Solectek 70MOB1 Broadband Wireless Base Station User Manual KA370MOB1
Solectek Corporation Broadband Wireless Base Station KA370MOB1
Solectek >
Users Manual
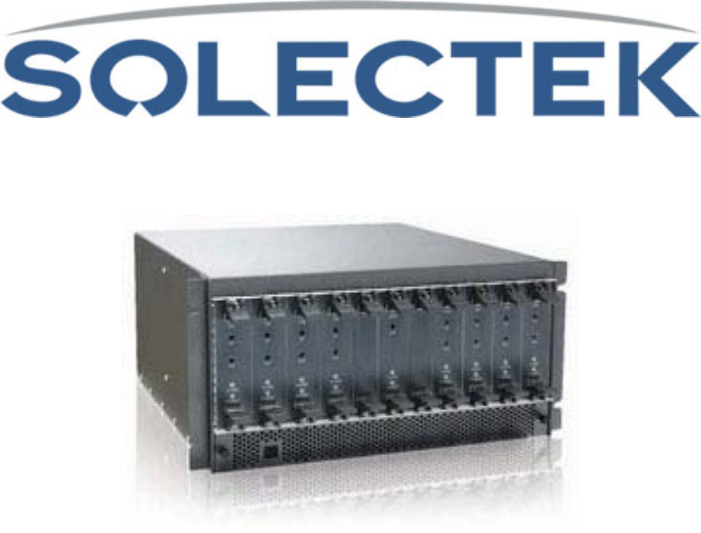
SKYWAY-MOBILE SERIES
Base Transceiver Station
User’s Guide
July 2008
Rev 1
Note: Any changes or modifications not expressly approved by the party responsible for
compliance could void the user’s authority to operate the equipment.
This device complies with Part 15 of the FCC Rules. Operation is subject to the following
(1) This device may not cause harmful interference, and
(2) This device must accept any interference received, including interference that may
cause undesired operation.
NOTE:This equipment has been tested and found to comply with the limits for a Class
A digital device, pursuant to Part 15 of the FCC Rules. These limits are designed to
provide reasonable protection against harmful interference when the equipment is
operated in a commercial environment. This equipment generates, uses, and can radiate
radio frequency energy and, if not installed and used in accordance with the instruction
manual, may cause harmful interference to radio communications. Operation of this
equipment in a residential area is likely to cause harmful interference in which case the
user will be required to correct the interference at his/her own expense.
1. Introduction
Congratulations on your purchase of a SkyWay-Mobile BTS system. This user’s guide
contains basic description of the system, basic installation and configuration steps to act as
a basic guideline for the end user. This guide is not to act as a step-by-step guide for self-
installation by end users.
This product requires a full professional installation services by Solectek’s field engineering
staff or authorized reseller officially certified by Solectek. The installation services will
include the following work:
Site survey and RF planning.
Drive test, mapping of the coverage area.
Physical mounting of the outdoor components on tower or rooftop
Antenna alignment
Configuration, calibration and troubleshooting
Commission of the service
Product Features
The SkyWay-Mobile BTS unit has the following features
Throughput – up to 15 Mbps in a 5 MHz channel BW.
Chanel BW – 1, 2, 3, 4, or 5 MHz, user configurable
Support for more than 300 subscribers
Support for 150 simultaneous phone calls
N=1 Frequency reuse
Voice service support – proprietary mode or VoIP
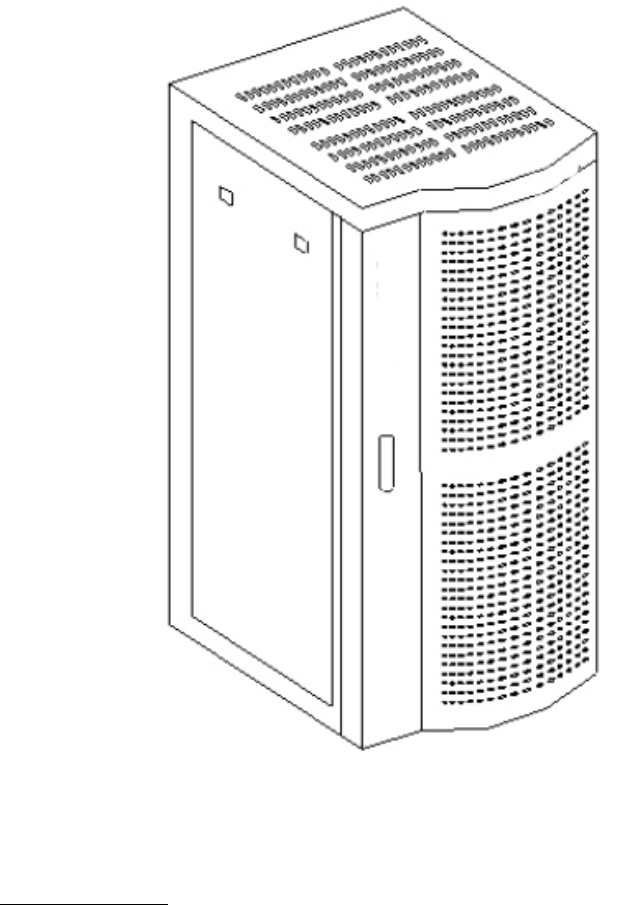
2. Installation
Installation Cabinet
The SkyWay-Mobile BTS is typically installed in a standard 19 inch cabinet. The outer
dimensions are:
Height x Width x Depth – 1550 mm x 600 mm x 722 mm
The following is a diagram of the cabinet, as an example.
Fig 2-1: SkyWay-Mobile BTS cabinet
2.2 Position and Installation of Cabinet
Layout of Cabinet
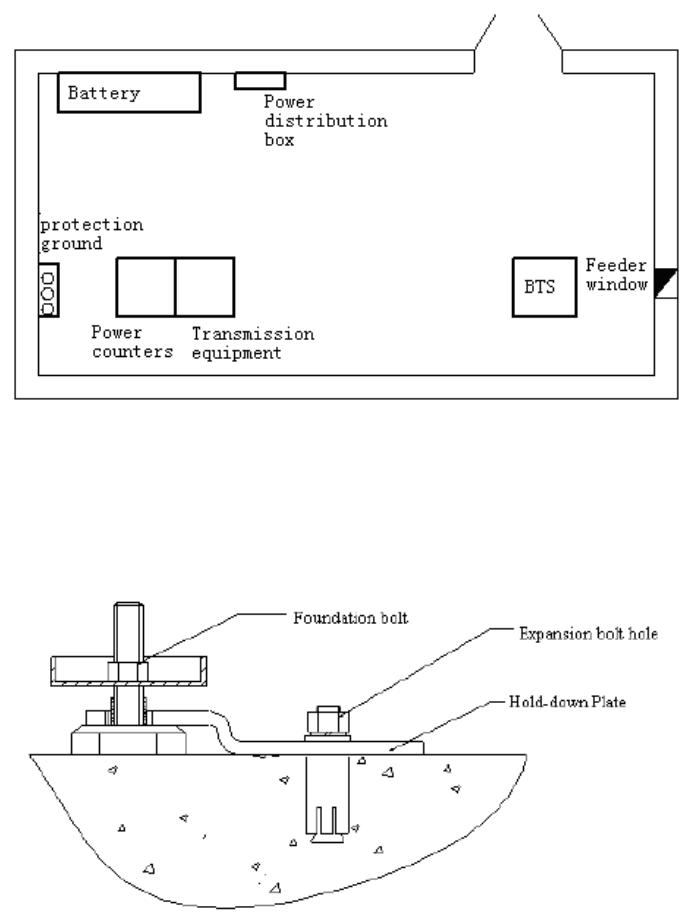
It is recommended to position the BTS cabinet as shown in Figure 2-2 in accordance
with the following guidelines.
The spacing between the rear side of the cabinet and the wall should be at least
600mm.
In the front side of the cabinet, at least 600mm spacing should be reserved as a work
area.
Fig 2-2: Layout of the network facility and location of BTS cabinet
Place the cabinets based on the engineering design requirements and accurately mark
out the positions of the supports on the floor. Install the accessories for cabinet
installation, as shown in Figure 2-3. Drill vertical holes with the appropriate punch drill
and drill bit, and then install M12 expansion bolts.
Figure 2-3: Installation of cabinet accessories
Do not over tighten the expansion bolts so that the installation accessories can be easily
moved if necessary. Install the cabinet in the preset position, and then rotate the
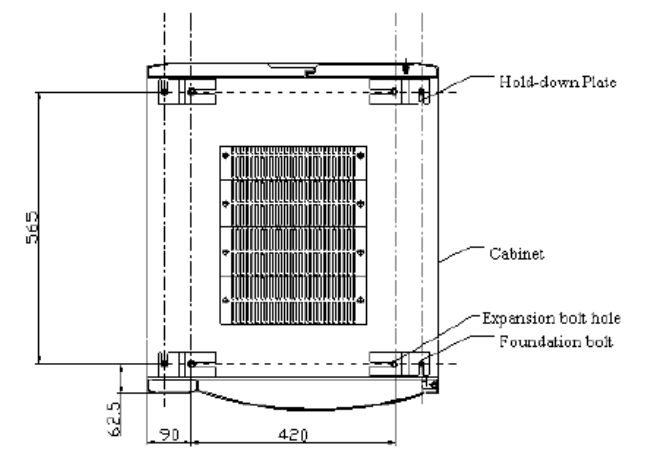
accessories to move the U-shape opening on the corresponding round steel bar of the
cabinet support, as show in Figure 2-5.
Figure 2-4 Bottom of the cabinet
Position the cabinet, make it sit flat by using a level and then tighten the expansion bolts.
Check the insulation impedance with a meg-ohmmeter between the cabinet and the floor
and make sure that the value is greater than 5MΩ.
2.3 BTS Installation
The overall structure of the BTS is shown in Figure 2-5.
Open the cabinet door, adjust the partition positions, push the BTS into the sub-rack.
Record the model and Factory No. of the BTS and cable loss data for future references.
Keep this set of information at an easily accessible location.
Make sure that any empty slot in the BTS enclosure is filled in with a cover panel.
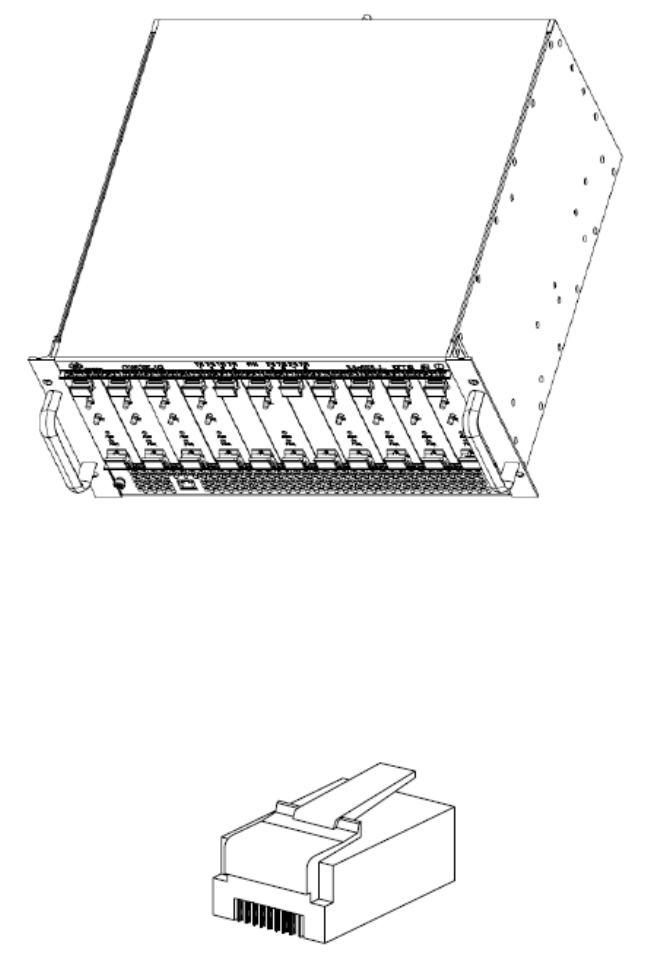
Figure 2-6: Rack-mount BTS Enclosure
2.4 Connection of Ethernet Cable
The following diagram (Fig 2-7) shows the connections between the BTS and a network
switch. The data interface on the BTS is Ethernet with standard RJ-45 connector, as
shown below in Figure 2-7.
