Rosemount Tank Radar 5900 Rosemount 5900S Radar Level Gauge User Manual
Rosemount Tank Radar AB Rosemount 5900S Radar Level Gauge
Contents
- 1. User Manual (preliminary)
- 2. User Manual part 2
User Manual (preliminary)
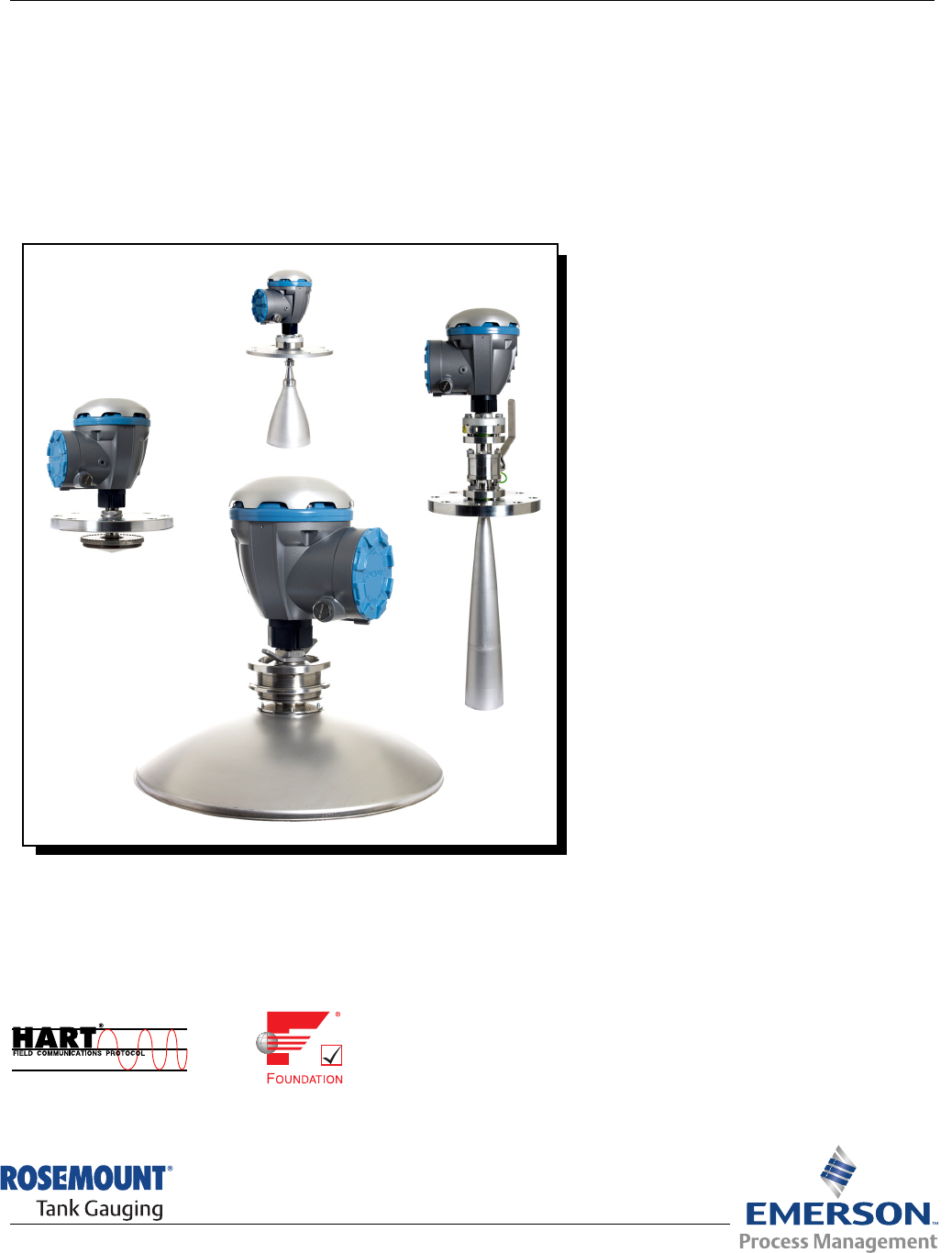
www.rosemount-tg.com
Reference Manual
300520EN, Rev AA
November 2009
Rosemount 5900
Radar Level Gauge
Preliminary
Preliminary
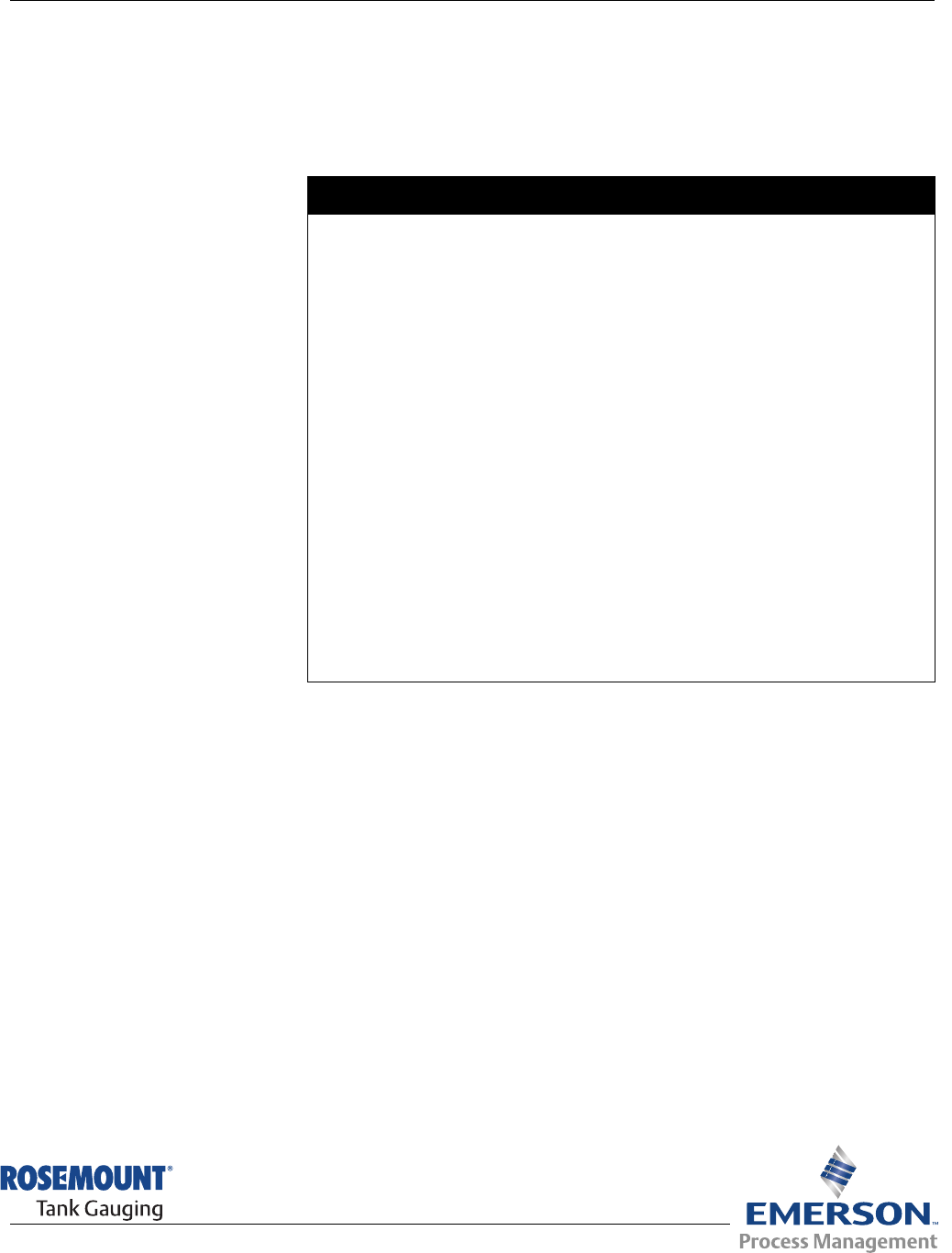
Reference Manual
300520EN, Rev AA
November 2009 Rosemount 5900
www.rosemount-tg.com
Rosemount 5900
Radar Level Gauge
Cover Photo: 5900_coverphoto.tif
NOTICE
Read this manual before working with the product. For personal and system safety, and for
optimum product performance, make sure you thoroughly understand the contents before
installing, using, or maintaining this product.
For equipment service or support needs, contact your local Emerson Process
Management/Rosemount Tank Gauging representative.
Spare Parts
Any substitution of non-recognized spare parts may jeopardize safety. Repair, e.g.
substitution of components etc, may also jeopardize safety and is under no circumstances
allowed.
Rosemount Tank Radar AB will not take any responsibility for faults, accidents, etc caused
by non-recognized spare parts or any repair which is not made by
Rosemount Tank Radar AB.
Specific FCC Requirements (USA only)
Rosemount 5900 generates and uses radio frequency energy. If it is not installed and used
properly, that is, in strict accordance with the manufacturer´s instructions, it may violate
FCC regulations on radio frequency emission.
Rosemount TankRadar 5900 has been FCC certified under test conditions which assume a
metallic tank. Installation on a non-metallic tank is not certified, and is not allowed.
The FCC certificate for Rosemount 5900 requires that the tank is closed as far as emitted
radio energy is concerned. Tanks with open manholes, external-floating-roof tanks without
still pipes etc. are not covered by the certificate.
Preliminary
Preliminary
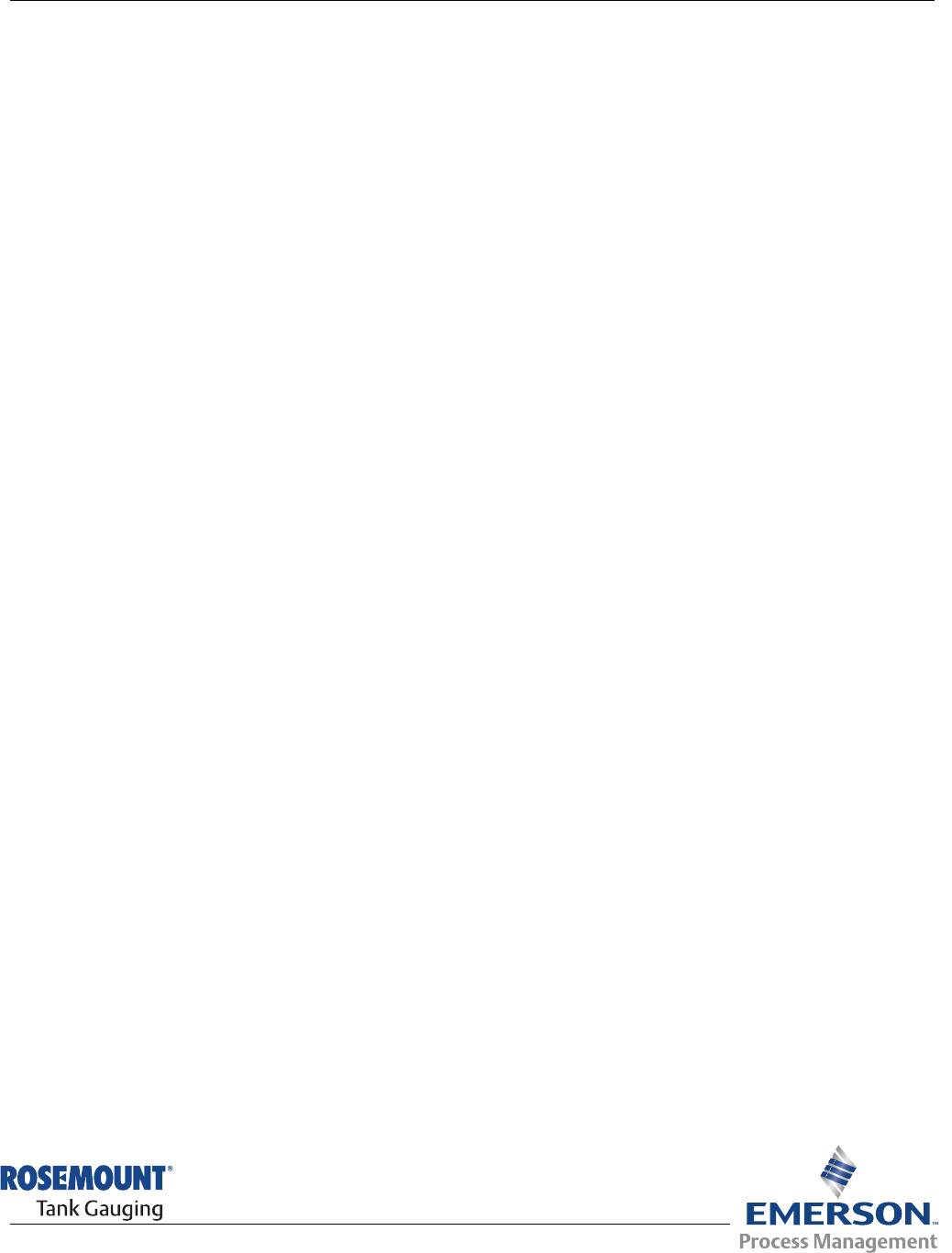
Reference Manual
300520EN, Rev AA
November 2009 Rosemount 5900 Series
www.rosemount-tg.com
Table of Contents
SECTION 1
Introduction
1.1 Safety Messages . . . . . . . . . . . . . . . . . . . . . . . . . . . . . . . . . . . . 1-1
1.2 Symbols. . . . . . . . . . . . . . . . . . . . . . . . . . . . . . . . . . . . . . . . . . . 1-2
1.3 Manual Overview. . . . . . . . . . . . . . . . . . . . . . . . . . . . . . . . . . . . 1-3
1.4 Service Support. . . . . . . . . . . . . . . . . . . . . . . . . . . . . . . . . . . . . 1-4
1.5 Product Recycling/
Disposal1-5
1.6 Packing Material . . . . . . . . . . . . . . . . . . . . . . . . . . . . . . . . . . . . 1-5
1.6.1 Reuse. . . . . . . . . . . . . . . . . . . . . . . . . . . . . . . . . . . . . 1-5
1.6.2 Recycling . . . . . . . . . . . . . . . . . . . . . . . . . . . . . . . . . . 1-5
1.6.3 Energy recovery . . . . . . . . . . . . . . . . . . . . . . . . . . . . . 1-5
SECTION 2
Overview
2.1 Introduction . . . . . . . . . . . . . . . . . . . . . . . . . . . . . . . . . . . . . . . . 2-1
2.2 Components . . . . . . . . . . . . . . . . . . . . . . . . . . . . . . . . . . . . . . . 2-2
2.3 System Overview. . . . . . . . . . . . . . . . . . . . . . . . . . . . . . . . . . . . 2-3
2.4 Antennas . . . . . . . . . . . . . . . . . . . . . . . . . . . . . . . . . . . . . . . . . . 2-7
2.5 Installation Procedure . . . . . . . . . . . . . . . . . . . . . . . . . . . . . . . . 2-9
SECTION 3
Installation
3.1 Safety Messages . . . . . . . . . . . . . . . . . . . . . . . . . . . . . . . . . . . . 3-1
3.2 Installation Considerations . . . . . . . . . . . . . . . . . . . . . . . . . . . . 3-3
3.2.1 Horn Antenna Requirements . . . . . . . . . . . . . . . . . . . 3-4
3.2.2 Parabolic Antenna Requirements . . . . . . . . . . . . . . . 3-6
3.2.3 Still Pipe Antenna Requirements . . . . . . . . . . . . . . . 3-10
3.2.4 LPG/LNG Antenna Requirements . . . . . . . . . . . . . . 3-13
3.3 Mechanical Installation . . . . . . . . . . . . . . . . . . . . . . . . . . . . . . 3-18
3.3.1 Horn Antenna . . . . . . . . . . . . . . . . . . . . . . . . . . . . . . 3-18
3.3.2 Parabolic Antenna . . . . . . . . . . . . . . . . . . . . . . . . . . 3-20
3.3.3 Array Antenna - Fixed version . . . . . . . . . . . . . . . . . 3-29
3.3.4 Array Antenna - Hinged Hatch . . . . . . . . . . . . . . . . . 3-32
3.3.5 LPG/LNG Antenna . . . . . . . . . . . . . . . . . . . . . . . . . . 3-36
3.4 Electrical Installation . . . . . . . . . . . . . . . . . . . . . . . . . . . . . . . . 3-39
3.4.1 Cable/conduit entries . . . . . . . . . . . . . . . . . . . . . . . . 3-39
3.4.2 Grounding . . . . . . . . . . . . . . . . . . . . . . . . . . . . . . . . 3-39
3.4.3 Cable Selection . . . . . . . . . . . . . . . . . . . . . . . . . . . . 3-40
3.4.4 Hazardous Areas . . . . . . . . . . . . . . . . . . . . . . . . . . . 3-40
3.4.5 Power Requirements . . . . . . . . . . . . . . . . . . . . . . . . 3-40
3.4.6 Power Budget. . . . . . . . . . . . . . . . . . . . . . . . . . . . . . 3-40
3.4.7 The Raptor Tankbus . . . . . . . . . . . . . . . . . . . . . . . . 3-41
3.4.8 Typical installations . . . . . . . . . . . . . . . . . . . . . . . . . 3-42
3.4.9 Wiring . . . . . . . . . . . . . . . . . . . . . . . . . . . . . . . . . . . . 3-43
3.4.10 Terminal Blocks . . . . . . . . . . . . . . . . . . . . . . . . . . . . 3-44
3.4.11 Wiring Diagrams. . . . . . . . . . . . . . . . . . . . . . . . . . . . 3-47
Preliminary
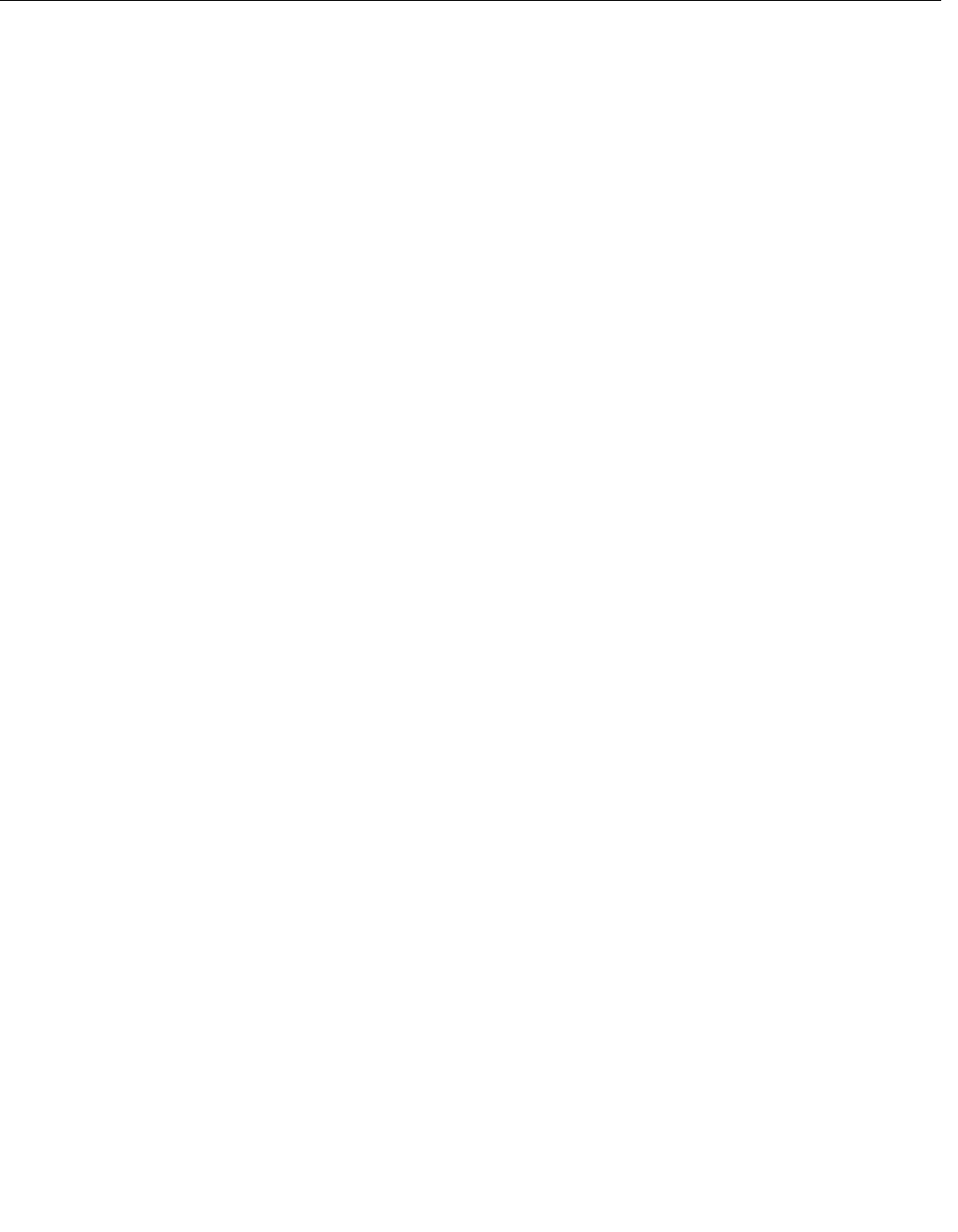
Reference Manual
300520EN, Rev AA
November 2009
Rosemount 5900 Series
TOC-2 Table of Contents
SECTION 4
Configuration
4.1 Safety Messages . . . . . . . . . . . . . . . . . . . . . . . . . . . . . . . . . . . . 4-1
4.2 Overview . . . . . . . . . . . . . . . . . . . . . . . . . . . . . . . . . . . . . . . . . . 4-2
4.2.1 Basic Configuration . . . . . . . . . . . . . . . . . . . . . . . . . . 4-3
4.2.2 Advanced Configuration. . . . . . . . . . . . . . . . . . . . . . . 4-3
4.2.3 Configuration Tools . . . . . . . . . . . . . . . . . . . . . . . . . . 4-3
4.3 Basic Configuration . . . . . . . . . . . . . . . . . . . . . . . . . . . . . . . . . . 4-4
4.3.1 Tank Geometry . . . . . . . . . . . . . . . . . . . . . . . . . . . . . 4-4
4.3.2 Environment . . . . . . . . . . . . . . . . . . . . . . . . . . . . . . . . 4-6
4.3.3 Tank Shape . . . . . . . . . . . . . . . . . . . . . . . . . . . . . . . . 4-6
4.4 Configuration Using Rosemount TankMaster . . . . . . . . . . . . . . 4-7
4.4.1 Installation Wizard . . . . . . . . . . . . . . . . . . . . . . . . . . . 4-8
4.5 LPG Configuration . . . . . . . . . . . . . . . . . . . . . . . . . . . . . . . . . . . 4-9
4.5.1 Preparations. . . . . . . . . . . . . . . . . . . . . . . . . . . . . . . . 4-9
4.5.2 LPG Configuration . . . . . . . . . . . . . . . . . . . . . . . . . . 4-10
SECTION 5
Operation
5.1 Safety Messages . . . . . . . . . . . . . . . . . . . . . . . . . . . . . . . . . . . . 5-1
5.2 Viewing Measurement Data . . . . . . . . . . . . . . . . . . . . . . . . . . . 5-2
5.3 Alarm Handling . . . . . . . . . . . . . . . . . . . . . . . . . . . . . . . . . . . . . 5-2
SECTION 6
Service and
Troubleshooting
6.1 Safety Messages . . . . . . . . . . . . . . . . . . . . . . . . . . . . . . . . . . . . 6-1
6.2 Service. . . . . . . . . . . . . . . . . . . . . . . . . . . . . . . . . . . . . . . . . . . . 6-2
6.2.1 Viewing Input and Holding Registers . . . . . . . . . . . . . 6-2
6.2.2 Backing Up the Gauge Configuration. . . . . . . . . . . . . 6-4
6.2.3 To Recover a Backup Configuration Database . . . . . 6-6
6.2.4 Diagnostics. . . . . . . . . . . . . . . . . . . . . . . . . . . . . . . . . 6-7
6.2.5 Upgrading the Gauge Software . . . . . . . . . . . . . . . . . 6-8
6.2.6 Write Protection . . . . . . . . . . . . . . . . . . . . . . . . . . . . 6-10
6.2.7 Write Protection Switch . . . . . . . . . . . . . . . . . . . . . . 6-11
6.2.8 Logging Measurement Data. . . . . . . . . . . . . . . . . . . 6-12
6.2.9 Exchanging Gauge Electronics . . . . . . . . . . . . . . . . 6-13
6.2.10 Calibration Using the WinSetup Calibrate function . 6-14
6.2.11 Loading the Default Database . . . . . . . . . . . . . . . . . 6-19
6.3 Troubleshooting. . . . . . . . . . . . . . . . . . . . . . . . . . . . . . . . . . . . 6-20
6.3.1 Device Status . . . . . . . . . . . . . . . . . . . . . . . . . . . . . . 6-22
6.3.2 Warning Messages . . . . . . . . . . . . . . . . . . . . . . . . . 6-23
6.3.3 Error Messages . . . . . . . . . . . . . . . . . . . . . . . . . . . . 6-25
6.3.4 Measurement Status . . . . . . . . . . . . . . . . . . . . . . . . 6-27
APPENDIX A
Reference Data
A.1 Specifications . . . . . . . . . . . . . . . . . . . . . . . . . . . . . . . . . . . . . .A-1
A.2 Dimensional drawings . . . . . . . . . . . . . . . . . . . . . . . . . . . . . . . .A-4
A.3 Ordering Information . . . . . . . . . . . . . . . . . . . . . . . . . . . . . . . . .A-8
A.3.1 Transmitter Head (TH) . . . . . . . . . . . . . . . . . . . . . . . .A-8
A.3.2 Horn Antenna . . . . . . . . . . . . . . . . . . . . . . . . . . . . . . .A-9
A.3.3 Parabolic Antenna . . . . . . . . . . . . . . . . . . . . . . . . . . .A-9
A.3.4 Still-pipe Array Antenna . . . . . . . . . . . . . . . . . . . . . .A-10
A.3.5 LPG/LNG Antenna . . . . . . . . . . . . . . . . . . . . . . . . . .A-11
A.3.6 5900S Radar Level Gauge Options . . . . . . . . . . . . . A-11
APPENDIX B
Product Certifications
B.1 Safety Messages . . . . . . . . . . . . . . . . . . . . . . . . . . . . . . . . . . . . B-1
B.2 EU Conformity . . . . . . . . . . . . . . . . . . . . . . . . . . . . . . . . . . . . . .B-2
B.3 Hazardous Locations Certifications . . . . . . . . . . . . . . . . . . . . . .B-3
B.3.1 Factory Mutual US Approvals . . . . . . . . . . . . . . . . . .B-3
Preliminary
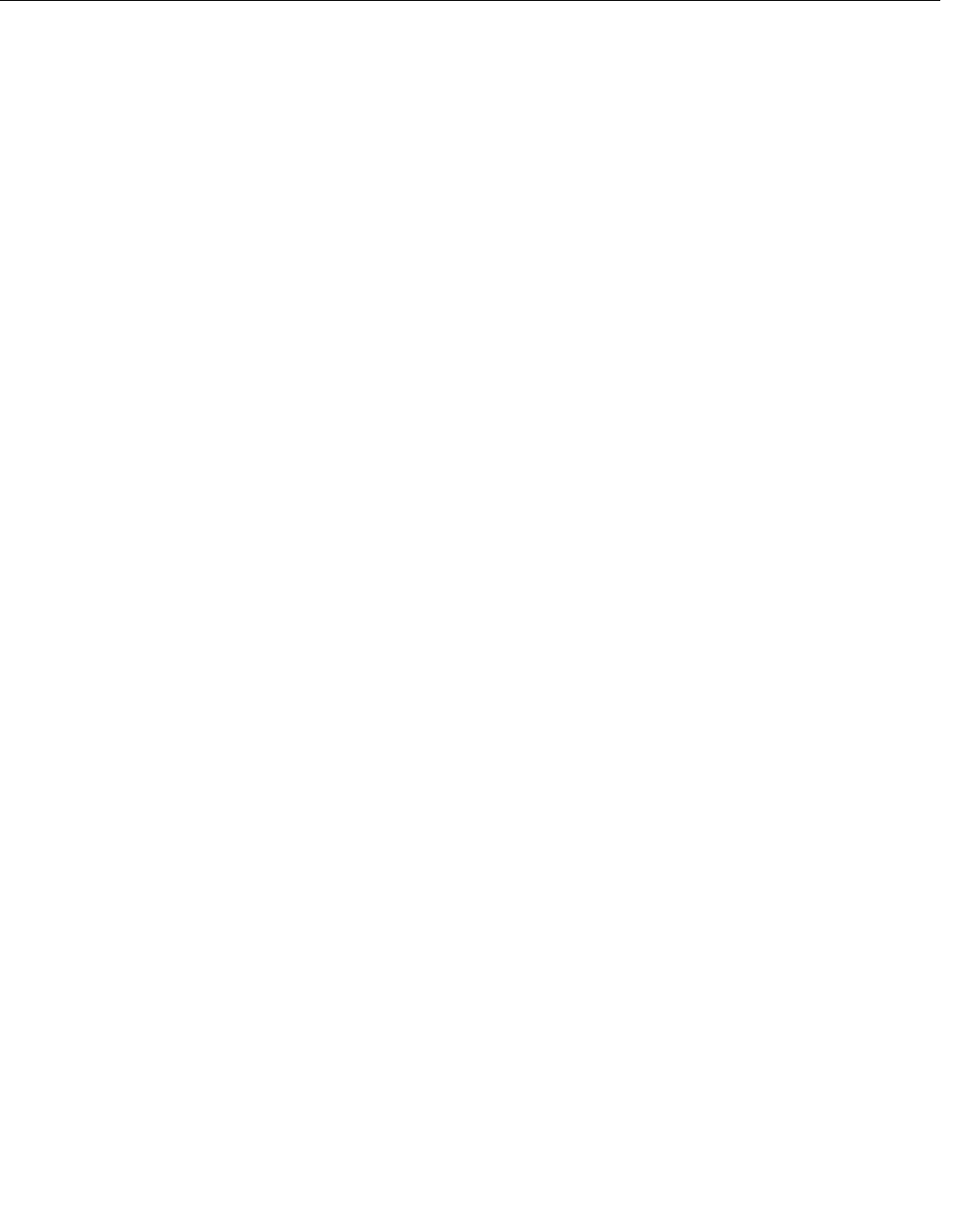
Reference Manual
300520EN, Rev AA
November 2009
TOC-3
Rosemount 5900 Series
Table of Contents
B.3.2 Factory Mutual Canadian Approvals . . . . . . . . . . . . .B-4
B.3.3 European ATEX Directive Information . . . . . . . . . . . .B-5
B.3.4 IECEx Approval . . . . . . . . . . . . . . . . . . . . . . . . . . . . . B-6
B.4 Approval Drawings . . . . . . . . . . . . . . . . . . . . . . . . . . . . . . . . . . B-7
APPENDIX C
Advanced Configuration
C.1 Safety messages . . . . . . . . . . . . . . . . . . . . . . . . . . . . . . . . . . . .C-1
C.2 Winsetup Advanced Configuration . . . . . . . . . . . . . . . . . . . . . .C-3
C.3 Tank Scan . . . . . . . . . . . . . . . . . . . . . . . . . . . . . . . . . . . . . . . . .C-4
C.4 Empty Tank Handling . . . . . . . . . . . . . . . . . . . . . . . . . . . . . . . .C-5
C.5 Surface Echo Tracking . . . . . . . . . . . . . . . . . . . . . . . . . . . . . . .C-9
C.6 Filter Setting . . . . . . . . . . . . . . . . . . . . . . . . . . . . . . . . . . . . . .C-11
Preliminary
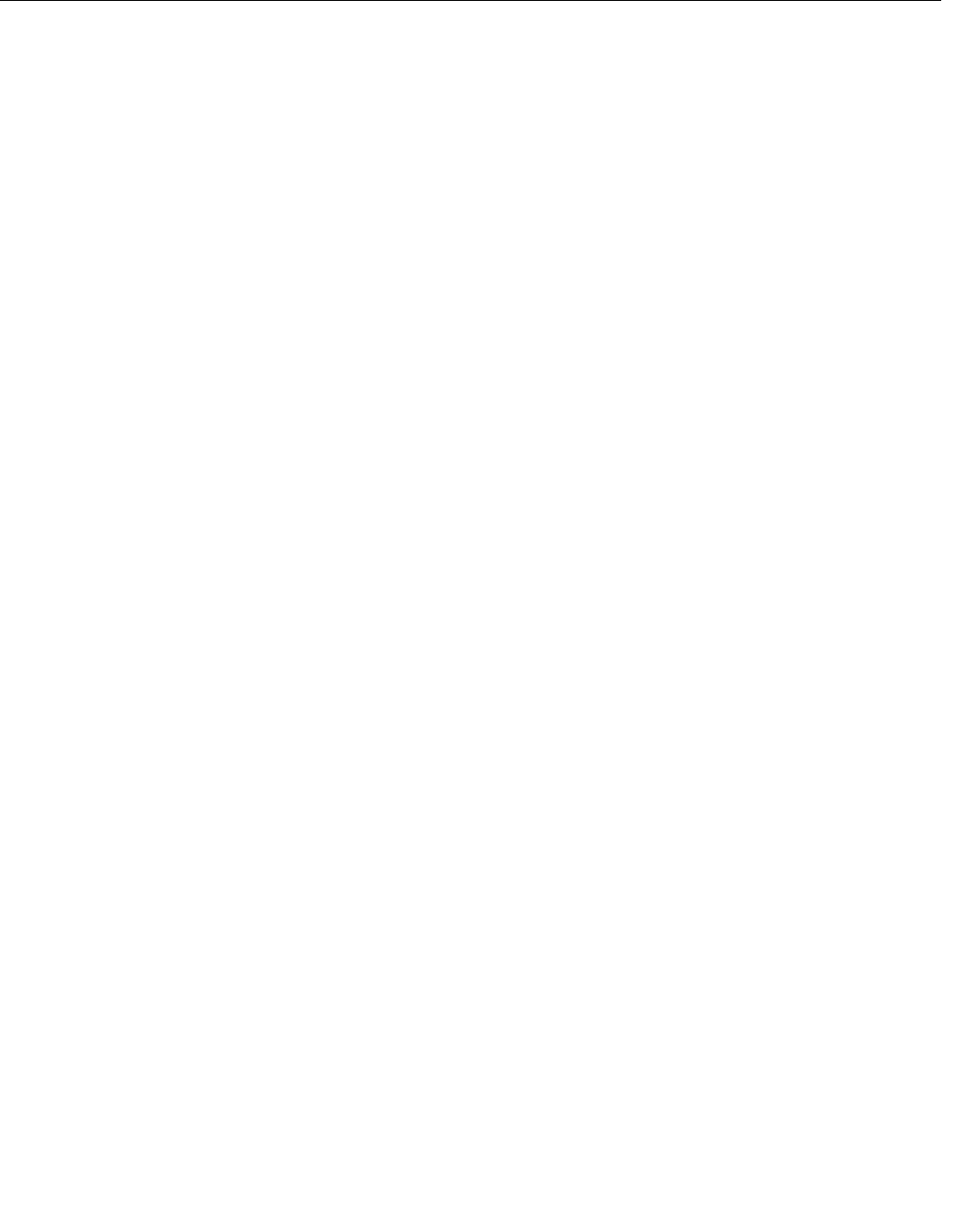
Reference Manual
300520EN, Rev AA
November 2009
Rosemount 5900 Series
TOC-4 Table of Contents
Preliminary
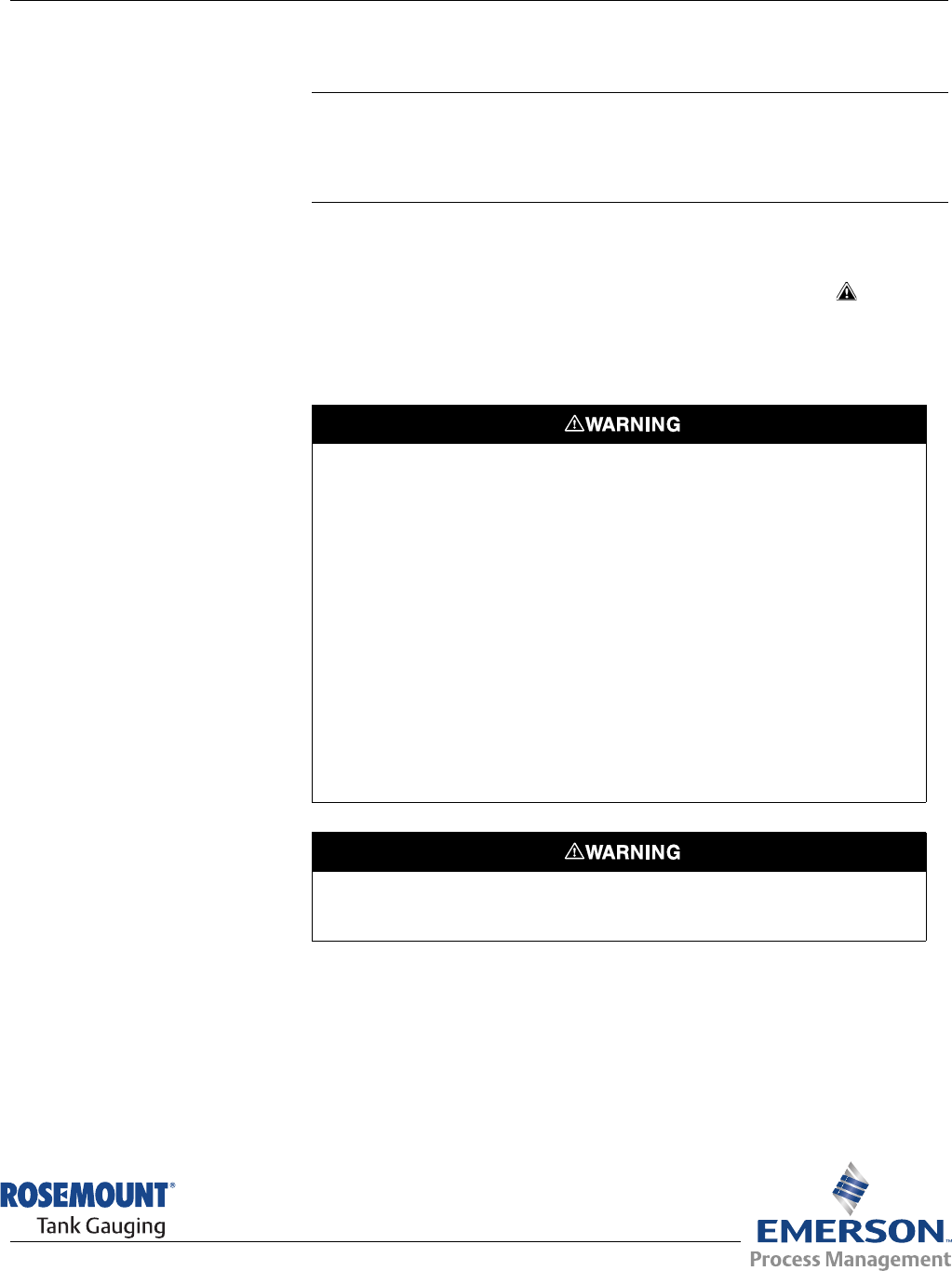
Reference Manual
300520EN, Rev AA
November 2009 Rosemount 5900 Series
www.rosemount-tg.com
Section 1 Introduction
1.1 Safety Messages . . . . . . . . . . . . . . . . . . . . . . . . . . . . page 1-1
1.2 Symbols . . . . . . . . . . . . . . . . . . . . . . . . . . . . . . . . . . . page 1-2
1.3 Manual Overview . . . . . . . . . . . . . . . . . . . . . . . . . . . page 1-3
1.4 Service Support . . . . . . . . . . . . . . . . . . . . . . . . . . . . page 1-4
1.1 SAFETY
MESSAGES
Procedures and instructions in this manual may require special precautions to
ensure the safety of the personnel performing the operations. Information that
raises potential safety issues is indicated by a warning symbol ( ). Refer to
the safety messages listed at the beginning of each section before performing
an operation preceded by this symbol.
Failure to follow these installation guidelines could result in death or serious
injury:
• Make sure only qualified personnel perform the installation.
• Use the equipment only as specified in this manual. Failure to do so may
impair the protection provided by the equipment.
Explosions could result in death or serious injury:
• Verify that the operating environment of the transmitter is consistent with the
appropriate hazardous locations certifications.
• Before connecting a communicator in an explosive atmosphere, make sure the
instruments in the loop are installed in accordance with intrinsically safe or
non-incendive field wiring practices.
• Do not remove the gauge cover in explosive atmospheres when the circuit is
alive.
Electrical shock could cause death or serious injury.
• Use extreme caution when making contact with the leads and terminals.
Any substitution of non-recognized parts may jeopardize safety. Repair, e.g. substitution
of components etc., may also jeopardize safety and is under no circumstances allowed.
Preliminary
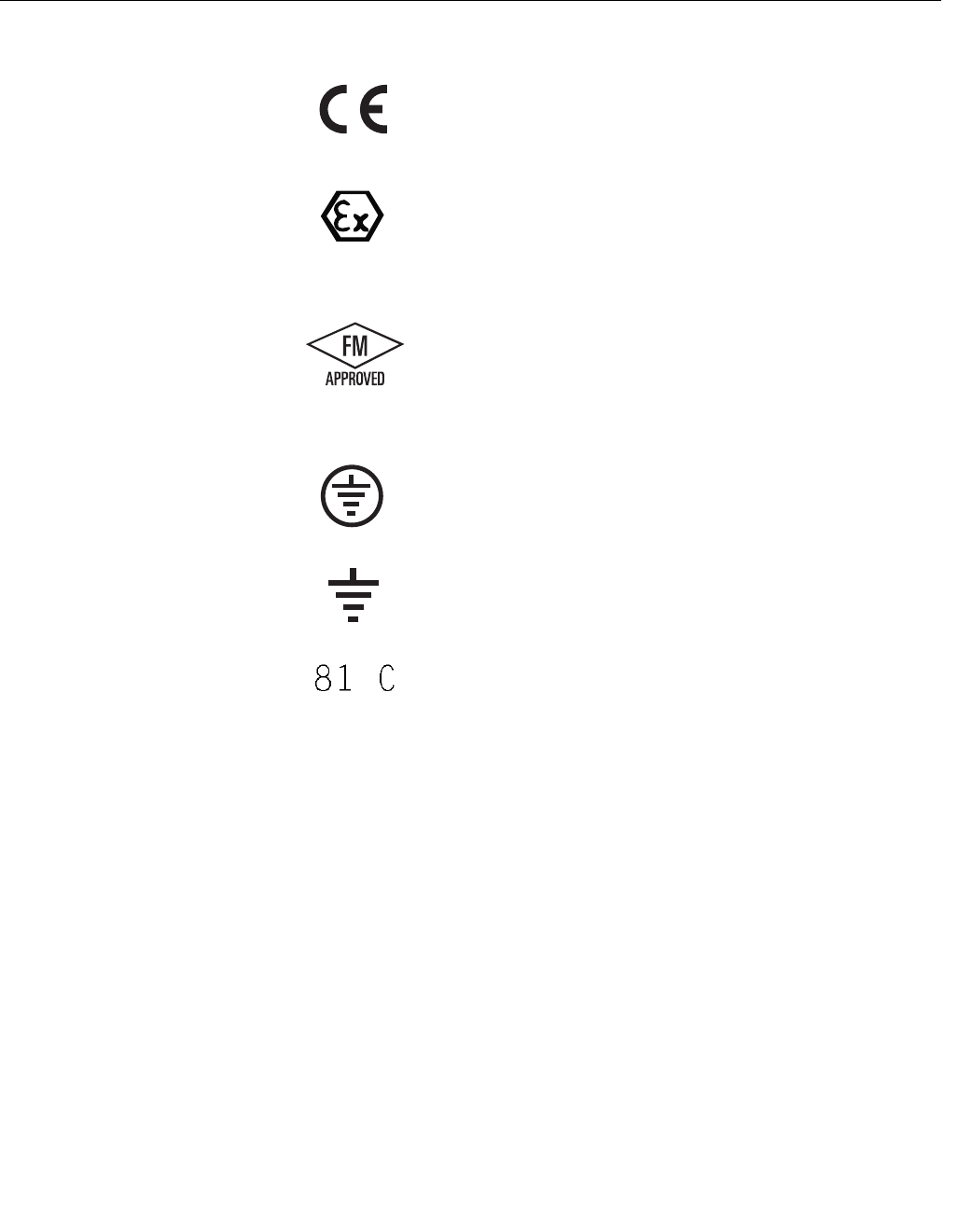
Reference Manual
300520EN, Rev AA
November 2009
Rosemount 5900 Series
1-2 Section 1. Introduction
1.2 SYMBOLS
The CE marking symbolises the conformity
of the product with the applicable European
Community Directives.
The EC-Type Examination Certificate is a
statement of a Notified Certification Body
declaring that this product meets the
Essential Health and Safety Requirements
of the ATEX directive
The FM APPROVED Mark indicates that the
equipment is approved by FM Approvals
according to applicable Approval Standards
and is applicable for installation in
hazardous locations
Protective Earth
Ground
External cabling must be approved for use in
min. 81°C
Preliminary
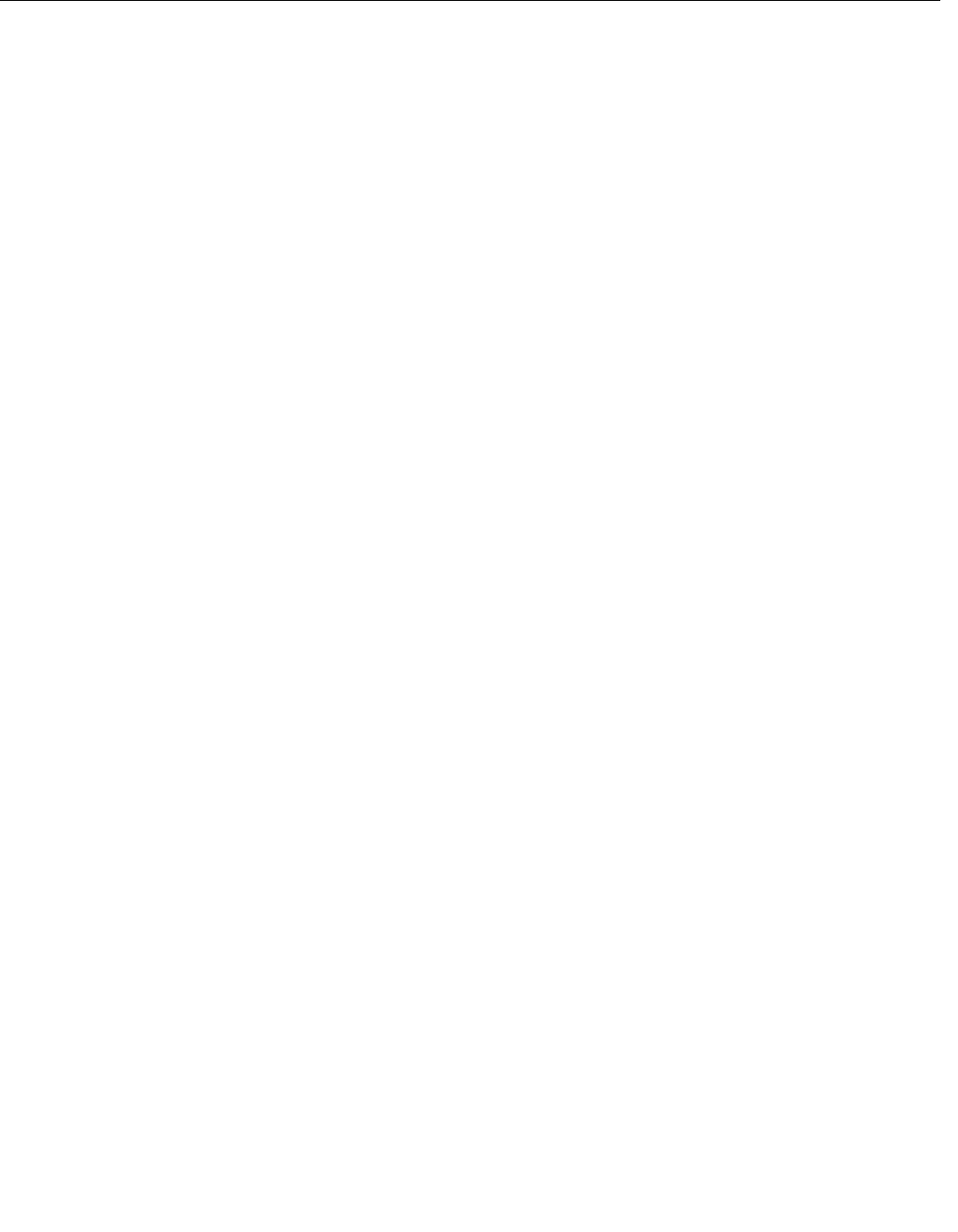
Reference Manual
300520EN, Rev AA
November 2009
1-3
Rosemount 5900 Series
Section 1. Introduction
1.3 MANUAL
OVERVIEW
This manual provides installation, configuration, and maintenance information
for the Rosemount 5900 Series Radar Level Gauge.
Section 2: Overview
• Gauge components
• System overview
• Antenna types
• Installation procedure
Section 3: Installation
• Installation considerations
• Mechanical installation
• Electrical installation
Section 4: Configuration
• Basic configuration
• Configuration using TankMaster WinSetup
• LPG configuration
Section 5: Operation
• Viewing measurement data
• Alarm handling
Section 6: Service and Troubleshooting
• Serivce functions
• Troubleshooting
• Device and measurement status
• Error and warning codes
Appendix A: Reference Data
• Specifications
• Ordering Information
Appendix B: Product Certifications
• European ATEX Directive information
• FM approvals
• Labels
•Drawings
Appendix C: Advanced Configuration
•Tank scan
• Empty tank handling
• Surface echo tracking
• Filter settings
Preliminary
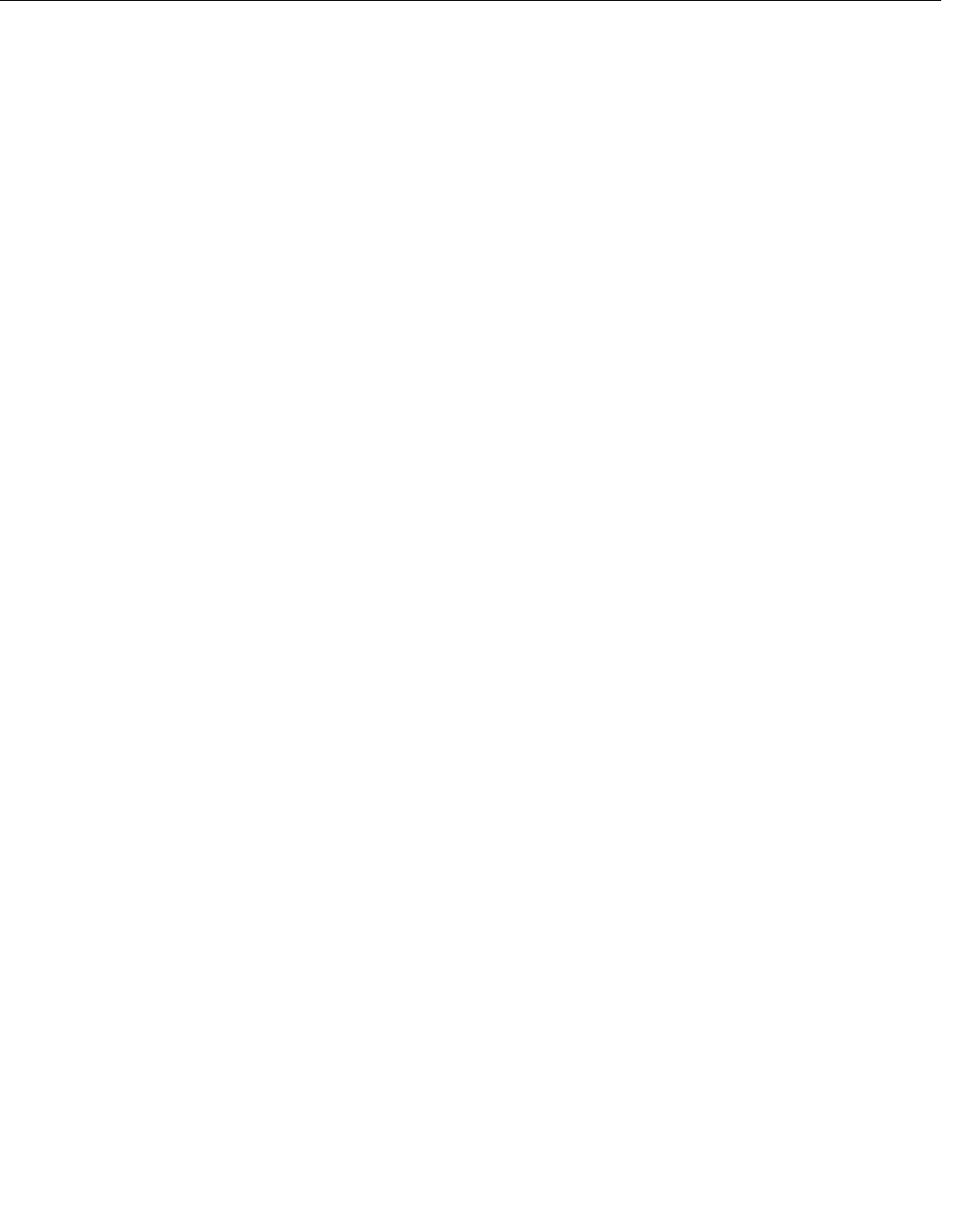
Reference Manual
300520EN, Rev AA
November 2009
Rosemount 5900 Series
1-4 Section 1. Introduction
1.4 SERVICE SUPPORT To expedite the return process contact the nearest Emerson Process
Management/Rosemount Tank Gauging representative.
Preliminary
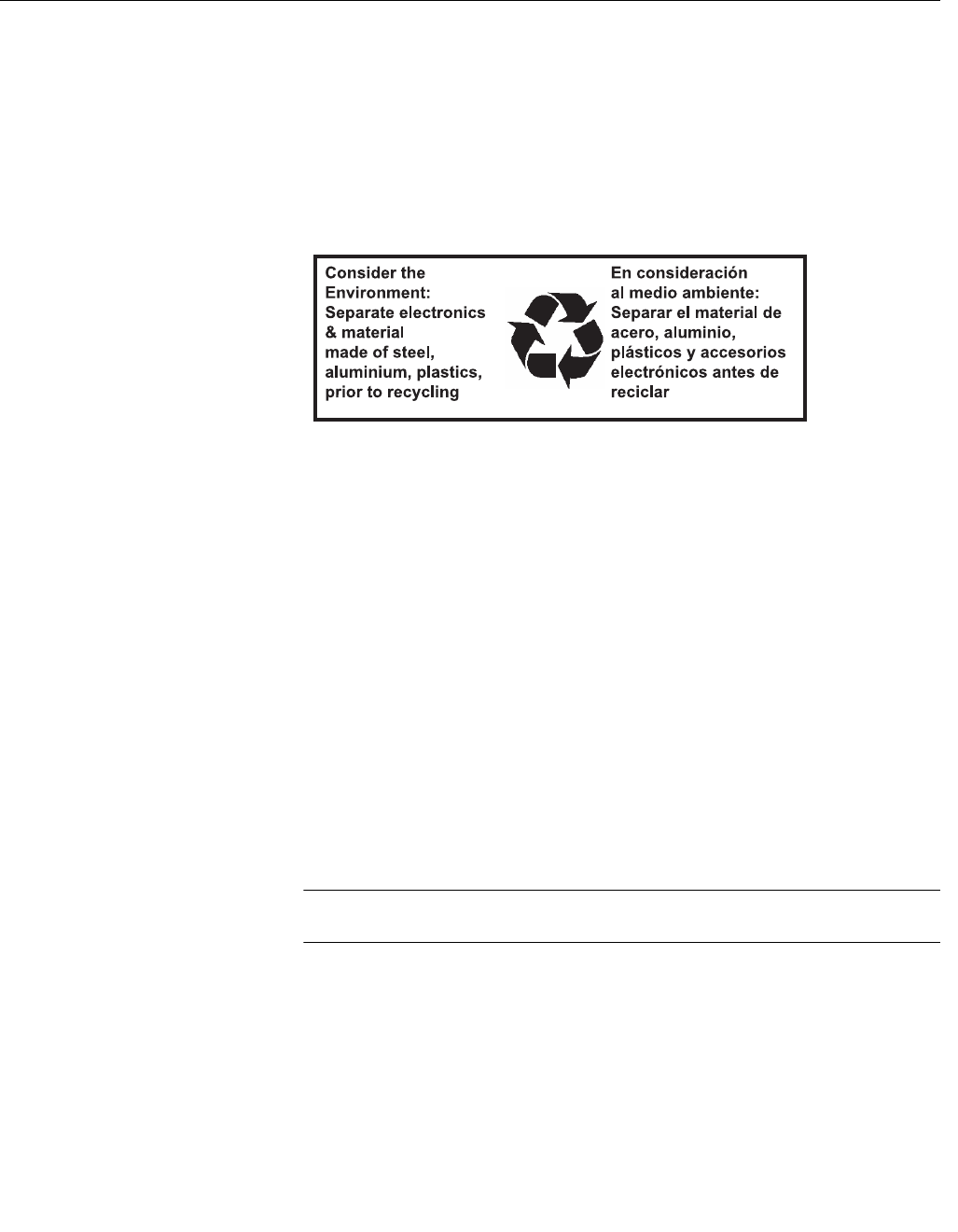
Reference Manual
300520EN, Rev AA
November 2009
1-5
Rosemount 5900 Series
Section 1. Introduction
1.5 PRODUCT
RECYCLING/
DISPOSAL
Recycling of equipment and packaging should be taken into consideration
and disposed of in accordance with local and national legislation/regulations.
