1272 2 Liberty Elv280 Instructions Pump OilTector Installation Rev. 7235000G User Manual
1271 2 Liberty Elv250 Instructions 1271_2_Liberty ELV250 Instructions
510 2 Liberty Elv280Hv Instructions 510_2_Liberty ELV280HV Instructions
516 2 Liberty Elv290 Instructions 516_2_Liberty ELV290 Instructions
540 2 Liberty Elv290Hv Instructions 540_2_Liberty ELV290HV Instructions
562 2 Liberty Otc-230 Instructions 562_2_Liberty OTC-230 Instructions
User Manual: Pump 1272 2 Liberty Elv280 Instructions
Open the PDF directly: View PDF .
Page Count: 6
- Liberty Pump OilTector Installation Instructions Rev. 7235000G Page 1
- Liberty Pump OilTector Installation Instructions Rev. 7235000G Page 2
- Liberty Pump OilTector Installation Instructions Rev. 7235000G Page 3
- Liberty Pump OilTector Installation Instructions Rev. 7235000G Page 4
- Liberty Pump OilTector Installation Instructions Rev. 7235000G Page 5
- Liberty Pump OilTector Installation Instructions Rev. 7235000G Page 6
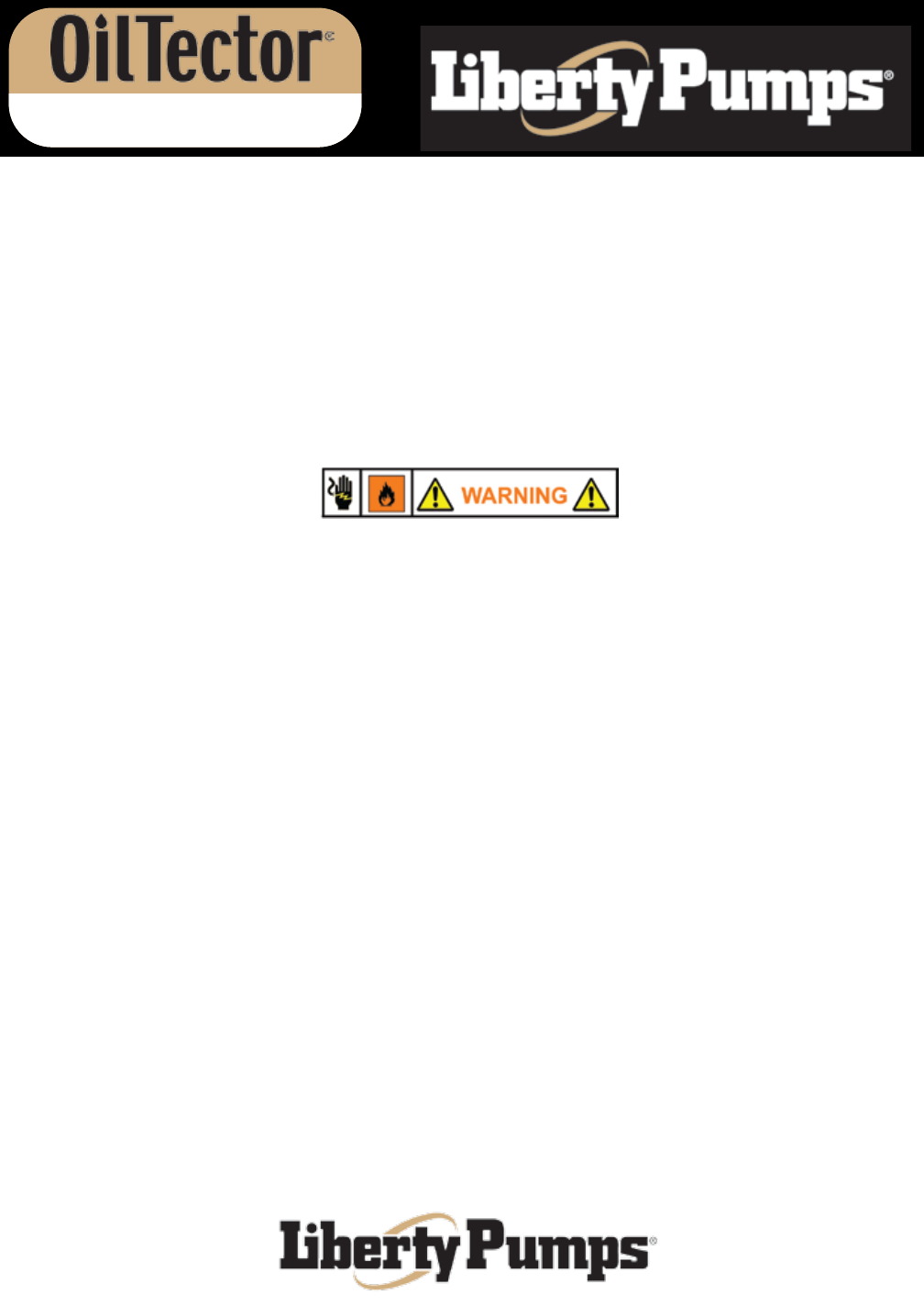
Introduction
Read all instructions thoroughly. Installation of the OilTector must comply with all Federal, State and Local Codes, Regulations
and Practices. The OilTector must be installed by qualified personnel familiar with all applicable local electrical and mechani-
cal codes. Refer to the National Electrical Code (NFPA 70). Failure to properly install and test this product can result in
personal injury or equipment malfunction.
