Trane Voyager 12 5 To 25 Tons Catalogue 1/2 20 60 Hz
2015-04-02
: Trane Trane-Voyager-12-5-To-25-Tons-Catalogue-684201 trane-voyager-12-5-to-25-tons-catalogue-684201 trane pdf
Open the PDF directly: View PDF .
Page Count: 60
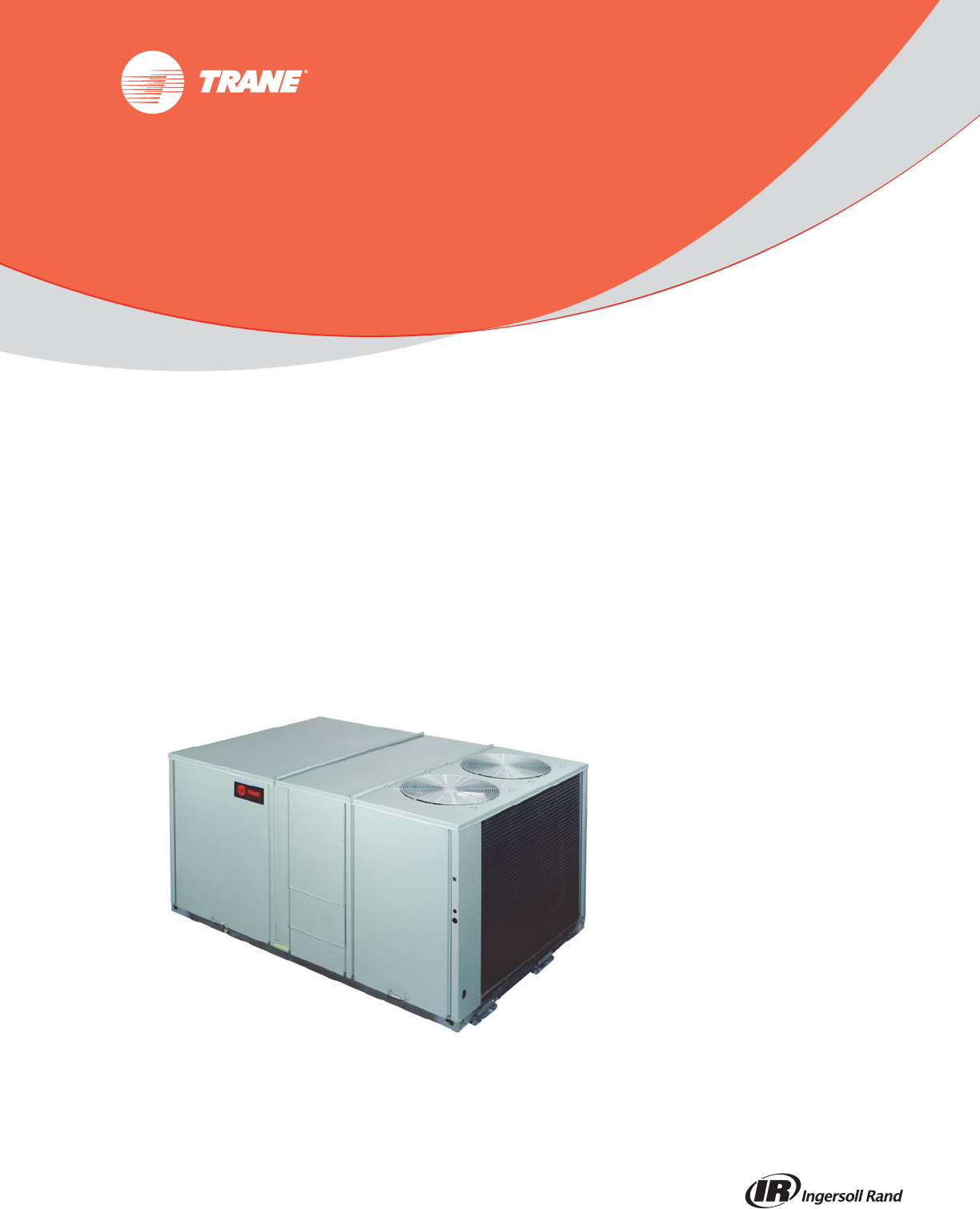
Packaged Rooftop Air Conditioners
Voyager™ – Heat Pump
12½ – 20 Tons – 60 Hz
June 2014 PKGP-PRC012M-EN
Product Catalog

© 2014 Trane All rights reserved PKGP-PRC012M-EN
Introduction
Packaged Rooftop Air Conditioners
Through the years, Trane has designed and developed the most complete line of Packaged Rooftop
products available in the market today. Trane was the first to introduce the Micro—microelectronic
unit controls—and has continued to improve and revolutionize this design concept.
The ReliaTel control platform offers the same great features and functionality as the original Micro,
with additional benefits for greater application flexibility.
Voyager continues to provide the highest standards in quality and reliability, comfort, ease of
service, and the performance of Trane light commercial products.
Trane customers demand products that provide exceptional reliability, meet stringent performance
requirements, and are competitively priced. Trane delivers all of this with Voyager.
Voyager features cutting edge technologies: reliable compressors, Trane engineered ReliaTel
controls, computer-aided run testing, and Integrated Comfort™ Systems.
So whether you’re the contractor, the engineer or the owner, you can be certain Voyager Products
are built to meet your needs.
It’s Hard To Stop A Trane®.
Copyright
This document and the information in it are the property of Trane, and may not be used or
reproduced in whole or in part without written permission. Trane reserves the right to revise this
publication at any time, and to make changes to its content without obligation to notify any person
of such revision or change.
Trademarks
Trane and the Trane logo, Frostat, Integrated Comfort, ReliaTel, Tracer, are trademarks of Trane in
the United States and other countries. All trademarks referenced in this document are the
trademarks of their respective owners.
Revision Summary
PKGP-PRC012M-EN (12 Jun 2014)
• Updated Low Leak Economizer Factory and Field Installed Option
• Updated Features & Benefits, Model Number Description, Performance Data, Weights, and
Mechanical Specifications

Table of Contents
PKGP-PRC012M-EN 3
Features and Benefits . . . . . . . . . . . . . . . . . . . . . . . . . . . . . . . . . . . . . . . . . . . . . . . . . . . 4
Standard and Optional Features at a Glance . . . . . . . . . . . . . . . . . . . . . . . . . . . 4
Standard Features . . . . . . . . . . . . . . . . . . . . . . . . . . . . . . . . . . . . . . . . . . . . . 4
Factory Installed Options . . . . . . . . . . . . . . . . . . . . . . . . . . . . . . . . . . . . . . . 5
Factory or Field Installed Options . . . . . . . . . . . . . . . . . . . . . . . . . . . . . . . . 5
Field Installed Options . . . . . . . . . . . . . . . . . . . . . . . . . . . . . . . . . . . . . . . . . 5
Other Benefits . . . . . . . . . . . . . . . . . . . . . . . . . . . . . . . . . . . . . . . . . . . . . . . . 6
Outstanding Standard Features . . . . . . . . . . . . . . . . . . . . . . . . . . . . . . . . . . . . . . 6
Variety of Options . . . . . . . . . . . . . . . . . . . . . . . . . . . . . . . . . . . . . . . . . . . . . . . . . . 8
Factory Installed Options . . . . . . . . . . . . . . . . . . . . . . . . . . . . . . . . . . . . . . . 8
Factory or Field Installed Options . . . . . . . . . . . . . . . . . . . . . . . . . . . . . . . 11
Field Installed Options . . . . . . . . . . . . . . . . . . . . . . . . . . . . . . . . . . . . . . . . 12
Other Benefits . . . . . . . . . . . . . . . . . . . . . . . . . . . . . . . . . . . . . . . . . . . . . . . . . . . . 13
Application Considerations . . . . . . . . . . . . . . . . . . . . . . . . . . . . . . . . . . . . . . . . . . . . . 16
Selection Procedure . . . . . . . . . . . . . . . . . . . . . . . . . . . . . . . . . . . . . . . . . . . . . . . . . . . 17
Cooling Capacity . . . . . . . . . . . . . . . . . . . . . . . . . . . . . . . . . . . . . . . . . . . . . . . . . . 17
Heating Capacity . . . . . . . . . . . . . . . . . . . . . . . . . . . . . . . . . . . . . . . . . . . . . . . . . . 18
Model Number Description . . . . . . . . . . . . . . . . . . . . . . . . . . . . . . . . . . . . . . . . . . . . . 19
Model Number Notes . . . . . . . . . . . . . . . . . . . . . . . . . . . . . . . . . . . . . . . . . 20
General Data . . . . . . . . . . . . . . . . . . . . . . . . . . . . . . . . . . . . . . . . . . . . . . . . . . . . . . . . . . 21
Performance Data . . . . . . . . . . . . . . . . . . . . . . . . . . . . . . . . . . . . . . . . . . . . . . . . . . . . . 23
Controls . . . . . . . . . . . . . . . . . . . . . . . . . . . . . . . . . . . . . . . . . . . . . . . . . . . . . . . . . . . . . . 34
Field Installed Control Options . . . . . . . . . . . . . . . . . . . . . . . . . . . . . . . . . . . . . . 34
Zone Sensors . . . . . . . . . . . . . . . . . . . . . . . . . . . . . . . . . . . . . . . . . . . . . . . . 34
Electrical Data . . . . . . . . . . . . . . . . . . . . . . . . . . . . . . . . . . . . . . . . . . . . . . . . . . . . . . . . . 36
Dimensional Data . . . . . . . . . . . . . . . . . . . . . . . . . . . . . . . . . . . . . . . . . . . . . . . . . . . . . . 39
Weights . . . . . . . . . . . . . . . . . . . . . . . . . . . . . . . . . . . . . . . . . . . . . . . . . . . . . . . . . . . . . . 44
Typical Wiring . . . . . . . . . . . . . . . . . . . . . . . . . . . . . . . . . . . . . . . . . . . . . . . . . . . . . . . . . 46
Jobsite Connections . . . . . . . . . . . . . . . . . . . . . . . . . . . . . . . . . . . . . . . . . . . . . . . . . . . 50
Mechanical Specifications . . . . . . . . . . . . . . . . . . . . . . . . . . . . . . . . . . . . . . . . . . . . . . 51
General . . . . . . . . . . . . . . . . . . . . . . . . . . . . . . . . . . . . . . . . . . . . . . . . . . . . . . . . . . 51
Factory Installed Options . . . . . . . . . . . . . . . . . . . . . . . . . . . . . . . . . . . . . . . . . . . 53
Factory or Field Installed Options . . . . . . . . . . . . . . . . . . . . . . . . . . . . . . . . . . . 55
Field Installed Options . . . . . . . . . . . . . . . . . . . . . . . . . . . . . . . . . . . . . . . . . . . . . 56

4 PKGP-PRC012M-EN
Features and Benefits
Voyager has the features and benefits that make it first class in the light commercial rooftop market.
Designed with input from field contractors and engineers, its U-shaped airflow performance is
outstanding.
Standard and Optional Features at a Glance
Standard Features
• 2” throwaway filters
• 5 year Limited Compressor Warranty
• 1 year Limited Parts Warranty
• Anti-Short Cycle Timer
• Belt Drive Motors
• Colored and Numbered Wiring
• Crankcase Heaters
• Dedicated Airflow
• Easy Access Low Voltage Terminal Board (LTB)
• Foil-Faced and Edge Captured Insulation
• High Pressure Cutout
• IAQ Sloped Condensate Drain Pan
• Liquid Line Refrigerant Drier
• Low Ambient Cooling to 0°F
• Operating Charge of R-410A
• Patented Hybrid Condenser Coil for Easy Cleaning
•Phase Monitor
• Quick Access Panels
• Quick Adjust Idler Arm Pulley
• ReliaTel™ Microprocessor Controls
• Single Point Power
• Single Side Service
• Standardized Components
Figure 1. Voyager features
A
B
C
D
E
F
H
I
J
G
Foil-Faced Insulation
Quick Adjust Idler Pulley
ReliaTel™ Microprocessor Controls
Colored and Numbered Wiring
Low Ambient Cooling to Zero° F
High and Low Pressure Switches
Scroll Compressors (R-410A)
Available in R-410A refrigerant
Hinged Access Doors
Single Side Service
Smoke Detector
Fan Failure Switch
Clogged Filter Switch
Through-the-Base Electrical
Disconnect Switch or Circuit Breaker
Convenience Outlet
A
B
C
D
E
F
G
H
I
J
K
L
M
N
O
P
L
M
N
K
O
P
Q
Variable Frequency DriveQ

PKGP-PRC012M-EN 5
Features and Benefits
• U-shaped Airflow Pattern
• Variable Frequency Drive (Multispeed Indoor Fan and Single Zone VAV)
Factory Installed Options
• 2” MERV 8 or MERV 13 Filters5 with Filter Removal Tool
• Black Epoxy Pre-Coated Coils
•CO
2 Sensor Wiring (Wiring Only)15
• Condensate Overflow Switch
• Fault Detection & Diagnostics (FDD)
• High Efficiency Motors5
• High Short Circuit Current Rated (SCCR) Electrical Subsystem16
• Hinged Access Doors
• Human Interface - 5 inch Color Touchscreen
• Multi-Speed Fan
• Powered or Unpowered Convenience Outlet4
• Single Zone Variable Air Volume (SZVAV)
• Stainless Steel Drain Pan
• Supply and/or Return Air Smoke Detector2, 9
• Through the Base Electrical with Circuit Breaker10, 11
• Through the Base Electrical With Disconnect Switch6, 10, 11
• Through the Base Utilities Access
Factory or Field Installed Options
• BACnet™ Communication Interface1
• Barometric Relief1
• Clogged Filter/Fan Failure Switch2, 5
• Discharge Air Sensing Kit2, 5
• Economizer - Standard, Downflow1
• Electric Heaters5, 7, 11
• Frostat™2, 5
• Indoor Fan Motor Shaft Grounding Ring14
• LonTalk® Communications Interface5
• Low Leak Economizer - Downflow
• Oversized Motors5
• Reference or Comparative Enthalpy3, 5
• ReliaTel Options Module8
• Tool-less Hail Guards5
• Trane Communications Interface (TCI)5, 13
Field Installed Options
•CO
2 Sensor
• Digital Display Zone Sensor
• Dual Thermistor Remote Zone Sensor
• Economizer - Standard, Horizontal
• High Static Drive
• Low Leak Economizer - Downflow
• Manual Outside Air Damper
• Motorized Outside Air Dampers
• Powered Exhaust
• Roof Curb (Downflow only)
• Remote Potentiometer

6 PKGP-PRC012M-EN
Features and Benefits
• Ventilation Override Accessory2
• Zone Sensors and Remote Zone Sensors
Note: Explanation of Note1 - Note16 located in “Model Number Description,” p. 19.
Other Benefits
• Cabinet Design Ensures Water Integrity
• Ease of Service, Installation and Maintenance
• Mixed Model Build Enables “Fastest in the Industry” Ship Cycle Times
• Outstanding Airflow Distribution
• ReliaTel Controls Benefits
• Rigorous Testing
• Unmatched Product Support
•Varitrac
Outstanding Standard Features
Anti-Short Cycle Timer
Provides a 3 minute minimum “ON” time and 3 minute “OFF” time for compressors to enhance
compressor reliability by assuring proper oil return.
Colored and Numbered Wiring
Save time and money tracing wires and diagnosing the unit.
Compressors
Voyager contains the best compressor technology available to achieve the highest possible
performance. Dual compressors are outstanding for humidity control, light load cooling conditions
and system back-up applications. Dual compressors are available on all models.
Controls—ReliaTel
ReliaTel microprocessor controls provide unit control for heating, cooling and ventilating utilizing
input from sensors that measure indoor and outdoor temperature and other zone sensors. ReliaTel
also provides outputs for building automation systems and expanded diagnostics. For a complete
list of ReliaTel offerings, refer to “Other Benefits,” p. 13.
Conversion-less Units
The dedicated design units (either downflow or horizontal) require no panel removal or alteration
time to convert in the field — a major cost savings during installation. Horizontal units come
complete with duct flanges so the contractor doesn’t have to field fabricate them. These duct
flanges are a time and cost saver.
Crankcase Heaters
These band or insertion heaters provide improved compressor reliability by warming the oil to
prevent migration during off-cycles or low ambient conditions. These are standard on all Voyager
models.
Condenser Coil
Voyager boasts a patent-pending 1+1+1 condenser
coil (pictured right), permanently gapped for easy
cleaning.