The label below is put on Rosemount Tank Gauging products as a
recommendation to customers if scrapping is considered.
Recycling or disposal should be done following instructions for correct
separation of materials when breaking up the units.
Figure 1-1. A green label is
placed on the housing of the
level gauge
1.6 PACKING
MATERIAL
Rosemount Tank Radar AB is fully certified according to ISO 14000
environmental standards. By recycling the plywood boxes material used for
shipping our products you can contribute to take care of the environment.
1.6.1 Reuse Experience has shown that NEFAB ExPak packaging can be used 4-5 times.
1.6.2 Recycling After careful disassembly the plywood sides may be reused. Metal waste may
be converted.
1.6.3 Energy recovery Products which have served their time may be divided into wood and metal
components and the wood can be used as fuel in sufficient ovens.
Due to its low moisture content (approximately 7%) this fuel has a higher
calorific value than ordinary wood fuel (moisture content approximately 20%).
When burning interior plywood the nitrogen in the adhesives may increase
emissions of nitrogen oxides to the air 3-4 times more than when burning bark
and splinter.
NOTE!
Landfill is not a recycling option and should be avoided.
Preliminary
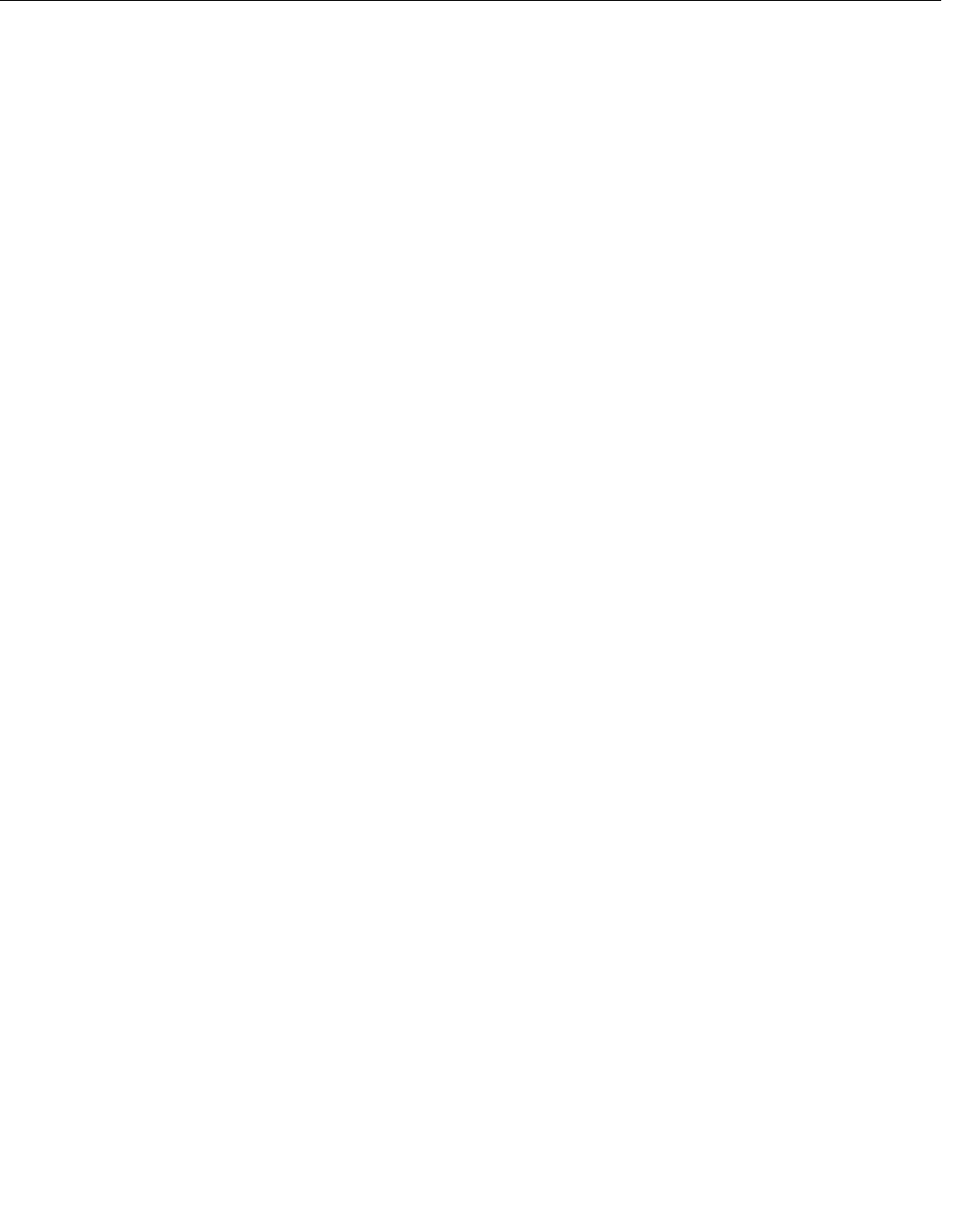
Reference Manual
300520EN, Rev AA
November 2009
Rosemount 5900 Series
1-6 Section 1. Introduction
Preliminary
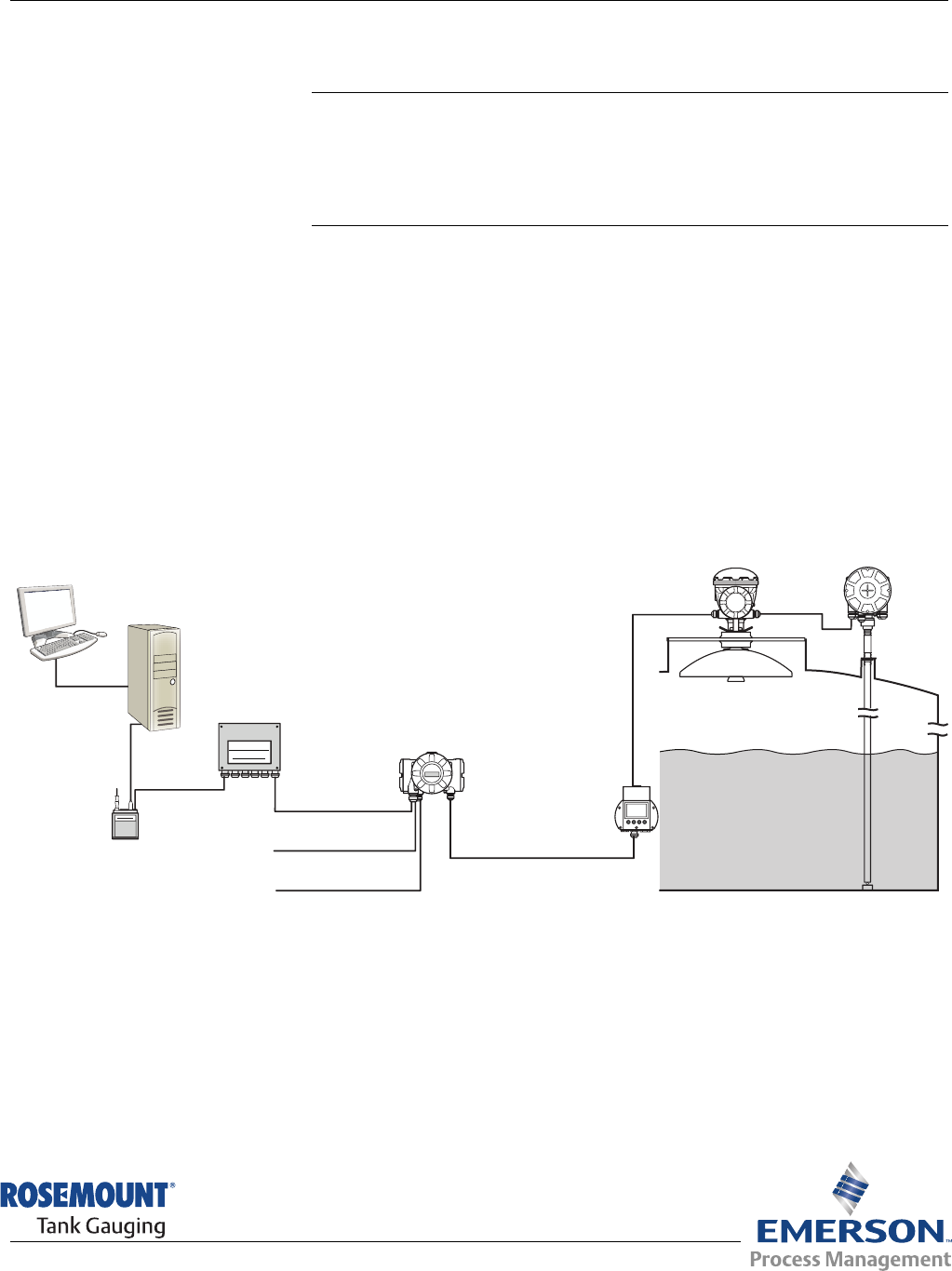
Reference Manual
300520EN, Rev AA
November 2009 Rosemount 5900 Series
www.rosemount-tg.com
Section 2 Overview
2.1 Introduction . . . . . . . . . . . . . . . . . . . . . . . . . . . . . . . . page 2-1
2.2 Components . . . . . . . . . . . . . . . . . . . . . . . . . . . . . . . page 2-2
2.3 System Overview . . . . . . . . . . . . . . . . . . . . . . . . . . . page 2-3
2.4 Antennas . . . . . . . . . . . . . . . . . . . . . . . . . . . . . . . . . . page 2-7
2.5 Installation Procedure . . . . . . . . . . . . . . . . . . . . . . . page 2-9
2.1 INTRODUCTION The Rosemount 5900 is a two-wire radar level gauge for high accuracy
non-contact measurements. The gauge continously emits a radar signal with
varying frequency towards the product surface. This allows very accurate
level measurements by processing the different frequencies between the
emitted and received radar signals.
The Rosemount 5900 is an integral part of the flexible Rosemount Raptor
system. The advanced and robust design makes it suitable for a vast range of
applications. It is capable of high accuracy level measurements as well as
handling obstacles that may interfere with measurement signals.
Figure 2-1. System integration
The Rosemount 5900 delivers measurement data and status information to a
Rosemount 2410 tank hub via the intrinsically safe Tankbus.
Data from a group of tanks is buffered by a 2160 Field Communication Unit
(FCU), and is distributed via the Group Bus to a TankMaster PC, or a host
system, whenever the FCU receives a request for data.
TankMaster
Rosemount 2410 Tank Hub
Modem
FCU 2160
Relay outputs
Secondary bus
Primary Bus
Intrinsically
safe Tankbus
Rosemount 5900 Rosemount 2240
Rosemount 2230
Group Bus
Preliminary
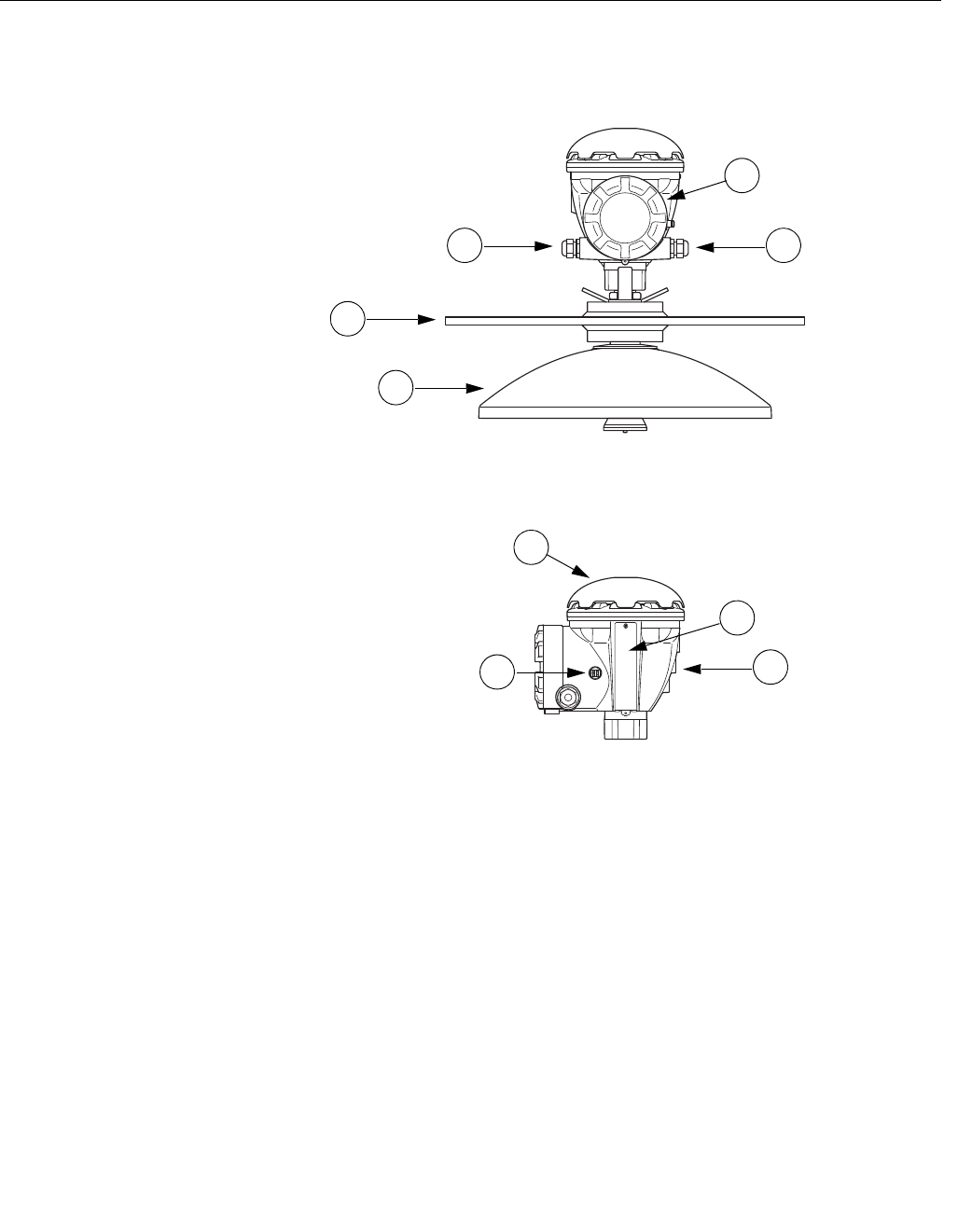
Reference Manual
300520EN, Rev AA
November 2009
Rosemount 5900 Series
2-2 Section 2. Overview
2.2 COMPONENTS
Figure 2-2. Rosemount 5900
components
1. Terminal compartment
2. Cable entries
3. Flange
4. Antenna
5. Grounding terminal
6. Weather protection hood
7. Label
8. Transmitter head with signal processing electronics
22
1
4
6
58
3
7
Preliminary
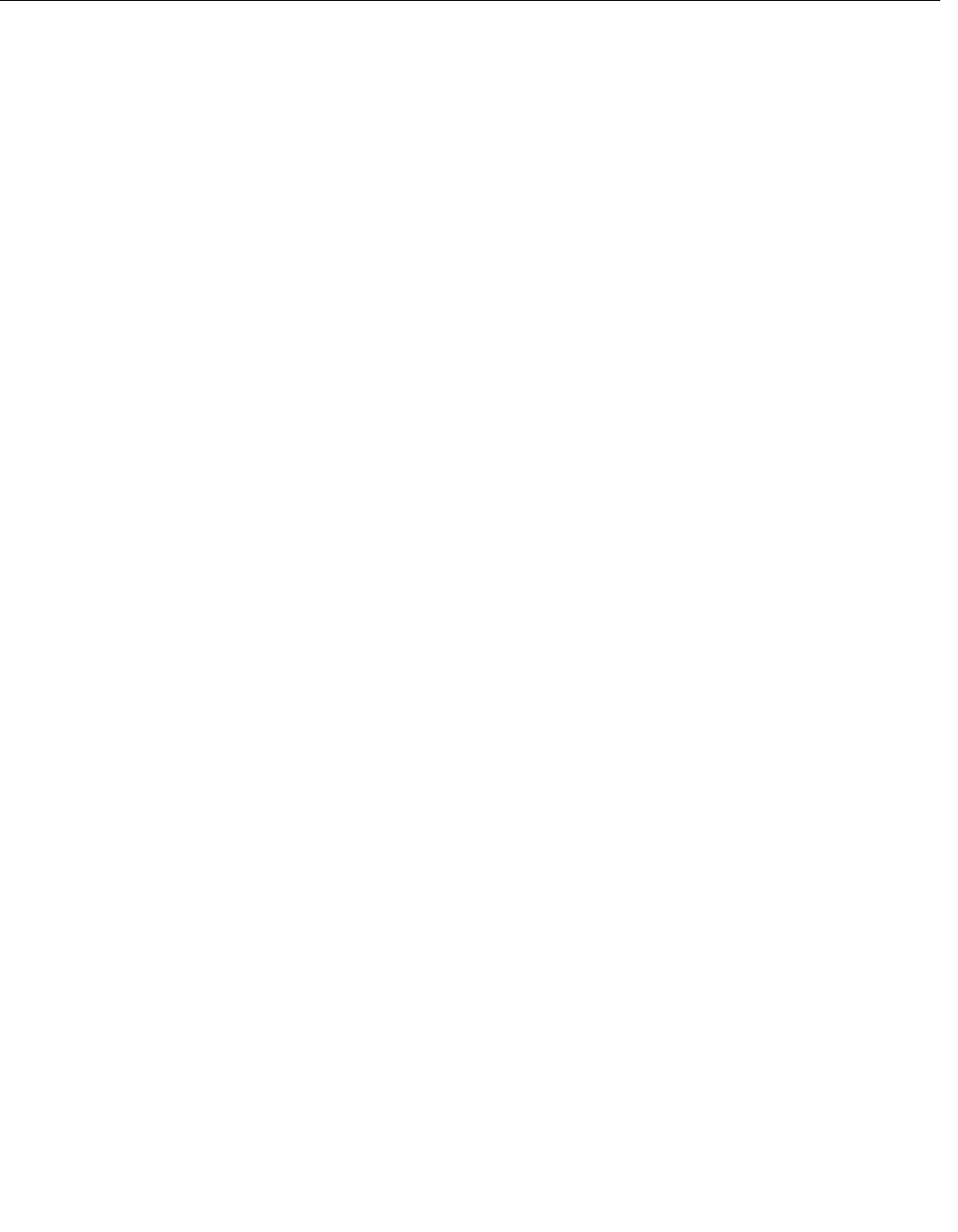
Reference Manual
300520EN, Rev AA
November 2009
2-3
Rosemount 5900 Series
Section 2. Overview
2.3 SYSTEM
OVERVIEW
Rosemount Raptor is a revolutionary, state-of-the art, inventory and custody
transfer radar tank level gauging system. It is developed for a wide range of
applications at refineries, tank farms and fuel depots, and fulfills the highest
requirements on performance and safety.
The Rosemount Raptor product portfolio includes a wide range of
components to build small or large customized tank gauging systems. The
system includes various devices, such as radar level gauges, temperature
transmitters, and pressure transmitters for complete inventory control. Such
systems are easily expanded thanks to the modular design.
Rosemount Raptor is a versatile system that is compatible with and can
emulate all major tank gauging systems. Moreover, the well-proven emulation
capability enables step-by-step modernization of a tank farm, from level
gauges to control room solutions.
It is possible to replace old mechanical or servo gauges with modern
Rosemount Raptor gauges, without replacing the control system or field
cabling. It is further possible to replace old HMI/SCADA-systems and field
communication devices without replacing the old gauges.
There is a distributed intelligence in the various system units which
continously collect and process measurement data and status information.
When a request for information is received an immediate response is sent
with updated information.
The field devices on the tank communicate over the intrinsically safe
Rosemount Raptor Tankbus. The Tankbus is based on a standardized
fieldbus, the FISCO(1) FOUNDATION™ fieldbus, and allows integration of any
device supporting that protocol. By utilizing a 2-wire field bus the power
consumtion is minimized. The standardized field bus also enables integration
of other vendors’ equipment on the tank.
The flexible Rosemount Raptor system supports several combinations to
achieve redundancy, from control room to the different field devices.
Redundant network configuration can be achived at all levels by doubling
each unit and using multiple control room work stations.
(1) See reference document IEC/TS 60079-27
Preliminary
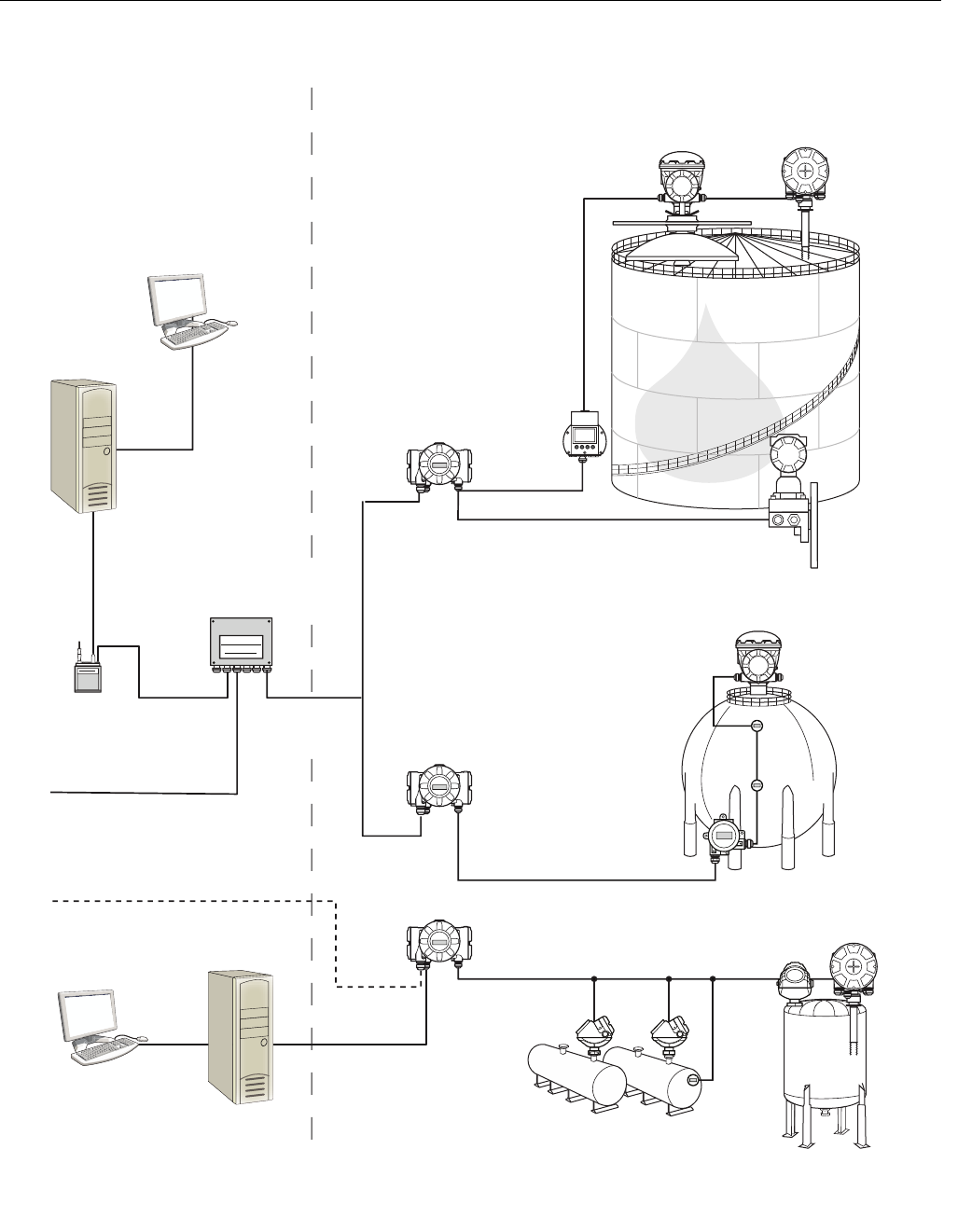
Reference Manual
300520EN, Rev AA
November 2009
Rosemount 5900 Series
2-4 Section 2. Overview
Figure 2-3. Raptor system
architecture
Rosemount 2230
Graphical Field
Display
Rosemount 2240
Multi-input Temperature
Transmitter
Rosemount 5900
Radar Level Gauge
Raptor Tankbus
Rosemount 2410
Tank Hub
Intrinsically safe Tankbus
Rosemount 5300
Level Transmitter
2240
Rosemount 5400
Radar Level
Transmitter
Rosemount 5900
Rosemount 3051S
Pressure Transmitter
TRL2 Modbus
/ 485 Modbus
Group bus
Field Bus
Modem
Rosemount 2160
Field Communication Unit
TankMaster PC
Plant Host
Computer 644
644
644
Rosemount 644
Temperature
Transmitter
TankMaster PC
Plant Host
Computer
Non-Hazardous area Hazardous area
Rosemount 2410
Tank Hub
Rosemount 2410
Tank Hub
Preliminary
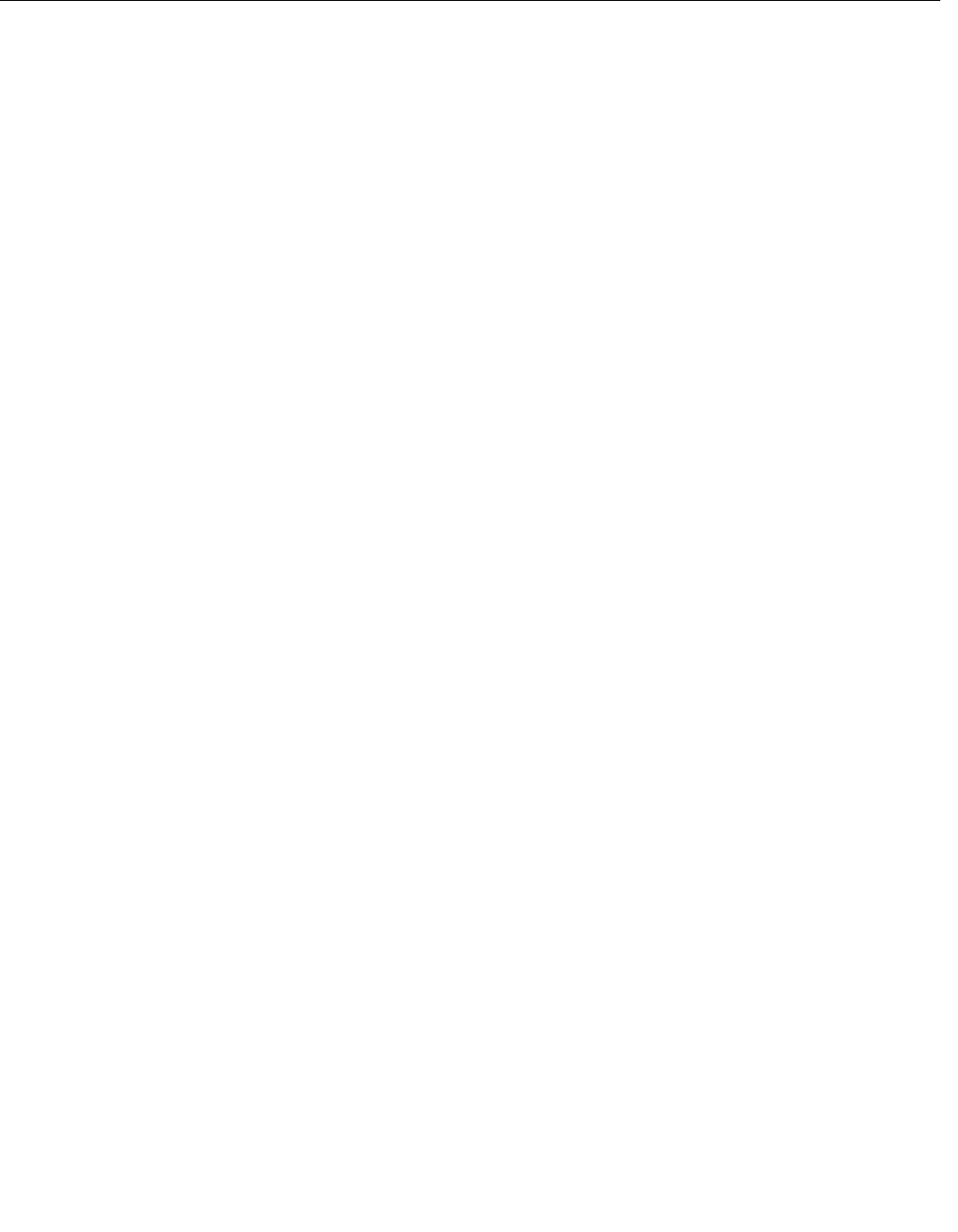
Reference Manual
300520EN, Rev AA
November 2009
2-5
Rosemount 5900 Series
Section 2. Overview
TankMaster HMI Software
TankMaster is a powerful Windows-based Human Machine Interface (HMI) for
complete tank inventory management. It provides configuration, service,
set-up, inventory, and custody transfer functions for Rosemount Raptor
systems and other supported instruments.
TankMaster is designed to be used in the Microsoft® Windows XP and Vista
environment providing easy access to measurement data from your Local
Area Network.
The TankMaster WinOpi program lets the operator monitor measured tank
data. It includes alarm handling, batch reports, automatic report handling,
historical data sampling as well as inventory calculations such as Volume,
Observed Density and other parameters. A plant host computer can be
connected for further processing of data.
The TankMaster WinSetup program is a graphical user interface for
installation, configuration and service of the different devices in the
Rosemount Raptor system.
Rosemount 2160 Field Communication Unit
The 2160 field communication unit (FCU) is a data concentrator that
continuously polls and stores data from field devices such as radar level
gauges and temperature transmitters in a buffer memory. Whenever a request
for data is received, the FCU can immediately send data from a group of tanks
from the updated buffer memory.
Rosemount 2410 Tank Hub
The Rosemount 2410 tank hub acts as a power supply to the connected field
devices in the hazardous area using the intrinsically safe Raptor Tankbus.
The Rosemount 2410 tank hub collects measurement data and status
information from field devices on a tank. It has two external buses for
communication with various host systems.
Rosemount 5900 Radar Level Gauge
The Rosemount 5900 radar level gauge is an intelligent instrument for
measuring the product level inside a tank. Different antennas can be used in
order to meet the requirements of different applications. The 5900 can
measure the level of almost any product, including bitumen, crude oil, refined
products, aggressive chemicals, LPG and LNG.
The Rosemount 5900 sends microwaves towards the surface of the product
in the tank. The level is calculated based on the echo from the surface. No
part of the 5900 is in actual contact with the product in the tank, and the
antenna is the only part of the gauge that is exposed to the tank atmosphere.
The 5900 2-in-1 option makes the radar level gauge redundant to electric
circuit failure. Two separate radar units in the same transmitter head allows
two independent level measurements using one antenna.
Preliminary
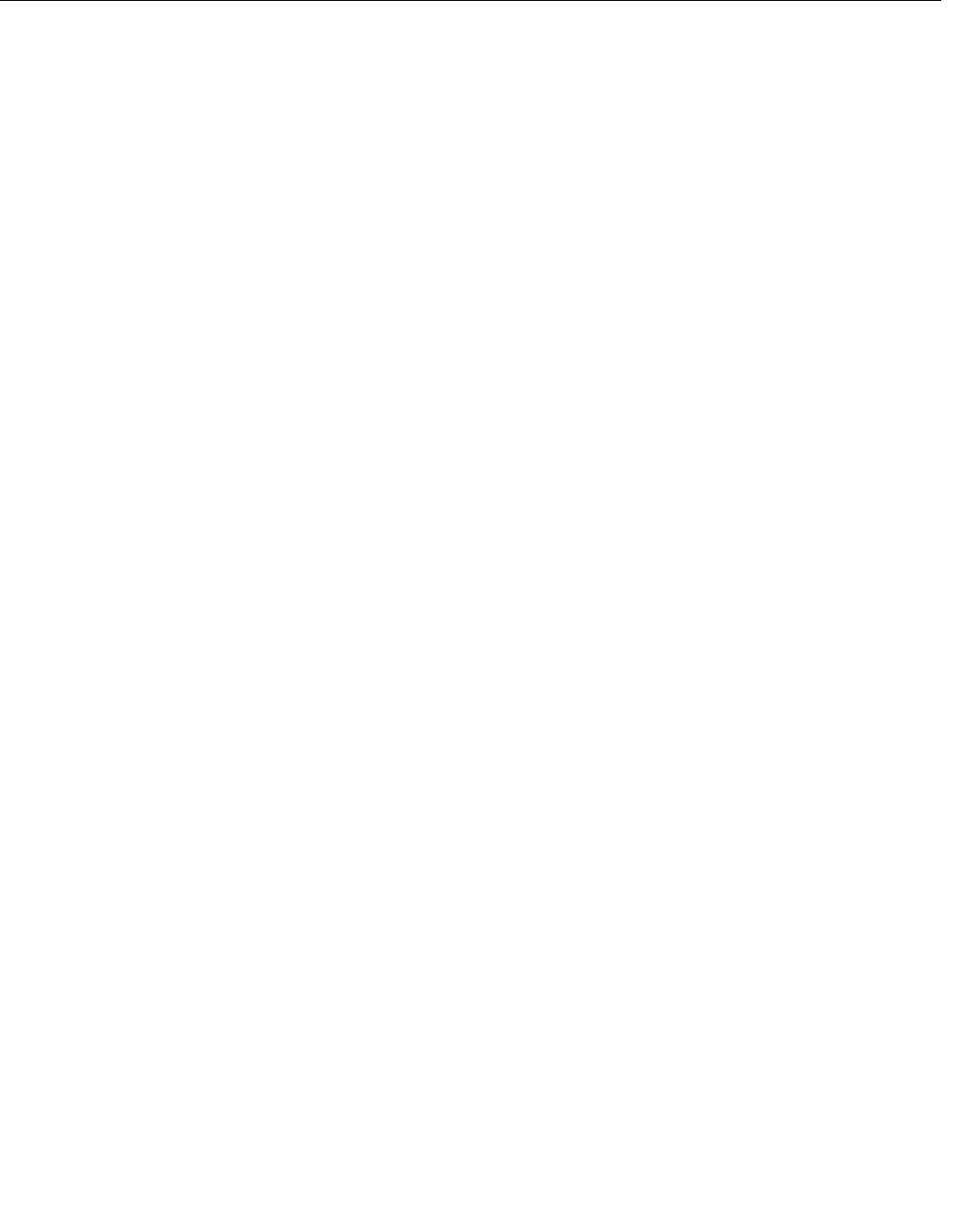
Reference Manual
300520EN, Rev AA
November 2009
Rosemount 5900 Series
2-6 Section 2. Overview
Rosemount 2240 Multi-Input Temperature Transmitter
The Rosemount 2240 multi-input temperature transmitter can connect up to
16 temperature spot sensors and an integrated water level sensor.
Rosemount 2230 Graphical Field Display
The Rosemount 2230 graphical field display presents inventory tank gauging
data such as level, temperature, and pressure. The four softkeys allow you to
navigate through the different menus to provide all tank data, directly in the
field. The Rosemount 2230 supports up to 10 tanks.
Rosemount 644 Temperature Transmitter
The Rosemount 644 is used with single spot temperature sensors.
Rosemount 3051S Pressure Transmitter
The 3051S series consists of transmitters and flanges suitable for all kinds of
applications, including crude oil tanks, pressurized tanks and tanks with /
without floating roofs.
When a radar level gauge is connected to a pressure transmitter near the
bottom of the tank, the density of the product can be calculated and
presented. One or more pressure transmitters with different scalings can be
used on the same tank to measure vapor and liquid pressure.
Rosemount 2180 Field Bus Modem
The Rosemount 2180 field bus modem (FBM) is used for connecting a
TankMaster PC to the TRL/2 communication bus. The 2180 is connected to
the PC using either the RS232 or the USB interface.
Preliminary
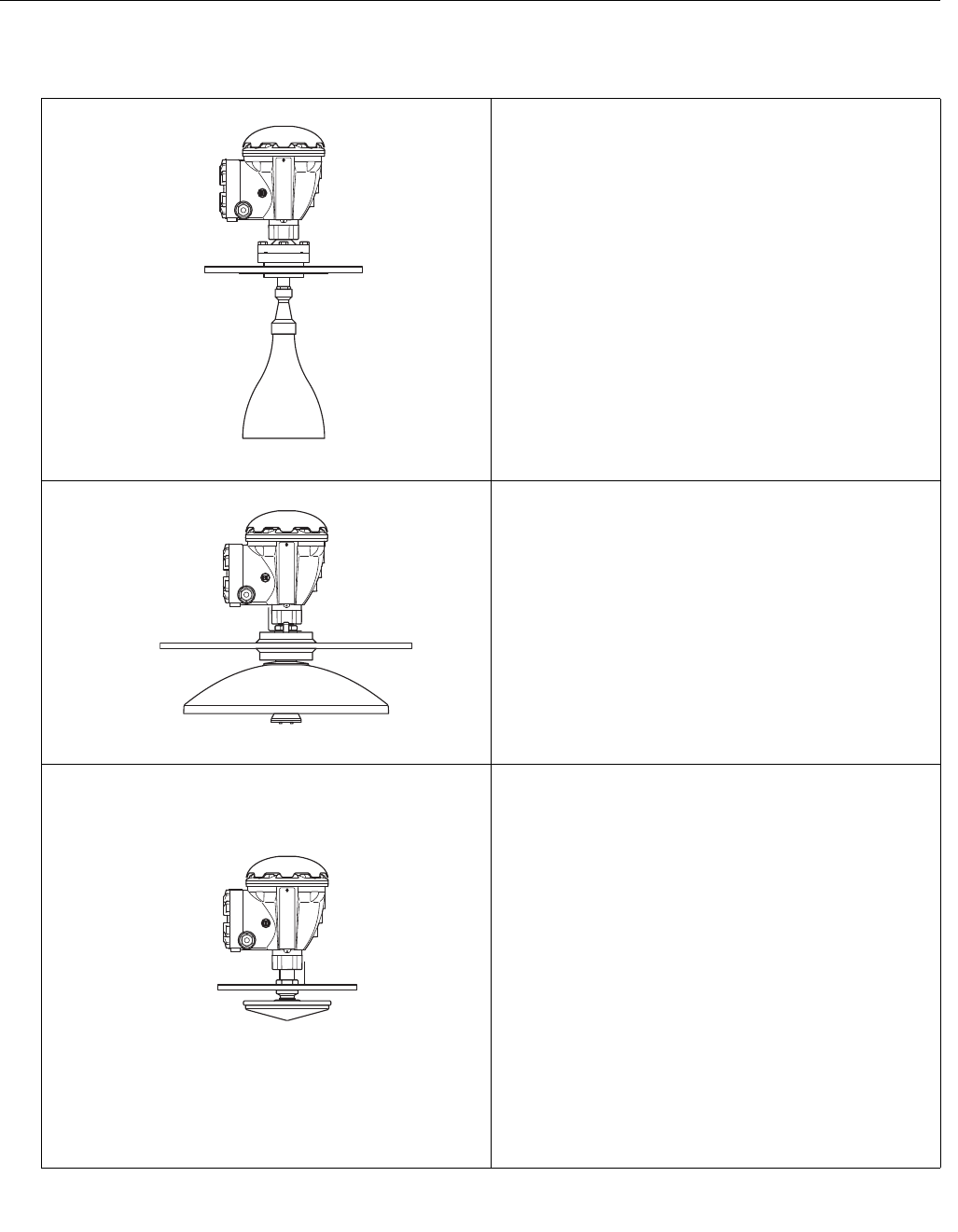
Reference Manual
300520EN, Rev AA
November 2009
2-7
Rosemount 5900 Series
Section 2. Overview
2.4 ANTENNAS
The Rosemount 5900 with horn antenna is designed
for an 8” antenna to be used in small size openings
on fixed roofs tanks.
The 5920 is designed for measurements of a variety
of oil products and chemicals. However, for
bitumen/asphalt and similar products the Parabolic
antenna is recommended.
The Rosemount 5900 with parabolic antenna
measures level of all types of liquids, from light
products to bitumen/asphalt. The gauge is designed
for mounting on tanks with fixed roofs and has
custody transfer accuracy.
The design of the parabolic antenna provides
extreme tolerance against sticky and condensing
products. The narrow beam of this antenna makes it
very suitable in narrow tanks with internal structures.
The Rosemount 5900 with still pipe array antenna is
used on tanks with still pipes and with all products
suited for still pipes.
The gauge uses a low-loss radar propagation mode
which virtually eliminates the influence of the still pipe
condition. Measurement is made with highest
accuracy even when the pipe is old, rusty and
covered with deposits.
The Still Pipe Gauge fits 5”, 6", 8", 10" and 12" pipes.
It can be mounted on an existing still pipe and there
is no need to take the tank out of operation during
installation.
There are two versions of the 5900 with still pipe
array antenna: fixed and hinged hatch. The hinged
hatch enables full pipe size product sampling or
verification hand-dips.
Preliminary

Reference Manual
300520EN, Rev AA
November 2009
Rosemount 5900 Series
2-8 Section 2. Overview
The Rosemount 5900 with LPG/LNG antenna is
designed for level measurements in LPG and LNG
tanks. A 4” still pipe is used as a wave guide for the
measurement and prevents a wavy or boiling surface
from disturbing the measurement. Radar signals are
transmitted inside the pipe towards the surface.
The pressure sealing is a quarts window approved for
use in pressure vessels. As standard the gauge is
also equipped with a fire-proof block valve and a
vapor space pressure sensor.
The Rosemount 5960 is available in two versions, a
150 PSI version and a 300 PSI version.
The patented reference pin function enables
verification of measurement without opening the tank.
By setting the gauge into “test mode” the measured
distances are compared with the actual distances.
Preliminary
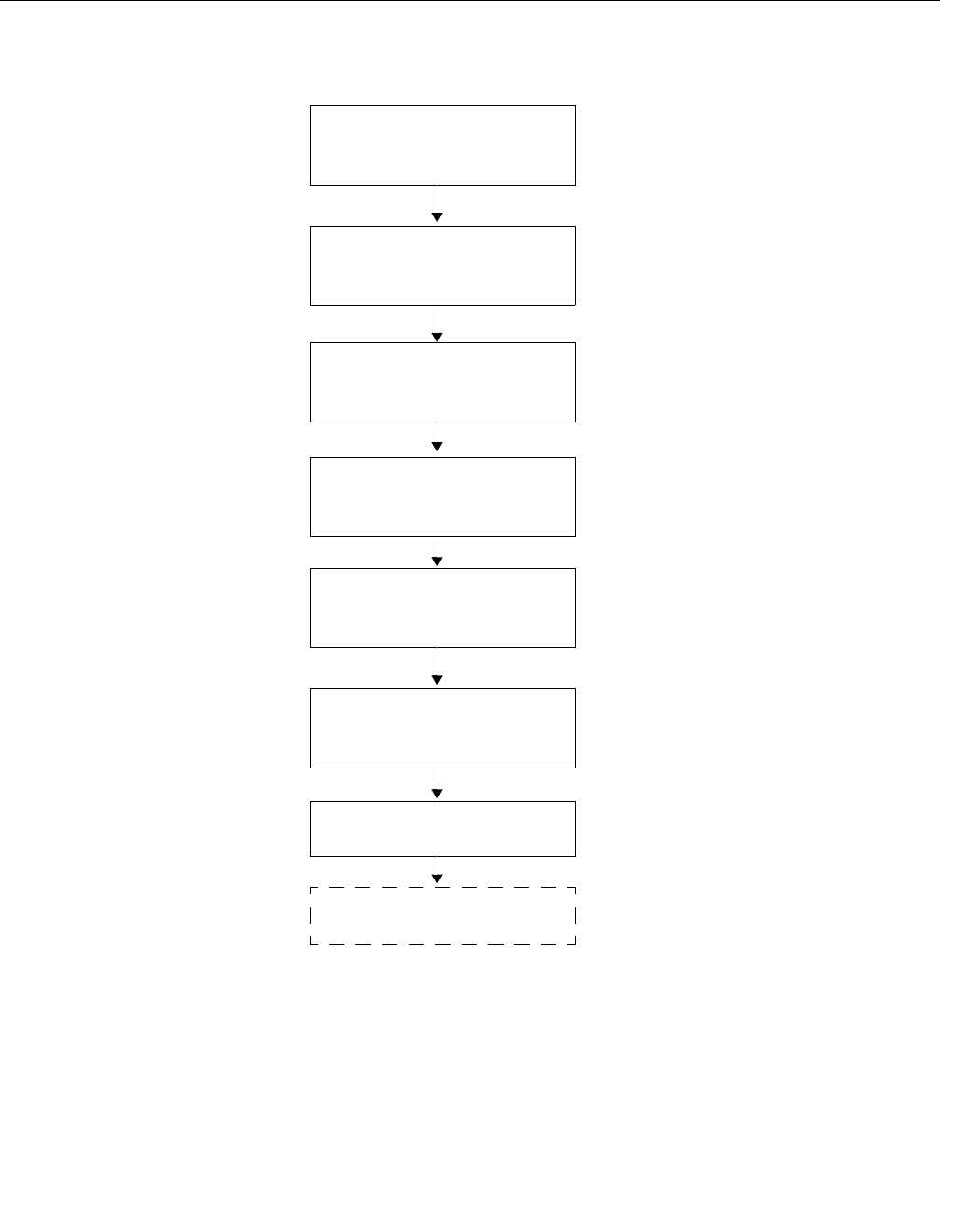
Reference Manual
300520EN, Rev AA
November 2009
2-9
Rosemount 5900 Series
Section 2. Overview
2.5 INSTALLATION
PROCEDURE
Follow these steps for proper installation:
Review Mounting Considerations.
See “Installation Considerations”
on page 3-3.
Mount the transmitter.
See “Mechanical Installation” on
page 3-18.
Wire the transmitter.
See “Electrical Installation” on
page 3-39.
Make sure covers
and cable/conduit
connections are tight
Power Up the
transmitter
Configure the transmitter.
See Section 4: Configuration.
Verify measurements
Set the Write
Protection
Preliminary
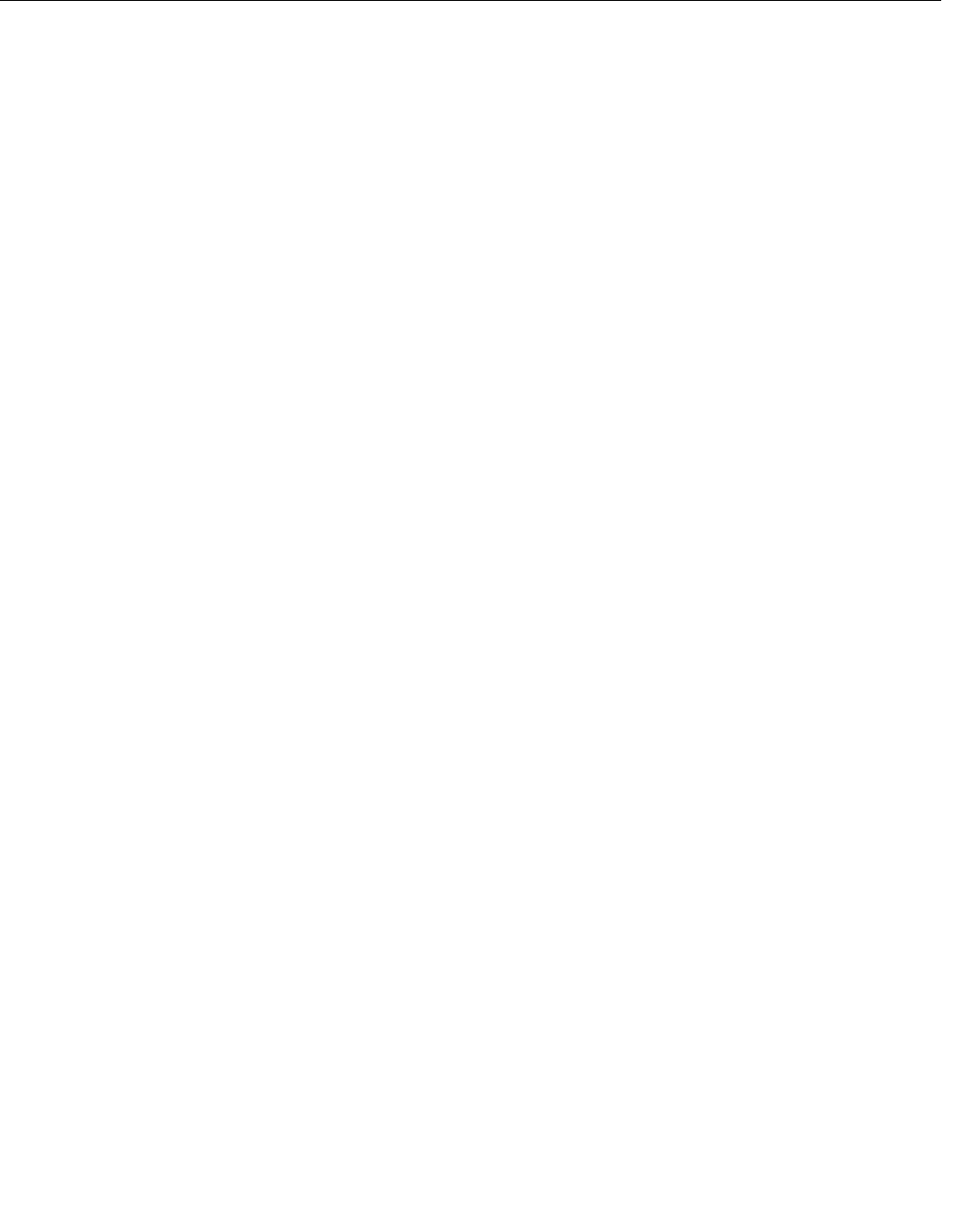
Reference Manual
300520EN, Rev AA
November 2009
Rosemount 5900 Series
2-10 Section 2. Overview
Preliminary
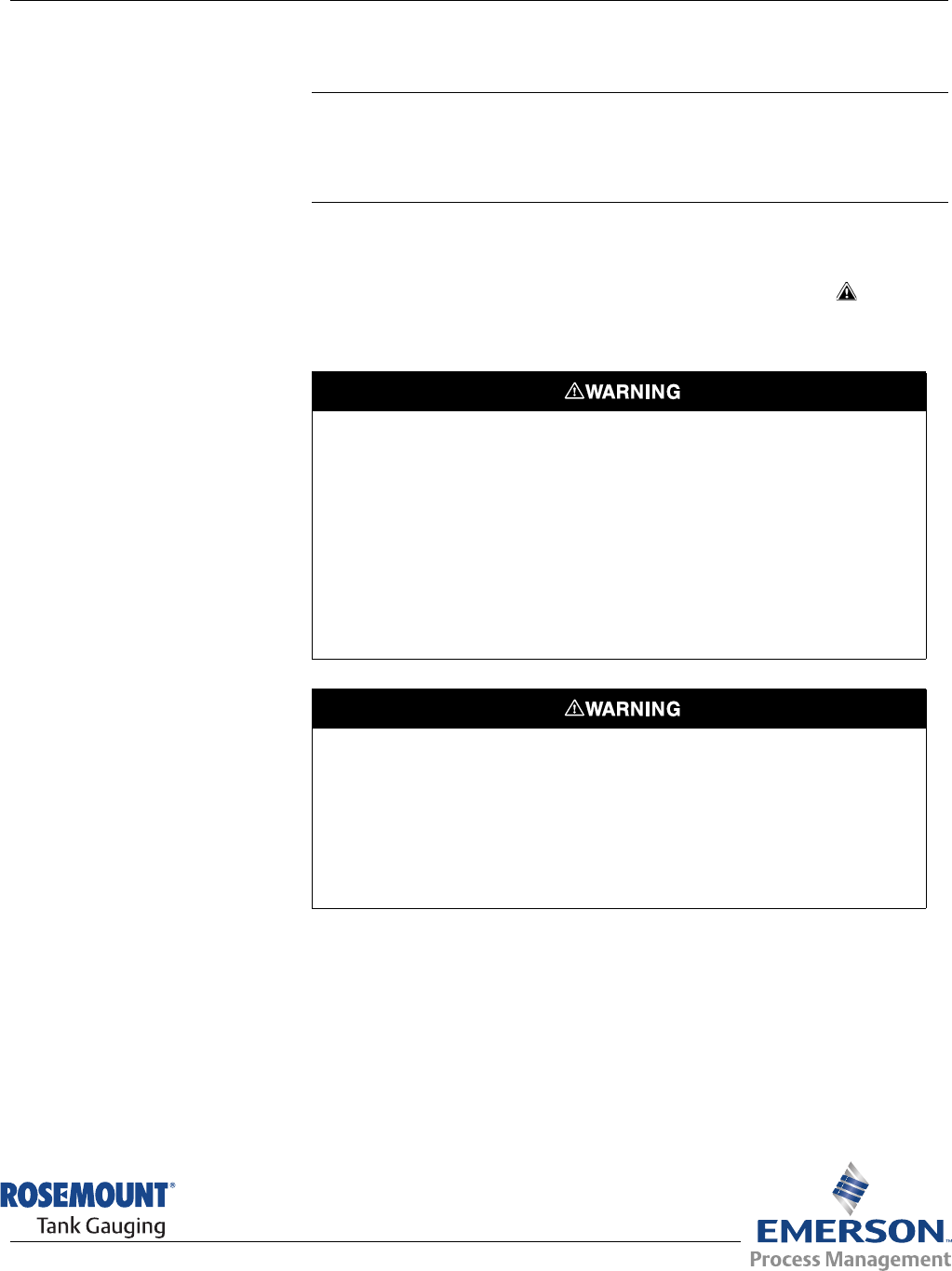
Reference Manual
300520EN, Rev AA
November 2009 Rosemount 5900 Series
www.rosemount-tg.com
Section 3 Installation
3.1 Safety Messages . . . . . . . . . . . . . . . . . . . . . . . . . . . . page 3-1
3.2 Installation Considerations . . . . . . . . . . . . . . . . . . . page 3-3
3.3 Mechanical Installation . . . . . . . . . . . . . . . . . . . . . . page 3-18
3.4 Electrical Installation . . . . . . . . . . . . . . . . . . . . . . . . page 3-39
3.1 SAFETY
MESSAGES
Procedures and instructions in this section may require special precautions to
ensure the safety of the personnel performing the operations. Information that
raises potential safety issues is indicated by a warning symbol ( ). Please
refer to the following safety messages before performing an operation
preceded by this symbol.
Failure to follow safe installation and servicing guidelines could result in death or
serious injury:
Make sure only qualified personnel perform the installation.
Use the equipment only as specified in this manual. Failure to do so may impair the
protection provided by the equipment.
Do not perform any service other than those contained in this manual unless you are
qualified.
To prevent ignition of flammable or combustible atmospheres, disconnect power before
servicing.
Substitution of components may impair Intrinsic Safety.
Explosions could result in death or serious injury:
Verify that the operating environment of the transmitter is consistent with the appropriate
hazardous locations certifications.
Before connecting a communicator in an explosive atmosphere, make sure the
instruments in the loop are installed in accordance with intrinsically safe or
non-incendive field wiring practices.
Do not remove the gauge cover in explosive atmospheres when the circuit is alive.
Preliminary
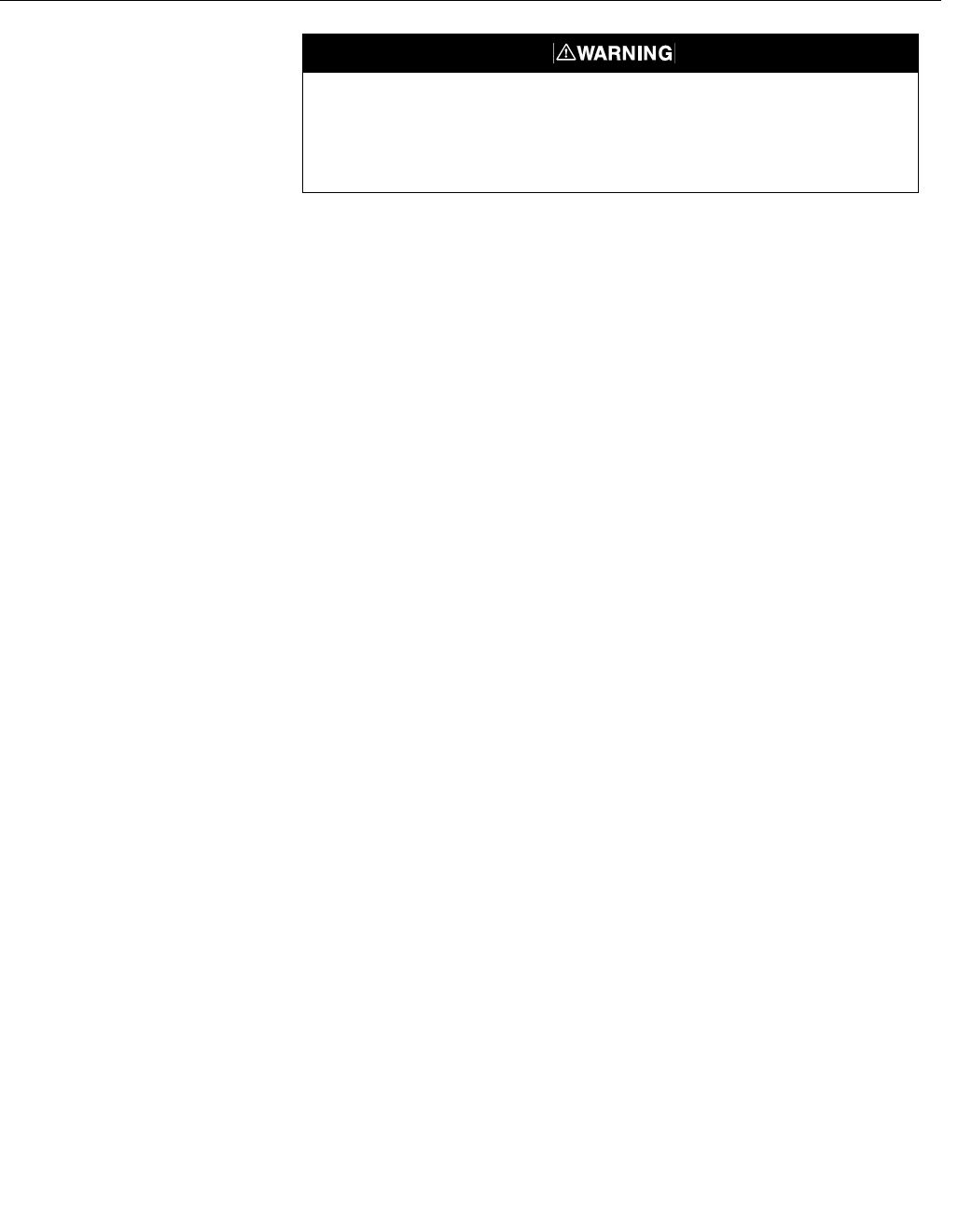
Reference Manual
300520EN, Rev AA
November 2009
Rosemount 5900 Series
3-2 Section 3. Installation
High voltage that may be present on leads could cause electrical shock:
Avoid contact with leads and terminals.
