TransCore 2611SS IT2611 RF Transmitter User Manual install
TransCore IT2611 RF Transmitter install
NEW Users Manual
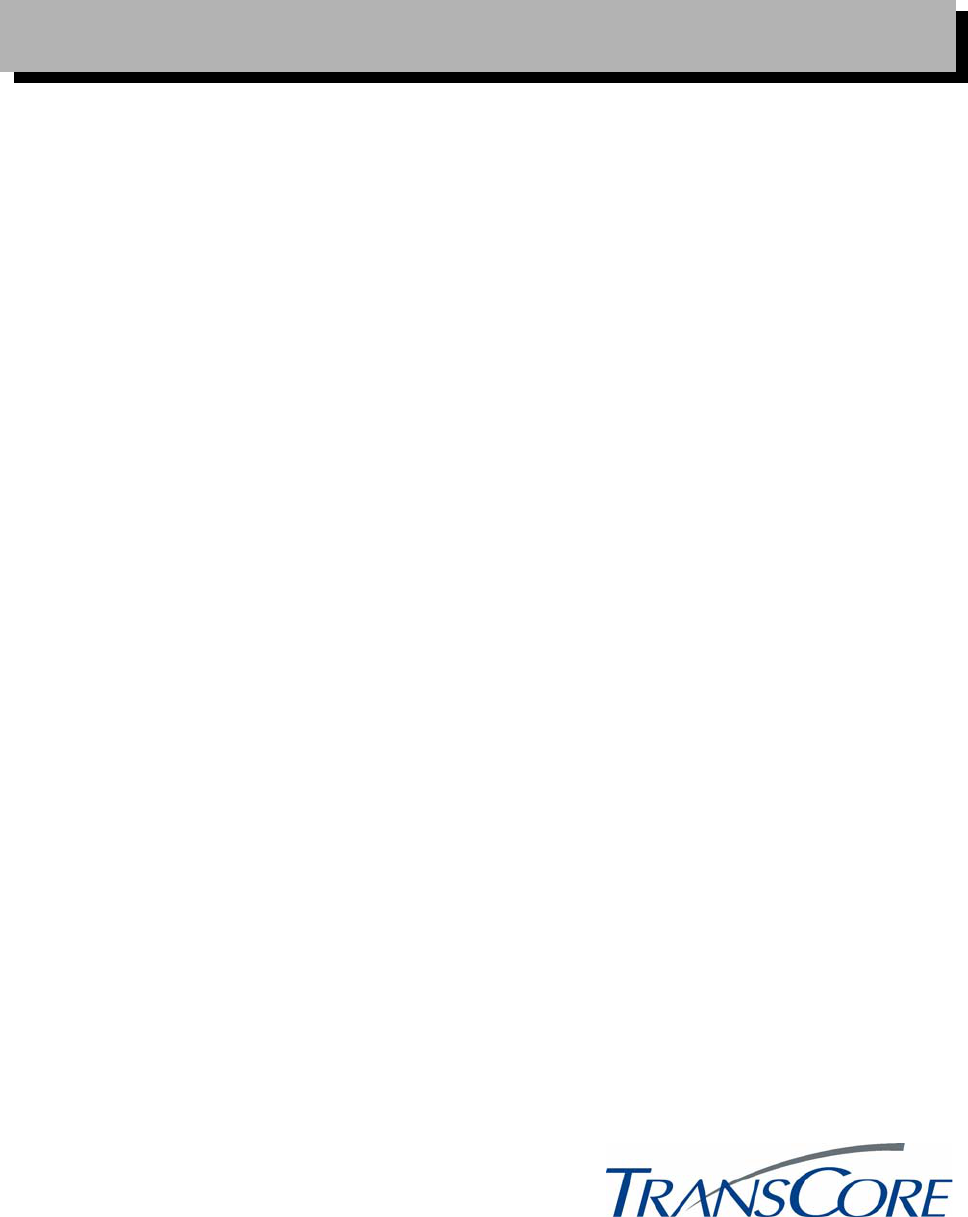
IT2200 Reader System
P/N 411554
Installation & Maintenance/Service Guide
with Multimode Capability
Information in this document is subject to change and does not represent a commitment on the part of
TransCore, Inc.
©2002 TransCore, Inc. All rights reserved. TransCore, TollTag, and Dynamic Tag are trademarks and
Amtech, SmartPass, Dynicom, and PassKey are registered trademarks of TransCore, Inc. The PassKey system
is covered by U.S. Patents 5,414,624 and 5,737,710. All other trademarks listed are the property of their
respective owners. Printed in the U.S.A.
For further information, contact:
TransCore
19111 Dallas Parkway, Suite 300
Dallas, Texas 75287-3106 USA
Phone: (972) 733-6600
Fax: (972) 733-6699
TransCore Action Center (TrAC)
19111 Dallas Parkway, Suite 300
Dallas, Texas 75287-3106 USA
Phone: (972) 733-6681
Fax: (972) 733-6695
WARNING TO USERS IN THE UNITED STATES
FEDERAL COMMUNICATIONS COMMISSION (FCC) RADIO FREQUENCY
INTERFERENCE STATEMENT
47 CFR §15.105(a)
NOTE: This equipment has been tested and found to comply with the limits for a Class A digital device
pursuant to Part 15 of the Federal Communications Commission (FCC) rules. These limits are designed to
provide reasonable protection against harmful interference when the equipment is operated in a
commercial environment. This equipment generates, uses, and can radiate radio frequency (RF) energy
and may cause harmful interference to radio communications if not installed and used in accordance with
the instruction manual. Operating this equipment in a residential area is likely to cause harmful
interference, in which case, depending on the laws in effect, the users may be required to correct the
interference at their own expense.
NO UNAUTHORIZED MODIFICATIONS
47 CFR §15.21
CAUTION: This equipment may not be modified, altered, or changed in any way without permission
from TransCore, Inc. Unauthorized modification may void the equipment authorization from the FCC and
will void the TransCore warranty.
USE OF SHIELDED CABLES IS REQUIRED
47 CFR §15.27(a)
Shielded cables must be used with this equipment to comply with FCC regulations.
A license issued by the FCC is required to operate this RF identification device in the United States.
Contact TransCore, Inc. for additional information concerning licensing requirements for specific devices.
TransCore, Inc.
USA
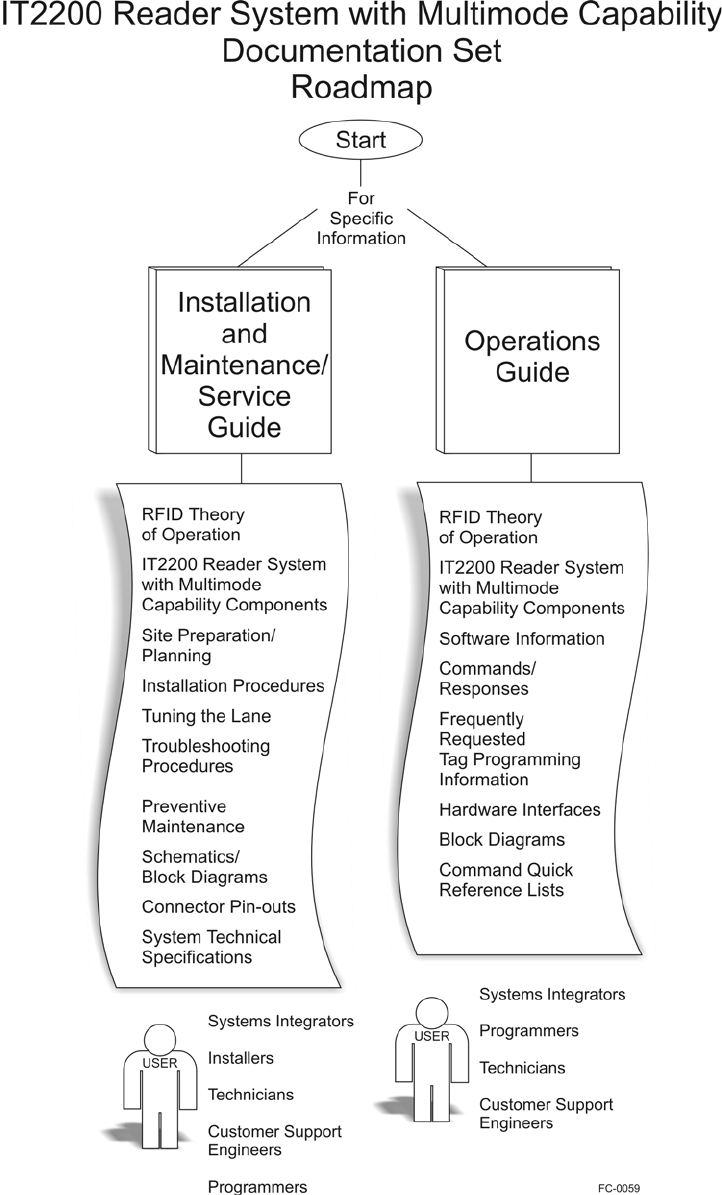

Contents

ix
Contents
1 Before You Begin
Purpose . . . . . . . . . . . . . . . . . . . . . . . . . . . . . . . . . . . . . . . . . . . . . . . . . . . . . . . . . 1-3
Intended Audience . . . . . . . . . . . . . . . . . . . . . . . . . . . . . . . . . . . . . . . . . . . . . . . . 1-3
Guide Topics . . . . . . . . . . . . . . . . . . . . . . . . . . . . . . . . . . . . . . . . . . . . . . . . . . . . . 1-3
Related Documents . . . . . . . . . . . . . . . . . . . . . . . . . . . . . . . . . . . . . . . . . . . . . . . 1-4
Typographical Conventions . . . . . . . . . . . . . . . . . . . . . . . . . . . . . . . . . . . . . . . . . 1-4
Licensing Requirements . . . . . . . . . . . . . . . . . . . . . . . . . . . . . . . . . . . . . . . . . . .1-5
U.S. Licensing . . . . . . . . . . . . . . . . . . . . . . . . . . . . . . . . . . . . . . . . . . . . . . . . . . 1-5
Health Limits . . . . . . . . . . . . . . . . . . . . . . . . . . . . . . . . . . . . . . . . . . . . . . . . . . . . . 1-6
2 Theory of Operation
Overview of RFID Theory 2-3
Components 2-3
Reader 2-4
RF Module 2-5
Antennas 2-5
Tags 2-7
Host Computer 2-8
Operational Characteristics 2-8
Reading Range 2-9
Reading Speed 2-9
Number of Characters Stored in Tag 2-9
Number of Characters Written to an IT2200-Series Tag 2-9
Coding Format of the Tag Data 2-9
Tag Orientation and Placement 2-10
Noise and Interference Immunity 2-10
Frequency and Power 2-11
Tag Lifetime 2-11
Tag Read/Write Accuracy Rate 2-11
Amtech RF Technology 2-11
Signal Transmission and Acquisition 2-12

IT2200 Reader System with Multimode Capability Installation & Maintenance/Service Guide
x
Automatic Vehicle Identification Transaction Process 2-12
Types of RFID Transactions 2-12
3 System Components
Overview 3-3
IT2020 Reader Logic Card 3-5
Functions 3-5
Features 3-6
IT2611 RF Module (Bistatic and Monostatic) 3-7
RF Module Connections 3-9
Transmit Connector (Bistatic RF Module) 3-9
Receive Connector (Bistatic RF Module) 3-9
Transmit/Receive Connector (Monostatic RF Module) 3-9
Check Tag Connector 3-10
Data Connector 3-10
Power Supply Connector 3-10
Functions 3-10
Features 3-10
Type Testing 3-11
RF Emissions 3-11
Antennas 3-13
AA3152 Universal Toll Antenna 3-13
Functions 3-13
Features 3-14
AA3153 Beacon Antenna 3-14
Functions 3-14
Features 3-14
IT2502 Check Tag Antenna 3-14
Check Tag 3-14
Tags 3-15
IT2221 Tag 3-15
Functions 3-17
Features 3-18
IT2211 Exterior Tag 3-18
IT2235 Tag 3-19
Functions 3-20
Features 3-21
ATA Tag 3-23
Tag Programmer 3-23
IT2410 Tag Programmer 3-24
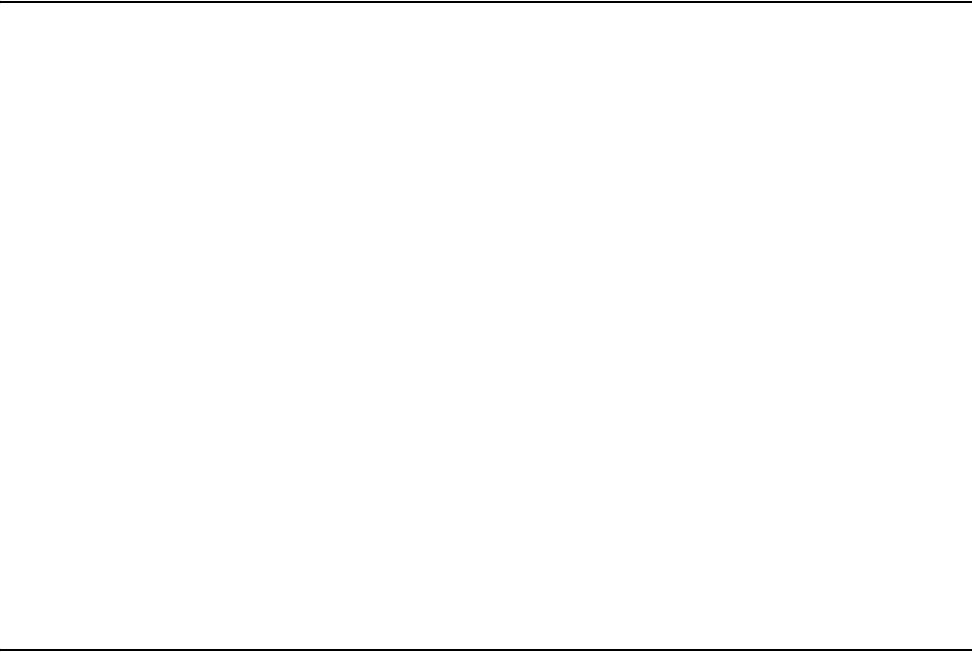
Contents
xi
Functions 3-24
Features 3-25
4 Installing the IT2200 Reader System
Assessing the Site and Formulating a Frequency Plan 4-3
Site Preparation Checklist 4-4
Components Checklist 4-4
Task Checklist 4-5
Where to Mount the Components 4-5
Canopy Mount 4-6
Overhead Gantry Mount 4-7
Overpass Mount 4-8
Cantilever Arm Mount 4-9
Lane-side “Pillbox” Mount 4-11
Installing the IT2200 Reader System 4-13
Installing the IT2020 Reader Logic Card 4-14
Installing the IT2611 RF Module 4-17
Installing the AA3152 UTA 4-19
Installing the AA3153 Beacon Antenna 4-21
Installing the IT2502 Check Tag Antenna with a UTA 4-23
Installing the IT2502 Check Tag Antenna with a Beacon Antenna 4-24
5 Tuning the Lane
Why You Need to Tune a Lane 5-3
Required Equipment 5-4
Optional Equipment 5-4
Tuning the Lane 5-5
Starting the Engineering Host 5-5
Lane Tag Test 5-6
Check Tag Test 5-9
IT2000 Check Tag Test 5-9
ATA Check Tag Test 5-11
Testing the Footprint 5-11
Running the CAM Test for IT2200-Series Tags 5-11
Tag-on-a-Stick Test for IT2235 Tag 5-12
Running the CAM Test for ATA-Type Tags 5-13
Tag-on-a-Stick Test Using ATA-Type Tag 5-13

IT2200 Reader System with Multimode Capability Installation & Maintenance/Service Guide
xii
Vehicle-Mounted Tag Test Using IT2235 Tag 5-13
Vehicle-Mounted Tag Test Using ATA-Type Tag 5-14
Dynamic Performance Test 5-15
Starting the Dynamic Performance Test 5-15
IT2235 Dynamic Performance Drive-Through Tag Test 5-16
IT2221 Dynamic Performance Drive-Through Tag Test 5-16
ATA Tag Dynamic Performance Drive-Through Tag Test 5-17
Adjusting the Read/Write Zone 5-18
Completing Antenna Connections 5-18
6 Troubleshooting the Installation
Required Equipment 6-3
Cross-Lane Interference in RFID Systems 6-3
What Is Cross-Lane Interference? 6-3
Determining Acceptable Lane Performance 6-4
Identifying Cross-Lane Interference 6-4
Diagnosing Cross-Lane Interference 6-5
Remedying Cross-Lane Interference 6-5
Frequency Separation 6-6
RF Power 6-6
Time Division Multiplexing 6-6
Physical Remedies 6-8
Troubleshooting Indications and Actions 6-10
Removal and Replacement Procedures 6-17
Reader Logic Card 6-17
Removal 6-17
Replacement 6-17
RF Module 6-18
Removal 6-18
Replacement 6-18
Transmit/Receive Antennas 6-18
Removal 6-18
Replacement 6-18
Check Tag Antenna 6-19
Removal 6-19
Replacement 6-19
Data Cable 6-20
Removal 6-20
Replacement 6-20
Antenna Cable 6-20
Removal 6-20
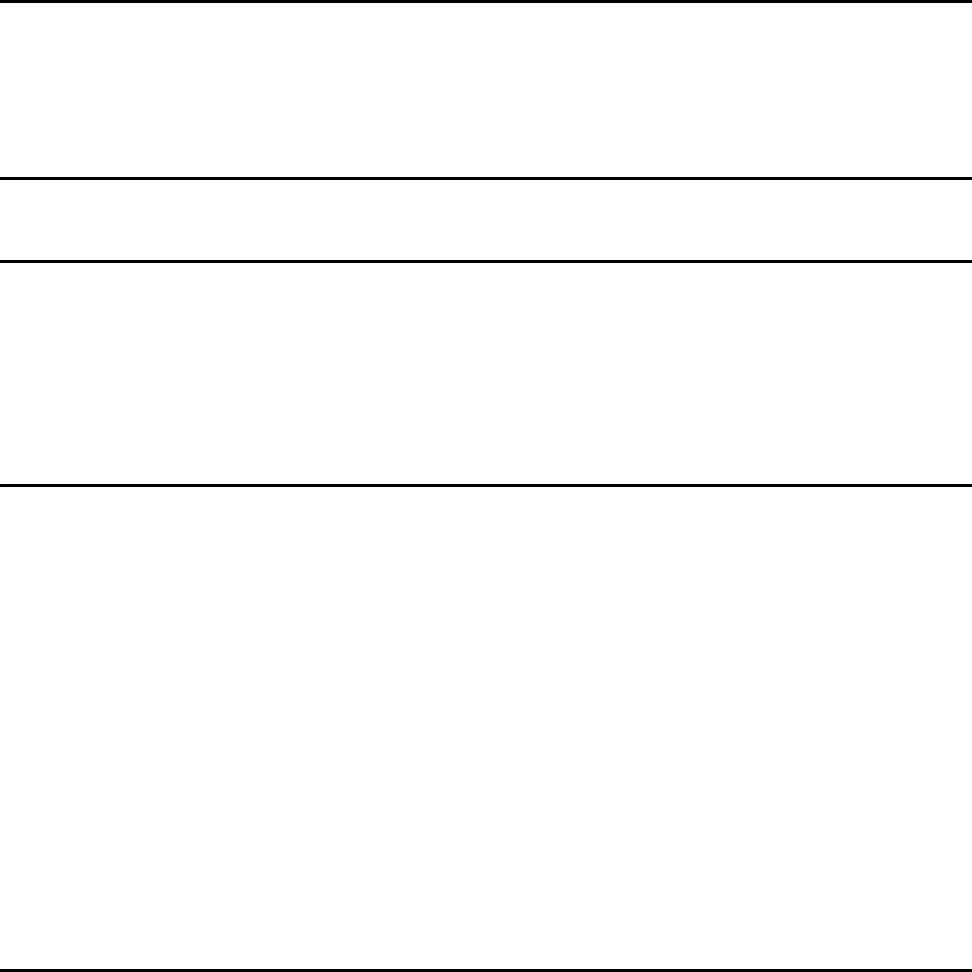
Contents
xiii
Replacement 6-20
7 Preventive Maintenance
Preventive Maintenance Schedule 7-3
Visual Inspection 7-3
A Acronyms and Glossary
B Block Diagrams
IT2200 Reader System with Multimode Capability B-3
IT2020 Reader Logic Card B-5
IT2611 RF Module B-9
C System Technical Specifications
Component Specifications C-3
IT2020 Reader Logic Card C-3
Electrical Specifications C-3
Environmental Specifications C-4
Physical Specifications C-4
IT2611 RF Module C-5
Interfaces C-5
Electrical Specifications C-5
Environmental Specifications C-5
Physical Specifications C-6
Housing Specifications C-6
AA3152 Universal Toll Antenna and
AA3153 Beacon Antenna C-6
Environmental Specifications C-7
IT2502 Check Tag Antenna C-7
D Hardware Interfaces
Reader Logic Card Hardware Interconnection D-3
16 Bit ISA Bus D-4
Optional External Power D-5
Expansion Interfaces (Industry Pack) D-5
LEDs D-6
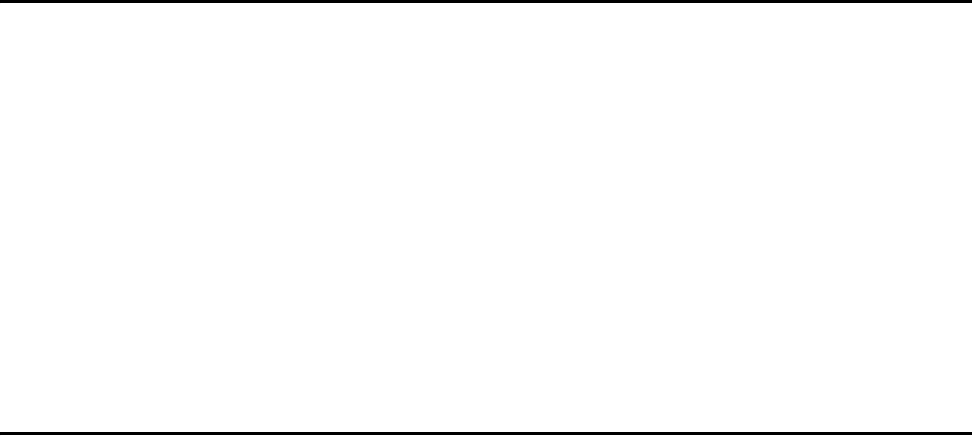
IT2200 Reader System with Multimode Capability Installation & Maintenance/Service Guide
xiv
Time Division Multiplexing Connector D-6
Background Debugger Connector D-7
General Purpose I/O Port (IT2020-004 Reader) D-8
Hardware Diagnostic Port D-8
RS-232 D-10
IT2020 Reader Logic Card Interface D-11
Pin Designations D-11
IT2020 ISA Card Interface Connector D-11
Interface Connector D-19
Power Connector D-20
Reader-to-RF Module Communications D-20
RF Module Interface Connector D-21
IT2410 Tag Programmer Hardware Interconnection D-23
E Connector Pinouts
IT2020 Reader Logic Card E-3
Tag Data/Control E-3
TDM E-5
ISA Bus E-5
IP Module Logic Interface E-9
IP Module I/O Connector E-11
Auxiliary Power E-13
BDM E-14
General Purpose I/O E-15
HW Diagnostics Port E-16
RS-232 E-17
IT2611 RF Module E-18
Index
(Index to be supplied with final version of guide.)
List of Figures
xv
List of Figures
Figure 2-1 Typical RFID Components for a Bistatic (Two-Antenna) Configuration . . . . . . . . . . . 2-4
Figure 2-2 Field Size, Shape, and Antenna Polarization Define the Reading Range
(Bistatic Configuration) . . . . . . . . . . . . . . . . . . . . . . . . . . . . . . . . . . . . . . . . . . 2-6
Figure 2-3 Field Size, Shape, and Antenna Polarization Define the Reading Range
(Monostatic Configuration) . . . . . . . . . . . . . . . . . . . . . . . . . . . . . . . . . . . . . . . . 2-6
Figure 2-4 Tag Orientation with Linear Polarized Antenna . . . . . . . . . . . . . . . . . . . . . . . . . . 2-10
Figure 2-5 Typical Read/Write Transaction Using the IT2200 Reader System and an
IT2200-Series Tag . . . . . . . . . . . . . . . . . . . . . . . . . . . . . . . . . . . . . . . . . . . . . 2-13
Figure 2-6 Four Transactions Can Occur Within 96 Milliseconds . . . . . . . . . . . . . . . . . . . . . 2-14
Figure 2-7 Typical Read-only Transaction Using the IT2200 Reader System in
ATA Mode Operation with an ATA-Type Tag . . . . . . . . . . . . . . . . . . . . . . . . . . . 2-15
Figure 2-8 Typical Dedicated Read-Only Transaction Using the IT2200 Reader System in
Multimode Operation with an ATA-Type Tag . . . . . . . . . . . . . . . . . . . . . . . . . . . 2-15
Figure 2-9 Typical Read-Only Transaction Using the IT2200 Reader System in
ATA Mode Operation with an ATA-Type Tag . . . . . . . . . . . . . . . . . . . . . . . . . . . 2-16
Figure 3-1 Relationship of the IT2200 Reader System Components
(Bistatic Installation Shown) . . . . . . . . . . . . . . . . . . . . . . . . . . . . . . . . . . . . . . . 3-3
Figure 3-2 IT2020 Reader Logic Card . . . . . . . . . . . . . . . . . . . . . . . . . . . . . . . . . . . . . . . . . 3-5
Figure 3-3 IT2020 Reader Logic Card Block Diagram . . . . . . . . . . . . . . . . . . . . . . . . . . . . . . 3-7
Figure 3-4 IT2611 RF Module Connections (Bistatic Configuration) . . . . . . . . . . . . . . . . . . . . 3-8
Figure 3-5 IT2611 RF Module Connections (Monostatic Configuration) . . . . . . . . . . . . . . . . . . 3-9
Figure 3-6 Tag Orientation with Linear Polarized Antenna . . . . . . . . . . . . . . . . . . . . . . . . . . 3-13
Figure 3-7 IT2221 Tag Block Diagram . . . . . . . . . . . . . . . . . . . . . . . . . . . . . . . . . . . . . . . 3-16
Figure 3-8 Alternative Mounting Locations for IT2221 Tag . . . . . . . . . . . . . . . . . . . . . . . . . 3-17
Figure 3-9 IT2211 Tag Placement . . . . . . . . . . . . . . . . . . . . . . . . . . . . . . . . . . . . . . . . . . 3-18
Figure 3-10 IT2235 Tag Block Diagram . . . . . . . . . . . . . . . . . . . . . . . . . . . . . . . . . . . . . . 3-19
Figure 3-11 IT2235 Tag Display Features . . . . . . . . . . . . . . . . . . . . . . . . . . . . . . . . . . . . . 3-22
Figure 3-12 IT2410 Tag Programmer System . . . . . . . . . . . . . . . . . . . . . . . . . . . . . . . . . . 3-24
Figure 3-13 Tag Programming Head . . . . . . . . . . . . . . . . . . . . . . . . . . . . . . . . . . . . . . . . 3-25
Figure 4-1 Canopy Mount . . . . . . . . . . . . . . . . . . . . . . . . . . . . . . . . . . . . . . . . . . . . . . . . 4-6
Figure 4-2 Overhead Gantry Mount . . . . . . . . . . . . . . . . . . . . . . . . . . . . . . . . . . . . . . . . . . 4-7
Figure 4-3 Overpass Mount . . . . . . . . . . . . . . . . . . . . . . . . . . . . . . . . . . . . . . . . . . . . . . . 4-8
Figure 4-4 Cantilever Arm Mount (Bistatic Configuration) . . . . . . . . . . . . . . . . . . . . . . . . . . . 4-9
Figure 4-5 Cantilever Arm Mount (Monostatic Configuration) . . . . . . . . . . . . . . . . . . . . . . . 4-10
Figure 4-6 Bistatic Laneside Mount . . . . . . . . . . . . . . . . . . . . . . . . . . . . . . . . . . . . . . . . . 4-11
Figure 4-7 Monostatic Laneside Mount . . . . . . . . . . . . . . . . . . . . . . . . . . . . . . . . . . . . . . 4-12
Figure 4-8 Antenna Placement for Pillbox Mount . . . . . . . . . . . . . . . . . . . . . . . . . . . . . . . . 4-13
Figure 4-9 IT2020 Reader Logic Card Installed in Typical Host Computer or Lane Controller
Chassis (Top View) . . . . . . . . . . . . . . . . . . . . . . . . . . . . . . . . . . . . . . . . . . . . 4-14
Figure 4-10 IT2020 Reader Logic Card Factory Dipswitch Settings . . . . . . . . . . . . . . . . . . . . 4-15
Figure 4-11 Frequency Enable Switch on Rear of IT2020 Reader Logic Card . . . . . . . . . . . . . 4-16
Figure 4-12 Location of Battery Jumper (J8) in Relation to Battery . . . . . . . . . . . . . . . . . . . . 4-16
Figure 4-13 IT2611 RF Module Mounting and Components for Both Monostatic
and Bistatic Configurations . . . . . . . . . . . . . . . . . . . . . . . . . . . . . . . . . . . . . . 4-18
IT2200 Reader System with Multimode Capability Installation & Maintenance/Service Guide
xvi
Figure 4-14 IT2611 RF Module Connectors (Monostatic RF Module Shown) . . . . . . . . . . . . . 4-19
Figure 4-15 AA3152 UTA Mounting and Connections . . . . . . . . . . . . . . . . . . . . . . . . . . . . . 4-20
Figure 4-16 AA3153 Beacon Antenna Mounting . . . . . . . . . . . . . . . . . . . . . . . . . . . . . . . . . 4-22
Figure 4-17 IT2502 Check Tag Antenna Mounting . . . . . . . . . . . . . . . . . . . . . . . . . . . . . . . 4-23
Figure 5-1 Background Status Information Screen . . . . . . . . . . . . . . . . . . . . . . . . . . . . . . . . 5-6
Figure 5-2 Sample RF Attenuation Statistics for Check Tag . . . . . . . . . . . . . . . . . . . . . . . . . . 5-7
Figure 5-3 Acceptable RF Attenuation Statistics . . . . . . . . . . . . . . . . . . . . . . . . . . . . . . . . . 5-8
Figure 5-4 Ranges of RF Attenuation Statistics . . . . . . . . . . . . . . . . . . . . . . . . . . . . . . . . . . 5-9
Figure 5-5 Sample Continuous Check Tag Read Request Display . . . . . . . . . . . . . . . . . . . . . 5-10
Figure 5-6 Typical Read/Write Zone for a Reader (Bistatic Configuration) . . . . . . . . . . . . . . . 5-12
Figure 5-7 Location of LEDs on Reader Logic Card . . . . . . . . . . . . . . . . . . . . . . . . . . . . . . 5-17
Figure 6-1 RF Footprint Extends Beyond Lane Boundaries (Bistatic Configuration Shown) . . . . . 6-5
Figure 6-2 TDM Synchronization . . . . . . . . . . . . . . . . . . . . . . . . . . . . . . . . . . . . . . . . . . . . 6-7
Figure 6-3 Antenna Tilt Angle Adjustment . . . . . . . . . . . . . . . . . . . . . . . . . . . . . . . . . . . . . 6-9
Figure 6-4 Downlink Antenna Side Angle Adjustment . . . . . . . . . . . . . . . . . . . . . . . . . . . . . 6-10
Figure 6-5 Location of Battery Jumper (J8) in Relation to Battery . . . . . . . . . . . . . . . . . . . . 6-12
Figure 6-6 Frequency Enable Switch on Rear of IT2020 Reader Logic Card . . . . . . . . . . . . . . 6-12
Figure 7-1 Visual Inspection Process . . . . . . . . . . . . . . . . . . . . . . . . . . . . . . . . . . . . . . . . . 7-4
Figure B-1 IT2200 Bistatic Reader System Functional Block Diagram . . . . . . . . . . . . . . . . . . . B-3
Figure B-2 IT2200 Monostatic Reader System Functional Block Diagram . . . . . . . . . . . . . . . . B-4
Figure B-3 IT2020 Reader Logic Card Functional Block Diagram . . . . . . . . . . . . . . . . . . . . . . B-5
Figure B-4 IT2020 Reader Logic Card Interface . . . . . . . . . . . . . . . . . . . . . . . . . . . . . . . . . . B-6
Figure B-5 Minimum Connections for the IT2020 Reader Logic Card Interface
(Bistatic Application) . . . . . . . . . . . . . . . . . . . . . . . . . . . . . . . . . . . . . . . . . . . B-7
Figure B-6 Minimum Connections for the IT2020 Reader Logic Card Interface
(Monostatic Application) . . . . . . . . . . . . . . . . . . . . . . . . . . . . . . . . . . . . . . . . . B-8
Figure B-7 IT2611 RF Module Functional Block Diagram (Bistatic Configuration) . . . . . . . . . . . B-9
Figure B-8 IT2611 RF Module Functional Block Diagram (Monostatic Configuration) . . . . . . . B-10
Figure D-1 Locations of Switches on IT2020 Reader Logic Card . . . . . . . . . . . . . . . . . . . . . . D-4
Figure D-2 Typical TDM Installation . . . . . . . . . . . . . . . . . . . . . . . . . . . . . . . . . . . . . . . . . D-6
Figure D-3 Locations of LEDs on IT2020 Reader Logic Card . . . . . . . . . . . . . . . . . . . . . . . . D-18
Figure D-4 Bistatic RF Module Interface . . . . . . . . . . . . . . . . . . . . . . . . . . . . . . . . . . . . . . D-19
Figure D-5 Monostatic RF Module Interface . . . . . . . . . . . . . . . . . . . . . . . . . . . . . . . . . . . D-19
Figure D-6 Twenty-six Pin Connector Showing Terminal Designators (RF Module) . . . . . . . . . D-20
Figure D-7 IT2410 Tag Programmer Power Connections . . . . . . . . . . . . . . . . . . . . . . . . . . . D-24
List of Tables
xvii
List of Tables
Table 1-1 Typographical Conventions . . . . . . . . . . . . . . . . . . . . . . . . . . . . . . . . . . . . . . . . 1-4
Table 2-1 Time and Distance Required to Complete Payment Zone . . . . . . . . . . . . . . . . . . . 2-14
Table 3-1 IT2611 RF Module Uplink and Downlink Specifications . . . . . . . . . . . . . . . . . . . . 3-12
Table 3-2 Example of Condition Code Bit Programming for IT2235 Tag . . . . . . . . . . . . . . . . . 3-21
Table 3-3 Audio/Visual Options Bits Decoding for IT2235 Tag . . . . . . . . . . . . . . . . . . . . . . . 3-23
Table 3-4 IT2410 Tag Programmer Indicator LEDs and Descriptions . . . . . . . . . . . . . . . . . . . 3-26
Table 4-1 Example Frequency Plan for Four-Lane Plaza . . . . . . . . . . . . . . . . . . . . . . . . . . . . 4-4
Table 4-2 Listing of Shorted Pins for Loopback Connector . . . . . . . . . . . . . . . . . . . . . . . . . . 4-14
Table 6-1 Frequency Plan for Four-Lane Toll Plaza . . . . . . . . . . . . . . . . . . . . . . . . . . . . . . . 6-6
Table 6-2 Frequency Settings Using TDM for Four-Lane Toll Plaza with TDM . . . . . . . . . . . . . . 6-8
Table 6-3 Failure Indicated by Host Software Diagnostics . . . . . . . . . . . . . . . . . . . . . . . . . . 6-11
Table 6-4 Failure During Check Tag Test . . . . . . . . . . . . . . . . . . . . . . . . . . . . . . . . . . . . . 6-13
Table 6-5 Unacceptable RF Attenuation Statistics Using Check Tag . . . . . . . . . . . . . . . . . . . 6-13
Table 6-6 Unacceptable RF Attenuation Statistics Using Vehicle-Mounted Tag . . . . . . . . . . . 6-13
Table 6-7 Self-Test Fail LED on Reader Logic Card Lights . . . . . . . . . . . . . . . . . . . . . . . . . . 6-14
Table 6-8 Spotty Pattern or Low Handshake Counts . . . . . . . . . . . . . . . . . . . . . . . . . . . . . . 6-15
Table 7-1 Preventive Maintenance Schedule . . . . . . . . . . . . . . . . . . . . . . . . . . . . . . . . . . . . 7-3
Table C-1 IT2020 Reader Logic Card Electrical Requirements . . . . . . . . . . . . . . . . . . . . . . . . C-3
Table C-2 IT2020 Reader Logic Card Power Consumption . . . . . . . . . . . . . . . . . . . . . . . . . . . C-4
Table C-3 IT2020 Reader Logic Card Environmental Tolerances . . . . . . . . . . . . . . . . . . . . . . C-4
Table C-4 IT2020 Reader Logic Card Physical Specifications . . . . . . . . . . . . . . . . . . . . . . . . C-4
Table C-5 IT2611 RF Module Electrical Requirements . . . . . . . . . . . . . . . . . . . . . . . . . . . . . C-5
Table C-6 IT2611 RF Module Environmental Specifications . . . . . . . . . . . . . . . . . . . . . . . . . . C-6
Table C-7 IT2611 RF Module Physical Specifications . . . . . . . . . . . . . . . . . . . . . . . . . . . . . . C-6
Table C-8 Antenna Environmental Tolerances . . . . . . . . . . . . . . . . . . . . . . . . . . . . . . . . . . . C-7
Table D-1 Optional External Power Pin Definition . . . . . . . . . . . . . . . . . . . . . . . . . . . . . . . . D-5
Table D-2 TDM Connector . . . . . . . . . . . . . . . . . . . . . . . . . . . . . . . . . . . . . . . . . . . . . . . . D-7
Table D-3 BDM Connector . . . . . . . . . . . . . . . . . . . . . . . . . . . . . . . . . . . . . . . . . . . . . . . . D-7
Table D-4 General Purpose I/O Connector . . . . . . . . . . . . . . . . . . . . . . . . . . . . . . . . . . . . . . D-8
Table D-5 Hardware Diagnostic Port . . . . . . . . . . . . . . . . . . . . . . . . . . . . . . . . . . . . . . . . . D-9
Table D-6 RS-232 Connector . . . . . . . . . . . . . . . . . . . . . . . . . . . . . . . . . . . . . . . . . . . . . . D-10
Table D-7 IT2020 Reader Logic Card Default I/O Settings . . . . . . . . . . . . . . . . . . . . . . . . . . D-11
Table D-8 IT2020 Reader Logic Card Default IRQ Settings . . . . . . . . . . . . . . . . . . . . . . . . . D-11
Table D-9 ISA Bus Pin Definition . . . . . . . . . . . . . . . . . . . . . . . . . . . . . . . . . . . . . . . . . . . D-11
Table D-10 Optional External Power Pin Definition . . . . . . . . . . . . . . . . . . . . . . . . . . . . . . D-15
Table D-11 IP Module Logic Interface Connector . . . . . . . . . . . . . . . . . . . . . . . . . . . . . . . . D-15
Table D-12 IP Module I/O Connector . . . . . . . . . . . . . . . . . . . . . . . . . . . . . . . . . . . . . . . . D-17
Table D-13 LEDs . . . . . . . . . . . . . . . . . . . . . . . . . . . . . . . . . . . . . . . . . . . . . . . . . . . . . . D-18
Table D-14 RF Module-to-Reader Logic Card Interface Connector . . . . . . . . . . . . . . . . . . . . D-21
Table D-15 RF Module Power . . . . . . . . . . . . . . . . . . . . . . . . . . . . . . . . . . . . . . . . . . . . D-23
Table D-16 RF Module-Antenna Connectors for Bistatic Operation . . . . . . . . . . . . . . . . . . . . D-23
Table D-17 RF Module-Antenna Connectors for Monostatic Operation . . . . . . . . . . . . . . . . . D-23
Table D-18 IT2410 Tag Programmer Interconnection . . . . . . . . . . . . . . . . . . . . . . . . . . . . . D-24
IT2200 Reader System with Multimode Capability Installation & Maintenance/Service Guide
xviii
Table E-1 Tag Data/Control Interface Connector . . . . . . . . . . . . . . . . . . . . . . . . . . . . . . . . . E-3
Table E-2 TDM Connector . . . . . . . . . . . . . . . . . . . . . . . . . . . . . . . . . . . . . . . . . . . . . . . . E-4
Table E-3 ISA Bus Pin Definition . . . . . . . . . . . . . . . . . . . . . . . . . . . . . . . . . . . . . . . . . . . . E-5
Table E-4 IP Module Logic Interface Connector . . . . . . . . . . . . . . . . . . . . . . . . . . . . . . . . . . E-9
Table E-5 IP Module I/O Connector . . . . . . . . . . . . . . . . . . . . . . . . . . . . . . . . . . . . . . . . . E-11
Table E-6 Auxiliary Power Connector . . . . . . . . . . . . . . . . . . . . . . . . . . . . . . . . . . . . . . . . E-13
Table E-7 BDM Connector . . . . . . . . . . . . . . . . . . . . . . . . . . . . . . . . . . . . . . . . . . . . . . . E-14
Table E-8 General Purpose I/O Connector . . . . . . . . . . . . . . . . . . . . . . . . . . . . . . . . . . . . . E-15
Table E-9 Hardware Diagnostics Port Connector . . . . . . . . . . . . . . . . . . . . . . . . . . . . . . . . E-16
Table E-10 RS-232 Connector . . . . . . . . . . . . . . . . . . . . . . . . . . . . . . . . . . . . . . . . . . . . . E-17
Table E-11 RF Module-To-Reader Logic Card Interface Connector . . . . . . . . . . . . . . . . . . . . E-18
Table E-12 RF Module Power . . . . . . . . . . . . . . . . . . . . . . . . . . . . . . . . . . . . . . . . . . . . . E-19
Table E-13 RF Module-Antenna Connectors . . . . . . . . . . . . . . . . . . . . . . . . . . . . . . . . . . . E-19

1
Before You Begin
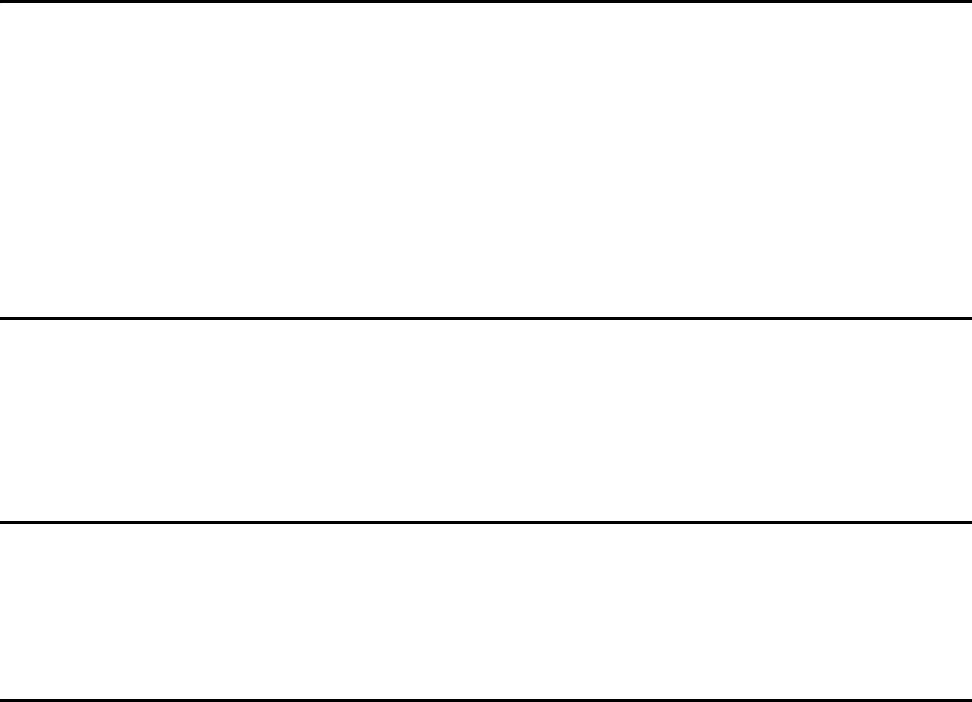
1-3
Chapter 1
Before You Begin
This chapter describes this guide’s purpose and intended audience. It
provides a list of topics covered in each section, a list of related
documents, and the symbols and typographical conventions used. A
discussion on licensing requirements and health limits for radio
frequency devices is also included.
Purpose
This guide provides the information necessary for TransCore-certified personnel to
successfully install an Amtech® IT2200 Reader System with Multimode Capability at
an electronic toll collection (ETC) site that has been designed and built to use this sys-
tem.
Intended Audience
This guide should be used by TransCore-certified personnel who will design, config-
ure, program, and test the Amtech® IT2200 Reader System with Multimode Capabil-
ity in the field.
Guide Topics
This installation guide contains the following chapters and appendixes:
Chapter 1 – Before You Begin Describes the purpose, intended audience, guide topics, related
documentation, and document conventions. Also contained are
licensing requirements and health limits for the RFID equipment.
Chapter 2 – Theory of Operation Provides an overview of RFID theory, Amtech® RFID
technology, and operational characteristics of the IT2200 Reader
System with Multimode Capability.
Chapter 3 – Overview of the IT2200
Reader System Describes the individual components and their
interrelationships.
Chapter 4 – Installing the IT2200
Reader System Provides instructions for installing the system.
Chapter 5 – Tuning the Lane Provides instructions for testing and tuning an installed system.

IT2200 Reader System with Multimode Capability Installation & Maintenance/Service Guide
1-4
Related Documents
Refer to the following documents for more information about operating the IT2200
Reader System with Multimode Capability components and for programming IT2200-
series tags:
•IT2200 Reader System with Multimode Capability Operations Guide
•IT2410 Tag Programmer User Guide
Chapter 6 – Troubleshooting the
Installation Describes problems that might occur during installation and
tests and provides workable solutions.
Chapter 7 – Preventive Maintenance Provides schedules and instructions for performing preventive
maintenance on the IT2200 Reader System with Multimode
Capability components.
Appendix A – Acronyms and Glossary Provides an alphabetical list of abbreviations, acronyms, and
terms used in this guide.
Appendix B – Block Diagrams Provides block diagrams of the system components.
Appendix C – System Technical
Specifications Provides product information and technical specifications for the
system components.
Appendix D – Hardware Interfaces Describes the physical interconnections within the IT2200
Reader System with Multimode Capability.
Appendix E – Connector Pin-outs Provides connector pin-outs for the IT2020 Reader Logic Card
and IT2611 RF Module.
Index Provides alphabetical listing of key information in this guide. (To
be supplied with final version of guide.)
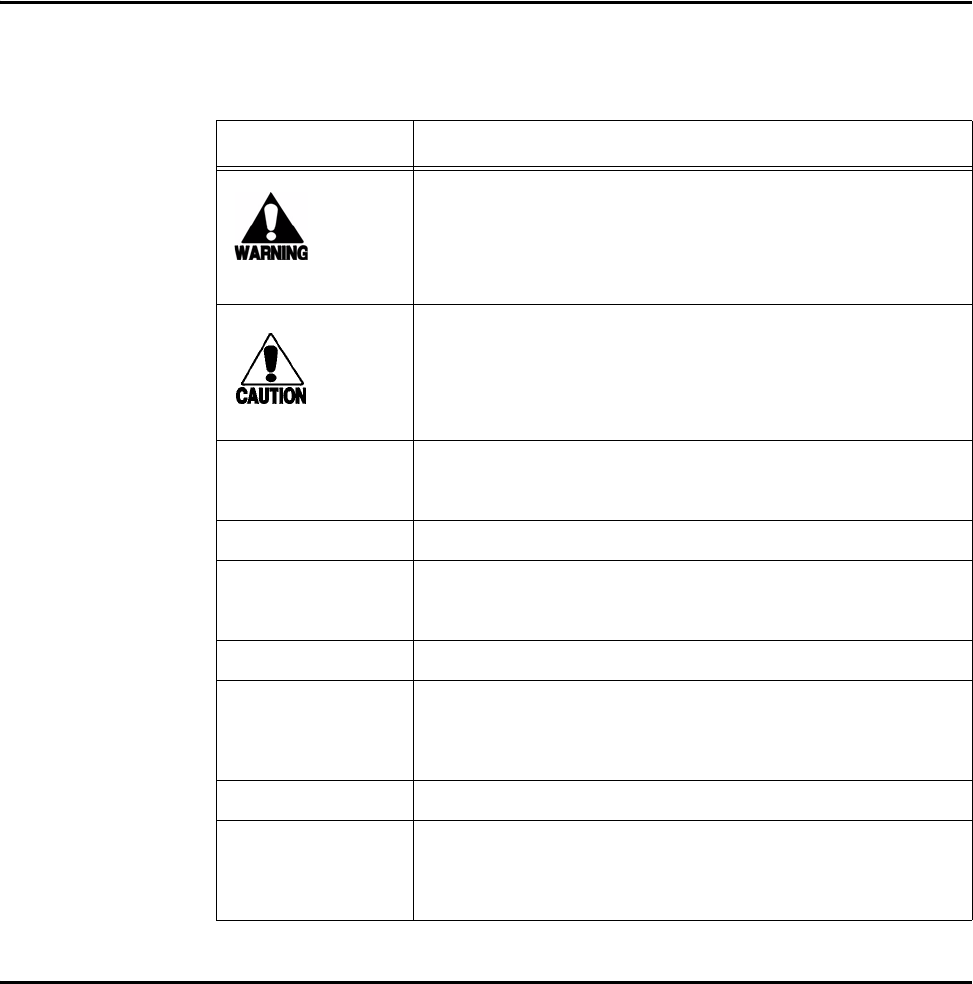
Before You Begin
1-5
Typographical Conventions
The following conventions are used in this manual:
Licensing Requirements
To operate a radio frequency (RF) system in a given country, the user must first obtain
permission from the regulatory agency that controls radio operations in that country.
Most countries require type and safety approval, as well as licensing for RF transmit-
ters.
Amtech® data and literature are available to assist approval and licensing activities.
Table 1-1 Typographical Conventions
Convention Indication
This procedure might cause harm to the equipment and/or
the user.
Concerns about a procedure.
Code Code, including keywords and variables within text and as
separate paragraphs, and user-defined program elements
within text appear in courier typeface.
Dialog Box Title Title of a dialog box as it appears on screen.
Function Start with the characters G4 and add mixed case with no
underscores, and include parentheses after the name, as in
G4FunctionName().
Menu Item Appears on a menu.
Note
Auxiliary information that further clarifies the current
discussion. These important points require the user’s
attention. The paragraph is in italics and the word Note is
bold.
NUL Zero-value ASCII character or a zero-value byte.
NULL Zero-value pointers are null-terminated strings that refer to
strings of printable ASCII characters with a zero-value byte
placed in memory directly after the last printable character of
the string.

IT2200 Reader System with Multimode Capability Installation & Maintenance/Service Guide
1-6
U.S. Licensing
IT2200 Reader System with Multimode Capability users in the U.S. must obtain a
license from the Federal Communications Commission (FCC). The authorized fre-
quency bands in the U.S. are 902 to 904 and 909.75 to 921.75 MHz.
The user is responsible for filing the FCC license according to FCC regulations, but
the Amtech® dealer should provide assistance and support as necessary to complete
these forms.
An FCC license provides the user with the legal authorization to operate the IT2200
Reader System with Multimode Capability on the licensed frequencies at the site
specified in the license. Only an authorized installer or service technician can set the
IT2200 series of readers’ frequency to that specified in the FCC site license.
The FCC license also provides the user with protection and authorization to maintain
the system should any other RF identification product be used in the licensed area
after the IT2200 equipment is installed.
Health Limits
Within the United States, environmental guidelines regulating safe exposure levels are
issued by the Occupational Safety and Health Administration (OSHA).
Section 1910.97 of OSHA Safety and Health Standards 2206 legislates a maximum
safe exposure limit of 10 milliwatts per square centimeter (mW/cm 2) averaged over 6
minutes at both 915 and 2450 MHz.
Although not binding, other organizations such as the American National Standards
Institute (ANSI) have issued similar guidelines that are more restrictive than the
OSHA limits (ANSI C95.1). ANSI guidelines recommends the following maximum
safe power density in mW/cm2:
Thus, the maximum safe power density at 915 MHz is 0.61mW/cm2. The power limit
is a 6-minute average. At 915 MHz, Exclusion 4.2(2) provides an exclusion of the lim-
its if transmitted power is 7 W or less.
The RF power density generated by Amtech® equipment was calculated using an
antenna gain that is equivalent to that typically used in an IT2200 installation. At 1.0
W transmitted power and a distance of 1 m (3 ft) from the antenna, the maximum
power density recorded was 0.16mW/cm2. Personnel must remain at least 0.46 m
(1.5 ft) from antennas when system is operating.
The data confirm that the Amtech® system effectively meets OSHA requirements and
does not represent an operating hazard to either the general public or maintenance per-
sonnel.
Frequency
(in MHz)
1500
-------------------------------------------------------

