Sensors and Software NOGGIN500 NOGGIN 500 User Manual SmartSystemsV11
Sensors & Software Inc. NOGGIN 500 SmartSystemsV11
Contents
- 1. Users Manual Pages 1 to 40
- 2. Users Manual Pages 41 to 80
- 3. Users Manual Pages 801 to end
- 4. Revsied Users Manual
Users Manual Pages 801 to end

Smart Systems User’s Manual Version 1.1
67
6.3 Nogginplus Setup
Pressing the number 1 on the main menu selects the Setup item. Setup lists the various
parameters that can be edited. These parameters are organized under the following
headings:
1 - System Parameters
2 - Cart Parameters
3 - Line Parameters
4 - Grid Parameters
5 – GPS Parameters
6 – Set Defaults
To select a setting to edit, press the corresponding number button. Then use the
numbered buttons to select the new setting. It is also possible to change all the settings
back to the factory default settings by pressing the 6 button (labelled Set Defaults).
The SETUP options are outlined below.
6.3.1 System Parameters
The System Parameters settings allow the user to view and modify settings specific to
the data collection of the Noggin system. This includes the type of Noggin system, the
desired depth of investigation, the velocity of the material being surveyed, the units of
depth and position, the number of stacks and the amount of linear gain.
Depth
The depth setting is how deep the radar will try to probe in to the subsurface. It is
important to realize that the depth setting is an estimated value that is dependent on the
velocity of the material being probed.
Ground penetrating radar systems record the time for a radio wave to travel to a target
and back. They do not measure the depth to that target directly. The depth to a target is
calculated based on the velocity at which the wave travels to the target and back. It is
calculated as:
D = V x T/2
Where D is Depth (m)
V is Velocity (m/ns)
T is Two-way travel time (ns)
The Depth units can be changed to metres, feet or time in nanoseconds. For details,
see Depth Units below in this section.
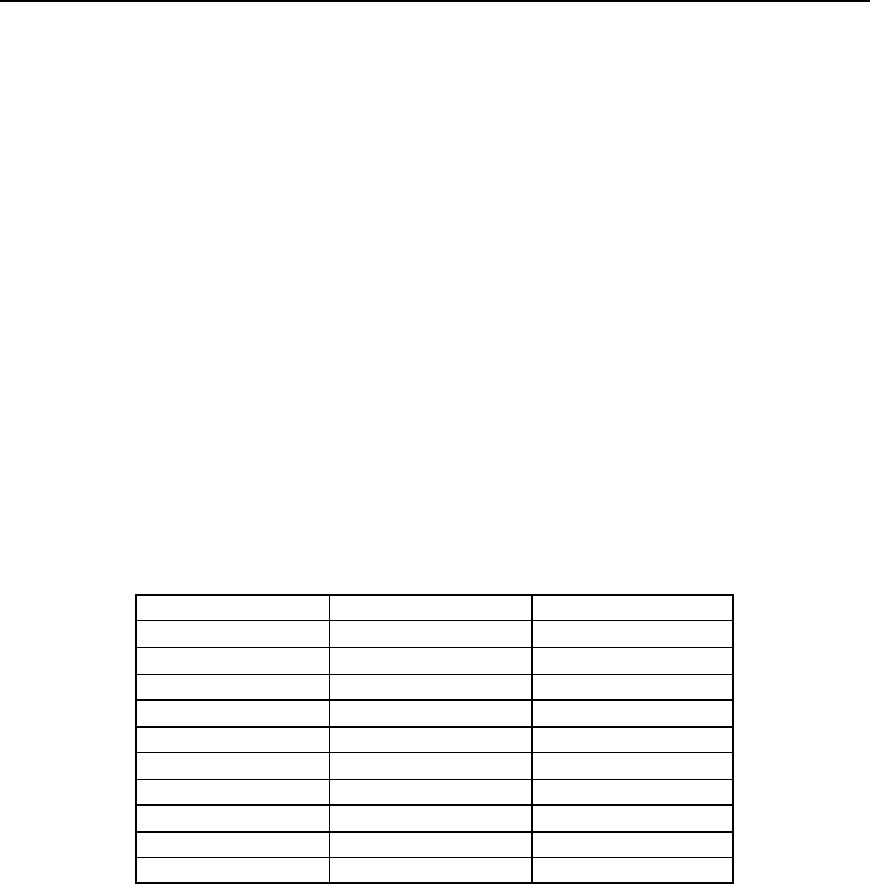
Smart Systems User’s Manual Version 1.1
68
It is important to remember that just because the Depth setting is set to a certain
value, it does not necessarily mean that the Noggin is able to penetrate to that
depth and collect data. For example, if the Depth setting is 5 metres but the
material penetration is only 3 metres the last 2 metres of the image will not
contain subsurface information. Some materials will absorb the Noggin signal and
limit penetration to less than the selected depth.
If the depth setting is deeper than the Noggin signals penetrate, the data in the lower
part of the data screen will look blank or speckled rather than signal with continuity.
Velocity
The wave velocity depends on the properties of the material. The Nogginplus software
allows the user to input a velocity, which changes the total time window collected by the
system.
See Section 6.2.8 for a discussion about determining velocity.
A table of typical radar velocities in various materials is given below. If in doubt, use a
value of 0.10 m/ns. This is a good average velocity that will provide a good estimate of
depth in most situations.
Material Velocity (m/ns) (ft/ns)
Air 0.300 1.000
Ice 0.170 0.558
Dry Soil 0.130 0.427
Dry Rock 0.120 0.394
Soil 0.100 0.328
Wet Rock 0.100 0.328
Concrete 0.100 0.328
Pavement 0.100 0.328
Wet Soil 0.065 0.213
Water 0.033 0.108
If units are metres then velocities will appear in metres per nanosecond (m/ns). If units
are feet then velocities will appear in feet per nanosecond (ft/ns). To change units see
Section 6.3.1 – Depth Units.
The Noggin will accept units in metres/nanosecond or feet/nanosecond depending on
the Depth Units setting.
Depth Units
This is the setting for the units of the horizontal depth lines that appear on the screen.
The available settings are metres, feet or nanoseconds (ns). If nanoseconds are
selected the “depth” lines (see Section 6.2.2) are actually time lines.
1. metres
2. feet
3. nanoseconds

Smart Systems User’s Manual Version 1.1
69
Noggin System
The Noggin System should be set to the type of Noggin currently in use on the Smart
System. The Noggins available are:
1. Noggin 250
2. Noggin 500
3. Noggin 1000
Stacks
Some materials tend to absorb radar signals and limit penetration. These materials are
said to be lossy. When collecting data in lossy areas or areas with a lot of radio
frequency noise, one way of increasing data quality is to collect more than one trace at
each survey position, average them and save the averaged trace. This is known as
“stacking”. Data quality improves because the noise, which is usually random (like white
noise on a TV screen with no station in the area), tends to zero when averaged.
Consequently, the usable signal is easier to see. This is known as increasing the “signal-
to-noise ratio”.
The amount of Stacking can vary from 1 to 2048 by factors of 2.
While stacking improves data quality, it also forces the user to slow down survey
production. The more stacks the longer it takes to collect data at each survey position.
Therefore, it is important to find the lowest number of stacks that still reveal the target
adequately. For most surveys, stacking 4 times is suitable.
See the warning in Section 6.2.7 about losing data if the Smart System is moving too
quickly for the Noggin system to keep up.
Linear Time Gain
As described in Section 6.2.6, the weak signals must be amplified or “gained” to see
them on the display. The Gain button described in Section 6.2.6 can be set to a value
from 1 to 9 depending on the amount of gain required (1 is lowest gain, 9 is highest
gain).
There is also a second level of gain available to the user and that is the Linear Gain
setting. The default Linear Gain setting of 2.0 is usually adequate for most ground
conditions, however, if advanced users find that they are surveying in areas where high
Gain button settings are always required to see data, it may be advantageous to
increase the Linear Gain setting. Conversely, if the user finds that low Gain button
values work to see the data, it may be useful to decrease the Linear Gain setting.
For the experienced user, the setting indicates the gain increases per nanosecond.
The Linear Gain setting can vary from 0.0 to 5.0 in steps of 0.5.

Smart Systems User’s Manual Version 1.1
70
Position Units
This is the setting for the position units used by the odometer. The available options are:
1. metres (default)
2. feet
6.3.2 Cart Parameters
The Cart Parameters settings allow the user to view and modify settings specific to the
Smart Cart or Smart Handle system. This includes the direction the Noggin will move to
collect data, whether or not the odometer is active and whether Auto Start is on or off.
Cart Direction
This setting determines whether data are collected as the Noggin is pushed forward or
pulled in reverse. The back up arrow (see Section 6.2.7) will work in the direction
opposite to this setting. The available options are:
1. Push (default)
2. Pull
Odometer Active
This setting determines whether the odometer is used to collect data. If no, then the
system runs continuously.
1. Yes (use the odometer) (default)
2. No (operate continuously)
Auto Start
If the Auto Start option is set to ON (the default), after the user presses Run to collect a
data line, the system will automatically boot up and be ready for data acquisition, rather
than having the Start button appear. This prevents the user from having to press the
Start button at the start of every new line. This setting is especially useful when
collecting numerous lines as occurs when collecting grid data. If Auto Start is set
to OFF the user must press the Start button to begin data acquisition for each line.
Arrow Offset
Section 6.2.7 describes the Back-up Arrow that appears when the Smart System is
backed up. The Back-up Arrow allows the user to pinpoint the exact ground position
corresponding to a target response on the data image. The Arrow Offset value is used
to change the physical position that corresponds to the Back-up Arrow. If the Arrow
Reference value is set to the default value of zero (0.0) metres, the Back-up arrow

Smart Systems User’s Manual Version 1.1
71
position corresponds with the centre point of the Noggin.
However, the Arrow Offset value can be changed so that the Back-up Arrow
corresponds to a position at any offset from the centre of the Noggin. For example,
setting the Arrow Offset value to +0.25 metres moves the Back-up Arrow to line up with
a position 25 centimetres in front of the Noggin centre point (on the Noggin 500 Smart
Cart this roughly corresponds to the front axle). Setting the Arrow Reference value to -
0.25 metres moves the Back-up Arrow to line up with a position 25 centimetres in behind
the Noggin centre point (on the Noggin 500 Smart Cart this roughly corresponds to the
back axle). In this way, the Arrow Offset value can be changed to correspond with any
position desired by the user.
One reason the user may want to change the Arrow Offset value is to ensure that the
Noggin does not cover the actual target location. This makes it easier to spray paint a
mark or put a flag on the ground where the target occurs.
Positive values correspond to positions in front of the Noggin and negative values are
positions behind the Noggin. Note that the Arrow Offset value is always expressed in
metres regardless of the settings of the other units.
Trip Menu
The software records the total distance the cart has travelled. This value is displayed in
Setup but cannot be changed.
The software also records a distance that can be reset by the user. To reset the
distance counter, move to the Reset Counter option and press the Zero button.
Transfer Rate
Transfer Rate is a variable from 1 to 8 that corresponds to the speed of the data transfer
from the Noggin to the DVL. A value of 8 provides the fastest transfer speed while a
value of 1 is the slowest.
For standard Smart Systems like the Smart Cart system and Smart Handle system
the Transfer Rate value must be set to 8.
The Transfer Rate value will only be decreased for systems with data cables longer than
standard lengths. Please contact Sensors & Software before changing the Transfer
Rate on your system.
Odometer Number
Noggin Smart Systems can take input from several different odometers.
It is very important that the user selects and calibrates the odometer appropriate
for their Smart System.
When Odometer Number is selected, the user is prompted to select the odometer that is
being used with the Smart System.

