Siemens Canada Siemens Milltronics Process Instruments LR400-1 RADAR LAVEL GAUGE User Manual 7ML19985FH05
Siemens Canada Ltd. - Siemens Milltronics Process Instruments RADAR LAVEL GAUGE 7ML19985FH05
USERS MANUAL
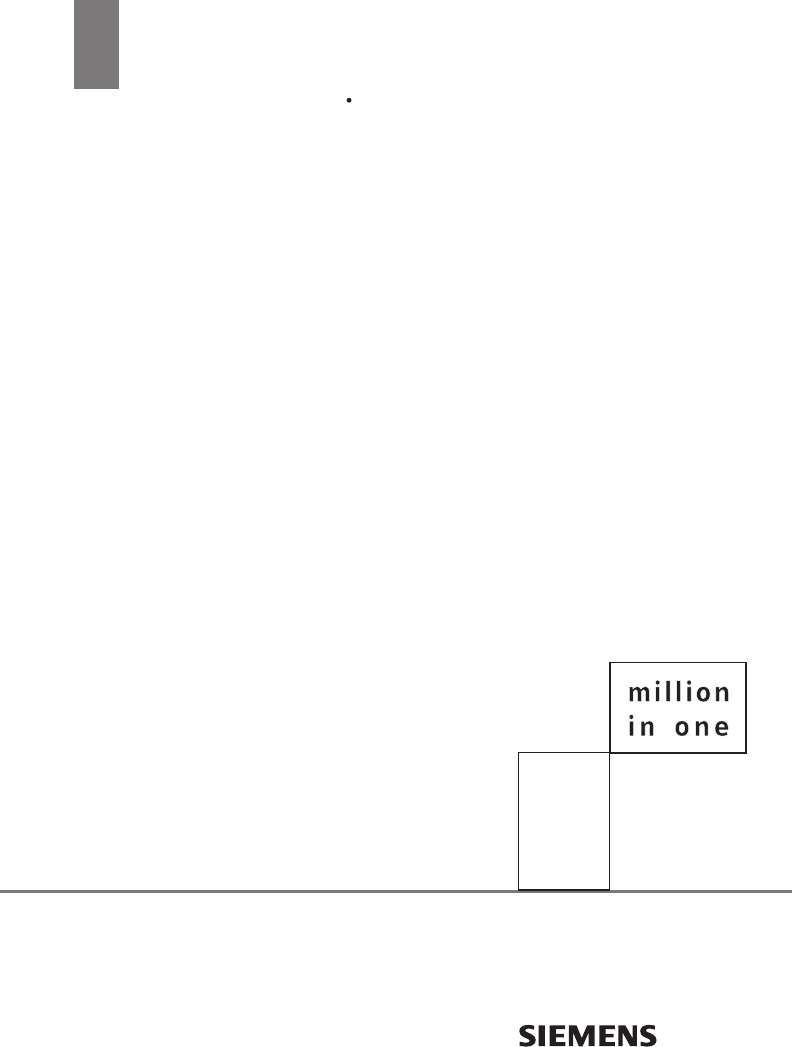
Instruction Manual October 2004
LR 400
sitrans
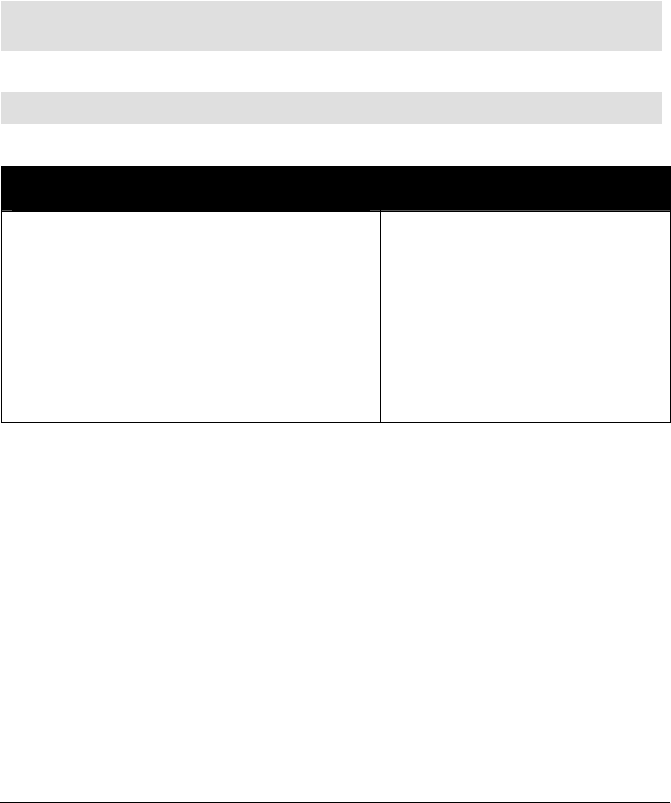
© Siemens Milltronics Process Instruments Inc. 2004
Safety Guidelines: Warning notices must be observed to ensure personal safety as well as that of
others, and to protect the product and the connected equipment. These warning notices are
accompanied by a clarification of the level of caution to be observed.
Qualified Personnel: This device/system may only be set up and operated in conjunction with this
manual. Qualified personnel are only authorized to install and operate this equipment in accordance with
established safety practices and standards.
Unit Repair and Excluded Liability:
• The user is responsible for all changes and repairs made to the device by the user or the user’s
agent.
• All new components are to be provided by Siemens Milltronics Process Instruments Inc.
• Restrict repair to faulty components only.
• Do not reuse faulty components.
Warning: This product can only function properly and safely if it is correctly transported, stored,
installed, set up, operated, and maintained.
Note: Always use product in accordance with specifications.
Copyright Siemens Milltronics Process
Instruments Inc. 2004. All Rights Reserved
Disclaimer of Liability
This document is available in bound version and in
electronic version. We encourage users to purchase
authorized bound manuals, or to view electronic versions
as designed and authored by Siemens Milltronics Process
Instruments Inc. Siemens Milltronics Process Instruments
Inc. will not be responsible for the contents of partial or
whole reproductions of either bound or electronic
versions.
While we have verified the contents of this
manual for agreement with the
instrumentation described, variations
remain possible. Thus we cannot
guarantee full agreement. The contents of
this manual are regularly reviewed and
corrections are included in subsequent
editions. We welcome all suggestions for
improvement.
Technical data subject to change.
MILLTRONICS®is a registered trademark of Siemens Milltronics Process Instruments Inc.
Contact SMPI Technical Publications at the following address:
Technical Publications
Siemens Milltronics Process Instruments Inc.
1954 Technology Drive, P.O. Box 4225
Peterborough, Ontario, Canada, K9J 7B1
Email: techpubs.smpi@siemens.com
• For a selection of Siemens Milltronics level measurement manuals, go to:
www. siemens.com/processautomation. Under Process Instrumentation, select Level
Measurement and then go to the manual archive listed under the product family.
• For a selection of Siemens Milltronics weighing manuals, go to:
www. siemens.com/processautomation. Under Weighing Technology, select Continuous
Weighing Systems and then go to the manual archive listed under the product family.
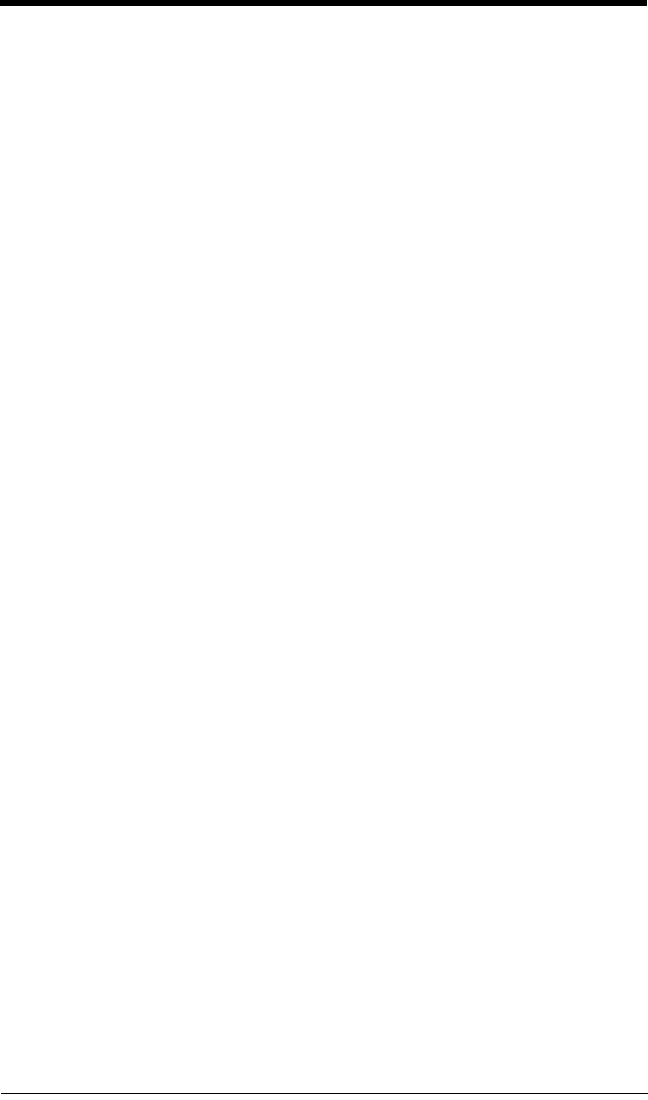
i
Table of Contents
General Information ...........................................................................................................1
Safety Notes .............................................................................................................................................1
The Manual ...............................................................................................................................................1
Abbreviations and Identifications .......................................................................................................2
SITRANS LR 400 ......................................................................................................................................3
Structure ....................................................................................................................................................3
System Implementation .........................................................................................................................5
Specifications ......................................................................................................................6
SITRANS LR 400 ............................................................................................................................6
Dimensions .............................................................................................................................................11
Purging System .................................................................................................................17
Installation ......................................................................................................................... 18
Mounting Location ................................................................................................................................18
Beam Spreading ..........................................................................................................................19
Correct Installation in Mounting Nozzle ................................................................................19
Installation using Easy Aimer LR .............................................................................................19
Electrical Connection ...........................................................................................................................20
Start Up ...............................................................................................................................22
Self-test ....................................................................................................................................................22
Multi-display ...........................................................................................................................................22
Local Programming ...............................................................................................................................22
Auto-Setup ..............................................................................................................................................22
Operation ............................................................................................................................24
General Information ..............................................................................................................................24
Measuring Principle .............................................................................................................................24
Operating the SITRANS LR 400 .........................................................................................................26
Selecting a Parameter .........................................................................................................................26
Structure of Parameters ............................................................................................................27
Changing a Parameter Value ..............................................................................................................27
Disabling and Enabling Programming ..............................................................................................29
Operating Examples ..............................................................................................................................30
Parameters (HART) ...........................................................................................................32
Functional Dimensions ..............................................................................................................33
Required Parameters ............................................................................................................................33
Additional Parameters .........................................................................................................................35
Parameters (PROFIBUS PA) ............................................................................................63
Troubleshooting .................................................................................................................75
Classification of Faults .........................................................................................................................75

ii
Self-test ....................................................................................................................................................75
Symptoms, Causes and Their Remedy ............................................................................................75
Fault Messages .....................................................................................................................................76
Unit Repair and Excluded Liability ..........................................................................................77
Maintenance ......................................................................................................................78
Cleaning the Antenna ..........................................................................................................................78
Glossary ..............................................................................................................................79
Appendix I: Parameter List ..............................................................................................80
Appendix II: Programming Chart ...................................................................................84
Appendix III ........................................................................................................................88
Ambient/Operating Temperature Specification .............................................................................88
Appendix IV ........................................................................................................................90
Process Pressure/Temperature De-rating ......................................................................................90
Appendix V .........................................................................................................................92
HART Communications for the SITRANS LR 400 ..........................................................................92
HART Device Descriptor (DD) ..................................................................................................92
SIMATIC Process Device Manager (PDM): ..........................................................................92
HART Communicator 275: ..........................................................................................................93
Appendix VI ........................................................................................................................98
PROFIBUS PA Communications for the SITRANS LR 400 ..........................................................98
Device Descriptor ........................................................................................................................98
The GSD file ..................................................................................................................................98
Bus address (Device Address) .................................................................................................98
Power Demands ..........................................................................................................................99
Cyclic versus Acyclic Data ........................................................................................................99
Cyclic Data ....................................................................................................................................99
Status Word ................................................................................................................................101
Extended Diagnostics ............................................................................................................. 102
Acyclic Data ............................................................................................................................... 102
Configuration Example: ........................................................................................................... 102
Hazardous Installation ................................................................................................... 103

7ML19985FH04 SITRANS LR 400 – INSTRUCTION MANUAL Page 1
mmmmm
General Information
General Information
Safety Notes
Special attention must be paid to warnings and notices highlighted from the rest of the
text by grey boxes.
• These instructions do not claim to cover all details or variations in equipment, or to
provide for every possible contingency that may arise during installation, operation,
or maintenance.
• For further information or to resolve issues not covered in the manual, consult your
Siemens Milltronics representative.
The Manual
WARNING: relates to a caution symbol on the product, and means
that failure to observe the necessary precautions can result in
death, serious injury, and/or considerable material damage.
WARNING: means that failure to observe the necessary
precautions can result in death, serious injury, and/or considerable
material damage.
CAUTION: means that failure to observe the necessary precautions can
result in considerable material damage.
Note: means important information about the product or that part of the operating
manual.
IMPORTANT: All specifications are subject to change without notice.
Please ensure that any safety-related information is confirmed with a
qualified Siemens Milltronics representative.
WARNINGS:
• Changes or modifications not expressly approved by Siemens Milltronics
could void the user’s authority to operate the equipment.
• This equipment is intended to be used only in fully enclosed metal and
concrete containers.
Note: This equipment has been tested and found to comply with the limits for a Class
A digital device, pursuant to Part 15 of the FCC Rules. These limits are designed to
provide reasonable protection against harmful interference when the equipment is
operated in a commercial environment. This equipment generates, uses, and can
radiate radio frequency energy and, if not installed and used in accordance with the
instruction manual, may cause harmful interference to radio communications.
Operation of this equipment in a residential area is likely to cause harmful
interference in which case the user will be required to correct the interference at his
own expense.
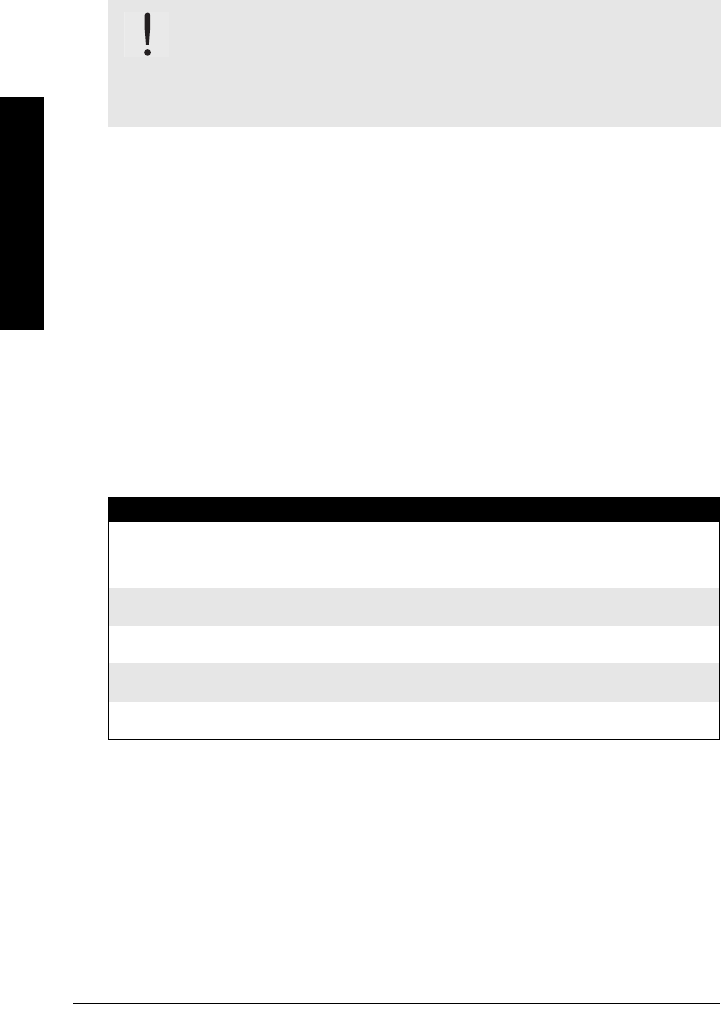
Page 2 SITRANS LR 400 – INSTRUCTION MANUAL 7ML19985FH04
mmmmm
General Information
This manual will help you set up your SITRANS LR 400 for optimal performance. We
alwasy welcome suggestions and comments about manual content, design, and
accessibility.
Please direct your comments to techpubs.smpi@siemens.com. For the complete library of
Siemens Milltronics manuals, go to www.siemens.com/processautomation
Qualified personnel
Qualified personnel are familiar with the installation, commissioning, and operation of
this equipment. In addition the person must be:
• trained and authorized to operate and service equipment/systems in accordance
with established safety procedures relating to electrical circuits, high pressures and
aggressive media.
• trained in the proper care and use of protective equipment in accordance with
established safety practices.
• trained in rendering first aid.
Abbreviations and Identifications
HART is a registered trademark of the HART Communication Foundation.
WARNINGS:
• Installation shall only be performed by qualified personnel and in
accordance with local governing regulations.
• The SITRANS LR 400 is to be used only in the manner outlined in this
manual, otherwise protection provided by equipment may be impaired.
Short form Long form Description
CE / FM / CSA Conformitè Europèene / Factory Mutual /
Canadian Standards Association
safety approval
ESD Electrostatic Discharge
HART® Highway Adressable Remote Transducer
IS Intrinsically Safe safety approval
PED Pressure Equipment Directive safety approval
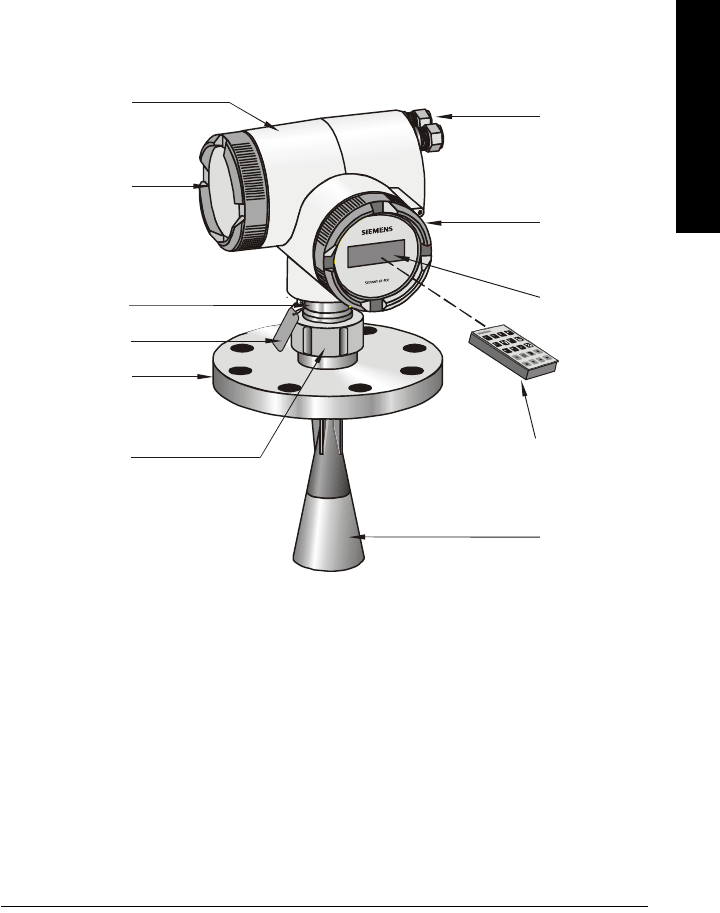
7ML19985FH04 SITRANS LR 400 – INSTRUCTION MANUAL Page 3
mmmmm
General Information
SITRANS LR 400
The SITRANS LR 400 is a long-range FMCW radar level instrument. A liquids version (L) is
available for use in liquids storage, performing well on low dielectric liquids or sticky
materials requiring a purging unit. A solids version (S) incorporates the Easy Aimer design
for use in solids, especially conditions of extreme dust. On both versions, the narrow
antenna beam results in a sharp radiation cone, which makes the SITRANS LR 400 quite
insensitive to vessel interferences.
Structure
housing
connection
cover
intermediate
flange
horn antenna
process flange
threaded ring
display module
electronics cove
r
cable gland
device tag
hand programme
r
(ordered
separately)
Liquids Version
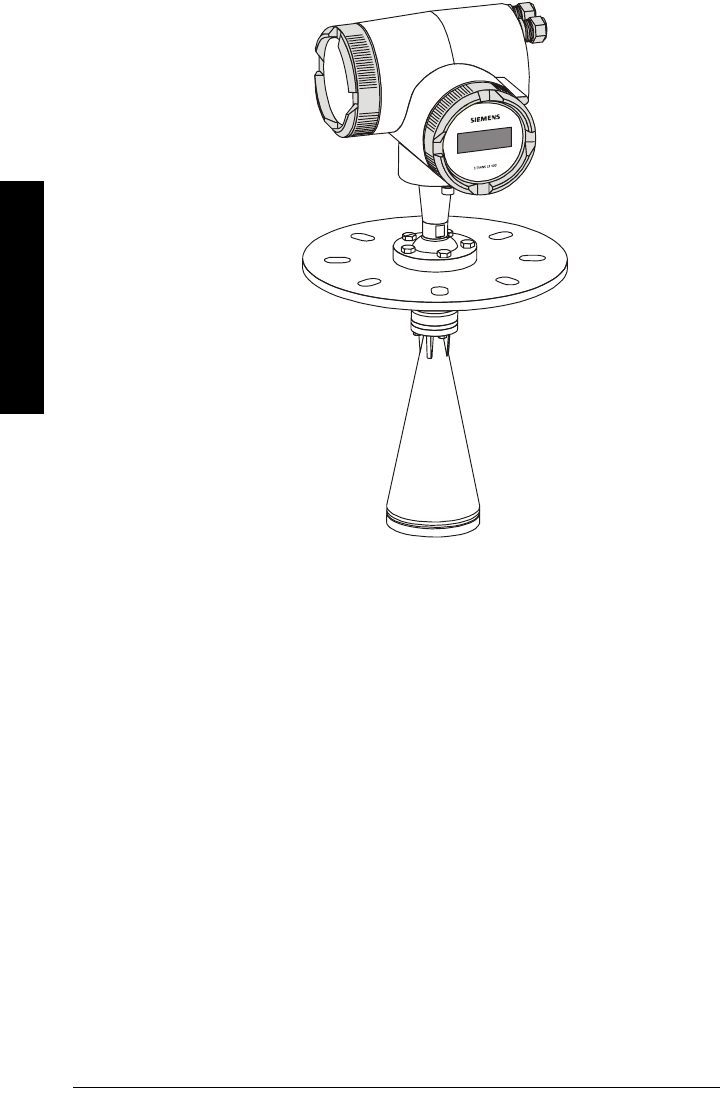
Page 4 SITRANS LR 400 – INSTRUCTION MANUAL 7ML19985FH04
mmmmm
General Information
The terminals for the power cable and the signal cable are behind the connection cover
on the left side of the housing. The signal cable must be fed in from the right through the
cable glands.
The end of the antenna must reach inside the vessel through the vessel nozzle (see
page 19).
If the device is rotated, return the orientation of the housing to its previous position with
reference to the flange, to ensure similar performance.
housing
connection
cover
intermediate
flange
horn antenna
process flange
threaded ring
display module
electronics cove
r
cable gland
device tag
hand programme
r
(ordered
separately)
Solids Version
Arrows required
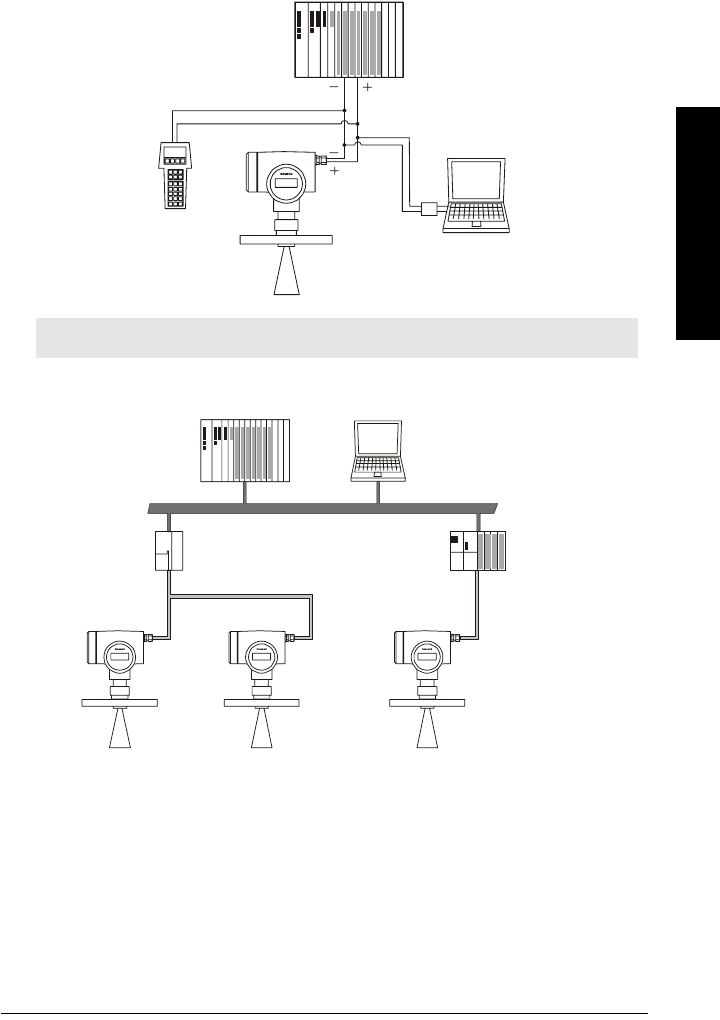
7ML19985FH04 SITRANS LR 400 – INSTRUCTION MANUAL Page 5
mmmmm
General Information
System Implementation
SITRANS LR 400 supports HART communication protocol, and SIMATIC PDM software.
Typical PLC/mA configuration with HART
Typical PLC/mA configuration with PROFIBUS PA
Note: A 250 ohm loop resistor may be required, depending on PLC input resistance.
SI TR A N S L R 400
PLC with mA
input card
HART
HART Communicator 275
SITRANS LR 400
PC/laptop with HART
modem running PDM
SITR AN S LR 40 0 SIT R AN S L R 40 0 SIT R AN S L R 40 0
PDM Class 2
Master
Class 1
Master PLC
DP/PA
Coupler ET200
HART
PROFIBUS PA
SITRANS LR 400 SITRANS LR 400 SITRANS LR 400
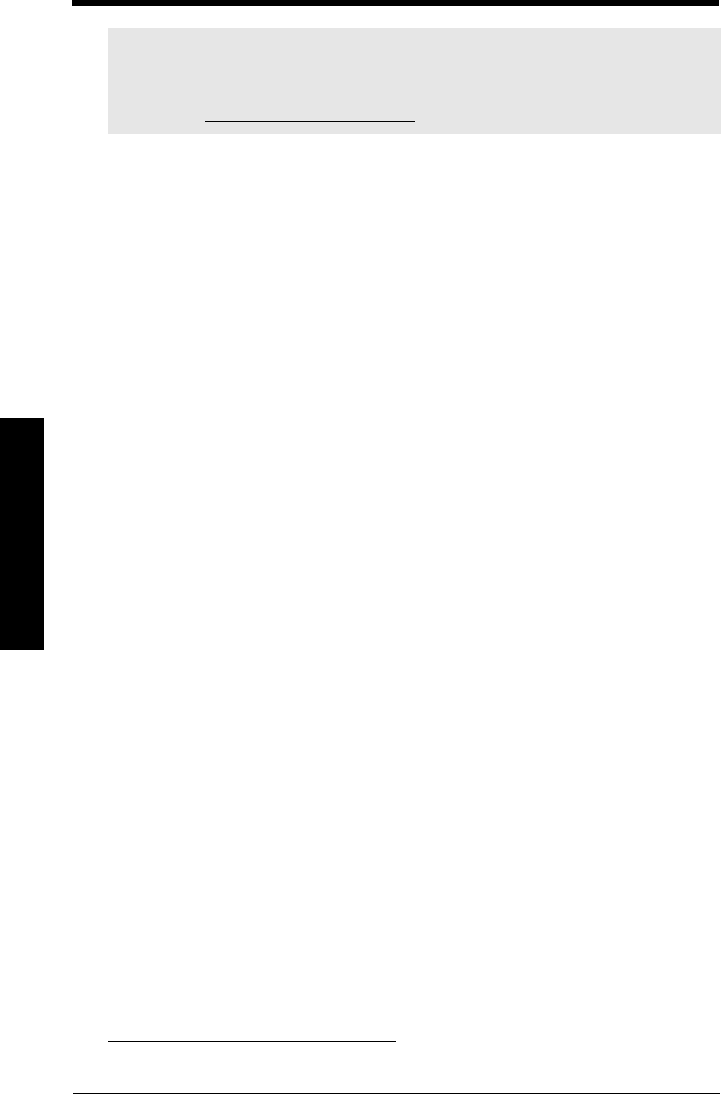
Page 6 SITRANS LR 400 – INSTRUCTION MANUAL 7ML19985FH04
mmmmm
Specifications
Specifications
SITRANS LR 400
Power
• Power Supply 120 to 230 V AC, ±15%, 50/60 Hz, 6W (12VA) or
24 V DC, +25/-20%, 6W
Power failure: bridge of at least 1 mains period (> 20 ms)
Fuse
• Fuse (both AC and DC versions)
SI1 Fast acting ceramic, 4 x 20 mm, 1A, 250 V AC
SI2 Slow-Blow, 4 x 20 mm, 0.63 A, 250 V AC
Performance
Measured value error (under reference conditions)
• Measuring error ≤ ± 5 mm at 1 to 10 m distance
≤ ± 15 mm at 10 to 45 m distance
• Dead zone 0 to 350 mm from bottom edge of flange
• Additional contribution of ≤ 0.1% of the measured value
analog output ≤ 0.05 % of full scale
• Long-term stability ≤ ± 1 mm/year
• Repetitive accuracy ≤ ± 1 mm at 0 to 45 m, damping ≥ 1 s
Interface
• Analog output (Not applicable to PROFIBUS PA option)
Signal range 4 to 20 mA
Upper Limit 20 to 22.5 mA adjustable
Fail signal 3.6 mA; 22 mA; 24 mA or last value
Load Max. 600 Ω; for HART®1 communication min. 230 Ω
• Digital output
Function Configurable as a device status or limit value
(level, volume, mass)
Note: Siemens Milltronics makes every attempt to ensure the accuracy of these
specifications, but reserves the right to change them at any time. Please ensure
these are the most recent specifications. Contact your representative, or check our
web site at www. siemens.com/milltronics for the most up-to-date information.
1. HART is a registered trademark of HART Communication Foundation.
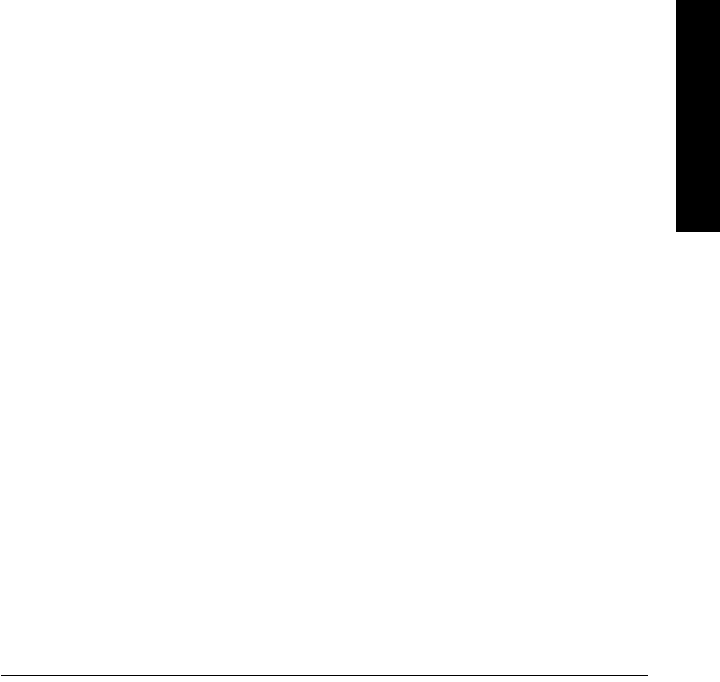
7ML19985FH04 SITRANS LR 400 – INSTRUCTION MANUAL Page 7
mmmmm
Specifications
Signal type Relay, either NCC or NOC function
max. 50 V DC, max. 200 mA, rating max. 5 W.
Self-resetting fuse, Ri = 9 Ω
• Electrical isolation Outputs electrically isolated from the power supply and
from each other
• Display LCD, two lines of 16 characters each,
configurable for the following displays:
level, volume, mass, amplitude, digital output,
temperature, validity, signal-to-noise ratio
Multi–display: 2 freely selectable measured values are
displayed simultaneously
Programmer (infrared keypad)
Siemens Milltronics Infrared IS (Intrinsically Safe) Hand Programmer for hazardous and
all other locations (battery is non-replaceable)
• approval: ATEX II 1 G, EEx ia IIC T4, certificate SIRA 01ATEX2147
CSA and FM Class I, Div. 1, Gr. A, B, C, D T6 @ max. ambient
temperature of 40 °C (104 °F)
• ambient temperature: −20 to 40 °C (−5 to 104 °F)
• interface: proprietary infrared pulse signal
• power: 3 V lithium battery
• weight: 150 g (0.3 lb)
• color: black
Mechanical
Flange
• Process Connection Flange DIN 2527, ANSI B16.5, or JIS B2238 equivalent bolt
pattern
• Materials of the wetted Stainless steel flange and horn, PTFE
parts – in contact with emitter (or glass/PTFE, Zone 0 and Zone 20 devices)
the process
• Pressure (vessel) Varies with connection type. Refer to Appendix IV for
specifications.
Solids version (including integral Easy
Aimer) is rated at 0.5 bar (7.5 psi) maximum.
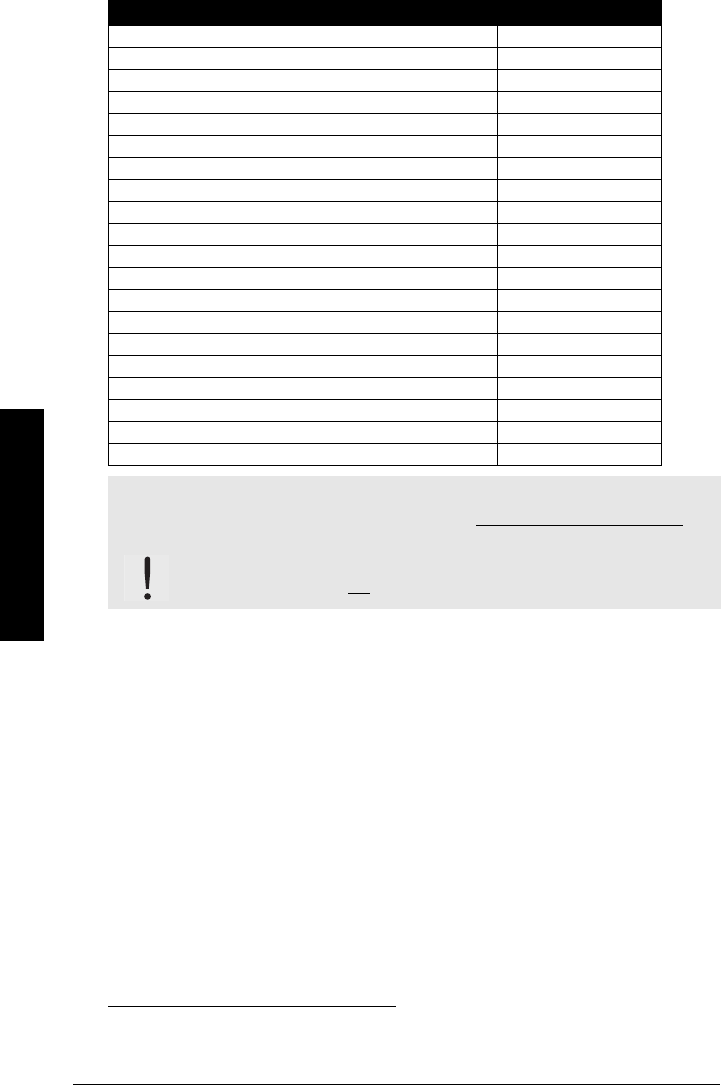
Page 8 SITRANS LR 400 – INSTRUCTION MANUAL 7ML19985FH04
mmmmm
Specifications
Weight
• Weight of instrument and flange
Enclosure
• construction Die-cast aluminum, painted
• conduit 2 x M20
or 2 x ½” NPT
• ingress protection Type 4X/NEMA 4X, Type 6/NEMA 6, IP671
Environmental2
location: indoor/outdoor
altitude: 2000 m max
ambient temperature: -40 to 65 °C (-40 to 149 °F)
relative humidity: suitable for outdoor (Type / NEMA 4X, 6/ IP67)
installation category II
pollution degree 4
• Process Temperature -40 to 200 °C (-40 to 392 °F)
Optional (Liquids version) -40 to 250 °C (-40 to 482 °F)
Process Connection Weight
Universal, 2" / 50 mm, flat faced, 0.5 bar maximum 5.3 kg (11.7 lbs)
Universal, 3" / 80 mm, flat faced, 0.5 bar maximum 6.1 kg (13.4 lbs)
Universal, 4" / 100 mm, flat faced, 0.5 bar maximum 6.8 kg (15.0 lbs)
Universal, 6" / 150 mm, flat faced, 0.5 bar maximum 8.5 kg (18.7 lbs)
DN80 PN16, flat faced 11.9 kg (26.1 lbs)
DN80 PN40, flat faced 12.9 kg (28.4 lbs)
DN100 PN16, flat faced 13.2 kg (28.9 lbs)
DN100 PN40, flat faced 15.5 kg (34.1 lbs)
DN150 PN16, flat faced 19.2 kg (42.1 lbs)
DN150 PN40, flat faced 24.1 kg (43.1 lbs)
3", 150 lb class, raised faced 12.2 kg (26.8 lbs)
3", 300 lb class, raised faced 14.3 kg (31.5 lbs)
4", 150 lb class, raised faced 14.8 kg (32.5 lbs)
4", 300 lb class, raised faced 20.2 kg (44.4 lbs)
6", 150 lb class, raised faced 20.1 kg (44.2 lbs)
6", 300 lb class, raised faced 31.8 kg (69.9 lbs)
JIS DN80 10K, flat faced 11.9 kg (26.1 lbs)
JIS DN100 10K, flat faced 13.2 kg (28.9 lbs)
JIS DN150 10K, flat faced 19.2 kg (42.1 lbs)
Easy Aimer with purge option 11.8 kg (26 lbs)
Note: Please ensure these are the most recent specifications. Contact your Siemens
Milltronics representative, or check our web site at www.siemens.com/milltronics for
the most up-to-date information.
WARNING: This product is designated as a Pressure Accessory per
Directive 97/23/EC and is not intended for use as a safety device.
1. Use only approved, suitable sized hubs for watertight applications.
2. See Process/Ambient de-rating curves in Appendix III.
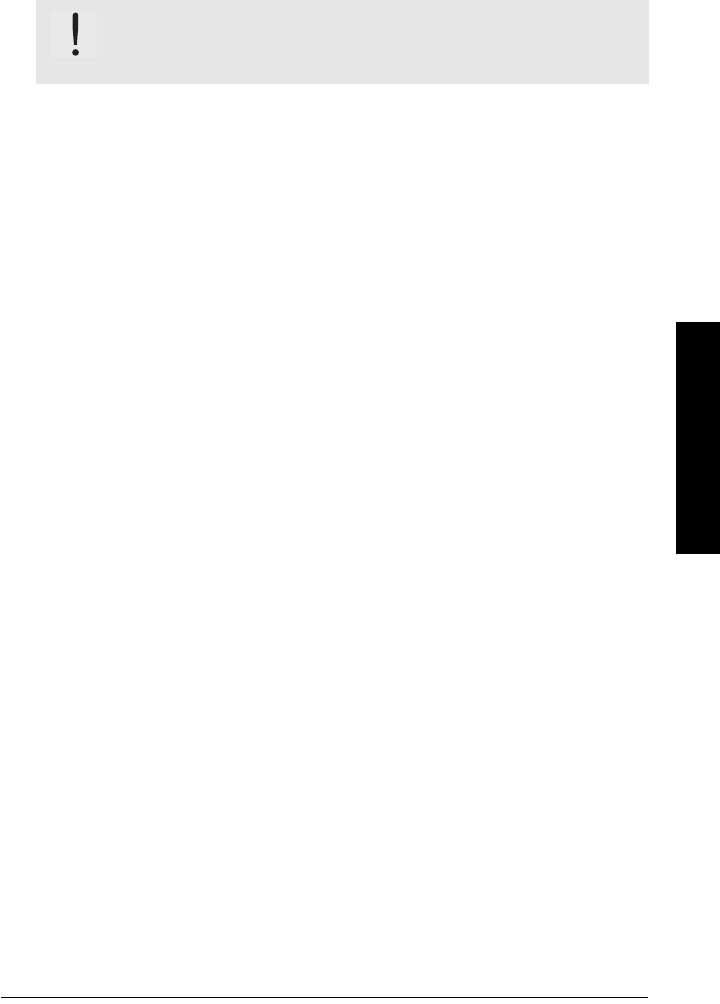
7ML19985FH04 SITRANS LR 400 – INSTRUCTION MANUAL Page 9
mmmmm
Specifications
• Electromagnetic compatibility
Spurious emission according to EN 50 081
Interference strength according to EN 50 082
• Perm. ambient -40 to 65 °C (-40 to 149 °F) (non-hazardous version)
temperature LCD: -10 to 55 °C (14 to 131 °F)
Observe the temperature classes in hazardous areas!
Communication
• Communication: HART
Load 230 to 600 Ω, 230 to 500 Ω when connecting a coupling
module
Line two-wire shielded: ≤ 3 km
multi-wire shielded: ≤ 1.5 km
Protocol HART, Version 5.1
• Communication: PROFIBUS PA
Protocol Layer 1 and 2 PROFIBUS PA,
technology: IEC 61158-2, slave-functionality
Device Class A
Device Profile 3.0
• PC/Laptop requirements IBM-compatible
RAM ≥ 64 Mbytes
Hard disk ≥ 100 Mbytes
RS 232-C interface
VGA graphic card (≥ 640 x 480)
• Software for PC/Laptop Windows 95/98/2000/XP or NT 4.0
SIMATIC® PDM
WARNING: Materials of construction are chosen based on their chemical
compatibility (or inertness) for general purposes. For exposure to specific
environments, check with chemical compatibility charts before installing.
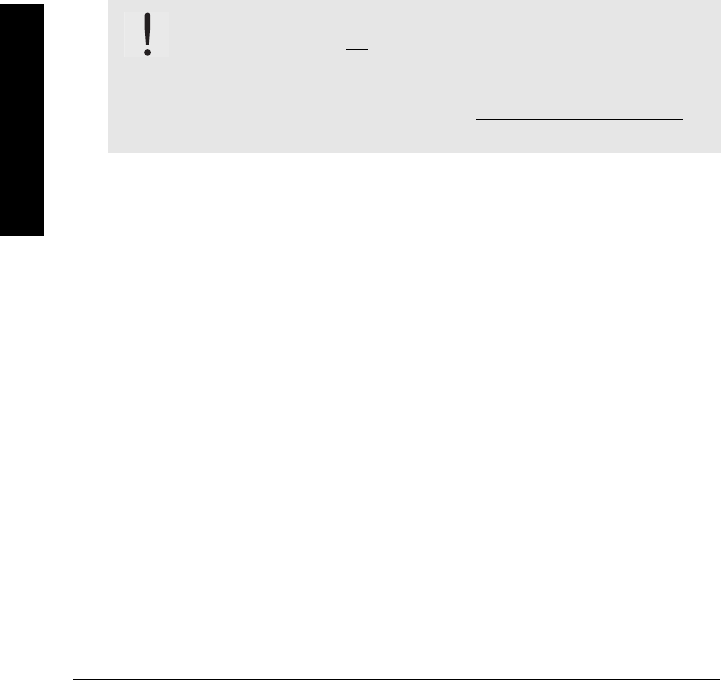
Page 10 SITRANS LR 400 – INSTRUCTION MANUAL 7ML19985FH04
mmmmm
Specifications
Approvals (verify against device nameplate)
• Explosion Protection (Liquids)Certificate No. PTB 00 ATEX 1024
*Refer to device II 1/2G EEx d IIC T6II 2G EEx d IIC T6
nameplate II 1/2G EEx dem IIC T6II 2G EEx dem IIC T6
II 1/2G EEx dem [ib] IIC T6II 2G EEx dem [ib] IIC T6
II 1/2G EEx dem [ia] IIC T6II 2G EEx dem [ia] IIC T6
FM/CSA Class I, Div. 1, Groups B, C, D; Class II/III, Div. 1,
Groups E, F, G
• Explosion Protection (Solids)FM/CSA Class II, Div. 1, Groups B, C,D; Class II/III, Div. 1,
Groups E,F and G
Certificate No. DMT 01 ATEX E 038
II 1/2 D IP 65 (dust zone 20, zone 21 approval)
• General CSAus/c, FM
• Radio FCC, Industry Canada, European Radio
• Shipping (Liquids version) Lloyd’s Register of Shipping, Categories ENV1, ENV2,
ENV3, and ENV5
WARNING: This product is designated as a Pressure Accessory per
directive 97/23/EC and is not intended for use as a safety device.
Note: Please ensure these are the most recent specifications. Contact your Siemens
Milltronics representative, or check our web site at www.siemens.com/milltronics for
the most up-to-date information.
