Roseman Engineering FG3E Car Data Logger User Manual
Roseman Engineering Ltd. Car Data Logger Users Manual
Contents
- 1. Users Manual
- 2. User Manuel
Users Manual
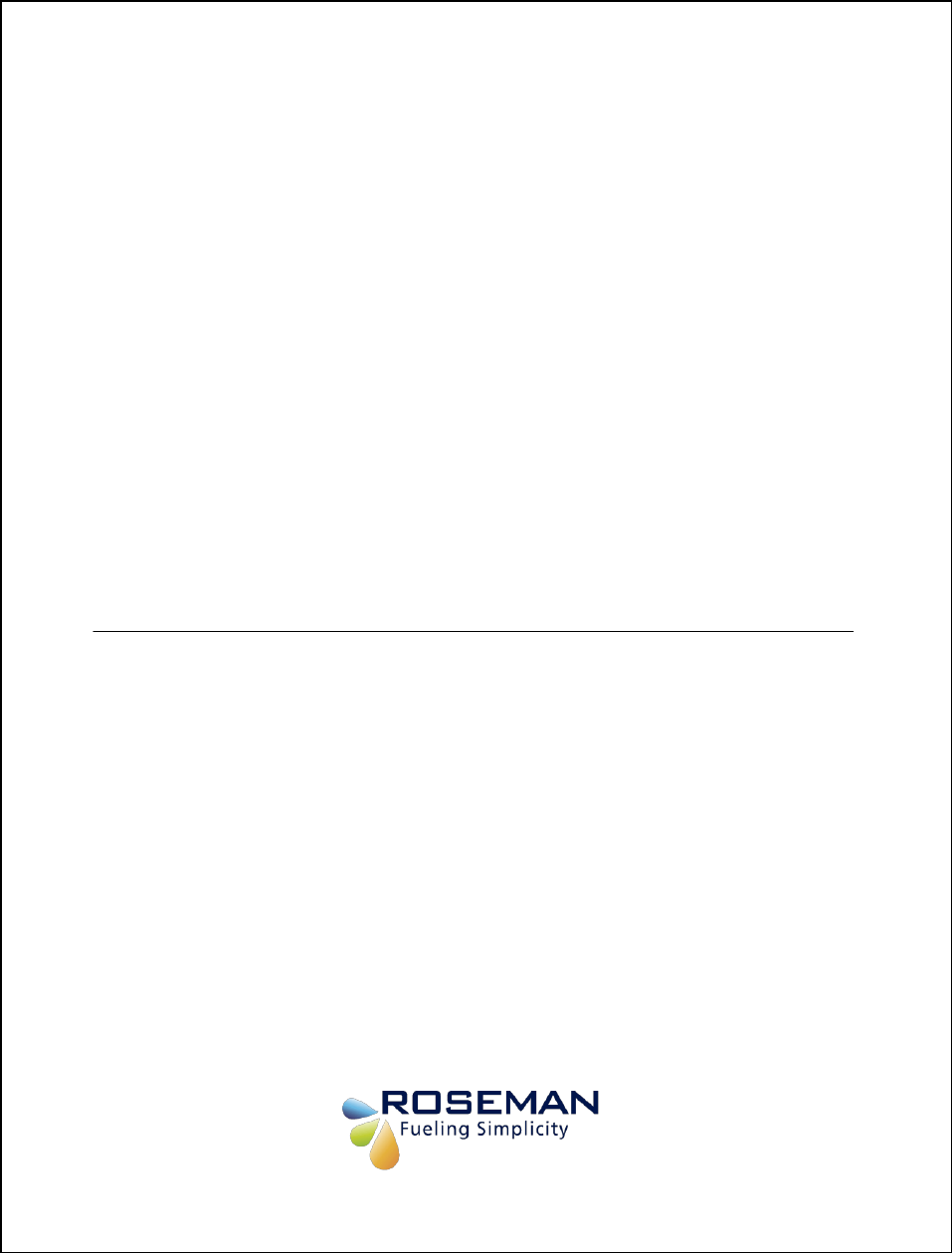
ROSEMAN FMS System
Modular Car/Driver Fleet Gate Type-3
#RID-FG3-XX
Installation Guide
Ver. 2.0
Roseman engineering ltd
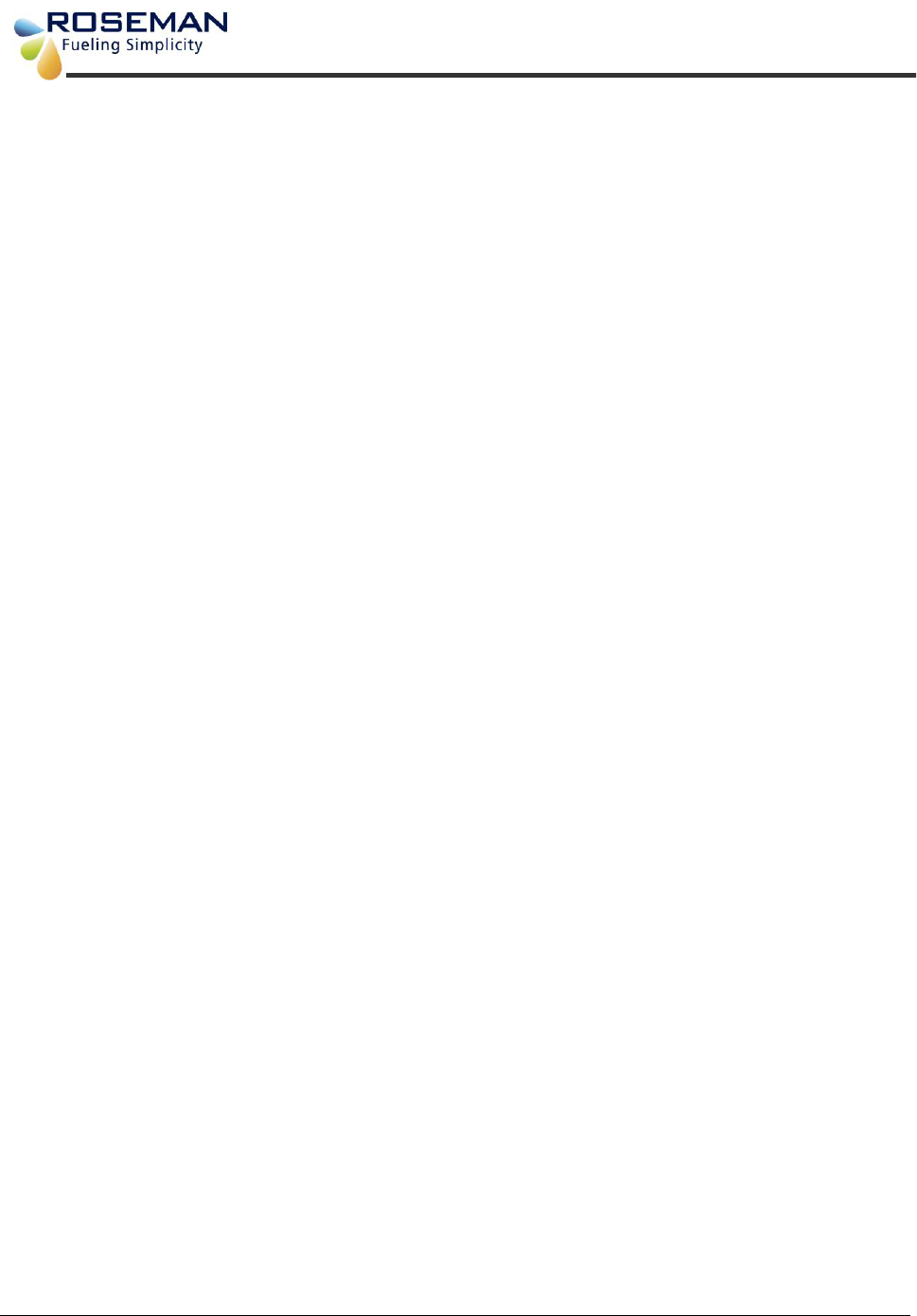
Fleet Gate Installation Guide Roseman Engineering Ltd
2
The Fueling Division of Roseman Engineering Ltd.
TABLE OF CONTENT
1. INTRODUCTION .......................................................................................................................... 4
2. INSTALLATION ............................................................................................................................ 7
3. FG3 MOUNTING AND INSTALLATION ............................................................................. 9
4. WIRING THE DUAL INPUT PULSE VEHICLES ............................................................ 12
5. WIRING THE CAN BUS VEHICLES ................................................................................... 16
6. WIRING THE DALLAS TAG READER SET ..................................................................... 20
7. WIRING THE J1708 VEHICLES .......................................................................................... 23
8. COMPLETION OF INSTALLATION .................................................................................... 26
9. PREPARATION AND PROGRAMMING ............................................................................ 27
10. FLASHING TOOL ....................................................................................................................... 33
11. APPENDIXES............................................................................................................................... 38
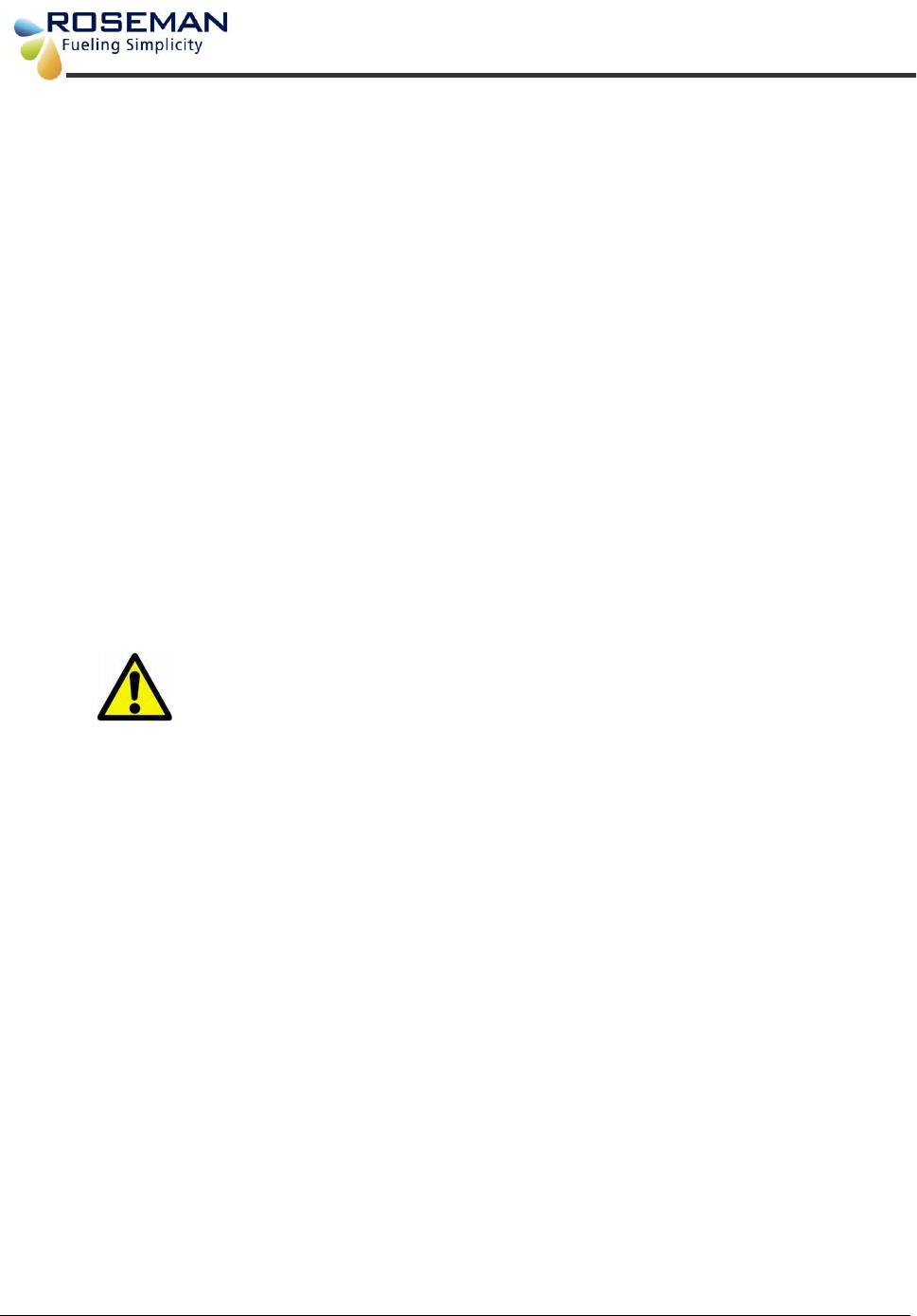
Fleet Gate Installation Guide Roseman Engineering Ltd
3
The Fueling Division of Roseman Engineering Ltd.
Important Notice
Roseman Inc. cannot guarantee the RF Vehicle ID Box installation techniques discussed
herein are complete and effective on every make, model and year of vehicle and
equipment now in the marketplace or coming in the future. At times vehicle manufacturers
make changes to the engine computer, wiring and/or electronics with new model years
and in fact also during mid-year production. After market accessories may also impact the
installation of the RF Vehicle ID Box. Roseman provides updates as soon possible after
discovering installation challenges, new OBD types or anything effecting proper operation.
We request feedback from the many very knowledgeable Automotive Technicians working
with this technology. If installation issues arise with new model years or unique
equipment we request immediate and detailed feedback so corrections and enhancement
may be made in a timely fashion. Working together we can assure that the Roseman
system remains the finest available. Information on updates and new programs or
procedures will be made available via the Fuel Focus installation trainers, the newsletter
and the customer support desk. Roseman urges all trained Technicians , Supervisors and
Managers to avail themselves of the newsletter by contacting " Roseman Support"
<fuelsupport@Roseman.com> to be included on the subscription list.
FCC Warning
To comply with FCC requirements, a distance of at least 20cm between the equipment and
all persons should be maintained during the operation of the equipment.
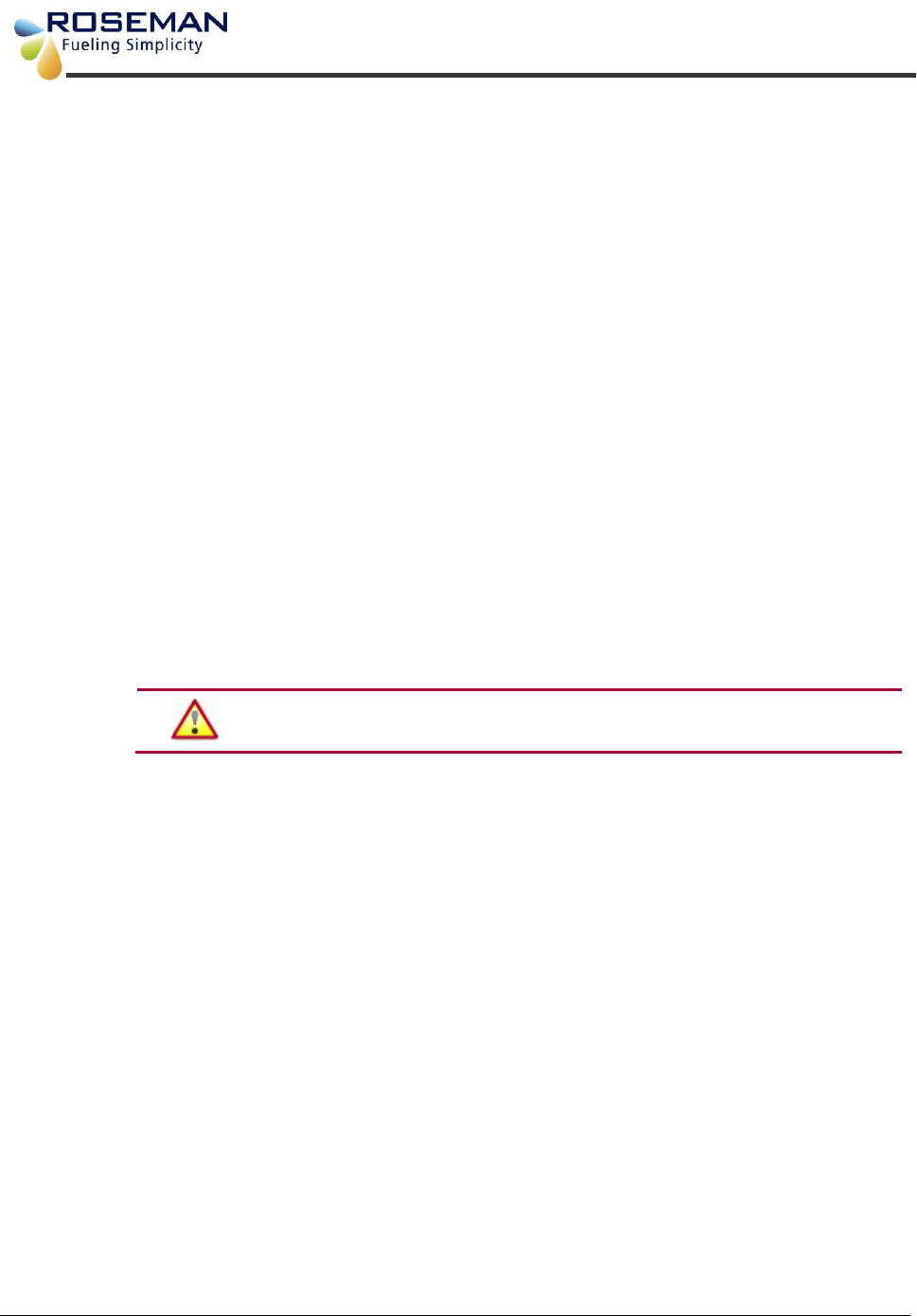
Fleet Gate Installation Guide Roseman Engineering Ltd
4
The Fueling Division of Roseman Engineering Ltd.
1. Introduction
1.1 Purpose
This Vehicle Subsystem Installation Manual is provided to assist you in installing
the Modular Fleet Gate Type 3 (FG3). Review this manual prior to the installation
of the FG3 to ensure proper installation practices. Incorrect installations are the
major cause of system malfunctions.
The FG3 must be installed as described in this manual to ensure the reliability and
proper operation of the system.
Please read this entire manual before starting your first installation.
1.2 System Overview
The Roseman FG3 is the integral component of the vehicle subsystem of the
Roseman FMS System. To properly install and utilize the FG3 the following is
required:
Roseman Fuel Management System Island Controllers
Pumps/dispensers modified using nozzle tags
WAF Receiver Upgrade Kit installed in the Island Controller
Failure to use a shielded cable as described in this manual will
void the warranty.
1.3 Components Overview
This section describes the various components that operate as part of the
Roseman System. Use this information to determine the equipment needed for
your particular fleet of vehicles.
Each Vehicle Unit includes the following components:
SVID (Small Vehicle Identification Device) Type 3
Modular Fleet GateType 3 (FG3)
Fuel inlet Antenna
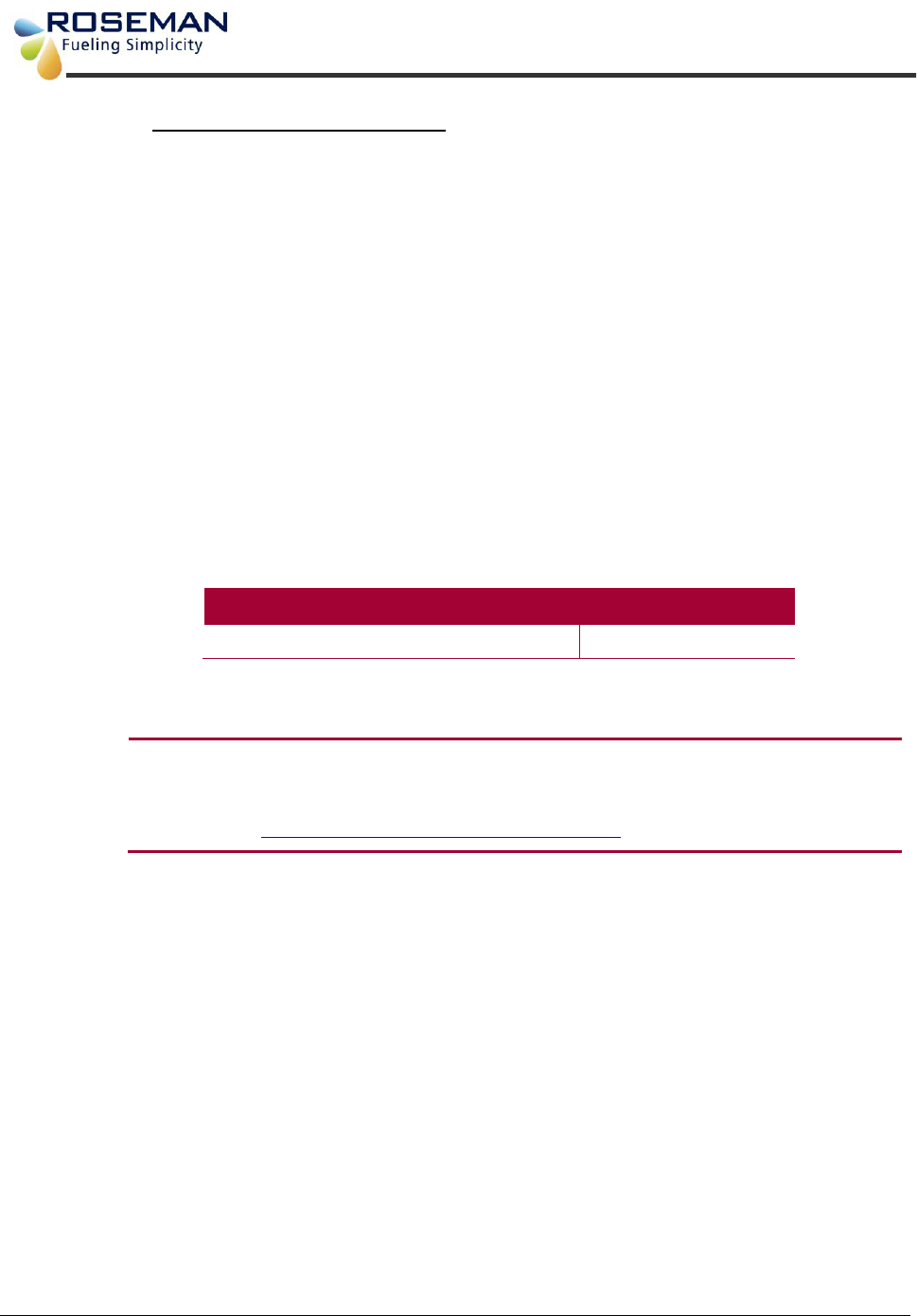
Fleet Gate Installation Guide Roseman Engineering Ltd
5
The Fueling Division of Roseman Engineering Ltd.
1.3.1 Modular Fleet Gate (FG3)
The FG3 is a main component of the Fleet Journal system installed in the vehicle
and stores the vehicle usage data, including each ride start and end times, initial
and final odometer reading, maximum speed, and ride participants etc, provides
the fleet manager full supervision and control over the use of all fleet vehicles.
The FG3 stores the vehicle usage data, this data is automatically transferred via
the WAF unit to Fleet Journal application. The FG3 process the data and
generates required reports for the use of the fleet manager.
The FG3 can be configured to record either odometer or engine hour readings;
and gets its power from the vehicle's battery.
The Vehicle data is uploaded in one of the following methods:
2.4GHz Wireless connection with fuel station controller.
2.4GHz Wireless connection at parking lot garage etc.
On line connection via cellular Modem.
All the data is collected into a central data base server.
This document describes the installation procedures for the FG3 (2.4 GHz).
Description
Part No.
Modular Fleet Gate Type 3
RID-FG3-XX
The FG3’s power is supplied from the vehicle’s battery. It requires either a 12 VDC
or a 24 VDC system, and draws a maximum 150mA of current.
Note
If you experience battery drain difficulties, we recommend the use of the
Battery Brain, or similar devices, available via the automotive after-market.
More information is available from
http://www.batterybrain.com/batterybrain.pl.
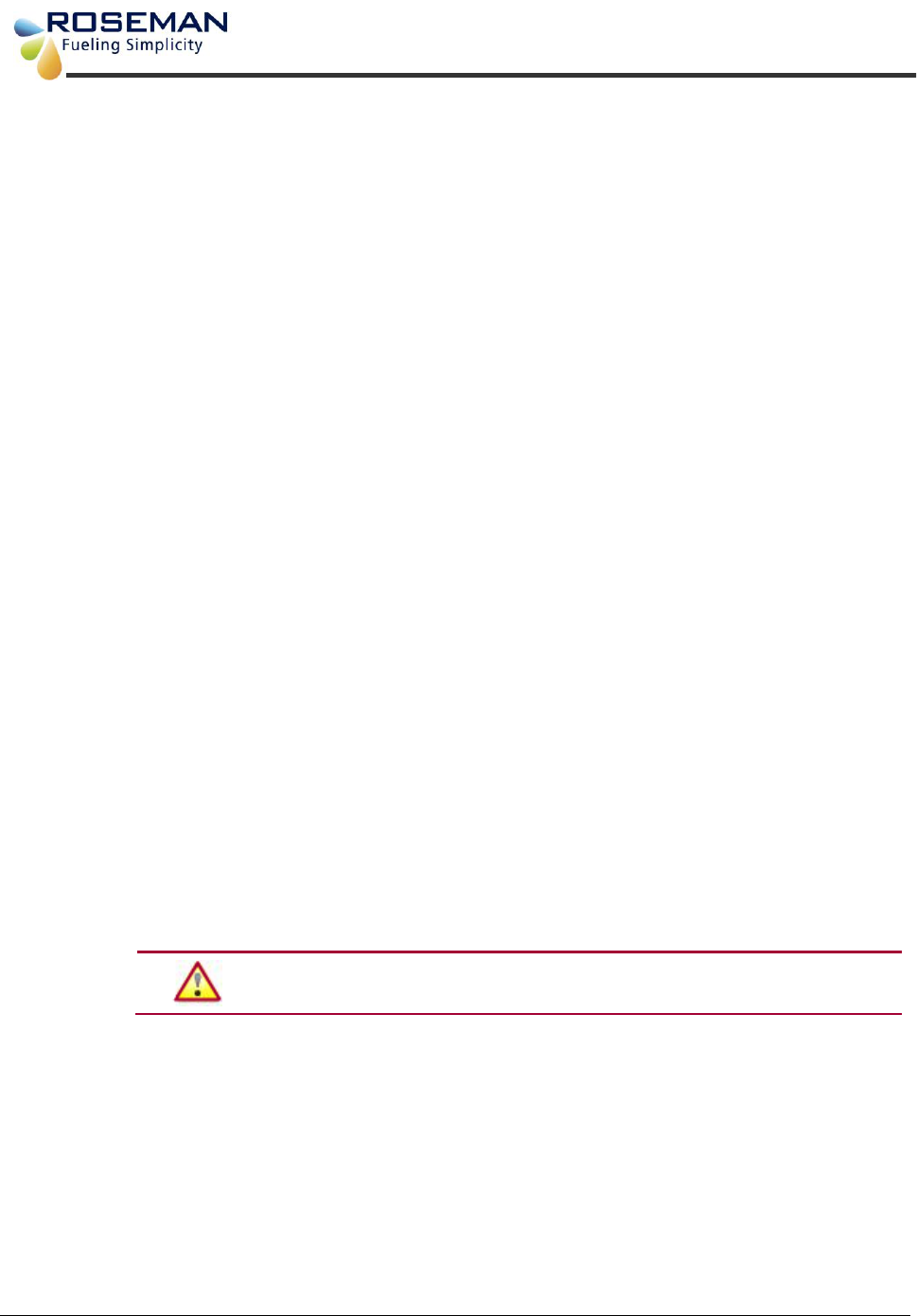
Fleet Gate Installation Guide Roseman Engineering Ltd
6
The Fueling Division of Roseman Engineering Ltd.
