Trane Modular 20 To 35 Tons Installation And Maintenance Manual SCXG SVX01H EN (06/2014)
2015-04-02
: Trane Trane-Modular-20-To-35-Tons-Installation-And-Maintenance-Manual-684229 trane-modular-20-to-35-tons-installation-and-maintenance-manual-684229 trane pdf
Open the PDF directly: View PDF .
Page Count: 114 [warning: Documents this large are best viewed by clicking the View PDF Link!]
- Introduction
- Table of Contents
- Model Number Descriptions
- General Data
- Pre-Installation Considerations
- Dimensions & Weights
- Installation - Mechanical
- Installation - Electrical
- Unit Wiring Diagrams
- Supply Power Wiring
- Selection Procedures
- Variable Frequency Drive Option (VFD)
- Static Pressure Transducer Installation (VAV units only)
- Electric Heat Installation
- Zone Sensor Options for IntelliPak Control Units
- Integrated Comfort™ Systems Sensors for CV and VAV Applications
- Zone Sensor Installation
- Programmable Zone Sensors
- Time Clock Option
- Remote Human Interface Panel Installation
- Mounting the Remote Human Interface (RHI) Panel
- Wiring the Remote Human Interface
- Connecting to Tracer Summit
- Programming the Time Clock Option
- Operating Principals
- Controls
- Points List
- Tracer™ LCI-I Module
- BCI-Points List
- Phase Monitor
- Unit Control Components
- RTM Module Board - Standard on all Units
- Compressor Module (MCM) - Standard on all Units
- Human Interface Module - Standard on all Units
- Remote Human Interface Module Option
- Waterside Module - Standard on all water- cooled units
- Heat Module
- Ventilation Override Module (VOM) Option
- Trane IntelliPak Communications Modules
- Exhaust/Comparative Enthalpy (ECEM) Module
- Ventilation Control Module (VCM)
- Generic Building Automation System Module Option
- Input Devices and System Functions
- Pre-Startup
- Start-up
- Maintenance
- Diagnostics
- Wiring Diagrams

SAFETY WARNING
Only qualified personnel should install and service the equipment. The installation, starting up, and servicing
of heating, ventilating, and air-conditioning equipment can be hazardous and requires specific knowledge and
training. Improperly installed, adjusted or altered equipment by an unqualified person could result in death or
serious injury. When working on the equipment, observe all precautions in the literature and on the tags,
stickers, and labels that are attached to the equipment.
Intellipak™
Commercial Self-Contained
Modular Series
20 to 35Tons
Installation, Operation,
and Maintenance
Models SCWG -020, -025, -030, -032, -035
SIWG -020, -025, -030, -032, -035
SCRG -020, -025, -032
SIRG -020, -025, -032
SCXG-SVX01H-EN
June 2014

© 2014Trane All rights reserved SCXG-SVX01H-EN
Introduction
Read this manual thoroughly before operating or servicing
this unit.
Warnings, Cautions, and Notices
Safety advisories appear throughout this manual as
required.Your personal safety and the proper operation of
this machine depend upon the strict observance of these
precautions.
Important Environmental Concerns
Scientific research has shown that certain man-made
chemicals can affect the earth’s naturally occurring
stratospheric ozone layer when released to the
atmosphere. In particular, several of the identified
chemicals that may affect the ozone layer are refrigerants
that contain Chlorine, Fluorine and Carbon (CFCs) and
those containing Hydrogen, Chlorine, Fluorine and
Carbon (HCFCs). Not all refrigerants containing these
compounds have the same potential impact to the
environment.Trane advocates the responsible handling of
all refrigerants-including industry replacements for CFCs
such as HCFCs and HFCs.
Important Responsible Refrigerant
Practices
Trane believes that responsible refrigerant practices are
important to the environment, our customers, and the air
conditioning industry. All technicians who handle
refrigerants must be certified.The Federal Clean Air Act
(Section 608) sets forth the requirements for handling,
reclaiming, recovering and recycling of certain
refrigerants and the equipment that is used in these
service procedures. In addition, some states or
municipalities may have additional requirements that
must also be adhered to for responsible management of
refrigerants. Know the applicable laws and follow them.
The three types of advisories are defined as follows:
WARNING Indicates a potentially hazardous
situation which, if not avoided, could
result in death or serious injury.
CAUTIONsIndicates a potentially hazardous
situation which, if not avoided, could
result in minor or moderate injury. It
could also be used to alert against
unsafe practices.
NOTICE Indicates a situation that could result in
equipment or property-damage only
accidents.
WARNING
Refrigerant under High Pressure!
System contains oil and refrigerant under high
pressure. Recover refrigerant to relieve pressure before
opening the system. See unit nameplate for refrigerant
type. Do not use non-approved refrigerants, refrigerant
substitutes, or refrigerant additives. Failure to recover
refrigerant to relieve pressure or the use of non-
approved refrigerants, refrigerant substitutes, or
refrigerant additives could result in an explosion which
could result in death or serious injury or equipment
damage.
WARNING
Personal Protective Equipment (PPE)
Required!
Installing/servicing this unit could result in exposure to
electrical, mechanical and chemical hazards.
• Before installing/servicing this unit, technicians
MUST put on all PPE required for the work being
undertaken (Examples; cut resistant gloves/sleeves,
butyl gloves, safety glasses, hard hat/bump cap, fall
protection, electrical PPE and arc flash clothing).
ALWAYS refer to appropriate Material Safety Data
Sheets (MSDS)/Safety Data Sheets (SDS) and OSHA
guidelines for proper PPE.
• When working with or around hazardous chemicals,
ALWAYS refer to the appropriate MSDS/SDS and
OSHA/GHS (Global Harmonized System of
Classification and Labelling of Chemicals) guidelines
for information on allowable personal exposure
levels, proper respiratory protection and handling
instructions.
• If there is a risk of energized electrical contact, arc, or
flash, technicians MUST put on all PPE in accordance
with OSHA, NFPA 70E, or other country-specific
requirements for arc flash protection, PRIOR to
servicing the unit. NEVER PERFORM ANY
SWITCHING, DISCONNECTING, OR VOLTAGE
TESTING WITHOUT PROPER ELECTRICAL PPE AND
ARC FLASH CLOTHING. ENSURE ELECTRICAL
METERS AND EQUIPMENT ARE PROPERLY RATED
FOR INTENDED VOLTAGE.
Failure to follow instructions could result in death or
serious injury.

Introduction
SCXG-SVX01H-EN 3
Copyright
This document and the information in it are the property of
Trane, and may not be used or reproduced in whole or in
part without written permission.Trane reserves the right
to revise this publication at any time, and to make changes
to its content without obligation to notify any person of
such revision or change.
Trademarks
Trane, Intellipak,Tracer and theTrane logo are trademarks
ofTrane in the United States and other countries.All
trademarks referenced in this document are the
trademarks of their respective owners.
Revision History
SCXG-SVX01H-EN (24 Jun 2014)
Updated to correct input line current for 575V, 15HP, with
bypass.
SCXG-SVX01G-EN (23 Oct 2012)
Updated fan motor FLA data.
WARNING
Proper Field Wiring and Grounding
Required!
Failure to follow code could result in death or serious
injury. All field wiring MUST be performed by qualified
personnel. Improperly installed and grounded field
wiring poses FIRE and ELECTROCUTION hazards.To
avoid these hazards, you MUST follow requirements for
field wiring installation and grounding as described in
NEC and your local/state electrical codes.
NOTICE:
Use Copper Conductors Only!
Unit terminals are not designed to accept other types
of conductors. Failure to use copper conductors could
result in equipment damage.

4 SCXG-SVX01H-EN
Table of Contents
Model Number Descriptions .............. 6
Modular Series Self-Contained .......... 6
Self-Contained Ship-With Accessory Model
Number .............................. 8
Remote Air-Cooled Condenser .......... 8
General Data ............................ 9
Modular Series Self-Contained Unit
Components .......................... 9
General Data ......................... 11
Pre-Installation Considerations ........... 13
Receiving ............................ 13
Contractor Installation Responsibilities .. 13
Unpackaging ......................... 13
Dimensions & Weights .................. 16
Service Clearances .................... 24
Installation - Mechanical ................ 25
Unit Handling Procedures ............. 25
Skid Removal ...................... 27
Installation Preparation ................ 27
Split-Apart Unit Assembly ............ 28
Unit Vibration Isolator Option .......... 29
Duct Connections ..................... 30
Plenum .............................. 30
Airside Economizer Installation ......... 31
Water Piping ......................... 32
Condenser Connections .............. 32
Condensate Drain Connections ........ 32
General Waterside Recommendations:
Cooling Towers .................... 32
Waterside Piping Arrangements ....... 33
Water Temperature Requirements ..... 33
Waterside Economizer Installation
Procedure ........................... 34
Waterside Economizer with right-hand
factory piping components ........... 35
Hydronic Coil Installation .............. 36
Refrigerant System ................... 36
Interconnecting Piping ............... 37
Preliminary Refrigerant Charging ....... 37
Installation - Electrical ....................39
Unit Wiring Diagrams ..................39
Supply Power Wiring ..................39
Selection Procedures ..................40
Variable Frequency Drive Option (VFD) ...41
Variable Frequency Drive Without ByPass 41
Variable Frequency Drive With ByPass . .45
Static Pressure Transducer Installation
(VAV units only) .......................49
Electric Heat Installation ................49
Standard with All IntelliPak Units .......51
Zone Sensor Options for IntelliPak
Control Units .........................51
CV and VAV Unit Zone Sensor Options . .52
Integrated Comfort™ Systems Sensors
for CV and VAV Applications ............52
Zone Sensor Installation ................53
Programmable Zone Sensors ...........54
Time Clock Option .....................56
Remote Human Interface Panel Installation 56
Mounting the Remote Human Interface
(RHI) Panel ...........................57
Wiring the Remote Human Interface .....59
Connecting to Tracer Summit ...........61
Programming the Time Clock Option .....61
Operating Principals .....................63
Control Sequences of Operation .........63
Unoccupied Sequence of Operation ......63
Occupied Sequence ....................64
Thermostatic Expansion Valve ..........66
Compressors .........................66
Unit Airside Components ...............71
Controls ................................74
Points List ............................74
RTM Module ........................74
GBAS Module .......................74
ECEM Module .......................74
Tracer™ LCI-I Module ..................74
Constant Volume (CV) Points ..........74

Table of Contents
SCXG-SVX01H-EN 5
Variable Air Volume (VAV) Points ...... 75
BCI-Points List ........................ 76
Phase Monitor ....................... 76
Unit Control Components .............. 76
RTM Module Board -
Standard on all Units ................ 76
Compressor Module (MCM) -
Standard on all Units ................ 78
Human Interface Module -
Standard on all Units ................ 78
Remote Human Interface Module Option 78
Waterside Module -
Standard on all water-cooled units ..... 78
Heat Module ....................... 78
Ventilation Override Module
(VOM) Option ...................... 78
Trane IntelliPak Communications
Modules .......................... 79
Exhaust/Comparative Enthalpy (ECEM)
Module ........................... 80
Ventilation Control Module (VCM) ..... 80
Generic Building Automation System
Module Option ..................... 80
Input Devices and System Functions . . . 82
Pre-Startup ............................. 85
Pre-Startup Checklist .................. 85
Start-up ................................ 86
Final Refrigerant Charge ............... 87
Start-up Procedure .................... 87
Startup Log .......................... 88
Maintenance ........................... 90
Service Access ....................... 90
Variable Frequency Drive (VFD) ....... 90
Variable Frequency Drive (VFD) -
Remote Mounted ................... 90
Air Filters ............................ 90
Inspecting and Cleaning Drain Pan ...... 90
Inspecting and Cleaning the Fan ........ 91
Supply Fan .......................... 91
Fan Drive .......................... 91
Fan Bearings ....................... 92
Fan Belt Tension .................... 93
Adjusting Belt Tension ...............94
Refrigerant System ....................95
Refrigerant Leak Test Procedure ........95
Brazing Procedures ..................96
System Evacuation Procedures ........97
Compressors .........................98
Scroll Compressor Failure Diagnosis
and Replacement ....................98
Components ..........................99
Coil Fin Cleaning .....................100
Piping Components ...................102
Maintenance Periodic Checklists ........102
Diagnostics ............................104
Troubleshooting ......................104
System Checks .....................104
Diagnostics ..........................104
Wiring Diagrams .......................113

6 SCXG-SVX01H-EN
Model Number Descriptions
Modular Series Self-
Contained
Digit 1 - Unit Model
S = self contained
Digit 2 - Unit Type
C = commercial
I = industrial
Digit 3 - Condenser Medium
W = water-cooled
R = remote air-cooled
Digit4-Development Sequence
G = modular series
Digit 5 - Refrigerant Circuit
Configuration
U = independent, R-410A refrigerant
Digits 6, 7 - Unit Nominal
Capacity
20 = 20Tons (water or air cooled)
25 = 25Tons (water or air cooled)
30 = 30Tons (water cooled only)
32 = 32Tons (air cooled only)
35 = 35Tons (water cooled only)
Digit 8 - Unit Voltage
6 = 200 volt/60 hz/3 ph
4 = 460 volt/60 hz/3 ph
5 = 575 volt/60 hz/3 ph
Digit 9 - Air Volume/Temp
Control
2 = I-Pak & VFD & supply air temp
ctrl
3 = I-Pak & VFD w/ bypass & supply
air temp ctrl
4 = I-Pak w/o vol. ctrl, w/ zone temp
cool
5 = I-Pak w/o vol. ctrl, w/ zone temp
heat/cool
6 = I-Pak w/o vol. ctrl, w/ supply air
temp ctrl
8 = thermostat interface
Digits 10, 11 - Design Sequence
** = Factory Assigned
Digit 12 - Unit Construction
A = vertical discharge
B = vertical discharge with double
wall
C = horizontal discharge
D = horizontal discharge w/ double
wall
E = vertical discharge, ship separate
F = vert. dis. w/ double wall,
ship sep.
G = horizontal discharge, ship
separate
H = horiz. dis. w/ double wall,
ship sep.
Digit 13 - PlenumType
B = std plenum w/ factory cut holes
C = low plenum w/ factory cut holes
E = std plenum w/ field cut holes
F = low plenum w/ field cut holes
H = std plenum double wall (perf)
w/ field cut holes
J = low plenum double wall (perf)
w/ field cut holes
L = std. plenum w/factory cut holes,
ship separate
M = low plenum w/ factory cut holes,
ship separate
P = std plenum w/ field cut holes,
ship
separate
R = low plenum w/ field cut holes,
ship separate
U = std plenum double wall (perf) w/
field cut holes, ship separate
V = low plenum double wall (perf) w/
field cut holes, ship separate
0 = without plenum
Digit 14 - Motor Type
2 = ODP motor
3 = TEFC motor
Digits 15, 16 - Motor HP
05 = 5 hp
07 = 7.5 hp
10 = 10 hp
15 = 15 hp
20 = 20 hp
25 = 25 hp
Digits 17, 18, 19 - Fan RPM
085 = 850 rpm
090 = 900 rpm
095 = 950 rpm
100 = 100 0 rpm
105 = 1050 rpm
110 = 110 0 r p m
115 = 1150 rpm
120 = 1200 rpm
125 = 1250 rpm
130 = 1300 rpm
135 = 1350 rpm
140 = 1400 rpm
145 = 1450 rpm
150 = 1500 rpm
155 = 1550 rpm
160 = 1600 rpm
165 = 1650 rpm
170 = 1700 rpm
175 = 1750 rpm
180 = 1800 rpm
185 = 1850 rpm
Digit 20 - Heating Type
A = steam coil, LH
B = hot water coil, LH
C = electric heat, 1 stage
F = hydronic heat ctrl interface
G = elec. heat ctrl interface,1 stage
K = steam coil ship separate, LH
L = hot water coil ship separate, LH
M = steam coil, RH
N = hot water coil, RH
P = steam coil ship separate, RH
R = hot water coil ship separate, RH
T = hi-cap. hot water coil, LH
U = hi-cap hot water coil, LH, ship
sep
V = hi-cap hot water coil, RH
W = hi-cap hot water coil, RH, ship
sep
0 = none
Digit 21 - Unit Isolators
A = isopads
B = spring isolators
0 = none
Digit 22 - Unit Finish
1 = paint - slate gray
2 = protective coating
3 = protective coating w/ finish coat
Digit 23
0 = none
Digit 24 - Unit Connection
1 = disconnect switch
2 = terminal block
3 = dual point power
Digit 25 - Industrial Options
A = protective coated evaporator coil
B = silver solder
C = stainless steel screws
D = A and B
E = A and C
F = B and C
G = A, B and C
0 = none
Digit 26 - Drain Pan Type
A = galvanized sloped
B = stainless steel sloped
Digit 27 - Waterside Economizer
A = mechanical clean full capacity
(4-row)
B = mechanical clean low capacity
(2-row)
C = chemical clean full capacity
(4-row)
D = chemical clean low capacity
(2-row)
E = mechanical clean full capacity
(4-row) ship separate
F = mechanical clean low capacity
(2-row) ship separate
G = chemical clean full capacity
(4-row) ship separate
H = chemical clean low capacity
(2-row) ship separate
0 = none

Model Number Descriptions
SCXG-SVX01H-EN 7
Digit 28 - Ventilation Control
B = airside econ w/Traq™ damper
(top O/A inlet)
C = airside econ w/ standard
dampers (top O/A inlet)
E = airside econ w/Traq™ damper
and comparative enthalpy
(top O/A)
F = airside econ w/ std dampers and
comparative enthalpy (top O/A)
H = none/ventilation for 2-position
control interface
J = airside economizer interface
K = airside economizer interface w/
comparative enthalpy
0 = None
Digit 29 - Water Piping
A = RH condenser connection
B = LH condenser connection
C = RH basic piping
D = LH basic piping
E = RH intermediate piping
F = LH intermediate piping
J = RH basic w/ flow switch
K = LH basic w/ flow switch
L = RH intermediate w/ flow switch
M = LH intermediate w/ flow switch
0 = none
Digit 30 - Condenser Tube Type
A = standard condenser tubes
B = 90/10 CuNi condenser tubes
0 = none
Digit 31 - Compressor Service
Valves
1 = with service valves
0 = none
Digit 32 - Miscellaneous System
Control
1 = timeclock
2 = interface for remote HI (IPCB)
3 = dirty filter switch
4 = 1 and 2
5 = 1 and 3
6 = 2 and 3
7 = 1, 2, and 3
0 = none
Digit 33 - Control Interface
Options
A = Generic BAS Module; 0-5 VDC
(GBAS)
B = Ventilation Override Module
(VOM)
D = Remote Human Interface (RHI)
G = GBAS & VOM
H = GBAS & RHI
J = VOM & RHI
M = GBAS & VOM & RHI
N = BACnet Communications
Interface (BCI)
P = BCI and GBAS
Q = BCI and VOM
R = BCI and RHI
T = BCI and GBAS and VOM
U = BCI and GBAS and RHI
V = BCI and VOM and RHI
W = BCI and GBAS and VOM and RHI
0 = None
1 = LonTalk Comm5 Interface (LCI)
2 = LCI and GBAS
3 = LCI and VOM
4 = LCI and RHI
5 = LCI and GBAS and VOM
6 = LCI and GBAS and RHI
7 = LCI and VOM and RHI
8 = LCI and GBAS and VOM and RHI
Digit 34 - Agency
T = UL agency listing
0 = none
Digit 35 - Filter Type
1 = 2-inch construction throwaway
2 = 2-inch med eff. throwaway
Digit 36 - Miscellaneous Control
Option
A = low entering air temp. protect
device (LEATPD)
B = high duct temp t-stat
C = plenum high static switch
D = kit for heat mode output (w/t’stat)
E = A and B
F = A and C
G = B and C
H = A, B, and C
0 = None

Model Number Descriptions
8 SCXG-SVX01H-EN
Self-Contained Ship-
With Accessory
Model Number
Digit1-Parts/Accessories
P = parts/accessories
Digit 2 - Unit Model
S = self-contained
Digit 3 - Shipment
W = with unit
Digit4-Development Sequence
F = signature series
G = modular series
Digit5-Sensors and Other
Accessories
S = sensors
Digit6-Sensors and
Thermostats (Field Installed)
A = BAYSENS077 - zone temp only
(CV and VAV)
B = BAYSENS073- zone temp with
timed override button (CV and
VAV)
C = BAYSENS074 - zone temp with
timed override button, setpoint
dial (CV and VAV)
E = BAYSENS108 - CV zone sensor
-dual setpoint, man/auto
changeover
F = BAYSENS110 - CV zone sensor-
dual setpoint, man/auto
changeover w, indicastor lights
G = BAYSENS119 - CV/VAV program-
mable night setback Sensor
H = BAYSENS021 - VAV zone sensor
with indicator lights
K = BAYSTAT150 2H/2C ProgTstat w/
BAYSTAT077 Remote Sensor
L = outside air temperature sensor
kit
M = outside air humidity sensor kit
N = BAYSTAT155 3H/2CTstat
P = BAYSTAT150 2H/2C
ProgrammableTstat
0 = none
Digit 7 - Mixed Air Temperature
Protection Kit (Field Installed)
1 = mixed air temperature protection
kit
0 = none
Digit 8 - Carbon Dioxide Sensor
(Field Installed)
1 = carbon dioxide sensor kit
0 = none
Digit9-Future Option
0 = none
Digits 10, 11 - Design Sequence
** = Factory Assigned
Remote Air-Cooled
Condenser
Digit 1 - Unit Model
C = Condenser
Digit 2 - Unit Type
C = Commercial
I = Industrial
Digit 3 - Condenser Medium
R = Remote
Digit4-Development Sequence
C=C
Digits 5, 6, 7 - Nominal Capacity
020 = 20Tons
029 = 29Tons
032 = 32Tons
Digit 8 - Unit Voltage
4 = 460 Volt/60 Hz/3 ph
5 = 575 Volt/60 Hz/3 ph
6 = 200 Volt/60 Hz/3 ph
Digit 9 - Control Option
0 = No Low Ambient, I-Pak
A = No Low Ambient,T-stat
B = Low Ambient, I-Pak
C = Low Ambient,T-stat
Digits 10, 11 - Design Sequence
** = Factory Assigned
Digit 12 - Unit Finish
1 = Paint (Slate Gray)
2 = Protective Coating
3 = Protective Coating with
Finish Coat
4 = Unpainted Unit
Digit 13 - Coil Options
A = Non-Coated Aluminum
C = Protective Coated Aluminum
Digit 14 - Unit Isolators
0 = None
A = Spring Isolators
B = Isopads
Digit 15 - Panels
0 = None
1 = Louvered Panels
Digit 16 - Agency
0 = None
T = UL Listing

SCXG-SVX01H-EN 9
General Data
Modular Series Self-Contained
Unit Components
Commercial self contained units are complete HVAC
systems used in floor-by-floor applications. Units are easy
to install because they feature a single point power
connection, factory installed and tested controls, single
water point connection, factory installed options, and an
internally trapped drain connection. Modular self-
contained units can ship as split-apart units for installation
ease. Split-apart units ship with a dry nitrogen charge and
require field refrigerant charging.
Units consist of multiple hermetically sealed 3-D scroll
compressors, water-cooled condensers (water-cooled
units only), an evaporator coil, dual forward curved fans,
and control panel. Air-cooled units require a remote air-
cooled condenser, model CXRC. Unit controls are either
electromechanical thermostat or microprocessor controls
on IntelliPak unit.
Hermetically sealed 3-D scroll compressor motors utilize
internal motor protection and time delays to prevent
excessive cycling.
Water-cooled condensers are shell and tube type with
internal subcooler. Condensers are available as
mechanically or chemically cleanable. Evaporator fan is
double width, double inlet and forward curved with a fixed
pitch belt drive assembly. Variable frequency drives are
optional. EISA efficiency open drip proof (ODP) and totally
enclosed fan cooled (TEFC) motor options are available.
Package water-cooled units ship with full refrigerant and
compressor oil charge. Split apart water cooled, and air
cooled, units ship with dry nitrogen charge and complete
compressor oil charge.
Split apart water cooled units require field connection of
suction and liquid lines. Air-cooled units require field-
piping discharge and liquid lines to remote air cooled
condenser.
All units have two refrigerant circuits that include filter
drier (field installed in air cooled), liquid line service valve,
sight glass/moisture indicator, thermal expansion valve
with a sensing bulb and external equalizing line, suction
and discharge line access ports, and high and low pressure
cutout switches. Water-cooled units also include pressure
relief valve. Air cooled units include liquid line solenoid
valve and discharge line check valve.
Control Options
Units may be ordered with conventional thermostat
interface or IntelliPak™ Direct Digital Control (DDC).
IntelliPak controls include a Human Interface (HI) panel
with two line by forty (40) character clear English display
for easy operator interface to unit setup and control
parameters. All basic setup parameters are preset from
factory.
Human Interface Panel
HI is unit mounted and accessible without opening unit’s
front panel. It allows easy setpoint adjustment using HI
keypad. HI displays all unit operating parameters and
conditions in a clear language display, which can be
configured for either English, French, or Spanish.
Optional remote human interface (RHI) will control up to
four self-contained units, each containing an
interprocessor communications bridge (IPCB). It has the
same features as unit-mounted HI except for service
mode.
For more information on setpoint defaults, ranges and unit
programming, see IntelliPak Self-Contained Programming
Guide, PKG-SVP01*-EN that ships with each unit.
IntelliPak™ DDC Control
IntelliPak™ DDC Control provides “smart” unit control
with safety features and control relays for pumps,
dampers, etc. Modular Series IntelliPak self-contained unit
is controlled by microelectronic control system consisting
of a network of modules.These modules are referred to as
unit control modules (UCM). In this manual, acronym UCM
refers to the entire control system network.
These modules perform specific unit functions using
proportional/integral control algorithms.They are
mounted in the unit control panel and are factory wired to
their respective internal components. Each module
receives and interprets information from other unit
modules, sensors, remote panels, and customer binary
contacts to satisfy the applicable request; i.e.,
economizing, mechanical cooling, heating, ventilation.
See the Operation section of this manual for a detailed
description of each module’s function.
Optional Controls
Optional controls include a disconnect switch, dirty filter
switch, water flow switch (water-cooled only), supply air
temperature reset, or external setpoint inputs. Daytime
heating is available on units with electric, steam, or hot
water heat control options. Morning warmup operation is
available on all units.
The static pressure probe, zone night heat/morning
warmup, supply air temperature reset sensor options ship
separate inside the unit control panel for field installation.
For more detailed information on the unit control options,
see the Owner’s section of this manual.

General Data
10 SCXG-SVX01H-EN
Unit Nameplate
Unit nameplate, mounted on left end of unit control panel,
identifies unit model number, service literature, and
wiring diagram numbers.
Figure 1. IntelliPak™ commercial self-contained
modular series unit

General Data
SCXG-SVX01H-EN 11
General Data
Table 1. SCWG/SIWG/SCRG/SIRG general data
Water-Cooled Units Air-Cooled Units
Unit Size 20 25 30 35 20 25 32
Compressor Data
Quantity 2 2 1/1 2 2 1/1 2
Nominal Ton/Comp 10 10 10/15 15 10 10/15 15
Circuits 2 2 2 2 2 2 2
Evaporator Coil Data
Rows 2 4 4 4 3 4 4
Sq. Ft. 22.5 25.0 25.0 25.0 25.0 25.0 25.0
FPF 144 144 144 144 144 144 144
Condenser Data
Minimum GPM w/o Econ 36 36 46 54 - - -
Minimum GPM w/ Econ 41 41 60 65 - - -
Maximum GPM 80 80 102 119 - - -
Evaporator Fan Data
Quantity 2 2 2 2 2 2 2
Size (Dia. x width - inches) 12 5/8"x8" 12 5/8"x9" 12 5/8"x11" 12 5/8 x11" 12 5/8"x8" 12 5/8"x9" 12 5/8"x11"
Minimum HP 5 5 5 5 5 5 5
Maximum HP 20 25 25 25 20 25 25
Minimum Design CFM 6350 7250 7250 7250 7250 7250 7250
Maximum Design CFM 8500 10,625 12,750 14,875 8500 10,625 13600
R-410A Refrigerant Data
EER 14.0 14.3 14.1 14.0 10.0 10.1 10.4
IEER (CV) 14.1 14.8 15.4 15.6 10.8 11.8 11.9
IEER (VFD) 17.1 18.1 18.2 17.7 13.4 13.3 13.8
Refrigerant Charge - lb (kg)
Circuit A 19.0 (8.6) 24.0 (10.9) 24.5 (11.1) 23.0 (10.4) See Note 3 See Note 3 See Note 3
Circuit B 19.0 (8.6) 24.0 (10.4) 23.0 (10.4) 23.0 (10.4) See Note 3 See Note 3 See Note 3
Capacity Steps - % 100/53/0 100/53/0 100/65/42/6 100/53/0
Filter Data
Quantity 4 4 4 4 4 4 4
Size (inches) 16x25x2 16x25x2 16x25x2 16x25x2 16x25x2 16x25x2 16x25x2
Quantity 4 4 4 4 4 4 4
Size (inches) 20x25x2 20x25x2 20x25x2 20x25x2 20x25x2 20x25x2 20x25x2
CCRC/CIRC Condenser
Match - - - - 20 29 32
Notes:
1. Compressors are Trane 3-D™scroll.
2. EER and IEER are rated in accordance to the AHRI Standard 340/360-2010. Based on 80/67°F (26.7/19.4°C) to the evaporator coil, nominal airflow
and 85-95°F (29.4-35°C) condenser water or 95° F (35° C) ambient.
3. All units operate with R-410A. Water Cooled units ship with full operating charge. Air-cooled units ship with dry nitrogen charge. Field refrigerant
system charge required. Refer to Table 2, p. 12 for amounts required.
4. Maximum cfm limits are set to prevent moisture carryover on the evaporator coil.
5. Minimum cfm limits are set to ensure stable thermal expansion valve operation at low load conditions.
6. Filter sizes are for units without hot water or steam heating coils

General Data
12 SCXG-SVX01H-EN
Table 2. SCRG/SIRG self-contained and CCRC/CIRC
remote air-cooled condenser
SCRG/SIRG & CCRC/CIRC
Unit Size 20/20 25/29 32/32
No. of Refrigerant Circuits 2 2 2
Operating Charge - lbs R-410A 36.5/36.5 48.5/36 46/46
Operating Charge - kg R-410A 16.6/16.6 22/16.3 20.9/20.9
Cond. Storage Cap. - lbs R-410A 37/37 51/37 51/51
Cond. Storage Cap. - kg R-410A 16.8/16.8 23.1/16.8 23.1/23.1
Notes:
1. Refrigerant charges are listed as circuit 1/circuit 2 and provide only an
estimate. Final charge requires sound field charging practice.
2. Operating charge estimate includes the air-cooled self-contained,
remote air-cooled condenser, and 25 feet of interconnecting
refrigerant piping.
3. At conditions of 95°F (35°C), condenser storage capacity is 95% full.
4. To determine the correct amount of refrigerant needed for a particular
application, reference the Trane Reciprocating Refrigeration Manual.
5. Field piping over 25 feet requires additional refrigerant. See Table 25,
p. 37 and Table 26, p. 38 to determine amounts.
Table 3. CCRC/CIRC remote air-cooled condenser
general data
Unit Size 20 29 32
Condenser Fan Data
Number/Type/Drive 4/Prop/Direct 4/Prop/Direct 4/Prop/Direct
Size (inches) 26 26 26
HP ea. 1 1 1
Nominal Cfm 18,800 21,200 32,000
Condenser Coil Data
Circuit 1 Size (in.) 1/46x71 1/46x71 1/64x71
Circuit 2 No./Size (in.) 1/46x71 1/64x71 1/64x71
Face Area (sq. ft.) 45.4 54.2 63.1
Rows/fpf 4/144 4/144 4/144
Ambient Temperature Operating Range
Standard Ambient (°F) 50-115 50-115 50-115
Low Ambient Option
(°F) 0-115 0-115 0-115
Table 4. SCWG/SIWG/SCRG/SIRG self-contained
heating coil
Filter Data for Heating Coil
Quantity 4
Size (inches) 20x18x2
Size (mm) (508x457x51)
Quantity 8
Size (inches) 20x20x2
Size (mm) (508x508x51)
Coil Data Type Row
sNo.
Size (in) No.
Size (mm) fpf
Steam Coil NS 1 2
24 x 58
2
609.6x1473.
242
Hot Water Coil,
std. cap 5W 1 1
48 x 62 1
1219 x 1575 80
Hot Water Coil,
hi-cap. 5W 2 1
48 x 62 1
1219 x 1575 108
Notes:
1. Hot water and steam heating coils have Prima-Flo® fins and do not
have turbulators.
2. For coil capacities, use TOPSS™ (Trane Official Product Selection
Program).
Table 5. Waterside economizer coil physical data -
SCXG 20, 25, 30, 35
Type Rows FPF Height
(in) Length
(in)
Chemically Cleanable 2 108 50 72
Mechanically Cleanable 2 108 50 72
Chemically Cleanable 4 108 50 72
Mechanically Cleanable 4 108 50 72

SCXG-SVX01H-EN 13
Pre-Installation Considerations
Receiving
Receiving Checklist
Complete the following checklist immediately after
receiving unit shipment to detect possible shipping
damage.
• Inspect individual cartons before accepting. Check for
rattles, bent carton corners, or other visible indications
of shipping damage.
• If a unit appears damaged, inspect it immediately
before accepting the shipment. Make specific
notations concerning the damage on the freight bill.
Do not refuse delivery.
• Inspect the unit for concealed damage before it is
stored and as soon as possible after delivery. Report
concealed damage to the freight line within the allotted
time after delivery. Check with the carrier for their
allotted time to submit a claim.
• Do not move damaged material from the receiving
location. It is the receiver’s responsibility to provide
reasonable evidence that concealed damage did not
occur after delivery.
• Do not continue unpacking the shipment if it appears
damaged. Retain all internal packing, cartons, and
crate.Take photos of damaged material if possible.
• Notify the carrier’s terminal of the damage
immediately by phone and mail. Request an
immediate joint inspection of the damage by the
carrier and consignee.
Notify yourTrane representative of the damage and
arrange for repair. Have the carrier inspect the damage
before making any repairs to the unit.
Ship-Separate Accessories
Field-installed sensors ship separately inside unit’s main
control panel. Extra filters, sheaves, and belts ship in unit’s
fan motor section. Condenser plugs, spring isolators, and
isopads ship in unit’s bottom left side.
Contractor Installation
Responsibilities
Complete the following checklist before beginning final
unit installation.
• Verify the unit size and tagging with the unit
nameplate.
• Make certain the floor or foundation is level, solid, and
sufficient to support the unit and accessory weights.
Level or repair the floor before positioning the unit if
necessary.
• Allow minimum recommended clearances for routine
maintenance and service. Allow space at end of the
unit for shaft removal and servicing. Refer to unit
submittals for dimensions. See also “Service
Clearances,” p. 24.
• Allow three fan diameters above the unit for the
discharge ductwork. Return air enters the rear of the
unit and conditioned supply air discharges through the
top.
• Electrical connection knockouts are on the top, left side
of the unit.
• Allow adequate space for piping access and panel
removal. Condenser water piping, refrigerant piping,
and condensate drain connections are on the lower left
end panel.
Note: Unit height and connection locations will change if
using vibration isolators.The unit height may
increase up to 5 7/8” with spring type isolators.
• Electrical supply power must meet specific balance
and voltage requirements as described in section
“Installation - Electrical,” p. 39.
•Water-cooled units only:The installer is responsible for
providing a condenser main, standby water pump,
cooling tower, pressure gauges, strainers, and all
components for waterside piping. See “Water Piping,”
p. 32 for general waterside recommendations.
•Air-cooled units only:The installer is responsible for
providing and installing the remote air-cooled
condenser and refrigerant piping.
Unpackaging
Commercial self-contained units ship assembled with
protective coverings over the coil and discharge openings.
Figure 2, p. 14 illustrates a typical shipping package.
Unit Protective Covers
Remove the shipping protection coverings from the
human interface panel (HI) at the control panel, the filter
box (or air inlet opening), the discharge air opening, and
optional variable frequency drive (VFD).
Supply Fan Isolators
Remove the shipping channels and mounting bolts from
beneath the fan. See Figure 4, p. 15. Open both fan
compartment access doors to access the channels.There
are four mounting points for 20-38 ton units.
Note: For 20-38 ton units, do not remove the fan
assembly shipping blocks and tie down bolts if the
fan speed is 750 rpm or less.
While keeping the fan mounting frame level, turn the fan
isolator height adjusting bolts until the fan housing P-
gasket compresses 1/4” against the roof transition piece.
See Figure 4, p. 15.

Pre-Installation Considerations
14 SCXG-SVX01H-EN
Figure 2. Typical unit mounting on shipping skid
Figure 3. Fan isolator locations

Pre-Installation Considerations
SCXG-SVX01H-EN 15
Figure 4. Supply fan horizontal isolation shipping
bracket

16 SCXG-SVX01H-EN
Dimensions & Weights
Table 6. SCWG/SIWG weight, lbs.
Unit Tons Base Weight - lb (kg)
20 2227 (1010)
25 2697 (1223)
30 2765 (1254)
35 2834 (1286)
Notes:
1. All unit weights include refrigerant, water and controllers, electric
heat and valves.
2. Add 150 lbs. to total weight to obtain approximate shipping weight.
3. Split-apart unit weights are approximately: 60% total unit weight =
compressor section, 40% total unit weight = fan section.
Table 7. SCRG/SIRG weight, lbs (kg)
unit tons base weight
20 2311 (1048)
25 2380 (1079)
32 2448 (1110)
Notes:
1. All unit weights include refrigerant, water and controllers, electric
heat and valves.
2. Add 150 lbs. to total weight to obtain approximate shipping weight.
3. Split-apart unit weights are approximately: 60% total unit weight =
compressor section, 40% total unit weight = fan section.

Dimensions & Weights
SCXG-SVX01H-EN 17
Figure 5. SCWG/SIWG, in.
6.75”

Dimensions & Weights
18 SCXG-SVX01H-EN
Figure 6. SCRG/SIRG, in.
6.75”

Dimensions & Weights
SCXG-SVX01H-EN 19
Note: When unit is ordered with horizontal supply,
ensure that all applicable codes are considered
when installing equipment. Special attention
should be made to over head clearances of unit/
ducting to meet code requirements.
Table 8. Detail dimensions, in.
Model A B C D E F
SCWG/SCRG 20 20 10 3/4 58 1/2 5 1/8 13 1/4 11 1/2
SCWG/SCRG 25 19 1/4 12 1/4 57 5/8 5 1/8 13 1/4 11 1/2
SCWG 30 - 35
SCRG 32 18 14 5/8 56 1/2 5 1/8 13 1/4 11 1/2
Figure 7. SCRG/SIRG/SCWG/SIWG detail “A”
electrical connections, in.
Figure 8. Detail “B” discharge options, in.

