Sanwa Electronic Instrument Co 90408 6CH 2.4GHz Radio Control Systems User Manual Manual Part 2
Sanwa Electronic Instrument Co Ltd 6CH 2.4GHz Radio Control Systems Manual Part 2
Contents
- 1. Manual Part 1
- 2. Manual Part 2
Manual Part 2
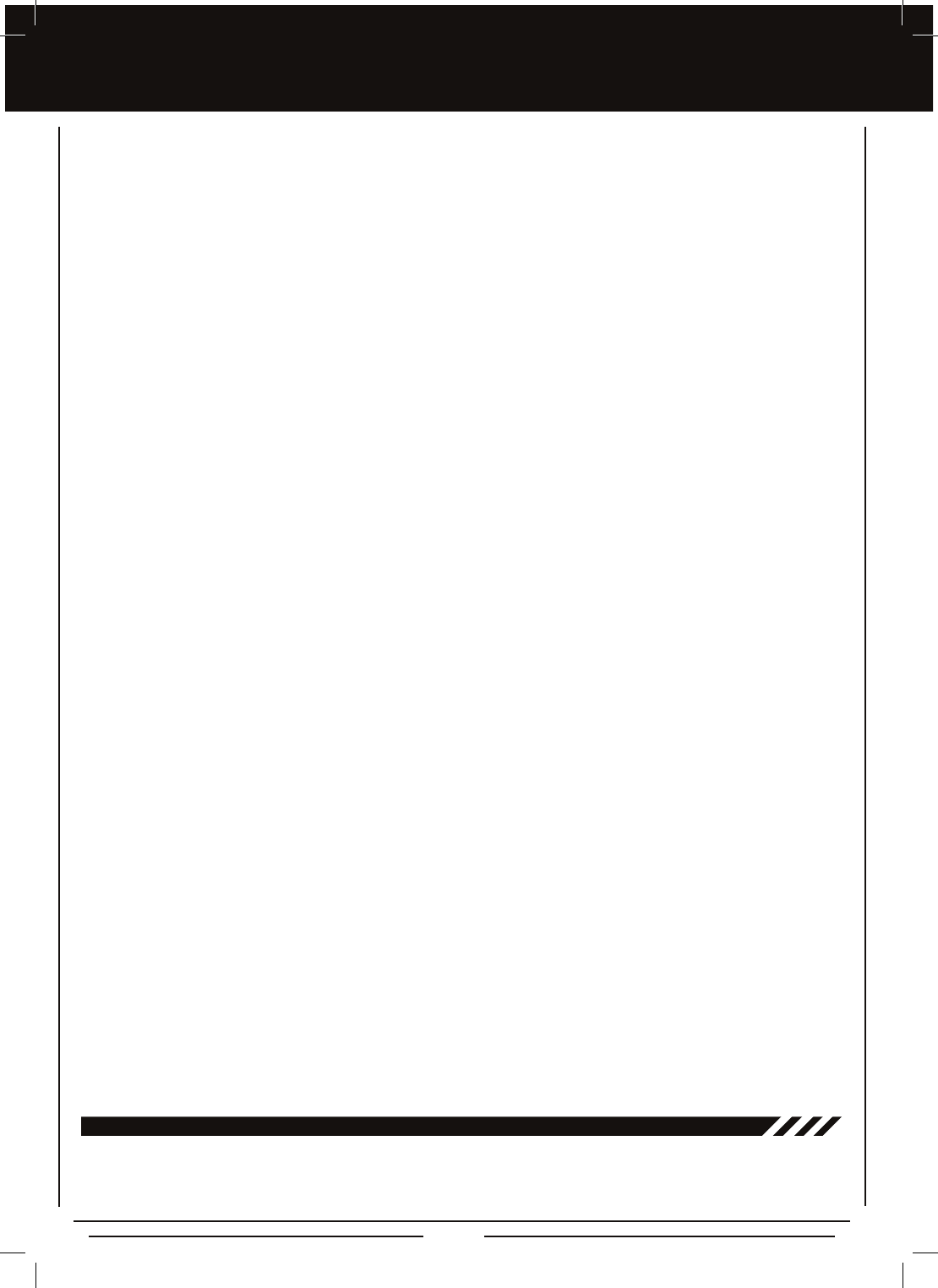
Page 2
Packaging
The packaging of your Airtronics TM-160 2.4GHz FHSS-1 radio control system has been specially designed for the safe
transportation and storage of the radio control system's components. After unpacking your radio control system, do not discard
the packaging materials. Save the packaging materials for future use if you ever need to send your radio control system to us
for service, or to store your radio control system if you don't plan on using it for an extended period of time.
TaBLE OF cOnTEnTS
Introduction......................................................................................................................................................................... Page 3
Additional Receiver Information ................................................................................................................................. Page 3
Transmitter Signal Range ............................................................................................................................................ Page 3
FCC Compliance Statement ........................................................................................................................................ Page 3
Safety and Usage Precautions.......................................................................................................................................... Page 4
General Safety .............................................................................................................................................................. Page 4
2.4GHz Frequency Band Precautions......................................................................................................................... Page 4
Transmitter Precautions .............................................................................................................................................. Page 4
Receiver Precautions ................................................................................................................................................... Page 5
AMA Information........................................................................................................................................................... Page 5
Features and Specications.............................................................................................................................................. Page 6
General System Features ............................................................................................................................................ Page 6
Aircraft-Specic Features............................................................................................................................................ Page 6
Helicopter-Specic Features ....................................................................................................................................... Page 6
System Specications ................................................................................................................................................. Page 6
Features Familiarization .................................................................................................................................................... Page 7
Transmitter Features Diagrams................................................................................................................................... Page 7
Receiver Features Diagram ......................................................................................................................................... Page 8
Features Descriptions.................................................................................................................................................. Page 8
Servo Connections....................................................................................................................................................... Page 9
Transmitter Alarms....................................................................................................................................................... Page 9
Servo Recommendations .......................................................................................................................................... Page 10
Optional Items............................................................................................................................................................. Page 10
Quick-Start Basic Model Setup ..................................................................................................................................Page 11
Tips and Suggestions .................................................................................................................................................Page 11
System Connections........................................................................................................................................................ Page 13
Transmitter Battery Installation................................................................................................................................. Page 13
Airborne System Connections .................................................................................................................................. Page 13
Transmitter and Receiver Battery Charging ............................................................................................................ Page 14
LCD and Programming Keys........................................................................................................................................... Page 15
Programming Keys Overview and Functions .......................................................................................................... Page 15
Multi-Function LCD Overview.................................................................................................................................... Page 16
System Setup Installation................................................................................................................................................ Page 17
Transmitter and Receiver Binding ............................................................................................................................ Page 17
Fail Safe Programming .............................................................................................................................................. Page 17
Mounting the Receiver ............................................................................................................................................... Page 18
Range Checking - Low-Power Mode......................................................................................................................... Page 19
Control Stick Length Adjustment.............................................................................................................................. Page 19
Flight Modes ..................................................................................................................................................................... Page 20
General Information ................................................................................................................................................... Page 20
Flight Mode Warning Alarm ....................................................................................................................................... Page 20
Aero Model Type Contents .............................................................................................................................................. Page 21
Aero Model Type - All Programming............................................................................................................................... Page 22
Heli Model Type Contents................................................................................................................................................ Page 51
Heli Model Type - All Programming ................................................................................................................................ Page 52
Reference .......................................................................................................................................................................... Page 81
Troubleshooting Guide .............................................................................................................................................. Page 81
Glossary of Terms ...................................................................................................................................................... Page 82
Index ............................................................................................................................................................................ Page 85
Setup Sheets..................................................................................................................................................................... Page 90
Service Information.................................................................................................................................................... Back Cover
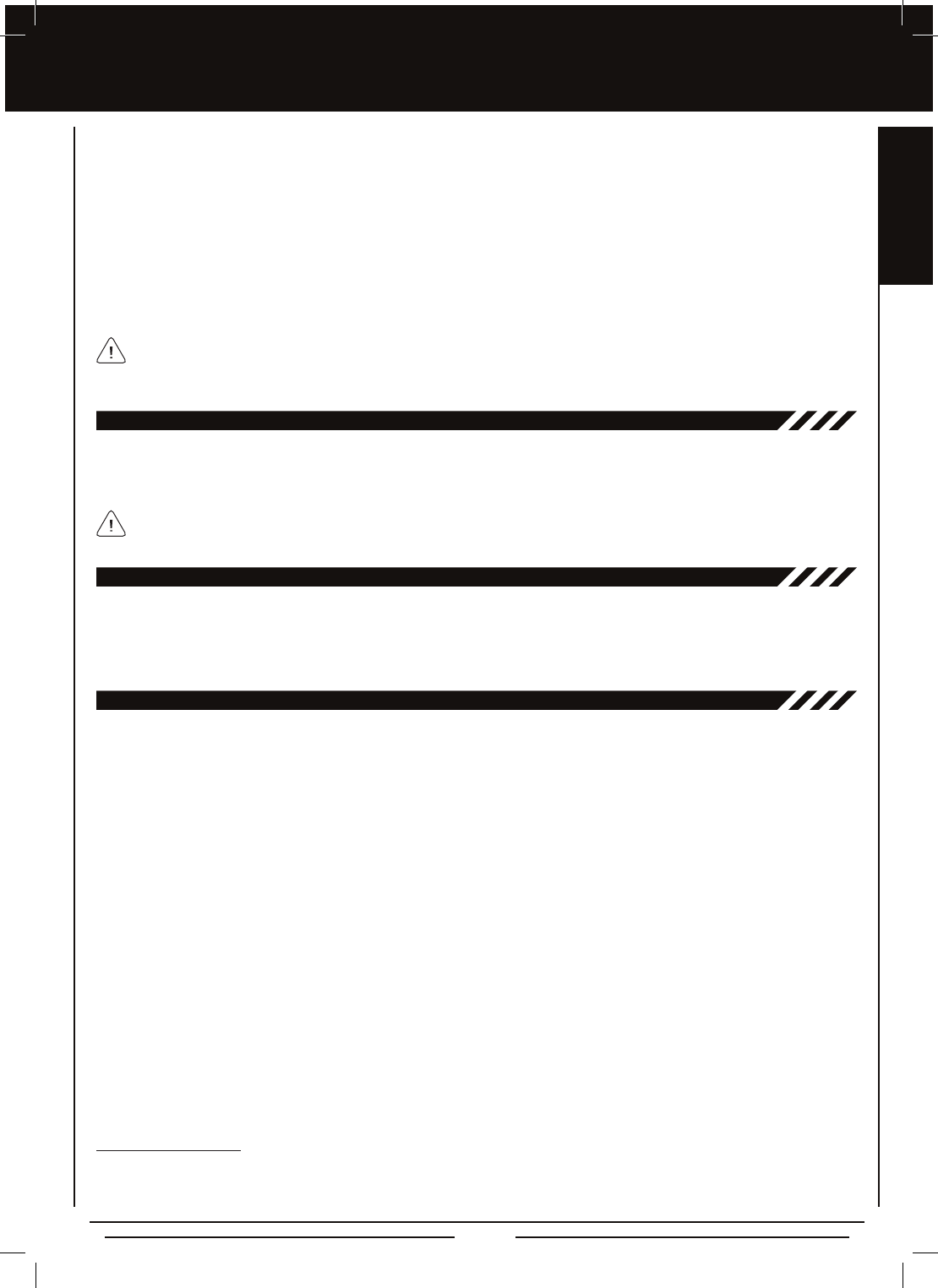
Page 3
Due to differences in the implementation of 2.4GHz technology among different manufacturers, only Airtronics brand
2.4GHz FHSS-1 aircraft receivers are compatible with your radio control system.
inTRODUcTiOn
Fcc cOMPLiancE STaTEMEnT
aDDiTiOnaL REcEivER inFORMaTiOn
Additional Airtronics 2.4GHz FHSS-1 aircraft receivers can be purchased and paired with the TM-160 transmitter through the
Binding procedure. For more information about the current receivers available, please visit your local Airtronics dealer or our
website at http://www.airtronics.net.
This equipment has been tested and found to comply with the limits for a Class B digital device, pursuant to Part 15 of the FCC
Rules. These limits are designed to provide reasonable protection against harmful interference in a residential installation. This
equipment generates, uses, and can radiate radio frequency energy and, if not installed and used in accordance with the operating
instructions, may cause harmful interference to radio communications, however, there is no guarantee that interference will not
occur in a particular installation.
If this equipment does cause harmful interference to radio or television reception, which can be determined by turning the
equipment off and on, the user is encouraged to try to correct the interference by one or more of the following measures:
lReorient or relocate the receiving antenna.
lIncrease the separation between the equipment and the receiver.
lConnect the equipment into an outlet on a circuit different from that to which the receiver is connected.
lConsult the dealer or an experienced technician for help.
This device complies with Part 15 of the FCC Rules and with RSS-210 of Industry Canada. Operation is subject to the following
two conditions:
1) This device may not cause harmful interference, and....
2) This device must accept any interference received, including interference that may cause undesired operation.
WARNING: Changes or modications made to this equipment not expressly approved by Airtronics may void the FCC authorization
to operate this equipment.
RF Exposure Statement
The TM-160 transmitter has been tested and meets the FCC RF exposure guidelines when used with the Airtronics accessories
supplied or designated for this product, and provided at least 20cm separation between the antenna the user's body is
maintained. Use of other accessories may not ensure compliance with FCC RF exposure guidelines.
We appreciate your purchase of the Airtronics TM-160 2.4GHz FHSS-1 radio control system. This Operating Manual is intended
to acquaint you with the many unique features of your new radio control system. In designing the TM-160 2.4GHz FHSS-1 radio
control system, our engineers listened to input from our test-pilots and feedback from our users to design a radio control system
that will allow you to extract the maximum performance from your model, while at the same time making the programming
process as easy as possible to accomplish.
Because the TM-160 2.4GHz FHSS-1 radio control system is advanced and is packed with many features for aircraft and helicopter
models, this Operating Manual is quite long. Don't be intimidated! This Operating Manual is laid out in such a way as to make it
as easy as possible to nd, understand, and learn to use the features you require. Please read this Operating Manual carefully
so that you may obtain maximum success and enjoyment from the operation of your new radio control system. This radio control
system has been designed for the utmost in comfort and precise control of your aircraft and helicopter models. We wish you the
best of success and fun with your new purchase.
An index is provided in the back of this Operating Manual to make it easy to nd the information that you're looking for.
Keep this Operating Manual in a safe place with your TM-160 transmitter so that you can use it as a reference book for any
questions you might have regarding your radio control system.
This is a high-output full-range radio control system that should well exceed the range needed for any model. For safety, the
user should perform a range check at the area of operation to ensure that the radio control system has complete control of the
model at the farthest reaches of the operational area. A range check can be accomplished using Low-Power Mode. For more
information, see page 19.
TRanSMiTTER SignaL RangE
GENERAL
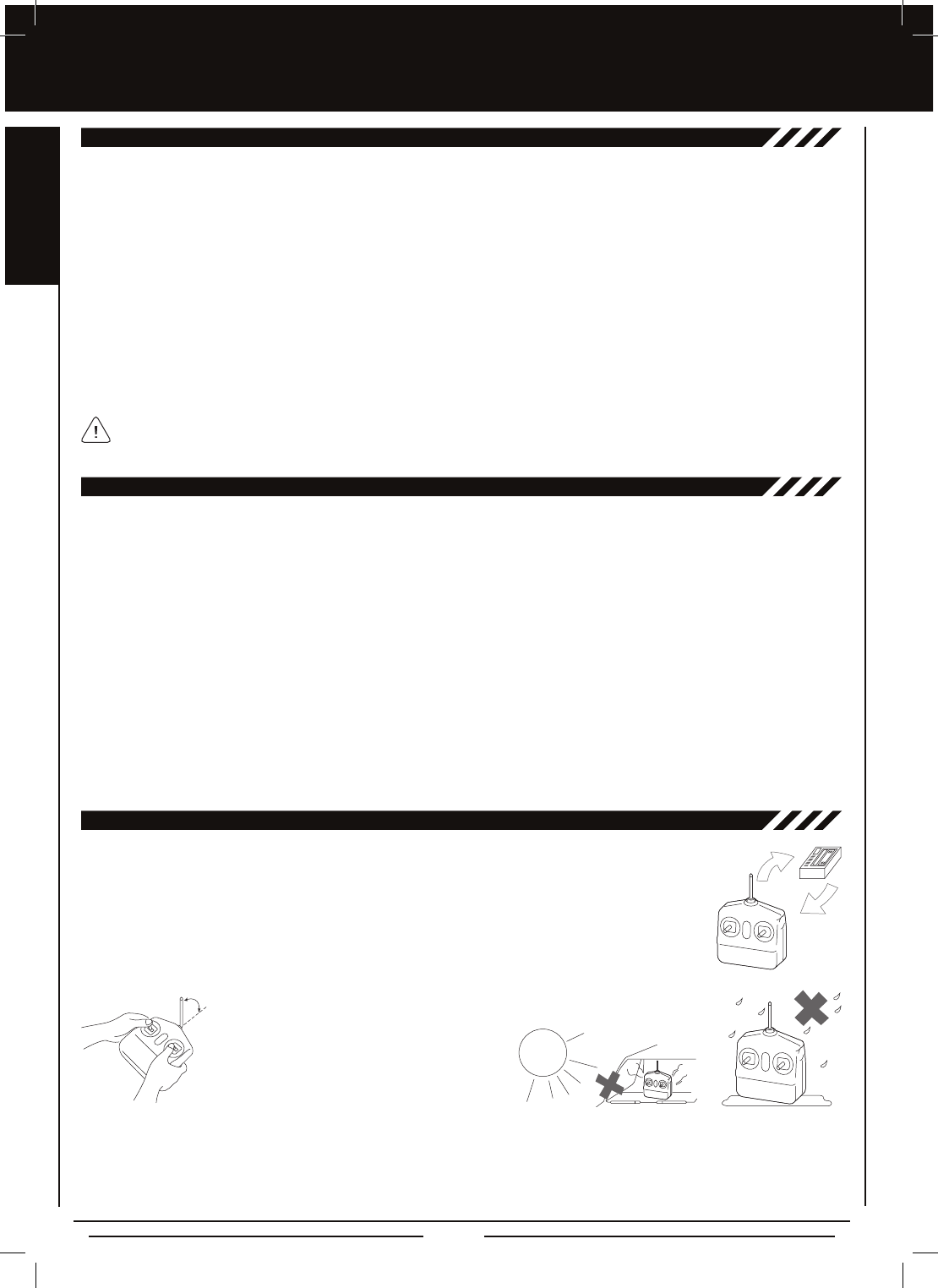
Page 4
SaFETy anD USagE PREcaUTiOnS
gEnERaL SaFETy
lBe certain to read this Operating Manual in its entirety.
l'Safety First' for yourself, for others, and for your equipment.
lObserve all the rules of the ying site or anywhere you
operate your radio control equipment.
lIf at any time during the operation of your model should
you feel or observe erratic operation or abnormality, end
your operation as quickly and safely as possible. DO NOT
operate your model again until you are certain the problem
has been corrected. TAKE NO CHANCES.
lYour model can cause serious damage or injury, so please
use caution and courtesy at all times.
lDo not expose the radio control system to water or excessive
moisture.
lPlease waterproof the receiver and servos by placing them
in a water-tight radio box when operating model boats.
lIf you have little to no experience operating models, we
strongly recommend you seek the assistance of experienced
modelers or your local hobby shop for guidance.
lThe low voltage alarm will sound when the transmitter
battery voltage drops to 6.7 volts. If this occurs, stop
using the transmitter as soon as possible, then replace or
recharge the transmitter batteries.
TRanSMiTTER PREcaUTiOnS
lTurn the transmitter ON rst, then turn the receiver ON. After using your model, turn the receiver OFF
rst, then turn the transmitter OFF. It can be dangerous if you activate the components in reverse order
as the servos may start up inadvertently.
lBefore use, double-check that the transmitter and receiver batteries have sufcient power and/or are
sufciently charged (if using Ni-Cd/Ni-MH batteries).
lNever touch the transmitter antenna during use. Doing so may cause loss of transmitter output, making
it impossible to control your model.
lThe transmitter antenna should be rotated and angled so that the antenna is
as close to perpendicular to the ground as
possible during use. After use, to prevent
any chance of damaging the antenna, the
antenna should be rotated and moved into
the horizontal stowed position.
lDo not expose the transmitter to excessive heat, moisture, fuel, exhaust residue, etc.
lDo not expose the transmitter to excessive heat or direct sunlight. Leaving the transmitter in direct sunlight can damage the LCD.
lDo not press the Bind Button during use. The signal is interrupted while the Bind Button is pressed. It may also require a short time
to restore the signal after releasing the Bind Button, which can be dangerous.
ON
OFF
Keep Antenna
Perpendicular
to Ground
Do Not Expose to Moisture
or Direct Sunlight
2.4ghz FREqUEncy BanD PREcaUTiOnS
lThe 2.4GHz frequency band may be used by other devices, and other devices in the immediate area may cause interference
on the same frequency band. Always before use, conduct a bench test to ensure that the servos operate properly. Also,
conduct a range check at the area of operation to ensure that the radio control system has complete control of the model at
the farthest reaches of the operational area.
lThe response speed of the receiver can be affected if used where multiple 2.4GHz transmitters are being used, therefore,
carefully check the area before use. Also, if response seems slow during use, discontinue use as quickly as possible.
lIf the 2.4GHz frequency band is saturated (too many transmitters on at once), as a safety precaution, the radio control system
may not bind. This ensures that your radio control system does not get hit by interference. Once the frequencies have been
cleared, or the saturation level has dropped, your radio control system should be able to bind without any problems.
lObserve any applicable laws and regulations in place at your ying site when using the 2.4GHz radio control system.
lUnlike frequency bands used with earlier radio control systems, reception with this 2.4GHz radio control system can be
adversely affected by large obstructions and concrete or steel structures between your model and the transmitter. Also, wire
mesh and similar barriers can adversely affect operation. Keep this mind to ensure the safety of your model.
This radio control system operates on the 2.4GHz frequency band. The 2.4GHz connection is determined by the transmitter
and receiver pair. Unlike ordinary crystal-based systems, your model can be used without frequency control.
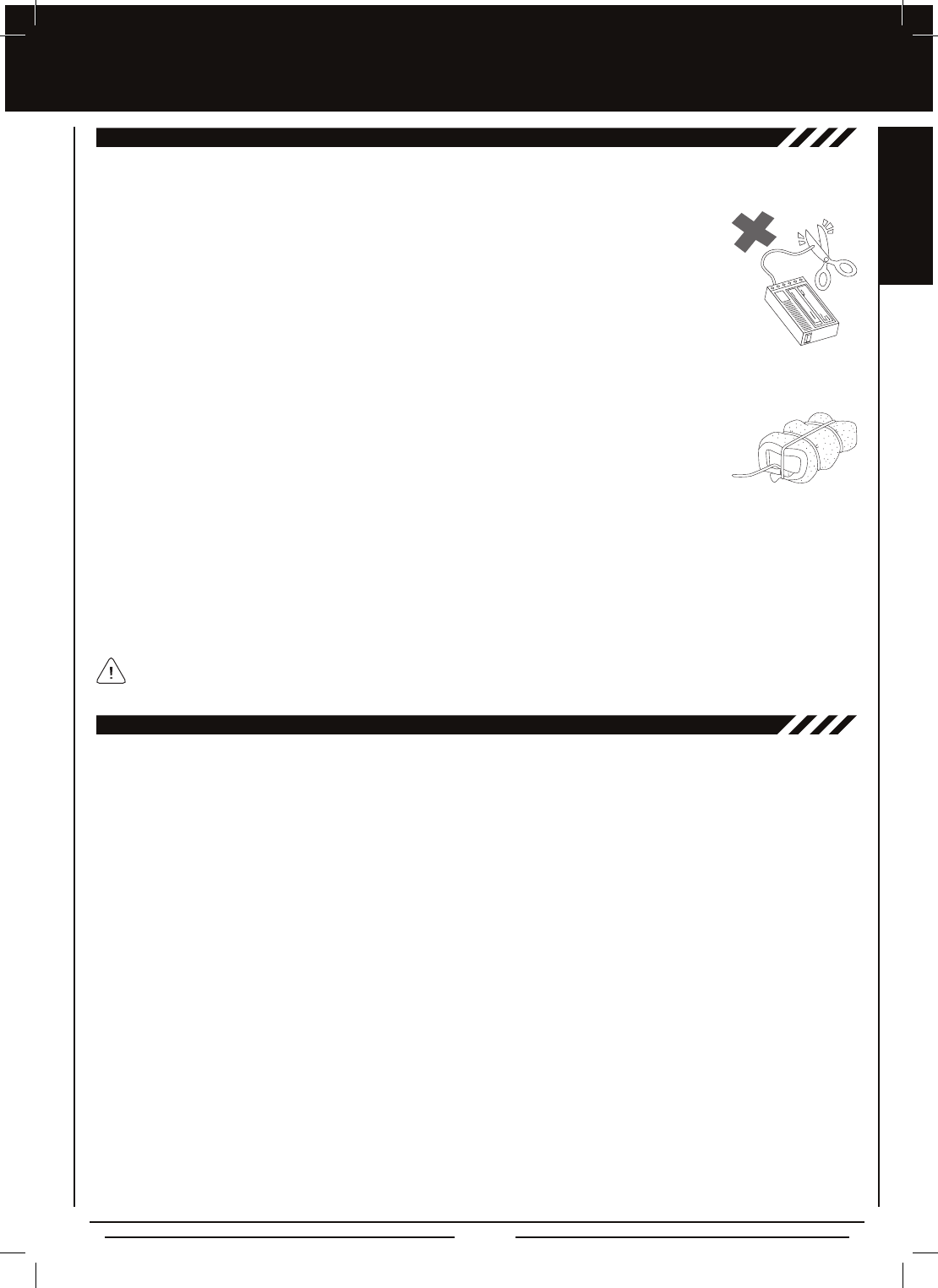
Page 5
SaFETy anD USagE PREcaUTiOnS
lThe receiver antenna wires consist of two coaxial cables and two reception wires (the thin tip at the end of the coaxial cables).
When you mount the receiver antenna wires, do not bend the reception wires. Reception performance decreases if the reception
wires are bent.
lThe receiver antenna wires are delicate, therefore, handle with care. Do not pull on the receiver
antenna wires with force. Do not cut or extend the receiver antenna wires.
lThe coaxial cables can be bent into gentle curves, however, do not bend the coaxial cables acutely, or
repeatedly bend them, or the antenna cores can be damaged.
lWhen installed in an electric-powered model, keep the receiver antenna wires as far away as possible
from the motor, battery, and electronic speed control (ESC).
lThere is a danger of runaway operation if connectors shake loose during use. Make sure that the receiver, servo(s), and switch
harness connectors are securely tted.
lThe receiver is susceptible to vibration and moisture. Take appropriate measures to
protect against vibration and moisture. The receiver should be wrapped in foam and the
foam should be secured around the receiver to hold it in place. The foam should not be
secured too tightly or the vibration dampening quality will be reduced. Failure to take
appropriate measures could result in damage to the receiver.
lWhen installing the receiver, the antenna reception wires (the thin tip at the end of the coaxial cables) should not come into
contact with any carbon or metal components (conductive components). Aircraft fuselages and helicopter frames may contain
conductive components. If mounting the receiver surrounded by conductive materials (for example, a carbon ber fuselage),
mount the receiver so that the antenna reception wires can be extended outside of the model. Reception can be blocked if the
antenna reception wires are shielded inside a carbon ber fuselage.
lThe manufacturer disclaims all responsibility for damages resulting from use of components other than genuine Airtronics
components.
It is extremely important to install the receiver and route the receiver antenna wires correctly in your model. This will ensure
that your model receives control signals no matter what its posture, attitude, or heading. For more information, see page 18.
Wrap Receiver
in Foam to Protect From
Vibration and Damage
REcEivER PREcaUTiOnS
aMa inFORMaTiOn
Academy of Model Aeronautics
5151 East Memorial Drive
Muncie, IN 47302
Phone (800) 435-9262
Fax (765) 741-0057
www.modelaircraft.org
The Academy of Model Aeronautics (AMA) is a national organization representing modelers in the United States. We urge you
to examine the benets of membership, including liability protection in the event of certain injuries. The Academy has adopted
simple and sane rules which are especially pertinent for radio controlled ight as the Ofcial AMA National Model Aircraft Safety
Code, which we have partially reprinted below:
lI will not y my model aircraft in sanctioned events, airshows or model ying demonstrations until it has been proven to be
airworthy by having been previously, successfully ight tested.
lI will not y my model higher than approximately 400 feet within 3 miles of an airport without notifying the airport operator.
I will give the right-of-way and avoid ying in the proximity of full-scale aircraft. Where necessary, an observer shall be
utilized to supervise ying to avoid having models y in the proximity of full-scale aircraft. Where established, I will abide by
the safety rules for the ying site I use, and I will not willfully and deliberately y my models in a careless, reckless and/or
dangerous manner.
lI will have completed a successful radio equipment ground range check before the rst ight of a new or repaired model.
lI will not y my model aircraft in the presence of spectators until I become a qualied yer, unless assisted by an experienced
helper.
lI will perform my initial turn after takeoff away from the pit or spectator areas, unless beyond my control.
GENERAL
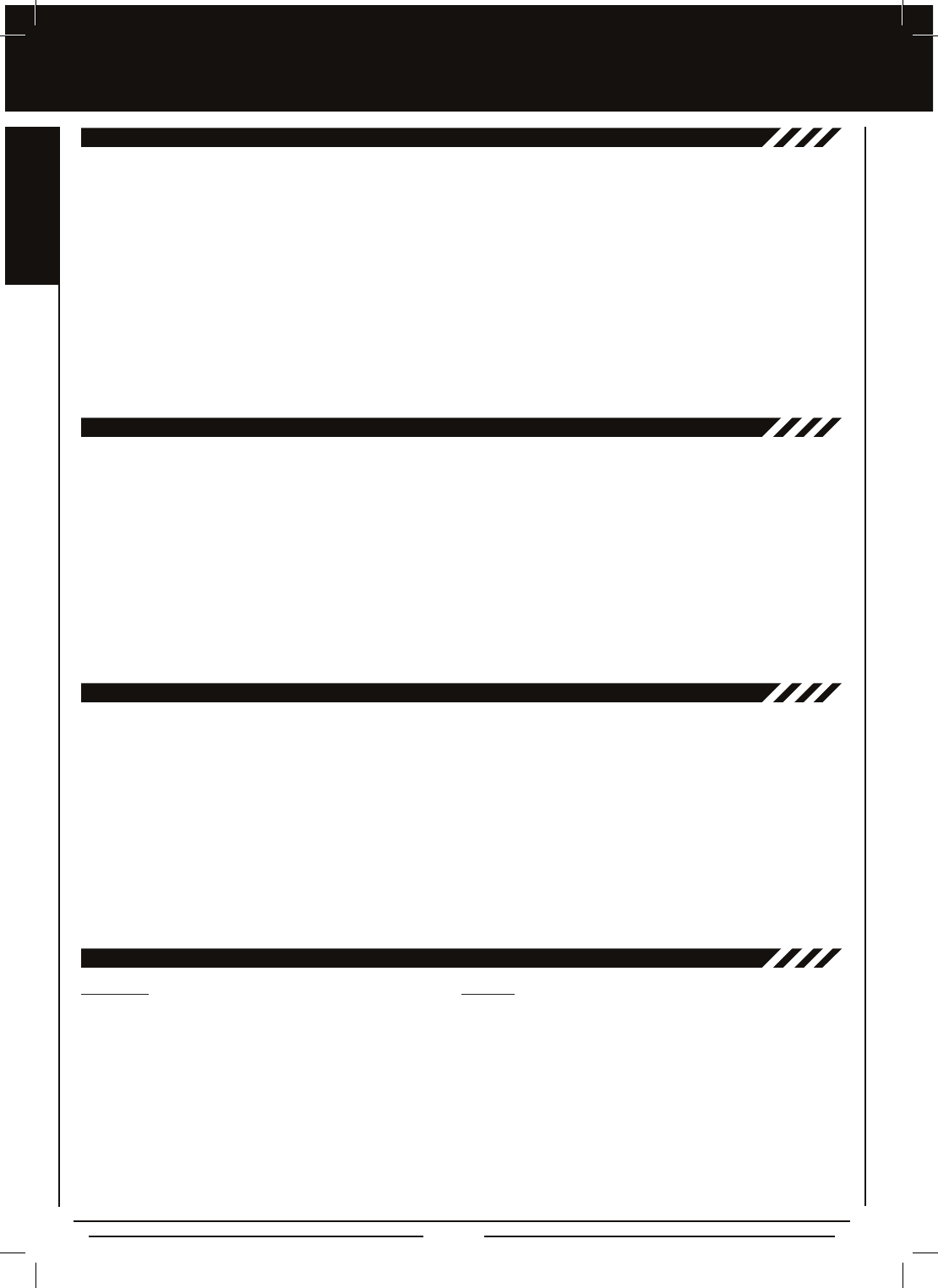
Page 6
l6-Channel 2.4GHz FHSS-1 Digital Proportional Computer Radio Control System for Aircraft and Helicopters
lFull-Range 92224 (RX600) 6-Channel 2.4GHz FHSS-1 Receiver
l6 Cell Battery for Lighter Weight and Better Feel
l10 Model Memory
lDirect Model Select (Models 1~3)
lEasy-to-Read Multi-Function LCD with Digital Voltage Display
lUser-Selectable Model Type Templates
lDigital Trims
lTrainer System Compatible with SD-5G and SD-10G Transmitters
lModel Naming
FEaTURES anD SPEciFicaTiOnS
gEnERaL SySTEM FEaTURES
lModel Select
lAudible Low Voltage Alarm
lLow-Power Range Check Mode
lProgrammable Fail Safe
lUser-Selectable Flight Modes
lStop Watch and Count Up Timers
lData Copy and Data Reset
aiRcRaFT-SPEciFic FEaTURES
lServo Monitor
l3 Flight Modes (FN/F1/F2)
lAileron, Elevator, and Rudder Dual Rate
lAileron, Elevator, and Rudder Exponential
lServo Reversing
lServo Centering Sub-Trim
lEnd Point Adjustment
lThrottle Cut
l5-Point Programmable Throttle Curve
lAileron Differential
lFlaperon Mixing
lFlap to Elevator Mixing
lDual Elevator Mixing with End Point Adjustment
lAilvator Mixing
lV-Tail Mixing with End Point Adjustment
lDelta (Elevon) Mixing with End Point Adjustment
l2 Programmable Compensation Mixers
lCommon or Flight Mode-Specic Trim with Throttle Trim Lock
hELicOPTER-SPEciFic FEaTURES
lServo Monitor
l3 Flight Modes (FN/F1/F2)
l9 Preprogrammed Swashplate Templates
lAileron, Elevator, and Rudder Dual Rate
lAileron, Elevator, and Rudder Exponential
lServo Reversing
lServo Centering Sub-Trim
lAdvanced Swashplate Adjustment
lCCPM End Point Adjustment
lEnd Point Adjustment
lThrottle Cut
l5-Point Programmable Throttle Curve
lThrottle Hold
l5-Point Programmable Pitch Curve
lRevolution Mixing
l2 Remote Gyro Gains
l2 Programmable Compensation Mixers
lCommon or Flight Mode-Specic Trim with Throttle Trim Lock
SySTEM SPEciFicaTiOnS
Transmitter
Model: TM-160
Output Power: 100mW
Operating Voltage: 6.7v~9.6v
Current Drain: 130mA~200mA
Temperature Range: 32ºF~122ºF (0ºC~50ºC)
Pulse Width: 0.9msec~2.1msec
Weight with Batteries: 26.45oz (750gr)
Frequency/Modulation Type: 2.4GHz/FHSS-1
Model Memory: 10
Receiver
Model: 92224 (RX600)
Frequency/Modulation Type: 2.4GHz/FHSS-1
Nominal Input Voltage: 4.8v~6.0v
Weight: 0.27oz (7.8gr) with Case
Weight: 0.20oz (5.9gr) without Case
Dimensions: 1.64 x 0.85 x 0.47in (41.7 x 21.5 x 12.0mm)
Fail Safe Support: Yes (CH 1~CH 4)
Connector Type: Universal 'Z'
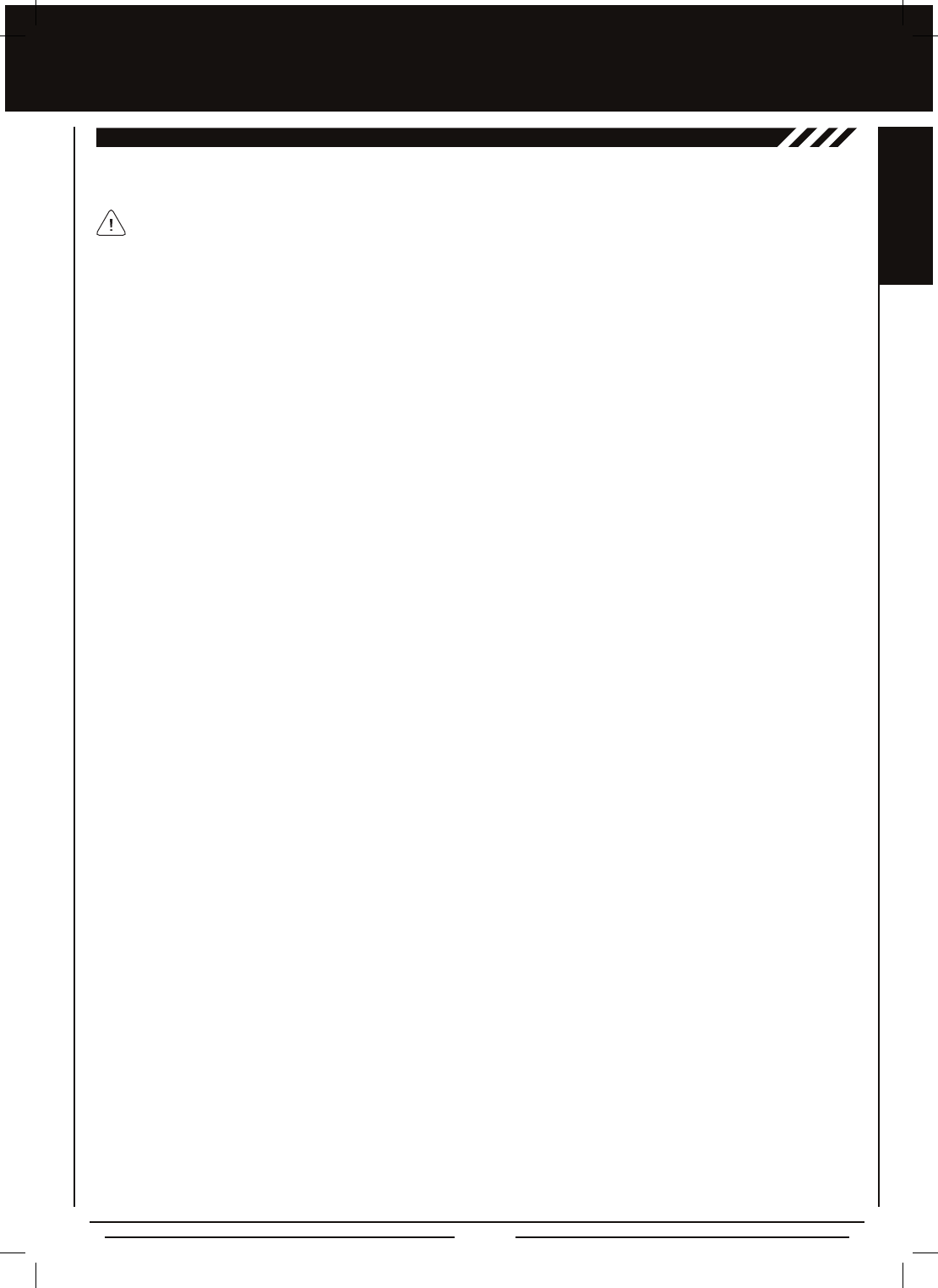
Page 7
FEaTURES FaMiLiaRizaTiOn
TRanSMiTTER FEaTURES DiagRaMS
Use the diagrams below to familiarize yourself with the basic features of your TM-160 2.4GHz FHSS-1 transmitter. Descriptions
of these features can be found on pages 8 and 9.
The transmitter antenna is adjustable. It should be adjusted so that when you're holding the transmitter while you're ying,
the antenna is orientated as close to perpendicular to the ground as possible at all times. This provides the best signal
between the transmitter and the receiver. You should never point the antenna directly at your aircraft, as this results in a weakened
signal. For more information, see page 4.
GENERAL
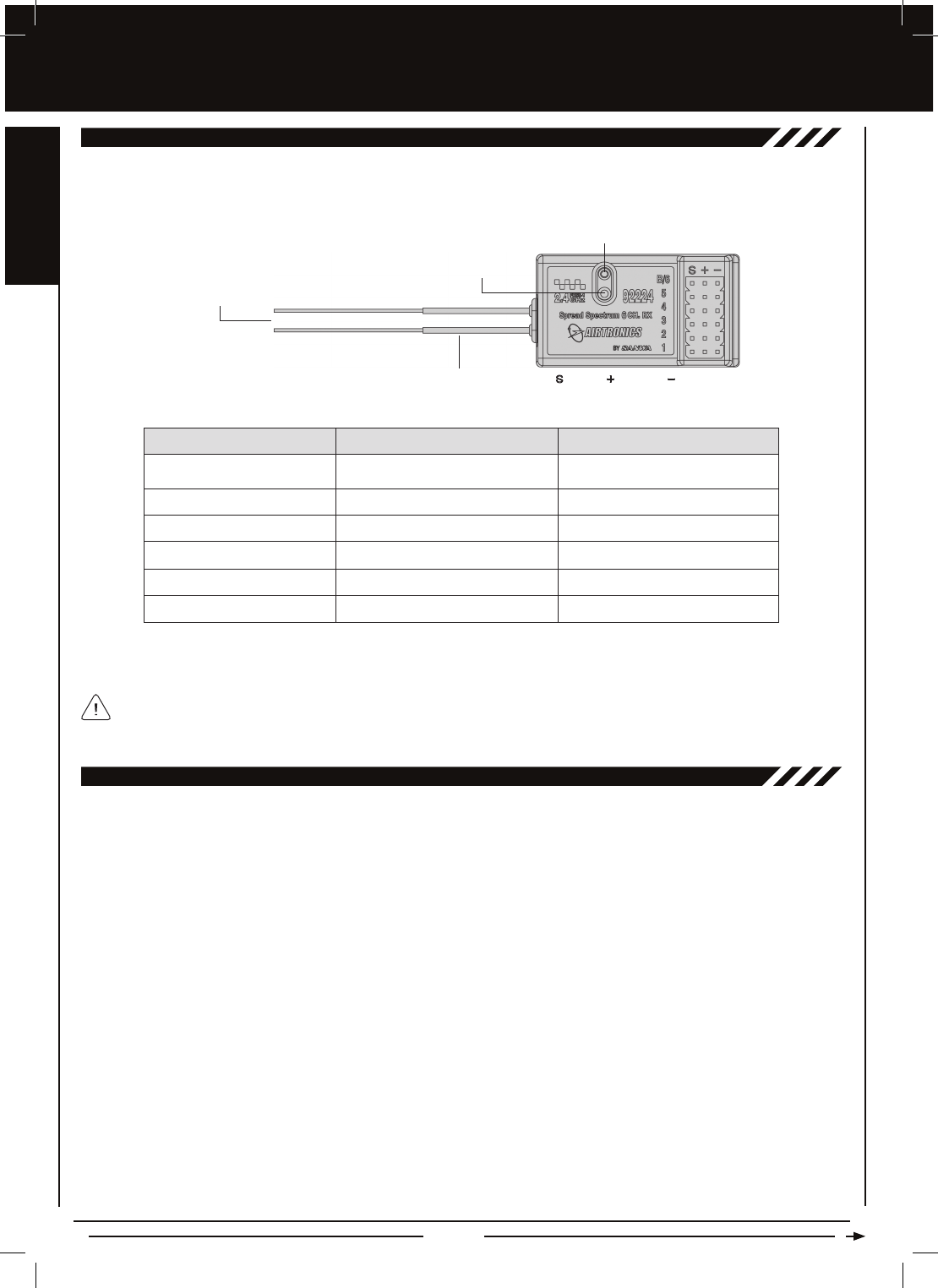
Page 8
FEaTURES FaMiLiaRizaTiOn
Use the diagram below to familiarize yourself with the 92224 (RX600) 6-Channel receiver included with your TM-160 2.4GHz
FHSS-1 radio control system. Descriptions of these features can be found below and on the next page.
REcEivER FEaTURES DiagRaM
*To utilize this channel and power the receiver at the same time, you must use a Y-Harness (available separately). For more
information, see page 13.
Aileron/Elevator Control Stick: Controls the Aileron and Elevator axes. The Aileron/Elevator Control Stick length is adjustable
to suit your preference. For more information, see page 19.
Aileron Trim Switch: Used to control the Aileron axis Right and Left trim.
Antenna: Transmits the signal from the transmitter to the receiver in the model. The Antenna should be pivoted into the vertical
position during use. When not in use, the Antenna should be collapsed into the horizontal position to prevent damage during
handling and transport.
Antenna Reception Wires: The portion of each of the receiver antenna wires that actually receives the transmitter signal. The
Antenna Reception Wires should never be bent or they could be damaged and limit the range of the receiver.
Battery Compartment: Houses the 6 cells that power the transmitter. The transmitter uses 6 cells for lighter weight and better
feel, while still providing long usage time and high power output.
Bind Button: Used to Bind the transmitter and receiver. Also used to enter Low-Power Range Check mode.
Bind LED: Displays the current status of the transmitter and receiver pair.
Charging Jack: Used for onboard charging of the Ni-Cd or Ni-MH batteries.
Coaxial Cables: The portion of each antenna wire that extends the Antenna Reception Wires. The Coaxial Cables can be bent
into gentle curves, however, do not bend the Coaxial Cables acutely, or repeatedly bend them, or the antenna wire's cores can
be damaged. For information on mounting the receiver and orientating the receiver antenna wires, see page 18.
Elevator Trim Switch: Used to control the Elevator axis Up and Down trim.
FEaTURES DEScRiPTiOnS
Bind Button
Coaxial Cables
Antenna
Reception
Wires
Bind LED
= Signal = Positive = Negative
(Antenna Wires Not to Scale)
The default channel slot assignments shown in the table above will vary based on the Model Type selection options you have
programmed in the TYPE menu. For example, in AERO mode with TAIL>2xEL selected in the TYPE menu, Channel Slot 1
will control the Left Elevator and Channel Slot 5 will control the Right Elevator. For more information, see page 25.
CHANNEL SLOT AERO CHANNEL ASSIGNMENT
Channel Slot 1
Channel Slot 2
Channel Slot 3
Channel Slot 4
Channel Slot 5
Channel Slot 6/BATT*
Elevator
Aileron
Throttle
Rudder
Gear
Flaps
Elevator (Fore/Aft Cyclic)
Aileron (Left/Right Cyclic)
Throttle
Rudder (Tail Rotor)
Gyro
Pitch (Collective)
HELI CHANNEL ASSIGNMENT
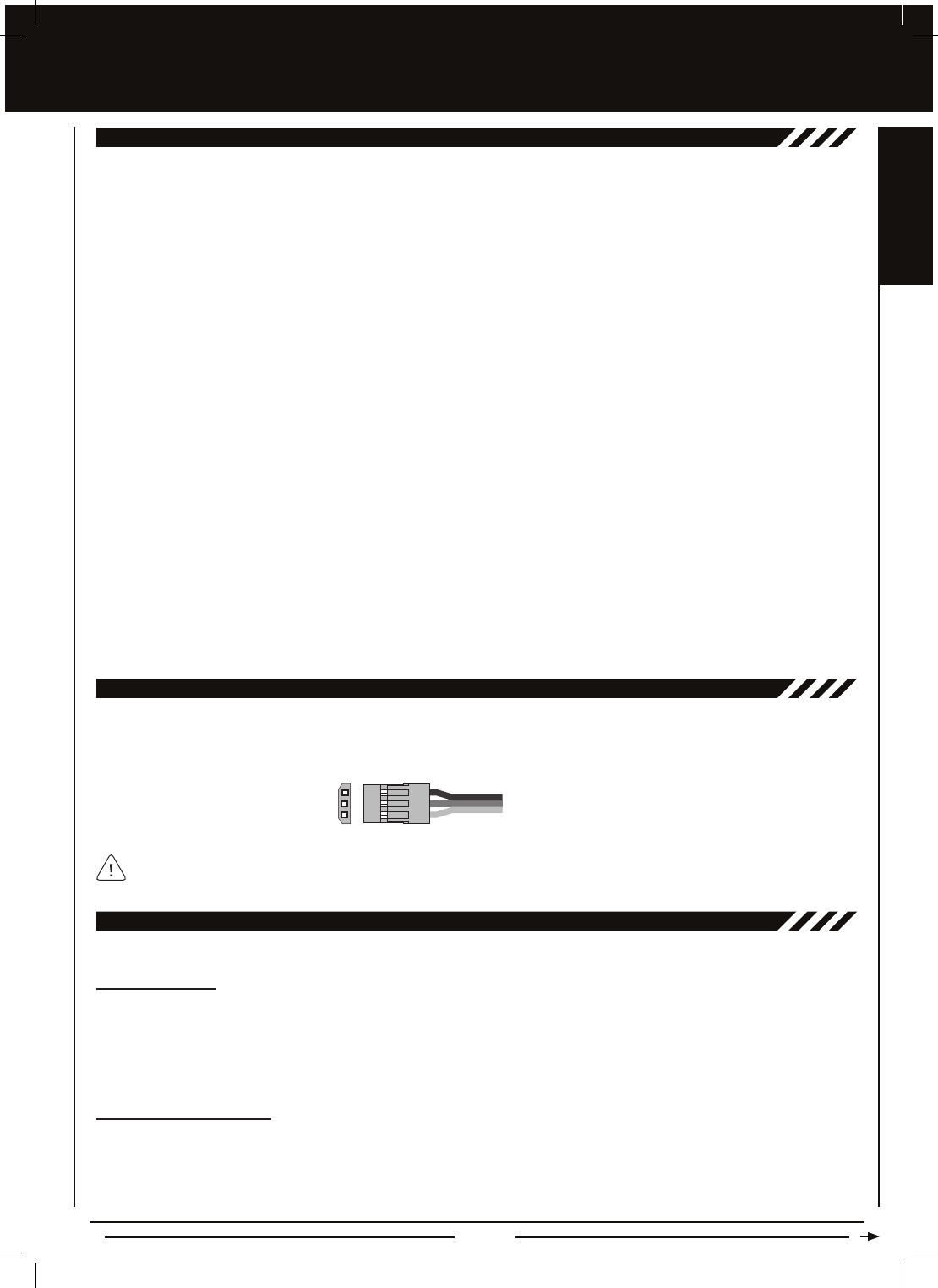
Page 9
FEaTURES FaMiLiaRizaTiOn
Multi-Function LCD: The heart of the programming and display features of the transmitter. All programming and transmitter
display functions are shown on the Multi-Function LCD.
Navigation Pad: The Navigation Pad is used in conjunction with the Programming Keys to facilitate transmitter programming.
The Navigation Pad allows you to quickly and easily move the Programming Cursor up and down, and right and left. The ENTER
key in the center of the Navigation Pad is used to open the selected menu or programming option.
Neck Strap Anchor: Used to attach your neck strap (available separately) to the transmitter.
Power Indicator: Indicates that there is power to the transmitter. When the battery voltage drops to 6.7 volts, the audible Low
Voltage Alarm will sound. For more information, see the Transmitter Alarms section below.
Power Switch: Turns the transmitter ON and OFF.
Programming Keys: The Programming Keys are used to facilitate transmitter programming and select models stored in
memory. The four Programming Keys consist of the INC+/M1 (Increase/Model 1) key, the DEC-/M2 (Decrease/Model 2) key, the
END/M3 (End/Model 3) key, and the F-MODE (Flight Mode) key.
Rudder Trim Switch: Used to control the Rudder axis Right and Left trim.
Throttle/Rudder Control Stick: Controls the Throttle and Rudder axes. The Throttle/Rudder Control Stick length is adjustable
to suit your preference. For more information, see page 19.
Throttle Trim Switch: Used to control the Throttle axis Up and Down trim.
Trainer Port: The Trainer Port is where the trainer cable (available separately) is plugged into. An adapter to use the transmitter
with a ight simulator can also be plugged into the Trainer Port.
RF Output Indicator: Illuminates when the transmitter is turned ON and transmitting a signal. If the RF Output Indicator fails
to illuminate, RF output is limited or non-existent. In this case, you should not y. The RF Output Indicator will ash when the
transmitter Trainer mode is set to Slave.
FEaTURES DEScRiPTiOnS, cOnTinUED....
The 92224 (RX600) 6-Channel receiver included with your TM-160 2.4GHz FHSS-1 radio control system uses universal Airtronics
'Z' connectors which are electronically compatible with the servos of other radio control system manufacturers. The connectors
are rugged, but should be handled with care.
When unplugging the servo connector, it's best not to pull on the servo wire itself. This could result in damage to the servo
wire pins in the plastic plug. Always grasp the plastic connector itself.
SERvO cOnnEcTORS
- = Negative (Black)
+ = Positive (Red)
S = Signal (Blue)
The TM-160 transmitter is equipped with several safety alarms to warn you of an abnormal transmitter condition.
TRanSMiTTER aLaRMS
Low Voltage Alarm
The TM-160 transmitter is equipped with a Low Voltage Alarm to warn you when the transmitter batteries need to be replaced or
recharged. The Low Voltage Alarm will sound when the transmitter batteries reach 6.7 volts. If the Low Voltage Alarm sounds
while you are ying, you should land immediately, then replace or recharge the transmitter batteries. If the Low Voltage Alarm
sounds after replacing or recharging the transmitter batteries, there may be a problem with the transmitter. If this occurs, please
contact Airtronics Customer Service using the information on the back cover of this Operating Manual.
Flight Mode Warning Alarm
The TM-160 transmitter is equipped with a safety feature that will not allow you to use the transmitter if the Flight Mode is not set
to FN (Normal) when you turn the transmitter ON. If the Flight Mode is not set to FN when you turn the transmitter ON, the Flight
Mode Warning alarm will sound continuously, the RF Output Indicator will ash, and the LCD will read F-MODE NOT 'N' ! To clear
the Flight Mode Warning, set the Flight Mode to FN using the Flight Mode Switches (move both Flight Mode switches forward).
The LCD will read normally, the Flight Mode Warning alarm will cease, and RF Output Indicator will stop ashing.
GENERAL
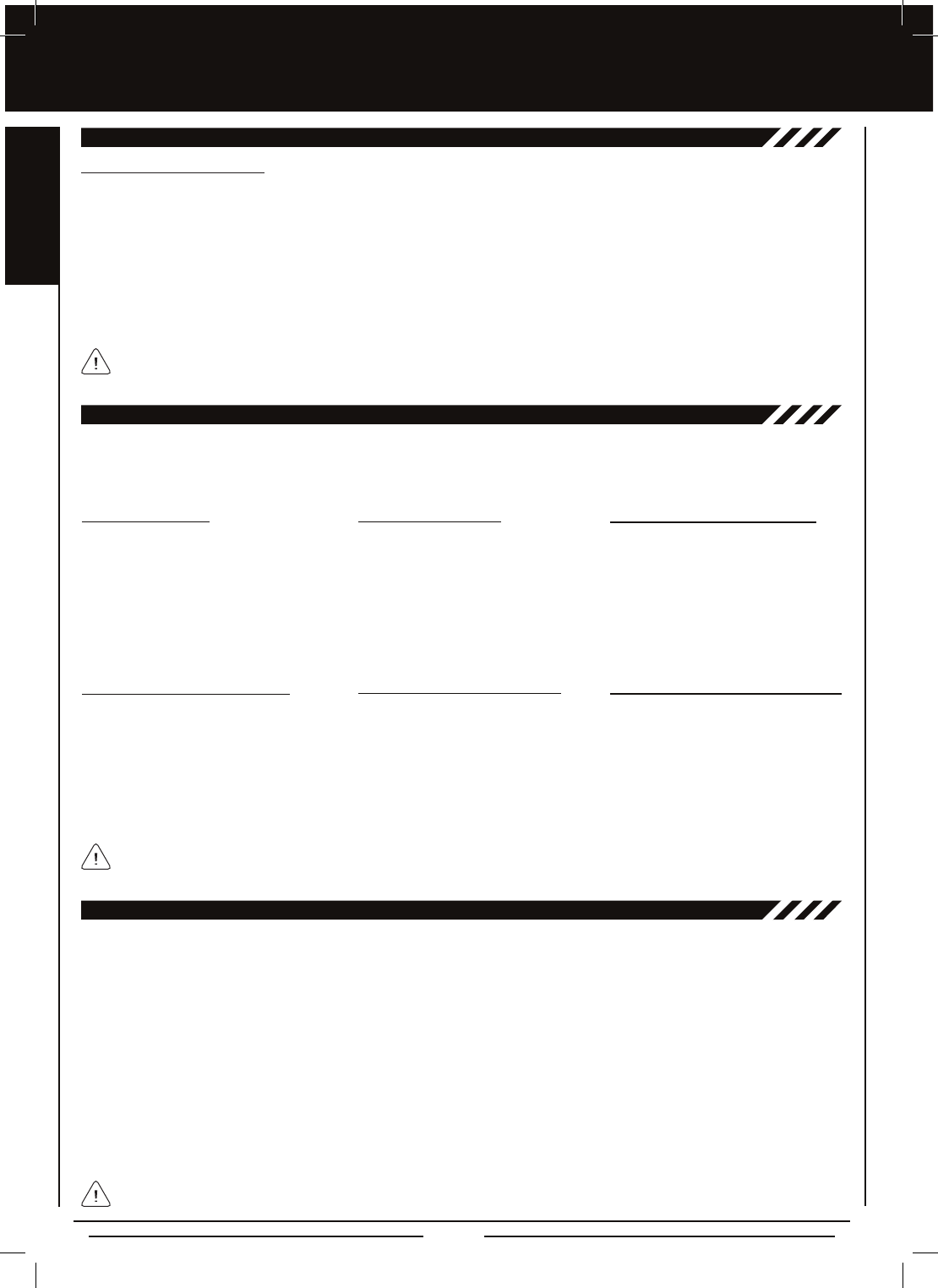
Page 10
FEaTURES FaMiLiaRizaTiOn
TRanSMiTTER aLaRMS, cOnTinUED....
Trainer Mode Warning Alarm
The TM-160 transmitter is equipped with a safety feature that will warn you when the transmitter is set to Trainer>Master or
Trainer>Slave when the transmitter is turned ON. If the transmitter is set to Trainer>Master when you turn the transmitter ON, the
Trainer Mode Warning alarm will sound continuously, the RF Output Indicator will blink, and the LCD will read TRAINER MODE
MASTER ! If the transmitter is set to Trainer>Slave when you turn the transmitter ON, the Trainer Mode Warning alarm will sound
continuously, the RF Output Indicator will blink, and the LCD will read TRAINER MODE SLAVE !
To clear either of the Trainer Mode Warnings, press any of the Programming Keys or the ENTER key. The LCD will read normally,
the Trainer Mode Warning alarm will cease, and the RF Output Indicator will stop ashing (if set to Slave, the RF Output Indicator
will continue to ash).
Clearing the Trainer Mode Warning does not change the Trainer setting of the transmitter. When the Trainer Mode Warning
is cleared, the transmitter will still be in Trainer Mode - either set to Master or set to Slave as indicated on the LCD.
Although most current brand servos will work with your TM-160 2.4GHz FHSS-1radio control system, we recommend using
Airtronics brand servos. For pricing, availability, and more selection, please visit your local Airtronics dealer or our website at
http://www.airtronics.net.
SERvO REcOMMEnDaTiOnS
Both analog and digital servos will work with your TM-160 2.4GHz FHSS-1 radio control system. To get the most out of your
experience though, we recommend the use of digital servos.
Torque: 115oz/in (8.3kg/cm @ 4.8v)
144oz/in (10.4kg/cm @ 6.0v)
Speed: 0.23 sec/60º @ 4.8v
0.18 sec/60º @ 6.0v
Dimensions: 1.54 x 0.79 x 1.61in
(39.1 x 20.0 x 40.9mm)
Weight: 2.36oz (67gr)
Torque: 42oz/in (3.0kg/cm @ 4.8v)
53oz/in (3.8kg/cm @ 6.0v)
Speed: 0.20 sec/60º @ 4.8v
0.16 sec/60º @ 6.0v
Dimensions: 1.54 x 0.79 x 1.42in
(39.1 x 20.0 x 36.0mm)
Weight: 1.59oz (45gr)
94102Z Standard Bushing
94162Z High Torque MG Dual Ball Bearing 94842 Digital Precision Dual Ball Bearing
Torque: 111oz/in (8.0kg/cm @ 4.8v)
132oz/in (9.5kg/cm @ 6.0v)
Speed: 0.16 sec/60º @ 4.8v
0.13 sec/60º @ 6.0v
Dimensions: 1.57 x 0.77 x 1.56in
(40.0 x 19.5 x 39.6mm)
Weight: 1.62oz (45.8gr)
Torque: 18oz/in (1.3kg/cm @ 4.8v)
23oz/in (1.7kg/cm @ 6.0v)
Speed: 0.12 sec/60º @ 4.8v
0.10 sec/60º @ 6.0v
Dimensions: 0.91 x 0.44 x 0.87in
(23.0 x 11.2 x 22.1mm)
Weight: 0.32oz (9gr)
94091Z Super Micro Bushing
94856 Digital High Speed MG Dual Ball Bearing
Torque: 125oz/in (9.0kg/cm @ 4.8v)
150oz/in (10.8kg/cm @ 6.0v)
Speed: 0.14 sec/60º @ 4.8v
0.11 sec/60º @ 6.0v
Dimensions: 1.50 x 0.79 x 1.49in
(38.0 x 20.0 x 37.8mm)
Weight: 2.04oz (58.0gr)
Torque: 22oz/in (1.6kg/cm @ 4.8v)
26oz/in (1.9kg/cm @ 6.0v)
Speed: 0.18 sec/60º @ 4.8v
0.15 sec/60º @ 6.0v
Dimensions: 0.91 x 0.35 x 0.90in
(23.0 x 9.0 x 22.8mm)
Weight: 0.26oz (7.4gr)
94802 Digital Sub-Micro Dual Ball Bearing
OPTiOnaL iTEMS
The following optional items (available separately) can be used with your TM-160 2.4GHz FHSS-1 radio control system. For
pricing and availability, please visit your local Airtronics dealer or our website at http://www.airtronics.net.
233819 Hi-Energy 4.8v 2200mAh Ni-MH Square Receiver Battery*
233808 Hi-Energy 6.0v 2200mAh Ni-MH Flat Receiver Battery*
96750 Stick Tip Extensions
99103 Adjustable Neck Strap
978411 Aluminum Carry Case
97020Z 8" Y-Harness
97011Z 12" Servo Extension
97107 Trainer Cable
96506 Airtronics Baseball Cap
978425 Airtronics Folding Field Chair
*Not an Airtronics brand product, however, this product is available through most Airtronics dealers.
Many more accessories, such as servos, servo extension leads, male and female plugs, receiver battery packs, and more
are available through your local Airtronics dealer or our website at http://www.airtronics.net.
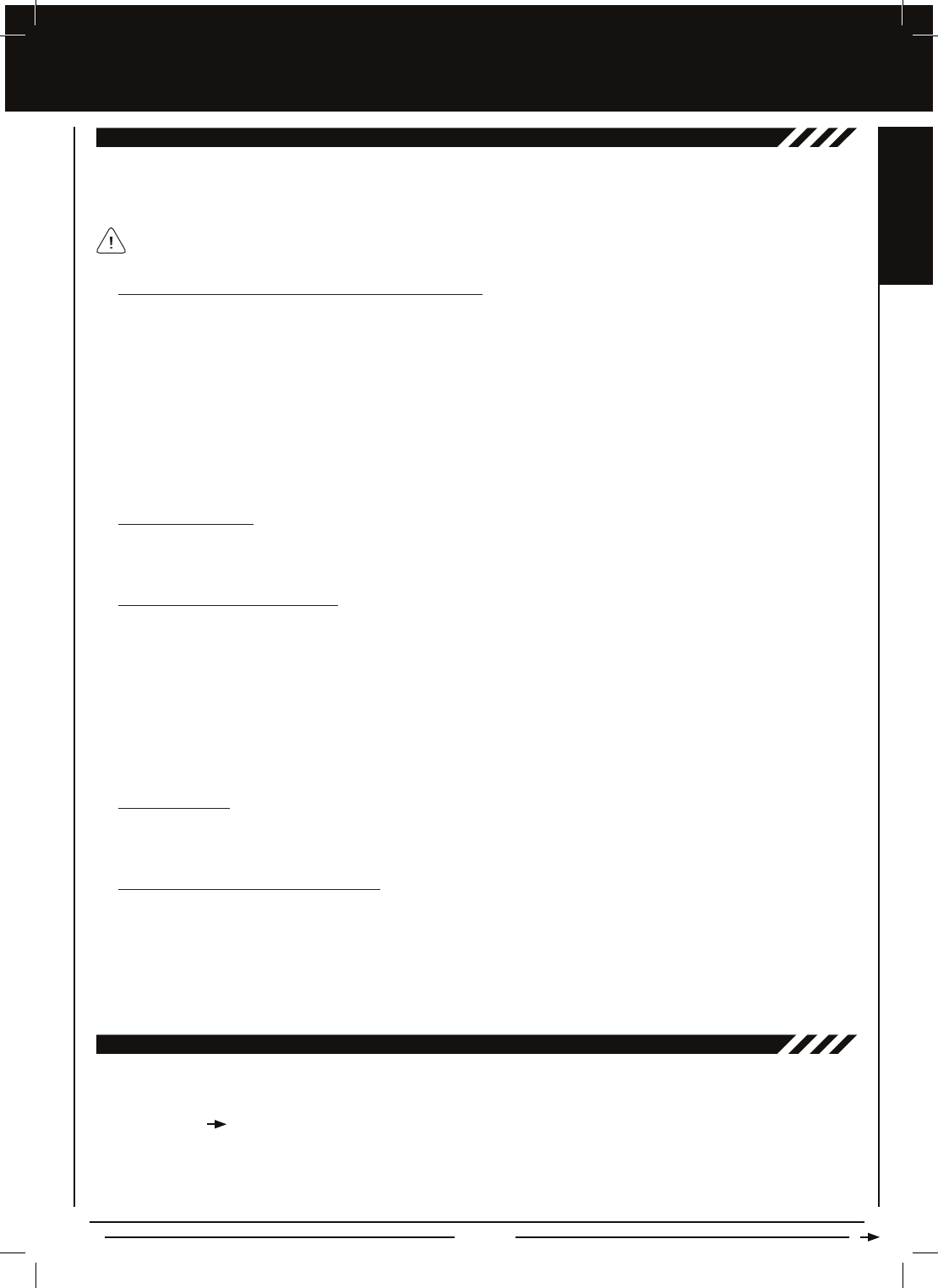
Page 11
qUick-STaRT BaSic MODEL SETUP
The information in this section describes the basic steps that you can use to quickly setup a new model. Regardless of the model
you are fying, using the basic functions of the TM-160transmitter for most applications is easy and will get your model setup
quickly. It's a simple ve-step process.
1) Bind the Receiver to the Transmitter and Install the Receiver:
lAfter connecting your airborne components and installing fully-charged transmitter and receiver batteries, turn the transmitter ON.
lHold down the Bind Button on the receiver. While holding down the Bind Button on the receiver, turn the receiver ON.
lRelease the Bind Button on the receiver. The Bind LED will slowly ash.
lPress the transmitter Bind Button. The receiver's Bind LED will ash rapidly, then the receiver's Bind LED will turn solid blue
indicating the system is paired.
lInstall the receiver in your model, making sure that the two receiver antenna wires are mounted 90º to each other.
lRotate the transmitter antenna so that it is positioned at a 45º angle toward you.
2) Choose a Model Type:
l Navigate to the TYPE menu, then press the INC+/M1 or DEC-/M2 keys to select the Model Type that matches your
model, either AERO (Aircraft) or HELI (Helicopter).
3) Make Model Type Selection Options:
lScroll down to choose the various options related to the Model Type you've chosen.
AERO - Select what type of wing (Normal or Delta), the type of tail (Normal, V-Tail, or Dual Elevator servos), and the
number of aileron servos in your wing (1 or 2).
HELI - Select what type of swashplate your model features, either Normal, or a CCPM swashplate. If choosing a CCPM
swashplate option, make sure that the CCPM swashplate type matches your model exactly.
lAfter making your selections, press the ENTER key, then the INC+/M1 key. The pre-programmed model template will be
loaded into the transmitter.
4) Name Your Model:
lNavigate to the MODEL NAME menu and input a name for your model. This will allow you to easily choose this model again
for later use. The Model Name will be displayed on the Display screen so that you know which model is currently in use.
5) Plug In Servos and Setup Control Surfaces:
lNavigate to the SX MONITOR menu and use the information displayed on the Servo Monitor to plug your servos into the
correct channel slots in the receiver based on the Model Type selection options you chose previously.
lNavigate to the REVERSE, CENTER, EPA, and D/R & EXPO menus to adjust direction of servo travel (REVERSE), servo
centering sub-trim (CENTER), desired servo travel in both directions (EPA), and if desired, the Dual Rate and Exponential
(D/R & EXPO) percentage values.
Many of the Tips and Suggestions on the following pages can be found throughout this Operating Manual, however, we have
listed what we feel are the more important ones in this section for your convenience.
TiPS anD SUggESTiOnS
FEaTURES FaMiLiaRizaTiOn
The information in this section is general in nature. For more in-depth instructions about the individual steps outlined below,
please make sure to read the pertinent sections of this Operating Manual.
lWhen you see in the lower right corner of a page, this indicates that the current section is continued at the top of the
next page.
lThe receiver’s nominal input voltage is 4.8 volts to 6.0 volts. If your receiver battery's nominal voltage rating is greater than
6.0 volts, you must use a voltage regulator plugged between the switch harness and the receiver battery to drop your battery's
voltage to 6.0 volts.