1.4 Required Tools
The following tools are required to complete the installation procedures:
Screwdrivers
Box wrenches
Crimping tool
Wire stripping tool
Drill with a 1/8" drill bit
Heat gun (for heat-shrink insulation)
1.5 Required Materials
The following materials are required to complete the installation procedures:
Two conductor twisted pair (with foil shield and drain wire) cable (18
gauge min)
Wire terminals. Do not use Scotch Locks.
3/8" inch self-tapping, sheet metal screws (Rittal SZ2487 or equivalent)
with matching flat washers and split washers
Grommets
Three amp fuse and fuse holder
1.6 Wiring Instructions
The general procedures for wiring the FG3 as follows:
Using a wire stripping tool, remove insulation to bare 3/8" of wire.
Press firmly on the connector locking tab.
Insert the exposed wire end.
Release the locking tab.
Check to make certain the wire is held firmly in place and that the wire
insulation is not pinched in the terminal.
Use gasoline and oil-resistant wiring only. Route wires away
from moving parts and the vehicle’s exhaust system.
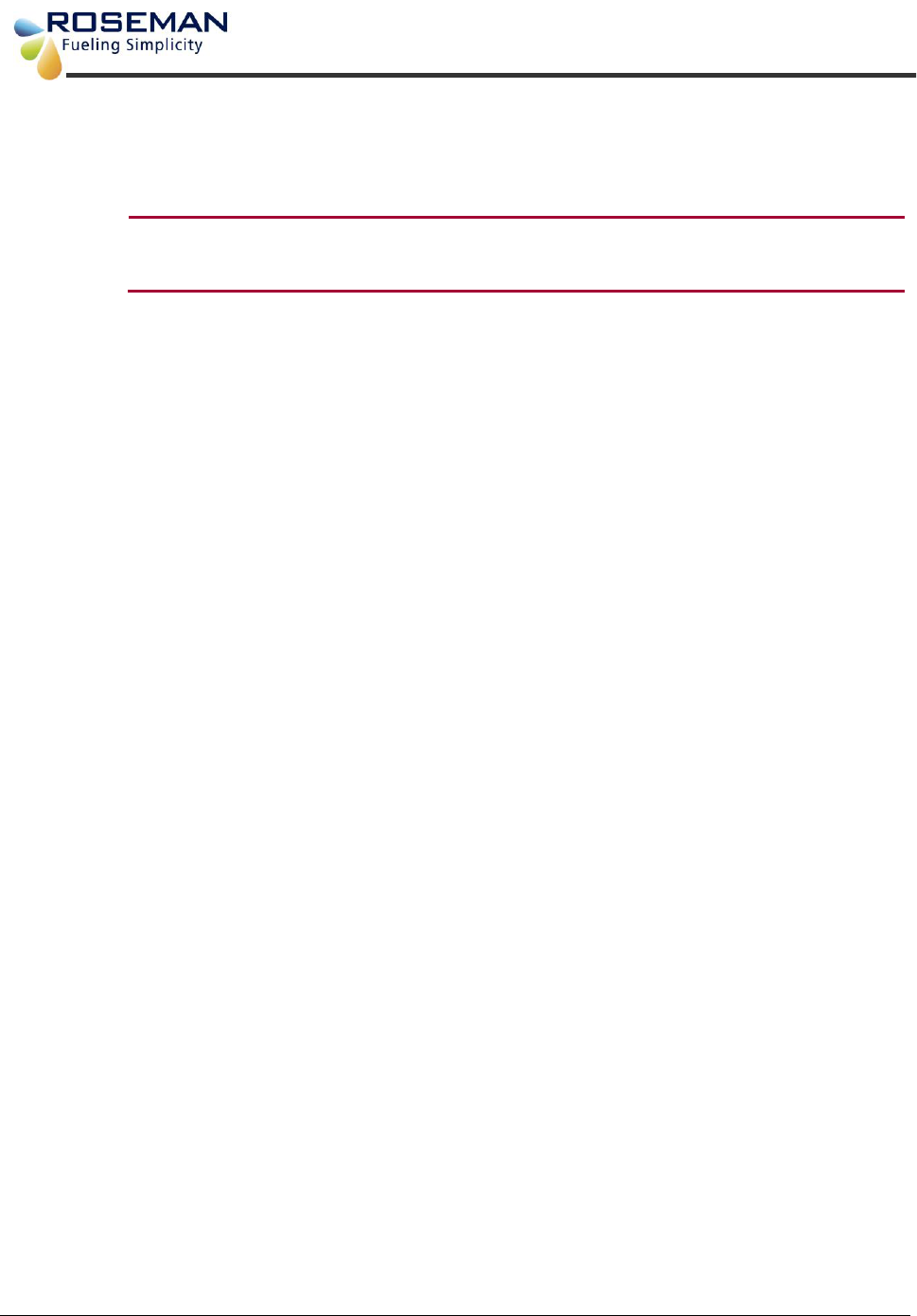
Fleet Gate Installation Guide Roseman Engineering Ltd
7
The Fueling Division of Roseman Engineering Ltd.
2. Installation
Follow the installation instructions detailed in the following sections.
Note
When performing wiring procedures, follow the instructions in Wiring
Instructions on page 6.
2.1 FG3 Mounting Location Considerations
Before mounting the FG3, give thought to where best to place it. Consider the
following four basic points:
Weather Protection – Select a weather-protected location. The FG3 is not
watertight. Water and/or moisture can seep in through the connectors
causing permanent damage! Consider an area where it will not be
exposed to water during vehicle operation or cleaning.
Cable Runs – The Fuel Inlet Antenna is mounted in a Class I, Division I,
and hazardous location. The wiring is intrinsically safe and therefore must
not come within two inches of any existing wires or cable harness.
Mounting the FG3 to minimize the FIA cable length makes it easier to
adhere to this safety rule. The VIB also requires connections to power and
ground, so it should be located in an area where you can tap into these
sources easily.
Cable Routing – It is important to keep cables from coming in contact with
moving parts, and away from parts that generate excessive heat, electrical
noise, or areas that may impede safety. Examples of these areas are the
drive shaft, fan blades, belts, adjustable steering column, alternators,
fluorescent lighting, foot pedals, radiator, and engine and exhaust
systems. Attempt to gather all conductors at a common point when routing
cables, allowing the cables to travel to the FG3 in a group. The FG3 must
be kept at least three feet from the fill pipe opening. This includes cases
where the FG3 is mounted in the trunk, as that is not a vapor-sealed area.
Wire loom is recommended for protection of the wiring.
Cable Clearance – Maintain a minimum of six (6) inches from devices with
a strong magnetic field such as fan motors or speakers.
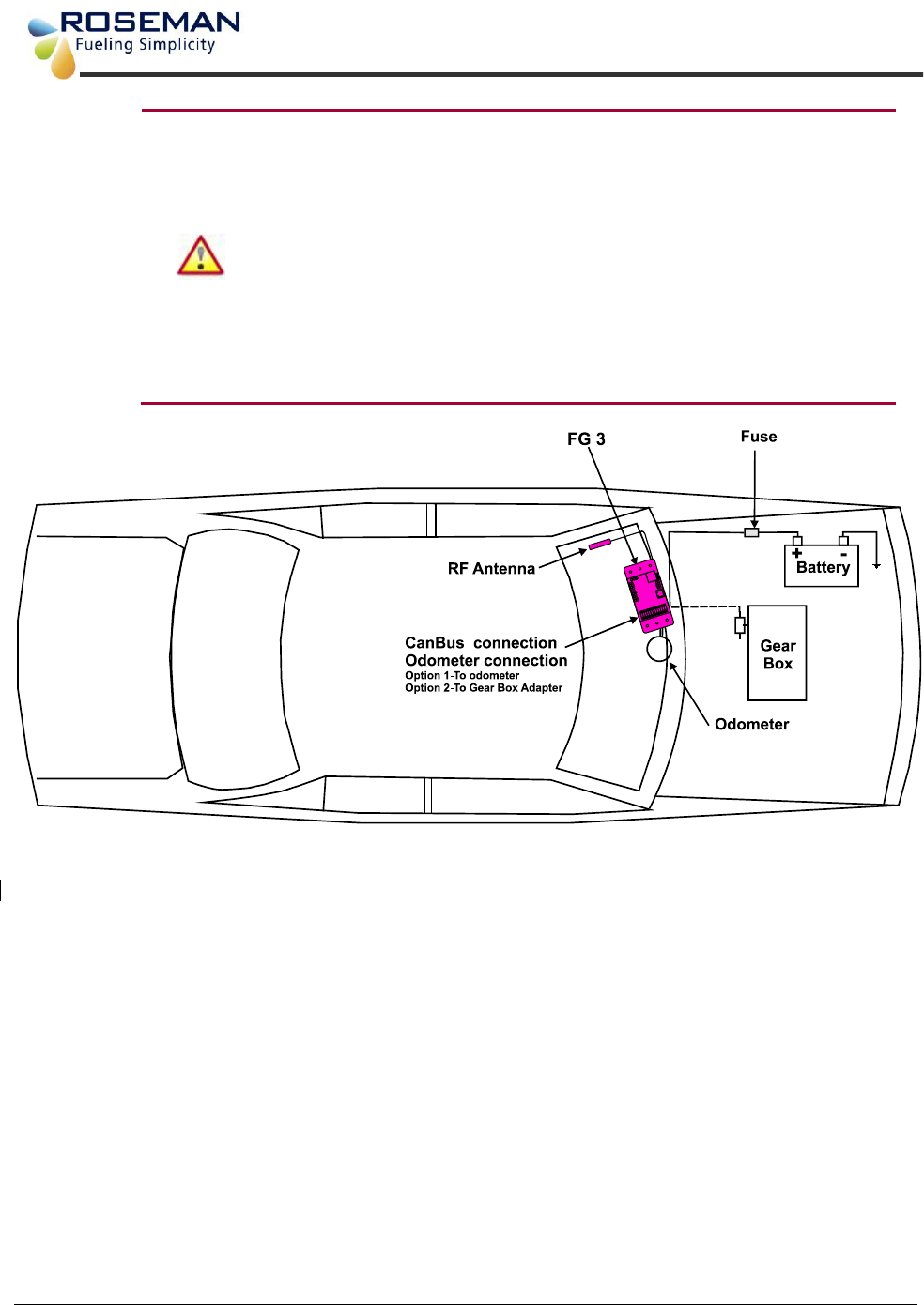
Fleet Gate Installation Guide Roseman Engineering Ltd
8
The Fueling Division of Roseman Engineering Ltd.
Do not use an electric drill or any other electrically-powered tools
within three feet of the filler neck or fuel tank, as this area is
considered a Class I, Group D hazardous location.
Do not use a heat gun or any other heating device within three feet
of the filler neck or fuel tank as this area is considered a Class I,
Group D hazardous location.
The Fuel Inlet Antenna and its wiring are intrinsically safe. You
must therefore ensure that there is complete separation between
the transmitter wiring and any existing auto wiring. You must also
avoid routing wires near the auto exhaust systems or fuel lines.
Mount the FG3 at least three running feet from the filler neck.
Figure 1: Typical Vehicle Wire Routing
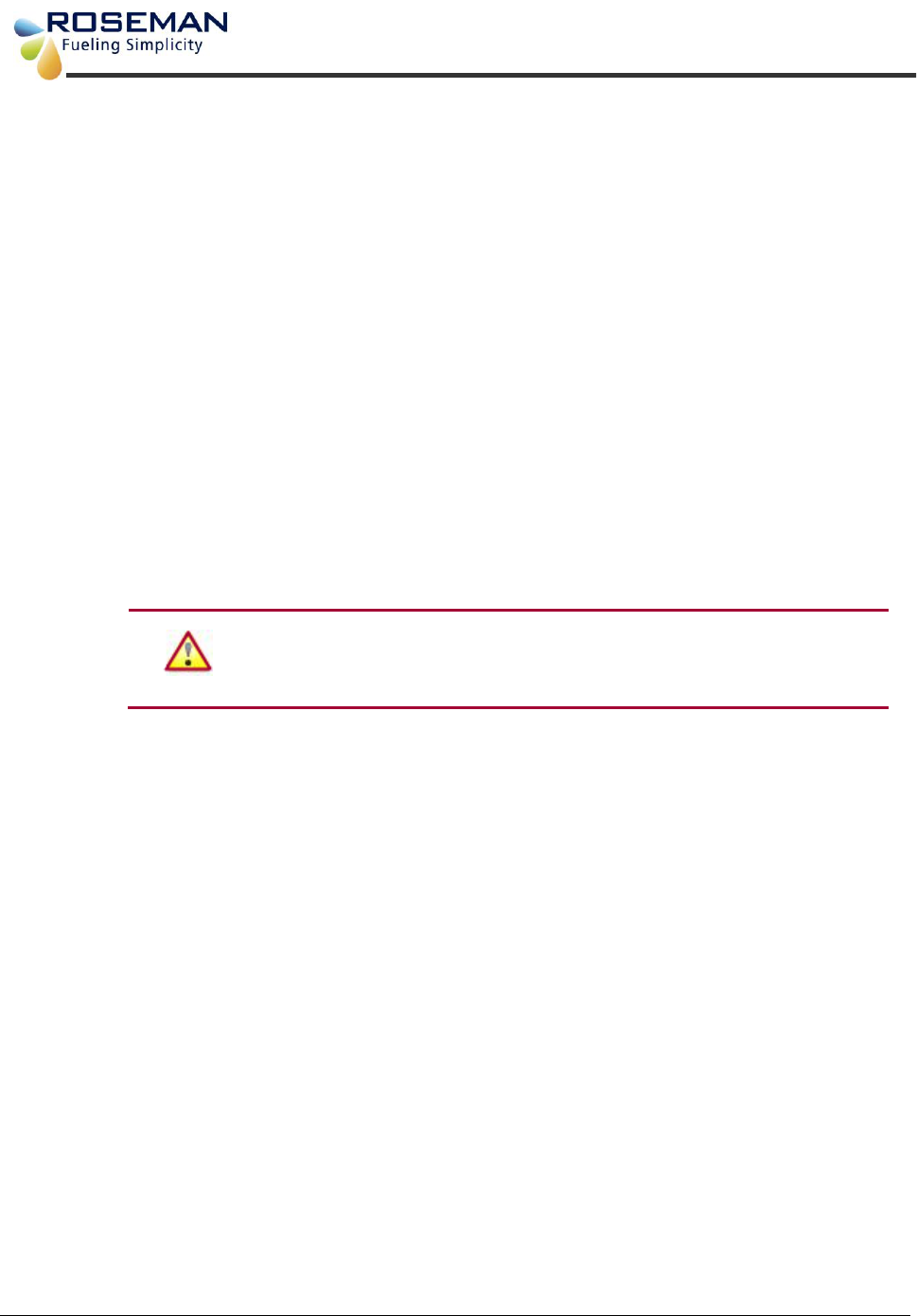
Fleet Gate Installation Guide Roseman Engineering Ltd
9
The Fueling Division of Roseman Engineering Ltd.
3. FG3 Mounting and Installation
3.1 Mounting the FG3
1. After reviewing the recommendations listed in the Vehicle Devices Mounting
Location Considerations, mount the FG3 as follows:
If possible, mount it on the same side of the vehicle as the filler neck.
For a passenger car, the FJ3 can be mounted under the dashboard or in the
trunk, provided that the unit is at least three running feet from the filler neck.
For a truck or bus, the FG3 can be mounted inside the vehicle's electric
enclosure.
2. Drill at least two 1/8" holes for the FG3 mounting. Use the FJ3 to mark the
holes (refer to Figure 2: FG3 Wiring Diagram)
3. Figure 2The FJ3 should be mounted on the vehicle chassis, or any other metal
portion of the vehicle whenever possible.
Do not use an electric drill or any other electrically powered
tools within three feet of the filler neck or fuel tank as this area
considered a Class I, Group D hazardous location.
4. Using the two 3/8" self-tapping mounting screws and two lock washers, mount
the FJ3 to the vehicle frame. You must use two self-tapping sheet metal
screws.
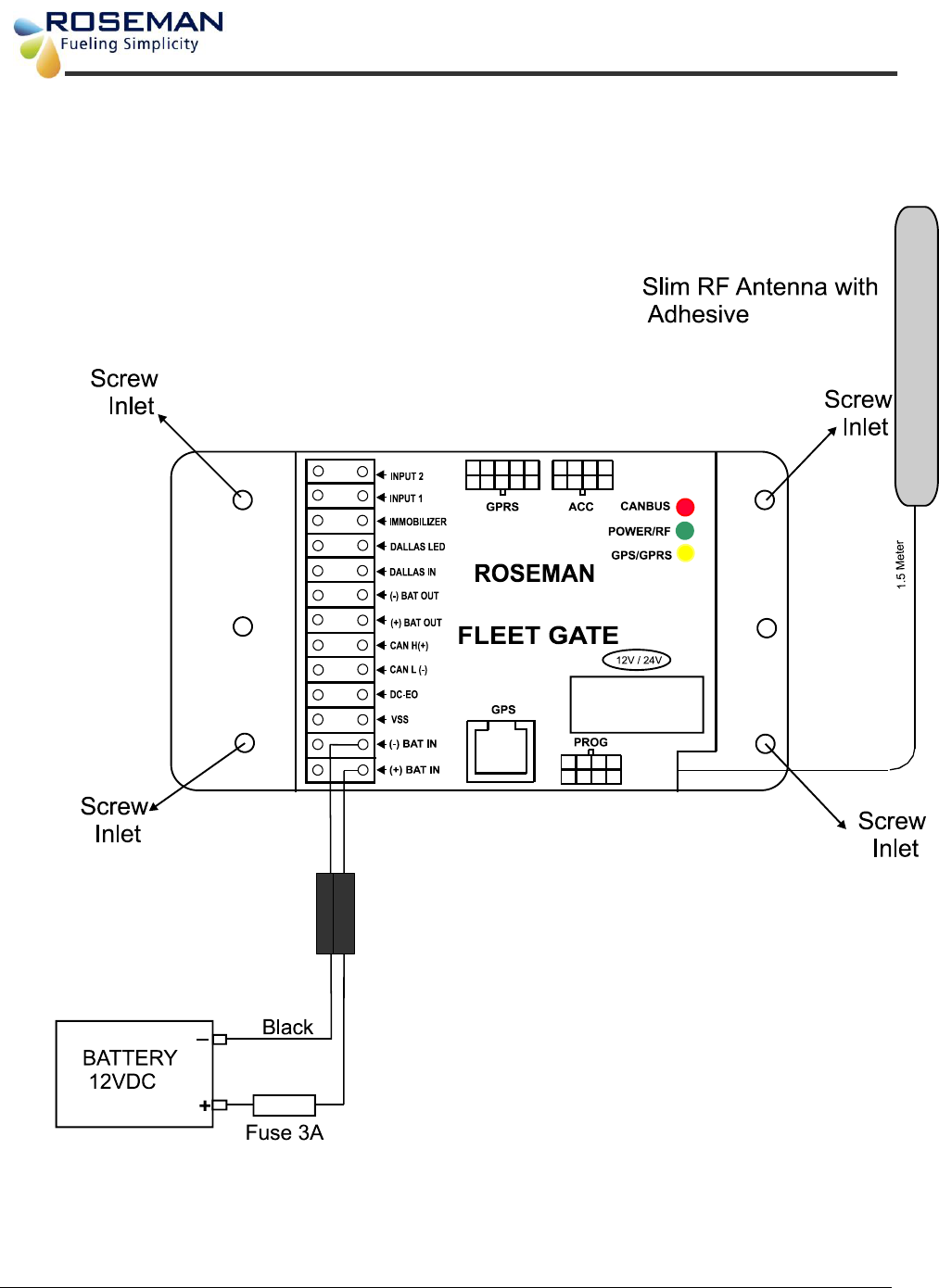
Fleet Gate Installation Guide Roseman Engineering Ltd
10
The Fueling Division of Roseman Engineering Ltd.
Figure 2: FG3 Wiring Diagram
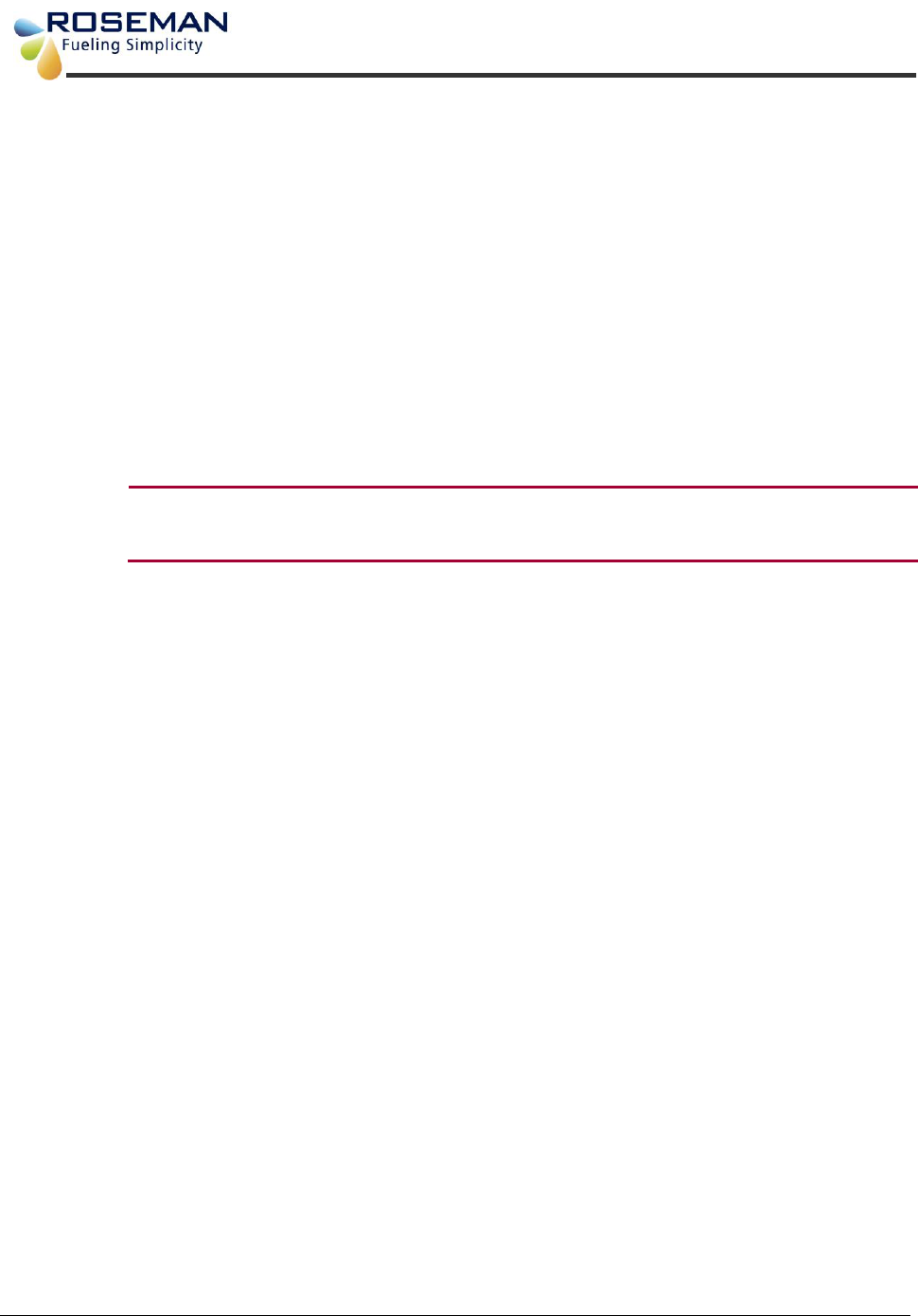
Fleet Gate Installation Guide Roseman Engineering Ltd
11
The Fueling Division of Roseman Engineering Ltd.
3.2 Mount the RF Antenna
The RF Antenna must be mounted so that it is vertical and is able to “see”
outside.
The RF Antenna can be mounted by removing the protective layer from the
adhesive back and attaching on the vehicle windshield.