Dimensions & Weights
20 SCXG-SVX01H-EN
Figure 9. CCRC/CIRC air-cooled condenser
Table 9. CCRC/CIRC air-cooled condenser dimensions & weight, in-lbs.
Model AA AB AC shipping weight operating weight
CCRC/CIRC 20 70 1/8 88 88 2030 1906
CCRC/CIRC 29 70 1/8 88 88 2084 1960
CCRC/CIRC 32 70 1/8 88 88 2138 2014
B
C
(LIQUID LINE CONNECTION REFRIG. CIRCUIT 1)
(HOT GAS CONNECTION REFRIG. CIRCUIT 1)
(LIQUID LINE CONNECTION REFRIG. CIRCUIT 2)
(HOT GAS CONNECTION REFRIG. CIRCUIT 2)
REFRIGERANT CIRCUIT 2
REFRIGERANT CIRCUIT 1
SUPPLY VOLTAGE WIRE ENTRY HOLE
SIZED FOR 1” CONDUIT
115 VOLT WIRE ENTRY HOLE SIZED FOR
3/4” CONDUIT
24 VOLT WIRE ENTRY HOLE SIZED
FOR 3/4” CONDUIT
OPTIONAL LOW
AMBIENT DAMPER
REFRIGERANT
LINE
CONNECTIONS
FRONTAL VIEW
OPTIONAL LOW
AMBIENT DAMPER
(ONE DAMPER PER
CIRCUIT)
AA
AB
AC
Table 10. CCRC/CIRC refrigerant connections, in.
Model E F G H J K L M N
CCRC/CIRC 20-32 66 7/8 14 3/8 18 1/2 24 3/4 29 5/8 7/8 5/8 7/8
Table 11. CCRC/CIRC electrical connections, in.
Model A B C
CCRC/CIRC 20-32 4 1/2 10 1/2 17 1/2

Dimensions & Weights
SCXG-SVX01H-EN 21
Figure 10. Hot water coil: left-hand connections
Table 12. Hot water coil dimensions & weight, in-lbs
A B C D E F G H J K Weight
one-row coil 53 3/4 4 7/8 73 1/2 16 5/8 6 3/4 7 1/2 23 1/8 37 1/4 1 3/4 2 1/2 415
two-row coil 53 3/4 5 1/8 73 1/2 16 5/8 6 3/4 7 1/2 22 3/8 37 1/4 2 3/4 3 5/8 510
Figure 11. Hot water coil: right-hand connections

Dimensions & Weights
22 SCXG-SVX01H-EN
Figure 12. Steam coil: left connections
53 13/16"
36 15/16"
22 1/2"
3 5/16"
15 7/8"
1"
40 15/16"
3 7/8"
9 3/8"
6 3/4"
16 15/16"
35"
CONDENSER
FITTINGS
1 1/2" NPTI
ELECTRICAL
CONNECTIONS
30 7/8"
2 1/8"
92 3/4"
73 1/2"
14 9/16" 64 1/2" 11"
3/4" (4X) ISOLATOR
MOUNTING LOCATION
ON BOTTOM OF UNIT
VERTICAL
DISCHARGE
TOP VIEW
LEFT VIEW
Note: Steam Coil Weight 460 Lbs.
Figure 13. Steam coil: right connections
40 15/16"
53 13/16"
22 1/2"
3 5/16"
15 7/8"
1"
36 15/16"
3 7/8"
9 3/8"
6 3/4"
16 15/16"
35"
PIPING CONNECTIONS
2 1/2" NPTE
STEAM INLET 1"
FEMALE CONN
CONDENSATE RETURN TRAP
1 1/2" FEMALE CONN
CONDENSATE RETURN TRAP
1" FEMALE CONN
VACUUM BREAKER 1"
FEMALE CONN
VACUUM BREAKER 1"
FEMALE CONN
30 7/8"
2 1/8"
92 3/4"
73 1/2"
10 15/16"
64 1/2"
11"
3/4" (4X) ISOLATOR
MOUNTING LOCATION
ON BOTTOM OF UNIT
VERTICAL
DISCHARGE
RIGHT VIEW
TOP VIEW
Note: Steam Coil Weight 460 Lbs.
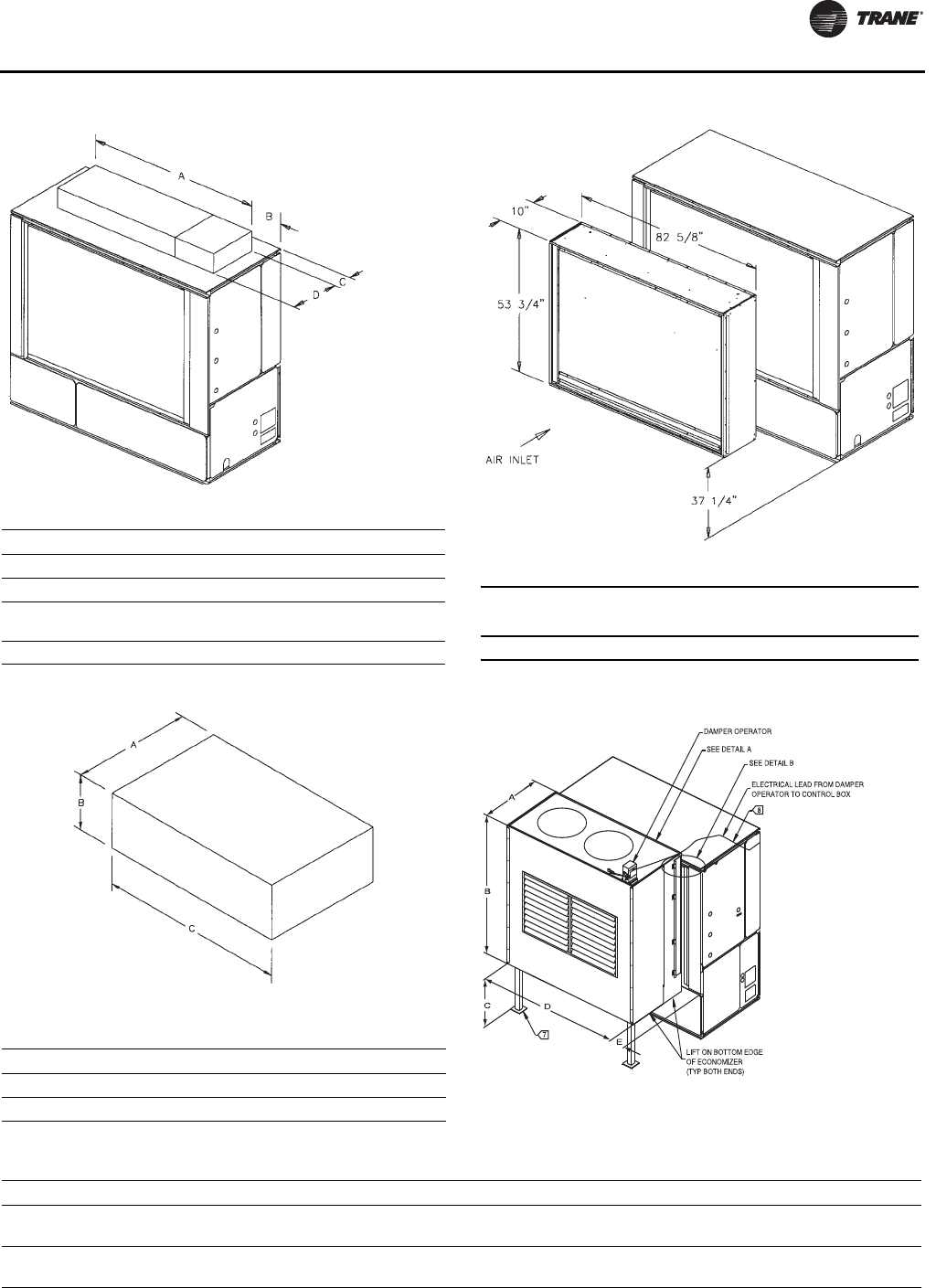
Dimensions & Weights
SCXG-SVX01H-EN 23
Figure 14. Electric Heat Coil
Table 13. Electric heat coil dimensions & weight, in-lbs.
Unit Size A B C D Weight
20 tons 70 1/4 4 7/8 11 1/2 19 460
25 tons 70 1/4 4 1/8 11 1/2 19 460
30 - 35
tons 70 1/4 2 7/8 11 1/2 19 460
Note: Coil box height is 8 in.
Figure 15. Flexible horizontal discharge plenum
Table 14. Flexible horizontal discharge plenum
dimensions & weights, in-lbs.
20-35 tons A B C Weight
Low height 35 17 1/4 86 1/2 262
Standard height 35 25 1/4 86 1/2 352
Figure 16. Waterside Economizer
Table 15. Waterside economizer weight, in-lbs.
Weight
Unit size 2-row 4-row
20 - 35 tons 488 584
Figure 17. Airside Economizer
Table 16. Airside economizer dimensions & weight, in-lbs.
Unit Size A B C D E F (1) F (2) G (1) G (2) H (1) H (2) J K L M Weight
SCWG/SIWG 20, 25
SCRG/SIRG 20 36 65 5/8 37 74 1/4 6 1/8 56 1/2 49 3/4 23 1/4 20 1/2 5 5/8 7 20 1/2 17 1/8 12 49 3/4 273
SCWG/SIWG 30, 35
SCRG/SIRG 25, 32 36 65 5/8 37 74 1/4 6 1/8 61 3/8 62 3/4 28 1/8 20 1/2 3 1/4 7 20 1/2 17 1/8 5 1/2 62 3/4 273
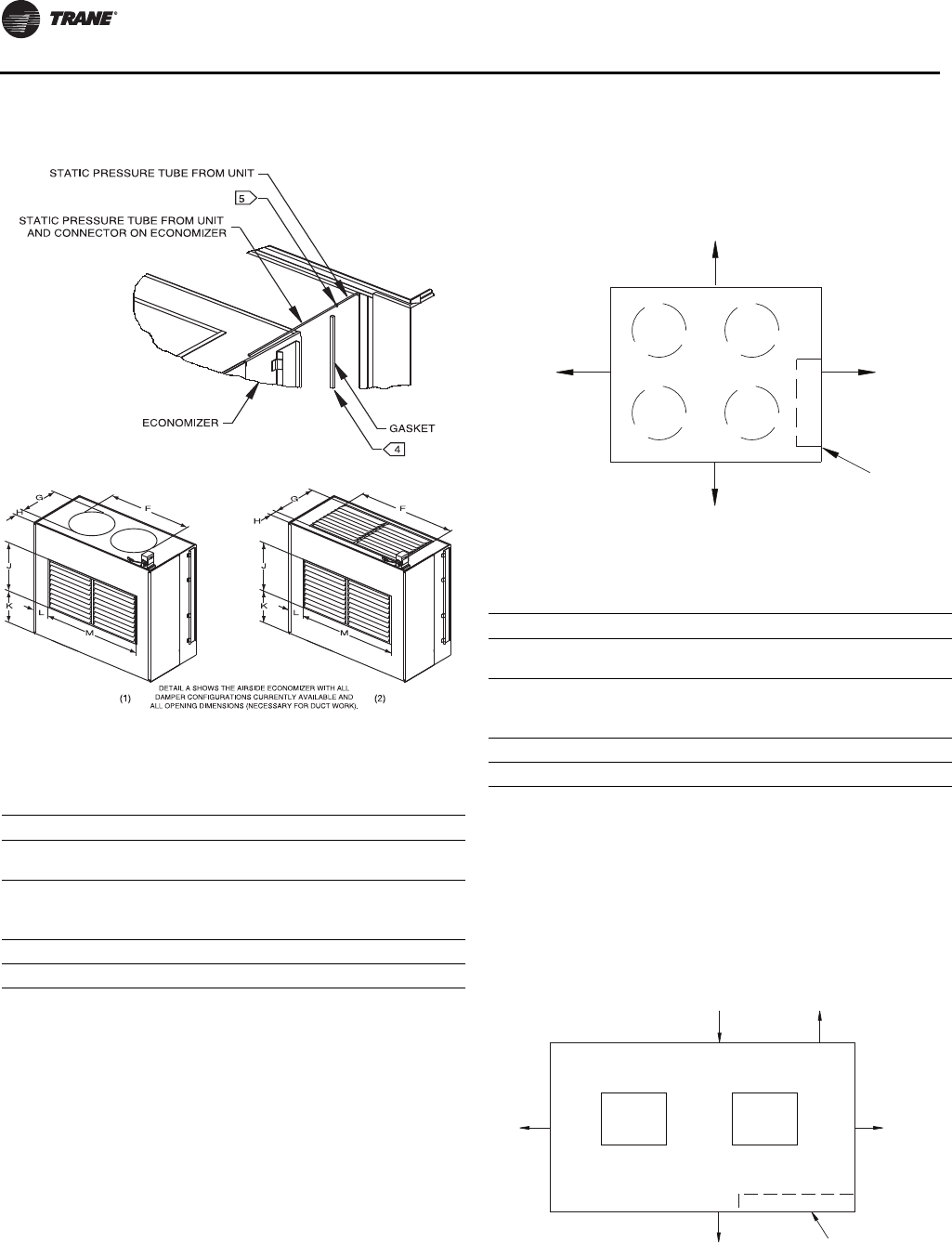
Dimensions & Weights
24 SCXG-SVX01H-EN
Service Clearances
See Figure 19, p. 24 and Figure 20, p. 24 for recommended
service and code clearances.
Note: When unit is ordered with horizontal supply,
ensure that all applicable codes are considered
when installing equipment. Special attention
should be made to overhead clearances of unit/
ducting to meet code requirements.
Figure 18. Detail “B” (top) and Detail “A” (bottom)
Table 17. Service and code clearance requirements
Side Distance Purpose
front 42 in.
(20-38 tons) NEC code requirement
left 18 in.
36 in.
77 in.
air-cooled units only
refrigeration & waterside component service
fan shaft removal
right 36 in. provides uniform airflow
inlet 18 in. provides uniform airflow
Figure 19. Top view CCRC/CIRC 20, 29, 32
Table 18. Service and code clearance requirements
Side Distance Purpose
front 42 in.
(20-38 tons) NEC code requirement
left 18 in.
36 in.
77 in.
air-cooled units only
refrigeration & waterside component service
fan shaft removal
right 36 in. provides uniform airflow
inlet 18 in. provides uniform airflow
Figure 20. Top view of self-contained unit showing
recommended service and code clearances
96” (2132 mm)
48”
(1066 mm)
Control
Panel
96” (2132 mm)
48”
(1066 mm)
air inlet 18” minimum
See
table
42” minimum
36”
minimum
Control Panel

SCXG-SVX01H-EN 25
Installation - Mechanical
Unit Handling Procedures Before lifting the unit or modular component, determine
the approximate center of gravity for lifting safety. See
Figure 21, p. 25 for assembled modular units and
Figure 22, p. 26 for split-apart units.The center of gravity
may vary slightly within the gravity block depending on
unit options.
Always test-lift the unit to determine the exact unit balance
and stability before hoisting it to the installation location.
See Figure 23, p. 26 and Figure 24, p. 27 for typical rigging
procedures and proper rigging equipment usage.
WARNING
Improper Unit Lift!
Test lift unit approximately 24 inches to verify proper
center of gravity lift point. To avoid dropping of unit,
reposition lifting point if unit is not level. Failure to
properly lift unit could result in unit dropping and
possibly crushing operator/technician which could
result in death or serious injury and possible equipment
or property-only damage.
WARNING
Heavy Objects!
Ensure that all the lifting equipment used is properly
rated for the weight of the unit being lifted. Each of the
cables (chains or slings), hooks, and shackles used to
lift the unit must be capable of supporting the entire
weight of the unit. Lifting cables (chains or slings) may
not be of the same length. Adjust as necessary for even
unit lift. Other lifting arrangements could cause
equipment or property damage. Failure to follow
instructions above or properly lift unit could result in
unit dropping and possibly crushing operator/
technician which could result in death or serious injury.
Table 19. Gravity block dimensions
Model A B C D
SCWG 36 14 38 12
SCRG 36 16 40 12
Figure 21. Assembled unit gravity block location

Installation - Mechanical
26 SCXG-SVX01H-EN
Figure 22. Split-apart unit gravity block location
Fan Section Only
Compressor Section Only
Figure 23. Split-apart modular unit proper rigging (L) and fan section (R)

Installation - Mechanical
SCXG-SVX01H-EN 27
Skid Removal
The unit ships on skids to provide forklift locations from
the front or rear.The skid allows easy maneuverability of
the unit during storage and transportation. Remove the
skids before placing the unit in its permanent location.
Remove the skids using a forklift or jack. Lift one end of the
unit off of the skids. See Figure 21, p. 25 and Figure 22,
p. 26 for unit gravity block location. Slide the skids out and
lower the unit at the installation location.
1. Position rigging sling under wood shipping skid.
2. Use spreader bars to avoid unit damage.
3. When using a forklift, exercise caution to prevent unit
damage.
4. Use the standard fork length to lift one end and drag or
pull unit while skidding the opposite end.
5. The unit center of gravity will fall within center of
gravity block at various locations depending on unit
options.
6. Use hooks to lift fan section only. Do not hook into open
channels to lift unit.
7. See unit nameplate for unit weight.
8. Do not stack units.
Installation Preparation
Important: Before installing the unit, perform the
following procedures to ensure proper unit
operation.
Before installing the unit, perform the following
procedures to ensure proper unit operation.
1. Position the unit and skid assembly in its final location.
If unit shipped split-apart, follow the procedure in the
“Split-Apart Unit Assembly,” p. 28 before completing
this step.Test lift the unit to determine exact unit
balance and stability before hoisting it to the
installation location. See Figure 23, p. 26 and
Figure 24, p. 27 for typical rigging procedures,
including cautions and proper uses of such equipment
as fork lifts, spreader bars, and hooks.
2. Test lift the unit to determine exact unit balance and
stability before hoisting it to the installation location.
See “Unit Handling Procedures,” p. 25 for proper
rigging procedures and cautions.
3. Remove the skids from under the unit. See “Skid
Removal,” p. 27.
4. Remove the protective shipping covers from the unit.
5. Verify isolators are properly tightened for operation.
See “Unit Vibration Isolator Option,” p. 29.
Note: Unit height and connection locations will change if
external vibration isolators are used.The unit may
be raised an additional 5-7/8 inches with spring-
type isolators.
Note: Unit height and connection locations will change if
the unit is constructed to be split-a-part in the field.
See unit submittal drawings for connection
locations.
6. Tighten compressor isolator mounting bolts.Torque to
18 ft. lbs. (± 2 ft. Lbs.)
7. Electrical supply power must meet specific balance
and voltage requirements, as described in section
“Installation - Electrical,” p. 39.
8. Water-cooled units only (model SCWG):The installer
must furnish and install a condenser main and standby
water pump, cooling tower, pressure gauges and all
components for the waterside piping. See “General
Waterside Recommendations: CoolingTowers,” p. 32.
9. Air-cooled units only (model SCRG):These units
require field-installation of a remote air-cooled
condenser and refrigerant piping. See “Refrigerant
System,” p. 36.
Figure 24. Assembled modular unit proper rigging
NOTICE:
Equipment Damage!
Do not use hooks to lift unit or hook into open channels
to lift unit.This could cause unit damage

Installation - Mechanical
28 SCXG-SVX01H-EN
Split-Apart Unit Assembly
1. Ensure the tagging information on the fan section
nameplate matches that on the compressor
nameplate.
2. Remove the connector brackets holding the sheet
metal shipping cover on compressor section. Retain
brackets and screws.
3. Remove shipping cover from the compressor section
and verify the ship-with package contains:
a. suction and liquid line couplings
b. insulation
c. sheet metal screws
4. Lift fan section onto the compressor section using the
rigging method in Figure 23, p. 26.
5. Remove skid from the fan section, placing the fan
section onto the compressor section. Reference
Figure 26, p. 29.
6. Install the connection brackets with the sheet metal
screws (referenced in step 2) on all sides of the unit.
Reference Detail “A” in Figure 26, p. 29.
7. Remove the unit panels labeled RU and RL in Figure 25,
p. 28. To remove panels, first remove the four shipping
screws located in the corner of each panel. Next, turn
the remaining 1/4 turn fasteners to the unlatch
position.The panel is supported by a “lip” channel. So,
lift the panel up and off the unit to remove it. See Detail
“A” i n Figure 26, p. 29.
8. Connect the drain hose to the drainpan outlet fitting
and secure it with the drain hose clamp provided.
9. See “Refrigerant System,” p. 36 for piping procedures.
10. Remove panel FLR and open the bottom control panel
door, FLL. Pull the fan motor leads (coiled in the fan
section) through the knockout in the bottom of the fan
section to the control panel. Ensure that the bushing is
installed in the hole to prevent the wires from chafing.
Refer to the unit wiring diagrams to connect the fan
motor leads properly and ensure correct phase
sequencing.
IntelliPak Units (UCM) Only
11. Remove panels FML, FMM, and FMR.
12. Pull the circular plug connector (CPC) from the
compressor section through the knockouts into the fan
section. Install the bushings (provided on the wiring
harnesses) in the knockouts.\
13. Using the CPC wiring diagram, connect the male CPC
to the female CPC in the top control panel.
14. If the unit has the mixed air temperature option, route
the capillary tube on back of the filter rack.
Units with Thermostat Only
15. Remove panel FMR. See Note 1 on Figure 25, p. 28.
16. Pull frost protection wires from the bottom control
panel through knockouts in bottom of fan section.
Route wires to the appropriate frost protection
switches on the evaporator coil. Reference the unit
wiring diagrams to connect frost protection wiring
connectors.
Air-Cooled Units Only
17. Route the refrigerant circuit wires for circuits 1 and 2
from the bottom control panel through the knockouts
to the solenoid valves.The solenoid valves are located
in the liquid refrigerant lines on the right-hand side of
the unit. Refer to the unit wiring diagrams to make
splice connections.
Figure 25. Modular unit panel description and internal connections

Installation - Mechanical
SCXG-SVX01H-EN 29
Unit Vibration Isolator Option
If your job requires external vibration isolation, two
options are available: isopads or spring-type isolators.
Isopads should be placed under the unit at locations
indicated on the factory-provided isolator sheet.
Set the spring-type isolators (Figure 27, p. 29) in position
after the unit is removed from skids before making
electrical, piping, or duct connections. All units require a
minimum of four isolators per unit. But some may require
six isolators, depending upon unit options.
Note: Trane strongly recommends you consult a
vibration specialist before double-isolating the
unit. Double isolation is not recommended.
If you decide to externally isolate the unit, use spring-flex,
type CP isolators.The spring number is marked on the
outer housing. See Figure 27, p. 29.
To install external isolators, complete the
following procedure.
1. Locate the isolators under unit base at the locations
indicated on the factory-provided isolator placement
sheet. Lift one end of the unit at a time to position
isolators to the floor, using anchor bolts.
2. Level the unit by adjusting isolator heights. Unit
weight may cause the upper housing to rest on the
lower housing of the spring isolators.The isolator
clearance shown in the side view of Figure 27, p. 29,
must be 1/4 - 1/2 inches.To increase the clearance, lift
the unit off the isolator and turn the leveling bolt
counterclockwise. Recheck the unit level and the
housing clearances. Maximum allowable difference
between isolator heights is 1/4 inch. Shim as required
under the isolators.
Note: The compressors and fan assembly are internally
isolated on most units. Due to this, the addition of
external isolation devices (spring mounting
isolators) is at the discretion of the building or
HVAC system designer.
Figure 26. How to assemble the modular unit
Figure 27. Optional spring isolator dimensional data

Installation - Mechanical
30 SCXG-SVX01H-EN
Duct Connections
Return air enters the rear of the unit and conditioned
supply air discharges through the top. Attach supply air
ductwork directly to the unit’s top panel, around the fan
discharge opening. A duct collar is not provided.
Note: Units equipped with the flexible horizontal
discharge plenum option may include a duct collar
when holes are factory cut. If discharge openings
are field-cut, refer to the “Plenum Installation”
section.
Install all air ducts according to the National Fire Protection
Association standards for the “Installation of Air
Conditioning and Ventilation Systems other than
ResidenceType (NFPA 90A) and ResidenceType Warm Air
Heating and Air Conditioning Systems (NFPA 90B).
Make duct connections to the unit with a flexible material
such as heavy canvas. If a fire hazard exists,Trane
recommends using Flexweave 1000, type FW30 or
equivalent canvas. Use three inches for the return duct
and three inches for the discharge duct. Keep the
material loose to absorb fan vibration.
Note: The compressors and fan assembly are internally
isolated.Therefore, external isolation devices
(spring mounting isolators) are at the discretion of
a vibration specialist consulted by the building or
HVAC system designer.
Run the ductwork straight from the opening for a
minimum of three fan diameters. See Figure 28, p. 30.
Extend remaining ductwork as far as possible without
changing size or direction. Do not make abrupt turns or
transitions near the unit due to increased noise and
excessive static losses. Use elbows with splitters or
turning vanes to minimize static losses.
Poorly constructed turning vanes may cause airflow
generated noise. Align the fan outlet properly with the
ductwork to decrease noise levels in the duct and to
increase fan performance. To complete trunk ductwork to
the VAV terminal units, refer to the VAV box manuals for
specific requirements. Check total external static
pressures against fan characteristics to be sure the
required airflow is available throughout the ductwork.
To achieve maximum acoustical performance, minimize
the duct static pressure setpoint
Plenum
Before installing the plenum attach the insulation strip that
ships with the plenum. See Figure 29, p. 31 for proper
insulation location. Align the plenum front with the
control panel side of the unit. Using the strips and screws
provided, secure the plenum to the unit.
Treat field-cut holes to prevent fiberglass from entering
the airstream.
Note: Plenum insulation must be applied properly to
prevent air bypass around the plenum. See
Figure 29, p. 31.
WARNING
Hazardous Voltage w/Capacitors!
Disconnect all electric power, including remote
disconnects and discharge all motor start/run
capacitors before servicing. Follow proper lockout/
tagout procedures to ensure the power cannot be
inadvertently energized. For variable frequency drives
or other energy storing components provided by Trane
or others, refer to the appropriate manufacturer’s
literature for allowable waiting periods for discharge of
capacitors. Verify with an appropriate voltmeter that all
capacitors have discharged. Failure to disconnect power
and discharge capacitors before servicing could result
in death or serious injury.
For additional information regarding the safe discharge
of capacitors, see PROD-SVB06A-EN
Figure 28. Duct connection recommendations
3 Fan
Diameters
Discharge
Duct
3-inch
Flexible
Duct
Return
Air

Installation - Mechanical
SCXG-SVX01H-EN 31
Airside Economizer Installation
Unit Handling
1. Hoist the damper cabinet to the installation location
with straps positioned under the skid as shown in
Figure 30, p. 32. Use spreader bars to prevent unit
damage during lifting.
2. With the damper cabinet at its final location (near the
unit), remove the screws securing it to the skid from the
side flanges. Retain these screws for later use.
Unit Preparation
3. The support legs are secured to the skid, and the
hanging bracket is secured with wire ties to an inside
flange near the cabinet’s base. Remove the C-channel
collar and install it on the unit, if not already installed.
4. Remove the roll of 1/8” thick gasket from the damper
cabinet’s W-supports, and apply it to the C-channel
collar mounted on the rear of the unit.This gasket will
provide a seal between the damper cabinet and the
unit.
5. Attach the legs (with screws provided) to the leg
brackets located on the damper’s base.
6. Attach a field-provided clevis of suitable strength ( > 1/
2” ), to each of the corner lifting brackets through the
7/8” diameter holes.
7. Attach to the clevises a means of lifting the damper
cabinet from its skid.
Unit Installation
8. Slowly raise the damper cabinet from its skid.
9. Attach the hanging bracket across the front of the
damper cabinet. Position it with its short flange
pointing to four o’clock, and secure it with screws
provided. See Figure 30, p. 32.
10. Lift the damper cabinet and position it such that the
hanging bracket is positioned over the unit’s C-channel
collar.
11. Lower the damper cabinet until the holes in its side
flanges are aligned with the holes in the C-channel
collar. Install screws removed in step 3 through the
damper cabinet’s side flanges and into the C-channel’s
corresponding holes.
12. Attach ductwork to the top and back dampers
according to local codes.
Field Wiring Connections
13. Open the damper cabinet’s door and connect the
factory-provided plug from the actuator to the
factory-provided plug in the unit’s filter section.
14. Cabinets withTRAQ dampers only: Unroll the two
rolls of pneumatic tubing located inside the damper
cabinet. Route these tubes through the cabinet’s front
upper panel (0.25 dia. holes provided). Connect them
to the two pneumatic tubes protruding from the
customer electrical connection panel on the unit. Be
sure to connect like tubes to each other (black to black,
white stripe to white stripe).
15. Cabinets with TRAQ dampers only: Locate the
“bullet” sensor and rolled up wiring in the unit’s filter
section. Route it into the damper cabinet and insert the
sensor into the sensor mounting clip attached to
underside of one of theTraq dampers.
Figure 29. Correct plenum insulation placement
Plenum Bottom View
Dashed line indicates correct insulation placement.
WARNING
Proper Field Wiring and Grounding
Required!
All field wiring MUST be performed by qualified
personnel. Improperly installed and grounded field
wiring poses FIRE and ELECTROCUTION hazards.To
avoid these hazards, you MUST follow requirements for
field wiring installation and grounding as described in
NEC and your local/state electrical codes. Failure to
follow code could result in death or serious injury.
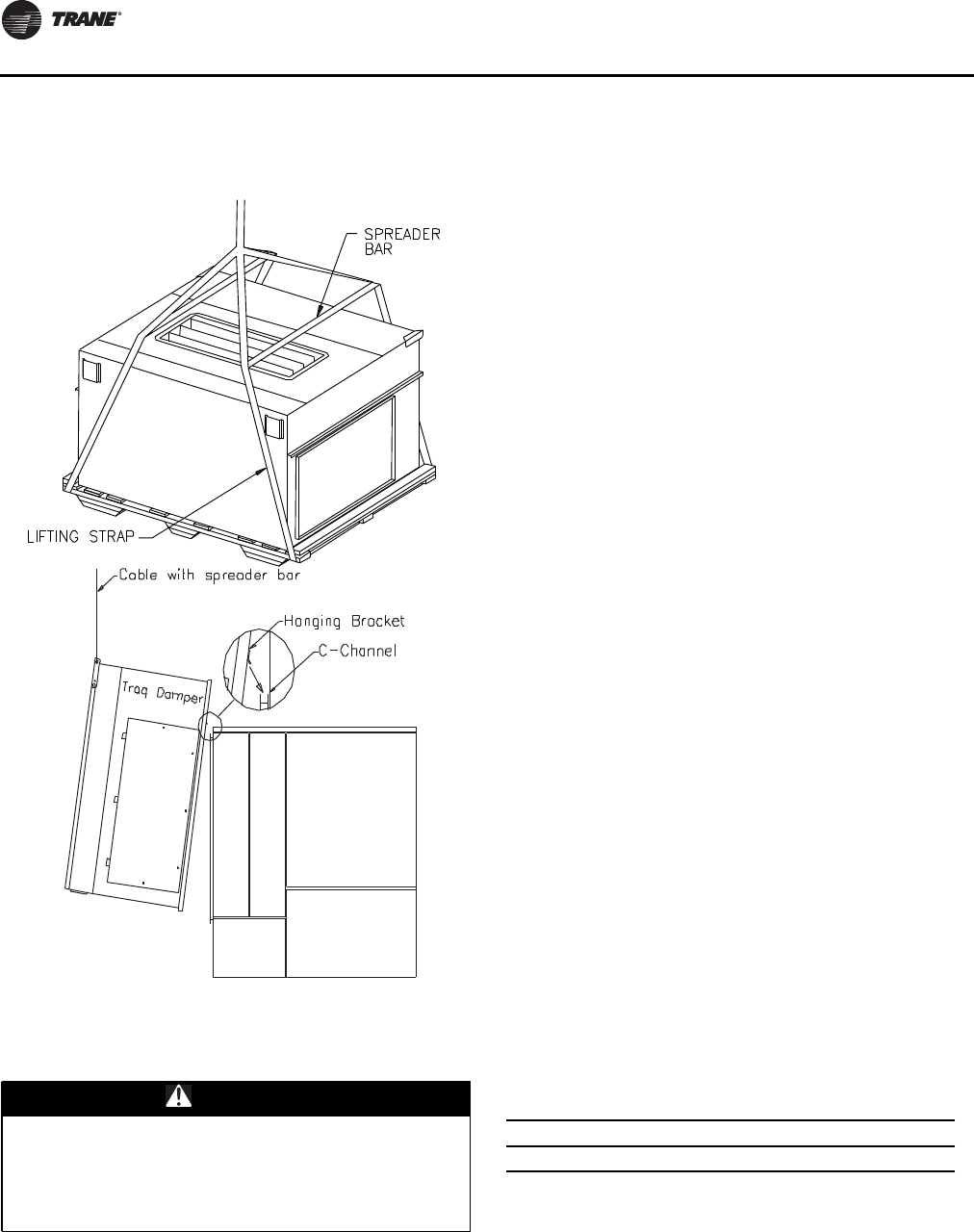
Installation - Mechanical
32 SCXG-SVX01H-EN
Water Piping
Condenser Connections
Condenser water piping knockouts are in the lower left end
panel. If necessary, remove insulation to gain access. All
field installed piping must conform to applicable local,
state, and federal codes.To complete condenser water
connections follow the procedure below.
Note: Four condenser waterline drain plugs ship in a bag
in the unit’s left end.The installer must field install
these four plugs using pipe thread sealer. An
additional plug is provided for units with a
waterside economizer.
1. Install the vent plugs in the economizer coil headers
and condenser manifolds.These plugs ship in a bag
with the condenser drain plugs.
2. Attach the water supply line to the inlet connection,
and the return line to the outlet connection. Entering
and leaving water connections for all condensers are
factory manifolded and require only single
connections for entering and leaving water. If the unit
has a waterside economizer and/or control valves, the
factory pipes between these components.
3. If using a cooling tower, refer to Figure 32, p. 33 for a
typical piping circuit from the unit.
4. Ensure the water pressure to the unit does not exceed
400 psig.
Note: To prevent water pump damage, design system
piping to provide relief when using energy saving
waterside economizer valves.
Condensate Drain Connections
The condensate drain is internally trapped. Condensate
drain connections are on the unit’s right side. Connect
condensate drain piping to the 1 1/4“ NPT female fitting,
using at least 7/8” OD copper or 3/4” OD iron pipe. Pitch the
condensate line downward a minimum of 1/2” for each 10'
of horizontal run, away from the unit. Be sure to install the
condensate drain “P” trap drain plug. Before starting the
unit, fill the trap with water to prevent negative pressure in
the fan section from impeding condensate flow.To
facilitate drain pipe cleaning, install plugged tees in place
of 90°elbows.
General Waterside Recommendations:
Cooling Towers
Cooling tower control affects the unit cycle rates.
Condenser water temperature swings from 10-15°F may
cause excessive compressor, water valve, and unit
cycling. Be sure to set the tower controls to minimize
compressor/unit cycling.
Figure 30. Proper lifting of the airside economizer (top)
and proper installation of the airside
economizer option (bottom)
WARNING
High Pressure Water!
Provide relief valves on system water piping to prevent
instantaneous release of high pressure water. Failure to
provide relief valves could result in death or serious
injury or water pump damage or unit failure.
Table 20. Water connection sizes
Unit Size Direct Condenser Factory Piped
SCWG 20-35 1-1/2 NPT 2-1/2 NPT
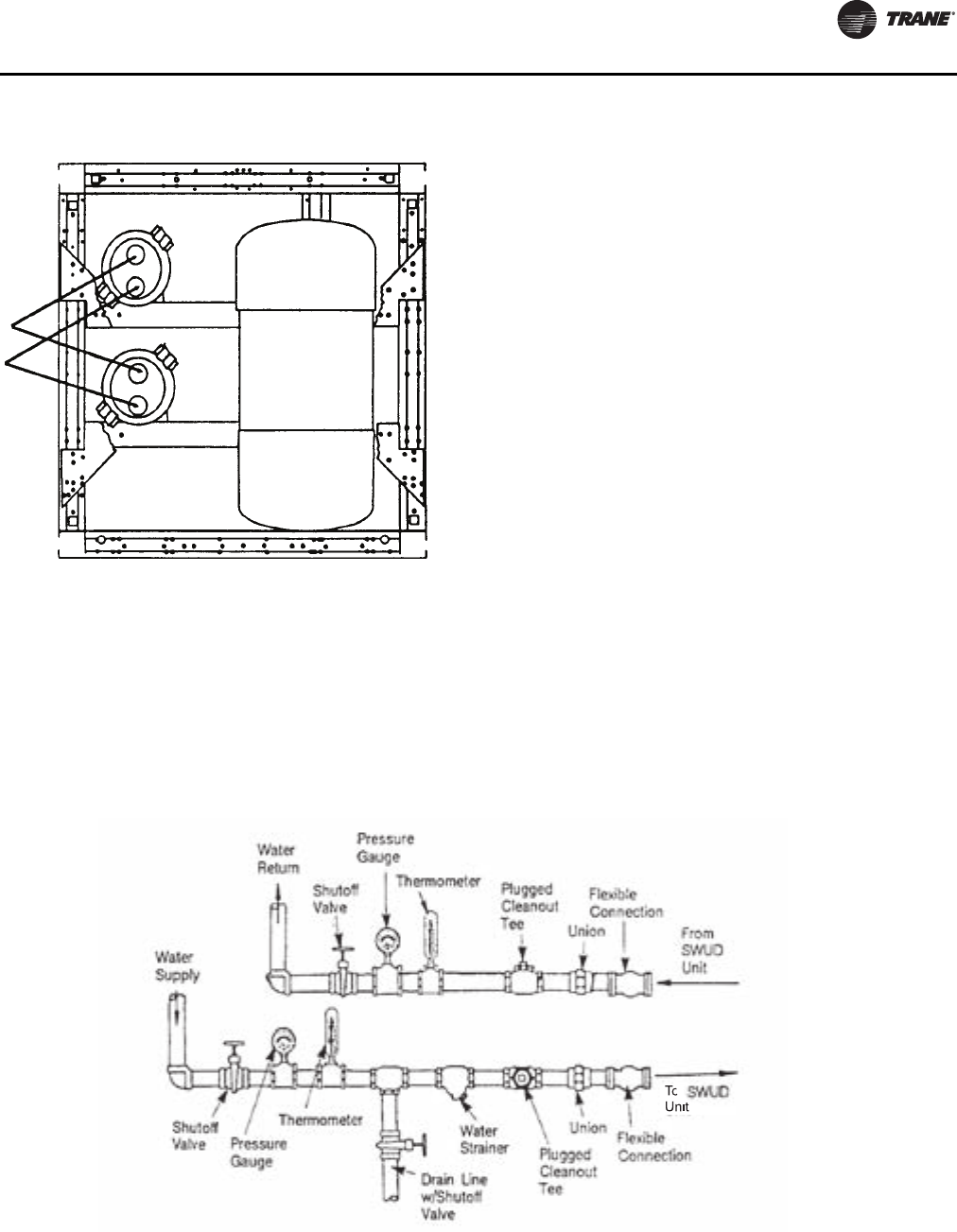
Installation - Mechanical
SCXG-SVX01H-EN 33
Waterside Piping Arrangements
Install a condenser water pump between the cooling tower
(either open or closed) and the self-contained unit. Lay out
the remainder of the system’s condenser piping in reverse
returns.This helps balance the system by equalizing the
length of supply and return pipes. Multistory buildings
may use a direct return system with balancing valves at
each floor.
Install the supply riser and its return in close proximity.
Furnish both with permanent thermometers to check the
waterside balance during start-up and routine
maintenance checks.
Also, include strainers at each pump inlet and unit. Install
drain valves at the riser’s base to allow drainage points for
system flushing during start-up and routine maintenance.
For condenser draining and header removal, include a
shutoff/balancing valve on the entering and leaving
waterside pipes, drain tees, and unions of each unit.
Note: Unit does not have floor drains.
Water Temperature Requirements
Do not allow the entering water temperature to go below
54°F (12.2°C) on units with constant water flow (basic
piping).This will cause the compressors to shut down and
the mechanical cooling function will lockout. However, the
economizer (if enabled) will continue to function.The
compressors will reset when the entering water
temperature reaches 58°F (15°C).
Units with variable water flow (intermediate piping) have
a modulating condensing pressure control valve that
allows compressor operation down to entering water
temperatures of 35°F (2°C).
For more information on constant and variable water flow,
see the Sequence of Operation section of this manual.
Note: Units with a waterside economizer can be set from
the human interface panel for variable or constant
water flow.
Figure 31. Direct condenser connections
Figure 32. Condenser water piping components for cooling tower system