Figure 2-7 RJ-45 Ethernet Connector
Fabricate the Ethernet cable using the RJ-45 connectors shown in Fig 2-7. Connect one
end to the Ethernet port located on the bottom left side of the BTS front panel as shown
in Fig 2-8 and the other to a network switch or other transmission equipment.
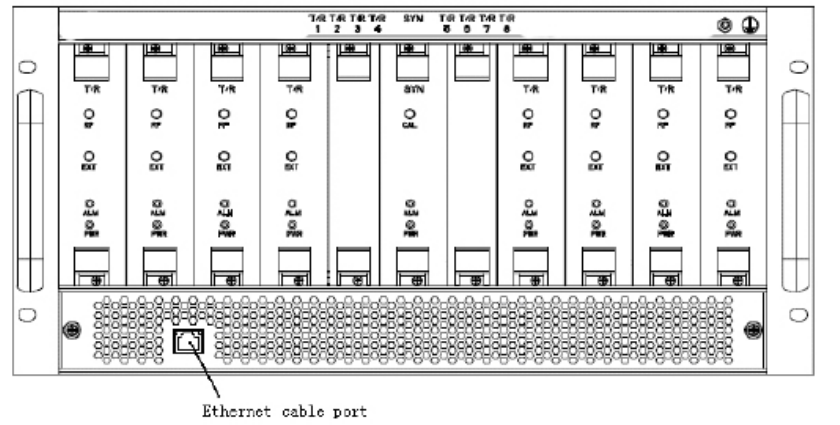
Fig 2-8: Front panel of the BTS with the Ethernet port
2.5 Connect Power Cable
The BTS uses a DC+24V power supply. A +24V power source may be locally available
as part of telco closet facility. Solectek supplies either of the following power supply
options in case that the user needs to use a separate stand-alone power supply.
220/120 V AC to +24V DC power supply unit.
-48V DC to 24V DC power supply unit (in case -48V DC is available on site).
A stand-along power supply must be securely installed in the cabinet. An example of a
typical power supply is shown in Figure 2-9.
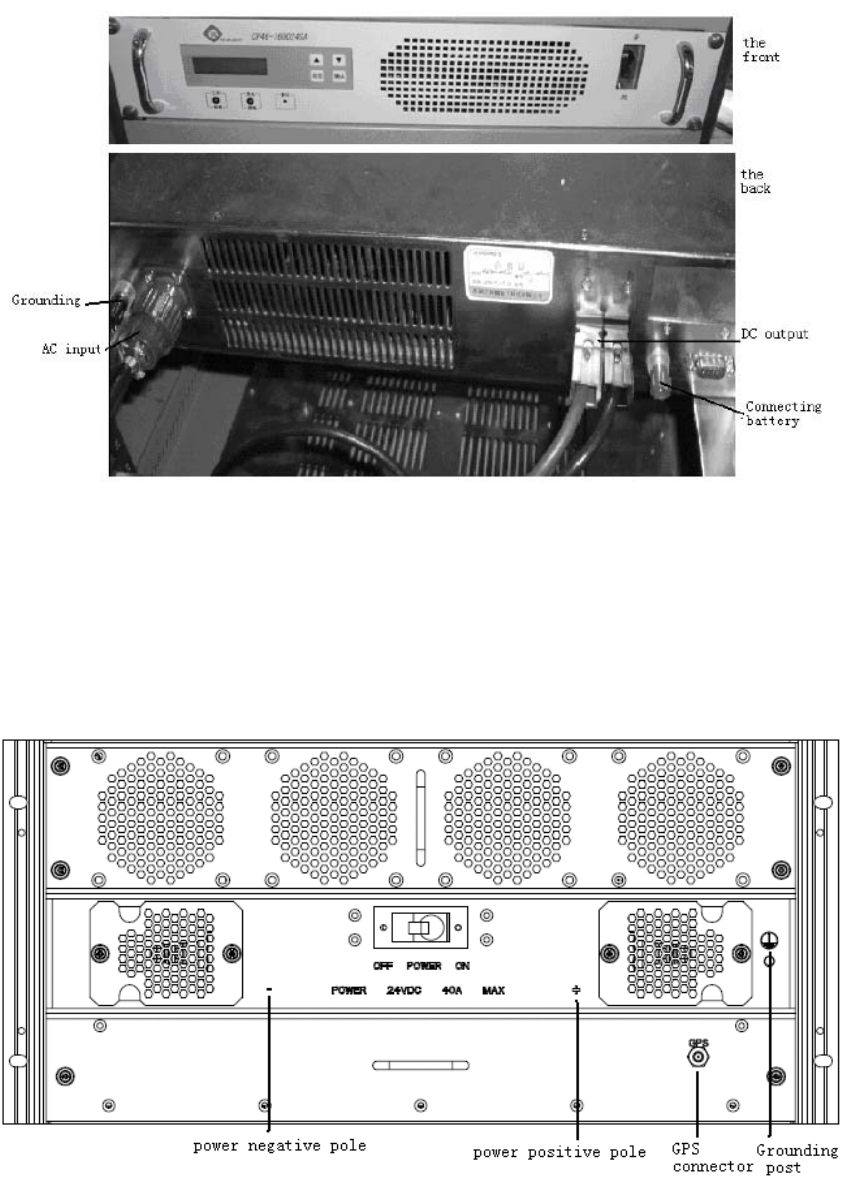
Fig 2-9: An example of a stand alone power supply to be installed in the cabinet
In case of an AC installation, first use a standard electrical cord to bring 120/220V AC to
the power supply’s AC input, connect the equipment’s DC output to the cabinet’s circuit
breaker and then the grounding to the cabinet’s pooling current bar.
WARNING: AC/DC equipment installation and use must strictly comply with the AC/DC
equipment instruction requirements, and reliable grounding must be finished through
grounding cable
Figure 2-10: BTS rear panel with BTS power cable connections shown.
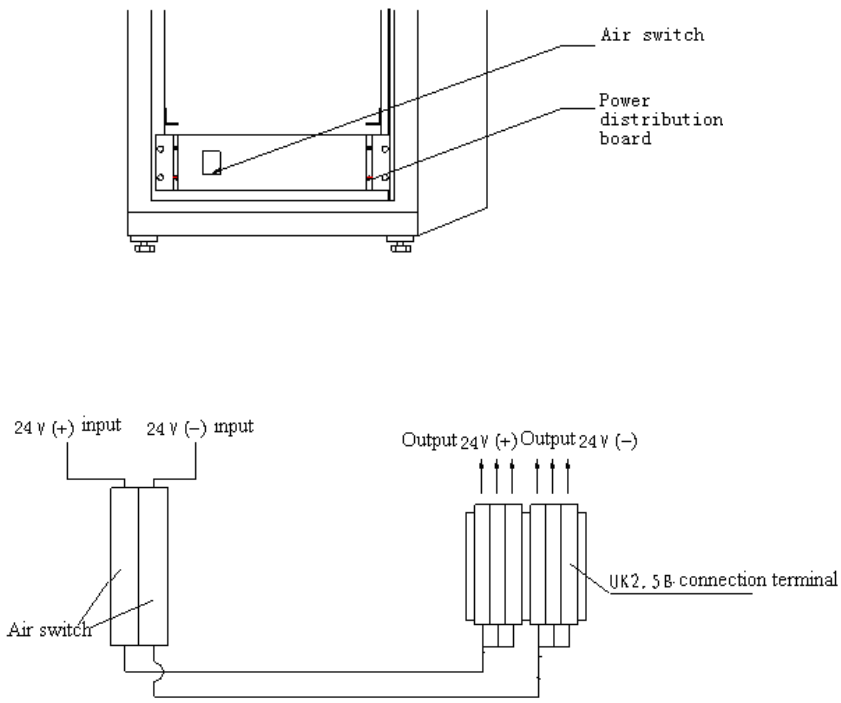
Use flame retardant cables as base station power cables, press them out through Ф6
copper lug, and screw down on the base station power wire posts, as shown in Figure 2-
10.
Connect one end of the DC+24V power cable to the air switch at the cabinet’s bottom,
the red is connected to the positive pole, and the blue is connected to the negative pole.
Connect the other end to DC power cabinet’s output terminal correspondingly, the red is
connected to the positive pole (the working ground), and the blue is connected to the
negative pole. One end of the greenish yellow is connected to the pooling current bar of
the base station cabinet, and the other end is connected to the protection grounding bus
bar in the equipment room, as shown in Figure 2-11.
Figure 2-11: Power distribution board
Connect one end of the power cable to the power distribution board underneath the rear
of the cabinet, and the other end to base station power wire posts. Complete the
connection for the air switch and the power distribution board as shown in Figure 2-12.
Figure 2-13 Connection map of the power
Connect the power cables to the connection at the side of electric power distribution
cabinet and label the connection as well. Connect the grounding bus bar to grounding
cable via connection and tighten it with bolts. The carrier’s staff are required to
cooperate on the scene when connect power cable to power distribution cabinet,
connecting the cables after having cut designated branch switch. After connection, close
the branch switch (make sure to close the air switch firstly), then connect the black pen
of the multi-meter with voltage grade to air switch working grounding and the red pen to
air switch +24V end, if measurement value shows 24(±3) V, connection is correct.
And then close designated branch switch.
WARNING: Do not bundle power cables with other cables. They must be cabled
separately.
2.6 Cabling Requirements in the Equipment Room
The following installation requirements must be followed in order to prevent accidents or
damages to the equipment.
In the equipment room, transmission cables on the cable ladder should be cabled
separately from power cables and grounding wires, without any cross connection.
The cabling should be done in a tidy and nice order. Excessive cables should be
bundled up with cable ties and then placed on the cable ladder in the equipment
room. Attached white cable ties should be used in an internal less than 400mm.
The RF feeders between the cable ladder and the RF feeder, any elbow should
be kept smooth without cross connection. The elbow angle should be ≥90º.
Some cables, such as the GPS cable from the cable ladder to the cabinet, 7D-FB
feeder, Ethernet cable, power cables of the BTS and the cabinet’s grounding
wires, should be vertically led into the cabinet’s cabling holes from the cable
ladder.
Both ends of Ethernet cable should be labeled clearly. Make sure to check the
Ethernet cable to ensure good contact;
Both ends of the ground wire should be connected with specific connectors
(copper lug). After checking the connectors, wrap the connection between the
grounding wire and the connector with insulation tape. On the grounding wire
provided upon delivery, no connection is allowed in the middle. Both ends should
be tightened with bolts;
On the power cables configured along with delivery, no connection is allowed in
the middle. After connection, label the power cables clearly close to the switch.
Close the branch switch on the power distribution cabinet to check the power to
be connected to the BTS. If the power is correct, switch it off and connect it to the
BTS.
Power cable and signal cable in the cabinet should be distributed separately,
leading power cable (connect to circuit breaker) and protection grounding cable
should be laid in the cabling troughs’ outboard on the left of the cabinet (see
behind), GPS cable should be laid in the cabling troughs’ middle, and Ethernet
cable should be laid in the cabling troughs’ indoor. Base station power cable
should be laid in the cabling troughs on the right of the cabinet.
3. Startup Process
3.1 Base station overview
As the core element in the SkyWay-Mobile system, the BTS is the bridge between
wireless transmission and wired backbone network. After the packet data signal is
received at the base station from backbone network, the message is mapped with EID of
the terminal and then forwarded to MDM board. After digital modulation at the DMD
board, the modulated signal undergoes channel packing and processing at the CHP
board and is converted into base-band signal, which is received by IF board from CHP
board. Then the signal transformed to intermediate frequency and transmitted to RFC
board. The signal, after transformation, is converted by RFC board to radio frequency,
forwarded to TTA and transmitted after amplification.
In the same way, the uplink signal is transmitted to cable backbone network via base
station in a reverse order. The routine operation of base station mainly focuses on the
power and system capacity of the base station system.
3.2 EMS configuration
Before power-on the base station, some basic parameters have to be input to
substations through serial port on the main board. These configuration parameters are
often used as “boot parameters", with which the base station can establish
communication with EMS server so that all configuration parameters can be downloaded
to base station from EMS.