2
Theory of Operation
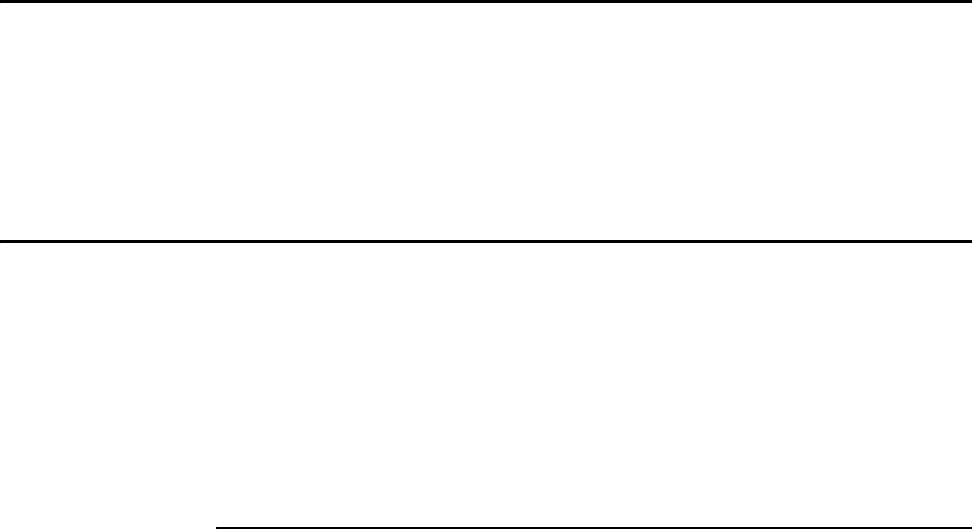
2-3
Chapter 2
Theory of Operation
This chapter provides the theory of operation for radio frequency
identification (RFID) systems and describes Amtech
®
RFID technology.
Overview of RFID Theory
The term radio frequency, or RF, describes the electromagnetic waves in the 10-kHz
to 10-GHz range. Television, cellular phones, two-way radios, and radar are among
the common technologies using RF energy. Many automatic door-opening systems
are also RF based.
Electronic identification (EID) systems automatically transfer data from an object to
the user’s data management system, usually through an optical (barcode or laser),
magnetic, or RF link. Radio frequency identification (RFID) provides the benefits of
optical and magnetic systems, while overcoming many of their limitations.
Components
The primary components of a RFID system are
•Readers (scanners, interrogators) that process the signal returned by the tag, and
send the tag message to a host computer or control system.
•RF sources (transmitters/receivers) that generate and send out a radio signal to the
tag and preprocess the signal returned from the tag.
•Antennas that transmit the RF signal into the environment and retrieve the
reflected signal from the tag.
•Tags (transponders) that carry unique codes and are attached to objects to be
identified.
An RFID system can include readers, RF modules, antennas, tags, and software,
usually under the control of a host computer (Figure 2-1). Various additional
equipment, such as vehicle detectors, gates, and lights, can be included in the system.
Software can be included in a system, usually to process the data gathered from the
tags.
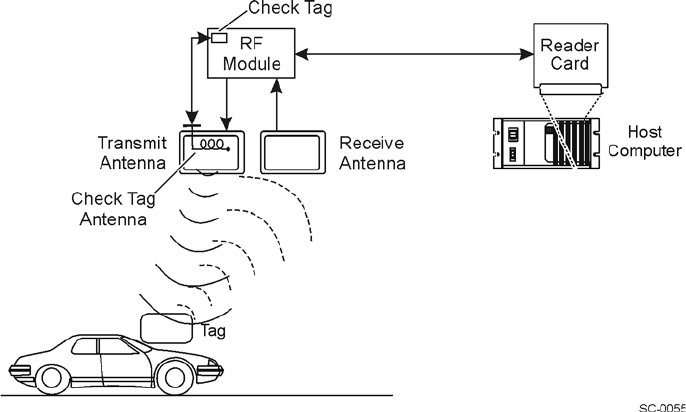
IT2200 Reader System with Multimode Capability Installation & Maintenance/Service Guide
2-4
Figure 2-1 Typical RFID Components for a Bistatic (Two-Antenna)
Configuration
The core RFID system components are described in the following sections.
Reader
Readers provide an operational link between tagged objects and host information
management systems. The reader receives a demodulated signal from the RF module,
decodes the identification information, validates the identification code, and transmits
the code along with any appended information to the host computer system. The
reader also controls the RF module, sending it a command to generate the RF signal.
The reader’s basic operation is to
•Direct the RF module to transmit RF.
•Receive the encoded signal from the tag through the RF module.
•Decode the tag’s ID code.
•Validate the ID code.
•Transmit the ID along with any other data from the tag to the host computer
system.
•Send single or multiple requests to the tag to return data or write to tag memory.
The reader may also have other functions, including accepting data from other input
devices, such as the vehicle detector, and controlling the toll lane gate and signal
lights.
Theory of Operation
2-5
Permanent programming (firmware) in the reader controls reader operation. The
firmware can accept commands from the user through the host computer system or a
local terminal; thus, the user can customize the reader’s operations to the user’s needs.
RF Module
The RF module is the RF source. It is mounted with the antennas. An RF module is a
radio transmitter/receiver that is controlled by a reader. Upon command from a reader,
the RF module generates an RF signal and delivers the signal to one of the antennas
for transmission. The RF module receives and demodulates the reflected tag signal
returned through the antenna(s). It then amplifies and conditions the signal before
sending it to the reader.
Antennas
The antenna is the transmitter and/or receiver for the RF. Each RFID system includes
at least one transmitting and receiving device, or antenna. In some systems, a single
antenna may be used to transmit the RF and receive the encoded RF signal from the
tag (monostatic); in others, one antenna transmits the RF and another receives the
signal returned by the tag (bistatic).
The sophistication of this device depends on the application and the type of tag used.
Antenna type is very important for the application; one type of antenna may transmit a
focused, strong field suitable for highly controlled, high-speed applications such as
rail. Another type may transmit a broad but relatively weak field suitable for relatively
open, slower-speed applications such as access control. Antennas may be stationary or
mobile, depending upon the application.
Transmission field size, shape, and polarization (directional sensitivity of energy
emitted from the antenna) are used to further define the reading range to desired
specifications.
Each type of antenna transmits RF energy generated by the RF module in a
characteristic pattern. The shape of the reading range generated by each antenna can
be related directly to the radiation pattern. In the AA3152 Universal Toll Antenna and
AA3153 Beacon Antenna, this pattern is balloon shaped (Figure 2-2 and Figure 2-3).
This type of antenna is ideal when the reading range must be relatively symmetrical.
When mounted with its elements oriented horizontally, the AA3152 and AA3153
Antennas are horizontally polarized.
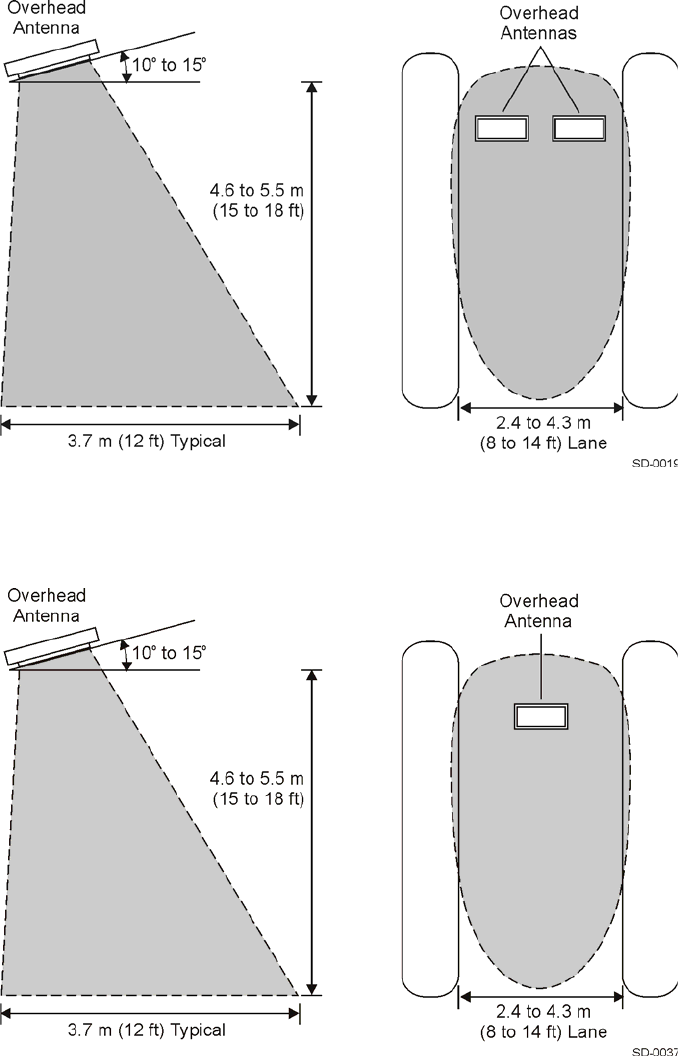
IT2200 Reader System with Multimode Capability Installation & Maintenance/Service Guide
2-6
Figure 2-2 Field Size, Shape, and Antenna Polarization Define the Reading
Range (Bistatic Configuration)
Figure 2-3 Field Size, Shape, and Antenna Polarization Define the Reading
Range (Monostatic Configuration)
Theory of Operation
2-7
Tags
Tags are small, self-contained RFID devices that are capable of bidirectional
communications with a reader. Tag circuitry contains an internal antenna through
which the tag modulates RF signals. Tags are available for interior and exterior
installation, and for system diagnostics (check tags).
Electronic circuitry in the tag can send a message to a reader either continuously or
upon command from a reader, depending on the tag type and application.
Tags and readers must be compatible. The RF generated by the reader system must be
compatible to the tag. For example a 915-MHz RF reader system will not be able to
read from or write to 2450-MHz tags.
Tags also have different memory sizes, varying according to application. Some
applications require only a small amount of memory, for example, 128 bits; while
others may require more memory, e.g., 256 bytes (2048 bits), to contain more data.
Read-Only and Read/Write Tags
Tags can be read-only or read/write. Electronic tags may simply return a fixed or
programmed message such as an ID code. This is referred to as a tag read. With a read/
write tag, data can be transmitted to the tag for archiving. This is referred to as a tag
write.
A read-only tag has an ID number preprogrammed either at the factory or the end
user's facility. This ID number cannot be changed; it can only be read. Read-only
applications have been used successfully for many applications, including high-
performance electronic toll systems. In these applications, the tag’s only function is to
signal its presence to the reader and provide the reader with its ID number.
Read/write tags have two general types. One type has memory that can be written into
only once, but can be read many times (called WORM memory). A second, more
flexible type has nonvolatile (EEPROM) memory that can be read and written to
repeatedly. Thus, information on the tag can be changed repeatedly by commands
issued by the host computer. With this advanced technology, the user can store
information on, or exchange information with, the RFID tag.
Both read-only and read/write tags can be programmable by the end user or
programmed by the manufacturer.
Beam-Powered and Battery-Powered Tags
In systems designed for short-range reading, beam-powered tags are energized by a
carrier signal sent by the reader. The tag returns a signal to the reader that is derived
from the energizing signal and that carries tag information as a sequentially coded
binary message. This type of beam-powered tag system is less expensive than a
battery-powered system.
Battery-powered tags use power from an internal battery to power circuitry that is
used to decode modulated data sent from a reader and to encode signals sent back
using modulated backscatter. Battery-powered tags are more expensive than beam-
powered tags, but they offer greater reading range and faster response time. Battery-
powered tags may offer increased capabilities and range, but they are limited by the
life of the internal tag battery. An additional benefit of battery-powered tag systems is
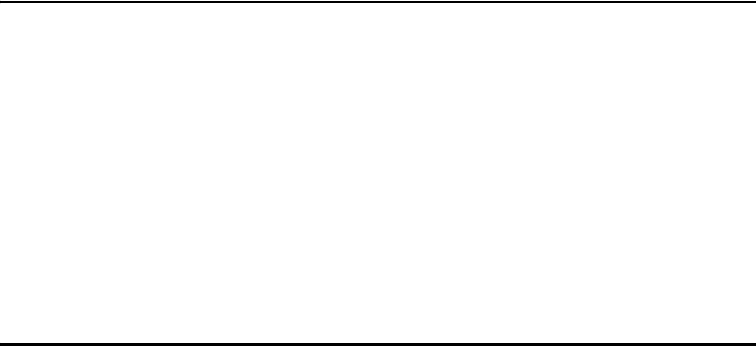
IT2200 Reader System with Multimode Capability Installation & Maintenance/Service Guide
2-8
that they are better able to distinguish between a nearby tag to be read and one slightly
more distant that is not to be read.
Passive backscatter tags do not transmit any RF, they merely modulate and reflect the
RF signal sent to them by the antenna. Beam-powered tags use the power from the RF
signal to reflect the modulated signal back, much as a mirror simply reflects light.
Beam-powered tags have an indefinite life expectancy, but are limited by a shorter
range.
When responding to a reader, active tags (ones that generate their own signal) add to
radio noise background whereas passive backscatter tags do not.
Depending upon the application, implementers can choose from read-only or read/
write models. Passive tags that are battery-powered or beam-powered, or active tags
(which are always battery-powered) can be chosen. Tags can also be selected with
different memory capacities.
Host Computer
The host computer must be capable of accepting data from the specific type(s) of
reader(s) being used in the system and variable bit formats, while offering flexibility
and expandability. Finally, the host computer must support multi-user, multi-tasking,
and multi-operating system environments.
The host computer performs many functions aside from directing the reader(s), such
as transferring the data received from the reader(s) to designated users, displaying it in
required form, and archiving it for reference.
The host computer may be used to provide other services such as controlling the
vehicle detectors, exit gates, and lights at a toll plaza.
Operational Characteristics
The performance of a given electronic identification system varies with the principles
of the systems and the details of implementation. The operational characteristics are
determined primarily by the following factors:
•Reading range, or the maximum distance between the antennas and tag allowing a
successful read and/or write transaction
•Maximum speed at which a tag on a moving object can be successfully read
•Number of characters stored in the tag
•Number of characters to be written to the tag
•Coding format of the tag data
•Sensitivity to tag orientation and placement
•Immunity of the system to noise and interference
Theory of Operation
2-9
•Frequency and power
•Tag lifetime
•Tag read/write accuracy rate
Reading Range
A well-defined reading range (sometimes called a capture window) is required for
successful performance of any ID system. This region is a volume of space extending
outward primarily from the front of the antenna.
Tags outside the reading range do not reflect enough RF signal to be processed by the
reader. Read/write tags may not receive a strong enough modulated signal from the
reader to be able to interpret the command being transmitted.
Reading Speed
Reading speed capability of a system is limited by the need to receive a complete code
frame (a tag's encoded message) while the tag is within reading range. Because signal
reception does not always start at the beginning of the tag's message, the system must
be designed to receive 10 full code frames to ensure reading an entire message.
Reading speed can be extended by
•Decreasing the number of characters (length of message) stored in the tag
•Increasing the volume of the reading range
Number of Characters Stored in Tag
For the IT2200-series tags, the number of characters stored in the tag consists of 16
pages of 16 bytes (128 bits) for a total of 256 bytes of data.
Number of Characters Written to an IT2200-Series Tag
From 1 to 16 bytes of data can be written to a specified frame during a write
command. If you only want to write one byte of data, then that byte has to be the most
significant byte. The IT2200-series tags do not support byte addressing.
Coding Format of the Tag Data
The coding format of the data written to the tag varies depending on tag configuration
and customer requirements.
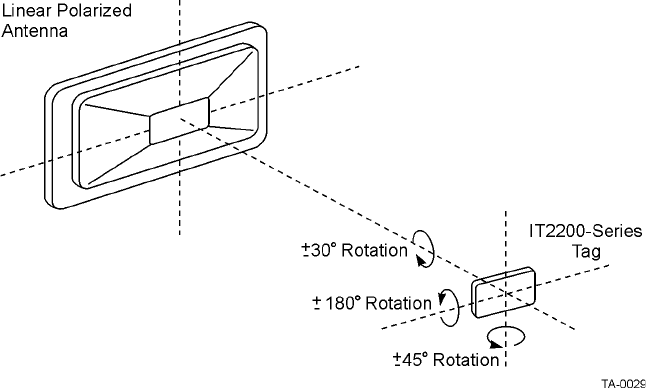
IT2200 Reader System with Multimode Capability Installation & Maintenance/Service Guide
2-10
Tag Orientation and Placement
Ideally, in any RFID system, the tag to be read is oriented such that the polarization of
its internal antenna is aligned favorably with the polarization of the system antenna
(Figure 2-4).
Figure 2-4 Tag Orientation with Linear Polarized Antenna
Tags can be mounted on the inside of a vehicle’s windshield or mounted on the license
plate area of the front of the vehicle.
The surface upon which tags are mounted can affect the tag's performance by
directing the reflected signal toward the transmitting/receiving antenna, or in some
cases, by reflecting the signal away from the antenna. Interior tags cannot be mounted
on metallic surfaces because the metal will interfere with the tag’s operation. Exterior
tags can be mounted on metallic or non-metallic surfaces.
Noise and Interference Immunity
Electrical noise and interference, as well as physical obstructions between the tag and
antenna, can degrade communications between a tag and the reader system.
Electrical Noise and Interference
Common sources of noise and interference are other communication devices such as
TVs, cellular phones, two-way radios, radar, and other tags and readers. Other noise
sources include motors, fans, digital equipment, automobile ignition systems,
fluorescent lights, and neon signs.
Physical Obstructions
Some types of obstructions or materials between the tag and antenna can cause little or
moderate to substantial interference with the tag signal. Radio waves penetrate
nonconducting materials (such as snow, ice, dirt, wood, paper, plastic, and cured
concrete) with only moderate attenuation.

Theory of Operation
2-11
More conductive materials, such as water (especially salty water), not only attenuate
the RF signal, but can also reflect a portion of the RF energy from the surface of the
material, resulting in poor system performance. The amount of reflection produced is
related to the dissimilarity in electromagnetic impedances of adjacent materials.
Multipath and Signal Diffraction
Many fundamental properties of radio waves influence the RFID system. Radio waves
are reflected from dielectric (nonconducting) as well as metallic surfaces. These RF
reflections can allow tags outside the antenna's line of sight to be read, and can cause
multipath effects as well.
Multipath occurs when two or more favorable radio paths exist between the tag and
antenna. Multipath can cause high fields (extended reading range areas) and low fields
(null regions), which must be taken into account in system configuration.
Signal diffraction can also affect system performance. Diffraction is the bending of
radio waves around an obstacle. The combined effects of signal diffraction and
multipath reflections can allow tags to be read under seemingly impossible
circumstances.
Frequency and Power
All RFID systems must operate within national and international laws and guidelines
with respect to frequency and power. The common frequency bands available are near
888 MHz, 915 MHz, and 2450 MHz. (The authorized frequency bands in the United
States are 902 to 904 MHz and 909.75 to 921.75 MHz.)
Tag Lifetime
The housing and internal electronics of the IT2200-series tags, excluding the battery,
have an operational life of at least 10 years.
Tag Read/Write Accuracy Rate
By using the specified equipment and system configuration outlined in this chapter, a
tag read/write accuracy rate greater than 99.97% has been achieved with the IT2200
Reader System with Multimode Capability.
Amtech
®
RF Technology
The Amtech® system operates on the principle of modulated backscatter. The system
sends an unmodulated RF signal toward the tag, which acts as a field disturbance
device. The tag signal is varied in a coded fashion so that the tag reflects a coded
signal back toward the antenna at the same frequency transmitted by the RF module.
Modulated backscatter technology is similar to systems used in air-traffic control and
police radar systems, as well as in marine sonar systems.
To provide enhanced lane-to-lane selectivity and the ability to isolate and operate in
noisy RF environments, the IT2200 Reader System with Multimode Capability uses
backscatter technology for tag-to-reader communications. In this system, the reader
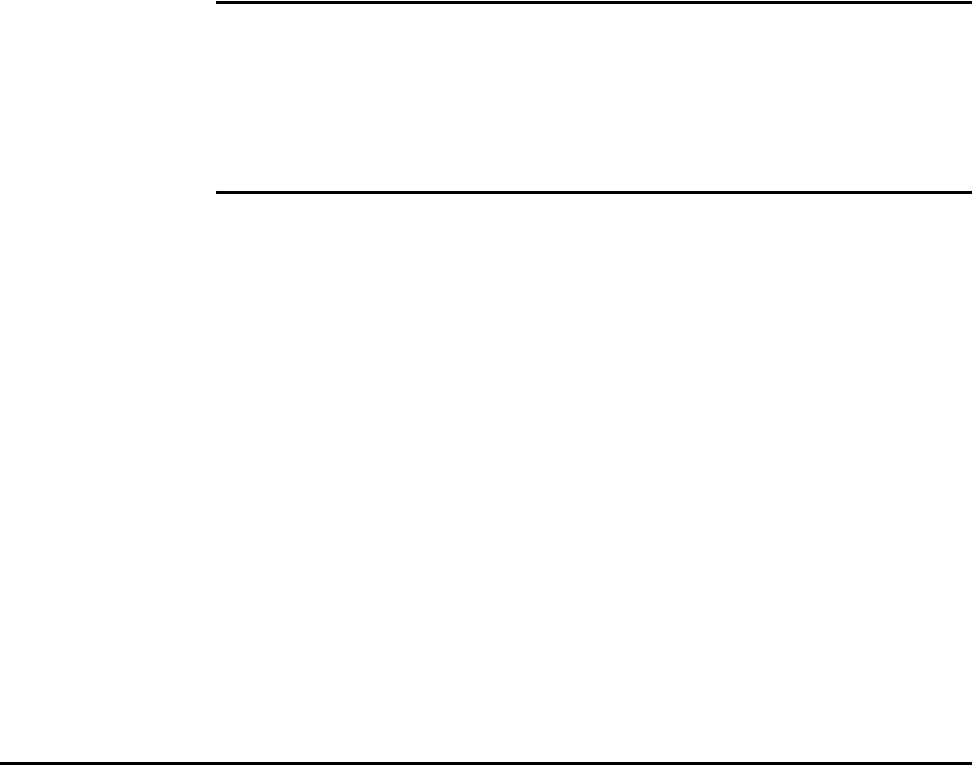
IT2200 Reader System with Multimode Capability Installation & Maintenance/Service Guide
2-12
communicates the initial polling message to the tag. It then transmits an unmodulated
continuous RF wave so that when a tag is within range of the antenna, it can
backscatter its data to the reader. The reader and tag continue this two-way
communications until the transaction has been completed. Normally, at this point, the
reader transmits an encoded acknowledgment (sign-off) message to the tag, and the
tag does not respond to further reader request messages for a programmable period of
time—from 1 to 128 seconds—allowing the vehicle time to travel through the antenna
pattern. During this time-out period, the reader starts communications with the next
tag in the same lane.
In ATA mode, the tags are read-only and do not use a reader-to-tag modulated signal.
When powered, and in the presence of an unmodulated signal, ATA tags always
attempt to backscatter.
Signal Transmission and Acquisition
Amtech® technology uses a single frequency, continuous-wave signal, transmitted
from the reader to the tag, and receives an amplitude modulated form of the same
signal from the tag. This homodyne system uses a sensitive multi-channel
preamplifier to distinguish the return signal from the transmitted signal.
Automatic Vehicle Identification Transaction
Process
Operationally, each tagged vehicle is processed identically whether the toll is
collected on a ticket or barrier system, or the lane is a confined plaza lane or an open,
high-speed express lane. Typical automatic vehicle identification (AVI) operations are
performed as follows:
1. The reader polls for a tag to respond with an identification (ID) number.
2. Once a tag enters the read zone, it responds with its ID number.
3. The reader sends single or multiple requests to the tag to return data or write to
tag memory.
4. At the end of the transaction, the reader sends an acknowledge (ACK) message.
5. The tag goes into a time-out state.
6. The reader polls for the next tag.
If the IT2200 tags respond in ATA mode, the tag identification is read. This completes
the transaction.
Types of RFID Transactions
There are two types of RFID transactions: read-only and read/write. A read-only
transaction is the simplest and consists of a tagged item entering an RF field where the
reader queries the tag’s information. The exchange of information is from the tag to
the reader, no information is returned to the tag.
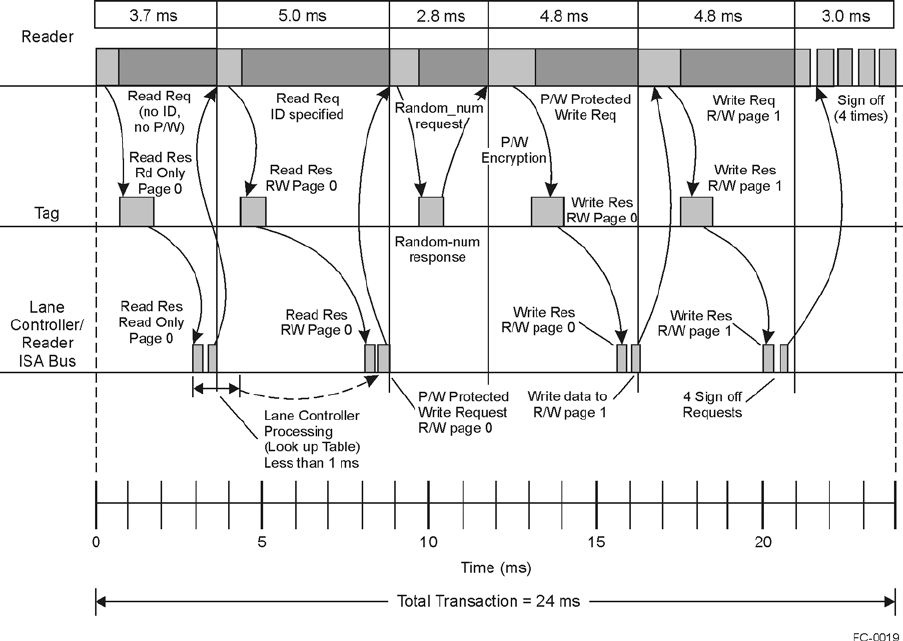
Theory of Operation
2-13
A read/write transaction consists of the following processes:
•The reader modulates a message to all tags until it receives a response from a sin-
gle tag that has been activated by the reader message
•The reader communicates with that individual tag by using the tag’s unique identi-
fication.
•The reader retrieves data from any of that tag’s memory location, and can also
write data to any of that tag’s memory locations.
This process is called read/write because the reader needs to write a message to the tag
to obtain a response. The reader can then write data to memory also, if required.
A read/write transaction is more complicated because not only does it entail commu-
nication between the tag and a reader, but the reader can also modify information that
is stored in the tag memory.
The total transaction time for this RFID system is less than one-tenth of a second.
Within that timeframe, a number of transactions occur. Figure 2-5 shows a timeline
for a representative read/write transaction using the IT2200 Reader System with Mul-
timode Capability and an IT2200-series tag that is controlled by an IT2200 reader
with multimode capability housed in a lane controller.
Figure 2-5 Typical Read/Write Transaction Using the IT2200 Reader System and
an IT2200-series Tag
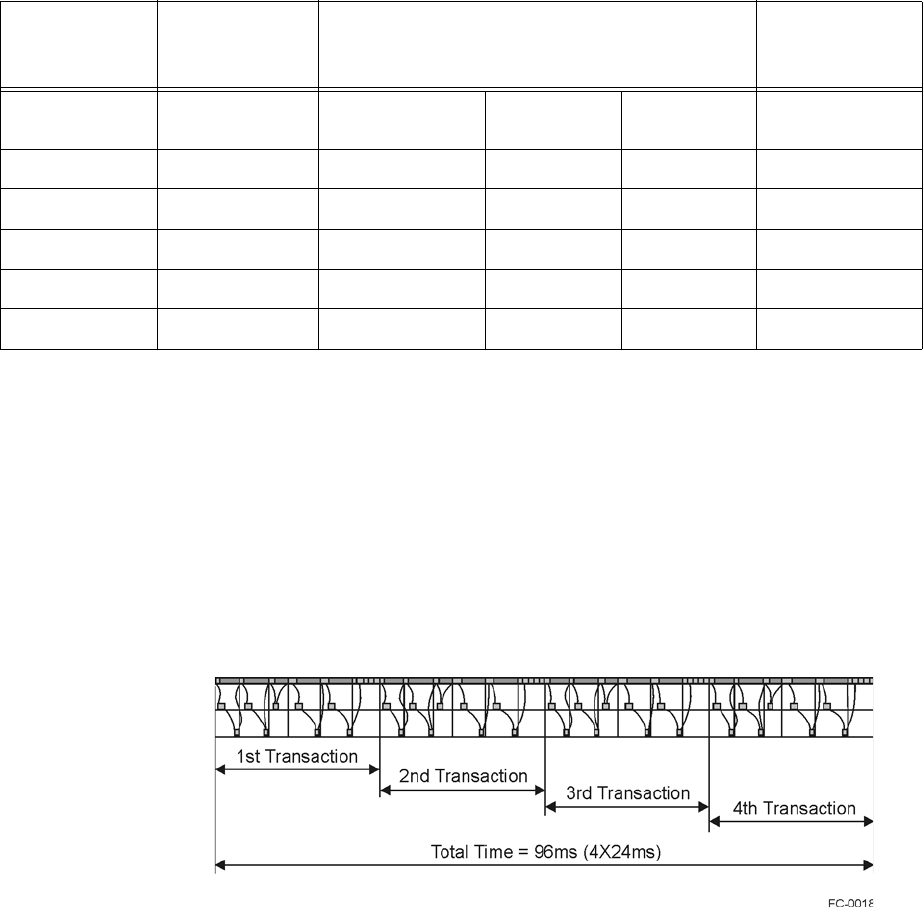
IT2200 Reader System with Multimode Capability Installation & Maintenance/Service Guide
2-14
Each sequence is equal to one valid transaction, and is composed of six RF data
packets. If the amount of time it takes to complete one transaction is equal to the total
length of the RF payment zone, then, because of a 95% effective RF link coverage, the
probability of completing that transaction is 73.51% (.956). The probability of
obtaining each transaction if the RF footprint is greater than the time for one
transaction is shown in Table 2-1.
Table 2-1 Time and Distance Required to Complete Payment Zone
The value of 95% RF effective coverage is derived from variables such as nulls and
multipath in the RF field because of reflections and various forms of interference. A
properly mounted tag in a vehicle exhibits at least this 95% value. A 95% coverage for
a 3m (10-ft) zone would mean that 0.15 m (0.5 ft) of the 3 m (10 ft) is a null or no RF.
As shown in Table 2-1, the minimum footprints or payment zones for each lane to
achieve an accuracy of 99.97% are 1.7 m (5.6 ft) at 64 kph (40 mph), 2.8 m (9.2 ft) at
105 kph (65 mph), and 4.3 m (14 ft) at 161 kph (100 mph).
Figure 2-6 illustrates that a minimum of four transactions must be allowed to occur to
achieve the required accuracy. The minimum time for these four transactions is 96 ms.
Figure 2-6 Four Transactions Can Occur Within 96 Milliseconds
Figure 2-7 shows a timeline for a sample read-only transaction using the IT2200
reader system with Multimode Capability operating in ATA mode and an ATA-type
tag.
Number of
Transactions
Time to
Complete
Payment Zone
Distance to Complete Payment Zone (in
meters (feet)) Probability (%)
64 kph (40
mph) 105 kph (65
mph) 161 kph
(100 mph)
1 24 ms 0.4 (1.4) 0.7 (2.3) 1.1 (3.5) 73.5092
2 48 ms 0.8 (2.8) 1.4 (4.6) 2.1 (7.0) 98.5093
3 72 ms 1.3 (4.2) 2.1 (6.9) 3.2 (10.5) 99.9250
4 96 ms 1.7 (5.6) 2.8 (9.2) 4.3 (14) 99.9963
5 120 ms 2.1 (7.0) 3.5 (11.5) 5.3 (17.5) 99.9998
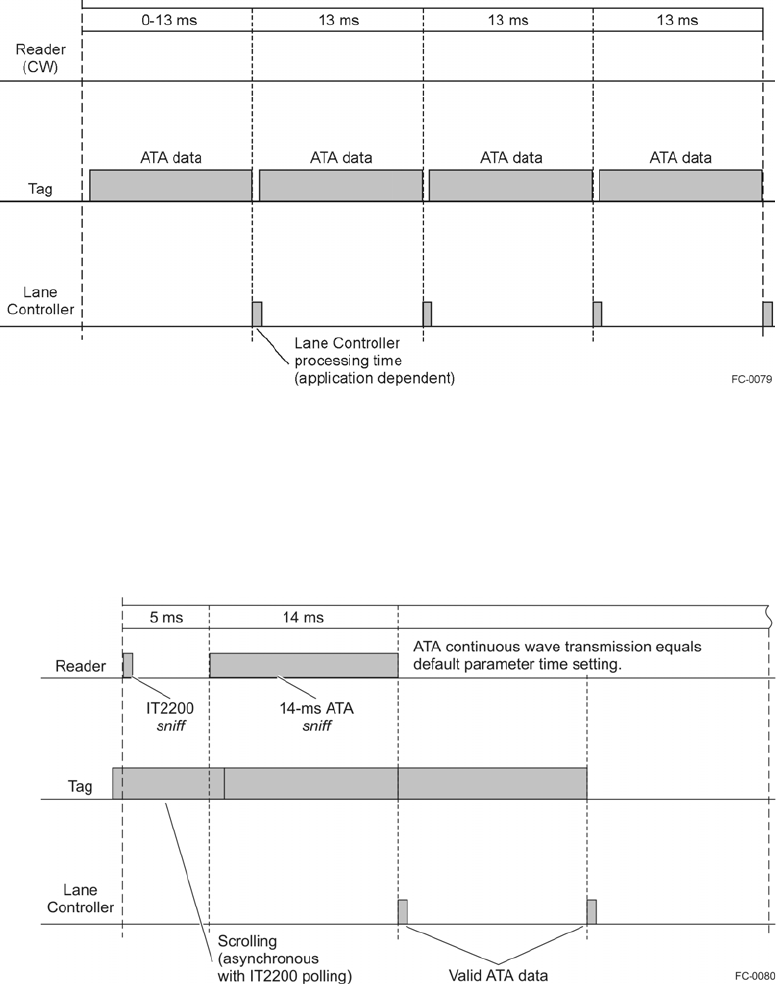
Theory of Operation
2-15
Figure 2-7Typical Read-only Transaction Using the IT2200 Reader System in
ATA Mode Operation with an ATA-Type Tag
Figure 2-8 shows a timeline for a sample read-only transaction using the IT2200
Reader System with Multimode Capability operating in multimode and an ATA-type
tag.
Figure 2-8Typical Dedicated Read-Only Transaction Using the IT2200 Reader
System in Multimode Operation with an ATA-Type Tag
Figure 2-9 shows a timeline for a sample read-only transaction using the IT2200
Reader System with Multimode Capability in ATA mode and an ATA-type tag.
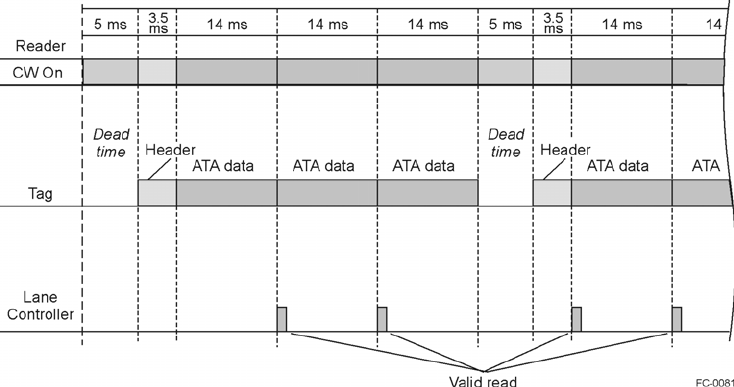
IT2200 Reader System with Multimode Capability Installation & Maintenance/Service Guide
2-16
Figure 2-9Typical Read-Only Transaction Using the IT2200 Reader System in
ATA Mode Operation with an ATA-Type Tag

3
System Components
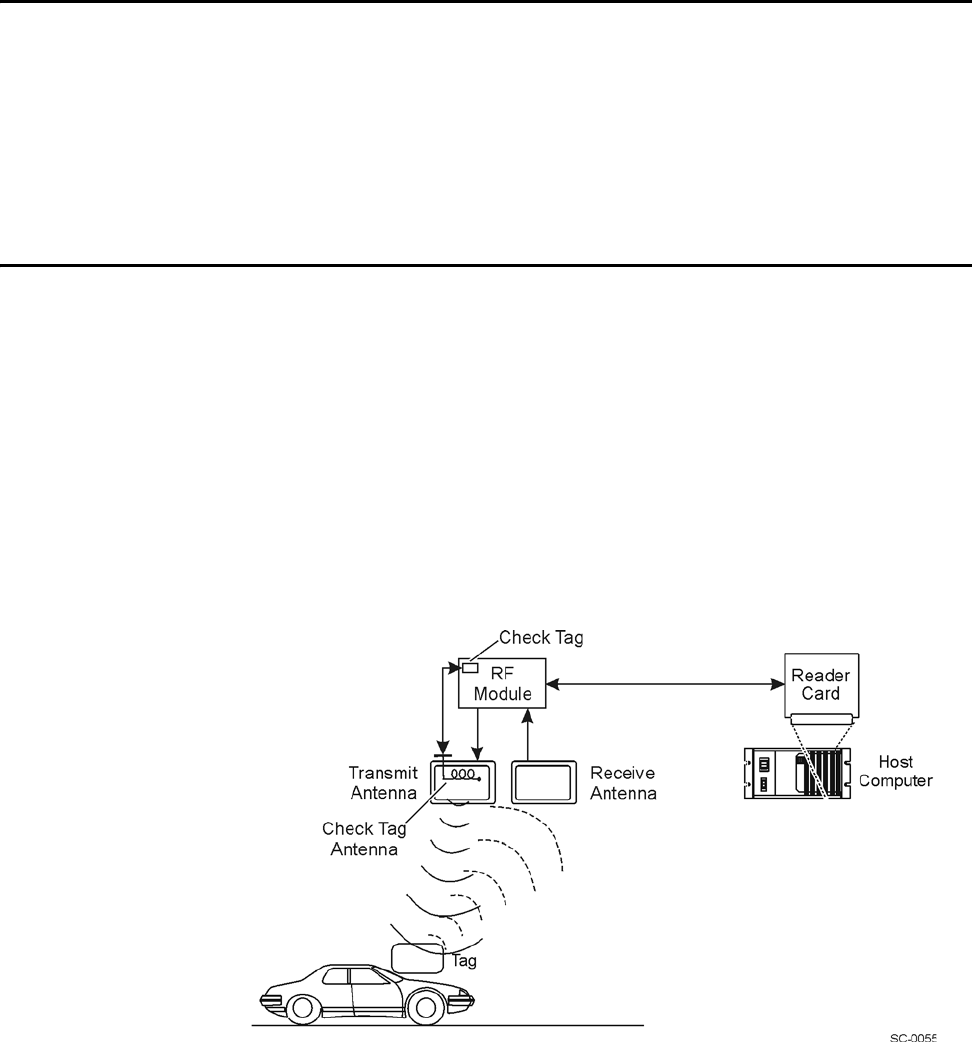
3-3
Chapter 3
System Components
This chapter presents an overview of the IT2200 Reader System with
Multimode Capability and then describes the individual components of
the reader system and their relationship to each other.
Overview
The components of the IT2200 Reader System with Multimode Capability are as
follows (Figure 3-1):
•IT2020 Reader Logic Card
•IT2611 RF Module
•AA3152 Universal Toll Antenna (UTA) or AA3153 Beacon Antenna
•IT2502 Check Tag Antenna
•IT2221, IT2211, IT2235, and ATA-type Tags
•IT2410 Tag Programmer
Figure 3-1 Relationship of the IT2200 Reader System Components (Bistatic
Installation Shown)
The IT2200 Reader System with Multimode Capability consists of the reader, RF
module, antennas, tags, and tag programmer. The reader's RF source is a separate
IT2200 Reader System with Multimode Capability Installation & Maintenance/Service Guide
3-4
component. The reader broadcasts RF energy over an adjustable area called the read
zone or reader footprint. The tag on the vehicle reflects a small part of this RF energy
back to the antenna. The reflected radio waves denote the tag's unique identification
code and other stored data.
The antenna relays the signal to the reader, which can add information such as date/
time to the tag's identification code, and stores it in a buffer. The reader can transmit
the tag's identification code to the customer's information management system. The
entire process takes only milliseconds.
The IT2020 Reader Logic Card is housed within a lane controller or PC chassis,
eliminating the need for a stand-alone reader. The reader logic card uses application-
specific software to communicate with the lane controller or host computer. All reader
commands and logic functions are incorporated into a single IT2020 Reader Logic
Card.
The IT2611 RF Module is connected to and works in conjunction with the IT2020
Reader Logic Card to provide two-way RF communications with tags. It is mounted
near the antennas to reduce signal losses to and from the antennas. The RF module
attaches to the antennas with low-loss coaxial cables.
The antennas, along with the RF module, provide the radio signal required to achieve
the bidirectional wireless communications link between the tag and the reader.
A check tag is a special purpose tag that can be permanently installed in an antenna or
is installed near an antenna that does not have an internal check tag. For the IT2200
Reader System, the check tag is integrated into the RF module and has a separate
check tag antenna.
The check tag can simulate a toll transaction, thereby providing a means for the reader
to check the system operation. The check tag, activated on command by the lane
controller or host computer, provides a test of the antennas, RF source, preamplifier,
encoder/decoder, microprocessor, communications port, and input/output (I/O)
control.
The IT2502 Check Tag Antenna is used to communicate with a check tag that is
located inside the RF module. The check tag antenna is placed directly in front of the
transmit antenna.
IT2200-series tags are self-contained RFID devices that are capable of bidirectional
communications with a reader. ATA tags are read-only that communicate from tag to
reader. Tags are available for interior or exterior installation.
The IT2410 Tag Programmer is used to read data from and write data to tags used in
an RFID system.
Each of the system components listed above is described in detail in this chapter.
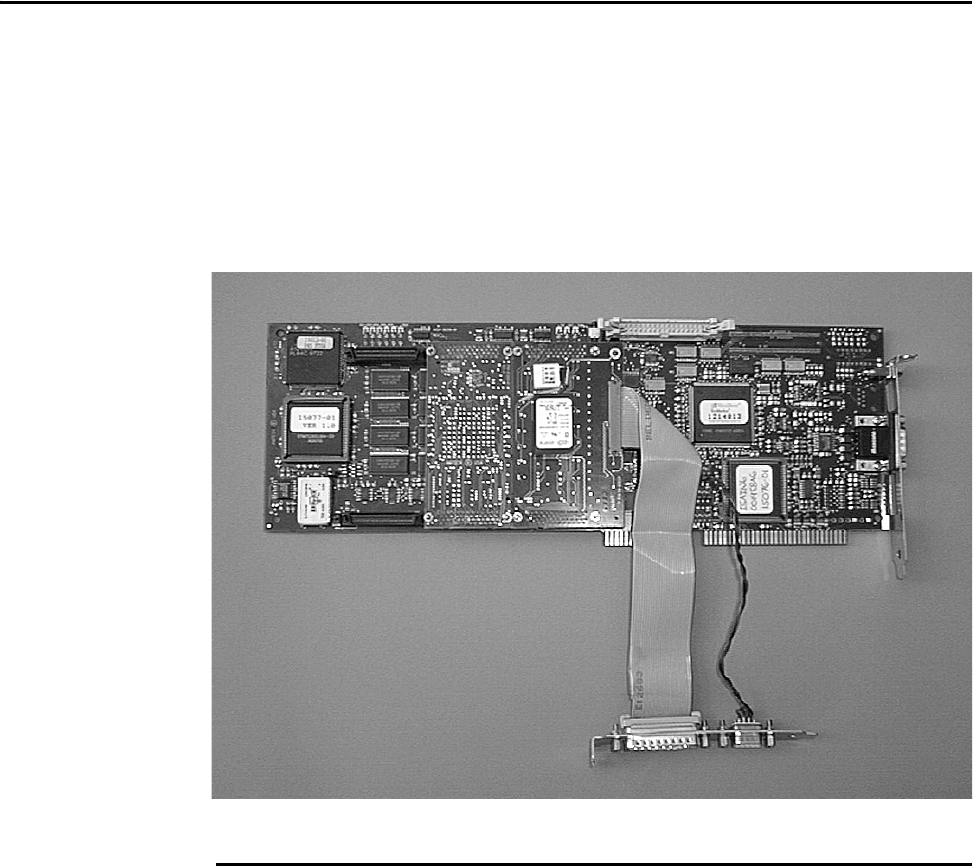
System Components
3-5
IT2020 Reader Logic Card
The IT2020 Reader Logic Card is a full-size ISA card, bus-operated, modular
component (see Figure 3-2). The IT2020 Reader Logic Card communicates with a
governing device, such as a lane controller or personal computer (PC), using
application-specific software. Readers control the two-way communications with any
tags that are compatible with the IT2200 protocol. All reader commands and logic
functions are incorporated into a single IT2020 Reader Logic Card. The IT2020
Reader Logic Card is housed within a lane controller or PC chassis, eliminating the
need for stand-alone readers. The IT2020 Reader Logic Card requires two adjacent
slots in the host PC.
Figure 3-2 IT2020 Reader Logic Card
Functions
The IT2020 Reader Logic Card establishes a direct interface with the lane controller
or PC and acts as a switchboard for communications between the ground-based
electronics and the mobile tags. The instructions executed by the reader logic card
determine the data flow and processing rates and perform read-only and read/write
transactions with tags.
The reader communicates with the tags over a radio frequency (RF) communications
link generated by the RF module and transmitted by the antenna. The communications
link uses a protocol specifically designed to minimize transaction time and provide the

IT2200 Reader System with Multimode Capability Installation & Maintenance/Service Guide
3-6
most flexible set of capabilities available in electronic toll collection (ETC)
equipment.
Features
The IT2020 Reader Logic Card provides the following features:
•Program memory—The reader logic card contains 2 MB of flash memory.
•Data memory—The reader logic card contains 1 MB of RAM.
•Battery-backed data memory—The reader logic card uses battery backup to
preserve data in the event of a power loss for 512K of SRAM in Bank1.
•Password security—The reader logic card contains circuitry to encrypt/decrypt
the tag password.
•Direct access protocol—The reader logic card uses this protocol to communicate
with a target tag even if many tags are present between the target tag and the
reader.
•Internal synchronization—Multiple readers can be placed in close proximity
without requiring RF synchronization by the lane controller.
•Extensive self-diagnostic capability—Extensive self-diagnostics are built into the
hardware and software.
•Expandable for future options—Both hardware and firmware features can be
expanded in the reader.
•Processor—The processing is based on the Motorola MC68EN360
microprocessor.
•Frequency operation—The reader operates in the 902 to 904 MHz and 909.75 to
921.75 MHz bands.
•Multiple tag—The reader with multimode capability can read IT2200-series tags
alone, ATA tags alone, and/or a mixed population of IT2200-series and ATA tags.
•FCC compliant—The reader is Part 15 verified and Part 90 type accepted.
•Host interface—The host interface is a 16-bit ISA interface.
By using the reader logic card approach, as opposed to a stand-alone reader, the user
can employ available ISA card slots in existing lane controllers. This approach
eliminates or diminishes expenses associated with stand-alone reader packaging, such
as additional power supplies, electrostatic discharge (ESD) protection, and more
robust environmental design factors, which require more expensive components and a
higher level of maintenance.
Additionally, the IT2020 Reader Logic Card is designed for integration into an
industrial-level processor, such as a host computer or lane controller.
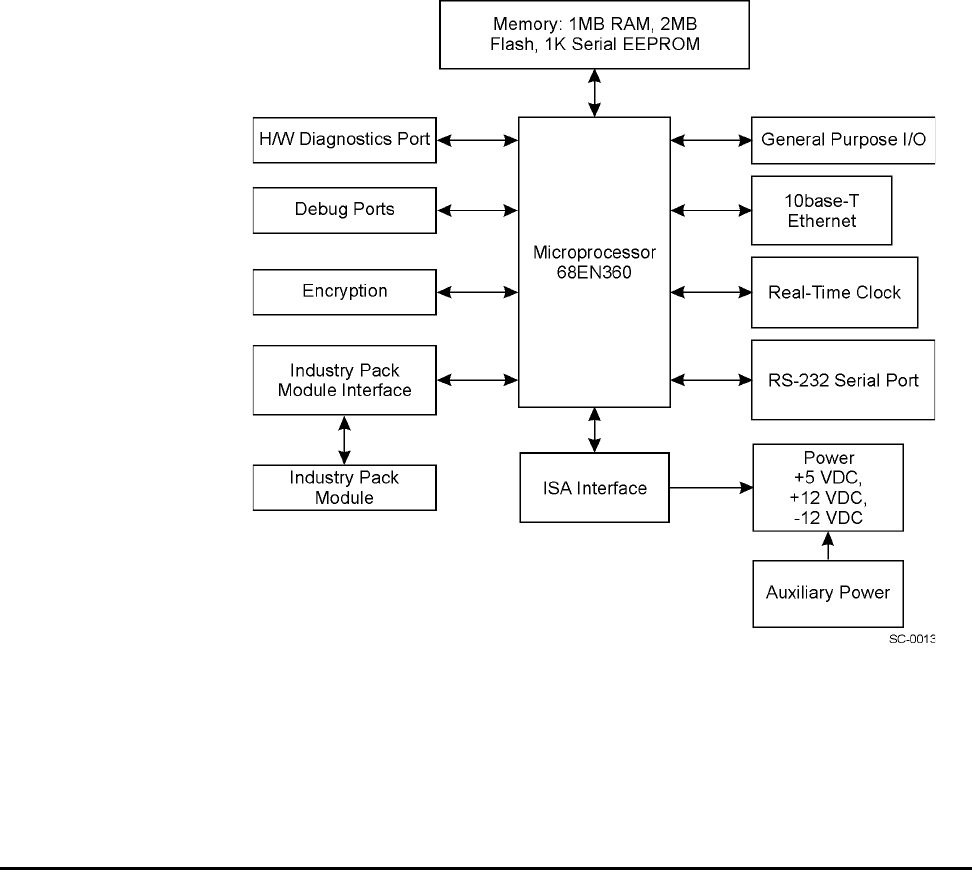
System Components
3-7
Because the IT2020 Reader Logic Card is integrated into the lane controller or host
computer, lightning protection is unnecessary at the reader logic card; however,
lightning protection is provided with the RF module. The RF module is contained in
the vicinity of the antenna housing for simplified installation and maintenance.
External signals are optically isolated to ensure that any potentially damaging
transients do not propagate into the reader. A block diagram of the IT2020 Reader
Logic Card is shown in Figure 3-3.
Figure 3-3 IT2020 Reader Logic Card Block Diagram
The reader logic card acts as the carrier for industry pack (IP) modules that expand the
reader’s functionality. The IP modules are expansion boards that interface to other
processing, status, and control components, such as the RF module. One spare IP slot
allows for an additional module to interface with the reader logic card.
IT2611 RF Module (Bistatic and Monostatic)
The IT2611 RF Module communicates with the IT2020 Reader Logic Card and the
antennas to provide two-way RF communications with tags. It is mounted near the
antennas to reduce signal losses to and from the antennas.
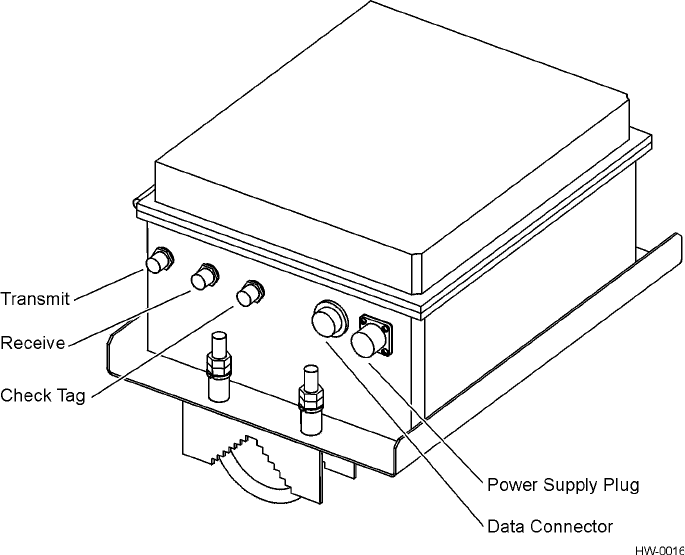
IT2200 Reader System with Multimode Capability Installation & Maintenance/Service Guide
3-8
The RF module housing consists of the following components:
•Fiberglass enclosure
•Bulkhead Type N connectors for antenna connections
•Bulkhead circular waterproof connectors for power and interface
•Stainless steel mounting hardware
The RF module connects to a 19- to 28-VAC or 16- to 28-VDC power source and
interfaces back to the lane controller and the IT2020 Reader Logic Card. These
connections are illustrated in Figure 3-4 (bistatic) and Figure 3-5 (monostatic).
Figure 3-4 IT2611 RF Module Connections (Bistatic Configuration)
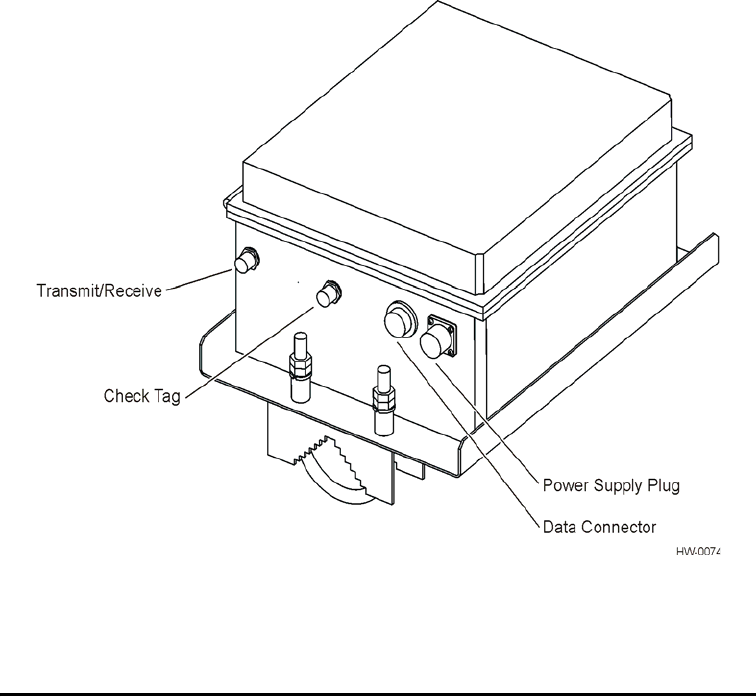
System Components
3-9
Figure 3-5 IT2611 RF Module Connections (Monostatic Configuration)
The interface connector connects to the reader logic card to supply tag data
information and communication to the RF module.
RF Module Connections
Connections to the IT2200 Reader System devices are made through connectors at the
front of the RF module.
Transmit Connector (Bistatic RF Module)
This Type N RF connector connects the RF module to the transmitting (downlink)
antenna through a short low-loss coaxial RF flexible cable.
Receive Connector (Bistatic RF Module)
This Type N RF connector connects the RF module to the receiving (uplink) antenna
through a short low-loss coaxial RF flexible cable.
Transmit/Receive Connector (Monostatic RF Module)
This Type N RF connector connects the RF module to the transmitting/receiving
antenna through a short low-loss coaxial RF flexible cable.
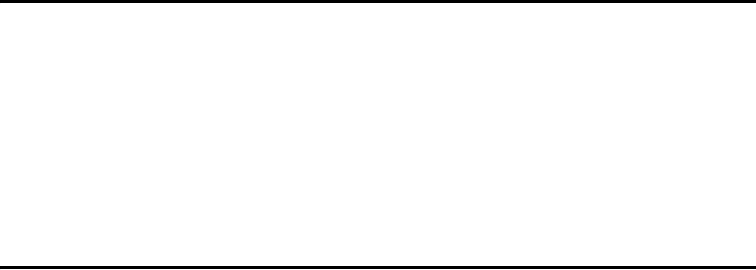
IT2200 Reader System with Multimode Capability Installation & Maintenance/Service Guide
3-10
Check Tag Connector
This Type N RF connector links the check tag, which is housed inside the RF module
and is used to test the reader system, to its accompanying antenna.
Data Connector
This connector links the RF module to the reader logic card. Data transfer between the
reader logic card and the tag occurs through this data connector. The interface to the
reader logic card is connected using the RF module interface connector.
Power Supply Connector
This connector provides the primary power for the RF module. The power interface is
19 to 28 VAC or 16 to 28 VDC. It typically connects to a power supply in the host lane
controller system.
Functions
The RF module sends the RF signal to the antenna, receives the modulated tag signal,
demodulates, amplifies, and filters the received tag signal, then forwards the digital
data to the reader for processing. This technique is known as modulated backscatter.
The RF module transmits the modulated signal at a reader-set discrete frequency
within the 902- to 904-MHz and 909.75- to 921.75-MHz frequency bands. The
transmitted signal is then received by a selected tag that backscatters or re-radiates the
signal and modulates the signal to reflect tag information.
Features
The RF module features include the following:
•FCC Part 90 type accepted and Part 15 verified
•Two RF sources, one to downlink (write) and one to uplink (read)
•Programmable RF—The transmitted carrier frequency can be adjusted. However,
this can be performed only by trained, authorized dealers or service personnel.
•Programmable RF power—Programmable control of RF output power is possible.
•RF operation—Two-antenna (bistatic) operation for enhanced performance
•Phase-lock loop (PLL) synthesizer with 250-kHz steps programmable
•One-watt (W) maximum power output to each channel (downlink and uplink)
•Power attenuation is programmable in 1dB steps to -15dB by digital-to-analog
converter control of each channel
•Check tag integrated into RF module with separate check tag antenna
•Three-channel differential receiver with pre-amplifier
System Components
3-11
•Interface-to-ISA reader logic board used to control RF module sources and
functions
The generated RF levels fall well below IEEE C95.1-1991 and international health
limits. The RF module transmits radio energy at a fixed frequency and is classified as
a low-power radio transmitter. Maximum peak RF power is 1W for each channel—
less than the power generated by many common radios, including ham radios and
citizen band radios.
A PLL crystal-controlled oscillator of the RF module makes degradation over time
unlikely. The PLL is resistant to temperature, humidity, and power fluctuations.
Transmitter failure does not result in the generation of more than the maximum
specified power output of 1 W.
Type Testing
The RF module has passed testing for type acceptance of FCC Part 90 as a location
and monitoring service transceiver and verification of FCC Part 15 as Class A
equipment, unintentional radiator. The end user will be required to obtain and
maintain site licenses.
RF Emissions
To confine the read/write coverage to a single lane, the RF module can be adjusted to
emit much less than the maximum 1 W. Depending on the particular installation site,
typical RF emission is an estimated 0.05 to 0.5 W. The RF module connects to an
automatic vehicle identification antenna that has a gain of approximately 10.5dB. This
gain produces energy levels and specific absorption rates far below IEEE C95.1-1991-
specified limits at any point around the antenna.
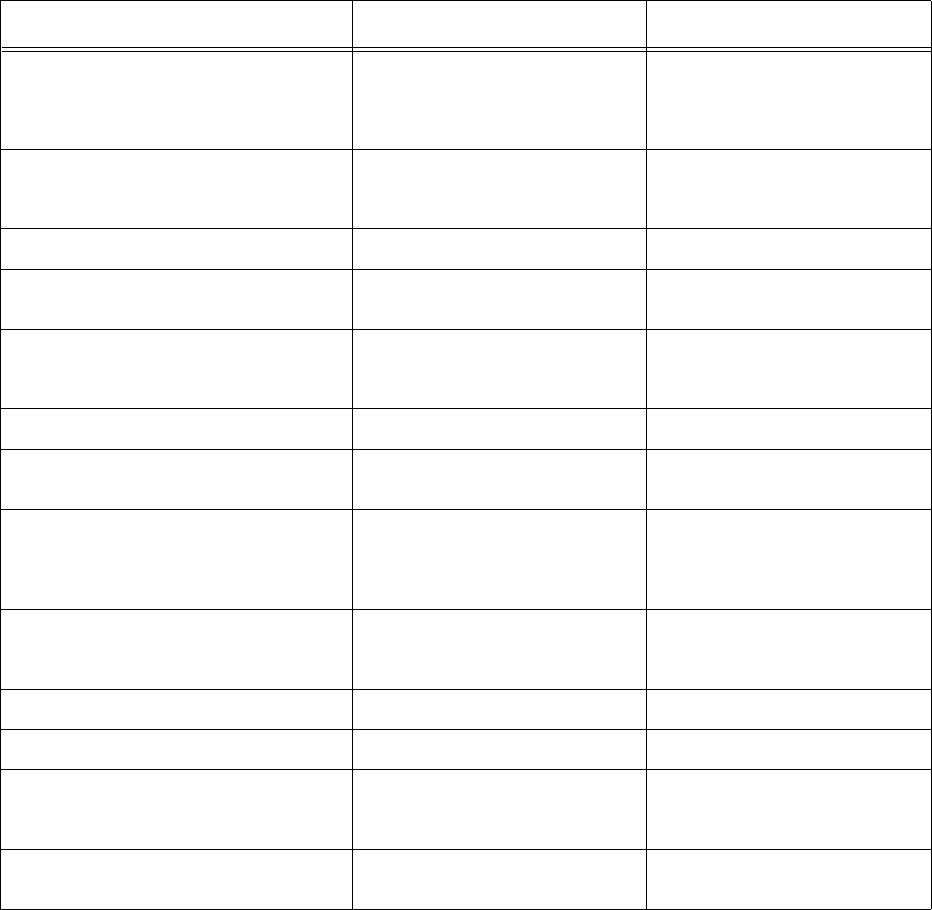
IT2200 Reader System with Multimode Capability Installation & Maintenance/Service Guide
3-12
Table 3-1 shows the downlink and uplink specifications.
Table 3-1 IT2611 RF Module Uplink and Downlink Specifications
Description Specification Comments
Downlink frequency selection Adjustable from 912 to 918.75
MHz Other frequencies locked out
by software control. Set by
qualified technicians at the
time of installation.
Downlink frequency stability ≤20 ppm Minimizes lane-to-lane
interference for ATA tag
mode.
Downlink frequency control step size ≤250 kHz N/A
Downlink RF power output 1 W maximum Minimum attenuation/
Maximum gain
Downlink RF power control 0 to ≥15dB
attenuation control
Set by host computer
command; facilitates lane
tuning
Downlink RF power control steps 1dB nominal N/A
Downlink modulation depth/spectrum Tailored to meet tag
requirements An example is Title 21
Uplink frequency selection Adjustable from 902 to 904
MHz and from 909.75 to
921.75 MHz
Other frequencies locked out
by software control. Set by
qualified technicians at the
time of installation.
Uplink frequency stability ≤20 ppm Minimizes lane-to-lane
interference for ATA tag
mode.
Uplink frequency control step size ≤250 kHz N/A
Uplink RF power output (transmit) 1 W maximum N/A
Uplink RF power control (transmit) 0 to ≥15dB attenuation Set by host computer
command; facilitates lane
tuning
Uplink RF power control steps
(transmit) 1dB nominal N/A
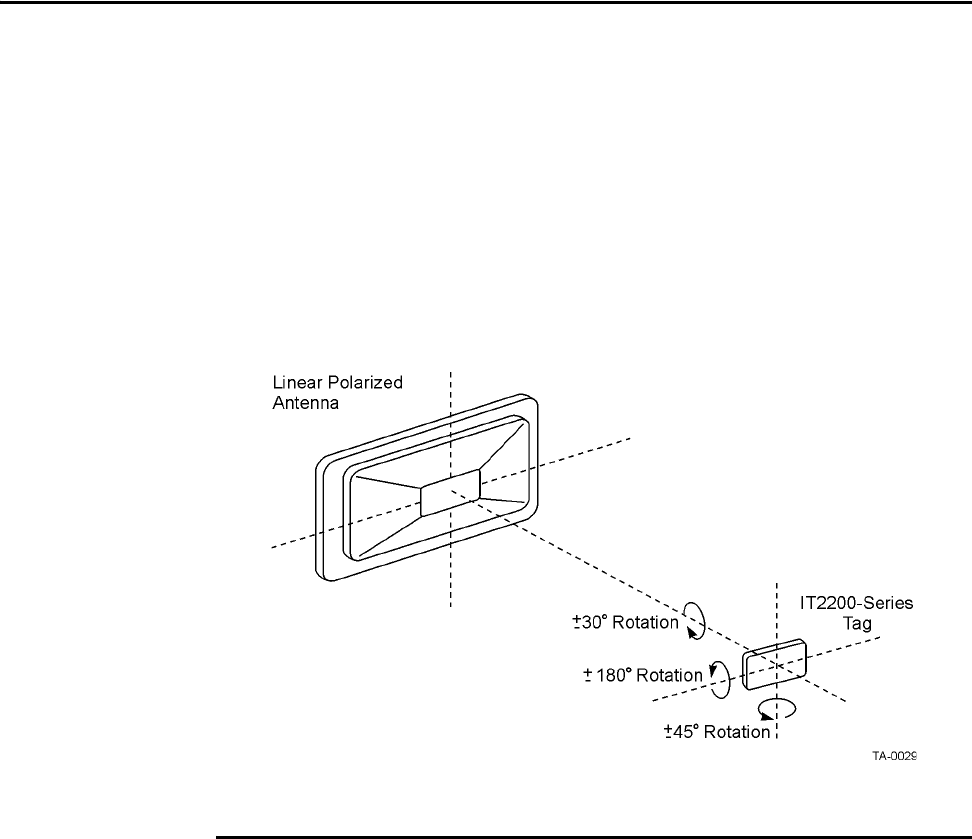
System Components
3-13
Antennas
The antennas transmit and receive the radio signal generated by the RF module and
receive the backscatter signal from the tag.
The IT2200 Reader System with Multimode Capability uses either a pair of AA3152
or AA3153 Antennas for bistatic configuration or a single AA3152 or AA3153
Antenna for monostatic configuration depending on the installation. The AA3152
Antennas are used in overhead installations and AA3153 Antennas are used in side-
mount installations.
Ideally, in any RFID system, the tag to be read is oriented such that the polarization of
its internal antenna is aligned favorably with the polarization of the system antenna.
Figure 3-6 illustrates the linear polarization of an antenna and tag.
Figure 3-6 Tag Orientation with Linear Polarized Antenna
AA3152 Universal Toll Antenna
The IT2200 Reader System with Multimode Capability uses either one or two
AA3152 Universal Toll Antennas (UTA) for overhead and gantry plaza installations.
Functions
In a monostatic configuration, the AA3152 UTA acts as the downlink antenna
transmitting signals to the tag, and also acts as the uplink antenna receiving signals
from a vehicle tag. In a bistatic configuration, an AA3152 UTA acts as the downlink
antenna transmitting signals to the tag, and another AA3152 UTA acts as the uplink
antenna receiving signals from a vehicle tag.
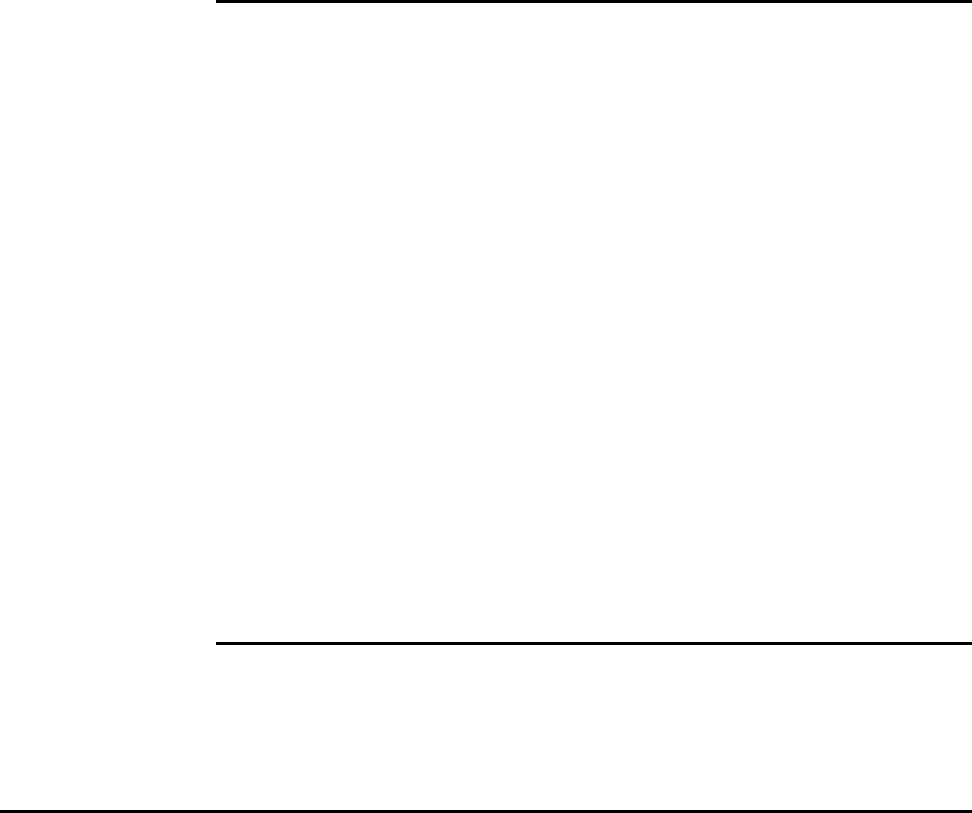
IT2200 Reader System with Multimode Capability Installation & Maintenance/Service Guide
3-14
Features
This antenna is specifically designed for use in toll lane applications, and it transmits
and receives RF signals in the 902- to 928-MHz RF range. The AA3152 UTA
transmission pattern has virtually no side or back lobes, which helps to confine
antenna coverage to a single lane width. The antenna is enclosed in a weatherproof
radome, which is made of materials selected for favorable electrical characteristics
and resistance to ultraviolet radiation.
The AA3152 UTA is designed for outdoor use. The antenna operates without
performance degradation in hot or cold temperature extremes, strong wind, or
vibrations caused by passing vehicles.
AA3153 Beacon Antenna
The IT2200 Reader System with Multimode Capability uses either one or two
AA3153 Beacon Antennas for pillbox-type plaza installations.
Functions
In a monostatic configuration, the AA3153 Beacon Antenna acts as the downlink
antenna transmitting signals to the tag, and the uplink antenna receiving signals from a
vehicle tag. In a bistatic configuration, an AA3153 Antenna acts as the downlink
antenna transmitting signals to the tag, and another AA3153 Antenna acts as the
uplink antenna receiving signals from a vehicle tag.
Features
This antenna is specifically designed for use in toll lane applications, and transmits
and receives RF signals in the 902- to 928-MHz RF range. The AA3153Antenna
broadcast patter has virtually no side or back lobes, which helps to confine antenna
coverage to a single lane width. The antenna is enclosed in a weatherproof radome,
which is made of materials selected for favorable electrical characteristics and
resistance to ultraviolet radiation.
The beacon antenna is designed for outdoor use. The antenna operates without
performance degradation in hot or cold temperature extremes, strong wind, or
vibrations caused by passing vehicles.
IT2502 Check Tag Antenna
The IT2502 Check Tag Antenna is used to communicate with the check tag that is
located inside the RF module.
Check Tag
A check tag is a special-purpose tag that is integrated in the RF module and has a
separate check tag antenna.
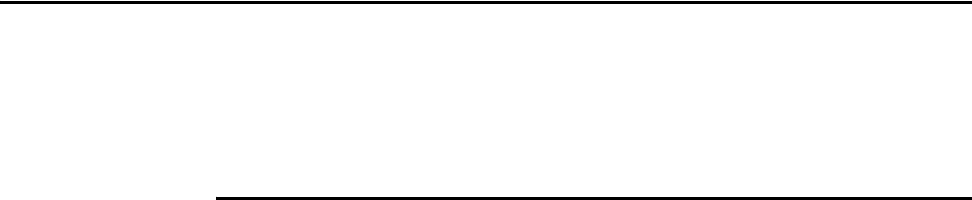
System Components
3-15
The check tag simulates a toll transaction, thereby providing a means for the reader to
check system operation. The check tag, activated on command by the lane controller,
provides a test of the antennas, RF source, preamplifier, encoder/decoder,
microprocessor, communications port, and I/O control.
The reader controls the check tag operation with an enable logic signal that lets the
check tag communicate through the reader in a manner similar to that of reading a
normal tag. The host computer can set the check tag to operate automatically at a
periodic rate or under command from the lane controller.
Check tag status failures permit troubleshooting and repair of sections of the system
(e.g., a lane), while the rest of the system remains operational.
Any data that is written to the check tag is erased if system power is lost. The default
check tag data is reloaded when system power is restored.
Tags
Tags are self-contained RFID devices that are capable of two-way communications
with a reader. Tags are available for interior or exterior installation. The IT2200
Reader System with Multimode Capability can read and write to IT2221, IT2211, and
IT2235 tags, and can read ATA tags. Tags used with the IT2200 system are passive,
battery powered. These tags are described in the following sections.
IT2221 Tag
The IT2221 Tag communicates with a reader via RF using an open protocol that has
been adopted by various transportation agencies. In addition, the IT2221Tag com-
mand set provides powerful capabilities for read/write access control and a non-pro-
prietary time division, multiple access (TDMA) protocol that can communicate with
multiple tags within an open-road configuration using a single reader. The multimode
version of this tag (IT2200 and ATA) is also available.
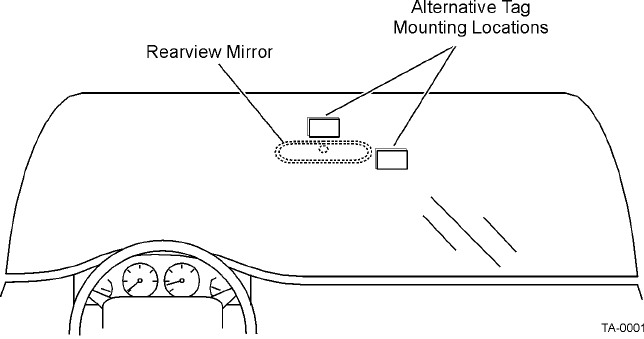
System Components
3-17
The IT2221 Tag is designed to be mounted inside a vehicle on the windshield (see
Figure 3-8). This tag has no visual displays or indicators and is used in all applications
where driver feedback is not necessary. The tag can be used on any vehicle.
Figure 3-8 Alternative Mounting Locations for IT2221 Tag
The remainder of this section describes the IT2221 Tag function and features.
Functions
The IT2221 Tag has the following technical and functional capabilities:
•Built-in self-test (BIST) capability to indicate random access memory (RAM)
failure or low battery
•Operational life of eight years, from time of manufacture
•-20°C to +75°C (-4°F to +167°F) operating temperature
•915-MHz band operation
•300kbps data rate transfer
•Read/write capability and 16 pages (256 bytes) of RAM
•Full data retention provided during a power loss
•Eight-year battery from time of manufacture
•Data protection using read and write passwords for each individual page
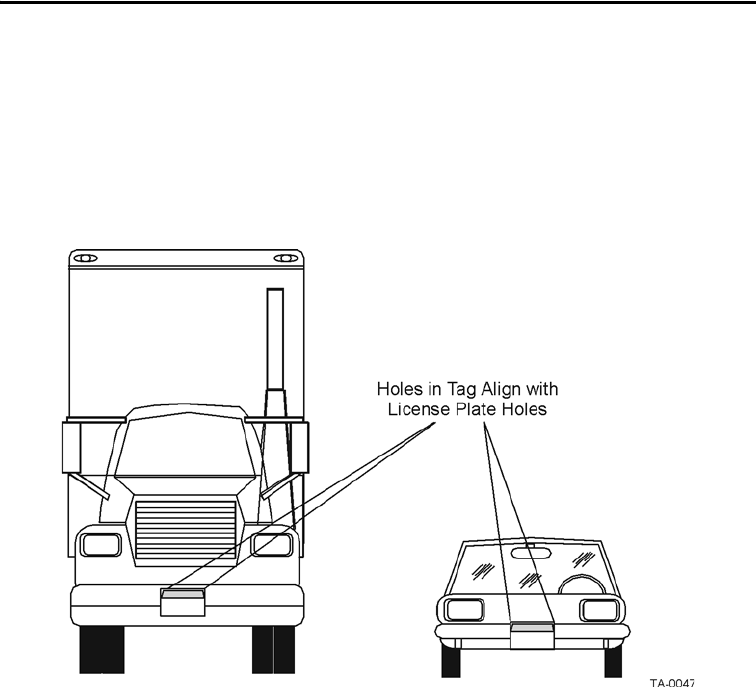
IT2200 Reader System with Multimode Capability Installation & Maintenance/Service Guide
3-18
Features
The IT2221 Tag design provides full internal diagnostics indicating status of the
following:
•Internal RAM
•Low battery voltage indication
•Splash resistant (sealed, waterproof version is also an option)
Results of the BIST are in the form of single-bit characters that are transmitted to a
lane controller the next time the tag enters a read zone. One of the following two mes-
sages is generated and sent to the lane controller if BIST results reveal a problem:
•Memory failure
•Low battery
IT2211 Exterior Tag
The IT2211 Exterior Tag is identical in functions and features to the IT2221 Tag, but
the IT2211 Exterior Tag circuitry is enclosed in a sealed watertight case that makes it
ideal for mounting on the exterior of a vehicle (see Figure 3-9). The tag's case pro-
vides resistance to chemicals and other agents typically found in transportation envi-
ronments and is UV stabilized. The IT2211 Tag can be mounted on either metallic or
non-metallic surfaces. A multimode version of this tag is planned for release in mid-
2001.
Figure 3-9 IT2211 Tag Placement
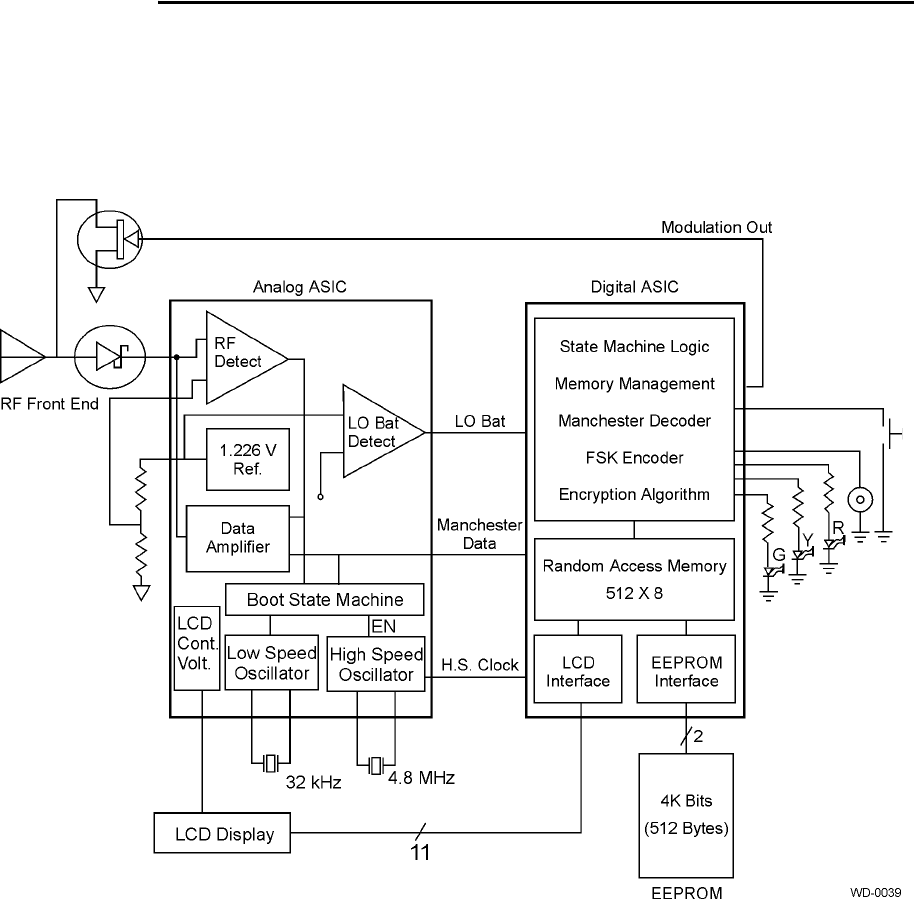
System Components
3-19
IT2235 Tag
The functionality of the IT2235 Tag is the same as that of the IT2221 Tag. However,
the IT2235 Tag has audio tones, LED lights, and an indicator screen to display trans-
action activity to the driver.
Figure 3-10 shows an IT2235 Tag block diagram.
Figure 3-10 IT2235 Tag Block Diagram
The IT2235 Tag is designed to be mounted inside a vehicle on the windshield (see
Figure 3-8). This tag uses visual and audio displays or indicators to provide the driver
with tag status and account information. The tag can be used on any vehicle.
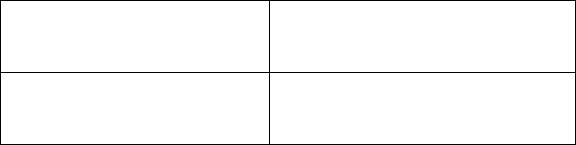
IT2200 Reader System with Multimode Capability Installation & Maintenance/Service Guide
3-20
Functions
The IT2235 Tag has the same BIST capability as the IT2221 Tag. Results of the
self-tests are stored and accessed in the same manner described for the IT2221 Tag. A
unique visual and/or audio indication can be activated on the tag by either a
programmer, portable reader, or in-lane reader as a means of providing notification of
these test results.
The rates for downlink messages and uplink messages are as follows:
The LCD alphanumeric display of the IT2235 Tag is activated in the following man-
ner:
•The LCD automatically displays messages during a transaction.
•The LCD displays on demand by pressing the button.
The tag’s alphanumeric LCD is automatically activated during the transaction to
display the messages indicated in this section. These messages have an automatic
shut-off after a time delay of 4 seconds and require no intervention from the patron. If
the patron wants to view additional messages sent by the toll agency, they are
available by scrolling through using the button. After a time delay of 4 seconds, the
LCD display clears itself, allowing the tag to go to a low power mode.
The alphanumeric LCD is also activated by pressing the button. The message readout
consists of 16 characters. The message displays on a single line for ease of reading.
Table 3-2 shows the condition code bits. These condition code bits each represent a
condition applicable to a tolling environment. There are 8 different conditions that can
arise, and there can be multiple conditions. The condition with the highest priority is
the sequence that is displayed upon receipt of a general ACK request. The other
conditions can be accessed by cycling to them using the pushbutton switch on the tag.
Downlink data rate Encoded: 300 kbps
Manchester decoded: 300 kbps
Uplink data rate Encoded: 600/1200 kHz
FSK decoded: 300 kbps
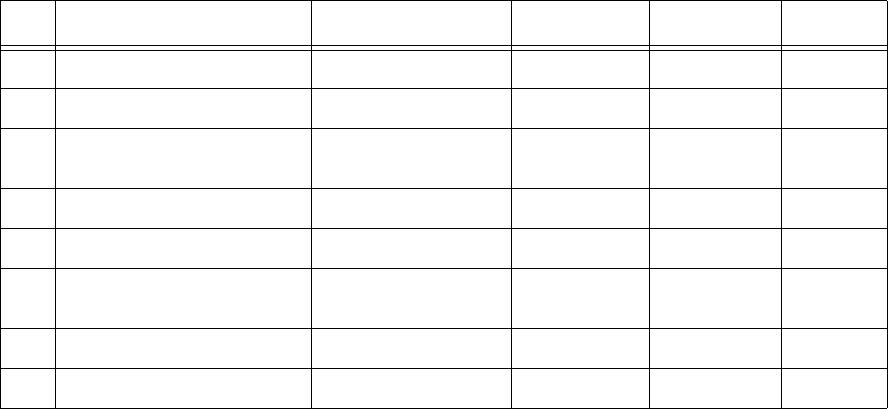
System Components
3-21
Table 3-2 Example of Condition Code Bit Programming for IT2235 Tag
Note: * Denotes that the data to be inserted in ±XXX.XX is pulled from the balance/
tolling page specified in page 0000 configuration.
Another method of displaying a message on the IT2235 tag is by using the LCD
custom message feature. This method allows the user to write a 16-byte maximum
ASCII message to a page in the tag and then command the message written to that
page to display upon receipt of the sign-off command. The tag is commanded to
display this information by setting a hex data field in the sign-off command, which is
called the LCD message page pointer.
The LCD message page pointer is a one-byte field that points to the page where the
LCD message to display is stored in ASCII. The valid range for the page pointer is
02H to 0FH. If this field is non-zero, the tag, upon receipt of a general ACK
command, displays this ASCII data to the LCD display from the page specified in this
field. The A/V sequence specified in the A/V options bits are associated with this
action. All condition code bits are stored for later retrieval by cycling with the
pushbutton.
Features
The IT2235 Tag features include an alphanumeric LCD; red, yellow, and green
light-emitting diode (LED) visual indicators; an audio buzzer with varying tonal
qualities; and a pushbutton for displaying the last reported toll balance and the last
message written to the tag (see Figure 3-11). The alphanumeric display is visible in all
daylight and nighttime conditions by use of LCD technology and backlighting.
Bit Condition Message Indicator Tone Priority
7 Negative list Invalid Red Low 1
6 Insufficient funds Insuff Bal Red Low 2
5 Low battery Low Battery Flash red Low-Low-
Low 3
4* Conversion to cash/ticket Cur Bal=±XXX.XX Flash green Low-High 4
3* Account replenishment New Bal=±XXX.XX Flash green High-High 5
2 Good read/low balance Low Balance Yellow High-Low-
High-Low 6
1* Good read Toll=±XXX.XX Green High 7
0 Good read/Pass used Pass used Green High 8
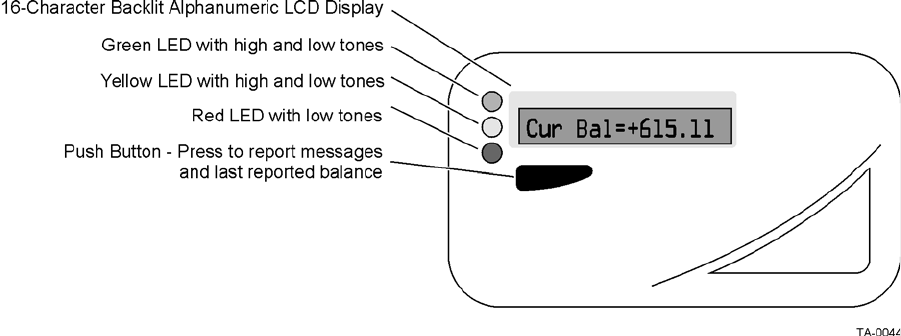
IT2200 Reader System with Multimode Capability Installation & Maintenance/Service Guide
3-22
Figure 3-11 IT2235 Tag Display Features
The IT2235 Tag is suitable for mounting inside a vehicle and operates from the
interior of any vehicle type. The IT2235 Tag has read/write capability and the same 16
pages of random access memory (RAM) as those described in the IT2221 section.
The IT2235 Tag is capable of displaying a variety of messages on the alphanumeric
LCD with additional signals provided through audible tones and lights. The light,
tone, LCD indications, and a subset of the tag messages are provided in the tables
shown in this section.
The character height of 5 mm (0.2 in) provides ample viewing detail from
approximately 0.9 m (3 ft) or less from the display. To provide sufficient readability in
all light conditions, backlighting is supplied and is activated while a message displays.
The IT2235 Tag has a pushbutton that provides a method of cycling through the
last-sent message and the last-reported patron account balance. The pushbutton is in
compliance with the environmental requirements of the tag. Because the LCD
displays a message when the button is pressed, backlighting will also be activated.
Each push of the button causes the next condition code to display, with a short beep
(100-ms ±10% duration) to confirm key press, until all of the conditions are cycled
through. The balance will then display at the end of all other stored conditions or LCD
messages. This cycle repeats until the tag times out (four seconds) and goes into idle
mode. At a minimum, the balance will be displayed upon button push, and nothing
else cycles on subsequent pushes. At a maximum, eight conditions can be cycled by
subsequent pushes. RF commands always have priority over the display of any LED,
LCD, or audio tones.
The IT2235 Tag has LED-type lights to provide visual alarms and messages in the
form of on/off or flashing signals. Three LEDs will accommodate red, yellow, and
green signals in a variety of sequences (Table 3-3).