PKGP-PRC012M-EN 7
Features and Benefits
Discharge Line Thermostat
A bi-metal element discharge line thermostats installed as a standard feature on the discharge line
of each system. This standard feature provides extra protection to the compressors against high
discharge temperatures in case of loss of charge, extremely high ambient and other conditions
which could drive the discharge temperature higher.
Low Ambient Cooling
All Voyager microprocessor units have cooling capabilities down to 0°F as standard.
Pressure Cutouts
Low and high pressure cutouts are standard on all Voyager models.
Phase Monitor
The phase monitor provides 100% protection for motors and compressors against problems
caused by phase loss, phase imbalance, and phase reversal. It is also equipped with an LED that
provides an ON or FAULT indicator.
Quick-Access Panels
Remove three or fewer screws for access to the standardized internal components and wiring.
Easy Access Low Voltage Terminal Board Foil Faced Insulation
Voyager’s Low Voltage Terminal Board is
external to the electrical control cabinet. It is
extremely easy to locate and attach the
thermostat wire and test operation of all unit
functions. This is another cost and time saving
installation feature.
All panels in the evaporator section of the unit
have cleanable foil-faced insulation. All edges
are either captured or sealed to ensure no
insulation fibers get into the airstream.
Low Voltage Connections
The wiring of the low voltage connections to the unit and
the zone sensors is as simple as 1-1, 2-2, and 3-3. This
simplified system makes it easy for the installer to wire.
Motors
All indoor fan motors are belt drive as standard.

8 PKGP-PRC012M-EN
Features and Benefits
Single Side Service
Single side service is standard on all units.
Sloped Drain Pans
Standard on every unit.
Standardized Components
Components are placed in the same location on all Voyager units. Familiarize yourself with one
Voyager and you are familiar with every Voyager. Due to standardized components throughout the
Voyager line, contractors/owners can stock fewer parts.
U-Shaped Airflow Pattern
The U-shaped airflow allows for improved static capabilities.
Variable Frequency Drives - VFD (Multispeed Indoor Fan and SZ VAV Only)
Variable Frequency Drives are factory installed and tested to provide supply fan motor speed
modulation, as well as modulating gas heat. VFDs on the supply fan, as compared to inlet guide
vanes or discharge dampers, are quieter, more efficient, and are eligible for utility rebates. All VFDs
are designed to allow bypass if required. Bypass control will simply provide full nominal airflow
in the event of drive failure. Modulating gas heat models with VFDs allow tighter space temperature
control with less temperature swing.
Variety of Options
Factory Installed Options
Black Epoxy Pre-Coated Coils
The pre-coated coils are an economical option for protection in mildly corrosive environments.
CO2 Sensor Wiring
This unit wiring for field installed C02 sensors. Factory-installed C02 sensor wiring saves time and
ensures proper unit connections for the field installed C02 sensor kits.
Condensate Overflow Switch
A condensate overflow switch is available to shut the unit down in the event that the condensate
drain line becomes clogged. This option protects the unit from water overflowing from the drain
pan and entering the base of the units.
Fault Detection & Diagnostics (FDD)
This offering meets the mandatory requirement of CA Title 24 of fully configurable diagnostics
allowing fault history and reading fault codes at the unit.This option provides detection of the
Quick-Adjust Idler Arm
With the Quick-Adjust Idler Arm (pictured right), the
belt and sheaves can be quickly adjusted without
moving the mounted fan motor. The result is a major
savings in time and money.
Single Point Power
A single electrical connection powers the unit.

PKGP-PRC012M-EN 9
Features and Benefits
following faults: Air temperature sensor failure/fault and notification of acceptable economizer
mode.The FDD system shall be certified by the Energy Commission as meeting the requirements.
High Efficiency Filtration
Voyager units offer a variety of high efficiency filtration options. MERV 8 and MERV 13 filters
provide additional filtration beyond the capabilities of typical 2” throwaway filters. Also, when
MERV 8 or MERV 13 filters are ordered, units come equipped with a filter removal tool.
High Efficiency Motors
This option is available with efficiency ratings from 86.5 up to 91.0. It is not available for all models.
High Short Circuit Current Rating (SCCR)
Voyager rooftop units now have an optional high short circuit current rated electrical subsystem
for units with an MOP above 60A. This option is a perfect fit for applications that need protection
against high potential fault currents. This option also includes individual over current protection
for each compressor and the indoor fan, as well as a dedicated over current protection to the
condenser fan motor(s). When the high SCCR is ordered, the control box will have components
separated into two sections - high and low voltage components.
Hinged Access Doors
These doors permit easy access to the filter, fan/heat, and compressor/control sections. They
reduce the potential roof damage from screws or sharp access door corners.
Multi-Speed Indoor Fan System
Multi-speed indoor fan system is designed for use in applications for meeting the minimum
requirement of CA Title 24. This system incorporates a multi-speed fan control to change the speed
of the fan to 67% of full airflow based off compressor stages.
Powered or Unpowered Convenience Outlet
This option is a GFCI, 120V/15amp, 2-plug, convenience outlet, either powered or unpowered. This
option can only be ordered when Through the Base Electrical with either the Disconnect Switch or
Circuit Breaker option is ordered. This option is available on all models.
Human Interface
The 5 inch Color Touchscreen Human Interface provides
an intuitive user interface to the rooftop unit that speeds
up unit commissioning, shortens unit troubleshooting
times, and enhances preventative maintenance
measures. The human interface includes several
features such as:
• Data trending capabilities by means of time series
graphs
• Historical alarm messages
• Real-time sensor measurements
• On board system setpoints
• USB port that enables the downloading of
component runtime information as well as trended
historical sensor data
• Customizable reports

10 PKGP-PRC012M-EN
Features and Benefits
Single Zone VAV - One Zone Variable Air Volume Mode
Note: Single Zone VAV is designed to be used with a zone sensor. If a unit is configured for Single
Zone VAV operation but is connected to a thermostat, the control will revert to multi-speed
(2-Speed) indoor fan control. (See "Multi-Speed Indoor Fan System" above.)
Single Zone VAV is designed for use in single zone applications like gymnasiums, auditoriums,
manufacturing facilities, retail box stores, and any large open spaces, where there is a lot of
diversity in the load profile. Single Zone VAV (SZ VAV) is an ideal replacement to "yesterday's"
constant volume (CV) systems, by reducing operating costs while improving occupant comfort. SZ
VAV systems combine Trane application, control and system integration knowledge to exactly
match fan speed with cooling and heating loads, regardless of the operating condition. Trane
algorithms meet/exceed ASHRAE 90.1- 2010, SZ VAV energy-saving recommendations, and those
of CA Title 24. The result is an optimized balance between zone temperature control and system
energy savings. Depending on your specific application, energy savings can be as much as 20%.
Note: Building system modeling in energy simulation software like TRACE is recommended to
evaluate performance improvements for your application.
SZ VAV is fully integrated into the ReliaTel Control system and is available today. It provides the
simplest and fastest commissioning in the industry through proven factory-installed, wired, and
tested system controllers. All control modules, logic and sensors are factory installed, and tested
to assure the highest quality and most reliable system available. This means no special
programming of algorithms, or hunting at the jobsite for sensors, boards, etc. that need to be
installed in the field. Single Zone VAV is a quick and simple solution for many applications and is
available from your most trusted rooftop VAV system solution provider- Trane.
Stainless Steel Drain Pan
For excellent corrosion and oxidation resistance, the optional stainless steel drain pan provides a
cleanable surface that complement other IAQ solutions such as high efficiency filtration (MERV 8
or 13), and demand control ventilation (CO2).
Through the Base Electrical/Horizontal Side Access with Circuit Breaker
This option is a factory installed thermal-magnetic, molded case, HACR Circuit Breaker with
provisions for through the base electrical connections.
Through the Base Electrical/Horizontal Side Access with Disconnect Switch
Factory installed 3-pole, molded case, disconnect switch with provisions for through the base
electrical connections are available.
Through the Base Utilities Access
An electrical service entrance shall be provided allowing electrical access for both control and main
power connections inside the curb and through the base of the unit. This option will allow for field
installation of liquid-tight conduit and an external, field-installed disconnect switch.
Supply, Return, and Plenum Air Smoke Detector
With this option (pictured right) installed, if smoke is detected,
all unit operation will be shut down. Reset will be manual at the
unit. Return Air Smoke Detectors require minimum allowable
airflow when used with certain models.
Supply and/or Return Smoke Detectors may not be used with
the Plenum Smoke Detector.

PKGP-PRC012M-EN 11
Features and Benefits
Factory or Field Installed Options
BACnet™ Communications Interface
The BACnet communications interface allows the unit to communicate directly with a generic open
protocol BACnet MS/TP Network Building Automation System Controls.
Barometric Relief
Designed to be used on downflow units, barometric relief is an unpowered means of relieving
excess building pressure.
Clogged Filter/Fan Failure Switch
A dedicated differential pressure switch is available to achieve active fan failure indication and/or
clogged filter indication.
Discharge Air Sensing Kit
Provides true discharge air sensing in heating models. The kit is functional only with the ReliaTel™
Options Module.
Economizer - Standard, Downflow
Economizers are equipped with either dry bulb, reference, or comparative enthalpy sensing. These
economizers provide free cooling as the outdoor temperature and/or humidity decreases. Correctly
installed, they offer a valuable energy savings. Factory-installed economizers save time and ensure
proper installation.
Note: Factory-installed economizers require some field set-up.
Economizer - Low Leak, Downflow
This accessory meets low leak requirements for ASHRAE 90.1, IECC, and CA Title 24 standards (3
cfm/ft^2@1" wg exterior air, 4 cfm/ft^2@1" wg return air). This option allows 100% outdoor air
supply from 0-100% modulating dampers and is standard with barometric relief. It can be paired
with powered exhaust for additional building pressure relief. This option can be paired with or
without Fault Detection & Diagnostics (FDD) to meet current mandatory CA Title 24 requirements.
Available on downflow units only. The economizers come with three control options, dry bulb and
reference or comparative enthalpy (optional).
Electric Heaters
Electric heat modules are available within the basic unit. If ordering the Through the Base Electrical
option with an Electrical Heater, the heater must be factory installed.
Frostat™
This capillary bulb embedded in the face of the evaporator coil monitors coil temperature to
prevent evaporator icing and protect the compressor. Recommended for applications with low
leaving air temperatures, low airflow and/or high latent load applications.
Indoor Fan Motor Shaft Grounding Ring
Shaft grounding rings are used on all VFD driven motors to provide a conductive discharge path
away from the motor bearings to ground. Bearing Protection Rings shall be maintenance free
circumferential rings of conductive micro fibers that discharge voltages to ground.
LonTalk® Communications Interface
The LonTalk communications interface allows the unit to communicate as a Tracer™ LCI-V device
or directly with generic LonTalk Network Building Automation System Controls.
Oversized Motors
Factory or field installed oversized motors are available for high static applications.

12 PKGP-PRC012M-EN
Features and Benefits
Reference or Comparative Enthalpy
Measures and communicates humidity while maximizing comfort control.
ReliaTel Options Module (RTOM)
The RTOM monitors the supply fan proving, clogged filter, supply air temperature, exhaust fan
setpoint, dehumidification setpoint, supply air tempering, Frostat™ and smoke detector.
Field Installed Options
CO2 Sensor - Demand Control Ventilation (DCV)
Demand-controlled ventilation (DCV) is a control strategy that responds to the actual demand
(need) for ventilation by regulating the rate at which the HVAC system brings outdoor air into the
building. A CO2 sensor measures the concentration (parts per million, ppm) of CO2 (Carbon
Dioxide) in the air. As the CO2 concentration changes, the outside air damper modulates to meet
the current ventilation needs of the zone. The CO2 sensor kit is available as a field installed
accessory. Two field installed kits are offered; C02 sensor and wiring or C02 sensor only. The C02
Sensor only kit should be ordered with factory installed C02 sensor wiring. Factory installed C02
sensor wiring saves set-up time and ensures proper unit connections for the C02 sensor.
Dampers
0–25 percent manual or 0–50 percent motorized outside air dampers are available.
Digital Display Zone Sensor
The Digital LCD (Liquid Crystal Display) zone sensor has the look and functionality of standard zone
sensors.
Economizer - Standard, Horizontal
Economizers are equipped with either dry bulb or reference or comparative enthalpy sensing.
These economizers provide free cooling as the outdoor temperature and/or humidity decreases.
Correctly installed, they offer a valuable energy savings.
Economizer - Low Leak, Downflow
This accessory meets low leak requirements for ASHRAE 90.1, IECC, and CA Title 24 standards (3
cfm/ft^2@1" wg exterior air, 4 cfm/ft^2@1" wg return air). This option allows 100% outdoor air
supply from 0-100% modulating dampers and is standard with barometric relief. It can be paired
with powered exhaust for additional building pressure relief. Available on downflow units only.
High Static Drive Accessory
Available on many models, this high static drive accessory extends the capability of the standard
motor. Avoid expensive motors and operating costs by installing this optimized sheave accessory.
Powered Exhaust
This option is available on downflow units and provides exhaust of the return air, when using a
downflow economizer, to maintain proper building pressurization. Great for relieving most
building overpressurization problems.
Tool-less Hail Guards
Tool-less, hail protection quality coil guards (pictured right) shall be
either factory or field-installed for condenser coil protection. This
option protects the condenser coil from vandalism and/or hail
damage.
Trane Communication Interface (TCI)
Available factory or field installed. This module when applied with the
ReliaTel™ easily interfaces with Trane’s Integrated Comfort™ System.

PKGP-PRC012M-EN 13
Features and Benefits
Remote Potentiometer
When properly installed in the economizer control circuitry, this accessory provides a remote
variable resistance to enable the operator to adjust the minimum damper position.
Roof Curbs
Available for downflow units. Only two roof curbs for the entire Voyager line simplifies curb
selection.
Ventilation Override Accessory
With the Ventilation Override Accessory installed, the unit can be set to transition to up to 3 different
pre-programmed sequences for Smoke Purge, Pressurization and Exhaust. The transition occurs
when a binary input on the RTOM is closed (shorted). This would typically be a hard wired relay
output from a smoke detector or fire control panel. The ventilation override kit is available as a field
installed accessory.
Zone Sensors/Thermostats
Available in programmable, automatic and manual styles.
Note: Zone sensors required for units configured for Single Zone VAV indoor fan system control
to enable Single Zone VAV functionality.
Other Benefits
Cabinet Integrity
For added water integrity, Voyager has a raised 1-1/8” lip around the supply and return of the
downflow units to prevent water from blowing into the ductwork.
Easy to Install, Service and Maintain
Because today’s owners are very cost-conscious when it comes to service and maintenance,
Voyager was designed with direct input from service contractors. This valuable information helped
to design a product that would get the serviceman off the job quicker and save the owner money.
Voyager does this by offering outstanding standard features enhanced by a variety of factory and
field installed options, multiple control options, rigorously tested proven designs and superior
product and technical support.
Outstanding Airflow Distribution
Airflow is outstanding. The Voyager can replace an older machine with old ductwork and, in many
cases, improve the comfort through better air distribution.
ReliaTel™ Controls Benefits
ReliaTel controls provide unit control for heating, cooling
and ventilating by utilizing input from sensors that
measure outdoor and indoor temperature.
Quality and Reliability are enhanced through ReliaTel
control and logic:
– Prevents the unit from short cycling, considerably
improving compressor life.
– Ensures the compressor will run for a specific
amount of time which allows oil to return for better
lubrication, enhancing the reliability of the
compressor.

14 PKGP-PRC012M-EN
Features and Benefits
Voyager with ReliaTel reduces the number of components required to operate the unit, thereby
reducing possibilities for component failure.
ReliaTel Makes Installing and Servicing Easy
ReliaTel eliminates the need for field installed anti-shortcycle timer and time delay relays.
ReliaTel controls provide these functions as an integral part of the unit. The contractor no longer
has to purchase these controls as options and pay to install them. The wiring of the low voltage
connections to the unit and the zone sensors is as easy as 1-1, 2-2, and 3-3. This simplified system
makes wiring easier for the installer.
ReliaTel Makes Testing Easy
ReliaTel requires no special tools to run Voyager unit through its paces. Simply place a jumper
between Test 1 and Test 2 terminals on the Low Voltage Terminal Board and the unit will walk
through its operational steps automatically.
The unit automatically returns control to the zone sensor after stepping through the test mode a
single time, even if the jumper is left on the unit.
As long as the unit has power and the “system on” LED is lit, ReliaTel is operational. The light
indicates that the controls are functioning properly.
ReliaTel features expanded diagnostic capabilities when utilized with Trane Integrated Comfort™
Systems.
Some zone sensor options have central control panel lights which indicate the mode the unit is in
and possible diagnostic information (dirty filters for example).
Other ReliaTel Benefits
The ReliaTel built-in anti-shortcycle timer, time delay relay and minimum “on” time control
functions are factory tested to assure proper operation. ReliaTel softens electrical “spikes” by
staging on fans, compressors and heaters. Intelligent Fallback is a benefit to the building occupant.
If a component goes astray, the unit will continue to operate at predetermined temperature
setpoint.
Intelligent Anticipation is a standard ReliaTel feature. It functions continuously as ReliaTel and zone
sensor(s) work together in harmony to provide much tighter comfort control than conventional
electro-mechanical thermostats.
The same ReliaTel Board fits all Packaged Gas/Electric, Cooling, and Heat Pump models. This
provides standardization of parts for contractors. Less money is tied up in inventory with ReliaTel.
Rigorous Testing
All of Voyager’s designs were rigorously rain tested at the factory to ensure water integrity. Voyager
units incorporate either a one piece top or the Trane-Tite-Top (T3). Each part of the top (either two
or three pieces) overlaps in such a way that water cannot leak into the unit. These overlapped edges
are gasketed and sealed to ensure superior water integrity.
Actual shipping tests were performed to determine packaging requirements. Units were test
shipped around the country to determine the best packaging. Factory shake and drop tests were
used as part of the package design process to help assure that the unit arrives at the job site in top
condition.
Rigging tests include lifting a unit into the air and letting it drop one foot, assuring that the lifting
lugs and rails hold up under stress.
We perform a 100% coil leak test at the factory. All coils are pressure and leak tested at a minimum
of 450 psig. The completely assembled refrigerant system is leak tested at a minimum of 240 psig
with a refrigerant and nitrogen mixture.
All parts are inspected at the point of final assembly. Sub-standard parts are identified and rejected
immediately. Every unit receives a 100 percent unit run test before leaving the production line to
make sure it lives up to rigorous Trane requirements.