Installation - Mechanical
34 SCXG-SVX01H-EN
Waterside Economizer
Installation Procedure
1. Loosen and pull all end devices that go through the
bushing on the filter rack (upper right corner of rack).
2. Remove the filter rack from the back of the unit by
removing the 1/4” hex head screws from the top and
bottom of the filter rack assembly. The filter rack
assembly will hang on the unit when the screws are
removed. Remove the filter rack by lifting it up off the
unit.
3. Remove the economizer from the crate and position it
behind the unit with the headers on the left side, when
facing the back of the unit. Remove the plastic
envelope that is taped to the economizer box
assembly.This envelope contains the gasket that must
be installed onto the vertical side flanges of the box.
4. Install the pressure sensitive gasket to the unit side of
the vertical flange on the economizer box.
5. Hang the economizer on the unit as shown in
Figure 33, p. 34. Lift the economizer by using the holes
provided in the top panel of the economizer.
6. Align economizer holes with the holes in the unit
channel. Install screws in the top (6x) and bottom (6x)
of the economizer.
7. Remove the unit’s rear middle panel and unbraze the
two copper pipes in the 2 5/8” water pipe. Do not
remove the pipe outlet blockoff panel.
8. Remove the economizer tubing assemblies from the
shipping box. Check ship-separate parts against those
shown in Figure 34, p. 34,Figure 35, p. 35,Figure 36,
p. 35, and Figure 37, p. 35. Face the front of the unit to
see which side the water pipe exits to determine if the
unit has either right or left-hand piping.
9. Assemble tubing as shown in Figure 34, p. 34 or
Figure 37, p. 35.Tack all tubes in place before brazing to
ensure proper fit-up. For right-hand piped units, install
the ball valve actuator assembly and actuator as
shown in Figure 35, p. 35. Refer to the unit wiring
diagram for wiring connection points.
10. Install the pipe insulation on all pipe line to prevent
sweating
11. Install the rear panels.
12. Re-install the filter rack on the back of the economizer
coil box and affix with screws provided.
Waterside Economizer with left-hand factory
piping components
Figure 33. Installing the waterside economizer
Figure 34. Detail view of ship-separate tubing
assemblies for waterside economizer left-
hand piping
Install screws in
top (6x) and
bottom (6x)
Waterside economizer must
be lifted and hooked over
flange in the opening of the
unit channel. Unit
Top
Economizer

Installation - Mechanical
SCXG-SVX01H-EN 35
Waterside Economizer with right-hand
factory piping components
Figure 35. Waterside economizer with left-hand factory
piping tubing assembly
Table 21. Waterside economizer ship-separate parts list -
left-hand piping
Factory
Piping Item Part # Qty. Description
Left-Hand 4001 2 Tube; 2 5/8" x 9"
X17110026250 5 Elbow; 2 5/8" x 2 5/8"
4003 1 Tube; 2 5/8" x 26 1/8"
4740 1 Tube; 2 5/8" x 33 1/2"
4009 1 *Tube; 2 5/8" x 14 7/8"
X21040098390 10 ft. *Gasket
X21080406110 1 *Insulation; 2 5/8" Rubatex
X16120203570 1 Plug; 1 1/2" Brass
X17150027060 1 Bushing; 2 1/2" ftg. x 1 1/2"
X17170031210 1 Tee; 2 5/8" x 2 1/8" x 2 5/8"
4738 1 *Tube; 2 5/8" x 19 3/4"
4007 1 Tube; 2 5/8" x 14 1/2"
X45000032020 1 roll Tape, 1.5' wide
4006 1 Tube; 2 5/8" x 19 15/16"
Table 22. Waterside economizer part descriptions - left-
hand piping
Item Part Description
A Assembly #1
B Assembly #2
C Assembly #3
D Assembly #4
E Tube; 2 5/8" x 16 7/8"
F Tube; 2 5/8" x 22 5/8"
B
E
A
FDC
Figure 36. Waterside economizer with right-hand
factory piping tubing assembly
Figure 37. Detail view of ship-separate tubing
assemblies for waterside economizer right-
hand piping
A
G
F
D
B
E
C

Installation - Mechanical
36 SCXG-SVX01H-EN
Hydronic Coil Installation
Installation Procedure
These instructions are for steam and hot water coil
installation. Hydronic coil assembly has a full coil, piping,
a modulating temperature control valve, and a disc
temperature limit device located in unit near fan on motor
frame. Hydronic coils are available with either right or left-
hand pipe connections. Piping connections are identical to
unit piping. For example, for right-hand unit piping,
hydronic coil will have right-hand connections.The
hydronic coil assembly has temperature controls to keep
the unit’s internal cabinet temperature below 105°F to
prevent motor and bearing damage.
1. Remove filter rack from back of unit. Remove the 1/4-
inch hex head screws from the top and bottom of the
filter rack assembly.The filter rack assembly will hang
on the unit when the screws are removed.The filter
rack can now be removed by lifting up on the filter rack.
2. Remove the hydronic coil from crate and position it
behind unit with open side facing unit evaporator coil
inlet. Remove the plastic envelope taped to coil box
assembly.This envelope contains the mounting
screws needed to attach the coil box to the unit and the
gasket required on the vertical side flanges of the box.
3. Install the pressure sensitive gasket to the unit side of
the vertical flange on the coil box in two places.
4. Install 2” x 1/2” standard thread eyebolts into coil lift
plates to raise coil to height necessary to attach it to the
unit.Top panel includes a “J” hook to allow hanging,
similar to filter rack. Align holes so coil hangs on unit.
If unit has dirty filter option, connect static pressure
tube to unit before bolting coil in place. Locate static
pressure tubing on unit evaporator coil and route
through the knockout in the top corner of the coil box.
5. Align the hydronic coil with the holes in the unit
channel or waterside economizer option. Move the coil
box up against the unit and install using six mounting
screws in the top and six in the bottom of the coil box.
6. Remove the valve and pipe cover on the coil box.
Connect the wires that are coiled in the coil box,
referring to the wiring diagram installed on the unit
control panel door. Route wires into the unit through
knockouts in the top of the box.
7. Reinstall the filter rack on the back of the heating coil
rack. If the unit has the waterside economizer option,
the filter rack will require additional support legs.
Refrigerant System
Trane Water Cooled Self Contained units are available in
complete system or a "Split Apart" configuration.
Complete systems are factory charged with R-410A
refrigerant. Split Apart modules have a nitrogen holding
charge and require field connection and charging.
Trane Air Cooled Commercial Self Contained and
Condenser units ship with a dry nitrogen holding charge.
Before installing refrigerant piping verify holding charge is
present. Momentarily depress the CSC suction or
discharge line (and Condenser liquid line) access port
valves.
If charge is present continue with piping installation.
Table 23. Waterside economizer ship-separate parts list -
right-hand piping
Factory
Piping Item Part # Qty. Description
Right-Hand 4001 1 Tube; 2 5/8" x 9"
4607 1 Tube; 2 5/8" x 17"
X17110026250 5 Elbow; 2 5/8" x 2 5/8"
4605 2 Tube; 2 5/8" x 9 1/2"
X15330177010 1 Water Valve
4008 1 *Tube; 2 5/8" x 20 1/4"
X17170031210 1 Tee; 2 5/8" x 2 1/8" x 2 5/8"
X16120203570 1 Brass Plug, 1 1/2"
X17150027060 1 Bushing; 2 1/8" ftg. x 1 1/
2"
4007 1 Tube; 2 5/8" x 14 1/2"
4031 1 Tube; 2 5/8" x 62
4603 1 *Tube; 2 5/8" x 11 3/4"
4006 1 Tube; 2 5/8" x 19 1/4"
X13610256010 1 *Actuator with wires
X19110028040 2 *90 Degree Conduit Fitting
X19110028040 3 ft. *1/2" Conduit
X210804060110 14 ft. *Rubatex Insulation, 2 5/8"
X45000032020 1 roll Tape, 1.5' wide
X21040098390 10 ft. *Gasket
Table 24. Waterside economizer part descriptions - right-
hand piping
Item Part Description
A Assembly #1
B Assembly #2
C Assembly #3
D Assembly #4
E Tube; 2 5/8" x 11 3/4"
F Tube; 2 5/8" x 20 1/4"
G Actuator Assembly
WARNING
Unit Structural Integrity!
Unit panels provide structural integrity. Do not remove
more than two non-adjacent panels at one time as this
could cause the plenum frame to collapse. Failure to
follow these recommendations could result in death,
serious injury or equipment damage.

Installation - Mechanical
SCXG-SVX01H-EN 37
If no nitrogen escapes the access valve, leak test the unit
refrigerant system to determine the leak source, and
repair. See Maintenance section, “Refrigerant LeakTest
Procedure,” p. 95. After finding leak, remove test pressure
and repair leak using proper brazing procedures. See
Maintenance section, “Brazing Procedures,” p. 96. Retest
unit(s) to ensure all leaks are repaired. Continue with
piping installation.
Interconnecting Piping
Refrigerant piping must be properly sized and applied.
These two factors have a significant effect on both system
performance and reliability.
Split Apart Units Only: Join liquid and suction lines with
pipe sections provided. Use proper brazing procedures.
Using Table 25, p. 37, select proper liquid and discharge
line size. Unit connection sizes are also shown. Install
interconnecting piping using proper installation and
brazing procedures.
Work on only one circuit at a time to minimize system
exposure to potentially harmful moisture in the air.
Before installing piping verify compressor oil levels are
near top of sight glass or above.
Note: CSC units (and replacement compressors) ship
fully charged with POE oil from the factory. Scroll
compressors use POE oil (OIL00079, quart
container or OIL00080, gallon container), DO NOT
substitute.
Capped discharge and liquid line connections are located
near bottom, left side of the indoor unit. CCRC/CIRC
connections are located in the unit front, at top.
Remove caps with a tube cutter to minimize risk of getting
chips inside piping.
Note: When facing the control panel side of the unit.
Circuit #2 is always on the left and Circuit #1 is
always on the right.
Cleanliness is extremely important during system
installation to minimize residual contaminants, such as
oxidization and scale.
Attach vacuum pump and begin evacuation as soon as
piping installation is complete.This starts system
dehydration and helps prevent POE compressor oil
contamination.This will also indicate large leaks if
vacuum does not hold (below 400 microns and hold for 2
hours). Complete LeakTest and Evacuation (for
procedures, see “Refrigerant Leak Test Procedure,” p. 95
and “System Evacuation Procedures,” p. 97 in
Maintenance section) before starting “,” p. 37..
Note: Installation of a field supplied discharge line access
port near indoor units with optional discharge line
ball valve will make high side pressure
measurements easier during leak test.
Note: UseType “L” refrigerant grade copper tubing only.
Preliminary Refrigerant Charging
NOTICE:
Equipment Damage!
Compressors contain POE oil which readily absorbs
moisture directly from the air. Moisture absorbed by
POE oil is very difficult to remove by evacuation and can
cause compressor failure.To prevent contamination,
this unit shipped sealed containing dry nitrogen.
Minimize the amount of time the system is open to the
atmosphere. When open, flow dry nitrogen through the
piping to prevent atmospheric moisture from
contacting compressor POE oil.
Table 25. Refrigerant piping sizes
Air Cooled Modular Connection Size (in)
Circuit 1 Circuit 2
SXRG Size Liquid Discharge Liquid Discharge
20, 25, 32 5/8 7/8 5/8 7/8
Remote Condenser Connection Size (in)
Circuit 1 Circuit 2
CXRC Size Liquid Discharge Liquid Discharge
20, 29, 32 5/8 7/8 5/8 7/8
Interconnecting Tube Size (in)
Circuit 1 Circuit 2
SXRG/
CXRC Size Liquid Discharge Liquid Discharge
20/20 5/8 7/8 5/8 7/8
25/29 5/8 1 1/8 5/8 7/8
32/32 5/8 1 1/8 5/8 1 1/8
WARNING
Confined Space Hazards!
Do not work in confined spaces where refrigerant or
other hazardous, toxic or flammable gas may be
leaking. Refrigerant or other gases could displace
available oxygen to breathe, causing possible
asphyxiation or other serious health risks. Some gases
may be flammable and or explosive. If a leak in such
spaces is detected, evacuate the area immediately and
contact the proper rescue or response authority. Failure
to take appropriate precautions or to react properly to
such potential hazards could result in death or serious
injury.

Installation - Mechanical
38 SCXG-SVX01H-EN
To charge the system:
1. Verify system leak check (including interconnecting
piping for air cooled systems) and evacuation are
complete before adding refrigerant. See “Refrigerant
LeakTest Procedure,” p. 95 and “System Evacuation
Procedures,” p. 97 in Maintenance section
2. Ensure field supplied unit disconnect is "OFF". Verify
that the unit 115 volt control circuit switch is "OFF" and
reset relays have been unplugged, to prevent
inadvertent compressor starts.
3. Turn field supplied unit disconnect "ON" to energize
crankcase heaters. Verify crankcase heaters are
operating.
4. Verify all service valves are open.
5. See CSC General data Table 1, p. 11 or Table 2, p. 12 for
unit refrigerant charge.
6. See Table 26, p. 38 for additional charge required
based on field piping size and length. Add this to the
charge amount fromStep 5 for the total charge.
Note: Step 6 not required for field piping under 25
feet, or for water cooled system.
7. At the liquid line angle valve add as much R-410A
LIQUID as possible up to, but not exceeding, total
charge amount. Depending on conditions, it may not
be possible to add more than 60% of the total charge.
This will be adequate for compressor startup. More
charge will be added after compressors are started.
Use an accurate scale to measure and record
preliminary amount of R-410A added to each circuit.
•Air Cooled Only: Add charge at the condenser
access valve or field supplied discharge line access
valve. If angle valve is used for charging, liquid line
solenoid valve should be open.
8. DO NOT add refrigerant in the suction line during
preliminary charging to minimize refrigerant in system
low side prior to compressor start.
9. Record charge amount added.
10. If total charge is not reached see “Final Refrigerant
Charge,” p. 87.
11. Verify wiring has been returned to original.
•Air Cooled Only: Verify liquid line solenoid valve
has been returned to original.
WARNING
Hazard of Explosion!
Use only dry nitrogen with a pressure regulator for
pressurizing unit. Do not use acetylene, oxygen or
compressed air or mixtures containing them for
pressure testing. Do not use mixtures of a hydrogen
containing refrigerant and air above atmospheric
pressure for pressure testing as they may become
flammable and could result in an explosion.
Refrigerant, when used as a trace gas should only be
mixed with dry nitrogen for pressurizing units. Failure
to follow these recommendations could result in death
or serious injury or equipment or property-only
damage.
WARNING
Hazardous Pressures!
If a heat source is required to raise the tank pressure
during removal of refrigerant from cylinders, use only
warm water or heat blankets to raise the tank
temperature. Do not exceed a temperature of 150°F. Do
not under any circumstances apply direct flame to any
portion of the cylinder. Failure to follow these safety
precautions could result in a violent explosion, which
could result in death or serious injury.
CAUTION
Freezing Temperatures!
Do not allow liquid refrigerant to contact skin. If it
does, treat the injury similar to frostbite. Slowly warm
the affected area with lukewarm water and seek
immediate medical attention. Direct contact with liquid
refrigerant could cause minor or moderate injury.
NOTICE:
Compressor Damage!
If it becomes necessary to remove or recharge the
system with refrigerant, it is important that the
following actions are taken. To prevent cross
contamination of refrigerants and oils, use only
dedicated R-410A service equipment.
• Disconnect unit power before evacuation and do not
apply voltage to compressor while under vacuum.
• Due to presence of POE oil, minimize system open
time. Do not exceed 1 hour.
• Allow the crankcase heater to operate a minimum of
24 hours before starting compressors.
• Do not allow liquid refrigerant to enter the suction
line. Excessive liquid accumulation in the liquid lines
could result in compressor damage.
• Do not operate the compressors without some
refrigerant in each circuit.
Failure to follow these instructions could result in
compressor failure.
Table 26. Charge add (R-410A) - lbs per 10 ft of line(a)
(a)Amounts listed are for 10 ft of pipe above 25’. Actual requirements will
be in direct proportion to the actual length of piping.
Charge (lbs)
Piping Size (in) Liquid Line Discharge Line
5/8 1.07 -
7/8 2.23 0.31
1 1/8 - 0.53

SCXG-SVX01H-EN 39
Installation - Electrical
Unit Wiring Diagrams
Specific unit wiring diagrams are provided on the inside of
the control panel door. Use these diagrams for
connections or trouble analysis.
Supply Power Wiring
It is the installer’s responsibility to provide power supply
wiring to the unit terminal block or the non-fused
disconnect switch option. Wiring should conform to NEC
and all applicable code requirements.
Bring supply wiring through the knockout in the lower left
side of the unit control panel. Connect the three phase
wires to the power terminal block or the non-fused
disconnect switch in the control box terminals. Refer to
specific wiring diagrams and fuse information in the unit’s
control panel.
Voltage Range
Voltages must be within +- 10% the nameplate voltage.
Ensure the unit voltage is balanced by measuring at the
compressor terminals. Voltage imbalance on three phase
systems can cause motor overheating and premature
failure. Maximum allowable imbalance is 2.0%.
Voltage Imbalance
Read the voltage at the compressor terminals to determine
if it is balanced.Voltage imbalance on three phase systems
can cause motor overheating and premature failure.The
maximum allowable imbalance is 2.0%. Voltage
imbalance is defined as 100 times the sum of the deviation
of the three voltages from the average (without regard to
sign) divided by the average voltage. For example, if the
three measured voltages are 221, 230, and 227, the average
voltage would be:
The percentage of voltage imbalance is then:
100 * (226-221)/226 = 2.2%
Phase Monitor
Unit is equipped with phase monitor in control box.The
phase monitor will protect against phase loss, imbalance
and reversal of line voltage. If a fault occurs, the red LED
will energize. While the fault condition is present, the
phase monitor interrupts the 115V control circuit. If no
faults are observed, a green LED will be energized.
Control Power
In this example, 2.2% imbalance is not acceptable.
Whenever a voltage imbalance of more than 2.0% exists,
check the voltage at the unit disconnect switch. If the
imbalance at the unit disconnect switch does not exceed
2.0%, faulty unit wiring is causing the imbalance. Conduct
a thorough inspection of the unit electrical wiring
connections to locate the fault, and make any repairs
necessary.
Access the connection terminal block through the control
panel on the unit’s upper left side. All wiring should
conform to NEC and applicable local code requirements.
Be sure all wiring connections are secure. Reference the
unit specific diagrams inside the control panel.
WARNING
Hazardous Service Procedures!
The maintenance and troubleshooting procedures
recommended in this section of the manual could result
in exposure to electrical, mechanical or other potential
safety hazards. Always refer to the safety warnings
provided throughout this section concerning these
procedures. Unless specified otherwise, disconnect all
electrical power including remote disconnect and
discharge all energy storing devices such as capacitors
before servicing. Follow proper lockout/tagout
procedures to ensure the power can not be
inadvertently energized. When necessary to work with
live electrical components, have a qualified licensed
electrician or other individual who has been trained in
handling live electrical components perform these
tasks. Failure to follow all of the recommended safety
warnings provided, could result in death or serious
injury.
NOTICE:
Use Copper Conductors Only!
Unit terminals are not designed to accept other types
of conductors. Failure to use copper conductors could
result in equipment damage.
NOTICE:
Motor Damage!
Correct phase sequence is critical. If phase sequence of
the incoming line voltage is not correct, it could result
in motor damage.
NOTICE:
Component Damage!
Unit transformers IT1, IT3, IT4, and IT5 are sized to
provide power to the unit only. Do not use these
transformers to supply power to field equipment. Field
connections to these transformers could create
immediate or premature component failures.
221 230 227++
3
----------------------------------------------------226volts=

Installation - Electrical
40 SCXG-SVX01H-EN
Selection Procedures
RLA = rated load amps
Compressor LRA = locked rotor amps
Fan motor LRA = locked rotor amps, N.E.C. table 430 - 150
FLA = full load amps, N.E.C.
Table 430 - 150
Voltage utilization range is ±10%
Determination of minimum circuit ampacity (MCA).
MCA = 1.25 x largest motor amps/VFD amps (FLA or RLA)
+ the sum of the remaining motor amps.
Determination of maximum fuse size (MFS) and maximum
circuit breaker size (MCB).
MFS and MCB = 2.25 x largest motor amps (FLA or RLA) +
the sum of the remaining motor amps.
For units with the dual power option, there are two
electrical circuits that need calculations using the formulas
above:
• circuit #1 - fans
• circuit #2 - compressors
If rating value determined does not equal a standard
current rating of over current protective device, use next
lower standard rating for the marked maximum rating.
Table 27. Number of compressors per unit
SCWG/SIWG
SCRG/SIRG 20
20 25 30
25 35
32
10 HP 2 2 1 -
15 HP - - 1 2
Table 28. SxWG & SxRG compressor motor electrical
data
200V 460V 575V
HP RLA LRA RLA LRA RLA LRA
10 41.4 267 18.6 142 15.8 103
15 56.9 351 25.5 197 23.1 146
Table 29. Electric heat - single stage
SCWG/SIWG SCRG/SIRG Heat 200V 460V
Size Size Kw Amps Amps
20 20 16 44.8 19.6
25 25 20 55.6 24.2
30 - 24 66.8 29.0
- 32 26 72.4 31.6
35 - 28 78 34.0
Note: Electric heat amperage should not be considered when determining
minimum circuit ampacity. The current of the unit in the heating
mode will not exceed the current of the unit in the cooling mode.
Table 30. CCRC/CIRC condenser electrical data
Unit
Size
Tons Rated
Voltage #
Fans FLA
(ea.) LRA
(ea.) MCA MFS/
MCB
20, 29, 32
200 4 4.1 20.7 17.4 20
230 4 4.1 20.7 17.4 20
460 4 1.8 9.0 7.7 15
575 4 1.4 7.2 6.0 15
Note: All motors for CCRC/CIRC units are rated at 1 hp (.7457 kW).
Table 31. Fan motor electrical data
200V 460V 575V
HP TYPE FLA LRA FLA LRA FLA LRA
5ODP 15.7 107 6.8 48 5.4 40
TEFC 15 125 6.7 52 5.3 41
7.5 ODP 22.3 199 9.7 84.8 7.8 61.4
TEFC 23.2 162 9.4 74 7.6 58.5
10 ODP 29.5 260 12.6 118 10.1 72.3
TEFC 27.4 195 11.9 103 9.6 83.9
15 ODP 43.4 271 18.9 118 15.1 94
TEFC 42.5 235 18.5 122.9 14.8 99
20 ODP 57.0 373 24.5 160.8 19.6 130
TEFC 56.4 320 24.5 175 19.6 140
25 ODP 69.0 438 30.4 190 24.3 152
Table 32. VFD electrical data
VFD L.I.C.
Without Bypass With Bypass
HP 200V 460V 575V 200V 460V 575V
7.5 23.8 10.6 8.8 25 11.3 9.3
10 32.2 14 11.1 31.6 14.3 11.3
15 48.3 21 16.6 47.7 21.3 15.6
20 61.9 27.6 21.4 60.9 27.3 22.3
25 78.2 34 26.3 76.5 34.3 27.3
Note: Values are at the maximum VFD input rating and not the reduced
motor values.

Installation - Electrical
SCXG-SVX01H-EN 41
Variable Frequency Drive Option
(VFD)
Variable frequency drive (VFD) option can only be used
with IntelliPak units. TraneTR200 VFD and VFD w/bypass
is available from 5 to 25 hp. All VFDs are pre-configured
and run tested at factory. VFD is wall mounted.
Mounting Requirements
Proper location of the VFD is important to achieve proper
performance and normal operating life. Installation must
be in an area where it will be protected from:
• Direct sunlight, rain or moisture.
• Corrosive gases or liquids.
• Vibration, airborne dust, or metallic particles.
For effective cooling and proper maintenance, install the
VFD vertically to the ground using four mounting screws.
To ensure sufficient air space for cooling there must be a
minimum eight inch clearance above and below VFD. A
minimum 2” clearance is required on each side. Allow
enough clearance to VFD cabinet door.
See Figure 38, p. 41 through Figure 45, p. 48 for VFD
dimensions and weights.
Electrical Installation Procedure
Refer to the National Electric Code, section 310-16 for
sizing power wires. All other control wires should be
twisted shielded or twisted pair shielded, 20 - 14 AWG,
with lead length not to exceed 164 feet. When using
shielded wire, the shield sheath must be connected at the
VFD only. Refer to Unit Schematic and connection
diagrams for VFD wiring.
Variable Frequency Drive Without ByPass
Weight = 14 lbs (6.350 Kg)
WARNING
Hazardous Voltage w/Capacitors!
Disconnect all electric power, including remote
disconnects and discharge all motor start/run
capacitors before servicing. Follow proper lockout/
tagout procedures to ensure the power cannot be
inadvertently energized. For variable frequency drives
or other energy storing components provided by Trane
or others, refer to the appropriate manufacturer’s
literature for allowable waiting periods for discharge of
capacitors.Verify with an appropriate voltmeter that all
capacitors have discharged. Failure to disconnect
power and discharge capacitors before servicing could
result in death or serious injury.
For additional information regarding the safe discharge
of capacitors, see PROD-SVB06A-EN
NOTICE:
Use Copper Conductors Only!
Unit terminals are not designed to accept other types
of conductors. Failure to use copper conductors could
result in equipment damage.
Table 33. W/O Bypass VFD Frame Sizes
HP
200V 460V 575V
Frame Frame Frame
7.5 B1 A3 A3
10 B1 A3 B1
15 B1 B1 B1
20 B2 B1 B1
25 C1 B1 B1
Notes:
1. See Figure 38, p. 41 through Figure 41, p. 44 for frame size details.
2. VFD wall-mounted by others
Figure 38. Frame A3: without bypass
0.22
0.20
0.31
0.22
0.26
0.43
14.65
8.07
13.19
10.12 10.56
4.33
5.28
Trane TR200
OK
Status
Cancel
Back
Info
Reset
On
Warn.
Alarm
Quick
Menu Menu
Main
Log
Alarm
On
Hand
Reset
Off
On
Auto
BDETAIL
ADETAIL
MOUNTING BASE
BSEE DETAIL
ASEE DETAIL
0.48
0.39

Installation - Electrical
42 SCXG-SVX01H-EN
Weight = 51 lbs (23.133 Kg)
Figure 39. Frame B1: without bypass
0.63
0.63
Auto
On
Off
Reset
Hand
On
Alarm
Log
Main
MenuMenu
Quick
Alarm
Warn.
On
Reset
Info
Back Cancel
Status
OK
Trane TR200
9.56
19.45
0.35
0.47
0.35
0.75
0.35
0.35
DETAIL A
DETAIL B
10.28
17.87
8.27
AIR
OUTLET
AIR
INLET
MOUNTING BASE
SEE DETAIL A
SEE DETAIL B

Installation - Electrical
SCXG-SVX01H-EN 43
Weight = 60 lbs (27.216 Kg)
Figure 40. Frame B2: without bypass
Trane TR200
OK
Status
Cancel
Back
Info
Reset
On
Warn.
Alarm
Quick
Menu Menu
Main
Log
Alarm
On
Hand
Reset
Off
On
Auto
0.35
0.35
0.75
0.47
0.35
0.35
BDETAIL ADETAIL
26.14
9.57
INLET
AIR
OUTLET
AIR
10.28
MOUNTING BASE
BSEE DETAIL
ASEE DETAIL
24.57
8.27
0.64
0.64

Installation - Electrical
44 SCXG-SVX01H-EN
Weight = 91 lbs (41.277 Kg)
Figure 41. Frame C1: without bypass
Trane TR200
OK
Status
Cancel
Back
Info
Reset
On
Warn.
Alarm
Quick
Menu Menu
Main
Log
Alarm
On
Hand
Reset
Off
On
Auto
BDETAIL
ADETAIL
0.39
0.35
0.75
0.49
0.39
0.35
27.28
12.17
MOUNTING BASE
BSEE DETAIL
ASEE DETAIL
INLET
AIR
OUTLET
AIR
25.51
10.71
12.17 0.72
0.72

Installation - Electrical
SCXG-SVX01H-EN 45
Variable Frequency Drive With ByPass
Weight = 35 lbs (15.876 Kg)
Table 34. With Bypass VFD Frame Sizes
HP
200V 460V 575V
Frame Frame Frame
7.5 B1 A3 A3
10 B1 A3 A3
15 B2 B1 B1
20 B2 B1 B1
25 C1 B1 B1
Notes:
1. See Figure 42, p. 45 through Figure 45, p. 48 for frame size details.
2. VFD wall-mounted by others.
Figure 42. Frame A3: with bypass
7.63
4.72
30.81
31.92
SEE DETAIL A
SEE DETAIL B
9.73
.59
DETAIL A
.39
.35
.28
.35
DETAIL B
.39
1.45
.72
1.45 4.72
.98
2.42
3.99
5.37
Trane TR200
Status Menu
Quick
Menu
Main
Log
Alarm
Back Cancel
Info
OK
On
Warn.
Alarm
On
Hand
Reset
Off
On
Auto Reset

Installation - Electrical
46 SCXG-SVX01H-EN
Weight = 85 lbs (38.555 Kg)
Figure 43. Frame B1: with bypass
8.86 8.86
19.09
20.1021.48
12.65
0.35
0.69
0.75
0.69
0.35
SEE DETAIL A
TYP. 3 PLCS.
DETAIL A
DETAIL B
0.47
.69
SEE DETAIL B
TYP. 3 PLCS.
Trane TR200
Status Quick
Menu Menu
Main
Log
Alarm
Cancel
Back
OK InfoOn
Warn.
Alarm
On
Hand
Reset
Off
On
Auto Reset

Installation - Electrical
SCXG-SVX01H-EN 47
Weight = 105 lbs (47.627 Kg)
Figure 44. Frame B2: with bypass
.47
.35
.75
.69
.35
.69
8.868.86
19.09
28.17
26.79
12.65
.69
SEE DETAIL B
SEE DETAIL A
DETAIL A DETAIL B
Trane TR200
OK
Status
Cancel
Back
Info
Reset
On
Warn.
Alarm
Quick
Menu Menu
Main
Log
Alarm
On
Hand
Reset
Off
On
Auto
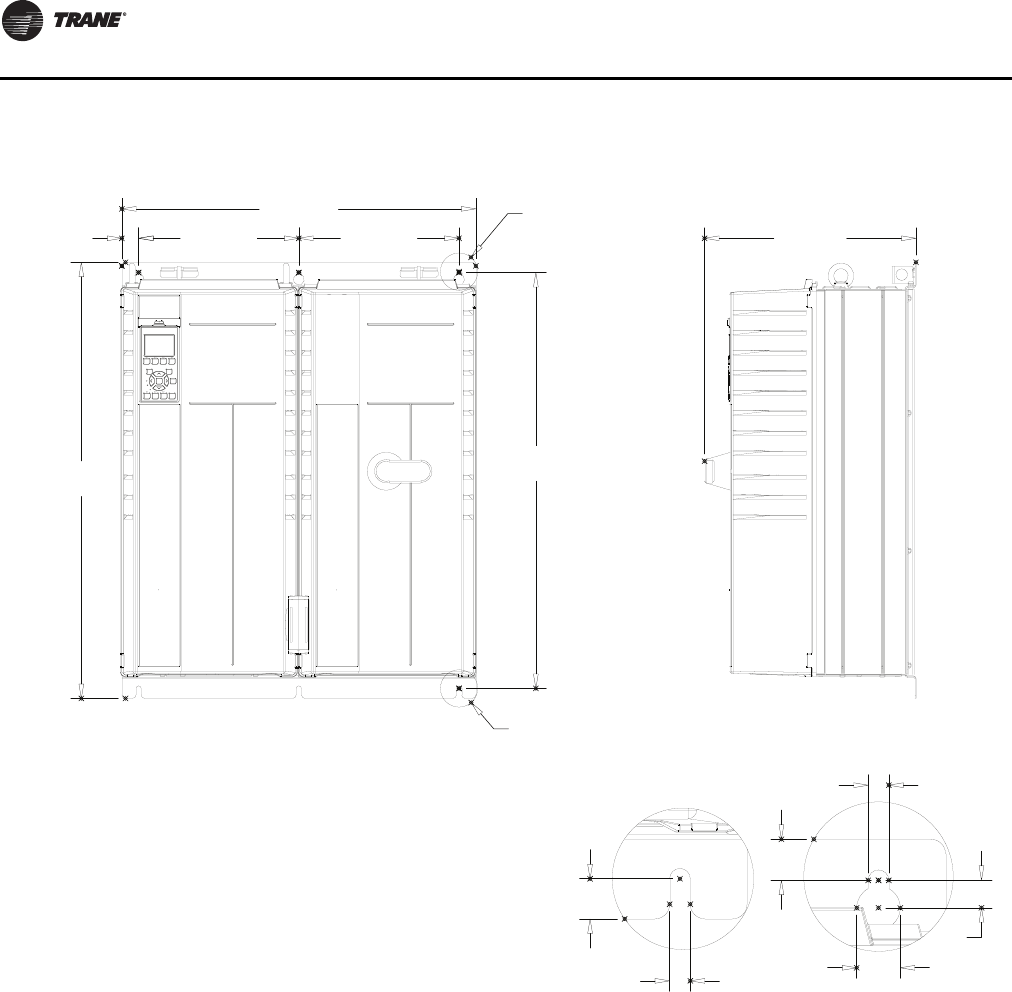
Installation - Electrical
48 SCXG-SVX01H-EN
Weight = 145 lbs (65.771 Kg)
Figure 45. Frame C1: with bypass
11.0011.00
24.30
14.51
29.94 28.55
1.15
1.42
2.76
1.42
2.99
2.82
1.89
SEE DETAIL B
TYP. 3 PLCS.
SEE DETAIL A
TYP. 3 PLCS.
DETAIL B DETAIL A
Trane TR200
OK
Status
Cancel
Back
Info
Reset
On
Warn.
Alarm
Quick
Menu Menu
Main
Log
Alarm
On
Hand
Reset
Off
On
Auto

Installation - Electrical
SCXG-SVX01H-EN 49
Static Pressure Transducer
Installation (VAV units only)
Supply air static pressure controls the inverter option. A
static pressure head assembly ships separate in control
panel for field installation in the supply air duct work.
Installer is responsible for providing pneumatic tubing.
Transducer Location
Place head assembly in an area of ductwork that will
provide an average and evenly distributed airflow pattern.
Use the following guidelines to determine an appropriate
installation location.
1. Locate static head assembly 2/3 to 3/4 down longest
duct run, in an area approximately 10 duct diameters
downstream and 2 duct diameters upstream of major
interferences, turns, or changes in duct diameter.
2. When installing pneumatic tubing between head
assembly and transducer in control panel, don’t
exceed 250ft for ¼”OD tubing or 500ft for 3/8”OD
tubing.
Installing the Transducer
To properly install the static pressure transducer:
1. Mount pressure sensing head assembly in duct with
sensing tip is in middle of the duct so that it will provide
a proper pressure measurement. See Figure 46, p. 49.
2. Connect the pneumatic tubing from the sensing head
to the push-on tubing connection in the control panel.
Use a plastic static pickup tubing. Do not exceed 250
feet for 1/4“ OD tubing or 500 feet for 3/8” OD tubing.
Transducer inside control panel picks up low side or
reference pressure.
Note: If plastic tubing pulls away from a connection, trim
it back before replacing it on the fitting. Stretched
tubing may leak and cause faulty control.
Electric Heat Installation
Electric heat option consists of a single stage heater and is
used in IntelliPak™ units or units with a field-installed
thermostat. Electric heater ships separate for field
installation and wiring. See Table 35, p. 49 for heater kW
per unit size. Electric heat can be installed on units with
vertical discharge. It cannot be installed on units with
plenums. See Figure 47, p. 50 and Table 36, p. 50 for
electric heat dimensional data.
Installation Procedure
1. Remove fan discharge shipping covers, if not
previously done.
2. Install open-cell gasket around discharge opening on
heater.
3. Position electric heater so unit fan discharge openings
line up with electric heater openings. For a vertical
discharge unit, position electric heater as shown in
Figure 47, p. 50.
4. Use hole pattern in electric heat as a template to mark
and drill 3/16” diameter holes in unit.
5. Bolt electric heaters to unit with ¼” sheetmetal screws.
Figure 46. Static pressure sensor installation
Duct
Pressure
Sensor
Static Pressure
Head Assembly
Connector
for 1/4”
Tubing
Sheet Metal Screws
(provided by installer) NOTE: Place sensor inlet
perpendicular to airflow.
Table 35. Available electric heat kW
Unit Size Heater kW
20 Tons 16
25 Tons 20
30 Tons 24
32 Tons 26
35 Tons 28
WARNING
Hazardous Voltage w/Capacitors!
Disconnect all electric power, including remote
disconnects and discharge all motor start/run
capacitors before servicing. Follow proper lockout/
tagout procedures to ensure the power cannot be
inadvertently energized. For variable frequency drives
or other energy storing components provided by Trane
or others, refer to the appropriate manufacturer’s
literature for allowable waiting periods for discharge of
capacitors.Verify with an appropriate voltmeter that all
capacitors have discharged. Failure to disconnect
power and discharge capacitors before servicing could
result in death or serious injury.
For additional information regarding the safe discharge
of capacitors, see PROD-SVB06A-EN
NOTICE:
Use Copper Conductors Only!
Unit terminals are not designed to accept other types
of conductors. Failure to use copper conductors could
result in equipment damage.