Safety Guidelines
1. DO NOT USE WITH FLAMMABLE OR EXPLOSIVE FLUIDS SUCH AS GASOLINE, FUEL OIL, KERO-
SENE, ETC. DO NOT USE IN EXPLOSIVE ATMOSPHERES. PROBE/FLOAT SWITCH SHOULD
ONLY BE USED WITH WATER.
2. DO NOT HANDLE THE OILTECTOR SYSTEM WITH WET HANDS OR WHEN STANDING ON A WET
OR DAMP SURFACE OR IN WATER.
3. DISCONNECT ALL ELECTRICAL SERVICE BEFORE WORKING OR HANDLING THE OIL ALERT
SYSTEM.
4. INCOMING VOLTAGE MUST MATCH OILTECTOR SYSTEM VOLTAGE.
5. TO PREVENT ELECTRICAL SHOCK AND EQUIPMENT MALFUNCTION, USE ONLY WITH A PUMP
SUPPLIED WITH A GROUNDING CONDUCTOR AND GROUNDING-TYPE ATTACHMENT PLUG. BE
CERTAIN TO PLUG THE OILTECTOR PANEL INTO A PROPERLY GROUNDED, GROUNDING-TYPE
RECEPTACLE.
6. CONTROL PANEL AND ALARM MUST BE MOUNTED INDOORS. FOR OUTDOOR APPLICATIONS
CONSULT FACTORY.
7. SECURE LEVEL SENSOR ON DISCHARGE PIPE AT A LEVEL THAT GUARANTEES PARTIAL PUMP
SUBMERGANCE WHEN WATER LEVEL IS JUST BELOW THE “OFF” PROBE (THE LONGEST
PROBE). (See Figure 5 on page 3 of this manual). FAILURE TO PROPERLY MOUNT THE LEVEL
SENSOR MAY CAUSE THE PUMP TO ACTIVATE EVEN WHEN OIL IS PRESENT IN THE SUMP.
8. CAUTION! REMOVE ANY FLOAT SWITCH THAT IS CURRENTLY USED OR SUPPLIED WITH THE
PUMP. IF THE FLOAT CANNOT BE REMOVED, SECURE SWITCH SO THAT IT IS ALWAYS ON.
Part Numbers
OTC-115 - OilTector 115 volt Oil Sensor Control System (Control Panel, Alarm Panel, Level
Sensor). NEMA 4X enclosure.
OTC-230 - OilTector 230 volt Oil Sensor Control System (Control Panel, Alarm Panel, Level
Sensor). NEMA 4X enclosure.
7000 Apple Tree Avenue, Bergen, NY 14416 Phone: (800) 543-2550-Fax: (585) 494-1839-www.libertypumps.com
DWG#7235000G
Manual 7235000G
The OilTector control system is designed and approved for the safe operation of pumping, alarming and monitoring of elevator
sump pits, transformer vaults and leachate well applications. The OilTector will activate a pump to remove water from elevator
pits in accordance with ASME A17.1. The OilTector stops the pump before oil or other harmful substances enter our water
supply. Indicator lights will illuminate on the control panel for the following: power, pump running, high alarm, high oil. The panel
has a set of auxiliary contacts that activate on power loss or high Oil/Water conditions. These contacts can be connected to the
OilTector remote panel which contains audio/visual alarming along with auxiliary contacts for connection to building automation
system or SCADA system. The recommended minimum sump size is Ø18” x 30” high.
Operation and Maintenance Manual
Operation and Maintenance Manual
Page 1 of 6

Oil “Film”
Detection Level
Pump “On”
Level
Pump “Off”
Level
120 V
Receptacle
Elevator Sump
Control Panel
Remote Alarm has
additional auxiliary
contacts for building
alarm system.
Figure 1
60500A0
Remote alarm can be mounted
2500 ft. from control panel!
