TransCore MPRX Multiprotocol Reader Extreme User Manual
TransCore Multiprotocol Reader Extreme
User Manual
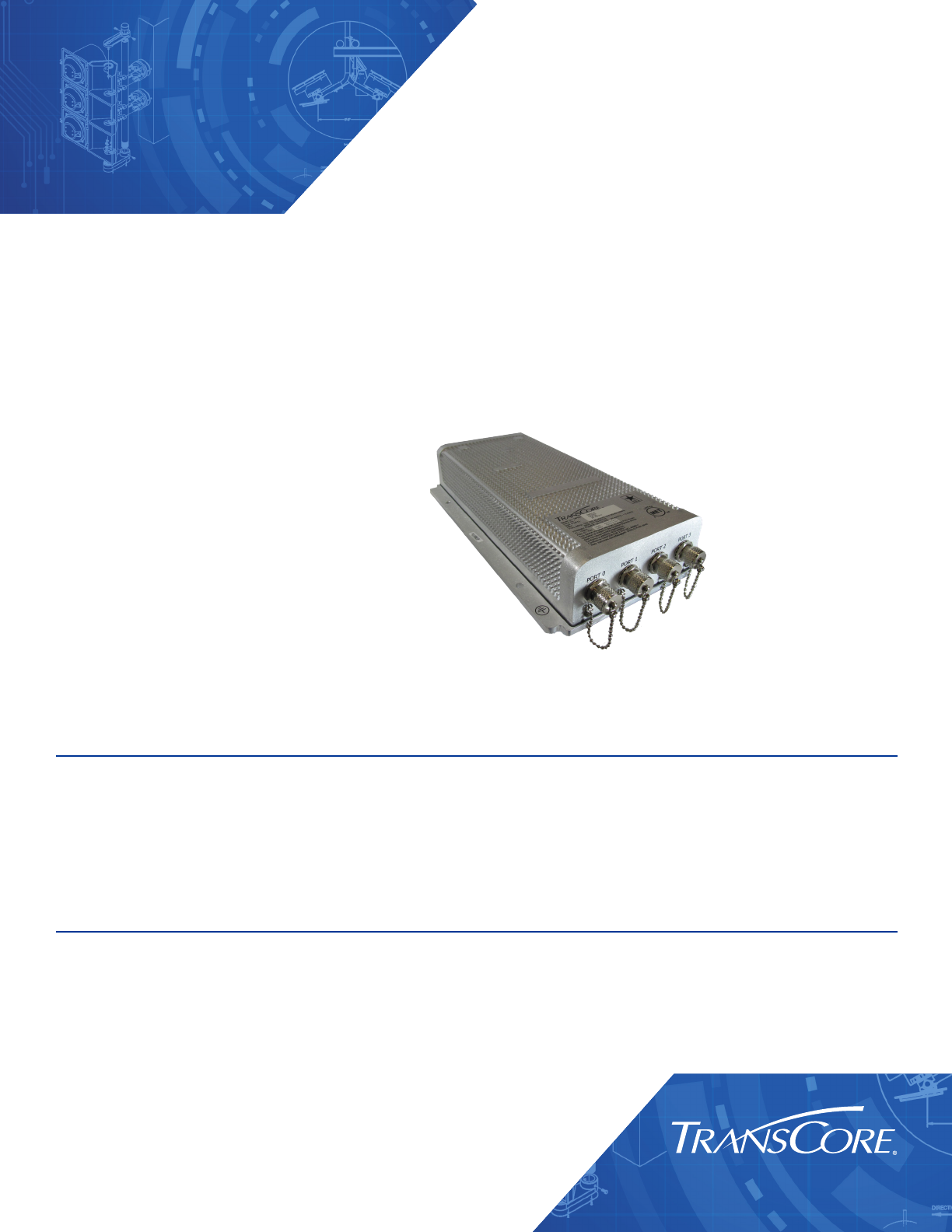
Multiprotocol
Reader Extreme (MPRX)
System Guide
Trusted Transportation Solutions
16-0079-001 Rev A 11/16
TransCore’s Multiprotocol Reader Extreme (MPRX) is a radio frequency
identification (RFID) reader that is specifically designed for harsh
environment applications.
Purpose of This Guide
This guide provides site planning and testing, installing, and operating instructions for
TransCore’s Multiprotocol Reader Extreme (MPRX) System, which reads Association of
American Railroads (AAR) formatted tags and TransCore Super eGo® (SeGo) protocol tags.
Before you begin installing the MPRX, TransCore recommends that you familiarize yourself
with this manual.
Intended Audience
This document is intended for use by authorized TransCore MPRX dealers, installers,
and service personnel. Because the MPRX has no operator or end-user serviceable
components or features, no end-user manual or operator guide exists. Once the system
is set up and tested by the authorized installer, MPRX operation requires no end-user
intervention. Information in this document is subject to change and does not represent a
commitment on the part of TransCore, LP.

System Guide
TransCore Proprietary
ii
© 2016 TransCore, LP. All rights reserved. TRANSCORE, AMTECH, EGO, TRU, and ENCOMPASS are
registered trademarks and are used under license. All other trademarks are the property of their respective
owners. Contents are subject to change. Printed in the U.S.A.
For further information, contact:
TransCore
8600 Jeerson Street NE
Albuquerque, New Mexico 87113 USA
TransCore Technical Support
Web: www.transcore.com/rfidsupport
Phone: (505) 856-8007
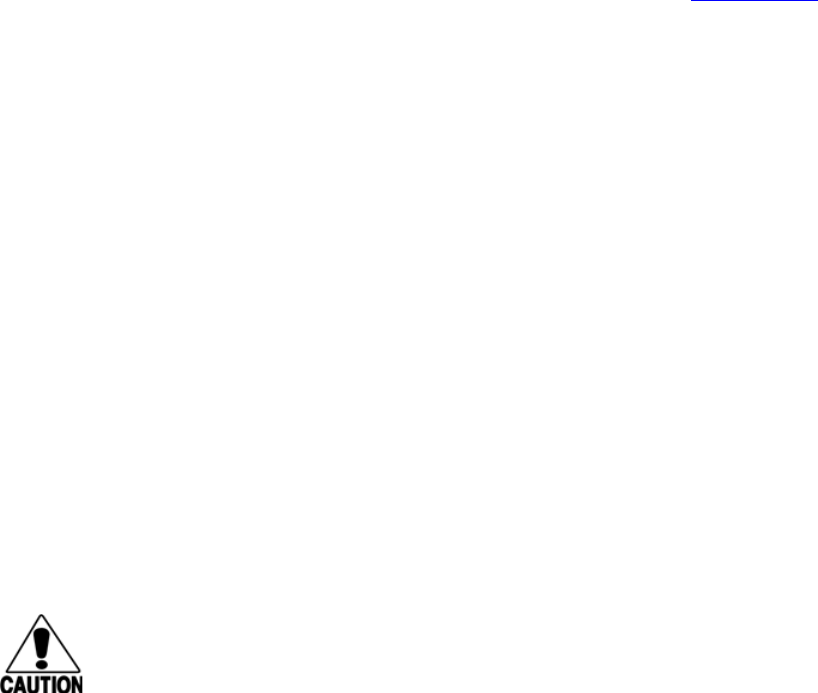
MPRX
TransCore Proprietary iii
WARNING TO USERS IN THE UNITED STATES
FEDERAL COMMUNICATIONS COMMISSION FCC
LOCATION AND MONITORING SERVICE STATEMENT
47 CFR §90.351
NOTE: The user is required to obtain a Part 90 site license from the Federal Communications
Commission (FCC) to operate this radio frequency identification (RFID) device in the United States.
The FCC ID number is FIHMPRX. Access the FCC website at www.fcc.gov to obtain additional
information concerning licensing requirements.
NOTE: Users in all countries should check with the appropriate local authorities for licensing
requirements.
FCC RADIO FREQUENCY INTERFERENCE STATEMENT
47 CFR §15.105A
NOTE: This equipment has been tested and found to comply with the limits for a Class A digital
device pursuant to Part 15 of the FCC rules. These limits are designed to provide reasonable
protection against harmful interference when the equipment is operated in a commercial
environment. This equipment generates, uses, and can radiate RF energy and may cause harmful
interference to radio communications if not installed and used in accordance with the instruction
manual. Operating this equipment in a residential area is likely to cause harmful interference, in
which case, depending on the laws in eect, the user may be required to correct the interference
at their own expense.
NO UNAUTHORIZED MODIFICATIONS
47 CFR §15.21
CAUTION: This equipment may not be modified, altered, or changed in any way without
permission. Unauthorized modification may void the equipment authorization from the FCC and
will
void the warranty.
USE OF SHIELDED CABLES AND GROUNDING
47 CFR §15.27A
NOTE: Shielded cables and earth grounding the unit is recommended for this equipment to comply
with FCC regulations.
TRANSCORE, LP
USA
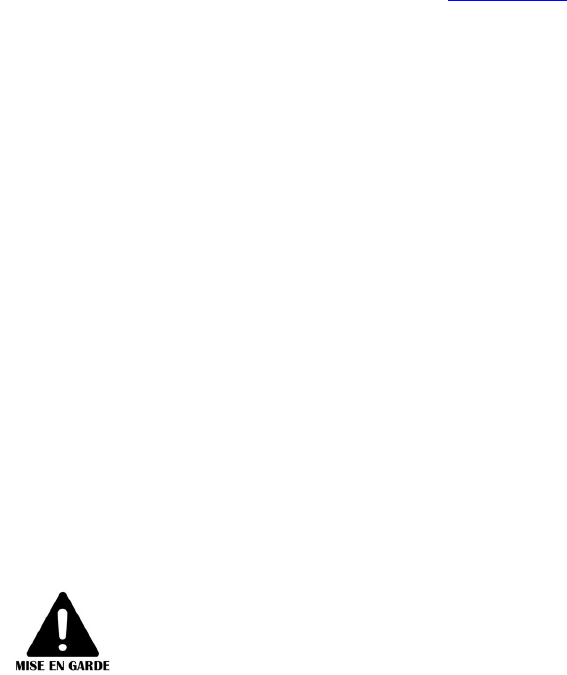
System Guide
TransCore Proprietary
iv
AVERTISSEMENT À L’ATTENTION DES
UTILISATEURS AUX ÉTATSUNIS
DÉCLARATION 47 CFR §90.351 CODE DES
RÈGLEMENTS FÉDÉRAUX DE LA FEDERAL
COMMUNICATIONS COMMISSION FCC SUR LES
SERVICES DE LOCALISATION ET DE CONTRÔLE
REMARQUE : L’utilisateur est tenu d’obtenir une licence d’utilisation sur site Partie 90 auprès de
la Federal Communications Commission (FCC) afin de pouvoir utiliser ce dispositif RFID (radio-
identification) aux États-Unis ou au Canada. Le numéro d’identification de la FCC est FIHMPRX.Pour
obtenir de plus amples informations concernant les exigences relatives aux licences, prière de
consulter le site web de la FCC à www.fcc.gov.
REMARQUE : Il est recommandé à tous les utilisateurs, quel que soit leur pays, de consulter les
autorités locales compétentes sur les exigences de licence.
DÉCLARATION 47 CFR §15.105A DE LA FCC SUR
LES INTERFÉRENCES DES FRÉQUENCES RADIO
REMARQUE : Cet appareil a été testé et déclaré conforme à la catégorie d’un appareil numérique
de classe A en accord avec la partie 15 des directives de la FCC. Ces normes visent à assurer
une protection raisonnable contre les interférences nuisibles lorsque l’appareil est utilisé dans
un environnement commercial. Cet appareil génère, utilise et peut émettre de l’énergie RF et
peut être à l’origine d’interférences nuisibles aux communications radio s’il n’est pas installé et
utilisé en suivant les directives du manuel d’instructions. Si cet appareil est utilisé dans une zone
résidentielle, il est probable qu’il cause des interférences nuisibles. Dans ce cas, l’utilisateur
pourrait être amené à remédier aux interférences à ses propres frais, selon les lois du pays en
vigueur.
AUCUNE MODIFICATION NON AUTORISÉE
47 CFR §15.21
MISE EN GARDE : Il est interdit de modifier, d’altérer ou d’apporter des changements à cet appareil
de quelque manière que ce soit sans autorisation. Toute modification non autorisée peut annuler
l’autorisation d’utilisation accordée par la FCC et annulera la garantie.
UTILISATION DE CÂBLES BLINDÉS ET MISE À LA TERRE
47 CFR §15.27A
REMARQUE : Il est recommandé d’utiliser des câbles blindés et une mise à la terre avec cet
appareil afin de répondre aux réglementations de la FCC
TRANSCORE, LP
ÉTATSUNIS
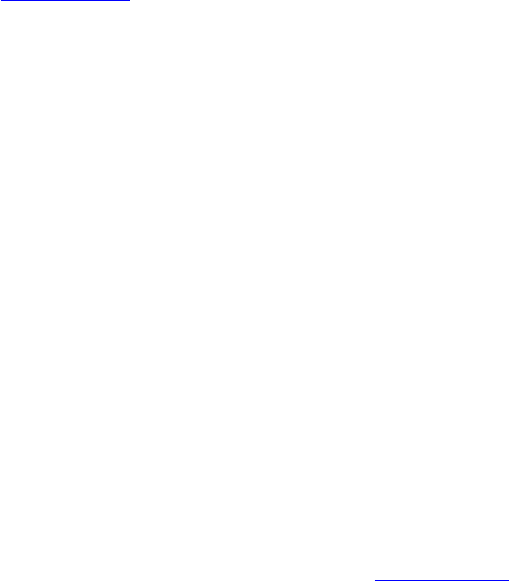
MPRX
TransCore Proprietary v
WARNING TO USERS IN CANADA
INDUSTRY CANADA IC INDUSTRY CANADA’S RADIO STANDARD SPECIFICATIONS RSS137 LOCATION
AND MONITORING SERVICE IN THE BAND 902928 MHZ SECTION 2.1
NOTE: The user is required to obtain a license from Industry Canada (IC), to operate this radio
frequency identification (RFID) device in Canada. The IC ID number is 1584A-MPRX, access the IC
website at www.ic.gc.ca to obtain additional information concerning licensing requirements.
Industry Canada (IC) Industry Canada’s Radio Standard Specifications General Requirements
(RSS-GEN) for Compliance of Radio Apparatus Statement Section 8.4
This device complies with Industry Canada’s license-exempt RSSs. Operation is subject to the
following two conditions:
1 ) This device may not cause interference; and
2 ) This device must accept any interference, including interference that may cause
undesired operation of the device.
AVERTISSEMENT AUX UTILISATEURS AU CANADA
INDUSTRIE CANADA IC INDUSTRIE CANADA RADIO STANDARD SPECIFICATIONS CNR137
EMPLACEMENT ET SERVICE DE SURVEILLANCE DANS LA BANDE 902928 MHZ, SECTION 2.1
Remarque : L’utilisateur est tenu d’obtenir une licence d’Industrie Canada (IC), afin d’exploiter
ce dispositif d’identification par radiofréquence au Canada. Le numéro d’identification d’IC est
1584A-MPRX. Pour obtenir de plus amples informations concernant les exigences relatives aux
licences, prière de consulter le site web de d’IC à www.ic.gc.ca .
Radio Standard Spécifications exigences générales Industrie Canada (IC) Industrie Canada
(CNR-GEN) pour s’acquitter du Radio appareil déclaration article 8.4
Le présent appareil est conforme aux CNR d'Industrie Canada applicables aux appareils radio
exempts de licence. L'exploitation est autorisée aux deux conditions suivantes :
1 ) l'appareil ne doit pas produire de brouillage, et
2 ) l'utilisateur de l'appareil doit accepter tout brouillage radioélectrique subi, même si le
brouillage est susceptible d'en compromettre le fonctionnement.
System Guide
TransCore Proprietary
vi
RADIO FREQUENCY HEALTH LIMITS FOR MPRX READER
USING AN EXTERNAL ANTENNA IN FREQUENCY BAND
OF 902.25 TO 903.75 AND 910.00 TO 921.50 MHZ
Several agencies (OSHA, FCC, IC) have environmental guidelines regulating maximum permissible
exposure (MPE) or “safe” exposure levels that this product falls under. To ensure that proper safety
guideline for the end users of this product, i.e. Occupational (Controlled) and General Population/
Public (Uncontrolled), the recommended levels for each of the agencies are presented in the next
sections with TransCore’s recommendations for safety in the last section.
OSHA (Occupational Safety and Health Administration)
OSHA (an agency of The United States of America) legislates in the Code of Federal Regulations
(CFR) Title 29 Part 1910 Subpart G 1910.97 titled “Nonionizing radiation”, a maximum safe exposure
limit of 10 milliwatts per square centimeter (mW/cm2) during any 0.1-hour period (i.e. 6 minutes).
Using the frequency (in the middle of the band of operation of this equipment) of 915 MHz and the
highest antenna gain that this equipment is certified for use in a final installation, the minimum safe
distance was calculated to be 8in (20cm).
FCC (Federal Communication Commission)
FCC (an agency of The United States of America) legislates in the Code of Federal Regulations
(CFR) Title 47 Chapter I Subchapter A Part 1 Subpart I Section 1.1310 titled “Radiofrequency radiation
exposure limits” that the maximum permissible exposure (MPE) is the following:
Occupational/Controlled Exposure
Power density = frequency (in MHz)/300 mW/cm2 with an Averaging time of 6 Min
General Population/Uncontrolled Exposure
Power density = frequency (in MHz)/1500 mW/cm2 with an Averaging time of 30 Min
Using the frequency (in the middle of the band of operation of this equipment) of 915MHz and the
highest antenna gain that this equipment is certified for use in a final installation, the minimum
safe distance was calculated. The MPE minimum distances are 14in (36cm) for the Occupational/
Controlled environment, and 31.5in (80.5cm) for the General Population/Uncontrolled environment.
Industry Canada (Innovation, Science and Economic Development Canada)
Industry Canada (a Department of the Government of Canada) sets out the requirements in Radio
Standards Specification RSS-102, Issue 5 guidelines, recommending a maximum safe
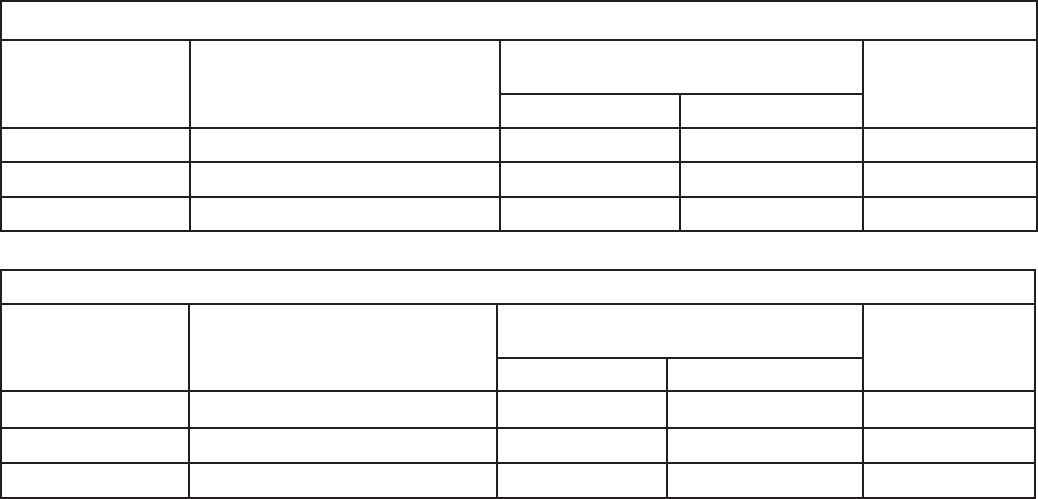
MPRX
TransCore Proprietary vii
Occupational/Controlled Environment
Agency Power Density (mW/cm2) MPE minimum distance Time (min)
in cm
OSHA 10 7 18 6
FCC 3.05 13 32 6
IC 1.95 16 40 6
General Population/Public/Uncontrolled Environment
Agency Power Density (mW/cm2) MPE minimum distance Time (min)
In cm
OSHA 10 7 18 6
FCC 0.61 28 72 30
IC 0.28 42 106 6
power density in W/m2. Thus, the maximum permissible exposure for general population/
uncontrolled exposure at 915MHz is 2.77 W/m2. The average time is 6 minutes. The maximum
permissible exposure (MPE) is the following:
Controlled Environment
Power density = 0.6455*frequency (in MHz)0.5 W/m2 with a Reference Period time of 6 Min
General Public/Uncontrolled Environment
Power density = 0.02619*frequency (in MHz)0.6834 W/m2 with a Reference Period time of 6 Min
Using the frequency (in the middle of the band of operation of this equipment) of 915MHz and the
highest antenna gain that this equipment is certified for use in a final installation, the minimum
safe distance was calculated. The MPE minimum distances are 18in (45cm) for the Controlled
environment and 47in (120cm) for the General Public/Uncontrolled environment.
TransCore Recommendation on MPE (Maximum Permissible Exposure)
The calculated power densities and MPE distance for each of the agencies respective to the
environment is shown below.
System Guide
TransCore Proprietary
viii
With the equipment installed and running at the maximum transmit power of 1.6W (32dBm),
0dB transmit attenuation, using the highest gain antenna that the equipment is certified for, the
recommendation for each of the operation environments is as follows:
1 ) The antenna should be installed at least 42in (106cm) from the General Population/
Public i.e. Uncontrolled Environment.
2 ) Maintenance personnel (i.e. Occupational/Controlled Environment) must remain at least
16in (40cm) from the antenna and limit their time in the environment to 6 minutes when
the system is operating.
MPRX
TransCore Proprietary ix
LIMITES D’EXPOSITION AUX RADIOFRÉQUENCES POUR LE LECTEUR MPRX
UTILISANT UNE ANTENNE EXTERNE SUR LA BANDE
DE FRÉQUENCES DE 902.25 À 903.75 ET DE 910.00 À 921.50 MHZ
Plusieurs organismes (OSHA, FCC, IC) publient des directives environnementales qui
recommandent des limites d’exposition maximale autorisée (normes MPE) ou des niveaux
d’exposition «sûrs» auxquels cet appareil se conforme. Pour faire en sorte que chaque utilisateur
final ait connaissance des directives de sécurité qui le concerne, que ce soit dans son travail
(accès contrôlé) ou pour la population générale/le grand public (accès non contrôlé), TransCore
présente les niveaux recommandés par chaque organisme dans ses recommandations sécuritaires
détaillées dans la dernière section.
OSHA (Occupational Safety and Health Administration)
Dans le Code des réglementations fédérales (CFR), Titre 29, Partie 1910, Sous-partie G 1910.97,
intitulée «Nonionizing radiation» (Rayonnements non ionisants), l’OSHA (organisme américain)
recommande un plafond d’exposition maximale de 10 milliwatts par centimètre carré (mW/cm2)
pendant une période de 0,1 heure (soit 6 minutes). En utilisant la fréquence de 915 MHz (milieu de
la bande de fréquences de cet appareil) et le gain d’antenne maximal pour lequel cet appareil a
reçu une certification d’utilisation dans une installation finale, la distance minimale sécuritaire est
de 20 cm (8 po).
FCC (Federal Communication Commission)
Dans le Code des réglementations fédérales (CFR), Titre 47, Chapitre I, Sous-chapitre A, Partie
1, Sous-partie I, Section 1.1310 intitulée «Radiofrequency radiation exposure limits» (Limites
d’exposition aux rayonnements de radiofréquence), la FCC (organisme américain) établit les limites
d’exposition maximale autorisée (normes MPE) comme suit :
Exposition professionnelle/contrôlée
Densité de puissance = fréquence (en MHz)/300 mW/cm2 avec une durée moyenne de 6 min.
Exposition de la population générale/non contrôlée
Densité de puissance = fréquence (en MHz)/1500 mW/cm2 avec une durée moyenne de 30 min.
En utilisant la fréquence de 915 MHz (milieu de la bande de fréquences de cet appareil) et le
gain d’antenne maximal pour lequel cet appareil a reçu une certification d’utilisation dans une
installation finale, la distance minimale sécuritaire est la suivante : les distances MPE minimales
sont de 36 cm (14 po) pour l’environnement professionnel/contrôlé et de 80,5 cm (31,5 po) pour la
population générale/environnement non contrôlé.
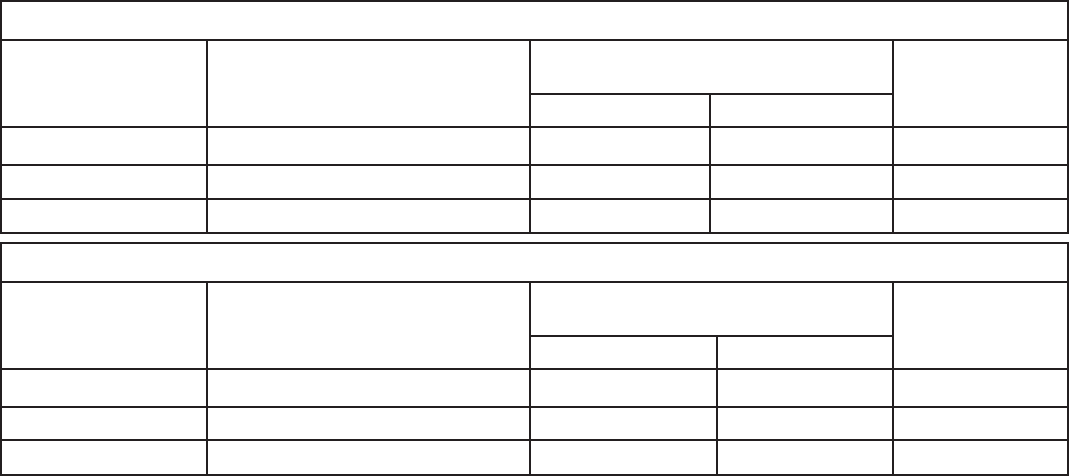
System Guide
TransCore Proprietary
x
Industrie Canada (Innovation, Sciences et Développement économique Canada)
Le Cahier des charges sur les normes radioélectriques 102, 5e édition, d’Industrie Canada (un
ministère du Gouvernement du Canada) établit des recommandations pour une densité de
puissance maximale sécuritaire en W/m2. Ainsi, l’exposition maximale admissible pour la population
générale/non contrôlée à 915 MHz est calculée à 2,77 W/m2. La durée moyenne est de 6 minutes.
Les limites d’exposition maximale autorisée (normes MPE) sont les suivantes :
Environnement contrôlé
Densité de puissance = 0,6455*fréquence (en MHz)0,5 W/m2 avec une durée de référence de 6 min.
Grand public/environnement non contrôlé
Densité de puissance = 0,02619*fréquence (en MHz)0,6834 W/m2 avec une durée de référence de 6 min.
En utilisant la fréquence de 915 MHz (milieu de la bande de fréquences de cet appareil) et le
gain d’antenne maximal pour lequel cet appareil a reçu une certification d’utilisation dans une
installation finale, la distance minimale sécuritaire est la suivante : les distances MPE minimales
sont de 45 cm (18 po) pour l’environnement professionnel/contrôlé et de 120 cm (47 po) pour le
grand public/environnement non contrôlé.
Recommandations de TransCore sur les limites d’exposition maximale autorisée (normes MPE)
Les densités de puissance et la distance MPE calculées par chaque organisme pour un
environnement donné sont présentées ci dessous.
Exposition professionnelle/environnement contrôlé
Organisme Densité de puissance (mW/
cm2)
Distance MPE minimale Durée (en min.)
po cm
OSHA 10 7 18 6
FCC 3,05 13 32 6
IC 1,95 16 40 6
Population générale/environnement non contrôlé
Organisme Densité de puissance (mW/
cm2)
Distance MPE minimale Durée (en min.)
po cm
OSHA 10 7 18 6
FCC 0,61 28 72 30
IC 0,28 42 106 6
MPRX
TransCore Proprietary xi
Avec l’appareil installé et fonctionnant à la puissance de transmission maximale de 1,6W (32dBm),
0dB d’atténuation de transmission, et en utilisant le gain d’antenne maximal pour lequel l’appareil
a reçu une certification, les recommandations pour chaque environnement d’exploitation sont les
suivantes :
1 ) L’antenne devrait être installée à au moins 106 cm (42 po) de la population générale/du
grand public, c’est-à-dire d’un environnement non contrôlé.
2 ) Le personnel d’entretien (c’est-à-dire dans un environnement professionnel/contrôlé)
doit rester à au moins 40 cm (16 po) de l’antenne et limiter son temps d’exposition à 6
minutes lorsque l’appareil est en fonctionnement.
-

MPRX
TransCore Proprietary i–i
Table of Contents
Purpose of This Guide ................................................i
Intended Audience .................................................... i
Chapter 1 Introduction ..........................................1–2
Licensing Requirements ........................................... 1–4
Technical Support................................................. 1–4
Chapter 2 Developing the Site Plan ...............................2–2
System Description ...............................................2–2
Overview of Site Planning..........................................2–3
Reading of Mixed Population Tags .......................................2–3
Antenna and Tag Alignment ........................................2–4
Antenna Selection ................................................2–6
Site Layout and Trac Flow . . . . . . . . . . . . . . . . . . . . . . . . . . . . . . . . . . . . . . . . 2–6
Electrical and Communications Requirements.........................2–9
Chapter 3 Choosing, Installing, Removing Tags .....................3–2
Compatible Tag Types ................................................3–2
Recommended Mounting Locations .................................3–2
Locomotive Mounting Guidelines ...................................3–6
Rail Car Mounting Guidelines.......................................3–8
Tank Car Mounting Guidelines .....................................3–10
Chapter 4 Installing the MPRX.............................................4–2
Installation Process ...............................................4–2
Pre-installation Testing of the MPRX .................................4–3
Mounting the MPRX...............................................4–9
Mounting the Antenna Rail-Side ....................................4–11
Connecting the Power Supply ......................................4–11
Connecting Communications ......................................4–12
Connecting Sense Input and Sense Output Circuits................... 4–12
Marking the Read Zone ........................................... 4–13
Chapter 5 General Software Information ..........................5–2
Command Entry Conventions........................................ 5–2
Command Response Conventions ................................... 5–3
System Guide
TransCore Proprietary
ii
Operating Parameters .............................................. 5–3
Power Fail ......................................................... 5–4
Program Download ...............................................5–4
Startup ..........................................................5–4
Tag/Message Buer . . . . . . . . . . . . . . . . . . . . . . . . . . . . . . . . . . . . . . . . . . . . . . . 5–5
Chapter 6 Communications Protocols .............................6–2
Introduction......................................................6–2
Basic Protocol ....................................................6–3
Error Correcting Protocol...........................................6–3
Data Inquiry Protocol ..............................................6–4
Basic Protocol and ECP Format .....................................6–4
Host-Addressed Failure Conditions..................................6–11
ECP Reliability...................................................6–12
CRC Calculation .................................................6–12
Manually Disabling ECP for Maintenance............................6–15
Chapter 7 Commands ...........................................7–2
Introduction......................................................7–2
Operating Modes .................................................7–2
Command List....................................................7–4
Chapter 8 Configuring the MPRX..................................8–2
Configuring the Reader ............................................8–2
Configuring Parameters with Terminal Emulation Software..............8–3
Configuring MPRX Parameters.......................................8–11
Chapter 9 Troubleshooting and Maintenance ......................9–1
Error Messages ................................................... 9–1
MPRX Repair .....................................................9–4
Technical Support .................................................9–4
Marketing Support . . . . . . . . . . . . . . . . . . . . . . . . . . . . . . . . . . . . . . . . . . . . . . . . 9–5
Chapter 10 Interface to Train Recording Unit ..................... 10–2
TRU System Overview............................................10–2
MPRX to TRU Connection.........................................10–3
Chapter 11 AT5720 Check Tag-to-MPRX Assembly.................. 11–2
MPRX
TransCore Proprietary iii
Required Supplies ................................................11–2
Appendix A Glossary............................................A–2
Appendix B Technical Specifications...............................B–2
Reader Specifications .............................................B–2
Appendix C Wiring Information ...................................C–2
Appendix D Command Quick Reference ...........................D–2
Command Syntax .................................................D–2
Factory Default Settings ...........................................D–2
Numerical Command List ..........................................D–3
Alphabetical Command List .......................................D–14
Appendix E Compatible Tag Information ...........................E–2
Tag Configurations ...............................................E–2
Tag Data Formats .................................................E–4

System Guide
TransCore Proprietary
iv
List of Figures
Figure 2 – 1 MPRX End Views ........................................................................................................ 2–2
Figure 2 – 2 Tag and Antenna Orientation (horizontal polarization) .....................................2–4
Figure 2 – 3 Horizontally Polarized Tag ........................................................................................................2–5
Figure 2 – 4 Antenna Location Relative to Tag Position ..........................................................2–6
Figure 2 – 5 Location of Host Port on MPRX..............................................................................2–11
Figure 2 – 6 Pin Assignments for Host Connector ...................................................................2–11
Figure 2 – 7 Location of Sense Port on MPRX .......................................................................... 2–12
Figure 2 – 8 Pin Assignments for Sense Connector ............................................................... 2–12
Figure 3 – 9 Clear Zone –Side View .............................................................................................3–4
Figure 3 – 10 Clear Zone –End View ............................................................................................ 3–4
Figure 3 – 11 Mounting Location Examples ..................................................................................3–5
Figure 3 – 12 Tag Placement Window for Locomotives – Right Front .....................................3–6
Figure 3 – 13 Right Front Placement of Tag on Locomotive .................................................... 3–7
Figure 3 – 14 Tag Placement Window Location for Locomotives — Left Rear ...................... 3–7
Figure 3 – 15 Optimal Tag Placement for Locomotives ...........................................................3–8
Figure 3 – 16 Tag Placement Window Location for Rail Cars –“A” Right Side ...................3–9
Figure 3 – 17 Tag Placement Window Location for Rail Cars -“B” Left Side ...........................3–9
Figure 3 – 18 Optimal Tag Placement for Rail Cars ................................................................... 3–10
Figure 3 – 19 Tag Placement Window Location for Tank Cars –“B” Left Side ...................3–11
Figure 3 – 20 Optimal Tag Placement for Tank Cars ..............................................................3–11
Figure 4 – 1 Wiring for Audible Circuit Tester ........................................................................... 4–4
Figure 4 – 2 Connect RF N-type Load or Attenuator to Reader Cable End .......................4–5
Figure 4 – 3 Short Load to Earth Ground .....................................................................................4–5
Figure 4 – 4 MPRX Showing Antenna Ports ................................................................................ 4–6
Figure 4 – 5 Location of MPRX Ground Stud .............................................................................. 4–7
Figure 4 – 6 Location of Communications/Power Port on MPRX .........................................4–8
Figure 4 – 7 MPRX Outer Dimensions and Mounting Hole Locations (not to scale) ....... 4–10
Figure 4 – 8 Sample Read Zone Marking Pattern ..................................................................... 4–15
Figure 8 – 1 Connection Description Dialog Box ........................................................................... 8–4
Figure 8 – 2 Phone Number Dialog Box ........................................................................................... 8–4
Figure 8 – 3 COM 1 Properties Dialog Box ........................................................................................ 8–5
Figure 8 – 4 Hyper Terminal Main Screen....................................................................................8–6
Figure 8 – 5 Sign-on Message ........................................................................................................ 8–7
MPRX
TransCore Proprietary v
Figure 8 – 6 Tag and Antenna Orientation (horizontal polarization) ..................................... 8–9
Figure 8 – 7 Successful Tag Read ................................................................................................. 8–10
Figure 8 – 8 Second Successful Tag Read ................................................................................ 8–10
Figure 8 – 9 MPRX RF Control Options ....................................................................................... 8–14
Figure 10 – 1 TRU Front Panel Showing Operational LEDs.................................................. 10–2
Figure 10 – 2 TRU-MPRX Communications Interface Cable Port (bottom of TRU) .......... 10–3
Figure 10 – 3 MPRX-TRU Communications Interface Cable .................................................. 10–4
Figure 11 – 1 Place Nut and Grommet Over Exposed Check Tag Wires .............................11–3
Figure 11 – 2 Feed Check Tag Wires through Plastic Housing Connector ........................... 11–3
Figure 11 – 3 Connect Check Tag Wires ........................................................................................11–3
Figure 11 – 4 Two Check Tag Assemblies Connected to Terminal Strip .................................11–4
Figure 11 – 5 Securing Terminal Strip into Connector Housing .............................................. 11–5
Figure 11 – 6 Plastic Nuts with Grommets ....................................................................................11–5
Figure 11 – 7 Nylon Cap Securely Fastened in Unused Port ..................................................11–6
Figure 11 – 8 Check Tag Assembly Secured to MPRX Port .....................................................11–6