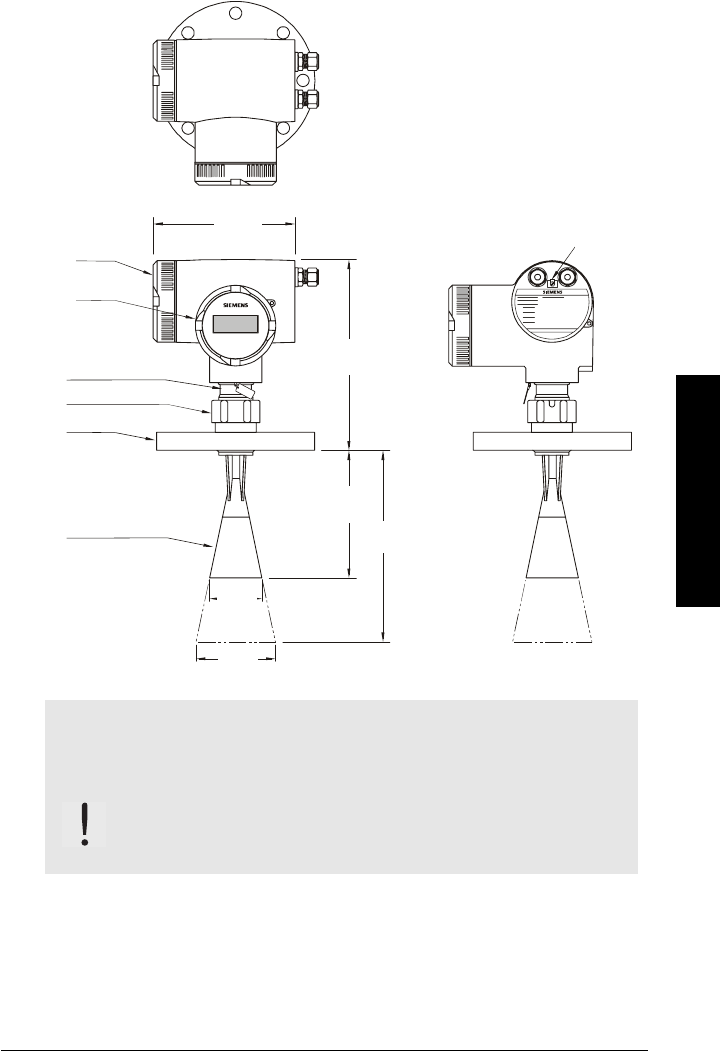
7ML19985FH04 SITRANS LR 400 – INSTRUCTION MANUAL Page 11
mmmmm
Specifications
Dimensions
SITRANS LR 400 Version for Liquids (without Temperature Extension)
*Flange acc. to DIN 2527 / ANSI B16.5 / JIS B2238 bolt hole pattern
**An optional purging system can be installed between the flange and the horn antenna.
The system provides a 1/8” NPT inlet on the flange where cooling air or cleaning fluid
passes through the universal flange and exits the inside of the horn to clean it. The
customer will supply the purging medium by manual or automatic valve system. This
option is only available with universal flanges.
SITRANS LR 400
Note: Process temperature and pressure capabilities are dependent upon
information on the process device tag. See Appendix IV (Process Pressure/
Temperature de-Rating). Reference drawing listed on the tag is available upon
request.
WARNING: The user is responsible for the selection of bolting and
gasket materials which will fall within the limits of the flange and its
intended use and which are suitable for the service conditions.
204 mm
(8.0")
281 mm
(11.1")**
191 mm
(7.5") 238 mm
(9.4")
74 mm
(2.9")
93 mm
(3.7")
horn
process
flange*
threaded
ring
intermediate
flange
electronics
cover
connection
cover
earth
terminal
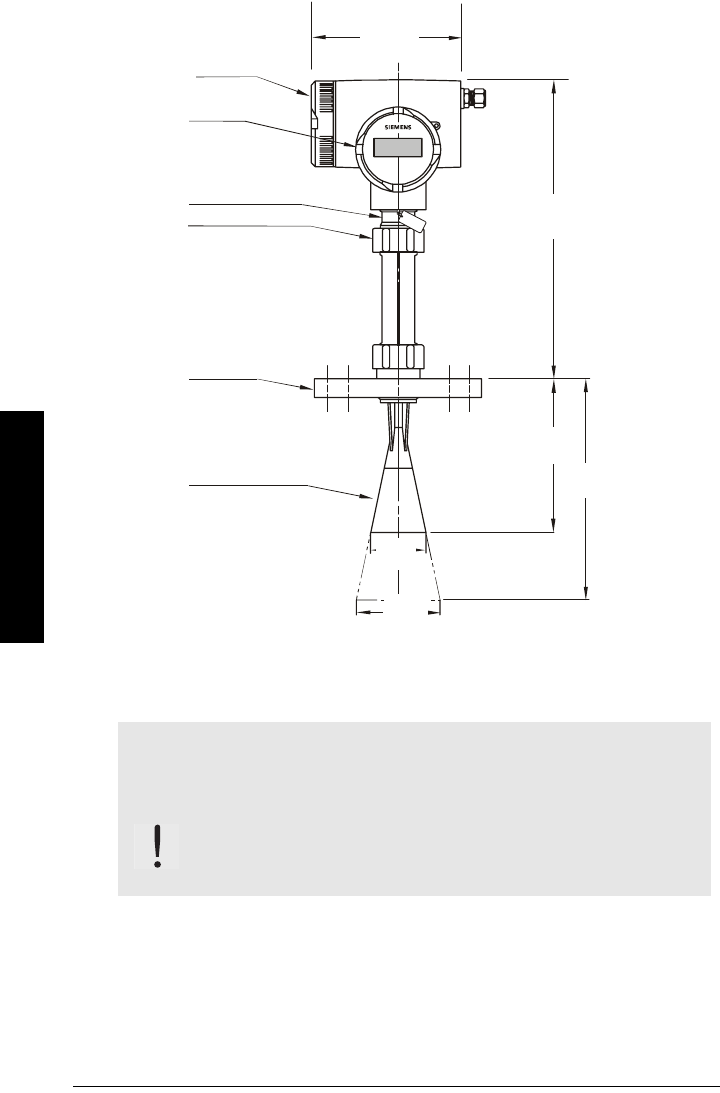
Page 12 SITRANS LR 400 – INSTRUCTION MANUAL 7ML19985FH04
mmmmm
Specifications
SITRANS LR 400 Version for Liquids with optional Temperature Extension
SITRANS L R 40 0
process
flange*
*Flange acc. to DIN 2527 / ANSI B16.5 / JIS B2238 bolt hole pattern
Note: Process temperature and pressure capabilities are dependent upon
information on the process device tag. See Appendix IV (Process Pressure/
Temperature de-Rating). Reference drawing listed on the tag is available upon
request.
WARNING: The user is responsible for the selection of bolting and
gasket materials which will fall within the limits of the flange and its
intended use and which are suitable for the service conditions.
204 mm
(8.0")
384 mm
(15.1")
191 mm
(7.5")
238 mm
(9.4")
74 mm
(2.9")
93 mm
(3.7")
horn
threaded
ring
electronics
cover
connection
cover
intermediate
flange
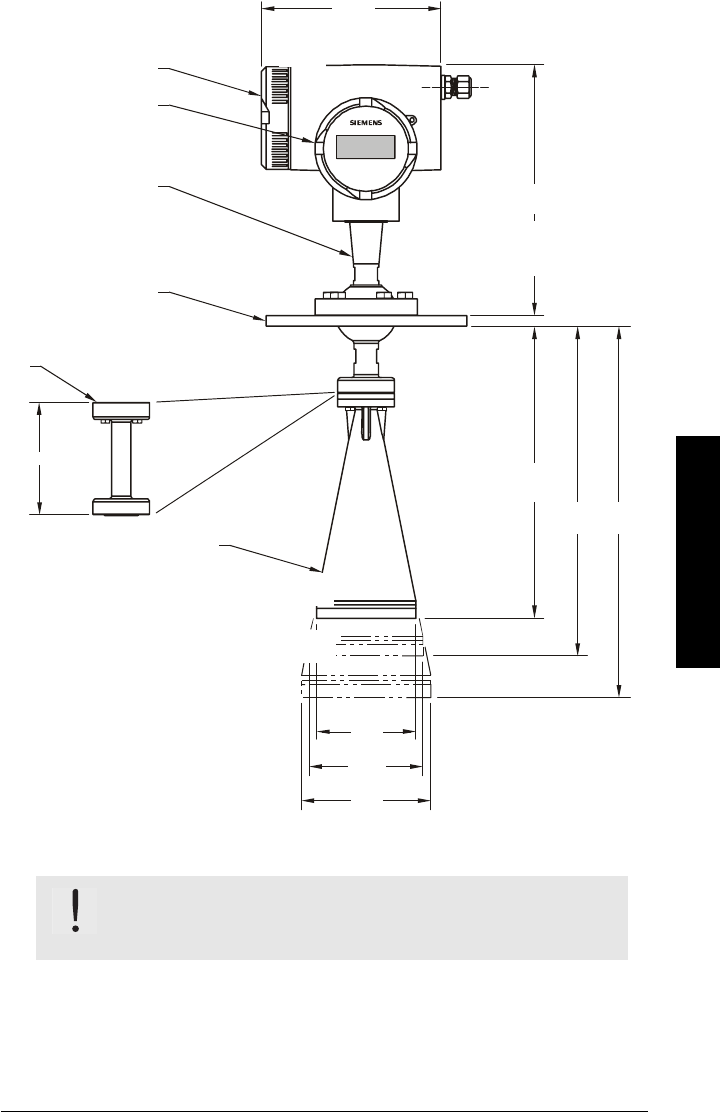
7ML19985FH04 SITRANS LR 400 – INSTRUCTION MANUAL Page 13
mmmmm
Specifications
SITRANS LR 400 Version for Solids
*Flange acc. to DIN 2527 / ANSI B16.5 / JIS B2238 bolt hole pattern
WARNING: The user is responsible for the selection of bolting and
gasket materials which will fall within the limits of the flange and its
intended use and which are suitable for the service conditions.
SITRANS LR 400
204 mm
(8.0")
285 mm (11.2")
412 mm (16.2") with
temperature extension
threaded
ring
electronics
cover
connection
cover
Easy Aimer
Flange*
horn
74 mm
(2.9")
93 mm
(3.7")
188.2 mm
(7.4")
9.6 mm
(0.38")
intermediate
flange
235.2 mm
(9.3")
Graphic labels to be up-
dated. New graphic to be
included for Optional
Horn Extension and dust
cover version
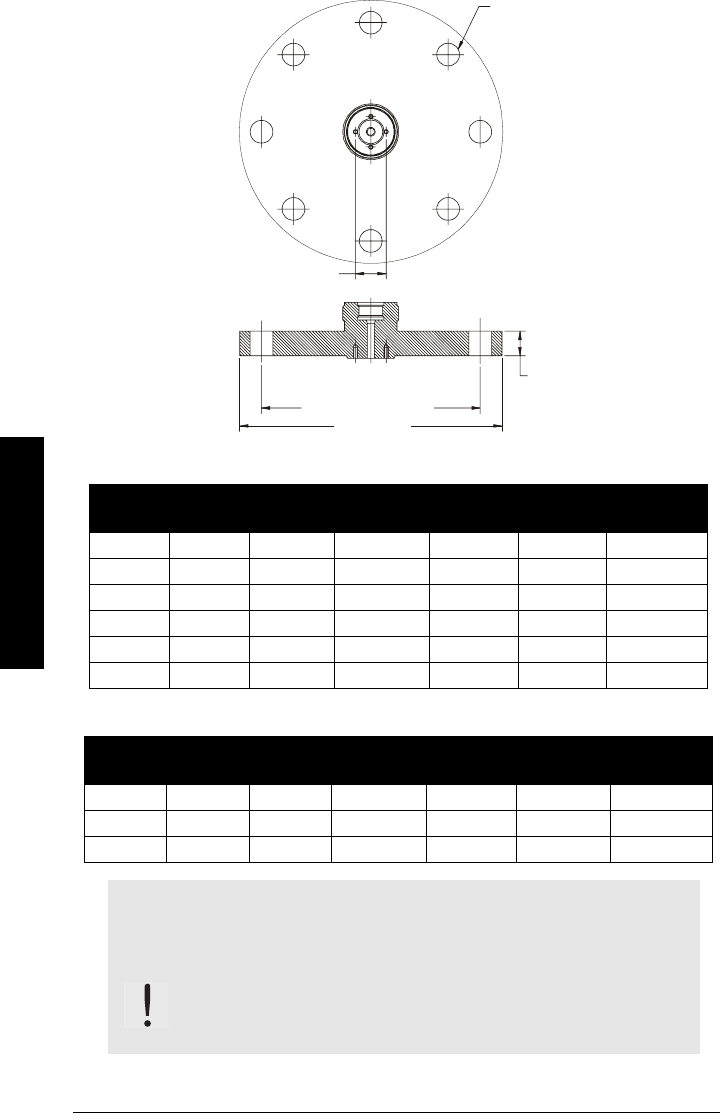
Page 14 SITRANS LR 400 – INSTRUCTION MANUAL 7ML19985FH04
mmmmm
Specifications
DIN / JIS Flat Face Flange Diagram (for Liquids version only)
Flange according to DIN 2527 (see Flange Diagram above)
Flange according to JIS B 2238
Pipe Size Flange
Size
Flange
O.D.
Thickness
(s)
Bolt Hole
Circle Ø
Bolt Hole
Ø
Number of
Bolts
80 mm PN 16 200 mm 20.0 mm 160 mm 18.0 mm 8
100 mm PN16 220 mm 20.0 mm 180 mm 18.0 mm 8
150 mm PN 16 285 mm 22.0 mm 240 mm 22.0 mm 8
80 mm PN 40 200 mm 24.0 mm 160 mm 18.0 mm 8
100 mm PN 40 235 mm 24.0 mm 190 mm 22.0 mm 8
150 mm PN 40 300 mm 28.0 mm 250 mm 26.0 mm 8
Pipe Size Flange
Size
Flange
O.D.
Thickness
(s)
Bolt Hole
Circle Ø Bolt Hole Ø Number of
Bolts
80 mm 10 K 185 mm 20.0 mm 150 mm 19.0 mm 8
100 mm 10 K 210 mm 22.0 mm 175 mm 19.0 mm 8
150 mm 10 k 280 mm 24.0 mm 240 mm 23.0 mm 8
Note: Process temperature and pressure capabilities are dependent upon
information on the process device tag. See Appendix IV (Process Pressure/
Temperature de-Rating). Reference drawing listed on the tag is available upon
request.
WARNING: The user is responsible for the selection of bolting and
gasket materials which will fall within the limits of the flange and its
intended use and which are suitable for the service conditions.
bolt hole
Ø
thickness (s)
flange O.D.
bolt hole circle Ø
horn mounting holes
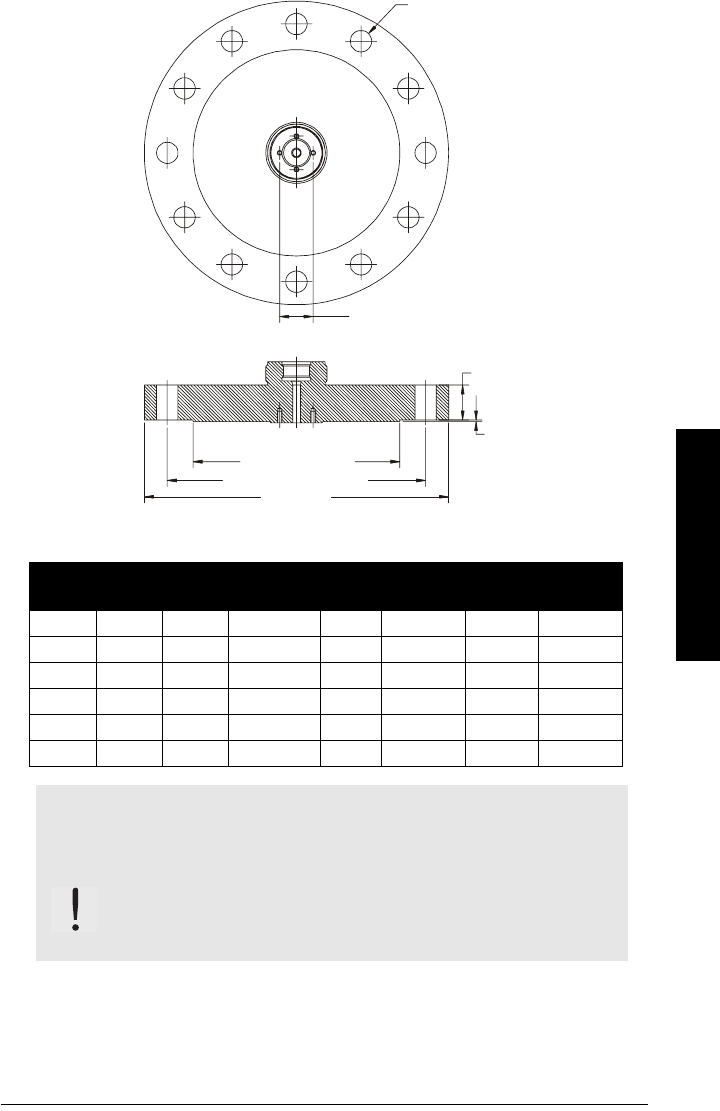
7ML19985FH04 SITRANS LR 400 – INSTRUCTION MANUAL Page 15
mmmmm
Specifications
ANSI Raised Face Flange Diagram (for Liquids version only)
Flange according to ANSI B 16.5 (see Flange Diagram above)
Pipe
Size
Flange
Size
Flange
O.D.
Thickness
(s)
Face
O.D.
Bolt Hole
Circle Ø
Bolt
Hole Ø
Number
of Bolts
3" 150 # 7.50" 0.941" 5.0" 6.00" 0.75" 4
4" 150 # 9.00" 0.941" 6.19" 7.50" 075" 8
6" 150 # 11.00" 1.00" 8.5" 9.50" 0.88" 8
3" 300 # 8.25" 1.12" 5.0" 6.62 0.88" 8
4" 300 # 10.00" 1.25" 6.19" 7.88" 0.88" 8
6" 300 # 12.51" 1.44" 8.5" 10.62" 0.88" 12
Note: Process temperature and pressure capabilities are dependent upon
information on the process device tag. See Appendix IV (Process Pressure/
Temperature de-Rating). Reference drawing listed on the tag is available upon
request.
WARNING: The user is responsible for the selection of bolting and
gasket materials which will fall within the limits of the flange and its
intended use and which are suitable for the service conditions.
thickness (s)
raised face thickness
0.063" (mm)
bolt hole Ø
horn mounting holes
flange O.D.
bolt hole circle Ø
face O.D.
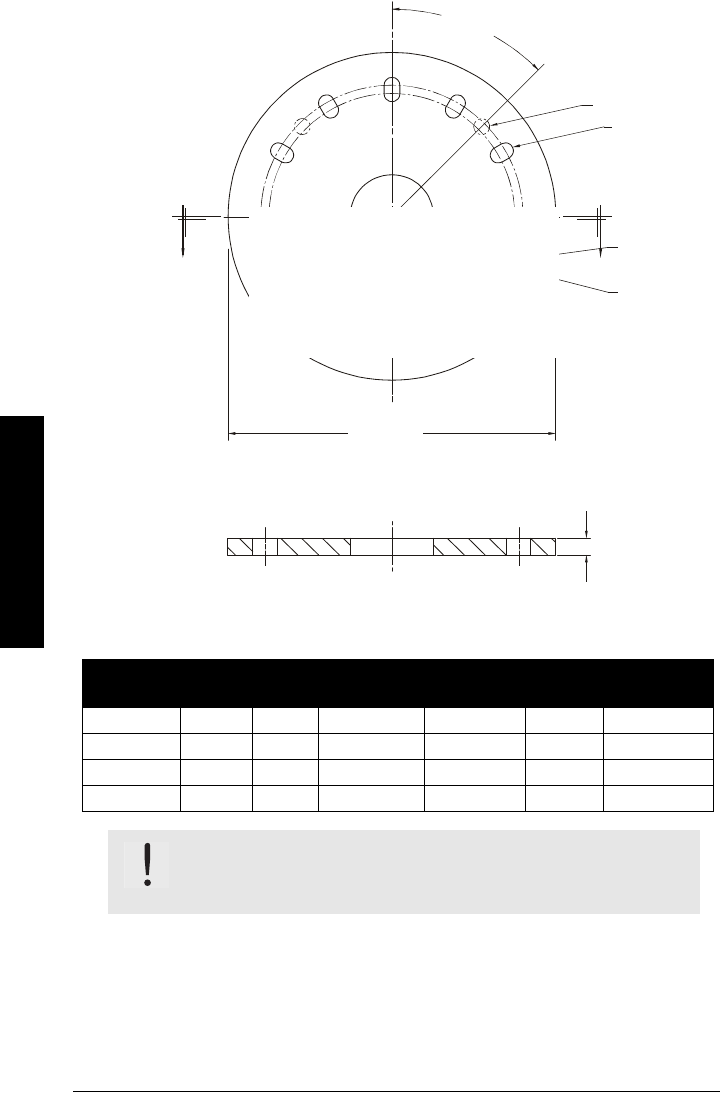
Page 16 SITRANS LR 400 – INSTRUCTION MANUAL 7ML19985FH04
mmmmm
Specifications
Universal Slotted Flange Diagram
Flange according to Universal Slotted Flange (see Flange Diagram above)
Pipe
Size
Flange
O.D.
Thick-
ness (s)
Bolt Hole
Circle Max Ø
Bolt Hole
Circle Min Ø
Bolt Hole
radius
Number of
Slotted Holes
3" or 80 mm 7.87" 0.40" 6.30" 5.90" 0.38" 8
4" or 100 mm 9.00" 0.40" 7.50" 6.89" 0.38" 8
6" or 150 mm 11.22" 0.40" 9.50" 9.44" 0.45" 8
8" or 200 mm 13.5" 0.40" 11.75" 11.4" 0.45" 12
WARNING: The user is responsible for the selection of bolting and
gasket materials which will fall within the limits of the flange and its
intended use and which are suitable for the service conditions.
45°
flange O.D.
section A-A
thickness
only available on pipe
size 8" (200 mm)
number of
slotted bolt
holes
bolt hole
circle min Ø
bolt hole
circle max Ø
AA
New Univeral Flange graphic
required for Solids version.
Replaces current Universal
Flange diagram.
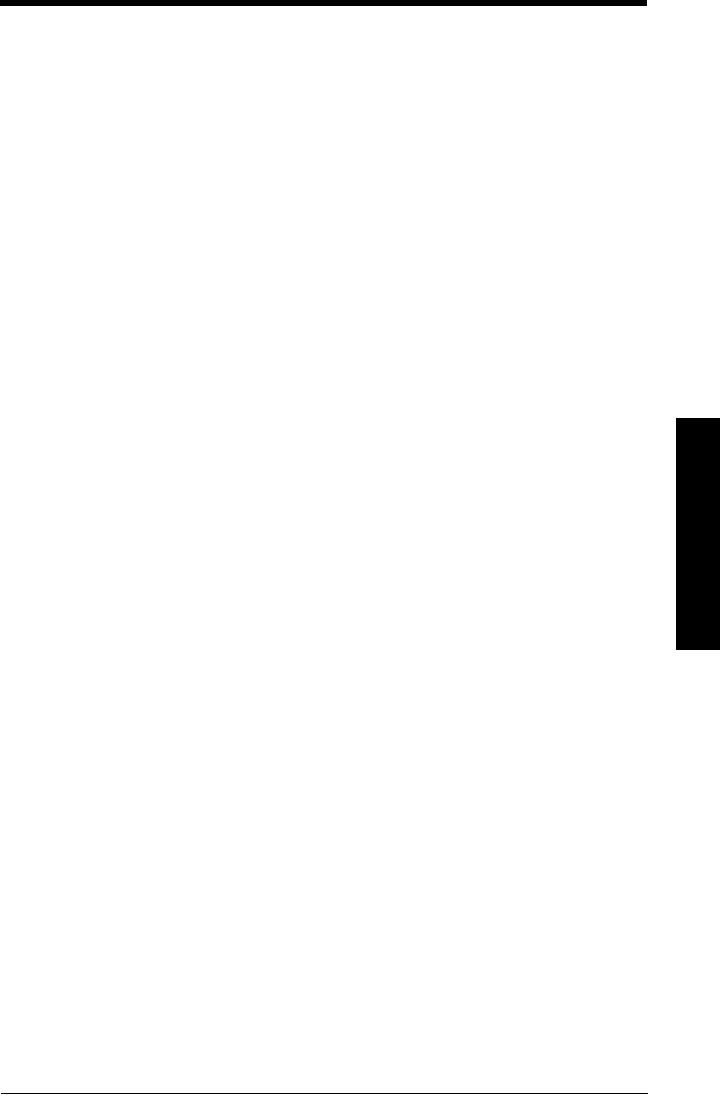
7ML19985FH04 SITRANS LR 400 – INSTRUCTION MANUAL Page 17
mmmmm
Specifications
Purging System
For more frequent cleaning, a purging system can be installed between the flange and the
horn antenna. The system provides an inlet on the flange where cooling air or cleaing fluid
passes through the flange and exits the inside of the horn to clean it. The customer will
supply the purging medium by manual or automatic valve system. This option is only
available with universal flanges on the Liquids version of the SITRANS LR 400.
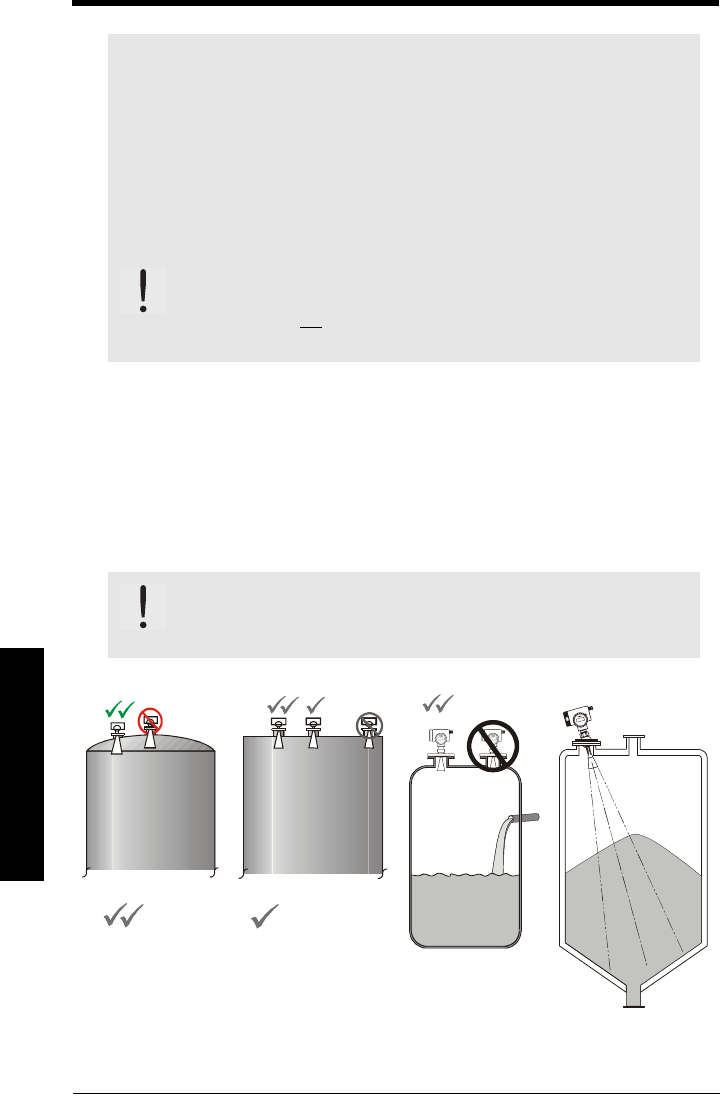
Page 18 SITRANS LR 400 – INSTRUCTION MANUAL 7ML19985FH04
mmmmm
Installation
Installation
Mounting Location
• Do not mount in direct sunlight without the use of a sun shield. Refer to Appendix III
(Ambient/Operating Temperature Specification) on page 88.
• Mount the unit more than 1 m away from the vessel walls, pipes and other
assemblies as well as the filling stream, because all these influences will become
noticeable as reflective interference. Align the antenna so that the radar cone
intersects the surface of the measuring medium as vertically as possible
Notes:
• The SITRANS LR 400 is rated for Type 4X/NEMA 4X, Type 6/NEMA 6,
IP67. Follow all installation and operating instructions to meet the
requirements of this type of protection. Use only approved, suitable
sized hubs for watertight applications.
• Observe all maximum permissible ambient and process temperatures.
Refer to Appendix III (Ambient/Operating Temperature Specification).
Provide a warning sign and/or touch guard if the surface of the measuring
instrument can become hotter than 70 °C in use.
WARNINGS:
• This product is designated as a Pressure Accessory per directive
97/23/EC and is not intended for use as a safety device.
• Improper installation may result in loss of process pressure.
WARNING: For vessels with conical or parabolic tops, avoid
mounting the unit at the center. The concavity of the top can focus
echoes into the centre, giving false readings.
Flat
P a ra b o lic
SITRANS LR 400 SITRANS LR 400
SIT
RA
NS LR
400
Parabolic or Conical Flat
is preferred
location
is acceptable
location
Easy Aimer
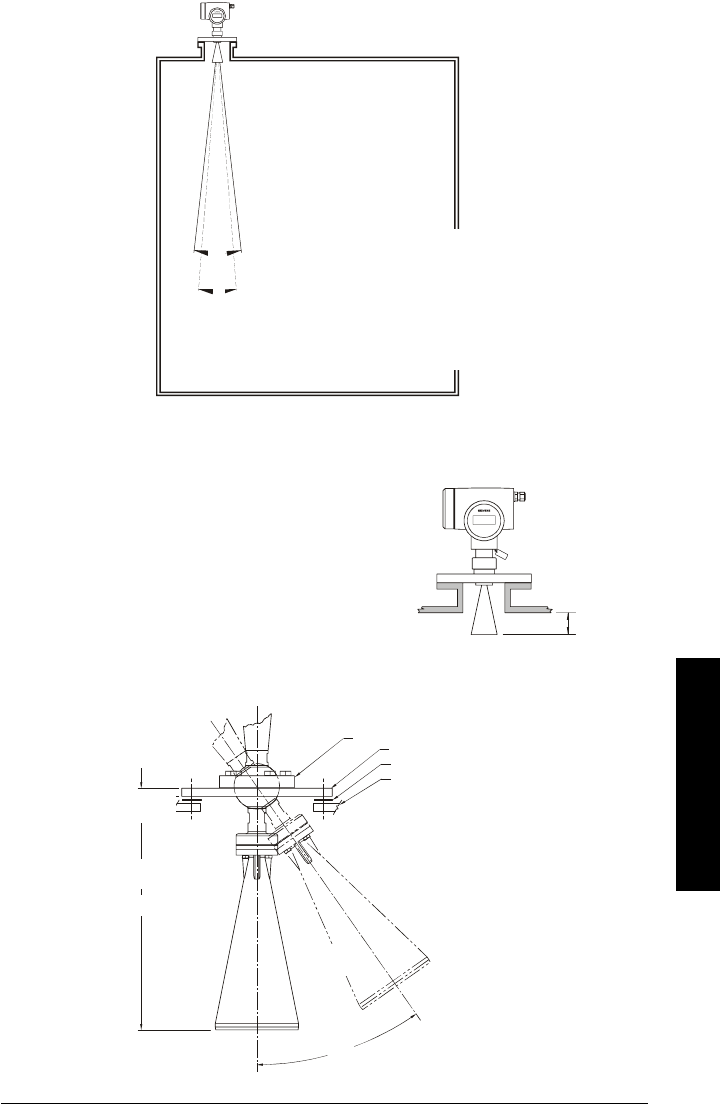
7ML19985FH04 SITRANS LR 400 – INSTRUCTION MANUAL Page 19
mmmmm
Installation
Beam Spreading
Correct Installation in Mounting Nozzle
The bottom edge of the antenna must project
into the vessel to avoid reflective interference
at the wall of the nozzle. Above flange size
DN 150/6", the antenna need not project beyond
the nozzle unless the radiation cone (the
extension of the antenna’s angle) touches the
nozzle wall.
Installation using Easy Aimer LR
SITRANS LR 400
13°
9°
Keep the emission cone
(9° or 13° depending on
configuration), free of
obstructions.
short horn antenna
long horn antenna
Updated graphic
required showing 2",
3" and 4" horn
SITRANS LR 400
10 mm
top clamping plate (upper socket)
bottom clamping plate (lower socket
)
customer gasket [recommended
thickness 1.5 to 1.8 mm (0.06 to
0.07")], as required
customer mounting plate with at
least ø 4" (102 mm) central
opening, as required
30°
max.
long horn 9.3"(235 mm)
short horn 7.4"(188 mm)
0.38"
(10 mm)
Graphic
labels to be
updated
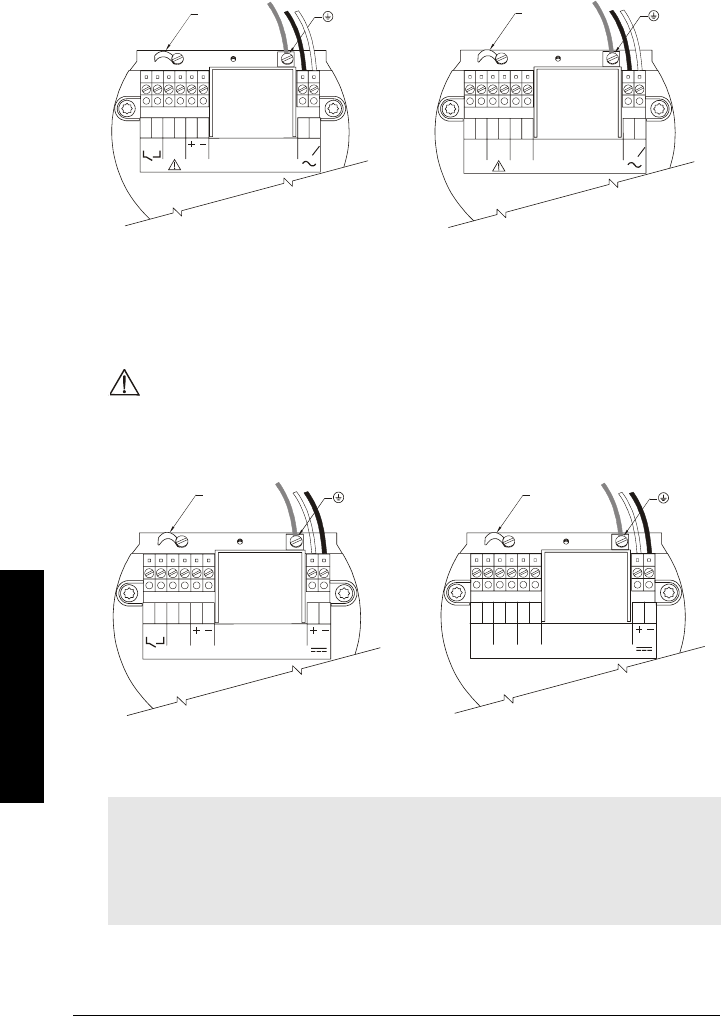
Page 20 SITRANS LR 400 – INSTRUCTION MANUAL 7ML19985FH04
mmmmm
Installation
Electrical Connection
AC version:
• The equipment must be protected by a 15A fuse or circuit breaker in the building
installation.
• A circuit breaker or switch in the building installation, marked as the disconnect
switch, shall be in close proximity to the equipment and within easy reach of the
operator.
All field wiring must have insulation suitable for at least 250 V.
DC version:
• DC input terminals shall be supplied from an SELV source in accordance with IEC
1010-1 Annex H.
Notes (AC and DC versions):
• 4-20 mA, PROFIBUS PA, DC input circuits, 14 - 20 AWG, shielded copper
wire
• AC input circuit, min 14 AWG copper wire
Recommended torque on terminal clamping screws, 0.5 - 0.6 Nm.
1264 5
378
L
1
L
2
N
mA
Rated temperature of
connection cables must
exceed m aximum ambient
temperature by at least 15 K
1264 5
378
L
1
L
2
N
Rated temperature of
connection cables must
exceed maximum ambient
temperature by at least 15 K
PROFI-
BUS PA
HART wiring PROFIBUS wiring
earth
terminal
earth
terminal
cable clamp cable clamp
1264 5
378
mA
19-3 0 V
Rated temperature of
connection cables must
exceed maximum ambient
temperature by at least 15 K
12645378
PROFI-
BUS PA
19-30 V
Rated temperature of
connection cables must
exceed m aximum ambient
temperature by at least 15 K
HART wiring PROFIBUS wiring
earth
terminal
earth
terminal
cable clamp cable clamp
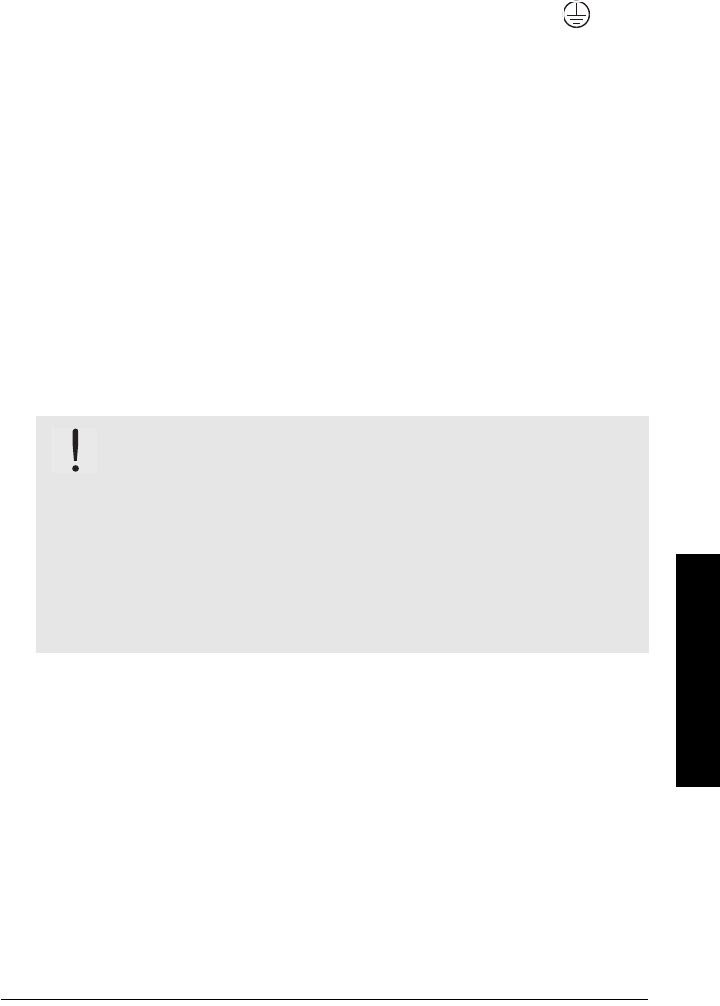
7ML19985FH04 SITRANS LR 400 – INSTRUCTION MANUAL Page 21
mmmmm
Installation
Connecting the SITRANS LR 400:
1. Release the cover lock on the connection box with a 3 mm Allen key.
2. Unscrew the cover from the connection box.
3. Push the power cable and signal cable through the cable gland on the right of the
unit, up to the terminal strip. Lay the cable in a bend before the cable gland so that
moisture cannot enter the connection box.
4. Connect the earth conductor of the power supply to the earth terminal in the
connection box. Adjust the cable length so that the earth conductor will be
disconnected last if you pull on the cable.
5. In devices with ignition protection types II 1/2G EEx dem [ia] IIC T6 and II 1/2G EEx
dem [ib] IIC T6 or II 2G EEx dem [ia] IIC T6 and II 2G EEx dem [ib] IIC T6 (Liquids
version), mount the cover for the power supply terminals.
6. Tighten the cable screw gland and check the strain relief (pull and turn).
7. In devices with ignition protection type II 1/2G EEx D IIC T6 or II 2G EEx d IIC T6
(Liquids version), replace unused screw-type cable glands with a certified dummy
plug.
8. Screw the cover onto the housing and tighten it without using a tool. The sealing
ring must be clean and undamaged.
9. Mount the cover lock of the connection box cover.
10. Connect the earth terminal located between the screw-type cable glands to a
ground connection at your vessel by using a cable of a cross-section at least
2.5 mm2.
For error-free communication via the HART protocol, a load of at least 230 Ω must be
available in the signal circuit.
WARNING:
• To avoid short-circuits, do not connect a load resistance with bare wires in
the connection box.
• The housing cover may not be unscrewed in a hazardous area when the
device is under voltage (power supply, digital outputs on external supply).
• In devices with ignition protection types II 1/2G EEx dem [ia] IIC T6 and II 1/
2G EEx dem [ib] IIC T6 II 2G EEx dem [ia] IIC T6 and II 2G EEx dem [ib]
IIC T6 (Liquids version), only the cover of the connection box may be
unscrewed for test purposes. The cover on the power supply terminals may
not be removed!
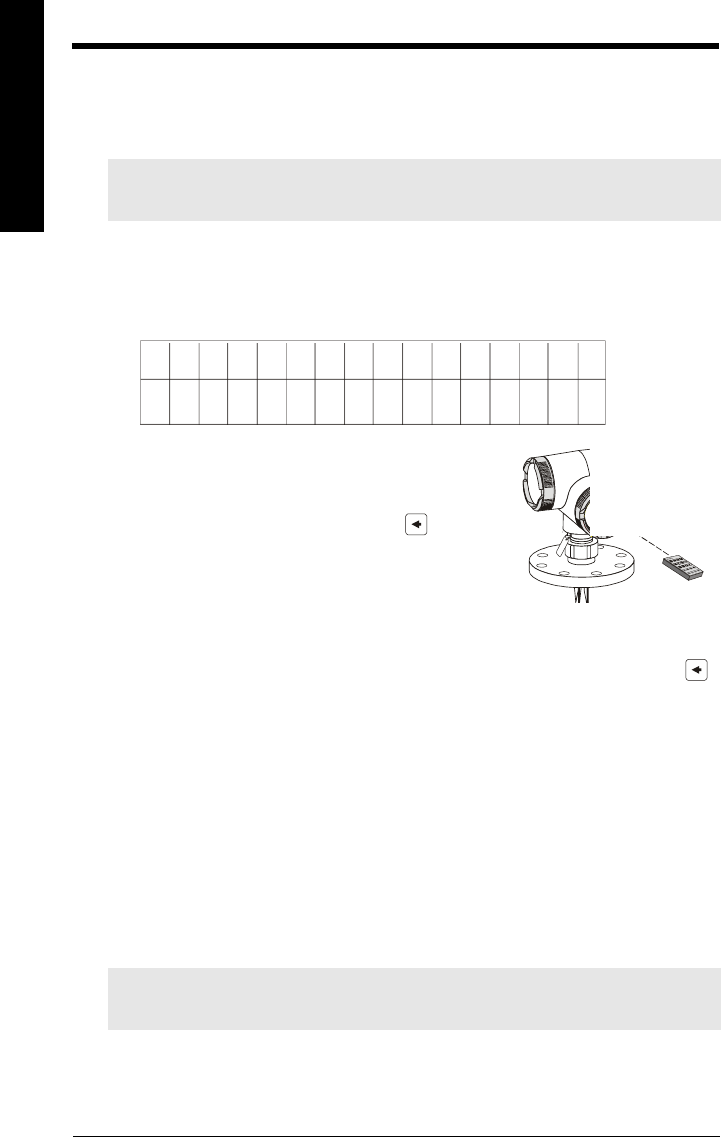
Page 22 SITRANS LR 400 – INSTRUCTION MANUAL 7ML19985FH04
mmmmm
Start Up
Start Up
Self-test
The device performs a self-test after power is supplied. Then, the unit is ready for
programming when the multi-display appears.
Multi-display
The multi-display shows on the LCD after a successful self-test with the output of the
level in the first line and the signal-to-noise ratio in the second line (factory setting):
Local Programming
When the multi-display appears on the LCD, begin
local programming using the hand programmer. To
access the parameter settings, press LEFT once.
Main Menu is displayed in the first line of the LCD.
Then program the unit beginning with the Auto-Setup
parameters.
Auto-Setup
After switching on the SITRANS LR 400, and after a successful self test, press LEFT
to access the parameters. Set the Auto-Setup parameters to make the system
operational: (see page 33)
• The language of the local user interface
• The unit of length of the measured level
• The nozzle height in the selected unit of length
•The vessel height in the selected unit of length
• The LRV as a distance from the bottom of the vessel
• The URV as a distance from the bottom of the vessel
• The damping of the measured level in sec
• The application type
• The bus-address by PROFIBUS PA communication (on PROFIBUS models)
Enter the necessary values as described in Parameters on page 33.
If the multi-display does not appear or displays incorrect measured values after Auto-
Setup, proceed as described in Troubleshooting on page 75.
Refer to the Parameter section that begins on page 32 for a list of available parameters.
Note: Frequent switching off and on of the device causes aging of the electronics
(see Parameter 3.1).
Note: It is strongly recommended that a Customer Code (Parameter 5.2) be entered
after all programming is completed to secure the programmed values from changes.
+1 2 300 m
bd03+
.
Updated
graphic
required
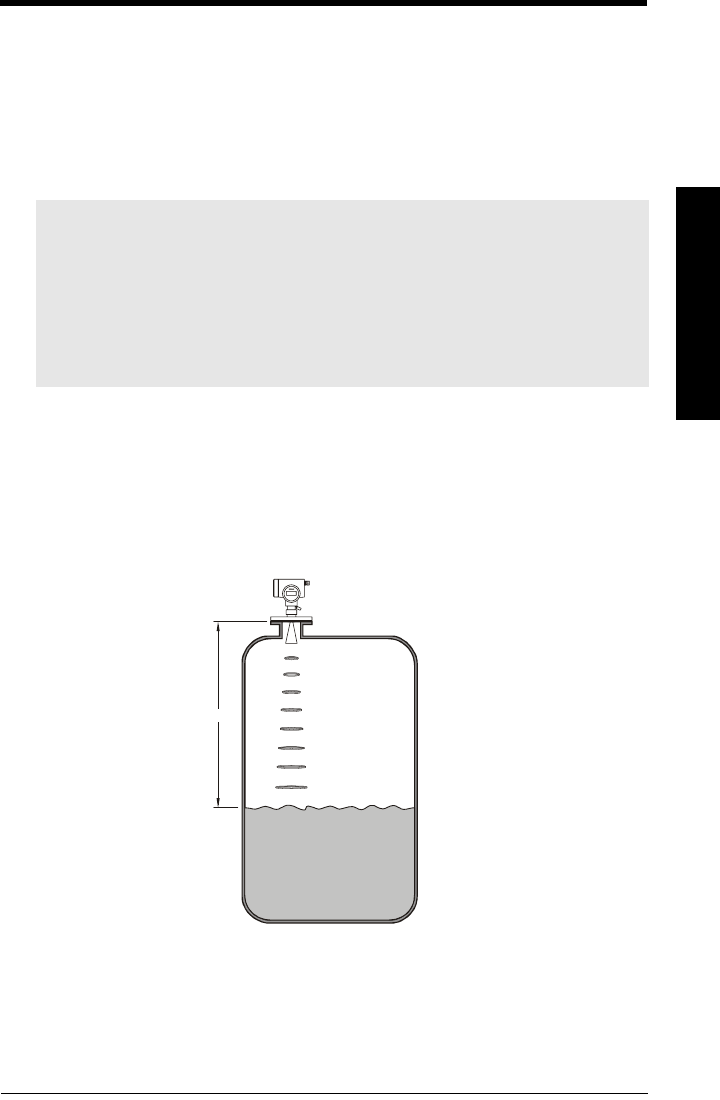
7ML19985FH04 SITRANS LR 400 – INSTRUCTION MANUAL Page 24
mmmmm
Operation
Operation
General Information
You can operate the SITRANS LR 400 with:
• Hand-held infrared programmer
• HART Communicator or PROFIBUS PA
• PC/Laptop and SIMATIC PDM software (recommended)
Measuring Principle
The SITRANS LR 400 operates according to the FMCW (Frequency Modulated Continuous
Wave) method. Its antenna sends microwaves to the surface of the measuring medium.
The wave frequency is modulated continuously (see Determining the Differential
Frequency on page 25). A receiver registers the reflection at the surface of the measuring
medium and links it with the simultaneously radiated signal.
The propagation speed of microwaves in gases corresponds to the speed of light. The
distance d is proportional to the propagation time t:
d= distance, t = measured time, c = speed of light
Notes:
• The SITRANS LR 400 can be operated and programmed most comfortably
with the SIMATIC PDM software. This software gives you the added
possibility of saving and archiving your application-specific parameters and
copying them back into the device if necessary.
• It is best to perform the operations described in the following sections
directly on the device to familiarize yourself with the operation.