Installation of the Control Panel
Description of Operation
9.75"
5.25"
8.82"
.50"
4.02"
Figure 2
7000 Apple Tree Avenue, Bergen, NY 14416 Phone: (800) 543-2550-Fax: (585) 494-1839-www.libertypumps.com
Operation and Maintenance Manual
Page 2 of 6
DWG#7235000G
Manual 7235000G
Operation and Maintenance Manual
On water rise, level reaches pump “start” probe to start the pump. Pump will remain on until level is below
“off” probe. The “off” probe senses air or oil and turns the pump off so the oil layer will not be pumped out of
the sump. If the liquid level reaches alarm probe and mechanical float, the system will differentiate between
water and oil and activate the remote alarm.
1. It is highly recommended to mount the control panel in the same area as the sump pump to eliminate any
splicing of sensor and pump wires. See “Installation of Preset Level Sensor Holder” for more information on
splicing.
2. Determine mounting location for the control panel. Mount panel at the desired location making sure the
mounting location of the control panel is within 6 feet of electrical receptacle.
3. Plug pump cable into control panel receptacle cable. Plug power cable into receptacle only when ready for
testing. See Testing System installation.
4. If the panel is to be installed with conduit, the cables and cord seals must first be removed. Please make
note of wire locations. The incoming power 115V is connected to L1 and L2 of the contactor, pump recep-
tacle is T1 and T2 on the contactor. Low voltage cable from the level sensing module: green - TB1 off probe,
yellow - TB2 start probe, red - TB3 alarm probe, white - TB4 float, black - TB5 float. Low voltage auxiliary
contacts are TB6 and TB7. Do not mix low voltage probe wires or auxiliary contacts in high voltage conduits.
See figure 3 and figure 6.
Figure 3
Conduit
A Conduit – Low Voltage Preset Level Sensor
B Conduit – High Voltage Pump Cable
C Conduit – High Voltage Incoming Power Cable
D Conduit – Low Voltage Auxiliary Contact for Remote Alarm