Installation - Electrical
50 SCXG-SVX01H-EN
Note: It is very important that electric heaters are selected
based on unit voltage and tonnage because
discharge opening sizes vary by unit tonnage.
Electric Heat Coil Wiring Procedure
• Before wiring the electric heater, remove the unit
wiring diagram from the unit control panel and refer to
the connection points.
Table 36. Electric heat dimensions - english - (inches)
Unit Size B1 B2 Z
20 Tons 10 3/4 15 5/8 27 3/4
25 Tons 12 1/4 15 5/8 26 3/4
30, 32, 35 Tons 14 3/4 15 5/8 23 3/4
Figure 47. Vertical discharge electric heat installation (L) and electric heater dimensions

Installation - Electrical
SCXG-SVX01H-EN 51
Standard with All
IntelliPak Units
BAYSENS077
(zone temperature sensor only)
CV Unit Zone Sensor
Options
BAYSENS108
(Dual setpoint, manual/automatic
changeover sensor, accessory
model number digit6=E)
BAYSENS110
(Dual setpoint, manual/automatic
changeover sensor with system
function lights, accessory model
number digit6=F)
Zone Sensor Options for IntelliPak Control Units
Zone sensor options are available and be ordered with the unit or after the unit ships.
Following is a full description of zone sensors and their functions. See Table 44, p. 77
for the zone sensor temperature vs. resistance coefficient curve.
BAYSENS077* Description
This zone sensor module ships with all units, and can be used with BAYSENS019,
BAYSENS020, or BAYSENS021 remote sensors. When this sensor is wired to one of
these remote zone sensors, wiring must be 18AWG shielded twisted pair (Belden 8760
or equivalent). Refer to the specific zone sensor for wiring details. It provides the
following features and system control functions:
• Remote temperature sensing in the zone
• Morning warmup sensor
• Zone sensor for ICS™ systems
• Zone temperature averaging
When used as a remote sensor for standard zone sensor, the thermistor sensor must
be disabled.
(Possible Schematic Designation(s): 5U23, 5U26, 5U30, and 5RT5.)
BAYSENS108 & BAYSENS110 Description
These zone sensor modules are for use with cooling/heating constant volume units.
They have four system switch settings (heat, cool, auto, and off) and two fan settings
(on and auto).The zone sensor provides either manual or automatic changeover
control with dual setpoint capability.
BAYSENS108 and BAYSENS110 features and system control functions include:
• System control switch to select heating mode (HEAT), cooling mode (COOL),
automatic selection of heating or cooling as required (AUTO), or to turn the
system off (OFF).
• Fan control switch to select automatic fan operation while actively heating or
cooling (AUTO), or continuous fan operation (ON).
• Dual temperature setpoint levers for setting desired temperature.The blue lever
controls cooling, and the red lever controls heating.
• Thermometer to indicate temperature in the zone. This indicator is factory
calibrated.
(Possible Schematic Designation: 5U29)
BAYSENS110-Specific Feature: Function status indicator lights:
•SYSTEM ON glows continuously during normal operation, or blinks if system
is in test mode.
•COOL glows continuously during cooling cycles, or blinks to indicate a cooling
system failure.
•HEAT glows continuously during heating cycles, or blinks to indicate a heating
system failure.
•SERVICE blinks or glows to indicate a problem.These signals vary depending
on the particular equipment being used.
(Possible Schematic Designation: 5U29)

Installation - Electrical
52 SCXG-SVX01H-EN
CV and VAV Unit Zone
Sensor Options
BAYSENS074
(Zone temperature sensor w/timed override
and local setpoint adjustment,
accessory model number digit 6 =
C)
BAYSENS073
(Zone temperature sensor w/timed
override , accessory model
number digit6=B)
Integrated Comfort™ Systems Sensors for CV and
VAV Applications
These zone sensor options are for use with cooling/heating Integrated Comfort
System (ICS) systems.
BAYSENS074 Description
This electronic analog sensor features single setpoint capability and timed override
with override cancellation. BAYSENS074 features and system control functions
include:
• Remote temperature sensing in the zone
• A timed override button to move an ICS or a building management system from
its “unoccupied” to “occupied” mode.
• Thumbwheel for local setpoint adjustment
• A cancel button to cancel the “unoccupied override” command.
(Possible Schematic Designation: 5U23)
BAYSENS073 Description
This electronic analog sensor features single setpoint capability and timed override
with override cancellation. It is used with aTrane Integrated Comfort system.
BAYSENS073 features and system control functions include:
• Remote temperature sensing in the zone
• A timed override button to move an ICS or a building management system from
its “unoccupied” to “occupied” mode.
• Cancel button to cancel the “unoccupied override” mode.
(Possible Schematic Designation: 5U23)
Figure 48. Zone sensor mounting hole locations for: BAYSENS077, BAYSENS073, BAYSENS074, BAYSENS108, and
BAYSENS110.
RIGHT BACK
1-3/32 [27,43 mm]
3/32 [2,00 mm]
1-3/8 [35,00 mm]
19/32 [15,00 mm]
15/64 [6,00 mm]
3-5/32 [80,00 mm]
1-1/32 [26,16 mm]
5/32 [3,81 mm] 4X

Installation - Electrical
SCXG-SVX01H-EN 53
Zone Sensor Installation
All sensor options ship in the main control panel and are
field-installed. Programmable option installation
procedures.
Mounting the Subbase
Remove the zone sensor cover from subbase, and mount
subbase on the wall or on a 2 x 4 junction box. Route wires
through the wire access hole in the subbase. See
Figure 49, p. 54. Seal the hole in the wall behind the
subbase.
Note: Guidelines for wire sizes and lengths are shown in
Table 37, p. 53.The total resistance of these low
voltage wires must not exceed 2.5 ohms per
conductor. Any resistance greater than 2.5 ohms
may cause the control to malfunction due to
excessive voltage drop.
Note: Do not run low-voltage control wiring in same
conduit with high-voltage power wiring.
Wiring
1. Run wires between the unit control panel and the zone
sensor subbase.To determine the number of wires
required, refer to the unit wiring diagrams.
2. Connect the wiring to the appropriate terminals at the
unit control panel and at the zone sensor subbase. In
general, zone sensor connections to the unit use the
convention of connecting zone sensor terminals to like
numbered unit terminals (1 to 1, 2 to 2, etc.).The
connection detail is shown on the unit wiring
diagrams, which are located in the unit control panel.
3. Replace the zone sensor cover back on the subbase and
snap securely into place.
Standard Remote Sensor (BAYSENS077)
When using the remote sensor, BAYSENS077, mount it in
the space that is to be controlled. Wire according to the
interconnecting wiring diagrams on the unit.
Mounting Location
Mount the sensor on the wall in an area with good air circulation
at an average temperature. Avoid mounting space temperature
sensor is areas subject to the following conditions:
• Drafts or “dead” spots behind doors or in corners
• Hot or cold air from ducts
• Radiant heat from the sun or appliances
• Concealed pipes and chimneys
• Unheated or non-cooled surfaces behind the sensor, such as
outside walls
• Airflows from adjacent zones or other units
To mount the sensors, remove the dust cover and mount the
base on a flat surface or 2" x 4" junction box. Sensors ship with
mounting screws.
WARNING
Hazardous Voltage w/Capacitors!
Disconnect all electric power, including remote
disconnects and discharge all motor start/run
capacitors before servicing. Follow proper lockout/
tagout procedures to ensure the power cannot be
inadvertently energized. For variable frequency drives
or other energy storing components provided by Trane
or others, refer to the appropriate manufacturer’s
literature for allowable waiting periods for discharge of
capacitors. Verify with an appropriate voltmeter that all
capacitors have discharged. Failure to disconnect power
and discharge capacitors before servicing could result
in death or serious injury.
For additional information regarding the safe discharge
of capacitors, see PROD-SVB06A-EN
NOTICE:
Use Copper Conductors Only!
Unit terminals are not designed to accept other types
of conductors. Failure to use copper conductors could
result in equipment damage. Table 37. Zone sensor maximum lengths and wire size
Distance from Unit to
Controller Recommended Wiring Size
0-150 feet 22 gauge
151--240 feet 20 gauge
241-385 feet 18 gauge
386- 610 feet 16 gauge
611-970 feet 14 gauge

Installation - Electrical
54 SCXG-SVX01H-EN
Programmable Zone Sensors
A Check FilterTimer function is included. Filter service
countdown time can be set in one-day increments.
Activation of theTest/Configuration button located on the
bottom of the sensor performs a sensor self-diagnostic
routine and indicates hours in service.
When the BAYSENS119 is programmed for Constant
Volume or VAV control, Night Setback is initiated through
the scheduled Unoccupied time setting. When the sensor
switches to Night Setback, the outdoor dampers close and
heating/cooling functions are enabled/disabled based on
set up parameters. As building load changes, If heating/
cooling functions are enabled, the Sensor energizes self-
contained unit and evaporator fan operation.The unit will
cycle heating/cooling operation throughout the
Unoccupied period as required to maintain Unoccupied
space temperature setpoints. When the Unoccupied time
period has expired, all heating/cooling functions return to
normal operation.
When Night Setback options are used with VAV heating/
cooling, maintain airflow through the self-contained unit
by electronically tying the VAV terminals to the
unoccupied output relay contacts on the self-contained
units low voltage terminal board, or by using changeover
thermostats. Either of these methods will assure adequate
airflow through the unit and satisfactory temperature
control of the space.
Note: Refer to BAS-SVX17*-EN for complete Installation,
Operation, and Maintenance Instructions.
Figure 49. Typical zone sensor installation for vertically-oriented sensors
Junc-
tion
Mounting to Junction Box
Mounting Directly to the Wall
The BAYSENS119 programmable night set back sensor
provides multi functional flexibility for both Constant Volume
and Variable Air Volume control.This electronic programmable
sensor includes auto or manual cooling and heating
changeover with 7 day programming. Five tactile feel buttons
located on the sensor front panel provide interface for all
programming, including initial setup for CV or VAV control.
Sensor functionality includes up to four daily programmable
periods for Occupied/Unoccupied operation, and Override. The
dynamic LCD display indicates status for System On/Off, Heat,
Cool, Fan Status,Time of Day, Occupied/Unoccupied mode,
SpaceTemperature, Space or Discharge Air Heating and
Cooling Setpoints. Additional features include Service
Indication for Heat Failure, Cool Failure, Fan Failure, andTest
Mode if system is operating in test mode.

Installation - Electrical
SCXG-SVX01H-EN 55
Figure 50. Zone sensor mounting hole locations for: BAYSENS119
2.9 in (73.5 cm)
1.08 in (27.5 mm)
4.68 in (118.9 mm)
1.34 in (34.14 mm)
0.58 in (14.76 mm)
0.31 in (8 mm)
0.12 in (3 mm)
TYP R.07 in
(R1.80 mm)
3.39 in (86 mm)
0.24 in (6.00 mm)
2.62 in (66.5 mm)

Installation - Electrical
56 SCXG-SVX01H-EN
Time Clock Option
Time Clock Installation
1. Ensure operating temperature is between 4°F and
131°F.
2. Locate the time clock at least 5 feet away from any large
electrical contact or machinery to avoid possible
electrical interference problems.
3. Provide a separate independent circuit for the time
clock power supply.
4. Since all electronic instruments are sensitive to
voltage spikes, pay close attention tot he following:
a. If possible, supply power to the electronic time
clock from a phase different than the one
supplying power to the load.
b. Provide a suitableVaristor or RC network across the
INDUCTIVE LOADS supply terminals to reduce
voltage spikes.
c. Place a diode across the DC OPERATED INDUCTOR
terminals to eliminate back EMF.
d. HIGHLY INDUCTIVE LOADS, especially fluorescent
lights, may require a relay in which case step a. and
c. apply.
The time clock can be surface or flush mounted. Lift off the
front cover and loosen the two screws on opposite
corners. Pull off the base’s plug with a left to right rolling
motion.
Time Clock Installation Checklist
1. Ensure operating temperature is 4°F to 131°F.
2. Locate the time clock at least 5 feet away from any large
electrical contact or machinery to avoid possible
electrical interference problems.
3. Provide a separate independent circuit for the time
clock power supply.
4. Since all electronic instruments are sensitive to
voltage spikes, pay close attention to the following:
a. If possible, supply power to the electronic time
clock from a phase different than the one supplying
power to the load
b. Provide a suitableVaristor or RC network across the
INDUCTIVE LOADS supply terminals to reduce
voltage spikes.
c. Place a diode across the DC OPERATED INDUCTOR
terminals to eliminate back EMF.
d. HIGHLY INDUCTIVE LOADS, especially fluorescent
lights, may require a relay in which case (A) and (C)
apply.
The Digi 20A time clock unit can be surface or flush
mounted. Lift off the front cover and loosen the two
screws on opposite corners. Pull off the base’s plug with a
left to right rolling motion.
Surface Mounting Inside Panel
Place screws through the base’s preset holes and screw to
back of panel or wall.
Wire according to the instructions in the following section.
Depending upon the specific installation, you may find it
more convenient to complete wiring before attaching the
base.
Place the terminal cover over the terminal block by
aligning the two screws with the corner holes in the base.
Push the timer firmly onto the plug in the base.Tighten the
two screws. A base for DIN rail mounting is optional.
Wiring the Time Clock
1. Wire 24, 120, or 220VAC to input terminals. Make sure
to apply correct voltage. Using incorrect voltage will
void the warranty.
2. Connect wire to the screw terminals according to the
unit wiring diagrams. Use 12 to 22 AWG wire.
Remote Human Interface Panel
Installation
Human Interface (HI) Panel
The HI enables the user to communicate necessary unit
operating parameters and receive operating status
information from within the occupied space.
Figure 51. Grasslin time clock option
The time clock option has a programmable timer that is factory
wired to the unoccupied input to provide on/off control.The
time clock will not allow the unit to pass through the night
setback/morning warm-up mode, except on units with optional
night heat/morning warm up, or programmable night setback.
See Figure 51, p. 56.
The timeclock, a “Digi 20” by Grasslin, is inside the control
panel, but accessible with the control panel door closed.This
same type timer is also used for programmable night setback/
morning warm up. Programming instructions for the “Digi 20”
timer are in the “Programming” section.

Installation - Electrical
SCXG-SVX01H-EN 57
The HI displays top level information in the LCD window,
unless the operator initiates other displays, for the various
unit functions. It also displays menu readouts in a clear
language 2 line, 40 character format.The 16-key keypad
allows the operator to scroll through the various menus to
set or modify the operating parameters. See Figure 52,
p. 57 to reference the HI keypad.
Remote Human Interface Panel
The remote human interface (RHI) panel is identical to the
unit mounted HI with the exception of the“unit select” key.
This key allows the operator to switch from one unit to the
next to program or view status information regarding a
particular unit.
The RHI functions the same as the unit mounted HI with
two exceptions.The first is the “test start” function.The
operator can view the service parameters, but can only
initiate the service test function at the unit.The RHI door
has a locking screw to deter access by unauthorized
personnel. Additionally, the RHI can control up to four
different units.
Location Recommendations
The HI microprocessor module is mounted inside a
molded plastic enclosure for surface mounting. It is not
weatherproof.Therefore, it is only applicable for indoor
use.
Locate the RHI panel in an area that will ensure the
communication link between the panel and the unit(s)
does not exceed 5,000 feet maximum or pass between
buildings. See Table 39, p. 57.
The run length of the low voltage AC power wiring to the
remote HI must not exceed three (3) ohms/conductor.
Refer to Table 39, p. 57.
Ambient Temperature and Humidity Limits
Ambient Operating Conditions
• Temperature: 32 to 120°F
• Relative humidity: 10 to 90%, non-condensing
Ambient Storage Conditions
• Temperatures: -50 to 200°F
• Relative humidity: 5 to 95%, non-condensing
distance to remote HI recommended wire size
0-460 feet 18 gauge
461-732 feet 16 gauge
733-1000 feet 14 gauge
Mounting the Remote Human
Interface (RHI) Panel
The installer must provide all mounting hardware such as;
hand tools, electrical boxes, conduit, screws, etc. Refer to
Figure 53, p. 59 for the mounting hole and knockout
locations.
Procedure
Refer to Figure 53, p. 59 and follow the procedure below
for mounting the remote HI panel on a 4” by 4” electrical
junction box. Place the microprocessor in a clean dry
location during the enclosure mounting procedures to
prevent damage.
1. Mount an electrical junction box in the wall so that the
front edge of the box will be flush with the finished wall
surface.
2. Prior to mounting the panel, the microprocessor
module must be carefully removed from the enclosure.
To remove the module:
a. Lay the remote panel face up on a flat surface and
remove the locking screw from the right hand
bottom end of the panel.
b. Remove the recessed hinge screw from the left
hand bottom end of the panel.
Figure 52. Human interface (HI) panel keypad
Table 38. Maximum communication link wiring length
max. wire length max. capacitance between
conductors
1,000 ft up to 60 pf/ft
2,000 ft up to 50 pf/ft
3,000 ft up to 40 pf/ft
4,000 ft up to 30 pf/ft
5,000 ft up to 25 pf/ft
Note: pf/ft = picofarads/foot
Table 39. Wiring recommendations for the remote HI
panel

Installation - Electrical
58 SCXG-SVX01H-EN
c. Unlatch the door of the enclosure as if to open it,
and slide the left hand side of the door upward away
from the hinge. Lay it aside.
d. With the key pad visible, remove the two (2) screws
located on the right hand side of the key pad.
e. Carefully slide the key pad plate upward from the
bottom, releasing the extruded hinge pin from its
socket at the top.
f. Set the microprocessor aside until mounting is
complete.
3. Remove the junction box knockout in the back of the
enclosure.
Note: The top of the enclosure is marked “TOP.”
4. With the enclosure in the correct position; align the
mounting holes around the knockout in the enclosure
with the screw holes in the electrical handy box and
secure with the appropriate screws.
5. Replace the microprocessor within the enclosure as
follows:
a. Verify that the terminal block jumpers are
connected properly.
b. Slide the extruded hinge pin at the top left of the key
pad plate into the hole located at the top left hand
side of the enclosure.
c. Slide the bottom of the plate into place, aligning the
two (2) clearance holes with the screw holes on the
right. Install the screws but do not tighten.
Note: If the two screws are not installed as called out in
the previous step, hold against the key pad plate
while installing the door in the next step, to prevent
it from falling out.
d. Slide the extruded hinge pin at the top left of the
door into the hole located under the bottom left side
of the display.
e. Install and tighten the hinge screw located at the
bottom left side of the enclosure.
Wall Mounting the RHI Panel
1. Prior to mounting the panel, the microprocessor
module must be removed from the enclosure.
Complete step 2 in the previous discussion,“Mounting
on a 4 in. x 4 in. Electrical Box,” before proceeding.
2. With the microprocessor removed, refer to Figure 53,
p. 59 for the location of the mounting holes to be used
for wall mounting.
3. Place the enclosure against the mounting surface and
mark the mounting holes.
Note: The top of the enclosure is marked with “TOP.”
4. With the enclosure in the correct position, remove the
enclosure and drill the necessary holes in the surface
for the appropriate fasteners, (plastic anchors, molly
bolts, screws, etc.)
5. Remove the necessary knockouts for the wire or
conduit entry before mounting the panel.
6. Place the enclosure back onto the surface and secure it
with the appropriate screws.
7. Follow step 5 in the previous section, “Mounting on a
4” by 4” Electrical Box,” to replace the microprocessor
within the enclosure.

Installation - Electrical
SCXG-SVX01H-EN 59
Wiring the Remote Human
Interface
Figure 53. Remote HI mounting holes and knockout locations
WARNING
Proper Field Wiring and Grounding
Required!
All field wiring MUST be performed by qualified
personnel. Improperly installed and grounded field
wiring poses FIRE and ELECTROCUTION hazards.To
avoid these hazards, you MUST follow requirements for
field wiring installation and grounding as described in
NEC and your local/state electrical codes. Failure to
follow code could result in death or serious injury.

Installation - Electrical
60 SCXG-SVX01H-EN
The remote human interface requires 24 VAC+4volts
power source and a shielded twisted pair communication
link between the remote panel and the interprocessor
communication bridge (ICPB) module at the self-
contained unit.
Field wiring for both the low voltage power and the
shielded twisted pair must meet the following
requirements:
Important: To prevent control malfunctions, do not run
low voltage wiring (30 volts or less) in
conduit with higher voltage circuits.
1. All wiring must be in accordance with NEC and local
codes.
2. Reference Table 39, p. 57 for recommended wiring
distance and size.
3. Communication link wiring must be 18 AWG shielded
twisted pair (Belden 8760, or equivalent).
4. Communication link must not exceed 5,000 feet
maximum for each link. See Table 38, p. 57.
5. Do not run communication link between buildings.
Low Voltage (AC) Field Wiring Connections
To access the wire entry locations, open the RHI panel door
and remove the two screws on the right-hand side of the
key pad. Swing the keypad open, exposing both the wire
entries and the back of the HI module. Refer to Figure 53,
p. 59 and connect one end of the three conductor 24 volt
wires to the remote panel terminal strip (+), (-), and
(ground).
Communication Link (Shielded Twisted Pair)
Wiring
Trim the outer covering of the shielded cable back
approximately 1 inch. See Figure 54, p. 60. Do not cut the
bare shield wire off. Strip approximately 1/2-inch of
insulation from each insulated wire to connect them to the
terminal strip at the remote panel.
Connect the white lead to the positive (+) terminal, the
black lead to the negative (-) terminal, and the bare shield
wire to the terminal at the remote human interface panel.
Close the key pad plate. Install and tighten the two screws
removed earlier. Close the outer door and install the
recessed locking screw at the bottom right hand side of the
enclosure to prevent accidental starting of the unit by
unauthorized personnel while completing the wiring at the
self-contained unit.
At the Self-Contained Unit
Connect the opposite end of the three conductor 24-volt
wire to the appropriate terminal strip as follows:
Note: Although the 24 volt power is not polarity sensitive,
do not connect either the + (plus) or - (minus)
terminals from the remote panel to ground at the
self-contained unit.
Connect the wire connected to the positive (+) terminal at
the remote panel. Connect the wire connected to the
negative (-) terminal at the remote panel. Connect the
ground wire from the remote panel to the unit control
panel casing.
WARNING
Hazardous Voltage w/Capacitors!
Disconnect all electric power, including remote
disconnects and discharge all motor start/run
capacitors before servicing. Follow proper lockout/
tagout procedures to ensure the power cannot be
inadvertently energized. For variable frequency drives
or other energy storing components provided by Trane
or others, refer to the appropriate manufacturer’s
literature for allowable waiting periods for discharge of
capacitors.Verify with an appropriate voltmeter that all
capacitors have discharged. Failure to disconnect
power and discharge capacitors before servicing could
result in death or serious injury.
For additional information regarding the safe discharge
of capacitors, see PROD-SVB06A-EN
Figure 54. Dressing shielded twisted wire

Installation - Electrical
SCXG-SVX01H-EN 61
Interprocessor Communication Bridge Module
Wiring
Trim outer covering of shielded cable back approximately
1”.SeeFigure 54, p. 60. Cut bare shield wire even with
outer covering. Strip approximately 1/2” of insulation
from each insulated wire to connect to terminal strip at
unit. Wrap tape around any exposed foil shield and base
shield wire.
Note: The communication link is polarity sensitive.
See unit wiring diagram and connect white lead to positive
(+) terminal and black lead to negative (-) terminal. (These
terminals are numbered. Reference to color is for
clarification to maintain polarity).
Note: To maintain polarity, do not connect the base shield
wire to ground at the self-contained unit.
Connecting to Tracer Summit
IntelliPak commercial self-contained (CSC) units operate
withTrane building automation software,Tracer Summit
version 10.0.4 or later or any OS2 operating system.
Note: Tape non-insulated end of shield on shielded wire
at unit. Any connection between shield and ground
will cause a malfunction. If daisy-chained in unit,
splice and tape shields to prevent contact with
ground.
Communication Wiring
Note: Communication link wiring is shielded, twisted pair
of wire and must comply with applicable electrical
codes.
An optional communication link provides a serial
communication interface (SCI) betweenTracer Summit
and each commercial self-contained (CSC) unit in the
system.The CSC system can have a maximum of 12 CSC
units per connection link toTracer Summit. Use a single 18
AWG shielded, twisted pair wire with stranded, thinned
copper conductors to establish each communication link
betweenTracer Summit and each unit.
Programming theTime Clock
Option
Setting the Time
Important: Depress the reset key before beginning to
set time and program.
1. Select military (24:00 hr.) or AM/PM (12:00 hr.) time
mode by depressing and holding the “h” key while
pressing “+ 1h” key to toggle between military and
AM/PM. (AM appears in the display when in AM/PM
mode.)
2. Press and hold down “” key.
3. If setting the time when daylight savings time is in
effect, press “+ 1h” key once (+ 1h will appear in
display).
4. Set hour with “h” key. If AM or PM does not appear in
display, the unit is in military time. See note above to
change display.
5. Set minutes with “m” key.
6. Press “Day” key repeatedly to the day of the week. (1
is Monday, 7 is Sunday)
7. Release “” key, colon will begin flashing.
Note: If keys h + or m + are kept depressed for longer than
2 seconds, a rapid advance of figures will result.
The “Digi 20” electronic time switch is freely
programmable for each day of the week in one minute
increments. For easy and quick programming, the
following 4 block programs are available:
• Monday through Sunday
• Monday through Saturday
• Monday through Friday
• Saturday and Sunday
Programming
Follow the instructions below for programming the time
clock.
1. Press “Prog.” key. 1234567 AM—:— will appear in
display. (Pressing “Prog.” key again, display will show
the number of free programs “Fr 20”). Press again to
RETURN to 1st program.
2. Press “”key,“” ON symbol will appear. Pressing
the key again will toggle to OFF “”. Select ON or OFF
for the program.
3. Press “h+” to select hour for switching time.
4. Press “m+” to select minute for switching time.
5. If the program is to occur every day of the week, (24
hour time control) ignore “Day” key and press “Prog.”
key to advance to program.
6. For 7 day time control, press “Day” key. 123456
(Monday through Saturday) block of days appears in
display. Pressing “Day” key again,12345(Monday
WARNING
Hazardous Voltage w/Capacitors!
Disconnect all electric power, including remote
disconnects and discharge all motor start/run
capacitors before servicing. Follow proper lockout/
tagout procedures to ensure the power cannot be
inadvertently energized. For variable frequency drives
or other energy storing components provided by Trane
or others, refer to the appropriate manufacturer’s
literature for allowable waiting periods for discharge of
capacitors.Verify with an appropriate voltmeter that all
capacitors have discharged. Failure to disconnect
power and discharge capacitors before servicing could
result in death or serious injury.
For additional information regarding the safe discharge
of capacitors, see PROD-SVB06A-EN

Installation - Electrical
62 SCXG-SVX01H-EN
through Friday) appears in display. Repeated presses
will cycle through all days of the week and back to 1
through 7 (Monday through Sunday). Select day or
block of days desired.
7. Press “Prog.” key and repeat steps 2 through 6a to
enter additional programs of ON and OFF times. (Note
that more than one OFF time may be programmed,
enabling automatic control or manual overrides.)
8. Press “” key to enter run mode.
To review and change programs:
1. To review a program at any time, press “Prog.” key.
Programs display in the sequence they were entered
with repeated presses of “Prog.” key.
2. To change a program, select that program as outlined
in step 1. Enter the time of day and days of week just as
in the programming steps above.The old program is
overwritten with the new selections. Press “Prog.” to
store the new program.
3. To delete an individual program, select the program as
in step 1 and press “h” and “m” keys until “—:—”
appears in the display. Press either “Prog.” or “¹” key
until “—:—” flashes.The program is deleted after a few
seconds.
Manual Override
While in the “run” mode (“” symbol is displayed),
pressing the “” key will reverse the load status (switch
load off if it is on, or switch it on if it is off). A hand symbol
appears in the display to indicate the override is active. At
the next scheduled switching time, automatic time control
resumes, eliminating the override.
Pressing the “” key a second time “” appears in the
display indicating the load is permanently on.
Pressing the “” key a third time “” appears in the
display indicating the load is permanently off.
Pressing the “” key a fourth time returns to automatic,
“” appears in the display.
All days shown in the respective blocks will switch on (or
off) at the selected hour and minute.

SCXG-SVX01H-EN 63
Operating Principals
Control Sequences of Operation
Occupied/Unoccupied Switching
There are four ways to switch occupied/unoccupied:
1. Night setback zone sensor
2. Field-supplied contact closure (hard wired binary input
to RTM)
3. Tracer Summit
4. Factory-mounted time clock
Field Supplied Occupied/Unoccupied Input on
the RTM
This input accepts a field supplied switch or contacts
closure, such as a time clock, with a rating of 12 mA at 24
VDC minimum.
Tracer Summit System
TheTracer Summit system can control the occupied/
unoccupied status of the self-contained unit.
Factory Mounted Time Clock
A time clock can control the occupied/unoccupied status of
the self-contained unit.
Unoccupied Sequence of
Operation
The unoccupied mode helps conserve energy during
times when a building is usually unoccupied. When in
unoccupied mode, the unit will control to the unoccupied
setpoints (usually a lower heating setpoint and higher
cooling setpoint). Setpoints can be programmed at the HI,
Tracer Summit, or the night setback zone sensor.
The unit enters the unoccupied mode when the RTM
receives a closed signal on the unoccupied input for more
than five seconds. For units with supply air temperature
control entering unoccupied mode, the following
sequence will occur:
• Heating/cooling functions cease and the economizer
option closes fully.The supply fan shuts down for
proper cool-down time of the heat exchanger.
However, the supply fan may remain on for a short
period of time.
• After the supply fan shuts down, the occupied/
unoccupied relay energizes. Also, the VAV box stroke
time begins.The VAV box stroke time is field
adjustable to allow time forVAV boxes to go to the full
open airflow position.
• After the max VAV box stroke time expires, the supply
fan, economizer (if enabled), compressors, and heat
are enabled to satisfy the unoccupied zone
temperature setpoints.
Note: Unoccupied economizer operation can be enabled
or disabled at the HI or usingTracer Summit.
For units without volume control entering unoccupied
mode, the following sequence will occur:
• The occupied/unoccupied relay energizes and the
economizer option fully closes.
• The fan mode is set to auto and the unit will control to
the unoccupied zone temperature setpoints.
With MWU enabled at the HI, if the zone temperature is
below the MWU setpoint, the unit enters the MWU mode.
Morning Warmup
This feature can be enabled at the HI, and can be used with
factory or field-installed heat. If MWU is not required
disable the function in the setup menu at the HI. MWU
transitions the zone from unoccupied to occupied. It will
heat until the MWU setpoint is met.The unit is then
released to occupied mode. Supply duct static pressure is
maintained during this sequence. MWU can be set (at the
HI) to function as either full or cycling capacity.
Full Capacity Morning Warmup (MWU)
Full capacity morning warmup uses full heating capacity
to heat the zone as quickly as possible. Full heating
capacity is provided until the morning warmup setpoint is
met. At this point, the unit is released to daytime mode.
Cycling Capacity Morning Warmup (MWU)
Cycling capacity morning warmup provides a more
gradual heating to overcome“building sink” as the zone is
heated. Normal zone temperature control with varying
capacity is used to raise the zone temperature to the MWU
zone temperature setpoint.This method of warmup is
used to overcome the “building sink” effect.
See Figure 55, p. 63 for a pictorial explanation of the
cycling MWU sequence. Cycling capacity MWU will heat
until MWU temperature setpoint is reached. Next a 60
minute timer begins. If the building load reaches the MWU
ventilation setpoint, or the 60 minutes expire, whichever is
first, the airside economizer will control to the minimum
position. MWU will end when the zone temperature rises
above the MWU terminate setpoint.
Figure 55. Typical cycling morning warmup cycle

Operating Principals
64 SCXG-SVX01H-EN
Timed Override Activation - ICS™
This function is operational whenever the unit’s RTM
module is used as the zone temperature sensor source,
which can be set at the HI panel. When this function is
initiated by the push of the override button on the zone
sensor, the unit will switch to the occupied mode. Unit
operation (occupied mode) during timed override is
terminated by a signal fromTracer.
Timed Override Activation - Non-ICS
This function is active whenever the unit’s RTM module
board is selected as the zone temperature source, which
can be set at the human interface panel. When this
function is initiated by the push of the override button on
the zone sensor, the unit will switch to the occupied mode.
Automatic cancellation of the timed override mode occurs
after three hours of operation.
VAV Drive Max Output
This is a single-pole, double-throw relay rated at a
maximum voltage of 24 vac, two amps max.The relay
contacts of this relay switch when the unit goes from the
occupied mode to the unoccupied mode by means of the
unoccupied binary input, night setback zone sensor, or
Tracer Summit.The contacts will stay switched during the
unoccupied and morning warmup mode.They will return
to the position shown on the unit wiring diagram when the
unit returns to the occupied mode. The intent of this
binary output is to signal the VAV boxes or other terminal
devices to go to a full open airflow position.
Occupied Sequence
All setpoints can be adjusted using the HI panel. Also,
cooling/heating setpoints can be adjusted in the zone, if
using one of the zone sensor options (BAYSENS020,
BAYSENS021, BAYSENS108, BAYSENS110, BAYSENS019,
or BAYSENS074). For a complete list of unit setpoint
default values and ranges, see the IntelliPak Self-
Contained Programming Guide, PKG-SVP01*-EN.
Occupied Zone Temperature - Cooling
The unit transitions from unoccupied to occupied when
the occupied/unoccupied input on the RTM is open for
more than five seconds after having been closed.This
input can be received fromTracer Summit, the remote
NSB zone sensor, the timed override function, or a field
supplied contact. Dependent on unit options and the HI
programming, the following sequence will occur:
• The unit will begin MWU and then switch to the
occupied mode after the MWU setpoint is met.
• Purge will be enabled byTracer Summit.ThenTracer
Summit will enable the occupied mode.
• The unit will switch from unoccupied to occupied
control immediately.
Upon entering occupied mode, the supply fan remains on.
The occupied/unoccupied relay will de-energize.
Zone Temperature Control (Unit Model
NumberDigit9=4or5)
A zone sensor located directly in the space sends input to
the RTM while the CV unit is in occupied cooling mode.
When the unit is in occupied cooling, the RTM controls the
zone temperature within the cooling setpoint deadband by
modulating the economizer option and/or staging
mechanical cooling on and off as required.
Supply Air Temperature Control (Unit Model
NumberDigit9=1,2,3,or6)
When the VAV unit is in occupied cooling, the RTM
controls the supply air temperature to the specified supply
air cooling setpoint by modulating the economizer option
and/or staging mechanical cooling on and off as required.
The changeover relay contacts (field supplied) must be
open on units with hydronic heat for cooling to operate.
Cooling
Upon entering occupied mode, the RTM receives an input
from either the HI, RHI,Tracer Summit, or the GBAS to start
the supply fan.The RTM supply fan contacts close and
energize the supply fan contactor. When the supply fan
starts, the fan proving switch closes, signaling the RTM
that airflow is established.The VFD will ramp the fan, and/
or the airside economizer dampers will open to the user-
defined minimum position.
When a cooling request is sent to the RTM from the zone
sensor, the RTM evaluates the system operating
conditions using the supply air and outdoor temperature
input before sending the request to the MCM for
mechanical cooling. If outdoor conditions (temperature
and humidity) are suitable or the EWT is within specified
setpoints, the RTM will attempt to use “free cooling”
without using any compressors.The RTM will use either
the airside or waterside economizer option.When outdoor
air conditions are not suitable, only mechanical cooling
will function and outside air dampers will remain at their
minimum position. If the unit does not have an
economizer, mechanical cooling will operate to satisfy
cooling requirements.
Units With Economizer
If the entering condenser water temperature (units with a
WSE) or the outside air enthalpy (units with an ASE) is
appropriate to use “free cooling,” the economizer will
attempt to satisfy the cooling zone temperature setpoint.
Note: When using an ASE with economizer enabled, O/A
temperature enable can be used instead of
comparative enthalpy if the O/A temperature falls
below the economizer setpoint.
Then compressors will stage on as necessary to maintain
supply air temperature setpoint, which is user-defined at
the HI. Minimum on/off timing of compressors prevents
rapid cycling.
When both airside and waterside economizers are on a
single unit, priority must be set at the HI.The economizer

Operating Principals
SCXG-SVX01H-EN 65
with the highest priority attempts cooling first. Once it is
operating at its maximum, and if additional cooling is
necessary, the other economizer enables before
mechanical cooling begins.
Cooling/Waterside Economizer
Waterside economizing enables when the unit’s entering
water temperature is below the unit’s entering mixed air
temperature by 4°F plus the user adjustable economizer
approach temperature.The approach temperature default
is 4°F.
Waterside economizing disables when the unit’s entering
water temperature is not below the unit’s entering mixed
air temperature by at least the water economizer approach
temperature (default value of 4°F).The economizer acts as
the first stage of cooling. If the economizer is unable to
maintain the zone (CV units) or supply air (VAV units)
temperature setpoint, the compressor module will bring
on compressors as required to meet the setpoint.
Cooling/Airside Economizer
On units with an airside economizer, a call for cooling will
modulate the fresh air dampers open.The rate of
economizer modulation is based on deviation of the zone
temperature from setpoint; i.e., the further away from
setpoint, the faster the fresh air damper will open.The first
stage of cooling will start after the economizer reaches full
open.
Note: The airside economizer will only function freely if
ambient conditions are below the enthalpy control
settings or below the return air enthalpy if unit has
comparative enthalpy installed. If outside air is not
suitable for “economizing,” the fresh air dampers
drive to the minimum open position. A field
adjustable, factory default setting at the HI panel or
Tracer Summit can provide the input to establish
the minimum damper position.
When outdoor air conditions are above the setpoint or
comparative enthalpy control setting, only mechanical
cooling will function and outside air dampers will remain
at their minimum position.
Mechanical Cooling
If the zone temperature cannot be maintained within the
setpoint deadband using the economizer option or if there
is no economizer, the RTM sends a cooling request to the
MCM.The compressor module checks the compressor
protection circuit before closing stage one. After the first
functional stage starts, the compressor module monitors
the saturated refrigerant temperature and closes the
condenser fan output contact when the saturated
refrigerant temperature rises above the lower limit
setpoint.
Air-Cooled Units Only
The compressor module closes the condenser fan output
contact when the saturated refrigerant temperature rises
above the lower limit setpoint.
Water-Cooled Units Only
The WSM modulates the condenser coil water valves to
maintain condenser temperature, if applicable. Otherwise,
it will check the entering condenser water temperature to
ensure it is greater than 54°F or if not, it will lock out
cooling.
Auto Changeover (Units with Heat Only)
When the system mode is in auto, the mode will change to
cooling or heating as necessary to satisfy the zone cooling
and heating setpoints.The zone cooling and heating
setpoints can be as close as 2°F (1.1°C).
Occupied Zone Temperature - Heating
Relies on input from a sensor directly in the space, while
a system is in occupied heating mode or an unoccupied
period, to stage electric heat on and off or modulate the
hydronic heating valve as required to maintain the zone
temperature within the heating setpoint deadband.The
supply fan will operate when there is a request for heat.
Electric Heat
On units with electric heat, the zone temperature can be
controlled to a heating setpoint during the occupied mode
by cycling a single stage electric heater. An interface is
provided for field supplied single stage electric heat.The
zone temperature heating setpoint and deadband are user
defined at the HI panel.
Hydronic Heat: Hot Water or Steam
On units with hot water or steam heating, the zone
temperature can be controlled to a heating setpoint during
the occupied mode.The zone temperature heating
setpoint and deadband are user defined at the HI panel or
zone sensor. VAV occupied heating initiates by closing a
field-supplied switch or relay contacts connected to the
changeover input on the RTM. Supply air static pressure is
maintained.
Supply Air Setpoint Reset (VAV Units Only)
Supply air reset can be used to adjust the supply air
temperature setpoint on the basis of a zone temperature or
outdoor air temperature. Supply air reset adjustment is
available at the HI panel for supply air heating and supply
air cooling control.
Reset based on outdoor air temperature
Outdoor air cooling reset is sometimes used in
applications where the outdoor temperature has a large
effect on building load.When the outside air temperature
is low and the building cooling load is low, the supply air
setpoint can be raised, thereby preventing subcooling of
critical zones.This reset can lower usage of mechanical
cooling, thus savings in compressor kW, but an increase in
supply fan kW may occur.
Outdoor air heating reset is the inverse of cooling, with the
same principles applied.