To maintain normal communication links, EMS server is usually connected to the main
board of the base station through hub or switch (10/100 Base-T), while the debugging
computer is connected to the serial port on the main board through RS-232 serial cable.
The serial ports on the main board and debugging computer should be available at this
time. After this, the base station is initialized and configured through some general
communication software, such as HyperTerminal, the standard terminal emulation
software.
3.2.1 Basic procedures
Make sure that all RF cables at the base station are correctly connected. There are 8
data RF cables and 1 calibration RF cable, as indicated on the front panel of the BTS
unit.
Connect the Ethernet interface on the main board of the base station to a network switch
using a standard Ethernet cable and then connect the switch to the PC with EMS server
installed using another Ethernet cable.
Connect the serial port on the main board of BTS to the serial port of debugging
computer through RS-232 cable (DB-9 male-female). Power-on EMS server and start
debugging computer. Configure FTP server tool. It can be installed on any computer that
can communicate with BTS or EMS.
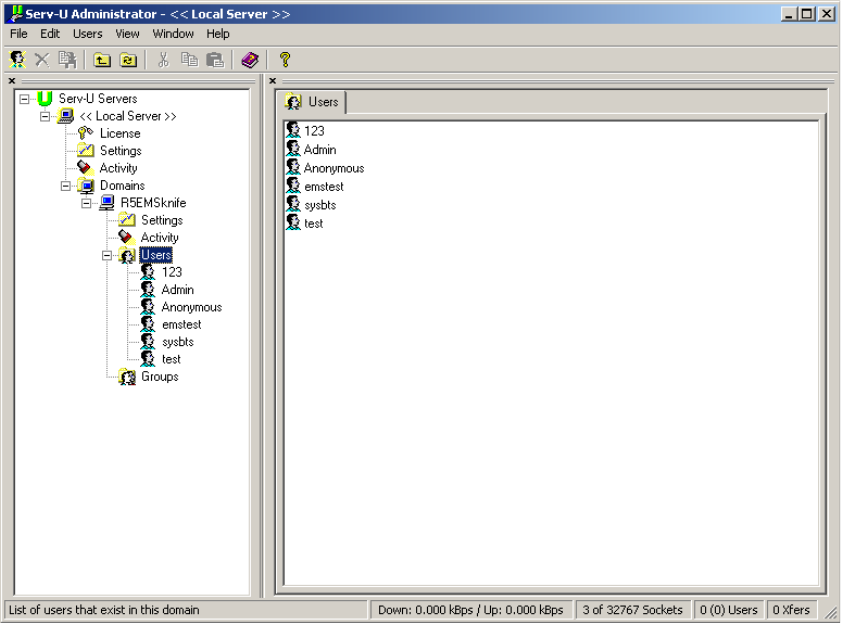
Start EMS server and client in EMS server computer. Make sure that EMS server and
client application are installed and configured properly
Enter EMS SERVER IP and port in IE address bar to enter EMS client GUI interface
(refer to the EMS server user’s guide for details). Input user name and password in EMS
client login screen to start the process.
3.2.2 FTP Server Configuration
Add the base station load program to the server with the FTP server and make sure that
there is a link between the FTP server, the EMS server and the BTS as shown in Fig 3-1.
Start installed FTP server software, such as serv-u, sonicftp, etc. Add user after staring
and specify the path for user to read as the path where Load programs are located, for
example, user name: emstest, path: d:\release0.3.2.1.
Fig 3-1: Window to enable addition of users
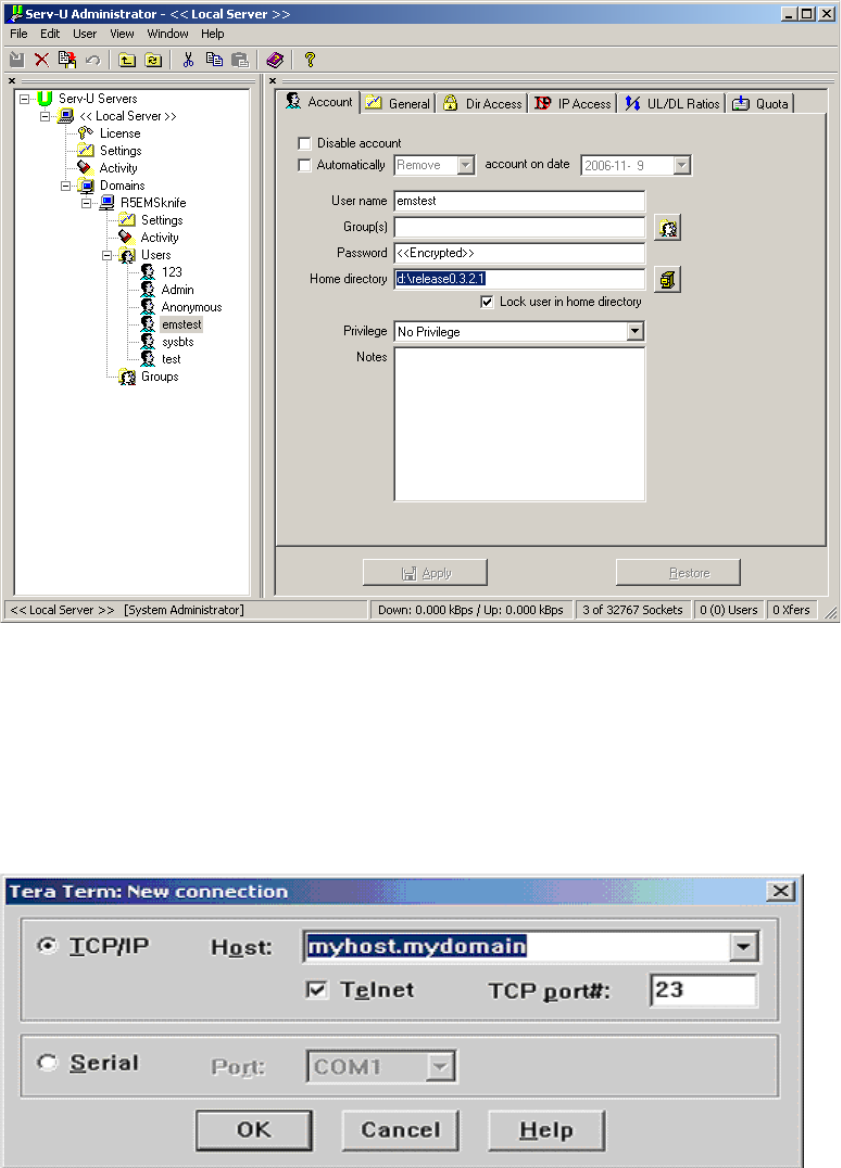
Fig 3-2: Window to specify the server path
3.2.3 HyperTerminal configuration
Make sure that the computer is furnished with HyperTerminal software. Tera Term Pro
software is strongly recommended and it can be downloaded from a shareware website.
Click desktop shortcut to run HyperTerminal software. The following screen will show
upon startup:
Fig 3-3 HyperTerminal configuration
Select “serial”, “COM1” port and click [OK] button (Fig 3-4)

Fig 3-4: HyperTerminal configuration – Serial port
Clicking OK in Fig 3-4 should prompt the following screen (Fig 3-5). Go to “Setup” on the
menu and select “Serial port”.
Fig 3-5 HyperTerminal configuration – Serial port setup
In the serial port setup screen (Fig 3-6), set the baud rate of the serial port to 19200. The
serial port will not function at any other baud rate value.
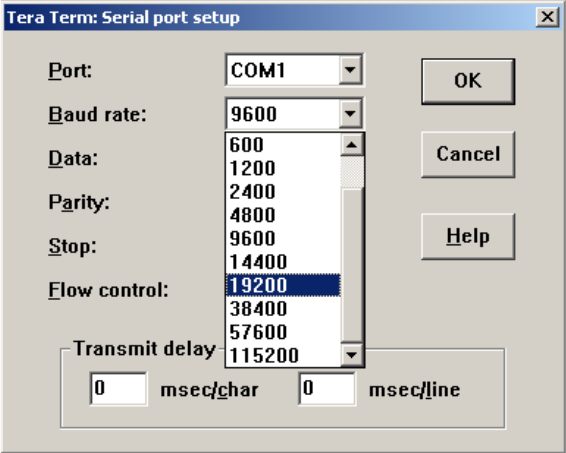
Fig 3-6 HyperTerminal configuration (4)
The serial port is now successfully configured and can be used for configuring
information (such as IP address) for connected base station so that the base station is
linked to the EMS server.
3.3 Add a BTS in EMS Server
If the client program is running in EMS Server computer, click [Resource Management]
to add new base station. Here only some necessary configurations are required, such as
base station name, ID, IP address, subnet mask and network gateway, etc, which should
be filled in according to your system network plan design.
Go to “Net Element” and select “Add Net Element” (Fig 3-7) and the “Add Net Element”
screen will be shown (Fig 3-8).
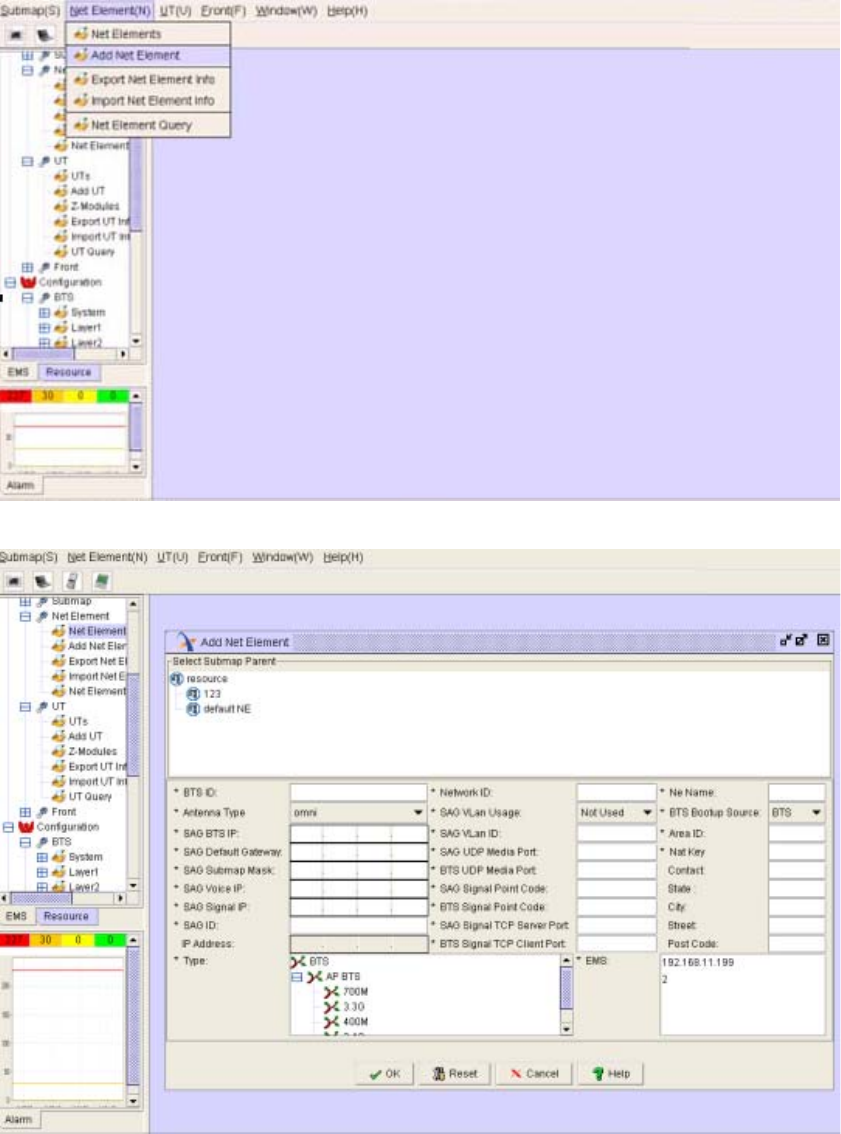
Fig 3-7 Add a net element (Base Station)
Fig 3-8 “Add Net Element” screen
All entries with the asterisk “*” are required according to the parameters below (content
and writing specifications).