Smart Systems User’s Manual Version 1.1
72
If a Smart Cart System is being used, select one of the two Smart Cart odometers
(usually #1).
If a Smart Handle system is being used, select one of the two Smart Handle odometers
(usually #1).
If the system is being towed behind a vehicle and using the transmission odometer to
trigger the system, select one of the two Vehicle odometers (usually #1).
The odometers labelled Other are to be used in future configurations.
The number after the odometer is the current Odometer Calibration value for that
odometer. To calibrate the odometer, see Section 6.5.2.
6.3.3 Line Parameters
The Line Parameters settings allow the user to view and modify settings specific to
collecting data as individual lines, namely, the starting position of the line and line
direction.
Start Position
The Start Position is the position value at the very beginning of a line. This will usually
be set to zero (0.0). However, if the user wants a data file to start at a position other
than zero, this value can be edited.
Line Direction
The Line Direction setting specifies which direction that line will be collected, either
Forward or Reverse. Data are usually collected in a forward direction.
If data are collected in the Forward direction the position stepsize is positive, that is, the
position value of each data collection point increments positively. For example, for a
Noggin 250 system, if the Start Position is 10.0 and the Line Direction is Forward, the
positions on the line will increment 10.00, 10.05, 10.10, 10.15 ….
If data are collected in the Reverse direction the position stepsize is negative, that is, the
position value of each data collection point increments negatively. For example, for a
Noggin 250 system, if the Start Position is 10.0 and the Line Direction is Reverse, the
positions on the line will decrement 10.00, 9.95, 9.90, 9.85 ….
Station Interval
As Smart Systems moves, the odometer triggers the system to collect a data trace at
fixed distance intervals. This interval is called the “station interval”.
The station interval can be changed to allow a longer or shorter distance between
traces. For a successful survey, it is important that several traces be collected over a
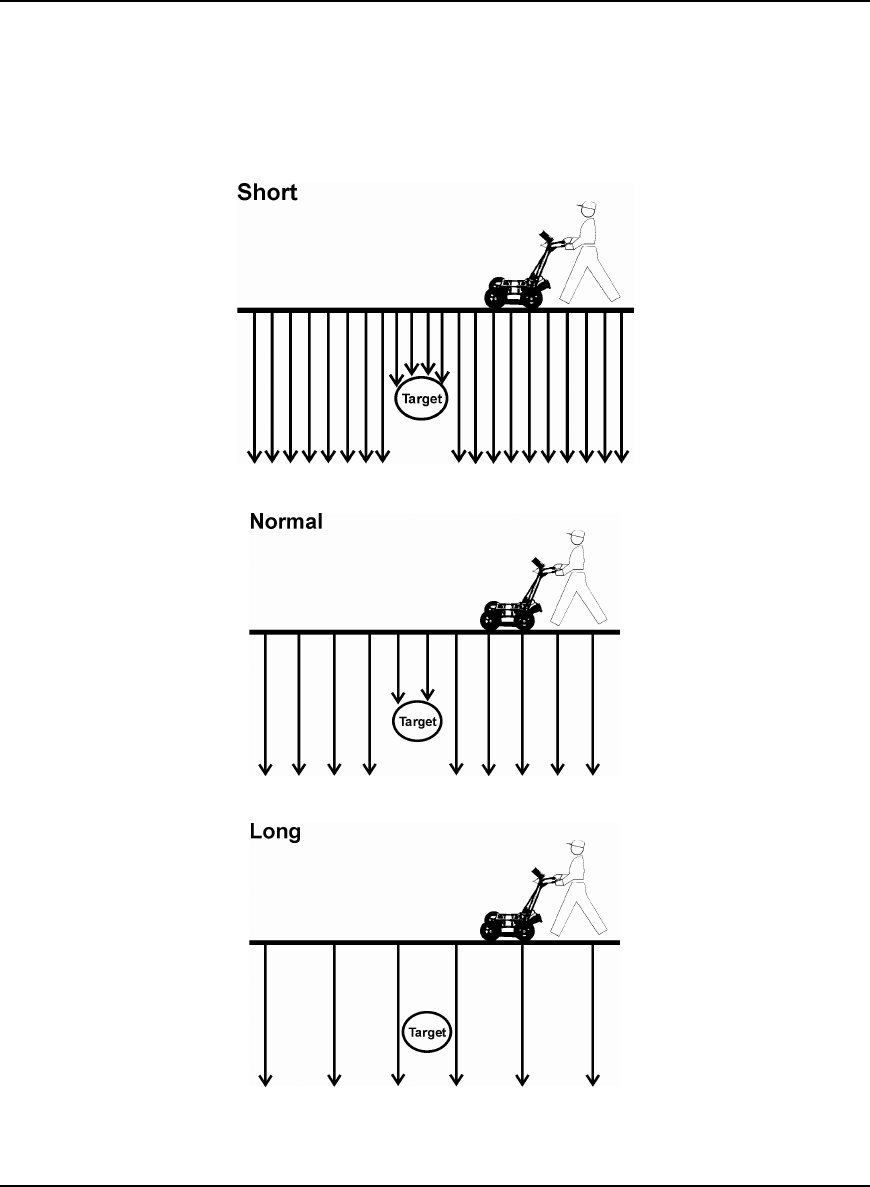
Smart Systems User’s Manual Version 1.1
73
target. If the target is small, the user may want to shorten the station interval to ensure
that data traces are collected over the target. Conversely, if the target is very large or is
a flat-lying feature it is probably not necessary to collect a lot of traces over the target, in
fact, sometimes this can make the target more difficult to see in the data. In this case it
may be beneficial to increase the station interval.
Figure 6-5: The Station Interval is the distance between sample points on the ground. Be careful
not to choose a Station Interval that is larger than the smallest target to be detected.
Note that decreasing the station interval increases the data volume and increasing the
station interval reduces the data volume.