GENERAL
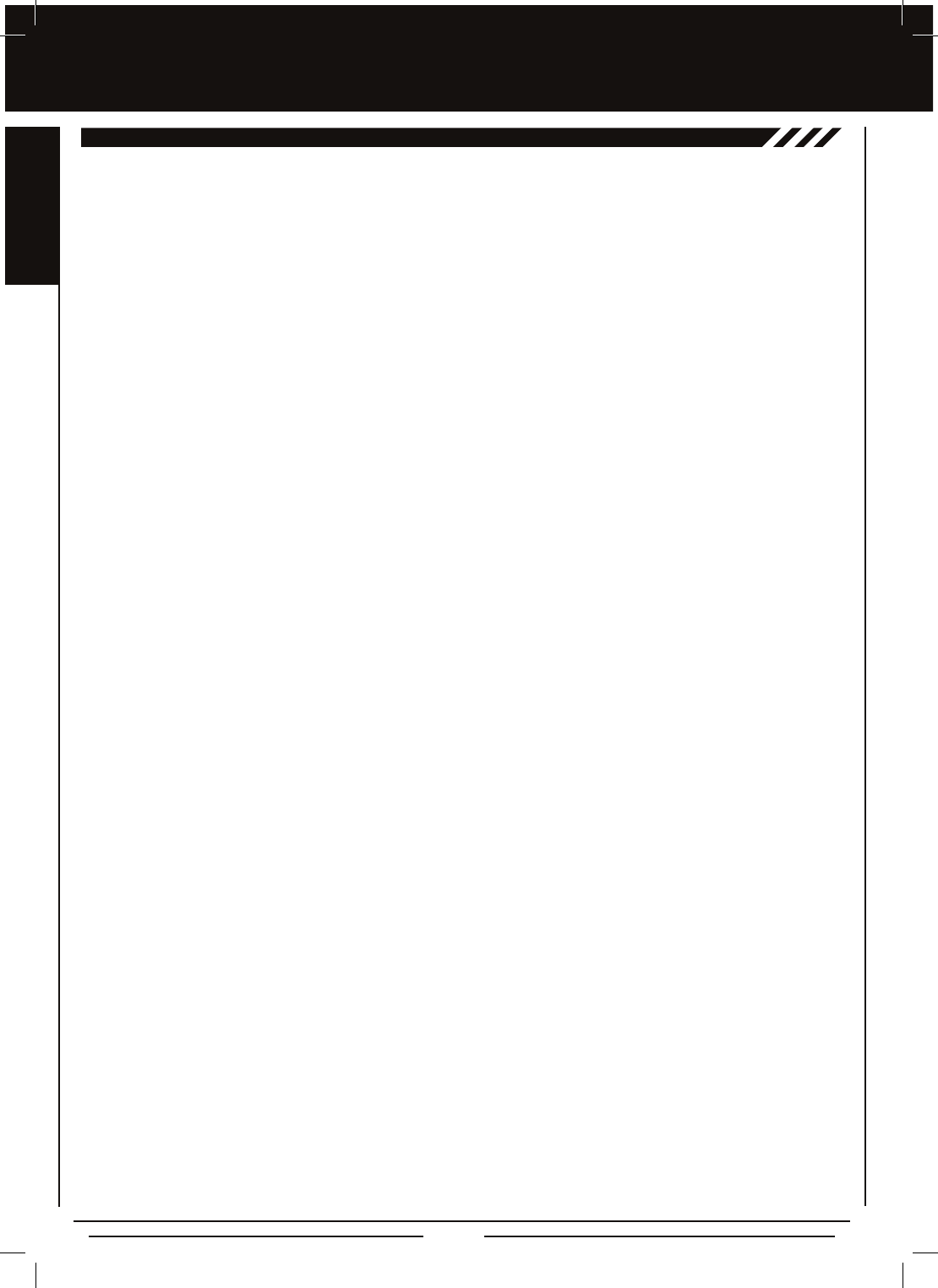
Page 12
FEaTURES FaMiLiaRizaTiOn
TiPS anD SUggESTiOnS, cOnTinUED....
lAn after-market peak-detection charger, cycler, or fast charger should NOT be used to charge Ni-Cd or Ni-MH rechargeable
batteries through the transmitter. The circuitry within the transmitter can interfere with the peak-detection charger's normal
operation, resulting in over-charging and damaging the batteries, and possibly the transmitter itself. In addition, a fast
charger can damage the transmitter's circuitry. These chargers can be used, but ONLY if the batteries are charged outside of
the transmitter.
lUp to 6 servos can be plugged into the receiver separately. To utilize the Channel 6/BATT slot along with the receiver battery,
you must plug a Y-Harness into the channel slot, then plug the servo into one side of the Y-Harness and the battery switch
harness into the other side of the Y-Harness.
lIt is extremely important that the receiver antenna wires be mounted as described. This will ensure that your model receives
control signals no matter what its posture, altitude, or heading.
lThe radio control system is range checked using the Low-Power Mode function. Do not attempt to y with the transmitter in
Low-Power Mode. You will be unable to control your model once it is a certain distance away from you.
lThe TM-160 transmitter features a Type function which allows you to quickly set up the transmitter's low-level mixing based on
the type of model you're ying. Common templates for AERO (Aircraft) and HELI (Helictopter) model types are provided. For
example, if your model features two aileron servos and dual elevator servos, choosing these options will automatically change
the transmitter's programming to accommodate this setup. This takes the guess-work out of setting up more complex models.
lThe TM-160 transmitter features an audible Flight Mode Warning alarm. If you turn your TM-160transmitter ON and it beeps,
the transmitter is more than likely in Flight Mode F1 or Flight Mode F2. Putting the transmitter in Flight Mode FN (Normal), will
silence the Flight Mode Warning alarm.
lIn the default conguration, the Model Select List contains 5 AERO model types and 5 HELI model types. The Model Type for any
of the 10 models in the Model Select List can be changed using the Type menu.
lThe Direct Model Select function allows you to select one of three of your most-used models from memory without going
through the Model Select menu. This makes it much quicker and easier to load the programming for your three favorite models.
lPressing both the INC+/M1 and DEC-/M2 keys together will Reset the highlighted programming selection to the Factory Default
Setting.
lWhen the Display screen is displayed, pressing the INC+/M1 key will Start and Stop the Timer. Pressing the INC+/M1 and
DEC-/M2 keys together will Reset the Timer.
lUnless otherwise noted, all programming changes take effect immediately.
lAn audible double-tone is heard when the trim switches reach the center position. This allows you to know when the trim
switches reach the center position without the need to look at the Trim Indicators on the Display screen.
lThe TM-160 transmitter features Digital Trim Memory. Any amount of control surface trim that you set during fight using the
trim switches is automatically stored in memory for that specic channel and for that specic model. The Digital Trim values for
each model will automatically be loaded when the transmitter is turned ON.
lThere is always one Flight Mode Active at all times. In the default conguration, Flight Mode FN (Normal) is Active.
lThe F-MODE key is used to facilitate programming the individual Flight Modes only and does not turn the Flight Modes ON
or OFF. Flight Modes are turned ON and OFF using the two Flight Mode switches.
lPrior to takeoff, check the position of the Dual Rate switch to ensure that it is in the position you want.
lUse the Servo Monitor to determine which receiver channel slots to plug your servos into. The channels displayed on the Servo
Monitor will vary based on the Model Type selection options chosen in the TYPE menu. For example, if you chose TAIL>2xEL
and AILE>2 in the TYPE menu, LE (Left Elevator), RE (Right Elevator), LA (Left Aileron), and RA (Right Aileron) will be
displayed along with the corresponding receiver channel slot numbers.
lMany menu functions feature Common or Separate choices. When set to COMMON the function settings will be the same
regardless of which Flight Mode the transmitter is operating in. When set to SEPARATE, you can program different function
settings separately for each Flight Mode.
lWhen setting up a CCPM swashplate helicopter, you may want to use the CP-EPA function instead of the standard EPA
function. The CCPM End Point Adjustment function allows you to adjust servo travel in each direction for the elevator, aileron,
and pitch servos independently. Unlike the standard End Point Adjustment function, which affects all the cyclic servos, CCPM
End Point Adjustment allows you to adjust each cyclic servo independently without any affect on the other cyclic servos. This
allows you to also quickly and easily level the swashplate.
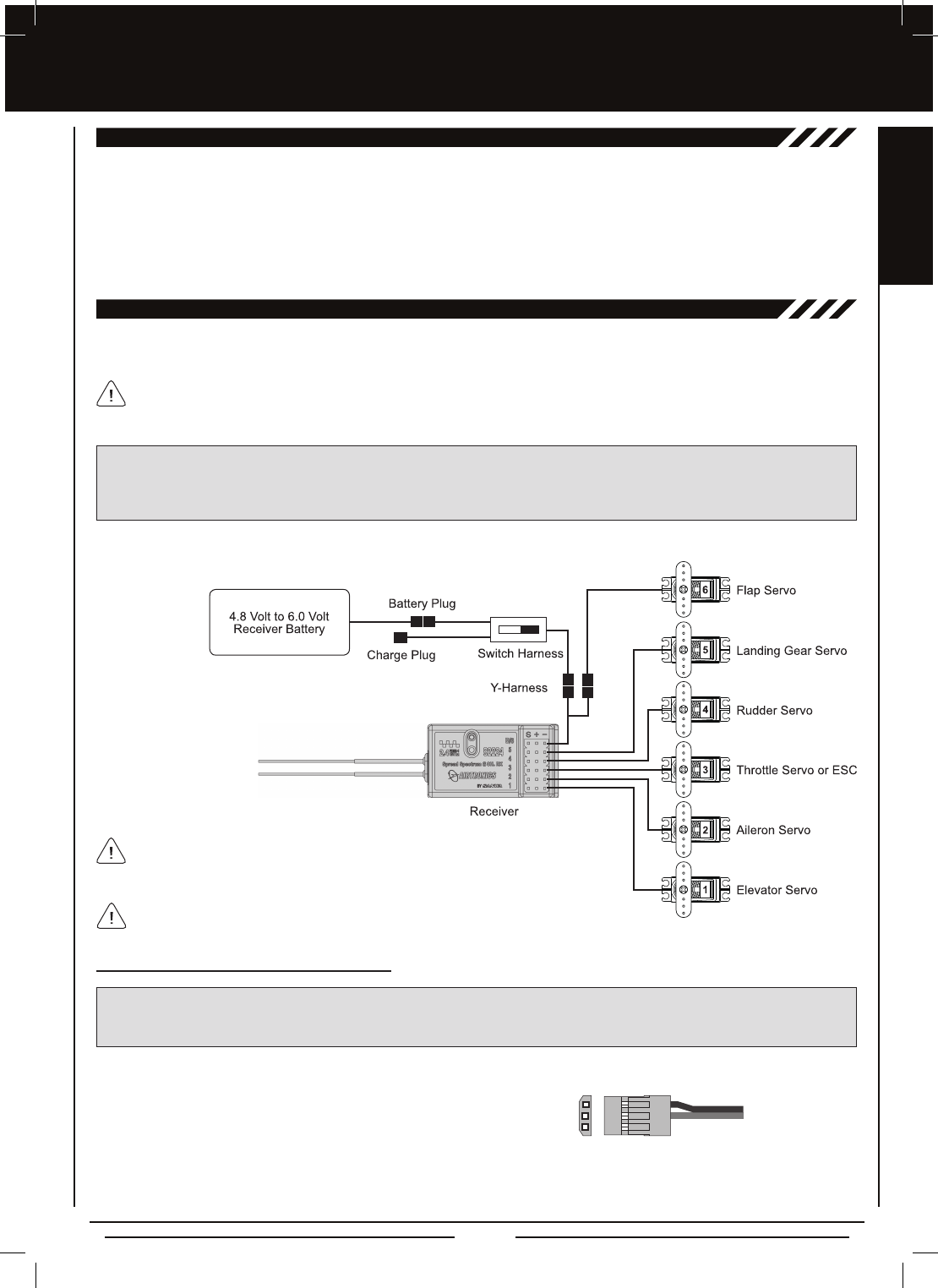
Page 13
SySTEM cOnnEcTiOnS
Use the diagram below to familiarize yourself with how to connect the switch harness, servos (available separately), and receiver
battery (available separately) to your 92224 (RX600) 6-Channel receiver.
A receiver battery is not included. The receiver can be powered by a 4.8 volt (4 cell) or a 6.0 volt (5 cell) Ni-Cd or Ni-MH
battery of desired capacity. The receiver can also be powered by a 2 cell Li-Fe/A123 or a 2 cell Li-Po battery of desired
capacity as long as you use a voltage regulator. See WARNING below.
WARNING The receiver’s nominal input voltage is 4.8 volts to 6.0 volts. If your receiver battery's nominal voltage rating is
greater than 6.0 volts, you must use a voltage regulator plugged between the switch harness and the receiver battery to drop
your battery's voltage to 6.0 volts. If you do not use a voltage regulator, damage to the receiver could result. We recommend a
switching type regulator and it must be able to handle the amperage demands of the servos used in your model.
If you decide to power the receiver using a 2 cell Li-Fe/A123 battery or a 2 cell Li-Po battery, please observe the following:
lUse ONLY a 2 cell Li-Fe or Li-Po battery of desired capacity with a voltage
regulator. You MUST use a voltage regulator.
lWhen changing the plug on your battery to be compatible with the switch harness, please observe correct polarity. Connecting
with reverse polarity could damage the switch harness and/or the receiver. See plug polarity diagram above.
lObserve all safety precautions provided with your battery before use, during use, and during the charging process.
WARNING The nominal voltage rating of a 2 cell Li-Fe/A123 battery or a 2 cell Li-Po battery is greater than 6.0 volts.
Because of the higher voltage, you MUST use a voltage regulator plugged between the switch harness and the receiver
battery to drop the battery voltage to 6.0 volts. If you do not use a voltage regulator, damage to the receiver could result.
- = Negative (Black)
+ = Positive (Red)
TRanSMiTTER BaTTERy inSTaLLaTiOn
1) Remove the battery cover on the back of the transmitter by pushing down rmly on the tab in the top of the battery cover and
pulling the battery cover out.
2) Install six 'AA' batteries into the battery tray, making sure that the polarity is correct. The direction that each battery should be
installed is molded into the battery tray (+ Positive and - Negative).
3) Set the bottom of the battery cover back onto the transmitter and push it rmly until it 'clicks' closed.
aiRBORnE SySTEM cOnnEcTiOnS
Using an Li-Fe/A123 or Li-Po Receiver Battery
If necessary, the receiver battery can be plugged into any of the channel slots and
still power the receiver without causing damage.
*
*To utilize this channel and power the receiver at the same time,
you must use a Y-Harness (available separately).
The receiver channel slots that you plug your servos into will vary based on the
TYPE menu options you choose. After making TYPE menu option selections, use
the Servo Monitor to determine which receiver channel slots to plug your servos into.
GENERAL
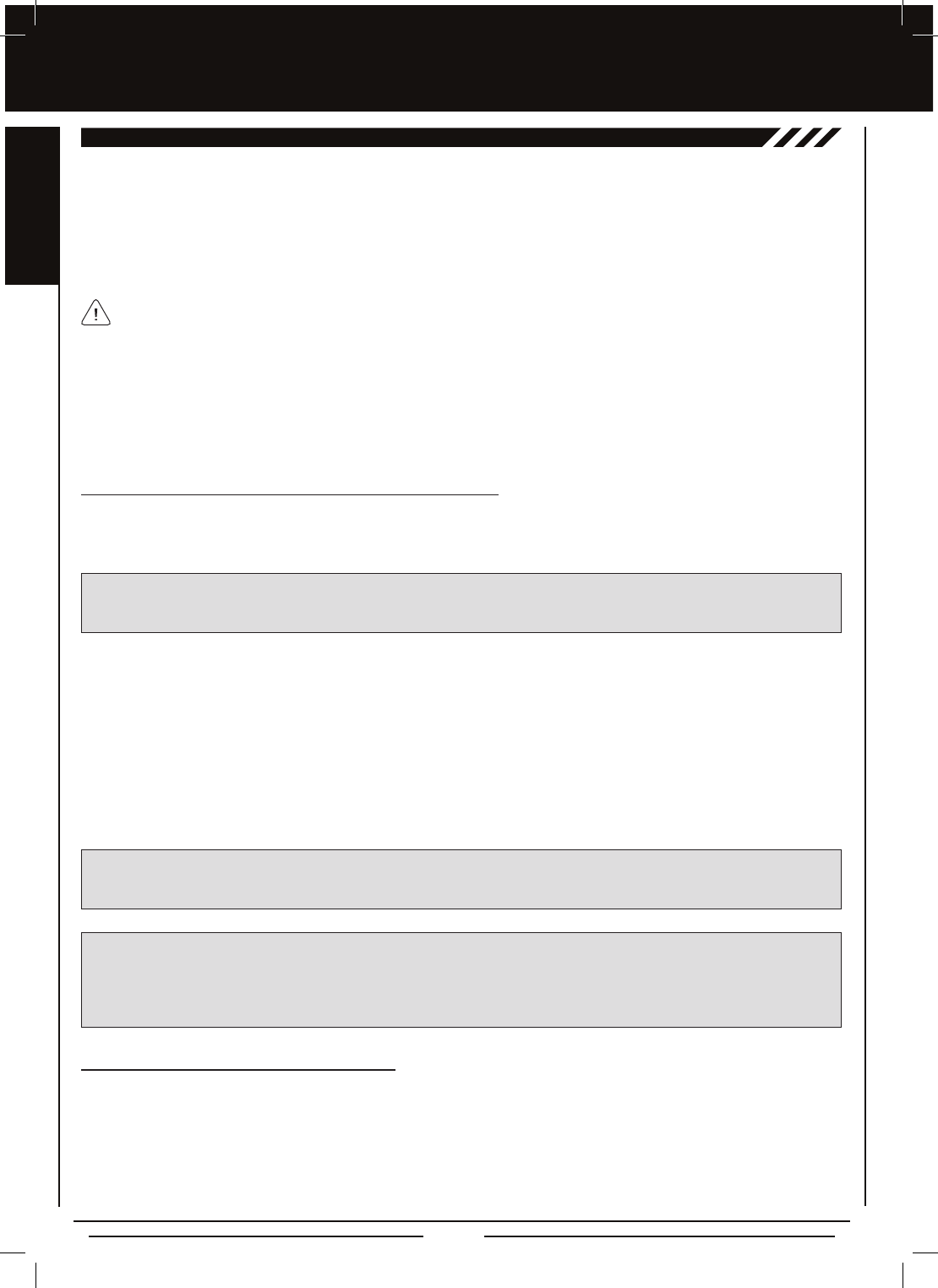
Page 14
SySTEM cOnnEcTiOnS
TRanSMiTTER anD REcEivER BaTTERy chaRging
The TM-160 transmitter features a Charging Jack, which can be used with the Airtronics 95034 110v AC Transmitter and Receiver
Dual Charger to recharge the batteries without removing them from the transmitter. In addition, this charger can also be used to
recharge a 4.8v (4 cell) or 6.0v (5 cell) rechargeable Ni-Cd or Ni-MH receiver battery pack at the same time. We recommend
one of the following receiver battery packs:
Hi-Energy 4.8v 2200mAh Ni-MH Rechargeable Flat Battery Pack for Receiver (1 PC.)
Hi-Energy 6.0v 2200mAh Ni-MH Rechargeable Flat Battery Pack for Receiver (1 PC.)
Warnings About Charging the Transmitter and Receiver Batteries
The TM-160 transmitter features a Charging Jack located on the right side of the transmitter, allowing you to recharge the Ni-Cd
or Ni-MH rechargeable batteries without removing them from the transmitter. Use ONLY the recommended optional Airtronics
95034 110v AC Transmitter and Receiver Dual Charger or damage to the transmitter and/or batteries could result.
WARNING Do NOT attempt to recharge Alkaline batteries. Do NOT attempt to charge any type of batteries other than those
recommended and use ONLY the recommended charger. Do not use the Charging Jack with any other after-market fast
charger or Peak-Detection charger or the transmitter could be damaged.
Charging the Transmitter and Receiver Batteries
1) Plug the Airtronics 95034 110V AC Transmitter and Receiver Dual Charger into a 110v AC wall socket.
2) Plug the round connector from the charger into the Charging Jack in the transmitter and plug the female connector from the
charger into the switch harness charge plug. The charger LEDs will illuminate red, indicating that the charger is charging.
3) Both transmitter and receiver charger outputs are 150mAh, therefore, it will take approximately 15 hours to recharge
fully-discharged 2200mAh batteries (2200/150=14.6). Charge time will vary depending on the mAh capacity of the batteries
you're charging. For example, 1200mAh batteries would require an 8 hour charge (1200/150=8).
lAlways follow the charging procedures described below to ensure the safe and correct use of the rechargeable batteries and
charger.
lBefore charging the batteries, double-check that both the transmitter and the receiver are turned OFF.
lOvercharging reduces the life of the batteries and can result in overheating and bursting. This may cause personal injury
and/or property damage.
lDo not plug the recommended charger into anything other than an AC 110v power outlet. Plugging the charger into anything
other than AC 110v outlet may result in smoking, sparks, or re.
lDo not throw the batteries or abuse them in any manner. Do not dispose of the batteries in the re or allow them to overheat.
lDo not short-circuit the battery terminals with wire or any other object.
WARNING If you're using a Li-Fe or Li-Po receiver battery, do NOT attempt to charge either of these types of batteries with
the optional Airtronics 95034 110v AC Transmitter and Receiver Dual Charger. You MUST use a charger that is specically
designed to charge Li-Fe or Li-Po batteries.
Depending on the region in which your purchase your TM-160 2.4GHz FHSS-1 radio control system, rechargeable
transmitter batteries and an overnight charger may or may not be included. If these items are NOT included, we recommend
using the following:
Hi-Energy 1200mAh Ni-MH 'AA' Rechargeable Batteries (4-Pack) for Transmitter (2 PCS.)
Airtronics 95034 110v AC Transmitter and Receiver Dual Charger (1 PC.)
WARNING An after-market peak-detection charger, cycler, or fast charger should NOT be used to charge Ni-Cd or Ni-MH
rechargeable batteries through the transmitter. The circuitry within the transmitter can interfere with the peak-detection
charger's normal operation, resulting in over-charging and damaging the batteries, and possibly the transmitter itself.
In addition, a fast charger can damage the transmitter's circuitry. These chargers can be used, but ONLY if the batteries are
charged outside of the transmitter.
Instead of using Alkaline batteries to power the transmitter, you can use rechargeable Ni-Cd or Ni-MH batteries. This will provide
longer usage time and reduced cost in the long run, since you won't need to continuously purchase new Alkaline batteries.
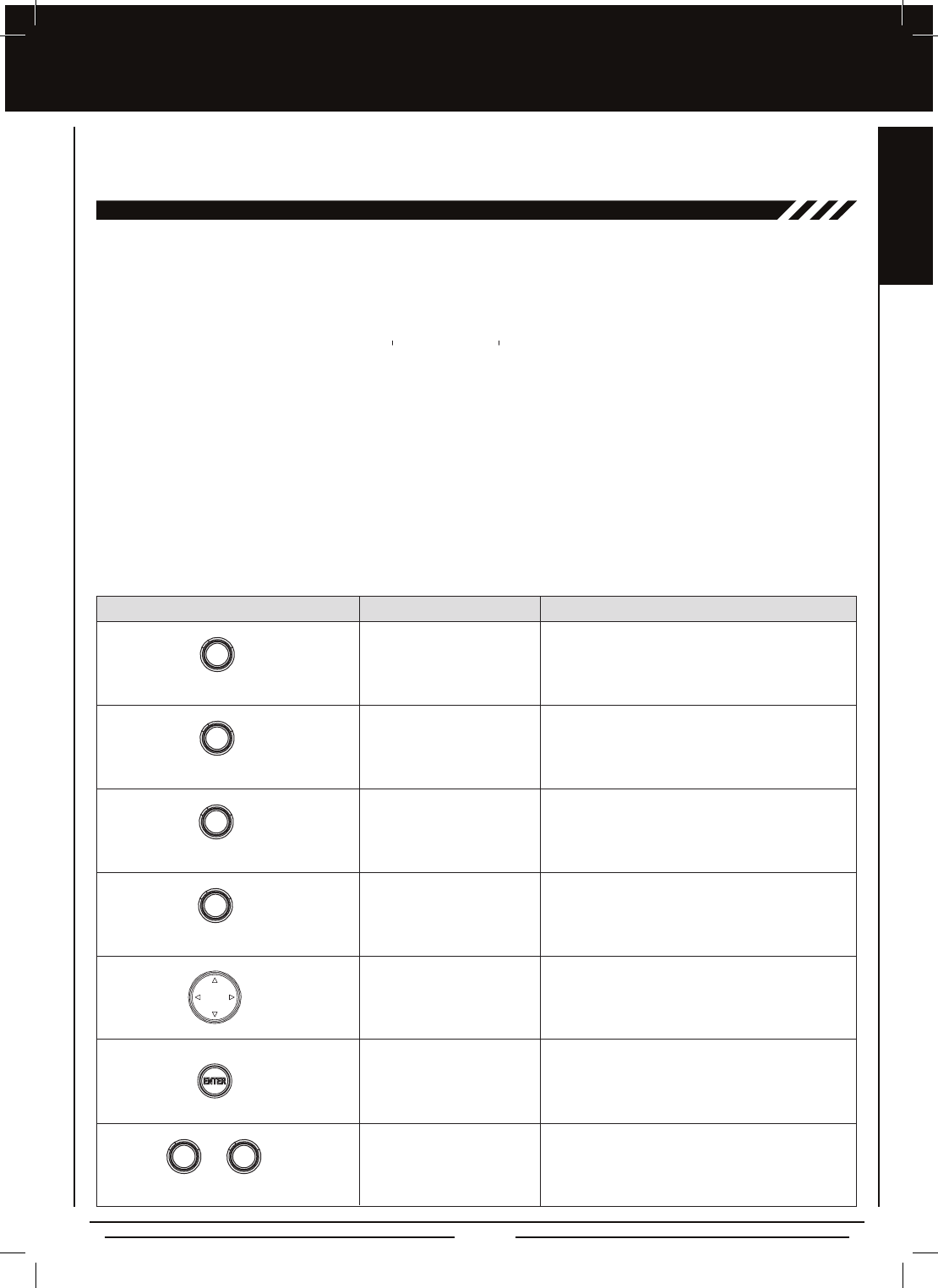
Page 15
The TM-160 transmitter features four Programming Keys, a Navigation Pad and an ENTER key, all used in conjunction to facilitate
transmitter programming. This section summarizes the functions of these features in addition to detailing the main areas of the
Multi-Function LCD.
PROgRaMMing kEyS OvERviEw anD FUncTiOnS
Increases Programming Values and is used to
select Model 1, using the Direct Model Select
function.
Decreases Programming Values and is used to
select Model 2, using the Direct Model Select
function.
END/M3
(End/Model 3)
Returns to the previous menu. Press several times to
return to the Display screen. Is also used to select
Model 3, using the Direct Model Select function.
F-MODE
(Flight Mode Select)
Cycles through the three Flight Modes during
programming. Does NOT switch between Flight
Modes during use.
INC+/M1
(Increase/Model 1)
DEC-/M2
(Decrease/Model 2)
INC+/M1
DEC-/M2
END/M3
F-MODE
LcD anD PROgRaMMing kEyS
INC+/M1 DEC-/M2
+Rest Default Shortcut
Pressing both keys at the same time within a
Programming Menu resets the Programming
Value to the Default value.
PROGRAMMING KEY NAME FUNCTION
Moving around the LCD and programming the transmitter is accomplished using the Navigation Pad, the ENTER key, and the
four Programming Keys positioned on the right half of the transmitter.
Navigation Pad Moves the Programming Cursor Up 5, Down 6,
Right 4, and Left 3.
ENTER Key Opens the selected menu or programming option.
Advances the cursor in the Model Name menu.
GENERAL
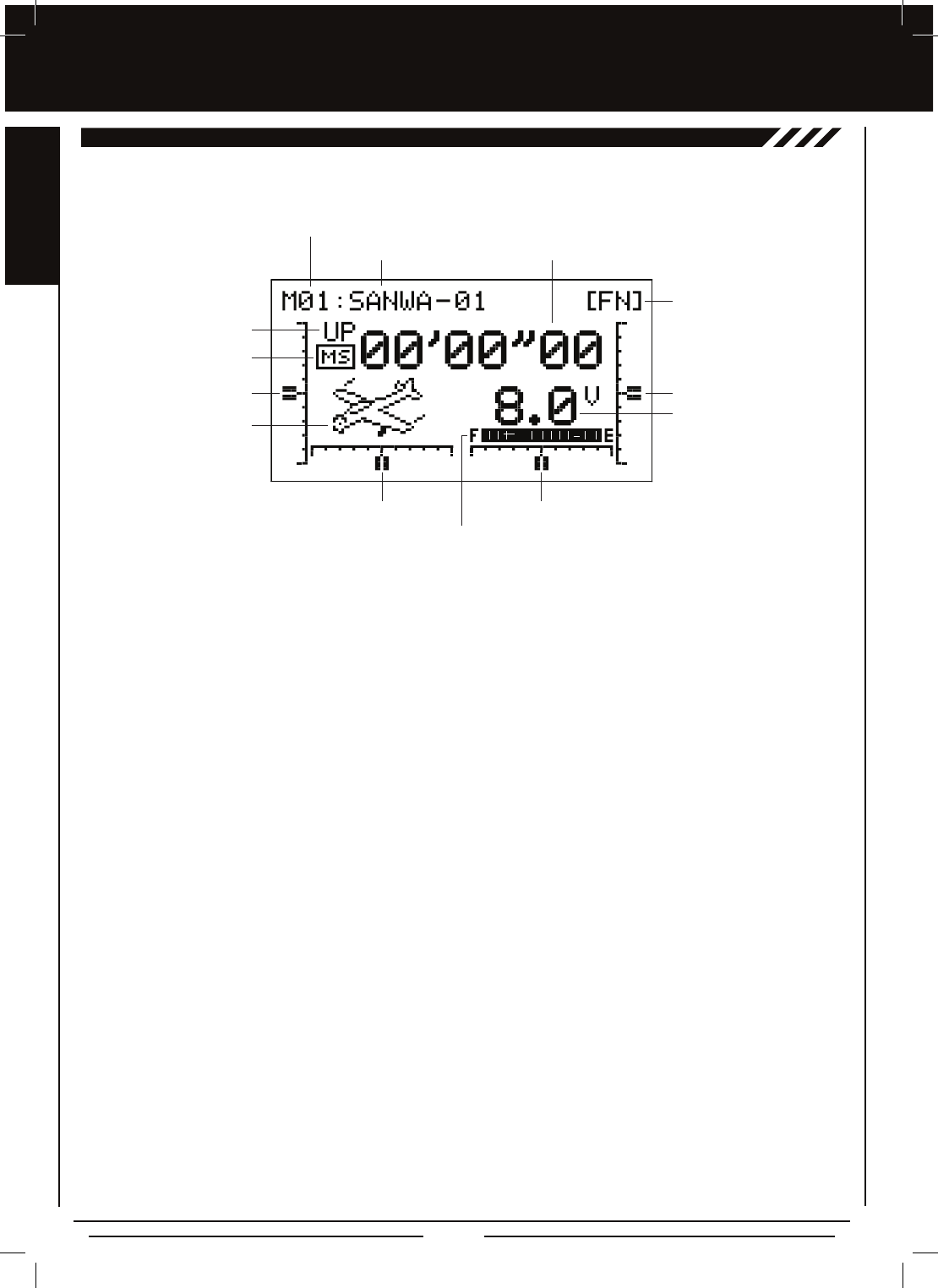
Page 16
LcD anD PROgRaMMing kEyS
MULTi-FUncTiOn LcD OvERviEw
Use the diagram below to familiarize yourself with the layout and different indicators that make up the Multi-Function LCD.
Model Number
Model Type Icon
Rudder Trim
Elevator Trim
Trainer Status Indicator
Model Name Timer
Active Flight Mode
Voltage Indicator
Throttle Trim
Aileron Trim
Battery Capacity Indicator
Active Flight Mode: Displays the Flight Mode number that is currently Active.
Aileron Trim: Displays the current position of the Aileron trim switch*.
Battery Capacity Indicator: Indicates the current remaining usable capacity of the transmitter batteries.
Count Up Timer Indicator: Displayed when the Count Up Timer is chosen.
Elevator Trim: Displays the current position of the Elevator trim switch*.
Model Name: Displays the Name of the currently selected Model.
Model Number: Displays the Number of the currently selected Model.
Model Type Icon: Displays the current Active Model Type loaded into memory, either AERO (Aircraft icon) or HELI (Helicopter icon).
Rudder Trim: Displays the current position of the Rudder trim switch*.
Timer: Displays the Stop Watch Timer or the Count Up Timer.
Throttle Trim: Displays the current position of the Throttle trim switch*.
Trainer Status Indicator: Displays when the transmitter Trainer function is Active. If the transmitter is in Master mode, MS will be
displayed. If the transmitter is in Slave mode, SL will be displayed.
Voltage Indicator: Displays the current voltage of the transmitter batteries. When the voltage reaches 6.7 volts, the Low Voltage
Alarm will sound.
Count Up Timer Indicator
*An audible tone will sound each time a trim switch is pressed. When the trim reaches the center, an audible double-tone will
sound. This allows you to know when the trim is centered without needing to look down at the transmitter during ight.
THIS SPACE INTENTIONALLY LEFT BLANK
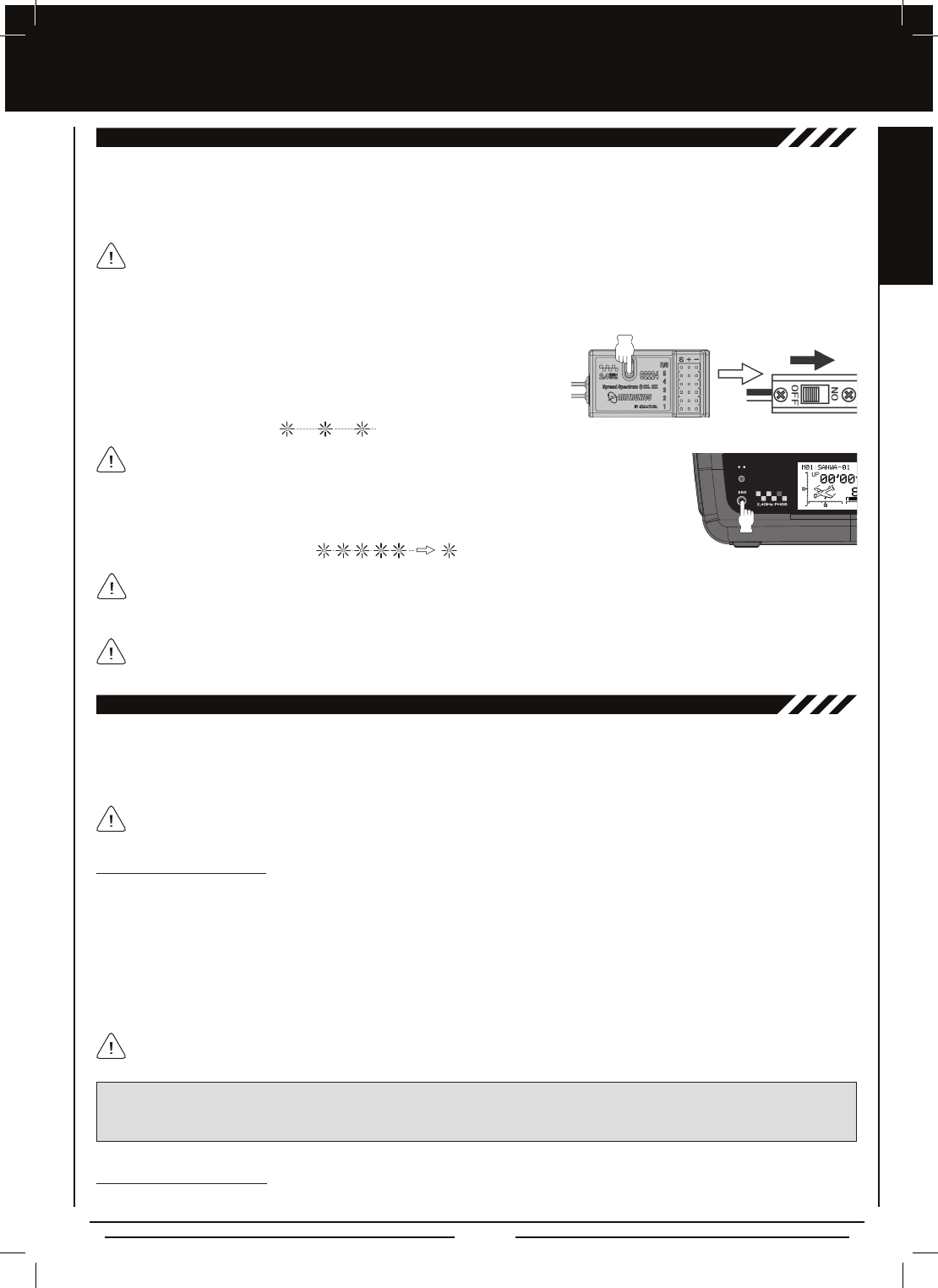
Page 17
SySTEM SETUP anD inSTaLLaTiOn
TRanSMiTTER anD REcEivER BinDing
The Binding function allows you to Bind the transmitter and receiver pair. When new, it is necessary to pair the transmitter and
receiver to prevent interference from transmitters operated by other users. This operation is referred to as 'binding'. Once the
binding process is complete, the setting is remembered even when the transmitter and receiver are turned OFF. Therefore,
this procedure usually only needs to be done once.
Under some circumstances, the receiver may not operate after turning the transmitter and receiver ON. If this occurs,
perform the binding process again.
Before beginning the binding process, connect the switch harness, servos, and the receiver battery to your 92224 (RX600)
6-Channel receiver, using the diagram on page 13. Make sure that both the transmitter and the receiver are turned OFF.
When the binding procedure is successful, the Bind LED on the receiver will stay solid blue when both the transmitter and
receiver are turned ON. If the Bind LED on the receiver is ashing rapidly or not ON at all, the transmitter and receiver are
not paired. In this case, turn both the transmitter and receiver OFF, then repeat the binding procedure.
1) Ensure that the throttle control stick is in the LOW position (pulled all the way back).
2) Turn the transmitter ON. The Bind LED on the transmitter will illuminate solid green.
Use the tip of a pencil or a 1.5mm hex wrench to press the Bind Button on the receiver.
3) While holding down the Bind Button on the receiver, turn the receiver ON.
The Bind LED on the receiver will ash slowly. After ~2 seconds release
the Bind Button. The Bind LED on the receiver will continue to ash slowly.
4) Quickly press the Bind Button on the transmitter. The Bind LED on the receiver will ash rapidly
for ~3 seconds, go out momentarily, then illuminate solid blue, indicating the Binding process
is complete.
FaiL SaFE PROgRaMMing
The Fail Safe function automatically sets the servos to a predetermined position in the event that the signal between the transmitter and
the receiver is interrupted, whether due to signal degradation or to a low transmitter battery. For example, the Fail Safe function
can be set so that the throttle returns to idle, the elevator moves slightly up, and the ailerons move slightly right or left to result in
a shallow downward decent of your aircraft.
The Fail Safe function is available on channels 1 through 4 only. We suggest programming the Fail Safe function prior to
mounting the receiver into your aircraft if you will be unable to access the receiver's Bind Button after mounting.
Setting Fail Safe Positions
1) Turn the transmitter ON, then turn the receiver ON. Move the transmitter control sticks to verify correct servo movement.
2) Move the transmitter control sticks to the desired Fail Safe positions. While holding the transmitter control sticks in those
positions (generally throttle at idle and a minimal amount of elevator and/or aileron), press and HOLD the Bind Button on the
receiver. After ~2 seconds, the Bind LED will begin to ash slowly. Continue holding the Bind Button until the Bind LED begins
to ash rapidly (~2 more seconds). Once the Bind LED begins to ash rapidly, release the Bind Button.
3) Turn the transmitter OFF to test the Fail Safe operation. The servos should move to the positions that you set in step 2.
The Fail Safe settings will be erased if you re-bind the transmitter and receiver pair. If you bind the same transmitter and
receiver pair you MUST repeat these procedures to setup the Fail Safe function again.
IMPORTANT If you don't program the Fail Safe function, if the signal between the transmitter and receiver is lost, the servos
will stay in the last position they were in when the signal was lost. However, the servos will be free to move under load. They
will NOT be locked in the last position they were in.
Clearing Fail Safe Settings
1) To clear the currently programmed Fail Safe settings, re-bind the transmitter and receiver pair.
GENERAL
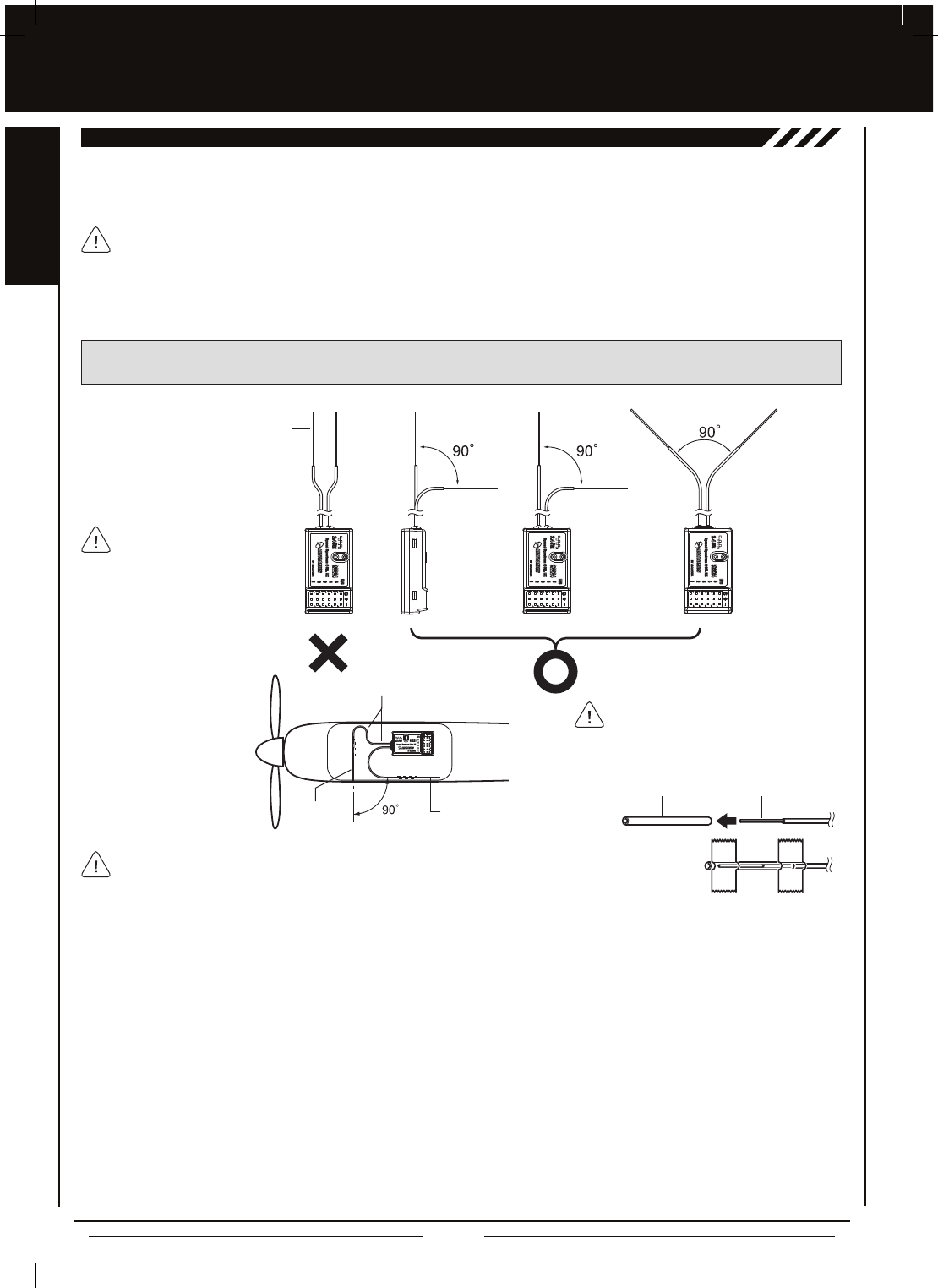
Page 18
SySTEM SETUP anD inSTaLLaTiOn
When mounting the receiver into your model, it's important to mount the receiver exactly as described. In addition, the receiver
should be wrapped in foam rubber to protect it from vibration. Failure to mount the receiver antenna wires as described can
result in poor reception, or in some cases, complete loss of reception.
We recommend that you bind the transmitter and receiver, and program the Fail Safe function, prior to mounting the
receiver into your model, otherwise, it may be difcult or impossible to access the Bind Button on the receiver.
The receiver should be mounted securely in your model and the receiver antenna wires installed per the diagram below. The two
receiver antenna wires should be mounted to a wood or plastic non-conductive part of your model and angled so that the antenna
reception wires (thin, silver-colored antenna tips) are positioned 90º apart.
WARNING It is extremely important that the receiver antenna wires be mounted as described. This will ensure that your
model receives control signals no matter what its posture, attitude, or heading.
lThe receiver antenna wires consists of two coaxial cables and two reception wires (the thin tip at the end of the coaxial cables).
When you mount the receiver antenna wires, do not bend the reception wires. Reception performance decreases if the
reception wires are bent.
lThe receiver antenna wires are delicate, therefore, handle with care. Do not pull on the receiver antenna wires with force. Do
not cut or extend the receiver antenna wires.
lThe coaxial cables (the thicker portion of the receiver antenna wires) can be bent into gentle curves, however, do not bend
the coaxial cables acutely, or repeatedly bend them, or the antenna cores can be damaged.
lWhen installed in an electric-powered model, keep the receiver antenna wires as far away from the motor, battery, and
electronic speed control (ESC) as possible.
lWhen installing the receiver, the antenna reception wires (the thin tip at the end of the coaxial cables) should not come into
contact with any carbon or metal components (conductive components). Aircraft fuselages may contain conductive components.
If mounting the receiver surrounded by conductive materials (for example, a carbon ber fuselage), mount the receiver so that
the antenna reception wires can be extended outside of the model. Reception can be blocked if the antenna reception wires
are shielded inside a carbon ber fuselage.
Tape can be used to secure the antenna reception wires to your model. Alternatively, cut two
short pieces of plastic tube and slide one antenna reception wire into each piece of tube, then
tape or glue the tube to your model. The tubes will protect the antenna reception wires from damage.
If mounting inside a carbon fiber
fuselage, the antenna reception wires
must be run outside of the model as
described in the notation below.
MOUnTing ThE REcEivER
The Coaxial cables can
be mounted parallel to
each other, but under no
circumstances should the
antenna reception wires be
mounted parallel to each other.
Reception Wire
Coaxial Cable
Coaxial Cables
Reception Wire
Reception
Wire
Reception Wire
Plastic Tube
OR OR
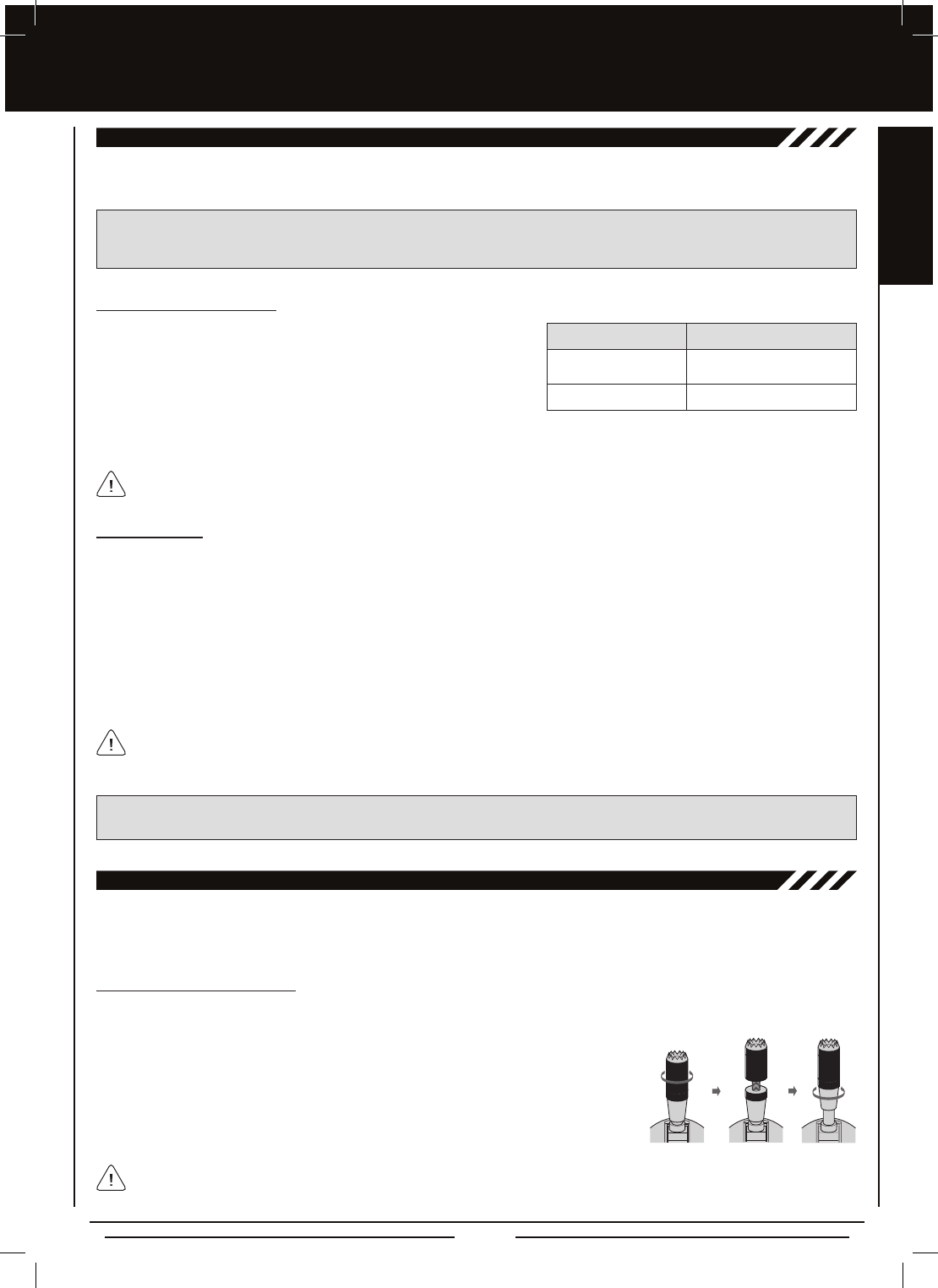
Page 19
SySTEM SETUP anD inSTaLLaTiOn
RangE chEcking - LOw-POwER MODE
When lengthening the control sticks, we strongly suggest that you leave at least four threads inside the top half of each
control stick. This will ensure that the control sticks maintain optimum mechanical security. If you thread the control sticks
out too far, the control sticks might come loose during use.
cOnTROL STick LEngTh aDjUSTMEnT
The length of the control sticks can be adjusted to best suit the way you hold them. In general, pilots who place their thumbs on
top of the control sticks prefer the control sticks to be shorter, and pilots who grasp the control sticks prefer the control sticks to
be longer. In the default conguration, the control sticks are adjusted as short as possible.
Activating Low-Power Mode
1) Press and HOLD the Bind Button on the transmitter, then turn the
transmitter ON. The Bind LED will ash.
2) Continue to HOLD the Bind Button for approximately 5 seconds. After
approximately 5 seconds, the Bind LED will ash rapidly, then go out.
3) Release the Bind Button and the Bind LED should begin to ash again. The transmitter is now in Low-Power Mode and you
can begin the Range Check process.
IMPORTANT The radio control system should be Range Checked prior to the day's rst ight and prior to the rst ight after
a hard landing or after a repair. This will ensure that the transmitter and receiver are communicating properly prior to ight.
This ensures the safety of your aircraft, yourself, and the people around you.
Low-Power Mode
Normal Mode
POWER MODE TRANSMITTER STATUS
Bind LED Flashing
Bind LED Solid
The Low-Power Mode function lowers the transmitter's RF output level to check radio signal reception (Range Check). Use
this function to check radio signal reception on the ground, prior to ight.
Range Checking
1) Turn the receiver in your aircraft ON.
2) With the transmitter in Low-Power Mode (Bind LED ashing), walk approximately 30 paces from your aircraft (approximately
90 feet) and, with the help of another person, check to make sure that the servos move without any problems. If there is a
problem with servo movement, try moving to a different position while still maintaining the same distance from your aircraft,
then check servo movement again. If there is still a problem, DO NOT FLY. Check to make sure that all receiver, servos,
switch, and onboard battery connections are correct and secure. Check to ensure that the receiver antenna wires are correctly
mounted as described previously.
3) When satised that the system is operating correctly, turn the transmitter OFF, then back ON to resume use in Normal Mode.
WARNING Do not attempt to y with the transmitter in Low-Power Mode. You will be unable to control your aircraft once it is
a certain distance away from you. Always verify that the Bind LED is solid prior to ight.
The transmitter will revert to Normal Mode after approximately 3 minutes. If you haven't completed your Range Check
within that time, turn the transmitter OFF, then repeat steps 1 through 3 to re-enter Low-Power Mode.
If after checking all airborne system components and verifying correct antenna wire mounting, your radio control system
still fails the Range Check, DO NOT FLY. Please contact Airtronics Customer Service using the information on the back
cover of this Operating Manual.
Adjusting Control Stick Length
1) While holding the base of the control stick, turn the top half of the control stick counter-clockwise to loosen it.
2) To lengthen the control stick, turn the top half of the control stick counter-clockwise. To
shorten the control stick, turn the top half of the control stick clockwise.
3) Once your are satised with the length of the control stick, thread the bottom half of the
control stick up and tighten it gently against the top half of the control stick.
GENERAL
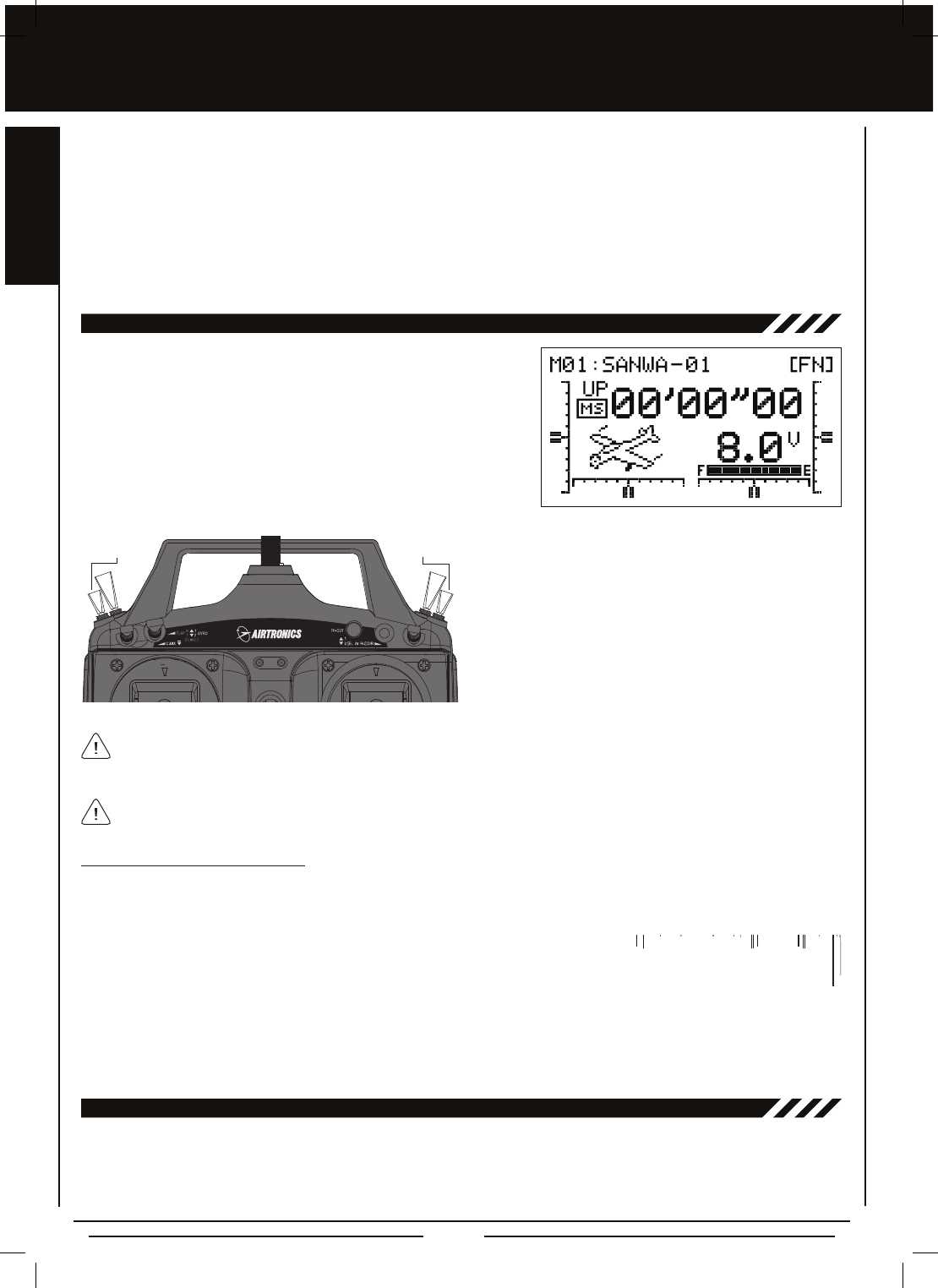
Page 20
FLighT MODES
The TM-160 transmitter model programming is based around Flight Modes. Each Model Type (AERO and HELI) feature three
independently programmable Flight Modes. Flight Mode FN (Normal), Flight Mode F1, and Flight Mode F2. Within these Flight
Modes is where the core of the model programming takes place. Features such as Dual Rate, Exponential, Throttle Curve, Pitch
Curve, Mixing, Compensation Mixing, and much more can be individually programmed to each of the three Flight Modes. Each
Flight Mode is controlled by a switch so that they can be turned ON and OFF during ight.
Flight Modes allow you to change the ying characteristics of your model with the ip of a switch. For example, if you y
helicopters, you can have one Flight Mode for normal ying and a second Flight Mode for aerobatic ying. Flip the Flight Mode
switch from FN (Normal) to F1 and your helicopter is now programmed with all of your 'Aerobatic' Flight Mode programming. With
three programmable Flight Modes available for each Model Type, the combinations of model programming is highly-congurable.
FLighT MODE waRning aLaRM
The TM-160 transmitter is equipped with a safety feature that will not allow you to use the transmitter if the Flight Mode is not set
to FN (Normal) when you turn the transmitter ON. If the Flight Mode is not set to FN when you turn the transmitter ON, the Flight
Mode Warning alarm will sound continuously, the RF Output Indicator will ash, and the LCD will read F-MODE NOT 'N' ! To clear
the Flight Mode Warning, set the Flight Mode to FN using the Flight Mode Switches (move both Flight Mode switches forward).
The LCD will read normally, the Flight Mode Warning alarm will cease, and RF Output Indicator will stop ashing.
There are three Flight Modes that can be individually programmed for
each Model Type. The currently Active Flight Mode (FN, F1, or F2) is
displayed in the upper right corner of the Display screen.
There is always one Flight Mode active at all times and will vary based on the positions of the two Flight Mode switches.
When both Flight Mode switches are pushed away from you (OFF), Flight Mode FN (Normal) will be Active.
gEnERaL inFORMaTiOn
The F-MODE key is used to facilitate programming the individual Flight Modes only and
does not turn the Flight Modes ON or OFF or switch between Flight Modes during use.
It's important to note that higher numbered Flight Modes override lower numbered Flight Modes. For example, if you have
Flight Mode F1 and Flight Mode F2 Active at the same time (both Flight Mode switches pulled toward you), Flight Mode F2
will override Flight Mode F1.
Common or Separate Flight Modes
Many Flight Mode programming options can be agged either COMMON or SEPARATE. Options agged as Common are
common across all Flight Modes. Options agged as Separate can be programmed separately for each Flight Mode from the
same Programming Menu.
Flight Modes are turned ON and OFF using the two Flight
Mode switches, as described below:
Flight Mode FN (Normal) - Both Flight Mode switches pushed
forward (OFF).
Flight Mode F1 - Flight Mode F1 Switch pulled toward you
(ON) and Flight Mode F2 switch pushed away from you (OFF).
Flight Mode F2 - Flight Mode F2 switch pulled toward you
(ON).
Flight Mode F1
Switch
Flight Mode F2
Switch
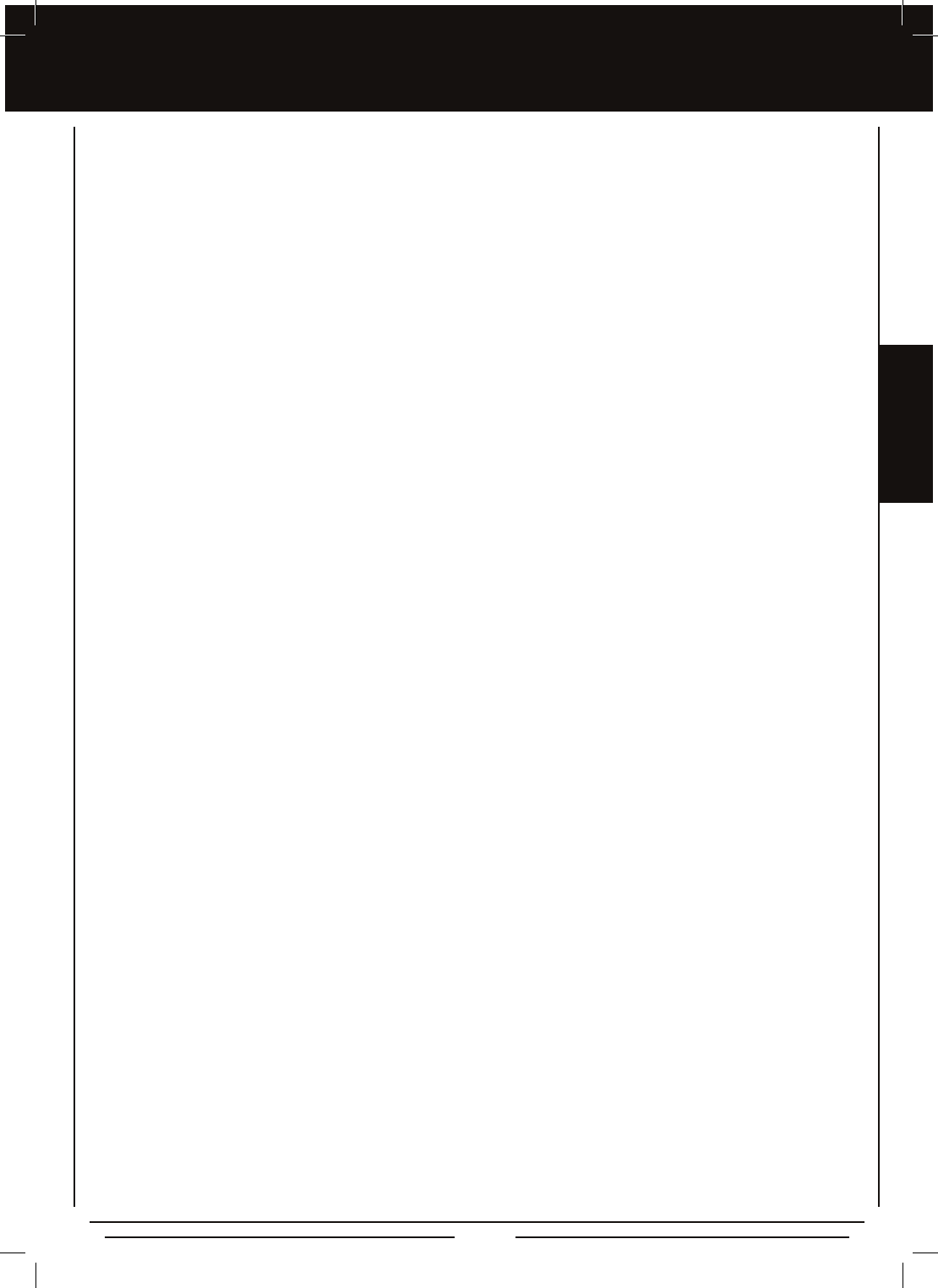
Page 21
aERO MODEL TyPE cOnTEnTS
General Information ......................................................................................................................................................... Page 22
AERO Model Type Menu Flow Chart .............................................................................................................................. Page 22
AERO Model Type Transmitter Layout........................................................................................................................... Page 23
MODEL SELE (Model Select)........................................................................................................................................... Page 23
MODEL NAME (Model Naming)....................................................................................................................................... Page 24
TYPE (Model Type) ........................................................................................................................................................... Page 25
TRAINER (Trainer System) .............................................................................................................................................. Page 26
STOP WATCH (Stop Watch and Count Up Timer).......................................................................................................... Page 28
DATA COPY (Model Programming Data Copy) .............................................................................................................. Page 29
DATA RESET (Model Programming Data Reset) ........................................................................................................... Page 29
REVERSE (Servo Reversing)........................................................................................................................................... Page 30
CENTER (Servo Centering Sub-Trim)............................................................................................................................. Page 31
EPA (End Point Adjustment)............................................................................................................................................ Page 32
TH-CUT (Throttle Cut) ...................................................................................................................................................... Page 33
D/R & EXP (Dual Rate and Exponential)......................................................................................................................... Page 34
TRIM (Digital Trim)............................................................................................................................................................ Page 36
TH-CURVE (Throttle Curve)............................................................................................................................................. Page 37
AI-DIFF (Aileron Differential) ........................................................................................................................................... Page 39
FLAPERON (Flaperon Mixing)......................................................................................................................................... Page 40
FL>EL (Flap to Elevator Mixing)...................................................................................................................................... Page 41
DUAL EL (Dual Elevator Mixing End Point Adjustment)............................................................................................... Page 42
AILVATOR (Ailvator/Taileron Mixing).............................................................................................................................. Page 44
V-TAIL (V-Tail Mixing End Point Adjustment)................................................................................................................. Page 45
DELTA (Delta Mixing End Point Adjustment) ................................................................................................................. Page 46
C-MIX1 (Compensation Mixing 1).................................................................................................................................... Page 47
C-MIX2 (Compensation Mixing 2).................................................................................................................................... Page 47
SX MONITOR (Servo Monitor) ......................................................................................................................................... Page 50
AERO MODEL TYPE
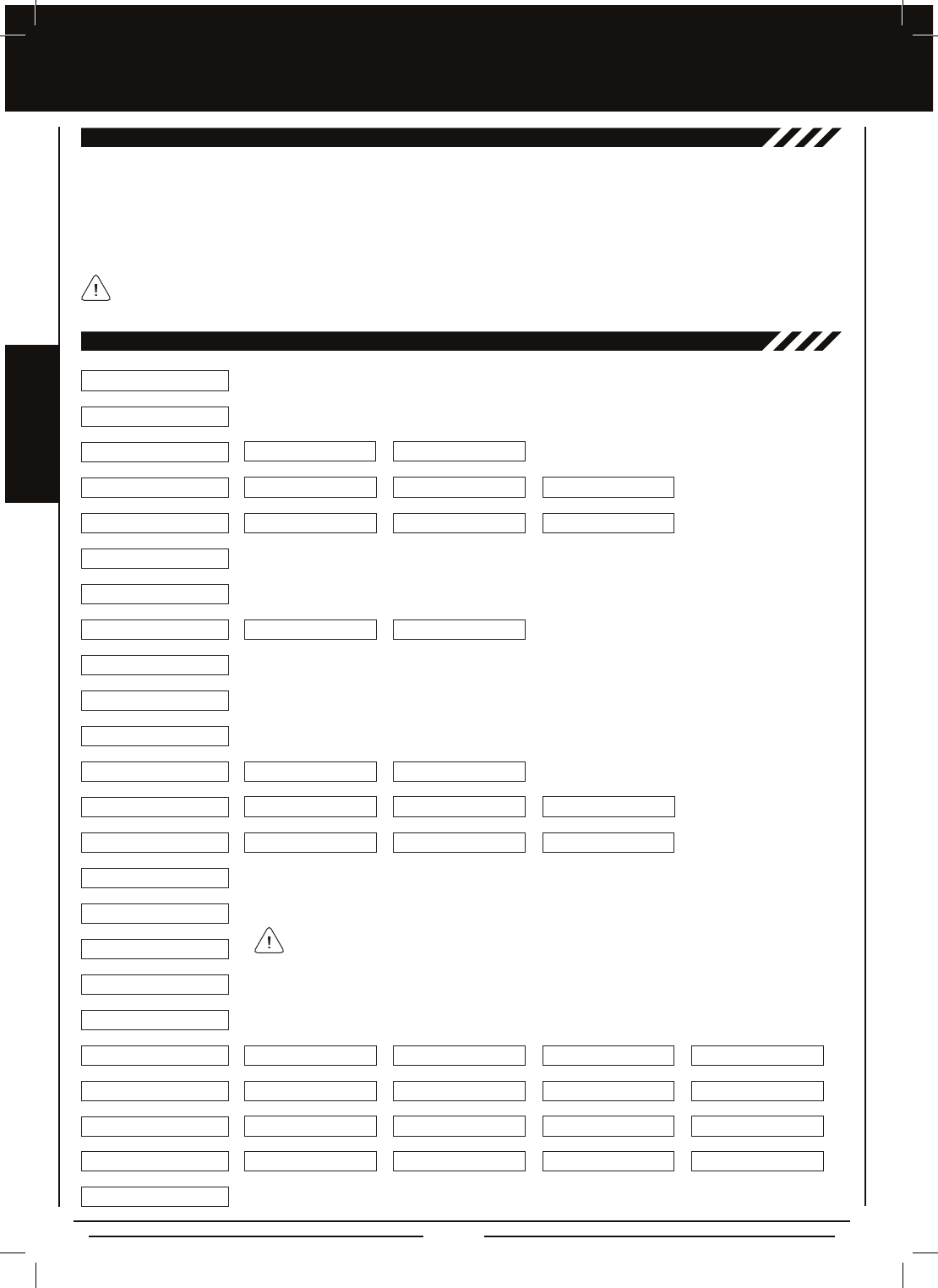
Page 22
aERO MODEL TyPE
aERO MODEL TyPE PROgRaMMing MEnU FLOw chaRT
Use this Flow Chart to familiarize yourself with the AERO Model Type Programming Menu structure.
Descriptions regarding all AERO Model Type functions and programming are found on pages 23
through 50.
04.TRAINER
03.TYPE
02.MODEL NAME
01.MODEL SELE
05.STOP WATCH
06.DATA COPY
07.DATA RESET
08.REVERSE
09.CENTER
10.EPA
11.TH-CUT
12.D/R & EXP
13.TRIM
14.TH-CURVE
15.AI-DIFF
16.FLAPERON
17.FL>EL
18.DUAL EL
19.AILVATOR
20.V-TAIL
21.DELTA
22.C-MIX1
6
6
6
6
6
6
6
6
6
6
6
6
6
6
6
6
6
6
6
6
6
AERO HELI
6
6
23.C-MIX2
24.SX MONITOR
6
6
To access the AERO Model Type Programming Menus, turn the transmitter ON. From the Display screen, press the ENTER key
to display the Programming Menus, then press the Navigation Pad 56to scroll to the desired Programming Menu. Press the
ENTER key to access the desired Programming Menu.
From within any Programming Menu, press the END/M3 key continuously to return to the Display screen. Unless otherwise
noted, all programming changes take effect immediately.
If the Display screen is not displayed when you turn the transmitter ON, continuously press the END/M3 key until the
Display screen is displayed.
gEnERaL inFORMaTiOn
INH MASTER
6
6
SLAVE
6
NOR REV
6
6
MIN SEC
6
6
1/10
6
D/R [1] - D/R [2] EXP [1] - EXP [2]
6
6
COMMON SEPARATE
6
6
HOLD POINT
6
6
RATE
6
MASTER SLAVE
6
6
RATE HIGH / RATE LOW
6
OFFSET
6
MASTER SLAVE
6
6
RATE HIGH / RATE LOW
6
OFFSET
6
ELEVATOR (DOWN) ELEVATOR (UP)
6
6
AILERON (LEFT)
6
AILERON (RIGHT)
6
ELEVATOR (DOWN) ELEVATOR (UP)
6
6
RUDDER (LEFT)
6
RUDDER (RIGHT)
6
Some Programming Menus cannot be accessed unless certain Model Type selection options
are chosen rst. For example, you cannot access the AI-DIFF menu unless you have chosen
AILE>2 in the TYPE menu.
TH-TRIM LOCK (F1)
6
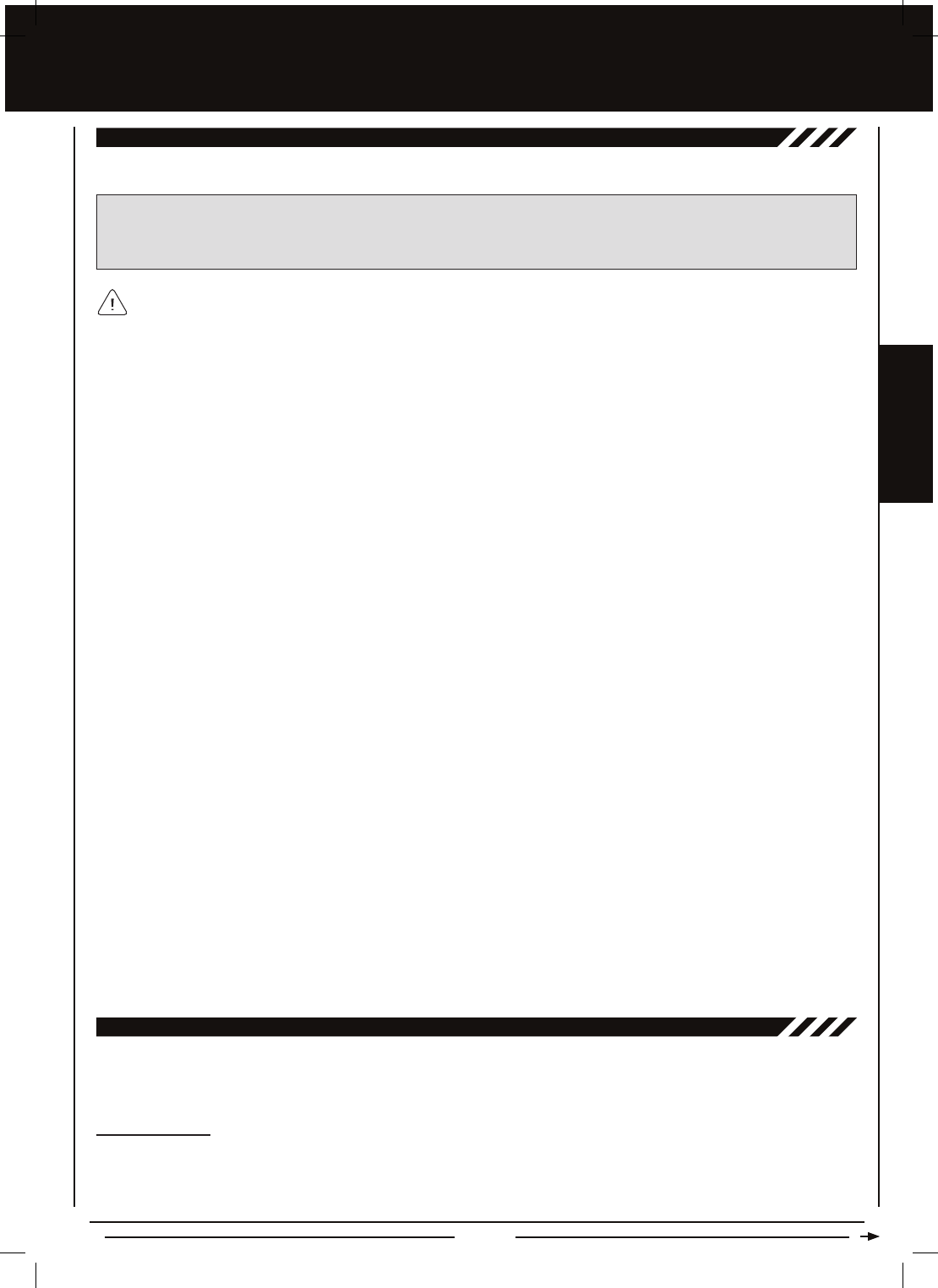
Page 23
aERO MODEL TyPE
The diagram below shows the transmitter control stick and switch layout in the AERO Model Type conguration.