Warning – Do not mix high and low voltage circuits in the
same conduit, failure to do so will cause system malfunc-
tion. The Preset Level Sensor and Auxiliary
Contact wires are low voltage class 2 circuits
- Do not install sensor cables in conduits
with main power or pump cables.
60500A0
A B C D
A
B
C
D
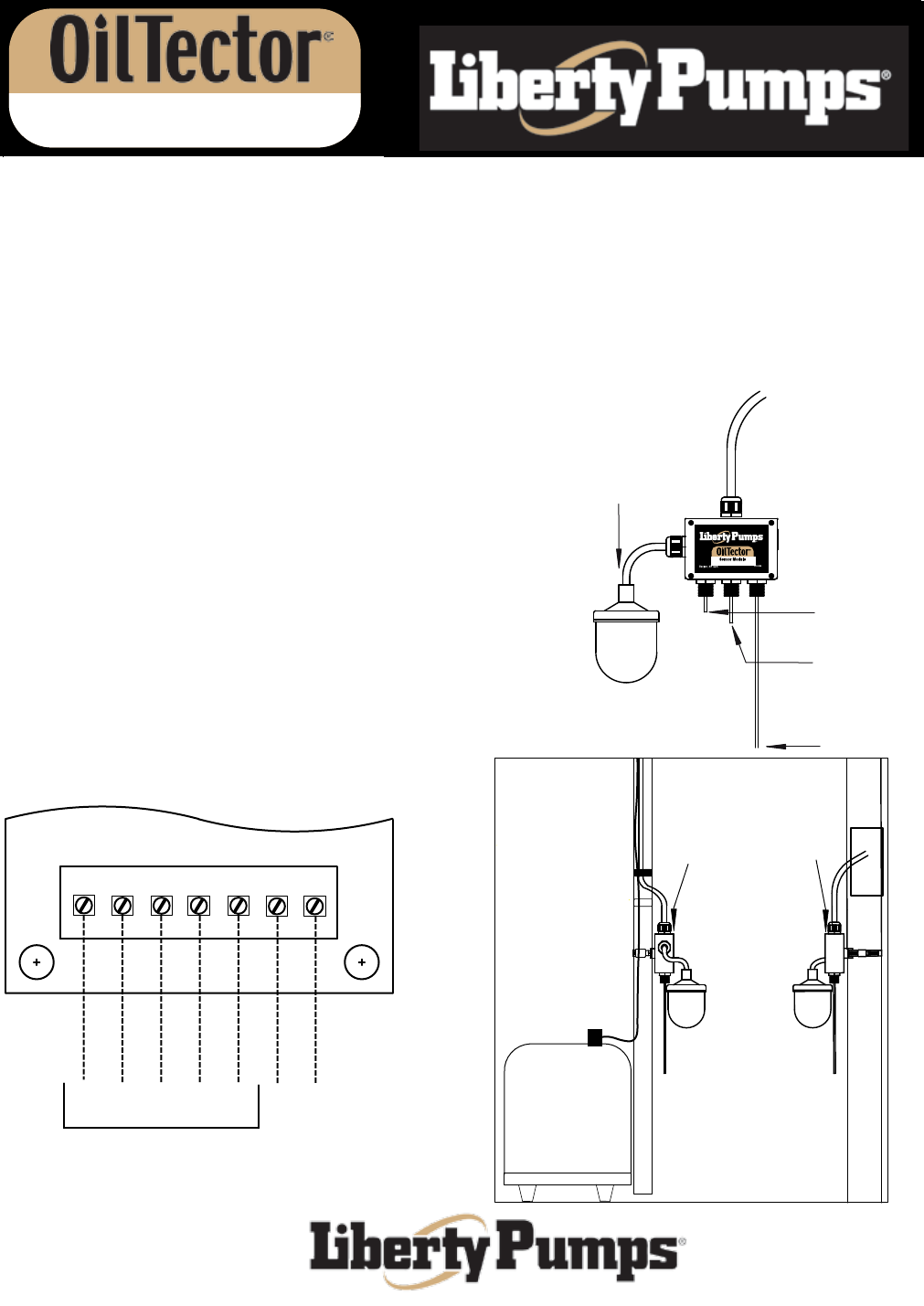
Installation of Preset Level Sensor Holder
Side Wall
Mount
Figure 5
Discharge Pipe
Mount
Page 3 of 6
Operation and Maintenance Manual
7000 Apple Tree Avenue, Bergen, NY 14416 Phone: (800) 543-2550-Fax: (585) 494-1839-www.libertypumps.com
Pump
Start
High Level
Probe
High Level
Float
5
1 2 3 4 6 7
Auxiliary Contacts
24VDC, 1A
Conect to Remote Alarm
Or BAS/SCADA System
Off
Probe
Start
Probe
Alarm
Probe
Float Float
Circuit Board
Green
Yellow
Red
White
Black
5 Conductor Cable from
Preset Level Sensor
Figure 6
Figure 4
DWG#7235000G
Manual 7235000G
Off
Probe
Operation and Maintenance Manual
Operation and Maintenance Manual
1. Review figures 4, 5 and 6.
2. Attach sensor holder to discharge pipe or separate pipe (mounted to side wall) using the stainless
steel pipe clamp. Make sure sensor is clear of inlet water and at least 1” to 2” away from any conductive
material. Make sure the bottom probe (off level) is at the same height as the top of the pump or just slightly
below ensuring submergence of the pump. See figure 5.
3. Route the five conductor cable to the control panel through the liquid tight cord connector and tighten
compression nut.
4. Connect the wires from the level sensor to the terminal strip inside the control panel. See figure 6.
5. If splicing on sensor cable is required:
A. For any splicing longer than 100 feet, consult factory.
B. Use liquid tight junction boxes and appropriate liquid tight
connectors and/or conduit.
C. Do not mix high and low voltage circuits in same junction box.
D. For level sensor splice, it is recommended to use 5 conductor,
18 AWG shielded cable. Only ground the shield on one end of
the cable – easiest to ground shield wire in panel to the ground lug.