Operating Principals
66 SCXG-SVX01H-EN
For both outdoor air cooling reset and heating reset, there
are three user defined parameters that are adjustable
through the human interface panel.
• Beginning reset temperature
• Ending reset temperature
• Maximum amount of temperature reset
Reset based on zone temperature
Zone reset is applied to the zone(s) in a building that tends
to overcool or overheat. The supply air temperature
setpoint is adjusted based on the temperature of the
critical zone(s).This can have the effect of improving
comfort and/or lowering energy usage.The user-defined
parameters are the same as for outdoor air reset.
Supply Air Tempering
(Hot Water and Steam VAV Units Only)
When supply air temperature falls below the supply air
temperature deadband low end, the heating valve
modulates open to maintain the minimum supply air
temperature setpoint.
Daytime Warmup(Units with Supply Air
Temperature Control Only)
During occupied mode, if the zone temperature falls to a
preset, user-defined zone low limit temperature setpoint,
the unit is put into daytime warmup.The system changes
over to CV heating, the VAV boxes drive full open.
However, unit airflow modulation control operates to
maintain duct static setpoint, and full heating capacity is
provided until the daytime warmup setpoint is reached.
The unit is then returned to normal occupied mode.
Supply Air Tempering
Supply air tempering is available on units without volume
control and with hot water, steam, or electric heat or units
with supply air temperature control with steam or electric
heat. When the unit is in heat mode but not actively
heating, if the supply air temperature drops to 10°F (5.5°C)
below the occupied zone heating temperature setpoint,
electric heat will stage on or the hydronic valve will
modulate to maintain a minimum supply air temperature.
The unit transitions out of heat mode if the supply air
temperature rises to 10°F (5.5°C) above the occupied zone
heating temperature setpoint.
Changeover
This mode only functions on units with supply air
temperature control with hydronic heat. When the
changeover binary input is closed the unit will control to a
discharge air heating setpoint.This setpoint is entered
from the HI, and can be a higher temperature than the
supply air cooling setpoint.This function maintains duct
static pressure.
Thermostatic Expansion Valve
Refrigerant system reliability and performance is heavily
dependent upon proper superheat.The importance of
maintaining the proper superheat cannot be
overemphasized. Accurate measurements of superheat
will provide the following information:
• How well expansion valve is controlling refrigerant
flow.
• Efficiency of the evaporator coil.
• Amount of protection compressor is receiving against
flooding.
The expected range for superheat is 14-20°F at full load
conditions. At part load, expect a properly adjusted
expansion valve to control to 8-12°F superheat. Systems
operating with lower superheat could cause serious
compressor damage due to refrigerant floodback.
Compressors
Units use two compressors of 10 and 15 hp.When viewing
the front of the unit, compressors are identified A and B
from left to right.The second compressor from the left, or
B compressor, is always the first to come on, unless locked
out for a malfunction or shut off on frost protection. Refer
to Table 40, p. 67 for compressor cycling stages and
Table 1, p. 11 for percent cooling capacity by stage.
The control system logic permits compressor operation
only after the supply fan is on. If the supply fan shuts down,
compressors will not operate. Units without head
pressure control (units with intermediate piping packages)
will lock out mechanical cooling when the entering
condenser water temperature falls below 54°F. Mechanical
cooling will resume when the entering condenser water
temperature exceeds 58°F.
Compressor Cycling
Compressors cycle to maintain the operating state
required by the temperature controls. In the event of a
compressor failure, the next available compressor turns
on. Refer to Table 40, p. 67 for compressor cycling by unit
model and tons.
During normal conditions, compressors will not shut off
until they have been on for at least three minutes and will
not turn on until they have been off for at least three
minutes. Normal operating conditions are established on
an individual compressor basis. When a compressor
starts, its timer also starts.The compressor evaporator
NOTICE:
Compressor Damage!
Systems operating with lower superheat than
recommended could cause serious damage to the
compressor.

Operating Principals
SCXG-SVX01H-EN 67
circuit frost protection can override the “minimum” timer
and reduce the five minute minimum required time
period.
When the unit is powered up, or manually reset there will
be a three to eight minute delay before the first
compressor may be turned on as requested by the unit
temperature control algorithm.
Compressor Lead/Lag Operation
Compressor lead/lag is a user-selectable feature at the HI
panel and is available on all units. After each request for
compressor operation, the lead refrigeration circuit or
compressor switches, thereby causing a more equitable or
balanced run time among compressors.
When lead/lag is enabled, each time the system cycles, it
will alternate between the standard compressor staging
and the lead/lag staging. Using Table 40, p. 67, a SXWG
30-ton unit will first stage compressor B then A, then AB
for first cycle and A, then AB for the second cycle.
Appropriate condenser valves (water-cooled and
condenser fans (air-cooled) will stage with appropriate
compressors to maintain saturated condensing
temperature. Enabling lead/lag may drop a cooling stage
when compared to standard staging. See Table 40, p. 67
for compressor staging.
Step Control
Steps of mechanical cooling are control based on supply
air or zone temperature. See Table 40, p. 67 for
compressor staging.
Capacity is based on an integrating control concept.The
unit capacity matches the existing load and maintains an
average supply air temperature within the supply air
setpoint temperature control band region.
The supply air temperature control band is centered
around supply air temperature setpoint and is adjustable
from 2 to 12°F. In a steady state, the unit will either
maintain a constant level of cooling capacity with the
supply air temperature within the control band, or the
highest active cooling level will cycle to provide an
average supply air temperature equal to the setpoint.
If the supply air temperature swings outside the limits of
the control band, the mechanical cooling capacity will
increase or decrease by one level accordingly.The change
occurs by integrating the temperature offset from the
control band limit.
A minimum time delay of five minutes follows each
change in cooling level.This time delay promotes stability
by allowing the system to respond to the change before
any further control action occurs. As the supply air
temperature approaches setpoint, the time duration
between changing levels of cooling capacity increases.
See Figure 56, p. 68 for the typical unit operating curve.
Figure 57, p. 68 shows typical unit performance when
supply air temperature swings exceed the control band
limits.
Adjust the supply air temperature control band according
to the desired unit performance. Increasing the control
band reduces the equipment cycle rate and increases the
maximum potential supply air temperature deviation from
setpoint. Conversely, decreasing the control band reduces
the maximum potential temperature deviation, but
increases the compressor cycle rate.
Follow these recommendations concerning the supply air
temperature control band settings based on expected unit
sizing:
2 Cooling stage unit: 9°F
3 Cooling stage unit: 7°F
4 Cooling stage unit: 6°F
Table 40. Compressor stages.
Unit Size
Refrigerant
Circuit Type
Model # Digit 5
Compressor HP
by Stage Standard
Compressor
Staging
Lead/Lag
Compressor
Staging
SCM
or
MCMAB
SXWG 20, 25
SXRG 20 Independent 10 10 B/AB A/AB MCM
SXWG 30
SXRG 25 Independent 15 10 B/A/AB A/AB MCM
SXWG 35
SXRG 32 Independent 15 15 B/AB A/AB MCM

Operating Principals
68 SCXG-SVX01H-EN
Compressor Safety Devices
If a compressor low pressure cutout opens during
compressor start-up, the UCM will not shut the
compressor off during the first two to three minutes after
start-up.This prevents possible nuisance trips during low
ambient start conditions. SeeTable 41.
Each compressor’s discharge line contains a high pressure
cutout. Under abnormal operating conditions, the cutout
will open to stop compressor operation.
Low Ambient Compressor Lockout
This function will lock out the compressor if the outdoor air
temperature sensor reads an outdoor temperature below
the low ambient compressor lockout temperature
setpoint.This setpoint is adjustable at the human interface
panel. Compressors will lock out when outdoor air
temperature falls below that selected temperature and will
start again when the temperature rises 5°F above the
setpoint.
Evaporator Coil Frost Protection FROSTAT™
The FROSTAT™ system eliminates the need for hot gas
bypass. It utilizes an evaporator temperature sensor
mounted on the suction line near theTXV bulb of each
circuit to protect the evaporator from freezing.
If the evaporator temperature approaches the specified
setpoint (adjustable between 25 and 35°F at the HI) the
compressor(s) will cycle off.The supply fan remains on to
help de-ice the coil.The compressors will restart when the
evaporator temperature has risen 10°F above the specified
cutout temperature and when the compressor(s) have
been off a minimum of three minutes.This prevents rapid
cycling of the compressors.
Service Valve Option
If ordered, service valves are factory installed on each
circuit before and after the compressor to allow
compressor isolation for servicing.Waterside
Components.
Waterside Components
Waterside components consist of water piping, water
valves, water flow switch option, water cooled condensers
(SXWG only), and the economizer option.
Figure 56. Typical pulldown curve for unit operating properly within control band
Figure 57. Typical pulldown curve for unit operating improperly outside control band
Table 41. Pressure cutouts (open/close)
Unit Model High Pressure
Cutout Low Pressure
Cutout
SXWF 553/424 49/74
SXRF 650/500 36/61

Operating Principals
SCXG-SVX01H-EN 69
Water Purge
This user-definable feature allows the user to select a
purge schedule to automatically circulate water through
the economizer and condensers periodically during non-
operational times.This allows fresh chemicals to circulate
in waterside heat exchangers. This feature is on all units
and is defined at the HI.
Water Piping Options
Water piping is factory-installed with left-hand
connections on units without a waterside economizer.
Units can be ordered with either basic piping or
intermediate piping. Also, units with waterside
economizers can be set for either variable or constant
water flow at the HI. SeeFigure 58, p. 70 and Figure 59,
p. 70 for detailed piping configuration information.
With compatible piping configurations, the unit can be
configured to provide:
1. Constant water flow with basic or intermediate piping
or
2. Variable water flow (head pressure control) with
intermediate piping only.
Constant water flow is for condenser pumping systems
that are not capable of unloading the water-pumping
system. Variable water flow maximizes energy saving by
unloading the water pumping system.
Basic Water Piping
This option is available on units without a waterside
economizer and with condenser water applications above
54°F (12.2°C) that do not require condensing pressure
control. Left hand water connections and piping are
extended to the unit exterior. Manifold piping is factory
installed.
Intermediate Water Piping
This option provides condensing temperature control
when the unit is configured (user defined at the HI) for
variable water flow with or without a waterside
economizer. A two-way modulating control valve is wired
and installed in the unit to maintains a specific range of
water temperature rise through the condenser when
entering fluid temperature is less than 58°F (15°C).This
option allows the compressor to operate with entering
fluid temperature down to 35°F (2°C).The minimum valve
position to maintain minimum condenser flow rates is
user-defined at the HI.This valve drives closed if the unit
shuts down or if a power failure occurs.
Water Flow Switch Option
A water flow switch is factory installed in the condenser
water pipe within the unit. Whenever the flow switch
detects a water flow loss prior to or during mechanical
cooling, compressor operation locks out and a diagnostic
code displays. If water flow is restored, the compressor
operation automatically restores.
Water-Cooled Condensers
Units that are set up for variable water flow will modulate
a water valve to maintain a user-defined condensing
temperature setpoint. Condensing temperature will be
referenced utilizing factory installed sensors located at
each condenser.
Waterside Economizer Option
The waterside economizer option takes advantage of
cooling tower water to either precool the entering air to aid
the mechanical cooling process or, if the water
temperature is low enough, provide total system cooling.
Waterside economizing enables when the unit’s entering
water temperature is below the unit’s entering mixed air
temperature by a minimum of 4°F plus the economizer’s
approach temperature.The approach temperature default
is 4°F. Waterside economizing disables when the unit’s
entering water temperature is not below the unit’s
entering mixed air temperature by at least the water
economizer approach temperature.The approach
temperature defaults to 4°F.The economizer acts as the
first stage of cooling. If the economizer is unable to
maintain the supply air setpoint, the unit control module
brings on compressors as required to meet the setpoint.
The waterside economizer includes a coil, modulating
valves, controls, and piping with cleanouts.The coil
construction is ½-inch (13 mm) OD seamless copper tubes
expanded into aluminum fins.The evaporator and
economizer coils share a common sloped (IAQ) drain pan.
Drain pan options are either galvanized or stainless steel,
and are insulated and internally trapped.
The waterside economizer coil is available with either a
two or four row coil, with no more than 12 fins per inch.
The tubes are arranged in a staggered pattern to maximize
heat transfer.The coil has round copper supply and return
headers with removable cleanout and vent plugs.The
optional mechanical cleanable economizer has removable
cast iron headers to allow easy mechanical cleaning of the
tubes.The waterside working pressure is rated for 400
psig (2758 kPa).
NOTICE:
Proper Water Treatment!
The use of untreated or improperly treated water could
result in scaling, erosion, corrosion, algae or slime. It is
recommended that the services of a qualified water
treatment specialist be engaged to determine what
water treatment, if any, is required.Trane assumes no
responsibility for equipment failures which result from
untreated or improperly treated water, or saline or
brackish water.
Table 42. Condenser water piping connection sizes
Unit Size Inlet Pipe Outlet Pipe
SXWG 20, 25, 30, 32, 35 2 1/2 NPT 2 1/2 NPT

Operating Principals
70 SCXG-SVX01H-EN
Waterside Economizer Flow Control
Units equipped with a waterside economizer can be set
from the human interface panel for variable or constant
water flow.
Constant Water Flow
Two-way modulating control shutoff valves are wired,
controlled, and installed in the unit. One valve is located in
the economizer’s water inlet, and the other is in the
condenser bypass water inlet. When the waterside
economizer enables, the two-way valves modulate to
maintain the discharge air temperature setpoint. As the
economizer valve opens, the condenser bypass valve
closes, and vice versa. Full water flow is always
maintained through the condensers. Both valves will close
in the event of a power failure.
Variable Water Flow
Two-way modulating control shutoff valves are wired,
controlled, and installed in the unit. One valve is located in
the economizer’s water inlet, and the other is in the
condenser water inlet. When the economizer valve is
active, the condenser bypass valve closes.The
economizer valve modulates, thus water flow through the
unit modulates. If the water is cool enough for
economizing, but mechanical cooling is also required, the
economizer valve fully opens to establish full water flow
through the condensers. Whenever the water is too warm
for economizing and there is a call for cooling, the
economizer valve fully closes and the bypass valve fully
opens, establishing full water flow through the
condensers. Full water flow is always maintained through
the condensers when mechanical cooling is required. Both
valves close whenever cooling is not required, and in the
event of a power failure.
Figure 58. Intermediate piping with waterside economizer, variable or constant water flow
V2
Condenser 2
V1
Economizer
Condenser 1
Figure 59. Intermediate water piping, variable water flow (L) and basic water piping, constant water flow (R)
Condenser 1
Condenser 2
V2
Condenser 1
Condenser 2

Operating Principals
SCXG-SVX01H-EN 71
Unit Airside Components
The unit’s air delivery system consists of dampers,
enthalpy switch option, airside economizer option, filters,
low ambient sensors, and factory mounted single or
double wall plenums.
Supply Air Fan
The unit has a single supply fan that runs at a constant
speed. However, the fan may have the VFD option that
modulates airflow based on supply air temperature
control. Pressing the stop key on the HI will turn the supply
fan off.The fan is on continuously when a CV unit is in
occupied mode and except when a unit is in the night heat/
morning warmup mode. During the night heat and setback
mode the fan cycles on and off in response to a call for
heat.
Low Entering Air Temperature Sensor
This is standard on all units with a hydronic coil or
waterside economizer. It can also be ordered as an option.
A thermostat limit switch is factory mounted on the unit’s
entering air side with a capillary tube serpentine across the
coil face. If the temperature falls below 35°F (2°C), the fan
shuts down and the waterside economizer and/or
hydronic heat valve options open to allow full water flow.
The heat output also energizes.A manual reset is required.
The low entering air temperature setpoint is adjustable at
the HI.
High Duct Temperature Thermostat
A factory-supplied temperature limit switch with reset
element detects the supply air duct temperature.This
sensor should be field-installed downstream from the
unit’s discharge in the supply air duct. If the supply air duct
temperature exceeds 240°F (115.6°C), the unit shuts down
and displays a diagnostic.A manual reset is required at the
unit.The high duct temperature can be adjusted at the
thermostat.
Dirty Filter Sensor Option
A factory installed pressure switch senses the pressure
differential across the filters. When the differential
pressure exceeds 0.9-inches (23 mm)WG, contact closure
occurs and the HI will display a diagnostic.The unit will
continue to run until you replace the air filters.
A field installed indicator device may be wired to relay
terminals to indicate when filter service is required.
Contacts are rated at 115 VAC and are powered by a field
supplied transformer.
Low Ambient Sensor (Air-Cooled Units)
The low ambient sensor is field-installed on air-cooled
units. Position it in a location subject to ambient
temperatures only and not exposed to direct sunlight or
exhaust fans.
The low pressure cutout initiates based on the ambient
temperature. A time delay on the low pressure cutout
initiates for ambient temperatures between 50 (zero
minutes) and 0°F (10 minutes).This helps to prevent
nuisance low pressure cutout trips.
Supply Air Static Pressure Limit
The opening of the VAV boxes coordinate during unit
startup and transition to/from occupied/unoccupied
modes to prevent supply air duct over pressurization.
However, if for any reason the supply air pressure exceeds
the user-defined supply air static pressure limit set at the
HI panel, the supply fan VFD shuts down.The unit will
attempt to restart, up to three times. If the over
pressurization condition still occurs on the third restart,
the unit shuts down and a manual reset diagnostic sets
and displays at the HI.
Variable Frequency Drive Option
The variable frequency drive (VFD) is driven by a
modulating 0-10 vdc signal from the RTM module. A
pressure transducer measures duct static pressure, and
the VFD adjusts the fan speed to maintain the supply air
static pressure within an adjustable user-defined range.
The range is determined by the supply air pressure
setpoint and supply air pressure deadband, which are set
at the HI panel.
VFDs provide supply fan motor speed modulation.The
drives will accelerate or decelerate as required to maintain
the supply air static pressure setpoint.
VFD with Bypass
Bypass control is an option that provides full nominal
airflow in the event of drive failure.The user must initiate
the bypass mode at the HI panel. When in bypass mode,
VAV boxes need to be fully open.The self-contained unit
will control heating and cooling functions to maintain
setpoint from a user-defined zone sensor. Supply air static
pressure limit is active in this mode.
For more detailed information on VFD operation,
reference the VFD technical manual that ships with the
unit.
Airside Economizer Option
Units with the airside economizer option are equipped
with the necessary control sequences to use outside air for
the first stage of cooling, in occupied or unoccupied mode
and when ambient conditions are favorable for
economizing. Inherent in the unit controller is the ability to
suppress the setpoint below the normal unit setpoint.This
allows the building to improve comfort levels when
possible, and at the same time, optimize building
mechanical cooling operation for peak operating
efficiency. An outside air temperature and relative
humidity sensor are provided to allow monitoring of
reference enthalpy and are field installed.
If the unit has the ECEM board, economizer operation
enables when the outside air enthalpy is less than 25
BTU’s/lb. default (adjustable 19-28 BTU’s/lb). During
occupied mode, the outside air damper opens to 15%

Operating Principals
72 SCXG-SVX01H-EN
(adjustable 0-100% at the HI) for ventilation purposes.
Also, the ability to alter the outside air damper position to
compensate for VAV supply air modulation is inherent in
the unit controls, and can be enabled by the operator.
If the unit does not have an ECEM board, it will economize
when the O/A temperature falls below the O/A economizer
setpoint.
The mixing box fabrication is galvanized steel. Opposed
low leak damper blades are fabricated from galvanized
steel and rotate on rustproof nylon bushings. A factory
installed 24V modulating spring return actuator controls
both damper positions.
When outdoor conditions are not suitable for economizer
cooling, the enthalpy control disables the economizer
function and permits the outdoor air damper to open only
to the minimum position.
On water-cooled units, compressor operation lockout will
not occur at low ambient air temperatures. However,
lockout will still occur via low condenser water
temperature.
The outdoor air dampers drive fully closed whenever the
supply air fan is off, provided there is power to the unit.
Comparative Enthalpy Control
Comparative enthalpy controls the economizer operation
and measures temperature and humidity of both return air
and outside air to determine which source has lower
enthalpy.This allows true comparison of outdoor air and
return air enthalpy by measurement of outdoor air and
return air temperatures and humidities.A factory-installed
control board, with field-installed outside and return air
temperature and relative humidity sensors, allows
monitoring of outside and return air.
Note: If comparative enthalpy is not ordered, the
standard method is to compare outdoor air
enthalpy with the fixed reference enthalpy.The
reference enthalpy is set through the human
interface panel.
Units with comparative enthalpy control are equipped
with the necessary control sequences to allow using
outside air for the first stage of cooling, in occupied or
unoccupied mode and when ambient conditions are
favorable for economizing. Inherent in the unit controller
is the ability to suppress the setpoint below the normal
unit setpoint.This allows the building to improve comfort
levels when possible, and at the same time, optimize
building mechanical cooling operation for peak operating
efficiency.
Economizer operation enables when the outside air
enthalpy is 3 BTu/lb less than the return air enthalpy.
During occupied mode, the outside air damper opens to
15% (adjustable 0-100%) for ventilation purposes. Also,
the ability to alter the outside air damper position to
compensate for VAV supply air modulation is inherent in
the unit controls, and can be enabled by the operator.
The mixing box fabrication is galvanized steel. Opposed
low leak damper blades are fabricated from galvanized
steel and rotate on rustproof nylon bushings. A factory
installed 24V modulating spring return actuator controls
both damper positions.
Airside Economizers withTraq™ Damper
Outside air enters the unit through theTraq damper
assembly and is measured by velocity pressure flow rings.
The velocity pressure flow rings are connected to a
pressure transducer/solenoid assembly, which
compensates for temperature swings that could affect the
transducer.The ventilation control module (VCM) utilizes
the velocity pressure input, the RTM outdoor air
temperature input, and the minimum outside air cfm
setpoint to modify the volume (cfm) of fresh air entering
the unit as the measured airflow deviates from setpoint.
When the optional preheat temperature sensor is installed
at the auxiliary temperature on the VCM and the preheat
function is enabled, the sensor will monitor the combined
(averaged) fresh air and return air temperatures. As this
mixed air temperature falls below the preheat actuate
temperature setpoint, the VCM activates the preheat
binary output to control a field-installed heater.The output
deactivates when the temperature rises 5°F above the
preheat actuate temperature setpoint.
Using a field-installed CO2sensor with CO2reset enabled,
as the CO2concentration increases above the CO2reset
start value, theVCM modifies the minimum outside air cfm
setpoint to increase the amount of fresh air entering the
unit.The setpoint adjusts upward until reaching the CO2
maximum reset value.The maximum effective (reset)
setpoint value for fresh air is limited to the system’s
operating cfm. As the CO2concentration decreases, the
effective (reset) setpoint value adjusts downward toward
the minimum outside air cfm setpoint. See Figure 60, p. 73
for an airflow cfm vs. CO2concentration curve.
Standard Two-Position Damper Interface
Units with the two-position damper interface are provided
with a 0-10 VDC control output suitable for controlling a
field-provided modulating actuator. In occupied mode, the
output drives to the maximum position.
Airside Economizer Interface
Units with airside economizer interface are equipped with
the necessary control sequences to allow using outside air
for the first stage of cooling, in occupied or unoccupied
mode and when ambient conditions are favorable for
economizing. Inherent in the unit controller is the ability to
suppress the setpoint below the normal unit setpoint.This
allows the building to improve comfort levels when
possible, and at the same time, optimize building
mechanical cooling operation for peak operating
efficiency. An outside air temperature and relative
humidity sensor are provided for field installation to
monitor reference enthalpy. Economizer operation
enables when the outside air enthalpy is less than 25 BTu/

Operating Principals
SCXG-SVX01H-EN 73
lb (adjustable 19-28 BTu/lb.). During occupied mode, the
outside air damper opens to 15% (adjustable 0-100%) for
ventilation purposes. Also, the ability to alter the outside
air damper position to compensate for VAV supply air
modulation is inherent in the unit controls, and can be
enabled by the operator. An analog 2-10 VDC output
(adjustable (0-10 VDC) is provided to modulate the field-
provided 30 second damper actuators (adjustable 1-255
seconds).
Airside Economizer Interface with
Comparative Enthalpy
Units with airside economizer interface and comparative
enthalpy are equipped with the necessary control
sequences to allow using outside air for the first stage of
cooling, in occupied or unoccupied mode and when
ambient conditions are favorable for economizing.
Inherent in the unit controller is the ability to suppress the
setpoint below the normal unit setpoint.This allows the
building to improve comfort levels when possible, and at
the same time, optimize building mechanical cooling
operation for peak operating efficiency. A factory-installed
control board, with outside and return air temperature and
relative humidity sensors, are provided for monitoring
outside and return air.The sensors are field installed.
Economizer operation enables when the outside air
enthalpy is 3 BTU’s/lb. less than the return air enthalpy.
During occupied mode, the outside air damper opens to
15% (adjustable 0-100%) for ventilation purposes. Also,
the ability to alter the outside air damper position to
compensate for VAV supply air modulation is inherent in
the unit controls, and can be enabled by the operator. An
analog 2-10VDC output (adjustable (0-10 VDC) is provided
to modulate the field-provided 30-second damper
actuators (adjustable 1-255 seconds).
Air-Cooled Condensers
Model SXRG units are designed for use with the remote
air-cooled condenser, model CXRC. For more information,
see the air-cooled condenser Installation, Owner, and
Diagnostic Manual, CXRC-SVX01*-EN.
Verify head pressure control, standard or optional.
Condenser fans will stage per a user-defined setting. If the
condenser is equipped with head pressure control (air
modulation on last stage of condenser capacity), the
condenser airflow will modulate to maintain condensing
temperature setpoint. Condensing temperature is
determined by sensors located at each condenser coil.
Figure 60. CO2reset function, outside air vs. CO2
Increasing
Concentration
Maximum
Airflow
Increasing
Reset Amount
O.A CFM
Setpoint
Carbon Dioxide
Reset Start
Carbon Dioxide
Maximum Reset

74 SCXG-SVX01H-EN
Controls
Points List
RTM Module
Binary Inputs
• Emergency stop
• External auto/stop
• Unoccupied/occupied
• Dirty filter
• VAV changeover with hydronic heat
Binary outputs
• VAV box drive max (VAV units only)
• CV unoccupied mode indicator (CV units only)
• Alarm
• Fan run request
• Water pump request (water-cooled only)
Analog input
• Airside economizer damper minimum position
Analog output
• Outside air damper actuator
Heat Module:
• Analog output
GBAS Module
Binary inputs
• Demand limit contacts
Binary outputs
• Dirty filter relay
• Refrigeration fail relay
• Heat fail relay
• Supply fan fail relay
• Active diagnostics
Analog inputs
• Occupied zone cooling setpoint
• Occupied zone heating setpoint
• Unoccupied zone cooling setpoint
• Unoccupied zone heating setpoint or minimum
outside air flow setpoint
• Supply air cooling setpoint
• Supply air heating setpoint
• Supply air static pressure setpoint
ECEM Module
Analog inputs
• Return air temperature
• Return air humidity
In addition, units with a VOM have:
Binary inputs
• VOM mode A, unit off
• VOM mode B, pressurize
• VOM mode C, exhaust
• VOM mode D, purge
• VOM mode E, purge w/duct pressure control
Binary output
• V.O. relay
Tracer™ LCI-I Module
Constant Volume (CV) Points
Binary inputs
• Airside economizer enable/disable
• Condenser type (air or water cooled)
• Condenser water flow status
• Emergency shutdown
• Local fan switch enable/disable
• Mechanical cooling lockout
• Mechanical heating lockout
• Mixed air temperature
• Occupancy
• Occupancy override
• Occupancy sensor
Binary outputs
• Airside economizer status
• Alarm status
• Compressor on/off status
Controls
• Condenser circuit information
• Condenser water pump status
• Waterside economizer status
Analog inputs
• Airside economizer dry bulb setpoint
• Airside economizer minimum setpoint
• Building static pressure input

Controls
SCXG-SVX01H-EN 75
• Maintenance required time
• Occupancy bypass time
• Outdoor air damper minimum position setpoint
• Outdoor air relative humidity
• Outdoor air temperature
• Unit start delay time setpoint
• Zone temperature
• Zone temperature setpoint
• Zone temperature setpoint (default)
• Zone temperature setpoint limits
• Zone temperature setpoint offsets
• Zone temperature setpoint shift
Analog outputs
• Alarm message
• Building static pressure status
• Condenser saturated refrigerant temperature
• Condenser water temperature
• Cooling output status
• Effective occupancy
• Exhaust fan status
• Heating output status
• Heating/cooling mode
• Morning warm up sensor temperature
• Outdoor air damper position
• Outdoor air enthalpy
• Outdoor air relative humidity
• Return air temperature
• Supply air temperature
• Supply fan status
• Unit status mode
• Zone CO2
• Zone relative humidity
Variable Air Volume (VAV) Points
Binary inputs
• Airside economizer enable/disable
• Condenser water flow input
• Emergency override
• Local fan switch enable/disable
• Mechanical cooling lockout
• Mechanical heating lockout
• Occupancy
Binary outputs
• Airside economizer status
• Alarm status
• Compressor on/off status
• Condenser circuit information
• Condenser type (water or air cooled)
• Condenser waterflow status
• Condenser water pump status
Analog inputs
• Airside economizer dry bulb setpoint
• Airside economizer minimum position
• Building static pressure input
• Building static pressure setpoint
• Daytime warm up setpoint
• Daytime warm up terminate setpoint
• Maintenance required time
• Occupancy bypass time
• Outdoor air damp min position setpoint
• Outdoor airflow minimum setpoint
• Outdoor air relative humidity
• Outdoor air temperature
• Supply air cooling setpoint
• Supply air cooling setpoint (default)
Analog outputs
• Building static pressure status
• Alarm message
• Condenser saturated refrigerant temp.
• Condenser water temperature
• Condenser water temp (local)
• Cooling output status
• Exhaust fan status
• Heating output status
• Heating/cooling mode
• Mixed air temperature
• Morning warm up sensor temperature
• Outdoor air damper position
• Outdoor air enthalpy
• Outdoor air flow
• Outdoor air relative humidity status
• Outdoor air temperature status
• Return air temperature

Controls
76 SCXG-SVX01H-EN
BCI-Points List
Refer to ACC-SVP*-EN
Phase Monitor
Unit is equipped with phase monitor in control box.The
phase monitor will protect against phase loss, imbalance
and reversal of line voltage. If a fault occurs, the red LED
will energize. While the fault condition is present, the
phase monitor interrupts the 115V control circuit. If no
faults are observed, a green LED will be energized.
Unit Control Components
The Modular Series IntelliPak self-contained unit is
controlled by a microelectronic control system that
consists of a network of modules.These modules are
referred to as unit control modules (UCM). In this manual,
the acronym UCM refers to the entire control system
network.
These modules perform specific unit functions using
proportional/integral control algorithms.They are
mounted in the unit control panel and are factory wired to
their respective internal components. Each module
receives and interprets information from other unit
modules, sensors, remote panels, and customer binary
contacts to satisfy the applicable request; i.e.,
economizing, mechanical cooling, heating, ventilation.
Following is a detailed description of each module’s
function.
RTM Module Board - Standard on all Units
The RTM responds to cooling, heating, and ventilation
requests by energizing the proper unit components based
on information received from other unit modules, sensors,
remote panels, and customer supplied binary inputs. It
initiates supply fan, exhaust fan, exhaust damper, variable
frequency drive output, and airside economizer operation
based on that information.
Reference the RTM points list.
Note: Emergency stop and external auto/stop, stop the
unit immediately, emergency stop generates a
manual reset diagnostic that must be reset at the
unit human interface. External auto-stop will return
the unit to the current operating mode when the
input is closed, so this input is auto reset.
RTM Remote Economizer Minimum Position
The remote minimum position potentiometer,
BAYSTAT023A, provides a variable resistance (0-270
ohms) to adjust the economizer minimum position from 0
to 100% when connected to the economizer remote
minimum position input of the RTM. The RTM must be
selected as the source for economizer minimum position.
If the RTM is the selected source for economizer minimum
position, and if a valid resistance per Table 43, p. 76 is
provided to the RTM remote minimum position input, the
OA cfm compensation function will not operate, even if
enabled. “Default” is the only possible source for
economizer minimum position when using the OA cfm
compensation function.
RTM Analog Outputs
The RTM has two 0-10 vdc outputs: one for the supply fan
and one for the economizer option.These outputs provide
a signal for one or two damper actuators.There are no
terminal strip locations associated with these wires.They
go directly from pins on RTM circuit board to actuator
motor.
RTM Binary Outputs
The RTM has an output with pressure switch proving
inputs for the supply fan. There is a 40 second delay from
when the RTM starts the supply fan until the fan proving
input must close.A fan failure diagnostic will occur after 40
seconds.This is a manual reset diagnostic, and all heating,
cooling, and economizer functions will shut down. If this
proving input is jumped, other nuisance diagnostics will
occur. If the proving input fails to close in 40 seconds, the
economizer cycles to the minimum position.This is a
manual reset diagnostic. External control of the fan is not
recommended.
VAV Drive Max Output
This is a single-pole, double-throw relay rated at a
maximum voltage of 24 vac, two amps.The relay contacts
of this relay switch when the unit goes from the occupied
mode to the unoccupied mode by means of the occupied
binary input. The contacts will stay switched during the
unoccupied and morning warmup mode.They will return
to the position shown on the unit wiring diagram when the
unit returns to the occupied mode.This binary output
signals the VAV boxes or other terminal devices to go full
open.
RTM Alarm Relay
This is a single pole, double throw relay rated at a
maximum voltage of 24 vac, two amps max. Relay
contacts can be programmed from the unit human
interface.This relay can be programmed to pick up on any
one or group of diagnostics from the unit human interface.
Table 43. Economizer remote minimum position input
resistance
Input resistance Economizer min. position
0 - 30 ohms 0 %
30 - 240 ohms 0-100 % (linear)
240 - 350 ohms 100 %
> 350 ohms N/A (a)
(a) A resistance greater than 350 ohms is assumed to be an open
circuit. The system will use the default minimum position value.

