Pentair Two Speed Pool And Spa Pump Energy Master Users Manual
Hydropump to the manual 669c8dcf-5b14-c3d4-d185-84123663a5eb
2015-02-06
: Pentair Pentair-Two-Speed-Pool-And-Spa-Pump-Energy-Master-Users-Manual-518010 pentair-two-speed-pool-and-spa-pump-energy-master-users-manual-518010 pentair pdf
Open the PDF directly: View PDF .
Page Count: 4
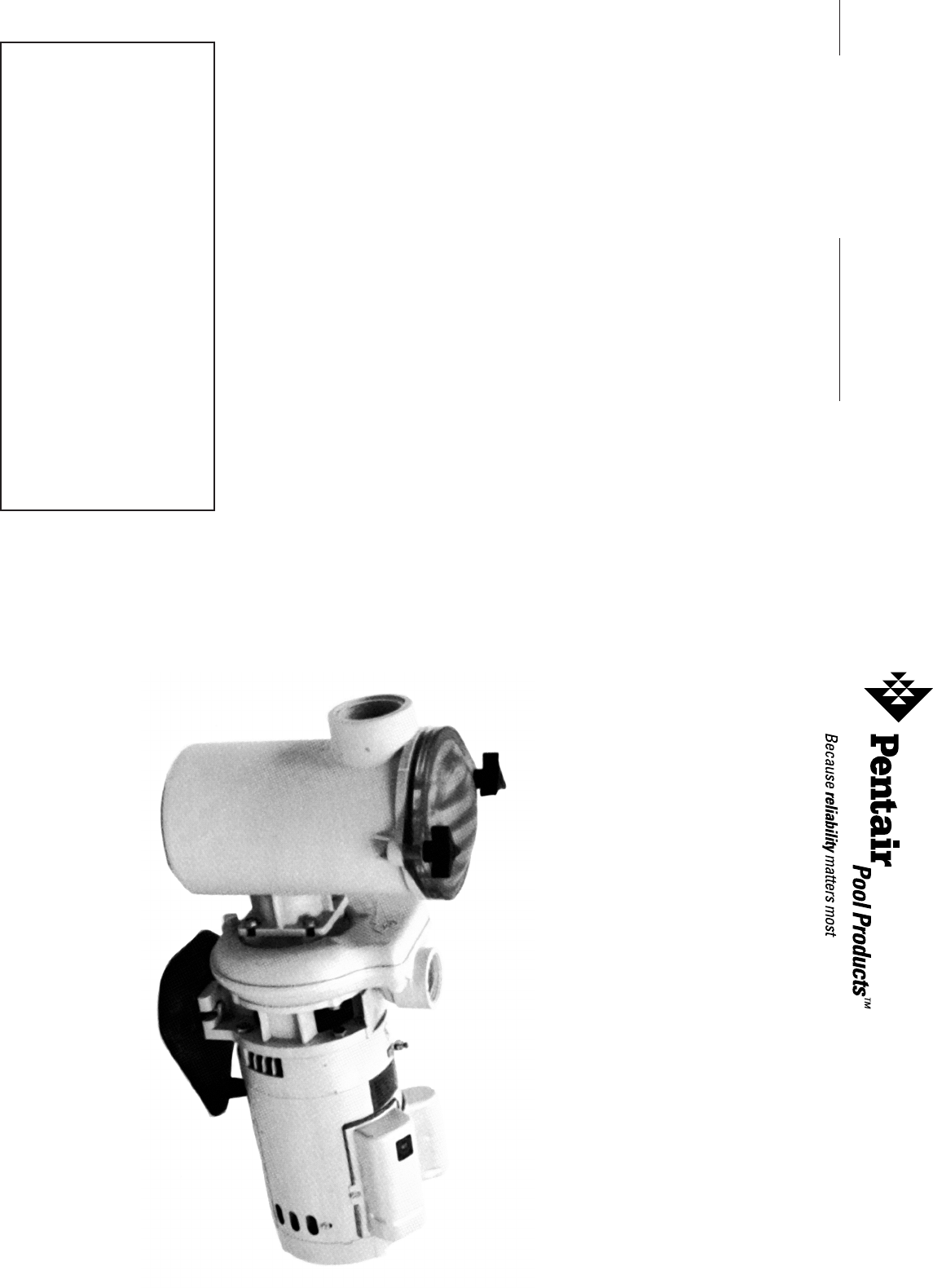
HYDROPUMP
®
AND
ENERGY MASTER
™
HYDROPUMP
®
TWO SPEED POOL AND SPA PUMP
INSTALLATION, OPERATION
& SERVICE MANUAL
TROUBLE GUIDE
THE FOLLOWING ARE SOME COMMON CAUSES OF PROBLEMS THAT MAY ARISE:
PROBLEMS POSSIBLE CAUSES & SOLUTIONS
A. PUMP WILL 1. Make sure pool water is midway of skimmer opening.
NOT PRIME: 2. Make sure strainer basket is not clogged.
3. Make sure strainer basket is positioned properly!
4. Tighten lid down snugly.
5. Make sure strainer pot is full of water.
6. TIghten all fittings and seal all joints on suction side.
7. Clean skimmer and pump strainer baskets.
8. Remove pump lid and check for clogging.
9. Open all valves in return and suction lines.
10. Remove and replace pump seal if needed.
11. Check voltage at pump to be sure it is same as motor specs.
B. LOW FLOW1. If filter gauge reads high.
a. Filter is dirty.
b. Clogged return lines.
2. If filter pressure gauge reads low.
a. Pump or skimmer strainer basket is clogged.
b. Skimmer or main drain valve is closed.
c. Air leak in suction line.
d. Impeller setting is incorrect.
e. Debris on impeller vanes.
C. MOTOR 1. Motors will run hot to the touch, however, they are designed this way. Thermal
RUNS HOT overload protector will function to turn the motor off if there is an overload problem.
2. Factors which will increase operating temperature:
a. Installed in direct sun.
b. Poor ventilation.
c. Low voltage.
d. Wiring is incorrect size for load.
D. MOTOR WILL 1. Check that all power switches are on, fuse not blown, and circuit breaker
NOT TURN is not tripped.
2. Timer improperly set.
3. Impeller is against volute face.
SAVE THESE INSTRUCTIONS.
LIMITED
WARRANTY
PUMPS
PENTAIR POOL PRODUCTS, INC. pumps are warranted to be free from defects in material and
workmanship.Should any of the operating parts become defective within one year from date of pur-
chase, they will be replaced or repaired if defect is proved to be the responsibility of PENTAIR POOL
PRODUCTS, INC.
All adjustments are to be based on list prices in effect at the time of adjustment. PENTAIR POOL
PRODUCTS, INC. will not be liable for the cost of labor or removing or replacing parts.Purchase
agrees to prepay all shipping charges to and from PENTAIR POOL PRODUCTS, INC. 1620 Hawkins
Ave., Sanford, NC 27330 or 10951 West Los Angeles Ave., Moorpark, CA 93021, whichever is clos-
er or more convenient.
This warranty does not cover failure in service due to fire, wreckage, freezing, willful abuse, improper repackaging
or damage incurred in shipping nor does it extend to consequential damages.
35-7000 Printed in the U.S.A.