In passenger cars, it is can usually be concealed behind the pillar molding on the
side of the windshield. The same location can be used near the rear window if
desired.
In busses, the RF Antenna can be mounted in the sign compartment area,
provided that it is manufactured of fiberglass.
The antenna cannot be concealed on all sides by metal.
Note
The RF Antenna should be fastened and secured appropriately.
Do not coil the antenna wire.
3.3 Connect the FG3 to the Battery or Power Source
Positive (+) connection can be from any 12 or 24 volt source.
If your power source is the battery, run a wire from the battery to the FG3
and connect it to BATT (+). This wire requires a 3 amp fuse to protect the
FG3.
3.4 Connect the FG3 to Ground
To connect the FG3 to ground, you can connect it to the vehicle metal
chassis, or to the negative (-) post on the vehicle's battery.
If you are connecting to the vehicle battery:
Prepare a black auto wire with a terminal on each end. Connect the black
(-) cable from BATT (-) on the FG3 to the negative (-) terminal on the
battery. Tie the wire to the vehicle frame.
If you are connecting to the vehicle metal chassis:
Connect a black ground cable from BATT (-) on the FG3 to one of the
FG3’s mounting screws. Loop the cable end around the screw, between
the screw head and the FG3 plate, and tighten the screw.
Note this will connect the FG3 to ground only if the FG3 is affixed to the
metal chassis of the car.
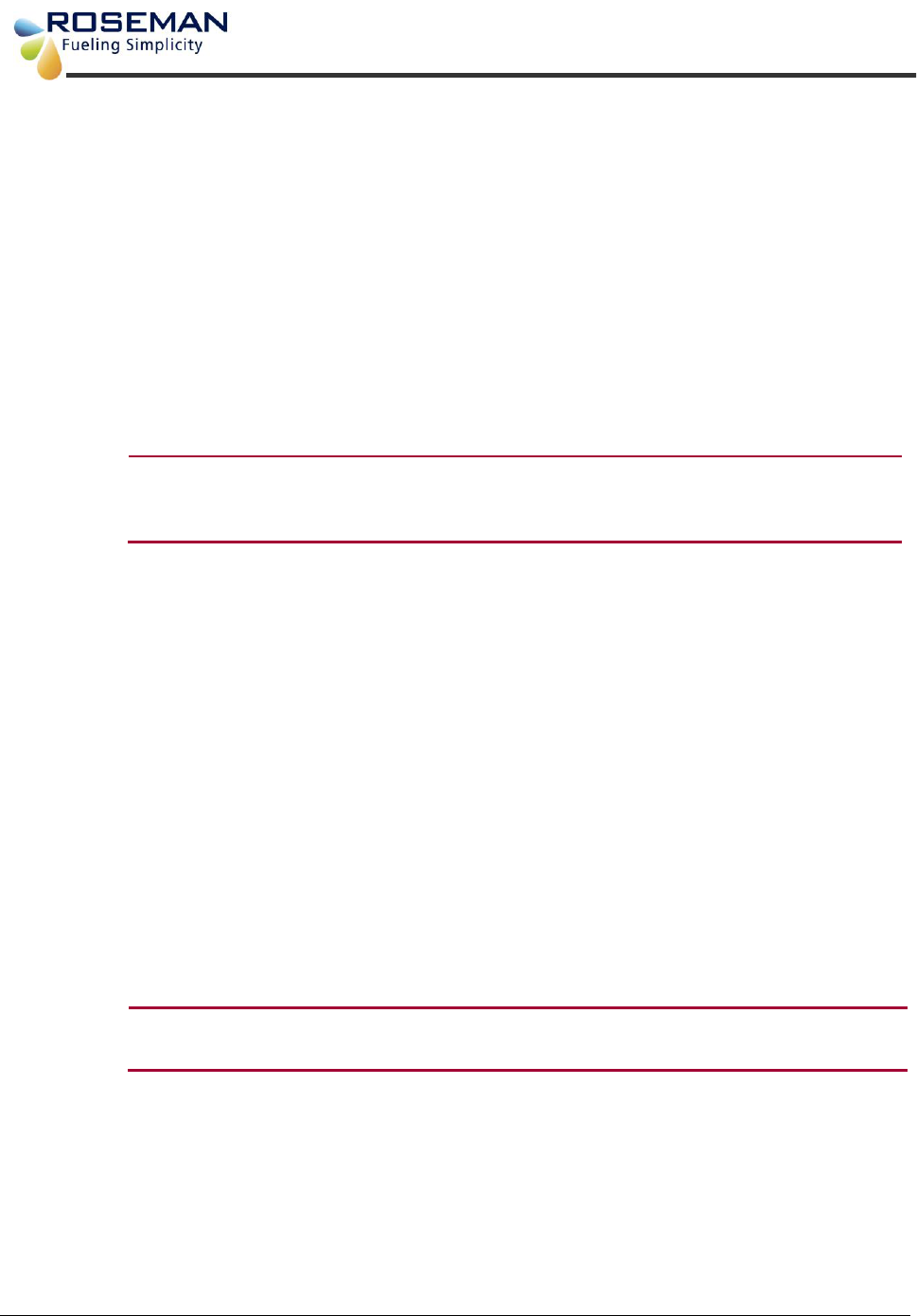
Fleet Gate Installation Guide Roseman Engineering Ltd
12
The Fueling Division of Roseman Engineering Ltd.
4. Wiring the Dual Input Pulse Vehicles
4.1 Locating the Vehicle Speed Sensor (VSS)
The VSS usually originates near the rear of the transmission case. From there
it usually travels to the engine control computer, speedometer and the cruise
control computer. Pick a location to tap the circuit near the engine control
computer interface as this will usually reduce risk of incorrect data due to
ignition noise. Also, as with any electronic accessory, a good ground is
imperative. Lack of proper ground could result in a ground loop condition which
could affect the accuracy of the unit.
Note
Roseman can provide you with an aftermarket catalog that details
where to find the VSS+ wire, what color it is and how many pulses
per mile the vehicle has. This is a good reference to use.
4.2 Connect the Data Interface to the FG3
The instructions for this procedure depend on the type of vehicle.
To view how to capture vehicle data, refer to Appendixes
Appendix A –Capturing vehicle data
on page 38.
4.2.1 Connect the FG3 to odometer
There are two possible odometer connections:
Direct from either an electronic odometer or speedometer.
From a mechanical odometer via a Reed type odometer adaptor. Also
known as a pulse transducer or “taxi tap”
Note
If you are recording the vehicle's engine hours, you
may skip this section and go on to "Engine Hours".
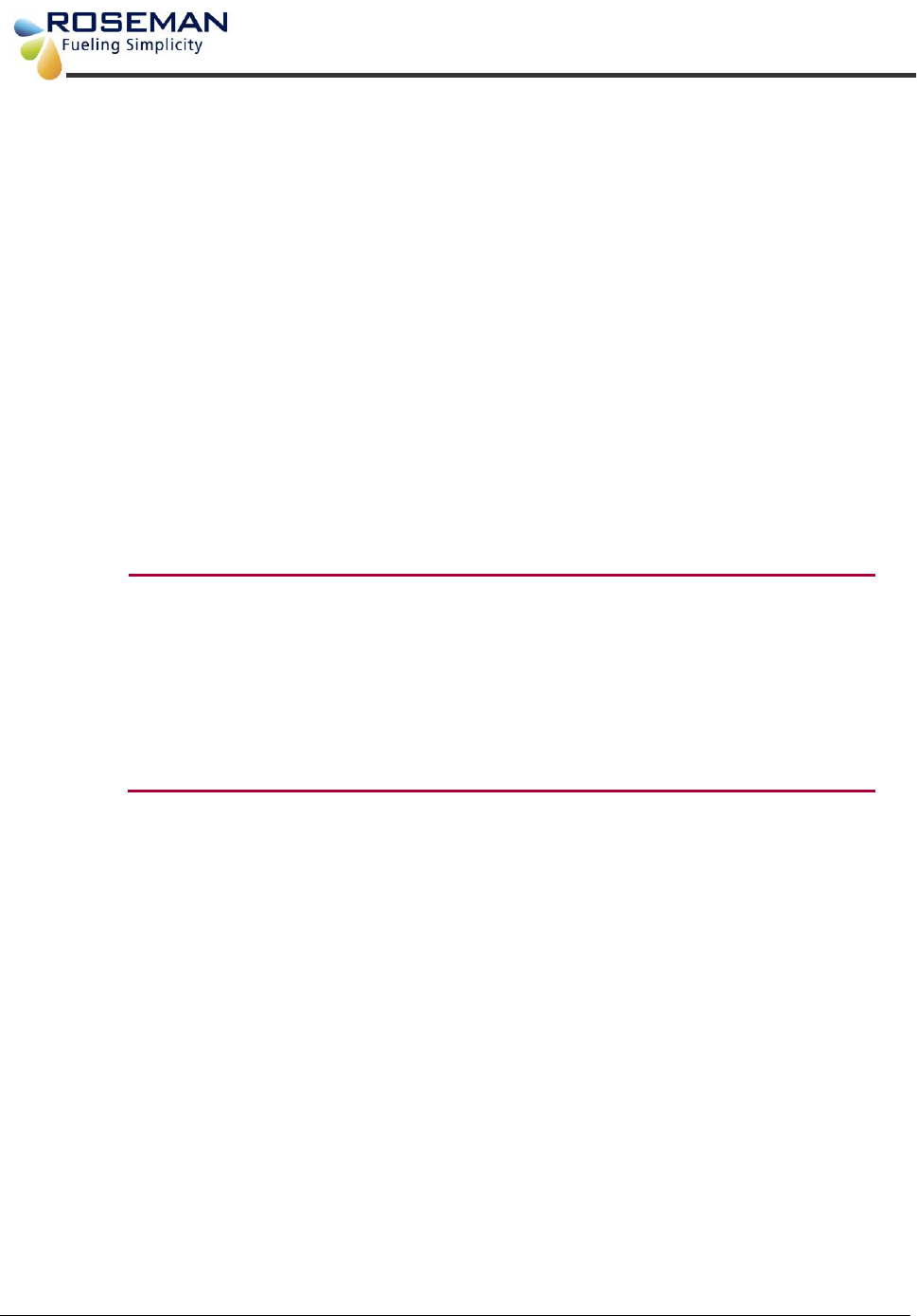
Fleet Gate Installation Guide Roseman Engineering Ltd
13
The Fueling Division of Roseman Engineering Ltd.
4.2.2 Electronic Odometer or Speedometer
If the vehicle has electronic instrumentation, run a single wire from the
vehicle speed sensor output VSS+ signal to the FG3 and connect to
"VSS".
4.2.3 Reed Type Mechanical Adaptor
If the vehicle has a mechanical odometer, and you are using a Reed type
adaptor, run two wires to the FG3 and connect to "BATT(+)" and "VSS".
4.2.4 Engine Hours
To record engine hours, run a single wire from the oil pressure sensor or
any other sensor which is at a continuous "high" state while the engine is
running. If you are using a single meter FG3, connect one wire to FG3
point VSS.
If you are using Dual input FG3 and only capturing hours, connect to FG3
point VSS.
Note
If you are using Dual input Vehicle and capturing hours by counter 2,
connect the engine running signal wire to FG3 terminal VSS or the
wire from the ignition switch.
In this case the FG3 will Power Off after the turning off the engine
even if the ignition switch is On.
You have completed the FG3 installation. Please go to the
instructions for programming the FG3.
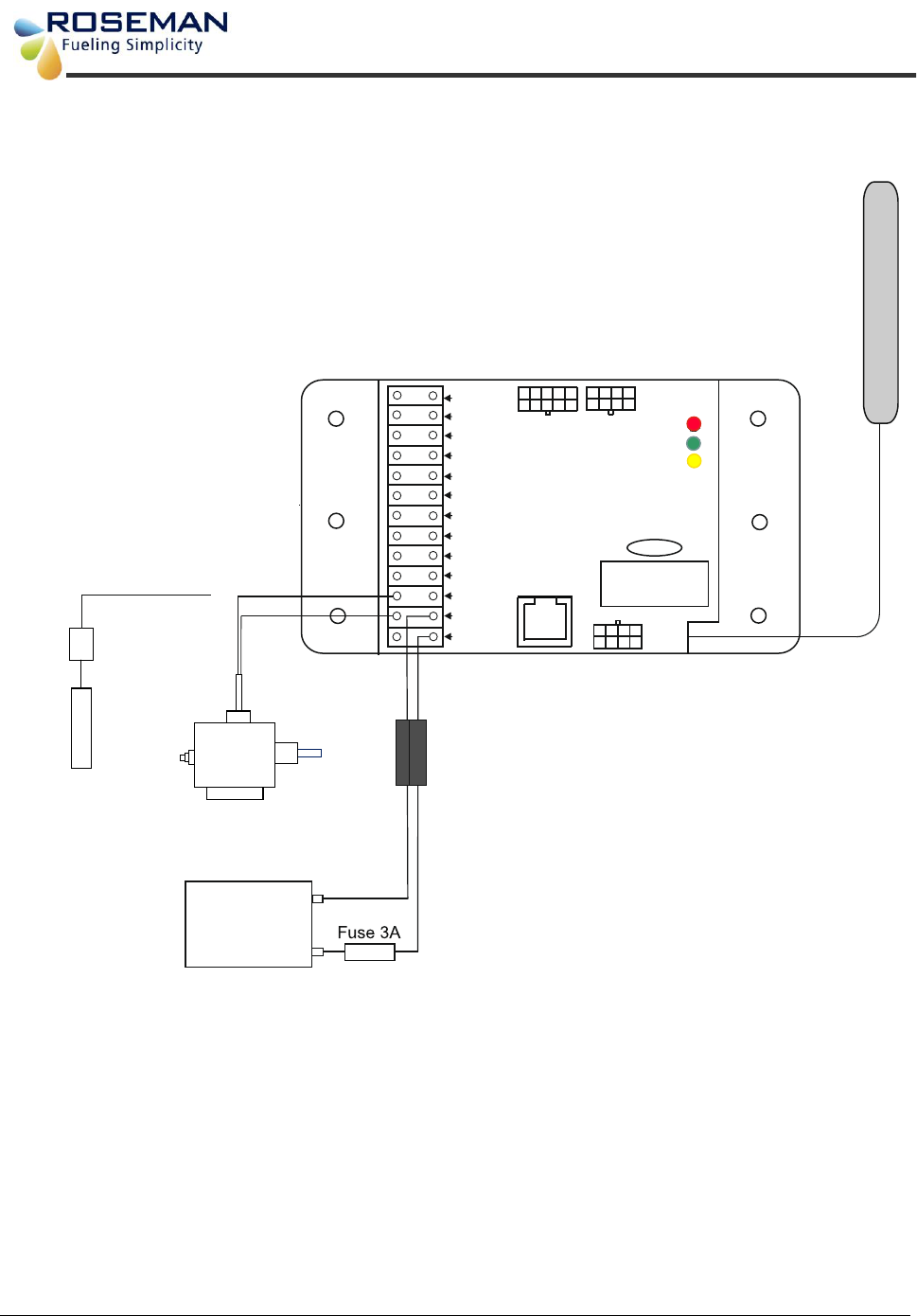
Fleet Gate Installation Guide Roseman Engineering Ltd
14
The Fueling Division of Roseman Engineering Ltd.
GPRS
Reed type Mechanical
Odometer Adapter
Electronic Odometer
Adapter
1.5 meter
Slim RF Antenna with
Adhesive
-Black
BATTERY
12VDC +
IN PUT 2
IN PUT 1
DALLAS LED
IMMOB ILIZER
DALLAS IN
(-) BAT OUT
(-) BAT IN
(+) BAT OUT
(+) BAT IN
CAN L (-)
ACC CANBUS
POWER/RF
GPS/GPRS
PROG
GPS
CAN H(+)
DC-EO
VSS
12V / 24V
ROSEMAN
FLEET GATE
RID-FG3-03
Figure 3: FG3 wiring diagram for speed pulse
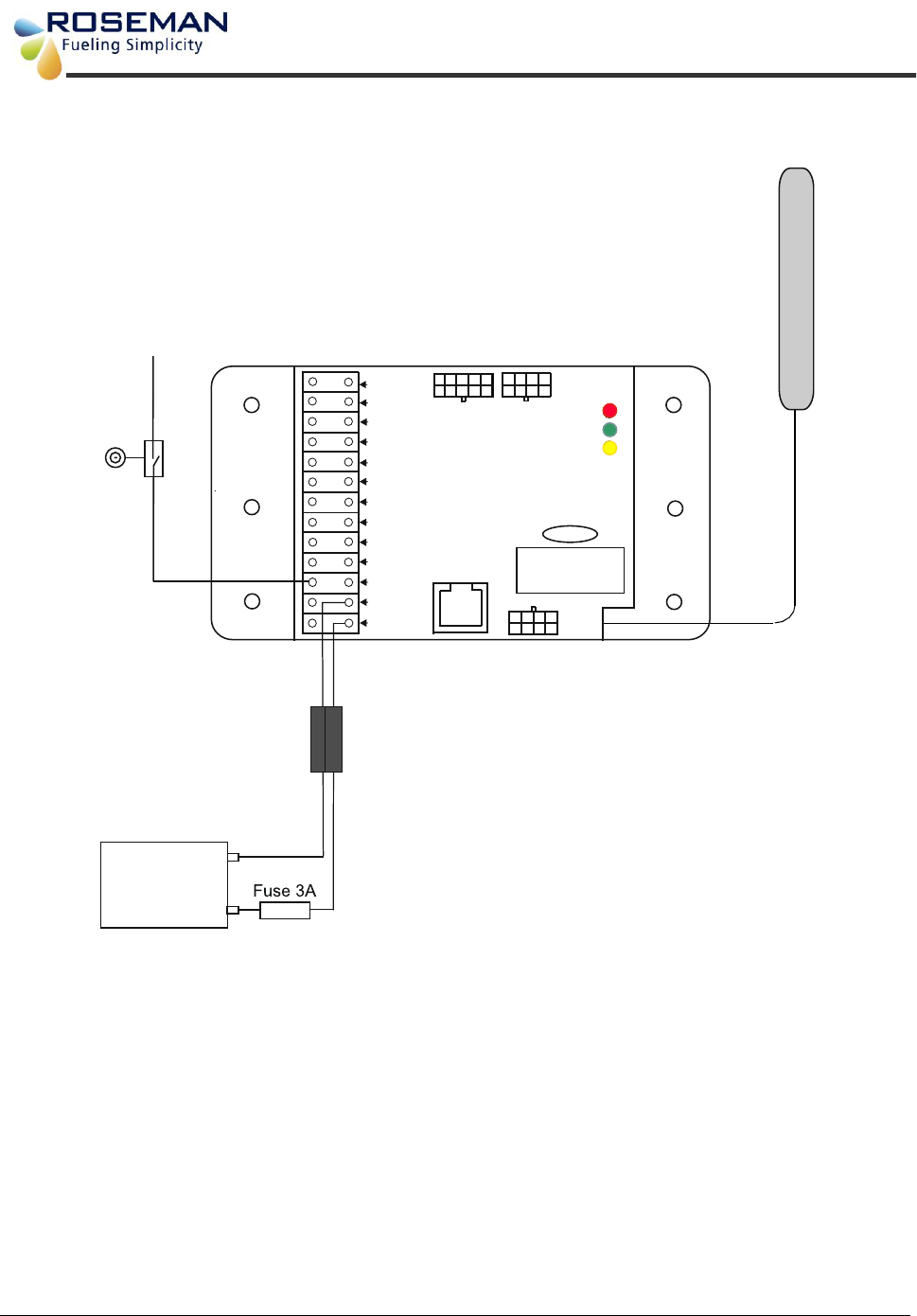
Fleet Gate Installation Guide Roseman Engineering Ltd
15
The Fueling Division of Roseman Engineering Ltd.
GPRS
+12V
Engine hours
oil pressure sensor
1.5 meter
Slim RF Antenna with
Adhesive
-Black
BATTERY
12VDC +
IN PUT 2
IN PUT 1
DALLAS LED
IMMOBILIZER
DALLAS IN
(-) BAT OUT
(-) BAT IN
(+) BAT OUT
(+) BAT IN
CAN L (-)
ACC CANBUS
POWER/RF
GPS/GPRS
PROG
GPS
CAN H(+)
DC-EO
VSS
12V / 24V
ROSEMAN
FLEET GATE
RID-FG3-03
Figure 4: FG3 wiring diagram for engine hour meter
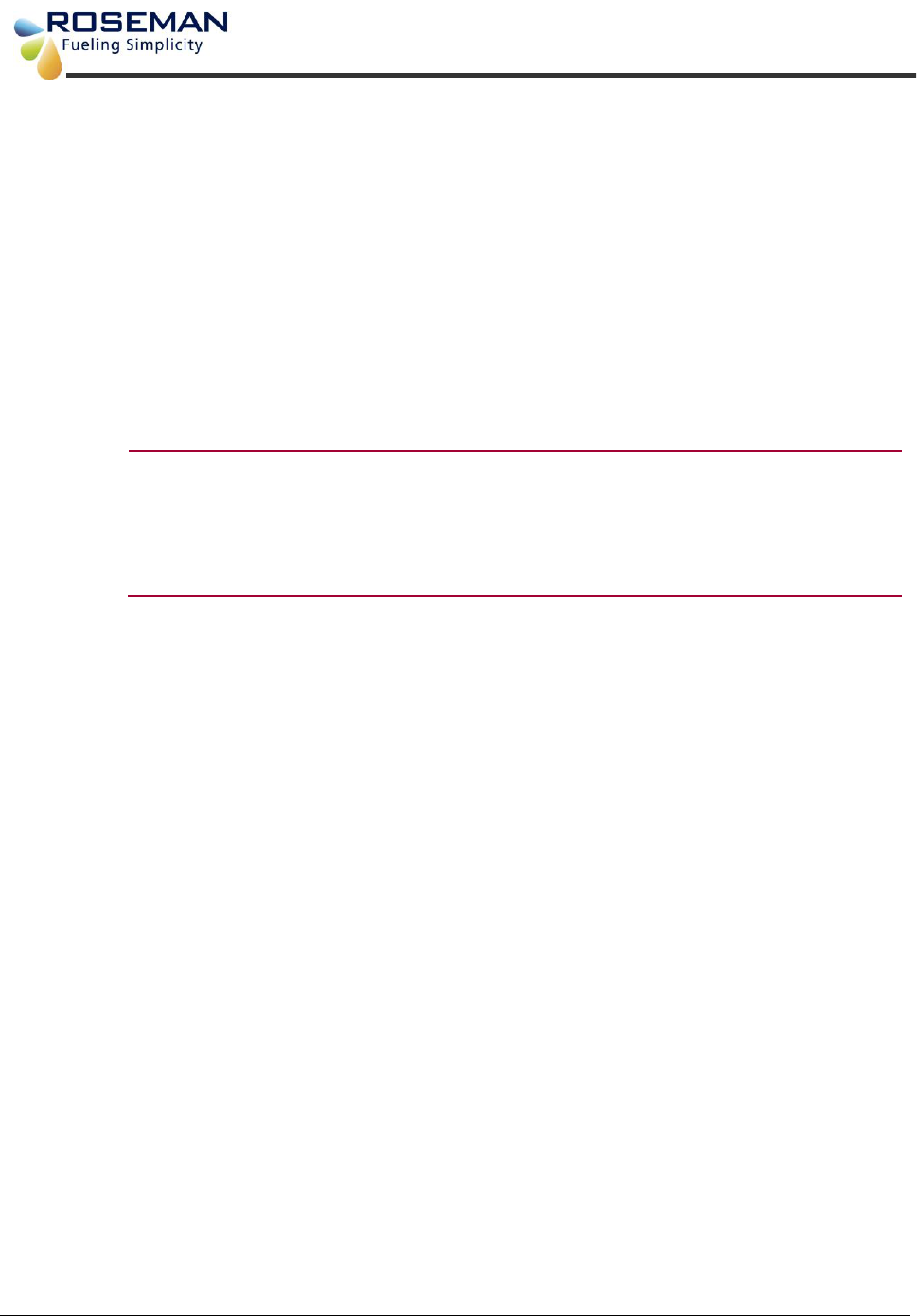
Fleet Gate Installation Guide Roseman Engineering Ltd
16
The Fueling Division of Roseman Engineering Ltd.
5. Wiring the CAN Bus Vehicles
5.1 Connect the Ignition Switch to the FG3
1. Run a wire from the vehicle ignition switch (or start/stop button on some hybrid
models) to the DC-EO terminal on the FG3 (refer to Figure 5: Wiring Diagram
for FG3 with CAN Bus Interface
for Light Duty Vehicles, Figure 6: Wiring Diagram for FG3 with CAN Bus
Interface for Heavy Duty Vehicles, Figure 7: Wiring Diagram for FG3 with CAN
Bus Interface (3-pin connector) for Heavy Duty Vehicles)
2. The FG3 needs a constant 12-24 volt signal at the BAT+ and BAT- terminals
when the vehicle is on and 0 volts when the vehicle is off.
Note
If the ignition wire is not connected, the FG3 will not function
properly. If the wire is connected, and the FG3 is functioning
properly, the FG3 will go into Sleep mode after turning off the
ignition. There is a 30-minute delay between the Off state of the
ignition and Sleep mode.
5.2 Connect the Data Interface to the FG3
The instructions for this procedure depend on the type of vehicle – whether it is a
heavy duty vehicle or a light duty vehicle. Light duty vehicles have an OBD II
connector for electronic instrumentation, while heavy duty vehicles have an SAE
J1939 connector. The following sections provide instructions for both types of
vehicles. To view the connectors’ pin out information, refer to Appendix B – CAN
Bus Data Connectors on page 38.
5.3 Connect the FG3 to an OBD II Connector (Light Duty
Vehicle)
If the vehicle has OBD II connector for electronic instrumentation, perform the
following:
Run a twin wire cable from the vehicle connector to the FG3 as follows:
Connect the FG3 CAN-H to pin - 6 of the OBD II connector.