System Components
3-23
Table 3-3 Audio/Visual Options Bits Decoding for IT2235 Tag
The IT2235 Tag produces two distinct and discernible audible signals. These signals
are in the form of high and low frequencies referred to as a beep (high frequency) HI,
or a buzz (low frequency) LO. These two different tones are used to generate the
various sequences as requested by the customer.
RF commands always have priority over the display of any LED, LCD, or audio tones.
ATA Tag
In ATA mode, the tags are read-only and do not use a reader-to-tag modulated signal.
When powered, and in the presence of an unmodulated signal, ATA tags always
attempt to backscatter.
Tag Programmer
Tag programmers are used to write data to and read data from tags that are used in an
RFID system.
Bit 4 Bit 3 Bit 2 Bit 1 Bit 0 LED
Sequence Audio
Sequence
00000None None
00001aLong Green
a. Denotes that the LED stays on for 1 second longer than the audio.
HI-HI-HI-HI
00010aLong Red LO-LO-LO-LO
00011aFlash Green LO-HI
00111aLong Red Long LO
01011aLong Yellow HI-LO-HI-LO
01111aFlash Red LO-LO-LO
10011aLong Green HI-HI-HI
10111aFlash Green HI-HI
11011aLong Green Long HI
11101aShort Red LO
11110Short GreenHI
11111bGreen-
Ye llow -R e d
b. Denotes that this sequence is used for testing.
HI
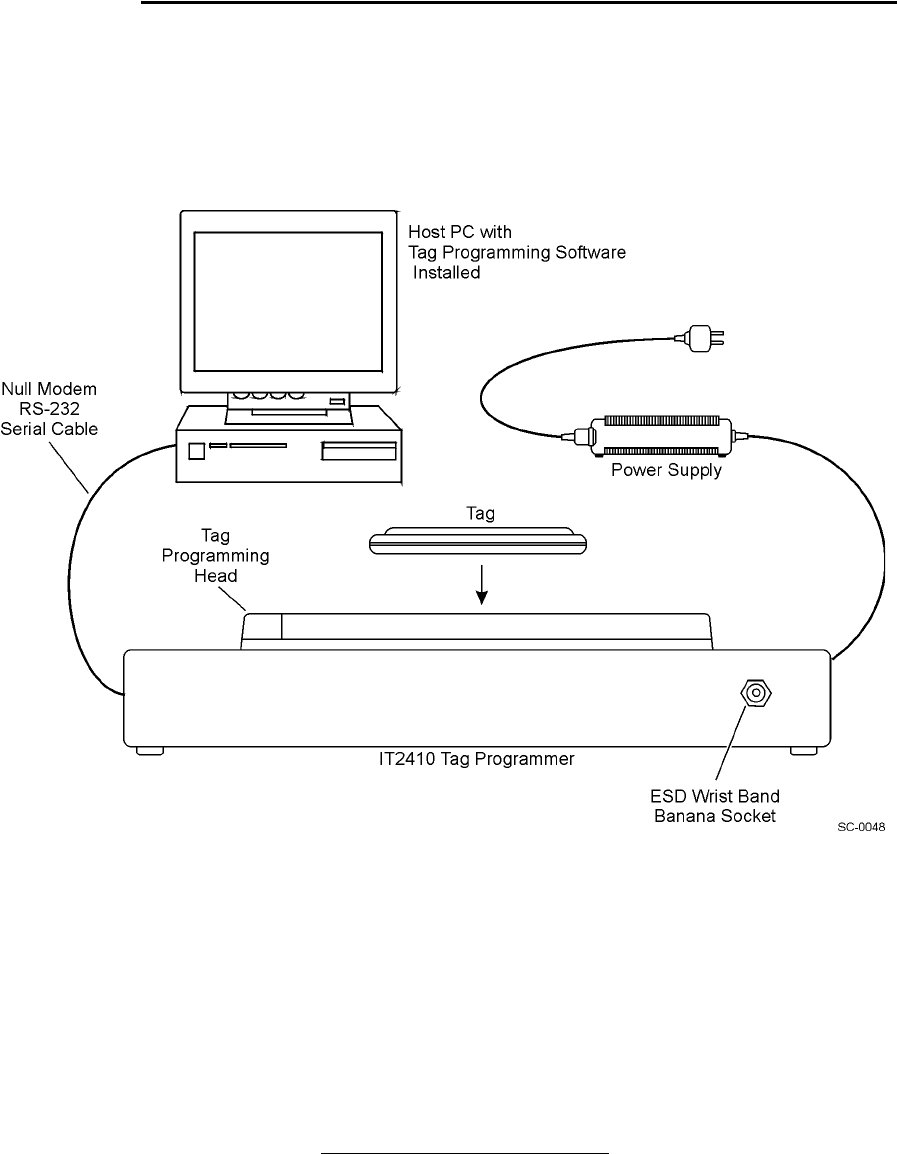
IT2200 Reader System with Multimode Capability Installation & Maintenance/Service Guide
3-24
IT2410 Tag Programmer
The IT2410 Tag Programmer1 is part of a system that is used to program IT2200-
series tags (Figure 3-12). The IT2410 Tag Programmer cannot program ATA tags.The
IT2410 Tag Programmer can be used to select a number of standard formats or
develop a unique, customized format to meet specific application needs.
Figure 3-12 IT2410 Tag Programmer System
Functions
Programmer functions include programming tag data pages, locking fixed data pages,
and interrogating all data pages. Tag data pages can be easily programmed and locked
with a password.
Transferring programmed data to the tag is simple. Once the code is downloaded or
entered into the host, the user issues a command to initiate code transfer to the tag
programmer. The programmer then automatically transfers data to or reads data from
the tag.
1. For complete installation and programming instructions for the tag programmer, refer to
Amtech® document Intellitag IT2000 Programmer User Guide (Document No. 411013).
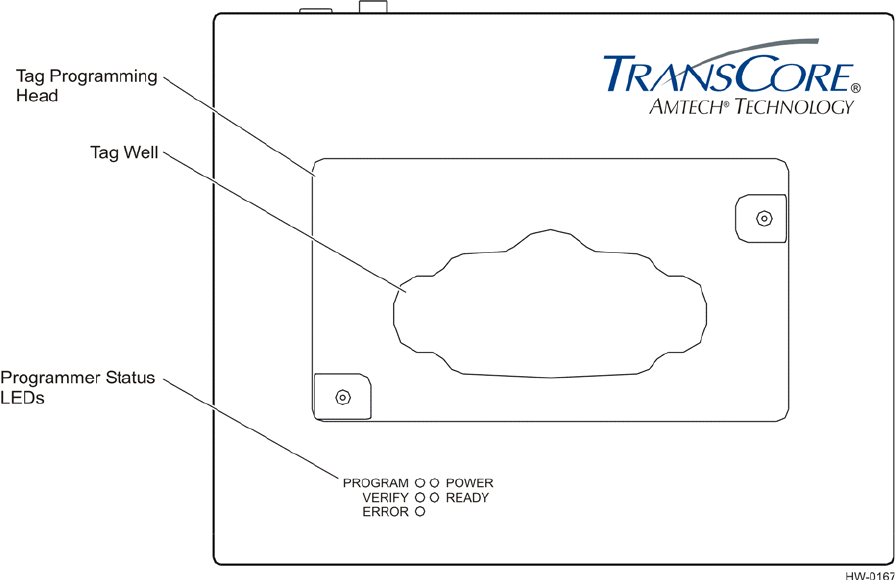
System Components
3-25
The tag programmer is connected to a PC port that complies with the RS-232
communications interface standard.
Features
The programming head on the top of the programmer provides a mechanical interface
to the tag. The programming head includes a drop-in tag well that is compatible with
the IT2200-series tags. By placing the tag in the tag well on the head, the tag is
correctly positioned to the programmer’s internal antenna. Figure 3-13 illustrates the
tag programming head.
Figure 3-13 Tag Programming Head
The IT2410 Tag Programmer includes a simple interface that is compatible with
computing equipment used in host computers. The link between the programmer and a
patron account workstation is provided by an RS-232 communications port running at
19200 bps. The programmer is designed to read from and write to a tag at distances up
to 5.08 cm (2 in) from the programmer head. The IT2410 Tag Programmer provides a
highly reliable and focused RF pattern for programming only the tag on the
programming head without interacting with any other tags in the area. The RF
transmission of the programmer is active only during the read/write operation.
All control and monitor accessories are easily available to the user from the outside of
the programmer.
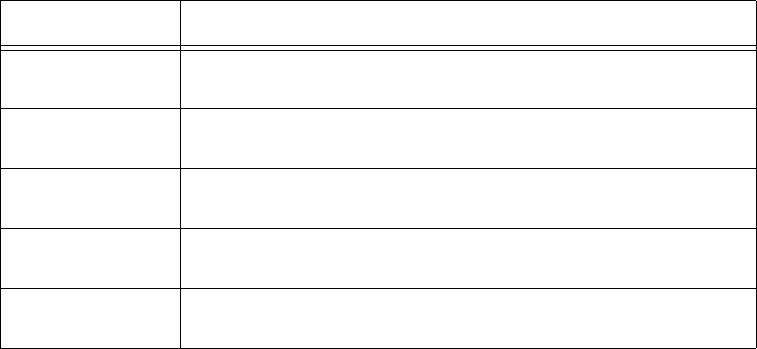
IT2200 Reader System with Multimode Capability Installation & Maintenance/Service Guide
3-26
As shown in Figure 3-13, all indicators are located on the top face of the programmer.
The functional indicators of the tag programmer are listed in Table 3-4.
Table 3-4 IT2410 Tag Programmer Indicator LEDs and Descriptions
The tag programmer also has the following features:
•FCC compliant—The programmer has been tested and found to comply with the
limits established by the FCC for a Class A computing device.
•AC power—The programmer is powered from a standard 120 VAC outlet. A UL-
approved 12 VDC power module is included.
Indicator LED Description
PROGRAM
(GREEN) The tag is being programmed with user-specified data.
VERIFY
(GREEN) The tag programmer has read valid data from the specified tag
frame.
ERROR (RED) The tag programmer has detected an error in the programming
or verifying process or during other operations.
POWER
(GREEN) Power is being supplied to the tag programmer.
READY
(GREEN) The tag programmer is ready to accept commands from the
PC.

4
Installing the IT2200 Reader System
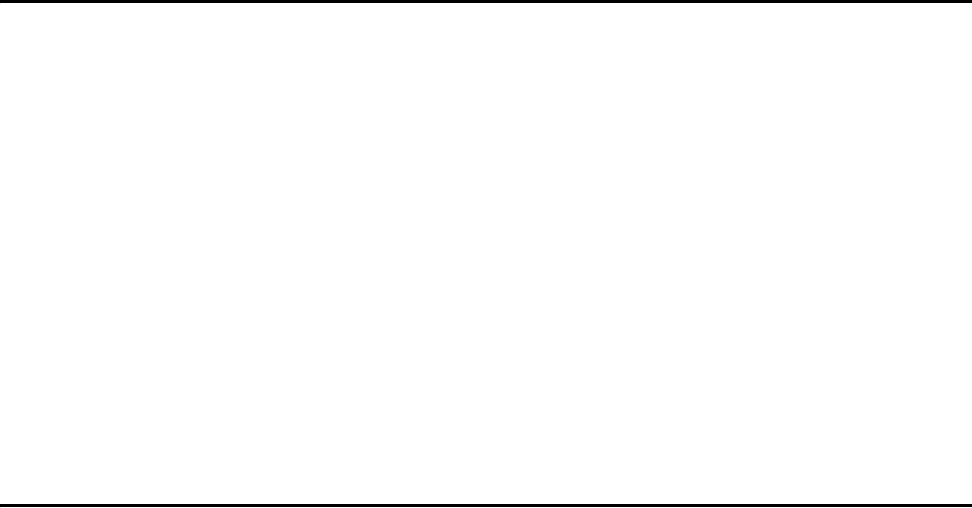
4-3
Chapter 4
Installing the IT2200 Reader System
This chapter includes information on:
Assessing the Site — Instructions for conducting an RF survey of the
chosen site and formulating a frequency plan.
Preparing the Site — Checklist of tasks involved in preparing a site for
installation.
Installing the System — Checklist of required components and a
checklist of installation tasks. Description of where to mount the reader
system components for several typical site configurations. Step-by-step
instructions for installing the system.
Assessing the Site and Formulating a Frequency Plan
Perform an RF site survey to check for RF noise sources near the toll plaza or toll lane
being installed. Use a spectrum analyzer and a horizontally polarized whip antenna.
(TransCore recommends a Agilent Technologies Model 8523 spectrum analyzer.)
•Set up the test equipment under the plaza canopy, if possible, or within a 15m (50-
ft) radius of the plaza.
•Record any frequencies operating in the 902 to 904 MHz or the 909.75 to 921.75
MHz bands.
•If you find frequencies within these bands, check the power level. Power levels
exceeding -10dBm could possibly alter the consideration of installing the system
at this site or the frequency plan for the system. Consult with Amtech® if you
encounter this problem.
Formulate a frequency plan for the plaza. There are two frequencies for each reader:
downlink (reader-to-tag communication) and uplink (tag-to-reader response). For this
system, all readers share the same downlink frequency, which is generally set to
918.75 MHz. Uplink frequencies should alternate between adjacent lanes. For exam-
ple, a four-lane plaza would have the frequencies shown in Table 4-1.
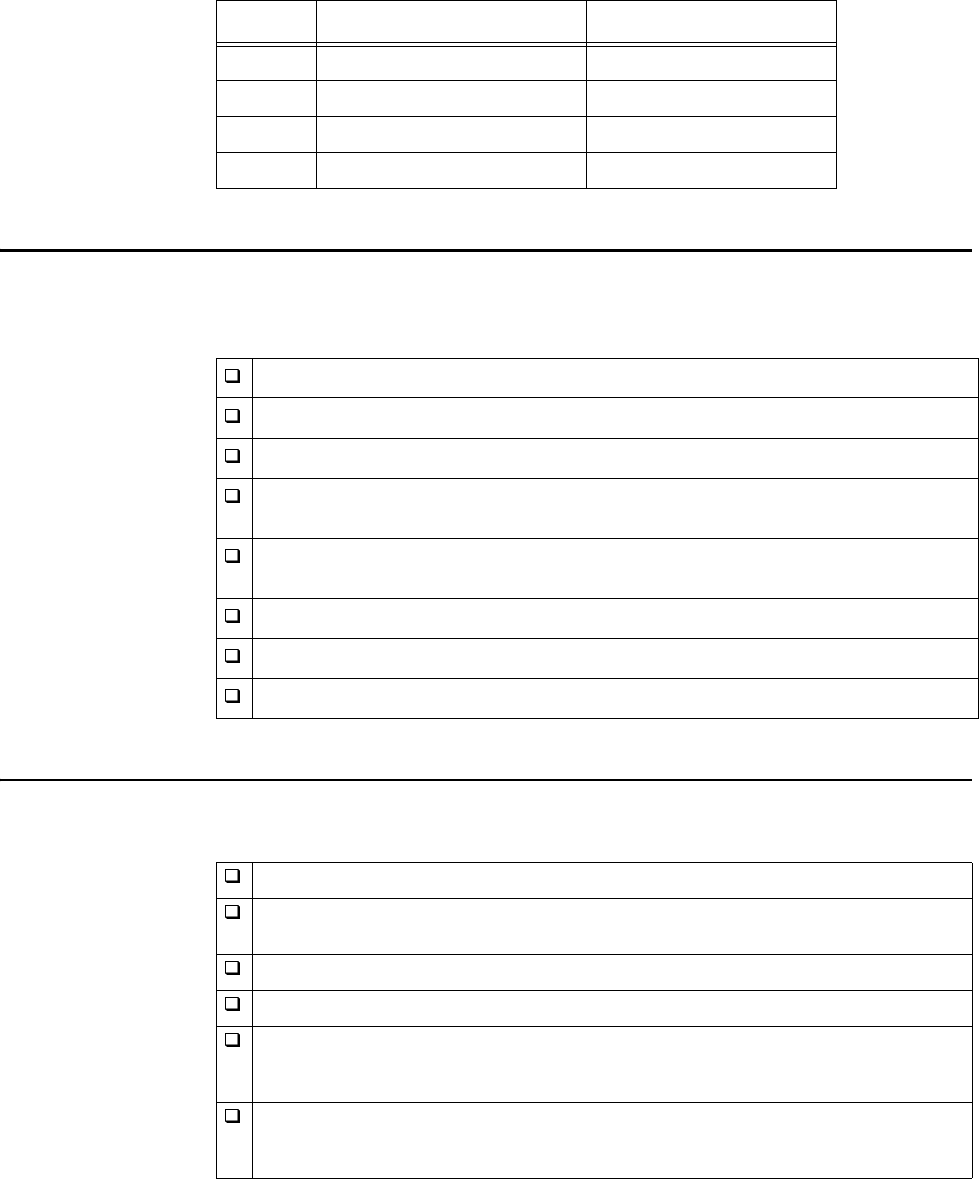
IT2200 Reader System with Multimode Capability Installation & Maintenance/Service Guide
4-4
Table 4-1 Example Frequency Plan for Four-Lane Plaza
Site Preparation Checklist
Prepare the site according to the design parameters determined by your system inte-
grator. Some of the tasks you should complete, depending on the individual site, are
Components Checklist
Ensure you have the following components available for each lane to be installed:
Lane Downlink Frequency Uplink Frequency
1 918.75 MHz 903.00 MHz
2 918.75 MHz 912.00 MHz
3 918.75 MHz 903.00 MHz
4 918.75 MHz 912.00 MHz
Acquire a construction license.
Acquire an FCC license.
Acquire an environmental assessment permit.
Ensure that you have assembled all the lights, buzzers, and vehicle detectors
that will interface with the system.
Ensure that you have software that allows a PC or laptop to interface with the
reader firmware.
Pull communications, coaxial, and power cables through outdoor-grade conduit.
Ensure that construction work required for mounting the equipment is completed.
Ensure that 120 V AC service is available.
IT2020 Reader Logic Card
One or two AA3152 or AA3153 antennas (depending on whether the installation
is monostatic or bistatic, and plaza type)
IT2502 Check Tag Antenna
IT2611 RF Module
One or two RF-grade coaxial cables with Type N connectors to link the
antennas to the RF module (depending on whether installation is monostatic or
bistatic)
Tag data/control cable (data cable) to link the RF module to the reader logic
card. The cable must have a DB-25 plug connector and a 26-pin circular socket
connector (Souriau 851-06RJ16-26S50 or equivalent).
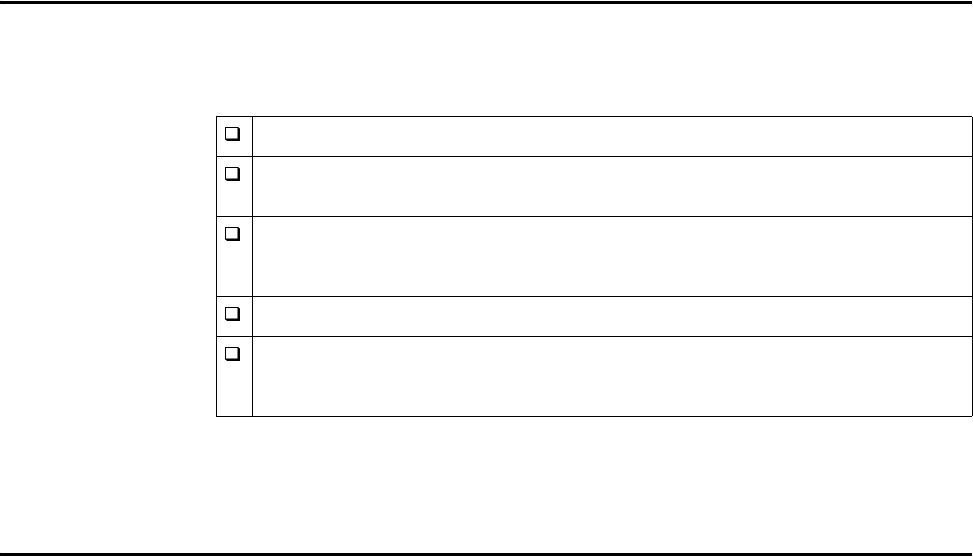
Installing the IT2200 Reader System
4-5
Task Checklist
This checklist summarizes the installation procedure. Instructions for each task are
provided in the “Installing the IT2200 Reader System” section later in this chapter.
After installing a reader system in each lane, it is necessary to tune each lane as
described in Chapter 5, “Tuning the Lane.”
Where to Mount the Components
The location for mounting the components is designated in the site installation plan.
Most Electronic Toll Collection (ETC) site layouts are similar. Four typical mounts
are the canopy, overhead gantry, overpass, and cantilever arm mounts. A fifth config-
uration is the laneside or pillbox antenna mount.
Test data cable for proper continuity and isolation.
Install reader logic card in host computer. Connect data cable to reader logic
card.
Mount RF module. Connect either 19 to 28 VAC or 16 to 28 VDC power to RF
module. Verify voltage with RF module powered (loaded voltage measurement).
Proper voltage is 19 to 28 VAC or 16 to 28 VDC.
Connect data cable to RF module.
Mount transmit and receive antennas (bistatic installation) or transmit/receive
antenna (monostatic installation), and check tag antennas. Connect antenna(s)
to RF module.
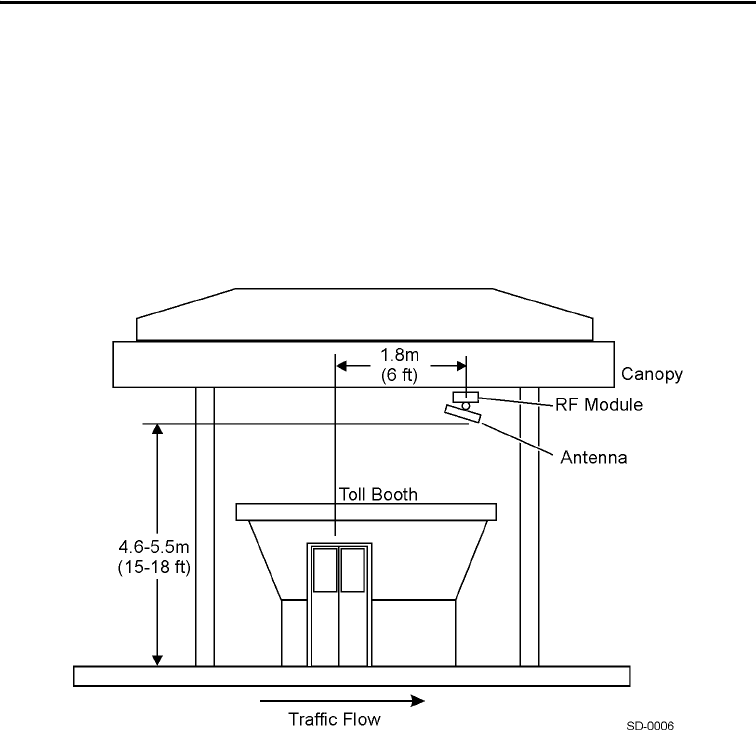
IT2200 Reader System with Multimode Capability Installation & Maintenance/Service Guide
4-6
Canopy Mount
The canopy mount is typically used for covered toll plazas. The reader logic card is
installed in the host computer. The RF module, Universal Toll Antenna(s) (UTA), and
check tag antenna are attached to a 5.0 to 7.6cm (2- to 3-in) pipe that is supported
from the plaza canopy. The pipe is located approximately 4.5 to 5.5 m (15 to 18 ft)
above the road surface and 1.8 m (6 ft) downstream of the collection point. The collec-
tion point is the centerline of the toll booth door, coin basket, or light curtain, depend-
ing on the site configuration. Figure 4-1 illustrates a typical canopy mount.
Figure 4-1 Canopy Mount
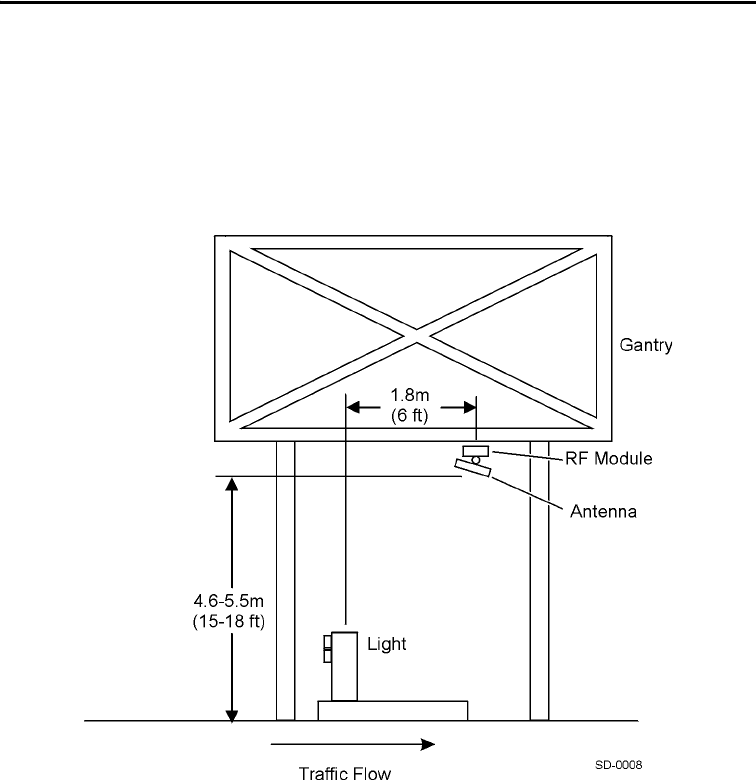
Installing the IT2200 Reader System
4-7
Overhead Gantry Mount
In the overhead gantry mount, the reader logic card is installed in the host computer,
and the RF module, UTA(s), and check tag antenna are attached to a 5.0- to 7.6-cm (2-
to 3-in) pipe that is supported from a gantry that spans the lanes. These components
are mounted approximately 4.5 to 5.5 m (15 to 18 ft) above the road surface.
Figure 4-2 illustrates a typical overhead gantry mount.
Figure 4-2 Overhead Gantry Mount
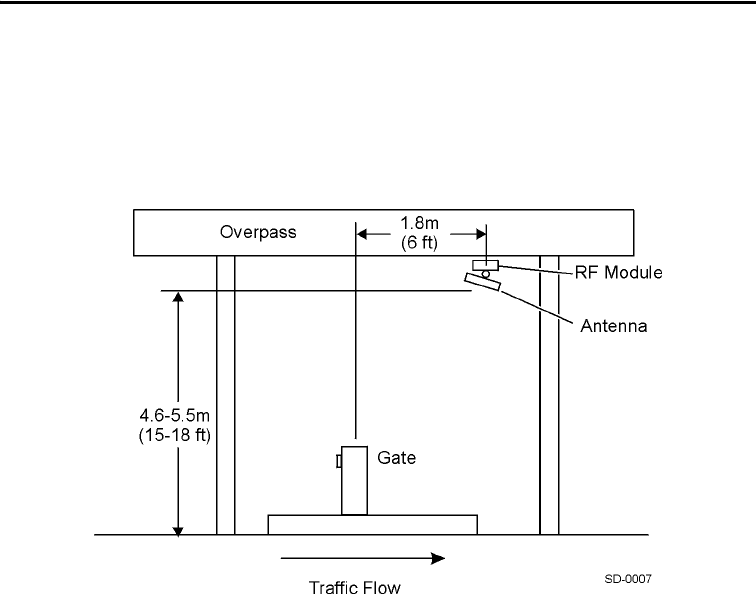
IT2200 Reader System with Multimode Capability Installation & Maintenance/Service Guide
4-8
Overpass Mount
In the overpass mount, the reader logic card is installed in the host computer, and the
RF module, UTA(s), and check tag antenna are attached to a 5.0 to 7.6cm (2- to 3-in)
pipe that is supported from an overpass. These components are mounted approxi-
mately 4.5 to 5.5 m (15 to 18 ft) above the road surface.
Figure 4-3 Overpass Mount
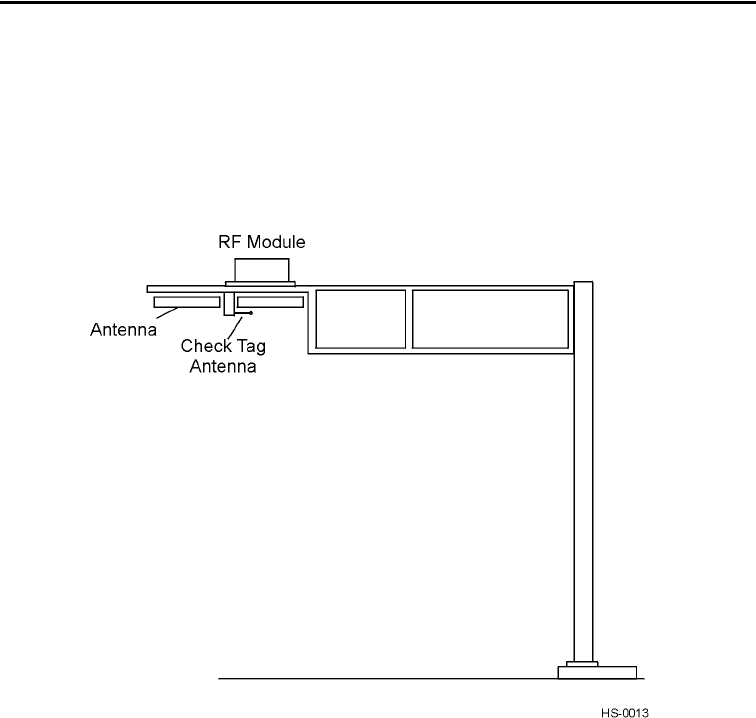
Installing the IT2200 Reader System
4-9
Cantilever Arm Mount
In the cantilever arm mount, the reader logic card is installed in the host computer, and
the RF module, UTA(s), and check tag antenna are attached to a 5.0 to 7.6cm (2- to 3-
in) pipe at the end of the cantilever arm. These components are mounted approxi-
mately 4.5 to 5.5 m (15 to 18 ft) above the road surface. Figure 4-4 illustrates a typical
bistatic laneside cantilever arm mount with two antennas.
Figure 4-4 Cantilever Arm Mount (Bistatic Configuration)
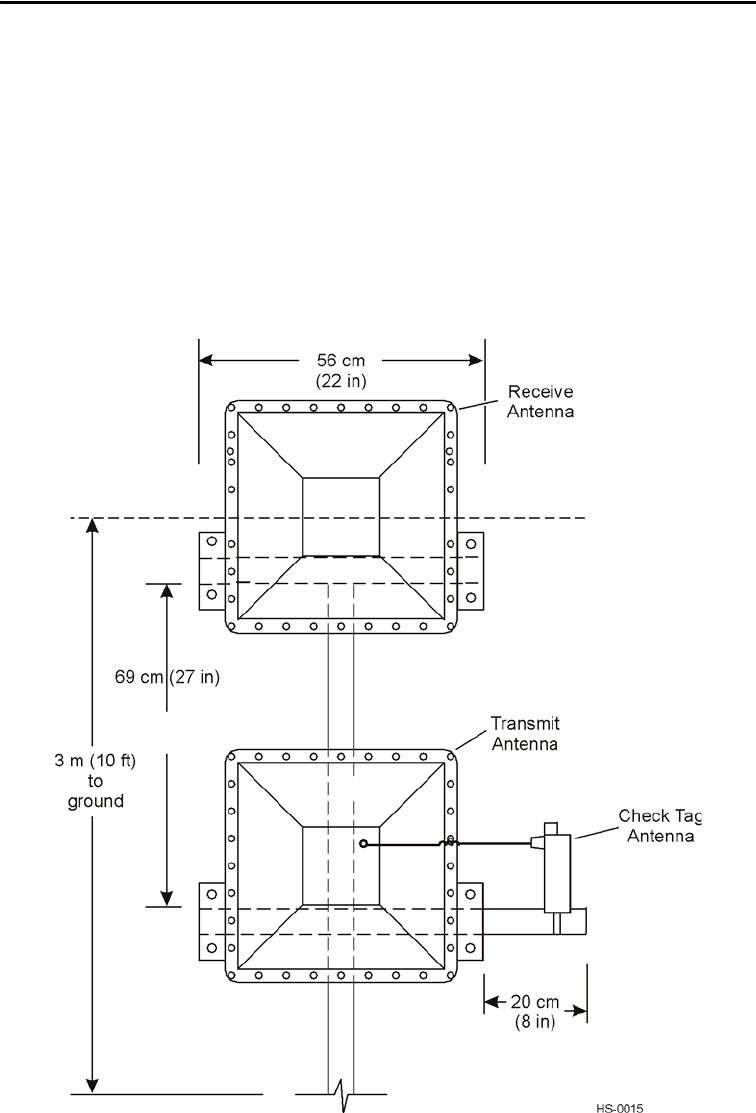
Installing the IT2200 Reader System
4-11
Laneside “Pillbox” Mount
The laneside mount is typically used with the AA3153 Beacon Antenna for pillbox
installations. The reader logic card is installed in the host computer. For bistatic con-
figuration, the receive antenna is mounted on a horizontal section of 5.0 to 7.6cm (2-
to 3-in) wide by 56-cm (22 in) long horizontal pipe mounted 3m (10 ft) above the
ground on a vertical pole. The transmit antenna is mounted to a horizontal section of
76cm (30-in) long pipe that is 69 cm (27 in) below the upper pipe. The check tag
antenna is mounted next to the transmit antenna. The RF module can be mounted next
to the antennas or in a sheltered location nearby. Figure 4-6 illustrates a typical bistatic
laneside mount.
Figure 4-6 Bistatic Laneside Mount
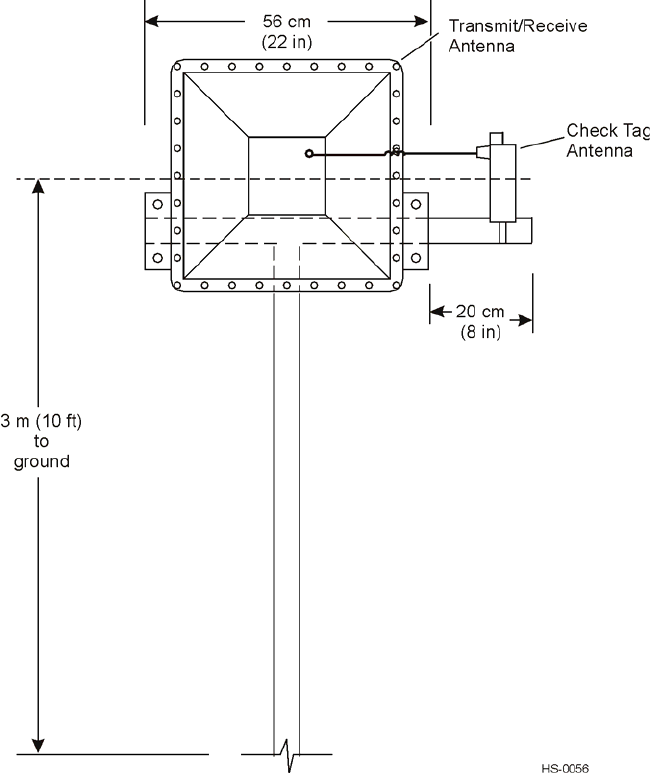
IT2200 Reader System with Multimode Capability Installation & Maintenance/Service Guide
4-12
For monostatic configuration, the transmit/receive antenna is mounted on a horizontal
section of 5.0 to 7.6cm (2- to 3-in) wide by 56cm (22-in) long horizontal pipe
mounted 3m (10 ft) above the ground on a vertical pole. The check tag antenna is
mounted next to the transmit/receive antenna. The RF module can be mounted next to
the antenna or in a sheltered location nearby. Figure 4-6 illustrates a typical mono-
static laneside mount.
Figure 4-7 Monostatic Laneside Mount
The exact placement of the antenna for a pillbox installation depends on the site con-
figuration. The placement is the same for both bistatic and monostatic configurations.
Figure 4-8 shows the antenna placement for a typical pillbox installation.
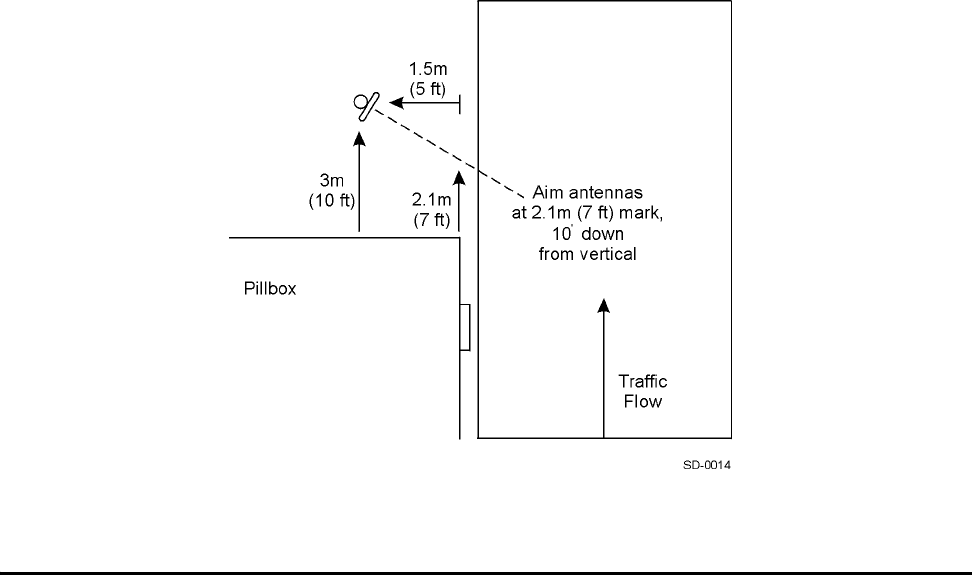
Installing the IT2200 Reader System
4-13
Figure 4-8 Antenna Placement for Pillbox Mount
Installing the IT2200 Reader System
This section contains instructions for installing each component of the reader system.
In addition to standard tools, you need the following equipment to install the system:
•Wrist strap for electrostatic discharge (ESD) protection
•Hydraulic lift
•Torque wrench
•Inclinometer
•Multimeter, Fluke 87 or equivalent
•Loopback connector for testing data cable. Use a DB-25 connector to make the
loopback connector. Short the pins listed in Table 4-2. Refer to Table D-13,
“LEDs,” on page 18 in Appendix D to this manual for a complete listing of
IT2611 RF Module-to-IT2020 Reader Logic Card interface connector pin-outs.
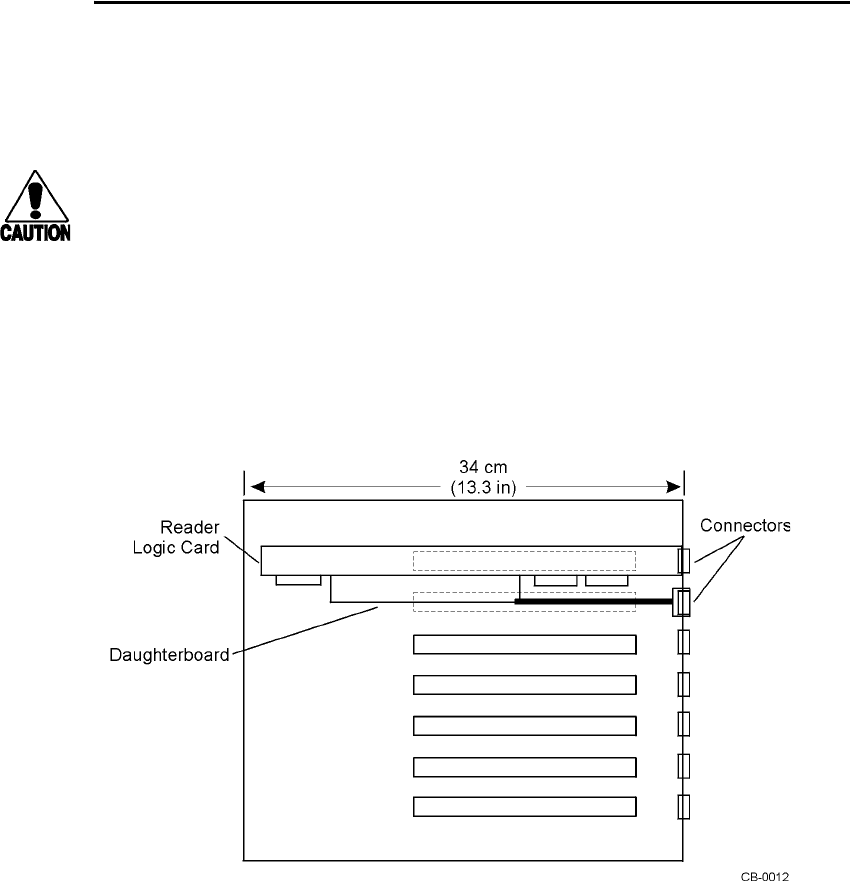
IT2200 Reader System with Multimode Capability Installation & Maintenance/Service Guide
4-14
Table 4-2 Listing of Shorted Pins for Loopback Connector
Installing the IT2020 Reader Logic Card
This section describes the installation of the IT2020 Reader Logic Card in a host com-
puter or lane controller. Details of installation may vary slightly depending on the site
configuration.
Caution
Wear a wrist strap when handling and installing the reader logic card. Failure to do
so can result in ESD damage to the card.
Figure 4-9 shows a reader logic card installed in a typical host computer or lane con-
troller chassis. Because of its daughterboard and two connector panels, the reader
logic card occupies two slots. One ISA slot provides power and communications
through the card’s edge connector and provides access to the frequency mode switch
and RS-232 port on the back of the card. The other slot provides space for the RF
module interface.
Figure 4-9 IT2020 Reader Logic Card Installed in Typical Host Computer or
Lane Controller Chassis (top view)
1 - 15
3 - 14
4 - 18
6 - 17
8 - 22
9 - 20
11 - 25
12 - 23
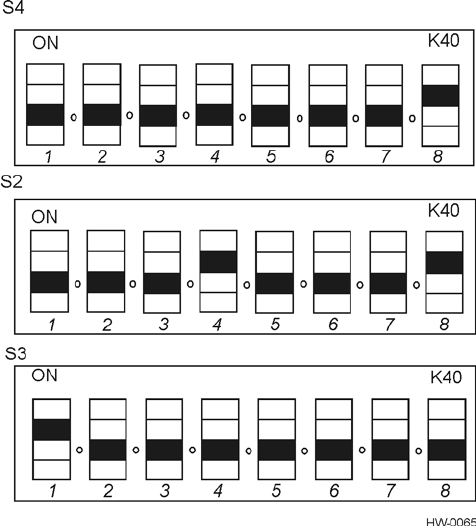
Installing the IT2200 Reader System
4-15
To install the reader logic card
1. Connect the loopback connector to the data cable, then test the cable for
continuity and isolation.
2. Remove the reader logic card, which is still in its ESD protective bag, from the
shipping box.
3. Put on the protective wrist strap; be sure it is properly grounded.
4. Remove the reader logic card from the ESD protective bag.
5. Verify that dipswitches S2, S3, and S4 are still set to the factory settings shown in
Figure 4-10. Refer to page D-3 in Appendix D to this document for configuration
settings information.
Figure 4-10 IT2020 Reader Logic Card Factory Dipswitch Settings
6. Set the frequency-enable switch (S1) to the left (normal) position as shown in
Figure 4-11.
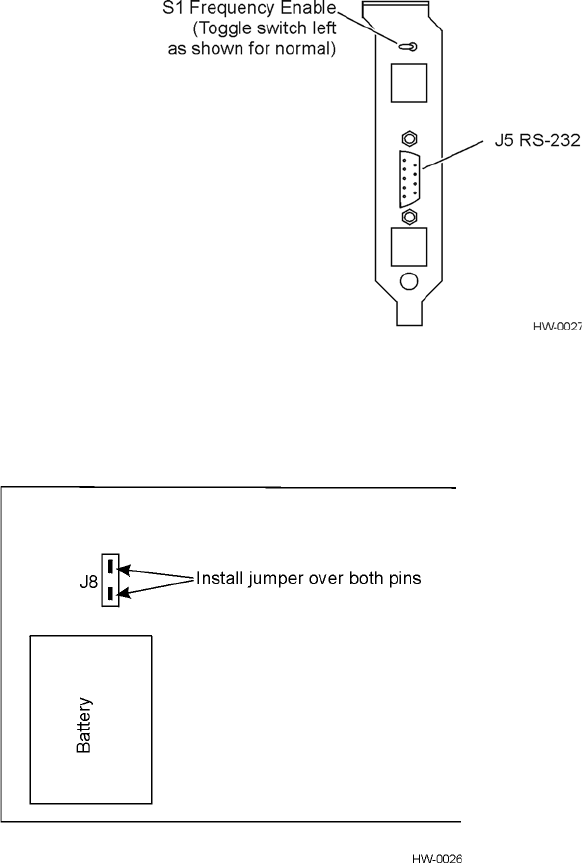
IT2200 Reader System with Multimode Capability Installation & Maintenance/Service Guide
4-16
Figure 4-11 Frequency Enable Switch on Rear of IT2020 Reader Logic Card
7. Locate the battery jumper (might be on J8 or be loose in the ESD bag) and install
over both J8 pins (see Figure 4-12).
Figure 4-12 Location of Battery Jumper (J8) in Relation to Battery
8. Turn off the host computer.
9. Insert the reader logic card in an ISA slot in the host computer. Be sure the card’s
edge connector is firmly seated, then secure the card with the retaining screw.
10. Install the reader logic card’s RF interface connector in a slot next to the reader
logic card, then secure the connector with the retaining screw.
11. Do not turn on the host computer until ready to test the system as described in
Chapter 5.