Rev.B 5/2005
P
P
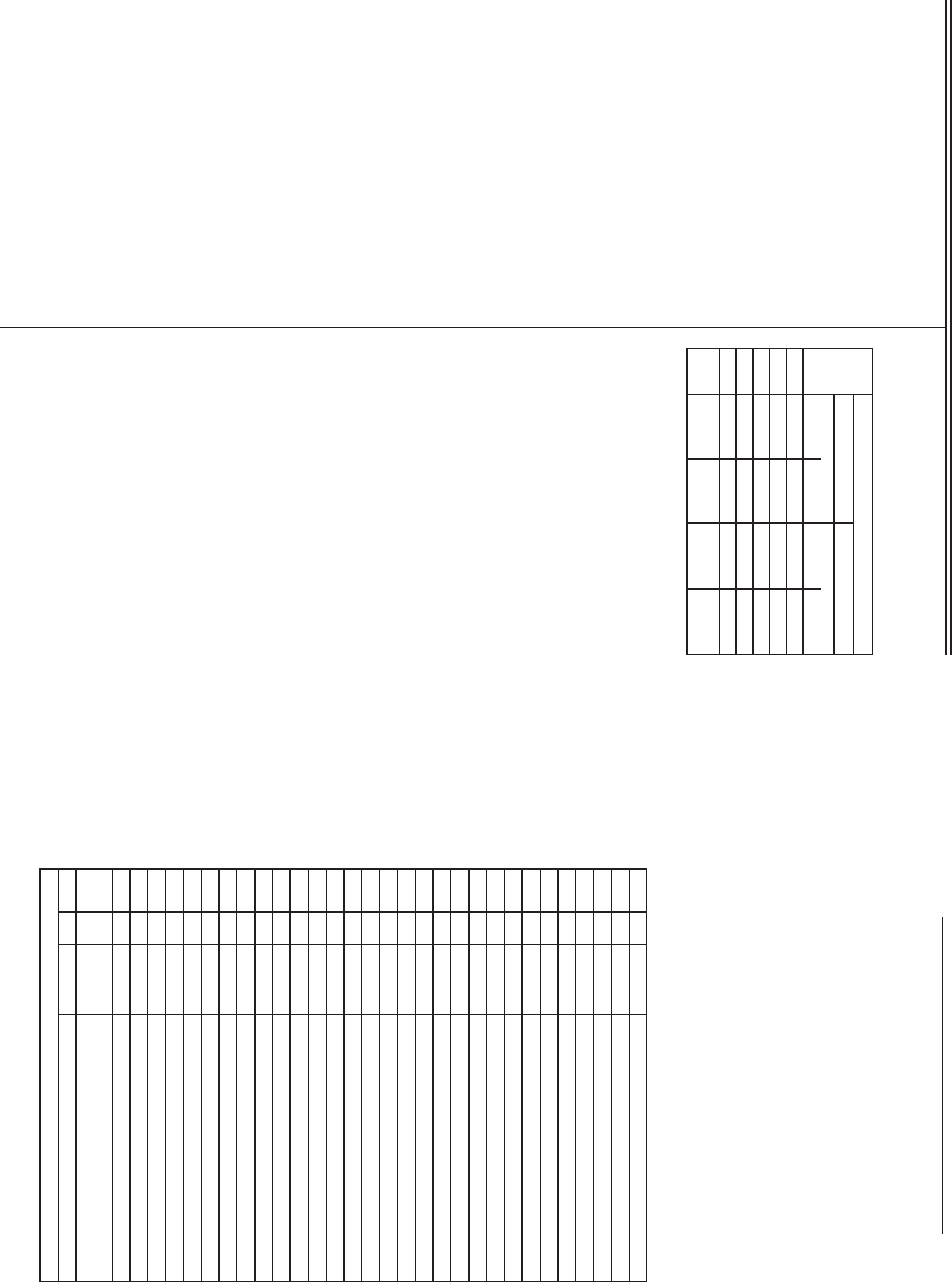
INSTRUCTIONS
READ AND FOLLOW ALL INSTRUCTIONS
GENERAL:
Our shipping container has been specifically
designed to prevent transit damage.However, any
indications of damage should be carefully noted on
the delivery ticket and a claim filed promptly with the
carrier.
LOCATION:
Locate the pump as close as possible to the pool.
Provide the necessary space around the pump for
future inspection and servicing of the unit. If possible,
allow several inches of clearance below the motor to
floor to allow easy access to mounting screw. Locate
away from pool chemicals to prevent spilling on or
near motor.
INSTALLATION:
The pump suction line should not be smaller than
the pipe size on the inlet of the pump.