PKGP-PRC012M-EN 15
Features and Benefits
Unmatched Support
Trane Sales Representatives are a Support Group that can assist you with:
VariTrac
When Trane’s changeover VAV System for light commercial applications is coupled with Voyager,
it provides the latest in technological advances for comfort management systems and can allow
thermostat control in every zone served by VariTrac.
Note: Varitrac is not recommended for SZ VAV and Multi-speed indoor fan applications.
• Product • Special Applications
• Application • Specifications
• Service • Computer Programs and much more
•Training
VariTr ac
TM

16 PKGP-PRC012M-EN
Application Considerations
Application of this product should be within the catalogued airflow and cooling considerations.
Low Ambient Cooling
This Voyager line features, as a standard, low ambient cooling down to 0°F. Contact your local Trane
Representative for more assistance with low ambient cooling applications.
Barometric Relief
This product line offers an optional barometric relief damper included in the downflow economizer
accessory. This accessory consists of gravity dampers which open with increased pressure. As the
building air pressure increases, the pressure in the unit return air section also increases, opening
the dampers and relieving the conditioned space.
Important: THE EFFECTIVENESS OF BAROMETRIC RELIEF DAMPER DURING ECONOMIZING
OPERATION IS SYSTEM RELATED. PRESSURE DROP OF THE RETURN AIR SYSTEM
SHOULD BE CONSIDERED TO CONTROL BUILDING PRESSURIZATION.
Power Exhaust Accessory
The power exhaust accessory is available on all downflow units. This accessory can be field
installed and will assist in relieving a building’s pressurization.
Condensate Trap
The evaporator is a draw-thru configuration. A trap must be field provided prior to start-up on the
cooling cycle.
Clearance Requirements
The recommended clearances identified with unit dimensions should be maintained to assure
adequate serviceability, maximum capacity and peak operating efficiency. Actual clearances which
appear inadequate should be reviewed with the local Trane sales personnel.
Unit Pitch
These units have sloped condensate drain pans. Units must be installed level, any unit slope must
be toward access side of unit.
VariTrac
Varitrac is not recommended for SZ VAV and Multi-speed indoor fan applications.

PKGP-PRC012M-EN 17
Selection Procedure
Cooling Capacity
Step 1
Calculate the building’s total and sensible cooling loads at design conditions. Use the Trane
calculation form or any other standard accepted method.
Step 2
Given the following building requirements:
A. Electrical Characteristics: 460/60/3
B. Summer Design Conditions: Entering Evaporator Coil: 80 DB/ 67 WB
Outdoor Ambient: 95 DB
C. Total Cooling Load: 172 MBh
D. Sensible Cooling Load: 122 MBh
E. Airflow: 6000 cfm
F. External Static Pressure: 0.50 in. w.g.
G. Rooftop - downflow configuration.
H. Accessories, Economizer, Supplementary Electric Heat
I. Heating Capacity 100 MBh
460 volt/3 phase Electric Supplemental Heat - at 6000 cfm
Size the equipment using Table 3, p. 24. As a starting point, a rough determination of the size of the
unit must be made. This selection will then be confirmed after examining the performance at the
given conditions. Divide the total cooling load by nominal BTUH per ton (12 MBh per ton); then
round up to the nearest unit size. 172 MBh/12 MBh = 14.33 (approx. 15 tons.)
Step 3
Table 3, p. 24 shows that a WSD180E4 has a gross cooling capacity of 186.2 MBh and 138.9 MBh
sensible capacity at 95°F ambient and 6000 cfm with 80 DB/67 WB air entering the evaporator.
To Find Capacity at Intermediate Conditions
When the design conditions are between two numbers that are in the capacity table, interpolation
is required to approximate the capacity.
Note: Extrapolation outside of the table conditions is not recommended.
Step 4
Verify that there will be enough capacity by determining net capacity. In order to select the correct
unit which meets the building’s requirements, the fan motor heat must be deducted from the gross
cooling capacity. The amount of heat that the fan motor generates is dependent on the effort by
the motor CFM and static pressure. To determine the total unit static pressure, add the following:
External Static: 0.50 in.
Standard Filter 1 in: 0.05 in. (from Table 12, p. 29)
Economizer Return Air: 0.04 in. (from Ta b l e 12 , p . 2 9 )
Electric Heater Size 18 kW: 0.06 in.
Total Static Pressure: 0.65 in.
Note: The Evaporator Fan Performance Table 6, p. 27 has already accounted for the pressure drop
for standard filters and wet coils.

18 PKGP-PRC012M-EN
Selection Procedure
Therefore, the actual Total Static Pressure is 0.65 - 0.05 = 0.6. With 6000 CFM and 0.60 inches,
Table 6, p. 27 shows 2.17 Bhp.
The note below Table 6, p. 27 gives a formula to calculate Fan Motor Heat:
3.15 x bhp = MBh
3.15 x 2.17 = 6.835 MBh
Now subtracting the fan motor heat from the gross cooling capacity of the unit:
Net Total Cooling Capacity =
186.2 - 6.835 = 179.36 MBh
Net Sensible Cooling Capacity =
138.9 - 6.385 = 132.065 MBh
Step 5
If the performance will not meet the required load of the building, try a selection at the next higher
size unit.
Heating Capacity
Step 1
Calculate the building heating load using the Trane calculation form or other standard accepted
method.
Step 2
Size the equipment using Tab l e 14 , p . 3 1 to match the heating loads at design conditions.
A. Total Heating Load: 100 MBh
B. Outdoor Ambient (Winter) 17 DB
C. Indoor Return Temperature: 70 DB
D . Airflow: 6000 CFM
Use the integrated portion of Table 14, p. 31 for the WSD180E4 to determine capacity at winter
design conditions. The mechanical heating portion of the heat pump will provide 85.4 MBh.
Step 3
Because 45 MBh is less than the building’s required heating capacity at winter design conditions,
a supplementary heater must be selected.
100.0 - 85.54 = 14.46 MBh
From Table 17, p. 32, at 480 volts, the 18 kW Heater will be adequate to do the job.
18 kW 61 MBh
From Table 17, p. 32 select heater AYDHTRK418A (18 kW 460/60/3).

PKGP-PRC012M-EN 19
Model Number Description
Digit 1 — Unit Type
W = Packaged Cooling, Electric Heat
Digit 2 — Efficiency
S = Standard Efficiency
Digit 3 — Airflow Configuration
D= Downflow
H= Horizontal
Digit 4, 5, 6 — Nominal Gross
Cooling Capacity (MBh)
150 = 12½ Tons
180 = 15 Tons
240 = 20 Tons
Digit 7 — Major Design
Sequence
E = R-410A Refrigerant
Digit 8 — Voltage Selection
3 = 208-230/60/3
4 = 460/60/3
W = 575/60/3
Digit 9 — Unit Controls
R = Reliatel
Digit 10 — Heating Capacity
0 = No Heat
G = 18 kW Electric Heat
N = 36 kW Electric Heat
P = 54 kW Electric Heat
R = 72 kW Electric Heat
Digit 11 — Minor Design
Sequence
Digit 12, 13 — Service Sequence
Digit 14 — Fresh Air Selection
0=No Fresh Air
A = Manual Damper
B = Motorized Damper
D = Econ Dry Bulb w/ Barometric
Relief1
F = Econ Reference Enthaply w/
Barometric Relief1
H = Econ Comparative Enthaply w/
Barometric Relief1
K = Low Leak Econ w/ Barometric
Relief1
M = Low Leak Econ Reference
Enthalpy w/ Barometric Relief1
P = Low Leak Econ Comparative
Enthalpy w/ Barometric Relief1
Digit 15 — Supply Fan/Drive
Type/Motor
0=Standard Motor
1=Oversized Motor
5
3 = High Efficiency Motor5
6 = Single Zone Variable Air Volume
Standard Motor
WSD 150 E 3 R G B **
123 456 7 8 9 10 11 1213
7 = Multi-Speed Standard Motor
8 = Single Zone Variable Air Volume
Oversized Motor
9 = Multi-Speed Oversized Motor
A = Single Zone Variable Air Volume
Standard Motor w/ Shaft Ground
Ring
B = Multi-Speed Standard Motor w/
Shaft Ground Ring
C = Single Zone Variable Air Volume
Oversized Motor w/ Shaft Ground
Ring
D = Multi-Speed Oversized Motor w/
Shaft Ground Ring
Digit 16 — Hinged Service
Access / Filters5
0 = Standard Panels/Standard
Filters17
A = Hinged Access/Standard Filters17
B = Standard Panels/2" MERV 8 Filters
C = Hinged Access/2" MERV 8 Filters
D = Standard Panels/MERV 13 Filters
E = Hinged Access/MERV 13 Filters
Digit 17 — Condenser Coil
Protection
0 = Standard Coil
1 = Standard Coil With Hail Guard
2 = Black Epoxy Pre-Coated Coil
3 = Black Epoxy Pre-Coated Coil with
Hail Guard
Digit 18 — Through The Base
Provisions
0 = No Through The Base Provisions
A = Through The Base Electric11
D = Through The Base Utilities Access
Digit 19 — Disconnect Switch/
Circuit Breaker10
0 = No Disconnect/circuit break
1 = Unit Mounted Non-Fused
Disconnect Switch
2 = Unit Mounted Circuit Breaker
Digit 20 — Convenience Outlet
Option
0 = Without Convenience Outlet
A = Unpowered Convenience Outlet4
B = Powered Convenience Outlet4
Digit 21 — Communications
Options
0 = Without Communications
Options
1 = Trane Communications
Interface5, 13
2 = Lontalk Communications
Interface5
6 = Building Automation Control
Network Communications
Interface
Digit 22 — Refrigeration System
Option
0 = Standard refrigeration system
Digit 23 — Refrigeration
Controls
0 = Without Refrigeration Controls
1 = Frostat™
Digit 24 — Smoke Detector2,9
0 = Without Smoke Detector
A = Return Air Smoke Detector
B = Supply Air Smoke Detector
C = Return/Supply Air Smoke
Detector
D = Plenum Smoke Detector
Digit 25 — System Monitoring
Controls2
0 = No Monitoring Controls
1 = Clogged Filter Switch
2 = Fan Failure Switch
3 = Discharge Air Sensing
4 = Clogged Filter Switch and Fan
Failure
5 = Clogged Switch and Discharge Air
Sensing
6 = Fan Failure Switch and Discharge
Air Sensing
7 = Clogged Filter Switch, Fan Failure
Switch and Discharge Air Sensing
A = Condensate Drain Pan Overflow
Switch
B = Clogged Filter Switch and
Condensate Drain Pan Overflow
Switch
C = Fan Failure Switch and
Condensate Drain Pan Overflow
Switch
D = Discharge Air Sensing and
Condensate Drain Pan Overflow
Switch
E = Clogged Filter Switch, Fan Failure
Switch and Condensate Drain Pan
Overflow Switch
F = Clogged Filter Switch, Discharge
Air Sensing Tube and Condensate
Drain Pan Overflow Switch
G = Fan Failure Switch, Discharge Air
Sensing Tube and Condensate
Drain Pan Overflow Switch
H = Clogged Filter Switch, Fan Failure
Switch, Discharge Air Sensing
and Condensate Drain Pan
Overflow Switch
Digit 26 - System Monitoring
Controls
0 = No Monitoring Controls
A = Demand Control Ventilation
(CO2)15
B = FDD (Fault Detection and
Diagnostics)
Model Number Description

20 PKGP-PRC012M-EN
Model Number Description
C = FDD (Fault Detection Diagnostics)
& Demand Control Ventilation
(CO2)15
Digit 27 - Unit Hardware
Enhancements
0 = No Enhancements
1 = Stainless Steel Drain Pan
Digit 28 - Short Circuit Current
Rating
0 = Standard SCCR
A = 65kA SCCR Option16
Digit 31 - Advanced Unit
Controls
0 = Standard Unit Controls
1=Human Interface
18
Note: Most Factory Installed Options
available for Downflow Air
Discharge units only. Please verify
with ordering system for
availability.
Model Number Notes
1. Some field set up required.
2. Requires ReliaTel Options Module.
3. Requires Economizer.
4. Must be ordered with Through-
the-Base Electrical option or
Horizontal-Side Access and either
Unit Mounted Disconnect or
Circuit Breaker.
5. Available factory installed on
downflow AND horizontal units.
Verify with ordering system.
6. Cannot be fused.
7. Must be factory installed when
using Through-the-Base Options.
8. ReliaTel Options Module is
required when ordering the
following accessories: Clogged
Filter Switch, Fan Fail Switch,
Condensate Overflow Switch,
Discharge Air Sensing Kit, Frostat,
Ventilation Override, and Smoke
Detector.
9. Option cannot be ordered in
conjunction with field installed
economizer on downflow units.
Must be factory installed. The
return air smoke detector may not
fit up or work properly on the
Voyager units when used in
conjunction with 3rd party
accessories (such as bolt on heat
wheels, economizers, and power
exhaust). Do not order the return
air smoke detectors when using
this type of accessory.
10. Unit mounted disconnect and
circuit breakers are mutually
exclusive of each other.
11. Through-the-base electrical
option or Horizontal-Side Access
must be ordered with either unit
mounted disconnect or circuit
breaker. When adding heat, you
must order Trane Electric Heat.
12. All Factory Installed Options are
Built-to-Order. Check order
services for estimated production
cycle.
13. TCI is for use with non-VariTrac
systems and VariTrac systems.
14. For use with multi-speed and
SZVAV units only.
15. Demand Control Ventilation
Option includes wiring only. The
C02 sensor is a field-installed only
option.
16. 575 VAC option is 25kA.
17. Standard filters are not available
with Low Leak Economizers.
18. Human Interface is standard with
FDD (Fault Detection Diagnostics).
Model Number Description

PKGP-PRC012M-EN 21
General Data
Table 1. General data — 12½ - 20 tons
12½ Tons
Downflow &
Horizontal Units
15 Tons
Downflow &
Horizontal Units
20 Tons
Downflow &
Horizontal Units
WS*150E3,4,W WS*180E3,4,W WS*240E3,4,W
Cooling Performance(a)
Gross Cooling Capacity 148,000 177,000 249,000
EER(b) 10.6 10.6 9.7
Nominal Airflow/ARI Rated Airflow (CFM) 5000 6000 / 5300 8000 / 6400
ARI Net Cooling Capacity 146,000 170,000 240,000
IEER(c) (One Speed Fan / Two or Variable
Speed Fan) 12/13.5 12/13.5 11.5/12.0
System Power (kW) 13.77 16.04 25.47
Heating Performance(a)
High Temp. Btuh Rating 136,000 170,000 210,000
COP 3.2 3.2 3.2
System Power (kW) 12.46 15.57 19.23
Low Temp. Btuh Rating 75,000 90,000 120,000
COP 2.1 2.1 2.1
System Power (kW) 10.47 12.56 16.75
Compressor
Number/Type 2 / Scrolls 2 / Scrolls 2 / Scrolls
ARI Sound Rating (BELS)(d) 9.2 9.2 9.4
Outdoor Coil — Type Hi-Performance Hi-Performance Hi-Performance
Refrigerant Control Expansion Valve Expansion Valve Expansion Valve
Tube Size (in.) OD 0.3125 0.3125 0.3125
Face Area (sq. ft.) 35.20 35.20 42.53
Rows/FPI 3 / 16 3 / 16 3 / 16
Indoor Coil — Type Hi-Performance Hi-Performance Hi-Performance
Tube Size (in.) ID 0.3125 0.3125 0.3125
Face Area (sq. ft.) 26.00 26.00 31.42
Rows/FPI 3 / 15 4 / 15 4 / 15
Refrigerant Control Short Orifice Short Orifice Short Orifice
Drain Connection Number/Size (in.) 1/1.00 NPT 1/1.00 NPT 1/1.00 NPT
Outdoor Fan — Type Propeller Propeller Propeller
Number Used/Diameter (in.) 2 / 26 2 / 26 2 / 28
Drive Type/No. Speeds Direct / 1 Direct / 1 Direct / 1
CFM 11,100 10,800 14,800
Number Motors/HP 2 / 0.5 2 / 0.5 2 / 1.0
Motor RPM 1,100 1,100 1,125