Make sure the main power to the transmitter is off and the lines to any other external
power source are disconnected or not powered while wiring the gauge.
Preliminary
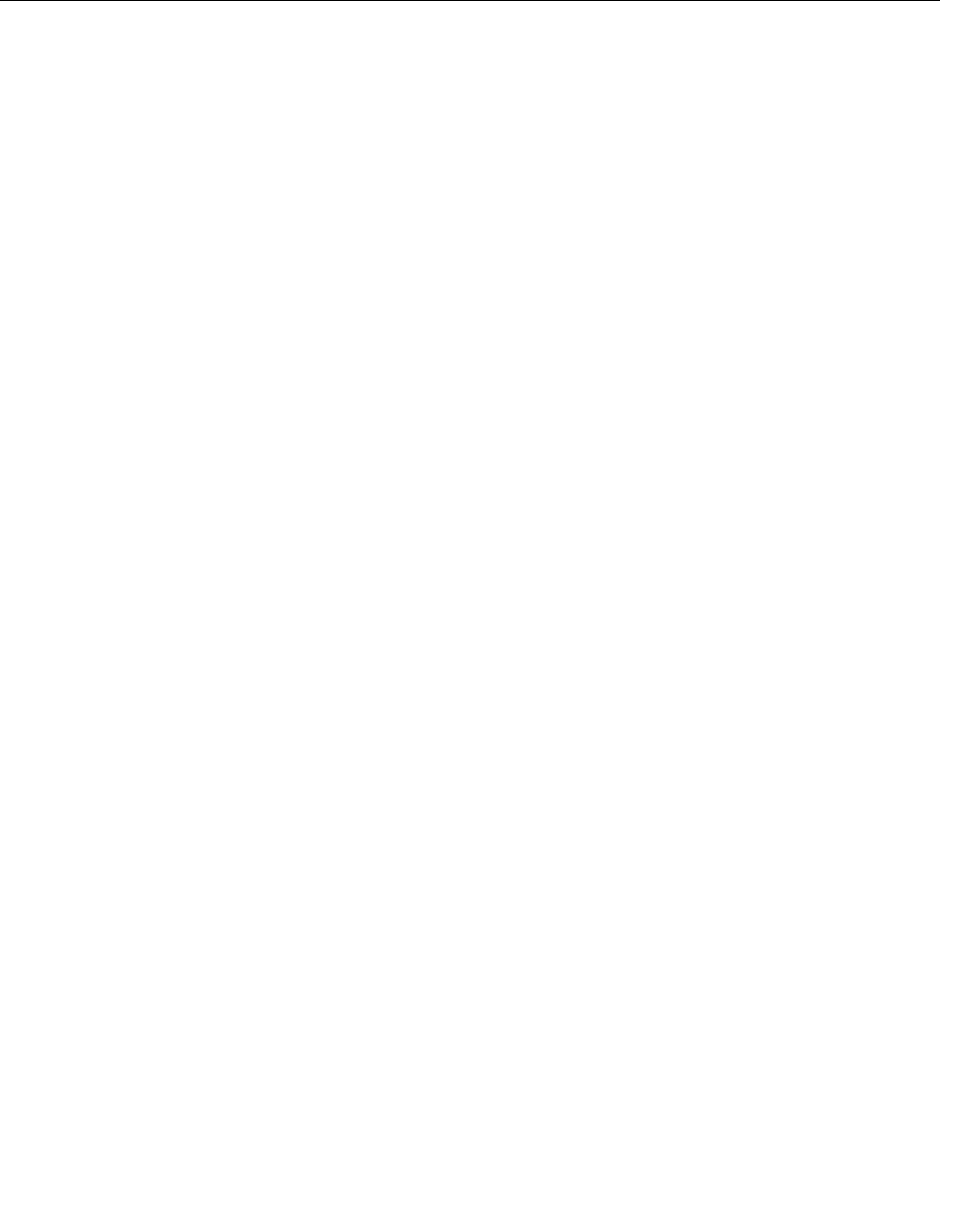
Reference Manual
300520EN, Rev AA
November 2009
3-3
Rosemount 5900 Series
Section 3. Installation
3.2 INSTALLATION
CONSIDERATIONS
When finding an appropriate location on the tank for a Rosemount 5900 radar
level gauge, the conditions of the tank must be carefully considered. The
5900 should be installed so that the influence of disturbing objects is kept to a
minimum, preferably outside the radar signal beam.
Ensure that environmental conditions are within specified limits as listed in
“Specifications” on page A-1.
Chapters 3.2.1 to 3.2.4 describe requirements and recommendations to
consider when installing a Rosemount 5900 radar level gauge with different
antenna types.
Preliminary
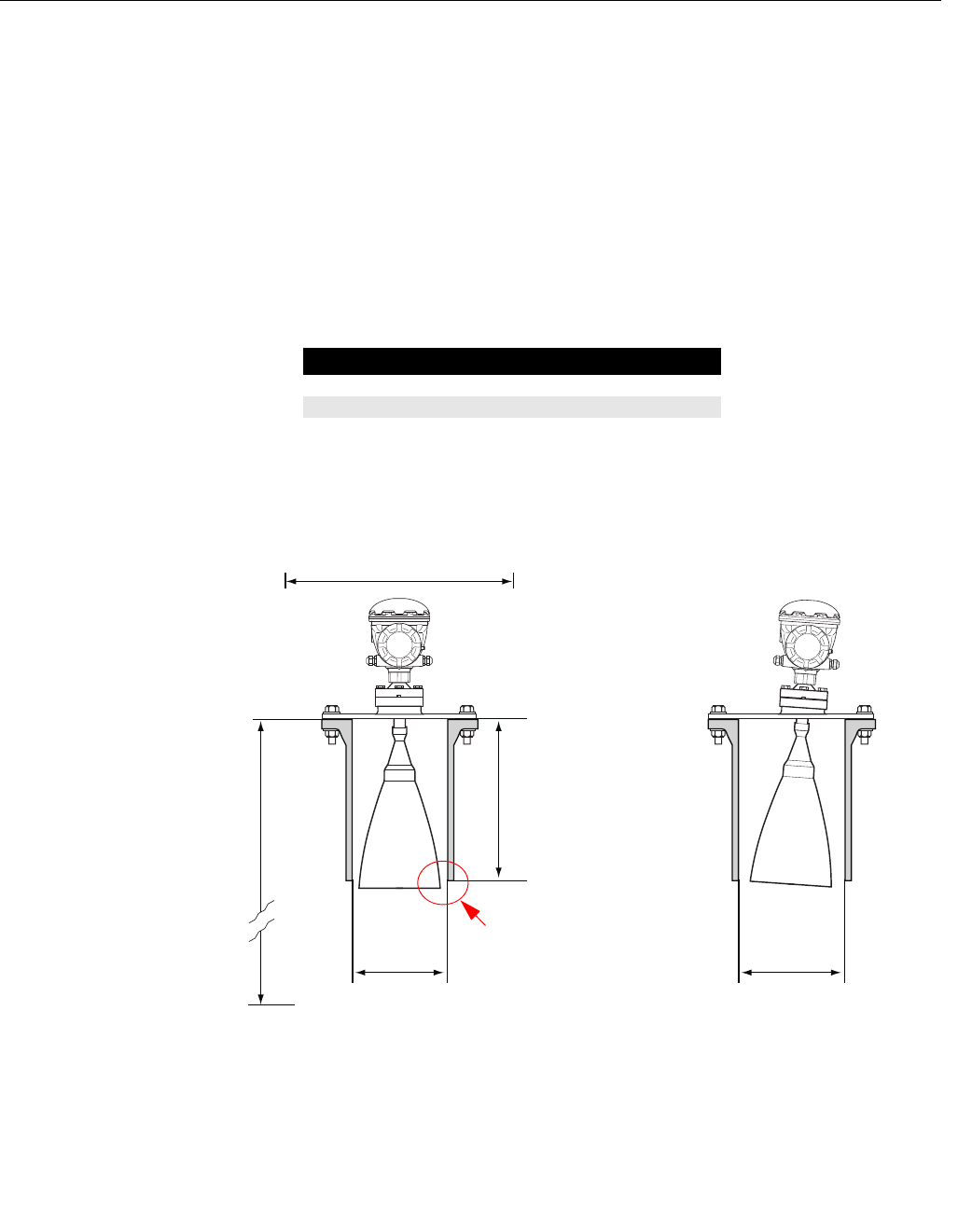
Reference Manual
300520EN, Rev AA
November 2009
Rosemount 5900 Series
3-4 Section 3. Installation
3.2.1 Horn Antenna
Requirements
The Rosemount 5920 with horn antenna must be installed so that there are no
pipes or other obstacles that could prevent the radar beam from reaching the
tank bottom unobstructed. There are two flanges available; a horizontal flange
for vertical installation, and an inclined flange for installation close to the tank
wall.
Please refer to mechanical installation drawings for more information on the
installation requirements of the Horn Antenna and service space
requirements.
Nozzle Requirements
Maximum nozzle height 330 mm.
Minimum nozzle diameter:
Table 3-1. Minimum nozzle
diameter for the 5900 with horn
antenna
Figure 3-1. Nozzle requirements
for the Horn Antenna Gauge
Flange Minimum nozzle diameter (mm)
Horizontal flange 180
4° flange 185
Maximum height: 330 mm
Note!
For best performance the
antenna should reach out
below the nozzle
Minimum nozzle
diameter 180 mm
Note!
Highest accuracy is
achieved for product
levels outside a region of
approximately 850 mm
below the flange.
Service space 400 mm
Minimum nozzle
diameter 185 mm
HORIZONTAL FLANGE 4° FLANGE
Preliminary
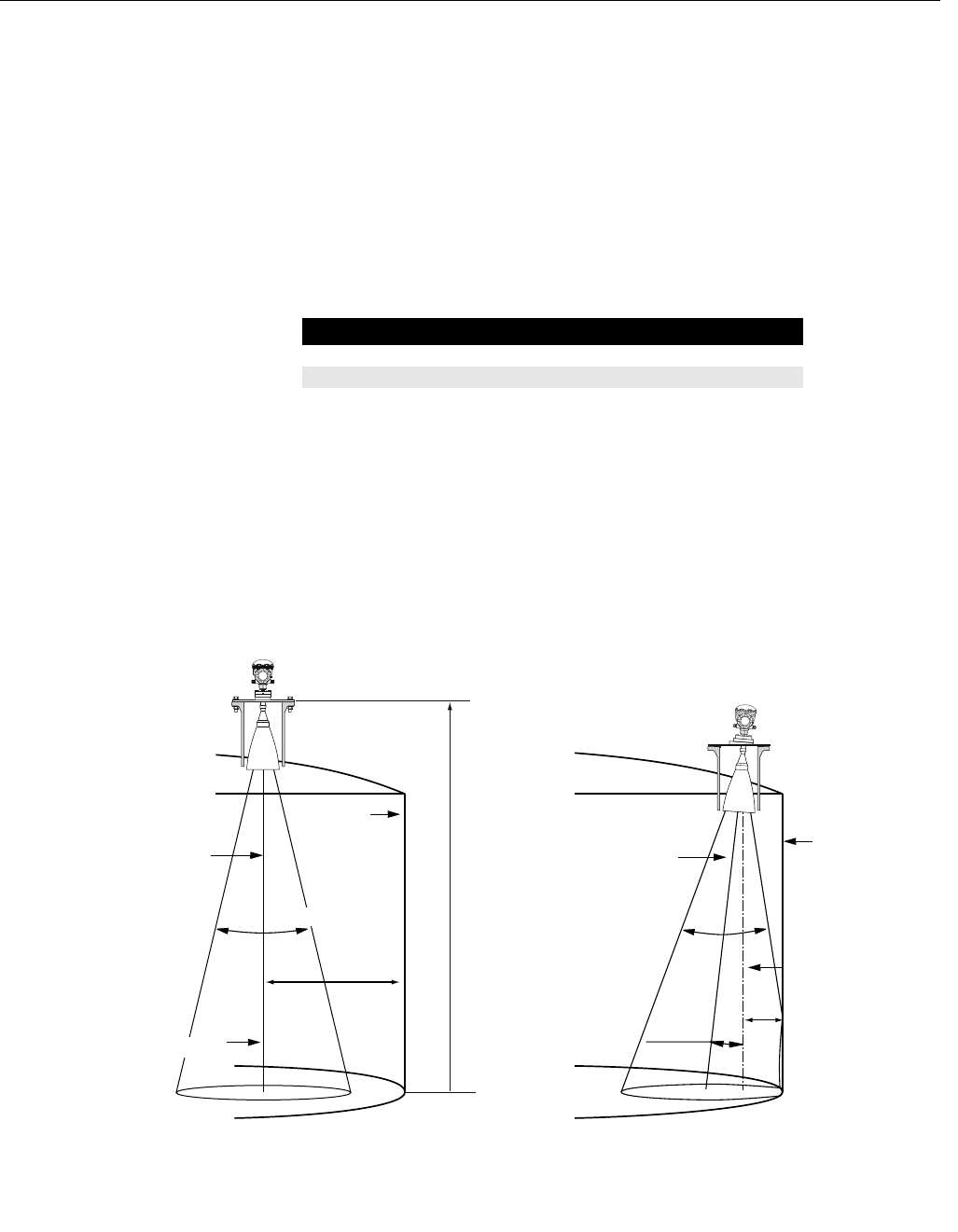
Reference Manual
300520EN, Rev AA
November 2009
3-5
Rosemount 5900 Series
Section 3. Installation
Free Space Requirements
There are two flanges available for the Horn Antenna Gauge. One flange has
an inclination of 4° and the other is horizontal. See installation drawing for
flange dimensions.
The horizontal flange can be used if the wall does not intrude into the 30° wide
radar beam of the Rosemount 5900. If a vertical antenna axis installation is
not possible without the tank wall intruding into the radar beam, the 5900 has
to be directed away from the wall by using the 4° flange. The inclination is
necessary to ensure maximum accuracy.
The minimum free space distance L:
Table 3-2. Minimum distance L
to tank wall for the 5900 with
horn antenna
In certain cases, when maximum accuracy is not required, the horizontal
flange can be used even if the wall intrudes into the radar beam. In doubtful
cases, please contact Emerson Process Management / Rosemount Tank
Gauging or one of its representatives for advice.
Figure 3-2. Two different flange
options are available
Flange Minimum distance L to tank wall (m)
Horizontal flange Rx0.27 (R=tank reference height)
4° flange 0.8(1)
(1) In exceptional cases the 5900 with Horn antenna can be installed closer to the
tank wall if required. Please contact Emerson Process Management /
Rosemount Tank Gauging for advice.
4° ± 1°
Tank wall
Antenna axis
30° radar beam
Vertical plumb line
Vertical plumb line
Antenna axis Tank wall
30° radar beam
L
HORIZONTAL FLANGE INCLINED FLANGE
L
Tank reference height (R)
Preliminary
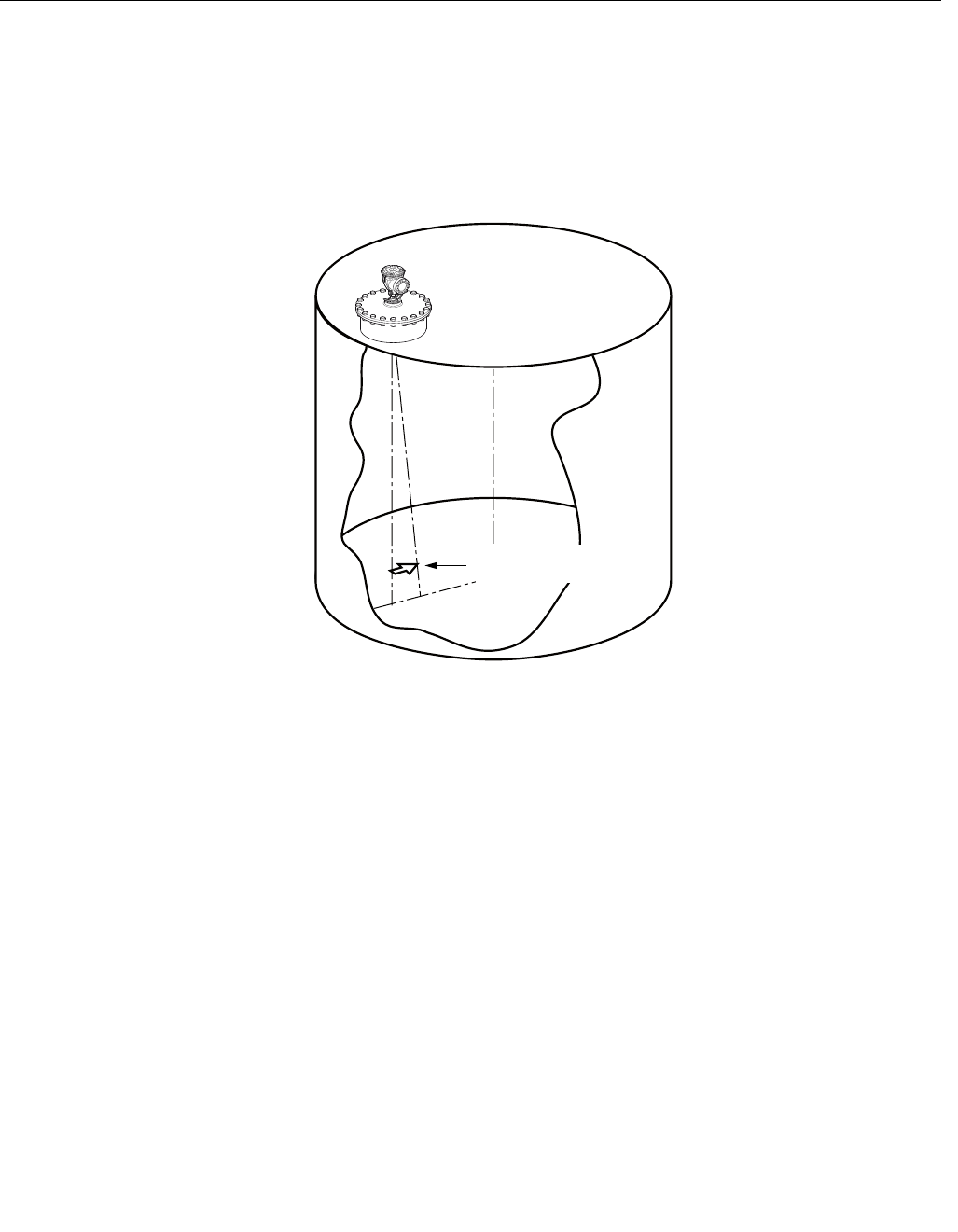
Reference Manual
300520EN, Rev AA
November 2009
Rosemount 5900 Series
3-6 Section 3. Installation
3.2.2 Parabolic
Antenna
Requirements
Inclination
The inclination of the Rosemount 5900 with parabolic antenna should not
exceed 1.5 ° towards the center of the tank. For products with high
condensation such as bitumen/asphalt applications, the radar beam should
be directed vertically without any inclination.
Figure 3-3. Maximum inclination
with parabolic antenna
Flange Requirements
The Rosemount 5900 with Parabolic antenna is mounted on the tank nozzle
by using the Flange Ball. It is designed for easy adjustment of gauge
inclination within the specified limits.
There are two versions of the Flange Ball: T30 and T38-W. Model T 38-W is
welded on the flange. Model T 30 is attached to the flange with a nut. The
Flange Ball has to be mounted on the tank flange prior to mounting the gauge
on the tank nozzle.
Certain flange requirements have to be fulfilled in order to ensure that the
radar beam is not disturbed by the tank wall, and maximum signal strength is
reflected from the product surface back to the level gauge.
With Flange Ball Model T30 the tank flange has to meet the following
inclination requirements (see Figure 3-4) in order to allow proper adjustment
of the antenna:
• maximum 4.5° away from the tank wall
• maximum of 2° towards the tank wall
• within ±3° horizontally along the tank wall
Maximum inclination 1.5°
Preliminary
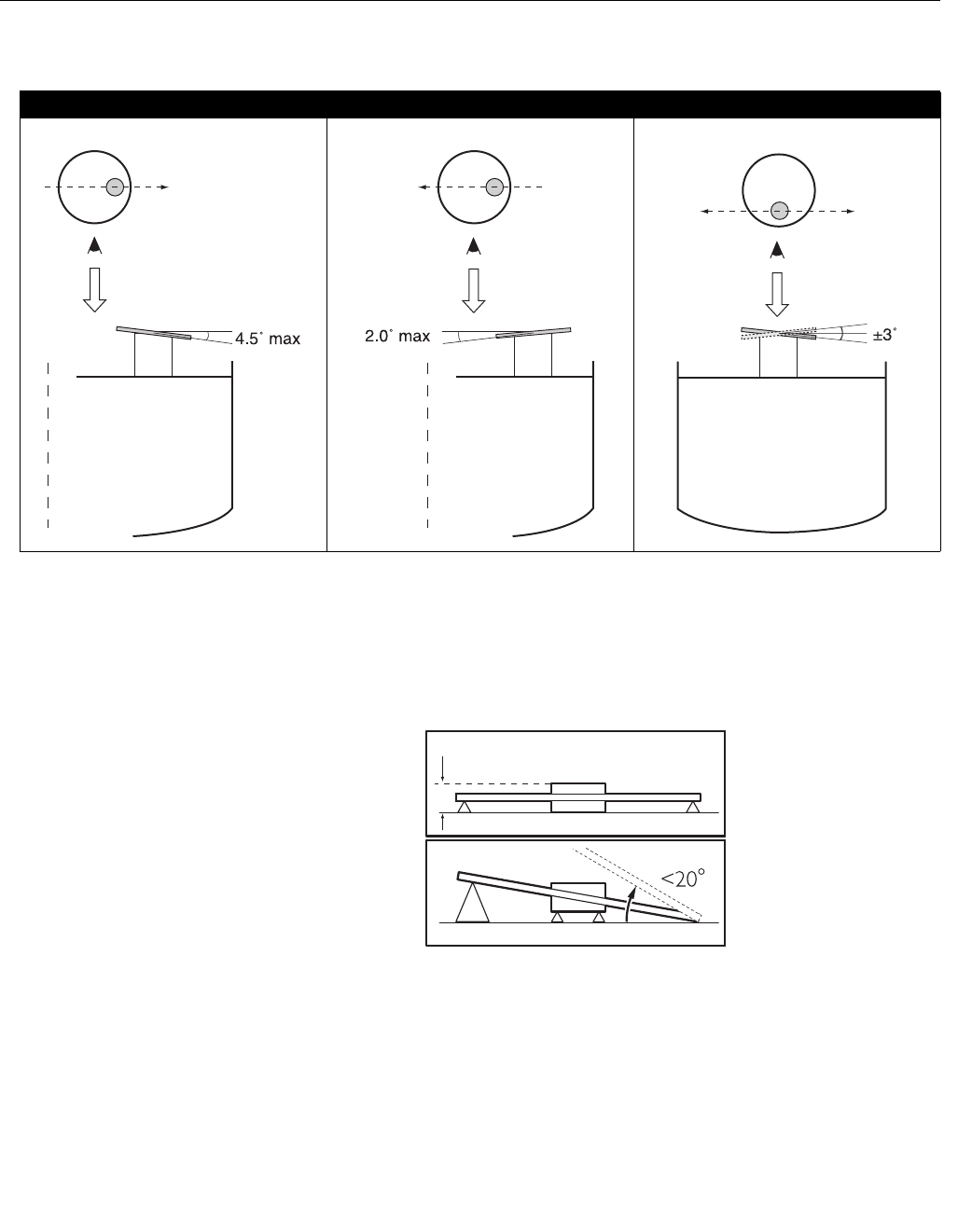
Reference Manual
300520EN, Rev AA
November 2009
3-7
Rosemount 5900 Series
Section 3. Installation
Figure 3-4. Maximum inclination
of tank flange
Flange Ball T38-W can be welded at a maximum angle of 20° between the
flange and the Flange Ball surface.
Figure 3-5. Maximum inclination
of welded flange with Flange
Ball T38W
Maximum inclination towards tank center Maximum inclination towards tank wall Max inclination along tank wall
60 mm
Preliminary
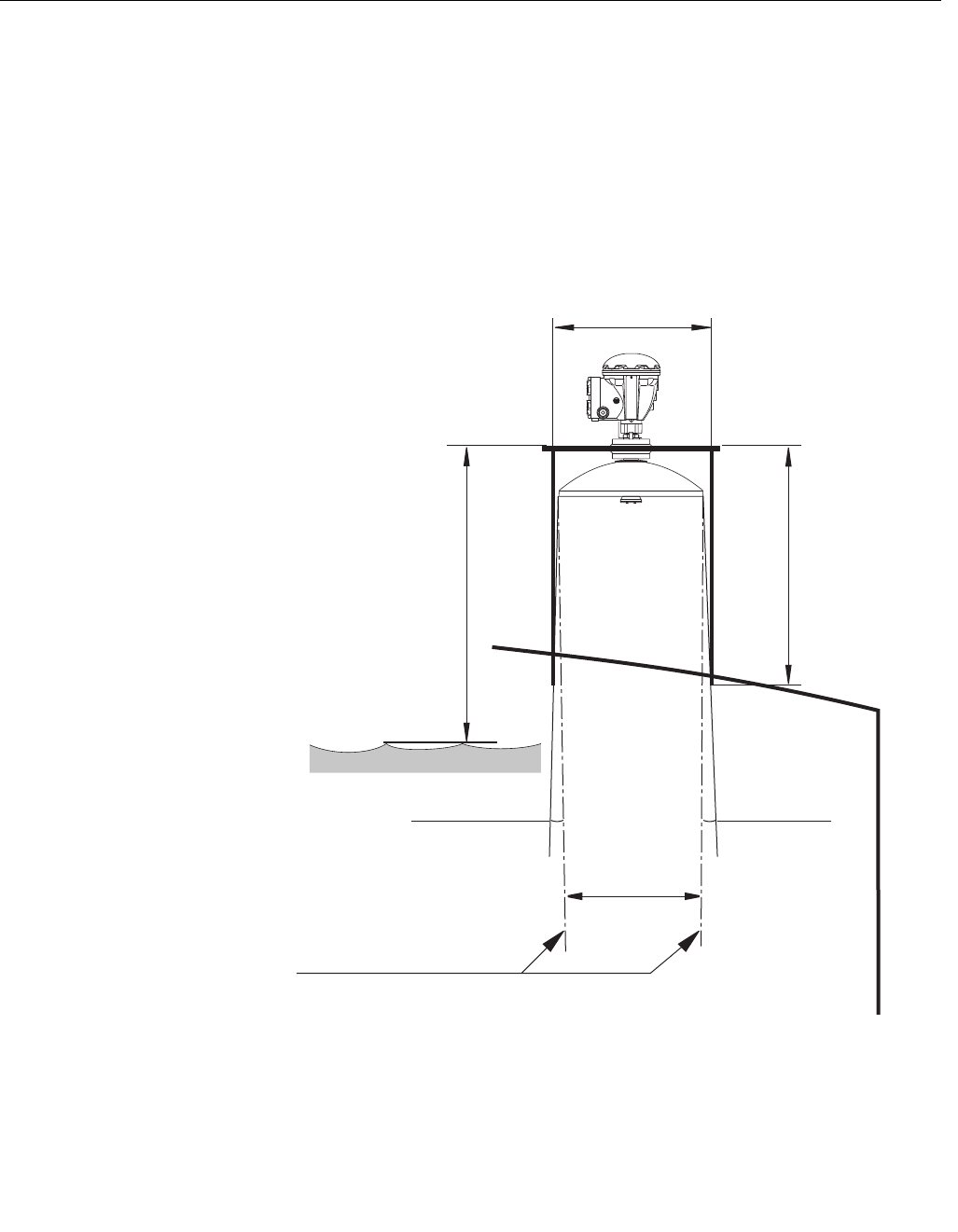
Reference Manual
300520EN, Rev AA
November 2009
Rosemount 5900 Series
3-8 Section 3. Installation
Nozzle Requirements
When using a Ø 20" nozzle the height of the nozzle must not exceed 0.5
meter. There has to be a free passage for the radar beam within a 5° angle
from the edge of the parabolic reflector to the lower end of the nozzle.
Nozzles with larger diameter may be higher than 0.5 meter as long as the 5°
requirement is fulfilled.
From the flange to the product surface the distance should not be less than
1.0 m. Highest accuracy is obtained from product levels 1.0 meter below the
flange downwards
Figure 3-6. Nozzle requirements
for the Rosemount 5900 with
Parabolic antenna
Ø > 500 mm (20 inch)
Mimimum 1.0 m to
product surface
Nozzle height
maximum 0.5 m
5° minimum5° minimum
Ø 441 mm
Vertical plumb line
Preliminary
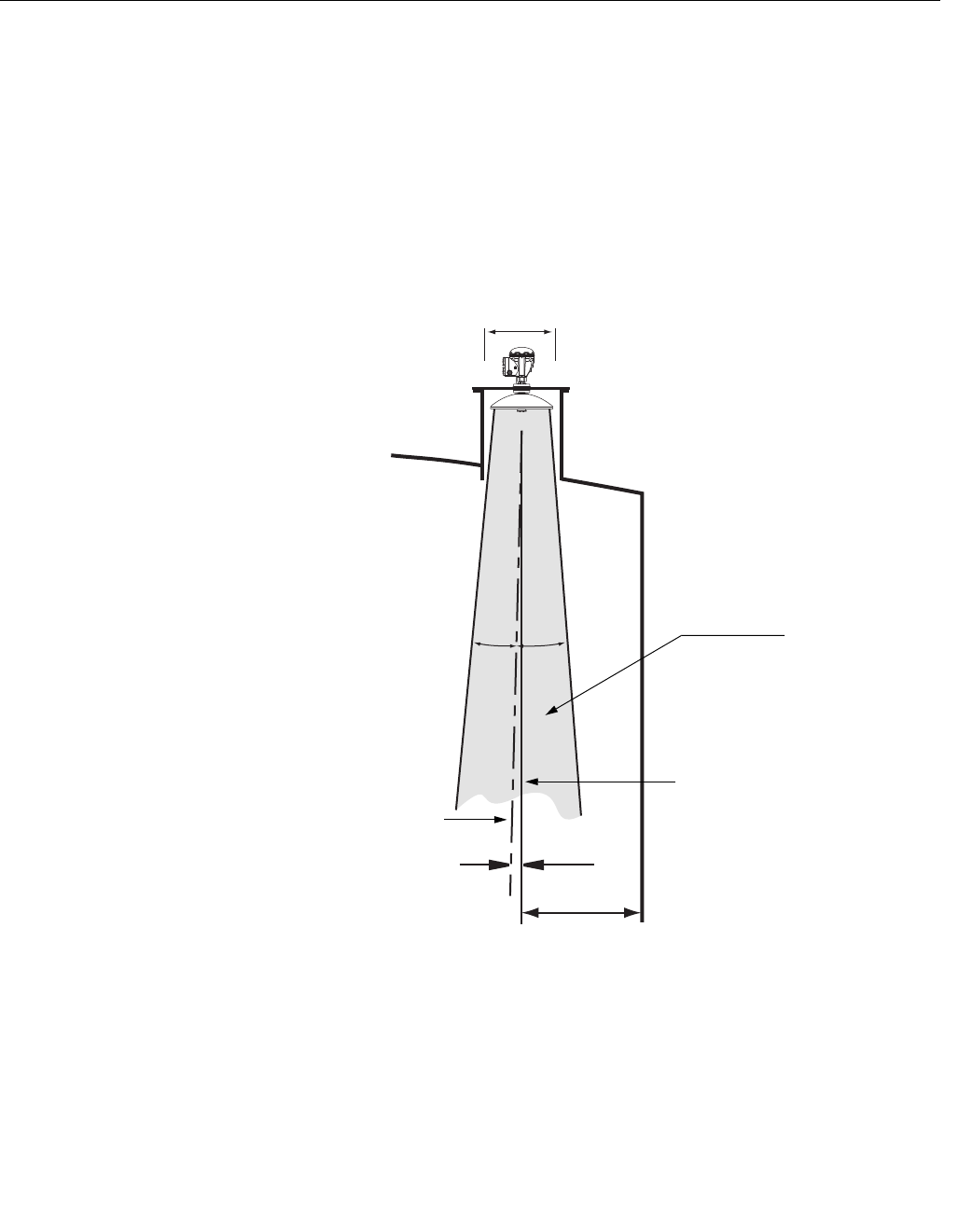
Reference Manual
300520EN, Rev AA
November 2009
3-9
Rosemount 5900 Series
Section 3. Installation
Free Space Requirements
The radar beam of the Parabolic Antenna Gauge is 10° wide. Obstacles
(construction bars, pipes larger than Ø 2", etc.) within the radar beam are
generally not accepted, as these may result in disturbing echoes. However, in
most cases, a smooth tank wall or heating coils will not have any significant
influence on the radar beam.
The distance from the tank wall to the antenna axis should be at least 0.8 m.
Figure 3-7. Free space
requirements for the Rosemount
5900 with Parabolic antenna
For evaluation contact Emerson Process Management / Rosemount Tank
Gauging.
Free passage
Vertical plumb line
Antenna axis
Min. 0.8 m
5°5°
1.5 °
Recommended service space 400 mm
Preliminary
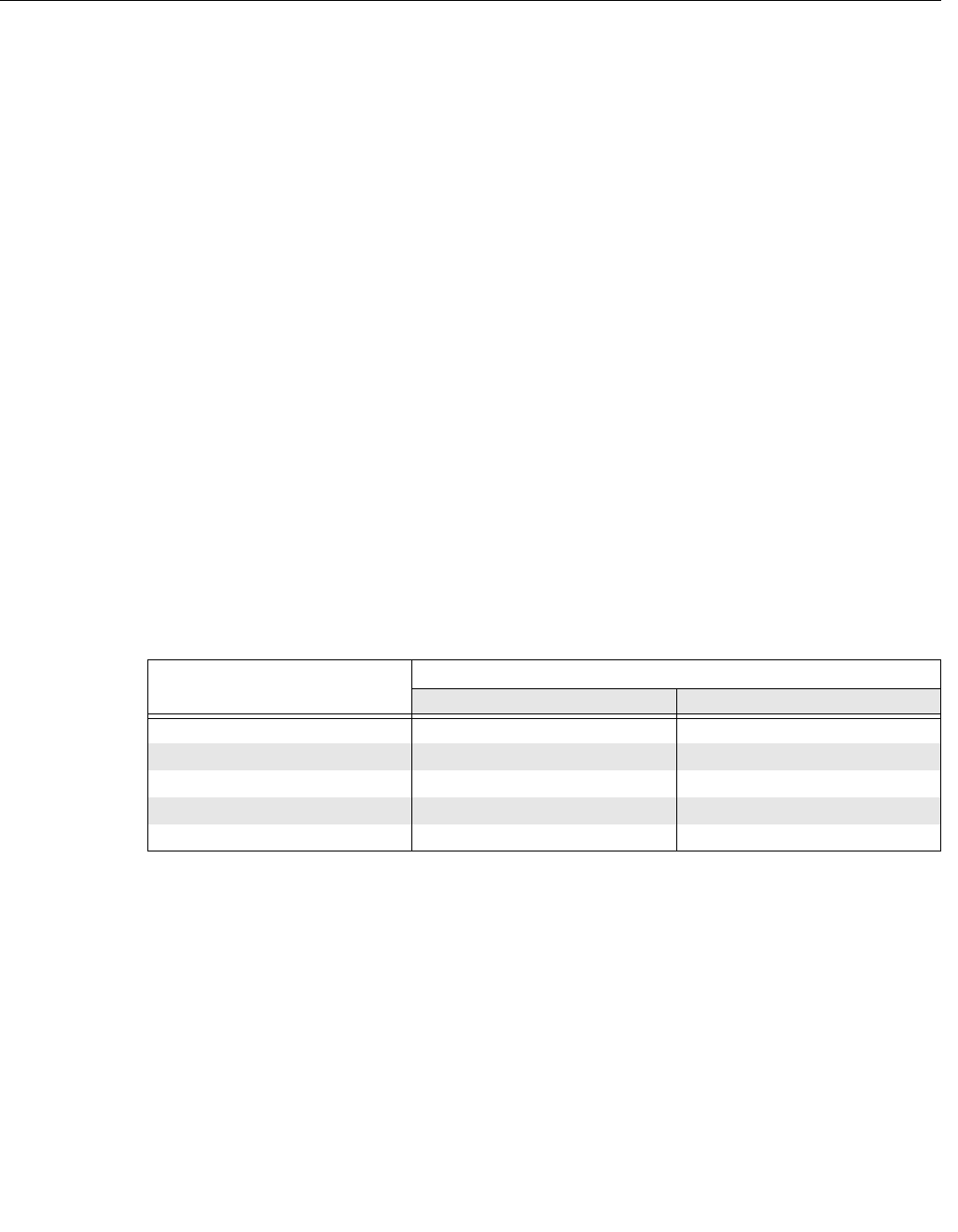
Reference Manual
300520EN, Rev AA
November 2009
Rosemount 5900 Series
3-10 Section 3. Installation
3.2.3 Still Pipe Antenna
Requirements
This instruction covers installation of the Rosemount 5900 Still-pipe Array
antenna available for pipe size 5, 6, 8, 10 and 12 inch.
The Rosemount 5900 is designed for still-pipe mounting and can be mounted
on existing still-pipe flanges without taking the tank out of operation.
There are two versions available in order to suit various requirements for easy
installation and maintenance:
• The Rosemount 5900 Still-pipe Array antenna Fixed version.
This version has a flange for easy mounting when there is no need for
opening the still-pipe for hand dipping.
• The Rosemount 5900 Still-pipe Array antenna Hinged Hatch version.
This version is suitable when the still-pipe needs to be opened for hand
dipping.
Still Pipe Requirements
The Rosemount 5900 Still-pipe Array antenna fits 5", 6", 8", 10" and 12"
flanges and pipes. The adaption is accomplished by selecting a suitable
Still-pipe Array antenna. The gauge has a flange to seal the tank.
The still pipe must be vertical within 0.5° (0.2 m over 20 m).
Table 3-3 shows the wide range of schedules and pipe inner diameters that
the Array antennas can be mounted in.
Table 3-3. Antenna size and
corresponding pipe inner
diameter
Antenna size (mm) Pipe
Size Inner diameter (mm)
120.2 5" SCH10-SCH60 134.5 - 125.3
145.2 6" SCH10-SCH60 161.5 - 150.3
189 8" SCH20-SCH80 206.3 - 193.7
243 10" SCH10-SCH60 264.7 - 247.7
293.5 12" SCH 10-40-XS 314.7 - 298.5
Preliminary
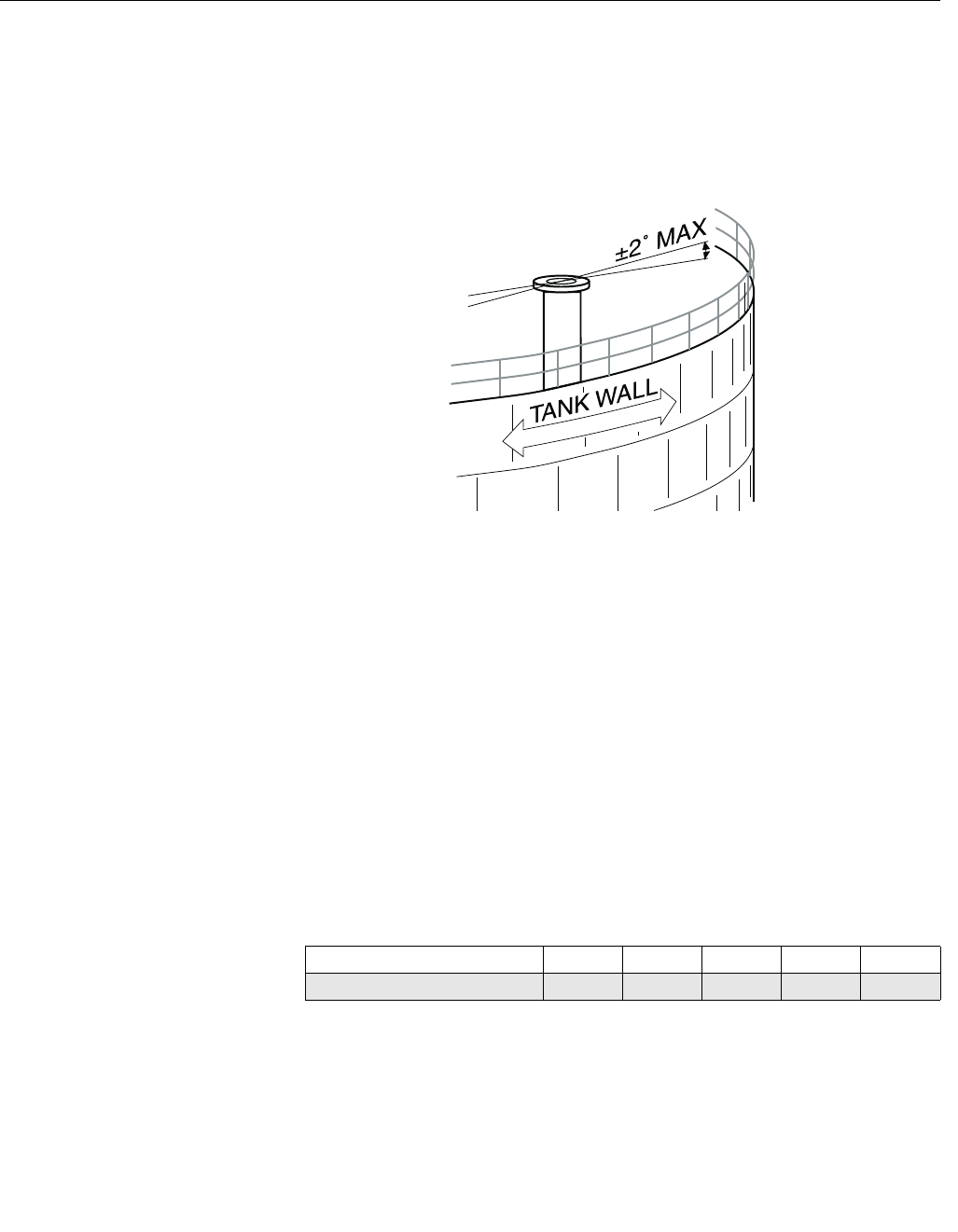
Reference Manual
300520EN, Rev AA
November 2009
3-11
Rosemount 5900 Series
Section 3. Installation
Flange Requirements
The Rosemount 5900 Still-pipe Array antenna fits flanges of size 5", 6", 8",
10" and 12". The gauge has a flange for sealing the tank. The flange must be
horizontal within ±2°.
Figure 3-8. The flange must be
horizontal within ±2°
Recommended Installation
When constructing new tanks, an 8" still pipe or larger is recommended. This
is especially relevant in tanks with sticky, viscous products. Before
manufacturing a new still pipe, we recommend that you contact Emerson
Process Management / Rosemount Tank Gauging for advice.
For highest performance, the total area of the slots or holes in the still pipe
must not exceed the values shown in Table 3-4 below. The listed values refer
to the total area of the holes over the entire length of the pipe, regardless of its
length. In some cases it is possible to allow a larger total area than stated in
Table 3-4. When the limits are exceeded, please contact Emerson Process
Management / Rosemount Tank Gauging for advice.
Table 3-4. Maximum area of the
slots or holes
Pipe Dimension (inch) 5 6 8 10 12
Max Area of Slots or Holes (m2)0.1 0.1 0.4 0.80 1.2
Preliminary
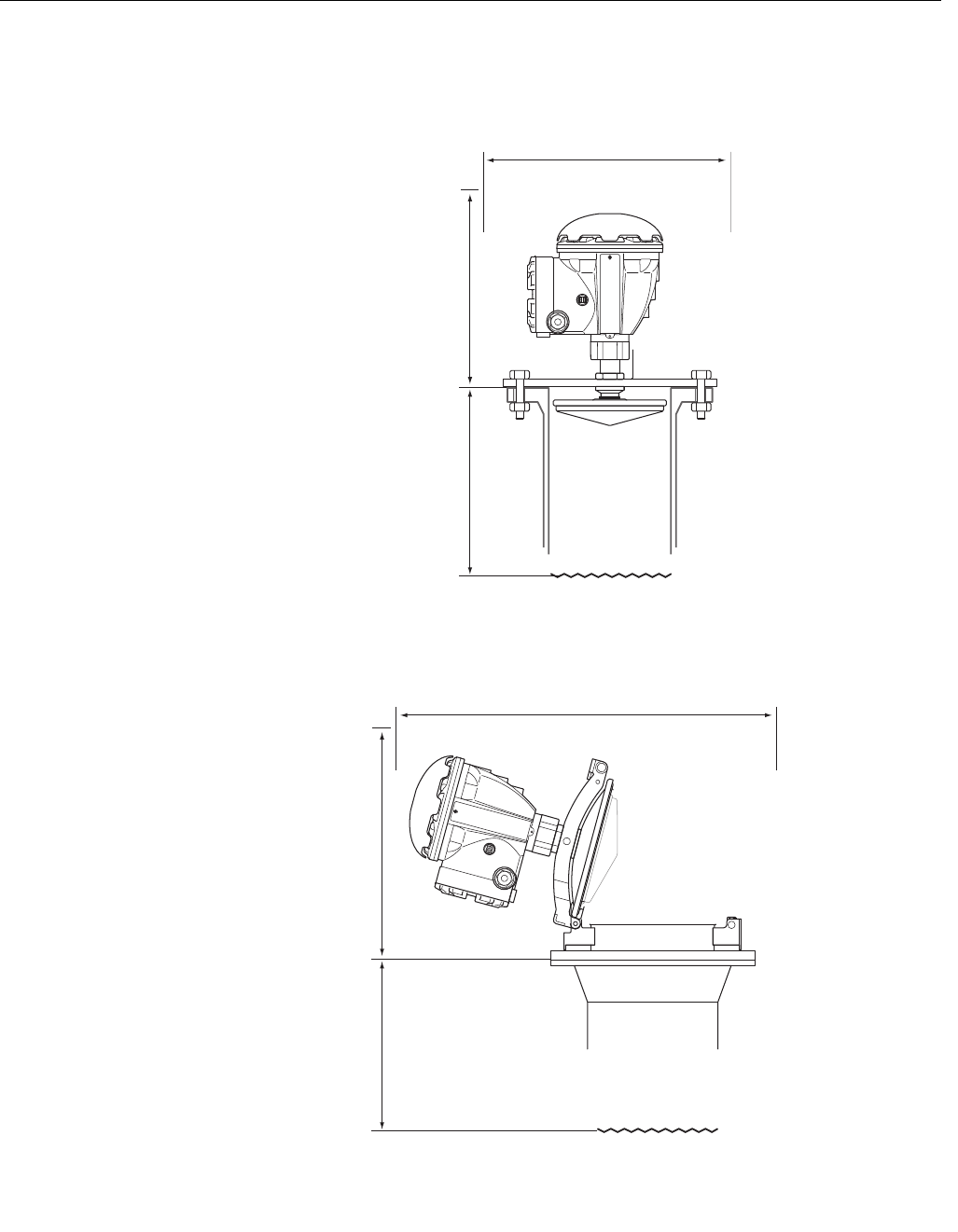
Reference Manual
300520EN, Rev AA
November 2009
Rosemount 5900 Series
3-12 Section 3. Installation
Free Space
The following free space is recommended for mounting the Still-pipe gauge:
Figure 3-9. Free space
requirements for 5900 with Array
antenna Fixed version
Figure 3-10. Free space
requirements for 5900 with Array
antenna Hinged H atch version
Minimum 500 mm
Service space 400 mm
Service space 400 mm
Minimum 500 mm
Service space 500 mm
Preliminary
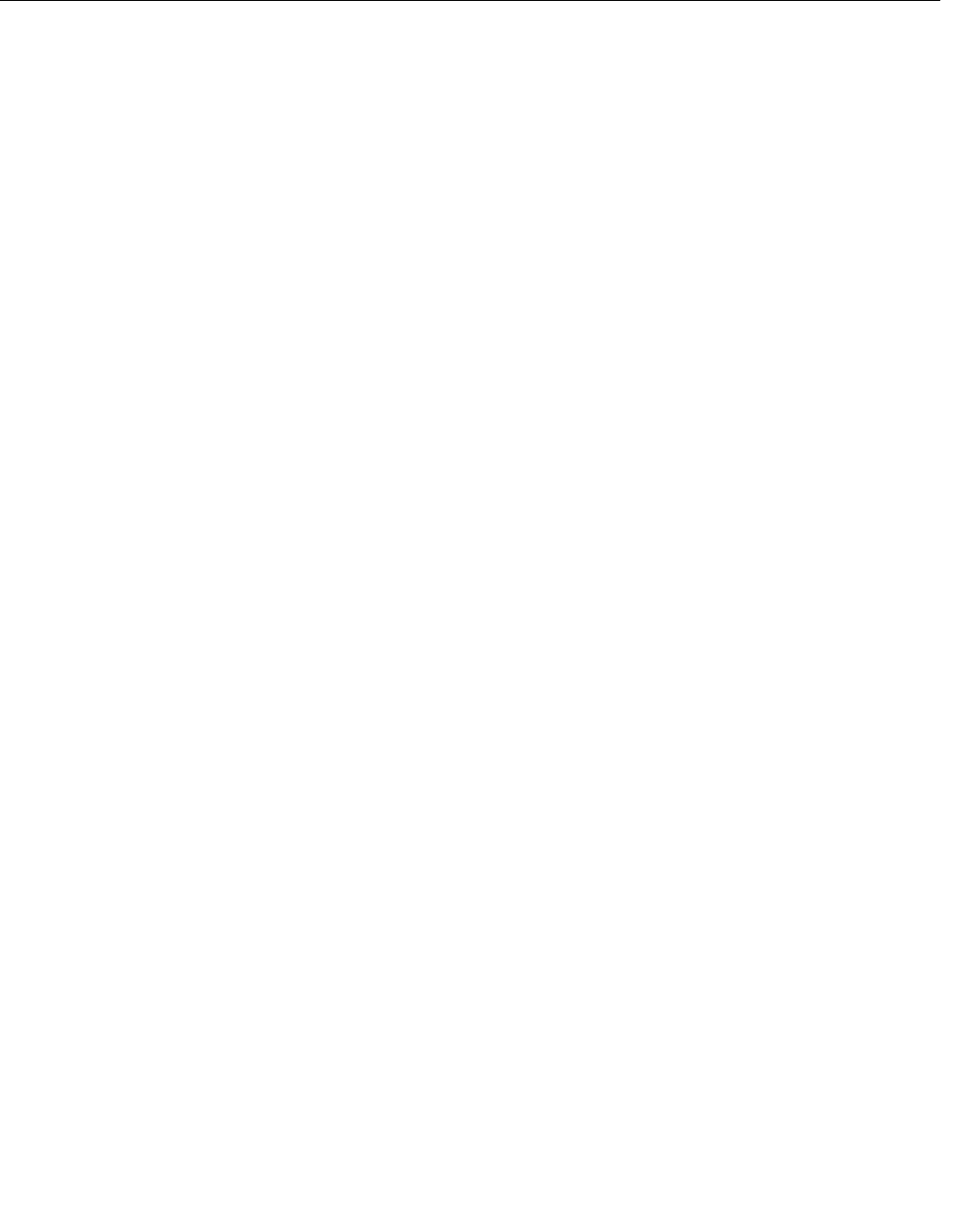
Reference Manual
300520EN, Rev AA
November 2009
3-13
Rosemount 5900 Series
Section 3. Installation
3.2.4 LPG/LNG
Antenna
Requirements
Temperature and Pressure Measurement
A prerequisite for high accuracy level-measurements in LPG/LNG tanks is
that temperature and pressure measurements are made. The Rosemount
5900 transmitter can interface pressure sensors and up to six temperature
sensors.
Still Pipe
A still-pipe must be installed prior to the gauge installation. The still-pipe is
customer supplied and should be manufactured according to the installation
drawings.
Three types of steel pipe can be used:
• DN100
• 4" SCH 10 stainless steel pipe
• 4" SCH 40 stainless steel pipe
When ordering the gauge specify the pipe type in the Required System
Information (RSI) form.
The still-pipe must be vertical within ±0.5° and the customer flange must be
horizontal within ±1° as illustrated in Figure 3-12 on page 3-14.
The still-pipe is manufactured with a number of holes in order to provide
pressure equalization so that the product level inside the pipe is equal to the
level in the rest of the tank. The diameter of the holes should be 20 mm or
3/4".
All holes in the upper pipe section must be placed along a line on one side of
the pipe and aligned with a bolt hole on the pipe flange as illustrated in Figure
3-11 on page 3-14. The position of the holes must be clearly marked on the
pipe flange. The Reference Pin must be directed towards the bolt hole. The
flange marking is used to properly align the gauge with the Reference Pin,
see Figure 3-11.
See the Raptor System Configuration Manual, Document No. 300510EN, for
more information on configuration and verification of the 5900 with LPG/LNG
antenna.