Your pump is made of the finest engineering
materials available today. A few simple precautions
taken during the initial installation, will insure many
long years of trouble-free operation.
The threads of pipe fittings screwed into pump
must be sealed with: pipe sealant, Teflon®Tape,
R.T.V.or other sealing materials approved for pipe
threads.
Tighten the pump fitting only as much as is
required to insure a tight connection. DO NOT OVER
TIGHTEN.
The piping should be supported independently
and not supported by the pump.
The pump motor must be wired for the proper
voltage, and rotation, in accordance with the wiring
diagram supplied with the motor.All wiring should be
done by a licensed electrician in accordance with
local codes, be certain that the motor frame is
grounded. Use lug on top of motor frame to bond
together motor and all metallic parts of pool, spa or
hot tub structure and to all electrical equipment,
metal conduit, and metal piping within 5 feet of the
inside walls of a swimming pool, spa or hot tub, when
the motor is installed within 5 feet of the inside walls
of the swimming pool, spa or hot tub structure with a
solid copper conductor not less than No.8 A.W.G.
Motor name plate has voltage, phase, ampere
draw and other motor information. Terminal cover
plate or name plate has wiring connection informa-
tion.
The wiring to motor should be kept as short as
possible and large enough to carry the necessary
current for required length without excessive voltage
drop.The following table should be followed to be
sure that the proper wire size is selected. Use as a
guide only.
TABLE OF A.W.G. WIRE SIZE
FOR
SINGLE-PHASE POOL PUMP MOTORS
WARNING - To reduce the risk of injury, do not
permit children to use this product unless they are
closely supervised at all times.
PRIMING:
Fill the pump pot with water before starting the
pump.This may be done by removing clear lid.
Pumps are self priming providing the pump pot is
filled with water.Should you lose this liquid from the
pot accidentally or by draining purposely, it will be
necessary to refill it with liquid before starting. High
Suction Lifts, require additional time for priming.
OPERATION:
After the pump has been filled with water, and the
motor started, allow a few moments for the pump to
start pumping water.If flow does not start within four
minutes, stop motor and refer to (THE TROUBLE
GUIDE). Be sure all suction and discharge valves are
open when the pump is running. Operating the pump
with a closed valve in the system can cause pump
damage.
WINTERIZING:
In areas subject to freezing winter temperatures,
protect pump by removing both drain plugs, one from
the pump volute and one from the pot. Do Not
Replace Plugs, store them in strainer basket for the
winter.
An alternate is to remove the pump and motor
from plumbing and store them indoors in a warm, dry
location.
MAINTENANCE:
The strainer basket in pump should be inspected
and cleaned twice each week. The strainer basket is
easy to clean. Loosen the knobs and remove the
clear lid. Remove the basket and clean. Inspect the
Lid “O”-Ring; if damaged, replace.Install the Clear
Lid, tightening knobs by hand only.The pump seal
requires no lubrication. Refer to motor service center
for motors.
WARNING: NEVER WORK ON PUMP WHILE IT IS RUNNING OR POWER IS STILL CONNECTED.
2 7
WIRE LENGTH
50 FEET 100 FEET
VOLTS VOLTS
115 230 115 230
1/3 14 14 14 14
1/2 14 14 12 14
3/4 12 14 12 14
112 14 10 14
1 1/2 10 14 10 14
210 12 812
3 - 12 -12
HOW TO ORDER PARTS
WHEN ORDERING PARTS, GIVE
H.P., PUMP SERIAL NO., MODEL NO.& ITEM NO.
TO YOUR LOCAL DEALER
--------------------
H.P., PUMP SERIAL NO.& MODEL NO.
ARE LOCATED ON PUMP
22 135-3450 Motor Support (for 5 1/2 Dia. Motor)
21 115-4909 Motor Outrigger
20 235-4256 Set Screw 1/4” x 20 x 3/8” S.S.
19 435-4290 Cap Screw 3/8 - 16 x 1” S.S.