Installing the IT2200 Reader System
4-17
Installing the IT2611 RF Module
The IT2611 RF Module should be mounted on a 5.0 to 7.6cm (2- to 3-in) pipe. A
mounting kit is provided with each RF module that includes:
•RF module
•Two U-bolts
•Two brackets
•Four spacers
•Eight nuts
•Four lock washers
•Shrink tubing
Figure 4-13 shows the correct way to mount the RF module.
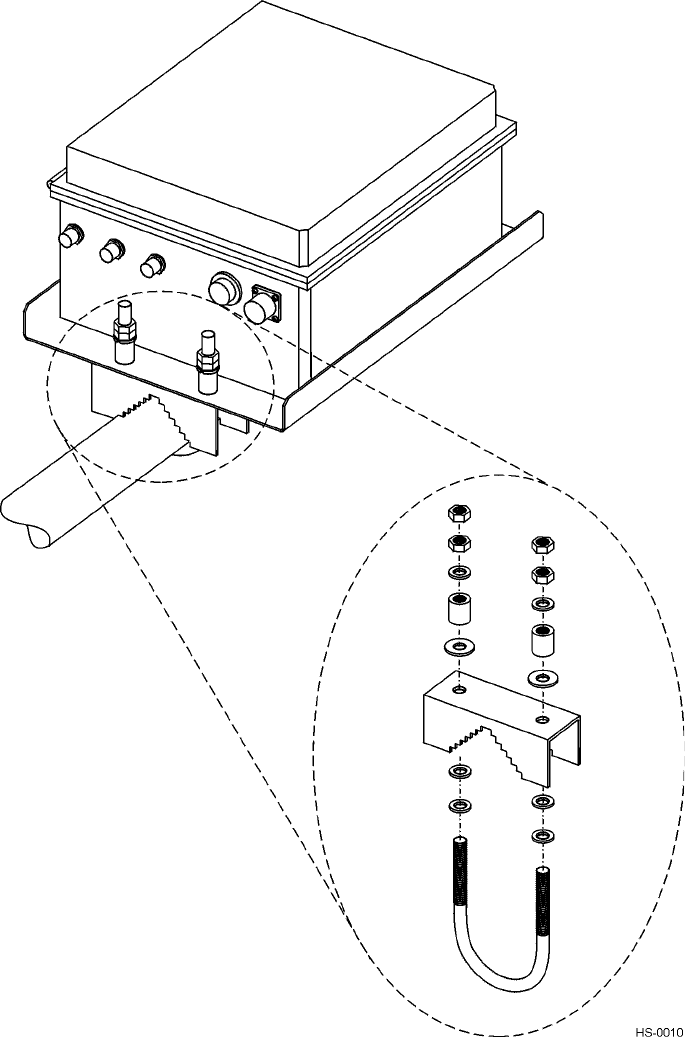
IT2200 Reader System with Multimode Capability Installation & Maintenance/Service Guide
4-18
Figure 4-13 IT2611 RF Module Mounting and Components for Both Monostatic
and Bistatic Configurations
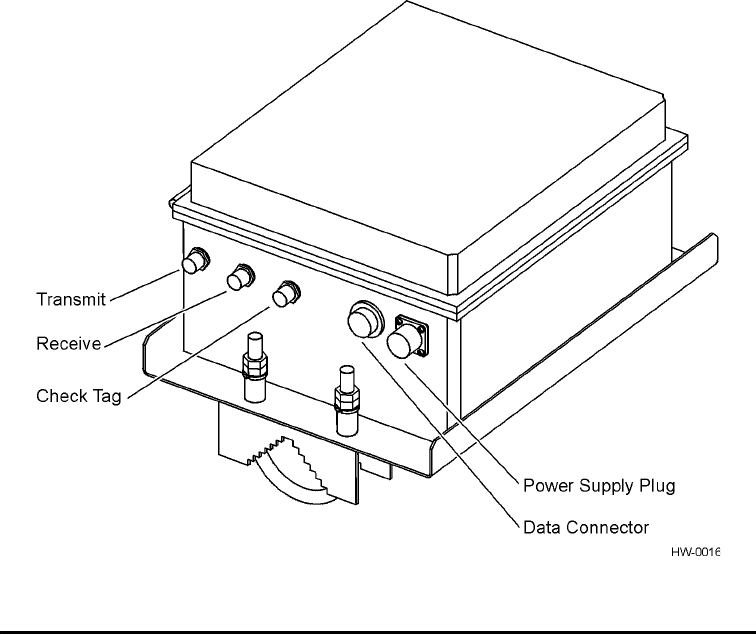
Installing the IT2200 Reader System
4-19
To install the RF module
1. Locate the RF module atop the mounting pipe and insert a U-bolt around the pole
and up through the bracket. Place a spacer over each section of the U-bolt
protruding through the bracket and place a lock washer and nut over each side of
the U-bolt. Repeat for the other U-bolt.
Note: Depending on pole diameter, spacers may or may not be needed.
2. Tighten nuts with torque wrench to 68 N-m (50 ft-lb). Tighten second nut over
first nut to lock it in place.
3. Check that 19 to 28 VAC or 16 to 28 VDC power is available at the module end
of the power cable. Measure the voltage across pins A and C of the power cable
connector.
4. Connect the power cable to the RF module’s power supply plug (Figure 4-14).
5. Connect the data cable to the RF module’s data connector.
Figure 4-14 IT2611 RF Module Connectors (Monostatic RF Module Shown)
Installing the AA3152 UTA
The UTA is mounted on a 5.0 to 7.6cm (2- to 3-in) pipe to accommodate various
angles for lane tuning. Two UTAs are required for each dedicated or mixed-use lane
in a bistatic configuration. One UTA is required for each dedicated or mixed-use lane
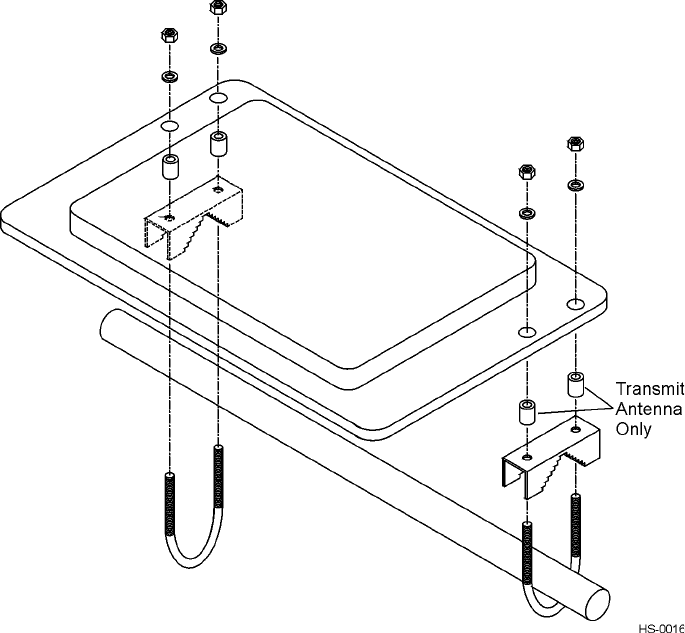
IT2200 Reader System with Multimode Capability Installation & Maintenance/Service Guide
4-20
in a monostatic configuration. A mounting kit is provided with each antenna that
includes:
•Antenna
•Two U-bolts
•Two brackets
•Four spacers
•Eight nuts
•Four lock washers
•One length of heat-shrink tubing
Figure 4-15 shows the correct way to mount and connect a UTA.
Figure 4-15 AA3152 UTA Mounting and Connections
Note: When installing the UTA use only the mounting hardware provided. Do not use
oversized washers to secure the plastic radome to the bracket. This practice can
weaken the radome material.

Installing the IT2200 Reader System
4-21
To install the UTA
1. Locate the UTA that will be used as the transmit antenna below the mounting
pipe and insert a U-bolt around the pole and down through the bracket on the side
of the antenna closest to the center of the lane. Place a lock washer and nut over
each side of the U-bolt, but do not tighten the nuts. Repeat for the other U-bolt,
but install two of the supplied spacers between the bracket and the antenna to
angle the antenna toward the center of the lane.
2. For bistatic installation, mount the second UTA the same way, but mount it on
the other side of the RF module from the transmit antenna and do not add
spacers.
3. Rotate each antenna up and toward oncoming traffic. Rotate up 15° from
horizontal for a dedicated lane or 10° up for a mixed-use lane. Use an
inclinometer to check the angle.
4. Tighten nuts with torque wrench to 68 N-m (50 ft-lb).
5. Slide the shrink tubing over the coaxial cable, but do not heat it.
6. Connect the coaxial cable to the antenna and to the appropriate connector on the
RF module. Leave the shrink tubing loose until you have finished tuning the lane.
Installing the AA3153 Beacon Antenna
Two beacon antennas are required for each lane in a bistatic configuration. One bea-
con antenna is required for each lane in a monostatic configuration.
A mounting kit is provided with each antenna that includes:
•Antenna
•Two U-bolts
•Two brackets
•Four spacers
•Eight nuts
•Four lock washers
•One length of heat-shrink tubing
Figure 4-16 shows the correct way to mount an AA3153 antenna.
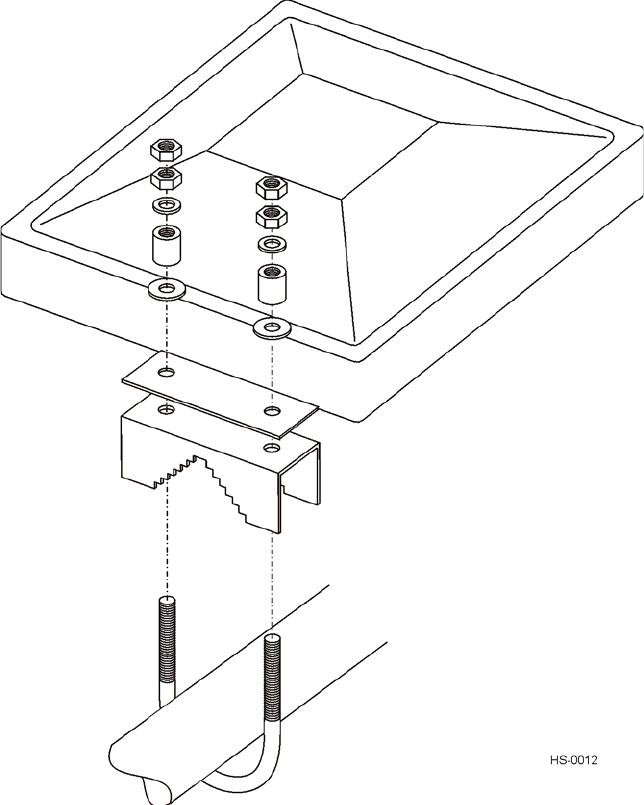
IT2200 Reader System with Multimode Capability Installation & Maintenance/Service Guide
4-22
Figure 4-16 AA3153 Beacon Antenna Mounting
Note: The location and positioning of the beacon antenna(s) can vary depending
on the site configuration. These instructions provide a starting point that will
work for many typical installations.
To install the beacon antenna
1. Locate the antenna along the mounting pipe and insert a U-bolt around the pole
and through the bracket. Place lock washer and nut over each side of U-bolt.
Repeat for the other U-bolt.
Note: For installations requiring horizontal polarization, mount the beacon antenna
with the Amtech® label horizontal to the horizon. For installations requiring vertical
polarization, rotate the antenna 90° so that the Amtech® label is perpendicular to the
horizon.
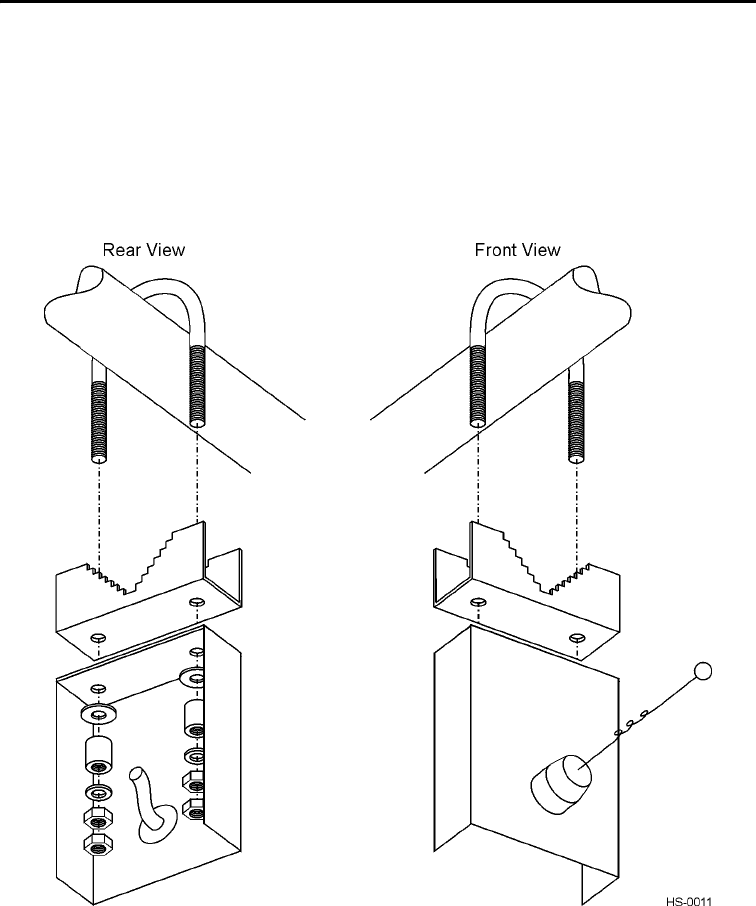
Installing the IT2200 Reader System
4-23
2. Rotate the antenna 10° down from vertical. For a pillbox mount, aim the antenna
toward oncoming traffic as shown in Figure 4-8. If there is no pillbox, rotate the
antenna 45° toward oncoming traffic. Use an inclinometer to check the angle.
3. Tighten nuts with torque wrench to 68 N-m (50 ft-lb) to prevent slippage.
Tighten second nut over first nut to lock it in place.
4. Slide the shrink tubing over the coaxial cable, but do not heat it.
5. Connect the coaxial cable to the antenna and to the appropriate connector on the
RF module. Leave the shrink tubing loose until you have finished tuning the lane.
Installing the IT2502 Check Tag Antenna with a
UTA
For bistatic configuration, install the check tag antenna on the mounting pipe between
the transmit and receive antennas. For monostatic configuration, install the check tag
antenna on the mounting pipe next to the transmit/receive antenna. Figure 4-17 shows
the correct way to mount a check tag antenna.
Figure 4-17 IT2502 Check Tag Antenna Mounting

IT2200 Reader System with Multimode Capability Installation & Maintenance/Service Guide
4-24
To install the check tag antenna
1. Locate the check tag antenna along the mounting pipe and insert a U-bolt around
the pole and through the bracket. Place lock washer and nut over each side of U-
bolt. Repeat for the other U-bolt.
2. For bistatic configuration, adjust the check tag antenna so it is about 2.5 cm (1 in)
from and centered on the transmit antenna. It should extend across about one
third of the transmit antenna’s width.
3. For monostatic configuration, adjust the check tag antenna so it is about 2.5 cm
(1 in) from and centered on the transmit/receive antenna. It should extend across
about one third of the transmit/receive antenna’s width.
4. Tighten the nuts with a torque wrench to 68 N-m (50 ft-lb). Tighten a second nut
over the first nut to lock it in place.
5. Slide the shrink tubing over the check tag antenna cable, but do not heat it. Leave
the shrink tubing loose until you have finished tuning the lane.
6. Connect the cable to the check tag antenna connector on the RF module. See
Figure 4-14 for the location of the RF module connectors.
Installing the IT2502 Check Tag Antenna with a
Beacon Antenna
Install the check tag antenna on the same mounting pipe as the transmit antenna
(bistatic configuration) and transmit/receive antenna (monostatic configuration). Fig-
ure 4-17 shows the correct way to mount a check tag antenna.
To install the check tag antenna
1. Locate the check tag antenna along the mounting pipe and insert a U-bolt around
the pole and through the bracket. Place lock washer and nut over each side of U-
bolt. Repeat for the other U-bolt.
2. For bistatic configuration, adjust the check tag antenna so it is about 2.5 cm (1 in)
from the transmit antenna and extends across about one third of the transmit
antenna’s width.
3. For monostatic configuration, adjust the check tag antenna so it is about 2.5 cm
(1 in) from the transmit/receive antenna and extends across about one third of the
transmit/receive antenna’s width.
4. Tighten nuts with torque wrench to 68 N-m (50 ft-lb) to prevent slippage.
Tighten second nut over first nut to lock it in place.
5. Slide the shrink tubing over the check tag antenna cable, but do not heat it. Leave
the shrink tubing loose until you have finished tuning the lane.
6. Connect the cable to the check tag antenna connector on the RF module. See
Figure 4-14 for the location of the RF module connectors.

5
Tuning the Lane
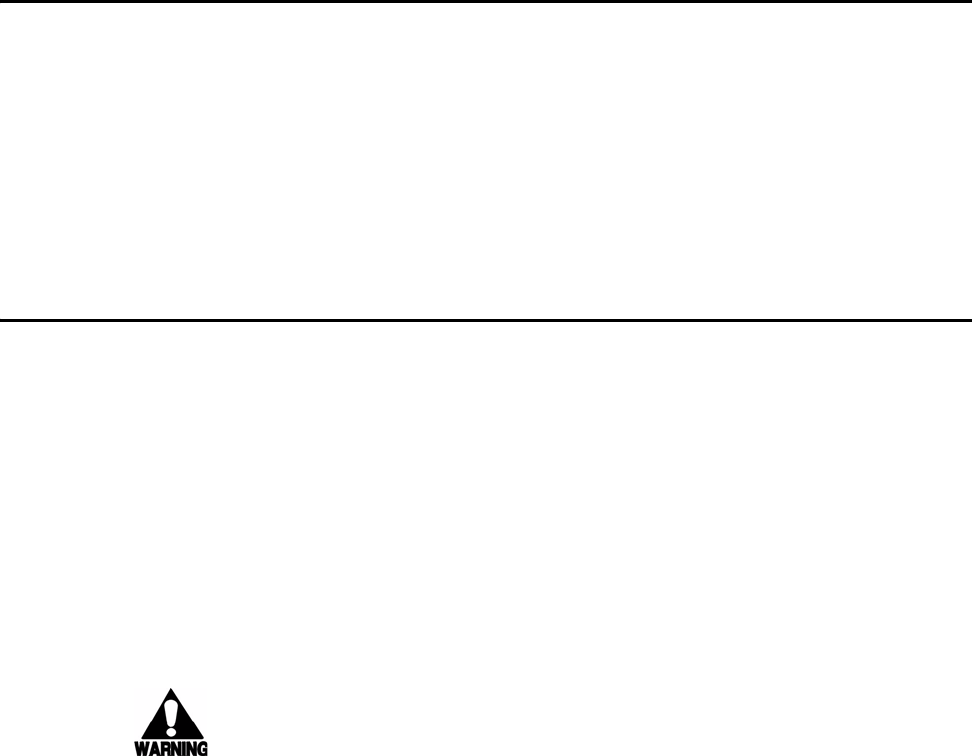
5-3
Chapter 5
Tuning the Lane
This chapter provides instructions for tuning the lane for optimum
performance and for verifying that the installed IT2200 Reader System is
functioning correctly.
Why You Need to Tune a Lane
You tune a lane to:
•Test the installed reader system
•Adjust the read/write zone footprint to guarantee reliable tag performance and
proper transaction framing
•Minimize the RF power output to decrease interference with adjacent lanes
The read/write zone is adjusted by changing the antenna position, antenna mounting
angle, and uplink and downlink RF power. The nominal antenna angle is 15° up from
horizontal in a dedicated lane and 10° up in a mixed-use lane.
Note: TransCore recommends that two people accomplish this procedure.
Warning
Switch off RF power before working on antennas.
The following procedure assumes that the equipment to be tested and commissioned
has been properly installed and that host computer power is available.
This lane tuning procedure tests the following equipment:
•IT2611 RF Module
•AA3152 or AA3153 antennas
•IT2502 Check Tag Antenna
•IT2020 Reader Logic Card
•Reader-to-RF module tag data/control cable (data cable)
•RF module power supply
•RF module power supply cable
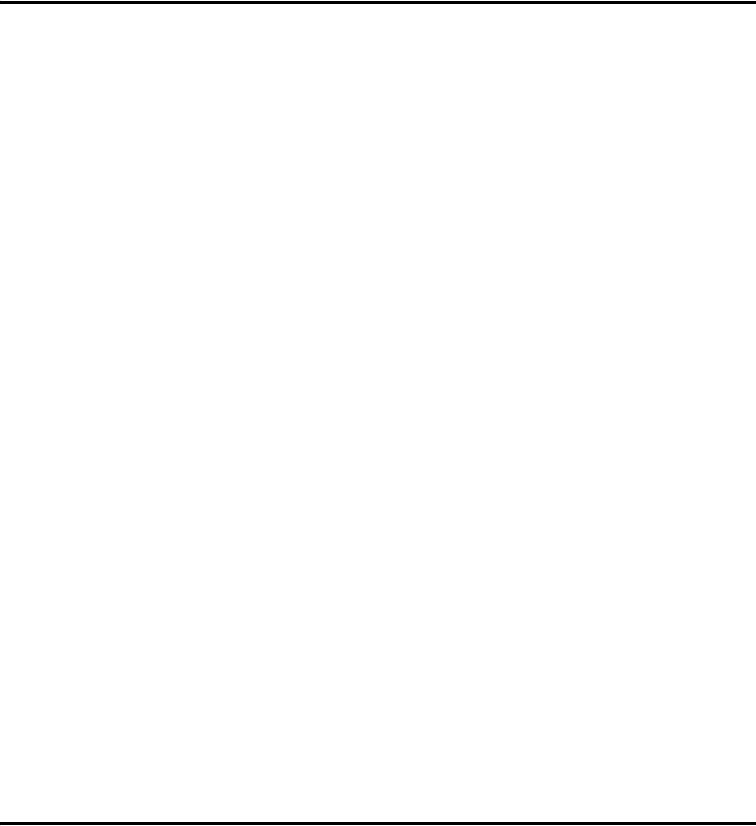
IT2200 Reader System with Multimode Capability Installation & Maintenance/Service Guide
5-4
Required Equipment
You need the following equipment to complete the tuning procedure:
•One IT2221 and one IT2235 tag to use as baseline tags for testing all lanes
•One ATA-type tag to use as a baseline tag for testing multimode lanes
Note: The ATA-type tag is required only if you are tuning a multimode lane.
•Plastic or wood stick. (A plastic kitchen spatula works well.)
•Rubber bands or hook-and-loop fastener to mount tag to stick
•Tape measure and masking tape
•Test computer (PC or lunch box type) with version 1.03 of the IT2200 engineering
host software (P/N 11254-00) and an available ISA slot for installing a reader
logic card
•Diskette with custom autonomous mode (CAM) files
•Data cable to use as an extension cable to the installed data cable. Use a 2m (6-ft)
DB-25, fully wired, plug and socket end cable
•One pair of walkie talkie radios, preferably UHF band
•Multimeter, Fluke 87 or equivalent
•Vehicle. Use a car or truck for interior tags or a truck for exterior tags
•Commercial grade heat gun
•Protective electrostatic device bag
Optional Equipment
TransCore manufactures diagnostic tools that you can use to check the reader system
functions.
•Breakout Box for the IT2020 Reader Logic Card. The breakout box is used to
access IT2020-series Reader Logic Card internal signals for analysis, and uses
light-emitting diodes (LEDs) to display various software signals. In addition, the
breakout box can set the RF signal modulation high.
•External Modulation Box for the IT2611 RF Module. The mod box is used to con-
trol radio frequency (RF) modulation and measure maximum downlink power and
depth of modulation using diagnostic equipment.
•Beeper Box for the IT2200 Reader System. The beeper box is used to verify tag
reads when diagnosing a reader system. The beeper box has internal audio/visual
indicators and can also power remote light or audible buzzer for lane-side tag test-
ing.
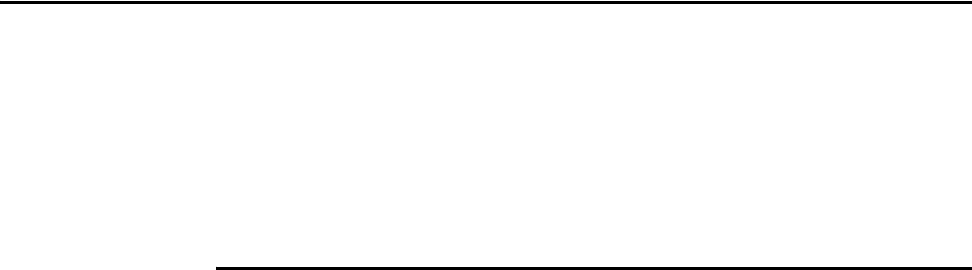
Tuning the Lane
5-5
Tuning the Lane
If you have installed multimode lanes (those using IT2200-series and
ATA-type tags), then you must follow all of the directions outlined in this
lane tuning section. If you have installed single-mode lanes (IT2200-
series tags only), you can ignore the ATA tag testing instructions.
This section provides instructions for installing and starting the IT2200 engineering
host software diagnostic tool to check the reader system status.
Starting the Engineering Host
To run the engineering host
1. Disconnect the data cable from the reader logic card in the host computer.
2. Remove the reader logic card from the host computer and install it in the test
computer.
3. Connect the data cable to the extension data cable, then connect the extension
data cable to the reader logic card in the test computer.
4. Start the test computer, then double-click the Host icon to start the host software.
Upon startup, the Background status information screen displays (see Figure
5-1).
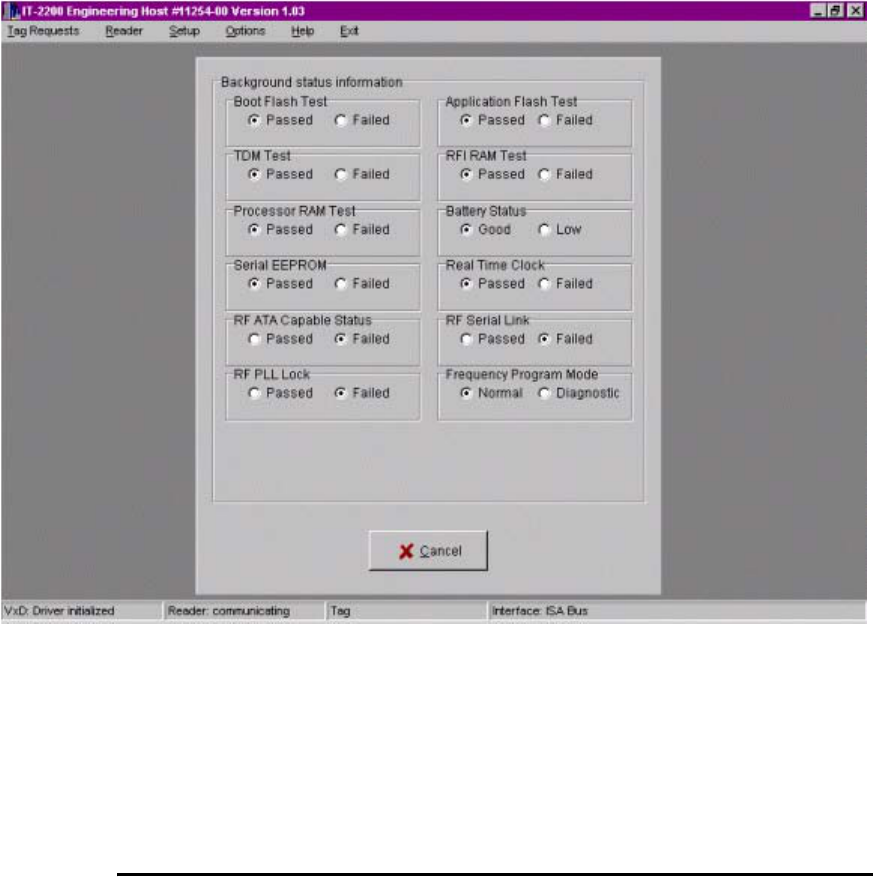
IT2200 Reader System with Multimode Capability Installation & Maintenance/Service Guide
5-6
Figure 5-1 Background Status Information Screen
If the system is operating correctly, all Passed blocks on the diagnostics page are
checked. Figure 5-1 shows a failure of the RF Data EEPROM, RF PLL Lock, and
RF Serial Link tests. Any condition that results in a Fail status must be corrected
before the testing proceeds. See Chapter Chapter 6, “Troubleshooting the
Installation,” for corrective actions.
5. Click Cancel to clear the Background status information screen.
Lane Tag Test
This procedure determines the correct RF attenuation settings for the installed reader
system.
If more than one lane is to be tuned, the other lanes should be operating to obtain valid
attenuation parameters. This might not be practical for the initial tuning, but final tun-
ing must be performed with all lanes operating. For untuned lanes, set the attenuation
to 9dB uplink and downlink. When these lanes are finally tuned, if their attenuation
settings differ by more than 2dB from the selected 9dB, some repeat tuning might be
necessary in other lanes.
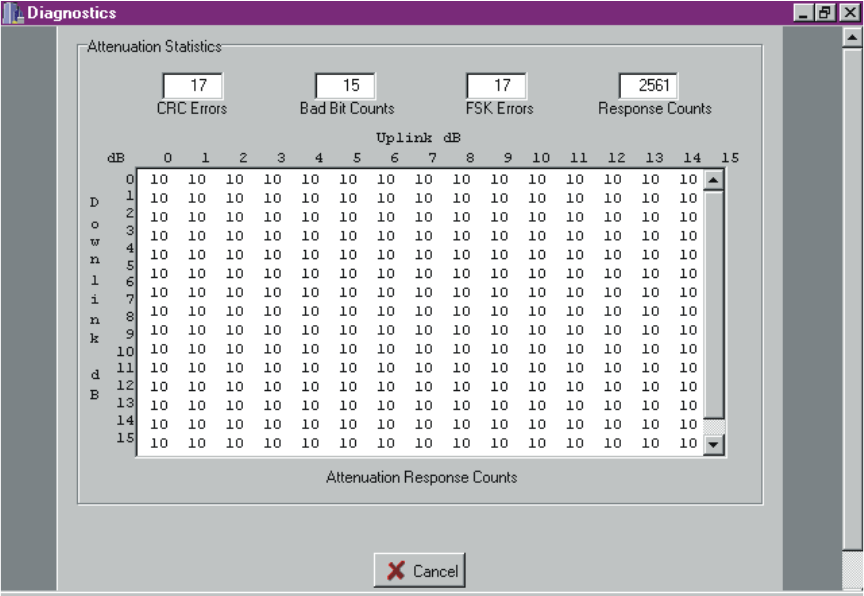
Tuning the Lane
5-7
1. From the Reader menu, select RF Attenuation. When the RF Attenuation
Parameters screen appears, set the downlink and uplink attenuation to 0, then
click Apply.
2. From the Options menu, select Diagnostics, then Attenuation Statistics. When
the Attenuation Statistics Control screen appears, click Read Frame #07, All
Tags, then click Run.
3. After about two minutes, a table of results displays (see Figure 5-2 for sample
results). Save the table using screen capture (press Alt-Print Scrn), paste it into a
word processing program such as Microsoft Word, and assign it a title.
An attenuation response count of 9 or 10 is ideal. A count of 5 at 14dB uplink and
downlink attenuation is acceptable.
If the count at 14dB uplink and downlink attenuation is less than 5, or if the count
at 15dB uplink and downlink attenuation is 0, go to Chapter Chapter 6,
“Troubleshooting the Installation.”
Figure 5-2 Sample RF Attenuation Statistics for Check Tag
4. From the Reader menu, select Check Tag Control. When the Check Tag
Control screen appears, select Check Tag Disabled, then click Apply.
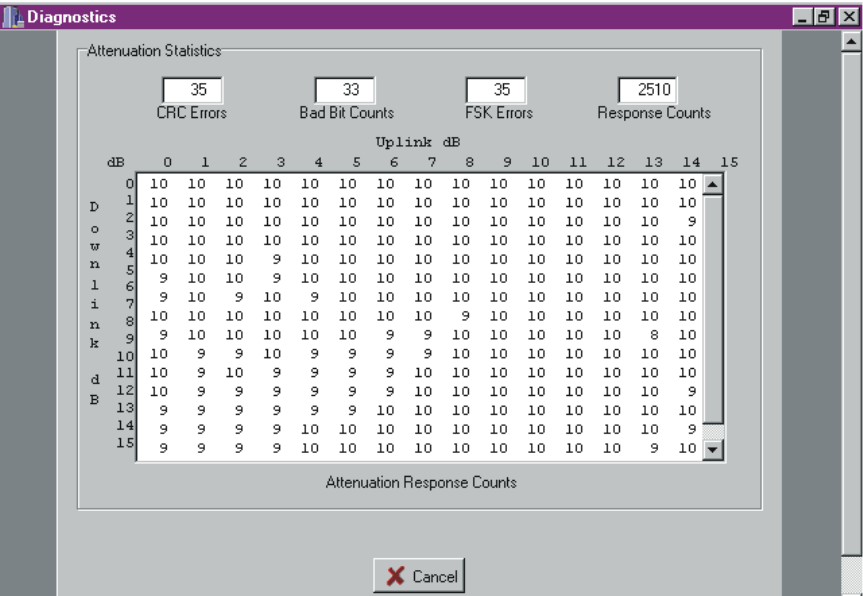
IT2200 Reader System with Multimode Capability Installation & Maintenance/Service Guide
5-8
5. Mount an IT2221 or IT2235 tag on the inside of the vehicle’s windshield. The tag
must be at least 5 cm (2 in) from the windshield frame or rear view mirror post,
and it must be below the tint line at the top of the windshield.
6. Park the vehicle with the tag exactly 3 m (10 ft) upstream of the antenna.
7. Run the attenuation statistics program (see Step 1 of this instructions section).
Save and label the tables.
8. Compare the attenuation statistics to those shown in Figure 5-3 and Figure 5-4.
Figure 5-3 shows an example of acceptable results. Notice that the screen shows
attenuation response counts of 9 or 10 at almost all attenuation settings. Figure 5-
4 shows attenuation response counts that range from acceptable to marginal to
unacceptable. If your results look like these, choose attenuation settings in the
acceptable range.
If the results are unacceptable, move the vehicle upstream 15 to 30 cm (6 to 12 in)
and repeat attenuation statistics. Then move the vehicle downstream of the
original position 15 to 30 cm (6 to 12 in) and repeat attenuation statistics. If
moving the vehicle results in a good report, the vehicle was in a small hole or poor
read area as a result of a standing wave pattern, and you can proceed with the
tuning.
If you are unable to achieve good attenuation statistics by moving the vehicle, go
to Chapter Chapter 6, “Troubleshooting the Installation.”
Figure 5-3 Acceptable RF Attenuation Statistics
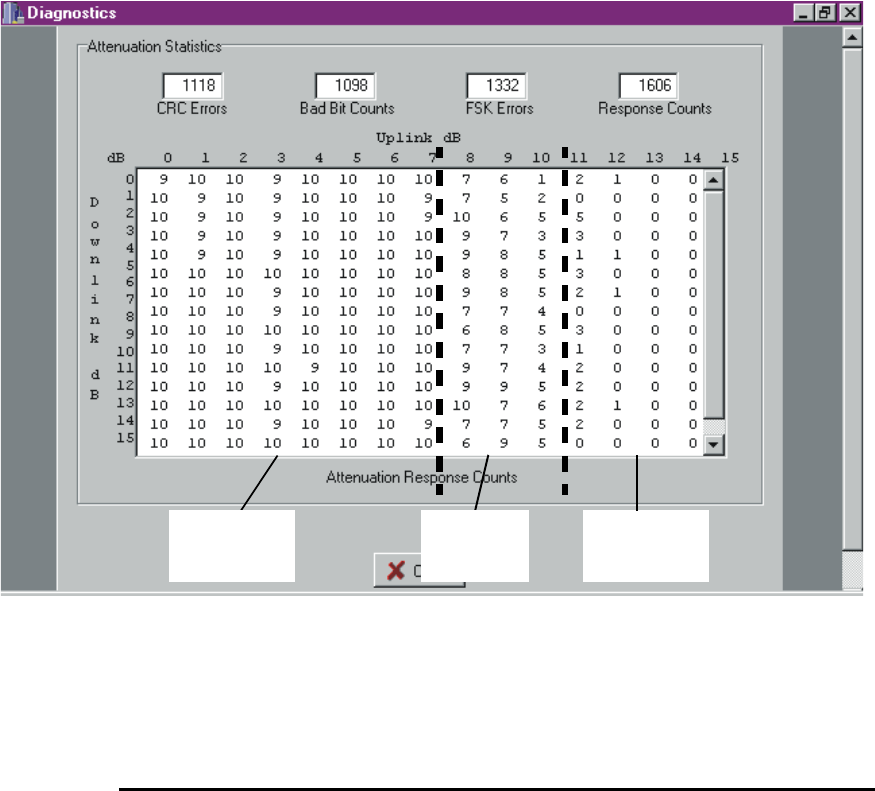
Tuning the Lane
5-9
Figure 5-4 Ranges of RF Attenuation Statistics
9. Select a pair of attenuation settings that give acceptable attenuation response
counts. (Do not use 15dB attenuation.) Attenuation settings close to 8dB
downlink and 12dB uplink are typical in many installations. In Figure 5-3,
settings of 13dB downlink and 7dB uplink are an acceptable choice.
Check Tag Test
The check tag works best if the check tag antenna whip is placed directly in front of
the active elements of the transmit antenna. If a UTA or beacon antenna is used for the
transmit antenna, the patches on the antenna lie directly down the center of the
radome, equidistant from the long edges. If the check tag antenna is mounted on the
same rail as the transmit antenna, the check tag antenna should be rotated down so that
the whip is directly in front of the center of the transmit antenna radome. This is a
good approximation for the check tag antenna placement. Ensure that the uplink and
downlink RF power levels are set at the lane tuning levels previously set in the Lane
Tag Test.
IT2000 Check Tag Test
This test verifies that the IT2000 check tag and check tag antenna are working cor-
rectly.
Acceptable RF
Attenuation
Settings
Marginal RF
Attenuation
Settings
Unacceptable
RF Attenuation
Settings
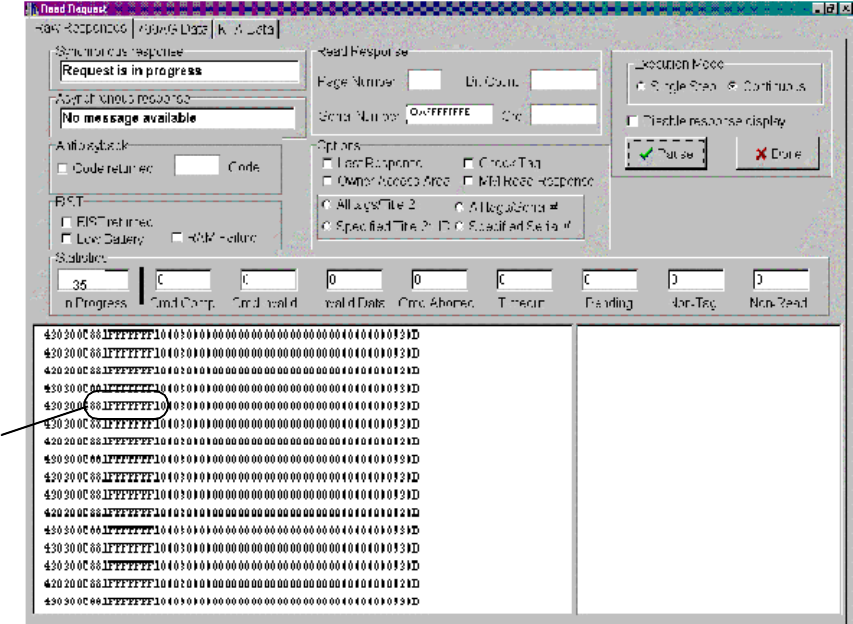
IT2200 Reader System with Multimode Capability Installation & Maintenance/Service Guide
5-10
1. Remove any tag from the read/write zone.
2. From the Reader menu, select Check Tag Control. When the Check Tag
Control screen appears, select IT-2000 Check Tag Enabled, then click Apply.
3. From the Reader menu, select RF Attenuation. When the RF Attenuation
Parameters screen appears, set the downlink and uplink attenuation to 6, then
click Apply.
4. From the Tag Requests menu, select Read. When the Read Request screen
appears, set Execution Mode to Continuous.
5. Click Run. Click the Raw Responses tab, if necessary. The tag read counter
should increment fast and steady, and the tag serial number should be
0xFFFFFFFE, the check tag signature as shown in Figure 5-5.
Figure 5-5 Sample Continuous Check Tag Read Request Display
6. In Execution Mode, select Continuous.
7. Rotate the check tag antenna to find the high-angle and low-angle points where
the check tag begins to get continuous reads. Note the high- and low-angle
positions of the check tag antenna.
If the check tag test fails, check that the check tag antenna is correctly positioned and
connected. If it is, replace the check tag antenna. See "Check Tag Antenna" on page
6-19.
Check Tag
Signature

Tuning the Lane
5-11
ATA Check Tag Test
Follow the steps outlined in the previous procedure for the IT2000 Check Tag Test.
The only exceptions are in Steps 2 and 6. In Step 2 you will select ATA Check Tag
Enabled instead of IT-2000 Check Tag Enabled. In Step 6 you will select the ATA
Tag Read Request screen instead of the Read Request screen, then in Execution
Mode, select Continuous.
If the check tag test fails, check that the check tag antenna is correctly positioned and
connected. If it is, replace the check tag antenna. See "Check Tag Antenna" on page 6-
19.
The optimum orientation for the antenna will be at a mounting angle that is located
within both solid read zones previously established for the IT2000 and ATA lane test
reads.
Testing the Footprint
Test the footprint using the custom autonomous mode (CAM) file. The CAM file
causes an IT2235 Tag to beep when the host successfully interacts with it. Access the
engineering host Background Status Information screen display.
Running the CAM Test for IT2200-Series Tags
1. Insert diskette with the Map4.cam files into the host computer’s floppy
diskette drive and copy the files to host. Remove the diskette from the
computer drive.
2. From the Reader menu, select Download CAM File.
3. Select the Map4.cam file. When the Map4.cam file has been successfully
downloaded, an information box appears indicating that the CAM file is
loaded into the reader logic card. Click OK to exit this screen.
4. From the Reader menu, select Cam Sequencing. From the Cam Sequencing
screen, select Non-Virtual Sequence. This command sets the host-reader
interface for this series of tests.
5. From the Reader menu, select Tag Command Mode. From the Tag
Command Mode screen, select Process Autonomous Commands. From the
Process Autonomous Commands screen, select Disable Response Display,
then click Run. This operating mode causes the IT2235 Tag to beep after
every read/write transaction. An IT2235 Tag should beep several times each
second.
Note: An IT2235 Tag produces two audible tones: a lower pitch tone indicating
a tag read and a higher pitch tone indicating a tag write.For this phase of lane
testing, only listen for the lower pitched tone.
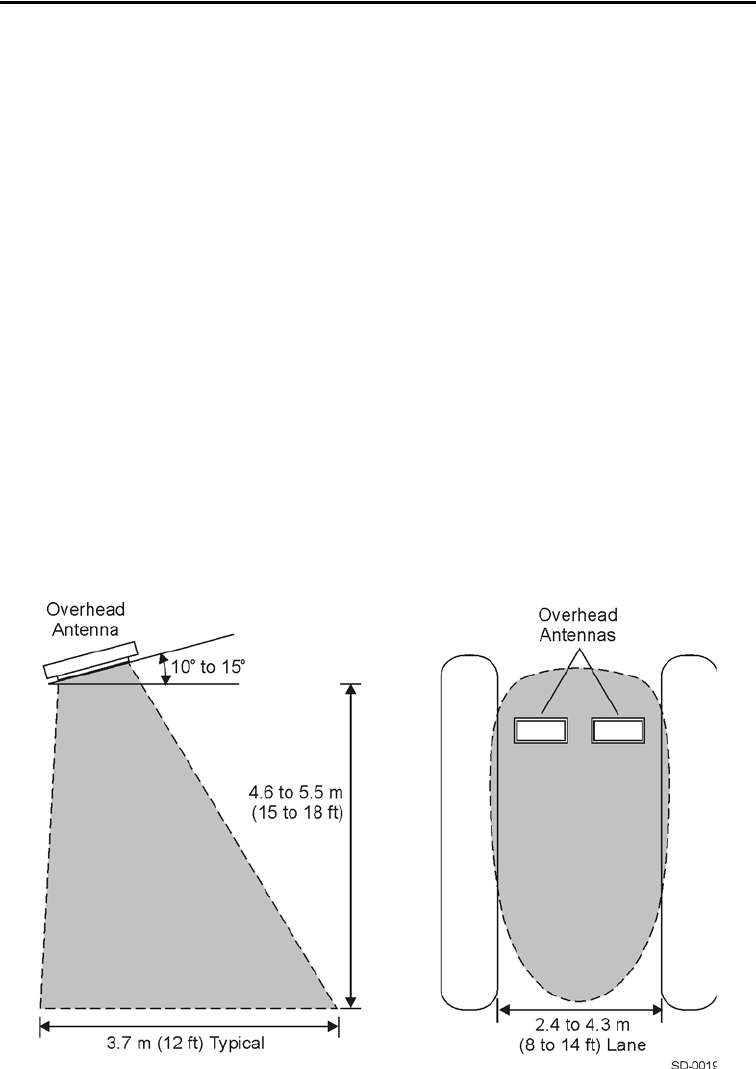
IT2200 Reader System with Multimode Capability Installation & Maintenance/Service Guide
5-12
Tag-on-a-Stick Test for IT2235 Tag
1. Mount the IT2235 Tag on the stick or rubber or plastic spatula using Velcro or a
rubber band.
2. Hold the tag on the stick with the long side horizontal.
3. Move the tag around the desired read/write zone, and note where the tag
beeps.
The read/write area is roughly an oval, or egg, shape. The zone should extend
from about 3 m (10 ft) ahead of the antenna to 0.9 m (3 ft) past the antenna (see
Figure 5-6). Near the center of the pattern, the read/write zone should extend
from one side of the lane to the other. This pattern width is necessary to read
motorcycles at the extreme edges of the lane. If the actual pattern is shorter or
narrower than desired, decrease both uplink and downlink attenuation 1dB and
repeat the pattern mapping. If it is larger than desired, increase the attenuation
1dB. Pattern mapping with a tag on a stick only gives a representation of the
actual pattern. The pattern probably will be different with the tag in a car. Also,
some “holes” in the pattern are unavoidable. As a general rule, if a hole or holes
does not occupy more than 10 percent of the total pattern, it is a good pattern.
Figure 5-6 Typical Read/Write Zone for a Reader (Bistatic Configuration)
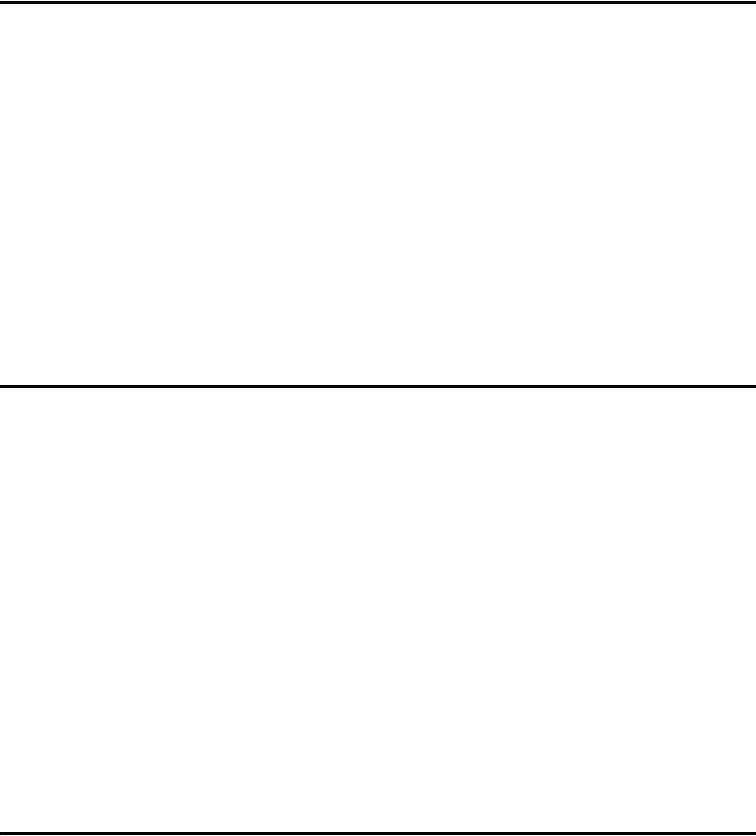
Tuning the Lane
5-13
Running the CAM Test for ATA-Type Tags
1. From the Main menu, select Options, then Sound. Click On.
2. From the Main menu, select Tag Requests. Select ATA Read. This operating
mode causes the ATA tag to cause the host PC to emit an audible click after
every read transaction.
3. From the ATA Tag Read Request screen, then in Execution Mode select
Continuous.
4. Leave all other setting at defaults. Select Run.
The IT2200 system is ready to read only single-mode or multimode ATA-type
tags.
Tag-on-a-Stick Test Using ATA-Type Tag
Note: TransCore recommends that two people accomplish this procedure. If only one
person is available, you can use the Beeper Box for the IT2200 Reader System (see
product description in “Optional Equipment” on page 5-4 for more information).
1. Replace the IT2235 Tag with an ATA-type tag. Place the IT2235 Tag in an ESD
bag.
2. Mount the ATA-type tag on the stick or rubber or plastic spatula using Velcro or a
rubber band.
3. Hold the tag on the stick with the long side horizontal.
4. Move the tag around the desired read/write zone, and watch the engineering
host screen for a tag read indication (tag ID appears on the screen) and listen
for an audible click from the host PC when the ATA tag is read.
Vehicle-Mounted Tag Test Using IT2235 Tag
Note: For the vehicle mounted tag test, you must mark the tag, not vehicle, location at
the point where the tag starts and stops beeping.
1. Mount an IT2235 Tag on the inside of the vehicle’s windshield. The tag must be
at least 5 cm (2 in) from the windshield frame or rear view mirror post, and it
must be below the tint line at the top of the windshield.
2. Drive the car at a speed of about 8 to 16 km/h (5 to 10 mph) through the center
of the lane.
3. Use a piece of masking tape on the road or curb to mark the location in the
lane where the tag starts to beep.

IT2200 Reader System with Multimode Capability Installation & Maintenance/Service Guide
5-14
4. Continue driving the car through the lane until the tag stops beeping.
5. Mark the location where the tag stops beeping.
6. Repeat this process of driving slowly through the pattern first along the left
and then along the right curbs.
7. Mark the pattern start and stop locations.
8. Measure the start and stop points.
All measurements are made with respect to the antenna-mounting pipe. In a toll
lane, the light curtain is usually centered between the treadles 1.8 m (6 ft)
upstream of the antenna. Measurements can be made from the light curtain but,
when recording the distances, add or subtract the 1.8 m (6 ft) as appropriate so
that the dimensions represent the distance to the antenna. Distance
measurements past the antenna are recorded as negative numbers. An ideal
pattern in the center of the lane is 3 m (10 ft) before the antenna to 0.9 m (3 ft)
past the antenna, or +3 m to -0.9 m (+10 ft to -3 ft). These distances can vary
by ±0.3 m (1 ft) and still be acceptable. With the car driving along the sides of
the lane, the pattern can be up to 0.6 m (2 ft) shorter overall.
If the pattern is larger or smaller than optimum, increase or decrease the
attenuation in 1dB steps until the optimum pattern is obtained.
Vehicle-Mounted Tag Test Using ATA-Type Tag
Note: For the vehicle mounted tag test, you must mark the tag, not vehicle, location at
the point where the tag starts and stops reading (indicated by audible clicks on host
PC or beeper box).
1. Replace the IT2235 Tag with an ATA-type tag. Place the IT2235 Tag in an ESD
bag.
2. Mount an ATA-type tag on the inside of the vehicle’s windshield. The tag must be
at least 5 cm (2 in) from the windshield frame or rear view mirror post, and it
must be below the tint line at the top of the windshield.
3. Drive the car at a speed of about 8 to 16 km/h (5 to 10 mph) through the center
of the lane.
4. Use a piece of masking tape on the road or curb to mark the location in the
lane where the tag starts to beep.
Note: For Step 5, you must either enable sound on the host PC or use a beeper box to
hear the audible clicks when the ATA tag is read.
5. Continue driving the car through the lane until the host PC or beeper box
stops clicking, indicating the end of the read zone.