SITRAN S LR 400
d
dct⋅
2
--------
=
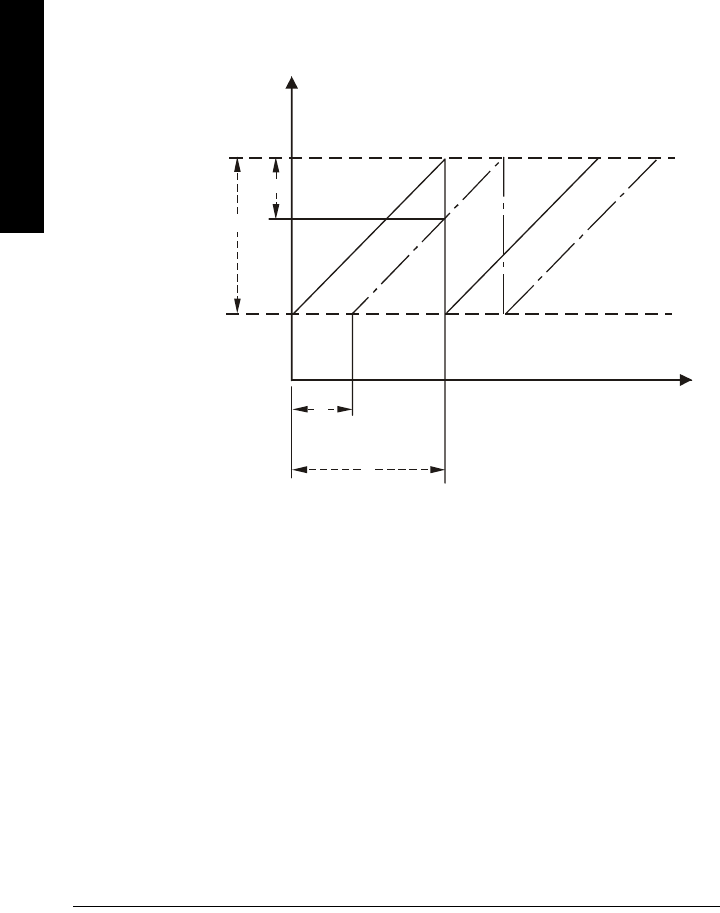
Page 25 SITRANS LR 400 – INSTRUCTION MANUAL 7ML19985FH04
mmmmm
Operation
As the transmission signal has changed its frequency until the reception signal arrives, the
linked signal gives a differential frequency fd, which is proportional to the distance d from
the reflecting surface.
The distance d is given by the ratio of the differential frequency fd to the frequency
deviation B and the duration of a frequency modulation phase T :
B = bandwidth (frequency deviation), d = distance, T = modulation duration,
c = speed of light
Determining the Differential Frequency
Example
The linear frequency deviation is 200 MHz at a modulation duration of 10 ms. The surface
of the measuring medium is 10 m away from the transmitting antenna. The difference
signal then has a frequency of:
Every reflection at a surface generates a different frequency. The reception signal
therefore consists of a frequency mix from which the disturbance frequencies must be
filtered. These can be caused by fixed targets like struts inside the vessel.
fd
2Bd⋅⋅
Tc⋅
------------------ d,fdTc⋅⋅
2B
-------------------
==
frequency
B
fd
t
T
time
transmission
signal
reception
signal
fd
2210
810⋅⋅ ⋅
10 3– 310
8
⋅⋅
----------------------------------13 333kHz,==
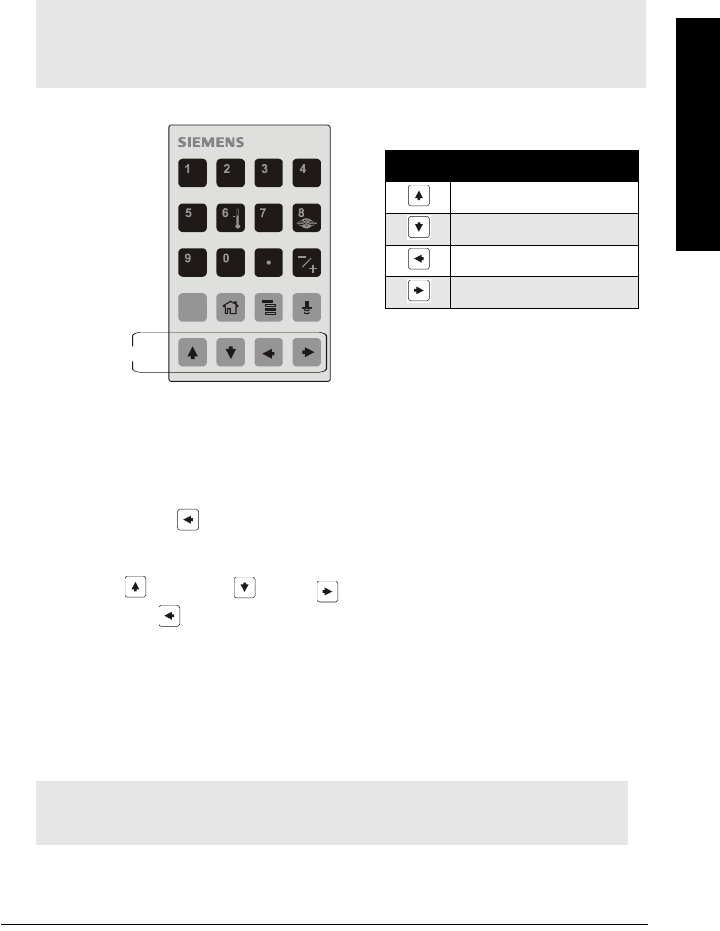
7ML19985FH04 SITRANS LR 400 – INSTRUCTION MANUAL Page 26
mmmmm
Operation
Operating the SITRANS LR 400
Use the arrow keys at the bottom of the hand programmer to program the SITRANS
LR 400. The two-line LCD displays the parameters. You can alter the setting or change to
other parameters using the arrows on the hand programmer (see page 27 for information
on navigating the menus using the arrow keys).
Hand Programmer
Selecting a Parameter
After a successful self-test, the SITRANS LR 400 displays the two-line multi-display.
Press LEFT ARROW to access the parameter menus. The first line of the display tells
you the current parameter menu level. The second line shows one of the parameters you
can access in the current parameter group. Scroll through the parameters in the group by
touching UP and DOWN . RIGHT accesses the parameter displayed on the
second line. LEFT closes this parameter and moves up one level until you return to the
multi-display.
When you select a parameter, its current value is displayed in the second line. When the
value flashes, programming is enabled, (see Disabling and Enabling Programming on
page 29) and you can change the current setting. If the parameter value cannot be
changed or if programming is disabled, the value will not flash.
Note: The ARROW buttons shown below are required for programming
this product. The additional buttons on the hand programmer do not
apply to the SITRANS LR 400.
Key Programming Mode
Parameter scroll UP
Parameter scroll DOWN
LEFT Arrow (or CANCEL)
RIGHT Arrow (or Enter)
Note: The background illumination of the LCD switches on as soon as you use a
button. It goes out about three minutes after last use of programming button.
C
SITRANS LR 400
buttons
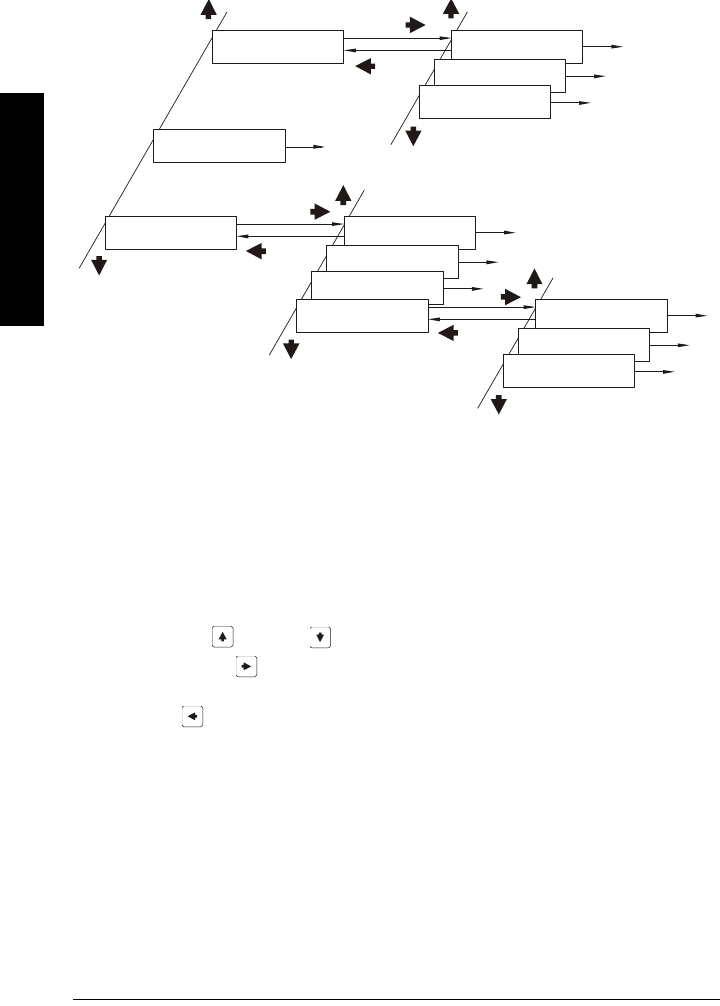
Page 27 SITRANS LR 400 – INSTRUCTION MANUAL 7ML19985FH04
mmmmm
Operation
Structure of Parameters
Operation is hierarchically structured: the parameters are arranged in groups and
assigned a numerical menu identification (see example below).
Changing a Parameter Value
Selecting a Parameter Value from a List
In many cases, you can assign a parameter a value from a list of options.
You will see a single item of the selection list in the second line of the display.
• Press UP or DOWN to cycle through the list and choose the desired entry.
Press RIGHT to assign the current entry to the parameter. The device accepts
the new setting, closes the input and returns to the next parameter level up.
• LEFT operates like a CANCEL key: When pressed, the device closes the
parameter input but keeps the originally displayed value. It does not save a changed
setting!
For an example of assigning a value from a selection list, see Operating Examples on
page 30.
Operating level 1
Operating level 2
Operating level 3
Function group
2 Display
Function group
3 Diagnostics
Function group
4 Device data
2. Display
1 Multi-display
2. Display
2 Level
2. Display
3 Volume
4. Device Data
1 Units
4. Device Data
2 Operating parameters
4. Device Data
3 Analog output
4. Device Data
3 Digital output
4.4 Digital output
1 Function DO
4.4 Digital output
2 Signal type DO
4.4 Digital output
3 Level parameters
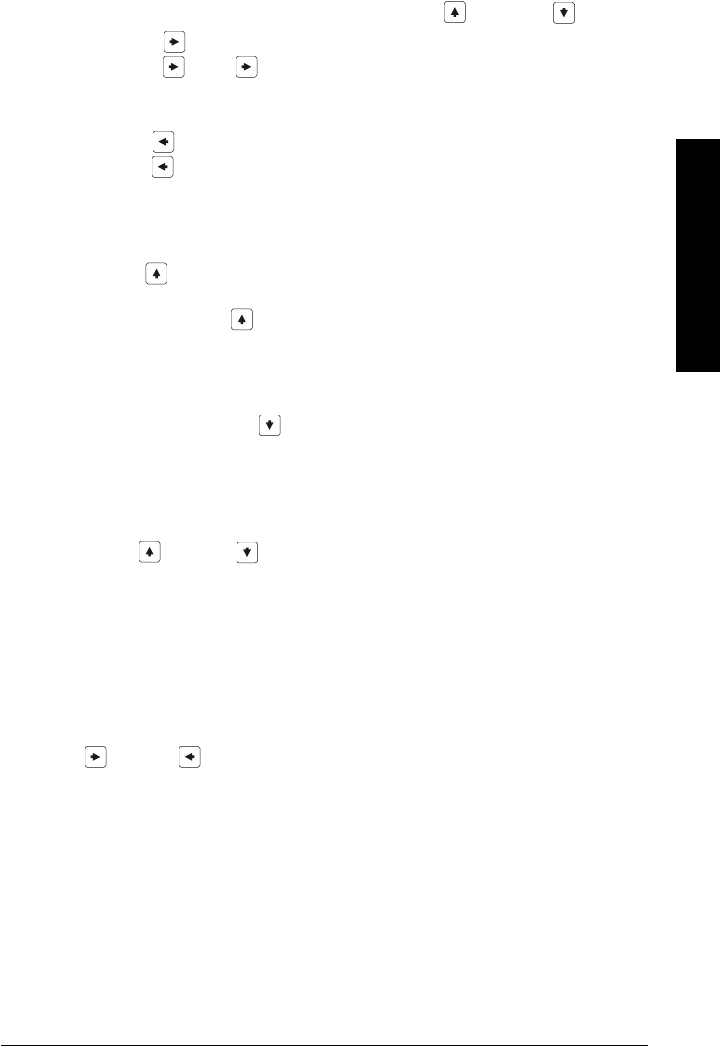
7ML19985FH04 SITRANS LR 400 – INSTRUCTION MANUAL Page 28
mmmmm
Operation
Entering a Parameter Value
The ARROW keys operate like a cursor control when entering a parameter value with the
input position marked by flashing of a single character.
• Increase or decrease a character’s value by using UP and DOWN .
• Press RIGHT to move the input position to the right. At the far right position,
press RIGHT again: operates like an ENTER key. The device saves the
changed value and closes the parameter unless the value is not within the
permissible input range. Then an error message is displayed.
• Press LEFT to move the input position to the left. At the farthest left position,
press LEFT again: it now functions as a CANCEL key. The device closes the
parameter input without saving the changed value.
Top or bottom of representable range
If you press UP when the value is at the top of the representable range,
SITRANS LR 400 automatically places the value at the next highest position. If 0.9 is
displayed and you press UP , the value becomes 1.0. So, 9 becomes 10, 90 or 99
become 100 (depending on whether you have set the input position to the second or first
9), etc.
This input system also works in the opposite direction: For example, when 100 is
displayed and you press DOWN on the first or second 0, the numeric value changes
to 90 or 99 and the device cancels the places in front of the decimal point.
Decimal point
You can also set the cursor to the decimal point (unless an integer value is currently
displayed). UP or DOWN then multiply or divide the displayed value by 10. The
necessary additional places in front of the decimal point appear. You cannot change the
number of displayed decimal places.
Display scrolling
Display text assigned to a parameter may sometimes be longer than the field of the
display. An arrow pointing outward on the right or left hand side of the display line
indicates that the text continues outside the display. You can move the text with
RIGHT and LEFT by moving the pointer past the end of the line, to allow you to
read the rest of the text.
See Operating Examples on page 30 for an example of manual input.
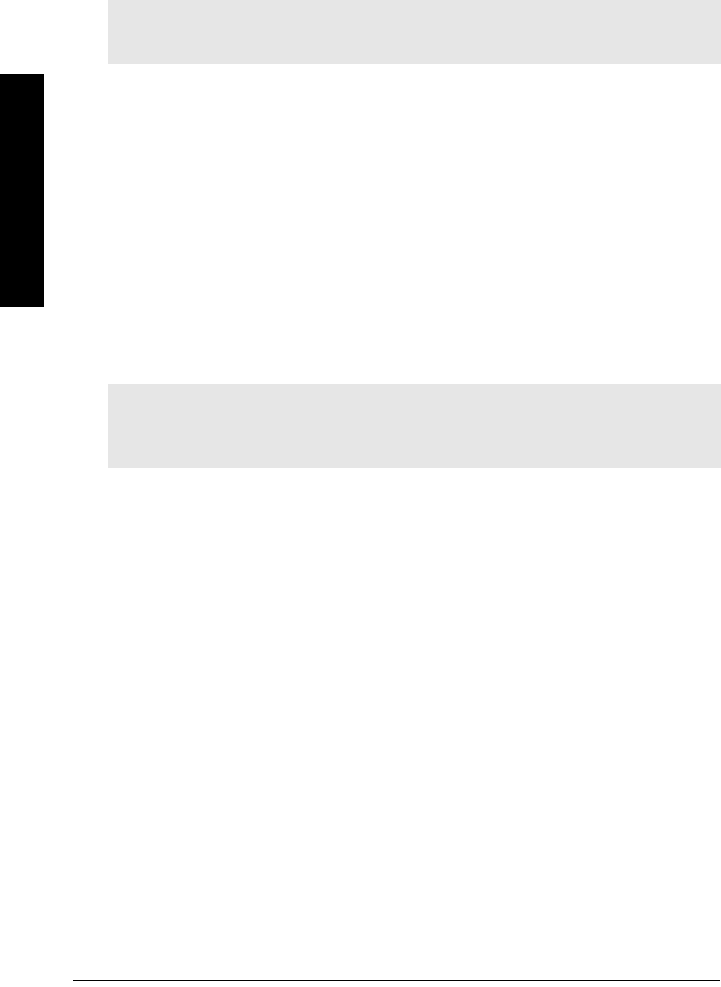
Page 29 SITRANS LR 400 – INSTRUCTION MANUAL 7ML19985FH04
mmmmm
Operation
Disabling and Enabling Programming
To prevent unauthorized personnel causing programming errors through the display
module, set a customer code – a personal, freely selectable code number up to 9 digits. A
device protected by a customer code still displays all functions and values but it requests
input of the code number before allowing a parameter to be reset.
Programming is enabled when you:
• enter the requested customer code for the current parameter. (Only the current
parameter is enabled for reprogramming. All the others are still waiting for input of
the customer code.)
or
• release the programming lock for all parameters at once using the Code Input
Parameter (see Parameter 5.1 on page 62).
The programming lock will be released for approximately 10 minutes.
When you return to the multi-display or enter a number in the Code Input parameter
which is different from the customer code, or do not operate the device for 10 minutes,
the programming lock is enabled.
Note: The customer code is activated 10 minutes after you have programmed
Parameter 5.2 Customer Code.
Note: If Customer Code (Parameter 5.2) is 0, programming of parameters is always
enabled. We strongly recommend that a customer code be entered after all
programming is completed to secure the programmed values from change.

7ML19985FH04 SITRANS LR 400 – INSTRUCTION MANUAL Page 30
mmmmm
Operation
Operating Examples
Example 1(HART)
The length unit should be changed from m to mm. The starting point is the multi-display.
Follow the bold path in the diagram above for input. The other paths lead to other device
functions and parameters which are not required in this example. Use the arrow buttons
shown next to the numbered operating steps.
1
Function group
1 Auto-Setup
+12,300 m
+30 dB
Function group
2 Display
Function group
3 Diagnostics
Function group
4 Device data 4. Device data
1 Units
4.1 Units
1 Length Unit 4.1.1 Length unit
m
4.1.1 Length unit
mm
4. Device data
2. Operating param.
4. Device data
3 Analog output
4.3 Analog output
1 AO select
4.3.1 AO select
Level
4.3 Analog output
2 Level param.
4.3.2 Level param.
1 Level URV
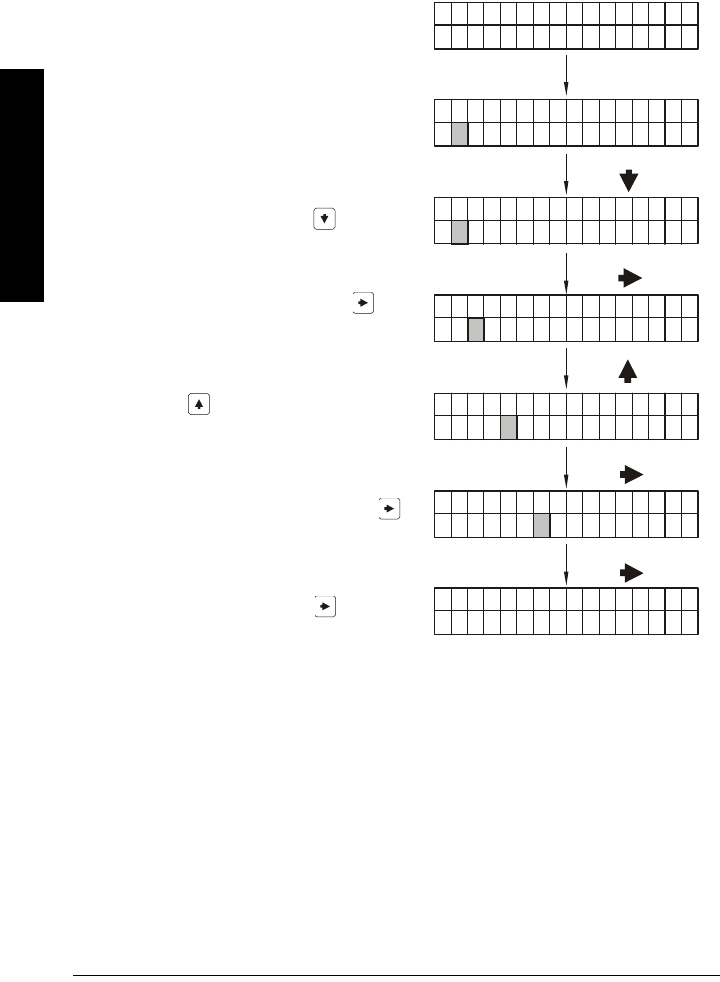
Page 31 SITRANS LR 400 – INSTRUCTION MANUAL 7ML19985FH04
mmmmm
Operation
Example 2
The filling speed should be changed from 2.0 cm/min to 100 cm/min.
Access the Fill speed parameter from the multi-display according to instructions on
page 27.
4.
4.
4.
4.
4.
4.
4.
+
5
2.
2.
2.
2.
2.
2.
2.
2.
2+0,
1+,
1+0,
1
1 x
1 x
1 x
2 x
2 x
0+
1,+
c
c
c
c
c
c
0
0
0000
0
000,
00
2.
2.
2.
2.
2.
2.
2.
5.
5.
5.
5.
5.
5.
0
f
f
f
f
f
f
M
f
i
i
i
i
i
i
e
i
m
m
m
m
m
m
l
l
l
l
l
l
a
l
/
/
/
/
/
/
l
l
l
l
l
l
s
l
m
m
m
m
m
m
i
i
i
i
i
i
u
i
i
i
i
i
i
i
n
n
n
n
n
n
r
n
n
n
n
n
n
n
g
g
g
g
g
g
.c
g
s
s
s
s
s
s
o
s
p
p
p
p
p
p
n
p
e
e
e
e
e
e
d
e
e
e
e
e
e
e
it
ed
The default setting appears in the display.
Enable the programming.
The second segment of the second display
line flashes.
Set the digit to 1 with DOWN arrow.
Select the decimal point with RIGHT
arrow.
Press UP arrow twice so that two other
places appear in front of the decimal point.
Select the last decimal place with RIGHT
arrow.
And end the input with RIGHT arrow
(ENTER function).
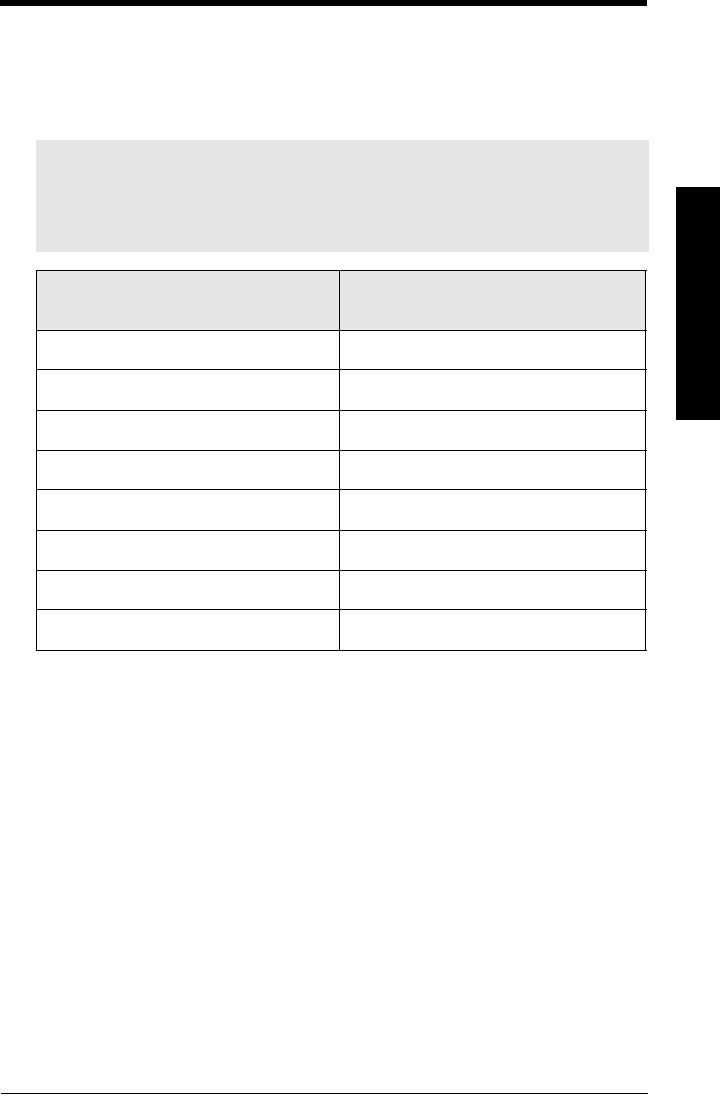
7ML19985FH04 SITRANS LR 400 – INSTRUCTION MANUAL Page 32
mmmmm
Operation
Parameters (HART)
The parameter groups are followed by the parameters within each group. The parameter
tables show the values you need to enter and are followed by additional information
when necessary. Factory settings are displayed after the parameter name, where
applicable.
Note: Parameter menus are dependent on selections made by the user.
In some cases, parameter menus are renumbered according to the
selection made at the previous menu level. See table below for an
example.
When User chooses Parameter 4.2.2.1:
Application Type = Liquids (Process)
When User chooses Parameter 4.2.2.1:
Application Type = User tank1
4.2.2.2: Surface (not available when 4.2.2.1 = User tank1)
4.2.2.3: Deadband 4.2.2.2: Deadband
4.2.2.4: Correction Factor 4.2.2.3: Correction Factor
4.2.2.5: Filling Speed (not available when 4.2.2.1 = User tank1)
4.2.2.6: Reflectivity (not available when 4.2.2.1 = User tank1)
4.2.2.7: Failsafe Level 4.2.2.4: Failsafe Level
4.2.2.8: Failsafe Timer 4.2.2.5: Failsafe Timer
4.2.2.9: Range Extension 4.2.2.6: Range Extension
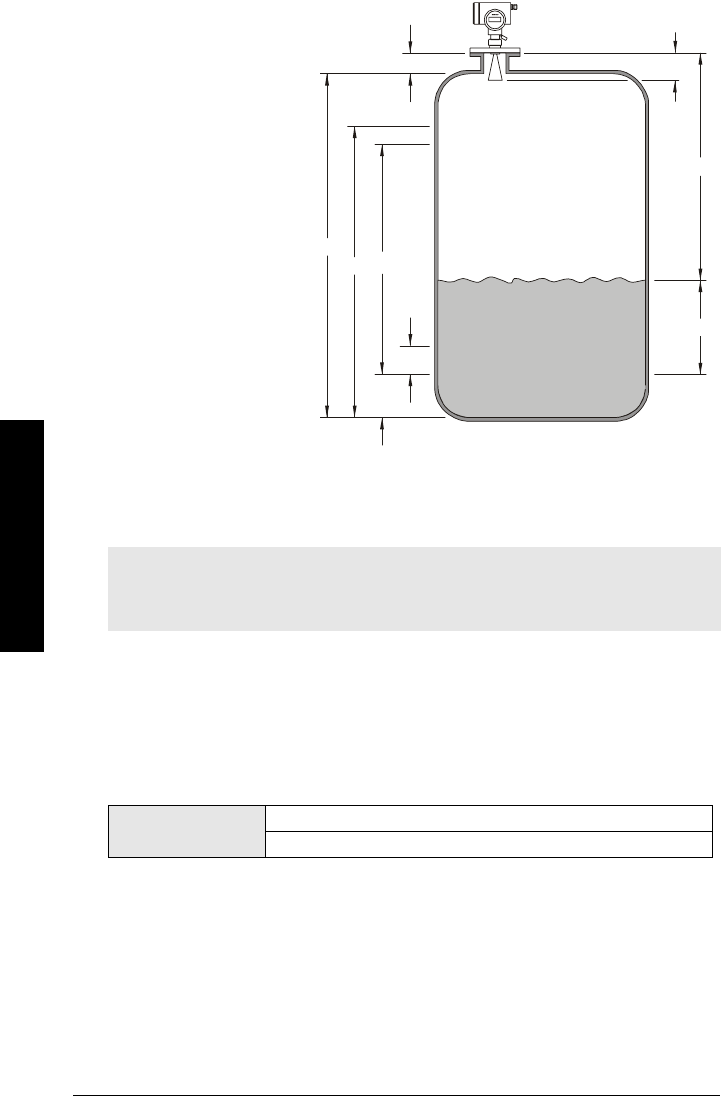
Page 33 SITRANS LR 400 – INSTRUCTION MANUAL 7ML19985FH04
mmmmm
Parameters (HART)
Functional Dimensions
Required Parameters
1. Auto-Setup
1.1: Language Local (F = English)
Language of the local user interface
Note: The following parameters are absolutely essential for proper operation of the
device. They apply to all applications and are required to make the system
operational.
Value English
Deutsch
SITRAN S LR 400
1. Nozzle height
2. Dead band
3. Raw value (measured)
4. Level (=calculated value)
5. Lower range value
6. Lower limit
7. Upper limit
8. Upper range value
9. Vessel height
1
2
3
4
5
6
7
8
9
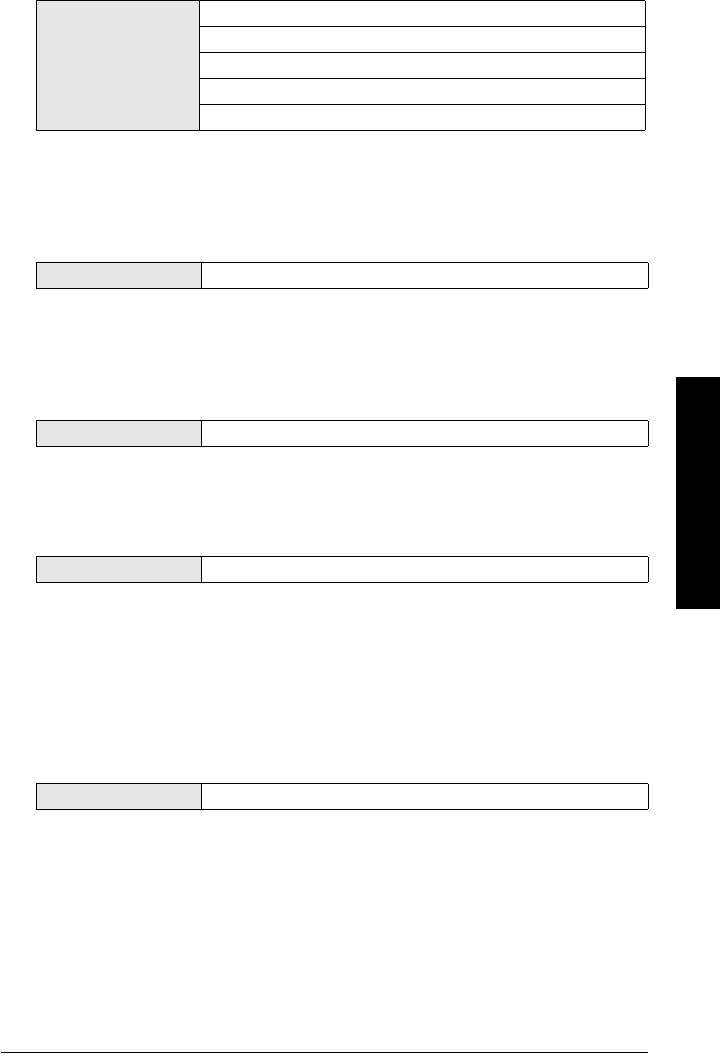
7ML19985FH04 SITRANS LR 400 – INSTRUCTION MANUAL Page 34
mmmmm
Parameters (HART)
1.2: Length Unit (F = m)
Units of measurement
1.3: Nozzle Height (F = 0 m)
Length of nozzle from top of flange to top of vessel (see Functional Dimensions on page
33)
1.4: Tank Height (F = 20 m)
Height of vessel from bottom of nozzle to bottom of vessel (see Functional Dimensions on
page 33)
1.5: Level URV (F = 20 m)
Full scale of level (see Functional Dimensions on page 33)
Set the URV as the level above the bottom of the vessel (see Functional Dimensions on
page 33) in the units system selected with Function 4.1.1. It corresponds to an output
current of 20 mA.
1.6: Level LRV (F = 0 m)
Empty scale of level (see Functional Dimensions on page 33)
Set the LRV as the level above the bottom of the vessel (see Functional Dimensions on
page 33) in the units system selected with Function 4.1.1. It corresponds to an output
current of 4 mA.
Value
cm
m
mm
ft
in
Value numerical value
Value numerical value
Value numerical value
Value numerical value
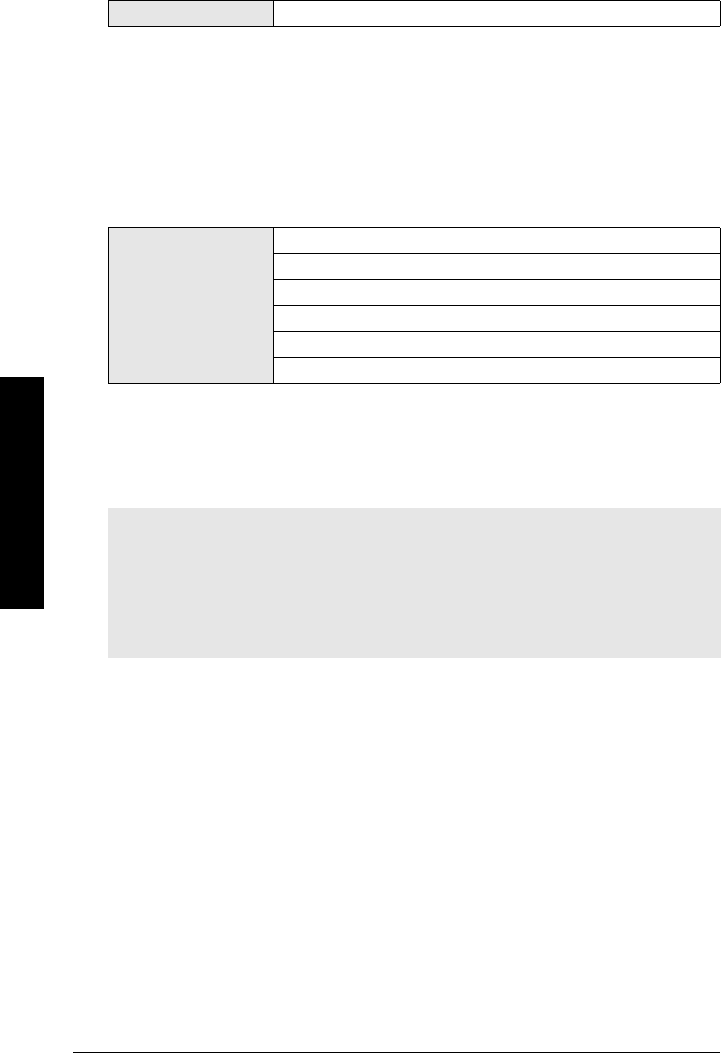
Page 35 SITRANS LR 400 – INSTRUCTION MANUAL 7ML19985FH04
mmmmm
Parameters (HART)
1.7: Level damping (F = 1 s)
Damping of level in s
Set the damping of the level value in seconds. It acts on the analog output, the limit value
monitor and the local display. For damping of the sensor signal, set Parameter 4.2.3.1. For
slow moving solids applications, use a value of 500.
1.8: Application Type (F - Liquid [process])
Use of the vessel
Select Silo1 (solids) for tall, narrow silos. Select Silo 2 (solids) for large diameter silos,
typically used for cement. In most cases, you set one of the pre-specified applications.
The user vessels may adopt configurations which deviate from the factory settings.
These are designed for special applications loaded at the factory or by service personnel.
Additional Parameters
2. Display
2.1: Multi-display (F = level in m
Signal to noise ratio in db)
Display of two measured values. Values are determined in Parameter 4.5.1.1 (Line 1 Local)
and in Parameter 4.5.1.4 (Line 2 Local).
2.2: Level (F = m)
Current level of measured medium (set unit using Length Unit in Auto-Setup)
Value numerical value
Value
Liquid (store)[Liquid]
Liquid (process)[Liquid]
Silo1 (solids)
Silo2 (solids)
User tank1
User tank2
Note: The following parameters cannot be accessed when you set a user vessel:
Parameter 4.2.2.2 (Surface), Parameter 4.2.2.5 (Filling Speed), Parameter 4.2.2.6
(Reflectivity), and Sensor Parameters 4.2.3.1 (Sensor Damping), 4.2.3.2 (Multiple
Echoes), 4.2.3.3 (Echo Motion), 4.2.3.4 (Window Tracking), and 4.2.3.5 (Tank Empty
Detect). However, the parameters that remain under 4.2.2.x will be renumbered. See
page 32 for more information on parameter renumbering.
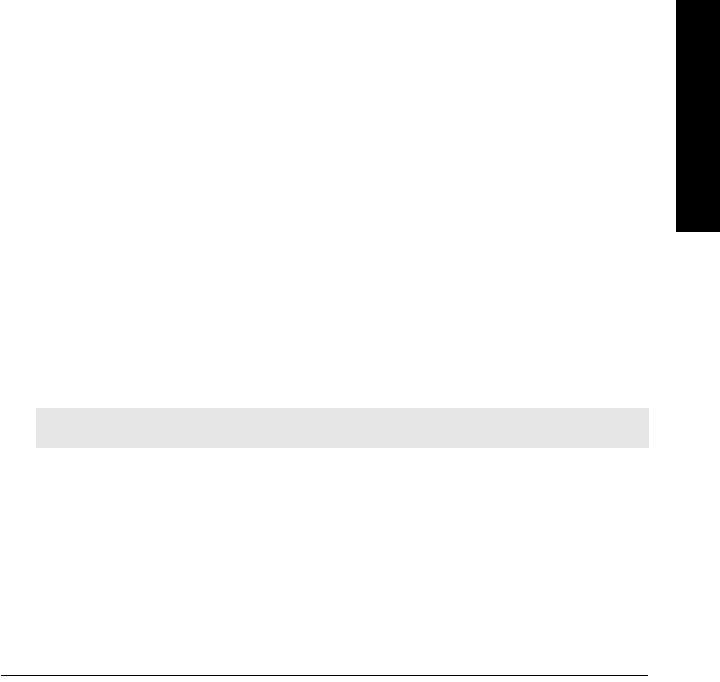
7ML19985FH04 SITRANS LR 400 – INSTRUCTION MANUAL Page 36
mmmmm
Parameters (HART)
2.3: Volume (F = m3)
Volume of measured medium (set unit using Parameter 4.1.2 [Volume Unit])
2.4: Mass (for qualified personnel only)
This parameter is for Factory Authorized Personnel Only.
2.5: Current Output
Value of the analog output in mA
When the device electronics are working properly, the displayed current value will
correspond to the measured output current.
2.6: Digital Output
State of digital output
3. Diagnostics
3.1: Status
Here you can access current status messages of the device. Parameter 3.1.1 is always
accessible; other parameters (Parameter 3.1.x) appear in the appropriate order if they
contain error messages.
3.1.1: Wear
3.1.1.1: Operating Hours
Total previous operating time of the device in hours (approximate value)
3.1.1.2: Maximum Temperature (F = 26 °C)
Previous maximum internal temperature of the device
3.1.1.3: Minimum Temperature (F = 26 °C)
Previous minimum internal temperature of the device
3.1.1.4: Aging
Approximate value for the previous life of the device in % (100% = approx. 10 years)
Note: This temperature must not exceed 85 °C (185 °F) or warranty may be void.
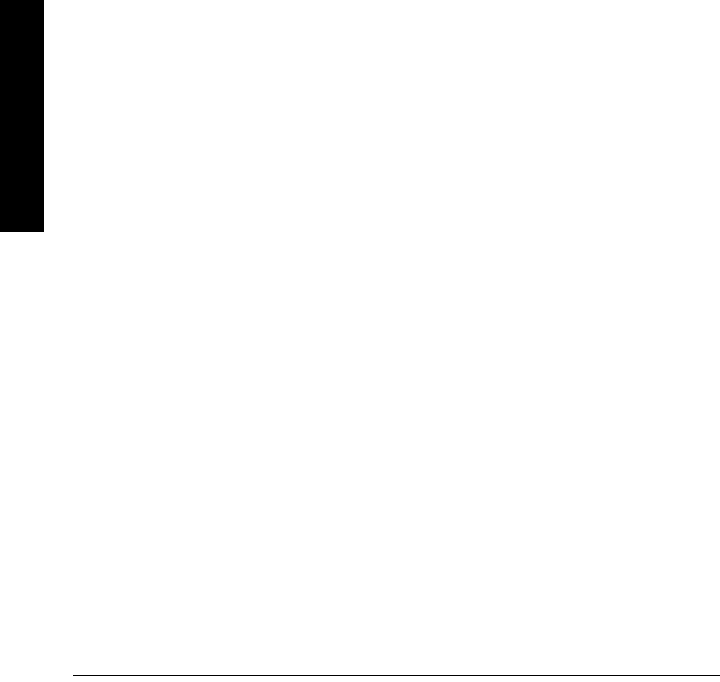
Page 37 SITRANS LR 400 – INSTRUCTION MANUAL 7ML19985FH04
mmmmm
Parameters (HART)
This parameter outputs a calculated percentage which estimates the wear of the device
due to aging.
3.1.1.5: Hours > 85 °C
Total time the maximum permissible internal temperature was exceeded, in hours
3.1.x: Sensor, electronics, software, application, parameters,
service
These parameters are only displayed if they contain an error message. The number of the
menu items matches the number of defective functions and can range in extreme cases
from 3.1.2 to 3.1.7.
See Troubleshooting on page 75 for the individual error messages and possible remedies.
3.1.x: Sensor
Diagnostic messages of the sensor
and/or
3.1.x: Electronics
Diagnostic messages of the electronics
and/or
3.1.x: Software
Diagnostic messages of the software
and/or
3.1.x: Application
Diagnostic messages to the application
and/or
3.1.x: Parameters
Display of the false parameters
and/or
3.1.x: Service
For service purposes only
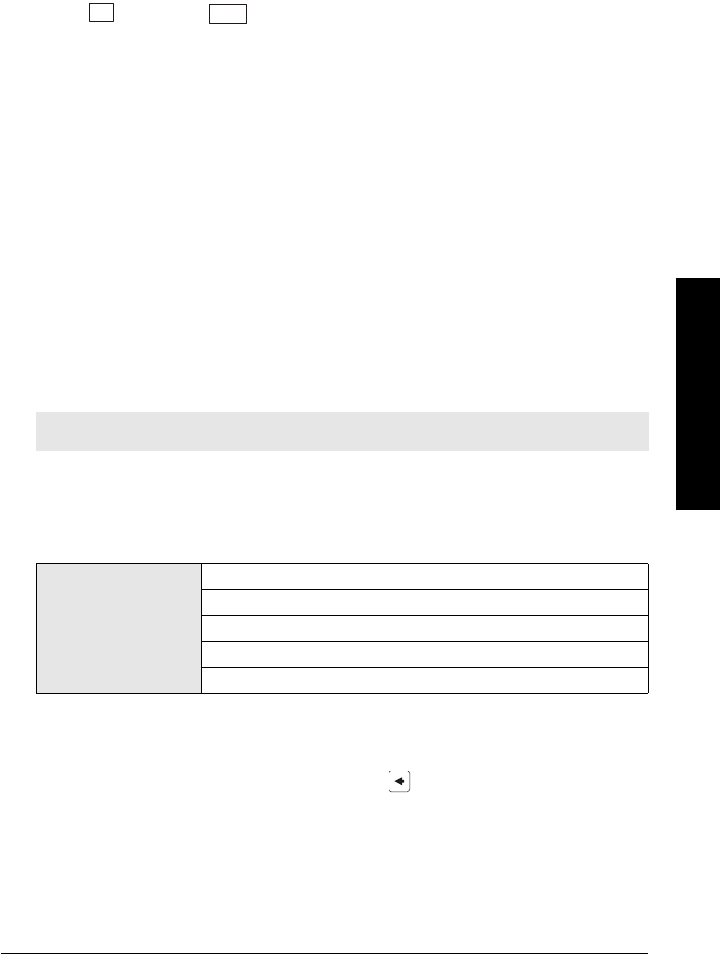
7ML19985FH04 SITRANS LR 400 – INSTRUCTION MANUAL Page 38
mmmmm
Parameters (HART)
3.2: Device Test
3.2.1: Self-test
Check device state
The device integrates the self-test routines in the ongoing measurements; it completes
them after approximately 10 seconds. It confirms a successful self-test with the
display . The display signals an error. Read out the error type according to
Parameter 3.1.x.
3.2.2: Display test
Visual check of LCD
During the test of the LCD, the display first goes blank for 5 seconds and then lights up for
another 5 seconds so that you can determine whether individual display points have
failed.
3.3: Simulation
This parameter can support testing the correct functions of the connections during
commissioning or maintenance of the device. With the two sub-parameters, you can
temporarily replace the measured values at the analog and digital output with known
simulated output values.
3.3.1: Simulate AO (F = 4 mA)
Simulation of the analog output signal
When this parameter is accessed and a value is entered, the device sets the defined
current value that can be validated.
Complete the parameter function by pressing LEFT so the analog output again gives
the measured value.
Note: The Simulation parameter influences output to the control system.
Value
4 mA
10 mA
12 mA
20 mA
Error signal
OK
not OK
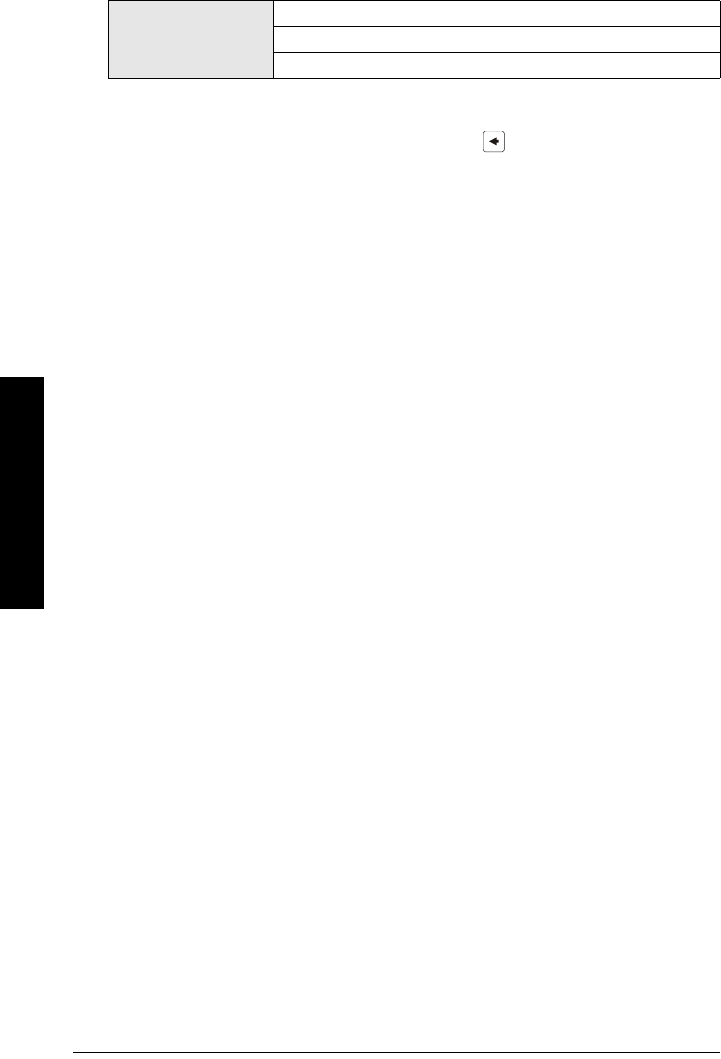
Page 39 SITRANS LR 400 – INSTRUCTION MANUAL 7ML19985FH04
mmmmm
Parameters (HART)
3.3.2: Simulate DO (F = End)
Simulation of the digital output signal
Select the applied output value (relay on or relay off).