22 PKGP-PRC012M-EN
General Data
Indoor Fan - Type FC Centrifugal FC Centrifugal FC Centrifugal
Number Used/Diameter (in.) 1 / 18x18 1 / 18x18 1 / 18x18
Drive Type/No. Speeds Belt / 1 Belt / 1 Belt / 1
Number Motors 111
Motor HP (Standard/Oversized) 3.0 / 5.0 3.0 / 5.0 5.0 / 7.5
Motor RPM (Standard/Oversized) 1740 / 3,450 1740 / 3,450 3450 / 3,470
Motor Frame Size (Standard/Oversized) 145T / 145T 145T / 145T 145T / 184T
Filters - Type Furnished Throwaway Throwaway Throwaway
Number Size Recommended
Downflow (4)20x20x2
(4)20x25x2 (4)20x20x2
(4)20x25x2 (8)20x20x2
(4)20x16x2
Horizontal (8)20x25x2 (8)20x25x2 (12)20x20x2
Refrigerant Charge Pounds of
R-410A(e)
Downflow 14 / 14.5 16.5 / 15.9 20.0 / 20.7
Horizontal 13.2 / 13.3 17 / 15.9
(a) Cooling Performance is rated at 35°C (95°F) ambient, 26.7°C (80°F) entering dry bulb, 19.4°C (67°F) entering wet bulb.
Heating Performance is rated at 20°C (68°F) ambient, 8.3°C (47°F) entering dry bulb, 6.1°C (43°F) entering wet bulb.
Gross capacity does not include the effect of fan motor heat. ARI capacity is net and includes the effect of fan motor heat.
Units are suitable for operation to ±20% of nominal airflow. Rated in accordance with ARI Standard 210/240 or 340/360.
(b)EER is rated at ARI conditions and in accordance with DOE test procedures.
(c) Integrated Energy Efficiency Ratio (IEER) is rated in accordance with AHRI standard 210/240 or 360.
(d)Sound Rating shown is tested in accordance with ARI Standard 270 or 370.
(e)Refrigerant charge is an approximate value. For a more precise value, see unit nameplate and service instructions.
Table 1. General data — 12½ - 20 tons (continued)
12½ Tons
Downflow &
Horizontal Units
15 Tons
Downflow &
Horizontal Units
20 Tons
Downflow &
Horizontal Units
WS*150E3,4,W WS*180E3,4,W WS*240E3,4,W

PKGP-PRC012M-EN 23
Performance Data
Table 2. Gross cooling capacities (MBh) 12½ tons three phase WS*150E
Air
Flow
CFM
Ent
DB
°F
Ambient Temperature (°F)
85 95 105
Entering Wet Bulb (F)
61 67 73 61 67 73 61 67 73
MBH SHC MBH SHC MBH SHC MBH SHC MBH SHC MBH SHC MBH SHC MBH SHC MBH SHC
4000
75 140.4 110.8 152.3 74.7 156.2 39.1 131.7 108.1 146.6 75.2 153.1 35.5 118.1 103.1 138.7 73.6 148.3 33.9
80 146.6 139.5 156.7 99.7 160.5 60.9 135.0 131.4 148.6 98.4 155.7 59.5 123.4 123.4 140.6 97.0 150.9 58.0
85 148.1 148.1 156.5 121.3 161.4 85.3 141.9 141.9 150.7 121.6 158.5 83.4 135.0 135.0 142.6 120.3 153.1 81.9
90 155.8 155.8 159.4 144.5 163.7 106.3 150.5 150.5 153.8 145.1 160.6 107.3 144.0 144.0 146.2 143.6 156.0 105.8
4500
75 144.5 117.5 156.4 77.9 157.1 37.5 136.4 115.5 149.0 77.1 154.1 36.7 125.1 111.9 141.7 76.3 149.6 33.1
80 147.8 143.2 158.8 103.5 159.8 61.1 139.9 139.6 151.2 102.9 157.1 63.3 131.5 131.5 143.7 102.3 152.3 60.1
85 153.8 153.8 158.8 127.9 162.4 85.0 148.2 148.2 153.8 128.8 159.9 89.0 141.3 141.3 146.4 129.1 155.0 86.6
90 160.1 160.1 161.6 152.9 165.3 108.6 156.0 156.0 157.4 153.7 162.5 113.9 150.0 150.0 150.9 150.8 157.6 113.0
5000
75 147.7 123.7 154.9 78.7 157.8 33.9 139.8 122.3 150.7 78.4 154.7 36.9 129.6 119.6 143.9 79.1 150.9 33.7
80 151.6 150.4 160.1 107.3 160.2 60.0 144.2 144.2 153.1 107.3 158.0 64.7 136.9 136.9 146.1 107.3 153.1 63.5
85 157.3 157.3 160.3 135.3 162.7 86.8 152.6 152.6 156.4 136.0 160.8 91.1 146.2 146.2 149.3 136.4 156.5 92.2
90 162.3 162.3 163.0 158.0 165.4 112.7 159.4 159.4 159.9 159.1 163.6 116.5 154.2 154.2 154.2 154.2 159.3 120.2
5500
75 149.9 129.7 155.6 82.5 158.0 31.8 142.5 128.7 151.9 80.6 155.5 34.1 133.3 126.6 145.6 81.1 153.0 36.3
80 154.1 154.0 158.4 112.6 160.5 62.6 148.3 148.3 154.5 111.6 158.7 63.3 141.2 141.2 148.2 112.6 154.5 66.6
85 159.4 159.4 161.0 140.5 163.3 91.2 155.8 155.8 157.9 142.7 160.9 90.9 150.0 150.0 151.8 143.2 157.3 96.9
90 163.8 163.8 164.2 160.8 165.7 118.4 161.1 161.1 161.4 161.2 164.1 119.0 157.1 157.1 157.2 157.2 160.3 125.5
6000
75 153.7 136.6 156.6 85.7 159.3 32.9 145.0 134.8 152.1 83.2 155.8 31.7 136.2 132.9 147.0 83.8 151.9 35.3
80 156.4 156.4 159.2 116.6 161.8 65.1 151.2 151.2 155.4 116.6 159.2 63.2 144.6 144.6 149.8 117.7 155.3 68.4
85 160.3 160.3 161.9 143.5 163.7 95.1 157.8 157.8 159.0 148.8 164.6 97.9 152.7 152.7 156.1 154.1 158.2 99.2
90 164.7 164.7 164.9 162.7 166.3 122.2 162.7 162.7 164.7 164.7 164.5 123.4 158.7 158.7 158.6 158.6 161.3 128.5
Air
Flow
CFM
Ent
DB
°F
Ambient Temperature (°F)
115
Entering Wet Bulb (F)
61 67 73
MBH SHC MBH SHC MBH SHC
4000
75 104.6 98.2 129.1 71.4 141.4 33.8
80 114.1 114.1 130.8 94.5 143.9 58.3
85 127.1 127.1 132.8 118.1 145.8 82.1
90 136.7 136.7 136.9 136.9 148.1 105.6
4500
75 111.4 107.2 132.2 74.6 143.0 32.2
80 122.5 122.5 134.1 100.7 145.4 59.5
85 133.6 133.6 137.3 127.3 147.8 85.6
90 142.8 142.8 142.9 142.9 150.6 112.4
5000
75 116.2 114.7 134.8 77.8 144.4 31.3
80 128.8 128.8 136.9 106.9 146.7 60.7
85 138.6 138.6 140.6 135.6 149.5 90.1
90 147.3 147.3 147.5 147.5 152.6 119.3
5500
75 121.4 121.1 136.7 80.5 144.9 32.0
80 133.0 133.0 139.2 112.5 148.0 63.8 Notes:
1. Dry Coil Condition. Total Gross Cooling Capacity (MBh) shown to the left is not
applicable. In this case the Sensible Heat Capacity (SHC) is the total capacity.
2. All capacities shown are gross and have not considered indoor fan heat. To obtain net
cooling subtract indoor fan heat.
3. MBH = Total Gross Capacity
4. SHC = Sensible Heat Capacity
* stands for both downflow and horizontal unit.
85 142.5 142.5 143.5 142.0 150.9 95.4
90 150.4 150.4 150.5 150.5 153.8 126.7
6000
75 125.5 125.5 138.4 83.4 145.6 32.6
80 136.5 136.5 141.1 117.9 148.8 66.6
85 145.6 145.6 146.1 145.9 151.8 100.4
90 152.7 152.7 152.6 152.6 155.0 132.6

24 PKGP-PRC012M-EN
Performance Data
Table 3. Gross cooling capacities (MBh) 15 tons three phase WS*180E
Air
Flow
CFM
Ent
DB
°F
Ambient Temperature (°F)
85 95 105
Entering Wet Bulb (F)
61 67 73 61 67 73 61 67 73
MBH SHC MBH SHC MBH SHC MBH SHC MBH SHC MBH SHC MBH SHC MBH SHC MBH SHC
4800
75 172.4 137.8 185.0 97.2 190.7 51.2 157.4 132.2 181.5 98.1 189.5 52.1 141.1 123.6 169.8 95.1 185.3 54.1
80 175.2 164.2 185.9 124.4 191.5 73.3 165.6 159.0 182.5 125.2 190.5 80.5 151.3 150.2 179.0 126.0 186.2 82.1
85 182.7 182.4 204.9 161.7 192.5 98.7 176.3 176.3 183.4 152.4 190.9 107.9 167.0 167.0 161.9 143.1 187.8 110.5
90 186.4 187.2 188.2 173.6 192.9 123.3 185.2 185.2 186.8 175.9 191.9 134.5 178.6 178.6 180.1 173.1 188.8 137.3
5400
75 176.7 146.7 186.4 97.4 192.2 43.3 163.9 141.3 183.8 102.8 190.8 53.1 148.9 134.8 174.0 99.6 187.4 51.8
80 185.0 177.6 187.1 128.6 192.7 68.8 173.2 169.4 185.4 133.4 191.9 82.7 161.4 161.2 175.2 130.2 188.4 82.7
85 185.9 186.3 188.2 157.9 193.7 99.4 183.4 183.4 186.4 163.3 192.8 110.9 171.2 171.2 178.2 160.1 188.9 112.5
90 189.2 190.2 189.9 181.4 193.9 129.3 188.2 188.7 188.9 182.3 193.7 138.7 183.8 183.8 185.0 181.5 190.0 143.1
6000
75 180.7 154.7 186.9 103.2 193.2 37.0 169.6 151.6 186.2 105.9 192.0 51.1 154.9 143.9 177.5 103.9 189.4 51.7
80 184.3 179.0 193.7 140.1 193.9 70.8 179.0 177.4 186.2 138.9 193.4 81.3 163.3 163.3 178.8 137.7 190.0 85.0
85 187.7 188.5 189.9 165.8 194.6 104.4 186.5 186.5 188.1 168.9 194.3 111.2 171.3 172.9 182.7 169.1 190.4 119.4
90 191.3 192.2 191.6 184.4 194.5 135.3 190.5 191.3 190.7 187.4 195.1 140.8 187.5 187.7 187.4 186.9 191.8 152.7
6600
75 189.8 168.9 188.4 106.3 193.8 36.5 175.1 160.4 186.7 106.8 193.3 46.9 160.4 151.9 180.2 109.6 189.7 51.0
80 185.9 182.8 189.6 140.4 194.2 73.1 182.9 182.6 195.4 150.8 194.5 77.7 152.3 152.3 181.8 146.4 190.7 88.8
85 188.8 189.7 190.9 168.8 195.1 108.9 188.3 188.7 189.2 174.2 195.3 110.6 181.0 181.0 185.1 175.2 191.4 125.5
90 192.3 193.5 192.7 186.1 195.8 141.0 191.3 192.3 192.4 191.2 196.0 145.8 189.6 190.1 189.5 190.0 192.9 158.2
7200
75 184.1 166.8 189.6 107.7 193.7 36.2 177.0 165.0 187.4 110.1 194.3 40.6 165.9 159.8 185.2 112.5 191.1 51.1
80 187.8 187.0 190.5 141.8 194.6 73.2 185.5 185.5 188.5 148.8 195.4 76.1 156.3 157.7 183.6 152.6 191.9 91.6
85 190.2 191.0 191.1 170.0 195.6 113.4 189.8 190.4 190.4 180.2 196.5 115.6 186.6 186.6 187.3 180.0 192.9 129.7
90 193.5 194.7 193.5 190.5 196.5 145.2 193.2 194.0 194.0 193.4 196.2 152.3 191.5 192.2 191.4 192.1 194.0 161.4
Air
Flow
CFM
Ent
DB
°F
Ambient Temperature (°F)
115
Entering Wet Bulb (F)
61 67 73
MBH SHC MBH SHC MBH SHC
4000
75 125.9 115.6 153.3 88.3 177.8 55.8
80 137.6 137.6 154.4 115.9 179.0 83.1
85 154.5 154.5 158.9 143.5 179.8 110.1
90 168.6 168.6 169.3 167.4 180.8 137.7
4500
75 132.7 125.6 158.2 94.1 180.4 54.5
80 147.7 147.7 159.7 125.2 181.4 84.8
85 164.1 164.1 166.5 155.1 182.2 116.3
90 176.1 176.1 176.4 176.3 183.2 146.8
5000
75 139.5 135.4 162.3 99.8 182.0 52.6
80 155.6 155.6 164.6 134.3 182.9 87.6
85 170.4 170.4 171.8 163.3 183.6 121.0
90 180.9 180.9 180.9 180.9 184.7 153.1
5500
75 145.6 143.4 165.6 104.6 183.0 51.6
80 162.2 162.2 168.3 142.1 183.9 89.0 Notes:
1. Dry Coil Condition. Total Gross Cooling Capacity (MBh) shown to the left is not
applicable. In this case the Sensible Heat Capacity (SHC) is the total capacity.
2. All capacities shown are gross and have not considered indoor fan heat. To obtain net
cooling subtract indoor fan heat.
3. MBH = Total Gross Capacity
4. SHC = Sensible Heat Capacity
* stands for both downflow and horizontal unit.
85 175.2 175.2 176.2 170.7 184.8 126.0
90 184.1 184.1 184.2 184.2 186.5 161.7
6000
75 150.4 149.6 168.3 108.5 184.1 51.5
80 167.2 167.2 171.0 148.6 184.8 93.7
85 179.5 179.5 179.9 177.1 186.0 132.8
90 185.5 185.7 186.3 186.4 187.8 168.8