Tuning the Lane
5-15
6. Mark the location where the tag stops beeping. Ensure that you mark the tag,
not vehicle, location.
7. Repeat this process of driving slowly through the pattern first along the left
and then along the right curbs.
8. Measure the ATA tag footprint.
Pay close attention to the point of the first read. You may find that the first read
point for the ATA tag differs from the first read point of the IT2235 Tag. If this
difference is undesirable, you can adjust the ATA tag range independent of the
IT2235 Tag read range by changing the uplink attenuation. ATA tags respond to
uplink RF power only; the IT2235 Tag response is relatively independent of
uplink power.
To increase the ATA footprint, increase the uplink power. To decrease the ATA
footprint, decrease the uplink power.
Once the ATA and IT2235 footprints have been matched to a satisfactory degree,
recheck the IT2235 Tag footprint to ensure that the ATA adjustments have not
adversely affected the IT2235 footprint.
Dynamic Performance Test
This test evaluates the host computer performance for continuous reads of a tag in the
field.
Starting the Dynamic Performance Test
1. From the Reader menu, select Download CAM File. Select the
HDSKS.cam file. When the HDSKS.cam file has been successfully
downloaded, an information box appears indicating that the CAM file is
loaded into the reader logic card. Click OK to exit this screen.
2. From the Reader menu, select CAM Sequencing. When the CAM
Sequencing screen appears, select Non-Virtual Sequence. This command
initiates the host-reader interaction for this type of CAM file.
3. From the Reader menu, select Tag Command Mode. When the Tag
Command Mode screen appears, select Process Autonomous Commands.
When the Process Autonomous Commands screen appears, select Disable
Response Display, then click Run.
The CAM file issues continuous reads to any tag in the field, and the host
software counts the transactions. This is a very useful index of dynamic lane
performance.
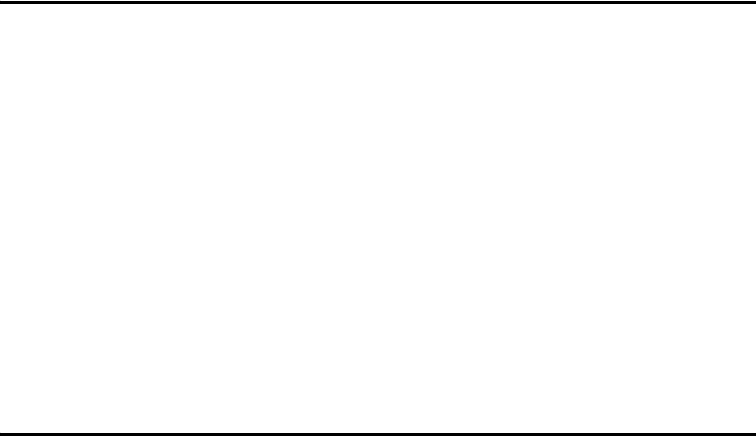
IT2200 Reader System with Multimode Capability Installation & Maintenance/Service Guide
5-16
IT2235 Dynamic Performance Drive-Through Tag
Test
1. Mount an IT2235 Tag on the inside of the vehicle’s windshield. The tag must be
at least 5 cm (2 in) from the windshield frame or rear view mirror post, and it
must be below the tint line at the top of the windshield. Drive the vehicle through
the center of the lane at 48 km/h (30 mph).
2. Toggle Run/Pause on the host computer to clear the counter.
3. If a message appears signifying a buffer overflow, the total number of
handshakes is too high for the host to process. To continue this test, drive
faster through the lane to reduce the handshake count.
4. Drive the vehicle through the lane three times. The handshake count should be
between 65 and 100 for each run.
IT2221 Dynamic Performance Drive-Through Tag
Test
1. Replace the IT2235 Tag with an IT2221 Tag and repeat Step 3 of “Starting the
Dynamic Performance Test” on page 5-15.
Note: Remove the IT2235 Tag from the vehicle or place it in a sealed protective
electrostatic device bag.
2. Drive the vehicle through the lane three times at 48 km/h (30 mph). The
handshake count should be between 65 and 100 for each run.
3. Close the host software.
4. Connect the data cable to the reader logic card in the host computer. Tighten the
connector and ensure that the cable’s ground wire is securely grounded to the
host computer enclosure.
5. Switch on the host computer. It should initiate automatically. In 30 to 45 seconds,
the three LEDs (Transmit Active, Uplink Source On, and Downlink Source On)
farthest from the bracket on the reader logic card should light (see Figure 5-7). If
the Self-test Fail LED lights, go to Chapter Chapter 6, “Troubleshooting the
Installation.”
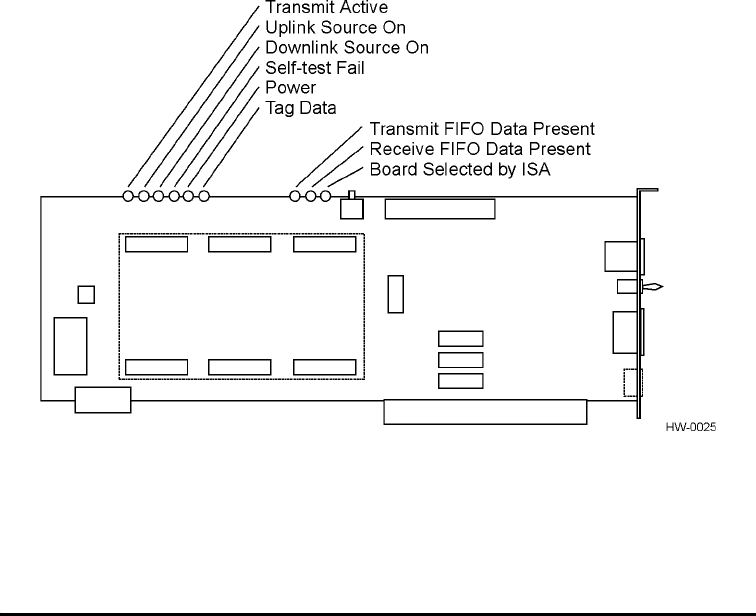
Tuning the Lane
5-17
Figure 5-7 Location of LEDs on Reader Logic Card
If the lane performs to the stated standards, tuning is complete. If not, perform trouble-
shooting procedures listed in Chapter Chapter 6, “Troubleshooting the Installation” of
the IT2200 Reader System Installation & Maintenance/Service Guide.
ATA Tag Dynamic Performance Drive-Through Tag
Test
1. Replace the IT2221 Tag with an ATA-type Tag.
Note: Remove the IT2221 Tag from the vehicle or place it in a sealed protective
electrostatic device bag.
2. From the Reader menu, select Download CAM File. Select the
HDSKS_ATA.cam file. When the HDSKS_ATA.cam file has been successfully
downloaded, an information box appears indicating that the CAM file is loaded
into the reader logic card. Click OK to exit this screen.
3. From the Reader menu, select CAM Sequencing. When the CAM
Sequencing screen appears, select Non-Virtual Sequence. This command
initiates the host-reader interaction for this type of CAM file.
4. From the Reader menu, select Tag Command Mode. When the Tag
Command Mode screen appears, select Process Autonomous Commands.
When the Process Autonomous Commands screen appears, select Disable
Response Display, then click Run.
5. Toggle Run/Pause on the host computer to clear the counter.
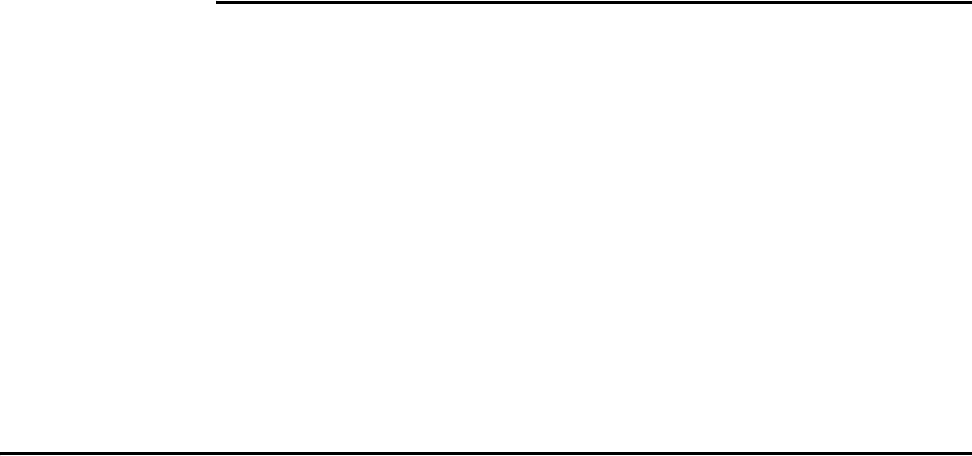
IT2200 Reader System with Multimode Capability Installation & Maintenance/Service Guide
5-18
6. If a message appears signifying a buffer overflow, the total number of
handshakes is too high for the host to process. To continue this test, drive
faster through the lane to reduce the handshake count.
7. Drive the vehicle through the lane three times. The handshake count should be
significantly lower than the number obtained with the IT2200-series tags. A
good handshake count for an ATA tag tested at 40 km/h (25 mph) is
approximately 12 handshakes. Handshake counts of 7 to 8 are acceptable
when targeting an 80 km/h (50 mph) application.
Adjusting the Read/Write Zone
The read/write zone is adjusted by changing the antenna position, antenna mounting
angle, and uplink and downlink RF power. The nominal antenna angle is 15° up from
horizontal in a dedicated lane and 10° up in a mixed-use lane.
ATA-type tags are unaffected by downlink power. The read range for ATA tags can be
adjusted by increasing or decreasing uplink power levels, or by adjusting antenna
uptilt angles.
IT2200-series tags are relatively insensitive to uplink power changes. You need uplink
power to communicate with IT2200-series tags, but you can set uplink power at mid-
dle to low power levels with little effect on performance. However, downlink power
significantly affects the read/write zone for IT2200-series tags. Antenna uptilt angle
and placement are also important in determining the read zone length for IT2200-
series tags.
Completing Antenna Connections
When all tests and connections are completed, shrink the tubing by using a commer-
cial heat gun at the connections between the antennas and the coaxial cables to water-
proof the connections.

6
Troubleshooting the Installation
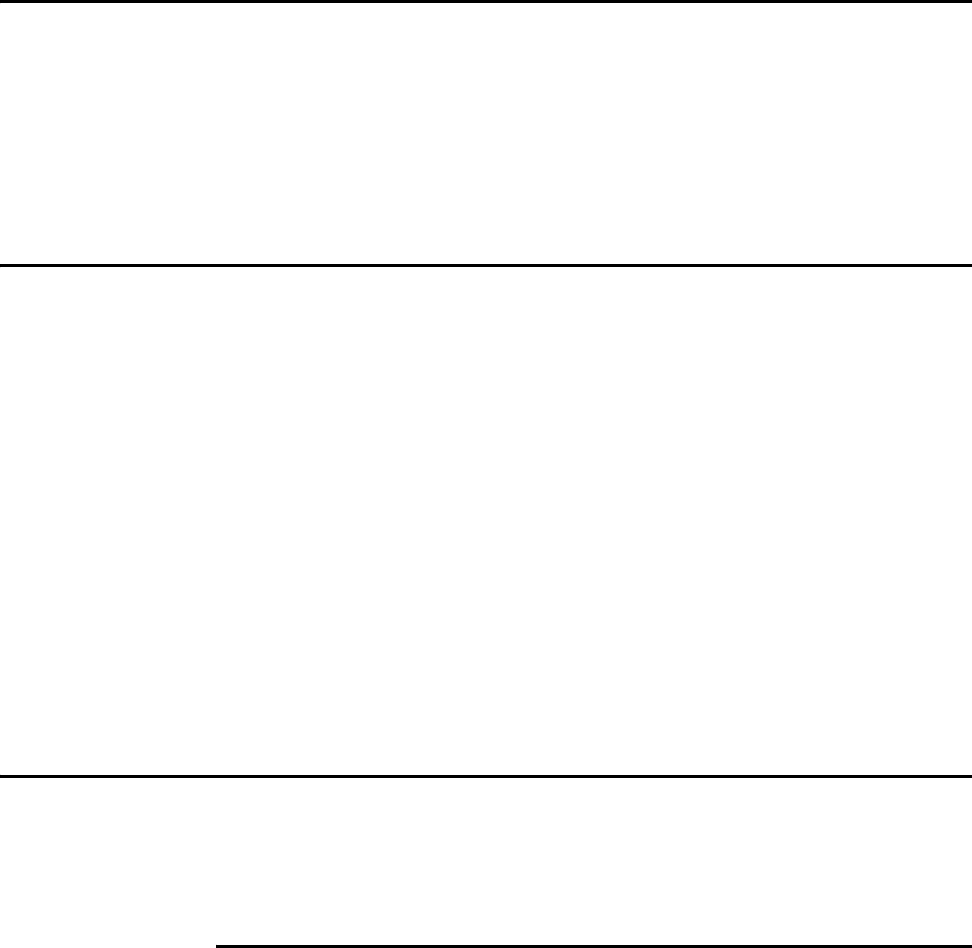
6-3
Chapter 6
Troubleshooting the Installation
This chapter provides information on cross-lane interference and
troubleshooting instructions for use when installing and testing the
IT2200 Reader System with Multimode Capability.
Required Equipment
You need the following equipment to complete the tuning procedure:
•Hydraulic lift
•Test computer (PC or lunch box type) with the IT2200 Engineering Host #11254-
00 software, Version 1.03 installed and an available ISA slot for installing a
reader logic card
•Data cable to use as an extension cable to the installed data cable. Use a 2m (6-ft)
DB-25, fully wired, plug and socket end cable.
•One pair of walkie talkie radios, preferably UHF band
•Multimeter, Fluke 87 or equivalent
•Vehicle. Use a car or truck for interior tags or a truck for exterior tags.
•Commercial grade heat gun
Cross-Lane Interference in RFID Systems
As discussed in “Noise and Interference Immunity” on page 2-10, RFID systems are
subject to various types of interference that can affect the level of communications
between a tag and reader system. Another type of interference that can result from the
operation of the reader system is called cross-lane interference.
What Is Cross-Lane Interference?
Cross-lane interference occurs when the RF generated in one toll lane interrupts the
RFID operation in another lane thereby causing the affected lane to perform poorly.
Before diagnosing cross-lane interference, it is necessary to understand what consti-
tutes a satisfactorily performing lane.
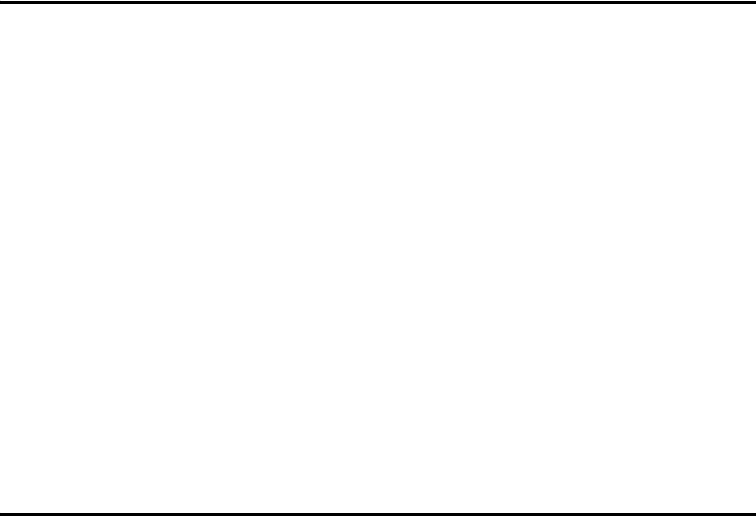
IT2200 Reader System with Multimode Capability Installation & Maintenance/Service Guide
6-4
Determining Acceptable Lane Performance
The criteria for optimal lane performance are usually set by the customer and can vary
according to the site requirements. In testing, acceptable lane operation criteria typi-
cally are determined by the length of the RF footprint and the speed of the test vehicle.
Usually, a test vehicle’s speed is limited by the amount of the toll lane that can be used
for starting and stopping distances. Usually, testing speed is limited to 32 kph (20
mph) or less.
An ideally performing toll lane will produce one handshake for every 4 ms of transac-
tion time. At 32 kph (20 mph), the vehicle is using 34 ms to travel through 0.3 m (1.0
ft) of the footprint. If the footprint is 2.4 m (8 ft), this means that the vehicle will
spend approximately 272 ms in the footprint. Based on a vehicle speed of 32 kph (20
mph) and an 2.4m (8-ft) footprint, this yields an ideal maximum number of 68 hand-
shakes. Nulls and voids within the RF footprint will lower this number, as will any
other local sources of RF noise and stray reflections. A rule of thumb for lane perfor-
mance is to have 40 to 60 handshakes within an 2.4m (8-ft) footprint with a test vehi-
cle traveling at 32 kph (20 mph). A system that operates with less than 40 handshakes
should be tested for cross-lane interference.
Identifying Cross-Lane Interference
Cross-lane interference is identified by an area in the RF read zone, or footprint,
which has areas where a tag cannot be read. If a toll lane has been operating satisfacto-
rily and then begins to show a degradation in system performance, that is, an increas-
ing number of missed reads or a spotty read pattern, there is a probability that cross-
lane interference is occurring.
Cross-lane interference can be caused by several factors, including:
•A downlink antenna transmitting strong RF beyond its lane boundaries
•Reflection of RF from fixed objects (e.g., toll plazas with low, metal roofs)
•Reflection of RF from moving objects (e.g., a passing tractor-trailer in an adjacent
lane)
A typical toll lane application encompasses more than a single lane. In some cases a
toll plaza can have more than eight lanes with each lane having separate RF transmit-
ting (downlink) and receiving (uplink) antennas. As shown in Figure 6-1, the RF
transmitted within a lane is not bound by physical dividers such as lane barriers. With
multiple-lane applications, this can create areas of possible cross-lane interference.
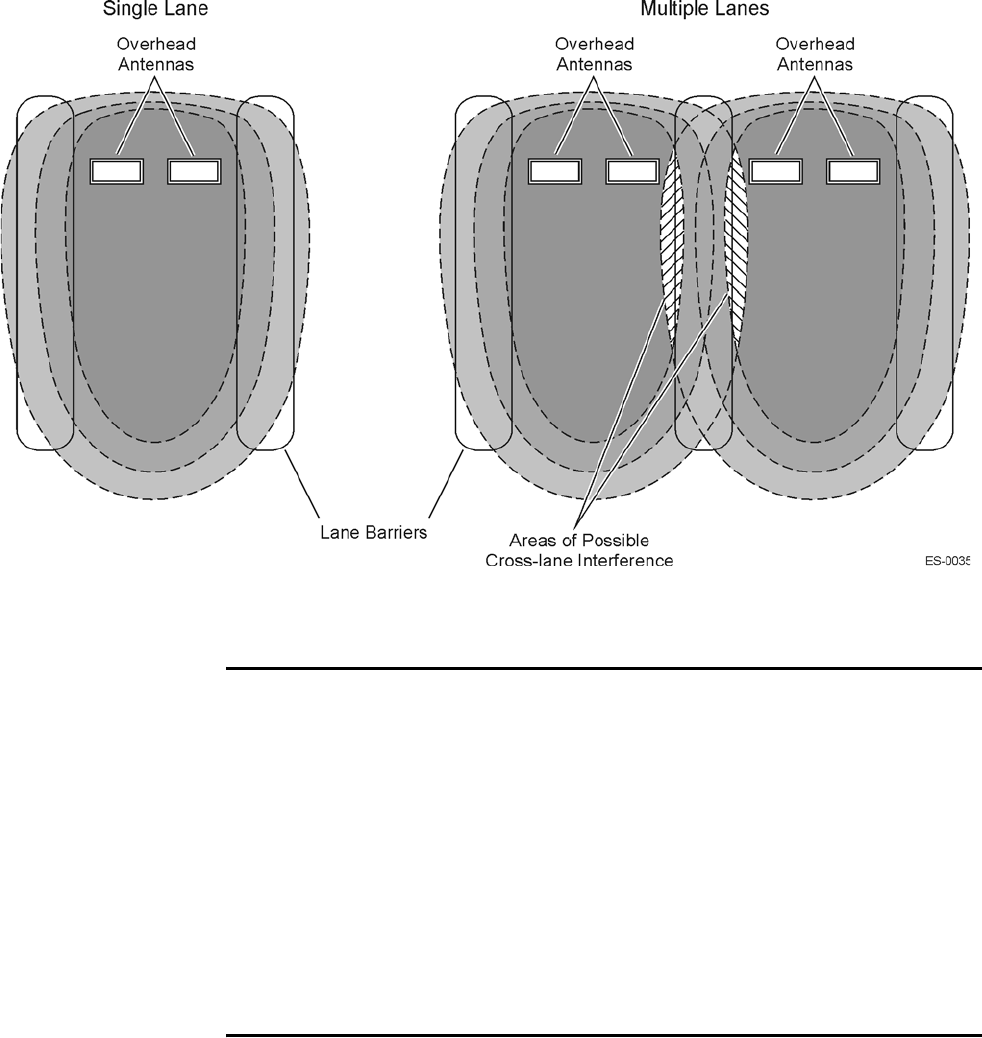
Troubleshooting the Installation
6-5
Figure 6-1 RF Footprint Extends Beyond Lane Boundaries (Bistatic
Configuration Shown)
Diagnosing Cross-Lane Interference
To diagnose this type of interference, first set the RF power in all lanes to a moderate
setting (6 to 9 dB) for both downlink and uplink antennas. Follow the procedures out-
lined in “Why You Need to Tune a Lane” on page 5-3. Next, tune a single lane by fol-
lowing the lane tuning procedure outlined in that section. When tuning a lane be sure
to use a tag and vehicle that have been used consistently at your site.
Once the lane has been tuned and you determine that it is working satisfactorily, per-
form lane tuning procedures in the adjacent lane. Continue for each lane in the toll
plaza.
If each adjacent lane tuning causes the previously tuned lane to start performing
poorly (i.e., spotty read zone or areas of no reads), cross-lane interference is indicated.
Remedying Cross-Lane Interference
There are several methods that can be used to remedy cross-lane interference. These
are accomplished by software or hardware changes, or a combination of both. A rem-
edy at one site may not be appropriate at another site, so iterative methods of correct-
ing this interference are necessary.
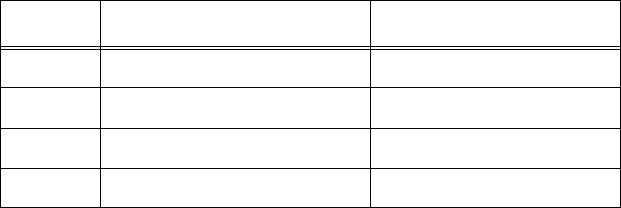
IT2200 Reader System with Multimode Capability Installation & Maintenance/Service Guide
6-6
Frequency Separation
Review the toll plaza frequency plan that was developed during the IT2200 Reader
System with Multimode Capability installation phase. There are two frequencies for
each reader: downlink and uplink. For the IT2200 Reader System with Multimode
Capability, all readers share the same downlink frequency, which is generally set to
918.75 MHz. Uplink frequencies should alternate between 903.00 MHz and 912.00
MHz in adjacent lanes. For example, a four-lane plaza would have the frequencies
shown in Table 6-1.
RF Power
A good rule of thumb when configuring a toll plaza is to set the RF attenuation at a
lower output and increase the level as needed for optimal system operation (see “Lane
Tag Test” on page 5-6 for procedures to set the RF output). This practice may provide
you with RF attenuation settings at which your reader system can operate with mini-
mal adjustment for cross-lane interference.
Time Division Multiplexing
If after tuning each lane your toll plaza is still experiencing cross-lane interference,
you may want to configure the IT2200 Reader System with Multimode Capability
using time division multiplexing, or TDM. Time division multiplexing offers the
option of isolating each lane in the system so that it operates as a stand-alone reader
for a brief fraction of the transaction time. Time-division multiplexing permits the
antennas in each individual lane to operate apart from the other antennas in the toll
plaza. This results in one lane or alternating lanes transmitting and receiving RF at a
time. Figure 6-2 shows how TDM can delay the reader period and isolate lanes from
each other.
Table 6-1 Frequency Plan for Four-Lane Toll Plaza
Lane Downlink Frequency Uplink Frequency
1 918.75 MHz 903.00 MHz
2 918.75 MHz 912.00 MHz
3 918.75 MHz 903.00 MHz
4 918.75 MHz 912.00 MHz
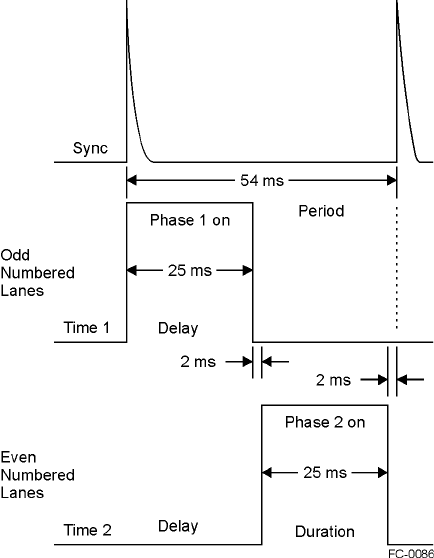
Troubleshooting the Installation
6-7
Figure 6-2 TDM Synchronization
Benefits of Using TDM
TDM may remedy the problem of cross-lane interference by removing the possibility
of the RF footprint transmitting into an actively transmitting and receiving adjacent
lane. In this case no physical changes to the plaza or antennas is necessary.
Drawbacks of Using TDM
Based on site criteria, TDM may not be the best solution for correcting cross-lane
interference. By using TDM, you may unintentionally introduce a period of dead time
within the transaction time when a vehicle could pass through the lane unrecorded.
For example, if a toll plaza has five lanes and you choose to use TDM, each lane will
be operating only 20% of the time. If you have window of 80 ms when the lane is
dead, this might be sufficient time for a vehicle to travel through the lane undetected.
The TDM configuration for each lane can be adjusted so that more than one lane is
switched on at the same time. This reduces the amount of time that a lane is off and
reduces the probability of a vehicle passing through undetected. However, by config-
uring the site in this manner, you may reintroduce cross-lane interference across alter-
nating lanes.
Frequency Settings Using TDM
As discussed in “Frequency Separation” on page 6-6, there are two frequencies for
each reader: downlink and uplink. When using TDM to reduce cross-lane interfer-
ence, alternating lanes are switched off for a specified duration. For the IT2200
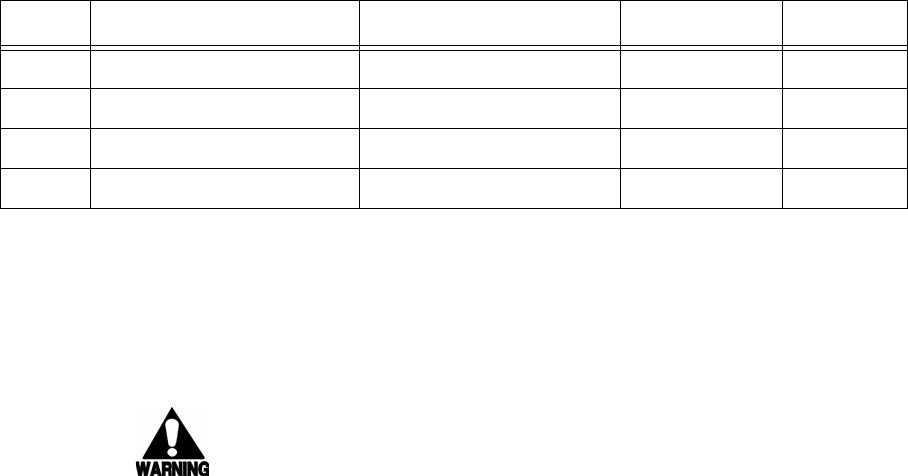
IT2200 Reader System with Multimode Capability Installation & Maintenance/Service Guide
6-8
Reader System with Multimode Capability, all readers share the same downlink fre-
quency, which is generally set to 918.75 MHz. When using TDM, adjacent lanes can
be set to any of the uplink frequencies that are specified in the frequency plan (see
Table 6-1). The uplink frequencies in the adjacent lanes can be set to the same fre-
quency because one of the lanes is switched off when using TDM. This differs from
the traditional lane frequency plan. For example, a four-lane plaza using TDM could
have the frequencies shown in Table 6-2. Compare these settings with the frequency
settings for a system not using TDM as shown in Table 6-1.
Note: Where X delay and corresponding period and direction meet system needs.
Physical Remedies
By adjusting the angle or position of the downlink and uplink antennas, you may be
able to minimize cross-lane interference.
Warning
Switch off RF power before working on antennas.
Adjusting the Antenna’s Uptilt Angle
Lowering an antenna’s uptilt angle (the angle between the antenna cover and the hori-
zon) generally tends to reduce the interference (Figure 6-3).
Table 6-2 Frequency Settings Using TDM for Four-Lane Toll Plaza with TDM
Lane Downlink Frequency Uplink Frequency TDM Phase Delay
1 918.75 MHz 903.00 MHz 1 0
2 918.75 MHz 903.00 MHz 2 X
3 918.75 MHz 912.75 MHz 1 0
4 918.75 MHz 912.75 MHz 2 X
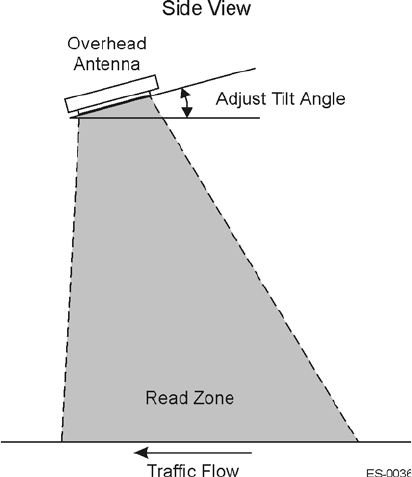
Troubleshooting the Installation
6-9
Figure 6-3 Antenna Tilt Angle Adjustment
Adjusting the Downlink Antenna Side Angle
In the IT2200 Reader System with Multimode Capability, the downlink antenna side
angle is adjusted so that the RF transmits toward the center of the toll lane, placing the
RF footprint where it is useful. If the side angle is too small the footprint can project
into the lane nearest to the downlink antenna. If the side angle is too great, and that the
RF footprint is projecting toward the uplink antenna, you can reduce the side angle so
that the antenna’s RF footprint is evenly placed within the correct lane boundaries
(Figure 6-4).
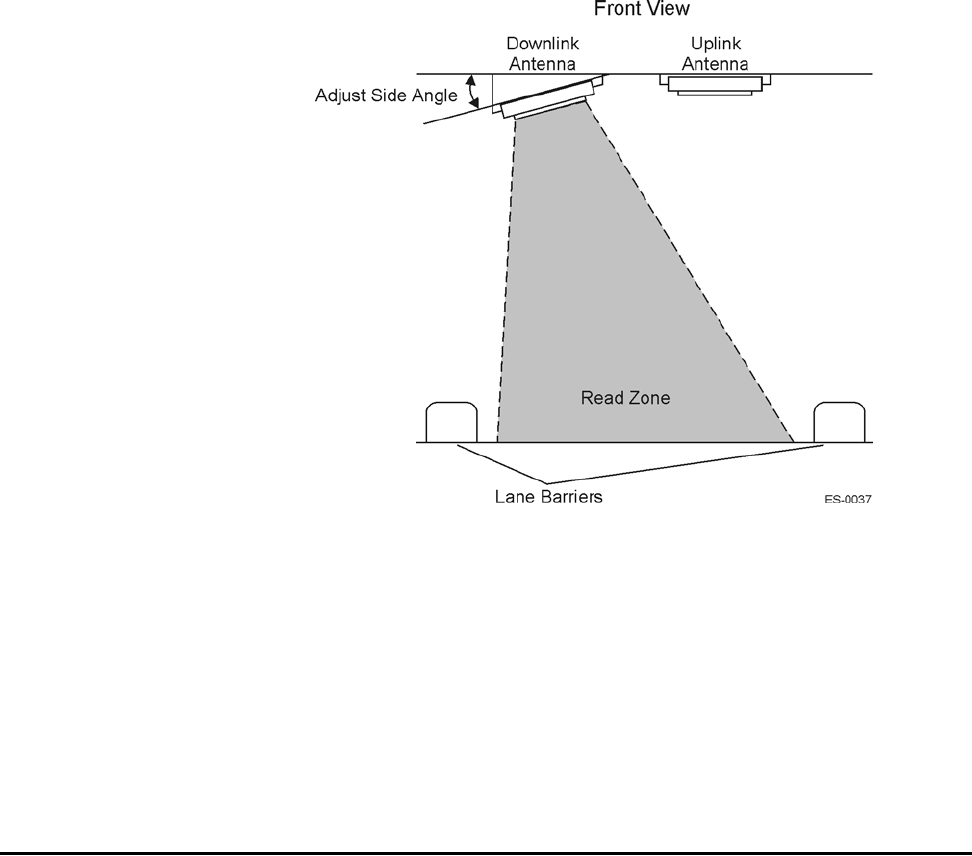
IT2200 Reader System with Multimode Capability Installation & Maintenance/Service Guide
6-10
Figure 6-4 Downlink Antenna Side Angle Adjustment
Adjusting the Antenna Placement
Besides adjusting the antenna angles, you can also move the antenna farther back into
its overhead location so that the read zone does not extend as far in front of the trans-
action area. By shortening the read zone you may be able to reduce the required RF
output power. This will result in reduced probability of cross-lane interference.
Other Site Modifications
In rare instances, applying radar absorbing foam to fixed areas of the toll plaza (e.g.,
metal roof) may reduce the incidence of interference.
Troubleshooting Indications and Actions
This section includes troubleshooting information for the listed problems. Refer to the
appropriate table for detailed instructions. If applicable, the table refers you to the
removal and replacement procedure later in this section.
•Table 6-3, ”Failure Indicated by Host Software Diagnostics
•Table 6-4, ”Failure During Check Tag Test
•Table 6-5, ”Unacceptable RF Attenuation Statistics Using Check Tag
•Table 6-6, ”Unacceptable RF Attenuation Statistics Using Vehicle-Mounted Tag
•Table 6-7, ”Self-Test Fail LED on Reader Logic Card Lights
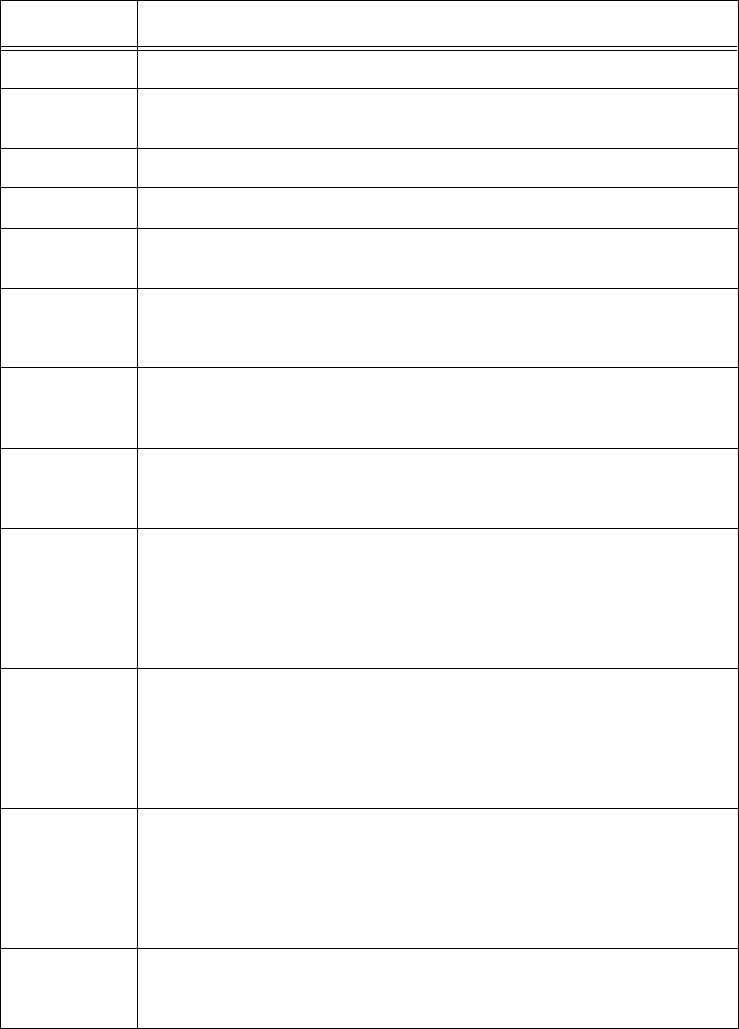
Troubleshooting the Installation
6-11
•Table 6-8, ”Spotty Pattern or Low Handshake Counts
Note: The troubleshooting procedures in this chapter test only the Amtech® IT2200
Reader System with Multimode Capability. For other problems, such as host computer
or power supply failure, refer to the manufacturer’s documentation for the correct
troubleshooting procedures.
Table 6-3 Failure Indicated by Host Software Diagnostics
Failed Test Action
Boot Flash Boot sector of flash memory failed. Replace reader logic card.
Application
Flash Application sector of flash memory failed. Replace reader logic
card.
TDM Incorrect TDM settings.
RFI RAM RFI RAM failed. Replace reader logic card.
Processor
RAM Processor RAM failed. Replace reader logic card.
Battery
Status Battery might be low or dead. Check that battery jumper J8 is
shorted (see Figure 6-5). If the jumper is shorted, the battery
failed. Replace the reader logic card.
Serial
EEPROM Serial EEPROM might have failed. Save configuration to
nonvolatile RAM. If the problem persists, the serial EEPROM
failed. Replace the reader logic card.
Real Time
Clock Clock or battery might have failed. Check that battery jumper J8 is
shorted (see Figure 6-5). If the jumper is shorted, the clock failed.
Replace the reader logic card.
RF Data
EEPROM Data cable, RF module data EEPROM, or RF module power
supply failed. Open the RF module and check for 19 to 28 VAC or
16 to 28 VDC at terminals A and C. If the voltage setting meets
your requirements, test the data cable using a loopback
connector. If the cable is good, the RF module data EEPROM
failed. Replace the RF module.
RF Serial
Link Data cable, RF module reader port, or RF module power supply
failed. Open the RF module and check for 19 to 28 VAC or 16 to
28 VDC at terminals A and C. If the voltage setting meets your
requirement, test the data cable using a loopback connector. If
the cable is good, the RF module reader port failed. Replace the
RF module.
RF PLL
Lock Data cable, RF module PLL lock, or RF module power supply
failed. Open the RF module and check for 19 to 28 VAC or 16 to
28 VDC at terminals A and C. If the voltage setting meets your
requirements, test the data cable using a loopback connector. If
the cable is good, the RF module PLL lock failed. Replace the RF
module.
Frequency
Program
Mode
Check that the frequency enable switch SW1 on the reader logic
card is set to diagnostic or normal as needed (see Figure 6-6).
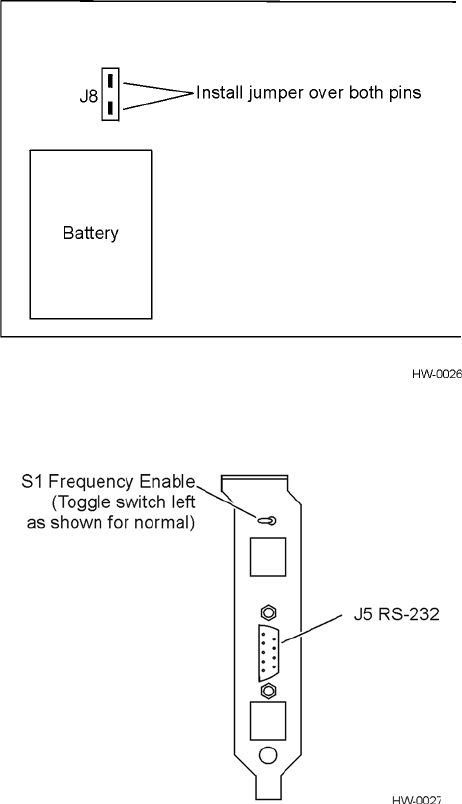
IT2200 Reader System with Multimode Capability Installation & Maintenance/Service Guide
6-12
Figure 6-5 Location of Battery Jumper (J8) in Relation to Battery
Figure 6-6 Frequency Enable Switch on Rear of IT2020 Reader Logic Card
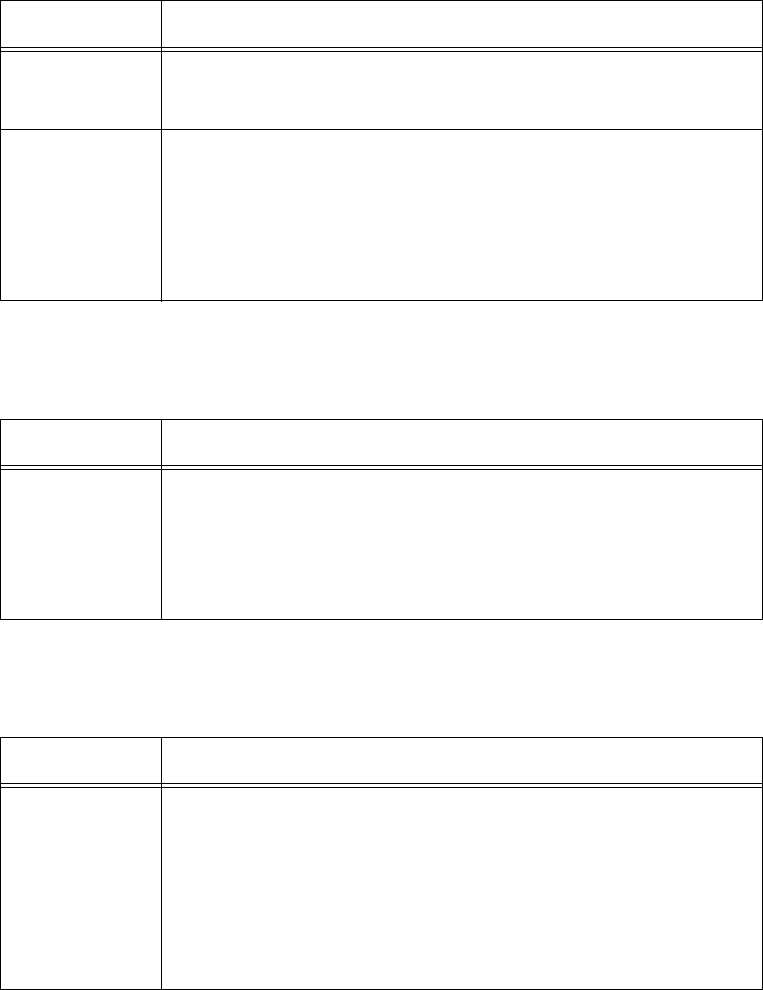
Troubleshooting the Installation
6-13
Table 6-4 Failure During Check Tag Test
Indication Action
No response to
check tag read
request
Repeat the check tag test, being careful to verify that all test
parameters are correctly set.
Slow or
intermittent
read count or
incorrect serial
number
The check tag antenna might have failed. Verify that the check tag
antenna is correctly positioned in relation to the transmit antenna
(see Figure 4-17 on page 4-23). Be sure that the check tag
antenna cable is securely fastened to the check tag antenna port
on the RF module.
Repeat the check tag test. If the problem persists, replace the
check tag antenna.
Table 6-5 Unacceptable RF Attenuation Statistics Using Check Tag
Indication Action
Unacceptable
RF attenuation
statistics using
check tag
Verify that the check tag antenna is correctly positioned in relation
to the transmit antenna (see Figure 4-17 on page 4-23). Be sure
that the check tag antenna cable is securely fastened to the check
tag antenna port on the RF module.
Repeat the check tag test. If the problem persists, replace the
check tag antenna.
Table 6-6 Unacceptable RF Attenuation Statistics Using Vehicle-Mounted Tag
Indication Action
Unacceptable
RF attenuation
statistics using
vehicle-
mounted tag
If, after moving vehicle to check for holes in the read pattern, the
problem persists, repeat the test using a different tag.
If the problem persists with a new tag, verify that the transmit and
receive antennas are correctly positioned (see Figure 4-15 on
page 4-20). Check that the antenna cables are securely
connected to the RF module.
If no problem can be found with the antennas or antenna cables,
contact the TransCore Action Center (TrAC).
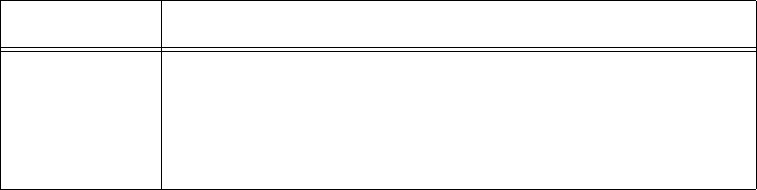
IT2200 Reader System with Multimode Capability Installation & Maintenance/Service Guide
6-14
Table 6-7 Self-Test Fail LED on Reader Logic Card Lights
Indication Action
SELF-TEST
FAIL LED on
reader logic
card lights
during startup
Data cable or RF module power supply failed. Open the RF
module and check for 24 VAC at terminals A and C. The voltage
should be 19.2V to 28.8 VAC or 16 to 28 VDC. If voltage setting
meets your requirements, test the data cable using a loopback
connector. If the cable is good, the RF module failed. Replace
the RF module.
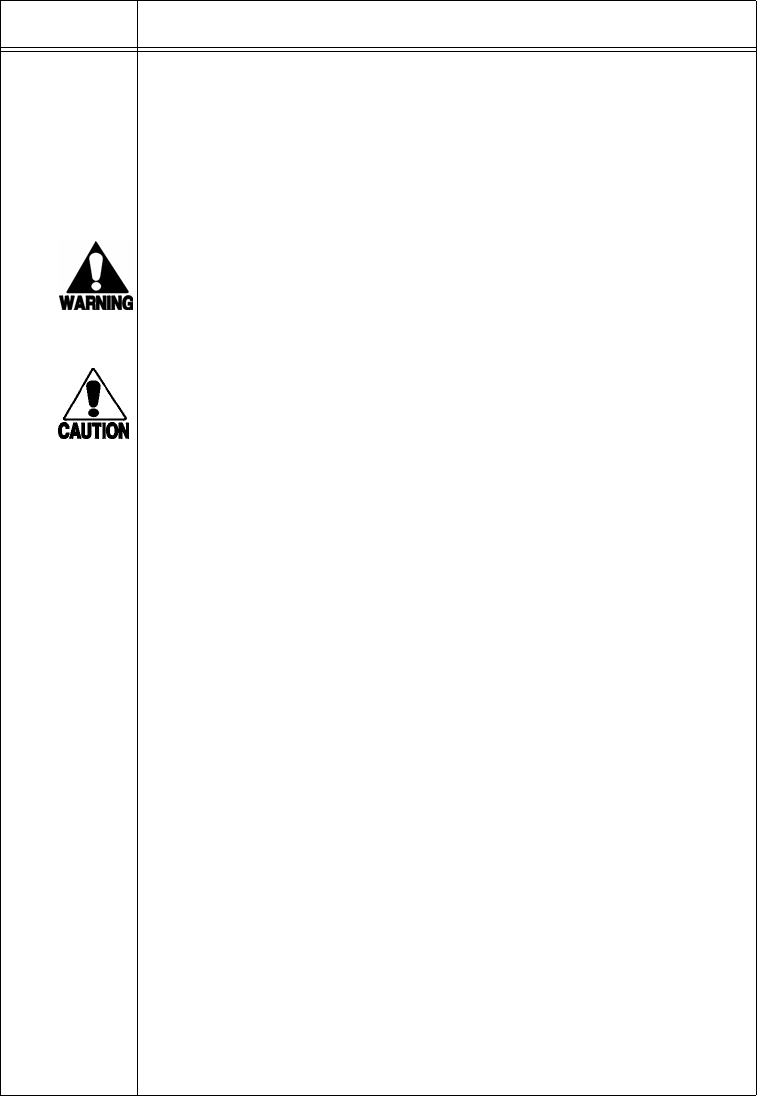
Troubleshooting the Installation
6-15
Table 6-8 Spotty Pattern or Low Handshake Counts
Indication Action
Spotty
pattern or
low
handshake
counts
This is a two-person operation. Person 1 checks commands and
responses using the host software. Person 2 uses a hydraulic lift to
check the physical connections.
The problems of spotty pattern or low handshake counts usually
have the same cause: either a defective RF coaxial cable between
the RF module and an antenna or a defective antenna. This
procedure checks both cables and antennas.
Warning
Switch off RF power before working on antennas.
Caution
Only switch on RF power when the RF module transmit port is
connected to an antenna or other load device.
Troubleshooting at the Lane
1. Person 1: Disconnect the data cable from the reader logic card
in the lane controller.
2. Connect the data cable to the extension data cable, then
connect the extension data cable to the reader logic card in the
PC.
3. Person 2: Open the RF module cover and measure the voltage
at Terminals A and C. The voltage should be 19 to 28 VAC or
16 to 28 VDC depending on your requirements.
Using Engineering Host Software Diagnostics
1. Person 1: Start the PC, then double-click the Host icon to start
the host software. Upon startup, the Power On Status
Information screen appears. Click Cancel to clear this screen.
2. From the Reader menu, select RF Attenuation. When the RF
Attenuation Parameters screen appears, set the downlink and
uplink attenuation to 0, then click Apply.
3. From the Options menu, select Diagnostics, then Diagnostics
Control.
4. Person 2: Disconnect the transmit antenna cable from the RF
module.
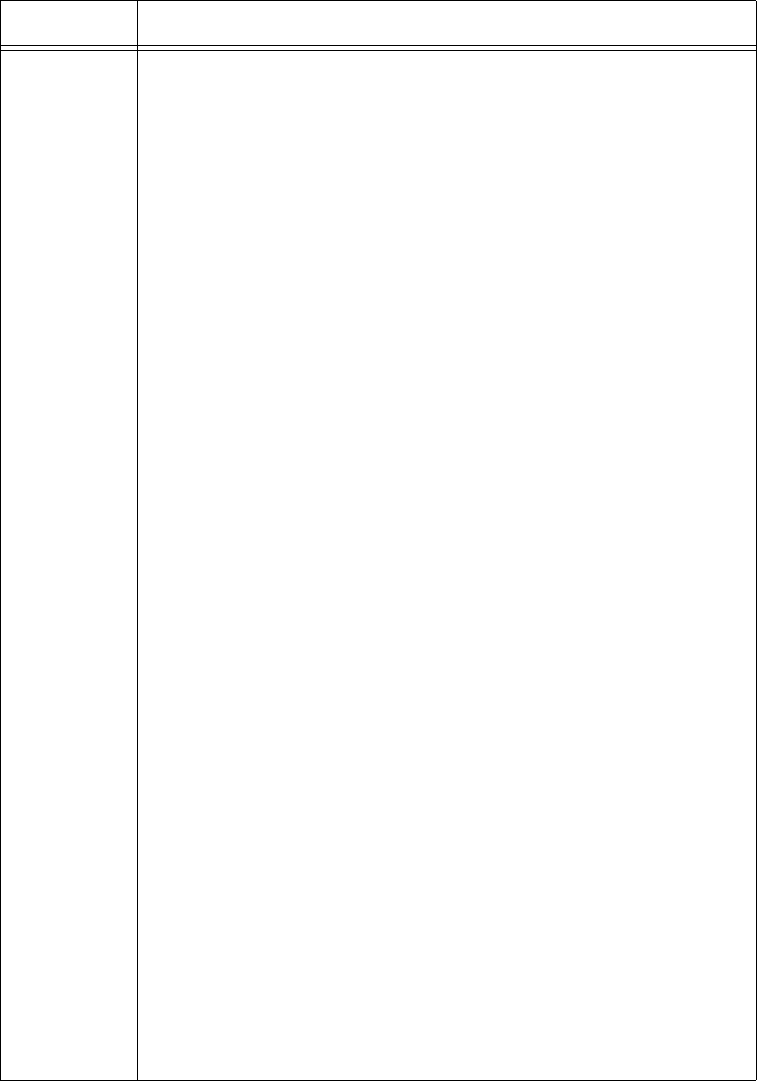
IT2200 Reader System with Multimode Capability Installation & Maintenance/Service Guide
6-16
Measuring Power and VSWR
1. Connect the RF jumper cable from the RF module transmit
port to the wattmeter input port.
2. Connect the antenna cable to the wattmeter output port.
3. Person 1: Select Continuous Uplink on the host software.
4. Person 2: Measure uplink power. It should be 28 to 30 dBm.
5. Measure the VSWR of the transmit antenna. It should be a
maximum of 1.6:1.
6. If VSWR is out of tolerance, test the antenna cable near the
connectors by moving it. Any significant change in VSWR
indicates a poorly terminated connection. Have Person 1
disable the continuous uplink, then replace the antenna cable
and repeat Steps 10 and 12. If the VSWR is still out of
tolerance, replace the transmit antenna.
7. Person 1: Disable the uplink.
8. Person 2: Disconnect the transmit antenna from the wattmeter
and connect the receive antenna.
9. Person 1: Select Continuous Uplink on the engineering host
software diagnostics.
10. Person 2: Measure the VSWR of the receive antenna. It should
be a maximum of 1.6:1.
11. If VSWR is out of tolerance, test the antenna cable near the
connectors by moving it. Any significant change in VSWR
indicates a poorly terminated connection. Have Person 1
disable the continuous uplink, then replace the antenna cable
and repeat Steps 16 and 17. If the VSWR is still out of
tolerance, replace the receive antenna.
12. Person 1: Disable the uplink and select Continuous
Downlink RF.
13. Person 2: Measure downlink power. It should be 20 to 27
dBm.
If the previous procedures did not reveal a problem, replace the
reader logic card and retest the system.
Table 6-8 Spotty Pattern or Low Handshake Counts (continued)
Indication Action
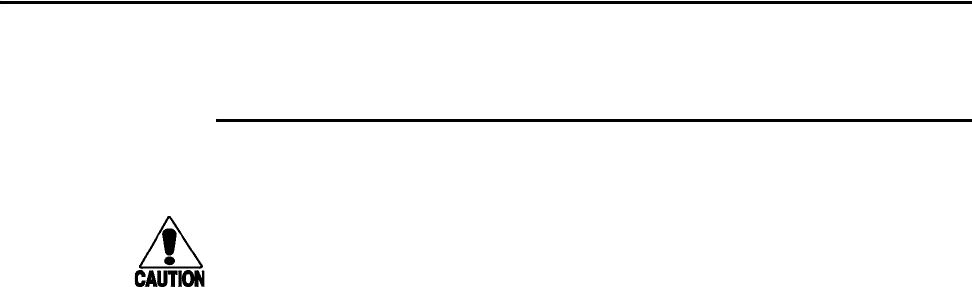
Troubleshooting the Installation
6-17
Removal and Replacement Procedures
This section outlines the procedures to remove or replace IT2200 Reader System with
Multimode Capability components.
Reader Logic Card
Caution
To prevent electrostatic discharge damage (ESD) be sure to wear a properly
grounded wrist strap before handling the reader logic card. Be sure the host com-
puter or lane controller is switched off before removing or replacing the card.
Removal
To remove the reader logic card
1. Record frequency and attenuation settings.
2. Turn off power to the host computer or lane controller.
3. Disconnect the data cable from the reader logic card.
4. Remove the screws holding the card brackets.
5. Remove the card.
Replacement
To install the replacement reader logic card
1. Check the dip switch settings on the new card.
2. Short the battery jumper on the new card.
3. Install the card in an ISA slot in the host computer or lane controller.
4. Fasten both connector brackets.
5. Connect the data cable to the reader logic card
6. Set the frequency and attenuation levels.
7. Check the lane tuning as described in “Testing the Footprint” on page 5-11.
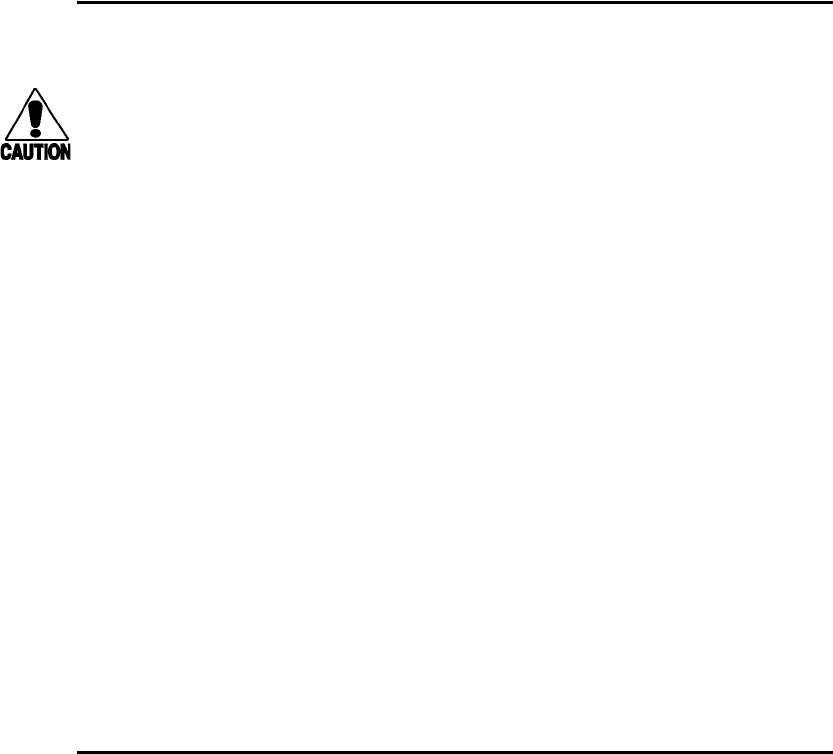
IT2200 Reader System with Multimode Capability Installation & Maintenance/Service Guide
6-18
RF Module
Caution
Only switch on RF power when the RF module transmit port is connected to an
antenna or other load device.
Removal
To remove the RF module
1. Turn off power to the RF module.
2. Disconnect the RF module power cable, data cable, and all three antenna cables.
3. Remove the nuts holding the mounting bracket U-bolts, then remove the RF
module.
Replacement
To install the replacement RF module
1. Position the RF module on the mounting pipe.
2. Insert the U-bolts through the mounting brackets and secure with lock washers
and nuts.
3. Tighten the nuts to 50 ft/lb.
4. Place a length of heat shrink tubing over each antenna cable.
5. Connect the data cable, all three antenna cables, and the power cable.
6. Check the lane tuning as described in “Testing the Footprint” on page 5-11.
Transmit/Receive Antennas
Removal
To remove a transmit or receive antenna
1. Turn off power to the RF module and disconnect the power cable.
2. Remove shrink tubing covering connector.
3. Disconnect the antenna cable from the antenna.
4. Check the antenna mounting angle using an inclinometer and record the angle.
5. If removing the transmit antenna, note the position of the spacers on the outside
mounting bracket.
6. Remove the nuts holding the mounting bracket U-bolts, then remove the antenna.

Troubleshooting the Installation
6-19
Replacement
To install a replacement antenna
1. Position the new antenna along the mounting pipe.
2. Insert the U-bolts through the mounting brackets and secure with lock washers
and nuts. If replacing the transmit antenna, add spacers in the same position as
before.
3. Set the antenna mounting angle to match the original antenna.
4. Tighten the nuts to 68 N-m (50 ft/lb).
5. Put a length of heat shrink tubing over the antenna cable and connect the cable to
the antenna.
6. Check the lane tuning as described in “Testing the Footprint” on page 5-11.
7. When lane tuning is complete, heat the shrink tubing covering the antenna cable
connection.
Check Tag Antenna
Removal
To remove the check tag antenna
1. Turn off power to the RF module and disconnect the power cable.
2. Disconnect the check tag antenna cable.
3. Note the position of the check tag antenna with relation to the transmit antenna
(see Figure 3-1 on page 3-3.
4. Remove the nuts holding the mounting bracket U-bolts, then remove the antenna.
Replacement
To install the replacement check tag antenna
1. Position the new antenna along the mounting pipe.
2. Insert the U-bolts through the mounting brackets and secure with lock washers
and nuts.
3. Position the check tag antenna to match the original antenna (see Figure 3-1 on
page 3-3).
4. Tighten the nuts to 68 N-m (50 ft/lb).
5. Put a length of heat shrink tubing over the antenna cable and connect the cable.
6. Perform the check tag test described on “Check Tag Test” on page 5-9.
7. When lane tuning is complete, heat the shrink tubing covering the check tag
antenna cable connection.

IT2200 Reader System with Multimode Capability Installation & Maintenance/Service Guide
6-20
Data Cable
Removal
To remove the data cable
1. Turn off power to the RF module and computer housing the reader logic card.
2. Disconnect the data cable.
Replacement
To install the replacement data cable
1. Connect the loopback connector to the new cable and test the cable for continuity.
2. Connect the new cable to the RF module and reader logic card.
3. Turn on power to the RF module.
4. Check the lane tuning as described in “Testing the Footprint” on page 5-11.
Antenna Cable
Removal
To remove an antenna cable
1. Turn off power to the RF module.
2. Disconnect the antenna cable.
Replacement
To install a replacement antenna cable
1. Connect the new cable to the RF module.
2. Place a piece of heat shrink tubing over the antenna cable.
3. Connect the cable to the antenna.
4. Turn on power to the RF module.
5. Check the lane tuning as described in “Testing the Footprint” on page 5-11.
6. When lane tuning is complete, heat the shrink tubing covering the antenna cable
connectors.