The parameter function is completed by pressing LEFT so that the digital output again
gives an alarm/limit.
3.4: Sensor Variables
You can read out device-internal data with this parameter group. The displayed values
depend on the respective application. You can access the following data:
3.4.1: Raw Value (for service purposes only)
Distance from the flange to measuring medium
The measured distance from the flange to the surface of the measuring medium.
3.4.2: Echo Amplitude
Measure of quality of reflection
This dimensionless value is an absolute measure of the strength of reflection at the
measuring medium. Its display can be evaluated as follows:
•x > 1: very good
•1 > x > 0.5: good
•0.5 > x > 0.05: satisfactory
•x < 0.05: uncertain
3.4.3: S/N Ratio
Signal-to-noise ratio of the measured value in dB
S/N ratio provides a relative measure of the strength of reflection of the measuring
medium in dB. Its display can be evaluated as follows:
•x > 20: very good
•20 > x > 10: good
•x < 10: satisfactory
Value
Relay on
Relay off
End
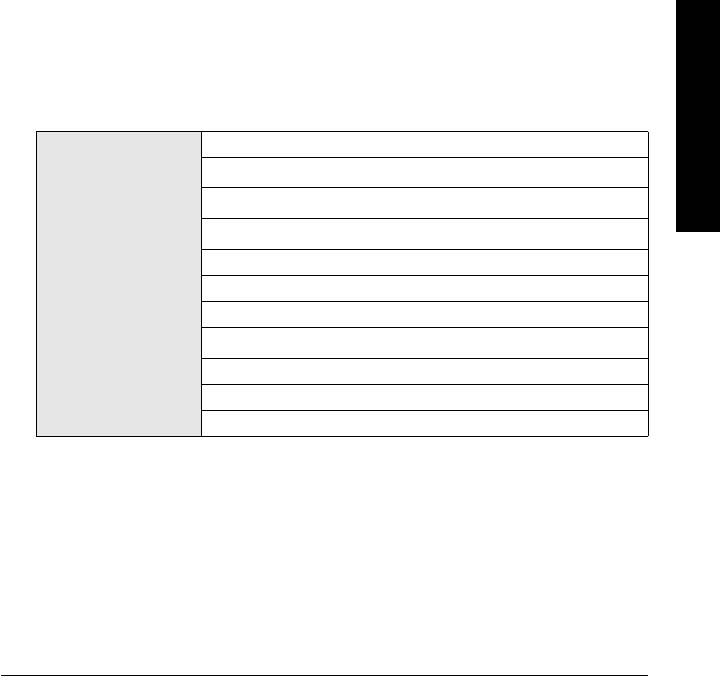
7ML19985FH04 SITRANS LR 400 – INSTRUCTION MANUAL Page 40
mmmmm
Parameters (HART)
3.4.4: Validity
Validity of the measured value in %
This parameter provides a percentage measure of the certainty that the displayed
measured value corresponds to the real level and does not represent a multiple echo or a
fixed target. Its display can be evaluated as follows:
•x > 70: very good
•70 > x > 50: good
•50 > x > 20: uncertain
•x < 20: no plausible measured value
3.4.5: Sensor Temp
Sensor temperature
4. Device Data
4.1: Units
4.1.1: Length Unit = Parameter 1.2
4.1.2: Volume unit (F = m3)
4.1.3: Mass Unit (for qualified personnel only)
This parameter is for Factory Authorized Personnel Only.
Value
bbl
yd3
ft3
in3
bush
bbl (liq)
l
m3
hL
Gal
ImpGal
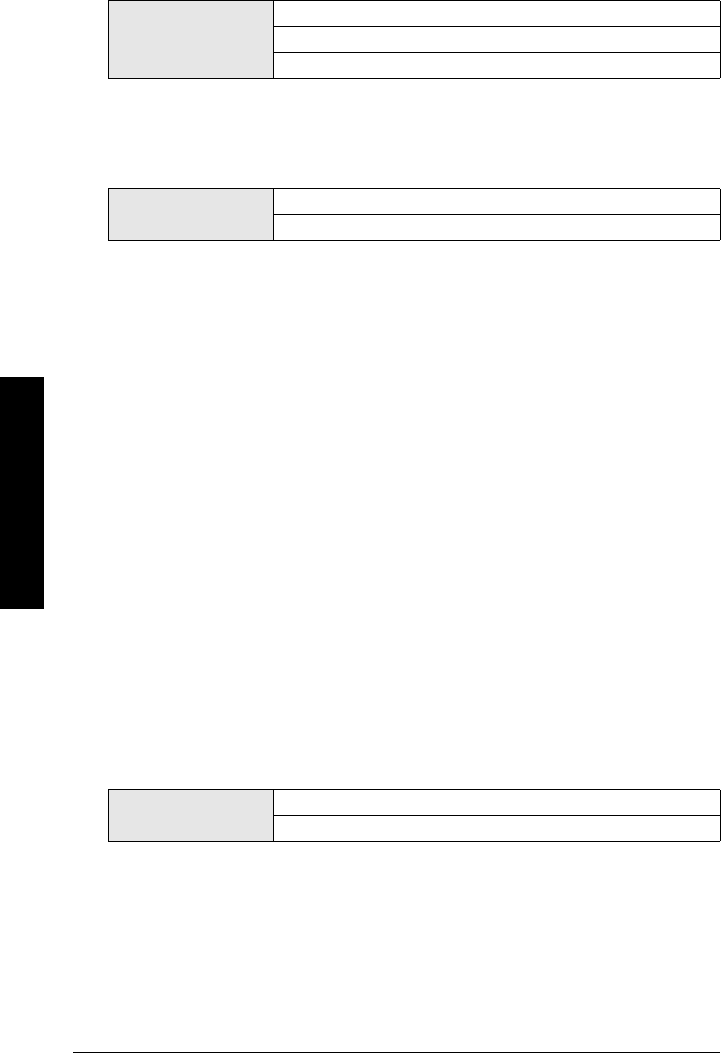
Page 41 SITRANS LR 400 – INSTRUCTION MANUAL 7ML19985FH04
mmmmm
Parameters (HART)
4.1.4: Temperature Unit (F = °C)
Unit of the sensor temperature
4.1.5: Other units (F = SI)
Units system for all other units
With this function, determine whether you want to enter the operating parameters (see
Parameter 4.2) in SI or in British Imperial (US/UK) units. The selected units of the
measured value output and sensor temperature as well as the decimal point are not
influenced by this setting.
4.2: Operating Parameters
With this parameter group, define the parameters of your vessel, the measuring medium
and the calculation of the measured signal. Signal-specific default settings such as the
failure signal or the upper current limit of the analog output signal are assigned to the
functions of the respective outputs (see Parameters 4.3 and 4.4).
4.2.1: Tank Geometry
4.2.1.1: Nozzle Height = Parameter 1.3
4.2.1.2: Tank Height = Parameter 1.4
4.2.1.3: Stilling Pipe? (F = no) [Liquids]
Stilling pipe available?
By selecting yes or no, you specify whether the device is mounted on a stilling pipe. If you
select yes, Parameter 4.2.1.3.2 is enabled so you can specify the internal diameter of the
stilling pipe.
Value
°C
°F
K
Value SI unit
US/UK unit
Value Yes
No
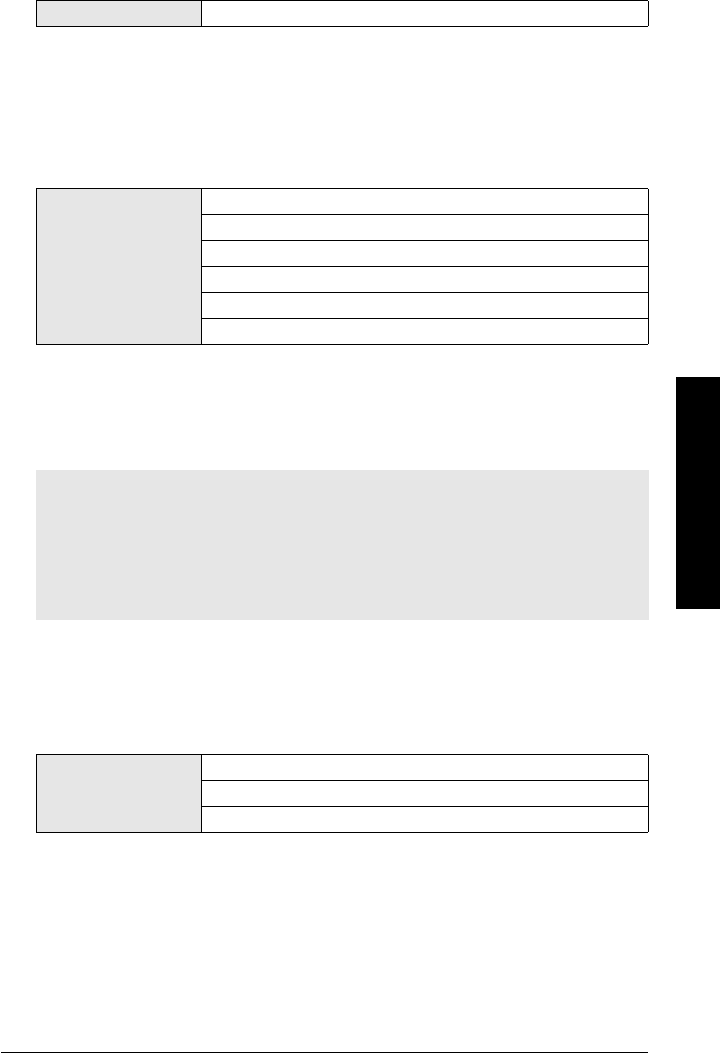
7ML19985FH04 SITRANS LR 400 – INSTRUCTION MANUAL Page 42
mmmmm
Parameters (HART)
4.2.1.3.2: Pipe Diameter (F = 100 mm) [Liquids]
Internal diameter of the stilling pipe
4.2.2: Measuring Conditions
4.2.2.1: Application Type (F - Liquid [process])
Use of the vessel
Select Silo1 (solids) for tall, narrow silos. Select Silo 2 (solids) for large diameter silos
typically used for cement. In most cases you set one of the pre-specified applications
here. The user vessels may adopt configurations which deviate from the factory settings.
These are designed for special applications loaded at the factory or by service.
4.2.2.2: Surface (F = wavy)
Surface structure of the measuring medium. Not displayed if a user vessel is selected in
Parameter 4.2.2.1.
This parameter is not displayed when a user vessel is selected in Parameter 4.2.2.1. When
used with poorly reflecting measuring media, you may be able to improve measuring
results by setting a different surface structure here. If your measuring medium forms
waves more than 1 cm in height, you should select the wavy setting. The turbulent setting
is recommended for waves greater than 10 cm.
Value numerical value
Value
Liquid (store) [Liquids]
Liquid (process) [Liquids]
Silo1 (solids)
Silo2 (solids)
User tank1
User tank2
Note: The following parameters cannot be accessed when you set a user vessel:
Parameter 4.2.2.2 (Surface), Parameter 4.2.2.5 (Filling Speed), Parameter 4.2.2.6
(Reflectivity), and Sensor Parameters 4.2.3.1 (Sensor Damping), 4.2.3.2 (Multiple
Echoes), 4.2.3.3 (Echo Motion), 4.2.3.4 (Window Tracking), and 4.2.3.5 (Tank Empty
Detect). However, the parameters that remain under 4.2.2.x will be renumbered. See
page 32 for more information on parameter renumbering.
Value
Smooth
Wavy
Turbulent
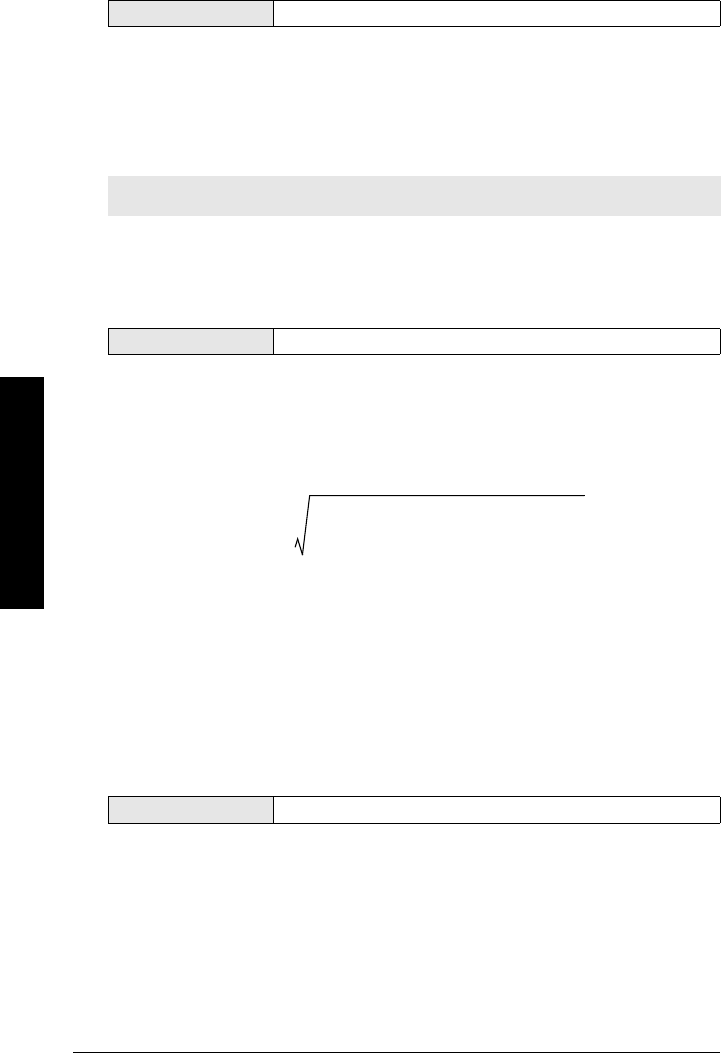
Page 43 SITRANS LR 400 – INSTRUCTION MANUAL 7ML19985FH04
mmmmm
Parameters (HART)
4.2.2.3: Dead band (F = 0.4 m)
Area below the flange in which measured values are ignored
Specification of a dead band in the units system selected according to Parameter 4.1.5
defines a minimum distance from the flange which the measuring medium must have for
the device to accept the measured values as valid. This suppresses reflective
interference generated by the nozzle, close obstacles, or the antenna.
For solids applications, a dead band setting of 1 m minimum is recommended
4.2.2.4: Correction Factor (F = 1.0)
Correction factor for physical measuring influences
The propagation time of the microwaves between the antenna and the measuring
medium changes slightly depending on the pressure inside the vessel. If this pressure is
constant, however, it can be included in the evaluation according to the equation:
K = correction factor, p = pressure inside the vessel in bar, Tgas = gas temperature in °C,
εr, G as = dielectric of the overlying gas, e.g. ερ, air = 1.00059
Enter the correction factor K as a dimensionless value.
4.2.2.5: Filling Speed (F = 200 mm/min)
Typical speed of change of the level. Not displayed if user vessel is selected in Parameter
4.2.2.1 (Application Type).
This parameter is not displayed when a user vessel is selected in Parameter 4.2.2.1. When
you determine that the displayed measured value does not follow the change in the
height of the level in the vessel, you can enter a value for the speed with which it
generally changes. This assigns a greater probability to measuring targets which move at
this speed.
Value numerical value, Minimum value = Length of the antenna
Note: The dead band should exceed the antenna’s length.
Value numerical value
Value numerical value
K1
1εrGas,1–()+273 p⋅
TGas 273+
--------------------------
⋅
-------------------------------------------------------------------------
=
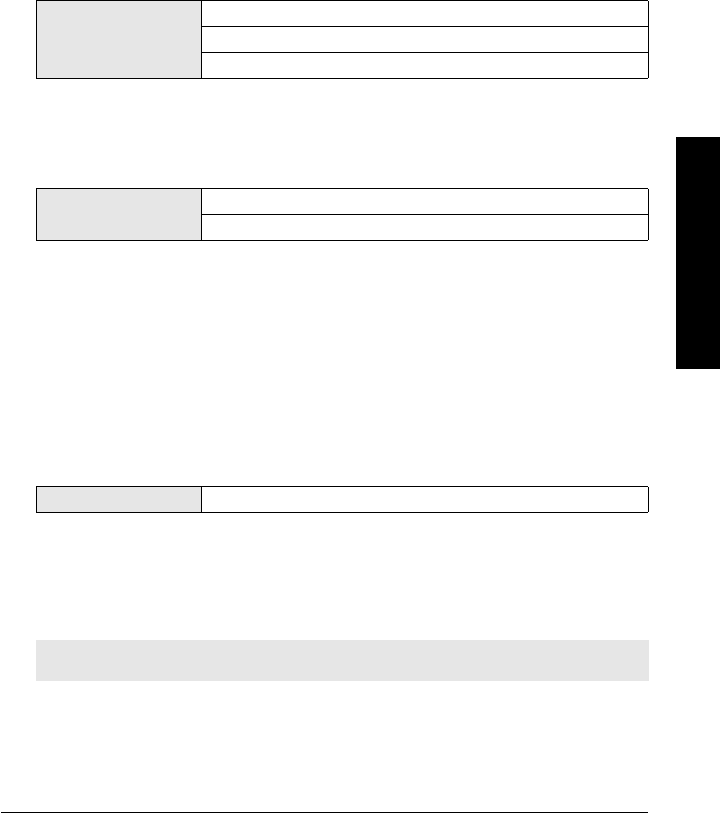
7ML19985FH04 SITRANS LR 400 – INSTRUCTION MANUAL Page 44
mmmmm
Parameters (HART)
If the display does not follow the level height continuously but in abrupt jumps, you should
choose a higher filling speed. If multiple echoes are indicated during filling/emptying a
vessel, select a lower filling speed. In the case of very low filling speeds (a few mm/min)
switch off Parameter 4.2.3.3. If different filling/emptying speeds occur, select the higher
speed.
4.2.2.6: Reflectivity (for qualified personnel only)
This parameter is for Factory Authorized Personnel Only.
4.2.2.7: Failsafe Level (F = Hold Continuously)
Selects the default measurement in the event that the failsafe timer expires
4.2.2.8: Failsafe Timer (F = 10 min)
Sets the time delay, in minutes, before entering failsafe level
The failsafe timer begins when there is a loss of echo condition. This loss of echo
condition will occur when there is no signal available above the Auto False Echo
Suppression threshold as defined in Parameter 4.2.3.9.
4.2.2.9: Range Extension (F = 3 m)
Sets the amount of range extension as measured from the tank height and extending
beyond the measurement range. For vessels with conical or parabolic bottoms, you may
need to increase this value to ensure an empty vessel reads empty.
4.2.3: Sensor Parameter
Here you can view and change the sensor parameters which you have selected
according to Parameter 4.2.2 (Measuring Conditions).
Value
100 %
0 %
Hold Continuously
Value 1 min
2 min, etc.
Value numerical
Note: The factory settings for the user vessels are not editable.

Page 45 SITRANS LR 400 – INSTRUCTION MANUAL 7ML19985FH04
mmmmm
Parameters (HART)
4.2.3.1: Sensor Damping (F = 1 s)
Averaging of measuring signal. Not displayed if a user vessel is selected in Parameter
4.2.2.1 (Application Type).
Enter the damping in seconds.
This parameter is not displayed when a user vessel is selected in Parameter 4.2.2.1
(Application Type). The sensor damping influences the evaluation of the measuring
signal. If the level generally only changes slowly and continuously, a time constant set
here can improve the measuring accuracy and the validity in poorly reflecting measuring
media or those with a restless surface. The sensor damping must always be smaller than
the interval of the time of change of the level (e.g. 1 mm/10 s), because too high a value
would have a negative influence on the measuring result.
4.2.3.2: Multiple Echo (F = on)
Evaluate multiple echo
The multiple echo evaluation suppresses multiple reflections by assigning them a lower
probability than the measuring signal.
4.2.3.3: Echo Motion (F = off)
Evaluate echo motion
Dynamic processes in the vessel are included in the evaluation of the measuring targets.
The typical filling speed can be set in Parameter 4.2.2.5. If the measured value still does
not follow the level height, switching off echo motion may improve the result.
Value numerical
Note: Specification of damping directly influences the evaluation of the measuring
signal. If you only want to dampen the calculated outputs at the analog output, you
should set the damping of level, volume or mass described in Function 4.2.4.4 (MinLim
Level).
Value On
Off
Value On
Off
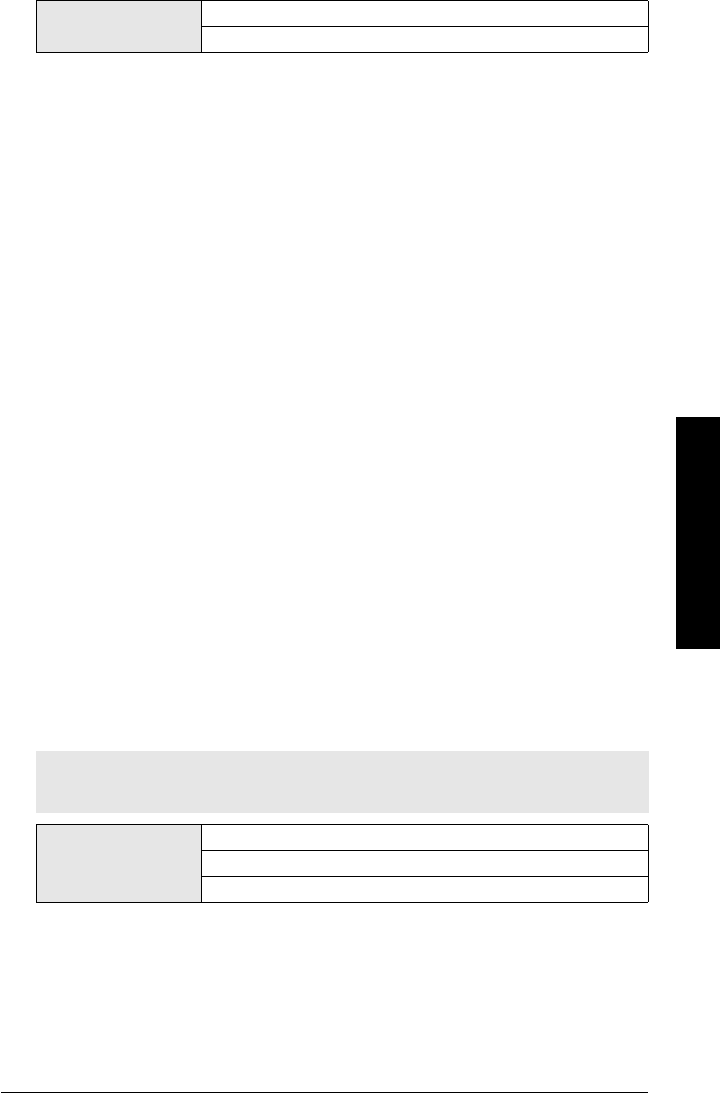
7ML19985FH04 SITRANS LR 400 – INSTRUCTION MANUAL Page 46
mmmmm
Parameters (HART)
4.2.3.4: Window Tracking (F = Off)
A window follows the measured value which it is forced to track. The window size is
calculated from the set filling speed. Switch off window tracking for applications where
the SITRANS LR 400 is unable to keep up to level changes. By using SIMATIC PDM, you
can display a list of all echoes in your vessel. It provides the distance between the flange
and the measuring medium’s surface, as well as the distances of fixed targets. These
may be directly used and transferred to the fix distance list.
4.2.3.5: Tank Empty Detect (for qualified personnel only)
This parameter is for Factory Authorized Personnel Only.
4.2.3.6: Auto Fix Distance (for qualified personnel only)
This parameter is for Factory Authorized Personnel Only.
4.2.3.7: Fix Distance List (for qualified personnel only)
This parameter is for Factory Authorized Personnel Only.
4.2.3.7.1 to 4.2.3.7.9: Fix Distance Values (for qualified
personnel only)
These parameters are for Factory Authorized Personnel Only
4.2.3.8: Auto False Echo Suppression (F = Use)
Learns and records the current signal up to the suppression distance setting. These
signals are then ignored during operation.
If all signals fall below this defined threshold, then the failsafe timer is initiated.
Value On
Off
Note: This function works best when the vessel is nearly empty. For best results, do
not record or learn when the vessel is completely empty.
Value
Off
Record
Use

Page 47 SITRANS LR 400 – INSTRUCTION MANUAL 7ML19985FH04
mmmmm
Parameters (HART)
4.2.3.9: Auto False Echo Suppression Distance (F = 2/3 tank
height)
Defines the end point of the auto false echo suppression distance
4.2.3.A: Hover Level (F = 40%)
Defines (in percent) how high the TVT (Time Varying Threshold) curve is placed above the
profile, relative to the largest echo. When SITRANS LR 400 is located in the center of the
vessel, lower this parameter to prevent multiple echo detections.
4.2.3.B: Window Trigger (F = 80%)
Defines the position of the window on the leading edge of the selected echo, relative to
the amplitude. Used only on Silo1 and Silo2 applications (see Application Type on
page 35).
4.2.4: Level Parameter
4.2.4.1: Level URV (F = 20 m)
Full scale of level (see Functional Dimensions on page 33)
Set the URV as the level above the bottom of the vessel (see Functional Dimensions on
page 33) in the units system selected with Parameter 4.1.1. It corresponds to an output
current of 20 mA.
4.2.4.2: Level LRV (F = 0 m)
Empty scale of level (see Functional Dimensions on page 33)
Set the LRV as the level above the bottom of the vessel (see Functional Dimensions on
page 33) in the units system selected with Parameter 4.1.1. It corresponds to an output
current of 4 mA.
Value variable
Values Range: 0 to 100%
Values Range: 0 to 100%
Value numerical value
Note: This parameter is also set using Parameter 1.5 (Level URV).
Value numerical value
Note: This parameter is also set using Parameter 1.6 (Level LRV).
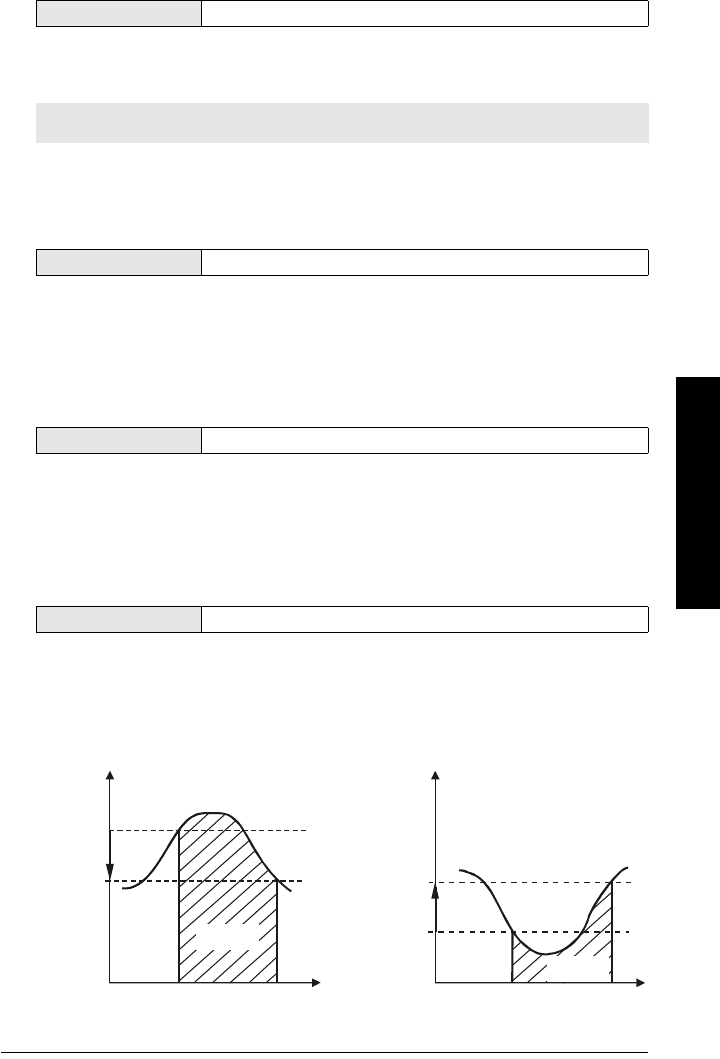
7ML19985FH04 SITRANS LR 400 – INSTRUCTION MANUAL Page 48
mmmmm
Parameters (HART)
4.2.4.3: Level damping (F = 1 s)
Damping of level in s
Set the damping of the level value in seconds. It acts on the analog output, the limit value
monitor and the local display. For damping of the sensor signal, set Parameter 4.2.3.1.
4.2.4.4: MinLim Level (F = 0 m)
Lower limit value of the level (see Functional Dimensions on page 33)
Set the lower limit value of the level as a height above the LRV.
4.2.4.5: MaxLim Level (F = 20 m)
Upper limit value of the level (see Functional Dimensions on page 33)
Set the upper limit value of the level as a height above the LRV.
4.2.4.6: HYST Level (F = 0.5 m)
Hysteresis of the level limit values
Set the hysteresis of the limit values in the units system selected according to Parameter
4.1.1 (see diagram below).
Limit value alarm
Value numerical value
Note: This parameter is also set using Parameter 1.7 (Level Damping).
Value numerical value
Value numerical value
Value numerical value
measuring variable measuring variable
upper limit
value
hysteresis
lower limit
value
limit value
alarm
hysteresis
limit value
alarm
time
time
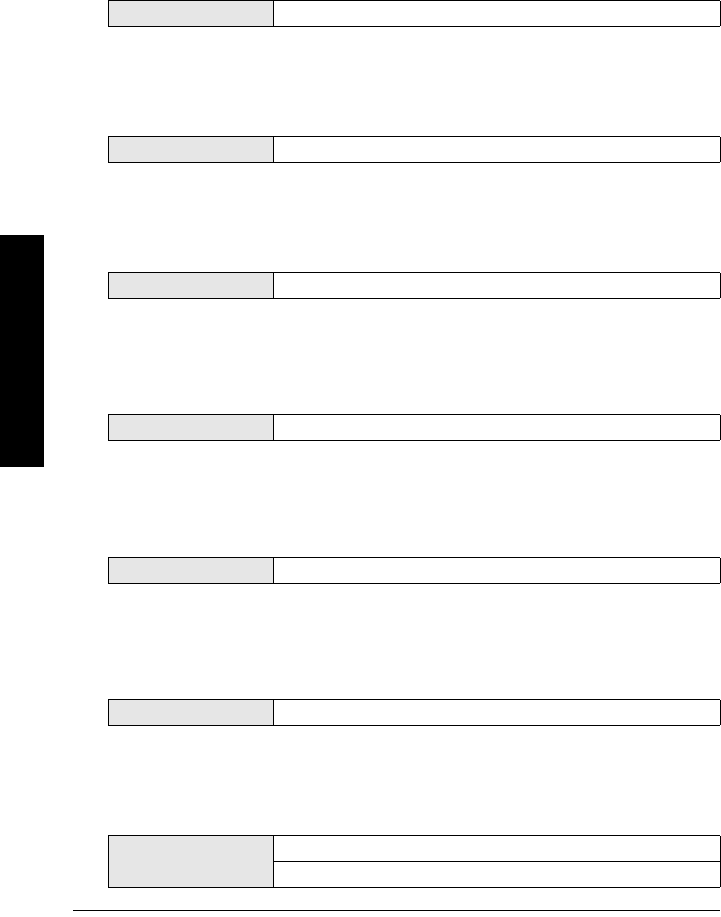
Page 49 SITRANS LR 400 – INSTRUCTION MANUAL 7ML19985FH04
mmmmm
Parameters (HART)
4.2.5: Volume Parameters
To calculate the volume of the measuring medium, you need the level parameters
(Parameter 4.2.4) in the units selected according to Parameter 4.1.1 and additionally a tank
characteristic (Parameter 4.2.5.7).
4.2.5.1: Volume URV (F = 20 m3)
Full scale of volume
4.2.5.2: Volume LRV (F = 0 m3)
Start of scale of volume
4.2.5.3: Volume Damping (F = 1 s)
Damping of volume
4.2.5.4: MinLim Volume (F = 0 m3)
Lower limit value of volume
4.2.5.5: MaxLim Volume (F = 20 m3)
Upper limit value of volume
4.2.5.6: HYST Volume (F = 0.5 m3)
Hysteresis of the volume limit values
4.2.5.7: Tank Characteristic (F = Calculate)
Determining the vessel characteristic
Value numerical value
Value numerical value
Value numerical value
Value numerical value
Value numerical value
Value numerical value
Value Calibrate/table
Calculate
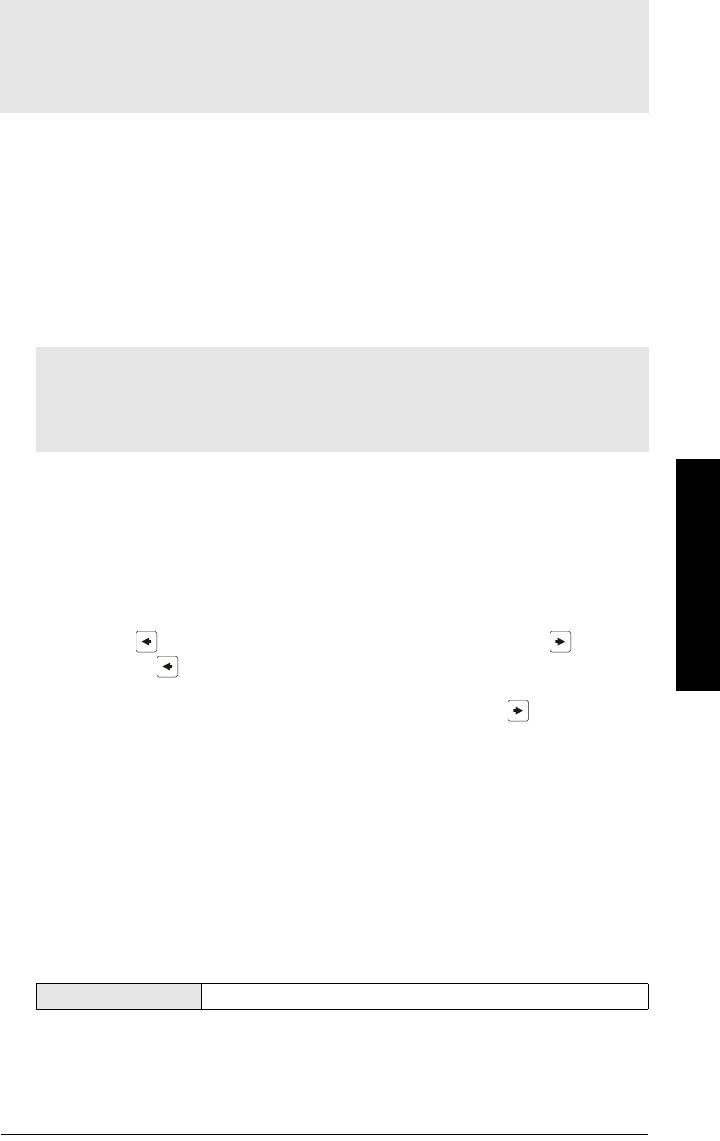
7ML19985FH04 SITRANS LR 400 – INSTRUCTION MANUAL Page 50
mmmmm
Parameters (HART)
4.2.5.8: Calibrate/table
If your vessel deviates from the forms offered, the necessary data is not available or is
unknown, or you need a vessel characteristic with greater accuracy, you will need to use
a level/volume calibration table. You can enter reference values from a table provided by
the vessel manufacturer or do the calibration manually and enter the determined
reference values.
You can only enter pairs of values consisting of level and volume.
The 4.2.5.8 Calibrate/table parameter offers the following selection possibilities:
4.2.5.8.1: Calibrate
Here you can enter up to 50 reference values whose levels SITRANS LR 400 measures.
Enter the appropriate volume (determined by manual calibration).
If you access this parameter, first the currently measured level is displayed. Accept it by
pressing LEFT . Enter the appropriate volume: save it by pressing RIGHT or reject it
by pressing LEFT .
Then the device displays Calibrate. Access again by pressing RIGHT to select a
further reference value. The device automatically offers you the next undefined reference
value.
We recommend entering a maximum of two or three reference values for the linear range
of the vessel and to use the others for the non-linear portion.
If you enter a second volume value for the same level, the reference value saved earlier is
overwritten.
4.2.5.8.2: Enter table
Manual entry of a table
Here you can enter up to 50 reference values provided by the vessel manufacturer in any
order.
Note: Select the option Calibrate/table or Calculate as required. The
selection controls the display of Parameter 4.2.5.8. The possibilities of each
parameter are listed below. For the values associated with Parameter 4.2.5.8:
Calculate, go to page 51.
Note: Entering the vessel characteristic with the hand programmer can be a time-
consuming procedure. It can be done more quickly and comfortably with the SIMATIC
PDM software. There, an entered table can be edited simply – an option which is only
conditionally possible with the hand programmer.
Value numerical value
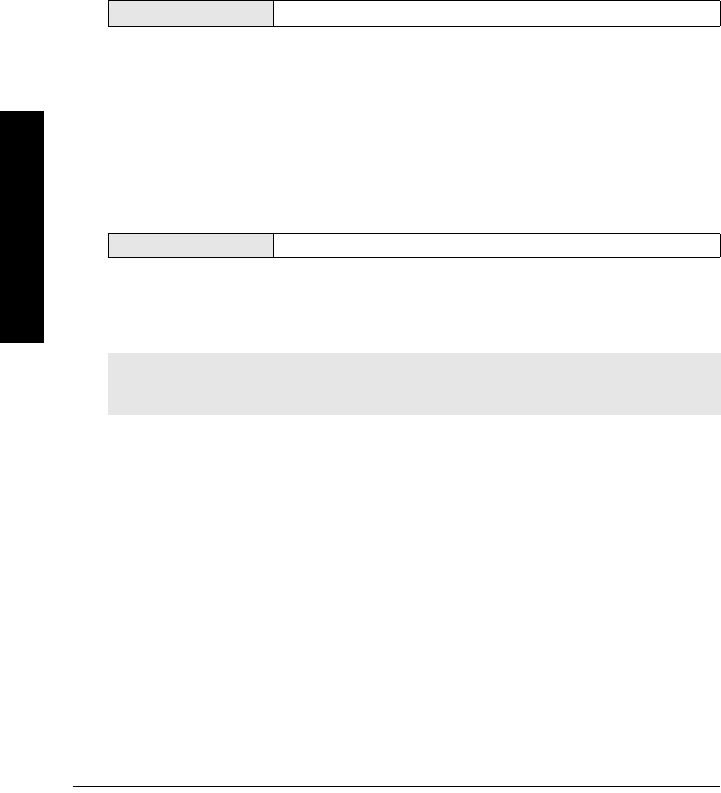
Page 51 SITRANS LR 400 – INSTRUCTION MANUAL 7ML19985FH04
mmmmm
Parameters (HART)
The first reference value is offered when you access the parameter. Enter the level as a
distance from the floor of the vessel in the units selected according to Parameter 4.1.1
(Enter level) and the volume corresponding to the level (Enter volume).
The device then displays Enter table again. Access again to enter a further reference
value. The device automatically offers you the next undefined reference value.
We recommend entering a maximum of two or three reference values for the linear range
of the vessel. Use the other reference values for the non-linear section.
If you enter a second volume value for the same level, the reference value saved earlier is
overwritten.
4.2.5.8.3: Show table
Display table
Here you can display the entered reference values sorted on levels. In the second line,
the level corresponding to the first reference value appears first and then the
corresponding volume value when you switch further. Each switching accesses a further
reference value.
4.2.5.8.4: Clear table
Delete table
If you choose all in this parameter, the entire saved table is deleted. You can delete
individual reference values with the selection 1st, 2nd etc. that were displayed in
Parameter 4.2.5.8.3.
or
4.2.5.8: Calculate
Automatic calculation of a vessel characteristic is faster than manual entry by calibrating
or a table. However, the calculated vessel characteristic is not as accurate as a manually
calibrated characteristic – especially in the non-linear sections of the vessel when errors
of ≤ 1 % may occur. As well, the necessary data which you can get from the design
documents of your vessel must still correspond to the real conditions.
The 4.2.5.8: Calculate parameter requires the following parameters:
Value selection
Value selection
Note: The reference values are sorted in order of filling states and do not
necessarily correspond to the order of the value pairs you have entered.
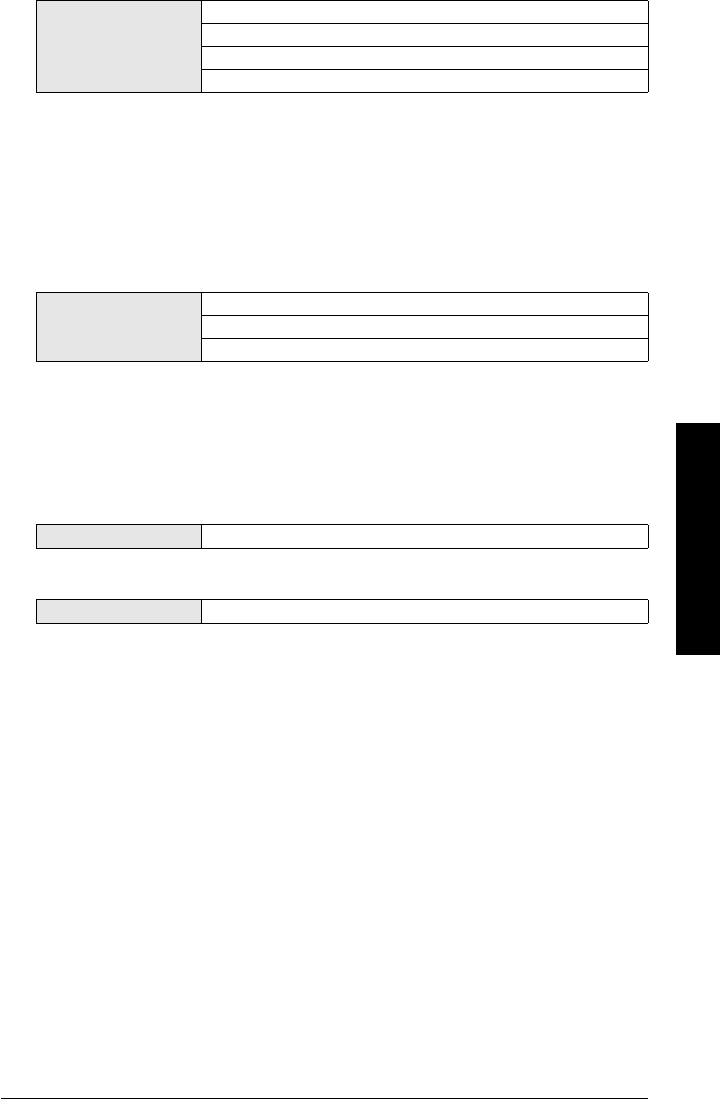
7ML19985FH04 SITRANS LR 400 – INSTRUCTION MANUAL Page 52
mmmmm
Parameters (HART)
4.2.5.8.1: Tank Design (F = Vertical Cylinder)
Enter the external form of your vessel. You can choose from:
• Linear (any form with vertical walls and a flat floor)
• Vertical cylinder (vertically standing cylindrical form with curved covers)
• Horizontal cylinder (horizontal cylindrical form with curved caps)
• Sphere
4.2.5.8.2: Bottom Design (F = Dished end)
Enter the form of the two vessel cover caps. You can choose from:
• Dished (according to DIN 28011)
• Basket (according to DIN 28013)
• Bullet (hemispherical shaped floor)
4.2.5.8.3: Tank volume (F = 20 m3)
4.2.5.8.4: Tank height (F = 20 m)
4.2.6: Mass Parameters (for qualified personnel only)
Mass parameters 4.2.6.1 to 4.2.6.9 are for Factory Authorized Personnel Only.
4.2.6.1: Mass URV (for qualified personnel only)
4.2.6.2: Mass LRV (for qualified personnel only)
4.2.6.3: Mass Damping (for qualified personnel only)
4.2.6.4: MinLim Mass (for qualified personnel only)
4.2.6.5: MaxLim Mass (for qualified personnel only)
4.2.6.6: HYST Mass (for qualified personnel only)
4.2.6.7 Tank Characteristic (for qualified personnel only)
Value
Linear
Vertical cylinder
Horizontal cylinder
Sphere
Value
Dished end
Basket end
Bullet bottom
Value numerical value
Value numerical value
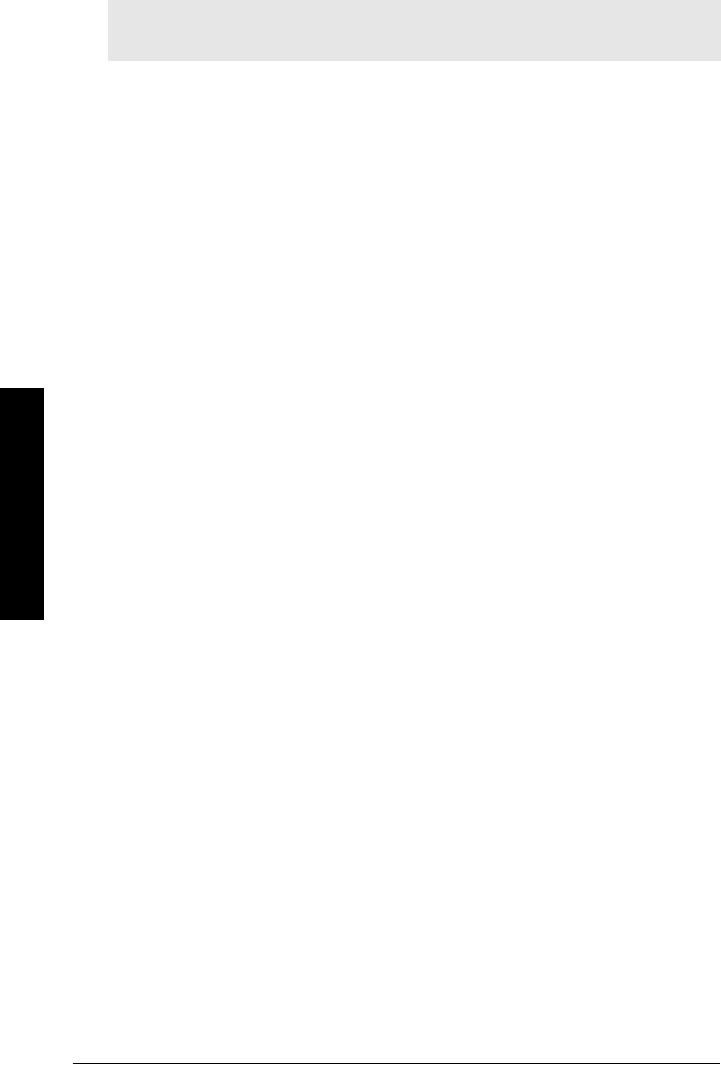
Page 53 SITRANS LR 400 – INSTRUCTION MANUAL 7ML19985FH04
mmmmm
Parameters (HART)
4.2.6.8 Calibrate/table or Calculate (for qualified personnel
only)
4.2.6.8 Calibrate/table
4.2.6.8.1: Calibrate (for qualified personnel only)
4.2.6.8.2: Enter table (for qualified personnel only)
4.2.6.8.3: Show table (for qualified personnel only)
4.2.6.8.4: Clear table (for qualified personnel only)
or
4.2.6.8 Calculate
4.2.6.8.1: Tank design (for qualified personnel only)
4.2.6.8.2: Bottom design (for qualified personnel only)
4.2.6.8.3: Tank volume (for qualified personnel only)
4.2.6.8.4: Tank height (for qualified personnel only)
4.2.6.9: Density (for qualified personnel only)
4.2.7.x: User1 Parameters (for qualified personnel only)
All parameters in range 4.2.7.x are for Factory Authorized Personnel Only. Advanced echo
processing parameters should only be modified by qualified personnel.