IMPORTANT Since each of the three Flight Modes can be programmed separately, before making programming changes,
verify that you are in the Flight Mode you want to make programming changes to. To avoid confusion, we suggest leaving both
Flight Mode switches pushed away from you (OFF) and use the F-MODE key from within the programming menus to choose
which Flight Mode you would like to make programming changes to.
aERO MODEL TyPE TRanSMiTTER LayOUT
01.MODEL SELE (MODEL SELEcT)
The Model Select function allows you to load the Programming Data for the particular model you wish to y. The MODEL SELECT
menu displays the currently selected model, along with a list of available models that can be selected. The specic Model Type
(AERO or HELI) is displayed for each of the models. The TM-160 can store Programming Data for up to 10 different models.
Selecting a Model
1) From the Display screen, press the ENTER key to display the Programming Menus.
2) Press the Navigation Pad 56 to highlight MODEL SELE, then press the ENTER key to display the MODEL SELECT menu.
The currently selected model in the Model Select List will be highlighted.
When any switch is moved into the Up or Forward position (pushed away from you), this is considered the OFF position.
When moved into the Down position or Back position (pulled toward you), this is considered the ON position.
AERO MODEL TYPE
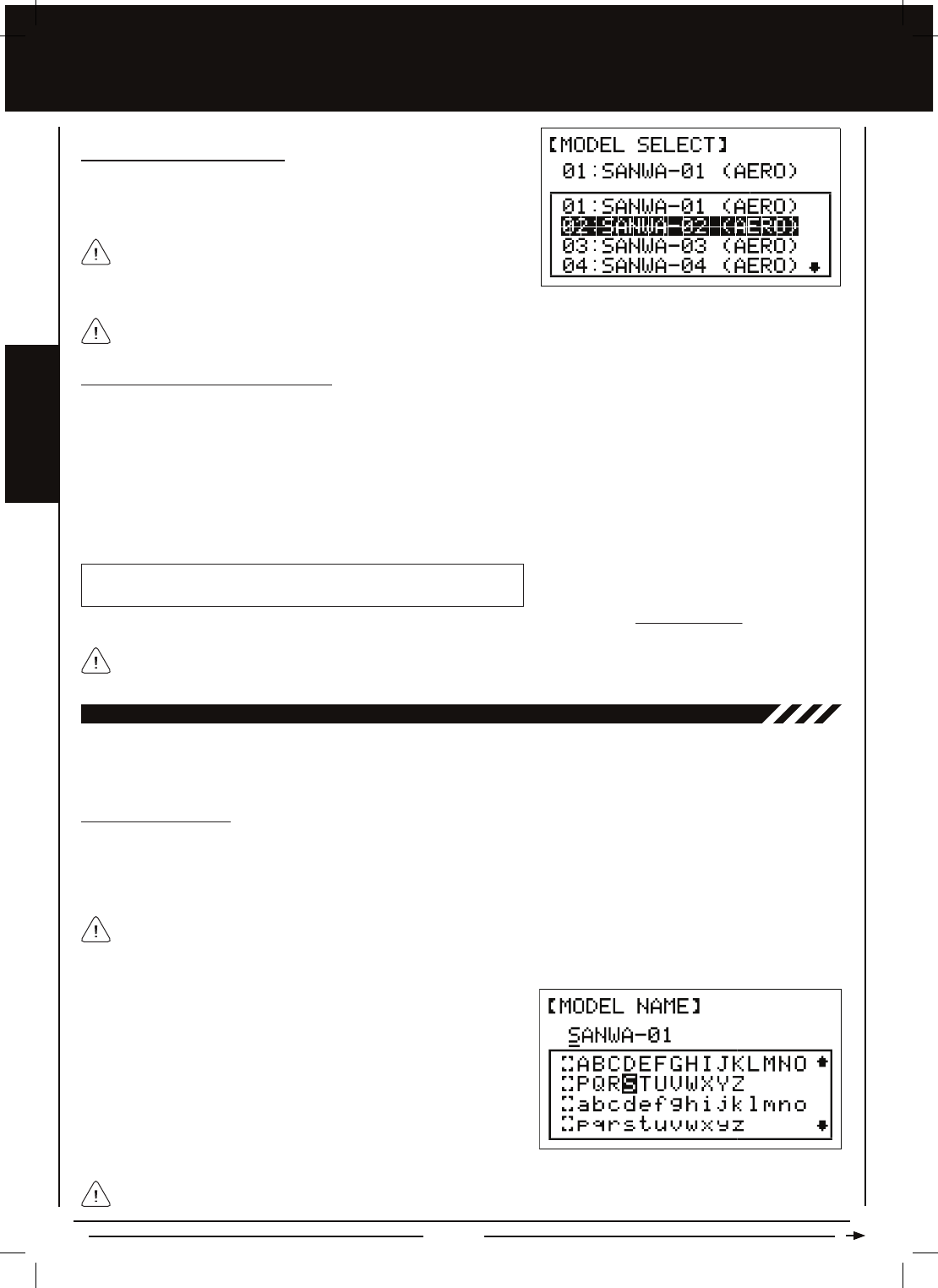
Page 24
aERO MODEL TyPE
In the default conguration, the Model Select List contains 5 AERO Model Types and 5 HELI Model Types. The Model Type
for any of the 10 models in the Model Select List can be changed using the TYPE menu. For more Information, see page 25.
Using the Direct Model Select Function
The Direct Model Select function allows you to select one of rst three models from memory without going through the MODEL
SELECT menu. This makes it much quicker and easier to load the Programming Data for your three most-used models.
Before ying, verify that the Model Name displayed at the top of the Display screen is the actual model that you'll be ying.
1) Turn the transmitter OFF.
2) Press and HOLD the programming key of the model you wish to setup
or y, then turn the transmitter ON. The Model Name will be displayed
at the top of the Display screen.
INC+/M1 selects Model 1, DEC-/M2 selects Model 2, and END/M3
selects Model 3.
02.MODEL naME (MODEL naMing)
The Model Naming function allows you to name each of the 10 individual models. This makes it easy to keep track of multiple
models. The Model Name can consist of up to 8 letters, numbers, or symbols. Choose from capital letters, lower case letters,
numbers, and various symbols.
Entering a Model Name
1) From the Display screen, press the ENTER key to display the Programming Menus.
2) Press the Navigation Pad 56 to highlight MODEL NAME, then press the ENTER key to display the MODEL NAME menu.
The cursor will default to the left side of the top row of letters and an underscore will appear under the rst character in the name.
A model must be selected before a Model Name can be entered or modied. In the default conguration, M01:SANWA-1
is selected. To enter a Model Name for another model, that model must rst be selected using the MODEL SELECT menu
or the Direct Model Select function. For more information, see the 01.MODEL SELECT section on page 23.
When you press the ENTER key to select a model, the Programming
Data for that model will be loaded immediately.
Selecting a Model, Continued....
3) Press the Navigation Pad 56 to highlight the model you would like to
select, then press the ENTER key to select the highlighted model. That
model will be displayed above the Model Select List.
3) Press the Navigation Pad 5634 to highlight a character, then press
the ENTER key to select the highlighted character. That character will be
displayed and the underscore will move to the next space.
4) Repeat step 3 to enter the rest of the characters. Up to eight characters
can be entered. The name of your model will be displayed on the
top of the Display screen.
Press the Navigation Pad 56 repeatedly to scroll up and down the list of characters. In addition, press the INC+/M1 and
DEC-/M2 keys to move the underscore left and right respectively.
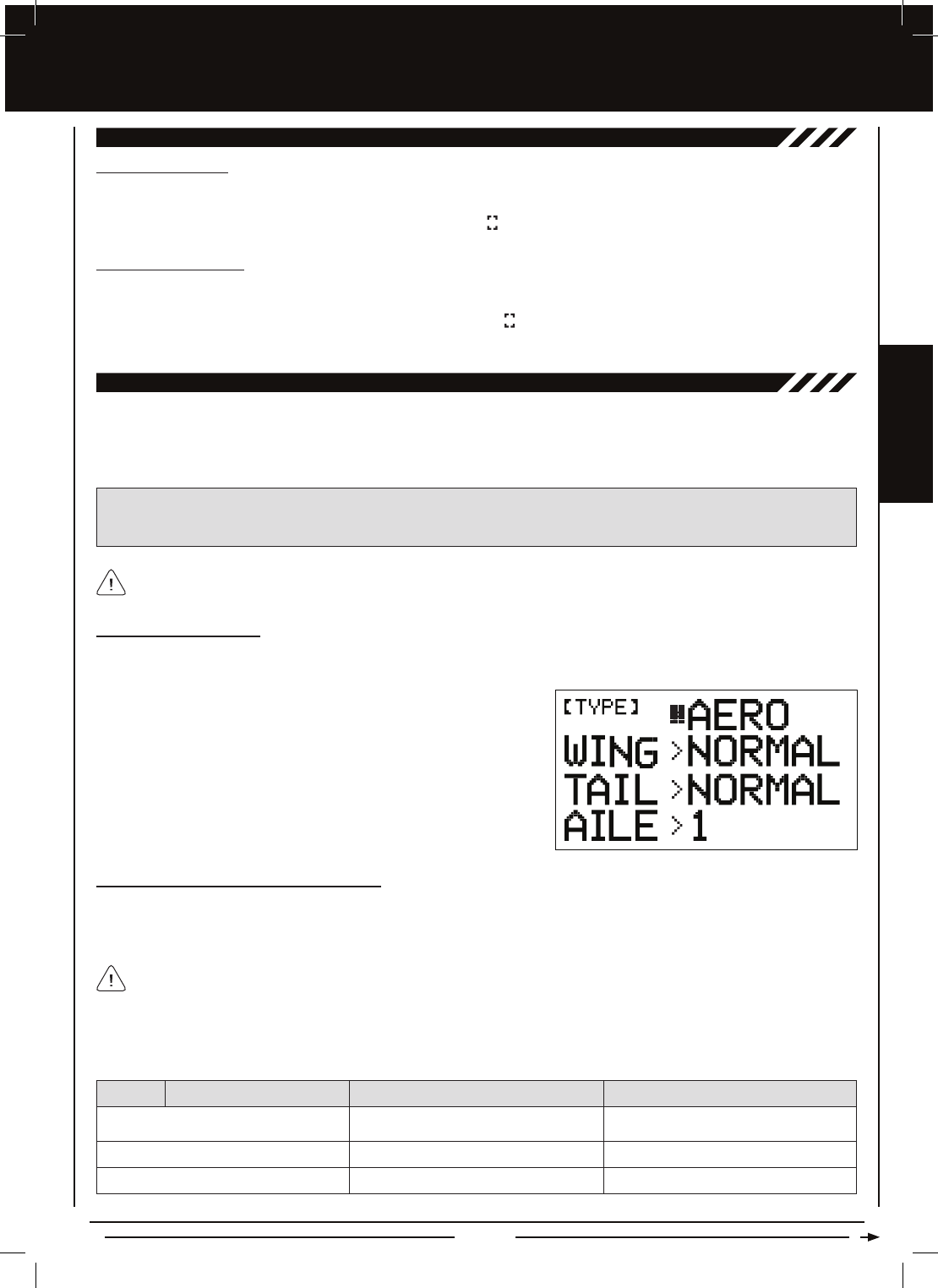
Page 25
aERO MODEL TyPE
Deleting a Character
1) Press the INC+/M1 or DEC-/M2 keys to move the underscore under the character you want to erase.
2) Press the Navigation Pad 5634 to highlight the Erase Bracket , then press the ENTER key to erase the underscored character.
Deleting a Model Name
1) Press the INC+/M1 and DEC-/M2 keys at the same time to move the underscore under the rst character.
2) Press the Navigation Pad 5634 to highlight the Erase Bracket , then press the ENTER key repeatedly to erase the entire
Model Name.
03.TyPE (MODEL TyPE)
The Model Type function allows you to quickly set up the transmitter's low-level mixing based on the type of model you're
ying. Common templates for AERO and HELI Model Types are provided. For example, if your aircraft features two aileron servos
and dual elevator servos, choosing these options will automatically change the transmitter's programming to accommodate this
setup. This takes the guess-work out of setting up more complex models.
WARNING The Model Type function is used when setting up a new model and should be done prior to making any
programming changes to your model. When Model Type selection options are changed for the currently selected model,
all Programming Data for that model will be reset.
Individual Model Type selection options can be reset to the default setting by pressing the INC+/M1 and DEC-/M2 keys at
the same time.
2) Press the Navigation Pad 56 to highlight TYPE, then press the ENTER
key to display the TYPE menu. The cursor will default to >AERO or
>HELI depending on the particular model you've selected.
3) If the current Model Type is >HELI, press the INC+/M1 or DEC-/M2
keys to change the selection option to >AERO.
Changing the Model Type
1) From the Display screen, press the ENTER key to display the Programming Menus.
02.MODEL naME (MODEL naMing), cOnTinUED....
Making AERO Model Type Selection Options
Choose AERO Model Type selection options that suit the aircraft that you're setting up. For example, if your aircraft is a ying
wing and is controlled by elevons, choose WING>DELTA. If your aircraft features separate aileron servos and split elevator
halves that use one elevator servo on each elevator half, choose AILERON>2 and TAIL>2xEL, and so on.
Receiver channel slot assignments will change based on the selection options chosen. To verify which receiver channel
slots to plug your servos into, navigate to the SX MONITOR menu after saving your Model Type selection options. For more
information, see page 50. Depending on the Model Type selection options chosen, not all channel functions will be available for use.
1) From within the TYPE menu, verify that >AERO is displayed. If >HELI is displayed, change the Model Type to AERO by
following the steps in the Changing the Model Type section above.
SELECTION DEFAULT OPTION
WING (Type)
TAIL (Type)
AILERON (Servos)
NORMAL
NORMAL
1
DELTA* (Elevons)
V-TAIL or 2xEL**
2
AERO
*Delta mixing is sometimes referred to as Elevon mixing. **If you require both servos to move the same direction, you will need to Reverse one of the channels.
AERO MODEL TYPE
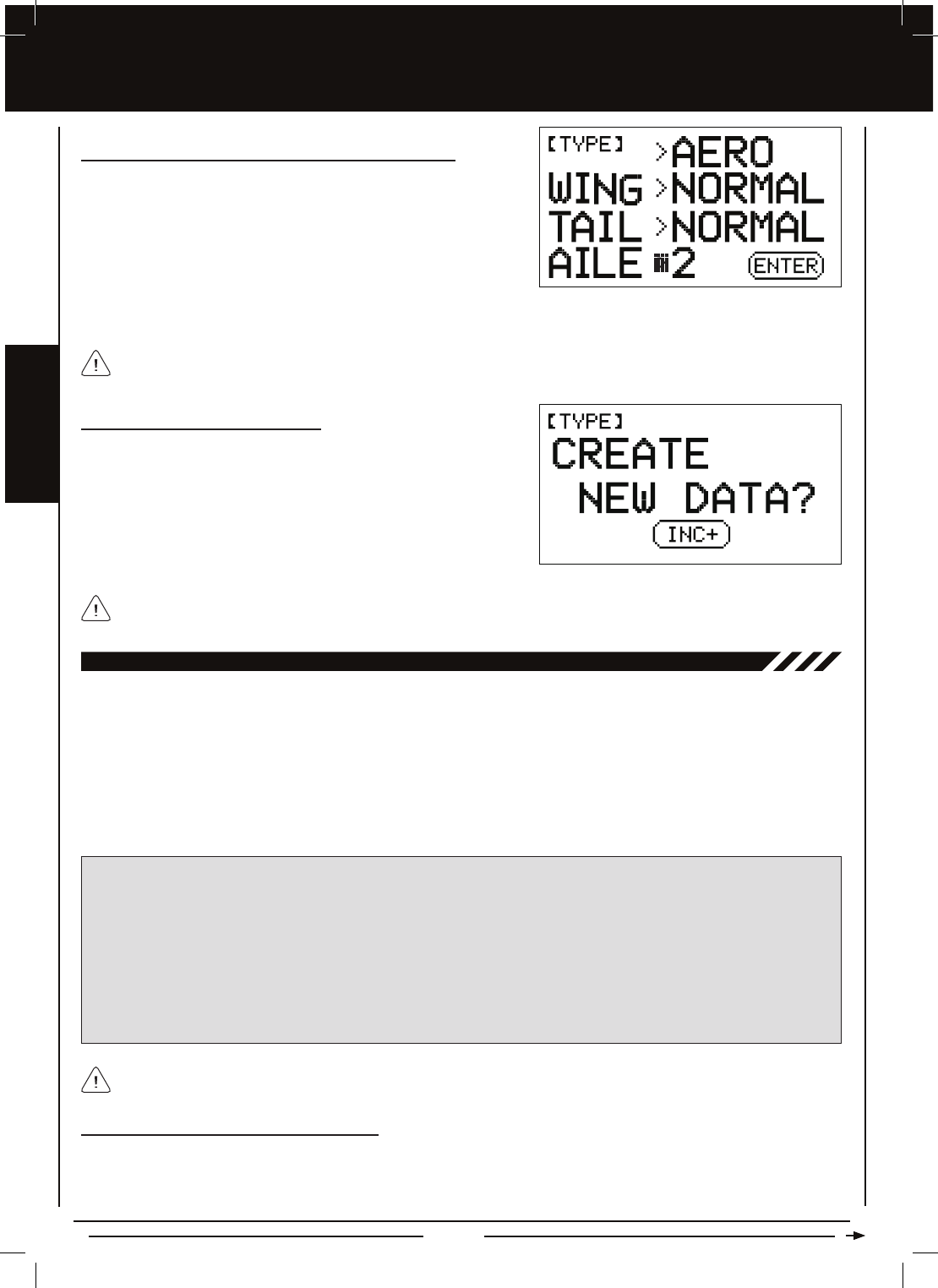
Page 26
aERO MODEL TyPE
Some selection options are dependent on other selection options and may not be able to be changed.
If you want to go back and change the settings or if you don't want to create the new settings for any reason, press the
DEC-/M2 or END/M3 keys.
Saving Model Type Selection Options
1) After making your choices, press the ENTER key. CREATE NEW
DATA? will be displayed and INC+ will ash in the Programming Window.
2) Press the INC+/M1 key to Create New Data. After ~10 seconds, the
new Programming Data will be loaded into the transmitter as indicated
by the progress bar, and COMPLETE!! will be displayed in the
Programming Window. Press any key to return to the TYPE menu.
04.TRainER (TRainER SySTEM)
The TM-160 transmitter features a Trainer System that allows you to connect two TM-160 transmitters to one another, or connect
one TM-160 transmitter to one SD-5G transmitter or to one SD-10G transmitter, for the purpose of training a new pilot or for training
a more experienced pilot on a new model.
During use, one transmitter acts as the Master (Instructor) and the other transmitter acts as the Slave (Student). The Instructor
controls the Student's model as long as the Trainer switch is released. For example, once the Instructor maneuvers the model to a
safe altitude, the Instructor pulls and holds the Trainer switch to give control of the model to the Student. The Student will have
control of the model as long as the Instructor holds the Trainer switch. Once the Trainer switch is released, the Instructor will have
control of the model once again. If at any time the Instructor feels that the Student is in a situation that endangers the model, the
Instructor releases the Trainer switch and control of the model returns instantly to the Instructor.
Making AERO Model Type Selection Options, Continued....
2) Press the Navigation Pad 56 to highlight the AERO Model Type
selection option you wish to change, for example, AILE>1.
3) Press the INC+/M1 or DEC-/M2 keys to change the selection option.
When a Model Type selection option is changed, ENTER will ash in
the Programming Window.
IMPORTANT INFORMATION ABOUT THE TRAINER SYSTEM
lThe Trainer System is currently compatible ONLY with another TM-160transmitter or an SD-5G or SD-10G transmitter and
you MUST use the Airtronics 97107 Trainer Cable. See your local Airtronics dealer for more information and availability.
lDuring use, both the Master transmitter and the Slave transmitter should be turned ON. If using an SD-10G transmitter as
the Slave transmitter, to save battery power only the transmitter LCD needs to be turned ON, using the DISPLAY key.
lBoth transmitters must be programmed identically for the Trainer System to function properly. For example, Servo Reversing,
Servo End Point Adjustments, etc. must be identical.
lThe Instructor transmitter Trainer System function must be set to MASTER and the Student transmitter Trainer System
function must be set to SLAVE.
If using the Trainer System with an Airtronics SD-5G transmitter or an SD-10G transmitter, please refer to those transmitter's
Operating Manuals for more information on the correct setup and use of those transmitter's Trainer functions.
Connecting the Master and Slave Transmitters
1) Turn both transmitters OFF.
2) Plug one end of the Airtronics 97107 Trainer Cable (available separately) into the back of one TM-160 transmitter, then
plug the other end of the Trainer Cable into the back of the second TM-160 transmitter or an SD-5G or SD-10G transmitter.
4) Repeat steps 2 and 3 to change the options for any of the other AERO Model Type selection options you wish to change.
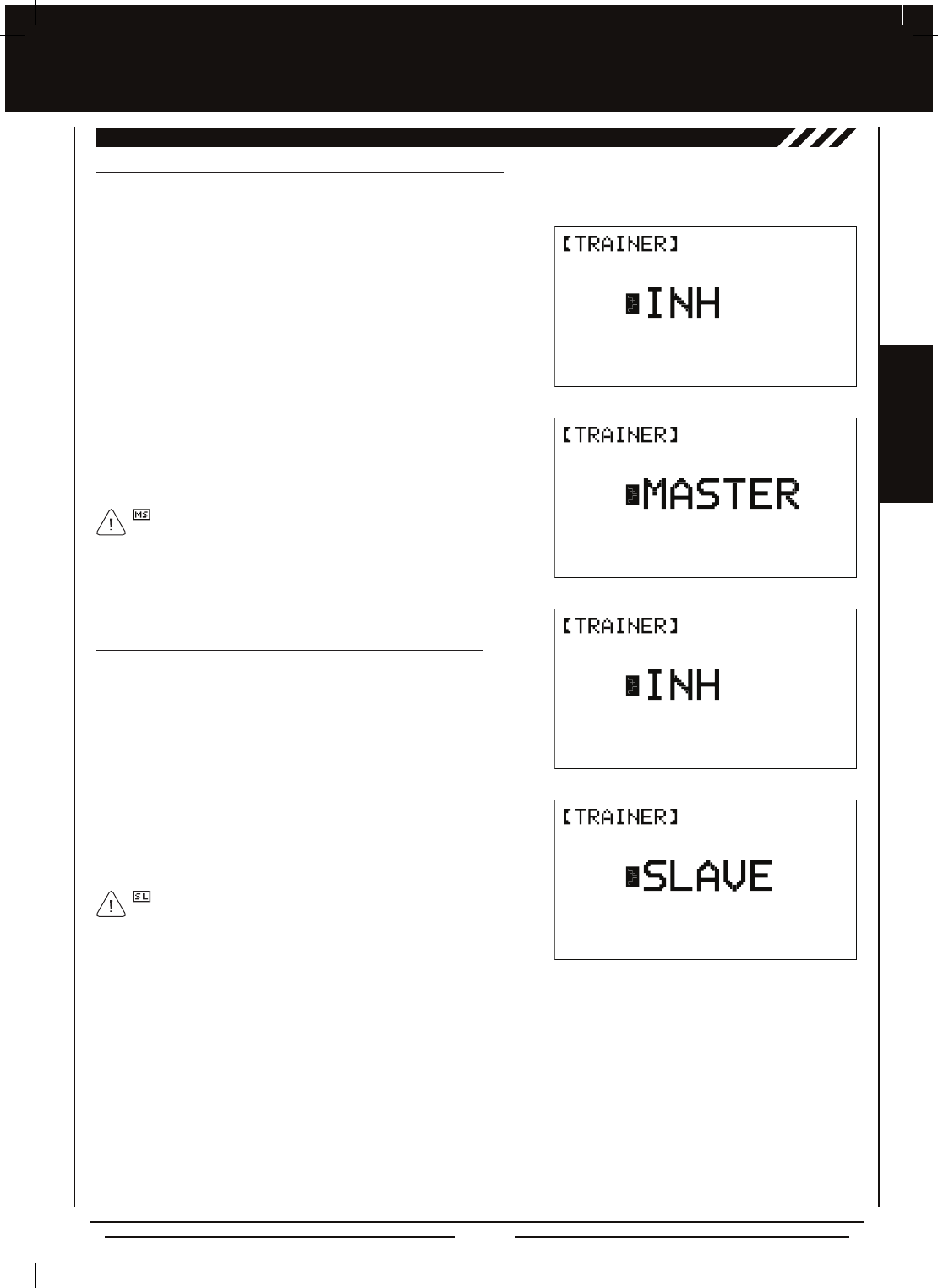
Page 27
aERO MODEL TyPE
04.TRainER (TRainER SySTEM), cOnTinUED....
Activating the Trainer Function - Master (Instructor) Transmitter
1) Turn the Master (Instructor) transmitter ON. From the Display screen, press the ENTER key to display the Programming
Menus.
Activating the Trainer Function - Slave (Student) Transmitter
1) Turn the Slave (Student) transmitter ON. From the Display screen,
press the ENTER key to display the Programming Menus.
2) Press the Navigation Pad 56 to highlight TRAINER, then press the
ENTER key to display the TRAINER menu. The cursor will default to >INH.
Using the Trainer Function
1) The Trainer Cable should be connected between the two transmitters and the Trainer function on both transmitters should
be Activated as described previously. Both the Master (Instructor's) transmitter and the Slave (Student's) transmitter should
be turned ON. If using an SD-10G transmitter as the Slave transmitter, to save battery power only the transmitter LCD
needs to be turned ON, using the DISPLAY key.
2) Turn the receiver ON in the model you're using for training and verify that the Instructor's transmitter controls the model's
control surfaces correctly.
3) Activate the Trainer function by pulling and HOLDING the Trainer switch on the Instructor's transmitter continuously and verify
that the Student's transmitter controls the model's control surfaces correctly.
4) When the Trainer switch is released, the Instructor will have full control over the model. When the Trainer switch is pulled
toward you and held continuously, the Student has control over the model. As soon as the Trainer switch is released, the
Instructor will have full control over the model once again.
2) Press the Navigation Pad 56 to highlight TRAINER, then press the
ENTER key to display the TRAINER menu. The cursor will default to >INH.
3) Press the INC+/M1 key to change the current transmitter's Trainer
mode to MASTER. >MASTER will be displayed.
will be displayed on the Display screen, indicating that the
transmitter is operating in MASTER mode.
will be displayed on the Display screen, indicating that the
transmitter is operating in SLAVE mode.
3) Press the INC+/M1 key to change the current transmitter's Trainer
mode to SLAVE. >SLAVE will be displayed.
AERO MODEL TYPE
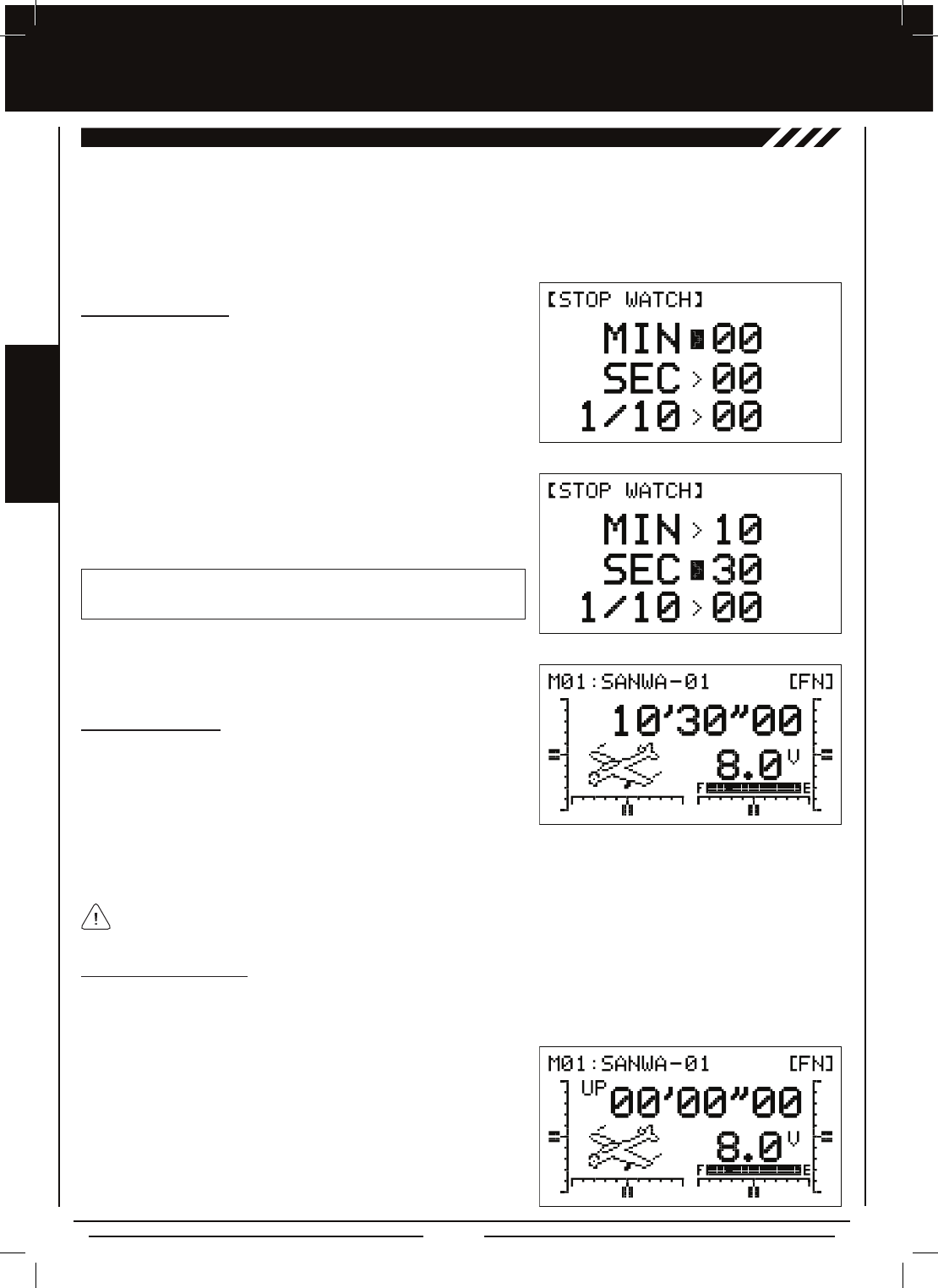
Page 28
aERO MODEL TyPE
05.STOP waTch (STOP waTch anD cOUnT UP TiMER)
The Stop Watch function is used to either count down from a programmed Start time (Count Down mode) or to count up from zero
if no Start time is programmed (Count Up mode). In Count Down mode, an audible tone will sound in 1 second intervals when the
Stop Watch reaches 10 seconds from zero. When zero is reached, a long audible tone will sound and the Stop Watch will begin
to count up. In Count Up mode, an audible tone will sound at 1 minute intervals to remind you that the count down time (zero)
has been surpassed. The Stop Watch function has a number different uses, but one of the more popular uses is to use it as a fuel
usage indicator to remind you to land within an allotted amount of time to ensure that your model doesn't run out of fuel.
Setting the Stop Watch
1) From the Display screen, press the ENTER key to display the Programming
Menus.
2) Press the Navigation Pad 56 to highlight STOP WATCH, then press
the ENTER key to display the STOP WATCH menu. The cursor will
default to MIN>00.
The Stop Watch is displayed in Minutes, Seconds, and 1/10 Seconds. 00' (Minutes) 00" (Seconds) 00 (1/10 Seconds).
Using the Stop Watch
1) Press the END/M3 key two times to return to the Display screen. The
Start time that you programmed will be displayed.
Using the Count Up Timer
The Stop Watch function can also be used as a Count Up timer when the Stop Watch is set to 00'00"00. When the Count Up timer
runs, UP will be displayed on the Display screen and an audible tone will sound at 1 minute intervals.
1) Set the Stop Watch Start time to 00'00"00 as described in the Setting
the Stop Watch section above.
2) To Start the Count Up timer, press the INC+/M1 key. To Stop the Count
Up timer, press the INC+/M1 key a second time. To Reset the Count Up
timer to 00'00"00, press the INC+/M1 and DEC-/M2 keys at the same time.
2) To Start the Stop Watch, press the INC+/M1 key. To Stop the Stop Watch, press the DEC-/M2 key a second time. To Reset
the Stop Watch to the programmed Start time, press the INC+/M1 and DEC-/M2 keys at the same time.
3) The Minute, Second, and 1/10 Second times can be set independently.
Press the Navigation Pad 56 to highlight the time interval you would
like to program, then press the INC+/M1 or DEC-/M2 keys to set the
desired Start time.
MIN setting range is 0 to 59', SEC setting range is 0 to 59" and 1/10
setting range is 0 to 90. The default setting for each is 0.
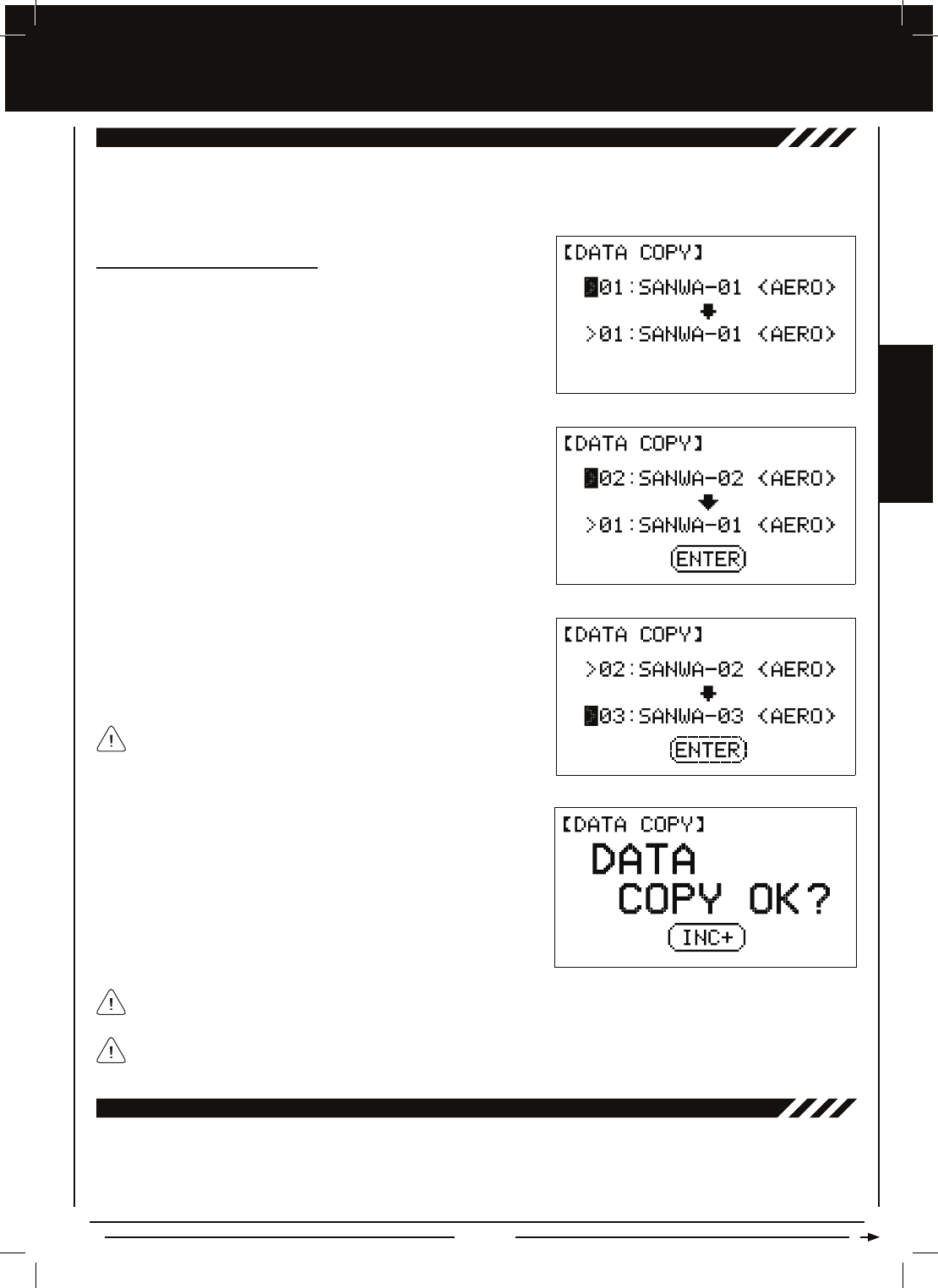
Page 29
aERO MODEL TyPE
06.DaTa cOPy (MODEL PROgRaMMing DaTa cOPy)
The Data Copy function allows you to copy the Programming Data from one model to another model. This is convenient if you
have similar Model Types. For example, if you have two models that are similar, you can copy the Programming Data from the
rst model to the second model to use as a base to start ne-tuning the programming for the second model.
Copying Model Programming Data
1) From the Display screen, press the ENTER key to display the Programming
Menus.
2) Press the Navigation Pad 56 to highlight DATA COPY, then press the
ENTER key to display the DATA COPY menu. The cursor will default to
the currently selected model, for example >01:SANWA-01 <AERO>.
3) With the cursor adjacent to the top model number, press the INC+/M1
or DEC-/M2 keys to select the model you would like to copy Programming
Data FROM. ENTER will ash in the Programming Window.
4) Press the Navigation Pad 6to move the cursor to the bottom model
number, then press the INC+/M1 or DEC-/M2 keys to select the model
you would like to copy Programming Data TO. ENTER will continue to
ash in the Programming Window.
It's not possible to copy Programming Data from one model to the
same model. If you attempt this, ENTER will not be displayed.
5) Press the ENTER key. DATA COPY OK? will be displayed and INC+
will ash in the Programming Window.
6) Press the INC+/M1 key to Copy the model Programming Data. After ~10
seconds, the Programming Data will be copied as indicated by the
progress bar, and COMPLETE!! will be displayed in the Programming
Window. Press any key to return to the DATA COPY menu.
All model-specic Programming Data, including the Model Name will be copied to the selected model.
If you want to go back and change models or you don't want to copy the Programming Data for any reason, press the
DEC-/M2 or END/M3 keys.
07.DaTa RESET (MODEL PROgRaMMing DaTa RESET)
The Data Reset function allows you to Reset model-specic Programming Data for any model back to the factory default settings.
As described previously, individual programming settings can be Reset to the factory default settings by pressing the INC+/M1
and DEC-/M2 keys at the same time, however, this is time consuming if you want to change all of the selected model's programming
settings back to default. Using the Data Reset function makes doing this much quicker and more accurate, since nothing will
be missed.
AERO MODEL TYPE
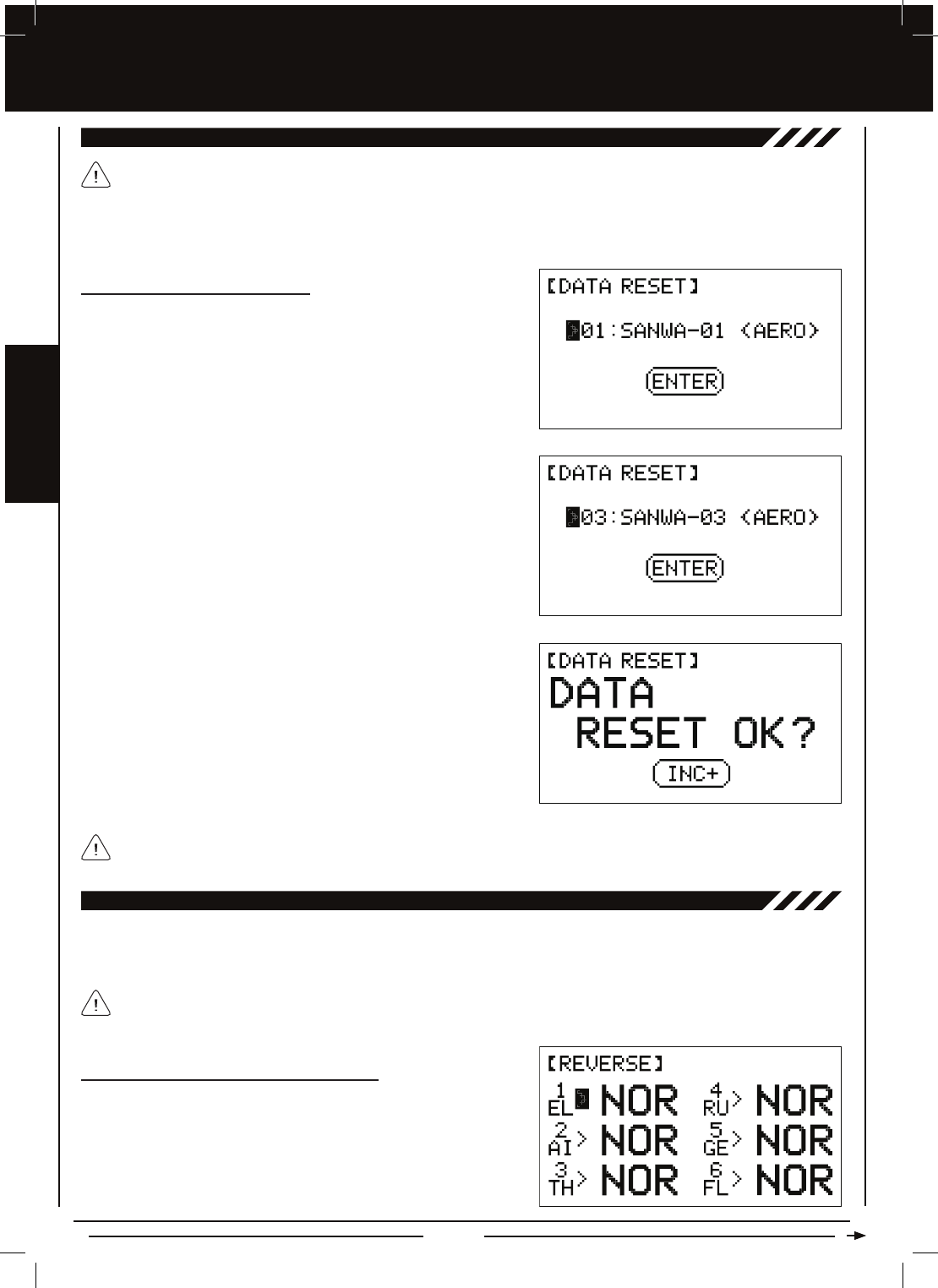
Page 30
07.DaTa RESET (MODEL PROgRaMMing DaTa RESET), cOnTinUED....
Although Model Type selection options are model-specic, the Data Reset function does NOT Reset them. This is useful if
you have two similar models, but different programming needs for each. For example, if you have two similar aircraft that
use the same Model Type selection options (e.g., TAIL>2xEL and AILE>2) but different Programming Data (e.g., Servo Reversing,
End Point Adjustments, etc), you can copy the rst model's Programming Data, using the Data Copy function, then use the Data
Reset function to Reset all of the Programming Data except Model Type selection options. This saves time by not needing to
re-program Model Type selection options.
Resetting Model Programming Data
1) From the Display screen, press the ENTER key to display the Programming
Menus.
2) Press the Navigation Pad 56 to highlight DATA RESET, then press
the ENTER key to display the DATA RESET menu. The cursor will
default to the currently selected model, for example >01:SANWA-01
<AERO> and ENTER will flash in the Programming Window.
3) Press the INC+/M1 or DEC-/M2 keys to select the model you would like
to Reset the Programming Data for. ENTER will continue to ash in the
Programming Window.
4) Press the ENTER key. DATA RESET OK? will be displayed and INC+
will ash.
5) Press the INC+/M1 key to Reset the Programming Data for the selected
model. After ~10 seconds, the Programming Data will be Reset as
indicated by the progress bar, and COMPLETE!! will be displayed in
the Programming Window. Press any key to return to the DATA RESET
menu.
If you want to go back and change the model or you don't want to Reset the Programming Data for any reason, press
the DEC-/M2 or END/M3 keys.
aERO MODEL TyPE
08.REvERSE (SERvO REvERSing)
The Servo Reversing function electronically switches the direction of servo travel. For example, if you pull the elevator control
stick back for Up elevator, but the elevator moves Down, you can use the Servo Reversing function to switch the direction of
servo travel to make the elevator move Up.
Changing Servo Reversing Adjustment Values
1) From the Display screen, press the ENTER key to display the Programming
Menus.
2) Press the Navigation Pad 56 to highlight REVERSE, then press the
ENTER key to display the REVERSE menu. The cursor will default
to 1EL>NOR.
The channel numbers will differ based on the Model Type selection options you chose previously in the TYPE menu.
For example, if you chose AILE>2, channel 2 will be displayed as LA (Left Aileron) and channel 5 will be displayed as
RA (Right Aileron).
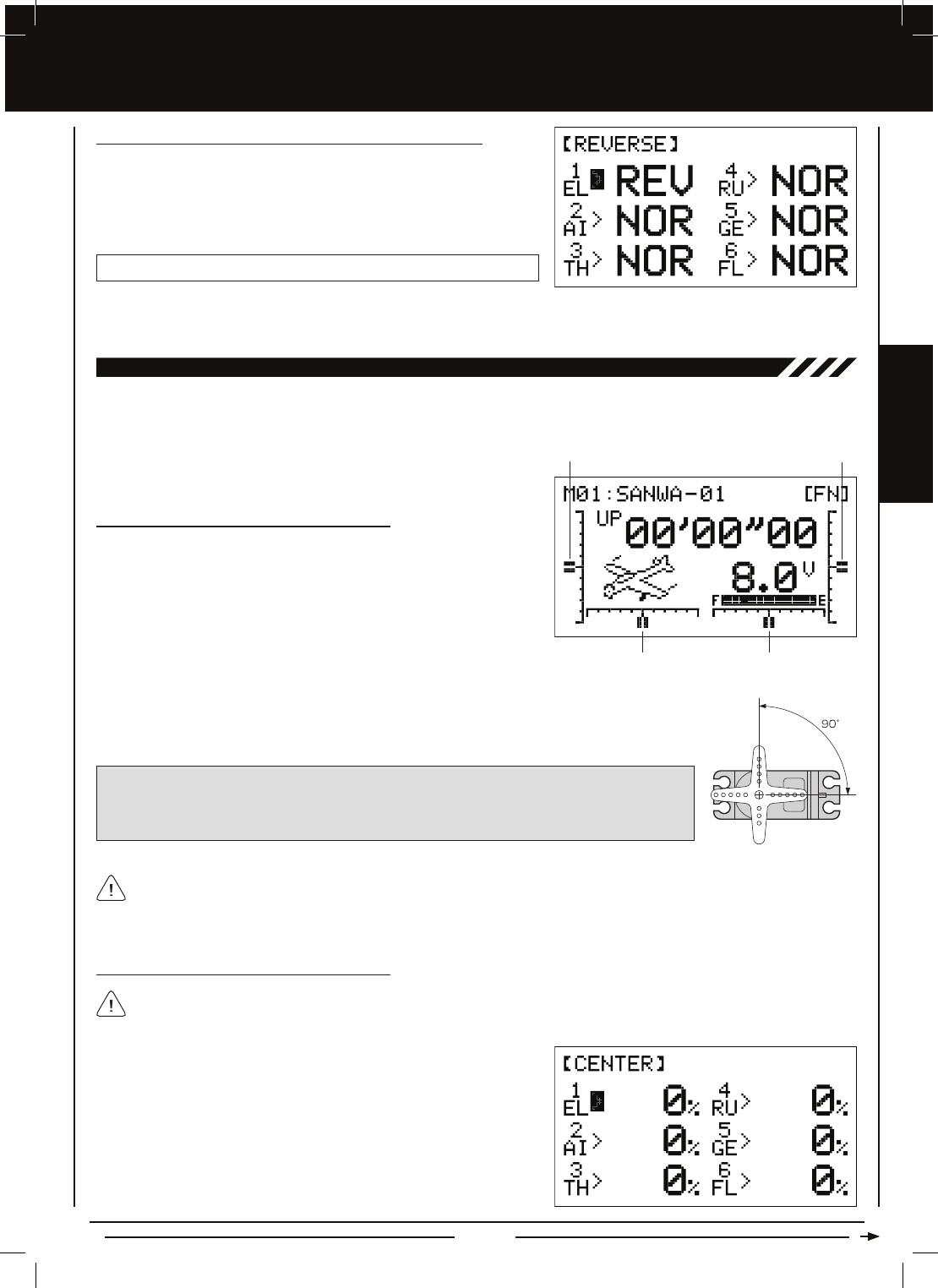
Page 31
aERO MODEL TyPE
Changing Servo Reversing Adjustment Values, Continued....
3) Press the Navigation Pad 5634 to highlight the channel that you
would like to change the Servo Reversing adjustment value for.
4) Press the INC+/M1 or DEC-/M2 keys to change the REV adjustment
value to set the desired direction of servo travel.
REVERSE setting range is NOR/REV. The default setting is NOR.
5) Repeat steps 3 and 4 to set the desired direction of servo travel for the desired remaining channels.
09.cEnTER (SERvO cEnTERing SUB-TRiM)
The Servo Centering function allows you to ne-tune the Center (Neutral) position of each servo. It's not unusual that when you
install the servo horn onto your servo that the servo horn is not perfectly centered. The Servo Centering function allows you to center
the servo horn perfectly.
1) From the Display screen, press the ENTER key to display the Programming
Menus.
2) Press the Navigation Pad 56 to highlight CENTER, then press the
ENTER key to display the CENTER menu. The cursor will default
to 1EL>0%.
The channel numbers will differ based on the Model Type selection options you chose previously in the TYPE menu.
For example, if you chose AILE>2, channel 2 will be displayed as LA (Left Aileron) and channel 5 will be displayed as
RA (Right Aileron).
Centering the Trim Switches and Servo Horns
1) Before changing the Servo Centering percentage values you must rst
adjust each of the four trim switches so that the control surface trims
are centered as displayed on the Display screen. In addition, an audible
double-tone is heard when the trim switches reach the center position.
The TM-160 transmitter features Digital Trim Memory. Any amount of trim that you set during fight using the trim
switches is automatically stored in memory for that specic channel and model, and for that specic Flight Mode (if
Enabled). The Trim percentage values for each model will automatically be loaded when the transmitter is turned ON and your
model is selected. For more information, see page 36.
2) Install the servo horn onto the servo, making sure that the servo horn is as close to being centered
as possible. In some cases you can get the servo arm closer to being centered by rotating the
servo arm 180º and reinstalling it.
IMPORTANT It is always recommended to install the servo horns as close to being centered
as possible, prior to changing the Servo Centering percentage values. After you change the Servo
Centering percentage values to center the servo horns, only then should you manually adjust the
control linkages to center the control surfaces.
TH Trim
RU Trim
EL Trim
AI Trim
Changing Servo Centering Percentage Values
AERO MODEL TYPE
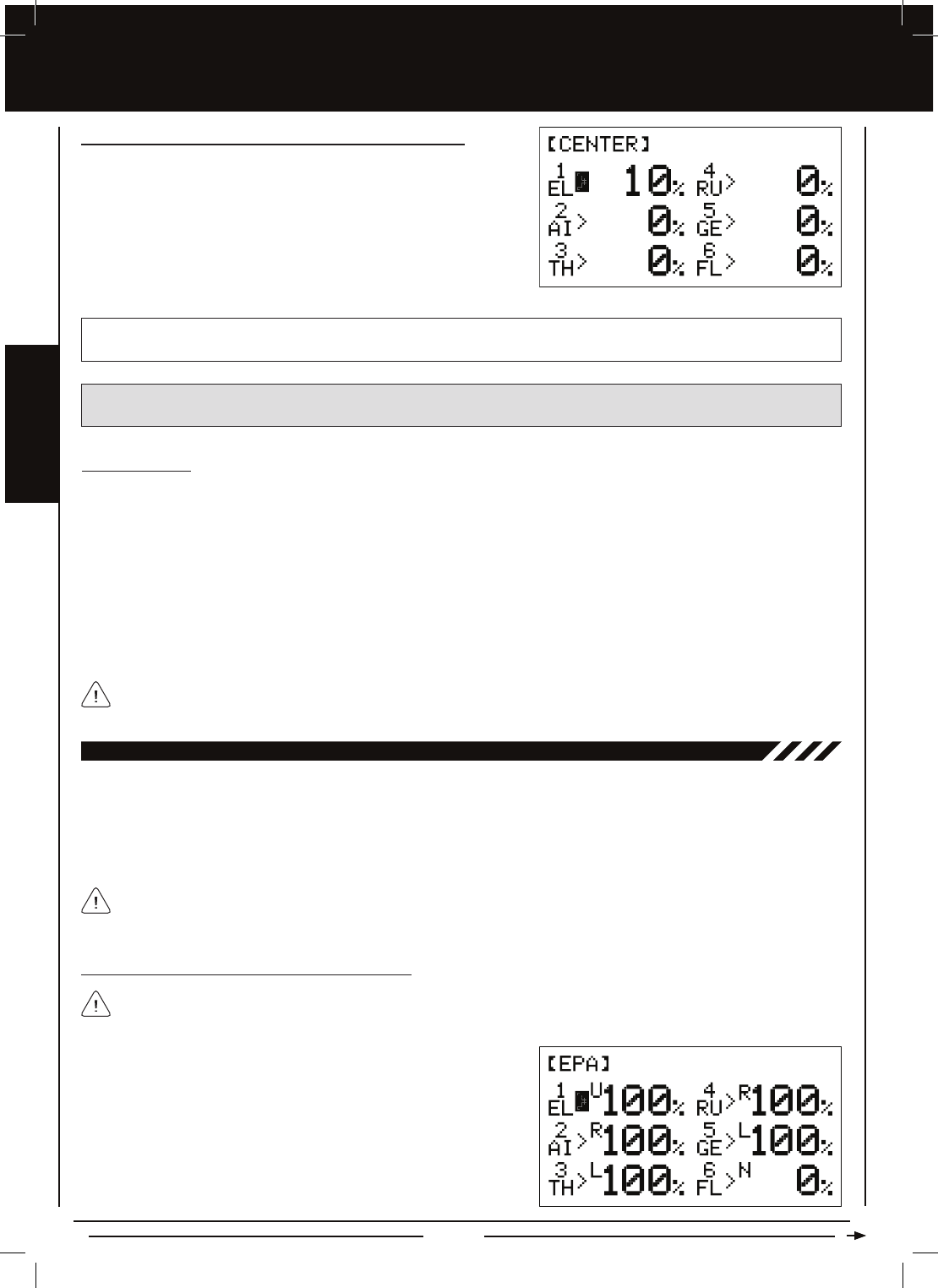
Page 32
aERO MODEL TyPE
Changing Servo Centering Percentage Values, Continued....
3) Press the Navigation Pad 5634 to highlight the channel that you
would like to change the Servo Centering percentage value for.
4) Press the INC+/M1 or DEC-/M2 keys to change the Servo Centering
percentage value to center the servo horn.
5) Repeat steps 3 and 4 to center the servo horns for the desired remaining
channels.
CENTER setting range is -150% to 150%. The default setting is 0%. Increase or decrease the Servo Centering percentage
values to center the servo horns.
WARNING We don't recommend using a Servo Centering percentage value outside the range of approximately -40% to
40%. Using a percentage value outside of this range can result in limited maximum servo travel.
Zeroing Out Trim
Although trim switch settings are automatically stored in memory for each individual model, some users may wish to always keep
their trim switch settings at zero (centered) for all models. For example, after test-ying your model, if you have had to add trim to
make your model y straight and level, you can use the Servo Centering function to add that amount of trim back into the servo(s),
then move the trim switches back to center. This ensures that your trim switches are always centered.
1) After ying your model, check your model's control surfaces to see how much trim was necessary to achieve straight and level ight.
2) From within the CENTER menu, highlight the channel you need to add Centering trim to.
3) Recenter the trim switch, then change the Servo Centering percentage value until the control surface is in the same position
it was prior to recentering the trim switch. Double-check the control throws to ensure the End Points haven't changed.
In the default conguration, the same trim settings are stored across all Flight Modes. This option can be changed to
allow you to store different trim settings for each individual Flight Mode. For more information, see page 36.
10.EPa (EnD POinT aDjUSTMEnT)
The End Point Adjustment function allows you to adjust servo travel in each direction. This makes it possible to balance control
surface throw in both directions and set the maximum desired control throw. For example, if you want your elevator to move Up
and Down two inches in each direction, but the elevator moves Down more than two inches, decrease the End Point Adjustment
in the Down direction, so that the elevator moves Up and Down the same amount. Another example is with ailerons. If your
aircraft rolls faster to the right than to the left, increase the End Point Adjustment in the Left direction until the aircraft rolls the
same speed in both directions.
The End Point Adjustment function is designed to balance the control throw on both sides of servo travel and can be
overridden by other settings, such as Dual Rate. For example, if you have your End Point Adjustment percentage value set
to 100%, and you set your Dual Rate percentage value to 150%, the servo will travel more than 100% when Dual Rate is ON.
1) From the Display screen, press the ENTER key to display the Programming
Menus.
2) Press the Navigation Pad 56 to highlight EPA, then press the ENTER
key to display the EPA menu. The cursor will default to 1EL>U100% or
1EL>D100% depending on the last position of the elevator control stick.
The channel numbers will differ based on the Model Type selection options you chose previously in the TYPE menu.
For example, if you chose AILE>2, channel 2 will be displayed as LA (Left Aileron) and channel 5 will be displayed as
RA (Right Aileron).
Changing End Point Adjustment Percentage Values
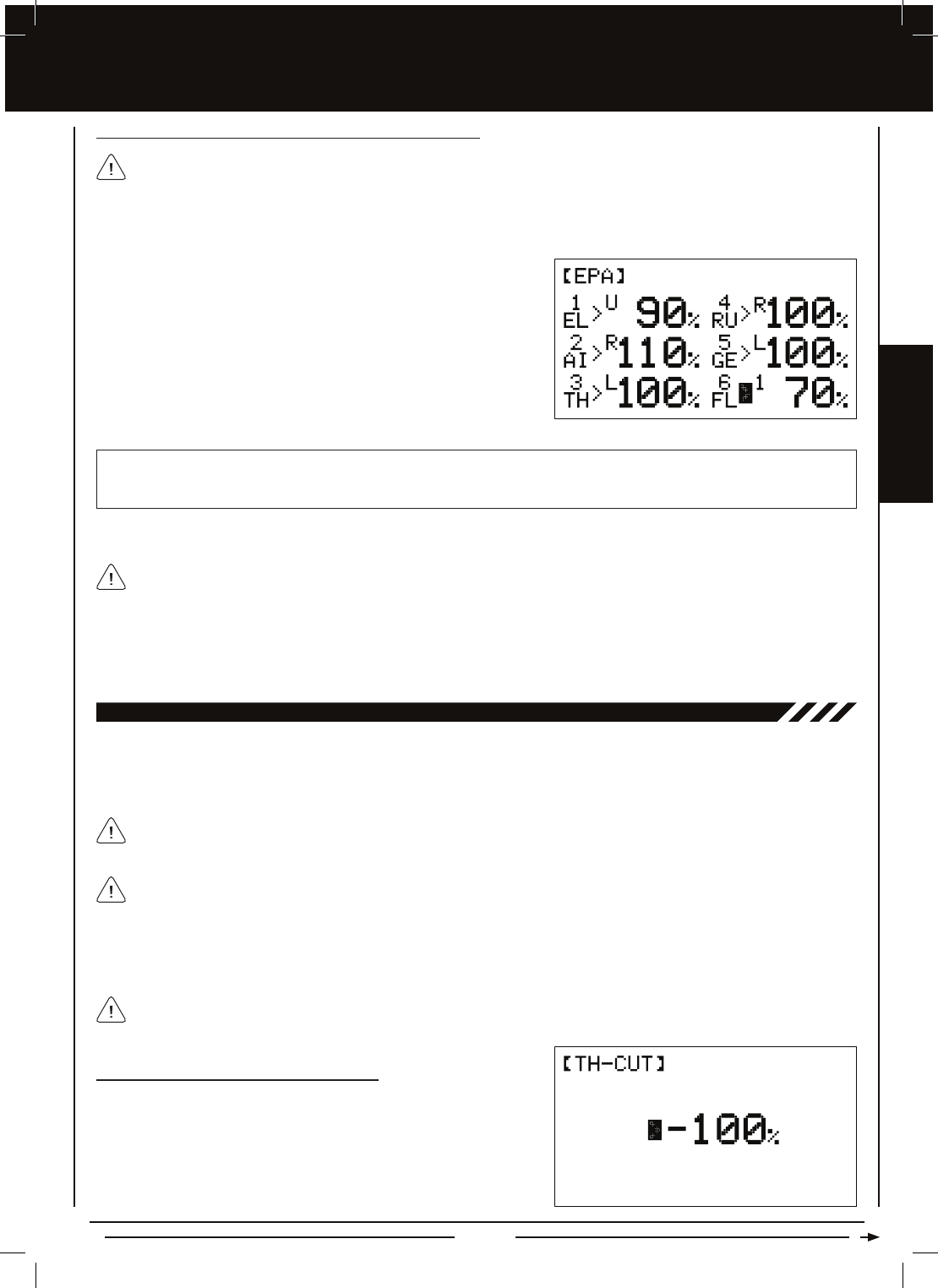
Page 33
aERO MODEL TyPE
Changing Servo End Point Percentage Values, Continued....
In front of each End Point Adjustment percentage value is a specic icon. To set the End Point Adjustment percentage
value for the desired direction of servo travel, the control stick or switch must be moved in the direction of servo travel you
want to change the End Point Adjustment percentage value for. For example, if you want to change the End Point Adjustment
percentage value for Down elevator, push the elevator control stick forward, then release it. 'D' will be displayed in front of the
Elevator End Point Adjustment percentage value.
3) Press the Navigation Pad 5634 to highlight the channel that you
would like to change the End Point Adjustment percentage value for.
4) Press the INC+/M1 or DEC-/M2 keys to change the End Point Adjust-
ment percentage value.
EPA setting range for the primary ight controls is 0% to 150%. The default setting is 100%. EPA setting range for Flaps is
-150% to 150%. Increasing the End Point Adjustment percentage value increases servo travel and decreasing the End Point
Adjustment percentage value decreases servo travel.
Although the End Point Adjustment function is used to balance and adjust maximum control surface deection, we suggest
adjusting the control linkages rst to try to achieve as close to the desired control surface deection as possible, then use
the End Point Adjustment function to make nal adjustments.
To increase control surface deection, you can either move the pushrod further out on the servo arm or move the pushrod closer
to the control surface. To decrease control surface deection, you can either move the pushrod closer to the center of the servo
arm or move the pushrod further away from the control surface.
11.Th-cUT (ThROTTLE cUT)
The Throttle Cut function allows you to set a specic position that the throttle servo will move to when you press the Throttle Cut
button. The Throttle Cut function is primarily used to shut down your engine after ight. You are able to adjust the Throttle
Cut percentage value to ensure that when you press the Throttle Cut button to shut down your engine, the carburetor will close
completely, yet not bind.
Changing the Throttle Cut Percentage Value
1) From the Display screen, press the ENTER key to display the Programming
Menus.
2) Press the Navigation Pad 56 to highlight TH-CUT, then press the
ENTER key to display the TH-CUT menu. The cursor will default to
>-100%.
Before using the Throttle Cut function, make sure that the idle stop screw on your carburetor (if featured) is adjusted to
allow the carburetor barrel to close completely.
When the Throttle Cut function is Activated, throttle control will be disabled.
There are several different methods that can be used to set up your throttle control linkage and the Throttle Cut function. To
prevent any chance of causing your throttle control linkage to bind, possibly resulting in damage to your throttle servo when
you use the Throttle Cut function, we rst suggest adjusting the Throttle Low End Point Adjustment percentage value so that
when the throttle control stick is pulled all the way back the carburetor barrel closes completely without binding. Next, increase
the throttle trim (using the throttle trim switch) to adjust your engine's idle. Now change the Throttle Cut percentage value to close
the carburetor barrel without binding when you press the Throttle Cut button.
5) Repeat steps 3 and 4 to change the End Point Adjustment percentage values for the desired remaining channels.
AERO MODEL TYPE
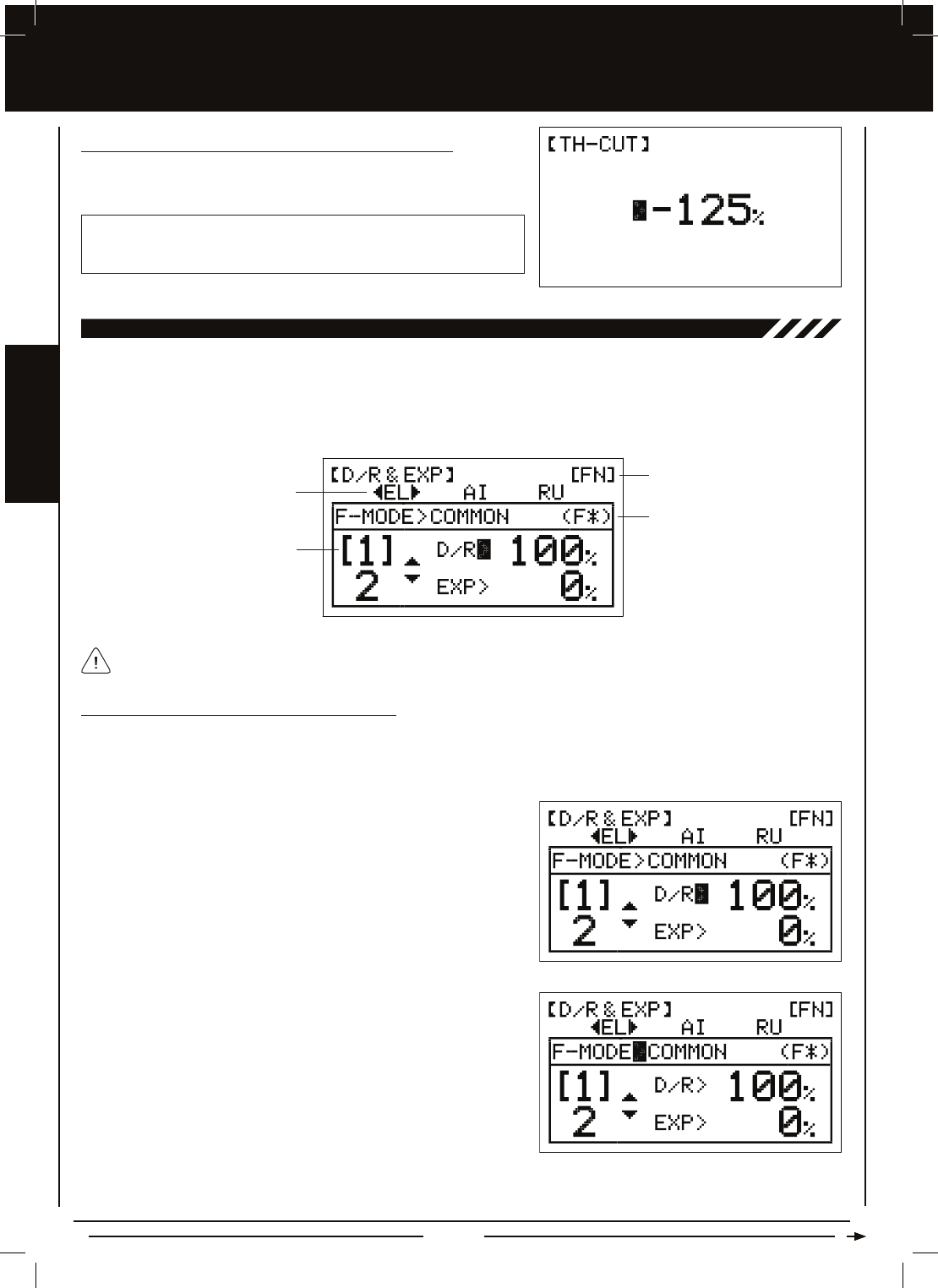
Page 34
aERO MODEL TyPE
TH-CUT setting range is -150% to 0%. The default setting is -100%.
Decreasing the Throttle Cut percentage value will increase throttle servo
travel when the Throttle Cut button is pressed.
Changing the Throttle Cut Percentage Value, Continued....
3) Press the INC+/M1 or DEC-/M2 keys to set the position you would like
the throttle servo to move to when you press the Throttle Cut button.
12.D/R & EXP (DUaL RaTE anD EXPOnEnTiaL)
The TM-160 transmitter features one Dual Rate switch that controls Dual Rate for the elevator, aileron, and rudder channels
at the same time. In addition, the Dual Rate percentage value for each channel can be programmed independently. The
Exponential function is linked directly to the Dual Rate switch, allowing you to program Exponential for each of the two Dual Rate
positions separately. For greater exibility, both Dual Rate and Exponential can be programmed either the same for all Flight
Modes or separately for each of the three Flight Modes.
Current Channel
Dual Rate Switch Position
Transmitter F-MODE
Programming F-MODE
Transmitter F-MODE refers to the Flight Mode that the transmitter is currently operating in. Programming F-MODE refers
to the Flight Mode that you would like to change the programming for.
Choosing the Flight Mode - Common or Separate
When set to COMMON, the Dual Rate and Exponential percentage values you program will be the same regardless of which
Flight Mode the transmitter is operating in. You cannot program Dual Rate and Exponential percentage values separately for
each Flight Mode. When set to SEPARATE, you can program Dual Rate and Exponential percentage values separately for each
Flight Mode. This allows for greater exibility.
1) From the Display screen, press the ENTER key to display the Programming
Menus.
2) Press the Navigation Pad 56 to highlight D/R & EXP, then press the
ENTER key to display the D/R & EXP menu. The cursor will default to
D/R>100%.
3) Press the Navigation Pad 5to move the cursor to F-MODE>COMMON.
4) Press the INC+/M1 or DEC-/M2 keys to choose either SEPARATE OR
COMMON.
5) If you choose SEPARATE, press the F-MODE key to choose the F-MODE number you would like to program the Dual Rate
and Exponential functions for. Choose from FN, F1 or F2.