Preset Level
Sensor Holder
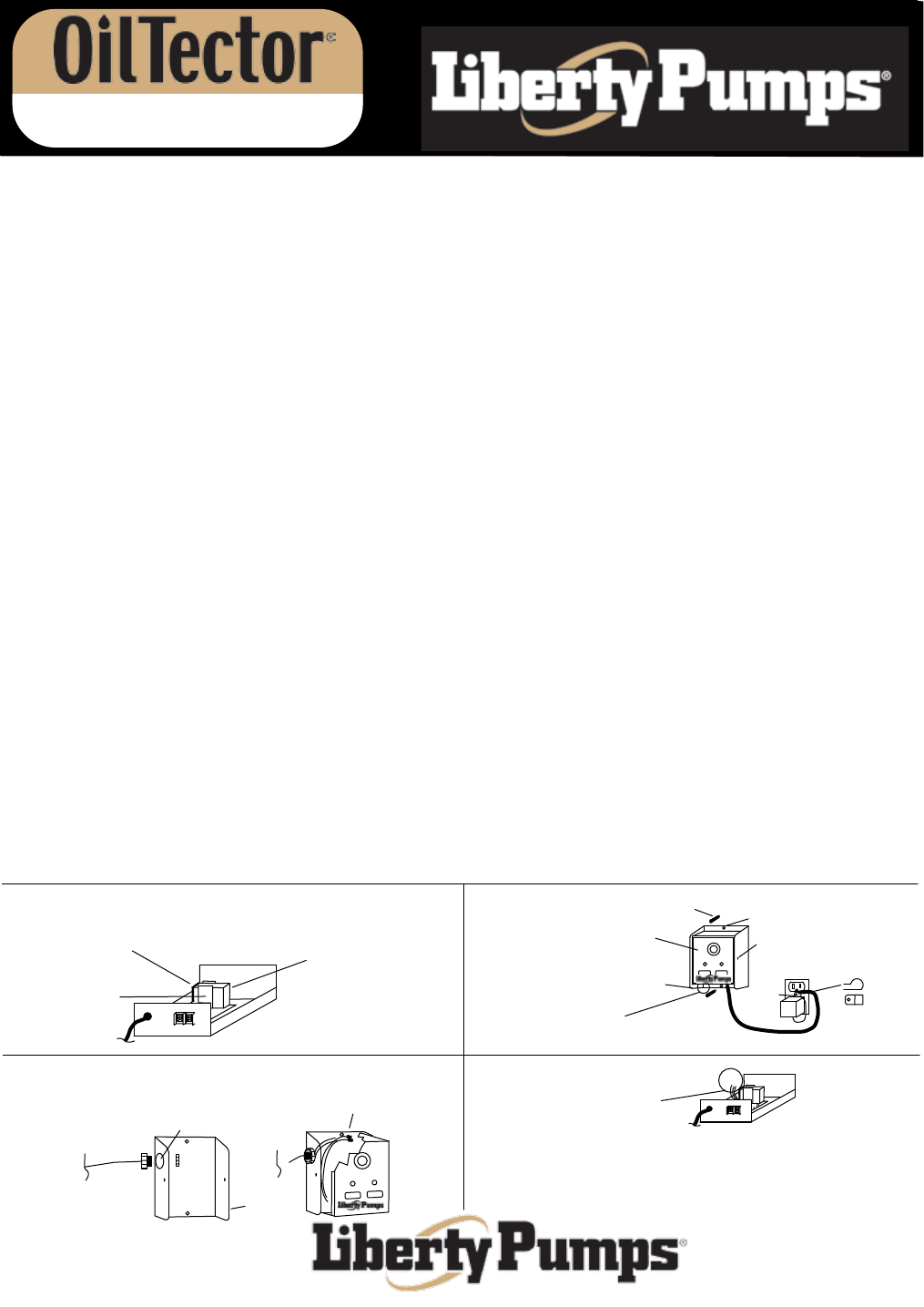
Mounting Hole (2)
Figure 8 - Mounting
Side Screw
120VAC Wallmount
Receptacle
Figure 7 - Installing/Replacing Battery
Battery Strap
Connector Duracell Model
MX1604B2
9 VDC Battery
Battery
Holder
Figure 9 - Installing Field Wiring for
Auxiliary Contacts
Connects to BAS/SCADA system
Auxiliary Contacts
White - Common
Red - Normally Closed
Black - Normally Open
Class 2, 24 VDC/VAC(50/60HZ)
500 milliamps MAXIMUM!
Jam
Nut
2 wire cable
To BAS/SCADA
1/2" Strain
Relief
Use #8 X 1 1/4"
Self Tapping Screws
1/2" Electrical
Knockout
Center
Screw
Base
Base
Wire Nuts
Plastic
Cord
Holder
OilTector
Cover
Terminal Block
connects to terminal
blocks 6 & 7 of the
CONTROL PANEL
Figure 10
7000 Apple Tree Avenue, Bergen, NY 14416 Phone: (800) 543-2550-Fax: (585) 494-1839-www.libertypumps.com
Operation and Maintenance Manual
Page 4 of 6
DWG#7235000G
Manual 7235000G
The OilTector Remote Alarm Panel is powered by 120 VAC coming from standard wall outlets and is transformed to 9VDC.
Installing a 9 Volt battery provides battery back-up.
When the OilTector Control Panel’s Auxiliary Contacts “close” the buzzer and light will turn “on” and the alarm panel’s auxiliary
contacts will be activated. Pressing the “silence switch deactivates the buzzer and auxiliary contacts. When the OilTector Control
Panel’s Auxiliary Contacts reset, the remote alarm panel will automatically reset itself.
Test product weekly. Make sure the green ”power on” light is “on”. Press the “Test” switch; the red alarm light and buzzer should
turn “on”. If the battery back up system is utilized, unplug the wall mount power supply (the green light will be off). Now press the
“Test” switch; the red alarm light and buzzer will turn “on”. If the buzzer sounds less loudly than when tested with the normal power
supply, then replace the battery.