Preliminary
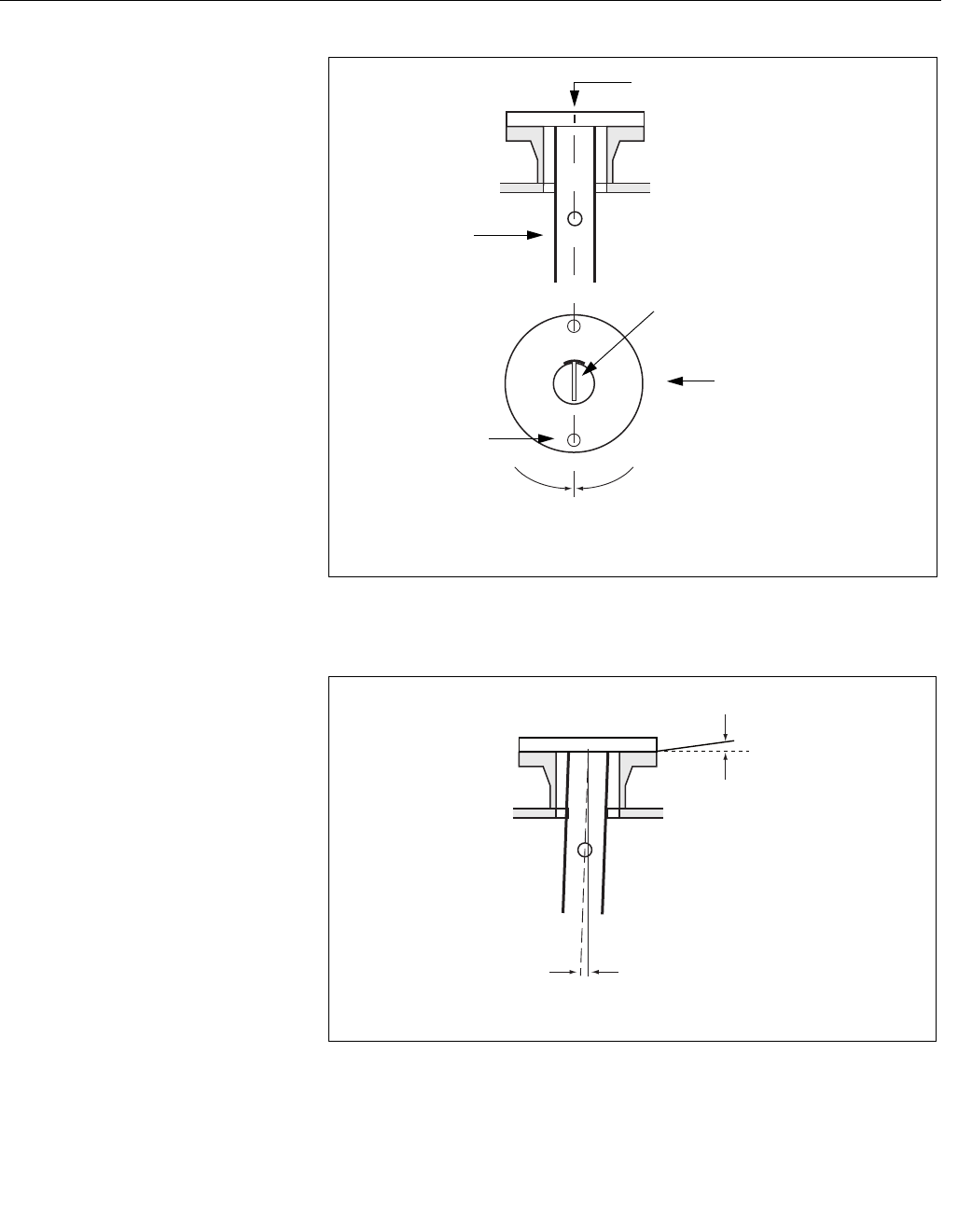
Reference Manual
300520EN, Rev AA
November 2009
Rosemount 5900 Series
3-14 Section 3. Installation
Figure 3-11. Reference pin
installation
Figure 3-12. Still-pipe and flange
inclination requirements
Marking
Align Reference Pin
and bolt hole within 1°
Flange seen from above
The Reference Pin is directed
towards the bolt hole on the
pipe flange
Bolt hole
Still Pipe
REFERENCE PIN
Maximum 0.5°
Maximum 1°
FLANGE
Preliminary
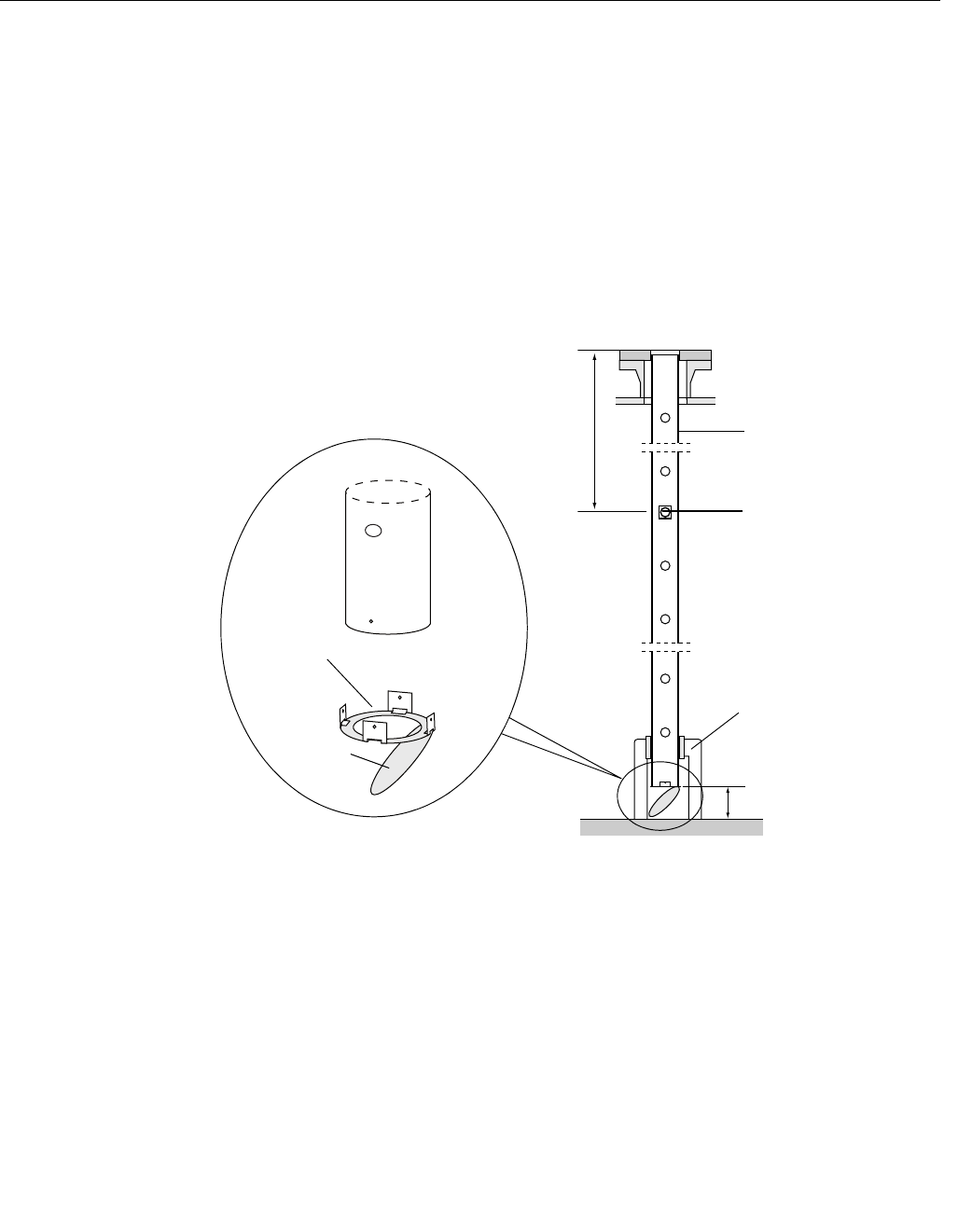
Reference Manual
300520EN, Rev AA
November 2009
3-15
Rosemount 5900 Series
Section 3. Installation
Reference Pin and Reflector
One of the holes on the still-pipe is used for mounting a Reference Pin which
enables verification of the measurement when the tank is pressurized.
The Reflector is mounted at the lower end of the still-pipe and is integrated
with a ring that is used for calibrating the gauge during the installation phase
when the tank is empty.
See installation drawings for LPG/LNG Still-pipe for information on where to
put the reference pin in the still-pipe. Installation instructions are enclosed
with the reference pin and reflector.
Figure 3-13. Still-pipe with
reflector and reference pin
The reflector can be attached to the Still Pipe by using one of three methods:
• Welding
• M4 screw and nut
• Riveting
For pipe dimensions 4 inch SCH 40 and DN 100 an extra ring is needed for
the reflector as illustrated below in Figure 3-14 and Figure 3-15:
Reference pin
Support
Calibration ring
Reflector
Still Pipe
Min. 150 mm
2000 ±500 mm
Preliminary
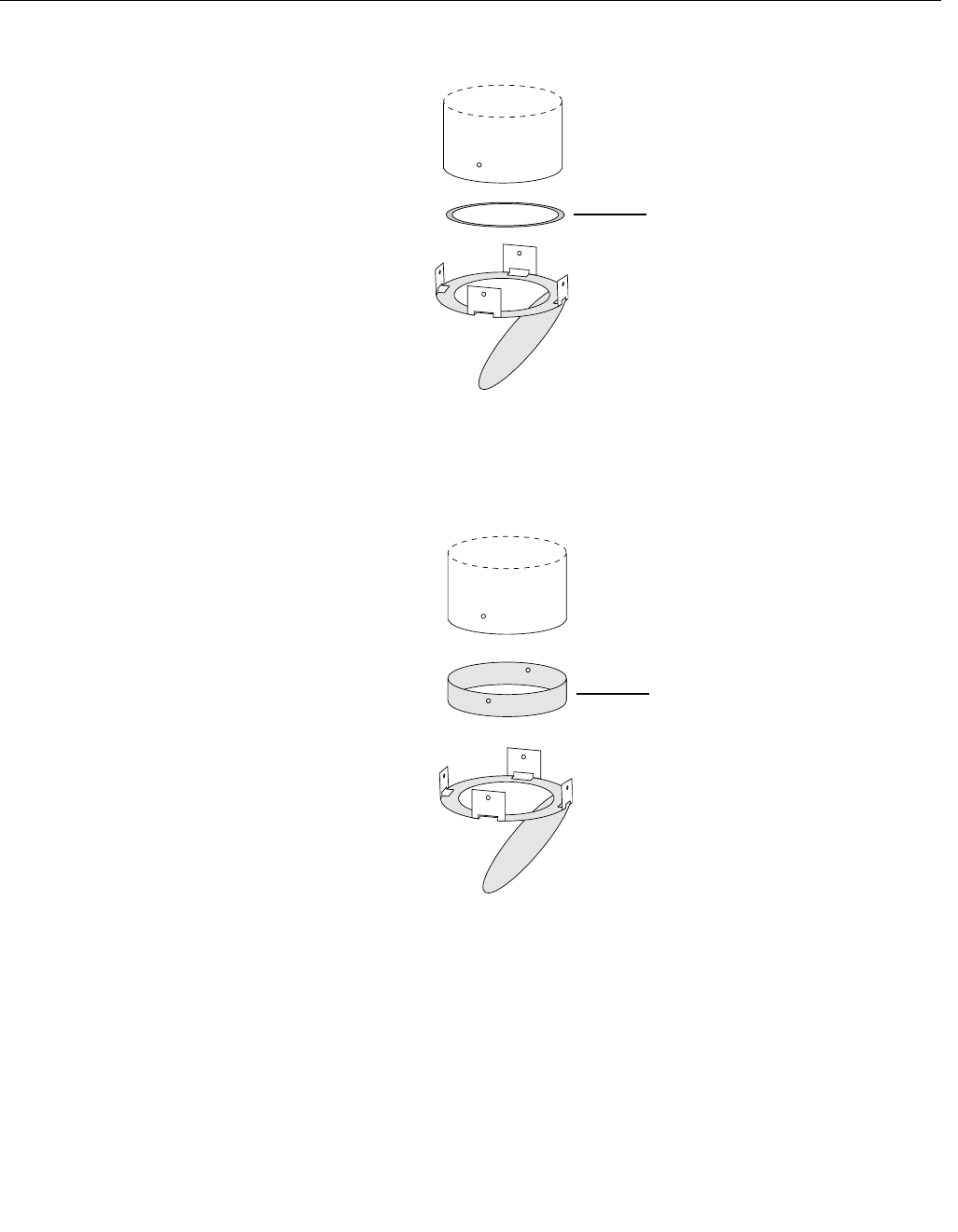
Reference Manual
300520EN, Rev AA
November 2009
Rosemount 5900 Series
3-16 Section 3. Installation
Figure 3-14. Mounting the
reflector on pipe 4 inch SCH 40
Figure 3-15. Mounting the
reflector on pipe DN 100
Ring is marked 4” SCH40
Ring is marked DN100
Preliminary
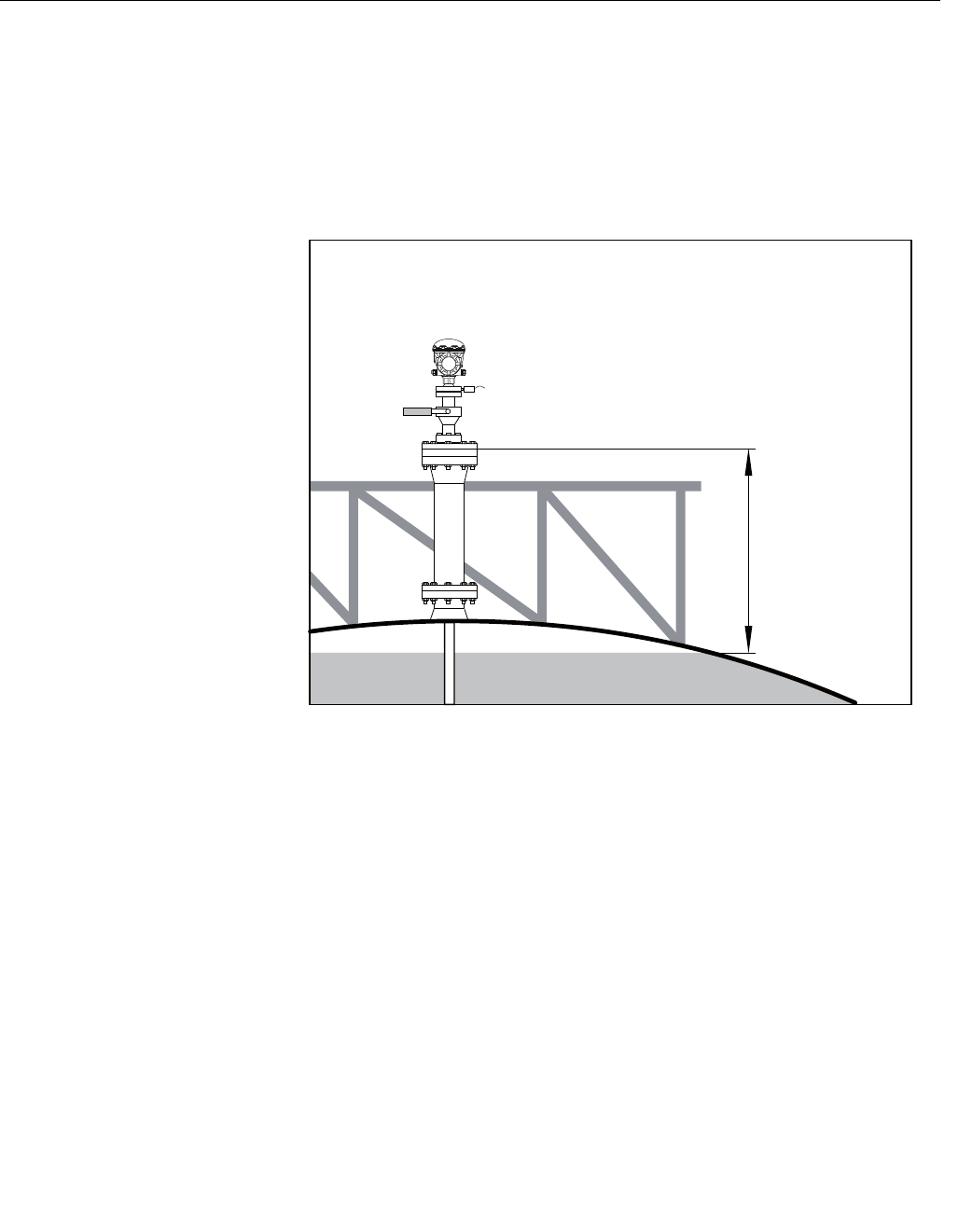
Reference Manual
300520EN, Rev AA
November 2009
3-17
Rosemount 5900 Series
Section 3. Installation
Extension Pipe for Minimum Distance.
The radar level gauge should be placed so that there is always 800 mm or
more between the flange and the maximum product level. If the tank is filled
above the maximum product level, an extension pipe can be mounted to raise
the radar level gauge so that it measures correctly all the way up to the
maximum level, see Figure 3-16.
Figure 3-16. Rosemount 5900
with extension pipe
Minimum 800 mm
to product surface
Preliminary
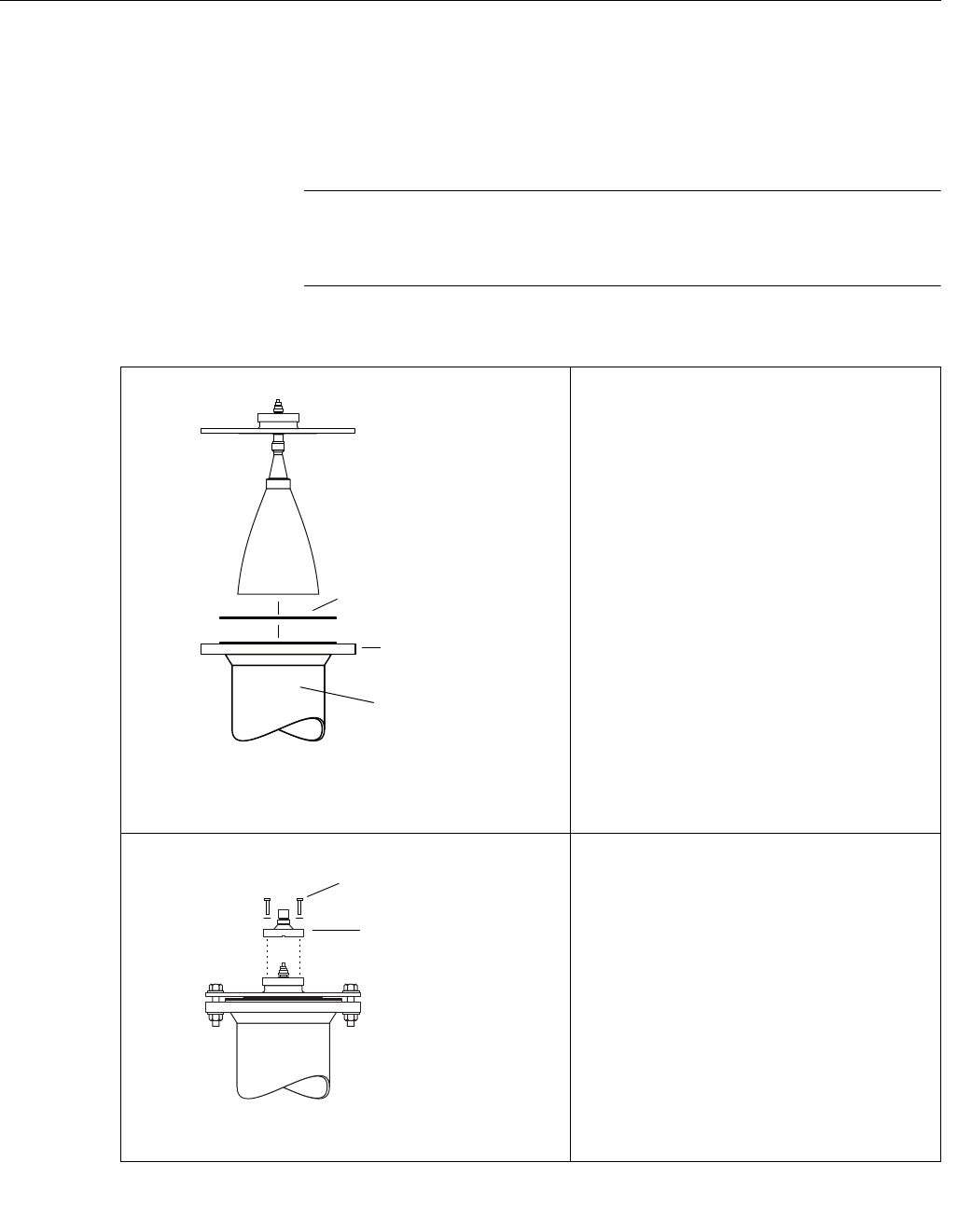
Reference Manual
300520EN, Rev AA
November 2009
Rosemount 5900 Series
3-18 Section 3. Installation
3.3 MECHANICAL
INSTALLATION
3.3.1 Horn Antenna Follow this instruction when installing the Rosemount 5900 with Horn
Antenna. See “Horn Antenna Requirements” on page 3-4 for information on
mounting considerations before installing the gauge on the tank.
NOTE!
When determining conduit dimensions (if used), note that the Horn Antenna
Gauge may be inclined 4° towards the center of the tank (see Figure 3-2 on
page 3-5). Use flexible conduits close to the Radar Tank Gauge.
1. Check that all parts and tools are
available before carrying them up to
the tank roof.
2. Put a gasket on the socket and
carefully insert the horn antenna and
flange assembly.
3. Tighten the flange onto the socket by
using suitable screws and nuts
(customer supplied).
4. Put the adapter on the flange.
Tighten the four M10 screws with
washers by hand so that the adapter
can be rotated.
Horn antenna and
flange assembly
Gasket (Customer supplied)
Customer supplied
flange
Nozzle
Adapter
Four M10 screws and
washers
Preliminary
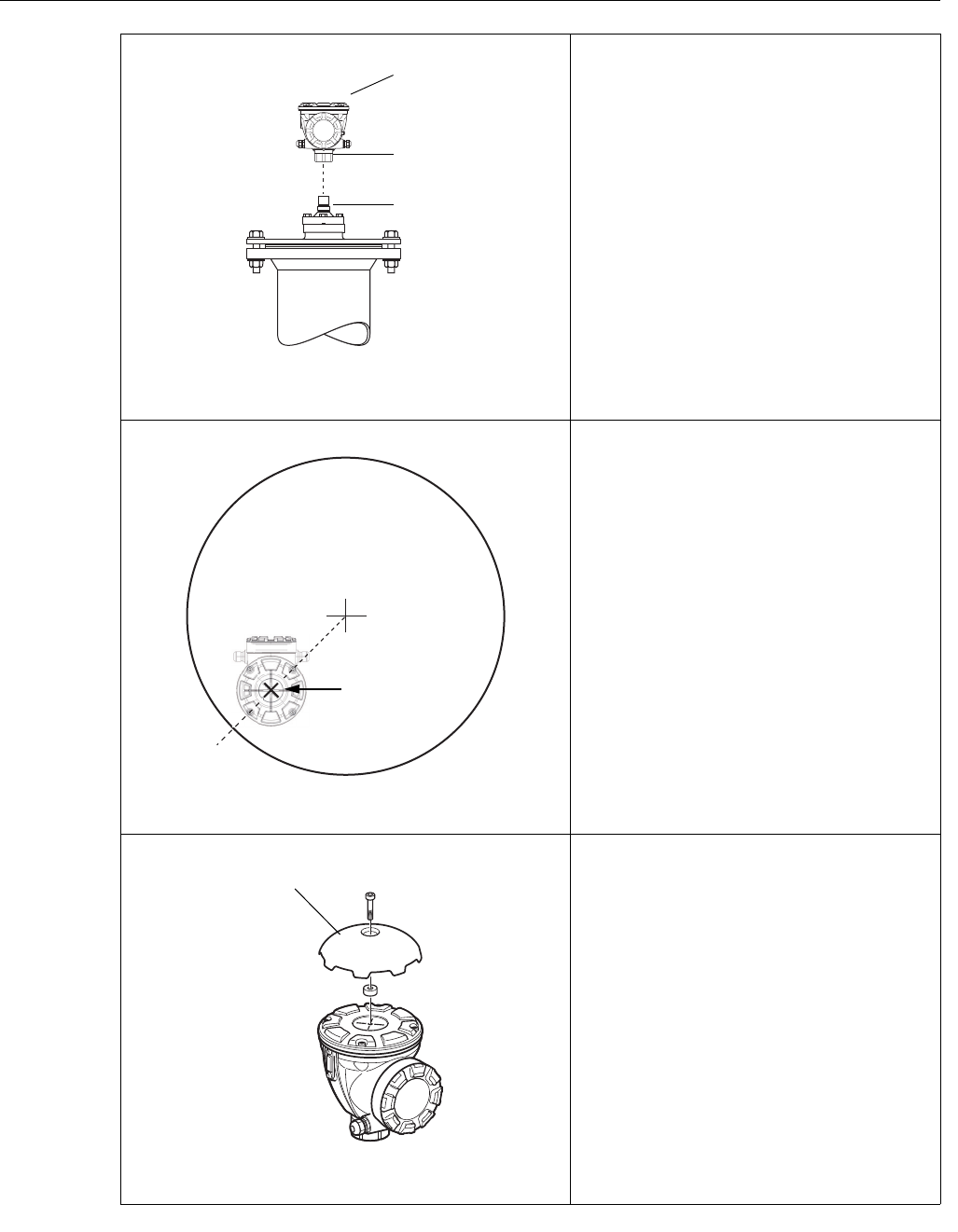
Reference Manual
300520EN, Rev AA
November 2009
3-19
Rosemount 5900 Series
Section 3. Installation
5. Put the transmitter head onto the
antenna adapter.
6. Ensure that the guide pin inside the
transmitter head base fits the groove
on the adapter.
7. Tighten the nut that connects the
transmitter head to the adapter.
8. Ensure that the gauge is directed so
that the cross hairs on top of the
transmitter head points towards the
center of the tank.
9. Tighten the adapter screws
(4 M10).
10. Put the Weather Protection Hood on
top of the transmitter head and
tighten the screw.
11. Connect the electrical cabling and
configure the gauge by using the
TankMaster WinSetup software (see
the Raptor System Configuration
Manual, Document No. 300510EN)
Transmitter head
Nut
Adapter
Tank
Tank center
Cross hairs
Weather
Protection Hood
Preliminary
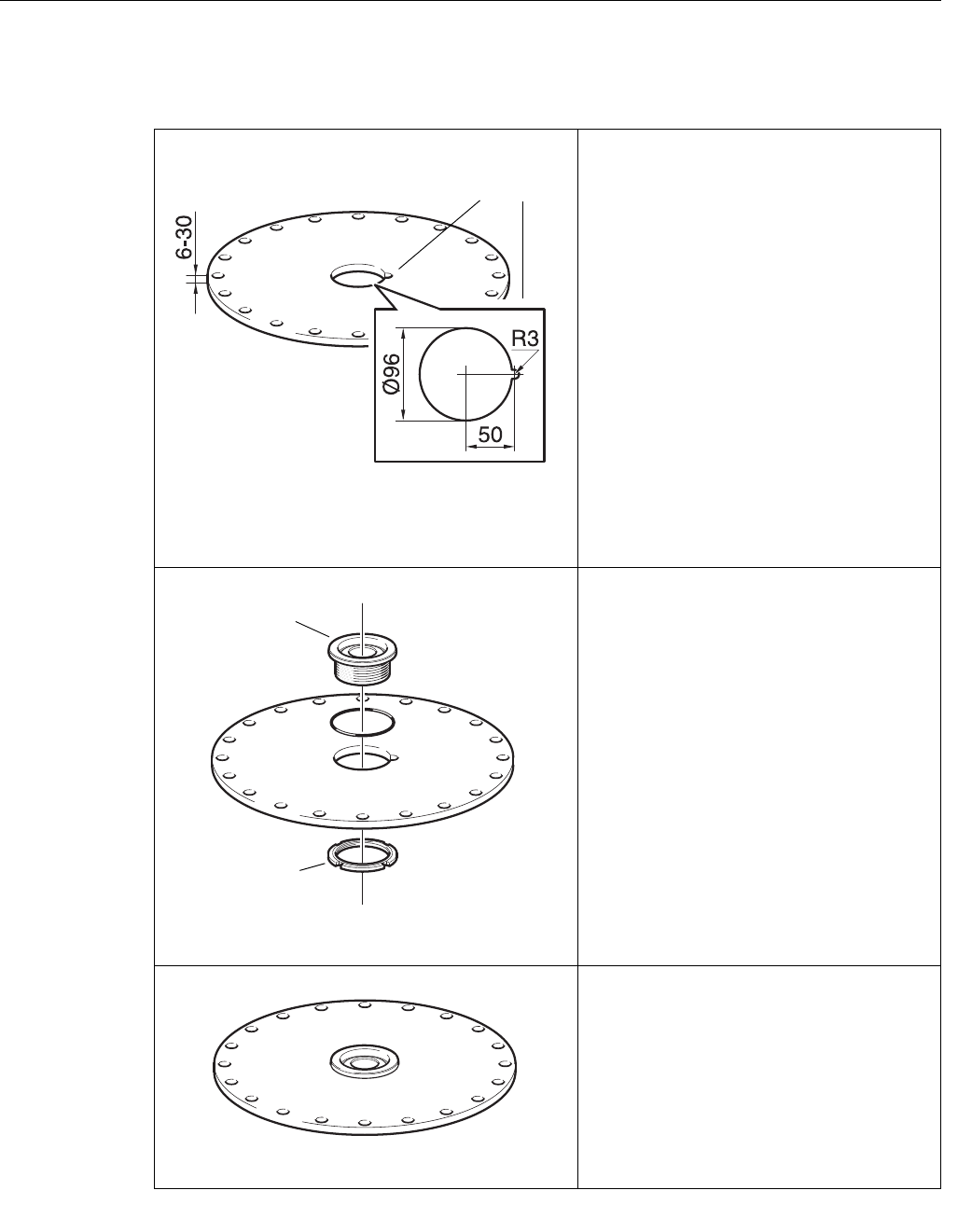
Reference Manual
300520EN, Rev AA
November 2009
Rosemount 5900 Series
3-20 Section 3. Installation
3.3.2 Parabolic
Antenna
Mounting the Flange Ball model T30
1. Use a flange of thickness 6 - 30 mm.
2. Make sure that the diameter of the
hole is 96 mm.
Make a small recess at one side of
the flange hole.
3. Put the O-ring on the flange and
insert the Flange Ball into the hole.
Make sure that the pin on the side of
the Flange Ball fits into the recess
on the flange.
4. Tighten the nut so that the Flange
Ball fits tightly to the flange (torque
50 Nm).
Recess
Flange Ball
Nut
Preliminary
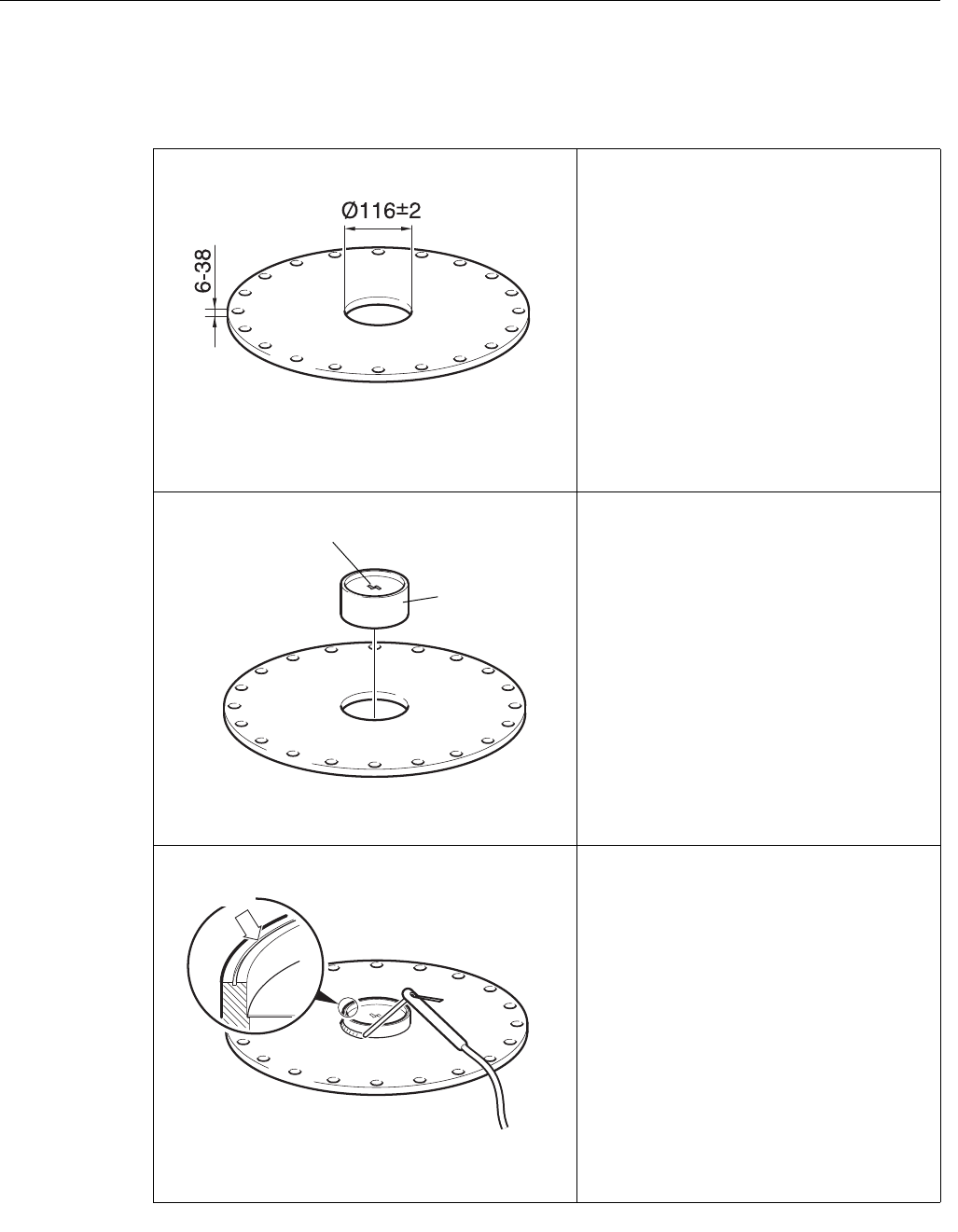
Reference Manual
300520EN, Rev AA
November 2009
3-21
Rosemount 5900 Series
Section 3. Installation
Mounting the Flange Ball model T38-W
The Flange Ball T38 is welded to the flange. To mount the
T38 do the following:
1. Make sure that the diameter of the
hole is 116 ± 2 mm.
2. Let the protection plates remain on
the Flange Ball until the welding is
finished. These plates protect the
surface of the Flange Ball from
welding sparks.
3. Make sure that the Flange Ball is
mounted in such a way that the
grove is directed upwards when the
flange is mounted on the tank
nozzle.
Protection plate
Flange Ball
Groove
Preliminary
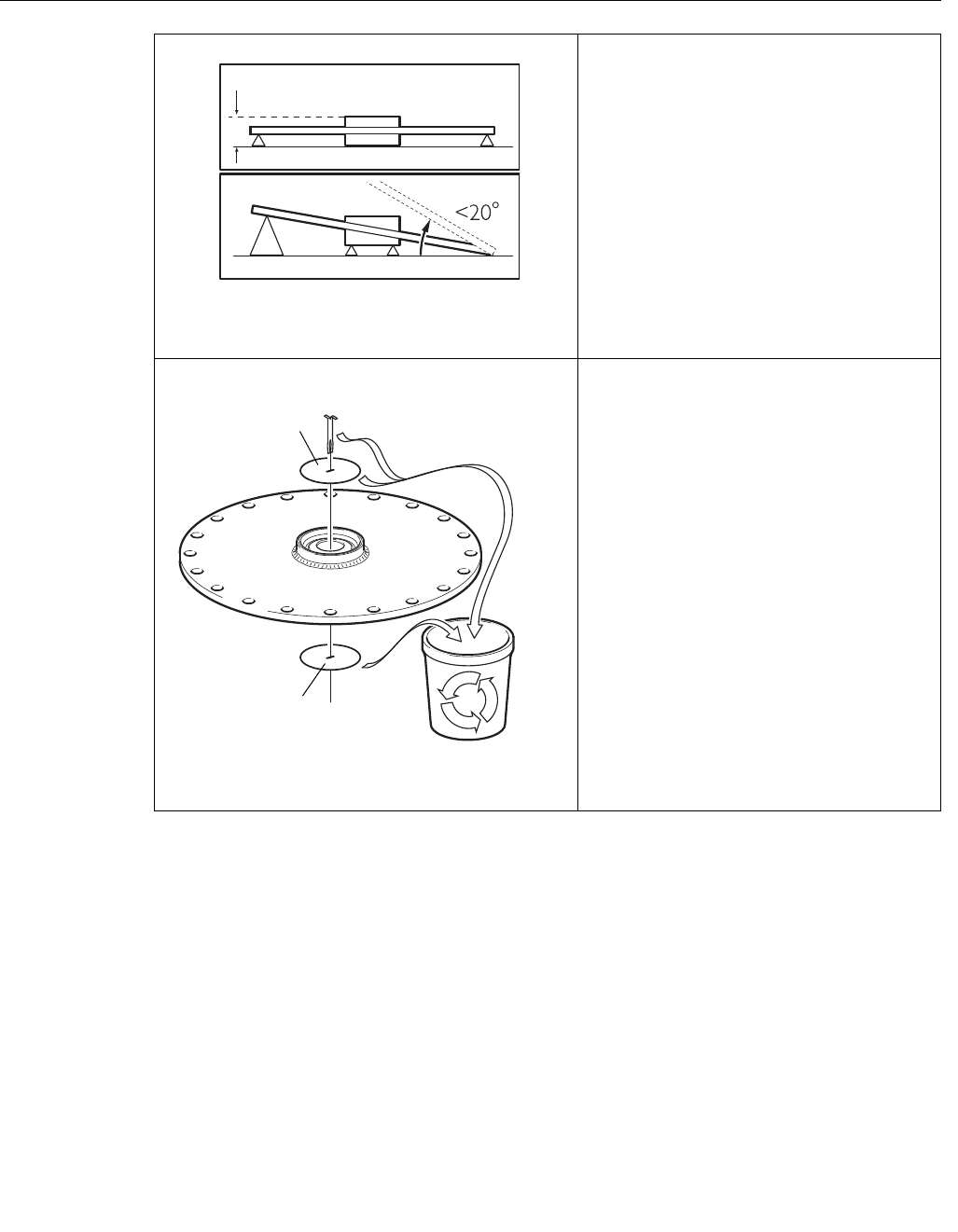
Reference Manual
300520EN, Rev AA
November 2009
Rosemount 5900 Series
3-22 Section 3. Installation
4. If the tank flange is inclined, make
sure that the Flange Ball is welded
so that the Flange Ball is horizontal
when it is mounted on the tank.
The tank flange inclination should
not exceed 20 degrees.
5. Remove the protection plates when
the Flange Ball is welded to the
flange.
60 mm
Protection plate
Protection plate
Preliminary
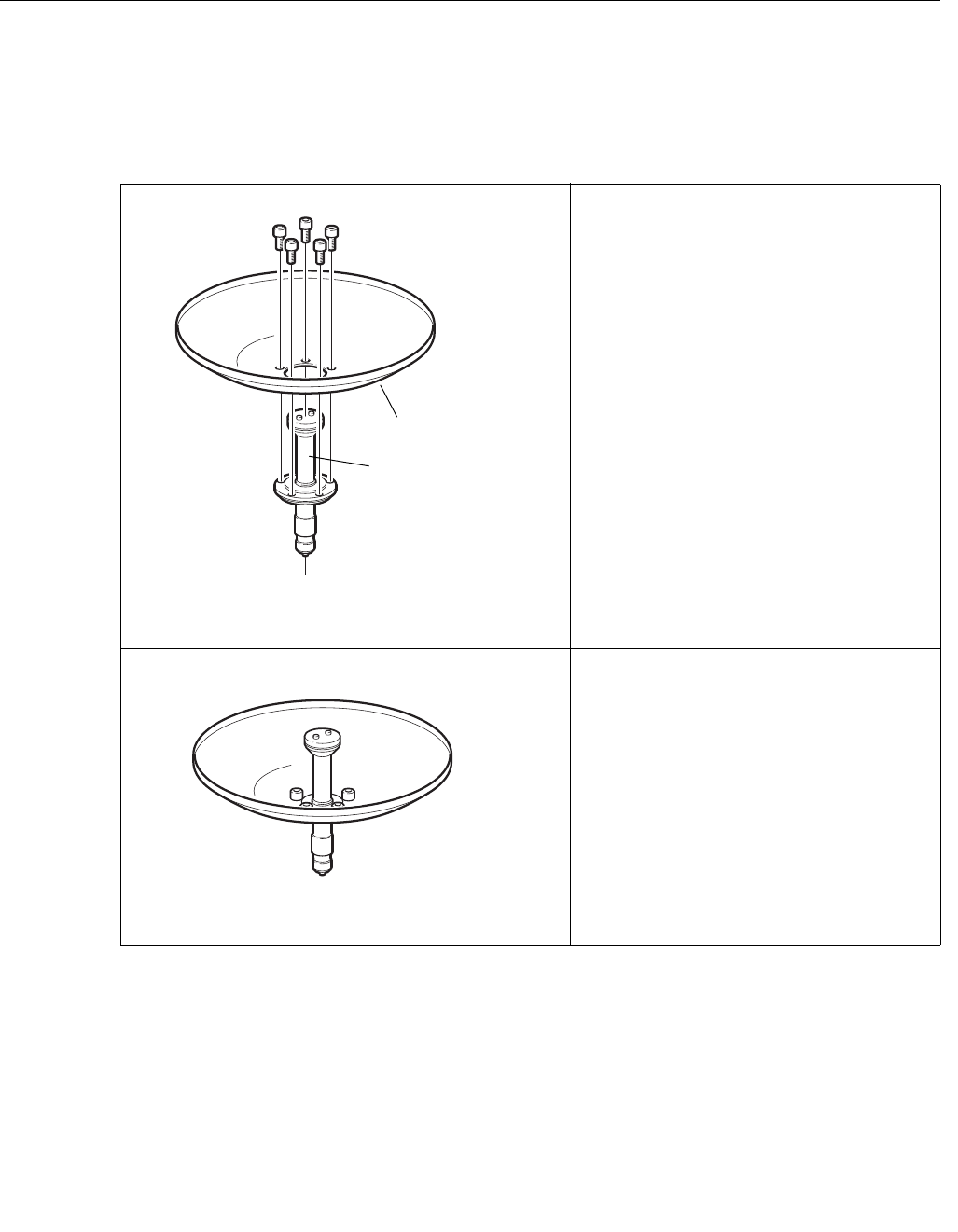
Reference Manual
300520EN, Rev AA
November 2009
3-23
Rosemount 5900 Series
Section 3. Installation
Mounting the Parabolic Antenna
Follow this instruction when installing the the Parabolic antenna. See
“Parabolic Antenna Requirements” on page 3-6 for considerations before
installing the gauge on the tank.
1. Check that all parts and tools are
available before carrying them up to
the tank top.
2. Fit the Parabolic Reflector onto the
Antenna Feeder and mount the five
M5 screws
3. Tighten the screws.
Parabolic reflector
Antenna feeder
M5x5
Preliminary
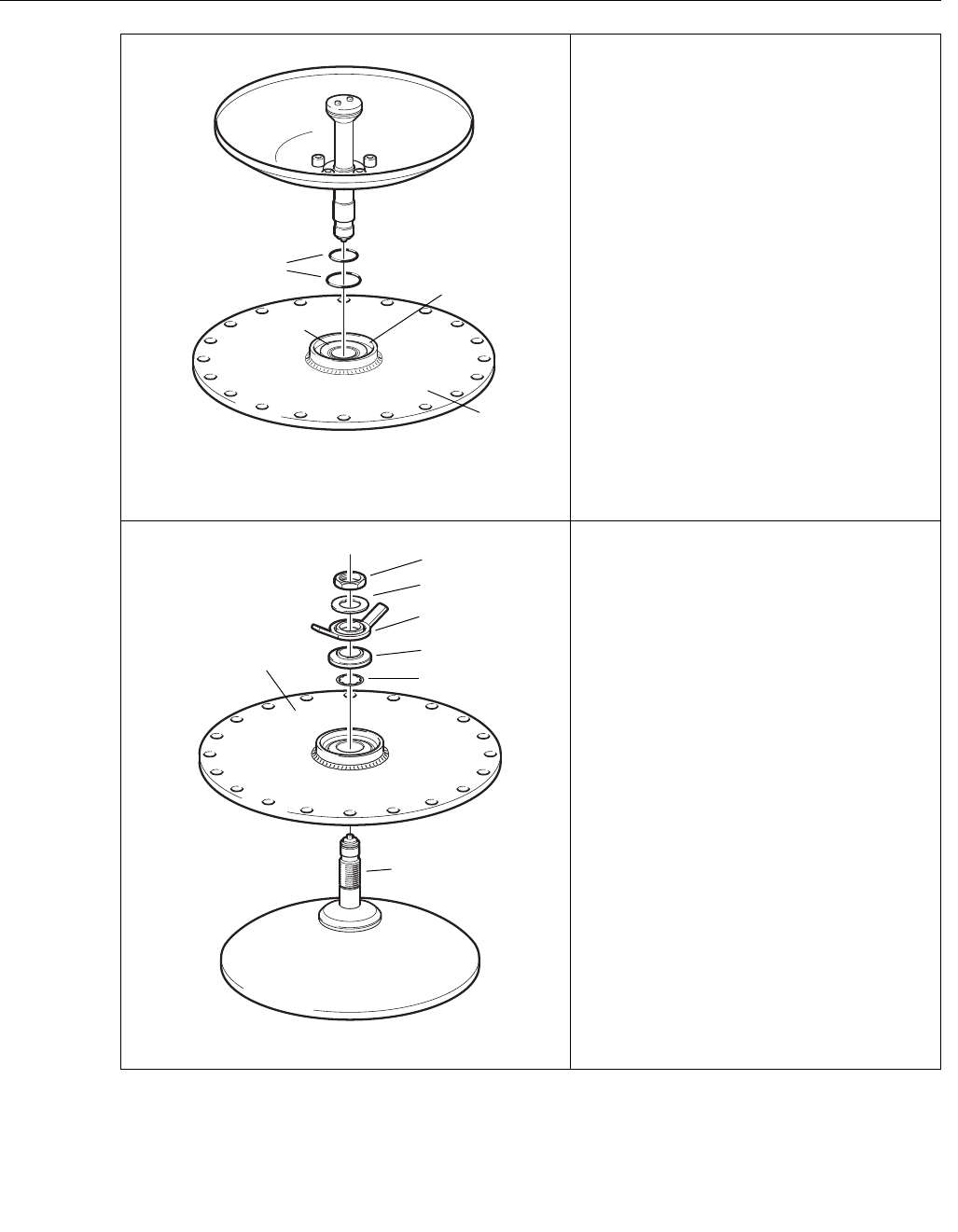
Reference Manual
300520EN, Rev AA
November 2009
Rosemount 5900 Series
3-24 Section 3. Installation
4. Put the two O-rings in the grooves on
the upper surface of the Flange Ball.
5. Turn the flange around and insert the
antenna feeder into the flange hole.
Mount the washers and nuts.
Flange Ball
Flange
2 O-rings
Grooves
Nut
Tab Washer
Finger Nut
Washer Ball
Stop Washer
Antenna Feeder
Flange
Preliminary
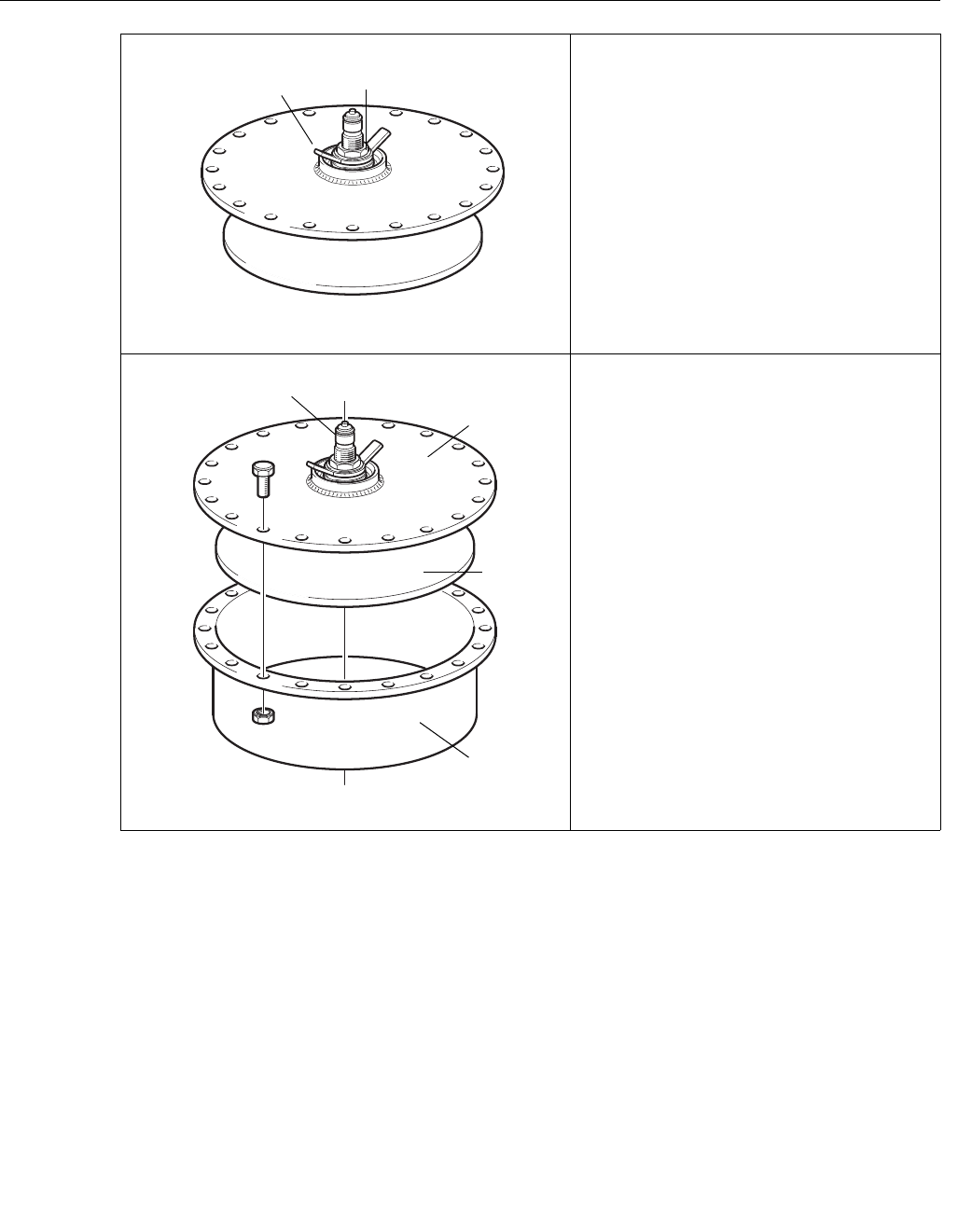
Reference Manual
300520EN, Rev AA
November 2009
3-25
Rosemount 5900 Series
Section 3. Installation
6. Tighten the finger nut and the upper
nut by hand.
7. Place the antenna and flange
assembly on the tank nozzle and
tighten the flange screws.
Finger Nut Upper Nut
Antenna
Flange
Nozzle
Antenna Feeder
Preliminary
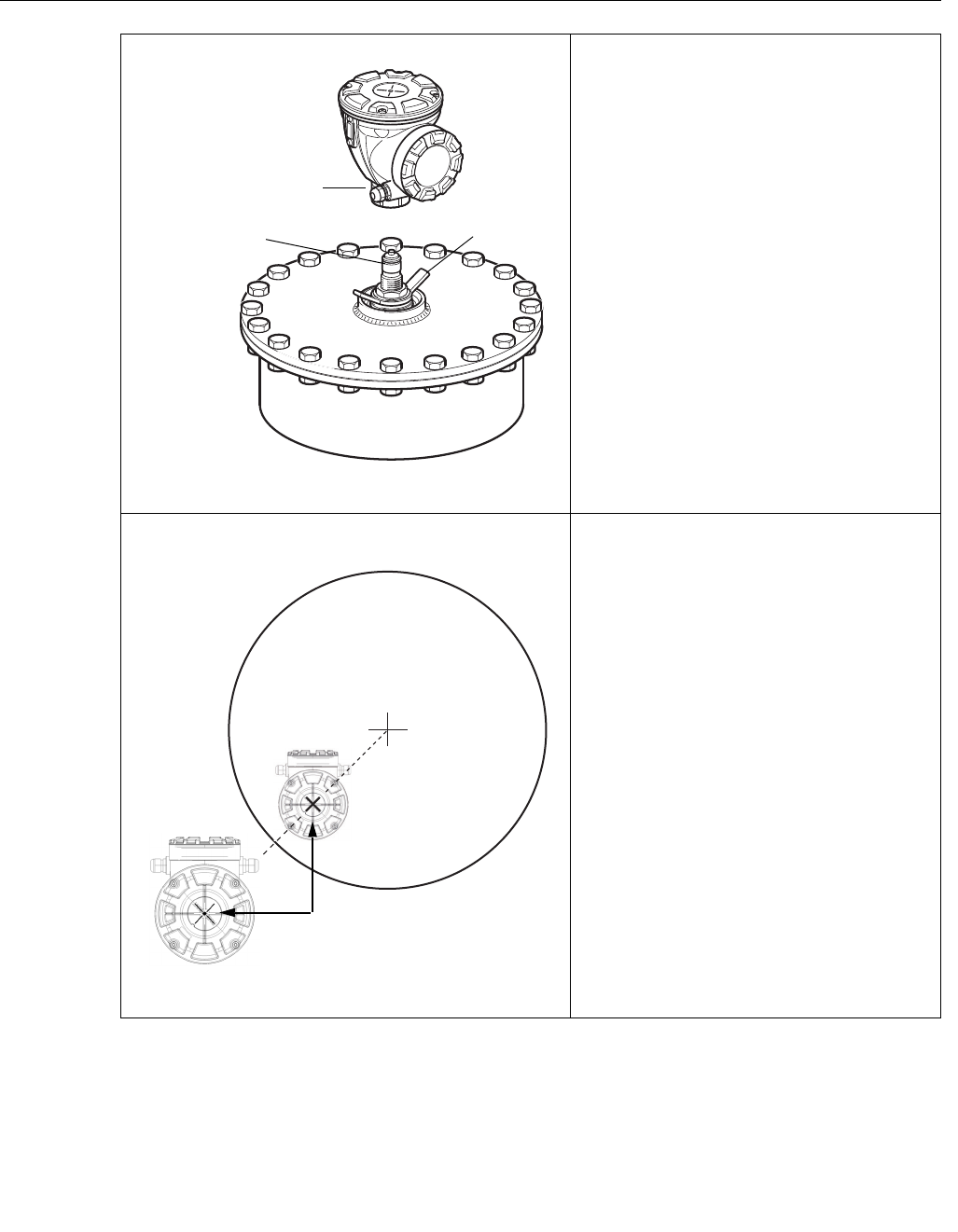
Reference Manual
300520EN, Rev AA
November 2009
Rosemount 5900 Series
3-26 Section 3. Installation
8. Put the gauge on the antenna feeder.
Ensure that the guide pin inside the
base of the transmitter head fits the
groove on the antenna feeder.
9. Tighten the nut that connects the
transmitter head to the antenna.
10. Loosen the finger nut slightly.
11. Rotate the gauge so that the cross
hairs on top of the 5900 head is
directed towards the center of the
tank.
Nut
Antenna Feeder Finger Nut
Tank center
Cross hairs
TANK
Preliminary
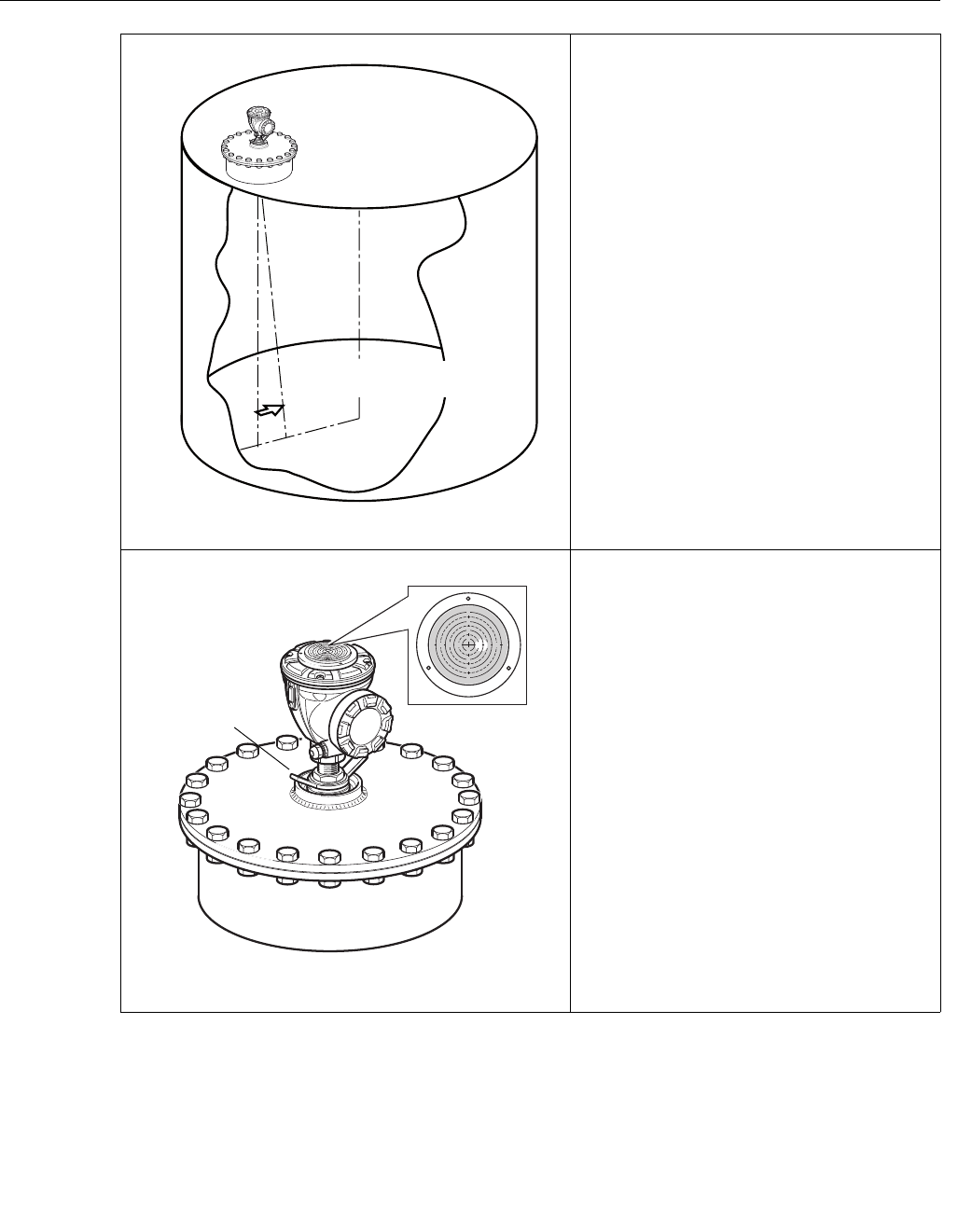
Reference Manual
300520EN, Rev AA
November 2009
3-27
Rosemount 5900 Series
Section 3. Installation
12. Use the marks on the Washer Ball to
adjust the gauge so that the antenna
is inclined roughly 1.5° towards the
center of the tank.
Note: For bitumen tanks, the gauge
should be mounted with 0°
inclination.
13. Tighten the finger nut.
14. Place the level on top of the
transmitter head and check that the
inclination of the gauge is 1.5°
towards the tank center. If not, loosen
the finger nut and adjust the gauge.
Note: Make sure the air bubble
touches, but doesn´t overlap the 1.5°
mark.
Note: For bitumen tanks, the gauge
should be mounted with 0°
inclination.