PKGP-PRC012M-EN 25
Performance Data
Table 4. Gross cooling capacities (MBh) 20 tons three phase WS*240E
Air
Flow
CFM
Ent
DB
°F
Ambient Temperature (°F)
85 95 105
Entering Wet Bulb (F)
61 67 73 61 67 73 61 67 73
MBH SHC MBH SHC MBH SHC MBH SHC MBH SHC MBH SHC MBH SHC MBH SHC MBH SHC
6400 75 231.1 183.1 268.4 137.9 289.8 77.1 208.1 173.6 253.0 133.2 279.2 76.0 183.1 163.6 232.4 126.5 264.7 75.0
80 235.6 220.5 270.5 174.4 293.4 114.9 213.9 209.8 254.8 169.7 282.0 114.4 194.5 194.4 233.8 162.8 266.8 111.7
85 247.9 247.9 273.1 211.7 297.1 153.0 233.1 233.1 256.8 206.6 284.9 152.1 217.4 217.4 236.3 199.8 269.0 149.2
90 266.0 266.0 276.3 249.1 300.8 190.8 253.6 253.6 260.8 244.3 288.0 189.7 238.1 238.1 241.6 236.3 271.5 186.7
7200 75 242.5 197.1 274.8 142.3 292.9 73.3 219.0 187.9 259.9 138.5 283.2 74.2 194.4 178.4 239.9 132.8 269.1 72.5
80 247.6 238.6 277.5 183.8 297.1 115.8 227.3 226.2 261.8 179.8 286.4 115.6 209.7 209.7 241.8 174.2 271.7 114.5
85 262.8 262.8 280.9 225.7 301.5 158.1 248.8 248.8 265.0 221.7 290.1 158.4 233.0 233.0 245.7 216.1 274.7 156.5
90 279.8 279.8 286.0 268.1 305.8 200.4 267.3 267.3 270.9 263.1 294.0 200.7 253.1 253.1 254.3 253.2 278.1 199.5
8000 75 251.1 209.8 279.7 146.5 295.4 70.6 229.7 202.0 265.1 143.6 285.9 70.7 204.3 192.2 247.0 139.0 272.5 70.2
80 258.3 254.4 283.0 192.7 299.9 117.4 240.8 240.6 267.8 189.7 289.8 117.8 222.4 222.4 249.6 185.1 275.6 117.0
85 274.0 274.0 287.2 239.1 304.5 164.0 260.7 260.7 271.9 236.4 294.0 164.5 245.2 245.2 253.4 231.5 279.0 163.6
90 290.9 290.9 293.8 284.4 309.4 210.2 278.4 278.4 279.8 277.3 298.5 210.9 263.8 263.8 264.2 264.2 283.2 210.9
8800 75 258.4 222.0 283.4 150.7 297.2 69.0 237.8 214.9 269.4 148.5 288.1 69.4 212.9 204.9 251.4 144.7 275.1 69.2
80 266.2 265.3 287.2 201.2 302.1 120.4 251.2 251.2 272.7 199.1 292.5 120.1 233.8 233.8 254.5 195.4 278.7 120.1
85 283.3 283.3 292.2 251.8 307.1 170.5 270.0 270.0 277.7 250.1 296.9 170.3 254.9 254.9 260.0 246.0 282.6 171.1
90 298.9 298.9 300.3 296.3 312.4 219.9 287.3 287.3 288.0 287.6 302.1 221.9 273.0 273.0 273.3 273.3 287.4 222.7
9600 75 263.4 233.2 286.3 154.9 298.8 68.8 243.6 226.7 272.9 153.4 289.9 67.5 220.3 216.0 255.4 150.4 277.1 68.5
80 273.7 273.6 290.6 209.2 303.9 123.4 259.6 259.6 276.6 208.6 294.5 123.2 242.4 242.4 258.5 205.2 281.0 123.0
85 290.4 290.4 296.3 263.8 309.1 176.8 277.9 277.9 282.6 263.4 299.2 177.8 262.7 262.7 265.5 258.0 285.3 178.3
90 304.8 304.8 305.5 304.1 314.5 229.2 294.2 294.2 294.4 294.4 304.9 232.6 280.3 280.3 280.6 280.6 290.7 234.1
Air
Flow
CFM
Ent
DB
°F
Ambient Temperature (°F)
115
Entering Wet Bulb (F)
61 67 73
MBH SHC MBH SHC MBH SHC
6400 75 158.5 152.9 206.9 118.1 246.1 71.0
80 177.1 177.1 208.6 154.5 247.1 108.6
85 201.1 201.1 212.3 192.1 249.1 144.9
90 222.0 222.0 223.1 223.0 251.3 182.3
7200 75 168.6 165.4 216.4 125.7 251.0 70.1
80 191.7 191.7 218.4 166.8 252.7 111.5
85 214.8 214.8 223.1 209.0 255.1 153.3
90 236.2 236.2 236.5 236.5 257.9 195.5
8000 75 179.2 177.5 223.0 132.4 254.7 68.8
80 204.0 204.0 225.4 178.2 257.0 115.2
85 227.3 227.3 230.9 223.5 259.6 161.8
90 247.3 247.3 247.7 247.7 263.3 208.7
8800 75 188.7 188.1 227.6 138.7 257.4 67.5
80 214.2 214.2 230.3 189.1 260.3 118.2
Notes:
1. Dry Coil Condition. Total Gross Cooling Capacity (MBh) shown to the left is not
applicable. In this case the Sensible Heat Capacity (SHC) is the total capacity.
2. All capacities shown are gross and have not considered indoor fan heat. To obtain net
cooling subtract indoor fan heat.
3. MBH = Total Gross Capacity
4. SHC = Sensible Heat Capacity
* stands for both downflow and horizontal unit.
85 237.3 237.3 239.4 236.4 263.6 170.1
90 256.1 256.1 256.3 256.3 267.8 221.7
9600 75 197.1 197.0 231.8 145.0 259.8 67.1
80 223.4 223.4 235.9 200.1 262.9 122.0
85 245.1 245.1 246.0 245.3 266.7 178.3
90 263.4 263.4 263.6 263.6 271.7 234.3

26 PKGP-PRC012M-EN
Performance Data
Table 5. Evaporator fan performance 12½ tons WS*150E downflow or horizontal
External Static Pressure (Inches of Water)
CFM 0.10 0.20 0.30 0.40 0.50 0.60 0.70 0.80 0.90 1.00
RPMBHPRPMBHPRPMBHPRPMBHPRPMBHPRPMBHPRPMBHPRPMBHPRPMBHPRPMBHP
3HP Standard Motor & Low Static Drive Accessory 3HP Standard Motor & Drive
4000 — — 382 0.56 420 0.66 459 0.79 496 0.91 531 1.05 564 1.19 595 1.34 625 1.50 654 1.67
4500 — — 410 0.73 446 0.85 479 0.97 514 1.11 548 1.26 578 1.40 610 1.56 639 1.72 666 1.89
5000 400 0.80 440 0.95 473 1.07 504 1.20 534 1.34 566 1.50 597 1.66 625 1.81 653 1.98 681 2.16
5500 431 1.03 470 1.19 502 1.34 531 1.48 559 1.62 586 1.77 615 1.95 643 2.12 670 2.30 695 2.47
6000 463 1.30 500 1.48 531 1.65 559 1.80 585 1.95 611 2.11 636 2.28 662 2.46 689 2.66 714 2.85
3HP Standard Motor & High Static Drive Accessory
Continued External Static Pressure (Inches of Water)
1.10 1.20 1.30 1.40 1.50 1.60 1.70 1.80 1.90 2.00
CFM RPMBHPRPMBHPRPMBHPRPMBHPRPMBHPRPMBHPRPMBHPRPMBHPRPMBHPRPMBHP
3HP Standard Motor & Low Static Drive Accessory 3HP Standard Motor & High Static Drive Accessory
4000 682 1.83 708 1.99 734 2.16 758 2.32 782 2.49 804 2.66 826 2.83 847 3.01 867 3.19 886 3.38
4500 693 2.07 719 2.25 745 2.44 769 2.62 793 2.80 815 2.99 838 3.17 859 3.36 880 3.55 900 3.74
5000 707 2.34 732 2.53 757 2.72 780 2.92 804 3.13 826 3.33 848 3.54 870 3.74 891 3.95 911 4.15
5500 721 2.66 747 2.86 771 3.05 794 3.26 816 3.46 838 3.68 860 3.90 881 4.13 902 4.36 922 4.58
6000 738 3.04 760 3.22 784 3.43 808 3.65 831 3.86 852 4.08 873 4.30 893 4.53 913 4.77 933 5.01
5HP Oversized Motor & Drive
Notes:
1. Fan motor heat (MBH) = 3.15 x Fan BHP.
2. Data includes pressure drop due to wet coils and filters.
3. No accessories or options are included in pressure drop data.
4. Refer to Table 12, p. 29 to determine add’l static pressure drop due to other options/accessories.
5. Factory supplied motors, in commercial equipment, are definite purpose motors, specifically designed and tested to operate reliably and continuously
at all cataloged conditions. Using the full horsepower range of our fan motors as shown in our tabulated data will not result in nuisance tripping or
premature motor failure. Our product's warranty will not be affected.

PKGP-PRC012M-EN 27
Performance Data
Table 6. Evaporator fan performance 15 tons WS*180E downflow or horizontal
External Static Pressure (Inches of Water)
CFM 0.10 0.20 0.30 0.40 0.50 0.60 0.70 0.80 0.90 1.00
RPMBHPRPMBHPRPMBHPRPMBHPRPMBHPRPM BHP RPMBHPRPMBHPRPMBHPRPM BHP
3HP Standard Motor & Low Static Drive Accessory 3HP Standard Motor Drive
4800 397 0.75 435 0.88 469 1.00 501 1.13 533 1.28 566 1.43 596 1.59 625 1.74 655 1.92 682 2.09
5400 435 1.02 473 1.18 504 1.32 533 1.46 562 1.60 590 1.76 620 1.94 648 2.11 674 2.28 700 2.46
6000 475 1.36 510 1.53 541 1.70 568 1.85 594 2.01 620 2.17 645 2.34 672 2.53 698 2.73 723 2.92(a)
6600 514 1.76 549 1.96 578 2.15 604 2.33 629 2.49 653 2.66 676 2.84 699 3.02 722 3.23 747 3.44
7200 555 2.25 588 2.46 616 2.68 641 2.89 665 3.06 687 3.24(b) 709 3.43 730 3.62 751 3.82 772 4.02
5HP Oversized Motor & Drive
Continued External Static Pressure (Inches of Water)
1.10 1.20 1.30 1.40 1.50 1.60 1.70 1.80 1.90 2.00
CFM RPM BHP RPM BHP RPM BHP RPM BHP RPM BHP RPM BHP RPM BHP RPM BHP RPM BHP RPM BHP
3HP Standard Motor & High Static Drive Accessory 5HP Oversized Motor & Drive
4800 708 2.27 734 2.46 758 2.66 782 2.86 806 3.06 829 3.25 850 3.45 872 3.65 893 3.85 913 4.04
5400 727 2.65 752 2.85 776 3.05 799 3.25 821 3.47 843 3.69 865 3.91 886 4.13 907 4.36 927 4.58
6000 747 3.11 770 3.30 794 3.51 817 3.73 839 3.95 861 4.17 881 4.40 902 4.63 922 4.87 942 5.12
6600 770 3.66 793 3.87 815 4.08 835 4.28 857 4.51 879 4.74 900 4.98 — — — — — —
7200 794 4.25 817 4.49 839 4.73 860 4.96 — — — — — — — — — — — —
Notes:
1. Fan motor heat (MBH) = 3.15 x Fan BHP.
2. Data includes pressure drop due to wet coils and filters.
3. No accessories or options are included in pressure drop data.
4. Refer to Table 12, p. 29 to determine add’l static pressure drop due to other options/accessories.
5. Factory supplied motors, in commercial equipment, are definite purpose motors, specifically designed and tested to operate reliably and continuously at
all cataloged conditions. Using the full horsepower range of our fan motors as shown in our tabulated data will not result in nuisance tripping or
premature motor failure. Our product's warranty will not be affected.
(a) 3HP Standard Motor & High Static Drive Accessory
(b)5-hp Oversized Motor & Field Supplied Fan Sheave BK160 x 1 3/16 with BX75 (DF) or BX90 (HZ) Belt Required.

28 PKGP-PRC012M-EN
Performance Data
Table 7. Evaporator fan performance 20 tons WS*240E downflow or horizontal
External Static Pressure (Inches of Water)
CFM 0.10 0.20 0.30 0.40 0.50 0.60 0.70 0.80 0.90 1.00
RPMBHPRPMBHPRPMBHPRPMBHPRPMBHPRPMBHPRPMBHPRPMBHPRPMBHPRPM BHP
5HP Standard Motor Drive & low Static Drive Accessory 5HP Standard Motor Drive
6400 — — — — 507 1.72 535 1.88 560 2.07 584 2.27 607 2.46 631 2.66 654 2.86 677 3.07
7200 — — 519 2.10 549 2.30 576 2.48 600 2.67 623 2.88 644 3.10 665 3.32 686 3.54 707 3.76
8000 531 2.50 563 2.77 592 3.00 617 3.21 641 3.41 663 3.62 684 3.86 704 4.10 723 4.34 742 4.58
8800 578 3.26 607 3.56 634 3.83 659 4.08 683 4.31 704 4.54 724 4.77 744 5.01 762 5.27 779 5.54
9600 626 4.19 653 4.51 679 4.81 703 5.10 725 5.36 746 5.62 765 5.85 784 6.11 802 6.36 819 6.64
7.5HP Oversized Motor & Drive
Continued External Static Pressure (Inches of Water)
1.10 1.20 1.30 1.40 1.50 1.60 1.70 1.80 1.90 2.00
CFM RPMBHPRPMBHPRPMBHPRPMBHPRPMBHPRPMBHPRPMBHPRPMBHPRPMBHPRPM BHP
5HP Standard Motor Drive
6400 699 3.30 721 3.52 742 3.75 762 3.98 780 4.20 798 4.42 815 4.66 832 4.89 849 5.12 866 5.36
7200 727 3.98 748 4.22 768 4.46 789 4.71 808 4.97 827 5.22 845 5.48 861 5.73 878 5.98 893 6.24
8000 760 4.82 779 5.07 798 5.32 816 5.57 834 5.83 853 6.11 871 6.38 889 6.67 906 6.95 923 7.23(a)
8800 797 5.81 814 6.07 831 6.34 848 6.60 865 6.88 882 7.15 898 7.42 — — — — — —
9600 836 6.93 852 7.22 868 7.51 — — — — — — — — — — — — — —
7.5HP Oversized Motor & Drive
Notes:
1. Fan motor heat (MBH) = 3.15 x Fan BHP.
2. Data includes pressure drop due to wet coils and filters.
3. No accessories or options are included in pressure drop data.
4. Refer to Table 12, p. 29 to determine add’l static pressure drop due to other options/accessories.
5. Factory supplied motors, in commercial equipment, are definite purpose motors, specifically designed and tested to operate reliably and continuously at
all cataloged conditions. Using the full horsepower range of our fan motors as shown in our tabulated data will not result in nuisance tripping or
premature motor failure. Our product's warranty will not be affected.
6. For multi-speed or single zone VAV applications, minimum "full" speed airflow must be set to 6800 cfm or higher to prevent VFD overheating during
heating operation.
(a)7.5-hp Oversized Motor & Field Supplied Motor Sheave 1VP50 x 1 1/8 Required.
Table 8. Standard motor & drive/fan speed (Rpm)
Tons Unit Model No. 6 Turns
Open 5 Turns
Open 4 Turns
Open 3 Turns
Open 2 Turns
Open 1Turn
Open Closed
12½ WS*150E3,4,W 500 537 574 611 648 685 N/A
15 WS*180E3,4,W 500 537 574 611 648 685 N/A
20 WS*240E3,4,W 605 650 695 739 784 829 N/A
Note: Factory set at 3 turns open.
Table 9. Standard motor & low static fan drive
Tons Unit Model No. 6 Turns
Open 5 Turns
Open 4 Turns
Open 3 Turns
Open 2 Turns
Open 1Turn
Open Closed
12½ WS*150E3,4,W 379 407 435 463 491 519 N/A
15 WS*180E3,4,W 379 407 435 463 491 519 N/A
20 WS*240E3,4,W 506 544 581 619 656 694 N/A

PKGP-PRC012M-EN 29
Performance Data
Table 10. Standard motor & high static drive accessory/fan speed (rpm)
Tons Unit Model No. 6 Turns
Open 5 Turns
Open 4 Turns
Open 3 Turns
Open 2 Turns
Open 1Turn
Open Closed
12½ WS*150E3,4,W 685 722 759 796 833 870 N/A
15 WS*180E3,4,W 685 722 759 796 833 870 N/A
Table 11. Oversized motor & drive/fan speed (rpm)
Tons Unit Model No. 6 Turns
Open 5 Turns
Open 4 Turns
Open 3 Turns
Open 2 Turns
Open 1Turn
Open Closed
12½ WS*150E3,4,W 695 747 798 850 901 953 N/A
15 WS*180E3,4,W 695 747 798 850 901 953 N/A
20 WS*240E3,4,W 694 739 784 829 874 919 N/A
Table 12. Static pressure drops through accessories (inches water column)
Tons Unit Model
No. CFM Standard
Filters(a)
2”
MERV 8
Filters(b)
2”
MERV 13
Filters(b)
Standard
Economizer
with OA/RA
Dampers(c)
Low Leak
Economizer
with OA/RA
Dampers(d) Electric Heater
Accessory (KW)(e)
100%
OA 100%
RA 100%
OA 100%
RA 5-12 14-
23 36 54 72
12½ WS*150E
4000 0.02 0.04 0.08 0.20 0.02 0.16 0.10 — 0.03 0.03 0.04 —
5000 0.03 0.05 0.11 0.26 0.03 0.24 0.16 — 0.04 0.05 0.06 —
6000 0.05 0.07 0.14 0.35 0.04 0.33 0.24 — 0.06 0.07 0.09 —
15 WS*180E
4800 0.03 0.05 0.10 0.24 0.03 0.22 0.15 — 0.04 0.04 0.05 —
6000 0.05 0.07 0.14 0.35 0.04 0.33 0.24 — 0.06 0.07 0.08 —
7200 0.07 0.09 0.17 0.42 0.05 0.45 0.35 — 0.09 0.10 0.12 —
20
WSH240E
6400 0.04 0.01 0.11 0.22 0.04 — — — — 0.06 0.08 0.09
8000 0.06 0.09 0.14 0.31 0.05 — — — — 0.10 0.12 0.14
9600 0.09 0.12 0.18 0.44 0.07 — — — — 0.14 0.17 0.20
WSD240E
6400 0.05 0.08 0.12 0.22 0.04 0.37 0.27 — — 0.06 0.08 0.09
8000 0.08 0.10 0.15 0.31 0.05 0.54 0.43 — — 0.10 0.12 0.14
9600 0.11 0.14 0.19 0.44 0.07 0.75 0.62 — — 0.14 0.17 0.20
(a) Tested with: 2” filters 12 - 20 tons.
(b)Difference in pressure drop should be considered when utilizing optional 2” pleated filters.
(c) OA = Outside Air and RA = Return Air.
(d)OA = Outside Air and RA = Return Air.
(e) Nominal KW ratings at 240, 480, 600 volts.