1. To install/replace the battery for the backup power feature, remove the two side screws and install 9 VDC battery (Duracell
model MX 1604B2). After installing battery, press the test button to activate the alarm to make sure the battery works properly.
Reinstall side screws. See Figures 7.
2. Determine mounting location for the Alarm Panel. Make sure power outlet is within 6 feet of the alarm. Make sure the outlet
is on a separate circuit breaker from any other device and not on a switched receptacle to maintain power integrity. Mount the
alarm using two #8 x 1 1/4" self tapping screws (not included). Use #8 plastic anchor if mounting to sheet rock. See Figure 8.
The alarm can be mounted up to 2500 feet from the panel using 18 ga wire.
3. If Auxiliary Contacts are used, continue; otherwise go to step 4. Remove cover from base and remove 1/2" electrical knockout
from base. Use 16 - 2 AWG stranded wire - make sure there is at least 6" of wire inside of enclosure. Install a 1/2" strain relief
with jam nut. Connect wires for required application using wire nuts. Caution ! - When installing wires, route all wires away from
sharp objects & internal components. See figures 9 & 10.
4. There are two terminals on the bottom of the alarm panel. Connect a wire from the first terminal to the CONTROL PANEL
terminal #6 and connect another wire from the second terminal of the alarm panel to CONTROL PANEL terminal #7. See Figure
8
5. Plug the power supply into a 120VAC, 50/60 HZ standard wall outlet. For UL applications, remove center screw on receptacle
and place cord from wallmount transformer inside the plastic cord holder. Secure plastic cord holder to the receptacle by reinstall
ing screw to the center hole of receptacle. See Figure 8. For Canadian applications DO NOT INSTALL Plastic Cord Holder! The
green "Normal" light should come on.
6. Test the system by pressing the "Test" switch. The buzzer and the red warning light will be "on". The green "Normal" light will
be "off". While holding the “Test” switch, press the “Silence” switch. The buzzer will silence, but the alarm light will remain “on”.
Let go of the “Test” switch and the alarm light will turn “off” and the green “Normal” light will turn “On” indicating the system is now
in a normal condition.
Operation and Maintenance Manual
Operation and Maintenance Manual
Operation and Maintenance Manual
Installation of the Alarm Panel
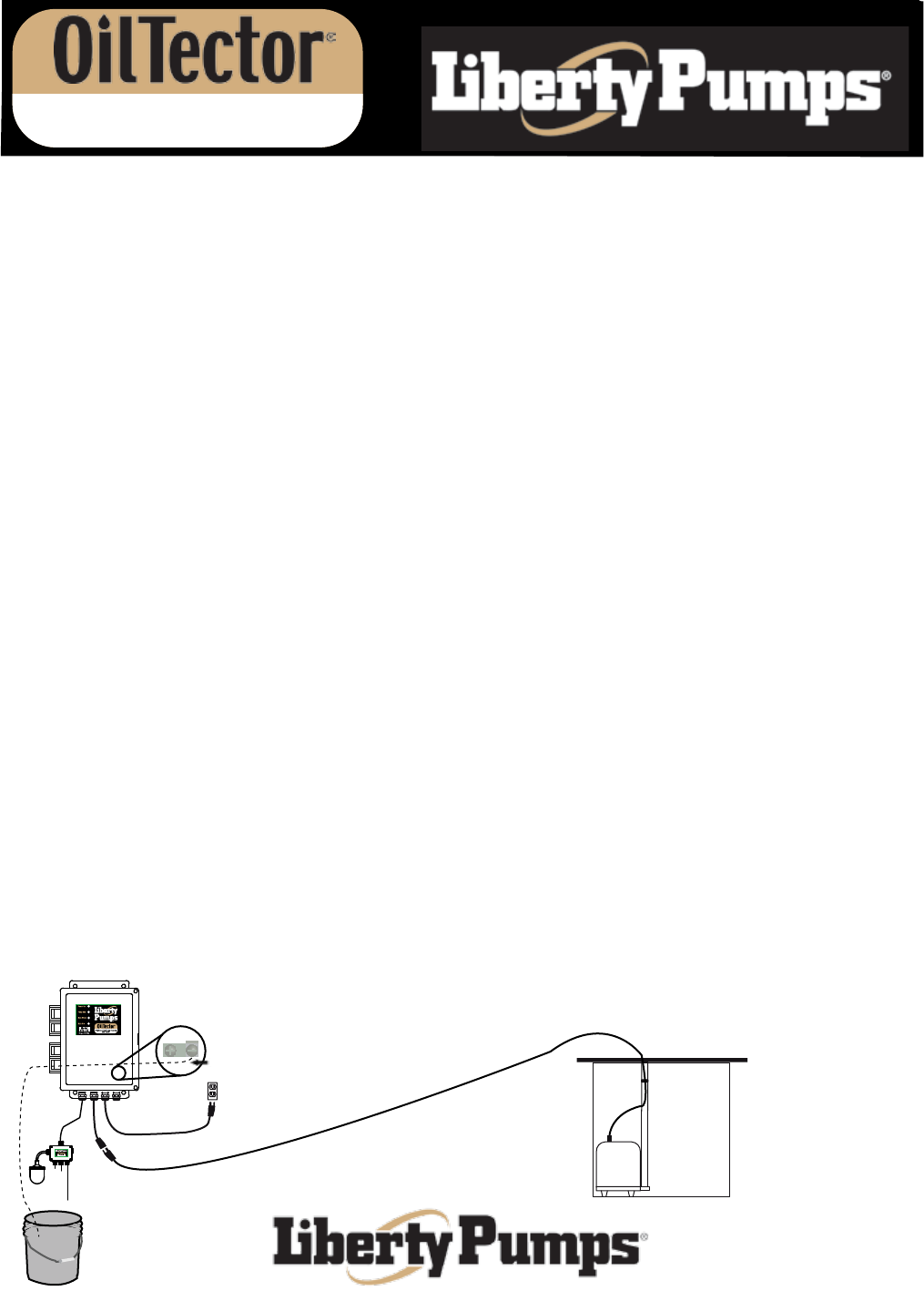
7000 Apple Tree Avenue Bergen, NY 14416 Phone: (800) 543-2550-Fax: (585) 494-1839-www.libertypumps.com
Operation and Maintenance Manual
P
age 5 of 6
DWG#7235000G
Manual 7235000G
:
Operation and Maintenance Manual
Operation and Maintenance Manual
Operation and Maintenance Manual
Testing the complete system