BTS ID: in digits, the id assigned to the BTS
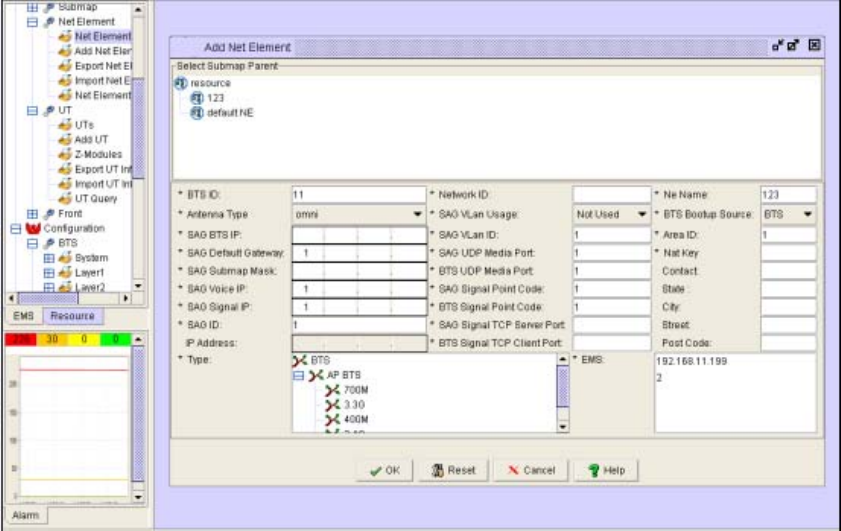
SAG signal IP:IP address of sag signaling connected to the BTS
SAG voice IP:IP address of sag voice connected to the BTS
SAG ID: sag id connected to bts in digits
Signaling sending port: signaling sending port specified
Sag media port: media port specified
Sag signaling code: manner of signaling coding
Antenna type: omni-direction or directional
Network element type: the frequency range used by network elements; at present 4
types are available: 3.3 G, 2.4G, 1.8G and 400M
Network element name: name specified for BTS, with digits, letters and Chinese
characters
Acceptable Network element ip: ip address specified to the base station
Network id: id assigned by carrier
Region id: in digits
Signaling receiving port: signaling receiving port specified
BTS media port: media port specified
BTS signaling coding: manner of signaling coding
EMS: name of the front-end processor connected to the base station
Fig 3-9: “Add Net Element” screen with input values filled in.
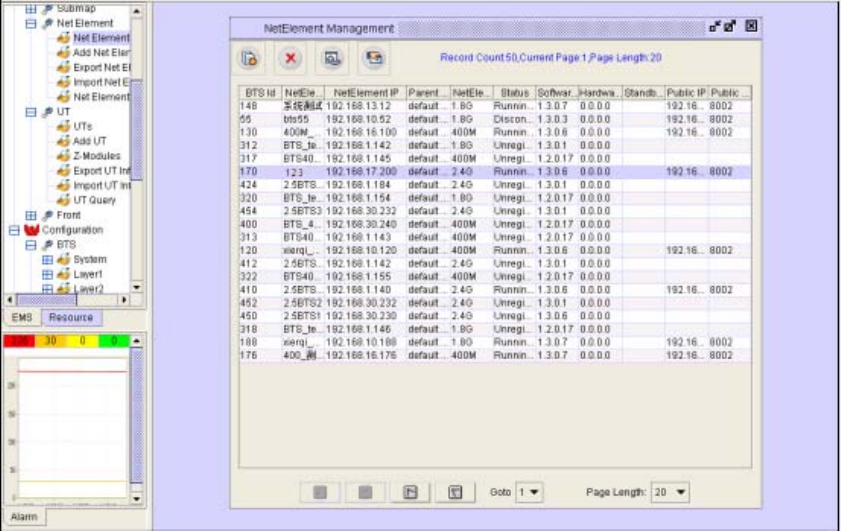
Fig 3-10: Net Element Management Screen
3.4 Base Station Startup
3.4.1 Base station normal startup
Base station power-on
For startup, the base station power, RF cables, calibration cable and GPS etc. must be
correctly connected. In particular make sure that the L3 network cable is connected. Also
the serial port cable of the base station can be connected to PC to update BTS IP
information or view startup message, etc. When everything is connected, switch on the
power, then switch on the main switch at the back of BTS and the base station will enter
startup.
Base station boot
The following is the content displayed and to be configured in HyperTerminal window
during base station startup.
bootrom booting!!!!!!!
VxWorks System Boot
Copyright 1984-2002 Wind River Systems, Inc.
CPU: 7447A Power PC
Version: VxWorks5.5.1
BSP version: 1.0/0
Creation date: Aug 4 2006, 13:44:28
Press any key to stop auto-boot...
Configuration of Parameters
Press any key on the keyboard to stop automatic startup and input configuration
information to configure base station:
Now there will be a boot message in HyperTerminal screen: [VxWorks Boot]:
This message provides some operations of simple commands. Input “?” or “h” and press
[Enter] to display a set of commands (and examples). To use any command, just input
character
command with optional parameters and press [Enter].
Boot Commands
[VxWorks Boot]: ?
? - print this list
@ - boot (load and go)
p - print L3 boot params
P - print L2 boot params
c - change L3 boot params
C - change L2 boot params
l - load boot file
g adrs - go to adrs
d adrs[,n] - display memory
m adrs - modify memory
f adrs, nbytes, value - fill memory
t adrs, adrs, nbytes - copy memory
e - print fatal exception
v - print boot logo with version
n netif - print network interface device address
$dev(0,procnum)host:/file h=# e=# b=# g=# u=usr [pw=passwd] f=#
tn=targetname s=script o=other
boot device: ata=ctrl,drive file name: /ata0/vxWorks
Boot flags:
0x02 - load local system symbols
0x04 - don't autoboot
0x08 - quick autoboot (no countdown)
0x20 - disable login security
0x40 - use bootp to get boot parameters
0x80 - use tftp to get boot image
0x100 - use proxy arp
available boot devices:Enhanced Network Devices
mv0 ata
Explanations of all commands:
@ -Used when all parameters are set as required. This command will continue to
execute previously cancelled boot initialization process.
p - This command will display a brief description of L3 parameters in current boot
configuration.
P - This command will display a brief description of L2 parameters in current boot
configuration.
c - This command can be used to change current L3 boot parameters. Once this
command is selected, a detailed option list will be displayed. Modify and overwrite it.
When all options are modified, the system will return to [VxWorks Boot]: message.
During these processes, press [Enter] to accept current parameters value or input
new parameters value and press [Enter] to confirm. Besides, input “.” and press
[Enter] to clear current value of this entry and restore it to default. If any error occurs,
process “-(hyphen)” and [Enter] to return to previous option. Or you can continue this
erroneous entry and modify it when returning to [VxWorks Boot]: command line.
C - This command can be used to change current L2 boot parameters. Once this
command is selected, a detailed option list will be displayed. Modify and overwrite it.
When all options are modified, the system will return to [VxWorks Boot]: message.
During these processes, press [Enter] to accept current parameters value or input
new parameters value and press [Enter] to confirm. Besides, input “.” and press
[Enter] to clear current value of this entry and restore it to default. If any error occurs,
process “-(hyphen)” and [Enter] to return to previous option. Or you can continue this
erroneous entry and modify it when returning to [VxWorks Boot]: command line.
d - display memory usage; the user-defined base station memory to be displayed can
be viewed here. This operation can only be conducted by Solectek certified technical
support engineer.
m - modify memory. This option allows the user to change allocation of base station
memory as per the user’s requests. This operation can only be conducted by
Solectek certified technical support engineer.
f - fill memory. This option allows changing BTS memory with a set mode. This
operation can only be conducted by Solectek certified technical support engineer.
t - fill memory. This option allows changing BTS memory with a set mode from other
memory area. This operation can only be conducted by Solectek certified technical
support engineer.
Input “c” to configure L3.
[VxWorks Boot]: c
'.' = clear field; '-' = go to previous field; ^D = quit
boot device : mv0 :Boot BTS from ftp server
processor number : 0
host name : hy :host username
file name : l3_image :filename of L3 startup
inet on ethernet (e) : 192.168.17.160:ffffff00 :IP and subnet mask
of L3
inet on backplane (b): 10.0.0.1 :IP of L3’s BP
host inet (h) : 192.168.11.199 :IP of ftp server
gateway inet (g) : 192.168.17.1 :IP of L3’s gateway
user (u) : emstest :username of ftp server
ftp password (pw) (blank = use rsh): emstest :FTP password
flags (f) : 0x0
target name (tn) :
startup script (s) :
other (o) :
[VxWorks Boot]:
Input “C” to configure L2.
[VxWorks Boot]: C
'.' = clear field; '-' = go to previous field; ^D = quit
boot device : mv0 :Boot BTS from ftp server
processor number : 0
host name : hy :host username
file name : l2_image.bin :filename of L2 startup
inet on ethernet (e) : 192.168.17.161:ffffff00 :IP and subnet
mask of L2
inet on backplane (b): 10.0.0.2 :IP of L2’s BP
host inet (h) : 192.168.11.199 :IP of ftp server
gateway inet (g) : 192.168.17.1 :IP of L3’s gateway
user (u) : emstest :username of ftp server
ftp password (pw) (blank = use rsh): emstest :FTP password
flags (f) : 0x0
target name (tn) :
startup script (s) :
other (o) : 0.250.0.37
[VxWorks Boot]:
Input “p” to view L3 configuration.
[VxWorks Boot]: p
boot device : mv
unit number : 0
processor number : 0
host name : hy
file name : l3_image
inet on ethernet (e) : 192.168.17.160:ffffff00
inet on backplane (b): 10.0.0.1
host inet (h) : 192.168.11.199
gateway inet (g) : 192.168.17.1
user (u) : emstest
ftp password (pw) : emstest
flags (f) : 0x0
Input “P” to view L2 configuration.
[VxWorks Boot]: P
boot device : mv
unit number : 0
processor number : 0
host name : hy
file name : l2_image.bin
inet on ethernet (e) : 192.168.17.161:ffffff00
inet on backplane (b): 10.0.0.2
host inet (h) : 192.168.11.199
gateway inet (g) : 192.168.17.1
user (u) : emstest
ftp password (pw) : emstest
flags (f) : 0x0
other (o) : 0.250.0.37
Boot process
[VxWorks Boot]: @
boot device : mv
unit number : 0
processor number : 0
host name : hy
file name : l3_image
inet on ethernet (e) : 192.168.17.160:ffffff00
inet on backplane (b): 10.0.0.1
host inet (h) : 192.168.11.199
gateway inet (g) : 192.168.17.1
user (u) : emstest
ftp password (pw) : emstest
flags (f) : 0x0
Attached TCP/IP interface to mv0.
Attaching network interface lo0... done.
Loading... 4365424
Starting at 0x10000...
ataDrv returned ERROR from usrRoot.
ataDrv returned ERROR from usrRoot.
Error during ataDevCreate: d0003
Attached TCP/IP interface to mv unit 0
Attaching interface lo0...done
Adding 8580 symbols for standalone.
]]]]]]]]]]]]]]]]]]]]]]]]]]]]]]]]]]]]]]]]
]]]]]]]]]]]]]]]]]]]]]]]]]]]]]]]]]]]]]]]
]]]]]]]]]]]]]]]]]]]]]]]]]]]]]]]]]]]]]]
]]]]]]]]]]] ]]]] ]]]]]]]]]] ]] ]]]]
(R)
] ]]]]]]]]] ]]]]]] ]]]]]]]] ]] ]]]]
]] ]]]]]]] ]]]]]]]] ]]]]]] ] ]] ]]]]
]]] ]]]]] ] ]]] ] ]]]] ]]] ]]]]]]]]] ]]]] ]] ]]]] ]]
]]]]]
]]]] ]]] ]] ] ]]] ]] ]]]]] ]]]]]] ]] ]]]]]]] ]]]] ]]
]]]]
]]]]] ] ]]]] ]]]]] ]]]]]]]] ]]]] ]] ]]]] ]]]]]]]
]]]]
]]]]]] ]]]]] ]]]]]] ] ]]]]] ]]]] ]] ]]]] ]]]]]]]]
]]]]
]]]]]]] ]]]]] ] ]]]]]] ] ]]] ]]]] ]] ]]]] ]]]] ]]]]
]]]]
]]]]]]]] ]]]]] ]]] ]]]]]]] ] ]]]]]]] ]]]] ]]]] ]]]]
]]]]]
]]]]]]]]]]]]]]]]]]]]]]]]]]]]]]
]]]]]]]]]]]]]]]]]]]]]]]]]]]]] Development System
]]]]]]]]]]]]]]]]]]]]]]]]]]]]
]]]]]]]]]]]]]]]]]]]]]]]]]]] VxWorks version 5.5.1
]]]]]]]]]]]]]]]]]]]]]]]]]] KERNEL: WIND version 2.6
]]]]]]]]]]]]]]]]]]]]]]]]] Copyright Wind River Systems, Inc.,
1984-2003
CPU: 7447A Power PC. Processor
#0.