Connect the FG3 CAN-L to pin -14 of the OBD II connector.
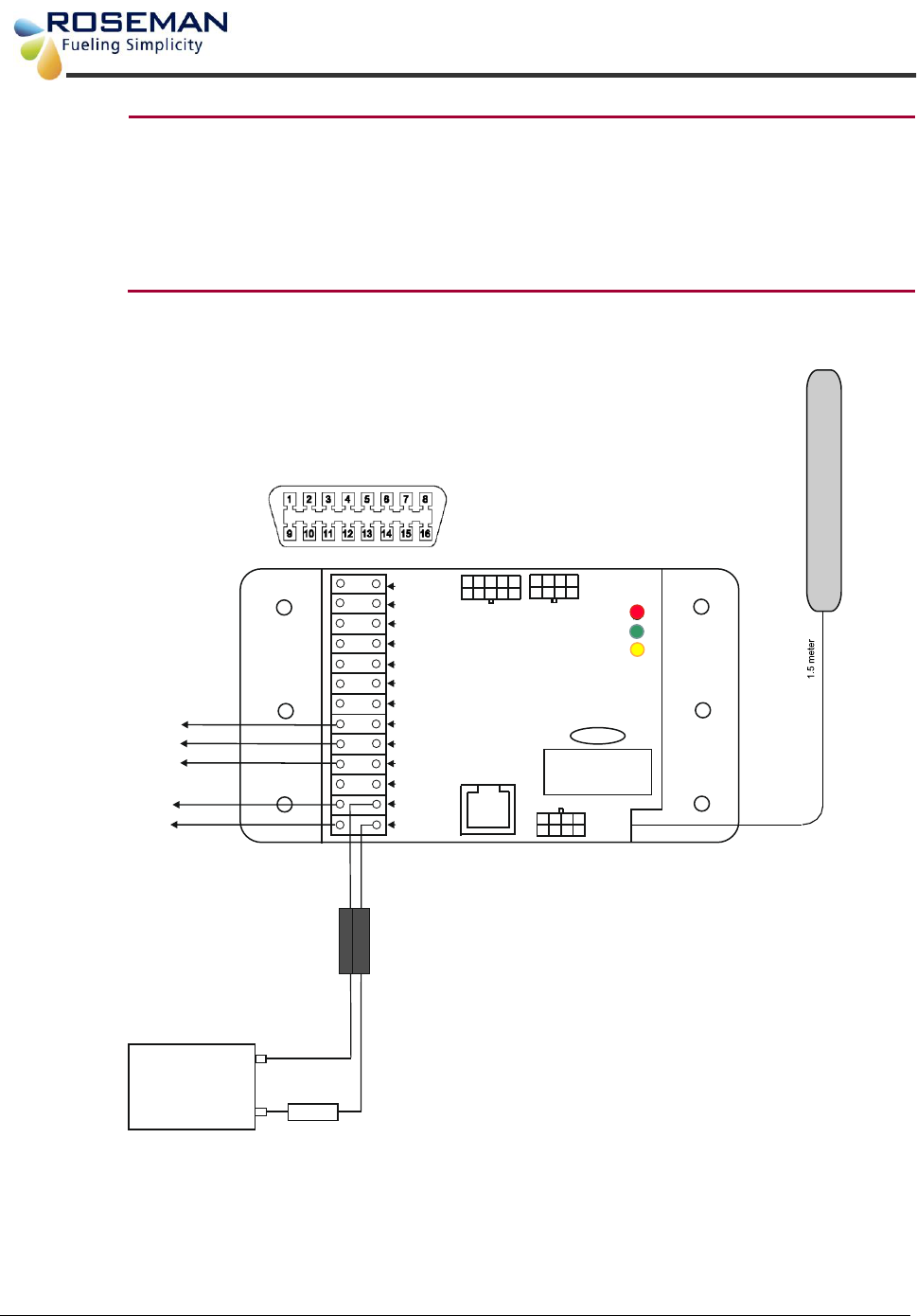
Fleet Gate Installation Guide Roseman Engineering Ltd
17
The Fueling Division of Roseman Engineering Ltd.
Note
Optional Power Supply Connection
It is possible to supply the power to the FG3 from the OBD II
connector as follows:
- Connect Pin 16 to BATT (+) on the FG3.
- Connect Pin 4 to BATT (-) on the FG3.
Slim RF Antenna with
Adhesive
-Black
BATTERY
12VDC +Fuse 3A
IN PUT 2
IN PUT 1
DALLAS LED
IMMOBILIZER
DALLAS IN
(-) BAT OUT
(-) BAT IN
(+) BAT OUT
(+) BAT IN
CAN L (-)
ACC CANBUS
POWER/RF
GPS/GPRS
PROG
GPS
CAN H(+)
DC-EO
VSS
12V / 24V
RID-FG3-03
OBD II CAN BUS Connector Pin Out
Pin 6
Pin 14
Optional- Pin 4
Ignition switch
Optional- Pin 16
GPRS
ROSEMAN
FLEET GATE
Figure 5: Wiring Diagram for FG3 with CAN Bus Interface
for Light Duty Vehicles
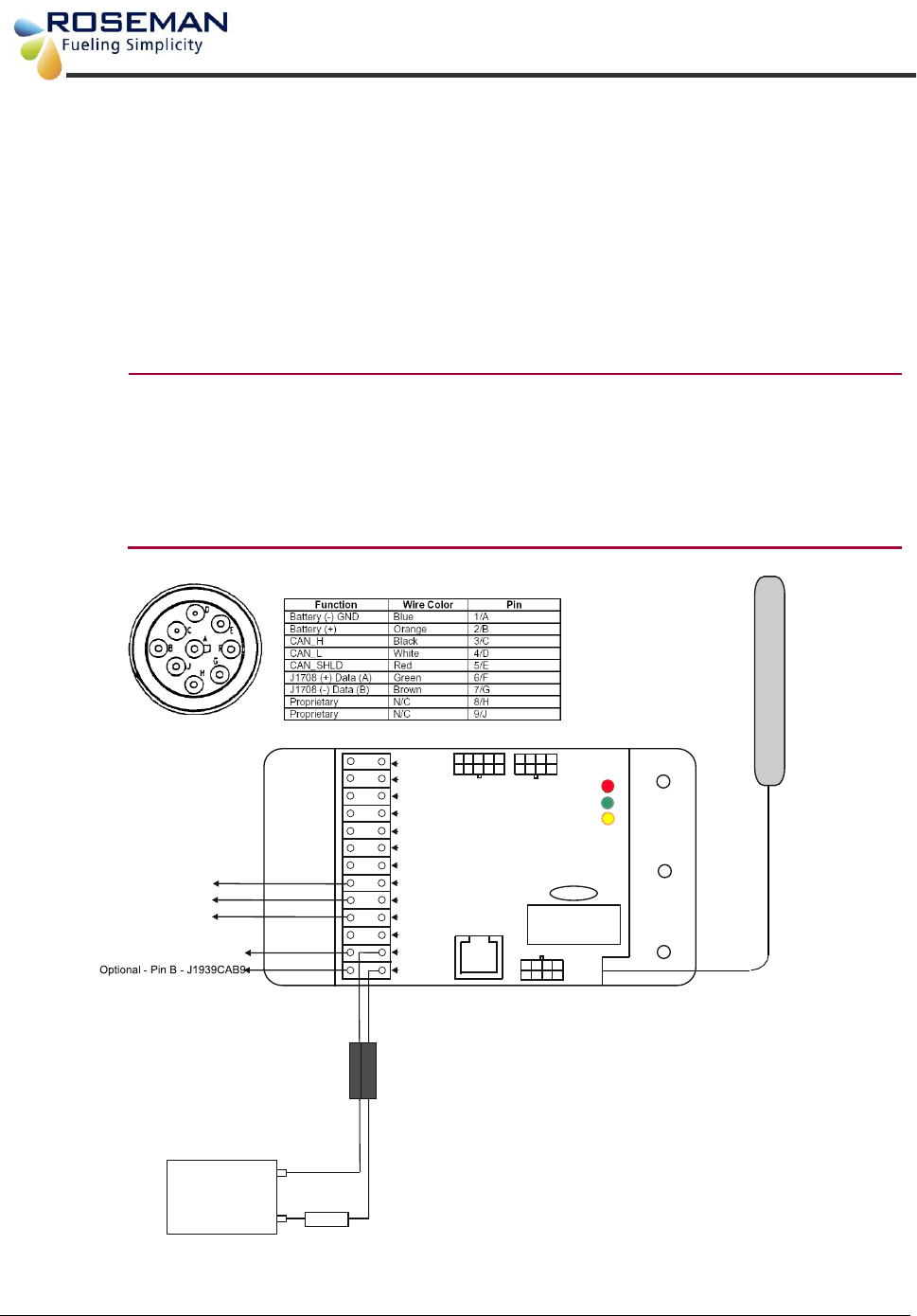
Fleet Gate Installation Guide Roseman Engineering Ltd
18
The Fueling Division of Roseman Engineering Ltd.
5.3.1 Connect the FG3 to a J1939 Connector (Heavy Duty Vehicle)
If the vehicle has a 9 pin Deutsch connector for electronic instrumentation,
perform the following:
Run a twin wire cable from the vehicle connector to the FG3 as follows:
1. Connect the CAN_H Black wire from pin 3/C of the Deutsch
connector to the FG3 point CAN_H.
2. Connect the CAN_L white wire from pin 4/D of the Deutsch
connector to the FG3 point CAN_L.
Note
Optional Power Supply Connection
It is possible to supply the power to the FG3 from the J1939CAB9
connector as follows:
- Connect Pin 2/B to BATT (+) on the FG3.
- Connect Pin 1/A to BATT (-) on the FG3.
Optional - Pin A - J1939CAB9
GPRS
1.5 meter
Slim RF Antenna with
Adhesive
-Black
BATTERY
12VDC +Fuse 3A
INPUT 2
INPUT 1
DALLAS LED
IMMOB ILIZER
DALLAS IN
(-) BAT OU T
(-) BAT IN
(+) BAT OUT
(+) BAT IN
CAN L (-)
ACC CANBUS
POWER/RF
GPS/GPRS
PROG
GPS
CAN H(+)
DC-EO
VSS
12V / 24V
RID-FG3-03
Ignition switch
Pin C - J1939CAB9
Pin D - J1939CAB9
View into SAE J1939 or
J1708CAB9 Connector
SAE J1939 or J1708CAB9 Deutsch Connector- Pin Out
ROSEMAN
FLEET GATE
Figure 6: Wiring Diagram for FG3 with CAN Bus Interface for Heavy Duty Vehicles
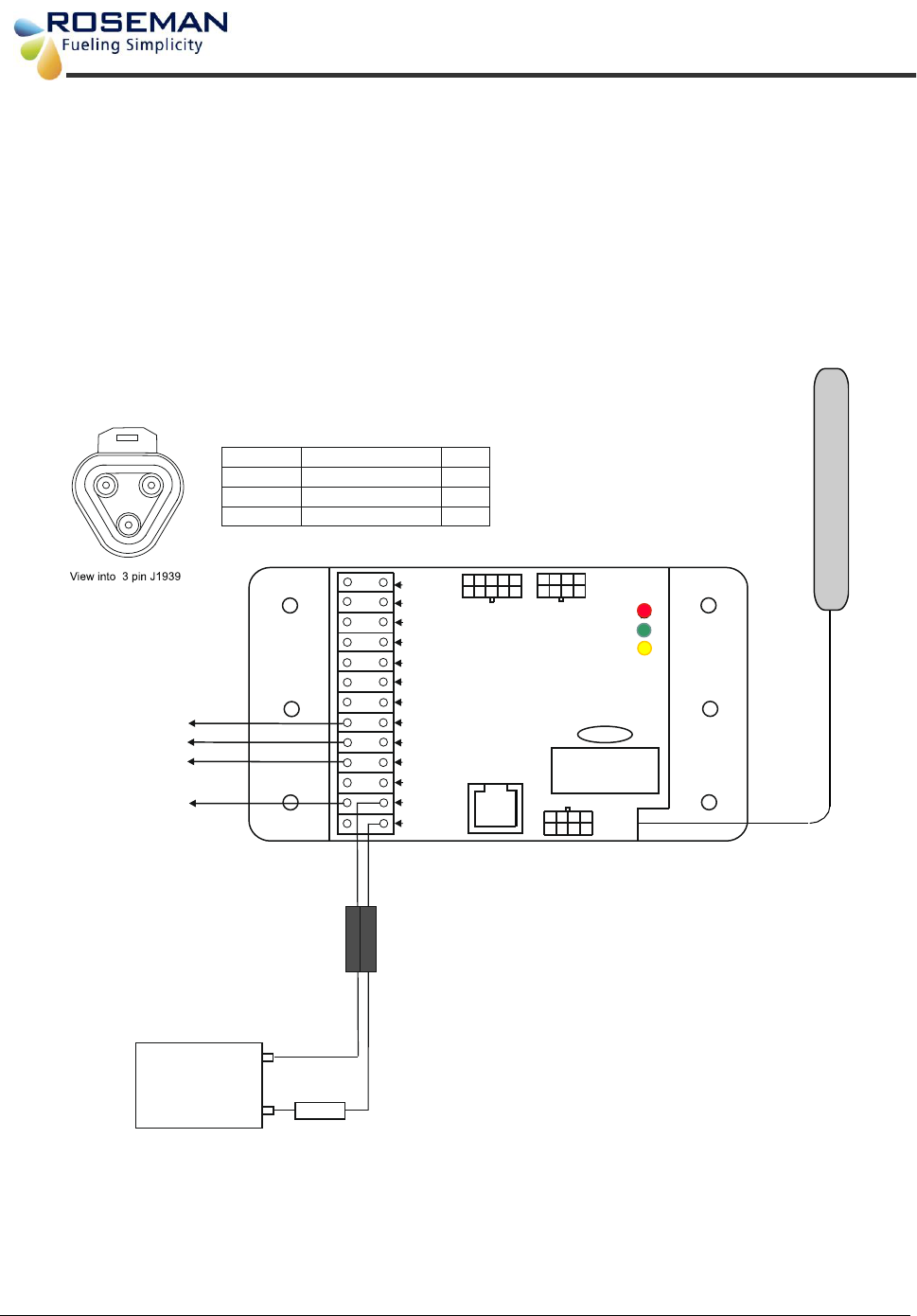
Fleet Gate Installation Guide Roseman Engineering Ltd
19
The Fueling Division of Roseman Engineering Ltd.
5.3.2 Connect the FG3 to a 3 pin J1939 Connector (Heavy Duty Vehicle)
If the vehicle has a 3 pin Deutsch connector for electronic instrumentation, perform the
following:
Run a twin wire cable from the vehicle connector to the FG3 as follows:
1. Connect the CAN_H from pin B of the Deutsch connector to the FG3 point CAN_H.
2. Connect the CAN_L pin A of the Deutsch connector to the FG3 point CAN_L.
3. Connect pin C ground of the Deutsch connector to the FG3 point BATT (-).
DT06-3S-E008 Connector
3 PIN Deutsch DT06-3S-E008 Connector- Pin Out
Pin
Function Description
CAN-L
CAN-H
CAN-GND CAN ground
CAN bus dominant low
CAN bus dominant high
A
B
C
A B
C
1.5 Meter
Slim RF Antenna with
Adhesive
-Black
BATTERY
12VDC +Fuse 3A
IN PUT 2
IN PUT 1
DALLAS LED
IMMOBILIZER
DALLAS IN
(-) BAT OUT
(-) BAT IN
(+) BAT OUT
(+) BAT IN
CAN L (-)
ACC CANBUS
POWER/RF
GPS/GPRS
PROG
GPS
CAN H(+)
DC-EO
VSS
12V / 24V
RID-FG3-03
Ignition switch
Pin C - J1939
Pin B - J1939
Pin A - J1939
GPRS
ROSEMAN
FLEET GATE
Figure 7: Wiring Diagram for FG3 with CAN Bus Interface (3-pin connector) for Heavy Duty Vehicles
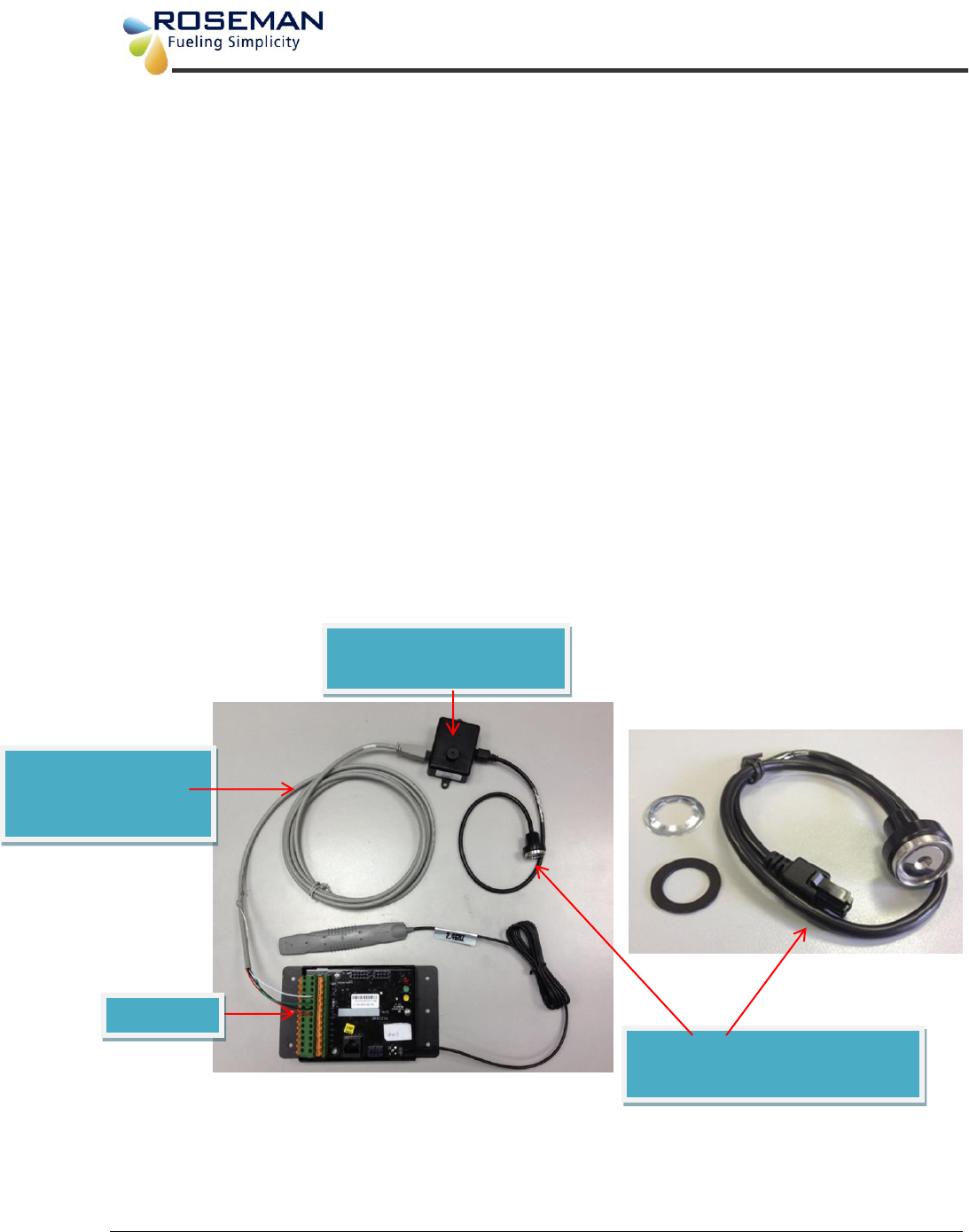
Fleet Gate Installation Guide Roseman Engineering Ltd
20
The Fueling Division of Roseman Engineering Ltd.
6. Wiring the Dallas TAG reader set
6.1 Mounting the Vehicle Dallas TAG Reader Set
1. Mount the Dallas TAG Reader Combined under the vehicle dashboard.
2. Route the Grey Cable #ACC-CB-15A from FJ3 to TAG Reader Combined.
3. Mount the Cable Reader Dallas TAG #ACC-CB-B7 on the dashboard near the driver.
6.2 Connecting the FJ3 to Dallas TAG reader set
1. Connect the 4 wire grey cable #ACC-CB-15A to FJ3 terminals as follows:
Connect the White wire to DALLAS LED terminal
Connect the Green wire to DALLAS IN terminal
Connect the Black wire to (-) BAT OUT terminal
Connect the Red wire to (+) BAT OUT terminal
2. Connect the 4 pin connector of cable #ACC-CB-B7 to TAG Reader Combined as
shown.
Figure 8: Wiring Dallas TAG Reader Set
Cable Button
Reader Dallas
#ACC-CB-15A
Cable Reader Dallas TAG
#ACC-CB-B7
TAG Reader Combined
#RDR-02-01
FJ3
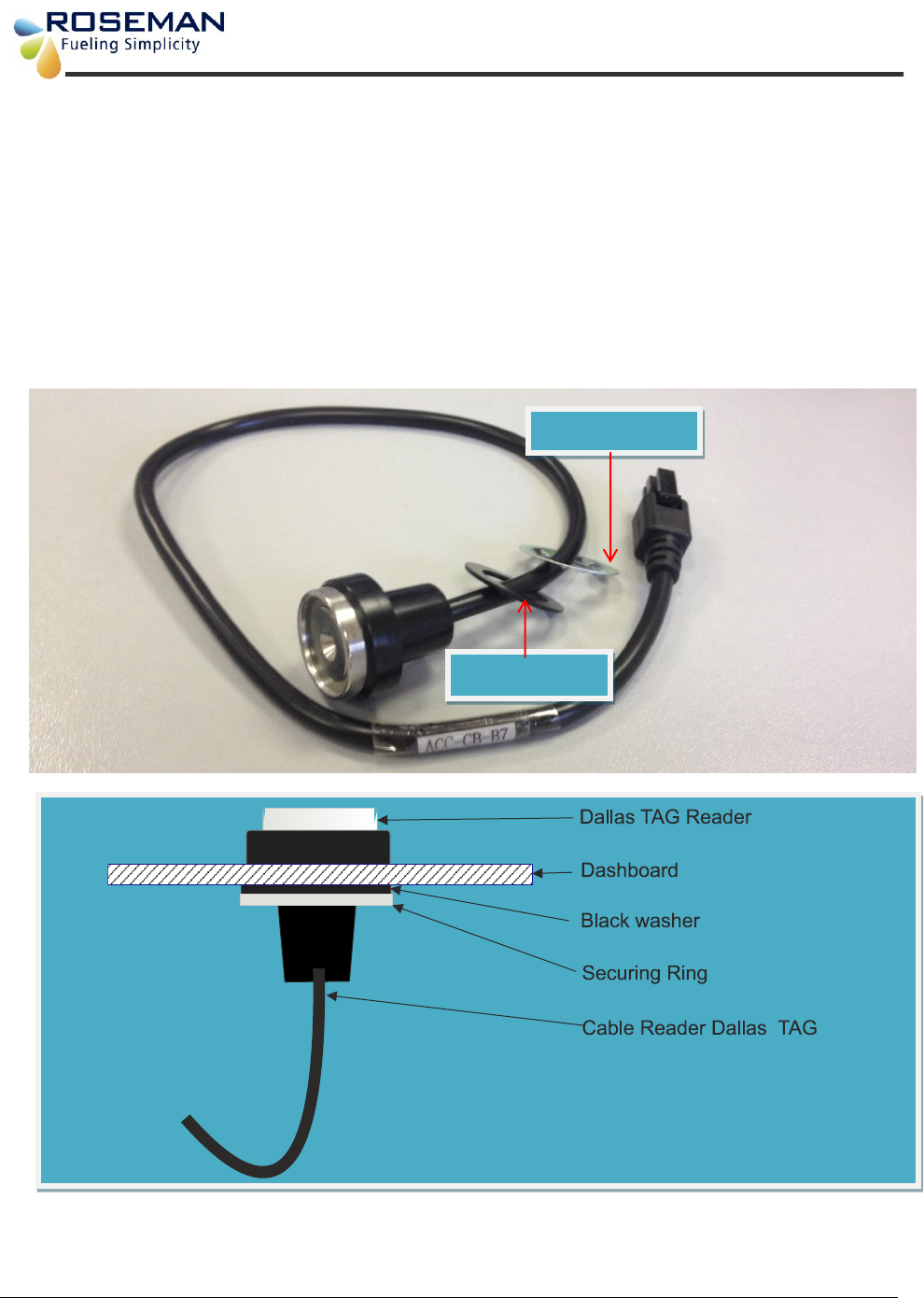
Fleet Gate Installation Guide Roseman Engineering Ltd
21
The Fueling Division of Roseman Engineering Ltd.
6.3 Installation of the Dallas TAG Reader
6.3.1 Drill a ½ “(12.7 mm) diameter hole on the dashboard near the driver.
6.3.2 Insert the Cable Reader Dallas TAG #ACC-CB-B7 into the hole and route it under
the dashboard by attaching the black washer and securing ring to the dashboard as
shown.
6.3.3 Connect the 4 pin connector of the Cable Reader Dallas TAG to the TAG Reader
Combined as shown.