15. Tighten the finger nut firmly.
Plumb line
Tank center
Incline antenna 1.5°
towards the tank center
0,5 0,5
1,5 1,5
2,5 2,5
0
0
1
1
2
2
3
3
Finger Nut
Preliminary
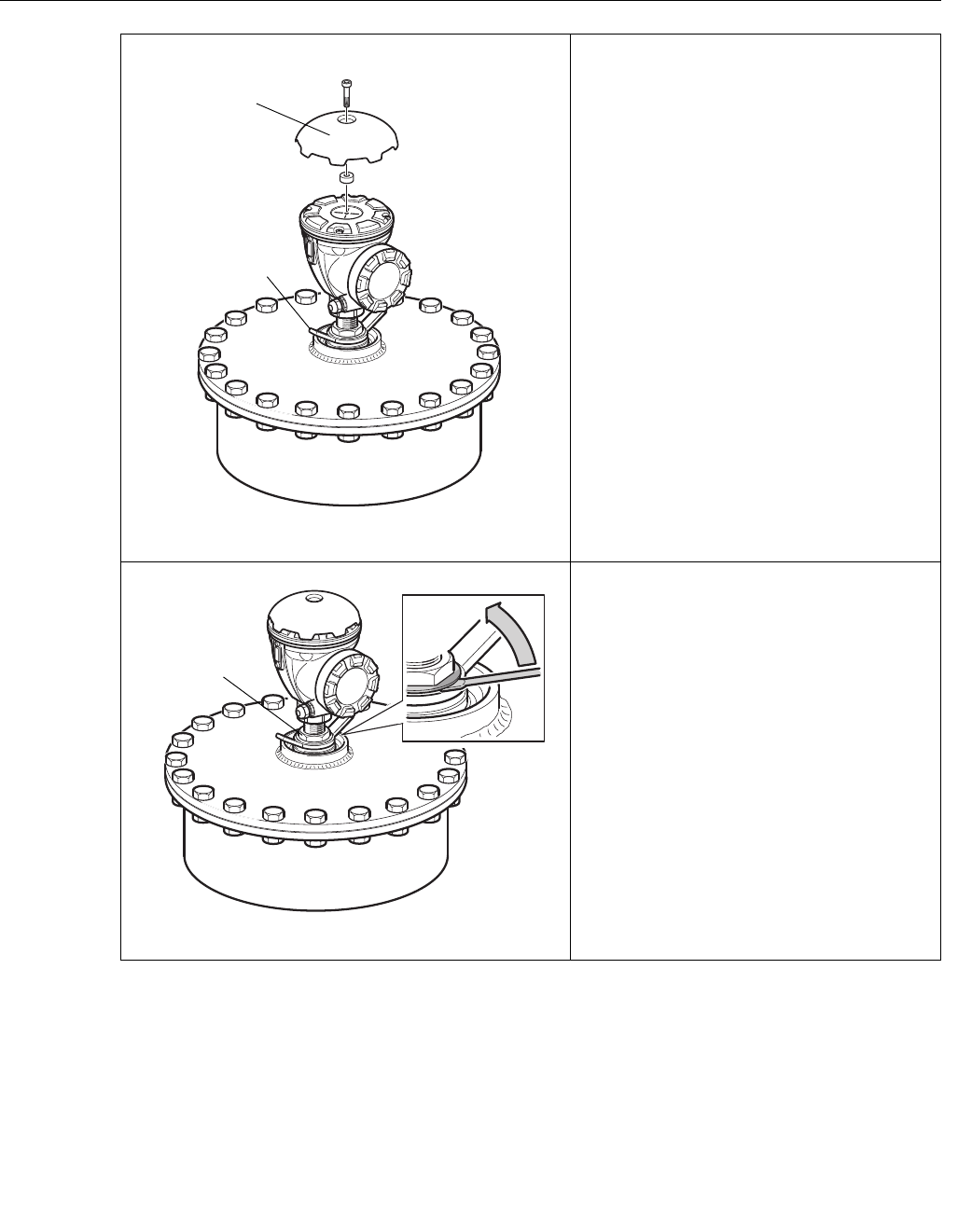
Reference Manual
300520EN, Rev AA
November 2009
Rosemount 5900 Series
3-28 Section 3. Installation
16. Put the Weather Protection Hood on
top of the transmitter head and
tighten the screw.
17. Tighten the upper nut to lock the
finger nut, and secure by folding the
tab washer over the nut.
18. Connect the electrical cabling and
configure the gauge by using the
TankMaster WinSetup software (see
the Raptor System Configuration
Manual, Document No. 300510EN).
Finger Nut
Weather
Protection Hood
Upper Nut
Preliminary
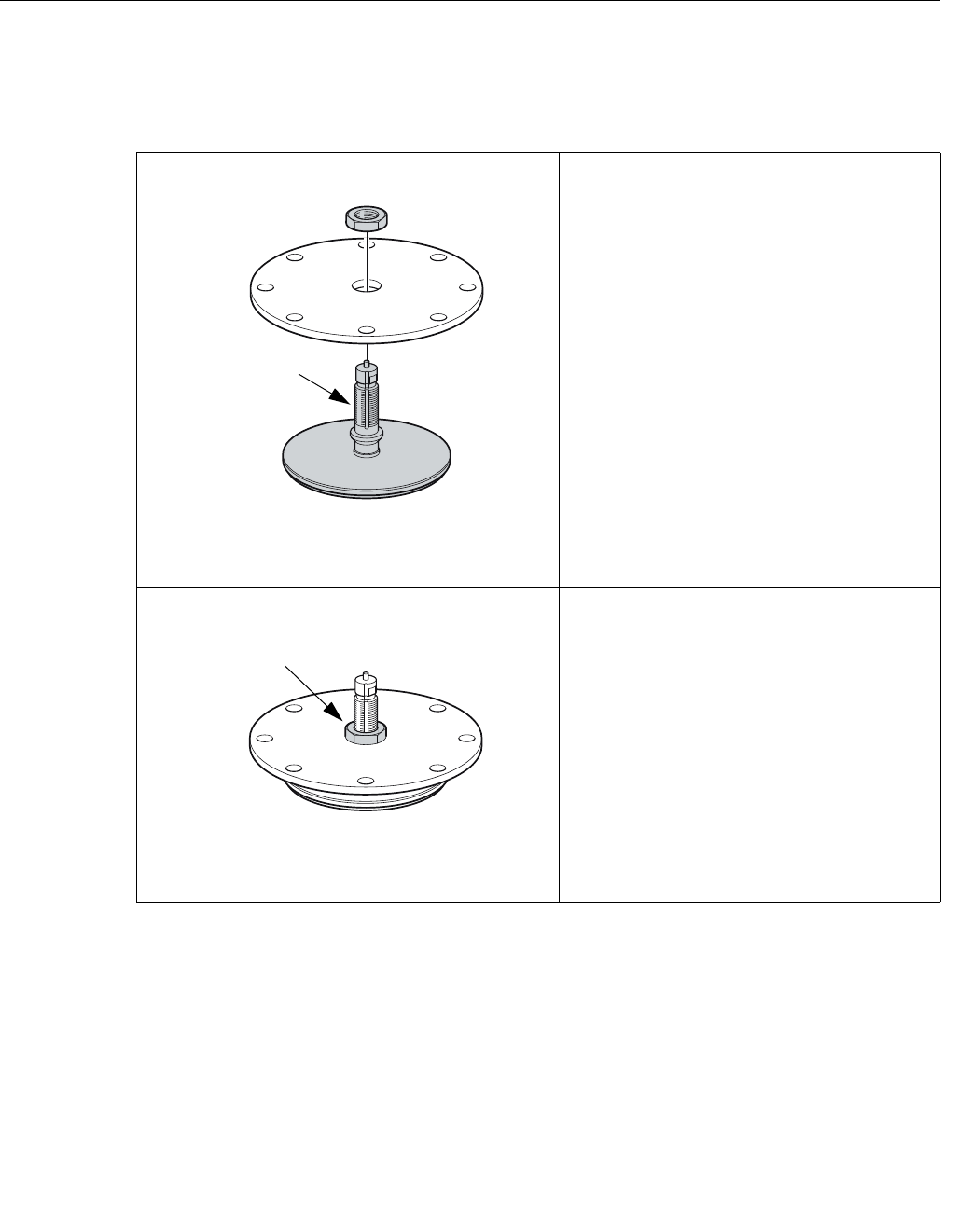
Reference Manual
300520EN, Rev AA
November 2009
3-29
Rosemount 5900 Series
Section 3. Installation
3.3.3 Array Antenna -
Fixed version
Follow this Step by Step instruction when installing the Array Antenna Fixed
version. See “Still Pipe Antenna Requirements” on page 3-10 for information
on mounting considerations before installing the gauge on the tank.
1. Insert the antenna feeder into the
flange hole.
2. Tighten the nut. Secure by folding the
tab washer over the nut.
Antenna
feeder
Nut
Preliminary
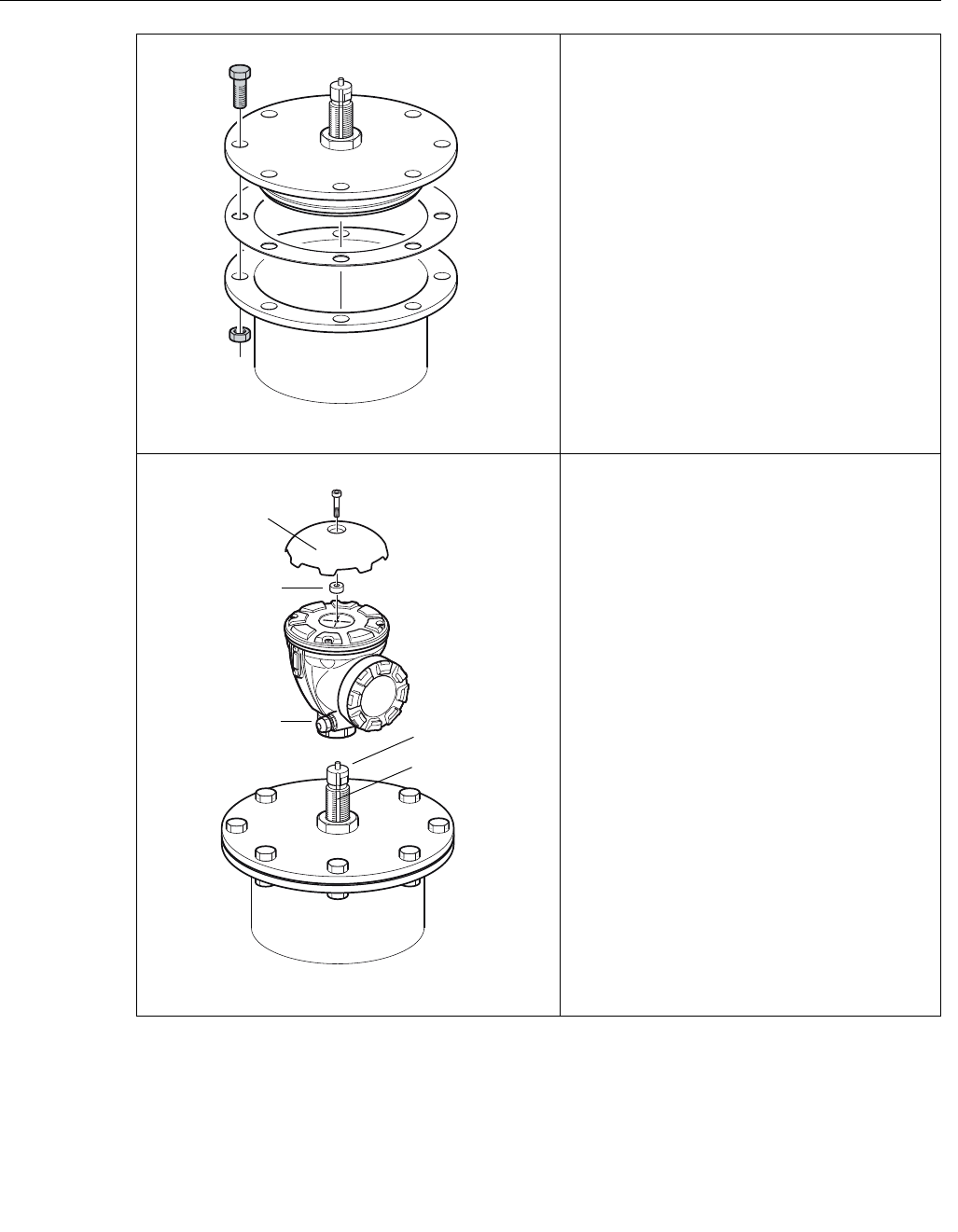
Reference Manual
300520EN, Rev AA
November 2009
Rosemount 5900 Series
3-30 Section 3. Installation
3. Put the antenna and flange assembly
on the tank nozzle and tighten the
flange screws.
4. Carefully put the gauge on top of the
antenna feeder and tighten the nut.
Ensure that the guide pin inside the
base of the transmitter head fits the
groove on the antenna feeder.
5. Put the Weather Protection Hood on
top of the transmitter head and tighten
the screw.
Nut
Groove
Weather
Protection Hood
Antenna feeder
Spacer
Preliminary
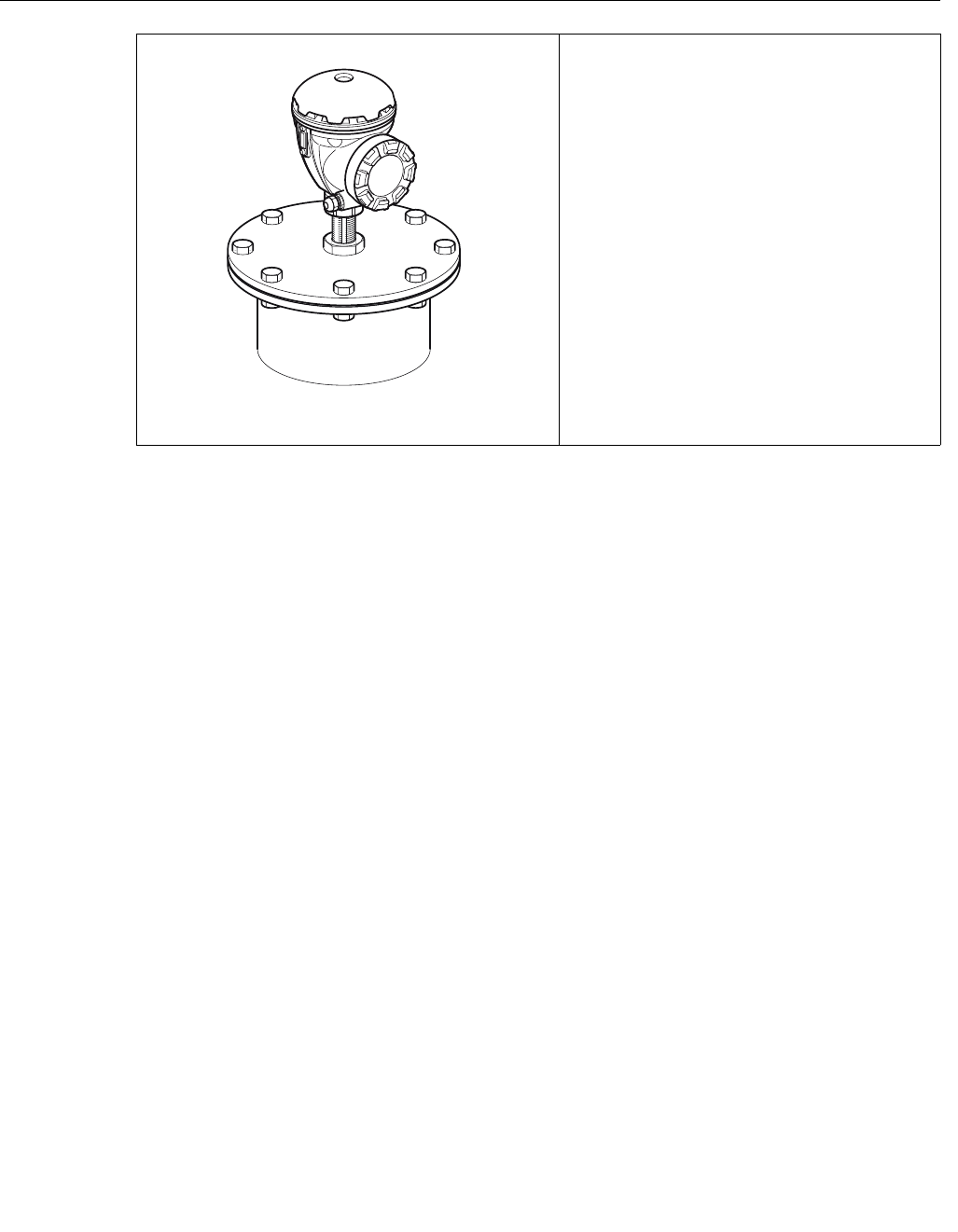
Reference Manual
300520EN, Rev AA
November 2009
3-31
Rosemount 5900 Series
Section 3. Installation
6. Connect the electrical cabling and
configure the 5900 by using the
TankMaster WinSetup software, see
the Raptor System Configuration
Manual (Document No. 300510EN).
Preliminary
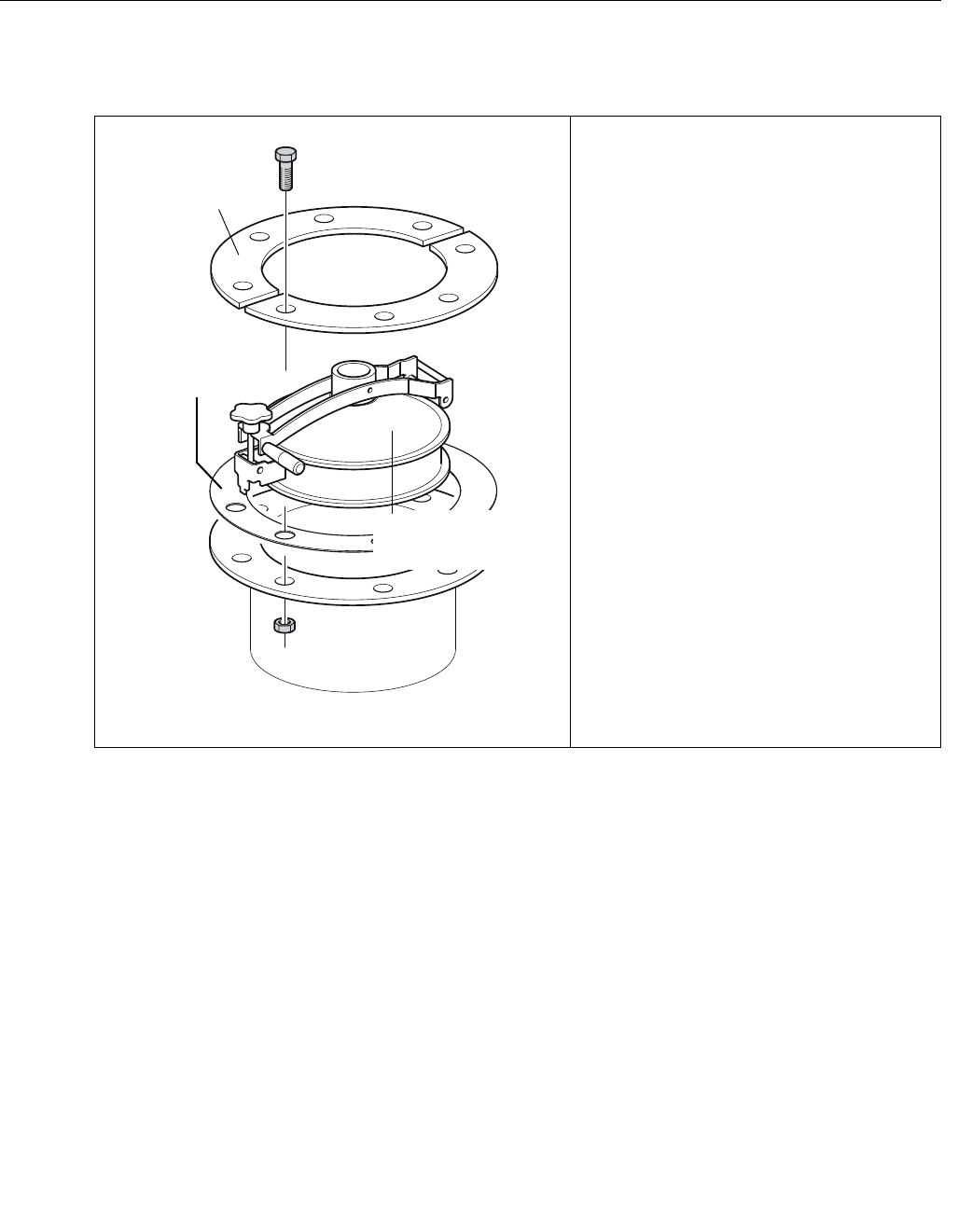
Reference Manual
300520EN, Rev AA
November 2009
Rosemount 5900 Series
3-32 Section 3. Installation
3.3.4 Array Antenna -
Hinged Hatch
Follow this instruction when installing the the Array antenna Hinged Hatch
version.
1. Mount the Fast Opening Cover and
flange on the nozzle. The flange
consists of two parts mounted on
each side of the cover.
(There is also a version available
with a flange welded on the cover).
2. Tighten the flange screws.
Fast Opening
Cover
Flange
Flange
Gasket
Preliminary
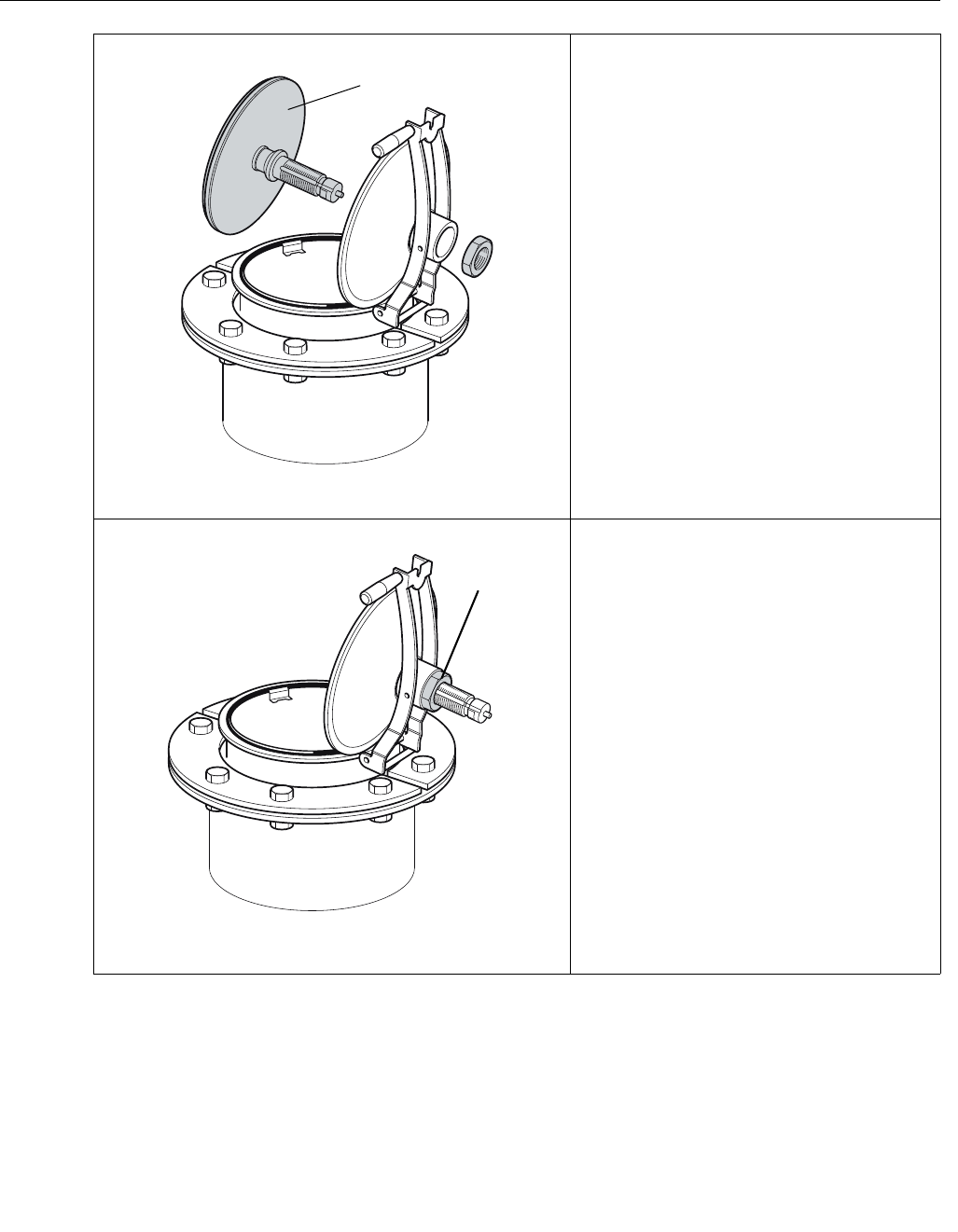
Reference Manual
300520EN, Rev AA
November 2009
3-33
Rosemount 5900 Series
Section 3. Installation
3. Mount the antenna on the lid.
4. Tighten the nut which holds the
antenna to the lid.
Antenna
Nut
Preliminary
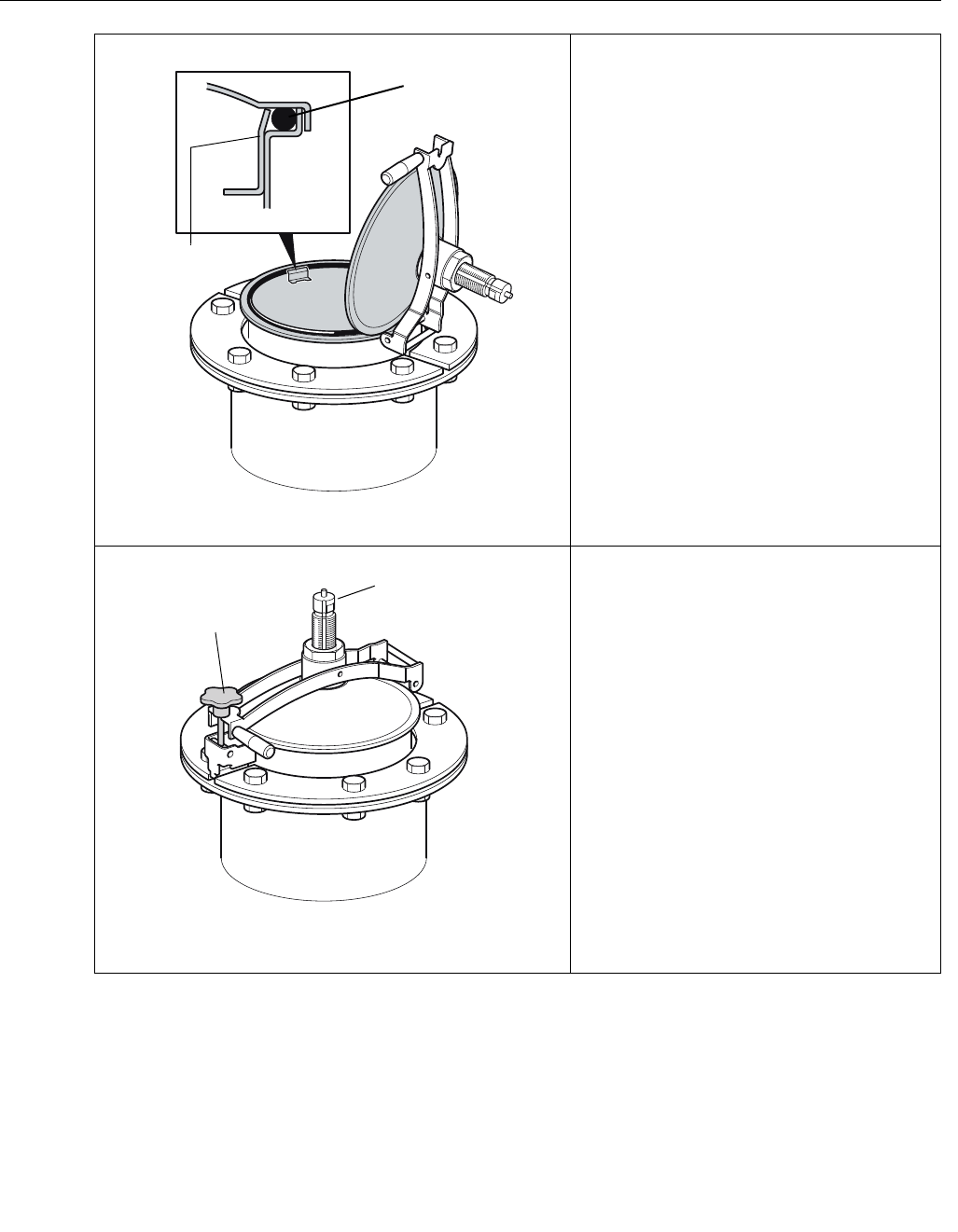
Reference Manual
300520EN, Rev AA
November 2009
Rosemount 5900 Series
3-34 Section 3. Installation
5. Check that the O-ring is properly
seated all around the cover and is
pressed down behind the Hand Dip
Plate.
6. Close the lid and tighten the locking
screw.
O-ring
Hand Dip Plate
Tighten the locking
screw
Antenna feeder
Preliminary
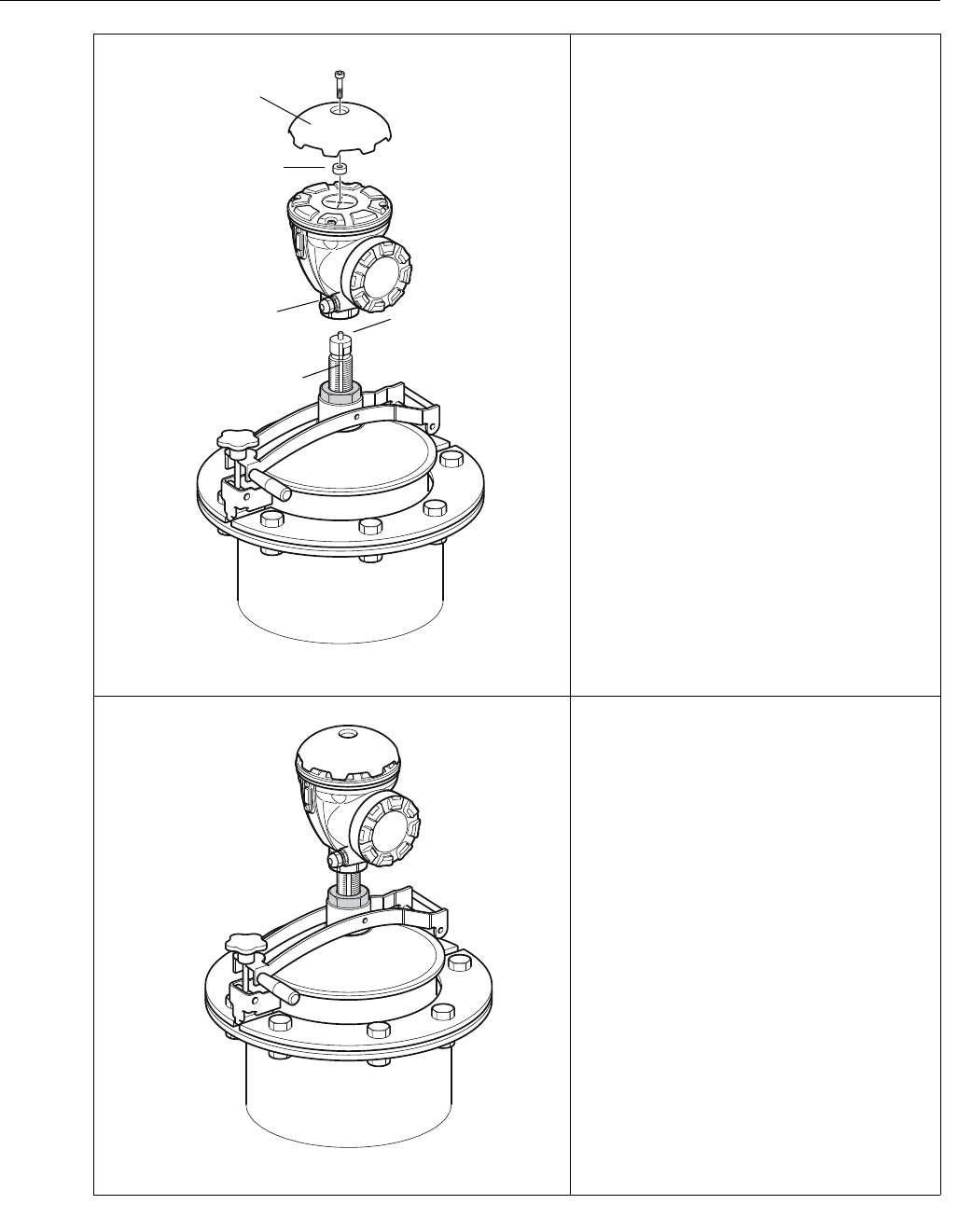
Reference Manual
300520EN, Rev AA
November 2009
3-35
Rosemount 5900 Series
Section 3. Installation
7. Carefully put the gauge on top of the
antenna feeder and tighten the nut.
Ensure that the guide pin inside the
base of the transmitter head fits the
groove on the antenna feeder.
8. Put the Weather Protection Hood on
top of the transmitter head and
tighten the screw.
9. Connect the electrical cabling and
configure the gauge by using the
TankMaster WinSetup software (see
the Raptor System Configuration
Manual, Document No. 300510EN)
Antenna feeder
Groove
Nut
Weather
Protection Hood
Spacer
Preliminary
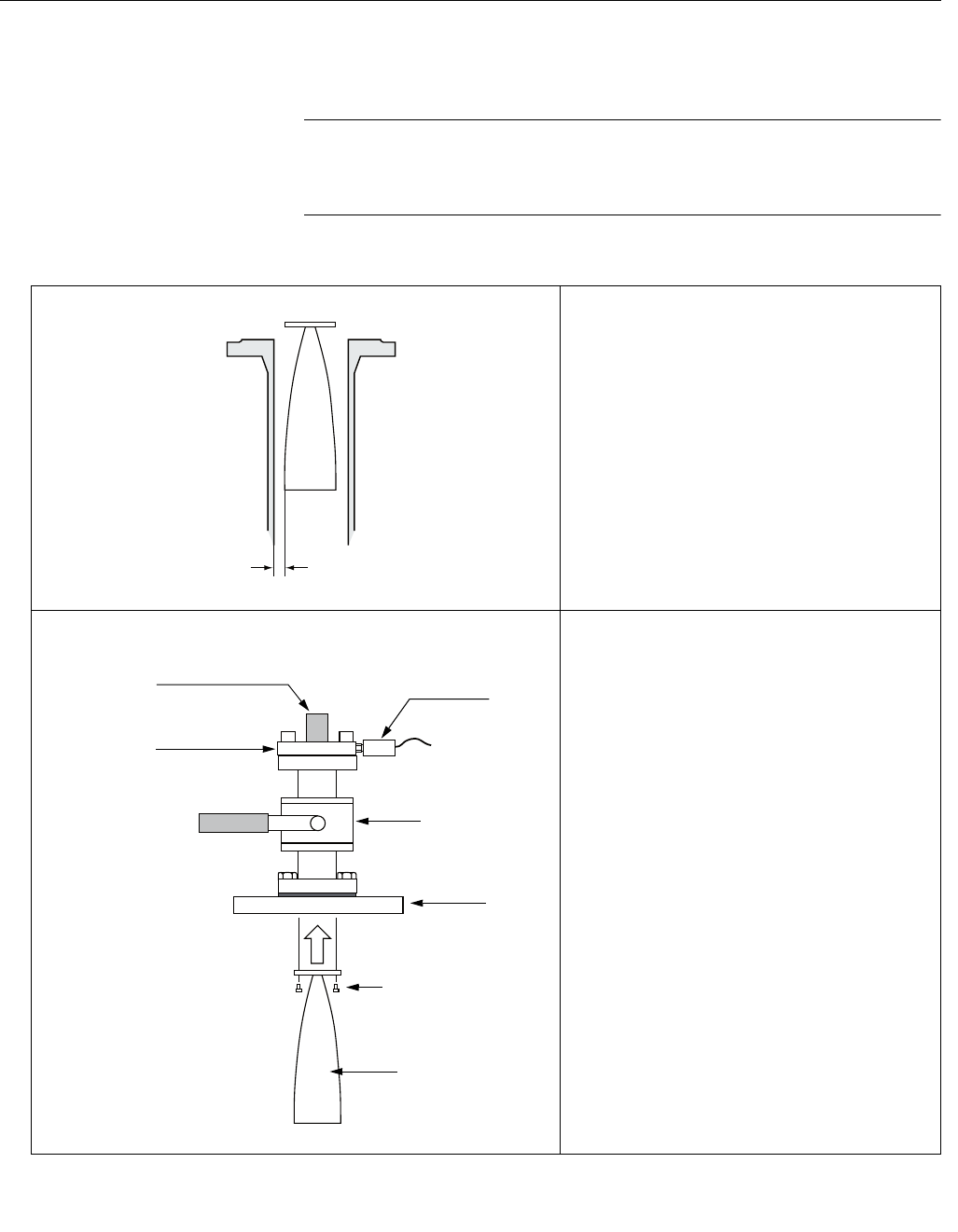
Reference Manual
300520EN, Rev AA
November 2009
Rosemount 5900 Series
3-36 Section 3. Installation
3.3.5 LPG/LNG
Antenna
Follow this step by step instruction when installing the LPG/LNG antenna.
See “LPG/LNG Antenna Requirements” on page 3-13 for information on
mounting considerations before installing the gauge on the tank.
NOTE!
There must be a mark on the pipe flange to show the direction of the
reference pins in the still pipe. Carefully check that the Closing is mounted in
the appropriate angle relative to that mark.
1. Ensure that all parts and tools are
available before carrying them to the
tank top.
2. Install the still pipe according to
mechanical installation drawing
9150072-924.
3. Check that the Cone antenna fits into
the still pipe. The gap between the
Cone antenna and the pipe must not
exceed 2 mm.
4. Mount the Pipe Cone onto the Closing
using four M6 Allen head screws. Be
careful when handling the Closing and
Pipe Cone assembly. It is important
that the Pipe Cone is undamaged.
Do not remove the yellow protective
cap.
Maximum 2 mm
Pressure
transducer
Do not remove this
protection cap
Lower flange
Closing
Four M6 screws
Pipe cone
Ball valve
Preliminary
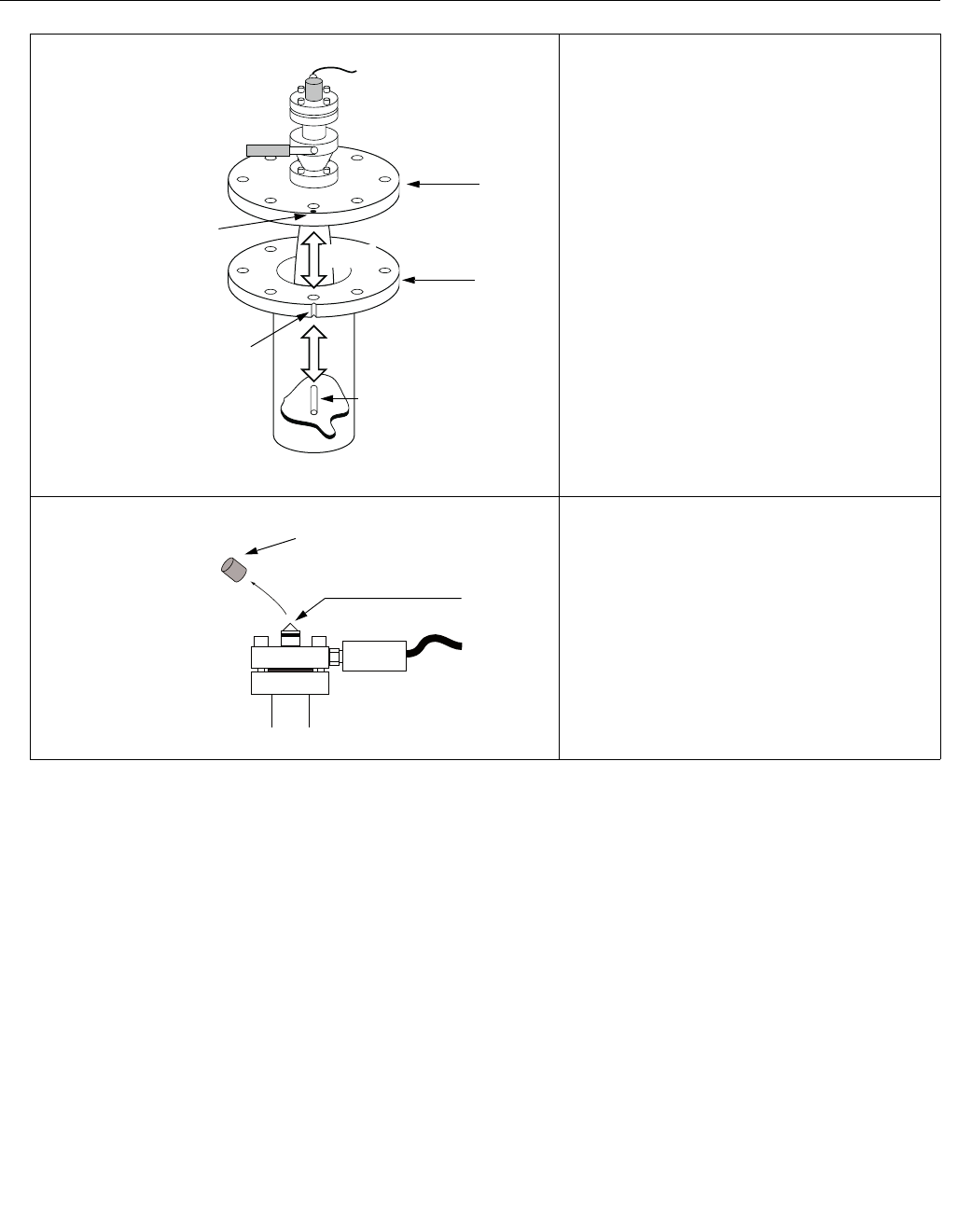
Reference Manual
300520EN, Rev AA
November 2009
3-37
Rosemount 5900 Series
Section 3. Installation
5. Place a gasket (customer supplied) on
the Mounting Flange.
6. Carefully fit the Pipe Cone into the still
pipe and tighten the Closing onto the
Mounting Flange (customer supplied
screws and nuts).
7. Direct the Closing so that the marking
hole aligns with the notch or mark on
the pipe flange.
8. The tank is now sealed and can, as far
as Rosemount Tank Gauging
equipment is concerned, be
pressurized
9. Remove the yellow protection cap.
Do not remove the rubber cone.
Closing
Mounting
Flange
Notch indicating the
direction of the
Reference Pin
Marking
hole Align!
Reference pin
Do not remove
this cone!
Protection cap
Preliminary
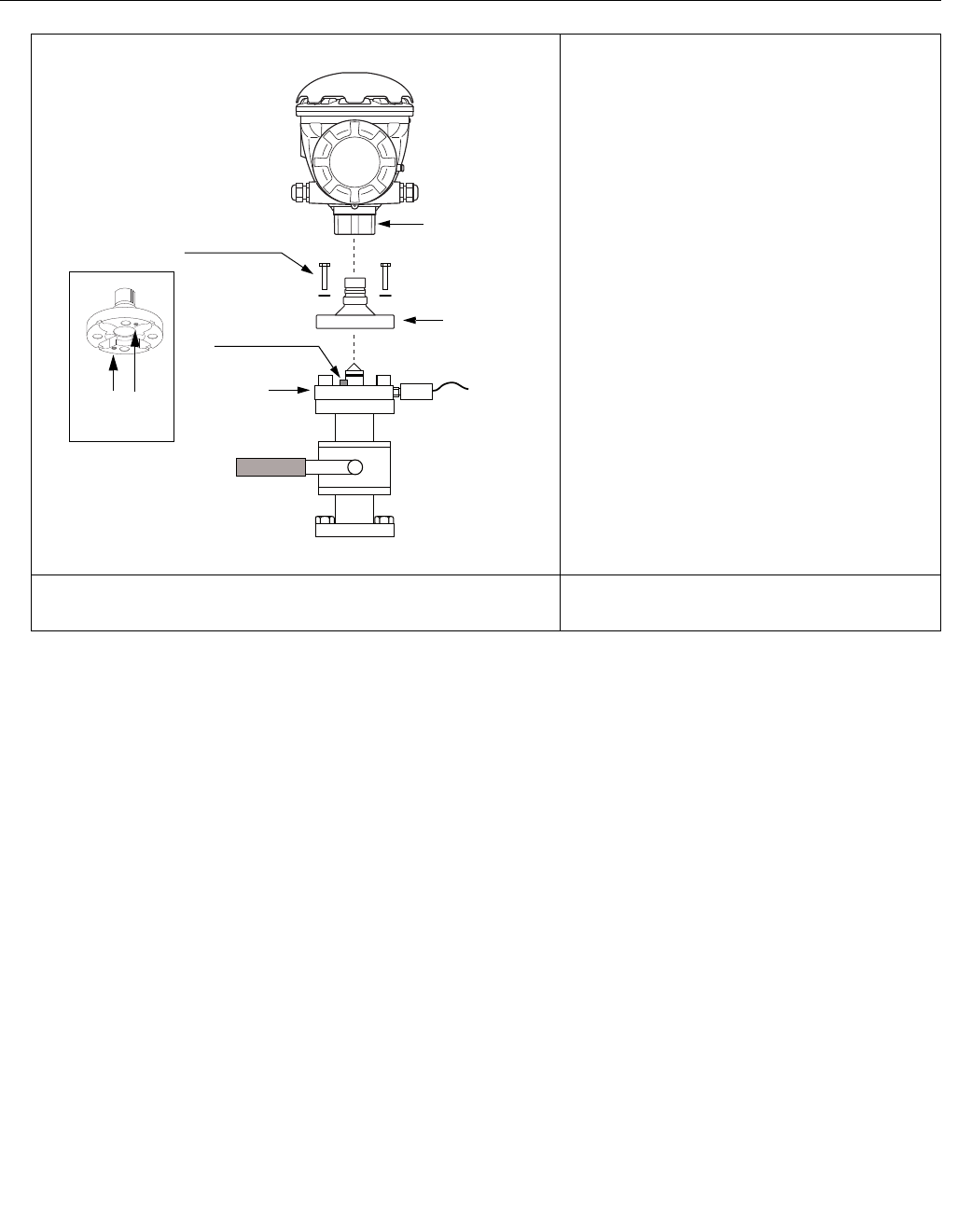
Reference Manual
300520EN, Rev AA
November 2009
Rosemount 5900 Series
3-38 Section 3. Installation
10. Put the adapter on the flange and
tighten the four M10 screws with
washers.
Ensure that the guide pins enter the
holes in the adapter.
11. Fit the Transmitter Head on the
adapter and tighten the nut that
connects the transmitter head to the
antenna
12. Connect the electrical cabling and
configure the gauge by using the
TankMaster WinSetup software, see
the Raptor System Configuration
Manual (Document no. 300510EN).
13. Configure the gauge for LPG
measurements (see “LPG
Configuration” on page 4-9).
4 M10 screws
and washers
Guide pins
Flange
Adapter
Nut
Holes for
guide pins
Preliminary
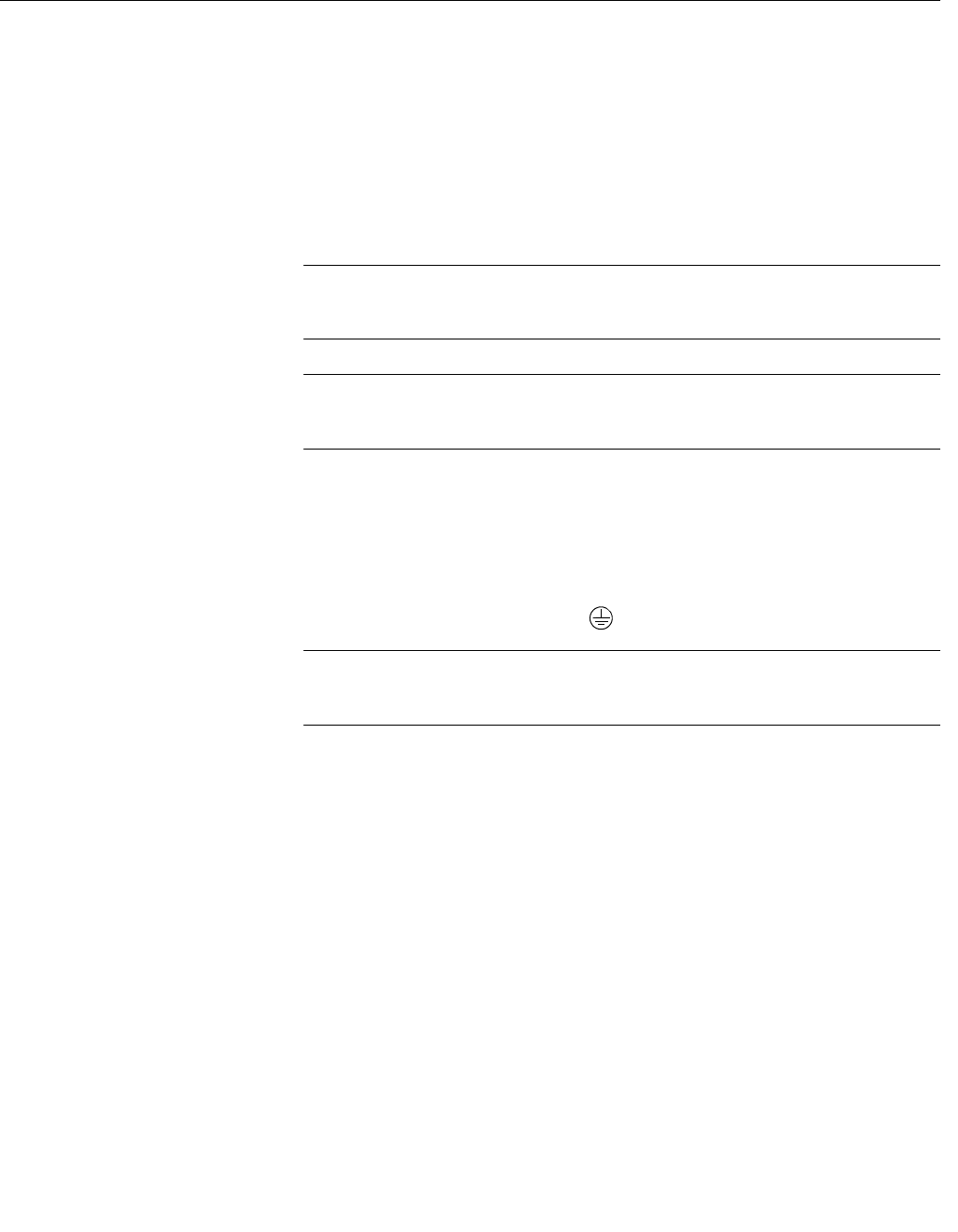
Reference Manual
300520EN, Rev AA
November 2009
3-39
Rosemount 5900 Series
Section 3. Installation
3.4 ELECTRICAL
INSTALLATION
3.4.1 Cable/conduit
entries
The electronics housing has entries for ½ - 14 NPT. Optional M20×1.5,
minifast and eurofast adapters are also available. The connections are made
in accordance with local or plant electrical codes.
Make sure that unused ports are properly sealed to prevent moisture or other
contamination from entering the terminal block compartment of the electronics
housing.
NOTE!
It is recommended that a sealant is used on the cable entry threads to prevent
water from entering the housing interior.
NOTE!
Use the enclosed metal plugs to seal unused ports. The orange plastic plugs
mounted at delivery are not sufficient as seal!
3.4.2 Grounding The housing should always be grounded in accordance with national and
local electrical codes. Failure to do so may impair the protection provided by
the equipment. The most effective grounding method is direct connection to
earth ground with minimal impedance. There are three grounding screw
connections provided. Two are located inside the Field Terminal side of the
housing and the third is located on the housing. The internal ground screws
are identified by a ground symbol: .
NOTE!
Grounding the transmitter via threaded conduit connection may not provide
sufficient ground.
Grounding - Foundation Fieldbus
Signal wiring of the fieldbus segment can not be grounded. Grounding out
one of the signal wires will shut down the entire fieldbus segment.
Shield Wire Ground
To protect the fieldbus segment from noise, grounding techniques for shield
wire usually require a single grounding point for shield wire to avoid creating a
ground loop. The ground point shall be located at the power supply.
The Raptor devices are designed for “daisy-chain” connection of shield wiring
in order to enable a continuous shield throughout the Tankbus network.
Preliminary
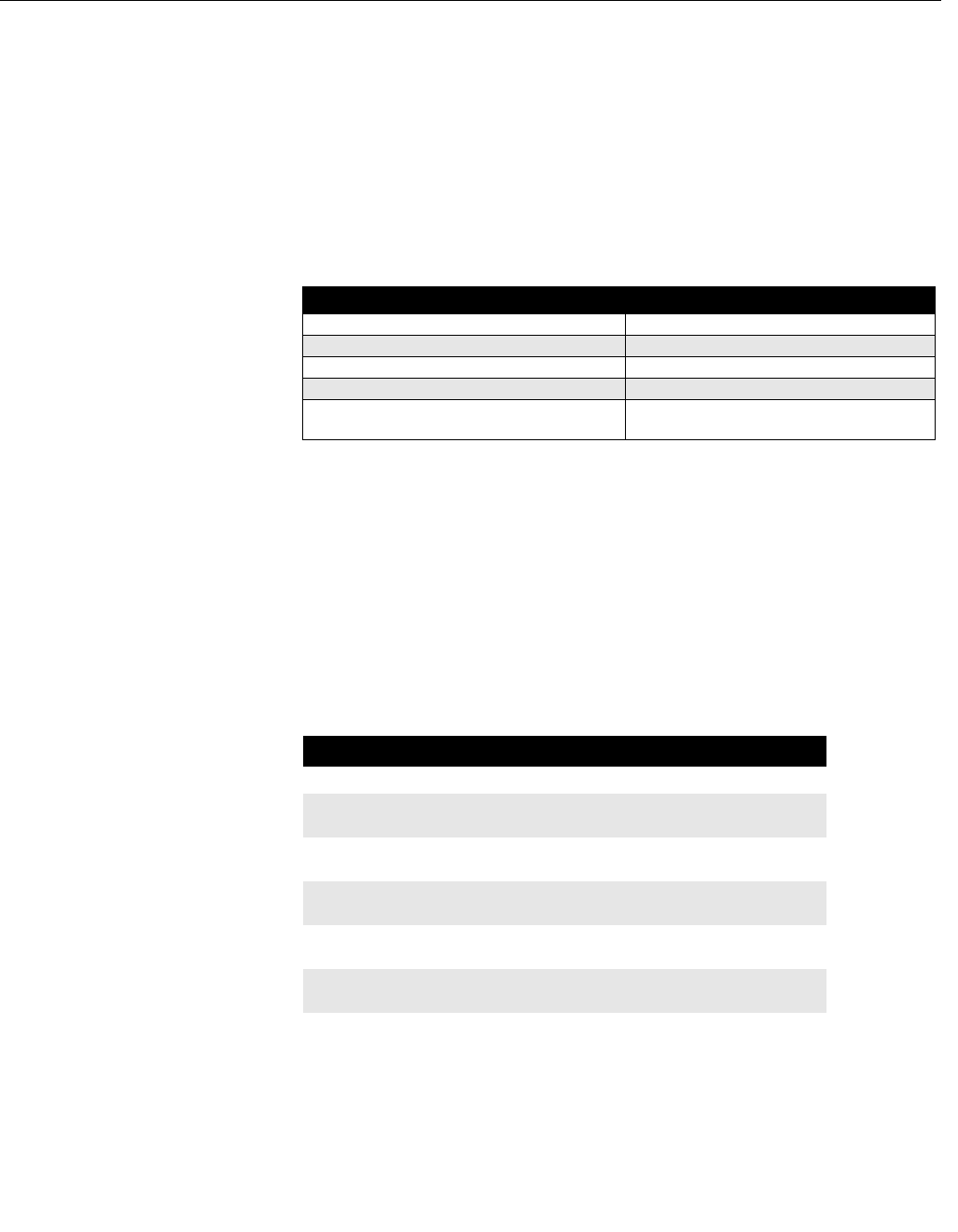
Reference Manual
300520EN, Rev AA
November 2009
Rosemount 5900 Series
3-40 Section 3. Installation
3.4.3 Cable Selection Use shielded twisted pair wiring for the Rosemount 5900 Series in order to
comply with EMC regulations and to ensure good fieldbus performance is
achieved. The cables must be suitable for the supply voltage and approved
for use in hazardous areas, where applicable. In the U.S. explosion-proof
conduits may be used in the vicinity of the vessel.
Use 22 AWG to 18 AWG in order to minimize the voltage drop to the
transmitter.
The FISCO(1) FOUNDATION™ fieldbus specification requires that cables for the
Raptor Tankbus comply with the following parameters:
Table 3-5. FISCO cable
parameters
3.4.4 Hazardous Areas When the Rosemount 5900 level gaugeis installed in hazardous area, local
regulations and specifications in applicable certificates must be observed.
3.4.5 Power
Requirements
The Rosemount 5900 is powered over the intrinsically safe Tankbus by the
Rosemount 2410 tank communication unit. The 2410 feeds the intrinsically
safe fieldbus segment by acting as a FISCO power supply on the Tankbus.
3.4.6 Power Budget The Rosemount 2410 tank hub delivers 250 mA to the Tankbus. The number
of tanks served by the 2410 depends on the type of connected field devices
and their power consumption(2). Power consumption per field device is listed
in Table 3-6 below:
Table 3-6. Power consumption
for various Raptor devices
The Rosemount 2410 tank hub supports a maximum of one tank for a
5900S-based configuration. In a 5300T- or 5400T-based configuration up to
10 tanks are supported.