30 PKGP-PRC012M-EN
Performance Data
Table 13. 12½ tons three phase heating capacities (net) WS*150E3, E4, EW at 5000 CFM
Outdoor
Temp (°F)
70% RH
Integrated Heating Capacity (MBh/1000)
at Indicated Dry Bulb Temp (°F) Total Power in Kilowatts at Indicated
Dry Bulb Temp (°F)
60 70 75 80 60 70 75 80
-8 50.9 48.5 47.2 45.9 9.6 10.3 10.8 11.3
-3 56.9 54.5 53.4 52.1 9.7 10.4 10.9 11.4
2 63.3 60.6 59.3 58.0 9.7 10.5 10.9 11.4
7 69.7 66.6 65.5 64.0 9.8 10.6 11.0 11.5
12 76.1 72.5 71.7 70.2 9.9 10.7 11.1 11.6
17 82.0 79.0 77.3 76.9 10.0 10.8 11.3 11.8
22 89.7 86.5 84.8 83.5 10.1 10.9 11.3 11.9
27 96.8 93.5 91.8 90.2 10.1 11.0 11.5 12.0
32 104.6 100.8 99.1 97.2 10.2 11.1 11.6 12.1
37 112.0 108.1 106.1 104.3 10.3 11.2 11.7 12.2
42 129.1 124.4 122.2 120.0 10.5 11.4 11.9 12.5
47 148.4 142.8 140.1 137.4 10.7 11.6 12.1 12.7
52 156.7 151.0 148.0 145.2 10.8 11.7 12.2 12.8
57 166.0 159.8 156.8 153.6 10.9 11.9 12.4 12.9
62 175.5 168.6 165.3 162.0 11.0 12.0 12.5 13.1
67 185.2 177.6 174.5 170.0 11.2 12.1 12.7 13.2
72 193.6 185.7 181.6 177.6 11.3 12.3 12.8 13.4
Notes:
1. For other airflow conditions, see heating capacity correction factor Net Heating Capacity and Power Input include indoor fan heat at
nominal CFM and 0.35 inch ESP. To obtain net heating at other conditions, subtract fan heat at this condition and add fan heat at new
condition.
2. Heating capacities and powers are integrated to include the effects of defrost in the frost region.
3. All heating capacities and power (kW) are at 70% OD relative humidity.

PKGP-PRC012M-EN 31
Performance Data
Table 14. 15 tons three phase heating capacities (net) WS*180E3, E4, EW at 6000 CFM
Outdoor
Temp (°F)
70% RH
Integrated Heating Capacity (MBh/1000)
at Indicated Dry Bulb Temp (°F) Total Power in Kilowatts at Indicated
Dry Bulb Temp (°F)
60 70 75 80 60 70 75 80
-8 56.3 54.8 54.0 53.2 10.5 11.5 12.0 12.5
-3 62.8 61.1 60.2 59.4 10.7 11.7 12.1 12.7
2 69.5 67.6 66.7 65.7 10.9 11.8 12.4 12.9
7 76.2 71.1 69.9 70.8 11.1 12.0 12.5 14.0
12 82.9 73.0 76.9 77.0 12.0 12.1 12.7 13.7
17 88.2 85.4 84.0 82.7 11.4 12.4 12.9 13.5
22 95.9 92.8 91.4 89.9 11.6 12.5 13.1 13.7
27 103.8 100.6 98.9 97.3 11.8 12.7 13.3 13.9
32 112.3 109.0 107.1 105.5 11.9 13.0 13.5 14.1
37 120.8 117.1 115.4 113.7 12.1 13.2 13.8 14.4
42 148.0 143.6 141.4 139.1 12.2 13.3 13.9 14.5
47 179.2 173.8 170.8 168.0 12.6 13.6 14.2 14.8
52 190.8 185.3 182.3 179.0 12.8 13.9 14.4 15.0
57 204.1 197.7 194.2 191.5 13.1 14.1 14.7 15.3
62 217.8 210.6 207.5 203.7 13.4 14.4 15.0 15.6
67 233.5 225.5 221.1 217.0 13.7 14.8 15.4 16.0
72 247.8 239.7 235.5 231.2 14.1 15.2 15.8 16.4
Notes:
1. For other airflow conditions, see heating capacity correction factor Net Heating Capacity and Power Input include indoor fan heat at
nominal CFM and 0.35 inch ESP. To obtain net heating at other conditions, subtract fan heat at this condition and add fan heat at new
condition.
2. Heating capacities and powers are integrated to include the effects of defrost in the frost region.
3. All heating capacities and power (kW) are at 70% OD relative humidity.

32 PKGP-PRC012M-EN
Performance Data
Table 15. 20 tons three phase heating capacities (Net) WS*240E3, E4, EW at 8000 CFM
Outdoor
Temp (°F)
70% RH
Integrated Heating Capacity (MBh/1000)
at Indicated Dry Bulb Temp (°F) Total Power in Kilowatts at Indicated
Dry Bulb Temp (°F)
60 70 75 80 60 70 75 80
-8 80.6 78.4 77.6 76.8 15.1 15.9 16.4 16.9
-3 87.5 85.3 84.5 83.4 15.3 16.0 16.5 17.0
2 96.3 93.9 92.8 91.7 15.4 16.2 16.7 17.2
7 106.0 103.2 102.3 101.0 15.5 16.3 16.8 17.3
12 118.3 116.2 115.5 114.7 15.7 16.5 17.0 17.5
17 131.1 128.2 127.4 126.3 15.9 16.7 17.2 17.7
22 142.9 140.3 138.8 137.2 16.1 16.9 17.4 17.9
27 154.1 151.3 150.0 148.6 16.4 17.3 17.8 18.3
32 165.5 162.4 161.2 159.6 16.5 17.4 17.9 18.4
37 180.9 177.6 175.7 174.5 16.8 17.7 18.2 18.7
42 196.5 191.9 189.8 188.2 17.0 17.9 18.4 18.9
47 213.3 209.1 207.0 205.4 17.1 18.0 18.5 19.0
52 228.9 224.2 221.4 219.8 17.4 18.3 18.8 19.3
57 243.4 237.7 235.6 233.0 17.8 18.8 19.3 19.8
62 261.9 255.7 252.6 250.0 20.0 21.1 21.6 22.1
67 279.6 272.0 268.9 265.3 20.1 21.2 21.7 22.2
72 298.5 291.1 287.9 283.8 20.4 21.5 22.0 22.6
Notes:
1. For other airflow conditions, see heating capacity correction factor Net Heating Capacity and Power Input include indoor fan heat at
nominal CFM and 0.35 inch ESP. To obtain net heating at other conditions, subtract fan heat at this condition and add fan heat at new
condition.
2. Heating capacities and powers are integrated to include the effects of defrost in the frost region.
3. All heating capacities and power (kW) are at 70% OD relative humidity.
Table 16. Heating capacity correction factors
% Variation of Nominal CFM - 20 - 10 0 + 10 + 20
Total Gross Capacity Multiplier 0.96 0.98 1.0 1.01 1.02
Table 17. Auxiliary electric heat capacity
Total(a) Stage 1 Stage 2
Unit KW MBh No. of KW MBh KW MBh
Tons Model No. Input(b) Output Stages Input(b) Output Input(b) Output
18.00 61.00 1 18.00 61.00 - -
12½, 15 WS*150E3, E4, EW 36.00 123.00 2 18.00 61.00 18.00 61.00
WS*180E3, E4, EW 54.00 184.00 2 36.00 123.00 18.00 61.00
36.00 123.00 2 18.00 61.00 18.00 61.00
20 WS* 240E3, E4, EW 54.00 184.00 2 36.00 123.00 18.00 61.00
72.00 246.00 2 36.00 123.00 36.00 123.00
(a)Heaters are rated at 240v,380v,480v and 600v. For other than rated voltage, CAP= (voltage/rated voltage)2 x rated cap.
(b)For all input/output categories, does not include fan power or heat.

PKGP-PRC012M-EN 33
Performance Data
Table 18. Electric heater voltage correction factors (applicable to auxiliary heat capacity)
Nominal Distribution Capacity
Voltage Voltage Multiplier
208 0.75
240 230 0.92
240 1.00
440 0.84
480 460 0.94
480 1.00
540 0.81
600 575 0.92
600 1.00
Table 19. Air temperature rise across electric heaters (°F)
KW Stages
12½ Ton
5000 CFM 15 Ton
6000 CFM 20 Ton
8000 CFM
Three Phase
WS*150E Three Phase
WS*180E Three Phase
WS*240E
9.00 1 - - -
17.30 1 - - -
18.00 1 11.4 9.5 -
27.00 2 - - -
36.00 2 23.0 19.0 14.2
54.00 2 34.1 28.4 21.3
72.00 2 - - 28.5
Table 20. Electric heater temperature rise correction factors
% Variation From Nominal CFM - 20 - 15 - 10 - 5 0 +5 +10 +15 +20
Temperature Rise Multiplier 1.25 1.17 1.11 1.05 1.00 0.95 0.91 0.87 0.83

34 PKGP-PRC012M-EN
Controls
Field Installed Control Options
Zone Sensors
Note: Zone sensor required for units configured for Single Zone VAV indoor fan system control
to enable Single Zone VAV functionality.
Zone Sensors are the building occupant’s comfort control devices forVoyager™ units with
ReliaTel:
RA Remote Sensor
Return Air Remote Sensor which can be mounted in the return air duct to report return air
temperature.
Manual Changeover Manual/Automatic
Changeover
Manual/Automatic
Changeover
Heat, Cool or Off System
Switch. Fan Auto or Off
Switch. One temperature
setpoint lever
Auto, Heat, Cool or Off System
Switch. Fan Auto or Off Switch.
Two temperature setpoint
levers
Auto, Heat, Cool or Off System
Switch. Fan Auto or Off
Switch. Two temperature
setpoint levers. Status
Indication LED lights, System
On, Heat, Cool, or Service.
Manual/Automatic
Changeover
Remote Sensor Integrated Comfort™
System
Auto, Heat, Cool or Off System
Switch. Fan Auto or Off
Switch. Two temperature
setpoint levers
Sensor(s) available for all zone
sensors to provide remote
sensing capabilities
Sensor(s) available with
optional temperature
adjustment and override
buttons to provide central
control through a Trane
Integrated Comfort™system.

PKGP-PRC012M-EN 35
Controls
Dual Thermistor Remote Zone Sensor
This sensor will allow the customer to reduce the total number of remote sensors to obtain space
temperature averaging. This sensor should be utilized with ReliaTel controls.
Room Remote Sensor
Space Remote Sensor which can be mounted on the wall to report/control from a remote location
in the space.
Programmable Night
Setback
Touchscreen
Programmable
Thermostat (2H/2C)
CO2 Sensor
Auto or manual changeover
with seven-day
programming. Keyboard
selection of Heat, Cool, Fan,
Auto, or On. All
programmable sensors have
System On, Heat, Cool,
Service LED/indicators as
standard. Night Setback
Sensors have one (1)
Occupied, one (1) Un-
occupied, and one (1)
Override program per day.
Two Heat/Two Cool
programmable thermostat
with touch screen digital
display. Menu-driven
programming. Effortless set-
up. Program each day
separately with no need to
copy multiple days. All
programming can be done on
one screen. Easy to read and
use. Large, clear backlit digital
display.
The CO2 sensor shall have
the ability to monitor the
concentration (parts per
million, ppm) of CO2 (Carbon
Dioxide) in the air. As the CO2
concentration changes, the
outside air damper
modulates to meet the
current ventilation needs of
the zone.
Digital Display Programmable
Thermostat (3H/2C)
Digital Display Thermostat
(3H/2C)
Two Heat/Two Cool auto changeover digital
display thermostat. 7-day programmable
stat with night setback shall be available
Three Heat, Two Cool auto changeover digital
display thermostat.
DONE WAKE LEAVE RETURN SLEEPEDIT CANCEL
MON TUE WED THU FRI SAT SUN
PM
FAN
ON
AUTO
CIRC
SYSTEM
EM HEAT
HEAT
OFF
COOL
AUTO
RESET
HEAT
COOL
DEHUMIDIFIER
CANCEL
PERIOD

36 PKGP-PRC012M-EN
Electrical Data
Table 21. Unit wiring
Standard Indoor Motor Oversize Indoor Fan Motor
Tons Unit Model # Unit Operating
Voltage Range Minimum Circuit
Ampacity
Max Fuse Size or
Max Circuit
Breaker(a) Minimum Circuit
Ampacity
Max Fuse Size or
Max Circuit
Breaker(a)
WS*150E3 187-253 68 80 74 90
12½ WS*150E4 414-506 32 40 35 45
WS*150EW 517-633 25 30 27 30
WS*180E3 187-253 74 90 80 100
15 WS*180E4 414-506 36 45 39 50
WS*180EW 517-633 30 35 32 40
WS*240E3 187-253 116 150 124 150
20 WS*240E4 414-506 56 70 59 70
WS*240EW 517-633 45 60 48 60
(a) HACR type circuit breaker per NEC.
Table 22. Unit wiring with electric heat (single point connection) — standard refrigeration system (downflow and
horizontal)
Standard Indoor Motor Oversize Indoor Motor
Tons Unit Model
Number Heater Model
Number(a) Heater kW
Rating Control
Stages MCA
Max Fuse Size
or Max Circuit
Breaker MCA
Max Fuse Size
or Max Circuit
Breaker(b)
208/230 Volts Three Phase
12½ WS*150E3
AYDHTRK318/AYHHTRM318 13.5/18.0 1 115/123 125/125 121/129 125/150
AYDHTRK336/AYHHTRM336 27.0/36.0 2 168/183 175/200 174/189 175/200
AYDHTRK354/AYHHTRM354 40.5/54.0 2 209/198 225/200 215/204 225/225
15 WS*180E3
AYDHTRK318/AYHHTRM318 13.5/18.0 1 121/129 125/150 127/135 150/150
AYDHTRK336/AYHHTRM336 27.0/36.0 2 168/183 175/200 174/189 175/200
AYDHTRK354/AYHHTRM354 40.5/54.0 2 215/204 225/225 221/210 225/225
20 WS*240E3
AYDHTRL336/AYHHTRN336 27.0/36.0 2 210/225 225/225 218/233 225/250
AYDHTRL354/AYHHTRN354 40.5/54.0 2 257/246 300/250 265/254 300/300
AYDHTRK372/AYHHTRN372 54.0/72.0 2 267/290 300/300 275/298 300/300
460 Volts Three Phase
12½ WS*150E4
AYDHTRK418/AYHHTRM418 18 1 60 60 63 70
AYDHTRK436/AYHHTRP436 36 2 87 90 90 90
AYDHTRK454/AYHHTRM454 54 2 97 100 100 100
15 WS*180E4
AYDHTRK418/AYHHTRM418 18 1 64 70 67 70
AYDHTRK436/AYHHTRM436 36 2 91 100 94 100
AYDHTRK454/AYHHTRM454 54 2 101 110 104 110
20 WS*240E4
AYDHTRL436/AYHHTRN436 36 2 111 125 114 125
AYDHTRL454/AYHHTRN454 54 2 121 125 125 125
AYDHTRK472/AYHHTRN472 72 2 143 150 146 150

PKGP-PRC012M-EN 37
Electrical Data
575 Volts Three Phase
12½ WS*150EW
AYDHTRKW18 (AYDHTRLW18)(a)
/AYHHTRMW18 (AYHHTRPW18) 18 1 47 50 49 50
AYDHTRKW36/AYHHTRMW36
(AYHHTRRW36)(a) 36 2 69 70 71 80
AYDHTRKW54/AYHHTRMW54 54 2 77 80 79 80
15 WS*180EW
AYDHTRKW18 (AYDHTRMW18)(a)
/AYHHTRMW18 (AYHHTRQW18) 18 1 52 60 54 60
AYDHTRKW36/AYHHTRMW36
(AYHHTRSW36)(a) 36 2 74 80 76 80
AYDHTRKW54/AYHHTRMW54 54 2 82 90 84 90
20 WS*240EW
AYDHTRLW36/AYHHTRNW36 36 2 89 90 92 100
AYDHTRLW54/AYHHTRNW54 54 2 97 110 100 110
AYDHTRKW72/AYHHTRNW72 72 2 115 125 118 125
(a) Heater model numbers in parenthesis apply to units with an optional high SCCR rating.
(b)Values do not include power exhaust accessory.
* Indicates both downflow and horizontal units.
Table 22. Unit wiring with electric heat (single point connection) — standard refrigeration system (downflow and
horizontal) (continued)
Standard Indoor Motor Oversize Indoor Motor
Tons Unit Model
Number Heater Model
Number(a) Heater kW
Rating Control
Stages MCA
Max Fuse Size
or Max Circuit
Breaker MCA
Max Fuse Size
or Max Circuit
Breaker(b)
Table 23. Electrical characteristics - power exhaust accessory
Tons Accessory Operating
Voltage Phase HP RPM Amps FLA LRA
208-230 1 3/4 1040 6.6 13.5
12½, 15, 20 460 1 3/4 1040 3.2 8.4
575 1 3/4 1040 2.1 5.2
Table 24. Electrical characteristics - evaporator fan motors - 60 cycle
Standard Evaporator Fan Motor Oversized Evaporator Fan Motor
Amps Amps
Tons Unit Model
No. No. Volts Phase HP FLA LRA No. Volts Phase HP FLA LRA
WS*150E3 1 208-230 3 3.00 10.6 81.0 1 208-230 3 5.00 16.7 109.8
12½ WS*150E4 1 460 3 3.00 4.8 40.5 1 460 3 5.00 7.6 54.9
WS*150EW 1 575 3 3.00 3.9 31.0 1 575 3 5.00 6.1 41.6
WS*180E3 1 208-230 3 3.00 10.6 81.0 1 208-230 3 5.00 16.7 109.8
15 WS*180E4 1 460 3 3.00 4.8 40.5 1 460 3 5.00 7.6 54.9
WS*180EW 1 575 3 3.00 3.9 31.0 1 575 3 5.00 6.1 41.6
WS*240E3 1 208-230 3 5.00 16.7 109.8 1 208-230 3 7.50 24.2 120.4
20 WS*240E4 1 460 3 5.00 7.6 54.9 1 460 3 7.50 11.0 74.0
WS*240EW 1 575 3 5.00 6.1 41.6 1 575 3 7.50 9.0 60.0