System Guide
TransCore Proprietary
vi
List of Tables
Table 1 – 1 MPRX System Guide Overview .................................................................................. 1–2
Table 1 – 2 Typographical Conventions .........................................................................................1–3
Table 2 – 1 Staggered Reader Frequencies for AAR-formatted Tag Operation .................2–8
Table 2 – 2 Staggered Reader Frequencies for Tag Operation Outside the U.S. ..............2–8
Table 2 – 3 Connector Cabling Accessory Kits ........................................................................ 2–10
Table 2 – 4 Power Supply Current Requirements ...................................................................... 2–10
Table 2 – 5 Reader to Antenna Cable Performance ................................................................. 2–13
Table 3 – 1 Tags Read by the MPRX ................................................................................................3–2
Table 4 – 1 Installation Accessories................................................................................................4–3
Table 4 – 2 MPRX-to-Host Communications Cable Pin Designations ..................................4–8
Table 4 – 3 Commands for Testing RF Port-0 ............................................................................. 4–14
Table 4 – 4 Commands for Testing RF PORT-1 ......................................................................................4–16
Table 4 – 5 Commands for Testing RF PORT-2 ....................................................................................4–16
Table 4 – 6 Commands for Testing RF PORT-3 ......................................................................... 4–16
Table 5 – 1 Four-Character Command Structure ........................................................................ 5–1
Table 5 – 2 Sample Command Sequence....................................................................................5–2
Table 7 – 1 Select Baud Rate Commands ..................................................................................... 7–6
Table 7 – 2 Select Stop Bits Commands ...................................................................................... 7–6
Table 7 – 3 Select Parity Commands ............................................................................................. 7–7
Table 7 – 4 Append Time and Date Commands .......................................................................7–9
Table 7 – 5 Append Auxiliary Information Commands ............................................................. 7–10
Table 7 – 6 Unique ID Code Criteria ..............................................................................................7–11
Table 7 – 7 Select Valid Code Commands and Frames ........................................................... 7–12
Table 7 – 8 Flow Control Commands ...........................................................................................7–25
Table 7 – 9 RF Control Commands ...............................................................................................7–26
Table 7 – 10 RF Attenuation Command Variables .....................................................................7–27
Table 7 – 11 Select RF Frequency Commands ............................................................................7–29
MPRX
TransCore Proprietary vii
Table 7 – 12 Presence Without Tag Report Commands .......................................................... 7–30
Table 7 – 13 RF Control Algorithm Commands .......................................................................... 7–31
Table 7 – 14 Timeout Period Values ..................................................................................................... 7–32
Table 7 – 15 Input Inversion Options .............................................................................................7–33
Table 8 – 1 MPRX Default Configuration Settings .....................................................................8–2
Table 8 – 2 Command Sequence to Verify Communications ................................................8–8
Table 9 – 1 Error Messages ............................................................................................................. 9–1
Table 9 – 2 Symptoms and Remedies ..........................................................................................9–2
Table 10 – 1 MPRX-to-TRU Interface Cable Pin and Signal Designations ......................... 10–4
Table 11 – 1 Check Tag Kit Parts List ...............................................................................................11–2
Table 11 – 2 Check Tag 0 Wire Assignments ................................................................................ 11–4
Table 11 – 3 Check Tag 1 Wire Assignments .................................................................................11–4
Table C – 1 Communications Interfaces and Conductor Requirements ...............................C–2
Table C – 2 MPRX Host Communications Cable Pin Designations ......................................C–2
Table C – 3 MPRX SENSE Communications Cable Pin Designations ..................................C–4
Table D – 1 MPRX Default Configuration Settings ...................................................................... D–2
Table D – 2 MPRX Commands Listed Numerically ....................................................................D–4
Table D – 3 MPRX Commands Listed Alphabetically ...............................................................D–14
Table E – 1 SeGo Protocol Tags ......................................................................................................E–2
Table E – 2 AAR-formatted Tags ..................................................................................................................E–3

Chapter 1
Introduction
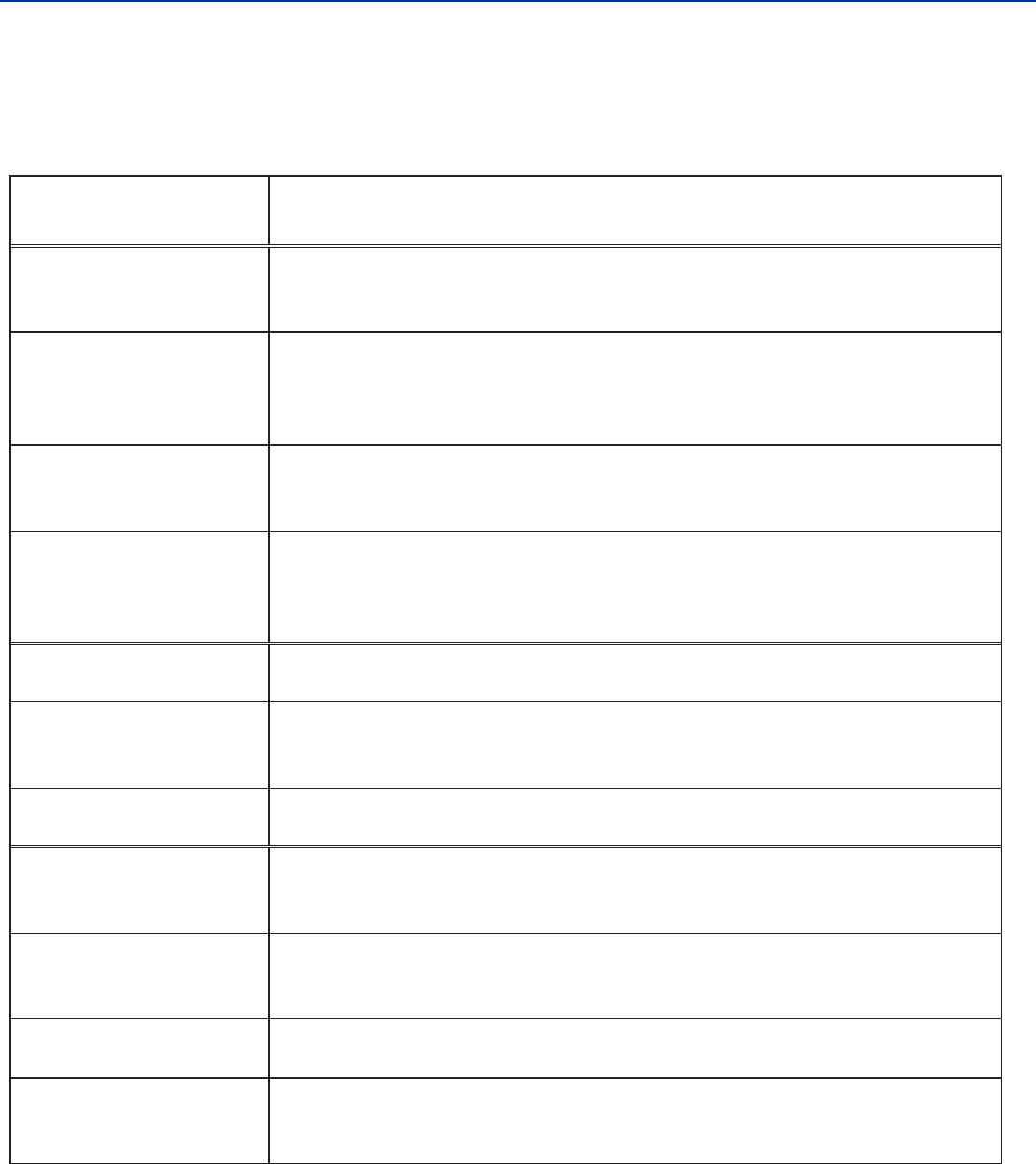
System Guide
TransCore Proprietary
1–2
Chapter 1 Introduction
This chapter presents an overview of the MPRX System Guide.
Table 1 – 1 describes the contents of each chapter.
Table 1 – 1 MPRX System Guide Overview
Chapter Number
and Title Description
Chapter 1 – Introduction Outlines the manual’s organization, provides a brief description of the
MPRX, and discusses Federal Communications Commission (FCC) licensing
requirements.
Chapter 2 – Developing
the Site Plan
Discusses factors to be considered when developing the site plan and before
ordering equipment and installing the MPRX. These considerations include
antenna and tag alignment, site layout and trac flow, and electrical and
communications requirements.
Chapter 3 – Choosing,
Installing, and Removing
Tags
Contains information on compatible tag models and provides procedures
for installing tags onto, and removing tags from, railcars where the MPRX is
installed.
Chapter 4 – Installing
the Multiprotocol Reader
Extreme
Lists the materials needed and provides procedures to install the MPRX,
including pre-installation testing, installing the MPRX in a railside hut or NEMA
enclosure, connecting power and communications, connecting to TransCore’s
Train Recording Unit (TRU™), and marking the read zone
Chapter 5 – General
Software Information
Provide reference information on various software-related topics
Chapter 6 –
Communications
Protocols
Provide reference information on various communications protocols.
Chapter 7 – Commands Discusses the host-transmitted commands that are used to control MPRX
configuration and operation.
Chapter 8 – Configuring
the Multiprotocol Reader
Extreme
Provides procedures for configuring and fine-tuning the MPRX after installing
it at the site, including marking the read zone.
Chapter 9 –
Troubleshooting and
Maintenance
Answers the most commonly asked questions about installing and maintaining
the MPRX.
Chapter 10 –Interface to
Train Recording Unit
Describes the interoperability between the MPRX and the TRU.
Chapter 11 – Connecting
AT5720 Check Tag-to-
MPRX Assembly
Explains how to connect one or two check tags to the MPRX.
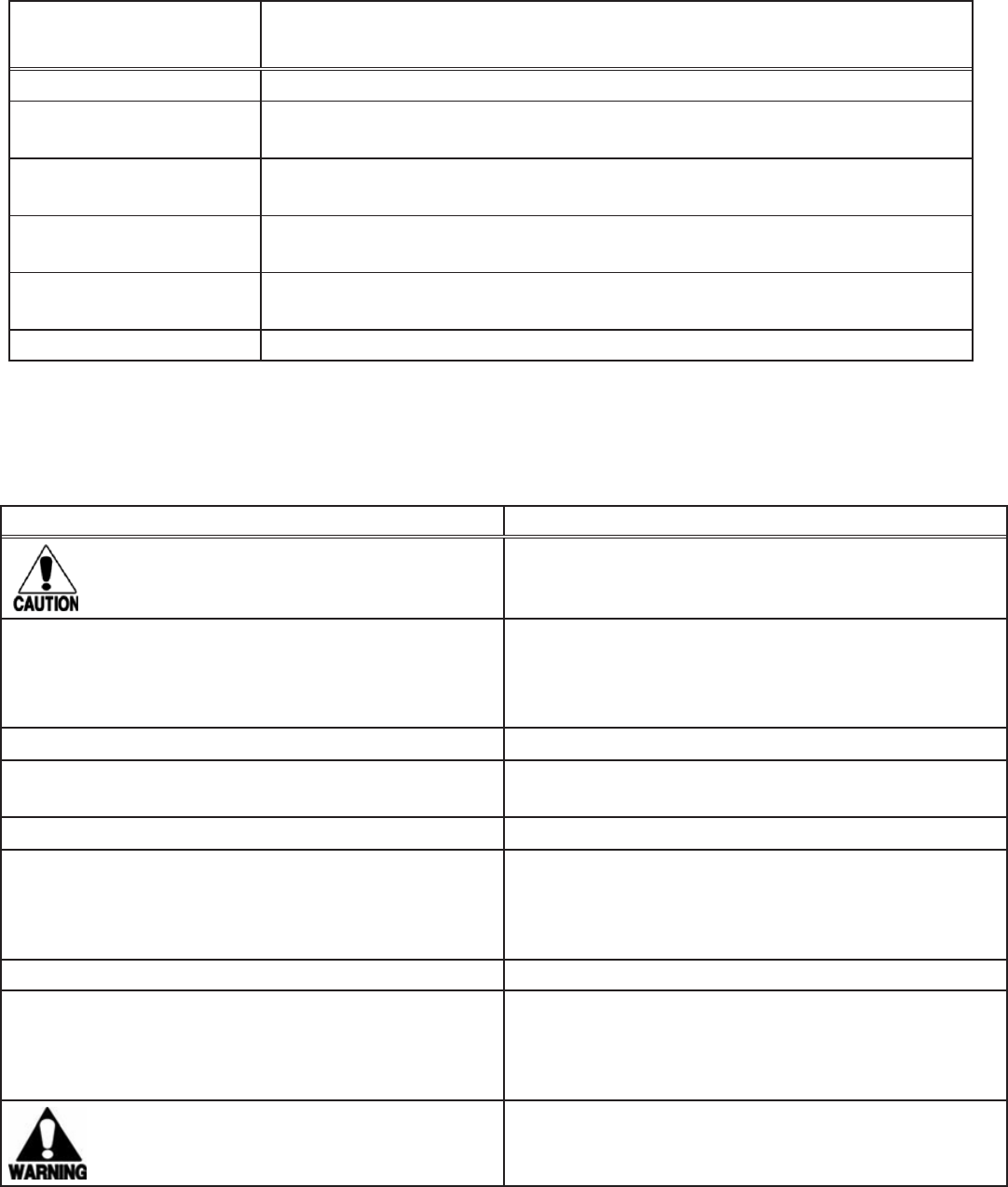
MPRX
TransCore Proprietary 1–3
Chapter Number
and Title Description
Appendix A – Glossary Contains frequently used terms.
Appendix B – Technical
Specifications
Provides the MPRX specifications.
Appendix C – Wiring
Information
Shows the wiring connections for the communications interfaces, electrical
cable connections, and the external interface signal wiring.
Appendix D – Command
Quick Reference
Lists the MPRX factory default configuration settings and provides host
software commands in numerical and alphabetical order.
Appendix E – Compatible
Tag Information
Provides helpful information about tags that are compatible with the MPRX.
Index Provides an alphabetical listing of guide topics.
Typographical Conventions
The conventions listed in Table 1 – 1 are used in this manual.
Table 1 – 2 Typographical Conventions
Convention Indication
Caution
Concerns about a procedure.
Code Code, including keywords and variables within
text and as separate paragraphs, and user-defined
program elements within text appear in courier
typeface.
Dialog Box Title Title of a dialog box as it appears on screen.
Menu Item Appears on a menu. Capitalization follows the
interface.
Factory Default Settings Identifies factory default settings
Note Auxiliary information that further clarifies the current
discussion. These important points require the user’s
attention. The paragraph is in italics and the word
Note is bold.
NUL Zero-value ASCII character or a zero-value byte.
NULL Zero-value pointers. Null-terminated string refers to
strings of printable ASCII characters with a zero-value
byte placed in memory directly after the last printable
character of the string.
This procedure might cause harm to the equipment
and/or the user.
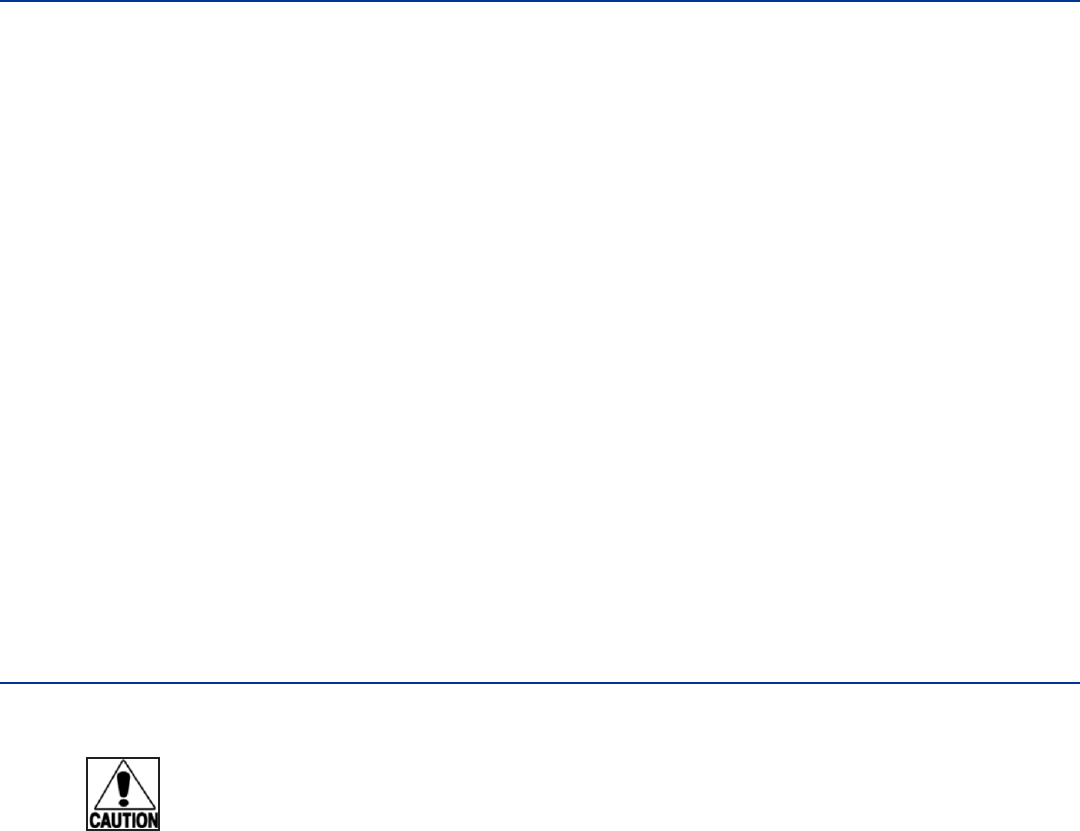
System Guide
TransCore Proprietary
1–4
Licensing Requirements
An FCC license provides the user with the legal authorization to operate the MPRX on the
licensed frequencies at the site specified in the license. Only an authorized installer or
service technician can set the RF frequency of the MPRX to the frequency specified in the
FCC site license. No end-user-operated controls exist on the MPRX.
The FCC license may provide the user with protection and authorization to maintain
the system should any other RFID product be used in the licensed area after the MPRX
equipment is installed.
Users of the MPRX in the United States must obtain a license from the FCC. In the United
States, the authorized modulated (SeGo protocol operation) frequency band for this
product is 911.75 to 919.75 MHz and the authorized continuous wave (AAR-formatted
operation) frequency band is 902.25 to 903.75 MHz and 910.00 to 921.50 MHz.
The user is responsible for filing the FCC license according to FCC regulations, but the
TransCore dealer will provide assistance and support as necessary to complete these
forms. Forms are available online at the FCC internet site http://wireless.fcc.gov/uls. For
further information on obtaining the license contact TransCore.
Caution
This equipment can be set to frequency ranges outside those authorized for use in
the U.S. by the FCC. Users in all countries should check with the appropriate local
authorities for licensing requirements.
Technical Support
Authorized dealers and distributors are responsible for the direct support of all customers.
Authorized dealers and distributors needing technical support can contact:
Technical Support: Phone: (505) 856-8007
Web: transcore.com/rfidsupport
Please be prepared to answer a series of questions that are designed to direct you to the
best support resource available.
MPRX
TransCore Proprietary 1–5

Chapter 2
Developing the Site Plan
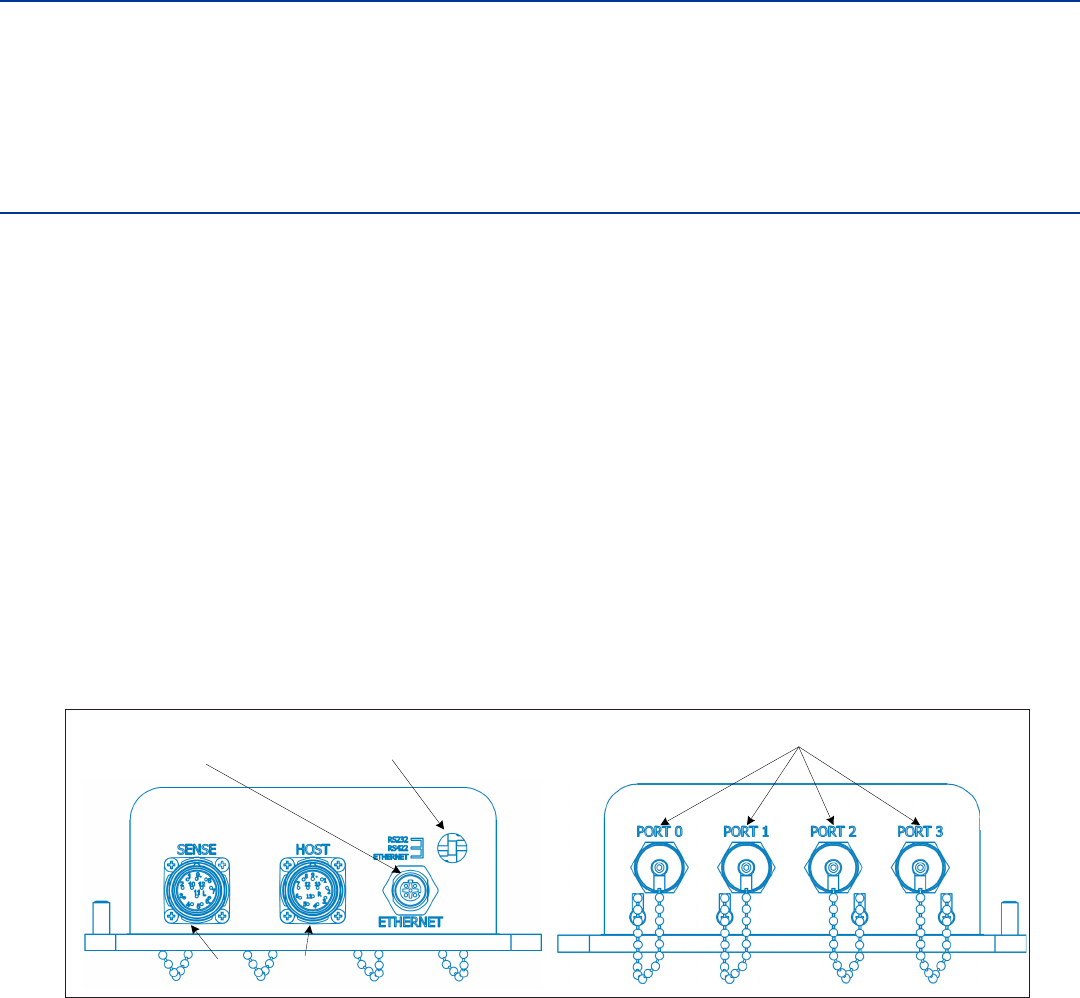
System Guide
TransCore Proprietary
2–2
Chapter 2 Developing the Site Plan
This chapter provides a brief description of the Multiprotocol Reader
Extreme (MPRX) and discusses site plan development for installing the
MPRX System.
System Description
The MPRX is a reader that supports Association of American Railroads (AAR) formatted
tags and TransCore’s low-cost, high-performance Super eGo® (SeGo) radio frequency
identification (RFID) technology.
The MPRX is a high-power unit that reads full frame tags. The reader output power can be
adjusted using reader commands.
The MPRX can multiplex up to four antennas, which allows a single reader to be used for
two tracks. The MPRX can support up to two AT5720 Check Tags.
Reader
The MPRX consists of an input/output (I/O) module, a power supply, a reader logic board
(also called a tag decoder), and a radio frequency (RF) transmitter/receiver (called the RF
module) in a compact enclosure. These MPRX components are contained in a highly
reliable, compact, and easy-to-install package. Figure 2 – 1 shows the Host connector,
Sense connector, Ethernet connector, Interface Selection Switch, and antenna ports
locations on opposite ends of the MPRX.
Figure 2 – 1 MPRX End Views
Antenna Ports
Interface Selection Switch
Host Port
Sense Port
Ethernet Port
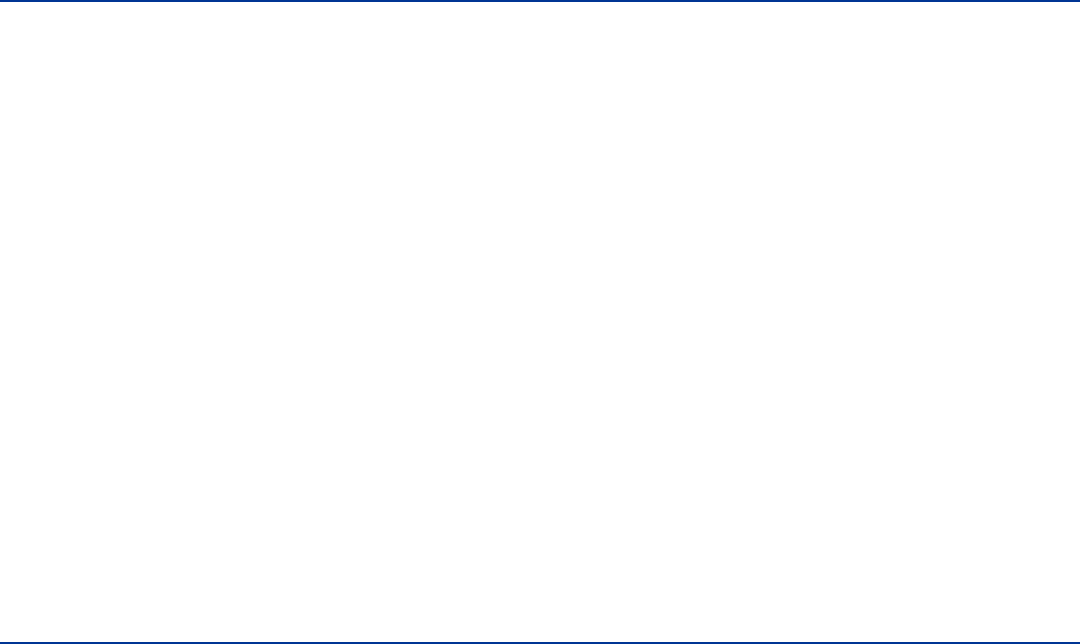
MPRX
TransCore Proprietary 2–3
Tags
The MPRX has the capability to read TransCore AAR formatted read-only full frame tags and
TransCore SeGo protocol tags, for example, the AT5118 Harsh Environment Transportation
Tag and the AT5120 Transportation Tag.
How It Works
The MPRX directs the RF module to generate an RF signal, which is broadcast through
the external antenna mounted railside. Entering the MPRX’s reading range, a TransCore
RFID tag installed on a railcar or other asset to be tracked adds its programmed
identification information to the signal and reflects the signal back to the MPRX. The
MPRX receives this modified, or modulated signal, and decodes the tag data carried by
the reflected signal and transmits this data to the Train Recording Unit (TRU) or local host
computer for processing.
Overview of Site Planning
Developing a site plan provides the foundation for the site’s system design and
establishes the following system configuration parameters:
• Number and general location of primary components
• Number of dierent radio frequencies required
Gathering relevant site information is crucial before applying for Federal Communications
Commission (FCC) or regulatory agency approval from the country where the equipment
is to be used and ordering and installing MPRX(s) and tags.
Also, consider the following factors when developing a site plan:
• Type of tags used
• Antenna and tag alignment
• Site layout and rail trac flow
• MPRX and/or antenna mounting requirements
• MPRX electrical requirements
• MPRX communications requirements
These factors provide relevant information regarding each site’s physical and
electromagnetic environment and the conditions under which the system must perform.
Reading of Mixed Population Tags
The MPRX reads AAR-formatted tags and TransCore’s SeGo protocol tags. The factors
that influence the readability include, but are not limited to, physical orientation and
configuration, type of read-only tag, ratio of backscatter cross-section of the tags, and
whether the tag is battery powered or beam powered.
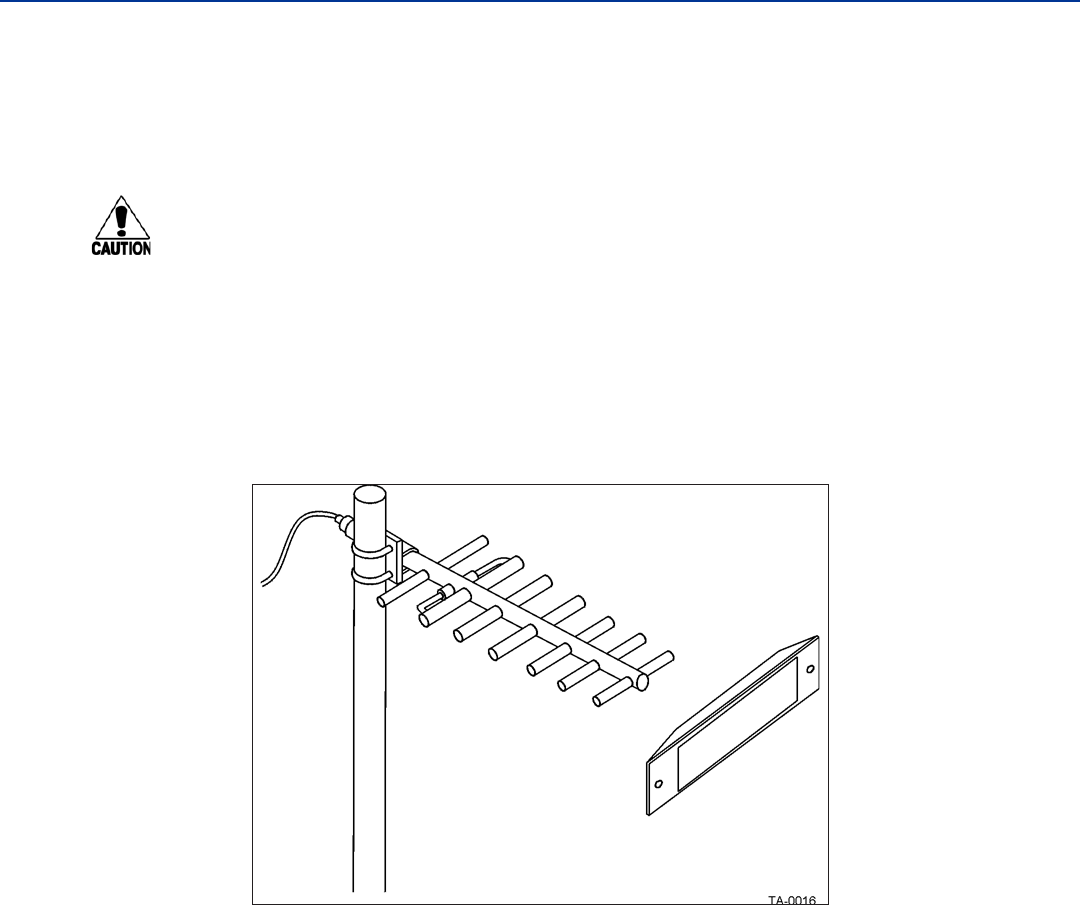
System Guide
TransCore Proprietary
2–4
Antenna and Tag Alignment
The position of the antenna and placement of the tag on the vehicle must be compatible.
Two primary criteria must be satisfied to achieve the highest read reliability:
• Tag and the antenna polarization, they must be aligned in the same direction —
both horizontal.
• The installed tag must be in a direct, unobstructed line of sight to the antenna.
Caution
A tag may not be reliably read unless the preceding criteria are met.
Polarization
The polarization of the tag must be aligned in the same direction as the antenna.
Figure 2 – 2 shows a horizontally polarized antenna and tag.
Note: Matching the tag and antenna polarization is critical to obtain optimal system
performance.
Figure 2 – 2 Tag and Antenna Orientation (horizontal polarization)
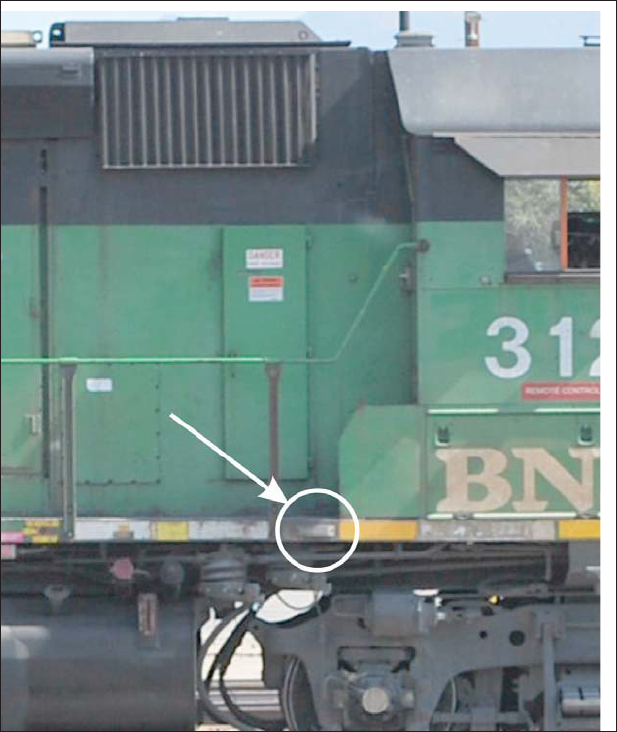
MPRX
TransCore Proprietary 2–5
Figure 2 – 3 shows a tag in correct polarization for the antenna.
Figure 2 – 3 Horizontally Polarized Tag
Unobstructed Line of Sight
For optimum readability, install the MPRX and antenna(s) and the railcar’s tag so that when
the railcar approaches the antenna(s), the tag is directly facing the antenna and the line of
sight is clear between the antenna and the tag. If there is a physical obstruction between
the tag and the antenna(s), the MPRX cannot reliably read the tags. Figure 2 – 4 illustrates
possible installation locations of an antenna in relation to a tag’s mounting location on a
railcar.
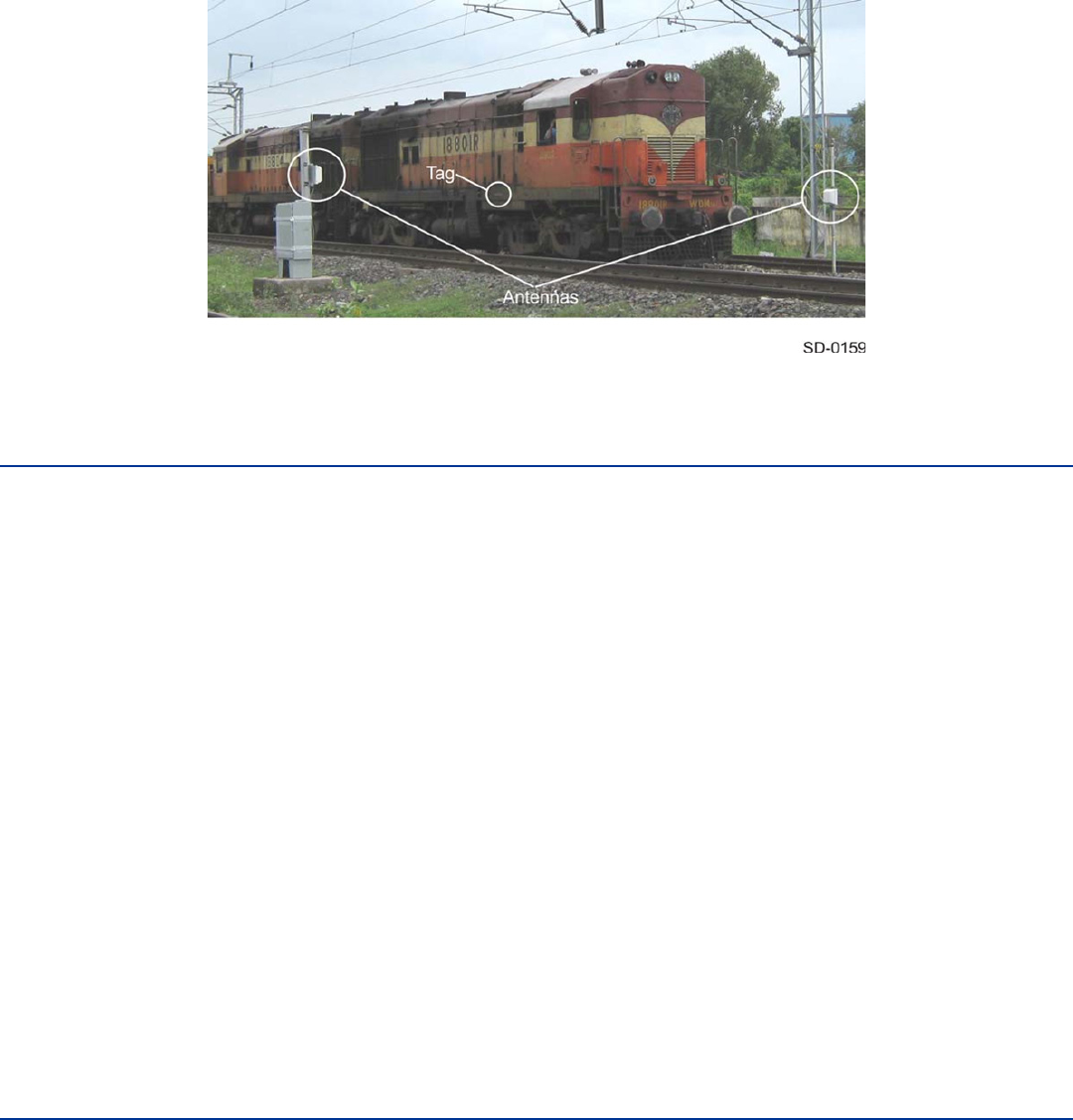
System Guide
TransCore Proprietary
2–6
Figure 2 – 4 Antenna Location Relative to Tag Position
Antenna Selection
This section contains guidelines to assist in antenna selection for an MPRX installation. The
following antennas are compatible with the MPRX installation.
AA3110 Parapanel
Appropriate for installations with the following requirements and conditions:
• 902 to 928 MHz operation
• Exposure to harsh environments
• Broad radiation pattern in one dimension, narrow in the other
• Low antenna profile
• Horizontal polarization
AA3140 PCB Log Periodic
Appropriate for installations with the following requirements and conditions:
• 845 to 950 MHz operation
• Exposure to harsh environments
• Maximum coverage at close range (<20 ft [6.1 m])
• Vertical or horizontal polarization
Site Layout and Trac Flow
The following site layout and trac flow considerations are critical when determining MPRX
installation locations:
• The MPRX read zone
MPRX
TransCore Proprietary 2–7
• Other MPRXs and antennas in the area
• Reflection, refraction, and diraction of RF signals
• Existing signal interference at the site
The MPRX Read Zone
The MPRX must be able to read the tag data properly within a specified area, called the
read zone, without reading other nearby tags or interfering with other MPRXs at the site.
The following are some of the factors that aect the size and shape of the read zone:
• Mounting method used for the antenna
• Mounting location of the antenna
• Height from the ground and mounting angle of the antenna
• RF output attenuation
• Range discrimination setting
• Other sources of interference and reflection
The railside antenna must be positioned so that the RF signal travels to and return from the
tags within the designated range and must be placed in an area where it is not likely to be
bumped out of alignment. If the antenna becomes misaligned or some nearby structure is
added or removed, system operation can be seriously aected.
For instructions on setting the read zone, refer to “Fine-Tuning and Verifying the Read
Zone” on page 8–17
Other MPRXs and Antennas in the Area — AAR-Formatted Tag
Operation
For AAR-formatted (continuous wave) tag operation, sites with more than one MPRX in
proximity should be configured with a frequency separation of at least 2 MHz from adjacent
readers. If more than one MPRX is in a multiple track application, the frequencies should
be staggered. MPRX antennas can face each other across a rail track as long as they are
multiplexed and controlled by the same MPRX. For installations where multiple antennas
are controlled by a host processor with multiple MPRXs, or where multiple MPRXs are
used in close proximity, ensure that there is adequate frequency separation between the
antennas. Contact TransCore Technical Support with any questions. Table 2 – 1 shows
examples of staggered reader frequencies in a site with up to seven readers.
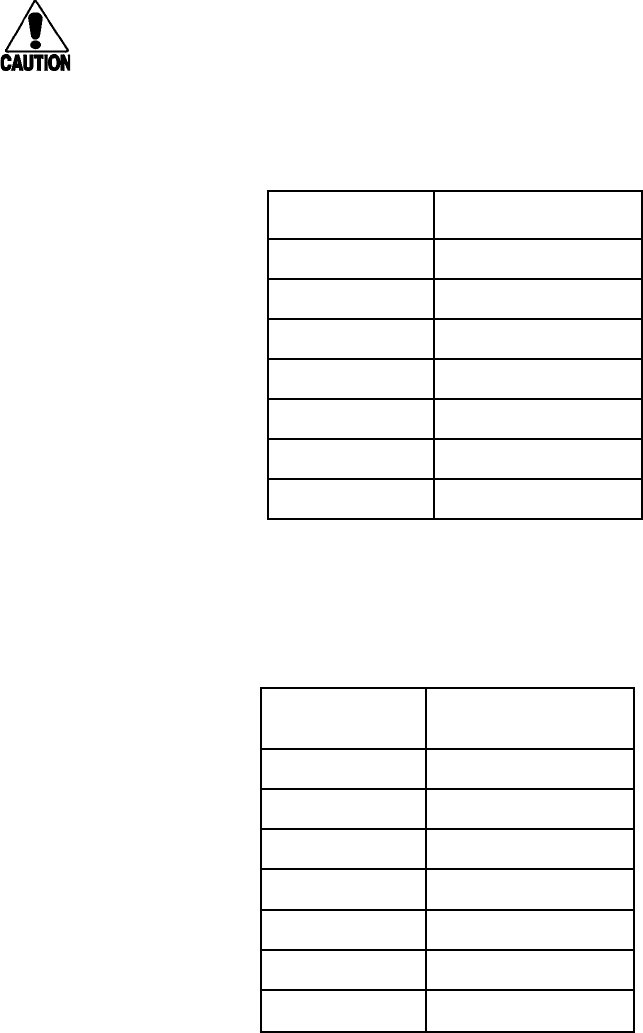
System Guide
TransCore Proprietary
2–8
Caution
TransCore advises locating antennas controlled by an MPRX at least 24 feet (7.3
meters) away from antennas that are controlled by another MPRX. There is no
minimum spacing for antennas connected to the same MPRX.
Table 2 – 1 Examples of Staggered Reader Frequencies for AAR-formatted Tag Operation
Table 2 – 2 shows examples of staggered reader frequencies in a site outside the U.S. with
up to four readers.
Table 2 – 2 Examples of Staggered Reader Frequencies for Tag Operation Outside the U.S.
Reflection, Refraction, and Diraction of RF Signals
RF signals can be reflected, refracted, or diracted by metal objects, walls, and even wet
pavement or ice. Any of these factors can alter or degrade system performance. When
designing your site plan, you must consider permanent structures and transient factors in
the vicinity that may aect RF signals being generated by the MPRX. Permanent structures
include buildings, chain link fences, guard shacks, and gates. Transient factors include
passing trac and local weather conditions, such as rain or snow. Symptoms of reflection,
Rail Number Reader Frequency
1 911.50
2 918.50
3 913.00
4 915.00
5 921.50
6 917.00
7 910.00
Rail Number Reader
Frequency*
1 865.25
2866.25
3865.50
4 866.50
5865.75
6866.75
7 866.00