(1) See also the reference document IEC/TS 60079-27
Parameter Value
Loop resistance 15/km to 150/km
Loop inductance 0.4 mH/km to 1 mH/km
Capacitance 45 nF/km to 200 nF/km
Maximum length of each spur cable 60 m in apparatus class IIC and IIB
Maximum cable length including trunk and
spurs
1000 m in apparatus class IIC and 1900 m in
apparatus class IIB
(2) May be fewer than the 16 devices per segment, stated in the FOUNDATION™ fieldbus stan-
dard.
Field device Power consumption
5900S Radar Level Gauge 50 mA
5300T or 5400T Series Radar Level
Gauge
20-25 mA
Rosemount 2230 Graphical Field
Display
25 mA
Rosemount 2240S Multi-input
Temperature Transmitter
30 mA including MST and WLS
Rosemount 644 Temperature
Transmitter
11 mA
Rosemount 3051 Pressure
Transmitter
17.5 mA
Preliminary
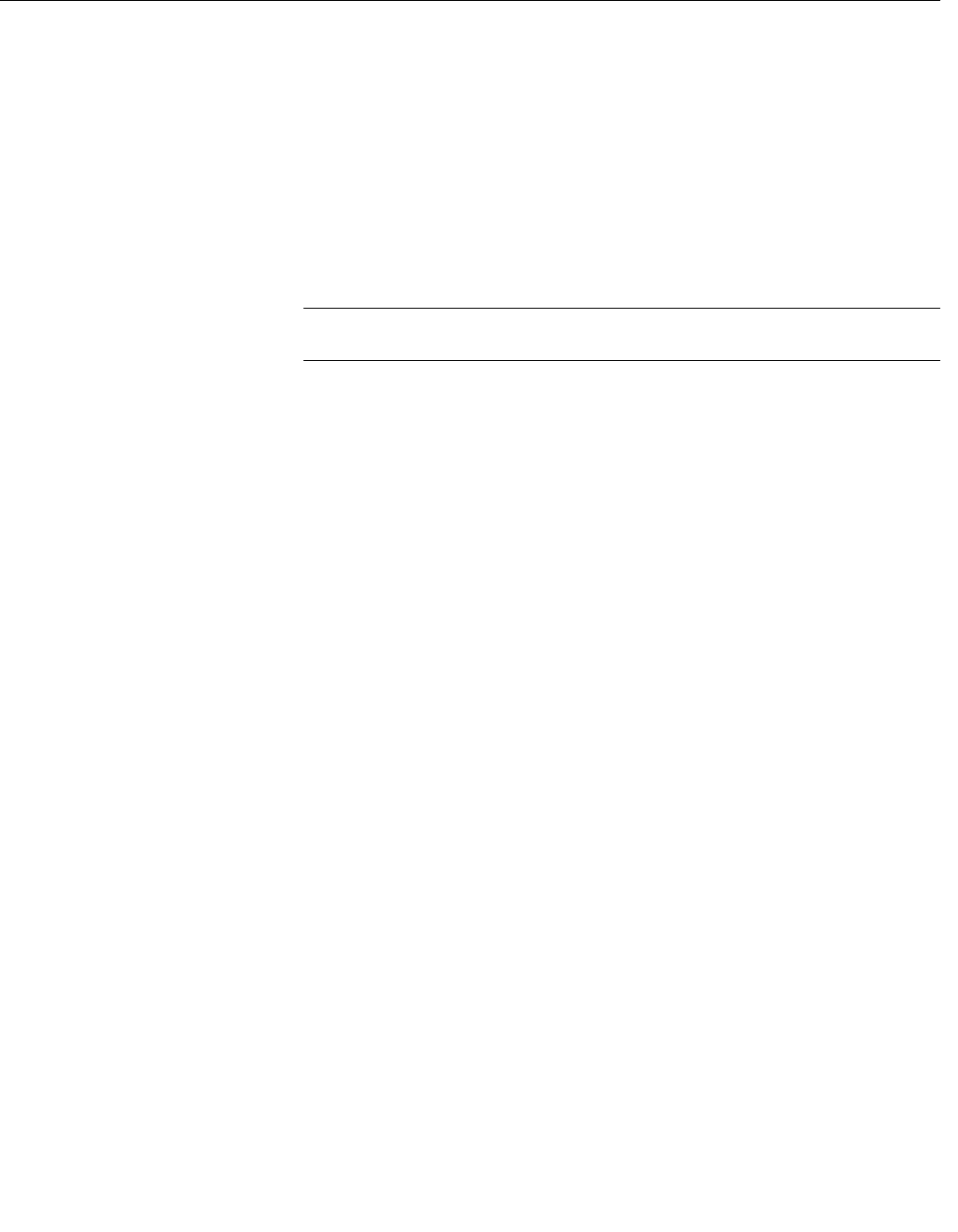
Reference Manual
300520EN, Rev AA
November 2009
3-41
Rosemount 5900 Series
Section 3. Installation
3.4.7 The Raptor
Tankbus
The Raptor system is easy to install and wire. Devices can be “daisy-chained”
thus reducing the number of external junction boxes.
In a Raptor system devices communicate with a Rosemount 2410 tank hub
via the intrinsically safe Tankbus. The Tankbus complies with the FISCO(1)
FOUNDATION fieldbus standard. The Rosemount 2410 acts as power supply to
the field devices on the Tankbus.
Termination
A terminator is needed at each end of a FOUNDATION Fieldbus network.
Generally, one terminator is placed in the fieldbus power supply, and the other
one in the last device in the fieldbus network.
NOTE!
Ensure that there are two terminators on the fieldbus.
In a Raptor system the Rosemount 2410 tank hub acts as power supply.
Since the 2410 normally is the first device in the fieldbus segment, the built-in
termination is enabled at factory
Other Raptor devices such as the Rosemount 5900 radar level gauge, the
Rosemount 2230 graphical display, and the Rosemount 2240 multi-input
temperature transmitter also have built-in terminators which can easily be
enabled by inserting a jumper in the terminal block when necessary.
Segment design
When designing a FISCO fieldbus segment a few requirements need to be
considered. Cabling has to comply with FISCO requirements as described in
“Cable Selection” on page 3-40.
You will also have to ensure that the total operating current of the connected
field devices is within the output capability of the Rosemount 2410 tank hub.
The 2410 is able to deliver 250 mA. Consequently, the number of field devices
has to be considered so that the total current consumption is less than
250 mA, see “Power Budget” on page 3-40.
Another requirement is to ensure that all field devices have at least 9 V input
voltage at their terminals. Therefore you will have to take into account the
voltage drop in the fieldbus cables.
Distances are normally quite short between the Rosemount 2410 tank hub
and field devices on the tank. In many cases you can use existing cables as
long as the FISCO requirements are fulfilled (see “Cable Selection” on
page 3-40).
See “The Raptor Tankbus” on page 3-7 in the Rosemount 2410 Reference
Manual (Document no. 305030EN) for more information on segment design
of a Raptor system.
(1) FISCO=Fieldbus Intrinsically Safe Concept
Preliminary
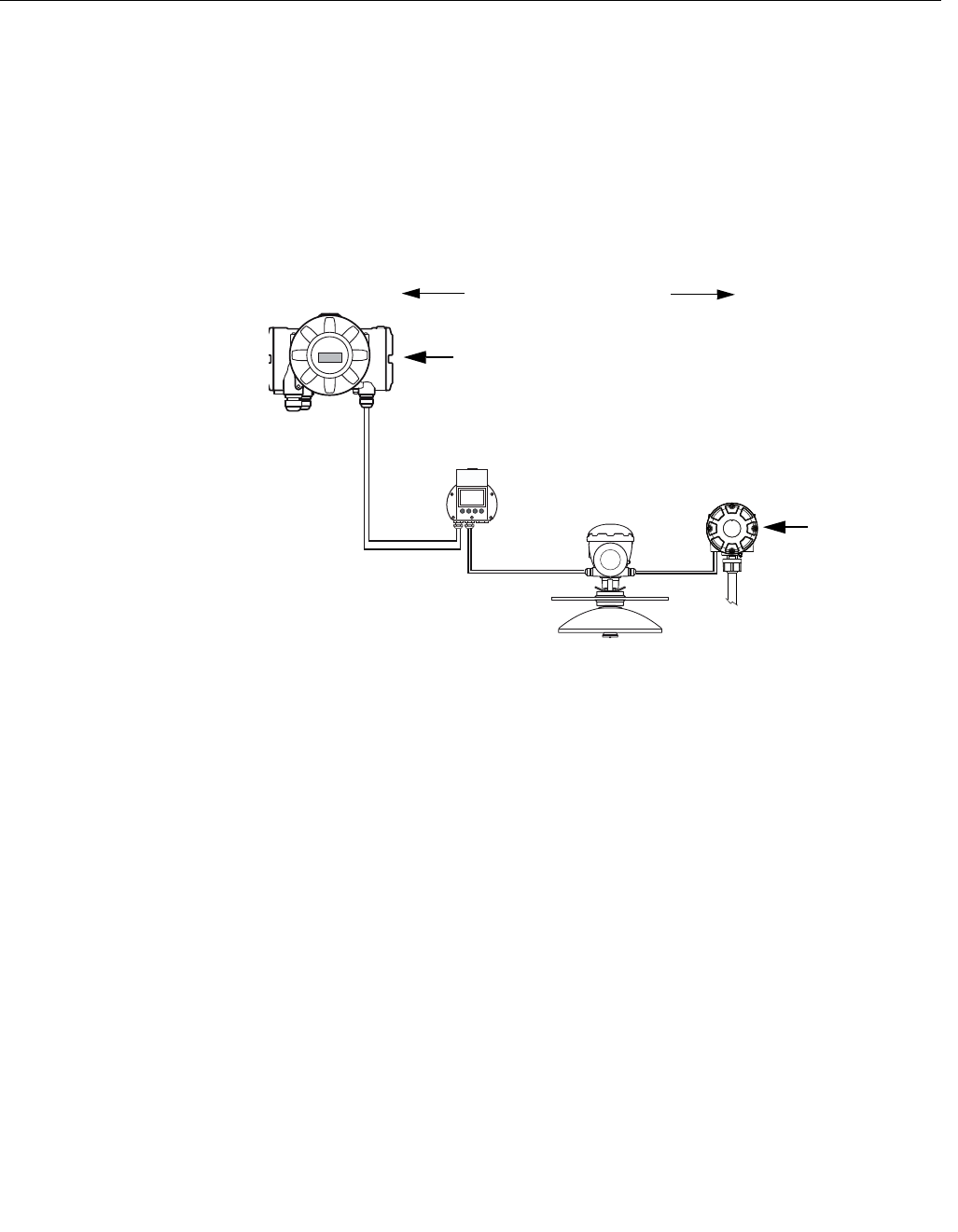
Reference Manual
300520EN, Rev AA
November 2009
Rosemount 5900 Series
3-42 Section 3. Installation
3.4.8 Typical
installations
The example below (Figure 3-17) illustrates a Raptor system with terminators
at both ends of the fieldbus segment as required in a FOUNDATION fieldbus
system. In this case terminators are enabled in the Rosemount 2410 tank hub
and a Raptor field device at the end of the network segment.
Figure 3-17. Example of a
Raptor Tankbus connection for a
single tank
See “Typical installations” on page 3-10 in the Rosemount 2410 Reference
Manual (Document no. 305030EN) for more Raptor system installation
examples.
Rosemount
5900 radar
level gauge
Rosemount 2240 multi-input
temperature transmitter
Built-in terminator
Intrinsically safe
Tankbus Built-in
terminator
enabled on the
last device
Rosemount
2230 display
Fieldbus segment
Maximum 1900 meter (class IIB)
Maximum 1000 meter (class IIC)
Rosemount 2410 tank hub
with intrinsically safe
power supply, integrated
power conditioner, and
built-in terminator
Preliminary
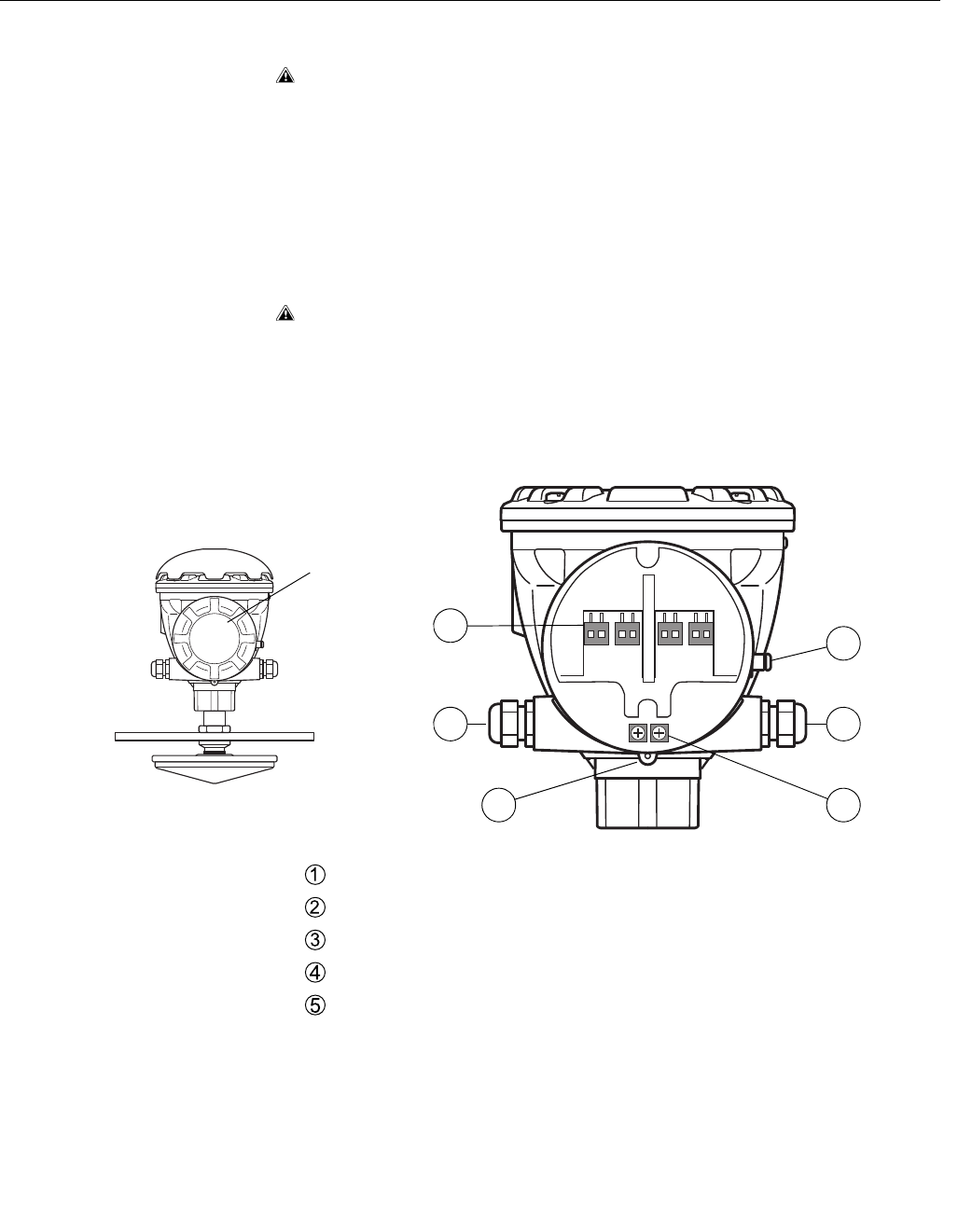
Reference Manual
300520EN, Rev AA
November 2009
3-43
Rosemount 5900 Series
Section 3. Installation
3.4.9 Wiring To connect the Rosemount 5900 Series transmitter:
1. Make sure that the power supply is switched off.
2. Remove the cover on the terminal compartment.
3. Run the wires through the appropriate cable gland/conduits.
Install wiring with a drip loop. The bottom of the loop must be lower than
the cable entry.
4. Connect wires as described in “Terminal Blocks” on page 3-44.
5. Connect the positive lead to the terminal marked (+) and the negative
lead to the terminal marked (-).
6. Use the enclosed metal plug to seal any unused port.
7. Replace the cover. Make sure that the cover is fully engaged.
8. Tighten the conduit/cable gland.
Note that adapters are required for M20 glands.
9. Switch on the power supply.
Figure 3-18. Terminal
compartment
Cable glands
Internal Ground screws
Terminals for signal and power supply
Locking screw (Flameproof version)
External Ground screw
11
24
5
3
Cover
Preliminary
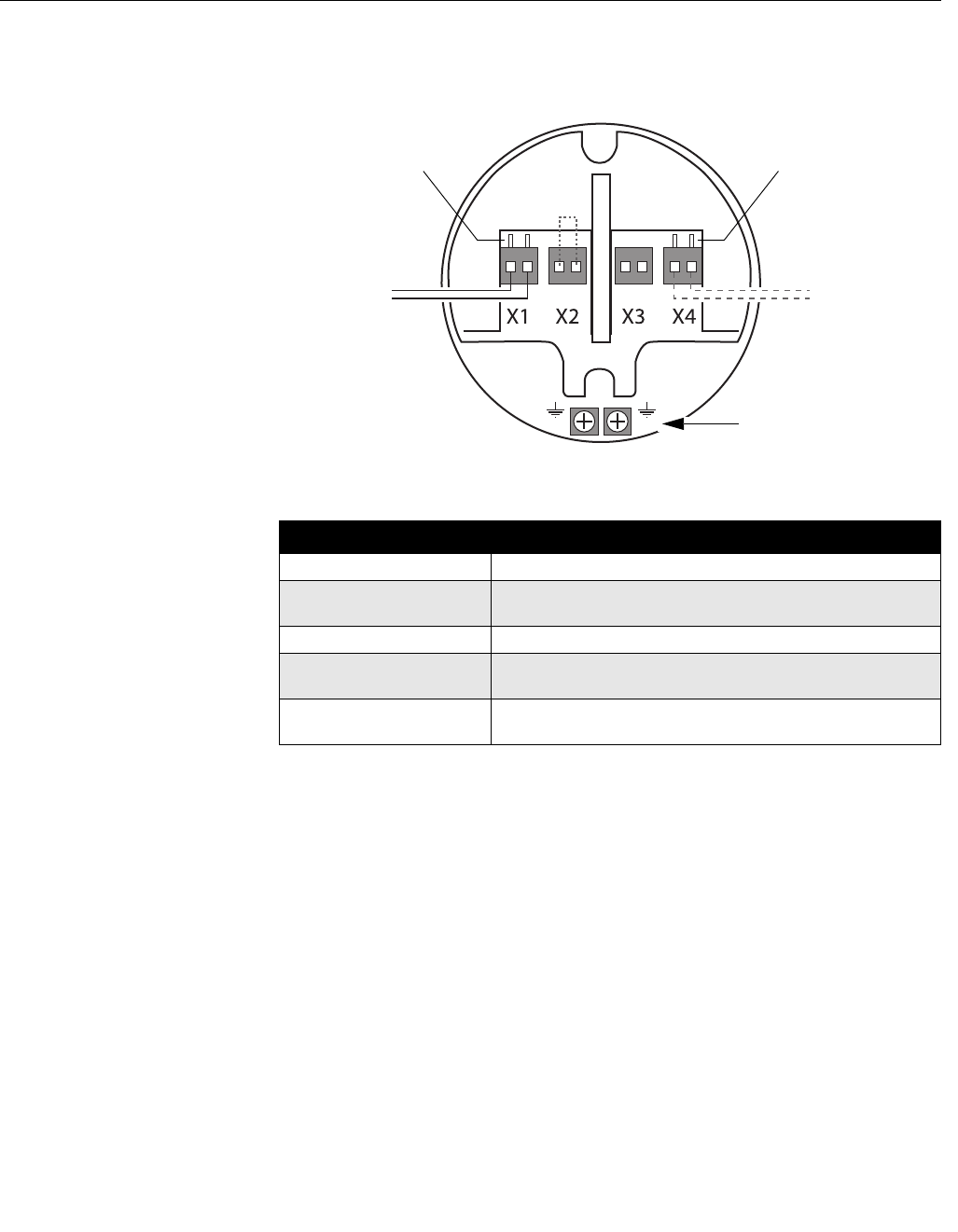
Reference Manual
300520EN, Rev AA
November 2009
Rosemount 5900 Series
3-44 Section 3. Installation
3.4.10 Terminal Blocks
Figure 3-19. Rosemount 5900
terminal compartment
Table 3-7. Standard terminal
block connections for the 5900
The X1 terminal is connected to the intrinsically safe Raptor Tankbus.
A jumper on the X2 terminal enables the built-in termination. The termination
should be used if the Rosemount 5900 gauge is installed at the end of a
Tankbus network. See “The Raptor Tankbus” on page 3-41 for more
information on how to terminate the Raptor Tankbus.
The X3 terminal is used for connecting the cable shield in order to enable a
continuous shield throughout the Tankbus network.
The X4 terminal can be used for “daisy-chain” connection to other Raptor
devices such as the 2240 tank temperature multiplexer, or the 2230 tank
display unit, see also Figure 3-22 on page 3-47.
Ground terminals, internal
Test terminalsTest terminals
Connection Standard
X1: Tankbus in Intrinsically safe Tankbus input, power and communication
X2: Terminate on The integrated line terminator is connected over the Tankbus
when a jumper is placed in the terminal block
X3: Shield loop through Cable shield daisy-chain connector (not grounded)
X4: Tankbus out Tankbus output connected to X1 for optional daisy-chain
connection to other devices
Test terminals Test terminals for temporary connection of a handheld
communicator such as the Rosemount 375 Field Communcator
Preliminary
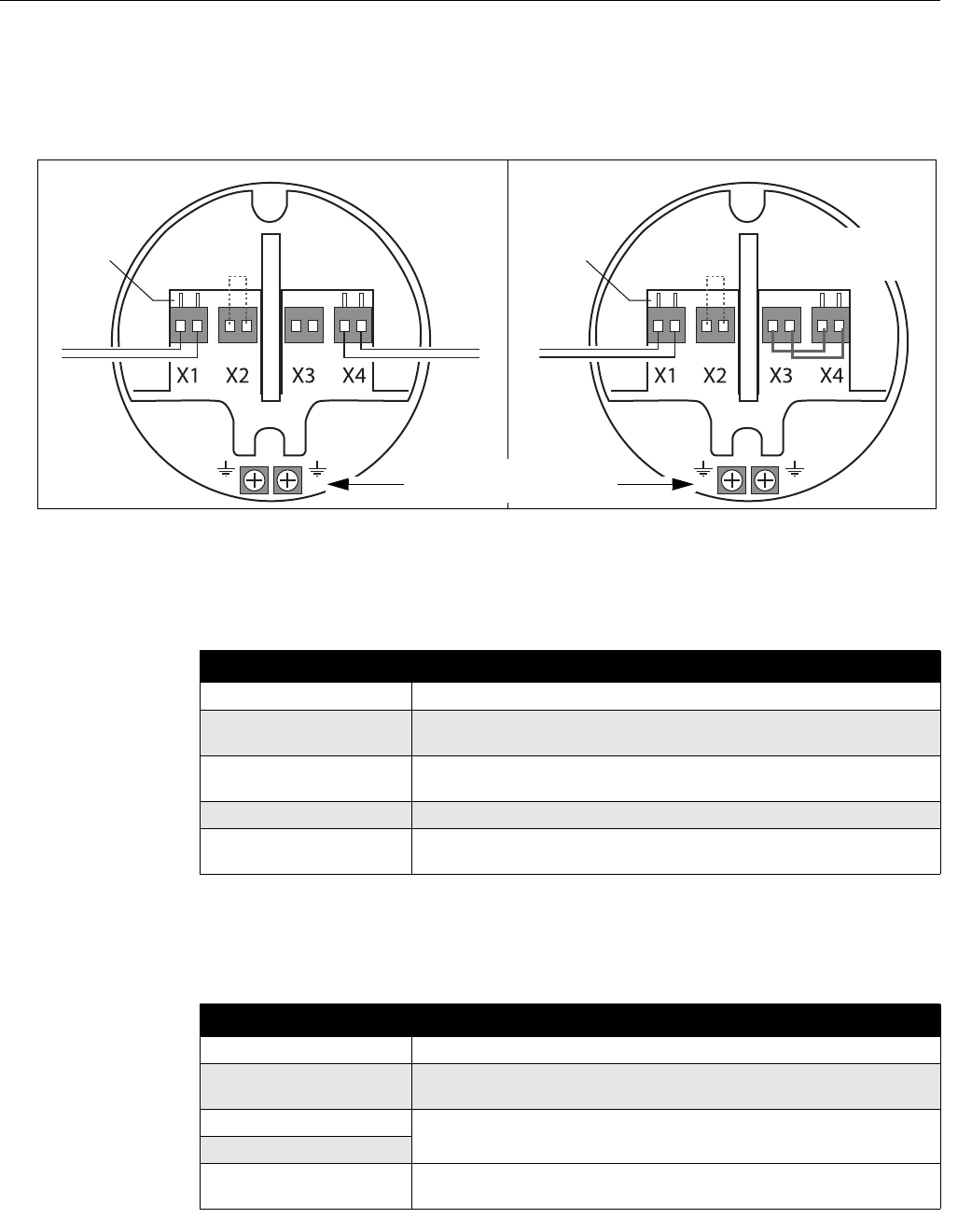
Reference Manual
300520EN, Rev AA
November 2009
3-45
Rosemount 5900 Series
Section 3. Installation
Terminal Block Two-in-One Version
The Rosemount 5900 Two-in-One version can be connected to a single
Tankbus or two separate Tankbuses.
Figure 3-20. Terminal
compartment.2-in-1 version
When using two separate tankbuses, connect X1 to Tankbus 1 and X4 to
Tankbus 2.
Table 3-8. Terminal Block
connections for the 5900 with
two tankbuses
Connect to X1 when using a single tankbus, and jumpers between X3 and X4.
Table 3-9. Terminal Block
connections for the 5900
with single tankbus
Single tankbusTwo tankbuses
Jumpers between
X3 and X4
Test
terminals
Test
terminals
Ground terminals, internal
Connection Two-in-One / Two tankbuses
X1: Primary Tankbus in Intrinsically safe Tankbus input for level gauge 1, power and communication
X2: Terminate on Termination for primary tankbus . The integrated line terminator is connected
over the Tankbus when a jumper is placed in the terminal block.
X3: Primary Tankbus out Primary Tankbus output connected to X1 for optional daisy-chain connection
to other devices
X4: Secondary Tankbus in Intrinsically safe Tankbus input for level gauge 2, power and communication
Test terminals Test terminals for temporary connection of a handheld communicator such as
the Rosemount 375 Field Communcator
Connection Two-in-One / Single tankbus
X1: Primary Tankbus in Intrinsically safe Tankbus input, power and communication
X2: Terminate on Termination for primary tankbus . The integrated line terminator is connected
over the Tankbus when a jumper is placed in the terminal block.
X3: Primary Tankbus out Jumpers between X3 and X4
X4: Secondary Tankbus in
Test terminals Test terminals for temporary connection of a handheld communicator such as
the Rosemount 375 Field Communcator
Preliminary
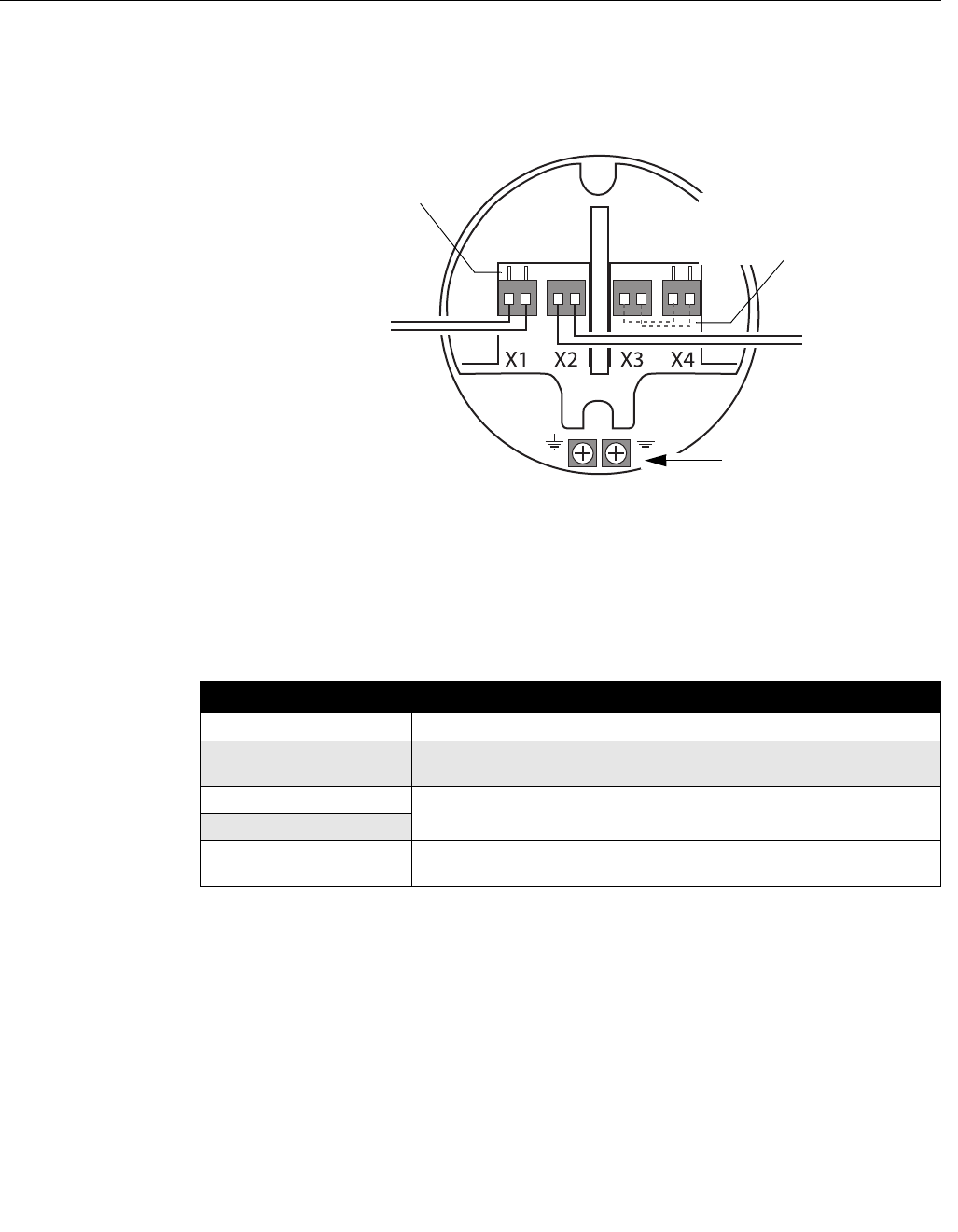
Reference Manual
300520EN, Rev AA
November 2009
Rosemount 5900 Series
3-46 Section 3. Installation
Gauge Terminal Block SIL Safety System
The Rosemount 5900 has a SIL alarm output which is connected to the
Rosemount 2410 Tank Hub.
Figure 3-21. Terminal
compartment
For the 2-in-1 SIL version of the Rosemount 5900, optional jumpers are
placed between terminals X3 and X4 for connection to the second radar level
gauge.
Table 3-10. Terminal Block
connections for the 5900 with
SIL option
2-in-1: optional jumpers between
X3 and X4 for connection to
second level gauge
Test terminals
Ground terminals, internal
SIL Alarm
Connection SIL Safety System
X1: Primary Tankbus in Intrinsically safe Tankbus input, power and communication
X2: Alarm SIL alarm output
(connect to Exi terminal block on Rosemount 2410 Tank Hub)
X3: Primary Tankbus out Optional jumpers between X3 and X4 for connection to second level gauge of
the Rosemount 5900 / 2-in-1 version
X4: Secondary Tankbus in
Test terminals Test terminals for temporary connection of a handheld communicator such as
the Rosemount 375 Field Communcator
Preliminary
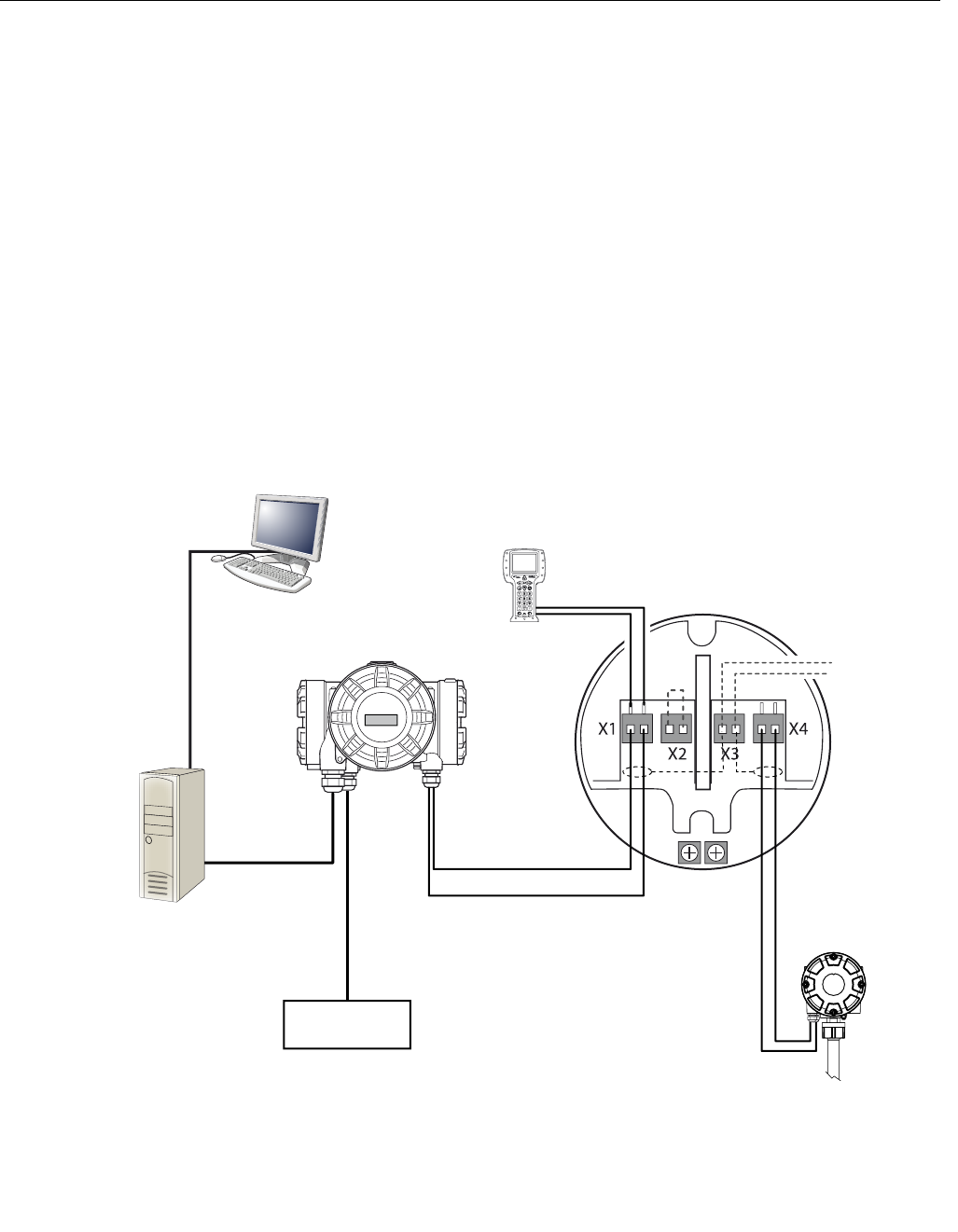
Reference Manual
300520EN, Rev AA
November 2009
3-47
Rosemount 5900 Series
Section 3. Installation
3.4.11 Wiring Diagrams The standard version of the Rosemount 5900 has a single intrinsically safe
fieldbus input. The 5900 has a built-in termination by short circuiting the X2
connector.
An intrinsically safe output on connector X4 can be used for “daisy-chain”
connection to other devices in a Raptor system.
Connector X3 is used for a fieldbus input/output cable shield connection
(separated from chassis ground).
Figure 3-22 illustrates a typical wiring diagram with a Rosemount 5900 level
gauge connected to a Rosemount 2240 multi-input temperature transmitter. In
this example the termination is enabled in the 2240 transmitter since this is
the last device on the Tankbus (see “The Raptor Tankbus” on page 3-41).
In case you prefer to connect the 2240 to the 2410 tank hub, you may
“daisy-chain” the 5900 to the 2240, and terminate the Tankbus by a jumper in
terminal X2 on the 5900 terminal block.
Figure 3-22. Rosemount 5900
standard wiring diagram
See also “Terminal Blocks” on page 3-44 for information on terminal block
connections.
Rosemount 2410 Tank Hub
Rosemount 2240 multi-input
temperature transmitter with
built-in terminator
TankMaster PC
Tankbus
Shield
ROSEMOUNT 5900
RADAR LEVEL GAUGE
Power supply
375 Field Communicator
Preliminary
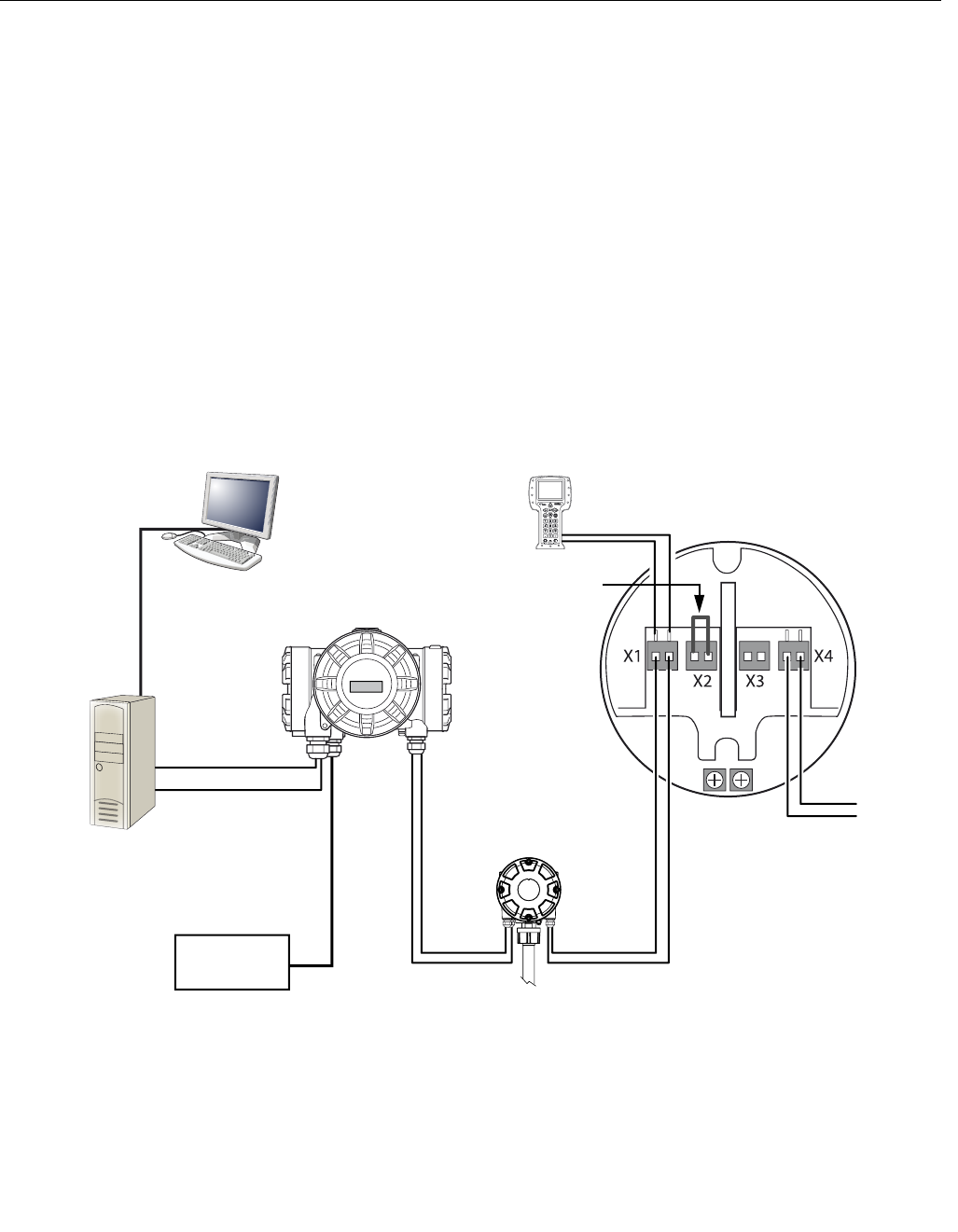
Reference Manual
300520EN, Rev AA
November 2009
Rosemount 5900 Series
3-48 Section 3. Installation
The Rosemount 5900 2-in-1 version
The 2-in-1 version of the Rosemount 5900 has two separate level gauges
placed in the same housing. One of the tankbuses can be terminated.
The 2-in-1 version can be connected to two separate tankbuses as illustrated
in Figure 3-23 and 3-24, or to a single tankbus as illustrated in Figure 3-25 on
page 3-50.
Terminal X1 is an intrinsically safe tankbus input for level gauge 1, and
terminal X4 connects to the second level gauge.
Figure 3-23 illustrates a wiring diagram with a 2-in-1 version of the
Rosemount 5900 level gauge which is “daisy-chained” to a Rosemount 2240
multi-input temperature transmitter. Note that the Primary Tankbus is
terminated in the 5900 terminal block (X2).
Figure 3-23. Rosemount 5900
wiring diagram for 2-in-1 version
with two tankbuses
See also “Terminal Blocks” on page 3-44 for information on terminal block
connections.
375 Field Communicator
ROSEMOUNT 5900 RADAR
LEVEL GAUGE (2-IN-1)
TankMaster PC
Power supply
Primary Tankbus
(gauge 1)
Rosemount 2240
multi-input temperature
transmitter
Rosemount 2410 Tank Hub
Secondary Tankbus
(gauge 2)
Termination
Preliminary
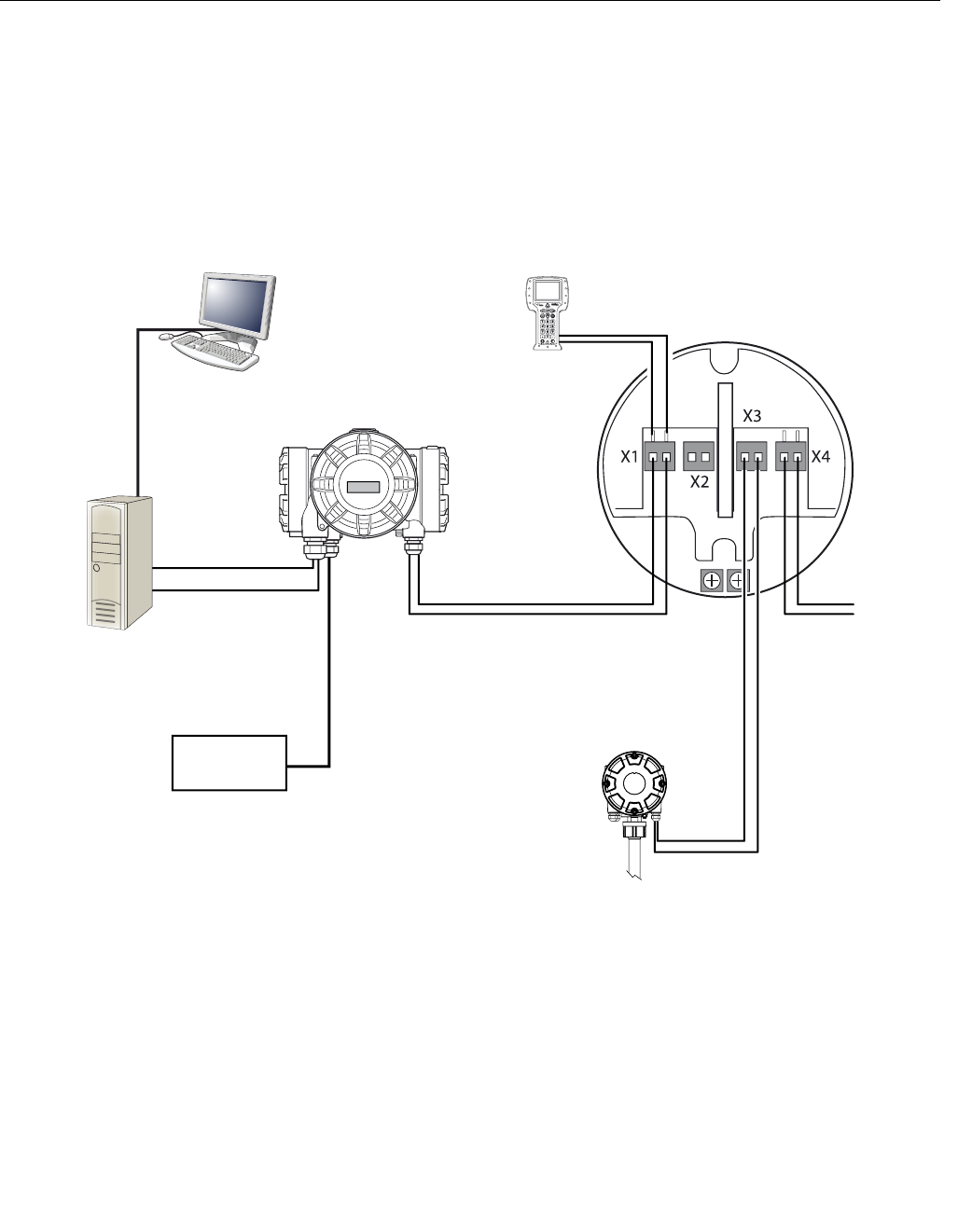
Reference Manual
300520EN, Rev AA
November 2009
3-49
Rosemount 5900 Series
Section 3. Installation
In Figure 3-24 a Rosemount 2240 transmitter is “daisy-chained” to a 2-in-1
version of the Rosemount 5900 level gauge.
The termination is enabled in the 2240 terminal block.
Figure 3-24. Wiring diagram for
Rosemount 5900 2-in-1 version
with two tankbuses
375 Field Communicator
TankMaster PC
Power supply
Primary Tankbus (gauge 1)
Rosemount 2240
multi-input temperature
transmitter with built-in
terminator
Rosemount 2410 Tank Hub
Primary Tankbus (gauge 1)
ROSEMOUNT 5900 RADAR
LEVEL GAUGE (2-IN-1)
Secondary Tankbus
(gauge 2)
Preliminary

Reference Manual
300520EN, Rev AA
November 2009
Rosemount 5900 Series
3-50 Section 3. Installation
Figure 3-25 illustrates the 2-in-1 version of the Rosemount 5900 with a single
intrinsically safe tankbus connected to both level gauges via terminal X1 by
setting a jumper between X3 and X4.
The Tankbus termination is enabled in the 5900 terminal block (X2).
Figure 3-25. Rosemount 5900
wiring diagram for 2-in-1 version
with a single tankbus
TankMaster PC
Tankbus
Rosemount 2240
multi-input temperature
transmitter
Rosemount 2410 Tank Hub
Power supply
375 Field Communicator
ROSEMOUNT 5900 RADAR
LEVEL GAUGE (2-IN-1)
Termination
Preliminary
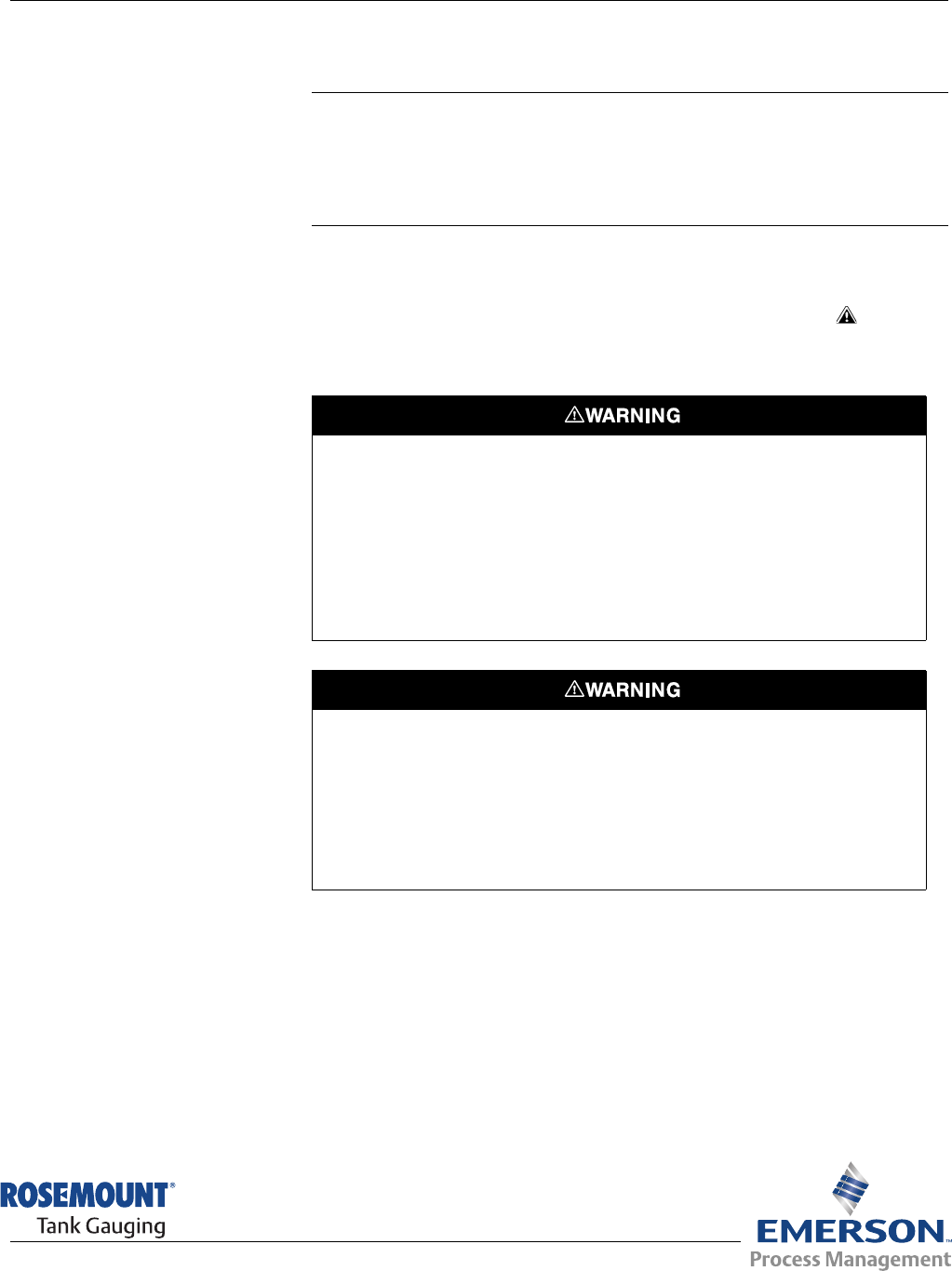
Reference Manual
300520EN, Rev AA
November 2009 Rosemount 5900 Series
www.rosemount-tg.com
Section 4 Configuration
4.1 Safety Messages . . . . . . . . . . . . . . . . . . . . . . . . . . . . page 4-1
4.2 Overview . . . . . . . . . . . . . . . . . . . . . . . . . . . . . . . . . . page 4-2
4.3 Basic Configuration . . . . . . . . . . . . . . . . . . . . . . . . . page 4-4
4.4 Configuration Using Rosemount TankMaster . . . . page 4-7
4.5 LPG Configuration . . . . . . . . . . . . . . . . . . . . . . . . . . page 4-9
4.1 SAFETY
MESSAGES
Procedures and instructions in this section may require special precautions to
ensure the safety of the personnel performing the operations. Information that
raises potential safety issues is indicated by a warning symbol ( ). Please
refer to the following safety messages before performing an operation
preceded by this symbol.
Failure to follow safe installation and servicing guidelines could result in death or
serious injury:
Make sure only qualified personnel perform the installation.
Use the equipment only as specified in this manual. Failure to do so may impair the
protection provided by the equipment.
Do not perform any service other than those contained in this manual unless you are
qualified.
Substitution of components may impair Intrinsic Safety.
Explosions could result in death or serious injury:
Verify that the operating environment of the transmitter is consistent with the appropriate
hazardous locations certifications.
Before connecting a communicator in an explosive atmosphere, make sure the
instruments in the loop are installed in accordance with intrinsically safe or
non-incendive field wiring practices.
Do not remove the gauge cover in explosive atmospheres when the circuit is alive.
Preliminary
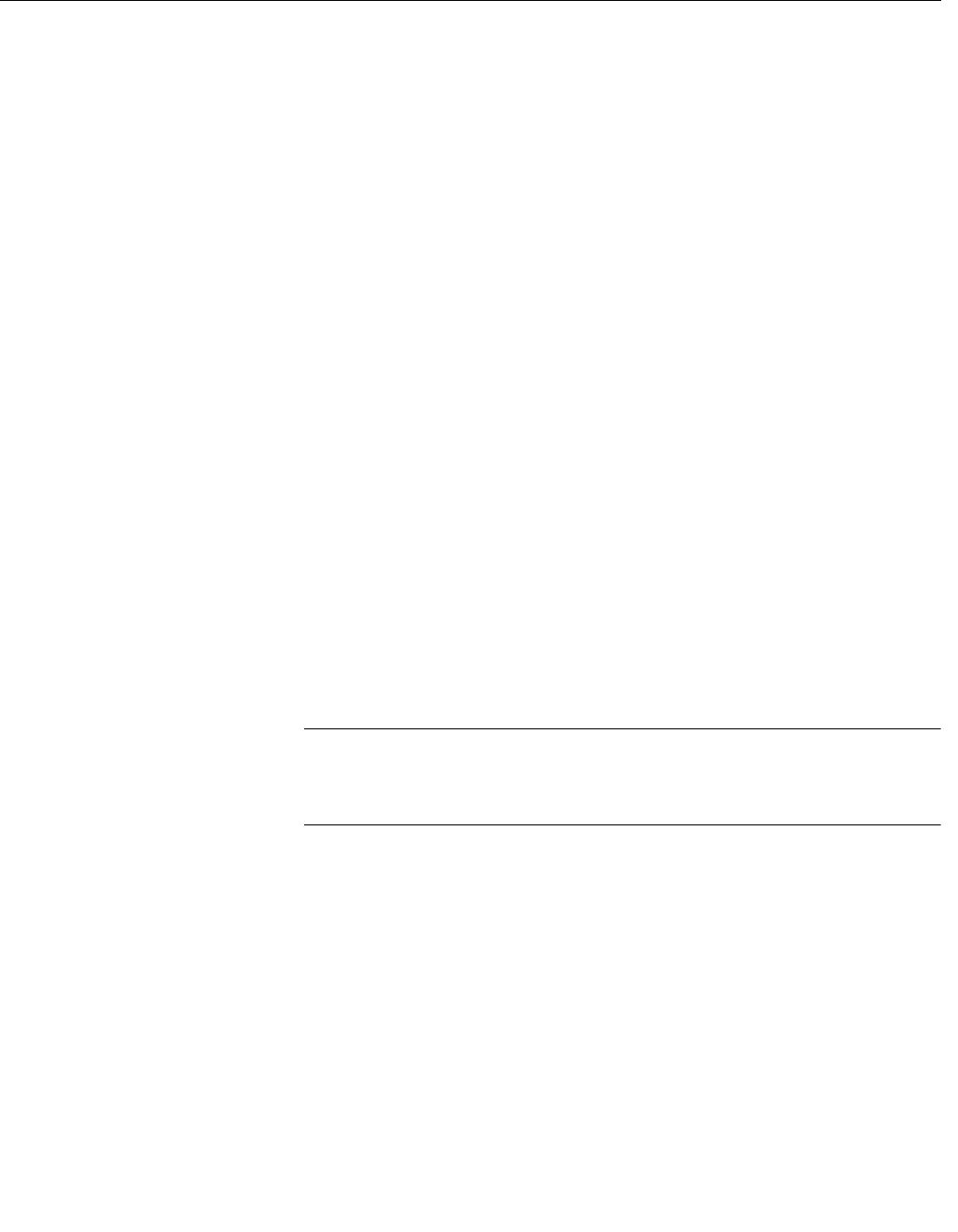
Reference Manual
300520EN, Rev AA
November 2009
Rosemount 5900 Series
4-2 Section 4. Configuration
4.2 OVERVIEW Installation and configuration of a Raptor system is a simple and
straight-forward procedure. It basically includes the following steps:
1. Setting up communication protocol and communication parameters.
2. Configuration of Field Communication Unit.
3. Configuration of Rosemount 2410 tank communication unit.
4. Configuration of measurement devices such as the Rosemount 5900
level gauge.
5. Calibration.
A detailed description of how to install and configure a Rosemount 5900 by
using the TankMaster WinSetup software is given in the Raptor System
Configuration manual (Document no. 300510EN).
The TankMaster WinSetup configuration is the recommended tool for
installation and configuration of a Rosemount 5900. The 5900 can be installed
as part of the procedure when installing a Rosemount 2410 tank
communication unit. This is the standard procedure when a new Raptor
system is installed:
a. Install and configure the 2410 tank communication unit by using the
device installation wizard in TankMaster WinSetup.
b. Finish the 2410 installation with “offline” installation of the 5900 level
gauge.
c. Configure the 5900 level gauge via the Properties window.
If a 5900 is added to an existing system the Rosemount 2410 Tank Database
must be updated before the 5900 is configured. The Tank Database maps the
5900 to the tank on which it is installed.
NOTE!
If the system contains a Field Communication Unit (FCU) it has to be installed
and configured before other devices such as level gauges and temperature
multiplexers.