4.2.8.x: User2 Parameters (for qualified personnel only)
All parameters in range 4.2.8.x are for Factory Authorized Personnel Only. Advanced echo
processing parameters should only be modified by qualified personnel.
Note: The value of Parameter 4.2.6.8 is determined by the selection (Calibrate/table
or Calculate) in Parameter 4.2.6.7.
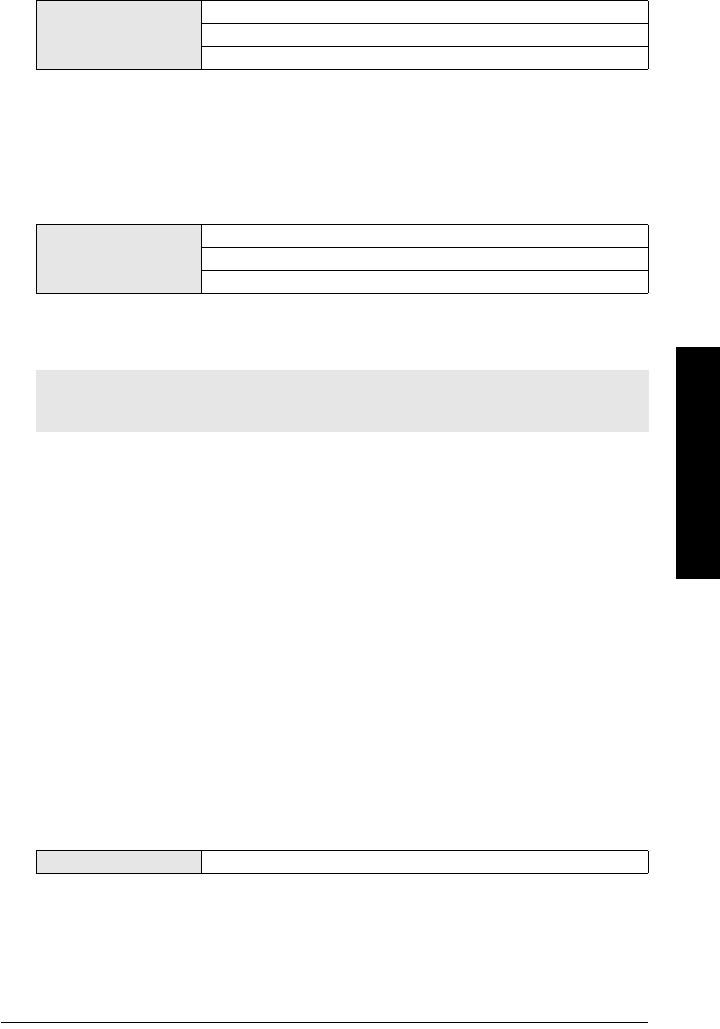
7ML19985FH04 SITRANS LR 400 – INSTRUCTION MANUAL Page 54
mmmmm
Parameters (HART)
4.3: Analog Output
4.3.1: Error Level (F = D: Error Signal)
Level for the error signal to alarm in Analog or Digital output
When D is selected, all errors are displayed. When D+F is selected, there is special
handling for failsafe. When D+F+W is selected, there is special handling for warnings.
4.3.2: AO Select (F = Level)
Assignment of a measured value to the analog output
Here you can set whether the analog output supplies the level, volume, or mass to the
control system.
If 4.3.2 (AO Select) = Level
4.3.3: Level Parameter (= Parameter 4.2.4)
If 4.3.2 (AO Select) = Volume
4.3.3: Volume Parameter (= Parameter 4.2.5)
If 4.3.2 (AO Select) = Mass
4.3.3: Mass Parameter (= Parameter 4.2.6)
4.3.4: Current Limit (F = 20 mA)
Upper current limit
Here you can set the upper current limit of the output signal in steps of 0.1 mA (see
Current limiting diagram on next page).
Value
D: Error Signal
D+F: Error Signal
D+F+W: Error Signal
Value
Level
Volume
Mass
Note: The value of Parameter 4.3.3 is determined by the selection (Level, Volume or
Mass) in Parameter 4.3.2 (AO select).
Value 20 - 22.5 mA
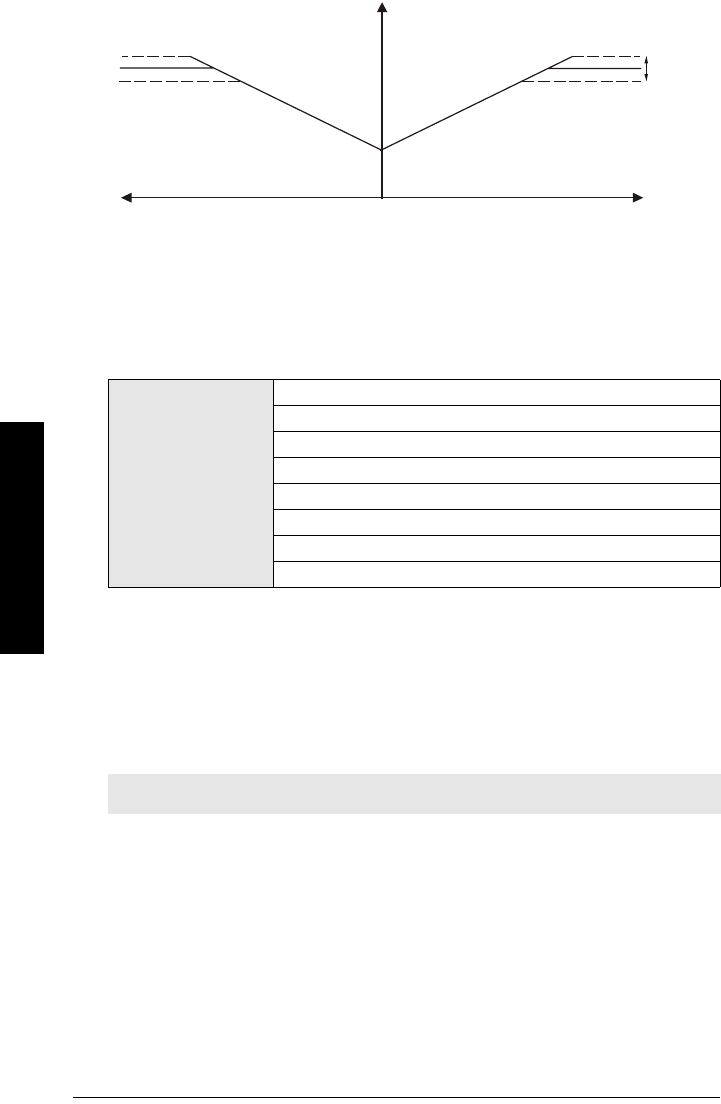
Page 55 SITRANS LR 400 – INSTRUCTION MANUAL 7ML19985FH04
mmmmm
Parameters (HART)
Current limiting
The URV is always at 20 mA. If you set the current limit to a higher value, you can have the
measured values output outside the measuring range (up to approx. 115%).
4.3.5: Error Signal (F = 3.6 mA)
Current value of the error signal
In the event of a fault the device applies the current defined here to the analog output.
You can choose between 3.6 mA, 22 mA, 24 mA, Hold 10 s, Hold 1 min, Hold 2 min, Hold 3
min and Hold continuously.
When the Hold... values are selected, the device outputs the last valid value until the set
time has run out or the fault has been eliminated. If the fault persists after the set time
runs out, the analog output switches to an error signal of 3.6 mA.
Value
3.6 mA
22.0 mA
24.0 mA
Hold 10 s
Hold 1 min
Hold 2 min
Hold 3 min
Hold continuously
Note: A fault is different from a loss of echo which indicates a failsafe condition.
current
22.5 mA
20.0 mA
setting
range
measured value
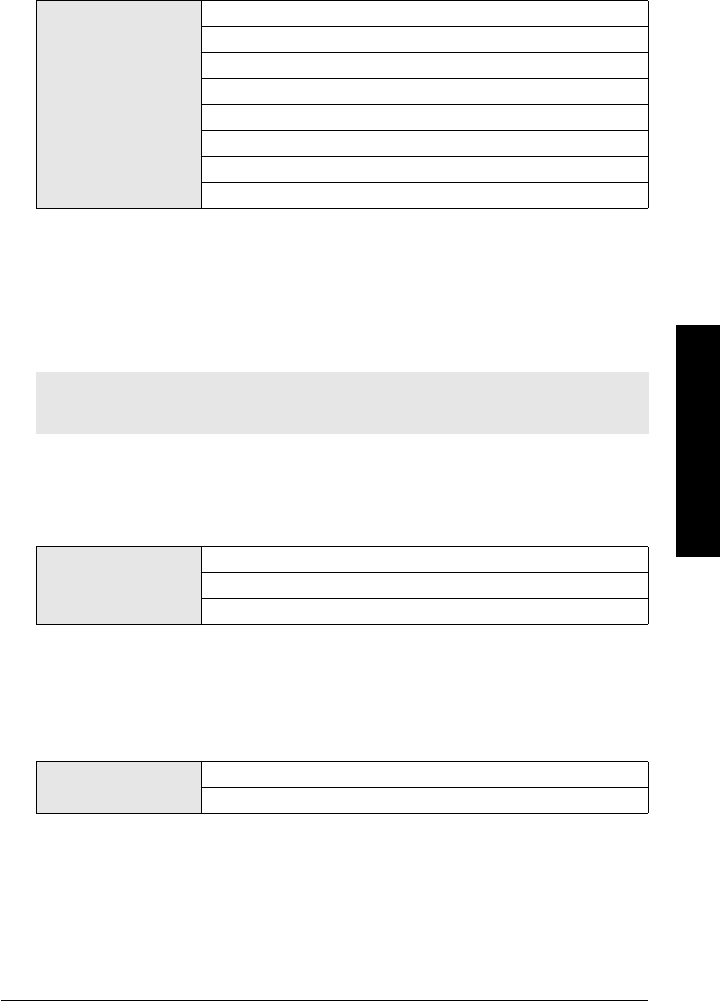
7ML19985FH04 SITRANS LR 400 – INSTRUCTION MANUAL Page 56
mmmmm
Parameters (HART)
4.4 Digital Output
4.4.1: Function DO (F = Alarm)
Assignment of the digital output
Here you can select whether the digital output supplies the upper or lower limit value of
level or volume or an alarm (device error, measurement error; see Parameter 3.1) to the
control system. If you select the No function option, the digital output is switched off.
Selection of a limit value enables Parameter 4.4.4. If you select Alarm or No function in
this parameter, Parameter 4.4.4 will not be visible.
4.4.2: Error Level (F = D: Error Signal)
Level for the error signal to alarm in Analog or Digital output
When D is selected, all errors are displayed. When D+F is selected, there is special
handling for failsafe. When D+F+W is selected, there is special handling for warnings.
4.4.3: Signal Type DO (F = Relay closes)
Value
MaxLim level
MinLim level
MaxLim volume
MinLim volume
MaxLim mass
MinLim mass
Alarm
No function
Note: The value of Parameter 4.4.4 is determined by the MaxLim or MinLim selection
chosen in 4.4.1 (Function DO).
Value
D: Error signal
D+F: Error signal
D+F+W: Error signal
Value Relay closes
Relay opens
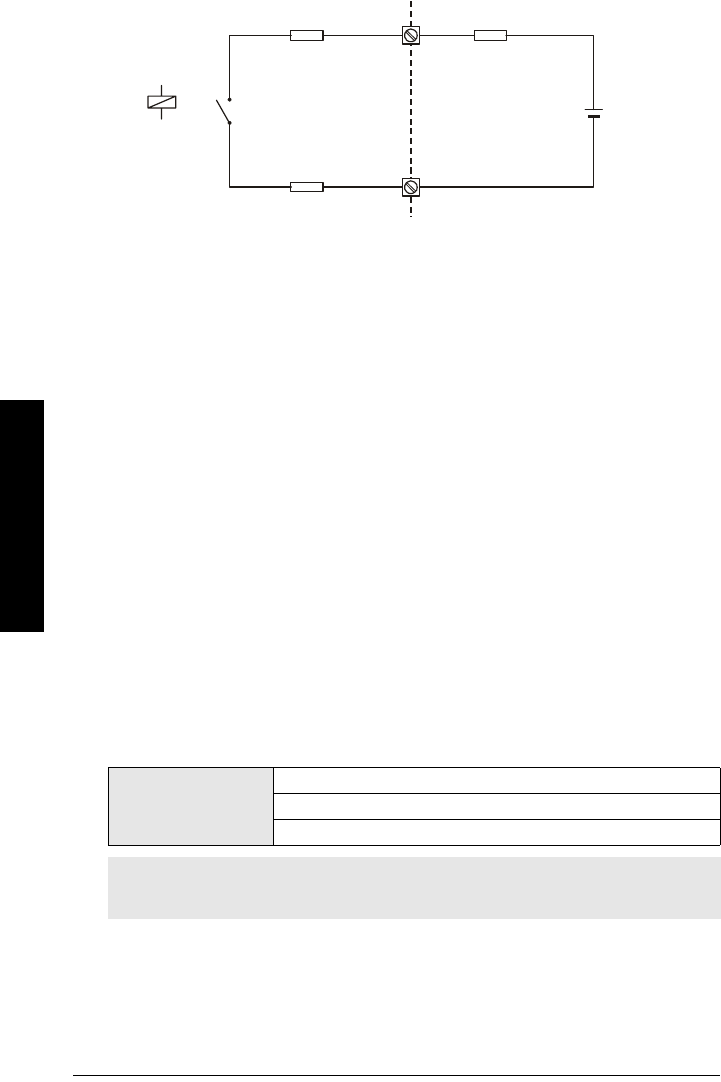
Page 57 SITRANS LR 400 – INSTRUCTION MANUAL 7ML19985FH04
mmmmm
Parameters (HART)
Here you can determine the behavior of the digital output. Select whether its contact
closes or opens at an event.
If 4.4.1 (Function DO) = MaxLim level or MinLim level
4.4.4: Level Parameter (= Parameter 4.2.4)
If 4.4.1 (Function DO) = MaxLim volume or MinLim volume
4.4.4: Volume Parameter (= Parameter 4.2.5)
If 4.4.1 (Function DO) = MaxLim mass or MinLim mass
4.4.4: Mass Parameter (= Parameter 4.2.6)
4.5: Display Parameters
4.5.1: Multi-Display
4.5.1.1: Line 1 Local (F = Level)
Choice of measured value in line 1
Value
Level
Volume
Mass
Note: The value of 4.5.1.3 is determined by the selection (Level, Volume or Mass) in
Parameter 4.5.1.1 (Line 1 Local).
electronic fuse
Device
9 Ω
External supply
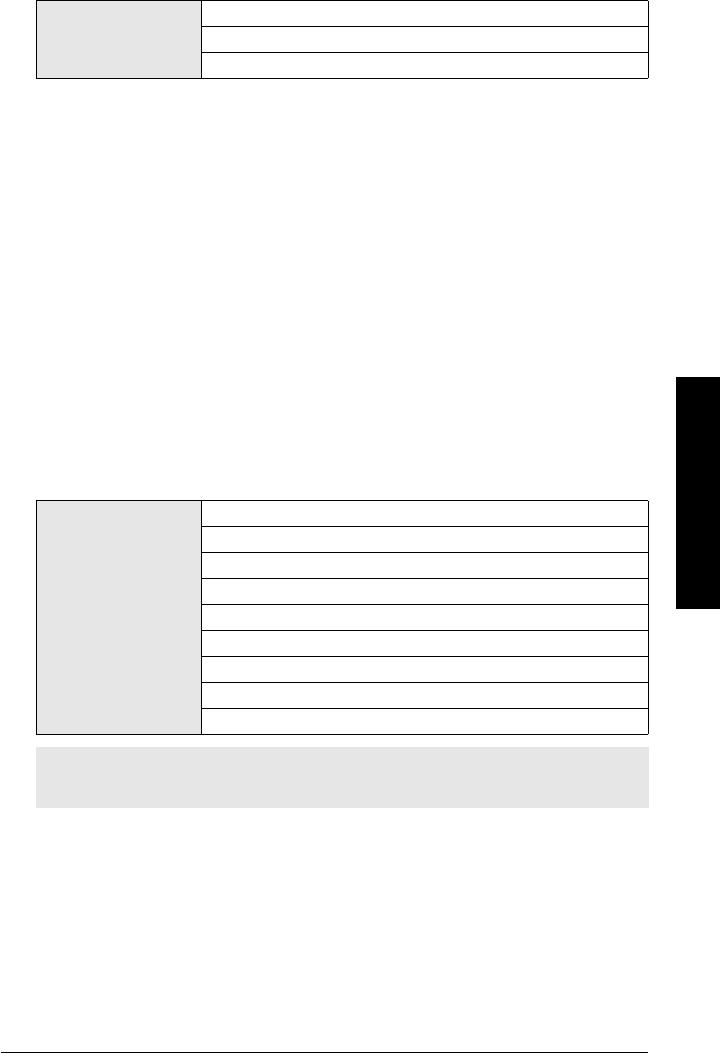
7ML19985FH04 SITRANS LR 400 – INSTRUCTION MANUAL Page 58
mmmmm
Parameters (HART)
4.5.1.2: Display Local (F = Eng Unit)
Method of display in line 1
If 4.5.1.1 (Line 1 Local) = Level
4.5.1.3: Level Parameter (= Parameter 4.2.4)
If 4.5.1.1 (Line 1 Local) = Volume
4.5.1.3: Volume Parameter (= Parameter 4.2.5)
If 4.5.1.1 (Line 1 Local) = Mass
4.5.1.3: Mass Parameter (= Parameter 4.2.6)
4.5.1.4: Line 2 Local (F = S/N ratio)
Display in line 2
If 4.5.1.4 (Line 2 Local) = Level
4.5.1.5: Level Parameter (= Parameter 4.2.4)
If 4.5.1.4 (Line 2 Local) = Volume
4.5.1.5: Volume Parameter (= Parameter 4.2.5)
Value
Eng unit
%
Bar graph
Value
Level
Volume
Mass
Temperature
Validity
S/N ratio
Amplitude
Digital output
Analog output
Note: Parameter 4.5.1.5 is displayed if Parameter 4.5.1.4 (Line 2 Local) = Level, Volume,
or Mass.
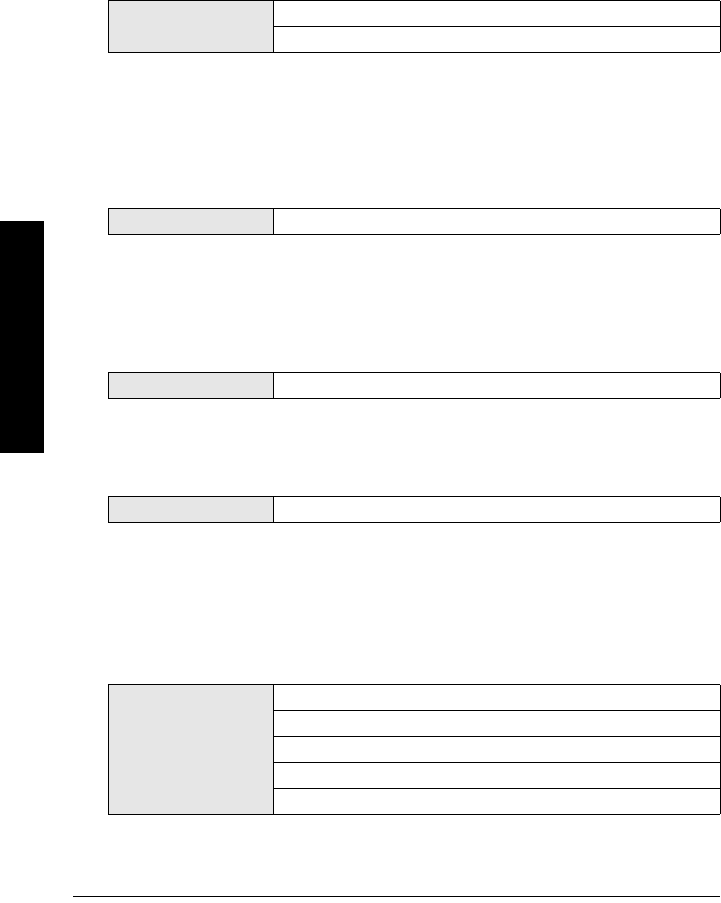
Page 59 SITRANS LR 400 – INSTRUCTION MANUAL 7ML19985FH04
mmmmm
Parameters (HART)
If 4.5.1.4 (Line 2 Local) = Mass
4.5.1.5: Mass Parameter (= Parameter 4.2.6)
4.5.2: Language Local (= Parameter 1.1)
4.5.3: LCD Backlight (F = off)
Background illumination of the LCD
4.6: Device Information
4.6.1: Power Supply (according to customer specifications)
Voltage range of the built-in power supply unit
4.6.2: Process Temperature (according to customer
specifications)
Temperature range of the flange in °C
4.6.3: Electrical Connection (according to customer
specifications)
4.6.4: Antenna and Flange
4.6.4.1: Flange Size (according to customer specifications)
Size of the flange
Value On
Off
Value non-editable
Value non-editable
Value non-editable
Value
DN 50, 2"
DN 80, 3"
DN 100, 4"
DN 150, 6"
Special design
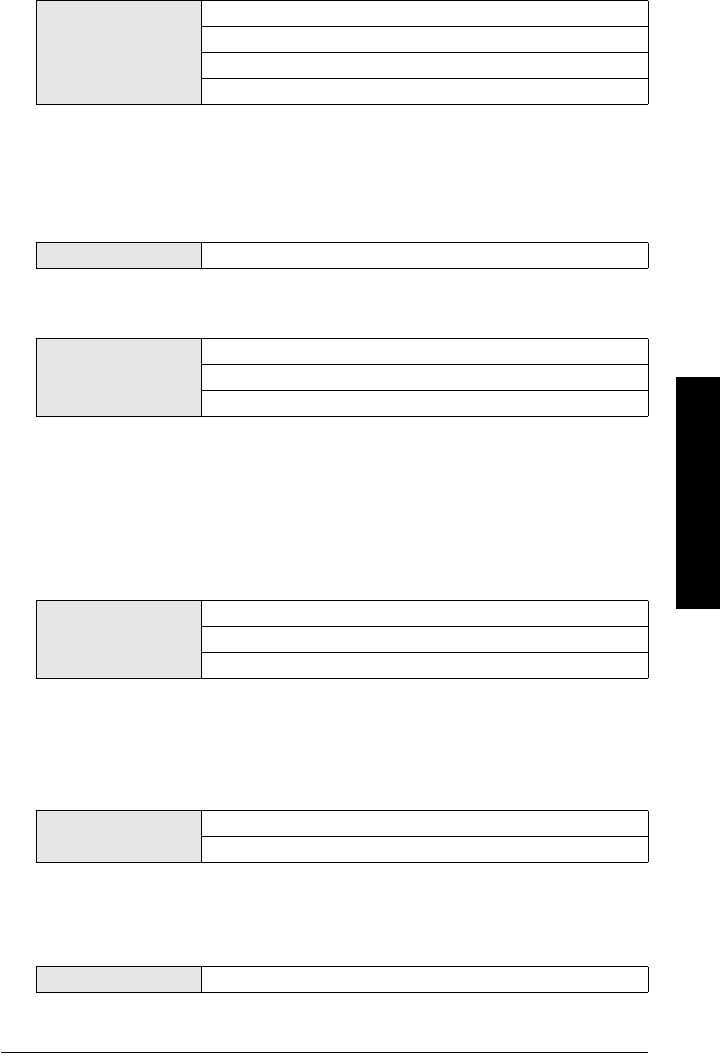
7ML19985FH04 SITRANS LR 400 – INSTRUCTION MANUAL Page 60
mmmmm
Parameters (HART)
4.6.4.2: Flange Type (according to customer specifications)
Type of flange
4.6.4.3: Pressure Stage (according to customer
specifications)
Pressure range of the process connection
4.6.4.4: Antenna Type (according to customer settings)
4.6.4.5: Antenna Extensions (for qualified personnel only)
This parameter is for Factory Authorized Personnel Only.
4.6.4.6: Flange Material (according to customer
specifications)
4.6.4.7: Seal Material (according to customer
specifications)
Sealing material
4.6.5: Tag (according to customer specifications)
Device identification
Value
DIN 2527
ANSI
JIS
Special design
Value non-editable
Value
Horn type 2" (51 mm)
Horn type 3" (76 mm)
Horn type 4" (102 mm)
Value
304
316/316L
Special design
Value PTFE
FKM
Value up to any eight characters
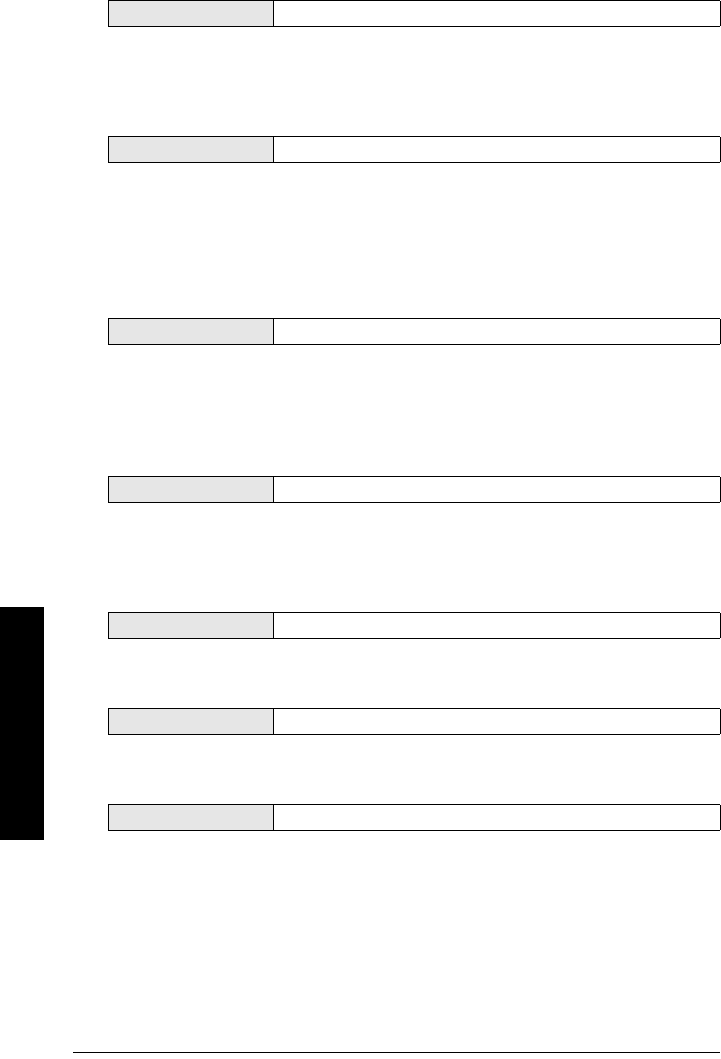
Page 61 SITRANS LR 400 – INSTRUCTION MANUAL 7ML19985FH04
mmmmm
Parameters (Profibus PA)
4.6.6: Descriptor (according to customer specifications)
Measuring point description
4.6.7: Message (according to customer specifications)
Measuring point message, e.g. the date of the last check or clean
4.6.8: Manufacturer Identification
4.6.8.1: Serial Number (F = unique number)
Factory serial number
4.6.8.2: Order Number (according to customer
specifications)
Device order number (delivery state)
4.6.8.3: Fld Device Revision (F = Number)
Device version
4.6.8.4: Software Revision (F = Number)
4.6.8.5: Hardware Revision (F = Number)
4.6.8.6: Antenna Offset (F = approx. 0.5 m [calibration value])
Distance from sensor to flange
The antenna offset defines the propagation time of the measuring signal between the
sensor and the flange as a distance. It is preset at the factory and cannot be changed.
Value up to any 16 characters
Value Up to any 32 characters
Value non-editable
Value non-editable
Value non-editable
Value non-editable
Value non-editable
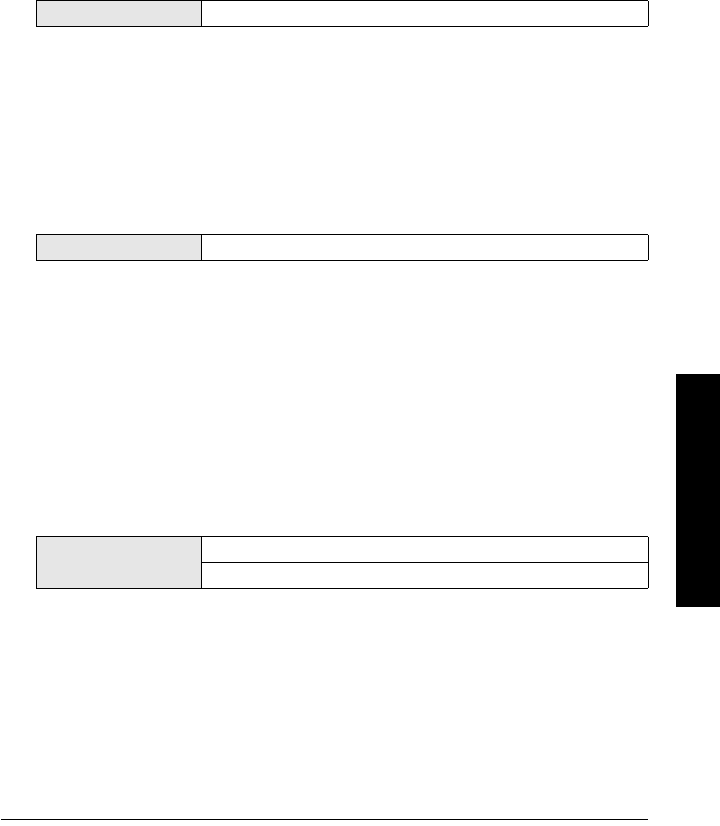
7ML19985FH04 SITRANS LR 400 – INSTRUCTION MANUAL Page 62
mmmmm
Parameters (Profibus PA)
4.6.8.7: Reference Difference (F = approx. 106 m [calibration
value])
Internal reference distance
The length of the reference distance in the units system selected according to Parameter
4.1.5 is view-only. The device uses this value to calibrate itself so that no manual
adjustment is necessary in long-term operation.
5. Options
5.1: Enter Code
Input of customer code to enable programmability
The device compares a code number which you enter here with the code defined in
Parameter 5.2. If your entry matches the customer code completely, it releases the
programming lock for all parameters. Any other code number locks and disables
programming.
5.2: Customer Code (F = 0)
Determination of customer code
Here you define the customer code (up to nine digits), with which you can protect the
device parameters against programming errors. It is strongly recommended that a
customer code be entered after all programming is completed to secure the programmed
values from changes.
Use of the customer code is explained in Disabling and Enabling Programming on page
29.
5.3: Factory Reset (F = no)
Reset all parameters to factory setting
This parameter allows you to reset all parameters to the original factory setting as
described in Parameters (HART) beginning on page 32.
Value Customer code
Value Up to 9-digit code
Value Yes
No
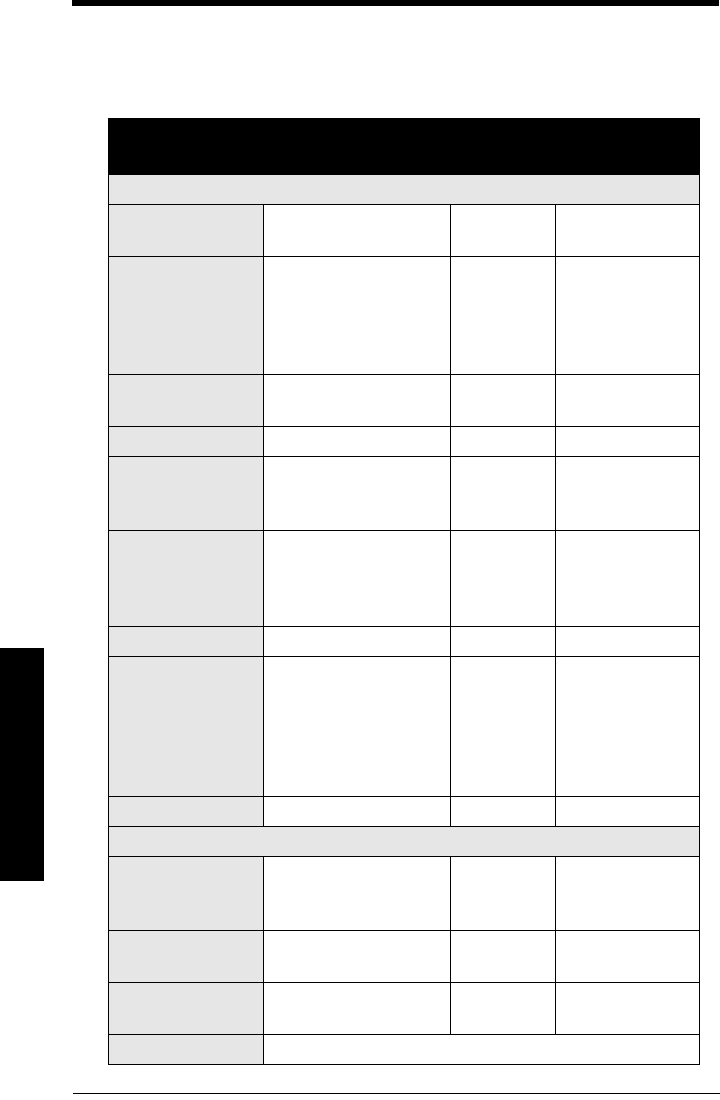
Page 63 SITRANS LR 400 – INSTRUCTION MANUAL 7ML19985FH04
mmmmm
Parameters (Profibus PA)
Parameters (PROFIBUS PA)
Parameters (PROFIBUS PA)
Note: For parameter descriptions, please refer to the associated HART parameters on
pages 30 to 58.
Parameter, menu
identification Description Factory
Setting
Setting
Possibilities
1: Auto-Setup
Language local Language of the local
user interface
English English
Deustch
Length unit m cm
m
mm
ft
in
Nozzle height Height flange to top of
tank
0 m numerical value
Tank height Height tank bottom to top 20 m numerical value
Level URV Full scale of level (see
Functional Dimensions
Diagram on page 33)
20 m numerical value
Level LRV Start of scale of level
(See Functional Dimen-
sions Diagram on
page 33)
0 m numerical value
Level damping Damping of level in s 1 s numerical value
Application type Use of the vessel Liquid (pro-
cess)
Liquid (store)
Liquid (process)
Silo1 (solids)
Silo2 (solids)
User tank1
User tank2
Bus address Current bus address 126 0 to 126
2: Display
2.1: Multi-display Display of two measured
values
Level/Signal-
to-noise ratio
in dB
non-editable
2.2: Level Level of measured
medium
m non-editable
2.3: Volume Volume of measured
medium
m3non-editable
2.4: Mass For qualified personnel only
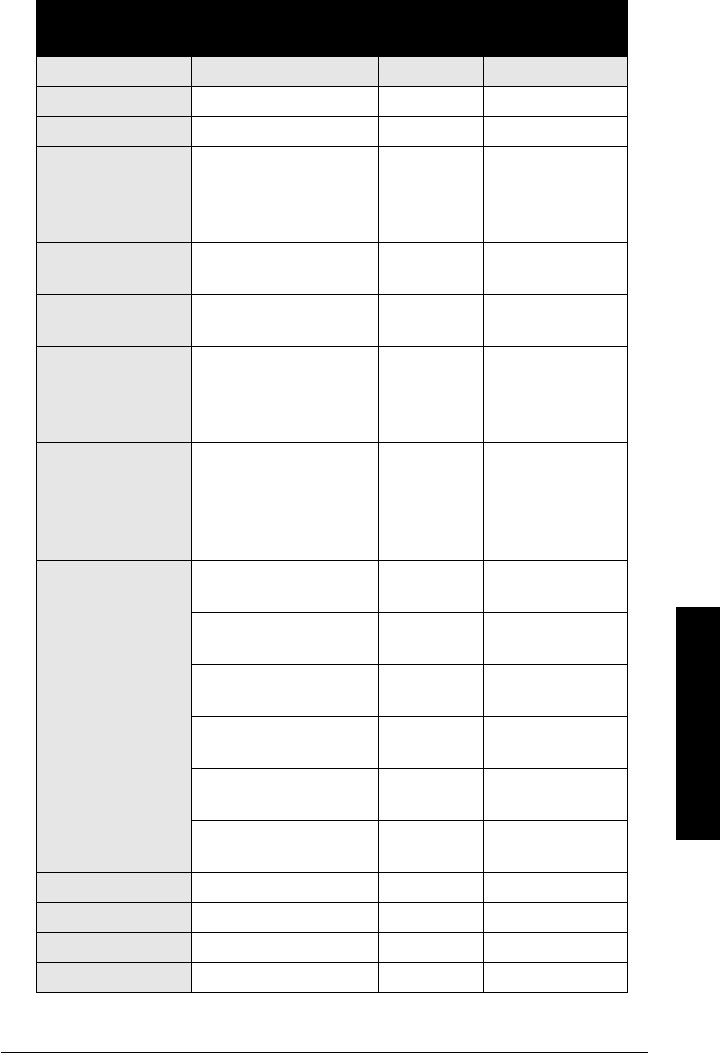
7ML19985FH04 SITRANS LR 400 – INSTRUCTION MANUAL Page 64
mmmmm
Parameters (Profibus PA)
3: Diagnostics
3.1: Status
3.1.1: Wear
3.1.1.1: Operating
hours
Total previous operating
time of the device in
hours (approximate
value)
non-editable
3.1.1.2: Maximum
temp.
Previous maximum tem-
perature of device
26°C non-editable
3.1.1.3: Minimum
temp.
Previous minimum tem-
perature of the device
26°C non-editable
3.1.1.4: Aging Approximate value for the
previous life of the device
in % (100% = approx. 10
years)
non-editable
3.1.1.5: Hours > 85°C Previous time during
which the maximum per-
missible sensor tempera-
ture was exceeded in
hours
non-editable
3.1.x: Sensor
and/or
3.1.x: Electronics
and/or
3.1.x: Software
and/or
3.1.x: Application
and/or
3.1.x: Parameters
and/or
3.1.x: Service
Diagnostic messages of
the sensor
non-editable
Diagnostic messages of
the electronics
non-editable
Diagnostic messages of
the software
non-editable
Diagnostic messages to
the application
non-editable
Display of the false
parameters
non-editable
For qualified personnel
only
non-editable
3.2: Device test
3.2.1: Self-test Check device state non-editable
3.2.2: Display test Visual check of LCD non-editable
3.3: Sensor variables
Parameters (PROFIBUS PA)
Note: For parameter descriptions, please refer to the associated HART parameters on
pages 30 to 58.
Parameter, menu
identification Description Factory
Setting
Setting
Possibilities
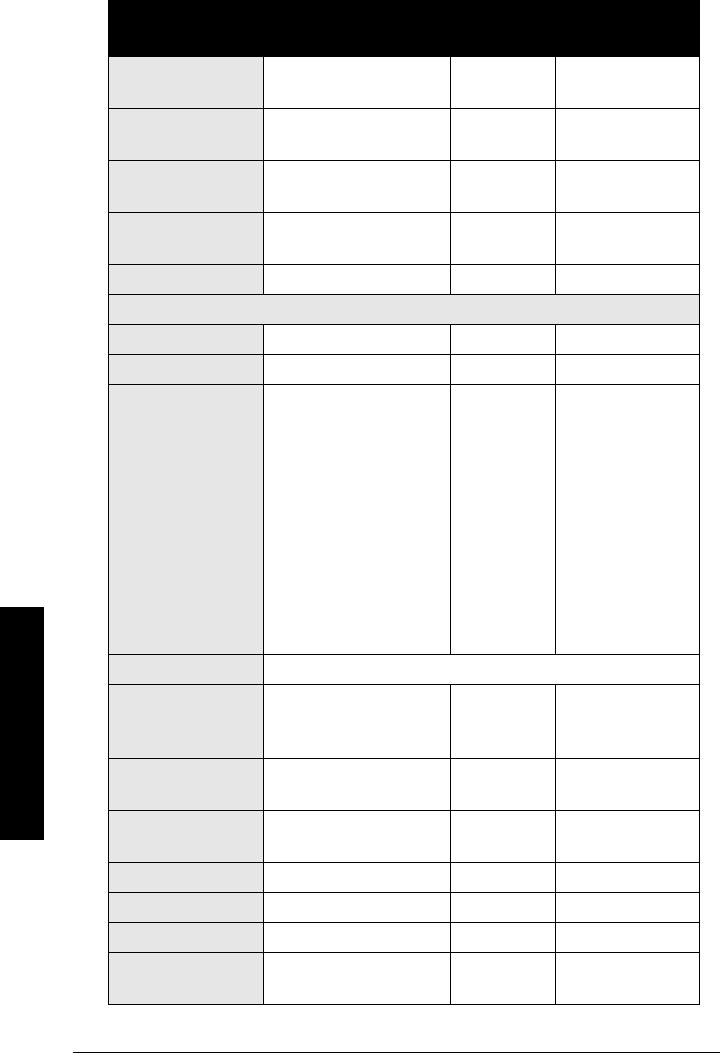
Page 65 SITRANS LR 400 – INSTRUCTION MANUAL 7ML19985FH04
mmmmm
Parameters (Profibus PA)
3.3.1: Raw value Distance from flange to
measured medium
3.3.2: Echo amplitude Measure of quality of
reflection
3.3.3: S/N ratio Signal-to-noise ratio of
the measured value in dB
3.3.4: Validity Validity of the measured
value in %
3.3.5: Sensor temp Sensor temperature
4: Device data
4.1: Units
4.1.1 Length unit = [1.2]
4.1.2: Volume unit m3bbl
yd3
ft3
in3
bush
bbl (fl.)
l
m3
hL
Gal
ImpGal
4.1.3: Mass unit For qualified personnel only
4.1.4: Temperature
unit
Unit of the sensor tem-
perature
°C °C
°F
K
4.1.5: Other units Units system for all other
units
SI SI unit
US/UK unit
4.2: Operating
parameters
4.2.1: Tank geometry
4.2.1.1: Nozzle height = [1.3]
4.2.1.2: Tank height = [1.4]
4.2.1.3: Stilling pipe?
[Liquids}
Stilling pipe available? no yes
no
Parameters (PROFIBUS PA)
Note: For parameter descriptions, please refer to the associated HART parameters on
pages 30 to 58.
Parameter, menu
identification Description Factory
Setting
Setting
Possibilities
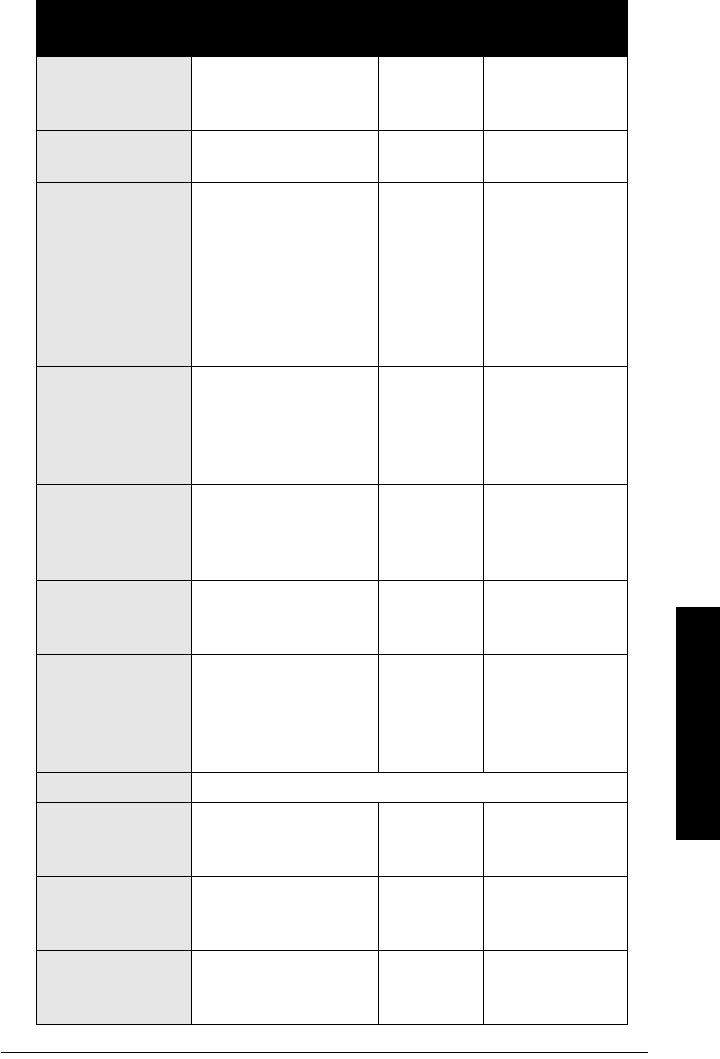
7ML19985FH04 SITRANS LR 400 – INSTRUCTION MANUAL Page 66
mmmmm
Parameters (Profibus PA)
If yes, 4.2.1.3.2: Pipe
diameter
[Liquids}
Diameter (internal) of the
stilling pipe
100 mm numerical value
4.2.2: Measuring
conditions
4.2.2.1: Applic. type Use of the tank Liquid (pro-
cess)
Liquid (store)
Liquid (process)
Silo1 (solids-pel-
lets)
Silo2 (solids-pow-
ders)
User tank1
User tank2
4.2.2.2: Surface Surface structure of the
measured medium
Not displayed if a user
tank is selected in
[4.2.2.1].
wavy smooth
wavy
turbulent
4.2.2.3: Dead band Area beneath the flange
in which measured val-
ues are ignored
0.4 m numerical value,
Minimum value =
Length of the
antenna
4.2.2.4: Correction
factor
Correction factor for
physical measuring influ-
ences
1.0 numerical value
4.2.2.5: Filling speed Typical speed of change
of the level
Not displayed if a user
tank is selected in
[4.2.2.1].
200 mm/min numerical value
4.2.2.6 Reflectivity For qualified personnel only
4.2.2.7: Failsafe level Selects the default mea-
surement in the event the
failsafe timer expires
Hold 100 %
0 %
Hold
4.2.2.8: Failsafe timer Sets the time delay, in
minutes, before going
into fail-safe level
10 min 1 min
2 min
etc.
4.2.2.9: Range exten-
sion
Sets the distance below
the tank height included
in the evaluation
3 m 1 m
2 m
etc.
Parameters (PROFIBUS PA)
Note: For parameter descriptions, please refer to the associated HART parameters on
pages 30 to 58.
