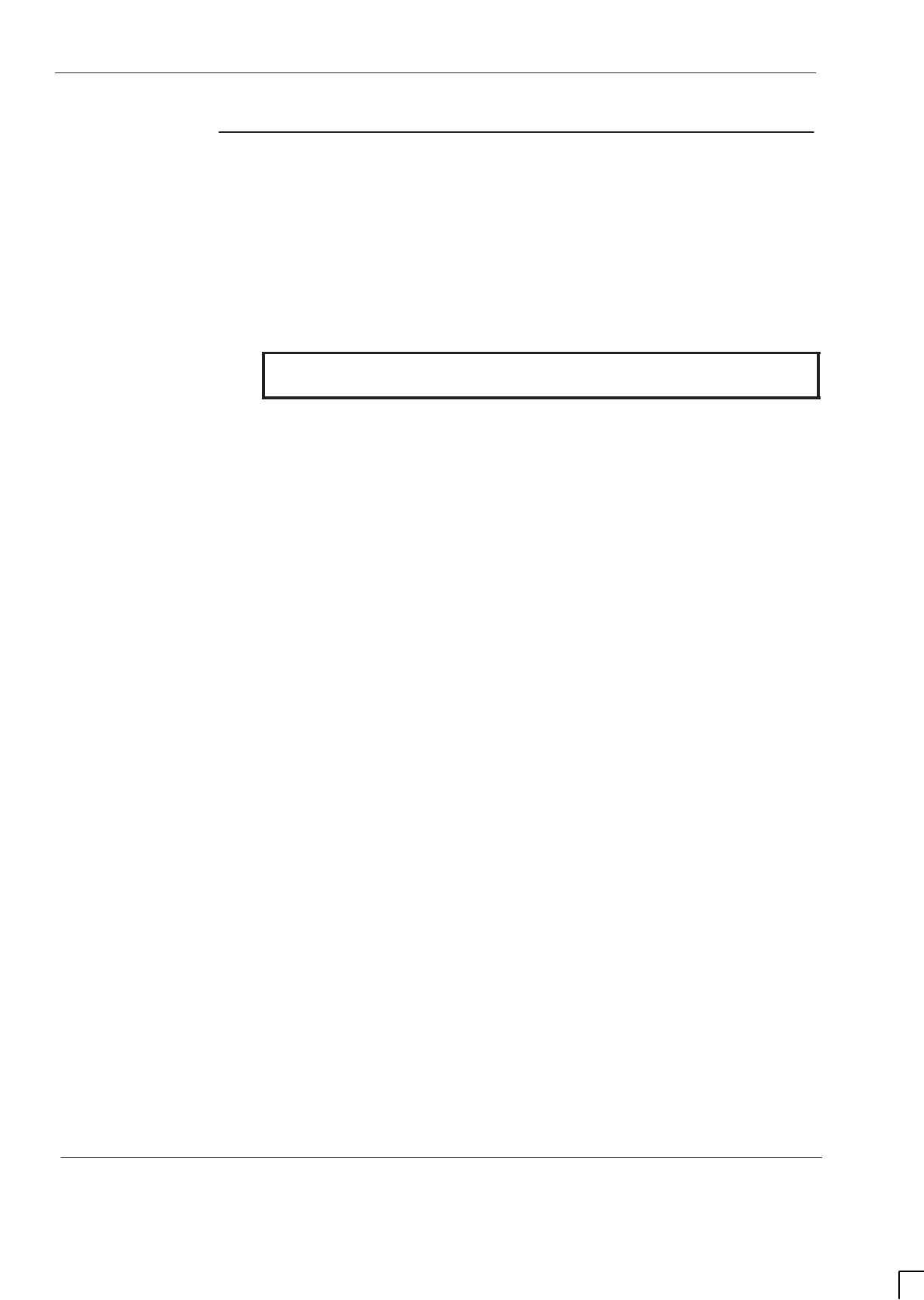
GSM-204-523
Replacing the lid
31st Oct 01
Maint. 3–6
Maintenance Information: Horizon
macro
outdoor
CONTROLLED INTRODUCTION
68P02902W04-A
Replacing a lid
Removing a faulty lid
To remove the lid proceed as follows:
1. Unscrew the M6 nut and star washer which secures the lid earth cable to
the cabinet.
2. Remove the circlips from the hinge pins.
3. Unbolt gas strut from the lid.
WARNING The cabinet lid weighs 15 kg. Handle with care and
observe proper lifting precautions.
4. Support the lid and unscrew the mechanical stay from the lid.
5. Remove the three hinge pins by pulling their lugs in the required direction,
using long nose pliers.
6. Remove the lid and place safely to one side.
Fitting a replacement lid
To install a replacement lid proceed as follows:
1. Support the lid in position, so that the hinges line up.
2. Insert the three hinge pins fully into the hinges.
3. Screw the mechanical stay to the lid.
4. Bolt the gas strut to the lid.
5. Fit the circlips into the recesses in the hinges.
6. Attach the lid earth cable to the cabinet using the M6 nut and star washer.
Tighten to the correct torque (see Overview of FRU replacement
procedures in this chapter).
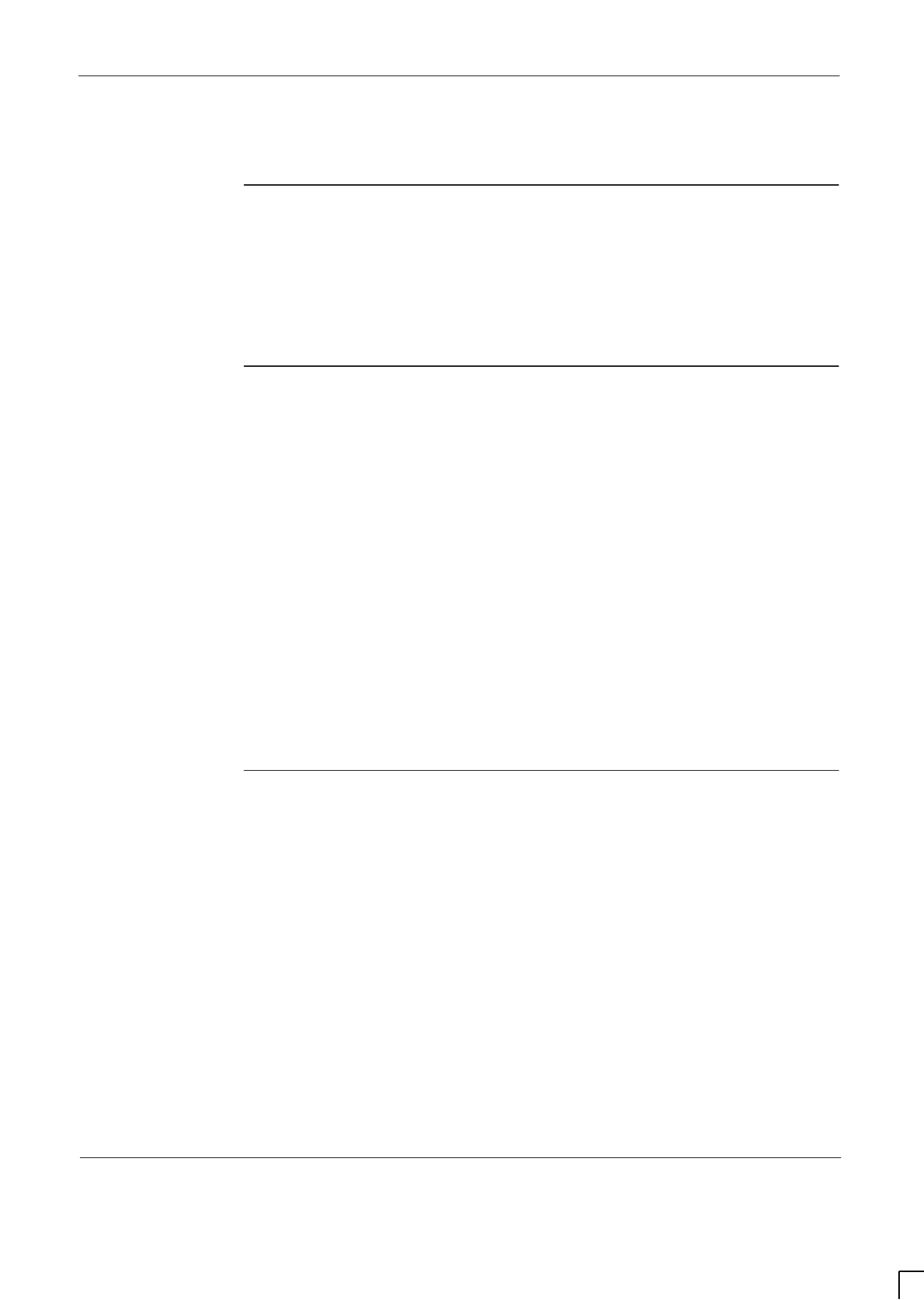
GSM-204-523 Replacing environmental seals
31st Oct 01
Maintenance Information: Horizon
macro
outdoor
68P02902W04-A
CONTROLLED INTRODUCTION
Maint. 3–7
Replacing environmental seals
Introduction to
environmental
seal
replacement
A faulty environmental seal can allow moisture to enter the cabinet, which in
turn can lead to equipment failure. It is important that the seals are inspected for
signs of wear or damage whenever the cabinet doors or lid are opened.
Replacing an
environmental
seal for the lid
The environmental seal for the lid consists of a U-shaped rubberized seal that
fits over the metal lip on the top of the cabinet (see Figure 3-3).
The procedure for replacing the seal for the lid is as follows:
1. Open the cabinet doors, release the lid catches and then lift the lid so that
it locks in position.
2. Pull the old seal off the metal lip.
3. Measure the length of the new seal against the old seal and trim to the
correct length, if necessary.
4. Starting at the centre, press the new seal firmly onto the metal lip all the
way around. Ensure that both ends of the seal meet at the centre of the
front lip.
5. Close the lid and the cabinet doors.
The procedure for replacing the environmental seal for the lid is now complete.
Replacing an
environmental
seal on a door
The environmental seals for the doors consist of four strips of self-adhesive
gasket, fixed to the inside panel of each door.
The procedure for replacing the seal for a door is as follows:
1. Open the cabinet doors.
2. Trace a line around the inside edge of each seal strip as a marker for
positioning the new seal strips.
3. Remove the old seal strips. Remove all traces of adhesive using a suitable
solvent.
4. Fit the new seal strips, ensuring that the inside edges align with the marks
made prior to removing the old seals.
5. Close the doors.
The procedure for replacing the environmental seal for a door is now complete.
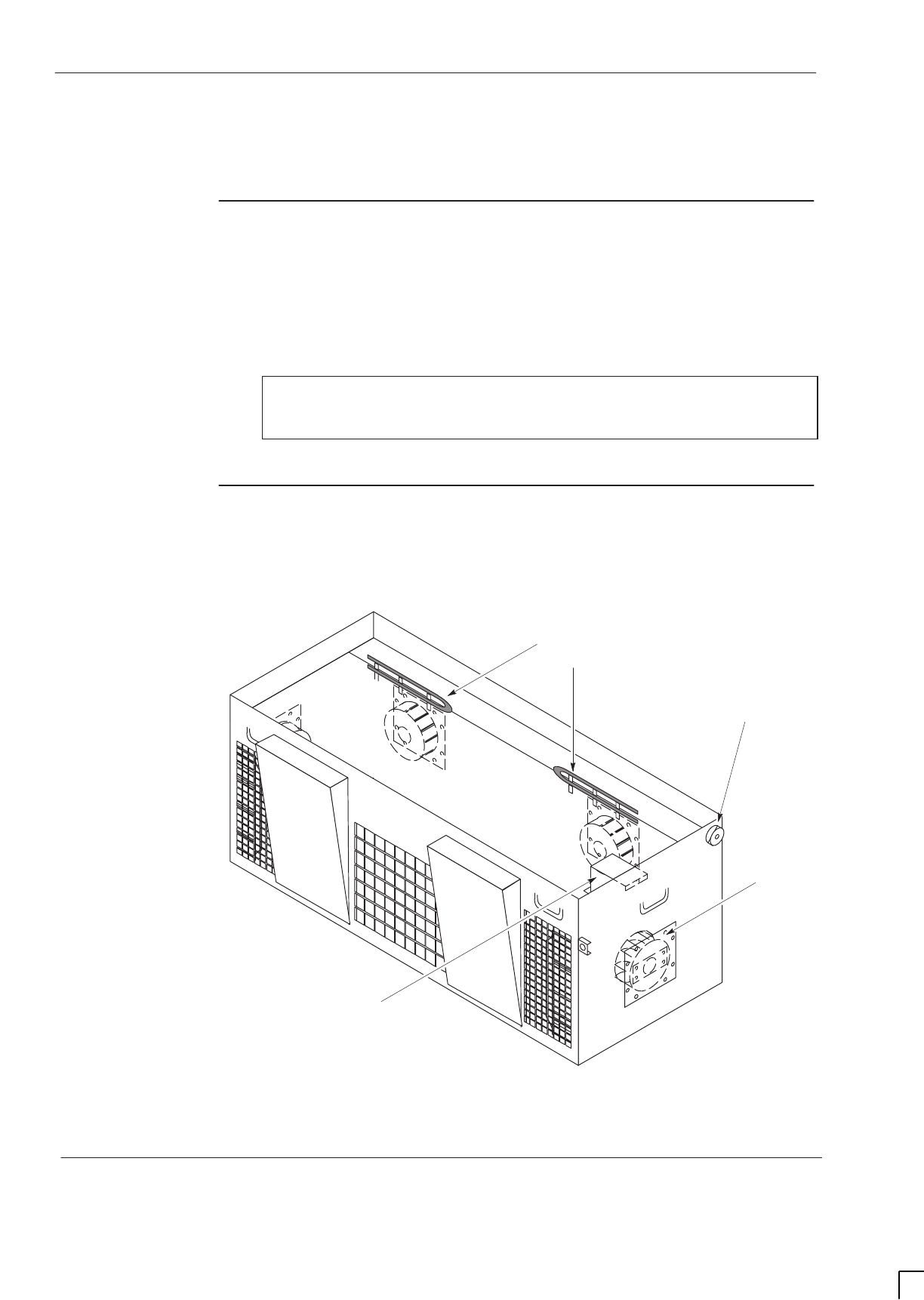
GSM-204-523
Replacing a thermal management system (TMS) unit
31st Oct 01
Maint. 3–8
Maintenance Information: Horizon
macro
outdoor
CONTROLLED INTRODUCTION
68P02902W04-A
Replacing a thermal management system (TMS) unit
Introduction
to TMS
replacement
The TMS units can be replaced while the cabinet is operational, but be aware
that forced air cooling is stopped and cooling is only by natural convection while
the TMS is out of service. This will raise equipment temperature, and could shut
down the cabinet by triggering the temperature sensors.
CAUTION If the cabinet is operational, this replacement procedure
should be completed without delay, in order to minimize
duration of air cooling disruption.
View of the TMS
unit
Figure 3-4 shows a view of the TMS unit, removed from the cabinet, with upper
panels and air ducts omitted for clarity.
HEATING
ELEMENTS
FAN
ACCESS
PANEL
CONTROL
BOARD COVER
MOUNTING RAIL
ROLLER
Figure 3-4 TMS unit showing major features
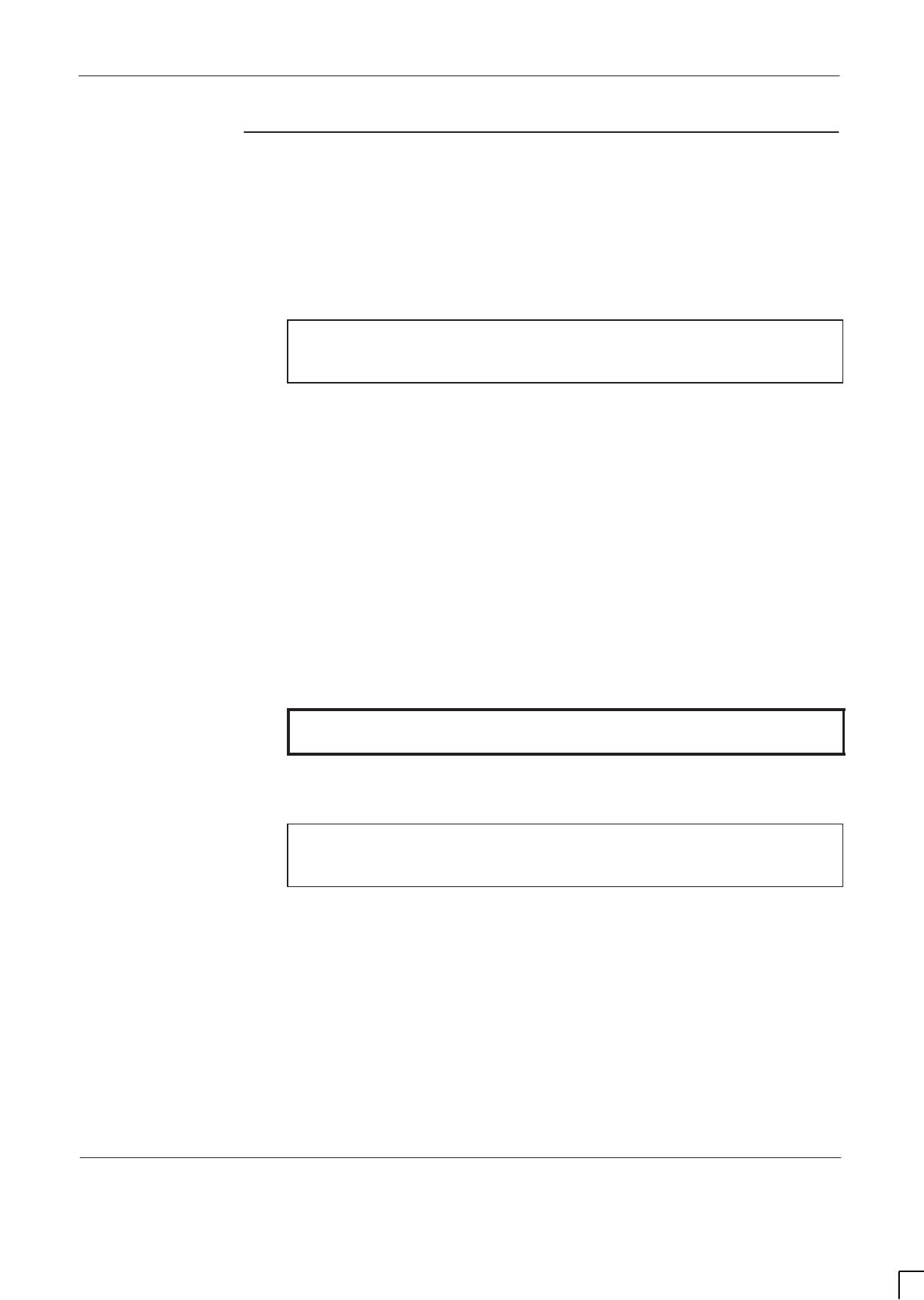
GSM-204-523 Replacing a thermal management system (TMS) unit
31st Oct 01
Maintenance Information: Horizon
macro
outdoor
68P02902W04-A
CONTROLLED INTRODUCTION
Maint. 3–9
Removing the
TMS unit
To remove the TMS unit:
1. Remove the TMS front access panel at the base of the cabinet.
2. Shut down the TMS by switching off the TMS FANS at the dc circuit
breaker panel and the TMS heater ac circuit breaker at the number 2 ac
power distribution box.
CAUTION Care must be taken at all times to avoid cable damage
caused by abrasion as cables pass through cabinet
apertures.
3. Disconnect the following TMS cables:
– The ac cable from the plug at the front right of the power supply
enclosure.
– The dc cable from the connector at the front left of the power supply
enclosure.
– The alarm cable from the connector PL5 at the alarms interface
board.
4. Feed the cables through the aperture into the cable well and tie them
safely out of the way.
5. Disconnect the earth bonding cable from the TMS unit.
6. Remove and retain the two TMS securing screws and washers, on the
front of the TMS unit, using a crosspoint screwdriver.
WARNING The TMS unit can weigh up to 40 kg. Handle with care
and observe proper lifting precautions.
7. Pull the unit forwards, using the front two built-in handles, lowering the
front edge to ease pressure on the seals.
NOTE The TMS unit is supported by rollers at the rear (see
Figure 3-4). These run on rails in the bottom wrap of the
cabinet.
8. When the TMS unit is fully withdrawn, carefully lift it out of cabinet, using
the built-in handles on the sides and place it on a dry surface in a position
suitable for further work.
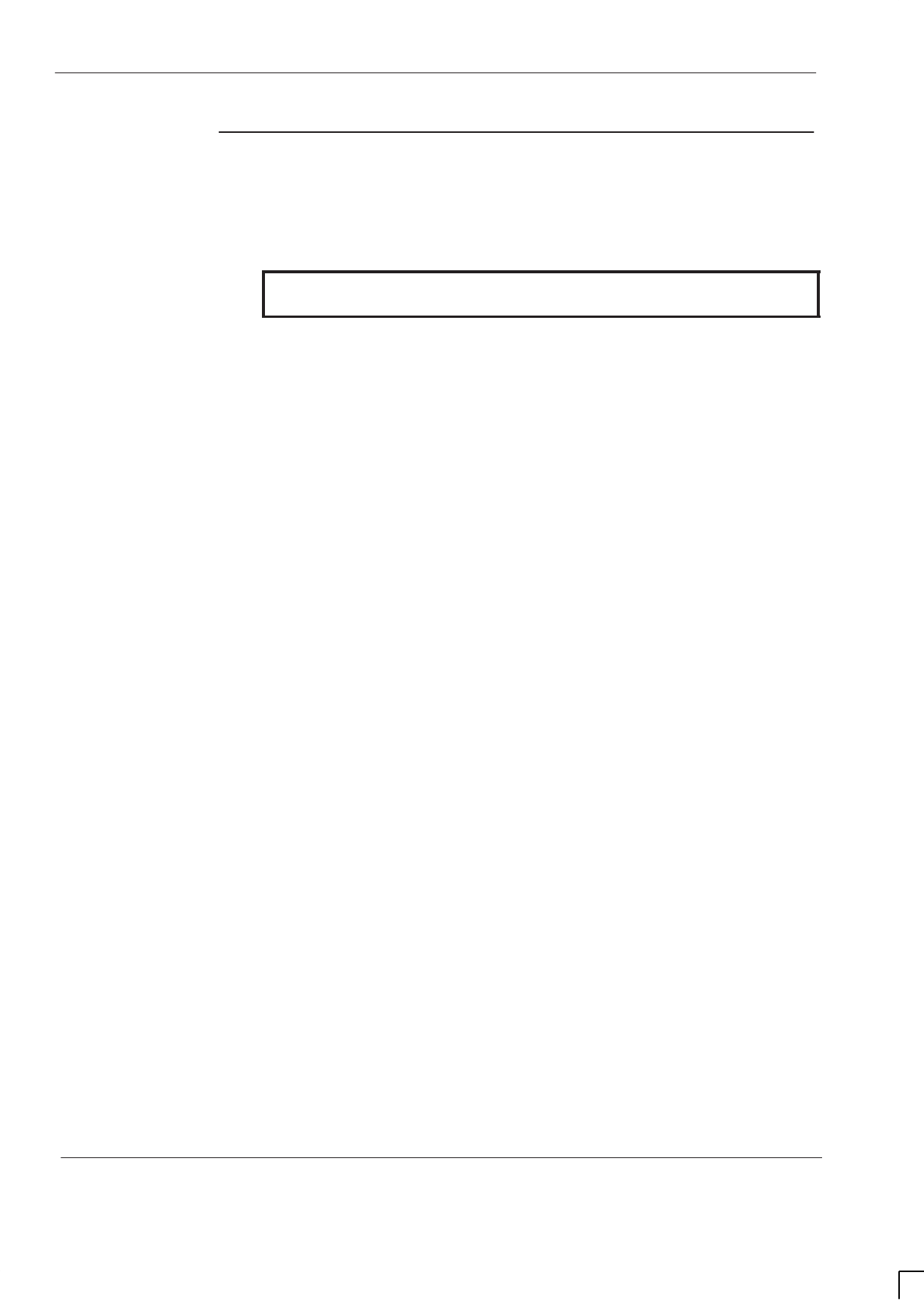
GSM-204-523
Replacing a thermal management system (TMS) unit
31st Oct 01
Maint. 3–10
Maintenance Information: Horizon
macro
outdoor
CONTROLLED INTRODUCTION
68P02902W04-A
Refitting the
TMS unit
To refit the TMS unit:
1. Examine the TMS unit gasket for damage or degradation, replace if
necessary as described in Replacing TMS unit components.
WARNING The TMS unit can weigh up to 40 kg. Handle with care
and observe proper lifting precautions.
2. Carefully lift the rear of the TMS unit into place, positioning the two rollers
onto the rails in the bottom wrap of the cabinet.
3. Push the TMS unit into place, lifting the front into position before locating
the front fixing brackets.
4. Feed the power supply and alarm cables through the aperture into the
power supply enclosure.
5. Fit the two, previously retained, screws and washers to secure the TMS
unit and tighten to the correct torque (see Overview of FRU replacement
procedures in this chapter).
6. Connect the earth bonding cable to the TMS unit.
7. Reconnect the following TMS cables:
– The ac cable to the plug at the front right of the power supply
enclosure.
– The dc cable to the connector at the front left of the power supply
enclosure.
– The alarm cable to the connector PL5 at the alarms interface board.
8. Switch on the TMS heater ac circuit breaker in the number 2 distribution
box and the TMS FANS at the dc circuit breaker panel.
9. Test the operation of the TMS unit as described in
Installation and
Configuration: (GSM-204-423)
Testing the thermal management
system.
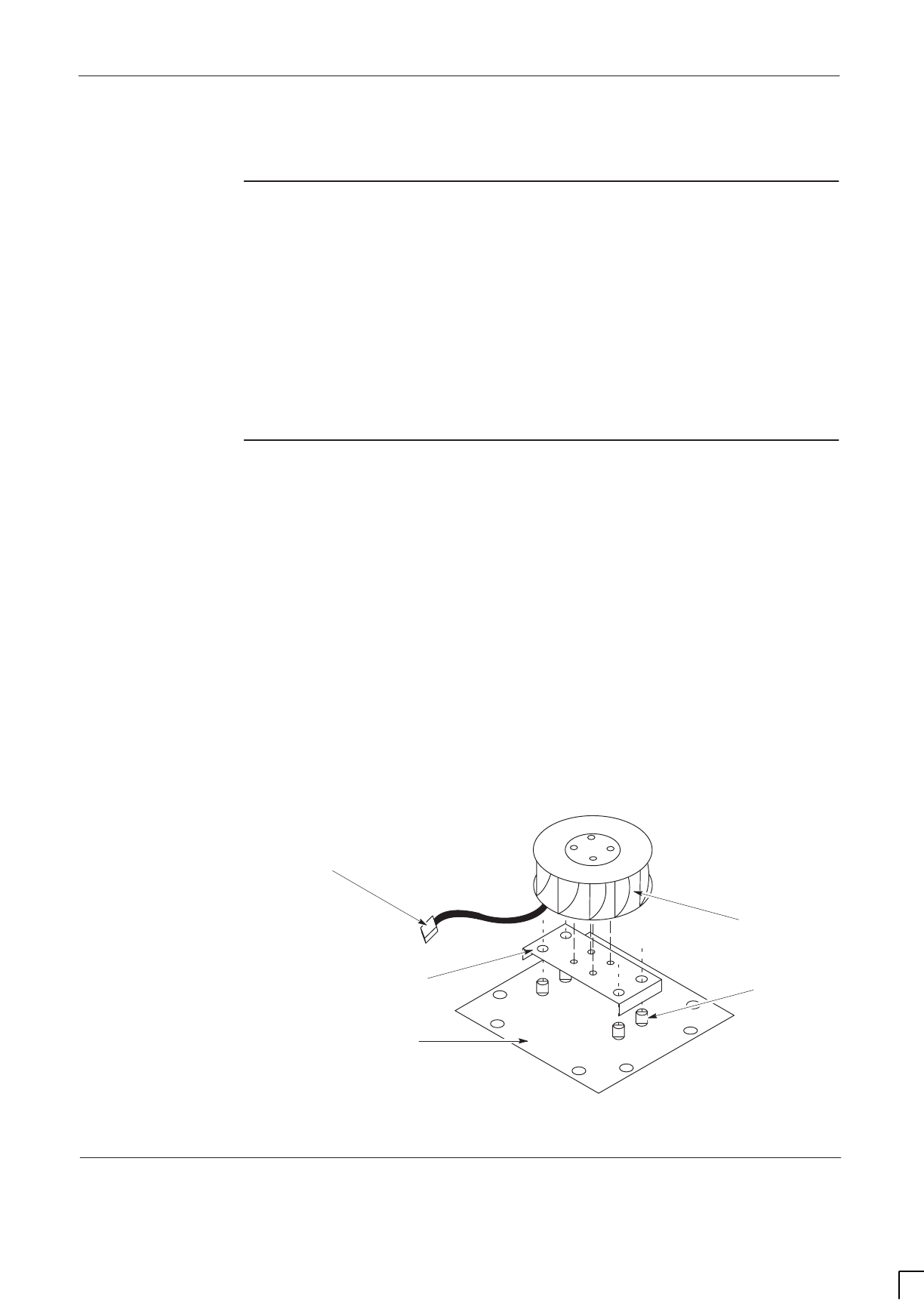
GSM-204-523 Replacing TMS unit components
31st Oct 01
Maintenance Information: Horizon
macro
outdoor
68P02902W04-A
CONTROLLED INTRODUCTION
Maint. 3–11
Replacing TMS unit components
Introduction to
TMS unit
component
replacement
The following TMS unit internal components can be replaced as FRUs:
TMS fans.
TMS control board.
TMS gasket (only needs to be checked when replacing other TMS FRUs).
The information contained here assumes that the TMS unit has been removed
from the Horizon
macro
outdoor cabinet, as previously described.
Replacing a
TMS fan
Each of the four fans in the TMS can be replaced as follows (refer to
Figure 3-5):
1. Remove the fan access panel by undoing the panel retaining screws using
a Torx screwdriver.
2. Gently lift off the access panel and partially withdraw the fan. (The fan is
bolted to the rear of the access panel.)
3. Unplug the floating connector and withdraw the fan assembly from the
TMS unit.
4. Place the fan assembly on a flat surface. Undo the four mounting plate
retaining bolts and remove the fan and mounting plate from the spacers
on the access panel.
5. Remove the fan from the mounting plate by undoing the four fan securing
bolts on the underside of the mounting plate.
Replacement is a reversal of the removal procedure.
FAN ACCESS PANEL
FAN MOUNTING PLATE
FAN
SPACER
POWER CONNECTOR
Figure 3-5 TMS fan assembly
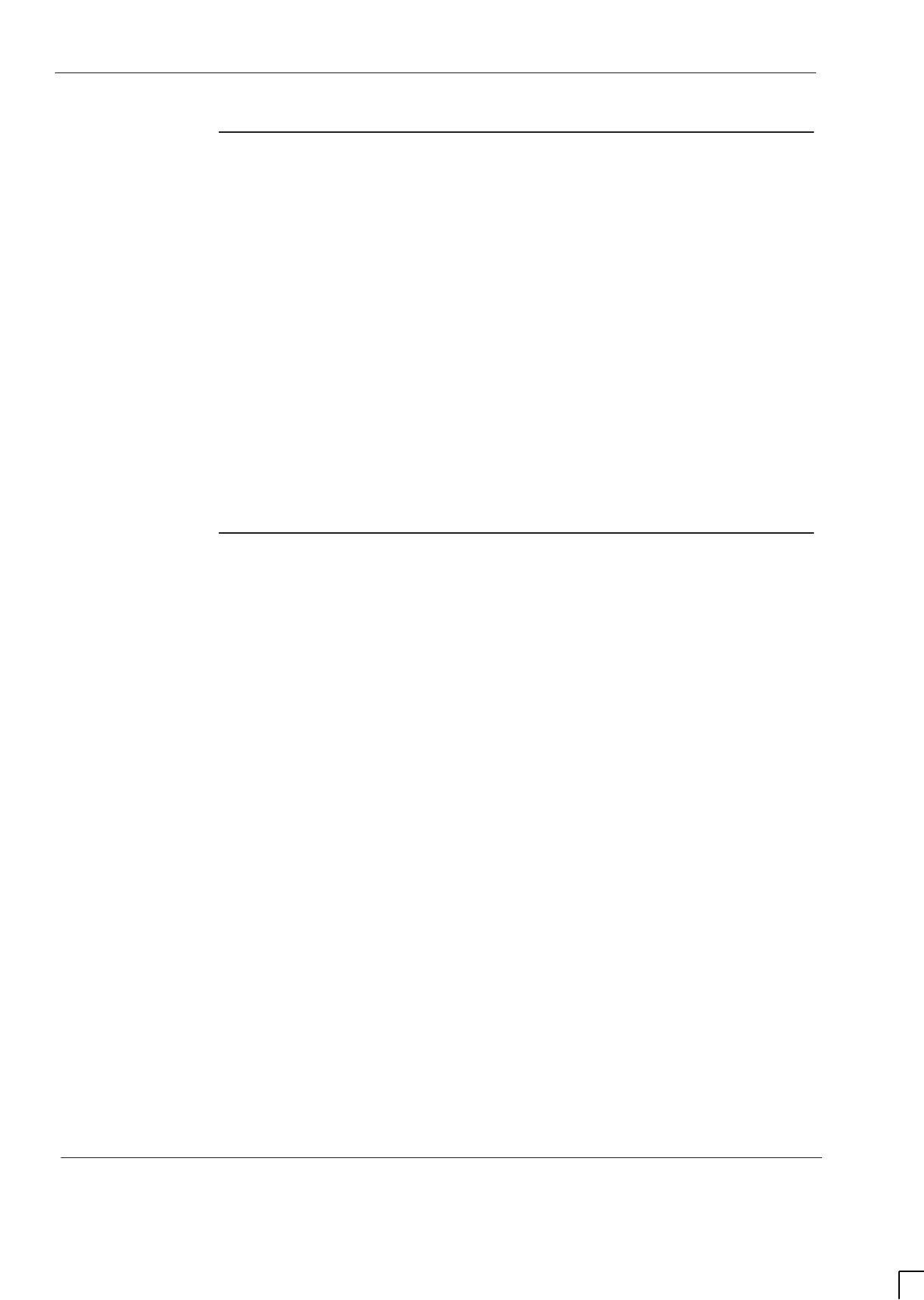
GSM-204-523
Replacing TMS unit components
31st Oct 01
Maint. 3–12
Maintenance Information: Horizon
macro
outdoor
CONTROLLED INTRODUCTION
68P02902W04-A
Replacing the
TMS control
board
The TMS control board is mounted under a metal cover on the right side of the
TMS (see Figure 3-4).
Carry out the following procedure to replace the control board:
1. Undo the two cover retaining screws and remove the cover.
2. Undo the six screws that secure the board in position.
3. One by one, unplug the connectors and plug them onto the corresponding
connectors on the new board. Remove the old board once all the
connectors have been removed.
4. Mount the new board and secure in position using the six screws.
5. Refit the metal cover and tighten the cover retaining screws.
The procedure for replacing the TMS control board is now complete.
Replacing the
TMS gasket
The TMS gasket is designed to last the lifetime of the equipment. However,
should it become damaged, it can easily be replaced as follows:
1. Strip off the old gasket from the flange.
2. Clean all traces of adhesive from the flange using a suitable solvent.
3. Carefully fit the new gasket onto the flange.
The procedure for replacing the gasket is now complete.
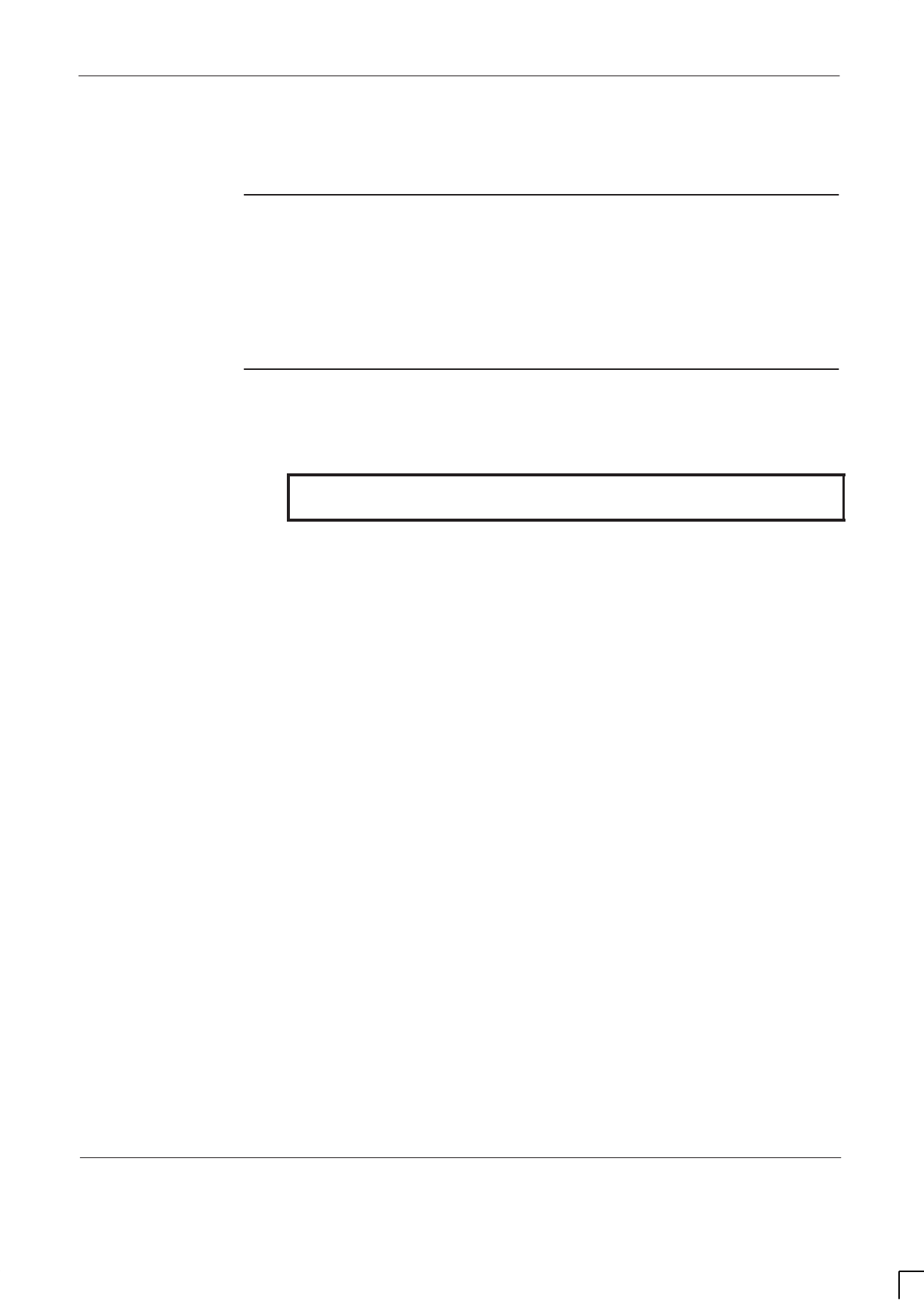
GSM-204-523 Replacing a cabinet temperature sensor
31st Oct 01
Maintenance Information: Horizon
macro
outdoor
68P02902W04-A
CONTROLLED INTRODUCTION
Maint. 3–13
Replacing a cabinet temperature sensor
Overview of
main cage
temperature
sensor FRUs
Three temperature sensors plug into the backplane from the front above the
CTUs. Each one can be removed separately, and a replacement inserted.
Replaceing a
main cage
temperature
sensor
WARNING Severe burns may result if CTU power is ON when RF
cables are disconnected.
The procedure for replacing a main cage temperature sensor is as follows:
1. Turn cabinet PSMs off, to ensure that the CTU power is OFF, before
disconnecting RF cables.
2. Remove the CTUs (see Replacing a CTU).
3. Identify the faulty temperature sensor.
4. Unplug the faulty temperature sensor.
5. Insert the replacement temperature sensor.
6. Install the CTUs (see Replacing a CTU).
The temperature sensors should now be operational.
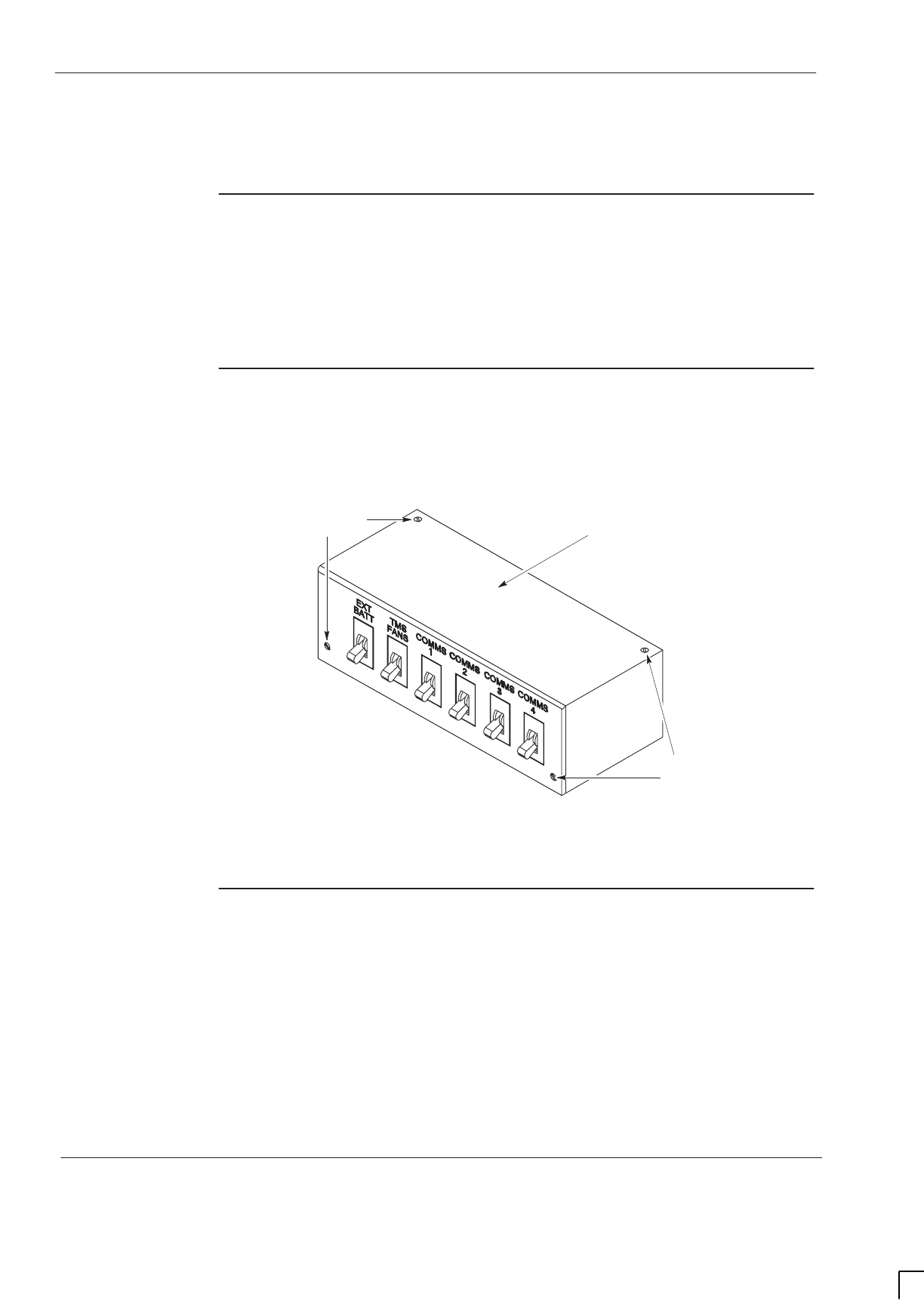
GSM-204-523
Replacing a dc circuit breaker
31st Oct 01
Maint. 3–14
Maintenance Information: Horizon
macro
outdoor
CONTROLLED INTRODUCTION
68P02902W04-A
Replacing a dc circuit breaker
Introduction to
dc circuit
breaker
replacement
The procedure for replacing an individual dc circuit breaker in the dc circuit
breaker panel is described here.
View of the dc
circuit breaker
panel
Figure 3-6 show a view of the dc circuit breaker panel.
COVER PLATE
COVER
RETAINING
SCREWS
COVER
RETAINING
SCREWS
Figure 3-6 DC circuit breaker panel
Replacing a dc
circuit breaker
The procedure for replacing a circuit breaker is as follows:
1. Remove the L-shaped cover plate by undoing the four retaining screws.
2. Pull out the faulty circuit breaker.
3. Push the new circuit breaker into the bullet type connector. Ensure that the
replacement circuit breaker is of the same rating as the one removed.
4. Refit the cover and tighten the four retaining screws.
The procedure for replacing the dc circuit breaker is now complete.
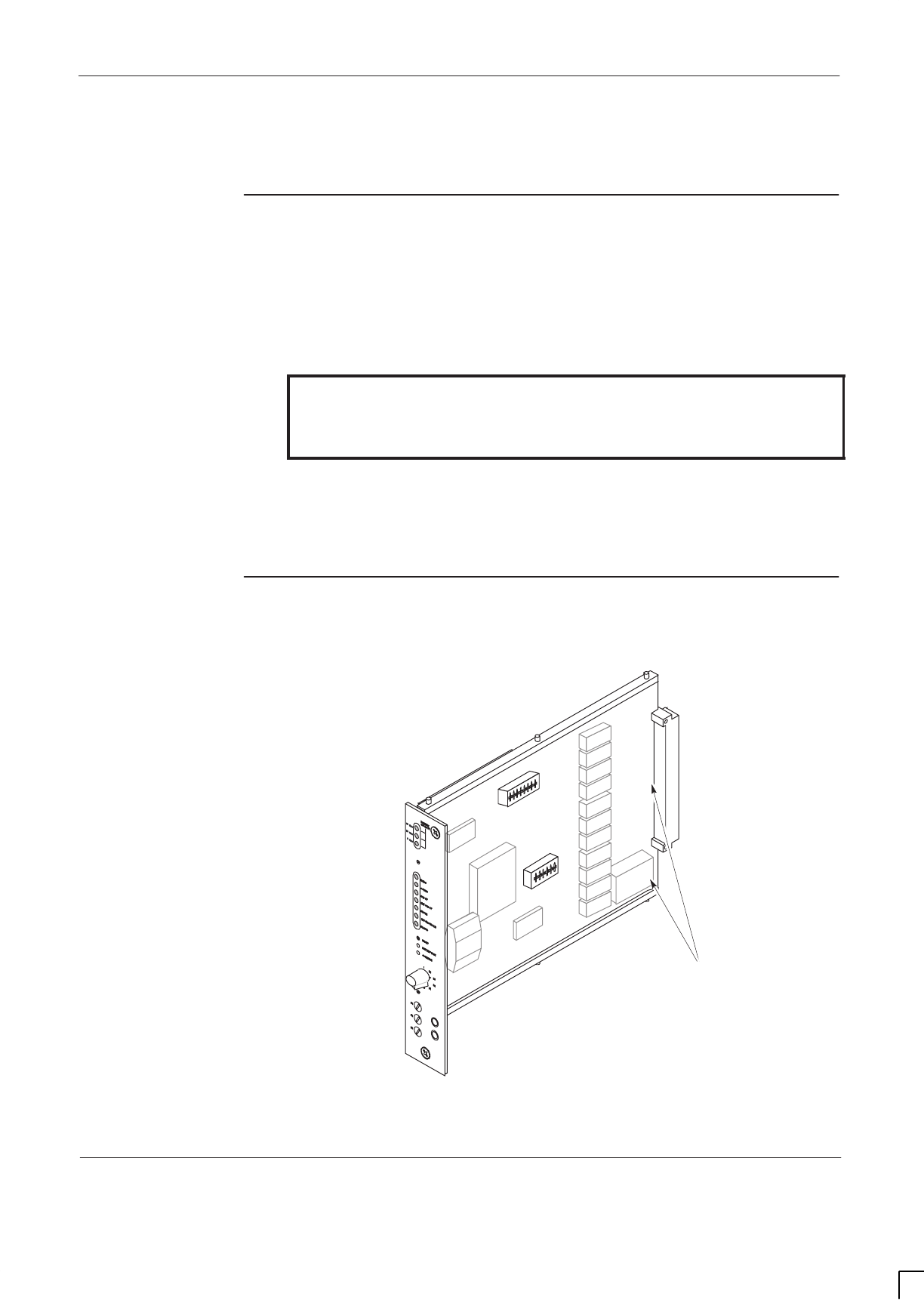
GSM-204-523 Replacing the control and alarm board (CAB)
31st Oct 01
Maintenance Information: Horizon
macro
outdoor
68P02902W04-A
CONTROLLED INTRODUCTION
Maint. 3–15
Replacing the control and alarm board (CAB)
Introduction
to CAB
replacement
This procedure describes how to remove and replace a CAB in the
Horizon
macro
outdoor cabinet PSU.
The CAB is located in the PSU cage in the power supply enclosure half of the
cabinet, to the left of the number 2 ac power distribution box.
WARNING Potentially lethal voltages, up to 415 V ac, and other high
energy sources are present within the cabinet when the ac
supply disconnect switch is set to the ON position and/or
batteries are connected.
Replacing a CAB does not require the removal of power. The CAB can be hot
swapped without harm to the module or affecting normal service operation.
Notify the OMC-R of imminent repair activity.
View of CAB
Figure 3-7 shows a typical CAB. The front panel and circuit board layout may
vary slightly, depending on the manufacturer.
DIP SWITCHES
SW2 AND SW4
(see Note below)
Figure 3-7 Control and alarm board (CAB)
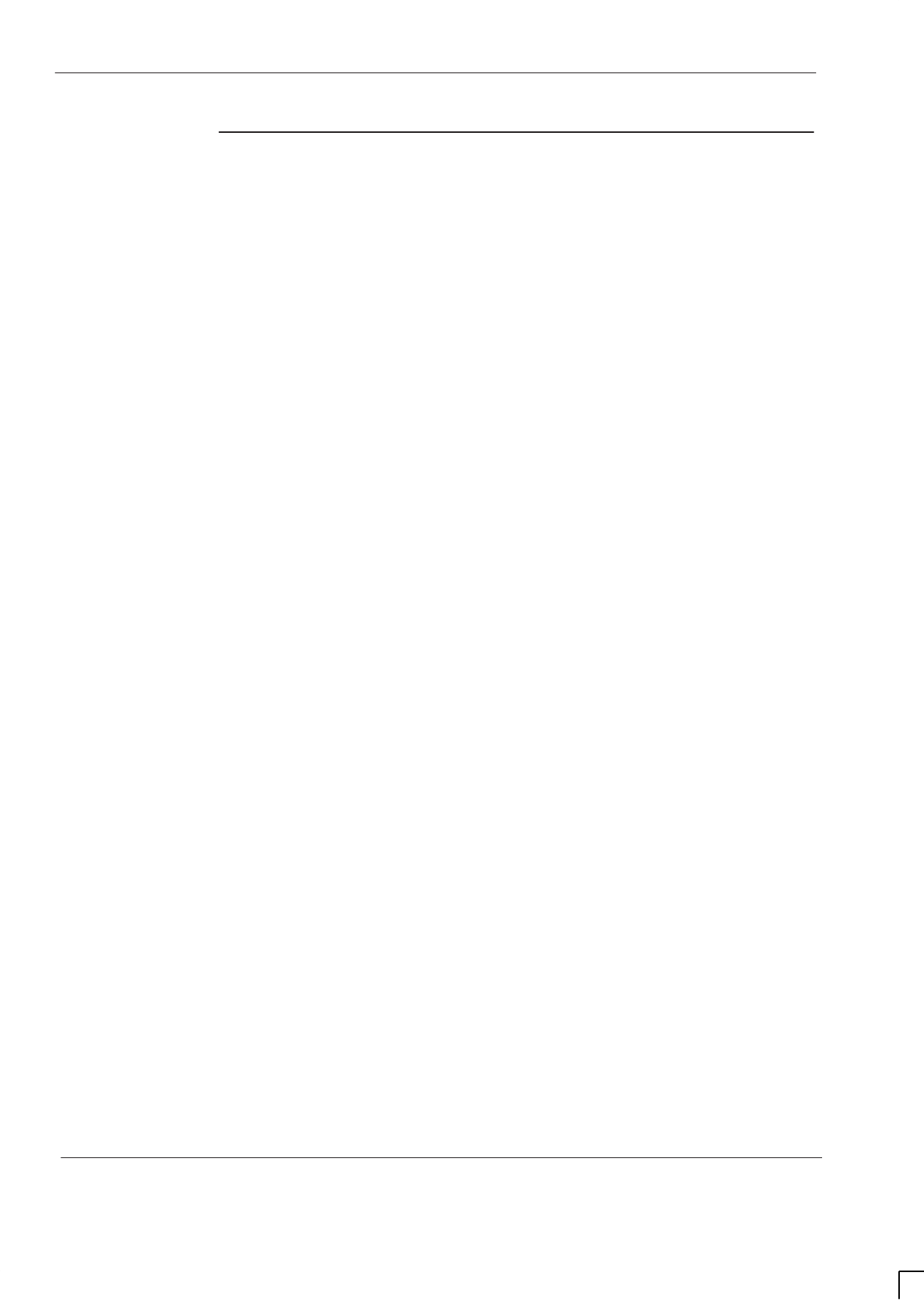
GSM-204-523
Replacing the control and alarm board (CAB)
31st Oct 01
Maint. 3–16
Maintenance Information: Horizon
macro
outdoor
CONTROLLED INTRODUCTION
68P02902W04-A
Replacing a
CAB
A faulty CAB may be replaced using the following procedure:
1. Unscrew the two front panel fasteners using a Torx driver or crosspoint
screwdriver.
2. Withdraw the CAB until the edge connector at the rear unplugs.
3. Carefully slide the CAB from its location.
4. Remove the replacement CAB from its anti-static storage container. Check
that the DIP switch settings on the replacement CAB match those on the
original board.
5. Place the original CAB in an anti-static storage container.
6. Slide the CAB along the guide rails and push firmly into place.
7. Tighten both front panel attachment screws. Tighten to the correct torque
(see Overview of FRU replacement procedures in this chapter).
8. Check the CAB front panel LEDs for alarm indications.
9. Notify the OMC-R of base station availability and log the maintenance
activity.