38 PKGP-PRC012M-EN
Electrical Data
Table 25. Electrical characteristics — compressor motor and condenser motor — 60 cycle
Compressor Motors Condenser Fan Motors
Amps(a) Amps
Tons Unit Model
Number No. Volts Phase HP(b) RPM RLA LRA No. Phase HP FLA LRA
12½
WS*150E3 2 208-230 3 5.6 3450 22.4 149 2 1 0.5 3.2 8.8
WS*150E4 2 460 3 5.6 3450 10.6 75 2 1 0.5 1.6 3.8
WS*150EW 2 575 3 5.6 3450 7.9/7.7 54 2 1 0.5 1.3 3.2
15
WS*180E3 2 208-230 3 6.9 3450 25 164 2 1 0.5 3.2 8.8
WS*180E4 2 460 3 6.9 3450 12.5/12.2 100 2 1 0.5 1.6 3.8
WS*180EW 2 575 3 6.9 3450 10.3/10.1 78 2 1 0.5 1.3 3.2
20
WS*240E3 2 208-230 3 10.4 3450 39.1 267 2 1 1 5.0 14.4
WS*240E4 2 460 3 10.4 3450 17.3 142 2 1 1 2.5 5.8
WS*240EW 2 575 3 10.4 3450 15.4 103 2 1 1 2 5.1
(a)For Compressor Motors and Condenser Fan Motors: Amp draw for each motor; multiply value by number of motors to determine total amps.
(b)HP for each compressor.
*Indicates both downflow and horizontal units.

PKGP-PRC012M-EN 39
Dimensional Data
Figure 2. Heat pump models - 12½ - 20 tons
* All dimensions are in inches/millimeters.
DOWNFLOW CONDENSATE
DRAIN CONN 1" (25.4MM) NPT
121 11/16"
6 7/16"
84 3/16"
33 3/16"
8 15/16"
1"
2 11/16"
56"
48 1/2"
6 13/16"
122 5/16"
85 5/16"
54"
13/16"
SINGLE POINT
POWER ENTRY
3" (76MM) DIA HOLE
(UNIT POWER WIRE)
7/8" (22.23MM) DIA. HOLE
(UNIT CONTROL
WIRE)
FILTER
ACCESS DOOR
HORIZONTAL
SERVICE GAUGE
PORT ACCESS
2167MM
3107MM
20MM
(1372MM) - 12.5-15T UNITS
2154MM
25.4MM
1231.90MM
173MM
3091MM
1422MM
163.51MM
843MM
227MM
68.26MM
64 1/8
" (1629MM) - 20T UNITS

40 PKGP-PRC012M-EN
Dimensional Data
Figure 3. Heat pump models - 12½ - 20 tons
* All dimensions are in inches/millimeters.
Figure 4. Heat pump models - 12½ - 20 tons
* All dimensions are in inches/millimeters.

PKGP-PRC012M-EN 41
Dimensional Data
Figure 5. Heat pump models - 12½ - 20 tons
* Duct flanges mount 7-7/16" down inside the curb on the 1-1½ curb flanges.
Roofcurb is intended for downflow use only.
* All dimensions are in inches/millimeters.
Figure 6. Heat pump models - 12½ - 20 tons
* All dimensions are in inches/millimeters.
9
1”
25.4 MM
CURB FLANGE
LONG SIDES
SHORT SIDES

42 PKGP-PRC012M-EN
Dimensional Data
Figure 7. Downflow & horizontal condensate locations
Table 26. Heat pump units
Tons Condensate
Drain Size
Condensate Drain Location
Downflow Only Downflow Horizontal
ABCDFGH J K
12½, 15, 20 26 7/16 28 3/4 19 15/16 4 1/4 4 1/4 76 5/16 68 11/16 1 NPT 26 3/4 5 3/8
Table 27. Swing clearances
Unit Model # A B C D E
WSD 150-240 29 1/2 56 38 1/2 18 1/2 N/A
WSH 150-240 29 1/2 N/A 38 1/2 18 1/2 14
Note: All dimensions are in inches.
SWING RADIUS (C)
OD SECTION
ACCESS PANEL
THROUGH THE
BASE ELECTRICAL
SWING RADIUS (A)
ID SECTION
ACCESS PANEL
TOP VIEW SHOWING THROUGH THE BASE
ELECTRICAL UTILITY LOCATIONS AND ACCESS PANEL SWING CLEARANCES.
SWING RADIUS (E)
HORIZONTAL FILTER
ACCESS PANEL
SWING RADIUS (D)
ID FAN SECTION
ACCESS PANEL
B
6 7/8"
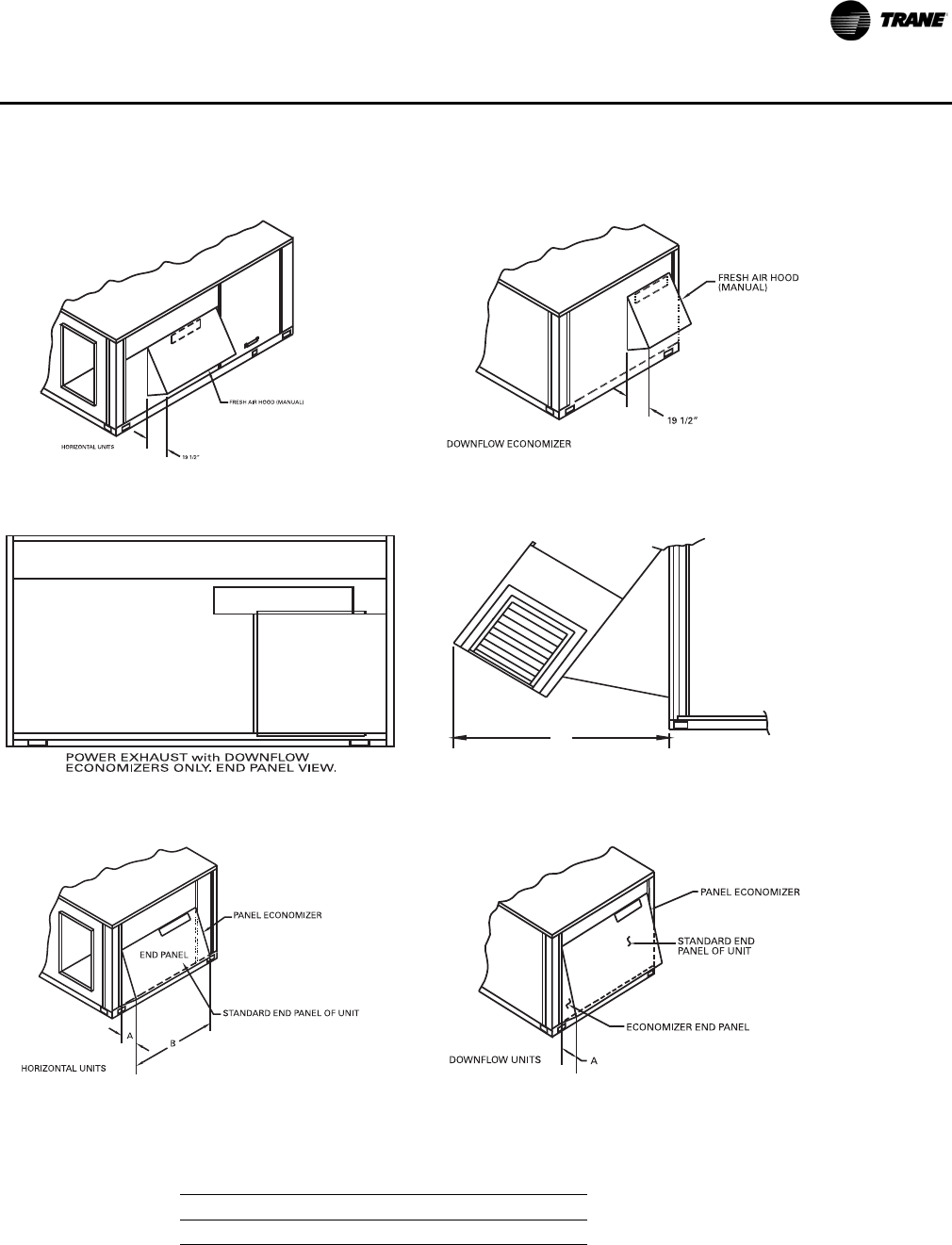
PKGP-PRC012M-EN 43
Dimensional Data
Figure 8. Fresh air hood (horizontal units) Figure 9. Fresh air hood (downflow units)
Figure 10. Power exhaust - downflow economizers Figure 11. Power exhaust - downflow economizers - side view
C
POWER EXHAUST with DOWNFLOW
ECONOMIZERS only, SIDE VIEW
Figure 12. Economizer - horizontal units Figure 13. Economizer - downflow units
Note: When applying economizer to horizontal units, connected
ductwork must be run full size to allow proper operation of
economizer damper.
Table 28. Power exhaust dimensions
Unit Model # A B(a)
(a)Horizontal dimension only. Downflow economizer is width of
end panel.
C(b)
(b)Power exhaust is applied on downflow economizer only.
WS* 150-240 19½ 64¾ 39

44 PKGP-PRC012M-EN
Weights
Table 29. Accessory net weights (lbs)
Tons Unit Model
No.
Std
Economizer
(a)
(a) Net weight should be added to unit weight when ordering factory installed economizer or oversize motor.
Low Leak
Economizer Outside Air
Damper Power
Exhaust
(b)
(b)Downflow only.
Roof
Curb
Oversized
Motor
Adder
High
Static
DriveNet Ship Net Manual Moto-
rized
12½, 15,
20 WSD150-240E 80 265 250 32 75 95 235 5 10
12½, 15,
20 WSH150-240E 65 210 - 32 75 - - 5 15
Table 30. Electric heaters weights
Tons Unit Model No. All Zone
Sensors
Electric Heaters(a)(b)
(a) For 600V heaters net weights are same as 480V heaters.
(b)To estimate shipping weight add 5 lbs to net weight.
5-18 kW
240/480V 23-36 kW
240/480V 54 kW
240/480V 72 kW
240/480V
12½-20 WS*150E, 180E, 240E 1 28/22 33/27 40/32 43/34
Table 31. Variable frequency drive weights
Motor Size WSD150-240E WSH150-240E
3(a) & 5 HP
(a)3 HP motors not applicable to WS*240E units.
32 34
7.5 HP(b)
(b)WS*240E units only.
63 65
Figure 14. Center of gravity

PKGP-PRC012M-EN 45
Weights
Table 32. Maximum unit & corner weights (lbs) and center of gravity dimensions (In.)
Maximum Weights
(Lbs) Corner Weights (Lbs) Center of Gravity (In.)
Tons Unit Model No. Shipping Net A B C D Length Width
12½ WS*150E 2430 1978 633 514 376 455 56 36
15 WS*180E 2435 1982 634 515 377 456 56 36
20 WS*240E 2566 2107 674 485 400 590 57 35
Table 33. Factory installed options (FIOPS) net weights (lbs)(a)(b)(c)
(a)Weights for FIOP accessories not listed are < 5 lbs.
(b)Net weight should be added to unit weight when ordering factory installed accessories.
(c) See Table 29, p. 44 for standard factory installed economizer and oversized motors.
Accessory Weight Unit Model No.
High Efficiency Motors(d)
(d)Standard factory installed motors are already included in unit net and shipping weights. Values shown for high
efficiency motors are in addition to the standard motor weight.
* Indicates both downflow and horizontal units.
49 WS*150-180 standard size motor
36 WS*240 standard size motor
WS*150-180 oversized motor
0 WS*240 oversized size motor
Hinged Doors 27 All WS* units
Powered Convenience Outlet 38 All WS* units
Through the Base Electrical 23 All WS* units
Unit Mounted Circuit Breaker 5 All WS* units except those with 54&72 kW heaters & 208/230V
10 All WS* units with 54&72 kW heaters & 208/230V
Unit Mounted Disconnect 5 All WS* units except those with 54&72 kW heaters & 208/230V
10 All WS* units with 54&72 kW heaters & 208/230V
Smoke Detectors (Supply/Return) 5 All WS* units
Tool-less Hail Guard 43 WS*150,180
51 WS*240
Stainless Steel Drain Pan 8.1 All WS* units

46 PKGP-PRC012M-EN
Typical Wiring

PKGP-PRC012M-EN 47
Ty p i c a l W i ri n g

48 PKGP-PRC012M-EN
Typical Wiring

PKGP-PRC012M-EN 49
Ty p i c a l W i ri n g

50 PKGP-PRC012M-EN
Jobsite Connections
Notes:
•For specific wiring information, see the installation instructions.
•All wiring except power wires is low voltage.
•All customer-supplied wiring should be copper and must conform to NEC or CEC and local
electrical codes.
•Wiring shown dotted is to be furnished and installed by the customer.
•Zone sensors are required for units configured for Single Zone VAV indoor fan system control
in order to enable Single Zone VAV functionality.
Table 34. Zone sensors - typical number of wires
Zone
Sensors
AManual Changeover.....................................................................4
Manual/Auto Changeover.............................................................5
Manual/Auto Changeover with Status Indication LED’s....................10
Programmable Night Setback with Status Indication LED’s...............7
Thermostats
B3 Power Wires + 1 Ground Wire (three phase)
2 Power Wires + 1 Ground Wire (single phase)
DISCONNECT
SWITCH
(BY OTHERS)
ZONE SENSOR OR
THERMOSTAT ROOFTOP
UNIT
A
B

PKGP-PRC012M-EN 51
Mechanical Specifications
General
The units shall be dedicated downflow or horizontal airflow. The operating range shall be between
115°F and 0°F in cooling as standard from the factory for all units. Cooling performance shall be
rated in accordance with ARI testing procedures. All units shall be factory assembled, internally
wired, fully charged with R-410A, and 100% run tested to check cooling operation, fan and blower
rotation and control sequence, before leaving the factory. Wiring internal to the unit shall be
colored and numbered for simplified identification. Units shall be UL listed and labeled, classified
in accordance to UL 1995/C 22.2, 236-05 3rd Edition.
Casing
Unit casing shall be constructed of zinc coated, heavy gauge, galvanized steel. Exterior surfaces
shall be cleaned, phosphatized, and finished with a weather-resistant baked enamel finish. Unit’s
surface shall be tested 500 hours in a salt spray test in compliance with ASTM B117. Cabinet
construction shall allow for all maintenance on one side of the unit. In order to ensure a water and
air tight seal, service panels shall have lifting handles and no more than three screws to remove.
All exposed vertical panels and top covers in the indoor air section shall be insulated with a 1/2 inch,
1 pound density foil-faced, fire-resistant, permanent, odorless, glass fiber material. The base of the
downflow unit shall be insulated with 1/2 inch, 1 pound density foil-faced, closed-cell material. The
downflow unit’s base pan shall have no penetrations within the perimeter of the curb other than
the raised 11/8 inch high supply/return openings to provide an added water integrity precaution,
if the condensate drain backs up. The base of the unit shall have provisions for forklift and crane
lifting.
Unit Top
The top cover shall be one piece, or where seams exist, double hemmed and gasket sealed to
prevent water leakage.
Filters
Two inch standard filters shall be factory supplied on all units. Optional two inch pleated MERV 8
and MERV 13 filters with filter removal tool shall be available.
Compressors
External high pressure cutout shall be provided on all 15 and 20 models. Low pressure switches
shall be standard. All units shall have direct-drive, hermetic, scroll type compressors with
centrifugal type oil pumps. Motor shall be suction gas-cooled and shall have a voltage utilization
range of plus or minus 10% of nameplate voltage. Internal overloads shall be provided with the
scroll compressors. Crankcase heaters shall be utilized with all scroll compressors.
Refrigerant Circuits
Each refrigerant circuit shall have independent fixed orifice or thermostatic expansion devices,
service pressure ports, and refrigerant line filter driers factory installed as standard. An area shall
be provided for replacement suction line driers.
Evaporator and Condenser Coils
Internally finned, 5/16” copper tubes mechanically bonded to a configured aluminum plate fin shall
be standard. Coils shall be leak tested at the factory to ensure the pressure integrity. All coils are
pressure and leak tested at minimum of 450 psig. The completely assembled refrigerant system
is leak tested at a minimum of 240 psig with a refrigerant and nitrogen mixture. All dual compressor
units shall have intermingled evaporator coils. Sloped condensate drain pans are standard. Patent-
pending 1+1+1 condenser coil, permanently gapped for easy cleaning is available.