(Typically 1=Maximum Control Throw
and 2=Reduced Control Throw)
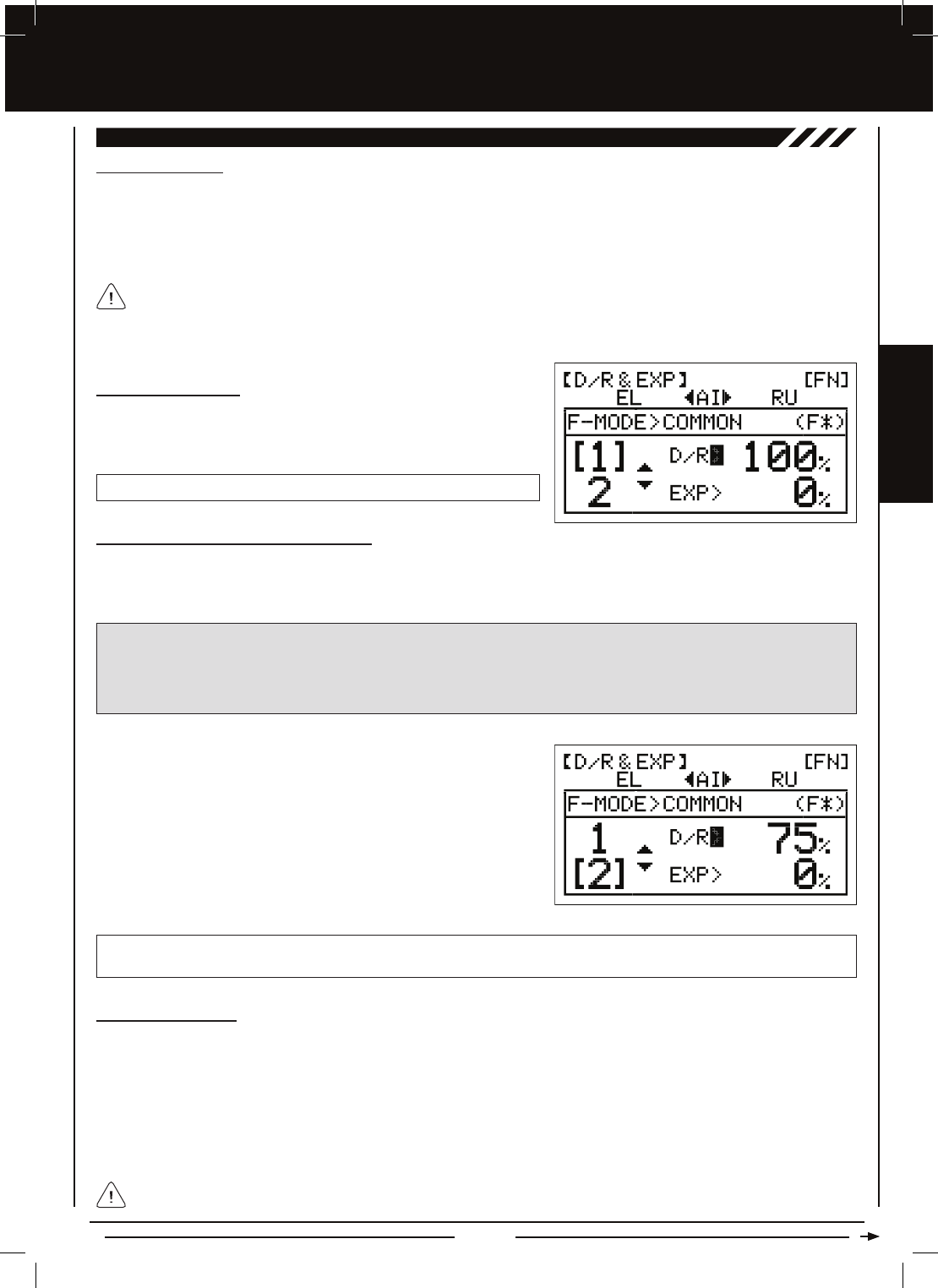
Page 35
aERO MODEL TyPE
Dual Rate is a percentage of End Point Adjustment. For example, if you set the Dual Rate 1 percentage value to 100%,
the control surfaces will travel the same amount as dened by your End Point Adjustment programming, and if you set the
Dual Rate 2 percentage value to 50%, the control surfaces will travel half that amount when Dual Rate 2 is Activated. Prior to
takeoff, check the position of the Dual Rate switch to ensure that it is in the position you want.
Dual Rate Overview
The Dual Rate function allows you to change the control authority of the control surfaces by changing the amount of servo travel.
For example, if you are ying an aerobatic aircraft that requires a lot of control throw for aerobatics, but that same amount of control
throw makes the aircraft difcult to control during normal ight, you can use the Dual Rate function to lower the control throw for
normal ight with just the ip of the Dual Rate switch. Two Dual Rate settings are available for the Elevator, Aileron, and Rudder
channels, and different Dual Rate settings can be programmed separately for each of the three Flight Modes.
Changing the Dual Rate Percentage Values
Two different Dual Rate settings can be programmed to the Dual Rate switch. We recommend that Dual Rate 1 be set to the
maximum control surface throw you desire, then set Dual Rate 2 to a different value that is less than maximum. For example,
set the Dual Rate 1 percentage value to 100% and the Dual Rate 2 percentage value to 75%.
WARNING Keep in mind that it's possible to set the Dual Rate percentage value higher than the End Point Adjustment
percentage value. For example, with the End Point Adjustment percentage value set to 100% and the Dual Rate percentage
value set to 150% the servo will move more than 100% when Dual Rate is turned ON. We strongly recommend that you set
the Dual Rate 1 percentage value to no more than 100%. This will prevent any chance of exceeding your End Point Adjustment
and overdriving your control linkage.
Choosing the Channel
1) Press the Navigation Pad 34 to highlight the channel you would like
to make Dual Rate percentage value changes to. Choose either <EL>,
<AI>, or <RU>.
Dual Rate can be set for EL (Elevator), AI (Aileron), and RU (Rudder).
D/R setting range is 0% to 150%. The default setting is 100%. Increasing the Dual Rate percentage value increases servo
travel and decreasing the Dual Rate percentage value decreases servo travel.
1) Move the Dual Rate switch to the position you would like to set a Dual
Rate percentage value for, either 1 or 2.
2) Press the INC+/M1 or DEC-/M2 keys to set the desired Dual Rate
percentage value for the channel you chose previously.
Exponential Overview
The Exponential function allows you to vary the amount of servo travel in relation to the movement of the elevator, aileron, and
rudder control sticks near the neutral positions to change the way the control surfaces react to control stick movement. Increasing
the Exponential value will soften the control feel around neutral and decreasing the Exponential value will heighten the control
feel around neutral. For example, using a positive Exponential percentage value allows for smoother control by lessening the
amount of servo travel in relation to the amount of control stick movement. Using a negative Exponential percentage value may
result in more 'twitchy' control response because the amount of servo travel will be increased in relation to the amount of control
stick movement. The Exponential function is linked directly to the Dual Rate switch. This allows you to program Exponential for
each of the two Dual Rate positions separately.
Exponential does not change the total amount of servo travel at maximum control stick deection. Exponential affects
the ratio between servo travel and control stick movement at less than maximum control stick deection.
12.D/R & EXP (DUaL RaTE anD EXPOnEnTiaL), cOnTinUED....
AERO MODEL TYPE
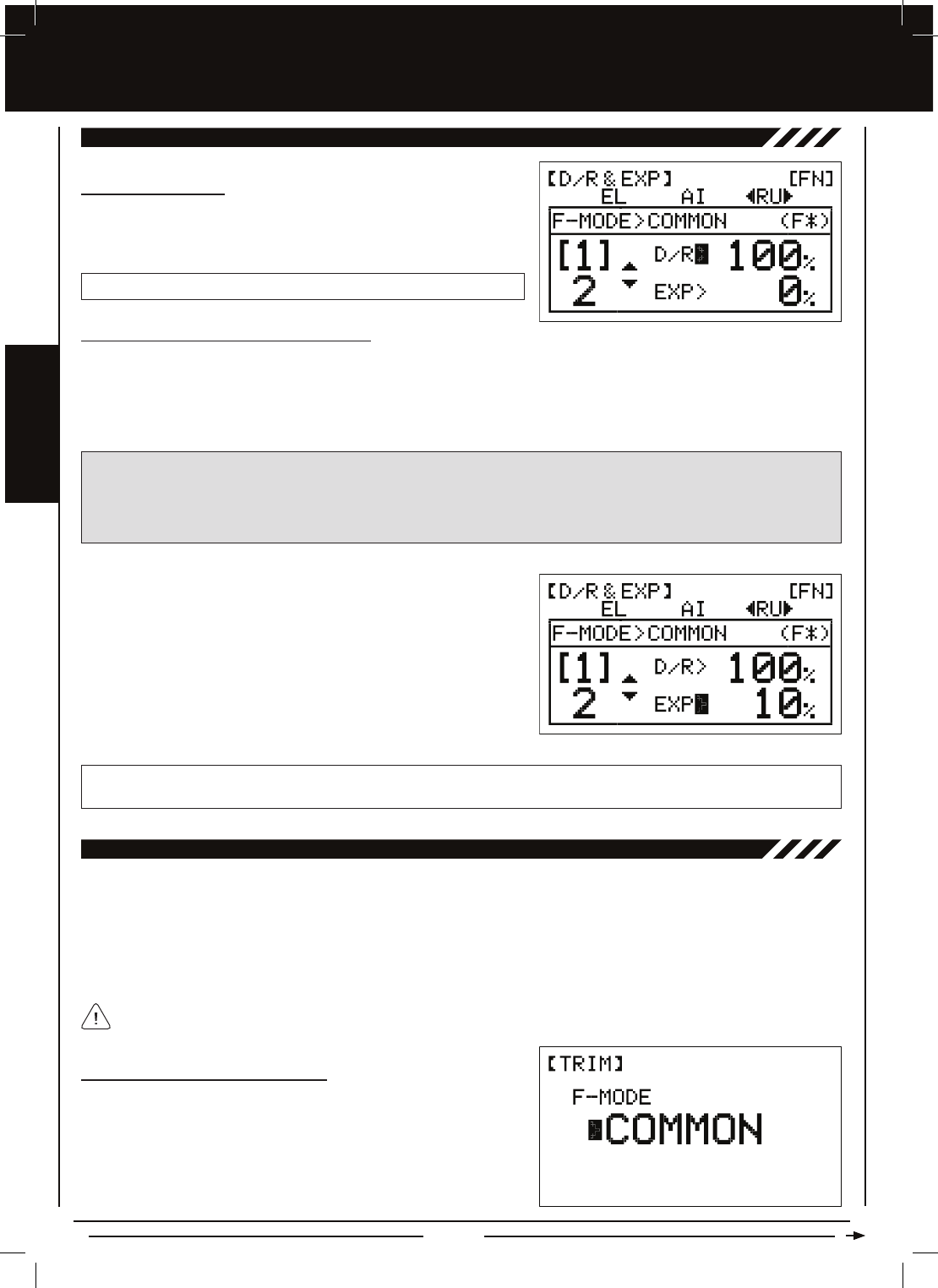
Page 36
aERO MODEL TyPE
Choosing the Channel
1) Press the Navigation Pad 34 to highlight the channel you would like to
make Exponential percentage value changes to. Choose either <EL>,
<AI>, or <RU>.
Exponential can be set for EL (Elevator), AI (Aileron), and RU (Rudder).
Changing the Exponential Percentage Values
The Exponential function is linked directly to the Dual Rate switch. This allows you to program Exponential for each of the two
Dual Rate positions separately. For example, with the Dual Rate switch in position 1 (maximum travel), you can set the Exponential
percentage value to 30% to soften the control feel around neutral and with the Dual Rate switch in position 2 (reduced travel) you
can set Exponential percentage value to 0%. When the Exponential percentage value is set to 0%, the ratio between servo travel
and control stick movement will be Linear throughout the entire range of deection.
WARNING If you have not used Exponential functions in the past, we suggest that you start with a small percentage
of Exponential (approximately 10%~20%) until you get used to the feel of how Exponential affects the control feel of
your model. You will find that Exponential is most useful where strong control response is desired at extreme control
stick positions, but softer control response to small control stick movements is desired in order to make very accurate
small corrections to the flight path.
1) Press the Navigation Pad 6 to move the cursor to EXP>0%.
2) Move the Dual Rate switch to the position you would like to set an
Exponential percentage value for, either 1 or 2.
3) Press the INC+/M1 or DEC-/M2 keys to set the desired Exponential
percentage value for the channel you chose previously.
EXP setting range is -100% to 100%. The default setting is 0% (Linear). Increasing the Exponential percentage value softens
the control feel around neutral. Decreasing the Exponential percentage value heightens the control feel around neutral.
13.TRiM (DigiTaL TRiM)
The TM-160 transmitter features Digital Trim Memory. Any amount of control surface trim that you set during fight using the trim
switches is automatically stored in memory for that specic channel and for that specic model. The Digital Trim values for each
model will automatically be loaded when the transmitter is turned ON. The Trim function allows you to choose whether you want
trim changes saved the same across all three Flight Modes or if you want trim changes saved separately for each of the three
Flight Modes. In addition, an option to lock the throttle trim in Flight Mode F1 is also available. This feature is convenient when
ying aerobatics with a custom Throttle Curve in Flight Mode F1, because if accidentally hit, the throttle trim could change your
Throttle Curve and cause unintended consequences.
An audible double-tone is heard when the trim switches reach the center position. This allows you to know when the trim
switches reach the center position without the need to look at the Trim Indicators on the Display screen.
Choosing the Trim Flight Mode Option
1) From the Display screen, press the ENTER key to display the Programming
Menus.
2) Press the Navigation Pad 56 to highlight TRIM, then press the
ENTER key to display the TRIM menu. The cursor will default to
F-MODE>COMMON.
12.D/R & EXP (DUaL RaTE anD EXPOnEnTiaL), cOnTinUED....
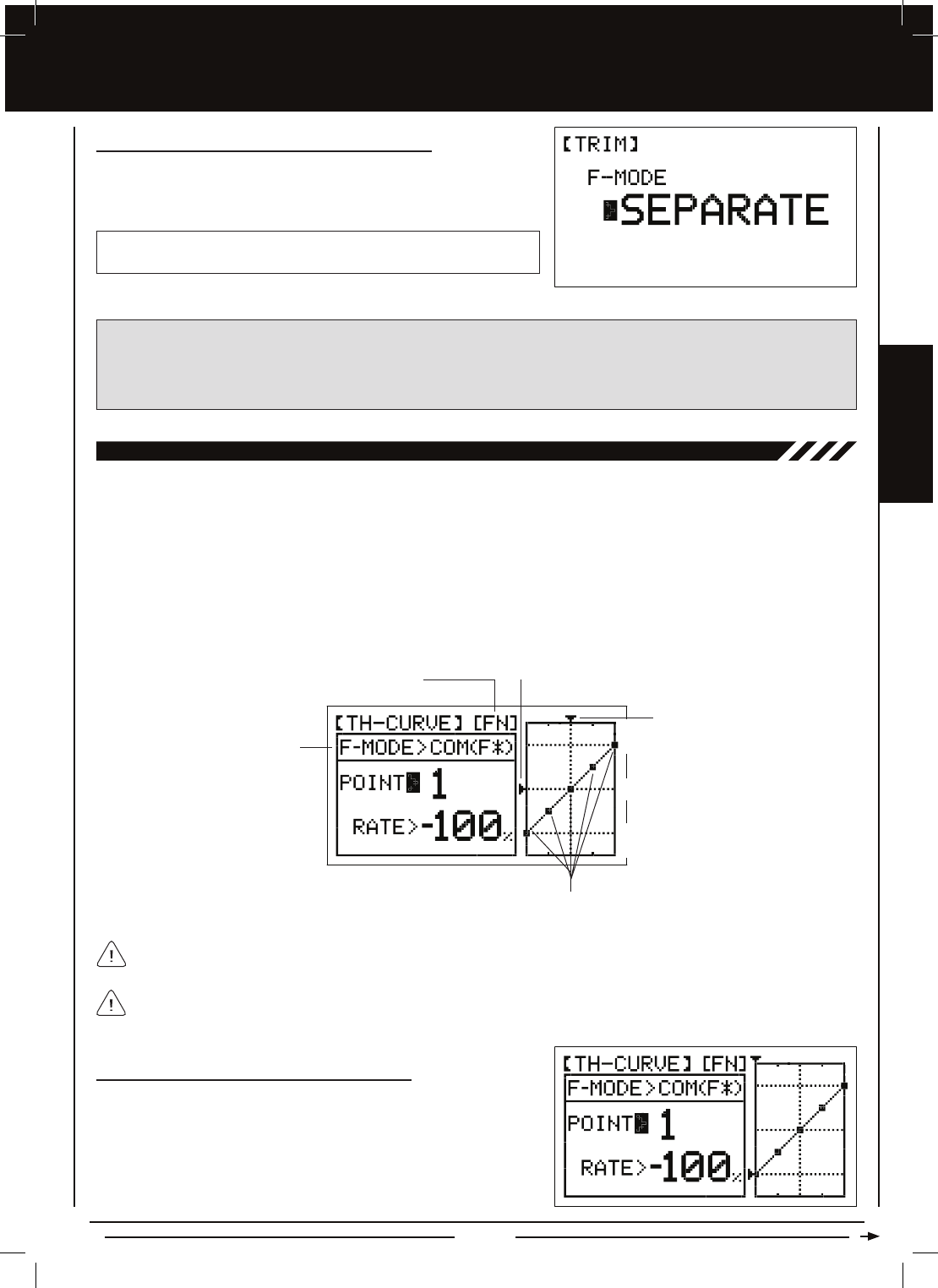
Page 37
aERO MODEL TyPE
WARNING When the Trim Flight Mode option is set to Separate or SEPARATE TH-TRIM LOCK (F1), Digital Trim values are
stored in the specic Flight Mode you're using when you change the trim using the trim switches. For example, you could have
10 'clicks' of Up elevator trim in Flight Mode FN (Normal) and 5 'clicks' of Up elevator trim in Flight Mode F1. Be cautious of
this when switching between Flight Modes during ight. In addition, if SEPARATE TH-TRIM LOCK (F1) is chosen, throttle
trim will NOT be adjustable when in Flight Mode F1.
Choosing the Trim Flight Mode Option, Continued....
3) Press the INC+/M1 or DEC-/M2 keys to choose the desired Trim Flight
Mode option, either COMMON, SEPARATE or SEPARATE TH-TRIM
LOCK (F1).
TRIM setting range is COMMON, SEPARATE, or SEPARATE TH-TRIM
LOCK (F1). The default setting is COMMON.
14.Th-cURvE (ThROTTLE cURvE)
The Throttle Curve function allows you to vary the amount of throttle servo travel in relation to the movement of the throttle control
stick at different points throughout the entire range of deection. Five custom-programmable Points ensure a precise Throttle
Curve to suit any situation. For example, many glow and gas engines are very non-Linear, meaning that when the throttle control
stick is at half, the engine is not at half power. In addition, many times the difference between three-quarter power and full power
is almost indistinguishable. Using the Throttle Curve function, you can change the way the engine reacts to power based on
the position of the throttle control stick. For example, you can change the Throttle Curve so that three-quarter stick feels like
three-quarter throttle.
For greater exibility, the Throttle Curve function can be programmed either the same for all Flight Modes or separately for each
of the three Flight Modes. A graph with Input and Output indicators help with programming visualization.
Transmitter F-MODE refers to the Flight Mode that the transmitter is currently operating in. Programming F-MODE refers
to the Flight Mode that you would like to change the programming for.
Transmitter F-MODE
Programming F-MODE
Stick Input
Function Output
150%
100%
100%
150%
0%
Point Positions
As you change the Point values and Rate percentage values, you can use the graph and Input and Output indicators to
visualize the ratio between control stick movement and servo travel throughout the entire deection range.
Choosing the Flight Mode - Common or Separate
1) From the Display screen, press the ENTER key to display the Programming
Menus.
2) Press the Navigation Pad 56 to highlight TH-CURVE, then press
the ENTER key to display the TH-CURVE menu. The cursor will
default to POINT>1.
AERO MODEL TYPE
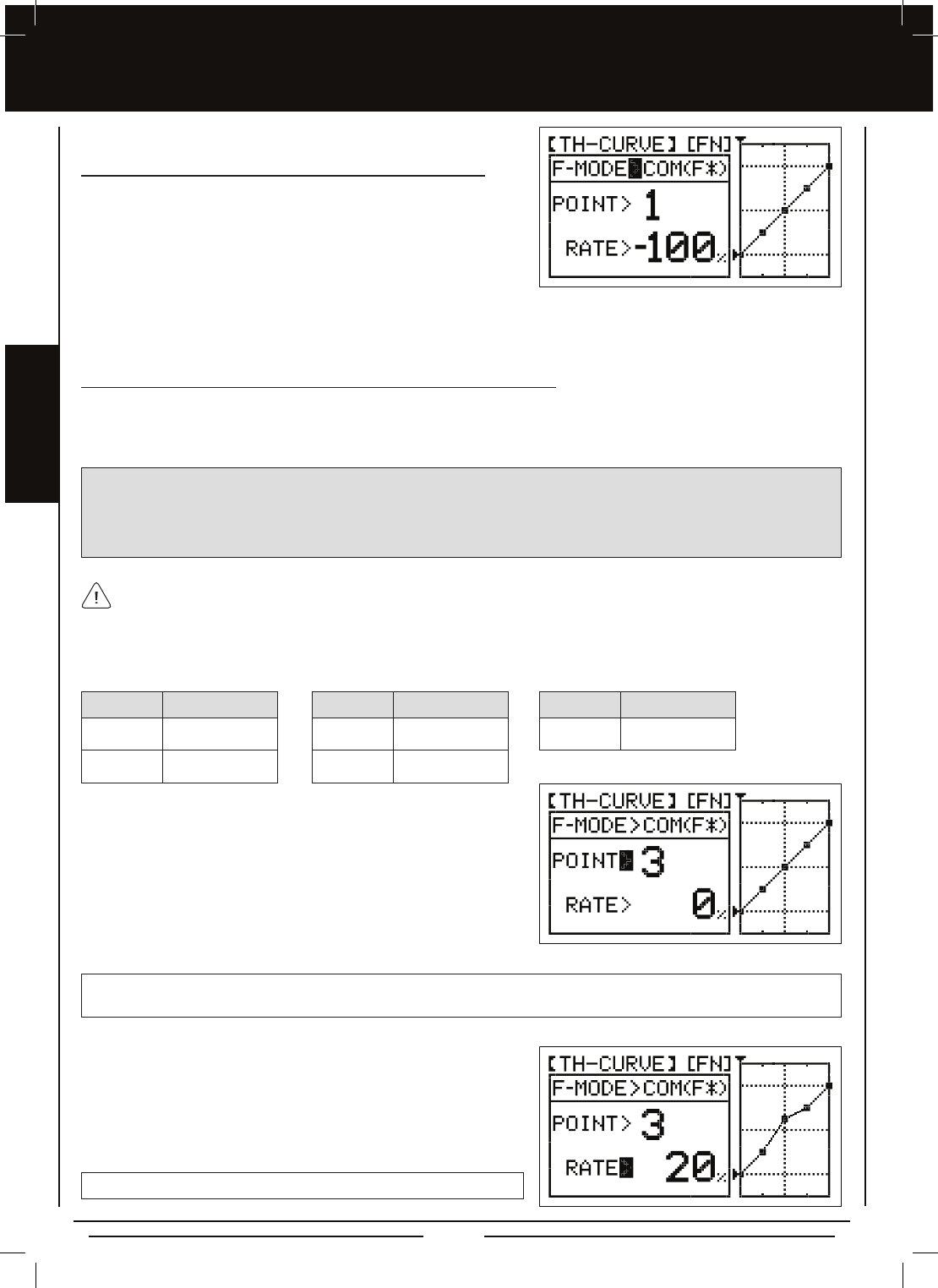
Page 38
aERO MODEL TyPE
Choosing the Flight Mode - Common or Separate, Continued....
3) Press the Navigation Pad 5 to move the cursor to F-MODE>COM.
4) Press the INC+/M1 or DEC-/M2 keys to choose either SEP OR COM
(SEParate or COMmon).
5) If you choose SEPARATE, press the F-MODE key to choose the F-MODE number you would like to program the Throttle
Curve function for. Choose from FN, F1 or F2.
Changing the Throttle Curve Point Values and the Rate Percentage Values
Five different Points with varying Rate percentage values can be programmed onto the Throttle Curve. Each Point will be displayed
on the graph to give you a visual interpretation of the position of the Point on the Throttle Curve. The Point that is currently selected
will ash.
WARNING Keep in mind that it's possible to set the Rate percentage values higher or lower than the throttle End
Point Adjustment percentage values. For example, with the throttle High End Point Adjustment percentage value set to 100%
and POINT>5 Rate percentage value set to 150% the servo will move 150%. We strongly recommend that you set the Throttle
Curve Point Rate percentage values no higher than your throttle End Point Adjustment percentage values unless specically
necessary for your particular setup. This will prevent any chance of overdriving your control linkage.
1) Press the Navigation Pad 6 to highlight POINT>1.
2) Press the INC+/M1 or DEC-/M2 keys to choose which Point you would
like to set a Rate percentage value for.
POINT setting range is 1 through 5. Point 1 is at the low end of the Throttle Curve and Point 5 is at the high end of the Throttle
Curve. Point 3 is a the center of the Throttle Curve.
RATE setting range for each Point is -150% to 150%.
3) Press the Navigation Pad 6 to highlight RATE>.
4) Press the INC+/M1 or DEC-/M2 keys to set the desired Rate percentage
value for the Point you chose previously, then repeat the previous
procedures to change the desired remaining Point and Rate percentage
values.
In the default conguration the Throttle Curve is Linear. For example, when you move the throttle control stick from 0%
to 100%, the throttle servo will travel from 0% to 100%, too. As long as the line on the graph remains straight, the Throttle
Curve will be Linear. When a Point Rate percentage value is changed, the line on the graph curves (displaying the Throttle Curve)
and throttle servo travel will vary in relation to throttle control stick movement.
100%
The tables below describe the default Point and Rate values.
1
2
-100%
-50%
POINT DEFAULT RATE
3
4
0%
50%
POINT DEFAULT RATE
5
POINT DEFAULT RATE
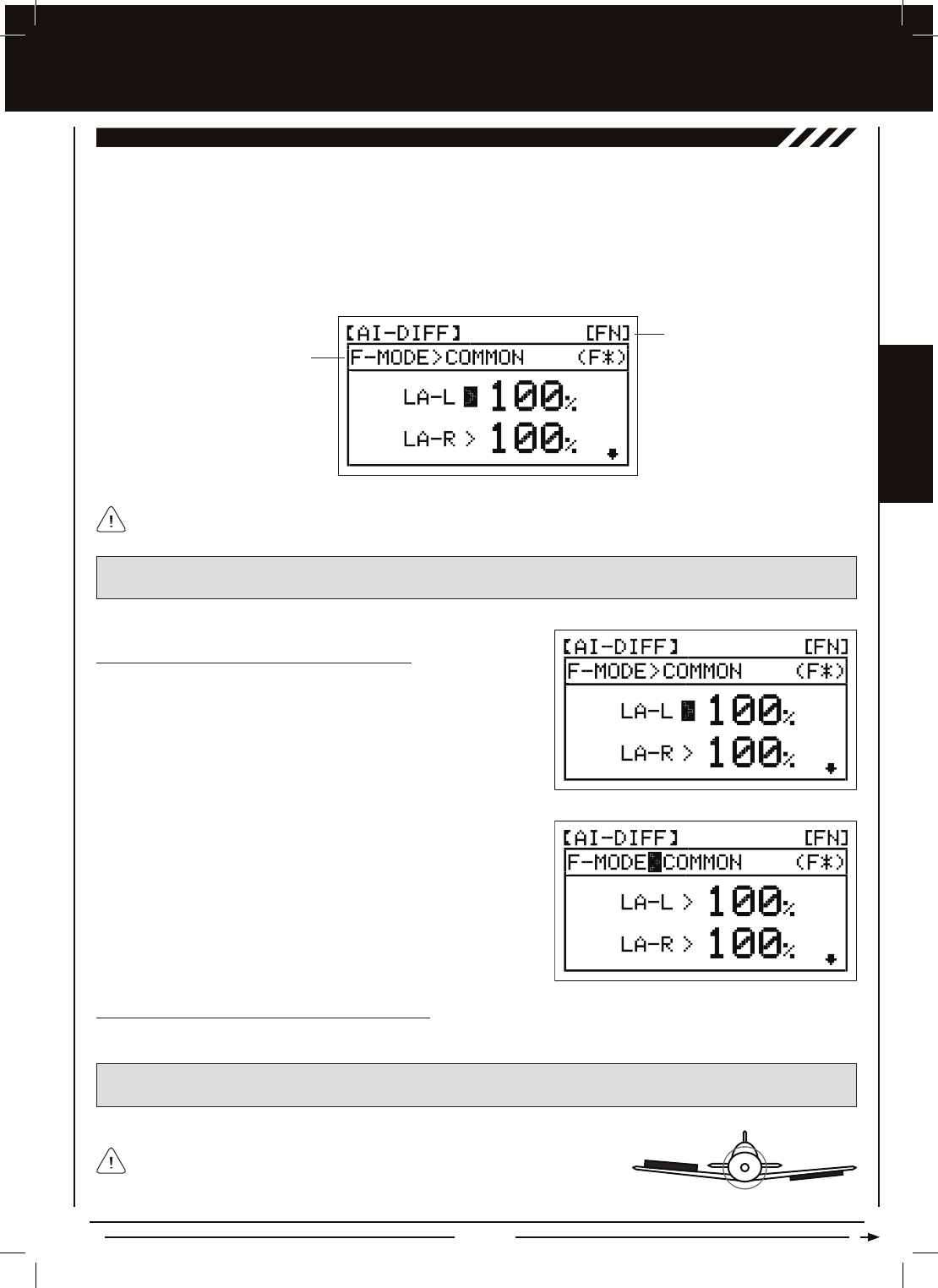
Page 39
aERO MODEL TyPE
15.ai-DiFF (aiLEROn DiFFEREnTiaL)
The Aileron Differential function allows you change the ratio of the Up to Down movement of each aileron. For example, many
aircraft exhibit a yaw tendency when the ailerons are used. Although this can affect any aircraft, it's noticed mostly on high-wing
aircraft and aerobatic aircraft. The Aileron Differential function can be used to eliminate the yaw tendency by adding more movement
to the upward moving aileron than the downward moving aileron. For example, if your aircraft tends not to stay in a straight line
during rolls, you can adjust the Aileron Differential to make the aircraft roll more axially and therefore in a straight line.
For greater exibility, the Aileron Differential function can be programmed either the same for all Flight Modes or separately for
each of the three Flight Modes.
Programming F-MODE
Transmitter F-MODE
Transmitter F-MODE refers to the Flight Mode that the transmitter is currently operating in. Programming F-MODE refers
to the Flight Mode that you would like to change the programming for.
IMPORTANT To be able to access the AI-DIFF menu and program the Aileron Differential function, your aircraft must feature
two separate aileron servos and you must choose the AILE>2 Model Type selection option in the TYPE menu.
Choosing the Flight Mode - Common or Separate
1) From the Display screen, press the ENTER key to display the Programming
Menus.
2) Press the Navigation Pad 56 to highlight AI-DIFF, then press the
ENTER key to display the AI-DIFF menu. The cursor will default to
LA-L>100%.
3) Press the Navigation Pad 5to move the cursor to F-MODE>COMMON.
4) Press the INC+/M1 or DEC-/M2 keys to choose either SEPARATE or
COMMON.
5) If you choose SEPARATE, press the F-MODE key to choose the F-MODE
number you would like to program the Aileron Differential function for.
Choose from FN, F1 or F2.
Changing the Aileron Differential Percentage Values
Aileron Differential is achieved by reducing the amount of DOWN movement in the required aileron.
Aileron Differential is a percentage of the control throw differential between the
ailerons. For example, if you set the LA-R (Left Aileron-Right) percentage value
to 90%, the Left Aileron will move Down less than what the Right Aileron moves Up.
IMPORTANT Prior to setting the Aileron Differential percentage values, you should use the End Point Adjustment function
to ensure that each aileron is moving UP and DOWN the same amount.
UP = More
Movement
DOWN = Less
Movement
Diagram of Differential
AERO MODEL TYPE
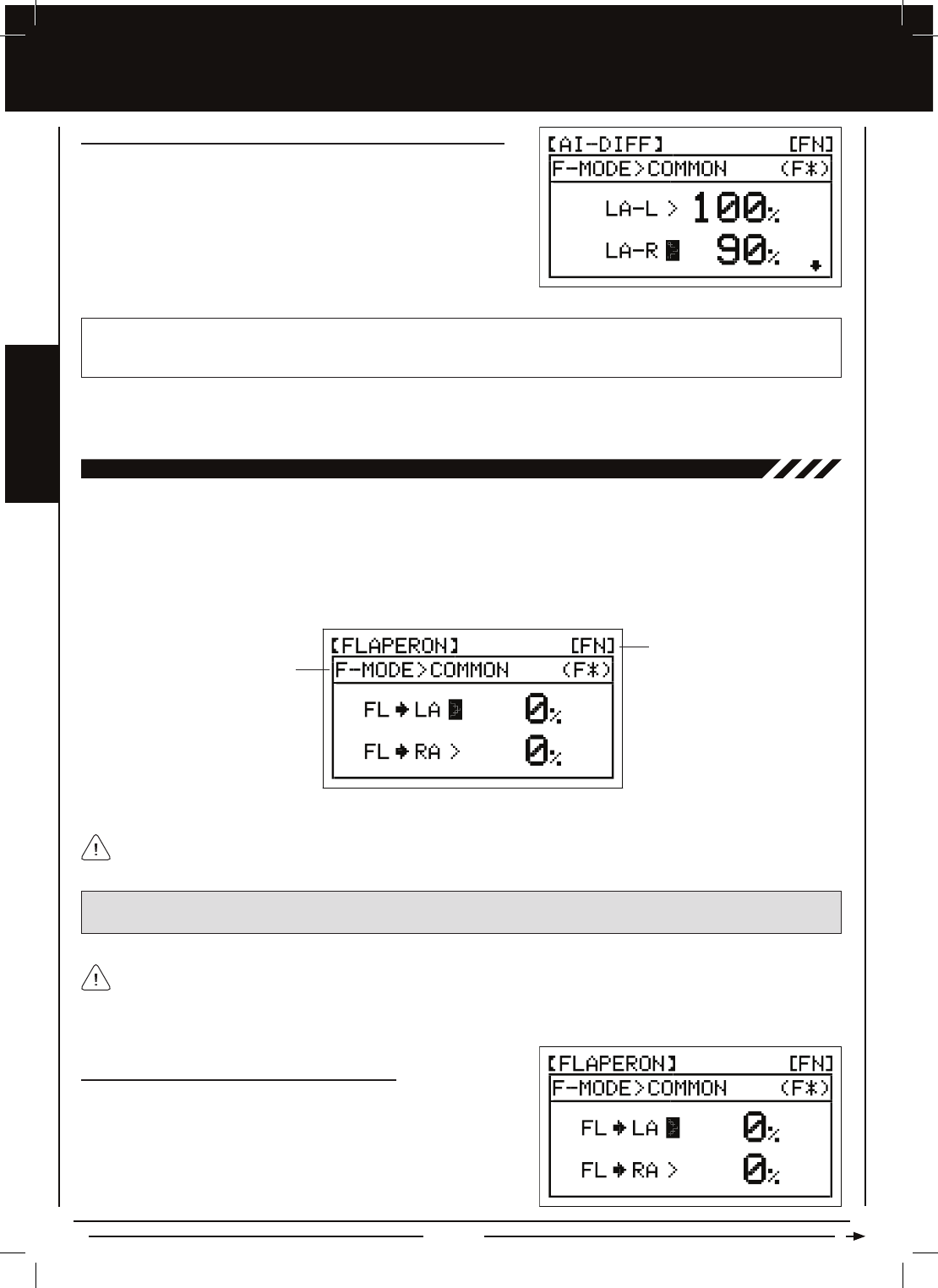
Page 40
aERO MODEL TyPE
Changing the Aileron Differential Percentage Values, Continued....
1) Press the Navigation Pad 56 to highlight the desired aileron travel
direction you would like to change the Aileron Differential percentage
value for. For example, if you need the Right Aileron to move Up more
than the Left Aileron moves Down (per the previous diagram), you would
decrease the LA-R>100% (Left Aileron-Right) percentage value.
2) Press the INC+/M1 or DEC-/M2 keys to set the desired Aileron Differential
percentage value.
AI-DIFF setting range is 0% to 100%. The default setting is 100%. Decreasing the Aileron Differential percentage value will
decrease the movement for that specic aileron and direction of travel. The Aileron Differential percentage value is a percentage
of End Point Adjustment.
3) Repeat the previous procedures to set the desired remaining Aileron Differential percentage values. Press the Navigation
Pad 6 to scroll to the RA-L and RA-R options.
16.FLaPEROn (FLaPEROn MiXing)
The Flaperon Mixing function mixes aps and ailerons, allowing you to use the ailerons as aps if your model does not feature
separate aps. During use, both ailerons move down at the same time to provide the function of aps, while still providing aileron roll
control. Both ailerons can also be programmed to move up at the same time (spoilerons) to rapidly decrease lift. On some aircraft,
moving both ailerons up slightly can induce greater speeds and also aid in trimming.
For greater exibility, the Flaperon Mixing function can be programmed either the same for all Flight Modes or separately for each
of the three Flight Modes.
Programming F-MODE
Transmitter F-MODE
Transmitter F-MODE refers to the Flight Mode that the transmitter is currently operating in. Programming F-MODE refers
to the Flight Mode that you would like to change the programming for.
IMPORTANT To be able to access the FLAPERON menu and program the Flaperon Mixing function, your aircraft must
feature two separate aileron servos and you must choose the AILE>2 Model Type selection option in the TYPE menu.
The Flaperons are controlled by the Flap switch, just as if your model featured separate aps. In most cases, you will
want to set the Flap channel End Point Adjustment percentage values prior to adjusting the Flaperon4Left Aileron and
Flaperon4Right Aileron percentage values.
Choosing the Flight Mode - Common or Separate
1) From the Display screen, press the ENTER key to display the Programming
Menus.
2) Press the Navigation Pad 56 to highlight FLAPERON, then press
the ENTER key to display the FLAPERON menu. The cursor will
default to FL4LA>0%.
Flaperons - Both ailerons down
Spoilerons - Both ailerons up
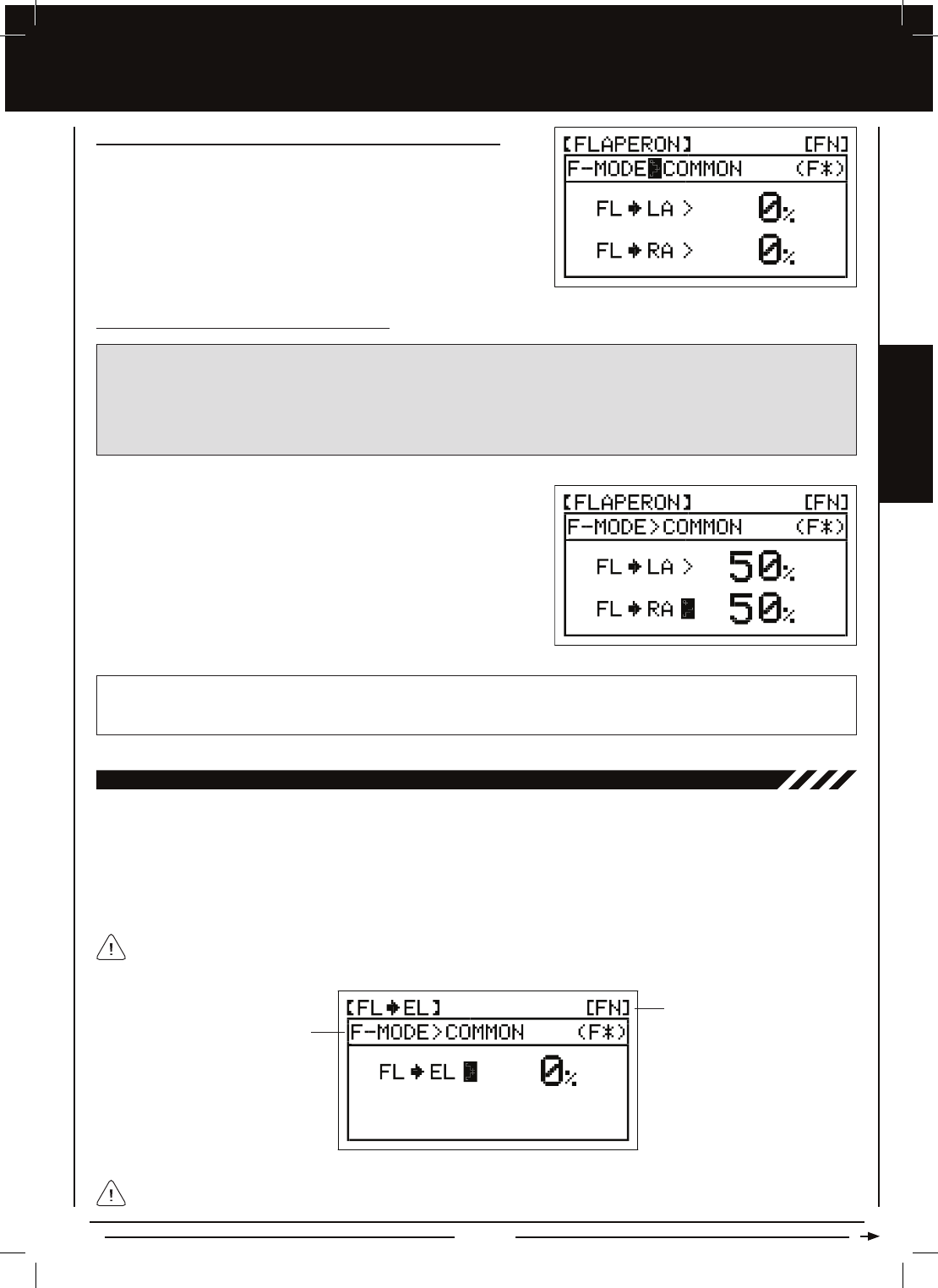
Page 41
aERO MODEL TyPE
Choosing the Flight Mode - Common or Separate, Continued....
3) Press the Navigation Pad 5to move the cursor to F-MODE>COMMON.
4) Press the INC+/M1 or DEC-/M2 keys to choose either SEPARATE or
COMMON.
5) If you choose SEPARATE, press the F-MODE key to choose the F-MODE
number you would like to program the Flaperon Mixing function for.
Choose from FN, F1 or F2.
IMPORTANT Adjusting the Flaperon4Left Aileron and Flaperon4Right Aileron percentage values changes the percentage
of Flaperon travel in relation to the Flap channel End Point Adjustment percentage value. For example, if the Flap Switch '1'
End Point Adjustment percentage value is set to 100% and the Flaperons move down 2", changing the Flaperon4Left Aileron
and Flaperon4Right Aileron percentage values to 50% will cause the Flaperons to move down 1". In addition, changing the
Flaperon4Left Aileron and Flaperon4Right Aileron percentage values to -50% will cause the Flaperons to move up 1"
(Spoilerons).
Changing Flaperon Mixing Percentage Values
FLAPERON setting range is -100% to 100%. The default setting is 0% (OFF). When the percentage value is increased from
0% to 100%, Flaperon travel will increase in one direction. When the percentage value is decreased from 0% to -100%,
Flaperon travel will increase in the opposite direction.
1) Press the Navigation Pad 6to highlight FL4LA>0%, then press the
INC+/M1 or DEC-/M2 keys to change the Flaperon4Left Aileron
Mixing percentage value.
2) Press the Navigation Pad 6to highlight FL4RA>0%, then press the
INC+/M1 or DEC-/M2 keys to change the Flaperon4Right Aileron
Mixing percentage value.
17.FL
4
EL (FLaP TO ELEvaTOR MiXing)
The Flap to Elevator Mixing function allows you to mix a percentage of elevator control with ap control. When you move the aps
up and down, the elevator will move up and down. The Flap to Elevator Mixing function is typically used to reduce the ballooning
tendency that most aircraft exhibit when the aps are lowered. The amount and the direction that the elevator moves with ap
control is adjusted by changing the Flap to Elevator mixing percentage value either positive or negative.
For greater exibility, the Flap to Elevator Mixing function can be programmed either the same for all Flight Modes or separately for
each of the three Flight Modes.
In the majority of cases, you will want to program the Flap to Elevator Mixing function to move the elevator down enough
to minimize ballooning when the aps are lowered.
Programming F-MODE
Transmitter F-MODE
Transmitter F-MODE refers to the Flight Mode that the transmitter is currently operating in. Programming F-MODE refers
to the Flight Mode that you would like to change the programming for.
AERO MODEL TYPE
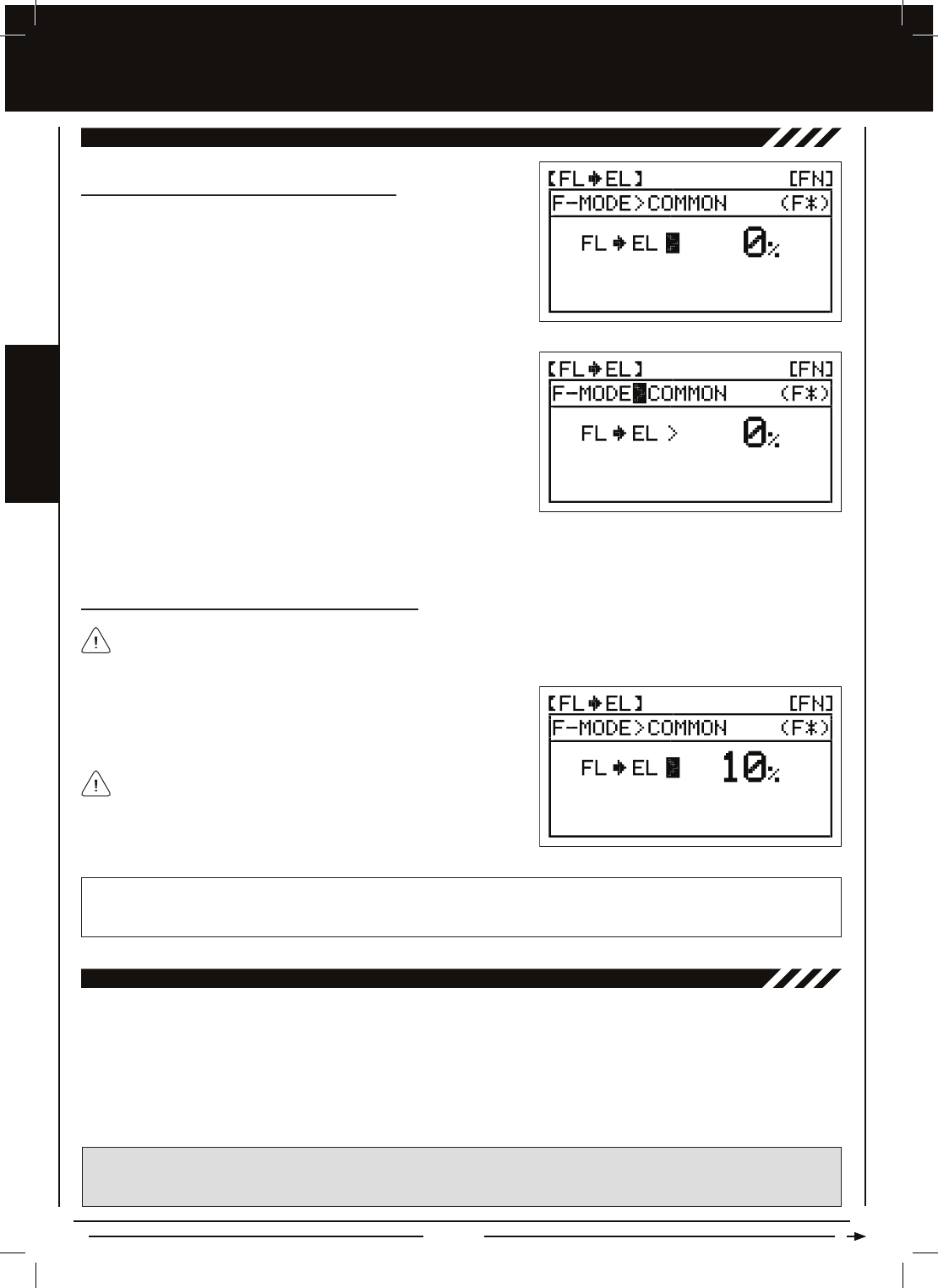
Page 42
aERO MODEL TyPE
Choosing the Flight Mode - Common or Separate
1) From the Display screen, press the ENTER key to display the Programming
Menus.
2) Press the Navigation Pad 56 to highlight FL4EL, then press the
ENTER key to display the FL4EL menu. The cursor will default to
FL4EL>0%.
The channel options displayed will differ based on the Model Type selection options you chose previously. For example, if
you chose TAIL>2xEL in the TYPE menu, FL4LE (Left Elevator) and FL4RE (Right Elevator) percentage values can be
changed separately.
3) Press the Navigation Pad 5to move the cursor to F-MODE>COMMON.
4) Press the INC+/M1 or DEC-/M2 keys to choose either SEPARATE or
COMMON.
17.FL
4
EL (FLaP TO ELEvaTOR MiXing), cOnTinUED....
Changing Flap to Elevator Mixing Percentage Values
FL4EL setting range is -100% to 100%. The default setting is 0% (OFF). When the percentage value is increased from 0% to
100%, elevator travel will increase in one direction in relation to flap travel. When the percentage value is decreased
from 0% to -100%, elevator travel will increase in the opposite direction in relation to ap travel.
The Flap4Elevator Mixing percentage value is a ratio of elevator
travel to ap travel. For example, when the Flap4Elevator Mixing
percentage value is set to 10%, the elevator will travel 1/10th the amount
that the aps travel. This mix is Linear.
1) Press the Navigation Pad 6to highlight FL4EL>0%, then press the
INC+/M1 or DEC-/M2 keys to change the Flap4Elevator Mixing
percentage value.
18.DUaL EL (DUaL ELEvaTOR MiXing EnD POinT aDjUSTMEnT)
The Dual Elevator Mixing End Point Adjustment function allows you to adjust the servo travel of each elevator servo independently
while the Dual Elevator Mixing option is Active. In some cases, when you use two separate elevator servos, minor differences in
control linkage geometry can result in one elevator half deecting more in one or both directions than the other elevator half. The
Dual Elevator Mixing End Point Adjustment function allows you to reduce the control deection of one or both elevator halves in
either direction to ensure that both elevator halves deect exactly the same amount.
For greater exibility, the Dual Elevator Mixing End Point Adjustment function can be programmed either the same for all Flight
Modes or separately for each of the three Flight Modes.
5) If you choose SEPARATE, press the F-MODE key to choose the F-MODE number you would like to program the Flap to Elevator
Mixing function for. Choose from FN, F1 or F2.
IMPORTANT Depending on the specic orientation of your elevator control linkages, in order for the Dual Elevator Mixing
function to work as intended, one of the elevator servos may need to be reversed (using the NOR/REV setting in the
REVERSE menu), so that both control surfaces move Up and Down together using the elevator control stick.
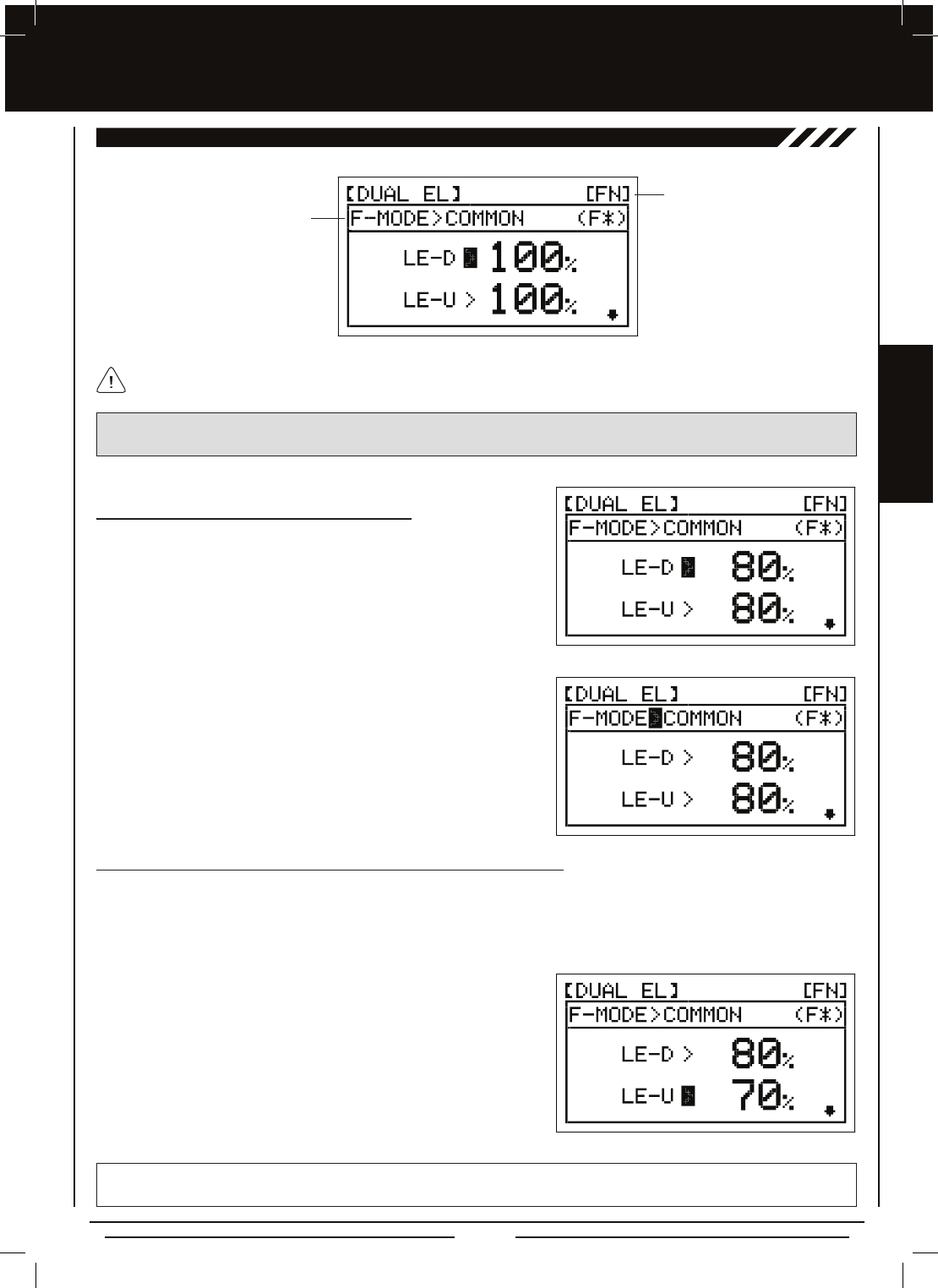
Page 43
aERO MODEL TyPE
Programming F-MODE
Transmitter F-MODE
Transmitter F-MODE refers to the Flight Mode that the transmitter is currently operating in. Programming F-MODE refers
to the Flight Mode that you would like to change the programming for.
18.DUaL EL (DUaL ELEvaTOR MiXing EnD POinT aDjUSTMEnT), cOnTinUED....
IMPORTANT To be able to access the DUAL EL menu and program the Dual Elevator End PointAdjustment function, your aircraft
must feature two separate elevator servos and you must choose the TAIL>2xEL Model Type selection option in the TYPE menu.
Choosing the Flight Mode - Common or Separate
1) From the Display screen, press the ENTER key to display the Programming
Menus.
2) Press the Navigation Pad 56 to highlight DUAL EL, then press the
ENTER key to display the DUAL EL menu. The cursor will default to
LE-D>80%.
3) Press the Navigation Pad 5to move the cursor to F-MODE>COMMON.
4) Press the INC+/M1 or DEC-/M2 keys to choose either SEPARATE or
COMMON.
5) If you choose SEPARATE, press the F-MODE key to choose the F-MODE
number you would like to program the Dual Elevator Mixing End Point
Adjustment function for. Choose from FN, F1 or F2.
Changing Dual Elevator Mixing End Point Adjustment Percentage Values
Both the Up and Down, and the Right and Left elevator percentage values can be changed separately. Prior to changing the
Dual Elevator Mixing End Point Adjustment percentage values, you should adjust the elevator End Point Adjustment percentage
values in the EPA menu to achieve the desired maximum amount of control deection in both directions. You can then lower the
required Dual Elevator Mixing End Point Adjustment percentage values to equalize the control deection of both elevator halves
in both directions.
1) Press the Navigation Pad 56 to highlight the desired elevator servo
and direction of travel you would like to change the Dual Elevator Mixing
End Point Adjustment percentage value for. For example, if the Left
elevator half moves Up more than the Right elevator half moves Up,
you would decrease the LE-U>80% (Left Elevator-Up) percentage value.
2) Press the INC+/M1 or DEC-/M2 keys to set the desired Dual Elevator
Mixing End Point Adjustment percentage value.
DUAL EL setting range is 100% to 0%. The default setting is 80%. Decreasing the Dual Elevator Mixing End Point Adjustment
percentage value will decrease the movement for that specic elevator half and direction of travel.
AERO MODEL TYPE
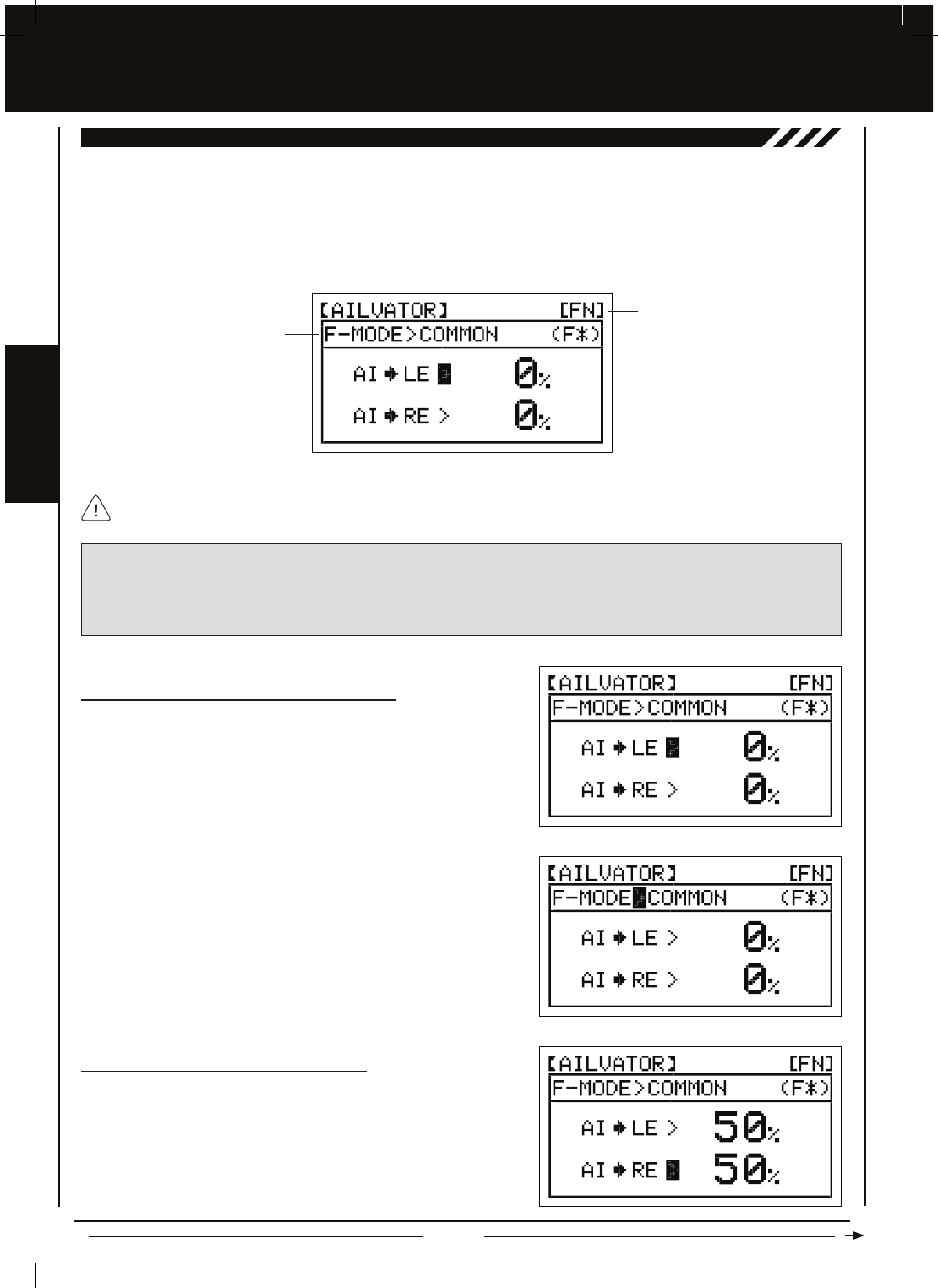
Page 44
aERO MODEL TyPE
19.aiLvaTOR (aiLvaTOR/TaiLEROn MiXing)
The Ailvator Mixing function mixes ailerons and elevator, allowing you to have both roll control and pitch control on the elevator,
separate from the ailerons. When Activated, not only will the two elevator halves move up and down together, but each elevator
half can move up and down independently like ailerons. This function is commonly referred to as tailerons (or stabilators), and
is normally found on aircraft that feature full-ying stabilizers.
For greater exibility, the Ailvator Mixing function can be programmed either the same for all Flight Modes or separately for each
of the three Flight Modes.
Transmitter F-MODE refers to the Flight Mode that the transmitter is currently operating in. Programming F-MODE refers
to the Flight Mode that you would like to change the programming for.
IMPORTANT To be able to access the AILVATOR menu and program the Ailvator Mixing function, your aircraft must feature
two separate elevator servos and you must choose the TAIL>2xEL Model Type selection option in the TYPE menu. In addition,
depending on the specic orientation of your elevator control linkages, in order for the Ailvator Mixing function to work as
intended, one of the elevator servos may need to be reversed (using the NOR/REV setting in the REVERSE menu), so that both
control surfaces move Up and Down together using the elevator control stick.
Programming F-MODE
Transmitter F-MODE
Choosing the Flight Mode - Common or Separate
1) From the Display screen, press the ENTER key to display the Programming
Menus.
2) Press the Navigation Pad 56 to highlight AILVATOR, then press
the ENTER key to display the AILVATOR menu. The cursor will
default to AI4LE>0%.
3) Press the Navigation Pad 5to move the cursor to F-MODE>COMMON.
4) Press the INC+/M1 or DEC-/M2 keys to choose either SEPARATE or
COMMON.
5) If you choose SEPARATE, press the F-MODE key to choose the F-MODE
number you would like to program the Ailvator Mixing function for.
Choose from FN, F1 or F2.
Changing Ailvator Mixing Percentage Values
1) Press the Navigation Pad 6to highlight AI4LE>0%, then press the
INC+/M1 or DEC-/M2 keys to change the Aileron4Left Elevator Mixing
percentage value.
2) Press the Navigation Pad 6to highlight AI4RE>0%, then press the
INC+/M1 or DEC-/M2 keys to change the Aileron4Right Elevator
Mixing percentage value.
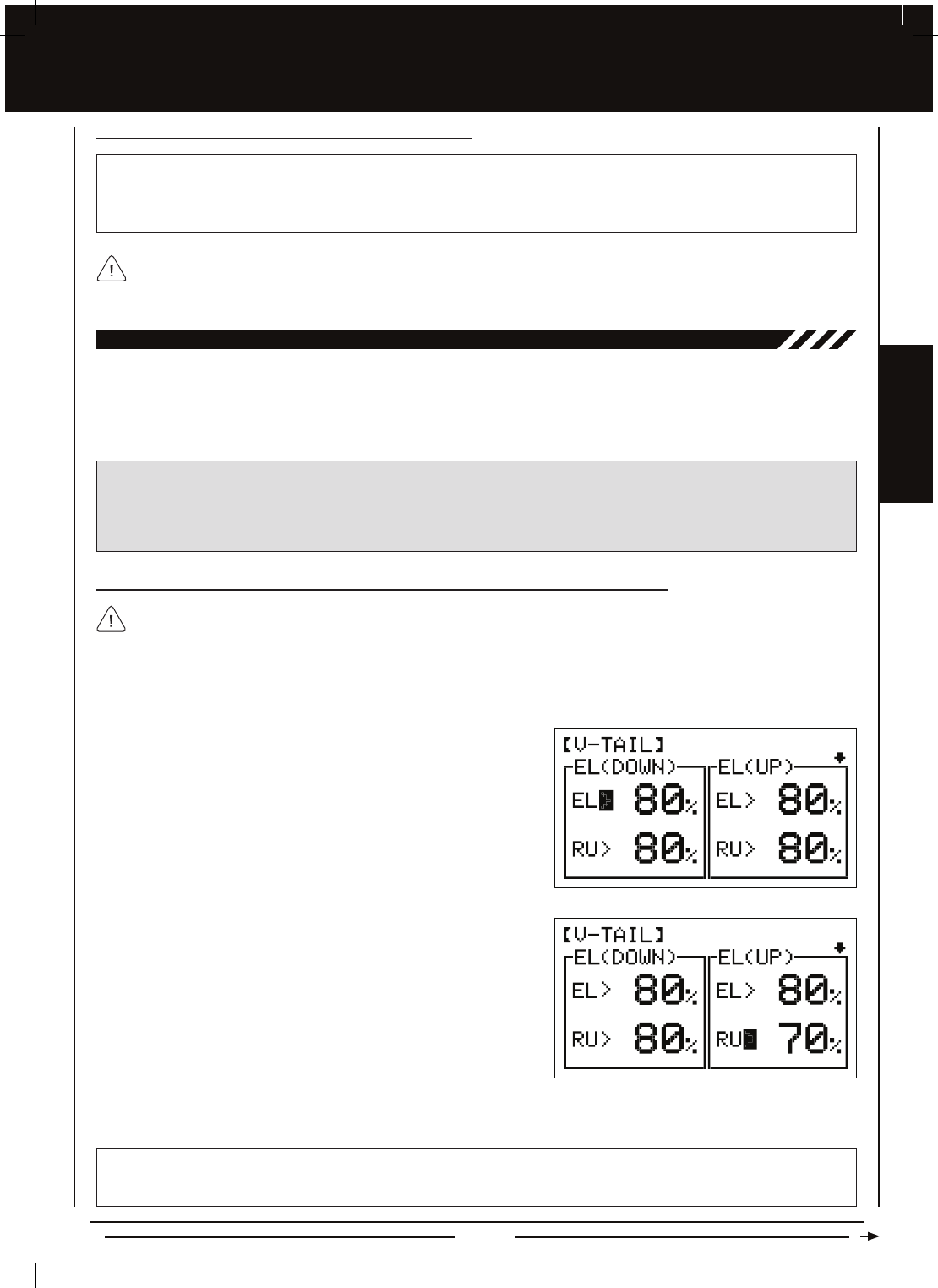
Page 45
aERO MODEL TyPE
AILVATOR setting range is -100% to 100%. The default setting is 0% (OFF). Adjusting the Ailvator Mixing percentage values
will change the ratio of elevator roll travel to elevator pitch travel. For example, when the Aileron4Left Elevator and the
Aileron4Right Elevator percentage values are both set to 50%, the elevator roll travel will be half the amount of the elevator
pitch travel at any given control stick position. This mix is Linear.
Setting one Ailvator Mixing percentage value opposite of the other Ailvator Mixing percentage value will cause both
elevator servos to move together when the elevator/aileron control stick is moved in both the up and down, and the right
and left directions.
Changing Ailvator Mixing Percentage Values, Continued....
20.v-TaiL (v-TaiL MiXing EnD POinT aDjUSTMEnT)
The V-Tail Mixing End Point Adjustment function allows you to adjust the servo travel of the elevator and rudder servos
independently while the V-Tail Mixing option is Active. In some cases, minor differences in the control linkage geometry can result
in unequal control deection. The V-Tail Mixing End Point Adjustment function allows you to equalize control deection, and
in addition, allows you the ability to change the control deection amount of each servo in both directions. This allows greater
exibility in making control surface adjustments versus using the elevator and rudder channel End Point Adjustments in the EPA menu.
IMPORTANT To be able to access the V-TAIL menu and program the V-Tail Mixing End Point Adjustment function, you must
choose the TAIL>V-TAIL Model Type selection option in the TYPE menu. In addition, depending on the specic orientation of
your control linkages, in order for the V-Tail Mixing function to work as intended, one of the servos may need to be reversed
(using the NOR/REV setting in the REVERSE menu) so that both control surfaces move Up and Down together using the
elevator control stick.
2) Press the Navigation Pad 56 to highlight V-TAIL, then press the
ENTER key to display the V-TAIL menu. The cursor will default to EL
(DOWN) EL>80%.
Changing V-Tail Mixing End Point Adjustment Percentage Values - Elevator Up and Down
Prior to changing the V-Tail Mixing End Point Adjustment percentage values, you should rst adjust the elevator and rudder
channel End Point Adjustment percentage values in the EPA menu to achieve the desired maximum amount of control
deection in all four directions (elevator Up and Down, and rudder Right and Left), then use the V-Tail Mixing End Point Adjustment
function to ne-tune the servo travel of each servo independently.
3) Press the Navigation Pad 5634 to highlight the desired servo (EL or
RU) and direction of travel (DOWN or UP) you would like to change the
V-Tail Mixing End Point Adjustment percentage value for. For example, if
the Rudder servo moves Up more than the Elevator servo moves Up
when you move the elevator control stick, you would decrease the EL
(UP) RU>80% percentage value.
4) Press the INC+/M1 or DEC-/M2 keys to set the desired V-Tail Mixing
End Point Adjustment percentage value.
V-TAIL EL (DOWN) and EL (UP) setting range is 100% to 0%. The default setting is 80%. Decreasing the V-Tail Mixing End
Point Adjustment percentage value will decrease the movement for that specic servo and direction of travel. Increasing the
V-Tail Mixing End Point Adjustment percentage value will increase the movement for that specic servo and direction of travel.
1) From the Display screen, press the ENTER key to display the Programming Menus.
5) Repeat the previous procedures to set the desired remaining V-Tail Elevator Mixing End Point Adjustment percentage values.
AERO MODEL TYPE
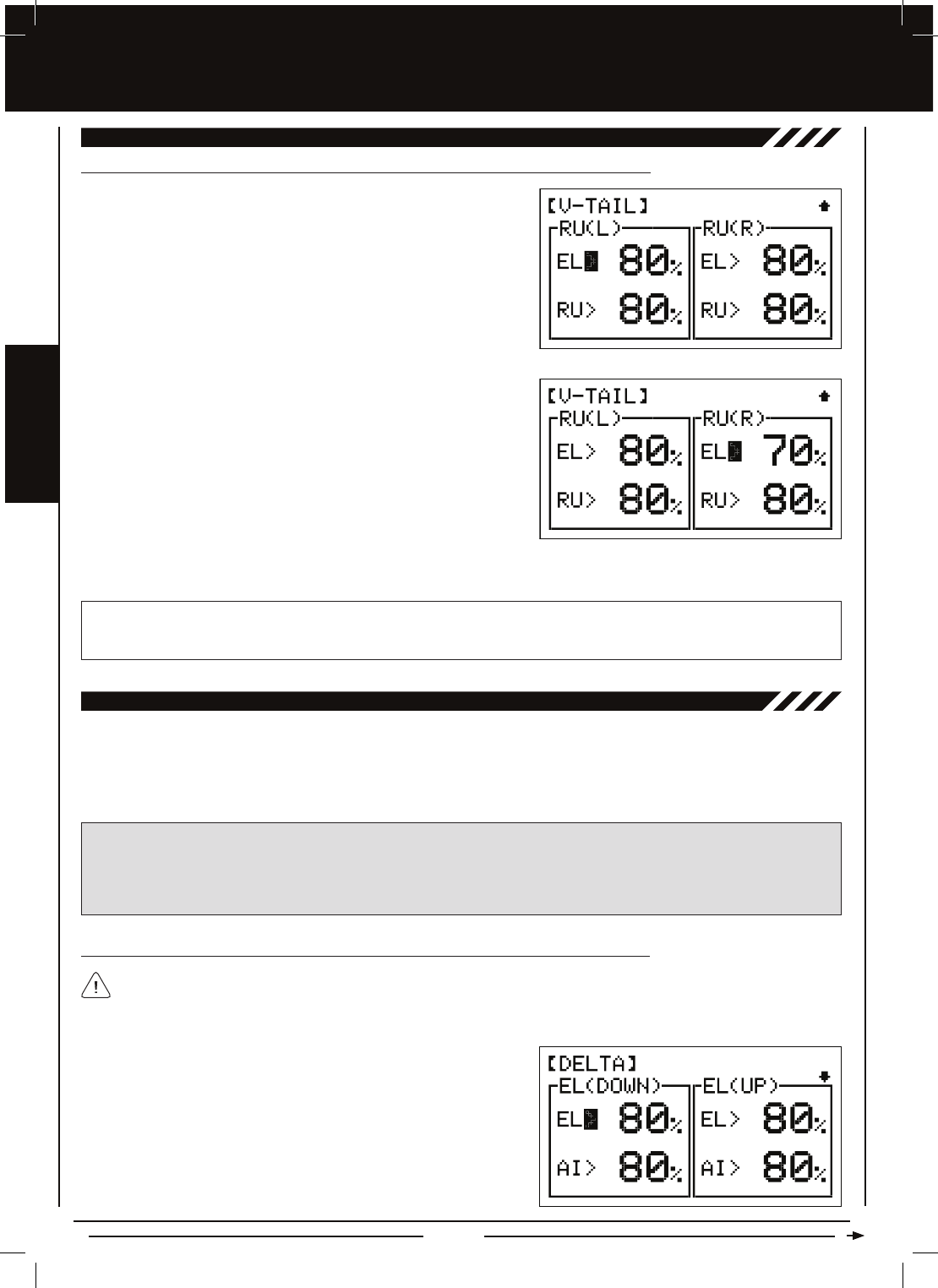
Page 46
aERO MODEL TyPE
21.DELTa (DELTa MiXing EnD POinT aDjUSTMEnT)
Changing V-Tail Mixing End Point Adjustment Percentage Values - Rudder Right and Left
1) Press the Navigation Pad 6to scroll down to display V-TAIL RU (L)
and RU (R).