Controls
SCXG-SVX01H-EN 77
Status/Annunciator Output
The status annunciator output is an internal function
within the RTM module on CV and VAV units. It provides:
a. diagnostic and mode status signals to the remote
panel (LEDs) and to the Human Interface.
b. control of the binary alarm output on the RTM.
c. control of the binary outputs on the GBAS module
to inform the customer of the operational status
and/or diagnostic conditions.
Occupied/Unoccupied Inputs
There are four ways to switch to occupied/unoccupied:
1. Field-supplied contact closure hard wired binary input
to the RTM
2. Programmable night setback zone sensor
3. Tracer Summit
4. Factory-mounted time clock
VAV Changeover Contacts
These contacts are connected to the RTM when daytime
heating on VAV units with internal or external hydronic
heat is required. Daytime (occupied) heating switches the
system to a CV unit operation. Refer to the unit wiring
diagram for the field connection terminals in the unit
control panel.The switch must be rated at 12 ma @ 24VDC
minimum.
External Auto/Stop Switch
A field-supplied switch may be used to shut down unit
operation.This switch is a binary input wired to the RTM.
When opened, the unit shuts down immediately and can
be cancelled by closing the switch. Refer to the unit wiring
diagrams (attached to the unit control panel) for proper
connection terminals.The switch must be rated for 12 ma
@ 24 VDC minimum.This input will override all VOM
inputs, if the VOM option is on the unit.
Occupied/Unoccupied Contacts
To provide night setback control if a remote panel with
night setback was not ordered, install a field-supplied
contact.This binary input provides the building’s
occupied/unoccupied status to the RTM. It can be initiated
by a time clock, or a building automation system control
output.The relay’s contacts must be rated for 12 ma @ 24
VDC minimum. Refer to the appropriate wiring diagrams
(attached to the unit control panel for the proper
connection terminals in the unit control panel.
Emergency Stop Input
A binary input is provided on the RTM board for
installation of a field-supplied normally closed (N.C.)
switch to use during emergency situations to shut down all
unit operations. When open, an immediate shutdown
occurs. An emergency stop diagnostic enters the human
interface and the unit will require a manual reset. Refer to
the unit wiring diagrams (attached to the unit control panel
for the proper connection terminals.The switch must be
rated for 12 ma @ 24 VDC minimum.This input will
override all VOM inputs, if the VOM option is on the unit.
VAV Box Option
To interlock VAV box operation with evaporator fan and
heat/cool modes, wire theVAV boxes/air valves toVAV box
control connections on the terminal block.
Supply Duct Static Pressure Control
The RTM relies on input from the duct pressure transducer
when a unit is equipped with VFD to set the supply fan
speed to maintain the supply duct static pressure to within
the static pressure setpoint deadband.
RTM Sensors
RTM sensors include: zone sensors with or without
setpoint inputs and modes, supply air sensor, duct static
pressure, outside air temperature, outside air humidity,
airflow proving, and dirty filter.
Table 44. RTM sensor resistance vs. temperature
Temperature
°F Resistance,
ohms Temperature
°F Resistance,
ohms
-40 346.1 71 11.60
-30 241.7 72 11.31
-20 170.1 73 11.03
-10 121.4 74 10.76
-5 103.0 75 10.50
0 87.56 76 10.25
5 74.65 77 10.00
10 63.8 78 9.76
15 54.66 79 6.53
20 46.94 80 9.30
25 40.40 85 8.25
30 34.85 90 7.33
35 30.18 100 5.82
40 26.22 105 5.21
45 22.85 110 4.66
50 19.96 120 3.76
55 17.47 130 3.05
60 15.33 140 2.50
65 13.49 150 2.05
66 13.15 160 1.69
67 12.82 170 1.40
68 12.50 180 1.17
69 12.19 190 0.985
70 11.89 200 0.830
Note: Mode boundaries are 1000 to 40,000 ohms. Other boundaries are
equal to the midpoint between the nominal mode resistance

Controls
78 SCXG-SVX01H-EN
Compressor Module (MCM) - Standard on
all Units
The compressor module, (single circuit and multiple
circuit) energizes the appropriate compressors and
condenser fans upon receiving a request for mechanical
cooling. It monitors the compressor operation through
feedback information it receives from various protection
devices.
Human Interface Module - Standard on all
Units
The human interface (HI) module enables the operator to
adjust the operating parameters for the unit using it's 16-
key keypad on the human interface panel.The HI panel
provides a two line, 40 character, clear language (English,
Spanish, or French) LCD screen with unit status
information and menus to set or modify operating
parameters. It is mounted in the unit’s main control panel
and accessible through the unit’s control panel door.
Remote Human Interface Module Option
The optional remote-mount human interface (RHI) panel
has all the functions of the unit-mounted version except
for service mode.To use a RHI, the unit must be equipped
with an optional interprocessor communications bridge
(IPCB). Model number digit 32 (=2) indicates if the ICPB
was ordered with the unit. If not, contact your localTrane
representative to order an ICPB kit for field installation.
The RHI can be located up to 1,000 feet (304.8 m) from the
unit. A single RHI can monitor and control up to four self-
contained units if each one contains an IPCB.The IPCB
switches must be set as SW1- off, SW2 - off, and SW3 - on.
Interprocessor Communications Board •
Option used with RHI
The interprocessor communication board expands
communications from the rooftop unit's UCM network to
a remote human interface panel. DIP switch settings on the
IPCB module for this application are; switches 1 and 2 “off,”
switch 3 “on.”
Waterside Module - Standard on all water-
cooled units
Waterside module (WSM) controls all water valves based
on unit configuration. In addition, the WSM monitors
waterflow proving and the following temperatures:
• entering water
• entering air low
• mixed air
• entering condenser water
• refrigerant circuit 3:
•saturated condenser
•evaporator frost
• refrigerant circuit 4:
•condenser
•evaporator
Cooling Tower Interlock
To interlock condenser pump/tower with cooling
operation, wire the cooling tower to an external 115 volt
control power source, to ground, and to control terminal
block. Normally open/closed contacts are provided.
Heat Module
The heat module is standard on all units with factory-
installed heat. It controls the unit heater to stage up and
down to bring the temperature in the controlled space to
within the applicable heating setpoint. Also, it includes a
freezestat, morning warmup, and heating outputs.
Ventilation Override Module (VOM) Option
The ventilation override module can be field-configured
with up to five different override sequences for ventilation
override control purpose. When any one of the module’s
five binary inputs are activated, it will initiate specified
functions such as; space pressurization, exhaust, purge,
purge with duct pressure control, and unit off.
Table 45. RTM setpoint analog inputs
Cooling or Heating
Setpoint Input, °F
(using RTM as zone
temp. source) ohms
Cooling Setpoint Input, °F
(using RTM as supply air temp.
source) resistance,
40 40 1084
45 45 992
50 50 899
55 55 796
60 60 695
65 65 597
70 70 500
75 75 403
80 80 305
NA 85 208
NA 90 111
Table 46. RTM resistance value vs. system operating
mode
Resistance applied
to RTM mode input
terminals, ohms
CV units VAV units
fan mode system
mode system
mode
2320 auto off off
4870 auto cool
7680 auto auto auto
10,770 on off
13,320 on cool
16,130 on auto
19,480 auto heat
27,930 on heat

Controls
SCXG-SVX01H-EN 79
Once the ventilation sequences are configured, they can
be changed unless they are locked using the HI. Once
locked, the ventilation sequences cannot be unlocked.
The compressors and condenser fans disable during the
ventilation operation. If more than one ventilation
sequence activates, the one with the highest priority (VOM
“A”) begins first, with VOM “E” having lowest priority and
beginning last.
A description of the VOM binary inputs follows below.
UNIT OFF sequence “A”
When complete system shut down is required, the
following sequence can be used.
• Supply fan – off
• Supply fan VFD – off (0 Hz)
• Outside air dampers – closed
• Heat – all stages – off, modulating heat output at 0 vdc
• Occupied/Unoccupied output – de-energized
• VO relay – energized
• Exhaust fan (field-installed) - off
• Exhaust damper (field-installed) - closed
PRESSURIZE sequence “B”
This override sequence can be used if a positively
pressured space is desired instead of a negatively
pressurized space.
• Supply fan – on
• Supply fan VFD – on (60 Hz)/VAV boxes – open
• Outside air dampers – open
• Heat – all stages – off, hydronic heat output at 0 vdc
• Occupied/ unoccupied output - energized
• VO relay - energized
• Exhaust fan (field-installed) - off
• Exhaust damper (field-installed) - closed
EXHAUST sequence “C”
With the building’s exhaust fans running and the unit’s
supply fan off, the conditioned space becomes negatively
pressurized.This is desirable for clearing the area of
smoke when necessary; i.e. from an extinguished fire, to
keep smoke out of areas that were not damaged.
• Supply fan – off
• Supply fan VFD – off (0 Hz)
• Outside air dampers – closed
• Heat – all stages – off, hydronic heat output at 0 vdc
• Occupied/Unoccupied output – de-energized
• VO relay – energized
• Exhaust fan (field-installed) - on
• Exhaust damper (field-installed) - open
PURGE sequence “D”
This sequence can purge the air out of a building before
coming out of unoccupied mode of operation in a VAV
system. Also, it can be used to purge smoke or stale air.
• Supply fan – on
• Supply fan VFD – on (60 hz)/VAV boxes – open
• Outside air damper – open
• Heat – all stages – off, modulating heat output at 0 vdc
• Occupied/Unoccupied output – energized
• VO relay – energized
• Exhaust fan (field-installed) - on
• Exhaust damper (field-installed) - open
PURGE with duct pressure control “E”
This sequence can be used when supply air control is
required for smoke control.
• Supply fan – on
• Supply fan VFD – on (if equipped)
• Outside air dampers – open
• Heat – all stages – off, hydronic heat output at 0 vdc
• Occupied/unoccupied output – energized
• VO relay – energized
• Exhaust fan (field-installed) - on
• Exhaust damper (field-installed) - open
Note: Each system (cooling, exhaust, supply air, etc.)
within the unit can be redefined in the field for each
of the five sequences, if required. Also the
definitions of any or all of the five sequences may
be locked into the software by simple key strokes at
the human interface panel. Once locked into the
software, the sequences cannot be changed.
Trane IntelliPak Communications Modules
BACnet Communications Interface (BCI-I)
Module
The BACnet Communication Interface for IntelliPak self-
contained (BCI-I) controller expands communications
from the unit UCM network toTracer SC or a 3rd party
building automation system, utilizing BACnet, and allows
external setpoint and configuration adjustment and
monitoring of status and diagnostics.The BCI-I utilizes the
BACnet defined MS/TP protocol as defined in ASHRAE
standard135-2004. This controller works in standalone
mode, withTracer SC or when connected to a 3rdparty
building automation system that supports BACnet.
LonTalk® Communications Interface (LCI-I)
Module
The LonTalk Communication Interface for IntelliPak self-
contained (LCI-I) controller expands communications
from the unit UCM network to aTraneTracer Summit or a

Controls
80 SCXG-SVX01H-EN
3rd party building automation system, utilizing LonTalk,
and allows external setpoint and configuration
adjustment and monitoring of status and diagnostics.The
LCI-I utilizes an FTT-10A FreeTopology transceiver, which
supports nonpolarity sensitive, free topology wiring,
which allows the system installer to utilize star, bus, and
loop architectures.This controller works in standalone
mode, peer-to-peer with one or more other units, or when
connected to aTraneTracer Summit or a 3rd party building
automation system that supports LonTalk.
Exhaust/Comparative Enthalpy (ECEM)
Module
(Option used on units with comparative enthalpy
option)
The exhaust/comparative enthalpy module receives
information from the return air humidity sensor, and the
RTM outside air temperature sensor and outside air
humidity sensor, the outside air humidity sensor and
temperature sensor to utilize the lowest possible enthalpy
level when considering economizer operation. In addition,
it receives space pressure information to maintain the
space pressure within the setpoint control band. Refer to
the Figure 61, p. 80 for humidity vs. voltage values.
Ventilation Control Module (VCM)
(Available only with Traq™ Damper Option)
The ventilation control module (VCM) is located in the
airside economizer section of the unit and linked to the
unit’s UCM network. Using a velocity pressure transducer/
solenoid (pressure sensing ring) in the fresh air section
allows the VCM to monitor and control fresh air entering
the unit to a minimum airflow setpoint. See Figure 62,
p. 80 for a detail view of the velocity pressure transducer/
solenoid assembly.
An optional temperature sensor can be connected to the
VCM to enable control of a field installed fresh air
preheater.
Also, a field-provided CO2sensor can be connected to the
VCM to control CO2reset.The reset function adjusts the
minimum cfm upward as the CO2concentrations increase.
The maximum effective (reset) setpoint value for fresh air
entering the unit is limited to the system’s operating cfm.
Table 47, p. 80 lists the minimum outside air cfm vs. input
voltage.
Generic Building Automation System
Module Option
The generic building automation system module (GBAS)
provides broad control capabilities for building
automation systems other thanTrane’sTracer system. A
field provided potentiometer or a 0-5 vdc signal can be
applied to any of the inputs of the GBAS to provide the
following points:
GBAS Analog Inputs
Four analog inputs that can be configured to be any of the
following:
5. occupied zone cooling
6. unoccupied zone cooling
7. occupied zone heating
8. unoccupied zone heating
9. SA cooling setpoint
10. SA heating setpoint
11. space static pressure setpoint
12. SA static pressure setpoint
Figure 61. Relative humidity vs. voltage
Figure 62. Velocity pressure transducer/solenoid
assembly
Tube from low side
of Transducer
Pressure
Transducer
Ventilation
Control Module
Solenoid
Tube from high side
of Transducer
Tube from
low side
of Velocity
Ring
Table 47. Minimum outside air setpoint w/VCM module
and Traq™ sensing
Unit Input Volts CFM
SXWG 20 0.5 - 4.5 vdc 6,350-8,500
SXWG 25 0.5 - 4.5 vdc 7,250-10,625
SXWG 30 0.5 - 4.5 vdc 7,250-12,750
SXWG 35 0.5 - 4.5 vdc 7,250-14,875
SXRG 20 0.5 - 4.5 vdc 7,250-8,500
SXRG 25 0.5 - 4.5 vdc 7,250-10,625
SXRG 32 0.5 - 4.5 vdc 7,250-13,600

Controls
SCXG-SVX01H-EN 81
GBAS Binary Outputs
Five binary outputs to provide diagnostics, signaling up to
five alarms. Each of the five (5) relay outputs can be
mapped to any/all of the available diagnostics. Each output
contains a dry N.O. and N.C. contact with a VA rating of 2
amps at 24 VAC.
GBAS Binary Input
One binary input for the self-contained unit to utilize the
demand limit function.This function is operational on
units with a GBAS and is used to reduce electrical
consumption at peak load times. Demand limiting can be
set at either 50% or 100%. When demand limiting is
needed, mechanical cooling and heating (with field-
provided 2-stage electric heat only) operation are either
partially (50%), or completely disabled (100%) to save
energy.The demand limit definition is user definable at the
HI panel. Demand limit binary input accepts a field
supplied switch or contact closure. When the need for
demand limiting has been discontinued, the unit’s cooling/
heating functions will again become fully enabled.
GBAS Communication (Analog Inputs)
The GBAS accepts external setpoints in the form of analog
inputs for cooling, heating, supply air pressure. Refer to
the unit wiring diagram for GBAS input wiring and the
various desired setpoints with the corresponding DC
voltage inputs.
Any of the setpoint or output control parameters can be
assigned to each of the four analog inputs on the GBAS
module. Also, any combination of the setpoint and/or
output control parameters can be assigned to the analog
inputs through the HI.To assign the setpoints apply an
external 0-5 vdc signal:
1. directly to the signal input terminals, or
2. to the 5 vdc source at the GBAS module with a 3-wire
potentiometer.
Note: There is a regulated 5 vdc output on the GBAS
module that can be used with a potentiometer as a
voltage divider.The recommended potentiometer
value is 1000-100,000 ohms.
The setpoints are linear between the values shown in
Table 48, p. 82. Reference Table 49, p. 82 for
corresponding input voltage setpoints. Following are
formulas to calculate input voltage or setpoint. SP =
setpoint, IPV = input voltage.
If the setpoint range is 50-90°F:
IPV = (SP - 50) (0.1) + 0.5
SP = [(IPV - 0.5)/0.1] + 50
If the setpoint range is 40-90°F:
IPV = (SP - 40)(0.8) + 0.5
SP = [(IPV - 0.5)/0.08] + 40
If the setpoint range is 40-180°F:
IPV = (SP - 40)(0.029) + 0.5
SP = [(IPV - 0.5)/0.029] + 40
If the static pressure range is 0.03-0.3 iwc:
IPV = (SP - 0.03)(14.8) + 0.5
SP = [(IPV - 0.5)/14.8] + 0.03
If the static pressure range is 0.0-5.0 iwc:
IPV = (SP)(0.8) + 0.5
SP = [IPV/(0.8 + 0.5)]
GBAS Demand Limit Relay (Binary Input)
The GBAS allows the unit to utilize the demand limit
function by using a normally open (N.O.) switch to limit the
electrical power usage during peak periods. Demand limit
can initiate by a toggle switch closure, a time clock, or an
ICS control output.These contacts must be rated for 12 ma
@ 24 VDC minimum.
When the GBAS module receives a binary input signal
indicating demand limiting is required, a command
initiates to either partially (50%) or fully (100%) inhibit
compressor and heater operation.This can be set at the HI
using the setup menu, under the “demand limit definition
cooling” and “demand limit definition heating” screens. A
toggle switch, time clock, or building automation system
control output can initiate demand limiting.
If the cooling demand limit is set to 50%, half of the cooling
capacity will disable when the demand limit binary input
closes.The heating demand limit definition can only be set
at 100%, unless the unit has field-provided two-stage
electric heat. In that case, if the heating demand limit is set
to 50%, half or one stage of heating disables when the
demand limit binary input closes. If the demand limit
definition is set to 100%, then all cooling and/or heating
will disable when the demand limit input closes.
GBAS Diagnostics (Binary Outputs)
The GBAS can signal up to five alarm diagnostics, which
are fully mappable through the setup menu on the HI.
These diagnostics, along with the alarm output on the
RTM, allow up to six fully mappable alarm outputs.
Each binary output has a NO and NC contact with a rating
of two amps at 24 VAC.The five binary outputs are factory
preset as shown on the unit wiring diagram (on the unit
control panel door). However, these outputs can be field
defined in a variety of configurations, assigning single or
multiple diagnostics to any output.
For a complete listing of possible diagnostics, see the
IntelliPak Self-Contained Programming Guide, PKG-
SVP01*-EN. For terminal strip locations, refer to the unit
wiring diagram for the GBAS.

Controls
82 SCXG-SVX01H-EN
Input Devices and System Functions
Following are basic input device and system function
descriptions used within the UCM network on IntelliPak
self-contained units. Refer to the unit wiring diagrams for
specific connections.
Water Purge
During the unoccupied mode, water-cooled units will
periodically circulate water through the condensers and
waterside economizer if the user has enabled the purge
function at the HI. The water purge function circulates
water to introduce fresh water-treatment chemicals and
help prevent water stagnation.The number of hours
between each periodic purge, or purge duration, is user-
defined at the HI between 1-999 hours. If the periodic purge
timer expires while the unit is in occupied mode, it will wait
for the next available unoccupied time before initiating
water purge. Contrary, if a request for cooling occurs
during a purge sequence, purge will terminate and cooling
will commence.
Compressor Circuit Breakers
The compressors are protected by circuit breakers that
interrupt the compressor power supply if the current
exceeds the breakers “must trip” value. During a request
for compressor operation, if the compressor module
(MCM or SCM) detects a problem outside of it’s normal
parameters, it turns any operating compressor(s) on that
circuit off, locks out all compressor operation for that
circuit, and initiates a manual reset diagnostic.
Low Pressure Control
Low pressure (LP) control is accomplished using a binary
input device mounted on the suction line, near the
compressor. If suction pressure drops to 49 (water-
cooled), 36 (air-cooled) ± 6 psig, or below, the switch
opens.
If the switch is open at start, no compressors on that circuit
will operate.They are locked out and a manual reset
diagnostic initiates. If the LP switch opens after a
compressor start, all compressors on that circuit will stop
and remain off a minimum 3 minutes before restarting. If
the LP cutout trips four times in the first three minutes of
operation, all compressors on that circuit lockout and a
manual reset diagnostic initiates.
Table 48. GBAS analog input setpoints
control parameter signal range setpoint range
occupied zone cooling setpoint 0.5 to 4.5 vdc 50 to 90°F
(CV units only)
unoccupied zone cooling
setpoint 0.5 to 4.5 vdc 50 to 90°F
(CV and VAV)
occupied zone heating setpoint 0.5 to 4.5 vdc 50 to 90°F
(CV units only)
unoccupied zone heating
setpoint 0.5 to 4.5 vdc 50 to 90°F
(CV and VAV)
supply air cooling setpoint 0.5 to 4.5 vdc 40 to 90°F
(VAV units only)
supply air hydronic heating
setpoint 0.5 to 4.5 vdc 40 to 180 °F
(VAV units only)
space static pressure setpoint 0.5 to 4.5 vdc 0.03 to 0.30 IWC
supply air pressure setpoint 0.5 to 4.5 vdc 0.0 to 5.0 IWC
(VAV units only)
Notes:
1. Input voltages less than 0.5 vdc are considered as 0.5 vdc input
signal is lost, the setpoint will "clamp" to the low end of the setpoint
scale. No diagnostic will result from this condition.
2. Input voltages greater than 4.5 vdc are considered to be 4.5 vdc.
3. The actual measured voltage is displayed at the HI.
Table 49. GBAS input voltage corresponding setpoints
Volts Temp.
°F Volts Temp.
°F Volts Temp.
°F Volts Temp.
°F
0.5 50 1.6 60 2.6 70 2.7 80
0.6 51 1.7 61 2.7 71 2.8 81
0.7 52 1.8 62 2.8 72 2.9 82
0.8 53 1.9 63 2.9 73 3.0 83
0.9 54 2.0 64 3.0 74 3.1 84
1.0 55 2.1 65 3.1 75 3.2 85
1.1 56 2.2 66 3.2 76 3.3 86
1.2 57 2.3 67 3.3 77 3.4 87
1.3 58 2.4 68 3.4 78 3.5 88
1.5 59 2.5 69 3.5 79 3.6 89
1.6 60
1.7 61
1.8 62
1.9 63
2.0 64
2.1 65
2.2 66
2.3 67
2.4 68
NOTICE:
Proper Water Treatment!
The use of untreated or improperly treated water in a
CenTraVac could result in scaling, erosion, corrosion,
algae or slime. It is recommended that the services of a
qualified water treatment specialist be engaged to
determine what water treatment, if any, is required.
Trane assumes no responsibility for equipment failures
which result from untreated or improperly treated
water, or saline or brackish water.

Controls
SCXG-SVX01H-EN 83
LP switches close at 74 (water-cooled) and 61 (air-cooled)
± 6 psig.
Evaporator Temperature Sensor Frostat™
The evaporator temperature sensor is an analog input
device used to monitor refrigerant temperature inside the
evaporator coil to prevent coil freezing. It is attached to the
suction line near the evaporator coil with circuits 1 and 2
connected to the SCM/MCM and circuits 3 and 4 connected
to theWSM.The coil frost cutout temperature is factory set
at 30°F. It is adjustable at the HI from 25-35°F.The
compressors stage off as necessary to prevent icing. After
the last compressor stages off, the compressors will
restart when the evaporator temperature rises 10°F above
the coil frost cutout temperature and the minimum three
minute “off” time elapses.
Saturated CondenserTemperature Sensors
The saturated condenser temperature sensors are analog
input devices.They are mounted inside a temperature well
located on a condenser tube bend on air-cooled units, and
in the condenser shell on water-cooled units.The sensors
monitor the saturated refrigerant temperature inside the
condenser coil and are connected to the SCM/MCM for
circuits 1 and 2 (air or water cooled), andWSM for circuits
3 and 4 (only water-cooled).
Head Pressure Control
Head pressure control is accomplished using two
saturated refrigerant temperature sensors on air-cooled
units and up to four sensors on water-cooled units.
Air-cooled units: During a request for compressor
operation when the condensing temperature rises above
the lower limit of the control band, the compressor
module (SCM/MCM) sequences condenser fans on. If the
operating fans cannot bring the condensing temperature
to within the control band, more fans turn on. As the
saturated condensing temperature approaches the lower
limit of the control band, fans sequence off.The minimum
on/off time for condenser fan staging is 5.2 seconds. If the
system is operating at a given fan stage below 100% for 30
minutes the saturated condensing temperature is above
the efficiency check point setting, a fan stage will be added.
If the saturated condensing temperature falls below the
efficiency check point setting, fan control remains at the
present operating stage. If the fan stage cycles four times
within a 10 minute period, the lower limit temperature is
redefined as being equal to the lower limit minus the
temporary low limit suppression setting.The unit will
utilize this new low limit temperature for one hour to
reduce condenser fan short cycling.
Water-cooled: Units without WSE, the condenser valve
modulates to maintain an average saturated condenser
temperature. Units with WSE, if economizing and
mechanical cooling is necessary the economize valve will
sacrifice free cooling and modulate to maintain
condensing saturated temperature. If not economizing,
the condenser valve will modulate to maintain condensing
saturated temperature. Water-cooled units without head
pressure control will lock out mechanical cooling at
entering condenser water temperatures below 54°F.
Mechanical cooling will resume when the entering
condenser water temperature exceeds 58°F.
Low Ambient Control (Air-Cooled Units Only)
The low ambient modulating output on the compressor
module is functional on all units with or without the low
ambient option. When the compressor module stages up
to it's highest stage (stage 2 or 3 depending on unit size),
the modulating output is 100% (10VDC). When the control
is at stage 1, the modulating output (0-10VDC) controls the
saturated condensing temperature to within the
programmable condensing temperature low ambient
control point.
Low Ambient Compressor Lockout (Air-Cooled
Units Only)
The low ambient compressor lockout utilizes an analog
input device. When the system is configured for low
ambient compressor lockout, the compressors will not
operate if the temperature of the outside air falls below the
lockout setpoint. When the temperature rises 5°F above
the lockout setpoint, the compressors will operate.The
setpoint for units without the low ambient option is 50°F.
For units with the low ambient option, the setpoint is 0°F.
The setpoints are adjustable at the human interface panel.
Return Air Temperature Sensor
The return air temperature sensor is an analog input
device used with a return humidity sensor on units with
the comparative enthalpy option.The sensor monitors the
return air temperature and compares it to the outdoor
temperature to establish which temperature is best suited
to maintain cooling requirements. It is mounted in the
return air path and connected to the ECEM.
Supply Fan Circuit Breaker, Fuses, and
Overloads
The supply fan motor is protected by either circuit
breakers fuses or a combination of fuses and overloads,
dependent upon unit configuration. Circuit breakers are
used on units without a VFD.They will trip and interrupt
the motor power supply if the current exceeds the breaker
trip value.The RTM shuts all system functions off when
detecting an open fan proving switch. Units with a VFD
have fuses to protect the VFD and motor. Units with a VFD
w/bypass have fuses to protect VFD circuit and overloads
to protect the motor when in bypass.
Supply Air Temperature Low Limit
The supply air temperature low limit function uses the
supply air temperature sensor input to modulate the
economizer damper to the minimum position if the supply
air temperature falls below the occupied heating setpoint
temperature.

Controls
84 SCXG-SVX01H-EN
Supply Air Temperature Sensor
The supply air temperature sensor is an analog input
device. It monitors the supply air temperature for supply
air temperature control, supply air temperature reset,
supply air temperature low limiting, and supply air
tempering. It is mounted in the supply air discharge
section of the unit and connected to the RTM.
Supply Airflow Proving Switches
This is binary input device used on units to signal the RTM
when the supply fan is operating. It is mounted in the
supply fan section and is connected to the RTM. During a
request for fan operation and if the differential switch
opens for 40 consecutive seconds, compressor operation
turns off, heat operation turns off, the request for supply
fan operation is turns off and locks out, economizer
damper option closes, and a manual reset diagnostic
initiates.
Low Entering Air Protection Device (LEATPD)
The low entering air protection device (LEATPD) is a binary
input on units with hydronic heat or a waterside
economizer. It is optional on water-cooled units.
If the LEATPD is on a unit with factory-installed heat, it is
mounted in the heat section and connected to the heat
module. If the entering air temperature to the heating coil
falls to 40°F, the normally open contacts on the LEATPD
close and cause the following events:
a. the hydronic heat actuator fully opens.
b. the supply fan turns off
c. the outside air damper closes
d. the SERVICE light at the remote zone sensor option
turns on.
e. a LEATPD diagnostic displays at the human
interface panel.
If the LEATPD is on a water-cooled unit without factory-
installed heat, it is wired to the WSM. It will trip if the
entering water temperature falls to 34°F, open the
economizer valve, and energize the pump output.
High Duct Temp Thermostat Option On Units
with an LCI-I
The high duct temperature thermostats are binary input
devices used on units with aTrane communication
interface module (Tracer/LCI-I).They provide a high limit
unit shutdown and require a manual reset.The
thermostats are factory set to open if the supply air
temperature reaches 240°F, or the return air temperature
reaches 135°F. Once tripped, the thermostat requires a
manual reset. Reset by pressing the sensor’s reset button
when the air temperature decreases approximately 25°F
below the cutout point.
Filter Switch
The filter switch is a binary input device that measures the
pressure differential across the unit filters. It is mounted in
the filter section and connected to the RTM. A diagnostic
SERVICE signal displays at the remote panel if the
pressure differential across the filters is at least 0.5” w.c.
The contacts automatically open when the pressure
differential across the filters decrease to 0.4” w.c.The
switch differential is field adjustable between 0.17” to 5.0”
w.c. ± 0.05 “.
High Duct Static Switch Option
The high duct static switch is field-mounted in the
ductwork or plenums with smoke dampers. It will cause a
manual reset diagnostic if the duct static exceeds the pre-
set static limit.The static limit is adjustable at the HI.

SCXG-SVX01H-EN 85
Pre-Startup
Pre-Startup Checklist
Complete this checklist after installing unit to verify all
recommended installation procedures are complete
before start-up.This does not replace the detailed
instructions in the appropriate sections of this manual.
Always read the entire section carefully to become familiar
with the procedures.
Supply Fan
• Verify the fan and motor shafts are parallel.
• Verify the fan and motor sheaves are aligned.
• Check the fan belt condition and tension. Adjust the
tension if belts are floppy or squeal continually.
Replace worn or fraying belts in matched sets..
• Ensure the fan rotates freely.
• Tighten locking screws, bearing set screws and
sheaves.
• Ensure bearing locking collars do not wobble when
rotated.
• Remove fan assembly tie down bolts. On 20 - 35 ton
units, do not remove the fan assembly tie down bolts
if the fan speed is 750 rpm or less.
• Ensure fan rotation is in direction of arrow on fan
housing. If incorrect, verify incoming power phasing is
correct. Switch wires on the fan contact to properly
phase fan if necessary.
Ductwork
• Ensure trunk ductwork to VAV boxes is complete and
secure to prevent leaks.
• Verify that all ductwork conforms to NFPA 90A or 90B
and all applicable local codes
Water-Cooled Unit Piping
• Verify condensate drain, water piping drain plugs,
economizer header, and condenser vent plug are
installed.
Air-Cooled Units Only
• Verify leak test was performed after refrigerant piping
was installed.
• Verify liquid line filter driers installed.
Units with Hydronic Heat
• Verify the entering water temperature sensor is
installed upstream of the hydronic coil.
Units with Electric Heat
• Verify the supply air temperature sensor is
downstream of the electric heat coil.
Electrical
• Verify electrical connections are tight.
Components
• Verify liquid line service valve, and suction and
discharge service valves if present, are open at startup.
Note: Each compressor suction line contains a low
pressure sensor that will shut the compressor
down in low pressure situations. See Table 41,
p. 68.
• Ensure system components are properly set and
installed.
Note: Thermal expansion valve superheat is factory set
and requires no field adjustment. Operating
superheat should be between 14-20°F. Actual
superheat depends on several factors (operating
conditions, system load step, system charge,
piping and condenser head pressure control.)

86 SCXG-SVX01H-EN
Start-up
To start the unit, complete the following steps in order.
Review “Preliminary Refrigerant Charging,” p. 37 in
Installation section if applicable. Confirm all steps were
completed.
Air Cooled Only
•Charging is more accurate at higher outdoor
temperatures, if the outdoor temperature is less
than 80°F, temporarily disable fan pressure control
switches. See unit wiring diagrams and disconnect
wires between the switches and terminal strip.
•Do not attempt to charge system with low ambient
dampers operating (if applicable). Disable low
ambient dampers in “Open” position before
proceeding.
Evaporator load should be at least 70°F return air and 350
CFM/ton.
Work on only one circuit at a time.
Important: R-410A compressors have belly band
crankcase heaters that must be energized
24 hours before starting compressor. Power
to the unit will energize the heaters. Heaters
will be energized during off-cycle as long as
the unit has power. Failure to perform these
pre-start instructions could result in
compressor damage.
3. Verify compressor crank case heaters have been on for
at least 24 hours.
4. Make sure all service valves are open.
5. Attach a thermocouple type temperature sensor on the
liquid line close to the liquid line service valve.To
ensure an accurate liquid temperature reading, clean
the line where the sensor is attached. After securing
sensor to line, insulate the sensor and line to isolate it
from ambient air.
6. Attach a set of service gauges onto the suction and
discharge gauge ports.
7. Check low side pressure. Low pressure cutout opens
below, and closes above, values in Table 41, p. 68.If
low side pressure is less than open psig, refrigerant
may need to be added to suction line before starting
compressor(s) to close the switch. SLOWLY meter into
the suction line only as much R-410A as needed to
close the low pressure cutout. Use theVAPOR charging
connection. If possible, plan to use this entire
refrigerant bottle on the same unit in order to minimize
fractionalization. Use an accurate scale to measure and
record the amount of R-410A added.
8. Switch field supplied unit disconnect “OFF”. Open the
unit control box and plug in reset relay only for circuit
being started.
9. Turn 115 volt control circuit switch “ON”. Close control
box and switch field supplied unit disconnect “ON”.
Unit power should be off no longer than 60 minutes to
prevent refrigerant migration to compressor sumps. If
power is off for longer than 60 minutes, allow time for
crankcase heaters to drive refrigerant from
compressor sumps before starting compressors.
10. Adjust setpoints at the HI.
Note: Sufficient cooling load must be visible to
refrigerant circuit controls for mechanical
refrigeration to operate. If necessary, temporarily
reduce discharge air setpoint to verify refrigeration
cycle operation.
11. Check voltage at all compressor terminals to ensure it
is within 10% of nameplate voltage.
12. Check voltage imbalance from these three voltage
readings at each compressor. Maximum allowable
voltage imbalance, phase to phase is 2%.
13. Start the first step compressor only.
WARNING
Live Electrical Components!
During installation, testing, servicing and
troubleshooting of this product, it may be necessary to
work with live electrical components. Have a qualified
licensed electrician or other individual who has been
properly trained in handling live electrical components
perform these tasks. Failure to follow all electrical safety
precautions when exposed to live electrical
components could result in death or serious injury.
NOTICE:
Compressor Damage!
Never manually or automatically pump down system
below 7 psig.This will cause the compressor to operate
in a vacuum and result in compressor damage.
NOTICE:
Compressor Damage!
Keep crankcase heaters on whenever refrigerant is in
the system. If crankcase heaters have not been on with
refrigerant in the system, turn the crankcase heaters on
for a minimum of 24hours before starting compressors.
Failure to follow the above could result in compressor
failure or reduced compressor life.
WARNING
Hazardous Voltage!
Disconnect all electric power, including remote
disconnects before servicing. Follow proper lockout/
tagout procedures to ensure the power can not be
inadvertently energized. Failure to disconnect power
before servicing could result in death or serious injury.

Start-up
SCXG-SVX01H-EN 87
14. Check amp draw at compressor terminals. RLA and
LRA are on the unit nameplate.
15. Measure amp draw at evaporator fan motor terminals.
FLA data is on the motor nameplate.
16. As soon as a compressor starts, verify correct rotation.
If a scroll compressor is allowed to run backwards for
even a very short period of time, internal compressor
damage could occur and compressor life could be
reduced.When rotating backwards scroll compressors
make a loud noise, do not pump, and draw about 1/2
expected amps, and the low side shell gets hot.
Immediately shut off a compressor rotating backwards
and correct wiring.
17. Air Cooled Only: Check condenser fans for proper
rotation. As viewed from the top of the unit, the correct
rotation direction is clockwise. If running backwards,
correct wiring.
18. After 10 minutes, start second compressor of manifold
circuits.
19. Allow 10 minutes for circuit operation to stabilize at full
load.
20. Complete charging, if required.
Final Refrigerant Charge
If full charge was not used during installation, follow these
steps:
1. Determine remaining charge required by subtracting
charge added during “Preliminary Refrigerant
Charging,” p. 37 from the total.
2. With all circuit compressors running, SLOWLY meter
remaining R-410A into suction line from LIQUID
charging connection.
3. Use an accurate scale to measure, then record amount
of R-410A added.
4. After unit has been operating for approximately 30
minutes at full load measure then record operating
pressures.
•Air Cooled Only: Operating pressure
measurement must be made with all condenser
fans running.
5. Repeat for other circuits.
Start-up Procedure
Using startup log on following pages, establish nominal
conditions for consistent measurements as follows:
•Leaving air greater than 60°F
•Entering air temperature = 70 to 90°F
•Entering water temperature > 60°F
With all compressors running at full load:
1. Compute superheat from the suction line pressure and
temperature at the compressor on each circuit. Adjust
the thermal expansion valve settings if necessary.
Superheat should be between 14 and 20°F.
2. Inspect refrigerant flow in the liquid line sight glass.
Flow should be smooth and even, with no bubbles
once the system has stabilized.
Note: Sight glass moisture indicator may show caution
or wet at start-up. May need up to 12 hours of
operation for system to reach equilibrium and
correctly show moisture.
Normal startup will occur provided thatTracer Summit is
not controlling the module outputs or the generic BAS is
NOTICE:
Compressor Damage!
Improper power phasing could cause the compressor
to run backward. Compressor could be running
backward if it is noisy, low side shell gets hot, suction
pressure does not drop within 5 seconds after startup
and compressor only draws half of the expected amps.
Stop the compressor immediately and have a qualified
electrician or technician properly trained in 3-phase
power correct the wiring. Failure to do the above could
result in compressor damage.
WARNING
Rotating Components!
During installation, testing, servicing and
troubleshooting of this product it may be necessary to
work with live and exposed rotating components. Have
a qualified or licensed service individual who has been
properly trained in handling exposed rotating
components, perform these tasks. Failure to follow all
safety precautions could result in rotating components
cutting and slashing technician which could result in
death or serious injury.
NOTICE:
Compressor Damage!
Avoid compressor liquid slugging. Only add liquid in
the suction line when the compressor is running. Use
extreme caution to meter liquid refrigerant in to the
suction line slowly. If liquid is added too rapidly,
compressor oil dilution and oil pump out could occur.
Failure to follow the above could result in compressor
failure or reduced compressor life.
NOTICE:
Compressor Damage!
Do not overcharge system. Excessive refrigerant
charging can cause compressor liquid slugging at
startup and compressor (and/or condenser fans short
cycle). Overcharging could result in compressor failure
or reduced compressor life.