Memory Size: 0xe000000. BSP version 1.0/
0.
WDB Comm Type: WDB_COMM_END
WDB: Ready.
Note that there are only 3 seconds to modify configuration: if the first letter is not “m”, the
system will automatically start up, causing configuration failure.
L3 booting
c -config, p - display, b -boot parameter, h/? - help, @ boot
[BOOT]: c
'.' = clear field; '-' = go to previous field; ^D = quit
btsId : 160 :Configure base station ID specified in EMS
vlanId (0~4095) : 0 :Configure vlan port
dataSource(0-bts/1ems): 0 :Configure base station startup source
ems IP : 192.168.17.125 192.168.11.199 :Configure EMS
server IP
emsRcvPort(D=3999) : 3999 :EMS port number, usually d
efault
btsRcvPort(D=8002) : 8002 :bts port number, usually d
efault
rtc year : 2006 :Configure year
rtc month : : 11 :Configure month
rtc day : 8 :Configure date
rtc hour : 11 :Configure hour
rtc minute : : 11 : Configure minute
rtc second : : 2 :Configure second
[BOOT]:BS booting
[BOOT]: @
L3 Application booting.............................. Done
Now bts is successfully started.
bts(160) L3->3b55bae0 tCleanUp:0000 L3DataEB.cpp( 840) :
CleanUp sta
rt monitoring.
SatellitesVisible = 0
StatellitesTrack = 0
BootSrc = 0
RfMask = 0X00FF
SyncCardTemperature = 0
DigitalBoardTemperature = 0
TimePassedSinceBtsBoot = 0 seconds
[2006/11/08 11:11:0] [tSys] BTS software version: 0.3.2.1
:Display BTS software version
[2006/11/08 11:11:0] [tSys] BTS boot normal!
[2006/11/08 11:11:0] tSys create ok!
[2006/11/08 11:11:0] tEmsRx create ok!
[2006/11/08 11:11:0] tEmsTx create ok!
[2006/11/08 11:11:0] [tDiagL2L3EMS] create m_sfdl2l3[15] ok!
[2006/11/08 11:11:0] [tDiagL2L3EMS] create m_sfdl3ems[16] ok!
[2006/11/08 11:11:0] tDiagL2L3Ems create ok!
[2006/11/08 11:11:0] [tDiagEMSL3L2] create m_sfdemsl3[17] ok!
[2006/11/08 11:11:0] [tDiagEMSL3L2] create m_sfdl3l2[18] ok!
[2006/11/08 11:11:0] tDiagEmsL3L2 create ok!.
[2006/11/08 11:11:0] tAlarm create ok!
[2006/11/08 11:11:0] tCfg create ok!
[2006/11/08 11:11:0] mode = tFileM create ok!
0
[2006/11/08 11:11:0] tFtpC create ok!
[2006/11/08 11:11:0] tCpeM create ok!.
mode 0: no hold; 1: enable position hold; 2:enable altitude hold; 3:
autosite survey
[2006/11/08 11:11:0] tGps create ok!
[2006/11/08 11:11:0] tPM create ok!
[2006/11/08 11:11:0] [tSys] All OAM tasks create ok! :system se
lf-test over
[2006/11/08 11:11:0] [tSys] Send Register Notify to EMS[192.168.11.
199] @state[0] bts send register message to ems server
[2006/11/08 11:11:0] [BTS boot] ==> BTS booting from FTP server
[2006/11/08 11:11:0] [tSys] BTS send to EMS register response, stat
e[0]
[2006/11/08 11:11:0] [tSys] BTS register SUCCEED. Bts register
succeed
[2006/11/08 11:11:0] [BTS boot] ==> Download file :l2_image.bin fin
ished
[2006/11/08 11:11:0] [BTS boot] ==> Download file :app_mcp.out fini
shed
[2006/11/08 11:11:0] [BTS boot] ==> Download file :app_aux.out fini
shed
[2006/11/08 11:11:0] [BTS boot] ==> Download file :app_fep.out fini
shed
[2006/11/08 11:11:0] [BTS boot] ==> Download file :fpga_L2.out fini
shed
[2006/11/08 11:11:0] [BTS boot] ==> Download file :fpga_L1.out fini
shed
[2006/11/08 11:11:0] [BTS boot] ==> Download file :fpga_FEP0.out fi
nished
[2006/11/08 11:11:0] [BTS boot] ==> Download file :fpga_FEP1.out fi
nished
Download booting file is now completed.
[2006/11/08 11:11:0] [BTS boot] ==> FPGA download started
[2006/11/08 11:11:0] [BTS boot] ==> FPGA download succeed
[2006/11/08 11:11:0] [BTS boot] ==> Reset FPGA
Start the FPGA circuit module.
[2006/11/08 11:11:0] [BTS boot] ==> Reset AUX :Start AUX cir
cuit module.
[2006/11/08 11:11:0] [BTS boot] ==> Reset L2 PowerPC system
[2006/11/08 11:11:0] [BTS boot] ==> L2 PreLoader is ready to accept
L2 Image
[2006/11/08 11:11:0] [BTS boot] ==> L2 PPC image download finished
[2006/11/08 11:11:0] L2 PCI interface is ready for message exchange
[2006/11/08 11:11:0] [tSys] BTS L2 boot up SUCCESS
BTS L2 boot is now completed
[2006/11/08 11:11:0] [BTS boot] ==> MCP 0 reset, start code download
[2006/11/08 11:11:0] [BTS boot] ==> MCP 1 reset, start code download
[2006/11/08 11:11:0] [BTS boot] ==> MCP 2 reset, start code download
[2006/11/08 11:11:0] [BTS boot] ==> MCP 3 reset, start code download
[2006/11/08 11:11:0] [BTS boot] ==> MCP 4 reset, start code download
[2006/11/08 11:11:0] [BTS boot] ==> MCP 5 reset, start code download
[2006/11/08 11:11:0] [BTS boot] ==> MCP 6 reset, start code download
[2006/11/08 11:11:0] [BTS boot] ==> MCP 7 reset, start code download
[2006/11/08 11:11:0] [BTS boot] ==> AUX Reset, start AUX code
download
[2006/11/08 11:11:0] [tSys] BTS MCP[0] boot up SUCCESS
[2006/11/08 11:11:0] [tSys] BTS MCP[1] boot up SUCCESS
[2006/11/08 11:11:0] [tSys] BTS MCP[2] boot up SUCCESS
[2006/11/08 11:11:0] [tCpeM] receive msg[0x3706] from task[57]
[2006/11/08 11:11:0] [tSys] BTS MCP[3] boot up SUCCESS
[2006/11/08 11:11:0] [tSys] BTS MCP[4] boot up SUCCESS
[2006/11/08 11:11:0] [tSys] BTS MCP[5] boot up SUCCESS
[2006/11/08 11:11:0] [tSys] BTS MCP[6] boot up SUCCESS
[2006/11/08 11:11:0] [tSys] BTS MCP[7] boot up SUCCESS
MSP circuit module boot is now completed
[2006/11/08 11:11:0] [tSys] BTS AUX boot up SUCCESS
[2006/11/08 11:11:0] [BTS boot] ==> Reset FEP 0
[2006/11/08 11:11:0] [BTS boot] ==> Reset FEP 1
[2006/11/08 11:11:0] [BTS boot] ==> FEP 0 reset, start code download
[2006/11/08 11:11:0] [BTS boot] ==> FEP 1 reset, start code download
[2006/11/08 11:11:0] [tSys] BTS FEP[0] boot up SUCCESS
[2006/11/08 11:11:0] [tSys] BTS FEP[1] boot up SUCCESS
FEP circuit module boot is now completed
[2006/11/08 11:11:0] [BTS boot] ==> Whole BTS boot finished
[2006/11/08 11:11:0] [tSys] BTS standby version: 0
[2006/11/08 11:11:0] [tSys] Send BTS Reset Notify to EMS.
[2006/11/08 11:11:0] [tSys] BTS boot from NvRam.
L2 AIR LINK DATA:####################################
btsid = 000000A0
networkid = 00000001
reset cnt = 0017
seqid = 00
subcgmask = 1F
timeslotn = 08
dltsnum = 04
BCHSCG = 02 FF FF FF FF FF FF FF FF FF
BCHTS = 01 FF FF FF FF FF FF FF FF FF
RRCHSCG = 02 FF FF FF FF FF FF FF FF FF
RRCHTS = 03 FF FF FF FF FF FF FF FF FF
RACHSCG = 02 FF FF FF FF FF FF FF FF FF FF FF FF FF FF FF FF FF FF F
F
RACHTS = 02 FF FF FF FF FF FF FF FF FF FF FF FF FF FF FF FF FF FF F
F
maxscale = 2000
premscale = E4F
BCHSCALE = 0EAE 0C8E 0EAE[2006/11/08 11:11:0] [tSys] BTS boot up SU
CCESS.
0EAE 0000 0000 0000 0000
TCHSCALE = 03D7 03D7 03D7 03D7 0000 0000 0000 0000
W0I = 1DB1 D8B5 E4BD 2CAB 2CAB E4BD D8B5 1DB1
W0Q = DF1B EBE8 2312 0000 0000 2312 EB65 0000 [2006/11/08 11:11:
0] [tCfg]
receive msg = 0x2012
[2006/11/08 11:11:0] [tCfg]Boot from NvRam! please wait...
[2006/11/08 11:11:0] [tCfg] receive msg = 0x2028
[2006/11/08 11:11:0] [tCfg] receive msg = 0x2025
[2006/11/08 11:11:0] [tCfg] receive msg = 0x2022
[2006/11/08 11:11:0] [tCfg] receive msg = 0x202b
[2006/11/08 11:11:0] [tCfg] receive msg = 0x0011
[2006/11/08 11:11:0] [tCfg] receive msg = 0x0029
[2006/11/08 11:11:0] [tCfg] receive msg = 0x0015
[2006/11/08 11:11:0] [tCfg] receive msg = 0x3038
[2006/11/08 11:11:0] [tCfg] receive msg = 0x3002
[2006/11/08 11:11:0] [tCfg] receive msg = 0x3005
[2006/11/08 11:11:0] [tCfg] receive msg = 0x3008
[2006/11/08 11:11:0] [tCfg] receive msg = 0x300b
[2006/11/08 11:11:0] [tCfg] receive msg = 0x3015
[2006/11/08 11:11:0] [tCfg] receive msg = 0x3018
[2006/11/08 11:11:0] [tCfg] receive msg = 0x301b
[2006/11/08 11:11:0] [tCfg] receive msg = 0x301b
[2006/11/08 11:11:0] [tCfg] receive msg = 0x301b
[2006/11/08 11:11:0] [tCfg] receive msg = 0x301b
[2006/11/08 11:11:0] [tCfg] receive msg = 0x301b
[2006/11/08 11:11:0] [tCfg] receive msg = 0x301b
[2006/11/08 11:11:0] [tCfg] receive msg = 0x301b
[2006/11/08 11:11:0] [tCfg] receive msg = 0x301b
[2006/11/08 11:11:0] [tCfg] receive msg = 0x301b
[2006/11/08 11:11:0] [tCfg] receive msg = 0x301b
[2006/11/08 11:11:0] [tCfg] receive msg = 0x301b
[2006/11/08 11:11:0] [tCfg] receive msg = 0x301b
[2006/11/08 11:11:0] [tCfg] receive msg = 0x301b
[2006/11/08 11:11:0] [tCfg] receive msg = 0x301b
[2006/11/08 11:11:0] [tCfg] receive msg = 0x301b
[2006/11/08 11:11:0] [tCfg] receive msg = 0x301b
[2006/11/08 11:11:0] [tCfg] receive msg = 0x301b
[2006/11/08 11:11:0] [tCfg] receive msg = 0x301b
[2006/11/08 11:11:0] [tCfg] receive msg = 0x301b
[2006/11/08 11:11:0] [tCfg] receive msg = 0x301b
[2006/11/08 11:11:0] [tCfg] receive msg = 0x301b
[2006/11/08 11:11:0] [tCfg] receive msg = 0x301b
[2006/11/08 11:11:0] [tCfg] receive msg = 0x301b
[2006/11/08 11:11:0] [tCfg] receive msg = 0x301b
[2006/11/08 11:11:0] [tCfg] receive msg = 0x301b
[2006/11/08 11:11:0] [tCfg] receive msg = 0x301b
[2006/11/08 11:11:0] [tCfg] receive msg = 0x301b
[2006/11/08 11:11:0] [tCfg] receive msg = 0x301b
[2006/11/08 11:11:0] [tCfg] receive msg = 0x301b
[2006/11/08 11:11:0] [tCfg] receive msg = 0x301b
[2006/11/08 11:11:0] [tCfg] receive msg = 0x301b
[2006/11/08 11:11:0] [tCfg] receive msg = 0x301b
[2006/11/08 11:11:0] [tCfg]Syn_Src[1] Antanna Mask in NvRam[00ff]
[2006/11/08 11:11:0] [tCfg]GPS not ready, config Antenna Mask with
0x0000
[2006/11/08 11:11:0] [tCfg]Antanna Mask:[0000]
[2006/11/08 11:11:0] [tCfg]Send L1GenData0[0001]:
[2006/11/08 11:11:0] [tCfg]Send L1GenData1[0000]:
[2006/11/08 11:11:0] [tCfg]Send L1GenData2[0000]:
[2006/11/08 11:11:0] [tCfg] receive msg = 0x3012
[2006/11/08 11:11:0] [tCfg] send Data Init Finish Notify to tSys
[2006/11/08 11:11:0] [tSys] receive Data Init Finish Notify from tC
fg
[2006/11/08 11:11:0] =====================
[2006/11/08 11:11:0] BTS IS WORKING STATUS
[2006/11/08 11:11:0] =====================
BTS startup is now successful.