Upon complete installation of controls, pump and piping, the complete system should be tested for quality assur-
ance.
1. Test high oil circuit by lifting the float switch with the sump empty of water. Oil is non conductive like “air”, and
when the float is lifted only the HIGH OIL indicator will be illuminated. The auxiliary contacts in the control panel
and the remote alarm will activate.
2. Test a pump cycle by slowly filling tank with water. Stop filling tank with water when the level touches middle
probe. When the water touches the middle probe, pump should start and pump down to the bottom probe at
which time the pump will stop. Check discharge plumbing for leads and make sure discharge is going to the
correct area.
3. Test high water circuit. Unplug the pump from the control panel and slowly fill the tank until the water level just
touches the upper probe. When the water touches the upper probe, the HIGH WATER indicator will be illumi-
nated. The auxiliary contacts in the control panel and the remote alarm will activate.
4. Test the remote alarm for power loss. Unplug the power cord on the control panel. The auxiliary contacts will
close and the remote alarm will activate.
Testing panel - Using 5 gallon pail.
If it is not possible to test the complete system outlined above, then test the panel operation using a 5 gallon pail
filled with water. The system requires a temporary ground wire run from the control panel into the liquid in the pail
for correct operation.
1. Run Temporary Ground wire (14 AWG Copper Wire) from the ground lug inside panel and into the pail of
water. Make sure at least ½” of copper wire is exposed and immersed in the water.
2. Before lowering the sensor probe into the pail, lift the float switch, the HIGH OIL indicator will be illuminated.
The auxiliary contacts in the control panel and the remote alarm will activate.
3. Lower the sensor probe into the bucket of water slowly so that the longest probe is immersed in the water.
Slowly continue to lower so the middle probe touches the water, the pump should activate. While the pump is
activated, slowly remove the sensor probe out of the water until the longest probe is no longer in the water, the
pump should turn off. Repeat a couple of times for quality assurance.
4. Lower the sensor probe into the bucket of water slowly so that the longest probe and the middle probe are
immersed in water, the pump will activate. Continue to lower sensor probe so that water touches the shortest
probe, the HIGH WATER indicator will be illuminated. The auxiliary contacts in the control panel and the remote
alarm will activate.
5. This completes testing. Remove temporary ground from panel and retighten ground lug with all the green
wires. Return to manual for “Installation of Preset Level Sensor Holder”.