Parameter, menu
identification Description Factory
Setting
Setting
Possibilities
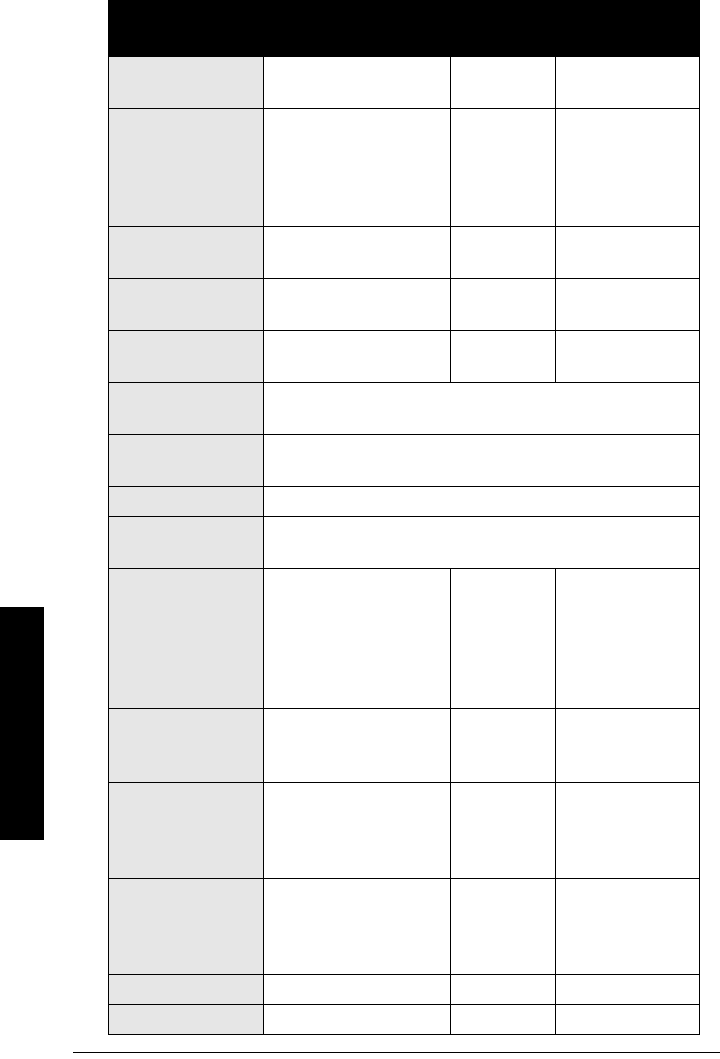
Page 67 SITRANS LR 400 – INSTRUCTION MANUAL 7ML19985FH04
mmmmm
Parameters (Profibus PA)
4.2.3: Sensor param-
eter
4.2.3.1: Sensor damp-
ing
Averaging of measuring
signal
Not displayed if a user
tank is selected in
[4.2.2.1].
1 s numerical value
4.2.3.2: Multiple echo Evaluate multiple echo on on
off
4.2.3.3: Echo motion Evaluate echo motion on on
off
4.2.3.4: Window
tracking
Evaluate moving targets off on
off
4.2.3.5: Tank empty
detect
For qualified personnel only
4.2.3.6: Auto fix dis-
tance
For qualified personnel only
4.2.3.7: Fix Dist List For qualified personnel only
4.2.3.7.1 to 4.2.3.7.9:
Fix Dist List values
For qualified personnel only
4.2.3.8: Auto False
Echo suppression
Learns and records the
current signal up to the
suppression distance set-
ting. These signals are
then ignored during oper-
ation.
use use
record
off
4.2.3.9: Auto False
Echo suppression
distance
Defines the end point of
the Auto False Echo
suppression distance
2/3 tank
height
variable
4.2.3.A Hover level Defines (in %) how high
the TVT curve is placed
above echo profile, rela-
tive to largest echo
40% 0 to 100%
4.2.3.B Window
Trigger
Defines position of win-
dow on leading edge of
selected echo, relative to
amplitude
80% 0 to 100%
4.2.4: Level param.
4.2.4.1: Level URV = [1.5]
Parameters (PROFIBUS PA)
Note: For parameter descriptions, please refer to the associated HART parameters on
pages 30 to 58.
Parameter, menu
identification Description Factory
Setting
Setting
Possibilities
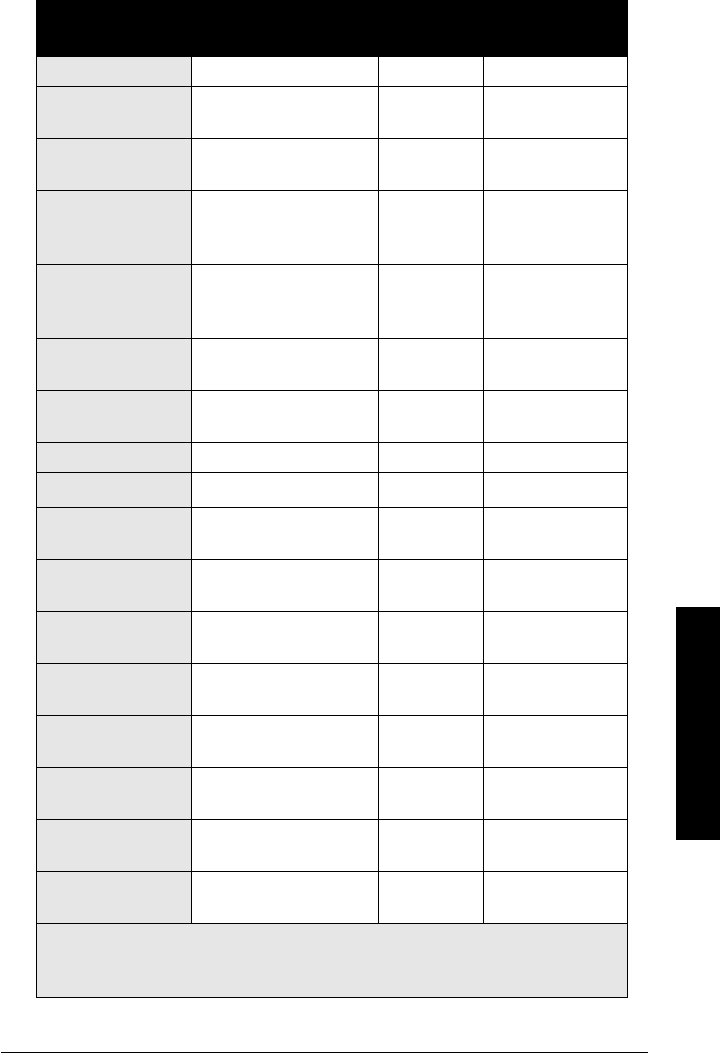
7ML19985FH04 SITRANS LR 400 – INSTRUCTION MANUAL Page 68
mmmmm
Parameters (Profibus PA)
4.2.4.2: Level LRV = [1.6]
4.2.4.3: Level damp-
ing
= [1.7]
4.2.4.4: MinWarn
level
Limit before reaching
lower limit value
0 m numerical value
4.2.4.5: MinLim level Lower limit value of the
level (See Functional
Dimensions Diagram)
0 m numerical value
4.2.4.6: MaxLim level Upper limit value of the
level (See Functional
Dimensions Diagram)
20 m numerical value
4.2.4.7: MaxWarn
level
Limit before reaching
upper limit value
20 m numerical value
4.2.4.8: HYST level Hysteresis of the level
limit values
0.5 m numerical value
4.2.5: Volume param.
4.2.5.1: Volume URV Full scale of the volume 20 m3numerical value
4.2.5.2: Volume LRV Start of scale of the vol-
ume
0 m3numerical value
4.2.5.3: Volume
damping
Damping of the volume 1 s numerical value
4.2.5.4: MinWarn vol-
ume
Limit before reaching
lower limit value
0 m3numerical value
4.2.5.5: MinLim vol-
ume
Lower limit value of the
volume
0 m3numerical value
4.2.5.6: MaxLim vol-
ume
Upper limit value of the
volume
20 m3numerical value
4.2.5.7: MaxWarn
volume
Limit before reaching
upper limit value
20 m numerical value
4.2.5.8: HYST volume Hysteresis of the volume
limit values
0.5 m3numerical value
4.2.5.9: Tank charac-
teristic
Determining the tank
characteristic
Calculate Calibrate/table
Calculate
4.2.5.A: Calibrate/table
or
4.2.5.A: Calculate
Parameters (PROFIBUS PA)
Note: For parameter descriptions, please refer to the associated HART parameters on
pages 30 to 58.
Parameter, menu
identification Description Factory
Setting
Setting
Possibilities
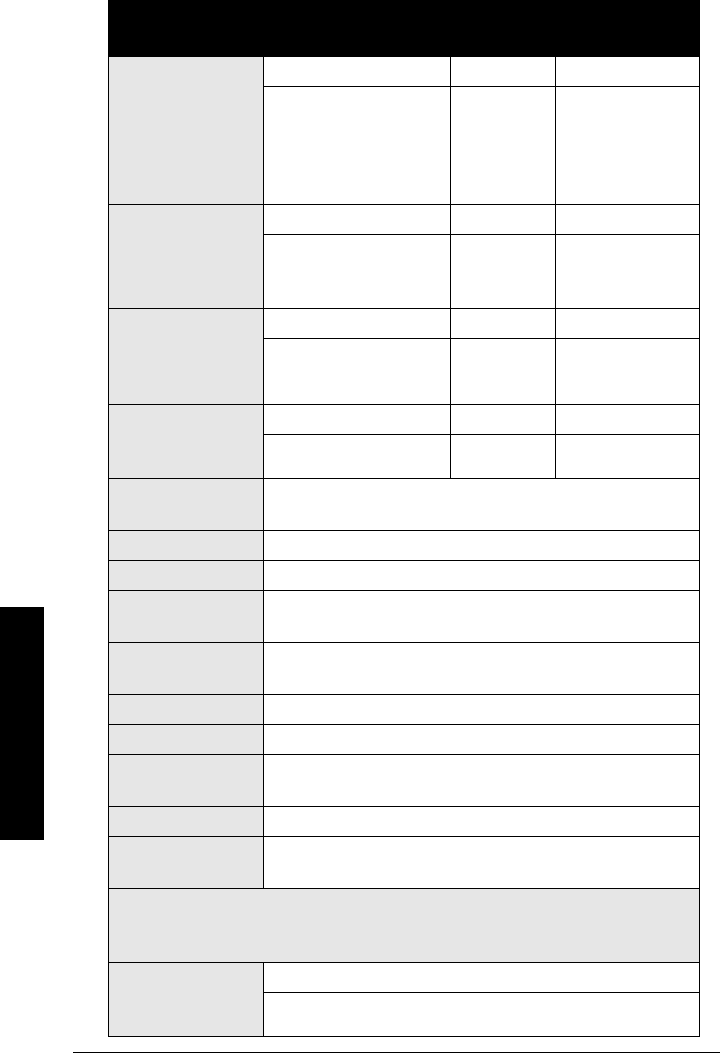
Page 69 SITRANS LR 400 – INSTRUCTION MANUAL 7ML19985FH04
mmmmm
Parameters (Profibus PA)
4.2.5.A.1: Calibrate
or
4.2.5.A.1: Tank design
Automatic litering Confirm input
Vertical cylin-
der
Linear
Vertical cylinder
Horizontal
Cylinder
Sphere
4.2.5.A.2: Enter table
or
4.2.5.A.2: Bottom
design
Manual entry of a table numerical value
Dished end Dished end
Basket end
Bullet bottom
4.2.5.A.3: Show table
or
4.2.5.A.3: Tank vol-
ume
Display table Selection
20 m3numerical value
4.2.5.A.4: Clear table
or
4.2.5.A.4: Tank height
Delete table Selection
= [4.2.1.2]
4.2.6: Mass Parame-
ters
For qualified personnel only
4.2.6.1: Mass URV For qualified personnel only
4.2.6.2: Mass LRV For qualified personnel only
4.2.6.3: Mass damp-
ing
For qualified personnel only
4.2.6.4: MinWarn
Mass
For qualified personnel only
4.2.6.5: MinLim mass For qualified personnel only
4.2.6.6: MaxLim mass For qualified personnel only
4.2.6.7: MaxWarn
Mass
For qualified personnel only
4.2.6.8: HYST Mass For qualified personnel only
4.2.6.9: Tank Charac-
ter
For qualified personnel only
4.2.6.A: Calibrate/table
or
4.2.6.A: Calculate
4.2.6.A.1: Calibrate
or
4.2.6.A.1: Tank design
For qualified personnel only
For qualified personnel only
Parameters (PROFIBUS PA)
Note: For parameter descriptions, please refer to the associated HART parameters on
pages 30 to 58.
Parameter, menu
identification Description Factory
Setting
Setting
Possibilities
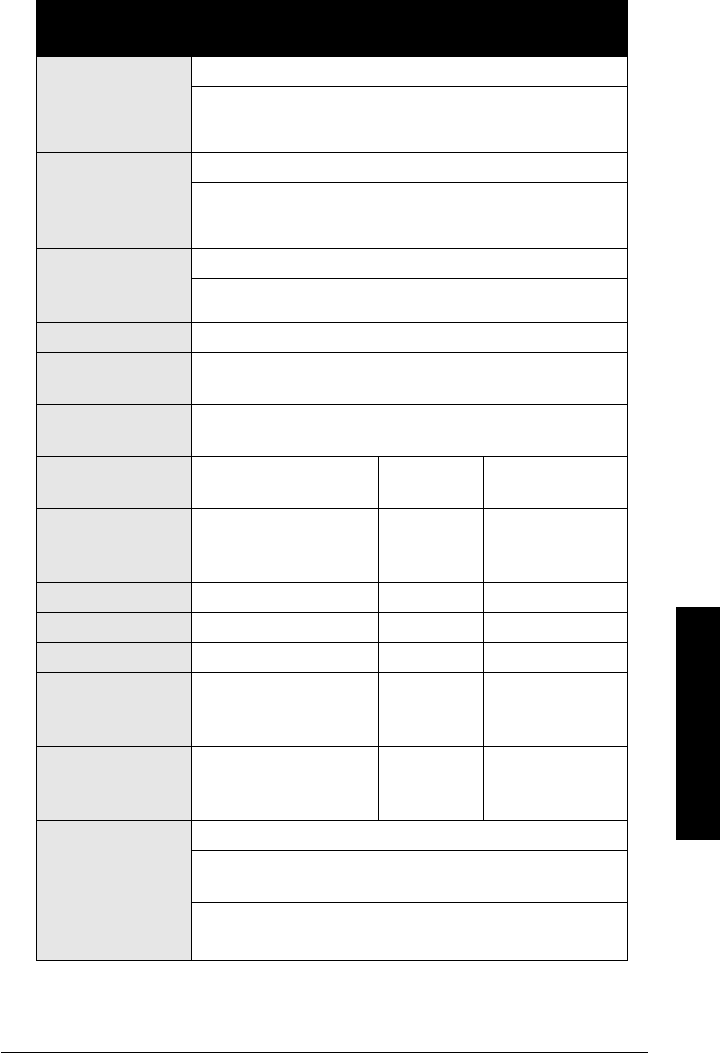
7ML19985FH04 SITRANS LR 400 – INSTRUCTION MANUAL Page 70
mmmmm
Parameters (Profibus PA)
4.2.6.A.2: Enter table
or
4.2.6.A.2: Bottom
design
For qualified personnel only
For qualified personnel only
4.2.6.A.3: Show table
or
4.2.6.A.3: Tank vol-
ume
For qualified personnel only
For qualified personnel only
4.2.6.A.4: Clear table
or
4.2.6.A.4: Tank height
For qualified personnel only
For qualified personnel only
4.2.6.B: Density For qualified personnel only
4.2.7.x: User Parame-
ters 1
For qualified personnel only
4.2.8.x: User Parame-
ters 2
For qualified personnel only
4.3: Output parame-
ter
4.3.1: BusIdentNr. Profile specific
Manufacturer spe-
cific
4.3.2: Bus address = [1.8}
4.4: Display param.
4.4.1: Multi display
4.4.1.1: Line 1 local Choice of measured
value in line 1
Level Level
Volume
Mass
4.4.1.2: Display local Method of display in line
1
Eng unit Eng unit
%
Bargraph
4.4.1.3: Level param.
or
4.4.1.3: Volume
param.
or
4.4.1.3: Mass param.
= [4.2.4]
= [4.2.5]
= [4.2.6]
Parameters (PROFIBUS PA)
Note: For parameter descriptions, please refer to the associated HART parameters on
pages 30 to 58.
Parameter, menu
identification Description Factory
Setting
Setting
Possibilities
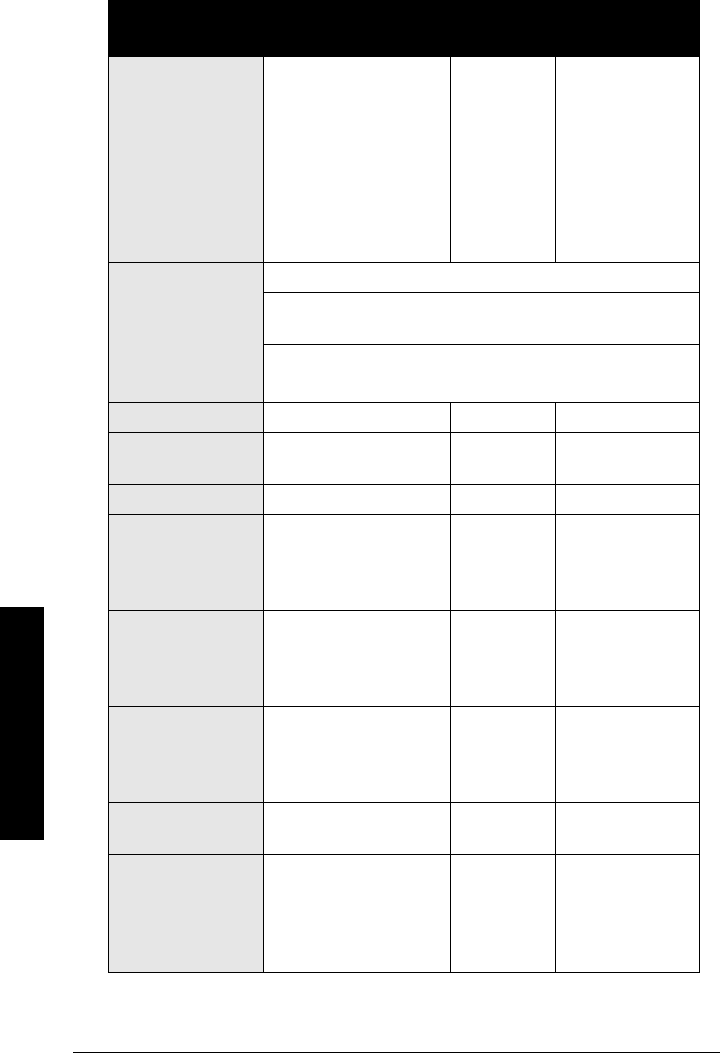
Page 71 SITRANS LR 400 – INSTRUCTION MANUAL 7ML19985FH04
mmmmm
Parameters (Profibus PA)
4.4.1.4: Line 2 local Display in line 2 S/N ratio Level
Volume
Mass
Temperature
Validity
S/N ratio
Amplitude
Digital output
Analog output
4.4.1.5: Level param.
or
4.4.1.5: Volume
param.
or
4.4.1.5: Mass param.
= [4.2.4]
= [4.2.5]
= [4.2.6]
4.4.2: Language local = [1.1]
4.4.3: LCD backlight Background illumination
of the LCD
off on
off
4.5: Device info
4.5.1: Power supply Voltage range of the built-
in power supply unit
according to
customer
specifica-
tions
non-editable
4.5.2: Process
temperature
Temperature range of the
flange in °C
according to
customer
specifica-
tions
non-editable
4.5.3: Electrical con-
nection
according to
customer
specifica-
tions
non-editable
4.5.4: Antenna and
flange
4.5.4.1: Flange size Rated size of the flange according to
customer
specifica-
tions
DN 50, 2"
DN 80, 3"
DN 100, 4"
DN 150, 6"
Special design
Parameters (PROFIBUS PA)
Note: For parameter descriptions, please refer to the associated HART parameters on
pages 30 to 58.
Parameter, menu
identification Description Factory
Setting
Setting
Possibilities
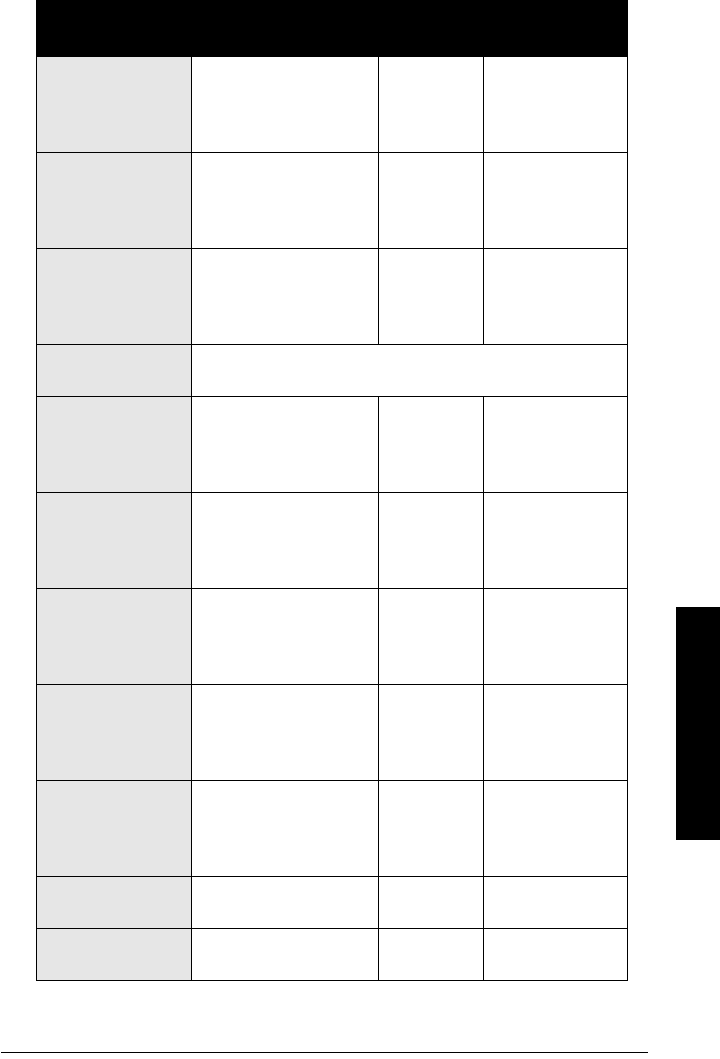
7ML19985FH04 SITRANS LR 400 – INSTRUCTION MANUAL Page 72
mmmmm
Parameters (Profibus PA)
4.5.4.2: Flange type Type of flange according to
customer
specifica-
tions
DIN
ANSI
JIS
Special design
4.5.4.3: Pressure
range
Pressure range of the
process connection
according to
customer
specifica-
tions
non-editable
4.5.4.4: Antenna type according to
customer
specifica-
tions
Horn type 2"
Horn type 3"
Horn type 4"
4.5.4.5: Antenna
extension
For qualified personnel only
4.5.4.6: Flange
material
according to
customer
specifica-
tions
304
316/316L
4.5.4.7: Seal material Sealing material according to
customer
specifica-
tions
PTFE
FKM
4.5.5: Tag Device identification according to
customer
specifica-
tions
up to any eight
characters
4.5.6: Descriptor Measuring point descrip-
tion
according to
customer
specifica-
tions
up to any 16 char-
acters
4.5.7: Message Measuring point mes-
sage, e.g. the date of last
check or clean
according to
customer
specifica-
tions
up to any 32 char-
acters
4.5.8: Manufacturer
identification
4.5.8.1: Serial no. Factory serial number unique num-
ber
non-editable
Parameters (PROFIBUS PA)
Note: For parameter descriptions, please refer to the associated HART parameters on
pages 30 to 58.
Parameter, menu
identification Description Factory
Setting
Setting
Possibilities
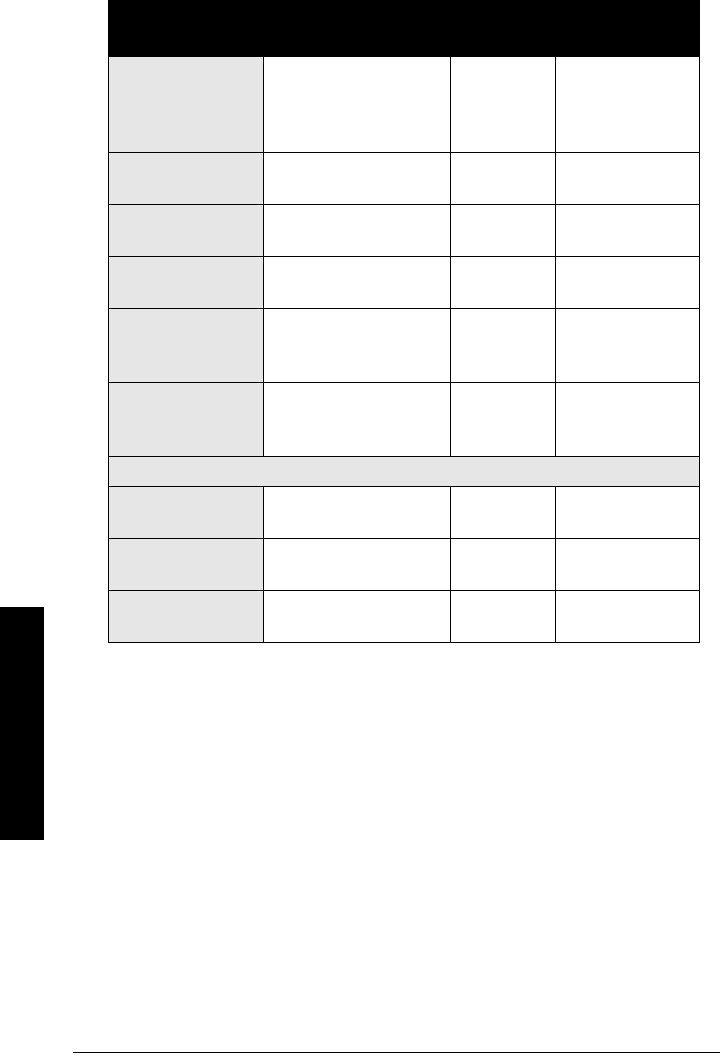
Page 73 SITRANS LR 400 – INSTRUCTION MANUAL 7ML19985FH04
mmmmm
Parameters (Profibus PA)
4.5.8.2: Order no. Delivery order no. (deliv-
ery state)
according to
customer
specifica-
tions
non-editable
4.5.8.3: Device revi-
sion
Device version Number non-editable
4.5.8.4: Software
revision
Number non-editable
4.5.8.5: Hardware
revision
Number non-editable
4.5.8.6: Antenna off-
set
Distance sensor/flange approx. 0.5 m
(calibration
value)
non-editable
4.5.8.7: Reference
distance
Internal reference dis-
tance
approx. 106 m
(calibration
value)
non-editable
5: Options
5.1: Enter code Input of customer code to
enable programmability
Customer code
5.2: Customer code Determination of cus-
tomer code
0 up to 9 digit code
5.3: Factory reset Reset all parameters to
factory setting
no yes
no
Parameters (PROFIBUS PA)
Note: For parameter descriptions, please refer to the associated HART parameters on
pages 30 to 58.
Parameter, menu
identification Description Factory
Setting
Setting
Possibilities
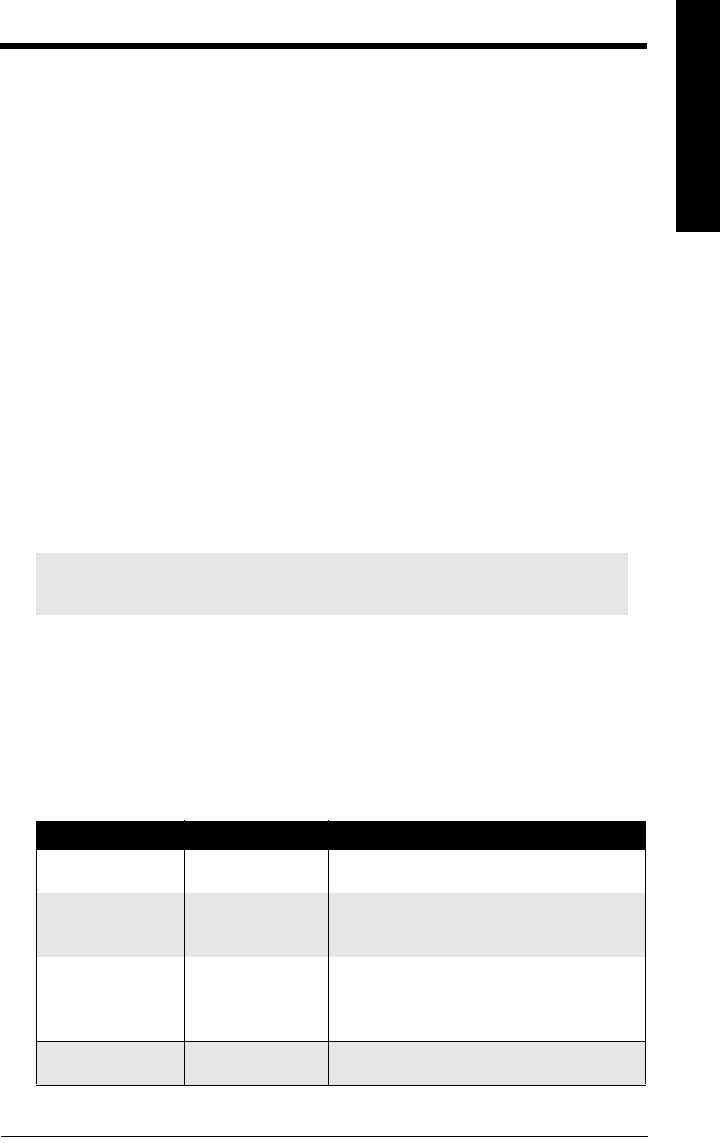
7ML19985FH04 SITRANS LR 400 – INSTRUCTION MANUAL Page 75
mmmmm
Troubleshooting
Troubleshooting
The SITRANS LR 400 is factory-tested. Carefully selected components and compliance
with prescribed quality standards guarantee the high reliability of the SITRANS LR 400.
Please review the instructions below for troubleshooting before contacting the
responsible customer services.
Classification of Faults
Faults occurring in the SITRANS LR 400 can be classified in the following groups:
• faults caused by ambient influences: over- and under-temperature, moisture,
contamination by the measuring medium and other substances, mains faults,
vibration
• faults in the device: display, electronics, mechanics, connections
Please try to determine the fault and localize it as accurately as possible.
If the fault cannot be eliminated with the measures described below, follow the
instructions in Maintenance on page 78.
Self-test
If you get fault messages after the self-test, please proceed according to Fault Messages
on page 76.
If there is a malfunction in the device, you can also activate the self-test manually with
Parameter 3.2.1.
Symptoms, Causes and Their Remedy
Note: The device performs a self-test every time it is switched on. It is ready for
operation when the LCD displays the multi-display.
Symptom Possible causes Remedy
No display on the LCD Defective or missing
power supply
Check that the power supply is connected
correctly.
LCD is defective
Connect a HART Communicator or a PC/Laptop
with SIMATIC PDM software. If the device can be
parameterized from there, the LCD is defective.
Electronics are
defective
Measure the analog current output. If the output
current is not between 3.6 mA < x < 22 mA, the
electronics are defective. Replace the electronics
unit as described in Maintenance on page 78.
A fault message is
displayed Internal fault Call the fault display in Function 3.1.
Proceed as described in Maintenance on page 78.
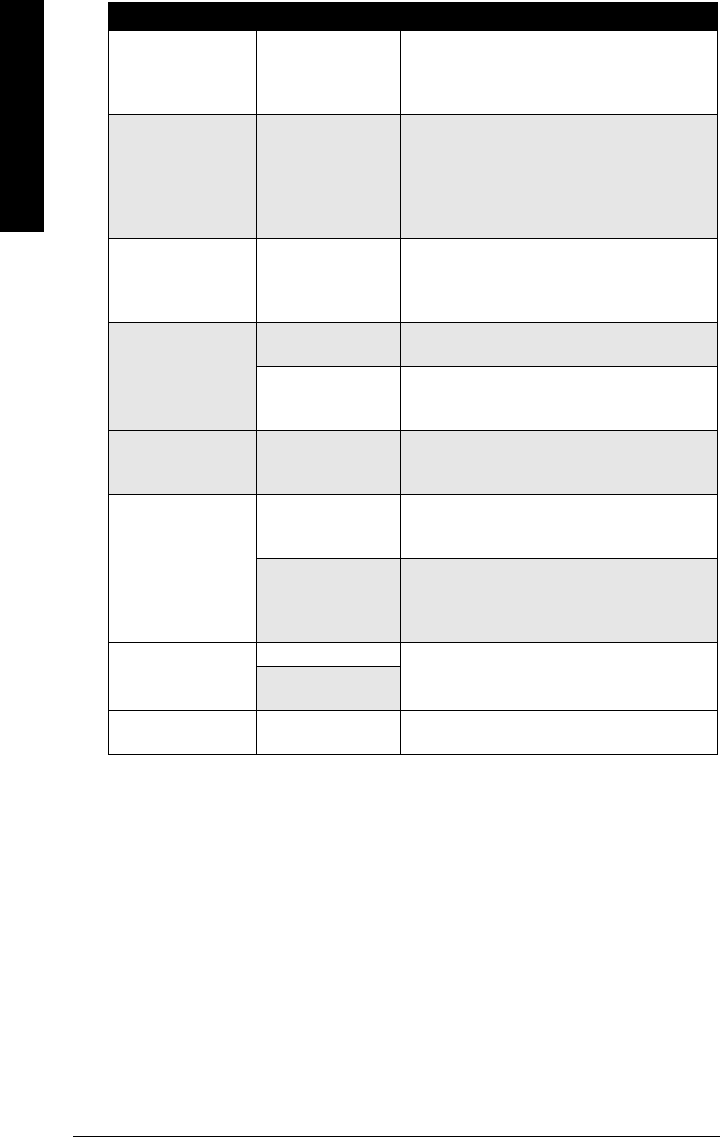
Page 76 SITRANS LR 400 – INSTRUCTION MANUAL 7ML19985FH04
mmmmm
Troubleshooting
Fault Messages
The device indicates faults with a flashing letter on the right of the first line of the display.
It has the following meaning:
• W: Warning – device is still ready for operation but faults may occur
• F: Fault – sporadic fault, device conditionally ready for operation
• D: Continuous fault – device is not ready for operation
Under Parameter 3.1.x, you will find a fault log which indicates the type of the fault(s) that
occurred. It indicates the device function status in which the fault occurred and outputs a
fault message in plain text.
An incorrect
measured value
appears after Auto-
Setup.
The device is not
parameterized
correctly according to
the application
Set the device parameters and functions
manually.
No measured value
appears after the
Auto-Setup
(measured value 0 and
the fault display
flashes)
Internal fault Call the fault display in Parameter 3.1.
Proceed as described in Maintenance on page 78.
Material movement
but output remains
constant
Varying signal moves
out of tracking
window too
frequently.
Set Window Tracking (4.2.3.4) to OFF.
SITRANS LR 400 reads
100% continually.
Check antenna for
material buildup. Clean antenna or order a purge (self-cleaning) kit.
Nozzle interference,
or end of horn is not
inside vessel
Shorten nozzle or lower position of SITRANS
LR 400.
SITRANS LR 400
reading stays above
actual level
False echo from
vessel (fixed
obstruction)
Use 4.2.3.8 and 4.2.3.9 Auto False Echo
Suppression function
SITRANS LR 400 reads
low or empty when
material level is high
Multiple or indirect
echo detected
instead of first echo.
Set 4.2.3.2 Multiple Echo Tracking to ON. Try using
Liquid Store application type 4.2.2.1.
Highly sloped surface
Aim the SITRANS LR 400 using shims or order an
Easy Aimer kit. Contact your Siemens
representative for service and possible User
parameter support.
SITRANS LR 400
reading is too slow.
Damping too high Decrease 4.2.3.1 Sensor Damping
Decrease Level Damping
Set 4.2.3.4 to OFF (Window Tracking)
Window Tracking
was too slow.
SITRANS LR 400
reading is drifting
Sloped material
surface Increase damping.
Symptom Possible causes Remedy
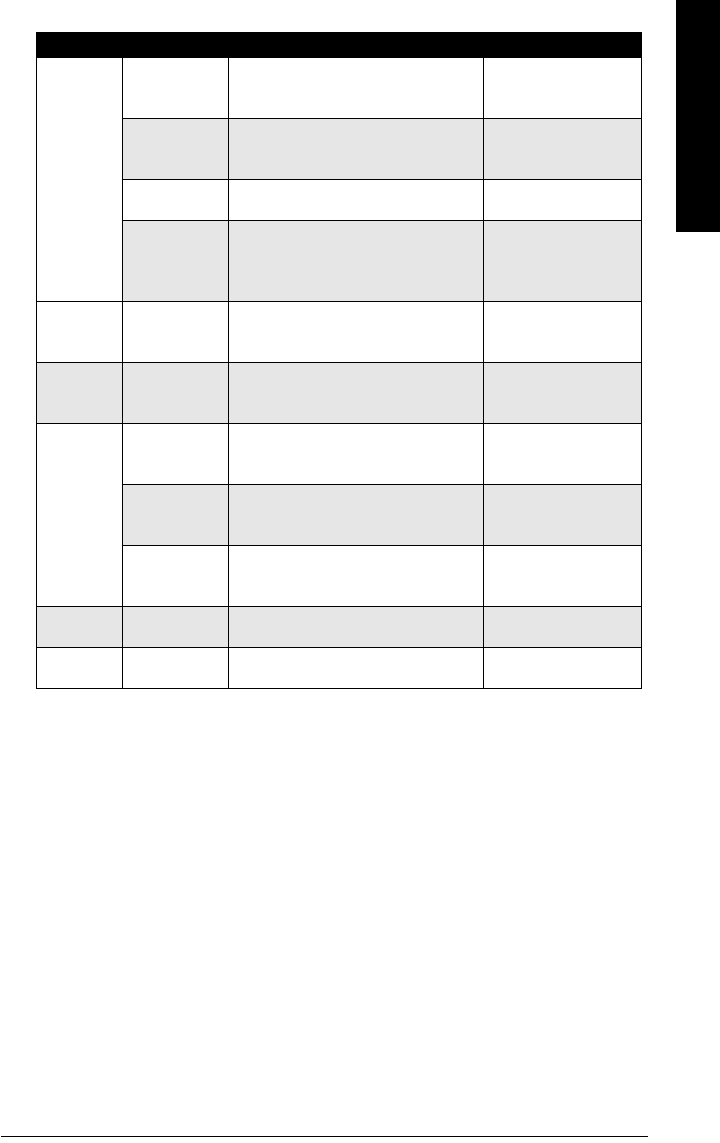
7ML19985FH04 SITRANS LR 400 – INSTRUCTION MANUAL Page 77
mmmmm
Troubleshooting
Possible fault messages:
1. Make the following modifications, starting with
a. Check whether the fault still occurs after every step.
b. Check the set measuring range and the deadband (Parameter 4.2.2.3).
c. Check whether the filling speed has been correctly set (Parameter 4.2.2.5).
d. Reduce the reflectivity (Parameter 4.2.2.6).
e. Switch off the automatic fixed target detection (Parameter 4.2.3.6) if necessary.
f. Switch off the multiple echo detection (Parameter 4.2.3.2) if necessary.
Unit Repair and Excluded Liability
All changes and repairs must be done by qualified personnel and applicable safety
regulations must be followed. Please note the following:
• The user is responsible for all changes and repairs made to the device.
• All new components must be provided by Siemens Milltronics Process
Instruments Inc.
• Restrict repair to faulty components only
• Do not re-use faulty components.
Function Message Possible causes Remedy
Sensor
MW cable
defective
Microwave cable not connected or line
break
Contact your Siemens
Milltronics
representative
Sensor
defective Overtemperature in device
Contact your Siemens
Milltronics
representative
Check antenna Antenna contaminated, damaged or not
mounted Check the antenna
Sensor too hot Sensor temperature exceeds 85 °C
Check the max.
permissible ambient
and process
temperature
Electronics all messages Internal fault
Contact your Siemens
Milltronics
representative
Software all messages Internal fault
Contact your Siemens
Milltronics
representative
Application
No valid meas.
value
fault in fixed target detection, fault in
multiple echo detection, poorly
reflecting measuring medium
1 (see below)
Tank e mpt y
detected
vessel is empty (only when sensor
parameter vessel empty detection
active)
Deactivate vessel
empty detection if
necessary
false param. incompatible parameters entered,
e. g.: URV = LRV
Correct the parameters
listed in the next
function
Parameters <Parameter to
be corrected> False parameterization Perform the correction
as indicated
Service (various) For service personnel
only
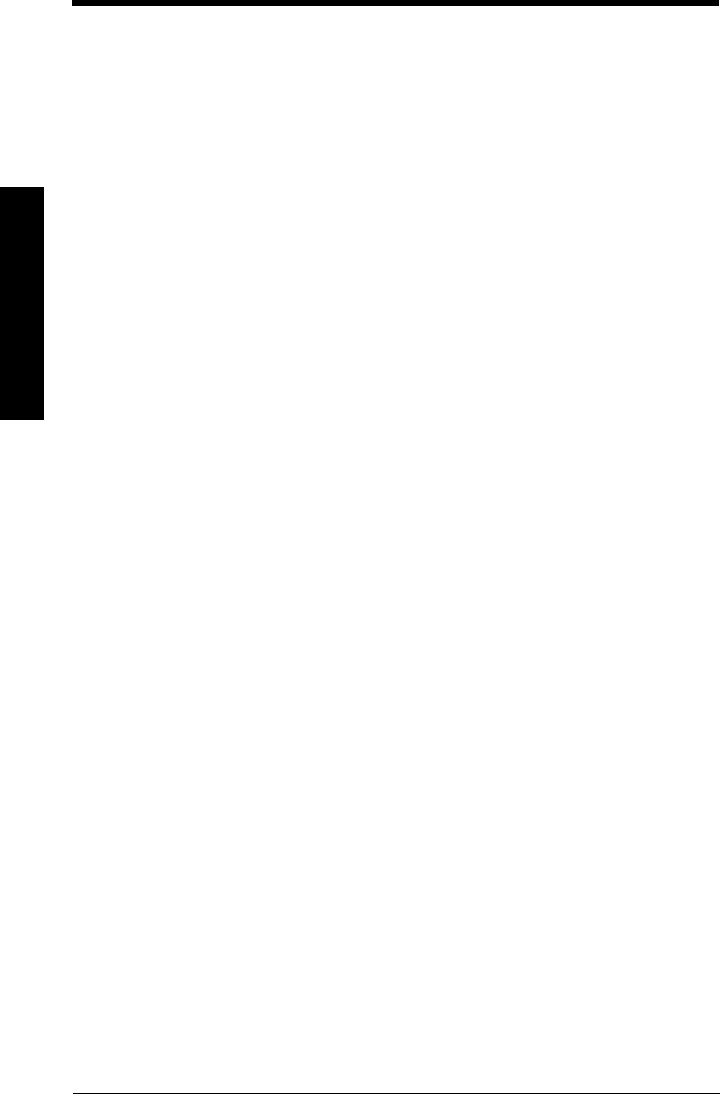
Page 78 SITRANS LR 400 – INSTRUCTION MANUAL 7ML19985FH04
mmmmm
Maintenance
Maintenance
Cleaning the Antenna
If the antenna is contaminated, any built-up material can be removed using air or soft
brushes. Be careful not to damage the PTFE emitter cone inside the antenna.
An optional purge kit is available from Siemens Milltronics if required. Contact your local
Siemens Millltronics representative for more details.
Solids Version
If the measured material is prone to build-
up, you may need to clean the antenna at
regular intervals to remove buildup that
may affect the measuring result. To
access the antenna, the flange must be
removed.
1. Disconnect the electronics by
turning off the connector waveguide,
located directly above the Easy
Aimer ball.
2. Remove the flange bolts. (position
label)
3. Lift off the process section (including
antenna).
4. Remove four Hex head M5 screws
holding the antenna. (position label)
5. Clean the inside of the antenna with
compressed air or soft brush.
6. Reattach the antenna and tighten the
screws (ensure the screws are
tightened according to the torque
shown opposite). (position label)
7. Insert the process section into the
vessel and fasten the flange bolts.
(position label)
8. Reattach the electronics to the
process section
Graphic
showing
expanded
diagram of LR
400 antenna
labelled with
torque of
appropriate
screws.
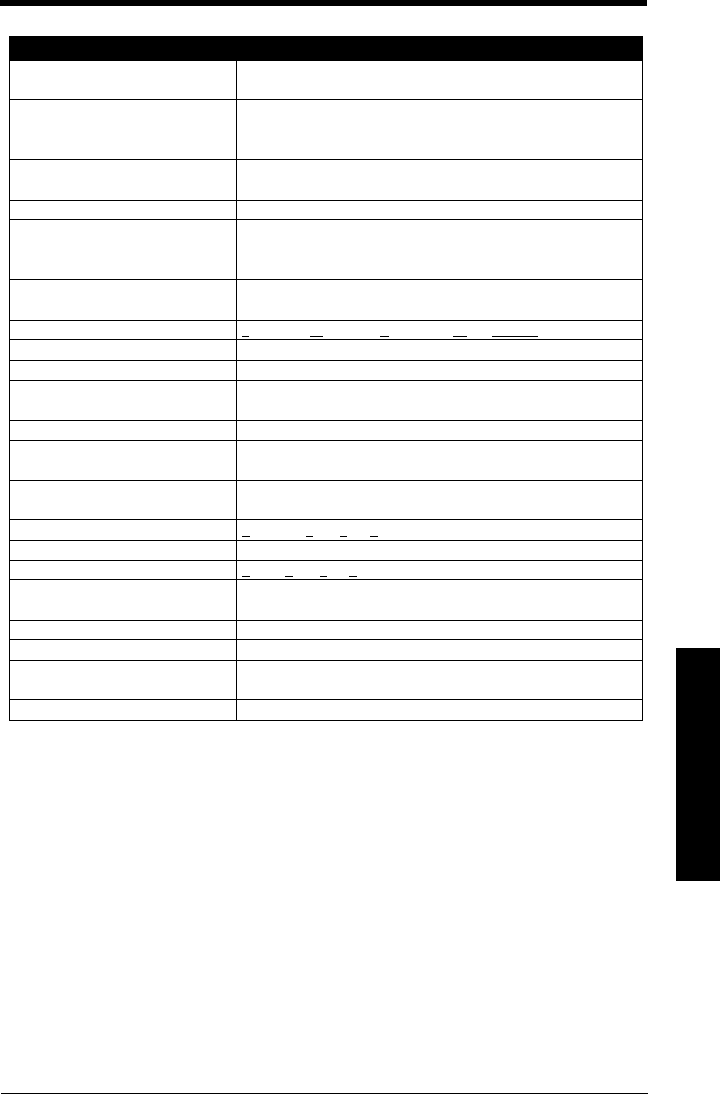
7ML19985FH04 SITRANS LR 400 – INSTRUCTION MANUAL Page 79
mmmmm
Glossary
Glossary
Term Explanation
Antenna offset Propagation time of the signal in the sensor, expressed as a dis-
tance
Current limit
The maximum possible value of the output signal in fault-free
operation in mA. The value of the fail signal may be above the
current limit with 24 mA.
Customer code User-defined code which protects the device against accidental
programming.
Dead band Value range below the device flange declared unmeasurable.