[2006/11/08 11:11:0] [tCfg]Boot from NvRam success!
[2006/11/08 11:12:0] [tGPS] send msg M_L3_L2_L1_GENERAL_SETTING_REQ
RF Mask[0x00ff]success!
[2006/11/08 11:12:0] [tGPS] GPS locked!
[2006/11/08 11:12:0] [tCpeM] receive msg[0x200b] from task[3]
[2006/11/08 11:12:0] [tCpeM] receive msg[0x3706] from task[57]
[2006/11/08 11:13:0] [tCpeM] receive msg[0x3706] from task[57]
When the status of the BTS that you just booted up is shown as “connected" or “In
operation warning” in net element information screen in EMS, the BTS boot-up
sequence has been successfully completed.
3.4.2 Base Station reboot
When base station needs to be rebooted due to incidents happening to BTS or other
causes:
First, if the base station is in normal working mode, i.e. there is data output from BTS
serial port (or level 3 of telnet), you can enter command “reboot” in L3 command line or
“rebootL2” for only rebooting L2.
Second, there is a “Reset” switch on the front panel. Press this button for several
seconds and the base station will reset and enter into the reboot sequence; A hard
reboot (disconnect main switch at the back of base station rear panel) is not
recommended in all circumstances except for severe equipment malfunction that causes
other reset options to be unavailable.
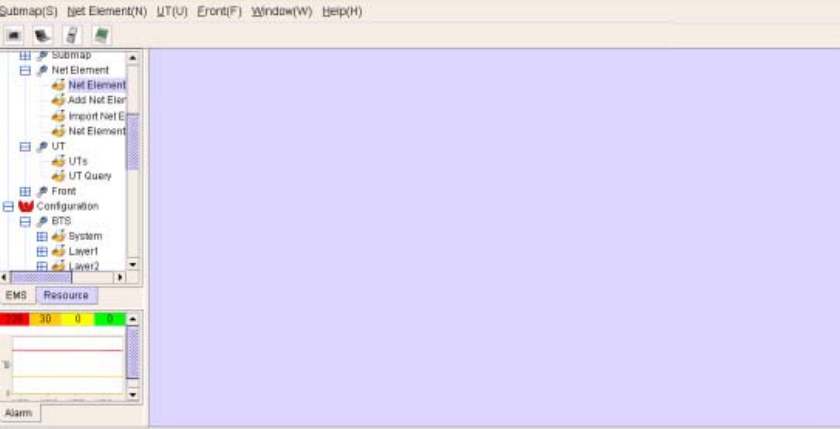
4. Calibration
When BTS is successfully started, some of its initializing data can be configured via
EMS client so that BTS is calibrated for normal work.
During base station calibration, the inter-antenna phase difference can be measured and
the all output power from RFS to antenna can be matched. The calibration should be
conducted at least three times to ensure its effectiveness. At least 20 minutes are
required for loading new software in RFC.
Complete calibration
As there may be changes in the system due to temperature and climate changes as well
as normal equipment aging in normal operation, the base station must be completely
calibrated before power-on after implementation. The calibration is based on the target
data set in EMS. In the SkyWay-Mobile BTS system complete calibration is adopted.
In complete calibration, calculation is conducted of the power and gain in each antenna
to get data for calibrating base station antenna. The calibration result covers calibration
data of the eight antennas, current sending and receiving amplitude and phase diagrams
of the current calibration results, comparison with history calibration data, etc.
In complete calibration a log file will be generated in the “calibration” folder in the
“system” of EMS installation folder (standard file location), with standard file name in
154_20061206163046 format. Here,154 is the base station ID and the digits are the time
of calibration (year, month, day, hour, minute, second, or YYYYMMDDhhmmss).
Calibration method
In EMS client computer, open IE and start EMS client GUI in IE address bar; input user
name and password in EMS client login window. Click [Resource Management| Network
Element Management] and select the bts just added and successfully started. Double
click to open BTS panel (Fig 4-1).
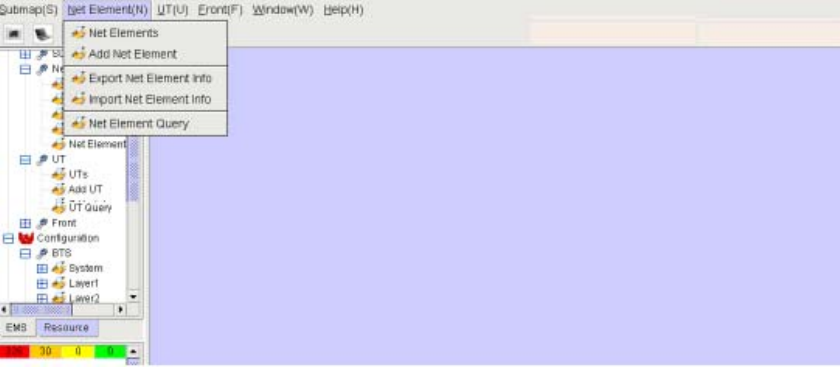
Fig 4-1 BTS Panel
Go to “Net Element” on the menu and select “Net Element” (Fig 4-2). The “Net Element
Management Screen” is shown in Fig 4-3.
Fig 4-2 Net Element Option on the menu
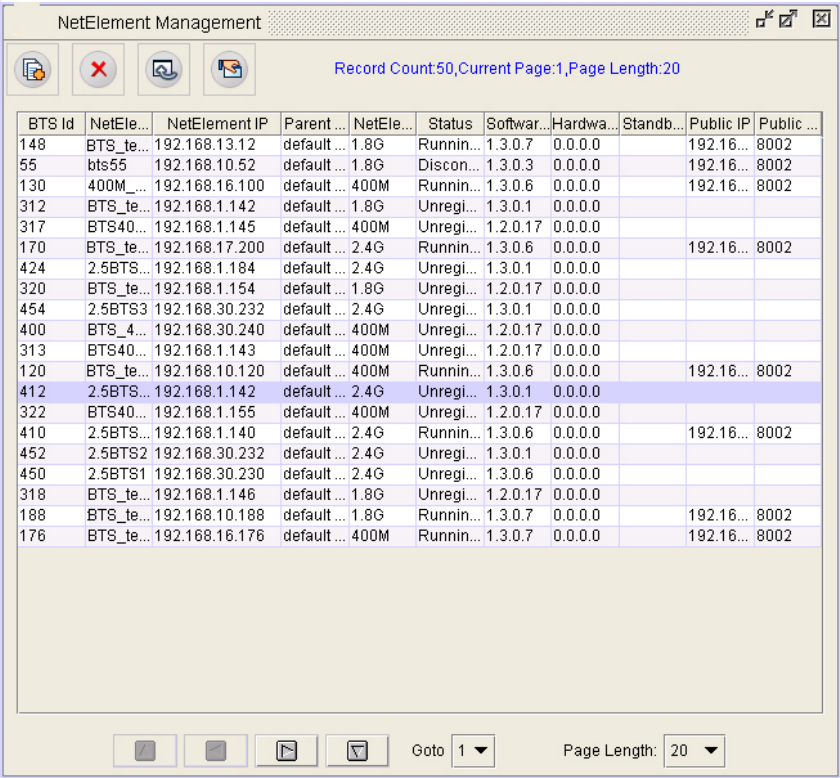
Fig 4-3: Net Element Management Screen
Some basic configurations are needed at this point:
Click [System Management-GPS Settings] and select the time zone of the base
station in [GMT difference] as shown in Fig 4-4. Click [OK] and the configuration
is successful.

Fig 4-4: BTS configuration for GPS time
Click [OK] in the confirmation window, as shown in Fig 4-5.
Fig 4-5: GPS Confirmation Window
Enter [System Configuration / Performance Log settings] and fill in [Server IP] with the
server IP for performance log uploading and storage. Please make sure that this IP
matches the IP address in front-end processor configuration. For other entries, just keep
the default value.
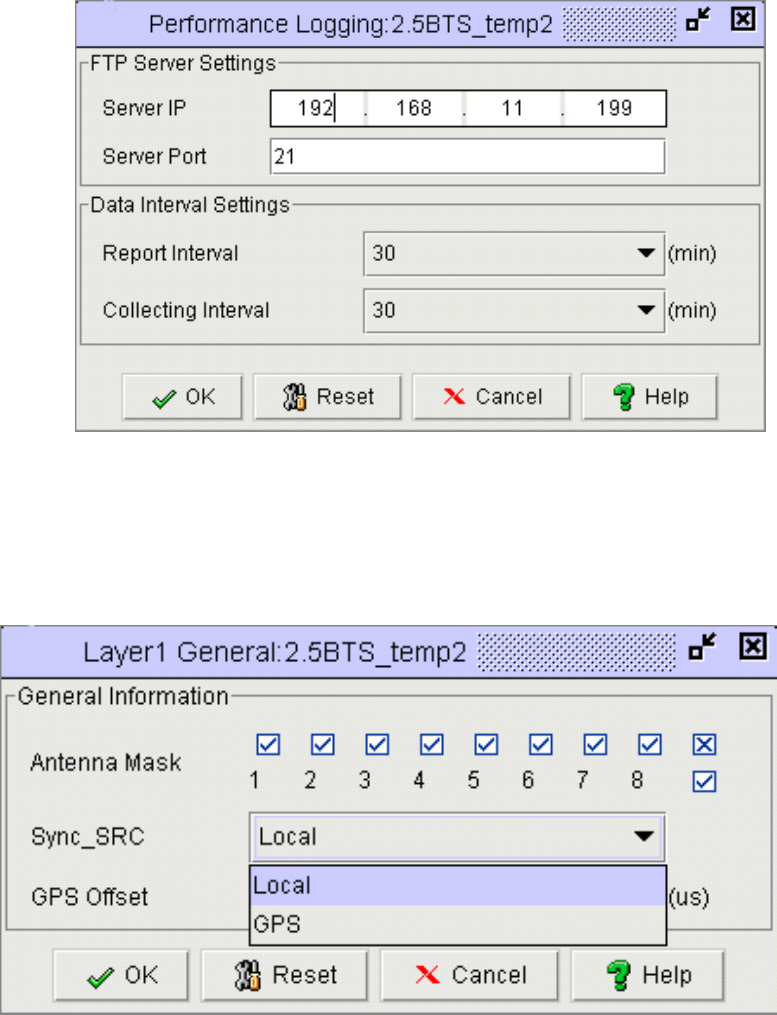
Fig 4-6: FTP server IP configuration
Click [Ok] and the configuration is successful.