Start-up
88 SCXG-SVX01H-EN
not keeping the unit off. To preventTracer Summit from
affecting unit operation, removeTracer wiring and make
required changes to setpoint and sensor sources.
Operating & Programming Instructions
Reference the IntelliPak™ Self-Contained Programming
Guide, PKG-SVP01B-EN, for available unit operating
setpoints and instructions.A copy ships with each unit. For
units with theVFD option, reference the installer guide that
ships with each VFD.
Startup Log
Complete this log at unit startup.
Unit: __________________________ Unit Location: _____________________________________
Unit Voltage: _____________________ _____________________ _____________________
ABC
Evaporator:
evaporator fan motor horsepower: _____________ evaporator fan
motor amps: __________ __________ __________
ABC
evaporator fan rpm (actual): _____________________________
evaporator system static (from test and balance report or actual readings):
supply duct static: __________
return duct static: __________
evaporator air conditions with both compressors operating:
entering: leaving:
dry-bulb °F: __________ dry-bulb °F: __________
wet-bulb °F: __________ wet-bulb °F: __________
evaporator system cfm (test and balance sheet or actual tested): _______________
Compressor Amp Draw:
circuit A: __________ __________ __________ circuit B: __________ __________ __________
AB C A B C
circuit C: __________ __________ __________ circuit D: __________ __________ __________
AB C A B C
circuit E: __________ __________ __________ circuit F: __________ __________ __________
AB C A B C
suction pressure, psig: circuit A: __________ circuit B: __________ circuit C: __________ circuit D: __________
circuit E: __________ circuit F: __________
discharge pressure, psig: circuit A: __________ circuit B: __________ circuit C: __________ circuit D: __________
circuit E: __________ circuit F: __________
super heat °F: circuit A: __________ circuit B: __________ circuit C: __________ circuit D: __________
circuit E: __________ circuit F: __________
liquid line pressure, psig: circuit A: __________ circuit B: __________ circuit C: __________ circuit D: __________
circuit E: __________ circuit F: __________
sub cooling °F: circuit A: __________ circuit B: __________ circuit C: __________ circuit D: __________
circuit E: __________ circuit F: __________

Start-up
SCXG-SVX01H-EN 89
Water Cooled Units:
Circuit A:
entering water temperature °F: __________ leaving water temperature °F: __________
entering water pressure, psig: __________ leaving water pressure, psig: __________
Circuit B:
enter water temperature °F: __________ leaving water temperature °F: __________
entering water pressure, psig: __________ leaving water pressure, psig: __________
Circuit C:
entering water temperature °F: __________ leaving water temperature °F: __________
entering water pressure, psig: __________ leaving water pressure, psig: __________
Circuit D:
enter water temperature °F: __________ leaving water temperature °F: __________
entering water pressure - psig: __________ leaving water pressure, psig: __________
Circuit E:
enter water temperature °F: __________ leaving water temperature °F: __________
entering water pressure - psig: __________ leaving water pressure, psig: __________
Circuit F:
enter water temperature °F: __________ leaving water temperature °F: __________
entering water pressure - psig: __________ leaving water pressure, psig: __________
Air Cooled Units:
(data taken from outside condensing unit)
voltage: __________ __________ __________ amp draw: __________ __________ __________
ABC A B C
entering air temperature °F:_______________________ leaving air temperature °F: __________
refrigerant pressures at condenser, psig:
____/____ sub cooling at condenser °F: __________

90 SCXG-SVX01H-EN
Maintenance
Service Access
See “Service Clearances,” p. 24 for recommended service
and code clearances. Access to thermostat unit controls is
through a hinged access panel door on the front, lower left
of the unit’s compressor section.
IntelliPak unit controls access is through a panel on the
middle right of the fan section.The panel is secured with
an automatic latch and quick-acting fasteners, which
require a screwdriver to open.
Removable front unit panels provide access to
compressors, fan, motor and belts.
Removable left side panels give access to drive side, fan
bearing, condensers, and waterside economizer control
valve.The compressor, condenser and fan motor access
panels are secured with quick-acting fasteners. Access
panels for evaporator coils, expansion and water valves,
and left fan bearing are sheet metal screws. Access to
other components for service requires removal of panels
secured with sheet metal screws. During operation, sight
glasses are viewable through portholes on the upper right
side panel of the fan section.
Variable Frequency Drives are shipped separately and field
installed. See section “Variable Frequency Drive Option
(VFD),” p. 41 for VFD related dimensions and weights.
Variable Frequency Drive (VFD)
The VFD access panel is hinged to allow service access to
the fan motor and belt drive components that are located
behind it.To swing the panel open:
• Remove the unit center cover panel to the left of the
VFD panel.
• Remove and discard the sheet metal shipping screws
along the top and bottom edges of the VFD panel.
• Disconnect the communications cable from the
keypad on the VFD door panel.
• Turn the two slotted-head fasteners on the right edge
of the VFD panel fully counterclockwise.
• Pull on the handle to swing the panel 180°.
To close and reattach the panel, reverse the procedures
listed above.
Note: To secure panel in open position during service
procedures, attach chain mounted to cabinet frame
behind the unit center cover panel to chain retainer
notch on the edge of the VFD panel.
Note: Verify all wires are in proper position and not
rubbing before replacing the panel.
Note: Panel weight rating = 225 lbs. total, including
factory-installed components.
Variable Frequency Drive (VFD) - Remote
Mounted
ReferenceTR200 operating instructions (BAS-SVX19A-
EN) for maintenance information on VFD.
Air Filters
Filter access doors are on the unit’s left side. Filter access
for the 2” filter rack on optional steam and hot water coils
and airside economizers is also on the left side of the unit.
To replace throwaway filters, remove the dirty elements
and install new filters with the filter’s directional arrows
pointing toward the fan. Verify that no air bypasses the
filters.
Inspecting and Cleaning Drain
Pan
Check the condensate drain pan and drain line to ensure
that the condensate drains properly at least every six
months or as dictated by operating experience.
WARNING
Hazardous Voltage w/Capacitors!
Disconnect all electric power, including remote
disconnects and discharge all motor start/run
capacitors before servicing. Follow proper lockout/
tagout procedures to ensure the power cannot be
inadvertently energized. For variable frequency drives
or other energy storing components provided by Trane
or others, refer to the appropriate manufacturer’s
literature for allowable waiting periods for discharge of
capacitors.Verify with an appropriate voltmeter that all
capacitors have discharged. Failure to disconnect
power and discharge capacitors before servicing could
result in death or serious injury.
For additional information regarding the safe discharge
of capacitors, see PROD-SVB06A-EN
WARNING
Hazardous Voltage w/Capacitors!
Disconnect all electric power, including remote
disconnects and discharge all motor start/run
capacitors before servicing. Follow proper lockout/
tagout procedures to ensure the power cannot be
inadvertently energized. For variable frequency drives
or other energy storing components provided by Trane
or others, refer to the appropriate manufacturer’s
literature for allowable waiting periods for discharge of
capacitors. Verify with an appropriate voltmeter that all
capacitors have discharged. Failure to disconnect power
and discharge capacitors before servicing could result
in death or serious injury.
For additional information regarding the safe discharge
of capacitors, see PROD-SVB06A-EN

Maintenance
SCXG-SVX01H-EN 91
If evidence of standing water or condensate overflow
exists, take steps to identify and remedy the cause
immediately. See “Troubleshooting,” p. 104 for possible
causes and solutions.
Clean drain pans using the following procedure:
1. Disconnect all electrical power to the unit.
2. Don the appropriate personal protective equipment
(PPE).
3. Remove all standing water.
4. Use a scraper or other tools to remove and solid
matter. Remove solid matter with a vacuum device that
utilizes high efficiency particulate arrestance (HEPA)
filters with a minimum efficiency of 99.97% at 0.3
micron particle size.
5. Thoroughly clean the contaminated area(s) with a mild
bleach and water solution or an EPA-approved sanitizer
specifically designed for HVAC use. Carefully follow
the sanitizer manufacturer’s instructions regarding
product use.
6. Immediately rinse drain pan thoroughly with fresh
water to prevent potential corrosion from cleaning
solution.
7. Allow the unit to dry thoroughly before putting the
system back into service.
8. Properly dispose of all contaminated materials and
cleaning solution.
Inspecting and Cleaning the Fan
Inspect the fan section every six months or more
frequently if operating experience dictates. Clean
accumulated dirt and organic matter on the fan interior
surfaces following the procedure below:
1. Disconnect all electrical power to the unit.
2. Wear the appropriate personal protective equipment
(PPE).
3. Use a portable vacuum with HEPA filtration to remove
the loose dirt and organic matter.The filter should be
99.97% efficient at 0.3 micron particle size.
4. Thoroughly clean the fan and associated components
with an industrial cleaning solution. Carefully follow
the cleaning solution manufacturer’s instructions
regarding personal protection and ventilation when
using their product.
5. Rinse the affected surfaces thoroughly with fresh
water and a fresh sponge to prevent potential
corrosion of metal surfaces.
6. Allow the unit to dry completely before putting it back
into service.
7. Properly dispose of all contaminated materials and
cleaning solution.
Supply Fan
Fan Drive
Perform the following procedures according to the
“Periodic Maintenance Check List”.
WARNING
Hazardous Voltage w/Capacitors!
Disconnect all electric power, including remote
disconnects and discharge all motor start/run
capacitors before servicing. Follow proper lockout/
tagout procedures to ensure the power cannot be
inadvertently energized. For variable frequency drives or
other energy storing components provided by Trane or
others, refer to the appropriate manufacturer’s literature
for allowable waiting periods for discharge of
capacitors. Verify with an appropriate voltmeter that all
capacitors have discharged. Failure to disconnect power
and discharge capacitors before servicing could result in
death or serious injury.
For additional information regarding the safe discharge
of capacitors, see PROD-SVB06A-EN
WARNING
Hazardous Voltage w/Capacitors!
Disconnect all electric power, including remote
disconnects and discharge all motor start/run
capacitors before servicing. Follow proper lockout/
tagout procedures to ensure the power cannot be
inadvertently energized. For variable frequency drives
or other energy storing components provided by Trane
or others, refer to the appropriate manufacturer’s
literature for allowable waiting periods for discharge of
capacitors.Verify with an appropriate voltmeter that all
capacitors have discharged. Failure to disconnect
power and discharge capacitors before servicing could
result in death or serious injury.
For additional information regarding the safe discharge
of capacitors, see PROD-SVB06A-EN

Maintenance
92 SCXG-SVX01H-EN
1. Rotate the fan wheel to ensure it turns freely in the
proper direction and is not rubbing on the fan housing
or inlet. If necessary, center the fan wheel again.
2. Check the position of both shafts. Fan and motor shafts
should operate parallel to each other for maximum belt
and bearing life. Shim as necessary under the motor or
fan bearings to obtain proper alignment.
3. Check the fan motor sheave alignment with straight
edge or a tightly pulled string. For sheaves of different
widths, place a string in the center groove of each
sheave and pull it tight for a center line. See Figure 64,
p. 94 for recommended torques.
4. Once sheaves are properly aligned, tighten sheave set
screws to proper torque. See Table 53 and Table 54,
p. 93.
5. Check belt tension. See “Measuring BeltTension,”
p. 93.
6. If required, adjust belt to the minimum recommended
tension. See “Adjusting BeltTension,” p. 94.
7. After aligning sheaves, retighten bearing set screws to
proper torques shown in Table 53, p. 93 and Table 54,
p. 93 .
8. Check the fan bearing locking collars for tightness on
the shaft.To tighten the locking collar, loosen the set
screw and slide the collar into its proper position over
the extended end of the inner case.Tighten the set
screw to torque value in Table 53, p. 93 and Table 54,
p. 93.
9. During air balancing, verify the sheave alignment, belt
tension, and that the shaft is parallel.
Fan Bearings
The opposite drive end bearing is a special bearing with
close tolerance fit of balls and races. Replace this bearing
with the same part number as the original bearing. Follow
the fan bearing lubrication schedules in Table 50, p. 92,
Table 51, p. 92, and Table 52, p. 93 to reference compatible
fan bearing grease for specific bearings.
WARNING
Hazardous Voltage w/Capacitors!
Disconnect all electric power, including remote
disconnects and discharge all motor start/run
capacitors before servicing. Follow proper lockout/
tagout procedures to ensure the power cannot be
inadvertently energized. For variable frequency drives or
other energy storing components provided by Trane or
others, refer to the appropriate manufacturer’s literature
for allowable waiting periods for discharge of
capacitors. Verify with an appropriate voltmeter that all
capacitors have discharged. Failure to disconnect power
and discharge capacitors before servicing could result in
death or serious injury.
For additional information regarding the safe discharge
of capacitors, see PROD-SVB06A-EN
Figure 63. Fan shaft and motor sheave alignment
NOTICE:
Bearing Failure!
Do not mix greases with different bases within the
bearing. Mixing grease within the bearing could result
in premature bearing failure.
Fixed
Sheave
Straight-
edge
For uneven width sheaves
use a taut string down the
center of both sides.
Table 50. Baldor fan bearing lubrication schedule
Baldor Rated Speed, rpm
NEMA/ (IEC) Frame Size 3600 1800 1200 900
up to 210 incl. (132) 5500 hrs 12,000 hrs 18,000 hrs 22,000 hrs
over 210 to 280 incl. (180) 3600 hrs 9500 hrs 15,000 hrs 18,000 hrs
over 360 to 5800 incl. (300) 2200 hrs 3500 hrs 7400 hrs 10,500 hrs
Table 51. AO smith bearing lubrication schedule
Speed Service Frame Standard Service Severe Service Extreme
Over 1800 rpm All 6 months 3 months 3 months
1800 rpm 140-180 3 yrs 1 yr 6 mths
210-280 2 1/2 yrs 10 1/2 mths 5 1/2 mths
320-360 2 yrs 9 mths 4 1/2 mths

Maintenance
SCXG-SVX01H-EN 93
Fan Belt Tension
Note: Check fan belt tension at least twice during the first
days of new belt operation since there is a rapid
decrease in tension until belts are run-in.
Proper belt tension is necessary to endure maximum
bearing and drive component life and is based on fan
brake horsepower requirements. If frayed or worn, replace
belts in matched sets.
Measuring Belt Tension
Measure fan belt tension with a Browning, Gates, or
equivalent belt tension gauge. Determine deflection by
dividing the belt span distance (in inches) by 64. See
Figure 64, p. 94. Follow the procedure below to measure
belt tension.
1. Measure belt span between centers of sheaves and set
the large “O” ring of the tensioning gauge at 1/64 inch
for each inch of belt span.
2. Set the load “O” ring at zero.
3. Place the large end of the gauge at the center of the belt
span. Press down until the large “O” ring is even with
the top of the belt line or the next belt as in Figure 64,
p. 94. Place a straight edge across the sheaves as a
reference point. See Figure 63, p. 92.
4. Remove the gauge. Note that the load “O” ring now
indicates a number on the plunger scale.This number
represents pounds of force required to deflect the belt.
5. Check the reading from step 4 against the values given
in Table 53, p. 93. If necessary, readjust belt tension.
400-440 1 1/2 yrs 8 mths 4 mths
Note: Service standard - 8 hrs/day, normal to lgith loading, 100°F ambient temp. max.Severe service - 24 hrs/day, shock loading, vibration, dirt or dust,
100 to 150°F ambient temp. Extreme service - heavy shock or vibration, dirt or dust, 100 to 150°F ambient temp.
Table 51. AO smith bearing lubrication schedule
Speed Service Frame Standard Service Severe Service Extreme
Over 1800 rpm All 6 months 3 months 3 months
Table 52. Compatible fan bearing grease
Type
Texaco Multi Fak 2
Shell Alvania 2
Mobile 532
Chevron Dura-Lith 2
Exxon Beacon
Keystone 84H
Table 53. Fan shaft bearing torques
Setscrew
size hex-size across
flats recommended torque
In-lb ft-lb
1/4"-20 1/8” 180 15
5-16"-18 5-32” 402 33.5
Table 54. Fan hub and sheave torques
unit size fan dia. setscrew size torque (ft-
lbs)
SCWG 20
16.5” 5/16” 12
SCWG 22
SCWG 25
SCRG 20
SCWG 29
18” 5/16” 12
SCWG 32
SCRG 25
SCRG 30
SCWG 35
20” 5/16” 14
SCWG 38
SCRG 30
SCRG 35
SCWG 42
25” 3/8” 24
SCWG 46
SCWG 52
SCWG 58
SCRG 40
SCRG 50
SCWG 65
27” 3/8” 24
SCWG 72
SCWG 80
SCRG 60
SCWG 90
SCWG C0
SCWG C1

Maintenance
94 SCXG-SVX01H-EN
Adjusting Belt Tension
To adjust belt tension refer to Figure 64, p. 94 and perform
the following procedure:
1. Loosen bolts A, B, and E on both sides of the sliding
motor base. See Figure 65, p. 94.
2. Loosen nuts C and D (as required for motor
horsepower) to slide the motor on its mounting plate
in the proper direction to tension or relieve tension on
the belt.
3. Adjust nuts A-D and bolt E. Do not stretch the belts over
the sheaves.
4. Retighten all nuts and bolts.
5. Verify tension is adjusted properly.
Recommended belt tension range values are on the unit
fan scroll.To access the fan scroll, face the right-hand side
of the unit and remove the top left panel.The belt tension
label is on the top right-hand corner of the fan scroll. See
Figure 65, p. 94.
The correct operation tension for a V-belt drive is the
lowest tension at which the belt will not slip under the peak
load conditions. It may be necessary to increase the
tension of some drives to reduce flopping or excessive
startup squealing.
Figure 64. Belt tension gauge (top) and fan belt
adjustment (bottom)
NOTICE:
Belt Tension!
Do not over-tension belts. Excessive belt tension will
reduce fan and motor bearing life, accelerate belt wear
and possibly cause shaft failure.
Figure 65. Location of fan belt label on fan scroll (top)
and belt tensioning with fan adjustment
points (bottom)

Maintenance
SCXG-SVX01H-EN 95
Refrigerant System
Should refrigerant system repair be required, LeakTest,
Brazing and Evacuation Procedures are described.
Preliminary Charging is described in the Installation-
Mechanical section, “Preliminary Refrigerant Charging,”
p. 37 and Final Charging is described in Start-up section,
“Final Refrigerant Charge,” p. 87.
Ignore Air Cooled Only steps for Water Cooled systems.
Refrigerant systems that have been opened must have
filter driers replaced and complete leak test and
evacuation before recharging.
Refrigerant Leak Test Procedure
Figure 66. Fan assembly
WARNING
Confined Space Hazards!
Do not work in confined spaces where refrigerant or
other hazardous, toxic or flammable gas may be
leaking. Refrigerant or other gases could displace
available oxygen to breathe, causing possible
asphyxiation or other serious health risks. Some gases
may be flammable and or explosive. If a leak in such
spaces is detected, evacuate the area immediately and
contact the proper rescue or response authority. Failure
to take appropriate precautions or to react properly to
such potential hazards could result in death or serious
injury.
WARNING
Hazard of Explosion!
Never use an open flame to detect gas leaks. It could
result in an explosion. Use a leak test solution for leak
testing. Failure to follow recommended safe leak test
procedures could result in death or serious injury or
equipment or property-only-damage.
WARNING
Hazard of Explosion!
Use only dry nitrogen with a pressure regulator for
pressurizing unit. Do not use acetylene, oxygen or
compressed air or mixtures containing them for
pressure testing. Do not use mixtures of a hydrogen
containing refrigerant and air above atmospheric
pressure for pressure testing as they may become
flammable and could result in an explosion.
Refrigerant, when used as a trace gas should only be
mixed with dry nitrogen for pressurizing units. Failure
to follow these recommendations could result in death
or serious injury or equipment or property-only
damage.
WARNING
Hazardous of Explosion!
Do not exceed unit nameplate design pressures when
leak testing system. Failure to follow these instructions
could result in an explosion causing death or serious
injury.

Maintenance
96 SCXG-SVX01H-EN
Note: These service procedures require working with
refrigerant. Do not release refrigerant to the
atmosphere!The service technician must comply
with all federal, state, and local laws.
When Leak-testing refrigerant systems, observe all safety
precautions.
Leak test only one circuit at a time to minimize system
exposure to potentially harmful moisture in the air.
Field Piping (air cooled discharge and liquid
lines)
1. Ensure all required field installed piping pressure tests
are completed in accordance with national and/or local
codes.
2. Close liquid line angle valve.
3. Connect R-410A refrigerant cylinder to high side
charging port (at Remote Condenser or field supplied
discharge line access port). Add refrigerant to reach
pressure of 12 to 15 psig.
4. Disconnect refrigerant cylinder. Connect dry nitrogen
cylinder to high side charging port and increase
pressure to 150 psig. Do not exceed high side
(discharge) unit nameplate design pressure. Do not
subject low side (suction) components to high side
pressure.
5. Check all piping joints, valves, etc. for leaks.
Recommend using electronic detector capable of
measuring 0.1 oz/year leak rate.
6. If a leak is located, use proper procedures to remove
the refrigerant/nitrogen mixture, break connections
and make repairs. Retest for leaks.
Make sure all service valves are open.
System Repair
1. If system is water cooled with service valves, or air
cooled, high and low side may be tested independently
by closing liquid line angle valve and water cooled unit
discharge line ball valve. Otherwise leave all valves
open and DO NOT exceed low side design pressure.
2. Connect R-410A refrigerant cylinder to charging port,
add refrigerant to reach pressure of 12 to 15 psig.
3. Disconnect refrigerant cylinder. Connect dry nitrogen
cylinder to high side charging port and increase
pressure to 150 psig. DO NOT exceed unit nameplate
design pressures. If testing complete system, low side
design pressure is maximum.
4. Check piping and/or components as appropriate for
leaks.
5. Recommend using electronic detector capable of
measuring 0.1 oz/year leak rate.
6. If a leak is located, use proper procedures to remove
the refrigerant/nitrogen mixture, break connections
and make repairs. Retest for leaks.
7. Make sure all service valves are open.
Brazing Procedures
Proper brazing techniques are essential when installing
refrigerant piping.The following factors should be kept in
mind when forming sweat connections.
1. When heating copper in the presence of air, copper
oxide forms.To prevent copper oxide from forming
inside the tubing during brazing, sweep an inert gas,
such as dry nitrogen, through the tubing. A nitrogen
flow of 1 to 3 cubic feet per minute is sufficient to
displace the air in the tubing and prevent oxidation of
the interior surfaces. Use a pressure regulating valve
or flow meter to control the flow.
2. Ensure that the tubing surfaces requiring brazing are
clean, and that the tube ends are carefully reamed to
remove any burrs.
3. Make sure the inner and outer tubes of the joint are
symmetrical and have a close clearance, providing an
easy ‘slip’ fit. If the joint is too loose, the connection’s
tensile strength is significantly reduced. Ensure the
overlap distance is equal to the inner tube diameter.
4. Wrap each refrigerant line component with a wet cloth
to keep it cool during brazing. Excessive heat can
damage the internal components.
Note: Use 40-45% silver brazing alloy (BAg-7 or BAg-28)
on dissimilar metals. Use BCup-6 brazing alloy on
copper-to-copper joints.
WARNING
R-410A Refrigerant under High Pressure!
The units described in this manual use R-410A
refrigerant. Use ONLY R-410A rated service equipment
or components with these units. For specific handling
concerns with R-410A, please contact your local Trane
representative. Failure to use R-410A rated service
equipment or components could result in equipment
exploding under R-410A high pressures which could
result in death, serious injury, or equipment damage.
WARNING
Hazard of Explosion and Deadly Gases!
Never solder, braze or weld on refrigerant lines or any
unit components that are above atmospheric pressure
or where refrigerant may be present. Always remove
refrigerant by following the guidelines established by
the EPA Federal Clean Air Act or other state or local
codes as appropriate. After refrigerant removal, use dry
nitrogen to bring system back to atmospheric pressure
before opening system for repairs. Mixtures of
refrigerants and air under pressure may become
combustible in the presence of an ignition source
leading to an explosion. Excessive heat from soldering,
brazing or welding with refrigerant vapors present can
form highly toxic gases and extremely corrosive acids.
Failure to follow all proper safe refrigerant handling
practices could result in death or serious injury.

Maintenance
SCXG-SVX01H-EN 97
5. If using flux, apply sparingly to joint. Excess flux will
contaminate refrigerant system.
6. Apply heat evenly over length and circumference of
joint.
7. Begin brazing when the joint is hot enough to melt the
brazing rod.The hot copper tubing, not the flame,
should melt the rod.
8. Continue to apply heat evenly around the joint
circumference until the brazing material is drawn into
the joint by capillary action, making a mechanically
sound and gas-tight connection.
9. Visually inspect the connection after brazing to locate
any pinholes or crevices in the joint. Use a mirror if
joint locations are difficult to see.
System Evacuation Procedures
Each refrigeration circuit must be evacuated before the
unit can be charged and started.
Use a rotary type vacuum pump capable of pulling a
vacuum of 100 microns or less.
Verify that the unit disconnect switch and the system
control circuit switches are “OFF”.
Oil in the vacuum pump should be changed each time the
pump is used with high quality vacuum pump oil. Before
using any oil, check the oil container for discoloration
which usually indicates moisture in the oil and/or water
droplets. Moisture in the oil adds to what the pump has to
remove from the system, making the pump inefficient.
When connecting the vacuum pump to a refrigeration
system, it is important to manifold the vacuum pump to
both the high and low side of the system (liquid line access
valve and suction line access valve). Follow pump
manufacturer’s directions for proper usage methods.
Lines used to connect the pump to the system should be
copper and of the largest diameter that can practically be
used. Using larger line sizes with minimum flow resistance
can significantly reduce evacuation time.
Important: Rubber or synthetic hoses are not
recommended for system evacuation
because they have moisture absorbing
characteristics which result in excessive
rates of evaporation, causing pressure rise
during the standing vacuum test.This
makes it impossible to determine if the
system has a leak, excessive residual
moisture, or a continual or high rate of
pressure increase due to the hoses.
Install electronic micron vacuum gauge in common line
ahead of vacuum pump shutoff valve, as shown in
Figure 67, p. 98. Close valves B and C, open valve A.
Start vacuum pump.After several minutes, gauge reading
will indicate maximum vacuum pump is capable of
pulling. Rotary pumps should produce vacuums of 100
microns or less.
OpenValves B and C. Evacuate the system to a pressure of
300 microns or less. As the vacuum is being pulled on the
system, there could be a time when it would appear that no
further vacuum is being obtained, yet the pressure is high.
It is recommended that during the evacuation process, the
vacuum be “Broken”, to facilitate the evacuation process.
To break the vacuum, shut valves A, B, & C and connect a
refrigerant cylinder to the charging port on the manifold.
Purge the air from the hose. Raise the standing vacuum
pressure in the system to “zero” (0 psig) gauge pressure.
Repeat this process two or three times during evacuation.
Note: It is unlawful to release refrigerant into the
atmosphere. When service procedures require
working with refrigerants, the service technician
must comply with all Federal, State, and local laws.
Standing Vacuum Test . Once 300 microns or less is
obtained, close Valve A, leave valves B and C, allowing
vacuum gauge to read actual system pressure. Let system
equalize for approximately 15 minutes.This is referred to
as a “standing vacuum test” where, time versus pressure
rise. Maximum allowable rise in 15 minutes is 200
microns. If pressure rise is greater than 200 microns but
levels off to a constant value, excessive moisture is
present. If pressure steadily continues to rise, a leak is
indicated. Figure 68, p. 98 illustrates three possible results
of the “standing vacuum test”.
If a leak is encountered, repair system and repeat
evacuation process until recommended vacuum is
obtained. Once the system has been evacuated, break the
vacuum with refrigerant and complete the remaining Pre-
Start procedures before starting the unit.
NOTICE:
Valve Damage!
Remove, do not wrap, water cooled condenser pressure
relief valves during brazing. Failure to do so could result
in valve damage.
NOTICE:
Motor Winding Damage!
Do not use a megohm meter or apply voltage to a
compressor motor winding while it is under a vacuum.
Voltage sparkover could cause damage to the motor
windings.

Maintenance
98 SCXG-SVX01H-EN
Compressors
Scroll Compressor Failure Diagnosis and
Replacement
If compressor failure is suspected, refer to COM-SVN01A-
EN for detailed information regarding compressor failure
diagnosis and replacement of scroll compressors.
Figure 67. Typical vacuum pump hookup
Figure 68. Evacuation time vs. pressure rise

Maintenance
SCXG-SVX01H-EN 99
Components
Important: On units ordered with a Design Special of Inlet Guide Vanes, refer to non-current IOM (SCXF-SVX01D-EN)
dated on or before March 2008 for maintenance procedure.
Figure 69. Typical water-cooled (SXWG) compressor section components

Maintenance
100 SCXG-SVX01H-EN
Coil Fin Cleaning
Keep coils clean to maintain maximum performance. For
operation at its highest efficiency, clean the refrigerant coil
often during periods of high cooling demand or when dirty
conditions prevail. Clean the coil a minimum of once per
year to prevent dirt buildup in the coil fins, where it may
not be visible.
Remove large debris from the coils and straighten fins
before cleaning. Remove filters before cleaning.
Clean refrigerant coils with cold water and detergent, or
with one of the commercially available chemical coil
cleaners. Rinse coils thoroughly after cleaning.
Economizer and evaporator coils are installed so the
evaporator is directly behind the economizer. To clean
between the coils, remove the sheet metal block off.
Access the block off by removing the corner panels on the
unit’s left or right rear side.
If the refrigerant coil is installed back to back with the
waterside economizer coil, use a cleaner that is acceptable
for cleaning both types of coils.
Inspecting and Cleaning Coils
Coils become externally fouled as a result of normal
operation. Coil surface dirt reduces heat transfer ability
and can cause comfort problems, increased airflow
resistance and thus increased operating energy costs.
Inspect coils at least every six months or more frequently
as dictated by operating experience. Cleaning frequently
is dependent upon system operating hours, filter
maintenance, efficiency, and dirt load. Following is the
suggested method for cleaning steam and hot water coils.
Steam and Hot Water Coils
1. Disconnect all electrical power to the unit.
2. Wear appropriate personal protective equipment
(PPE).
3. Access both sides of the coil section.
4. Use a soft brush to remove loose debris from both
sides of the coil.
5. Use a steam cleaning machine, starting from the top of
the coil and working downward. Clean the leaving air
side of the coil first, then the entering air side. Use a
block-off to prevent steam from blowing through the
coil and into a dry section of the unit.
6. Repeat step 5 as necessary. Confirm that the drain line
is open following completion of the cleaning process.
7. Allow the unit to dry thoroughly before putting the
system back into service.
8. Straighten any coil fins that may be damaged with a fin
rake.
WARNING
Hazardous Chemicals!
Coil cleaning agents can be either acidic or highly
alkaline and can burn severely if contact with skin
occurs. Handle chemical carefully and avoid contact
with skin. ALWAYS wear Personal Protective
Equipment (PPE) including goggles or face shield,
chemical resistant gloves, boots, apron or suit as
required. For personal safety refer to the cleaning agent
manufacturer’s Materials Safety Data Sheet and follow
all recommended safe handling practices. Failure to
follow all safety instructions could result in death or
serious injury.
WARNING
Hazardous Voltage w/Capacitors!
Disconnect all electric power, including remote
disconnects and discharge all motor start/run
capacitors before servicing. Follow proper lockout/
tagout procedures to ensure the power cannot be
inadvertently energized. For variable frequency drives
or other energy storing components provided by Trane
or others, refer to the appropriate manufacturer’s
literature for allowable waiting periods for discharge of
capacitors.Verify with an appropriate voltmeter that all
capacitors have discharged. Failure to disconnect
power and discharge capacitors before servicing could
result in death or serious injury.
For additional information regarding the safe discharge
of capacitors, see PROD-SVB06A-EN
NOTICE:
Equipment Damage!
Do not clean the refrigerant coil with hot water or
steam.The use of hot water or steam as a refrigerant
coil-cleaner agent could cause high pressure inside the
coil tubing and subsequent damage to the coil.
Do not use acidic chemical coil cleaners. Also, do not
use alkaline chemical coil cleaners with a pH value
greater then 8.5 (after mixing) without using an
aluminum corrosion inhibitor in the cleaning solution.
Use of the chemical could result in equipment damage.
WARNING
Hazardous Voltage w/Capacitors!
Disconnect all electric power, including remote
disconnects and discharge all motor start/run
capacitors before servicing. Follow proper lockout/
tagout procedures to ensure the power cannot be
inadvertently energized. For variable frequency drives
or other energy storing components provided by Trane
or others, refer to the appropriate manufacturer’s
literature for allowable waiting periods for discharge of
capacitors.Verify with an appropriate voltmeter that all
capacitors have discharged. Failure to disconnect
power and discharge capacitors before servicing could
result in death or serious injury.
For additional information regarding the safe discharge
of capacitors, see PROD-SVB06A-EN

Maintenance
SCXG-SVX01H-EN 101
9. Replace all panels and parts and restore electrical
power to the unit.
10. Ensure that contaminated material does not contact
other areas of the equipment or building. Properly
dispose of all contaminated materials and cleaning
solutions.
Refrigerant Coils
1. Disconnect all electrical power to the unit.
2. Wear the appropriate personal protective equipment
(PPE).
3. Access to the coil section of the unit (both sides).
4. Use a soft brush to remove loose debris from both
sides of the coil.
5. Mix a high quality coil cleaning detergent with water
according to the manufacturer’s instructions. If the
detergent is strongly alkaline after mixing (pH 8.5 or
higher), it must contain an inhibitor. Carefully follow
the cleaning solution manufacturer’s instructions
regarding product use.
6. Place the mixed solution in a garden pump-up sprayer
or high pressure sprayer. If using a high pressure
sprayer note the following:
•Maintain a minimum nozzle spray angle of 15°
•Spray perpendicular to the coil face
•Protect other areas of the equipment and internal
controls from contact with moisture or the cleaning
solution
•Keep the nozzle at least six inches from the coil
•Do not exceed 600 psig
Draining the Waterside Economizer Coil
Drain plugs are in the piping below each coil’s supply and
return header. Use these plugs to drain the coil and piping.
When draining the coil, open the vents at the top of the
supply and return headers. Also, a drain plug is at the
bottom of the inlet condenser manifold and in the outlet
pipe near the unit’s left side. Remove these plugs to drain
the condensers. Be sure to open the vent plugs at the top
of the condenser inlet and outlet manifold.
When refilling the condenser/waterside economizer coil
system with water, provide adequate water treatment to
prevent the formation of scale or corrosion.
Cleaning the Condenser
Condensing water contains minerals that collect on the
condenser tube walls. Cooling towers also collect dust and
foreign materials that deposit in the condenser tube.The
formation of scale or sludge in the condenser is indicated
by a decreased water flow, low temperature difference
between inlet and outlet water, and abnormally high
condensing temperatures.To maintain maximum
condenser efficiency, the condenser must remain free of
built-up scale and sludge. Clean the condenser either
mechanically or chemically.
Mechanical Cleaning of Condenser and
Economizer Coils
1. Turn off the condenser supply water. Remove drain
plugs discussed in the “Draining the Coil” section.
2. Remove condenser head to expose condenser tubes.
3. Rotate a round brush through tubes to loosen
contaminant.
4. Flush tubes with water to push the sludge out through
the drain opening in the bottom of the supply header
and the return pipe.
WARNING
Hazardous Voltage w/Capacitors!
Disconnect all electric power, including remote
disconnects and discharge all motor start/run
capacitors before servicing. Follow proper lockout/
tagout procedures to ensure the power cannot be
inadvertently energized. For variable frequency drives
or other energy storing components provided by Trane
or others, refer to the appropriate manufacturer’s
literature for allowable waiting periods for discharge of
capacitors.Verify with an appropriate voltmeter that all
capacitors have discharged. Failure to disconnect
power and discharge capacitors before servicing could
result in death or serious injury.
For additional information regarding the safe discharge
of capacitors, see PROD-SVB06A-EN
NOTICE:
Equipment Damage!
Properly drain and vent coils when not in use.Trane
recommends glycol protection in all possible freezing
applications. Use a glycol approved for use with
commercial cooling and heating systems and copper
tube coils. Failure to do so could result in equipment
damage.
NOTICE:
Proper Water Treatment!
The use of untreated or improperly treated water could
result in scaling, erosion, corrosion, algae or slime. It is
recommended that the services of a qualified water
treatment specialist be engaged to determine what
water treatment, if any, is required.Trane assumes no
responsibility for equipment failures which result from
untreated or improperly treated water, or saline or
brackish water.

Maintenance
102 SCXG-SVX01H-EN
5. To clean the economizer tubes, remove the cast iron
header plates at both sides of the coil between the inlet
and outlet headers (four-row coils only; two-row coils
do not have cover plates at right end). Rotate round
brush through tubes from left end to loosen
contaminants. Flush tubes with water.
6. Replace condenser end plates and clamps.The end
plates must be centered when tightening the clamp.
7. Replace coil headers with gaskets and torque bolts to
50 ft.-lb.
8. Replace drain and vent plugs.
Chemical Cleaning of Condenser and
Economizer Coil
Chemical cleaning removes scale deposits built up by
minerals in the water. For a suitable chemical solution,
consult a water treatment specialist.The condenser water
circuit is composed of copper, steel, and cast iron.The
chemical supply house should approve or provide all
materials used in the external circulating system, along
with the quantity of cleaning material, duration of cleaning
time, and safety precautions necessary for handling the
cleaning agent.
Piping Components
Water Valves
Water valves have a stern packing nut. If there is evidence
of water leakage at the valve stem, proceed as follows:
1. Remove actuator motor from support plate.
2. Remove shaft coupling.
3. Torque the packing nut to 10-ft.-lbs. of torque.
4. Replace shaft coupling.
5. Replace actuator motor.
Water Flow Switch
Flow switches have a magnet on the vane assembly that
attracts ferrous particulate may build up on the magnet to
the point that the vane will wedge and not operate
properly. When the flow switch does not operate, remove
and replace.
Maintenance Periodic Checklists
Monthly Checklist
The following check list provides the recommended
maintenance schedule to keep the commercial self-
contained equipment running efficiently.
1. Inspect unit air filters. Clean or replace if airflow is
blocked or if filters are dirty.
2. Inspect coils for excess moisture or icing. Icing on the
coils may indicate low airflow supply, restricted airflow
from dirty fins, evaporator frost protection sensor
problems, or a shortage of refrigerant flowing through
the coil.
3. Check that condensate from evaporator and
economizer coils flows freely through condensate
piping, traps, drain pan, and drainage holes. Remove
algae and or any airflow obstructions.
4. Check the condition and tension of fan belts. Adjust
tension if belts are floppy or squeal continually.
Replace worn or fraying belts in matched sets.
Note: Check belt tension and adjust it at least twice daily
the first days of new belt operation. Belt tension
will rapidly decrease until the belts are run in.
5. Check liquid line sight glasses during operation.
Bubbles in the sight glasses indicate a possible
shortage of refrigerant or an obstruction in the liquid
lines, e.g. dirty liquid line filter driers.
6. Inspect filter driers for leaks, flow obstructions, or
temperature drop across the filter drier. A noticeable
temperature differential, e.g. 5°F, in the liquid line may
indicate an obstruction. Replace the filter drier if it
appears clogged.
WARNING
Hazardous Voltage w/Capacitors!
Disconnect all electric power, including remote
disconnects and discharge all motor start/run
capacitors before servicing. Follow proper lockout/
tagout procedures to ensure the power cannot be
inadvertently energized. For variable frequency drives
or other energy storing components provided by Trane
or others, refer to the appropriate manufacturer’s
literature for allowable waiting periods for discharge of
capacitors.Verify with an appropriate voltmeter that all
capacitors have discharged. Failure to disconnect
power and discharge capacitors before servicing could
result in death or serious injury.
For additional information regarding the safe discharge
of capacitors, see PROD-SVB06A-EN
WARNING
Hazardous Service Procedures!
The maintenance and troubleshooting procedures
recommended in this manual could result in exposure
to electrical, mechanical or other potential safety
hazards. Always refer to the safety warnings provided
throughout this manual concerning these procedures.
Unless specified otherwise, disconnect all electrical
power including remote disconnect and discharge all
energy storing devices such as capacitors before
servicing. Follow proper lockout/tagout procedures to
ensure the power can not be inadvertently energized.
When necessary to work with live electrical
components, have a qualified licensed electrician or
other individual who has been trained in handling live
electrical components perform these tasks. Failure to
follow all of the recommended safety warnings
provided, could result in death or serious injury.

Maintenance
SCXG-SVX01H-EN 103
7. Inspect the optional waterside economizer coil. Clean
the coil to prevent airflow restrictions through the fins.
8. Check and record operating pressures.
Semi-Annual Maintenance
1. Verify the fan motor is properly lubricated. Follow
lubrication recommendations on the motor tag or
nameplate. Contact the motor manufacturer for more
information.
2. Lubricate fan bearings. For best results, lubricate
bearings during unit operation. Refer to the “Fan
Bearings” section.
3. With power disconnected, manually rotate the fan
wheel to check for obstructions in the housing or
interference with fan blades. Remove obstructions and
debris. Center the fan wheel if necessary.
4. Check the fan assembly sheave alignment.Tighten set
screws to their proper torques.
5. Check water valves for leakage at valve stem packing
nut.
Note: Perform this procedure monthly if the unit is in a
coastal or corrosive environment.
Annual Maintenance
Check and tighten all set screws, bolts, locking collars and
sheaves.
1. Inspect, clean, and tighten all electrical connections.
2. Visually inspect the entire unit casing for chips or
corrosion. Remove rust or corrosion and repaint
surfaces.
3. Visually check for leaks in refrigerant piping.
4. Inspect fan, motor, and control contacts. Replace badly
worn or eroded contacts.
5. Inspect the thermal expansion valve sensing bulbs for
cleanliness, good contact with the suction line, and
adequate insulation from ambient air.
6. Verify the superheat setting is 12 -17°F at the
compressor.
When checking operating pressures and conditions,
establish the following nominal conditions for consistent
measurements.
1. Leaving air temperature greater than 60°F
2. Entering air temperature is 80 - 90°F
3. Entering water temperature greater than 65°F
4. Compressors running at full load
5. Drain condensing water system, inspect thoroughly
for fouling. Clean condensers if necessary.