18 835-4265 Hex Washer Head Screw 5/16” - 18
17 135-4001 3/4 Mechanical Seal
16 135-2670 Basket w/Handle - Plastic 700
16 135-2656 Basket w/Handle - Plastic 590
15 135-2600 Lid O-Ring 700
15 135-2602 Lid O-Ring 590
14 135-3525 Clear Lid - 700 Plastic
14 135-3625 Clear Lid - 590 Plastic
13 235-4280 Knob - Pot Plastic
12 135-4127 Strainer Pot 700 (Plastic)
12 135-4125 Strainer Pot 590 (Plastic)
11 2154699 Plug-Wing .25” Drain Lgr
10 119-2323 O-Ring (Pot to Volute)
9 1 35-3912 Volute - Plastic
8 1 35-2626 O-Ring Volute to Bracket
7 1 35-3220 Impeller RPF 3HP
7 1 35-3050 Impeller RPF 2HP, 21/2HP
7 1 35-3049 Impeller RPF 1 1/2HP, RPA2HP
7 1 35-3013 Impeller RPF 1HP, 1 1/2HP
7 1 35-3044 Impeller RFP 3/4HP, RPA1HP
7 1 35-3043 Impeller RFP 1/2HP, RPA3/4HP
7 1 35-3041 Impeller, RPA 1/2 HP
6 2 15-4445 Hex Nut 3/8 - 16 Cad. Pltd.
5 1 35-4894 Pump Tri Pod Base Plastic
4135-3775 Seal Bracket - Plastic
3 2 35-4294 Screw, Cap 3/8 - 16 x 1 1/4” Cad. Pltd.
2 1 35-3750 Shaft Extension - Bronze
1Motor
Item Qty. Part No.NAME OR DESCRIPTION
LIST OF MATERIAL OR PARTS LIST
H.P.
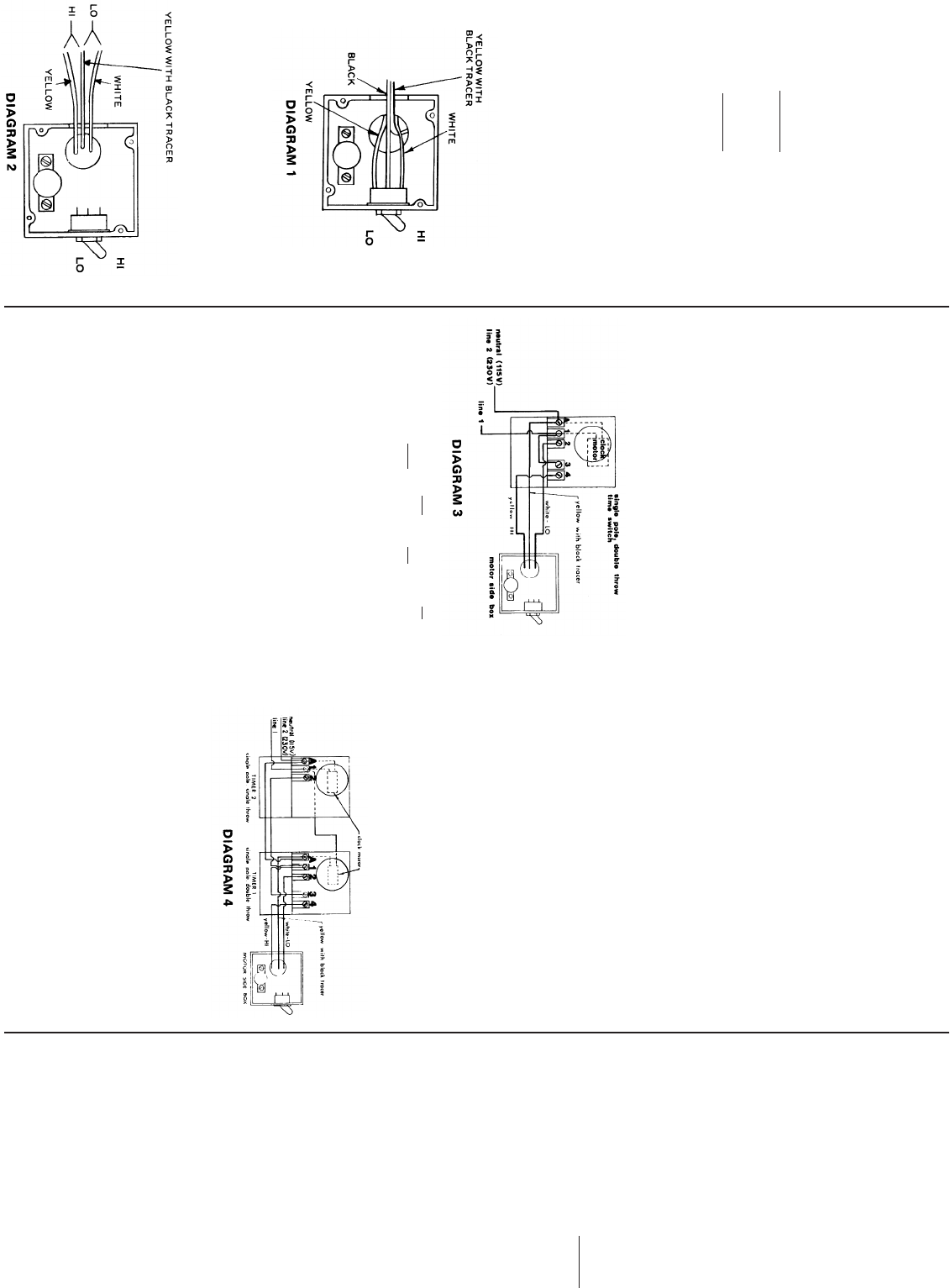
SPECIAL INSTRUCTION FOR TWO
SPEED ENERGY MASTER HYDROPUMP:
The performance of this pump will be the same at
high speed as the same model single speed pump,
both hydraulically and prime wise.At low speed the
pump will produce one half the flow and the pressure
will drop GREATLYwhich is due to much lower sys-
tem friction. These lower friction losses result in
GREAT energy savings.On low speed the electrical
energy savings are 60%.
Turn motor to high speed for vacuuming the pool,
reading the pressure gauge to determine if cleaning
or back washing of filter is required, for fast clean-up
of pool water, and for priming the system to rid it of all