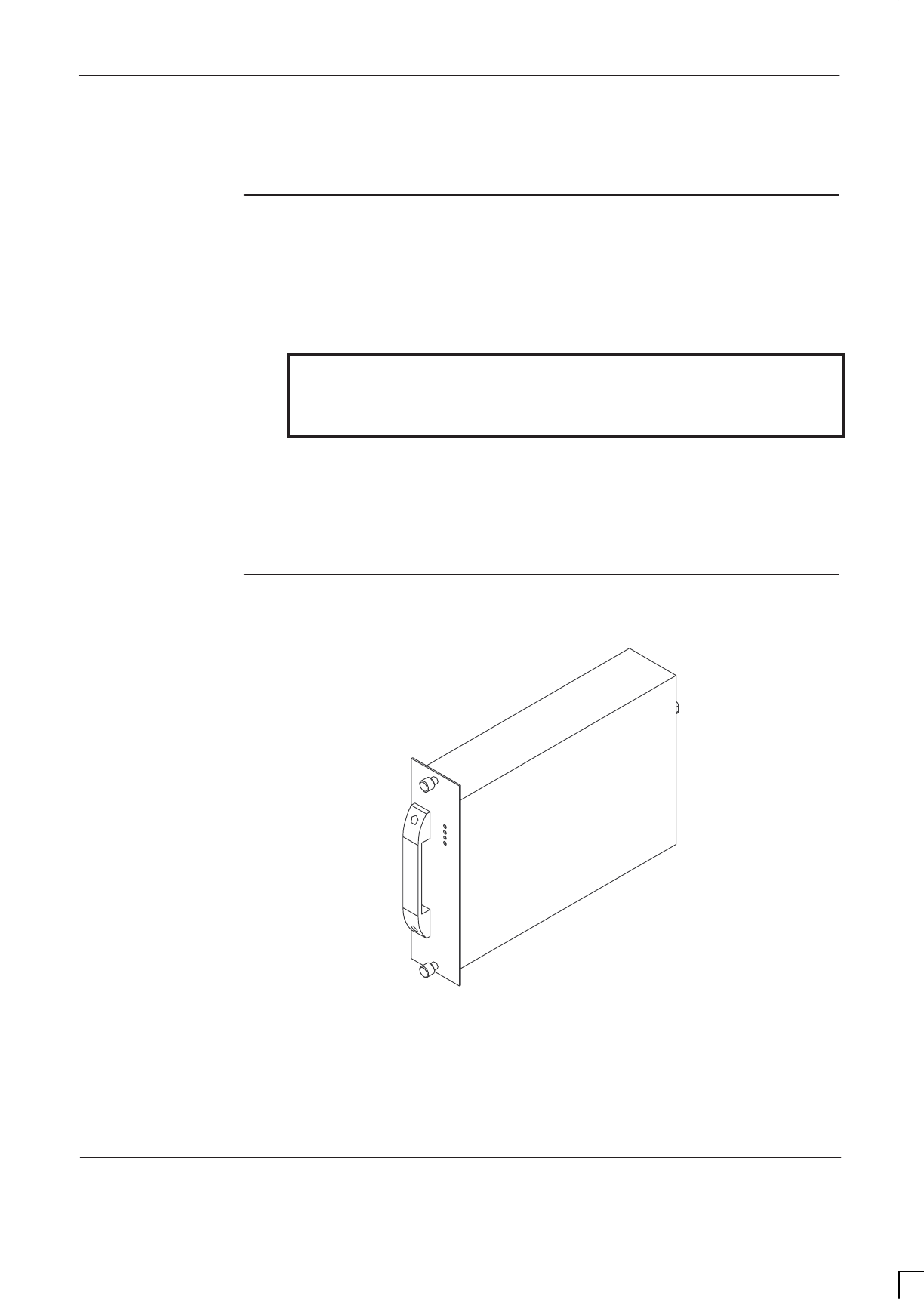
GSM-204-523 Replacing the outdoor power supply module (TOPSM)
31st Oct 01
Maintenance Information: Horizon
macro
outdoor
68P02902W04-A
CONTROLLED INTRODUCTION
Maint. 3–17
Replacing the outdoor power supply module (TOPSM)
TOPSM
replacement
This procedure describes how to remove and replace a TOPSM in an
Horizon
macro
outdoor cabinet.
Up to three TOPSMs can be located in the PSU cage in the power supply
enclosure half of the cabinet.
WARNING Potentially lethal voltages, up to 415 V ac, and other high
energy sources are present within the cabinet when the ac
supply disconnect switch is set to the ON position and/or
batteries are connected.
Replacing an TOPSM does not require the removal of power, however it is
advisable to perform this procedure during periods of low traffic, as available
power is reduced.
Notify the OMC-R of imminent repair activity.
View of TOPSM
Figure 3-8 shows a view of the TOPSM.
Figure 3-8 The outdoor power supply module (TOPSM)
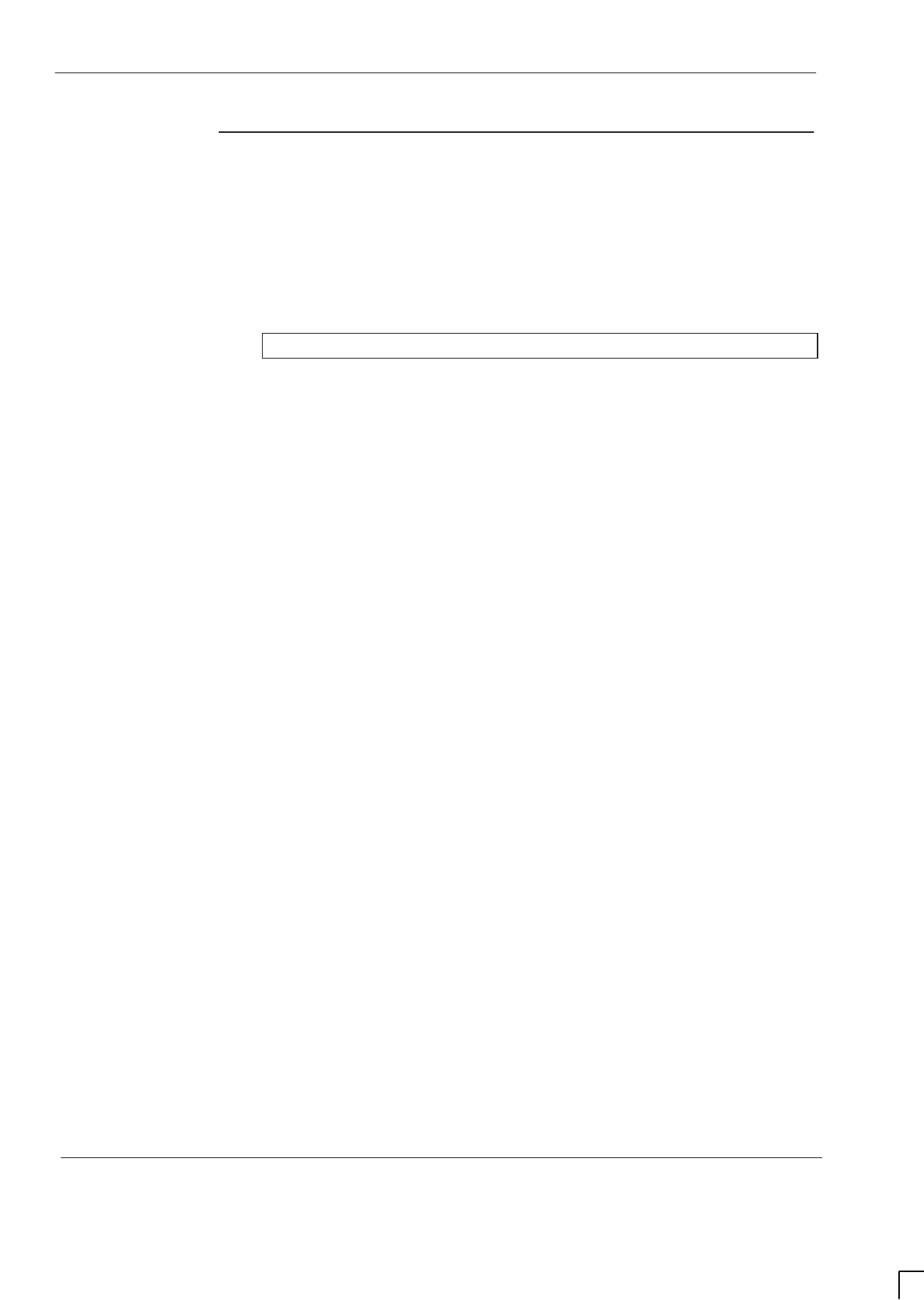
GSM-204-523
Replacing the outdoor power supply module (TOPSM)
31st Oct 01
Maint. 3–18
Maintenance Information: Horizon
macro
outdoor
CONTROLLED INTRODUCTION
68P02902W04-A
Replacing a
TOPSM
To remove a TOPSM
1. Switch OFF the appropriate circuit breaker for the TOPSM being replaced
(TOPSM 0 to TOPSM 2) on the number 2 ac distribution box.
2. Unscrew the two M6 captive fasteners that secure the TOPSM to the PSU
cage.
CAUTION Handle the TOPSM with care; the unit weighs 4.6 kg.
3. Slide the TOPSM out of the PSU cage, supporting it from beneath with the
other hand as it emerges. Place it securely to one side.
The procedure for removing the TOPSM is now complete.
To install a replacement TOPSM
1. Repeat the removal procedure in reverse order.
2. Ensure that the TOPSM is pushed fully home into its connector on the
backplane before tightening the two M6 screws. Tighten to a torque of 3.4
Nm.
3. Switch on the circuit breaker for the TOPSM.
4. Check the operation of the TOPSM LEDs, as described in
Installation
and Configuration, Category 423.
The procedure for replacing the TOPSM is now complete.
Notify the OMC-R of base station availability and log the maintenance activity.
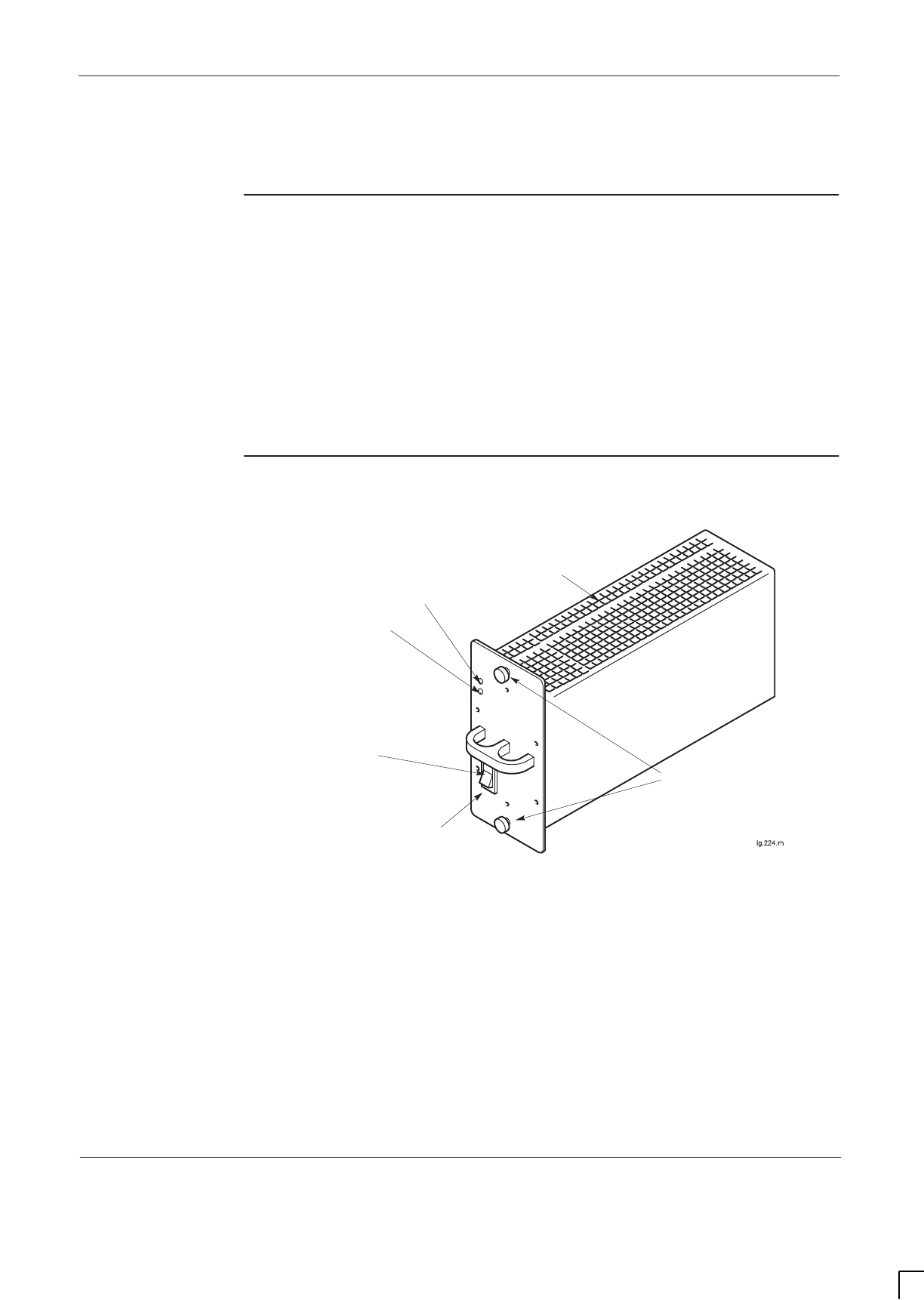
GSM-204-523 Replacing a power supply module (PSM)
31st Oct 01
Maintenance Information: Horizon
macro
outdoor
68P02902W04-A
CONTROLLED INTRODUCTION
Maint. 3–19
Replacing a power supply module (PSM)
Introduction
to PSM
replacement
Only one type of PSM is used in Horizon
macro
outdoor, –48V dc positive earth.
There are three slots for PSMs. A single PSM can power a cabinet containing
up to three CTUs therefore, a cabinet populated with six CTUs only requires two
PSMs to be fully operational. The third slot can be used for an additional power
supply to provide redundancy. A replacement PSM can be inserted into a vacant
slot without powering down, thereby avoiding any need to take the cabinet out
of service.
View of PSM
Figure 3-9 shows a view of the PSM with key features identified.
PSM FRONT PANEL
AIR VENTS ON
ENTIRE TOP AND
BOTTOM PANELS
GREEN LED
ACTIVE
RED LED
ALARM
OUTPUT DISABLE
SWITCH
M4 MODULE ATTACHMENT
SCREWS
Figure 3-9 View of PSM with key features identified
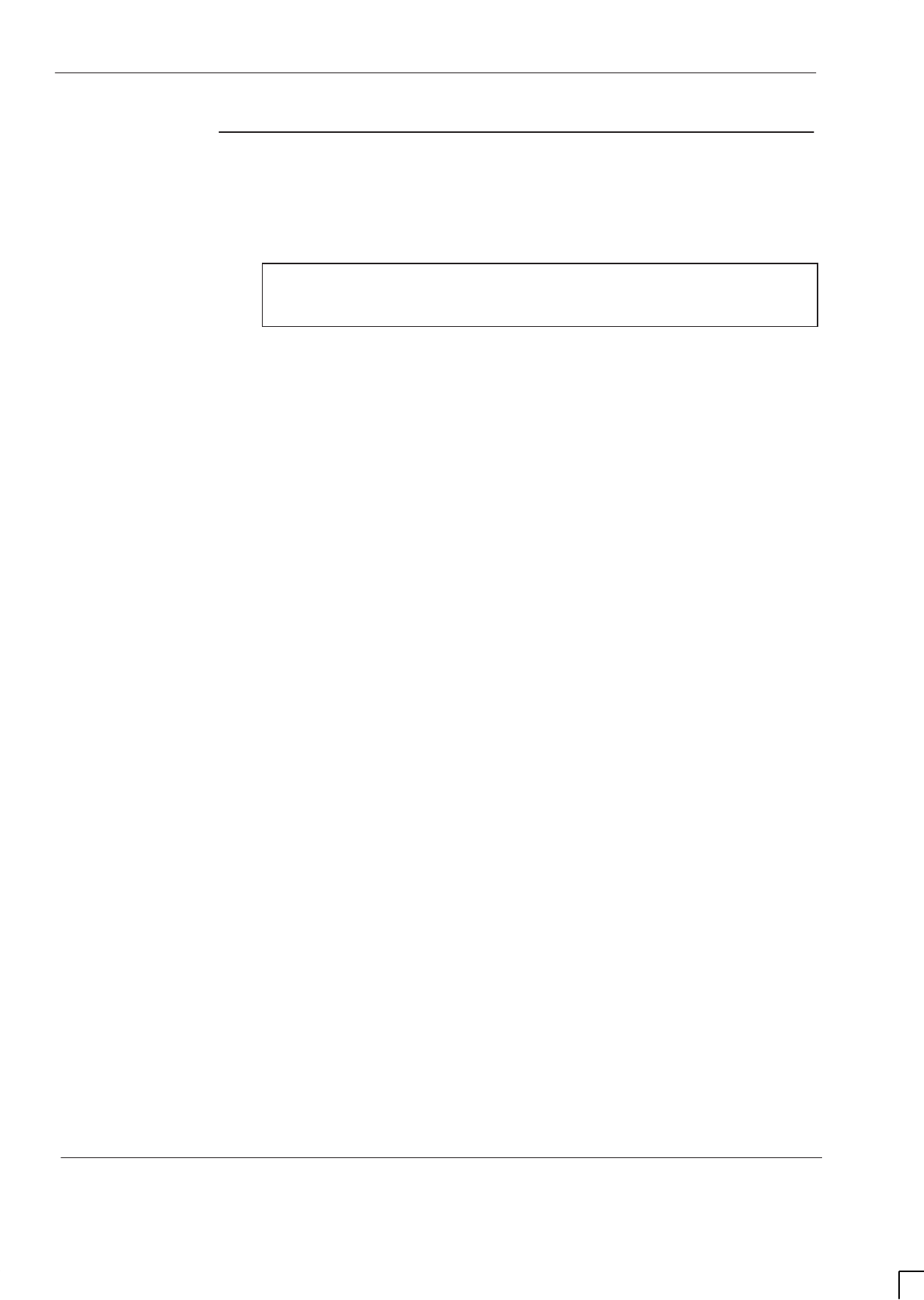
GSM-204-523
Replacing a power supply module (PSM)
31st Oct 01
Maint. 3–20
Maintenance Information: Horizon
macro
outdoor
CONTROLLED INTRODUCTION
68P02902W04-A
Replacing a
non-redundant
PSM
The following procedure should be followed if only two PSMs are fitted in the
cabinet:
CAUTION Only –48/60 V dc PSMs can be used in Horizon
macro
outdoor cabinets. Ensure that the replacement PSM is of
the appropriate type (kit number SVPN1221).
1. Verify that the switch of the replacement PSM is set to output disable.
2. Remove the blanking assembly of the spare slot, by unscrewing the
attachment screws using an M4 Torx driver.
3. Insert the replacement PSM in spare slot.
4. Ensure the replacement PSM is firmly in position and tighten both module
attachment screws using the M4 Torx driver. Tighten to correct torque (see
Overview of FRU replacement procedures in this chapter).
5. Set the switch to OUTPUT ENABLE. Check that the green LED (ACTIVE)
is lit.
6. Set the switch on the faulty PSM to OUTPUT DISABLE. The green
ACTIVE LED will go off (the green light may already be off if PSM failure
has resulted in output failure of that PSM). The red LED, if already ON due
to alarm state, will stay ON.
7. Undo the module attachment screws using the M4 Torx driver, and remove
the module. The red LED will go OFF.
8. Fit the cover plate by tightening the attachment screws using the M4 Torx
driver. Tighten to correct torque as stated in step 4.
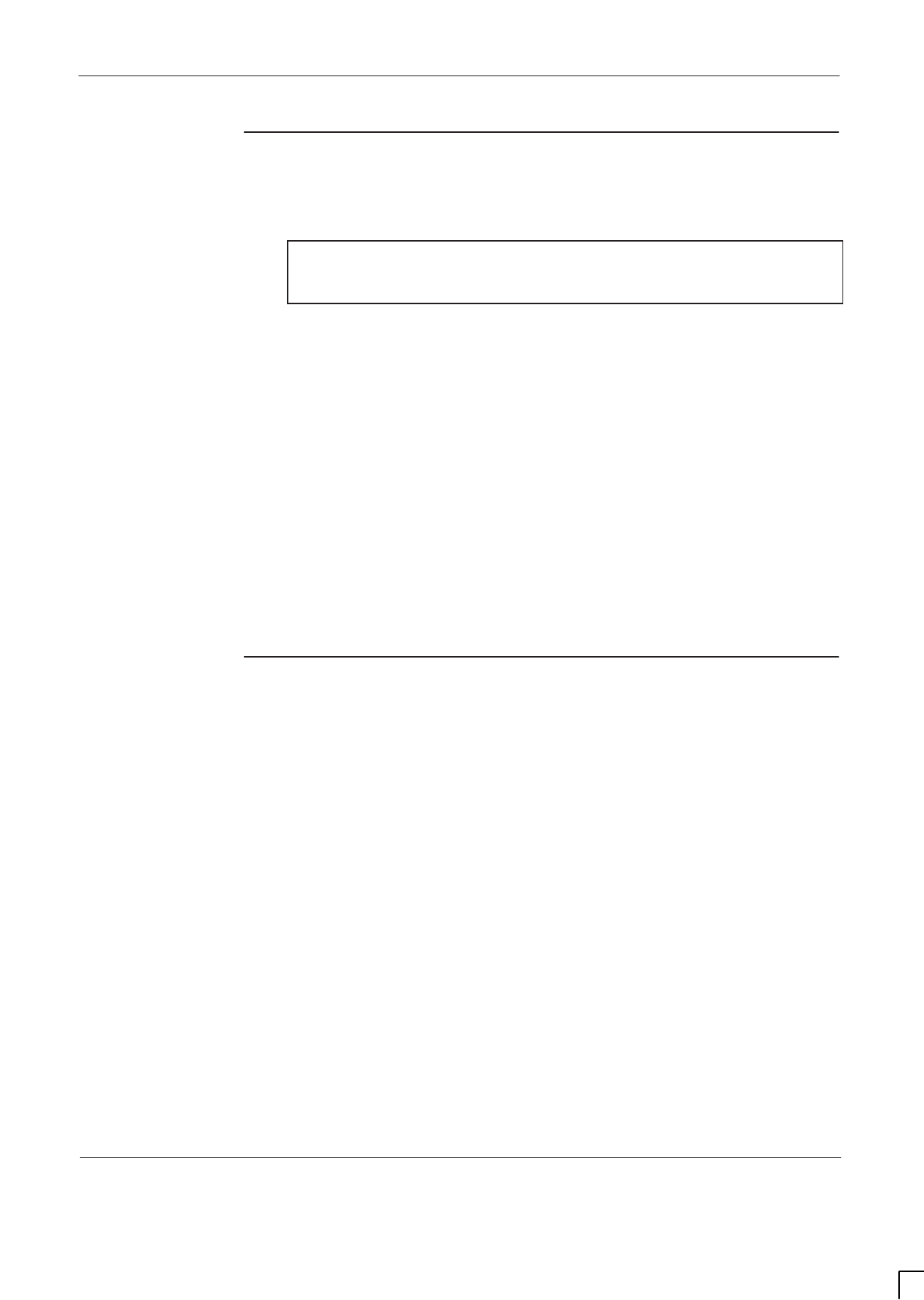
GSM-204-523 Replacing a power supply module (PSM)
31st Oct 01
Maintenance Information: Horizon
macro
outdoor
68P02902W04-A
CONTROLLED INTRODUCTION
Maint. 3–21
Replacing a
redundant PSM
The following procedure should be followed if three PSMs are fitted in the
cabinet:
CAUTION Only –48/60 V dc PSMs can be used in Horizon
macro
outdoor cabinets. Ensure that the replacement PSM is of
the appropriate type (kit number SVPN1221).
1. Verify that the switch of the replacement PSM is set to output disable.
2. Set the switch on the faulty PSM to OUTPUT DISABLE. The green LED
(ACTIVE) will go off (the green light may already be off if PSM failure has
resulted in output failure of that PSM). The red LED, if already ON due to
alarm state, will stay ON.
3. Undo the module attachment screws using an M4 Torx driver, and remove
module. The red LED will go OFF.
4. Insert the replacement PSM.
5. Ensure the replacement PSM is firmly in position and tighten both module
attachment screws using the M4 Torx driver. Tighten to correct torque (see
Overview of FRU replacement procedures in this chapter).
6. Set the switch to OUTPUT ENABLE. Check that the green ACTIVE LED is
lit.
BPSM
replacement
The procedure for replacing a BPSM is described in Digital module
replacement in this chapter.
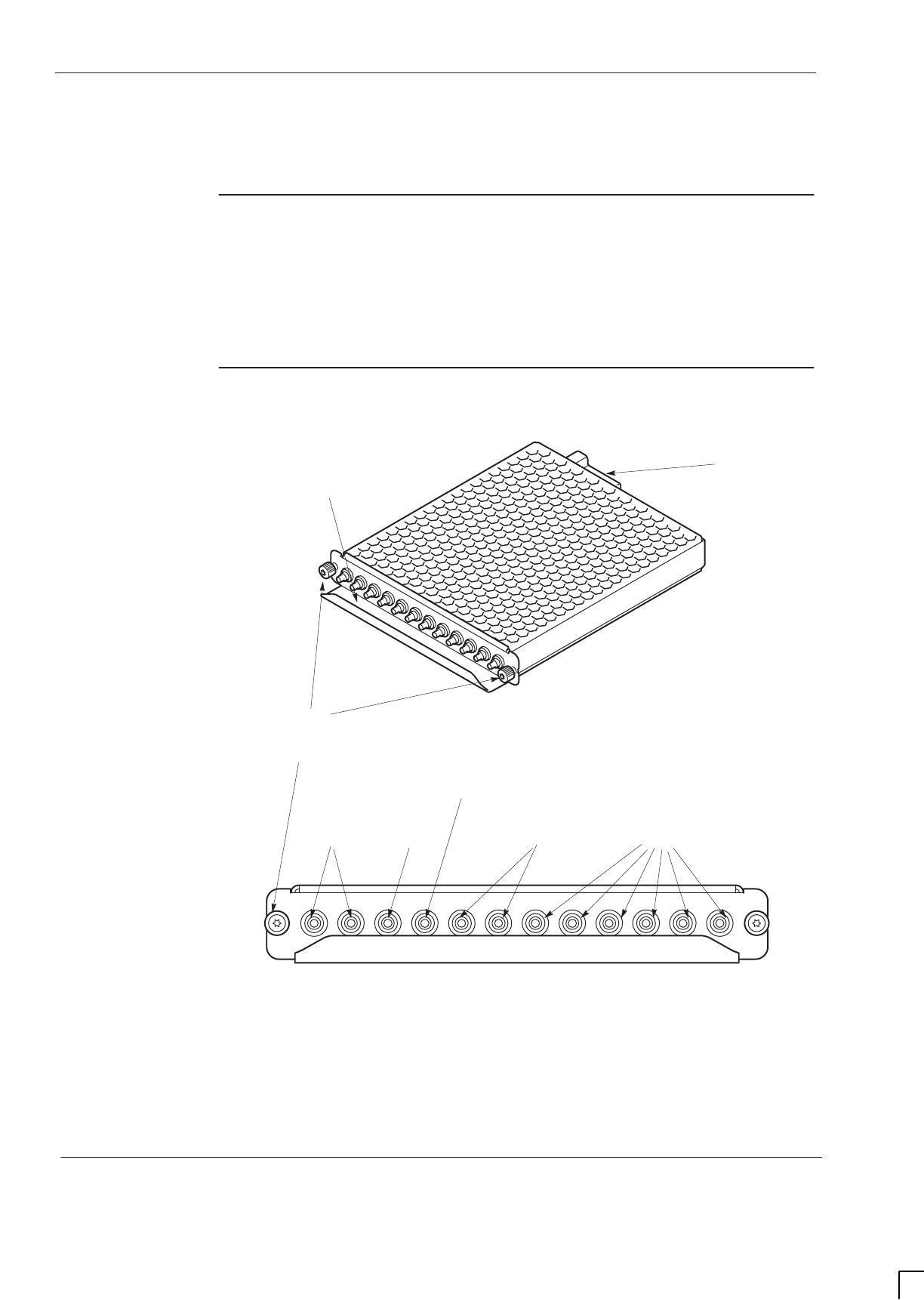
GSM-204-523
Replacing a circuit breaker module (CBM)
31st Oct 01
Maint. 3–22
Maintenance Information: Horizon
macro
outdoor
CONTROLLED INTRODUCTION
68P02902W04-A
Replacing a circuit breaker module (CBM)
Preconditions
for CBM
replacement
The CBM controls power for the power supply enclosure, apart from the PSMs.
Consequently, the replacement of a CBM can only take place after the cabinet
has been taken out of service, in agreement with the OMC-R.
Views of CBM
Figure 3-10 shows views of the CBM with circuit breaker buttons identified.
FRONT VIEW
BACKPLANE CONNECTOR
M4 MODULE ATTACHMENT
SCREWS
HANDLE-BAFFLE
ig.281.rh
6 CTUs (0 TO 5)
15 A2 A4 A
7 A
NOT USED SURF
NOT USED
BPSMs (A AND B)
7 A
Figure 3-10 Views of CBM with circuit breaker buttons identified
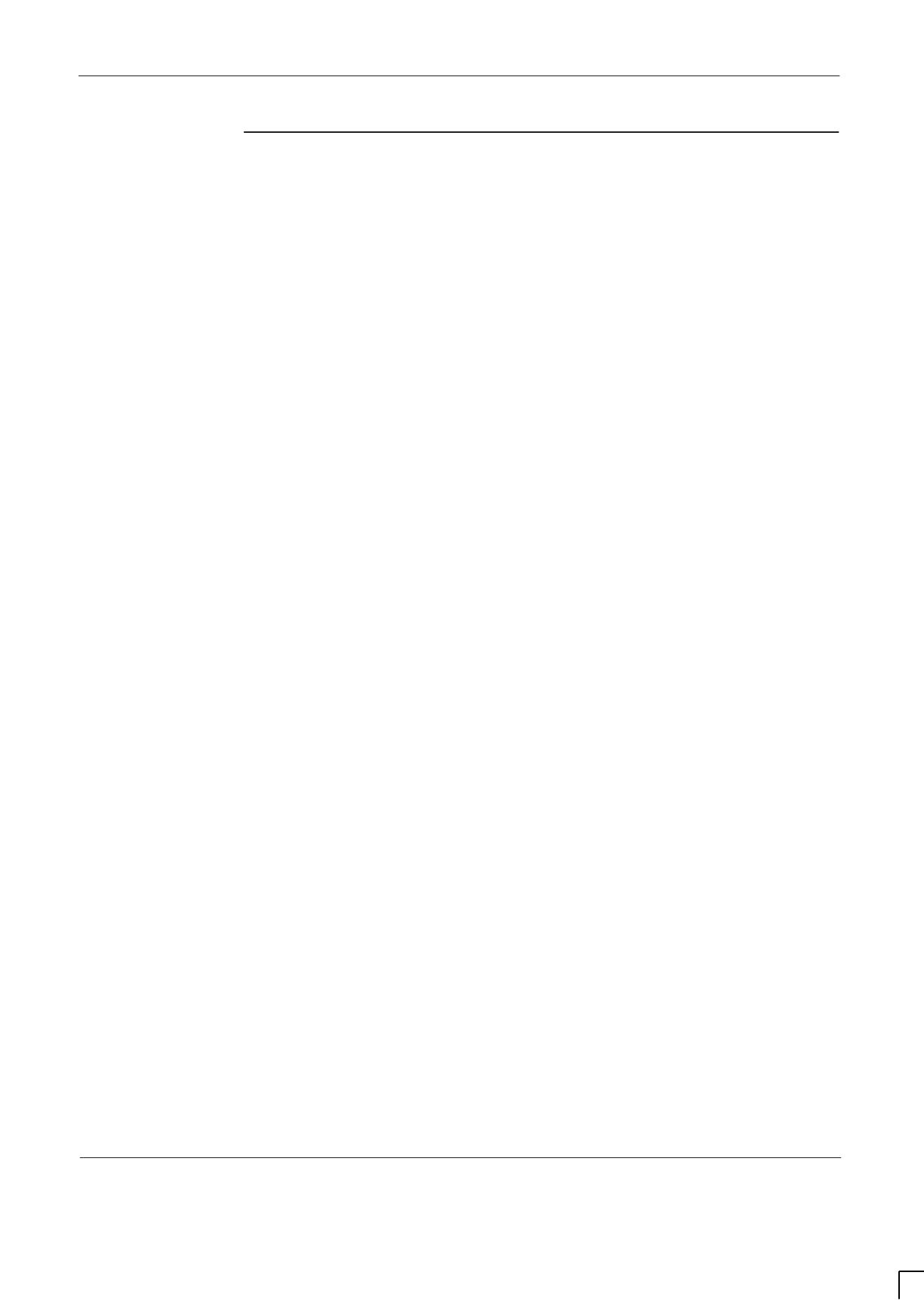
GSM-204-523 Replacing a circuit breaker module (CBM)
31st Oct 01
Maintenance Information: Horizon
macro
outdoor
68P02902W04-A
CONTROLLED INTRODUCTION
Maint. 3–23
Replacing a
CBM
To replace a CBM:
1. Set the main circuitbreaker in the number 1 ac distribution box to OFF.
2. Set the three PSUcircuit breakers in the number 2 ac distribution box to
OFF.
3. Set the switch of each PSM to the OUTPUT DISABLE position.
4. Unscrew both CBM module attachment screws (shown in Figure 3-10) by
using an M4 Torx driver.
5. Pull the module out, using the handle-baffle.
6. Check that all push on/push off circuit breaker buttons of the new CBM
module are in the out (off) position.
7. Install the new module and press firmly into place.
8. Tighten both module attachment screws to correct torque (see Overview
of FRU replacement procedures in ths Chapter), using an M4 Torx
driver.
To restore power to the cabinet:
1. Set the main circuitbreaker in the number 1 ac distribution box to ON.
2. Set the three PSUcircuit breakers in the number 2 ac distribution box to
ON.
3. Turn each PSM switch to the OUTPUT ENABLE position. Check that each
PSM has the ACTIVE (green) light on and the ALARM (red) light off.
4. Press the CBM circuit breaker button marked BPSM A and (if redundant
BPSM fitted) BPSM B. Check all associated digital module indicators
operate correctly.
5. Press the CBM circuit breaker button marked SURF.
6. Press the CBM appropriate circuit breaker buttons for the CTUs fitted, and
check that the LEDs for each CTU indicate correct operation.
7. Close the door to ensure correct ventilation.
This completes the CBM replacement and power up sequence for a cabinet.
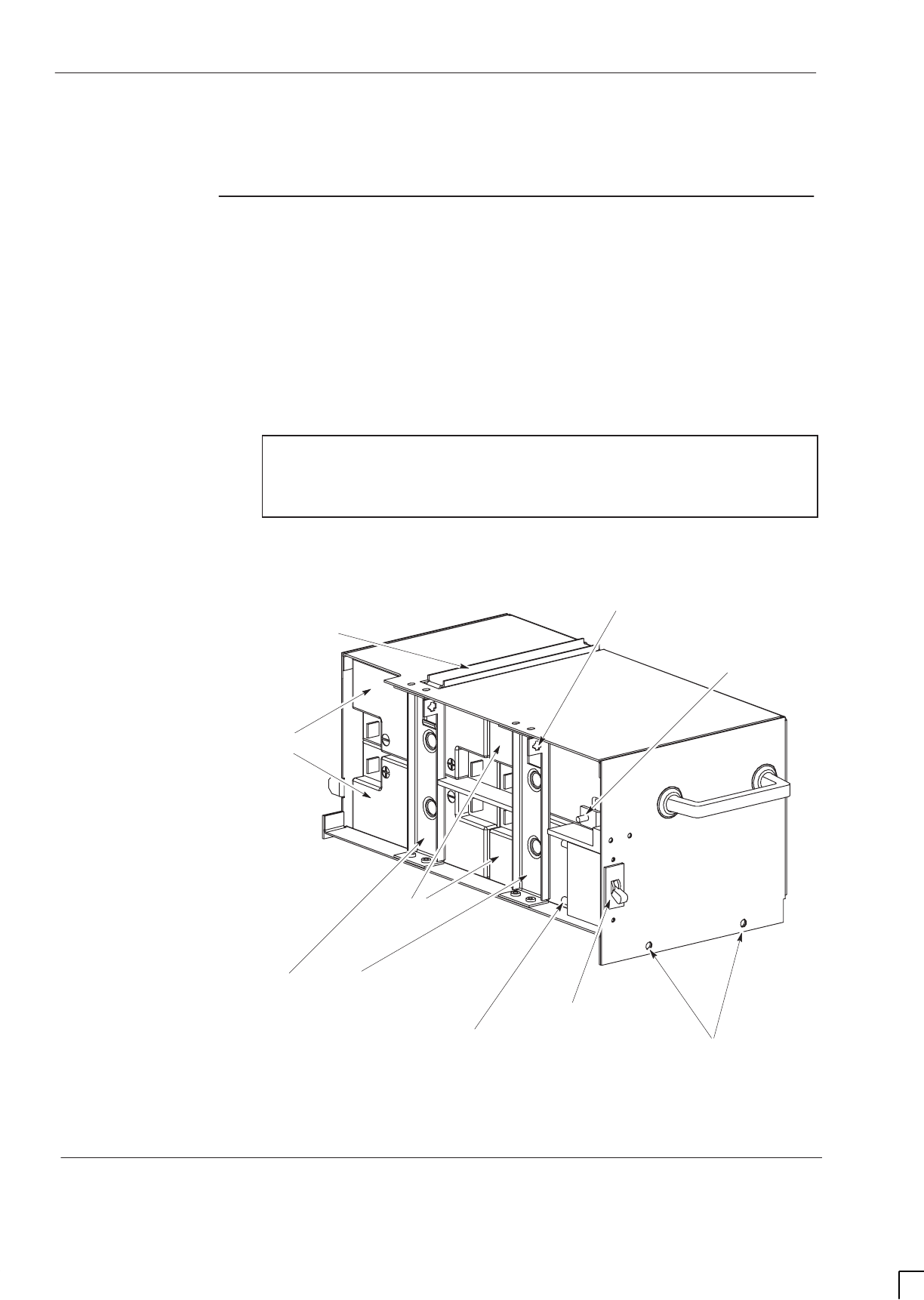
GSM-204-523
Replacing the internal batteries
31st Oct 01
Maint. 3–24
Maintenance Information: Horizon
macro
outdoor
CONTROLLED INTRODUCTION
68P02902W04-A
Replacing the internal batteries
Introduction to
internal battery
replacement
The internal backup battery tray is mounted in the lower right side of the PSU
cage, below the number 2 ac distribution box. Four 12 V batteries are mounted
on their sides in the battery tray, connected in series to provide –48 V dc.
It is usual to replace the battery tray, complete with Yuasa long life batteries as
an FRU item, although the batteries may be replaced separately, if required. Be
aware that if a different make of battery is fitted, however, the original cables
supplied may not fit and the cables may also have to be replaced.
NOTE Power does not need to be removed from the cabinet to
replace the batteries. Use the circuit breaker switch on the
battery tray front panel to isolate the batteries from the
system prior to removal.
Figure 3-11 shows the battery tray, with the batteries installed.
BATTERY TRAY
RETAINING SCREWS
RETRACTABLE
HANDLE
CIRCUIT BREAKER
SWITCH
BATTERIES
BATTERIES
BATTERY RETAINING STRAPS
FRONT +VE
TERMINAL
4-WAY BATTERY SENSE
LEAD MOLEX CONNECTOR
BOTTOM BREAKER
TERMINAL
Figure 3-11 Internal batteries, mounted in the battery tray
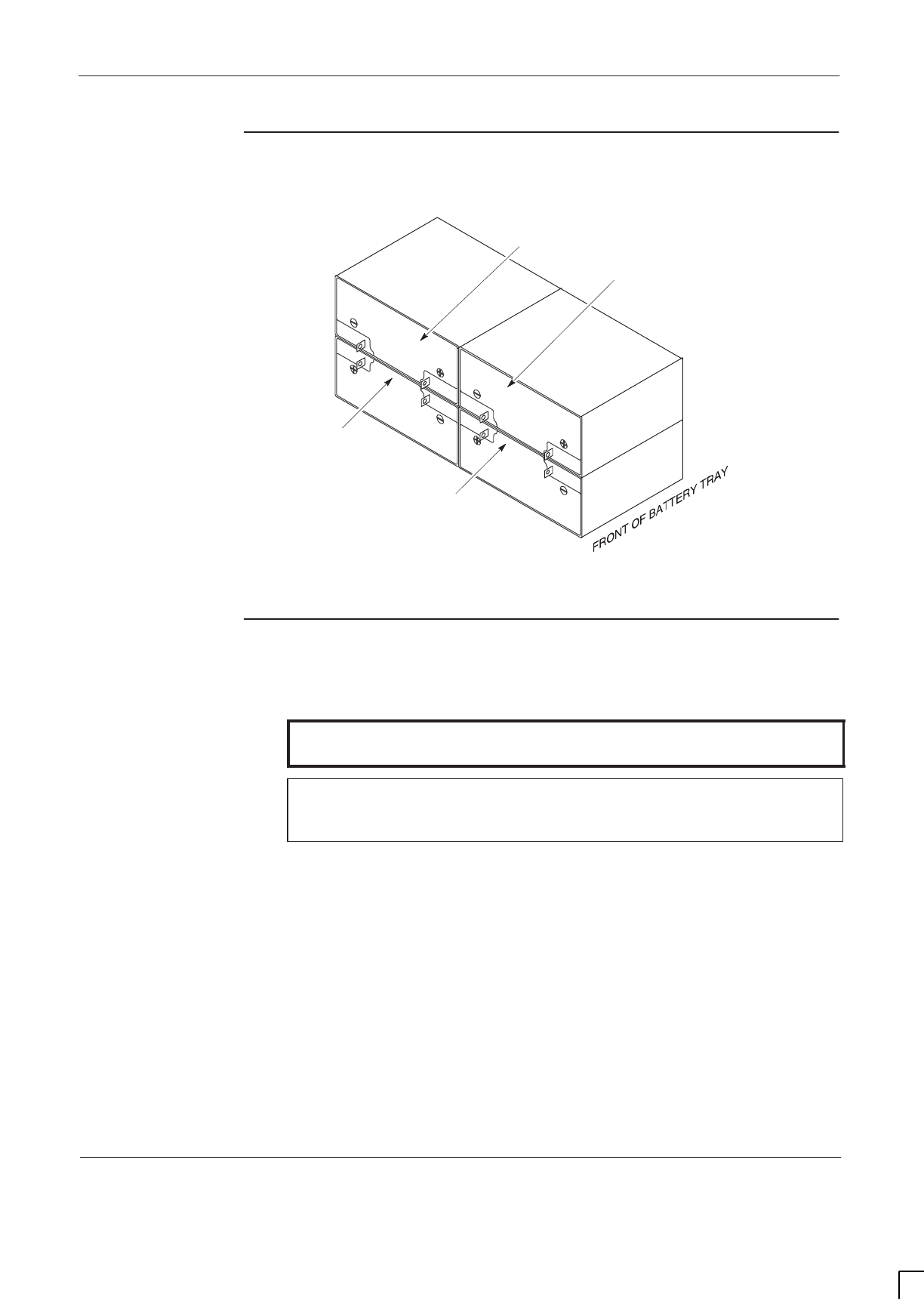
GSM-204-523 Replacing the internal batteries
31st Oct 01
Maintenance Information: Horizon
macro
outdoor
68P02902W04-A
CONTROLLED INTRODUCTION
Maint. 3–25
Battery
arrangement
Figure 3-12 shows how the batteries are arranged in the battery tray.
BATTERY 1
BATTERY 2
BATTERY 3
BATTERY 4
Figure 3-12 Internal battery arrangement in the battery tray
Removing the
battery tray
Carry out the following procedure to remove the internal battery tray from the
Horizon
macro
outdoor cabinet:
WARNING The batteries are capable of supplying high short circuit
currents and thus provide a high energy hazard.
CAUTION The battery tray is heavy. Take care when removing it from
the cage. Each battery cable must be insulated as soon
as it is disconnected from the terminal.
1. Isolate the batteries by switching off the circuit breaker on the battery tray
front panel.
2. Undo the two battery tray retaining screws on the lower front panel (see
Figure 3-11), and PARTIALLY withdraw the battery tray from the cage.
3. Using insulated spanners, disconnect the cables from the front positive
terminal and then the bottom breaker terminal. Disconnect the 4-way
battery sense lead Molex connector.
4. Slowly withdraw the tray until the retractable handle is exposed. With one
hand on the handle on the front panel and the other on the top handle, lift
the rear of the tray to disengage it from the cage and then gently pull the
tray completely out of the cage.
The procedure for removing the battery tray is now complete.
Replacement is a reversal of the removal procedure.
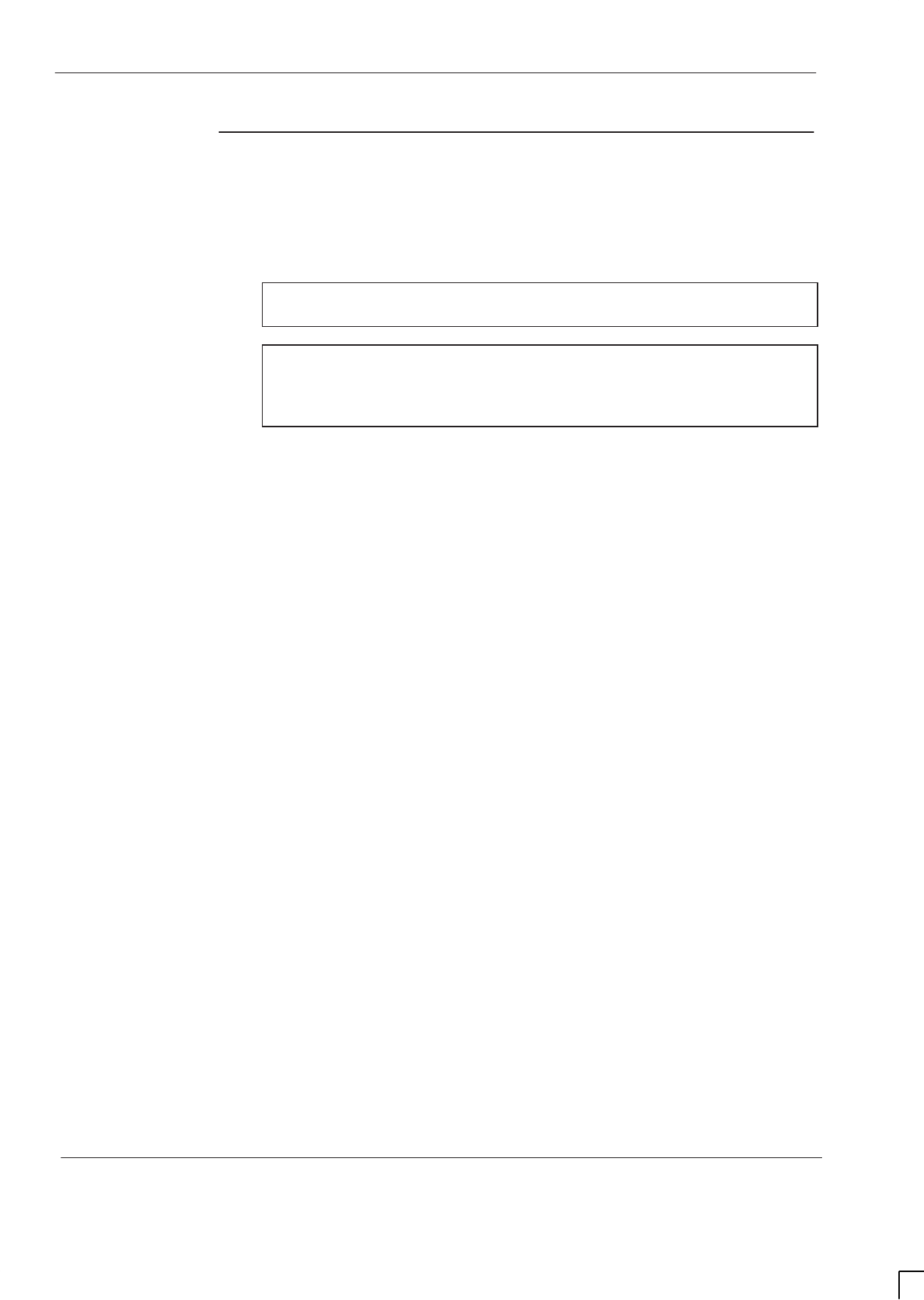
GSM-204-523
Replacing the internal batteries
31st Oct 01
Maint. 3–26
Maintenance Information: Horizon
macro
outdoor
CONTROLLED INTRODUCTION
68P02902W04-A
Removing and
replacing the
batteries
If it is necessary to remove the batteries from the battery tray, use the following
procedure (letters and numbers in parentheses refer to Figure 3-13). Table 3-2
details the wiring schedule of the battery sense lead for reference.
NOTE This procedure assumes that the battery tray has been
removed from the cabinet, as described previously.
CAUTION Each battery cable must be insulated as soon as it is
disconnected from the battery terminal.
Battery sense leads must be connected to the negative
terminal of the correct battery as shown in Figure 3-13.
1. Using spanners with insulated handles, undo the M5 screws and remove
the interconnection cable and the battery sense lead (B) from the rear
battery terminals (1).
2. Undo the M5 screws and remove the interconnection cables and battery
sense leads (C and D) from the middle battery terminals (2).
3. Disconnect the braid and battery sense lead (E) from the top terminal of
the circuit breaker (3).
4. Remove the two battery retaining brackets (4) by undoing the eight M4
screws.
5. Lift out the central insulation block (5) from between the middle terminals.
6. Remove the front insulator block (6) by undoing the two M4 screws on the
front panel of the battery tray.
7. Remove the circuit breaker (3) by undoing the two M3 screws on the front
panel of the battery tray.
8. Raise the upper rear battery (7) slightly, then disengage and remove the
handle (8).
9. Remove the rear battery, followed by the remaining batteries.
The procedure for removing the batteries is now complete. Remove the
L-shaped battery terminal (9) from from the upper battery terminal and fit onto
the new battery to be installed in that position.
Battery replacement is a reversal of the removal procedure.
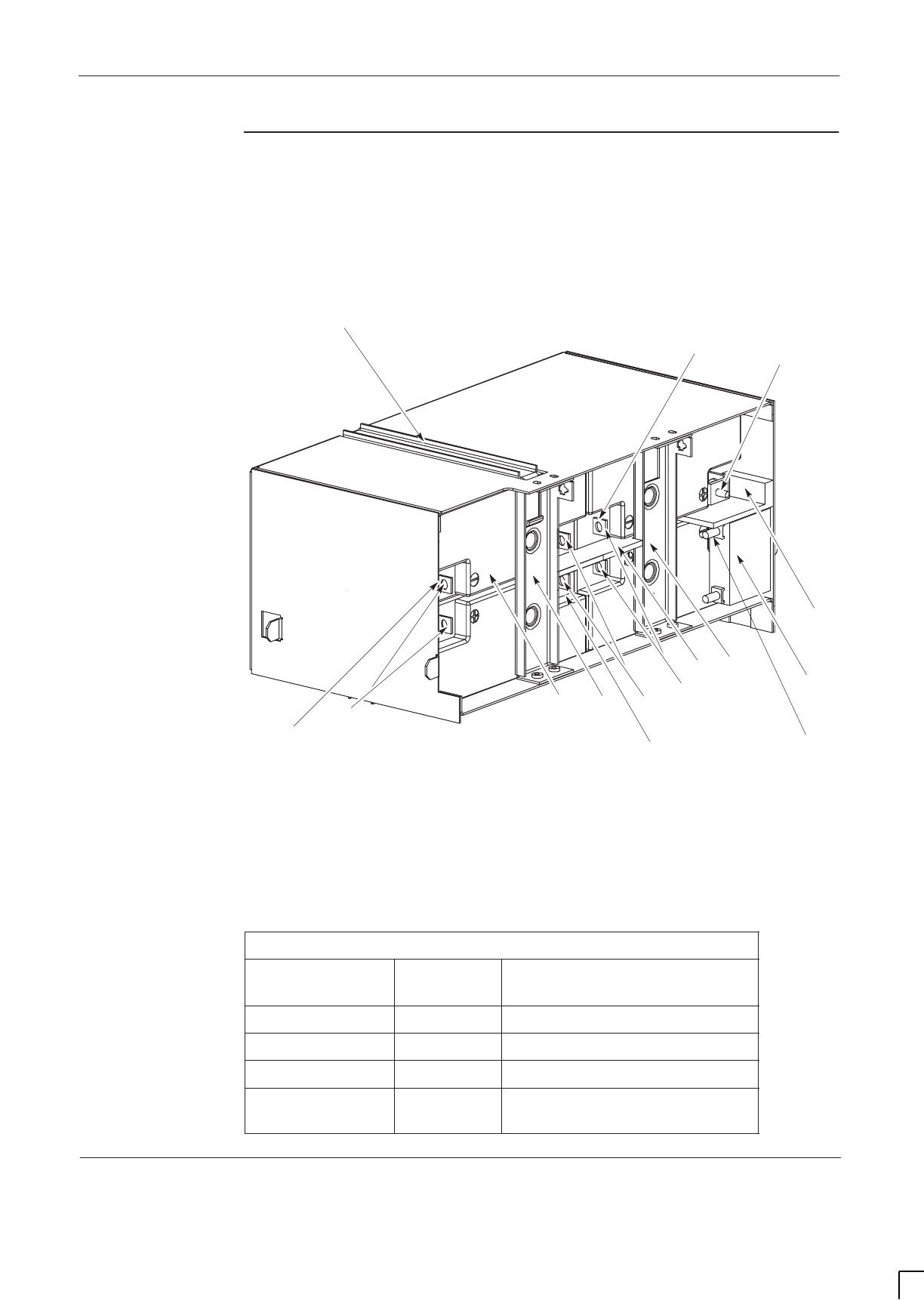
GSM-204-523 Replacing the internal batteries
31st Oct 01
Maintenance Information: Horizon
macro
outdoor
68P02902W04-A
CONTROLLED INTRODUCTION
Maint. 3–27
View showing
battery
replacement
components
Figure 3-13 shows a view of the internal batteries with the components identified
to assist in battery replacement.
(1) (2) (2) (3)
(4)
(4)
(5)
(6)
(7)
(8)
(9)
SENSE LEAD
TERMINAL (B) SENSE LEAD
TERMINAL (D)
SENSE LEAD
TERMINAL (C)
SENSE LEAD
TERMINAL (E)
(top breaker
terminal)
Figure 3-13 Component identification for battery replacement
Table 3-2 details the wiring schedule of the battery sense lead.