Figure 11: Cable Dallas TAG Reader Installation
Black Washer
Securing Ring
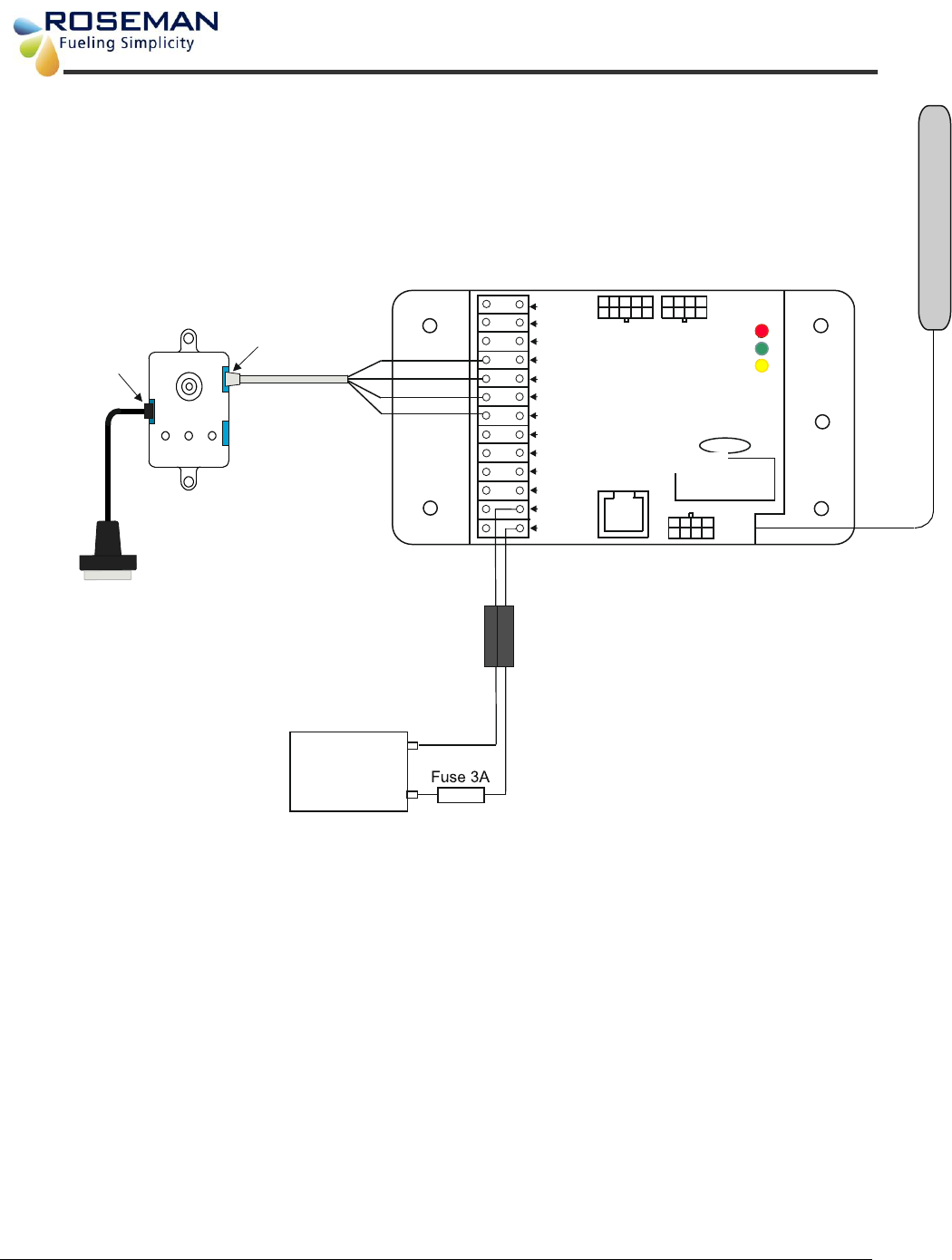
Fleet Gate Installation Guide Roseman Engineering Ltd
22
The Fueling Division of Roseman Engineering Ltd.
GPRS
Dallas TAG Reader Set
1.5 meter
Slim RF Antenna with
Adhesive
-Black
BATTERY
12VDC +
IN PUT 2
IN PUT 1
DALLAS LED
IMMOBILIZER
DALLAS IN
(-) B AT OUT
(-) BAT IN
(+) BAT OUT
(+) BAT IN
CAN L (-)
ACC CANBUS
POWER/RF
GPS/GPRS
PROG
GPS
CAN H(+)
DC-EO
VSS
12V / 24V
AssetWORKS
Fuel Focus
FleetJournal
RID-FG3-02
Cable from Fleet Journal
to Dallas TAG reader
#ACC-CB-15A
Cable Reader
Dallas TAG
#ACC-CB-B7
White
Black
Red
Green
4 pin connector
4 pin connector
Figure 12: Wiring Diagram for FJ3 to Dallas Tag Reader (4 pin connectors)
ROSEMAN
FLEET GATE
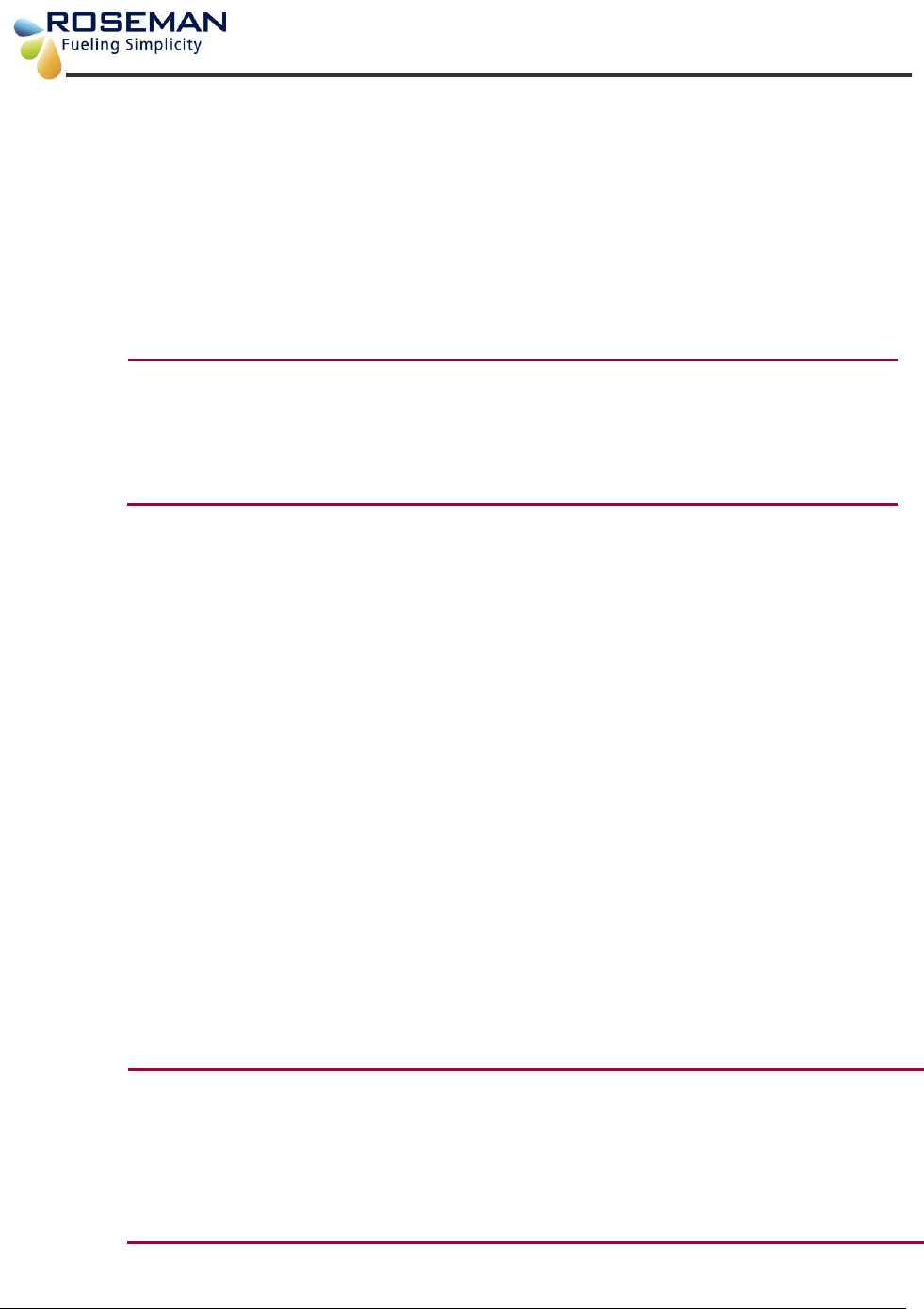
Fleet Gate Installation Guide Roseman Engineering Ltd
23
The Fueling Division of Roseman Engineering Ltd.
7. Wiring the J1708 Vehicles
7.1 Connect the Ignition Switch to the FG3
Run a wire from the vehicle ignition switch (or start/stop button on some
hybrid models) to the DC-EO terminal on the FG3 (refer to Figure 2).
Note
If the ignition wire is not connected, the FG3 will not function
properly. If the wire is connected, and the FG3 is functioning
properly, the FG3 will go into Sleep mode after turning off the
ignition. There is a 30-minute delay between the Off state of the
ignition and Sleep mode.
7.2 Connect the Data Interface to the FG3
The instructions for this procedure depend on the type of the connector equipped
with the vehicle – whether it is a J1708 CAB9 (9 pin) connector or a J1708 CAB (6
pin) connector. The following sections provide instructions for both types of
vehicles.
To view the connectors’ pin-out information, refer to the Appendixes
Appendix A –Capturing vehicle data
on page 38.
7.2.1 Connect the FG3 to a J1708 CAB9 Connector
If the vehicle has 9 pin Deutsch connector for electronic instrumentation,
perform the following:
Run a twin wire cable from the vehicle connector to the FG3 as follows:
1. Connect the J1708 Data link (+) wire from pin - F of the Deutsch
connector.
2. Connect the J1708 Data link (-) wire from pin - G of the Deutsch
connector.
Note
Optional Power Supply Connection
It is possible to supply the power to the FG3 from the J1708CAB9 if pin
2/B has 12-24 volts with the ignition in the off position:
- Connect Pin 2/B to BATT (+) on the FG3.
- Connect Pin 1/A to BATT (-) on the FG3.
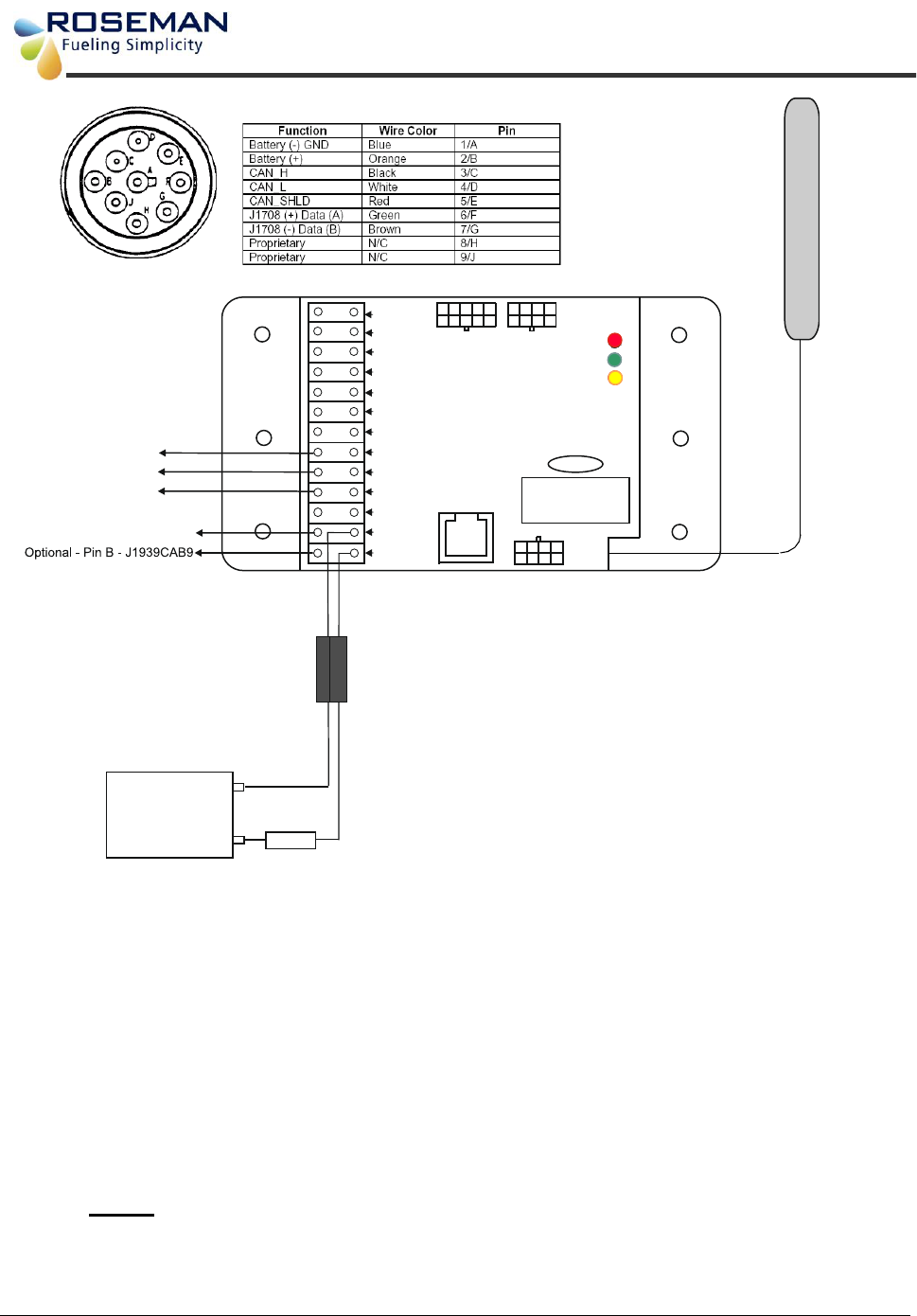
Fleet Gate Installation Guide Roseman Engineering Ltd
24
The Fueling Division of Roseman Engineering Ltd.
Optional - Pin A - J1939CAB9
GPRS
1.5 meter
Slim RF Antenna with
Adhesive
-Black
BATTERY
12VDC +Fuse 3A
IN PUT 2
IN PUT 1
DALLAS LED
IMMOBILIZER
DALLAS IN
(-) BAT OUT
(-) BAT IN
(+) BAT OUT
(+) BAT IN
CAN L (-)
ACC CANBUS
POWER/RF
GPS/GPRS
PROG
GPS
CAN H(+)
DC-EO
VSS
ROSEMAN
FLEET GATE
12V / 24V
RID-FG3-03
Ignition switch
Pin C - J1939CAB9
Pin D - J1939CAB9
View into SAE J1939 or
J1708CAB9 Connector
SAE J1939 or J1708CAB9 Deutsch Connector- Pin Out
Figure 9: Wiring Diagram for FG3 to J1708CAB9 (9 pin) connector
7.2.2 Connect the FG3 to an J1708 CAB Connector
If the vehicle has a 6 pin Deutsch connector for electronic instrumentation, perform the
following:
Run a twin wire cable from the vehicle connector to the FG3 as follows:
1. Connect the J1708 Data link (+) wire from pin - A of the Deutsch connector.
2. Connect the J1708 Data link (-) wire from pin - B of the Deutsch connector.
NOTE: Optional Power Supply Connection refer to Figure 8.
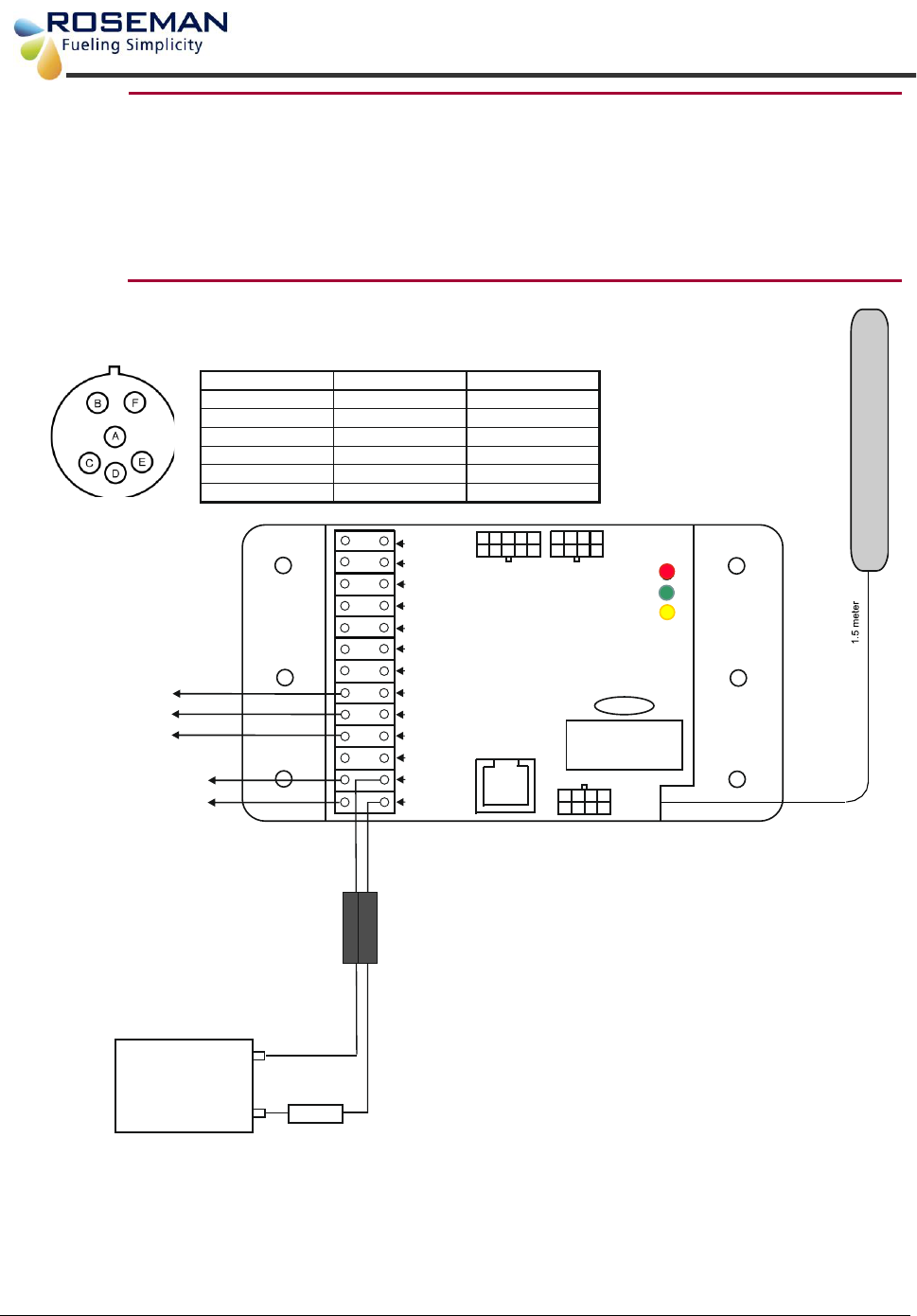
Fleet Gate Installation Guide Roseman Engineering Ltd
25
The Fueling Division of Roseman Engineering Ltd.
Note
Optional Power Supply Connection
There is a possibility to connect the power supply to the FG3 from
the J1708CAB connector if pin C has 12 – 24 volts with the ignition in
the off position:
- Connect Pin C to BATT (+) on the FG3.
- Connect Pin E to BATT (-) on the FG3.
Slim RF Antenna with
Adhesive
-Black
BATTERY
12VDC +Fuse 3A
INPUT 2
INPUT 1
DALLAS LED
IMMOBILIZER
DALLAS IN
(-) BAT OUT
(-) BAT IN
(+) BAT OUT
(+) BAT IN
CAN L (-)
ACC CANBUS
POWER/RF
GPS/GPRS
PROG
GPS
CAN H(+)
DC-EO
VSS
12V / 24V
RID-FG3-03
Ignition switch
View into SAE J1708CAB Connector
SAE J1708CAB Connector- Pin Out
Not standard function
Not standard function
V + (9-32V)
Function Wire color Pin
Data A (+) Orange
Yellow
Black
Red
Green
Brown
A
B
C
D
E
F
Data A (-)
Ground
GPRS
Optional - Pin C - J1708CAB
Pin B - J1708CAB
Pin A - J1708CAB
Optional - Pin E - J1708CAB
ROSEMAN
FLEET GATE
Figure 10: Wiring Diagram for FG3 to J1708CAB (6 pin) connector
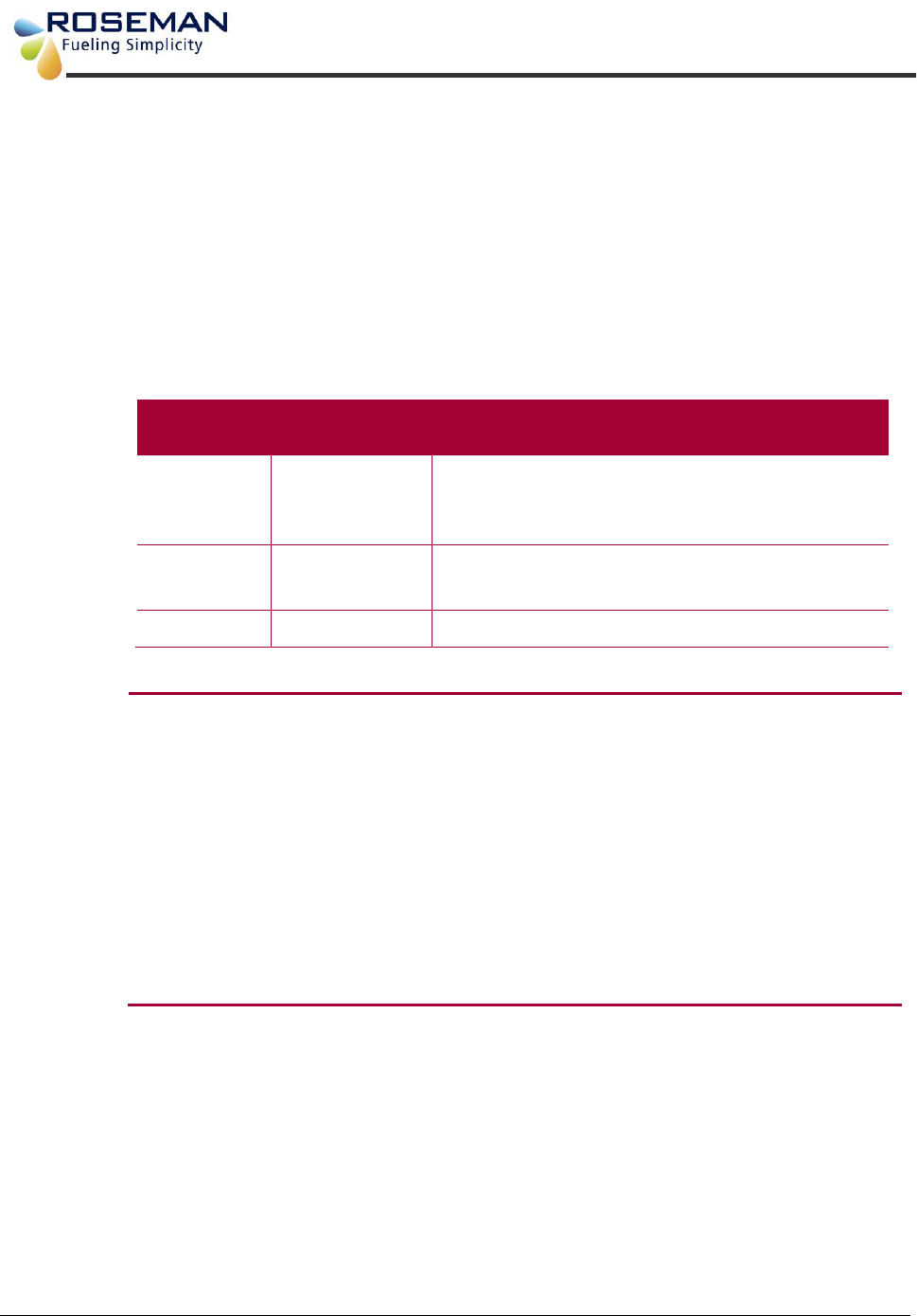
Fleet Gate Installation Guide Roseman Engineering Ltd
26
The Fueling Division of Roseman Engineering Ltd.
8. Completion of Installation
8.1 Verify Installation
When installation is complete, verify that the GREEN LED on the FG3 is
blinking every second. This indicates good power and grounding.
There are three indicator LEDs on the FG3 (refer to Figure 2) a RED, GREEN and
YELLOW LED :
LED COLOR
FUNCTION
INDICATION
RED
CAN BUS
When no data received blinks every 2 sec.
When data received blinks according to the
data rate
GREEN
Power and RF
RF transmission - Fast blinking
Power ON- Blinks every second
YELLOW
GPS/GPRS
Note
During normal operations, the green LED also blinks every time an
RF message is received, indicating that the FG3 is communicating
with the WAF or VDC antenna.
After power up, the green LED blinks every second. (Indicating a
good power and ground).
In addition the green LED blinks every time an RF message is
received. (Indicating the FG3 is communicating with the WAF or
VDC antenna)
When the FG3 is set to Hour counter and the input VSS set on, red
LED is on.
(Indicating good communication with the vehicle/equipment).
8.2 Post Installation Steps
The next step is to program the FG3 For instructions, refer to the FG3
Programming Guide.