air. Turn motor to low speed for quiet operation and
electrical cost savings.Since the pump should be
operated mostly at low speed for cost savings, minor
adjustments may be required in the automatic chlo-
rine dispenser, the skimmers and the heater due to
the lower flow. (See the equipment manufacturers
operation manuals).
All electrical work MUST be done by a licensed
electrician. Before working on motors be certain that
the electrical power is OFF at the main junction
box. TWO SPEED pumps have SINGLE VOLTAGE
motors which cannot be changed. See the motor
nameplate for the motor being installed. ALL electri-
cal connections should be made in the SIDE BOX
which also includes a prewired HI-LO switch. See
Diagram 1.
If an automatic timer is installed to change
speeds, the wiring connected to the switch should be
removed and the BLACK wire discarded. See
Diagram 2. The timer should then be installed and
connected to the motor as follows:
TIMER INSTALLATION FOR HI-LO SWITCHING
OF 2 SPEED HYDROPUMP®
An intermatic timer with single pole, double throw
switch may be used to automatically switch the
HYDROPUMP®between the high and low speed
modes at present intervals.
1) Check to see that timer voltage is the same as
that of the HYDROPUMP®motor.The following
intermatic timers should be used.
Hydropump H.P. Voltage Timer Model
3/4 115 T175*
1, 1 1/2, 2 230 T176*
*These models have skip-a-day wheel. Remove skip
screws if not needed.
2) Connect the timer to the motor following Diagram
3. All electrical connections to the motor should
be made in the side box.
NOTE: When time switch is ON - pump is on HI.
When time switch is OFF - pump is on LO.
CAUTION: Manual switch on motor side box must be
disconnected when HYDROPUMP®is being con-
trolled by the timer or the motor will be damaged.