Table 3-2 Battery sense lead to Molex connector
Molex
connector pin Terminal
ident Location
1 C Battery 1 –ve terminal
2 B Battery 2 –ve terminal
3 D Battery 3 –ve terminal
4 E Battery 4 –ve terminal at
circuit breaker top terminal
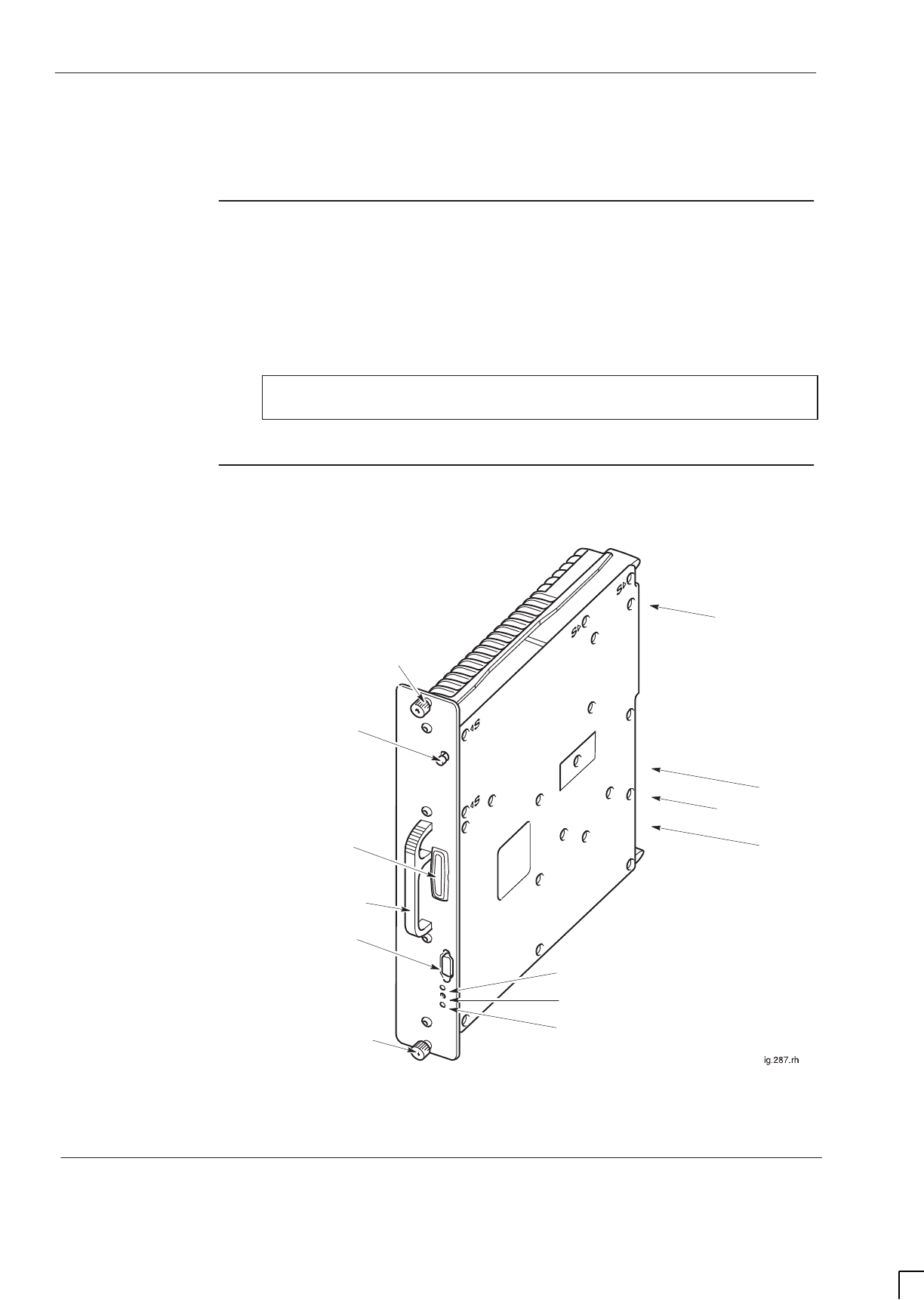
GSM-204-523
Replacing a CTU
31st Oct 01
Maint. 3–28
Maintenance Information: Horizon
macro
outdoor
CONTROLLED INTRODUCTION
68P02902W04-A
Replacing a CTU
Preconditions
to CTU
replacement
There are six CTUs in a cabinet. Replacing a CTU requires removal of RF
transmitter power for that CTU; it is therefore advisable to perform this
procedure during periods of low traffic. The OMC-R should be notified of
imminent repair activity.
NOTE The CTU replacement procedure is the same for all CTUs,
regardless of frequency rating.
View of CTU
Figure 3-14 shows a view of a CTU with key features identified.
Tx OUT
CONNECTOR
Tx STATUS LED
HANDLE
M4 MODULE ATTACHMENT
SCREW
M4 MODULE ATTACHMENT
SCREW
TTY INTERFACE
CONTROL
PROCESSOR
TEST INTERFACE
RADIO STATUS LED
RECESSED MANUAL
RESET BUTTON (if fitted)
Rx A
Rx B
LOOPBACK
TEST PORT (L)
BACKPLANE POWER AND
SIGNAL CONNECTOR
Figure 3-14 CTU view with key features identified
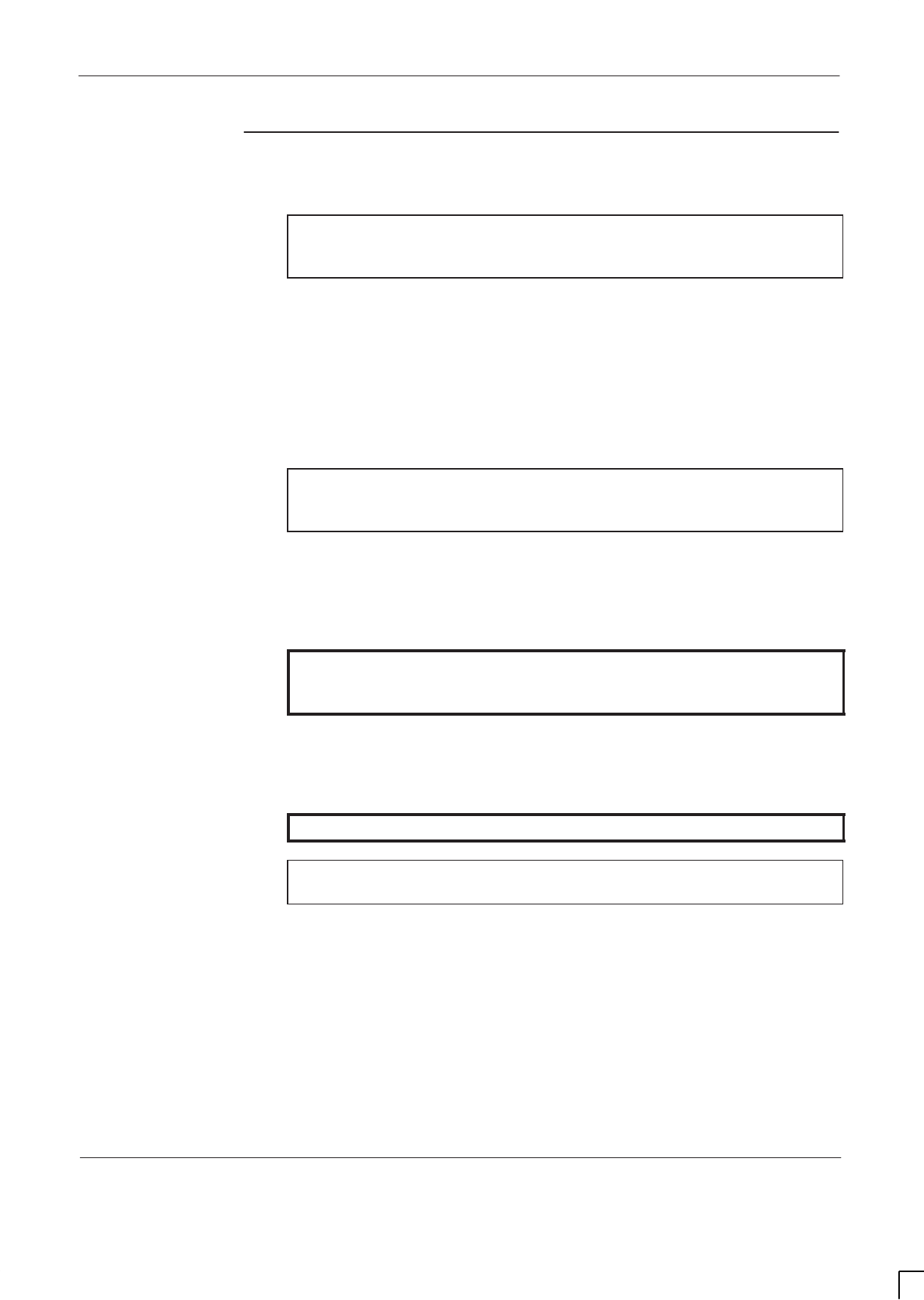
GSM-204-523 Replacing a CTU
31st Oct 01
Maintenance Information: Horizon
macro
outdoor
68P02902W04-A
CONTROLLED INTRODUCTION
Maint. 3–29
Replacement
procedure for
CTU
CAUTION An earthing wrist strap must be worn when handling
CTUs. An ESP earthing connection point is provided
above the leftmost PSM.
Removing a faulty CTU
To remove a CTU:
1. Locate the CTU to be replaced. CTUs are sequentially numbered, with
CTU 0 on the right, and CTU 5 on the left.
2. Disable the CTU transmit RF power by using the shutdown_device
command at the OMC-R, or from a PC connected to the MCUF.
NOTE Refer to
Technical Description: BSS Command Reference
(GSM-100-321)
for information on usage and specific
commands.
3. When the CTU has been shutdown, check that the Tx STATUS LED (solid
yellow) is extinguished.
4. Press and release the appropriate CTU circuit breaker button on the CBM
to the out (off) position. Ensure the RADIO STATUS LED is extinguished.
WARNING Ensure that RF power is OFF, before disconnecting RF
cables. Severe burns may result if RF power is ON when
cables are disconnected.
5. Unscrew the coaxial cable from the Tx OUT SMA connector at the top of
the CTU front panel.
6. Unscrew the two CTU attachment screws using an M4 Torx driver.
WARNING The CTU weighs 5 kg. Handle with care.
CAUTION Take care to avoid damaging the CTU rear connectors
when handling outside of the cabinet.
7. Withdraw the CTU using the handle. Support the unit from underneath as
it slides out.
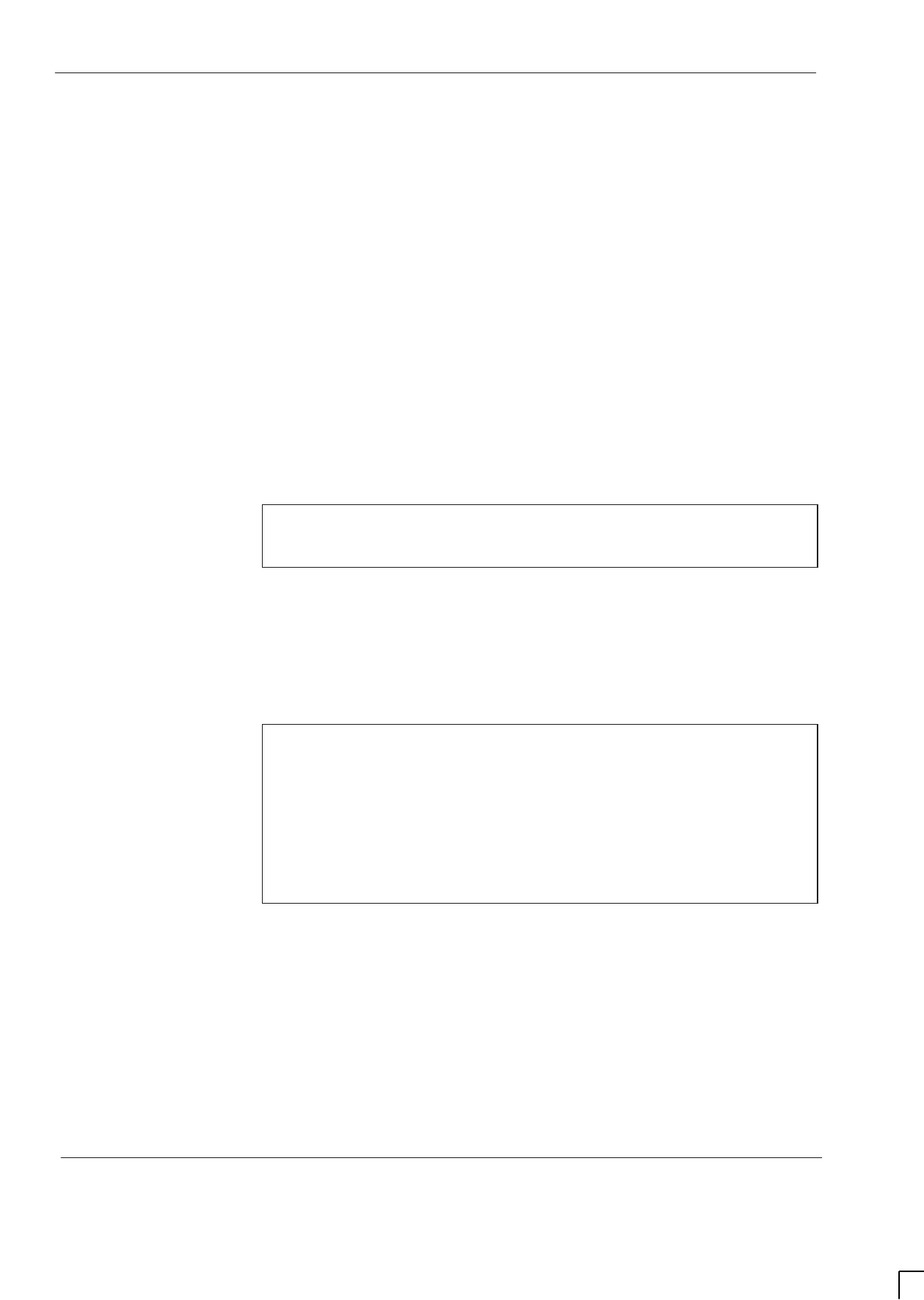
GSM-204-523
Replacing a CTU
31st Oct 01
Maint. 3–30
Maintenance Information: Horizon
macro
outdoor
CONTROLLED INTRODUCTION
68P02902W04-A
Fitting a replacement CTU
To fit a replacement CTU:
1. Ensure that the correct CTU push-on/push-off circuit breaker button on the
CBM has been pressed to the out (off) position.
2. Ensure that the transmit RF power of the correct CTU has been removed
using the shutdown_device command at the OMC-R or from a PC
connected to the MCUF.
3. Insert replacement CTU module, taking care to locate the module on the
guide rails. Press firmly in place.
4. Tighten both module attachment screws to the correct torque (see
Overview of FRU replacement procedures in this chapter), using an M4
Torx driver.
5. Attach the coax cable to the appropriate Tx block or feedthrough plate for
the CTU. Tighten to the correct torque (see Overview of FRU
replacement procedures in this chapter).
NOTE The Tx cable has a 90° SMA connector at one end, and a
straight SMA connector at the other. The 90° end is
designed for connection to the Tx port of a CTU.
6. Screw the coaxial cable onto the Tx OUT SMA connector at the top of the
CTU front panel. Tighten to the correct torque (see Overview of FRU
replacement procedures in this chapter).
7. Press and release the appropriate CTU circuit breaker button on the CBM.
The RADIO STATUS LED will flash green for about two minutes, and then
remain lit.
CAUTION If both RADIO STATUS and Tx STATUS LEDs are
flashing, the boot code is downloading into non-volatile
memory for software upgrade. Power should not be
removed, nor the cabinet reset, until downloading has
been completed, as this will corrupt the non-volatile
memory. If the boot code is corrupted, contact the
Motorola Customer Network Resolution Centre, requesting
the boot code restoration procedure and the appropriate
boot code file.
8. Enable the CTU transmit RF power by using the ins_device command
at the OMC-R, or from a PC connected to the MCUF. The Tx STATUS
LED (yellow) will be lit if the CTU is transmitting.
9. Notify the OMC-R of base station availability and log the maintenance
activity.
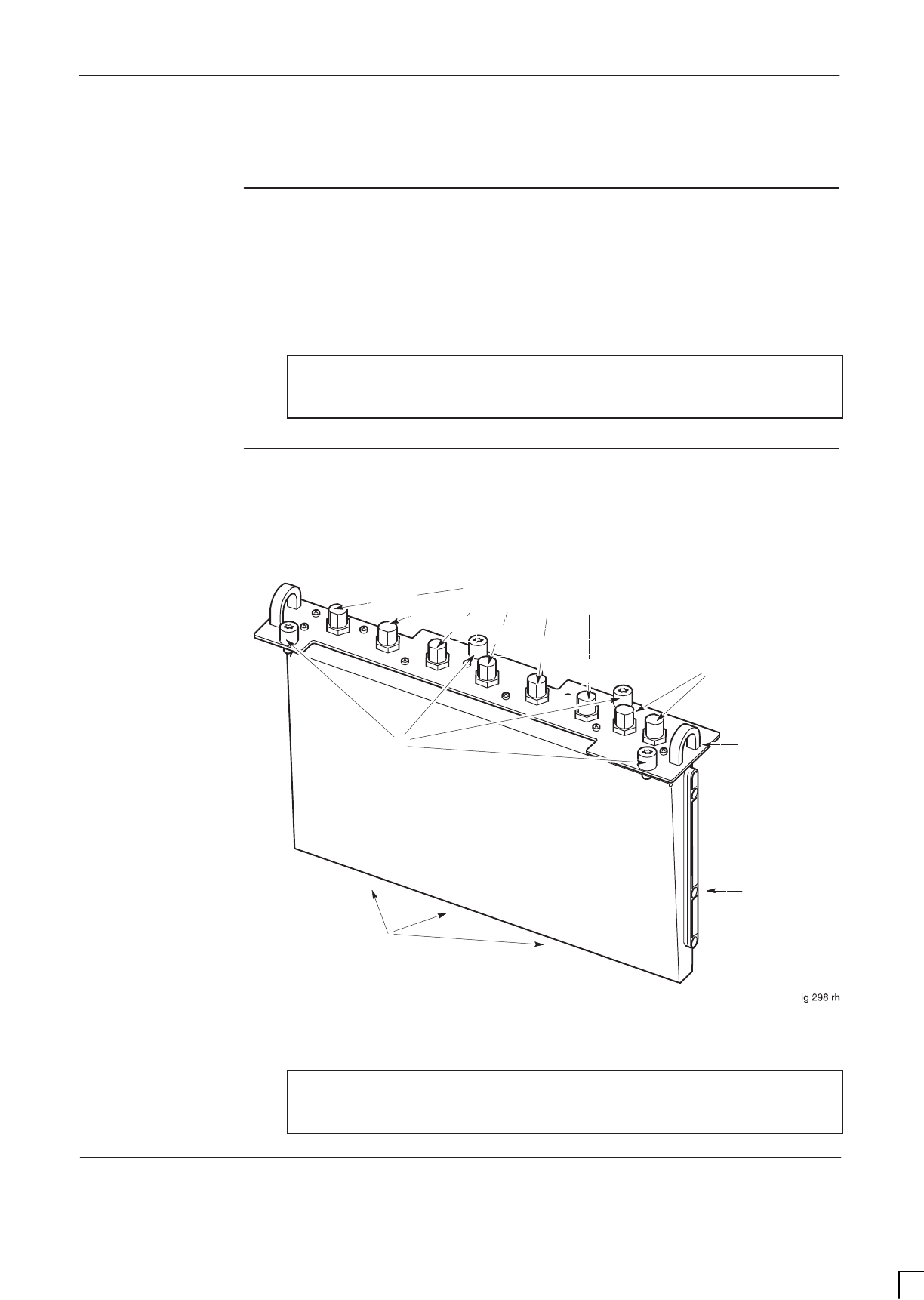
GSM-204-523 Replacing a SURF module
31st Oct 01
Maintenance Information: Horizon
macro
outdoor
68P02902W04-A
CONTROLLED INTRODUCTION
Maint. 3–31
Replacing a SURF module
Preconditions
for SURF
replacement
The cabinet contains only one SURF module, either a dual band SURF or a
single band SURF. Consequently, the replacement of a SURF module can only
take place after the cabinet has been taken out of service, in agreement with the
OMC-R.
CAUTION An earthing wrist strap must be worn when handling SURF
modules. An ESP earthing connection point is provided
above the leftmost PSM.
View of the
SURF
Figure 3-15 shows a single band SURF module. Where RXn appears in
Figure 3-15, the n may be 850, 900, 1800 or 1900, depending on the frequency
of the SURF module.
RXn
1B
RXn
2B
GUIDE RAIL FOR
INSERTION
SIX N-TYPE RECEIVE ANTENNA CONNECTIONS
(2 PER DLNB EQUIVALENT)
EXTENSION PORTS TO
OTHER CABINETS
3 CONNECTORS ON UNDERSIDE
TO SURF HARNESS
HANDLE FOR
MODULE
REMOVAL
FOUR M6 MODULE
ATTACHMENT
SCREWS
RXn
0A
RXn
1A
2A
RXn
RXn
0B
Single band SURF
Figure 3-15 View of a single band SURF module
NOTE The dual band SURF replacement procedure is almost
identical, with the addition of the extra two second
frequency antenna connections.
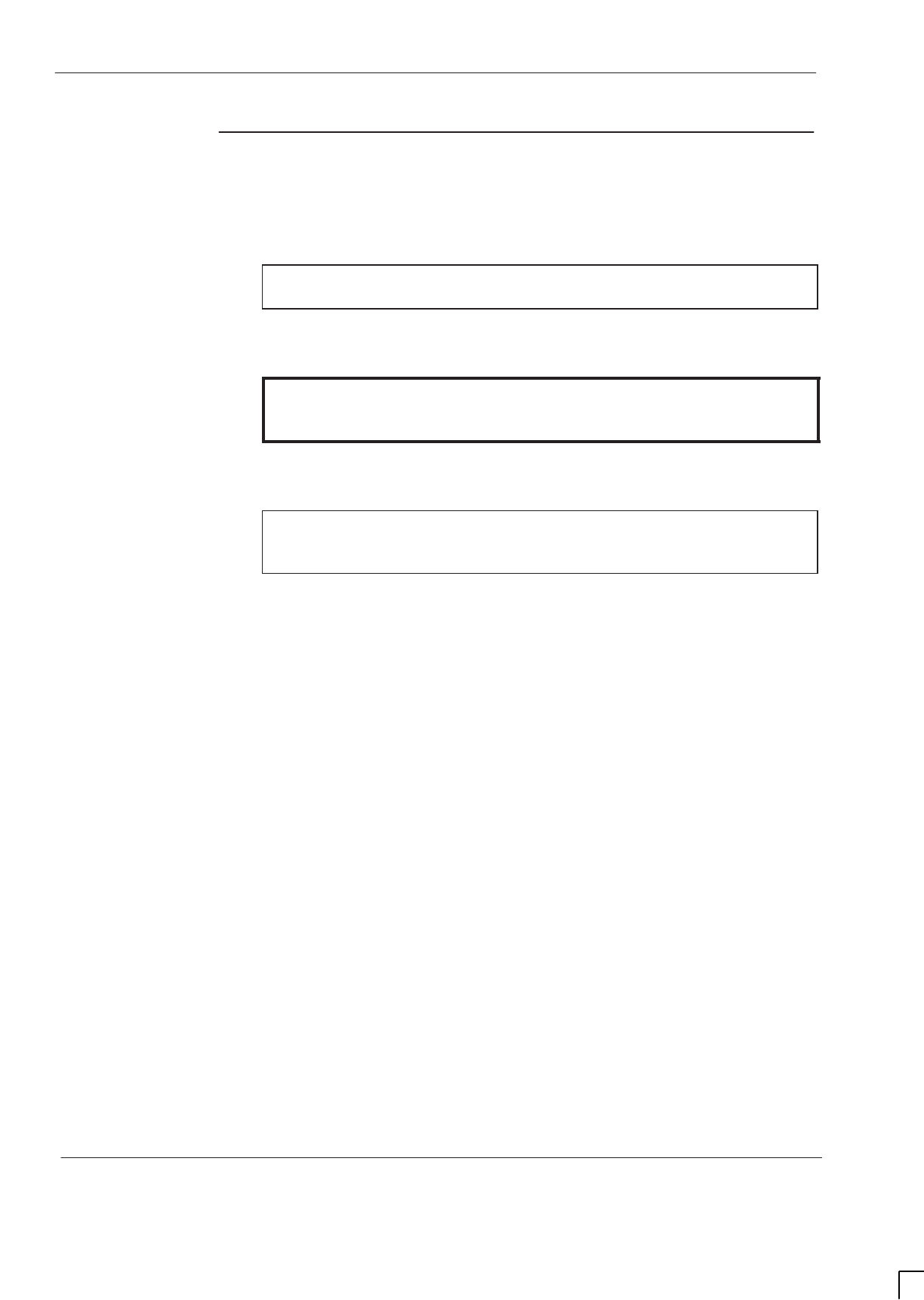
GSM-204-523
Replacing a SURF module
31st Oct 01
Maint. 3–32
Maintenance Information: Horizon
macro
outdoor
CONTROLLED INTRODUCTION
68P02902W04-A
Replacing a
SURF module
Removing a faulty SURF module
To remove a SURF proceed as follows:
NOTE The procedure for replacing a faulty SURF module is the
same for both single and dual band SURF variants.
1. Note the RF cable connections to the SURF module to enable correct
reconnection to the replacement module.
WARNING Ensure that RF power is OFF before disconnecting RF
cables. Severe burns may result if RF power is ON when
cables are disconnected.
2. Disable all CTU transmit RF power by using the shutdown_device
command at the OMC-R, or from a PC connected to the MCUF.
NOTE Refer to
Technical Description: BSS Command Reference
(GSM-100-321)
for information on usage and specific
device codes.
3. When all CTUs have been shutdown, check that the Tx STATUS LED
(yellow) is extinguished.
4. Press and release the CTU circuit breaker buttons on the CBM to the out
(off) position. Ensure that each RADIO STATUS LED is extinguished.
5. Press and release the SURF circuit breaker button on the CBM to the out
(off) position.
6. Disconnect the coaxial RF cables by carefully unscrewing and pulling
them out of the module sockets. Note the positions for correct
replacement.
7. Using a Torx driver, unscrew the four M6 torx captive screws holding the
SURF module to the top of the cabinet.
8. Using the handles, lift the SURF block from the slot.
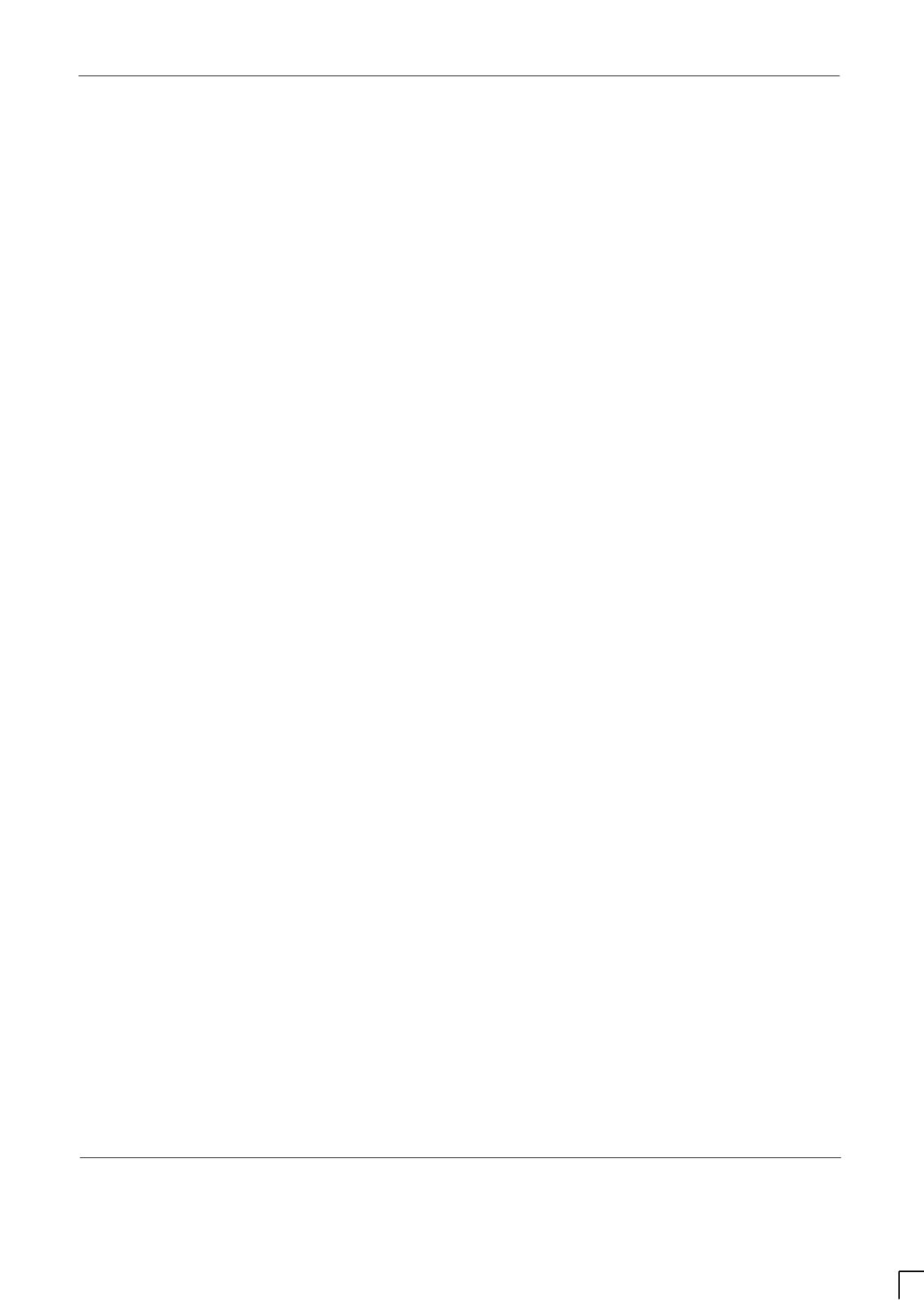
GSM-204-523 Replacing a SURF module
31st Oct 01
Maintenance Information: Horizon
macro
outdoor
68P02902W04-A
CONTROLLED INTRODUCTION
Maint. 3–33
Installing a replacement SURF module
To install a replacement SURF:
1. Transfer the protective caps on the RF connectors from the replacement
module to the faulty module.
2. Insert the replacement SURF module firmly into place. Take care to avoid
trapping cables as the module is seated.
3. Tighten the four captive M6 torx screws to the correct torque (see
Overview of FRU replacement procedures in this chapter).
4. Reconnect the coaxial RF cables to the positions noted in the removal
procedure. Tighten to the correct torque (see Overview of FRU
replacement procedures in this chapter).
5. Reset the SURF circuit breaker button on the CBM.
6. Reset the CTU circuit breaker buttons on the CBM. Each RADIO STATUS
LED will flash green for about two minutes and then remain lit.
7. Enable the CTU transmit RF power by using the ins_device command
at the OMC-R, or from a PC connected to the MCUF. The Tx STATUS
LED (yellow) will be lit if the CTU is transmitting.
8. Notify the OMC-R of base station availability and log the maintenance
activity.
The SURF module is now installed and operational.
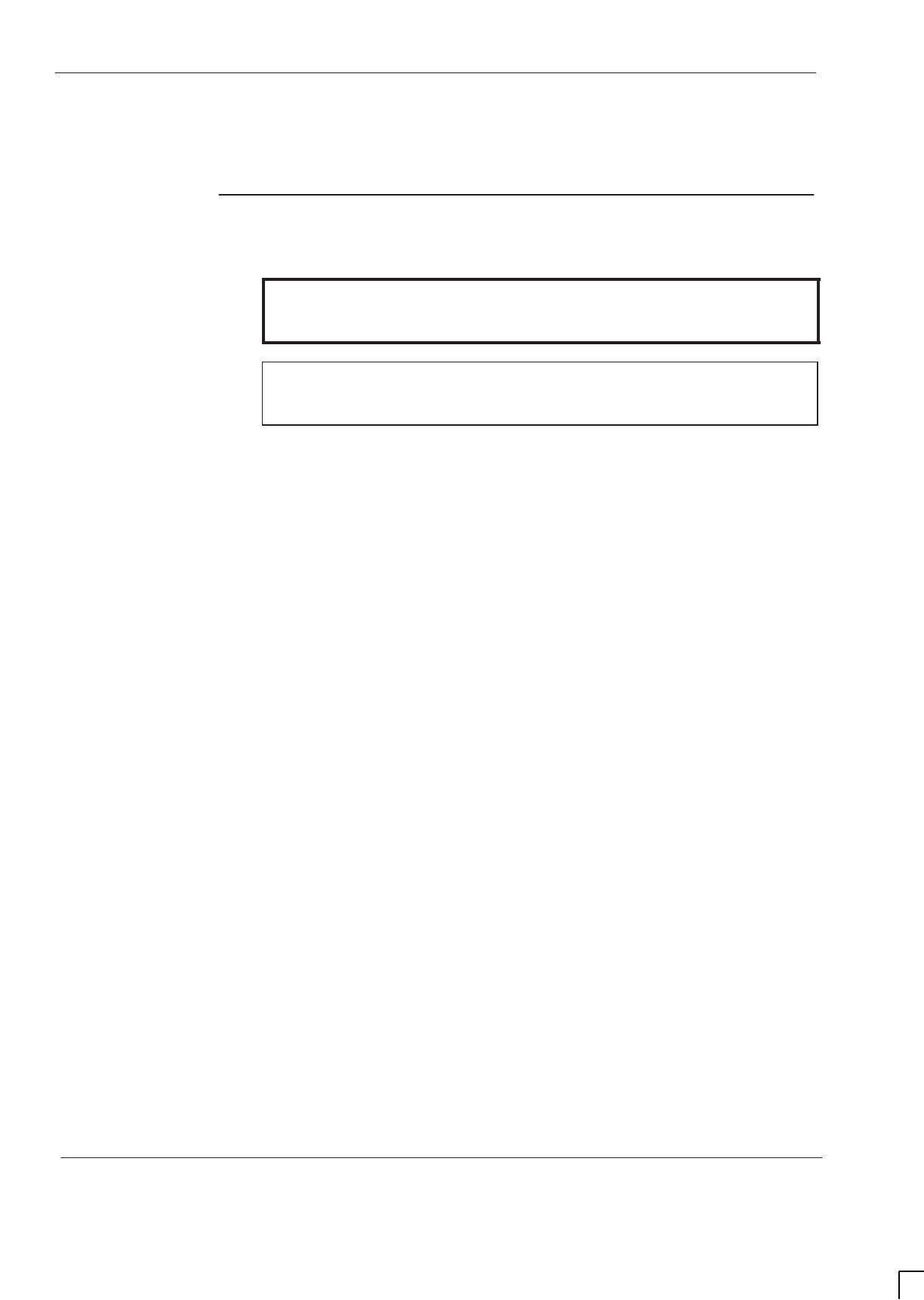
GSM-204-523
Replacing a Tx block
31st Oct 01
Maint. 3–34
Maintenance Information: Horizon
macro
outdoor
CONTROLLED INTRODUCTION
68P02902W04-A
Replacing a Tx block
Preconditions
to Tx block
replacement
WARNING Ensure that RF power is OFF before disconnecting RF
cables. Severe burns may result if RF power is ON when
cables are disconnected.
CAUTION An earthing wrist strap must be worn when handling Tx
blocks. An ESP earthing connection point is provided
above the leftmost PSM.
There are three slots for Tx blocks in the top panel basket of a cabinet, above
the CTUs. There are four types of Tx block: DCF, TDF, DDF and HCU.
Replacing a Tx block requires the removal of RF transmitter power for the
CTU(s) that connect with the faulty Tx block. It is therefore advisable to perform
this procedure during periods of low traffic. The OMC-R should be notified of
imminent repair activity.
It is important to ensure that all Tx Block M6 screw locations have a screw in
place and tightened to the correct torque (see Overview of FRU replacement
procedures in this chapter). This is to ensure correct EMC shielding and
general containment.
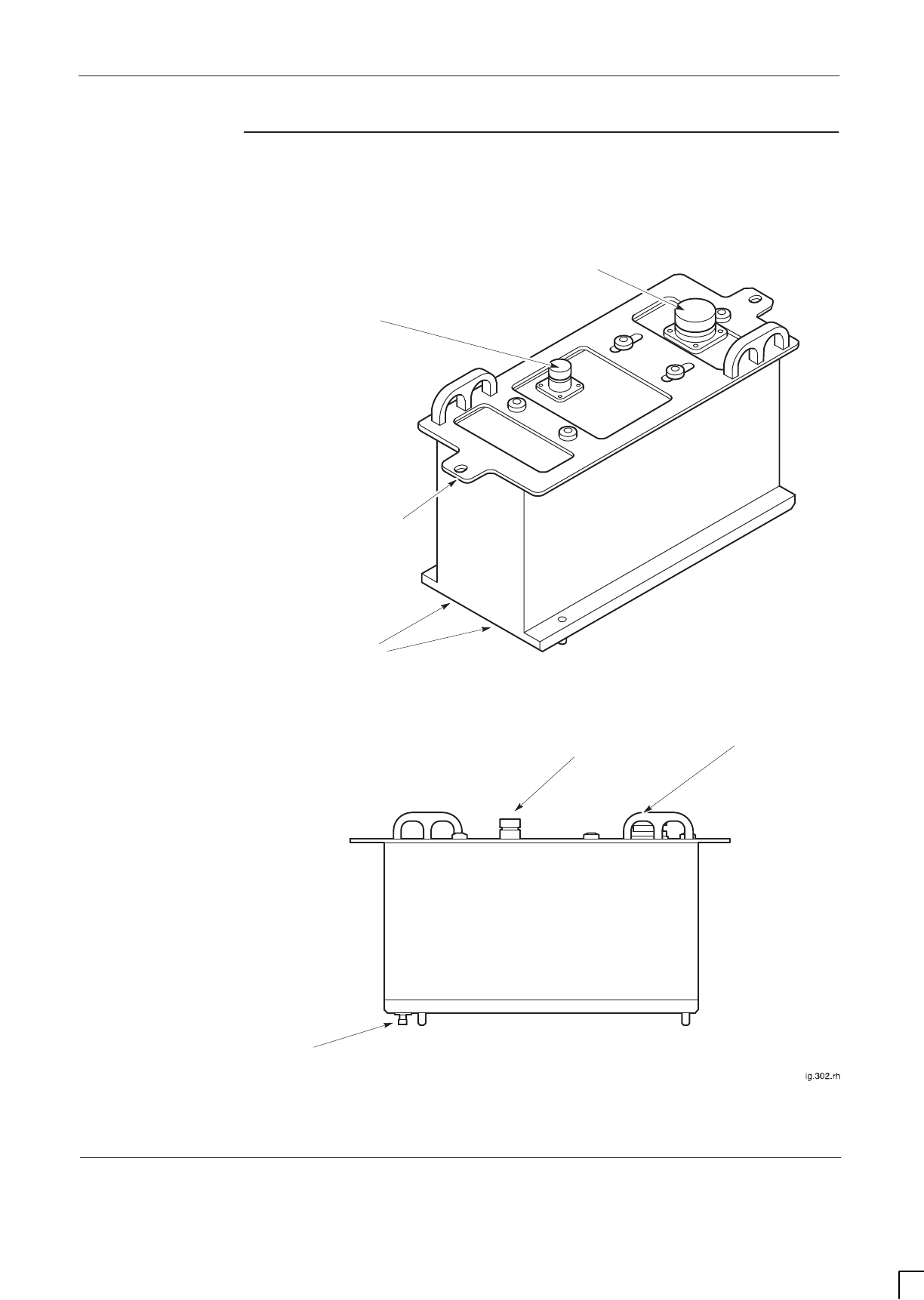
GSM-204-523 Replacing a Tx block
31st Oct 01
Maintenance Information: Horizon
macro
outdoor
68P02902W04-A
CONTROLLED INTRODUCTION
Maint. 3–35
Views of typical
Tx block
Figure 3-16 shows a typical Tx block module used in the Horizon
macro
outdoor
cabinet.
SMA Tx CONNECTORS
FROM CTUs
SIDE VIEW
ISOMETRIC VIEW
7/16 CONNECTOR TO
ANTENNA
N-TYPE CONNECTOR
TO SURF
HOLE FOR TOP
PANEL BASKET
ATTACHMENT
7/16 CONNECTOR TO
ANTENNA
N-TYPE CONNECTOR
TO SURF
SMA Tx CONNECTORS
FROM CTUs
Figure 3-16 View of a typical Tx block
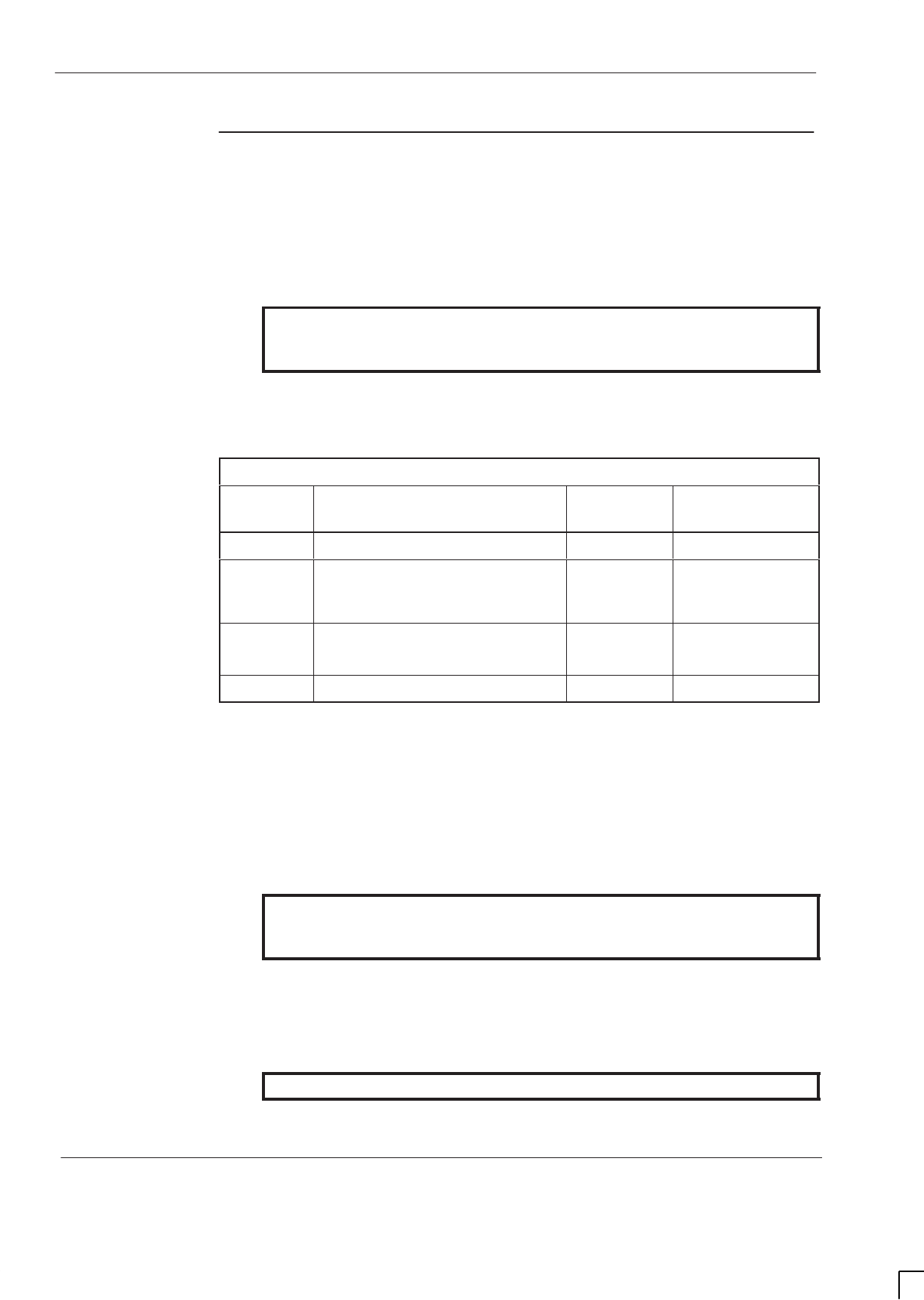
GSM-204-523
Replacing a Tx block
31st Oct 01
Maint. 3–36
Maintenance Information: Horizon
macro
outdoor
CONTROLLED INTRODUCTION
68P02902W04-A
Replacing a Tx
block
Removing a faulty Tx block
To remove a Tx block module:
1. Locate the faulty Tx block, and note the RF cable connections to enable
correct reconnection to the replacement module.
WARNING Ensure that all CTUs associated with the faulty Tx block
are identified (for example inputs to an HCU or
feedthrough plate connected to a DDF).
2. Identify the CTUs that make Tx connections to the underside of the faulty
Tx block (plus any CTUs connected to the third Tx connector on top of a
DDF). See Table 3-3.
Table 3-3 Connectors for each type of Tx block module
Tx block SMA from transceiver TX 7/16 Rx/Tx
to antenna N-type Rx to
SURF
DCF 2 (beneath Tx block) 1 1
TDF
(including
dual band)
2 (beneath Tx block) 2 2
DDF 3 (2 beneath Tx block)
(1 on top of Tx block from HCU)
1 1
HCU 2 0 1 to next Tx block
3. Disable each CTU transmit RF power by using the shutdown_device
command at the OMC-R, or from a PC connected to the MCUF. Refer to
Technical Description: BSS Command Reference (GSM-100-321)
for
information on usage and specific device codes.
4. When each CTU has been shutdown, check that the Tx status LED
(yellow) is extinguished.
5. Press and release each CTU circuit breaker button on the CBM to the out
(off) position. Ensure that all RADIO STATUS LEDs are extinguished.
WARNING Ensure that RF power is OFF, before disconnecting RF
cables. Severe burns may result if RF power is ON when
cables are disconnected.
6. Disconnect all coaxial RF cables by carefully unscrewing and pulling them
out of the Tx block sockets. Note the positions for correct replacement.
7. Using a Torx driver, unscrew and retain the two M6 Torx screws holding
the Tx block to the top of the cabinet.
WARNING Tx blocks can weigh as much as 5 kg. Handle with care.
8. Using the handles, lift the Tx block from the basket.
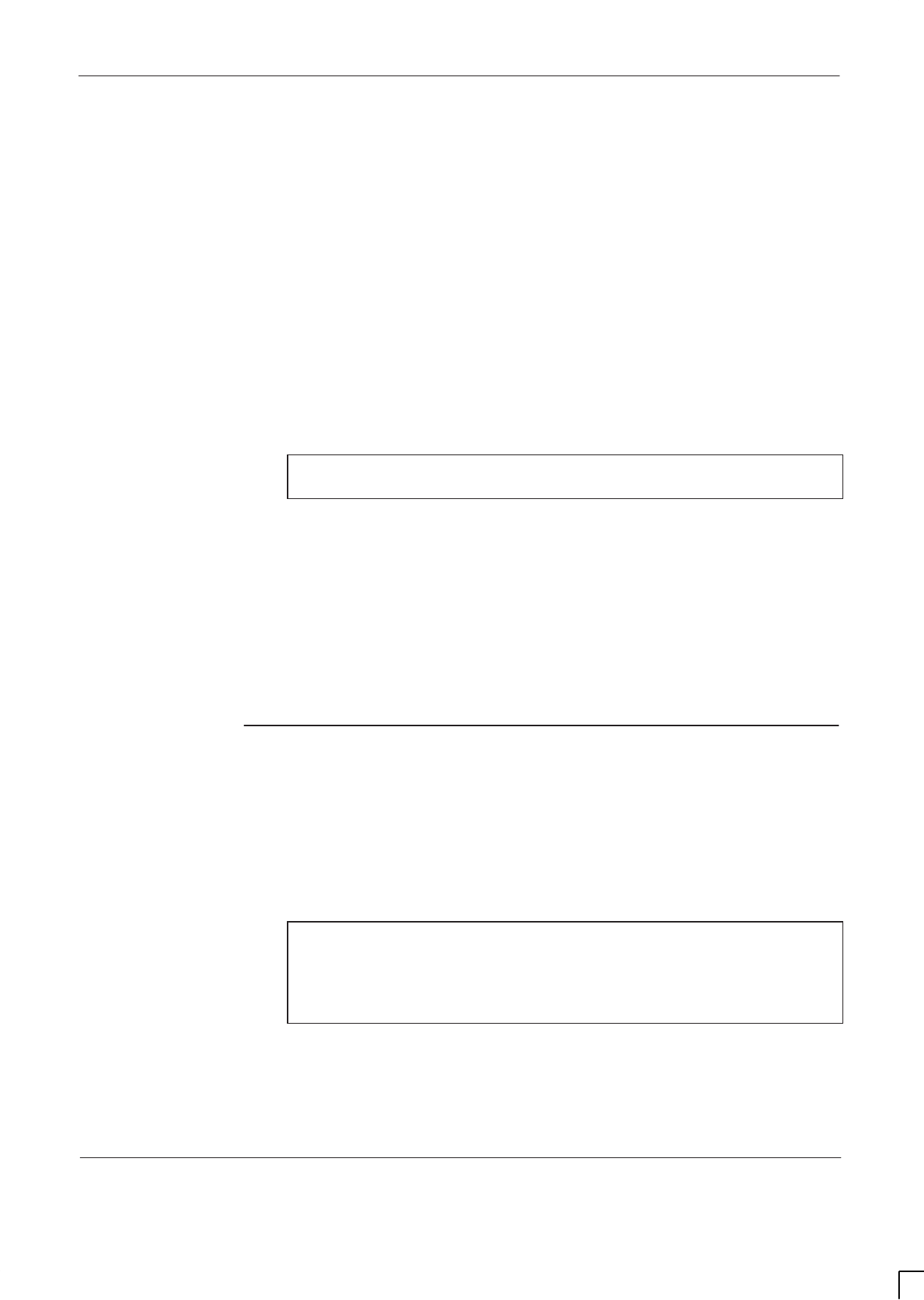
GSM-204-523 Replacing a Tx block
31st Oct 01
Maintenance Information: Horizon
macro
outdoor
68P02902W04-A
CONTROLLED INTRODUCTION
Maint. 3–37
Fitting a replacement Tx block
To install a replacement Tx block:
1. Transfer the protective caps on the RF connectors from the replacement
module to the faulty Tx block.
2. Carefully insert the replacement Tx block into its basket location on the top
panel, adjusting alignment for retaining screws. Take care to avoid
trapping cables as the Tx block is seated.
3. Fit the two M6 torx screws to hold the Tx block to the top of the cabinet.
Tighten to the correct torque (see Overview of FRU replacement
procedures in this chapter).
4. Reconnect the coaxial RF cables to the positions noted in the removal
procedure. Tighten to correct torque (see Overview of FRU replacement
procedures in this chapter).
NOTE Ensure all unused SMA inputs to DCF, DDF and HCU
modules are fitted with 50 ohm load terminations.
5. Reset the appropriate CTU circuit breaker buttons on the CBM. Each
RADIO STATUS LED will flash green for about two minutes, and then
remain lit.
6. Enable the CTU transmit RF power by using the ins_device command
at the OMC-R, or from a PC connected to the MCUF. The Tx STATUS
LED (yellow) will be lit if the CTU is transmitting.
7. Notify the OMC-R of base station availability and log the maintenance
activity.
Tx block
blanking plate,
feedthrough
plate or HCU
replacement
The procedure for plates is the same as for Tx blocks, but the plates are held by
six M4 screws in the base of the Tx block basket. The two M6 Tx block screw
locations are not used for plate attachment.
CAUTION Unused Tx block locations must be covered with a
blanking plate, with all screws fitted and tightened to the
correct torque (see Overview of FRU replacement
procedures in this chapter) to ensure correct airflow and
EMC shielding.

GSM-204-523
Krone block replacement
31st Oct 01
Maint. 3–38
Maintenance Information: Horizon
macro
outdoor
CONTROLLED INTRODUCTION
68P02902W04-A
Krone block replacement
Introduction to
Krone block
replacement
This procedure describes how to remove and replace a Krone block in
Horizon
macro
outdoor cabinet.
Two Krone blocks for external alarms and communications interfaces are
mounted on the top panel of the cabinet. Since they are an identical fit, the
following procedure describes how to replace either of them.
The Krone blocks can be replaced without interruption to normal operation of
the equipment, provided the associated customer alarms and communications
signal losses are accounted for.
Krone block
location
diagram
Figure 3-17 shows the location of the two Krone blocks on the top panel of a
Horizon
macro
outdoor cabinet.