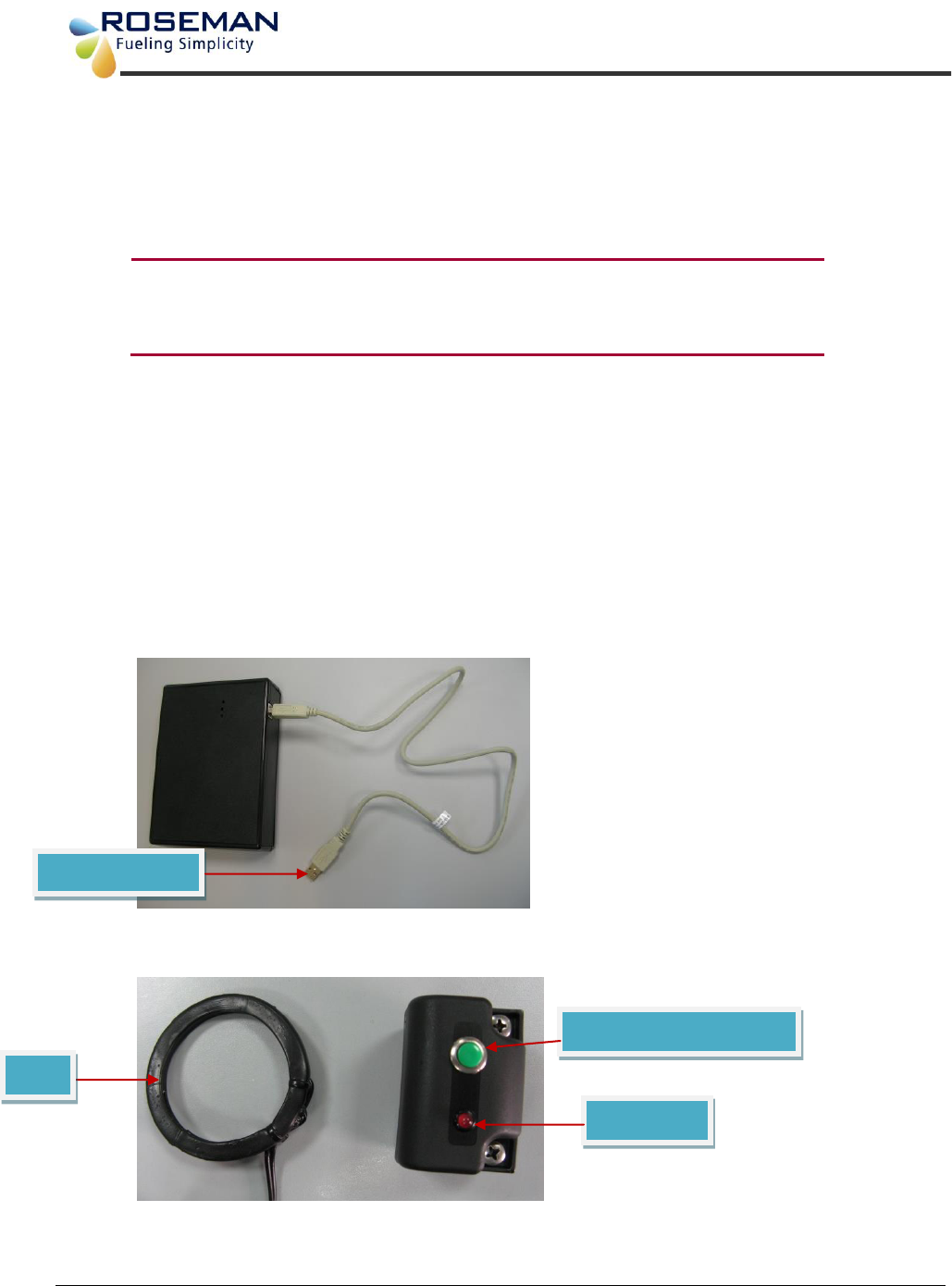
Fleet Gate Installation Guide Roseman Engineering Ltd
27
The Fueling Division of Roseman Engineering Ltd.
9. Preparation and Programming
9.1 Preparation Steps
Note
Make sure that the WAF is connected to the laptop or PC
otherwise when opening the software it will not open and
terminate.
1. Connect the USB cable from the programmer tool to your laptop (Refer to Figure10).
2. Run the Fleet Journal Application software from your laptop (Refer to page 31).
3. Use the Technician SVID Activation device and place it near the Fuel Inlet Antenna – FIA
(Refer to Figure11).
You can use the activator only while the Fleet Journal Application is ON
4. Press and Hold the SVID green activation button and verify that the red led is blinking
(The red led will blink approximately 5 seconds). When the red led will appear solid
meaning that SVID activation is completed successfully. The SVID Serial Number has
been transmitted to the Fleet Journal Application software.
SVID activation button
Figure 11: Technician SVID Activation Device
Figure 11: FJ3 Programmer
Indication
LED
USB to Laptop
FIA

Fleet Gate Installation Guide Roseman Engineering Ltd
28
The Fueling Division of Roseman Engineering Ltd.
9.2 Programming Steps
1. The Main Menu screen appears showing the following menu items:
Program Vehicle
Read FleetJournal
Read SVID
Calibrate Vehicle
Update FleetJournal Firmware
2. Verify the WAF is connected [comm] shows green.
3. Single click on the Program Vehicle menu item and the following screen appears showing
the devices serial numbers that are in range of the antenna.
4. Select the FJ3 Serial Number that you want to program and single click on it.
5. Click Next to continue.
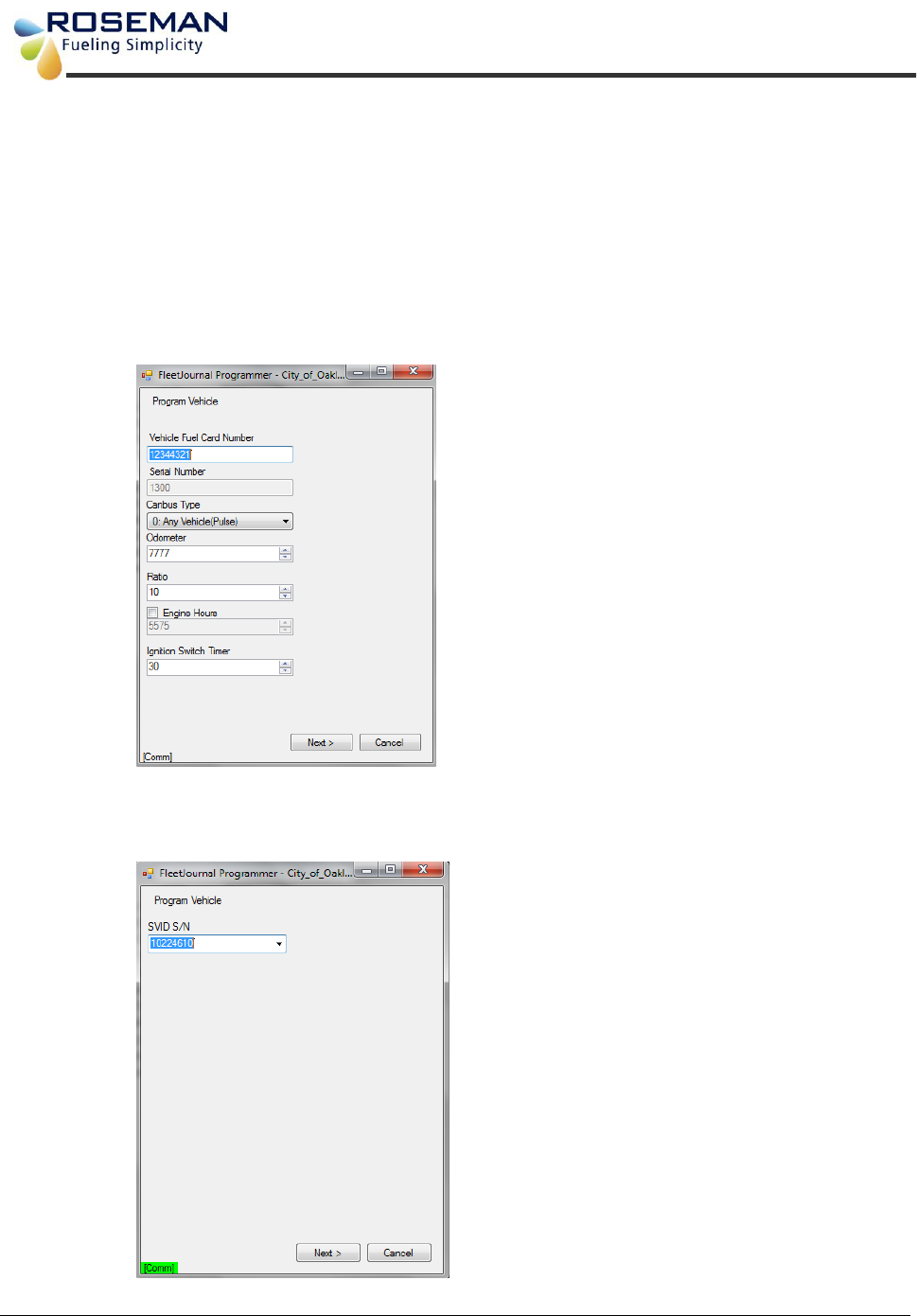
Fleet Gate Installation Guide Roseman Engineering Ltd
29
The Fueling Division of Roseman Engineering Ltd.
6. A
after clicking the Next button, the following screen will appear.
7. Fill in the details that apply to the vehicle that being is programmed (Example):
Vehicle Fuel Card Number: 12344321
Canbus Type: 0-Any Vehicle (Pulse)
Odometer: 7777
Ratio:10
Ignition switch timer: 30 min
8. Click Next button to continue.
9. The following screen will appear. Select the SVID serial number that you want to program
and click the Next button to continue.
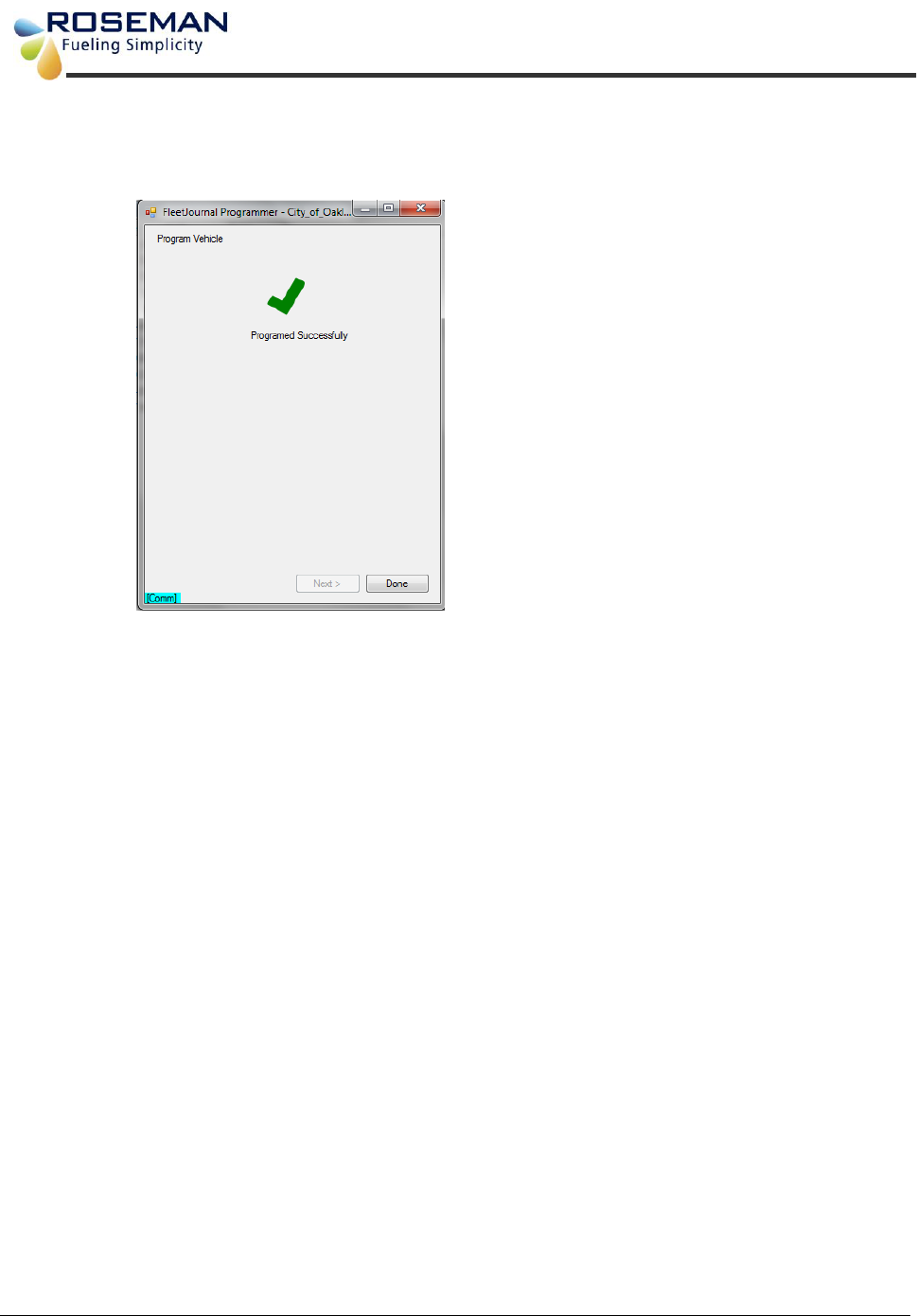
Fleet Gate Installation Guide Roseman Engineering Ltd
30
The Fueling Division of Roseman Engineering Ltd.
10. The following screen appears showing that the programming has completed
successfully.
11. Double click on Calibrate Vehicle menu and the following screen will appear.
12. Fill in the details for the vehicle to be calibrated:
Last Programmed Odometer
Current Odometer
Dashboard reading
Current Engine Hours
Dashboard Engine Hours
13. To do a Ratio calculation place a √ in the "Recalculate Ratio" box and the software
automatically will recalculate the ratio.
14. Click Next to continue
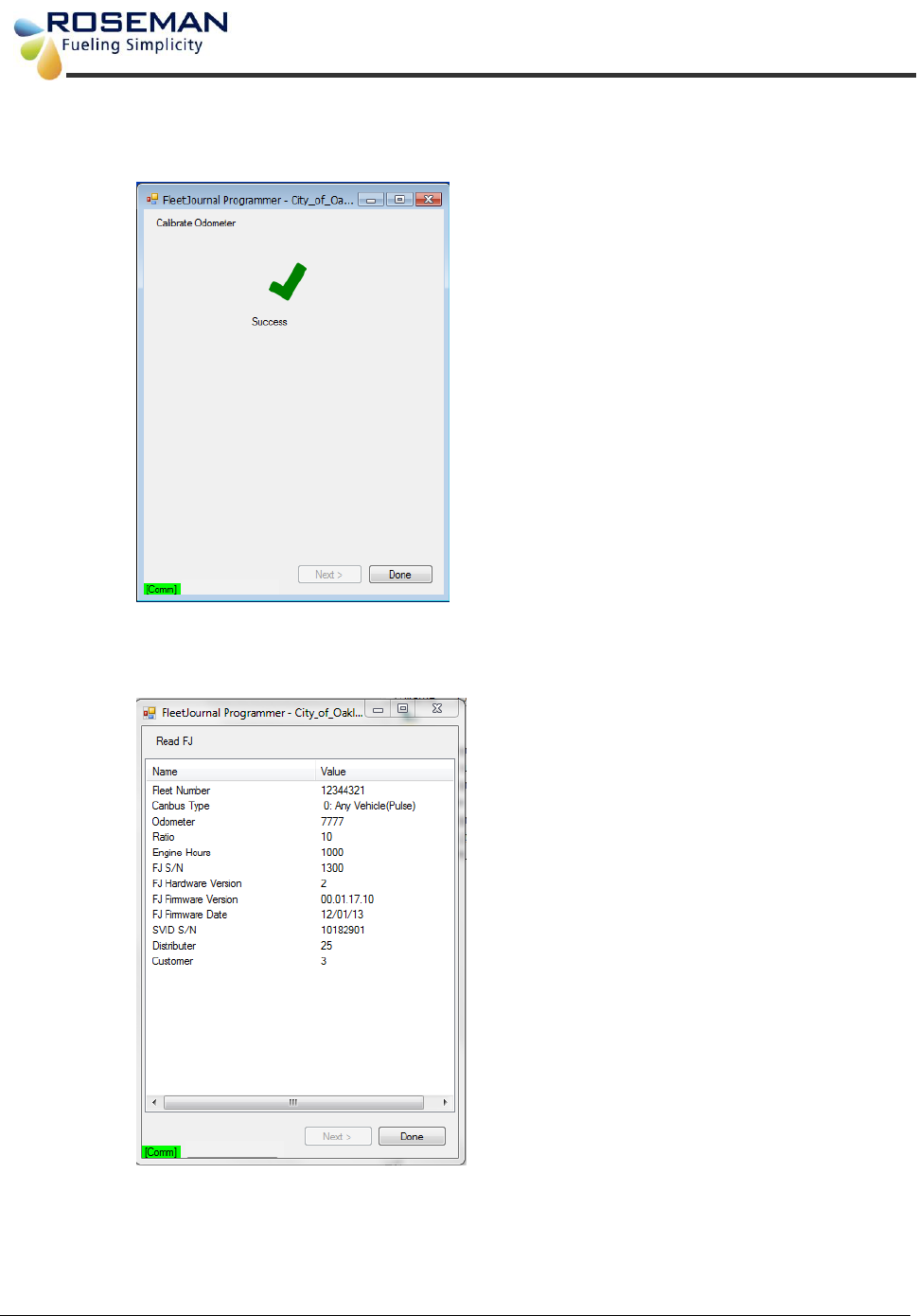
Fleet Gate Installation Guide Roseman Engineering Ltd
31
The Fueling Division of Roseman Engineering Ltd.
15. The following screen will appear showing that the odometer calibration has completed
successfully.
16. Double click the Read FleetJournal menu item and the following screen will appear
showing the details about what was programmed on the vehicle.
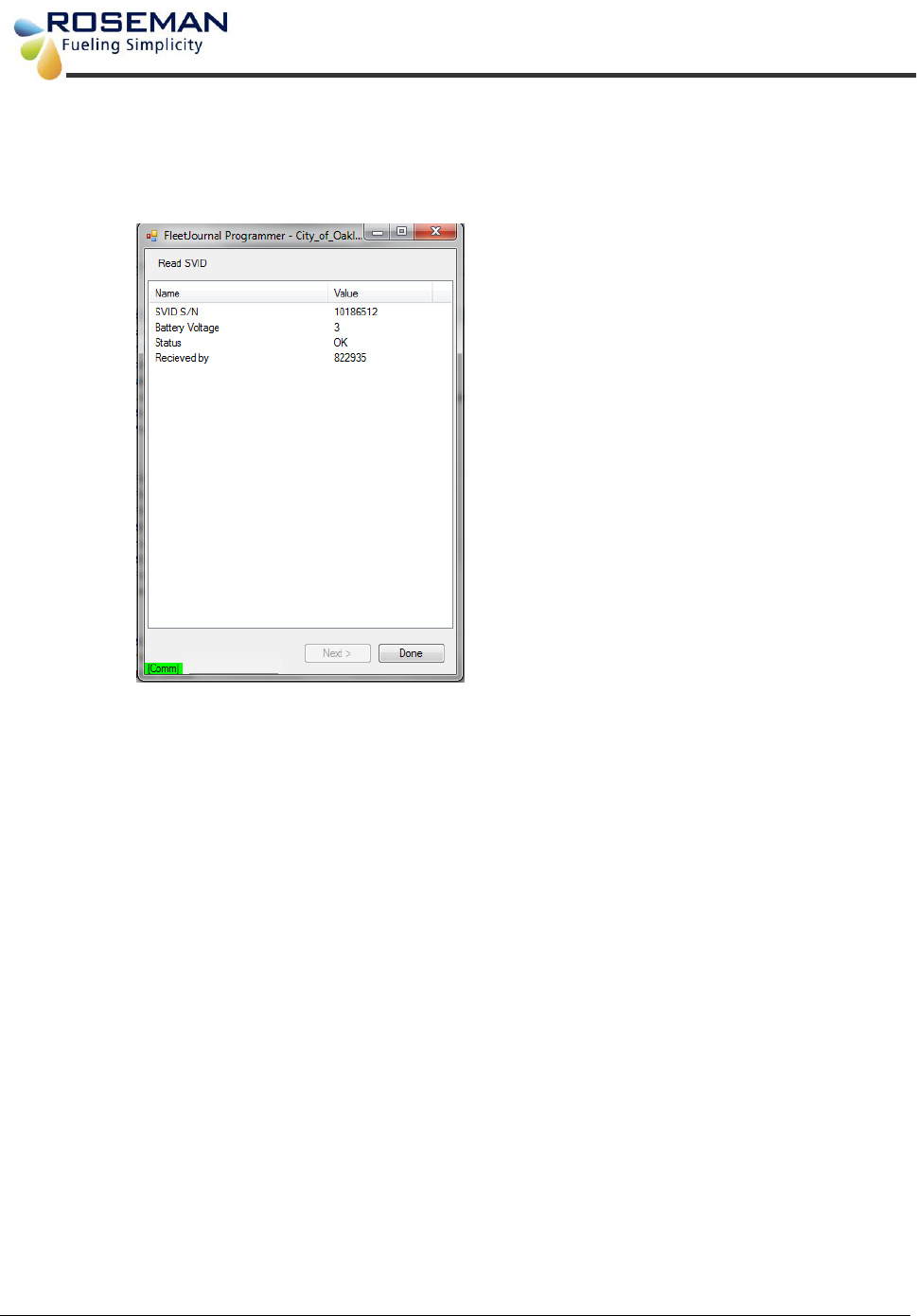
Fleet Gate Installation Guide Roseman Engineering Ltd
32
The Fueling Division of Roseman Engineering Ltd.
17. Double click on the Read SVID menu item and the following screen will appear showing
the Battery Voltage and Status.
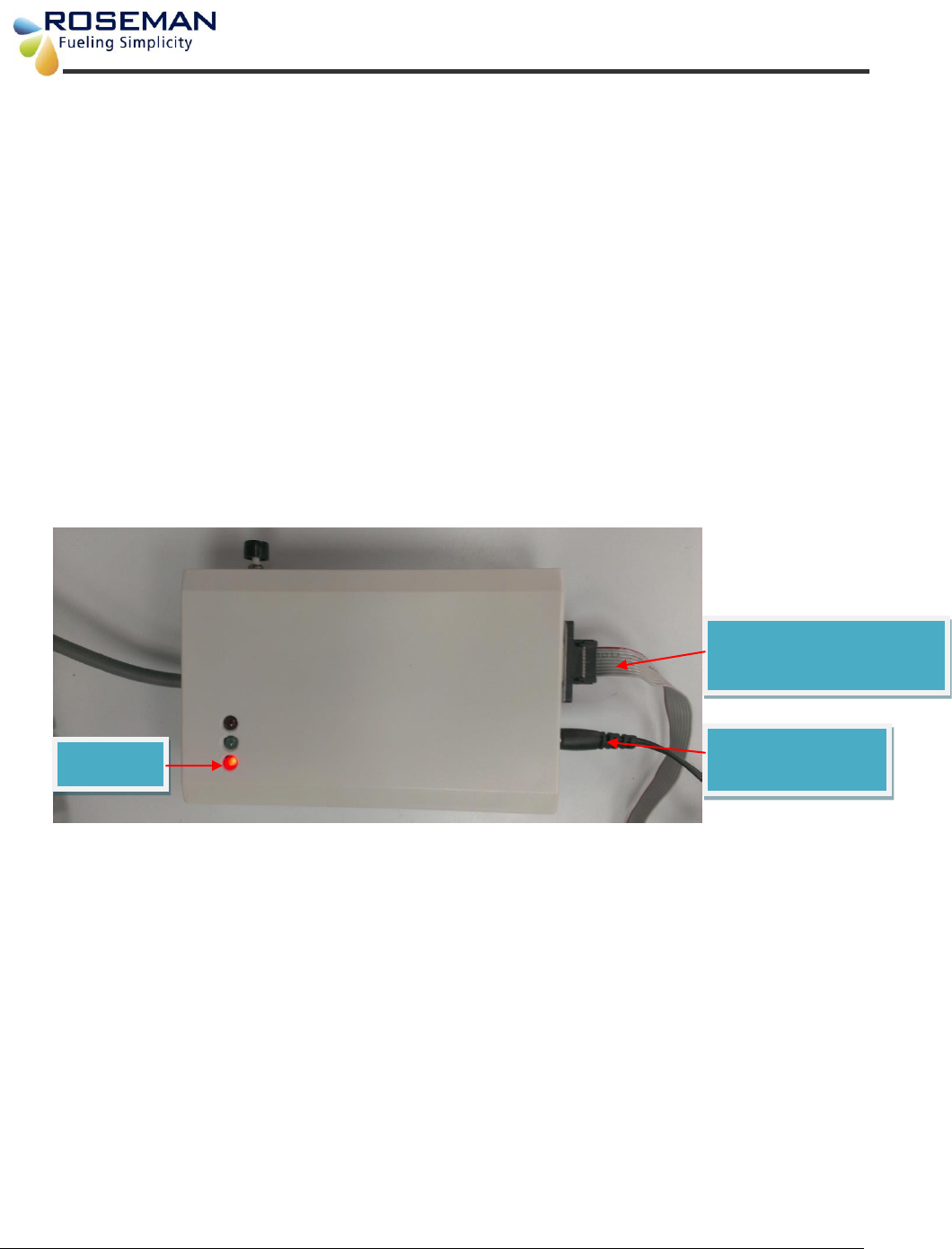
Fleet Gate Installation Guide Roseman Engineering Ltd
33
The Fueling Division of Roseman Engineering Ltd.
10. Flashing Tool
10.1 Purpose
The FJ3 Flashing Tool is part of the FouelFocus Vehicle Subsystem. These instructions
explains how to upload a new FJ3 version for the flashing tool and how to program the FJ3
after the new version has been loaded onto the tool.