[L1 Configuration—L1 Configuration]:
Antenna mask: Check or uncheck for each one of the 8 antenna masks.
Sync Source: “Local” or “GPS”. Please select “GPS” if GPS is connected.
Fig 4-7: Antenna Mask and GPS Configuration
Click [Ok] and the configuration is successful.
Drag the slider to select central frequency used by base station, as shown in Fig 4-8.
The values shown for antenna power, receiving sensitivity, cable loss and power splitter
loss are factory assigned.
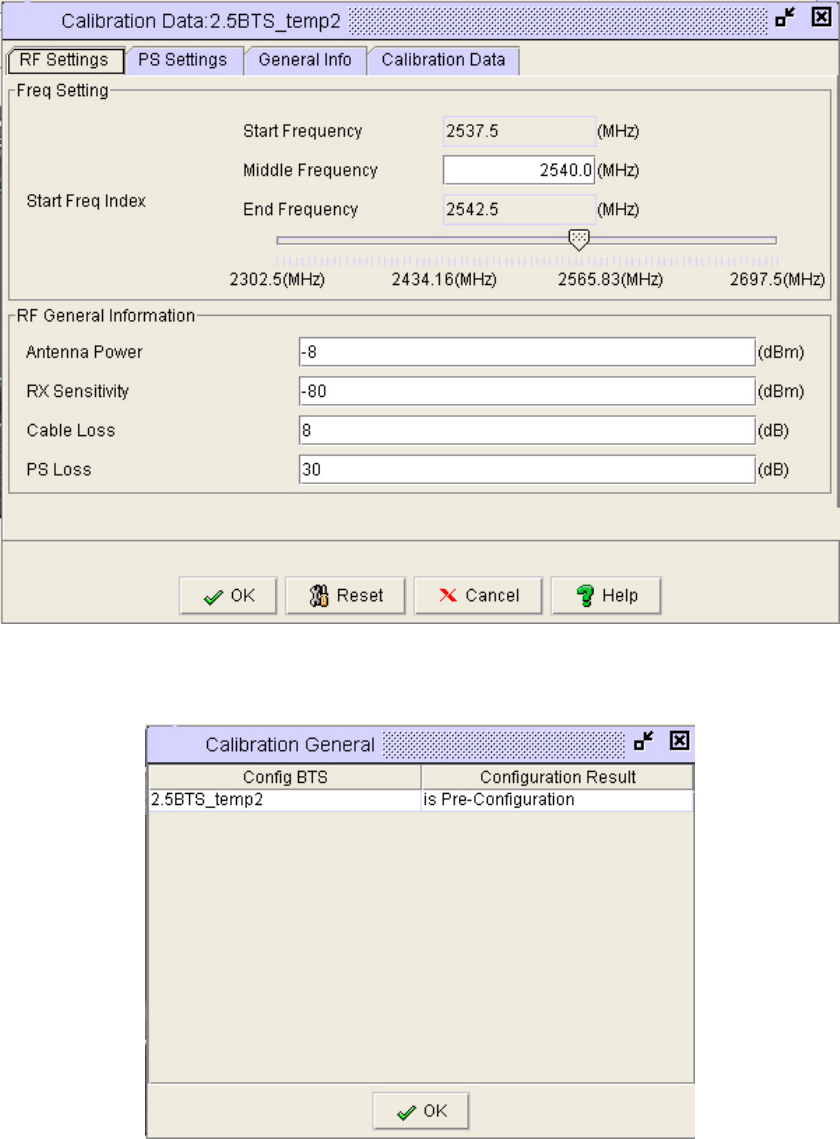
Fig 4-8: RF Calibration Setting Configuration
Click [Ok] and the configuration is successful in the confirmation window (Fig 4-9).
Fig 4-9: Calibration setting confirmation window
[L2 configuration—Air link] In this screen, the “Fronting Serial ID" supports intra-frequency
network. Different numbers should be used for Cell bits;
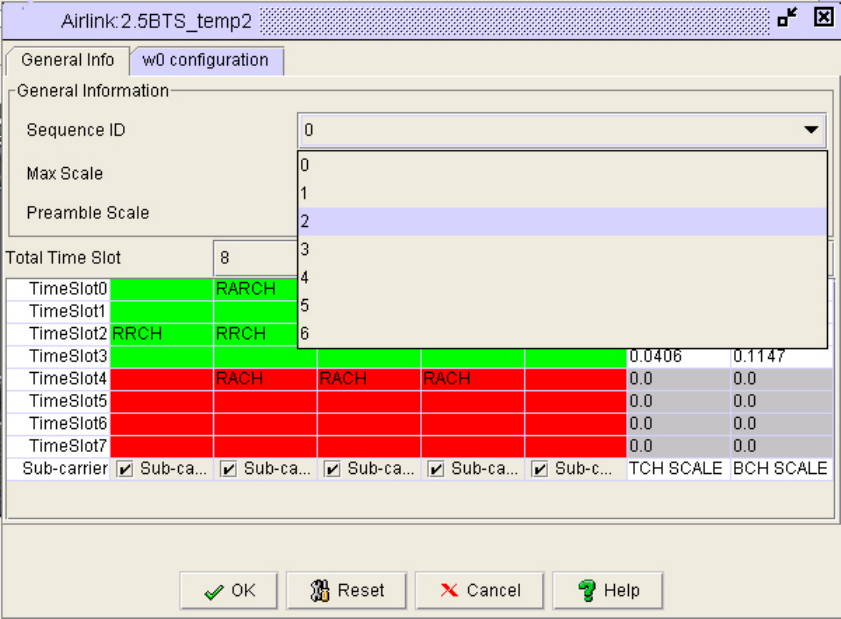
Fig 4-10: Choosing Sequence ID in the Airlink configuration
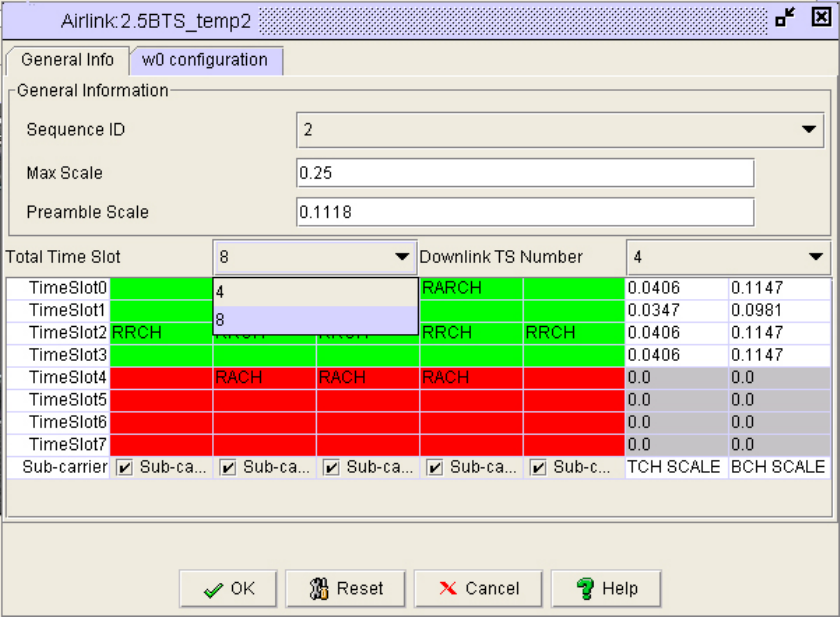
Fig 4-11: Choosing Time slot value in Airlink configuration window
The following default values can be used in most situations.
Select total time slot, default: 8
Select total downlink time slot, default: 4
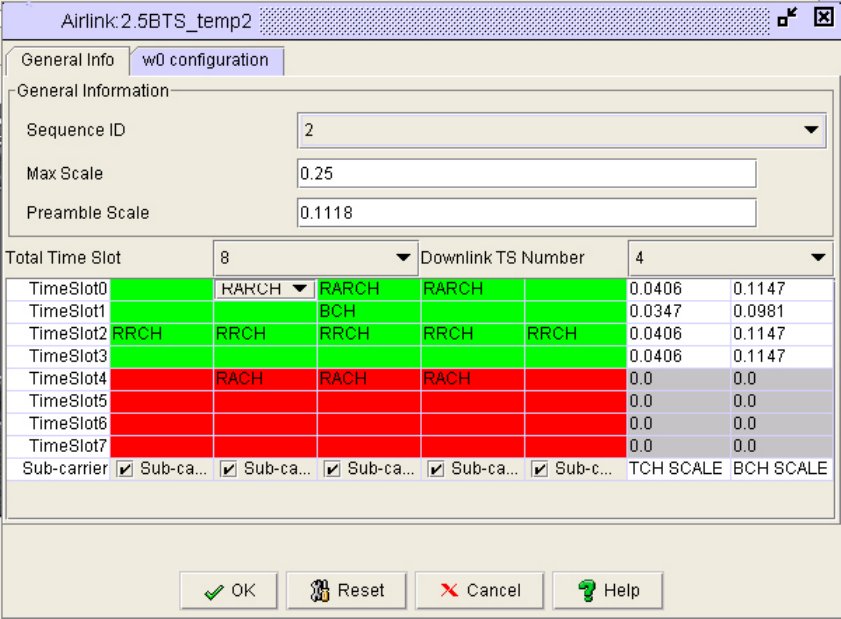
Fig 4-12: Airlink configuration window
Click [Ok] and the configuration is successful.
[L2 Configuration| Radio Resource Management Policy Configuration]: Configure the
modulation mode, power control and minimum bandwidth. The default, factory assigned
values are recommended.

Fig 4-13: Resource Management Policy Screen
Click the base station to be calibrated and select it.
Fig 4-14: BTS Calibration Screen
Click [L1 Configuration—Calibration Request]
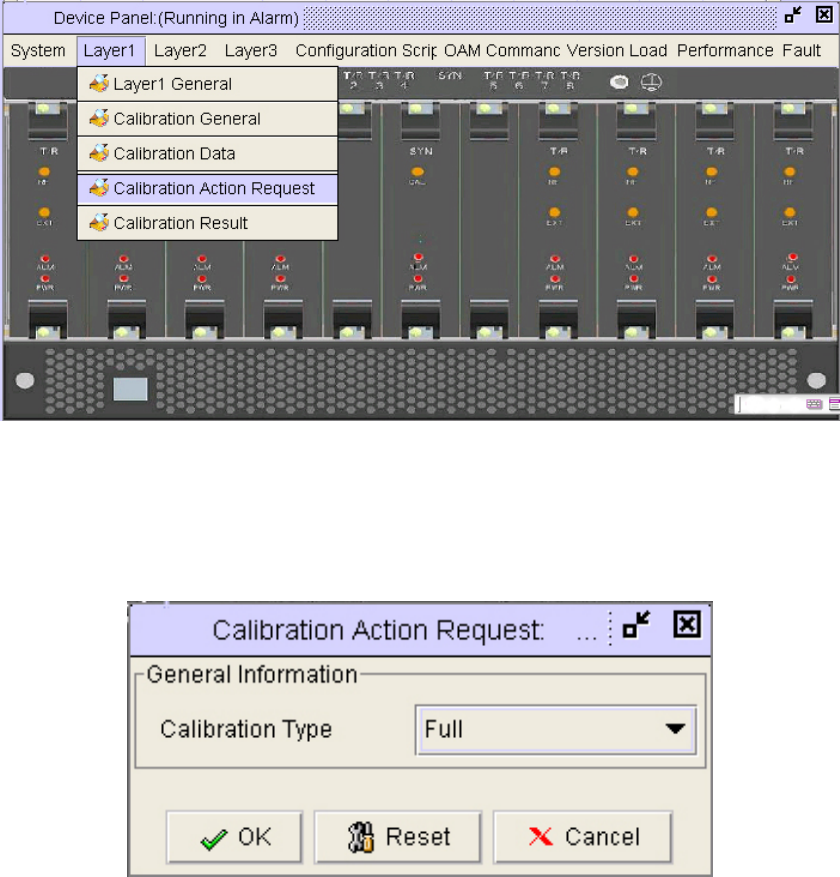
Fig 4-15: BTS Calibration Request
A dialogue box for calibration request pops up. Select calibration type between
“Complete calibration” and “Express calibration”, then click “OK” and the calibration is
successful.