Echo movement
Sensor parameter for a fuzzy rule which takes into account
dynamic procedures in the measuring medium, for example, and
therefore rules out fixed targets.
Fixed target Permanently installed objects inside the vessel which may cause
reflective interference, e.g. struts, agitators, feed pipes etc.
FMCW method Frequency Modulated Continuous Wave method
Frequency deviation Changing the transmission frequency in the FMCW method.
Level Distance from the LRV to the surface of the measuring medium.
LRV Lower limit of the valid measuring range as a distance from the
bottom inside of the vessel.
Measuring medium The (solid or liquid) contents of the vessel.
Multiple echo
evaluation
Sensor parameter for a fuzzy rule which detects and suppresses
multiple reflections of the measuring signal at the vessel walls.
Nozzle height Distance from the top of the inside of the vessel to the bottom of
the device flange.
PELV Protected Extra Low Voltage
PTFE Polytetrafluorethylene
SELV Safety Extra Low Voltage
Signal-to-noise ratio Measure of the strength of reflection of the measuring medium
in the current measuring situation in dB.
vessel height Distance between the floor and top of the vessel.
Triple reflector Metal instrument formed as a cubic segment with right angles.
URV Upper limit of the valid measuring range as a distance from the
bottom inside of the vessel.
Validity Measure of the certainty of the current measured value in %.
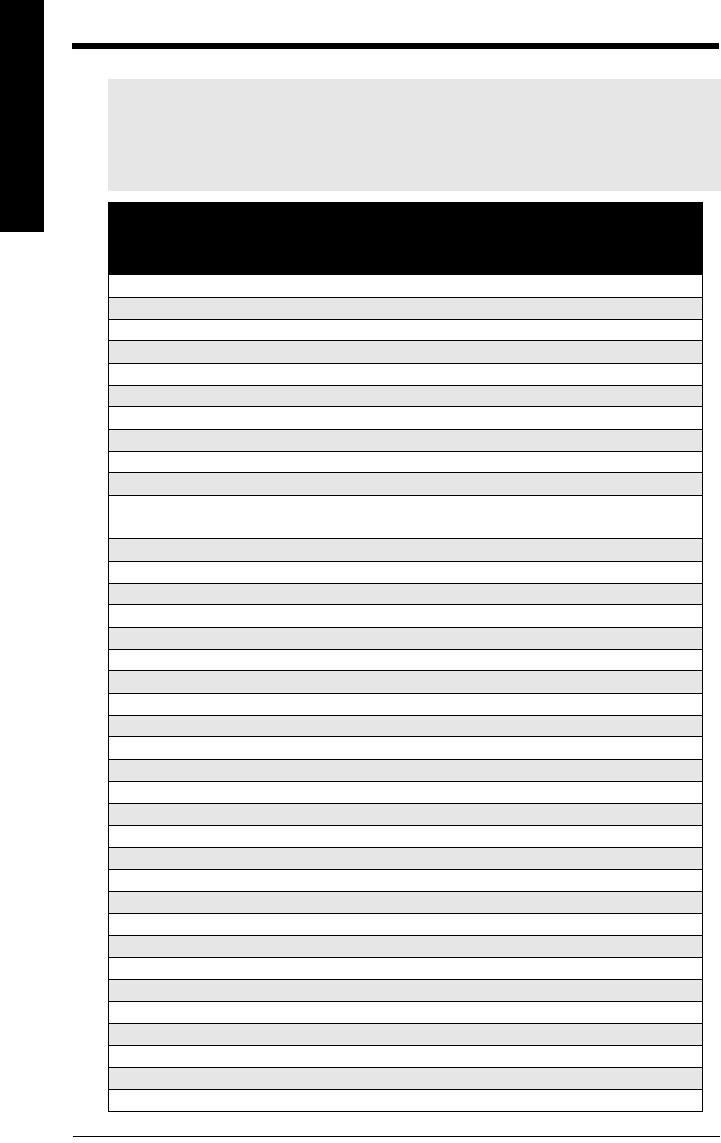
Page 80 SITRANS LR 400 – INSTRUCTION MANUAL 7ML19985FH04
mmmmm
Appendix I
Appendix I: Parameter List
Note: Parameter menus are dependent on selections made by the user.
In some cases, parameter menus are renumbered according to the
selection made at the previous menu level. Therefore, the parameter
numbering shown below includes the standard parameter numbering.
Parameter Name
Menu
Identification
Number
Page Number
Agin g 3.1.1. 4 36
Analog output 4.3 54
Antenna and flange 4.6.4 59
Antenna extensions 4.6.4.5 60
Antenna offset 4.6.8.6 61
Antenna type 4.6.4.4 60
AO select 4.3.2 54
Application type 1.8 35
Application type 4.2.2.1 42
Auto False Echo Suppression 4.2.3.8 46
Auto False Echo Suppression
Distance
4.2.3.9 47
Auto Fix Distance 4.2.3.6 46
Auto-Setup 1 33
Bottom design (volume) 4.2.5.8.2 52
Bottom design (mass) 4.2.6.8.2 53
Calculate (volume) 4.2.5.8 51
Calculate (mass) 4.2.6.8 53
Calibrate (volume) 4.2.5.8.1 50
Calibrate (mass) 4.2.6.8.1 53
Calibrate/table (volume) 4.2.5.8 50
Calibrate/table (mass) 4.2.6.8 53
Clear table (volume) 4.2.5.8.4 51
Clear table (mass) 4.2.6.8.4 53
Correction factor 4.2.2.4 43
Current limit 4.3.4 54
Current output 2.5 36
Customer code 5.2 62
Dead band 4.2.2.3 43
Descriptor 4.6.6 61
Device data 440
Device Information 4.6 59
Device revision 4.6.8.3 61
Device test 3.2 38
Diagnostics 336
Digital output 2.6 36
Digital output 4.4 56
Display 2 35
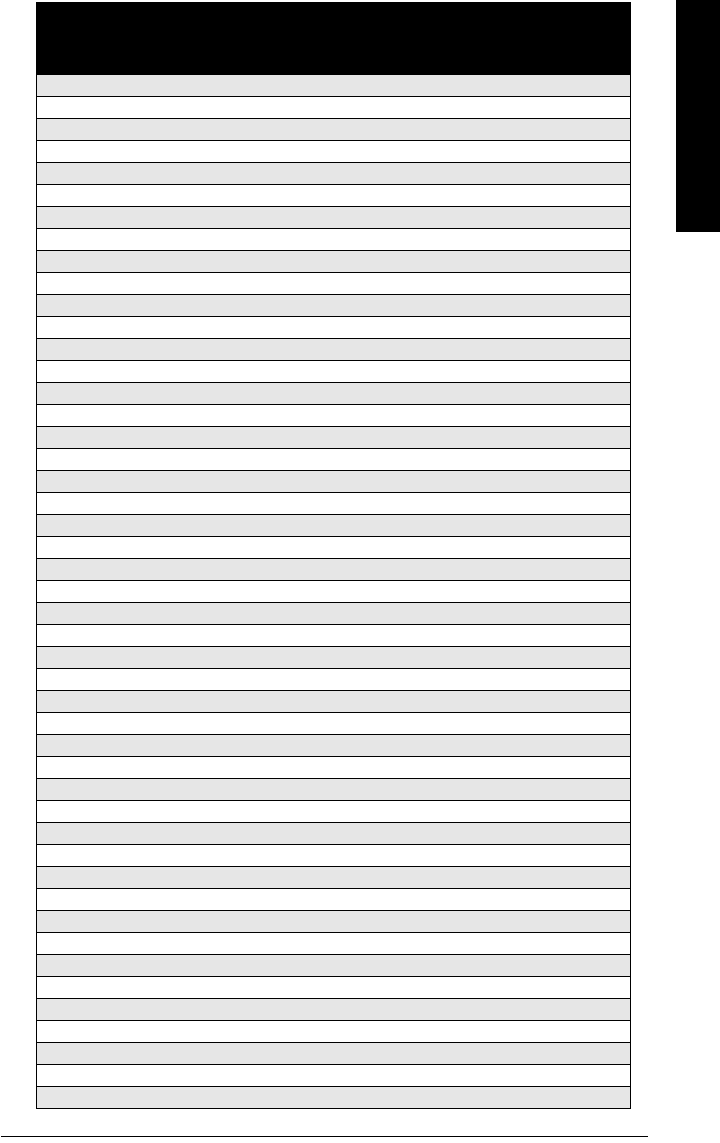
7ML19985FH04 SITRANS LR 400 – INSTRUCTION MANUAL Page 81
mmmmm
Appendix I
Display local 4.5.1.2 58
Display parameter 4.5 57
Display test 3.2.2 38
Echo amplitude 3.4.2 39
Echo motion 4.2.3.3 45
Electrical connection 4.6.3 59
Enter code 5.1 62
Enter table (volume) 4.2.5.8.2 50
Enter table (mass) 4.2.6.8.2 53
Error level (analog output) 4.3.1 54
Error level (digital output) 4.4.2 56
Error signal 4.3.5 55
Factory reset 5.3 62
Failsafe level 4.2.2.7 44
Failsafe timer 4.2.2.8 44
Filling speed 4.2.2.5 43
Fix distance list 4.2.3.7 46
Fix distance values 4.2.3.7.1 to 4.2.3.7.9 46
Flange material 4.6.4.6 60
Flange size 4.6.4.1 59
Flange type 4.6.4.2 60
Function DO 4.4.1 56
Hardware revision 4.6.8.5 61
Hours > 85°C 3.1.1.5 37
Hover level 4.2.3.A 47
HYST level 4.2.4.6 48
HYST mass 4.2.6.6 52
HYST volume 4.2.5.6 49
Language local 1.1 33
Language local (display) 4.5.2 59
LCD backlight 4.5.3 59
Length unit 1.2 34
Length unit 4.1.1 40
Level 2.2 35
Level damping 1.7 35
Level damping 4.2.4.3 47
Level LRV 1.6 34
Level LRV 4.2.4.2 47
Level parameters 4.2.4 47
Level parameter (analog output) 4.3.3 54
Level parameter (digital output) 4.4.4 57
Level parameter (line 1 local) 4.5.1.3 58
Level parameter (line 2 local) 4.5.1.5 58
Level URV 1.5 34
Level URV 4.2.4.1 47
Line 1 local 4.5.1.1 57
Line 2 local 4.5.1.4 58
Parameter Name
Menu
Identification
Number
Page Number
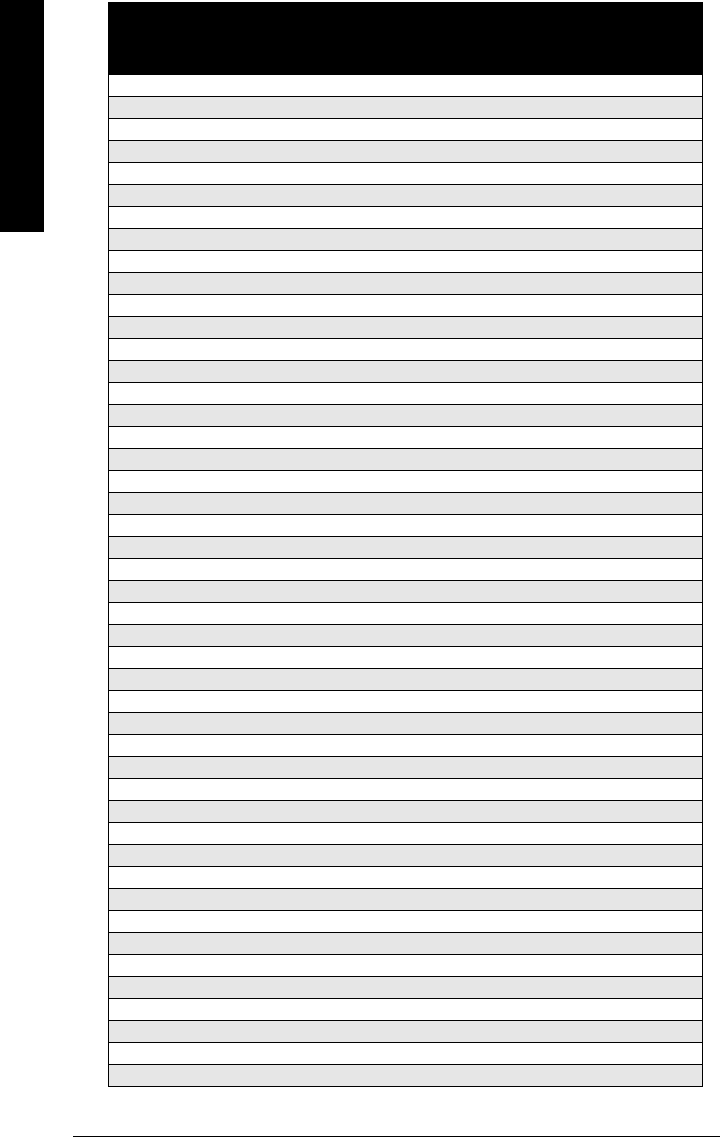
Page 82 SITRANS LR 400 – INSTRUCTION MANUAL 7ML19985FH04
mmmmm
Appendix I
Manufacturer identification 4.6.8 61
Mass 2.4 36
Mass damping 4.2.6.3 52
Mass LRV 4.2.6.2 52
Mass parameters 4.2.6 52
Mass parameter (analog output) 4.3.3 54
Mass parameter (digital output) 4.4.4 57
Mass parameter (line 1 local) 4.5.1.3 58
Mass parameter (line 2 local) 4.5.1.5 59
Mass unit 4.1.3 40
Mass URV 4.2.6.1 52
Maximum temperature 3.1.1.2 36
MaxLim level 4.2.4.5 48
MaxLim mass 4.2.6.5 52
MaxLim volume 4.2.5.5 49
Measuring conditions 4.2.2 42
Message 4.6.7 61
Minimum temperature 3.1.1.3 36
MinLim level 4.2.4.4 48
MinLim mass 4.2.6.4 52
MinLim volume 4.2.5.4 49
Multi-display 2.1 35
Multi-display 4.5.1 57
Multiple echo 4.2.3.2 45
Nozzle height 1.3 34
Nozzle height 4.2.1.1 41
Operating hours 3.1.1.1 36
Operating Parameters 4.2 41
Options 5 62
Order no. 4.6.8.2 61
Other units 4.1.5 41
Pipe diameter (if 4.2.1.3 = yes) 4.2.1.3.2 42
Power supply 4.6.1 59
Pressure stage 4.6.4.3 60
Process temperature 4.6.2 59
Range Extension 4.2.2.9 44
Raw value 3.4.1 39
Reference distance 4.6.8.7 62
Reflectivity 4.2.2.6 44
S/N ratio 3.4.3 39
Seal material 4.6.4.7 60
Self-test 3.2.1 38
Sensor damping 4.2.3.1 45
Sensor parameter 4.2.3 44
Sensor temperature 3.4.5 40
Sensor variables 3.4 39
Parameter Name
Menu
Identification
Number
Page Number
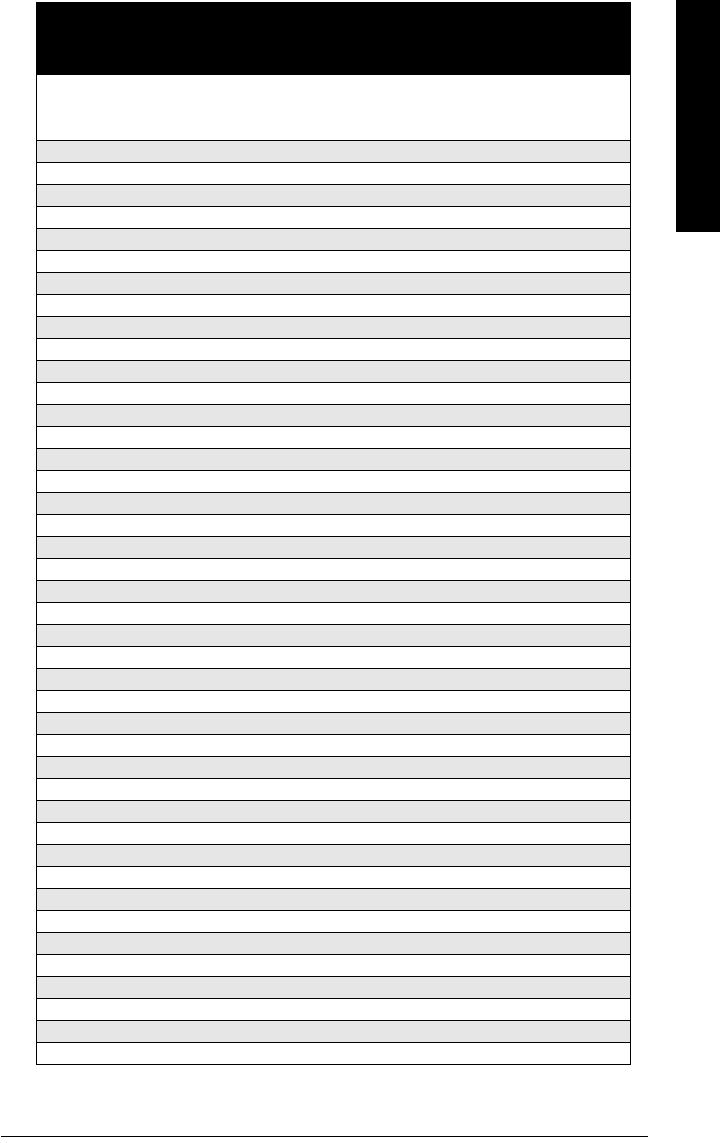
7ML19985FH04 SITRANS LR 400 – INSTRUCTION MANUAL Page 83
mmmmm
Appendix I
Sensor, electronics, software,
application, parameters and or
service
3.1.x 37
Serial no. 4.6.8.1 61
Show table (volume) 4.2.5.8.3 52
Show table (mass) 4.2.6.8.3 53
Signal type DO 4.4.3 56
Simulate AO 3.3.1 38
Simulate DO 3.3.2 39
Simulation 3.3 38
Software revision 4.6.8.4 61
Status 3.1 36
Stilling pipe? 4.2.1.3 41
Surface 4.2.2.2 42
Tag 4.6.5 60
Tank characteristic (volume) 4.2.5.7 49
Tank characteristic (mass) 4.2.6.7 52
Tank design (volume) 4.2.5.8.1 52
Tank design (mass) 4.2.6.8.1 53
Tank empty detect 4.2.3.5 46
Tank geometry 4.2.1 41
Tank height 1.4 34
Tank height 4.2.1.2 41
Tank height (volume) 4.2.5.8.4 52
Tank height (mass) 4.2.6.8.4 53
Tank volume (volume) 4.2.5.8.3 52
Tank volume (mass) 4.2.6.8.3 53
Temperature unit 4.1.4 41
Units 4.1 40
User1 parameters 4.2.7.x 53
User2 parameters 4.2.8.x 53
Validity 3.4.4 40
Volume 2.3 36
Volume damping 4.2.5.3 49
Volume LRV 4.2.5.2 49
Volume parameters 4.2.5 49
Volume parameter (analog output) 4.3.3 54
Volume parameter (digital output) 4.4.4 57
Volume parameter (line 1 local) 4.5.1.3 58
Volume parameter (line 2 local) 4.5.1.5 58
Volume unit 4.1.2 40
Volume URV 4.2.5.1 49
Wear 3.1.1 36
Window tracking 4.2.3.4 46
Window trigger 4.2.3.B 47
Parameter Name
Menu
Identification
Number
Page Number
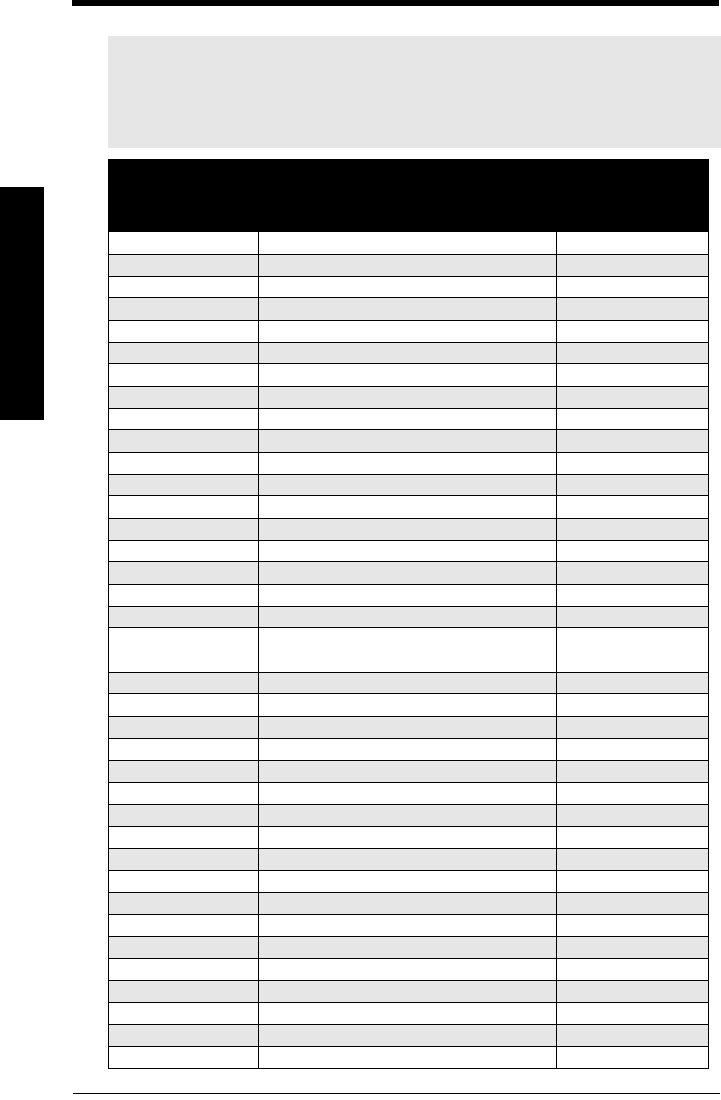
Page 84 SITRANS LR 400 – INSTRUCTION MANUAL 7ML19985FH04
mmmmm
Appendix II
Appendix II: Programming Chart
Note: Parameter menus are dependent on selections made by the user.
In some cases, parameter menus are renumbered according to the
selection made at the previous menu level. Therefore, the parameter
numbering shown below includes the standard parameter numbering.
Menu
Identification
Number
Parameter Name Value
1.1 Language local
1.2 Length unit
1.3 Nozzle height
1.4 Tank height
1.5 Level URV
1.6 Level LRV
1.7 Level damping
2.1 Multi-display
2.2 Level
2.3 Volume
2.4 Mass
2.5 Current output
2.6 Digital output
3.1.1.1 Operating hours
3.1.1.2 Maximum temperature
3.1.1.3 Minimum temperature
3.1.1.4 Aging
3.1.1.5 Hours > 85°C
3.1.x Sensor, electronics, software, application,
parameters and or service
3.2.1 Self-test
3.2.2 Display test
3.3.1 Simulate AO
3.3.2 Simulate DO
3.4.1 Raw value
3.4.2 Echo amplitude
3.4.3 S/N ratio
3.4.4 Validity
3.4.5 Sensor temperature
4.1 Units
4.1.1 Length unit
4.1.2 Volume unit
4.1.3 Mass unit
4.1.4 Temperature unit
4.1.5 Other units
4.2.1.1 Nozzle height
4.2.1.2 Tank height
4.2.1.3 Stilling pipe?

7ML19985FH04 SITRANS LR 400 – INSTRUCTION MANUAL Page 85
mmmmm
Appendix II
4.2.1.3.2 Pipe diameter (if 4.2.1.3 = yes)
4.2.2.1 Application type
4.2.2.2 Surface
4.2.2.3 Dead band
4.2.2.4 Correction factor
4.2.2.5 Filling speed
4.2.2.6 Reflectivity
4.2.2.7 Failsafe level
4.2.2.8 Failsafe timer
4.2.2.9 Range extension
4.2.3 Sensor parameter
4.2.3.1 Sensor damping
4.2.3.2 Multiple echo
4.2.3.3 Echo motion
4.2.3.4 Window tracking
4.2.3.5 Tank empty detect
4.2.3.6 Auto fix distance
4.2.3.7 Fix distance list
4.2.3.7.x Fix distance values (4.2.3.7.1 to 4.2.3.7.9)
4.2.3.8 Auto False Echo suppression
4.2.3.9 Auto False Echo suppression distance
4.2.3.A Hover level
4.2.3.B Window trigger
4.2.4.1 Level URV
4.2.4.2 Level LRV
4.2.4.3 Level damping
4.2.4.4 MinLim level
4.2.4.5 MaxLim level
4.2.4.6 HYST level
4.2.5.1 Volume URV
4.2.5.2 Volume LRV
4.2.5.3 Volume damping
4.2.5.4 MinLim volume
4.2.5.5 MaxLim volume
4.2.5.6 HYST volume
4.2.5.7 Tank characteristic
4.2.5.8 Calibrate/table
4.2.5.8.1 Calibrate
4.2.5.8.2 Enter table
4.2.5.8.3 Show table
4.2.5.8.4 Clear table
4.2.5.8 Calculate
4.2.5.8.1 Tank design
4.2.5.8.2 Bottom design
4.2.5.8.3 Tank volume
4.2.5.8.4 Tank height
4.2.6.1 Mass URV
Menu
Identification
Number
Parameter Name Value

Page 86 SITRANS LR 400 – INSTRUCTION MANUAL 7ML19985FH04
mmmmm
Appendix II
4.2.6.2 Mass LRV
4.2.6.3 Mass damping
4.2.6.4 MinLim mass
4.2.6.5 MaxLim mass
4.2.6.6 HYST mass
4.2.6.7 Tank characteristic
4.2.6.8 Calibrate/table
4.2.6.8.1 Calibrate
4.2.6.8.2 Enter table
4.2.6.8.3 Show table
4.2.6.8.4 Clear table
4.2.6.8 Calculate
4.2.6.8.1 Tank design
4.2.6.8.2 Bottom design
4.2.6.8.3 Tank volume
4.2.6.8.4 Tank height
4.2.6.9 Density
4.2.7.x User1 parameters
4.2.8.x User2 parameters
4.3.1 Error Level
4.3.2 AO Select
4.3.3 Level parameter
4.3.3 Volume parameter
4.3.3 Mass parameter
4.3.4 Current limit
4.3.5 Error signal
4.4.1 Function DO
4.4.2 Error Level
4.4.3 Signal type DO
4.4.4 Level parameter
4.4.4 Volume parameter
4.4.4 Mass parameter
4.5.1.1 Line 1 local
4.5.1.2 Display local
4.5.1.3 Level parameter
4.5.1.3 Volume parameter
4.5.1.3 Mass parameter
4.5.1.4 Line 2 local
4.5.1.5 Level parameter
4.5.1.5 Volume parameter
4.5.1.5 Mass parameter
4.5.2 Language local
4.5.3 LCD backlight
4.6.1 Power supply
4.6.2 Process temperature
4.6.3 Electrical connection
4.6.4 Antenna and flange
Menu
Identification
Number
Parameter Name Value
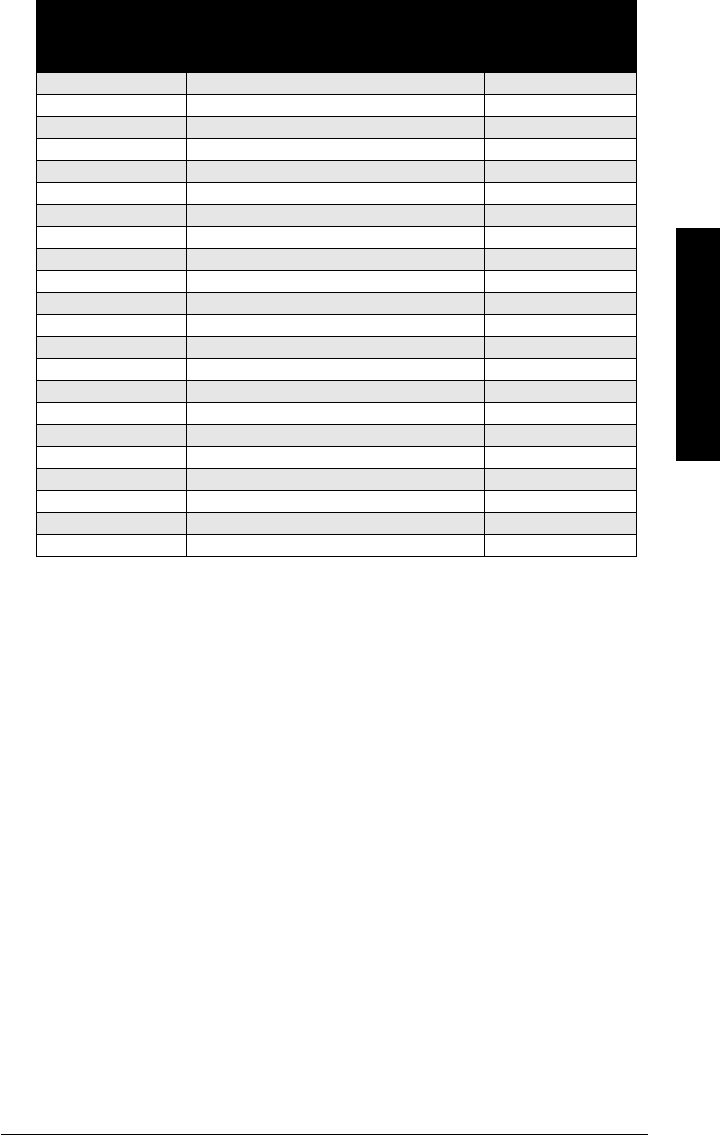
7ML19985FH04 SITRANS LR 400 – INSTRUCTION MANUAL Page 87
mmmmm
Appendix II
4.6.4.1 Flange size
4.6.4.2 Flange type
4.6.4.3 Pressure stage
4.6.4.4 Antenna type
4.6.4.5 Antenna extensions
4.6.4.6 Flange material
4.6.4.7 Seal material
4.6.5 Tag
4.6.6 Descriptor
4.6.7 Message
4.6.8 Manufacturer identification
4.6.8.1 Serial no.
4.6.8.2 Order no.
4.6.8.3 Device Revision
4.6.8.4 Software revision
4.6.8.5 Hardware revision
4.6.8.6 Antenna offset
4.6.8.7 Reference distance
5Options
5.1 Enter code
5.2 Customer code
5.3 Factory reset
Menu
Identification
Number
Parameter Name Value
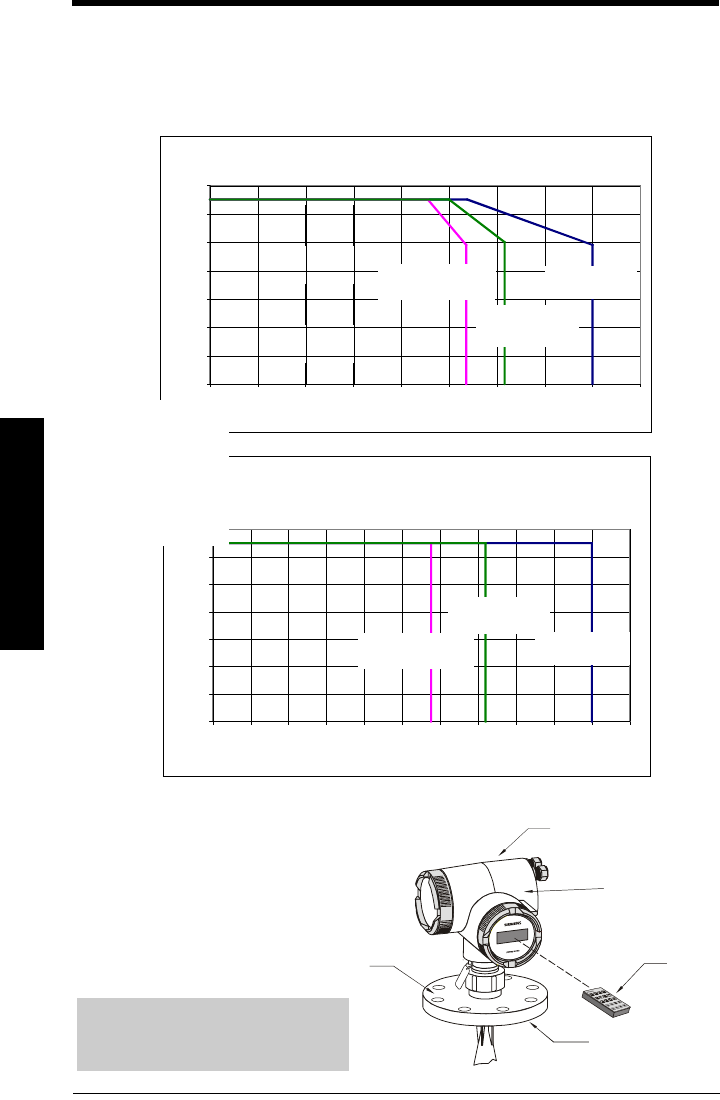
Page 88 SITRANS LR 400 – INSTRUCTION MANUAL 7ML19985FH04
mmmmm
Appendix III
Appendix III
Ambient/Operating Temperature Specification
Maximum Flange and Process Temperature Versus
Allowable Ambient
0
10
20
30
40
50
60
70
0 25 50 75 100 125 150 175 200 225
Process-Flange Temp Vs Ambient Temp (C)
Ambient (C)
Flange Temp
for Easy Aimer Process Temp for all
process connections
Flange Temp
for Standard (flanged)
Connection
Maximum Flange and Procss Temperature Versus
Allowable Ambient (Temperature Extension)
0
10
20
30
40
50
60
70
0 25 50 75 100 125 150 175 200 225 250 275
Process-Flange Temp Vs. Ambient (C)
Ambient (C)
Flange Temp
for Easy Aimer
Process Temp for all
process connections
Flange Temp
for Standard (flanged)
Connection
Process Flange
Temperature Process
Temperature
Process
Temperature
Process Flange
Temperature
Easy Aimer Flange
Temperature
Easy Aimer Flange
Temperature
U
PDATED
G
RAPHIC
R
EQUIRED
F
OR LIQUIDS
V
ERSION
am
bi
ent temperature
internal enclosure
temperature
hand
programmer
process temperature
Warning: Internal temperature
must not exceed 85 °C (185 °F)!
Warranty may be void.
flange
temperature
The chart above is provided for
guidance only. The chart does not
represent every possible process
connection arrangement. The chart
also does not take into consideration
heating from direct sunshine exposure.
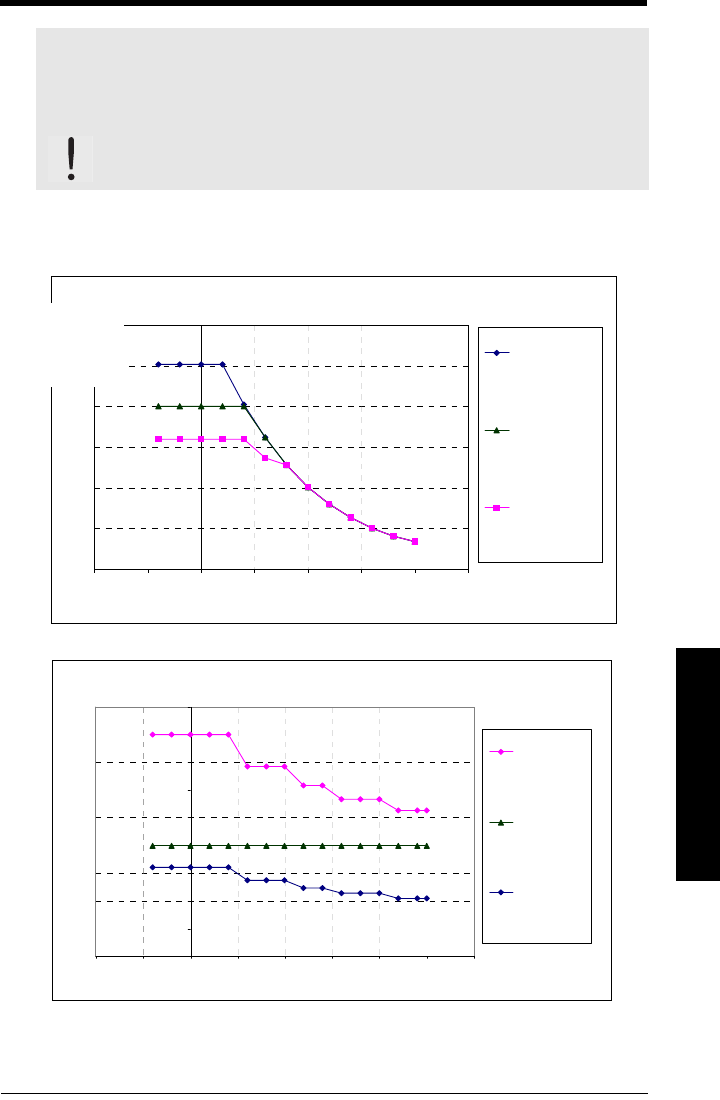
7ML19985FH04 SITRANS LR 400 – INSTRUCTION MANUAL Page 90
mmmmm
Appendix IV
Appendix IV
Process Pressure/Temperature De-rating
* standard process seal is rated to a max. of 200 °C of continuous duty.
**process seal for hazardous location is rated to a max. of 250 °C of continuous duty.
IMPORTANT: The information below is not applicable to the flanges
marked with serial numbers from 020102-001 to 020102-128. These flanges
are intended for non-pressure applications in North America only.
WARNING: Never attempt to loosen, remove, or disassemble process
connection or instrument housing with vessel contents.
Flange 22482 or 22487, FF Standard Process Seal*
0.0
5.0
10.0
15.0
20.0
25.0
30.0
-100 -50 0 50 100 150 200 250
Te mpe rature (°C)
Pressure (bar, gauge)
80 mm, 100 mm,
PN40
150 mm, PN40
80 mm, 100 mm ,
150 mm PN16 or
10K
UPDATE
GRAPHS
Flange 22482 or 22487, FF Process Seal for Hazardous Locations**
0.0
5.0
10.0
15.0
20.0
25.0
30.0
35.0
40.0
45.0
-100 -50 0 50 100 150 200 250 300
Temperature (°C)
Pressure (bar, gauge)
80 mm, 100
mm, PN40
150 mm, PN40
80 mm, 100
mm, 150 mm
PN16 or 10K
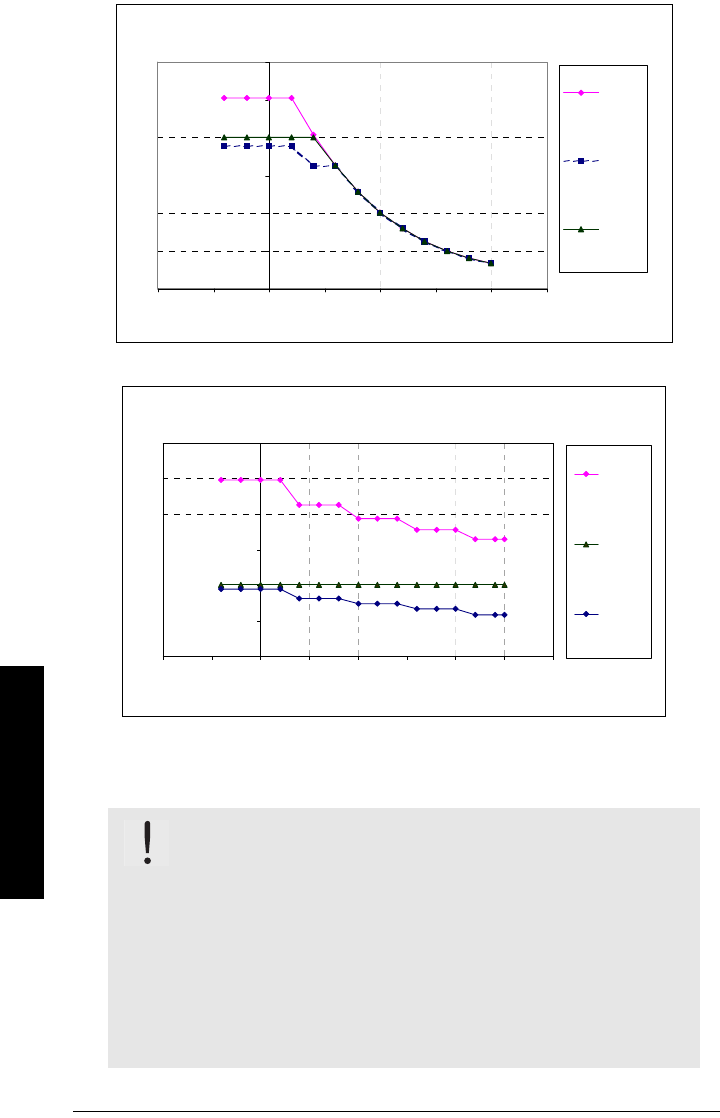
Page 91 SITRANS LR 400 – INSTRUCTION MANUAL 7ML19985FH04
mmmmm
Appendix IV
* standard process seal is rated to a max. of 200 °C of continuous duty.
**process seal for hazardous location is rated to a max. of 250 °C of continuous duty.
WARNINGS:
• Materials of construction are chosen based on their chemical
compatibility (or inertness) for general purposes. For exposure to
specific environments, check with chemical compatibility charts before
installing.
• The user is responsible for the selection of bolting and gasket materials
which will fall within the limits of the flange and its intended use and
which are suitable for the service conditions.
• Never attempt to loosen, remove, or disassemble process connection or
instrument housing with vessel contents.
• Improper installation may result in loss of process pressure.
Flange 22483 or 22488, FF Standard Process Seal*
0.0
5.0
10.0
15.0
20.0
25.0
30.0
-100 -50 0 50 100 150 200 250
Te mpe ratur e (°C)
Pressure (bar, gauge)
3", 4", 6"
300 #
3", 4", 6"
150 #
6", 300
#
Flange 22483 or 22488, RF Process Seal for Hazardous Locations**
0.0
10.0
20.0
30.0
40.0
50.0
60.0
-100 -50 0 50 100 150 200 250 300
Temperature (°C)
Pressure (bar, gauge)
3", 4", 6"
300 #
6", 300#
3", 4", 5"
300#
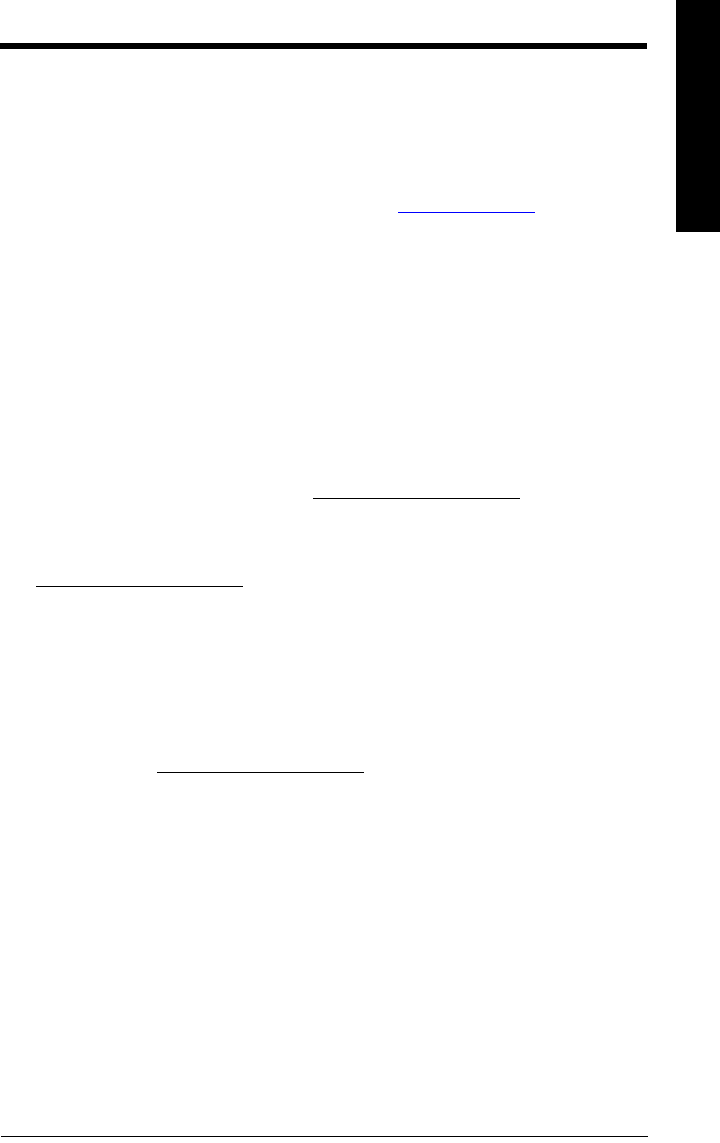
7ML19985FH04 SITRANS LR 400 – INSTRUCTION MANUAL Page 92
mmmmm
Appendix V
Appendix V
HART Communications for the SITRANS LR 400
Highway Addressable Remote Transducer, HART, is an industrial protocol that rides on
top of a 4-20 mA signal. It is an open standard, and full details about HART can be
obtained from the HART Communication Foundation www.hartcomm.org
The SITRANS LR 400 can be configured over the HART network using either the HART
Communicator 275 by Fisher-Rosemount, or a software package. There are a number of
different software packages available, and the SITRANS LR 400 should work well with
any of them. The recommended software package is the SIMATIC® Process Device
Manager (PDM) by Siemens.
HART Device Descriptor (DD)
In order to configure a HART device, the configurator must have the HART Device
Descriptor for the unit in question. HART DDs are controlled by the HART
Communications Foundation. The HART DD for the SITRANS LR 400 is available on the
SITRANS LR 400 page of our website at www.siemens.com/milltronics.
Older versions of the library will have to be updated in order to use all the features in the
SITRANS LR 400. If you do not see SITRANS LR 400 under Siemens Milltronics using the
configurator, you will need to download an update file from our website:
www.siemens.com/milltronics
SIMATIC Process Device Manager (PDM):
This software package is designed to permit easy configuration, monitoring and
troubleshooting of HART and PROFIBUS PA devices. The HART DD for the SITRANS
LR 400 was written with SIMATIC PDM in mind and has been extensively tested with this
software. The HART DD for the SITRANS LR 400 is available on the SITRANS LR 400 page
of our website at www.siemens.com/milltronics.