7
Preventive Maintenance
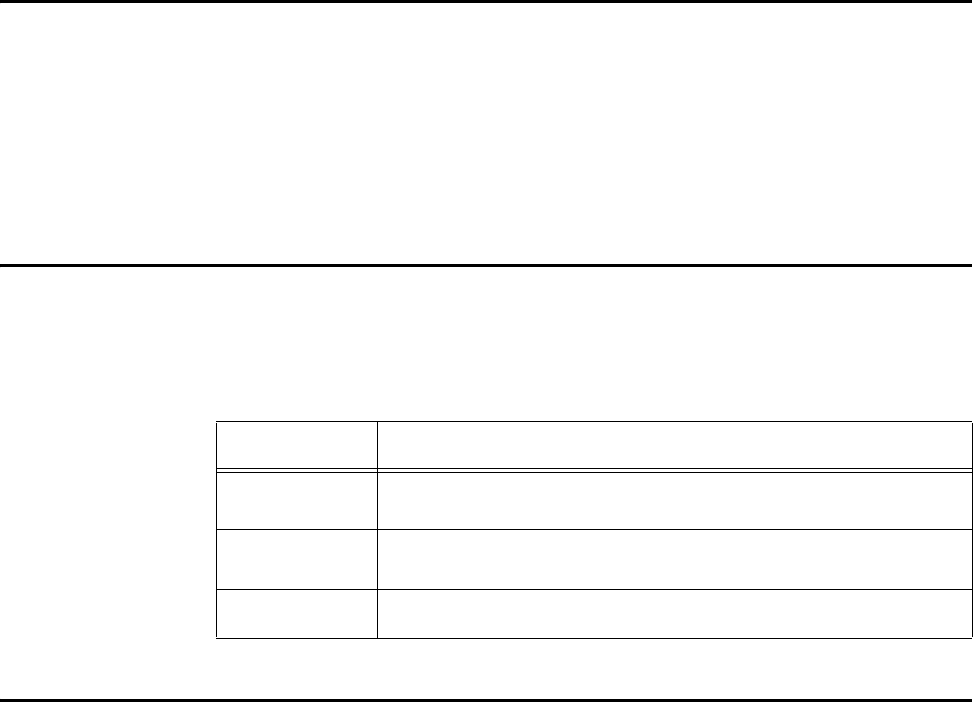
7-3
Chapter 7
Preventive Maintenance
This chapter provides schedules and instructions for performing
preventive maintenance on the IT2200 Reader System with Multimode
Capability components.
Preventive Maintenance Schedule
Table 7-1 lists the schedule of preventive maintenance activities for the IT2200
Reader System with Multimode Capability components.
Table 7-1 Preventive Maintenance Schedule
Visual Inspection
The IT2200 Reader System with Multimode Capability is very reliable, so many prob-
lems will be due to external causes, such as damage to components. Visually inspect
each system component and replace or repair components as needed. Replacement
procedures are listed later in this chapter.
To perform a visual inspection
1. Inspect the antennas for signs of damage or corrosion.
2. Check the RF module housing for signs of water leakage that might indicate a
broken or loose connector or a damaged seal.
3. Check cables between the RF module, antennas, and reader. Look for damage or
loose connections.
Use the flowchart in Figure 7-1 as a guide for performing visual inspections.
Period Task Description
Weekly Visually inspect the antennas and RF module housing for
physical damage such as cracks or stressed cables.
Quarterly Visually inspect all antenna and RF module cables for signs of
damage or water invasion.
Semiannually Check the lane tuning (see Chapter 5, "Tuning the Lane").
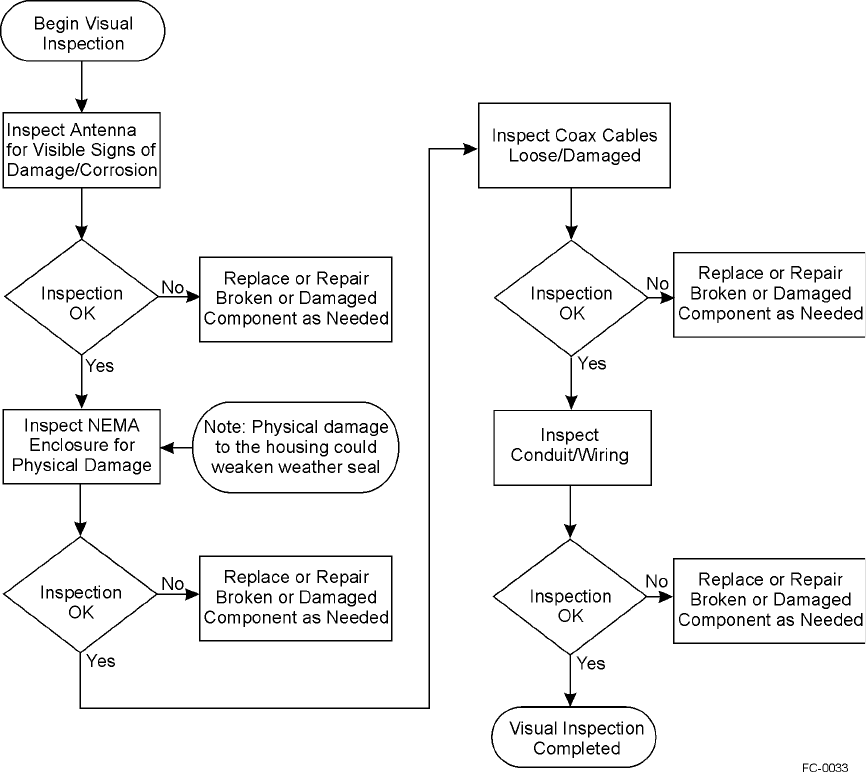
IT2200 Reader System with Multimode Capability Installation & Maintenance/Service Guide
7-4
Figure 7-1 Visual Inspection Process

A
Acronyms and Glossary

A-3
Appendix A
Acronyms and Glossary
A
A/V audiovisual
Aamp(s)
AAR Association of American Railroads
AC alternating current
ACK acknowledge (data valid)
active tag tag powered by a battery
antenna passive device that converts RF energy into magnetic energy (RF signal)
ASCII American Standard Code for Information Interchange
ATA American Trucking Association. This refers to a standard RF communications proto-
col and data storage method. ATA-type tags are read only.
AVI automatic vehicle identification
B
backscatter portion of an RF signal that is modulated by a tag and radiated back to the reader
baud measure of number of bits per second of a digital signal; for example, 9600 baud =
9600 bits per second
BDM background debugger mode
BIST built-in self test
bit The smallest unit of information, consisting of a 0 or 1 that is formed from binary digit
bps bits per second
byte binary character; for example, one 8-bit ASCII character
IT2200 Reader System with Multimode Capability Installation & Maintenance/Service Guide
A-4
C
CAM Custom autonomous mode used to run reader in semi-intelligent mode
check tag tag mounted inside IT2611 RF Module assembly
cm centimeter(s)
command data set that is recognized by the receiving device as intending to elicit a specific
response
conduit hardware portion of a particular interface; or, flexible steel pipe used for electrical wir-
ing
CR carriage return
CRC cyclic redundancy check
CTRL control
D
data information that is processed by a computing device
DC direct current
dB decibel(s)
dBM decibel(s)-milliwatts (30dBM = 1 watt; 1 dBM = 1 milliwatt)
dedicated lane lane that is restricted to tag-equipped vehicles
E
ECP error correcting protocol
eol end of line
eom end of message
EEPROM electrically erasable programmable read-only memory
EPROM erasable programmable read-only memory
ESD electrostatic discharge
ETC electronic toll collection
Acronyms and Glossary
A-5
F
FCC Federal Communications Commission
field physical area/space in which a tag can be read by the reader; also, an element of a data
record/frame. For example, division within a tag's data frame.
frame consecutive bits of data in memory that are read and written as a group
frequency bands range of RF frequencies assigned for transmission by an RF device
ft foot or feet
H
hex hexadecimal
hexadecimal base 16 numbering system that uses the characters 0–9 and A–F to represent the digits
0–15
host device, generally a computer, that is connected to the IT2200 Reader System compo-
nents through the communications port
Hz hertz
I
I/O input/output
ID identification; encoded information unique to a particular tag
in inch(es)
interface connection point for communication with another device
IP industry pack
ISA industry standard architecture
IRQ interrupt request
ISO International Organization for Standardization
IT2200 the IT2200 product line of equipment capable of communicating with read/write tags
IT2200 Reader System with Multimode Capability Installation & Maintenance/Service Guide
A-6
K
kkilo (103)
L
lane controller device that is used to integrate all the activity that occurs in a toll lane
lb pound(s)
LCD liquid crystal display
LED light-emitting diode
LSB least significant byte
M
message combination of fields, frames, and pages as required by the system to transmit or
receive associated command and response data to and from the reader and host
mmeter(s)
Mega million (106)
MB megabyte(s)
MHz megahertz
mixed-use lane lane equipped to handle cash transactions as well as tag-equipped vehicles
mode method of operation
ms milliseconds
MSB most significant byte
MTBF mean time between failure
MTTR mean time to replace
milli one-thousandth (10-3)
mW milliwatt(s)
Acronyms and Glossary
A-7
N
NNewton(s)
NACK negative acknowledgment (data not valid)
NEMA National Electrical Manufacturers Association
nibble sequence of four adjacent bits treated as a unit
NVM nonvolatile memory
NVRAM nonvolatile RAM used to hold data over power loss
P
page logical group of bytes representing data stored in a tag. A page is a maximum of 128
bits
PC personal computer
PDT portable data terminal
PLL phase locked loop
protocol specified convention for the format of data messages communicated between devices
PWA printed wiring assembly
R
RAM random access memory
read process of acquiring data from a device; for example, from a tag or from computer
memory
reader controlled interrogating device capable of acquiring data from a device; for example,
acquiring and interrupting data from a tag
read zone physical area in which a tag can be read by the reader system
RF radio frequency
RFID radio frequency identification
ROM read-only memory
IT2200 Reader System with Multimode Capability Installation & Maintenance/Service Guide
A-8
S
ssecond(s)
SCSI small computer systems interface
SRAM static random access memory
som start of message
system a reader, RF module, antenna, tag, and tag programmer, all described by their general
application and their interfaces with each other and any connected devices that are
defined as being outside the system
T
tag small, self-contained device acting as an identifying transponder
tag programmer initialization device that is capable of setting or programming a tag into its initial
functional mode of operation
TDM time division multiplexing, used in this document to refer to the use of time division
multiplexing of multiple readers within close proximity of each other
TDMA time division, multiple access refers to the capability to read multiple tags in an open-
road configuration by a single reader.
Title 21 State of California code of regulations, Chapter 16, Title 21, standard used for AVI/
DSRC (digital short-range communication) communication protocol
toll any application of the system equipment wherein the equipment is used to assist in the
orderly collection of money in exchange for the passage of a vehicle through a partic-
ular installation point
TrAC TransCore Action Center
transponder a tag
U
UPS uninterruptible power supply
UTA universal toll antenna
Acronyms and Glossary
A-9
V
Vvolt(s)
Ver version (software)
VSWR voltage standing wave ratio
W
Wwatt(s)
write process of recording data; for example, writing to computer memory or to a tag’s
memory. Writing writes over (erases) previous data stored at the specified memory
locations
IT2200 Reader System with Multimode Capability Installation & Maintenance/Service Guide
A-10

B
Block Diagrams
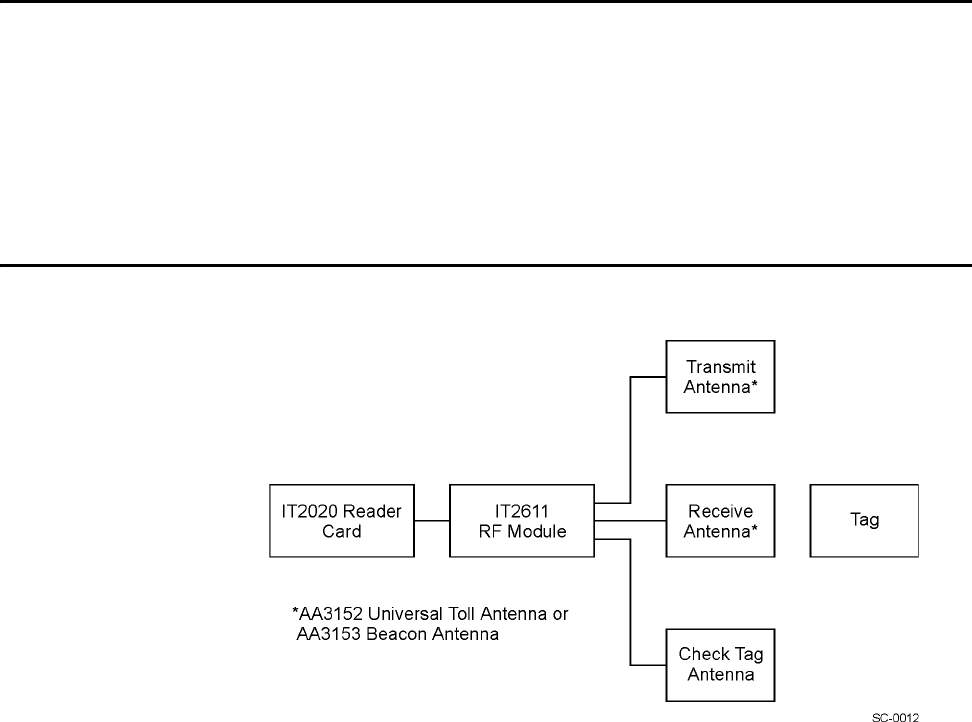
B
-3
Appendix B
Block Diagrams
This appendix shows the block diagrams for the individual IT2200
Reader System with Multimode Capability components as well as the
interface connections between the components.
IT2200 Reader System with Multimode Capability
Figure B-1 IT2200 Bistatic Reader System Functional Block Diagram
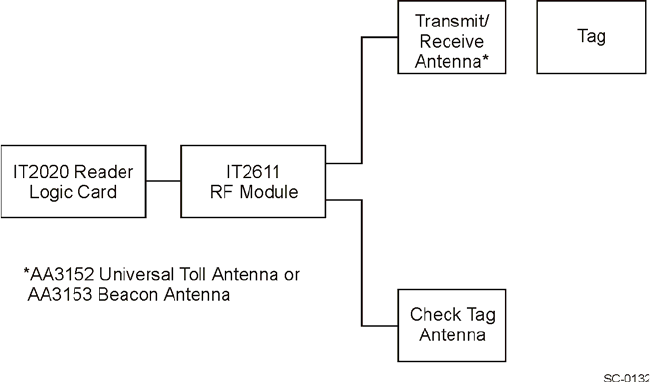
IT2200 Reader System with Multimode Capability Installation & Maintenance/Service Guide
B-4
Figure B-2 IT2200 Monostatic Reader System Functional Block Diagram
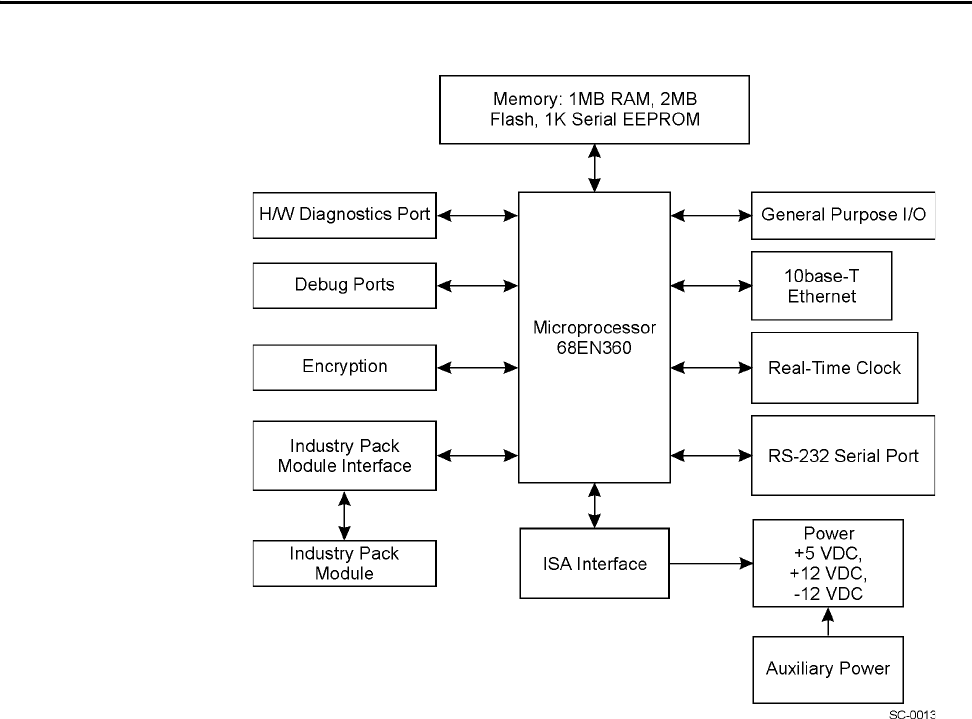
Block Diagrams
B-5
IT2020 Reader Logic Card
Figure B-3 IT2020 Reader Logic Card Functional Block Diagram
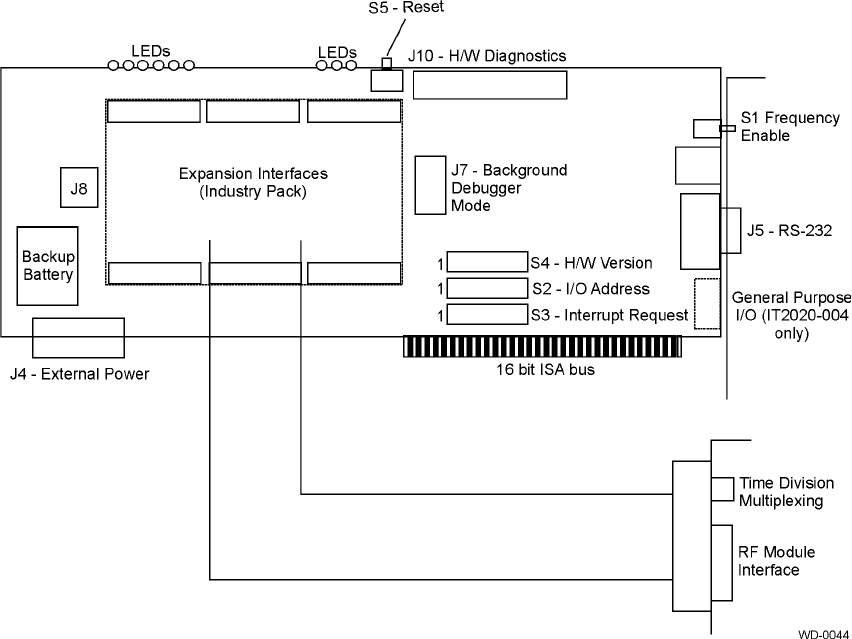
IT2200 Reader System with Multimode Capability Installation & Maintenance/Service Guide
B-6
Figure B-4 IT2020 Reader Logic Card Interface
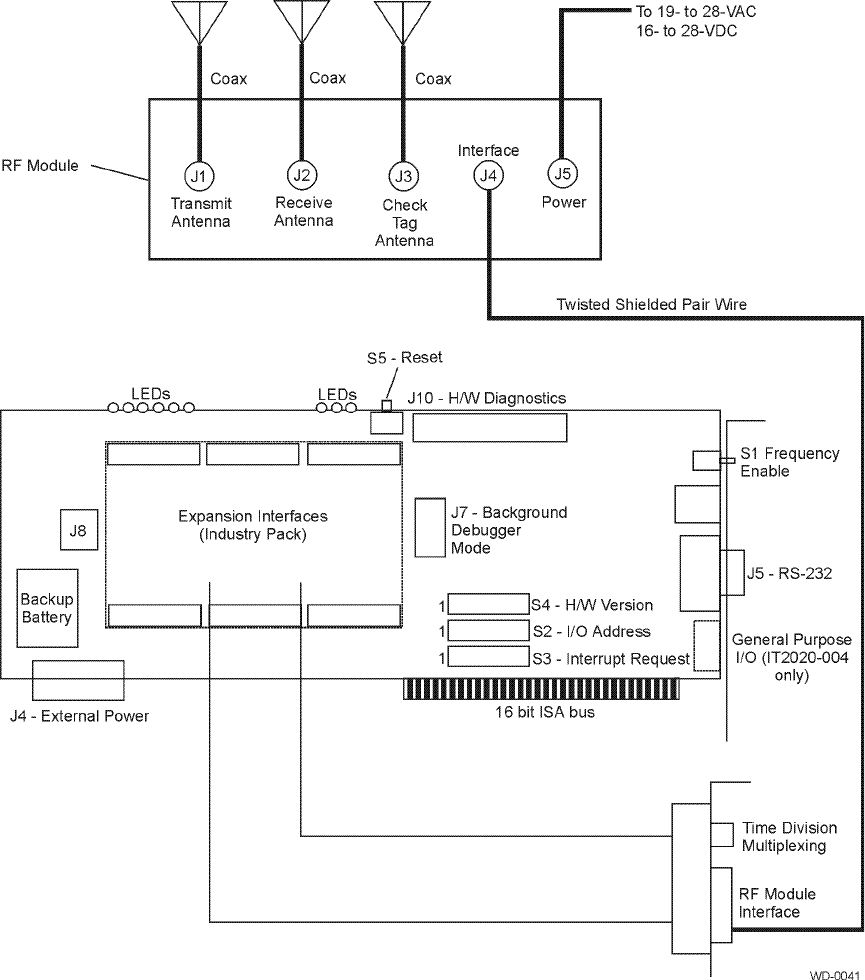
Block Diagrams
B-7
Figure B-5 Minimum Connections for the IT2020 Reader Logic Card Interface (Bistatic Application)
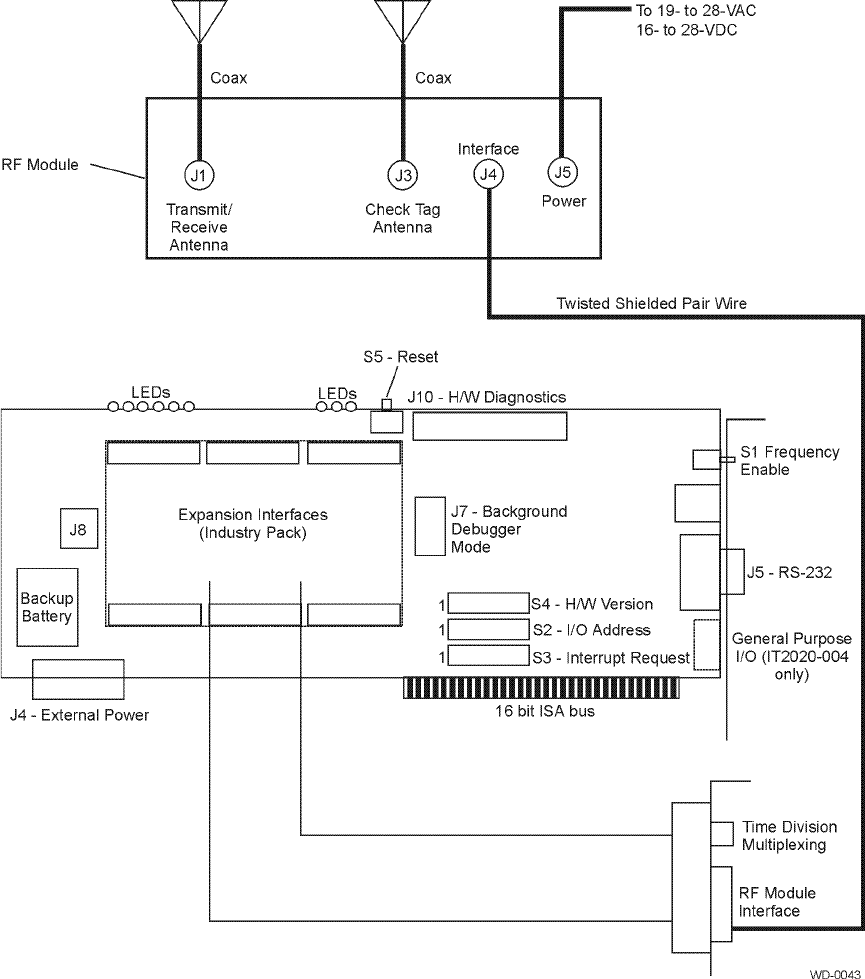
IT2200 Reader System with Multimode Capability Installation & Maintenance/Service Guide
B-8
Figure B-6 Minimum Connections for the IT2020 Reader Logic Card Interface (Monostatic Application)
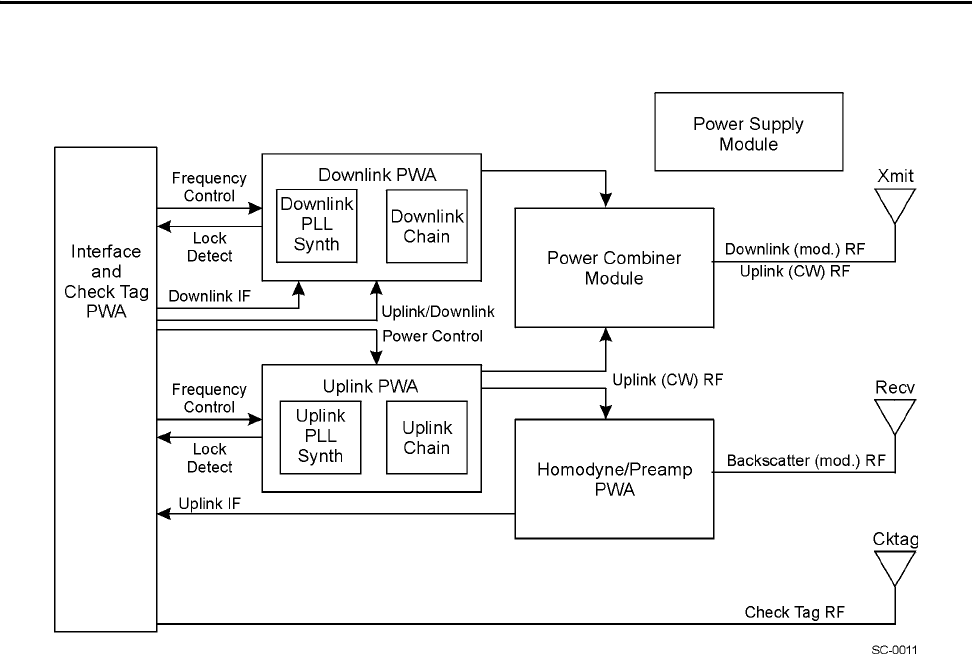
Block Diagrams
B-9
IT2611 RF Module
Figure B-7 IT2611 RF Module Functional Block Diagram (Bistatic Configuration)
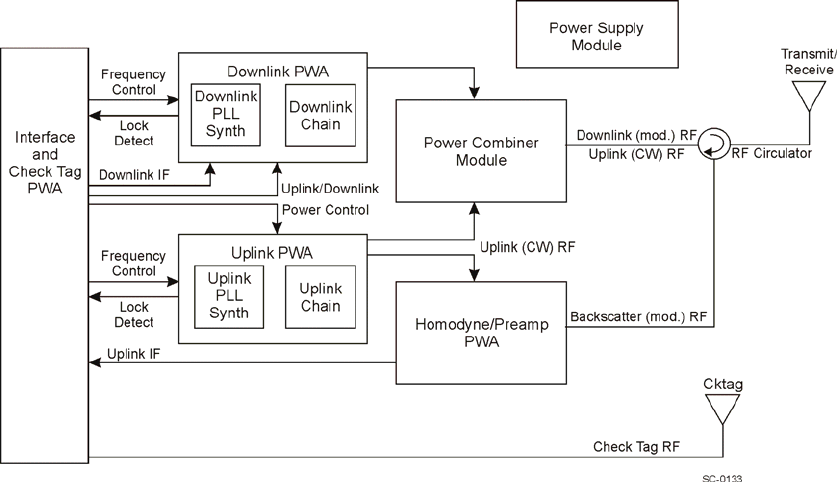
IT2200 Reader System with Multimode Capability Installation & Maintenance/Service Guide
B-10
Figure B-8 IT2611 RF Module Functional Block Diagram (Monostatic Configuration)

C
System Technical Specifications
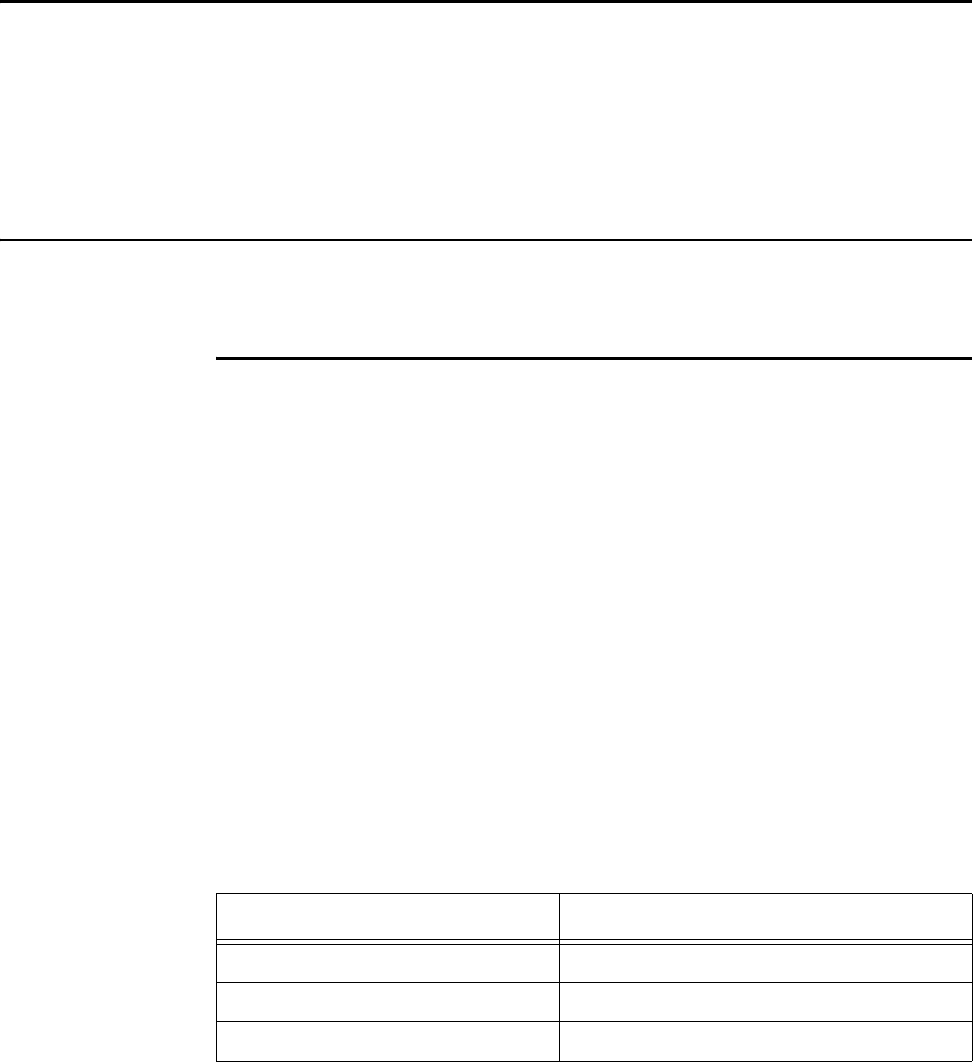
C-3
Appendix C
System Technical Specifications
This chapter provides reference information for the IT2200 Reader
System with Multimode Capability components.
Component Specifications
This appendix describes the engineering specifications for the IT2200 Reader System
components.
IT2020 Reader Logic Card
Electrical Specifications
The reader logic card requires +5 VDC and +12 VDC power, which is supplied by the
host computer or lane controller power supply.
Circuit breakers and disconnects are unnecessary with the reader logic card. Because
all input and output signals have limited short circuit current drive, there is no need to
include a circuit breaker. Lightning protection is achieved through the use of optically
coupled signals between the reader logic card and the RF module. These two units are
connected via copper wire with optical isolation on the reader logic card. The card
provides all of the following interfaces: card edge, ISA, RS-232, optically isolated
input/output interface, optional external power, background debugger mode (BDM),
TDM, diagnostics, and IP daughterboard.
Table C-1 shows the electrical requirements for the IT2020 Reader Logic Card.
Table C-2 shows the power consumption estimates for the card’s individual assem-
blies.
Table C-1 IT2020 Reader Logic Card Electrical Requirements
Specification Value
Input power <10W
Power connections ISA bus or direct
Warm-up time < 30 seconds
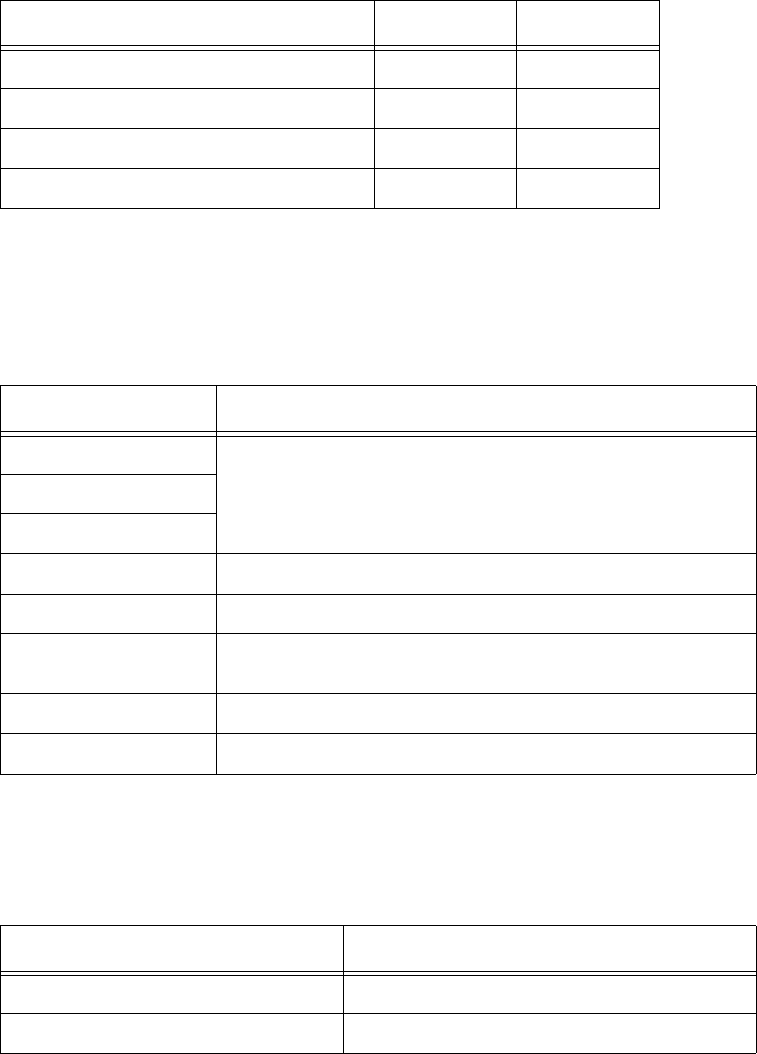
IT2200 Reader System with Multimode Capability Installation & Maintenance/Service Guide
C-4
Table C-2 IT2020 Reader Logic Card Power Consumption
Environmental Specifications
The IT2020 Reader Logic Card can withstand the environmental tolerances shown in
Table C-3.
Table C-3 IT2020 Reader Logic Card Environmental Tolerances
Physical Specifications
Table C-4 lists the physical specifications of the IT2020 Reader Logic Card.
Table C-4 IT2020 Reader Logic Card Physical Specifications
Component +5 VDC +12 VDC
ISA PWA 500 mA
Encoder/Decoder/TDM Module 200 mA
I/O Module 75 mA 200 mA
Total: 775 mA 200 mA
Environment Tolerance
Dust Reader logic card is installed in host computer or lane
controller Therefore it is not exposed to external
environmental tolerances.Rain
Corrosive resistance
Shock 5 G ½-sine pulse, 10 ms duration, 3 axis
Vibration 1.0 Grms 10-500 Hz
Operating
temperature -20° to +55°C (-4° to +131°F)
Storage temperature -20° to +70°C (-4° to +158°F) ambient air temperature
Humidity 10 to 95% noncondensing
Characteristic Specification
Size 33.3 x 12.2 x 1.5 cm (13.1 x 4.8 x 0.6 in)
Weight 0.45 kg (1 lb)
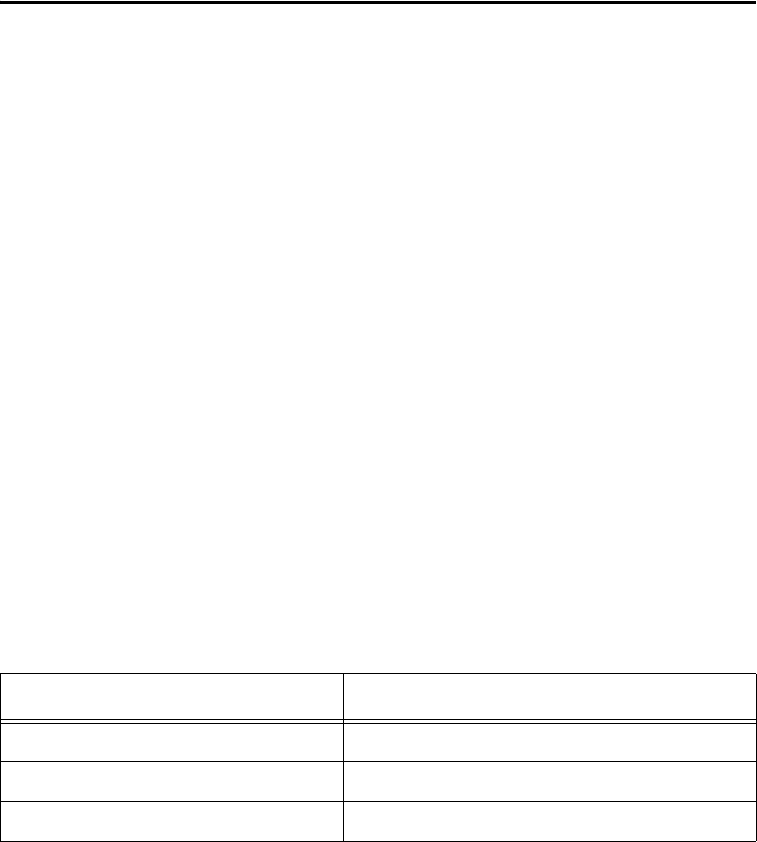
System Technical Specifications
C-5
IT2611 RF Module
The IT2611 RF Module provides two-way RF communication between the IT2020
Reader Logic Card and any tags compatible with the IT2200 protocol. It relays data
and control signals from the reader logic card to the tags and relays tag responses to
the reader logic card.
Interfaces
The RF module has five external interfaces:
•Antennas—Three Type N socket connectors are used to connect the RF module to
the transmit, receive, and check tag antennas using low-loss, coaxial RF cables.
•Tag data/control—A 26-pin connector is used to connect the RF module to the
reader logic card using the data cable.
•Power—A 3-pin connector is used to connect the RF module to a power supply
(19-28 VAC @47-63 Hz or 16-28 V DC).
The data connector connects to the logic card to supply tag data information and com-
munication to the RF module.
Electrical Specifications
Table C-5 shows the electrical requirements for the IT2611 RF Module.
Table C-5 IT2611 RF Module Electrical Requirements
Environmental Specifications
The IT2611 RF Module can withstand the environmental conditions shown in Table
C-6.
Characteristic Specification
Input power 19-28 VAC @47-63 Hz or 16-28 V DC
Power consumption 40 W maximum
Power connection 3-pin connector
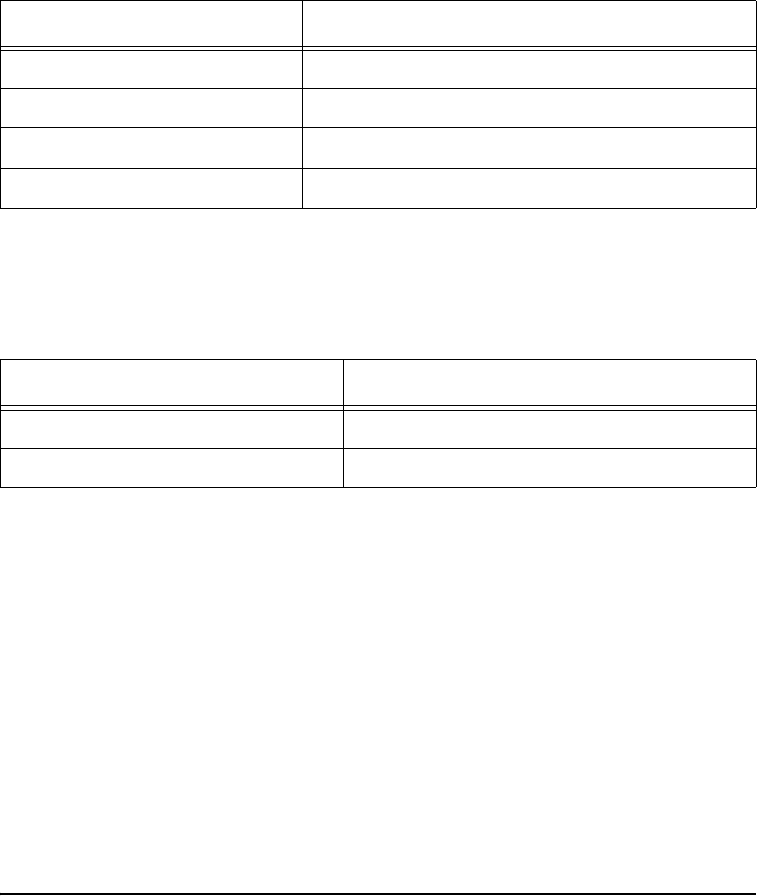
IT2200 Reader System with Multimode Capability Installation & Maintenance/Service Guide
C-6
Table C-6 IT2611 RF Module Environmental Specifications
Physical Specifications
Table C-7 lists the physical specifications of the IT2611 RF Module.
Table C-7 IT2611 RF Module Physical Specifications
Housing Specifications
The RF module housing consists of the following components:
•Fiberglass enclosure
•Bulkhead Type N connectors for antenna connections
•Bulkhead circular waterproof connectors for power and interface
•Stainless steel mounting hardware
Internal RF module printed wiring assemblies mount into a half-size ISA card cage.
This card cage mounts into the fiberglass enclosure for final mounting. All interface
connectors to the RF module are made through the fiberglass enclosure wall in bulk-
head style.
AA3152 Universal Toll Antenna and
AA3153 Beacon Antenna
Because the specifications for the AA3152 and AA3153 antennas are similar, this sec-
tion covers both antennas.
•Operates in the location and monitoring service band (902 to 928 MHz)
•Optimum radiation pattern—Virtually no side or back lobes help confine antenna
coverage to a single lane.
Environment Specification
Shock 5 G ½-sine pulse, 10 ms duration, 3 axes
Vibration 1.0 Grms 10 to 500 Hz
Operating temperature -20° to +55°C (-4° to +131°F)
Humidity 95% noncondensing
Specification Value
Size 33 x 35.6 x 21.6 cm (13 x 14 x 8.5 in)
Weight 11.34 kg (25 lb)
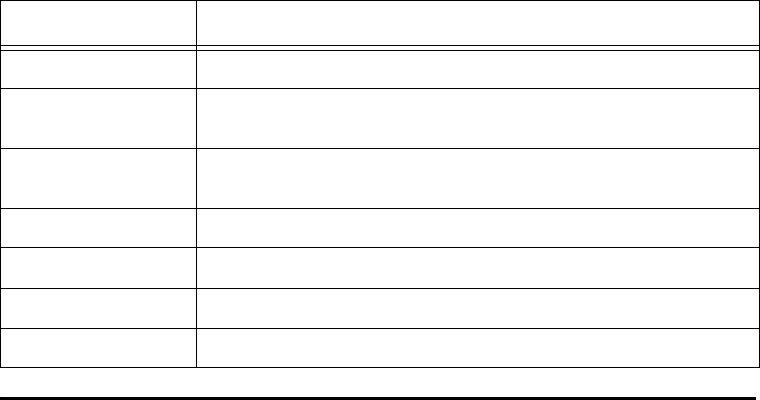
System Technical Specifications
C-7
•Weatherproof—Each antenna is housed in a radome made of materials with favor-
able electrical characteristics and resistance to ultraviolet radiation.
•Bandpass filtering helps to attenuate interference from other RF sources.
Environmental Specifications
The AA3152 and AA3153 antennas can withstand the environmental tolerances
shown in Table C-8.
Table C-8 Antenna Environmental Tolerances
IT2502 Check Tag Antenna
The IT2502 Check Tag Antenna allows the reader logic card and RF module to test
system operation using the check tag. The check tag antenna is mounted near the
transmit antenna and connected to the RF module through a low-loss, coaxial RF
cable.
Environment Specification
Dust NEMA pub 250-1991, Sec. 6.5, page 18
Rain NEMA pub 250-1991, Sec. 6.4, page 17 and Sec. 6.7, page
19
Corrosion
resistance NEMA pub 250-1991, Sec. 6.9, page 20
Shock 5 G ½-sine pulse, 10 ms duration, 3 axes
Vibration 0.5 Grms 10-500 Hz
Temperature range -40° to +75°C (-40° to +167°F)
Humidity 100% condensing
IT2200 Reader System with Multimode Capability Installation & Maintenance/Service Guide
C-8