MPRX
TransCore Proprietary 2–9
refraction, and diraction include reading tags that are out of the desired read zone or tags
being read from another track.
The most common RF reflectors are metallic surfaces. RF signals may also be partially
reflected by nonconducting materials such as dirt containing high concentrations of
metallic rail dust, wood, ice, asphalt, and concrete. When nonconducting materials in the
system environment become wet, they increase reflection of RF signals.
The antenna mounting location, aiming, and range control adjustment, and use of presence
detectors can reduce interference from RF reflections. When these actions cannot
adequately control reflections, other techniques such as shielding, absorbing, range
sensitivity adjustment, or barriers can also be used. Refer to “Chapter 9 Troubleshooting
and Maintenance” for information about troubleshooting and maintenance.
Existing Signal Interference at the Site
Interference from RF and electrical sources can degrade system performance and also
must also be considered in the site design. Fluorescent lights, neon signs, nearby radio
stations, or power lines can interfere with the optimal operation of the system.
Interference may degrade both reader and tag performance. Existing sources of
interference at the site should be shielded, removed, or positioned farther from the
antenna. In some cases, changing the operating frequency of the MPRX may provide a
simple solution. Readers in proximity should have at least a 2 MHz frequency separation.
Refer to “Other MPRXs and Antennas in the Area — AAR-Formatted Tag Operation” on
page 2–7. Strong RF sources of any frequency, in proximity to the tag, can preclude
the tag receiving the reader interrogation. Refer to “Chapter 4 Installing the MPRX” for
information about troubleshooting and maintenance.
Electrical and Communications Requirements
All construction work at the site must be completed before installing the MPRX. Electrical
and communications cables should be installed according to all applicable local and
federal building code requirements. Specific instructions for positioning and installing the
MPRX are discussed in “Chapter 4 Installing the MPRX”.
Power and Communications Cables
Cable length for power and communications depends on the physical characteristics of the
MPRX installation site. Table 2 – 3 lists accessory kits available for cabling options based
on your site’s requirements.
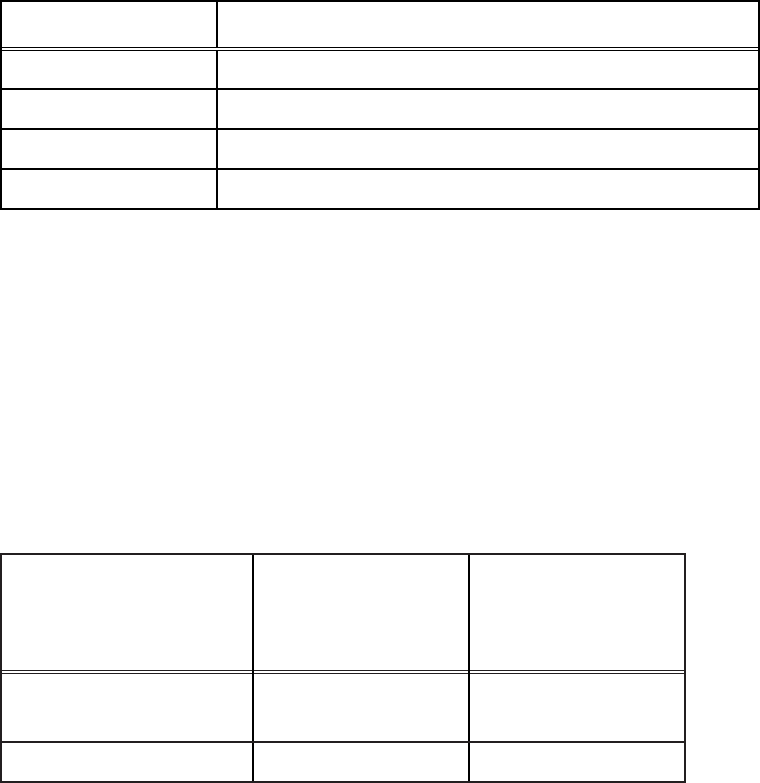
System Guide
TransCore Proprietary
2–10
Table 2 – 3 Connector Cabling Accessory Kits
Part Number Description
MPRX-to-TRU™ six-foot (1.8-m) cable assembly
MPRX-to-TRU 20-foot (6.1-m) cable assembly
MPRX cable assembly six feet (1.8 m), no TRU
MPRX cable assembly 20 feet (6.1 m), no TRU
Electrical Power
When connecting the MPRX to a TRU in a trackside hut, the MPRX draws its power directly
from the TRU. A dedicated power supply is only required when a MPRX is not connected to
a TRU.
The dedicated power must be 24-110VDC (Option 1) or 12-24VDC (Option 2). Consult your
local and national electrical codes for installation and safety requirements.
It is the installer’s responsibility to supply conversion equipment and wiring. Table 2 – 4
contains power supply current requirements.
Table 2 – 4 Power Supply Current Requirements
Supply
(RF On)
Worst Case
Maximum Current
at 68°F (20°C)
(RF O)
Worst Case
Maximum Current
at 68°F (20°C)
24 to 110VDC (Option 1) 1.7A at 24VDC 1A at 24VDC
12-24VDC (Option 2) 2.1A at 12VDC 1.4A at 12VDC
Power circuits are protected internally against power surges (±30%).
Host Communications
Your site design must include communications between the MPRX and the TRU or other
host device. The MPRX communicates with the TRU or other host device through an
asynchronous RS-232, RS-422, or Ethernet interface. Figure 2 – 5 shows the MPRX
communications ports and Figure 2 – 6 shows the connector pin designations.
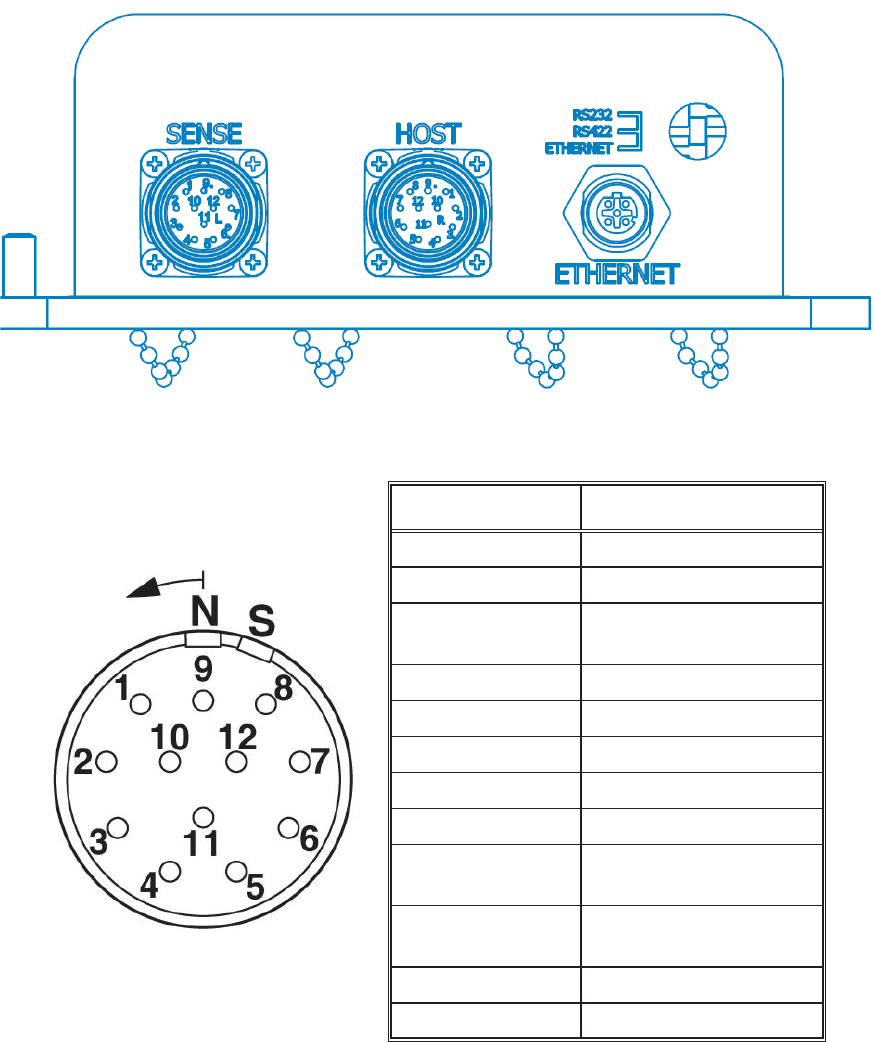
MPRX
TransCore Proprietary 2–11
Figure 2 – 5 Location of Host Port on MPRX
Figure 2 – 6 Pin Assignments for Host Connector
The standard RS-232/RS-422/Ethernet connection maximum distance depends on the
baud rate, cable type, and the receiving device at the other end.
Pin Number Operation
1RS232_TX
2RS232_RX
3 LOCK (Mechanical
Relay)
4LOCK_RTN
5RS422_TX+
6RS422_TX-
7RS422_RX+
8RS422_RX-
9 COM_GND (RS232
GND)
10 COM_GND (RS422
GND)
11 +V In
12 +V Return
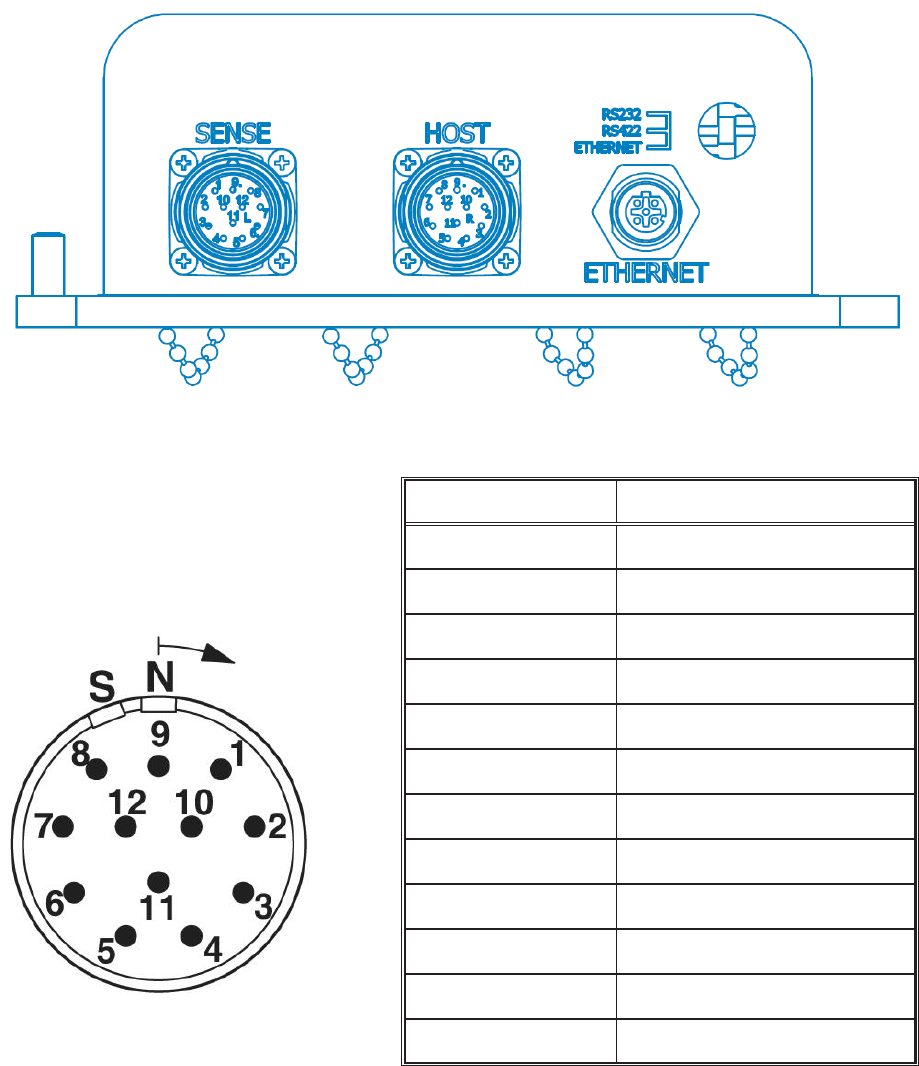
System Guide
TransCore Proprietary
2–12
Sense Connections
Figure 2 – 7 Location of Sense Port on MPRX
Figure 2 – 8 Pin Assignments for Sense Connector
The MPRX’s two RF sense input circuits are TTL (Logic Level, 0V/5V), designed to be
shorted to I/O Ground (0V) to provide sense.
Pin Number Operation
1+12VDC
2OUT1
3I/O GROUND
4I/O GROUND
5PULSE OUT
6OUT0
7CTAG 0
8CTAG 1
9I/O GROUND
10 I/O GROUND
11 SENSE 1
12 SENSE 0
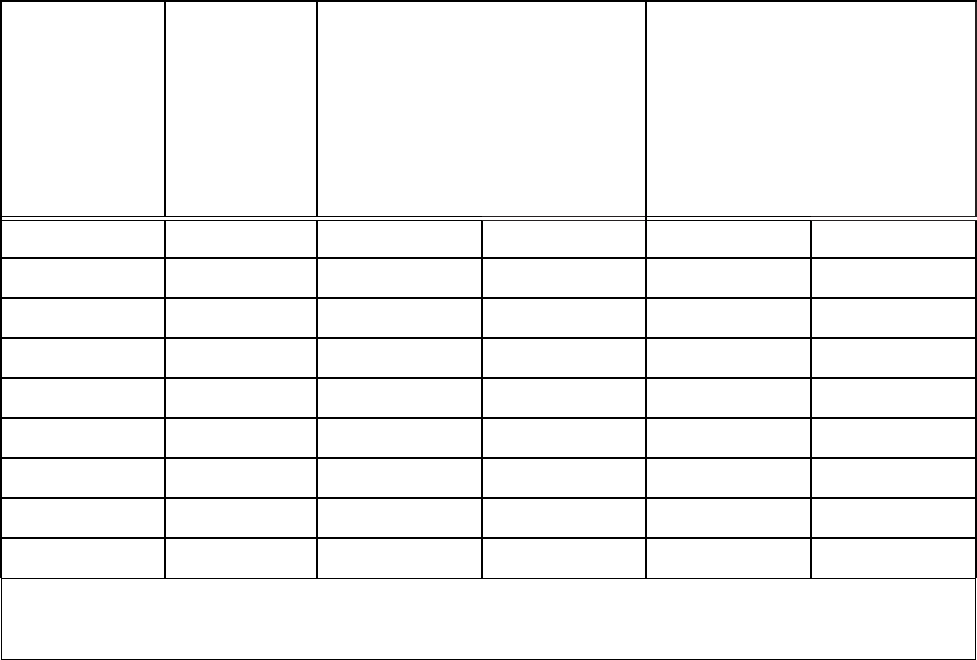
MPRX
TransCore Proprietary 2–13
The MPRX’s tag lock output circuit is a single-pole, double-throw relay providing a dry
contact closure. These contacts are rated at 42.2V AC peak (30Vrms) or 60V DC, at 1A
maximum with non-inductive load.
Output circuit is not intended for the direct control of electromechanical devices such as
motorized barrier arms. For such applications, the MPRX output circuit should be used to
drive a secondary, appropriately rated high-power relay.
Antenna Interface
The site design must include interface cable(s) between the MPRX and the compatible
antenna(s) chosen for the site. The antenna interface is RF coaxial cable with male Type
N sockets on each end.
Table 2 – 5 is a summary of coaxial cable performance. Figures indicate maximum
lengths of cable in feet.
Note: 1.1dB of cable loss is required for proper FCC operation.
Table 2 – 5 Reader to Antenna Cable Performance
Cable Typea
Overall
Diameter
(in.)
Cable Length (ft.)
915 MHz
Cable Length (ft.)
870MHz
Minimum
Lengthb
Maximum
Lengthc
Minimum
Lengthb
Maximum
Lengthc
RG–223 0.216 7.9 21.6 8.2 22.5
RG–214 0.425 14.4 39.3 14.9 41.1
FSJ1–50 0.25 19.4 52.8 19.9 54.6
LDF2–50 0.375 32.8 89.4 33.7 92.7
FSJ4–50B 0.5 32.1 87.6 33.1 90.6
LDF4–50A 0.5 52 141.9 53.4 146.7
LDF5–50A 0.875 92.2 251.4 94.8 260.4
LDF6–50 1.125 135.6 369.6 139.5 383.1
LDF7–50A 1.625 156.4 426.3 161.1 442.2
a. Suxes 50, 50A, and 50B indicate 50-ohm cables available from the Andrew Corporation.
b. These cable lengths ensure optimal system performance (1.1 dB loss).
c. These cable lengths ensure adequate, but not optimal, system performance (3 dB loss).