Smart Systems User’s Manual Version 1.1
74
The choices available are:
1) Short
2) Normal
3) Long
4) X-Long
5) 10x Normal
6) 20x Normal
7) 40x Normal
8) 50x Normal
9) 100x Normal
Here is a chart showing the station interval for each system and setting. The choices
available are:
Noggin 250 System
Setting
Station Interval Data per Screen
Short 2.5 cm or 0.96 in 8 m or 25.6 ft
Normal 5.0 cm or 1.92 in 16 m or 51.2 ft
Long 10.0 cm or 3.84 in 32 m or 102.4 ft
X-Long 25.0 cm or 9.6 in 80 m or 256 ft
Norm x10 50.0 cm or 19.20 in 160 m or 512 ft
Norm x20 100.0 cm or 38.4 in 320 m or 1024 ft
Norm x40 200.0 cm or 76.8 in 640 m or 2048 ft
Norm x50 250.0 cm or 96.0 in 800 m or 2560 ft
Norm x100 500.0 cm or 192.0 in 1600 m or 5120 ft
Noggin 500 System
Setting
Station Interval Data per Screen
Short 1.0 cm or 0.48 in 6.4 m or 25.6 ft
Normal 2.5 cm or 0.96 in 16 m or 51.2 ft
Long 5.0 cm or 1.92 in 32 m or 102.4 ft
X-Long 12.5 cm or 4.8 in 80 m or 256 ft
Norm x10 25 cm or 9.6 in 160 m or 512 ft
Norm x20 50 cm or 19.2 in 320 m or 1024 ft
Norm x40 100 cm or 38.4 in 640 m or 2048 ft
Norm x50 125 cm or 48.0 in 800 m or 2560 ft
Norm x100 250 cm or 96.0 in 1600 m or 5120 ft
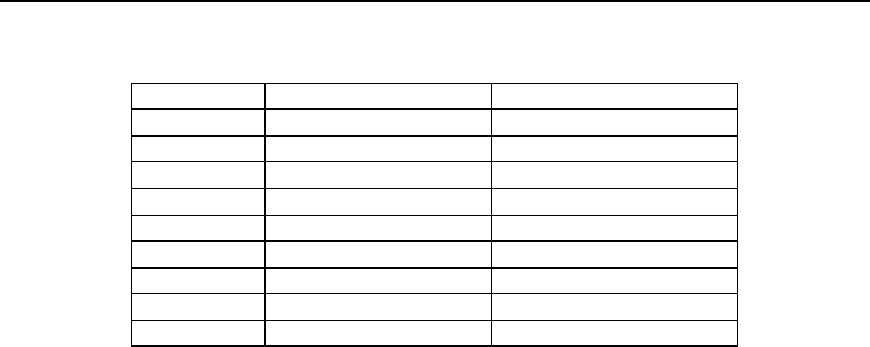
Smart Systems User’s Manual Version 1.1
75
Noggin 1000 System
Setting Station Interval Data per Screen
Short 0.5 cm or 0.24 in 3.2 m or 12.8 ft
Normal 1.0 cm or 0.48 in 6.4 m or 25.6 ft
Long 2.0 cm or 0.96 in 12.8 m or 51.2 ft
X-Long 5.0 cm or 2.4 in 32.0 m or 128 ft
Norm x10 10 cm or 4.8 in 64.0 m or 256 ft
Norm x20 20 cm or 9.6 in 128 m or 512 ft
Norm x40 40 cm or 19.2 in 256 m or 1024 ft
Norm x50 50 cm or 24.0 in 320 m or 1280 ft
Norm x100 100 cm or 48.0 in 640 m or 2560 ft
Note that Noggin 250 traces are plotted on the screen 2 pixels wide while traces from
the Noggin 500 and 1000 are plotted on the screen 1 pixel wide (see Section 6.2.7).
6.3.4 Grid Parameters
The Grid Parameters settings allow the user to view and modify settings specific to
collecting data in organized grids. This includes the grid dimensions, line spacing, grid
type and survey format.
Data are normally collected on a grid if the user is interested in displaying the data as a
3D volume (using the EKKO_3D software) or as a plan map (using the EKKO_Mapper
and/or EKKO_Pointer software). Producing accurate 3D volumes or plan maps is easier
if the field survey is properly designed and data are collected correctly.
Positional accuracy of each line is vital if the user wants to be able to relocate targets of
interest after the data have been processed.
For linear targets like pipes and utilities, the best GPR response occurs when the GPR
survey line crosses the target at right angles. If possible, it is always best to run GPR
survey lines perpendicular to the direction of linear targets.
Grid Type
The Grid Type asks specifically the way that the area of the grid is to be covered by the
survey lines. Survey lines can be either a set of parallel lines in the X axis direction
(Figure 6-6), a set of parallel lines in the Y axis direction (Figure 6-7), or, for complete
coverage, parallel lines in both the X and Y direction (Figure 6-8).
X Lines Only - Forward
Set up a first-quadrant XY grid. Data lines run in the X direction, distance increasing
from the Y axis baseline. Line numbers increase in the positive Y direction (see Figure
6-6). Lines must be equally spaced. It is not critical that all the lines are the same
length. However, it does make processing easier if all the lines start at the same
baseline position (usually defined as zero (0.0)).
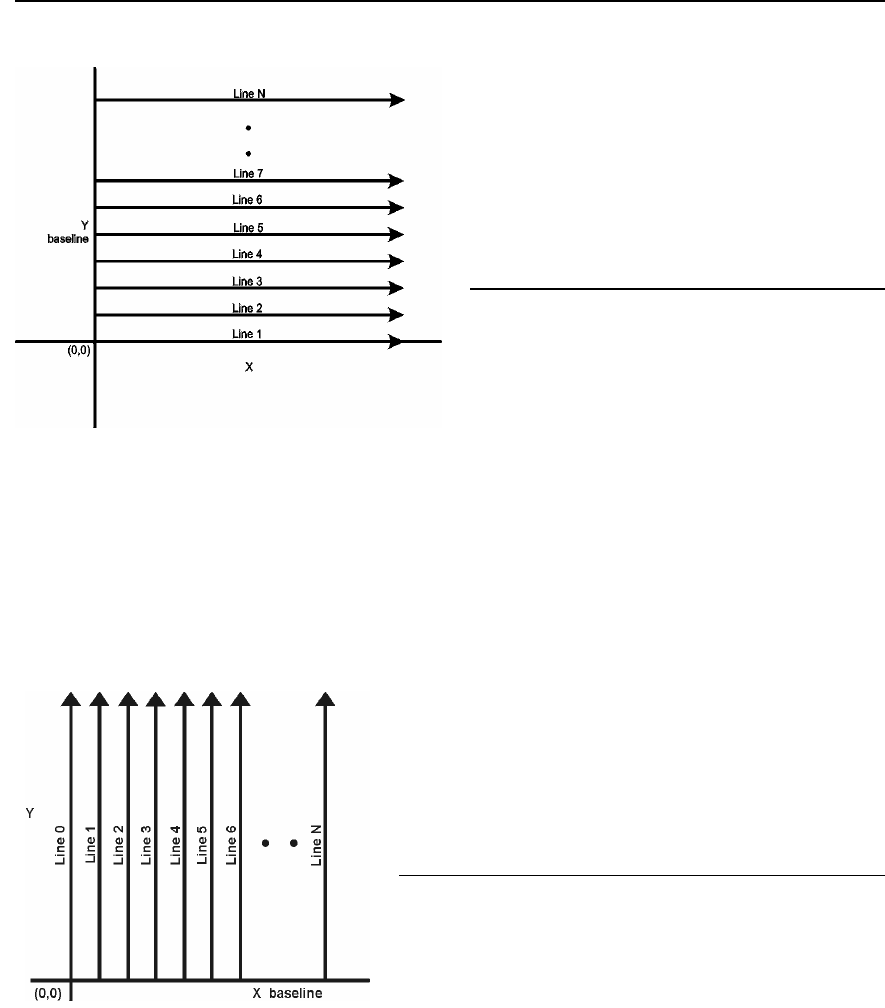
Smart Systems User’s Manual Version 1.1
76
Figure 6-6: Proper X Line surveying pattern.
Following this pattern and starting each line
from the same baseline minimizes the data
editing required to produce a spatially
accurate map of GPR data.
Y Lines Only - Forward
Set up a first-quadrant XY grid. Data lines run in the Y direction, distance increasing
from the X axis baseline. Line numbers increase in the positive X direction (see Figure
6-7). Lines must be equally spaced. It is not critical that all the lines are the same
length. However, it does make processing easier if all the lines start at the same
baseline position (usually defined as zero (0.0)).
Figure 6-7: Proper Y Line surveying pattern.
Following this pattern and starting each line from the
same baseline minimizes the data editing required to
produce a spatially accurate map of GPR data.
XY Lines - Forward
Set up a first-quadrant XY grid. X data lines run in the X direction, distance increasing
from the Y axis baseline. Line numbers increase in the positive Y direction (see Figure
6-8). Lines must be equally spaced. Y data lines run in the Y direction, distance
increasing from the X axis baseline. Line numbers increase in the positive X direction.
Lines should be equally spaced. The line spacing of the X lines and Y lines can be
different.
It is not critical that all the lines are the same lengths. However, it does make
processing easier if all the lines start at the same baseline position (usually defined as
zero (0.0)).
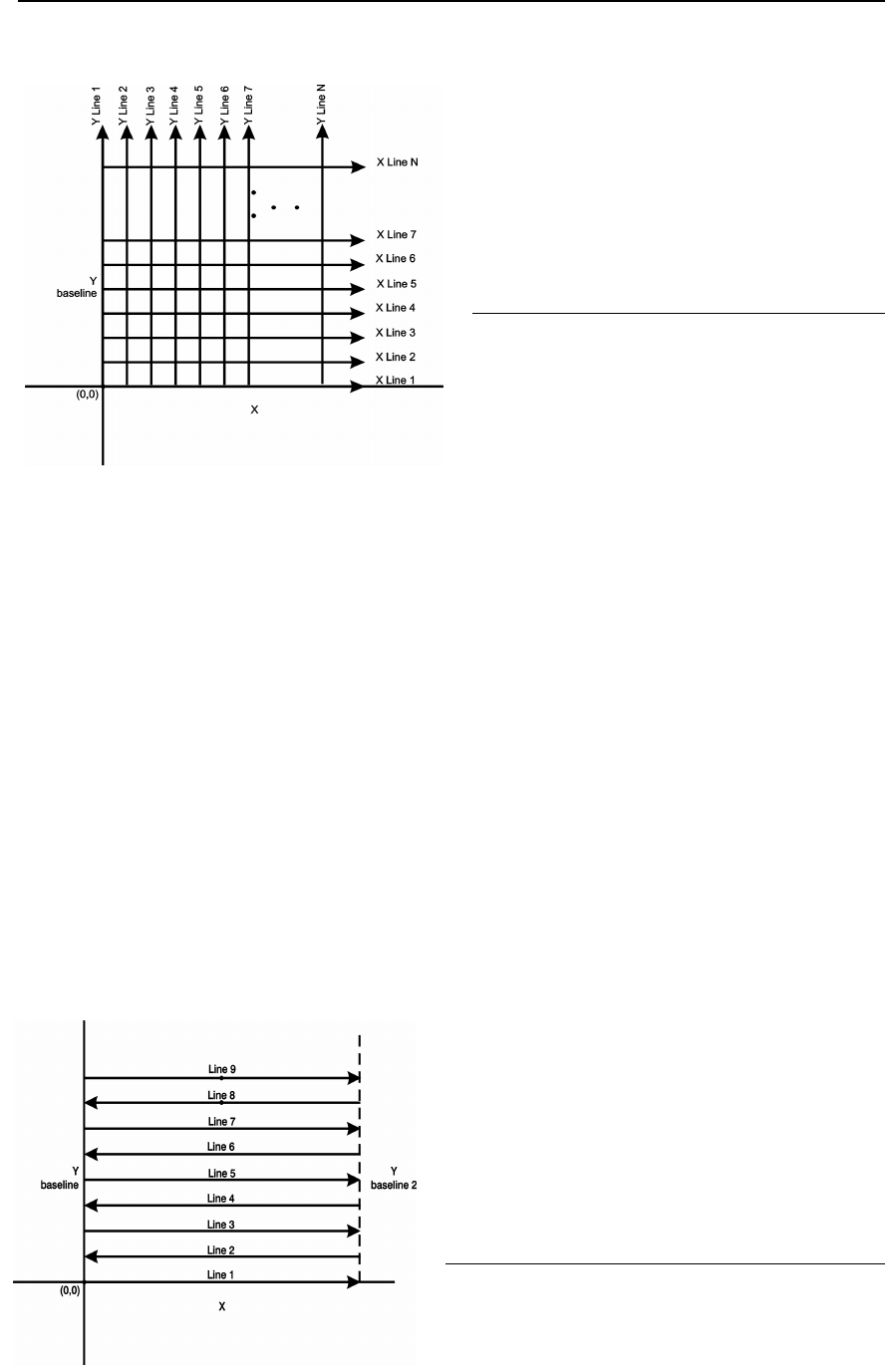
Smart Systems User’s Manual Version 1.1
77
Figure 6-8: Proper XY grid surveying pattern.
Following this pattern and starting each line
from the same baseline minimizes the data
editing required to produce a spatially
accurate map of GPR data
Survey Format
The Survey Format specifies how the lines will be collected. The lines shown in Figure
6-6, Figure 6-7, and Figure 6-8 are all collected in the Forward direction only. This
means that each line starts at the X or Y baseline.
When the length of the survey lines are more than about 20 metres, data acquisition
speed may be increased by collecting every second line in the reverse direction (Figure
6-9, Figure 6-10, and Figure 6-11). This is called a Forward and Reverse survey format.
Using forward and reverse format can speed acquisition but can lead to mapping
artifacts called “herringbone” if there are positional errors. It is important that the
odometer is calibrated (Section 6.5.2) and that the Grid Dimensions are correct (Section
6.3.4 – Grid Dimensions).
X Lines Only – Forward and Reverse
Using the Forward and Reverse survey format, X line data are collected in the pattern
shown in Figure 6-9.
Figure 6-9: For collecting GPR data consisting of
long data lines it makes more sense to follow a
forward and reverse surveying pattern. For the
final data to be spatially correct with a minimum
of editing, data collected in this pattern should be
on lines that extend completely from one
baseline to the other.
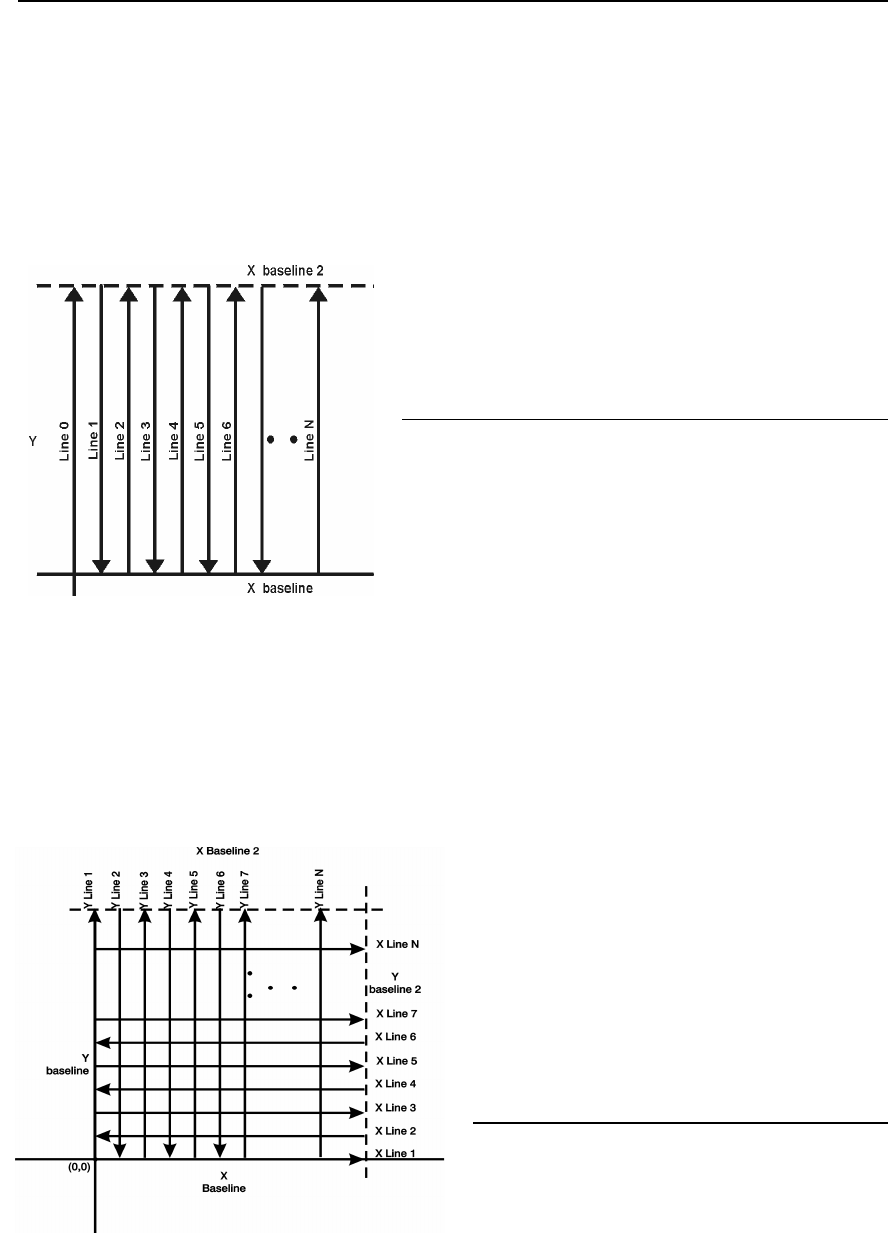
Smart Systems User’s Manual Version 1.1
78
Y Lines Only – Forward and Reverse
Using the Forward and Reverse survey format, Y line data are collected in the pattern
shown in Figure 6-10.
When data are collected like this, it is important that lines start and end on established
baselines, otherwise, when lines are reversed to the correct orientation for the display,
they may be offset from one another.
Figure 6-10: For collecting GPR data consisting of
long data lines it makes more sense to follow a
forward and reverse surveying pattern. For the final
data to be spatially correct with a minimum of editing,
data collected in this pattern should be on lines that
extend completely from one baseline to the other.
XY Lines – Forward and Reverse
Using the Forward and Reverse survey format, XY line data are collected in the pattern
shown in Figure 6-11.
When data are collected like this, it is important that lines start and end on established
baselines, otherwise, when lines are reversed to the correct orientation for the display,
they may be offset from one another.
Figure 6-11: For collecting GPR data on a grid
consisting of long data lines, it makes more
sense to follow a forward and reverse
surveying pattern. For the final data to be
spatially correct with a minimum of editing,
data collected in this pattern should be on
lines that extend completely from one
baseline to the other.