D
Hardware Interfaces
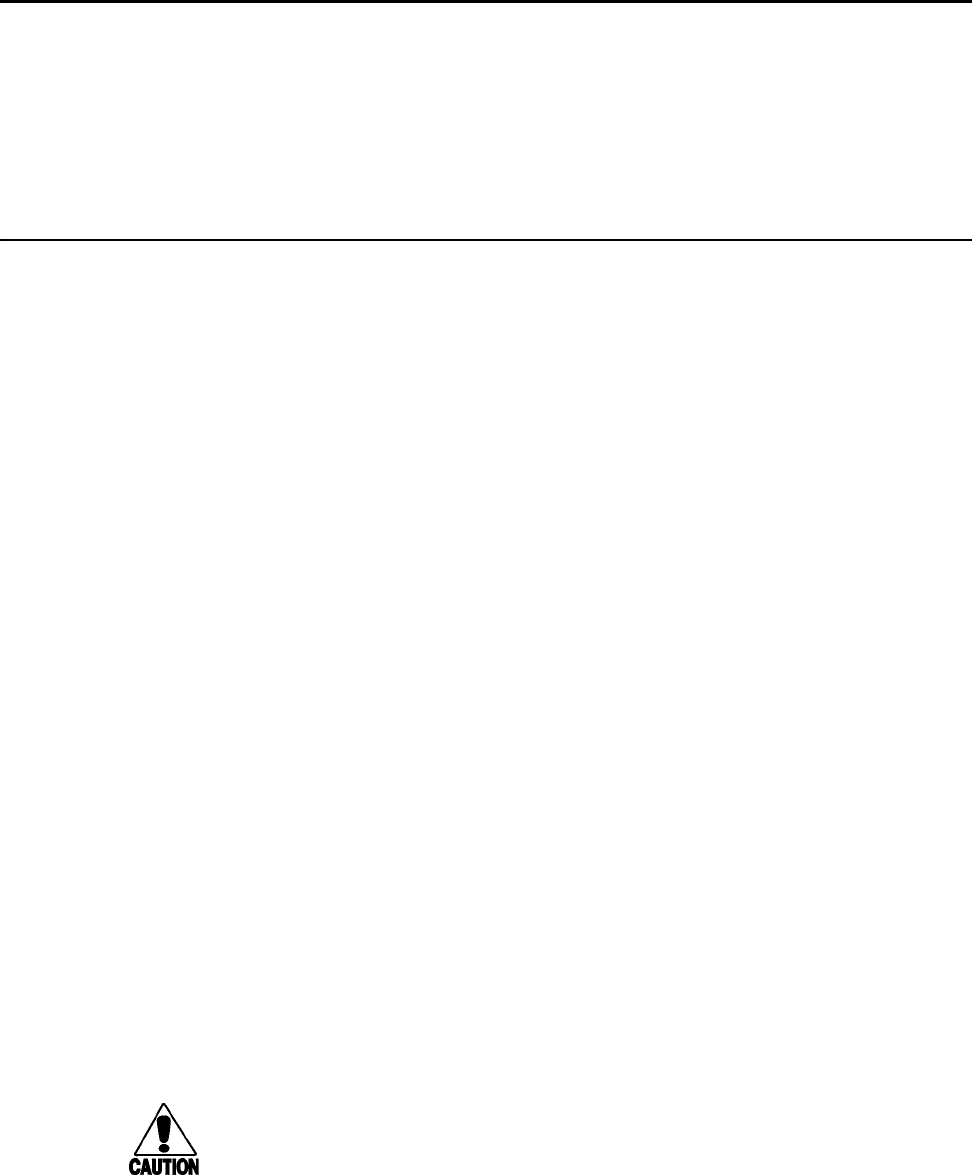
D-3
Appendix D
Hardware Interfaces
This appendix describes the physical interconnections within the IT2200
Reader System with Multimode Capability.
Reader Logic Card Hardware Interconnection
Interconnection to the IT2020 reader logic card includes an ISA bus interface. All
power and communications to the lane controller computer are routed through this
standard interface. Interface lines from the reader logic card to the RF module are
attached via an external connector.
The default configuration settings are
IRQ = 5 Possible range is 5, 6, 7, 10, 11, 12, 14, and 15
(Or no-interrupt with all switches off)
I/O (Input/Output) address = 220H Possible range 000H to 3FCH
Note: Many PCs that have an installed sound card use 5 as its IRQ and 220H for
its I/O address. If you are installing the IT2020 Reader Logic Card into a PC with a
sound card you must change the reader logic card I/O address and IRQ setting.
•Frequency Enable Switch (S1) Placing this switch to the right, places the reader
into Frequency Programming Mode, which lets the user change frequencies of the
RF. This switch enables the use of the Set RF Frequency command.
•I/O Address Switch (S2) The switch for setting the I/O address has 8 positions,
which controls the bit value for A9 through A2, with A1 and A0 defaulting to 0.
When the switch is placed in the ON position, it corresponds to a Hi State - 1. An
example of setting the switch to equal 220H (default) is shown below. The possi-
ble range of the I/O address switch S2 is from 000H to 3FCH.
•Interrupt Request (IRQ) Switch (S3) The IRQ switch provides selection of the
ISA interrupt. The switch has 8 positions and when on, corresponds to the Inter-
rupt selected. Note that all switches OFF will provide operation in the polled
mode. Setting a switch to ON selects that interrupt.
•Hardware (H/W) Version Switch (S4) The H/W Version Switch sets the hard-
ware version number on the logic board.
Caution
Switch S4 is set at the factory and should not be changed.
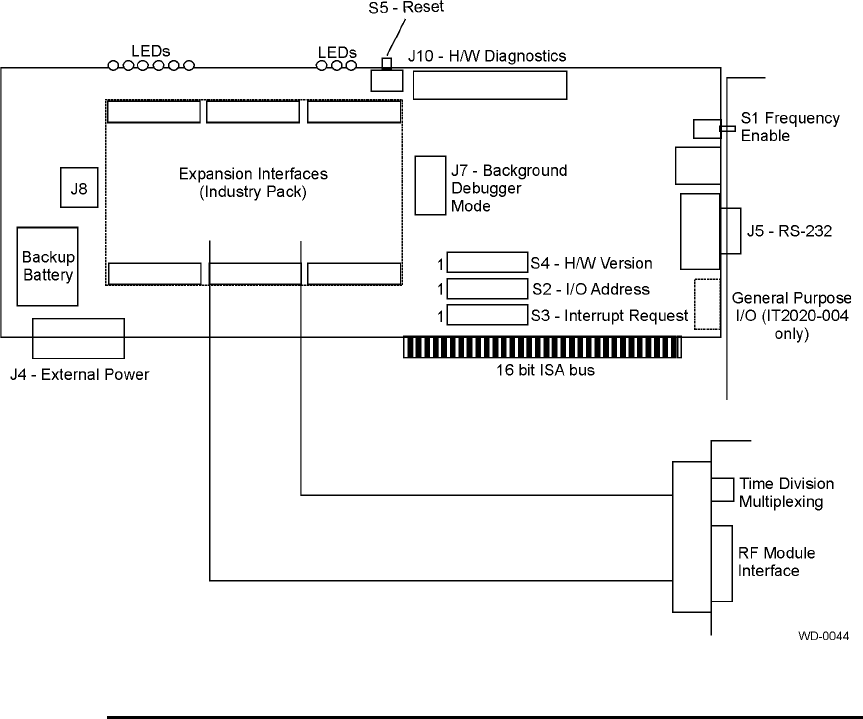
IT2200 Reader System with Multimode Capability Installation & Maintenance/Service Guide
D-4
•Battery Jumper (J8) This jumper must be installed for the battery to backup
SRAM in the event of a power loss. This jumper should remain open while this
reader logic card is in storage.
Figure D-1 shows the locations of the IT2020 Reader Logic Card switches.
Figure D-1 Locations of Switches on IT2020 Reader Logic Card
16 Bit ISA Bus
The card edge connector comprises two sets of contact pins on both sides of the board.
The set closest to the PC bracket and the back of the board is the signals for the origi-
nal 8-bit ISA bus. There are 31 contact pins on each side of the board in this set of
signals. The pins designated A1 through A31 are on the component side of the board,
while the pins designated B1 through B31 are on the back side of the board. A1 and
B1 are closest to the bracket end of the PC card. The second set of pins on the board
edge are all of the signals that were added when ISA expanded to a 16-bit data bus.
There are 18 contact pins on each side of the board in this set. The pins designated C1
through C18 are on the component side of the board, while the pins designated D1
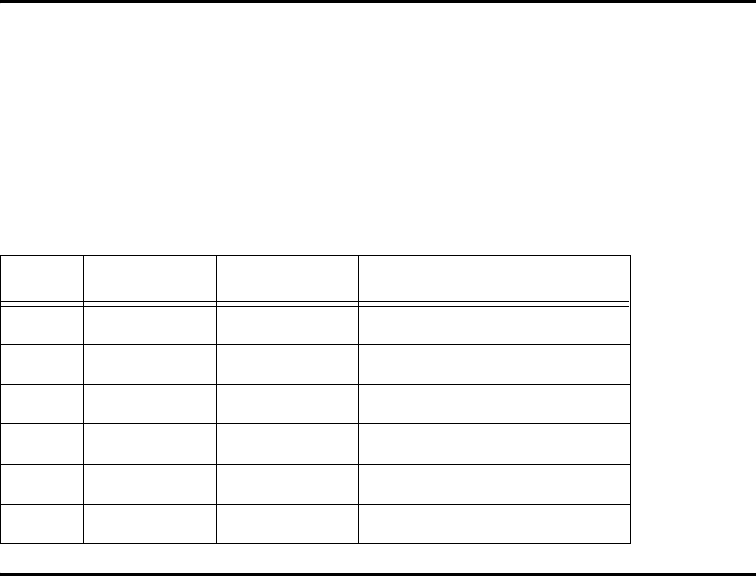
Hardware Interfaces
D-5
through D18 are on the back side of the board. Pins C1 and D1 are closest to the
bracket end of the PC card. Signal I/O is with respect to the ISA reader.
Optional External Power
Typically, the logic card receives power from the ISA bus. When the card is inserted
into an ISA bus backplane, this connector is not used. If the logic card is used in an
application where no ISA bus is present, the card receives power through this connec-
tor. Table D-1 lists definitions of the connector pins and the power supply require-
ments. The signal I/O is with respect to the ISA reader.
Expansion Interfaces (Industry Pack)
The ISA reader provides a minimum of two expansion slots on a mezzanine bus that
follows the definition of the Industry Pack (IP) Bus VITA 4-1995 draft document.
The clock speed for this bus is 8 MHz. The physical interface is made with two Type-
D connectors per each expansion slot. The connectors are AMP, Incorporated, part
173280-3 or equivalent on the ISA board. One connector contains all of the bus inter-
face and logic and the second is used for all user-defined I/O.
For implementing the IT2000 Encoder/Decoder daughterboard, the I/O connector
contains connections for a UART interface from the 68360 for the control interface to
the RF module, and discrete outputs used to control the RF power on/off of the RF
uplink and RF downlink of the RF module. All unused pins are reserved.
Signal I/O is with respect to the ISA printed wiring assembly (PWA).
The RF module interface connector is a 25-pin Type-D (DB-25F) socket connector. It
provides an interface to the RF module portion of the reader.
Table D-1 Optional External Power Pin Definition
Pin Signal In/Out Description
1 GND In/Out Ground
2 +5 VDC In +5 volt power
3 + 5VDC In +5 volt power
4 -12 VDC In -12 volt power
5 +12 VDC In +12 volt power
6 GND In/Out Ground
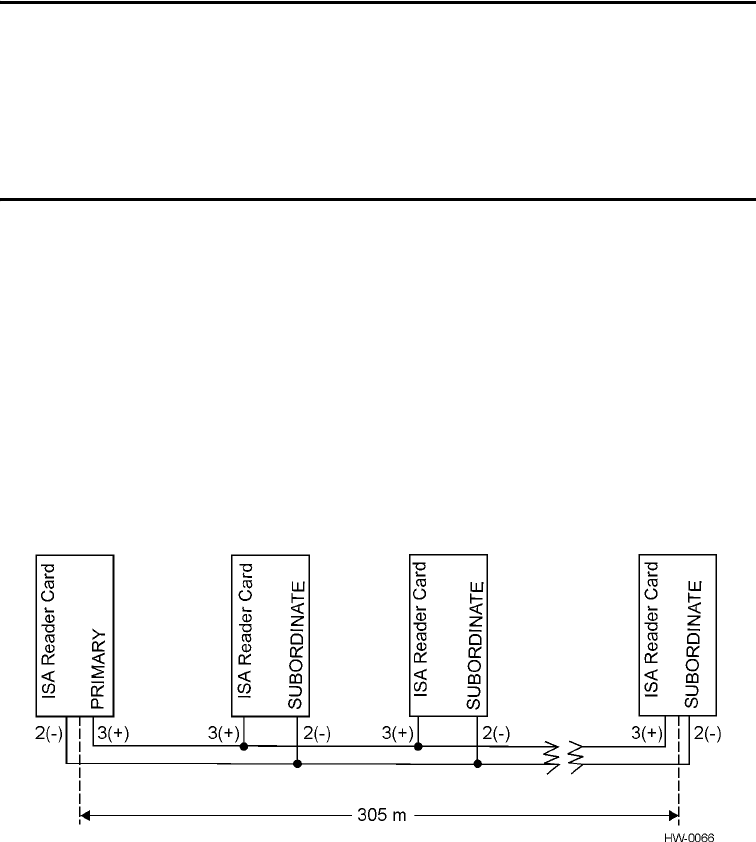
IT2200 Reader System with Multimode Capability Installation & Maintenance/Service Guide
D-6
LEDs
These LEDs denote the reader status. The LEDs are placed in logical groups along the
top edge of the board. The colors for the indicators were chosen to assist in trouble-
shooting. A software bit control circuit switches on all of the indicators in one of the
reader board’s initialization routines.
Time Division Multiplexing Connector
Interconnect for time division multiplexing (TDM) is provided by a differential RS-
485 interface with a DB-9 connector located on the expansion connector in slot 2. This
connection provides a synchronization interface between readers to provide multiplex-
ing in time. This interface connection can be daisy-chained from reader to reader dur-
ing installation (Figure D-2) and can operate by synchronizing the readers to each
other by a synchronization pulse from a primary reader. Because there are two sets of
the TDM synchronization pins, one set can be used and the incoming and the second
set can be used for outgoing signals. By daisy-chaining the readers on separate pins,
the downstream side (away from the primary reader) loses synchronization when dis-
connected. TransCore recommends that both upstream and downstream connections
be wired to the same positive (+) and negative (-) pins as shown in Figure D-2.
Figure D-2 Typical TDM Installation
With the use of low-loss/capacitance twisted pair cable, the maximum distance is 305
m (1000 ft), but can vary with installation and type of cable used. The suggested cable
is either Belden 89182 or 8132. Table D-2 shows the pin designations and descriptions
for the TDM connector.
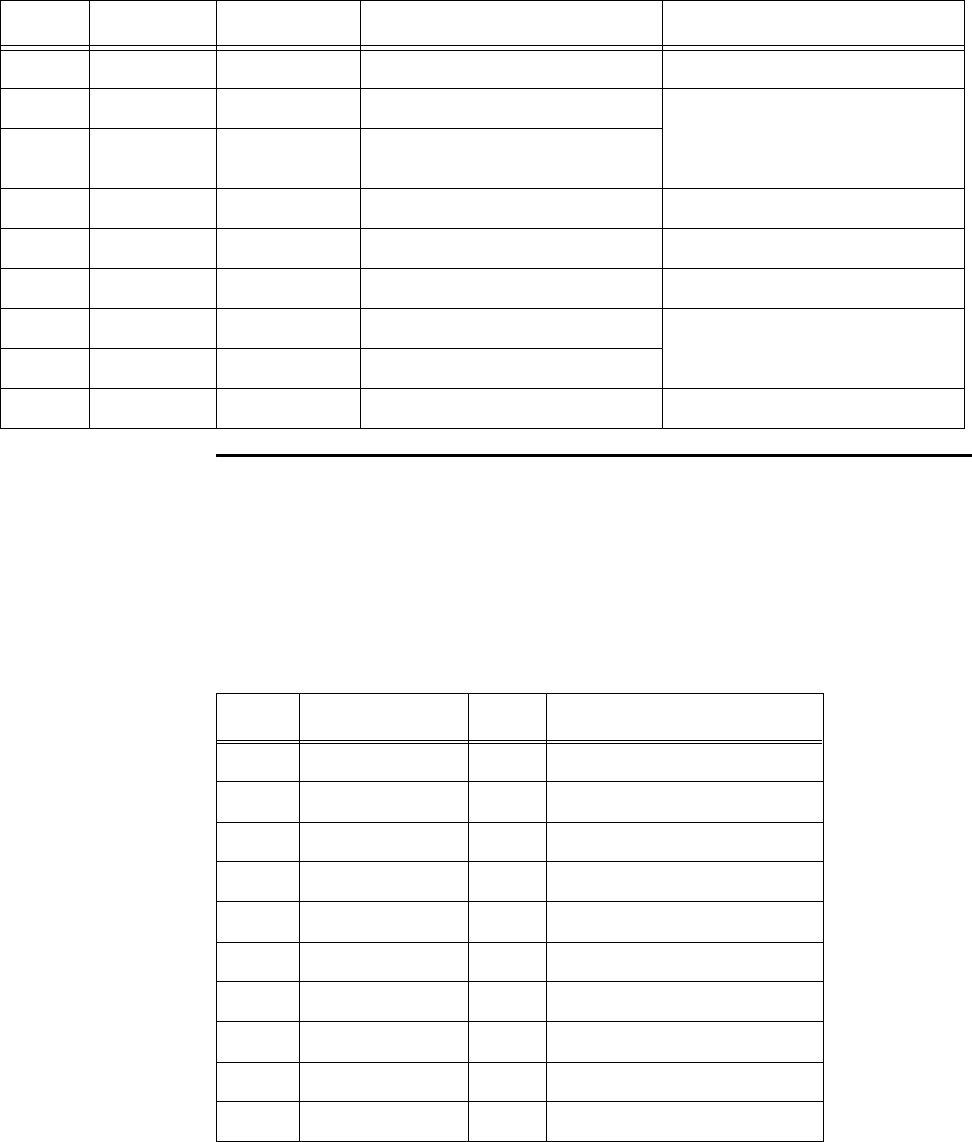
Hardware Interfaces
D-7
Table D-2 TDM Connector
Background Debugger Connector
The background debugger (BDM) connector is a 10-pin, 0.1-center dual-row header,
with a configuration is 2 by 5. This connector is used for debugging only and is a
Motorola proprietary interface.
Table D-3 shows the pin designations and descriptions for the BDM connector.
Table D-3 BDM Connector
Pin Name Type Description Recommended Connection
1 N/C N/A No connection
2 TDM (-) In/Out TDM synchronization negative Connect all negative
connections together. Connect
all positive connections
together.
3 TDM (+) In/Out TDM synchronization positive
4 N/C N/A No connection
5 N/C N/A No connection
6 N/C N/A No connection
7 TDM (+) In/Out TDM synchronization positive Ignore pins 7 and 8.
8 TDM (-) In/Out TDM synchronization negative
9 N/C N/A No connection
Pin Signal I/O Description
1 DS_L Data strobe
2 BERR_L Bus error
3 GND Ground
4 BKPT/DSCLK Development serial clock
5 GND Ground
6 FREEZE Breakpoint acknowledge
7 RESET_L Hard system reset
8 IFETCH/DSI Development serial input
9VCC +5 VDC
10 IPIPE0/DSO Development serial output
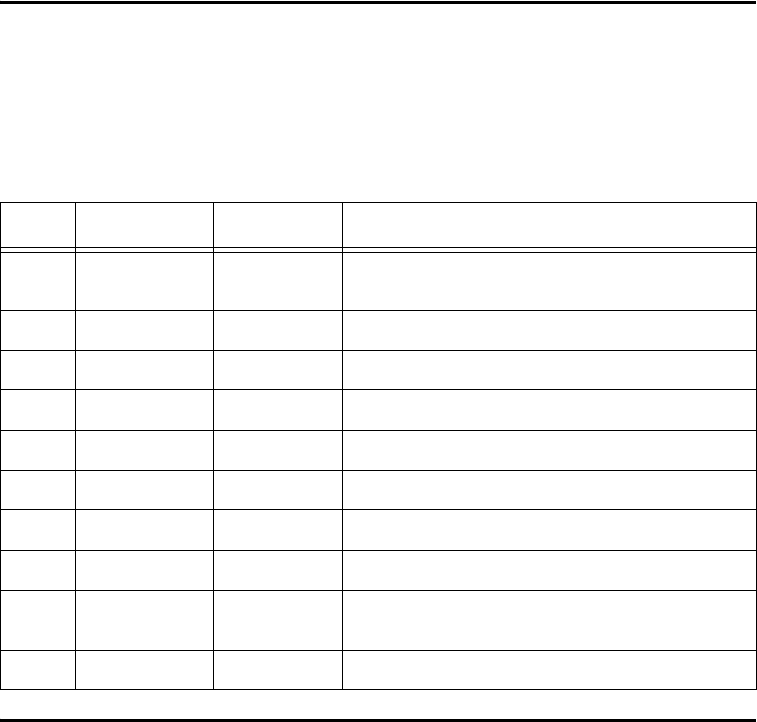
IT2200 Reader System with Multimode Capability Installation & Maintenance/Service Guide
D-8
General Purpose I/O Port (IT2020-004 Reader)
The connector is a 32-pin, 0.1-center dual-row header (2 by 16). This connector is for
future use only. Table D-4 shows the pin designations for the general purpose I/O con-
nector.
Table D-4 General Purpose I/O Connector
Hardware Diagnostic Port
The connector is a 34-pin, 0.1-center dual-row header (2 by 17). Signal I/O is with
respect to the ISA reader. Table D-5 shows the pin designations and descriptions for
the hardware diagnostic connector.
Pin Signal In/Out Description
1 EXT_INT+ In External interrupt input signal (IT2020-004
reader only)
2BIN1 In
2BIN2 In
3BIN3 In
4BIN4 In
5 BOUT4 Out
6 BOUT3 Out
7 BOUT2 Out
8 BOUT1 Out Good tag output signal (active low) (IT2020-
004 reader only)
9VCC
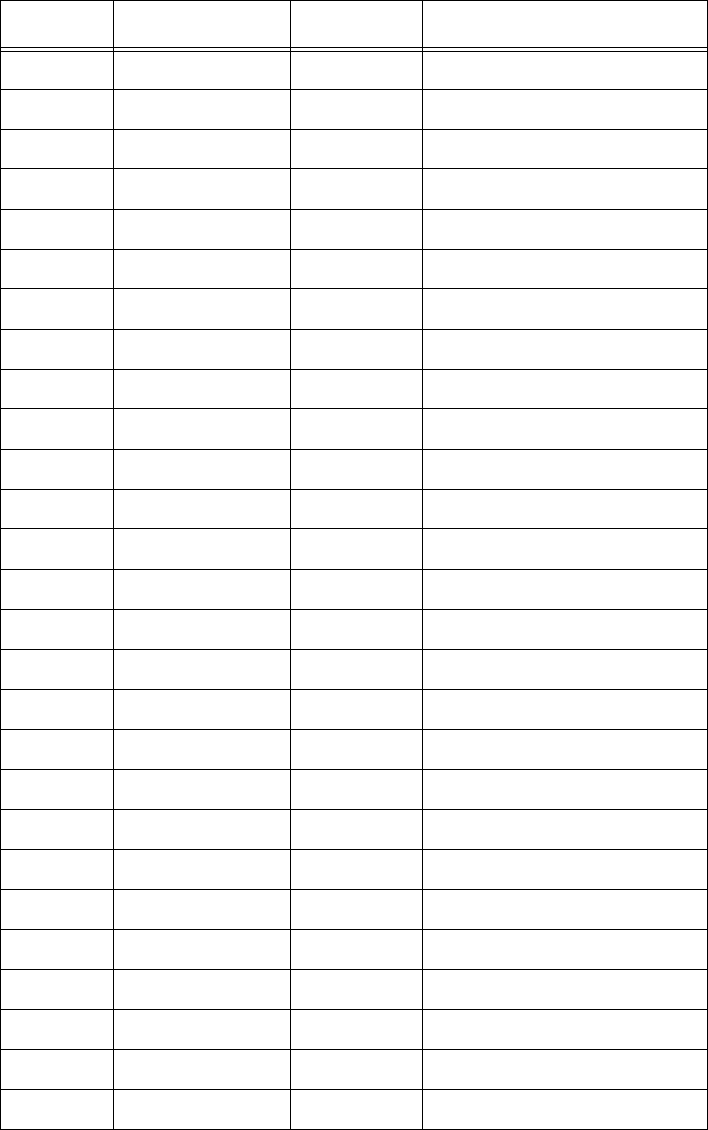
Hardware Interfaces
D-9
Table D-5 Hardware Diagnostic Port
Pin Signal In/Out Description
1 HDP_EN_L In Enables Output Buffers
2 GND Out Ground
3 CONT_CW_INP In Enable CW Mode
4VCC Out+5 volts
5 SWSIG0 Out SW Controlled Debug Bit
6 SWSIG1 Out SW Controlled Debug Bit
7 SWSIG2 Out SW Controlled Debug Bit
8 SWSIG3 Out SW Controlled Debug Bit
9 SWSIG4 Out SW Controlled Debug Bit
10 SWSIG5 Out SW Controlled Debug Bit
11 SWSIG6 Out SW Controlled Debug Bit
12 SWSIG7 Out SW Controlled Debug Bit
13 B_HDRDET Out Buffered Tag Data Present
14 B_MOD Out Modulation
15 B_DECINT_L Out Decoder Interrupt
16 B_TDMINT_L Out TDM Interrupt
17 B_MRESET_L Out 360 Reset from any Source
18 B_ISARES_L Out ISA Command or HW Reset
19 B_ISAIRQ_H Out IRQ to Host
20 B_IRQ1_L Out IRQ from Host
21 GND Out Ground
22 GND Out Ground
23 B_IF_A Out IF Data A
24 B_IF_B Out IF Data B
25 B_IF_C Out IF Data C
26 B_SPARE1 Out Spare
27 B_SPARE2 Out Spare
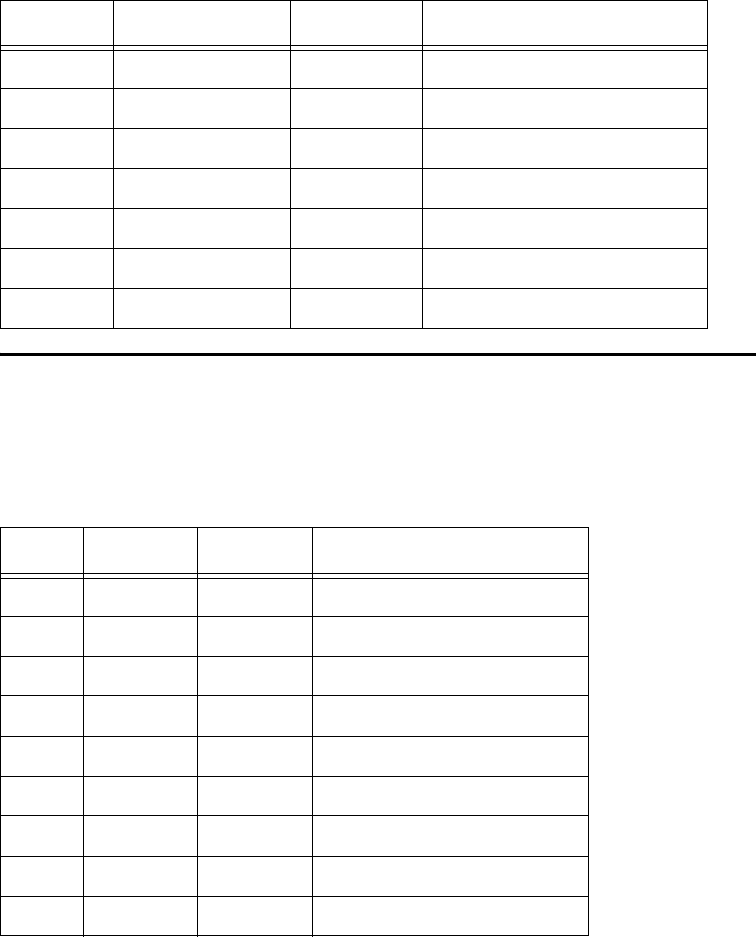
IT2200 Reader System with Multimode Capability Installation & Maintenance/Service Guide
D-10
RS-232
The connector is an industry standard DB-9M plug. Table D-6 shows the RS-232 con-
nector pin designations and descriptions for the RS-232 connector.
Table D-6 RS-232 Connector
28 B_SPARE3 Out Spare
29 B_SPARE4 Out Spare
30 B_SPARE5 Out Spare
31 VCC Out +5 volts
32 VCC Out +5 volts
33 GND Out Ground
34 GND Out Ground
Pin Signal In/Out Description
1 RSD N/C Received line signal detect
2 RXD In Receive data
3 TXD Out Transmit data
4 DTR N/C Data terminal ready
5 GND In/Out Ground
6 DSR N/C Data set ready
7 RTS Out Request to send
8 CTS In Clear to send
9 RI N/C Ring indicator
Table D-5 Hardware Diagnostic Port (continued)
Pin Signal In/Out Description
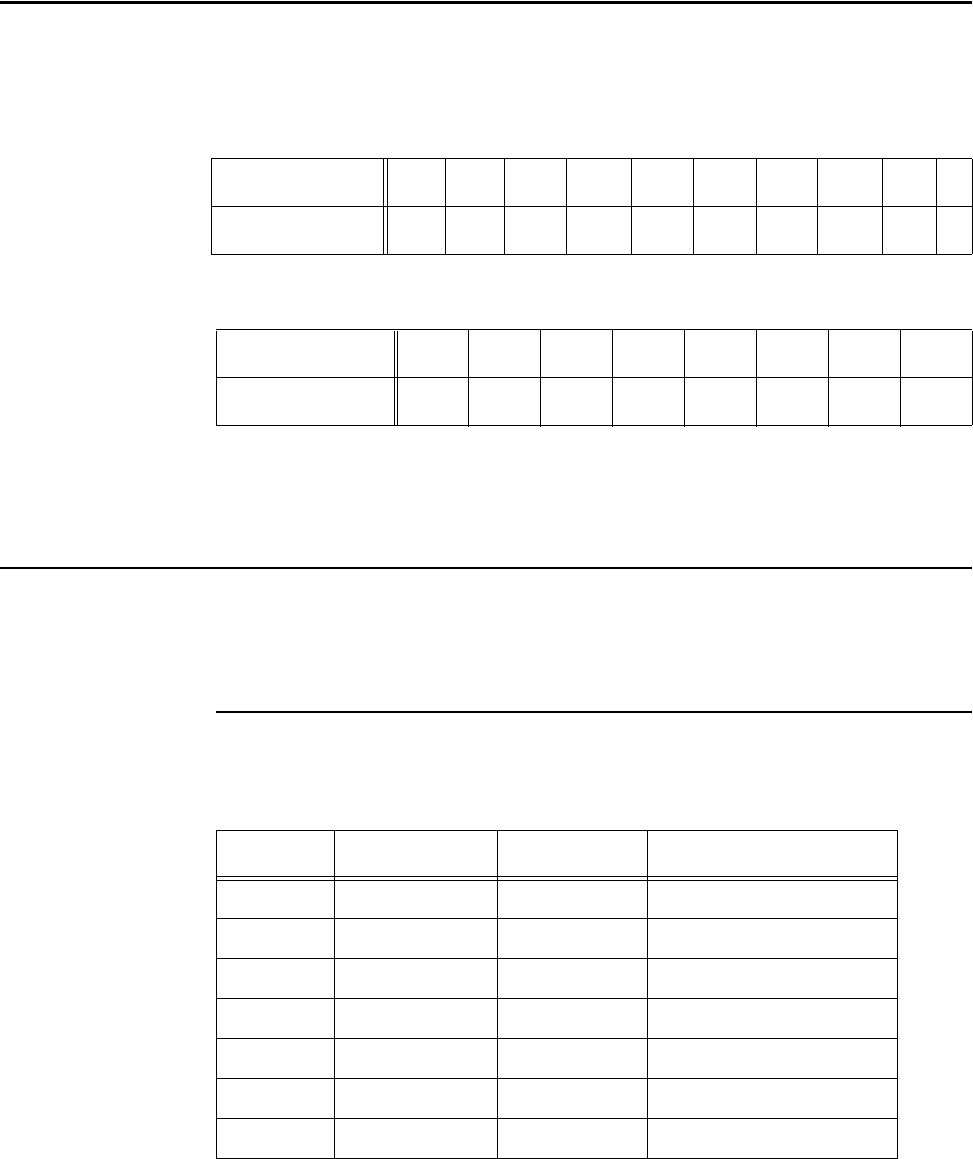
Hardware Interfaces
D-11
IT2020 Reader Logic Card Interface
This section shows the input/output and interrupt request line factory (default) config-
uration settings (Table D-7 and Table D-8) for the IT2020 Reader Logic Card.
Table D-7 IT2020 Reader Logic Card Default I/O Settings
Table D-8 IT2020 Reader Logic Card Default IRQ Settings
Note: Only one IRQ switch should be selected. If more than one switch is set, multiple
interrupts will occur.
Pin Designations
Tables D-9 through D-13 list the pin specifications for the IT2020 Reader Logic Card,
IT2611 RF Module, and IT2410 Tag Programmer. Figure D-3 shows the locations of
the LEDs on the IT2020 Reader Logic Board.
IT2020 ISA Card Interface Connector
Switch Number 8765 4321 xx
Switch State on off off off on off off off x x
Switch Number 87654321
IRQ 15 14 12 11 10 7 6 5
Table D-9 ISA Bus Pin Definition
Pin Signal In/Out Description
A1 IOCHK_L Out I/O channel check
A2 D7 In/Out Data bus, bit 7
A3 D6 In/Out Data bus, bit 6
A4 D5 In/Out Data bus, bit 5
A5 D4 In/Out Data bus, bit 4
A6 D3 In/Out Data bus, bit 3
A7 D2 In/Out Data bus, bit 2
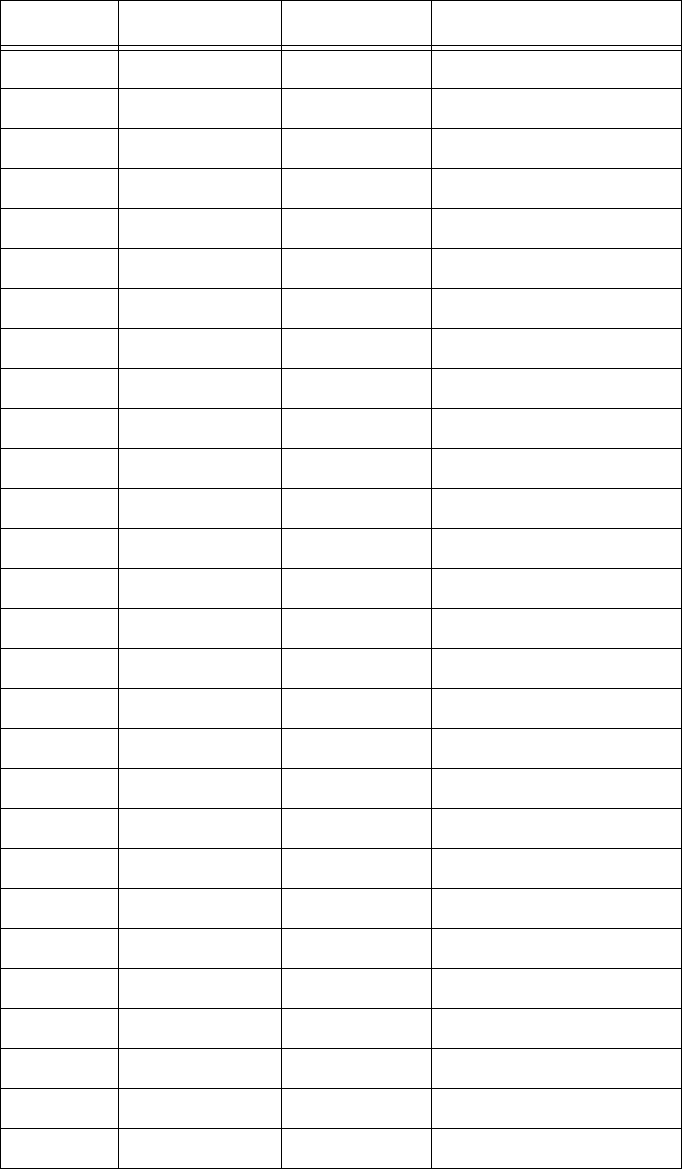
IT2200 Reader System with Multimode Capability Installation & Maintenance/Service Guide
D-12
A8 D1 In/Out Data bus, bit 1
A9 D0 In/Out Data bus, bit 0
A10 CHRDY Out I/O channel ready
A11 AEN In Address enable
A12 SA19 In System address, bit 19
A13 SA18 In System address, bit 18
A14 SA17 In System address, bit 17
A15 SA16 In System address, bit 16
A16 SA15 In System address, bit 15
A17 SA14 In System address, bit 14
A18 SA13 In System address, bit 13
A19 SA12 In System address, bit 12
A20 SA11 In System address, bit 11
A21 SA10 In System address, bit 10
A22 SA9 In System address, bit 9
A23 SA8 In System address, bit 8
A24 SA7 In System address, bit 7
A25 SA6 In System address, bit 6
A26 SA5 In System address, bit 5
A27 SA4 In System address, bit 4
A28 SA3 In System address, bit 3
A29 SA2 In System address, bit 2
A30 SA1 In System address, bit 1
A31 SA0 In System address, bit 0
B1 GND In/Out Ground
B2 RESDRV In Reset driver
B2 +5 VDC +5 volt power
B4 IRQ9 Out Interrupt request 9
Table D-9 ISA Bus Pin Definition (continued)
Pin Signal In/Out Description
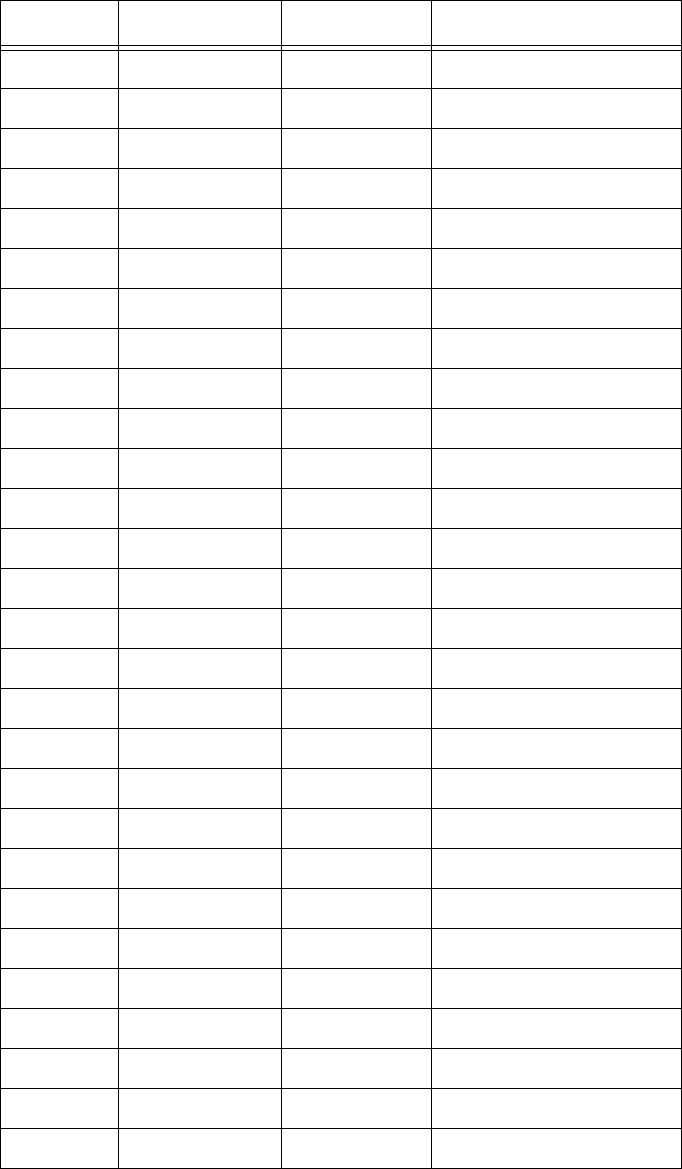
Hardware Interfaces
D-13
B5 -5 VDC -5 volt power
B6 DRQ2 Out DMA request 2
B7 -12 VDC -12 volt power
B8 NOWS_L Out No wait state
B9 +12 VDC +12 volt power
B10 GND In/Out Ground
B11 SMWT_L In System memory write
B12 SMRD_L In System memory read
B13 IOW_L In I/O write
B14 IOR_L In I/O read
B15 DAK3_L In DMA acknowledge 3
B16 DRQ3 Out DMA request 3
B17 DAK1_L In DMA acknowledge 1
B18 DRQ1 Out DMA request 1
B19 REFRESH_L In/Out DRAM refresh control
B20 BCLK In Bus clock
B21 IRQ7 Out Interrupt request 7
B22 IRQ6 Out Interrupt request 6
B23 IRQ5 Out Interrupt request 5
B24 IRQ4 Out Interrupt request 4
B25 IRQ3 Out Interrupt request 3
B26 DAK2_L In DMA acknowledge 2
B27 TC In Terminal count
B28 BALE In Bus address latch enable
B29 +5 VDC +5 volt power
B30 OSC In System oscillator
B31 GND In/Out Ground
C1 SBHE_L In System bus high enable
Table D-9 ISA Bus Pin Definition (continued)
Pin Signal In/Out Description
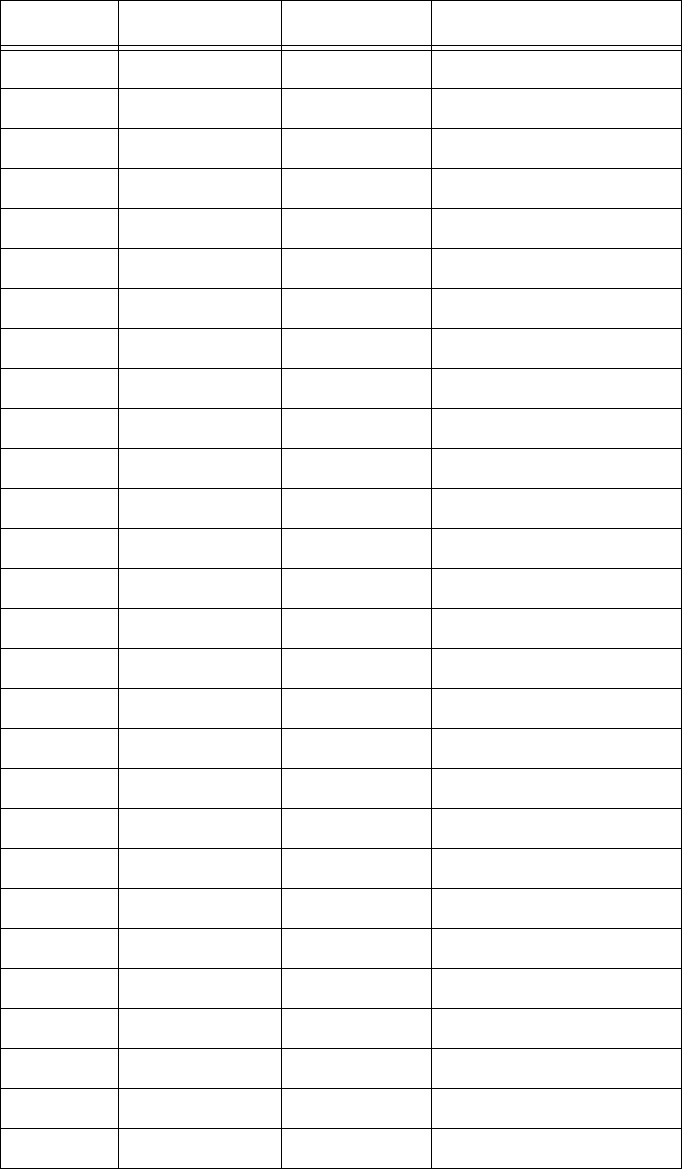
IT2200 Reader System with Multimode Capability Installation & Maintenance/Service Guide
D-14
C2 LA23 In Unlatched address, bit 23
C3 LA22 In Unlatched address, bit 22
C4 LA21 In Unlatched address, bit 21
C5 LA20 In Unlatched address, bit 20
C6 LA19 In Unlatched address, bit 19
C7 LA18 In Unlatched address, bit 18
C8 LA17 In Unlatched address, bit 17
C9 MRD_L In Memory write
C10 MWT_L In Memory read
C11 D8 In/Out Data bus, bit 8
C12 D9 In/Out Data bus, bit 9
C13 D10 In/Out Data bus, bit 10
C14 D11 In/Out Data bus, bit 11
C15 D12 In/Out Data bus, bit 12
C16 D13 In/Out Data bus, bit 13
C17 D14 In/Out Data bus, bit 14
C18 D15 In/Out Data bus, bit 15
D1 MCS16_L Out Memory chip select 16
D2 IO16_L Out I/O chip select 16
D3 IRQ10 Out Interrupt request 10
D4 IRQ11 Out Interrupt request 11
D5 IRQ12 Out Interrupt request 12
D6 IRQ15 Out Interrupt request 15
D7 IRQ14 Out Interrupt request 14
D8 DAK0_L In DMA acknowledge 0
D9 DRQ0 Out DMA request 0
D10 DAK5_L In DMA acknowledge 5
D11 DRQ5 Out DMA request 5
Table D-9 ISA Bus Pin Definition (continued)
Pin Signal In/Out Description
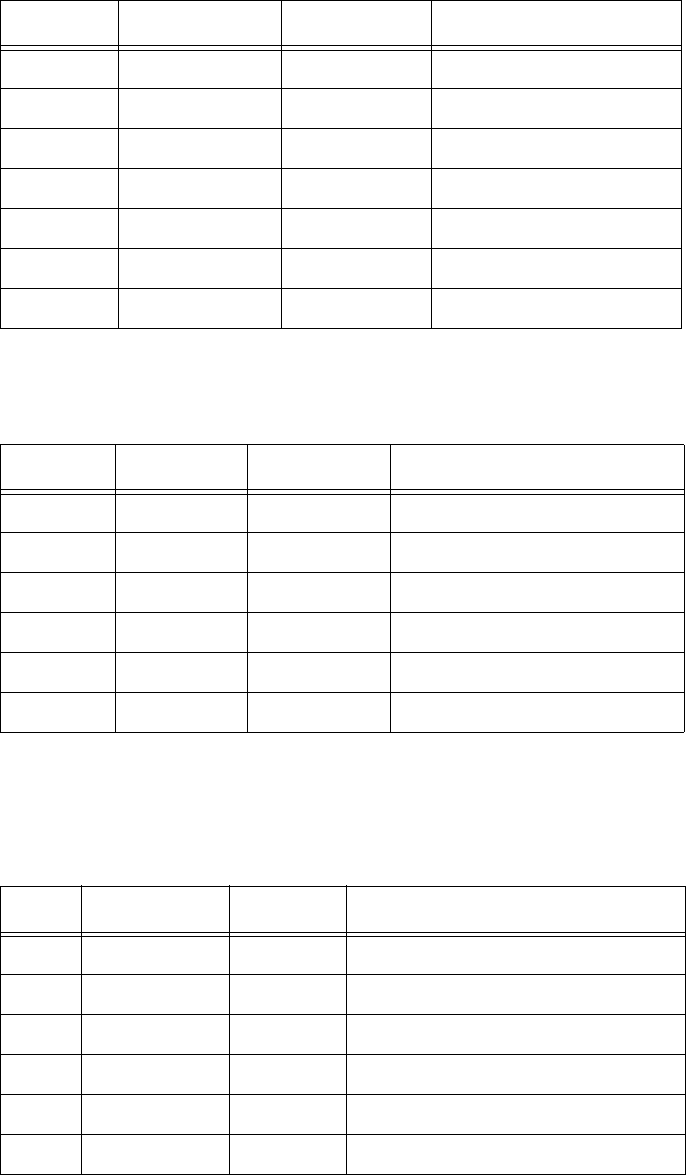
Hardware Interfaces
D-15
Table D-10 Optional External Power Pin Definition
D12 DAK6_L In DMA acknowledge 6
D13 DRQ6 Out DMA request 6
D14 DAK7_L In DMA acknowledge 7
D15 DRQ7 Out DMA request 7
D16 +5 VDC +5 volt power
D17 MASTER_L Out Primary
D18 GND In/Out Ground
Pin Signal In/Out Description
1 GND In/Out Ground
2 +5 VDC In +5 volt power
3 + 5VDC In +5 volt power
4 -12 VDC In -12 volt power
5 +12 VDC In +12 volt power
6 GND In/Out Ground
Table D-11 IP Module Logic Interface Connector
Pin Signal In/Out Description
1 GND Out Ground
2 CLK Out 8-MHz Clock
3 RESET_L Out Reset signal (active low)
4 D0 In/Out Data bit 0
5 D1 In/Out Data bit 1
6 D2 In/Out Data bit 2
Table D-9 ISA Bus Pin Definition (continued)
Pin Signal In/Out Description
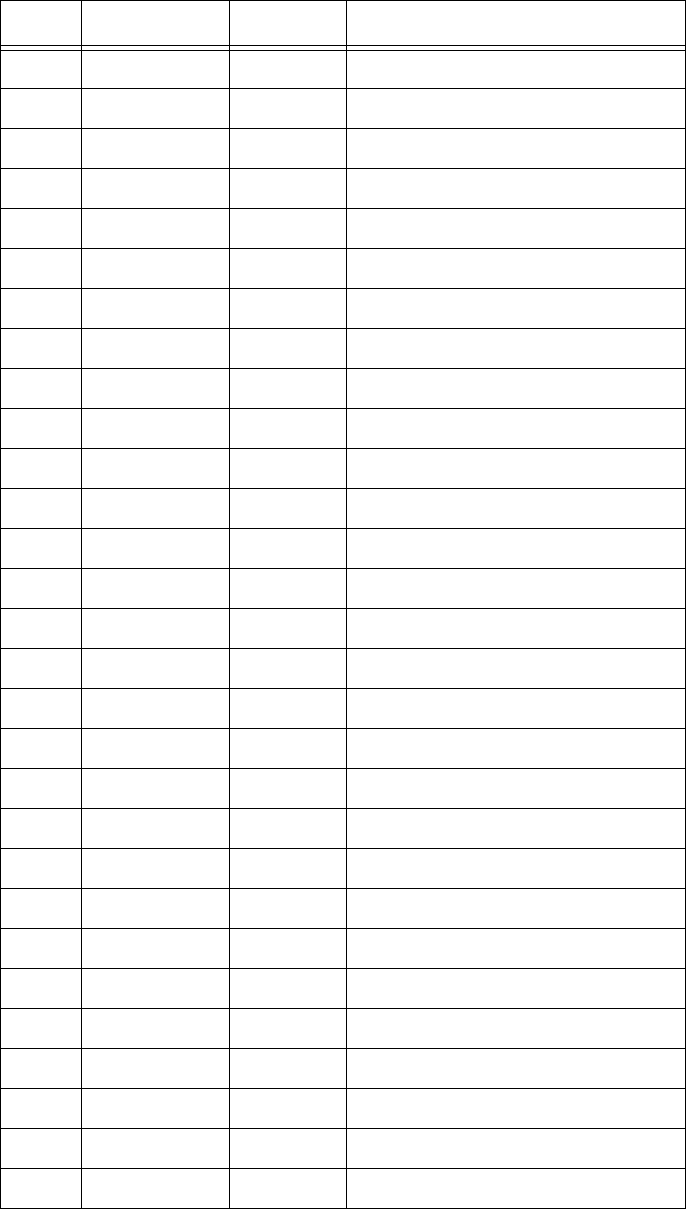
IT2200 Reader System with Multimode Capability Installation & Maintenance/Service Guide
D-16
7 D3 In/Out Data bit 3
8 D4 In/Out Data bit 4
9 D5 In/Out Data bit 5
10 D6 In/Out Data bit 6
11 D7 In/Out Data bit 7
12 D8 In/Out Data bit 8
13 D9 In/Out Data bit 9
14 D10 In/Out Data bit 10
15 D11 In/Out Data bit 11
16 D12 In/Out Data bit 12
17 D13 In/Out Data bit 13
18 D14 In/Out Data bit 14
19 D15 In/Out Data bit 15
20 BS0_L Out Byte select 0 (active low)
21 BS1_L Out Byte select 1 (active low)
22 -12 V Out +12 volt power
23 +12 V Out -12 volt power
24 +5 VDC Out +5 volt power
25 GND Out Ground
26 GND Out Ground
27 +5 VDC Out +5 volt power
28 R_W_L Out Data direction (read/write)
29 IDSEL_L Out IP module Identification
30 DMAREQ0_L In DMA request channel 0 (active low)
31 MEMSEL_L Out Memory select (active low)
32 DMAREQ1_L In DMA request channel 1 (active low)
33 INTSEL_L Out Read interrupt vector (active low)
34 DMACK_L Out DMA acknowledge (active low)
35 IOSEL_L Out I/O select (active low)
Table D-11 IP Module Logic Interface Connector (continued)
Pin Signal In/Out Description
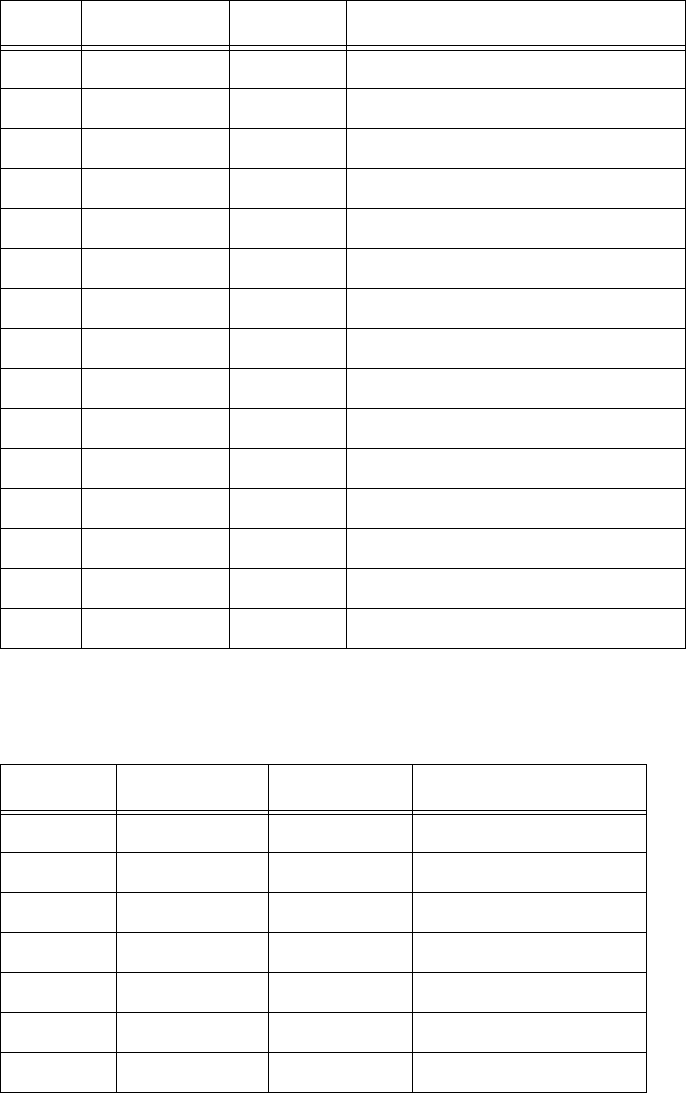
Hardware Interfaces
D-17
36 RESERVED N/C Reserved for future applications
37 A1 Out Address line A1
38 DMAEND In/Out DMA termination (active low)
39 A2 Out Address line A2
40 ERROR_L In IP module error (active low)
41 A3 Out Address line A3
42 INTREQ0_L In Interrupt request 0 (active low)
43 A4 Out Address line A4
44 INTREQ1_L In Interrupt request 1 (active low)
45 A5 Out Address line A5
46 STROBE_L In/Out Function strobe (optional)
47 A6 Out Address line A6
48 ACK_L In Data acknowledge (active low)
49 RESERVED N/C Reserved for future applications
50 GND Out Ground
Table D-12 IP Module I/O Connector
Pin Signal I/O Description
1 RCV In UART receive
2XMT Out UART transmit
3 GND In/Out System ground
4 GND In/Out System ground
5 RF_XMIT_EN Out RF downlink power on
6 RF_RCV_EN Out RF uplink power on
7-50 Reserved N/C Reserved
Table D-11 IP Module Logic Interface Connector (continued)
Pin Signal In/Out Description
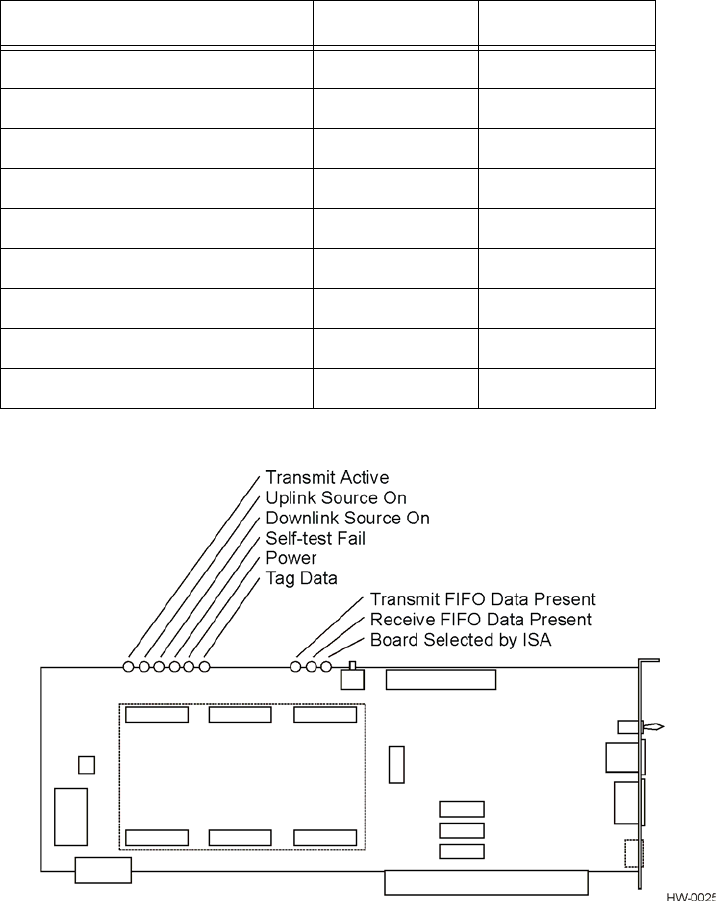
IT2200 Reader System with Multimode Capability Installation & Maintenance/Service Guide
D-18
Figure D-3 Locations of LEDs on IT2020 Reader Logic Card
The reader-to-RF module interfaces to the reader logic card by nonformatted differen-
tial signals. In addition to these nonformatted signals, for the bistatic version there are
two communications lines (one receive and one transmit) to send commands to the RF
module in the form of frequency control, power attenuation, and check tag command.
The reader-RF module also connects to the transmit (bistatic downlink), receive
(bistatic uplink), transmit/receive (monostatic downlink/uplink), and check tag anten-
nas (both bistatic and monostatic) (see Figure D-4 and Figure D-5).
Table D-13 LEDs
Action Color Stretched
Board Selected by ISA Green No
Receive FIFO Data Present Red No
Transmit FIFO Data Present Yellow Yes
Tag Data Green Yes
Power Green No
Self-Test Fail Red No
Downlink Source On Yellow No
Uplink Source On Red No
Transmit Active Yellow Yes

IT2200 Reader System with Multimode Capability Installation & Maintenance/Service Guide
D-20
Figure D-6 Twenty-Six Pin Connector Showing Terminal Designators (RF
Module)
The cabling, should be Belden 9732 or equivalent, nine-pair, twisted-shielded pair,
maximum length 152 m (500 ft).
Power Connector
This connector is a 3-pin circular plug.
Reader-to-RF Module Communications
The communication channel provides bi-directional communication between the
reader logic card and the RF module. This channel is a differential I/O that provides
two-way communication via half-duplex channels. Differential transmission provides
signal integrity over long cable distances and in electrically noisy environments. This
channel supports communication rates up to 19.2 Kbaud, with cable lengths up to 152
m (500 ft).
The command/response communication channel is implemented in a microchip
PIC16-series microcontroller, with the protocol executed in software that provides
flexibility for future applications. Frequency and power attenuation settings are stored
by the microcontroller in nonvolatile memory. A programming interface is provided
so that the new software can be downloaded into the PIC16 device.
The reader-to-RF module interface performs the following functions:
•Receives two discrete, differential input signals from the reader logic card for RF
power on/off control.
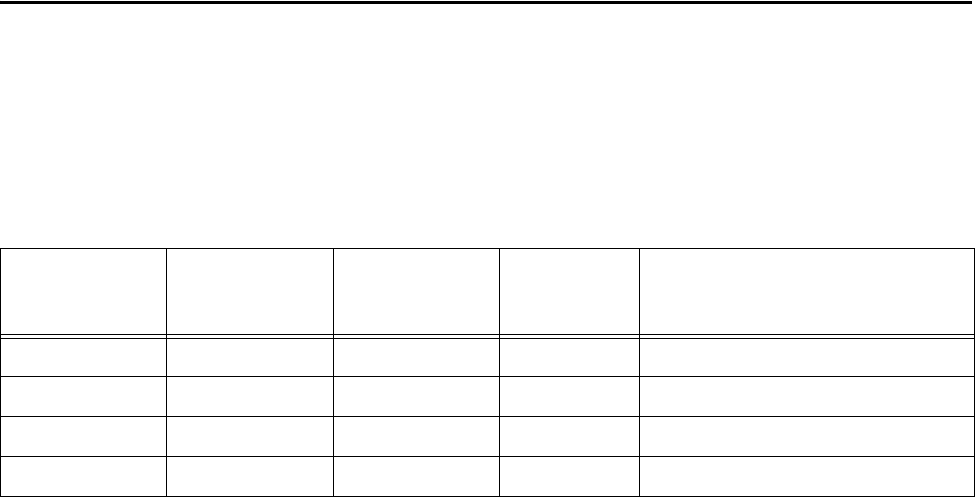
Hardware Interfaces
D-21
•Receives a differential input from the reader logic card and outputs a single-ended
signal to the RF downlink and uplink functions for control of the output stage
power. RF power on/off is also controlled via a microcontroller output under com-
mand from the reader logic card.
•Provides control output and status inputs for the RF uplink function — Initializes
the RF phase locked loop (PLL) frequency. Controls the RF output power attenu-
ation. Controls RF power on/off with a discrete differential input and reader com-
mand.
•Provides control output and status inputs for the RF downlink function — Initial-
izes the RF PLL frequency as in the RF uplink. Controls the RF output power
attenuation as in the RF uplink. Stores settings as in the RF uplink. Controls RF
power on/off with a discrete differential input and reader command as in the RF
uplink.
•Provides control for the check tag — The check tag simulates an automatic vehi-
cle identification (AVI) transaction thus providing a means for the reader to check
the AVI operation. The check tag, activated on command by the lane controller,
provides a test of the antenna, RF source, preamplifier, encoder/ decoder, micro-
processor, communications port, and I/O control.
The reader controls check tag operation with an enable logic signal, which
provides the check tag to communicate with the reader, as a normal tag. The check
tag may be set to operate automatically at a periodic rate, or under command from
the lane controller through the reader.
RF Module Interface Connector
Table D-14 lists the pin-socket signals and descriptions for the IT2611 RF Module-to-
IT2020 Reader Logic Card connector.
The cable shields are not connected at the IT2611 RF Module. Tie all the shielded
bare wires together and connect them to a good ground at the IT2020 Reader Logic
Card end.
Table D-14 RF Module-to-Reader Logic Card Interface Connector
IT2611 RF
Module Socket
IT2020 Reader
Logic Card
DB-25 Pin Signal In/Out Description
A 1 IF_A+_I2000 In Uplink tag data, channel A+
T 2 IF_A+_ATA In Uplink tag data, channel A+
D 3 IF_B- In Uplink tag data, channel B-
E 4 IF_C+ In Uplink tag data, channel C+
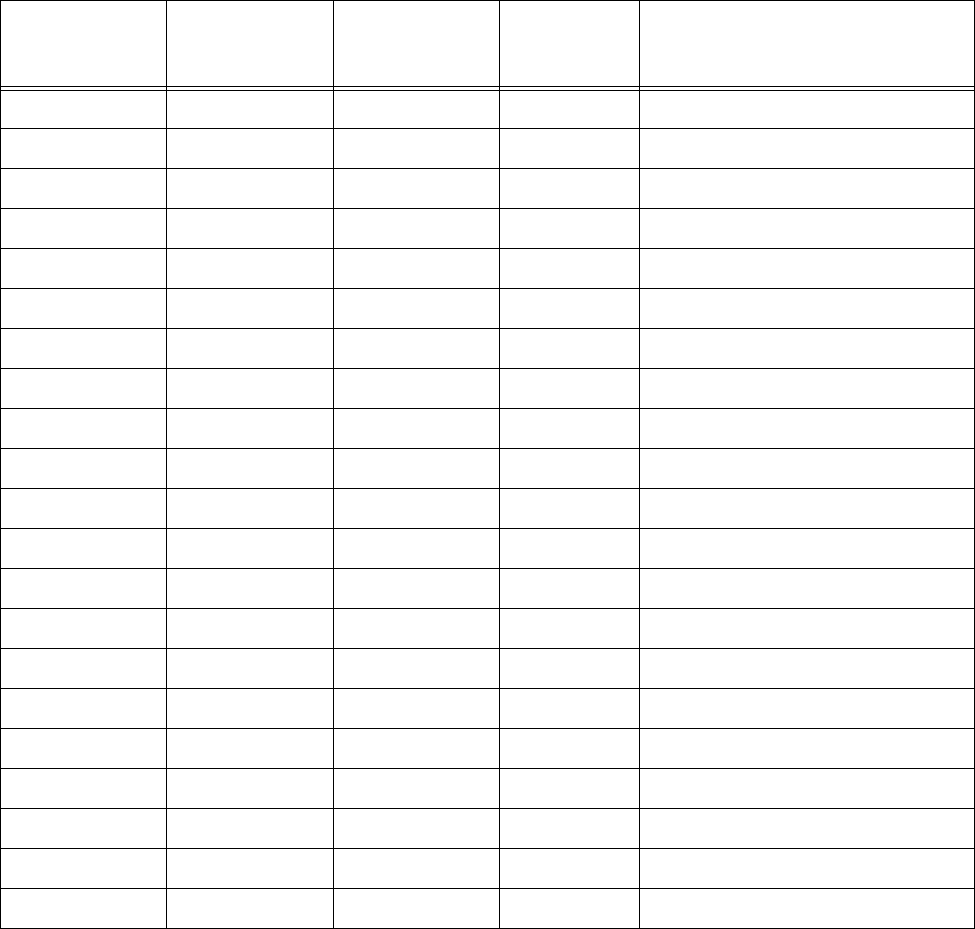
IT2200 Reader System with Multimode Capability Installation & Maintenance/Service Guide
D-22
Table D-15 shows the IT2611 RF Module power connector pin designations.
V 5 IF_B+_ATA In Uplink tag data, channel B+
H 6 MOD- Out Downlink modulation data, (-)
Z 7 IF_C+_ATA In Uplink tag data, channel C+
K 8 CTL_XMT- Out Control interface transmit, (-)
L 9 CTL_RCV+ In/Out Control interface receive, (+)
10 Reserved N/C Not connected
N 11 UL_OFF- Out RF uplink power on/off, (-)
P 12 DL_OFF+ Out RF downlink power on/off, (+)
13 Reserved N/C Not connected
B 14 IF_A- In Uplink tag data, channel A-
C 15 IF_B+ In Uplink tag data, channel B+
U 16 IF_A-_ATA In Uplink tag data, channel A-
F 17 IF_C- In Uplink tag data, channel C-
G 18 MOD+ Out Downlink modulation data, (-)
W 19 IF_B-_ATA In Uplink tag data, channel B-
J 20 CTL_XMT+ In/Out Control interface transmit, (+)
a 21 IF_C-_ATA In Uplink tag data, channel C-
Y 22 CTL_RCV- In Control interface receive, (-)
M 23 UL_OFF+ Out RF uplink power on/off, (+)
24 Reserved N/C Not connected
R 25 DL_OFF- Out RF downlink power on/off, (-)
Table D-14 RF Module-to-Reader Logic Card Interface Connector (continued)
IT2611 RF
Module Socket
IT2020 Reader
Logic Card
DB-25 Pin Signal In/Out Description

Hardware Interfaces
D-23
Table D-15 RF Module Power
Table D-16 shows the IT2611 RF Module-to-antenna connectors for bistatic operation
and Table D-17 shows the connectors for monostatic operation.
IT2410 Tag Programmer Hardware Interconnection
The IT2410 Tag Programmer requires only a small DC power supply and a DB-9
serial interface cable. Cabling for the two interconnections requires proper shielding
at both ends to meet Part 15 of FCC emission requirements.
The serial interface is RS-232 compatible. A null-modem adapter is required to con-
nect the programmer to RS-232 serial interfaces from most computers configured as
data terminal equipment (DTE). No hardware handshaking is employed; however,
handshaking is accomplished by firmware protocol as described in the interface defi-
nitions. Pin-outs of the RS-232 serial interface are shown in Table D-18.
Pin Description
A 19- to 28-VAC or
16- to 28-VDC
C 19- to 28 VAC Return or
16- to 28-VDC Return
B Not connected
Table D-16 RF Module-Antenna Connectors for Bistatic Operation
Connector Description Type
J1 RF uplink (receive) antenna N Socket
J2 RF downlink (transmit)
antenna N Socket
J3 Check tag antenna N Socket
Table D-17 RF Module-Antenna Connectors for Monostatic Operation
Connector Description Type
J1 RF uplink/downlink (receive/
transmit) antenna N Socket
J3 Check tag antenna N Socket
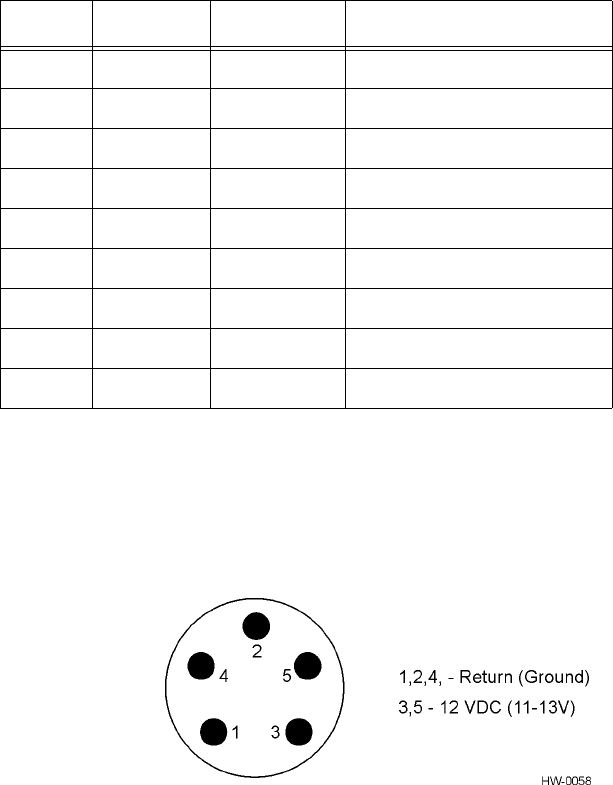
IT2200 Reader System with Multimode Capability Installation & Maintenance/Service Guide
D-24
Table D-18 IT2410 Tag Programmer Interconnection
The power is supplied to the programmer through a DIN-9 connector from a 40-W
power switching supply provided with each unit. Figure D-7 shows the connector on
the programmer.
Figure D-7 IT2410 Tag Programmer Power Connections
The power supply used with the programmer provides additional shielding to meet the
Class B, Part 15 FCC requirements. The cable used for the modification is an 18-
AWG, shielded, 2-conductor cable.
Pin Name Type Description
1RSDN/A
a
a. Not internally connected on the IT2410 Tag Programmer
Received line signal detect
2 TxD Output Transmit data
3 RxD Input Receive data
4 DTR Outputb
b. Connected, but not currently used in IT2410 Tag Pro-
grammer firmware
Data terminal ready
5 GND Ground Signal ground
6DSRN/A
aData set ready
7 RTS OutputbRequest to send
8 CTS InputbClear to send
9 RI N/A Ring indicator