10.2 Preparation steps
1. Connect a serial D type cable from the Flashing tool to your computer
2. Connect the Flashing tool to a 12V Power Supply
3. Locate the application on your computer to a new directory
Flashing Tool
#PRG-FG3-01
Serial Communication
to pc
12 V Power
Supply
Figure 12: Flashing Tool Preparation
Power
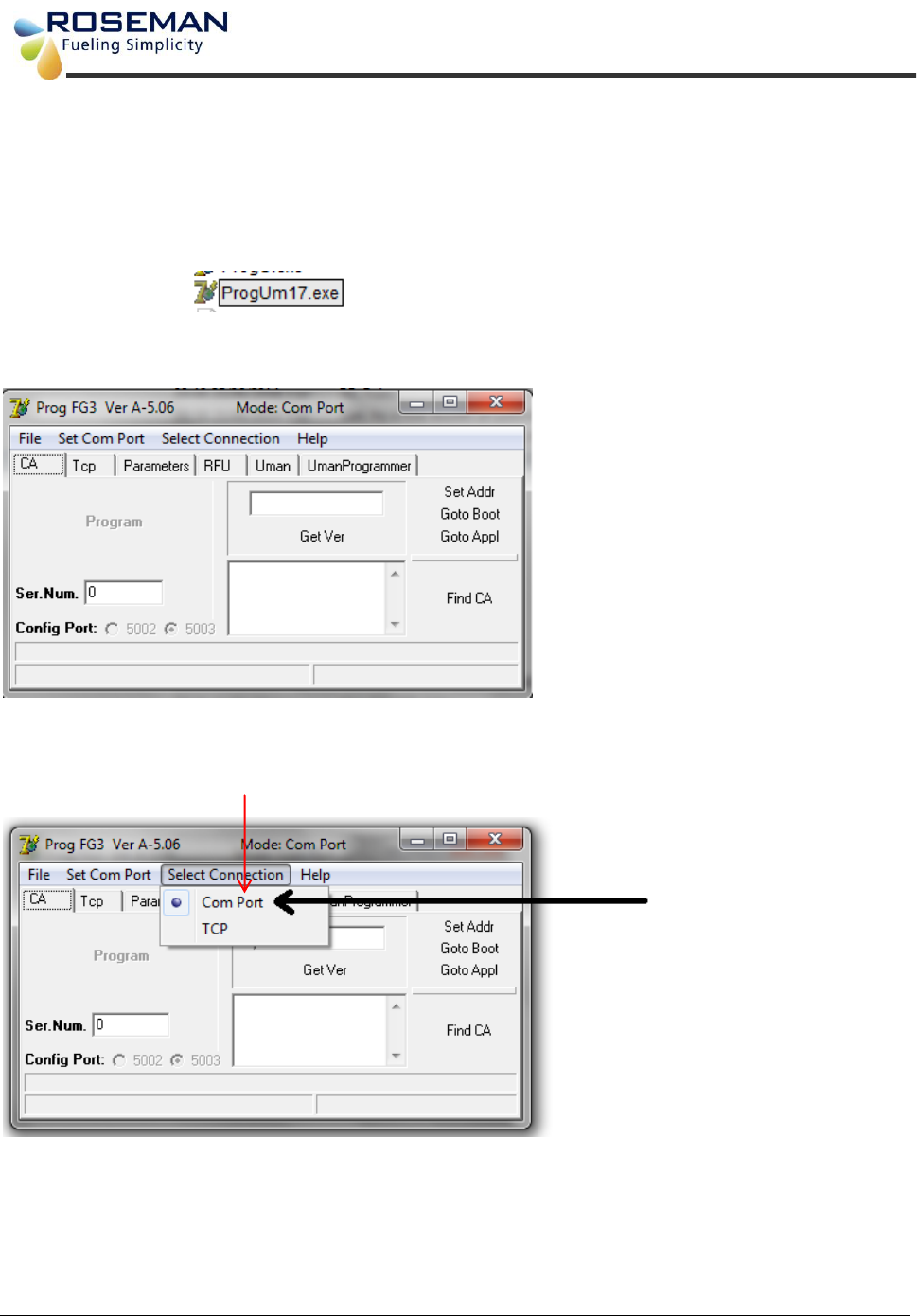
Fleet Gate Installation Guide Roseman Engineering Ltd
34
The Fueling Division of Roseman Engineering Ltd.
10.3 Updating version
Verify that the Flashing Tool program files has been installed on your comuter
Double click on icon
1. Prog FG3 Ver. 5.06 screen will appear
2. Click select Connection >Com Port
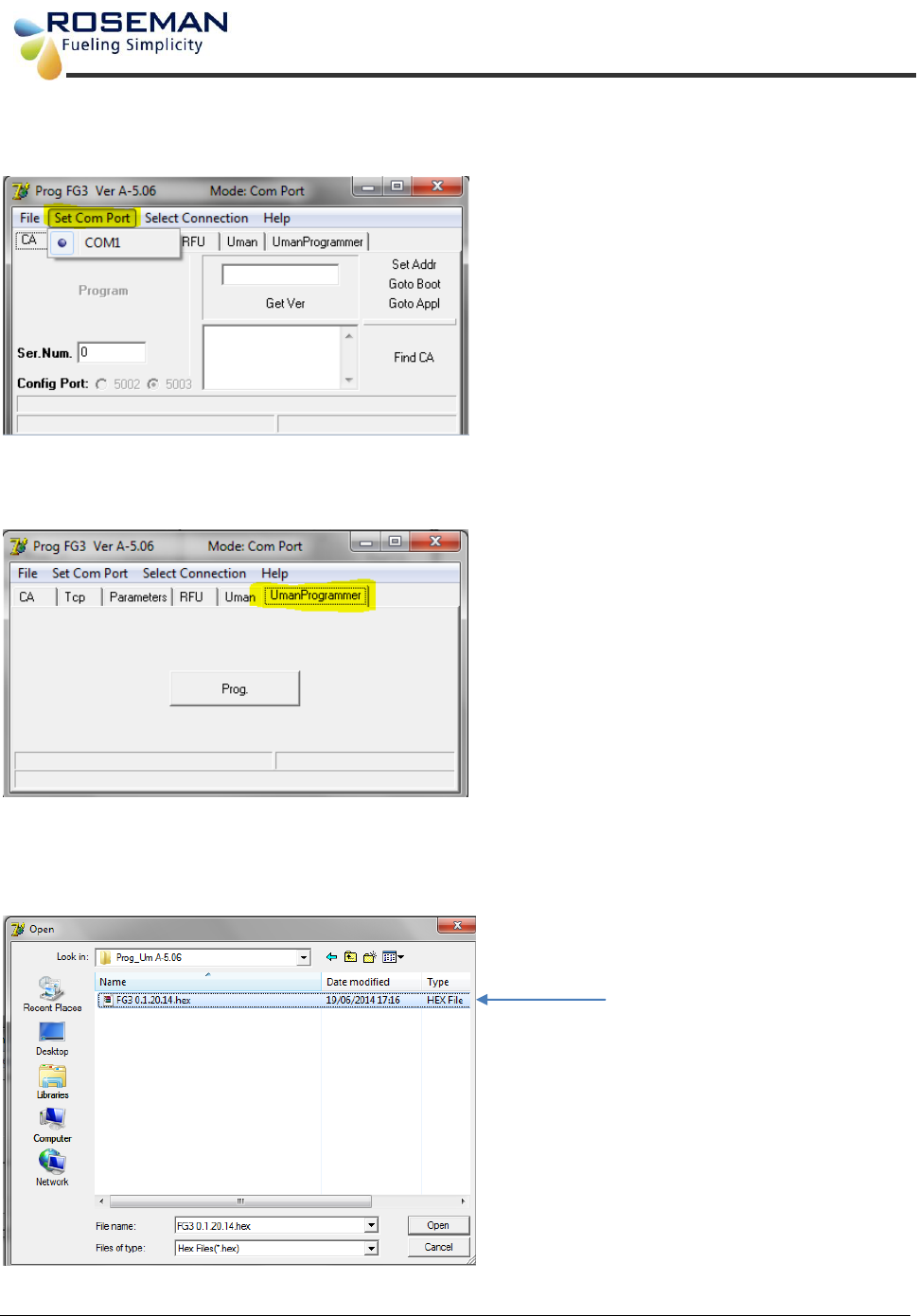
Fleet Gate Installation Guide Roseman Engineering Ltd
35
The Fueling Division of Roseman Engineering Ltd.
3. Click Set Com port selcet an available com of your comuter for example com3
4. Click File>Open
5. Open file screen will apppear
Select the required FG 0.1.20.14 hex file
Click Open Buttom to continue
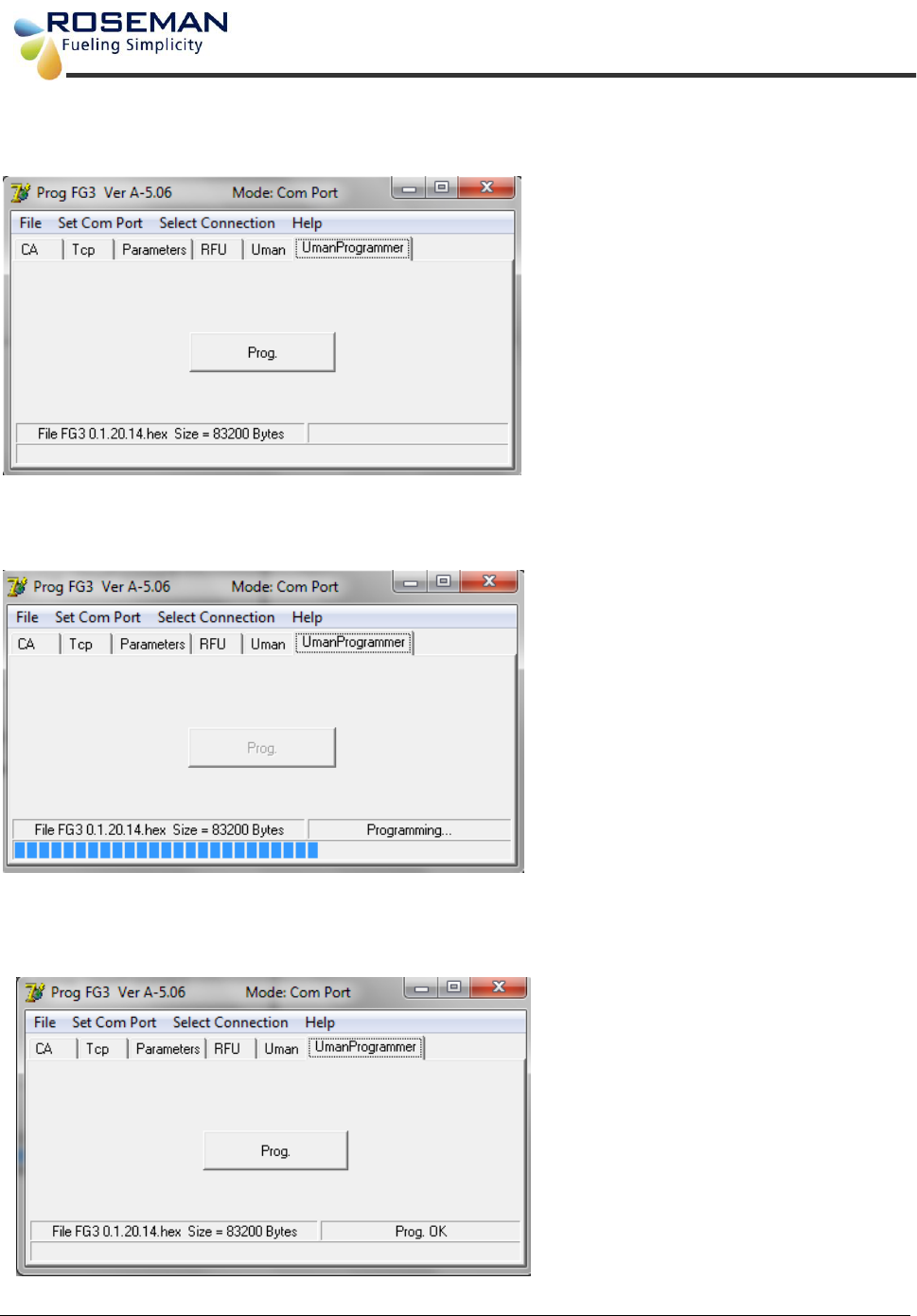
Fleet Gate Installation Guide Roseman Engineering Ltd
36
The Fueling Division of Roseman Engineering Ltd.
6. Press The Prog bottun and the following screen will appear.
7. Verify that the status bar is in progress
8. Verify that the Prog. is O.K
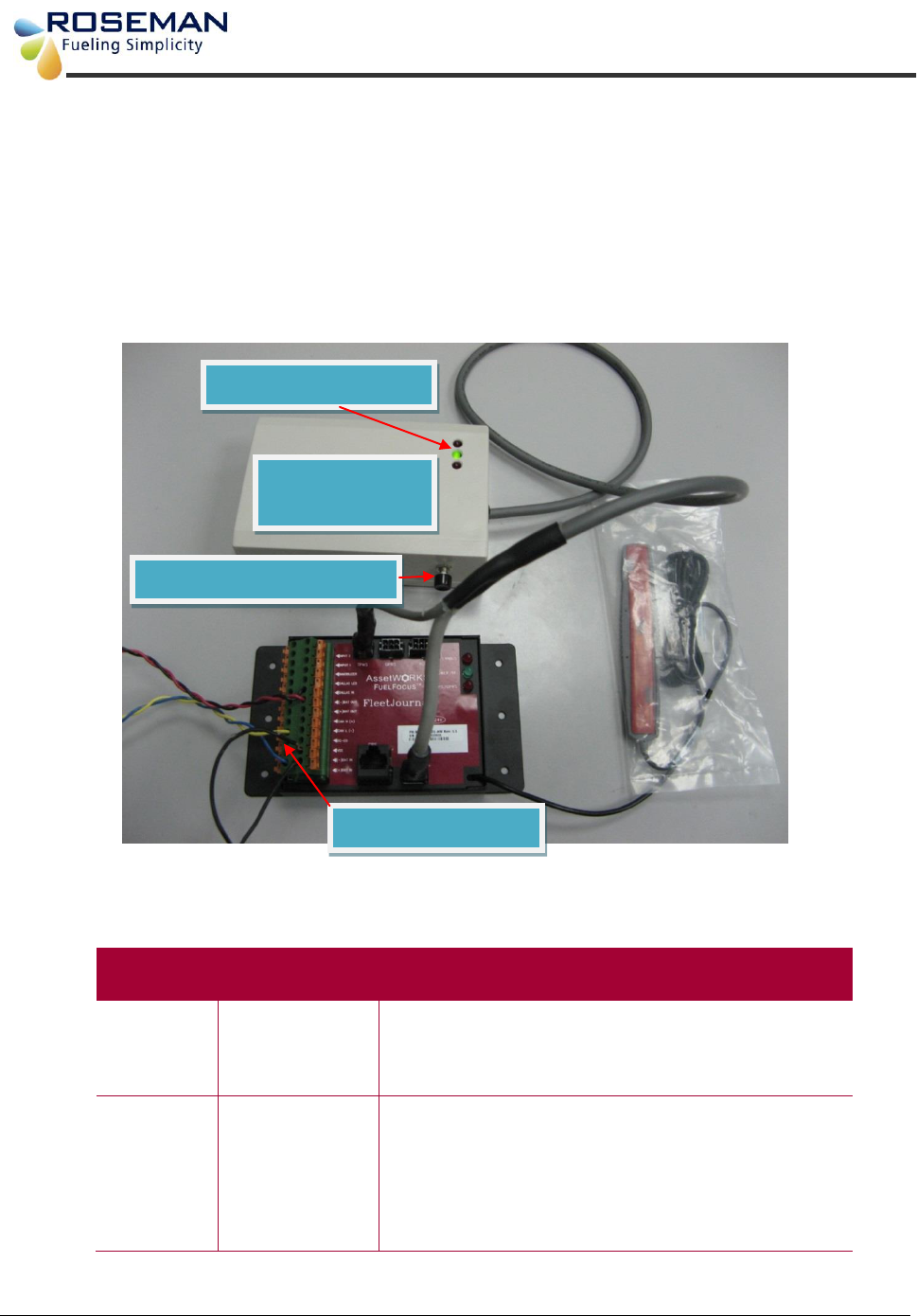
Fleet Gate Installation Guide Roseman Engineering Ltd
37
The Fueling Division of Roseman Engineering Ltd.
10.4 Flashing Steps
1. Connect the two connectors of the flashing tool # PRG-FG3-01 to the FJ3 as shown:
Connect the 4 pin plug to TPMS connector
Connct the 6 pin plug to the PROG connector
2. Ensure that the FJ3 has 12V
3. Press the Black Flasing Push Button for 2 seconds verify that the green led is flikering
during the flasing process and when the flashing has terminated it comes solid
There are 2 indicator LEDs on the Flashing Tool a GREEN LED and RED LED:
LED
COLOR
FUNCTION
INDICATION
RED
Power
Flickers when the power is connected to the
Flashing Tool
GREEN
Flashing
After pressing the e black push button The
green flickers while the Flash tool is
connected to the FJ3
the green is solid while the flashing is
completed successfully
Flashing Tool
#PRG-FG3-01
Power In 12VDC
Flashing Push Button
Indication LEDS
Figure 13: Flashing Tool connections
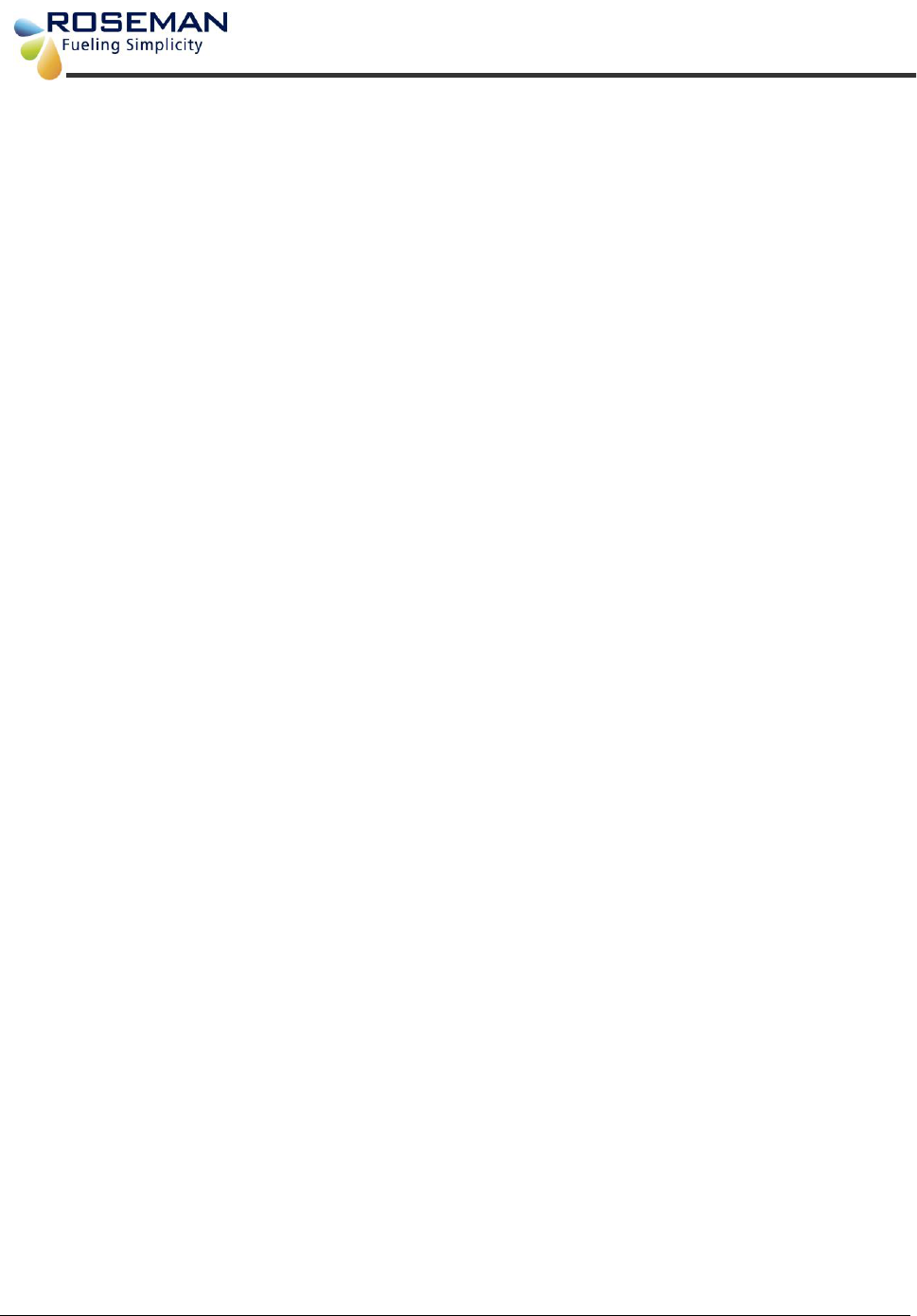
Fleet Gate Installation Guide Roseman Engineering Ltd
38
The Fueling Division of Roseman Engineering Ltd.
11. Appendixes
11.1 Appendix A –Capturing vehicle data
11.1.1 Capturing Odometer and Engine Hours Information
If the FG3 is to record the vehicle's odometer, you will need to obtain a pulse relevant to the
vehicle’s speed. This can be accomplished by either utilizing an Odometer Adaptor or by
receiving electronic pulses from the vehicle speed sensor (VSS) output. If your vehicle has a
cable driven speedometer, a transducer will be needed to convert the mechanical turns of
the speedometer cable into electronic pulses that the FG3 can read. Transducers may be
ordered through a local speedometer repair shop, through the vehicle manufacturer's parts
distributor, or directly from the sensor manufacturer.
11.1.2 Vehicle Data Collection (VDC) - Option
The Roseman VDC enables online wireless capture of odometer and/or engine hour
readings from vehicles equipped with the Roseman Vehicle Identification Fleet Gate (FG3).
This data capture occurs when a vehicle passes within range of the Wireless Automated
Fueling (WAF) Receiver installed in a parking area or at the fuel island. The pertinent
vehicle data is transmitted to a local PC, which has the Roseman proprietary VSU
application installed and running and will transmit it to the FleetFocus™ application client
server in REALTIME via TCP/IP protocol.
11.1.3 Vehicle Speed Sensor (VSS)
In order for a pulse counting FG3 to function properly, it requires an accurate speed signal
from the vehicle. This section provides a quick overview of what a speed signal is, and how
to identify a speed signal.
With the introduction of the electronic control module, or the “electronic brain”, found in all
modern day vehicles, engineers needed a way to report operational data to this computer
for processing. This is where sensors come in. There are sensors to measure just about
everything; pressure, speed, temperature, fluid levels, and so on. A sensor simply converts
one type of information into another, or more specifically, one type of energy into another.
The end result is used by the computer for calculations.
In almost all cases, the vehicle’s speed signal is generated at the output shaft of the
transmission. This shaft turns at a speed which is directly proportional to the vehicle speed.
There are usually two different types of sensors found at this location. The first type, and by
far the most common, is called a variable reluctance sensor. This is a fancy name for a
series of magnets mounted to “shag”, which spins past an inductor or coil. As the magnets’
lines of force cut through the inductor, a voltage, or pulse is induced in the circuit. So, the
end result is a signal which pulsates, or oscillates at a speed directly proportional to vehicle
speed. The second type of sensor, which is probably more modern, but less common, is the
Hall Effect sensor. The Hall Effect sensor works much the same as the variable reluctance
sensor, but instead of an inductor, the Hall Effect sensor is a tiny solid state switch which is
activated by a magnetic force. The end result is a smaller and lighter sensor generating a
cleaner signal.
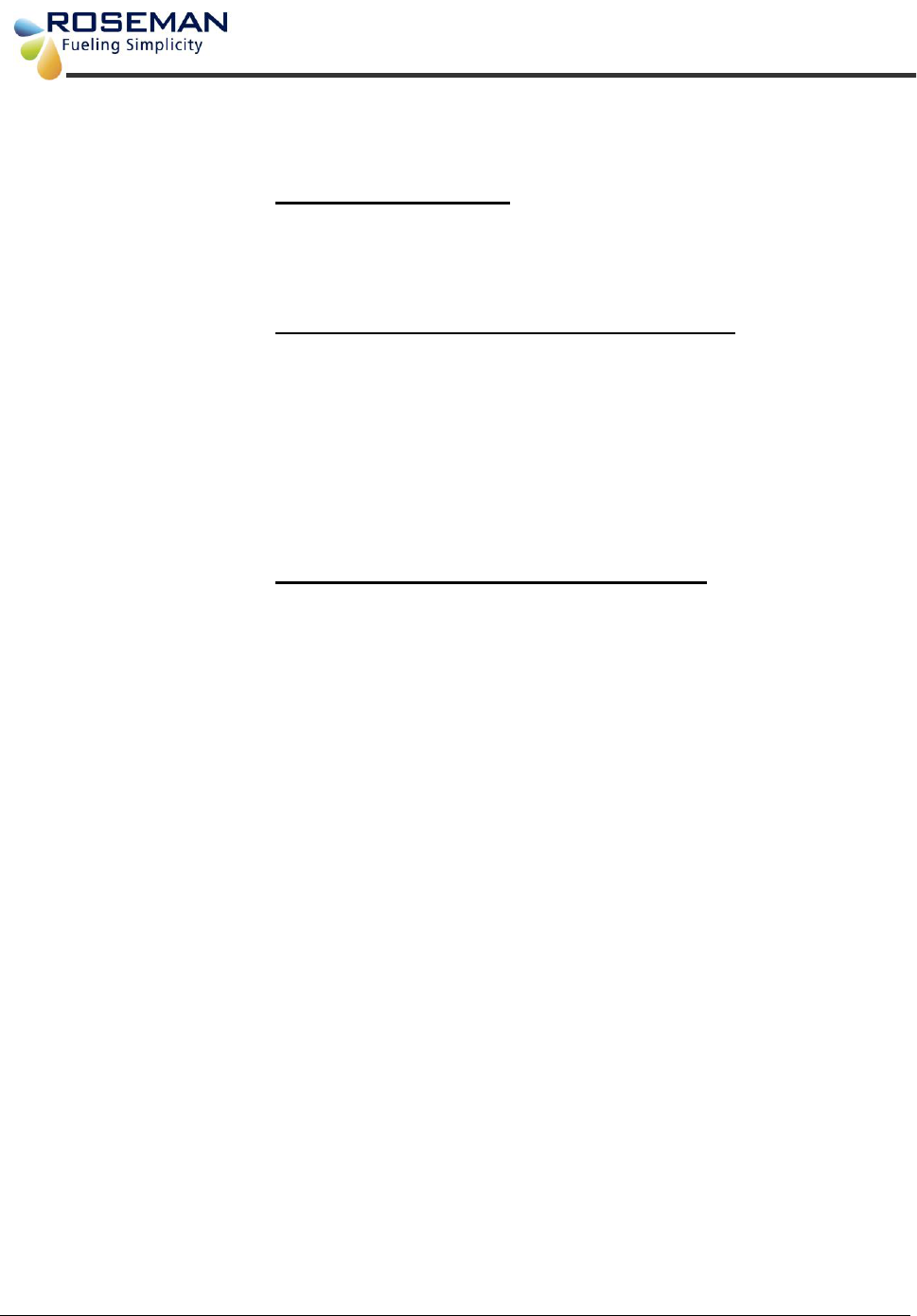
Fleet Gate Installation Guide Roseman Engineering Ltd
39
The Fueling Division of Roseman Engineering Ltd.