Choosing, Installing and
Removing Tags
Chapter 3
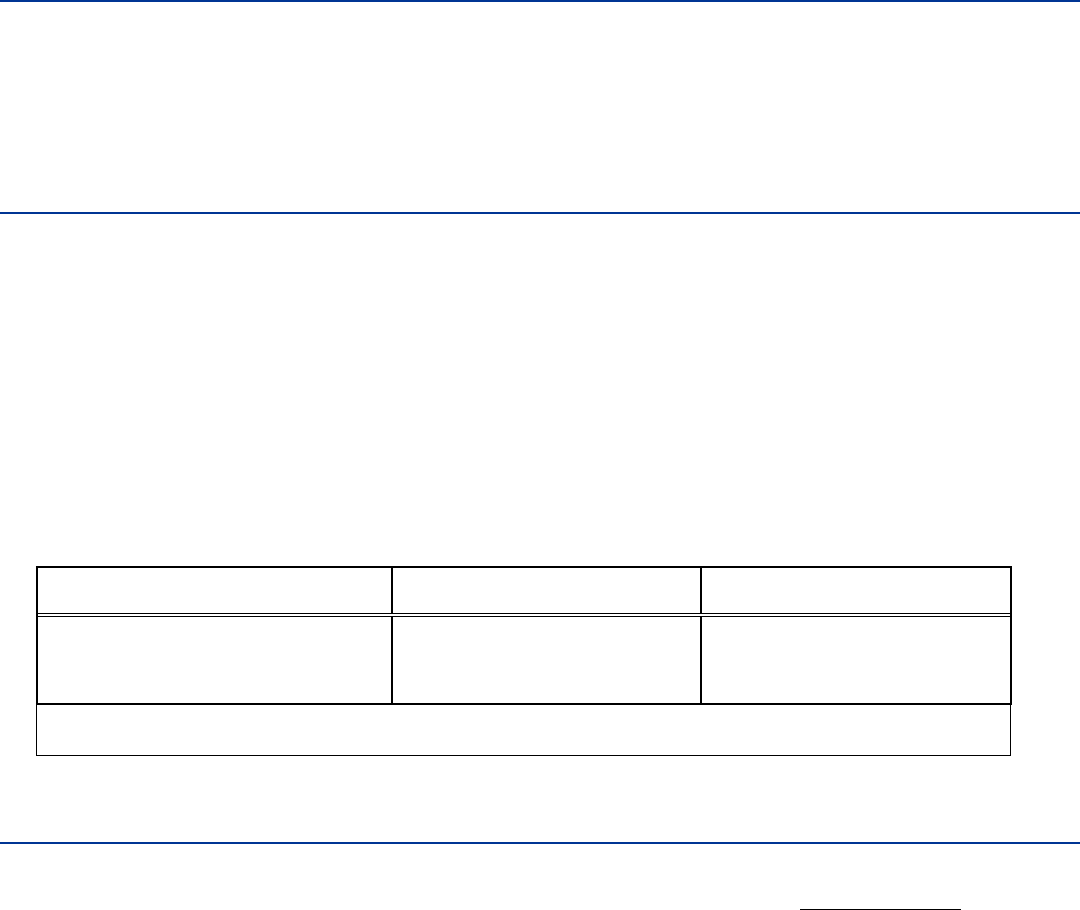
System Guide
TransCore Proprietary
3–2
Chapter 3 Choosing, Installing, Removing Tags
This chapter describes the various tag types compatible with the
Multiprotocol Reader Extreme (MPRX) and the procedures for installing
and removing compatible external tags.
Compatible Tag Types
The MPRX provides the capability to read Association of American Railroads (AAR)
formatted tags and TransCore Super eGo (SeGo) protocol tags. Refer to “Appendix E
Compatible Tag Information” on page E–2 for information about the numerous tag
models.
Reader and Tag Model Interoperability
Table 3 – 1 lists the tags that are read by the MPRX. Refer to www.transcore.com/pdf/
Tag- Reader-Matrix.pdf for most current information concerning readers and supported
tag protocols.
Table 3 – 1 Tags Read by the MPRX
Recommended Mounting Locations
Each piece of rail equipment has a specific area or window for optimum tag placement.
Tag positioning in the tag placement window is based on the center of the tag in
reference to window physical specifications.
Beam Tags Battery Tags External Power Tags
AT5110, AT5112, AT5118, AT5120*,
AT5125, AT5133, AT5412, AT5413,
AT5415
AT5114, AT5510, AT5414,
AT5549, AT5707, AT5910
AT5117, AT5119, AT5704
*The AT5120 Transportation Tag is used for applications in the 860 to 880 MHz frequency range.
MPRX
TransCore Proprietary 3–3
Required Materials
• Torque wrench (in/lb. range)
• Bolts and nuts (#10-24 NC threaded studs and nuts)
• Aluminum pop rivets
• Pop rivet gun
Mounting Surface
The mounting surface must be metal, vertical, and smooth within the area of the tag. If the
mounting area does not meet this requirement, you must use a metal mounting bracket.
If the mounting surface is irregular or non-metal (e.g., fiberglass), the tag must be
attached to a metal bracket to provide an electrical reflector for the tag. Use a 1/8-inch
(0.32-cm) or thicker smooth metal bracket that is the same size or larger than the tag.
The mounting bracket and tag must be in contact with each other to avoid interference
with transmission of radio waves.
Tag Positioning
Each piece of equipment has a specific area or tag placement window for optimum tag
placement. Tag positioning in the tag placement window is based on the center of the tag
in reference to window physical parameters.
The tag placement window is on opposite ends and opposite sides of the equipment.
The front and rear ends of the equipment are referred to as the “A” end and “B” end.
The “B” end represents the hand brake end and the “A” end represents the opposite
end looking forward. To determine left and right sides, stand at the “B” end and look
toward the front end of the equipment.
Refer to the appropriate section for tag placement window location on rail cars and
locomotive devices. Where possible, tags should be mounted in locations that minimize
the likelihood of damage from equipment such as forklifts, cranes, and other hazards.
Mount the tag on a plane perpendicular to the rail (back of the tag against the
equipment) with the long edge of the tag horizontal to the rail.
There is a clear zone surrounding the tag and toward the wayside that allows for
unobstructed data transmission. This zone must not be obstructed by any metallic
objects or protrusions.
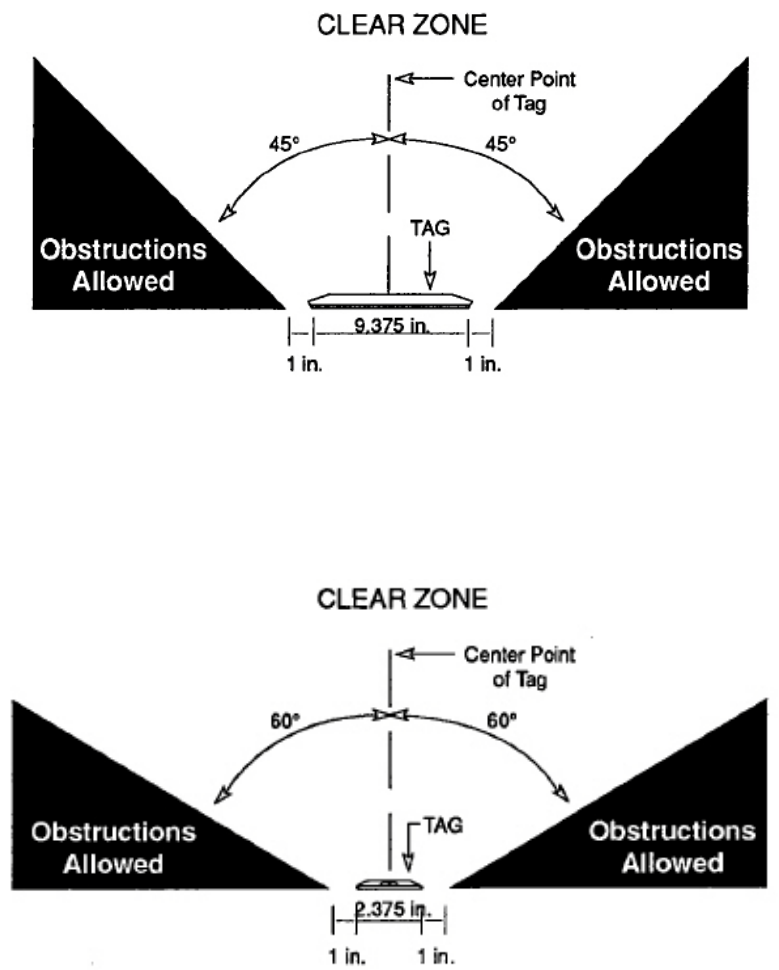
System Guide
TransCore Proprietary
3–4
As Figure 3 – 9 illustrates, there should be no obstructions in the area extending 45º from
the center line of the tag to one inch outside either narrow side of the tag. The side view
depicts the tag as viewed from the top of the equipment.
Figure 3 – 9 Clear Zone –Side View
Figure 3 – 10 illustrates that there should be no obstructions in the area extending 60º
from the center line of the tag to 1 inch outside either long side of the tag. The end view
depicts the tag as viewed from the end of the equipment.
Figure 3 – 10 Clear Zone –End View
Figure 3 – 11 shows examples of acceptable and unacceptable mounting locations based
on the clear zone. Any obstructions in the clear zone may introduce reading problems
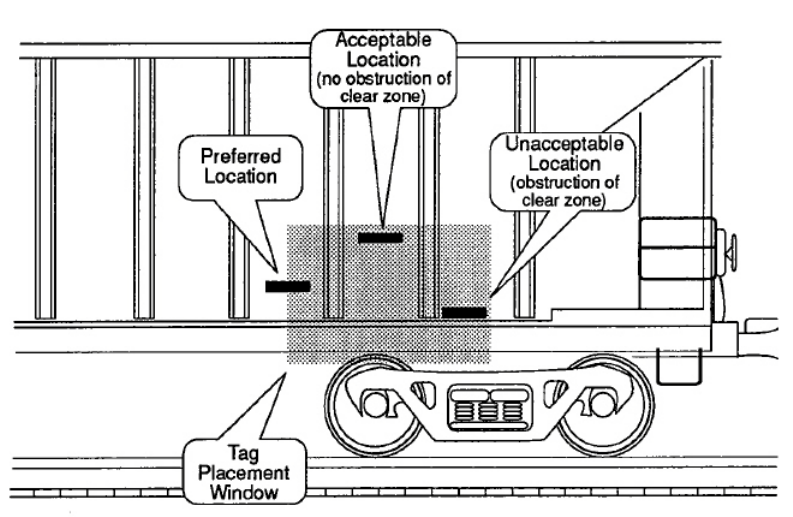
MPRX
TransCore Proprietary 3–5
with the tag. Refer to the mounting specifications chapters for each type of equipment for
tag placement window locations.
Figure 3 – 11 Mounting Location Examples
Surface Installation Techniques
Backing plates are preferred for attaching tags to equipment, but tags may be mounted
directly to the car at the owner’s discretion. Aluminum material is permitted as a
substitute for the mounting plate material specified, when required for compatibility with
the car surface.
When painting the backing plates, protect the studs from paint.
Two approved methods for mounting tags and backing plates on locomotives and
railcars are rivet and bolt mounting.
Note: Weld the backing plate to the freight car side sheet, but be certain the backing
plate is kept flat. If the car side sheet is deformed, spacing of welds may vary to
accommodate waviness of the freight car side.
Note: Allow the backing plate to cool after welding before mounting the tag.
Rivet/Bolt Mounting Guidelines
Select a means for mounting the tag that secures the tag but does not compromise the
tag case.
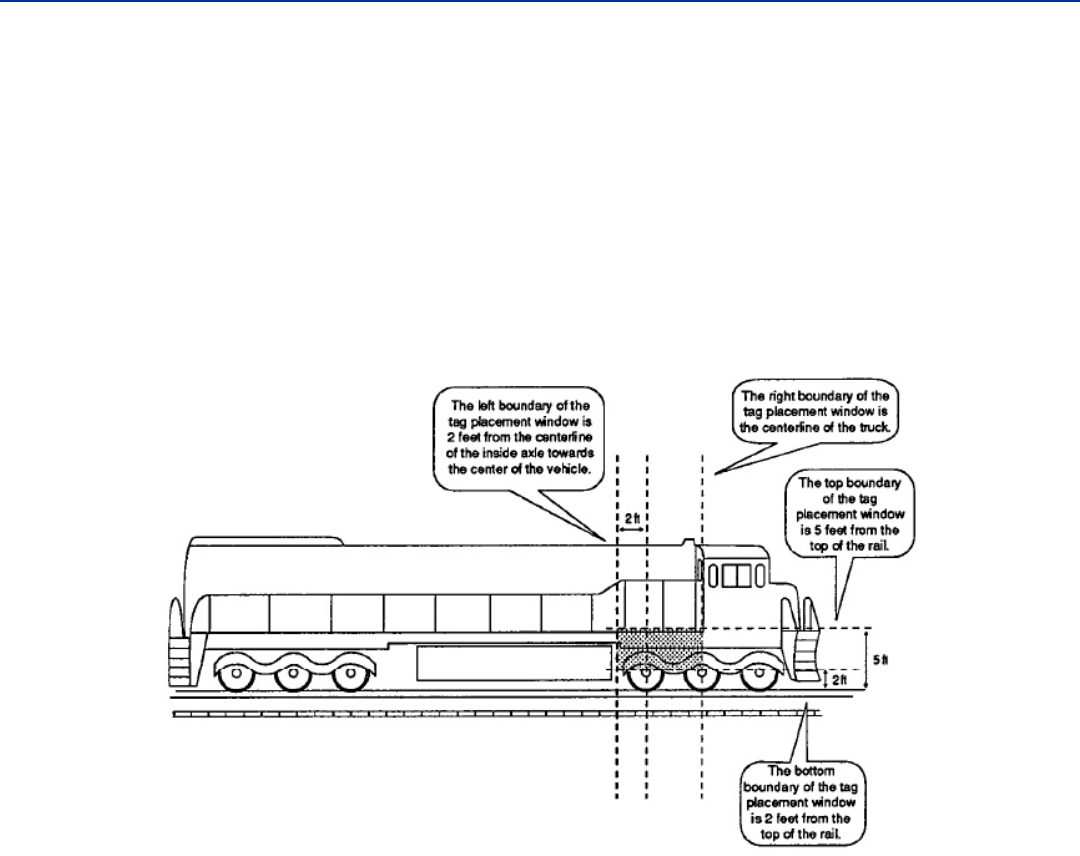
System Guide
TransCore Proprietary
3–6
Aluminum pop rivets are permissible, but TransCore advises against using high- pressure
rivets for mounting the tag.
If using bolts and nuts to mount the tag, avoid using excessive torque, which may crack
or break the tag case. Tighten the nut until snug, then tighten an additional 1/2 turn
only.
Locomotive Mounting Guidelines
Install two tags on each locomotive on opposite ends and opposite sides of the
equipment. Install one on the right front (engineer’s side) and another on the left rear
(fireman’s side).
Tag Placement Window Location
Horizontally, the tag placement window extends from the center line of the truck to two
feet from the center line of the inside axle (measure toward the center of the vehicle).
Vertically, the tag placement window begins two feet above the top of the rail and extends
to a maximum of five feet above the top of the rail.
Figure 3 – 12 illustrates the tag placement window on the right front portion (engineer’s
side) of the locomotive.
Figure 3 – 12 Tag Placement Window for Locomotives – Right Front

MPRX
TransCore Proprietary 3–7
Figure 3 – 13 shows the right front location of a tag on a locomotive.
Figure 3 – 13 Right Front Placement of Tag on Locomotive
Figure 3 – 14 illustrates the tag placement window on the left rear portion (brakeman’s
side) of the locomotive.
Figure 3 – 14 Tag Placement Window Location for Locomotives — Left Rear
Tag Placement
Optimal tag placement centers the tag on the left boundary line of the tag placement
window (Figure 3 – 15). Alternately, the center of the tag may be mounted anywhere
within the tag placement window, provided there are no obstructions to the tag’s clear
zone.
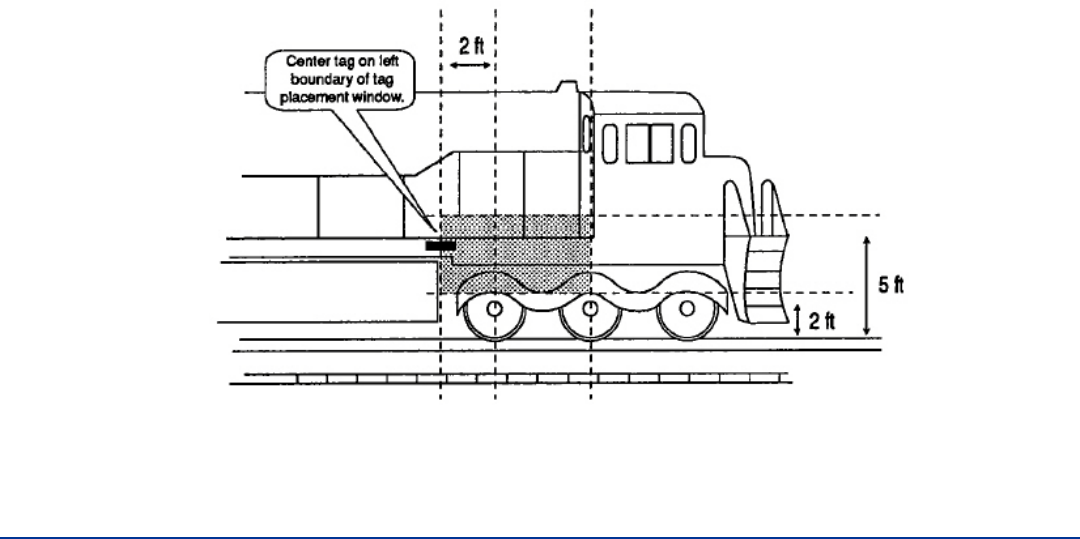
System Guide
TransCore Proprietary
3–8
Figure 3 – 15 Optimal Tag Placement for Locomotives
Rail Car Mounting Guidelines
Install two tags on each rail car on opposite ends and opposite sides of the equipment.
Install one on the right front (“A” end) and another on the left rear (“B” end).
Tag Placement Window Location
Horizontally, the tag placement window extends from the center line of the truck to two feet
from the center line of the inside axle (measure toward the center of the vehicle). Vertically,
the tag placement window begins at two feet above the top of the rail end and extends to
a maximum of five feet above the top of the rail. The tag should not cover car stenciling.
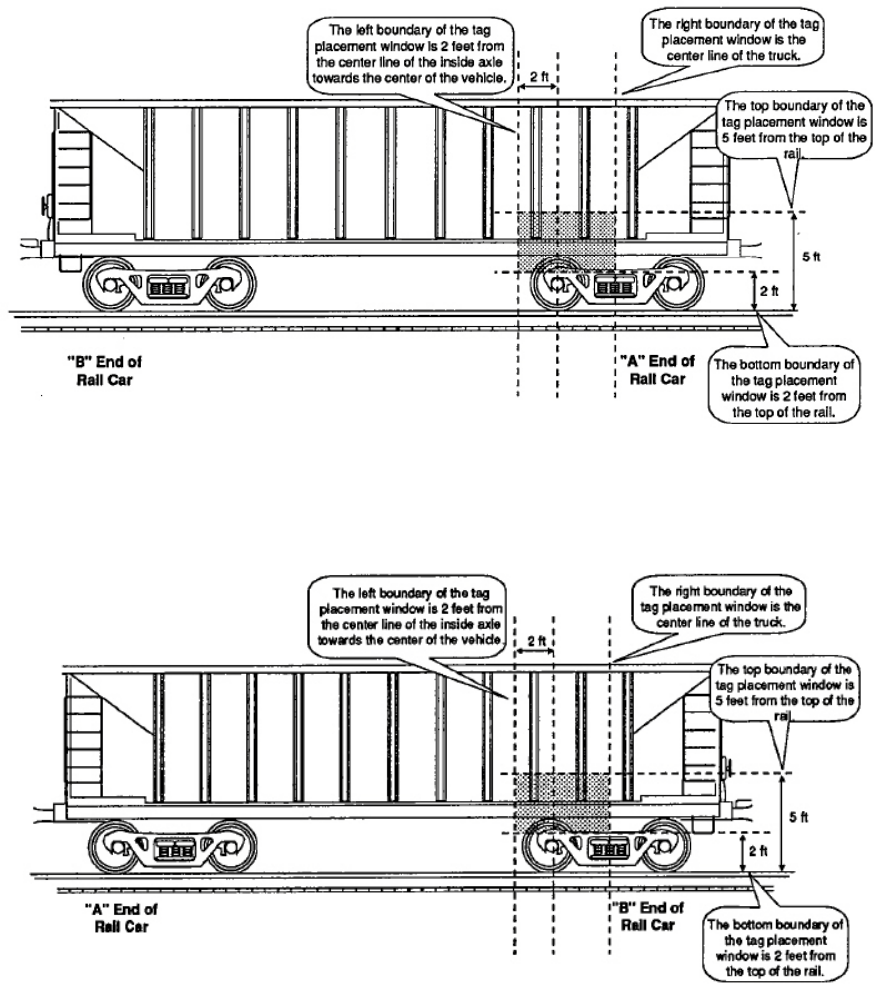
MPRX
TransCore Proprietary 3–9
Figure 3 – 16 illustrates the tag placement window on the right front portion (“A” end) of the
rail car.
Figure 3 – 16 Tag Placement Window Location for Rail Cars –“A” Right Side
Figure 3 – 17 illustrates the tag placement window on the left rear portion (“B” end) of the
rail car.
Figure 3 – 17 Tag Placement Window Location for Rail Cars -“B” Left Side
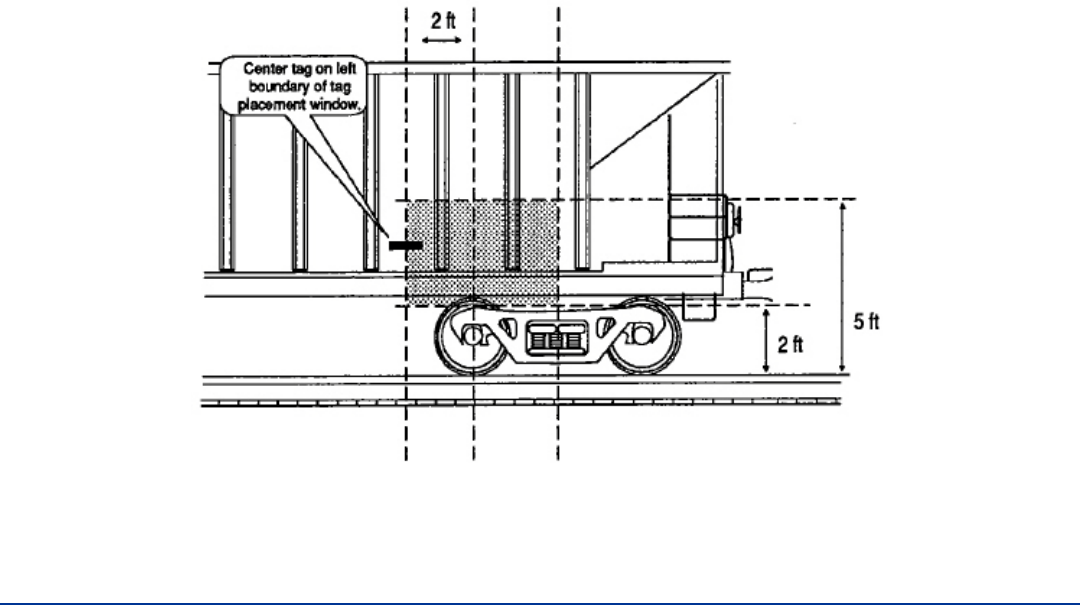
System Guide
TransCore Proprietary
3–10
Tag Placement
Optimal tag placement centers the tag on the left boundary line of the tag placement
window (Figure 3 – 18). Alternately, the tag may be mounted so that the center
of the tag falls anywhere within the tag placement window, provided there are no
obstructions of the tag’s clear zone.
Figure 3 – 18 Optimal Tag Placement for Rail Cars
Tank Car Mounting Guidelines
Tank car mounting is essentially the same as that for rail cars, except that the tag
placement window area has been expanded 18 inches to the right of the center of the
truck.
Tag Placement Window Location
Horizontally, the tag placement window extends from 18 inches to the right of the
center line of the truck to two feet from the center line of the inside axle (measured
toward the center of the vehicle). Vertically, the tag placement window begins at two
feet above the top of the rail and extends to a maximum of five feet above the top of
the rail. The tag should not cover car stenciling.
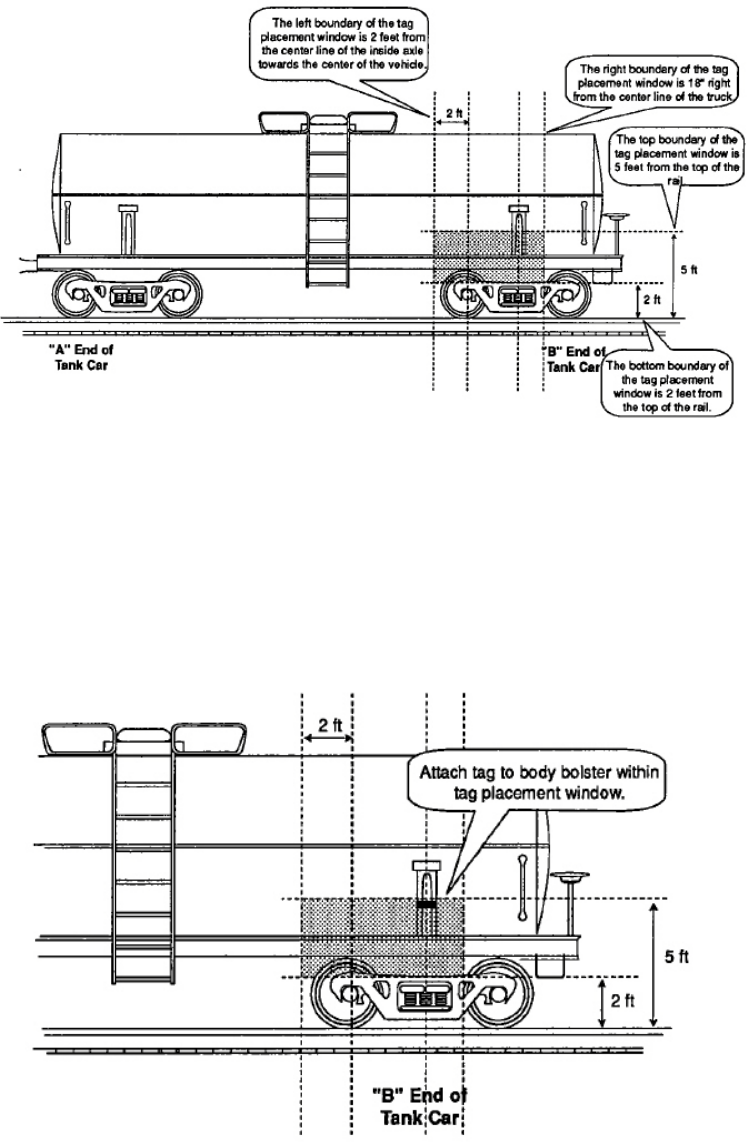
MPRX
TransCore Proprietary 3–11
Figure 3 – 19 illustrates the tag placement window on the left rear portion (“B” end) of the
tank car.
Figure 3 – 19 Tag Placement Window Location for Tank Cars –“B” Left Side
Tag Placement
Optimal tag placement positions the tag on the center line of the truck on the body bolster
(Figure 3 – 20). Alternately, the tag may be mounted so that the center of the tag falls
anywhere within the tag placement window, provided there are no obstructions of the tag’s
clear zone.
Figure 3 – 20 Optimal Tag Placement for Tank Cars