E
Connector Pin-outs
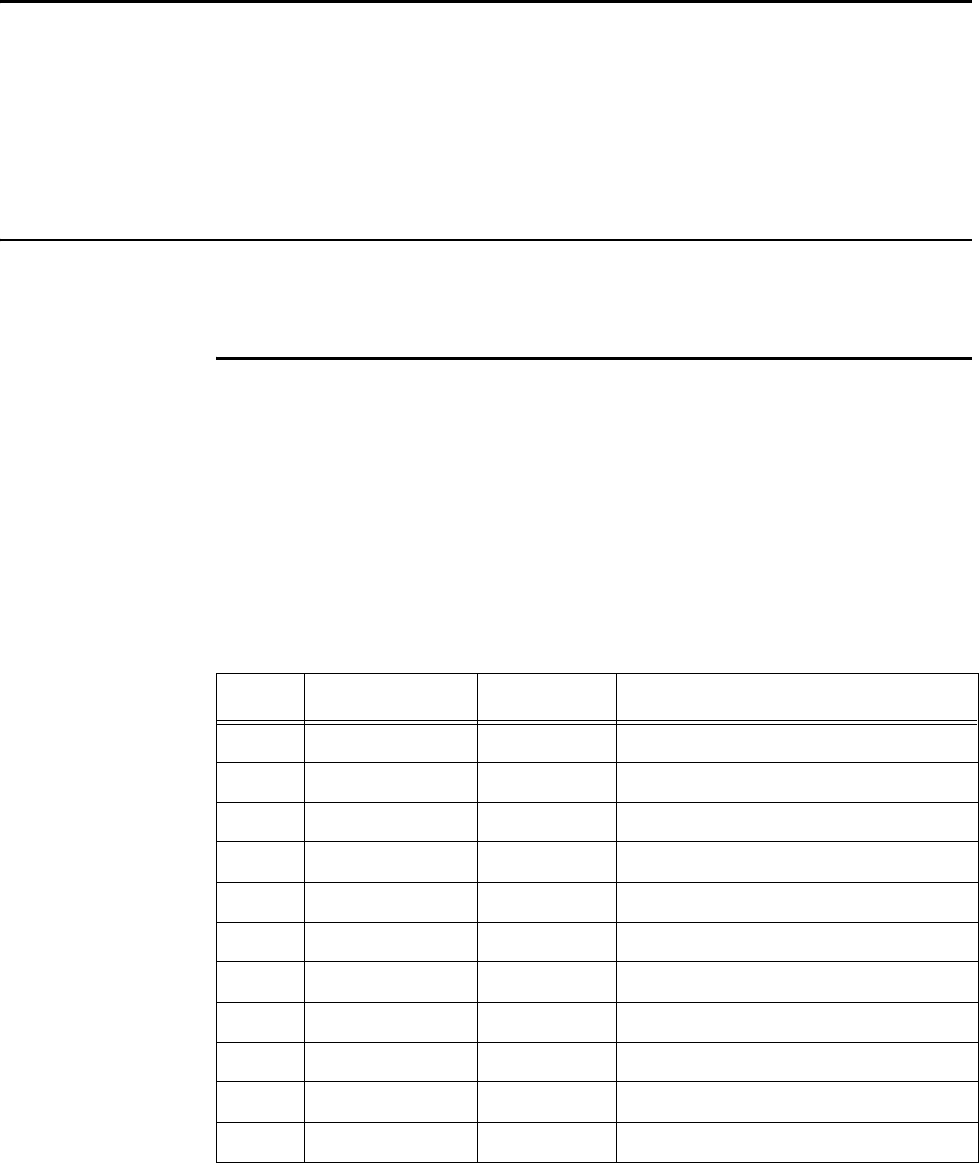
E-3
Appendix E
Connector Pin-outs
This appendix provides connector pin-out information for the IT2020
Reader Logic Card and the IT2611 RF Module.
IT2020 Reader Logic Card
This section provides pin-outs for the interface connectors on the IT2020 Reader
Logic Card.
Tag Data/Control
The communication path between the IT2020 Reader Logic Card and the IT2611 RF
Module runs through the input/output (I/O) module that is connected to IP slot A. The
I/O module connects to the RF module through a ribbon cable terminating at a DB-25
connector mounted on the RF module interface bracket. The tag data/control cable
from the RF module connects to this DB-25 connector.
Table E-1 shows the pinout of the DB-25 connector. Signal I/O is with respect to the
reader logic card.
Table E-1 Tag Data/Control Interface Connector
Pin Name Type Description
1 IF_A+ Input IT2200 tag data, channel A+
2 Unused N/A N/A
3 IF_B- Input IT2200 tag data, channel B-
4 IF_C+ Input IT2200 tag data, channel C+
5 Unused N/A N/A
6 MOD- Output Downlink modulation data, negative
7 Unused N/A N/A
8 CTL_RCV- Input Communication with RF module
9 CTL_XMT+ Output Communication with RF module
10 Unused N/A N/A
11 UL_RF_OFF- Output RF uplink power on/off, negative
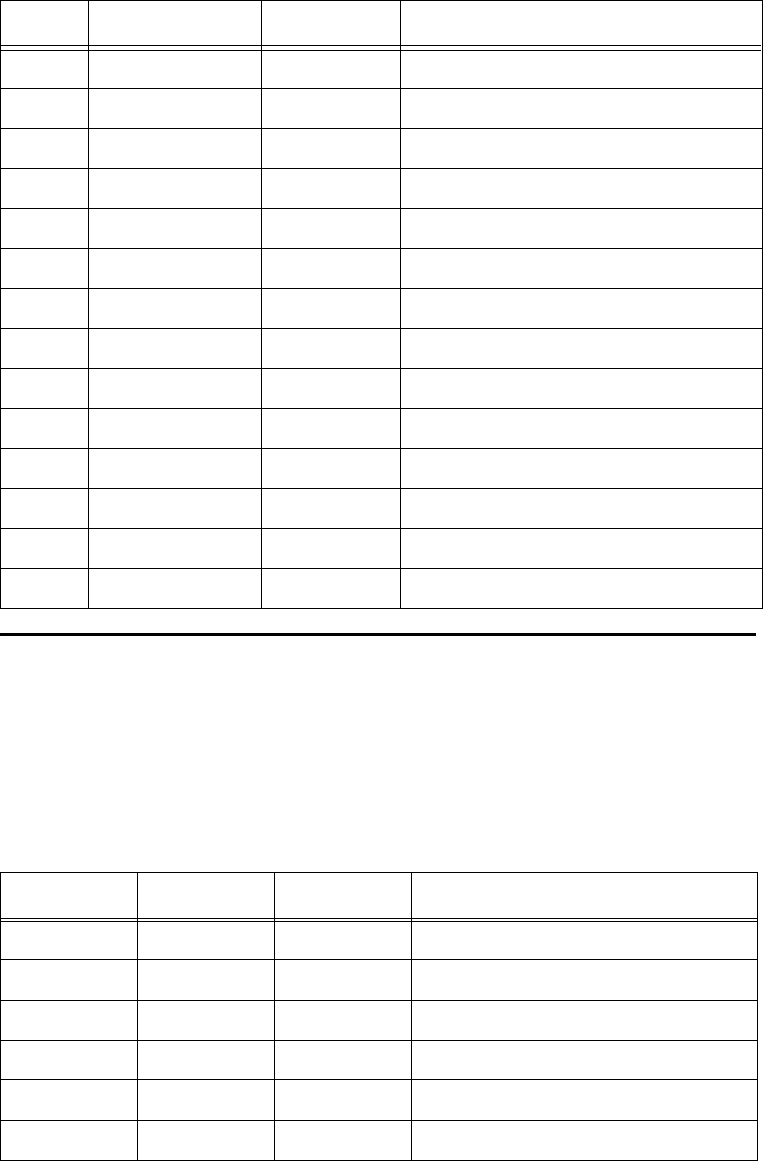
IT2200 Reader System with Multimode Capability Installation & Maintenance/Service Guide
E-4
TDM
The TDM (time division multiplexing) connector is located on the reader logic card
RF module interface bracket. The connector is a DB-9. The signals are RS-485. Two
identical pairs are provided for ease of wiring in the field.
Table E-2 shows the pinout of the TDM connector.
12 DL_RF_OFF+ Output RF downlink power on/off, positive
13 Unused N/A N/A
14 IF_A- Input IT2200 tag data, channel A-
15 IF_B+ Input IT2200 tag data, channel B+
16 Unused N/A N/A
17 IF_C- Input IT2200 tag data, channel C-
18 MOD+ Output Downlink modulation data, negative
19 Unused N/A N/A
20 CTL_RCV+ Input/output Communication with RF module
21 Unused N/A N/A
22 CTL_XMT- Output Communication with RF module
23 UL_RF_OFF+ Output RF uplink power on/off, positive
24 Unused N/A N/A
25 DL_RF_OFF- Output RF downlink power on/off, negative
Table E-2 TDM Connector
Pin Name Type Description
1 N/A N/A No connection
2 TDM- Input/output TDM synchronization negative
3 TDM+ Input/output TDM synchronization positive
4 N/A N/A No connection
5 N/A N/A No connection
6 N/A N/A No connection
Table E-1 Tag Data/Control Interface Connector (continued)
Pin Name Type Description
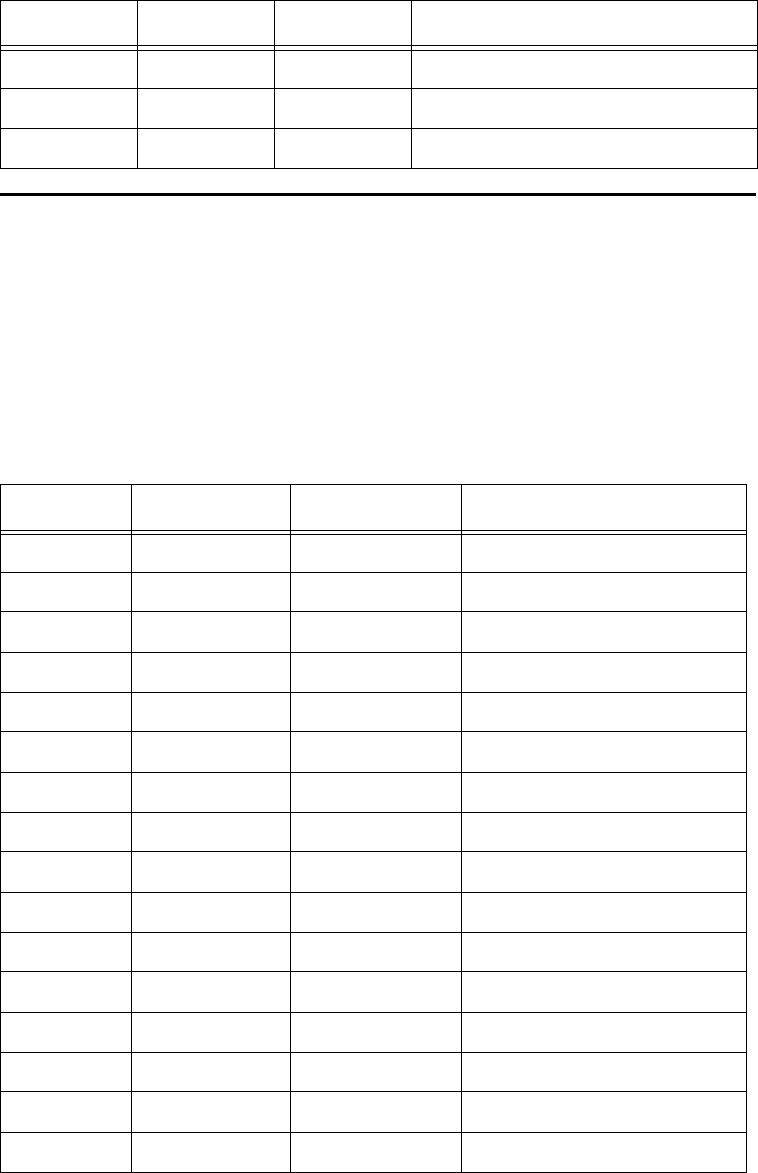
Connector Pin-outs
E-5
ISA Bus
The IT2020’s edge connector has two sets of contact fingers on each side of the board.
Pins A1 through A31 and C1 through C18 are on the component side of the card. Pins
B1 through B31 and D1 through D18 are on the other side. For all pin sets, the lower
numbers are toward the bracket end of the card.
Table E-3 shows the pinout of the ISA bus connector. Signal I/O is with respect to the
reader logic card.
7 TDM+ Input/output TDM synchronization positive
8 TDM- Input/output TDM synchronization negative
9 N/A N/A No connection
Table E-3 ISA Bus Pin Definition
Pin Name Type Description
A1 IOCHK_L Output I/O channel check
A2 D7 Input/output Data bus, bit 7
A3 D6 Input/output Data bus, bit 6
A4 D5 Input/output Data bus, bit 5
A5 D4 Input/output Data bus, bit 4
A6 D3 Input/output Data bus, bit 3
A7 D2 Input/output Data bus, bit 2
A8 D1 Input/output Data bus, bit 1
A9 D0 Input/output Data bus, bit 0
A10 CHRDY Output I/O channel ready
A11 AEN Input Address enable
A12 SA19 Input System address, bit 19
A13 SA18 Input System address, bit 18
A14 SA17 Input System address, bit 17
A15 SA16 Input System address, bit 16
A16 SA15 Input System address, bit 15
Table E-2 TDM Connector (continued)
Pin Name Type Description
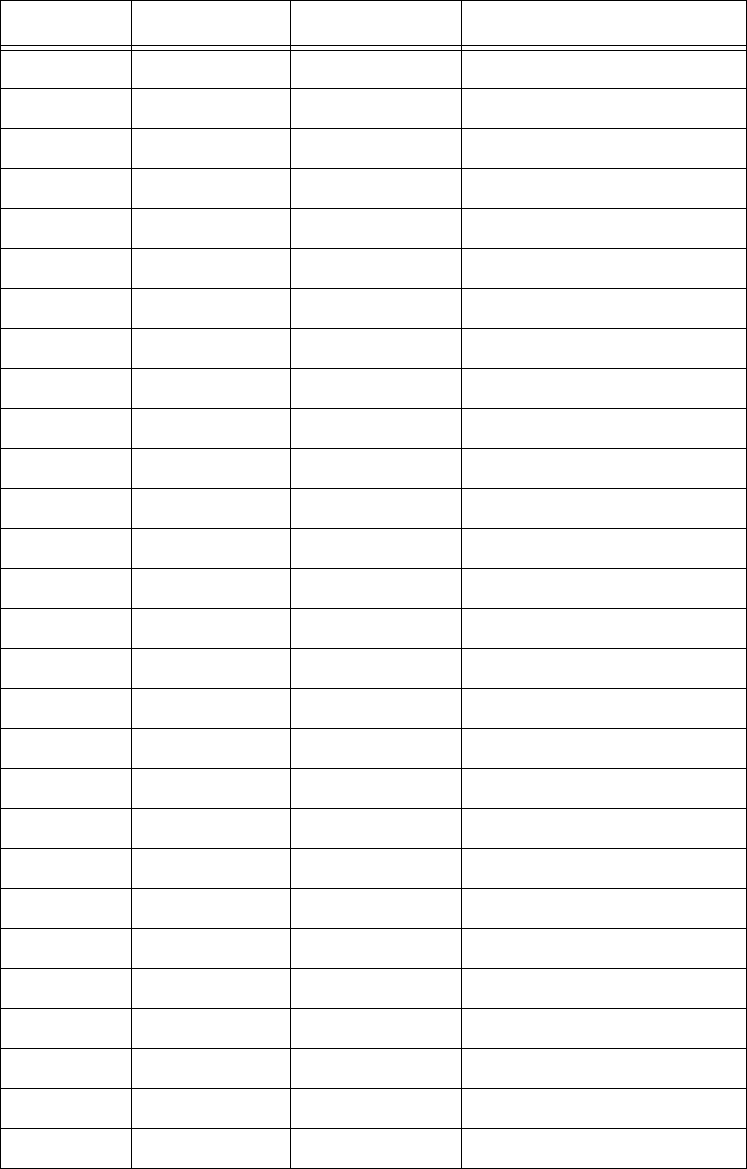
IT2200 Reader System with Multimode Capability Installation & Maintenance/Service Guide
E-6
A17 SA14 Input System address, bit 14
A18 SA13 Input System address, bit 13
A19 SA12 Input System address, bit 12
A20 SA11 Input System address, bit 11
A21 SA10 Input System address, bit 10
A22 SA9 Input System address, bit 9
A23 SA8 Input System address, bit 8
A24 SA7 Input System address, bit 7
A25 SA6 Input System address, bit 6
A26 SA5 Input System address, bit 5
A27 SA4 Input System address, bit 4
A28 SA3 Input System address, bit 3
A29 SA2 Input System address, bit 2
A30 SA1 Input System address, bit 1
A31 SA0 Input System address, bit 0
B1 GND Ground
B2 RESDRV Input Reset driver
B2 +5 VDC +5 volt power
B4 IRQ9 Output Interrupt request 9
B5 -5 VDC -5 V power
B6 DRQ2 Output DMA request 2
B7 -12 VDC -12 V power
B8 NOWS_L Output No wait state
B9 +12 VDC +12 V power
B10 GND Ground
B11 SMWT_L Input System memory write
B12 SMRD_L Input System memory read
B13 IOW_L Input I/O write
Table E-3 ISA Bus Pin Definition (continued)
Pin Name Type Description
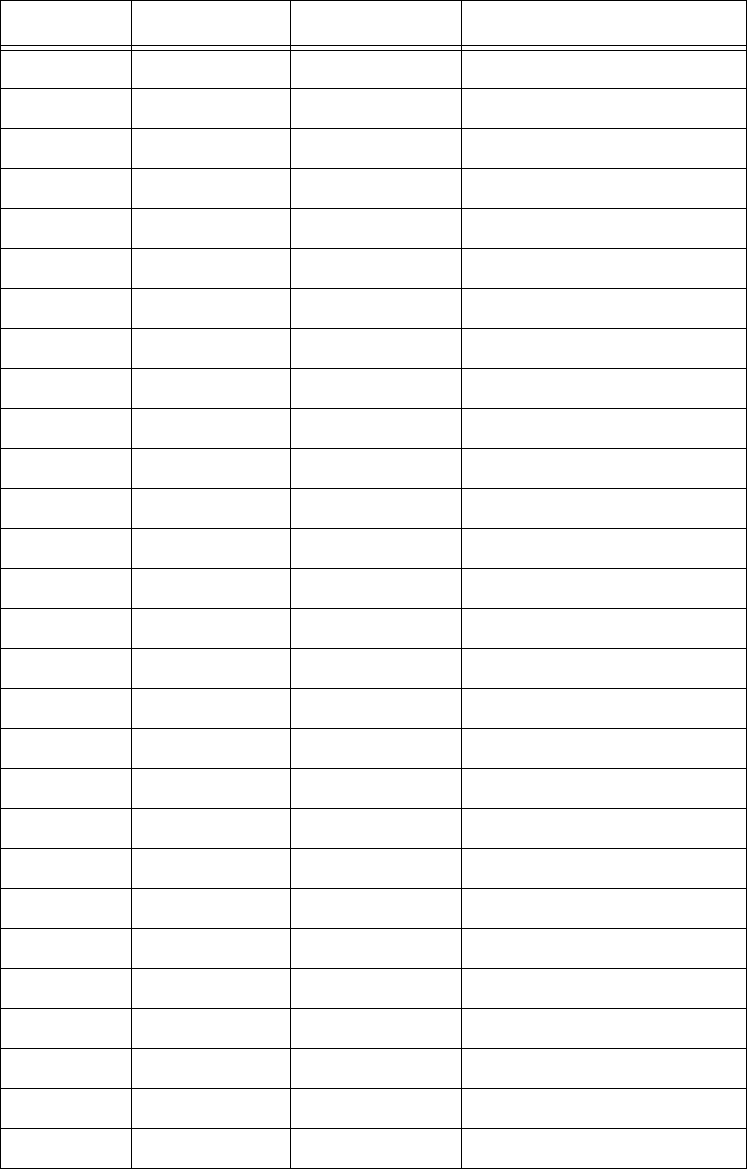
Connector Pin-outs
E-7
B14 IOR_L Input I/O read
B15 DAK3_L Input DMA acknowledge 3
B16 DRQ3 Output DMA request 3
B17 DAK1_L Input DMA acknowledge 1
B18 DRQ1 Output DMA request 1
B19 REFRESH_L Input/output DRAM refresh control
B20 BCLK Input Bus clock
B21 IRQ7 Output Interrupt request 7
B22 IRQ6 Output Interrupt request 6
B23 IRQ5 Output Interrupt request 5
B24 IRQ4 Output Interrupt request 4
B25 IRQ3 Output Interrupt request 3
B26 DAK2_L Input DMA acknowledge 2
B27 TC Input Terminal count
B28 BALE Input Bus address latch enable
B29 +5 VDC +5 volt power
B30 OSC Input System oscillator
B31 GND Ground
C1 SBHE_L Input System bus high enable
C2 LA23 Input Unlatched address, bit 23
C3 LA22 Input Unlatched address, bit 22
C4 LA21 Input Unlatched address, bit 21
C5 LA20 Input Unlatched address, bit 20
C6 LA19 Input Unlatched address, bit 19
C7 LA18 Input Unlatched address, bit 18
C8 LA17 Input Unlatched address, bit 17
C9 MRD_L Input Memory write
C10 MWT_L Input Memory read
Table E-3 ISA Bus Pin Definition (continued)
Pin Name Type Description
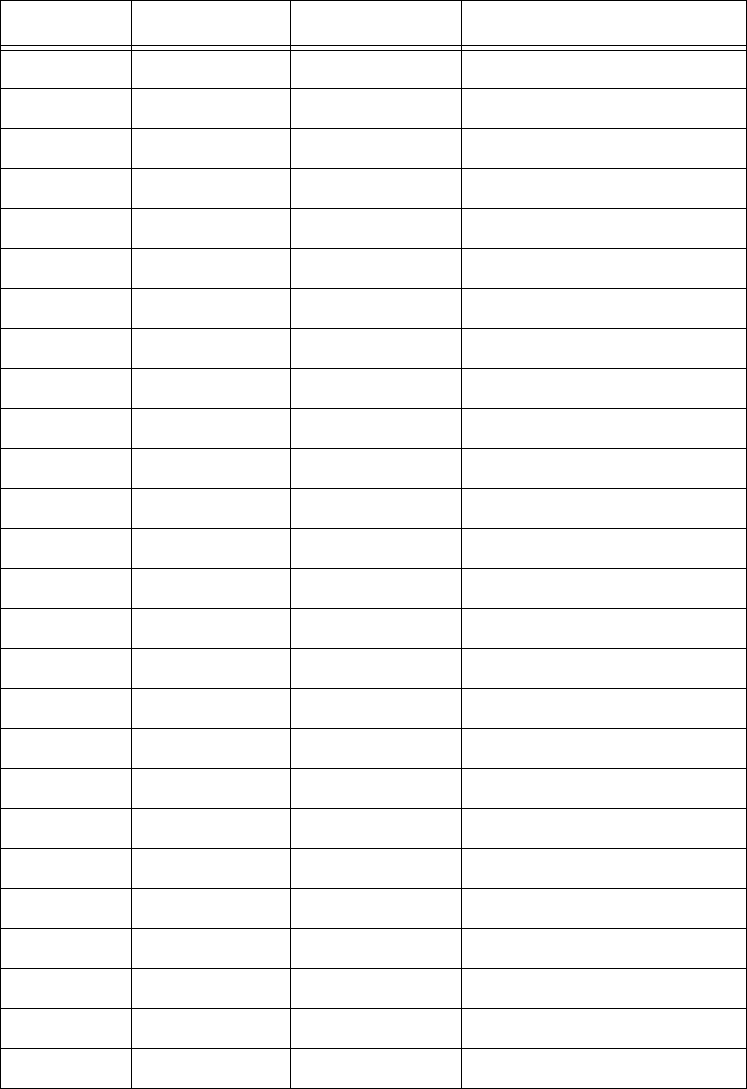
IT2200 Reader System with Multimode Capability Installation & Maintenance/Service Guide
E-8
C11 D8 Input/output Data bus, bit 8
C12 D9 Input/output Data bus, bit 9
C13 D10 Input/output Data bus, bit 10
C14 D11 Input/output Data bus, bit 11
C15 D12 Input/output Data bus, bit 12
C16 D13 Input/output Data bus, bit 13
C17 D14 Input/output Data bus, bit 14
C18 D15 Input/output Data bus, bit 15
D1 MCS16_L Output Memory chip select 16
D2 IO16_L Output I/O chip select 16
D3 IRQ10 Output Interrupt request 10
D4 IRQ11 Output Interrupt request 11
D5 IRQ12 Output Interrupt request 12
D6 IRQ15 Output Interrupt request 15
D7 IRQ14 Output Interrupt request 14
D8 DAK0_L Input DMA acknowledge 0
D9 DRQ0 Output DMA request 0
D10 DAK5_L Input DMA acknowledge 5
D11 DRQ5 Output DMA request 5
D12 DAK6_L Input DMA acknowledge 6
D13 DRQ6 Output DMA request 6
D14 DAK7_L Input DMA acknowledge 7
D15 DRQ7 Output DMA request 7
D16 +5 VDC +5 volt power
D17 MASTER_L Output Primary
D18 GND Ground
Table E-3 ISA Bus Pin Definition (continued)
Pin Name Type Description
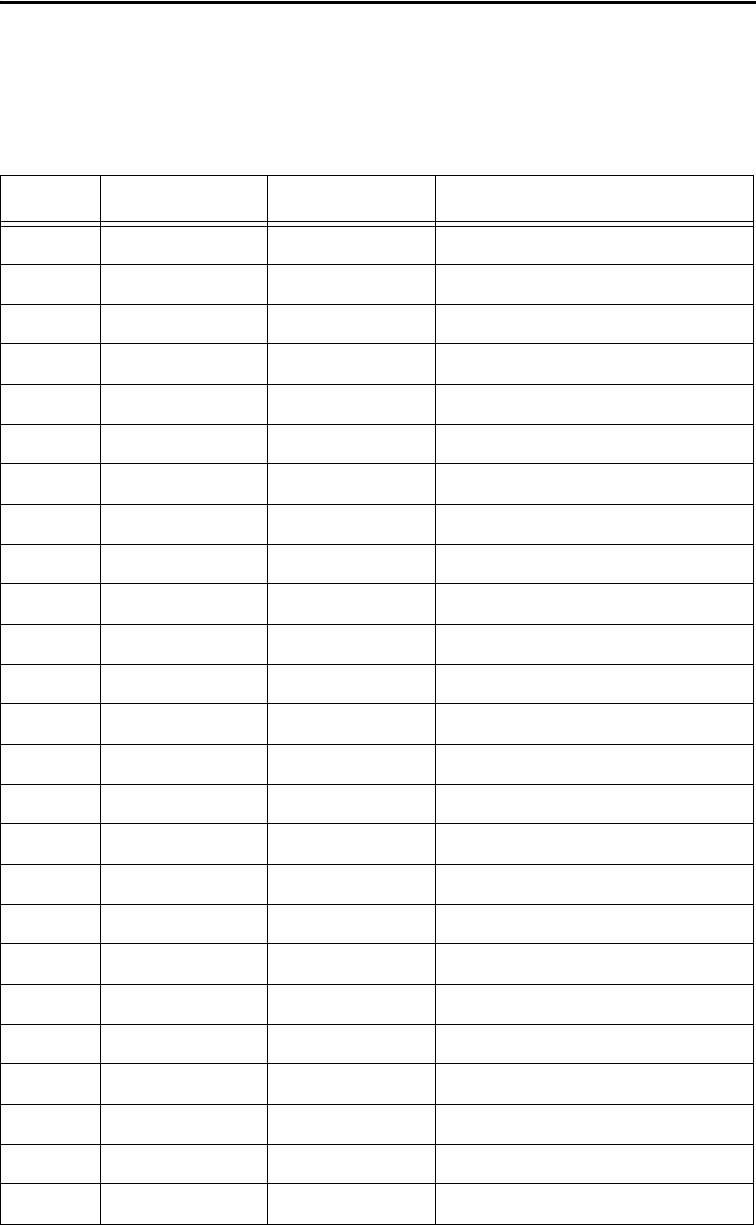
Connector Pin-outs
E-9
IP Module Logic Interface
Table E-4 shows the pinout of the IP module logic interface connector. Signal I/O is
with respect to the reader logic card.
Table E-4 IP Module Logic Interface Connector
Pin Name Type Description
1 GND Output Ground
2 CLK Output 8-MHz clock
3 RESET_L Output Reset signal (active low)
4 D0 Input/output Data bit 0
5 D1 Input/output Data bit 1
6 D2 Input/output Data bit 2
7 D3 Input/output Data bit 3
8 D4 Input/output Data bit 4
9 D5 Input/output Data bit 5
10 D6 Input/output Data bit 6
11 D7 Input/output Data bit 7
12 D8 Input/output Data bit 8
13 D9 Input/output Data bit 9
14 D10 Input/output Data bit 10
15 D11 Input/output Data bit 11
16 D12 Input/output Data bit 12
17 D13 Input/output Data bit 13
18 D14 Input/output Data bit 14
19 D15 Input/output Data bit 15
20 BS0_L Output Byte select 0 (active low)
21 BS1_L Output Byte select 1 (active low)
22 -12 V Output -12 volt power
23 +12 V Output +12 volt power
24 +5 VDC Output +5 volt power
25 GND Output Ground
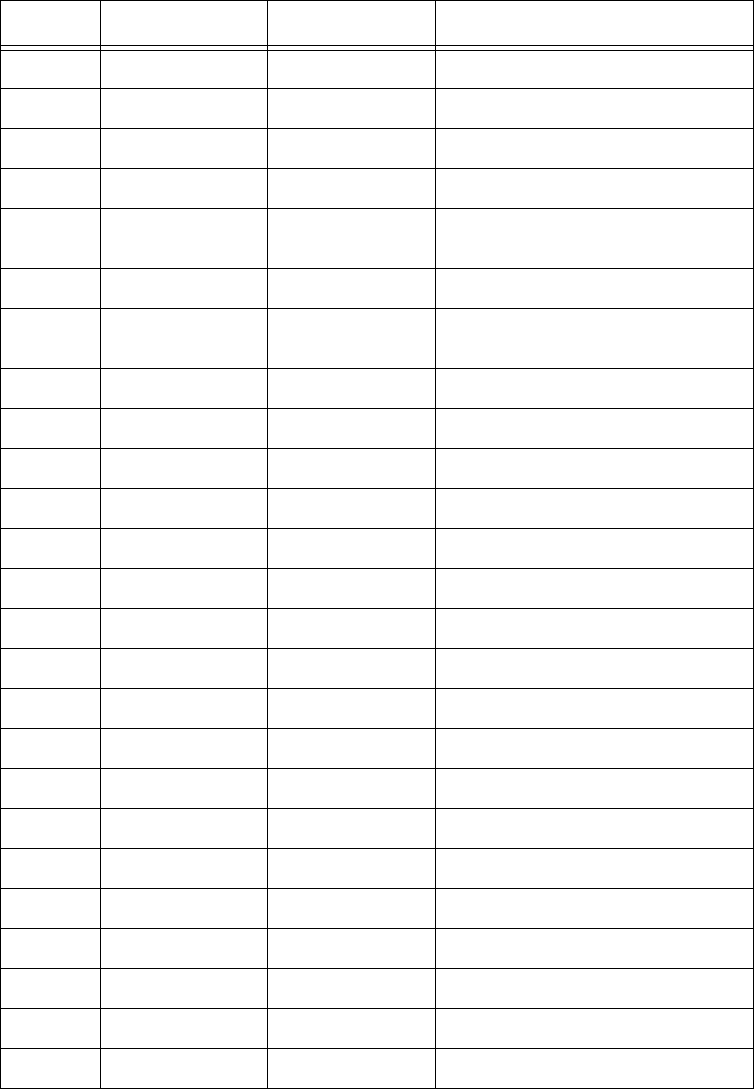
IT2200 Reader System with Multimode Capability Installation & Maintenance/Service Guide
E-10
26 GND Output Ground
27 +5 VDC Output +5 volt power
28 R_W_L Output Data direction (read/write)
29 IDSEL_L Output IP Module Identification
30 DMAREQ0_L Input DMA request channel 0 (active
low)
31 MEMSEL_L Output Memory Select (active low)
32 DMAREQ1_L Input DMA request channel 1 (active
low)
33 INTSEL_L Output Read Interrupt vector (active low)
34 DMACK_L Output DMA Acknowledge (active low)
35 IOSEL_L Output I/O select (active low)
36 RESERVED N/A Reserved for future applications
37 A1 Output Address line A1
38 DMAEND Input/output DMA Termination (active low)
39 A2 Output Address line A2
40 ERROR_L Input IP module error (active low)
41 A3 Output Address line A3
42 INTREQ0_L Input Interrupt request 0 (active low)
43 A4 Output Address line A4
44 INTREQ1_L Input Interrupt request 1 (active low)
45 A5 Output Address line A5
46 STROBE_L Input/output Function Strobe (optional)
47 A6 Output Address line A6
48 ACK_L Input Data Acknowledge (active low)
49 RESERVED N/A Reserved for future applications
50 GND Output Ground
Table E-4 IP Module Logic Interface Connector (continued)
Pin Name Type Description
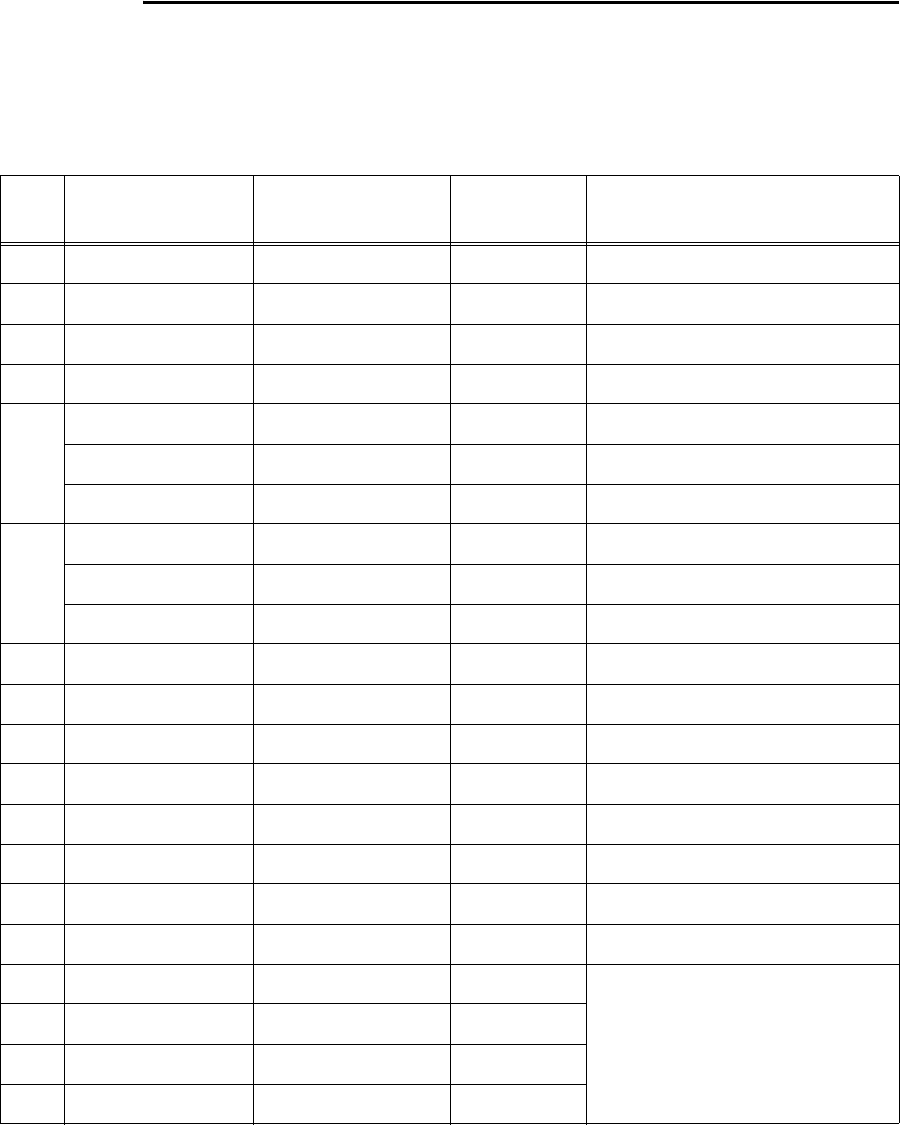
Connector Pin-outs
E-11
IP Module I/O Connector
Table E-5 shows the pinout of the IP module I/O connector. Signal I/O is with respect
to the reader logic card.
Table E-5 IP Module I/O Connector
Pin Slot A (Input/
output) Slot B (Encode/
Decode) Slot C
(Spare) Description
1 IPRXD Unused Unused Responses from RF module
2 B_IP_TXD Unused Unused Commands to RF module
3 GND GND GND Ground
4 GND GND GND Ground
5 DL_RF_ON High to turn downlink power on
BRF_XMITEN Buffered Port C, pin 2 of 360
Unused These two are wired in Flex10K
6 UL_RF_ON High to turn uplink power on
BRF_RCVEN Buffered Port C, pin 8 of 360
Unused These two are wired in Flex10K
7 Unused Unused Unused
8 IT2K_IF_A IT2K_IF_A Unused IT2200 IF channel A from RF
9 IT2K_IF_B IT2K_IF_B Unused IT2200 IF channel B from RF
10 IT2K_IF_C IT2K_IF_C Unused IT2200 IF channel C from RF
11 UNUSED DL_RF_ON Unused High to turn downlink power on
12 UNUSED UL_RF_ON Unused High to turn uplink power on
13 IT2K_MOD IT2K_MOD Unused IT2200 MOD from Flex10K
14 Unused XMTACT_PLS_L Unused Mod out has gone active
15 A_SPARE4 B_SPARE4 C_SPARE4 Extra Via’s added to board for
future upgrade
16 A_SPARE3 B_SPARE3 C_SPARE3
17 A_SPARE2 B_SPARE2 C_SPARE2
18 A_SPARE1 B_SPARE1 C_SPARE1
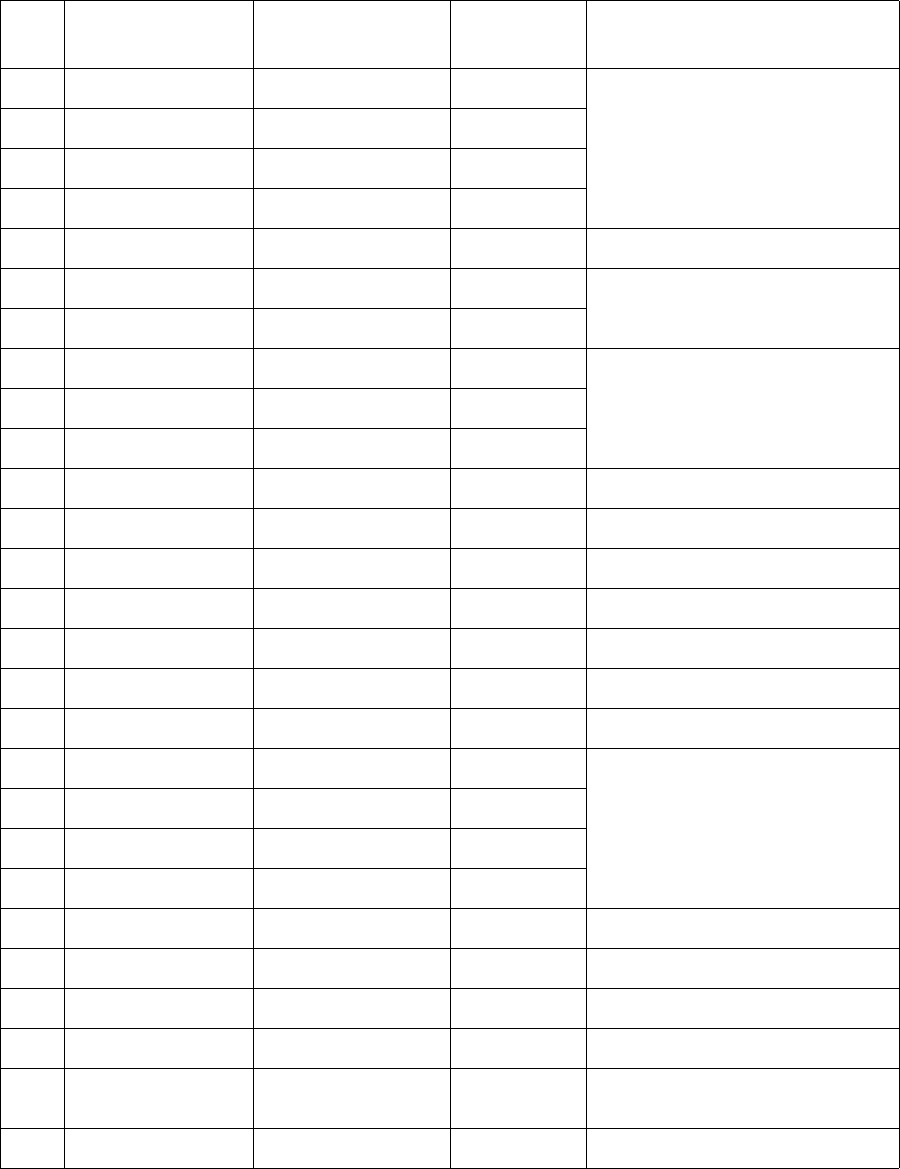
IT2200 Reader System with Multimode Capability Installation & Maintenance/Service Guide
E-12
19 IP_PARA_6 IP_PARA_6 IP_PARA_6 Route extra signals between all
expansion cards in anticipation
of future possibilities20 IP_PARA_5 IP_PARA_5 IP_PARA_5
21 IP_PARA_4 IP_PARA_4 IP_PARA_4
22 IP_PARA_3 IP_PARA_3 IP_PARA_3
23 Unused Unused Unused
24 IP_PARA_2 IP_PARA_2 IP_PARA_2 Route extra signals between all
cards for future possibilities
25 IP_PARA_1 IP_PARA_1 IP_PARA_1
26 Reserved N/A Reserved
27 Reserved N/A Reserved
28 Reserved N/A Reserved
29 Reserved N/A Reserved N/A
30 Reserved N/A Reserved N/A
31 TDM_SYNC_OUT TDM_SYNC_OUT Unused TDM output sync pulse
32 TDM_SYNC_IN TDM_SYNC_IN Unused TDM input sync pulse
33 TDM_SYNC_EN TDM_SYNC_EN Unused TDM enable active high
34 Unused Unused Unused
35 Unused TAGDPLS_L Unused Valid header detected
36 SWSIG7 SWSIG7 SWSIG7 These signals have no defined
functionality at this time. They
are run to the IP cards to give
software future control signals
37 SWSIG6 SWSIG6 SWSIG6
38 SWSIG5 SWSIG5 SWSIG5
39 SWSIG4 SWSIG4 SWSIG4
40 IP_A_PRES Unused Unused HI = I/O PWA installed properly
41 Unused IP_B_PRES Unused HI = ENC/DEC installed prop.
42 Unused Unused IP_C_PRES HI = Future Amtech board inst.
43 Unused IP_10KSTAT Unused LO = Flex10K not configured
44 Unused IP_10KCONF Unused LO to HI transition starts
configuration
45 Unused IP_10KDONE Unused HI = ready for normal operation
Table E-5 IP Module I/O Connector (continued)
Pin Slot A (Input/
output) Slot B (Encode/
Decode) Slot C
(Spare) Description
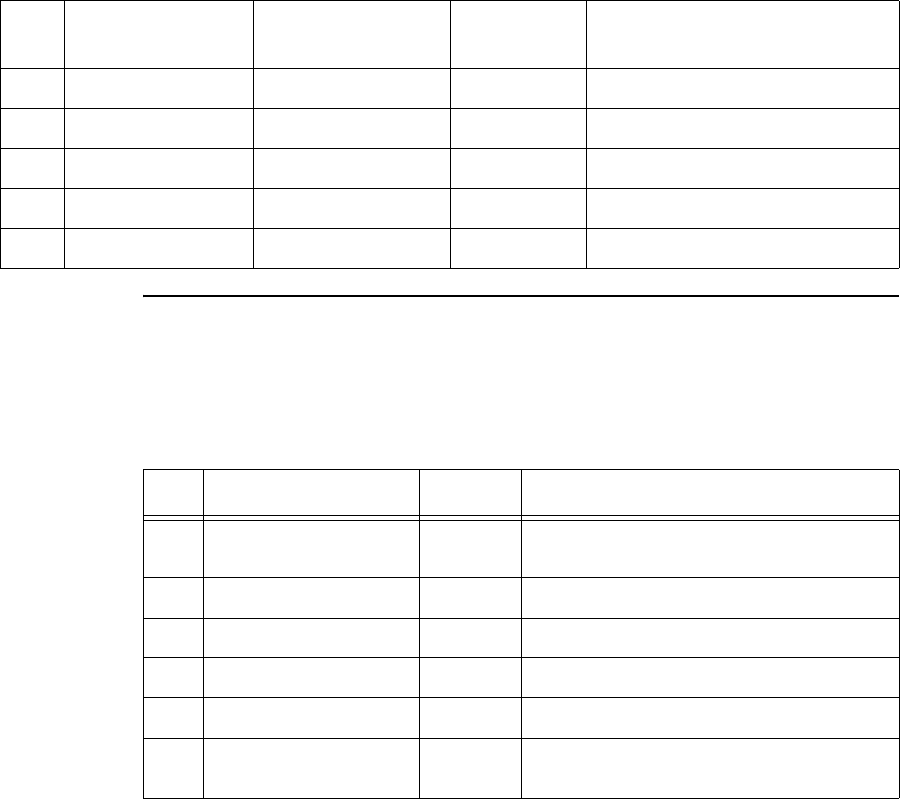
Connector Pin-outs
E-13
Auxiliary Power
Table E-6 shows the pinout of the auxiliary power connector. Signal I/O is with
respect to the reader logic card.
46 Unused CONT_CW_INP Unused Input - HI to turn CW on
47 Unused Unused Unused N/A
48 Unused Unused Unused N/A
49 Unused Unused Unused N/A
50 Unused Unused Unused N/A
Table E-5 IP Module I/O Connector (continued)
Pin Slot A (Input/
output) Slot B (Encode/
Decode) Slot C
(Spare) Description
Table E-6 Auxiliary Power Connector
Pin Name Type Description
1 GND Input/
output Ground
2 +5 VDC Input +5 V power
3 +5 VDC Input +5 V power
4 -12 VDC Input -12 V power
5 +12 VDC Input +12 V power
6 GND Input/
output Ground
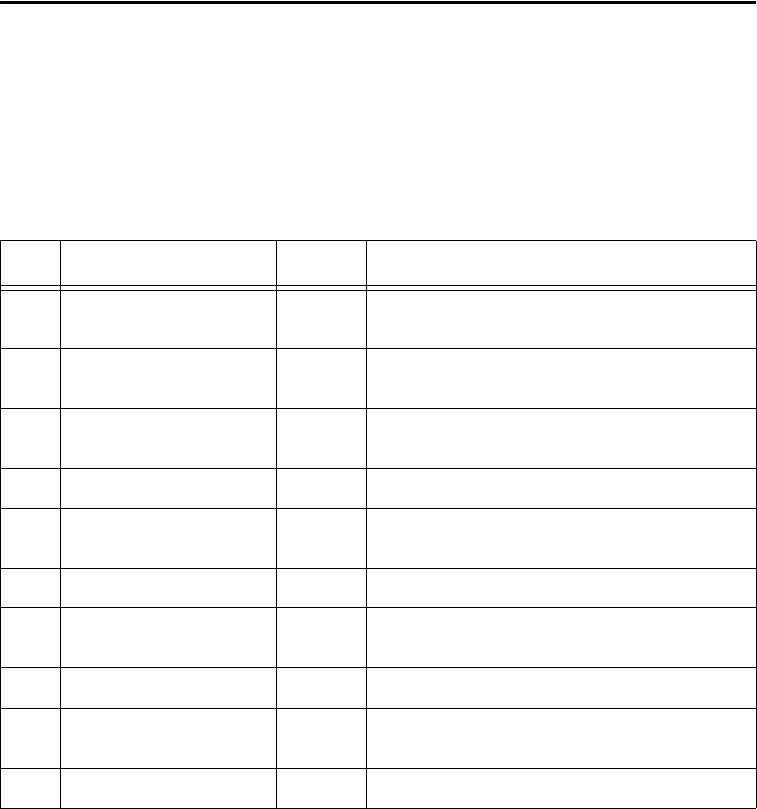
IT2200 Reader System with Multimode Capability Installation & Maintenance/Service Guide
E-14
BDM
The BDM (background debugger mode) connector is a 10-pin, 0.100 center, dual row
header with a 2 x 5 configuration.
Table E-7 shows the pinout of the BDM connector. Signal I/O is with respect to the
reader logic card.
Table E-7 BDM Connector
Pin Name Type Description
1 DS_L Input/
output Data strobe
2 BERR_L Input/
output Bus error
3 GND Input/
output Ground
4 BKPT/DSCLK Input Development serial clock
5 GND Input/
output Ground
6 FREEZE Output Breakpoint acknowledge
7 RESET_L Input/
output Hard system reset
8 IFETCH/DSI Input Development serial input
9 VCC Input/
output +5 VDC power
10 IPIPE0/DSO Output Development serial output
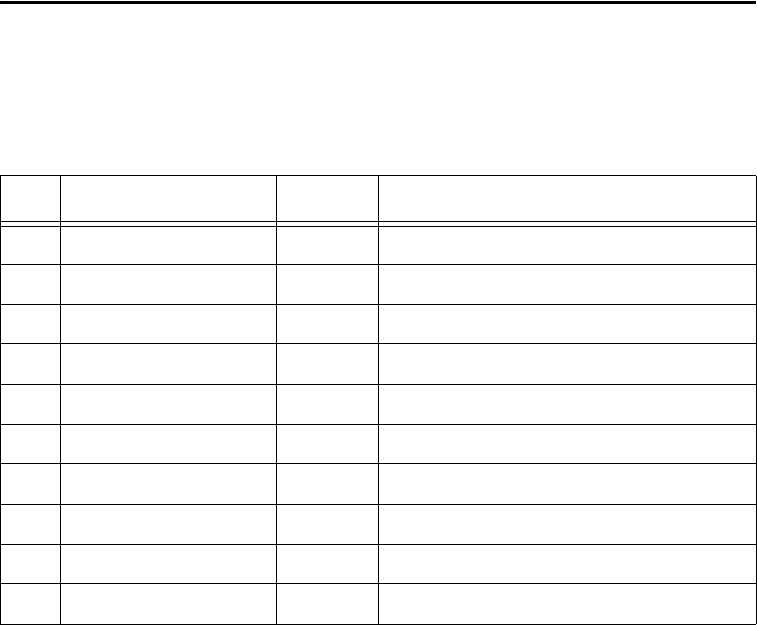
Connector Pin-outs
E-15
General Purpose I/O
Table E-8 shows the pinout of the general purpose I/O connector. Signal I/O is with
respect to the reader logic card.
Table E-8 General Purpose I/O Connector
Pin Name Type Description
1 BIN1 Input CMOS level status input
2 BIN2 Input CMOS level status input
3 BIN3 Input CMOS level status input
4 BIN4 Input CMOS level status input
5 BOUT4 Output CMOS drive output
6 BOUT3 Output CMOS drive output
7 BOUT2 Output CMOS drive output
8 BOUT1 Output CMOS drive output
9 VCC Output +5 VDC power
10 GND Output Ground
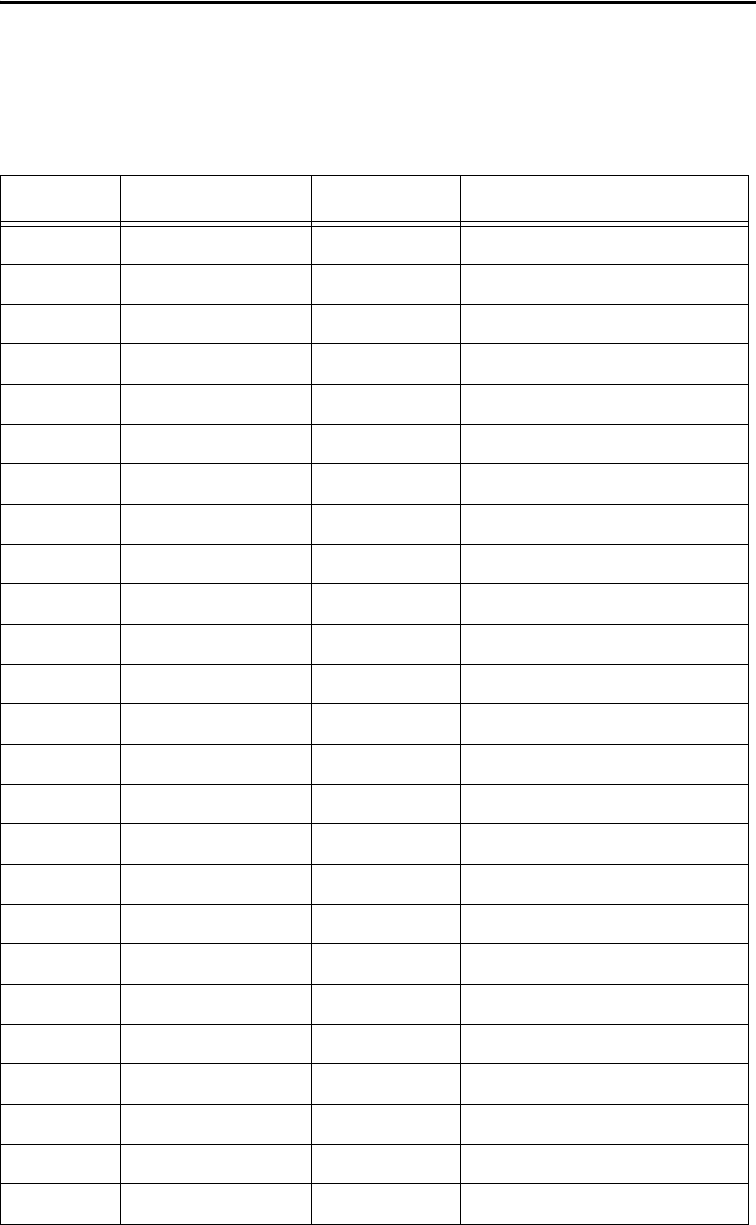
IT2200 Reader System with Multimode Capability Installation & Maintenance/Service Guide
E-16
HW Diagnostics Port
Table E-9 shows the pinout of the HW diagnostics port connector. Signal I/O is with
respect to the reader logic card.
Table E-9 Hardware Diagnostics Port Connector
Pin Name Type Description
1 HDP_EN_L Input Enables output buffers
2 GND Output Ground
3 CONT_CW_INP Input Enable CW mode
4 VCC Output +5 VDC power
5 SWSIG0 Output SW controlled debug bit
6 SWSIG1 Output SW controlled debug bit
7 SWSIG2 Output SW controlled debug bit
8 SWSIG3 Output SW controlled debug bit
9 SWSIG4 Output SW controlled debug bit
10 SWSIG5 Output SW controlled debug bit
11 SWSIG6 Output SW controlled debug bit
12 SWSIG7 Output SW controlled debug bit
13 B_HDRDET_L Output Buffered tag data present
14 B_MOD Output Modulation - IT2000
15 B_DECINT_L Output Decoder interrupt
16 B_TDMINT_L Output TDM interrupt
171 B_MRESET_L Output 360 reset from any source
18 B_ISARES_L Output ISA command or HW reset
19 B_ISAIRQ_H Output IRQ to host
20 B_IRQISA_L Output IRQ from host
21 Reserved N/A Reserved
22 Reserved N/A N/A
232 B_IF_A Output IF Data A - IT2200
24 B_IF_B Output IF Data B - IT2200
25 B_IF_C Output IF Data C - IT2200
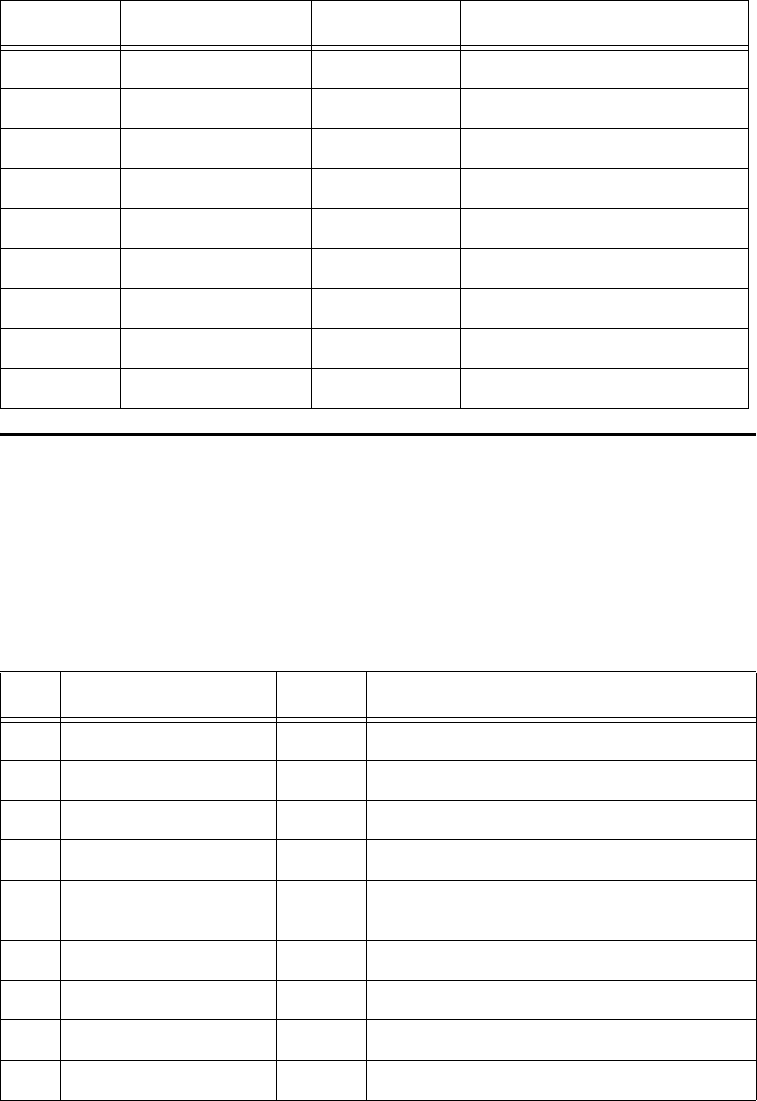
Connector Pin-outs
E-17
RS-232
The RS-232 connector is a standard DB-9 plug. The pinout of this connector is such
that it does not need a null modem cable to connect to a PC serial port.
Table E-10 shows the pinout of the DB-25 connector. Signal I/O is with respect to the
reader logic card.
26 Reserved N/A N/A
27 Reserved N/A N/A
28 Reserved N/A N/A
29 BHW_IP_RXD Output Buffered RF module receive
30 BHW_IP_TXD Output Buffered RF module transmit
31 VCC Output +5 VDC power
32 VCC Output +5 VDC power
33 GND Output Ground
34 GND Output Ground
Table E-10 RS-232 Connector
Pin Name Type Description
1 RSD N/A Received line signal detect
2 TXD Output Transmit data
3 RXD Input Receive data
4 DTR N/A Data terminal ready
5 GND Input/
output Ground
6 DSR N/A Data set ready
7 CTS Input Clear to send
8 RTS Output Request to send
9 RI N/A Ring indicator
Table E-9 Hardware Diagnostics Port Connector (continued)
Pin Name Type Description
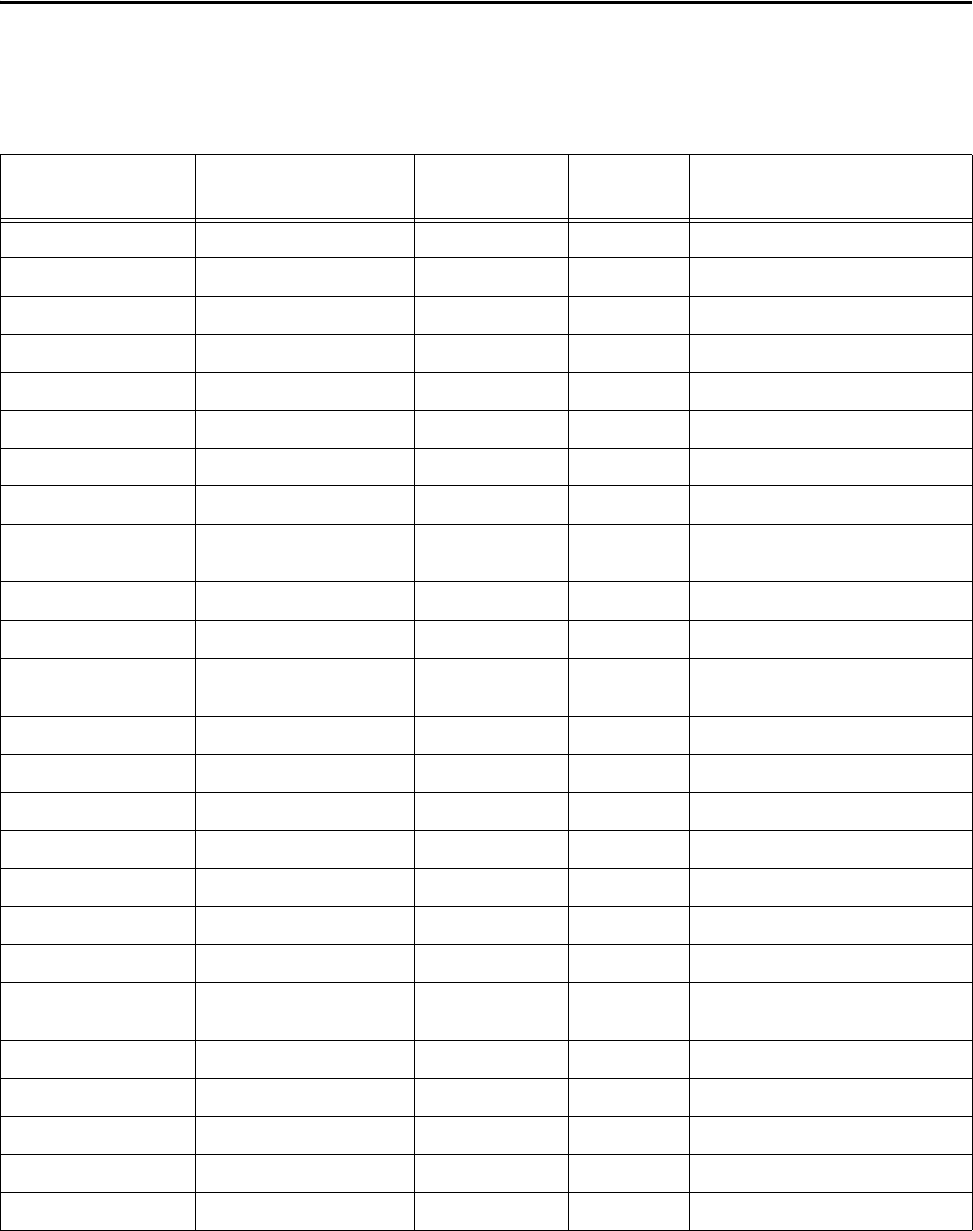
IT2200 Reader System with Multimode Capability Installation & Maintenance/Service Guide
E-18
IT2611 RF Module
Table E-11 lists the pin-socket names and descriptions for the IT2611 RF Module-to-
IT2020 Reader Logic Card connector.
Table E-11 RF Module-to-Reader Logic Card Interface Connector
IT2611 RF Module
Socket IT2020 Reader Logic
Card DB-25 Pin Name Type Description
A 1 IF_A+ Input Uplink tag data, channel A+
T 2 Reserved N/A
D 3 IF_B- Input Uplink tag data, channel B-
E 4 IF_C+ Input Uplink tag data, channel C+
V 5 Reserved N/A
H 6 MOD- Output Downlink modulation data, (-)
Z 7 Reserved N/A
K 8 CTL_XMT- Output Control interface transmit, (-)
L 9 CTL_RCV+ Input/
output Control interface receive, (+)
10 Reserved N/A
N 11 UL_OFF- Output RF uplink power on/off, (-)
P 12 DL_OFF+ Output RF downlink power on/off,
(+)
13 Reserved N/A
B 14 IF_A- Input Uplink tag data, channel A-
C 15 IF_B+ Input Uplink tag data, channel B+
U 16 Reserved N/A
F 17 IF_C- Input Uplink tag data, channel C-
G 18 MOD+ Output Downlink modulation data, (-)
W 19 Reserved N/A
J 20 CTL_XMT+ Input/
output Control interface transmit, (+)
a 21 Reserved N/A
Y 22 CTL_RCV- Input Control interface receive, (-)
M 23 UL_OFF+ Output RF uplink power on/off, (+)
24 Reserved N/A
R 25 DL_OFF- Output RF downlink power on/off, (-)
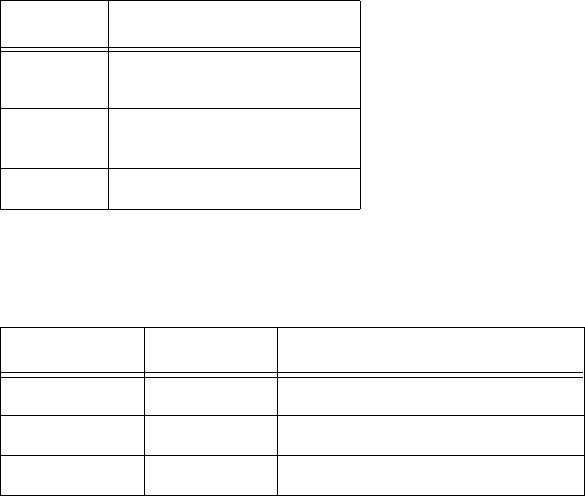
Connector Pin-outs
E-19
Table E-12 shows the IT2611 RF Module power connector pin designations.
Table E-13 shows the IT2611 RF Module-to-antenna connectors.
Table E-12 RF Module Power
Pin Description
A 19- to 28-VAC or
16- to 28-VDC
C 19- to 28 VAC Return or
16- to 28-VDC Return
BN/A
Table E-13 RF Module-Antenna Connectors
Connector Type Description
J1 N Socket RF uplink (receive) antenna
J2 N Socket RF downlink (transmit) antenna
J3 N Socket Check tag antenna
IT2200 Reader System with Multimode Capability Installation & Maintenance/Service Guide
E-20