104 SCXG-SVX01H-EN
Diagnostics
Troubleshooting
System Checks
Before proceeding with technical trouble charts or controls
checkout, complete the following system analysis:
1. Measure actual supply voltage at the compressor and
an motor terminals with the unit running.Voltage must
be within the range listed on the motor nameplate.
Phase imbalance must be less than 2.0%.
2. Check all wiring and connections to be sure that they
are intact, secure and properly routed.The as wired
system diagrams are provided in the unit control
panel.
3. Check that all fuses are installed and properly sized.
4. Inspect air filters and coils to be sure that airflow to the
unit is not restricted.
5. Check the zone thermostat settings.
6. Ensure that the fan is rotating in the proper direction.
If phasing is wrong at the main power terminal block,
the fan and compressors will not run correctly.
7. Inspect ductwork and duct connections for tightness.
Operating Procedures
Install pressure gauges on the discharge and suction line
access valves. When the unit has stabilized (after
operating approximately 15 minutes at full load), record
suction and discharge pressures. System malfunctions
such as low airflow, line restrictions, incorrect refrigerant
charge, malfunctioning of expansion valves, damaged
compressors, etc. will result in pressure variations which
are outside the normal range.
Note: If phasing at the main incoming power terminal is
incorrect, switch two of the three incoming power
leads. If a compressor has been replaced and the
phase is changed at the compressor, it will run
backwards and discharge pressure will be very low.
To resolve incorrect compressor wire phasing,
change phasing at the compressor.
It is important that pressures be measured under stable
and constant conditions in order for the readings to be
useful.
Voltage Imbalance
Voltage imbalance on three-phase systems can cause
motor overheating and premature failure. Maximum
allowable imbalance is 2.0%, and the readings used to
determine it must be measured at the compressor
terminals.
Voltage imbalance is defined as 100 times the sum of the
division of the three voltages from the average voltage. If,
for example, the three measured voltages are 221, 230,
227, the average is:
Therefore, the percentage of voltage imbalance is:
100*(226-221)/226 = 2.2%
In this example, 2.2% imbalance of more than 2.0% exists,
be sure to check the voltage at the unit disconnect and
terminal block switch. If an imbalance at the unit
disconnect switch does not exceed 2.0%, the imbalance is
caused by faulty wiring within the unit. Be sure to conduct
a thorough inspection of the unit electrical wiring
connections to locate the fault, and make any repairs
necessary.
Diagnostics
Refer to the IntelliPak Self-Contained Programming Guide,
PKG-SVP01B-EN, for specific unit programming and
troubleshooting information. In particular, reference the
“Service Mode Menu” and “Diagnostic Menu”sections in
the programming guide. Refer to the following text for
general diagnostic and troubleshooting procedures.
Common diagnostics and troubleshooting procedures
follow below.
WARNING
Live Electrical Components!
During installation, testing, servicing and
troubleshooting of this product, it may be necessary to
work with live electrical components. Have a qualified
licensed electrician or other individual who has been
properly trained in handling live electrical components
perform these tasks. Failure to follow all electrical
safety precautions when exposed to live electrical
components could result in death or serious injury.
Table 55. Common unit problems and solutions
Problem Possible Cause Remedy
Drain pan is
overflowing Plugged drain line
Unit not level Clean drain line
Level unit
Standing water in
drain pan Unit not level
Plugged drain line Level Unit
Clean drain line
Wet interior insulation
Coil face velocity too
high
Improper trap design
Drain pan leaks/
overflowing
Condensation on
surfaces
Reduce fan speed
Design trap per unit
installation
instructions
Repair Leaks
Insulate surfaces
Excess dirt in unit Missing filters
Filter bypass Replace filters
Reduce filter bypass
Microbial growth
(mold) Standing water in
drain pan See "Standing water in
drain pan" above
Moisture problems See “Wet interior
insulation” above
221 230 227++
3
----------------------------------------------------226volts=

Diagnostics
SCXG-SVX01H-EN 105
A
Auto Reset S/A Static Pressure Limit
Problem:The supply air static pressure went too high.
Reason for Diagnostic:The S/A static pressure exceeded
the S/A static pressure limit setpoint for at least one
second continuously.
UCM Reaction: A "supply air pressure shutdown" signal is
sent to the following functions:
a. Compressor staging control,
b. Economizer actuator control,
c. Heat operation,
d. Supply fan control,
e. VFD control,
f. Exhaust fan control,
g.Exhaust actuator control
Reset Required: (PAR) The supply fan is not allowed to
restart for 15 seconds after the diagnostic occurs. An auto
reset will also occur if the unit cycles out of occupied mode
and back.
C
CO2Sensor Failure
Problem:The VCM CO2sensor input signal is out of range.
Check: Check field/unit wiring between sensor and VCM.
Reason for Diagnostic:The unit is reading a signal that is
out of range for the CO2sensor transducer input.
UCM Reaction:The CO2reset function disables.
Reset Required: (PAR) An automatic reset occurs after the
CO2sensor transducer input receives a signal that is
within range for ten continuous seconds.
Compressor Contactor Fail - Circuit 1, 2, 3, or
4
Problem:The compressor contactor for Ckt. 1, 2, 3, or 4 has
malfunctioned.
Reason for Diagnostic:The circuit compressor proving
input is detected closed continuously for more than three
seconds while neither compressor output on that circuit
closes.
UCM Reaction:A "lockout ckt #1, 2, 3, or 4 request is issued
to the compressor staging control function.
Reset Required: (PMR) A manual reset is required after the
diagnostic is set. It can be reset by the HI orTracer Summit.
Compressor Trip - Ckt 1, 2, 3, or 4
Problem:The compressor ckt #1, 2, 3, or 4 has tripped.
Reason for Diagnostic:The ckt #1, 2, 3, or 4 compressor
proving input is detected open continuously for more than
3 seconds when either or both compressor outputs on that
circuit energize (as described in the compressor protection
function).
Reason for Diagnostic:The circuit compressor proving
input is detected open continuously for more than 3
seconds when either or both compressor outputs on that
circuit energize (as described in the compressor protection
function).
UCM’ Reaction: A “lockout ckt #1, 2, 3, or 4” request is
issued to the compressor staging control function.
Reset Required: (PMR) A manual reset is required after this
diagnostic occurs.The diagnostic can be reset by the unit
mounted HI module orTracer Summit.
Condenser Temp Sensor Failure - Circuit 1, 2,
3, or 4
Problem:The saturated condenser temperature input is
out of range for circuit #1, 2, 3, or 4.
Check: Sensor resistance should be between 830 ohms
(200°F) and 345.7 ohms (-40°F). If so, check field/unit
wiring between sensor and MCM/SCM.
Reason for Diagnostic:The unit is reading a signal that is
out of range for the circuit #1, 2, 3, or 4 saturated
condenser temperature sensor. (temp < -55°F or temp >
209°F).
UCM Reaction: A “Lockout Ckt # 1, 2, 3, or 4” request is
issued to the compressor staging control function.
Reset Required: (PAR) An automatic reset occurs after the
circuit 1, 2, 3, or 4 condenser temp input returns to its
allowable range within 10 seconds.
D
Dirty Filter
Problem:There is a dirty filter.
Reason for Diagnostic:The filter switch input on the RTM
is closed for more than 60 seconds continuously.
UCM Reaction: An information only diagnostic is set.
Reset Required: (INFO) An automatic reset occurs after the
dirty filter input reopens for 60 continuous seconds.
E
ECEM Communications Failure
Problem:The RTM has lost communication with the
ECEM.
Check: Field/unit wiring between RTM and ECEM module.
Reason for Diagnostic:The RTM has lost communication
with the ECEM.
UCM Reaction: If the unit has the comparative enthalpy
option, the economizer enable r.e. enthalpy function will
revert to level 2 enthalpy comparison.
Reset Required: (PAR) An automatic reset occurs after
communication has been restored.

Diagnostics
106 SCXG-SVX01H-EN
Emergency Stop
Problem:The emergency top input is open.
Reason for Diagnostic:An open circuit has occurred on the
emergency stop input caused either by a high duct temp t-
stat trip, or the opening of field-provided contacts, switch,
etc.
UCM Reaction: Off or close requests are issued as
appropriate to the following functions;
a. Compressor staging/chilled water cooling control
b. Heat operation
c. Supply fan control and proof of operation
d. Exhaust fan control and proof of operation.
e. Exhaust actuator control
f. Outside air damper control
g.On VAV units, VFD control
Reset Required: (PMR) A manual reset is required after the
emergency stop input recloses.The diagnostic can be
reset by the HI.
Entering Cond Water Temp Sensor Fail
Problem:
Activation Conditions: temperature < -50°F or temperature
> 209°F, and unit configured for water cooled condenser
c.Time to React: 10 sec <T < 20 sec
d. DiagnosticText (Human Interface Display) “ENT COND
WATERTEMP SENSOR FAIL”
e. Actions to be Initiated: A “Lockout All Ckts ” request is
issued to the “Compressor Staging Function”
f. Reset: An automatic reset occurs after the entering
condenser water temperature input returns to within
range continuously for 15 seconds.
Entering Water Temp Sensor Fail
a. Data used (module, packet, byte, bit): WSM, 01,18,05
b. Activation Conditions: temperature < -50°F or
temperature > 209°F, and unit configured with water
cooled condenser and/or economizer
c.Time to React: 10 sec <T < 20 sec
d. DiagnosticText (Human Interface Display) “ENTERING
WATERTEMP SENSOR FAIL”
e. Actions to be Initiated: A “Disable Water Side
Economizer” request is issued to “Water Side Economizer
Temperature Enable Function”
f. Reset: An automatic reset occurs after the EnteringWater
Temp. input returns to within range continuously for 10
seconds.
Evap Temp Sensor Failure - Circuit 1, 2, 3, or 4
Problem:The evaporator temperature sensor (ckt #1, 2, 3,
or 4) is out of range.
Check: Sensor resistance should be between 830 ohms
(200°F) and 345.7Kohms (-40°F). If so, check field/unit
wiring between sensor and MCM/SCM.
Reason for Diagnostic:The unit is reading a signal that is
out of range for the circuit #1 evaporator temperature
sensor input (temp < -55°F or temp > 209°F).
UCM Reaction:The coil frost protection function for the
refrigeration circuit (#1, 2, 3, or 4) only is disabled.
Reset Required: (PAR) An automatic reset occurs after the
#1, 2, 3, or 4 evap temp input returns to its allowable range
for 10 seconds.
G
GBAS 0-5 VDC Module Comm Failure
Problem:The RTM has lost communication with the GBAS
module.
Check: Field/unit wiring between RTM and GBAS.
Reason for Diagnostic:The RTM has lost communication
with the GBAS module.
UCM Reaction: The UCM will initiate the following actions;
a. If the demand limit input was closed prior to the
communications loss, then the demand limit commands
issued to the heat operation function (if applicable) and the
compressor staging/chilled water cooling function will be
cancelled.
b. If any of the GBAS setpoint control parameters are the
HI-selected setpoint sources, then those setpoints will
revert to the default HI setpoints.
c. Any active GBAS output control parameters will be
ignored.
d. A failsafe function in the GBAS module will cause all
GBAS outputs to be zeroed and deenergized.
Reset Required: (PAR) An automatic reset occurs after
communication has been restored.
H
Heat Failure
Problem:The heat has failed.
(Electric heat unit)Typically, this is because the electric
heat section became too hot.
Reason for Diagnostic:The heat fail input on the heat
module was closed:
a. for more than 80 seconds,
b. for ten consecutive occurrences (each lasting five
seconds or more) within a 210 second period.
UCM Reaction: An information only diagnostic is set.
Reset Required: (INFO) An automatic reset occurs after the
heat fail input remains open for 210 seconds continuously.

Diagnostics
SCXG-SVX01H-EN 107
Heat Module Auxiliary Temperature Sensor
Fail
Problem:The heat mod aux temp sensor input is out of
range.
Check: Sensor resistance should be between 830 ohms
(200°F) and 345.7 ohms (-40°F). If so, check field/unit wiring
between sensor and heat module.
Reason for Diagnostic: At least one enabled unit function
has the heat module auxiliary temperature input
designated as its sensor, and the unit is reading a signal
that is out of range for this input (temp < -55°F or temp >
209°F).
UCM Reaction:The functions that designated the heat
module auxiliary temperature input as their input are
disabled.
Reset Required: (PAR) An automatic reset occurs after the
heat module auxiliary temperature input returns to its
allowable range for 10 seconds.
Heat Module Comm Failure
Problem:The RTM has lost communication with the heat
module.
Check: Check field/unit wiring between RTM and heat
module.
Reason for Diagnostic:The RTM has lost communication
with the heat module.
UCM Reaction: An “all heat off” request is sent to the heat
operation function.
If the unit has staged gas or electric heat, all heat module
outputs will be zeroed and deenergized.
If the unit has hydronic heat or chilled water installed, the
unit will turn off the supply fan and close the outside air
damper upon the occurrence of a heat module comm
failure. A failsafe function in the heat module will cause all
water valves to be set to 100% to provide full water flow.
Unless used for switching purposes (air handlers with
chilled water and mod gas, or chilled water and hydronic
heat) all binary outputs will be deenergized.
Reset Required: (PAR) An automatic reset occurs after
communication has been restored.
L
Low Air Temp Limit Trip
Problem:The low air temp limit has tripped. (Units with
steam or hot water heating, or air handlers with chilled
water cooling)
Reason for Diagnostic: A low air temp limit trip is detected
continuously for more than one second.This can occur if
the hydronic heat low air temp limit input closes for > 1
second, or if the chilled water low air temp limit trip input
opens for > 1 second. On units with both hydronic heat and
chilled water, both low air temp limit inputs are active, and
the unit will respond in the same manner regardless of
which input is used.
UCM Reaction:The UCM will initiate the following actions;
a. An “open all water valves”request is issued to the heat
module function, causing any steam, hot water, or chilled
water valves on the unit to open.
b. An “all heat off” request is issued to the heat control
function.
c. A “fan off” request is sent to the supply fan control
function.
d. A “close damper” request is sent to the economizer
actuator control function.
Reset Required: (PMR) A manual reset is required after the
low air temp limit trip condition clears.The diagnostic can
be reset at the unit mounted human interface, byTracer
Summit, or by cycling power to the RTM.
Low Pressure Control Open - Circuit 1, 2, 3, or
4
Problem:The Low Pressure Control (LPC) for Ckt #1, 2, 3,
or 4 is open.
Check: State of refrigerant charge for ckt #1, 2, 3, or 4.
Reason for Diagnostic:The Ckt # 1 LPC input is detected
open as described in the compressor protection function.
UCM Reaction: A “Lockout Ckt # 1, 2, 3, or 4” request is
issued to the compressor staging control function.
Reset Required: (PMR) A manual reset is required anytime
after the diagnostic is set.The diagnostic can be reset by
the human interface,Tracer Summit, or by cycling power
to the RTM.
M
Manual Reset SA Static Press Limit
Problem:The supply air static pressure went too high for
the third consecutive time.
Reason for Diagnostic:The auto reset supply air static
pressure limit diagnostic has occurred for the third time
while the unit is operating in occupied mode.
UCM Reaction: A "supply air pressure shutdown" signal is
sent to the following functions;
a. Compressor staging control,
b. Economizer actuator control,
c. Heat operation,
d. Supply fan control,
e. VFD control,
f. Exhaust fan control
g. Exhaust actuator control
Reset Required: (PMR) A manual reset is required and can
be accomplished at the HI,Tracer Summit, or by cycling
power to the RTM.
MCM Communications Failure
Problem:The RTM has lost communication with the MCM.

Diagnostics
108 SCXG-SVX01H-EN
Check: Check field/unit wiring between RTM and MCM.
Reason for Diagnostic:The RTM has lost communications
with the MCM.
UCM Reaction: A “Lockout” request is sent to the
compressor staging control function. And a failsafe
function in the MCM will cause all MCM outputs to be
zeroed and deenergized.
Reset Required: (PAR) An automatic reset occurs after
communication has been restored.
Mode Input Failure
Problem:The RTM mode input is out of range.
Check: Sensor resistance should be between 1 ohm and 40
ohms. If so, check field/unit wiring between sensor and
RTM.
Reason for Diagnostic:The mode input signal on the RTM
is out of range (resistance < 1 ohm or resistance > 40
ohms).
UCM Reaction:The system mode reverts to the default (HI
set) system mode.
Reset Required: (INFO) An automatic reset occurs after the
mode input returns to its allowable range for 10 seconds.
N
NSB Panel Zone Temperature Sensor Failure
Problem:The NSB panel's zone temp sensor input is out of
range. (This input is at the NSB panel, not on the unit
itself).
Check: If have an external sensor connected to the NSB
panel zone sensor input, then the internal NSB panel zone
sensor should be disabled. Verify sensor resistance. If in
valid range, check wiring between the sensor and NSB
panel.
NSB Panel Comm Failure
Problem:The RTM has lost communications with the night
setback panel (programmable zone sensor).
Check: Field/unit wiring between RTM and NSB Panel.
Reason for Diagnostic:The RTM has lost communication
with the NSB panel.
UCM Reaction:The unit reverts to the next lower priority
mode switching source (typically the HI default mode). If
the NSB panel zone sensor is the designated sensor source
for any functions, those functions are disabled.
Reset Required: (PAR) An automatic reset occurs after
communication has been restored.
O
O/A Humidity Sensor Failure
Problem:The outside air humidity sensor data is out of
range.
Check: Check field/unit wiring between the sensor and
RTM.
Reason for Diagnostic:The unit is reading a signal that is
out of range for the outside air humidity sensor (humidity
< 5% or humidity > 100%).
UCM Reaction:The economizer enable enthalpy function
reverts to dry-bulb temperature changeover (“Level 1”)
control.
Reset Required: (PAR) An automatic reset occurs after the
OA humidity input returns to its allowable range for 10
seconds.
O/A Temp. Sensor Failure
Problem:The outside air temperature sensor input is out
of range.
Check: Sensor resistance should be between 830 ohms
(200°F) and 345.7 ohms (-40°F). If so, check field/unit wiring
between sensor and RTM.
Reason for Diagnostic:The unit is reading a signal that is
out of range for the outside air temperature input on the
RTM (temp. < -55°F or temp > 209°F).
UCM Reaction:These unit functions occur:
• low ambient compressor lockout disables
• O/A damper drives to minimum position
• on VAV units with S/A temp. reset type selected as O/A
temp. reset, the reset type reverts to “none” for the
duration of the failure
Reset Required: (PAR) an automatic reset occurs after the
O/A temperature input returns to its allowable range.To
prevent rapid cycling of the diagnostic, there is a 10 second
delay before the automatic reset.
Occupied Zone Heat Setpoint Failure
Problem:The occupied zone heat setpoint input is out of
range.
Reason for Diagnostic:The input designated as occupied
zone heating setpoint source is out of range for the outside
air temperature input on the RTM (temp. < 45°F or temp >
94°F).
UCM Reaction:The active occupied zone heating setpoint
reverts to the default value.
Reset Required: (PAR) an automatic reset occurs after the
occupied zone heating setpoint input returns to its
allowable range for 10 continuous seconds, or after a
different occupied zone heating setpoint selection source
is user-defined.
R
Return Air Humidity Sensor Failure
Problem: On units with both airside economizer and
comparative enthalpy installed, the return air humidity
sensor input is out of range.
Check: Check field/unit wiring between the sensor and
ECEM.

Diagnostics
SCXG-SVX01H-EN 109
Reason for Diagnostic:The unit is reading a signal that is
out of range for the return air humidity sensor (humidity
< 5% or humidity > 100%).
UCM Reaction:The economizer enable r.e. enthalpy
function reverts to reference enthalpy changeover (“Level
2”) control.
Reset Required: (PMR) An automatic reset occurs after the
RA humidity input returns to its allowable range
continuously for 10 seconds.
Return Air Temp Sensor Failure
Problem: On units with the comparative enthalpy option,
the return air temperature sensor input is out of range.
Check: Sensor resistance should be between 830 ohms
(200°F) and 345.7 ohms (-40°F). If so, check field/unit
wiring between the sensor and ECEM.
Reason for Diagnostic:The unit is reading a signal that is
out of range for the return air humidity sensor (temp < -
55°F or temp > 209°F).
UCM Reaction:The economizer enable r.e. enthalpy
function reverts to reference enthalpy changeover (“Level
2”) control.
Reset Required: (PAR) An automatic reset occurs after the
RA temp input returns to its allowable range continuously
for 10 seconds.
RTM Aux. Temp. Sensor Failure
Problem:The RTM auxiliary temperature sensor data is
out of range.
Check: Sensor resistance should be between 830 ohms
(200°F)and 345.7 ohms (-40°F). If so, check field/unit wiring
between sensor and RTM.
Reason for Diagnostic: At least one enabled unit function
has the RTM auxiliary temperature input designated as its
sensor, and the unit is reading a signal that is out of range
for this input (temp. < -55°F or temp > 209°F).
UCM Reaction:The functions with the RTM auxiliary
temperature input designated as their sensor are disabled.
Reset Required: (PAR) an automatic reset occurs after the
designated zone temperature signal returns to its
allowable range.To prevent rapid cycling of the
diagnostic, there is a 10 second delay before the automatic
reset.
RTM Data Storage Error
Problem:There was a data transmission error.
Check:This can be caused by an intermittent power loss.
Turn the unit off for 1-2 minutes, then back on again. If
diagnostic persists, then the RTM may need to be
replaced.
Reason for Diagnostic: An error occurred while the RTM
was writing data to its internal non-volatile memory
(EEPROM).
UCM Reaction: An information only diagnostic will be
displayed at the human interface.
Reset Required: (INFO) A manual reset may be made at the
human interface, atTracer Summit, or by cycling power to
the RTM.
RTM Zone Sensor Failure
Problem:The RTM zone temperature sensor input is out of
range.
Check: Sensor resistance should be between 830 ohms
(200°F) and 345.7 ohms (-40°F). If so, check field/unit wiring
between sensor and RTM.
Reason for Diagnostic: At least one enabled unit function
has the RTM zone temperature input designated as its
sensor, and the unit is reading a signal that is out of range
for this input (temp. < -55°F or temp > 150°F).
UCM Reaction:The functions with the RTM zone
temperature input designated as their sensor are disabled.
Reset Required: (PAR) an automatic reset occurs after the
designated zone temperature signal returns to its
allowable range.To prevent rapid cycling of the
diagnostic, there is a 10 second delay before the automatic
reset.
S
SCM Communication Failure
Problem:The RTM has lost communication with the SCM.
Check: Check field/unit wiring between the RTM and SCM.
Reason for Diagnostic:The RTM has lost communication
with the SCM.
UCM Reaction: A “lockout” request is sent to the
compressor staging control function. A failsafe function in
the SCM will cause all SCM outputs to be zeroed and
deenergized.
Reset Required: (PAR) An automatic reset occurs after
communication has been restored.
Space Static Press Setpt Failure
Problem:The active space static pressure setpoint is out of
range.
Check: Check setpoint value. Also, if space pressure
setpoint source is GBAS, but this setpoint has not been
assigned to any of the four analog inputs on GBAS, this
message will occur.
Reason for Diagnostic:The unit is reading a signal that is
out of range for the space static pressure setpoint (input <
0.03 iwc or input > 0.20 iwc).
UCM Reaction:The default space pressure setpoint will
become the active space pressure setpoint.
Reset Required: (PAR) An automatic reset occurs after the
designated space pressure setpoint source sends a signal
within range for 10 continuous seconds, or after a different
space pressure setpoint source is user-defined.

Diagnostics
110 SCXG-SVX01H-EN
Supply Air Pressure Sensor Failure
Problem:The supply air pressure sensor voltage input is
out of range.
Check: Check field/unit wiring between the sensor and
RTM.
Reason for Diagnostic:The unit is reading a signal that is
out of range for the supply air pressure sensor voltage
input (input < 40mV or input > 4.75V)
UCM Reaction:The supply fan is de-energized, and the
following functions are disabled;
a. SA pressure control
b. SA static pressure limit
Reset Required: (PAR) An automatic reset occurs after the
SA temp heating setpoint input returns to within range for
10 continuous seconds, or after a different SA temp
heating setpoint selection source is user-defined.
Supply Air Pressure Setpoint Failure
Problem:The SA pressure input signal is out of range.
Reason for Diagnostic:The SA pressure setpoint input is
sending a signal that is out of range (Input < 1.0 iwc or input
> 4.3 iwc)
UCM Reaction:The default SA pressure setpoint will
become the active SA pressure setpoint.
Reset Required: (PAR) An automatic reset occurs after the
designated SA pressure setpoint source sends a signal
within range for 10 continuous seconds, or after a different
SA pressure setpoint source is user-defined.
Supply Air Temp Cool Setpoint Fail
Problem:The active supply air temperature cooling
setpoint is out of range.
Reason for Diagnostic:The input designated as the SA
temp cooling setpoint is out is out of range (temp < 35°F or
temp > 95°F).
UCM Reaction:The default HI-set SA temp cooling
setpoint becomes the active SA temp cooling setpoint.
Reset Required: (PAR) An automatic reset occurs after the
SA temp cooling setpoint input returns to within range for
10 continuous seconds, or after a different SA temp
cooling setpoint selection source is user-defined.
Supply Air Temp Heat Setpoint Fail
Problem:The active supply air temperature cooling
setpoint is out of range.
Reason for Diagnostic:The input designated as the SA
temp heating setpoint is out is out of range (temp < 35°F
or temp > 185°F).
UCM Reaction:The default HI-set SA temp heating
setpoint becomes the active SA temp heating setpoint.
Reset Required: (PAR) An automatic reset occurs after the
SA temp heating setpoint input returns to within range for
10 continuous seconds, or after a different SA temp
heating setpoint selection source is user-defined.
Supply Air Temperature Failure
Problem:The supply air temperature sensor input is out of
range.
Check: Sensor resistance should be between 830 ohms
(200°F) and 345.7 ohms (-40°F). If so, check field/unit wiring
between sensor and RTM.
Reason for Diagnostic:The unit is reading a signal that is
out of range for the supply air temperature input on the
RTM (temp. < -55°F or temp > 209°F).
UCM Reaction:These unit functions are disabled:
• supply air tempering
• economizing
• supply air temperature low limit function (CV units)
• supply air temperature control heating and cooling
functions (VAV units)
Reset Required: (PAR) an automatic reset occurs after the
designated S/A temperature input returns to its allowable
range.To prevent rapid cycling of the diagnostic, there is
a 10 second delay before the automatic reset.
Supply Fan Failure
Problem:There is no supply airflow indication after the
supply fan is requested on.
Check: Check belts, linkages, etc. on the supply fan
assembly. If these are ok, check field/unit wiring between
RTM and supply fan. If the supply fan runs in service mode,
then verify airflow proving switch and wiring.
Reason for Diagnostic:The supply airflow input is detected
OPEN for 40 continuous seconds during any period of time
in which the supply fan binary output is ON. between 830
ohms (200°F) and 345.7 ohms (-40°F). If so, check field/unit
wiring between the sensor and MCM.
This input is ignored for up to 5 minutes after the supply
fan starts, until airflow is first detected.
UCM Reaction: “Off” or “Close” requests are issued as
appropriate to the following functions;
a. Compressor staging/chilled water control
b. Heat operation
c. Supply fan control & proof of operation
d. Exhaust fan control & proof of operation
e. Exhaust actuator control
f. Economizer actuator control
g. VFD control
Reset Required: (PMR) A manual reset is required anytime
after the diagnostic is set.The diagnostic can be reset at
the HI, Tracer Summit, or by cycling power to the RTM.
Supply Fan VFD Bypass Enabled
a. Data used (module,packet,byte,bit): RTM

Diagnostics
SCXG-SVX01H-EN 111
b. Activation conditions: supply fan VFD bypass has been
activated and supply fan vfd bypass is installed.
c.Time to React: 10 sec <T < 20 sec
d. Diagnostic text (human interface display)
SUPPLY FAN VFD BYPASS ENABLED”
e. Actions to be Initiated: NONE
f. Reset:The INFO diagnostic is cleared when the supply
fan VFD bypass is deactivated.
T
LCI Module Comm Failure
Problem:The RTM has lost communication with the LCI-I.
Check: Check field/unit wiring between RTM and LCI-I
module.
Reason for Diagnostic:The RTM has lost communication
with the LCI-I module.
UCM Reaction: All active commands and setpoints
provided byTracer Summit through the LCI-I will be
cancelled and/or ignored. And whereTracer Summit has
been designated as setpoint source, local HI default
setpoints will be used.
Reset Required: (PAR) An automatic reset occurs after
communication has been restored.
Tracer Communications Failure
Problem:The LCI-I has lost communication withTracer
Summit.
Check:Tracer Summit (building control panel) is powered
up and running properly. If so, check unit wiring between
LCI-I andTracer Summit (building control panel).
Reason for Diagnostic:The LCI-I has lost communications
withTracer Summit for > 15 minutes.
UCM Reaction: All active commands and setpoints
provided byTracer Summit through the LCI-I will be
cancelled and/or ignored. And whereTracer Summit has
been designated as the setpoint source, local HI default
setpoints are used.
Reset Required: (PAR) An automatic reset occurs after
communication betweenTracer Summit and the LCI-I is
restored.
U
Unit HI Communications Failure
Problem:The RTM has lost communication with the unit
mounted (local) human interface (HI).
Check: Field/unit wiring between RTM hand local HI.
Reason for Diagnostic:The RTM has lost communication
with the unit-mounted human interface.
UCM Reaction: A fail-safe function in the HI will cause the
following sequence:
a. disallow any interaction between the HI and the RTM (or
any other modules),
b. render all HI keystrokes ineffective
c. cause the following message to display on the unit-
mounted HI display: “Local HI communications loss.
Check comm link wiring between modules.” If the unit has
a remote HI option, then this diagnostic will display as any
other automatic reset diagnostic.
Reset Required: (INFO) An automatic reset occurs after
communication is restored between the RTM and the HI.
When the failure screen clears, the general display
restores to allow the HI to interact with the RTM again.
Unoccupied Zone Cool Setpoint Failure
Problem:The unoccupied zone cooling setpoint input is
out of range.
Reason for Diagnostic:The input designated as the
unoccupied zone cooling setpoint source is out of range
(temp < 45°F or temp > 94°F).
UCM Reaction:The active unoccupied zone cooling
setpoint reverts to the default value.
Reset Required: (PAR) An automatic reset occurs after the
designated unoccupied zone cool setpoint input returns to
its allowable range for 10 continuous seconds, or after the
user defines a different, valid unoccupied zone cool
setpoint selection source.
Unoccupied Zone Heat Setpoint Failure
Problem:The unoccupied zone heating setpoint input is
out of range.
Reason for Diagnostic:The input designated as
unoccupied zone heating setpoint source is out of range
(temp < 45 F or temp > 94 F).
UCM Reaction:The active unoccupied zone heating
setpoint reverts to the default value.
Reset Required: (PAR) An automatic reset occurs after the
designated unoccupied zone heat setpoint input returns to
its allowable range for 10 continuous seconds, or after the
user defines a different, valid unoccupied zone heating
setpoint selection source.
V
VCM Communication Failure
Problem:The RTM has lost communication with the VCM.
Verify: Check field/unit wiring between RTM and VCM.
Reason for Diagnostic:The RTM has lost communication
with the VCM.
UCM Reaction: All active commands and setpoints
provided by the VCM are canceled and/or ignored. A fail-
safe function in the VCM will cause all outputs to
deenergize and/or set to zero.The outside air damper
minimum position function will revert to using the O/A
flow compensation function if O/A flow compensation is

Diagnostics
11 2 SCXG-SVX01H-EN
enabled or set to the default minimum position function if
O/A flow compensation is disabled or not available.
Reset Required: (PAR) An automatic reset occurs after
communication is restored.
Velocity Pressure Sensor Failure
Problem:The velocity pressure input signal is out of range.
Check: Check field/unit wiring between sensor and VCM.
Reason for Diagnostic:The unit is reading a signal that is
out of range for the velocity pressure transducer input
(during calibration: V < 40 mV or V > 420 mV, during
operation: V < 40 mV or V > 0.75 V).
UCM Reaction:The minimum airflow control function is
disabled.The outside air damper minimum position
function reverts to using the O/A flow compensation
function if O/A flow compensation is enabled or to the
default minimum position function if O/A flow
compensation is disabled or not available.
Reset Required: (PAR) An automatic reset occurs after the
designated space pressure transducer sends a signal
within range for 10 continuous seconds.
VOM Communications Failure
Problem:The RTM has lost communication with the VCM.
Check: Field/unit wiring between RTM and VCM.
Reason for Diagnostic:The RTM has lost communications
with the VOM.
UCM Reaction: Ventilation override actions will not be
allowed, and the VO Output relay will be deenergized.
Reset Required: (PAR) An automatic reset occurs after
communication has been restored.
W
WSM Communications Fail
Problem:The RTM has lost communication with theWSM.
Check: Field/unit wiring between RTM and WSM.
Reason for Diagnostic:The RTM has lost communication
with the WSM.
UCM Reaction:The UCM will react as if a freezestat has
occurred by issuing:
• An “all heat on” or “mod output full open” request to
“heat control”
• A “fan off” request to “supply fan control”
• A “close damper” request to “economizer actuator
control”
•The water pump to turn on and position all water valves
to provide maximum flow through all water source heat
exchangers
• Disables preheat function ifWSM mixed air temp sensor
is selected as preheat sensor
Reset Required: An automatic reset occurs after one
complete set of IPC packets is received.
WSM Mixed Air Temp Sensor Fail
b. Activation Conditions: temperature < -50°For
temperature > 209°F, and sensor is selected for use by
“waterside economizer temperature enable function” or
“preheat function”
c.Time to React: 10 sec <T < 20 sec
e. Actions to be Initiated: “waterside economizer
temperature enable function” uses supply air cooling
setpoint instead of mixed air temperature. If xixed air
temperature is used for “preheat function”, issue a
“disable” request to “preheat function”.
f. Reset: An automatic reset occurs after the mixed air
temp. input returns to within range continuously for 10
seconds.
Water Flow Fail
a. Data used (module,packet,byte,bit): WSM, 01,19, 05
b. Activation Conditions:The water flow input is detected
open ;
1. at the end of precool water flow initiation state, or
2. continuously for five minutes while:
·water side economizer is open 100%,
· presetting of a head pressure valve, or
· demand for mechanical cooling.
Unit must be: a. configured with water cooled condenser
and/or water economizer and b. have water flow switch
installed.
c.Time to React: immediate
e. Actions to be Initiated: A “lockout all ckts” request is
issued to the “compressor staging function”
f. Reset: An automatic reset occurs after the water flow
input returns to within range continuously for 3 seconds,
the water pump is requested OFF, or the water flow switch
becomes not installed.
Z
Zone Cool Setpoint Failure
Problem:The occupied zone cooling setpoint is out of
range.
Reason for Diagnostic:The input designated as occupied
zone cooling setpoint source is out of range (temp. < 45°F
or temp > 94°F).
UCM Reaction:The active occupied zone cooling setpoint
reverts to the default occupied zone cooling setpoint.
Reset Required: (PAR) an automatic reset occurs after the
designated occupied zone CSP input returns to its
allowable range for 10 continuous seconds, or after a
different valid occupied zone CSP selection source is user-
defined.

SCXG-SVX01H-EN 11 3
Wiring Diagrams
Note: For easier access, published unit wiring diagrams (individual, separate diagrams for unitary product lines) will
become available via e-Library instead of through wiring manuals after 2007.
Drawing
Number Description
2307-8264 Field Wiring Diagram W/VFD S*WG 20 -35T & S*RF 20-32T
2307-8266 Schematic Diagram With VFD W/Bypass RTM Modual S*WG 20-35T S*RG 20-32T
2307-8272 Schematic Diagram With VFD W/Bypass S*WG 20-35T S*RG 20-32T
2307-8273 Schematic Diagram With VFD W/O Bypass RTM Modual S*WG 20-35T S*RG 20-32T
2307-8288 Connection Diagram With VFD W/ or W/O Bypass S*WG 20-35T S*RG 20-32T
2307-8419 Schematic Diagram With VFD W/Bypass Dual Power S*WG 20-35T S*RG 20-32T
2307-8423 Connection Diagram With VFD W/Bypass S*WG 20-35T S*RG 20-32T
2307-8265 Schematic Diagram CV S*WG 20-35T S*RG 20-32T
2307-8417 Schematic Diagram CV Dual Point Pwr S*WG 20-35T S*RG 20-32T
2307-8271 Schematic Diagram W/VFD Single Point Pwr S*WG 20-35T S*RG 20-32T
2307-8418 Schematic Diagram W/VFD Dual Point Pwr S*WG 20-35T S*RG 20-32T
2307-8267 Schematic Diagram CV RTM Module S*WG 20-35T S*RG 20-32T
2307-8268 Schematic Diagram Water-Cooled S*WG 20-35T
2307-8274 Schematic Diagram Air-Cooled S*RG 20-32T
2307-8269 Schematic Diagram Heat, Vent Cntrl & GBAS S*WG 20-35T S*RG 20-32T
2307-8270 Schematic Diagram ECEM, VOM LCI, IPCB, HI & RHI Mod S*WG 20-35T S*RG 20-32T
2307-8285 Connection Diagram CV S*WG 20-35T S*RG 20-32T
2307-8286 Connection Diagram CV S*WG 20-35T S*RG 20-32T
2307-8287 Connection Diagram CV S*WG 20-35T S*RG 20-32T
2307-8422 Connection Diagram CV S*WG 20-35T S*RG 20-32T
2307-8289 Connection Diagram W/VFD W/Bypass S*WG 20-35T S*RG 20-32T
2307-8290 Connection Diagram W/VFD W/Bypass S*WG 20-35T S*RG 20-32T
2307-8291 Connection Diagram Thermostat Interface S*WG 20-35T S*RG 20-32T
2307-8421 Connection Diagram Thermostat Interface S*WG 20-35T S*RG 20-32T
2307-8346 Lower 37 PIN CPC Connector S*WG 20-35T S*RG 20-32T
2307-8350 Upper 37 PIN CPC Connector S*WG 20-35T S*RG 20-32T
2307-8457 Electric Heat 9 PIN Connector S*WG 20-35T S*RG 20-32T
2307-8359 Field Wiring Diagram Ipak Controls CCRC 20-60 Ton
2307-8360 Schematic Diagram Thermostat Controls CCRC 20, 29 & 32 Ton
2307-8361 Schematic Diagram Thermostat Controls CCRC 20, 29 & 32 Ton
2307-8362 Connection Diagram Thermostat Controls CCRC 20, 29 & 32 Ton
2307-8363 Connection Diagram Thermostat Controls CCRC 20, 29 & 32 Ton
2307-8364 Field Wiring Diagram Thermostat Controls CCRC 20, 29 & 32 Ton
2307-8332 Schematic Diagram Ipak Controls CCRC 20, 29 & 32 Ton
2308-8284 Connection Diagram With Ipak Controls CCRC 20-60 Ton

Trane optimizes the performance of homes and buildings around the world. A business of Ingersoll Rand, the leader in
creating and sustaining safe, comfortable and energy efficient environments,Trane offers a broad portfolio of advanced
controls and HVAC systems, comprehensive building services, and parts. For more information, visit www.Trane.com.
Trane has a policy of continuous product and product data improvement and reserves the right to change design and specifications without notice.
We are committed to using environmentally
conscious print practices that reduce waste.
© 2014Trane All rights reserved
SCXG-SVX01H-EN 24 Jun 2014
Supersedes SCXG-SVX01G-EN (23 Oct 2012)