Installing the MPRX
Chapter 4
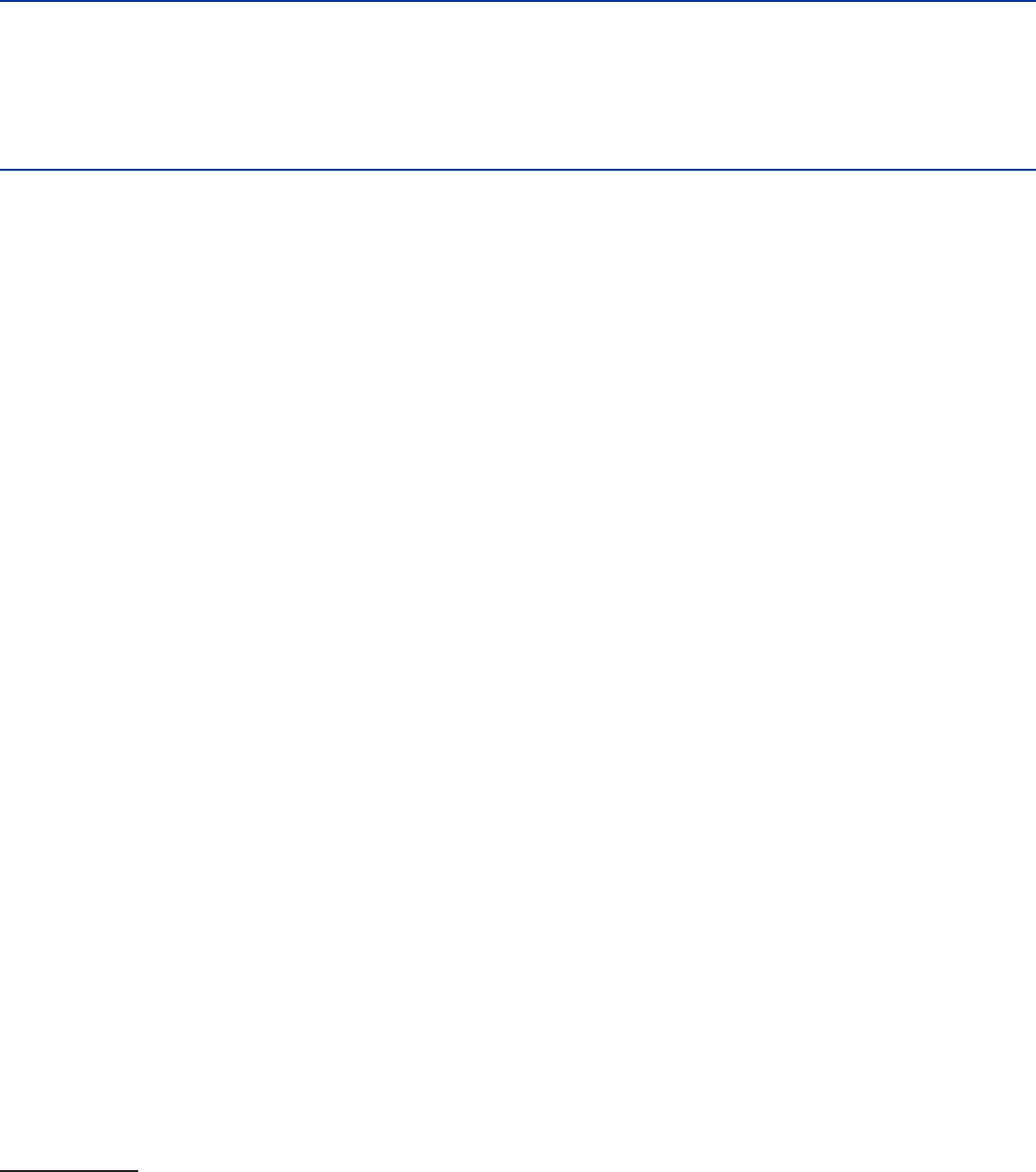
System Guide
TransCore Proprietary
4–2
Chapter 4 Installing the MPRX
This chapter lists the materials needed and presents the procedures to
pre-test and install the Multiprotocol Reader Extreme (MPRX).
Installation Process
After you have developed the site plan and identified the location to install the MPRX
and antennas1, if required, you are ready to install the equipment. Installation involves the
following tasks:
• Power and tag read capability testing prior to final installation of the MPRX
• Mounting the MPRX in a railside hut
• Mounting the railside antenna(s)
• Connecting the antenna(s)
• Connecting the MPRX to Earth Ground and power source
• Marking the read zone
• Connecting the MPRX host and sense input/sense output and communications
Materials Supplied by TransCore
You need the following materials to pre-test and install the MPRX. TransCore supplies
some of the materials; other materials must be obtained from other sources.
Contents of Shipping Carton
Ensure that you have received all parts before beginning your pre-installation MPRX tests.
Your MPRX is packaged with the following materials:
• One MPRX
• One Multiprotocol Reader Extreme Quick Start Guide
• Any accessories ordered as options as shown in Table 4 – 1
Required accessories are a power/communications cable harness and an AC/DC Converter
or a 24 to 110VDC/12 to 24VDC power source. You also require at least one MPRX-
compatible antenna and an antenna RF cable. These may be ordered as accessories from
TransCore or obtained from other sources.
For MPRX installation with TransCore’s Train Recording Unit (TRU™), refer to “Chapter 10
Interface to Train Recording Unit” on page 10–2.-
Installation Accessory Options
Table 4 – 1 lists optional TransCore MPRX installation accessory items.
1 The MPRX is designed with RF cable connectors for use with N-type RF Cables
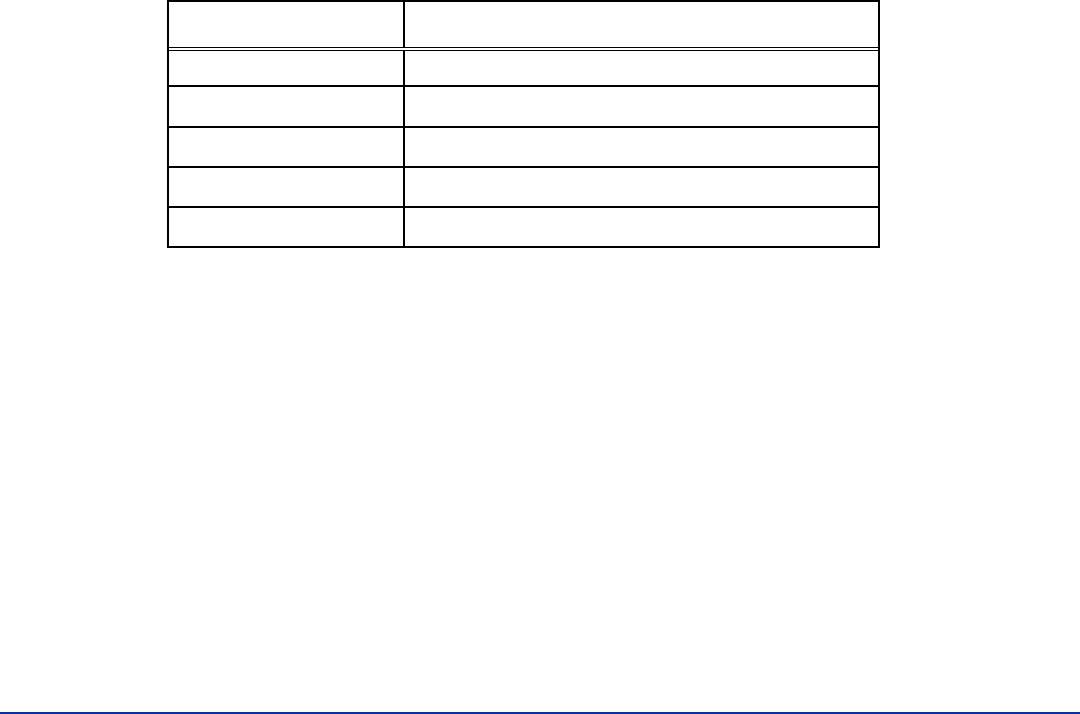
MPRX
TransCore Proprietary 4–3
Table 4 – 1 Installation Accessories
Additional Materials Needed for Testing
You need these additional materials to perform the pre-tests on the MPRX:
• Test tags, supplied by the TransCore dealer or distributor.
Note: The test tag must be mounted flush against a metal backplane.
• Suitable 24 to 110VDC or 12 to 24VDC power wiring for the MPRX
• Audible circuit tester and 9V DC battery for circuit tester power
• Wire stripper
• At least one MPRX-compatible antenna
• Suitable RF interface coaxial cable
Pre-installation Testing of the MPRX
Before installing the MPRX permanently at the site, you should use an audible circuit
tester to confirm that the MPRX has power and can read a tag that is in the tag read
zone.
Testing the MPRX Using an Audible Circuit Tester
An audible circuit tester is also called a buzz box. These boxes are available at some
electronic parts supply stores, or you can make a buzz box, as shown in Figure 4 – 1.
The buzz box is powered by a 9V DC battery and is equipped with two alligator-clip
leads. When you touch the leads together, the box makes an audible sound.
Part No. Description
MPRX Cable
MPRX Cable
MPRX Cable
MPRX Cable
20-7001-001 MPRX check tag accessory kit
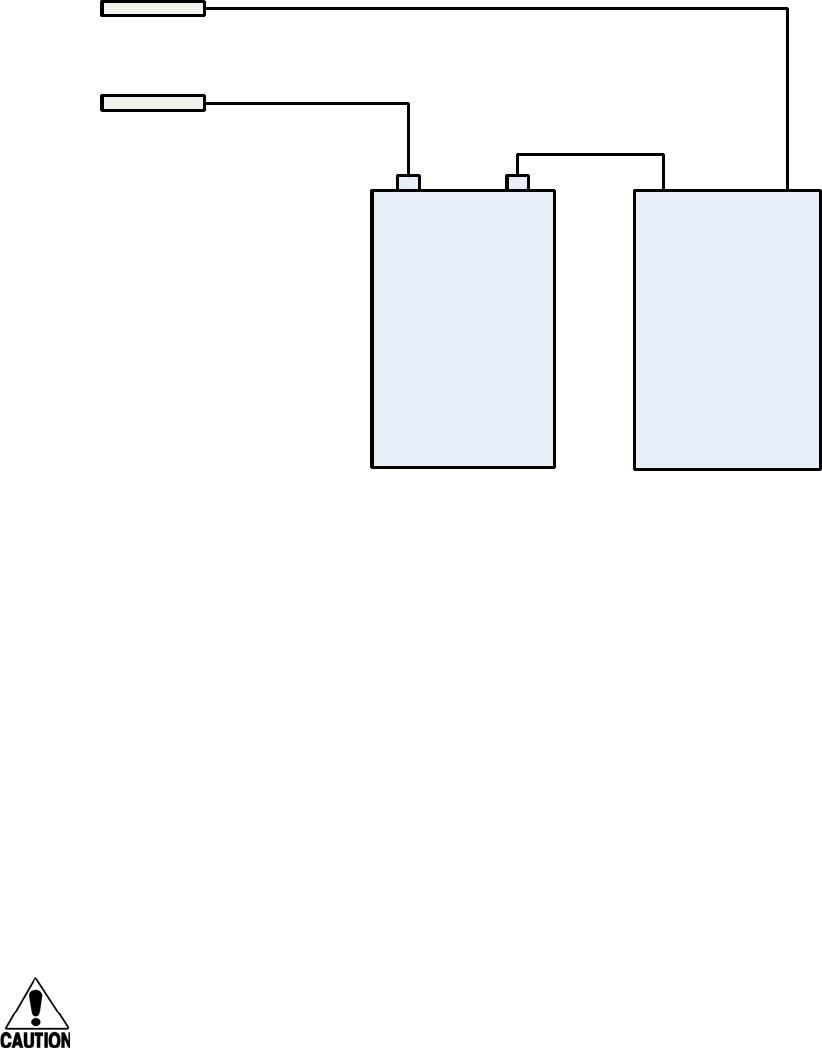
System Guide
TransCore Proprietary
4–4
Figure 4 – 1 Wiring for Audible Circuit Tester
To test the MPRX, connect the antenna and power supply as described in the appropriate
sections that follow.
Discharging Voltage from the Antenna
Use these instructions to discharge high voltage from the antenna before proceeding with
further pre-installation testing of the reader connected to an antenna.
Required Equipment
This procedure requires the following equipment.
• MPRX
• External antenna
• Grounding RF cable (long enough to reach Earth Ground source)
• N-type load (e.g., 50 Ω) or RF attenuator (e.g., 20 dB)
Caution
During shipping and installation, an antenna can build up a very high voltage charge.
The voltage needs to be discharged before connecting the antenna to the reader.
1. Terminate the reader end of the grounding RF cable with any N-type load or RF
attenuator (Figure 4 – 2).
9VDC
Battery
6-12VDC
Buzzer
+ -
Pin 4 on
Host Connector
Pin 3 on
Host Connector
- +
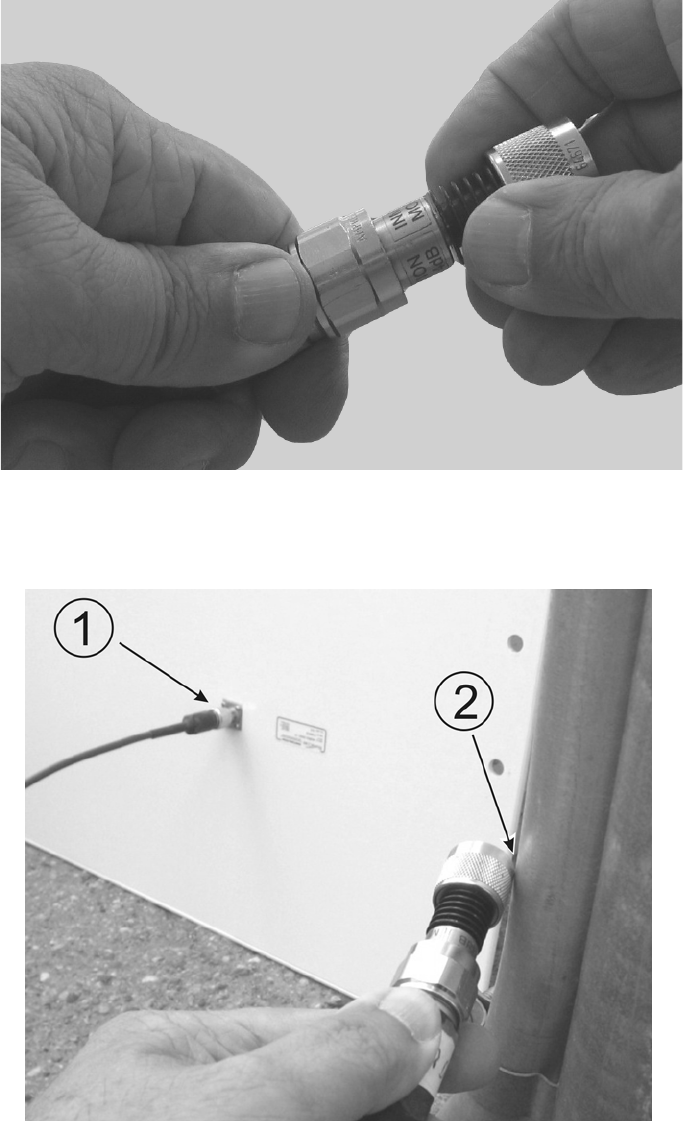
MPRX
TransCore Proprietary 4–5
Figure 4 – 2 Connect RF N-type Load or Attenuator to Reader Cable End
2. Connect the grounding RF cable to the antenna (refer to Item 1 in Figure 4 – 3.
Figure 4 – 3 Short Load to Earth Ground
3. Short the outer metal case of the load or attenuator to Earth Ground for approximately
10 seconds (refer to Item 2 in Figure 4 – 3). In this example, the operator is using the
mounting pole that has been properly connected to Earth Ground.
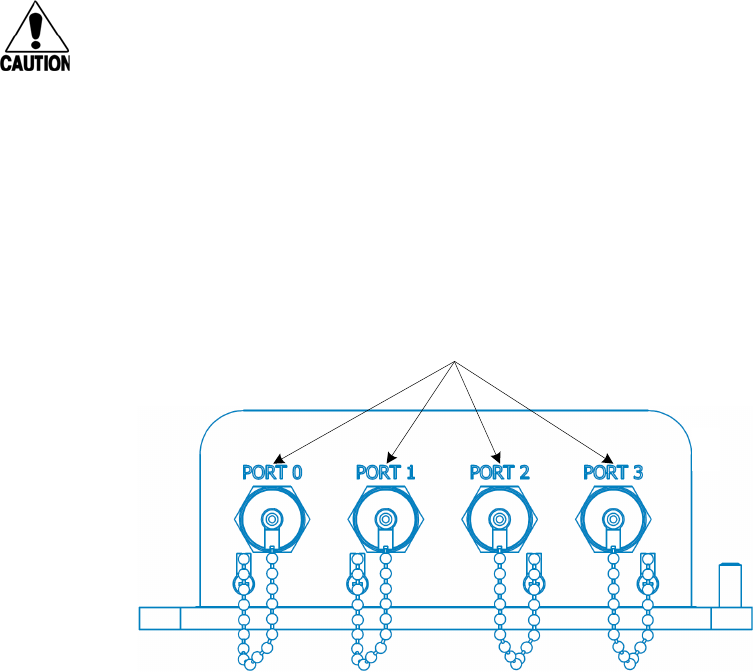
System Guide
TransCore Proprietary
4–6
4. Disconnect the grounding RF cable from the antenna and connect the permanent RF
cable to reader.
Once the antenna is discharged and properly connected to the reader, the reader
circuitry provides a DC path to keep any further charge from building up in the antenna.
Caution
TransCore does not recommend using a screwdriver or other tool to short the RF cable
center conductor to the outer ground of the cable. This grounding method can damage
the center pin or the threads of the connector.
TransCore strongly advises that you use adequate Earth Ground for this voltage
discharge procedure in accordance with the National Electric Code for the locale
where you are installing the MPRX.
Connecting the Antenna
This section explains the connection between the MPRX and antenna(s) (Figure 4 – 4).
Figure 4 – 4 MPRX Showing Antenna Ports
To connect the reader and antenna
1. Ensure the reader is turned o and unplugged.
2. Connect one end of the RF interface cable to the antenna.
3. Connect the other end of the RF interface cable to the appropriate antenna port on the
end of the MPRX (Figure 4 – 4).
4. For consistent performance, terminate unused antenna ports using a 50-Ohm, N–type
terminator.
Antenna Ports
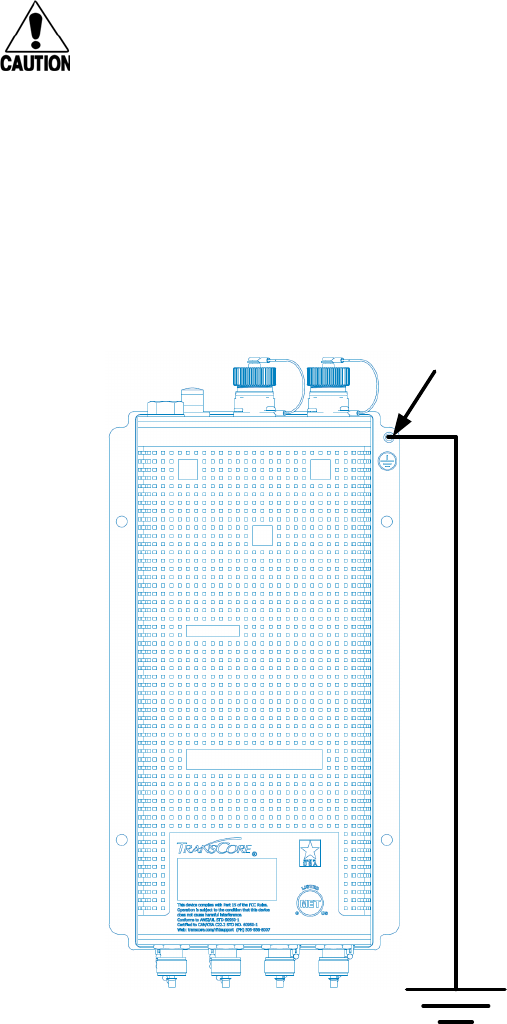
MPRX
TransCore Proprietary 4–7
Connecting the MPRX to a Power Supply
Caution
To avoid damage to the MPRX, first connect the reader to Earth Ground using a
ground cable and stake before powering up the reader or connecting to an antenna.
TransCore recommends that you follow the National Electric Code or equivalent code
for surge protection for the locale where you are installing the MPRX.
Connect any antenna(s) or terminate the antenna ports before applying power to the
reader.
To connect the MPRX to a power supply
1. Connect the MPRX to Earth Ground. Figure 4 – 5 shows the location of the MPRX
ground stud.
Figure 4 – 5 Location of MPRX Ground Stud
2. Connect the MPRX to a power supply using the interface cable.
The pin numbers for the reader M23 connector (Figure 4 – 6) are shown in Figure 4 – 7
and the pin assignments and corresponding wire numbers and colors are listed in
Ensure proper Earth
Ground for MPRX in
accordance with National
Electric Code for reader
installation locale.
Ground
Stud
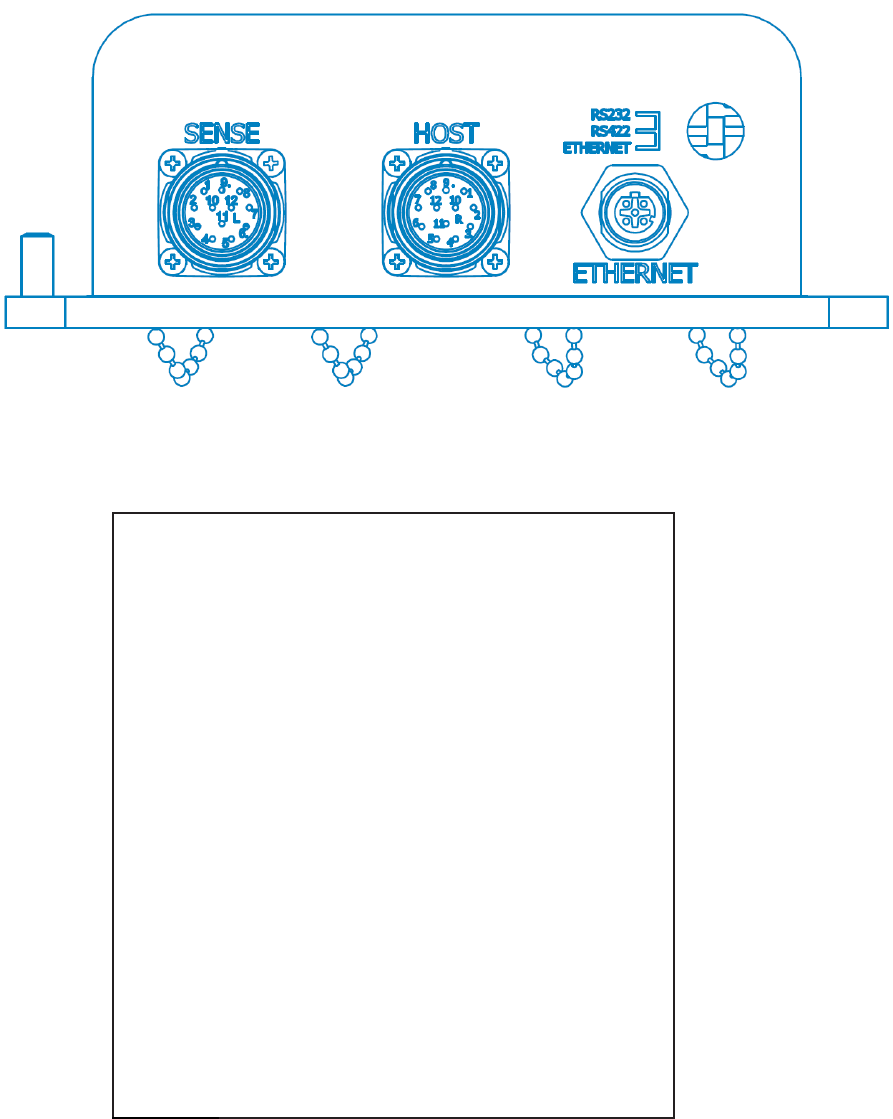
System Guide
TransCore Proprietary
4–8
Table 4 – 2. The TransCore part number (P/N) for the communication cable is 58-7001-
003 or 58-7001-004.
Figure 4 – 6 Location of Communications/Power Port on MPRX
Table 4 – 2 MPRX-to-Host Communications Cable Pin Designations
Host Cable
Pair Color Pin Number Name
Pair 1 White 9 SIG_GND
Black 1 RS232 TX
Pair 2 White 10 SIG_GND
Brown 2 RS232 RX
Pair 3 White 12 +V Return
Red 11 +V In
Pair 4 White 12 +V Return
Orange 11 +V In
Pair 5 White 12 +V Return
Yellow 11 +V In
Pair 6 White 3 Lock
Green 4 Lock Return
Pair 7 White 6 RS422 TX-
Blue 5 RS422 TX+
Pair 8 White 8 RS422 RX-
Violet 7 RS422 RX+
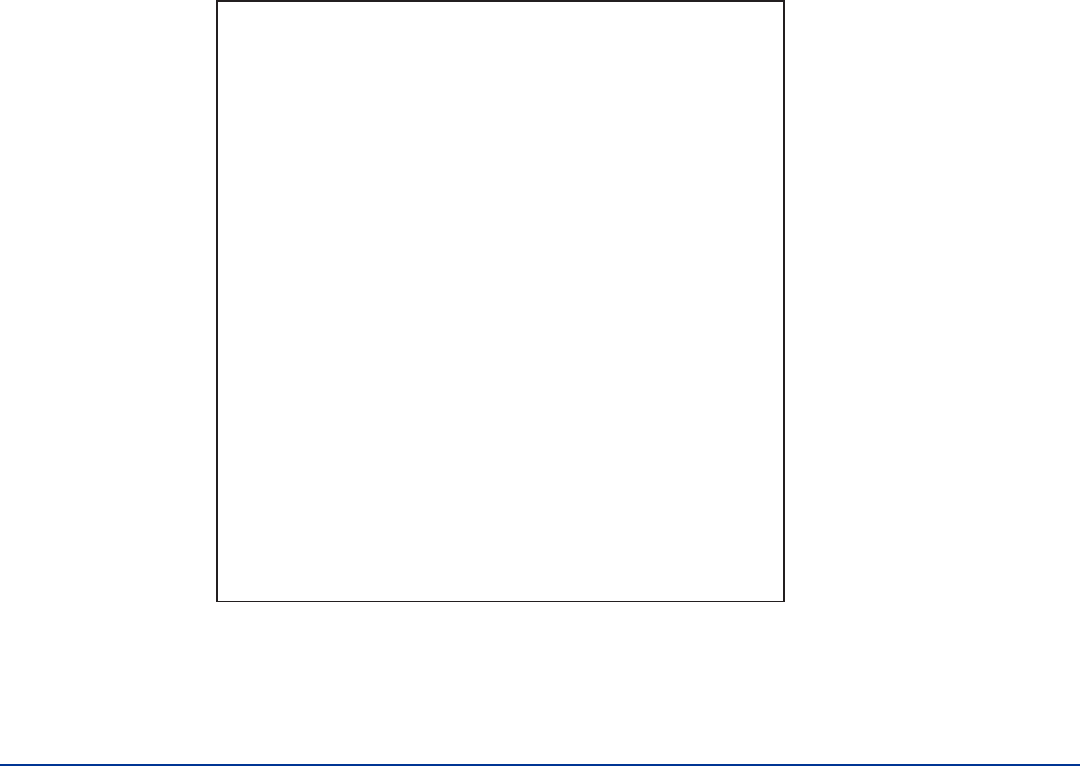
MPRX
TransCore Proprietary 4–9
Sense Cable
Pair Color Pin Number Name
Pair 1 White 3 I/O GND
Black 7 CTAG 0
Pair
2
White 3 I/O GND
Brown 8 CTAG 1
Pair
3
White 4 I/O GND
Red 1 +12V
Pair
4
White 4 I/O GND
Orange 1 +12V
Pair
5
White 6 OUT 0
Yellow 7 OUT 1
Pair
6
White 11 I/O GND
Green 5 PULSE OUT
Pair
7
White 9 I/O GND
Blue 12 SENSE 0
Pair
8
White 10 I/O GND
Violet 11 SENSE 1
If the MPRX is connected directly to a TRU, all power supply connections are made through
the MPRX-to-TRU cable assembly. Refer to Chapter 10, “Interface to Train Recording Unit”
on page 10–1 for wiring assignments.
Mounting the MPRX
This section lists procedures and materials required for mounting the MPRX on a wall or
other flat surface based on the site’s requirements.
In permanent installations the MPRX should be positioned as close as possible to the
antenna. Long cable runs increase system sensitivity to noise. Refer to Table 2 – 5 on page
2–13 for maximum RF cable lengths.
TransCore advises that for optimum heat dissipation, the MPRX should be mounted
vertically with the RF antenna ports at the bottom (refer to Figure 4 – 5). Figure 4 – 8
shows the outer dimensions and mounting hole locations for preparing to install the MPRX.
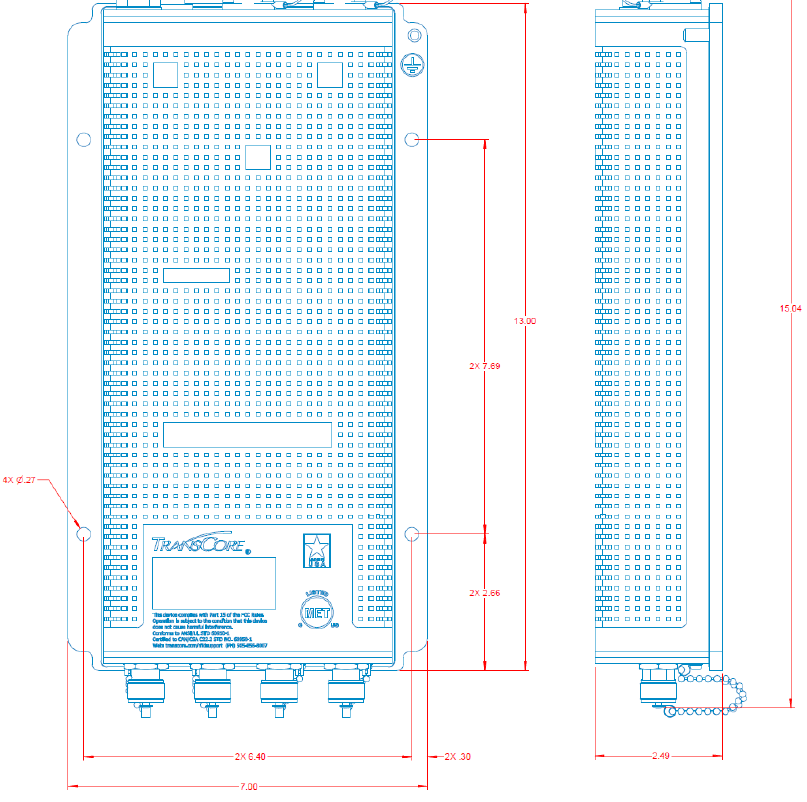
System Guide
TransCore Proprietary
4–10
Figure 4 – 7 MPRX Outer Dimensions and Mounting Hole Locations (not to scale)
Mounting to an Enclosure Wall or Flat Surface
Required Materials
You need the following materials to install the MPRX on an enclosure wall or flat surface.
Ensure the use of high-quality, corrosion-resistant anchor hardware.
Anchor hardware suitable for the surface on which you mount the MPRX
The MPRX weighs 5.7 lbs (2.6 kg) so choose mounting hardware that is adequate to secure
the unit to a wall.
After mounting the MPRX, you must connect it to a dedicated 12 to 24VDC or 24 to 110VDC
power supply.
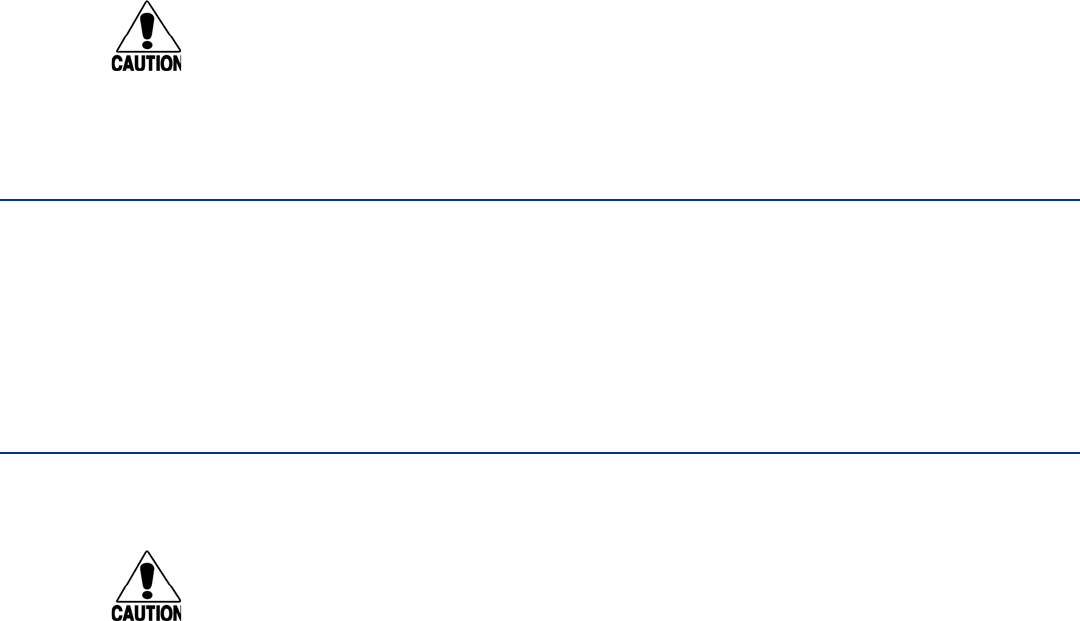
MPRX
TransCore Proprietary 4–11
Caution
To avoid damage to the MPRX, connect the antenna(s) before applying power
to the reader
Mounting the Antenna Rail-Side
Position the antenna as close as possible to the MPRX. Long cable runs increase system
sensitivity to noise. Refer to Table 2 – 5 on page 2–13 for maximum RF cable lengths.
After mounting the antenna, you must connect it to the MPRX. Follow the procedures
described previously in the section “Connecting the Antenna” on page 4–6.
Note: Adjust the antenna(s) to provide the most direct line of sight to the tags.
Connecting the Power Supply
After mounting the MPRX, connect the reader to a dedicated 12 to 24VDC or 24 to
110VDC power supply. If the MPRX is connected directly to a TRU, all power supply
connections are made through the MPRX-to-TRU cable assembly.
Caution
To avoid damage to the MPRX, connect the MPRX to ground before powering up the
reader or connecting the antenna(s).
Connect the antenna(s) before applying power to the reader.
Interface Selection Switch
The MPRX incorporates a communications interface selection switch, which allows on-
the-fly changes to the communications mode. This switch allows selecting the reader’s
receive communications interface. All communications interfaces are configured
for simultaneous transmit, but only the interface selected by the switch is active for
commands transmitted into the reader.
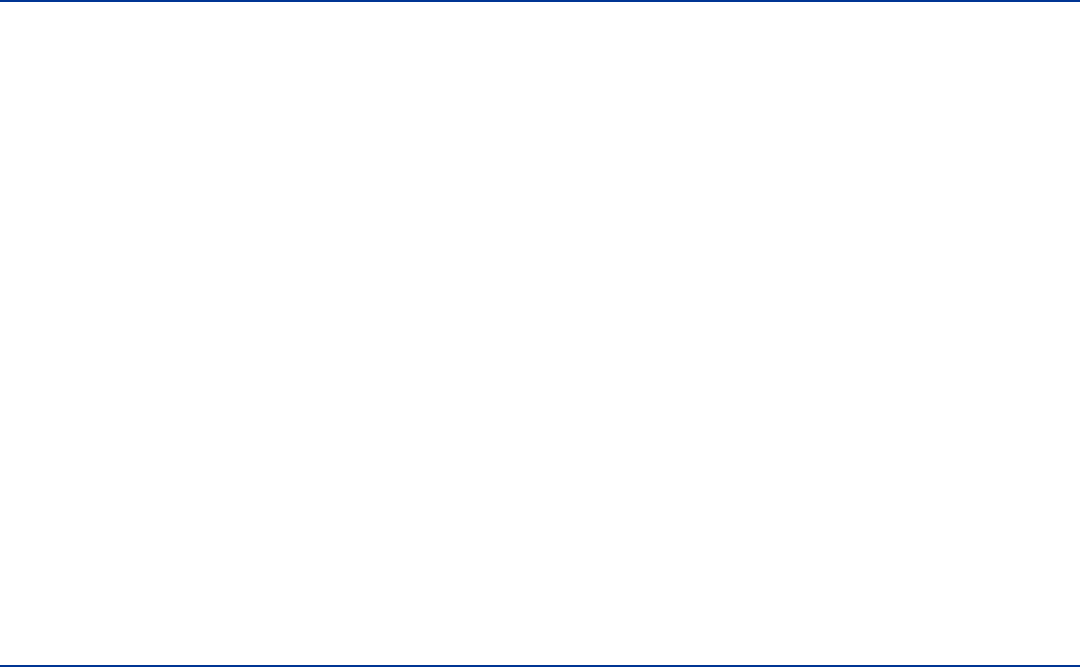
System Guide
TransCore Proprietary
4–12
Connecting Communications
The MPRX communicates through RS-232, RS-422, or Ethernet protocols.
Required Materials
You need the following materials to connect the communications cable to the host
device:
• Host device
• Any terminal emulation program such as Procomm Plus or Hyper Terminal operating
on a PC
• If the MPRX is connected directly to a TRU, all communications connections are
made through the MPRX-to-TRU cable assembly.
Connecting the MPRX to the Host
MPRX communications and customer interface signals are supplied from the MPRX to the
host through a multiwire cable. The connector for this cable is located on the end of the
MPRX (Figure 4 – 6).
Plug one end of the MPRX communications/power interface connector into the M23
Host connector at the MPRX and the other end into the customer-supplied host device
connector. Refer to Figure 4 – 7 and Table 4 – 2for the pin assignments, numbers, and
wire colors.
Connecting Sense Input and Sense Output Circuits
The MPRX has two sense input circuits and a tag lock output circuit available. SENSE0
is used to enable RF on antenna ports 0 and 1 if enabled, and SENSE1 is used to enable
RF on antenna ports 2 and 3. The sense input circuits are used to notify the MPRX of train
presence and are designed to be connected to a free-of-voltage dry contact. The tag
lock output circuit is a single-pole, double-throw relay that provides a normally closed
and normally open dry contact. The relay contact is rated at 42.2V AC peak (30 Vrms) or
60V DC at 1 A maximum. If controlling an external gate or device requiring high current,
an isolation transformer is required.
Sense Input Circuits
The MPRX supports two sense inputs – SENSE0 and SENSE1 – which require two
sense input lines (SENSEx and GND) for each loop sense or a total of four sense input
connections. SENSE0 is used to control RF power for the track that has antennas
connected to RF Ports 0 and 1. As shown in Figure 4 – 7, the sense inputs are wired through
the reader M23 Sense connector. The MPRX expects the SENSE0 circuit to close when a
railcar is present (on the track with antennas connected to MPRX ports 0 and 1).
SENSE1 must be closed when a railcar is present on the track connected to MPRX
antenna ports 2 and 3. The reader RF switches on to the appropriate RF ports
immediately upon detecting SENSEx.

MPRX
TransCore Proprietary 4–13
Sense Output Circuit
The sense output is dedicated for testing and reader setup. It is defined as the TAG_LOCK
signal, which indicates a valid tag is in the read field.
This sense output is a dry contact that provides a normally open and normally closed
sense output. The relay contacts are rated at 42.2V AC peak (30 Vrms) or 60V DC at 1
A maximum. If controlling an external gate or device requiring high current, an isolation
transformer is required.
Antenna Mux Channel Identification
With the MPRX in MPRX mode, it is possible to identify the tags read on the 4 channel
mux individually through the output I/O. Of course, it is still possible to enable antenna
stamping for the data transmissions on the selected communications interface as well.
Marking the Read Zone
Caution
Be sure to follow all applicable rail safety regulations when marking the read zone.
The area where the MPRX reads tags at the current RF range is called the read zone.
The antenna pattern, or read zone, of the MPRX would look roughly like a pearshaped
balloon if you were able to see it. When installing the MPRX, you should first mark the
unit’s read zone using the RF range set at the factory-default maximum. You can later
adjust the read zone using the techniques discussed in “Fine-Tuning and Verifying the
Read Zone” on page 8–17 .
If two MPRXs are installed near each other, TransCore recommends that you fine-tune
each reader for the ideal read zone before connecting it permanently to sense input/
sense output and communications cables. A minimum of 2 MHz frequency separation and
40 feet (12.2 m) of antenna separation between the two adjacent readers is required for
correct operation.
Required Materials
You need test tags, which can be supplied by your TransCore dealer or distributor to mark
the read zone. The test tag must be mounted flush against a metal backplane.
To mark the read zone
1. Confirm that you have correctly connected the power supply/communications cable as
described in this chapter.
2. Start the terminal emulation application Microsoft HyperTerminal by selecting
Programs>Accessories>Communications>HyperTerminal and press ENTER.
3. In the HyperTerminal dialog boxes choose the com port to which the communications
interface is attached and set the properties as:
• Bits per second: 9600 baud

System Guide
TransCore Proprietary
4–14
• Data bits: 8
• Parity: none
• Stop bits: 1
• Flow control: none
4. Cycle the power on the MPRX and ensure that the sign-on message displays.
5. To test the antenna connected to RF PORT-0, input the commands listed in Table 4-3.
Note: For testing purposes, the MPRX should not be in MPRX mode and should not
be multiplexing between multiple antennas.MPRX mode is used for rail track smart
multiplexing.
Note: Settings for RF, ATA range, SeGo range, and output power are the same for all
antennas.
Table 4 – 3 Commands for Testing RF Port-0
Entry Reader Response Notes
#01 <CR> #Done <CR/LF> Switches MPRX to command mode
#647XXX #Done <CR/LF> Sets operating frequency
#836 #Done <CR/LF> Disables MPRX mode
#850 #Done <CR/LF> Disables antenna multiplexing
#644XX #Done <CR/LF> Set desired RF power
#643XX #Done <CR/LF> Set desired ATA range control
#645XX #Done <CR/LF> Set desired SeGo range control
#6401 #Done <CR/LF> Turns on RF
#00 <CR> #Done <CR/LF> Returns MPRX to data mode
You can now connect the outer marks to draw the outer boundary of the read zone.
Figure 4 – 8 is a view of a sample read zone. The outer X marks show the outside edges
of the read zone.
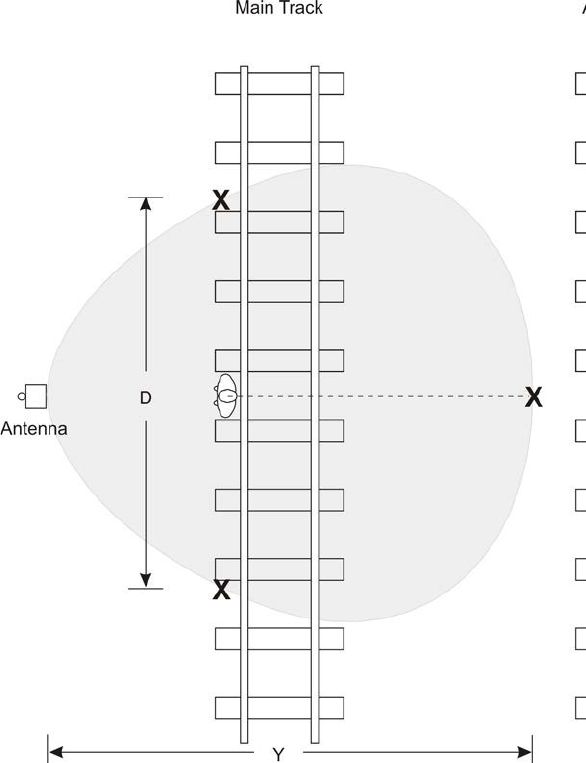
MPRX
TransCore Proprietary 4–15
Figure 4 – 8 Sample Read Zone Marking Pattern
6. Place the MPRX in single-antenna operation using the antenna of interest. Standing
at the edge of the rail sleepers closest to the antenna walk the metal- backed test tag
along the track to determine the farthest read point in both directions (Refer to item D in
Figure 4 – 8). Record the distance.
7. In a multiple track installation, walk the tag toward the adjacent track in a straight line
from the antenna face (refer to Figure 4 – 8) to determine whether the MPRX reads tags
from the adjacent track. Record that distance (item Y). If the MPRX reads tags on the
adjacent track, reduce the range control value, or increase RF attenuation until the
MPRX cannot read tags on the adjacent track.
To continue testing other antennas, ensure that the reader configurations used for RF
PORT-0 antenna (Table 4 – 3) are maintained. The following tables list the required
commands for testing PORT-1, PORT-2, and PORT-3.
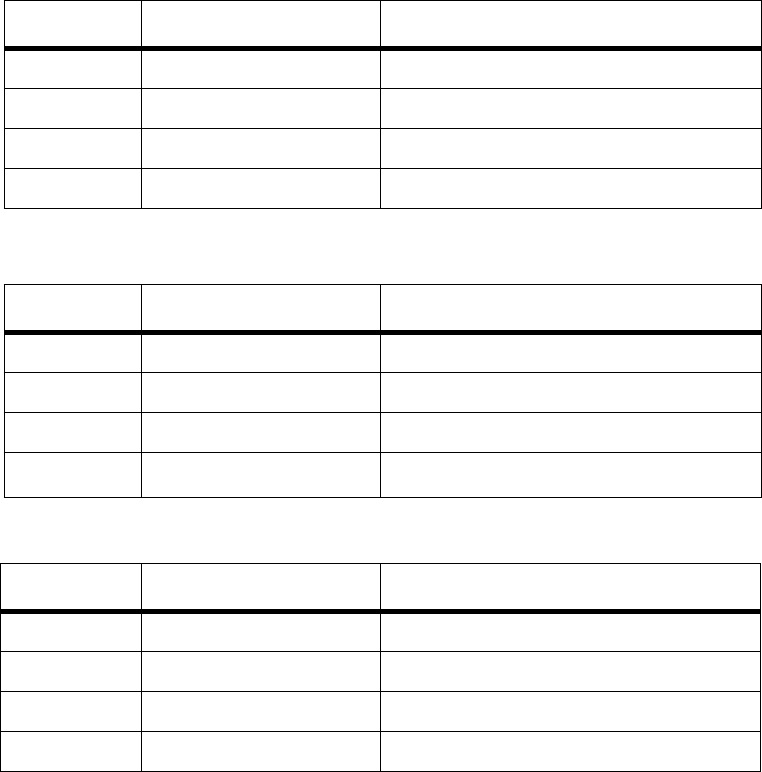
System Guide
TransCore Proprietary
4–16
Table 4 – 4 Commands for Testing RF PORT-1
Entry Reader Response Notes
#01 <CR> #Done <CR/LF> Switches MPRX to command mode
#891 #Done <CR/LF> Test mode, RF PORT-1 only
#6401 #Done <CR/LF> Turns on RF
#00 <CR> #Done <CR/LF> Returns MPRX to data mode
Table 4 – 5 Commands for Testing RF PORT-2
Entry Reader Response Notes
#01 <CR> #Done <CR/LF> Switches MPRX to command mode
#892 #Done <CR/LF> Test mode, RF PORT-2 only
#6401 #Done <CR/LF> Turns on RF
#00 <CR> #Done <CR/LF> Returns MPRX to data mode
Table 4 – 6 Commands for Testing RF PORT-3
Entry Reader Response Notes
#01 <CR> #Done <CR/LF> Switches MPRX to command mode
#893 #Done <CR/LF> Test mode, RF PORT-3 only
#6401 #Done <CR/LF> Turns on RF
#00 <CR> #Done <CR/LF> Returns MPRX to data mode
MPRX
TransCore Proprietary 4–17