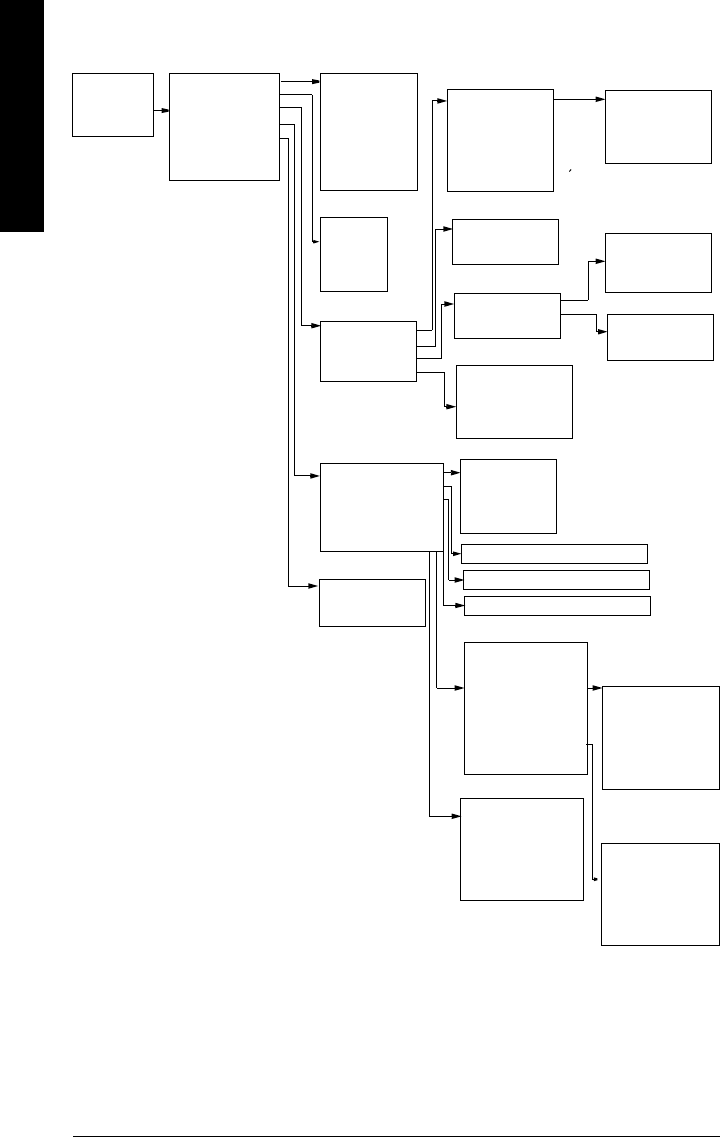
Page 93 SITRANS LR 400 – INSTRUCTION MANUAL 7ML19985FH04
mmmmm
Appendix V
HART Communicator 275:
Chart 1
1. Level
2. AO
3. Device Setup
4. Refresh
1. Auto-Setup
2. Display
3. Diagnostics
4. Device Data
5. Options
6. Review
1. Language Local
2. Length Unit
3. Nozzle Height
4. Tank Height
5. Level URV
6. Level LRV
7. Level Damping
8. Application Type
1. Level
2. Volume
3. Mass
4. AO
5. DO
1. Status
2. Device Test
3. Simulation
4. Sensor Variables
1. Units
2. Operating parameters
3. Output parameters
4. Display param (local)
5. Device information
6. HART info
1. Local keys ctrl mode
2. Customer code
3. Factory reset
On Line Device Setup Auto-Setup
Display
Diagnostics
Device Data
Options
1. Wear
2. Sensor Status
3. Electronic Status
4. Software Status
5. Application Status
6. Parameter Info
7. Service Info
Status
1. Operating hours
2. Maximum temp
3. Min temp
4. Aging
5. Hours > 85°C
Wear
1. Self-test
2. Local display test
3. Master reset
Device Test
1. Simulate AO
2. Simulate DO
Simulation
1. 4 mA
2. 20 mA
3. Other
4. End
Simulate AO
1. Relay on
2. Relay off
3. End
Simulate DO
1. Raw Value
2. Echo Amplitude
3. S/N Ratio
4. Validity
5. Sens Temp
Sensor Variables
1. Length unit
2. Volume unit\
3. Mass unit
4. Temp unit
5. Other unit
Units
Operating Parameters (see Chart 2)
Output Parameters (see Chart 3)
Display Parameters (see Chart 4)
1. Power supply
2. Process temp
3. Electrical connection
4. Local meter
5. Antenna and flange
6. Tag descriptor
7. Message
8. Last config
9. Manufacturer data
Device information
1. Manufacturer
2. Model
3. HART Dev. I.D.
4. Universal Rev.
5. Fld. dev. rev.
6. Software rev.
7. Hardware rev.
HART info
1. Serial number
2. Device order number
3. Actual order number
4. Software version
5. Hardware version
6. Antenna offset
7. Reference distance
Manufacturer Data
1. Flange size
2. Flange type
3. Pressure range
4. Antenna type
5. Antenna extension
6. Flange material
7. Seal material
Antenna and Flange
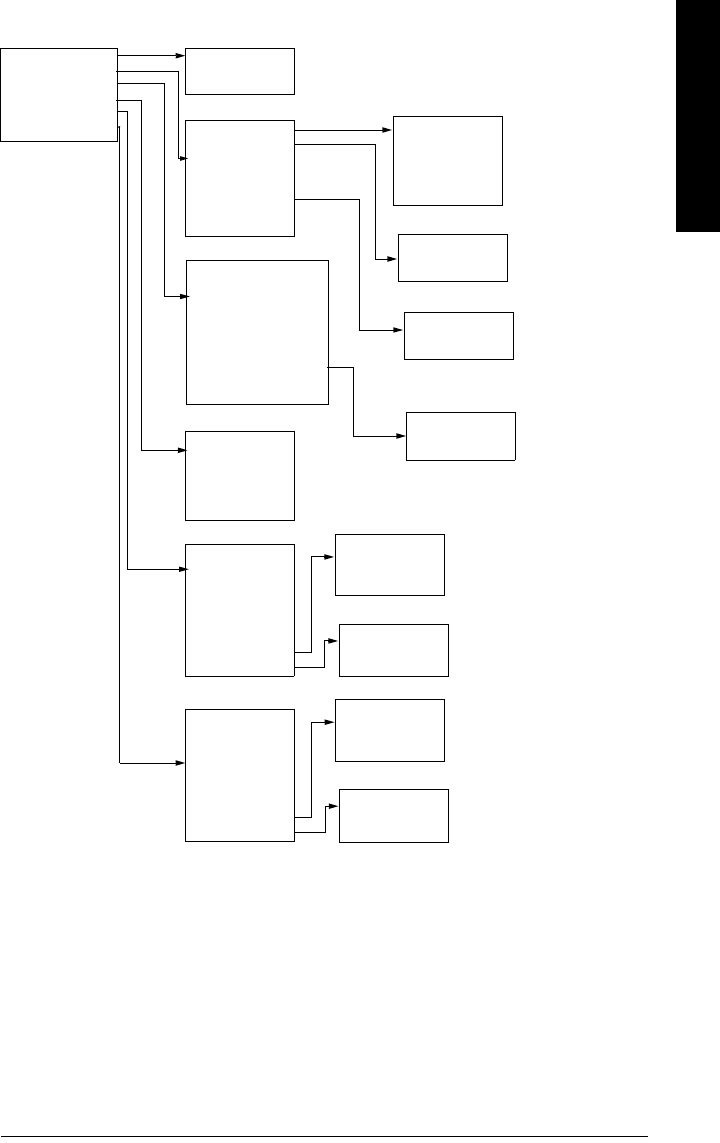
7ML19985FH04 SITRANS LR 400 – INSTRUCTION MANUAL Page 94
mmmmm
Appendix V
Chart 2
1. Tank geometry
2. Measuring conditions
3. Sensor parameters
4. Level parameters
5. Volume parameters
6. Mass parameters
1. Nozzle height
2. Tank height
3. Stilling pipe?
Operating Parameters Tank Geometry
1. Application type
2. Surface
3. Dead band
4. Correction factor
5. Filling speed
6. Failsafe level
7. Failsafe timer
8. Range extension
Measuring Conditions
1. Sensor damping
2. Multiple echo
3. Echo motion
4. Window tracking
5. Tank empty detection
6. Auto fix distance
7. Fix distance list
8. Echo suppress.
9. Echo suppress dist.
Sensor parameters
1. URV
2. LRV
3. Damping
4. Min limit
5. Max limit
6. HYST
Level Parameters
1. Volume URV
2. Volume LRV
3. Volume damping
4. MinLim Volume
5. MaxLim Volume
6. HYST Volume
7. Tank characteristic
8. Calibrate/table
or Calculate
Volume Parameters 1. Calibrate
2. Enter table
3. Show table
4. Clear table
Calibrate/table
1. Tank design
2. Bottom design
3. Tank volume
calculate
1. Liquid (store)
2. Liquid (process)
3. Silo1 (solids)
4. Silo2 (solids)
5. User tank1
6. User tank2
Application type
1. smooth
2. wavy
3. turbulent
Surface
1. 100%
2. 0%
3. Hold continuously
Failsafe Level
1. Off
2. Record
3. Use
False Echo Suppression
1. Mass URV
2. Mass LRV
3. Mass damping
4. MinLim Mass
5. MaxLim Mass
6. HYST Mass
7. Tank characteristic
8. Calibrate/table
or Calculate
Mass Parameters 1. Calibrate
2. Enter table
3. Show table
4. Clear table
Calibrate/table
1. Tank design
2. Bottom design
3. Tank volume
calculate
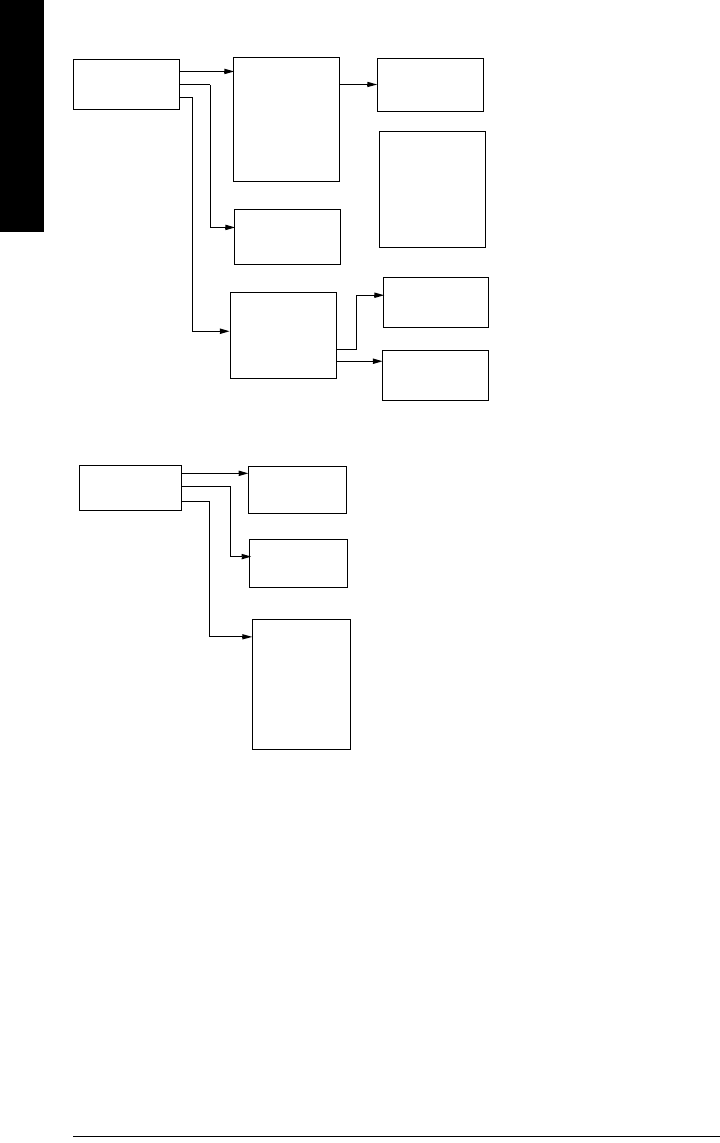
Page 95 SITRANS LR 400 – INSTRUCTION MANUAL 7ML19985FH04
mmmmm
Appendix V
Chart 3
Chart 4
Output Parameters
1. AO= (cust selection)
2. AO output select
3. PV parameters
4. Error level
5. Current limit
6. Error signal
7. AO
8. Level %range
Analog Output
1. Analog output
2. Digital output
3. HART output
1. Level
2. Volume
3. Mass
AO output select
1. Function DO
2. Error Level
3. Signal Type DO
Digital Output
1. Poll address
2. Num req preams
3. Num resp preams
4. Burst mode
5. Burst option
HART Output
1. On
2. Off
3. Not used
Burst Mode
1. Primary variable
2. %range/current
3. Process var/current
Burst Option
DO output select
1. MaxLim level
2. MinLim level
3. MaxLim volume
4. MinLim volume
5. MaxLim mass
6. MinLim mass
7. Alarm
8. No function
Line 1 LocalDisplay parameter
1. Line1 Local
2. Display Local
3. Line 2 Local
1. Level
2. Volume
3. Mass
Display Local
1. Eng unit
2. %
3. Bar graphic
Line 2 Local
1. Level
2. Volume
3. Mass
4. Temperature
5. Validity
6. S/N ratio
7. Amplitude
8. Digital output
9. Analog output
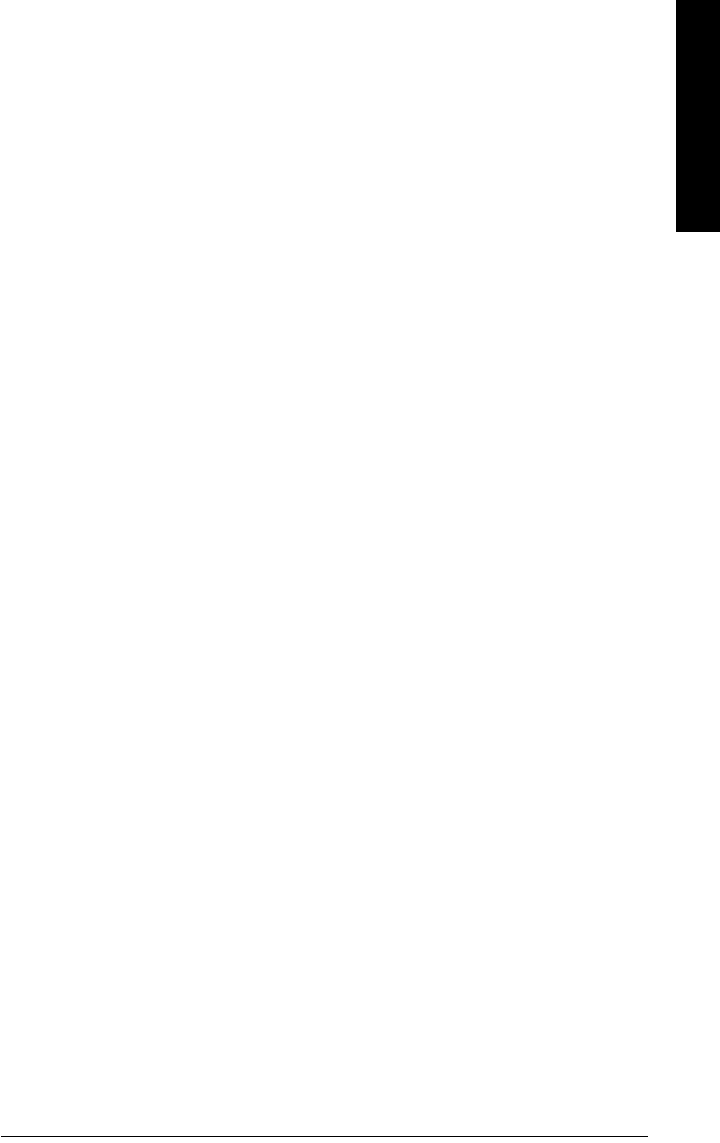
7ML19985FH04 SITRANS LR 400 – INSTRUCTION MANUAL Page 96
mmmmm
Appendix V
Supported HART Commands:
The SITRANS LR 400 conforms to HART rev. 5 and supports the following:
Universal Commands
0, 1, 2, 3, 6, 11, 12, 13, 14, 15, 16, 17, 18, 19
Common Practice Commands
33, 34, 35, 36, 37, 38, 40, 41, 42, 43, 44, 48, 50, 51, 53, 59, 108, 109, 110
Device Specific Commands
Command 128 Read static data material
Command 129 Write static data material
Command 130 Read dynamic variables 1
Command 131 Read dynamic variables 2
Command 132 Read tank parameters
Command 133 Write tank parameters
Command 134 Read tank design
Command 135 Write tank design
Command 136 Read calibration array
Command 137 Read calibration array
Command 138 Read stilling pipe conditions
Command 139 Write stilling pipe conditions
Command 140 Read measuring conditions
Command 141 Write measuring conditions
Command 142 Read sensor set-up 1
Command 143 Write sensor set-up 1
Command 144 Read fix distance
Command 145 Write fix distance
Command 146 Read customer code
Command 147 Write customer code
Command 148 Read sensor set-up 2
Command 149 Write sensor set-up 2
Command 150 Read analog parameters
Command 151 Write analog parameters
Command 152 Read temperature indicator
Command 154 Read trim values
Command 155 Write trim values
Command 156 Clear tank calibration
Command 157 Read device order number
Command 158 Read serial number
Command 159 Read local display select
Command 160 Write local display select
Command 161 Read display parameters
Command 162 Write display parameters
Command 163 Read digital out parameters 1
Command 164 Write digital out parameters 1
Command 165 Read digital out parameters 2
Command 166 Write digital out parameters 2
Command 167 Read lower range values
Command 168 Write lower range values
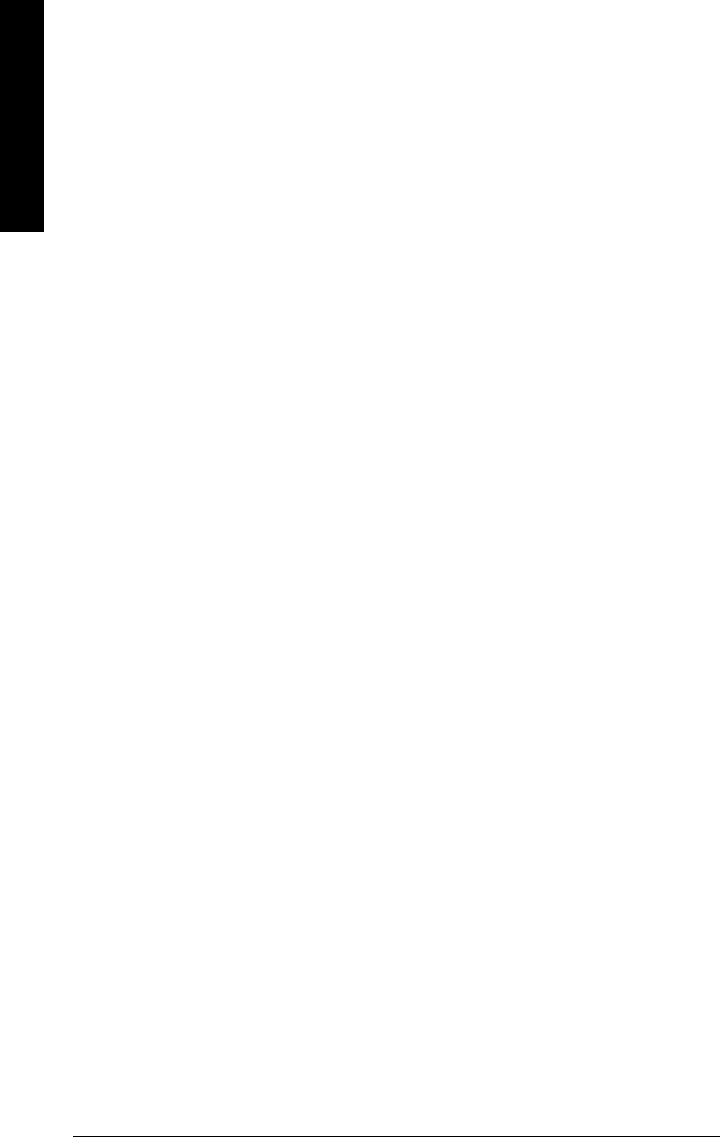
Page 97 SITRANS LR 400 – INSTRUCTION MANUAL 7ML19985FH04
mmmmm
Appendix V
Command 169 Read upper range values
Command 170 Write upper range values
Command 171 Read damping values
Command 172 Write damping values
Command 173 Read tank characteristic set
Command 174 Write tank characteristic set
Command 175 Execute display test
Command 176 Write digital out test code
Command 177 Read digital output
Command 178 Read service information
Command 179 Read parameter information
Command 180 Read software revision
Command 181 Read hardware revision
Command 182 Write factory reset
Command 183 Read analog lost echo and range extension
Command 184 Write analog lost echo and range extension
Command 196 Read tank noise action
Command 197 Write tank noise action
Command 198 Read error level
Command 199 Write error level
The HART commands are rarely if ever used by end users. For details on the Universal
and Common Practice Commands, please contact the HART Communication Foundation.
For details on the Device Specific Commands, please contact Siemens Milltronics.
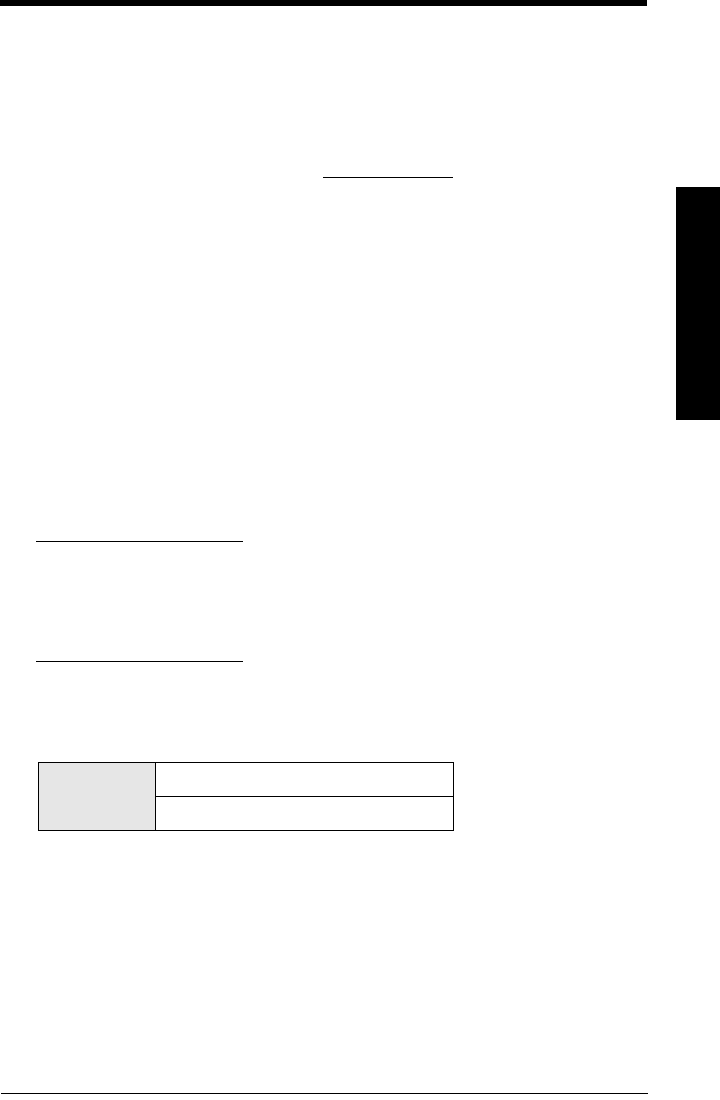
7ML19985FH04 SITRANS LR 400 – INSTRUCTION MANUAL Page 98
mmmmm
Appendix VI
Appendix VI
PROFIBUS PA Communications for the SITRANS
LR 400
PROFIBUS PA is an open industrial protocol. Full details about PROFIBUS PA can be
obtained from PROFIBUS International at www.profibus.com
The SITRANS LR 400 is a Class A, Profile Version 3.0, PA device. It supports Class 1
Master for Cyclic data exchange, and Class 2 for acyclic services: (See below for details).
The SITRANS LR 400 can be configured using a software package. There are a number of
different software packages available and the SITRANS LR 400 should work well with
any one of them. The recommended software package is the Simatic Process Device
Manager (PDM) by Siemens.
Device Descriptor
In order to use Process Device Manager (PDM) with PROFIBUS PA, you will need the
Device Descriptor, which will be included with new versions of PDM. Currently you can
locate the Device Descriptor in Device Catalog, under Level/Echo/Siemens Milltronics.
If you do not see SITRANS LR 400 under Siemens Milltronics, you will need to download
an update file from the SITRANS LR 400 product page on our website:
www.siemens.com/milltronics
The GSD file
The GSD file SM_062A.GSD can be obtained from Siemens Milltronics at our web site:
www.siemens.com/milltronics. (There is an example on page 102, To configure and use
PROFIBUS PA with an S7-300 PLC.)
Bus address (Device Address)
• This value can be set via Bus Address in the Auto-setup parameters, or over the
network. (After changing the value, turn the unit off and back on again in order for
the change to take effect.)
Values Range: 0 to 126
Pre-set: 126
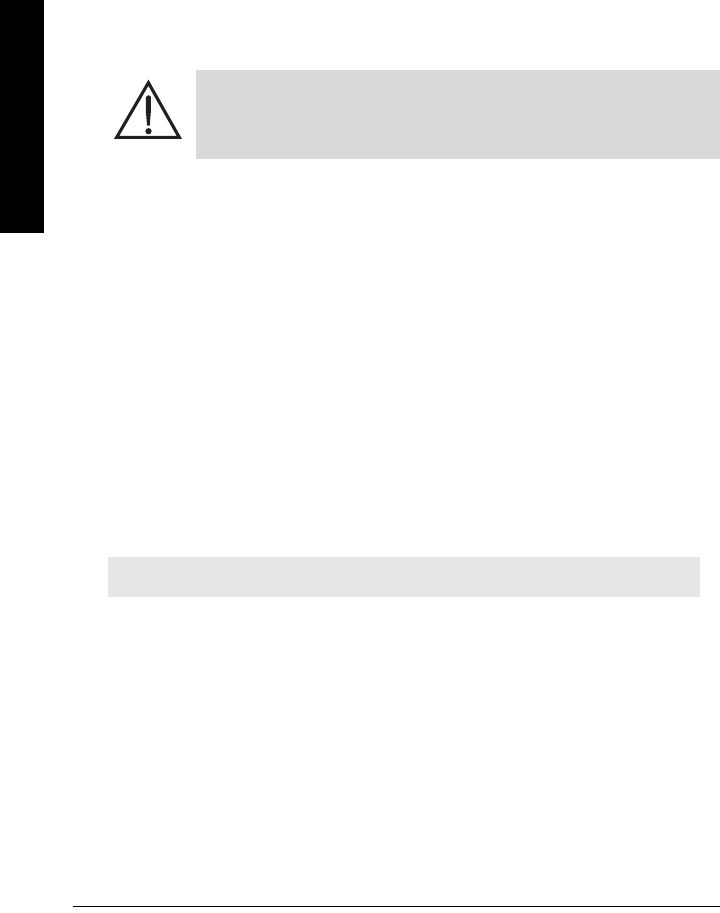
Page 99 SITRANS LR 400 – INSTRUCTION MANUAL 7ML19985FH04
mmmmm
Appendix VI
Power Demands
The maximum number of devices that can be connected to a bus line depends on their
current consumption and the respective application conditions. When operating in an
area where there is no risk of explosion, the couplers/links can feed up to 400 mA into the
bus.
When operating in explosion risk areas, the intrinsic safety is only guaranteed when the
maximum power fed into the bus does not exceed certain voltage and current values.
These are normally:
Current IS < 128 mA, voltage U0 < 15 V
The number of devices which can be connected to a bus line is determined by finding
the combined maximum current consumption of all the connected devices (10.5 mA for
the SITRANS LR 400). Plan to allow a current reserve for safety.
Cyclic versus Acyclic Data
When you request data from a device via PROFIBUS PA, you have two choices. Cyclic
data is provided at every bus scan: acyclic data is requested and provided as needed.
Input and output information is always requested at every bus scan and is set up as cyclic
data. Configuration information is only needed periodically and is set up as acyclic data.
Cyclic Data
When you configure the SITRANS LR 400 on the PROFIBUS PA bus, there are two slots
available for modules.
Slot 0 always transmits Level information and slot 1always Volume information. Slot2 is
always Mass information. If you do not wish to have data transmitted, then you must use
a Free Place module in that slot.
When you select a module, for the three values, there are two alternatives: a normal
version and a short version, for example, Level (short) and Level. The difference between
the two is the way each one identifies the function block used. Level uses both the
identifier and the extended identifier byte to determine which function block in the unit to
use. Level (short) uses only the identifier byte. In the current release of PROFIBUS PA
there is no functional difference between the short and normal versions. However, the
longer identifier is the preferred way to identify the function block and you should select
the normal version in each case.
Note: Each of the slots has to have a module defined in it.
WARNING: Only certified supply units (DP/PA couplers or DP/PA
links) may be used to feed the intrinsically safe PROFIBUS. See
the EC Type Examination Certificate for requirements.
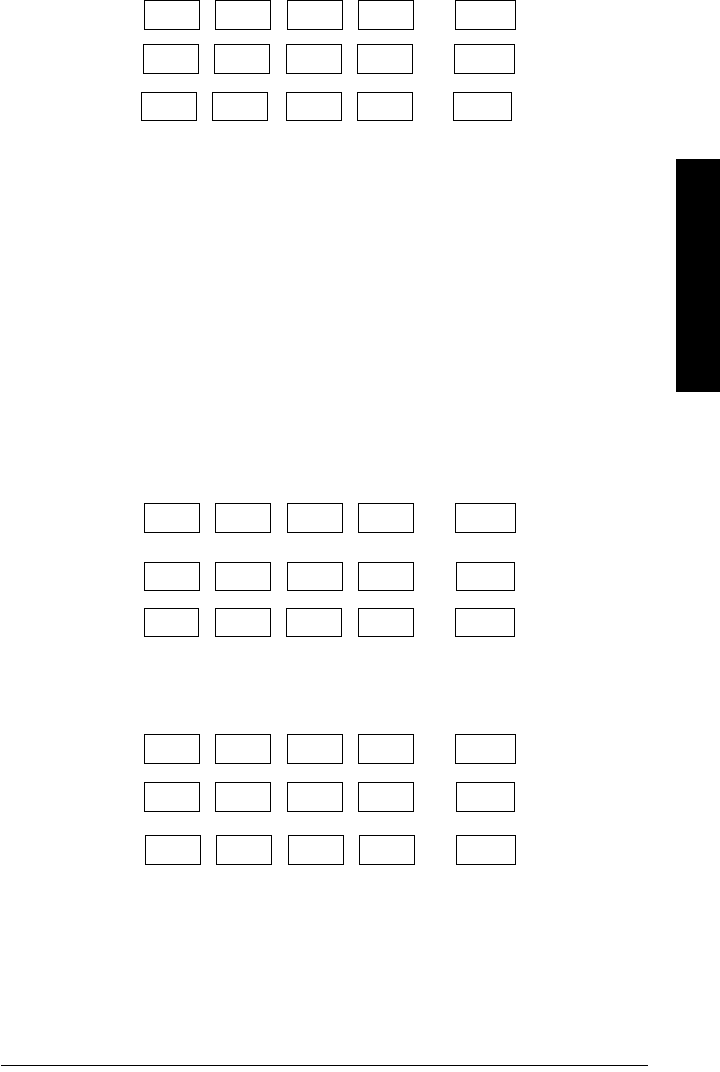
7ML19985FH04 SITRANS LR 400 – INSTRUCTION MANUAL Page 100
mmmmm
Appendix VI
The 3 function blocks (Level, Volume, Mass) return 5 bytes of data each:
The first 4 bytes are the floating point representation (IEEE) of the variable. The variables
are the outputs of the function block. The default setting for the variable level is meters.
The default setting for the variable volume is m3. The default setting for the variable mass
is kg. You can change the settings of the variables by changing the settings of the
function block. This is typically done using PDM.
The 5th byte is the status word and the list of possible values is given in the chart on
page 101.
The 5 bytes must be read consistently, in a contiguous chunk: they cannot be read byte by
byte, and cannot suffer an interrupt. If you are using an S7-300/400, you will need to use
SFC14 DPRD_DAT: Read Consistent Data of a Standard PD Slave.
If you select a Free Place module to fill one of the slots, this will affect the byte number.
Example 1:
Example 2:
Floating Point Status
Volume
Level byte 1 byte 2 byte 3 byte 4 byte 5
byte 6 byte 7 byte 8 byte 9 byte10byte10
Mass byte 11 byte 12 byte 13 byte 14 byte 15
Floating Point Status
Volume
Free
Place ———— —
byte 1 byte 2 byte 3 byte 4 byte 5
Mass byte 6 byte 7 byte 8 byte 9 byte 10
Floating Point Status
Level
Free
Place
byte1 byte 3 byte 4 byte 5
———— —
byte 2
Mass byte 6 byte 7 byte 8 byte 9 byte 10
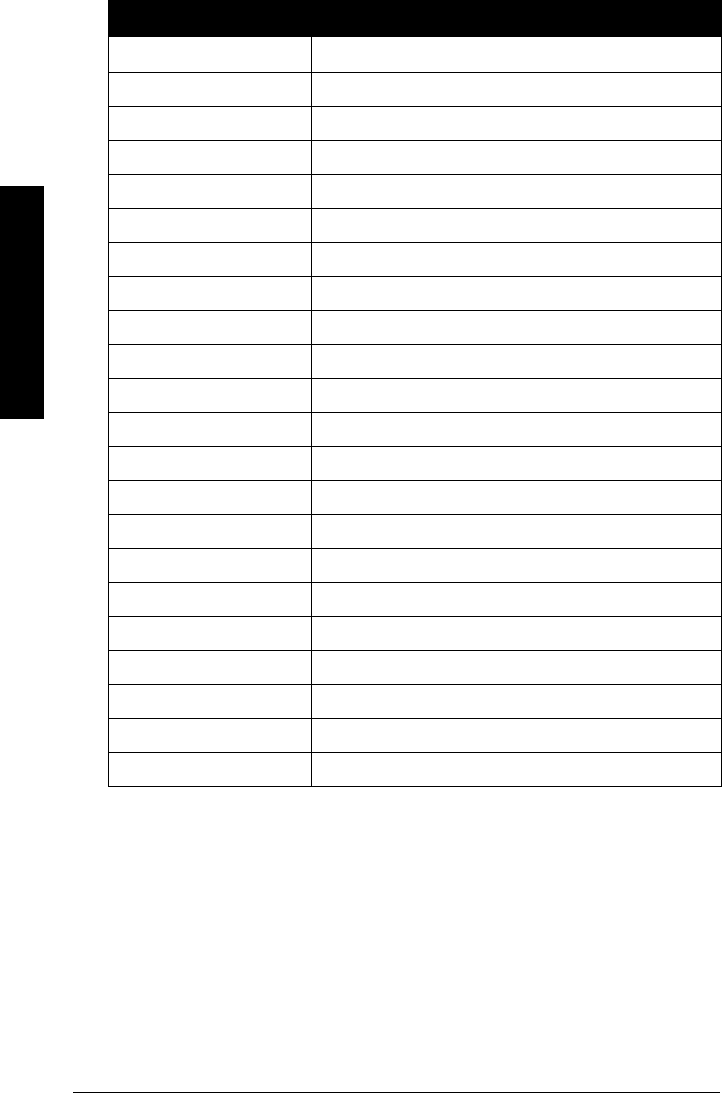
Page 101 SITRANS LR 400 – INSTRUCTION MANUAL 7ML19985FH04
mmmmm
Appendix VI
Status Word
Values in hex notation Description
0x1F out of service
0x0F constant device failure
0x0C device failure
0x13 constant sensor failure
0x12 high limited sensor failure
0x11 low limited sensor failure
0x10 sensor failure
0x07 constant configuration error
0x52 sensor conversion not accurate
0x4F initial value
0x4C uncertain: initial value
0x4B substitute set
0x47 last usable value
0x42 high limited non-specific
0x41 low limited non-specific
0x40 non-specific
0x8E high limited active critical alarm
0x8D low limited active critical alarm
0x8A high limited active advisory alarm
0x89 low limited active advisory alarm
0x84 active update event
0x80 ok
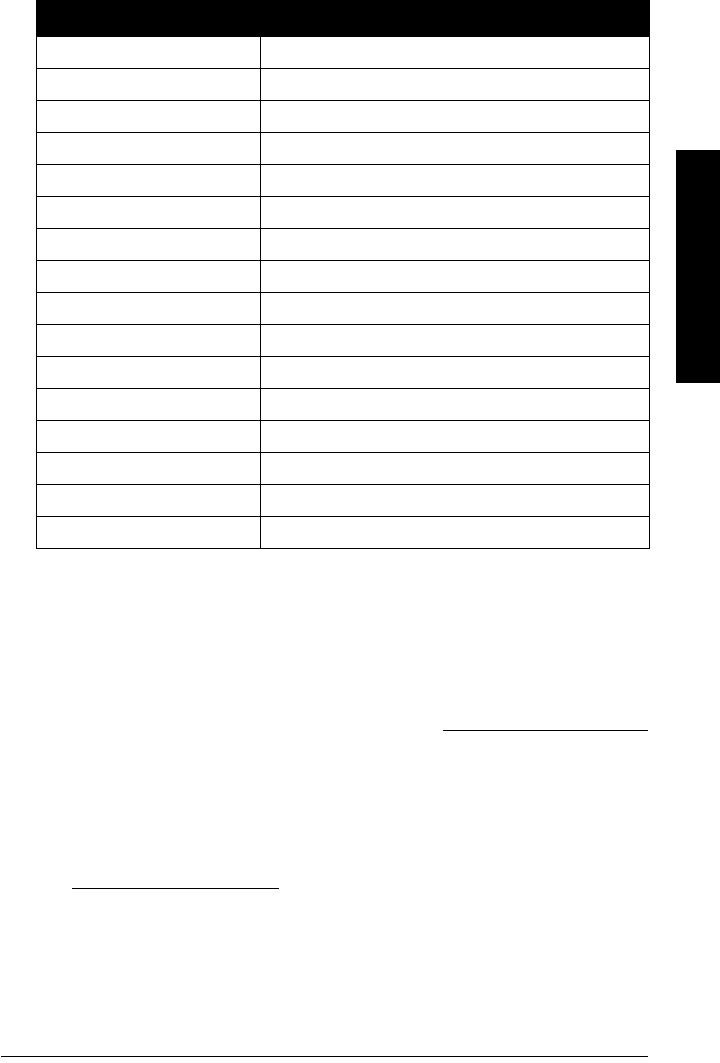
7ML19985FH04 SITRANS LR 400 – INSTRUCTION MANUAL Page 102
mmmmm
Appendix VI
Extended Diagnostics
The last four bytes of the extended diagnostics message are as follows:
Acyclic Data
The SITRANS LR 400 supports up to three simultaneous connections by a class 2 Master
(C2 connection). It does not support Master class 1 (C1 connection). A list of all
parameters including address (slot and index), format, range of values, start value and
attributes are compiled in a document which is available on request. Contact Siemens
Milltronics Technical Publications at the following address: techpubs.smip@siemens.com
Configuration Example:
To configure and use PROFIBUS PA with an S7-300/400 PLC
1. Import the GSD file SM_062A.GSD from the Siemens Milltronics Web site:
www.siemens.com/milltronics into Step 7 software.
2. Add the SITRANS LR 400 “rack”: click and drag the SITRANS LR 400 folder from the
hardware catalog.
3. Fill the rack with desired modules, by dragging and dropping them from the
hardware catalog.
4. After configuring PROFIBUS PA in steps 2 and 3, download it to the PLC.
5. Add code to the PLC program to read data consistently using the SFC14.
Values in hex notation Description
0x01000000 Electronics failure
0x02000000 Mechanical failure
0x04000000 Motor Temperature
0x08000000 Electronics temperature too high
0x10000000 Memory cheksum error
0X20000000 Measurement failure
0X40000000 Not initialized properly
0x80000000 Initial calibration error
0x00010000 Zero error
0x00020000 Power supply failure
0x00040000 Configuration invalid
0x00080000 Warm Start
0x00100000 Cold Start
0x00200000 Maintenance required
0x00400000 Characterization invalid
0x00000080 More information available
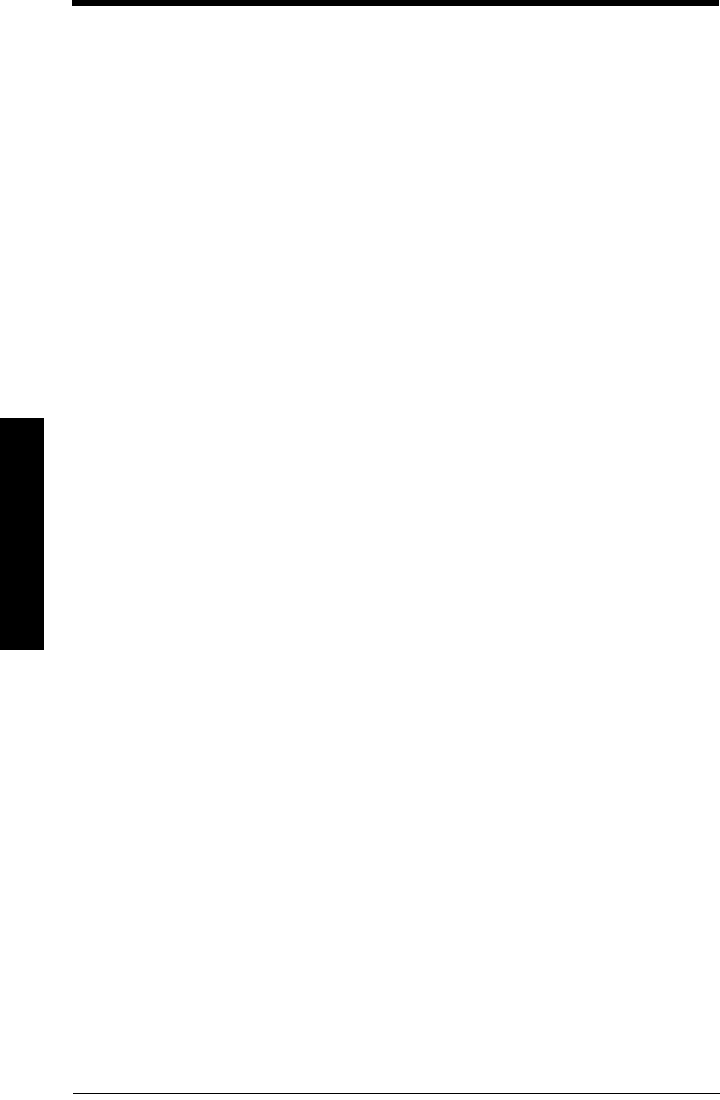
Page 103 SITRANS LR 400 – INSTRUCTION MANUAL 7ML19985FH04
mm
mmm
Certificates
Hazardous Installation
The necessary certificates are enclosed separately. Please refer to the SITRANS LR 400
Certificate manual 7ML19985FP82.
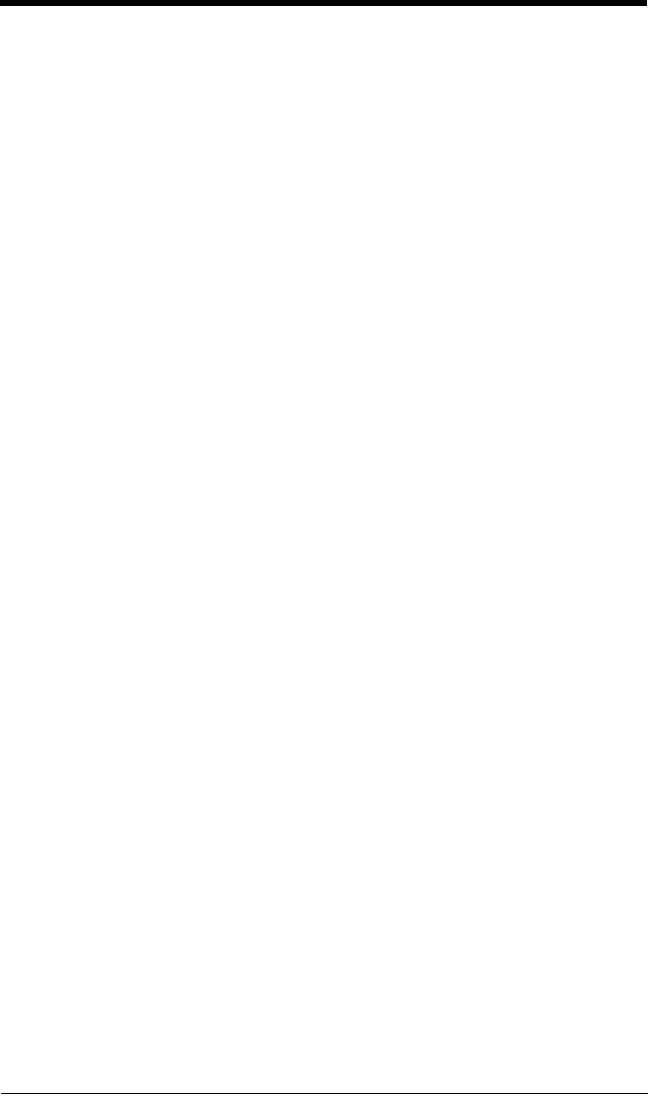
7ML19985FH04 SITRANS LR 400 – INSTRUCTION MANUAL Page 104
Index
A
analog output ............................................. 54
antenna
cleaning ............................................. 78
approvals ..................................................... 10
auto-setup ................................................... 22
B
beam spreading ......................................... 19
bus address (device address) ................ 98
C
certificates ................................................ 103
communication .............................................9
connection .................................................. 20
PROFIBUS ............................................5
cyclic data ................................................... 99
D
de-rating curves ........................................ 90
device descriptor ....................................... 98
digital output ............................................... 56
dimensions .................................................. 11
functional ........................................... 33
display parameters ................................... 57
E
Easy Aimer LR ............................................ 13
extended diagnostics ............................. 102
F
fault messages ........................................... 76
flanges ......................................................... 14
FMCW ...................................................24, 79
G
glossary ....................................................... 79
GSD file ........................................................ 98
H
hand programmer ..............................22, 26
HART Communications
detailed information ........................ 92
hysteresis .................................................... 48
M
maintenance ............................................... 78
mounting
location .............................................. 18
O
operation ..................................................... 26
output
analog .................................................54
digital ...................................................56
P
parameters
alphabetical .......................................80
analog output ....................................54
auto-setup ..........................................33
digital output ......................................56
display .................................................57
HART ...................................................32
hysteresis ...........................................48
measuring conditions ......................42
PROFIBUS ..........................................63
programming chart ..........................84
troubleshooting .................................37
PDM ..............................................................92
PROFIBUS ....................................................63
programming
disabling .............................................29
enabling ..............................................29
programming chart ....................................84
purging system ...........................................11
S
self-test .........................................................75
SIMATIC Process Device Manager ......92
specifications ................................................6
approvals ............................................10
communication ...................................9
de-rating curves ...............................90
performance ........................................6
power ....................................................6
temperature charts ..........................88
status word ................................................101
structure .........................................................3
T
troubleshooting ..........................................75
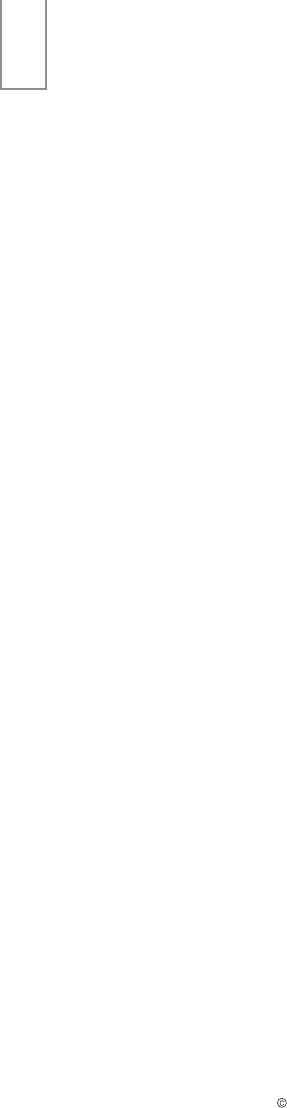
*7ml19985FH05* Rev. 5.0
www.siemens.com/processautomation
Siemens Milltronics Process Instruments Inc.
1954Technology Drive, P.O. Box 4225
Peterborough, ON, Canada K9J 7B1
Tel: (705) 745-2431 Fax: (705) 741-0466
Email: techpubs.smpi@siemens.com
Siemens Milltronics Process Instruments Inc. 2004
Subject to change without prior notice
Printed in Canada