KRONE BLOCK
KRONE BLOCK
Figure 3-17 Horizon
macro
outdoor cabinet top panel, showing the position of
the Krone blocks
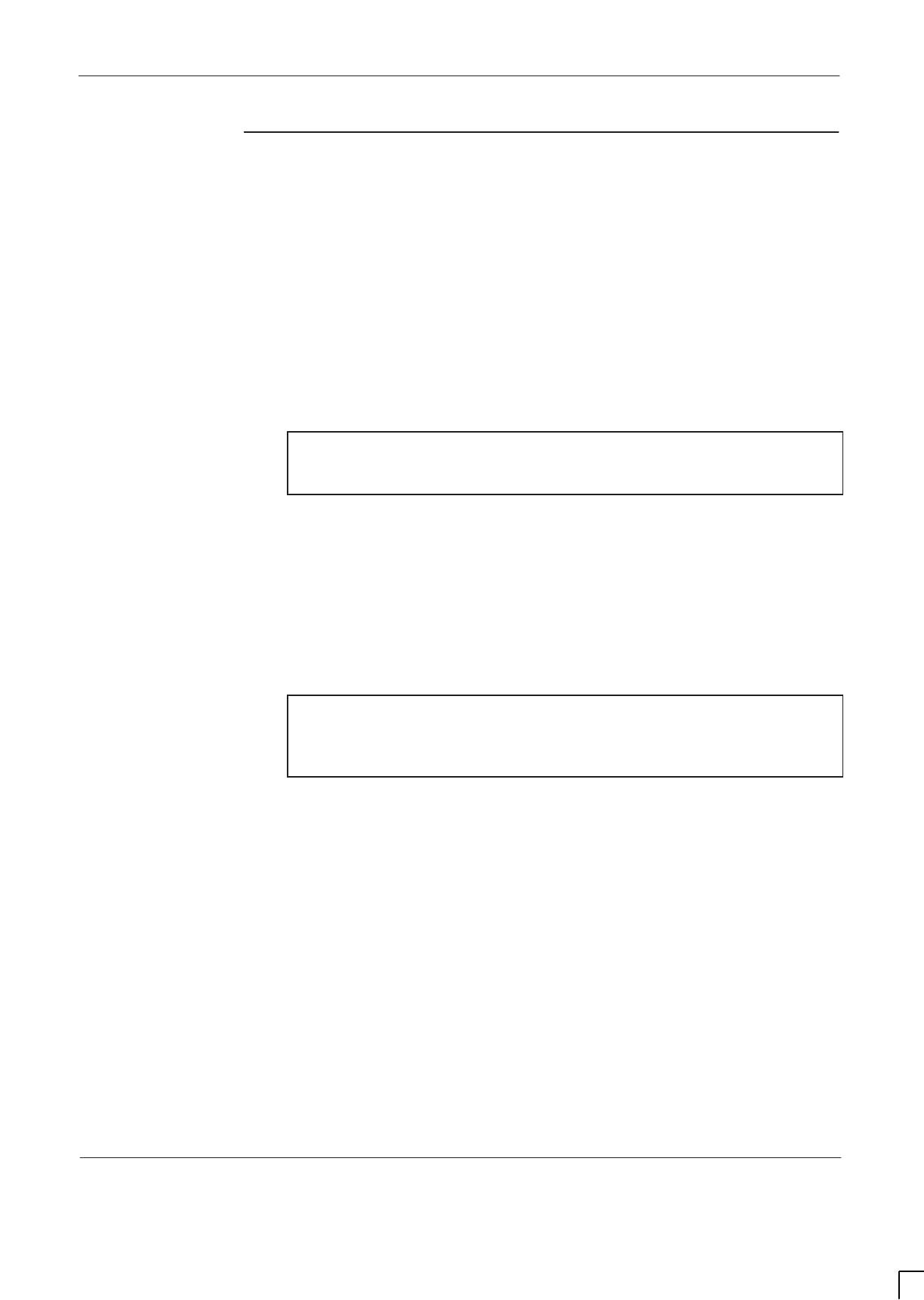
GSM-204-523 Krone block replacement
31st Oct 01
Maintenance Information: Horizon
macro
outdoor
68P02902W04-A
CONTROLLED INTRODUCTION
Maint. 3–39
Replacing a
Krone block
Removing a Krone block
To remove a Krone block:
1. Locate the Krone block to be replaced on the top panel and unscrew the
two 4 mm captive screws at diagonal corners of the block. Remove the
cover.
2. Note the location of the wires into the terminal blocks and cut them using
insulated wire cutters.
3. Undo the two screws securing the 37-pin D-type connector and remove
the cable along with all other wiring from the block.
CAUTION Take care in the following steps when removing the Krone
block not to drop the nuts or plain washers down the
interior of the cabinet.
4. Using a T20 Torx driver, unscrew and remove the four M3 x 8 screws
securing the block to the bulkhead.
The procedure for removing the Krone block is now complete.
Installing a replacement Krone block
To install a replacement Krone block:
1. Repeat the removal procedures in reverse order.
NOTE When refitting the nuts and washers, tighten to a torque of
1.0 Nm using a 5.5 mm torque wrench.
Re-insert the disconnected wires to the positions noted in
the removal procedure using an insertion tool.
2. Check the Krone block connections.
3. Notify the OMC-R of the base station availability and log the maintenance
activity.
The procedure for installing a new Krone block is now complete.
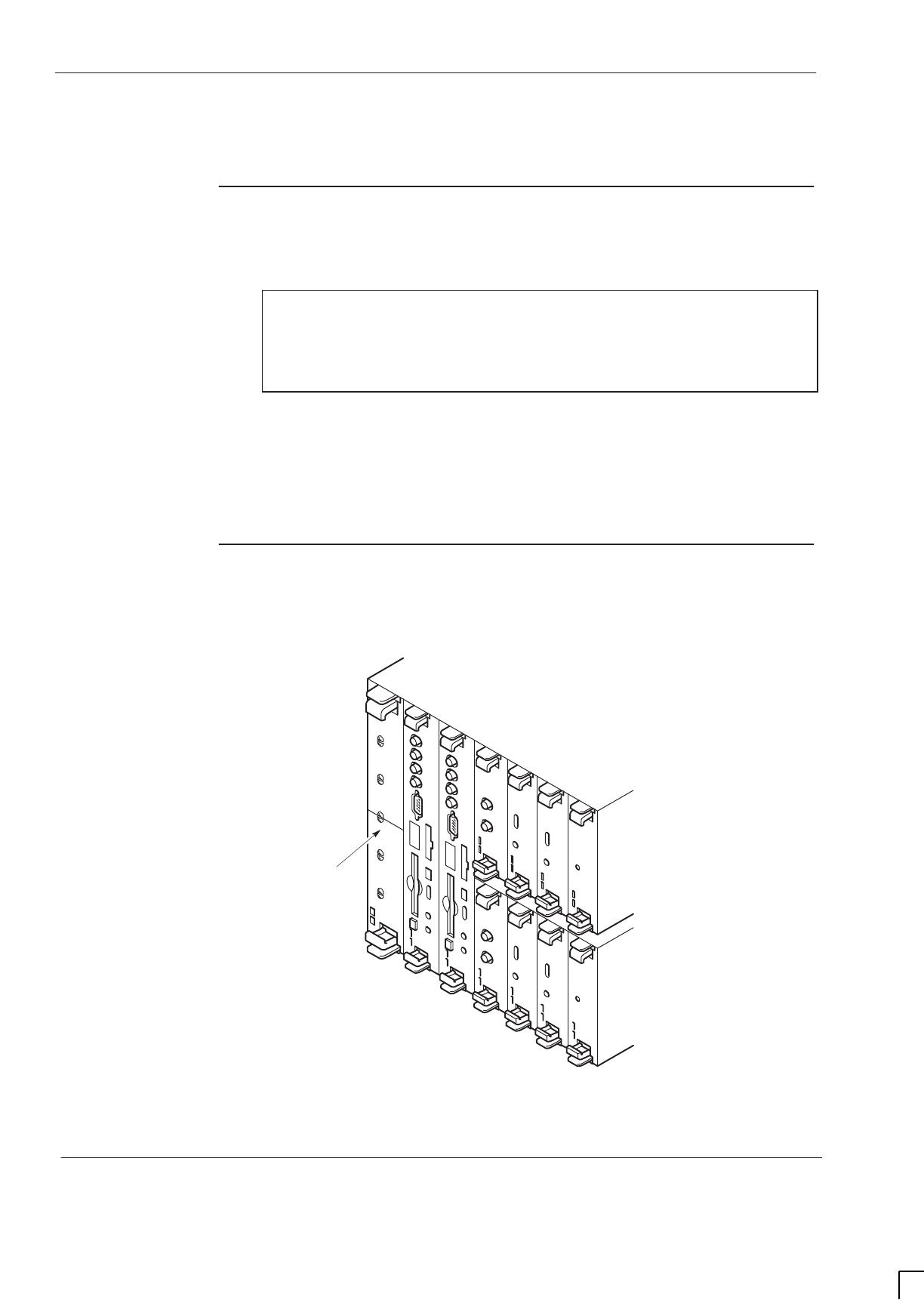
GSM-204-523
Digital module and BPSM replacement
31st Oct 01
Maint. 3–40
Maintenance Information: Horizon
macro
outdoor
CONTROLLED INTRODUCTION
68P02902W04-A
Digital module and BPSM replacement
Preconditions
for digital
module
replacement
CAUTION MCUF removal during flash memory programming may
result in boot code corruption. This is only repairable by
returning the MCUF to Motorola. For this reason, the
MCUF should not be removed while the code load is
taking place, indicated by a flashing LED.
A faulty master MCUF, FMUX or BPSM will enable a redundant module (if fitted)
to take over until the faulty module is replaced. Faulty MCUF, FMUX and BPSM
modules can be hot swapped without harm to the module or effect on normal
operation, provided the redundant module has taken over. Any faulty module
which has not had its function taken over by a redundant module will affect
service when removed. Inform the OMC-R before carrying out such procedures.
Digital module
location
diagram
Figure 3-18 shows the location of modules within the digital module shelf.
ig.322.rh
ALARM
MODULE
NIU B0
NIU B1
BPSM
BPSM
FMUX
FMUX
MCUF A
MCUF B
NIU A0
NIU A1
REDUNDANT (B)
MASTER (A)
DIGITAL
MODULE SHELF
Figure 3-18 Digital and BPSM module locations, including optional redundancy
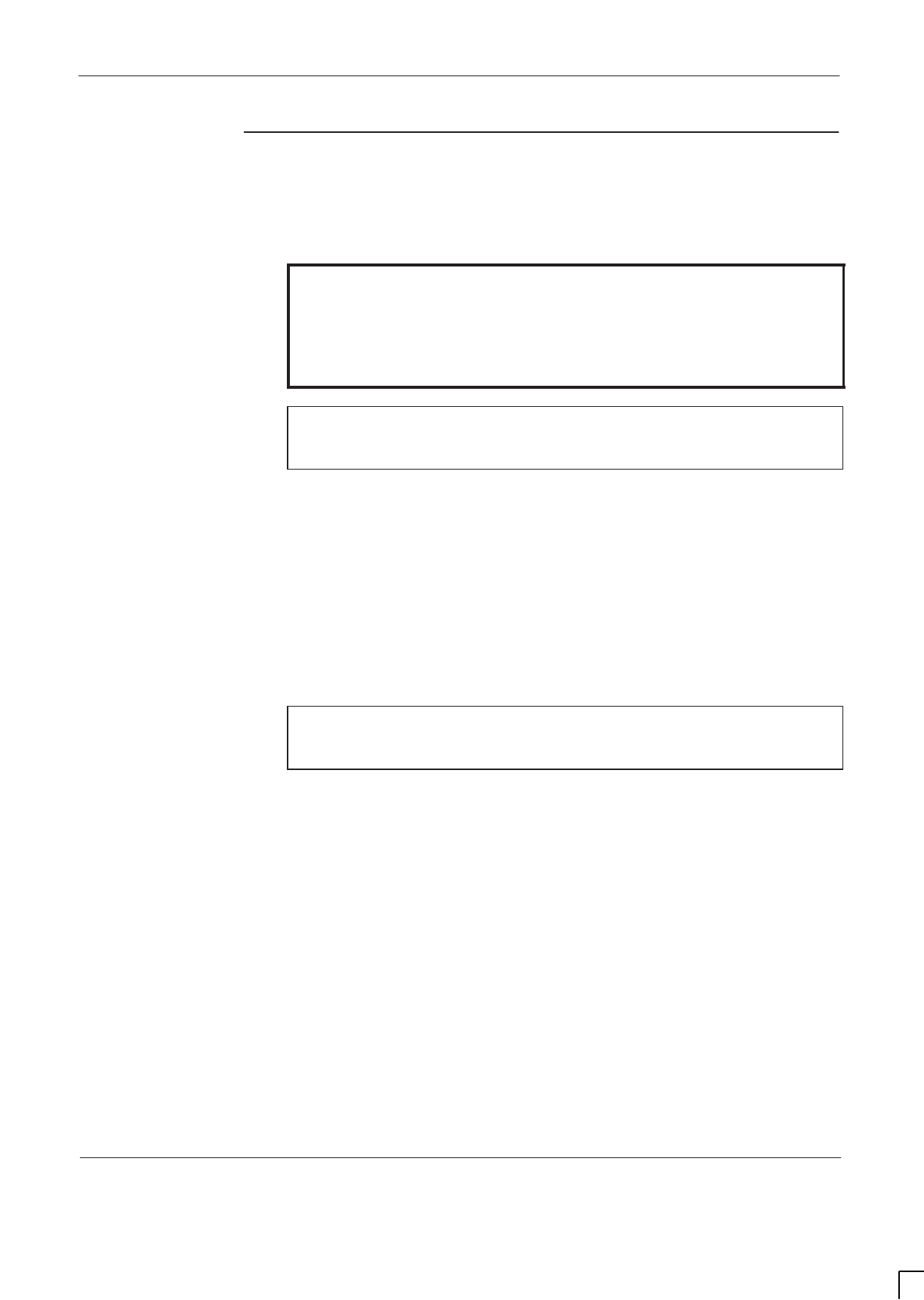
GSM-204-523 Digital module and BPSM replacement
31st Oct 01
Maintenance Information: Horizon
macro
outdoor
68P02902W04-A
CONTROLLED INTRODUCTION
Maint. 3–41
Replacing a
digital module
Removing a faulty digital module
To remove a digital module:
WARNING There is a possibility of laser radiation when fibre optic
cables are disconnected. Do not look directly into cables
with or without the use of any optical aids. Radiation can
come from either the data in/out connectors or
unterminated fibre optic cables connected to data in/out
connectors.
CAUTION An earthing wrist strap must be worn when handling digital
modules. An ESP earthing connection point is provided
above the leftmost PSM.
1. If the faulty digital module is still partially operating, due to no redundant
alternative module, inform the OMC-R before proceeding.
2. Locate the faulty module, as shown in Figure 3-18.
3. If an MCUF or FMUX module is being replaced, note any fibre optic cable
connections to the module, to enable correct reconnection to the
replacement module.
4. Disconnect each fibre optic cable by gently pushing the knurled connector
in and rotating it through a quarter-turn anti-clockwise to disengage, and
then carefully withdraw the cable.
NOTE It is advisable to protect the tips of the fibre optic cables
with a protective cover and then secure the cables to one
side.
5. Unseat the module by gripping the upper and lower pair of ejectors
between the thumb and first finger of each hand, then gently squeeze and
pull on the ejectors until the module unclips at the top and bottom of the
front panel and unplugs from the rear connector.
6. Carefully slide the module from its location and place it in an anti-static
storage container.
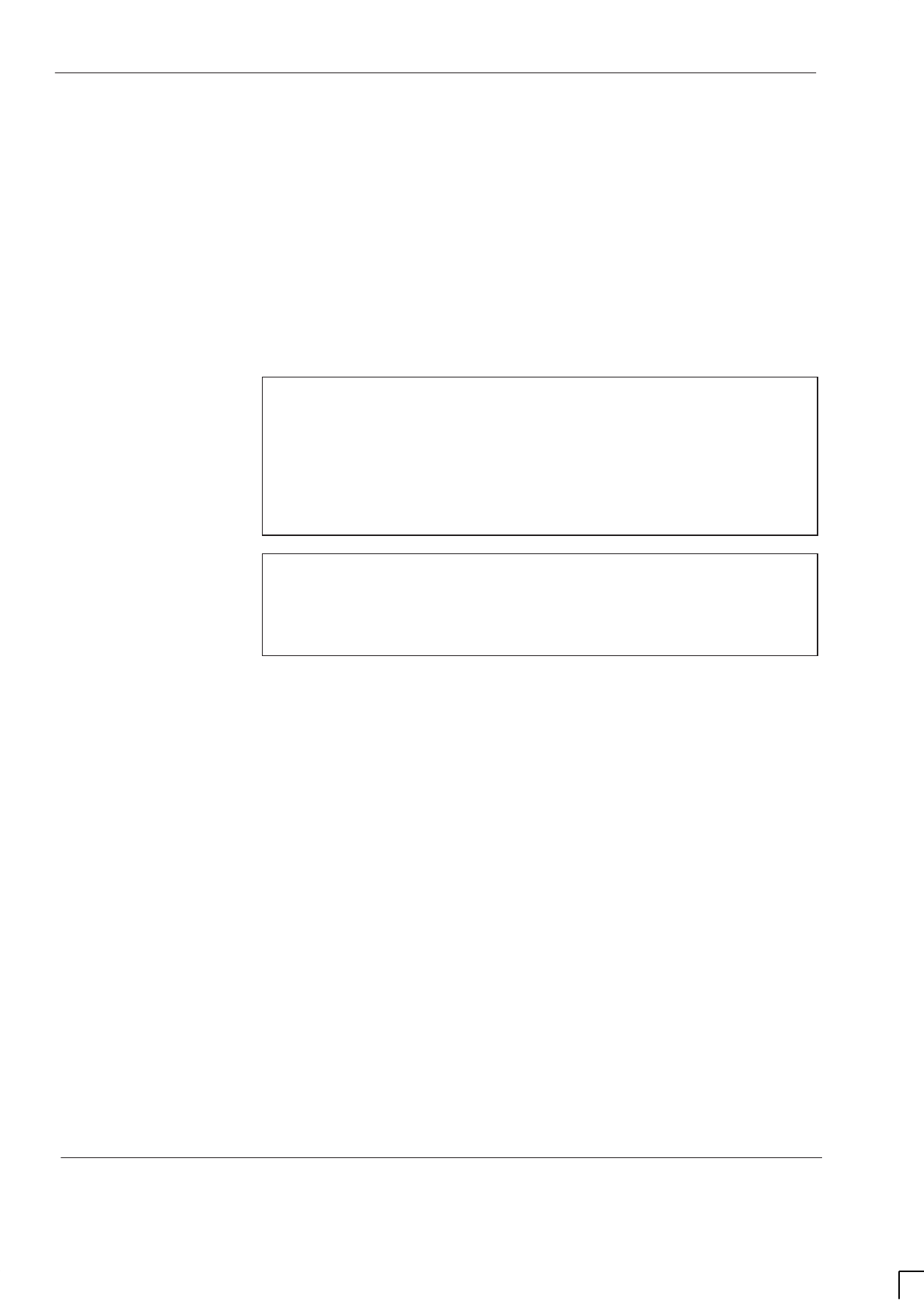
GSM-204-523
Digital module and BPSM replacement
31st Oct 01
Maint. 3–42
Maintenance Information: Horizon
macro
outdoor
CONTROLLED INTRODUCTION
68P02902W04-A
Fitting a replacement digital module
To install a replacement digital module:
1. Remove the replacement module from the anti-static storage container. In
the case of the NIU, ensure it is of the correct type (E1 or T1).
2. Slide the module into the guide rails and push firmly into place. The
ejectors will audibly click into place as confirmation of correct insertion.
3. Connect any fibre optic cables by inserting the connector and rotating a
quarter-turn clockwise to engage.
4. Ensure appropriate LEDs indicate correct operation.
CAUTION When the two LEDs of the MCUF, are flashing, the boot
code is downloading into non-volatile memory for software
upgrade. Power should not be removed, nor the cabinet
reset, until downloading has been completed, as this will
corrupt the non-volatile memory. If the boot code is
corrupted, contact the Motorola Customer Network
Resolution Centre, requesting the boot code restoration
procedure and the appropriate boot code file.
NOTE Following an NIU switch on or reboot, both red and green
LEDs are initially lit. After approximately 20 seconds, the
red LED will extinguish, indicating normal condition. This
waiting period may be extended to 50 seconds after
rebooting due to a code download.
5. When fitting a redundant MCUF refer to Redundant MCUF firmware
compatibility for details of further checks required.
6. Notify the OMC-R of base station availability and log the maintenance
activity.
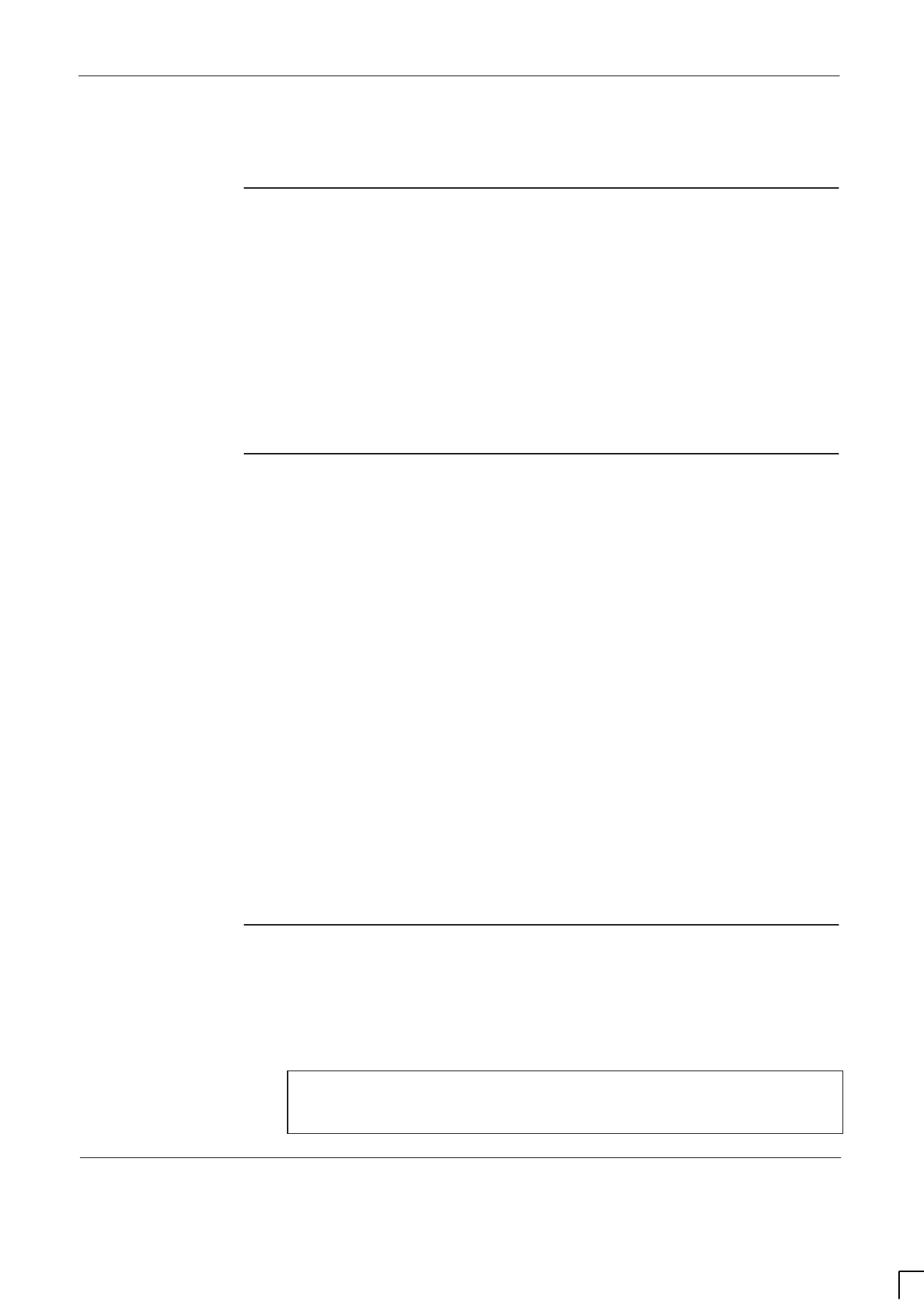
GSM-204-523 Redundant MCUF firmware compatibility
31st Oct 01
Maintenance Information: Horizon
macro
outdoor
68P02902W04-A
CONTROLLED INTRODUCTION
Maint. 3–43
Redundant MCUF firmware compatibility
Overview of
MCUF firmware
compatibility
In many installations a redundant MCUF is fitted and configured to assume
control in the event of a failure of the master MCUF. Under normal
circumstances, the redundant MCUF accepts code downloads from the master
MCUF and so remains updated and available for use.
If the redundant MCUF is replaced with a module containing firmware which is
incompatible with the master MCUF firmware, then the communicating link
between MCUFs will not be established. The redundant MCUF will therefore not
be updated and will not be available to take over when required.
Checking MCUF
firmware
compatibility
To check firmware compatibility between MCUFs, check the state of the base
transceiver processor (BTP) within each MCUF as follows:
1. Connect a PC to the TTY connection on the master MCUF.
2. At the CUST MMI prompt, enter:
state <site #> btp * *
Where <site #> is the site number.
The status of both BTPs will be displayed as follows:
BTP 0 0 0 B–U NO REASON
BTP 1 0 0 E–U NO REASON
or,
BTP 0 0 0 B–U NO REASON
BTP 1 0 0 D–U No Redundant Link
If No Redundant Link is indicated then the master MCUF is not in communication
with the redundant MCUF and firmware incompatibility may be assumed. Refer
to Updating redundant MCUF firmware.
Updating
redundant
MCUF firmware
The following procedure to update firmware in the redundant MCUF requires a
PCMCIA card containing current network configuration data. The procedure
assumes that the PCMCIA card is already in the master MCUF.
NOTE No call processing can take place during the MCUF
firmware update process. The entire process should take
approximately one hour.
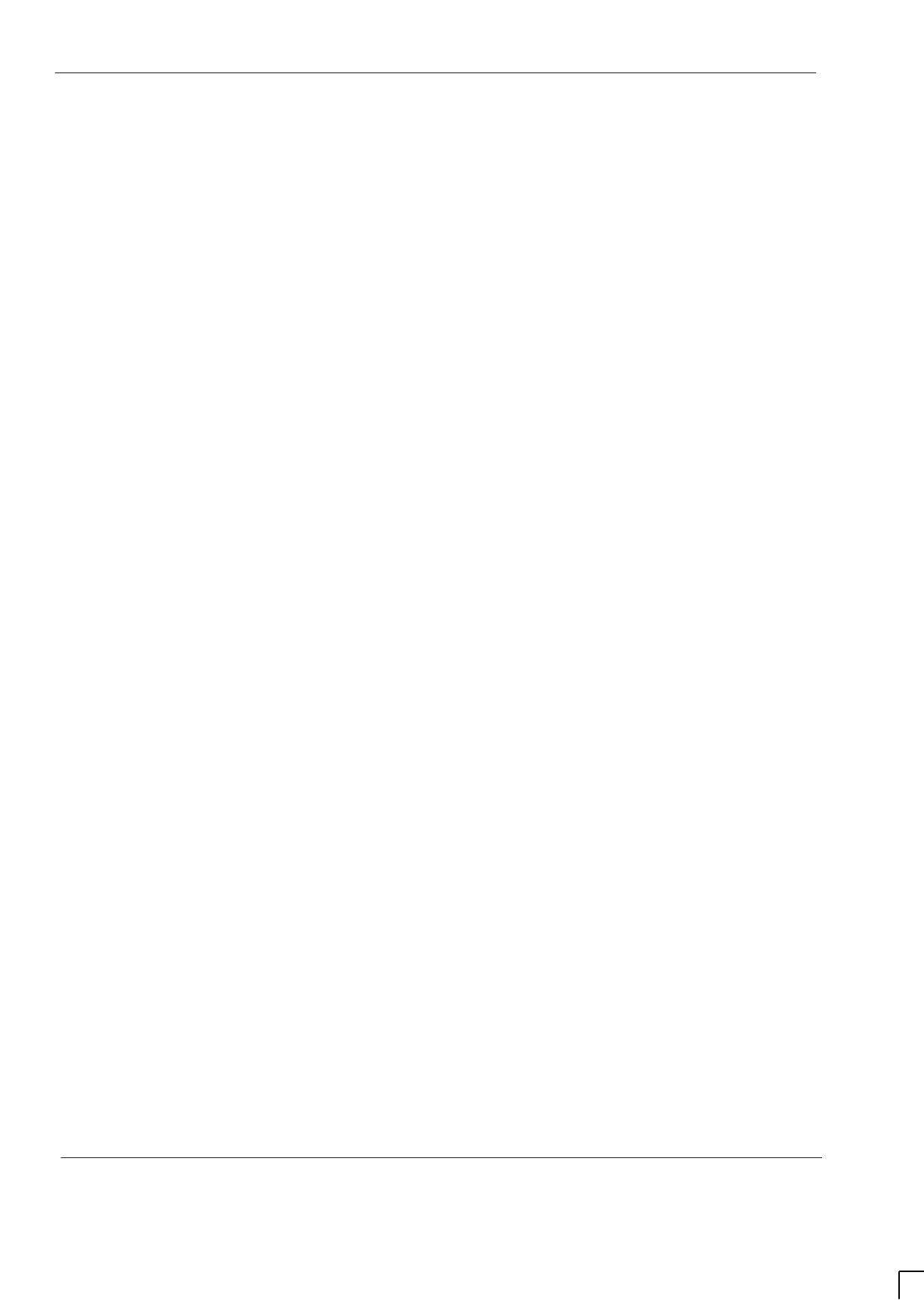
GSM-204-523
Redundant MCUF firmware compatibility
31st Oct 01
Maint. 3–44
Maintenance Information: Horizon
macro
outdoor
CONTROLLED INTRODUCTION
68P02902W04-A
Site preparation
To prepare for the firmware update the site must first be taken out-of-service as
follows:
1. Connect a PC to the TTY connection on the master MCUF.
2. At the CUST MMI prompt, disable all CTUs in turn by typing:
shutdown_device <site #> dri * * * <seconds>
Where <site #> is the site number, * * * is the DRI identifier and <seconds> is
the time delay before shutdown occurs.
3. Confirm this action by observing each CTU Tx status LED, which should
extinguish shortly after issuing the shutdown command.
4. Disconnect the 2.048 Mbit/s link
Redundant MCUF firmware update procedure
The following procedure shows how to update redundant MCUF firmware by
placing the redundant MCUF into the master position and downloading code
from a PCMCIA card.
1. Remove the uploaded PCMCIA card from the master MCUF, and ensure
that write protect is switched to OFF.
2. Remove both MCUFs. Insert the PCMCIA card into the original redundant
MCUF then insert this MCUF into the master position.
3. Connect a PC to the TTY connection on the MCUF front panel.
4. At the MMI-ROM prompt, type:
burn
This will flash object 8, the MCUF boot object, from the PCMCIA card onto the
MCUF card. The flash download takes approximately 30 seconds, then the
MCUF will reset.
5. At the MMI ROM prompt, type:
set_site <site #>
Where <site #> is the site number.
The MCUF now carries out a system initialization using data from the PCMCIA
card. After a short wait the screen displays:
Initialization complete. All commands accepted.
The MCUF firmware update is complete and both MCUFs now hold identical
firmware. The MCUF originally removed from the master position may now be
used in the redundant position.
6. Insert the original master MCUF into the redundant position.
The redundant MCUF now requires a 15 minute sync warm up period, followed
by a further delay of four minutes while the two MCUFs achieve phase lock.
Once phase lock is achieved the master MCUF immediately begins codeloading
to the redundant MCUF. Codeloading takes a further 15 minutes.
The process is complete when the following message is displayed on screen:
Redundant MSW is INS
<*><*><*> NEW STANDBY Switch CONFIGURED <*><*><*>
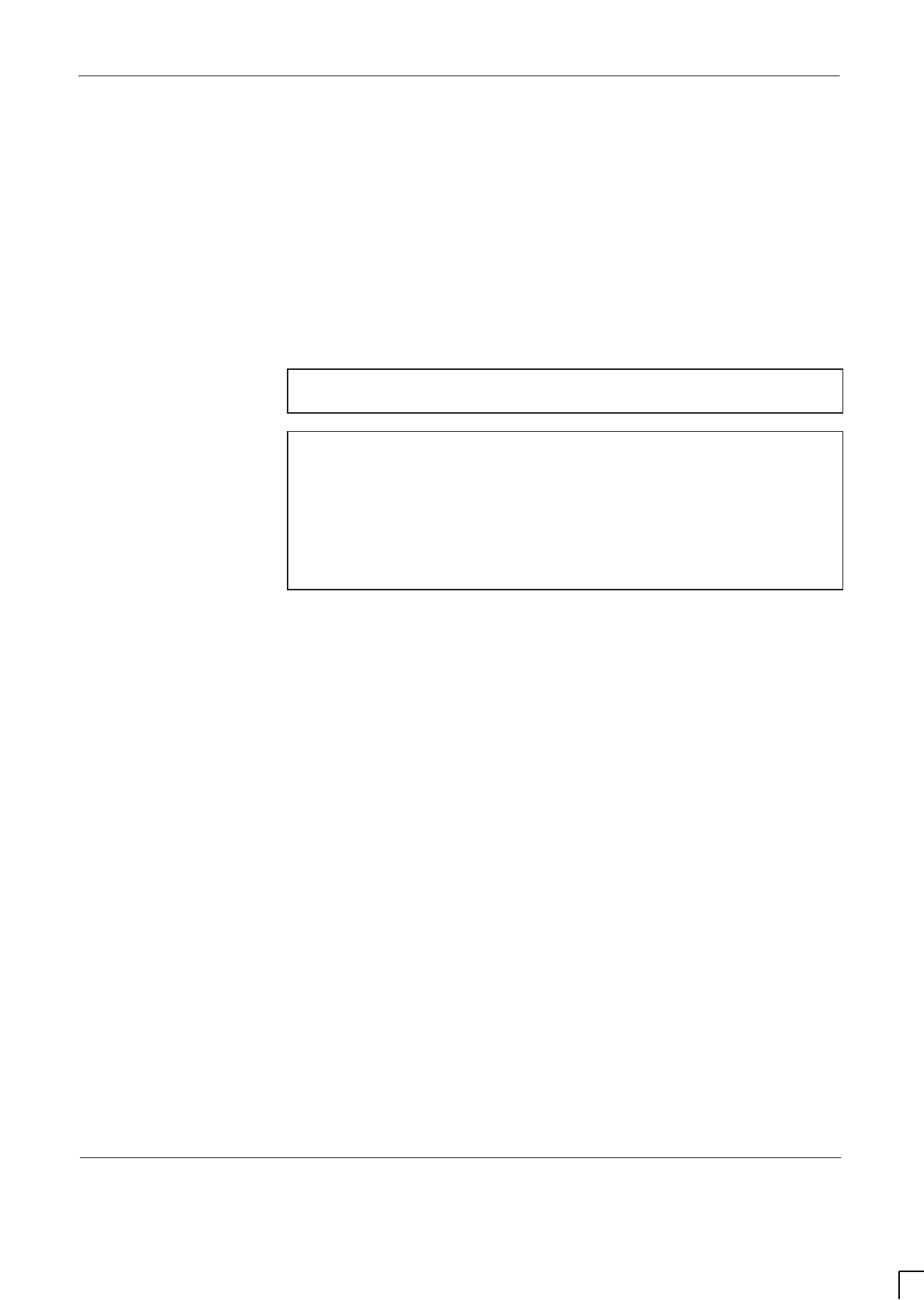
GSM-204-523 Redundant MCUF firmware compatibility
31st Oct 01
Maintenance Information: Horizon
macro
outdoor
68P02902W04-A
CONTROLLED INTRODUCTION
Maint. 3–45
7. To confirm correct MCUF status, at the CUST MMI prompt, enter:
state <site #> btp * *
Where <site #> is the site number.
The status of both BTPs will be displayed as follows:
BTP 0 0 0 B–U NO REASON
BTP 1 0 0 E–U NO REASON
Where B–U is busy unlocked (master) and E-U is enabled unlocked (redundant).
8. Reconnect the 2.048 Mbit/s link.
NOTE There is no need to unlock the CTUs as these are
automatically unlocked during the initialization procedure.
NOTE If a PCMCIA card is not available then the firmware in the
redundant MCUF may be updated by removing the master
MCUF and placing the redundant MCUF in the master
position. Code download from the BSC will ensure the
newly installed MCUF is fully updated. This procedure
however is likely to take up to 30 minutes longer than the
procedure involving a PCMCIA card, resulting in a longer
out of service time for the BTS.
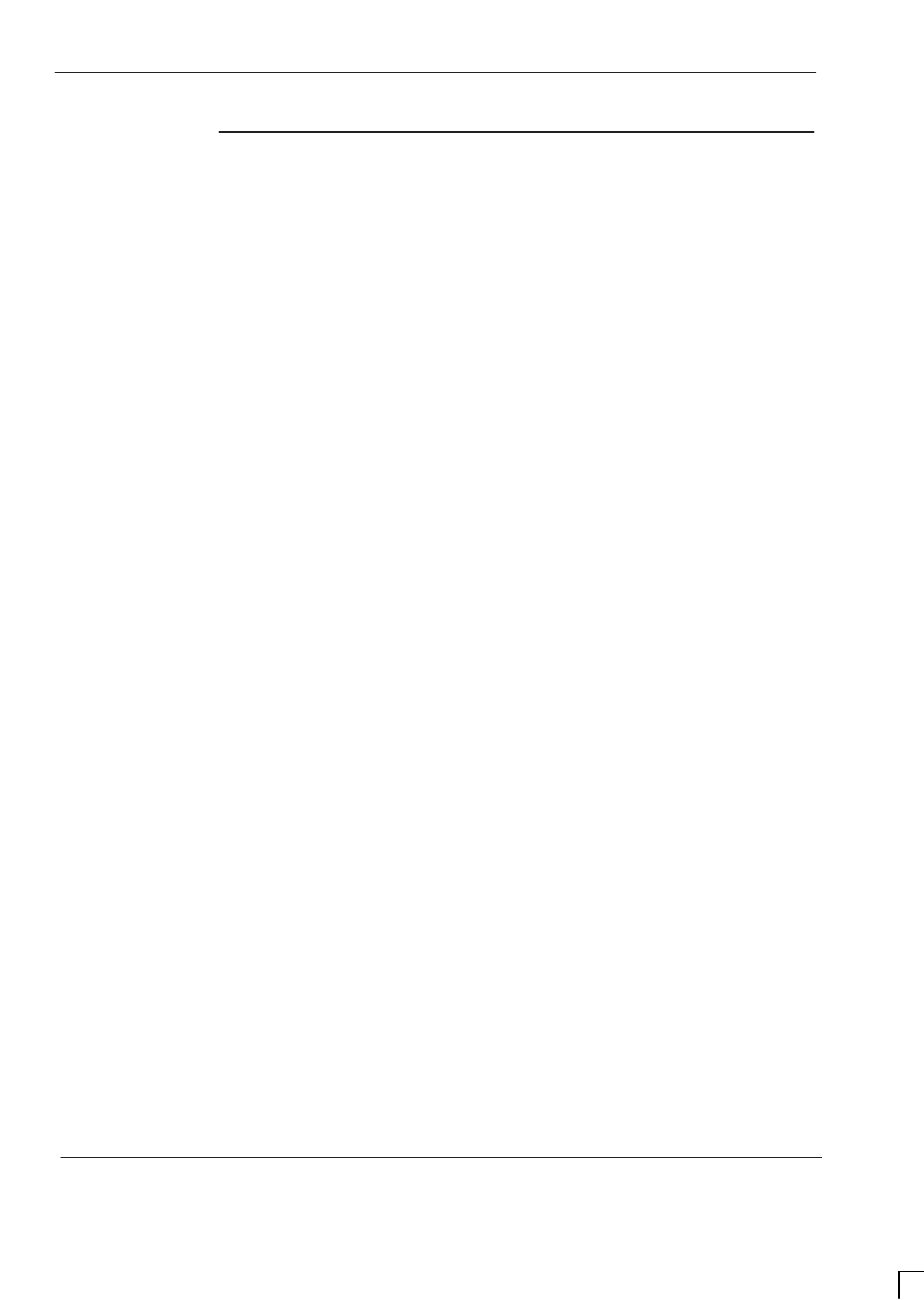
GSM-204-523
Redundant MCUF firmware compatibility
31st Oct 01
Maint. 3–46
Maintenance Information: Horizon
macro
outdoor
CONTROLLED INTRODUCTION
68P02902W04-A
Testing MCUF
redundancy
The following procedure tests MCUF redundancy by forcing the master and
redundant MCUFs to swap roles. The commands refer to the base transceiver
processors (BTPs) within each MCUF.
1. Connect a PC to the TTY connection on the master MCUF.
2. At the CUST MMI prompt, type:
state <site #> btp * *
Where <site #> is the site number.
The status of both BTPs will be displayed as follows:
BTP 0 0 0 B–U NO REASON
BTP 1 0 0 E–U NO REASON
Where B–U is busy unlocked (master) and E-U is enabled unlocked (redundant).
3. At the CUST MMI prompt type:
swap_devices <site #> btp 0 0 0 btp 1 0 0
Where <site #> is the site number, btp 0 0 0 is the master MCUF and btp 1 0 0
is the redundant MCUF.
This command will swap MCUF roles by forcing:
the redundant MCUF into a busy state , and making it master.
the master MCUF into an enabled state, and making it redundant.
4. At the CUST MMI prompt, confirm the swap by typing:
state <site #> btp * *
Where <site #> is the site number.
The status of both BTPs will now show changed roles:
BTP 0 0 0 E–U NO REASON
BTP 1 0 0 B–U NO REASON
5. Make test calls on the site to verify the new master MCUF.
6. At the CUST MMI prompt type, swap the MCUFs back to their original
states by typing:
swap_devices <site #> btp 1 0 0 btp 0 0 0
Where <site #> is the site number, btp 1 0 0 is the master MCUF and btp 0 0 0
is the redundant MCUF.
7. At the CUST MMI prompt, confirm the swap by typing:
state <site #> btp * *
Where <site #> is the site number.
Both BTPs have now reverted to their original roles:
BTP 0 0 0 B–U NO REASON
BTP 1 0 0 E–U NO REASON
8. Make test calls on the site to verify the new master MCUF.
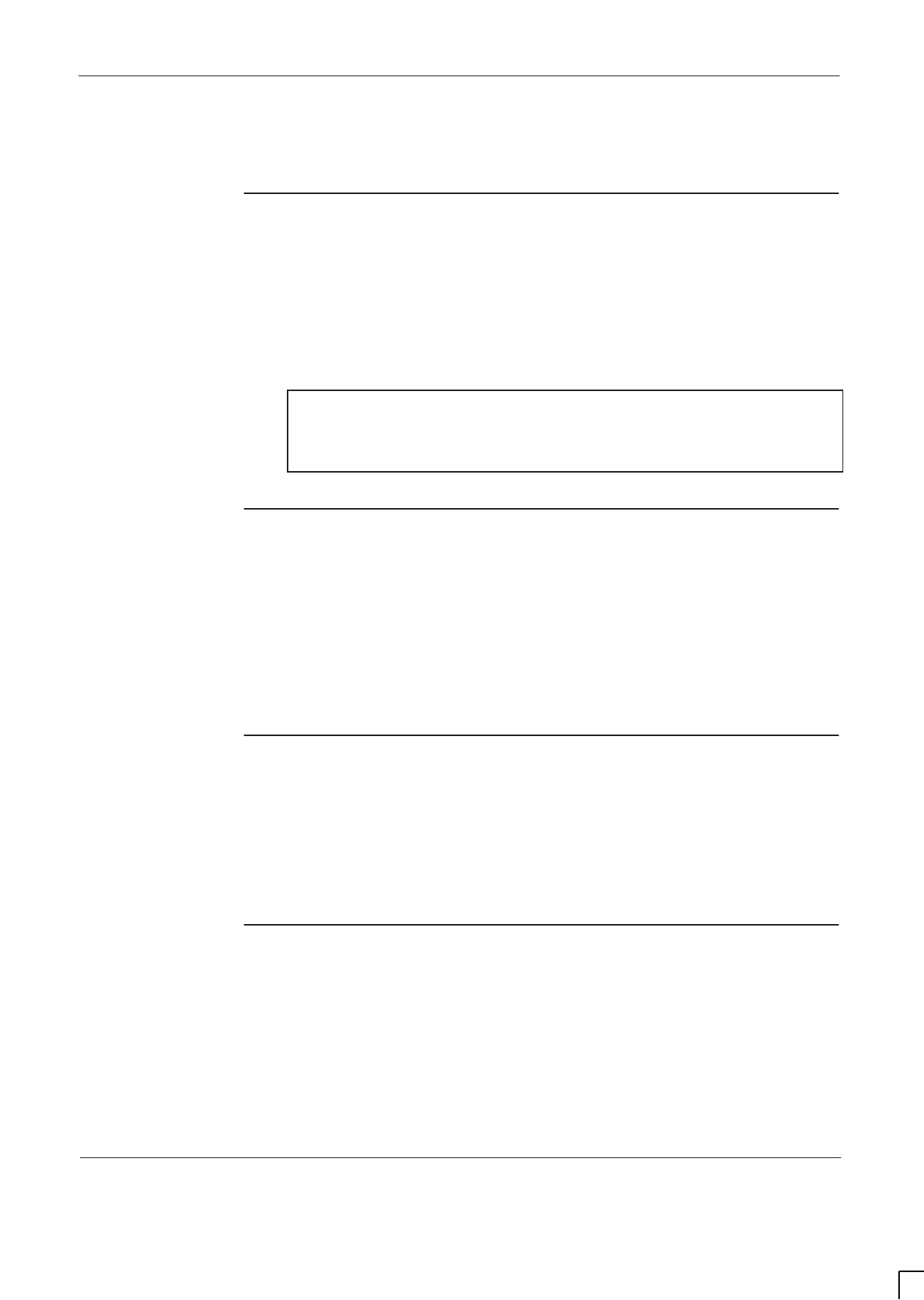
GSM-204-523 Additional replacement parts
31st Oct 01
Maintenance Information: Horizon
macro
outdoor
68P02902W04-A
CONTROLLED INTRODUCTION
Maint. 3–47
Additional replacement parts
Policy on
non-FRU parts
Non-FRU parts are:
Items unlikely to fail, but replacement of which is essential if failure occurs.
or
Subunits of FRUs, where local conditions may make it more economical to
repair the FRU.
CAUTION Only qualified personnel should attempt non-FRU
replacement, in order to minimize risk of equipment
damage. For example, the CBIA main cage requires care
in removal and installation.
List of non-FRU
parts
Non-FRU parts include the following:
Door lock.
Any part of CBIA: main cage, harness, interface panel, backplane.
The PSU cage.
The cabinet.
Procedure for
replacing
non-FRU parts
Customers requiring non-FRU replacement should:
1. Contact the local Motorola office for availability.
2. Seek advice from Motorola for fitting non-FRU parts.
CBIA
attachment
screws
The CBIA is attached to the cabinet by screws which should not be loosened:
Seven M4 screws to the SURF harness (two guide pins lock the cage into
position).
Four M6 (left side) and five M6 (right side) screws at the cabinet front.
Eight M6 T30 screws for interface panel attachment to the top panel.
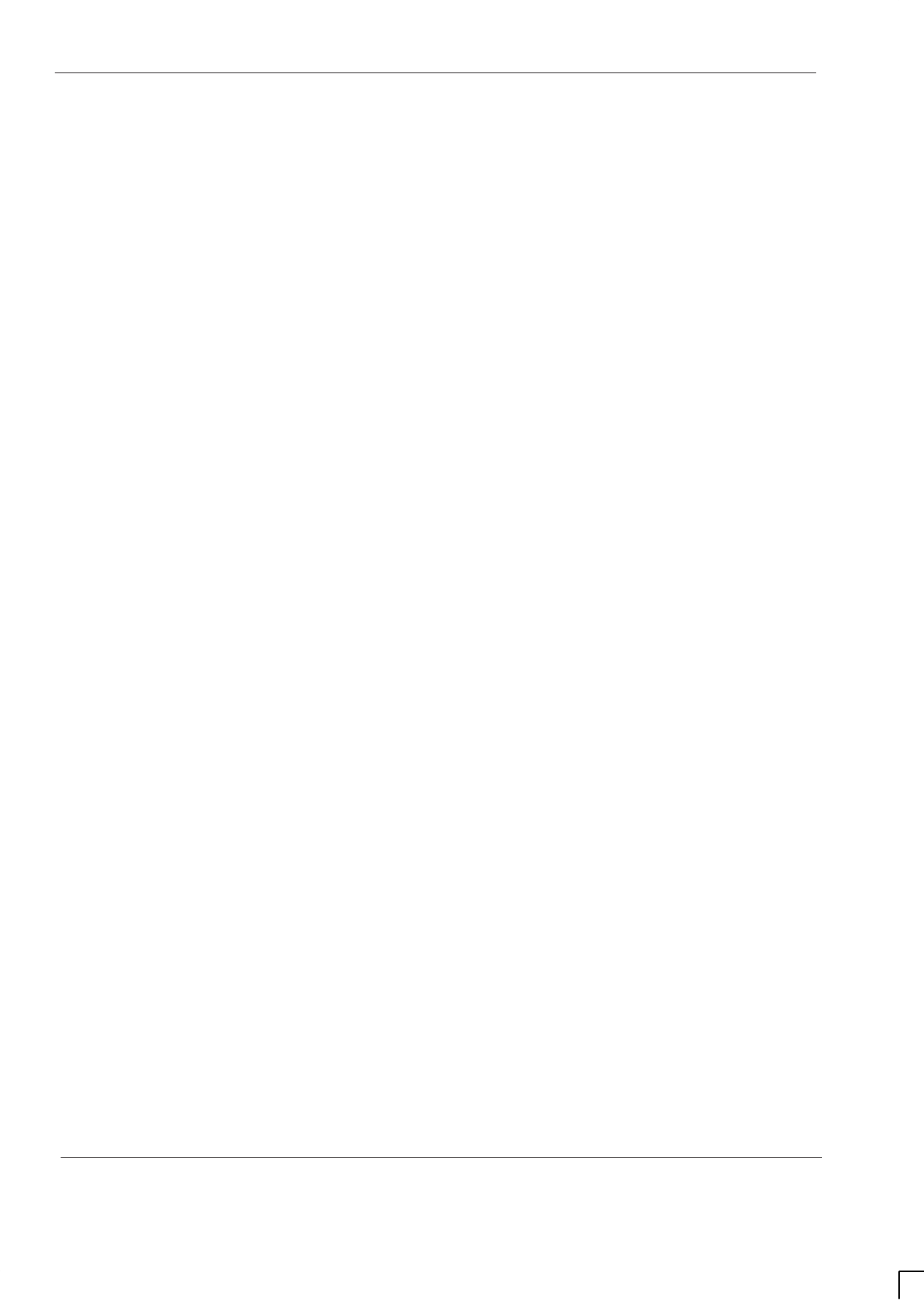
GSM-204-523
Additional replacement parts
31st Oct 01
Maint. 3–48
Maintenance Information: Horizon
macro
outdoor
CONTROLLED INTRODUCTION
68P02902W04-A
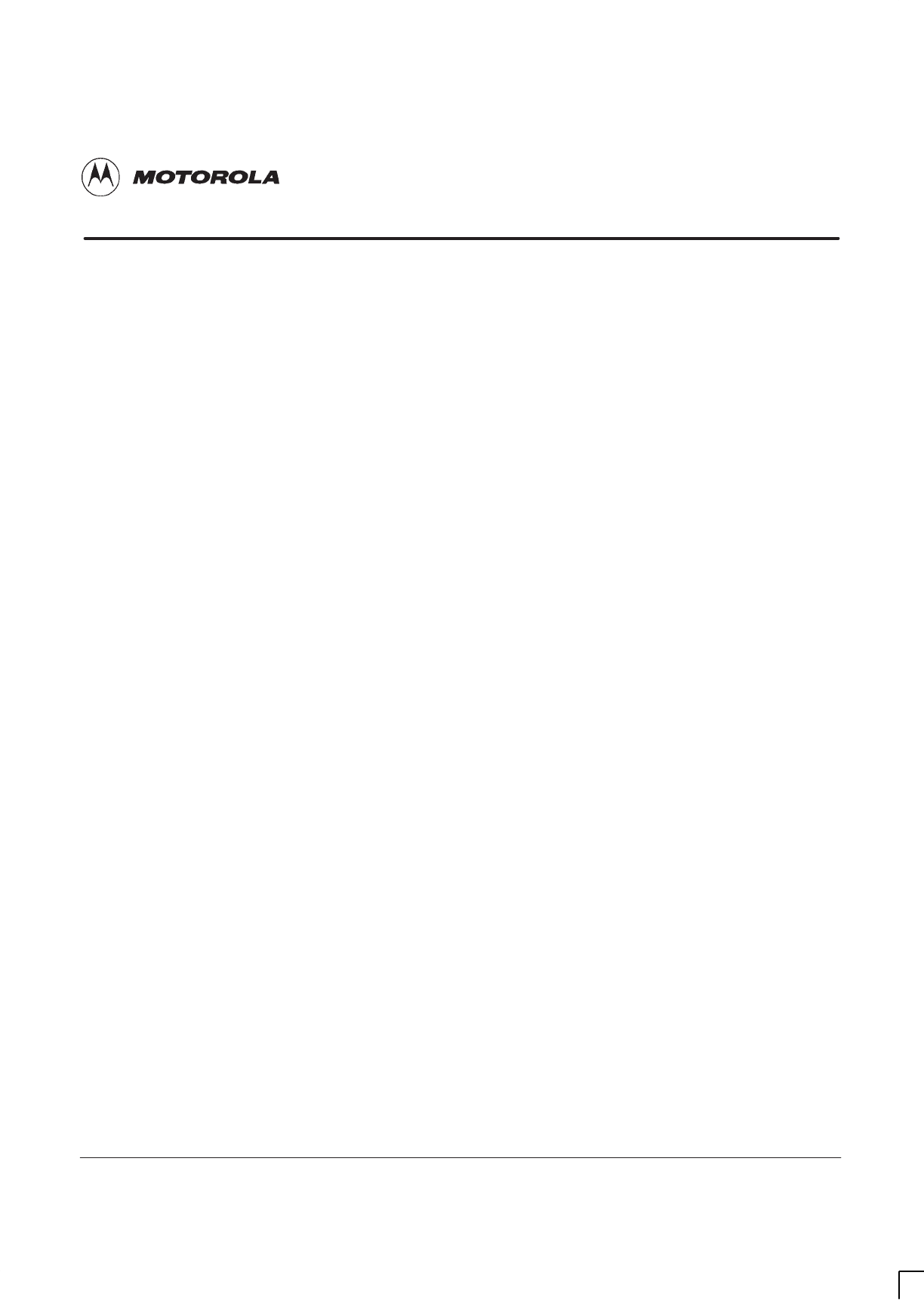
31st Oct 01
Maintenance Information: Horizon
macro
outdoor
68P02902W04-A
CONTROLLED INTRODUCTION
i
Chapter 4
Auxiliary equipment housing
maintenance
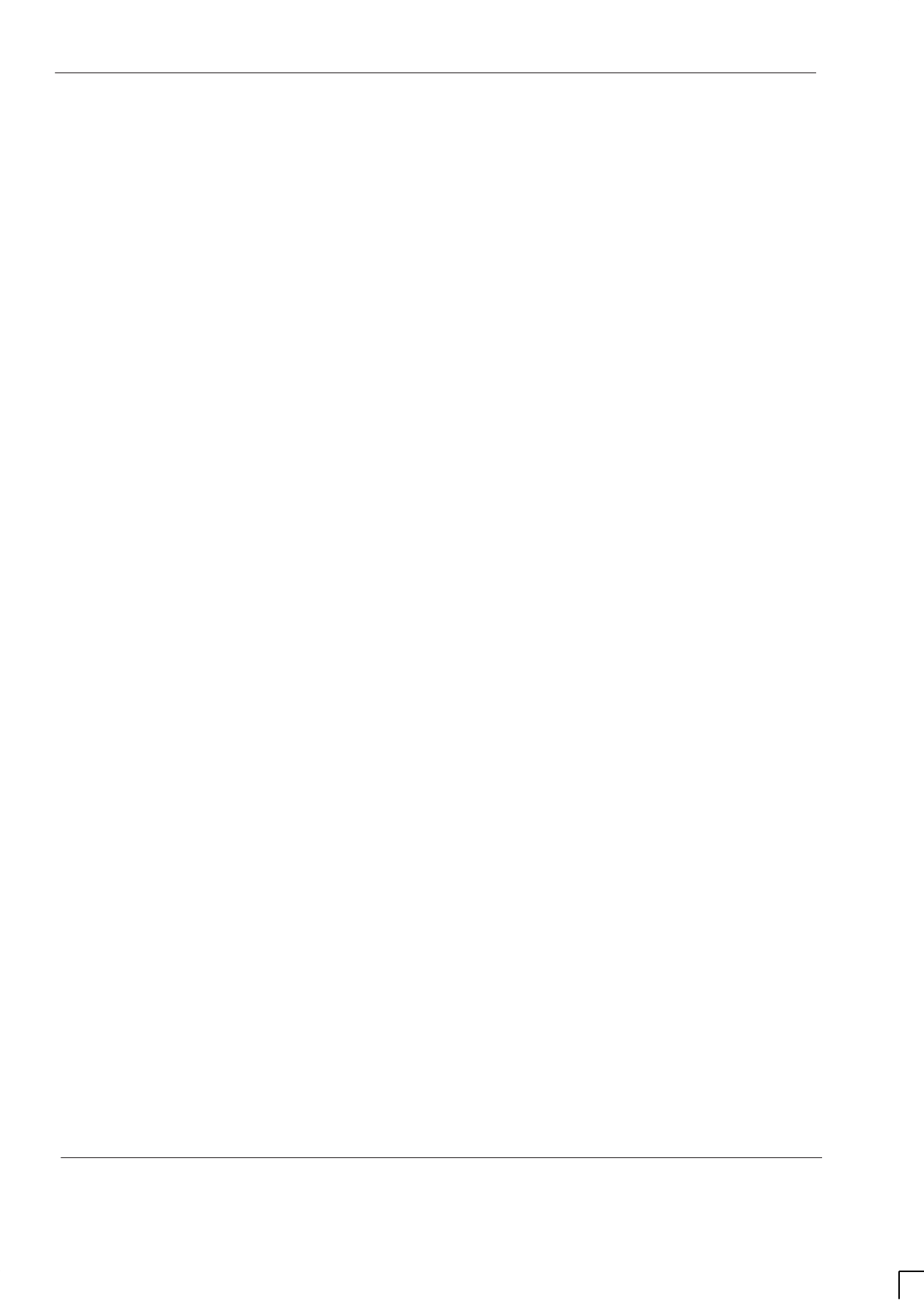
GSM-204-523
31st Oct 01
ii
Maintenance Information: Horizon
macro
outdoor
CONTROLLED INTRODUCTION
68P02902W04-A
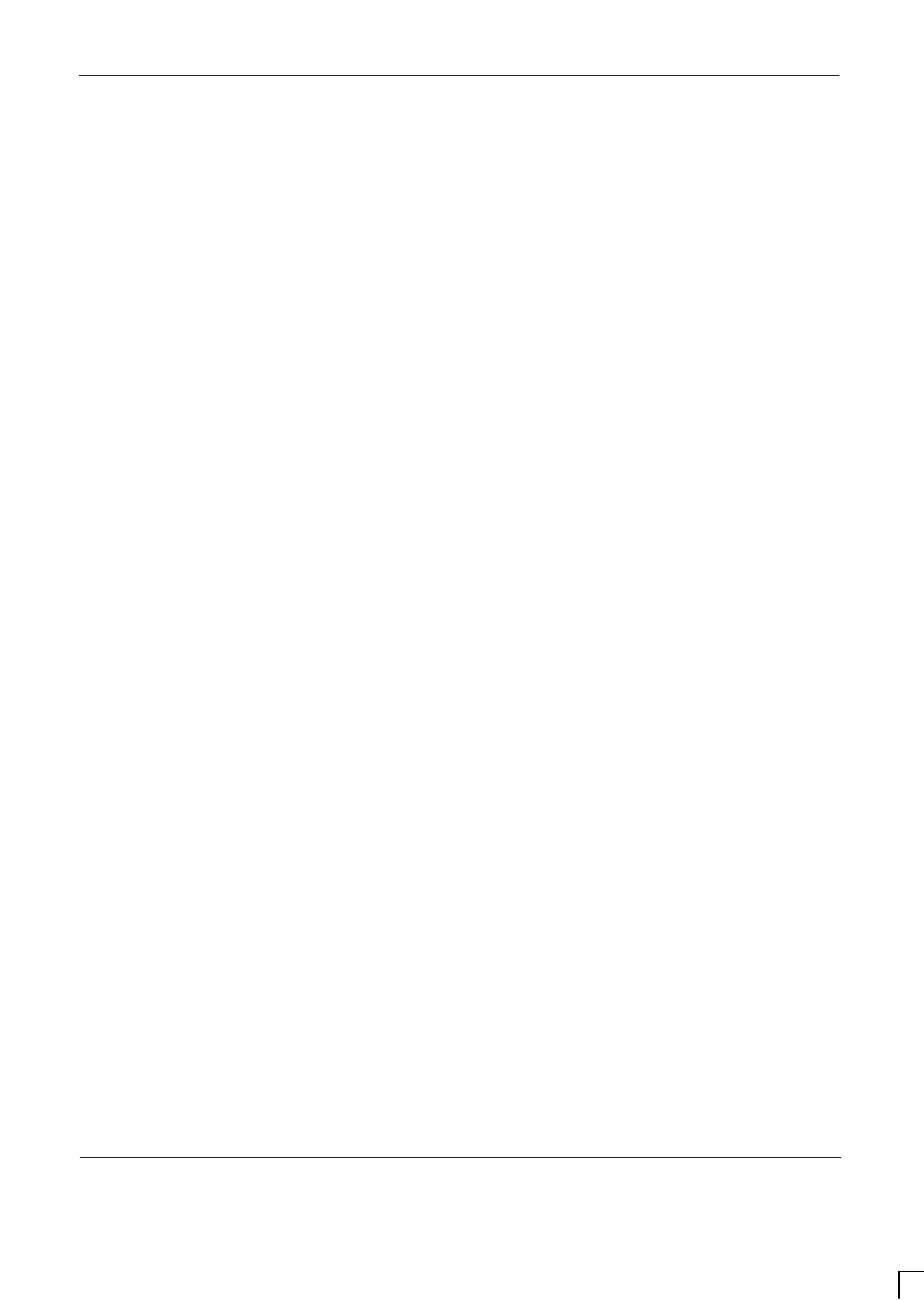
GSM-204-523
31st Oct 01
Maintenance Information: Horizon
macro
outdoor
68P02902W04-A
CONTROLLED INTRODUCTION
iii
Chapter 4
Auxiliary equipment housing maintenance i. . . . . . . . . . . . . . . . . . . . . .