2) Press the Navigation Pad 5634 to highlight the desired servo (EL or
RU) and direction of travel (L or R) you would like to change the V-Tail
Mixing End Point Adjustment percentage value for. For example, if the
Elevator servo moves Right more than the Rudder servo moves Right
when you move the rudder control stick, you would decrease the RU
(R) EL>80% percentage value.
3) Press the INC+/M1 or DEC-/M2 keys to set the desired V-Tail Mixing
End Point Adjustment percentage value.
V-TAIL RU (L) and RU (R) setting range is 100% to 0%. The default setting is 80%. Decreasing the V-Tail Mixing End Point
Adjustment percentage value will decrease the movement for that specic servo and direction of travel. Increasing the V-Tail
Mixing End Point Adjustment percentage value will increase the movement for that specic servo and direction of travel.
20.v-TaiL (v-TaiL MiXing EnD POinT aDjUSTMEnT), cOnTinUED....
The Delta Mixing End Point Adjustment function allows you to adjust the servo travel of the elevator and aileron servos
independently while the Delta Mixing option is Active. In some cases, minor differences in the control linkage geometry can result
in unequal control deection. The Delta Mixing End Point Adjustment function allows you to equalize control deection, and
in addition, allows you the ability to change the control deection amount of each servo in both directions. This allows greater
exibility in making control surface adjustments versus using the elevator and aileron channel End Point Adjustments in the EPA menu.
IMPORTANT To be able to access the DELTA menu and program the Delta Mixing End Point Adjustment function, you must
choose the WING>DELTA Model Type selection option in the TYPE menu. In addition, depending on the specic orientation
of your control linkages, in order for the Delta Mixing function to work as intended, one of the servos may need to be reversed
(using the NOR/REV setting in the REVERSE menu) so that both control surfaces move Up and Down together using the
elevator control stick.
Changing Delta Mixing End Point Adjustment Percentage Values - Elevator Up and Down
Prior to changing the Delta Mixing End Point Adjustment percentage values, you should rst adjust the elevator and aileron
channel End Point Adjustment percentage values in the EPA menu to achieve the desired maximum amount of control
deection in all four directions (elevator Up and Down, and Aileron Right and Left), then use the Delta Mixing End Point Adjustment
function to ne-tune the servo travel of each servo independently.
1) From the Display screen, press the ENTER key to display the Programming
Menus.
2) Press the Navigation Pad 56 to highlight DELTA, then press the
ENTER key to display the DELTA menu. The cursor will default to EL
(DOWN) EL>80%.
4) Repeat the previous procedures to set the desired remaining V-Tail Rudder Mixing End Point Adjustment percentage values.
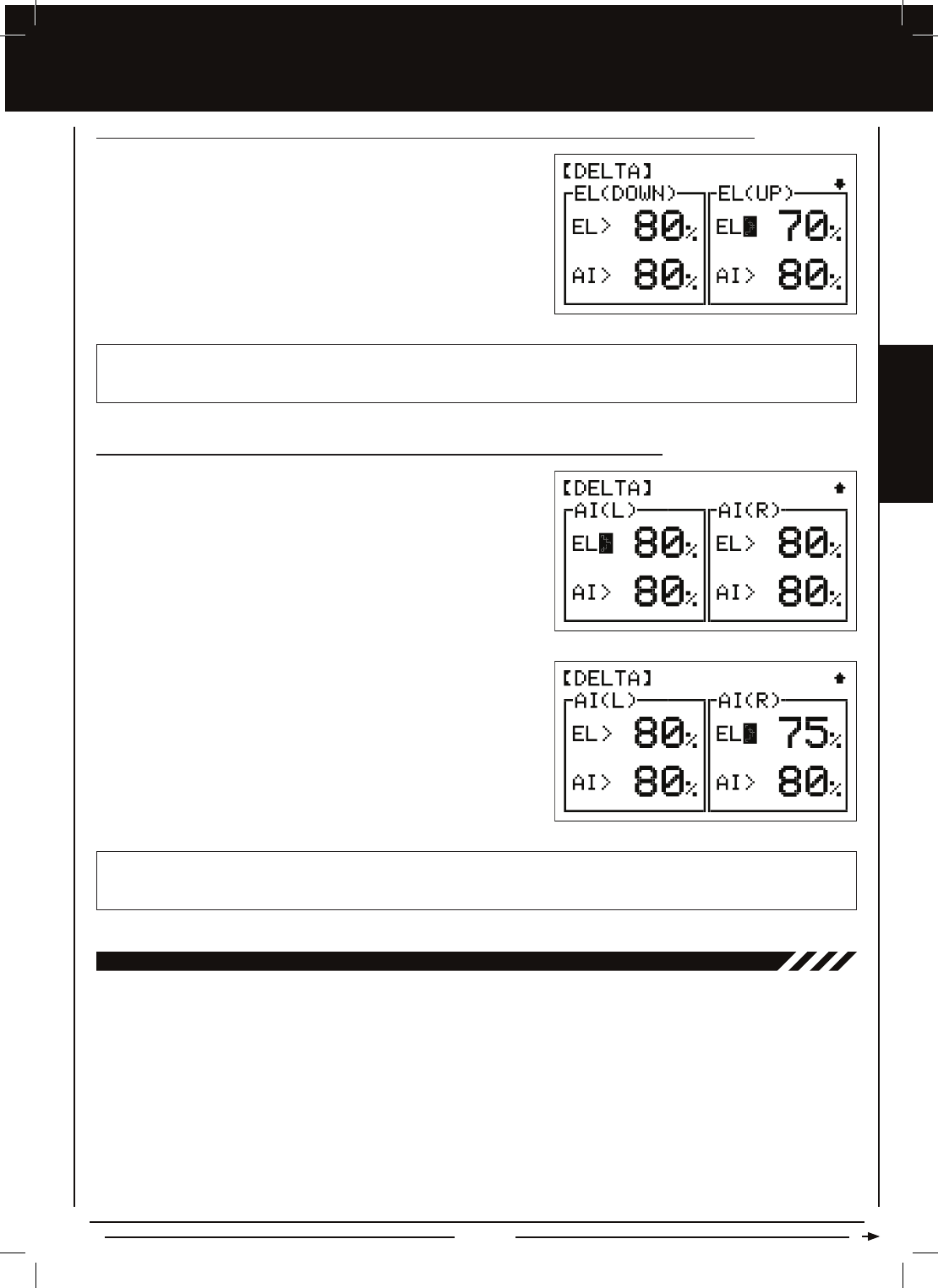
Page 47
aERO MODEL TyPE
3) Press the Navigation Pad 5634 to highlight the desired servo (EL
or AI) and direction of travel (DOWN or UP) you would like to change the
Delta Mixing End Point Adjustment percentage value for. For example, if
the Elevator servo moves Up more than the Aileron servo moves Up
when you move the elevator control stick, you would decrease the EL
(UP) EL>80% percentage value.
4) Press the INC+/M1 or DEC-/M2 keys to set the desired V-Tail Mixing
End Point Adjustment percentage value.
DELTA EL (DOWN) and EL (UP) setting range is 100% to 0%. The default setting is 80%. Decreasing the Delta Mixing End
Point Adjustment percentage value will decrease the movement for that specic servo and direction of travel. Increasing the
Delta Mixing End Point Adjustment percentage value will increase the movement for that specic servo and direction of travel.
Changing Delta Mixing End Point Adjustment Percentage Values - Elevator Up and Down, Continued....
Changing Delta Mixing End Point Adjustment Percentage Values - Aileron Right and Left
1) Press the Navigation Pad 6to scroll down to display DELTA AI (L) and
AI (R).
2) Press the Navigation Pad 5634 to highlight the desired servo (EL
or AI) and direction of travel (L or R) you would like to change the Delta
Mixing End Point Adjustment percentage value for. For example, if the
Elevator servo moves Right more than the Aileron servo moves Right
when you move the aileron control stick, you would decrease the RU
(R) EL>80% percentage value.
3) Press the INC+/M1 or DEC-/M2 keys to set the desired Delta Mixing
End Point Adjustment percentage value.
DELTA AI (L) and AI (R) setting range is 100% to 0%. The default setting is 80%. Decreasing the Delta Mixing End Point
Adjustment percentage value will decrease the movement for that specic servo and direction of travel. Increasing the Delta
Mixing End Point Adjustment percentage value will increase the movement for that specic servo and direction of travel.
22. & 23.c-MiX1 anD c-MiX2 (cOMPEnSaTiOn MiXing)
The Compensation Mixing function is used to create your own custom mix if one of the pre-programmed mixes is not suitable. For
example, you can create a custom mix that mixes aperons and spoilerons to elevator, so that when you move the elevator up
and down, both ailerons will move up and down, providing near-instantaneous extreme pitch changes while still enabling aileron
roll control. Another example would be to mix aileron to rudder, so that when you move the ailerons right and left, the rudder will
move right and left, resulting in a coordinated turn. Like with pre-programmed mixes, Compensation Mixes are composed of a
Master channel and a Slave channel. Any of the available six channels can be programmed as a Master or a Slave. The same
channel can even be programmed as both a Master and a Slave. For example, if you want to program throttle Dual Rate, you
can set both the Master and the Slave to throttle, then adjust the High and Low Rate percentage values to provide the amount of
travel you want when the Compensation Mixing function is Activated. In addition to programming the High and Low Rate percentage
values, the Slave channel Offset percentage value can be changed to move the neutral point of the Slave channel servo when
the Compensation Mixing function is Activated.
For greater exibility, both Compensation Mixing functions can be programmed either the same for all Flight Modes or sepa-
rately for each of the three Flight Modes.
AERO MODEL TYPE
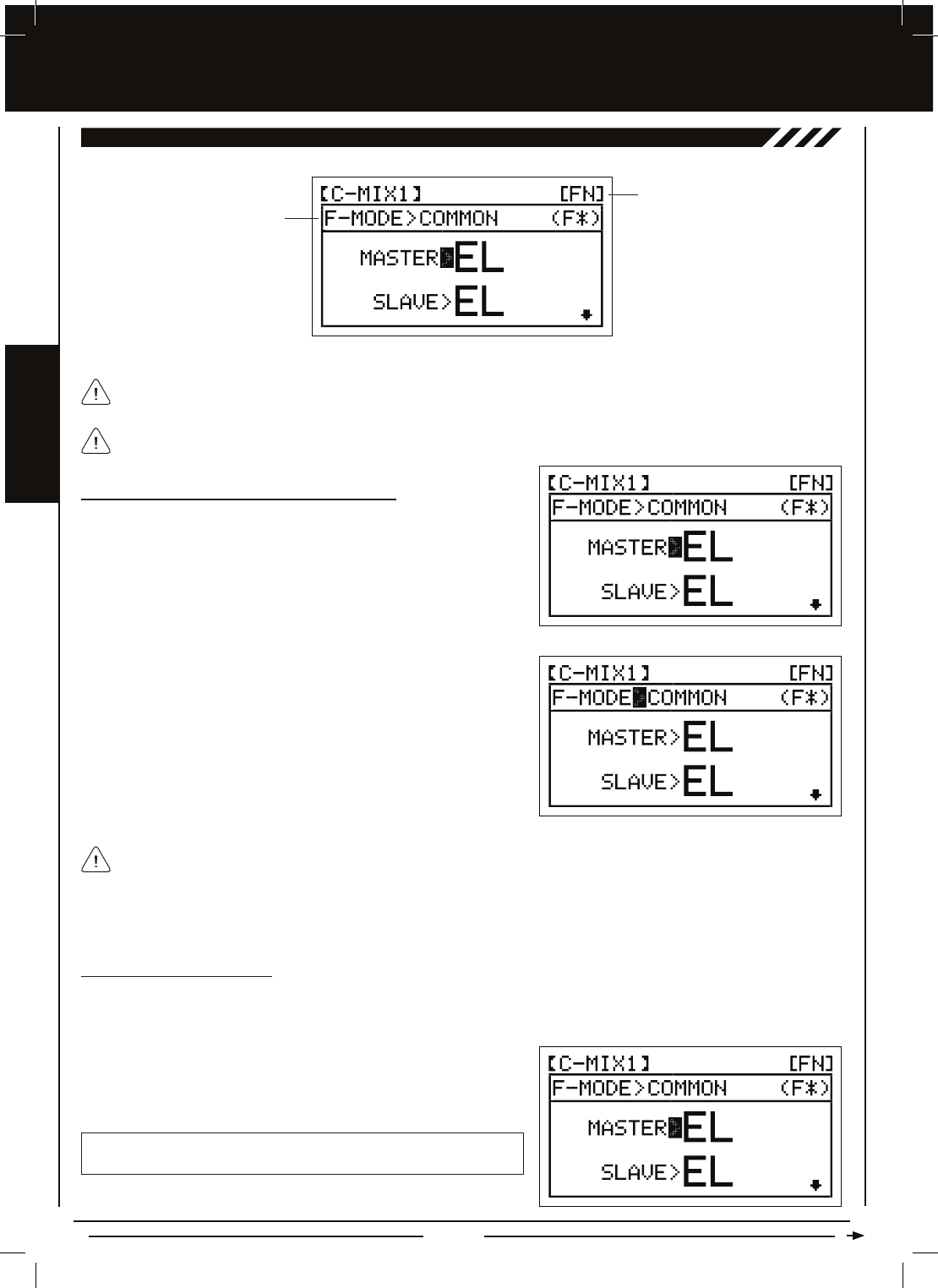
Page 48
Two Compensation Mixing functions are available, however, only one Compensation Mixing function can be Active at one
time. If F-MODE is set to COMMON, both Compensation Mixing functions will controlled by the Compensation Mixing
switch and Compensation Mixer 2 will always override Compensation Mixer 1. If F-MODE is set to SEPARATE, you can control
one Compensation Mixing function using the Compensation Mixing switch and control the second Compensation Mixing function
(programmed to a different Flight Mode) using a Flight Mode switch, however, keep in mind that higher numbered Flight Modes
will always override lower numbered Flight Modes.
aERO MODEL TyPE
22. & 23.c-MiX1 anD c-MiX2 (cOMPEnSaTiOn MiXing), cOnTinUED....
Transmitter F-MODE refers to the Flight Mode that the transmitter is currently operating in. Programming F-MODE refers
to the Flight Mode that you would like to change the programming for.
Programming F-MODE
Transmitter F-MODE
Choosing the Flight Mode - Common or Separate
1) From the Display screen, press the ENTER key to display the Programming
Menus.
2) Press the Navigation Pad 56 to highlight either C-MIX1 or C-MIX2,
then press the ENTER key to display the C-MIX1 or C-MIX2 menu. The
cursor will default to MASTER>EL.
3) Press the Navigation Pad 5to move the cursor to F-MODE>COMMON.
4) Press the INC+/M1 or DEC-/M2 keys to choose either SEPARATE or
COMMON.
5) If you choose SEPARATE, press the F-MODE key to choose the F-MODE
number you would like to program the Compensation Mixing function
for. Choose from FN, F1 or F2.
Choosing the Master Channel
The Master channel is the channel that controls the Slave channel. For example, if you set the Master channel to EL (Elevator),
when you move the elevator control stick, the Slave channel that's mixed to the elevator channel will move.
1) Press the Navigation Pad 6to highlight MASTER>EL, then press the
INC+/M1 or DEC-/M2 keys to change the desired Master channel.
MASTER setting range is EL (Elevator), AI (Aileron), TH (Throttle),
RU (Rudder), GE (Gear), and FL (Flap). The default setting is EL (Elevator).
In all cases, the Master channel always controls the Slave channel.
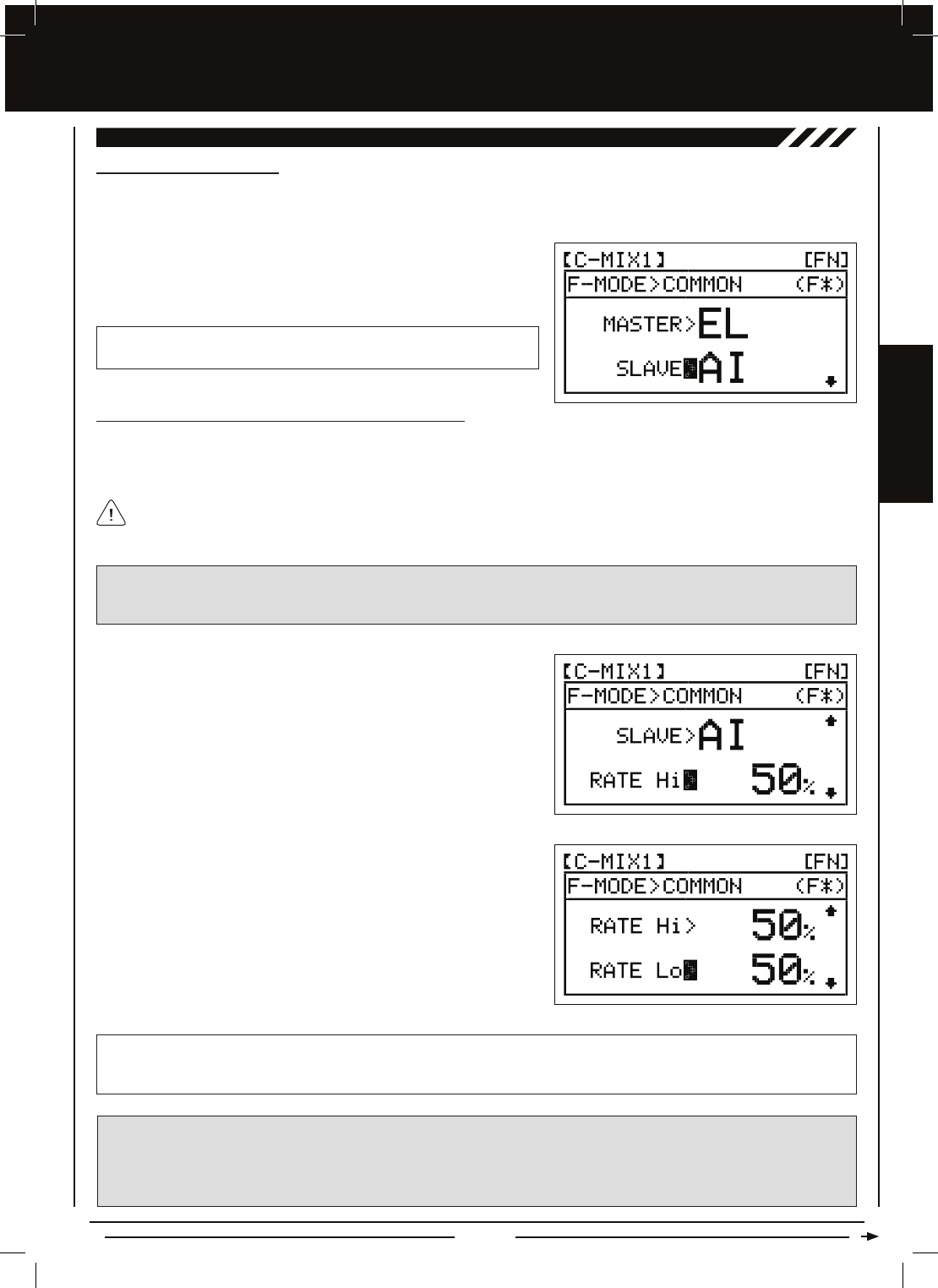
Page 49
aERO MODEL TyPE
22. & 23.c-MiX1 anD c-MiX2 (cOMPEnSaTiOn MiXing), cOnTinUED....
Choosing the Slave Channel
The Slave channel is the channel that is controlled by the Master channel. For example, if you set the Master channel to EL
(Elevator) and the Slave channel to AI (Aileron), when you move the elevator control stick, the ailerons will move.
1) Press the Navigation Pad 6to highlight SLAVE>EL, then press the
INC+/M1 or DEC-/M2 keys to change the desired Slave channel.
SLAVE setting range is EL (Elevator), AI (Aileron), TH (Throttle), RU
(Rudder), GE (Gear), and FL (Flap). The default setting is EL (Elevator).
Changing the Rate High and Rate Low Percentage Values
By changing the Rate High and Rate Low percentage values, you can program which direction the Slave channel servo
travels in relation to the Master channel servo, and program how far the Slave channel servo travels relative to how far the Master
channel servo travels.
1) Press the Navigation Pad 6 to highlight RATE Hi>0%.
2) Press the INC+/M1 or DEC-/M2 keys to change the Rate High Percentage
value.
RATE Hi and RATE Lo setting ranges are -150% to 150%. The default settings are 0%. Increasing or decreasing the Rate High
and Rate Low percentage values will change the direction that the Slave channel servo travels and the amount that it travels
relative to the Master channel servo.
The Rate High and Rate Low percentage values are a ratio of Slave channel servo travel to Master channel servo travel.
For example, if the Rate High percentage value is set to 10%, the Slave channel servo will travel 1/10th the amount in one
direction that the Master channel servo travels. This mix is Linear.
3) Press the Navigation Pad 6 to highlight RATE Lo>0%.
4) Press the INC+/M1 or DEC-/M2 keys to change the Rate Low Percentage
value.
WARNING When a Compensation Mixer is Activated, you still have separate control over the Slaved channel, however,
depending on the Rate High and Rate Low percentage values, the Slave channel End Point Adjustment could be exceeded. Be
cautious to prevent any chance of overdriving your control linkage when the Compensation Mixing function is used.
IMPORTANT When the Throttle channel is programmed as the Master channel, the Slave channel servo will not begin
to move relative to the position of the throttle control stick until the throttle control stick reaches half throttle and above. Once
the throttle control stick reaches half throttle, the Slave channel servo will begin to move. If you require the Slave channel
servo to move from Low throttle to High throttle, program the Compensation Mixer as shown in this example: MASTER>TH,
SLAVE>RU, Rate Hi>25%, RATE Lo>25%, OFFSET>-25%.
AERO MODEL TYPE
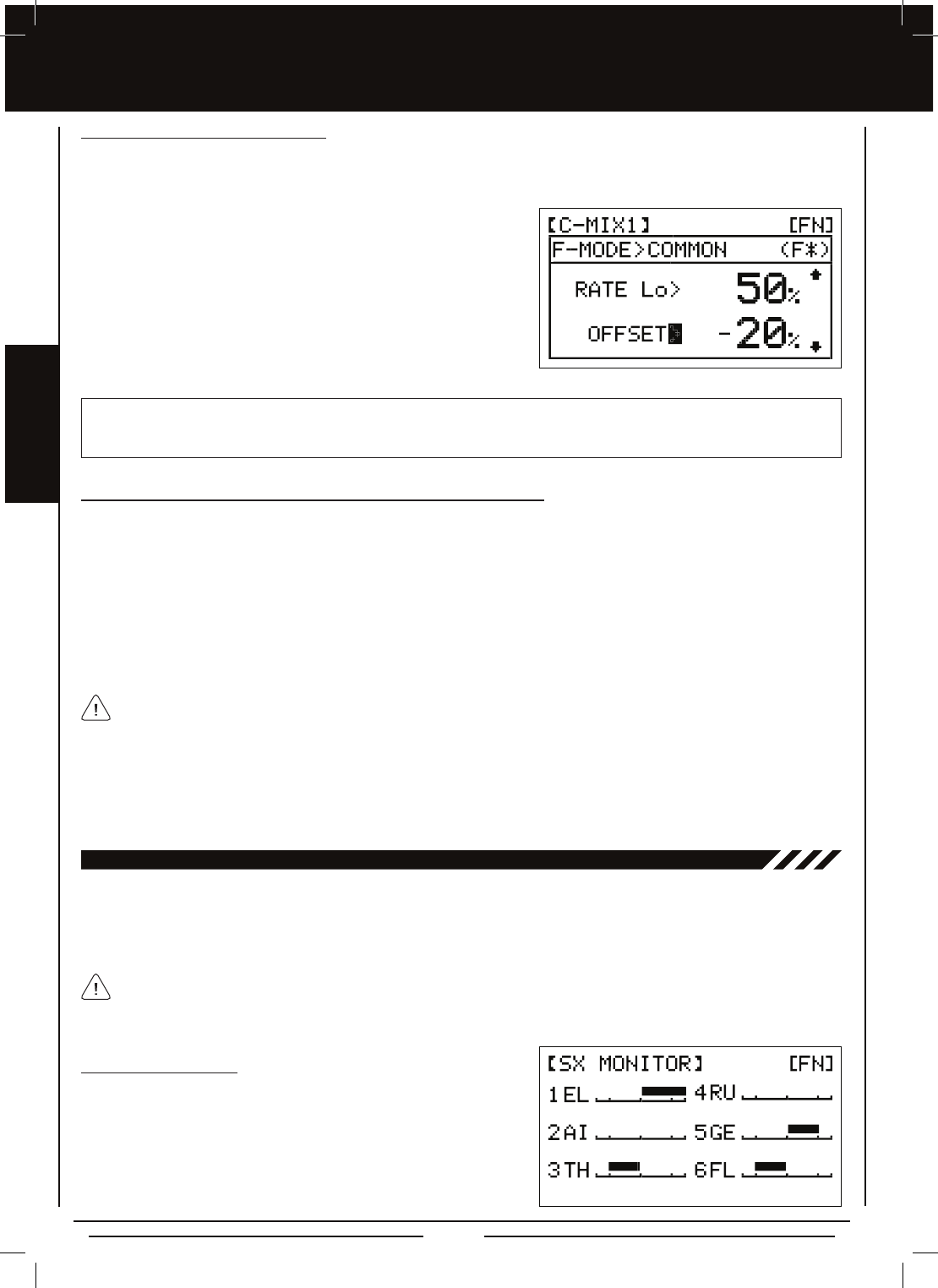
Page 50
24.SX MOniTOR (SERvO MOniTOR)
The Servo Monitor displays the output levels of each of the 6 channels in bar graph form, allowing you to monitor servo operation
in a virtual manner. This is helpful to see servo movement when the control sticks and switches are moved, and it allows you to
visualize what is occurring with servo movements when you apply different mixing values. The Servo Monitor also indicates which
channel slots in the receiver to plug your servos into (1 EL, 2AI, 3TH, 4RU, 5GE, and 6FL).
The channels displayed on the Servo Monitor will vary based on the Model Type selection options chosen in the TYPE
menu. For example, if you chose TAIL>2xEL and AILE>2 in the TYPE menu, LE (Left Elevator), RE (Right Elevator), LA
(Left Aileron), and RA (Right Aileron) will be displayed along with the corresponding receiver channel slot numbers.
aERO MODEL TyPE
Compensation Mixing Sample - Mixing Elevator to Flaperons/Spoilerons
The sample below describes how to mix elevator to aperons using Compensation Mixer 1 and control it using the Compensation
Mixing switch. This mix is common for use in 3D aerobatic aircraft where you want both ailerons to move up and down with the
elevator, yet still maintain full roll control. In order to use this mix, your aircraft must feature two separate aileron servos and you
must choose AILE>2 in the TYPE menu.
1) From within the FLAPERON menu, set the desired FL4LA> and FL4RA> percentage values. We suggest adjusting the
percentage values to achieve the maximum desired aperon control throw when the Flap switch is Activated.
In this example, the Master channel is the Elevator channel and the Slave channel is the Flap channel. The RATE Hi and RATE Lo
percentage values dene how far Up and Down the both ailerons will move together, and is a percentage of the FL4LA and FL4RA
percentage values you previously programmed in the FLAPERON menu. To Activate this mix, Activate Compensation Mixer 1 by
pulling the Compensation Mixer switch down. It's not necessary to use the Flap control switch when using this mix.
1) Press the Navigation Pad 6 to highlight OFFSET>0%.
2) Press the INC+/M1 or DEC-/M2 keys to change the Offset Percentage
value.
OFFSET setting range is -100% to 100%. The default setting is 0%. Increasing the Offset percentage value will shift the neutral
position of the Slave servo in one direction and decreasing the Offset percentage value will shift the neutral position of the
Slave servo in the opposite direction.
MASTER>EL
SLAVE>FL
RATE Hi>50%
RATE Lo>50%
OFFSET>0%
The positive and negative values shown in the example may vary based on the NOR/REV status
of your aileron and elevator servos. You may need to change the percentage values to suit.
2) Program the Compensation Mixer 1 options from the within the C-MIX1 menu, as shown at right.
Using the Servo Monitor
1) From the Display screen, press the ENTER key to display the Programming
Menus.
2) Press the Navigation Pad 56 to highlight SX MONITOR, then press
the ENTER key to display the Servo Monitor.
3) Moving the control sticks and channel switches will display the position
and movement of each of the servos.
Changing the Offset Percentage Value
The Offset percentage value changes the neutral position of the Slave channel servo when the Compensation Mixing function is
Activated. For example, when an Offset percentage value is programmed, the Slave channel servo neutral position and its two
End Point positions will 'shift' the programmed amount.
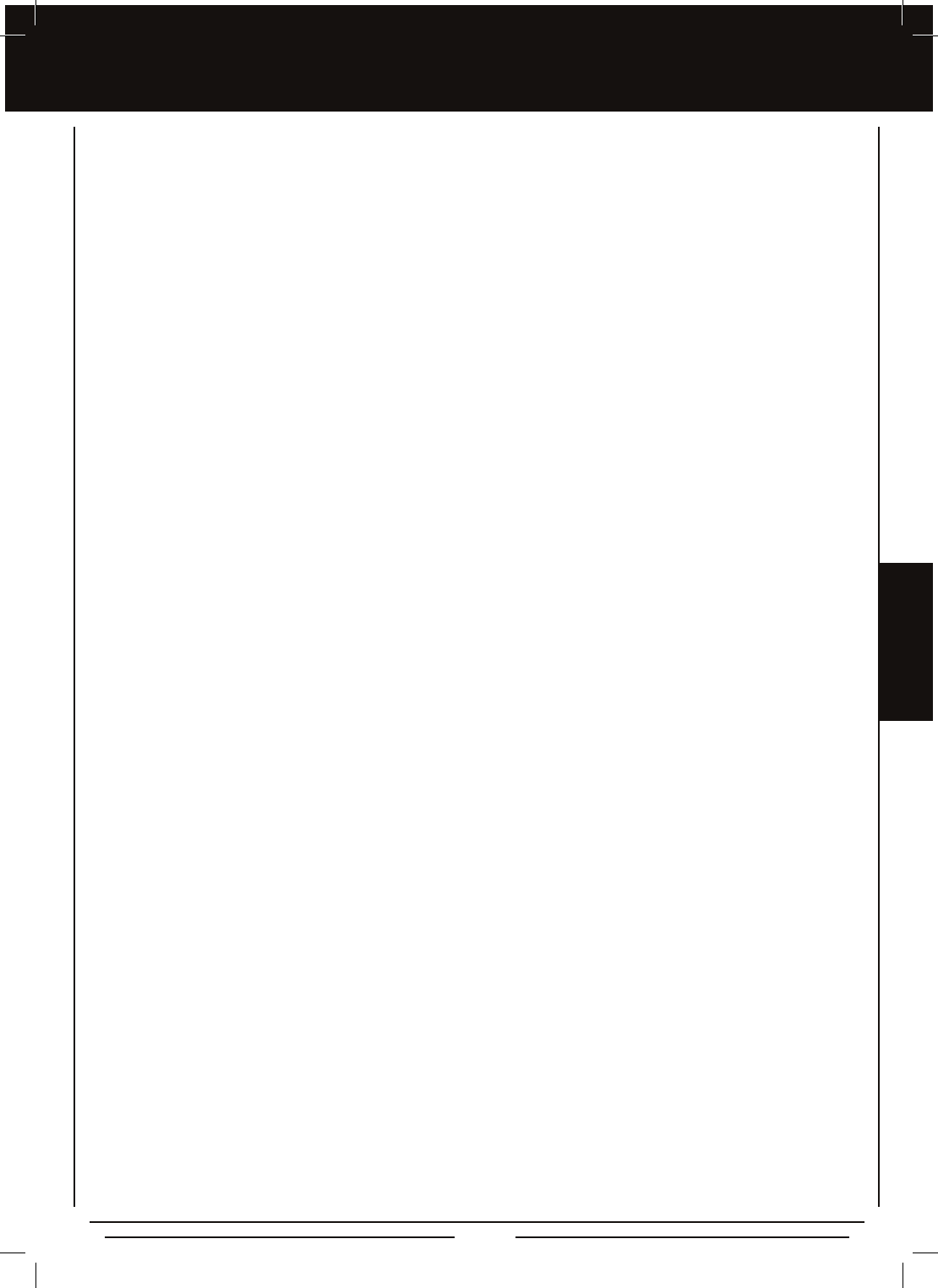
Page 51
hELi MODEL TyPE cOnTEnTS
General Information ......................................................................................................................................................... Page 52
HELI Model Type Menu Flow Chart................................................................................................................................. Page 52
HELI Model Type Transmitter Layout ............................................................................................................................. Page 53
MODEL SELE (Model Select)........................................................................................................................................... Page 53
MODEL NAME (Model Naming)....................................................................................................................................... Page 54
TYPE (Model Type) ........................................................................................................................................................... Page 55
TRAINER (Trainer System) .............................................................................................................................................. Page 57
STOP WATCH (Stop Watch and Count Up Timer).......................................................................................................... Page 58
DATA COPY (Model Programming Data Copy) .............................................................................................................. Page 59
DATA RESET (Model Programming Data Reset) ........................................................................................................... Page 60
REVERSE (Servo Reversing)........................................................................................................................................... Page 61
CENTER (Servo Centering Sub-Trim)............................................................................................................................. Page 61
EPA (End Point Adjustment)............................................................................................................................................ Page 63
CP-EPA (CCPM End Point Adjustment).......................................................................................................................... Page 64
SWASH (Swashplate Setup) ............................................................................................................................................ Page 64
TH-CUT (Throttle Cut) ...................................................................................................................................................... Page 65
D/R & EXP (Dual Rate and Exponential)......................................................................................................................... Page 66
TRIM (Digital Trim)............................................................................................................................................................ Page 69
TH-CURVE (Throttle Curve)............................................................................................................................................. Page 69
PI-CURVE (Pitch Curve)................................................................................................................................................... Page 72
REVO-MIX (Revolution Mixing) ....................................................................................................................................... Page 74
GYRO (Remote Gyro Control) ......................................................................................................................................... Page 75
C-MIX1 (Compensation Mixing 1).................................................................................................................................... Page 77
C-MIX2 (Compensation Mixing 2).................................................................................................................................... Page 77
SX MONITOR (Servo Monitor) ......................................................................................................................................... Page 80
HELI MODEL TYPE
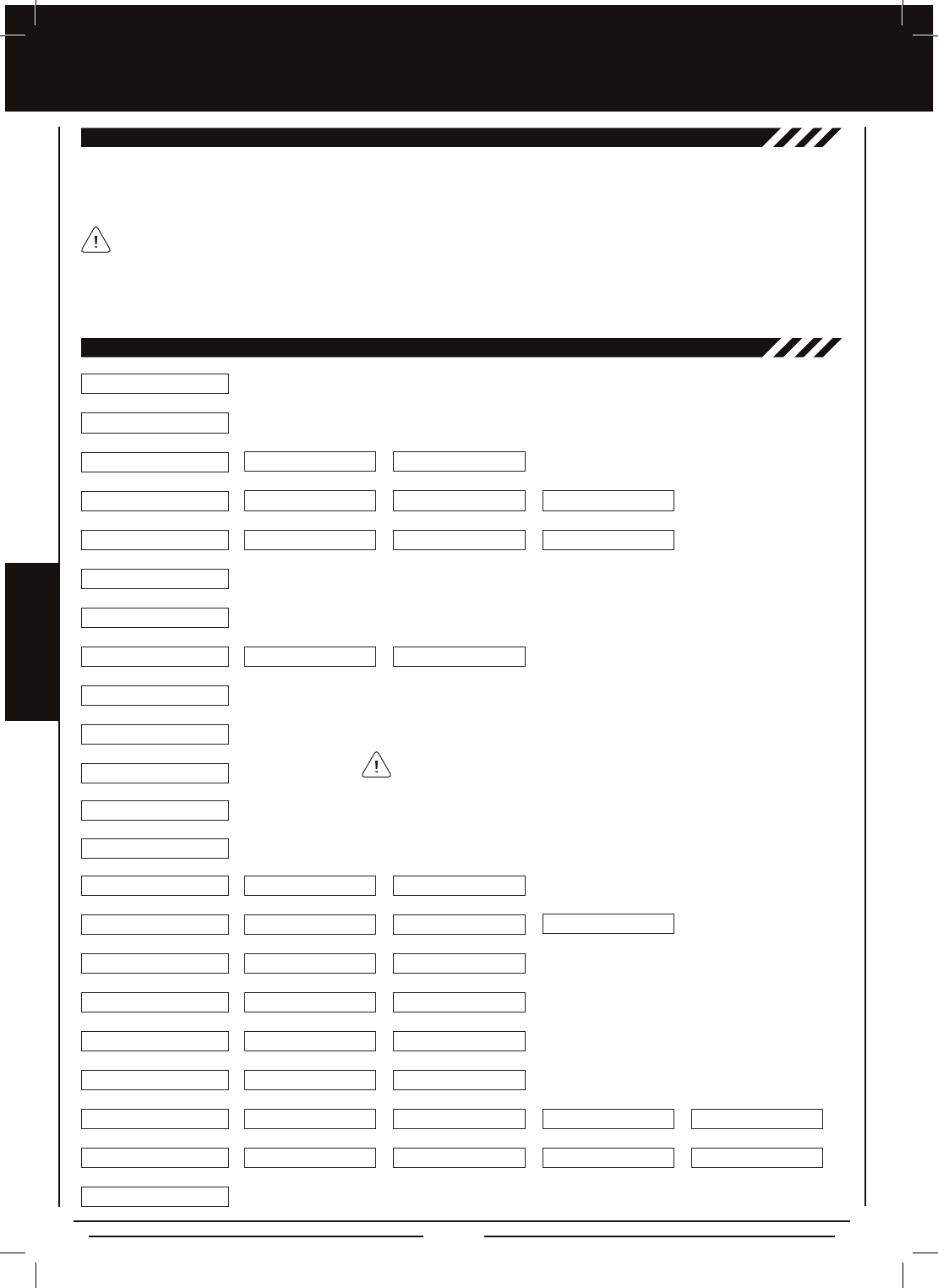
Page 52
hELi MODEL TyPE
hELi MODEL TyPE PROgRaMMing MEnU FLOw chaRT
Use this Flow Chart to familiarize yourself with the HELI Model Type Programming Menu structure.
Descriptions regarding all HELI Model Type functions and programming are found on pages 53
through 80.
04.TRAINER
03.TYPE
02.MODEL NAME
01.MODEL SELE
05.STOP WATCH
06.DATA COPY
07.DATA RESET
08.REVERSE
09.CENTER
10.EPA
6
6
6
6
6
6
6
6
6
6
HELI AERO
6
6
To access the HELI Model Type Programming Menus, turn the transmitter ON. A helicopter icon will be shown on the Display
screen. From the Display screen, press the ENTER key to display the Programming Menus, then press the Navigation Pad 56to
scroll to the desired Programming Menu. Press the ENTER key to access the desired Programming Menu.
gEnERaL inFORMaTiOn
From within any Programming Menu, press the END/M3 key continuously to return to the Display screen. If the Display screen
is not displayed when you turn the transmitter ON, continuously press the END/M3 key until the Display screen is displayed.
If a helicopter icon is not shown on the Display screen, use the Model Select function to select a HELI model. For more
information, see page 53.
INH MASTER
6
6
SLAVE
6
NOR REV
6
6
MIN SEC
6
6
1/10
6
11.CP-EPA
12.SWASH
6
6
13.TH-CUT
14.D/R & EXP
15.TRIM
16.TH-CURVE
17.PI-CURVE
18.REVO-MIX
19.GYRO
20.C-MIX1
21.C-MIX2
22.SX MONITOR
6
6
6
6
6
6
6
6
6
D/R [1] - D/R [2] EXP [1] - EXP [2]
6
6
COMMON SEPARATE
6
6
HOLD POINT
6
6
POINT RATE
6
6
HIGH LOW
6
6
GYRO [1] GYRO [2]
6
6
MASTER SLAVE
6
6
RATE HIGH / RATE LOW
6
OFFSET
6
MASTER SLAVE
6
6
RATE HIGH / RATE LOW
6
OFFSET
6
TH-TRIM LOCK (F1)
6
Unless otherwise noted, all programming changes take effect immediately.
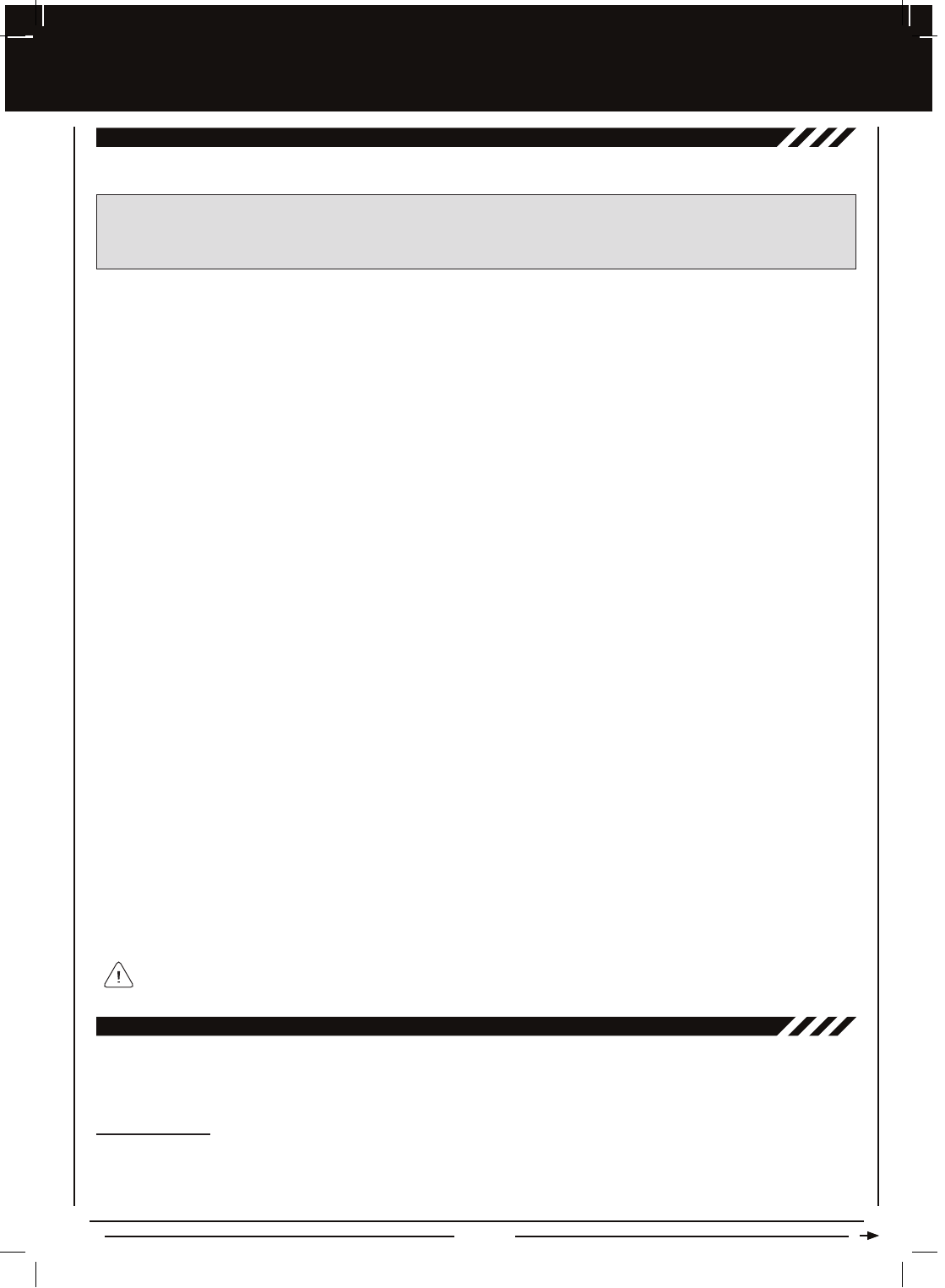
Page 53
hELi MODEL TyPE
The diagram below shows the transmitter control stick and switch layout in the HELI Model Type conguration.
IMPORTANT Since each of the three Flight Modes can be programmed separately, before making programming changes,
verify that you are in the Flight Mode you want to make programming changes to. To avoid confusion, we suggest leaving both
Flight Mode switches pushed away from you (OFF) and use the F-MODE key from within the programming menus to choose
which Flight Mode you would like to make programming changes to.
hELi MODEL TyPE TRanSMiTTER LayOUT
When any switch is moved into the Up or Forward position (pushed away from you), this is considered the OFF position.
When moved into the Down or Back position (pulled toward you), this is considered the ON position.
01.MODEL SELE (MODEL SELEcT)
The Model Select function allows you to load the Programming Data for the particular model you wish to y. The MODEL SELECT
menu displays the currently selected model, along with a list of available models that can be selected. The specic Model Type
(AERO or HELI) is displayed for each of the models. The TM-160 can store Programming Data for up to 10 different models.
Selecting a Model
1) From the Display screen, press the ENTER key to display the Programming Menus.
2) Press the Navigation Pad 56 to highlight MODEL SELE, then press the ENTER key to display the MODEL SELECT menu.
The currently selected model in the Model Select List will be highlighted.
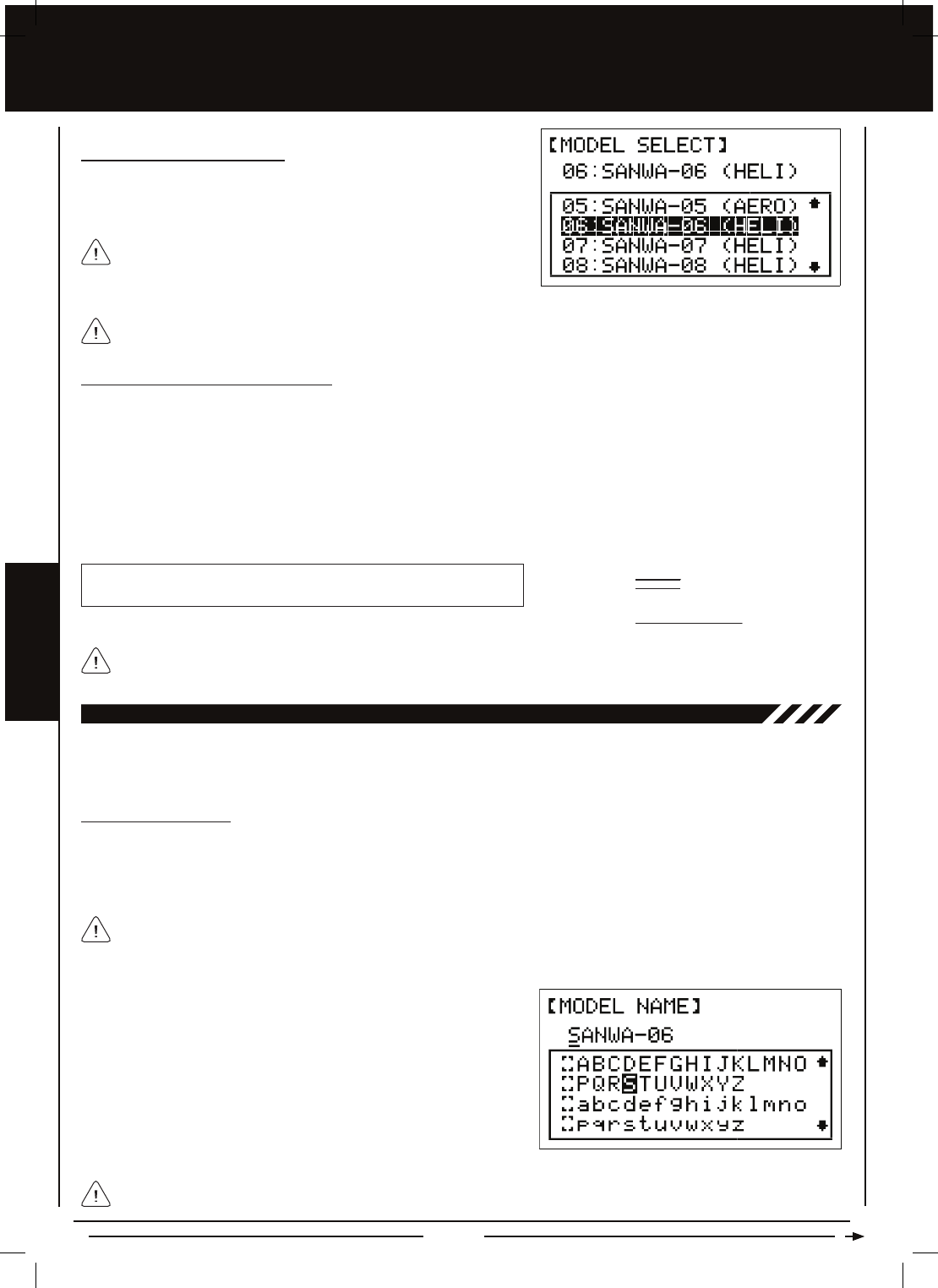
Page 54
hELi MODEL TyPE
In the default conguration, the Model Select List contains 5 AERO Model Types and 5 HELI Model Types. The Model Type
for any of the 10 models in the Model Select List can be changed using the TYPE menu. For more Information, see page 55.
When you press the ENTER key to select a model, the Programming
Data for that model will be loaded immediately.
Selecting a Model, Continued....
3) Press the Navigation Pad 56 to highlight the model you would like to
select, then press the ENTER key to select the highlighted model. That
model will be displayed above the Model Select List.
Using the Direct Model Select Function
The Direct Model Select function allows you to select one of rst three models from memory without going through the MODEL
SELECT menu. This makes it much quicker and easier to load the Programming Data for your three most-used models.
Before ying, verify that the Model Name displayed at the top of the Display screen is the actual model that you'll be ying.
1) Turn the transmitter OFF.
2) Press and HOLD the programming key of the model you wish to setup
or y, then turn the transmitter ON. The Model Name will be displayed
at the top of the Display screen.
INC+/M1 selects Model 1, DEC-/M2 selects Model 2, and END/M3
selects Model 3.
02.MODEL naME (MODEL naMing)
The Model Naming function allows you to name each of the 10 individual models. This makes it easy to keep track of multiple
models. The Model Name can consist of up to 8 letters, numbers, or symbols. Choose from capital letters, lower case letters,
numbers, and various symbols.
Entering a Model Name
1) From the Display screen, press the ENTER key to display the Programming Menus.
2) Press the Navigation Pad 56 to highlight MODEL NAME, then press the ENTER key to display the MODEL NAME menu.
The cursor will default to the left side of the top row of letters and an underscore will appear under the rst character in the name.
A model must be selected before a Model Name can be entered or modied. In the default conguration, M01:SANWA-1
is selected. To enter a Model Name for another model, that model must rst be selected using the MODEL SELECT menu
or the Direct Model Select function. For more information, see the 01.MODEL SELECT section on page 53.
Press the Navigation Pad 56 repeatedly to scroll up and down the list of characters. In addition, press the INC+/M1 and
DEC-/M2 keys to move the underscore left and right respectively.
3) Press the Navigation Pad 5634 to highlight a character, then press
the ENTER key to select the highlighted character. That character will be
displayed and the underscore will move to the next space.
4) Repeat step 3 to enter the rest of the characters. Up to eight characters
can be entered. The name of your model will be displayed on the
top of the Display screen.
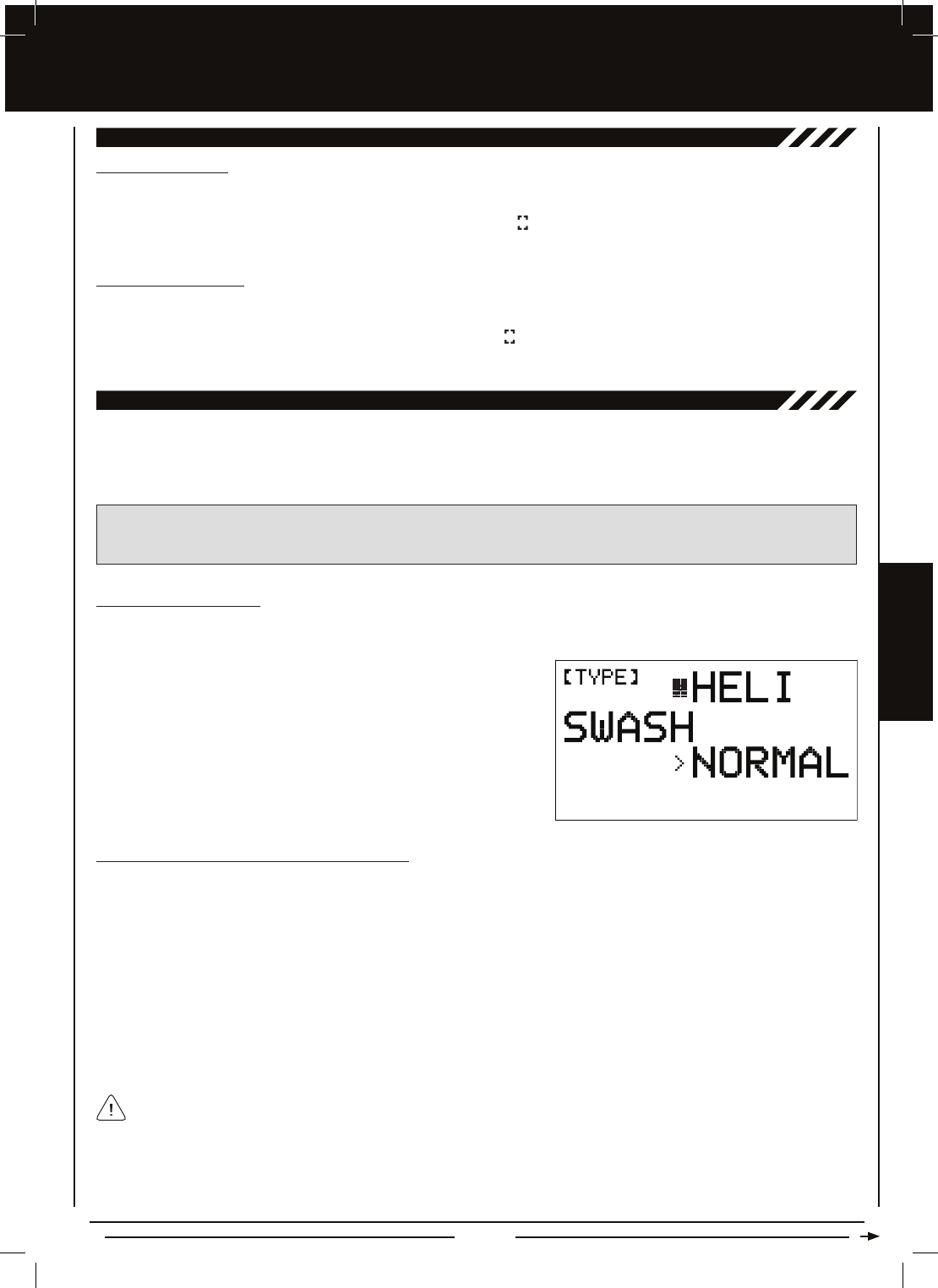
Page 55
hELi MODEL TyPE
Deleting a Character
1) Press the INC+/M1 or DEC-/M2 keys to move the underscore under the character you want to erase.
2) Press the Navigation Pad 5634 to highlight the Erase Bracket , then press the ENTER key to erase the underscored
character.
Deleting a Model Name
1) Press the INC+/M1 and DEC-/M2 keys at the same time to move the underscore under the rst character.
2) Press the Navigation Pad 5634 to highlight the Erase Bracket , then press the ENTER key repeatedly to erase the entire
Model Name.
02.MODEL naME (MODEL naMing), cOnTinUED....
03.TyPE (MODEL TyPE)
The Model Type function allows you to quickly set up the transmitter's low-level mixing based on the type of model you're
ying. Common templates for HELI and AERO Model Types are provided. For example, if your model features CP3F swashplate
mixing, choosing the CP3F option will automatically change the transmitter's programming to accommodate this setup. This
takes the guess-work out of setting up your model.
WARNING The Model Type function is used when setting up a new model and should be done prior to making any
programming changes to your model. When Model Type selection options are changed for the currently selected model,
all programming (including custom programming) for that model will be reset.
2) Press the Navigation Pad 56 to highlight TYPE, then press the
ENTER key to display the TYPE menu. The cursor will default to >HELI
or >AERO depending on the particular model you've selected.
3) If the current Model Type is >AERO, press the INC+/M1 or DEC-/M2
keys to change the selection option to >HELI.
Changing the Model Type
1) From the Display screen, press the ENTER key to display the Programming Menus.
Making HELI Swashplate Type Selection Options
Choose the HELI Swashplate Type that suits your helicopter. There are three basic Swashplate Types available:
Normal - In this conguration the swashplate does not control pitch. It only controls right, left, fore, and aft cyclic. Usually the
servos are installed 90º apart but do not mix with collective to control pitch. This conguration is generally used for xed-pitch
helicopters or helicopters that have a completely separate control system to control collective pitch.
3-Point CCPM - In this conguration the cyclic and collective controls are mixed. The servos that control the swashplate are
installed either 120º or 140º apart, depending on the conguration.
4-Point CCPM - In this conguration the cyclic and collective controls are mixed. The servos that control the swashplate are
installed 90º apart.
Receiver channel slot assignments will change based on the Swashplate Type selection options chosen. To verify which
receiver channel slots to plug your servos into, navigate to the SX MONITOR menu after saving your Swashplate Type
selection options. For more information, see page 80.
1) From within the TYPE menu, verify that >HELI is displayed. If >AERO is displayed, change the Model Type to HELI by
following the steps in the Changing the Model Type section above.
HELI MODEL TYPE
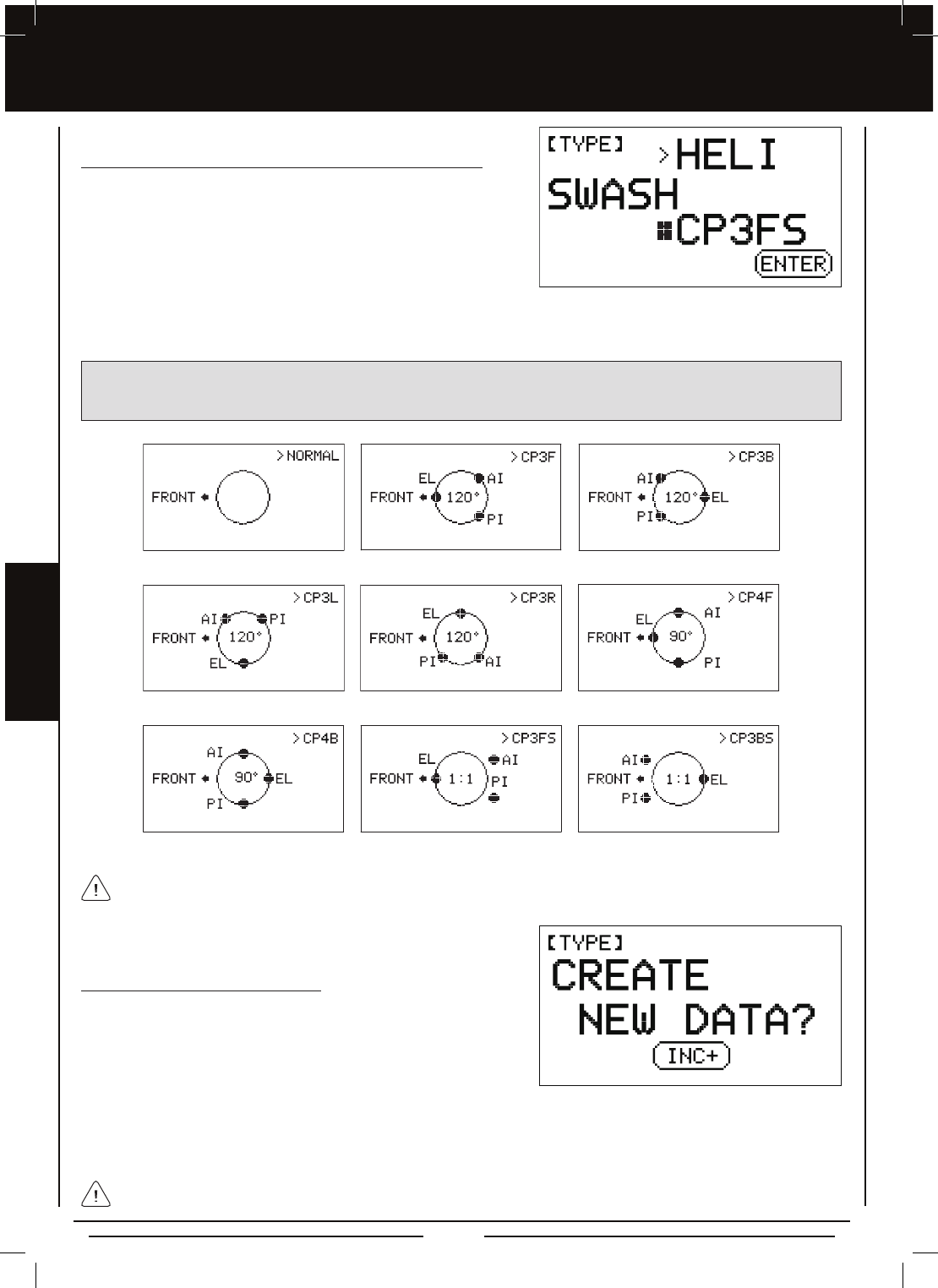
Page 56
hELi MODEL TyPE
Making HELI Swashplate Type Selection Options, Continued....
2) Press the Navigation Pad 6to highlight SWASH>NORMAL.
3) Press the INC+/M1 or DEC-/M2 keys to change the Swashplate Type
selection option. When a Swashplate Type selection option is changed,
ENTER will ash in the Programming Window.
WARNING There are a number of different Swashplate Type selection options available. Make sure that the Swashplate Type
selection option you choose matches exactly the Swashplate Type used by your helicopter. Refer to your helicopter's Operating
Manual for more information.
The following Swashplate Type selection options are available. The diagrams display the swashplate geometry, the number of
servos used, and the specic placement of those servos.
120º, 90º, and 1:1* refers to the physical relationship and geometry of the servo placements on the swashplate.
> NORMAL: Non-CCPM > CP3F 120º with 3 Servos > CP3B 120º with 3 Servos
> CP3L 120º with 3 Servos > CP3R 120º with 3 Servos
> CP3FS 1:1* with 3 Servos (2 Offset) > CP3BS 1:1* with 3 Servos (2 Offset)
> CP4F 90º with 3 Servos
> CP4B 90º with 3 Servos
*1:1 is sometimes referred to as 140º.
If you want to go back and change the settings or if you don't want to create the new settings for any reason, press the
DEC-/M2 or END/M3 keys.
Saving Model Type Selection Options
1) After making your choices, press the ENTER key. CREATE NEW
DATA? will be displayed and INC+ will ash in the Programming Window.
2) Press the INC+/M1 key to Create New Data. After ~10 seconds, the new Programming Data will be loaded into the transmitter
as indicated by the progress bar, and COMPLETE!! will be displayed in the Programming Window. Press any key to return to
the TYPE menu.
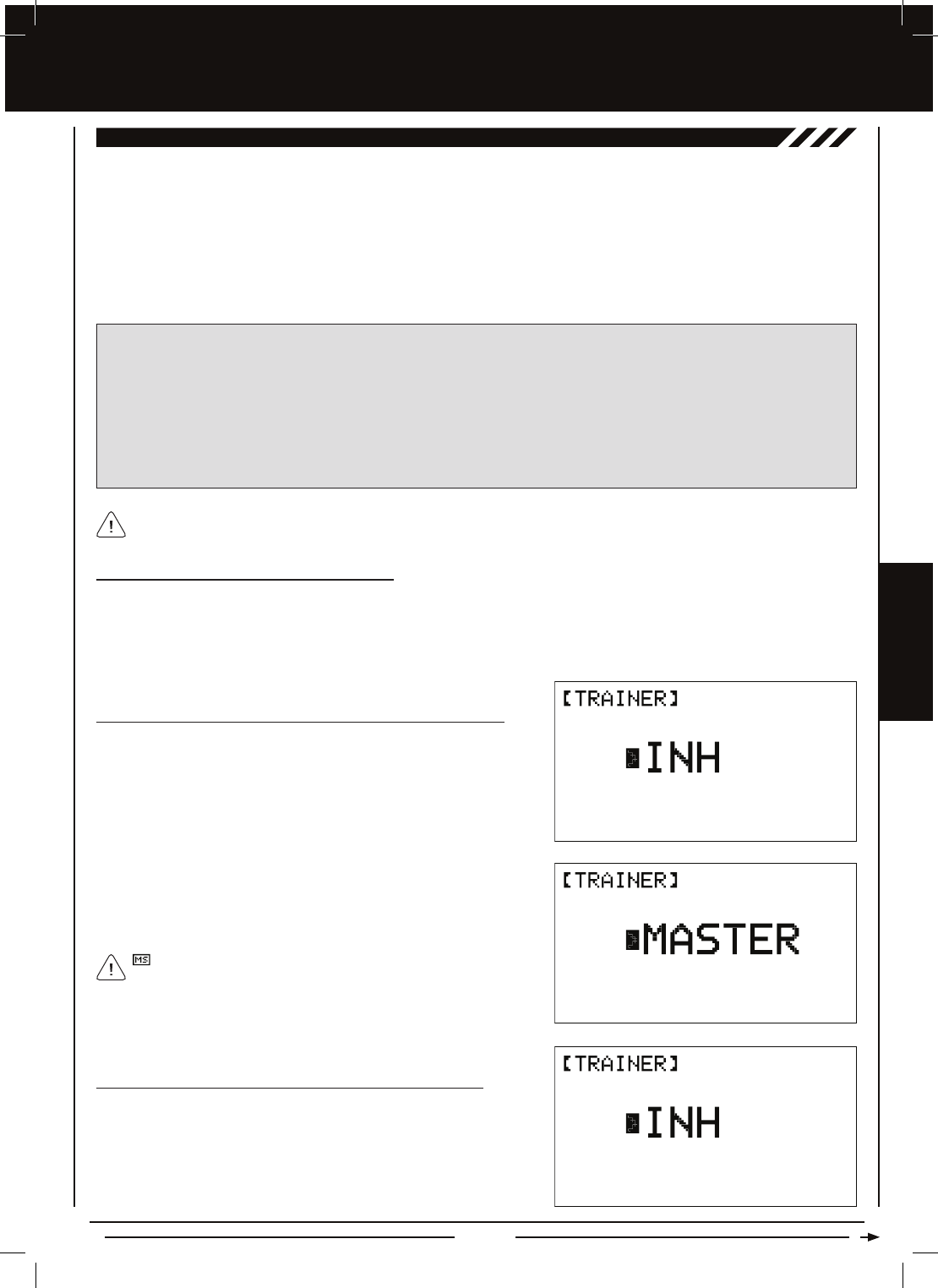
Page 57
hELi MODEL TyPE
04.TRainER (TRainER SySTEM)
The TM-160 transmitter features a Trainer System that allows you to connect two TM-160 transmitters to one another or connect
one TM-160 transmitter to one SD-5G transmitter or to one SD-10G transmitter for the purpose of training a new pilot or for training
a more experienced pilot on a new model. During use, one transmitter acts as the Master (Instructor) and the other transmitter
acts as the Slave (Student). The Instructor controls the Student's model as long as the Trainer switch is released. For example,
once the Instructor maneuvers the model to a safe altitude, the Instructor pulls and holds the Trainer switch to give control of the
model to the Student. The Student will have control of the model as long as the Instructor holds the Trainer switch. Once the
Trainer switch is released, the Instructor will have control of the model once again. If at any time the Instructor feels that the
Student is in a situation that endangers the model, the Instructor releases the Trainer switch and control of the model returns
instantly to the Instructor.
IMPORTANT INFORMATION ABOUT THE TRAINER SYSTEM
lThe Trainer System is currently compatible ONLY with another TM-160 transmitter or an SD-5G or SD-10G transmitter and
you MUST use the Airtronics 97107 Trainer Cable. See your local Airtronics dealer for more information and availability.
lDuring use, both the Master transmitter and the Slave transmitter should be turned ON. If using an SD-10G transmitter as
the Slave transmitter, to save battery power only the transmitter LCD needs to be turned ON, using the DISPLAY key.
lBoth transmitters must be programmed identically for the Trainer System to function properly. For example, Servo Reversing,
End Point Adjustments, etc. must be identical. In addition, the Instructor transmitter Trainer System function must be set to
MASTER and the Student transmitter Trainer System function must be set to SLAVE.
If using the Trainer System with an Airtronics SD-5G transmitter or an SD-10G transmitter, please refer to those transmitter's
Operating Manuals for more information on the correct setup and use of those transmitter's Trainer functions.
Connecting the Master and Slave Transmitters
1) Turn both transmitters OFF.
2) Plug one end of the Airtronics 97107 Trainer Cable (available separately) into the back of one TM-160 transmitter, then
plug the other end of the Trainer Cable into the back of the second TM-160 transmitter or an SD-5G or SD-10G transmitter.
Activating the Trainer Function - Master (Instructor) Transmitter
1) Turn the Master (Instructor) transmitter ON. From the Display screen,
press the ENTER key to display the Programming Menus.
2) Press the Navigation Pad 56 to highlight TRAINER, then press the
ENTER key to display the TRAINER menu. The cursor will default to >INH.
3) Press the INC+/M1 key to change the current transmitter's Trainer
mode to MASTER. >MASTER will be displayed.
will be displayed on the Display screen, indicating that the
transmitter is operating in MASTER mode.
Activating the Trainer Function - Slave (Student) Transmitter
1) Turn the Slave (Student) transmitter ON. From the Display screen,
press the ENTER key to display the Programming Menus.
2) Press the Navigation Pad 56 to highlight TRAINER, then press the
ENTER key to display the TRAINER menu. The cursor will default to >INH.