Smart Systems User’s Manual Version 1.1
79
Grid Dimensions
For grid data acquisition, the grid size needs to be specified. The user needs to input
the length of the X dimension and the length of the Y dimension. The dimensions
entered are assumed to be in the same units as the Position Units (see Section 6.3.1),
i.e. metres or feet.
On this screen the user needs to highlight the dimension to be changed. The user can
toggle between the X and Y fields by pressing the X/Y button.
The dimension value is incremented or decremented by pressing the +Line or –Line
buttons. The dimension value will change by a value equal to the current Line Spacing
in that dimension.
For example, if the Line Spacing (see below) in the X direction is 0.5 metres, the grid
dimension in the X direction will increment or decrement in 0.5 metre intervals.
Note that the maximum number of lines that can be collected in each direction is
100. Therefore, the X and Y grid dimensions cannot be set to a value that will
result in more than 100 lines being collected.
For example, if the Line Spacing between Y lines (defined as lines parallel to the Y axis)
is set to 0.25 metres, the maximum X dimension is (100-1) X 0.25 = 24.75 metres. (One
is subtracted because the first line is at position 0.0 metres.)
To increase the X dimension value, the Y line spacing must be increased. Using the
example above, if the Y Line Spacing is increased to 0.30 metres then the maximum X
dimension is (100-1) X 0.30 = 29.70 metres.
If the Grid Type is set to X Lines only or Y Lines only (see Section 6.3.4), the length of
those lines are not restricted by the Line Spacing parameter of the opposite dimension.
That is why if an X Lines only grid is selected, the X dimension can be input as a value
rather than an increment of the Y Line Spacing. Similarly, if a Y Lines only grid is
selected, the Y dimension can be input as a value rather than an increment of the X Line
Spacing.
Line Spacing
For grid data acquisition, the distance between survey lines needs to be specified.
If the grid type is X Lines only (see Section 6.3.4) then the spacing between the X lines
needs to be input.
If the grid type is Y Lines only (see Section 6.3.4) then the spacing between the Y lines
needs to be input.
If the grid type is XY Lines (see Section 6.3.4) then the spacing between the X lines and
Y lines need to be input. The line spacing can be different. The user can toggle between
the X line spacing and Y line spacing fields by pressing the X/Y button.

Smart Systems User’s Manual Version 1.1
80
Note that the maximum number of lines that can be collected in each direction is
100.
The calculation for determining an appropriate line spacing is complex. One has to
consider system frequency, target size and practical considerations. In general, the
Noggin 250 should have a line spacing of 0.5 metres or less, the Noggin 500 should
have a line spacing of 0.25 metres or less and the Noggin 1000 should have a line
spacing of 0.10 metres or less.
However, line spacing should really be determined by target size. In most cases the
system must pass over a target to detect it. Therefore, the line spacing needs to be on
the order of the size of the target or smaller, if practical. This can be adjusted to a larger
spacing for larger targets or targets with a linear extent. As well, these rules may have
to be bent for practical purposes like survey production rates. The fact is that a tighter
line spacing takes longer to collect and this may not be economically possible in all
circumstances.
6.3.5 GPS Parameters
The Global Positioning System (GPS) uses special satellites around the Earth to
determine the position of a GPS receiver located at any position on the surface of the
Earth. GPS receivers can be purchased from a number of manufacturers.
The DVL has a serial port on the back for attaching a GPS receiver. This port will
accommodate any GPS receiver that has a standard serial port output.
This feature allows GPS information to be logged while collecting Nogginplus data. The
GPS information may be useful for mapping where GPR surveys have been performed
(see Reading per Trace mode below) or determining where a specific target of interest is
located in GPS co-ordinates (see Fiducial Tagging mode below).
The DVL can be set up to read and log GPS information collected during data
acquisition with the Nogginplus system. GPS information can be logged in two different
ways: 1) for every trace collected by the Nogginplus system, or 2) every time the user
adds a fiducial to the data by pressing the A button (see Section 6.2.4 – Fiducial
Markers).
This feature provides a means of logging GPS information to an independent file. Note
that the GPS information is NOT automatically integrated with the Nogginplus data.
After data acquisition is complete, the data can be downloaded to a PC and the
Win_EKKO_Pro software can be used to integrate the GPS data with the Nogginplus
data.
In order for the DVL to read the GPS data string, the GPS settings for the specific GPS
receiver being used must be input into this menu. There are 4 important items that must
be specified correctly for the DVL to display the GPS strings. These items are Baud
Rate, Stop Bits, Data Bits and Parity. These are discussed in more detail below. The
default values listed below are the values that are typically used. Read the GPS
Receiver User’s Guide or experiment with the settings to find the correct ones.

Smart Systems User’s Manual Version 1.1
81
Once these 4 items are set correctly you should be able to run System Test #1 and have
GPS information written to the screen.
When the logging of GPS information is enabled, during data acquisition a message will
appear in the bottom left-hand corner of the DVL screen indicating whether GPS data is
successfully being received (see Section 6.2.4).
Mode
There are three GPS modes available:
1) Off mode means that a GPS receiver is not connected to the DVL so no GPS
information is being logged. This should be the setting if you do not have a GPS
receiver.
2) Reading every x traces mode means that every time the Nogginplus collects a
user-defined number of traces of GPR data, a data string of GPS information will
be added to a file. This file has the same name as the data file i.e. LINE6, but with
a GPS extension. This file can be accessed after transferring the GPR data files to
an external PC (see Section 6.4.1).
For example, if the number of traces is set to 1, the LINE6.GPS may look like this:
Trace #1
$GPGGA,134713.00,4338.221086,N,07938.421365,W,2,06,2.1,152.51,M,-35.09,M,5.0,0118*79
$GPVTG,34.0,T,,,001.4,N,002.5,K,D*70
$GPGSA,A,3,30,26,10,13,24,06,,,,,,,4.2,2.1,3.6*36
Trace #2
$GPGGA,134713.00,4338.221086,N,07938.421365,W,2,06,2.1,152.51,M,-35.09,M,5.0,0118*79
$GPVTG,34.0,T,,,001.4,N,002.5,K,D*70
$GPGSA,A,3,30,26,10,13,24,06,,,,,,,4.2,2.1,3.6*36
Trace #3
$GPGGA,134713.00,4338.221086,N,07938.421365,W,2,06,2.1,152.51,M,-35.09,M,5.0,0118*79
$GPVTG,34.0,T,,,001.4,N,002.5,K,D*70
$GPGSA,A,3,30,26,10,13,24,06,,,,,,,4.2,2.1,3.6*36
Trace #4
$GPGGA,134713.00,4338.221086,N,07938.421365,W,2,06,2.1,152.51,M,-35.09,M,5.0,0118*79
$GPVTG,34.0,T,,,001.4,N,002.5,K,D*70
$GPGSA,A,3,30,26,10,13,24,06,,,,,,,4.2,2.1,3.6*36
Note that when the Reading per Trace option is on, it is still possible to add fiducial
markers to the GPS file. These will appear as F1, F2 etc. between the trace
numbers. For example, a portion of LINE6.GPS may look like this:
Trace #85
$GPGGA,134850.00,4338.204868,N,07938.429003,W,2,06,2.1,152.60,M,-35.09,M,4.2,0118*74
$GPVTG,152.6,T,,,002.3,N,004.3,K,D*43
$GPGSA,A,3,30,26,10,13,24,06,,,,,,,4.2,2.1,3.7*37
F1
$GPGGA,134850.00,4338.204868,N,07938.429003,W,2,06,2.1,152.60,M,-35.09,M,4.2,0118*74
$GPVTG,152.6,T,,,002.3,N,004.3,K,D*43
$GPGSA,A,3,30,26,10,13,24,06,,,,,,,4.2,2.1,3.7*37
Trace #86
$GPGGA,134851.00,4338.204362,N,07938.428362,W,2,06,2.1,152.40,M,-35.09,M,5.2,0118*72
$GPVTG,136.9,T,,,002.8,N,005.2,K,D*45
$GPGSA,A,3,30,26,10,13,24,06,,,,,,,4.2,2.1,3.7*37
3) Fuducial Tagging mode means that whenever a fiducial marker (F1, F2 etc.) is
added to the data (see Section 6.2.4), a data string of GPS information will be added
to a file. This file has the same name as the data file i.e. LINE6, but with a GPS
extension. This file can be accessed after transferring the GPR data files to an

Smart Systems User’s Manual Version 1.1
82
external PC (see Section 6.4.1).
For example, LINE6.GPS may look like this:
F1
$GPGGA,134218.00,4338.190204,N,07938.438411,W,2,05,2.6,154.60,M,-35.09,M,4.0,0118*7B
$GPVTG,356.8,T,,,000.2,N,000.4,K,D*4B
$GPGSA,A,3,30,10,13,24,06,,,,,,,,4.3,2.6,3.4*36
F2
$GPGGA,134219.00,4338.190294,N,07938.438409,W,2,05,2.6,154.45,M,-35.09,M,5.0,0118*7C
$GPVTG,1.3,T,,,000.4,N,000.7,K,D*44
$GPGSA,A,3,30,10,13,24,06,,,,,,,,4.3,2.6,3.4*36
F3
$GPGGA,134221.00,4338.190261,N,07938.438285,W,2,05,2.6,154.05,M,-35.09,M,5.2,0118*79
$GPVTG,10.0,T,,,000.2,N,000.4,K,D*72
$GPGSA,A,3,30,10,13,24,06,,,,,,,,4.3,2.6,3.4*36
F4
$GPGGA,134222.00,4338.190397,N,07938.438255,W,2,05,2.6,153.95,M,-35.09,M,5.0,0118*73
$GPVTG,9.8,T,,,000.3,N,000.5,K,D*42
$GPGSA,A,3,30,10,13,24,06,,,,,,,,4.3,2.6,3.4*36
If the GPS mode is set to Reading per Trace or Fiducial Tagging AND the Nogginplus
is Run Without Saving Data (see Section 6.1.5), it is still possible to log GPS data
strings. Every time a fiducial marker is added to the data (see Section 6.2.4), a data
string of GPS information is added to a file. This file is called TAGGED.GPS and can
be exported and/or deleted using the Nogginplus File Management (see Section 6.4).
An example of a TAGGED.GPS file is shown below.
New File 09-18-2000 13:53:38
F1
$GPGGA,134227.00,4338.190520,N,07938.438280,W,2,05,2.6,153.98,M,-35.09,M,4.6,0118*7E
$GPVTG,347.7,T,,,000.3,N,000.5,K,D*44
$GPGSA,A,3,30,10,13,24,06,,,,,,,,4.3,2.6,3.4*36
F2
$GPGGA,134228.00,4338.190238,N,07938.438286,W,2,05,2.6,153.87,M,-35.09,M,4.4,0118*75
$GPVTG,5.4,T,,,000.2,N,000.4,K,D*42
$GPGSA,A,3,30,10,13,24,06,,,,,,,,4.3,2.6,3.4*36
F3
$GPGGA,134229.00,4338.190277,N,07938.438273,W,2,05,2.6,153.76,M,-35.09,M,5.4,0118*7A
$GPVTG,23.4,T,,,000.1,N,000.2,K,D*73
$GPGSA,A,3,30,10,13,24,06,,,,,,,,4.3,2.6,3.4*36
F4
$GPGGA,134231.00,4338.190127,N,07938.438362,W,2,05,2.6,154.59,M,-35.09,M,5.0,0118*7A
$GPVTG,20.2,T,,,000.2,N,000.3,K,D*74
$GPGSA,A,3,30,10,13,24,06,,,,,,,,4.3,2.6,3.4*36
********************************************************************************
New File 09-18-2000 13:55:36
F1
$GPGGA,134259.00,4338.192453,N,07938.449096,W,2,06,2.4,153.14,M,-35.09,M,5.4,0118*75
$GPVTG,310.9,T,,,000.5,N,001.0,K,D*4A
$GPGSA,A,3,04,30,10,13,24,06,,,,,,,3.2,2.4,2.1*32
F2
$GPGGA,134301.00,4338.192559,N,07938.449176,W,2,06,2.4,153.17,M,-35.09,M,5.0,0118*7A
$GPVTG,314.4,T,,,000.6,N,001.1,K,D*41
$GPGSA,A,3,04,30,10,13,24,06,,,,,,,3.2,2.4,2.1*32
F3
4) GPR data out port mode means that the GPR data stream will be output to the
serial port of the DVL. This is for users who wish to read the GPR data into their own
PC or other device. Contact Sensors & Software Inc. for more details if you want to
use this option.
Note that this option slows down data acquisition speeds.