Introduction to auxiliary equipment housing maintenance Maint. 4–1. . . . . . . . . . . . . . . . .
Auxiliary equipment housing FRUs Maint. 4–1. . . . . . . . . . . . . . . . . . . . . . . . . . . . . . . .
Auxiliary equipment housing FRU view Maint. 4–2. . . . . . . . . . . . . . . . . . . . . . . . . . . .
Replacing the power distribution box Maint. 4–3. . . . . . . . . . . . . . . . . . . . . . . . . . . . . . . . . . .
Introduction to power distribution box replacement Maint. 4–3. . . . . . . . . . . . . . . . . .
Removing the power distribution box Maint. 4–3. . . . . . . . . . . . . . . . . . . . . . . . . . . . . .
Fitting a replacement power distribution box Maint. 4–4. . . . . . . . . . . . . . . . . . . . . . . .
Replacing the lid on the auxiliary equipment housing Maint. 4–5. . . . . . . . . . . . . . . . . . . . .
Detailed view of the cabinet lid Maint. 4–5. . . . . . . . . . . . . . . . . . . . . . . . . . . . . . . . . . .
Removing the lid Maint. 4–6. . . . . . . . . . . . . . . . . . . . . . . . . . . . . . . . . . . . . . . . . . . . . . . .
Fitting a new lid Maint. 4–7. . . . . . . . . . . . . . . . . . . . . . . . . . . . . . . . . . . . . . . . . . . . . . . . .
Replacing the door on the auxiliary equipment housing Maint. 4–8. . . . . . . . . . . . . . . . . . .
Removing the cabinet door Maint. 4–8. . . . . . . . . . . . . . . . . . . . . . . . . . . . . . . . . . . . . . .
Fitting a replacement door Maint. 4–8. . . . . . . . . . . . . . . . . . . . . . . . . . . . . . . . . . . . . . .
Replacing the front panel or fan Maint. 4–9. . . . . . . . . . . . . . . . . . . . . . . . . . . . . . . . . . . . . . . .
Replacing the front panel Maint. 4–9. . . . . . . . . . . . . . . . . . . . . . . . . . . . . . . . . . . . . . . .
Replacing the fan Maint. 4–10. . . . . . . . . . . . . . . . . . . . . . . . . . . . . . . . . . . . . . . . . . . . . . .
Replacing a heater mat Maint. 4–11. . . . . . . . . . . . . . . . . . . . . . . . . . . . . . . . . . . . . . . . . . . . . . .
Introduction to heater mat replacement Maint. 4–11. . . . . . . . . . . . . . . . . . . . . . . . . . . .
Heater mat replacement procedure Maint. 4–11. . . . . . . . . . . . . . . . . . . . . . . . . . . . . . .
Replacing an environmental seal on the housing Maint. 4–12. . . . . . . . . . . . . . . . . . . . . . . . .
Introduction to replacing a seal Maint. 4–12. . . . . . . . . . . . . . . . . . . . . . . . . . . . . . . . . . .
Replacing the lid environmental seal Maint. 4–12. . . . . . . . . . . . . . . . . . . . . . . . . . . . . .
Replacing the door environmental seal Maint. 4–12. . . . . . . . . . . . . . . . . . . . . . . . . . . .
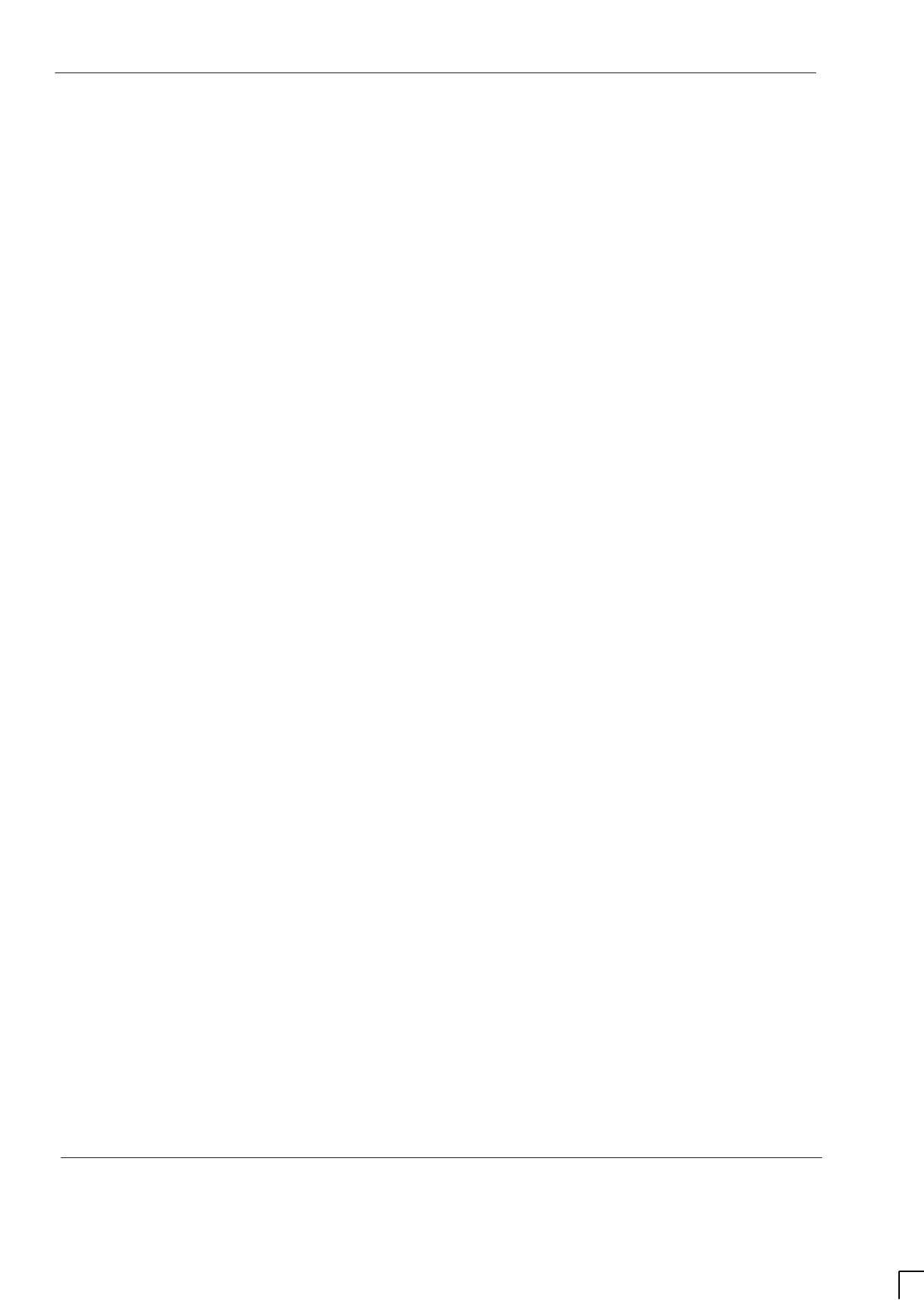
GSM-204-523
31st Oct 01
iv
Maintenance Information: Horizon
macro
outdoor
CONTROLLED INTRODUCTION
68P02902W04-A
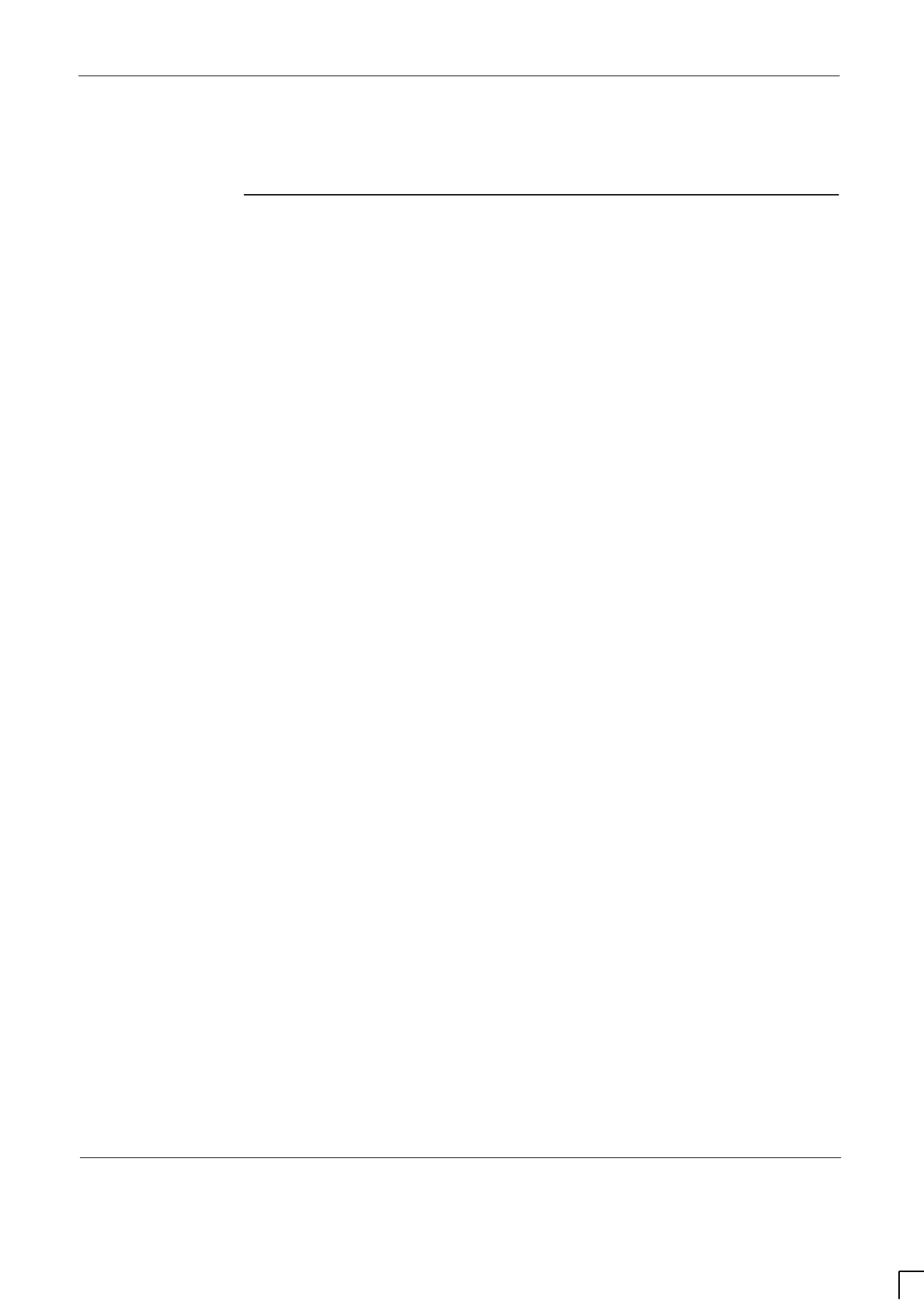
GSM-204-523 Introduction to auxiliary equipment housing maintenance
31st Oct 01
Maintenance Information: Horizon
macro
outdoor
68P02902W04-A
CONTROLLED INTRODUCTION
Maint. 4–1
Introduction to auxiliary equipment housing maintenance
Auxiliary
equipment
housing FRUs
The following items are considered as field replaceable units within the auxiliary
equipment housing (AEH):
Power distribution box.
Cabinet lid.
Cabinet door.
Front panel.
Fan.
Heater mats.
Environmental seals.
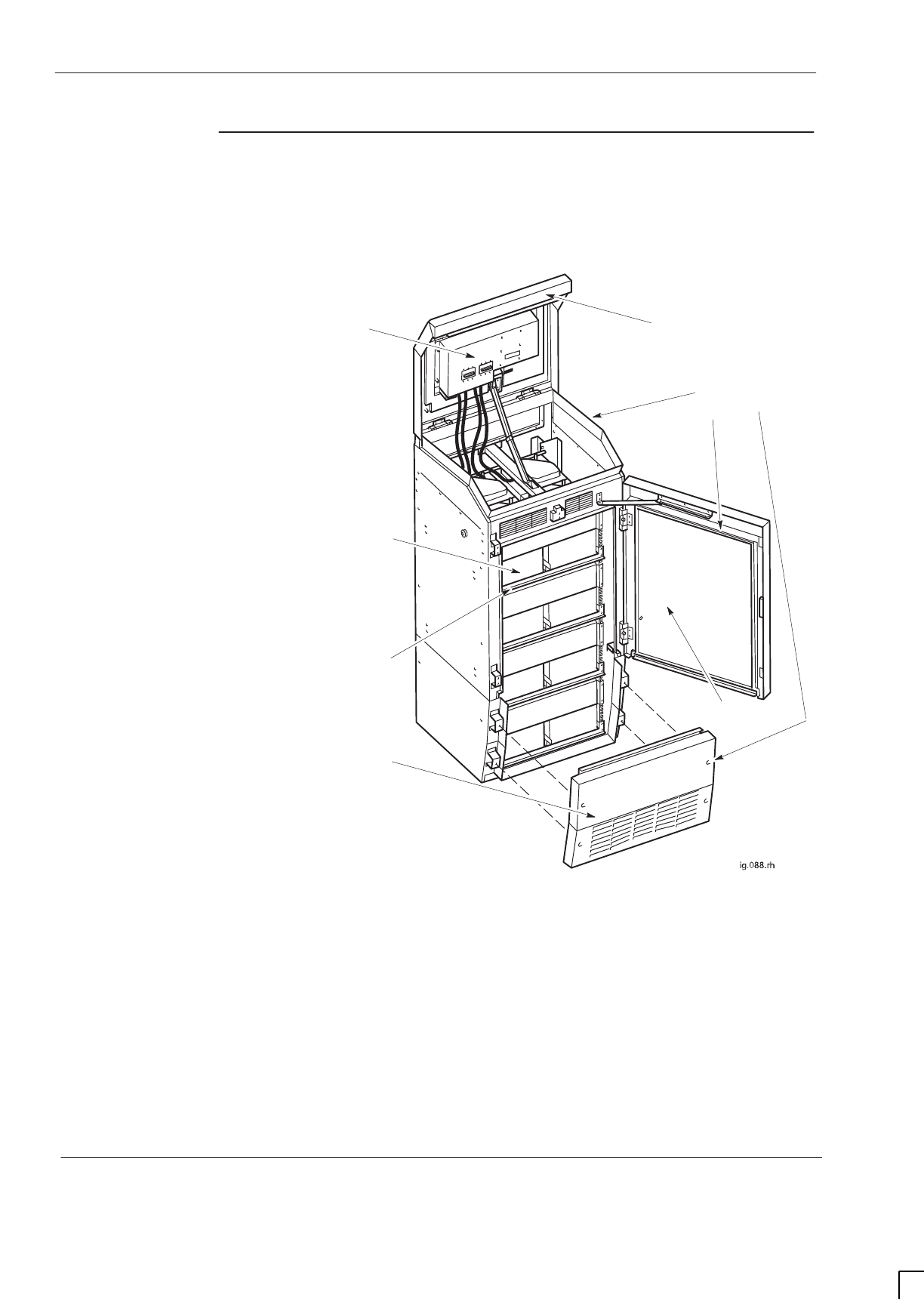
GSM-204-523
Introduction to auxiliary equipment housing maintenance
31st Oct 01
Maint. 4–2
Maintenance Information: Horizon
macro
outdoor
CONTROLLED INTRODUCTION
68P02902W04-A
Auxiliary
equipment
housing FRU
view
Figure 4-1 shows the auxiliary equipment housing, with FRUs identified.
POWER
DISTRIBUTION
BOX
FRONT PANEL
(CONTAINING FAN ASSEMBLY)
DOOR
ENVIRONMENTAL
SEALS
LID
HEATER MATS
(FITTED TO BATTERY
TRAYS BELOW
BATTERIES
BATTERY TRAY
Figure 4-1 Auxiliary equipment housing, showing field replaceable units
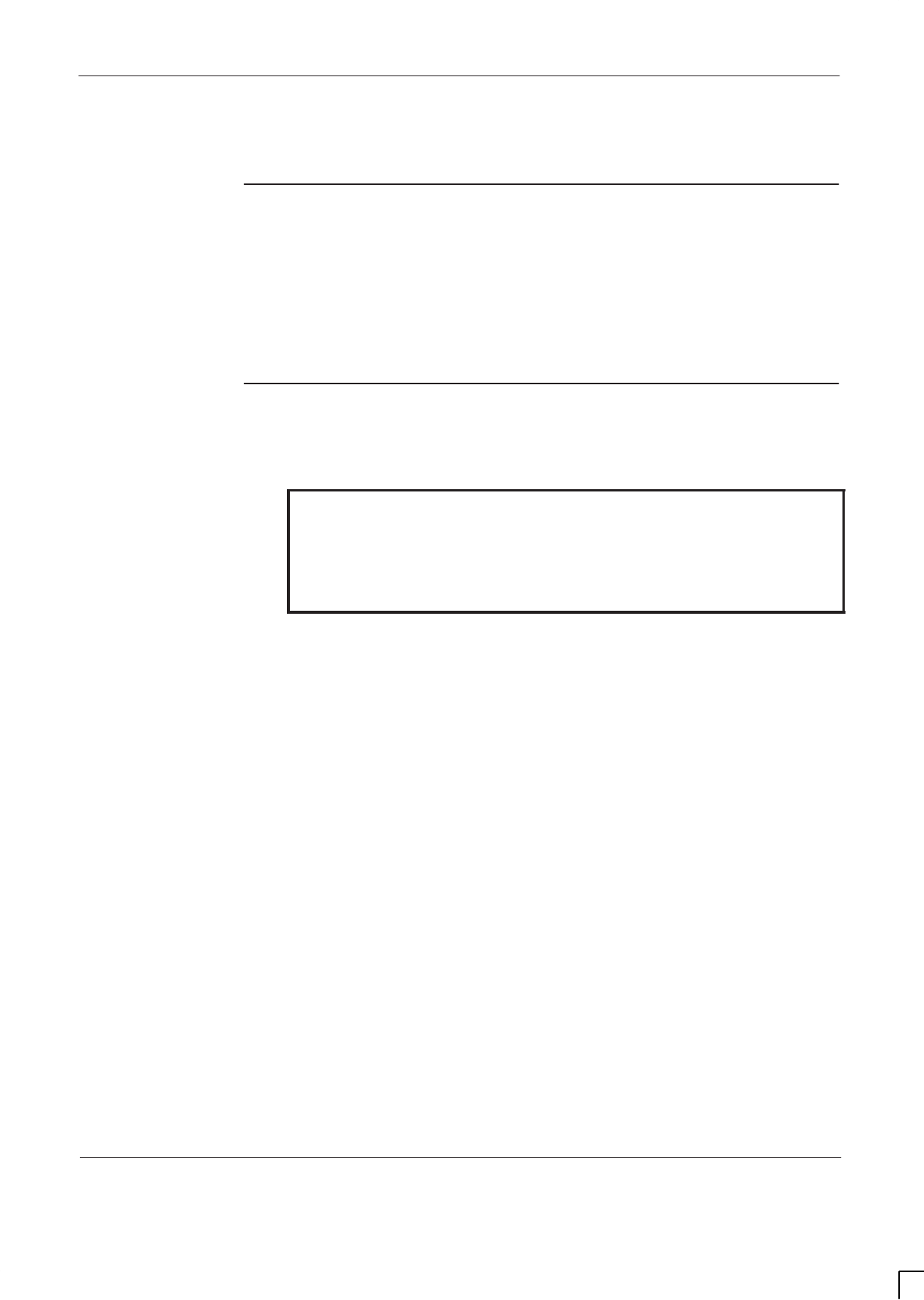
GSM-204-523 Replacing the power distribution box
31st Oct 01
Maintenance Information: Horizon
macro
outdoor
68P02902W04-A
CONTROLLED INTRODUCTION
Maint. 4–3
Replacing the power distribution box
Introduction to
power
distribution box
replacement
The circuit breakers in the power distribution box switch off if an
overtemperature alarm signal is received, and switch on again when the
temperature reset level is reached. The power distribution box will need to be
replaced if one or both of the circuit breakers fail to operate correctly.
Removing the
power
distribution box
To remove the power distribution box from the auxiliary equipment housing:
WARNING The batteries are capable of supplying high short circuit
currents and as such provides a high energy hazard.
Isolate the auxiliary equipment housing from the main
cabinet by switching off the EXT BATT circuit breaker on
the dc circuit breaker panel in the main cabinet before
commencing work.
1. Check that the AEH has been isolated from the main cabinet.
2. Open the cabinet door, release the lid latch and raise the lid.
3. Switch off the circuit breakers on the front of the power distribution box
and then disconnect the dc input cables from the rear pair of Anderson
connectors on the left side of the power distribution box. If used,
disconnect the extension cables to another cabinet from the front pair of
Anderson connectors.
4. Unplug the alarm signal cables from PL1, PL2 and PL3 on the front of the
power distribution box.
5. Disconnect the two cables which connect the top bank of batteries (bank
2, row 2) to the power distribution box and tie the cables safely out of the
way. Undo the battery terminal connections between bank 2, row 2 and
bank 2, row 1 and then remove the row 2 battery tray, followed by the row
1 battery tray.
6. Disconnect the two cables which connect battery bank 1, row 2 to the
power distribution box and tie the cables safely out of the way.
7. Undo the eight M4 nuts which secure the power distribution box to the lid
and then remove the box.
8. Unplug the door microswitch alarm cable from the external alarm interface
board.
9. Unplug the power cables for the heater mats and the fan from the external
alarm interface board.
The procedure for removing the power distribution box is now complete.
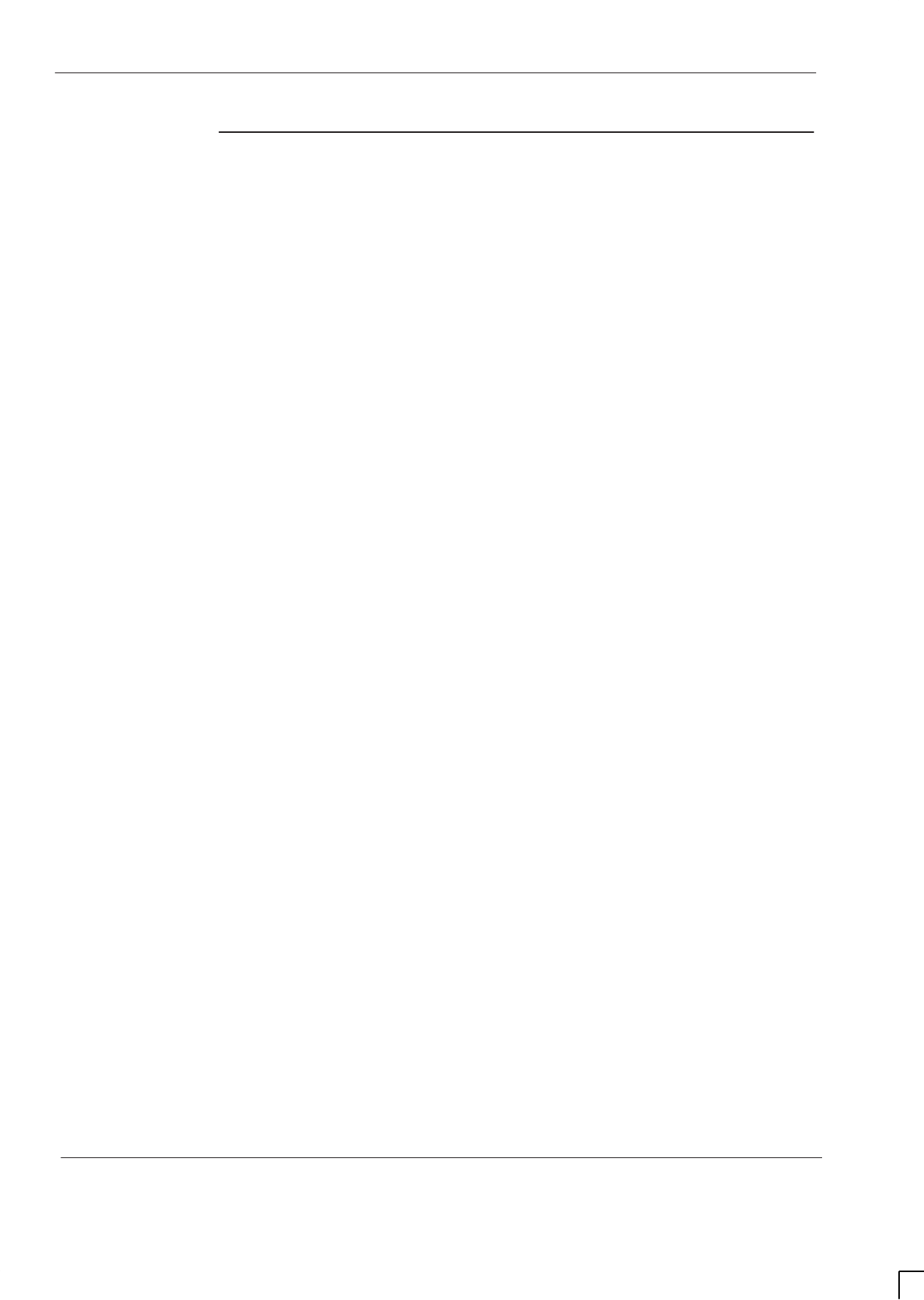
GSM-204-523
Replacing the power distribution box
31st Oct 01
Maint. 4–4
Maintenance Information: Horizon
macro
outdoor
CONTROLLED INTRODUCTION
68P02902W04-A
Fitting a
replacement
power
distribution box
To fit a new power distribution box:
1. Configure the new power distribution box to supply one or two BTS
cabinets as appropriate, see
Installation and Configuration:
(GSM-204-423)
Chapter 5 Configuring battery backup in this manual.
2. Connect the power cables for the heater mats and the fan to the external
alarm interface board.
3. Connect the alarm cables for the door microswitch to the external alarm
interface board.
4. Mount the new power distribution box onto the underside of the lid and
secure in position using the M4 nuts.
5. Connect the longer pair of battery cables from the power distribution box
to their terminals on battery bank 1, row 2. The blue cable connects to
negative and the black cable connects to positive.
6. Install the bank 2, row 1 battery tray, followed by the bank 2, row 2 battery
tray and then remake the terminal connections between the two rows
(refer to
Installation and Configuration: (GSM-204-423)
Installing
batteries in the auxiliary equipment housing if necessary. Connect the
remaining pair of battery cables to the positive and negative terminals on
the top bank of batteries.
7. Connect the alarm signal cables to PL1, PL2 and PL3 on the front of the
power distribution box.
8. Connect the dc power cable from the main cabinet to the rear pair of
Anderson connectors on the power distribution box. If used, connect the
extension cables from another cabinet to the front pair of Anderson
connectors.
9. Switch on the circuit breakers on the front of the power distribution box
and then close the lid and the cabinet door.
10. Switch on the EXT BATT circuit breaker on the dc circuit breaker panel in
the main cabinet.
The procedure for installing a new power distribution box is now complete.
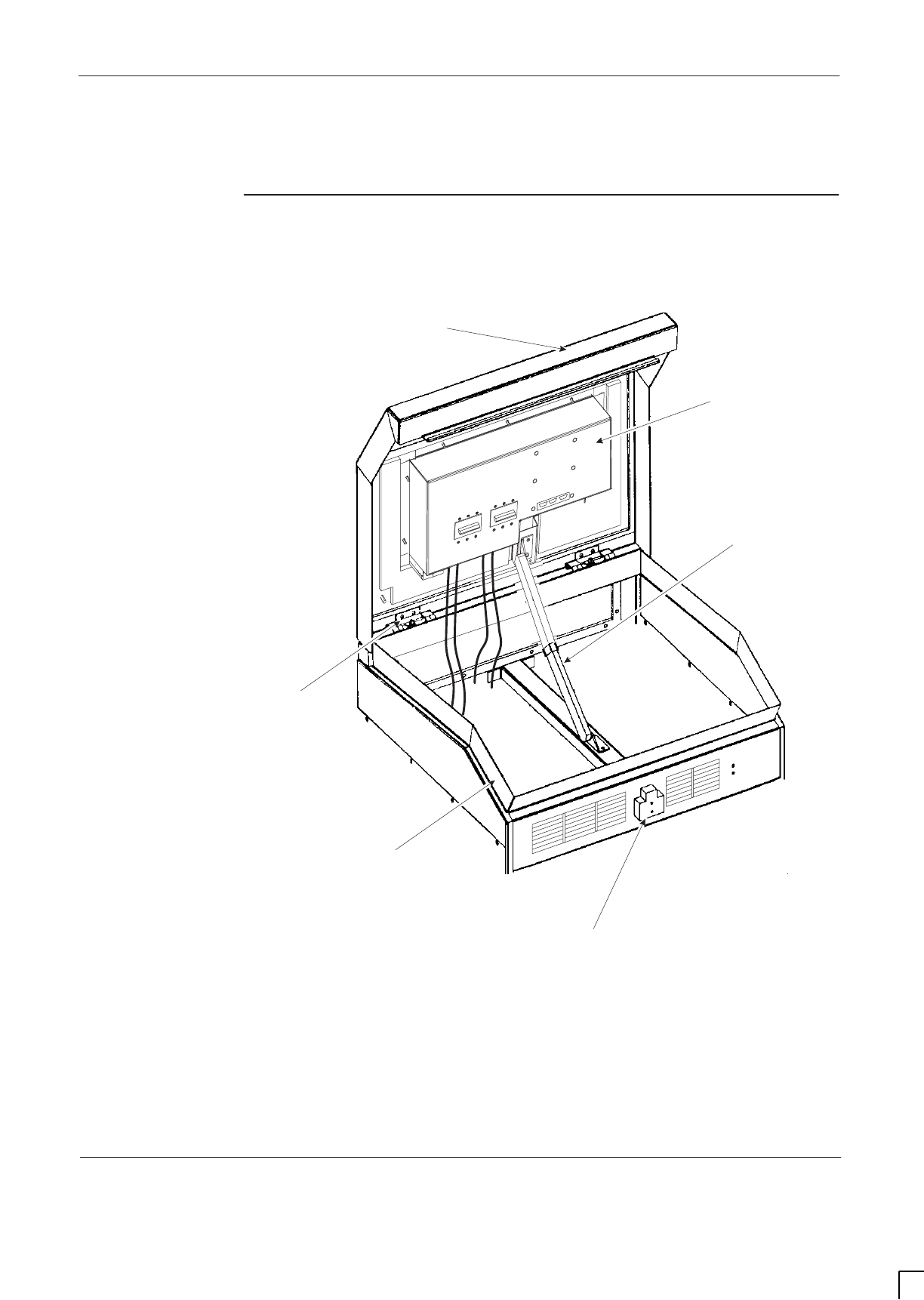
GSM-204-523 Replacing the lid on the auxiliary equipment housing
31st Oct 01
Maintenance Information: Horizon
macro
outdoor
68P02902W04-A
CONTROLLED INTRODUCTION
Maint. 4–5
Replacing the lid on the auxiliary equipment housing
Detailed view of
the cabinet lid
The major features of the auxiliary equipment housing lid are shown in
Figure 4-2.
MECHANICAL STAY
ENVIRONMENTAL SEAL
LID
POWER
DISTRIBUTION
BOX
LATCH
HINGE
Figure 4-2 Detailed view of the auxiliary equipment housing lid
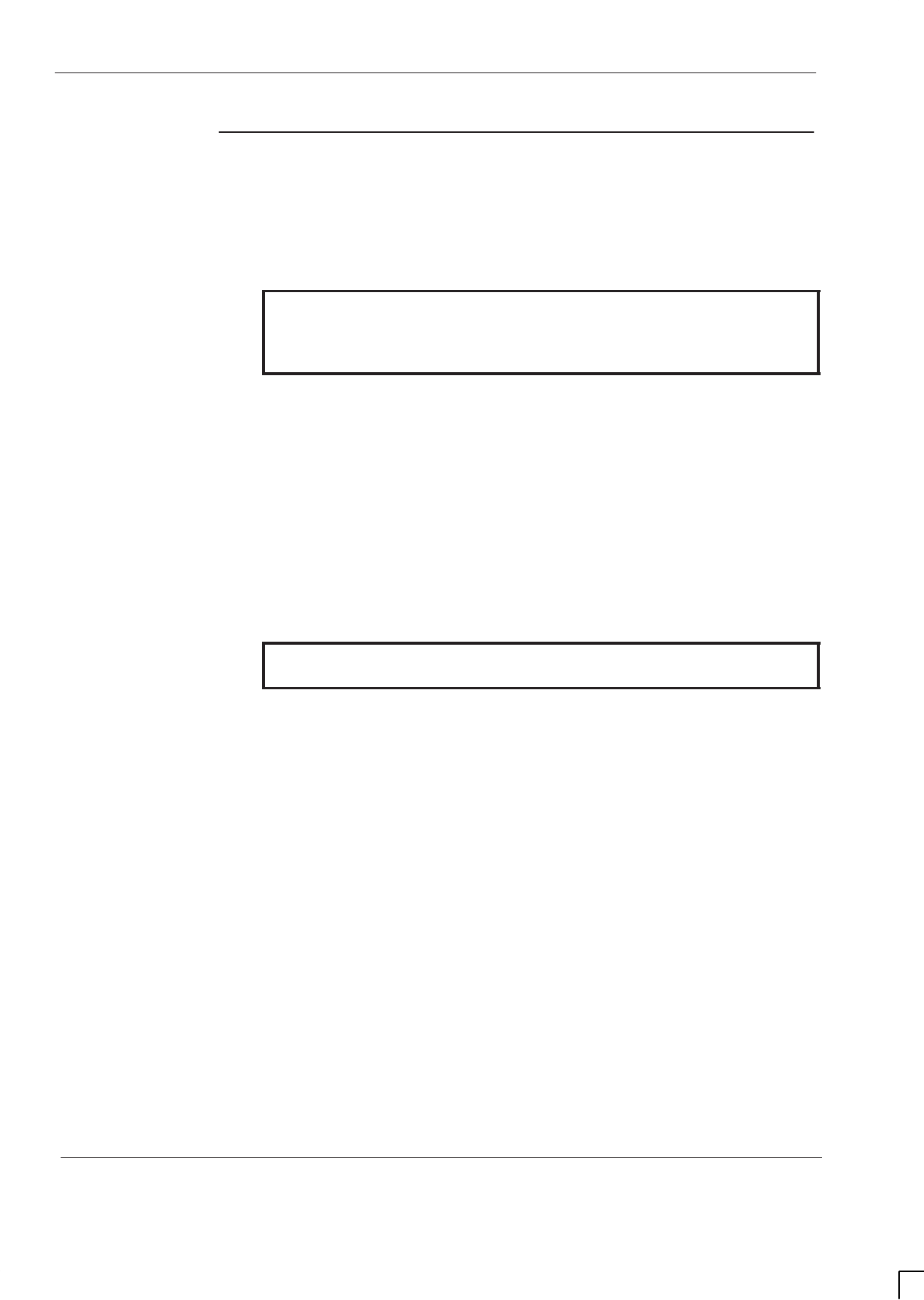
GSM-204-523
Replacing the lid on the auxiliary equipment housing
31st Oct 01
Maint. 4–6
Maintenance Information: Horizon
macro
outdoor
CONTROLLED INTRODUCTION
68P02902W04-A
Removing the
lid
The lid provides environmental protection for the equipment contained within.
For this reason, the following lid removal and replacement procedures should be
completed in one session and the cabinet then closed.
To remove the lid:
WARNING Isolate the auxiliary equipment housing from the main
cabinet by switching off the EXT BATT circuit breaker on
the dc circuit breaker panel in the main cabinet before
commencing work.
1. Open the cabinet door, release the lid latch and raise the lid until the
mechanical stay locks in position.
2. Switch off the circuit breakers on the front of the power distribution box
and then undo the eight M4 nuts which secure the box to the lid. Place the
power distribution box safely in the top area of the auxiliary equipment
housing.
3. Unscrew and remove, the M6 nut, plain washer and star washer which
secure the lid earth cable to the cabinet.
4. Remove the circlips from the hinge pins.
5. Support the lid and unscrew the mechanical stay from the lid.
WARNING The cabinet lid on its own weighs 8.5 kg. Handle with care
and observe proper lifting precautions.
6. Remove the two hinge pins by pulling their lugs in the required direction,
using long nose pliers.
7. Remove the lid and place safely to one side.
The procedure for removing the lid is now complete.
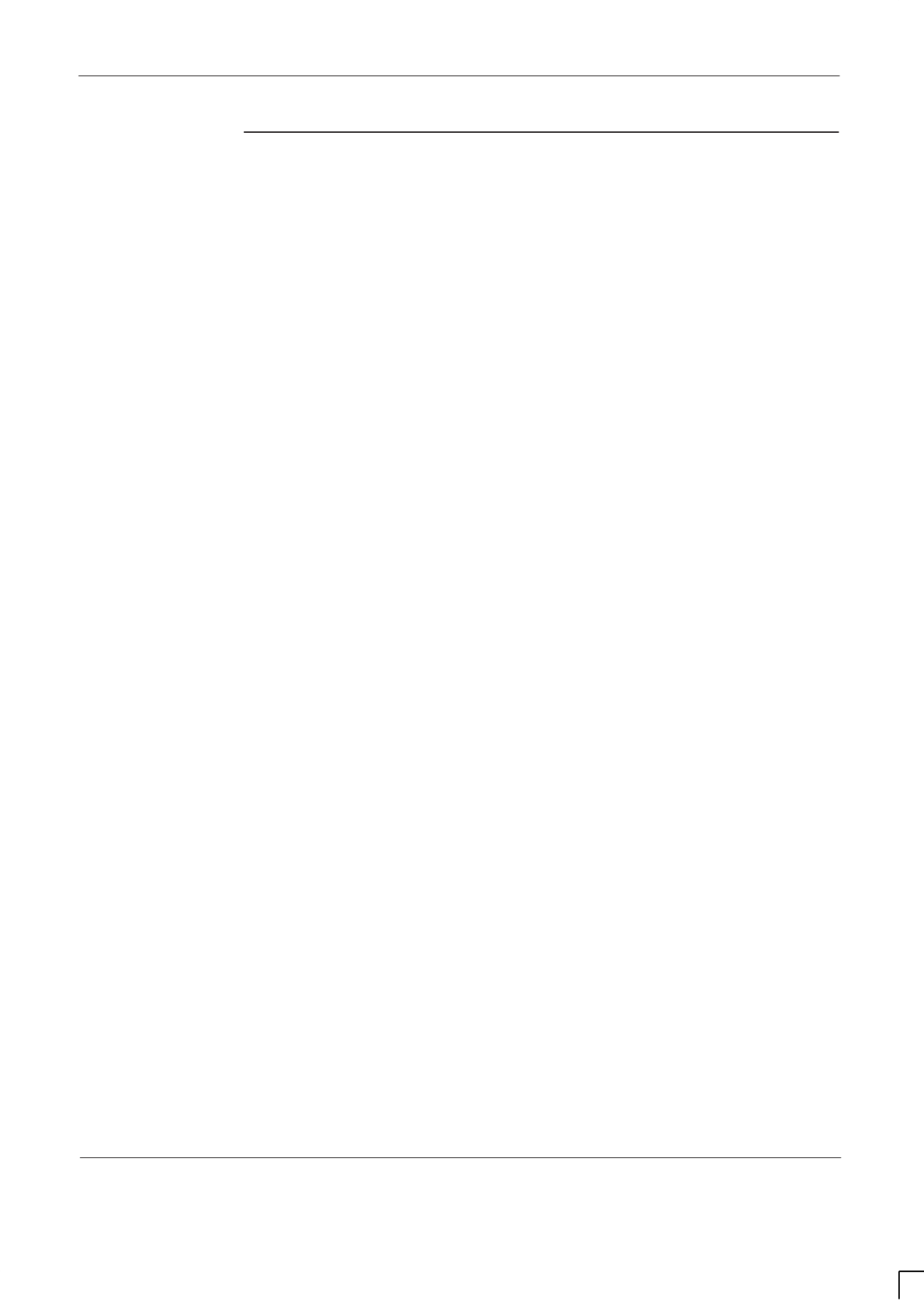
GSM-204-523 Replacing the lid on the auxiliary equipment housing
31st Oct 01
Maintenance Information: Horizon
macro
outdoor
68P02902W04-A
CONTROLLED INTRODUCTION
Maint. 4–7
Fitting a new lid
To fit a new lid:
1. Support the new lid in position, so that the hinges line up.
2. Insert the two hinge pins fully into the hinges.
3. Screw the mechanical stay to the lid.
4. Fit the circlips into the recesses in the hinges.
5. Attach the lid earth cable to the cabinet using the star washer, plain
washer and M6 nut. Tighten to the correct torque (see Overview of FRU
replacement procedures in Chapter 2 of this category).
6. Mount the power distribution box in position on the inside of the lid and
tighten the eight M4 nuts.
7. Switch on the circuit breakers on the front of the power distribution box
and then close the lid and the cabinet door.
8. Switch on the EXT BATT circuit breaker on the dc circuit breaker panel in
the main cabinet.
The procedure for fitting the new lid is now complete.
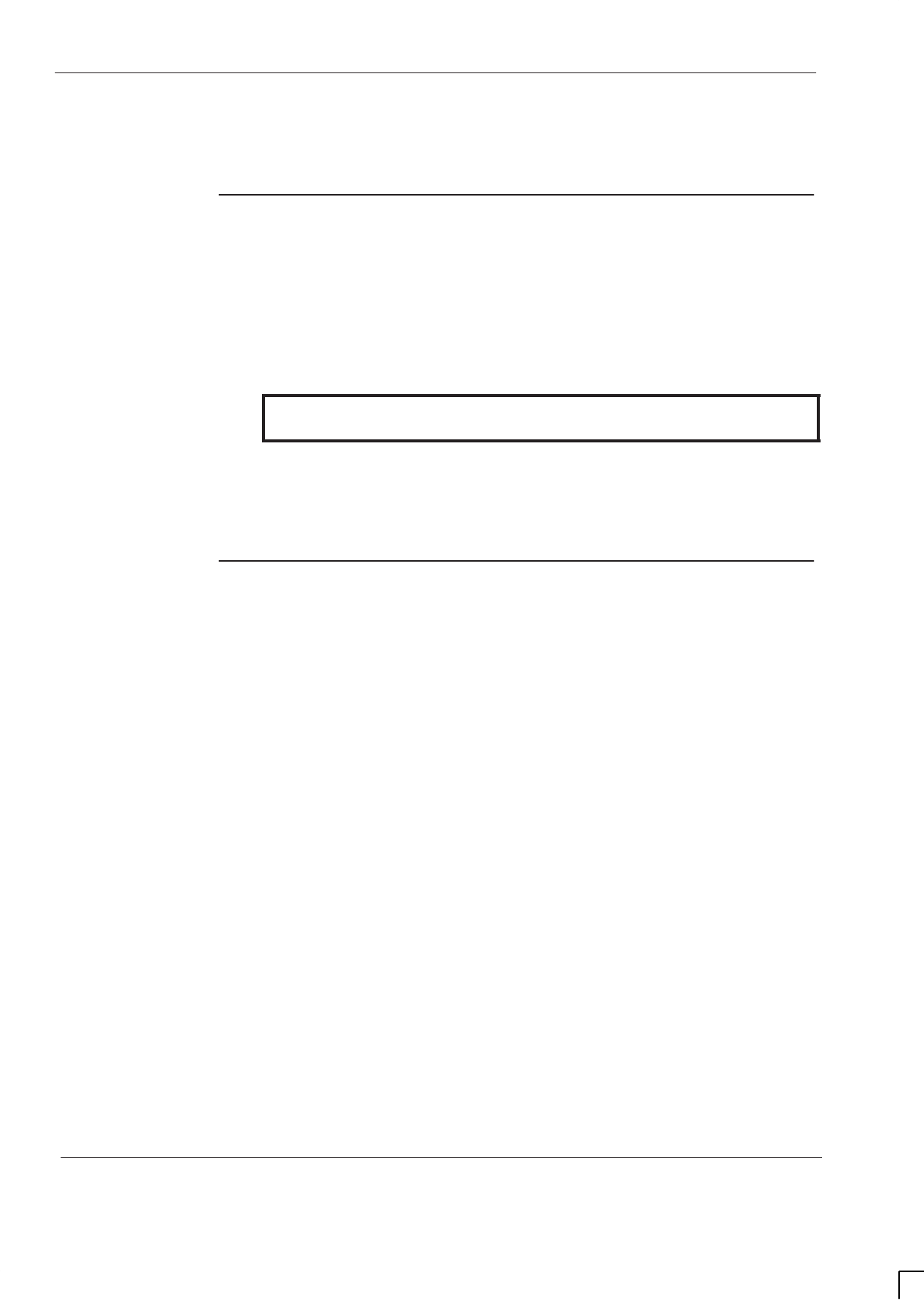
GSM-204-523
Replacing the door on the auxiliary equipment housing
31st Oct 01
Maint. 4–8
Maintenance Information: Horizon
macro
outdoor
CONTROLLED INTRODUCTION
68P02902W04-A
Replacing the door on the auxiliary equipment housing
Removing the
cabinet door
To remove the cabinet door:
1. Unscrew the M6 nut, plain washer and star washer which secures the door
earth cable to the cabinet body.
2. Unscrew the wind stop from the cabinet.
3. Remove the circlips from the bottom of the hinge pins.
WARNING The cabinet door weighs 15 kg. Handle with care and
observe proper lifting precautions.
4. Support the door and remove the two hinge pins by pulling their lugs in the
required direction, using long nose pliers.
5. Remove the door and place safely to one side.
Fitting a
replacement
door
To fit a replacement door:
1. Support the door in position, so that the hinges line up.
2. Insert the two hinge pins fully into the hinges.
3. Fit the circlips into the recesses in the bottom of the hinges.
4. Screw the wind stop to the cabinet.
5. Attach the door earth cable to the cabinet using the star washer, plain
washer and M6 nut. Tighten to the correct torque (see Overview of FRU
replacement procedures in Chapter 2 of this category).