HELI MODEL TYPE
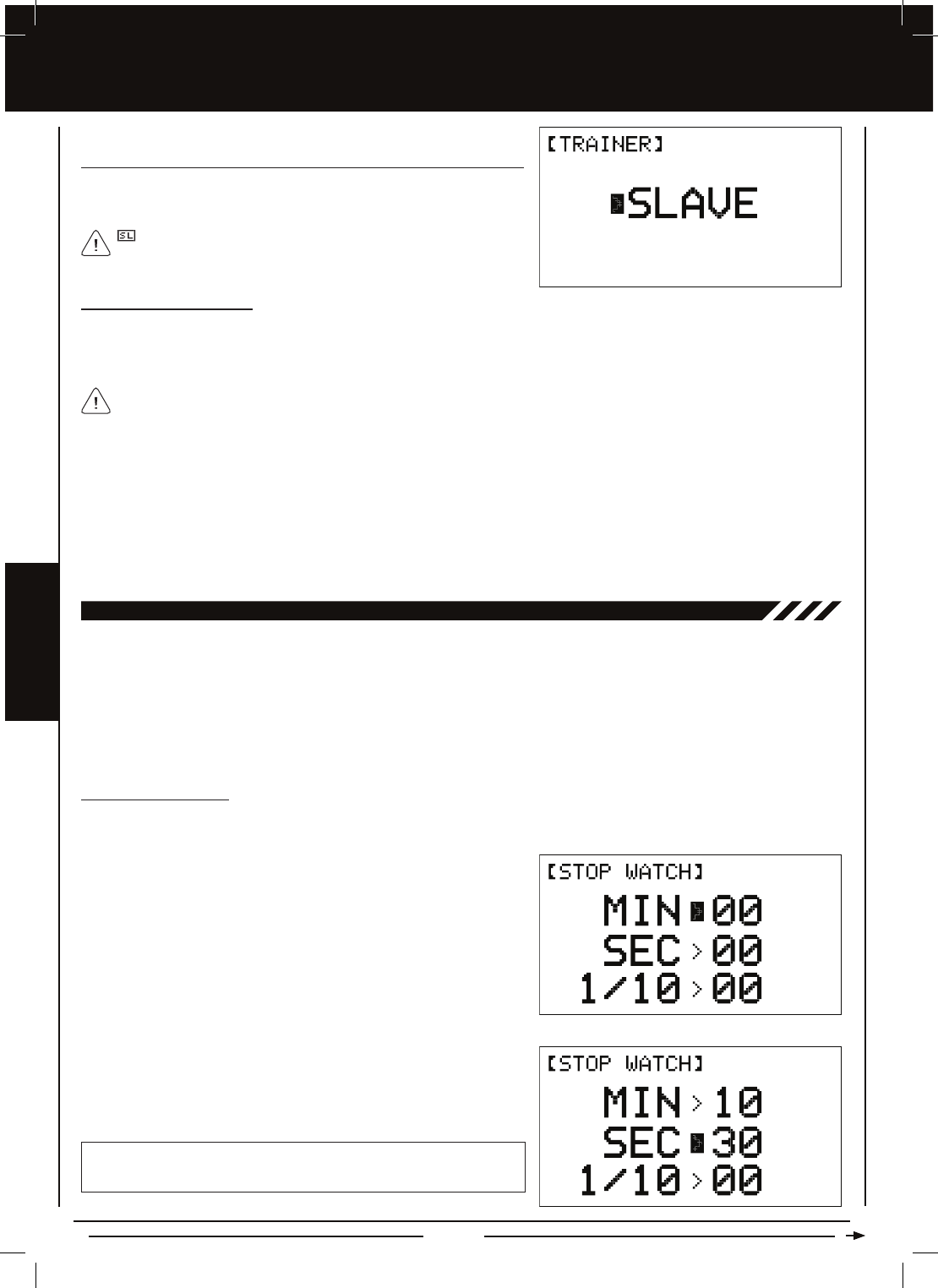
Page 58
hELi MODEL TyPE
Using the Trainer Function
1) The Trainer Cable should be connected between the two transmitters and the Trainer function on both transmitters should
be Activated as described previously. Both the Master (Instructor's) transmitter and the Slave (Student's) transmitter should
be turned ON.
will be displayed on the Display screen, indicating that the
transmitter is operating in SLAVE mode.
Activating the Trainer Function - Slave (Student) Transmitter, Continued....
3) Press the INC+/M1 key to change the current transmitter's Trainer
mode to SLAVE. >SLAVE will be displayed.
05.STOP waTch (STOP waTch anD cOUnT UP TiMER)
The Stop Watch function is used to either count down from a programmed Start time (Count Down mode) or to count up from
zero if no Start time is programmed (Count Up mode). In Count Down mode, an audible tone will sound in 1 second intervals
when the Stop Watch reaches 10 seconds from zero. When zero is reached, a long audible tone will sound and the Stop Watch
will begin to count up. In Count Up mode, an audible tone will sound at 1 minute intervals to remind you that the count down time
(zero) has been surpassed.
The Stop Watch function has a number different uses, but one of the more popular uses is to use it as a fuel usage indicator to
remind you to land within an allotted amount of time to ensure that your model doesn't run out of fuel.
Setting the Stop Watch
1) From the Display screen, press the ENTER key to display the Programming Menus.
2) Press the Navigation Pad 56 to highlight STOP WATCH, then press
the ENTER key to display the STOP WATCH menu. The cursor will
default to MIN>00.
2) Turn the receiver ON in the model you're using for training and verify that the Instructor's transmitter controls the model's
control surfaces correctly.
3) Activate the Trainer function by pulling and HOLDING the Trainer switch on the Instructor's transmitter continuously and verify
that the Student's transmitter controls the model's control surfaces correctly.
4) When the Trainer switch is released, the Instructor will have full control over the model. When the Trainer switch is pulled
forward and held continuously, the Student has control over the model. As soon as the Trainer switch is released, the Instructor
will have full control over the model once again.
If using an SD-10G transmitter as the Slave transmitter, to save battery power only the transmitter LCD needs to be
turned ON, using the DISPLAY key.
3) The Minute, Second, and 1/10 Second times can be set independently.
Press the Navigation Pad 56 to highlight the time interval you would
like to program, then press the INC+/M1 or DEC-/M2 keys to set the
desired Start time.
MIN setting range is 0 to 59', SEC setting range is 0 to 59" and 1/10
setting range is 0 to 90. The default setting for each is 0.
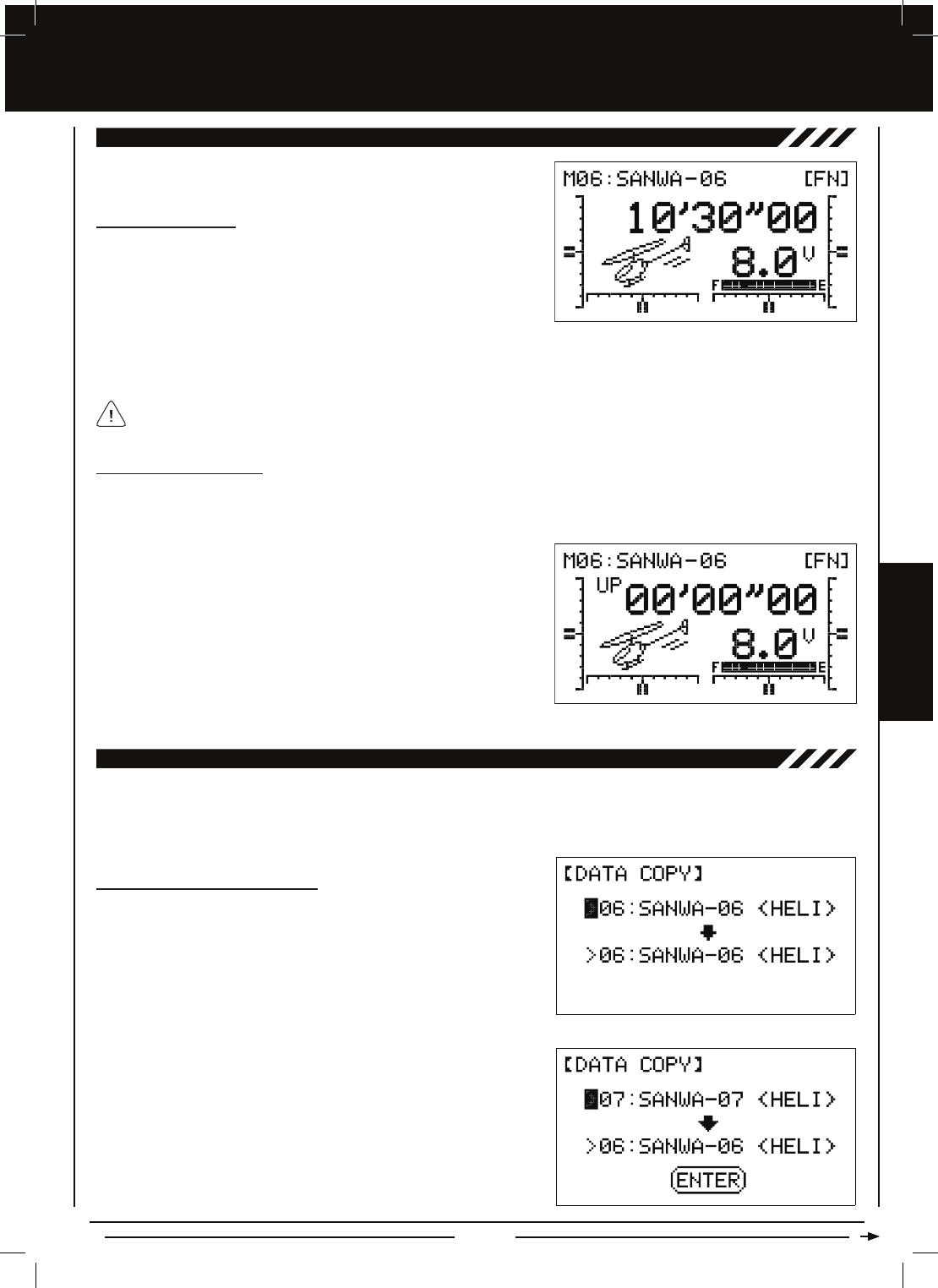
Page 59
hELi MODEL TyPE
The Stop Watch is displayed in Minutes, Seconds, and 1/10 Seconds. 00' (Minutes) 00" (Seconds) 00 (1/10 Seconds).
Using the Stop Watch
1) Press the END/M3 key two times to return to the Display screen. The
Start time that you programmed will be displayed.
Using the Count Up Timer
The Stop Watch function can also be used as a Count Up timer when the Stop Watch is set to 00'00"00. When the Count Up timer
runs, UP will be displayed on the Display screen and an audible tone will sound at 1 minute intervals.
1) Set the Stop Watch Start time to 00'00"00 as described in the Setting
the Stop Watch section above.
2) To Start the Count Up timer, press the INC+/M1 key. To Stop the Count
Up timer, press the INC+/M1 key a second time. To Reset the Count Up
timer to 00'00"00, press the INC+/M1 and DEC-/M2 keys at the same time.
2) To Start the Stop Watch, press the INC+/M1 key. To Stop the Stop Watch, press the DEC-/M2 key a second time. To Reset
the Stop Watch to the programmed Start time, press the INC+/M1 and DEC-/M2 keys at the same time.
05.STOP waTch (STOP waTch anD cOUnT UP TiMER), cOnTinUED....
06.DaTa cOPy (MODEL PROgRaMMing DaTa cOPy)
The Data Copy function allows you to copy the Programming Data from one model to another model. This is convenient if you
have similar Model Types. For example, if you have two models that are similar, you can copy the Programming Data from the
rst model to the second model to use as a base to start ne-tuning the programming for the second model.
Copying Model Programming Data
1) From the Display screen, press the ENTER key to display the Programming
Menus.
2) Press the Navigation Pad 56 to highlight DATA COPY, then press the
ENTER key to display the DATA COPY menu. The cursor will default to
the currently selected model, for example >06:SANWA-06 <HELI>.
3) With the cursor adjacent to the top model number, press the INC+/M1
or DEC-/M2 keys to select the model you would like to copy Programming
Data FROM. ENTER will ash in the Programming Window.
HELI MODEL TYPE
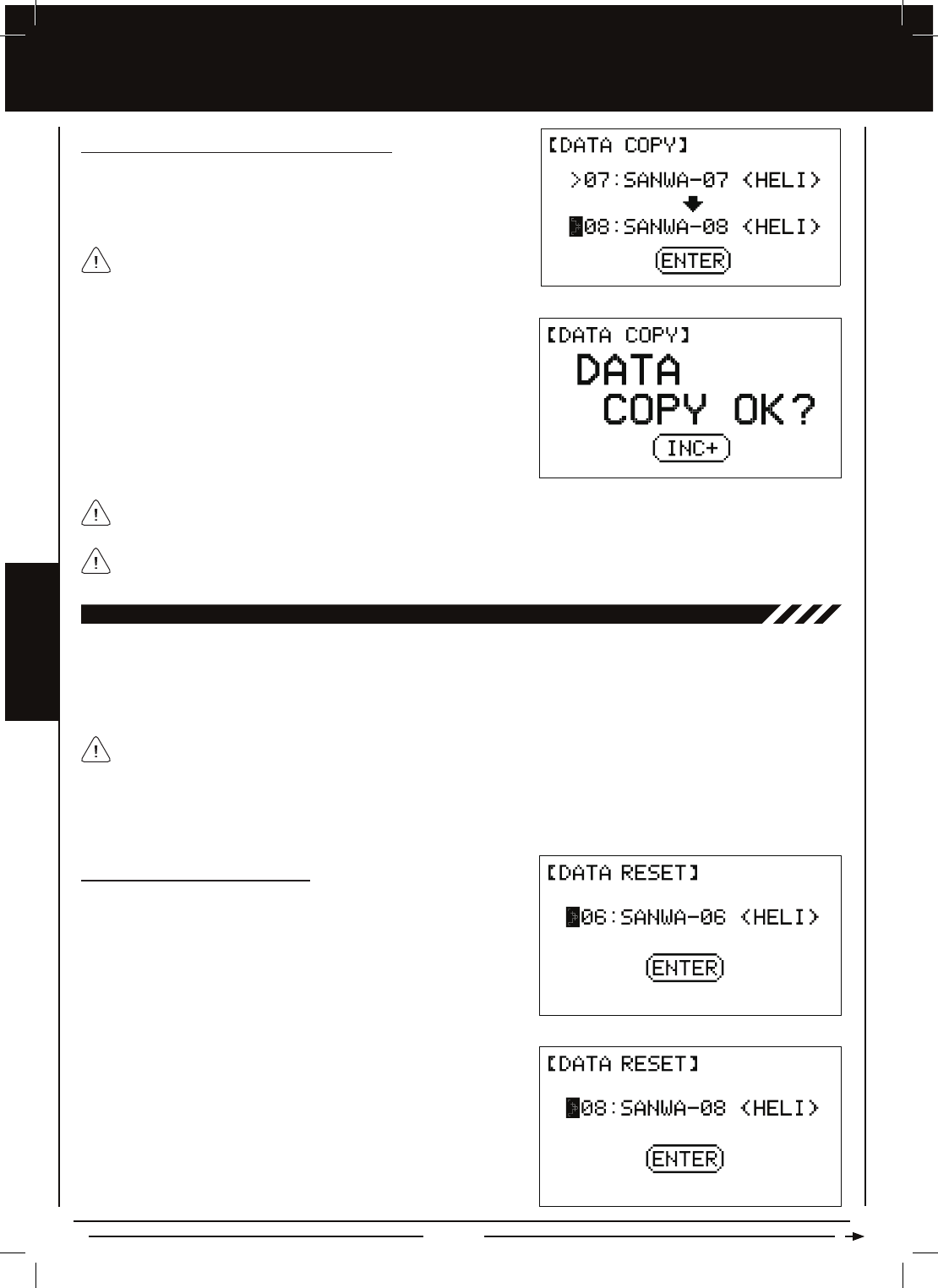
Page 60
hELi MODEL TyPE
Copying Model Programming Data, Continued....
4) Press the Navigation Pad 6to move the cursor to the bottom model
number, then press the INC+/M1 or DEC-/M2 keys to select the model
you would like to copy Programming Data TO. ENTER will continue to
ash in the Programming Window.
It's not possible to copy Programming Data from one model to the
same model. If you attempt this, ENTER will not ash.
5) Press the ENTER key. DATA COPY OK? will be displayed and INC+
will ash in the Programming Window.
6) Press the INC+/M1 key to Copy the model Programming Data. After ~10
seconds, the Programming Data will be copied as indicated by the
progress bar, and COMPLETE!! will be displayed in the Programming
Window. Press any key to return to the DATA COPY menu.
All model-specic Programming Data, including the Model Name will be copied to the selected model.
If you want to go back and change models or you don't want to copy the Programming Data for any reason, press the
DEC-/M2 or END/M3 keys.
07.DaTa RESET (MODEL PROgRaMMing DaTa RESET)
The Data Reset function allows you to Reset model-specic Programming Data for any model back to the factory default settings.
As described previously, individual programming settings can be Reset to the factory default settings by pressing the INC+/M1
and DEC-/M2 keys at the same time, however, this is time consuming if you want to change all of the selected model's programming
settings back to default. Using the Data Reset function makes doing this much quicker and more accurate, since nothing will
be missed.
Although Model Type selection options are model-specic, the Data Reset function does NOT Reset them. This is useful if
you have two similar models, but different programming needs for each. For example, if you have two similar models that
use the same Swashplate Type (e.g., CP3FS) but different Programming Data (e.g., Dual Rates, End Point Adjustments, etc),
you can copy the rst model's Programming Data, using the Data Copy function, then use the Data Reset function to Reset all
of the Programming Data except Model Type selection options. This saves time by not needing to re-program Swashplate Type
options.
Resetting Model Programming Data
1) From the Display screen, press the ENTER key to display the Programming
Menus.
2) Press the Navigation Pad 56 to highlight DATA RESET, then press
the ENTER key to display the DATA RESET menu. The cursor will
default to the currently selected model, for example >06:SANWA-06
<HELI> and ENTER will flash in the Programming Window.
3) Press the INC+/M1 or DEC-/M2 keys to select the model you would like
to Reset the Programming Data for. ENTER will continue to ash in the
Programming Window.
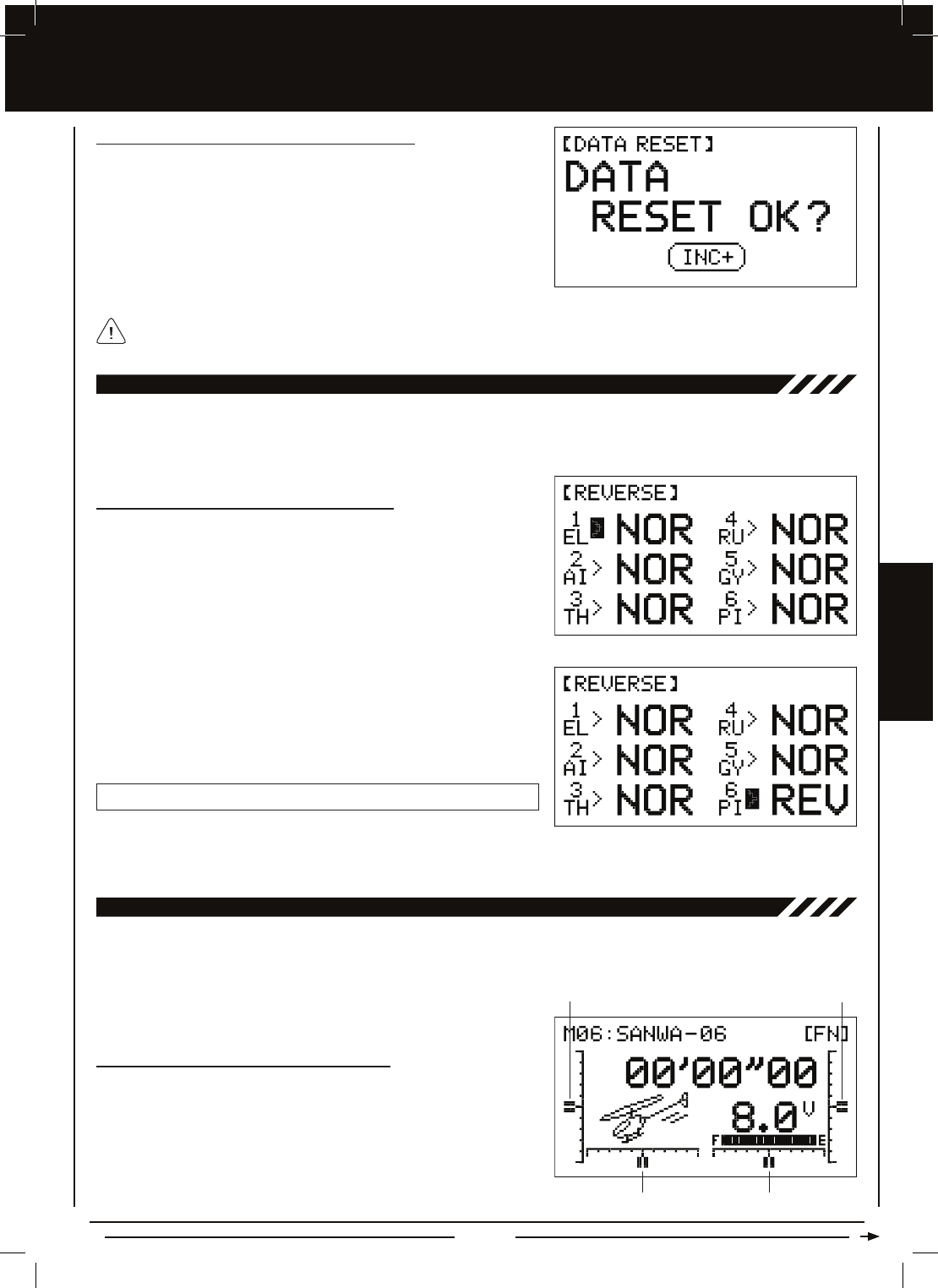
Page 61
hELi MODEL TyPE
Resetting Model Programming Data, Continued....
4) Press the ENTER key. DATA RESET OK? will be displayed and INC+
will ash.
5) Press the INC+/M1 key to Reset the Programming Data for the se-
lected model. After ~10 seconds, the Programming Data will be Reset
as indicated by the progress bar, and COMPLETE!! will be displayed in
the Programming Window. Press any key to return to the DATA RESET
menu.
If you want to go back and change the model or you don't want to Reset the Programming Data for any reason, press
the DEC-/M2 or END/M3 keys.
08.REvERSE (SERvO REvERSing)
The Servo Reversing function electronically switches the direction of servo travel. For example, if you push the throttle control
stick forward to increase pitch, but pitch decreases, you can use the Servo Reversing function to switch the direction of servo
travel to increase pitch when the throttle control stick is moved forward.
Changing Servo Reversing Adjustment Values
1) From the Display screen, press the ENTER key to display the Programming
Menus.
2) Press the Navigation Pad 56 to highlight REVERSE, then press the
ENTER key to display the REVERSE menu. The cursor will default
to 1EL>NOR.
3) Press the Navigation Pad 5634 to highlight the channel that you
would like to change the Servo Reversing adjustment value for.
4) Press the INC+/M1 or DEC-/M2 keys to change the REV adjustment
value to set the desired direction of servo travel.
REVERSE setting range is NOR/REV. The default setting is NOR.
5) Repeat steps 3 and 4 to set the desired direction of servo travel for the desired remaining channels.
09.cEnTER (SERvO cEnTERing SUB-TRiM)
The Servo Centering function allows you to ne-tune the Center (Neutral) position of each servo. It's not unusual that when you
install the servo horn onto your servo that the servo horn is not perfectly centered. The Servo Centering function allows you to center
the servo horn perfectly.
Centering the Trim Switches and Servo Horns
1) Before changing the Servo Centering percentage values you must rst
adjust each of the four trim switches so that the control surface trims
are centered as displayed on the Display screen. In addition, an audible
double-tone is heard when the trim switches reach the center position.
TH Trim
RU Trim
EL Trim
AI Trim
HELI MODEL TYPE
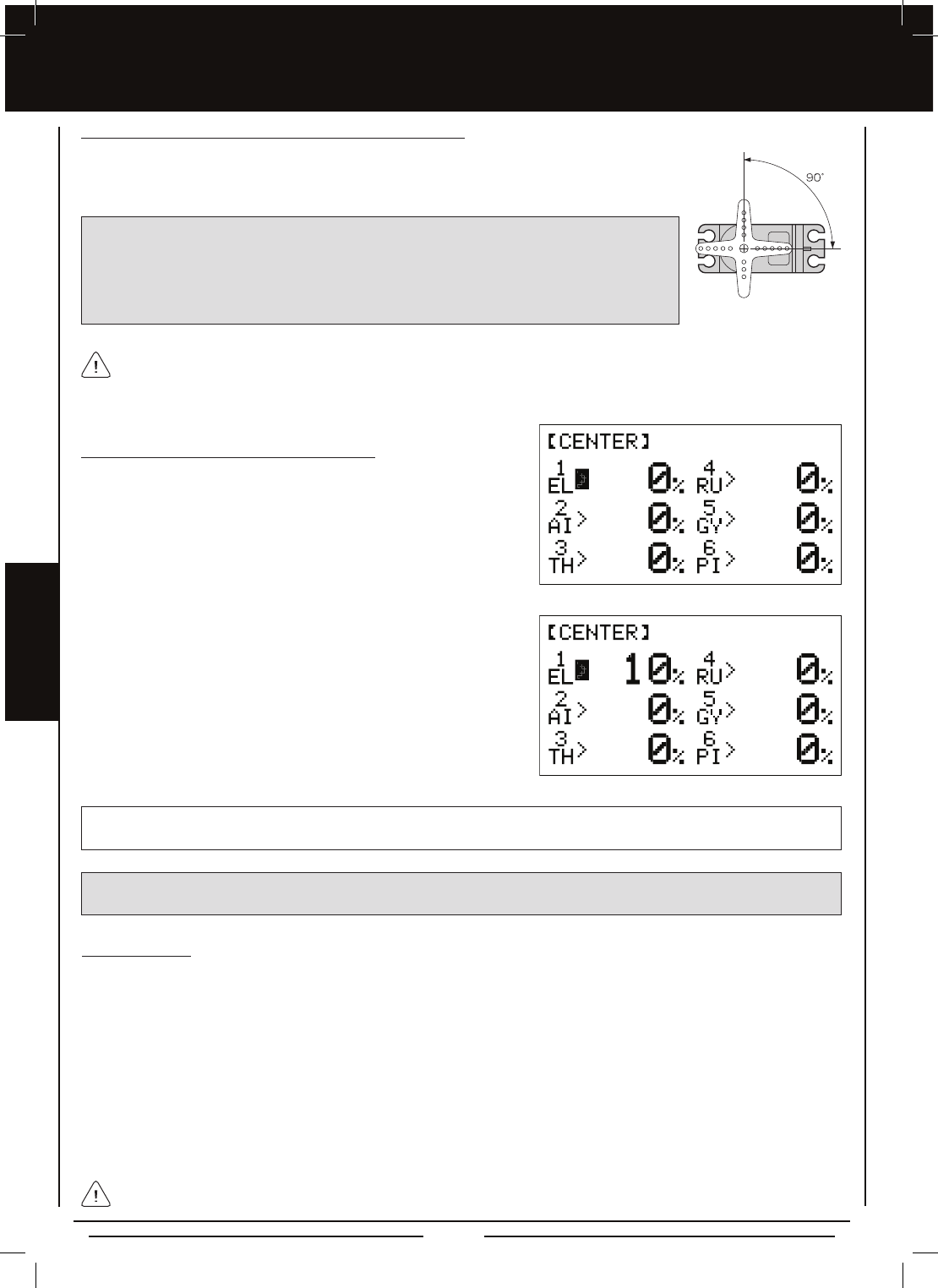
Page 62
hELi MODEL TyPE
Changing Servo Centering Percentage Values
1) From the Display screen, press the ENTER key to display the Programming
Menus.
2) Press the Navigation Pad 56 to highlight CENTER, then press the
ENTER key to display the CENTER menu. The cursor will default
to 1EL>0%.
The TM-160 transmitter features Digital Trim Memory. Any amount of trim that you set during fight using the trim
switches is automatically stored in memory for that specic channel and model, and for that specic Flight Mode (if
Enabled). The Trim percentage values for each model will automatically be loaded when the transmitter is turned ON and your
model is selected. For more information, see page 69.
Centering the Trim Switches and Servo Horns, Continued....
2) Install the servo horn onto the servo, making sure that the servo horn is as close to being centered
as possible. In some cases you can get the servo arm closer to being centered by rotating the
servo arm 180º and reinstalling it.
IMPORTANT It is always recommended to install the servo horns as close to being centered as
possible, prior to changing the Servo Centering percentage values. After you change the Servo
Centering percentage values to center the servo horns, only then should you manually adjust
the control linkages to center the control surfaces. When setting up your control linkages, it's
recommended that the servo arms and the control surfaces should be centered, and the control
linkages should be as close to perpendicular to the servo arms as possible.
3) Press the Navigation Pad 5634 to highlight the channel that you
would like to change the Servo Centering percentage value for.
4) Press the INC+/M1 or DEC-/M2 keys to change the Servo Centering
percentage value to center the servo horn.
5) Repeat steps 3 and 4 to center the servo horns for the desired remaining
channels.
CENTER setting range is -150% to 150%. The default setting is 0%. Increase or decrease the Servo Centering Percentage
Values to center the servo horns.
WARNING We don't recommend using a Servo Centering percentage value outside the range of approximately -40% to
40%. Using a percentage value outside of this range can result in limited maximum servo travel.
Zeroing Out Trim
Although trim switch settings are automatically stored in memory for each individual model, some users may wish to always keep
their trim switch settings at zero (centered) for all models. For example, after test-ying your model, if you have had to add trim to
make your model y straight and level, you can use the Servo Centering function to add that amount of trim back into the servo(s),
then move the trim switches back to center. This ensures that your trim switches are always centered.
1) After ying your model, check your model's control surfaces to see how much trim was necessary to achieve straight and
level ight.
2) From within the CENTER menu, highlight the channel you need to add Centering trim to.
3) Recenter the trim switch, then change the Servo Centering percentage value until the control surface is in the same position
it was prior to recentering the trim switch. Double-check the control throws to ensure the End Points haven't changed.
In the default conguration, the same trim settings are stored across all Flight Modes. This option can be changed to
allow you to store different trim settings for each individual Flight Mode. For more information, see page 69.
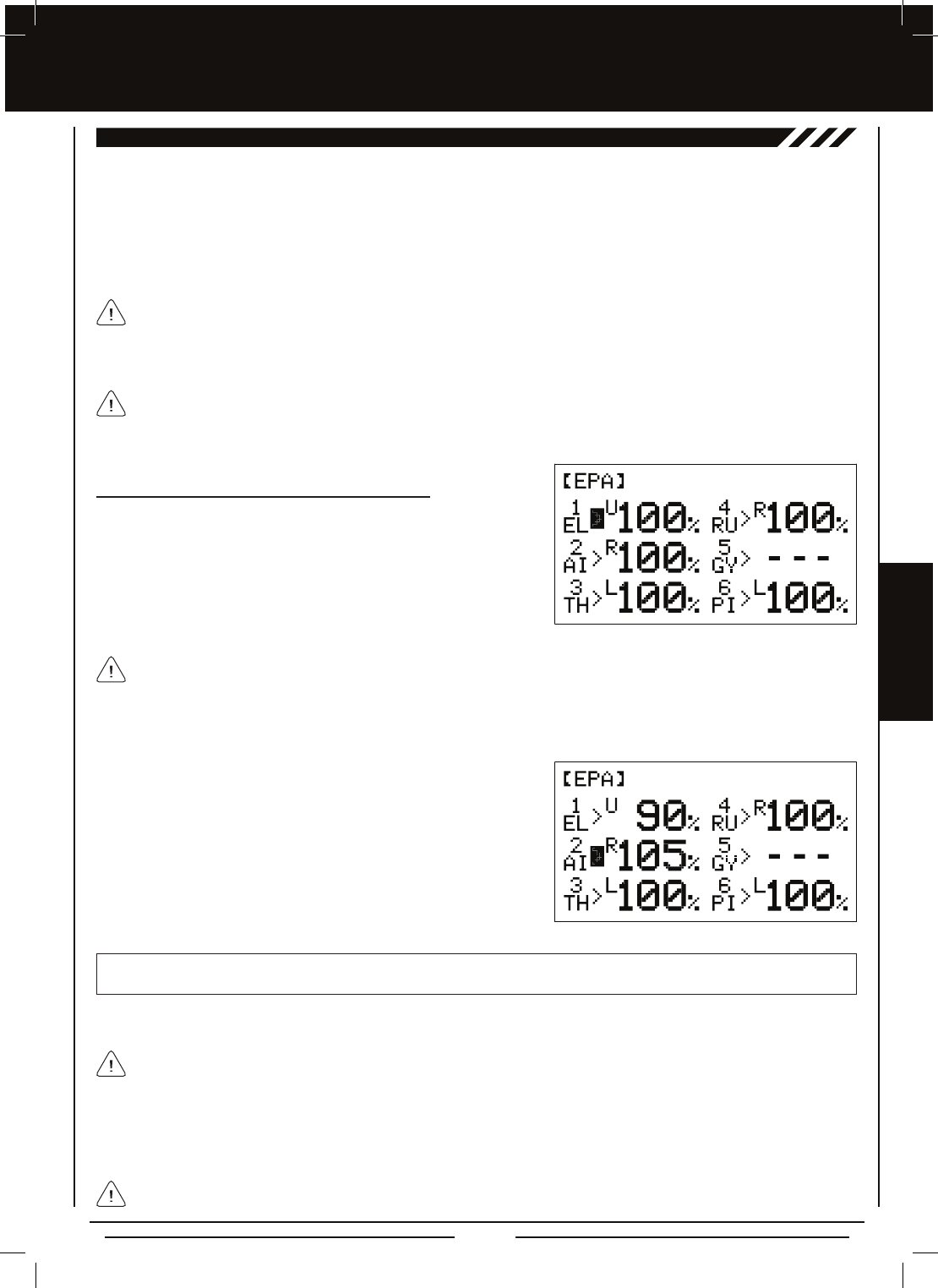
Page 63
hELi MODEL TyPE
10.EPa (EnD POinT aDjUSTMEnT)
The End Point Adjustment function allows you to adjust servo travel in each direction. This makes it possible to balance control
throw in both directions and set the maximum desired control throw. For example, if you want the elevator axis to move Up and
Down 4 degrees in each direction, but the elevator axis moves Down more than 4 degrees, decrease the End Point Adjustment
in the Down direction, so that the elevator axis moves Up and Down the same amount. In addition, the End Point Adjustment
function can be used to adjust the desired maximum control throw. For example, if your throttle binds when the throttle control
stick is at full, you can decrease the throttle End Point Adjustment to lower the control throw.
The End Point Adjustment function can be overridden by other settings, such as Dual Rate. For example, if you have your
End Point Adjustment percentage value set to 100%, and you set your Dual Rate percentage value to 150%, the servo will
travel more than 100% when Dual Rate is ON.
Changing End Point Adjustment Percentage Values
1) From the Display screen, press the ENTER key to display the Programming
Menus.
2) Press the Navigation Pad 56 to highlight EPA, then press the ENTER
key to display the EPA menu. The cursor will default to 1EL>U100% or
1EL>D100% depending on the last position of the elevator control stick.
In front of each End Point Adjustment percentage value is a specic icon. To set the End Point Adjustment percentage
value for the desired direction of servo travel, the control stick must be moved in the direction of servo travel you want to
change the End Point Adjustment percentage value for. For example, if you want to change the End Point Adjustment percentage
value for Down elevator, push the elevator control stick forward, then release it. 'D' will be displayed in front of the Elevator End
Point Adjustment percentage value.
3) Press the Navigation Pad 5634 to highlight the channel that you
would like to change the End Point Adjustment percentage value for.
4) Press the INC+/M1 or DEC-/M2 keys to change the End Point Adjustment
percentage value.
EPA setting range is 0% to 150%. The default setting is 100%. Increasing the End Point Adjustment percentage value
increases servo travel and decreasing the End Point Adjustment percentage value decreases servo travel.
Although the End Point Adjustment function is used to balance and adjust maximum control deection, we suggest adjusting
the control linkages rst to try to achieve as close to the desired control deection as possible, then use the End Point
Adjustment function to make nal adjustments.
To increase control surface deection, you can either move the pushrod further out on the servo arm or move the pushrod closer
to the control linkage. To decrease control surface deection, you can either move the pushrod closer to the center of the servo
arm or move the pushrod further away from the control linkage.
5) Repeat steps 3 and 4 to change the End Point Adjustment percentage values for the desired remaining channels.
When changing End Point Adjustment percentage values, changing the End Point Adjustment percentage value on one
channel, for example, pitch, affects all the cyclic servos (due to CCPM). If you need to make End Point Adjustments to individual
servos without affecting the other cyclic servos, use the CCPM End Point Adjustment function described on the next page.
The End Point Adjustment percentage value for the Gyro channel cannot be changed in the EPA menu. To change Gyro
Gain percentage values, see the Remote Gyro Gain Control section on page 75.
HELI MODEL TYPE
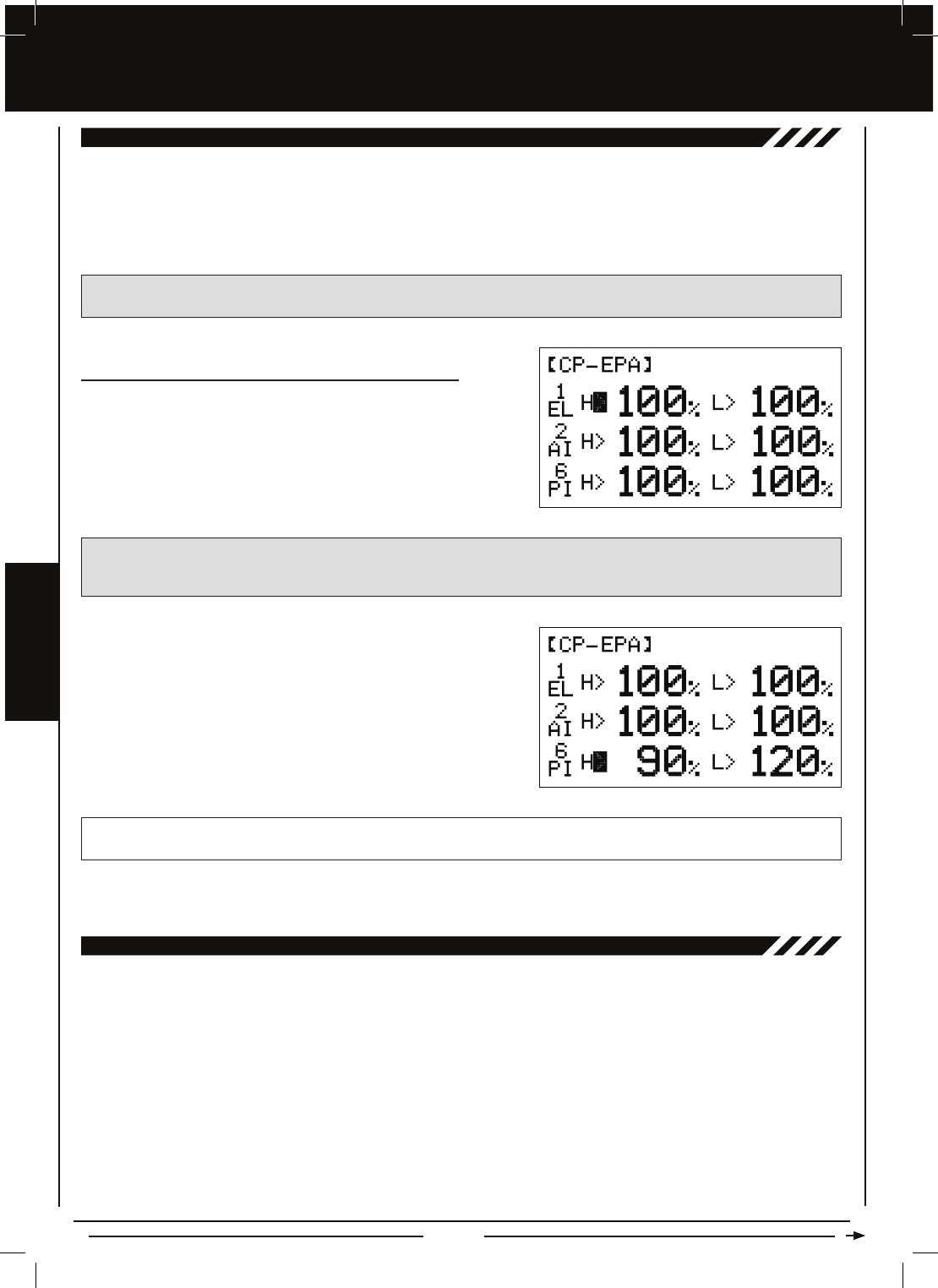
Page 64
hELi MODEL TyPE
11.cP-EPa (ccPM EnD POinT aDjUSTMEnT)
The CCPM End Point Adjustment function allows you to adjust servo travel in each direction for the elevator, aileron, and pitch
servos independently. Unlike the standard End Point Adjustment function, which affects all the cyclic servos, CCPM End Point
Adjustment allows you to adjust each cyclic servo independently without any affect on the other cyclic servos. For example, you
can change the End Point Adjustment on the pitch servo without affecting the End Point Adjustment of the elevator or the aileron
servos. This allows for the utmost control is setting up your swashplate for the most accurate movement and allows you to quickly
and easily level the swashplate.
Changing CCPM End Point Adjustment Percentage Values
1) From the Display screen, press the ENTER key to display the Programming
Menus.
2) Press the Navigation Pad 56 to highlight CP-EPA, then press the
ENTER key to display the CP-EPA menu. The cursor will default to
1EL H>100%.
IMPORTANT In front of each CP-EPA percentage value is an 'H' or 'L' icon (High or Low, respectively). Making adjustments
to the 'H' percentage value affects the High side of control stick travel and making adjustments to the 'L' percentage value
affects the Low side of control stick travel.
3) Press the Navigation Pad 5634 to highlight the channel and direction
that you would like to change the CCPM End Point Adjustment percentage
value for.
4) Press the INC+/M1 or DEC-/M2 keys to change the CCPM End Point
Adjustment percentage value.
CP-EPA setting range is 0% to 150%. The default setting is 100%. Increasing the CCPM End Point Adjustment percentage
value increases servo travel and decreasing the CCPM End Point Adjustment percentage value decreases servo travel.
5) Repeat steps 3 and 4 to change the CCPM End Point Adjustment percentage values for the desired remaining channels.
12.SwaSh (SwaShPLaTE SETUP)
The Swashplate Setup function allows you to control a number of different functions related to the swashplate. Using the
Swashplate Setup function, you are able to reverse individual elevator, aileron, and pitch functions.
For example, even if you select the correct Swashplate Type for your particular helicopter there may be a situation where instead
of the swashplate rising for positive collective it may be necessary for the swashplate to fall for positive collective. Instead of
'fooling' the swashplate by selecting the opposite Swashplate Type and swapping the aileron and pitch channels in the receiver,
then adjusting the servo reversing, the Swashplate Setup function allows you simply reverse the pitch function by changing the
PI (Pitch) adjustment value opposite to what is displayed (e.g., change 100 to -100) to change the direction of travel for the pitch
function. In addition, the Swashplate Setup function also allows you to control the overall throw of the elevator, aileron, and pitch
functions by increasing or decreasing the percentage values.
The Swashplate Setup function also allows you to mix elevator, aileron, and pitch functions together without the need to use a
separate mixer. For example, if you do a loop and the helicopter wants to roll out in one direction or another, you can change the
Mixing adjustment values of the Elevator Master to the Aileron Slave at either the low or the high collective stick to trim out
this tendency.
IMPORTANT To be able to access the CP-EPA menu and program the CCPM End Point Adjustment function, you must
choose a CCPM swashplate setup in the TYPE menu.
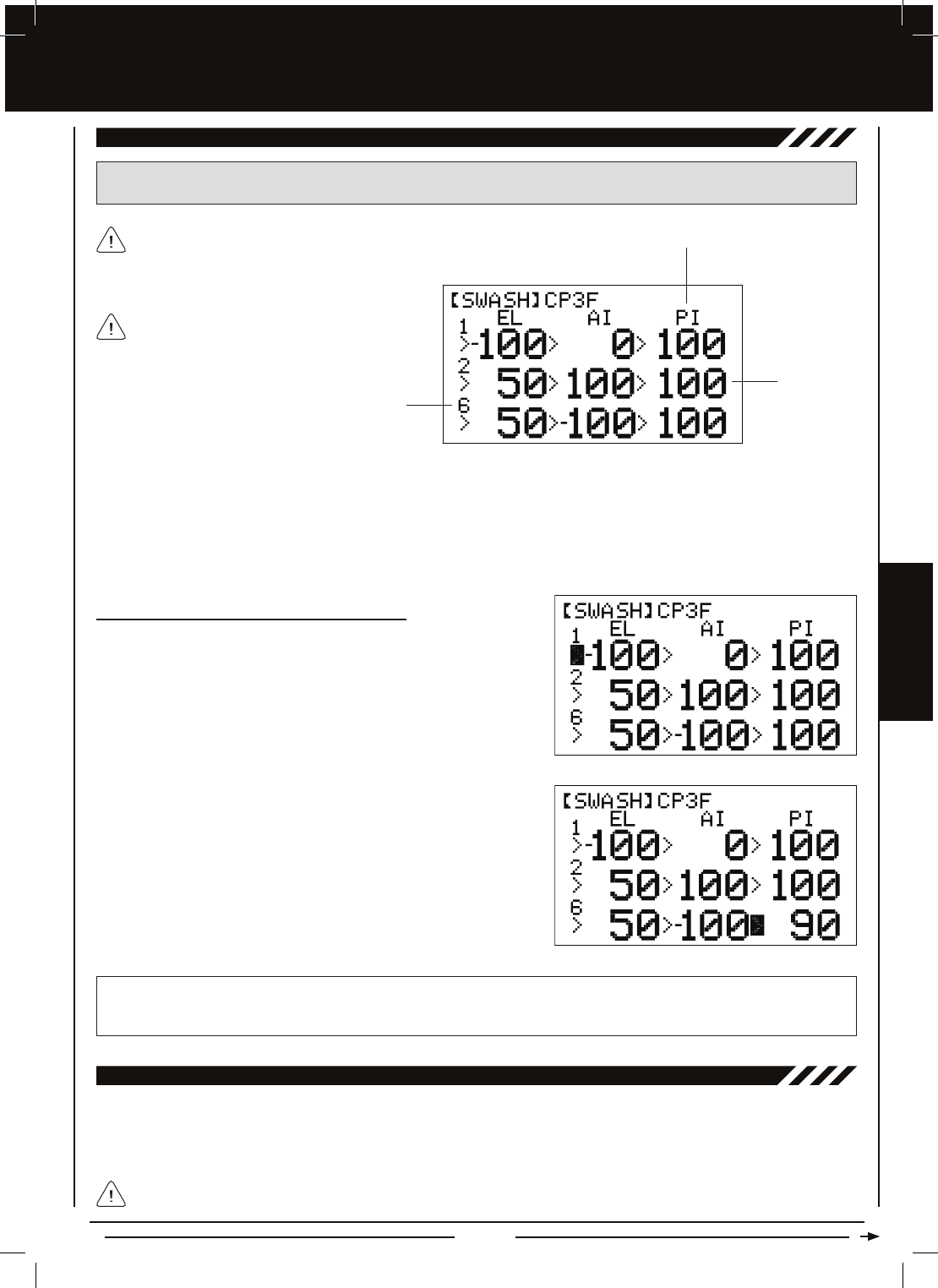
Page 65
hELi MODEL TyPE
12.SwaSh (SwaShPLaTE SETUP), cOnTinUED....
IMPORTANT To be able to access the SWASH menu and program the Swashplate Setup function, you must choose a
CCPM swashplate setup in the TYPE menu.
The SWASH menu consists of a row of MASTER functions along the top and a column of SLAVE functions along the left side. In
all cases, the MASTER function controls the SLAVE function. For example, if you want to increase the servo travel of the aileron
channel when the throttle control stick is moved forward, increase the PI MASTER/AI SLAVE adjustment value.
If you want to change the rotation of servo travel for a channel, for example, the pitch channel, highlight PI MASTER/PI SLAVE
and change the adjustment value to the opposite of the current adjustment value (e.g., 100 to -100).
SLAVE Functions
Adjustment
Values
MASTER Functions
Depending on your model's specic setup, it may
be necessary to decrease the adjustment values
to keep from over-driving the servos.
The SWASH menu displays the default adjustment values for the Swashplate
Type chosen in the TYPE menu. The currently selected Swashplate Type is
displayed.
Changing Swashplate Setup Adjustment Values
1) From the Display screen, press the ENTER key to display the Programming
Menus.
2) Press the Navigation Pad 56 to highlight SWASH, then press the
ENTER key to display the SWASH menu. The cursor will default to 1>
and the adjustment value displayed will vary based on the Swashplate
Type currently selected.
3) Press the Navigation Pad 3456 to highlight the adjustment value
you would like to change, then press the INC+/M1 or DEC-/M2 keys to
change the adjustment value.
4) Adjust the desired remaining SWASH menu adjustment values using
the same techniques.
SWASH menu setting range is -150 to 150. The default adjustment value varies based on Swashplate Type currently selected.
To display the default adjustment values, highlight a specic adjustment value and press the INC+/M1 and DEC-/M2 keys at
the same time.
13.Th-cUT (ThROTTLE cUT)
The Throttle Cut function allows you to set a specic position that the throttle servo will move to. The Throttle Cut function is
primarily used in glow- or gas-powered helicopters to shut down your engine after ight. You are able to adjust the Throttle Cut
percentage value to ensure that when you press the Throttle Cut button to shut down your engine, the carburetor will close
completely, yet not bind.
Before using the Throttle Cut function, make sure that the idle stop screw on your carburetor (if featured) is adjusted to
allow the carburetor barrel to close completely.
HELI MODEL TYPE
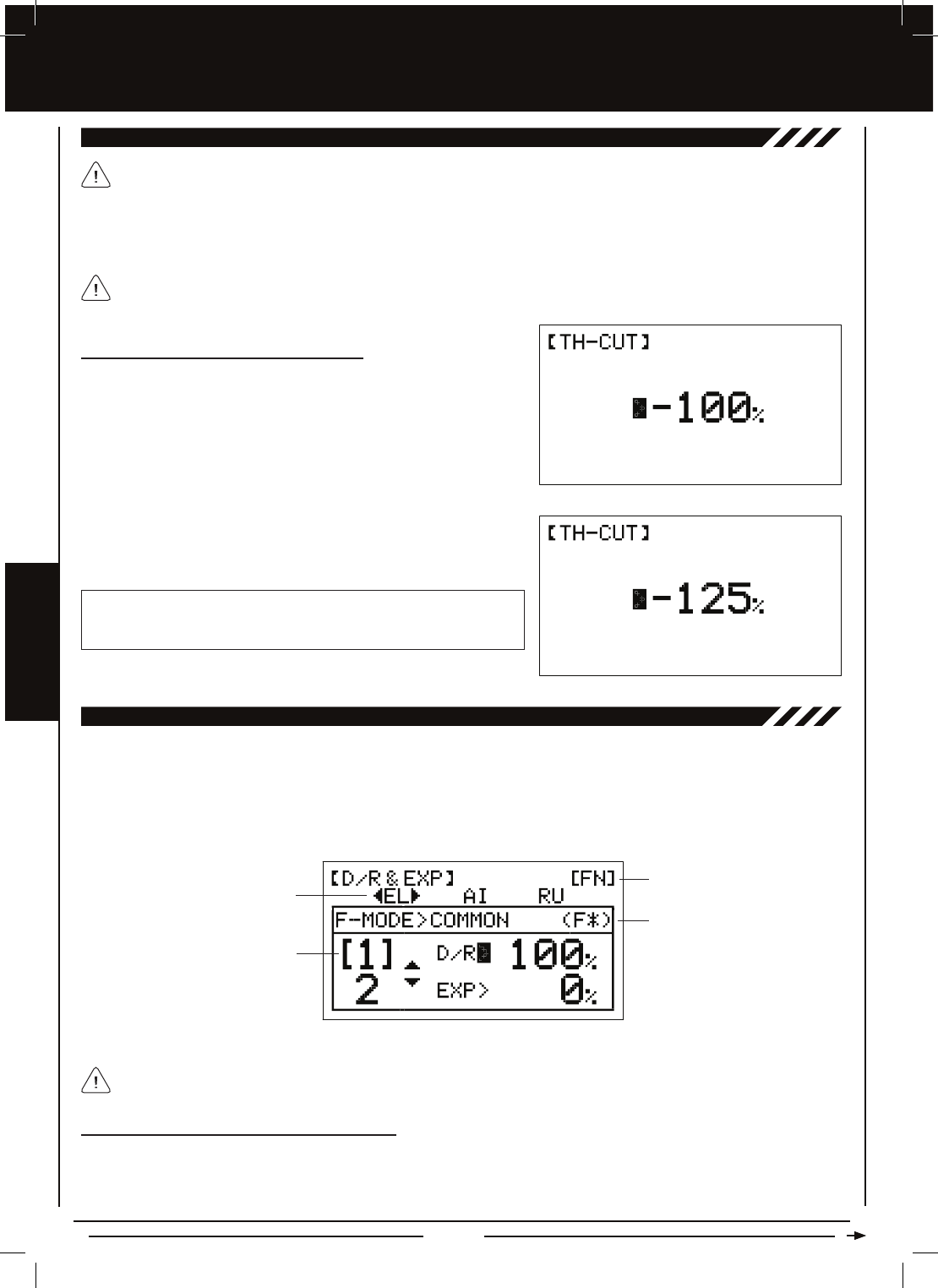
Page 66
hELi MODEL TyPE
14.D/R & EXP (DUaL RaTE anD EXPOnEnTiaL)
The TM-160 transmitter features one Dual Rate switch that controls Dual Rate for the elevator, aileron, and rudder channels
at the same time. In addition, the Dual Rate percentage value for each channel can be programmed independently. The
Exponential function is linked directly to the Dual Rate switch, allowing you to program Exponential for each of the two Dual Rate
positions separately. For greater exibility, both Dual Rate and Exponential can be programmed either the same for all Flight
Modes or separately for each of the three Flight Modes.
Current Channel
Transmitter F-MODE
Programming F-MODE
Transmitter F-MODE refers to the Flight Mode that the transmitter is currently operating in. Programming F-MODE refers
to the Flight Mode that you would like to change the programming for.
Choosing the Flight Mode - Common or Separate
When set to COMMON, the Dual Rate and Exponential percentage values you program will be the same regardless of which
Flight Mode the transmitter is operating in. You cannot program Dual Rate and Exponential percentage values separately for
each Flight Mode. When set to SEPARATE, you can program Dual Rate and Exponential percentage values separately for each
Flight Mode. This allows for greater exibility.
13.Th-cUT (ThROTTLE cUT), cOnTinUED....
Changing the Throttle Cut Percentage Value
1) From the Display screen, press the ENTER key to display the Programming
Menus.
2) Press the Navigation Pad 56 to highlight TH-CUT, then press the
ENTER key to display the TH-CUT menu. The cursor will default to
>-100%.
When the Throttle Cut function is Activated, throttle control will be disabled.
There are several different methods that can be used to set up your throttle control linkage and the Throttle Cut function. To
prevent any chance of causing your throttle control linkage to bind, possibly resulting in damage to your throttle servo when
you use the Throttle Cut function, we rst suggest adjusting the Throttle Low End Point Adjustment percentage value so that
when the throttle control stick is pulled all the way back the carburetor barrel closes completely without binding. Next, increase
the throttle trim (using the throttle trim switch) to adjust your engine's idle. Now change the Throttle Cut percentage value to close
the carburetor barrel without binding when you press the Throttle Cut button.
TH-CUT setting range is -150% to 0%. The default setting is -100%.
Decreasing the Throttle Cut percentage value will increase throttle servo
travel when the Throttle Cut button is pressed.
3) Press the INC+/M1 or DEC-/M2 keys to set the position you would like
the throttle servo to move to when you press the Throttle Cut button.
Dual Rate Switch Position
(Typically 1=Maximum Control Throw
and 2=Reduced Control Throw)
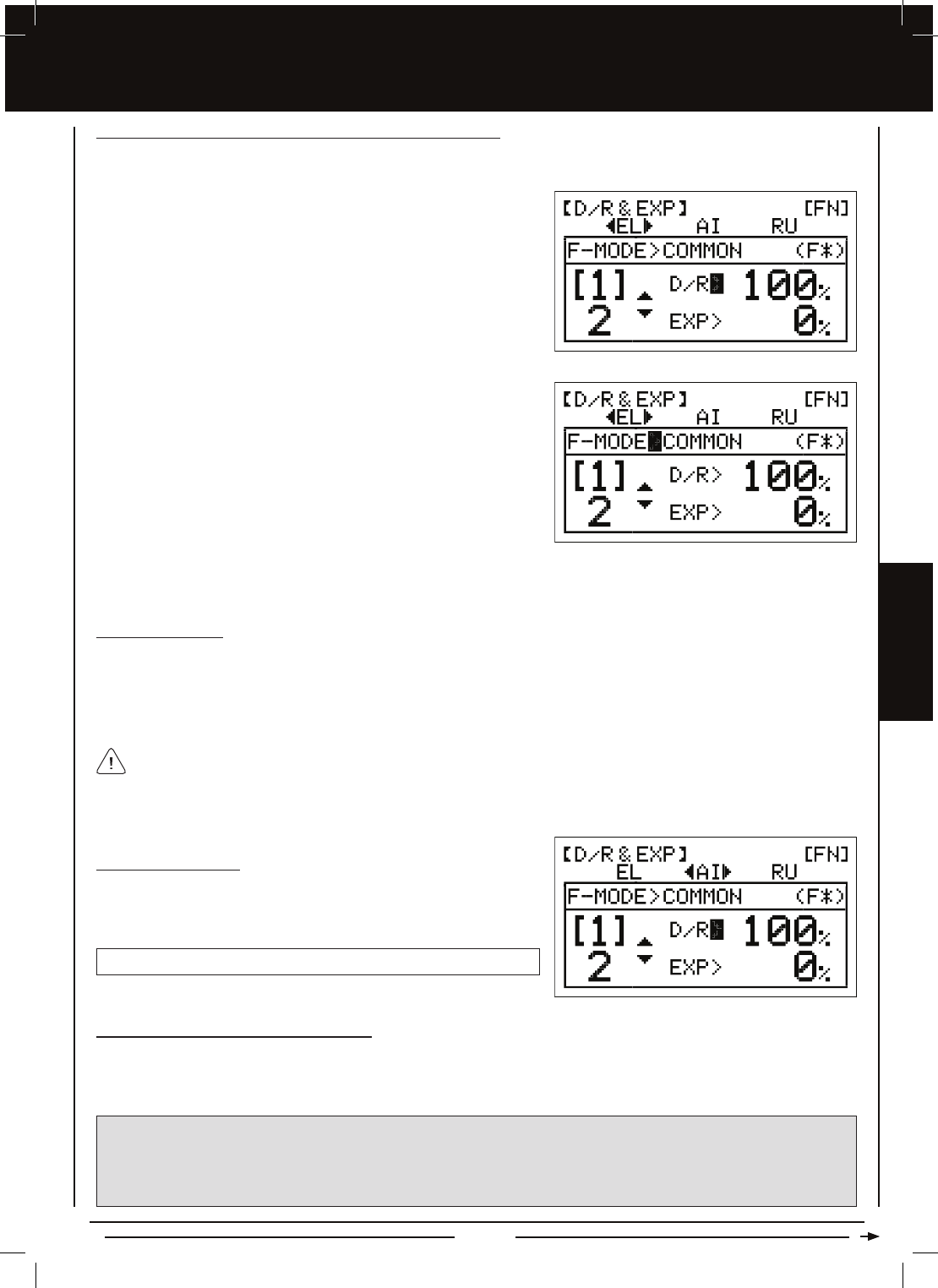
Page 67
hELi MODEL TyPE
Dual Rate is a percentage of End Point Adjustment. For example, if you set the Dual Rate 1 percentage value to 100%,
the control surfaces will travel the same amount as dened by your End Point Adjustment programming, and if you set the
Dual Rate 2 percentage value to 50%, the control surfaces will travel half that amount when Dual Rate 2 is Activated. Prior to
takeoff, check the position of the Dual Rate switch to ensure that it is in the position you want.
Dual Rate Overview
The Dual Rate function allows you to change the control authority of the control surfaces by changing the amount of servo travel.
For example, if you are ying an aerobatic helicopter that requires a lot of control throw for aerobatics, but that same amount of
control throw makes the helicopter difcult to control during normal ight, you can use the Dual Rate function to lower the control
throw for normal ight with just the ip of the Dual Rate switch. Two Dual Rate settings are available for the Elevator, Aileron, and
Rudder channels, and different Dual Rate settings can be programmed separately for each of the three Flight Modes.
Choosing the Channel
1) Press the Navigation Pad 34 to highlight the channel you would like
to make Dual Rate percentage value changes to. Choose either <EL>,
<AI>, or <RU>.
Dual Rate can be set for EL (Elevator), AI (Aileron), and RU (Rudder).
2) Press the Navigation Pad 56 to highlight D/R & EXP, then press the
ENTER key to display the D/R & EXP menu. The cursor will default to
D/R>100%.
3) Press the Navigation Pad 5to move the cursor to F-MODE>COMMON.
4) Press the INC+/M1 or DEC-/M2 keys to choose either SEPARATE OR
COMMON.
5) If you choose SEPARATE, press the F-MODE key to choose the F-MODE number you would like to program the Dual Rate
and Exponential functions for. Choose from FN, F1 or F2.
Choosing the Flight Mode - Common or Separate, Continued....
1) From the Display screen, press the ENTER key to display the Programming Menus.
Changing the Dual Rate Percentage Values
Two different Dual Rate settings can be programmed to the Dual Rate switch. We recommend that Dual Rate 1 be set to the
maximum control surface throw you desire, then set Dual Rate 2 to a different value that is less than maximum. For example,
set the Dual Rate 1 percentage value to 100% and the Dual Rate 2 percentage value to 75%.
WARNING Keep in mind that it's possible to set the Dual Rate percentage value higher than the End Point Adjustment
percentage value. For example, with the End Point Adjustment percentage value set to 100% and the Dual Rate percentage
value set to 150% the servo will move more than 100% when Dual Rate is turned ON. We strongly recommend that you set
the Dual Rate 1 percentage value to no more than 100%. This will prevent any chance of exceeding your End Point Adjustment
and overdriving your control linkage.
HELI MODEL TYPE
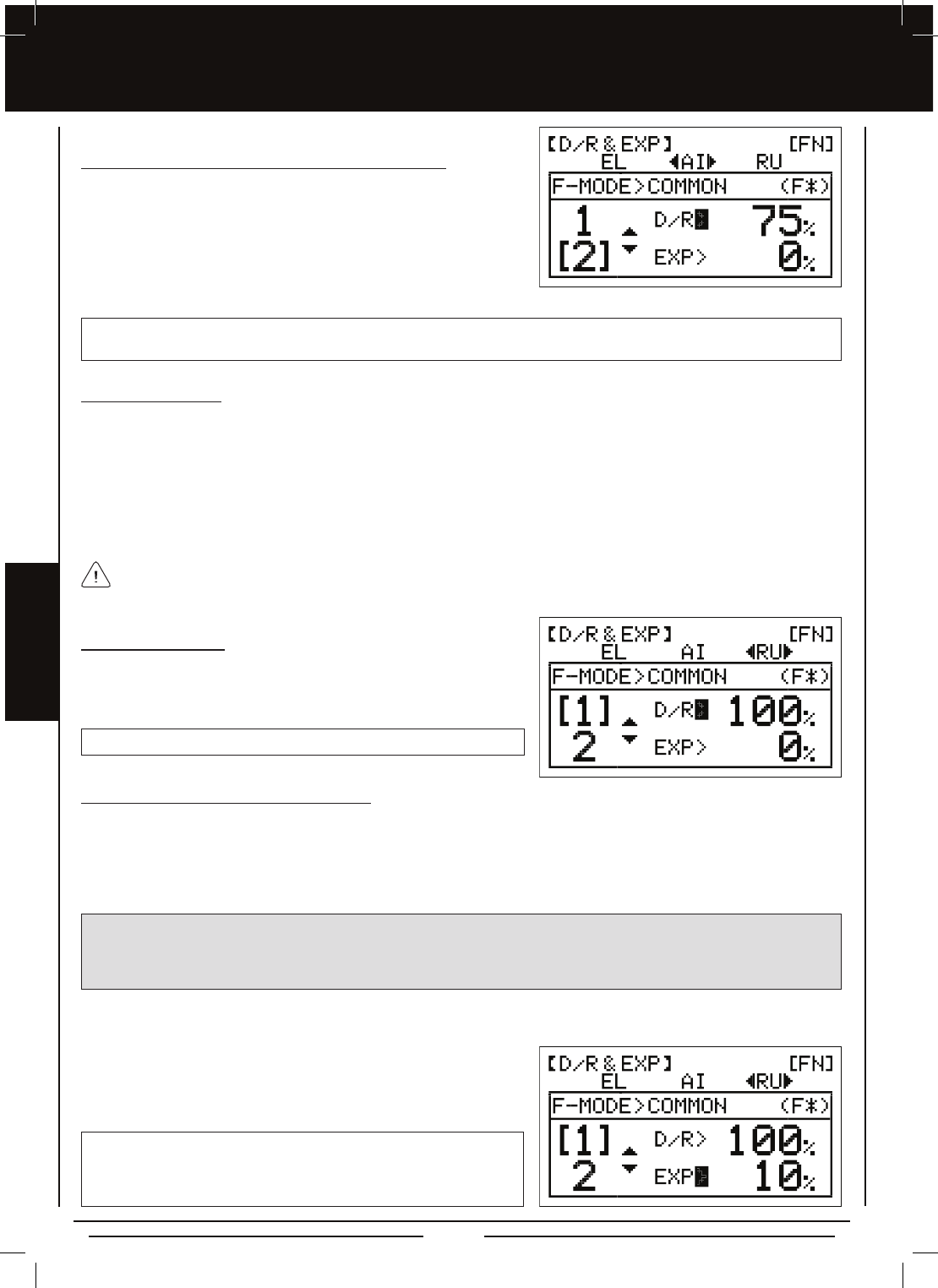
Page 68
hELi MODEL TyPE
Choosing the Channel
1) Press the Navigation Pad 34 to highlight the channel you would like to
make Exponential percentage value changes to. Choose either <EL>,
<AI>, or <RU>.
Exponential can be set for EL (Elevator), AI (Aileron), and RU (Rudder).
Changing the Exponential Percentage Values
The Exponential function is linked directly to the Dual Rate switch. This allows you to program Exponential for each of the two
Dual Rate positions separately. For example, with the Dual Rate switch in position 1 (maximum travel), you can set the Exponential
percentage value to 30% to soften the control feel around neutral and with the Dual Rate switch in position 2 (reduced travel) you
can set Exponential percentage value to 0%. When the Exponential percentage value is set to 0%, the ratio between servo travel
and control stick movement will be Linear throughout the entire range of deection.
WARNING If you have not used Exponential functions in the past, we suggest that you start with a small percentage of Exponential
(approximately 10%~20%) until you get used to the feel of how Exponential affects the control feel of your model. You will nd
that Exponential is most useful where strong control response is desired at extreme control stick positions, but softer control
response to small control stick movements is desired in order to make very accurate small corrections to the ight path.
1) Press the Navigation Pad 6 to move the cursor to EXP>0%.
2) Move the Dual Rate switch to the position you would like to set an
Exponential percentage value for, either 1 or 2, then press the INC+/M1
or DEC-/M2 keys to set the desired Exponential percentage value for
the channel you chose previously.
EXP setting range is -100% to 100%. The default setting is 0% (Linear).
Increasing the Exponential percentage value softens the control feel
around neutral. Decreasing the Exponential percentage value heightens
the control feel around neutral.
D/R setting range is 0% to 150%. The default setting is 100%. Increasing the Dual Rate percentage value increases servo
travel and decreasing the Dual Rate percentage value decreases servo travel.
Changing the Dual Rate Percentage Values, Continued....
1) Move the Dual Rate switch to the position you would like to set a Dual
Rate percentage value for, either 1 or 2.
2) Press the INC+/M1 or DEC-/M2 keys to set the desired Dual Rate
percentage value for the channel you chose previously.
Exponential Overview
The Exponential function allows you to vary the amount of servo travel in relation to the movement of the elevator, aileron, and
rudder control sticks near the neutral positions to change the way the control surfaces react to control stick movement. Increasing
the Exponential value will soften the control feel around neutral and decreasing the Exponential value will heighten the control
feel around neutral. For example, using a positive Exponential percentage value allows for smoother control by lessening the
amount of servo travel in relation to the amount of control stick movement. Using a negative Exponential percentage value may
result in more 'twitchy' control response because the amount of servo travel will be increased in relation to the amount of control
stick movement. The Exponential function is linked directly to the Dual Rate switch. This allows you to program Exponential for
each of the two Dual Rate positions separately.
Exponential does not change the total amount of servo travel at maximum control stick deection. Exponential affects
the ratio between servo travel and control stick movement at less than maximum control stick deection.
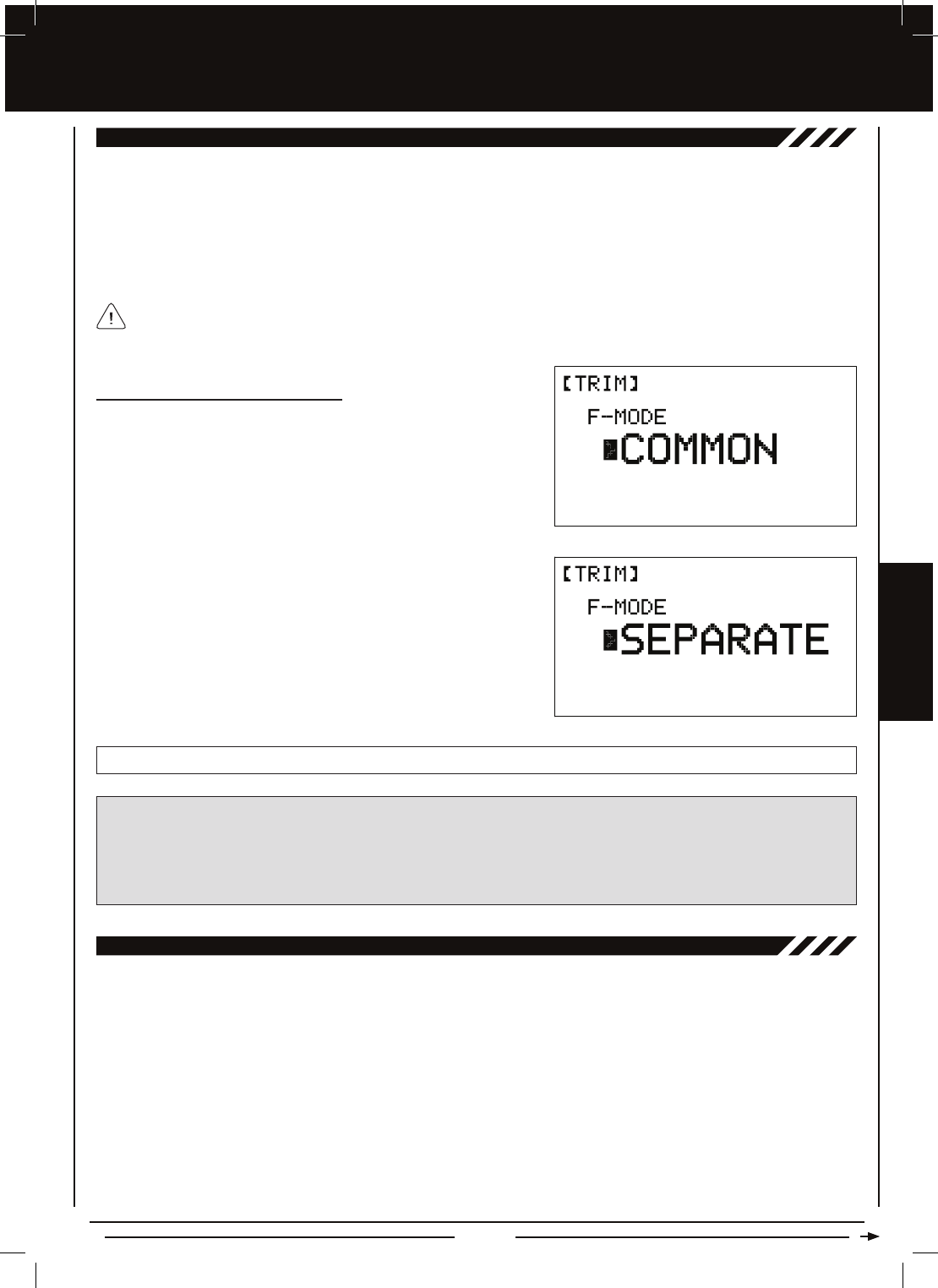
Page 69
hELi MODEL TyPE
16.Th-cURvE (ThROTTLE cURvE)
The Throttle Curve function allows you to vary the amount of throttle servo travel in relation to the movement of the throttle control
stick at different points throughout the entire range of deection. Five custom-programmable Points ensure a precise Throttle
Curve to suit any situation. For example, if you are doing 3D ying, you can adjust the Throttle Curve so that you have maximum
power and rotor head speed at both the low throttle control stick position and the high throttle control stick position when you have
full negative and positive collective pitch for aerobatics, but reduced power when the throttle control stick is near the center, so
that the rotor head will not overspeed with reduced collective.