Smart Systems User’s Manual Version 1.1
83
Baud Rate
The baud rate is the speed that data is sent from the GPS receiver to the serial port of
the DVL. The available options are: 2400, 4800, 9600 (default) or 19200.
Stop Bits
The available settings for Stop Bits are: 1 (default) or 2.
Data Bits
The available settings for Data Bits are: 7 or 8 (default).
Parity
The available settings for Parity are: none (default), odd or even.
End String
The GPS receiver can be set up to send one or more types of data strings. These
strings are called NMEA-0183 strings and each contains positional or other information
in specific formats. Each type of string is specified by a 5-character prefix. There are
numerous NMEA strings but examples of three different NMEA strings (GPGGA,
GPVTG and GPGSA) are shown below.
$GPGGA,134713.00,4338.221086,N,07938.421365,W,2,06,2.1,152.51,M,-35.09,M,5.0,0118*79
$GPVTG,34.0,T,,,001.4,N,002.5,K,D*70
$GPGSA,A,3,30,26,10,13,24,06,,,,,,,4.2,2.1,3.6*36
$GPGGA,134713.00,4338.221086,N,07938.421365,W,2,06,2.1,152.51,M,-35.09,M,5.0,0118*79
$GPVTG,34.0,T,,,001.4,N,002.5,K,D*70
$GPGSA,A,3,30,26,10,13,24,06,,,,,,,4.2,2.1,3.6*36
$GPGGA,134713.00,4338.221086,N,07938.421365,W,2,06,2.1,152.51,M,-35.09,M,5.0,0118*79
$GPVTG,34.0,T,,,001.4,N,002.5,K,D*70
$GPGSA,A,3,30,26,10,13,24,06,,,,,,,4.2,2.1,3.6*36
$GPGGA,134713.00,4338.221086,N,07938.421365,W,2,06,2.1,152.51,M,-35.09,M,5.0,0118*79
$GPVTG,34.0,T,,,001.4,N,002.5,K,D*70
$GPGSA,A,3,30,26,10,13,24,06,,,,,,,4.2,2.1,3.6*36
Before using the GPS with the Nogginplus, the DVL software needs to know the prefix of
the LAST string being sent in each group. In the example above, three strings are being
sent each time (GPGGA, GPVTG and GPGSA). Since GPGSA is the last one being
sent in each group, the End String needs to be specified as GPGSA.
To see what the End String is for your particular GPS, run System Test #1 and note the
first 5 characters on the last line after each series of strings is written to the screen.
These are the 5 characters that need to be filled in under End String.
The End String option allows the user to fill in the 5 character GPS prefix. Use the Left
and Right buttons to move left or right to different characters in the string. The currently
selected character will have an “^” under it. To change the letter of the current
character, use the Next button to change it to the next letter in the alphabet and the
Previous button to change it to the previous letter in the alphabet. Using these keys all 5

Smart Systems User’s Manual Version 1.1
84
characters can be filled in with the necessary GPS End String.
See the GPS Receiver User’s Guide for details on how to set up the receiver to output
specific NMEA strings or groups of NMEA strings.
System Test #1
After all the settings above have been input and the GPS receiver is attached to the
serial port on the DVL, the user can test that the DVL is receiving the GPS output by
using the Test option.
If the NMEA strings are successfully being read by the DVL they will appear on the DVL
screen. This is a good time to note the prefix of the last NMEA string in the list and input
it in the End String setting above.
If the NMEA strings do not appear, check that the port settings are correct. It is also
possible that a crossover cable is required between the output cable of the GPS receiver
and the serial port on the DVL.
System Test #2
Once the GPS system is running successfully, System Test #2 can be used to
graphically display the GPS data. This screen displays the GPS Time, Latitude,
Longitude and Altitude as well as other values indicating the accuracy of the GPS
reading. The GPS position is also displayed in a square that can be Zoomed from 2
metres square to 16384 metres square.
6.3.6 Set Defaults
To reset all the parameter settings back to the factory default settings press the 6 button
(labelled Set Defaults).
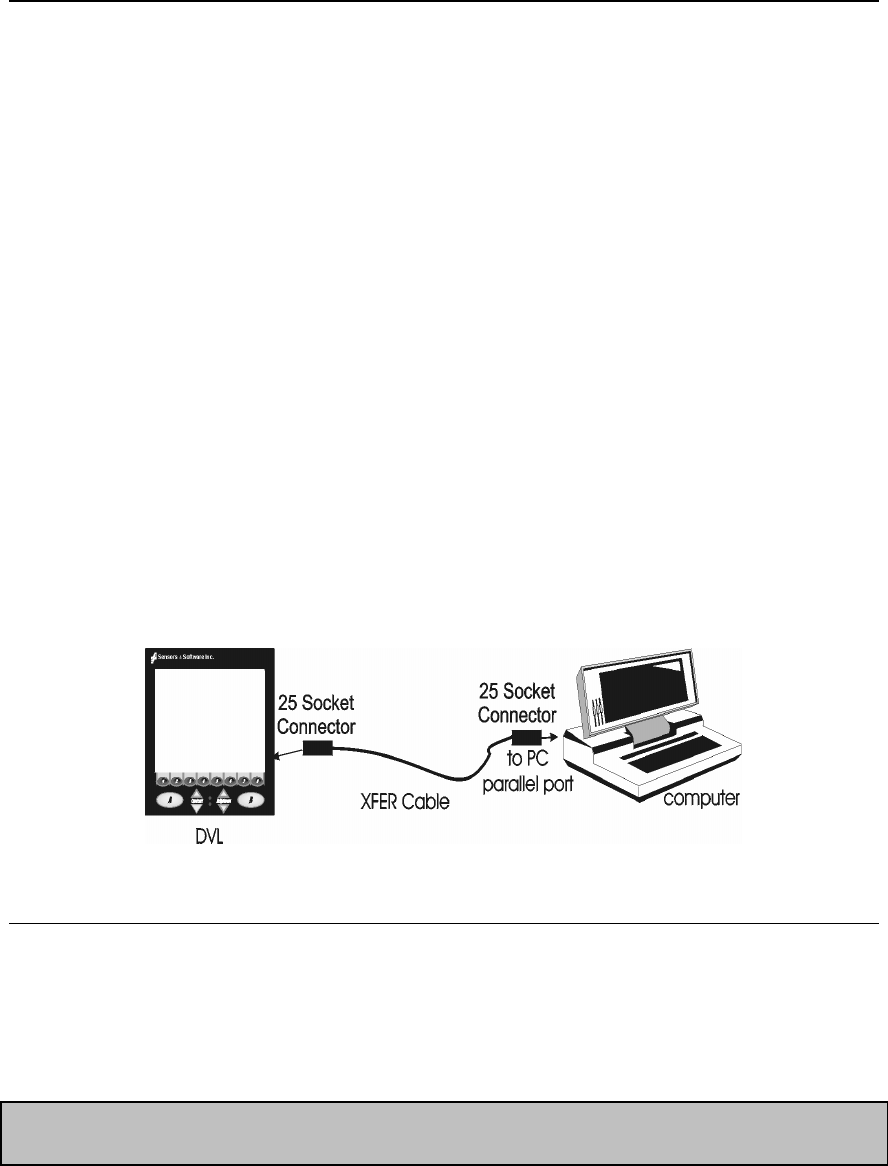
Smart Systems User’s Manual Version 1.1
85
6.4 Nogginplus File Management
The File Management option is available by pressing 2 from the main Nogginplus menu.
This option allows the user to export Nogginplus data or the TAGGED.GPS file (see
Section 6.3.5) to an external computer using the parallel XFER cable. It is also here that
the user can delete data from the DVL.
Before data export can take place, the DVL must be connected to the external computer
using the parallel XFER cable that is supplied with the system. As well, the WinPXFER
program must be installed and running on the external computer.
6.4.1 Transferring all Data Files to an External Computer
using the WinPXFER Program
Connecting the Digital Video Logger to an External Computer
Smart Systems come with a separate cable called the parallel XFER cable. This cable is
designed to connect the DVL to an external computer. Note that this is a special cable
and standard 25 pin to 25 pin or Laplink cables will not work.
Figure 6-12: Parallel XFER cable connections
The 2 connections that must be made before attempting to transfer data are:
3) Attach the 25 socket parallel connector to the 25 socket parallel port on back of
the Digital Video Logger, and
4) Attach the 25 socket parallel connector the parallel port of the external computer.
WARNING: To avoid damaging any of the components, turn off the DVL
and computer before making any of these connections.
Installing the WinPXFER Program
The Smart system comes with a CD-ROM containing the WinPXFER program.
To install the WinPXFER program, follow the directions in the “Getting Started”
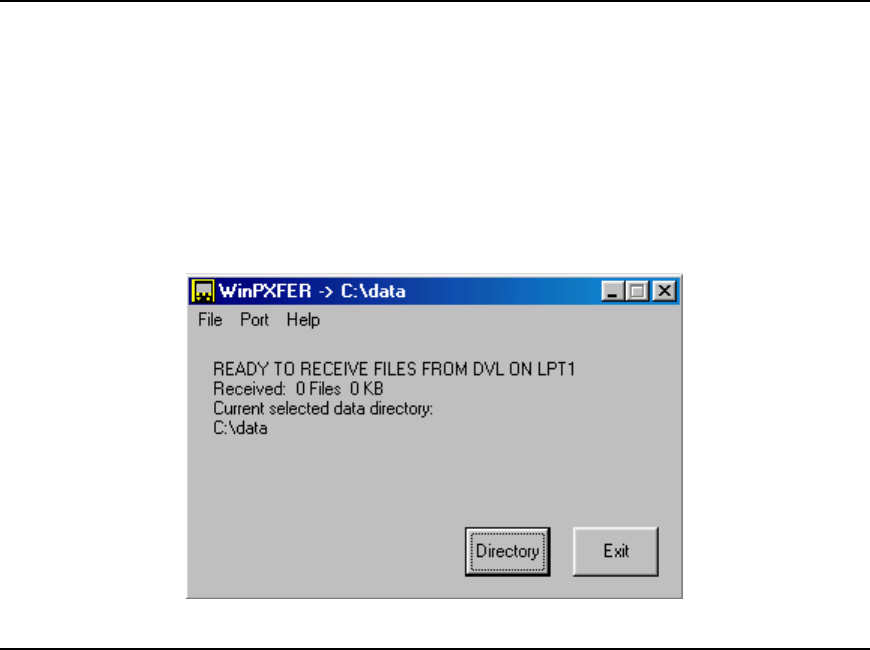
Smart Systems User’s Manual Version 1.1
86
document that accompanies the CD. Basically, running the SETUP.EXE program from
the WinPXFER folder on the CD will install WinPXFER on the computer.
Once the WinPXFER program has been installed on the computer and the user is ready
to transfer data to the computer, the WinPXFER program needs to be run. This can be
done using the WinPXFER shortcut on the Desktop, double-clicking the WinPXFER.EXE
program in Windows Explorer or pressing Start – Programs – Sensors & Software GPR
and finally WinPXFER.
Figure 6-13: WinPXFER main screen
When the WinPXFER program has been run, it will display a screen as shown in Figure
6-13:
This means that it is ready to receive data transferred from the DVL to the LPT port
number 1.
This command assumes that the data buffers are being transferred across Parallel Port
1 (LPT1). If using Parallel Port 2 (LPT2) or higher (LPT3, LPT4 etc.), specify the parallel
port number under the Port menu item from WinPXFER.
The name of the folder (or directory) that the Noggin data will be transferred into is listed
under the “Current selected data directory”. In the example in Figure 6-13, the data will
be transferred to the c:\data directory. The data directory can be changed by pressing
the Directory button and choosing another directory.
Exporting Data to an External Computer
Once the parallel XFER cable is connected (see above) and the WinPXFER software is
installed and running (see above), it is now possible to export data to the external
computer.
All the data in one or more Line or Grid Projects or the TAGGED.GPS file (see Section
6.3.5) can be transferred to an external computer. From the main File Management
menu, the user selects whether to export Line data, Grid data or the TAGGED.GPS file.
If Line or Grid data is selected, the next screen lists the current projects.