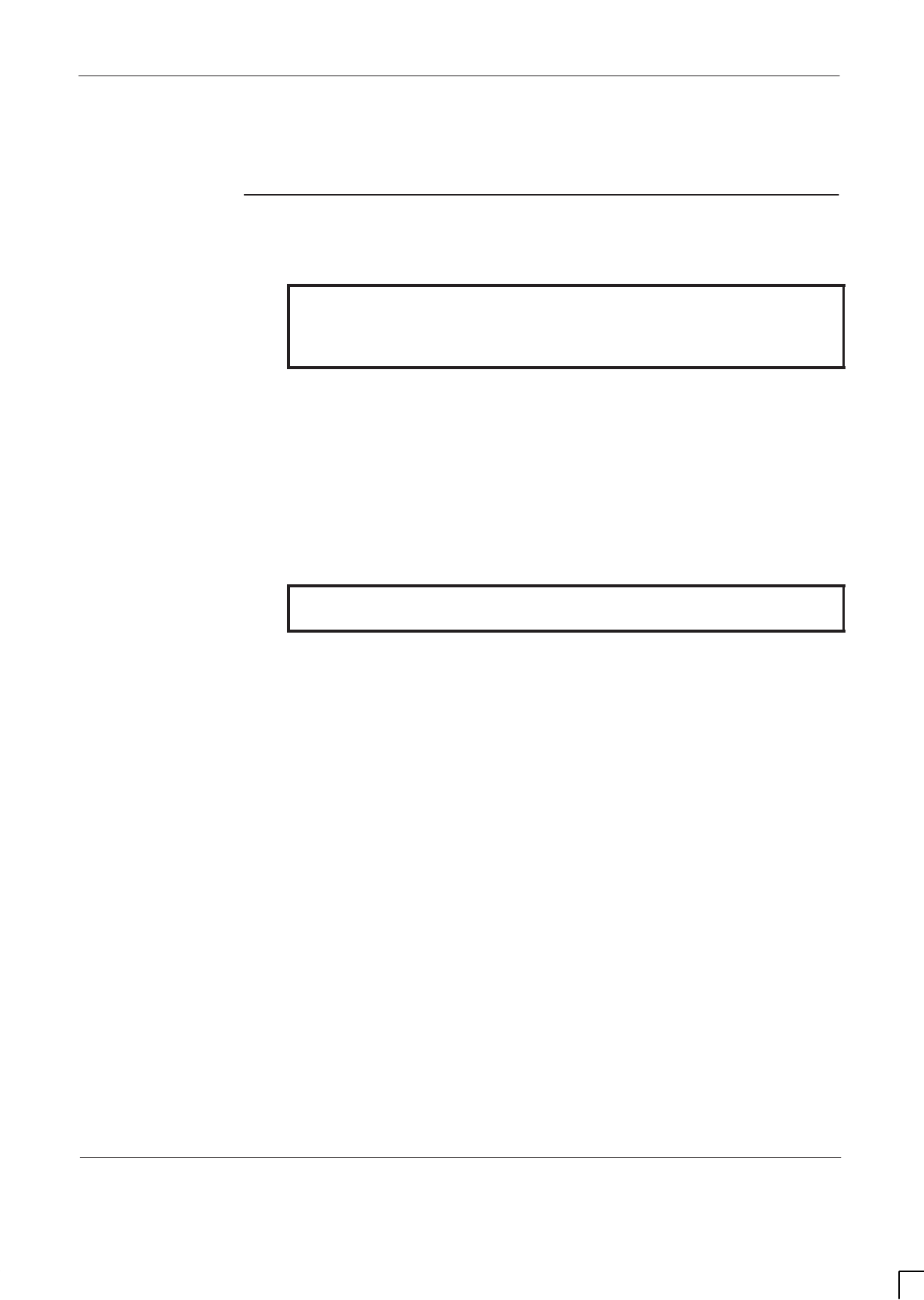
GSM-204-523 Replacing the front panel or fan
31st Oct 01
Maintenance Information: Horizon
macro
outdoor
68P02902W04-A
CONTROLLED INTRODUCTION
Maint. 4–9
Replacing the front panel or fan
Replacing the
front panel
To replace the front panel:
WARNING Isolate the auxiliary equipment housing from the main
cabinet by switching off the EXT BATT circuit breaker on
the dc circuit breaker panel in the main cabinet before
commencing work.
1. Open the cabinet door. Open the cabinet lid and switch off the circuit
breakers on the power distribution box.
2. Unplug the cable which supplies dc power to the fan from its connector,
fixed to a bracket on the right side of the rear of the front panel.
3. Unscrew and remove, the M6 nut, plain washer and star washer which
secure the front panel earth cable to the cabinet.
4. Undo the six screws which secure the front panel to the cabinet and lift the
panel away.
WARNING The front panel (excluding fan assembly) weighs 4.5 kg.
Handle with care and observe proper lifting precautions.
5. If the panel is to be replaced but the fan is to be retained, separate the fan
assembly from the front panel by following the instructions in the section
Removing the fan.
The procedure for removing the front panel is now complete.
Replacement is a reversal of the removal procedure. If the fan assembly has
been separated from the old front panel, refer to Installing the fan for
instructions about how to mount the fan assembly in the new front panel.
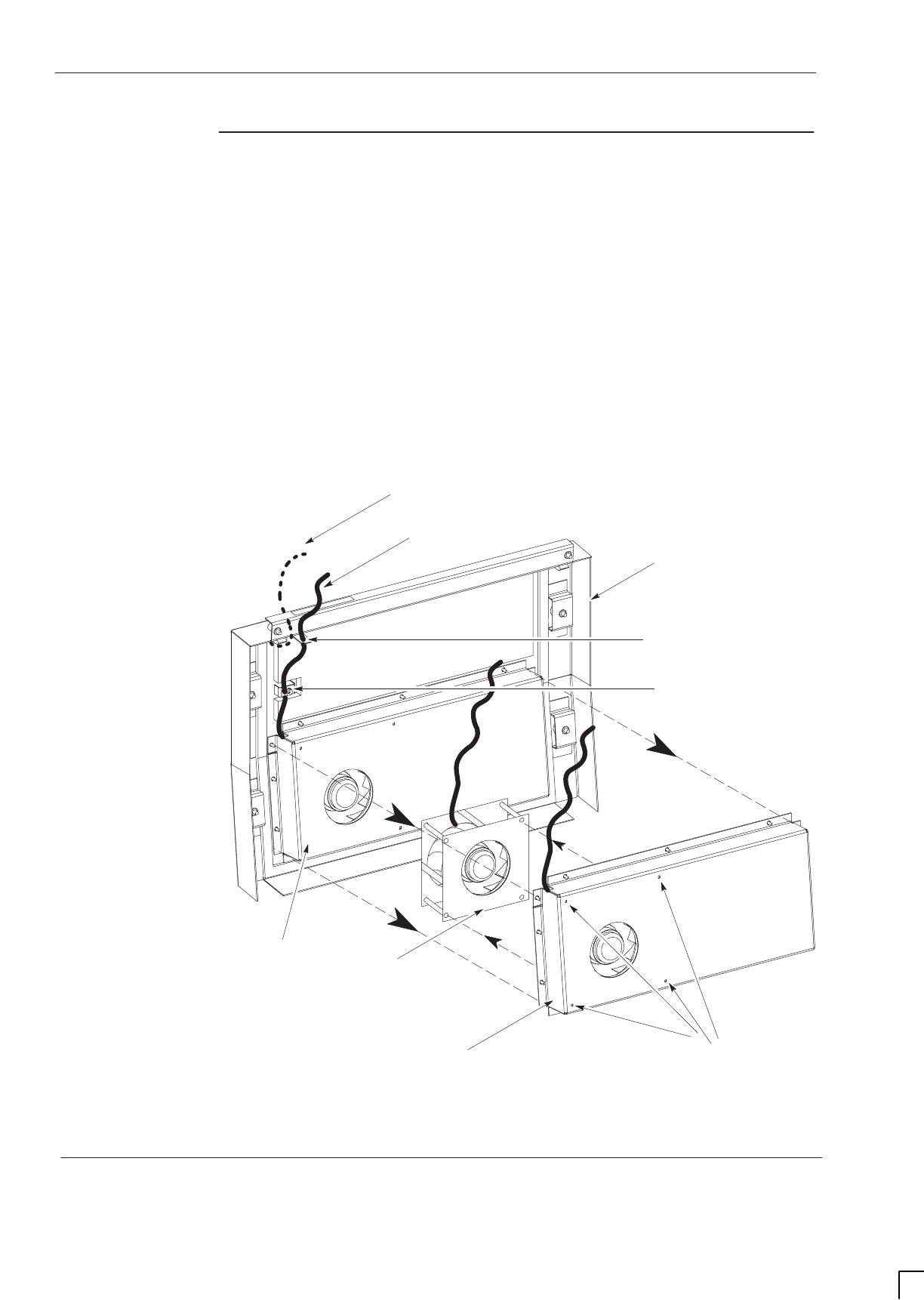
GSM-204-523
Replacing the front panel or fan
31st Oct 01
Maint. 4–10
Maintenance Information: Horizon
macro
outdoor
CONTROLLED INTRODUCTION
68P02902W04-A
Replacing the
fan
To remove the fan refer to Figure 4-3 and:
1. Remove the front panel, as described in Replacing the front panel.
2. Release the fan power cable from the cable clamp and feed through the
bracket on the rear of the front panel.
3. On the rear of the front panel, undo the 10 M4 nuts which secure the fan
cover to the front panel and then remove the cover and fan.
4. Undo the four screws that secure the fan assembly to the fan cover and
remove the fan assembly and its power cable.
The procedure for removing the fan is now complete.
The procedure for installing a new fan is a reversal of the removal procedure.
AEH FRONT
PANEL
FAN POWER CABLE
CABLE
CLAMP
CABLE
BRACKET
FAN COVER
FAN ASSEMBLY
EARTH BONDING
CABLE
FAN COVER FAN SECURING
SCREWS
Figure 4-3 Removing the fan assembly
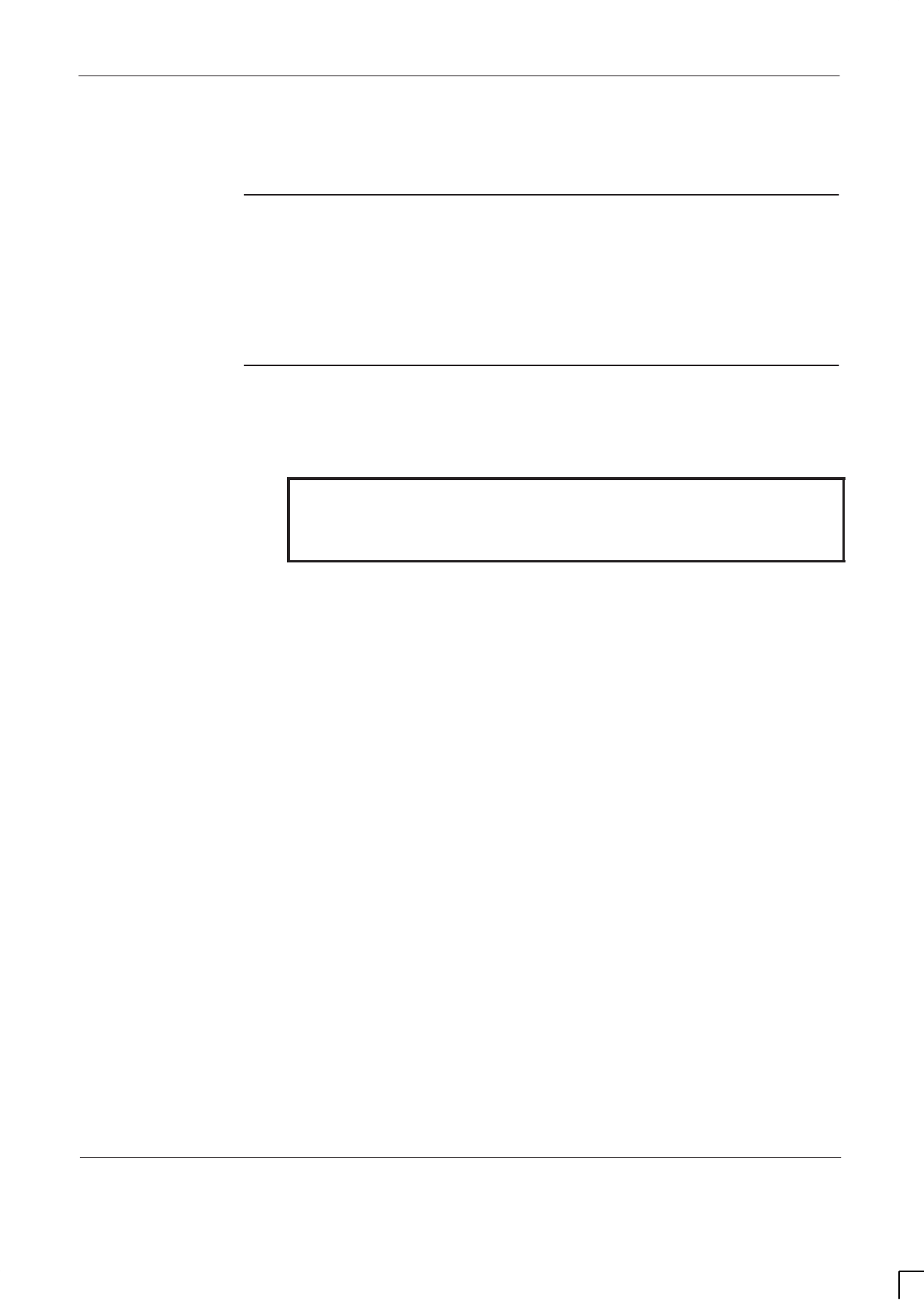
GSM-204-523 Replacing a heater mat
31st Oct 01
Maintenance Information: Horizon
macro
outdoor
68P02902W04-A
CONTROLLED INTRODUCTION
Maint. 4–11
Replacing a heater mat
Introduction to
heater mat
replacement
The auxiliary equipment housing contains four heater mats; mounted on each
battery tray. Equipment installed in the housing, such as batteries, must be
removed to gain access to the mats.
Heater mat
replacement
procedure
To replace a heater mat:
WARNING Isolate the auxiliary equipment housing from the main
cabinet by switching off the EXT BATT circuit breaker on
the dc circuit breaker panel in the main cabinet before
commencing work.
1. Open the cabinet door, then open the lid and switch off the circuit breakers
on the power distribution box.
2. Disconnect the fan cable, the front panel earth bonding cable and remove
the front panel.
3. Remove any equipment or batteries that are installed in the cabinet.
4. Unplug the power connector at the battery tray for the heater mat that is to
be replaced.
5. Remove the mat from the battery tray.
The procedure for removing the heater mat is now complete.
Replacement is a reversal of the removal procedure.
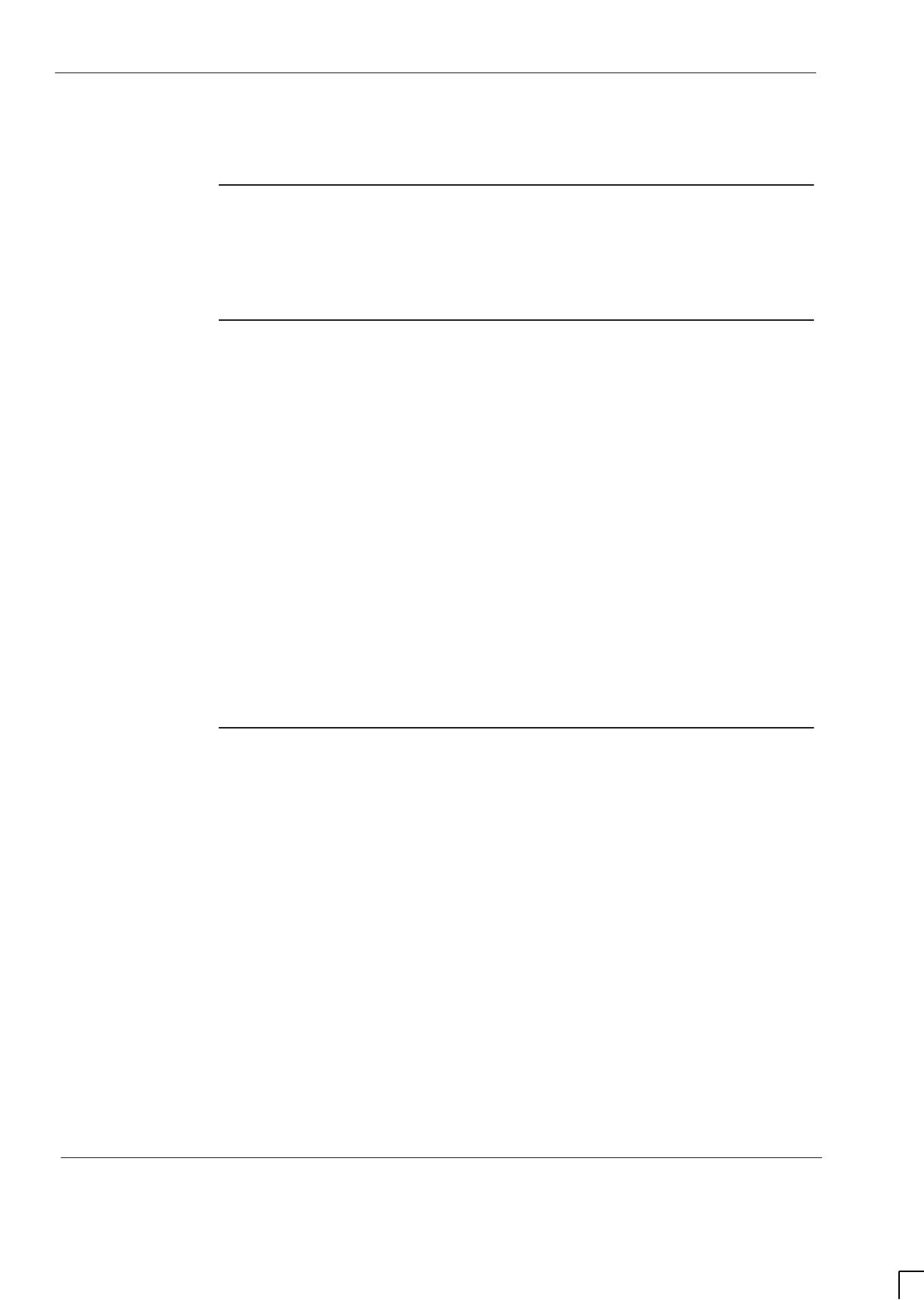
GSM-204-523
Replacing an environmental seal on the housing
31st Oct 01
Maint. 4–12
Maintenance Information: Horizon
macro
outdoor
CONTROLLED INTRODUCTION
68P02902W04-A
Replacing an environmental seal on the housing
Introduction to
replacing a seal
A faulty environmental seal can allow moisture to enter the housing, which in
turn can lead to equipment failure. It is important that the seals are inspected for
signs of wear or damage whenever the housing door or lid are opened.
Replacing the
lid
environmental
seal
The environmental seal for the lid consists of a U-shaped rubberized seal that
fits over the metal lip on the top of the housing (see Figure 4-1).
To replace the the lid seal:
1. Open the housing door, release the lid catch and then lift the lid so that it
locks in position.
2. Pull the old seal off the metal lip.
3. Measure the length of the new seal against the old seal and trim to the
correct length, if necessary.
4. Press the new seal firmly onto the metal lip all the way around and ensure
that the free ends meet centrally on the front edge.
5. Close the lid and the housing door.
The procedure for replacing the environmental seal for the lid is now complete.
Replacing the
door
environmental
seal
The environmental seal for the door consists of four strips of self-adhesive
gasket, fixed to the inside door panel.
To replace the door seal:
1. Open the housing door.
2. Trace a line around the inside edge of each seal strip as a marker for
positioning the new seal strips.
3. Remove the old seal strips. Remove all traces of adhesive using a suitable
solvent.
4. Fit the new seal strips, ensuring that the inside edges align with the marks
made prior to removing the old seals.
5. Close the door.
The procedure for replacing the environmental seal for the door is now
complete.

CHAPTER 1
PARTS LIST
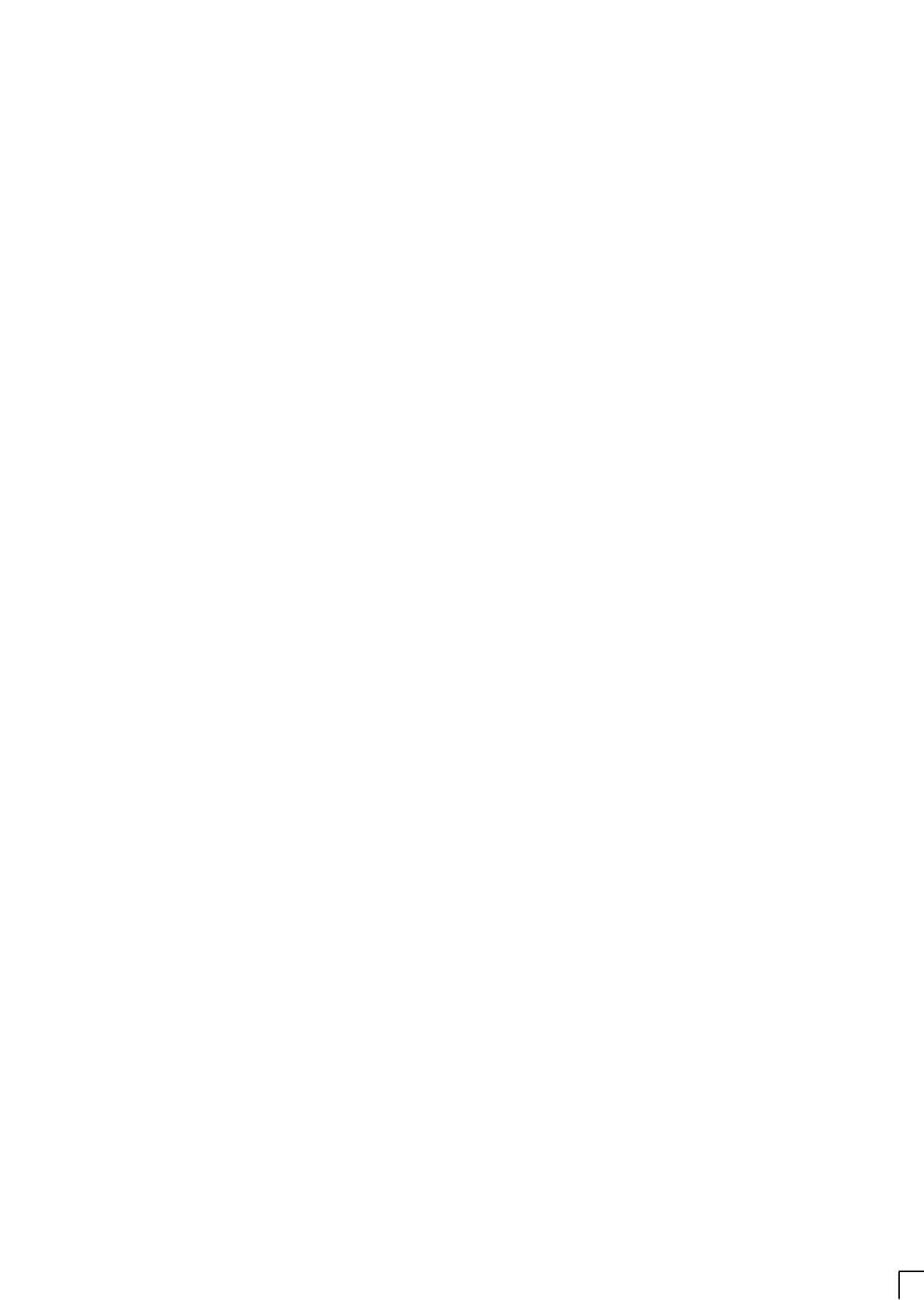
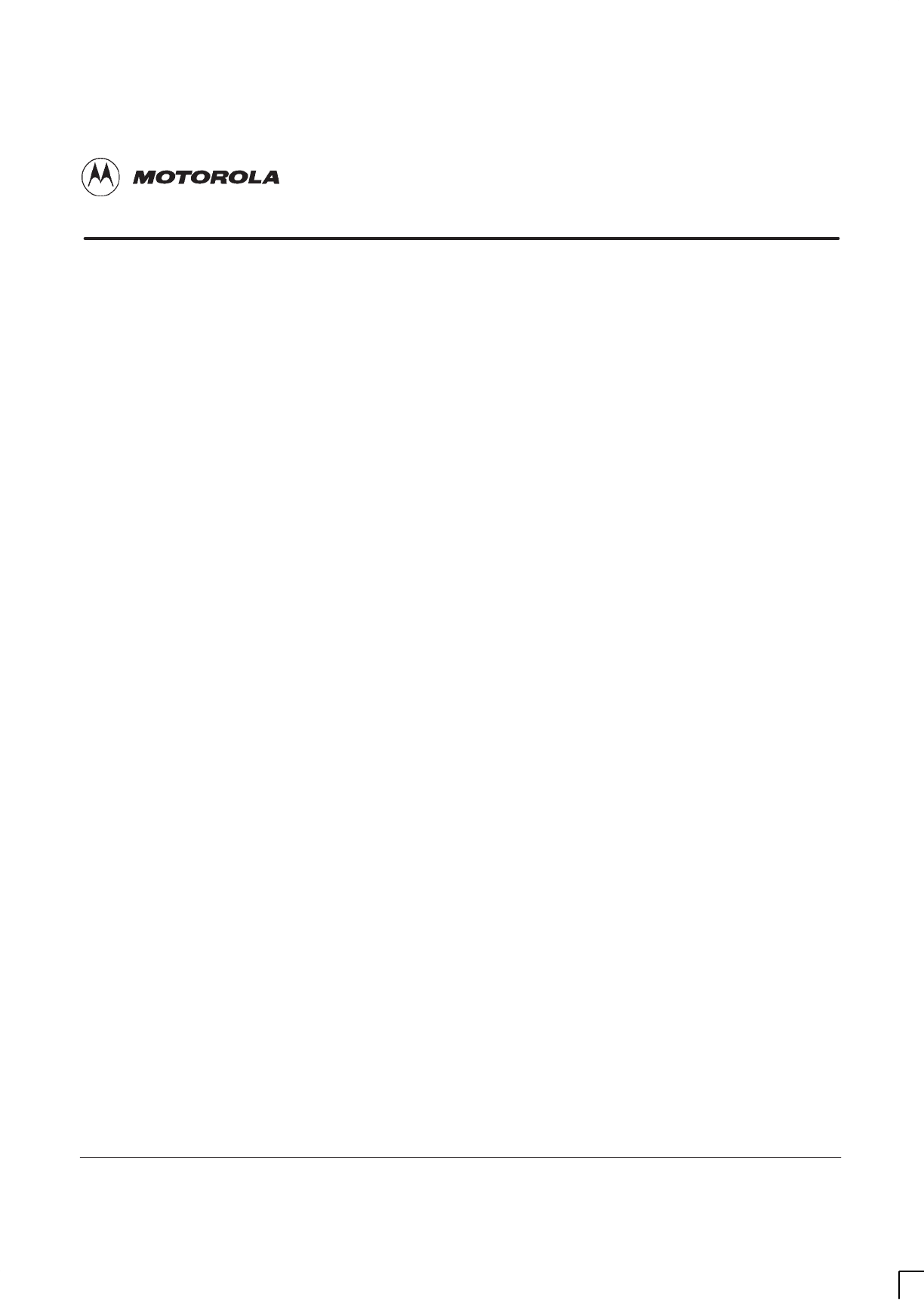
31st Oct 01
Parts Information: Horizon
macro
outdoor
68P02902W05-A
CONTROLLED INTRODUCTION
i
Category 623
Parts Information (Parts)
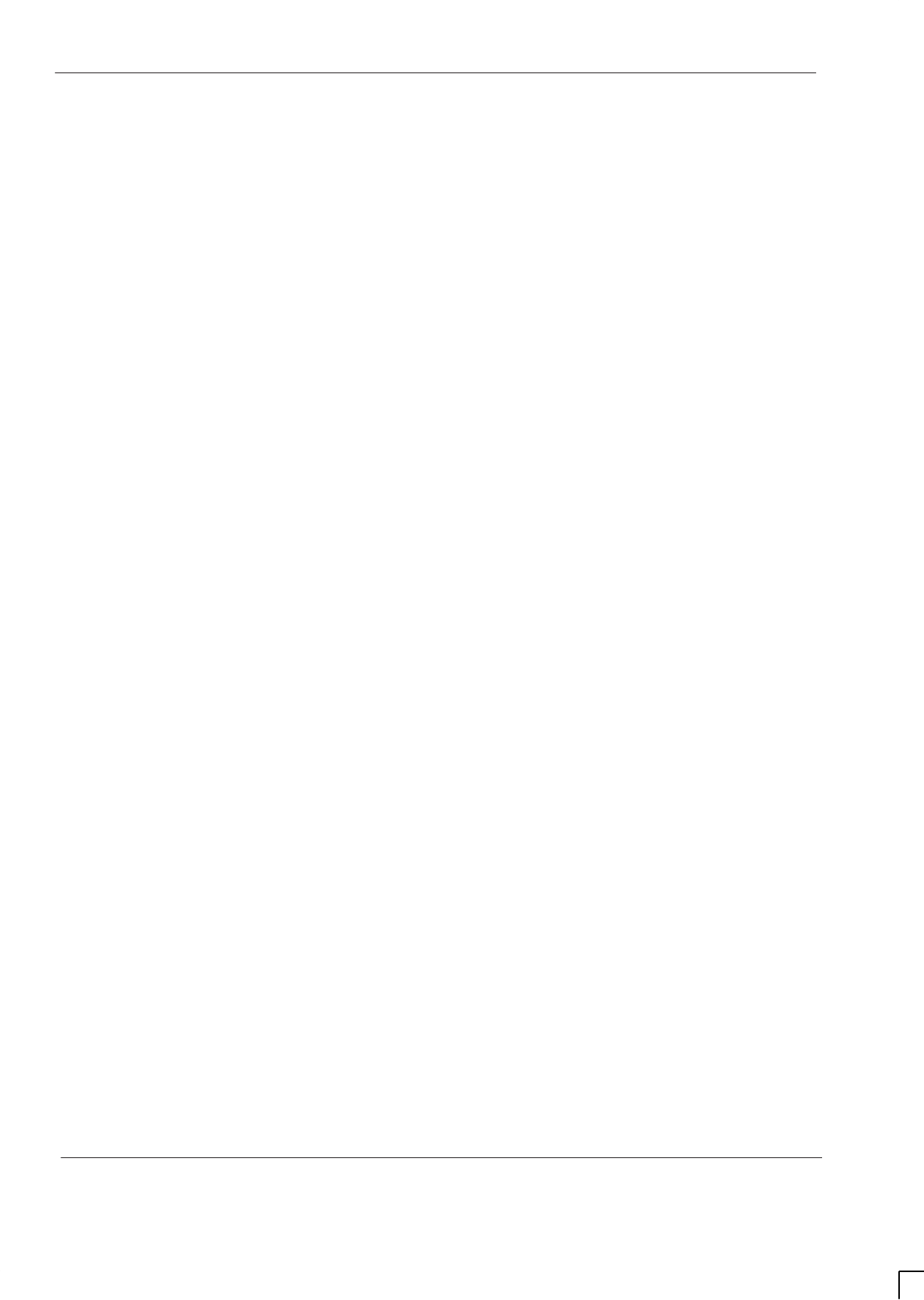
GSM-204-623
31st Oct 01
ii
Parts Information: Horizon
macro
outdoor
CONTROLLED INTRODUCTION
68P02902W05-A
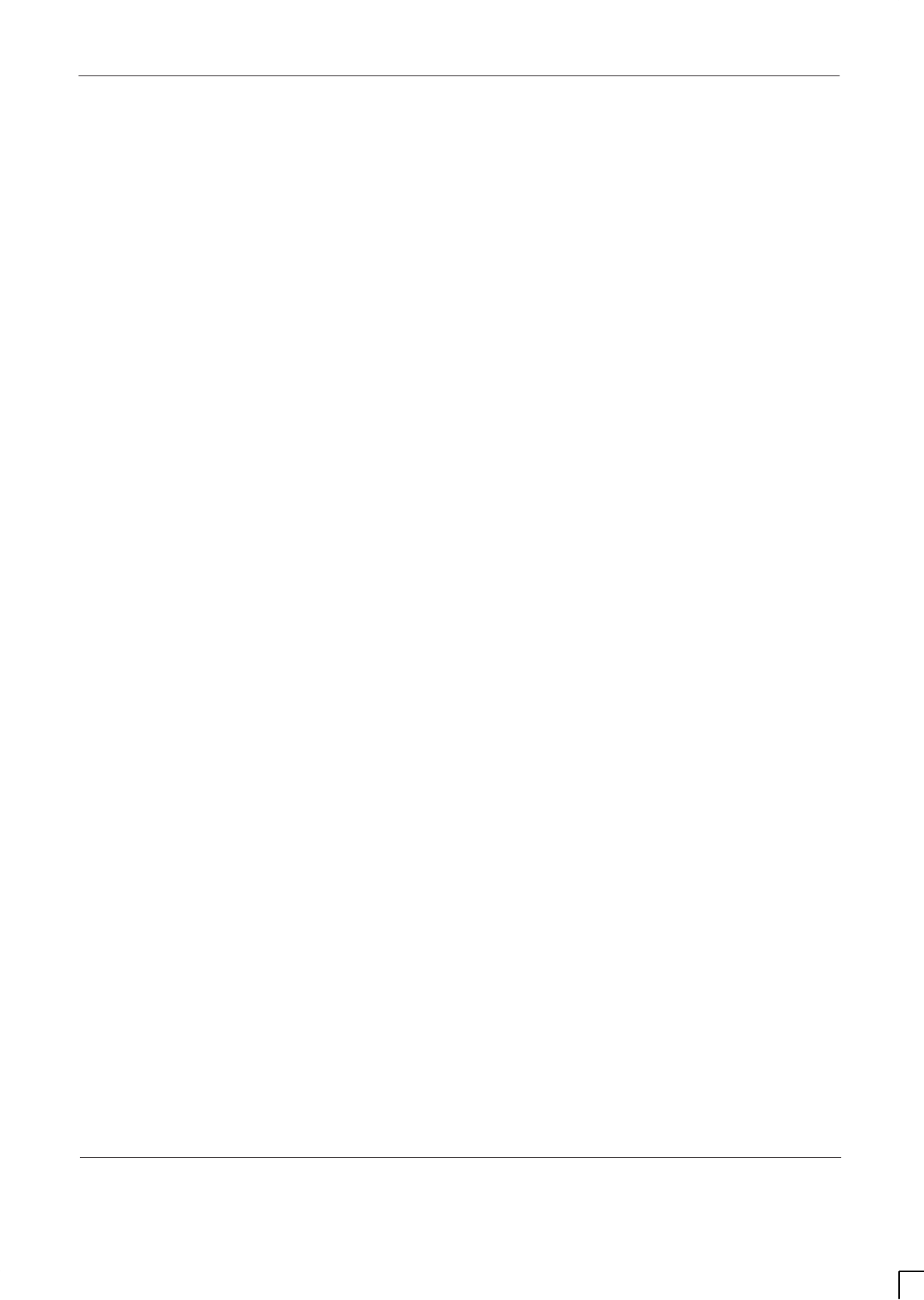
GSM-204-623
31st Oct 01
Parts Information: Horizon
macro
outdoor
68P02902W05-A
CONTROLLED INTRODUCTION
iii
Category 623
Parts Information (Parts) i. . . . . . . . . . . . . . . . . . . . . . . . . . . . . . . . . . . . . . . . . . .
Chapter 1
Parts list i. . . . . . . . . . . . . . . . . . . . . . . . . . . . . . . . . . . . . . . . . . . . . . . . . . . . . .
Parts information introduction Parts 1–1. . . . . . . . . . . . . . . . . . . . . . . . . . . . . . . . . . . . . . . . . .
Horizonmacro outdoor parts lists Parts 1–1. . . . . . . . . . . . . . . . . . . . . . . . . . . . . . . . . .
FRU items Parts 1–1. . . . . . . . . . . . . . . . . . . . . . . . . . . . . . . . . . . . . . . . . . . . . . . . . . . . .
Ordering method Parts 1–1. . . . . . . . . . . . . . . . . . . . . . . . . . . . . . . . . . . . . . . . . . . . . . . .
Diagram of Horizonmacro outdoor FRU modules Parts 1–2. . . . . . . . . . . . . . . . . . . .
Diagram of auxiliary equipment housing FRU modules Parts 1–3. . . . . . . . . . . . . . .
Parts for Horizonmacro outdoor Parts 1–4. . . . . . . . . . . . . . . . . . . . . . . . . . . . . . . . . . . . . . . .
Spares Table Parts 1–4. . . . . . . . . . . . . . . . . . . . . . . . . . . . . . . . . . . . . . . . . . . . . . . . . . .
Parts for optional equipment Parts 1–7. . . . . . . . . . . . . . . . . . . . . . . . . . . . . . . . . . . . . . . . . . .
Introduction to optional equipment parts lists Parts 1–7. . . . . . . . . . . . . . . . . . . . . . .
Spares table for the cable shroud Parts 1–7. . . . . . . . . . . . . . . . . . . . . . . . . . . . . . . . .
Spares table for the auxiliary equipment housing Parts 1–7. . . . . . . . . . . . . . . . . . . .
Glossary of terms unique to this equipment Parts 1–8. . . . . . . . . . . . . . . . . . . . . . . . . . . . . .
Overview of the glossary Parts 1–8. . . . . . . . . . . . . . . . . . . . . . . . . . . . . . . . . . . . . . . . .
Glossary of terms Parts 1–8. . . . . . . . . . . . . . . . . . . . . . . . . . . . . . . . . . . . . . . . . . . . . . .
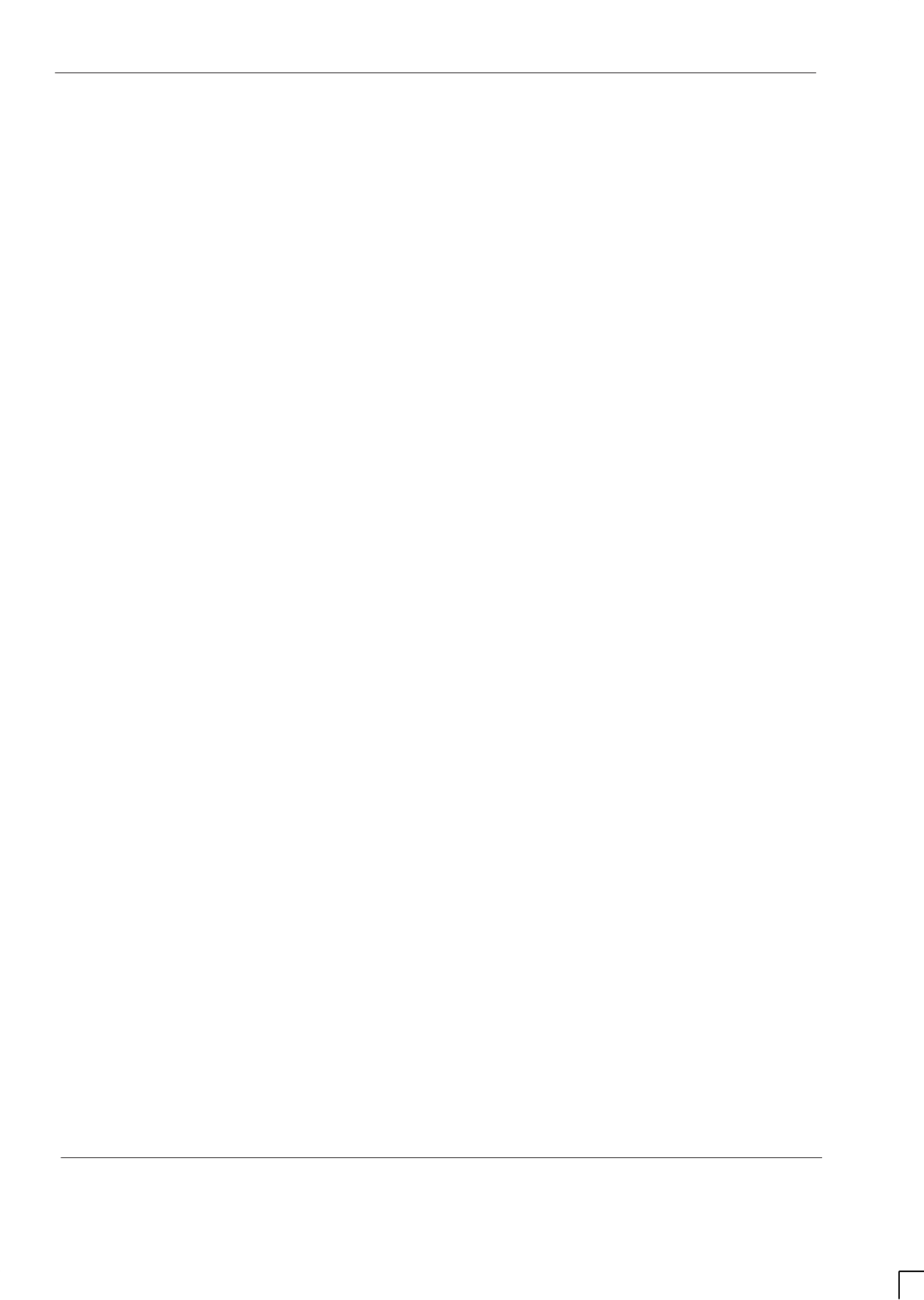
GSM-204-623
31st Oct 01
iv
Parts Information: Horizon
macro
outdoor
CONTROLLED INTRODUCTION
68P02902W05-A
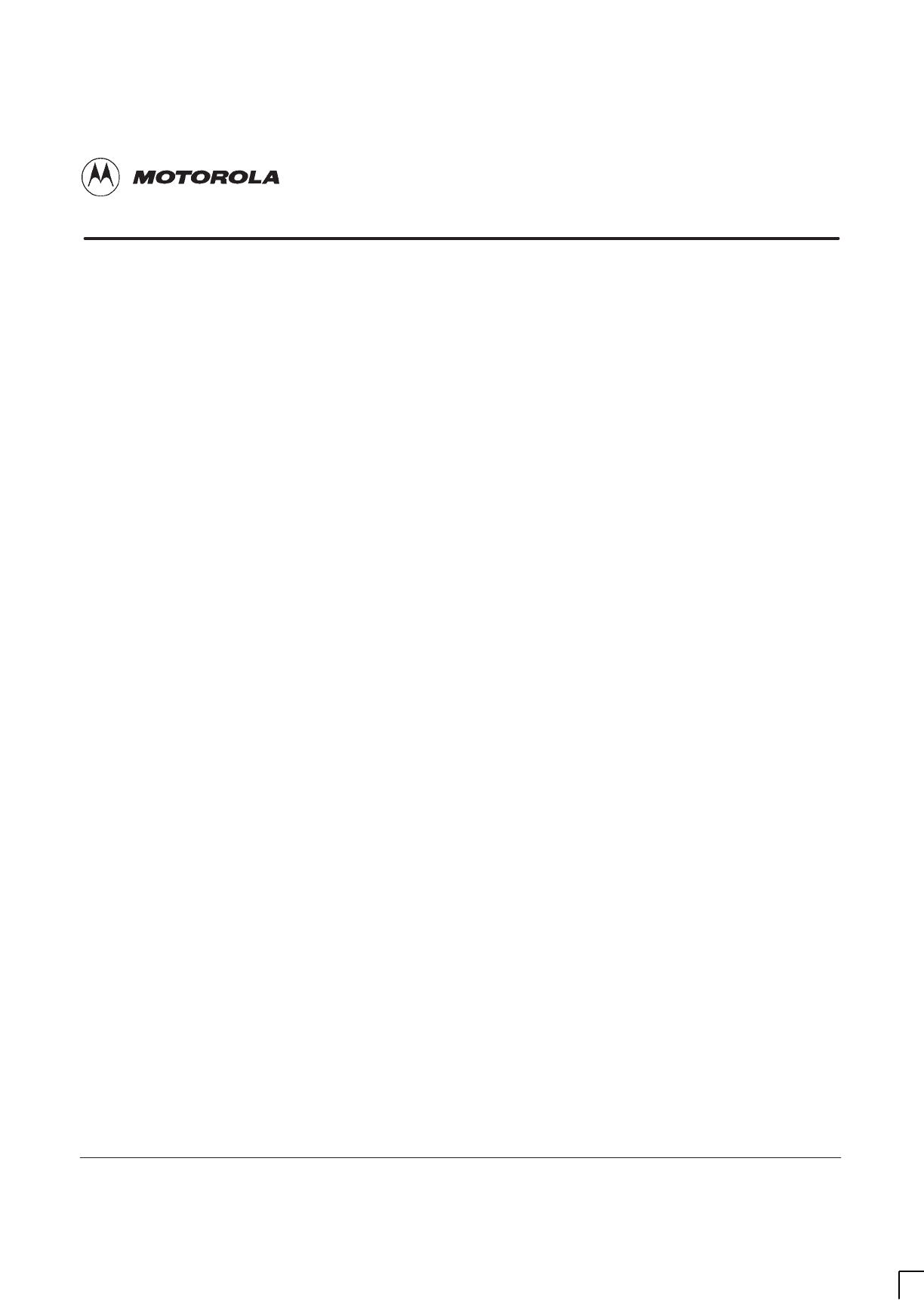
31st Oct 01
Parts Information: Horizon
macro
outdoor
68P02902W05-A
CONTROLLED INTRODUCTION
i
Chapter 1
Parts list
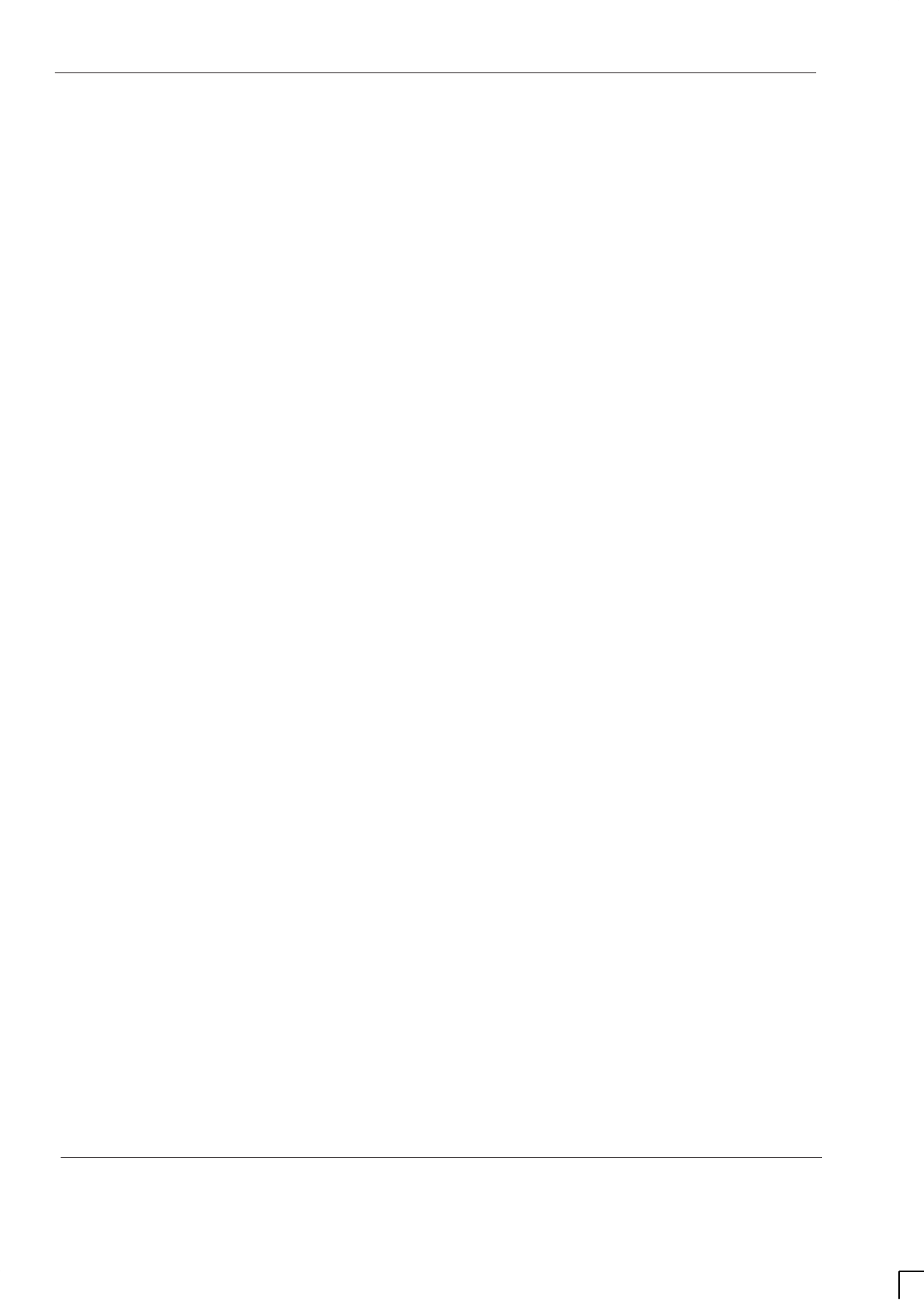
GSM-204-623
31st Oct 01
ii
Parts Information: Horizon
macro
outdoor
CONTROLLED INTRODUCTION
68P02902W05-A
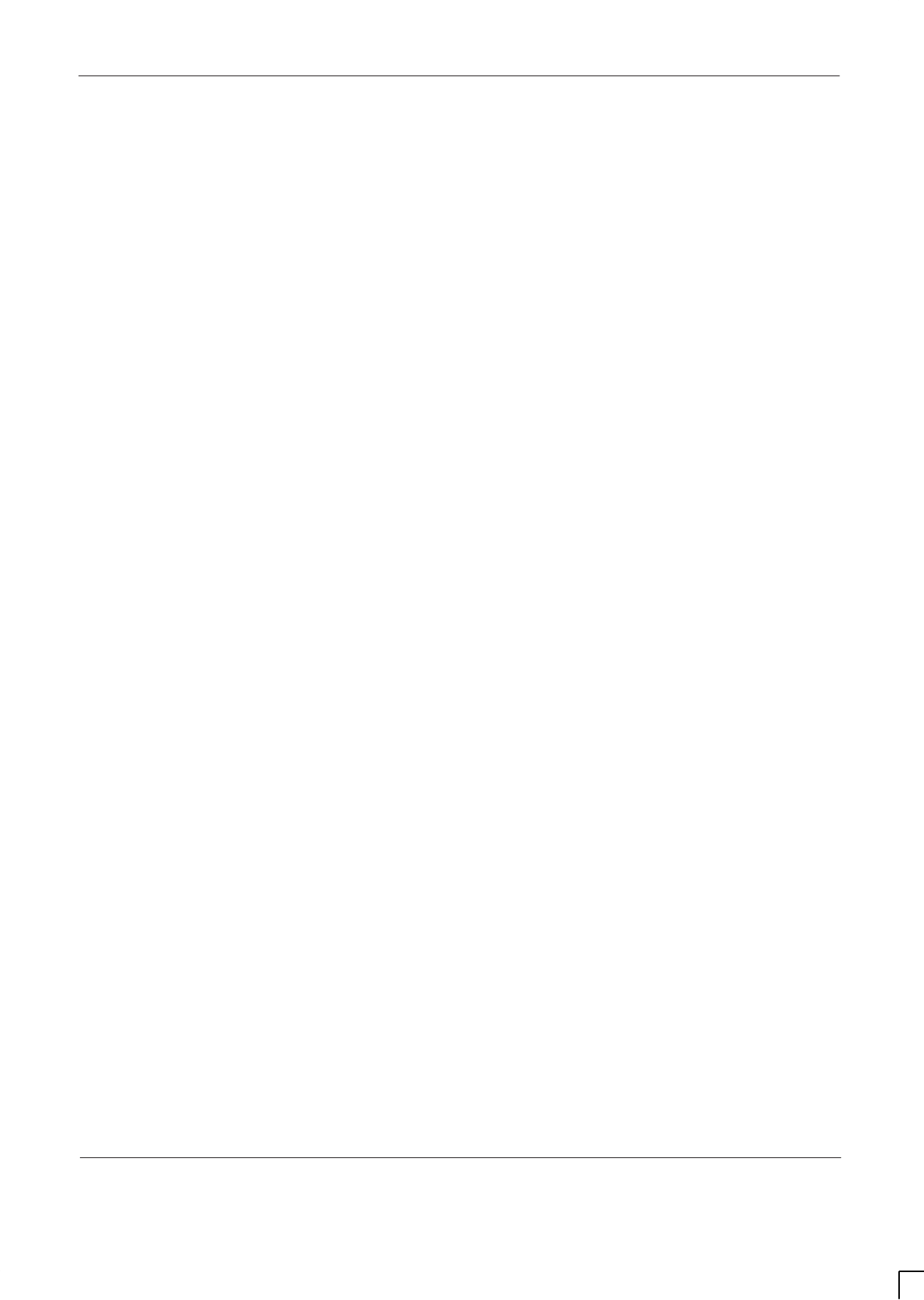
GSM-204-623
31st Oct 01
Parts Information: Horizon
macro
outdoor
68P02902W05-A
CONTROLLED INTRODUCTION
iii
Chapter 1
Parts list i. . . . . . . . . . . . . . . . . . . . . . . . . . . . . . . . . . . . . . . . . . . . . . . . . . . . . .
Parts information introduction Parts 1–1. . . . . . . . . . . . . . . . . . . . . . . . . . . . . . . . . . . . . . . . . .
Horizonmacro outdoor parts lists Parts 1–1. . . . . . . . . . . . . . . . . . . . . . . . . . . . . . . . . .
FRU items Parts 1–1. . . . . . . . . . . . . . . . . . . . . . . . . . . . . . . . . . . . . . . . . . . . . . . . . . . . .
Ordering method Parts 1–1. . . . . . . . . . . . . . . . . . . . . . . . . . . . . . . . . . . . . . . . . . . . . . . .
Diagram of Horizonmacro outdoor FRU modules Parts 1–2. . . . . . . . . . . . . . . . . . . .
Diagram of auxiliary equipment housing FRU modules Parts 1–3. . . . . . . . . . . . . . .
Parts for Horizonmacro outdoor Parts 1–4. . . . . . . . . . . . . . . . . . . . . . . . . . . . . . . . . . . . . . . .
Spares Table Parts 1–4. . . . . . . . . . . . . . . . . . . . . . . . . . . . . . . . . . . . . . . . . . . . . . . . . . .
Parts for optional equipment Parts 1–7. . . . . . . . . . . . . . . . . . . . . . . . . . . . . . . . . . . . . . . . . . .
Introduction to optional equipment parts lists Parts 1–7. . . . . . . . . . . . . . . . . . . . . . .
Spares table for the cable shroud Parts 1–7. . . . . . . . . . . . . . . . . . . . . . . . . . . . . . . . .
Spares table for the auxiliary equipment housing Parts 1–7. . . . . . . . . . . . . . . . . . . .
Glossary of terms unique to this equipment Parts 1–8. . . . . . . . . . . . . . . . . . . . . . . . . . . . . .
Overview of the glossary Parts 1–8. . . . . . . . . . . . . . . . . . . . . . . . . . . . . . . . . . . . . . . . .
Glossary of terms Parts 1–8. . . . . . . . . . . . . . . . . . . . . . . . . . . . . . . . . . . . . . . . . . . . . . .