Fig 4-16: Calibration action request window
After calibration, click calibration result to view whether the result is saved and whether
the calibration result is correct. If the result is not saved, "No calibration result" will be
displayed and if the calibration is not successful, the words will be displayed in red.
Meanwhile, please check calibration time to make sure that the calibration result is from
current calibration.
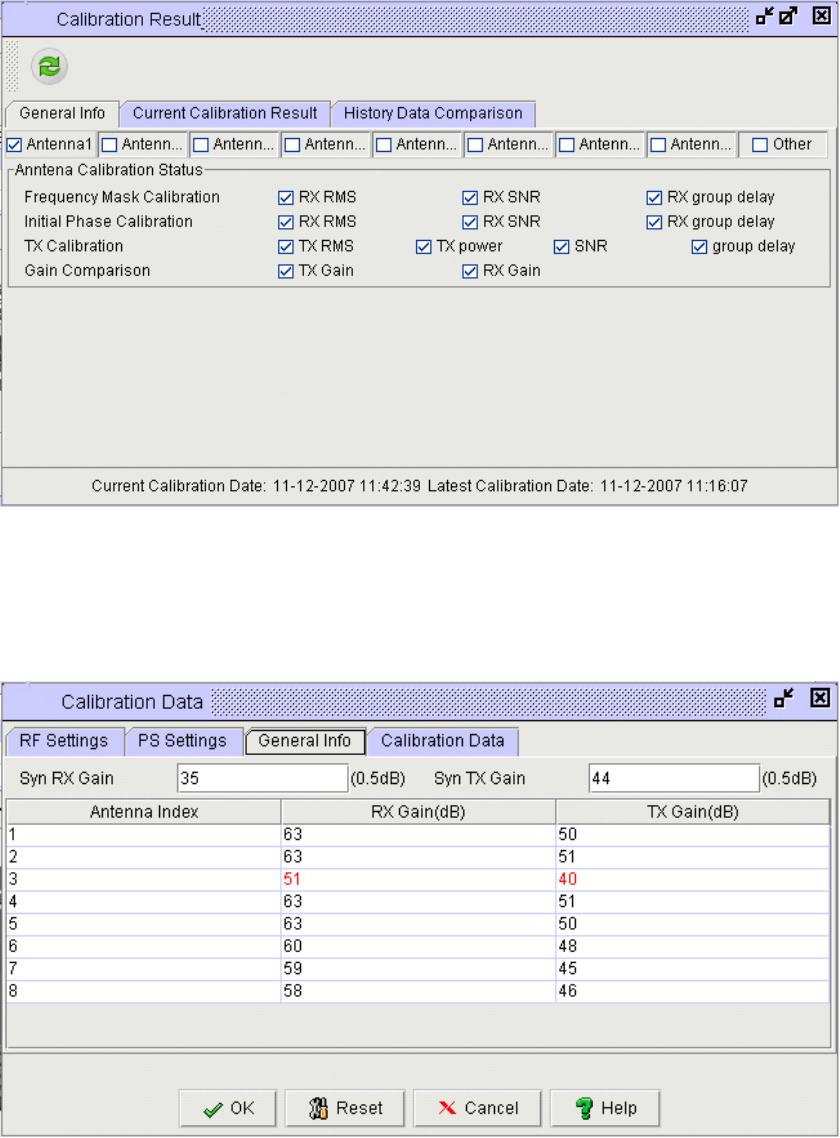
Fig 4-17: Calibration Status
The calibration process should be executed more than twice. Make sure that the values
are relatively stable(+/-3) and there is no “zero” in the result. After the second calibration
is conducted, click [Calibration Data] to show the data for second calibration in the
window.
Fig 4-18: Calibration Data: General Info
Calibrate Date
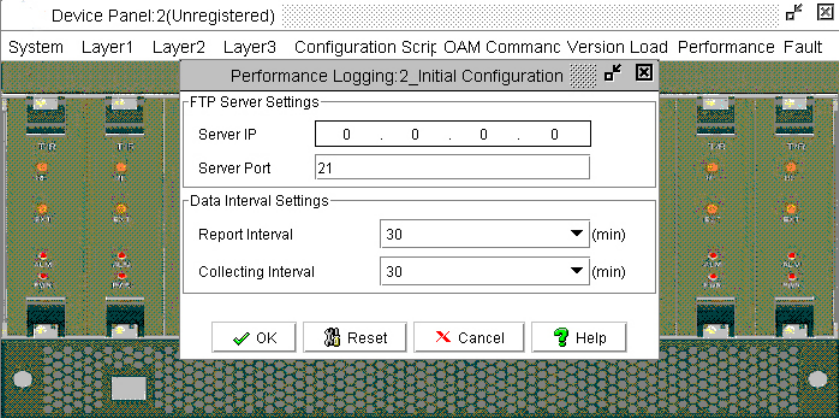
If the calibration date can’t be updated in base station calibration, the following two
solutions can be adopted: Make sure that ftp (Serve-U) is working properly: for example,
the user name and password for calibration are correctly matched; the folder of calibration
file is correct or not, etc. Make sure that the FTP IP information is correctly set in
performance logs.
Fig 4-19: Calibration of FTP settings
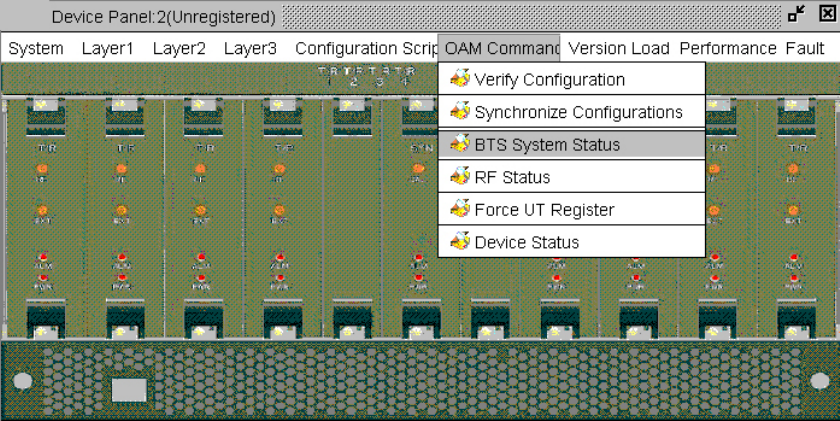
5. Operating Status
Any communication equipments must work within a certain range of temperatures
because over-high and over-low temperatures will affect its performance. For SkyWay-
Mobile BTS system the working temperature is between 0 and 50 centigrade degree.
At the digital panel of the base station there is temperature sensor for real time
monitoring of digital chipset board and transmitting detected temperature to EMS
network management system.
General steps for viewing base station status:
Enter the EMS screen and double click the base station to view, then select [OAM
Command—BTS System Status] and the corresponding information will pop up.
Fig 5-1: Accessing the BTS System Status

Fig 5-2: BTS Status Display
Current user number: the amount of CPE currently registered.
Satellites visible and satellites track: usually if the number of tracing satellites is
greater than 3, synchronization can be conducted.
BTS boot source: start data source of current base station.
SyncCard temperature: the temperature of frequency synthesizer board in the base
station.
Average Free UL Channel and DL channel: amount of currently available channels.
Time Passed Since BTS Boot: the time length for the continuous working of current
base station.
FR mask: the one with tick mark means the RF board is enabled and the one with
check mark means the RF board is disabled.
All the information above is shown graphically for easier view.

6. System Alert
Similar to any system management system, EMS maintains and stores messages of
failures or alerts from the base station, which can be viewed from failure console or alert
console.
Enter the EMS system and select [Fault—Console—Fault Console] to enter the screen as
below. Click the network element to view and click [View] button in the left top and the
detailed information of alert will be displayed.
Fig 6-1: Failure Console window
The operation of alert console is similar with failure console. For a simplified information
display, click a tab to sort, for example, sorting by network element.
Fig 6-2: Alert console window
Enter corresponding network element management and view by selecting the right end
[Failure Management—Events/Alerts] in its information panel.

Fig 6-3: Event and Alert View Console
Please refer to the EMS user’s guide for detailed information and measures for failures
and alerts. If it's confirmed that there is hardware failure, please consult relevant R&D or
maintenance personnel to update hardware versions, etc.
Solectek Warranty Policy
Scope
Warranty Policy applies to all new products purchased from Solectek or Solectek’s authorized
distributor, reseller or partner. The Warranty Policy does not cover the purchase of refurbished or
used equipment, or the purchase of equipment from non-authorized sources.
Standard Warranty Period
Standard Warranty period is 12 months beginning from date of shipment from Solectek or
authorized distributor.
Terms
Any defect, malfunction, or failure caused by fire, lightning, or other acts of God, accident,
negligence, vandalism or acts of war is excluded from this warranty. This warranty does not cover
removal, or reinstallation of this product.
This warranty policy covers only the initial, end-user of the product and is not transferable.
Customer is responsible for shipment of any unit to Solectek for warranty service or repairs.
Solectek will repair or replace, at Solectek’s option, such Solectek products or parts thereof,
which, on inspection by Solectek, are found to be covered by the terms stated in this warranty.
Except as noted below, Solectek is responsible for return shipping via ground services after
warranty service or repairs. Expedited return shipping is available at customer expense. Solectek
reserves the right to levy a service fee on any RMA unit deemed to be fully functional by Solectek
RMA services.
Repaired products will be warranted for 90 days or for the remaining balance of the original
warranty period, whichever is longer.
DOA
A DOA (“dead on arrival”) unit is defined to be a hardware failure diagnosed within 30 days of
initial user shipment, as determined by Solectek Support. Solectek attempts, but does not
guarantee, shipment of DOA replacements within 1-2 days, subject to inventory availability.
Solectek at its discretion, will replace a DOA unit with a new or refurbished unit, via UPS Ground.
Expedited shipping is available only at Customer expense. Customer’s faulty unit shall be
returned to Solectek as described in the Logistics section below.
Extended Warranty Plan (US only)
For US customers, Solectek may make available an optional Extended Warranty Plan which
extends warranty coverage beyond the Standard Warranty period. An Extended Warranty Plan
must be purchased prior to initial product delivery. All terms and conditions above apply to the
Extended Warranty Plan.
Rapid Replacement Service (US only)
For US customers, Solectek may make available a rapid replacement service. Such services
must be purchased prior to initial product delivery. During the applicable Rapid Replacement
period, units are eligible for 1-2 day replacement turn-around following diagnosis by Solectek
Support.
Solectek, at its discretion, will replace a unit with a new or refurbished unit and ship via Standard
Overnight Service. Customer’s faulty unit shall be returned to Solectek within 30 days, as
described in the Logistics section below. In the event that the faulty unit is not returned in the
stated time frame, or if upon inspection by Solectek, the faulty unit is determined to be outside the
scope of the Warranty Terms above, Customer shall be invoiced for the cost of the replacement
unit.
Out of Warranty Repairs
Out of warranty repairs are available for a fee to all customers. Please contact Solectek for rates
applicable to your specific product.
Logistics
1) Customer calls Solectek Technical support line at (858) 450-1220 x 6, or sends email to
support@solectek.com to initiate the RMA process. Solectek staff make all fault determinations
and authorizations.
2) Requests should include the following information:
i) Customer name, address and telephone number.
ii) Name of the Retailer for product and the purchase date.
iii) Model #.
iv) Serial #.
v) Length of Time unit was field deployed.
vi) A brief description of the issue.
vii) Return shipping address, if different from item #1.
3) Solectek provides RMA number within 5 days of request from customer.
4) Customer returns product to Solectek in the original box, or equivalent. A valid RMA is required
prior to any return. The RMA# should be prominent on the box when shipped to:
Solectek Corporation
6370 Nancy Ridge Drive, Suite 109
San Diego, CA 92121
RMA#
5) Upon receipt, Solectek will process and return ship the faulty unit to the customer within 4
weeks.