Smart Systems User’s Manual Version 1.1
87
One project can be highlighted and selected for export. Use the up and down arrows to
highlight the project and then press the XFER button to transfer to the PC.
It is also possible to use the TAG button to select several projects and export them all at
once. Use the up and down arrows to highlight the projects, the TAG button to tag each
project and then press the XFER button to transfer all the projects to the PC.
The data will be transferred from the DVL to the computer and saved in a sub-folder
from the current data directory indicated on the WinPXFER program, for example,
\DATA\PROJECT2. The progress of the data transfer will be displayed on the DVL
screen and the external computer.
When the data transfer is complete, exit from the WinPXFER program. Press any button
on the DVL to return to the main menu.
Parallel Port not bi-directional Error
Sometimes, when attempting to transfer data to the PC, the error message “LPT1 is not
bi-directional” may appear on the DVL screen. When transferring data from the DVL unit
to a PC, the printer port is used. The WinPXFER program utilizes the functions of a bi-
directional printer port for high-speed data transfer. A bi-directional port allows data to
be sent in both directions over the data lines. Most modern ports are bi-directional;
however, they may not be configured as such and may be configured as ‘output only’.
There are a number of ways the port can be reconfigured depending on the type and
manufacturer of your computer. Most computers configure the port using a BIOS setup
program. Again, different manufactures have different ways to start this program. Some
use the Delete key on boot up, some use the F1 or F2 key on boot up, some have a
special key sequence and others use a program run through DOS or Windows. Often
there is a line of text written to the screen during the boot-up sequence that indicates
which key must be pressed to run Setup. This key MUST be pressed BEFORE
Windows starts. If you miss pressing it, go into Windows, shut down, restart the
computer and try again. Consult your owners’ manual for details.
After the BIOS Setup program starts, the Parallel or Printer port configuration that needs
to be changed is normally under the ‘Peripheral’ or “Advanced” setting heading. If you
can’t find it under these headings, look under the various headings for some setting like
“Parallel Mode” or “Parallel Configuration”. Take note of what the current setting is. The
typical settings are Normal, ECP, EPP and bi-directional. It may require some
experimentation to find the correct setting that works with the WinPXFER program.
First, try changing the setting to bi-directional. Save the settings and exit the Setup
program (usually there is a special key like F10 to do this). Then allow the computer to
continue to boot up. Then, try transferring data again, as described above. If the “LPT1
is not bi-directional” error occurs again, reboot the PC, run the BIOS Setup program,
change the Parallel port setting to EPP, save the settings and try again. The settings
don’t appear standard so no one particular setting will solve the error on all computers.
Keep trying the different parallel port settings until one of them eliminates the error and
allows data transfer.

Smart Systems User’s Manual Version 1.1
88
Viewing Data Files on the External Computer
After transferring data files to the external computer the Nogginplus data files can be
viewed, processed and plotted using the Win_EKKO, EKKO_3D, EKKO_Mapper or
EKKO_Pointer software.
Appendix A contains details about the file format of Nogginplus data.
6.4.2 Deleting Data on the DVL
After data has been successfully transferred to an external computer or if the data is
longer required, the whole Line or Grid project can be deleted from the DVL. From the
File Management main menu, select Delete Line Project or Delete Grid Project. The
next screen lists all the current projects.
To delete a project, use the up and down arrows to highlight it and then press the DEL
button.
It is also possible to use the TAG button to select several projects and delete them all at
once. Use the up and down arrows to highlight the projects, the TAG button to tag each
project and then press the DEL button to delete the data from the DVL.
Before the project is deleted, the user is asked to confirm the deletion by pressing Yes or
No. If the answer to the question is No, the project is not deleted.
This menu also allows the user to delete the TAGGED.GPS file.

Smart Systems User’s Manual Version 1.1
89
6.5 Nogginplus Utilities
Pressing the number 4 on the main menu selects Utilities. This menu has utility
programs to change the date and time on the DVL and also calibrate the odometer.
6.5.1 Time and Date
The date and time are saved with the data files. The DVL date and time setting can be
changed by moving to one or more of the appropriate fields and editing the current
setting. The LEFT and RIGHT arrows are used to move between fields. To change any
of the numbers or months, use the UP and DOWN arrows to increase or decrease the
value. When the desired date and time are set, press ENTER to save the changes.
6.5.2 Odometer Calibration
The odometer should be calibrated periodically to ensure accuracy.
Noggin Smart Systems can take input from several different odometers.
It is very important that the user selects and calibrates the odometer appropriate
for their Smart System.
When Odometer Calibration is selected, the user is prompted to select the odometer that
is being used with the Smart System.
If a Smart Cart System is being used, select one of the two Smart Cart odometers
(usually #1).
If a Smart Handle system is being used, select one of the two Smart Handle odometers
(usually #1).
If the system is being towed behind a vehicle and using the transmission odometer to
trigger the system, select one of the two Vehicle odometers (usually #1).
The odometers labelled Other are to be used in future configurations.
Once an odometer is selected, the user is prompted to either 1) manually enter the
odometer calibration factor or 2) to actually calibrate the odometer over a known
distance. To achieve the highest accuracy, it is recommended that the user choose
option number 2 - Odometer Calibration.
When Odometer Calibration is selected, the user is prompted to select the length of the
line to calibrate on. There are 8 different choices in metres and 8 choices in feet. To
toggle the units between metres and feet, press the B button. Pressing the A button on
this screen gives the additional option to select a user-defined value. The user-defined
value can range from 0.01 to 5000 metres or 0.01 to 26400 feet.

Smart Systems User’s Manual Version 1.1
90
When the calibration distance has been selected follow the directions on the screen:
4) Set cart at zero and press A
5) Move the cart the selected distance and press B
6) Press A to exit.
Odometer calibration values for the Smart Cart odometer should be around 4000.
Odometer calibration values for the Smart Handle odometer should be around 1500.
Odometer calibration values for the Vehicle odometer vary but may be around 50.
6.5.3 Upgrade
This option is used to upgrade the software on the DVL. DO NOT press this button until
told to do so in the instructions accompanying the software upgrade.
6.5.4 System Information
This option can be used to list system information that may be useful to troubleshoot a
problem with the Noggin. The information is intended for the use of Sensors & Software
staff to assist in solving a problem with the Noggin system.
System information can be listed to the screen, printed directly to an attached printer or
transferred to a PC.
To print the information to a printer, attach the printer to the parallel port of the DVL and
then press the B button.
To transfer the information file to a PC, attach the parallel XFER cable from the parallel
port of the PC to the parallel port of the DVL. Then run the WinPXFER program on the
PC (see Section 6.4.1) and press the 1 button.
Sensors & Software technical staff may request that this information be sent to them. A
printed copy of the information can be faxed to Sensors & Software Inc. If the data is
transferred to a PC, the data file can be e-mailed to Sensors & Software Inc.

Smart Systems User’s Manual Version 1.1
91
7 Troubleshooting
Noggin Smart Systems are designed to minimize user problems; however, all electronic
devices are subject to possible failure. The following are troubleshooting hints in the
likelihood of occurrence if your Smart System fails to operate.
7.1 Power Supply
The most common problem that can occur while trying to run a system is insufficient
power. The battery may be dead or have a low voltage. If the system is being run from
AC, there may be a problem with the AC power supply or adapter.
If there is enough power to run the DVL, the upper red LED on the front of the DVL will
light up when the battery is plugged into the system. If this light is on and the DVL boots
up, runs and displays the main menu, next check that the red light on the connector to
the Noggin is on. If this light is off then there is a problem with the connection from the
DVL to the Noggin. Check the connection and this part of the cable.
If the DVL is running but the Noggin system will not run, go to the main menu and check
that battery voltage in the lower left corner (see Section 4) is above 10.5 volts. If not, the
battery needs to be recharged or replaced for the Noggin to run (see below).
If the battery voltage is less than about 10.5 volts, the DVL may not turn on and the
upper red LED will flash or not illuminate.
Check the battery voltage with a voltmeter. Try to do this while the system is still
attached to the Smart System to get a true measure of the voltage while under load (it
will be necessary to open the Smart Cart battery case and connect the voltmeter to the
positive and negative battery terminals). If the battery has a low voltage or seems dead,
try the system with another battery (if available), or give the battery a good 12-14 hour
charge and try running the system again.
If the battery does not charge up to 12 Volts or more, it should be replaced.
Smart System batteries are fused to protect the system. For the Smart Cart system,
open the battery case and check that the 10 Amp fuse is OK. If necessary, replace it
with one of the spare fuses available inside the battery case. The smaller belt batteries
available for the Smart Handle systems are also fused. Remove the battery from
padded casing and check the 5 Amp fuse. Replace the fuse if necessary.
7.2 System Communications
If the system power supply is OK but the Noggin does not respond there may be a
communication failure between the DVL and the Noggin. This type of failure is often
indicated by a 10000 series error number like 10012.