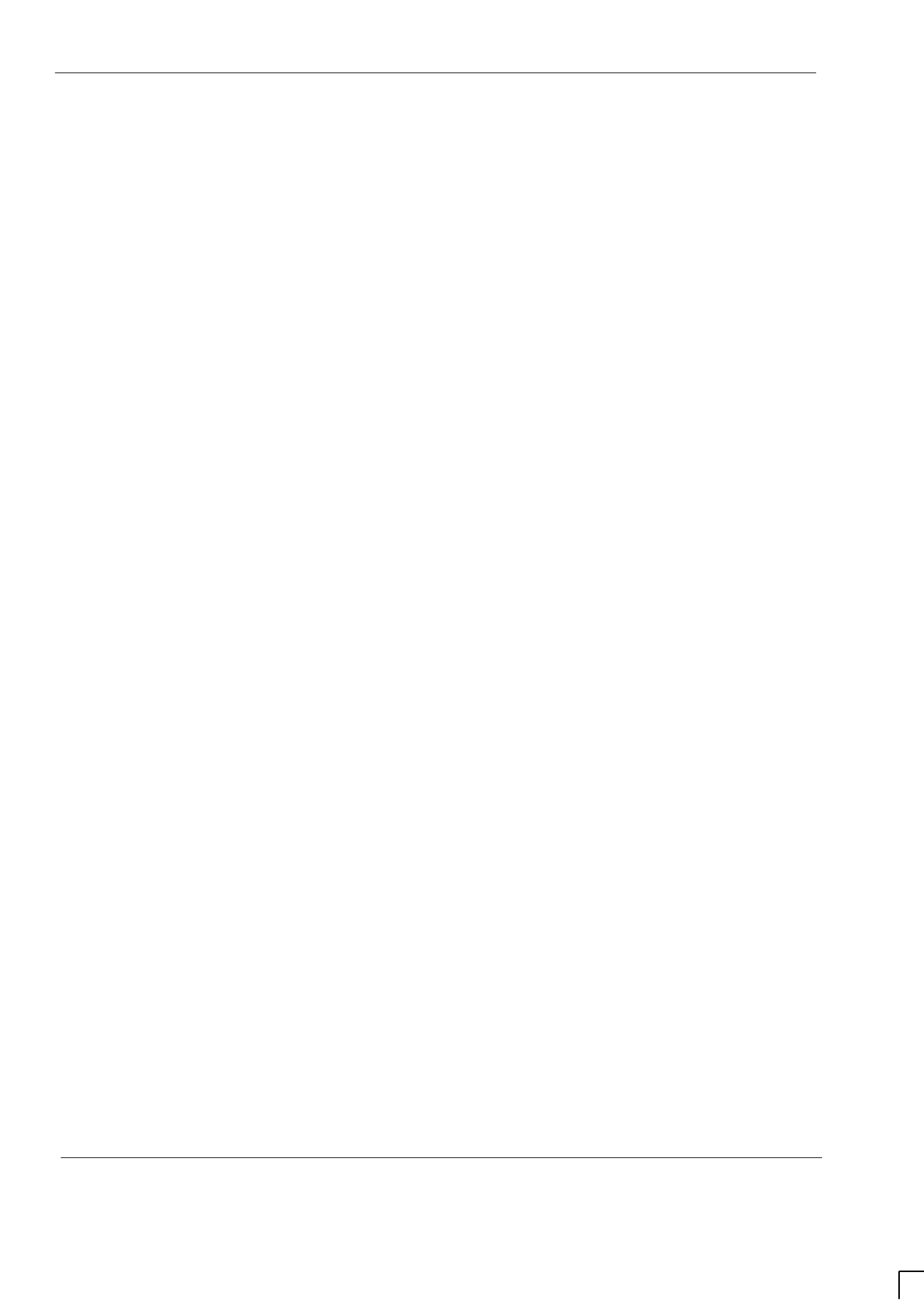
GSM-204-623
31st Oct 01
iv
Parts Information: Horizon
macro
outdoor
CONTROLLED INTRODUCTION
68P02902W05-A
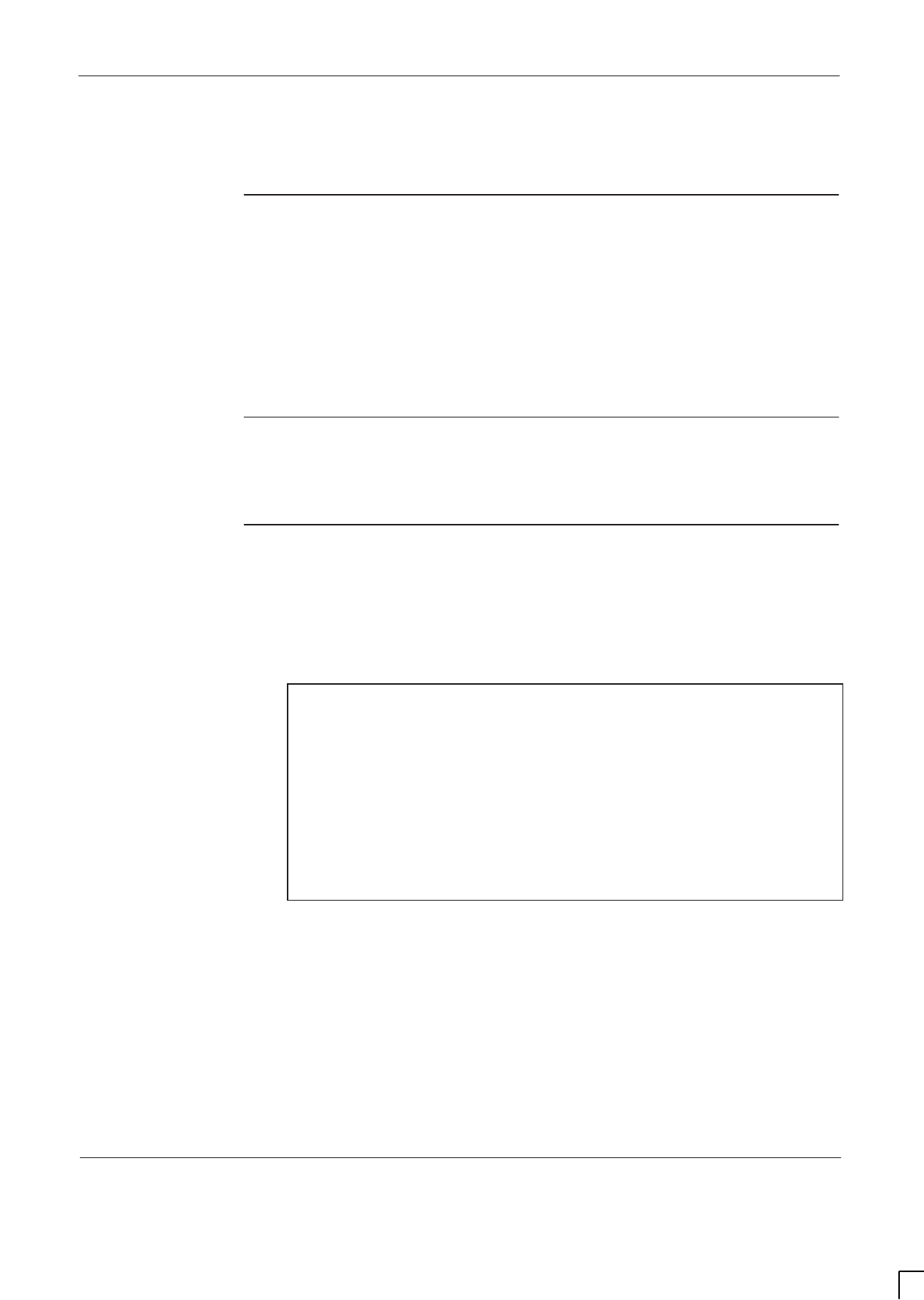
GSM-204-623 Parts information introduction
31st Oct 01
Parts Information: Horizon
macro
outdoor
68P02902W05-A
CONTROLLED INTRODUCTION
Parts 1–1
Parts information introduction
Horizon
macro
outdoor parts
lists
The parts lists for this manual reflect the availability of items for the product.
Each item consists of a description and an order number. This uniquely
identifies the required component. Some components are used in different
equipment in addition to Horizon
macro
outdoor. Some items are common to
both Horizon
macro
and M-Cell
6
.
FRU items
The majority of items on the parts list are Field Replaceable Units (FRUs). It is
not intended that sub-units of these parts will be supplied.
Ordering
method
Contact the local Motorola office for ordering information, including cost and
delivery.
If an item in a parts list is marked TBA, this means that the part number for the
item was not available at the time of publication of this manual.
NOTE Motorola reserves the right to change the design of the
product without notice. The information provided in this
chapter is intended as a guide. If the customer requires
the latest information, then consult the Motorola local
office who will be able to check on the web and confirm
the current situation.
Some items, for example PSMs, are produced by different
manufacturers, and so a replacement may appear slightly
different to the item it is replacing. All items bearing the
same order number, regardless of manufacturer, are fully
compatible.
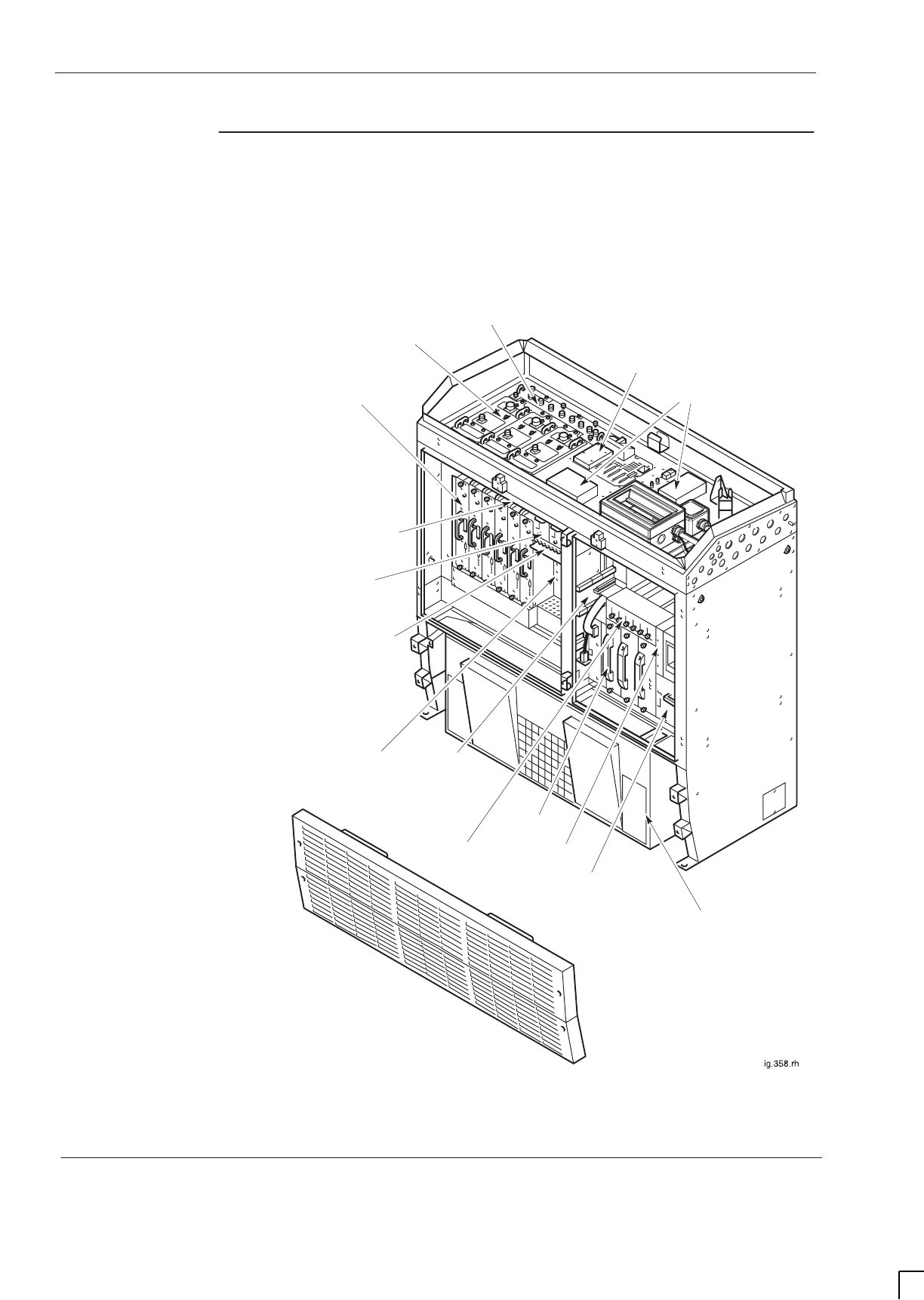
GSM-204-623
Parts information introduction
31st Oct 01
Parts 1–2
Parts Information: Horizon
macro
outdoor
CONTROLLED INTRODUCTION
68P02902W05-A
Diagram of
Horizon
macro
outdoor FRU
modules
Figure 1-1 shows the outdoor cabinet modules, including major FRUs, with
doors and lid omitted for clarity.
PSMs (x3)
Tx BLOCKS x3
(DCFs SHOWN AS
EXAMPLE) SURF (Rx)
CTUs (x6)
MAIN CAGE
TEMPERATURE SENSORS
(LOCATED ON
BACKPLANE)
DIGITAL
MODULES
ALARM BOARD
MCUF
FMUX/NIU/BPSM
CIRCUIT BREAKER
MODULE (CBM)
T43/BIB
TOPSMs
(x3)
ALARMS
INTERFACE
BOARD
CAB
INTERNAL
BATTERIES
TMS UNIT
KRONE BLOCKS
DC CIRCUIT
BREAKER PANEL
Figure 1-1 Horizon
macro
outdoor cabinet, showing major FRUs
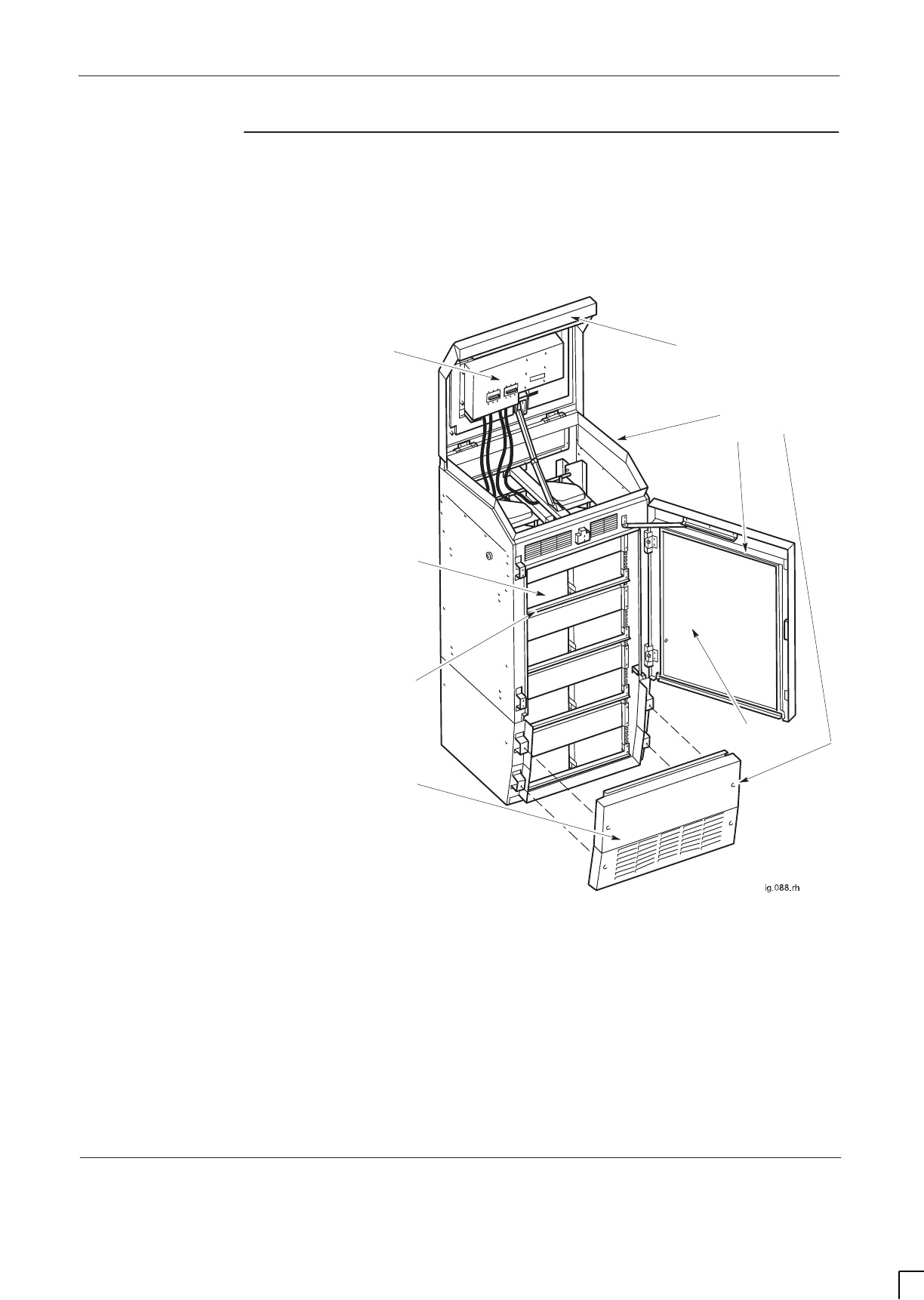
GSM-204-623 Parts information introduction
31st Oct 01
Parts Information: Horizon
macro
outdoor
68P02902W05-A
CONTROLLED INTRODUCTION
Parts 1–3
Diagram of
auxiliary
equipment
housing FRU
modules
Figure 1-2 shows the location of the FRUs for the auxiliary equipment housing.
POWER
DISTRIBUTION
BOX
FRONT PANEL
(CONTAINING FAN ASSEMBLY)
DOOR
ENVIRONMENTAL
SEALS
LID
HEATER MATS
(FITTED TO BATTERY
TRAYS BELOW
BATTERIES
BATTERY TRAY
Figure 1-2 Auxiliary equipment housing, showing FRUs
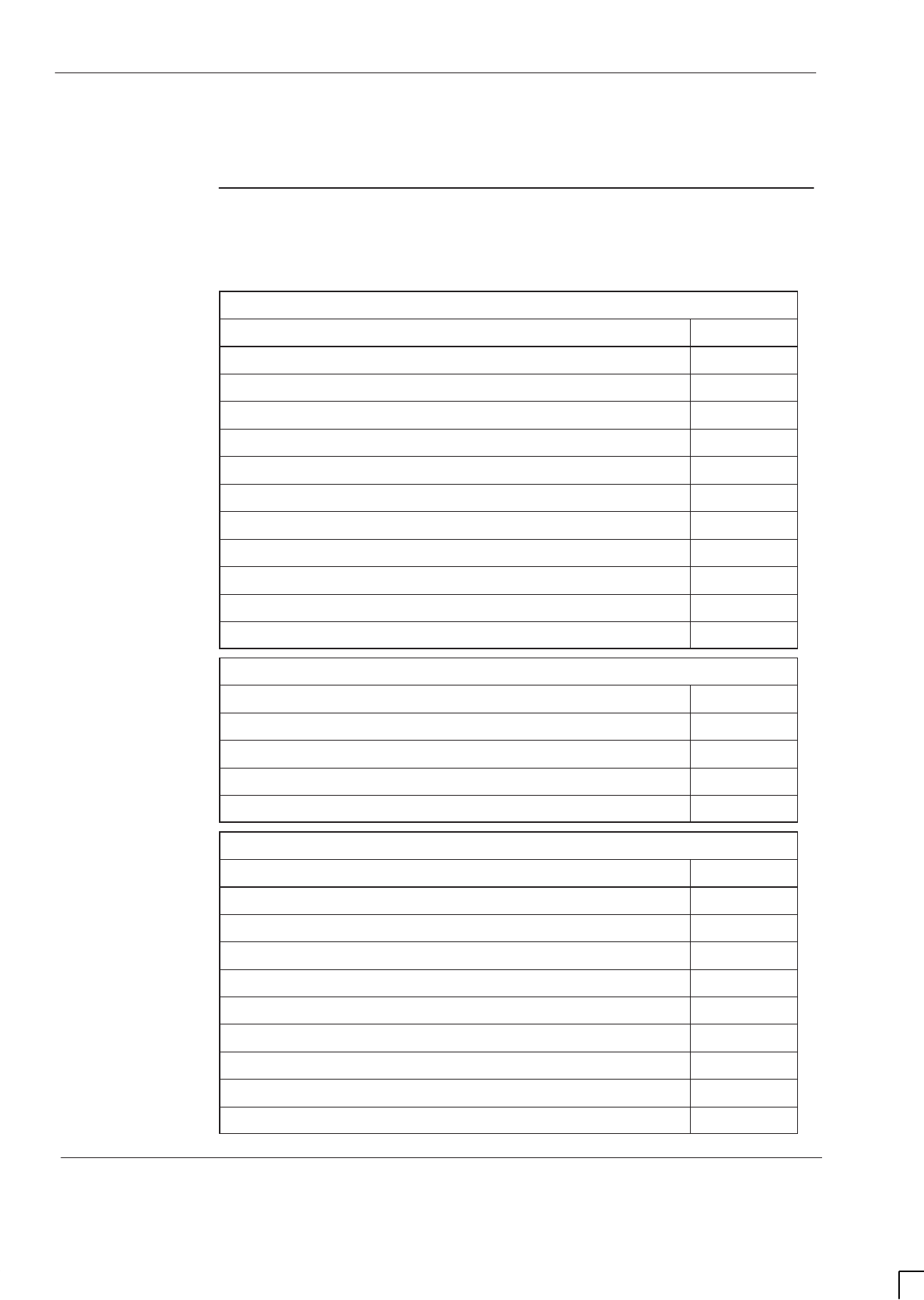
GSM-204-623
Parts for Horizonmacro outdoor
31st Oct 01
Parts 1–4
Parts Information: Horizon
macro
outdoor
CONTROLLED INTRODUCTION
68P02902W05-A
Parts for Horizon
macro
outdoor
Spares Table
The Horizon
macro
outdoor spares are listed in Table 1-1 to Table 1-7, available
as at October 2001. Contact the Motorola local office for an up to date list, or if
replacement parts are required that are not listed here.
Table 1-1 List of Horizon
macro
outdoor cabinet spares
Description Order No.
Outdoor BTS cabinet – standard colour SV1001
Outdoor BTS cabinet – M-Cell match SV1002
Outdoor BTS cabinet – dark green SV1003
Outdoor BTS cabinet – dark brown SV1004
Outdoor BTS cabinet – brick red SV1005
Gas strut for lid SVLN1332
Touch up paint – standard colour SVLN1333
Touch up paint – M-Cell match SVLN1335
Touch up paint – dark green SVLN1337
Touch up paint – dark brown SVLN1338
Touch up paint – brick red SVLN1339
Table 1-2 List of Horizon
macro
outdoor line interface spares
Description Order No.
Line interface NIU-E1 and CIM/T43 (75 ohm) SWLN2922
Line interface NIU-E1 and BIM/BIB (120 ohm) SWLN2923
BIM/BIB SWLN4024
CIM/T43 SWLN4025
Table 1-3 List of Horizon
macro
outdoor digital spares
Description Order No.
NIU-E1 SWLN4403
NIU-T1 SWLN4404
FMUX SWLN4406
MCUF SWLN5227
Alarm module SWLN5228
Alarm module with GPS functionality SWLN8510
GPS cable SWKN8115
PCMCIA memory card SWLN5239
BPSM SWPN2567
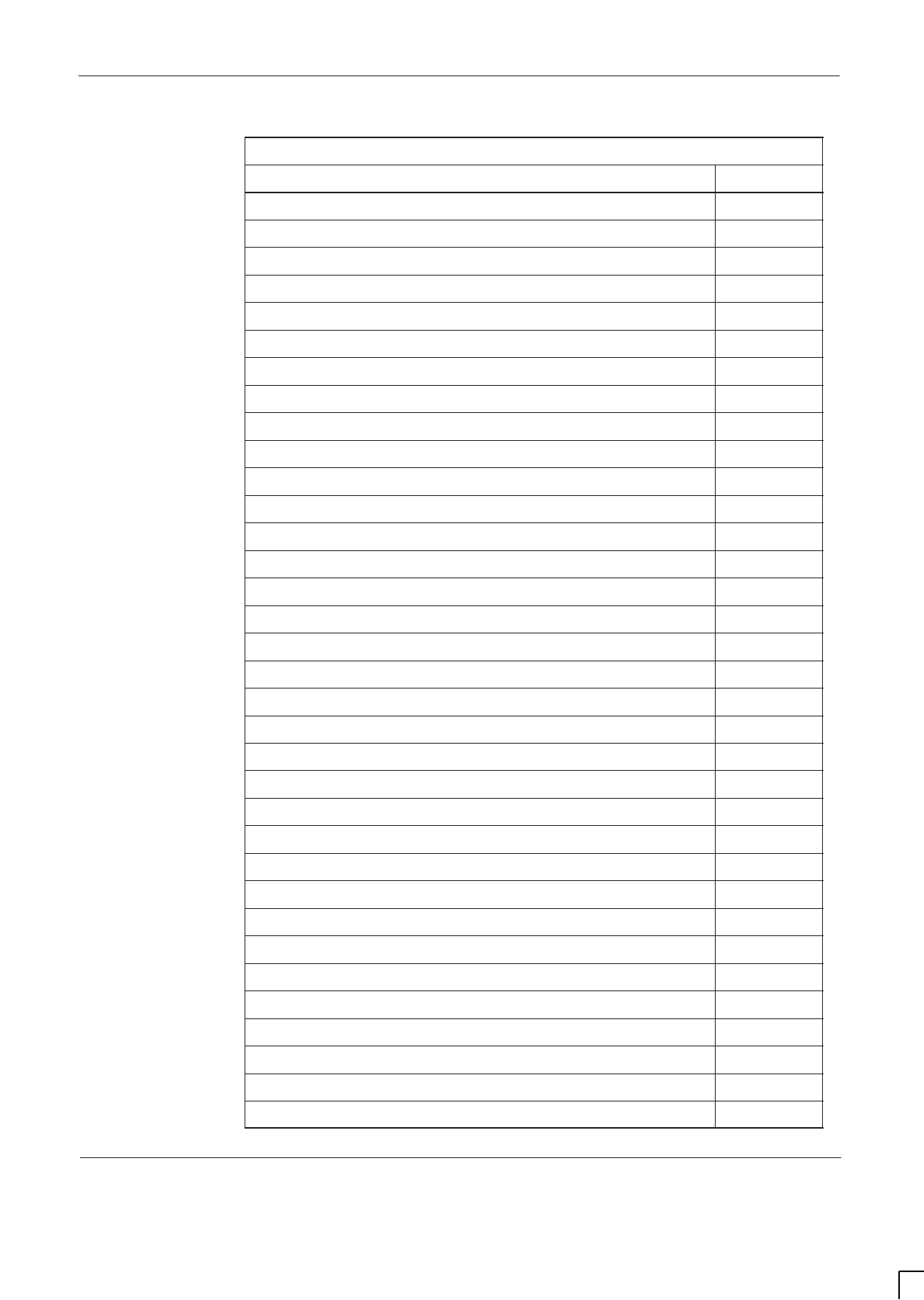
GSM-204-623 Parts for Horizonmacro outdoor
31st Oct 01
Parts Information: Horizon
macro
outdoor
68P02902W05-A
CONTROLLED INTRODUCTION
Parts 1–5
Table 1-4 List of Horizon
macro
outdoor RF spares
Description Order No.
CBIA SVLN1240
CTU Tx cable SVKN1304
Duplexer cable SVKN1305
SURF harness SWHN5538
850 CTU TBA
900 CTU SWRF5193
1800 CTU SWRG5197
1900 CTU TBA
850 SURF TBA
900 SURF (single band) TBA
900 SURF (dual band) SWRF2879
1800 SURF (single band) SWRG2880
1800 SURF (dual band) TBA
1900 SURF TBA
850 DCF TBA
850 DDF TBA
850 TDF TBA
850 HCU TBA
900 DCF SVLF1224
900 DDF SVLF1225
900 TDF SVLF1226
900 HCU SVLF1227
1800 DCF SVLG1224
1800 DDF SVLG1225
1800 TDF SVLG1226
1800 HCU SVLG1227
1900 DCF TBA
1900 DDF TBA
1900 TDF TBA
1900 HCU TBA
SMA 50 ohm load SVLN1230
Outdoor blanks set SVLN1236
Feedthrough plate assembly SVLN1243
Dual band TDF SVLX1198
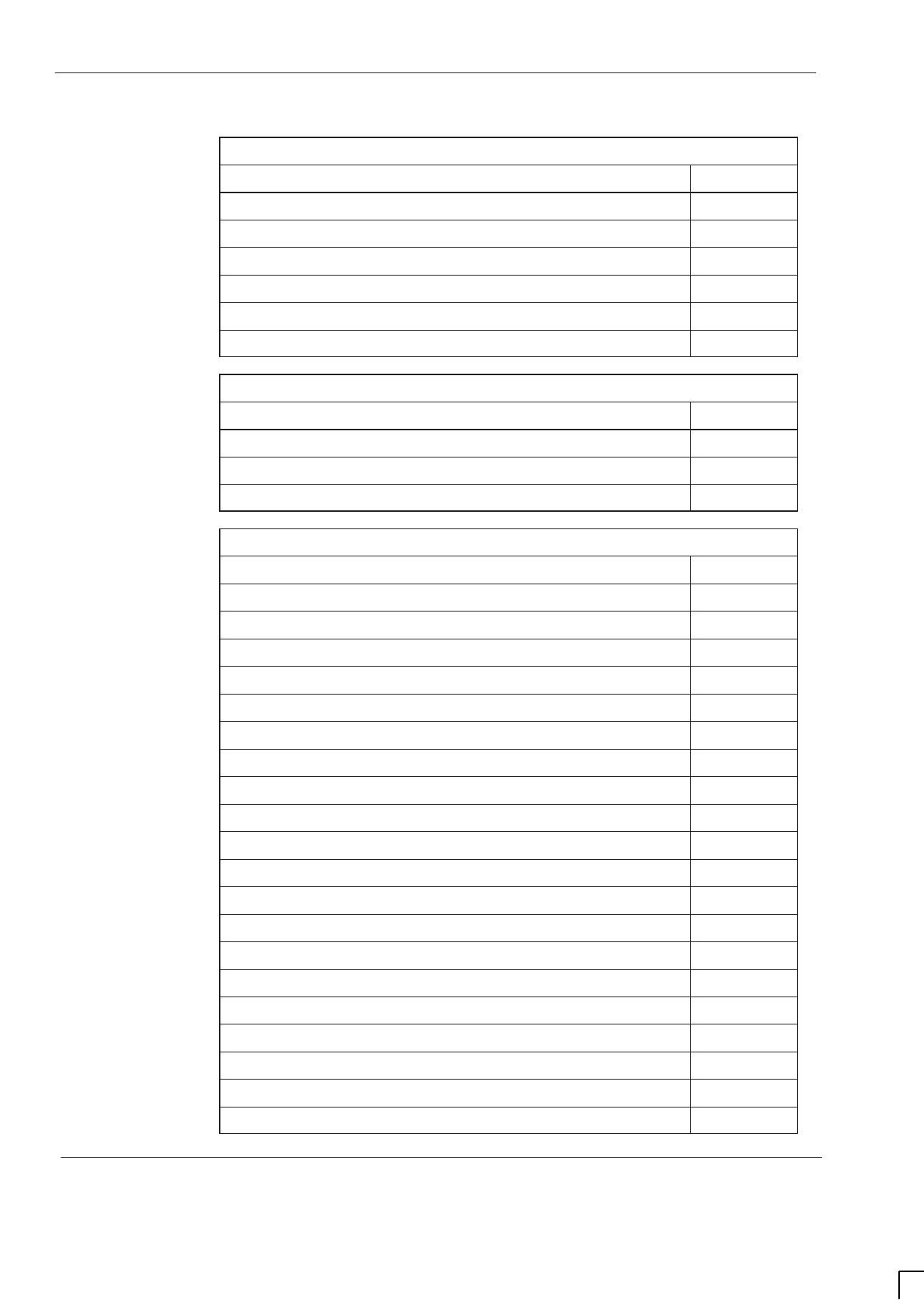
GSM-204-623
Parts for Horizonmacro outdoor
31st Oct 01
Parts 1–6
Parts Information: Horizon
macro
outdoor
CONTROLLED INTRODUCTION
68P02902W05-A
Table 1-5 List of Horizon
macro
outdoor power supply spares
Description Order No.
Outdoor internal battery tray SVPN1162
–48/60V PSM SVPN1221
CBM SWHN5519
Power cage SWHN5995
CAB SWLN6618
TOPSM SWPN5996
Table 1-6 List of Horizon
macro
outdoor temperature control spares
Description Order No.
TMS control board SVLN1330
TMS fan SVLN1331
TMS unit SWLN6001
Table 1-7 List of Horizon
macro
outdoor site expansion spares
Description Order No.
Outdoor Horizon
macro
to M-Cell
6
split sector cable pair SVKN1193
Outdoor Horizon
macro
to M-Cell
6
duplexer link cable SVKN1195
2nd (Extension) cabinet fibre SVKN1244
3rd (Extension) cabinet fibre SVKN1245
4th (Extension) cabinet fibre SVKN1246
Long SURF to SURF cable pair SVKN1313
Short SURF to SURF cable pair SVKN1314
Short DDF to HCU cable pair SVKN1315
Short SURF to earth plate cable SVKN1316
Long SURF to earth plate cable SVKN1317
Short Tx block to earth plate cable SVKN1318
Long Tx block to earth plate cable SVKN1319
3 input CBF 50 ohm load (used with M-Cell
6
) SVLN1196
RF cable plate (left) SVLN1320
RF cable plate (right) SVLN1321
Blanking panel (left) SVLN1322
Blanking panel (right) SVLN1323
Expansion plate assembly (left) SVLN1324
Expansion plate assembly (right) SVLN1325
Right side cable entry conversion kit SWKN5999
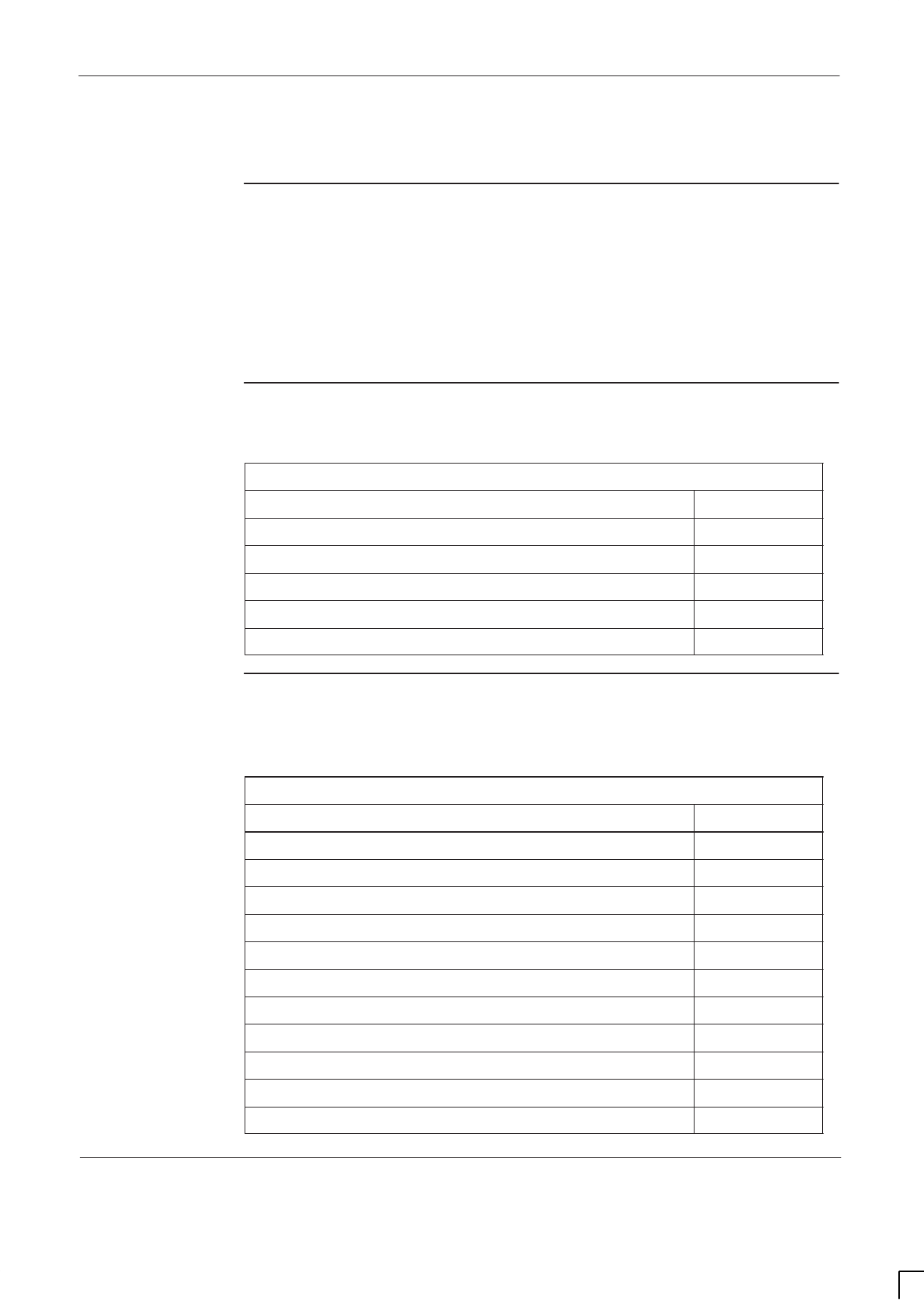
GSM-204-623 Parts for optional equipment
31st Oct 01
Parts Information: Horizon
macro
outdoor
68P02902W05-A
CONTROLLED INTRODUCTION
Parts 1–7
Parts for optional equipment
Introduction to
optional
equipment parts
lists
Table 1-8 and Table 1-9 list the spares for the optional equipment for the
Horizon
macro
outdoor, available as at October 2001. Contact the Motorola local
office for an up to date list, or if replacement parts are required that are not
listed here.
Spares table for
the cable
shroud
Table 1-8 List of spares for the cable shroud
Description Order No.
Cable shroud assembly – dark grey SVLN1217
Cable shroud assembly – M-Cell match SVLN1300
Cable shroud assembly – dark green SVLN1301
Cable shroud assembly – dark brown SVLN1302
Cable shroud assembly – brick red SVLN1303
Spares table for
the auxiliary
equipment
housing
Table 1-9 List of spares for the auxiliary equipment housing
Description Order No.
Long dc cable SVKN1352
Auxiliary equipment housing cabinet – dark grey SVLN1215
Battery tray SVLN1216
Auxiliary equipment housing cabinet – M-Cell match SVLN1296
Auxiliary equipment housing cabinet – dark green SVLN1297
Auxiliary equipment housing cabinet – dark brown SVLN1298
Auxiliary equipment housing cabinet – brick red SVLN1299
External alarm board SVLN1340
Fan SVLN1341
Heater mat SVLN1342
Battery pack SVPN1216
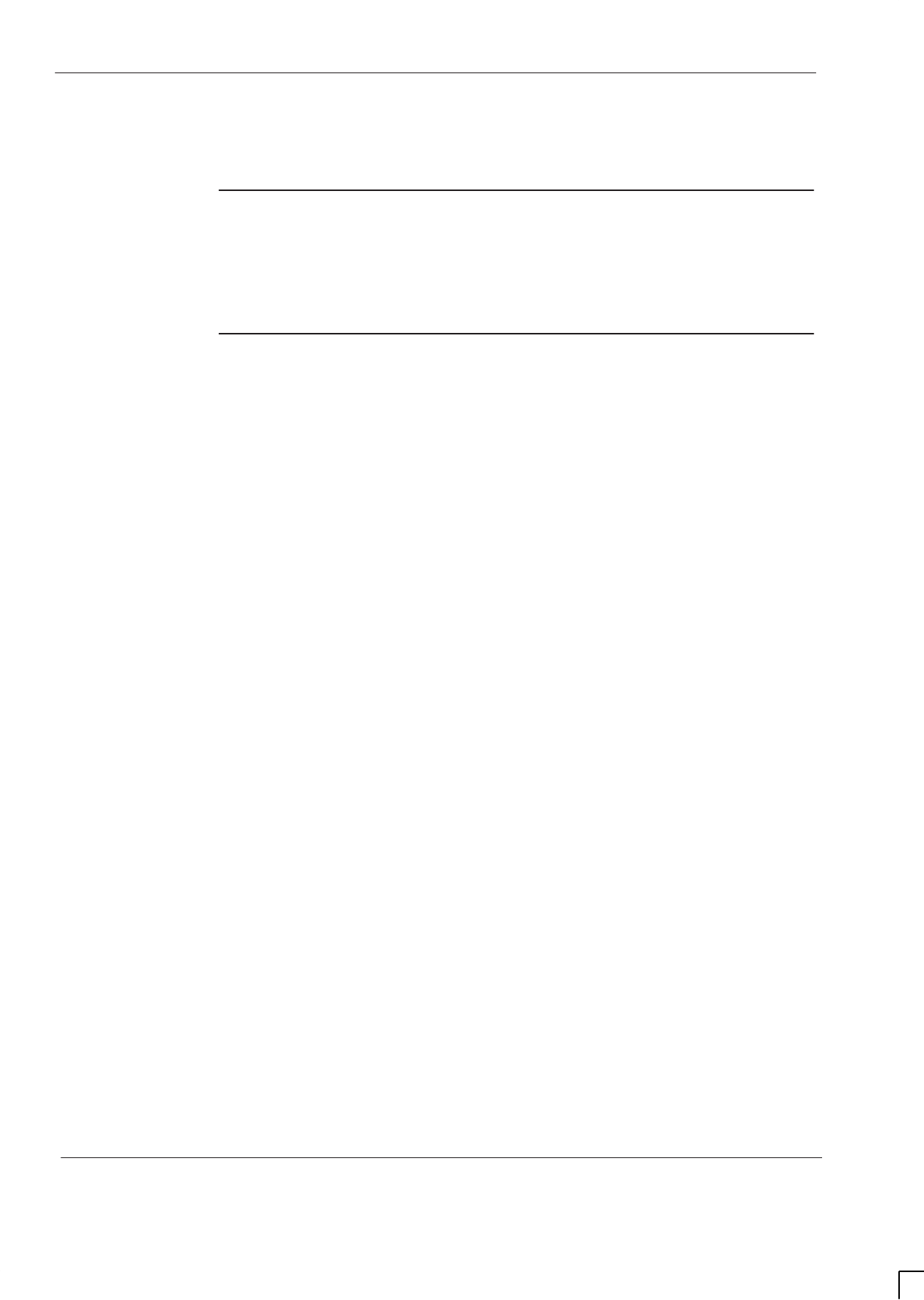
GSM-204-623
Glossary of terms unique to this equipment
31st Oct 01
Parts 1–8
Parts Information: Horizon
macro
outdoor
CONTROLLED INTRODUCTION
68P02902W05-A
Glossary of terms unique to this equipment
Overview of the
glossary
These glossary terms are unique to Horizon
macro
and M-Cell
6
equipment.
These and other GSM terms can be found in
System Information: General:
(GSM-100-101)
.
Glossary of
terms
AEH
Auxiliary Equipment Housing
BPSM
Micro BSU Power Supply Module
CAB
Control and Alarm Board
CBM
Circuit Breaker Module
CTU
Compact Transceiver Unit
DCF
Duplexed Combining bandpass Filter
DDF
Dual-stage Duplexed combining Filter
FMUX
Fibre optic Multiplexer
HCU
Hybrid Combining Unit
MCUF
Main Control Unit with dual FMUX
NIU
Network Interface Unit
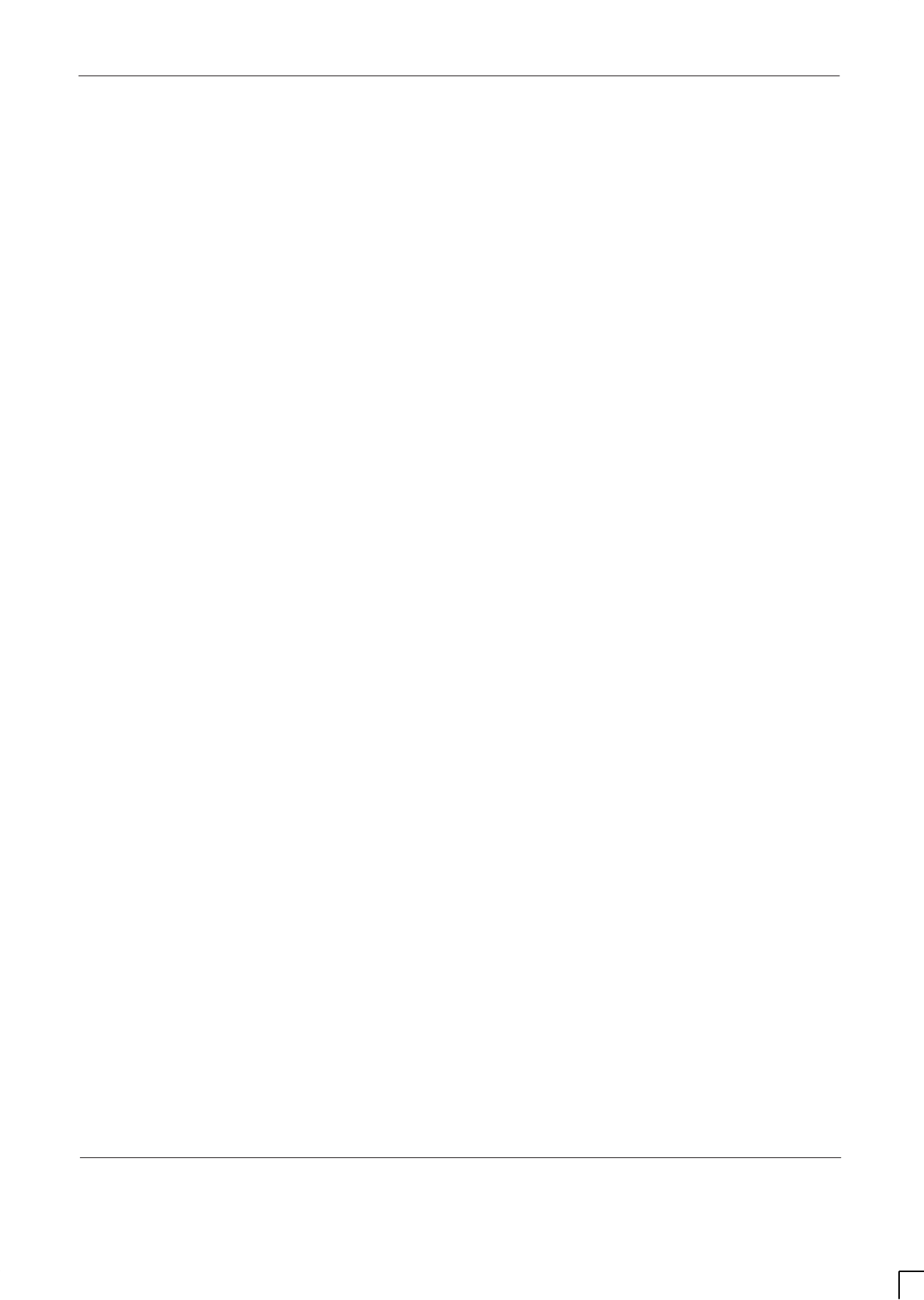
GSM-204-623 Glossary of terms unique to this equipment
31st Oct 01
Parts Information: Horizon
macro
outdoor
68P02902W05-A
CONTROLLED INTRODUCTION
Parts 1–9
SURF
Sectorized Universal Receiver Front-end
TDF
Twin Duplexed Filter
TMS
Thermal Management System
TOPSM
The Outdoor Power Supply Module
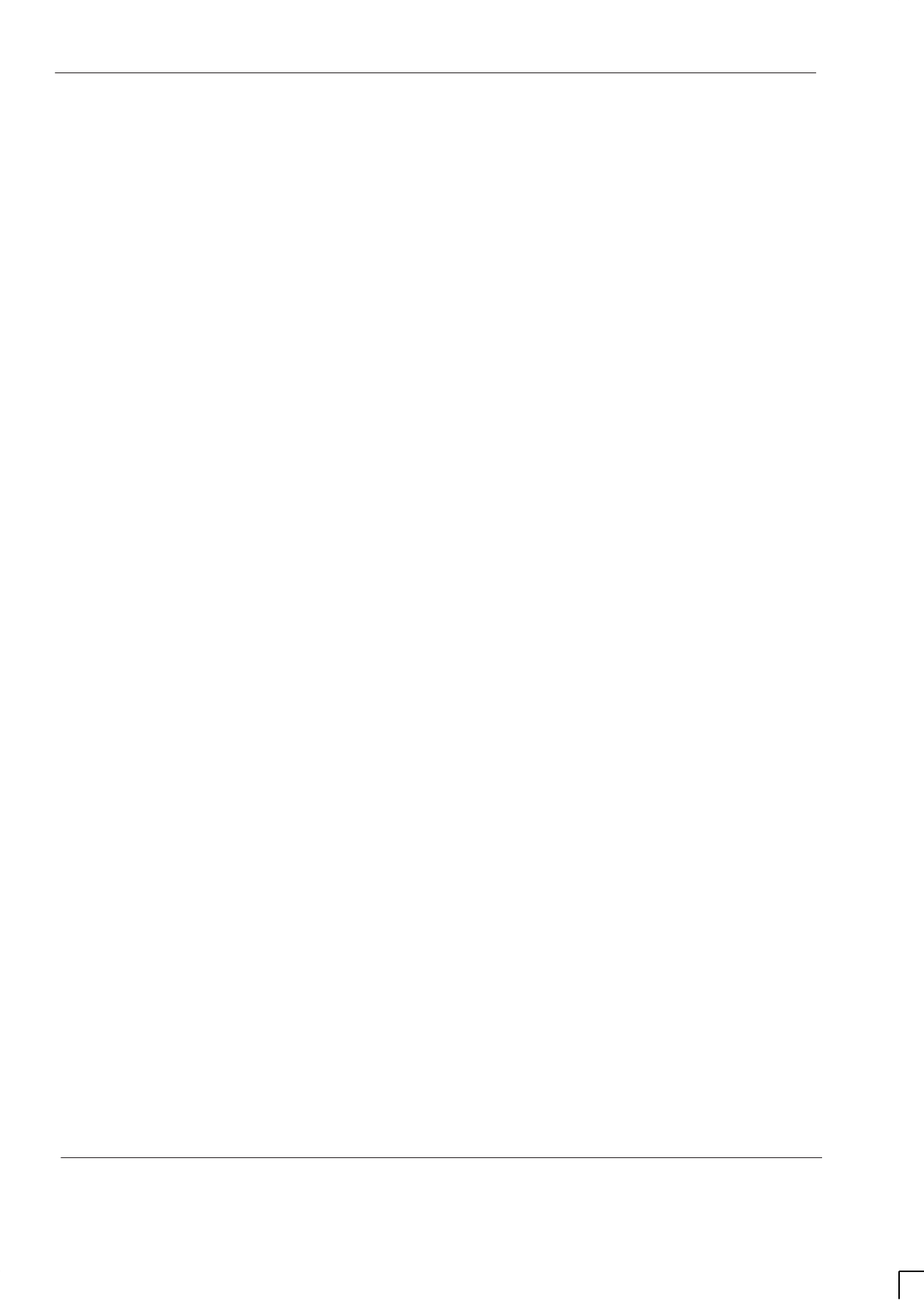
GSM-204-623
Glossary of terms unique to this equipment
31st Oct 01
Parts 1–10
Parts Information: Horizon
macro
outdoor
CONTROLLED INTRODUCTION
68P02902W05-A
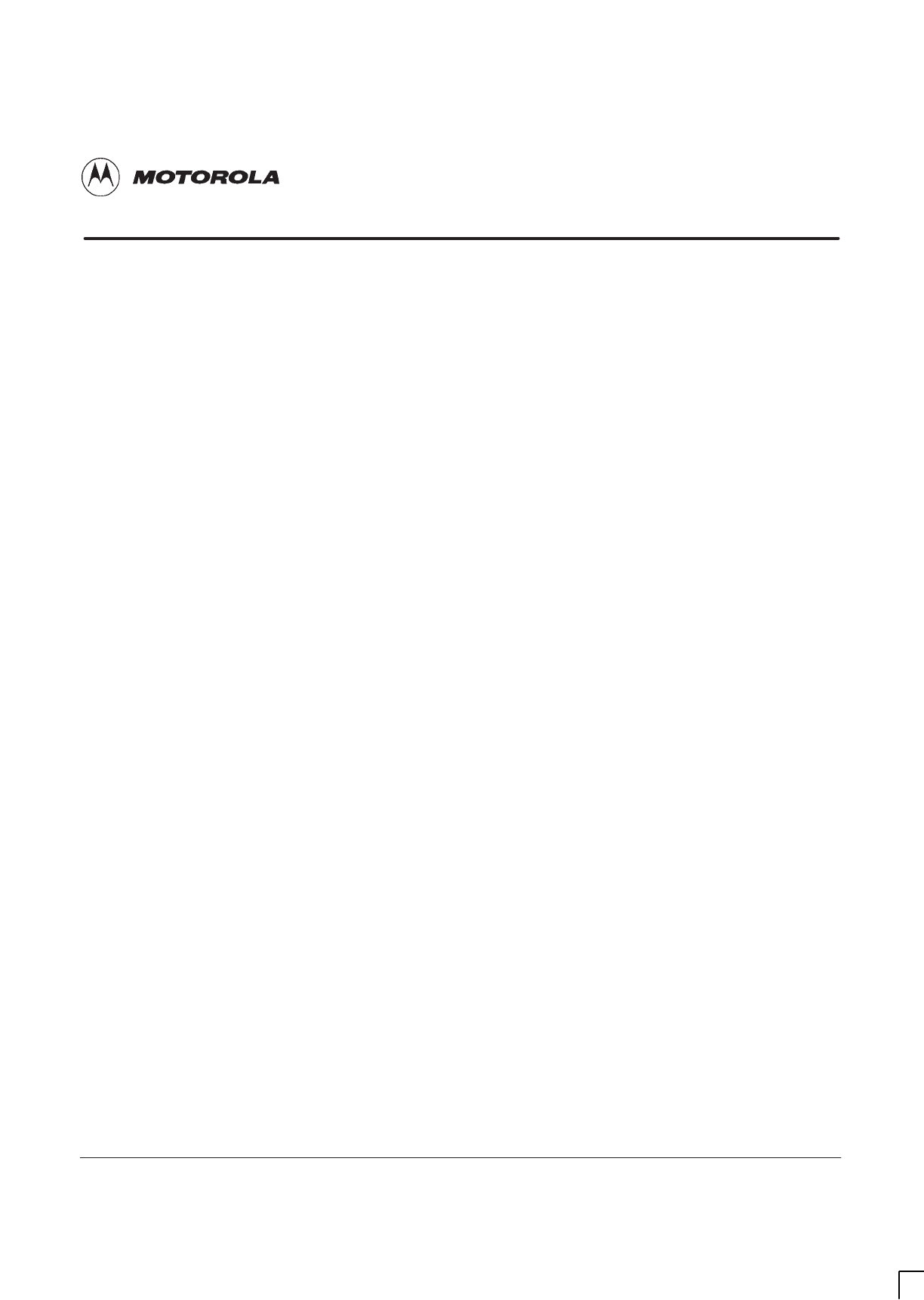
31st Oct 01
Service Manual: Horizon
macro
outdoor
68P02902W12-A
CONTROLLED INTRODUCTION
I–1
Index
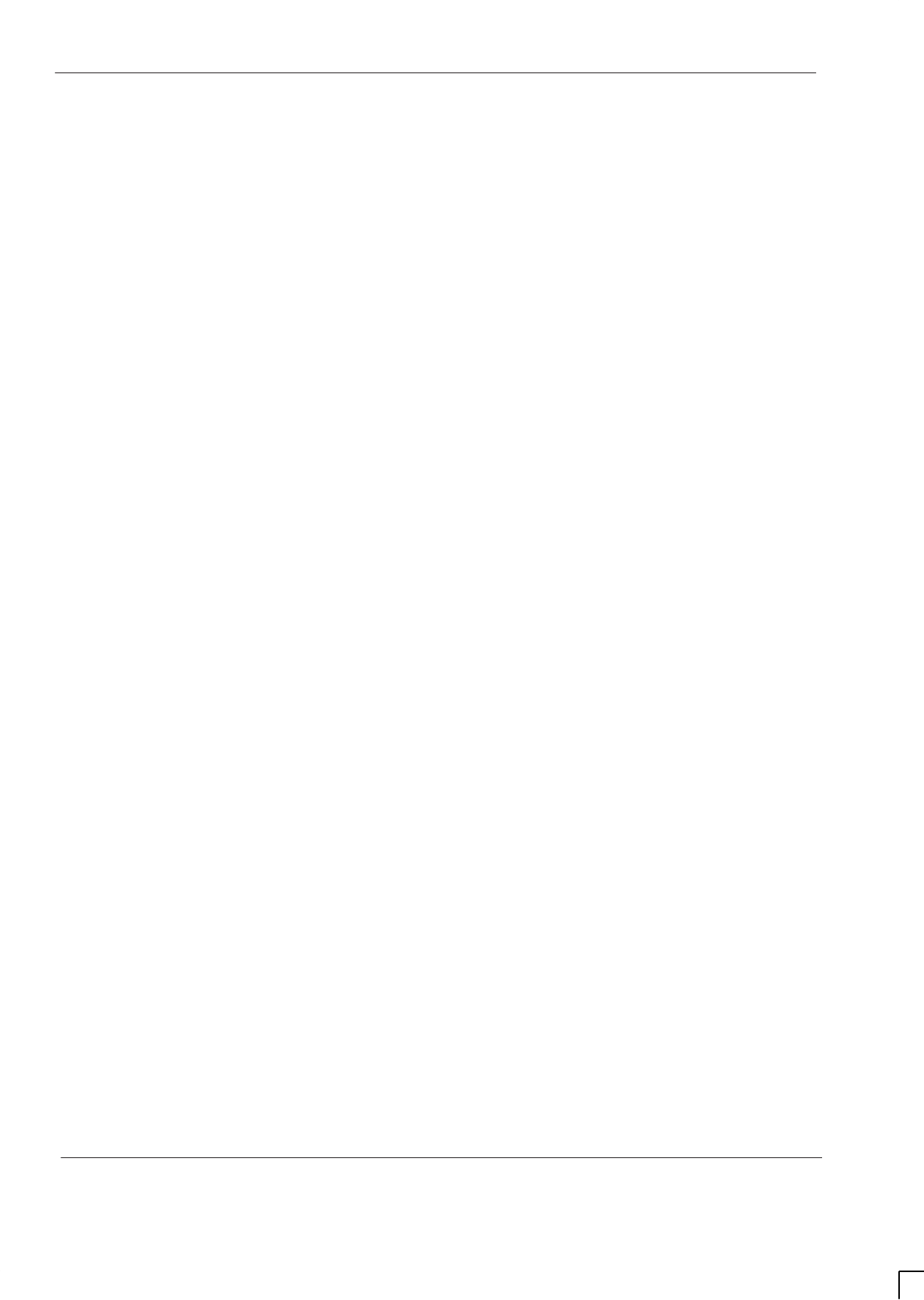
GSM-204-020
31st Oct 01
I–2
Service Manual: Horizon
macro
outdoor
CONTROLLED INTRODUCTION
68P02902W12-A
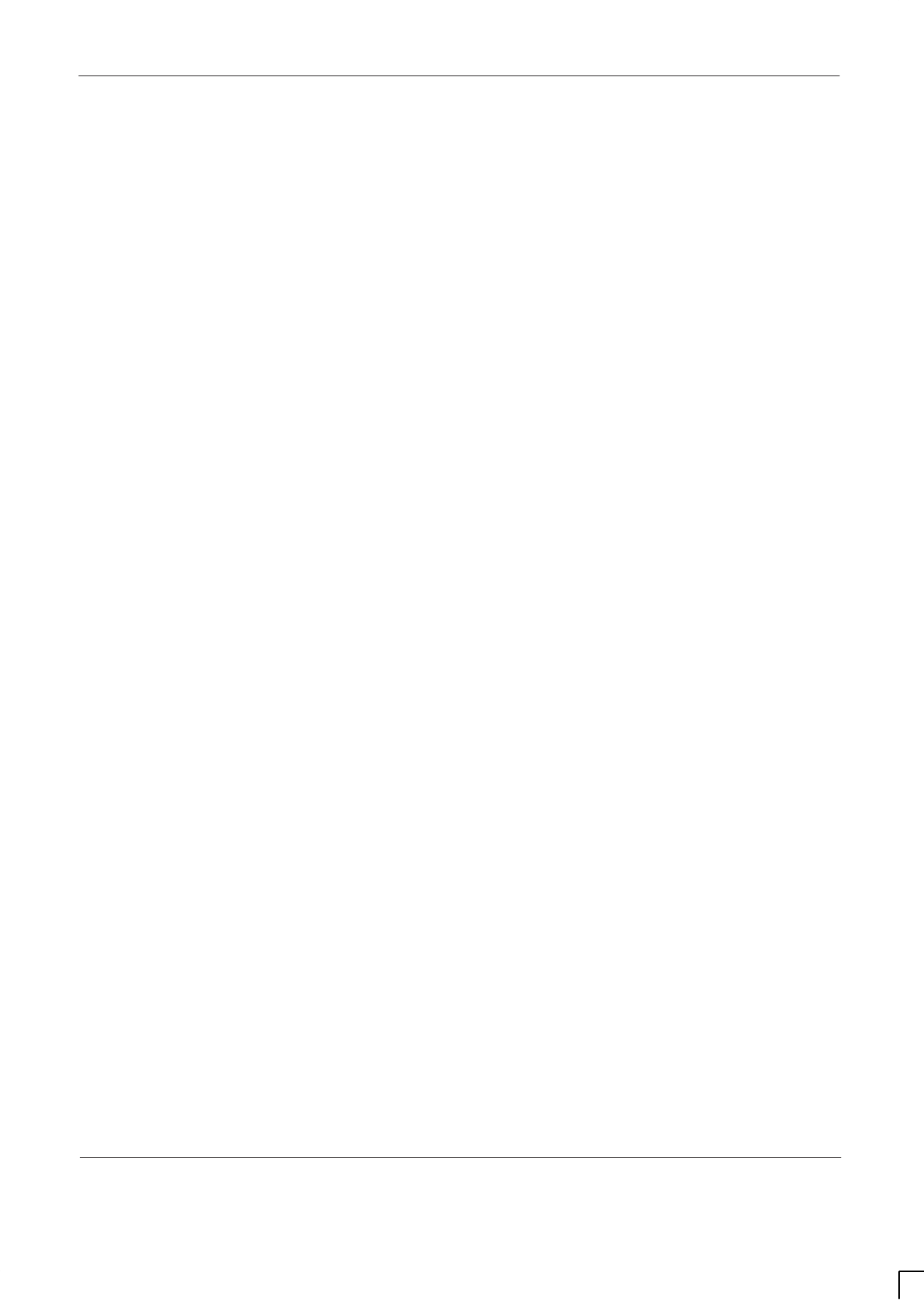
GSM-204-020
31st Oct 01
Service Manual: Horizon
macro
outdoor
68P02902W12-A
CONTROLLED INTRODUCTION
I–3
A
AC outlet socket, Tech. 4–8
AC power, insulation check, Inst. 7–5
AC power distribution box
number 1, Tech. 4–6
number 2, Tech. 4–7
AC supply
cable colour coding, Inst. 3–20
connecting to 3–phase (delta), Inst. 7–7
connecting to 3–phase (star), Inst. 7–7
connecting to single phase, Inst. 7–6
Acronyms, BTS cabinet, Tech. 1–2
Alarm module
extension cabinet, Tech. 6–26
functionality, Tech. 6–26
LED descriptions, Tech. 6–27
replacement, Maint. 3–40
view, Tech. 6–25
Alarm signals, auxiliary equipment housing,
Tech. 7–4
Alarms
door open, Tech. 4–21
extension cabinets, Tech. 6–26
external, pin connections, Inst. 3–68
power supply, Tech. 4–20
PSM, Tech. 4–32
site, Inst. 2–9
smoke, Tech. 4–21
TMS fail, Tech. 4–21
Alarms interface board
connections from auxiliary equipment
housing, Tech. 7–4
connectors, Tech. 2–17
layout diagram, Tech. 2–16, Inst. 7–18,
Maint. 2–9
Anderson connectors, auxiliary equipment
housing, Tech. 7–1
Antenna connections, Inst. 3–31
Attachment screws, CBIA, Maint. 3–47
Auxiliary equipment housing
cable connections, Inst. 5–10
cable shroud attachment points, Inst. 4–8
dimensions, Tech. 1–12
earthing, Inst. 5–10
external alarms interface board, Tech. 7–4
installation, Inst. 5–2
installing batteries, Inst. 5–6
major components, Tech. 7–2
mechanical design, Tech. 7–1
power connections, Inst. 5–10
temperature alarm sensors, Tech. 7–3
template installation, Inst. 5–3
weight, Tech. 1–13
B
Backplane, replacement, Maint. 3–47
Baseband hopping, Tech. 5–22
Batteries
arrangement in auxiliary equipment housing,
Inst. 5–6
configuring to supply two BTS cabinets, Inst.