Included within the Throttle Curve function is the Throttle Hold function. The Throttle Hold function allows you to set a specic
position that the throttle servo will Hold and not respond to the throttle control stick. This function is typically used to Hold the
throttle at idle or low speed, while still allowing you full pitch control. This is ideal for practicing auto-rotations and is also a good
safety feature on electric helicopters, because when Activated, the rotor head will not spin up if you accidentally bump the throttle
control stick up.
For greater exibility, the Throttle Curve and Throttle Hold functions can be programmed either the same for all Flight Modes
or separately for each of the three Flight Modes. A graph with Input and Output indicators help with programming visualization.
WARNING When the Trim Flight Mode option is set to Separate or SEPARATE TH-TRIM LOCK (F1), Digital Trim values are
stored in the specic Flight Mode you're using when you change the trim using the trim switches. For example, you could have
10 'clicks' of Up elevator trim in Flight Mode FN (Normal) and 5 'clicks' of Up elevator trim in Flight Mode F1. Be cautious of
this when switching between Flight Modes during ight.
If SEPARATE TH-TRIM LOCK (F1) is chosen, throttle trim will NOT be adjustable when in Flight Mode F1.
3) Press the INC+/M1 or DEC-/M2 keys to choose the desired Trim Flight
Mode option, either COMMON, SEPARATE or SEPARATE TH-TRIM
LOCK (F1).
TRIM setting range is COMMON, SEPARATE, or SEPARATE TH-TRIM LOCK (F1). The default setting is COMMON.
15.TRiM (DigiTaL TRiM)
The TM-160 transmitter features Digital Trim Memory. Any amount of control surface trim that you set during fight using the
trim switches is automatically stored in memory for that specic channel and for that specic model. The Digital Trim values for
each model will automatically be loaded when the transmitter is turned ON. The Trim function allows you to choose whether you
want trim changes saved the same across all three Flight Modes or if you want trim changes saved separately for each of the
three Flight Modes. In addition, an option to lock the throttle trim in Flight Mode F1 is also available. This feature is convenient
when ying aerobatics in Flight Mode F1, because if accidentally hit, the throttle trim could change your Throttle Curve and cause
unintended consequences.
An audible double-tone is heard when the trim switches reach the center position. This allows you to know when the trim
switches reach the center position without the need to look at the Trim Indicators on the Display screen.
Choosing the Trim Flight Mode Option
1) From the Display screen, press the ENTER key to display the Programming
Menus.
2) Press the Navigation Pad 56 to highlight TRIM, then press the
ENTER key to display the TRIM menu. The cursor will default to
F-MODE>COMMON.
HELI MODEL TYPE
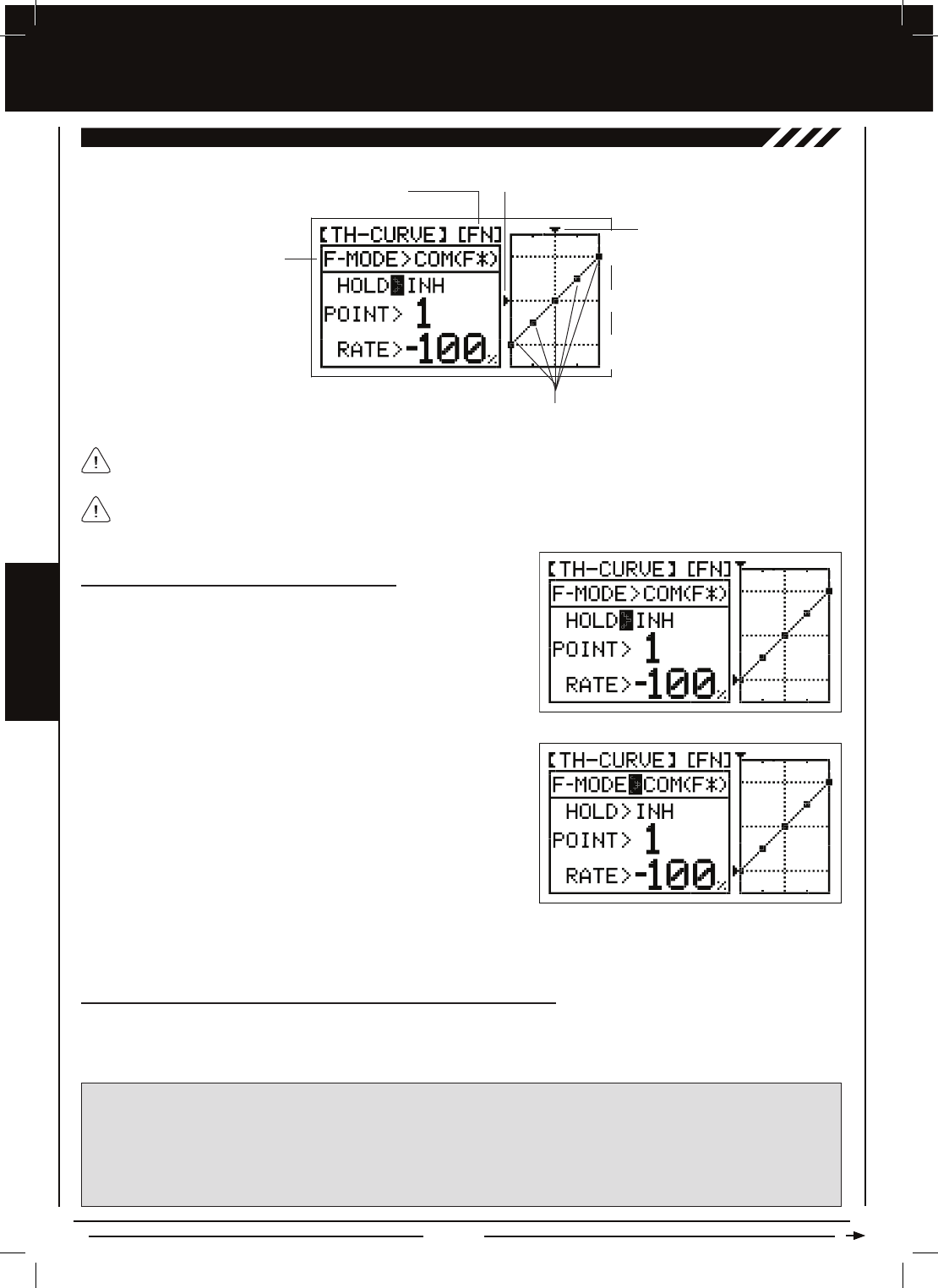
Page 70
Choosing the Flight Mode - Common or Separate
1) From the Display screen, press the ENTER key to display the Programming
Menus.
2) Press the Navigation Pad 56 to highlight TH-CURVE, then press
the ENTER key to display the TH-CURVE menu. The cursor will
default to HOLD>INH.
3) Press the Navigation Pad 5 to move the cursor to F-MODE>COM.
4) Press the INC+/M1 or DEC-/M2 keys to choose either SEP OR COM
(SEParate or COMmon).
5) If you choose SEPARATE, press the F-MODE key to choose the F-MODE number you would like to program the Throttle
Curve function for. Choose from FN, F1 or F2.
hELi MODEL TyPE
Changing the Throttle Curve Point Values and the Rate Percentage Values
Five different Points with varying Rate percentage values can be programmed onto the Throttle Curve. Each Point will be
displayed on the graph to give you a visual interpretation of the position of the Point on the Throttle Curve. The Point that is currently
selected will ash.
WARNING Keep in mind that it's possible to set the Rate percentage values higher or lower than the throttle End Point
Adjustment percentage values. For example, with the throttle High End Point Adjustment percentage value set to 100% and
POINT>5 Rate percentage value set to 150% the servo will move 150%.
We strongly recommend that you set the Throttle Curve Point Rate percentage values no higher than your throttle End Point
Adjustment percentage values unless specically necessary for your particular setup. This will prevent any chance of overdriving
your control linkage.
Transmitter F-MODE refers to the Flight Mode that the transmitter is currently operating in. Programming F-MODE refers
to the Flight Mode that you would like to change the programming for.
Transmitter F-MODE
Programming F-MODE
Stick Input
Function Output
150%
100%
100%
150%
0%
Point Positions
As you change the Point values and Rate percentage values, you can use the graph and Input and Output indicators to
visualize the ratio between control stick movement and servo travel throughout the entire deection range.
16.Th-cURvE (ThROTTLE cURvE), cOnTinUED....
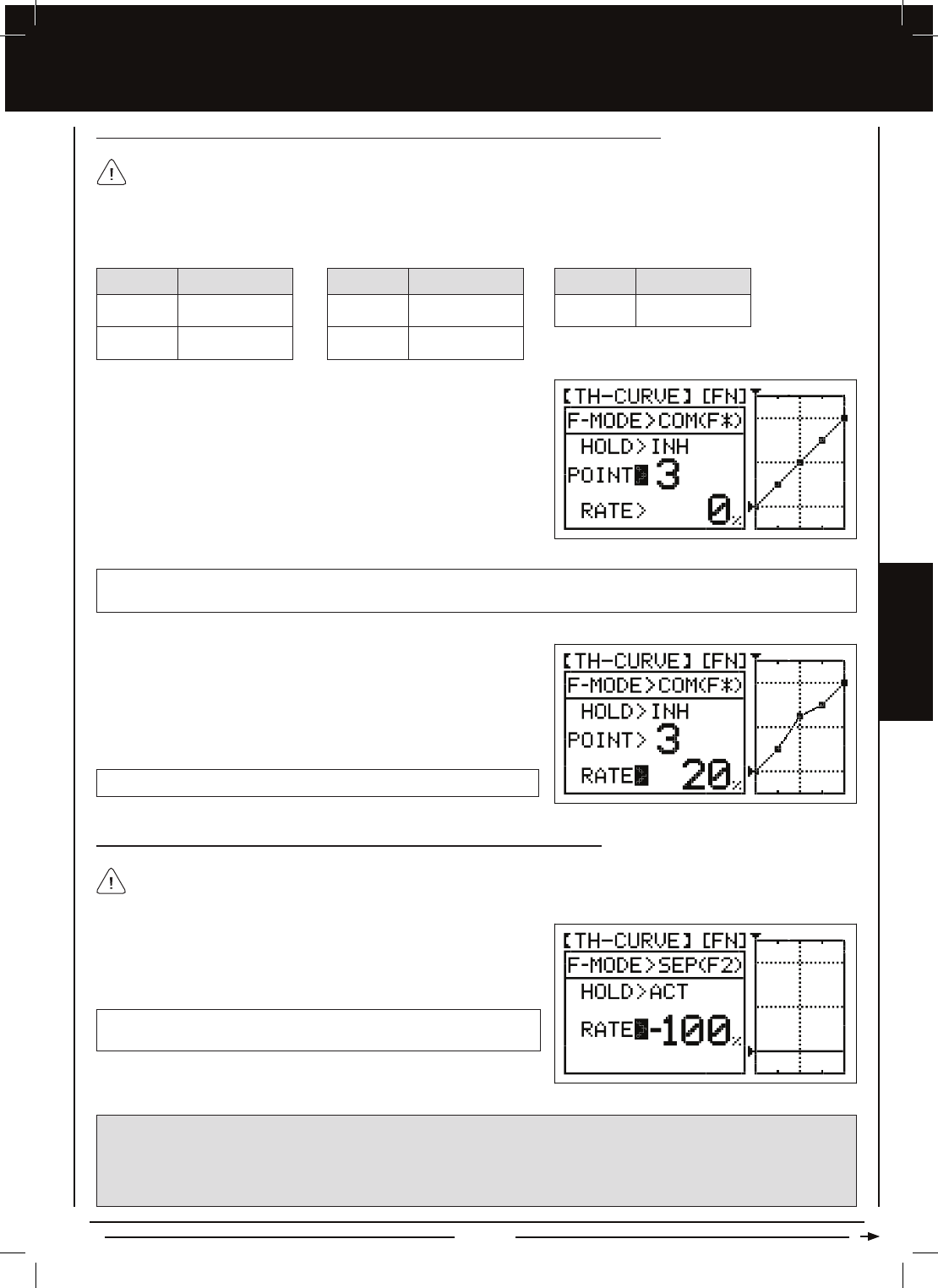
Page 71
hELi MODEL TyPE
1) Press the Navigation Pad 56 to highlight HOLD>INH, then press the
INC+/M1 or DEC-/M2 keys to change the INH/ACT setting to ACT.
HOLD setting range is INH/ACT. The default setting is INH. When
Activated, the Throttle Hold function will be Active for that Flight Mode.
When you Activate the Throttle Hold function, you will not be able to program the Throttle Curve Function. In addition,
when the Throttle Hold function is Activated, the throttle control stick will control Pitch only and the Throttle trim switch
will be Inhibited.
RATE setting range for each Point is -150% to 150%.
3) Press the Navigation Pad 6 to highlight RATE>.
4) Press the INC+/M1 or DEC-/M2 keys to set the desired Rate percentage
value for the Point you chose previously, then repeat the previous
procedures to change the desired remaining Point and Rate percentage
values.
Activating the Throttle Hold Function and Changing the Rate Percentage Value
WARNING Keep in mind that it's possible to set the Throttle Hold percentage value lower than the throttle End Point
Adjustment percentage value. For example, with the throttle End Point Adjustment percentage value set to -100% and the
Throttle Hold percentage value set to -150% the servo will move -150% when the Throttle Hold is Activated. We strongly
recommend that you set the Throttle Hold Rate percentage value no higher than your throttle End Point Adjustment percentage
values unless specically necessary for your particular setup. This will prevent any chance of overdriving your control linkage.
1) Press the Navigation Pad 6 to highlight POINT>1.
2) Press the INC+/M1 or DEC-/M2 keys to choose which Point you would
like to set a Rate percentage value for.
POINT setting range is 1 through 5. Point 1 is at the low end of the Throttle Curve and Point 5 is at the high end of the Throttle
Curve. Point 3 is a the center of the Throttle Curve.
In the default conguration the Throttle Curve is Linear. For example, when you move the throttle control stick from 0%
to 100%, the throttle servo will travel from 0% to 100%, too. As long as the line on the graph remains straight, the Throttle
Curve will be Linear. When a Point Rate percentage value is changed, the line on the graph curves (displaying the Throttle Curve)
and throttle servo travel will vary in relation to throttle control stick movement.
100%
The tables below describe the default Point and Rate values.
1
2
-100%
-50%
POINT DEFAULT RATE
3
4
0%
50%
POINT DEFAULT RATE
5
POINT DEFAULT RATE
Changing the Throttle Curve Point Values and the Rate Percentage Values, Continued....
HELI MODEL TYPE
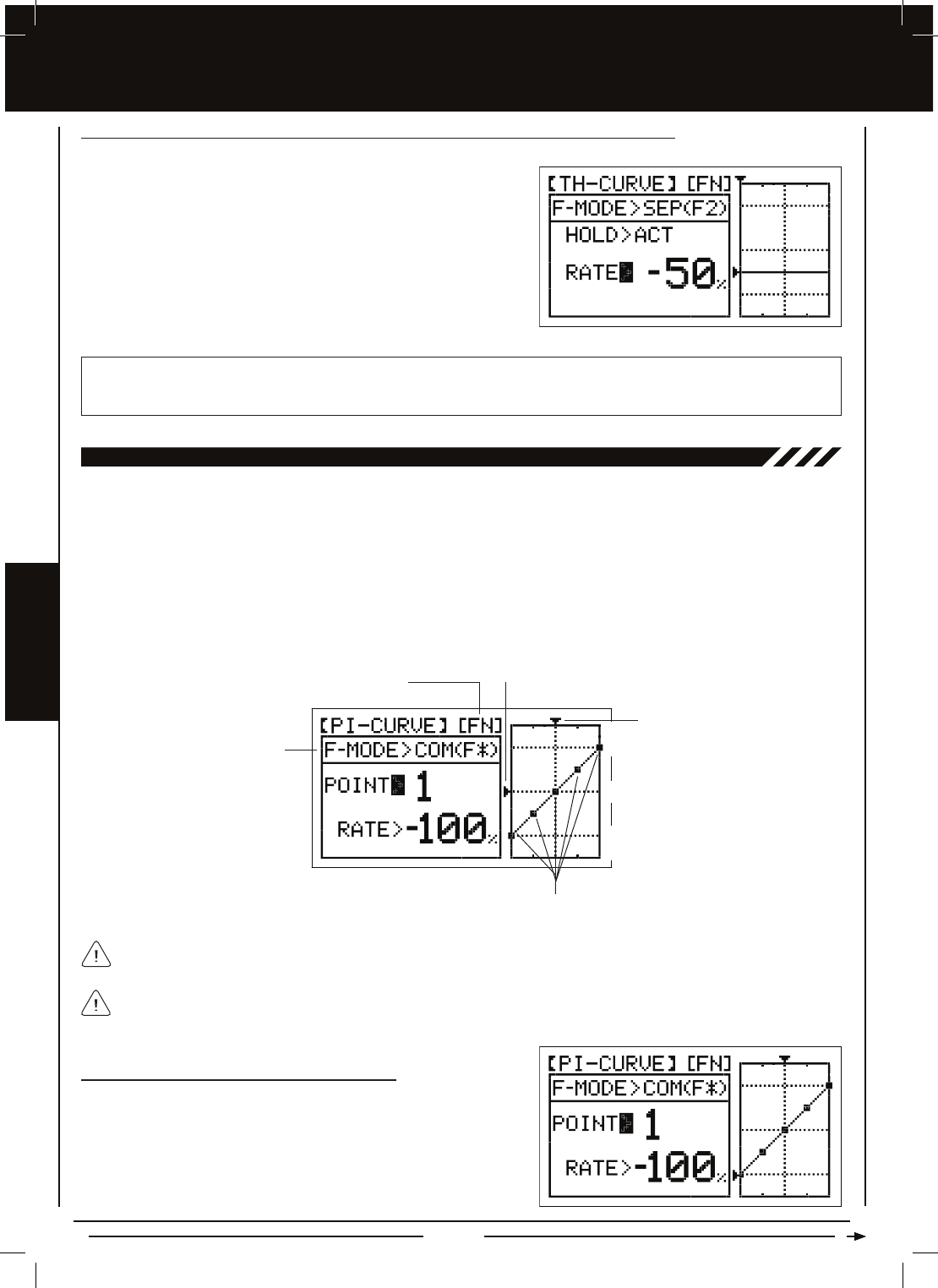
Page 72
hELi MODEL TyPE
17.Pi-cURvE (PiTch cURvE)
The Pitch Curve function allows you to vary the amount of pitch travel in relation to the movement of the throttle control stick
at different points throughout the entire range of deection. Five custom-programmable Points ensure a precise Pitch Curve
to suit any situation. For example, if you are doing 3D ying, you may want a Linear Pitch Curve with maximum negative pitch
when the throttle control stick is at low, maximum positive pitch when the throttle control stick is at high, and 0 degrees of pitch
when the throttle control stick is centered. Alternatively, for a more docile ying helicopter, you may want minimum negative
pitch when the throttle control stick is all the way back and gradually increase pitch in small increments as the throttle control
stick moves from low to high, to produce a smooth transition from low to high throttle.
For greater exibility, the Pitch Curve function can be programmed either the same for all Flight Modes or separately for each of
the three Flight Modes. A graph with Input and Output indicators help with programming visualization.
Transmitter F-MODE refers to the Flight Mode that the transmitter is currently operating in. Programming F-MODE refers
to the Flight Mode that you would like to change the programming for.
Transmitter F-MODE
Programming F-MODE
Stick Input
Function Output
150%
100%
100%
150%
0%
Point Positions
As you change the Point values and Rate percentage values, you can use the graph and Input and Output indicators to
visualize the ratio between control stick movement and servo travel throughout the entire deection range.
Choosing the Flight Mode - Common or Separate
1) From the Display screen, press the ENTER key to display the Programming
Menus.
2) Press the Navigation Pad 56 to highlight PI-CURVE, then press
the ENTER key to display the PI-CURVE menu. The cursor will
default to POINT>1.
1) Press the Navigation Pad 6 to highlight RATE>-100%.
2) Press the INC+/M1 or DEC-/M2 keys to set the position you would like
the throttle servo to Hold at.
HOLD setting range is -150% to 0%. The default setting is -100%. Increasing the Throttle Hold percentage value will increase
the position at which the throttle servo will Hold at and decreasing the Throttle Hold percentage value will decrease the position
at which the throttle servo will Hold at.
Activating the Throttle Hold Function and Changing the Rate Percentage Value, Continued....
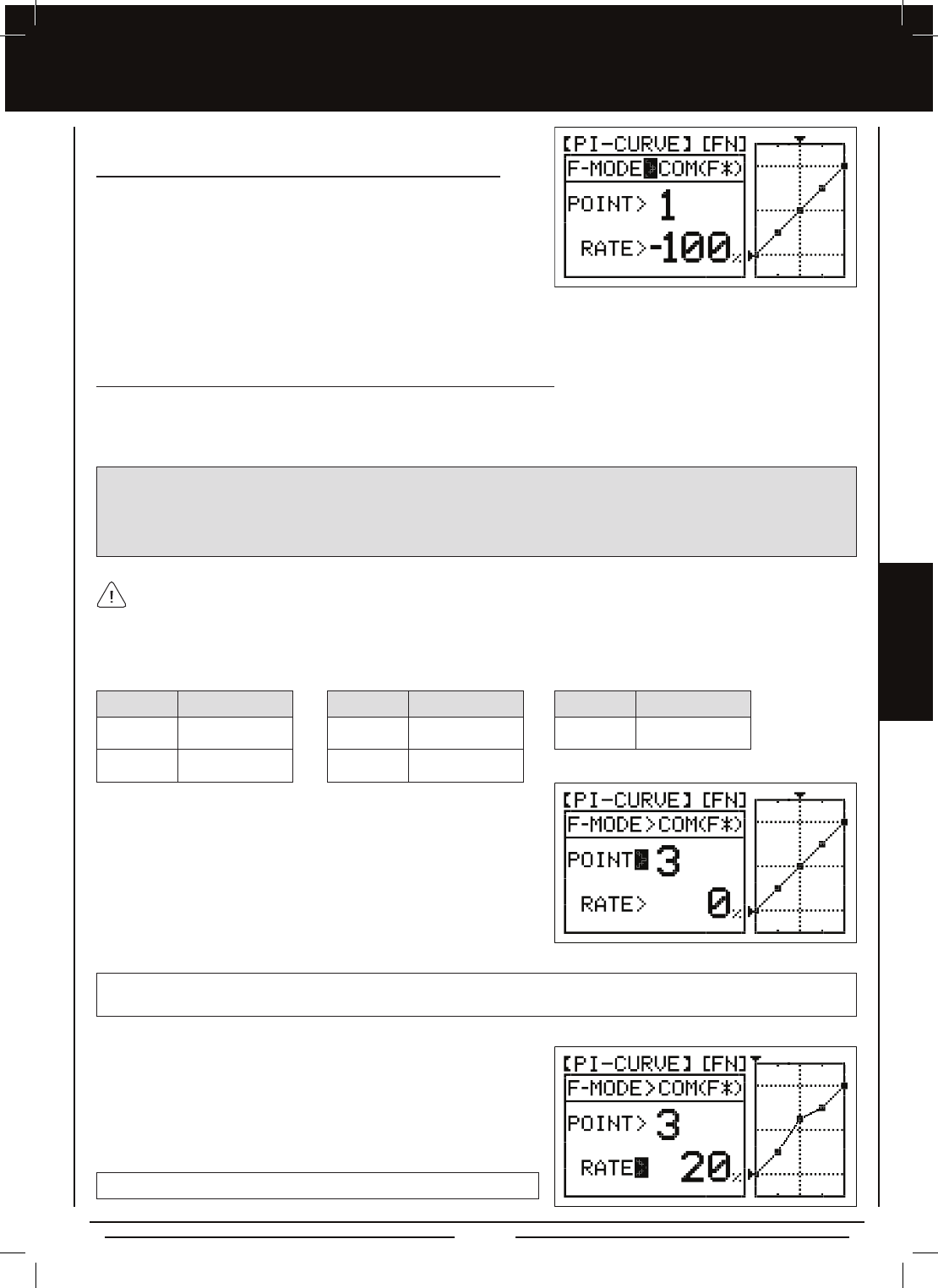
Page 73
hELi MODEL TyPE
Changing the Pitch Curve Point Values and the Rate Percentage Values
Five different Points with varying Rate percentage values can be programmed onto the Pitch Curve. Each Point will be displayed
on the graph to give you a visual interpretation of the position of the Point on the Pitch Curve. The Point that is currently selected
will ash.
WARNING Keep in mind that it's possible to set the Rate percentage values higher or lower than the pitch End Point
Adjustment percentage values. For example, with the pitch High End Point Adjustment percentage value set to 100% and
POINT>5 Rate percentage value set to 150% the collective servos will move 150%. We strongly recommend that you set the
pitch Curve Point Rate percentage values no higher than your pitch End Point Adjustment percentage values unless specically
necessary for your particular setup. This will prevent any chance of overdriving your control linkages.
1) Press the Navigation Pad 6 to highlight POINT>1.
2) Press the INC+/M1 or DEC-/M2 keys to choose which Point you would
like to set a Rate percentage value for.
POINT setting range is 1 through 5. Point 1 is at the low end of the Pitch Curve and Point 5 is at the high end of the Pitch Curve.
Point 3 is a the center of the Pitch Curve.
In the default conguration the Pitch Curve is Linear. For example, when you move the throttle control stick from 0% to
100%, the elevator, aileron, and pitch servos will travel from 0% to 100%, too. As long as the line on the graph remains
straight, the Pitch Curve will be Linear. When a Point Rate percentage value is changed, the line on the graph curves (displaying
the Pitch Curve) and throttle servo travel will vary in relation to throttle control stick movement.
100%
The tables below describe the default Point and Rate values.
1
2
-100%
-50%
POINT DEFAULT RATE
3
4
0%
50%
POINT DEFAULT RATE
5
POINT DEFAULT RATE
RATE setting range for each Point is -150% to 150%.
3) Press the Navigation Pad 6 to highlight RATE>.
4) Press the INC+/M1 or DEC-/M2 keys to set the desired Rate percentage
value for the Point you chose previously, then repeat the previous
procedures to change the desired remaining Point and Rate percentage
values.
Choosing the Flight Mode - Common or Separate, Continued....
3) Press the Navigation Pad 5 to move the cursor to F-MODE>COM.
4) Press the INC+/M1 or DEC-/M2 keys to choose either SEP OR COM
(SEParate or COMmon).
5) If you choose SEPARATE, press the F-MODE key to choose the F-MODE number you would like to program the Pitch Curve
function for. Choose from FN, F1 or F2.
HELI MODEL TYPE
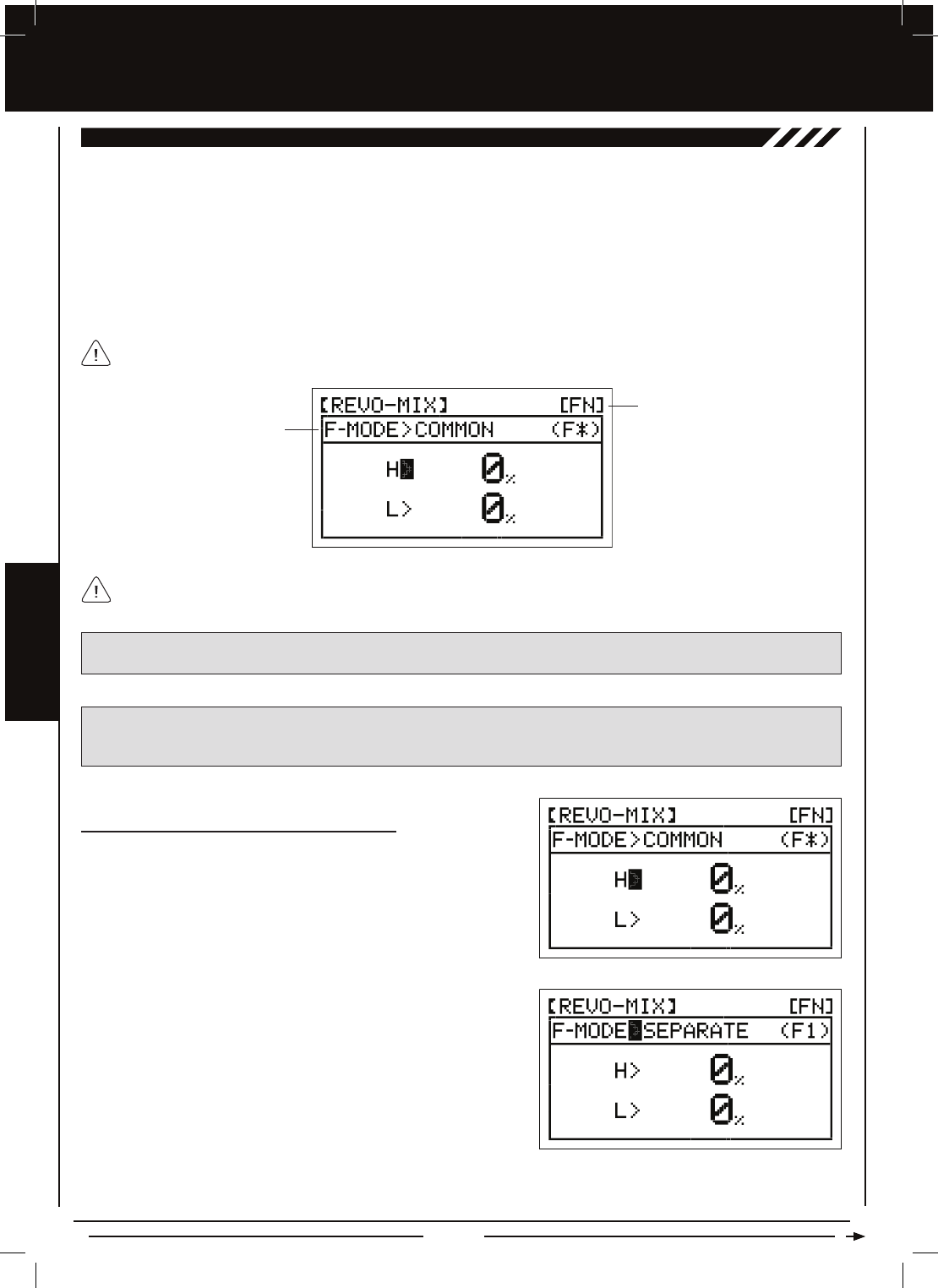
Page 74
hELi MODEL TyPE
18.REvO-MiX (REvOLUTiOn MiXing)
The Revolution Mixing function mixes rudder and collective pitch controls, which makes the helicopter more stable when collective
pitch is increased. For example, when you increase collective pitch, as the rotor head speed and pitch increase, the torque that
it creates can cause the tail of the helicopter to pivot. Adding Revolution mixing helps prevent this from occurring, which makes
the helicopter more stable in the yaw axis. The amount and the direction that the rudder moves with collective pitch control is
adjusted by changing the High side and Low side percentage values.
The Revolution Mixing function can be programmed for both the High and Low throttle sides independently.
For greater exibility, the Revolution Mixing function can be programmed either the same for all Flight Modes or separately for
each of the three Flight Modes.
Transmitter F-MODE refers to the Flight Mode that the transmitter is currently operating in. Programming F-MODE refers
to the Flight Mode that you would like to change the programming for.
Programming F-MODE
Transmitter F-MODE
IMPORTANT We DO NOT recommend using the Revolution Mixing function with a Heading Hold mode or AVCS mode gyro.
The Revolution Mixing function should only be used with a Rate mode gyro or in the event that no gyro is used.
IMPORTANT The Revolution Mixing function is not Activated directly by a switch. It is designed for use in a specic Flight
Mode (or Flight Modes). For example, you may have programmed your gyro for Heading Hold mode in Flight Mode FN
(Normal) and Rate mode in Flight Mode F1. In this case, you might program Revolution mixing only in Flight Mode F1.
Choosing the Flight Mode - Common or Separate
1) From the Display screen, press the ENTER key to display the
Programming Menus.
2) Press the Navigation Pad 56 to highlight REVO-MIX, then press
the ENTER key to display the REVO-MIX menu. The cursor will
default to H>0%.
3) Press the Navigation Pad 5 to move the cursor to F-MODE>COM.
4) Press the INC+/M1 or DEC-/M2 keys to choose either SEPARATE or
COMMON.
5) If you choose SEPARATE, press the F-MODE key to choose the F-MODE number you would like to program the Revolution
Mixing function for. Choose from FN, F1 or F2.
The Revolution Mixing function is typically used in conjunction with a gyro running in Rate mode only or if no gyro is used.
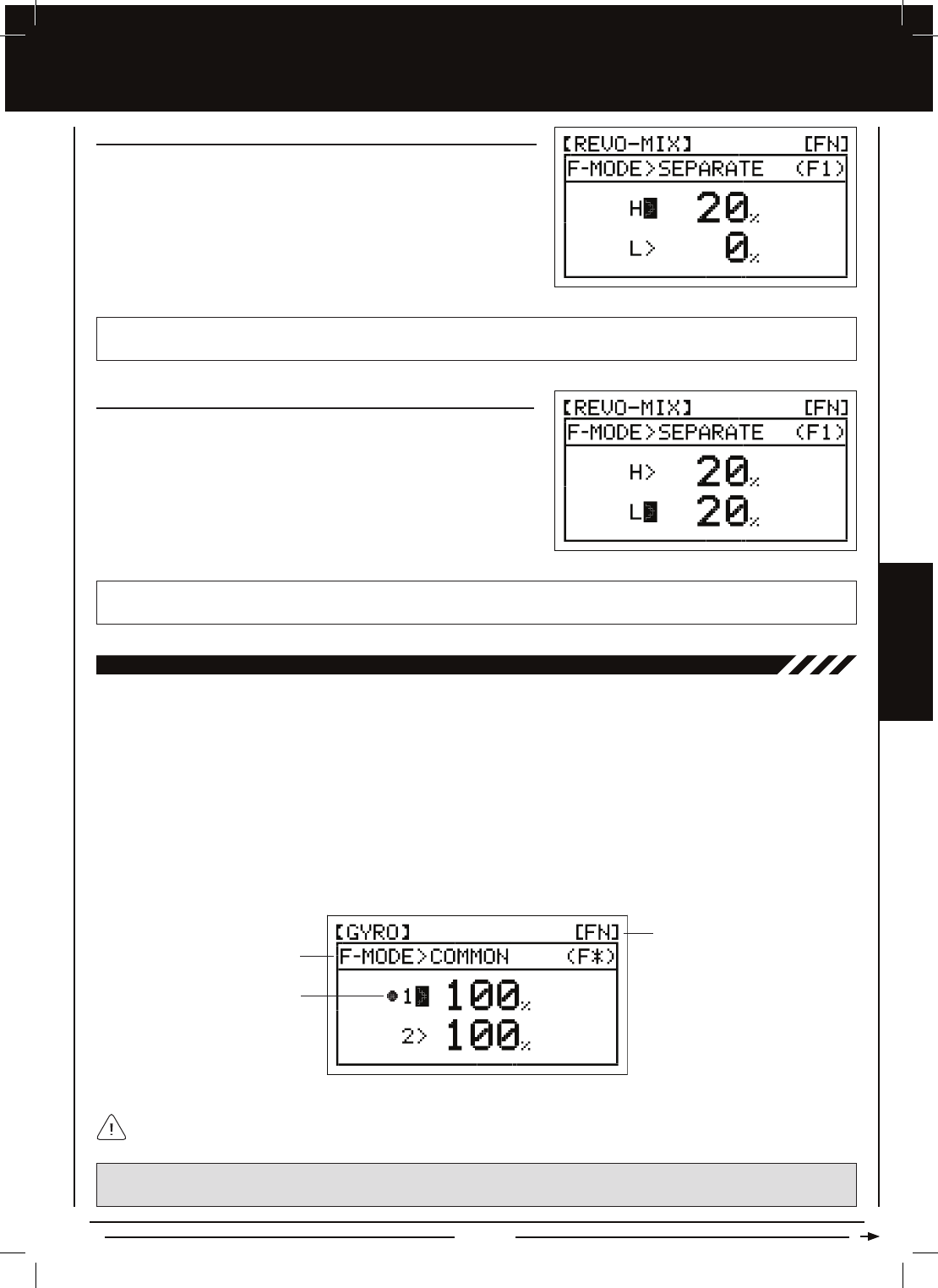
Page 75
hELi MODEL TyPE
Changing the Revolution Mixing Function High Side Percentage Value
Changing the High side percentage value affects the Revolution Mixing
function from half throttle stick to full throttle stick only. It has no effect on
the Low throttle side.
1) Press the Navigation Pad 6 to highlight H>0%.
2) Press the INC+/M1 or DEC-/M2 keys to choose the desired High
throttle side percentage value.
REVO-MIX H setting range is -150% to 150%. The default value is 0% (OFF). Using a positive or negative percentage value
will determine the direction the rudder travels when collective pitch is increased. This mix is Linear.
Changing the Revolution Mixing Function Low Side Percentage Value
Changing the Low side percentage value affects the Revolution Mixing
function from low throttle stick to half throttle stick only. It has no effect on
the High throttle side.
1) Press the Navigation Pad 6 to highlight L>0%.
2) Press the INC+/M1 or DEC-/M2 keys to choose the desired Low throttle
side percentage value.
REVO-MIX L setting range is -150% to 150%. The default value is 0% (OFF). Using a positive or negative percentage value will
determine the direction the rudder travels when collective pitch is increased. This mix is Linear.
19.gyRO (REMOTE gyRO gain cOnTROL)
The Remote Gyro Gain Control function allows you to control Heading Hold mode gain and Rate mode gain remotely. Two separate
Remote Gyro Gain Control function settings can be programmed and one can be selected at any time using the two-position
Gyro switch. For example, you might want 100% gain for aerobatic ight, but then switch to 75% gain for sport ying. In essence,
when you assign a Remote Gyro Gain Control percentage value to each of the two Remote Gyro Gain Control function settings,
you effectively have dual rates for your gyro, just like you have dual rates for your elevator, aileron, and rudder control surfaces.
Depending on the Remote Gyro Gain Control function percentage values, you can adjust the gain in either Heading Hold mode
or Rate mode. In addition, you can program a Heading Hold gain percentage value and a Rate gain percentage value separately,
then switch between the two to aid in setting up your gyro.
For greater exibility, the Remote Gyro Gain Control function can be programmed either the same for all Flight Modes or sepa-
rately for each of the three Flight Modes.
Transmitter F-MODE refers to the Flight Mode that the transmitter is currently operating in. Programming F-MODE refers
to the Flight Mode that you would like to change the programming for.
Programming F-MODE
Transmitter F-MODE
IMPORTANT In order to use this feature, your gyro must support Remote Gain. For more information, and before using this
function, please refer to your gyro's Operating Guide to familiarize yourself with its setup and use.
Current Gyro Switch Selection
HELI MODEL TYPE
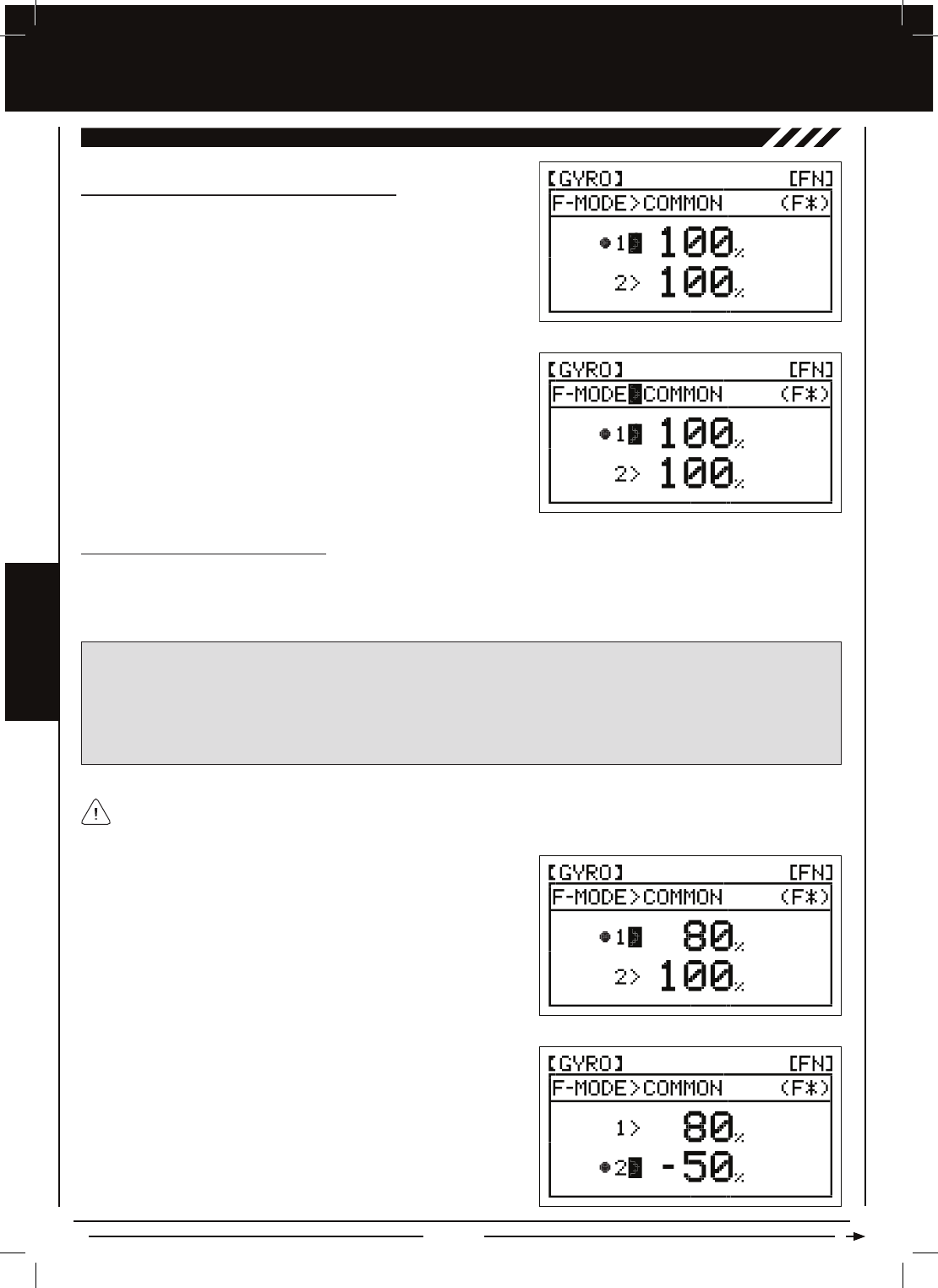
Page 76
hELi MODEL TyPE
Choosing the Flight Mode - Common or Separate
1) From the Display screen, press the ENTER key to display the Programming
Menus.
2) Press the Navigation Pad 56 to highlight GYRO, then press the
ENTER key to display the GYRO menu. The cursor will default to
1>100%.
3) Press the Navigation Pad 5to move the cursor to F-MODE>COMMON.
4) Press the INC+/M1 or DEC-/M2 keys to choose either SEPARATE or
COMMON.
5) If you choose SEPARATE, press the F-MODE key to choose the
F-MODE number you would like to program the Remote Gyro Gain
Control function for. Choose from FN, F1 or F2.
Changing the Gyro Percentage Values
The Gyro percentage values determine both the amount of gain and the gyro operating mode - either Heading Hold mode or Rate
mode. In general, positive values will result in your gyro operating in Heading Hold mode and negative values will result in your
gyro operating in Rate mode. The amount of gain is determined by the percentage value.
IMPORTANT Whether you use positive or negative Gyro percentage values to program your gyro in either Heading Hold
mode or Rate mode will be determined by the NOR/REV settings of the gyro channel in the REVERSE menu. For example,
if the gyro channel is set to NOR (Normal) in the REVERSE menu, positive Gyro percentage values may result in your
gyro operating in Heading Hold mode, but if the gyro channel is set to REV (Reverse) in the REVERSE menu, positive Gyro
percentage values may result in your gyro operating in Rate mode. You will need to test your gyro to ensure that it's operating
in the desired mode based on the percentage values, then adjust the percentage values accordingly to achieve the desired
amount of gain.
You can program two different Remote Gyro Gain Control functions and control them using the Gyro switch. When
programming Gyro percentage values, the 1> percentage value is controlled by the Gyro 1 switch position and the 2>
percentage value is controlled by the Gyro 2 switch position.
1) Press the Navigation Pad 6 to highlight 1>100%.
2) Press the INC+/M1 or DEC-/M2 keys to choose the desired Gyro 1
percentage value.
19.gyRO (REMOTE gyRO gain cOnTROL), cOnTinUED....
3) Press the Navigation Pad 6 to highlight 2>100%.
4) Press the INC+/M1 or DEC-/M2 keys to choose the desired Gyro 2
percentage value.
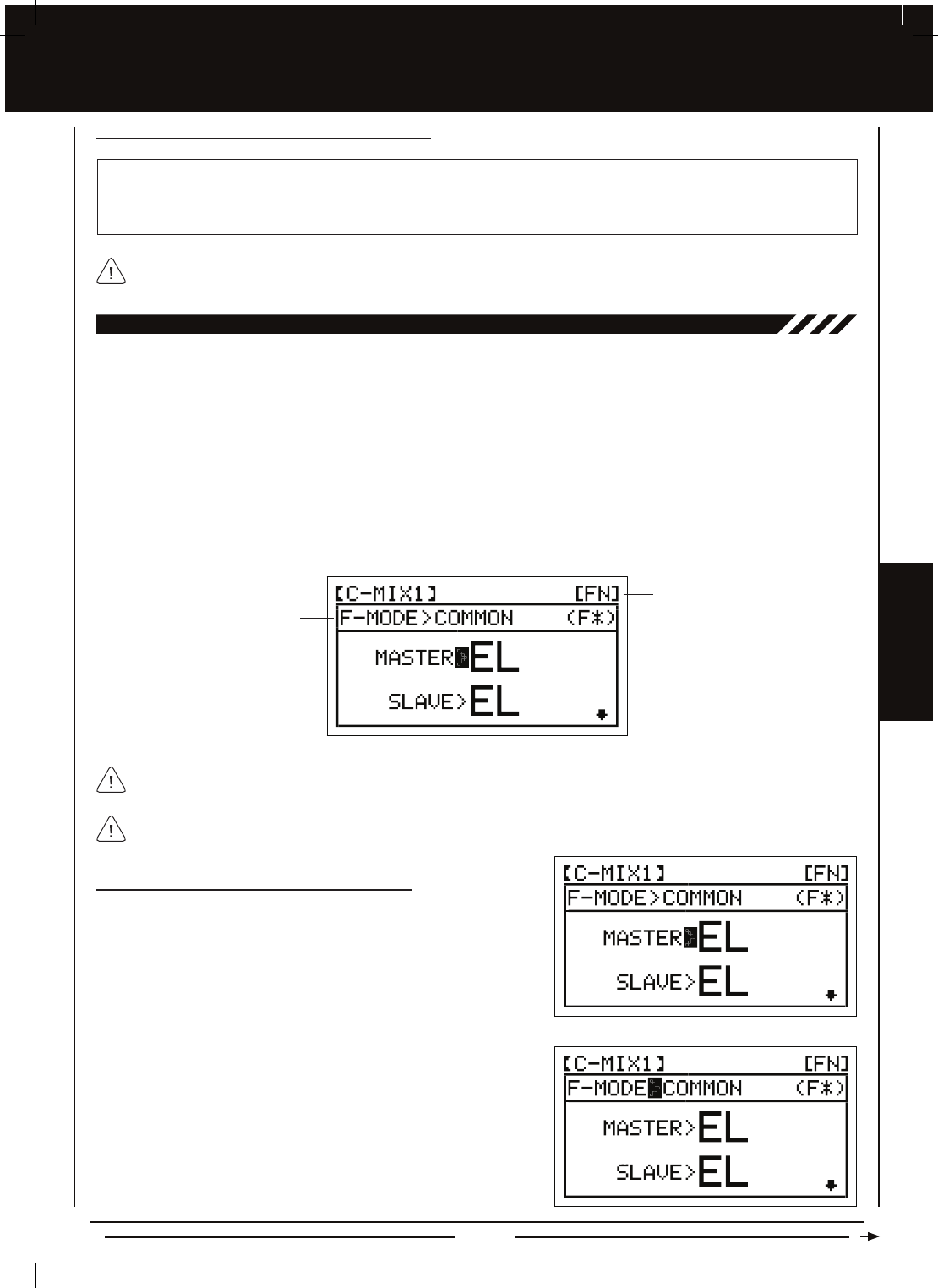
Page 77
hELi MODEL TyPE
GYRO 1 and GYRO 2 setting range is -150% to 150%. The default settings are 100%. Decreasing the GYRO percentage
values decreases gyro gain and increasing the GYRO percentage values increases gyro gain. See the IMPORTANT note on
the previous page regarding the use of positive and negative Gyro percentage values and how they may change your gyro
operating mode.
When the either the Gyro 1 or Gyro 2 percentage values are set to 0%, the gyro will be in 'pass-through' mode (e.g., OFF)
for that selected Gyro function only.
Changing the Gyro Percentage Values, Continued....
20. & 21.c-MiX1 anD c-MiX2 (cOMPEnSaTiOn MiXing)
The Compensation Mixing function is used to create your own custom mix if one of the pre-programmed mixes is not suitable. For
example, you can create a custom mix that mixes elevator to throttle or that mixes rudder to throttle. Elevator to throttle mixing is
typically used during 3D ying to provide a momentary burst of throttle under hard cyclic load. Rudder to throttle mixing is typically
used to reduce the tendency of the helicopter to slightly rise and fall as you pirouette.
Because any of the six channels can be programmed as a Master or a Slave, you are able to program custom mixes for just
about any situation required. Compensation Mixes are composed of a Master channel and a Slave channel. Any of the available
six channels can be programmed as a Master or a Slave. The same channel can even be programmed as both a Master and a
Slave. In addition to programming the High and Low Rate percentage values, the Slave channel Offset percentage value can be
changed to move the neutral point of the Slave channel servo when the Compensation Mixing function is Activated.
For greater exibility, both Compensation Mixing functions can be programmed either the same for all Flight Modes or separately
for each of the three Flight Modes.
Transmitter F-MODE refers to the Flight Mode that the transmitter is currently operating in. Programming F-MODE refers
to the Flight Mode that you would like to change the programming for.
Programming F-MODE
Transmitter F-MODE
In all cases, the Master channel always controls the Slave channel.
Choosing the Flight Mode - Common or Separate
1) From the Display screen, press the ENTER key to display the Programming
Menus.
2) Press the Navigation Pad 56 to highlight either C-MIX1 or C-MIX2,
then press the ENTER key to display the C-MIX1 or C-MIX2 menu. The
cursor will default to MASTER>EL.
3) Press the Navigation Pad 5to move the cursor to F-MODE>COMMON.
4) Press the INC+/M1 or DEC-/M2 keys to choose either SEPARATE or
COMMON.
5) If you choose SEPARATE, press the F-MODE key to choose the F-MODE
number you would like to program the Compensation Mixing function
for. Choose from FN, F1 or F2.
HELI MODEL TYPE
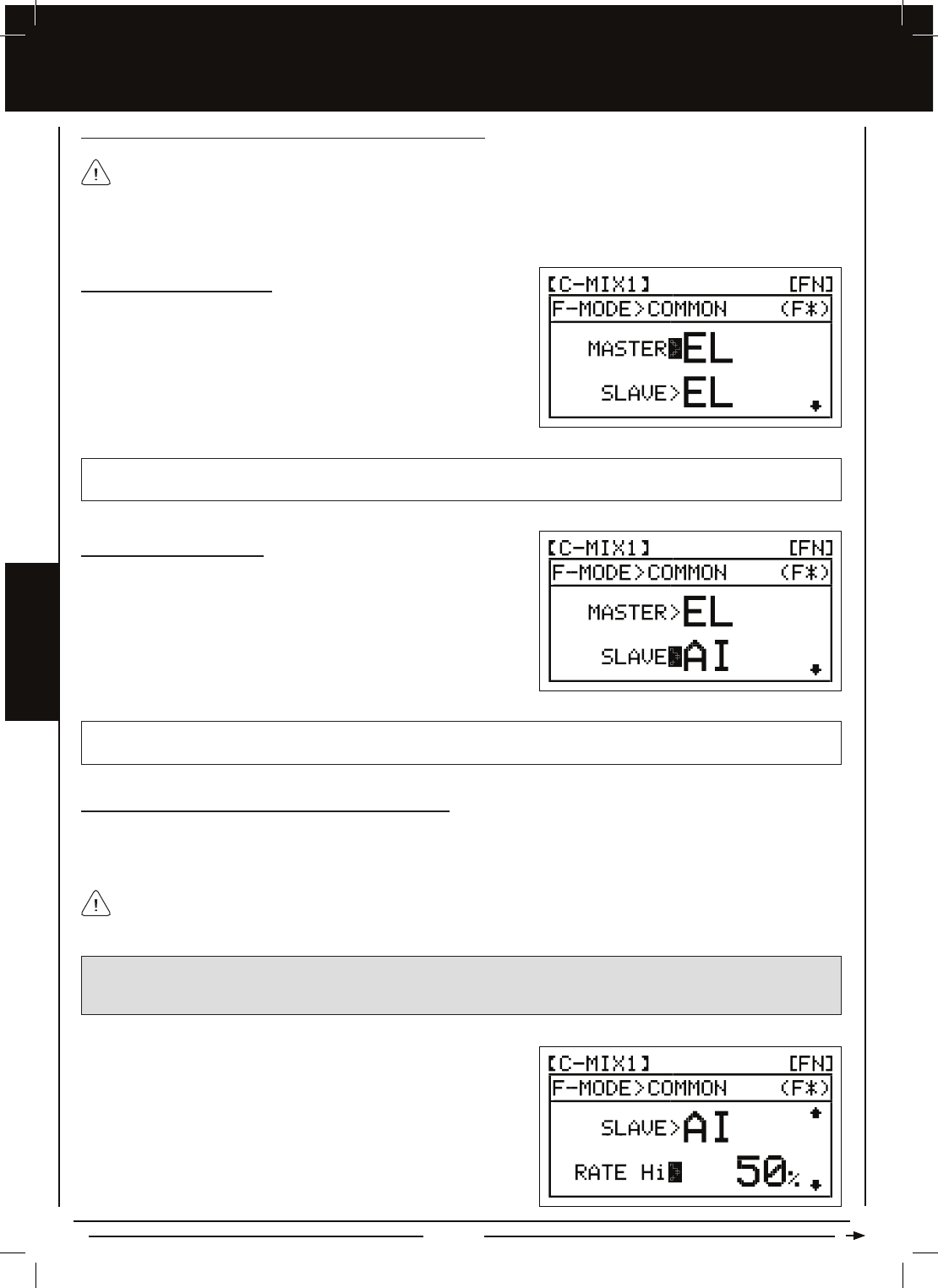
Page 78
hELi MODEL TyPE
Choosing the Flight Mode - Common or Separate, Continued....
Two Compensation Mixing functions are available, however, only one Compensation Mixing function can be Active at one
time. If F-MODE is set to COMMON, both Compensation Mixing functions will controlled by the Compensation Mixing
switch and Compensation Mixer 2 will always override Compensation Mixer 1. If F-MODE is set to SEPARATE, you can control
one Compensation Mixing function using the Compensation Mixing switch and control the second Compensation Mixing function
(programmed to a different Flight Mode) using a Flight Mode switch, however, keep in mind that higher numbered Flight Modes
will always override lower numbered Flight Modes.
Choosing the Master Channel
The Master channel is the channel that controls the Slave channel. For
example, if you set the Master channel to EL (Elevator), when you move
the elevator control stick, the Slave channel that's mixed to the elevator
channel will move.
1) Press the Navigation Pad 6to highlight MASTER>EL, then press the
INC+/M1 or DEC-/M2 keys to change the desired Master channel.
MASTER setting range is EL (Elevator), AI (Aileron), TH (Throttle), RU (Rudder), GY (Gyro), and PI (Pitch). The default
setting is EL (Elevator).
Choosing the Slave Channel
The Slave channel is the channel that is controlled by the Master channel.
For example, if you set the Master channel to EL (Elevator) and the Slave
channel to AI (Aileron), when you move the elevator control stick, the
aileron servo will move.
1) Press the Navigation Pad 6to highlight SLAVE>EL, then press the
INC+/M1 or DEC-/M2 keys to change the desired Slave channel.
SLAVE setting range is EL (Elevator), AI (Aileron), TH (Throttle), RU (Rudder), GY (Gyro), and PI (Pitch). The default setting
is EL (Elevator).
Changing the Rate High and Rate Low Percentage Values
By changing the Rate High and Rate Low percentage values, you can program which direction the Slave channel servo
travels in relation to the Master channel servo, and program how far the Slave channel servo travels relative to how far the Master
channel servo travels.
The Rate High and Rate Low percentage values are a ratio of Slave channel servo travel to Master channel servo travel.
For example, if the Rate High percentage value is set to 10%, the Slave channel servo will travel 1/10th the amount in one
direction that the Master channel servo travels. This mix is Linear.
WARNING When a Compensation Mixer is Activated, you still have separate control over the Slaved channel, however,
depending on the Rate High and Rate Low percentage values, the Slave channel End Point Adjustment could be exceeded. Be
cautious to prevent any chance of overdriving your control linkage when the Compensation Mixing function is used.
1) Press the Navigation Pad 6 to highlight RATE Hi>0%.
2) Press the INC+/M1 or DEC-/M2 keys to change the Rate High Percentage
value.
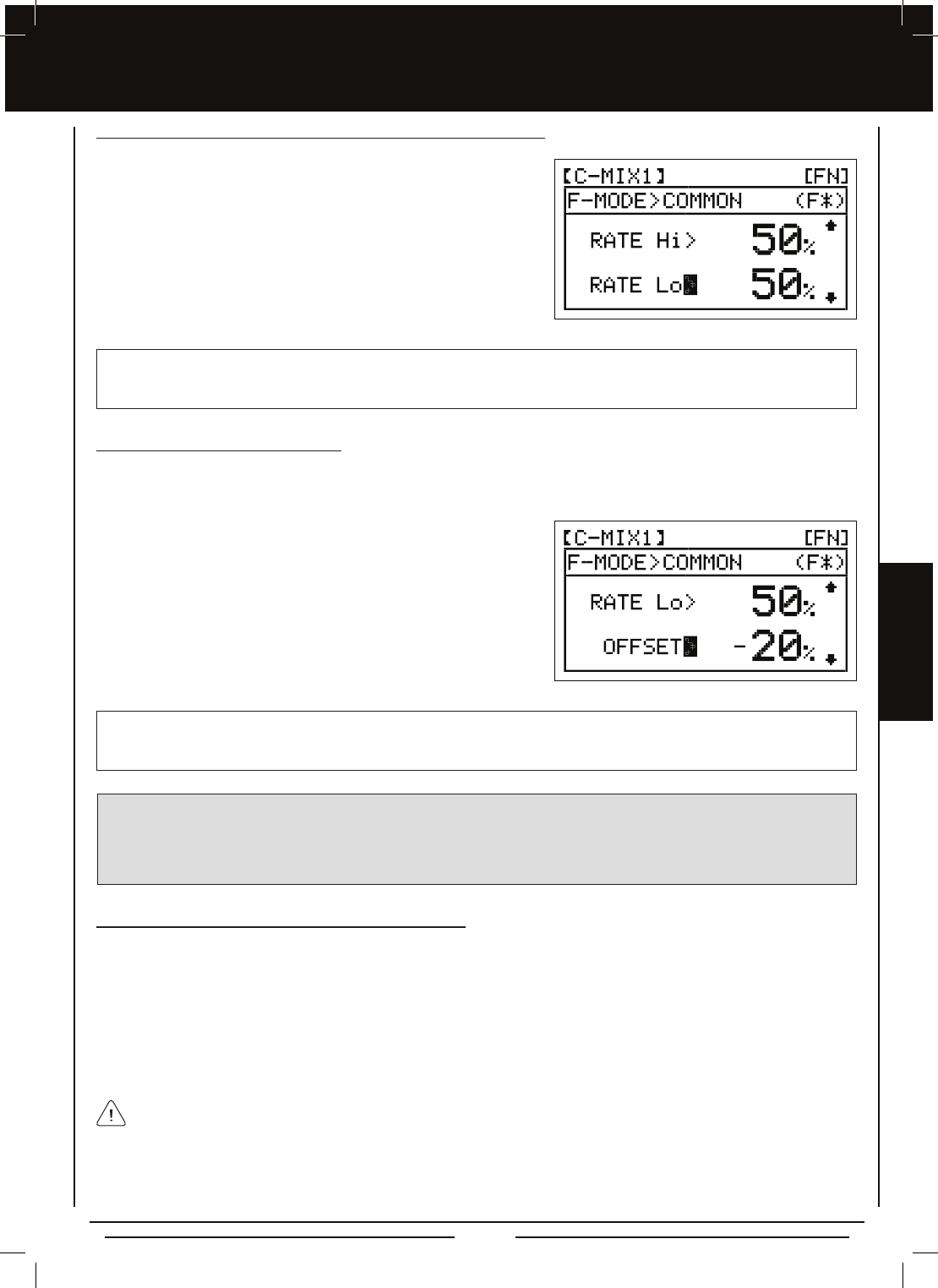
Page 79
hELi MODEL TyPE
RATE Hi and RATE Lo setting ranges are -150% to 150%. The default settings are 0%. Increasing or decreasing the Rate High
and Rate Low percentage values will change the direction that the Slave channel servo travels and the amount that it travels
relative to the Master channel servo.
3) Press the Navigation Pad 6 to highlight RATE Lo>0%.
4) Press the INC+/M1 or DEC-/M2 keys to change the Rate Low Percentage
value.
Changing the Rate High and Rate Low Percentage Values, Continued....
Changing the Offset Percentage Value
The Offset percentage value changes the neutral position of the Slave channel servo when the Compensation Mixing function is
Activated. For example, when an Offset percentage value is programmed, the Slave channel servo neutral position and its two
End Point positions will 'shift' the programmed amount.
1) Press the Navigation Pad 6 to highlight OFFSET>0%.
2) Press the INC+/M1 or DEC-/M2 keys to change the Offset Percentage
value.
OFFSET setting range is -100% to 100%. The default setting is 0%. Increasing the Offset percentage value will shift the neutral
position of the Slave servo in one direction and decreasing the Offset percentage value will shift the neutral position of the
Slave servo in the opposite direction.
Compensation Mixing Sample - Mixing Rudder to Throttle
The sample below describes how to mix rudder to throttle using Compensation Mixer 1 controlled by the Compensation Mixing
switch. This mix is typically used to reduce the tendency of the helicopter to slightly rise and fall as you pirouette. For example,
when you command a pirouette to the left, the helicopter will rise slightly and will require you to reduce throttle, and when you
command a pirouette to the right, the helicopter will fall slightly and will require you to increase throttle.
In this example, the Master channel is the Rudder channel and the Slave channel is the Throttle channel. The RATE Hi and RATE
Lo percentage values dene how far Up and Down the throttle will move when the rudder is moved, and is a percentage of the
amount the rudder is moved. To Activate this mix, Activate Compensation Mixer 1 by pulling the Compensation Mixer switch down.
IMPORTANT When the Throttle channel is programmed as the Master channel, the Slave channel servo will not begin to
move relative to the position of the throttle control stick until the throttle control stick reaches half throttle and above. Once the
throttle control stick reaches half travel and above, the Slave channel servo will begin to move. If you require the Slave channel
servo to move from Low throttle to High throttle, program the Compensation Mixer as shown in this example: MASTER>TH,
SLAVE>RU, Rate Hi>25%, RATE Lo>25%, OFFSET>-25%.
MASTER>RU
SLAVE>TH
RATE Hi>10%
RATE Lo>10%
OFFSET>0%
The positive and negative values shown in the example may vary based on the NOR/REV status
of your aileron and elevator servos. You may need to change the percentage values to suit.
1) Set up your swashplate, servo reversing, and control throws as desired.
2) Program the Compensation Mixer 1 options from the within the C-MIX1 menu, as shown at left.
HELI MODEL TYPE
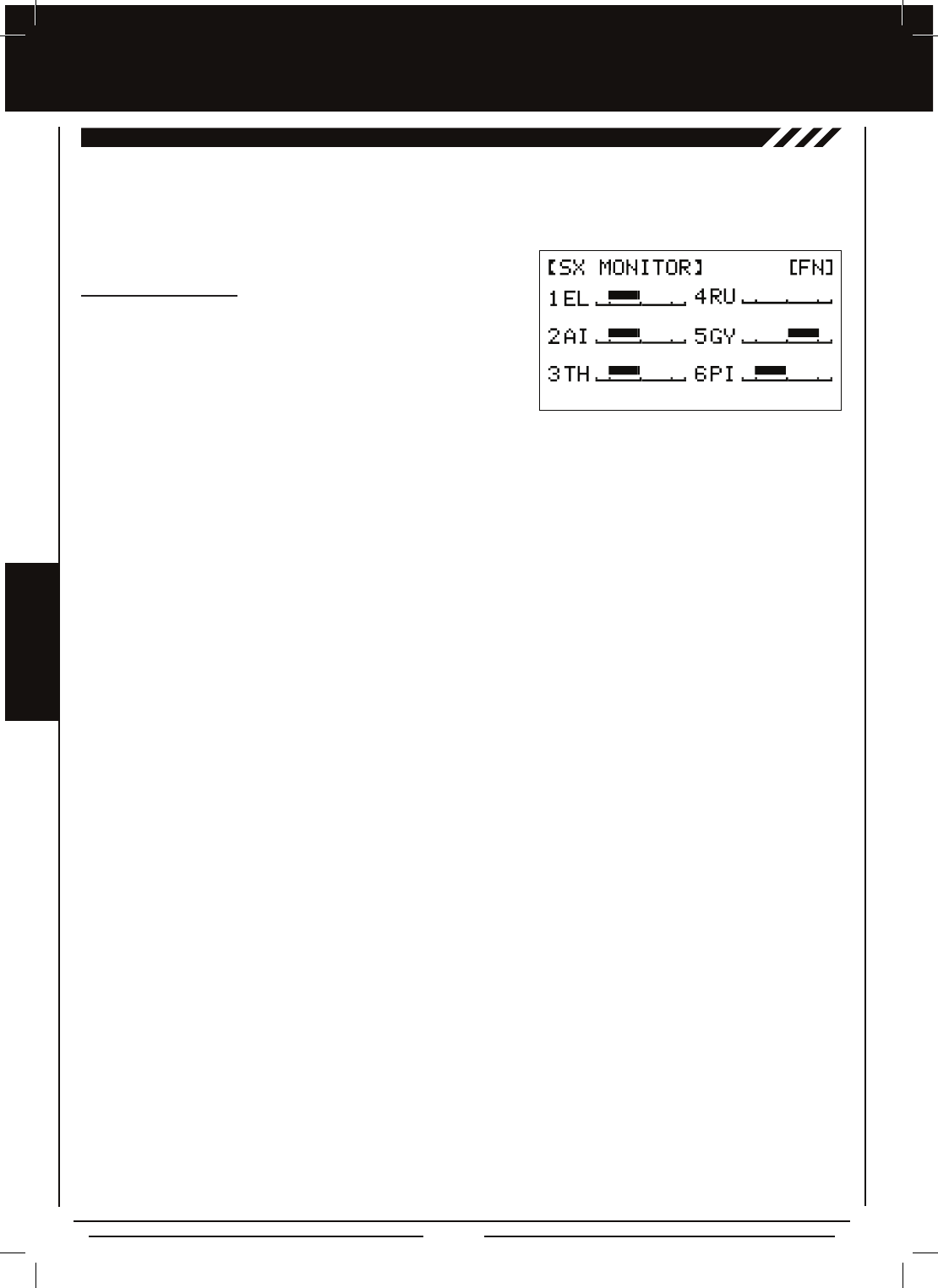
Page 80
hELi MODEL TyPE
22.SX MOniTOR (SERvO MOniTOR)
The Servo Monitor displays the output levels of each of the 6 channels in bar graph form, allowing you to monitor servo operation
in a virtual manner. This is helpful to see servo movement when the control sticks and switches are moved, and it allows you to
visualize what is occurring with servo movements when you apply different mixing values. The Servo Monitor also indicates which
channel slots in the receiver to plug your servos into (1 EL, 2AI, 3TH, 4RU, 5GY, and 6FL).
Using the Servo Monitor
1) From the Display screen, press the ENTER key to display the Programming
Menus.
2) Press the Navigation Pad 56 to highlight SX MONITOR, then press
the ENTER key to display the Servo Monitor.
3) Moving the control sticks and channel switches will display the position and movement of each of the servos.
THIS SPACE INTENTIONALLY LEFT BLANK
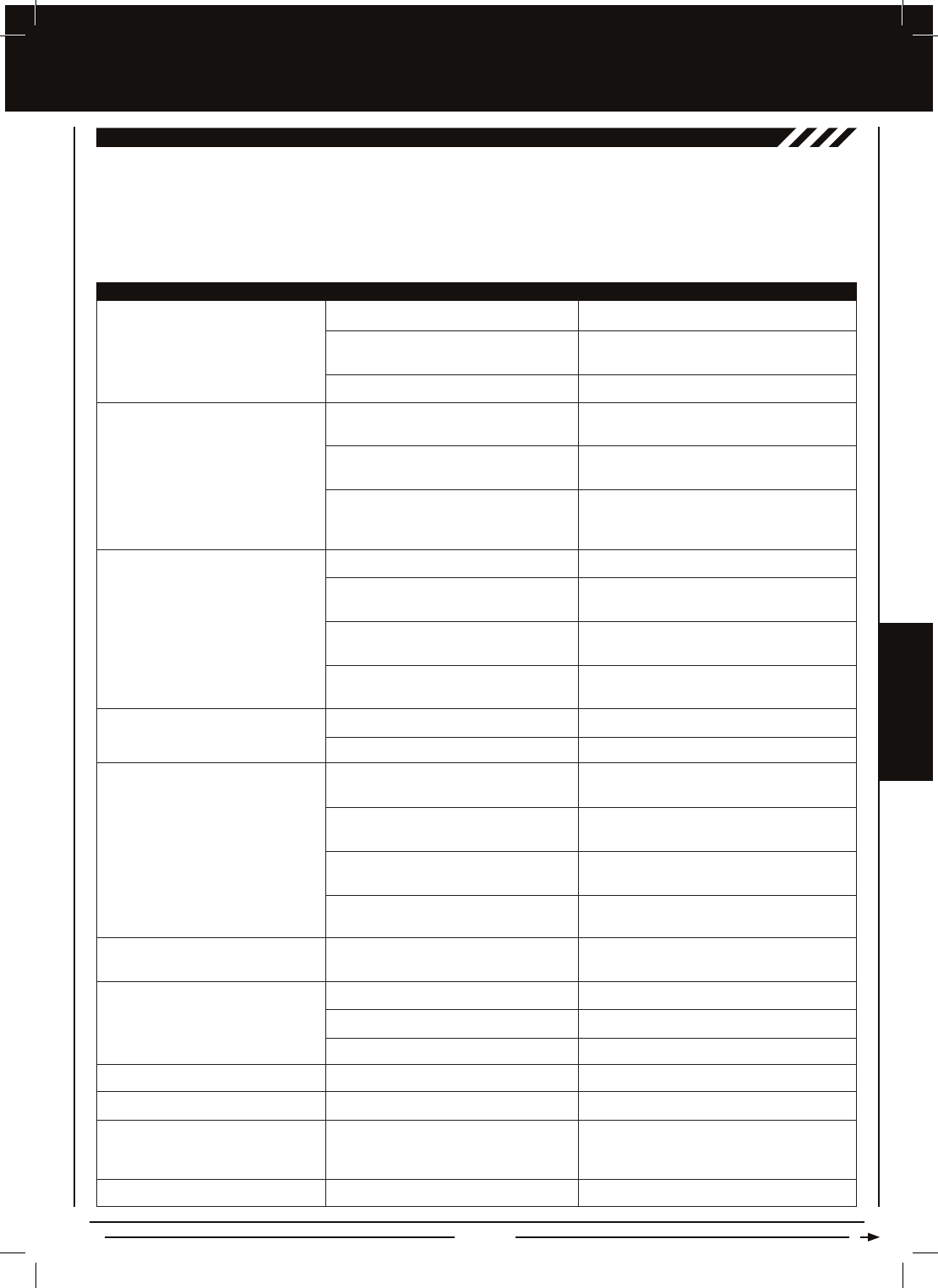
Page 81
Batteries not installed correctly
Damage caused by using incorrect charger
or reverse polarity
Low transmitter battery voltage
Too much time elapsed after pressing
receiver Bind Button
Attempting to bind incompatible receiver
Using ESC with BEC
Low transmitter battery voltage
Transmitter not in Flight Mode FN when
turned ON
Transmitter Trainer function set to
MASTER when turned ON
Transmitter Trainer function set to SLAVE
when turned ON
Control linkages binding
Low receiver battery voltage
Low transmitter or receiver battery
voltage
Receiver antennas not mounted correctly
in your model or are damaged
Transmitter antenna not angled to
optimum position
Transmitter in Low-Power Range Check
mode
Incorrect Servo Reversing setting
Servo horn not installed correctly
Trim switch not centered
Servo not centered
Too much servo travel
Transmitter Trainer function set to SLAVE
Transmitter in Low-Power mode
Transmitter Trainer function set to SLAVE
REFEREncE
This troubleshooting guide has been provided to help you diagnose and solve most problems that you may encounter with your
TM-160 2.4GHz FHSS-1 radio control system. Most problems encountered can be solved by following the problem-cause-solution
sections.