52 PKGP-PRC012M-EN
Mechanical Specifications
Outdoor Fans
The outdoor fan shall be direct-drive, statically and dynamically balanced, draw-through in the
vertical discharge position. The fan motor(s) shall be permanently lubricated and shall have built-
in thermal overload protection.
Indoor Fan
Units above shall have belt driven, FC centrifugal fans with adjustable motor sheaves. Units with
standard motors shall have an adjustable idler-arm assembly for quick-adjustment of fan belts and
motor sheaves. All motors shall be thermally protected. Oversized motors shall be available for
high static application. All indoor fan motors meet the U.S. Energy Policy Act of 1992 (EPACT).
Controls
Unit shall be completely factory- wired with necessary controls and contactor pressure lugs or
terminal block for power wiring. Unit shall provide an external location for mounting a fused
disconnect device. ReliaTel controls shall be provided for all 24-volt control functions. The resident
control algorithms shall make all heating, cooling, and/or ventilating decisions in response to
electronic signals from sensors measuring indoor and outdoor temperatures. The control
algorithm maintains accurate temperature control, minimizes drift from set point, and provides
better building comfort. A centralized control shall provide anti-short cycle timing and time delay
between compressors to provide a higher level of machine protection.
Defrost Controls
Adaptive demand defrost shall be provided to permit defrost wherever coil icing conditions begin
to significantly reduce unit capacity.
Discharge Line Thermostat
A bi-metal element discharge line thermostat is installed as a standard option on the discharge line
of each system. This standard option provides extra protection to the compressors against high
discharge temperatures in case of loss of charge, extremely high ambient and other conditions
which could drive the discharge temperature higher. Discharge line thermostat is wired in series
with high pressure control. When the discharge temperature rises above the protection limit, the
bi-metal disc in the thermostat switches to the off position, opening the 24 VAC circuit. When the
temperature on the discharge line cools down, the bi-metal disc closes the contactor circuit,
providing power to the compressor. When the thermostat opens the fourth time, the ReliaTel
control must be manually reset to resume operation on that stage.
Phase Monitor
The Phase Monitor is a 3 phase line monitor module that protects against phase loss, phase
reversal and phase unbalance. It is intended to protect compressors from reverse rotation. It has
an operating input voltage range of 190-600 VAC, and LED indicators for ON and FAULT. There are
no field adjustments and the module will automatically reset from a fault condition.
Variable Frequency Drive
Variable Frequency Drives are factory installed and tested to provide supply fan motor speed
modulation. VFDs on the supply fan, as compared to inlet guide vanes or discharge dampers, are
quieter, more efficient, and are eligible for utility rebates. All VFDs are designed to allow bypass
if required. Bypass control will simply provide full nominal airflow in the event of drive failure.

PKGP-PRC012M-EN 53
Mechanical Specifications
Factory Installed Options
Black Epoxy Pre-Coated Coils
The black epoxy coils have a thermoset vinyl coating that is bonded to the aluminum fin stock prior
to the fin-stamping process. The pre-coated coils are an economical option for protection in mildly
corrosive environments.
Condensate Overflow Switch
This option shall shut the unit down in the event that a clogged condensate drain line prevents
proper condensate removal from the unit.
Fault Detection & Diagnostics (FDD)
This offering meets the mandatory requirement of Title 24. This option provides detection of the
following faults: Air temperature sensor failure/fault, not economizing when it should,
economizing when it should not, damper not modulating, and excessive outdoor air. The FDD
system shall be certified by the Energy Commission as meeting the requirements.
High Efficiency Motors
This option is available with efficiency ratings from 86.5 up to 91.0. It is not available for all models.
High Short Circuit Current Rating
Unit shall be provided with electrical subsystem that will withstand fault currents up to 65kA (208/
230, 460 VAC) or 25kA (575 VAC) compliant with UL 1995 and NEC 440.4 (B). Each compressor circuit
and the indoor fan shall have dedicated overcurrent protection. Three phase motors shall be
protected by Class J time delay fuses. Single phase motors shall be protected by Class CC time
delay fuses. All transformers shall also be protected with Class CC time delay fuses. Contactors
shall be din rail mounted.
Hinged Access Doors
Sheet metal hinges are available on the Filter, Evaporator, ID Fan and Compressor/Control Access
Doors. This option is available on all models.
Horizontal Side Access with Circuit Breaker
This option is a thermal magnetic, molded case, HACR Circuit Breaker with provisions for through
the base electrical connections. The circuit breaker will be installed in a water tight enclosure in the
unit with access through a swinging door. Factory wiring will be provided from the switch to the
unit high voltage terminal block. The circuit breaker will provide overcurrent protection, be sized
per NEC and UL guidelines, and be agency recognized by UL/CSA.
Horizontal Side Access with Disconnect Switch
Three-pole, molded case, disconnect switch with provisions for through the base electrical
connections are available. The disconnect switch will be installed in the unit in a water-tight
enclosure with access through a swinging door. Factory wiring will be provided from the switch to
the unit high voltage terminal block. The switch will be UL/CSA agency recognized.
Note: The disconnect switch will be sized per NEC and UL guidelines but will not be used in place
of unit overcurrent protection. This option is available on all models.
Human Interface
The Human Interface shall have a 5 inch color touchscreen display that conforms to FCC Part 15
Class B with an Ingress Protection Rating of IP24. The display text shall be readable by a person
with 20/20 vision at a distance of 3 feet and 60° angle at lighting levels ranging from 100 lux - 25,000
lux. Also, the display shall operate at temperatures of -40° C to 70° C. Firmware and unit
configurations shall be able to be restored via a USB storage device.

54 PKGP-PRC012M-EN
Mechanical Specifications
Multi-Speed Indoor Fan System
Multi-speed indoor fan system is designed for use in applications for meeting the minimum
requirement of CA Title 24. This system incorporates a multi-speed fan control to change the speed
of the fan to 67% of full airflow based off of compressor stages.
Powered or Unpowered Convenience Outlet
This option is a GFCI, 120v/15amp, 2 plug, convenience outlet, either powered or unpowered. When
the convenience outlet is powered, a service receptacle disconnect will be available. The
convenience outlet is powered from the line side of the disconnect or circuit breaker, and therefore
will not be affected by the position of the disconnect or circuit breaker. This option can only be
ordered when the Through the Base Electrical with either the Disconnect Switch, or Circuit Breaker,
option is ordered. This option is available on all models.
Single Zone VAV
SZVAV systems combine Trane application, control and system integration knowledge to exactly
match fan speed with cooling and heating loads, regardless of the operating condition.
Stainless Steel Drain Pan
This option provides excellent corrosion and oxidation resistance. Drain pan shall be constructed
of 304 stainless steel.
Supply, Return and Plenum Air Smoke Detector
With this option installed, if smoke is detected, all unit operation will be shut down. Reset will be
manual at the unit. Return Air Smoke Detectors require minimum allowable airflow when used with
certain models. See the Installation, Operation, and Maintenance (IOM) manual for the models
affected and the minimum allowable airflow required. This option is available on all downflow
models. Supply and/or Return Detectors may not be used with the Plenum Smoke Detector.
Through the Base Electrical with Circuit Breaker
This option is a thermal magnetic, molded case, HACR Circuit Breaker with provisions for through
the base electrical connections. The circuit breaker will be installed in a water tight enclosure in the
unit with access through a swinging door. Factory wiring will be provided from the switch to the
unit high voltage terminal block. The circuit breaker will provide overcurrent protection, be sized
per NEC and UL guidelines, and be agency recognized by UL/CSA.
Through the Base Electrical with Disconnect Switch
Three-pole, molded case, disconnect switch with provisions for through the base electrical
connections are available. The disconnect switch will be installed in the unit in a water-tight
enclosure with access through a swinging door. Factory wiring will be provided from the switch to
the unit high voltage terminal block. The switch will be UL/CSA agency recognized.
Note: The disconnect switch will be sized per NEC and UL guidelines but will not be used in place
of unit overcurrent protection. This option is available on all models.
Through the Base Utilities Access
An electrical service entrance shall be provided allowing electrical access for both control and main
power connections inside the curb and through the base of downflow units, and through the front
of the horizontal units. Option will allow for field installation of liquid-tight conduit and an external
field-installed disconnect switch.
Two-Inch Pleated Filters
Two inch pleated MERV 8 or MERV 13 filters with filter removal tool shall be available on all models.

PKGP-PRC012M-EN 55
Mechanical Specifications
Factory or Field Installed Options
BACnet™ Communications Interface
This option shall be provided to allow the unit to communicate directly with a generic open protocol
BACnet MS/TP Network Building Automation System Controls.
Barometric Relief
This option shall provide a pressure operated damper for the purpose of space pressure
equalization and be gravity closing to prohibit entrance of outside air during the equipment “off”
cycle.
Clogged Filter/Fan Failure Switch
A dedicated differential pressure switch is available to achieve active fan failure indication and/or
clogged filter indication. These indications will be registered with either a zone sensor with status
indication lights or an Integrated Comfort™ System.
Differential Pressure Switches
These options allow for individual fan failure and dirty filter indication. The fan failure switch will
disable all unit functions and “flash” the Service LED on the zone sensor. The dirty filter switch will
light the Service LED on the zone sensor and will allow continued unit operation.
Discharge Air Sensing Kit
This kit provides true discharge air sensing in heating models. This sensor is a status indicator
readable through Tracer™or Tracker™. The kit is functional only with the ReliaTel Options Module.
Economizer - Standard, Downflow
The assembly includes fully modulating 0-100% motor and dampers, barometric relief, minimum
position setting, preset linkage, wiring harness with plug, fixed dry bulb and spring return actuator.
The barometric relief damper shall be standard with the downflow economizer and shall provide
a pressure operated damper that shall be gravity closing and shall prohibit entrance of outside air
during the equipment “off” cycle. Solid state enthalpy and differential enthalpy control shall be
field-installed.
Economizer - Low Leak, Downflow
This accessory meets low leak requirements for ASHRAE 90.1, IECC, and CA Title 24 standards (3
cfm/ft^2@1" wg exterior air, 4 cfm/ft^2@1" wg return air). This option allows 100% outdoor air
supply from 0-100% modulating dampers and is standard with barometric relief. It can be paired
with powered exhaust for additional building pressure relief.This option can be paired with or
without Fault Detection & Diagnostics (FDD) to meet current mandatory CA Title 24 requirements.
Available on downflow units only. The economizers come with three control options, dry bulb and
reference or comparative enthalpy (optional).
Electric Heaters
Electric heat modules shall be available for installation within the basic unit. Electric heater
elements shall be constructed of heavy-duty nickel chromium elements internally delta connected
for 240 volt, wye connected for 480 and 600 volt. Staging shall be achieved through ReliaTel. Each
heater package shall have automatically reset high limit control operating through heating element
contactors. All heaters shall be individually fused from the factory, where required, and shall meet
all NEC and CEC requirements when properly installed. Power assemblies shall provide single-
point connection. Electric heat modules shall be UL listed or CSA certified. If ordering the Through
the Base Electrical option with an Electric Heater, the heater must be factory installed.

56 PKGP-PRC012M-EN
Mechanical Specifications
Frostat™
This option is to be utilized as a safety device. The Frostat opens when temperatures on the
evaporator coil fall below 10°F. The temperature will need to rise to 50°F before closing. This option
should be utilized in low airflow or high outside air applications.
Indoor Fan Motor Shaft Grounding Ring
Shaft grounding rings are used on all VFD driven motors to provide a conductive discharge path
away from the motor bearings to ground. Bearing Protection Ring shall be maintenance free
circumferential ring of conductive micro fibers that discharges voltages to ground.
LonTalk® Communications Interface
The LonTalk communications interface, when installed in a Voyager unit, allows the unit to
communicate as a Tracer™LCI-V device or directly with generic LonTalk Network Building
Automation System Controls.
Oversized Motors
Oversized motors shall be available for high static applications.
Reference or Comparative Enthalpy
Reference Enthalpy is used to measure and communicate outdoor humidity. The unit receives and
uses this information to provide improved comfort cooling while using the economizer.
Comparative Enthalpy measures and communicates humidity for both outdoor and return air
conditions and return air temperature. The unit receives and uses this information to maximize use
of economizer cooling, and to provide maximum occupant comfort control. Reference or
Comparative Enthalpy option shall be available when a factory or field installed Downflow
Economizer is ordered. This option is available on all downflow models.
Tool-less Hail Guards
Tool-less, hail protection quality coil guards are available for condenser coil protection.
Trane Communication Interface
This factory or field-installed option shall be provided to interface ReliaTel™ controlled units with
the Trane Integrated Comfort™ systems.
Field Installed Options
CO2 Sensor
The CO2 sensor shall have the ability to monitor the concentration (parts per million, ppm) of CO2
(Carbon Dioxide) in the air. As the CO2 concentration changes, the outside air damper modulates
to meet the current ventilation needs of the zone.
Note: Choose factory-installed CO2 sensor wiring option to save time and ensure proper unit
connections for the field installed CO2 sensor kits.
Digital Display Zone Sensor
The Digital LCD (Liquid Crystal Display) zone sensor has the look and functionality of standard zone
sensors. This sensor includes a digital display of set point adjustment and space temperature in
°F (Fahrenheit) or °C (Celsius). Includes FAN and SYSTEM buttons (supports the service functions
of the standard sensor). E-squared memory stores last programmed set points. Requires 24 VAC
(Volts AC). This sensor should be utilized with ReliaTel™ controls.
Economizer - Standard, Horizontal
The horizontal economizer shall contain the same features as the downflow economizer with the
exception of barometric relief.

PKGP-PRC012M-EN 57
Mechanical Specifications
Economizer - Low Leak, Downflow
This accessory meets low leak requirements for ASHRAE 90.1, IECC, and CA Title 24 standards (3
cfm/ft^2@1" wg exterior air, 4 cfm/ft^2@1" wg return air).This option allows 100% outdoor air
supply from 0-100% modulating dampers and is standard with barometric relief. It can be paired
with powered exhaust for additional building pressure relief. Available on downflow units only.
High Static Drive
The high static drive option shall allow the standard motor on the 12½ and 15 ton units to operate
with improved external static capabilities.
Manual Outside Air Damper
The rain hood and screen shall provide up to 25% outside air.
Motorized Outside Air Dampers
Manually set outdoor air dampers shall provide up to 50% outside air. Once set, outdoor air
dampers shall open to set position when indoor fan starts. The damper shall close to the full closed
position when indoor fan shuts down.
Powered Exhaust
The powered exhaust shall provide exhaust of return air, when using an economizer, to maintain
better building pressurization.
Roof Curb - Downflow
The roof curb shall be designed to mate with the downflow unit and provide support and a water
tight installation when installed properly. The roof curb design shall allow field-fabricated
rectangular supply/return ductwork to be connected directly to the curb. Curb design shall comply
with NRCA requirements. Curb shall be shipped knocked down for field assembly and shall include
wood nailer strips.
Remote Potentiometer
The minimum position setting of the economizer shall be adjusted with this accessory.
Ventilation Override Accessory
With the Ventilation Override Accessory installed, the unit can be set to transition up to three
different pre-programmed sequences for Smoke Purge, Pressurization, and Exhaust. The transition
occurs when a binary input on the RTOM is closed (shorted). This would typically be a hard wired
relay output from a smoke detector or fire control panel.
Zone Sensors
This option shall be provided to interface with Voyager units and shall be available in either manual,
automatic, programmable with night setback, with system malfunction lights or remote sensor
options.
Note: Zone sensors are required for units configured for Single Zone VAV indoor fan system
control to enable Single Zone VAV functionality.

Trane optimizes the performance of homes and buildings around the world. A business of Ingersoll Rand, the leader in
creating and sustaining safe, comfortable and energy efficient environments, Trane offers a broad portfolio of advanced
controls and HVAC systems, comprehensive building services, and parts. For more information, visit www.Trane.com.
Trane has a policy of continuous product and product data improvement and reserves the right to change design and specifications without notice.
We are committed to using environmentally
conscious print practices that reduce waste.
© 2014 Trane All rights reserved
PKGP-PRC012M-EN 12 Jun 2014
Supersedes PKGP-PRC012L-EN (10 Jan 2014)