Smart Systems User’s Manual Version 1.1
92
If an error occurs, an error message will appear in the bottom left section of the Noggin
screen. EXIT the program and turn off the Digital Video Logger. Disconnect the power
source to completely shut down the system.
Make sure the cables are not damaged and that all cable connections are tightly
secured. Sometimes vibrations cause the cable connections to loosen just a bit and
break contact and this can cause errors. Disconnecting cables and reconnecting them
may provide a better contact and solve the problem. Turn the Digital Video Logger back
on and try running the system again.
If the power supply and cable are OK, the problem is likely a failure of the DVL. The
DVL has no user-serviceable parts so it will have to be returned to Sensors & Software
Inc for inspection and possible repair (see Section 7.6).
7.3 System Overheating
The Noggin systems are designed to operate to an internal temperature of 70 C or 158
F. In situations of high ambient temperatures or long exposure to direct sun, this
maximum internal temperature may be exceeded and cause the system to fail. While
the temperature displayed on the DVL in the lower left corner of the main menu indicates
the internal temperature of the DVL and not the Noggin, this temperature should give an
idea of whether the Noggin is overheating.
If you suspect that the Noggin system is overheating, shut it off and give it a chance to
cool down in a shady location before trying to run it again. Placing a wet cloth on top of
the Noggin may help in cooling it down.
If the situation is such that the high temperatures or direct sun cannot be avoided, it may
be a good idea to put some sort of shade over the Noggin.
Contact Sensors & Software Inc. if the problem persists as there may be defective
electronic components that need to be replaced (see Section 7.6).
7.4 DVL Problem
While the DVL has been ruggedized as much as possible, it should be handled in much
the same way a notebook computer is. If the DVL does not power up and boot up, there
may be a problem with the CPU or the storage media. If this occurs, contact Sensors &
Software Inc. (see Section 7.6).
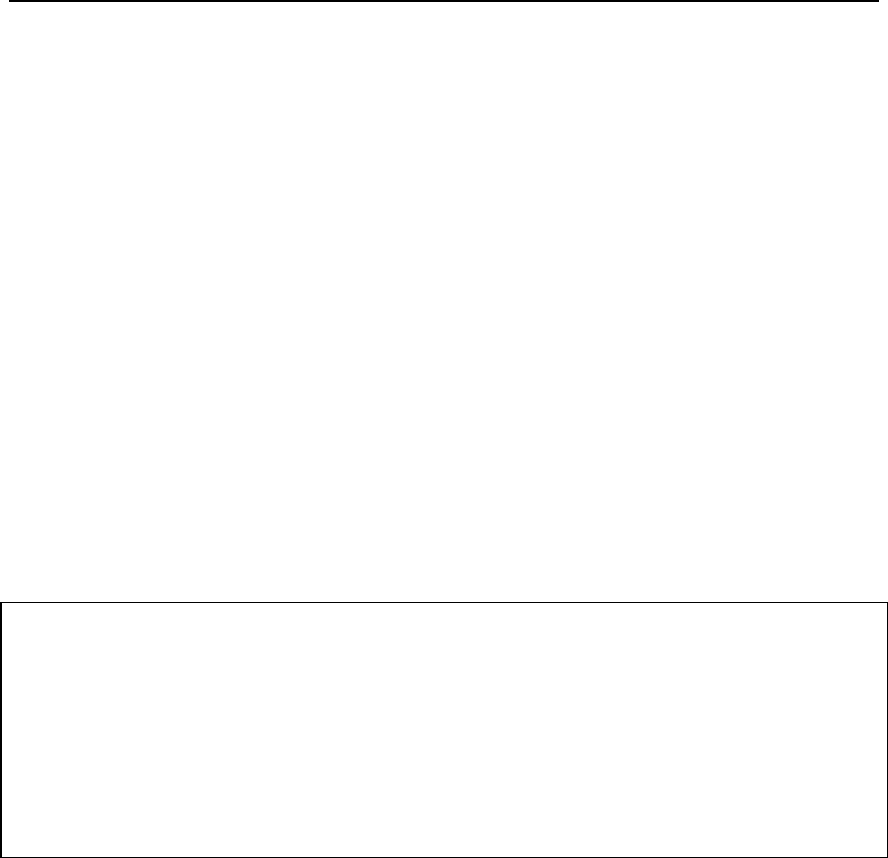
Smart Systems User’s Manual Version 1.1
93
7.5 Noggin Problem
When the Smart System is powered up and the user selects data acquisition in Noggin
or Nogginplus mode, the Noggin system goes through a self-calibration sequence. While
the self-calibration is occurring the user sees the words “Booting Noggin” in the lower left
corner of the DVL screen. These words are followed by a number that counts up from 1.
Normally, once the count reaches 6 the text disappears and the Noggin is ready to
collect data. Sometimes, however, this count goes beyond 6 and keeps going without
stopping. This indicates an internal problem with the Noggin. No error message will be
displayed on the screen and the only way to exit from the screen is to pull out the power
connection.
If this error occurs, power the system down, power it up again and retry data acquisition.
If the error persists, contact Sensors & Software Inc. (see Section 7.6).
7.6 Contacting Sensors & Software Inc.
If the Noggin system does not run, contact your agent or Sensors & Software Inc.
When contacting SSI, please have the following information available:
1) Noggin and/or DVL Serial Number.
2) Version number of the data acquisition software.
3) The error number or message appearing.
4) A brief description of when the error is happening and the operating conditions
(temperature, humidity, sunshine, system and survey setup, etc.).
5) Sensors & Software Inc. technical staff may request a copy of the System
Information file be sent to them by fax or e-mail. See Section 6.5.4 on how to view,
print and download this file.
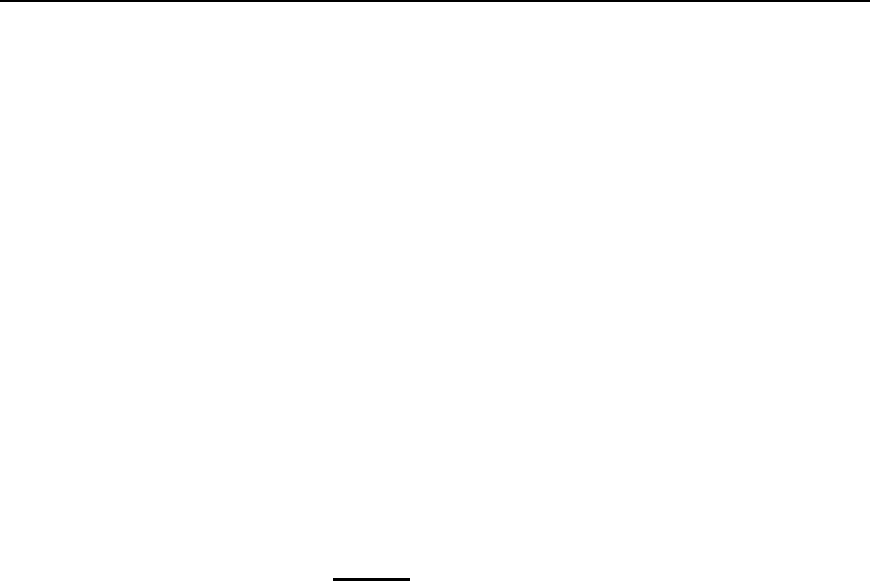
Smart Systems User’s Manual Version 1.1
94
8 Care and Maintenance
8.1 Battery Care
Smart Systems use 12-volt sealed lead acid batteries. They are fused with a 10 Amp
fuse to protect them from short circuit damage.
The Smart Cart battery unit uses contains a 15 Amp-hour battery. The battery unit
should run the Cart Noggin for 6-8 hours before recharging is necessary. If long days of
data surveying are typical, a second battery unit may be a useful item.
The Smart Handle belt battery has a 7 Amp-hour battery. This battery should run the
Smart Handle system for 2-3 hours before recharging is necessary. If long days of data
surveying are typical, more belt batteries may be a useful item.
If batteries are maintained in a charged condition they will give long life and reliable
service. Improper use and lack of maintenance will greatly reduce their life.
Sealed lead acid batteries should NEVER be left in a discharged condition for any period
of time. Charge the batteries as soon as possible after use.
Charge batteries at room temperature whenever possible.
The Noggin and DVL contain a voltage monitoring circuit that will turn off the unit when
the input voltage drops below 10.2 volts.
If a battery has been deeply discharged or left in a discharged condition for some period
of time it may not accept charge immediately when it is connected to the charger (The
fast charge LED will not light). If the fast charge light does not come on within 6 hours
the battery should be considered damaged and should be discarded.
Do not assume that a battery that is still charging after 8 hours is nearing the end of its
charge cycle. Typical charging time for an empty battery is 12-14 hours from start of fast
charge.
Ensure that the batteries are fully charged before storing. If practical, store the batteries
in a cool place, 10oc (a refrigerator is ideal), but make sure the temperature is not likely
to drop below -30oC or the electrolyte may freeze and possibly split the case.
8.2 DVL Internal Battery
If the Smart System has not been powered up for an extended period of time, the
internal battery will discharge. The dead battery causes the DVL time and date to reset
to January 1, 1988 at 12:00 PM. To correct the time and date see Section 5.5.1 or 6.5.1.
To recharge the internal battery the Smart System must be powered up and left running
for at least one hour and preferably longer.

Smart Systems User’s Manual Version 1.1
95
8.3 Skid Pads
The bottom of the Noggin unit is covered with one large wear-resistant skid pad. The
skid pad is designed to protrude from the bottom of the Noggin and take the majority of
the abrasive wear. If the pad wears down enough, the less-resistant plastic housing may
start to wear. If this occurs, it is best to replace the skid pad. It is easily removed with a
Phillips screwdriver and a new one can be purchased from Sensors & Software Inc.

Smart Systems User’s Manual Version 1.1
A-1
Appendix A NOGGIN PLUS DATA FILE FORMAT
Nogginplus data consists of two files, a Header file and a Data file. The files have the
same name but different extensions. The format details of these files are given below.
Header (.HD) File:
The header file, identified by the file extension .HD, is an ASCII file. An example is
shown below. The heading identifies what each piece of information represents.
1234
Data Collected with Noggin Plus
12/10/2000
NUMBER OF TRACES = 220
NUMBER OF PTS/TRC = 156
TIMEZERO AT POINT = 31
TOTAL TIME WINDOW = 62
STARTING POSITION = 0.0000
FINAL POSITION = 10.9500
STEP SIZE USED = 0.0500
POSITION UNITS = m
NOMINAL FREQUENCY = 250.00
ANTENNA SEPARATION = 0.3048
PULSER VOLTAGE (V) = 100
NUMBER OF STACKS = 4
SURVEY MODE = Reflection
This file can be read and/or printed using any Word Processor.
Data (.DT1) File:
The data file contains as many records as there are traces. Each record in turn consists
of a header section and a data section. The header section consists of an array of 25
real*4 numbers and a string of 28 characters which is used for annotation. The 25
element real array contains the following information:
Item # Description
1 Trace number
2 Position
3 Number of points per trace
4 Topographic data, if available
5 (not used)
6 # bytes/point (always 2 for Rev 3 firmware)
7 Time Window
8 # of stacks
9-10 reserved for GPS X position (double*8 number)
11-12 reserved for GPS Y position (double*8 number)
13-14 reserved for GPS Z position (double*8 number)

Smart Systems User’s Manual Version 1.1
A-2
15 reserved for receiver x position
16 reserved for receiver y position
17 reserved for receiver z position
18 reserved for transmitter x position
19 reserved for transmitter y position
20 reserved for transmitter z position
21 timezero adjustment
where:point(x)= point(x+adjustment)
22 Zero flag: 0 = data okay, 1=zero data
23 (not used)
24 Time of day data collected in seconds past midnight.
25 Comment flag: 1 = comment attached.
26 - 32 Comment
The data section consists of an array of two-byte integers, one value for every data
point.

Smart Systems User’s Manual Version 1.1
B-1
Appendix B HEALTH AND SAFETY CERTIFICATION
Radio frequency electromagnetic fields can pose a health hazard when the fields are
intense. Detailed discussions on the subject are contained in the references and the
web sites listed below.
The USA Federal Communication Commission (FCC) and Occupational Safety
and Health Administration (OSHA) both specify acceptable levels for
electromagnetic fields. Similar power levels are mandated by corresponding
agencies in other countries. Maximum permissible exposures and time duration
specified by the FCC and OSHA vary with excitation frequency. The lowest
threshold plane wave equivalent power cited is 0.2 mW/cm2 for general
population over the 30 to 300 MHz frequency band. All other applications and
frequencies have higher tolerances as shown in graphically in Figure 1.
Figure 1: FCC limits for maximum permissible exposure (MPE) plane-wave equivalent power density mW/cm2.
All Sensors & Software Inc. pulseEKKO, Noggin and Conquest products are
normally operated at least 1 m from the user and as such are classified as
“mobile” devices according to the FCC. Typical power density levels at a
distance of 1 m or greater from any Sensors & Software Inc. product are less
than 10-3 mW/cm2 which are 200 to 10,000 times lower than mandated limits. As
such, Sensors & Software Inc. products pose no health and safety risk when
operated in the normal manner of intended use.