General Software Information
5
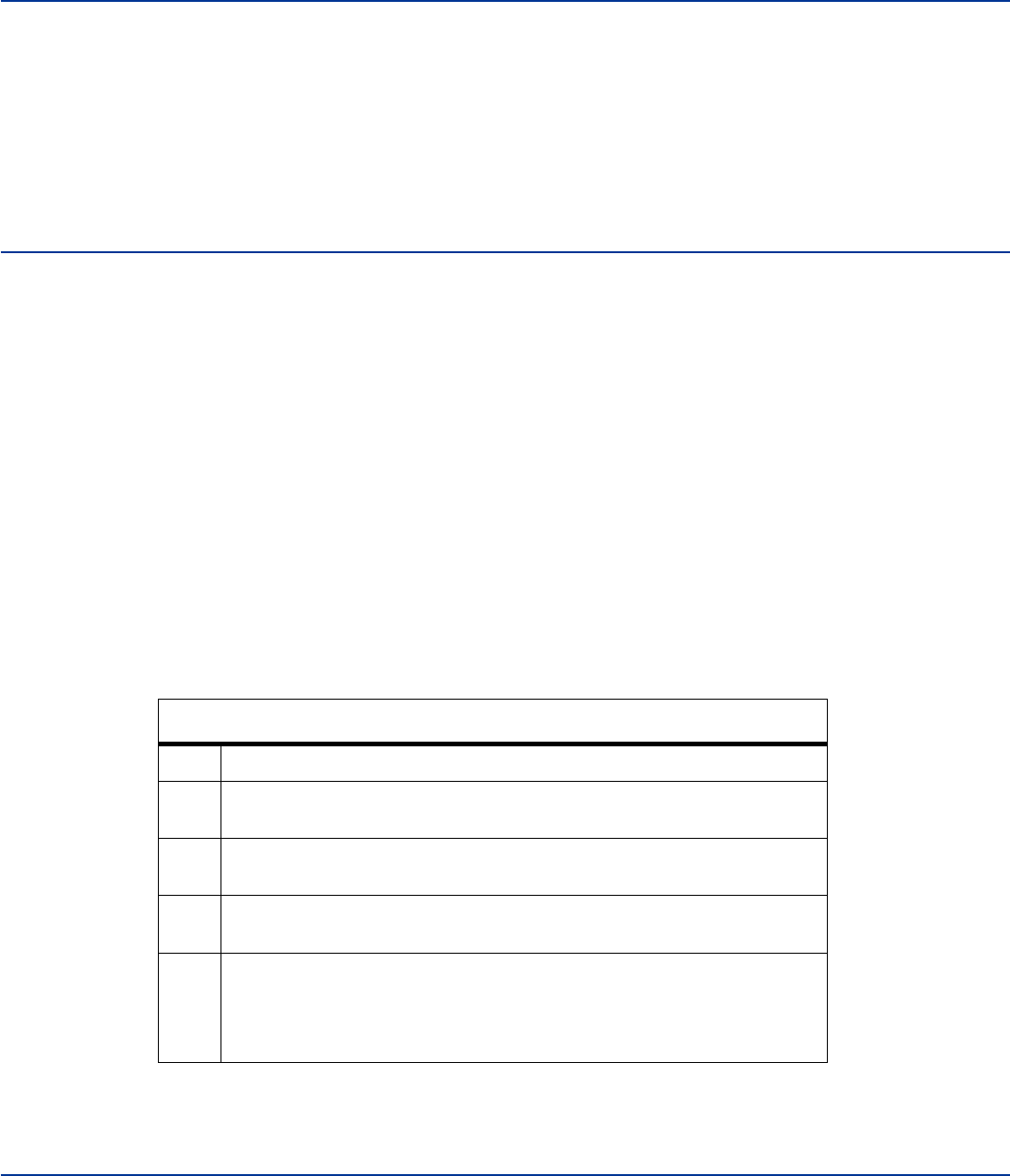
System Guide
TransCore Proprietary
5–2
Chapter 5 General Software Information
This chapter provides software-related information for the Multiprotocol
Reader Extreme (MPRX) System.
This chapter presents various software-related topics arranged in alphabetical order by
subject. In addition to this chapter, refer to “Chapter 6 Communications Protocols” on
page 6–2 and “Chapter 7 Commands” on page 7–2 ,” for more information.
Command Entry Conventions
All MPRX commands are preceded by the start-of-message character (#). The end-of-
message sequence expected from the host is a carriage return (CR). The MPRX terminates
messages with a return and a line-feed (CR/LF). For example, the command
#01 Switch To Command Mode is typed as follows:
#01<ENTER>
where <ENTER> is the Enter or Return key.
Some command characters may be represented by the letter N. This letter indicates
you are to supply a value. Maximum valid entries are the numbers 0 through 9 and the
uppercase letters A through F. These letters allow for as many as 16 available user
responses and are based on the hexadecimal numbering system.
Commands have at least two characters following the # character. Table 5 – 1 shows the
basic structure of a four-character command.
Table 5 – 1 Four-Character Command Structure
#1005 Set Baud Rate To 9600 Baud
# All commands are preceded by the # character.
1Indicates the command group. This command is in Group 1-
Communications Port Control.
0Indicates the command subgroup. In this example, all commands
with a second digit of 0 apply to the main port.
0The command digit. In this example, the 0 indicates that this
command aects the baud rate.
5
Indicates the setting. Normally this is a variable and is usually a
hexadecimal value from 0 through F. In this example, 5 sets the
baud rate to 9600, the factory setting. In some commands, this
digit may be a four-place hexadecimal string or a character string.
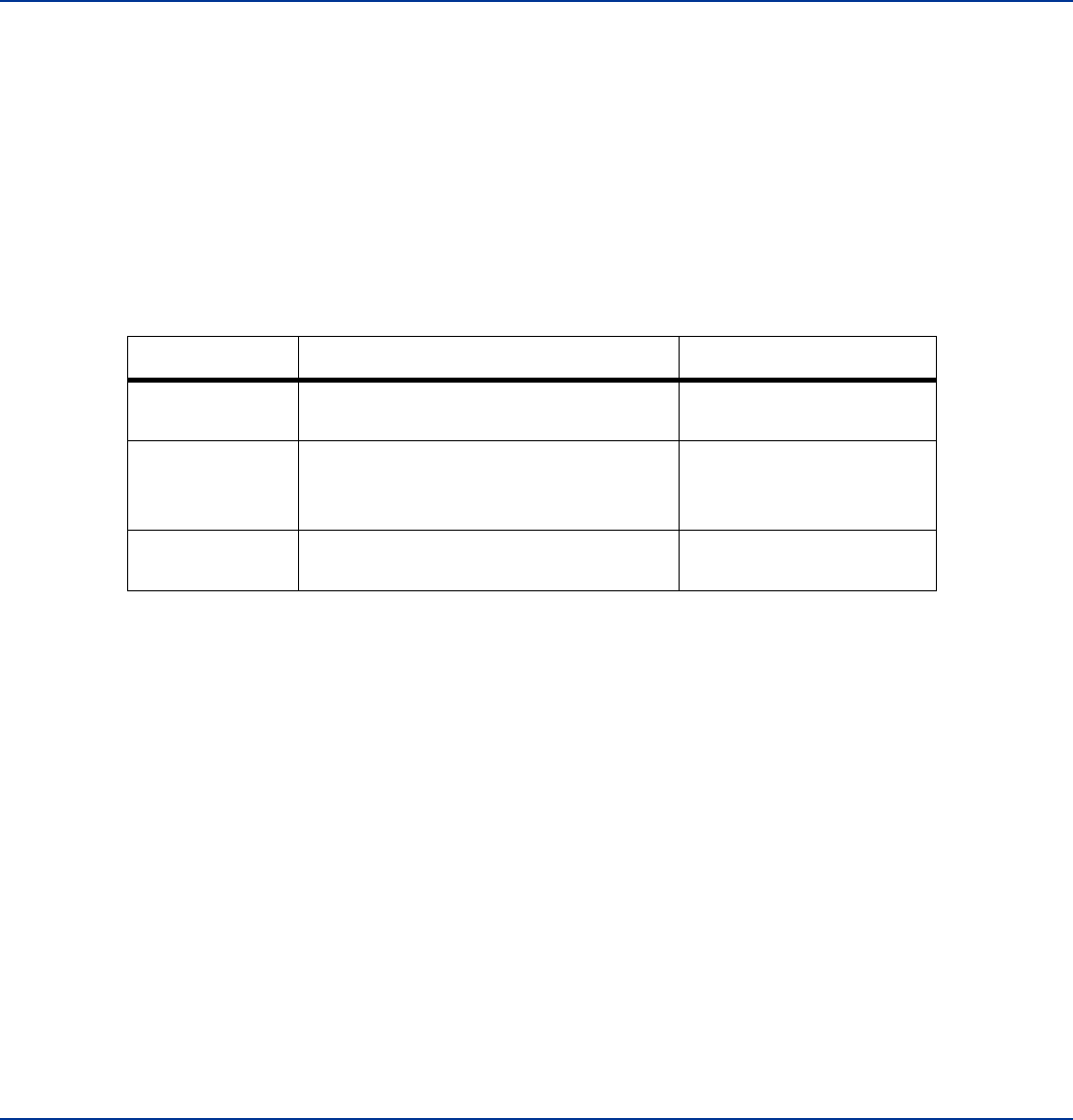
MPRX
TransCore Proprietary 5–3
Command Response Conventions
Like the MPRX commands, responses are preceded by the # character. Many MPRX
commands respond with #Done or #Error indicating the command was or was not
recognized and completed. Other commands respond with a four-character identifier
followed by one or more values.
Table 5 – 2 shows an example of a command/reply sequence. This example assumes
that an MPRX with serial number SN97001P running version X.XX software is connected
to a PC running a terminal emulation software package such as Windows Hyper Terminal
or Procomm Plus. The command sequence verifies that communications are working
correctly.
Table 5 – 2 Sample Command Sequence
In command discussions, MPRX response characters may be shown in brackets < >.
The use of brackets indicates that the response is a value in the range of characters.
The brackets are not part of the response. For example, the response to command
#520 Display Power Fail Bit is either a 0 or a 1. In the command discussion, the
response is shown as:
#PWRB <0-1>
with actual MPRX response being one of the following:
#PWRB 0
#PWRB 1
In this example, PWRB is the four-character identifier for power fail bit, and the 0 or 1 is the
value. All spaces shown in the response are actual spaces sent from the MPRX. In this
example, one space is between the letter B and the number.
Operating Parameters
The MPRXs maintain their operating parameters in nonvolatile memory (NVRAM) so that
the parameters are preserved after a power-down sequence.
Entry MPRX Response Notes
#01 <CR> #Done <CR/LF> Switches MPRX to
command mode
#505 <CR> #Model E4 Series Ver X.XX
SN08001P <CR/LF>
Reports the software
version and serial
number
#00 <CR> #Done <CR/LF> Returns MPRX to data
mode
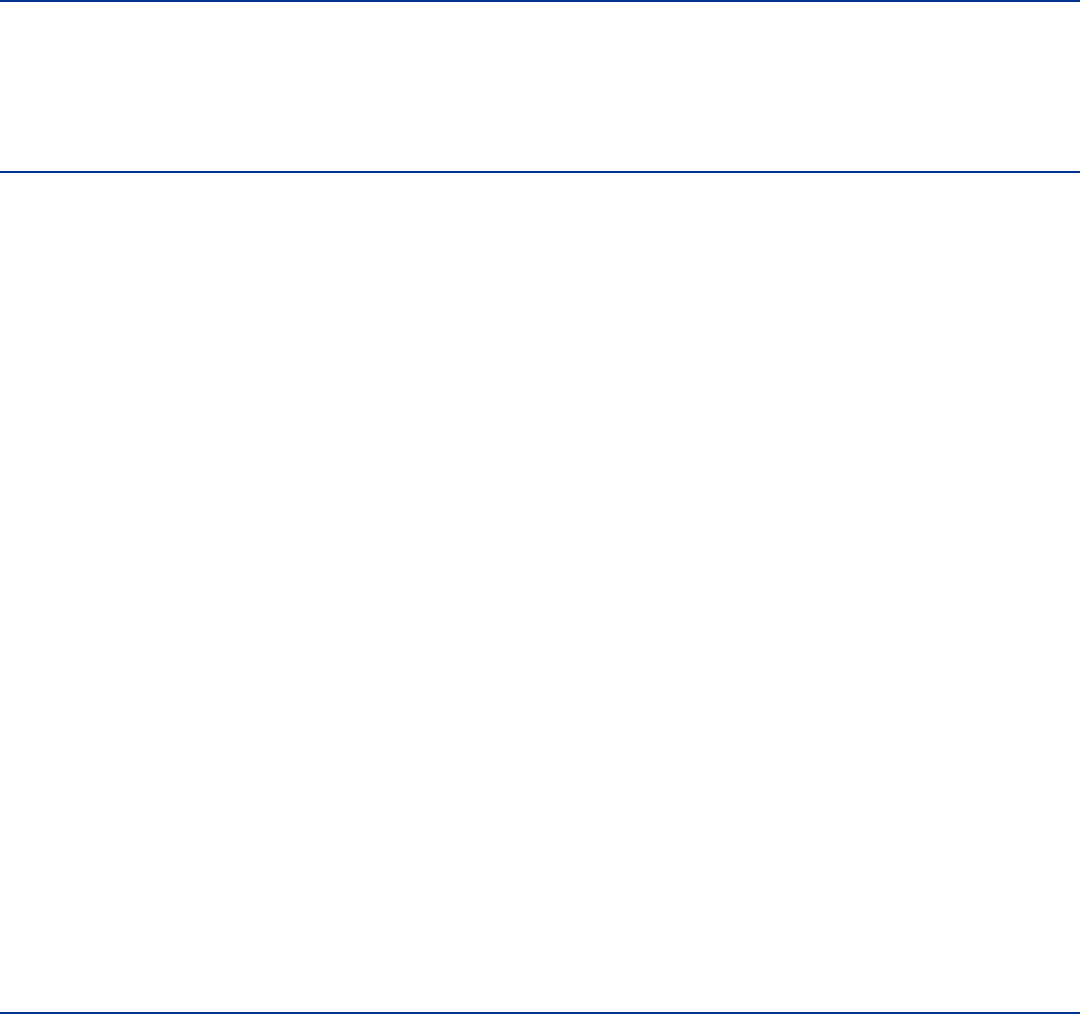
System Guide
TransCore Proprietary
5–4
Power Fail
The system maintains a power fail flag. The host transmits command #520 Display Power
Fail Bit to determine if a power down has occurred. This flag is cleared by both command
#63 Reset Reader and command #65 Reset Power Fail Bit.
Program Download
Program download stores the MPRX application software into the reader’s flash memory.
Program download is used to install program upgrades, add features, and to recover
from corrupted program data.
Note: Program download is a custom TransCore utility hosted process.
Download Considerations
You should consider the following factors when performing program download:
• The MPRX does not process tags while in download mode.
• The MPRX does not accept any program data unless a successful erase of flash
memory has been performed before transmitting the data. Erasing the flash memory
typically takes two seconds.
• Cycling reader power after exiting from download mode re-executes startup. If
the new software has been loaded without errors, the MPRX comes up in data
mode. If a flash checksum error is detected, the MPRX reenters download mode
and transmits a sign-on message with a boot version of 0.00x and without a serial
number.
Note: The MPRX uses default boot communications parameters when operating in
download mode – 38400 baud, 8 data bits, 1 stop bit, no parity, basic protocol – and
does not echo commands.
Download Procedures
If TransCore releases a new version of the MPRX software or if the MPRX does not
appear to be working properly, you may need to download the software to the MPRX.
Contact technical support or your TransCore MPRX sales representative.
Startup
Upon startup, MPRX transmits a sign-on message or a boot ROM failure message.
Sign-On Message
If startup is successful, the sign-on message appears as follows:
Model E4 Series [software version] SNSSSSSS [Copyright
notice]
where SSSSSS is the serial number assigned to the MPRX unit being used.

MPRX
TransCore Proprietary 5–5
Serial number 000000 is the default setting and is not a valid number. If this number
appears in the sign-on message, the serial number has never been stored into reader
memory. The serial number must be assigned by factory-authorized personnel using
command #695S...S Set Serial Number. Because only six digits are allowed in
the software, when setting the serial number skip the fourth (middle) digit of the seven-
digit number shown on the reader label.
If the flash memory checksum does not indicate verification, the sign-on message
appears as follows at a baud rate fixed at 38,400 bps:
Model [E4] Ver 0.00x
[Copyright notice]
Boot Failure Message
Upon powering up, the software performs a checksum verification on itself. The function
returns a specific value for the particular version of software. If the value returned is not
correct, the boot code assumes that the application code has been corrupted and a
failure condition exists. If the failure message does not transmit, a communications
error has occurred or the boot has failed to the extent that it cannot transmit the failure
message.
If the failure message version number equals 0.00 and no serial number exists, the
flash memory checksum has failed, and the MPRX is operating out of boot ROM. In this
case, the MPRX automatically enters download mode and waits for a new program to
be loaded into the flash memory. Contact TransCore Technical Support at 505-856-
8007 for assistance.
Tag/Message Buer
MPRXs maintain a tag buer in battery backed RAM to save tag IDs acquired when data
inquiry protocol is used. This buer holds up to 500 time-stamped messages.
When the buer fills, subsequent tag IDs will be lost.
System Guide
TransCore Proprietary
5–6

Communication Protocols
Chapter 6

System Guide
TransCore Proprietary
6–2
Chapter 6 Communications Protocols
This chapter describes the communications protocols for the
Multiprotocol Reader Extreme (MPRX).
Introduction
The MPRX supports the following communications protocols:
• Basic
• Error correcting
• Data inquiry
The following protocol information provides reference information relevant to developing
host software.
Communications are performed using the 7-bit ASCII code with optional parity, thus
providing easy setup, testing, and diagnostics with standard ASCII terminals and serial
printers.
Each message is framed within the start-of-message (som) and end-of-message (eom)
characters so that the host device can detect the beginning and end of each message.
This convention is most important under marginal communications conditions during which
the host may receive extraneous noise-induced characters between reader transmissions.
In such instances, the host is capable of ignoring any messages that do not conform to the
som...eom frame sequence.
Both data mode and command mode require a two-way message interchange when using
error correcting protocol (ECP). This interchange is completed by the message recipient
returning a message acknowledgment to the message sender.
With ECP, all transmissions require a message. If a message is not received, the sender will
time out with the same eect as if it had received a negative acknowledgment (from the
host) or an Error message from the MPRX.
Software (XON/XOFF) flow control is optionally supported. Be careful in the use of XON/
XOFF since noise-induced characters may be interpreted by the MPRX as the XOFF
character, which would suspend reader output without information reaching the host
device. For more information, refer to “Software Flow Control” on page 8–16.
Note: TransCore recommends that XON/XOFF flow control be disabled while using ECP.
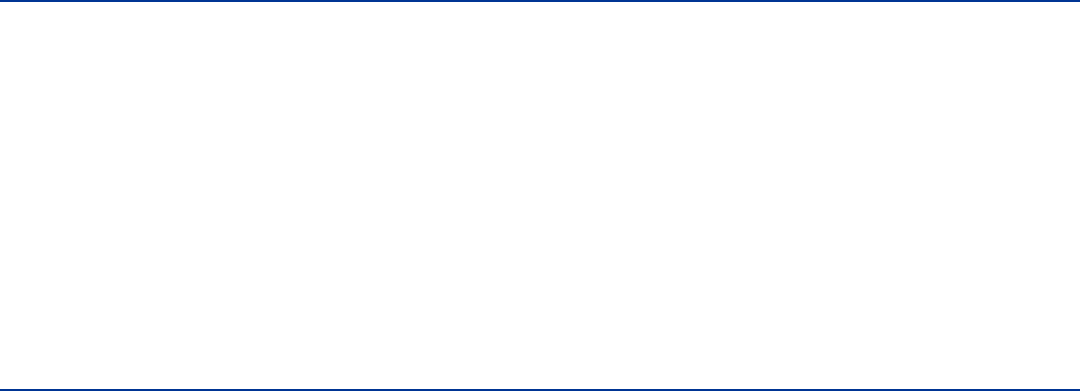
MPRX
TransCore Proprietary 6–3
Basic Protocol
With basic protocol, messages sent to and from the MPRX and the host are transmitted
without error checking. For each host transmission, the MPRX returns a Done or Error
message to the host.
When the host device is physically close to the MPRX and no sources of interference
exist, the basic protocol provides reliable communications.
The host must be ready to receive reader-transmitted messages because in basic
protocol the MPRX does not wait for the host to acknowledge a message before
transmitting the next message. If necessary, the host may halt reader transmissions by
using software flow control. Refer to “Chapter 8 Configuring the MPRX” on page 8–2
for flow control information.
Error Correcting Protocol
When the quality of data communications is imperative or may be suspect, you can
invoke ECP to ensure the integrity of data transmitted between the MPRX and the
host.
Note: TransCore recommends that basic protocol (not ECP) be used when commands
are entered manually at the keyboard.
Error correction is accomplished with the use of a cyclic redundancy check (CRC) value that
is based on the message data. The originator (reader or host) calculates the CRC value of a
message and includes it in the transmitted message.
The recipient (reader or host) also calculates a CRC value for the received message. If
the transmitted message data is correct, the CRC value calculated by the recipient will
agree with the CRC value calculated by the originator. If the CRC values do not agree, the
recipient rejects the message.
Message sequence numbers are also included when using ECP. These sequence numbers
are checked to determine if the message received has the correct sequence number; if
not, the recipient rejects the message.
Because the seven-bit ASCII code is used and there are eight data bits per character, the
eighth bit can optionally be used to support parity. Where parity is selected, the CRC value
calculation includes the parity of each character in the calculation of the CRC value.
Parity is required to achieve the most reliable communications. If parity is enabled, both
the MPRX and the host must issue a message if any received character has a parity error.
However, the message must not be transmitted before receipt of the eom character. If the
message is transmitted prematurely, the MPRX will issue an Error message, and the
host device will issue a negative acknowledgment message.
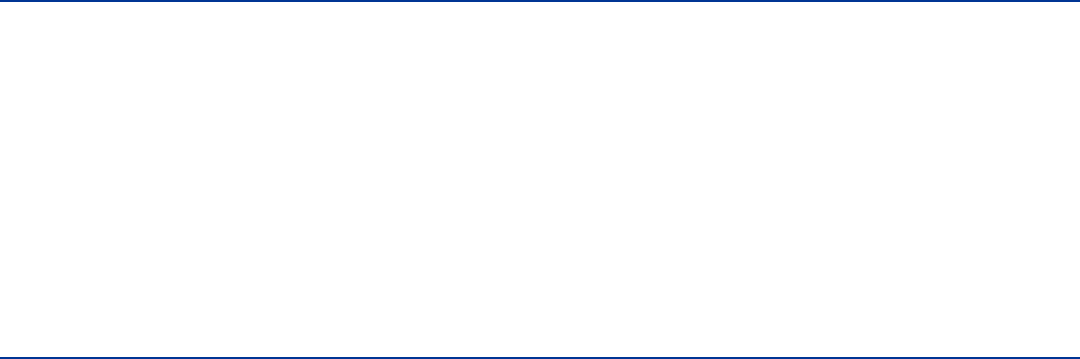
System Guide
TransCore Proprietary
6–4
Data Inquiry Protocol
Data inquiry protocol is a basic protocol option that allows the host to control transmission
of reader tag data. The selection of data inquiry protocol aects data mode operation. As
MPRX acquires tags, it buers them but does not transmit them. Instead, the host must
poll MPRX for each tag by sending a CTRL-E character (hex 5 digit). MPRX transmits one
message (tag ID or report data) for each CTRL-E it receives until the buer is empty.
Each tag request message sent by the host consists only of the CTRL-E character; no som
or eom characters are sent. MPRX data transmission (tag ID and report data) format is the
same as for basic protocol.
Selection of data inquiry protocol does not aect command mode operation.
Basic Protocol and ECP Format
Note: In the following text, the symbols < and > are used to represent required variable
message data, and the symbols [and] are used to represent optional data. These
symbols are not part of the message syntax.
Reader Transmissions
The basic protocol format and the data inquiry protocol format are as follows:
<som><data><eom>
The ECP format is as follows:
<som><seq><data><crc><eom>
where
<som> Start-of-message (ASCII # character)
<seq> Sequence number (ASCII hex) that represents an even number in
the
range 0–9, A–F (0, 2, 4, 6, 8, A, C, E). The MPRX maintains the number.
The host must acknowledge reader transmissions by sending an ACK
message with the same sequence number received from the MPRX. The
MPRX updates its sequence number upon receipt of a valid host ACK.
If an ACK is not received, the MPRX retransmits the message. A reader
transmission sequence is not considered complete until the MPRX
receives an ACK and updates its sequence number.
<data> ASCII string up to 72 characters long. This string may contain tag data; a
presence without tag report; an input status change report; an Error06,
Error07, Error08, or Error11 message; or a sign-on message.
Auxiliary data may also be included.
<crc> Field containing four ASCII digits that represent the 16-bit CRC value
calculated on the message. The CRC value is calculated on bytes between
the som character and the first <crc> byte.
MPRX
TransCore Proprietary 6–5
When the host receives a properly framed message, it can calculate
a 16-bit CRC value. The calculation is applied to the character string
that immediately follows the <som> and that ends with the character
immediately preceding the first <crc> character.
Transmitted CRC value can then be compared with the binary equivalent of
the received <crc> characters. If the transmitted and received CRC values
do not match, the recipient assumes the message was received in error,
and transmits a NAK message response.
<eom>
End-of-message characters (ASCII CR and LF). The system
includes both a
carriage return (CR) and line feed (LF) to facilitate the use of terminals and
printers.
If the host receives a <som> character in the middle of a data message, the
message in progress is aborted. The assumption is that an <eom> was lost
and the MPRX is in the process of retransmitting the previous message.
ECP Host ACK/NAK Response
With ECP, the host device responds to all data message transmissions from the MPRX
using the following acknowledgment or negative acknowledgment response format.
<som><seq><ack/nak><crc><eom>
where
<som> Start-of-message (ASCII # character)
<seq> Echo of the sequence number received from the MPRX. The sequence
number should correspond to the data message that is being positively
or negatively acknowledged by the host. If the MPRX receives an ACK
message with the incorrect sequence number, the data message is
retransmitted.
The host device resets the anticipated data message sequence number to
that of the MPRX before communications can resume without error.
<ack/nak> ASCII @ character for ACK response; ASCII ? character for NAK response
<crc> CRC value for the message
<eom> End-of-message character (ASCII CR)
The MPRX sets a user-programmable timeout delay at the time each
message is transmitted based on command #612NN Set Error Correcting
Protocol Timeout, where NN = timeout delay. To disable the timeout delay
for diagnostic purposes, issue the command #612FF Disable Error
Correcting Protocol Timeout.
System Guide
TransCore Proprietary
6–6
If the timeout delay expires before the MPRX receives an ACK or NAK
message from the host, a logical NAK condition will be declared. If the
MPRX receives a NAK or timeout, the reader retransmits the data message.
When the MPRX receives an ACK message, the system software treats
the message as having been properly received by the host. The software
increments the sequence number, and advances pointers to the next
message in the MPRX’s message queue to prepare for sending the next
message.
Switch to Command Mode Request
The host device may issue command #01 Switch to Command Mode while in data
mode.
The basic protocol format is as follows:
<som><cmd><eom>
The ECP format is as follows:
<som><seq><cmd><crc><eom>
where
<som> Start-of-message (ASCII # character)
<seq> Sequence number generated by the host device separately from
that
appearing in data messages transmitted by the MPRX
<cmd> Switch to command mode (ASCII characters 01)
<crc> CRC value for the message
<eom> End-of-message character (ASCII CR)
Host Transmission
The host device initiates synchronous communications between the MPRX and the host. The
host begins a sequence by issuing a command; the MPRX responds accordingly.
The data inquiry protocol format is as follows:
<CTRL-E>
The basic protocol format is as follows:
<som><cmd>[<data>]<eom>
The ECP format is as follows:
<som><seq><cmd>[<data>]<crc><eom>
where
<CTRL-E> ASCII Control E (hex 5 digit). When in data inquiry mode, each
transmission
of a CTRL-E by the host causes the MPRX to transmit one tag ID.
MPRX
TransCore Proprietary 6–7
<som> Start-of-message (ASCII # character)
<seq> Sequence number (ASCII hex digit) that represents an odd
number in the
range 0–9, A–F (1, 3, 5, 7, 9, B, D, F). The host should use odd sequence
numbers in its command since the MPRX uses even sequence numbers in
its transmissions. This method eliminates the possibility of a synchronous
host command and an asynchronous reader transmission having the same
sequence number.
Upon receiving a host command in ECP, the MPRX replies using the
command’s sequence number in its response. Therefore, the host device
updates its sequence number upon receipt of a valid reader response.
If the sequence number is not updated before transmission of the next
command, the MPRX will not service the new command; it will retransmit its
previous message. A command/message sequence is not complete until
the host updates its sequence number.
<cmd> Command code, a string that contains from two to four ASCII
hex characters
[<data>] Optional data field, an ASCII string of as many as 20 characters
in length. For
example, the store hardware configuration string command is #696S...S
or command #696 Store Hardware Configuration String followed by the
data string S...S.]
<crc> CRC value for the message
<eom> End-of-message character (ASCII CR)
Reader Command Response
The basic protocol format is
<som><resp><eom>
The ECP format is
<som><seq><resp><crc><eom>
where
<som> Start-of-message (ASCII # character)
<seq> Echo of sequence number received in host command message
<resp> Response string. The MPRX returns Done, Error, or another
ASCII string
depending on the host transmission. This string can be up to 72 characters
long.
<crc> CRC value for the message
<eom> End-of-message character (ASCII CR and LF)
Sample Messages
System Guide
TransCore Proprietary
6–8
This section contains examples of typical messages transmitted between the MPRX and
the host device.
Reader Transmissions
Basic protocol reader transmission
#KING 1302<eom>
Host response
No host response for non-ECP
ECP reader transmission
#4KING 1302 <crc><eom>
where
#
Start-of-message character
4
Message sequence number
KING 1302 Message data: Tag ID is shown.
Other sample message data could be as follows: IOST C0 O2 I0 D24
(display I/O status) Error06 (frequency not set)
<crc> CRC value for the message
<eom> End-of-message character
Host response
#4@<crc><eom>
where
#
Start-of-message character
4
Message sequence number
@
ACK (acknowledgment character)
(? returned for a negative acknowledgment)
<crc> CRC value for the message
<eom> End-of-message character
MPRX
TransCore Proprietary 6–9
Host Command Transmissions
Basic protocol host transmission
#647XXX<eom>
Reader response
#Done<eom> or #Error<eom>
#Error<eom> is returned if the host transmission is not a legal command with legal data.
ECP host transmission
#7647XXX<crc><eom>
where
#
Start-of-message character
7
Message sequence number
647XXX Select RF Operating Frequency command where
647XXX is the
command and XXX is a hexadecimal value from 000 to 118. In this example,
XXX sets the RF frequency to 903 MHz.
<crc> CRC value for the message
<eom> End-of-message character
Done Command has been invoked by the MPRX
Reader response
#7Done<crc><eom> or #7Error<eom>
For some commands, the MPRX responds with data that relates to the command, such
as T0F 0, to indicate the mode enabled for a #570 Display Operating Mode Status
command.
#7Error<eom> will be returned if host transmission is not a legal command with legal
data.
Timing and Synchronization
The ECP is largely independent of baud rate. The timeout delays previously described are
a function of baud rate.
The MPRX supports an ECP timeout, which applies equally to both transmit and receive.
The receiver’s minimum timeout delay equals the time to transmit/receive the longest
anticipated message at the current baud rate setting. Additional margin should be included
for idle periods between characters; for example, processing overhead, if any. The timeout
delay period can be expressed as follows:
Τrec (ms) = L x [Τchar + Τidle]
System Guide
TransCore Proprietary
6–10
where
Τchar (ms) 1000 x [ Bc / Rb ]
Bc
Bits per character, typically 10
Rb
Baud rate, 1200–38.4 K
L
Length of message in characters
Τidle Maximum idle period between characters (ms)
Note: The MPRX supports baud rates between 1200 and 38.4 K.
Likewise, the sender must set a timeout delay equal to the delay of nine characters at the
current baud rate setting. For example, the time required to shift out the <eom> character
plus the time to shift in the ACK or NAK message to be received plus a processing
allowance for the receiver to process the message and check for error conditions.
Thus, the sending timeout delay can be expressed as follows:
Τsend (ms) = 9 * Τchar + Τerrchk
where
Τerrckh (ms) Processing period to perform error checking by receiver
The host device can remotely set the MPRX’s communications parameters while in the
command mode, but TransCore does not recommend this action if communications
conditions are marginal.
After the MPRX receives new communications parameters, the MPRX issues the Done
message and switches to the new configuration immediately. The host device switches its
communications parameters immediately after the transaction is complete.
As noted, the message initiator, such as the MPRX in data mode and the host device
in command mode, starts a timeout counter at the time a message is transmitted. If the
timeout expires before receiving an acknowledgment message, a logical NAK condition is
declared, and the initiator assumes the message was received in error. In this instance, the
message is retransmitted until an acknowledgment message is received.
The message recipient, such as the host device in data mode and the MPRX in command
mode, starts a timeout counter when a <som> character is received. If the timeout expires
without the receipt of an <eom>, the message acquisition is aborted (reset), and the
receiver waits for the next <som> character.
If the message recipient receives a second <som> character before an <eom> character,
the message acquisition is aborted (reset), and retransmission of the previous message is
assumed to be underway.
These strategies allow for recovery during periods when communications are marginal or
lost completely.