The Rosemount 5900 supports basic configuration which is sufficient in most
cases. There are a number of advanced configuration options available as
well, which may be used for special applications when further fine-tuning is
needed.
Preliminary
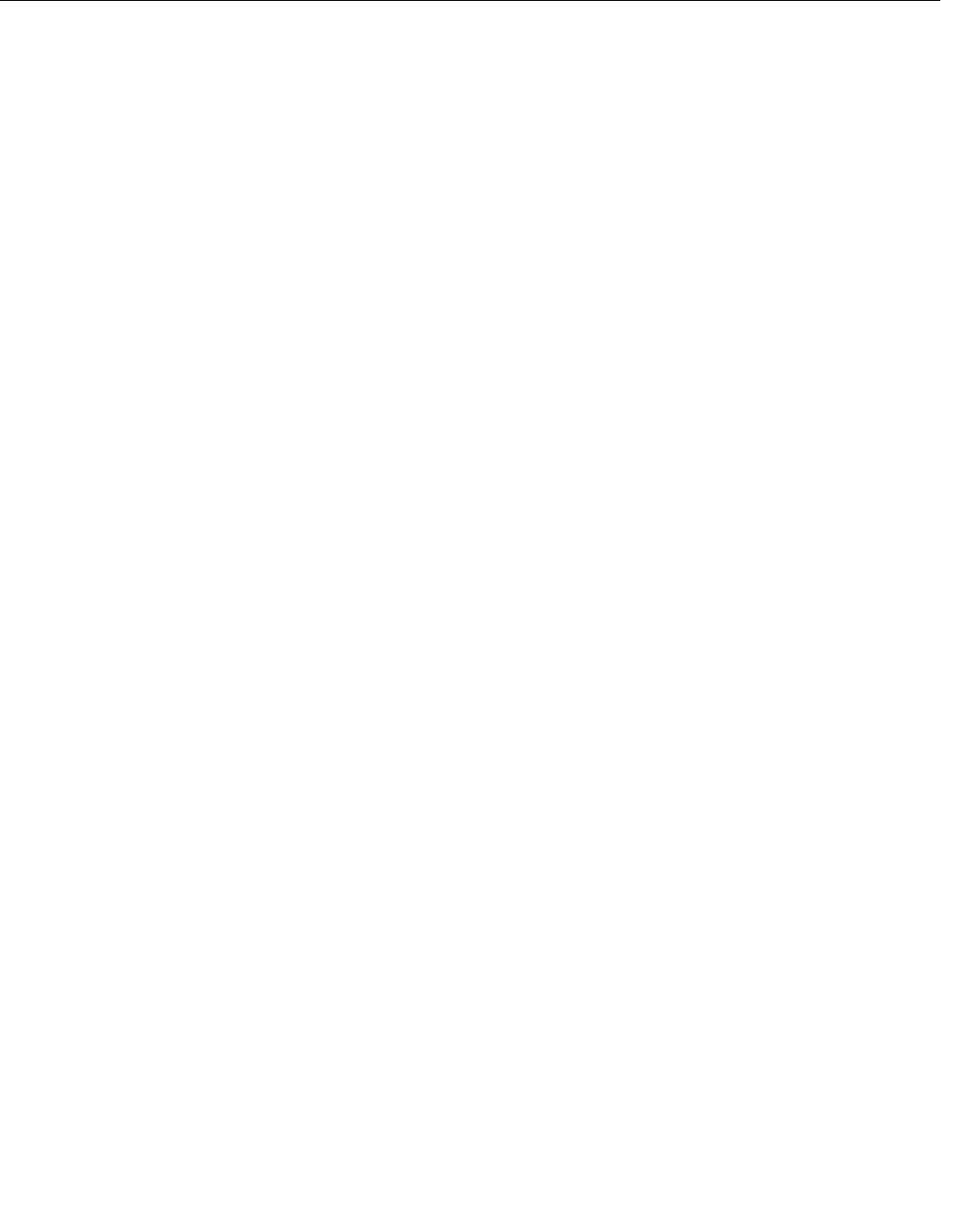
Reference Manual
300520EN, Rev AA
November 2009
4-3
Rosemount 5900 Series
Section 4. Configuration
4.2.1 Basic
Configuration
Basic configuration includes specifying parameters for a standard
configuration which is sufficient in most cases. It includes the following items:
• Measurement Units
• Tank geometry; tank height, tank type, tank bottom type, pipe diameter,
hold off disance, calibration distance etc.
• Process conditions; rapid level changes, turbulence, foam, solids,
product dielectric range
• Volume; standard tank types, strapping table
4.2.2 Advanced
Configuration
The Rosemount 5900 supports a number of advanced functions for optimizing
performance in advanced applications. Some applications may need further
configuration in addition to the basic configuration. This may be due to the
properties of the product or the tank shape.
Disturbing objects and turbulent conditions in the tank may also require
advanced measures to be taken.
Advanced functions supported by the Rosemount 5900 and the Rosemount
TankMaster program:
•Tank scan
• Empty tank handling
• Surface echo tracking
• Filter settings
4.2.3 Configuration
Tools
There are several tools available for configuration of a Rosemount 5900 level
gauge:
• Rosemount TankMaster Winsetup
• Rosemount 375 Field Communicator
The TankMaster Winsetup is a user-friendly software package that includes
basic configuration options as well as advanced configuration and service
functions.
Preliminary
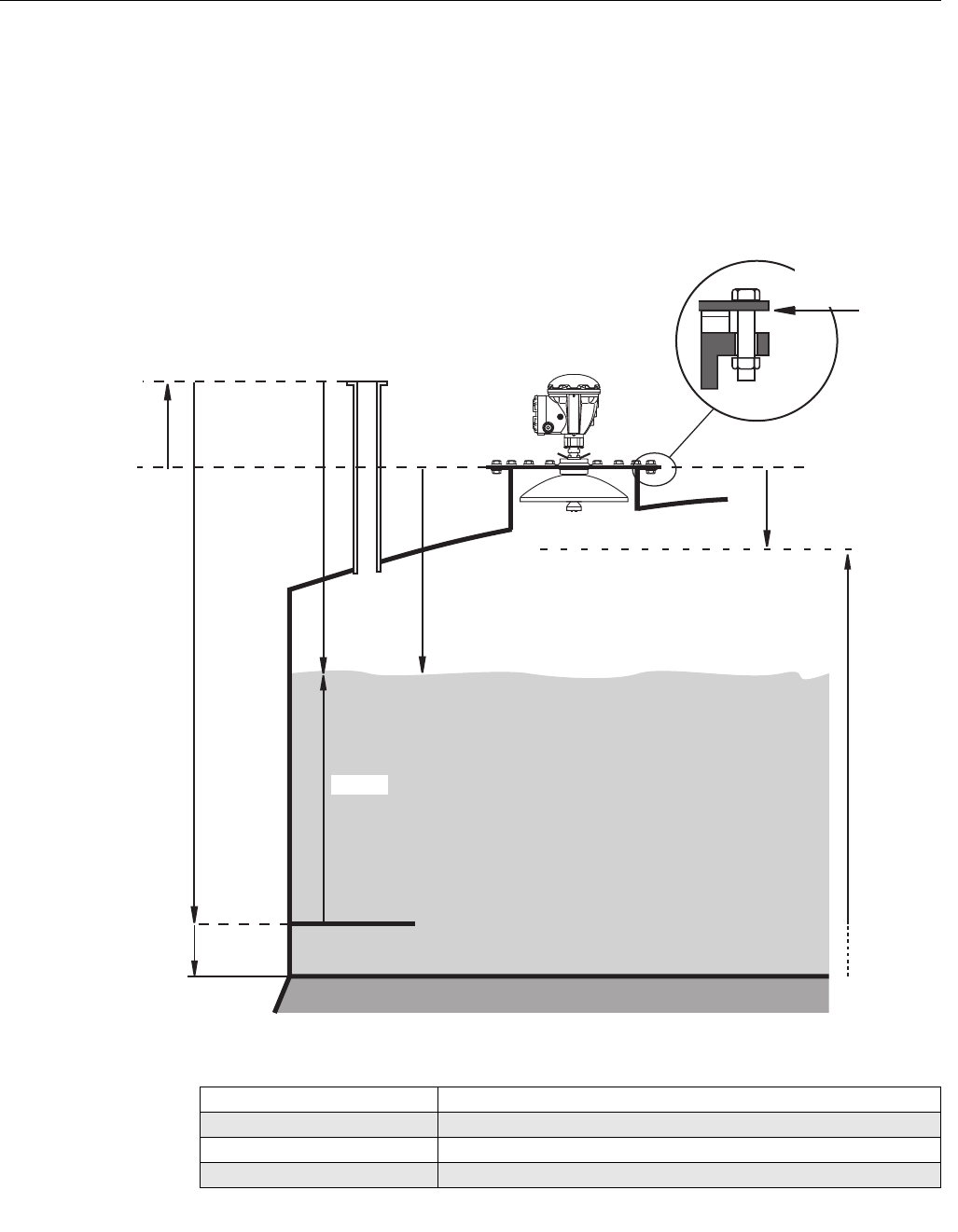
Reference Manual
300520EN, Rev AA
November 2009
Rosemount 5900 Series
4-4 Section 4. Configuration
4.3 BASIC
CONFIGURATION
4.3.1 Tank Geometry The following parameters are used for tank geometry configuration of a
Rosemount 5900 level gauge:
Figure 4-1. Illustration of the
various tank geometry
parameters
Table 4-1. Definition of tank
geometry parameters
Gauge Reference
Distance (G)
Tank Reference
Height (R)
Minimum Level Offset (C)
Hold Off Distance
Tank Ullage
Ullage
Gauge Reference
Point
Tank Reference Point
Gauge Reference Point
Zero Level
(Dipping Datum Point)
Level
MEASURING RANGE
Tank Height (R) Distance from Tank Reference Point to Zero level
Gauge Reference Distance (G) Distance from Tank Reference Point to the Gauge Reference Point
Minimum Level Offset (C) Distance from Zero Level to tank bottom
Hold Off Distance Defines how close to the Gauge Reference Point levels can be measured
Preliminary
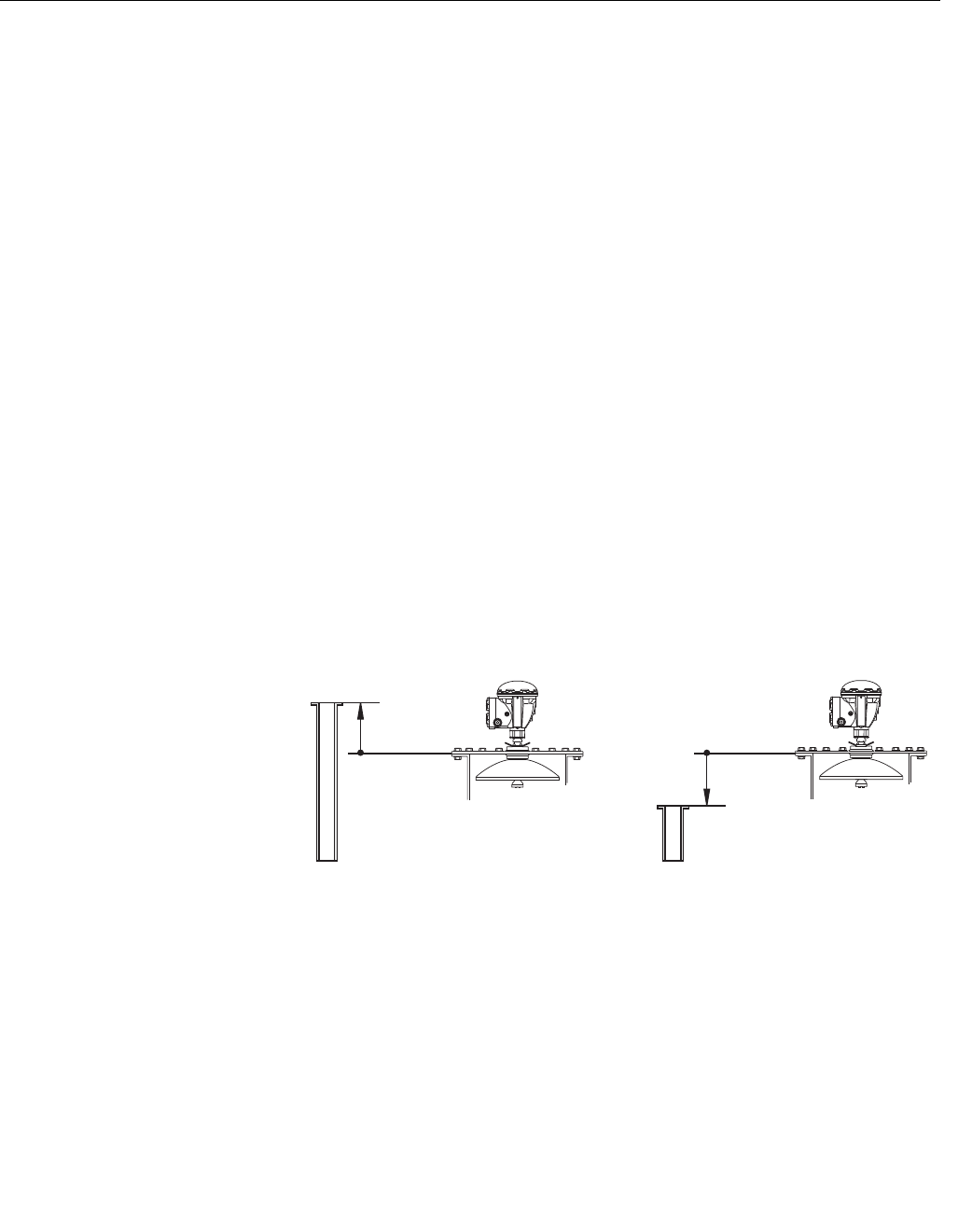
Reference Manual
300520EN, Rev AA
November 2009
4-5
Rosemount 5900 Series
Section 4. Configuration
Tank Reference Height (R)
The Tank Reference Height (R) is the distance from the hand dipping nozzle
(Tank Reference Point) to the Zero Level (Dipping Datum Plate) close to, or at
the bottom of the tank.
Gauge Reference Distance (G)
The RTG Reference Distance (G) is the distance between the Tank Reference
Point and the RTG Reference Point, which is located at the top surface of the
customer’s flange or manhole cover on which the gauge is mounted.
For Still Pipe Gauges the Gauge Reference Point is located at the hand-dip
mark on the Still Pipe Gauge Stand.
G is positive if the Tank Reference Point is located above the Gauge
Reference Point. Otherwise G is negative.
Minimum Level Offset (C)
The Minimum Level Distance (C) is defined as the distance between the Zero
Level (Dipping Datum Point) and the Minimum Level of the product surface
(tank bottom). By specifying a C-distance, the measuring range can be
extended to the bottom of the tank.
If C>0, negative level values will be displayed when the product surface is
below the Zero Level. Select the Show negative level values as zero check
box if you want levels below the Zero Level to be displayed as Level=0.
Measurements below the Zero Level will not be approved if the C-distance=0,
i.e. the RTG will report an invalid level.
Figure 4-2. Definition of RTG
Reference Distance
Hold Off Distance
The Hold Off distance defines how close to the Gauge Reference Point a level
value is accepted. Normally the Hold Off distance does not need to be
changed. However, if there are disturbing echoes in the upper part of the tank,
for example from the tank nozzle, you can increase the Hold Off distance in
order to avoid measurements in the region close to the antenna.
Calibration Distance
Use this variable to adjust the transmitter so that measured product levels
match hand dipped levels. Normally a minor adjustment is necessary when
the gauge is installed due to, for example, a minor deviation between the
actual tank height and the value stored in the transmitter database.
G>0
G<0
Gauge Reference Point
Preliminary
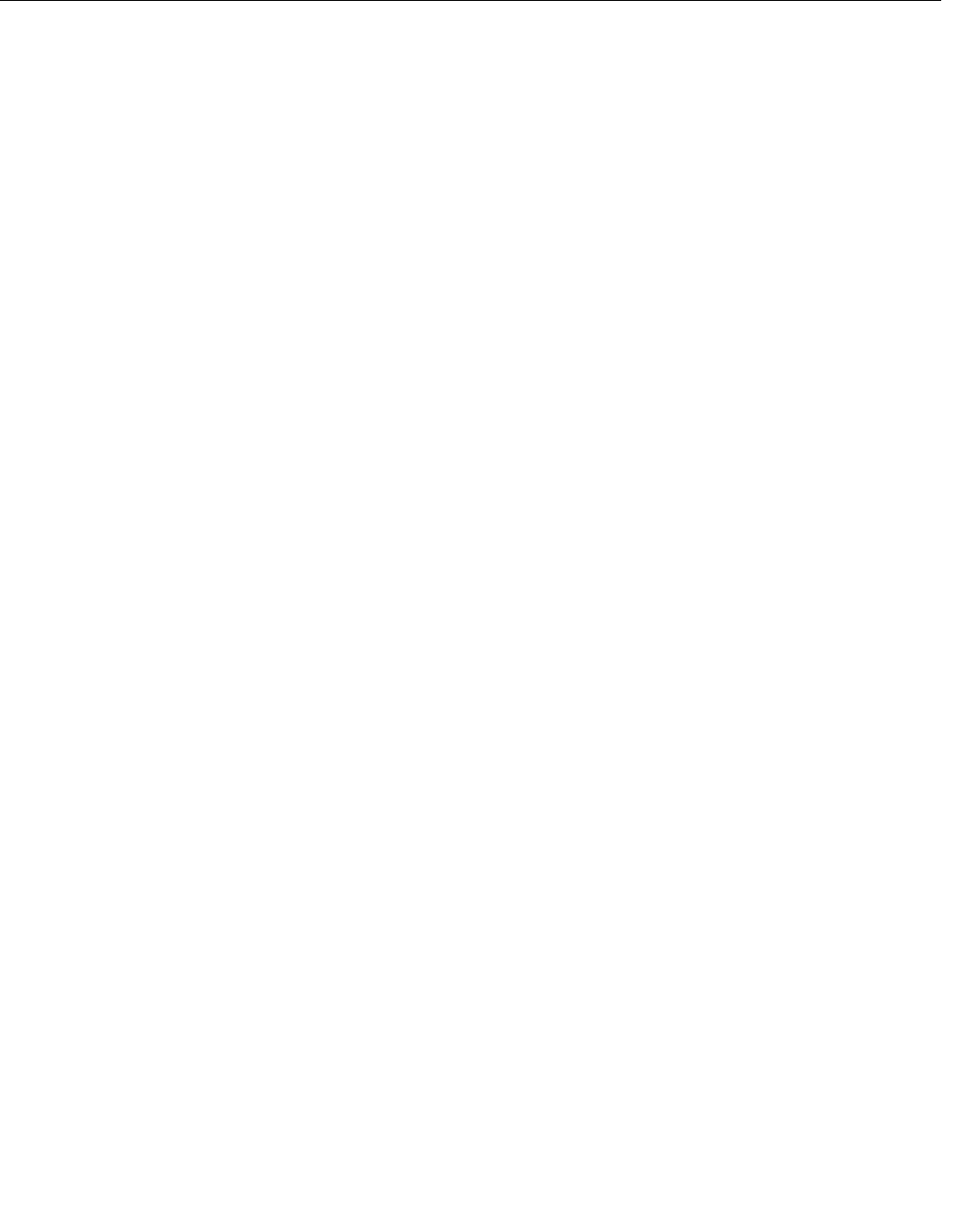
Reference Manual
300520EN, Rev AA
November 2009
Rosemount 5900 Series
4-6 Section 4. Configuration
Pipe Diameter
When a Rosemount 5900 level gauge is installed in a still pipe, the inner
diameter of the pipe must be specified. The Pipe Diameter is used to
compensate for the lower microwave propagation speed inside the pipe. An
incorrect value results in a scale factor error. If locally supplied still pipes are
used, make sure the inner diameter is noted before the pipe is installed.
4.3.2 Environment Foam
You can use this parameter to optimize the gauge for conditions with weak
and varying surface echo amplitudes such as foam. When the foam is light
and airy the actual product level is measured. For heavy and dense foam the
transmitter measures the level of the upper surface of the foam.
Turbulent Surface
Splash loading, agitators, mixers, or boiling products may cause a turbulent
surface. Normally the waves in a tank are quite small and cause local rapid
level changes. By setting the Turbulent Surface parameter the performance of
the transmitter will be improved when there are small and quickly changing
amplitudes and levels.
Rapid Level Changes
Optimize the level gauge for measurement conditions where the level
changes quickly due to filling and emptying of the tank. The Rosemount 5900
is able to track level changes of up to 1.5 inch/s (40 mm/s). The Rapid Level
Changes funtion allows the 5900 to track level changes of up to 8 inch/s (200
mm/s).
The Rapid Level Changes function shall not be used in normal conditions
when the product surface moves slowly.
Solid Products
Setting this parameter optimizes the transmitter for solid products, for
example concrete or grains, which are not transparent for radar signals. For
instance, this parameter can be used when the application is a silo with
product build-up.
Product Dielectric Range
The Dielectric Constant is related to the reflectivity of the product. This
parameter can be used to optimize measurement performance. However, the
level gauge will still be able to perform well even if the actual Dielectric
Constant differs from the configured value.
4.3.3 Tank Shape The Tank Type and Tank Bottom Type parameters optimize the Rosemount
5900 for various tank geometries and for measurements close to the tank
bottom.
Preliminary
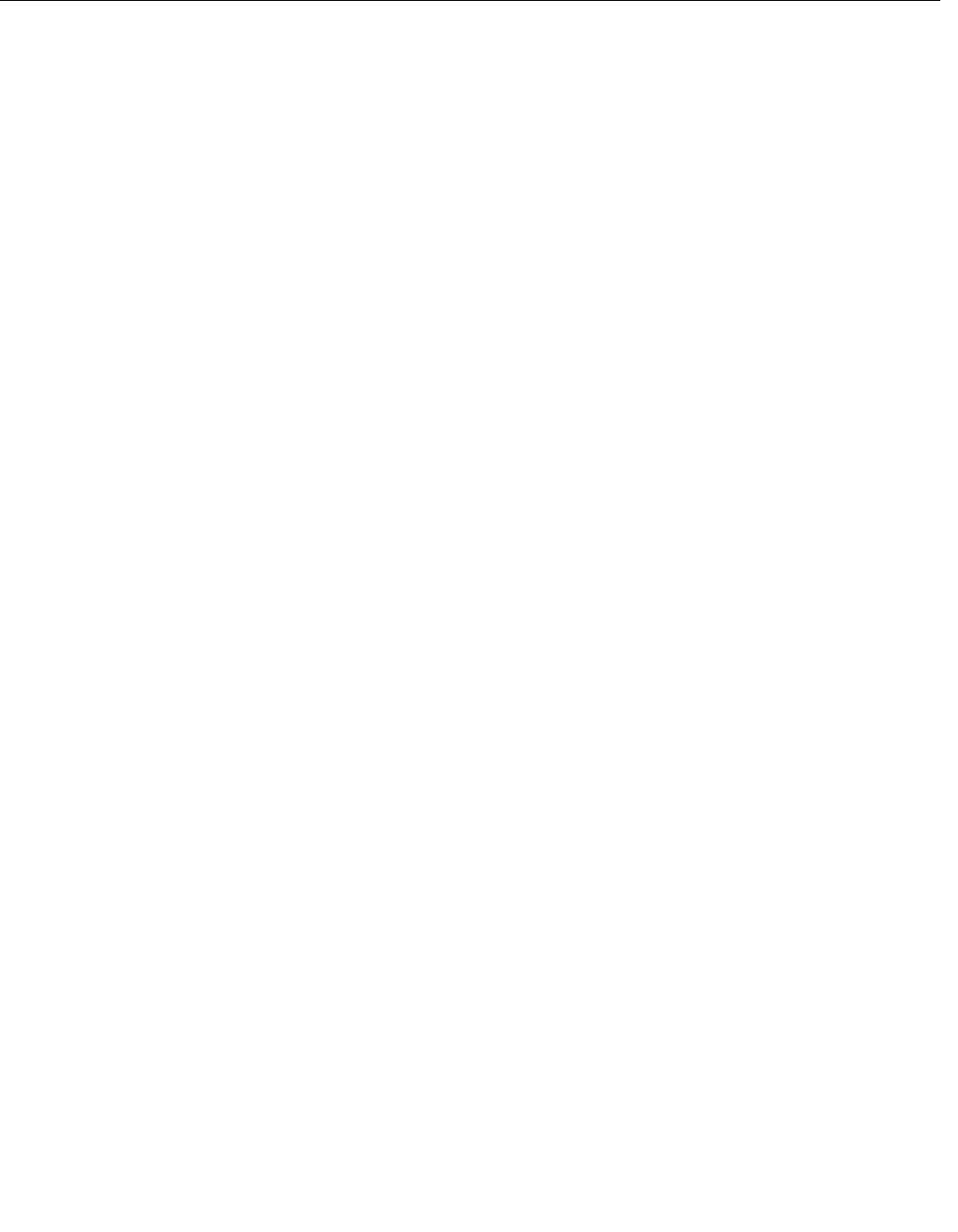
Reference Manual
300520EN, Rev AA
November 2009
4-7
Rosemount 5900 Series
Section 4. Configuration
4.4 CONFIGURATION USING ROSEMOUNT TANKMASTER
It is recommended that the Rosemount 5900 is configured by using the
TankMaster Winsetup configuration tool. Winsetup supports installation of the
Rosemount 5900 by one of the following methods:
• as part of the installation and configuration procedure of a Rosemount
2410 tank hub
• by using the TankMaster installation wizard
When a 5900 is installed as part of a 2410 installation procedure, it needs to
be configured in a separate stage.
See the Raptor System Configuration Manual (Document no. 300510EN) for
more information on using the TankMaster WinSetup software to configure a
Rosemount 5900 level gauge.
There are a number of advanced configuration options available which are not
included in the basic configuration wizard. See Section C: Advanced
Configuration for information on how to use the various advanced options
such as Tank Scan, Empty Tank Handling, Surface Echo Tracking and Filter
Settings.
Preliminary
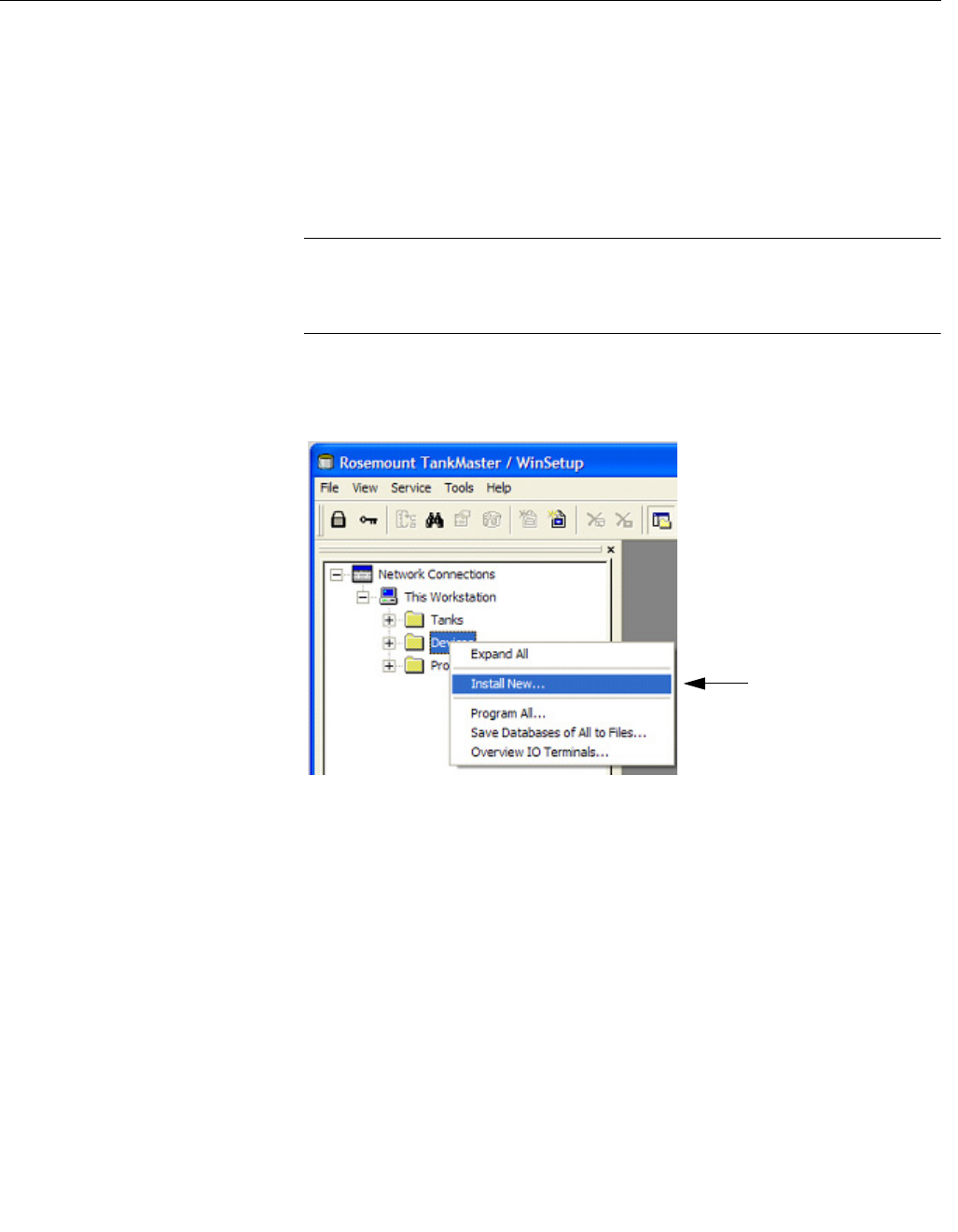
Reference Manual
300520EN, Rev AA
November 2009
Rosemount 5900 Series
4-8 Section 4. Configuration
4.4.1 Installation
Wizard
A Rosemount 5900 is typically installed as part of the installation procedure
when installing a Rosemount 2410 tank communication unit in TankMaster
WinSetup. Then the 5900 appears in the WinSetup workspace and is
configured via the Properties window. See the Rex II System Configuration
Manual (Document no. 300510EN) for more information.
The 5900 can also be installed by using the TankMaster WinSetup installation
wizard. The installation wizard in WinSetup is a tool that facilitates installation
and configuration of Rosemount 5900 and other devices.
NOTE!
In case the Rosemount 5900 level gauge was installed offline via a
Rosemount 2410 tank communication unit, it needs to be configured
separately via the Properties window.
To install a Rosemount 5900 do the following:
1. Start the installation wizard in TankMaster WinSetup.
2. Select the Devices folder.
3. Click the right mouse button and select Install New.
4. Follow the instructions.
See the Rex II System Configuration Manual (Document no. 300510EN) for
more information on using the TankMaster WinSetup program to configure the
Rosemount 5900.
Install New...
Preliminary
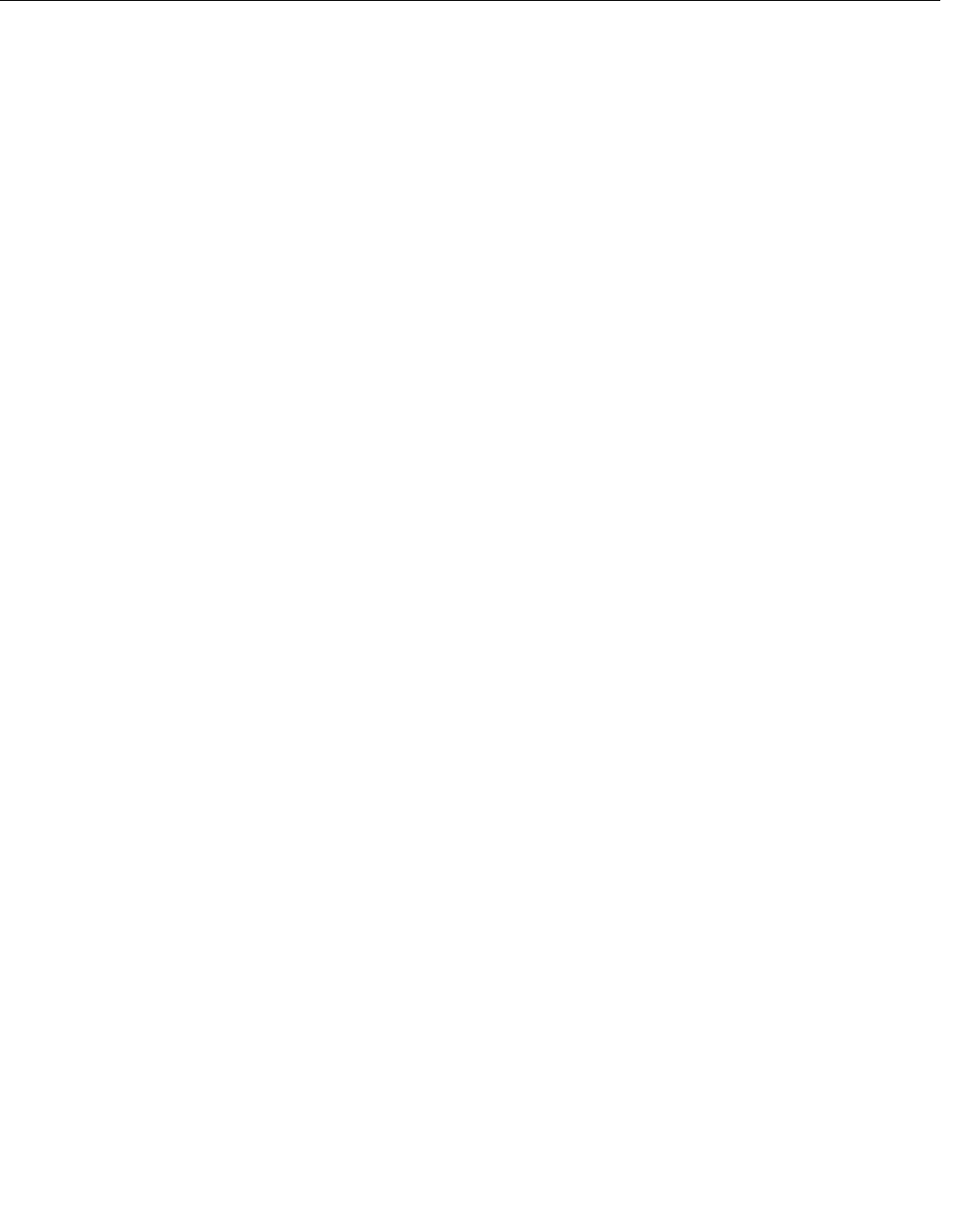
Reference Manual
300520EN, Rev AA
November 2009
4-9
Rosemount 5900 Series
Section 4. Configuration
4.5 LPG
CONFIGURATION
4.5.1 Preparations Ensure that all mechanical installations are made according to instructions,
and that all external sensors such as pressure and temperature sensors are
properly connected.
Make sure that the position of the reference pin is accurately measured and
the inner diameter of the still-pipe is available.
Before the actual LPG configuration can take place, install the tank and the
level gauge in TankMaster WinSetup as described in the REX II System
Configuration Manual (Document no. 300510EN). Ensure that the appropriate
tank and device types are selected and that the temperature and pressure
sensors are properly configured. Check that the gauge communicates with
the TankMaster PC.
Highly pressurized vapor above the product surface affects the progation
speed of microwaves. The Rosemount 5900 gauge is able to compensate for
this, thus avoiding deviations in measured level due to the vapor.
When the gauge is installed on the tank, and the tank is still empty, calibrate
the gauge and configure for LPG measurements.
Installing a Rosemount 5900 for LPG measurements can roughly be divided
into the following steps:
a. Mechanical installation. Install the 5900 gauge on the still-pipe.
Measure the position of the reference pin.
b. Start up. In TankMaster Winsetup configure the 5900 according to
the standard procedure for installing a Rosemount 5900 level gauge.
c. Calibration.
d. Configuration of temperature and pressure sensors.
e. Configuration of test pin.
f. Verification of LPG measurements.
g. Setting up the correction method that applies to the particular type of
product that is stored in the tank.
Preliminary
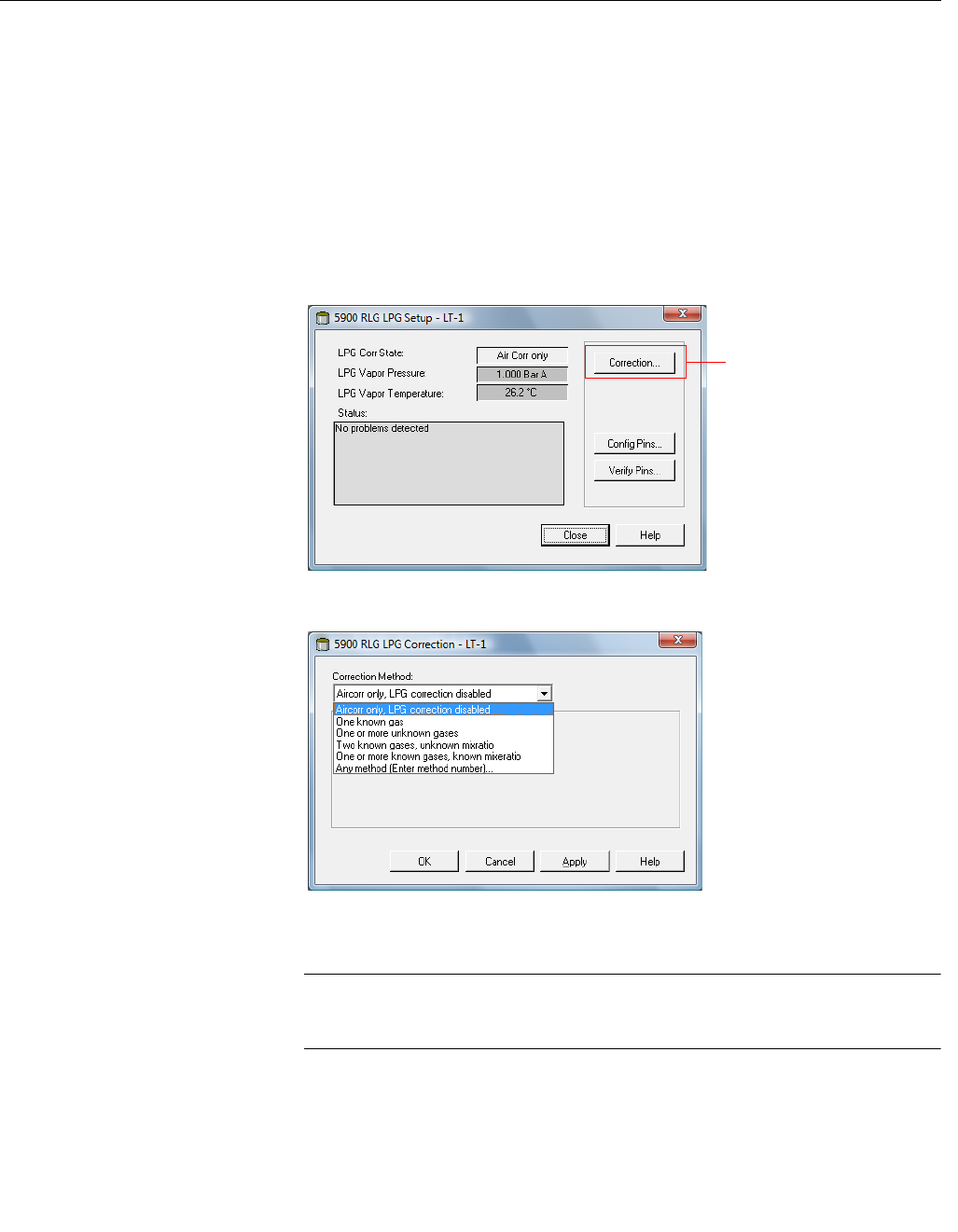
Reference Manual
300520EN, Rev AA
November 2009
Rosemount 5900 Series
4-10 Section 4. Configuration
4.5.2 LPG
Configuration
In the following description it is assumed that the Rosemount 5900 LPG
gauge is installed on the tank, and that a basic configuration is done as
described in the Rex II System Configuration Manual (Document no.
300510EN). Then it needs to be configured for LPG measurements. Do the
following:
1. Ensure that the tank is empty.
2. Check that the ball valve (optional) on the gauge is open.
In the TankMaster WinSetup work space choose the Logical View tab. Select
the icon that represents the radar level gauge, click the right mouse button
and choose LPG Setup.
3. In the LPG Setup window click the Correction button.
Choose Air Correction Only from the list of correction methods and click the
OK button.
NOTE!
The Air Correction Only option shall only be used when the tank atmosphere
contains air and no other gases.
When the LPG configuration is finished, the correction method needs to be
changed to a correction method that applies to the particular type of product
that is used.
Correction
Preliminary
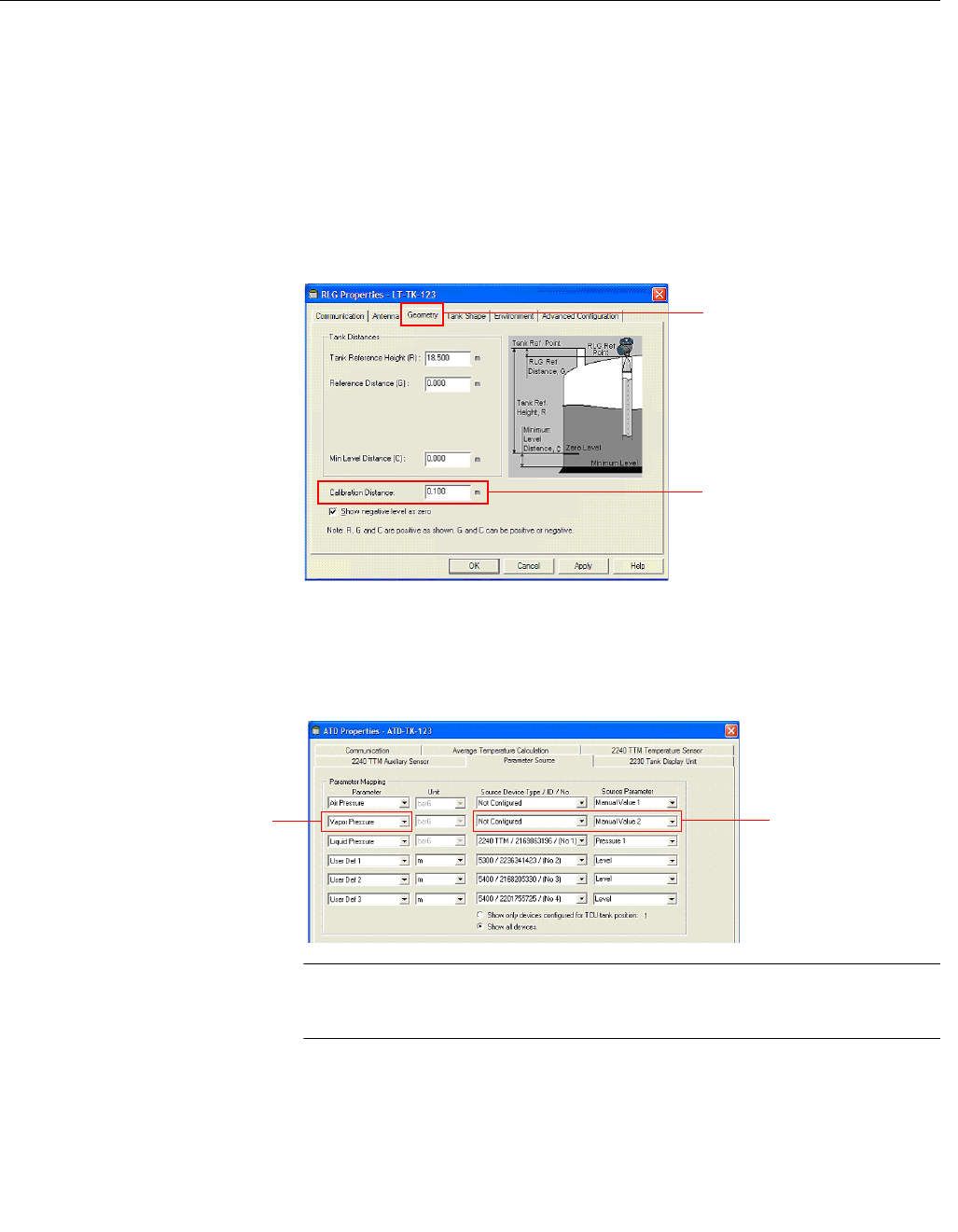
Reference Manual
300520EN, Rev AA
November 2009
4-11
Rosemount 5900 Series
Section 4. Configuration
4. Calibrate.
Make sure that there is no liquid above the calibration ring (or bottom plug) at
the end of the pipe.
Check the Ullage value measured by the transmitter:
Ullage = Tank Height R- Product Level L.
If the Ullage value is not equal to the actual distance between the RTG
Reference Point and the calibration ring, open the TankMaster WinSetup
Properties window (right-click the device icon and choose Properties), choose
the RTG Geometry tab and adjust the Calibration Distance:
5. Choose Vapor Pressure source device.
Open the ATD Properties window and select the Parameter Source tab.
This tab lets you map tank parameters such as Vapor Pressure to
source devices connected to the tankbus.
NOTE!
Pressure is not required for correction method One or more known gases,
known mixratio (see step 9 on page 4-15).
Calibration distance
Geometry
Tank parameter Vapor Presssure Source device and
source parameter
Preliminary
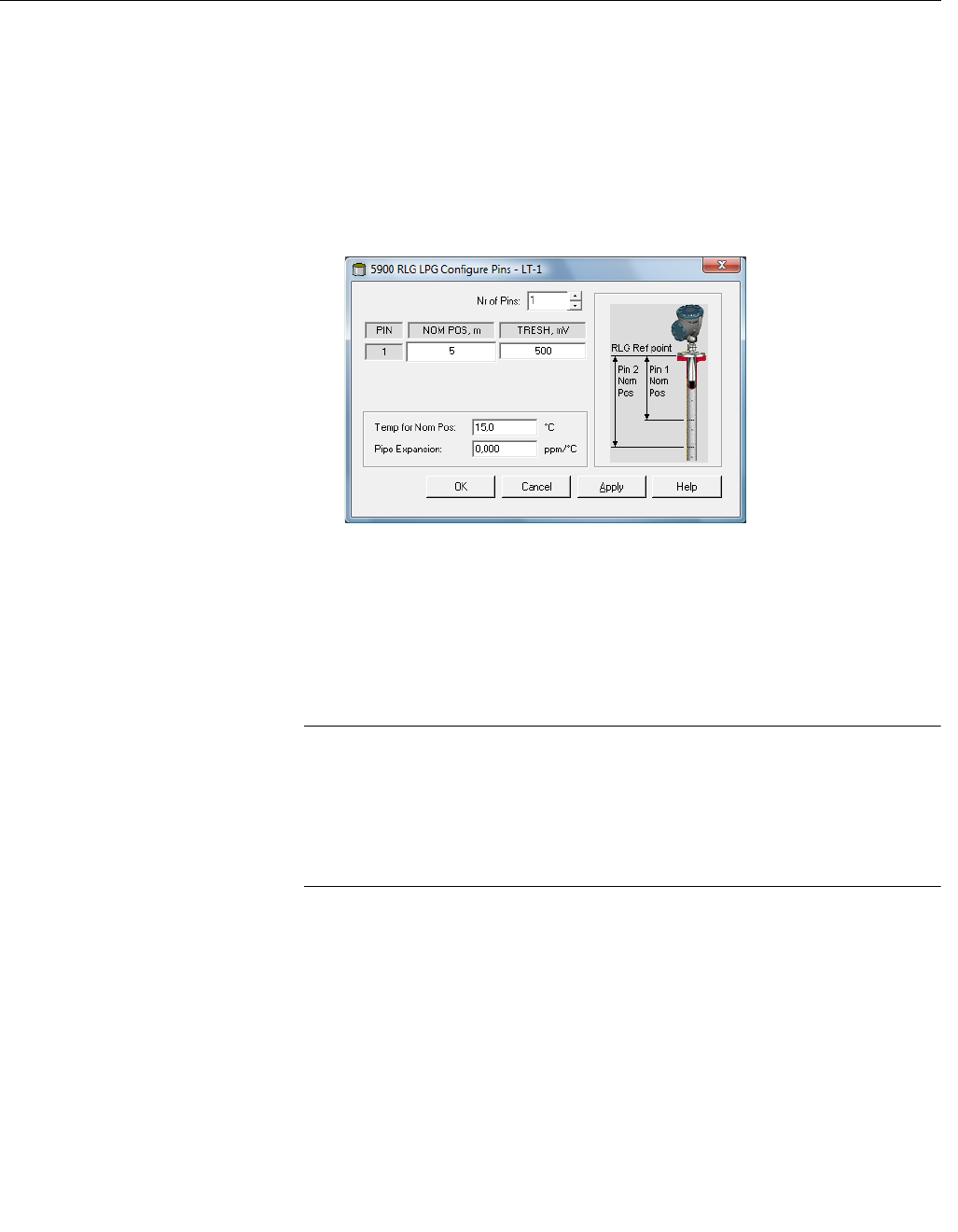
Reference Manual
300520EN, Rev AA
November 2009
Rosemount 5900 Series
4-12 Section 4. Configuration
6. When a Rosemount 2240 tank temperature multiplexer is used, the
vapor temperature is automatically mapped to the average temperature
of all spot sensors above the product surface. In case you like to map a
specific sensor, open the ATD Properties window and select the
Parameter Source tab to choose the desired temperature source device.
7. Configure the reference pins.
In the LPG Setup window click the Config Pins button to open the
LPG Configure Pins window:
Enter the reference pin position. The position is measured from the RTG
Reference Point to the actual position of the reference pin.
Since hand dipping can not be performed in high pressurized tanks, Emerson
Process Management / Rosemount Tank Gauging has developed a unique
method to verify level gauging in such tanks. The method is based on
measurements in a special radar wave propagation mode against a fixed
reference pin in order to verify the measurement.
NOTE!
The value entered in the Nominal Pos field refers to the mechanical distance
from the RTG reference point to the actual reference pin. This value will only
act as a starting point for the following verification process in which the
electrical distance from the RTG reference point to the reference pin is
calculated. In most cases the electrical distance deviates from the actual
mechanical distance.
Preliminary
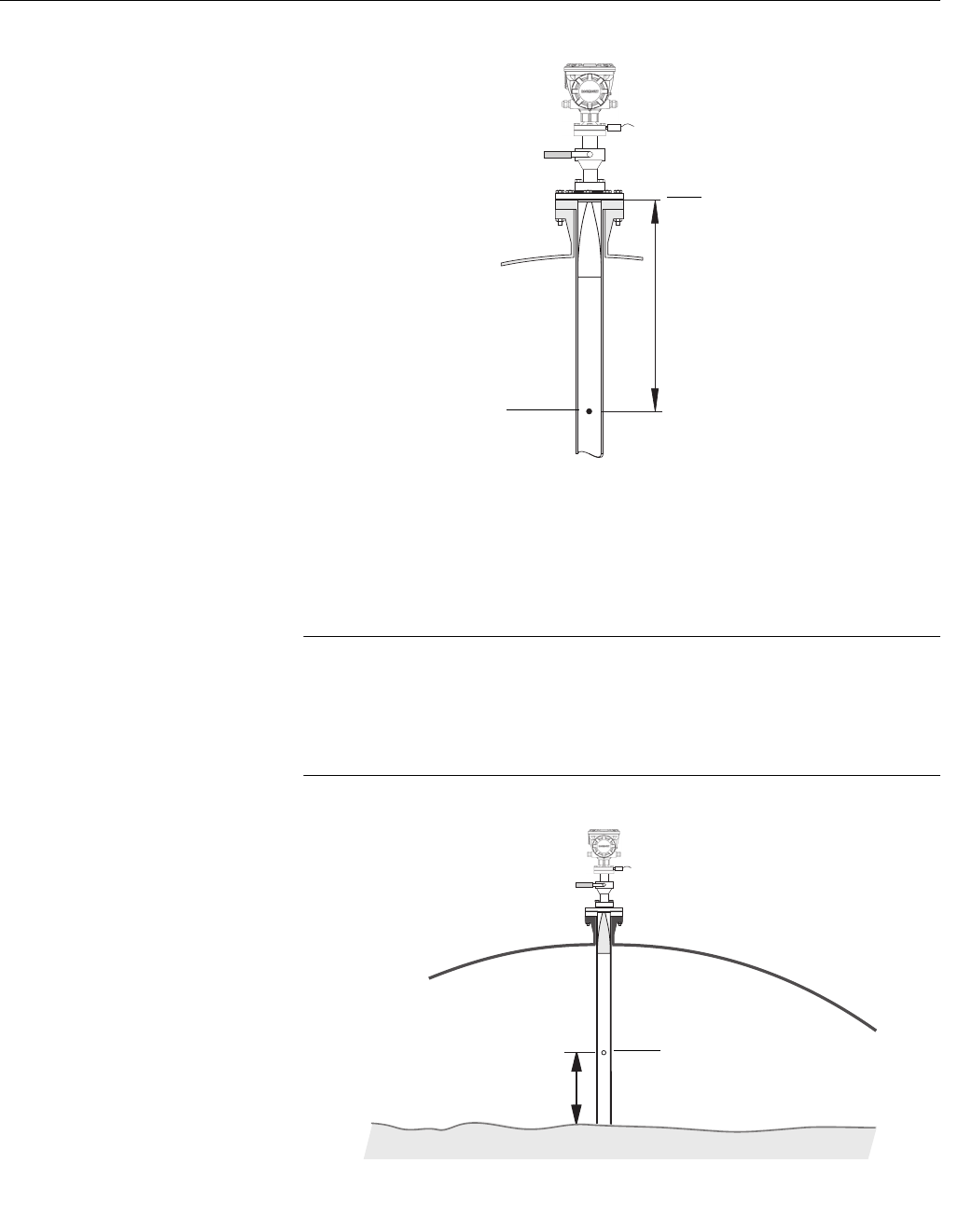
Reference Manual
300520EN, Rev AA
November 2009
4-13
Rosemount 5900 Series
Section 4. Configuration
Make sure that the Threshold value is 500 mV.
The amplitude of the echo from the reference pin must be above the threshold
value in order to appear in the LPGVerify window (see “Verify the gauge
measurement.” on page 4-14). In case the reference pin does not show up, it
is possible to use a smaller threshold value. Check that the product level is
not above the reference pin.
NOTE!
When the product surface is close to a reference pin, the radar echoes from
the reference pin and the product surface interfere. This may reduce the
accuracy of the measured distance to the reference pin. It is recommended
that verification is not performed if the distance between a reference pin and
the product surface is less than 900 mm.
RTG REFERENCE PIN
RTG REFERENCE POINT
Distance from RTG reference
point to reference pin
MINIMUM CLEARANCE 900 MM
REFERENCE PIN
Preliminary
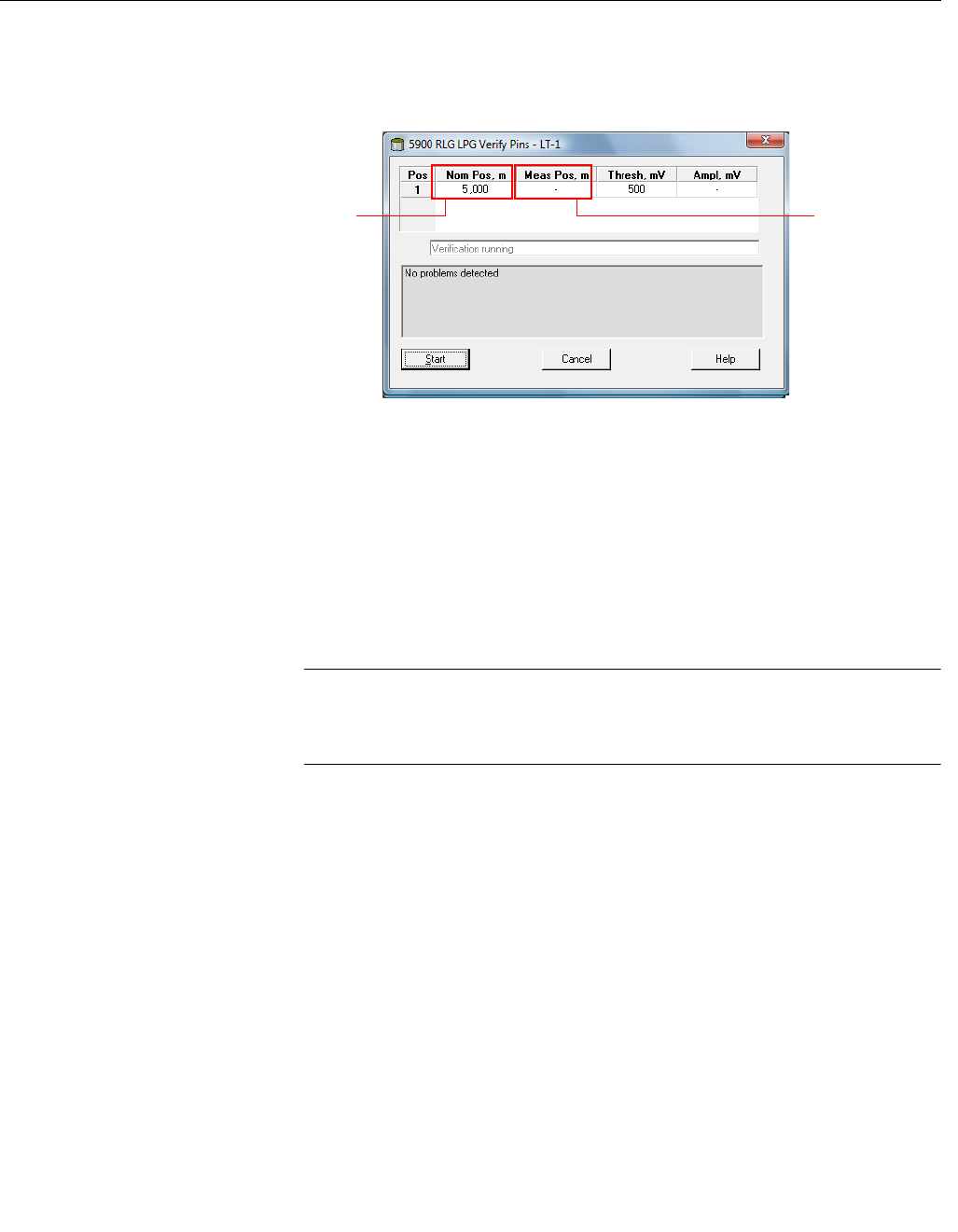
Reference Manual
300520EN, Rev AA
November 2009
Rosemount 5900 Series
4-14 Section 4. Configuration
8. Verify the gauge measurement.
a. Ensure that the reference pin appears in the LPG Setup window.