Smart Systems User’s Manual Version 1.1
C-1
Appendix C FCC REGULATIONS
This device complies with Part 15 of the FCC Rules. Operation is subject to the
following two conditions:
(1) this device may not cause harmful interference and
(2) this device must accept any interference received, including
interference that may cause undesired operation.
FCC Class A Digital Device or Peripheral – User Information
This equipment has been tested and found to comply with the limits for a Class A digital
device, pursuant to Part 15 of the FCC Rules. These limits are designed to provide
reasonable protection against harmful interference when the equipment is operated in a
commercial environment. This equipment generates, uses and can radiate radio
frequency energy and, if not installed and used in accordance with the instruction
manual, may cause harmful interference to radio communications. Operation of this
equipment in a residential area is likely to cause harmful interference in which case the
user will be required to correct the interference at his own expense.
WARNING
Changes or Modifications not expressly approved by Sensors & Software Inc. could void
the user’s authority to operate the equipment.
Certification of this equipment has been carried out using approved cables and
peripheral devices. The use of non-approved or modified cables and peripheral devices
constitutes a Change or Modification outlined in the warning above.
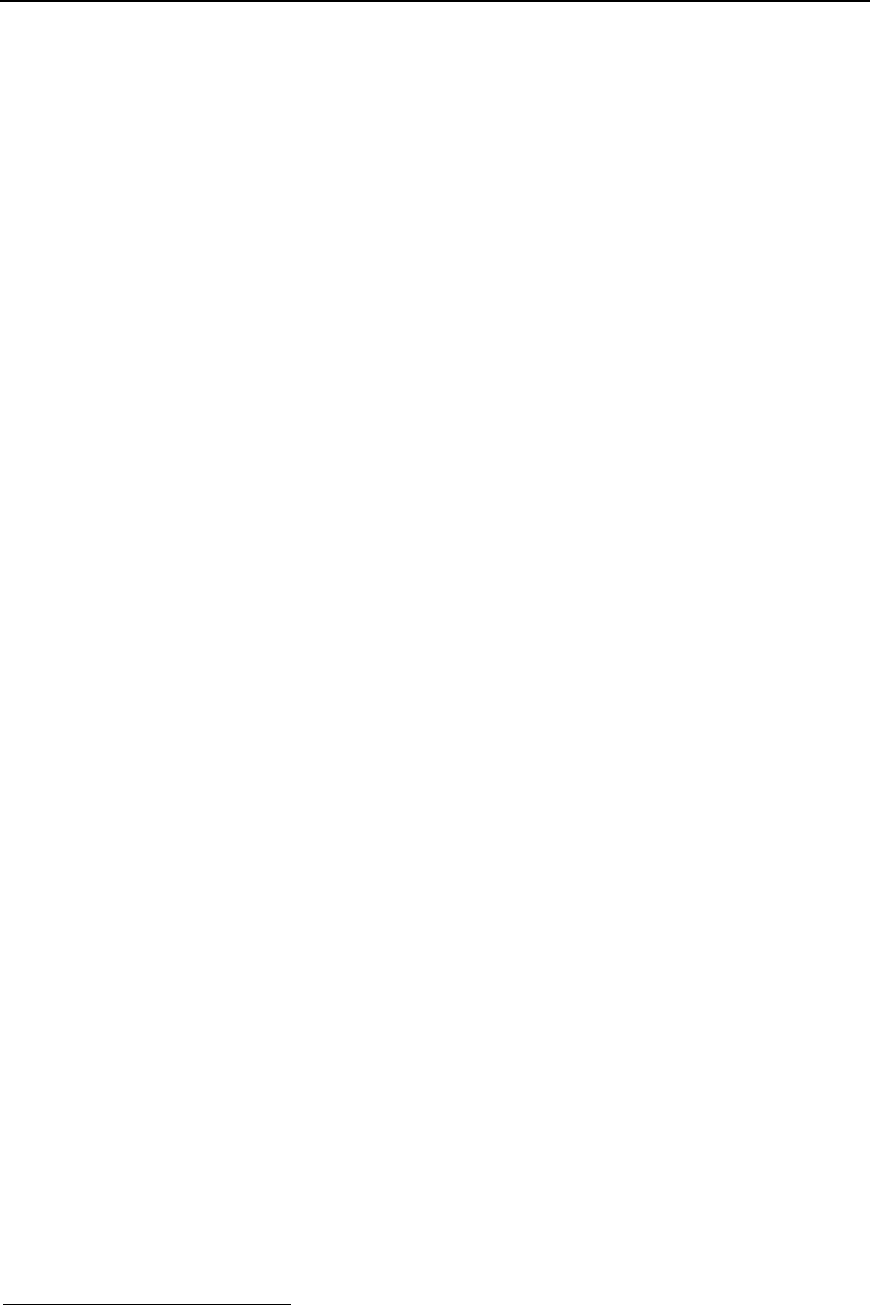
Smart Systems User’s Manual Version 1.1
C-2
Operating Restrictions
Operation of this device is restricted to law enforcement, fire and rescue officials,
scientific research institutes, commercial mining companies, and construction
companies. Operation by any other party is a violation of 47 U.S.C. §301 and could
subject the operator to serious legal penalties.
FCC Interpretation of this label issued July 12, 2002
The regulations contain restrictions on the parties that are eligible to operate imaging
systems. 1 Under the new regulations, GPRs and wall imaging systems may be used
only by law enforcement, fire and emergency rescue organizations, by scientific
research institutes, by commercial mining companies, and by construction companies.
Since the adoption of the Order, we have received several inquiries from the operators
of GPRs and wall imaging systems noting that these devices often are not operated by
the users listed in the regulations but are operated under contract by personnel
specifically trained in the operation of these devices. We do not believe that the recent
adoption of the UWB rules should disrupt the critical safety services that can be
performed effectively only through the use of GPRs and wall imaging systems. We
viewed these operating restrictions in the broadest of terms. For example, we believe
that the limitation on the use of GPRs and wall imaging systems by construction
companies encompasses the inspection of buildings, roadways, bridges and runways
even if the inspection finds no damage to the structure and construction does not
actually result from the inspection; the intended purpose of the operation of the UWB
device is to determine if construction is required. We also believe that the GPRs and
wall imaging systems may be operated for one of the purposes described in the
regulations but need not be operated directly by one of the described parties. For
example, a GPR may be operated by a private company investigating forensic evidence
for a local police department.
FCC Permitted Mode of Usage
The GPR antenna must be kept on the surface to be in compliance with FCC
regulations. Use of the antenna is not permitted if it is lifted off the surface.
1 See 47 C.F.R. §§ 15.509(b), 15.511(b), and 15.513(b).

Smart Systems User’s Manual Version 1.1
C-3
GPR Use Coordination
FCC regulation 15.525(c) requires users of GPR equipment to coordinate the use of
their GPR equipment as decribed below:
(a) UWB imaging systems require coordination through the FCC before the
equipment may be used. The operator shall comply with any constraints on equipment
usage resulting from this coordination.
(b) The users of UWB imaging devices shall supply detailed operational areas to
the FCC Office of Engineering and Technology who shall coordinate this information with
the Federal Government through the National Telecommunications and Information
Administration. The information provided by the UWB operator shall include the name,
address and other pertinent contact information of the user, the desired geographical
area of operation, and the FCC ID number and other nomenclature of the UWB device.
This material shall be submitted to the following address:
Frequency Coordination Branch., OET
Federal Communications Commission
445 12th Street, SW
Washington, D.C. 20554
ATTN: UWB Coordination
The form given on the following page is a suggested format for performing the
coordination.

Smart Systems User’s Manual Version 1.1
C-4
GROUND PENETRATING RADAR COORDINATION NOTICE
NAME:
ADDRESS:
CONTACT INFORMATION [contact name and phone number]:
AREA OF OPERATION [counties, states or larger areas]:
FCC ID: [e.g. QJQ-NOGGIN250 for Noggin 250 system)]
EQUIPMENT NOMENCLATURE: [ e.g. Noggin 250]
Send the information to:
Frequency Coordination Branch., OET
Federal Communications Commission
445 12th Street, SW
Washington, D.C. 20554
ATTN: UWB Coordination
Fax: 202-418-1944
INFORMATION PROVIDED IS DEEMED CONFIDENTIAL

Smart Systems User’s Manual Version 1.1
C-5
FCC Shut Off Switch
FCC regulation 15.509(c) requires that a GPR system incorporate a manually operated
switch that causes the transmitter to cease operation within 10 seconds of being
released by the operator.
Sensors & Software GPR systems will only operate when triggered by the operator. If
the system is not triggered by the operator it will cease transmitting within 10 seconds of
releasing the trigger.

Smart Systems User’s Manual Version 1.1
D-1
Appendix D OPERATION OF SHUT OFF SWITCH
Sensors & Software Inc.’s GPR systems transmitters will not operate in the free run
mode for more than 10 seconds without the shut off switch installed and depressed
by the user.
Installation
To install the switch, plug the 25 pin male connector into the printer port of the DVL-II
or the controlling PC. Software will automatically detect the switch.
Operation
To operate the switch, hold the button in the closed position. Releasing the button
for more than 10 seconds will cause the unit to stop functioning.
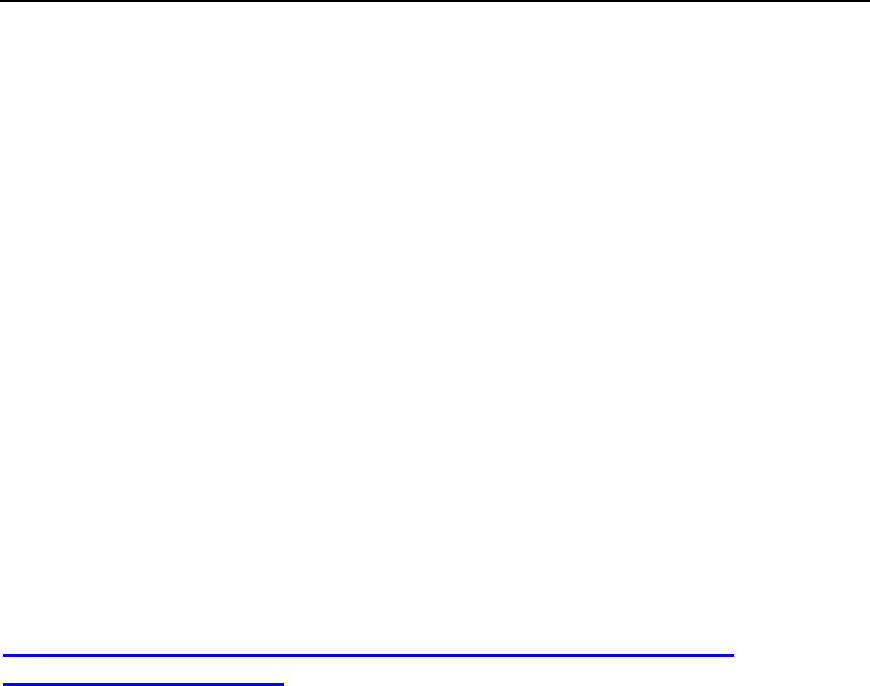
Smart Systems User’s Manual Version 1.1
References
1. Questions and answers about biological effects and potential hazards of
radio-frequency electromagnetic field
USA Federal Communications Commission, Office of Engineering &
Technology
OET Bulletin 56
(Contains many references and web sites)
2. Evaluation Compliance with FCC Guidelines for Human Exposure to
Radio Frequency Electromagnetic Fields.
USA Federal Communications Commission, Office of Engineering &
Technology
OET Bulletin 56
(Contains many references and web sites)
3. USA Occupational Safety and Health Administration regulations
paragraph 1910.67 and 1910.263.
Web Sites
www.fcc.gov/Bureau/EngineeringTechnlogy/Documents/bulletin
www.osha-slc.gov/SLTC (see radio frequency)