MPRX
TransCore Proprietary 6–11
Reader-Addressed Failure Conditions
The MPRX addresses the following failure conditions.
Illegal Sequence Number (not in the range 0–9, A–F)
If the MPRX detects an illegal sequence number in a host command message, it discards
the received message and sends no response. If it receives an illegal sequence number in
an ACK message, it responds as if a NAK had been received and retransmits the data.
Wrong Sequence Number
If the MPRX receives the wrong sequence number in an ACK message, it responds as if a
NAK had been received, and it retransmits the data.
Incorrect CRC
If the MPRX detects an incorrect CRC value in a host command message, it discards the
received message. No response is sent. If it receives an incorrect CRC value in an ACK
message, it responds as if a NAK had been received, and it retransmits the data.
Illegal Command
If the MPRX receives an illegal command, it returns its standard Error message.
Transmission Timeout
If the MPRX transmits an asynchronous message and the host does not send an ACK
before the ECP timeout occurs, the MPRX retransmits the message.
Receive Timeout
If the MPRX receives a <som> but does not receive a matching <eom> before the ECP
timeout occurs, it discards the incomplete message and resets its receiver.
Asynchronous Message/Command Message Collision
If the MPRX transmits asynchronous data at the same time that the host sends a command,
the MPRX gives priority to receiving the command. It processes the command and sends
a message before it retransmits the asynchronous data.
Host-Addressed Failure Conditions
The host device addresses the following failure conditions.
Illegal or Wrong Sequence Number
If the host detects an illegal or wrong sequence number in a reader response, it retransmits
the command with the same sequence number. If the host detects an illegal sequence
number in an asynchronous reader transmission, it sends a NAK message.
Incorrect CRC
If the host detects an incorrect CRC value in a reader message, it retransmits the command
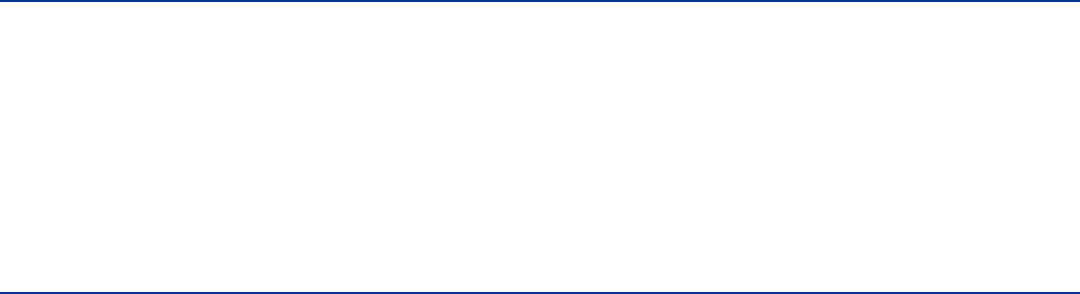
System Guide
TransCore Proprietary
6–12
with the same sequence number. If the host detects an incorrect CRC value in an
asynchronous reader transmission, it transmits a NAK message.
Transmission Timeout
If the MPRX does not respond to a host command within a specified interval, the host
software retransmits the command with the same sequence number.
Receive Timeout
If the host receives a <som> but does not receive a matching <eom> within a specified
timeout interval, it discards the incomplete message and resets its receiver.
Asynchronous Message/Command Message Collision
If the host receives an asynchronous reader transmission at the same time it transmits a
command, it ignores the asynchronous message and waits for the MPRX’s response. The
MPRX retransmits asynchronous data after it transmits the command message.
ECP Reliability
An undetected error is defined as a message having incorrect data or status but no parity
or CRC errors. An error transaction is defined as a message having either a parity or CRC
error. Laboratory testing indicates an undetected error rate of less than one undetected
error per 1,000,000 error transactions with parity enabled.
To ensure this error rate is not exceeded, the host must enable parity and adhere closely
to the timing specifications discussed previously in “Timing and Synchronization” on page
6–9.
CRC Calculation
The CRC used by the ECP is based on a 16-bit algorithm. The algorithm, as implemented,
operates on eight-bit characters, for example, a seven-bit ASCII character plus one optional
parity bit. The 16-bit result is converted to four ASCII hex characters and is appended to
messages transmitted by the MPRX.
The MPRX accepts four ASCII < ` > characters (60 hex) as a wild card CRC value in lieu of a
valid four-character CRC value to facilitate testing and diagnostic checkout.
The MPRX implements the algorithm with a 512-byte lookup table to reduce the processing
overhead requirements.
To simplify the implementation of the CRC algorithm by host software developers, several
examples of the calculation are provided in C source code on the following pages. The
calculation may be performed with or without a lookup table, depending on the trade-o
between code memory and processing overhead.
Example 1 presents an example of a function (CALCCRC) that calculates the CRC value
through a call to a separate function (UPDCRC).
MPRX
TransCore Proprietary 6–13
unsigned short calccrc(char *message)
{
unsigned short crc = 0;
for ( ; *message != (char)0;message++) crc =
updcrc(*message & 0xff, crc);
return (crc)
}
Example 2 shows an example of UPDCRC that does not require a lookup table.
#dene BITS_PER_CHAR 8
unsigned short updcrc (unsigned short ch, unsigned short crc)
{
register short counter = BITS_PER_CHAR;
register short temp = crc;
while (--counter >= 0) if
(temp & 0x8000) {
temp <<= 1;
temp += (((ch <<= 1) & 0x0100) != 0);
temp ^= 0x1021;
}
else { temp
<<= 1;
temp += (((ch <<= 1) & 0x0100) != 0);
}
return(temp);
}
Example 3 contains an example of UPDCRC that does require a lookup table.
#dene updcrc(cp, crc)( crctab[((crc >> 8) & 255)]^ (crc << 8) ^ cp static
unsigned short crctab [256] = {
0x0000, 0x1021, 0x2042, 0x3063, 0x4048, 0x50a5, 0x60c6, 0x70e7,
0x8108, 0x9129, 0xa14a, 0xb16b, 0xc18c, 0xd1ad, 0xe1ce, 0xf1ef,
0x1231, 0x0210, 0x3273, 0x2252, 0x52b5, 0x4294, 0x72f7, 0x62d6,
0x9339, 0x8318, 0xb37b, 0xa35a, 0xd3bd, 0xc39c, 0xf3ff, 0xe3de,
0x2462, 0x3443, 0x0420, 0x1401, 0x64e6, 0x74c7, 0x44a4, 0x5485,
0xa56a, 0xb54b, 0x8528, 0x9509, 0xe5ee, 0xf5cf, 0xc5ac, 0xd58d,
0x3653, 0x2672, 0x1611, 0x0630, 0x76d7, 0x66f6, 0x5695, 0x46b4,
0xb75b, 0xa77a, 0x9719, 0x8738, 0xf7df, 0xe7fe, 0xd79d, 0xc7bc,
0x48c4, 0x58e5, 0x6886, 0x78a7, 0x0840, 0x1861, 0x2802, 0x3823,
0xc9cc, 0xd9ed, 0xe98e, 0xf9af, 0x8948, 0x9969, 0xa90a, 0xb92b,
0x5af5, 0x4ad4, 0x7ab7, 0x6a96, 0x1a71, 0x0a50, 0x3a33, 0x2a12,
0xdbfd, 0xcbdc, 0xfbbf, 0xeb9e, 0x9b79, 0x8b58, 0xbb3b, 0xab1a,
0x6ca6, 0x7c87, 0x4ce4, 0x5cc5, 0x2c22, 0x3c03, 0x0c60, 0x1c41,
System Guide
TransCore Proprietary
6–14
0xedae, 0xfd8f, 0xcdec, 0xddcd, 0xad2a, 0xbd0b, 0x8d68, 0x9d49,
0x7e97, 0x6eb6, 0x5ed5, 0x4ef4, 0x3e13, 0x2e32, 0x1e51, 0x0e70,
0xff9f, 0xefbe, 0xdfdd, 0xcffc, 0xbf1b, 0xaf3a, 0x9f59, 0x8f78,
0x9188, 0x81a9, 0xb1ca, 0xa1eb, 0xd10c, 0xc12d, 0xf14e, 0xe16f,
0x1080, 0x00a1, 0x30c2, 0x20e3, 0x5004, 0x4025, 0x7046, 0x6067,
0x83b9, 0x9398, 0xa3fb, 0xb3da, 0xc33d, 0xd31c, 0xe37f, 0xf35e,
0x02b1, 0x1290, 0x22f3, 0x32d2, 0x4235, 0x5214, 0x6277, 0x7256,
0xb5ea, 0xa5cb, 0x95a8, 0x8589, 0xf56e, 0xe54f, 0xd52c, 0xc50d,
0x34e2, 0x24c3, 0x14a0, 0x0481, 0x7466, 0x6447, 0x5424, 0x4405,
0xa7db, 0xb7fa, 0x8799, 0x97b8, 0xe75f, 0xf77e, 0xc71d, 0xd73c,
0x26d3, 0x36f2, 0x0691, 0x16b0, 0x6657, 0x7676, 0x4615, 0x5634,
0xd94c, 0xc96d, 0xf90e, 0xe92f, 0x99c8, 0x89e9, 0xb98a, 0xa9ab,
0x5844, 0x4865, 0x7806, 0x6827, 0x18c0, 0x08e1, 0x3882, 0x28a3,
0xcb7d, 0xdb5c, 0xeb3f, 0xfb1e, 0x8bf9, 0x9bd8, 0xabbb, 0xbb9a,
0x4a75, 0x5a54, 0x6a37, 0x7a16, 0x0af1, 0x1ad0, 0x2ab3, 0x3a92,
0xfd2e, 0xed0f, 0xdd6c, 0xcd4d, 0xbdaa, 0xad8b, 0x9de8, 0x8dc9,
0x7c26, 0x6c07, 0x5c64, 0x4c45, 0x3ca2, 0x2c83, 0x1ce0, 0x0cc1,
0xef1f, 0xff3e, 0xcf5d, 0xdf7c, 0xaf9b, 0xbfba, 0x8fd9, 0x9ff8,
0x6e17, 0x7e36, 0x4e55, 0x5e74, 0x2e93, 0x3eb2, 0x0ed1, 0x1ef0,
};
Example 4 shows an example of a function that creates the lookup table.
#include <stdio.h>
#dene MAX_CHAR 256
#dene BITS_CHAR 8
#dene SIGN_BIT 0x8000
#dene POLY 0x1021
unsigned short crctab [MAX_CHAR]; main
()
{
unsigned short ch; unsigned
short workval; unsigned
short bit; unsigned short
carry;
for (ch = 0; ch != MAX_CHAR; ch++) {
workval = ch << BITS_CHAR;
for (bit = BITS_CHAR; bit != 0; bit--) {
carry = (workval & SIGN_BIT);
workval <<= 1; if
(carry) workval ^=
POLY;
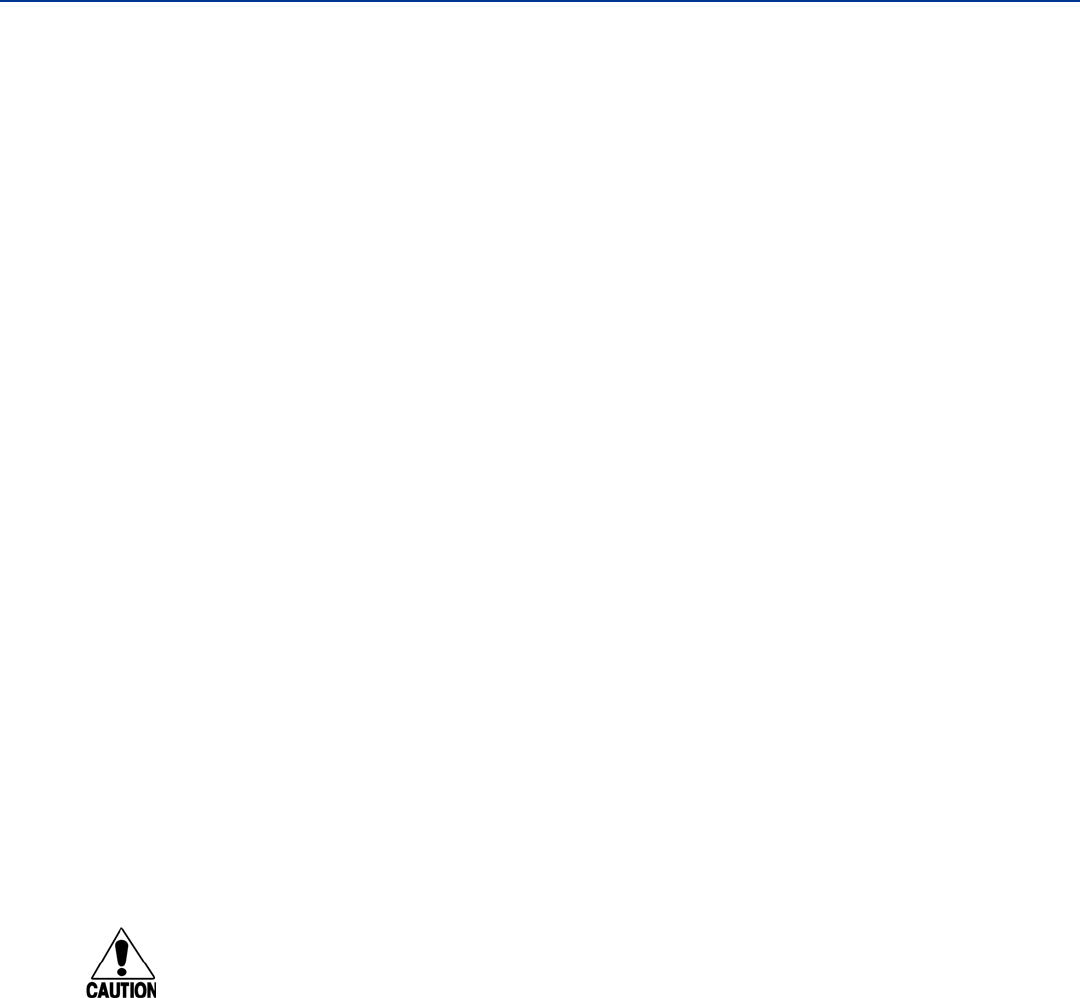
MPRX
TransCore Proprietary 6–15
}
crctab[ch] = workval;
}
for (ch = 0; ch != MAX_CHAR; ch++)
printf(“0x%04x\n”, crctab[ch]);
}
Manually Disabling ECP for Maintenance
Under certain conditions, communications between the host and MPRX may be lost
temporarily and maintenance may be required. The reader or host is sending out a
message and waiting for an acknowledgment. When the acknowledgment is not received,
the message is sent again. Additional messages are also buered. Often the first indication
that the MPRX software is in an ECP “loop” is when the user/technician sees a recurring
display of the same message repeated on the monitor. The procedure described in the
following paragraphs enables the maintenance technician to change configuration or test
tag reading manually.
Assuming that the ECP timeout is at the factory default of 12.7 seconds (or other value that
allows enough time for the commands to be manually entered) the following command
sequence may be used to break out of an ECP loop. This command sequence uses four
ASCII < ` > characters (60 hex) as wild card CRC values.
Note: The ASCII <`> character (60 hex) is commonly located on the ~ key.
You must acknowledge existing messages by issuing commands with the generic format:
#x@‘‘‘‘<eom>
where
#
Start-of-message character
x
Message sequence number. This must be the same as the
sequence
number of the message being acknowledged
@
ACK (acknowledgment character)
<‘‘‘‘> Wild card CRC value for the message
<eom> End-of-message character
The following is a typical sequence after power-on limiting buered messages.
Note: Ensure that no tags are in the field when you are performing this troubleshooting
procedure.
Caution
To avoid damage to the MPRX, ensure that you have connected the antenna or a
dummy load to the reader before applying power to the reader.
System Guide
TransCore Proprietary
6–16
Reader transmission on power-up:
#0 Model …. SN <crc><eom>
Manually enter: #0@````<eom>
Reader transmission #2 Copyright 2008 TransCore <crc><eom>
Manually enter: #2@````<eom>
Manually enter: #101‘‘‘‘<eom>
this puts reader into command mode
Reader response: #1Done<crc><eom>
Manually enter: #3610‘‘‘‘<eom> this puts reader into basic protocol,
disabling ECP
reader response: Done
Enter any other desired diagnostic or directive commands in basic protocol. After
maintenance is complete enter the commands:
#00 to return the reader to data mode
#611 to return to error correcting protocol
#100````<eom>
to return reader to data mode
MPRX
TransCore Proprietary 6–17

Chapter 7
Commands
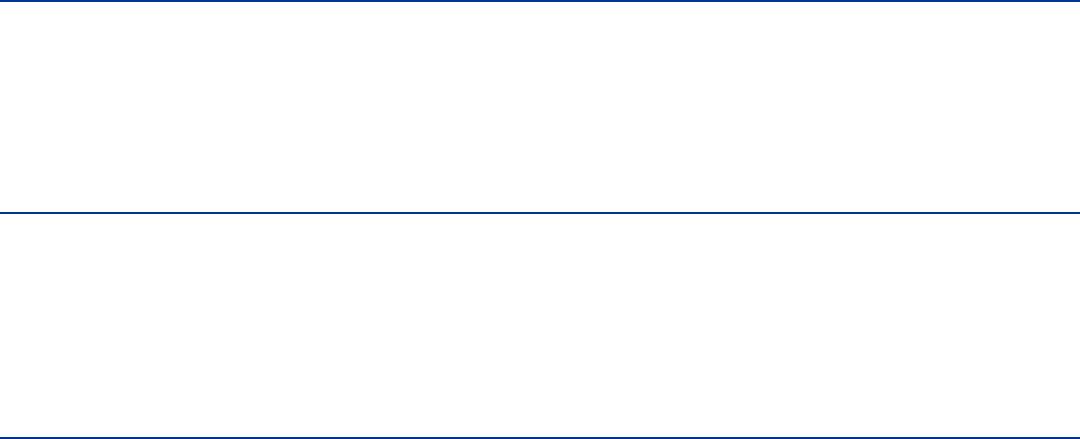
User Guide
TransCore Proprietary
7–2
Chapter 7 Commands
This chapter discusses the host-transmitted commands that are used
to control the Multiprotocol Reader Extreme (MPRX) configuration and
operation.
Introduction
The MPRX is delivered from the factory with specified default settings that determine how
the reader operates. Commands transmitted by the host device can change the default
settings and control additional features. The commands can be transmitted by manually
entering the commands at the host keyboard if the host is in terminal emulation mode.
The MPRX can also communicate with ASCII terminals.
Operating Modes
The MPRX has three modes of operation: data mode, command mode, and download
mode. The software for the MPRX contains two separate programs — boot and
application. The boot program has control of the MPRX on startup and when operating
in download mode. The application program has control of the MPRX during data mode
and command mode operation and holds the application code. Together, they control
the MPRX in the three modes of operation.
Data Mode
The MPRX is in the data mode upon power-up. While in the data mode, the MPRX sends
all communications, such as tag IDs and reports, as data messages to the host device.
Reports provide information on input status changes (input0 and input1), a presence
without tag report, and buer overflow information. When MPRX mode has been enabled
(#837) and while the MPRX is in data mode, the host device can send the following
commands the MPRX:
• Command #01 changes the MPRX from the data mode to the command mode.
• Command #440 provides a one-time reset of all tag uniqueness timers at which
point the previously set timeout interval resumes.
• Command #8110 turns on RF port0 and sends the command on Ctag pin 0 to fire o
Ctag address 0.
• Command #8111 turns on RF port1 and sends the command on Ctag pin 0 to fire o
Ctag address 1.

MPRX Reader
TransCore Proprietary 7–3
• Command #8112 turns on RF port2 and sends the command on Ctag pin 1 to fire o
Ctag address 0.
• Command #8113 turns on RF Port 3 and sends the command on Ctag pin 1 to fire o
Ctag address 1.
• Command #8150 sets the check tag address to 0 on check tag pin 0.
• Command #8151 sets the check tag address to 1 on check tag pin 0.
• Command #8152 sets the check tag address to 0 on check tag pin 1.
• Command #8153 sets the check tag address to 1 on check tag pin 1.
Note: The MPRX transmits ID codes to the host device when the MPRX is in data mode.
Command Mode
While the MPRX is in the command mode, the host device sends commands to the MPRX
that can be used to control the reader operation and configuration. After the MPRX
receives a command, it transmits a command response message. Typically, the command
message contains Error, Done, or data relating specifically to the command request. These
messages may be of variable length since some commands require information as part of
the message; for example, #570 Display Operating Mode Status.
Communication can be lost if the host device attempts to send certain commands under
marginal communication conditions. For example, if the host device transmits the command
request to change the baud rate and the MPRX properly receives the request and transmits
the Done message, one of the two following conditions may occur:
1. If the host device receives the Done message, then both the host and the MPRX switch
to the new baud rate, and communications are maintained.
Note: In many applications, the host must be set to the new baud rate as it does not
change automatically.
Note: The MPRX changes the baud rate immediately after issuing the Done message.
2. However, if the host does not receive the Done message transmitted by the MPRX, the
host assumes that the command was not properly sent and does not switch to the new
baud rate, causing a loss of communications.
Caution
The host device should not attempt to change communications parameters
or protocols during marginal communications conditions; otherwise, a loss of
communication can result.
Download Mode
In download mode, the host can download new software to the MPRX.
While in download mode, the reader communications port parameters are fixed at the
following factory-default settings: 38400 baud, 8 data bits, 1 stop bit, no parity, software
flow control (XON/XOFF), basic protocol.
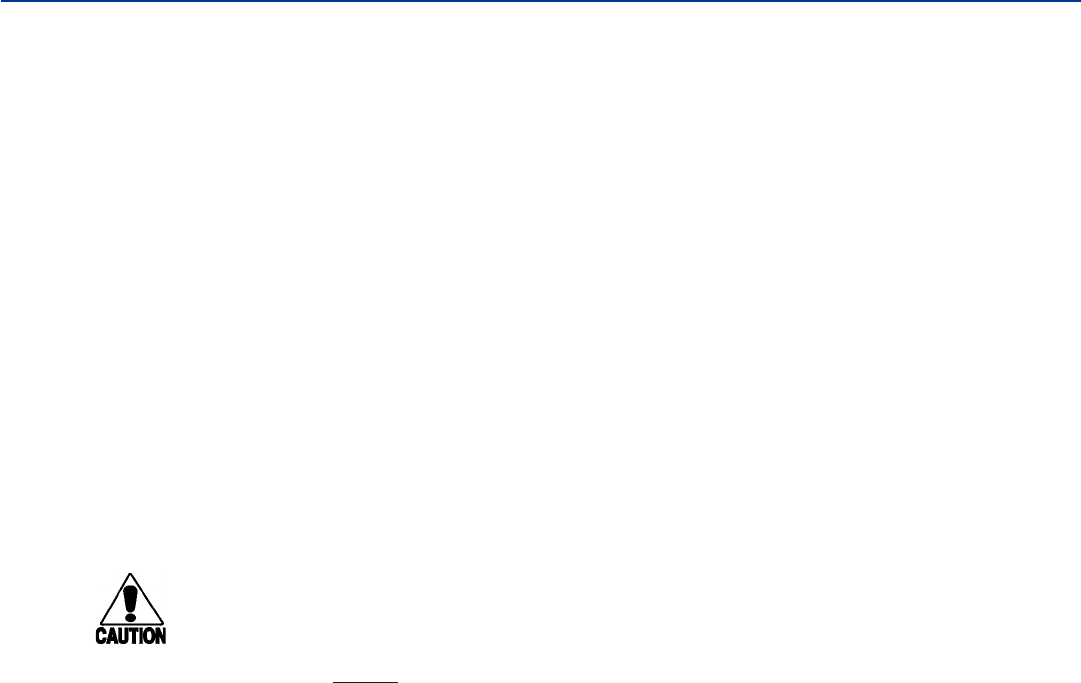
User Guide
TransCore Proprietary
7–4
While in download mode, the MPRX turns RF o, does not process tags, and does not
echo host commands.
Typically, TransCore trained personnel download new application code using a custom
firmware loader program.
Command List
Reader commands are divided into groups based on a primary function. The following
sections provide information about each command in command number order. Refer to
“Command Quick Reference” on page D–1 for listings of commands in numerical and
alphabetical order.
In the following text, the symbols < and > represent variable message data. These symbols
are not part of the message syntax.
Hex digits (0–9, A–F) in either uppercase or lowercase characters may be used in data
strings and for hex digits A–F.
Reader Mode Control — Command Group 0
Group 0 commands control reader mode. The mode determines whether the reader is
transmitting data to or receiving data from a host device or terminal.
00 Switch to Data Mode (Factory Default)
Command #00 switches the reader to data mode, which allows the reader to
transmit tag data (ID codes) to the host. In addition to switching the reader to data
mode, command #00 automatically saves to non-volatile memory (NVRAM) any user
parameters that had been changed during the command mode session. The reader
enters data mode on power up.
Caution
To save user parameter changes to non-volatile memory (NVRAM), you must send
command #00 before powering down the reader.
When MPRX mode has been enabled (#837) and while the MPRX is in data mode, the host
device can send the following commands to the MPRX:
• Command #01 Switch to Command Mode
Reader response:
Done
• Command #440 Reset Uniqueness
Reader response:
Done
• Command #8110 Switch on RF Port 0, Fire O Check Tag Address 0 on Check Tag
Pin 0
Reader response:
MPRX Reader
TransCore Proprietary 7–5
Done
• Command #8111 Switch on RF Port 1, Fire O Check Tag Address 1 on Check Tag Pin
0
Reader response:
Done
• Command #8112 Switch on RF Port 2, Fire O Check Tag Address 0 on Check Tag
Pin 1
Reader response:
Done
• Command #8113 Switch on RF Port 3, Fire O Check Tag Address 1 on Check Tag
Pin 1
Reader response:
Done
• Command #8150 Set Check Tag Address to 0 on Check Tag Pin 0.
Reader response:
Done
• Command #8151 Set Check Tag Address to 1 on Check Tag Pin 0.
Reader response:
Done
• Command #8152 Set Check Tag Address to 0 on Check Tag Pin 1.
Reader response:
Done
• Command #8153 Set Check Tag Address to 1 on Check Tag Pin 1.
Reader response:
Done
Note: The MPRX transmits ID codes to the host device when the MPRX is in data mode.
01 Switch to Command Mode
Command #01 switches the reader to command mode, which allows the reader to accept
commands from a host or terminal. While in command mode, the reader turns RF o and
does not acquire tags.
Reader response:
Done
Communications Port Control — Command Group 1
Group 1 commands configure the parameters used by the MPRX to communicate with a
host device or terminal. These commands set baud rate, stop bits, parity, and end-of- line
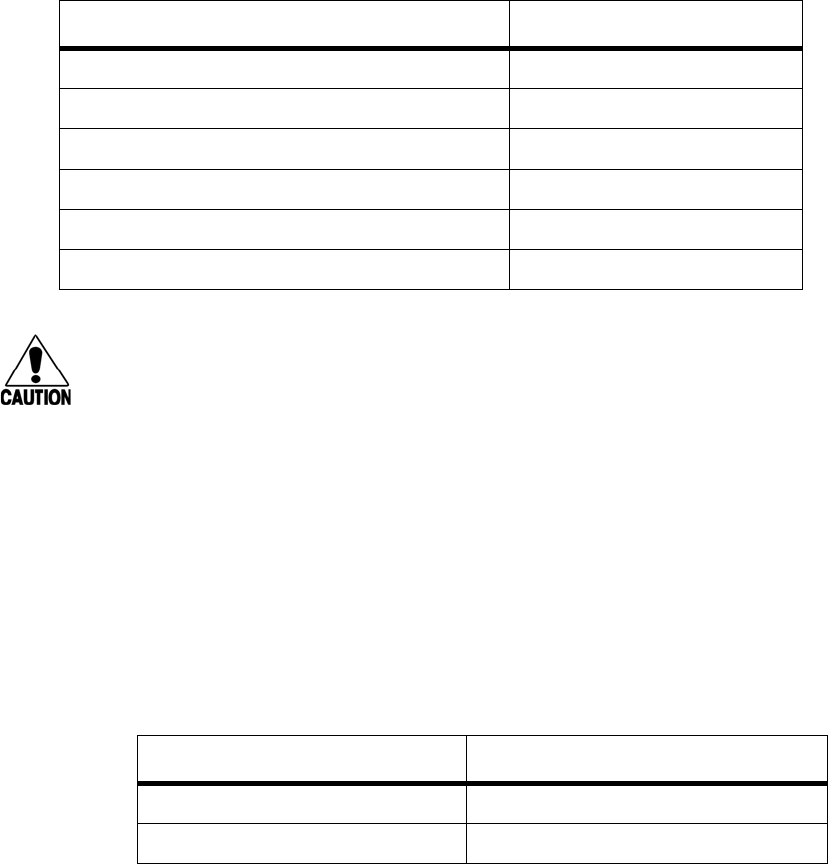
User Guide
TransCore Proprietary
7–6
delay.
100N Select Baud Rate
Command #100N selects the reader baud rate. The factory-default setting is 9600
baud. The N variable specifies the baud rate shown in Table 7 – 1.
Table 7 – 1 Select Baud Rate Commands
Caution
If ECP is enabled, ensure that the ECP timeout is sucient for the new baud rate.
Refer to “Timing and Synchronization” on page 6–9.
Reader response:
Done
101N Select Stop Bits
Command #101N selects the number of stop bits for reader character transmission. The
factory default setting is 1 stop bit. The N variable specifies the number of stop bits as
indicated in Table 7 – 2.
Table 7 – 2 Select Stop Bits Commands
Reader response:
Done
102N Select Parity
Command #102N selects the reader parity setting. The factory-default setting is parity
disabled. The N variable specifies parity as shown in Table 7 – 3.
Command Baud Rate Selected
1002 1200
1003 2400
1004 4800
1005 9600 (factory default)
1006 19.2 K
1007 38.4 K
Command Stop Bits Selected
1010 1 (factory default)
1011 2
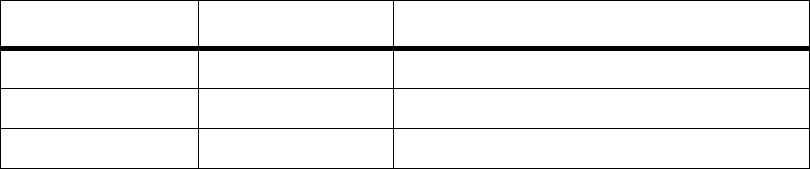
MPRX Reader
TransCore Proprietary 7–7
Table 7 – 3 Select Parity Commands
Reader response:
Done
Command Group 2
Group 2 commands control the real-time clock which maintains the MPRX internal time
and date. This time and date can be appended to IDs, error messages, and sensor input
reports. An internal battery supports the clock, so time and date are preserved if main
power is lost.
20 Set Time
Command #20 sets the time. Enter the time in the proper format: two-digit decimal entries
with no spaces between characters and using colons as delimiters.
The entry format is as follows:
20HH:MM:SS or 20HH:MM:SS:hh
where
HH
represents hours (00 to 23).
MM
represents minutes (00 to 59).
SS
represents seconds (00 to 59).
hh represents hundredths of a second (00 to 99).
:
is the time delimiter.
If hundredths of a second is not specified, the reader sets the hundredths register to 00.
Reader response:
Done
Command Data Bits Parity Selected
1020 8 Disable parity (factory default)
1021 7 Select even parity
1022 7 Select odd parity
User Guide
TransCore Proprietary
7–8
21 Set Date
Command #21 sets the date. Enter the date in the proper format: two-digit decimal entries
with no spaces between characters and using forward slashes “/” as delimiters. The entry
format is as follows:
21MM/DD/YY
where
MM
represents the month (01 to 12).
DD
represents the day (01 to 31).
YY
represents the last two digits of the year (00 to 99).
/
is the date delimiter.
Reader response:
Done
22 Display Time and Date
Command #22 displays the reader’s current time and date. One space separates the time
and the date output.
Reader response:
HH:MM:SS.hh MM/DD/YY
where
HH
represents hours.
MM
represents minutes.
SS
represents seconds.
hh represents hundredths of seconds.
:
is the time delimiter.
MM
represents the month.
DD
represents the day.
YY
represents the last two digits of the year.
/
is the date delimiter.