There are many ways to identify the vehicle speed signal. We will discuss a few of
these:
11.1.3.1 Using an Oscilloscope
By far the easiest way to view and identify the VSS signal is with an Oscilloscope.
This tool allows you to actually see a picture of the signal.
11.1.3.2 Using a Multi-Meter to measure frequency (Hz)
This is the easiest way to measure the speed signal without the use of a scope.
There are some things to watch out for, however. At rests, the meter may give
incorrect readings. This is because the meter uses A/C coupling to measure
frequency, and if it picks up some noise, it may try to measure it to determine its
frequency. The important thing is to measure frequency while the vehicle is
moving. The frequency will increase proportionately to vehicle speed. If the
measurements seem to bounce around, you probably don't have the correct circuit.
11.1.3.3 Using a Multi-Meter to measure A/C Voltage
This is yet another way to verify the VSS circuit. This method works poorly
however, with Hall Sensor outputs. The reason for this is that a Hall Sensor’s
output does not vary in amplitude, only frequency. Almost all A/C Multimeters
display voltage in RMS, which is about 70% of the peak value of the A/C waveform.
Since the peak voltage is constant with a Hall Sensor you will see only two
readings; the reading while the vehicle is stationary, and the reading while it is in
motion. Usually this is enough data to determine if you have the right circuit.
If you are using an A/C Multimeter to test a variable reluctance sensor, which are
by far the most common, it will work very well. As with frequency, the A/C voltage
should fluctuate in direct proportion to the vehicle speed.
Once the VSS circuit has been identified, the next step is to determine the number
of pulses per mile which are emitted from the sensor. In order to determine the
speed and mileage, the VIB must know how many pulses are emitted for a mile
traveled. Fortunately, there are only a few different calibration values. For
example, almost all Ford and Chrysler products emit 8000 pulses per mile.
Chevrolet commonly uses 4000 or 2000 at the control module, and 96000 at the
transmission.
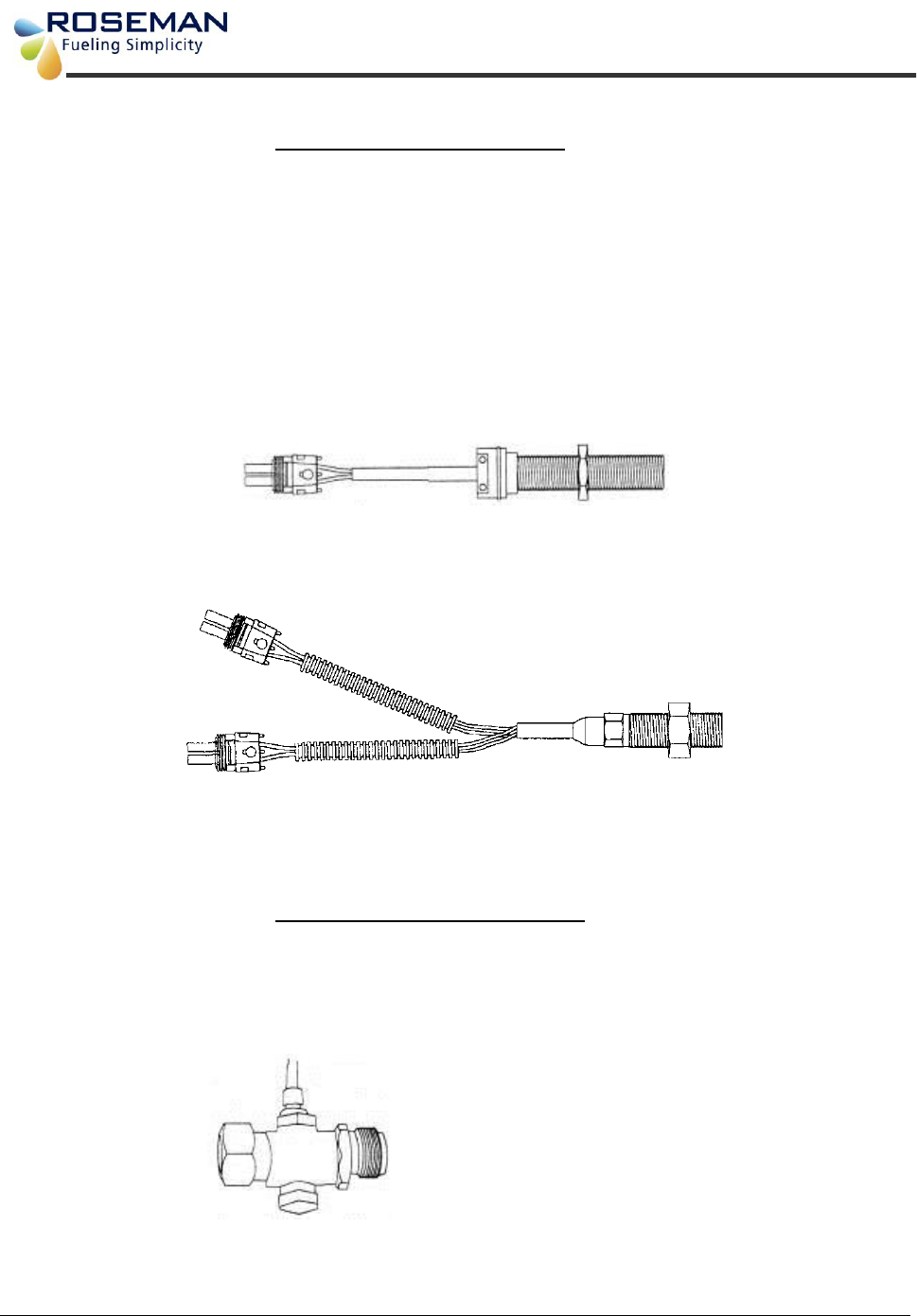
Fleet Gate Installation Guide Roseman Engineering Ltd
40
The Fueling Division of Roseman Engineering Ltd.
11.1.3.4 Electronic Odometer Adapter
If the vehicle is equipped with an electronic sending unit controlling the dashboard
speedometer, you need to simply connect a wire between the signal line and the
FG3. If the vehicle's electronic odometer line is also driving additional equipment,
such as a cruise control module or trip computer, there might not be enough signal
strength to add the FG3 to this line. In this case, you will need to replace the single
sensor with a dual-output sender, or add an additional single sender to the unused
sender port that is provided on some vehicles.
For connection instructions please refer to vehicle manufacturer.
Single Electronic Adaptor
Dual Electronic Adaptor
11.1.3.5 Reed Type Mechanical Adaptor
If the vehicle utilizes a mechanical cable between the dashboard speedometers to
the transmission, on a mechanical pulse Transducer (or taxi Tap) is required. Try to
order the sensor with 18 gauge shielded cable of sufficient length to reach the ID
Box without splicing. Consult Roseman on approved vendors for these
transducers.
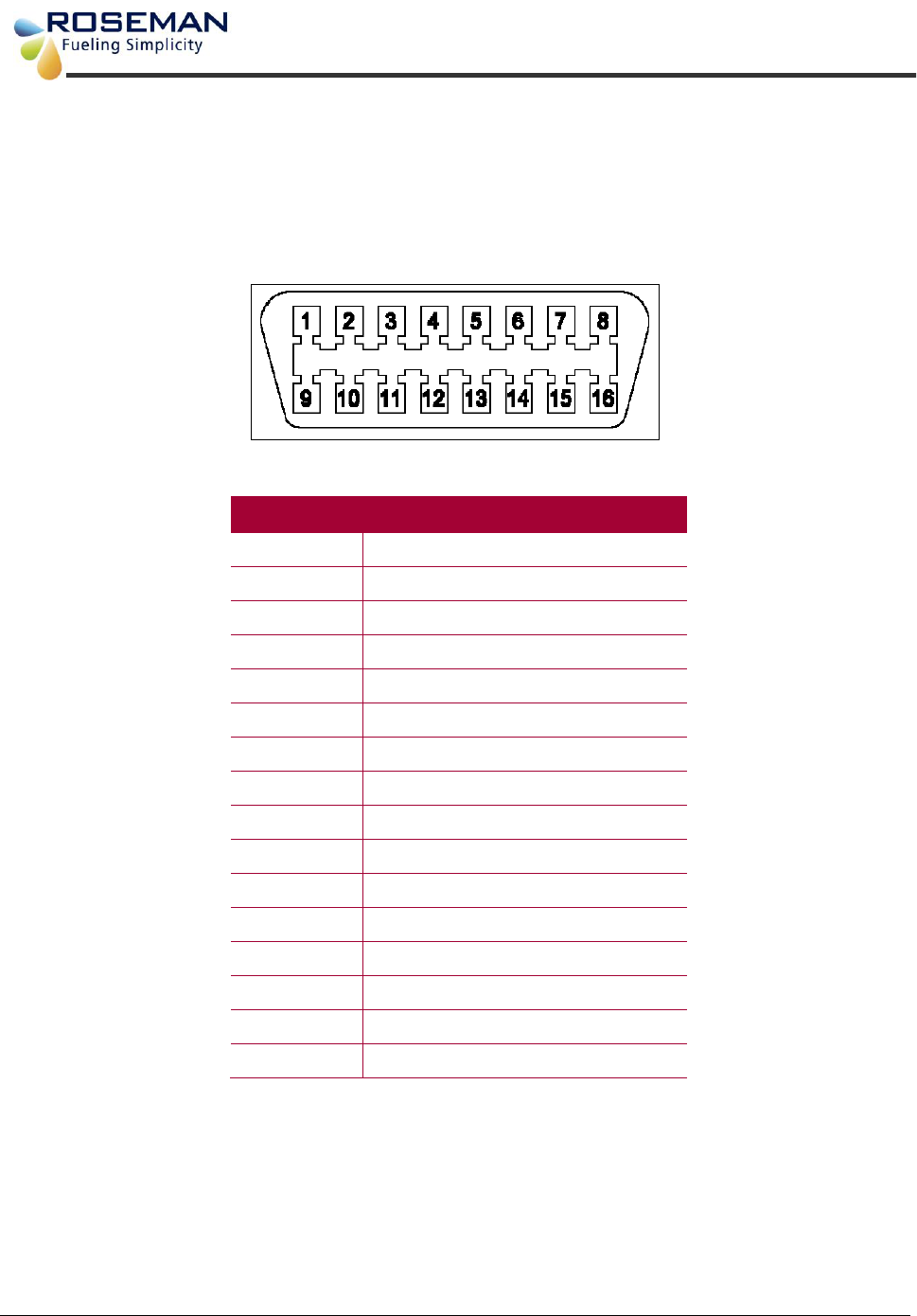
Fleet Gate Installation Guide Roseman Engineering Ltd
41
The Fueling Division of Roseman Engineering Ltd.
11.2 Appendix B – CAN Bus Data Connectors
11.2.1 Vehicle OBD-II Connector J1962
Figure 12: Car Diagnostic Connector (female)
Pin No.
Description
1
Manufacturer mandated
2
J1850 Bus+
3
Manufacturer mandated
4
Car ground
5
Signal ground
6
CAN High (J-2284)
7
ISO 9149-2 K output
8
Manufacturer mandated
9
Manufacturer mandated
10
J1850 Bus
11
Manufacturer mandated
12
Manufacturer mandated
13
Manufacturer mandated
14
CAN Low (J-2284)
15
ISO 9149-2 L output
16
Battery (+) voltage
Table 1: OBD-II Connector J1962 – Pin Description
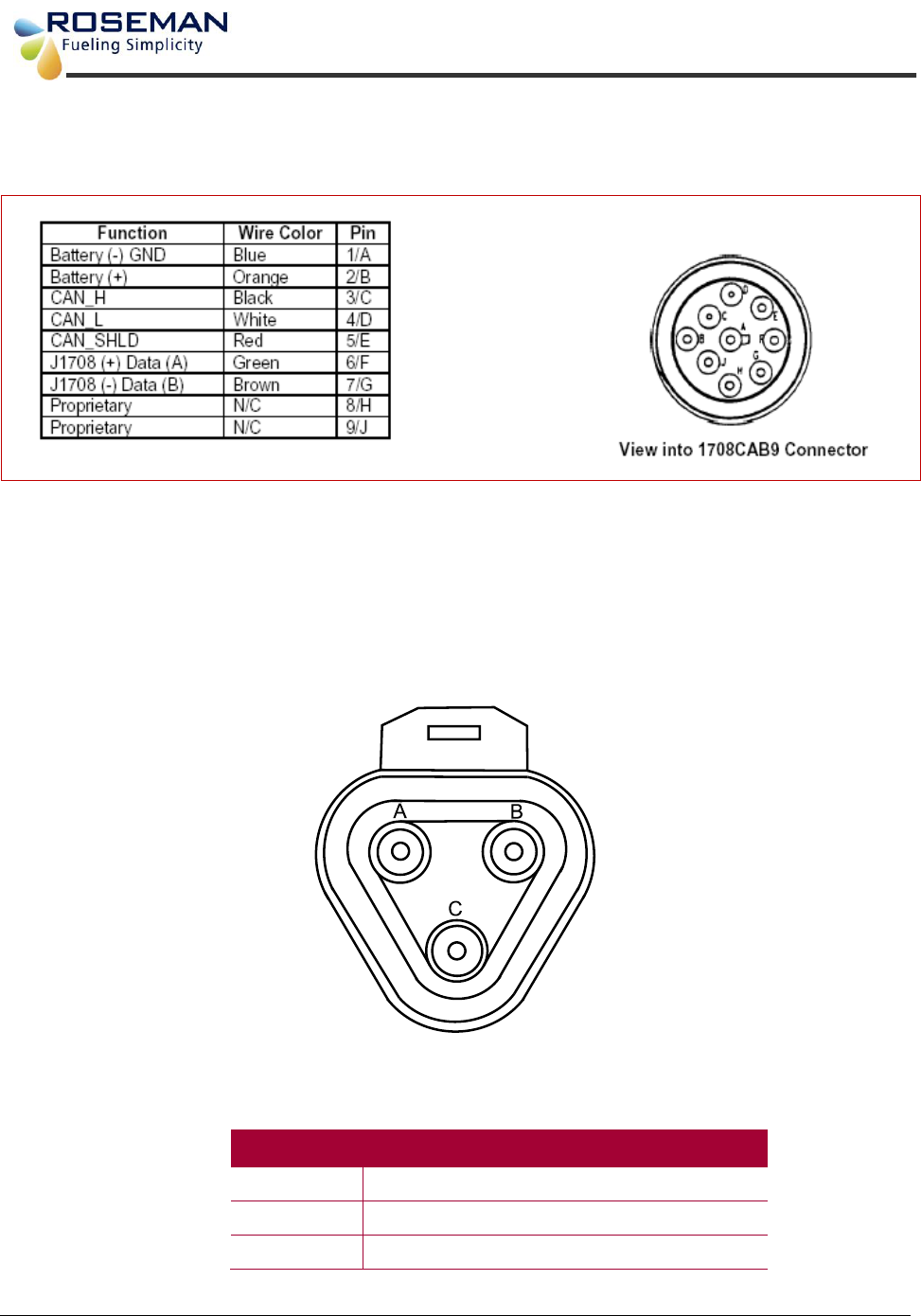
Fleet Gate Installation Guide Roseman Engineering Ltd
42
The Fueling Division of Roseman Engineering Ltd.
11.2.2 SAE J1939 Data Interface Connector
Figure 13: SAE J1939 Model 1708CAB9
11.2.3 3 PIN J1939 Data Interface Connector
Figure 14: 3-pin Deutsch J1939 DT06-3S-E008
Pin No.
Description
A
CAN bus line, dominant Low (J-1939)
B
CAN bus line, dominant High (J-1939)
C
CAN ground (Car ground)
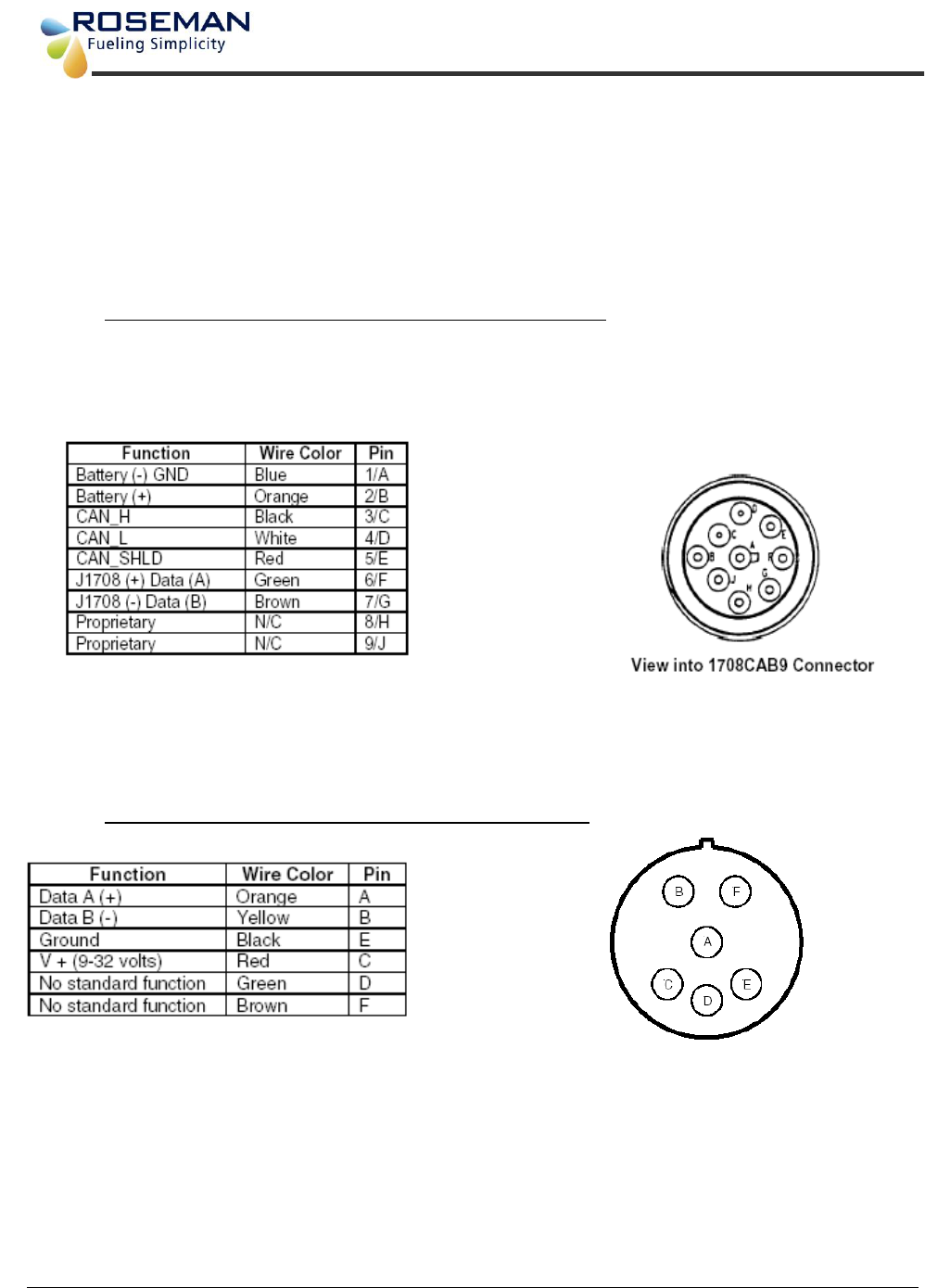
Fleet Gate Installation Guide Roseman Engineering Ltd
43
The Fueling Division of Roseman Engineering Ltd.
11.3 Appendix C – J1708 Data Connectors
11.3.1 SAE J1708 Data Interface Cables
Option 1: SAE J1708 Model 1708CAB9
Figure 15: SAE J1708 Model 1708CAB9
Option 2: SAE J1708 Model 1708CAB
Figure 16: SAE J1708 Model 1708CAB
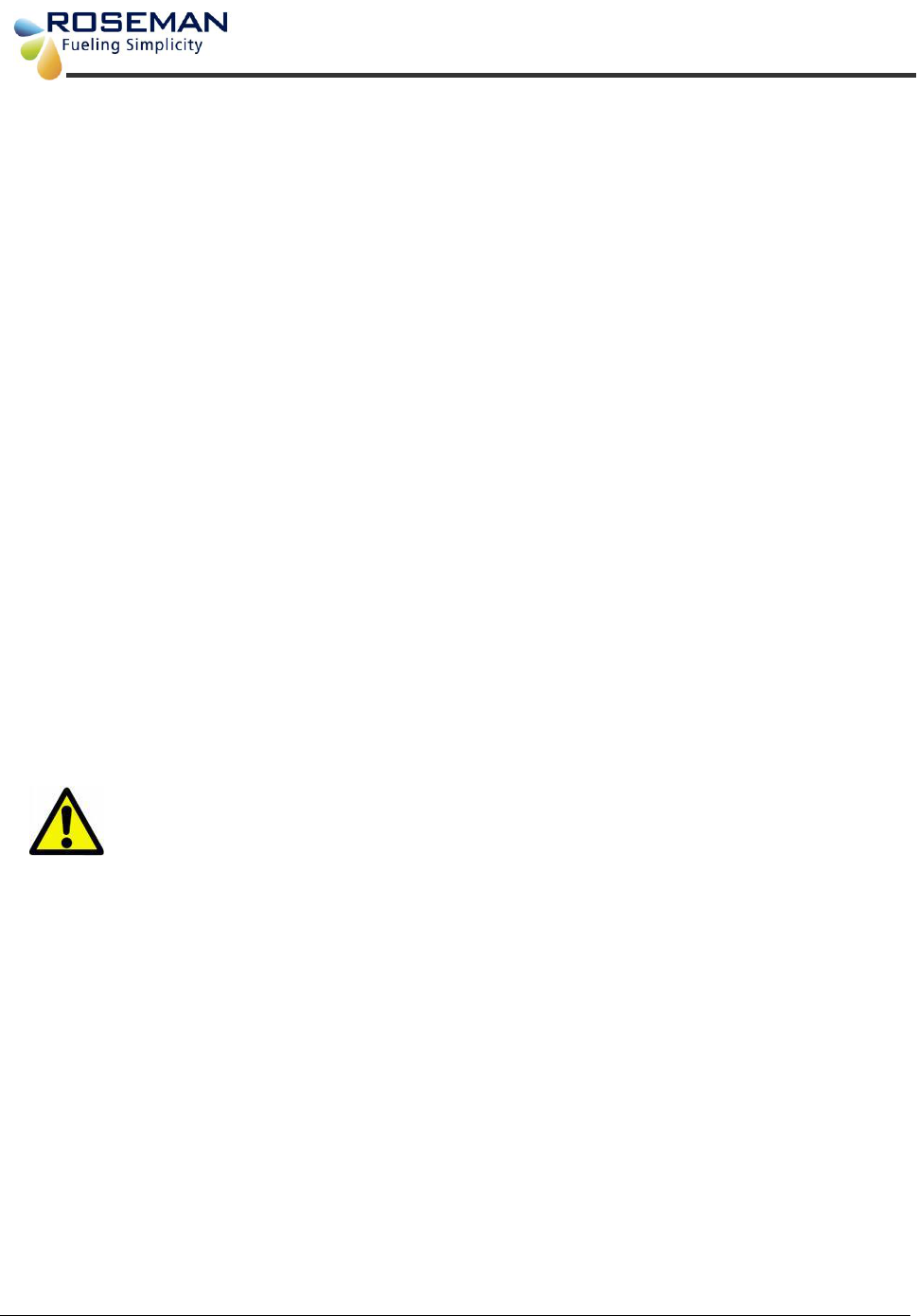
Fleet Gate Installation Guide Roseman Engineering Ltd
44
The Fueling Division of Roseman Engineering Ltd.
11.4 The FCC Wants You to Know
This equipment has been tested and found to comply with the limits for a Class B digital
device, pursuant to Part 15 of the FCC rules. These limits are designed to provide
reasonable protection against harmful interference in a residential installation. This
equipment generates uses and can radiate radio frequency energy and, if the equipment not
installed and used in accordance with the instructions, may cause harmful interference to
radio communications. However, there is no guarantee that interference will not occur in a
particular installation. If this equipment does cause harmful interference to radio or television
reception, which can be determined by turning the equipment off and on, the user is
encouraged to try to correct the interference by one or more of the following measures:
a) Reorient or relocate the receiving antenna.
b) Increase the separation between the equipment and receiver.
c) Connect the equipment to an outlet on a circuit different from that to which the
receiver is connected.
d) Consult the dealer or an experienced radio/TV technician.
FCC Warning
To comply with FCC requirements, a distance of at least 20cm between the equipment and all
persons should be maintained during the operation of the equipment.
Modifications not expressly approved by the manufacturer could void the user authority to
operate the equipment under FCC Rules.
This device complies with Part 15 of the FCC Rules. Operation is subject to the following
two conditions:
(1) This device may not cause harmful interference.
(2) This device must accept any interference received, including
interference that may cause undesired operation.