PROBLEM caUSE SOLUTiOn
Transmitter does not turn ON
Transmitter will not bind to receiver
Audible alarm beeps continuously
Servo movement is slow
Inadequate transmitting range
Servo(s) move the wrong direction
Servo horn(s) not centered
Control linkage(s) bind
RF Output Indicator ashes
Transmitter Bind LED ashes
Transmitter Bind LED goes out
Reinstall batteries. Observe correct polarity
Contact Airtronics Customer Service
Replace or recharge transmitter batteries
Quickly press the transmitter Bind Button after
releasing the receiver Bind Button
Transmitter compatible only with Airtronics
2.4GHz FHSS-1 aircraft receivers
Disconnect ESC and use standard receiver
battery for Binding procedure, then reconnect
ESC after binding
Replace or recharge transmitter batteries
Place transmitter in Flight Mode FN before
turning ON
Press any key to Inhibit alarm or use TRAINER
menu to Inhibit Trainer function.
Press any key to Inhibit alarm or use TRAINER
menu to Inhibit Trainer function.
Adjust control linkages to operate smoothly
Recharge receiver battery
Replace or recharge transmitter and receiver
batteries
Mount receiver antennas as recommended
or replace antennas
Adjust transmitter antenna so that it's angled
to the optimum position during use
Change transmitter to Normal mode
Change Servo Reversing setting assigned
to the channel affected in REVERSE menu
Turn servo horn 180º and reinstall
Center trim switch
Use CENTER menu to center servo horn
Adjust EPA to reduce servo travel
This is normal
Complete Range Check in Low-Power mode,
then turn transmitter OFF, then back ON to
enter Normal mode
This is normal
If you cannot solve the problem using this troubleshooting guide, please contact Airtronics Customer Service using the information
on the back cover of this Operating Manual.
TROUBLEShOOTing gUiDE
REFERENCE
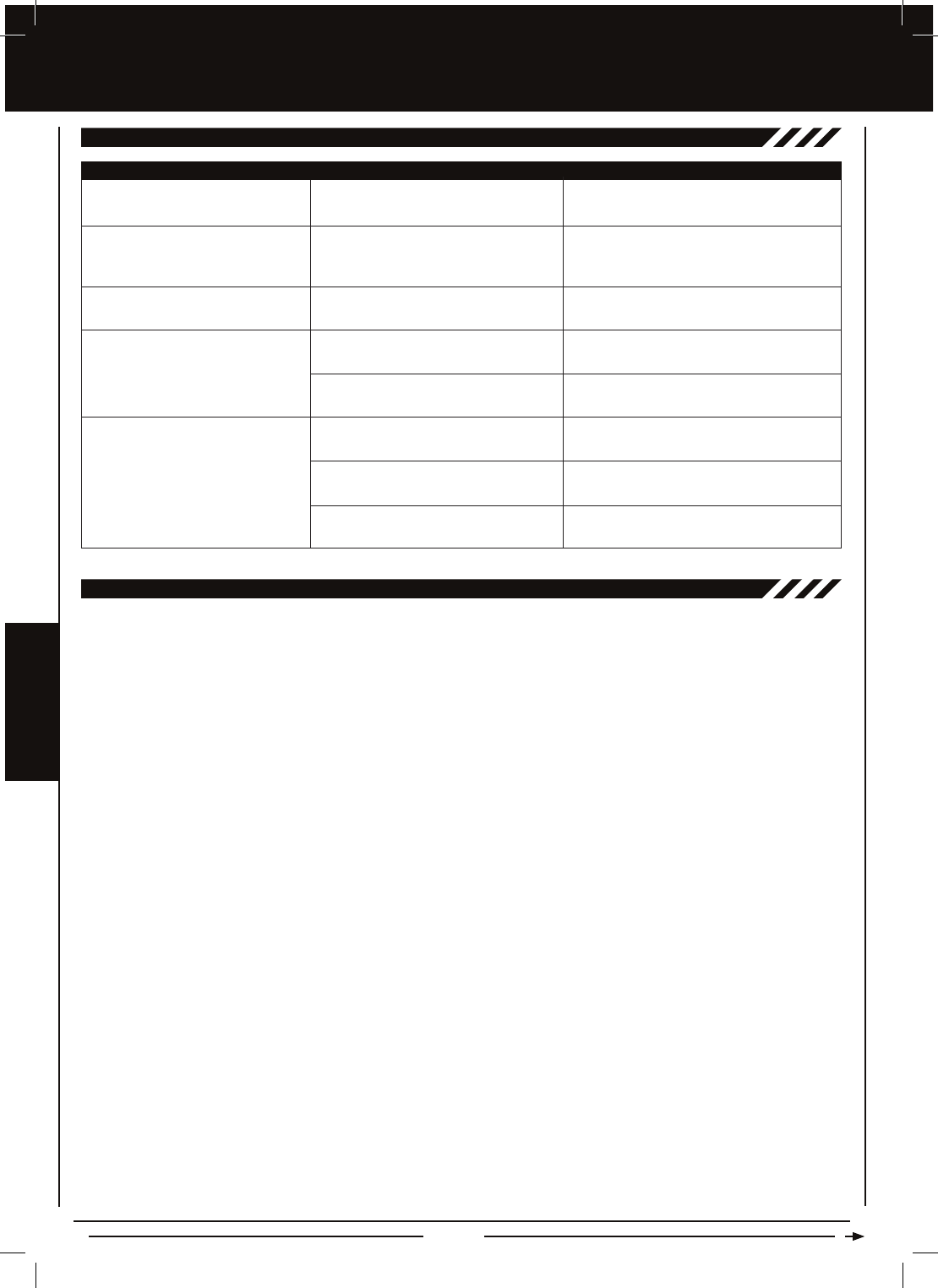
Page 82
REFEREncE
Attempting to copy Programming Data to
the same model number
Transmitter left in direct sunlight for too
long
Trim set to SEPARATE in TRIM menu
Too much control throw
No Exponential programmed
Low transmitter or receiver battery
voltage
Receiver antennas not mounted correctly
in your model or are damaged
Aircraft sitting in tall grass (usually
sailplanes only)
PROBLEM caUSE SOLUTiOn
Cannot copy Programming Data
LCD appears dark or hard to read
Trim changeswhen switching between
Flight Modes
Controls too sensitive
Range check fails
Copy Programming Data to a different model
number
Place transmitter in shade until LCD clears up.
Do not place transmitter in direct sunlight for
long periods of time
This is normal when Trim is set to SEPARATE,
otherwise, set Trim to COMMON
Turn Dual Rate switch ON to lower control
throw
Program positive Exponential percentage
value
Replace or recharge transmitter and receiver
batteries
Mount receiver antennas as recommended
or replace antennas
Lift model out of grass for range check
TROUBLEShOOTing gUiDE, cOnTinUED....
gLOSSaRy OF TERMS
Activate: To turn ON a particular function.
Aileron/Elevator Control Stick: Controls the Aileron and Elevator axes. The Aileron/Elevator Control Stick length is adjustable
to suit your preference.
Aileron Trim Switch: Used to control the Aileron axis Right and Left trim.
Ailvator: Ailvator mixes ailerons and elevator, allowing you to have both roll control and pitch control on the elevator, separate
from the ailerons. When Activated, not only will the two elevator halves move up and down together, but each elevator half can
move up and down independently like ailerons. This function is commonly referred to as tailerons or stabilators.
Antenna: Transmits the signal from the transmitter to the receiver in the model. The Antenna should be pivoted into the vertical
position during use. When not in use, the Antenna should be collapsed into the horizontal position to prevent damage during
handling and transport.
Antenna Reception Wires: The portion of each of the receiver antenna wires that actually receives the transmitter signal. The
Antenna Reception Wires should never be bent or they could be damaged and limit the range of the receiver.
Battery Compartment: Houses the 6 cells that power the transmitter. The transmitter uses 6 cells for lighter weight and better
feel, while still providing long usage time and high power output.
Binding: The act of pairing the transmitter and receiver to prevent interference from transmitters operated by other users. The
transmitter and receiver must be paired so that the two can 'talk' to each other. Once the Binding process is complete, the setting
is remembered even when the transmitter and receiver are turned OFF.
Bind Button: Used to Bind the transmitter and receiver. Also used to enter Low-Power Range Check mode.
Bind LED: Displays the current status of the transmitter and receiver pair.
CCPM: Collective, Cyclic, Pitch Mixing. CCPM is software-controlled mixing that allows control of the collective, cyclic and pitch
using three (and sometimes four) servos. This allows lower mechanical complexity and greater control precision. In this
conguration the cyclic and collective controls are mixed.
CCPM Servo End Point Adjustment: The CCPM End Point Adjustment function allows you to adjust servo travel in each direction
for the elevator, aileron, and pitch servos independently. Unlike standard End Point Adjustment, which affects all the cyclic servos,
CCPM End Point Adjustment allows you to adjust each cyclic servo independently without any affect on the other cyclic servos.
Charging Jack: Used for onboard charging of the Ni-Cd or Ni-MH transmitter batteries.
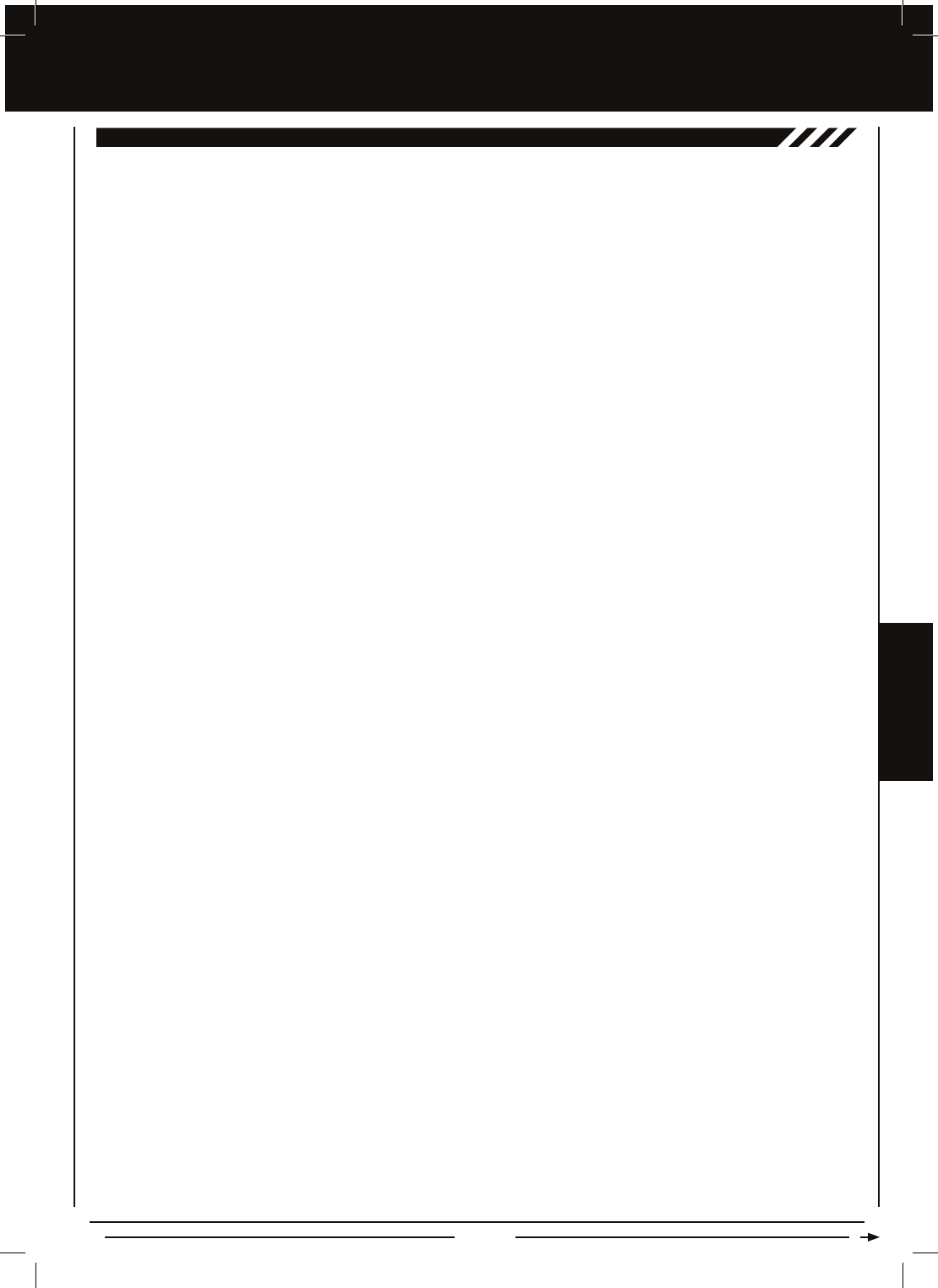
Page 83
REFEREncE
gLOSSaRy OF TERMS, cOnTinUED....
Coaxial Cables: The portion of each receiver antenna wire that extends the Antenna Reception Wires. The Coaxial Cables can
be bent into gentle curves, however, do not bend the Coaxial Cables acutely, or repeatedly bend them, or the antenna wire's
cores can be damaged.
Compensation Mixing: Allows you to mix two channels together, then apply that mixing to the channels themselves. Useful if
you need to program a mix that is not already pre-programmed.
Delta Mixing: Delta mixing, more commonly referred to as Elevon mixing, combines the use of aileron and elevator from two
separate control surfaces to provide both roll and pitch control.
Differential: The Differential function allows you change the ratio of the Up to Down movement of each aileron. The Aileron
Differential function can be used to eliminate aircraft yaw tendency by adding more movement to the upward moving aileron than
the downward moving aileron.
Digital Trim Memory: Allows the transmitter to store trim values in its memory. The amount of control surface trim that you
set during ight using the trim switches is automatically stored in memory for that specic channel and for that specic model.
The trim values for each model will automatically be loaded when the transmitter is turned ON.
Direct Model Select: Direct Model Select allows you to select one of three of your most-used models from memory without going
through the Model Select menu.
Dual Rate: The Dual Rate function allows you to change the control authority of the control surfaces by changing the amount of
servo travel. You can use Dual Rate to lower the control throw with just the ip of the Dual Rate switch.
Elevator Trim Switch: Used to control the Elevator axis Up and Down trim.
End Point Adjustment: The End Point Adjustment function allows you to adjust servo travel in each direction. This makes it
possible to balance control surface throw in both directions. For example, if you want your elevator to move Up and Down two
inches in each direction, but the elevator moves Down more than two inches, decrease the End Point Adjustment in the Down
direction, so that the elevator moves Up and Down the same amount.
Exponential: The Exponential function allows you to vary the amount of servo travel in relation to the movement of the
elevator, aileron, and rudder control sticks near the neutral positions to change the way the control surfaces react to control stick
movement. Increasing the Exponential value will soften the control feel around neutral and decreasing the Exponential value will
heighten the control feel around neutral.
Fail Safe: The Fail Safe function automatically sets the servos to a predetermined position in the event that the signal between
the transmitter and the receiver is interrupted, whether due to signal degradation or to a low transmitter battery.
FH1 Modulation: Frequency Hopping 1st generation FHSS technology.
FHSS: Frequency Hopping Spread Spectrum. FHSS is a modulation type which transmits data across the entire frequency
spectrum by transmitting data on different channels at an extremely fast interval.
Flaperons: Flaperons is a mix of aps and ailerons, allowing you to use the ailerons as aps if your model does not feature
separate aps. When Activated, both ailerons are moved down at the same time to provide the function of aps, while still providing
aileron roll control.
Flight Modes: Flight Modes allow you to change the ying characteristics of your model with the ip of a switch. For example,
you can have one Flight Mode for normal ying and a second Flight Mode for aerobatic ying. Flip the Flight Mode switch from
Flight Mode FN (Normal) to Flight Mode F1 and your model is now programmed with all of your 'Aerobatic' Flight Mode
programming. With three programmable Flight Modes available for each Model Type, the combinations of model programming
is highly-congurable.
Flight Mode Key: Allows you to cycle through the three different Flight Modes during programming.
Gyro: A Gyro is an electronic device, that coupled with a high-speed servo linked to the tail rotor control arm, is used to stabilize
a helicopter's yaw axis.
Inhibit: To deactivate or turn OFF a particular function.
Landing Gear Switch: Used to control the operation of the Landing Gear channel. This channel is a non-proportional channel,
and is ideal for controlling the retractable landing gear or any other non-proportional control function on your model.
Low-Power Mode: The Low-Power Mode function lowers the transmitter's RF output level to check radio signal reception
(Range Check). Use this function to check radio signal reception on the ground, prior to ight.
REFERENCE
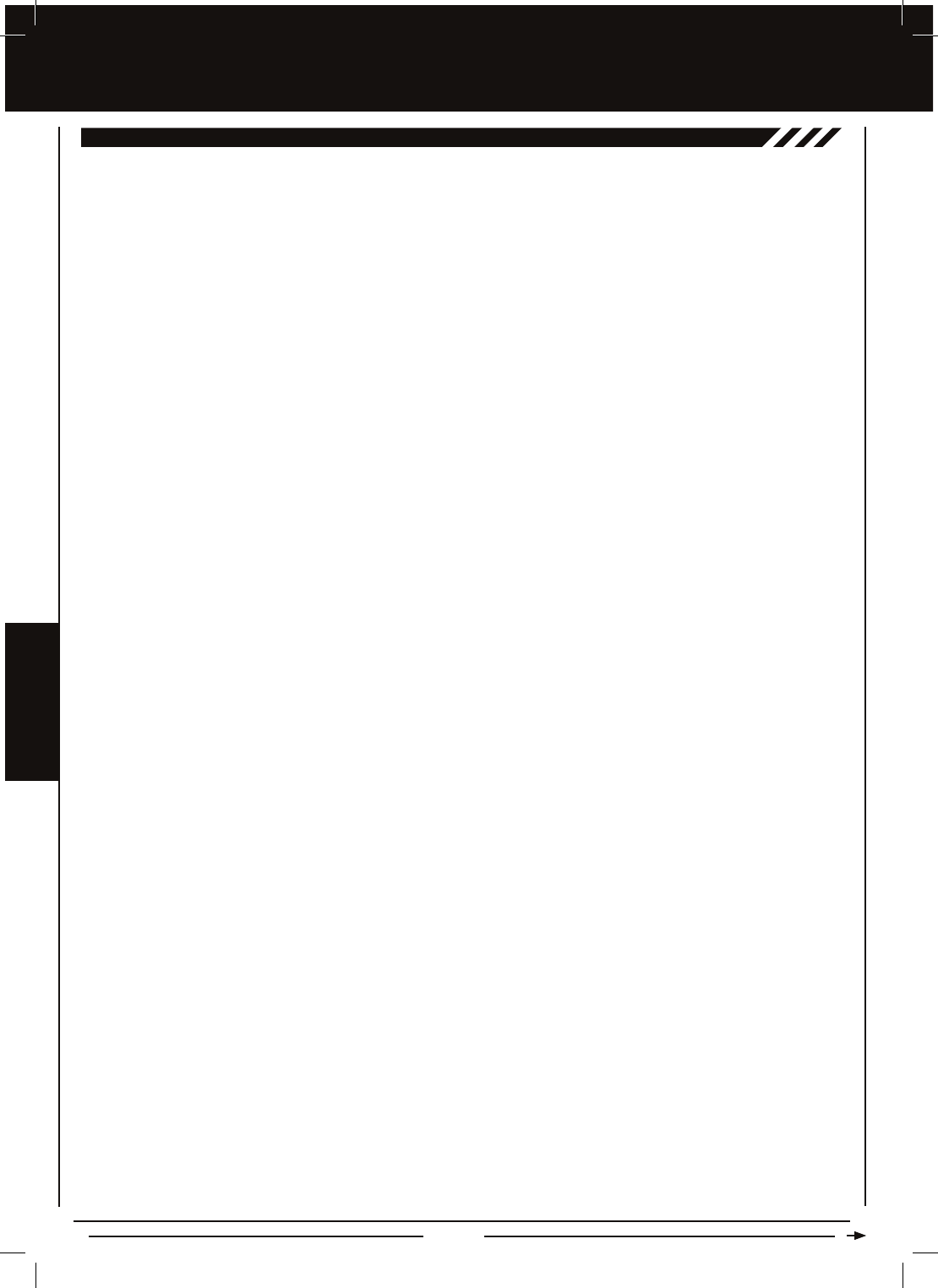
Page 84
gLOSSaRy OF TERMS, cOnTinUED....
Model Name: The Model Name function allows you to name each of your individual models. This makes it easy to keep track of
multiple models. The Model Name can consist of up to 8 letters, numbers, or symbols. Choose from capital letters, lower case
letters, numbers, and various symbols.
Model Select: The Model Select function allows you to load the programming for the particular model you wish to y. The
Programming Data for all of your models is accessed through the Model Select menu.
Multi-Function LCD: The heart of the programming and display features of the transmitter. All programming and transmitter
display functions are shown on the Multi-Function LCD.
Navigation Pad: The Navigation Pad is used in conjunction with the Programming Keys to facilitate transmitter programming.
The Navigation Pad allows you to quickly and easily move the Programming Cursor up and down, and right and left. The ENTER
key in the center of the Navigation Pad is used to open the selected menu or programming option.
Neck Strap Anchor: Used to attach your neck strap (available separately) to the transmitter.
Ni-MH: Short for Nickel Metal Hydride, a Ni-MH battery typically has about two to three times the capacity of an equivalently sized
Ni-Cd (Nickel Cadmium) battery, therefore, they are ideal for use to power both the transmitter and the receiver.
Offset: The Offset function allows you to shift and hold the neutral position of the Slave servo within a Compensation Mix.
Operating Voltage: The safe voltage that the transmitter or receiver can operate within. Exceeding the minimum operating voltage
can result in loss of power to the device(s). Exceeding the maximum operating voltage can result in damage to the devices(s).
Output Power: The power (in Milliwatts) that your transmitter transmits a signal. Output power is dened by government
guidelines and differs by region.
Pitch Curve: The Pitch Curve function allows you to vary the amount of pitch travel in relation to the movement of the throttle
control stick at different points throughout the entire range of deection.
Power Indicator: Indicates that there is power to the transmitter. When the battery voltage drops to 6.7 volts, the audible Low
Voltage Alarm will sound.
Power Switch: Turns the transmitter ON and OFF.
Programming Keys: The Programming Keys are used to facilitate transmitter programming and select models stored in
memory. The four Programming Keys consist of the INC+/M1 (Increase/Model 1) key, the DEC-/M2 (Decrease/Model 2) key, the
END/M3 (End/Model 3) key, and the F-MODE (Flight Mode) key.
RF Output Indicator: Illuminates when the transmitter is turned ON and transmitting a signal. If the RF Output Indicator fails
to illuminate, RF output is limited or non-existent. In this case, you should not y. The RF Output Indicator will ash when the
transmitter Trainer mode is set to Slave.
Rudder Trim Switch: Used to control the Rudder axis Right and Left trim.
Servo Centering Sub-Trim: The Servo Centering Sub-Trim function allows you to ne-tune the Center (Neutral) position of each
servo. It's not unusual that when you install the servo horn onto your servo that the servo horn is not perfectly centered. The
Servo Centering Sub-Trim function allows you to center the servo horn perfectly.
Servo Monitor: The Servo Monitor displays the output levels of each of the 6 channels in bar graph form, allowing you to monitor
servo operation in a virtual manner. This is helpful to see servo movement when the control sticks and switches are moved, and
it allows you to visualize what is occurring with servo movements when you apply different mixing values. The Servo Monitor also
indicates which channel slots in the receiver to plug your servos into
Servo Reversing: Electronically switches the direction of servo travel. For example, if you move the elevator control stick
forward, and the elevator moves up, you can use the Servo Reversing function to make the elevator move down.
Spoilerons: Spoilerons is a mix of spoilers and ailerons, allowing you to use the ailerons as spoilers if your model does not
feature separate spoilers. When Activated, both ailerons are moved up at the same time to provide the function of spoilers, while
still providing aileron roll control.
Stopwatch Timer: The Stop Watch timer is used to either count down from a programmed Start time (Count Down mode) or
to count up from zero if no Start time is programmed (Count Up mode). In Count Down mode, an audible tone will sound in 1
second intervals when the Stop Watch reaches 10 seconds from zero. When zero is reached, a long audible tone will sound and
the Stop Watch will begin to count up. In Count Up mode, an audible tone will sound at 1 minute intervals to remind you that the
count down time (zero) has been surpassed. One of its more popular uses is to use it as a fuel usage indicator to remind you to
land within an allotted amount of time to ensure that your model doesn't run out of fuel.
Swashplate: The swashplate changes the pilot's linear cyclic (and often collective) control inputs into rotary blade pitch angle
changes in the main rotor. It is the position of the swashplate that determines which direction the rotor disk will move in.
REFEREncE
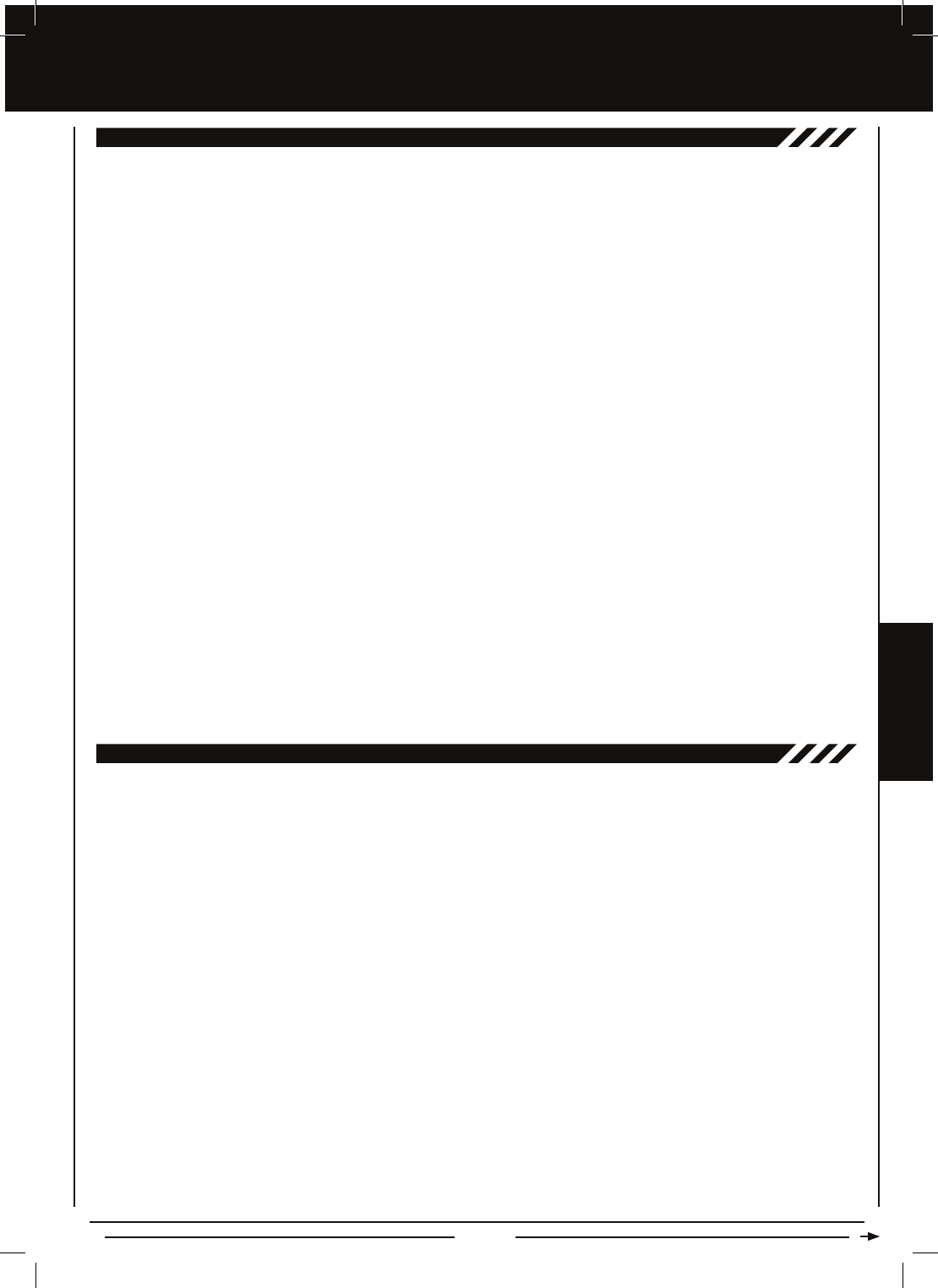
Page 85
Temperature Range: The range in temperature of the outside air that the transmitter can safely and reliably operate in.
Throttle/Rudder Control Stick: Controls the Throttle and Rudder axes. The Throttle/Rudder Control Stick length is adjustable
to suit your preference.
Throttle Cut: The Throttle Cut function allows you to set a specic position that the throttle servo will move to. The Throttle Cut
function is primarily used to shut down your engine after ight.
Throttle Hold: The Throttle Hold function allows you to set a specic position that the throttle servo will Hold and not respond to
the throttle control stick. This function is typically used when ying helicopters to Hold the throttle at idle or low speed, while still
allowing you full pitch control. This is ideal for practicing auto-rotations and is also a good safety feature on electric helicopters,
because when Activated, the rotor head will not spin up if you accidentally bump the throttle control stick up.
Throttle Trim Switch: Used to control the Throttle axis Up and Down trim.
Trainer Port: The Trainer Port is where the trainer cable (available separately) is plugged into. An adapter to use the transmitter
with a ight simulator can also be plugged into the Trainer Port.
Trainer System: Provides a way of training pilots to y. During use, one transmitter acts as the Master (Instructor) and the other
transmitter acts as the Slave (Student). The Instructor controls the Student's model as long as the Trainer Switch is released.
Once the Instructor maneuvers the model to a safe altitude, the Instructor holds the Trainer Switch and the Student has control
of the model. The Student will have control of the model as long as the Instructor holds the Trainer Switch. Once the Trainer
Switch is released, the Instructor will have control of the model once again. If at any time the Instructor feels that the Student is
in a situation that endangers the model, the Instructor releases the Trainer Switch and control of the model returns instantly to
the Instructor.
Trim Switch: Used to control the center trim of the channel that the Trim Switch is adjacent to.
Type (Model Type): The Type function allows you to quickly set up the transmitter's low-level mixing based on the type of model
you're ying. Common templates for AERO (Aircraft) and HELI (Helicopters) are provided. This takes the guess-work out of
setting up more complex models.
V-Tail Mixing: V-Tail mixing combines the use of elevator and rudder to provide pitch and yaw control. V-Tail mixing is commonly
found on gliders and sailplanes that don't feature a separate vertical n and horizontal stabilizer.
Z-Connector: The type of servo and battery connector used by Airtronics. The Z-Connector is a universal connector which is
electronically compatible with the airborne components of other radio control system manufacturers.
gLOSSaRy OF TERMS, cOnTinUED....
REFEREncE
inDEX
Symbols
2.4GHz Frequency Band, Precautions 4
A
Active Flight Mode, Diagram of 16
Aero Model Type, General Information 22
Aero Model Type, Programming Menu Flow Chart 22
Aero Model Type, Transmitter Layout 23
Aileron Control Stick, Diagram of 7
Aileron/Elevator Control Stick, Denition of 8, 82
Aileron Differential, Denition of. See Differential
Aileron Differential, Programming 39
Aileron Trim Switch, Denition of 8, 82
Aileron Trim Switch, Diagram of 7
Ailvator, Denition of 82
Ailvator Mixing, Programming 44
Airborne System Connections, Overview 13
Alarms, Flight Mode Warning 9
Alarms, Low Voltage 9
Alarms, Trainer Mode Warning 10
Analog Servos, Using and Recommendations 10
Antenna Reception Wires, Receiver - Denition of 8, 82
Antenna Reception Wires, Receiver - Diagram of 13
Antenna Reception Wires, Receiver - Mounting 18
Antenna, Transmitter - Denition of 8, 82
Antenna, Transmitter - Diagram of 7
Antenna, Transmitter - Orientation of 4, 7
B
Basic Model Setup 11
Battery, Receiver - Charging 14
REFERENCE
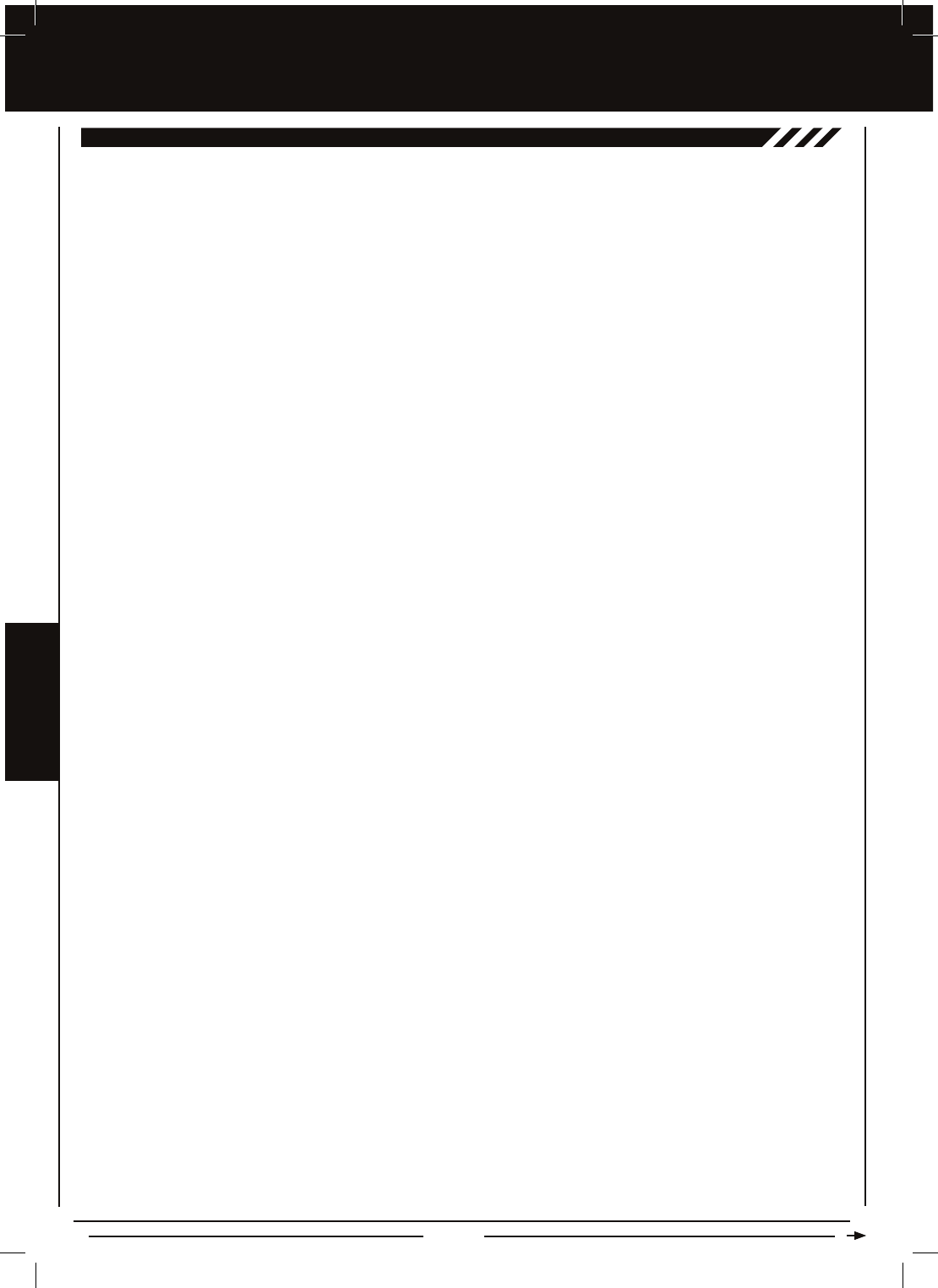
Page 86
REFEREncE
B
Battery, Receiver - Connection 13
Battery, Receiver - Options 10
Battery, Receiver - Using a Li-Po Battery 13
Batteries, Transmitter - Charging 14
Batteries, Transmitter - Installing 13
Battery Compartment, Denition of 8, 82
Battery Compartment, Diagram of 7
Battery Capacity Indicator, Denition of 16
Battery Capacity Indicator, Diagram of 16
Bind Button, Denition of 8, 82
Bind Button, Receiver - Diagram of 8
Bind Button, Transmitter - Diagram of 7
Binding. See Transmitter and Receiver Binding
Binding, Denition of 82
Bind LED, Denition of 8, 82
Bind LED, Receiver - Diagram of 8
Bind LED, Transmitter - Diagram of 7
C
CCPM, Denition of 82
CCPM End Point Adjustment, Denition of 82
CCPM End Point Adjustment, Programming 64
Centering. See Servo Centering Sub-Trim
Charging Jack, Denition of 8, 82
Charging Jack, Diagram of 7
Coaxial Cables, Denition of 8, 83
Coaxial Cables, Diagram of 8
Coaxial Cables, Mounting 18
Compensation Mixing, Denition of 83
Compensation Mixing, Programming - Aero Model Type 47
Compensation Mixing, Programming - Heli Model Type 77
Compensation Mixing Switch, Diagram of 7, 23, 53
Connector Type. See Servo Connectors
Control Sticks, Adjusting Length 19
Count Up Timer, Using - Aero Model Type 28
Count Up Timer, Using - Heli Model Type 59
Current Drain, Transmitter - Specication 6
D
Data Copy, Using - Aero Model Type 29
Data Copy, Using - Heli Model Type 59
Data Reset, Using - Aero Model Type 29
Data Reset, Using - Heli Model Type 60
DEC-/M2 Key, Overview 15
Delta Mixing, Denition of 83
Delta Mixing End Point Adjustment Programming 46
Differential, Denition of 83
Differential, Programming. See Aileron Differential
Digital Servos, Using and Recommendations 10
Digital Trim Memory, Denition of 83
Digital Trim, Programming - Aero Model Type 36
Digital Trim, Programming - Heli Model Type 69
Dimensions, Receiver - Specication 6
Direct Model Select, Denition of 83
Direct Model Select Keys, Overview 15
Direct Model Select, Using - Aero Model Type 24
Direct Model Select, Using - Heli Model Type 54
Dual Elevator Mixing End Point Adjustment, Programming 42
Dual Rate, Denition of 83
Dual Rate Switch, Diagram of 23, 53
Dual Rate, Overview - Aero Model Type 35
Dual Rate, Overview - Heli Model Type 67
Dual Rate, Programming - Aero Model Type 35
Dual Rate, Programming - Heli Model Type 67
Dual Rate, Using - Aero Model Type 34
Dual Rate, Using - Heli Model Type 66
E
Elevator Control Stick, Diagram of 7
Elevator Trim Switch, Denition of 8, 83
Elevator Trim Switch, Diagram of 7
Elevon Mixing. See Delta Mixing
End/M3 Key, Overview 15
inDEX, cOnTinUED....
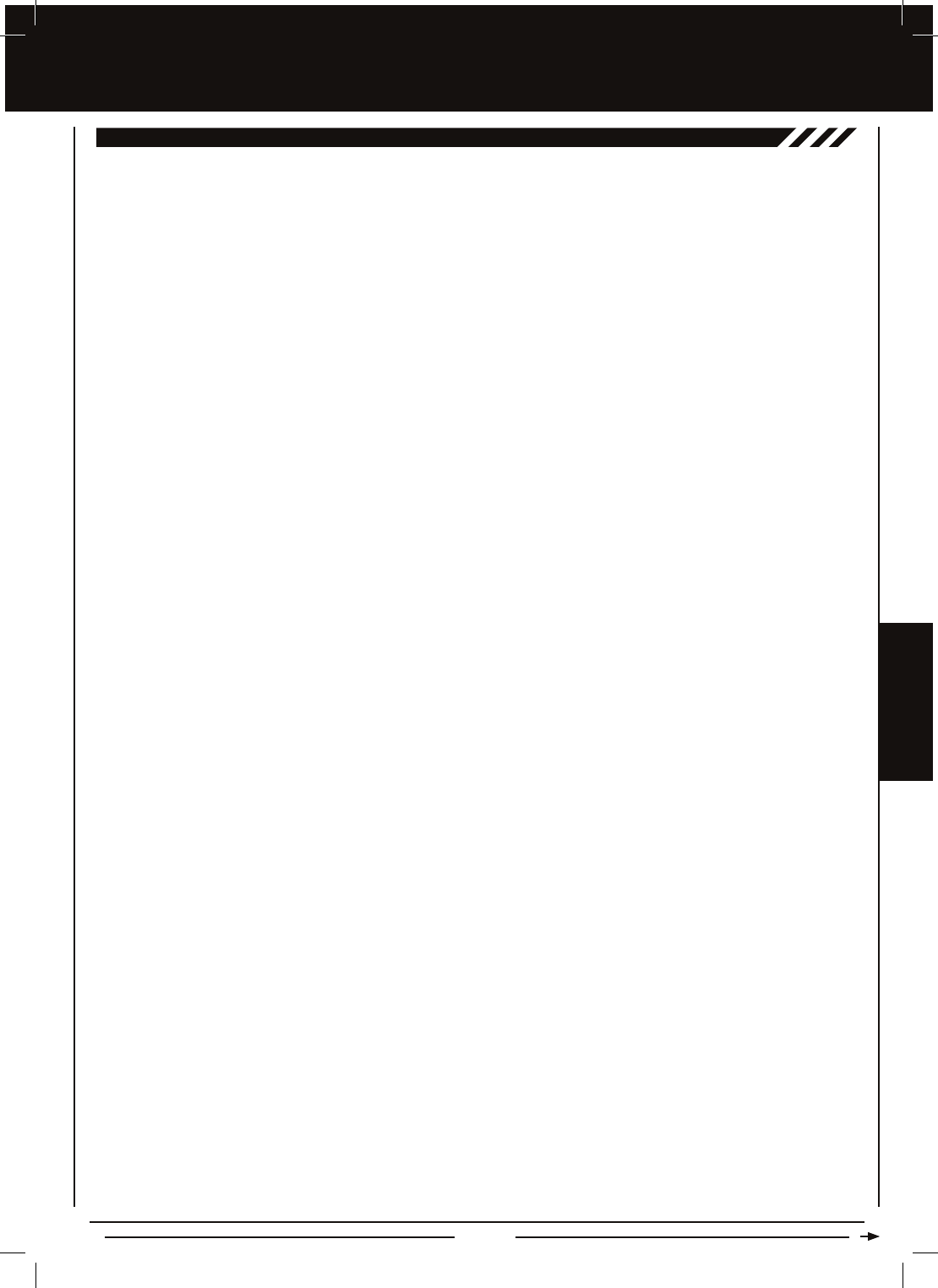
Page 87
REFEREncE
inDEX, cOnTinUED....
E
End Point Adjustment, Denition of 83
End Point Adjustment, Programming - Aero Model Type 32
End Point Adjustment, Programming - Heli Model Type 63
Enter Key, Overview 15
Exponential, Denition of 83
Exponential, Overview - Aero Model Type 35
Exponential, Programming - Aero Model Type 36
Exponential, Using - Aero Model Type 34
Exponential, Using - Heli Model Type 66
Exponential, Overview - Heli Model Type 68
Exponential, Programming - Heli Model Type 68
F
Fail Safe, Denition of 83
Fail Safe, Programming 17
FCC Compliance Statement 3
Features, General System 6
Features, Aircraft Specic 6
Features, Helicopter Specic 6
FH1 Modulation, Denition of 83
FHSS, Denition of 83
Flaperon Mixing, Programming 40
Flaperons, Denition of 83
Flap to Elevator Mixing, Programming 41
Flight Modes, Denition of 83
Flight Modes, Overview 15
Flight Modes, Using 15
Flight Mode Display. See Active Flight Mode
Flight Mode Key, Denition of 83
F-MODE (Flight Mode) Key, Overview 15
Flight Mode Switches, Diagram of 23, 53
Flight Mode Warning Alarm 9, 20
G
Gyro, Denition of 83
Gyro. See Remote Gyro Gain
H
Heli Model Type, Programming Menu Flow Chart 52
I
Inhibit, Denition of 83
Input Voltage, Receiver - Specication 6
INC+/M1 Key, Overview 15
L
Landing Gear Switch, Denition of 83
Landing Gear Switch, Diagram of 23
LCD. See Multi-Function LCD
Lithium Polymer (Li-Po) Battery, Using with Receiver 13
Low-Power Mode, Denition of 83
Low-Power Mode, Using 19
Low Voltage Alarm 9
M
Mixing, Ailvator. See Ailvator Mixing, Programming
Mixing, CCPM Swashplate Options 55, 56
Mixing, Delta. See Delta Mixing End Point Adjustment, Programming
Mixing, Dual Elevator. See Dual Elevator Mixing End Point Adjustment, Programming
Mixing, Elevator to Flaperon/Spoileron - Compensation Mixing Example 50
Mixing, Flap to Elevator. See Flap to Elevator Mixing, Programming
Mixing, Flaperon. See Flaperon Mixing, Programming
Mixing, Revolution. See Revolution Mixing, Programming
Mixing, Rudder to Throttle - Heli Model Type Compensation Mixing Example 79
Mixing, V-Tail. See V-Tail Mixing, Programming
Model Name, Denition of 84
Model Name, Display Overview 16
Model Name, Entering - Aero Model Type 24
Model Name, Entering - Heli Model Type 54
Model Name, Deleting a Character - Aero Model Type 25
Model Name, Deleting a Character - Heli Model Type 55
Model Name, Deleting - Aero Model Type 25
Model Name, Deleting - Heli Model Type 25
Model Number, Display Overview 16
REFERENCE
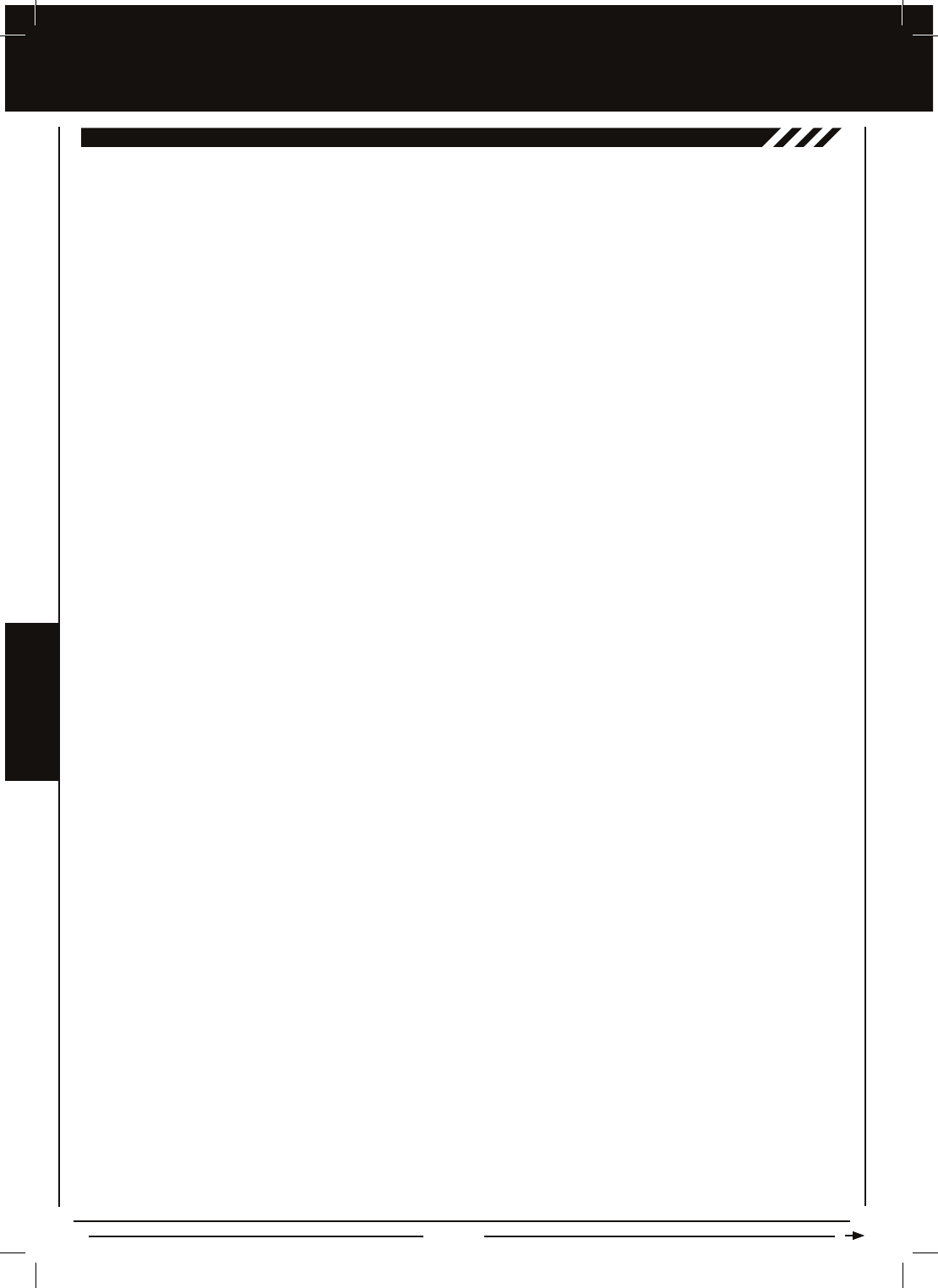
Page 88
inDEX, cOnTinUED....
M
Model Select, Denition of 84
Model Select, Using - Aero Model Type 23
Model Select, Using - Heli Model Type 53
Model Select. See Direct Model Select
Model Type, Changing - Aero Model Type 25
Model Type, Changing - Heli Model Type 55
Model Type, Options - Aero Model Type 25
Model Type, Options - Heli Model Type 56
Model Type, Saving - Aero Model Type 26
Model Type, Saving - Heli Model Type 56
Model Type Icon, Display Overview 16
Multi-Function LCD, Denition of 9, 24
Multi-Function LCD, Diagram of 7
Multi-Function LCD, Overview 16
N
Navigation Pad, Denition of 84
Navigation Pad, Diagram of 7
Navigation Pad, Overview 15
Neck Strap Anchor, Denition of 9, 84
Neck Strap Anchor, Diagram of 7
Ni-MH (Nickel-Metal Hydride), Denition of 84
Nominal Input Voltage, Receiver - Specication 6
O
Offset, Denition of 84
Offset, Programming. See Compensation Mixing, Programming
Operating Voltage, Denition of 84
Operating Voltage, Receiver. See Nominal Input Voltage, Receiver - Specication
Operating Voltage, Transmitter - Specication 6
Optional Items 10
Output Power, Denition of 84
Output Power, Transmitter - Specication 6
P
Packaging 2
Peak-Detection Charger, Warning Using with Transmitter 14
Pitch Curve, Denition of 84
Pitch Curve, Programming - Heli Model Type 72
Power Indicator, Denition of 9, 84
Power Indicator, Diagram of 7
Power Supply, Transmitter 6
Power Switch, Denition of 9, 84
Power Switch, Diagram of 7
Precautions, 2.4GHz Frequency Band. See 2.4GHz Frequency Band, Precautions
Precautions, Receiver. See Receiver, Precautions
Precautions, Transmitter. See Transmitter, Precautions
Programming Keys, Denition of 9, 84
Programming Keys, Diagram of 7
Programming Keys, Overview 15
Programming Menus Flow Chart, Aero Model Type 22
Programming Menus Flow Chart, Heli Model Type 52
Pulse Width, Transmitter - Specication 6
R
Range Checking. See Low-Power Mode, Using
Receiver, Additional Receiver Information 3
Receiver, Airborne System Connections 13
Receiver, Antenna Reception Wires. See Antenna Reception Wires
Receiver Battery, Options 10, 14
Receiver, Binding. See Transmitter and Receiver Binding
Receiver, Features 8
Receiver, Nominal Input Voltage - Specication 6
Receiver, Using a Li-Fe/A123 or Li-Po Battery 13
Receiver, Mounting 18
Receiver, Precautions 5
Revolution Mixing, Programming - Heli Model Type 74
RF Output Indicator, Denition of 84
RF Output Indicator, Diagram of 7
Rudder Control Stick, Diagram of 7
Rudder Trim Switch, Denition of 9, 84
Rudder Trim Switch, Diagram of 7
REFEREncE
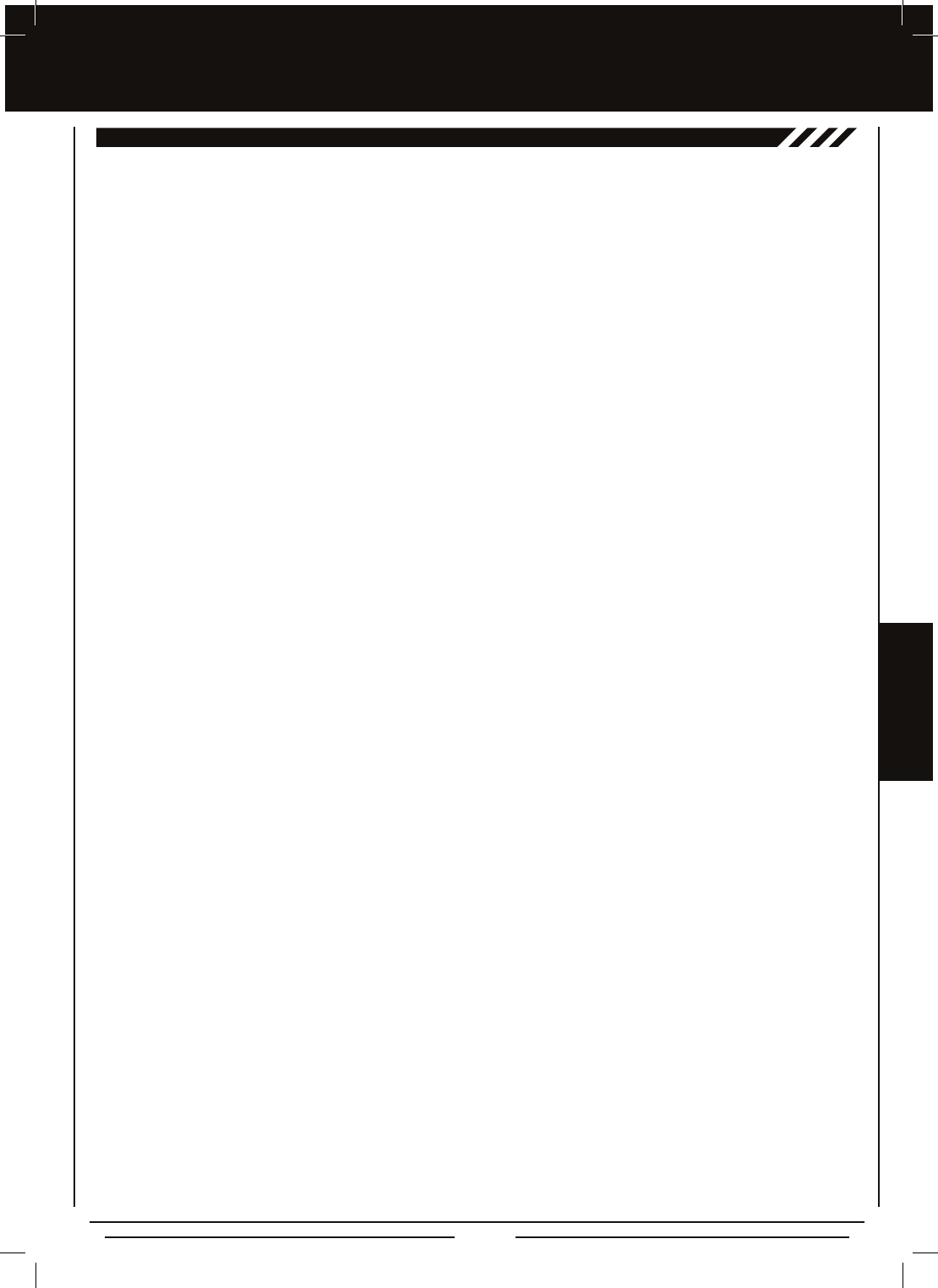
Page 89
inDEX, cOnTinUED....
S
Safety, General 4
Servo Centering Sub-Trim, Denition of 84
Servo Centering Sub-Trim, Programming - Aero Model Type 31
Servo Centering Sub-Trim, Zeroing out Trim - Aero Model Type 32
Servo Connectors, Overview 9
Servo Monitor, Denition of 84
Servo Monitor, Using - Aero Model Type 50
Servo Monitor, Using - Heli Model Type 80
Servo Recommendations 10
Servo Reversing, Denition of 84
Servo Reversing, Programming - Aero Model Type 30
Servo Reversing, Programming - Heli Model Type 61
Specications, System 6
Spoilerons, Denition of 84
Stopwatch Timer, Denition of 84
Stopwatch Timer, Setting - Aero Model Type 28
Stopwatch Timer, Setting - Aero Model Type 58
Stopwatch Timer, Using - Aero Model Type 28
Stopwatch Timer, Using - Aero Model Type 59
Swashplate, Denition of 84
Swashplate, Setup 64
Swashplate, Type Selection Options 55, 56
T
Temperature Range, Denition of 85
Temperature Range, Transmitter - Specication 6
Throttle Control Stick, Diagram of 7
Throttle/Rudder Control Stick, Denition of 9, 85
Throttle Curve, Programming - Aero Model Type 37
Throttle Curve, Programming - Heli Model Type 69
Throttle Cut, Denition of 85
Throttle Cut, Programming - Aero Model Type 33
Throttle Cut, Programming - Heli Model Type 51
Throttle Hold, Denition of 85
Throttle Hold, Activating and Programming - Heli Model Type 71
Throttle Trim Lock, Programming - Aero Model Type 37
Throttle Trim Lock, Programming - Heli Model Type 69
Throttle Trim Switch, Diagram of 7
Throttle Trim Switch, Denition of 9, 85
Timers. See Stopwatch Timer
Timers. See Count Up Timer
Tips and Suggestions 11, 12
Trainer Mode Warning Alarm 10
Trainer Port, Diagram of 7
Trainer Port, Denition of 9, 85
Trainer Cable, Optional Recommendation 10
Trainer Status Indicator, Display Overview 16
Trainer System, Activating - Aero Model Type 27
Trainer System, Activating - Heli Model Type 57
Trainer System, Denition of 85
Trainer System, Connections - Aero Model Type 26
Trainer System, Connections - Heli Model Type 57
Trainer System, Using - Aero Model Type 27
Trainer System, Using - Heli Model Type 58
Transmitter and Receiver Binding 17
Transmitter Batteries, Installing 13
Transmitter Batteries, Charging 14
Transmitter, Low Voltage Alarm 9
Transmitter, Precautions 4
Trim. See Digital Trim Memory
Troubleshooting 81, 82
Type. See Model Type
V
Voltage Indicator, Denition of 16
Voltage Indicator, Display Overview 16
Voltage Regulator, Using with Receiver 13
V-Tail Mixing, Denition of 85
V-Tail Mixing End Point Adjustment, Programming 45
Z
Z-Connector. See Servo Connectors
Z-Connector, Denition of 85
REFEREncE
REFERENCE
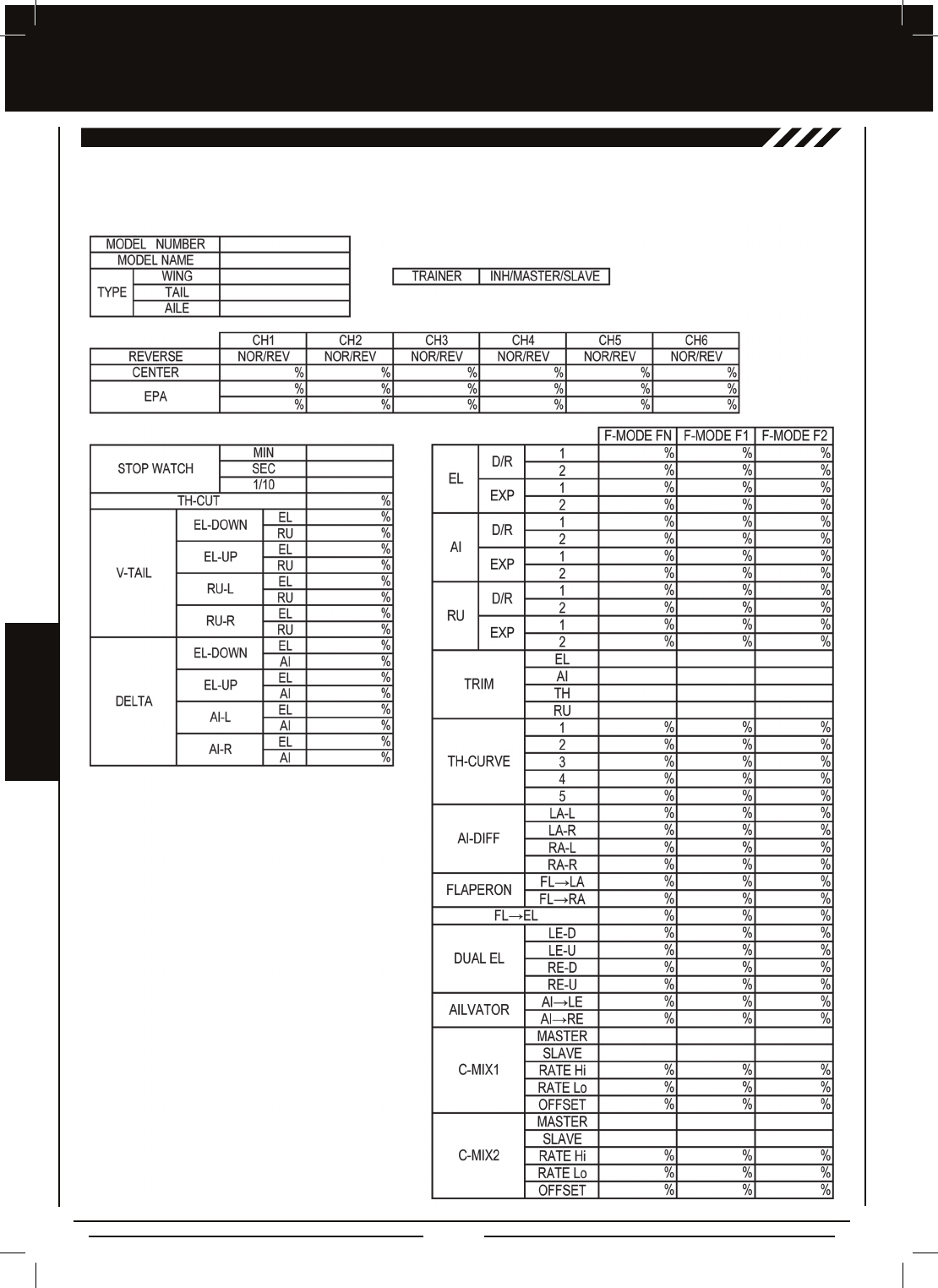
Page 90
SETUP ShEETS
aERO SETUP ShEET
Use this Aero Setup Sheet to help you keep track of each of your model's Programming Data. Before lling out this Setup Sheet
for the rst time, make several copies of it to use with multiple models.
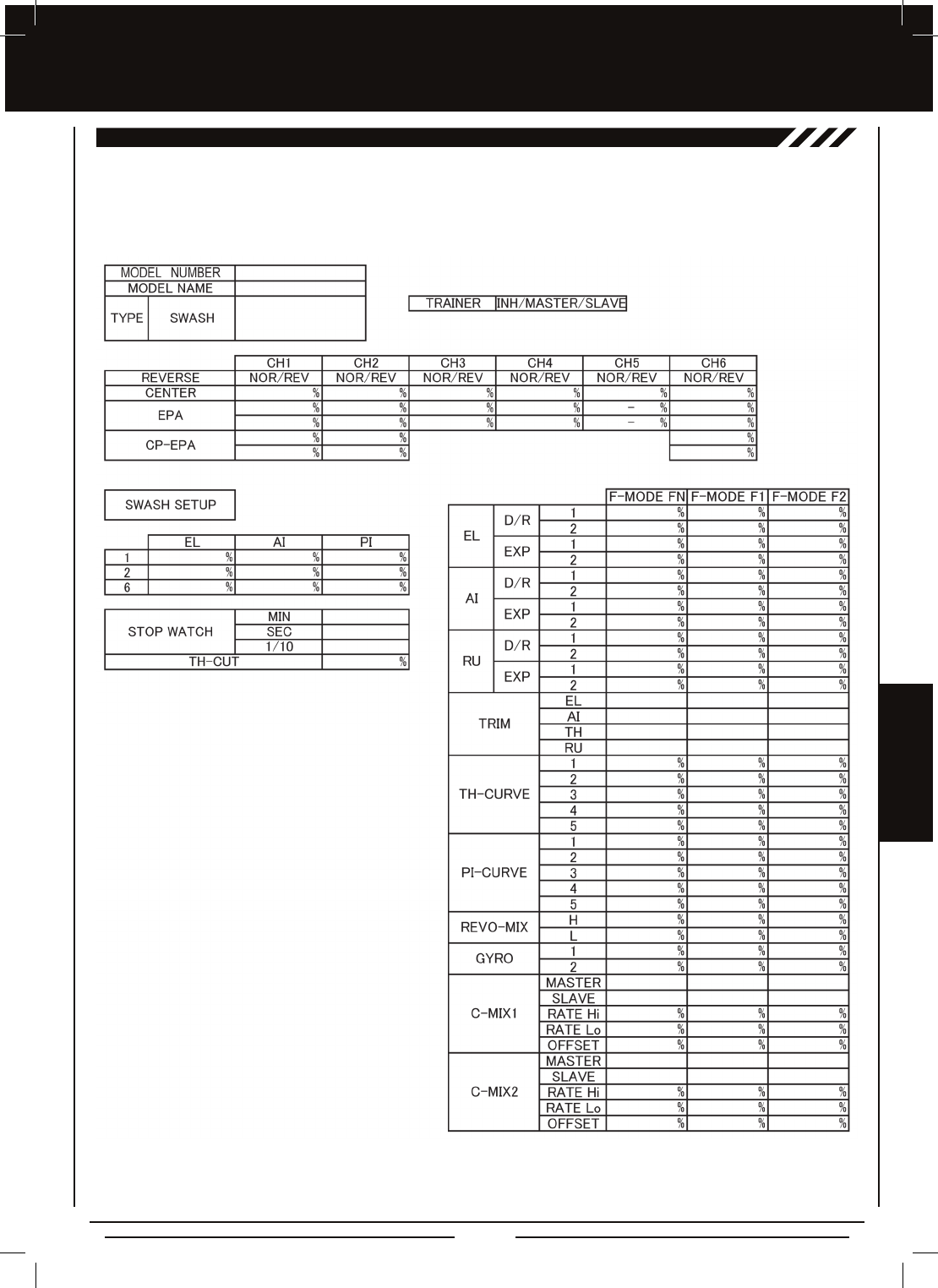
Page 91
SETUP ShEETS
SETUP SHEETS
hELi SETUP ShEET
Use this Heli Setup Sheet to help you keep track of each of your model's Programming Data. Before lling out this Setup Sheet
for the rst time, make several copies of it to use with multiple models.
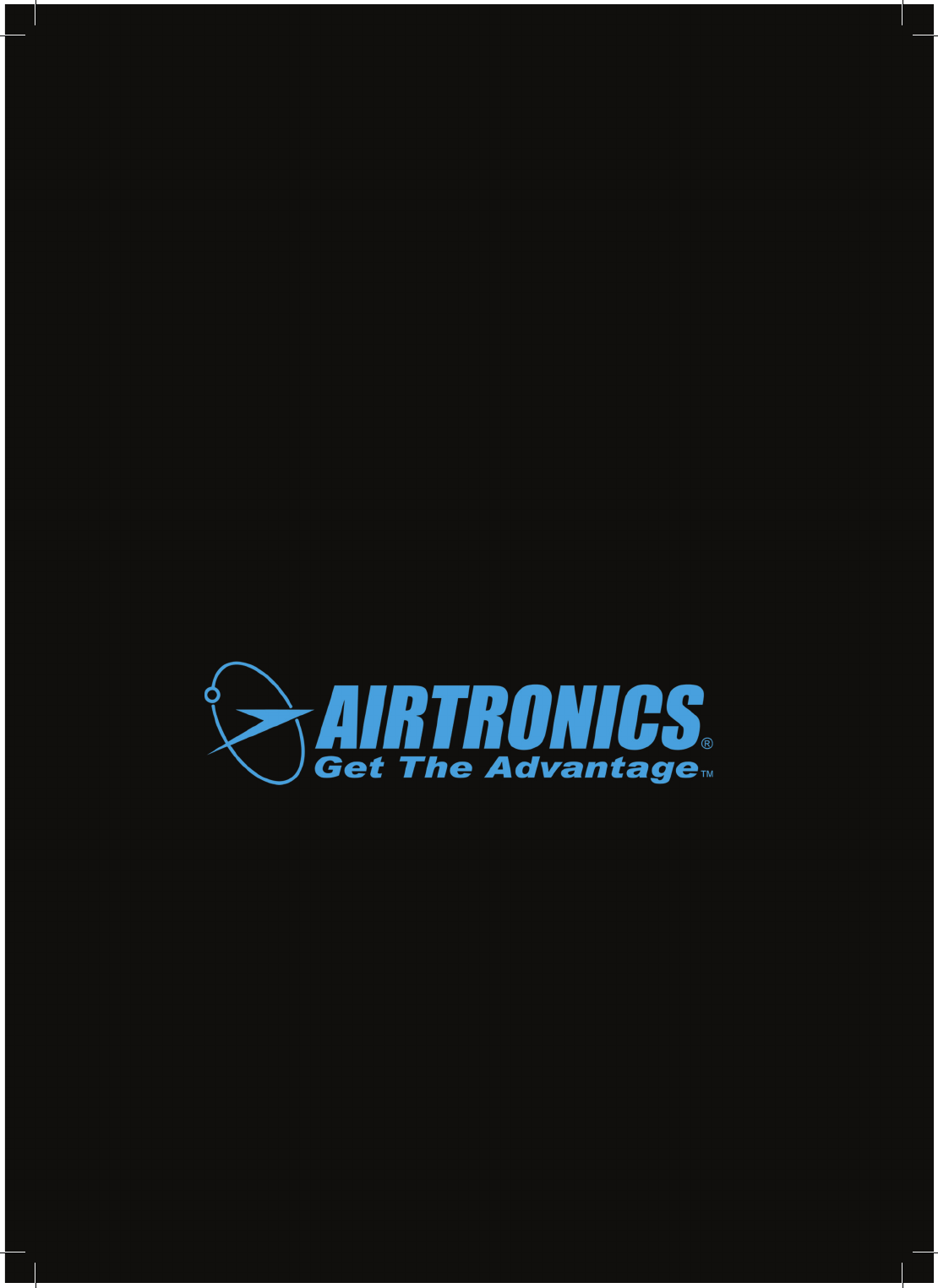
Page 92
Airtronics is Distributed Exclusively in North America by:
Global Hobby Distributors
18480 Bandilier Circle
Fountain Valley, CA 92708
Telephone: (714) 963-0329
Fax: (714) 964-6236
Email: service@airtronics.net
http://globalservices.globalhobby.com
http://www.airtronics.net
Features and Specications are Subject to Change Without Notice.
All contents © 2010 Airtronics, Inc.
All Rights Reserved. Revision 1-06.14.2010
The manufacturer disclaims all responsibility for damages resulting from use of components
other than those included with or designated for use with this product.