120 V
Receptacle
60500A0
Ground Lug
Temporary 14 AWG Ground Wire
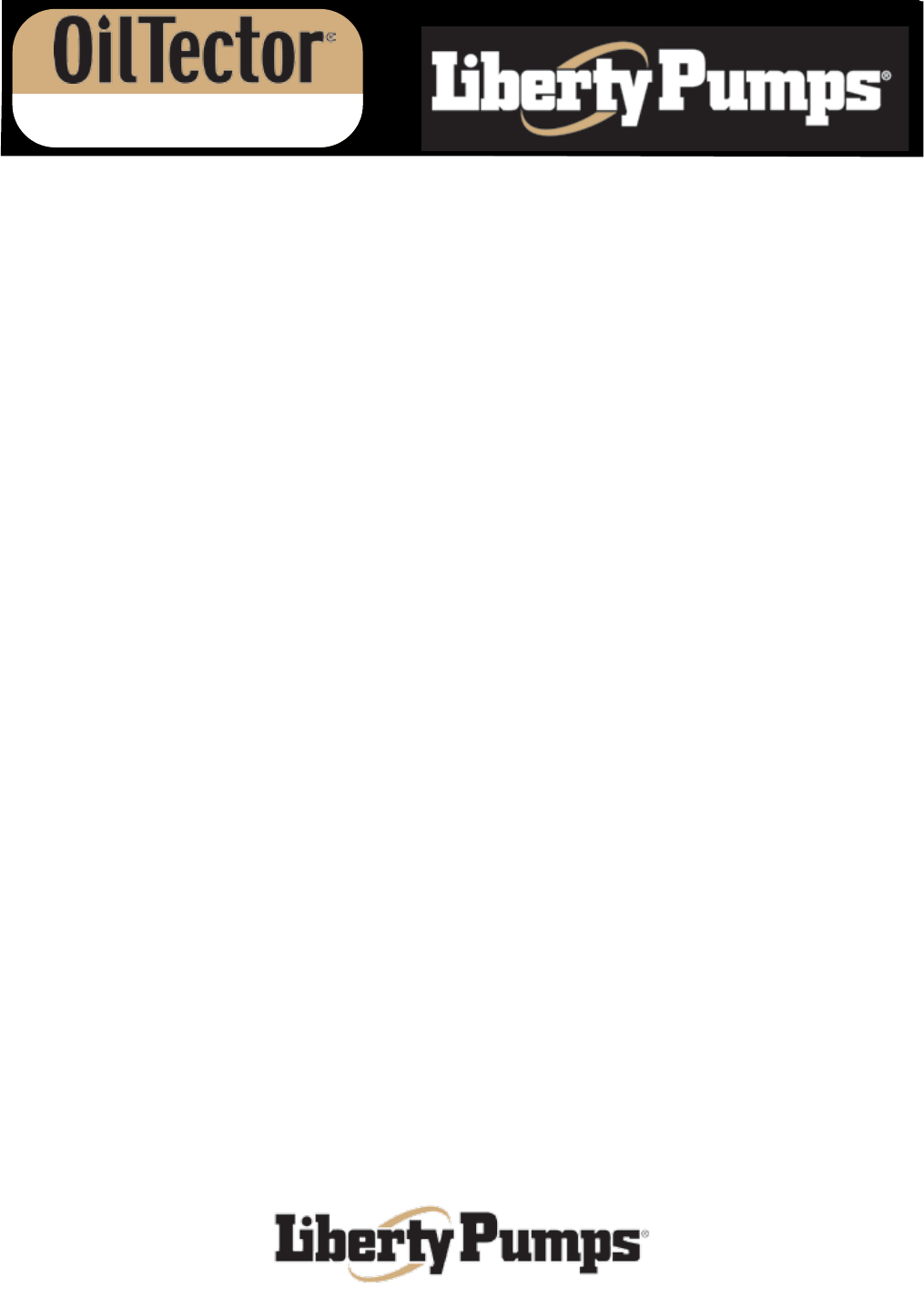
7000 Apple Tree Avenue Bergen, NY 14416 Phone: (800) 543-2550-Fax: (585) 494-1839-www.libertypumps.com
Operation and Maintenance Manual
P
age 6 of 6
DWG#7235000G
Manual 7235000G
:
Operation and Maintenance Manual
Operation and Maintenance Manual
Operation and Maintenance Manual
Maintenance
1. The preset level control must be kept clean and free of rust, mud, soap or any conductive material.
2. Every year clean probes keeping them free of debris, calcium or iron deposits.
3. Fuses in control panel are 5mm X 20mm 1/2amp for F1 and 5mm X 20mm 1amp for F2.
(Spare fuses are included for your convenience)
4. Every year replace 9 Volt Battery in Remote Alarm.
Trouble Shooting
Symptom Possible Cause Action
Pump does not run Panel Power Cord Unplugged Plug in Outlet, Check Power
Pump not plugged into panel Plug pump to panel plug
Defective Contactor Replace Contactor
Loose level sensor wires Tighten connections
Pump failure Replace pump
Pump turns off before Poor pump ground or system ground Check grounding system
bottom probe