TIMER INSTALLATION FOR PROGRAMMED
ON-OFF,HI-LO SWITCHING OF 2 SPEED
HYDROPUMP®
Automatic on-off and hi speed-lo speed control of
the ENERGYMASTER 2 speed pump can be
obtained by properly installing two appropriate
timers.One timer must have a single-pole, double
throw switch and the other must have a single-pole,
single throw switch. Both timers and the HYDRO-
PUMP®motor must be designed to operate on the
same voltage.
Only Intermatic timers are discussed below, but
other types may be used if desired. The following
timers are recommended for this installation:
Intermatic
Hydropump Timer Model No.
H.P. Voltage S.P.D.T. S.P.S.T.
3/4 115 T175* T101
1, 1 1/2, 2 230 T176* T102
•These models have skip-a-day wheel. Remove skip
screws if not needed.
1) Mount the timers side by side, between the power
supply and the HYDRO-PUMP®an Intermatic 2-
in-1 raintight case is ideal for this installation.
2) Timer No.1 will be used to control the hi speed-
lo speed switching of the motor.
3) Timer No.2 will be used to automatically switch
the HYDRO-PUMP®on and off.
The clocks of both timers must run continuously
for the proper operation of the switching circuits.
Therefore it is necessary to make a connection
between line 1 and the clock input of timer No.1. (See
Diagram 4.)
NOTE: When time switch 1 is ON - pump is on HI.
When time switch 1 is OFF - pump is on LO.
All wiring connections should be made with 12
A.W.G. or larger wire size.All wiring connections to
the HYDRO-PUMP®should be made inside the
motor side box. The 2 speed motor is designed to
operate on the voltage stamped on the nameplate
only.Wiring with a different line voltage will damage
the motor.
OPERATING INSTRUCTIONS
1) Set both clock dials to the exact time of day.
2) Locate the trippers on the clock dial of timer No.
2 to switch the HYDRO-PUMP®on and off at the
desired times.
3) Locate the trippers on the clock dial of timer No.
1 to switch the HYDRO-PUMP®between hi and
lo speed at the desired time.The timers should
always be programmed so that the HYDRO-
PUMP®will always operate for 10 minutes mini-
mum at hi speed when it is switched on. This
allows priming of the pump and evacuation of air
from the piping system.
4) The pump may be manually switched between hi
and lo speed by flipping the manual lever of timer
No.1, and may be switched on and off by flipping
the manual lever of timer No.2.
CAUTION: Always turn power off at main panel
before servicing switches or pumps.
CAUTION: Be certain the wiring CANNOTallow both
the HI and LO speed motor windings to be energized
at the same time.
CAUTION: This pump is for use with permanently
installed pools and may also be used with hot tubs
and spas if so marked. Do not use with storable
pools.A permanently installed pool is constructed in
or on the ground or in a building such that it cannot
be readily disassembled for storage.A storable pool
is constructed so that it may be readily disassembled
for storage and reassembled to its original integrity
and has a maximum dimension of 18 feet and a max-
imum wall height of 42 inches.
Do not install within an outer enclosure or
beneath the skirt of a hot tub or spa unless so
marked.
4 5

The Hydropump has an open face impeller
which was precisely set at the factory. Under
normal operating conditions it is not necessary
to make further adjustment, however, if the
pump draws excessive current a slight adjust-
ment may be required.
Loose the shaft extension set screws and
this will allow the mechanical seal spring to
force the impeller face to touch the volute.Place
a screwdriver between the motor bracket and
the shaft extension as depicted below. Move the
screwdriver handle away from the motor, this
will pull the impeller away from the volute. You
should move the shaft extension about 1/32”
and holding the screwdriver at this position firm-
ly tighten the shaft extension set screws.
Start the pump and check the amperage
draw. If the amperage exceeds the nameplate
rating or if the pump performs poorly the adjust-
ment needs to be redone.
6 3
IMPELLER CLEARANCE ADJUSTMENT