5–12
external dc connections, Tech. 4–13
internal battery tray, Tech. 4–11
testing backup operation, Inst. 7–19, Maint.
2–10
Battery backup, power duration, Tech. 1–12
Battery, internal, replacement, Maint. 3–24
BDM port, MCUF, Tech. 6–8
BIB, pinouts, Inst. 3–64
Blanking plate, Tx block screws, Tech. 5–31
Blanking plate (Tx block), Tech. 5–34
replacement, Maint. 3–37
Boot code download, Tech. 6–9
CTU status LEDs, Tech. 5–9
BPSM
dc power outputs, Tech. 4–37
LED display, Tech. 4–37
locations, Tech. 6–2
replacement, Maint. 3–40
BTS architectures, Horizonmacro and M–Cell6,
Inst. 6–2
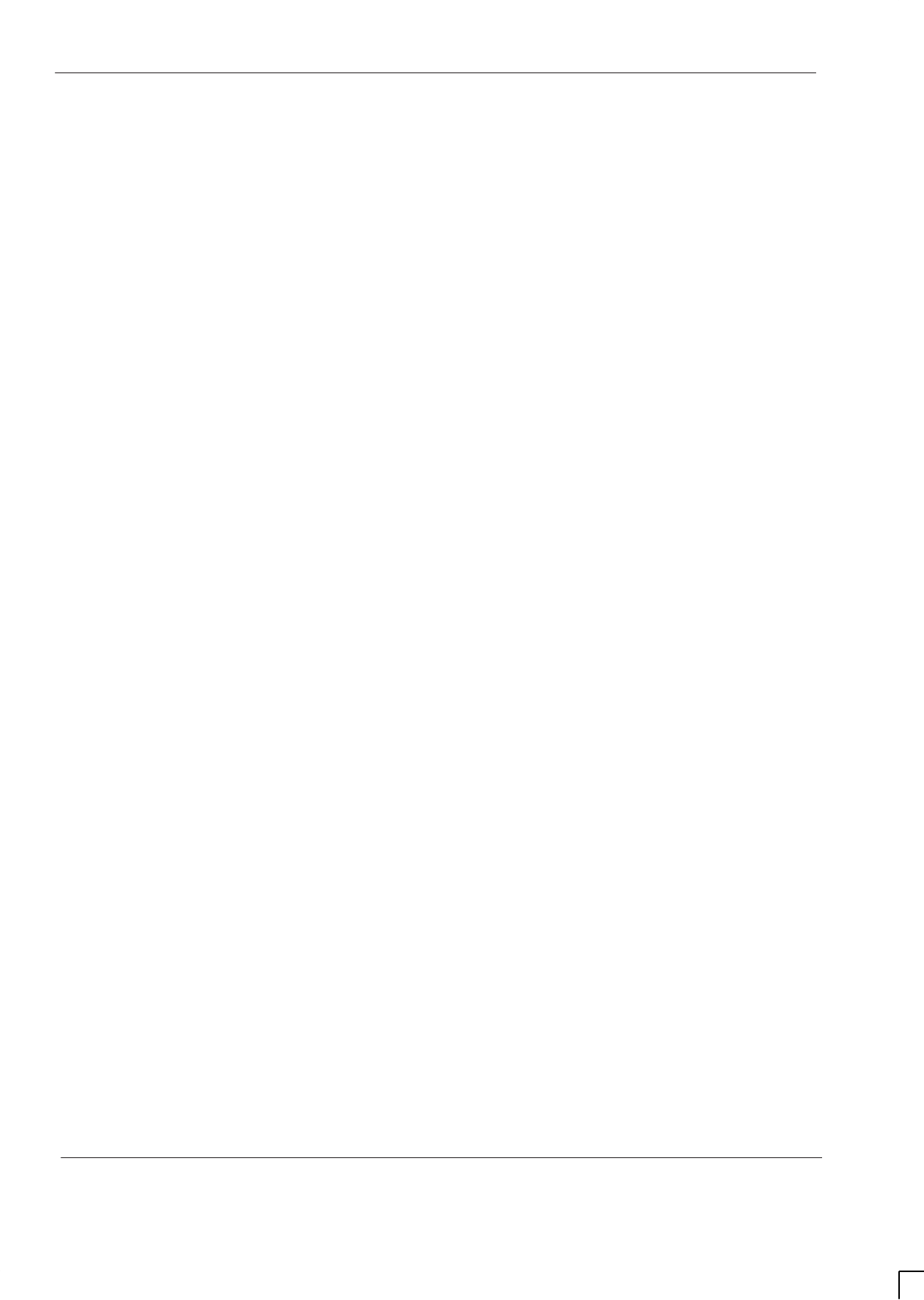
GSM-204-020
31st Oct 01
I–4
Service Manual: Horizon
macro
outdoor
CONTROLLED INTRODUCTION
68P02902W12-A
C
CAB
alarm functions, Tech. 4–20
debug, Tech. 4–24
DIP switch settings, Tech. 4–25
front panel indicators, Tech. 4–16
front panel switches and buttons, Tech. 4–17
removal and replacement, Maint. 3–16
Cabinet
attaching the cable shroud, Inst. 4–2
dimensions, Tech. 1–12, Tech. 1–17, Inst.
2–6
earthing, Inst. 3–20
internal layout, Tech. 2–3
lifting, Inst. 3–7, Inst. 3–10, Inst. 8–1
mechanical inspection, Maint. 2–7
power supply requirements, Inst. 2–3
powering up, Inst. 7–8
structural requirements, Inst. 2–5
temperature control, Tech. 3–1
template installation, Inst. 3–13
unpacking, Inst. 3–9
weight, Tech. 1–13
Cabinet modules, normal LED conditions, Maint.
2–6
Cable routeing, Inst. 3–19
Cable shroud
assembly diagram, Tech. 8–2
configurations, Tech. 8–1
installation considerations, Inst. 4–1
installation diagram, Inst. 4–3
installation procedure, Inst. 4–2
Cabling, power and earth, Inst. 3–19
Cage, replacement, Maint. 3–47
CAL port, MCUF, Tech. 6–8
Calibration, CTUs, Inst. 3–11
CBIA
attachment screws, Maint. 3–47
harness, backplane and interface panel,
Tech. 2–11
module locations in, Tech. 2–12
replacement, Maint. 3–47
CBIA interface panel, layout diagram, Tech.
2–14
CBM
front panel diagram, Tech. 4–34
operation, Tech. 4–35
overview, Tech. 4–34
replacement, Maint. 3–22
Checks, pre–power up, Inst. 7–3
CIM, pinouts, Inst. 3–65
CIM/BIM, (T43/BIB), Tech. 6–21
Circuit breaker module
operation, Tech. 4–35
overview, Tech. 4–34
Circuit breakers, auxiliary equipment housing,
Tech. 7–4
cleaning materials, Maint. 2–2
Clearance, cabinet positioning, Tech. 1–16
Code loading, MCUF, Tech. 6–10
Component identification, main cabinet, Tech.
1–5
Configuration, Site optimization, Inst. 7–14
Connectors, Fibre optic extension, Inst. 3–61
Crate, packaging, Inst. 3–4
CTU
automatic gain control, Tech. 5–13
block diagram, Tech. 5–12
calibration, Inst. 3–11
CCCP processor, Tech. 5–18
connections to MCUF, Tech. 6–4
downlink traffic data flow, Tech. 5–19
EQCP processor, Tech. 5–17
front panel connectors, Tech. 5–11
IF and exciter stages, Tech. 5–14
installing a replacement module, Maint. 3–30
interface function, Tech. 5–18
IQ modulator, Tech. 5–14
LED status indicators, Tech. 5–9
power amplifier board, Tech. 5–15
removal procedure, Maint. 3–29
RF output power, Inst. 2–4
RSS processor, Tech. 5–17
Rx functions, Tech. 5–2
TDM links, Tech. 5–17
testing Rx circuitry, Tech. 5–7
Tx functions, Tech. 5–3
uplink traffic data flow, Tech. 5–19
variants, Tech. 5–4
CTU frequency hopping, Tech. 5–20
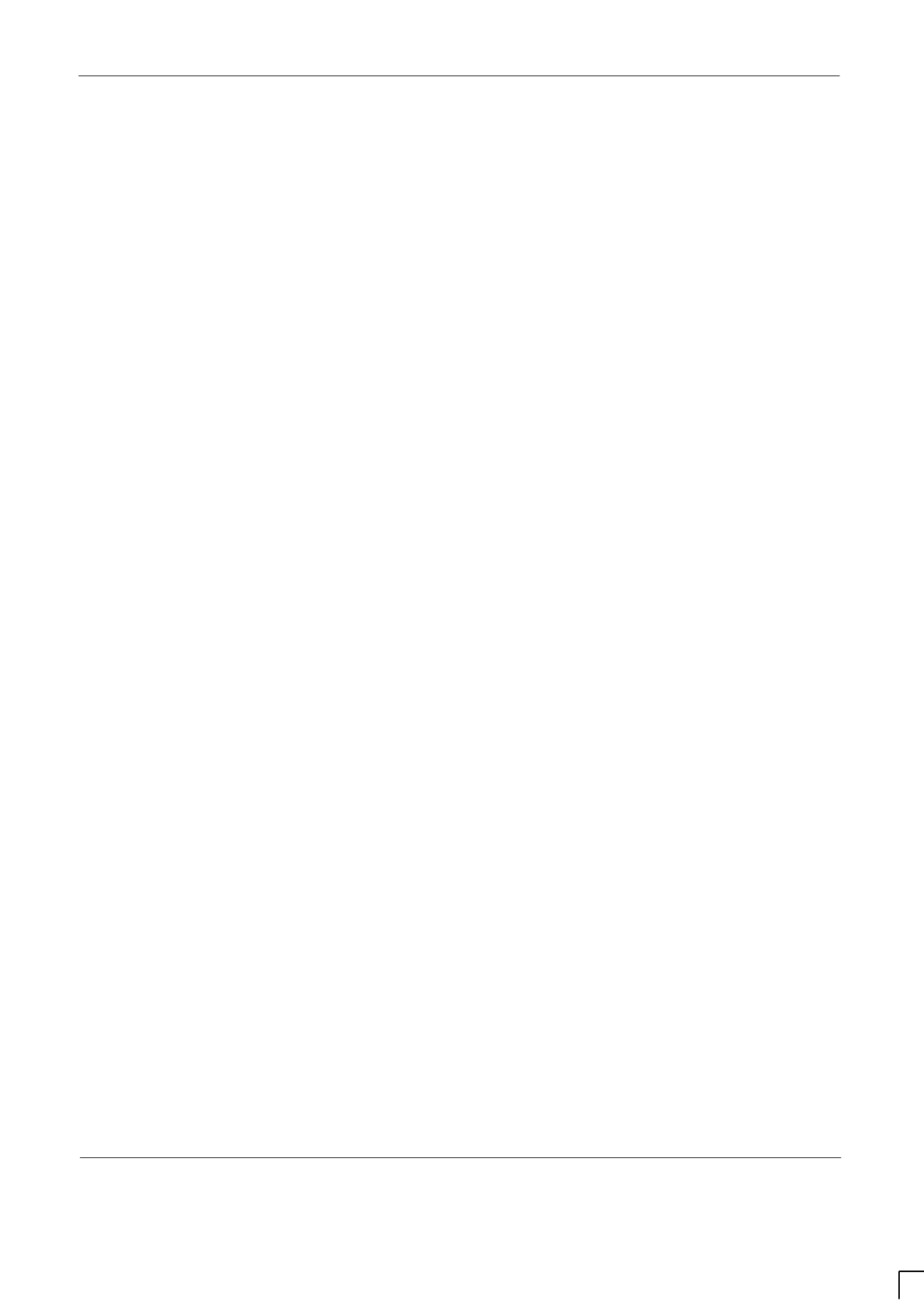
GSM-204-020
31st Oct 01
Service Manual: Horizon
macro
outdoor
68P02902W12-A
CONTROLLED INTRODUCTION
I–5
Customer equipment racking, Tech. 2–18
D
DC circuit breakers, replacement procedure,
Maint. 3–14
DC power
circuit breaker panel, Tech. 4–11
component diagram, Tech. 4–9
Internal battery backup, Tech. 4–11
DCF, Tech. 5–42
DDF, Tech. 5–44
Debug port, MCUF, Tech. 6–8
Decommissioning, BTS, Inst. 8–3
Diagnostics, loopback test function, Tech. 5–5
Diagram, interface panel, Inst. 3–61
Digital boards
power supply, Tech. 4–36
replacement, Maint. 3–40
Digital modules
locations, Tech. 6–2
overview, Tech. 6–1
redundancy, Tech. 6–1
replacement procedures, Maint. 3–41
Digital processing, on the CTU, Tech. 5–16
Dimensions
auxiliary equipment housing, Tech. 1–12,
Inst. 2–2
main cabinet, Tech. 1–12
outdoor cabinet, Inst. 2–2
site for cabinet, Tech. 1–17
Door
auxiliary equipment housing, replacement
procedure, Maint. 4–8
environmental seal replacement, Maint. 3–7
key, Tech. 2–19
locking angles, Maint. 2–3
opening and closing, Inst. 3–8, Maint. 2–3
operation, Maint. 2–3
replacement procedure, Maint. 3–4
Door lock, replacement, Maint. 3–47
Door sensor, replacement, Maint. 3–47
Doors, main cabinet, detail diagram, Tech. 2–19
Duplexing, Tech. 5–3
E
E1 NIU, Tech. 6–20
Earth, cabling, Inst. 3–19
Earth handling protection, ESP point, Inst. 3–20
Earth plates
cable connection, Inst. 3–32
fitting (left side), Inst. 3–34
Layout and function, Tech. 2–8
Earthing
auxiliary equipment housing, Inst. 5–10
cabinet, Inst. 3–16
continuity check, Inst. 7–5
site, Inst. 2–13, Inst. 2–14
Electricity supply
inspection certificate, Inst. 7–23
request for connection certificate, Inst. 7–4,
Inst. 7–6
request for connection form, Inst. 7–21
EMC, containment, Maint. 3–37
Environmental seal, auxiliary equipment
housing, replacement procedure, Maint.
4–12
ESP, connection point, Inst. 3–20
Extension cabinets, alarm transmission, Tech.
6–26
External alarm connector, pinouts, Inst. 3–68
External battery connectors, Tech. 4–13
Eyebolts, Inst. 3–7, Inst. 8–1
F
Fan
auxiliary equipment housing, Tech. 7–3
replacement procedure, Maint. 4–10
TMS, replacement procedure, Maint. 3–11
Fault finding, CAB debug facilities, Tech. 4–24
Feedthrough plate, Tech. 5–35
replacement, Maint. 3–37
Tx block screws, Tech. 5–31
Fibre optic extension, top sectionl, Tech. 2–6
Field replaceable units, Maint. 3–1
auxiliary equipment housing, Parts 1–3
location diagram, Maint. 3–2
main cabinet, Parts 1–2
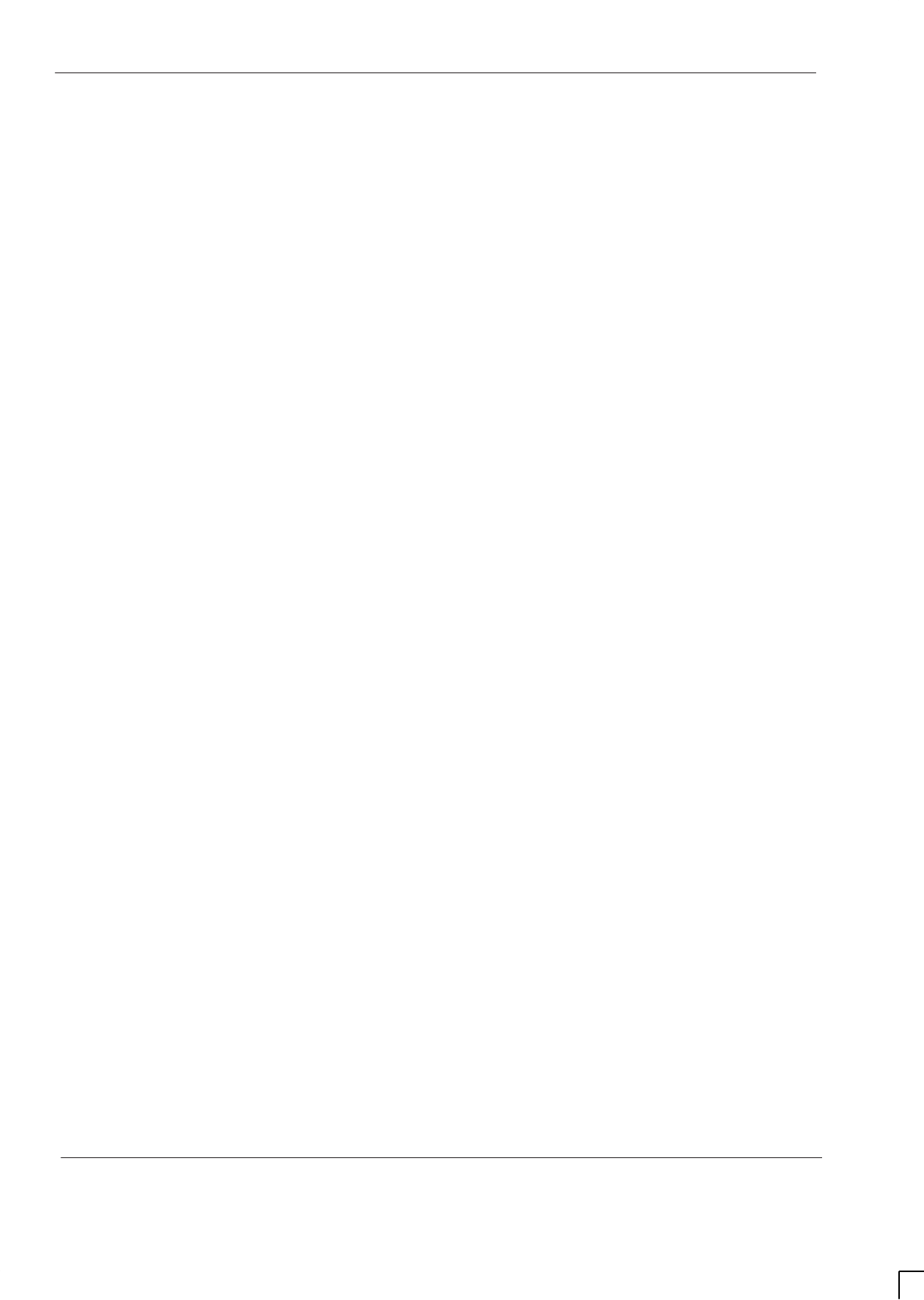
GSM-204-020
31st Oct 01
I–6
Service Manual: Horizon
macro
outdoor
CONTROLLED INTRODUCTION
68P02902W12-A
FMUX
connecting extension cabinets, Tech. 6–23
functional diagram, Tech. 6–24
internal to MCUF, Tech. 6–14
overview, Tech. 6–23
replacement, Maint. 3–40
FMUX fibre optic connections, MCUF, Tech. 6–8
Frequency band characteristics, Tech. 1–14
Front panel, auxiliary equipment housing,
replacement procedure, Maint. 4–9
FRU
blanking plate, Maint. 3–37
digital boards, Maint. 3–40
feedthrough plate, Maint. 3–37
HCU, Maint. 3–37
SURF, Maint. 3–31
FRUs, assumed procedures, Maint. 2–5
Fuses, CAB front panel, Tech. 4–17
G
Glossary of terms, Parts 1–8
GPS, pin connections, Inst. 3–62
H
Harness, cage, replacement, Maint. 3–47
HCU, replacement, Maint. 3–37
HCU plate, Tech. 5–36
Heat sensor, replacement procedure, Maint.
3–13
Heat sensors, description, Tech. 3–1
Heater mat, auxiliary equipment housing, Tech.
7–3
replacement procedure, Maint. 4–11
Hybrid Combining Unit, Tx block screws, Tech.
5–31
I
ICS connector, pinouts, Inst. 3–67
Interface panel
connector pinouts, Inst. 3–62
diagram, Inst. 3–61
replacement, Maint. 3–47
Interface panel cabling, Inst. 3–61
Interfaces, MCUF front panel, Tech. 6–8
Internal battery
removal and replacement, Maint. 3–26
removing the tray, Maint. 3–25
Internal battery
CAB selector switch, Tech. 4–23
capacity test, Tech. 4–22
K
Krone block, replacement procedure, Maint.
3–39
L
LAPD encoding, Tech. 6–20
LED indicators, transceiver, Tech. 5–9
Lid auxiliary equipment housing
fitting a new lid, Maint. 4–7
removal procedure, Maint. 4–6
environmental seal replacement, Maint. 3–7
main cabinet, detail diagram, Tech. 2–20
opening and closing, Inst. 3–8, Maint. 2–3
replacement procedure, Maint. 3–6
Lightning protection, E1/T1 lines, Inst. 3–16
Loopback test
availability software, Tech. 5–7
mode description, Tech. 5–7
Loopback test function, within SURF, Tech.
5–26, Tech. 5–29
Low voltage disconnect, Tech. 4–19
M
M–Cell2, Use of MCUF as MCU, Tech. 6–5
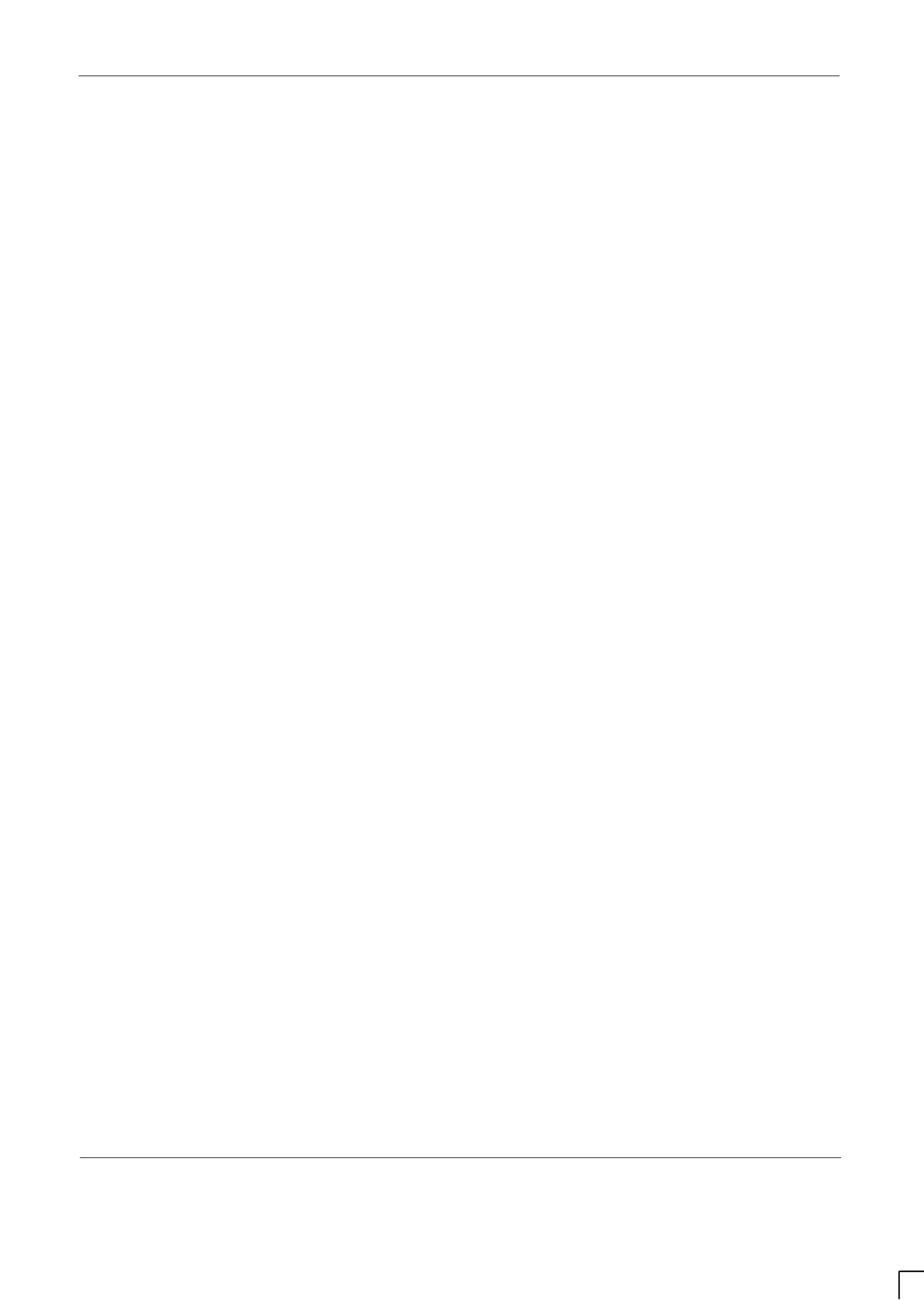
GSM-204-020
31st Oct 01
Service Manual: Horizon
macro
outdoor
68P02902W12-A
CONTROLLED INTRODUCTION
I–7
M–Cell6
cable gland for connection to Horizonmacro,
Inst. 6–14
Horizonmacro compatibility, Tech. 1–7
Horizonmacro hardware equivalents, Inst.
6–10
Horizonmacro component comparison, Tech.
1–8
Use of MCUF as MCU, Tech. 6–5
Maintenance cover, Inst. 3–6, Maint. 1–2
Manchester coding, Tech. 6–11
MCUF
code loading, Tech. 6–10
front panel interfaces, Tech. 6–8
front panel LEDs, Tech. 6–9
functional diagram, Tech. 6–7
GPROC functions, Tech. 6–6
redundancy, Tech. 6–3
replacement, Maint. 3–40
synchronization circuit, Tech. 6–19
technical description, Tech. 6–5
test cable connections, Inst. 7–1
Used as MCU, Tech. 6–5
MSC, Inst. 2–10
E1/T1 line testing, Inst. 3–1
notification on arrival on site, Inst. 2–9, Inst.
2–10
N
Names, main cabinet equipment, Tech. 1–2
NIU
block diagram, Tech. 6–18
connections to T43, Tech. 6–22
distance delay measurements, Tech. 6–20
front panel LEDs, Tech. 6–16
identity, Tech. 6–15
redundancy, Tech. 6–3
replacement, Maint. 3–40
reset, Tech. 6–19
TTY ports, Tech. 6–19
Number 1 ac distribution box, removing cover,
Inst. 3–21
O
OMC
alarm module replacement, Tech. 6–26
notification on arrival at site, Inst. 2–9, Inst.
2–10
Optimization procedures, Inst. 7–1
Over temperature trip, Tech. 4–19
P
PCMCIA card, Tech. 6–10
PCMCIA interface, MCUF, Tech. 6–9
Pinouts
BIB/BIM, Inst. 3–64
external alarm connector, Inst. 3–68
GPS connector, Inst. 3–62
ICS connector, Inst. 3–67
interface panel connectiors, Inst. 3–61
PIX connectors, Inst. 3–66
RTC connector, Inst. 3–63
T43/CIM, Inst. 3–65
pinouts, list of tables, Inst. 3–62
PIX, outputs and inputs, Inst. 3–66
PIX connectors, Tech. 6–25
pinouts, Inst. 3–66
PIX outputs, MCUF, Tech. 6–10
Plates, introduction, Tech. 5–31
Power
cabling install, Inst. 3–19
consumption, Tech. 1–10, Inst. 2–3
supply requirements, Tech. 1–10, Inst. 2–3
Power connections, auxiliary equipment
housing, Tech. 7–4, Inst. 5–10
Power distribution box, auxiliary equipment
housing, Tech. 7–1
replacement procedure, Maint. 4–3
Power down, Inst. 7–10, Inst. 8–2
Power supplies, BPSM, Tech. 4–36
Power supply enclosure, layout diagram, Tech.
2–15
Power supply unit
detail diagram, Tech. 4–2
main cabinet, Tech. 2–16
Power up
with code load, Inst. 7–11
without code load, Inst. 7–8
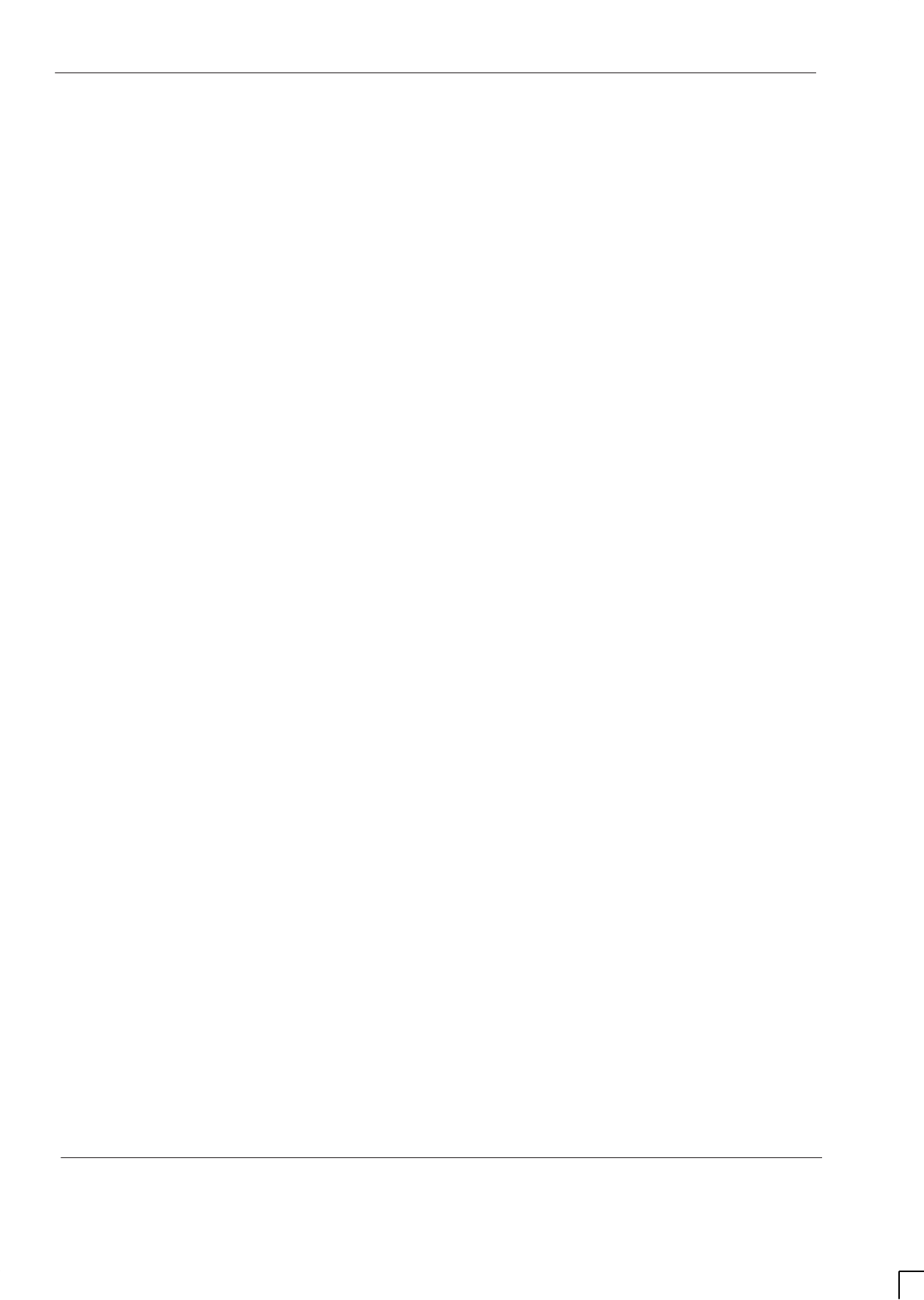
GSM-204-020
31st Oct 01
I–8
Service Manual: Horizon
macro
outdoor
CONTROLLED INTRODUCTION
68P02902W12-A
PSM
alarms, Tech. 4–32
front panel LEDs, Tech. 4–32
input currents, Tech. 4–31
redundancy, Tech. 4–31
replacement procedures, Maint. 3–20
R
Replacement
backplane, Maint. 3–47
blanking plate, Maint. 3–37
digital boards, Maint. 3–40
door sensor, Maint. 3–47
feedthrough plate, Maint. 3–37
HCU, Maint. 3–37
Main cage, Maint. 3–47
SURF, Maint. 3–31
Reporting faulty devices, Maint. 2–1
RF configuration diagrams, Inst. 3–37
loopback test function diagram, Tech. 5–6
main components, Tech. 5–4
multiple cabinet connection kits and cables,
Inst. 3–39
output power, Tech. 1–11, Inst. 2–4
receive hardware, Tech. 5–2
single cabinet connection kits and cables,
Inst. 3–38
test modes, Tech. 5–7
transmit hardware, Tech. 5–3
RF connectors, Inst. 3–33
RF equipment, overview, Tech. 5–1
RTC connector, pinouts, Inst. 3–63
S
Safety, during maintenance, Maint. 1–1
Safety equipment, Inst. 2–11
Sensitivity, Tech. 1–12
Site, foundation, Inst. 2–16
Site plan
multiple cabinet layouts, Tech. 1–18, Inst.
2–7
single cabinet layout, Inst. 2–6
Slave mode, MCUF, Tech. 6–8
Smoke trip, Tech. 4–19
Software requirements, Tech. 1–9
Specifications, Tech. 1–9
Structural cosiderations, Tech. 1–16
SURF
installing a replacement module, Maint. 3–33
module variants, Tech. 5–24
removal procedure, Maint. 3–32
replacement, Maint. 3–31
RF test function, Tech. 5–26, Tech. 5–29
test mode, Tech. 5–7
module variants, Tech. 5–4
SURF (dual band), Functional description, Tech.
5–29
SURF (single band), Functional description,
Tech. 5–26
SURF harness, detail diagram, Tech. 2–5
SURF module
1800 variant, Tech. 5–25
dual band capability, Tech. 5–29
Synthesizer frequency hopping, Tech. 5–20
T
T1 NIU, Tech. 6–20
T43, pinouts, Inst. 3–65
T43/BIB
(CIM/BIM), Tech. 6–21
Connector to NIU, Tech. 6–21
NIU mapping, Tech. 6–21
TDF, Tech. 5–38
Temperature, environmental limits, Tech. 1–9
Temperature alarm sensors, auxiliary equipment
housing, Tech. 7–3
Temperature control, sensors, Tech. 3–1
Temperature control sensors
power supply enclosure, Tech. 3–2
radio enclosure, Tech. 3–1
TMS, Tech. 3–4
Template
auxiliary equipment housing, Inst. 5–2
cable shroud, Inst. 5–2
main cabinet, Inst. 3–12
Templates, dimensions, Tech. 1–18, Inst. 2–7
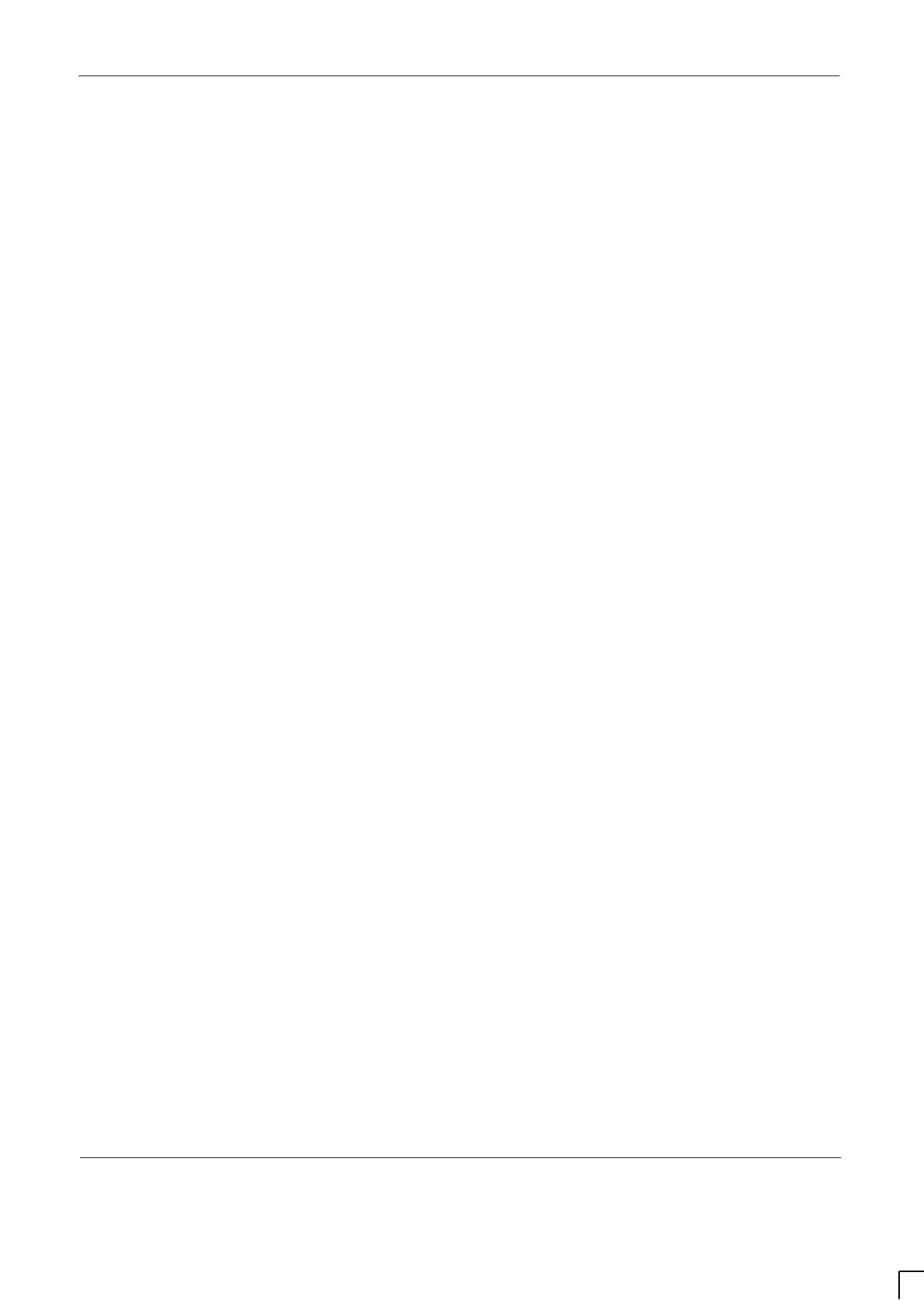
GSM-204-020
31st Oct 01
Service Manual: Horizon
macro
outdoor
68P02902W12-A
CONTROLLED INTRODUCTION
I–9
Test equipment, required for commissioning,
Inst. 7–2
Thermal dissipation, Tech. 1–11
TMS
air flow, Tech. 3–3, Tech. 3–6
air flow paths, Inst. 7–17
cleaning grilles, Maint. 2–5
control board replacement, Maint. 3–12
fan replacement, Maint. 3–11
front cover removal and refitting, Inst. 3–9,
Maint. 2–4
gasket replacement, Maint. 3–12
heat exchanger components, Tech. 3–4
refitting, Maint. 3–10
removal procedure, Maint. 3–9
test switch, Inst. 7–16, Maint. 2–8
test switches, Tech. 2–18
testing, Inst. 7–16, Maint. 2–8
Tools, required for installation, Inst. 1–3
Top section
blank and expansion plates, Tech. 2–9
description, Tech. 2–6
earth plates, Tech. 2–8
equipment locations, Tech. 2–7
fibre optic extension hole, Tech. 2–6
TOPSM
disable relay control, Tech. 4–18
external monitoring, Tech. 4–28
front panel LEDs, Tech. 4–27
internal monitoring, Tech. 4–28
pin connections, Tech. 4–30
protection circuits, Tech. 4–28
removal and replacement, Maint. 3–18
voltage trim, Tech. 4–18
Torque settings, screws, bolts, connectors, Tech.
1–13, Inst. 2–2
Transceiver link features, MCUF, Tech. 6–11
TRAU frames, Tech. 5–19
TTY interface, MCUF, Tech. 6–8
Tx block, Tech. 5–5
blanking plate, Tech. 5–34
connectors, Tech. 5–32
DCF, Tech. 5–42
DDF, Tech. 5–44
feedthrough plate, Tech. 5–35
fitting a replacement module, Maint. 3–37
HCU plate, Tech. 5–36
introduction, Tech. 5–31
removal procedure, Maint. 3–36
screw retention, Tech. 5–31
TDF, Tech. 5–38
Type approval, Tech. 1–9
V
VSWR test mode, Tech. 5–7
W
Weather
conditions for installation, Inst. 3–5
conditions for maintenance, Maint. 1–2
Weight
auxiliary equipment housing, Tech. 1–13,
Inst. 2–2
outdoor cabinet, Tech. 1–13, Inst. 2–2
Wiring diagram
110 V ac single phase, Inst. 3–25
230 V ac 3–phase (star), Inst. 3–27
230 V ac 3–phase (delta), Inst. 3–30
230 V ac single phase, Inst. 3–23
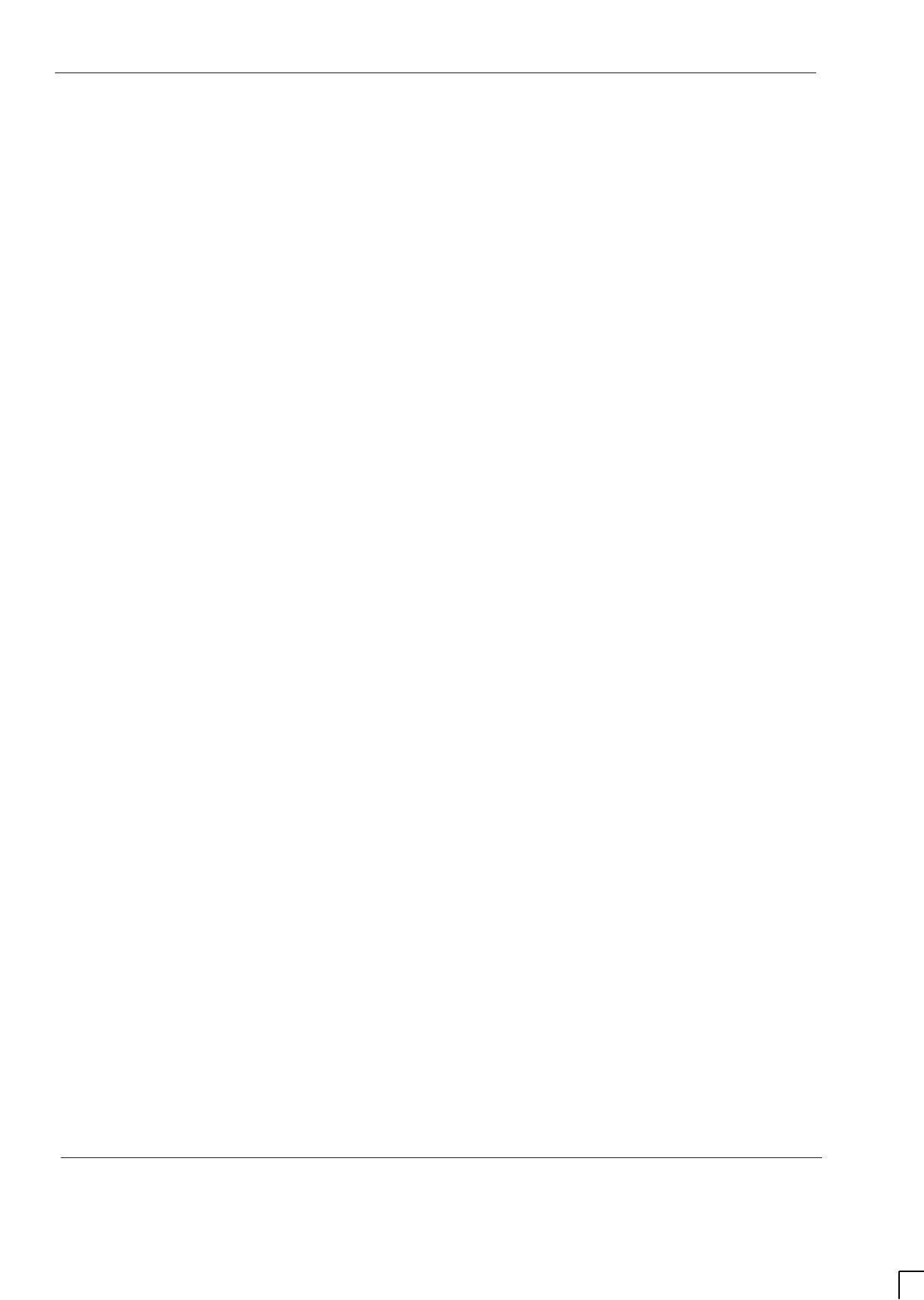
GSM-204-020
31st Oct 01
I–10
Service Manual: Horizon
macro
outdoor
CONTROLLED INTRODUCTION
68P02902W12-A