In the LPG Setup window click the Verify Pins button:
b. In the LPG Verify Pins window click the Start button to start the
verification process.
c. When verification is finished, the position appears in the Measured
Position field.
d. Note the position of the reference pin that is presented in the
Measured Position field. If the position deviates from the Nominal
Position, return to the LPG Configure Pins window (in the LPG
Setup window click the Config Pins button, see step 7 on
page 4-12) and enter the measured position in the Nominal
Position field.
NOTE!
The nominal position that was entered the first time refers to the mechanical
distance. The measured position refers to the electrical distance which is
the distance “seen” by the level gauge.
e. In the LPG Verify Pins window click the Start button again to start a
new verification. Repeat steps b to d until the nominal position in the
RTG LPG Configure Pins window is close to the measured position
that appears in the LPG Verify Pins window.
Nominal
position Measured
position
Preliminary
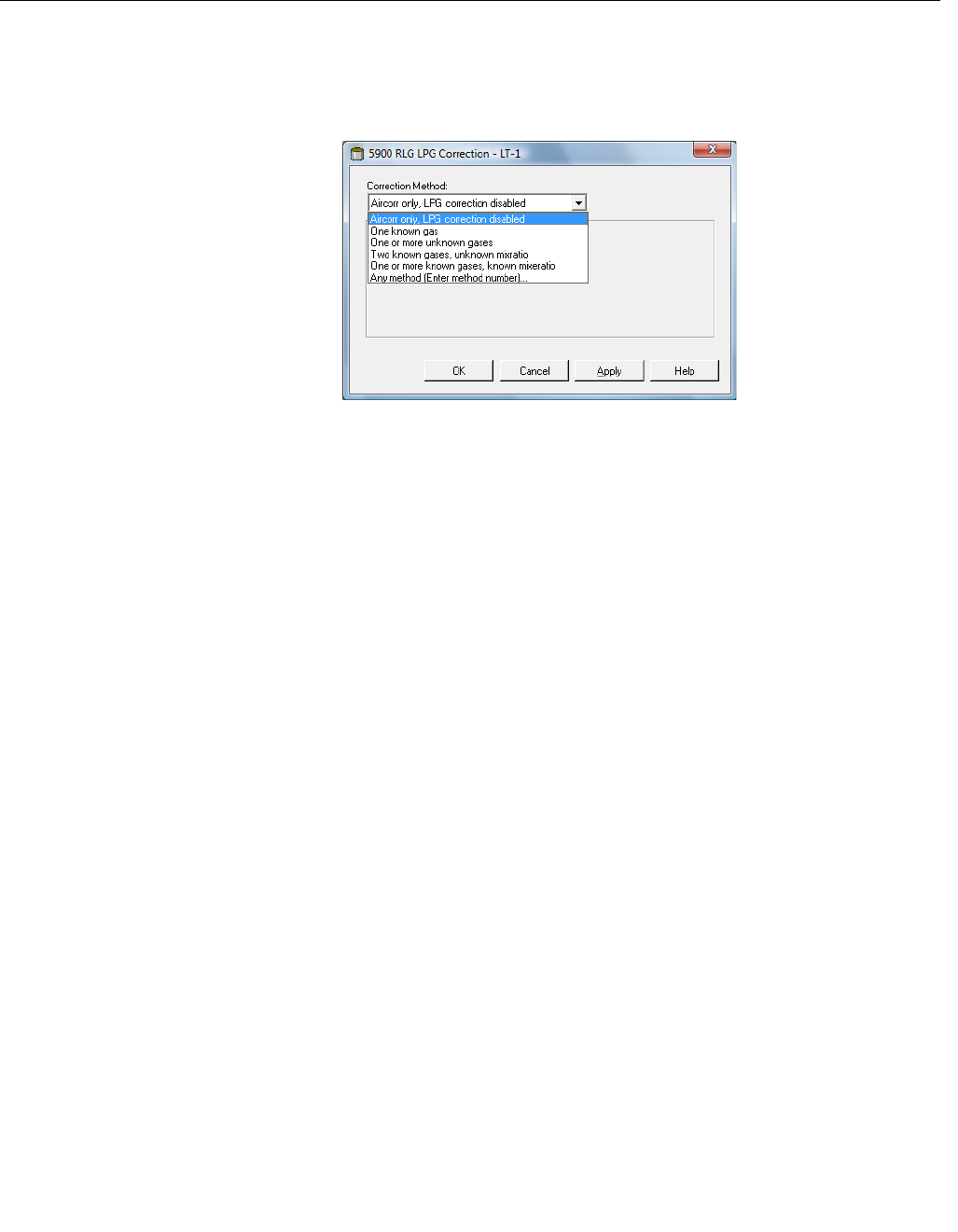
Reference Manual
300520EN, Rev AA
November 2009
4-15
Rosemount 5900 Series
Section 4. Configuration
9. Choose correction method.
There are several options available depending on the number of
products and product type.
In the LPG Setup window click the Correction button:
Choose one of the following correction methods:
a. Air Correction.
This method should only be used when there is no vapor in the tank,
i.e. when the tank is empty and contains air only. It is used in the
initial step when calibrating the 5900.
b. One known gas.
This method may be used when there is only one gas type in the
tank. It provides the highest accuracy among the different correction
methods. Note that even small amounts of another gas reduces the
accuracy.
c. One or more unknown gases.
Use this method for hydrocarbons, for example Propane/Buthane,
when the exact mixture is not known.
d. Two gases with unknown mixratio.
This method is suitable for a mixture of two gases even if the
mixratio is not known.
e. One or more known gases with known mixratio.
This method may be used when there is a well known mixture of up
to 4 products in the tank.
Now the Rosemount 5900 gauge is ready to measure the product level when
the tank is put into operation.
Preliminary
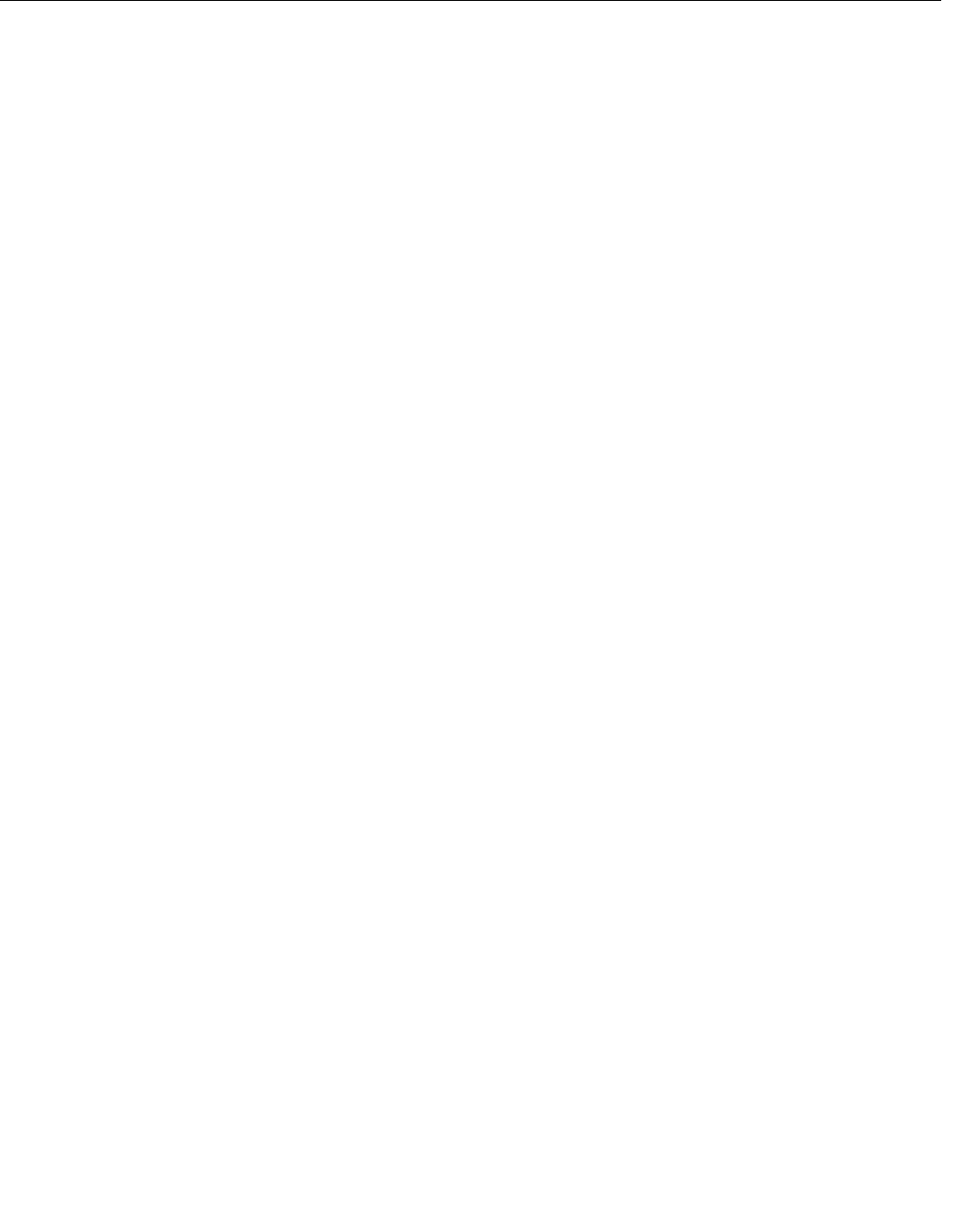
Reference Manual
300520EN, Rev AA
November 2009
Rosemount 5900 Series
4-16 Section 4. Configuration
Preliminary
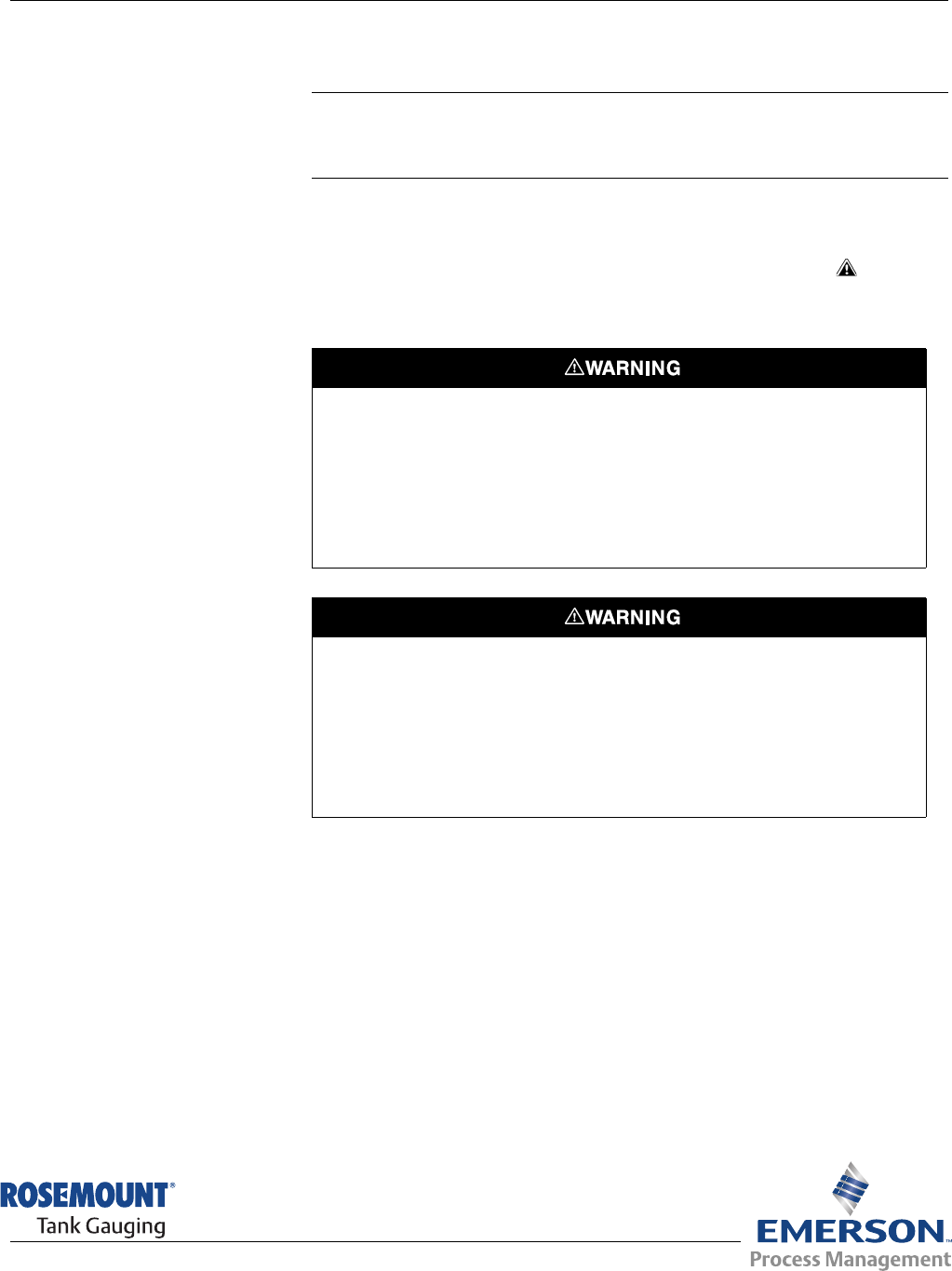
Reference Manual
300520EN, Rev AA
November 2009 Rosemount 5900 Series
www.rosemount-tg.com
Section 5 Operation
5.1 Safety Messages . . . . . . . . . . . . . . . . . . . . . . . . . . . . page 5-1
5.2 Viewing Measurement Data . . . . . . . . . . . . . . . . . . . page 5-2
5.3 Alarm Handling . . . . . . . . . . . . . . . . . . . . . . . . . . . . . page 5-2
5.1 SAFETY
MESSAGES
Procedures and instructions in this section may require special precautions to
ensure the safety of the personnel performing the operations. Information that
raises potential safety issues is indicated by a warning symbol ( ). Please
refer to the following safety messages before performing an operation
preceded by this symbol.
Failure to follow safe installation and servicing guidelines could result in death or
serious injury:
Make sure only qualified personnel perform the installation.
Use the equipment only as specified in this manual. Failure to do so may impair the
protection provided by the equipment.
Do not perform any service other than those contained in this manual unless you are
qualified.
Explosions could result in death or serious injury:
Verify that the operating environment of the transmitter is consistent with the appropriate
hazardous locations certifications.
Before connecting a communicator in an explosive atmosphere, make sure the
instruments in the loop are installed in accordance with intrinsically safe or
non-incendive field wiring practices.
Do not remove the gauge cover in explosive atmospheres when the circuit is alive.
Preliminary
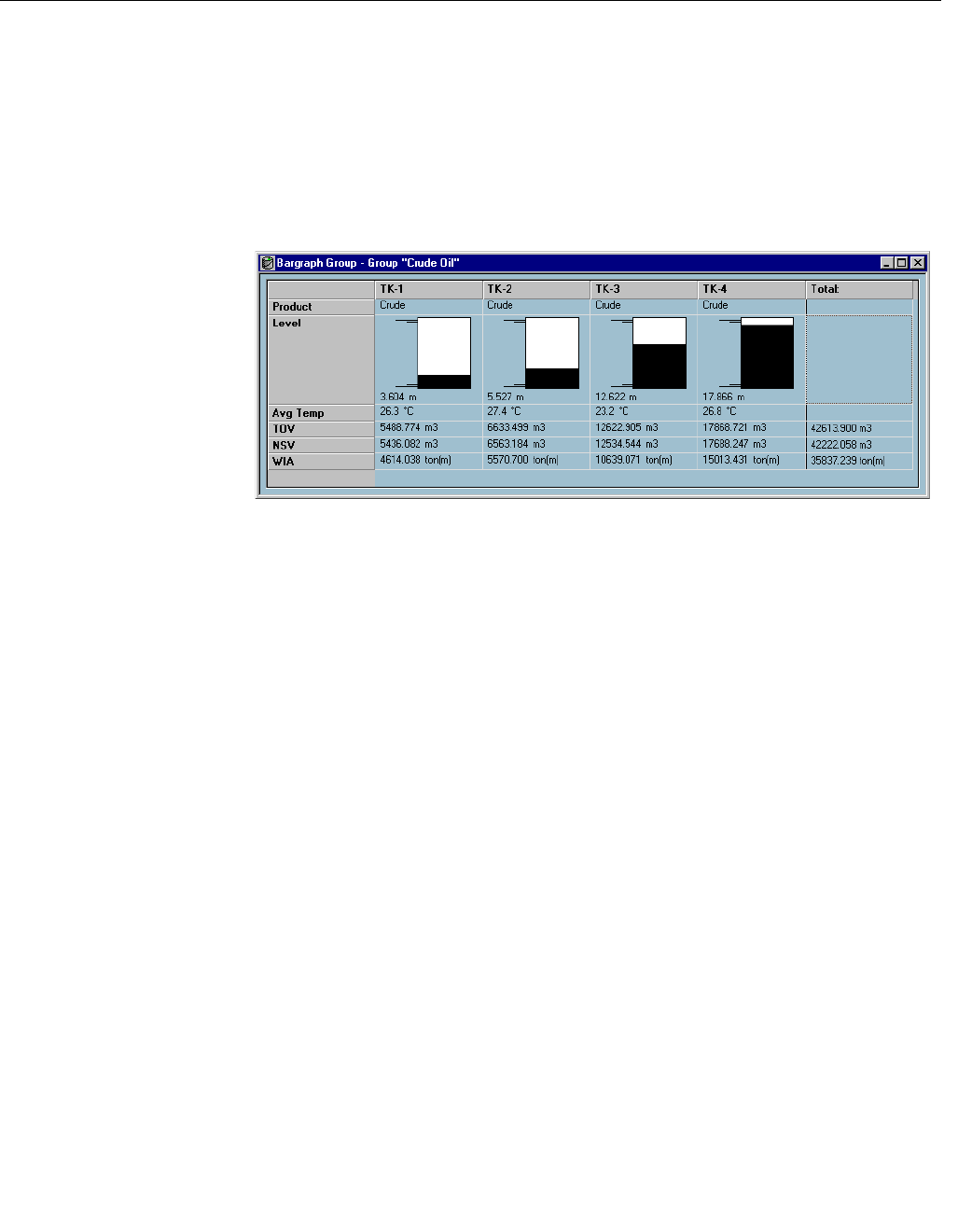
Reference Manual
300520EN, Rev AA
November 2009
Rosemount 5900 Series
5-2 Section 5. Operation
5.2 VIEWING
MEASUREMENT
DATA
The Rosemount TankMaster program has several options for viewing
measurement and inventory data for single tanks and for tank groups.
TankMaster also offers the option to create custom views with your own set of
parameters. See the TankMaster WinOpi Reference Manual (Document No.
303028EN) for more information.
Figure 5-1. Example of a
bargraph view in TankMaster
WinOpi
5.3 ALARM HANDLING The Rosemount TankMaster WinOpi program supports a wide range of alarm
functions. Alarms can be set for various measurement data such as Level,
Average Temperature, and Vapor Pressure. Alarm limits can also be set for
inventory data such as Net Standard Volume.
Active alarms can be shown in the Alarm Summary window. The Alarm Log
lets you view alarms that are no longer active. The Alarm Log can be saved to
disk for future reference.
See the TankMaster WinOpi Reference Manual (Document No. 303028EN)
for more information.
Preliminary
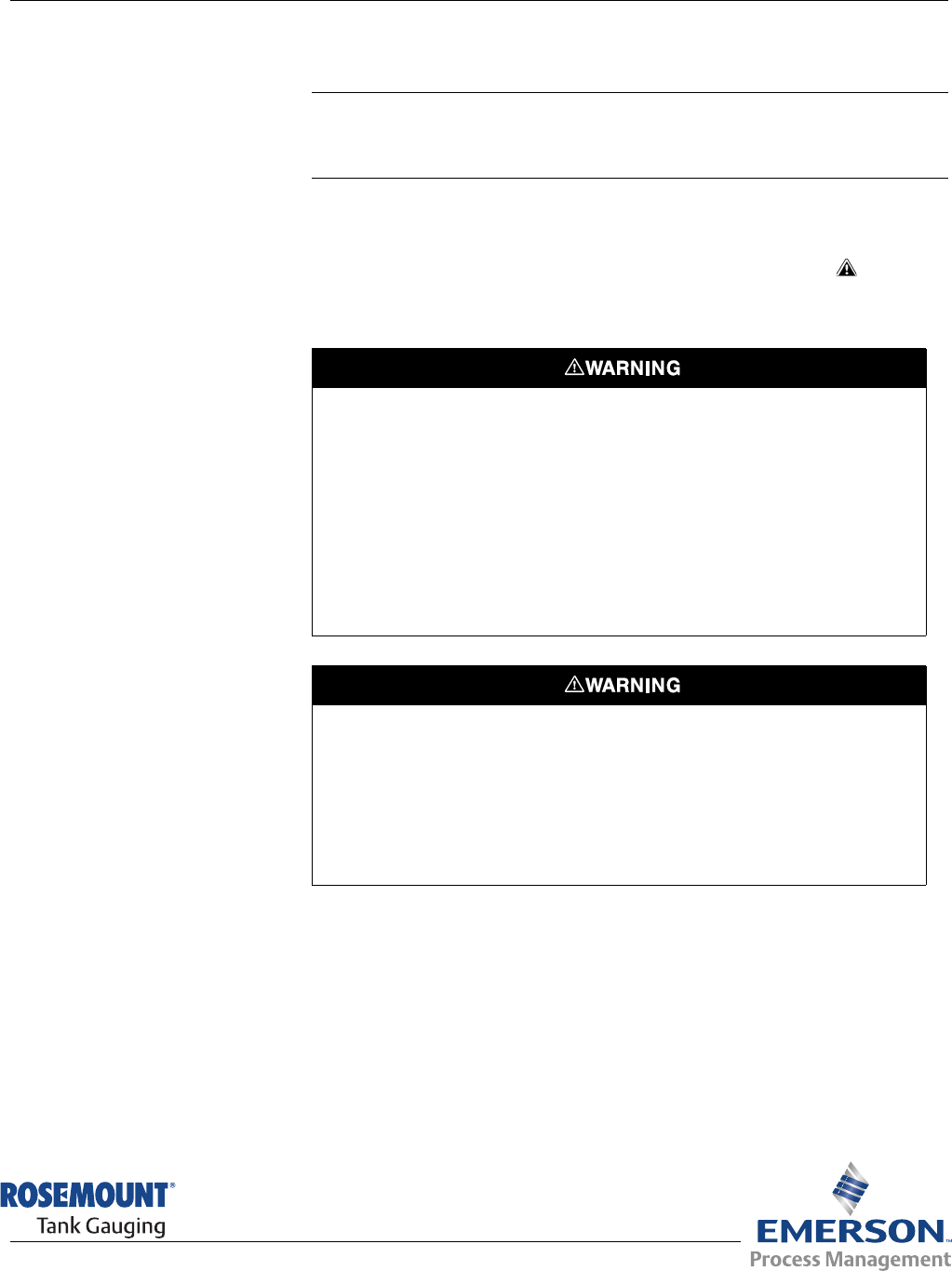
Reference Manual
300520EN, Rev AA
November 2009 Rosemount 5900 Series
www.rosemount-tg.com
Section 6 Service and Troubleshooting
6.1 Safety Messages . . . . . . . . . . . . . . . . . . . . . . . . . . . . page 6-1
6.2 Service . . . . . . . . . . . . . . . . . . . . . . . . . . . . . . . . . . . . page 6-2
6.3 Troubleshooting . . . . . . . . . . . . . . . . . . . . . . . . . . . . page 6-20
6.1 SAFETY
MESSAGES
Procedures and instructions in this section may require special precautions to
ensure the safety of the personnel performing the operations. Information that
raises potential safety issues is indicated by a warning symbol ( ). Please
refer to the following safety messages before performing an operation
preceded by this symbol.
Failure to follow safe installation and servicing guidelines could result in death or
serious injury:
Make sure only qualified personnel perform the installation.
Use the equipment only as specified in this manual. Failure to do so may impair the
protection provided by the equipment.
Do not perform any service other than those contained in this manual unless you are
qualified.
To prevent ignition of flammable or combustible atmospheres, disconnect power before
servicing.
Substitution of components may impair Intrinsic Safety.
Explosions could result in death or serious injury:
Verify that the operating environment of the transmitter is consistent with the appropriate
hazardous locations certifications.
Before connecting a communicator in an explosive atmosphere, make sure the
instruments in the loop are installed in accordance with intrinsically safe or
non-incendive field wiring practices.
Do not remove the gauge cover in explosive atmospheres when the circuit is alive.
Preliminary
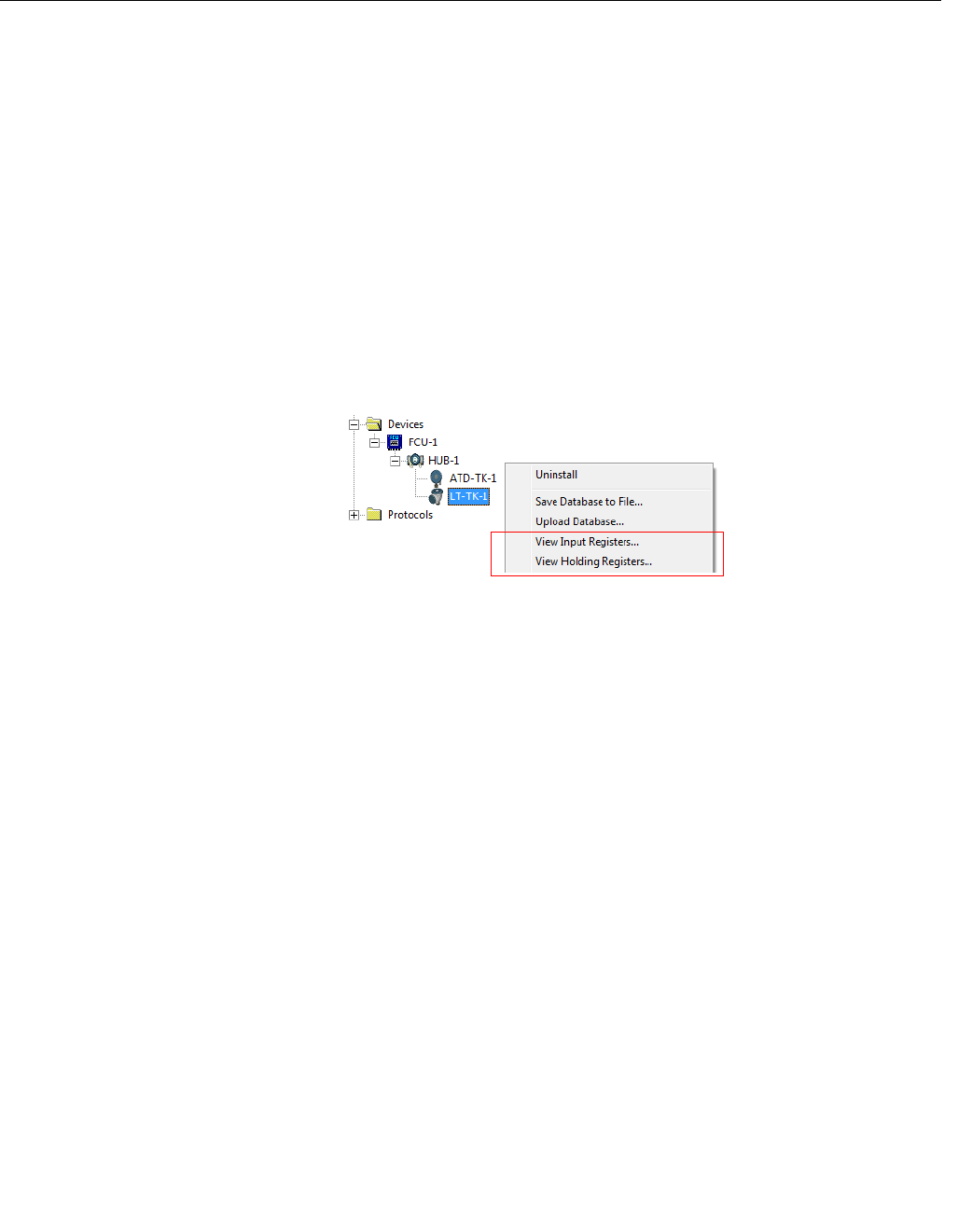
Reference Manual
300520EN, Rev AA
November 2009
Rosemount 5900 Series
6-2 Section 6. Service and Troubleshooting
6.2 SERVICE
6.2.1 Viewing Input
and Holding
Registers
Measured data is continuously stored in input registers of the Rosemount
5900 radar level gauge. By viewing the Input registers you can check that the
device is working properly.
The holding registers store various parameters which are used to configure
the 5900 gauge for various applications.
By using the Rosemount TankMaster WinSetup program, holding registers
can be edited simply by typing a new value in the appropriate value input field.
Some holding registers can be edited in a separate window. In this case
individual data bits can be changed.
To view input or holding registers of a device do the following:
1. Start the TankMaster WinSetup program.
2. In the TankMaster WinSetup workspace window select the 5900 gauge.
3. Click the right mouse button and choose the View Input/View Holding
Registers option, or from the Service menu choose Devices/View
Input/View Holding Registers.
Preliminary
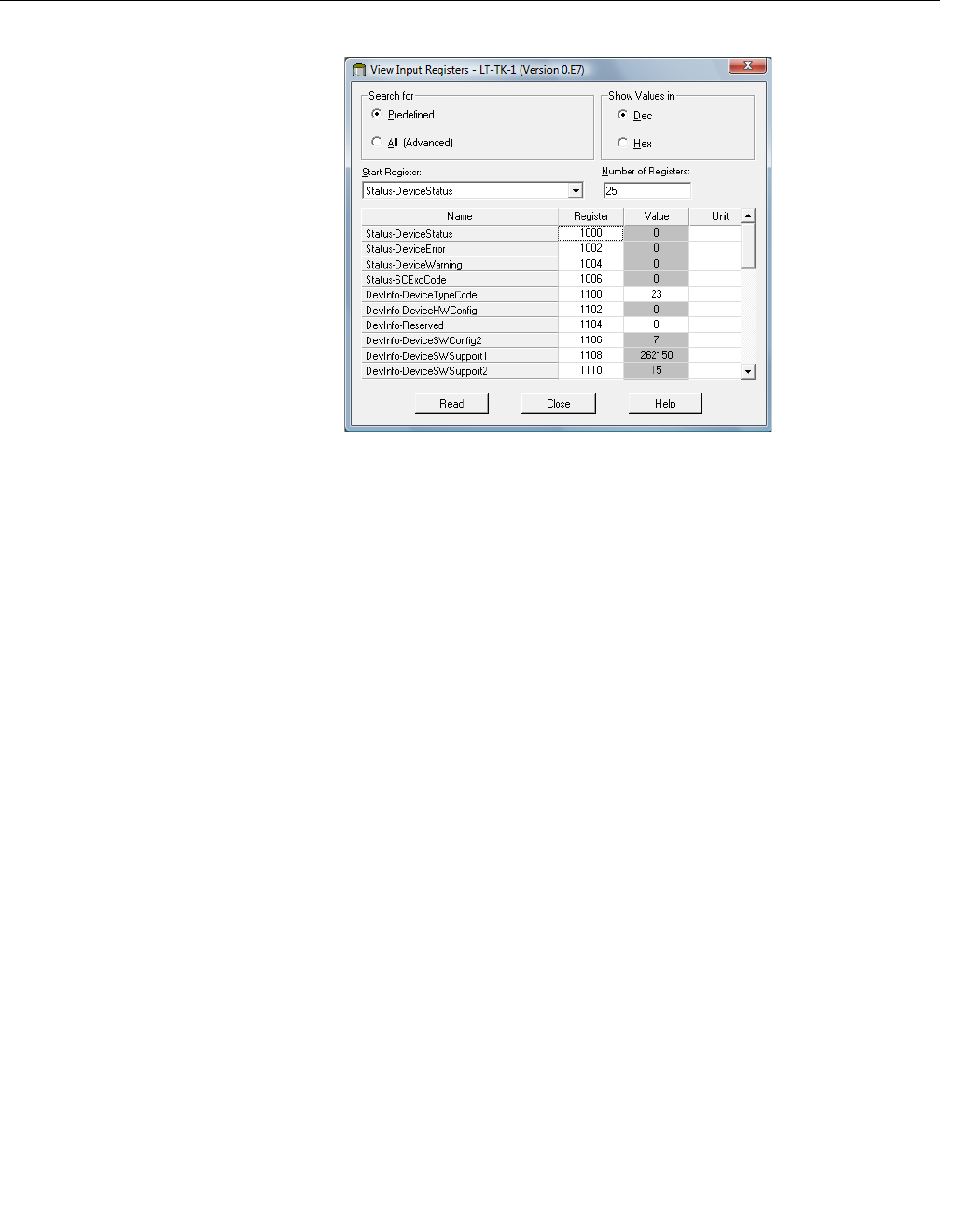
Reference Manual
300520EN, Rev AA
November 2009
6-3
Rosemount 5900 Series
Section 6. Service and Troubleshooting
4. Choose Predefined to see a basic selection of registers. Choose the All
option to view a range of registers by your own choice.
For the All option, you have to specify a range of registers by setting a
start value in the Start Register input field, and the total number of
registers to be displayed in the Number of Registers field (1-500).
5. Click the Read button. Now the Value column is updated with the current
register values.
See the Raptor System Configuration manual (Document No. 300510EN) for
more information on how to edit holding registers.
Preliminary
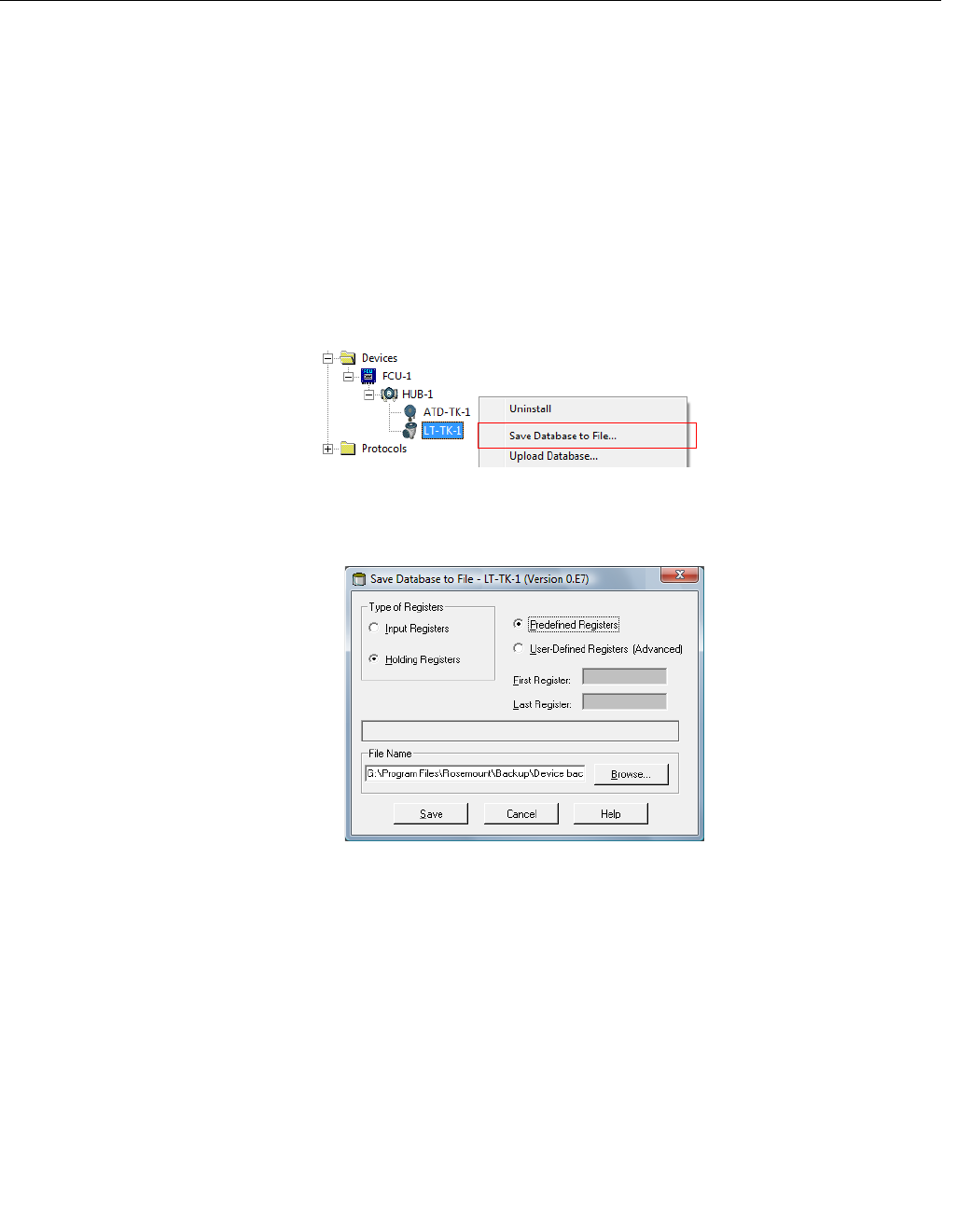
Reference Manual
300520EN, Rev AA
November 2009
Rosemount 5900 Series
6-4 Section 6. Service and Troubleshooting
6.2.2 Backing Up the Gauge Configuration
Input and holding registers of the Rosemount 5900 can be stored on disk.
This can be useful for backup purposes and troubleshooting. You can save a
predefined set of holding registers to make a backup copy of the current
gauge configuration. The backup file can be used to restore the transmitter
configuration at a later stage.
Single device
To save the current configuration to file for a single device do the following:
1. Start the TankMaster WinSetup program.
2. In the WinSetup workspace window, click the right mouse button on the
5900 icon.
3. Choose the Devices/Save Database to File option.
This option is also available from the Service/Devices menu.
4. Choose the Holding Registers and Predefined Registers options (the
User-Defined option should only be used for advanced service).
5. Click the Browse button, select a folder and type a name for the backup
file.
6. Click the Save button to start saving the database registers.
Preliminary
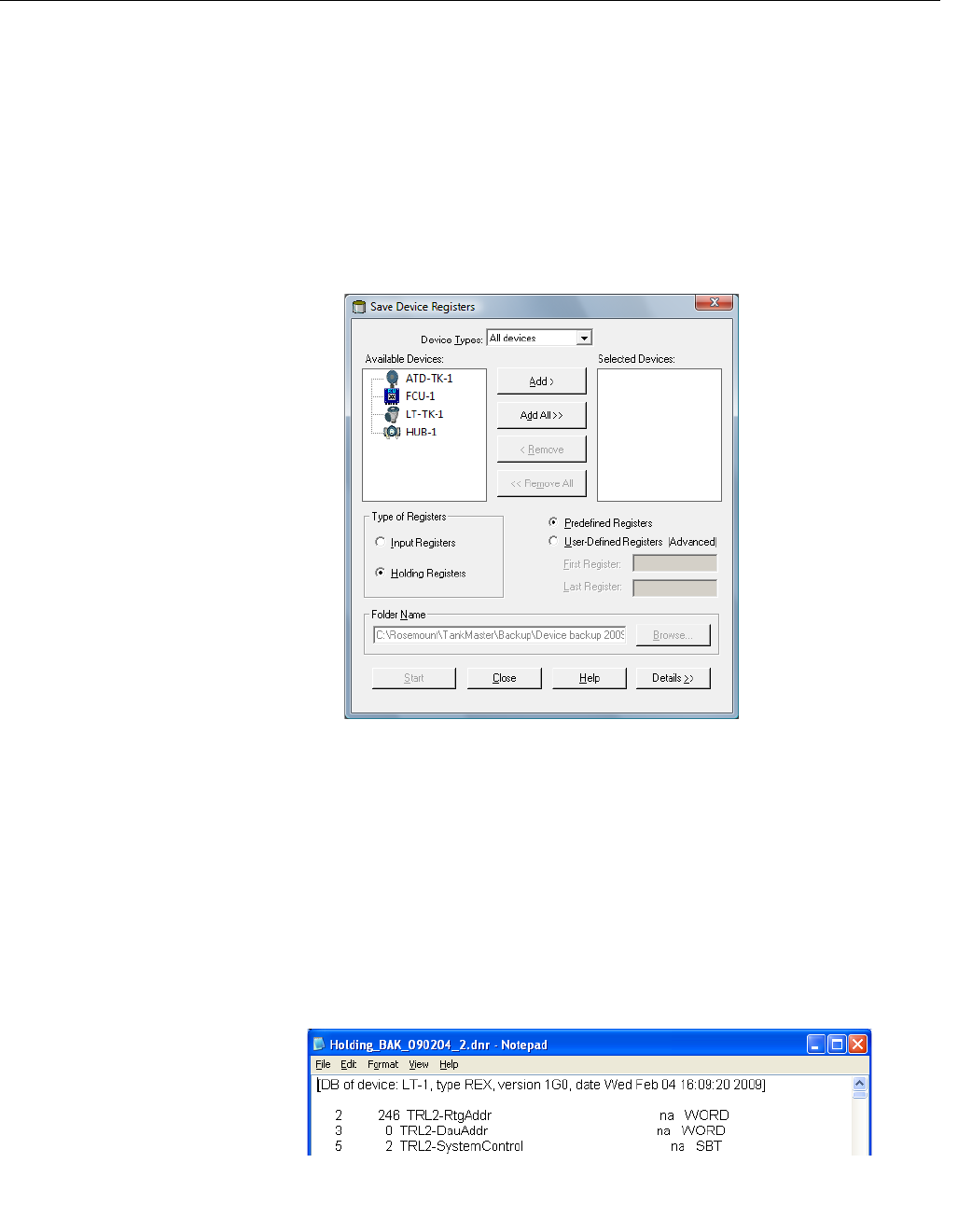
Reference Manual
300520EN, Rev AA
November 2009
6-5
Rosemount 5900 Series
Section 6. Service and Troubleshooting
Multiple devices
To save a backup copy of the current configuration for multiple devices, do the
following:
1. Start the TankMaster WinSetup program.
2. In the TankMaster WinSetup workspace window select the Devices
folder.
3. Click the right mouse button and choose the Devices/Save Database of
All to Files option.
This option is also available from the Service/Devices menu.
4. Select a device from the Available Devices pane and click the Add
button in order to move it to the Selected Devices pane. Repeat for all
devices you wish to include.
5. Choose the Holding Registers and Predefined Registers options (the
User-Defined option should only be used for advanced service).
6. Click the Browse button, select a folder and type a name for the backup
file.
7. Click the Start button to save the database backup.
The backup file can be viewed as a text file in a word processing program
such as the Microsoft Notepad:
Preliminary
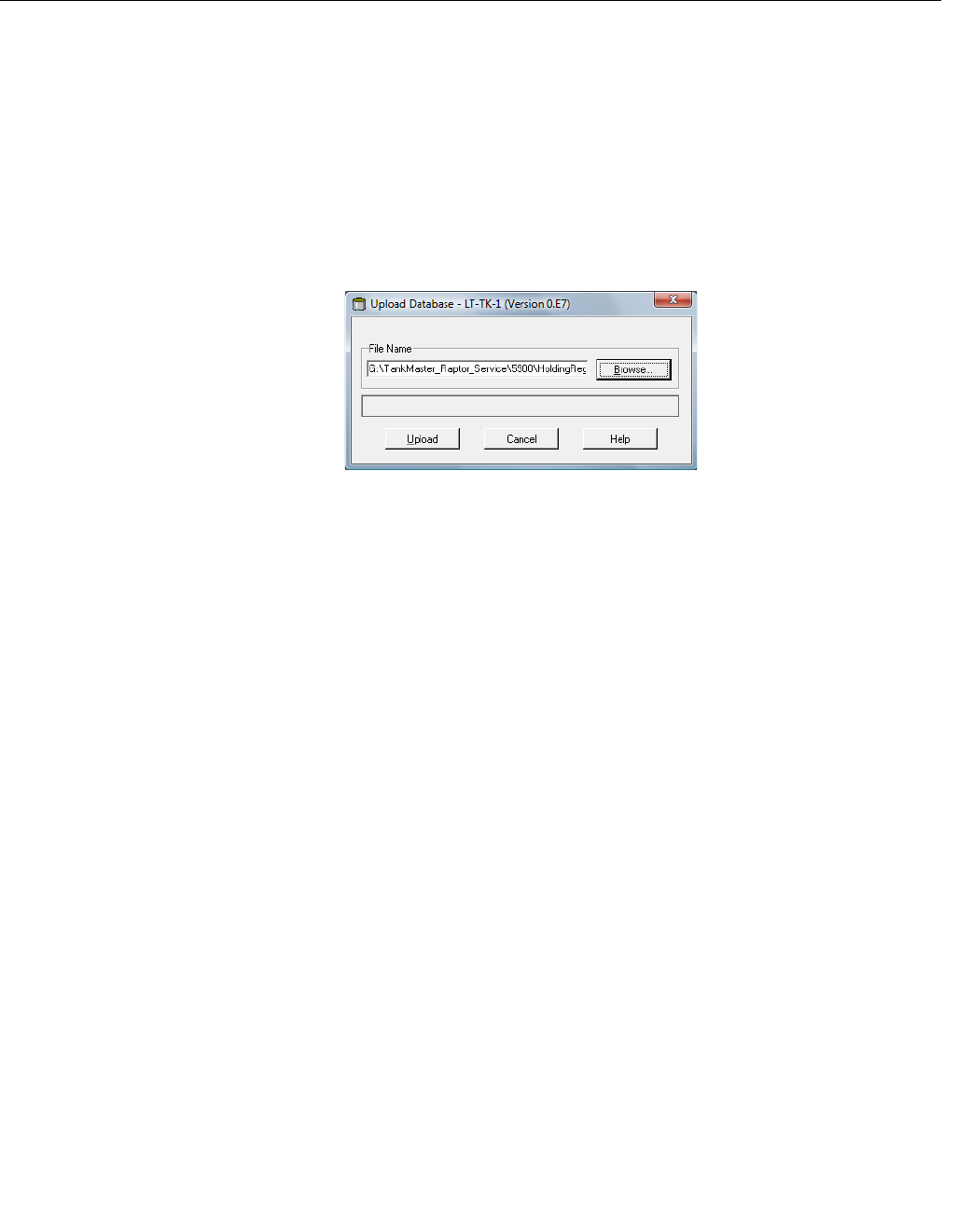
Reference Manual
300520EN, Rev AA
November 2009
Rosemount 5900 Series
6-6 Section 6. Service and Troubleshooting
6.2.3 To Recover a Backup Configuration Database
TankMaster WinSetup lets you replace the current Holding Register database
with a backup database stored on disk. This can be useful, for example, if you
want to recover lost configuration data.
To load a Holding Register database do the following:
1. Select the device in the Workspace window for which you want to load a
new database.
2. Click the right mouse button and choose the Devices/Upload Database
option, or from the Service menu choose Devices/Upload Database.
3. Click the Browse button and choose a database file to be uploaded, or
type a path and file name.
4. Click the Upload button.
Preliminary
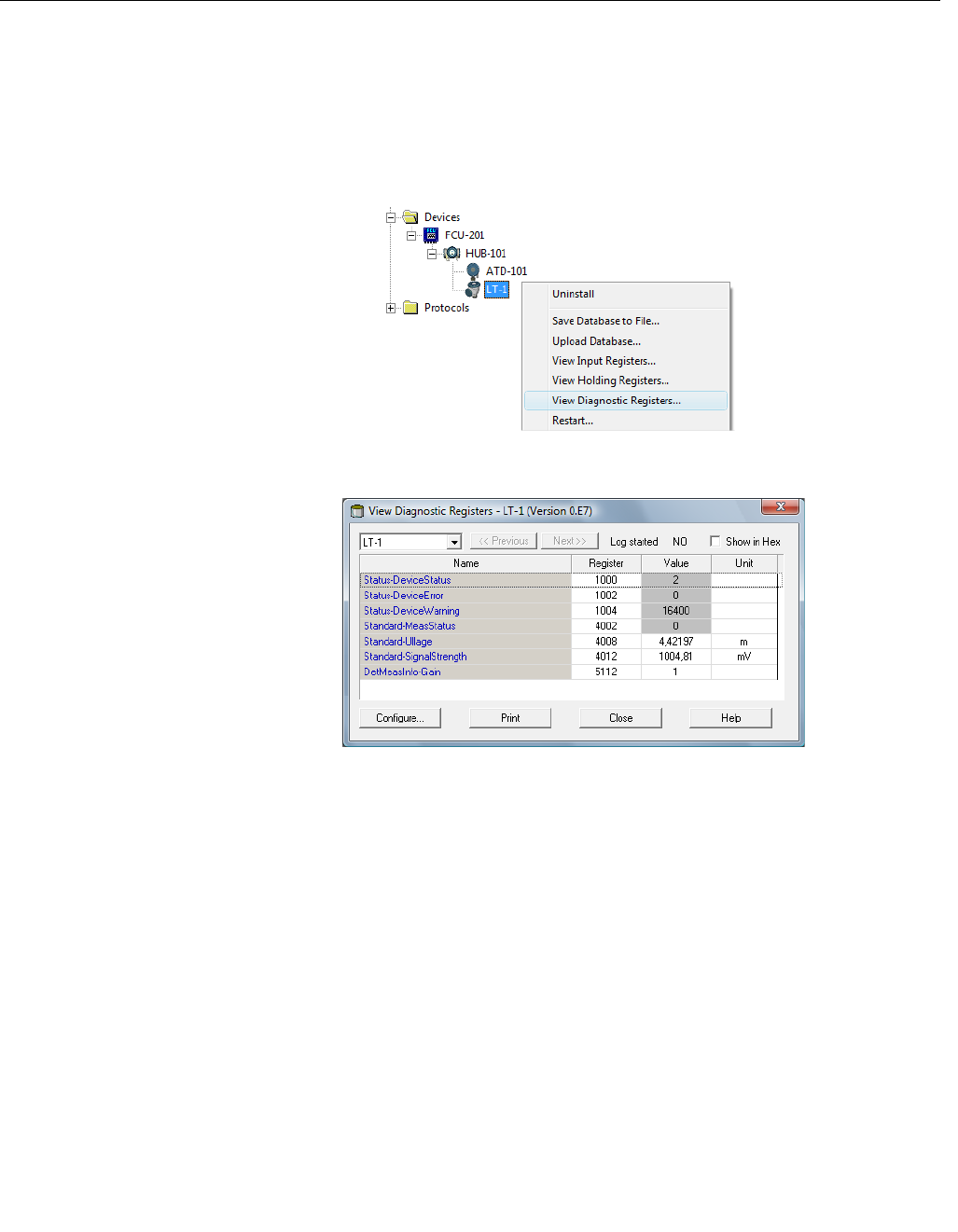
Reference Manual
300520EN, Rev AA
November 2009
6-7
Rosemount 5900 Series
Section 6. Service and Troubleshooting
6.2.4 Diagnostics The TankMaster WinSetup program lets you view the current device status.
The View Diagnostic Register window shows a selection of database registers
that gives you an instant view of how the gauge operates. You may also
configure the window by adding registers of special interest.
To view and configure the diagnostic registers:
1. Select the 5900 gauge icon in the TankMaster WinSetup workspace.
2. Click the right mouse button and choose View Diagnostic Registers.
The register values in the diagnostics window are of read only type. They are
loaded from the device as the window is opened.
A grey background color of the table cell in the Value column means that the
register is of either Bitfield or ENUM type. An expanded Bitfield/ENUM
window can be opened for this type of register. Double-click the cell to open
the Expanded Bitfield/ENUM window.
If needed, the values can be presented as hexadecimal numbers. This
applies to registers of the Bitfield and ENUM types. Select the Show in Hex
check box to present Bitfield and ENUM registers as hexadecimal numbers.
The Configure button lets you open the Configure Diagnostic Registers
window where you can change the list of registers to be displayed in the View
Diagnostic Registers window. See the Raptor System Configuration Manual
(Document No. 300510EN) for more information.
The Configure Diagnostic Registers window also has a Log Setup button for
access to the Register Log Scheduling window which allows you to setup a
log schedule for automatic start and stop of register logging. See “Logging
Measurement Data” on page 6-12 for more information.
Preliminary
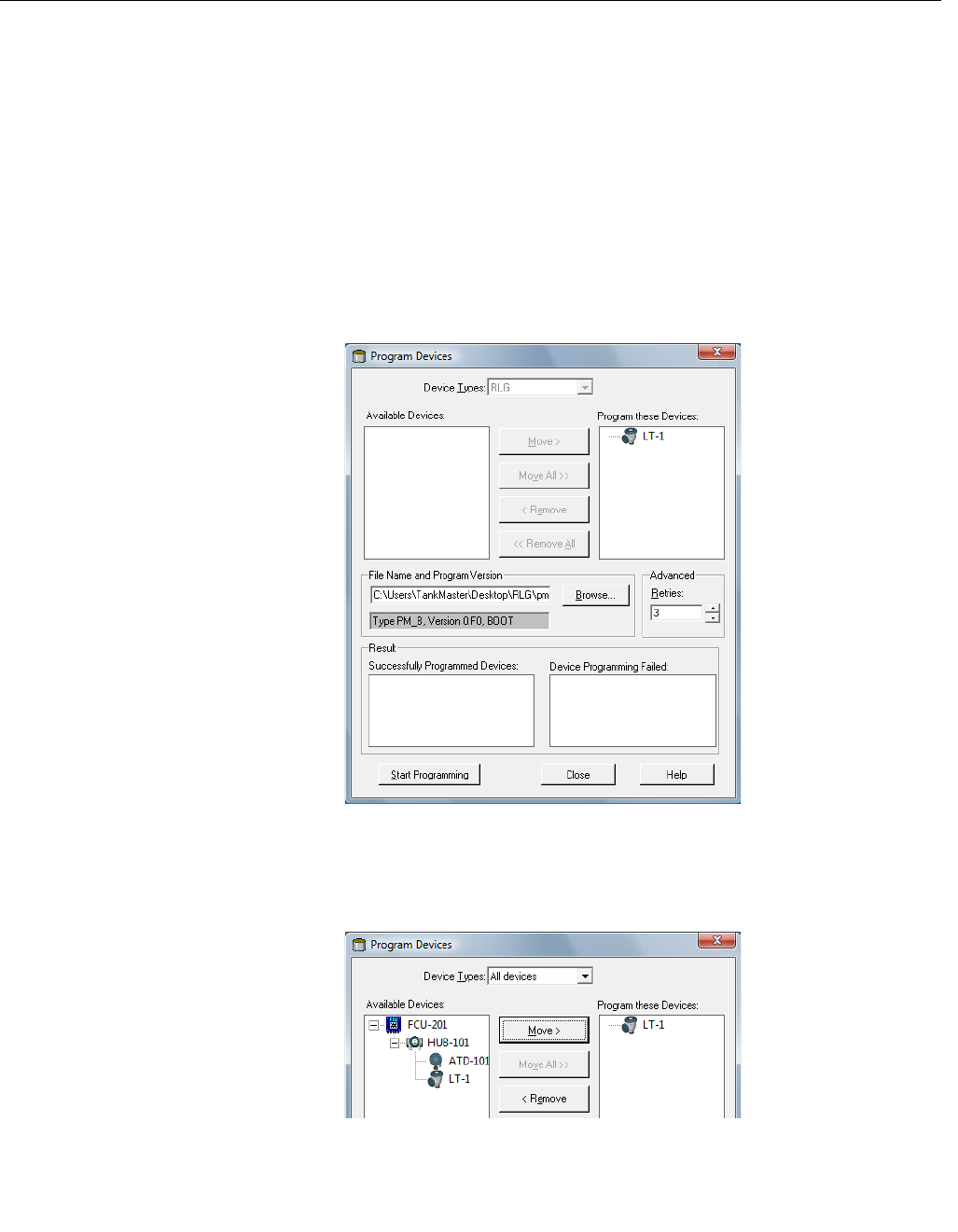
Reference Manual
300520EN, Rev AA
November 2009
Rosemount 5900 Series
6-8 Section 6. Service and Troubleshooting
6.2.5 Upgrading the Gauge Software
TankMaster WinSetup includes the option to upgrade Rosemount TankRadar
gauges with new application and boot software.
To upload a new program do the following:
1. Ensure that the 5900 level gauge has a stable communication with
TankMaster.
2. In the TankMaster WinSetup workspace window (Logical View) open the
Devices folder and select the 5900 level gauge to be upgraded (or select
the Devices folder to allow multiple devices programming).
3. Click the right mouse button and choose the Program option
(Program All option for multiple devices programming).
4. The 5900 will automatically appear in the Program These Devices pane
5. In case the Devices folder was selected for multiple programming,
choose the 5900 gauge to be programmed from the Available Devices
pane and click the Move button.
6. Repeat for each device to be programmed.
Use the Remove button if you want to change the list of devices to be
programmed.
Preliminary