MPRX Reader
TransCore Proprietary 7–9
Append Information — Command Group 3
Group 3 commands append useful information to reader transmissions, such as IDs, error
messages, and sensor input reports. Auxiliary information such as reader number, antenna
number (or manual entry code), number of times the previous tag was read, and sensor
input status can be appended to the ID using the Group 3 commands.
30N Append Time and Date Selection
Command #30N selects the option of appending the time and date to transmitted IDs,
error messages, presence without tag reports, and input status change reports. The factory
default setting is time and date appended (command #302).
The reader returns an Error message if its tag buer contains data. The reset reader
command #63 may be transmitted to clear the buer; however, tag ID data will not be
reported. If this is unacceptable, allow the buer to empty before reissuing append time
and date command #30N. Append Time and Date commands are shown in Table 7 – 4.
Table 7 – 4 Append Time and Date Commands
The reader transmits messages with time and date appended as follows. One space
separates the time from the date.
<string>&<HH:MM:SS.hh MM/DD/YY>
where
string
is a tag ID, error message, or report.
&
separates <string> from the time and date.
HH:MM:SS is the time delimiter.
MM/DD/YY is the date delimiter.
Reader response:
Done
31N Append Auxiliary Information Selection
Command #31N selects the option of appending auxiliary information to transmitted IDs,
presence-without-tag reports, and input status change reports. Auxiliary information is
not appended to error messages. The factory-default setting is no auxiliary information
appended. The N variable specifies whether or not auxiliary information is to be appended.
Append Auxiliary Information commands are shown in Table 7 – 5.
Command Append Option
300 No time and date appended
302 Time and date appended (factory default)

User Guide
TransCore Proprietary
7–10
Table 7 – 5 Append Auxiliary Information Commands
The reader transmits messages with auxiliary information appended as:
<message data>%<xx-y-zz-q-sss>
where
%
separates the auxiliary information and signals the host
computer that
auxiliary information is appended.
xx
reader ID. Value can be set with command #60NN.
-
auxiliary information delimiter
y
antenna number.
zz
number of reads (00 to FF hexadecimal) of the previous tag on
this antenna
q
current status of input0 and input1 (0 to 3)
sss
relative to tag read strength
Note: If the MPRX mode is enabled (#837) and you are using the Train Recording Unit
(TRU™) as a host, a relative tag strength is appended to the end of the auxiliary data.
Reader response:
Done
ID Filtering — Command Group 4
Group 4 commands set criteria for filtering (buering or discarding) ID codes. These
commands are useful for eliminating duplicate ID codes and selecting the type of tags read
by the MPRX.
40 Transmit All ID Codes
Command #40 instructs the reader to transmit all IDs without regard for uniqueness.
This command can be useful when tuning the read zone and mapping the footprint or
performing diagnostics.
Command Append Option
310 No auxiliary information appended (factory default)
311 Auxiliary information appended
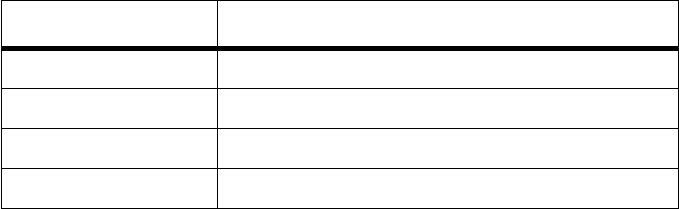
MPRX Reader
TransCore Proprietary 7–11
After diagnostics are complete, you may want to reinstate the uniqueness check using
command #410N Select Unique ID Code Criteria.
Reader response:
Done
410N Select Unique ID Code Criteria (Anti-passback Feature)
Command #410N instructs the reader to buer and transmit ID codes according to the
following test: an ID is read if previously decoded IDs have changed value at least N+1
times since the new ID was last received. IDs that do not pass the test are not reported. The
factory-default setting is command #4100, which selects a separation of one ID. Variable N
specifies ID separation as shown in Table 7 – 6.
Table 7 – 6 Unique ID Code Criteria
Each time the reader receives a tag ID, it compares the ID with the contents of a
comparison register. This register contains the following two items:
Item 1 Most recently acquired ID
Item 2 Second-most recently acquired ID
Item 3 Third-most recently acquired ID
Item 4 Fourth-most recently acquired ID
When the uniqueness filter is set to separation of one ID, the newly acquired ID is
transmitted only if it is dierent from the first item. Separation of two IDs allows transmission
if the new ID is dierent from Items 1 and 2 in the comparison register. Separation of three
and four IDs transmit the new ID only if it is dierent from the first three and the first four
items, respectively.
Note: A new ID can fail the filter test and not be transmitted; however, it remains stored
in the comparison register.
The uniqueness test has a time limit as set by command #44N. If an ID is buered, it will
not be accepted again unless it arrives at the reader more than the timeout value from the
previous arrival or until the receipt of one or more other IDs reset the uniqueness.
Command Uniqueness Criteria
4100 Separation of 1 ID (factory default)
4101 Separation of 2 IDs
4102 Separation of 3 IDs
4103 Separation of 4 IDs
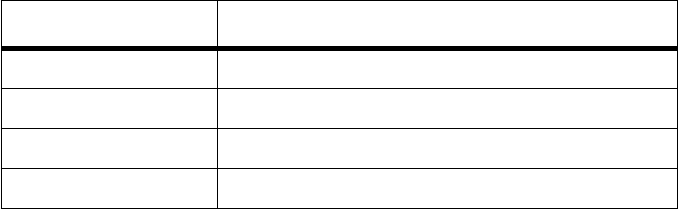
User Guide
TransCore Proprietary
7–12
Reader response:
Done
420N Select Valid ID Code Criteria
Command #420N directs the reader to validate an ID received only after it has been
obtained a specified number of times in sequence. Values for N are 1 through 4 (Table 7 – 7).
The factory setting is one acquisition (N = 0).
Table 7 – 7 Select Valid Code Commands and Frames
The validation procedure is executed before the unique ID test (Select Unique ID Code
Criteria [#410N] commands). IDs that do not pass the validation test are not reported.
For example, command #4203 specifies that the same ID must be obtained from the
antenna/RF module 4 times in succession before it is considered for the uniqueness test.
This feature is useful in installations where RF reflections may cause a single tag to be read
multiple times or where an occasional ID might be read from fringe areas
440 Reset Uniqueness
Command 440 causes the ID filtering process set by Select Unique ID Code Criteria
(#410N) to restart. It is used in conjunction with the Set Uniqueness Timeout
#44N) commands. This command provides a one-time reset at which point the previously set
timeout interval resumes. This command can be sent in data or command mode.
44N Set Uniqueness Timeout
Places a time limit on the uniqueness criterion set by Select Unique ID Code Criteria
(#410N). The parameter N sets the number of minutes on the timeout clock. The factory
setting is two minutes (N = 1).
Command Timeout Clock
#441 2 minutes (factory setting)
#442 15 seconds
#443 30 seconds
Entering these commands eectively expires the timeout clock, which erases all current
IDs in the comparison register. In eect, the first ID that is acquired after the clock expires
Command Valid Code Frames
4200 1 (factory default)
4201 2
4202 3
4203 4
MPRX Reader
TransCore Proprietary 7–13
always appears to be new and is stored. Newly acquired IDs are only tested against IDs
that are registered after the clock resets.
The timeout clock is continually reset (does not expire) as long as the reader receives the
same tag ID. For example, assume that the timeout clock is set for two minutes and there is
a railcar parked on a siding in front of the reader. Without this reset feature, the railcar’s ID
would be reported every two minutes (each time the timeout clock expired).
452 Disable Tag Translation Mode (Factory Default)
Command #452 disables tag translation mode. Incoming full-frame tags will be converted
directly to ASCII. They will not be translated from Association of American Railroads (AAR)
and American Trucking Associations (ATA) format to ASCII.
Reader response:
Done
453 Enable Tag Translation Mode
Command #453 enables the translation of tags in AAR and ATA formats. Specific data
fields, such as owner ID and car number, will be extracted from these tags, translated
according to AAR or ATA standards, and converted to ASCII. Tags that are not programmed
in AAR or ATA format will be converted directly to ASCII. The reader will not attempt to
translate data from half-frame or dual-frame tags.
Reader response:
Done
456 Enable SeGo Protocol Tag Initialization During Multi-tag Sort
(Factory Default)
Command #456 enables the reader to send the Super eGo® (SeGo) protocol tag initialize
command as part of the multi-tag sort function. When the reader sends the SeGo protocol
tag initialize command, all tags in the RF field reenter the sort process.
Reader response:
Done
457 Disable SeGo Protocol Tag Initialization During Multi-tag Sort
Command #457 disables the reader from sending the SeGo protocol tag initialize
command as part of the multi-tag sort function. Any SeGo protocol tags already identified
by the reader during the sort process will not be re-identified as long as they remain
powered in the RF field. The reader will only identify new tags that come into the RF field
or tags that do not remain powered in the RF field.
Reader response:
Done
480 Disable ATA
User Guide
TransCore Proprietary
7–14
Command #480 disables the reader from reading ATA protocol tags.
481 Enable ATA
Command #481 enables the reader to read ATA protocol data from tags if the reader is
programmed to read this tag protocol.
484 Disable SeGo
Command #484 disables the reader from reading SeGo protocol data from tags.
485 Enable SeGo
Command #485 enables the reader to read SeGo protocol data from tags if the reader is
programmed to read this tag protocol.
488 Disable eATA
Command #488 disables the reader from reading factory-programmed eATA data from
tags.
489 Enable eATA
Command #489 enables the reader to read factory-programmed eATA data from
SeGo protocol tags.
Reader Status — Command Group 5
Group 5 commands provide status reports on the parameters and operation of the reader.
505 Display Software Version
Command #505 displays the reader model number, software version information, and
assigned serial number.
Reader response:
Model E4 Series Ver X.XX SNSSSSSS
where
X.XX Version number
SSSSSS Serial number of the unit, skipping the fourth character printed on
the reader
product label
506 Display Hardware Configuration Information
Command #506 displays hardware configuration information stored in the reader memory
by the user. Hardware configuration information is empty by default until you set the
information to any 20 character ASCII string desired using command
#696S...S.
Reader response:
MPRX Reader
TransCore Proprietary 7–15
An ASCII string from 1 to 20 characters in length
520 Display Power Fail Bit
Command #520 displays the value of the reader power fail bit. The power fail bit changes
from 0 to 1 when power to the reader is interrupted. To reset the bit, use command #63
Reset Reader or command #65 Reset Power Fail Bit. On initial power-up, the host should
transmit one of these two commands to clear the power fail bit.
Reader response:
PWRB P<0 to 1> R0
where
P0
No power failure detected
P1
Power failure detected
R0
Not applicable to the MPRX
521 Display Reader ID Number
Command #521 displays the reader ID that is sent in the auxiliary data field. Reader
response:
RDID xx
where xx = 01 to FF (hexadecimal)
522 Display Communications Port Parameters
Command #522 displays the selected communications port parameters, including the baud
rate (#100N), the number of stop bits (#101N), the parity scheme (#102N), and the end-of-
line delay.
Reader response:
MAIN B<2 to 7> S<0 to 1> P<0 to 2> D0
where
B2
1200 baud
B3
2400 baud
B4
4800 baud
B5
9600 baud (factory default)
B6
19.2 kbps
B7
38.4 kbps
S0
one stop bit (factory default)
S1
two stop bits
User Guide
TransCore Proprietary
7–16
P0
no parity (factory default)
P1
even parity
P2
odd parity
D0
00 ms end-of-line delay (fixed)
One space is required between each value. For example, if factory default settings are
assigned, the reader message is
MAIN B5 S0 P0 D0
indicating 9600 baud, one stop bit, no parity, and 0-ms end-of-line delay.
Note: The information transmitted in response to command #522 applies to data and command
mode operation only. While operating in download mode, default communications parameters
are always used.
524 Display Appended Information Status
Command #524 displays the information being appended to the reader transmissions.
Command #31N appends information.
Reader response:
IDAP T<0 to 1> D<0 to 1> X<0 to 1>
where
T0
Time not appended
T1
Time appended
D0
Date not appended
D1
Date appended
X0
Auxiliary information not appended (factory default)
X1
Auxiliary information appended
One space is required between each value. For example, if factory-default settings are
assigned, the reader response is
IDAP T1 D1 X0
indicating time and date appended, and auxiliary information not appended.
525 Display Communications Protocol Status
Command #525 displays the status of command #610 Select Basic Communications
Protocol, command #611 Select Error Correcting Protocol, or #613 Enable Data Inquiry
Protocol, command #614N Selected Mode of Flow Control, and command
#612NN Error Correcting Protocol Timeout.
Reader response:
MPRX Reader
TransCore Proprietary 7–17
ECPS P<0 to 2> T<01 to FF> X<0 to 2> S0
where
P0
Basic protocol selected (factory default)
P1
ECP enabled
P2
data inquiry protocol enabled
Txx
ECP timeout where xx = 01 to FE (hexadecimal)
Timeout (ms) = 50 * xx
If xx = FF timeout disabled
X0
Flow control disabled
X1
Software flow control enabled (factory default)
S0
start of message character is #
For example, if factory default settings are assigned, the reader message is:
ECPS P0 TFE X1 S0
which means basic protocol selected, an ECP timeout of 254 (12,700 ms or 12.7 sec),
software flow control enabled, and start of message character is #.
527 Display RF Status
Command #527 displays the current status of the RF module. The reader response
indicates whether RF is controlled externally by the host, set by command #640N RF
Control, or internally by input set by command #641 (not applicable to the MPRX). RF always
is controlled by Sense0 and Sense1 when reader is in MPRX mode. Sense0 enables RF on
antenna ports 0 and 1, and Sense1 enables RF on antenna ports 2 and 3. Refer to “MUX
Operational Modes” on page 7–38. Command #527 also displays the current RF status
and the uniqueness timeout.
Note: If you enter RF settings using command #642NN, the display command for RF
output frequency, F is “Fxx” and indicates use of the backward-compatible frequency
entry method.
Reader response:
RFST C<0 to 1> O<0 to 1> T<1 to 3> Fxxx Rxx Gxx Axx Ixx
where
C0
RF controlled by host
C1
RF controlled by presence sensor on input0, the red/green pair
(factory
default)
O0
RF o
O1
RF on
User Guide
TransCore Proprietary
7–18
T1
Uniqueness timeout of two minutes
T2
Uniqueness timeout of 15 seconds
T3
Uniqueness timeout of 30 seconds
Fxxx RF output frequency, xxx = 000 to 118 hexadecimal oset in 250
kHz from
860 MHz. If an invalid frequency value is stored (corrupted NVRAM), then
xxx = “XXX” to indicate an error in the frequency setting.
Rxx
Tag decoder range (distance) for ATA tags, xx = 00 to 1F
hexadecimal range
value
Gxx
Tag decoder range (distance) for SeGo protocol tags, xx = 00 to
1F
hexadecimal range value
Axx
RF power attenuation, where 00 is maximum output power and
0A is
minimum output power (10dB less than maximum power).
I04
Fixed
For example, if factory default settings are assigned, the reader message is
RFST C1 O0 T1 Fxxx R1F G1F A00 I04
which means that RF is enabled by presence sensor on input0, RF signal o, uniqueness
timeout of two minutes, RF output frequency has not been set, maximum RF output range
for ATA tags, maximum RF output range for eGo and eGo Plus tags, full RF power, and IAG
power set at 4 dB attenuation.
529 Display Presence Input Status
Command #529 displays the parameters associated with presence detection and RF
control. The reader’s message indicates if presence without tag reports are enabled/
disabled (#690N Select Presence without Tag Report Option), if input inversion is enabled/
disabled (#694N Select Input Inversion Option), and the minimum presence true period
(always true). The reader’s message also reports the selected RF timeout (#693N Select
RF Timeout Period) and the selected means of RF-o control (#692N Select RF Control
Algorithm). If presence without tag reports is enabled (#6901 Enable Presence without
Tag Report Option), the reader transmits a report if a presence is detected without the
subsequent acquisition of a valid tag.
Note: RF timeout values vary depending on the operative tag read mode and the type
of tag in the read field. All times are approximate.
Reader response:
PRST P<0 to 1> D0 A<0 to 2> T<0 to F> I<0 to 1>
where
P0
Presence without tag reports disabled (factory default)
P1 Presence without tag reports enabled
MPRX Reader
TransCore Proprietary 7–19
D0 Minimum presence true period of 0 ms (fixed)
A0 RF o on timeout only
A1 RF o on timeout or tag
A2 RF o on timeout or presence condition false (factory default)
T0 RF timeout of 0 ms (always expired)
T1 4 ms
T2 8 ms
T3 12 ms
T4 20 ms
T5 24 ms
T6 32 ms
T7 48 ms
T8 60 ms
T9 92 ms
TA 152 ms
TB 300 ms
TC 452 ms
TD 600 ms
TE 752 ms
TF RF timeout infinite, never expires (factory default)
I0 input inversion disabled (factory default)
I1 input inversion enabled
For example, if factory default settings are assigned, the reader message is
PRST P0 D0 A2 TF I0
which means that presence without tag reports is disabled, minimum presence true period
is 0, RF o control on timeout or presence false, infinite RF timeout, and input inversion
disabled.
User Guide
TransCore Proprietary
7–20
530 Display RF0 Filter Status
Command #530 displays the parameter set for the RF input, including the selected unique
ID code criteria (#410N Select Unique ID Code Criteria) and the valid ID code criteria,
which are fixed at one acquisition.
Reader response:
RF0S U<0 to 4> V<0 to 3>
where
U0
One ID separation (factory default)
U1
Two ID separations
U2
Three ID separations
U3
Four ID separations
U4
Transmit all IDs
V0
Valid ID code criteria of one acquisition (factory default)
V1
Valid ID code criteria of two acquisitions
V2 Valid ID code criteria of three acquisitions
V3
Valid ID code criteria of four acquisitions
For example, if factory default settings are assigned, the reader message is
RF0S U0 V0
which means separation of one ID for uniqueness filtering and a valid ID code criteria of one
acquisition.
534 Display Tag Translation Mode Status
Command #534 displays tag translation mode status, enabled or disabled. If tag
translation mode is enabled, incoming full-frame tags in AAR or ATA format are translated
according to ISO standards. Refer to “452 Disable Tag Translation Mode (Factory
Default)” on page 7–13 and “453 Enable Tag Translation Mode” on page 7–13 for more
information.
Reader response:
TT <0 to 1>
where
0
tag translation mode disabled
1
tag translation mode enabled
MPRX Reader
TransCore Proprietary 7–21
537 Display Echo Status
Command #537 displays echo mode status. In basic protocol (#610 Select Basic
Communication Protocol) and data inquiry protocol (#613 Enable Data Inquiry Protocol), the
reader may be configured to enable (#6171 Enable Echo Mode) or disable (#6170 Disable
Echo Mode) the echo of received commands. Refer to sections 6170 Disable Echo Mode
and “6171 Enable Echo Mode (Factory Default)” on page 7-26 for more information.
Reader response:
ECHO <0 to 1>
where
0
Echo status disabled (factory default)
1
Echo status enabled
540 Display Flash Checksum
Command #540 displays the flash memory checksum. Reader response:
PCKS I0000 Exxxx
where
0000 Not applicable to the MPRX
xxxx Represents the four-byte ASCII representation of the flash
memory
checksum
543 Display Boot Checksum
Command #543 displays the boot ROM checksum. Reader response:
BCKS xxxx
where xxxx represents the four-byte ASCII representation of the boot ROM checksum.
549 Get User-Programmable Group Select Equals (GSE) Filter Data
Command #549 queries the reader for the user-programmable GSE filter data programmed
in the reader using command #697. The response data is formatted similar to the data in the
configuration command.
For example, if the command string shown in command #697 (refer to “697 Set User-
Programmable Group Select Equals (GSE) Filter” on page 7–34) was sent to a given
reader, the response to the #549 query command would be:
#A4 0A 0005014202024133
The reader response contains all the data fields repeated in the same sequence as
displayed in the User-Programmable GSE configuration command.
User Guide
TransCore Proprietary
7–22
552 Display Antenna Multiplexing Mode
Command #552 displays the antenna multiplexing mode When the MPRX mode is enabled,
the response is
Reader response:
MUX x<0 to 3> <MPRX>
where
x = 0 antenna multiplexing disabled, RF on port 0 only
x = 1 antenna multiplexing between RF ports 0 and 1 when sense0 active
x = 2 antenna multiplexing between RF ports 0 and 1 when sense0 active and RF
port 2 when sense1 active
x = 3 antenna multiplexing between RF ports 0 and 1 when sense0 active and RF
ports 2 and 3 when sense1 active
MPRX = MPRX mode selected
560 Request Sensor Status Change
Command #560 displays the sensor status change reporting. Not applicable to the MPRX
Reader response:
SSTC E<0 to 1> M<0 to 3>
where
E0
Input status change reports disabled (factory default)
E1
Input status change reports enabled
M0
Reporting disabled (factory default)
M1
Changes on input0 reported
M2
Changes on input1 reported
M3
Changes on either input reported
For example, if factory default settings are assigned, the reader message is
SSTC E0 M0
which means that input status change reports are disabled on both input0 and input1.
570 Display Operating Mode Status
Command #570 displays the currently selected tag read mode. Reader response:
ATA:<E, D> eGo:<I, F, D> SeGo:<I, F, D> IAG:<E, D> Sort:<E, D>
TMM0
where
MPRX Reader
TransCore Proprietary 7–23
I ID (64 bits)
E Enabled
F Full transaction (eATA)
D Disabled
TMM0 Fixed
577 Report Buered Handshakes
Command #577 reports the buered handshakes. When in MPRX mode and/or if antenna
multiplexing is enabled, the response is
Reader response:
HDSH C0 <ww> C1 <xx> C2 <yy> C3 <zz>
where
ww
count from port 0
xx
count from port 1
yy
count from port 2
zz
count from port 3.
Reader Control Functions — Command Group 6
Group 6 commands set reader control functions such as reader ID, communication
protocol, output pulse, and RF control.
60NN Set Reader ID Number
Command #60NN sets the reader ID that will be sent in the auxiliary data field (command
#311). Uppercase or lowercase characters are allowed for NN; for example, hex digits A
though F or a through f
where NN = 00 to FF (hex for 0 to 255, factory default = 00). Reader
response:
Done
610 Select Basic Communication Protocol (Factory Default)
Command #610 enables the basic communications protocol.
Reader response:
Done
611 Select Error Correcting Protocol
Command #611 enables the error correcting protocol.
Reader response:
Done

User Guide
TransCore Proprietary
7–24
Caution
Do not switch to ECP (command #611 Select Error Correcting Protocol) unless the host is
prepared to acknowledge each reader transmission.
612NN Select Error Correcting Protocol Timeout
Command #612NN selects the timeout interval for ECP. This timeout applies to the
transmission of tag, report, and error messages and to the receipt of host commands.
The transmit timeout is initiated immediately after the end-of-message sequence CR/ LF is
transmitted. If the host does not acknowledge the message within the specified interval,
the reader times out and retransmits the message.
The receive timeout is initiated upon receipt of the start-of-message character (#). If the
end-of-message character (CR) is not received within the specified interval, the reader
discards the partially received message and resets its receiver.
Uppercase or lowercase characters are allowed for NN; for example, hex digits A through F
or a through f.
The value for NN specifies the timeout interval as follows:
ms
50 * NN for NN = 01 to FE (1–254)
FE
Factory default (12,700 ms or 12.7 seconds)
FF
Disables the ECP timeout
Reader response:
Done
Caution
Ensure that the ECP timeout is sucient for a given baud rate. Refer to “Timing and
Synchronization” on page 6–9.
613 Enable Data Inquiry Protocol
Command #613 enable the data inquiry protocol. Refer to “Data Inquiry Protocol” on page
6–4 “ for more information.
Reader response:
Done
614N Select Flow Control Option
Command #614N selects the flow control option for reader-to-host communications. The
factory default setting is software flow control (XON/XOFF) enabled. In download mode,
flow control is not host-selectable; it is fixed at the default setting. However, during data
mode and command mode operation, the following flow control options are available. The
N variable specifies flow control as shown inTable 7 – 8.

MPRX Reader
TransCore Proprietary 7–25
Table 7 – 8 Flow Control Commands
Done
If the reader is configured for software flow control (XON/XOFF), it stops transmitting if it
receives an XOFF character (host software command 13H). It does not resume transmitting
until it receives an XON character (host software command 11H).
Note: TransCore recommends that XON/XOFF flow control be disabled while using the
ECP.
6170 Disable Echo Mode
Command #6170 disables the reader’s echo of received host commands. If operating
in basic protocol or data inquiry protocol, the reader echoes by default. As the reader
receives a host command, it echoes each character of the command. Once the entire
command has been received and processed, the reader transmits its response. If echoing
is disabled with command #6170, the reader does not echo the command, but only
transmits its response. The reader never echoes while in ECP or download mode operation.
Reader response:
Done
6171 Enable Echo Mode (Factory Default)
Command #6171 enables the reader to echo received host commands. Command
#6170 disables echo mode.
Reader response:
Done
63 Reset Reader
Command #63 resets the power fail bit, clears all buers, resets tag uniqueness, turns o
both output lines, transmits the sign-on message, and returns to the data mode.
Note: This command does not reset any other configuration parameters.
Command Flow Control Option
6140 Disable flow control
6141 Enable software flow control (factory default)
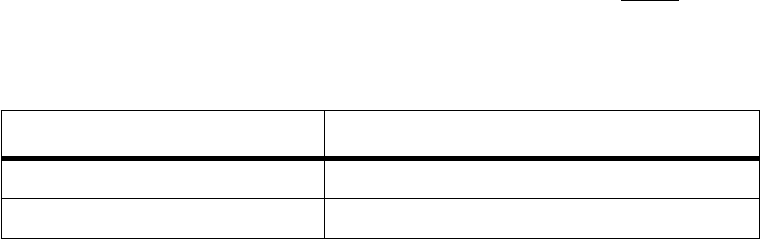
User Guide
TransCore Proprietary
7–26
Reader response:
Model E4 Series Ver X.XX SNSSSSSS
Copyright 2008 TransCore
where
X.XXD Version number
SSSSSS Serial number of the unit, skipping the fourth character printed on
the reader
product label.
640N RF Control
Command #640N directly controls the RF module. The N value controls the RF power as
shown in Table 7 – 9.
Note: These commands only have an eect when the reader is not in MPRX mode.
Refer to commands #836 and #837.
Table 7 – 9 RF Control Commands
Command #6400 disables RF-by-input control command #641 Select RF-by-Input
Control.
Reader response:
Done
Command RF Power
6400 Turns o RF
6401 Turns on RF
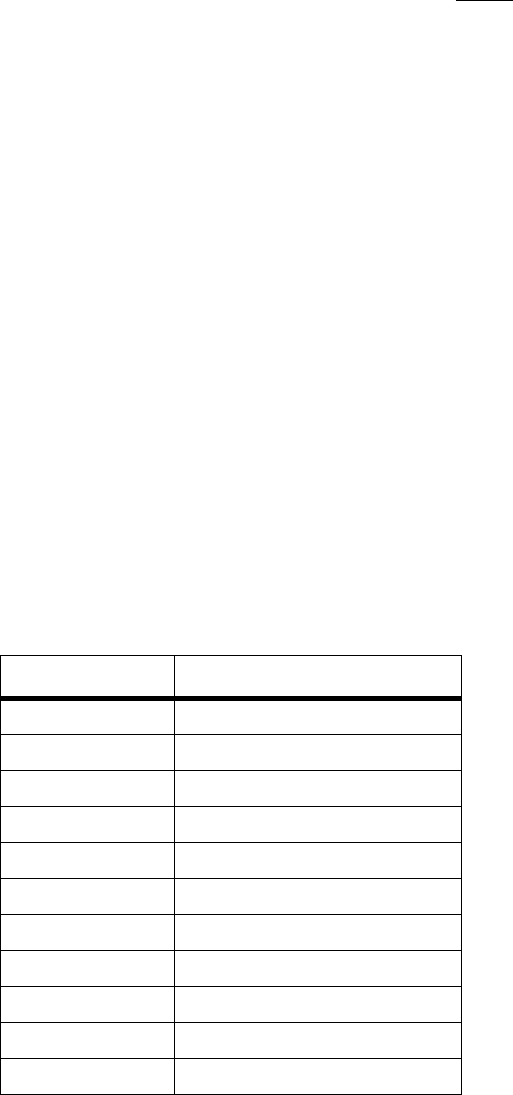
MPRX Reader
TransCore Proprietary 7–27
641 Select RF-by-Input Control (Factory Default)
Command #641 configures the reader for RF-by-input control. The reader automatically
turns on RF when it detects a presence through sense0. The reader turns o RF
according to the selected RF control algorithm (#692N Select RF Control Algorithm).
Note: This command only has an eect when the reader is not in MPRX mode.
Reader response:
Done
643NN Select ATA Operating Range (Distance)
Command #643NN selects the read range for ATA tags where NN is a hexadecimal value
from 00 to 1F; the range increases with increasing NN value. The range can be adjusted for
32 discrete values where 00 is the shortest range and 1F is the longest range. The default
range value is 1F.
Reader response:
Done
644NN Set RF Attenuation
Command #644NN sets the attenuation control for the output RF power where NN is a
hexidecimal value from 00 to 0A. Settings for attenuation are 1.0 dB increments over
a range of 10 dB of attenuation from the maximum power setting of 2 watts at 0dB
attenuation to a minimum power level of 200 milliwatts at 10-dB attenuation.
The Set RF Attenuation command NN variables and corresponding attenuation settings
are shown in Table 7 – 10.
Table 7 – 10 RF Attenuation Command Variables
Variable (NN) Attenuation Setting (dB)
00 0 (factory default)
01 1
02 2
03 3
04 4
05 5
06 6
07 7
08 8
09 9
0A 10
User Guide
TransCore Proprietary
7–28
Reader response:
Done
645NN Set SeGo Protocol Operating Range (Distance)
Command #645NN sets the read range for SeGo protocol tags where NN is a hexadecimal
value from 00 to 1F; the range increases with increasing NN value. The range can be
adjusted for 32 discrete values where 00 is the shortest range and 1F is the longest range.
The default range value is 1F.
Reader response:
Done
647XXX Select RF Operating Frequency
Command #647XXX sets the reader RF from 860 to 930 MHz in 250-kHz steps, where
XXX is a hexadecimal value from 000 to 118. After the reader’s frequency is set, the value is
stored in NVRAM. This value is not altered by power-down.
If the NVRAM becomes corrupted, the correct operating frequency cannot be guaranteed. In
this circumstance, the RF section shuts down and the reader sends an Error06 message to
the host. Until the frequency is reset using command
#647XXX, the unit displays the same error message each time it is powered up or if an
attempt is made to enable the RF by host or by external sensor.
Note: The authorized continuous wave (CW) frequency band for the MPRX in the U.S.
is 902.25 to 903.75 MHz and 910.00 to 921.50 MHz and the authorized modulated
frequency band for the MPRX in the U.S. is 911.75 to 919.75 MHz. The RF for each MPRX
at the site must be set according to the frequency specified in the FCC site license. Only
trained, authorized installation and maintenance personnel are permitted by FCC to set
the RF.
The commands to set the RF frequency are presented in Table 7 – 11.
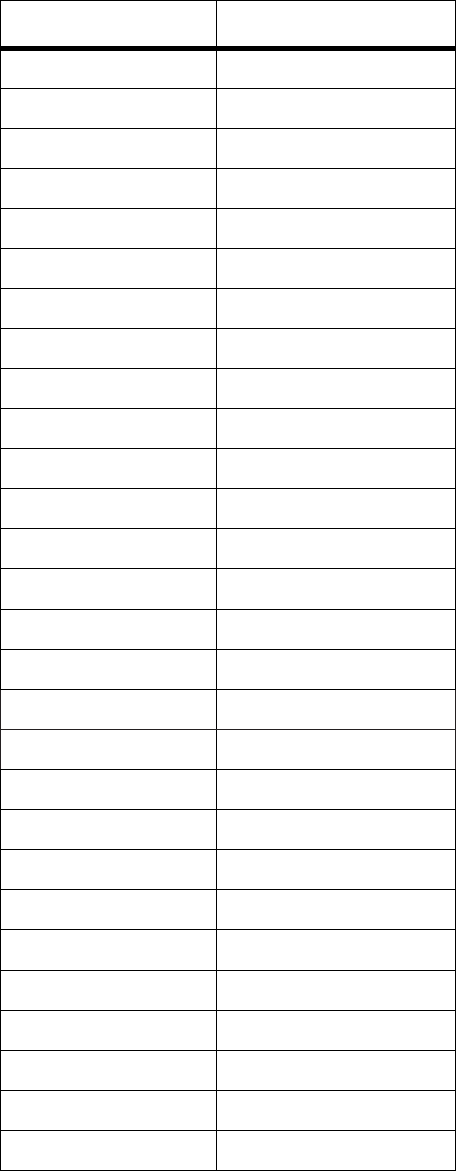
MPRX Reader
TransCore Proprietary 7–29
Table 7 – 11 Select RF Frequency Commands
Command RF Frequency (MHz)
647000 860.00
. .
. .
.
6470CF 911.75
6470D0 912.00
6470D1 912.25
6470D2 912.50
6470D3 912.75
6470D4 913.00
. .
. .
. .
6470EA 918.50
6470EB 918.75
6470EC 919.00
6470ED 919.25
6470EE 919.50
6470EF 919.75
. .
. .
.
657113 928.75
647114 929.00
647115 929.25
647116 929.50
647117 929.75
647118 930.00
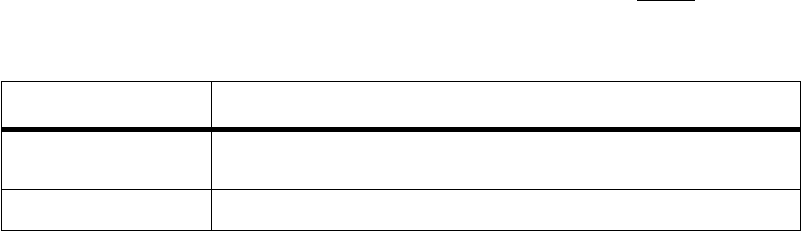
User Guide
TransCore Proprietary
7–30
Reader response:
Done
65 Reset Power Fail Bit
Command #65 resets the power fail bit to 0. The bit changes from 0 to 1 when power is
restored to the reader. Upon reader power-up, the host transmits either command
#65 or #63 Reset Reader to properly initialize this bit. The current state of the power
fail bit may be displayed. Refer to “520 Display Power Fail Bit” on page 7-16 for more
information.
Reader response:
Done
66F Load Default Operating Parameters
Command #66F loads all the factory default operating parameters except RF operating
frequency. Refer to Table 8-1, MPRX Default Configuration Settings” for a listing of the
defaults.
Reader response:
Done
All parameters loaded OK
Error
A parameter load failed
690N Select Presence Without Tag Report Option
Command #690N enables or disables the presence without tag report option. If the
presence without tag reporting option is enabled using command #6901, input reports are
transmitted when a tag presence is detected without the subsequent acquisition of a valid
tag. The value for N specifies the reports as shown in Table 7 – 12.
Note: These commands only have an eect when the reader is not in MPRX mode.
Table 7 – 12 Presence Without Tag Report Commands
Reader response:
Done
Refer to “Basic Protocol and ECP Format” on page 6-5 for message format information.
Command Report Option
6900 Disable presence without tag reports (factory default)
6901 Enable presence without tag reports
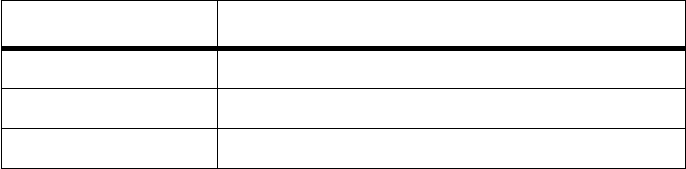
MPRX Reader
TransCore Proprietary 7–31
692N Select RF Control Algorithm
Command #692N selects the algorithm for turning o RF power when RF-by-input control
is enabled using command #641 Select RF-by-Input Control.
The values for N specify the RF control algorithms as shown in Table 7 – 13.
Table 7 – 13 RF Control Algorithm Commands
Command #6920 turns o RF power based on the timeout established by command
#693N Select RF Timeout Period.
Command #6921 allows RF power to be turned o either after the timeout period or upon
acquisition of a valid tag ID, whichever occurs first.
Command #6922 turns o RF power either after the timeout period or upon the presence
false condition, whichever occurs first.
Reader response:
Done
693N Select RF Timeout Period
Command #693N selects the RF timeout period used by command #692N Select RF
Control Algorithm. Values for N range from 0 through F.
Command #693F disables the RF timeout. The reader turns o the RF immediately
following the acquisition of a valid tag, whether or not it is unique.
Uppercase or lowercase characters are allowed for N; for example, hex digits A through F
or a through f. The commands and corresponding timeouts are shown in Table 7 – 14.
Command RF Power O
6920 On timeout only
6921 Timeout or tag ID acquired
6922 Timeout or presence false (factory default)
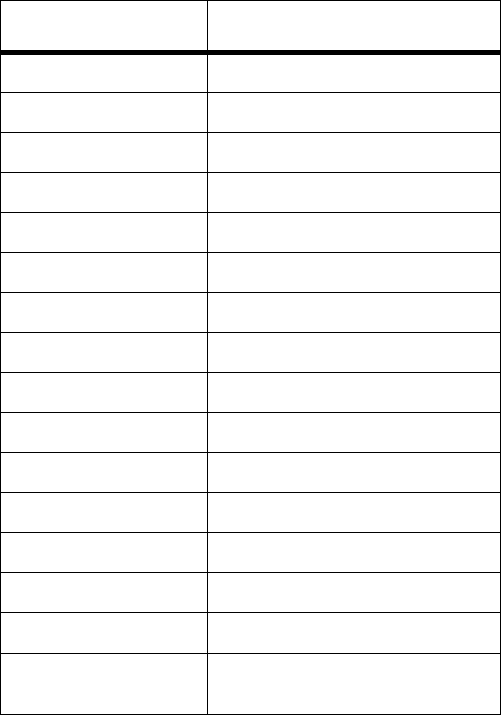
User Guide
TransCore Proprietary
7–32
Table 7 – 14 Timeout Period Values
Reader response:
Done or Error.
The reader returns an Error message if a valid hexadecimal digit is not substituted for N in
command #693N.
Note: This command only has an eect when the reader is not in MPRX mode.
694N Select Input Inversion Option
Command #694N enables or disables input inversion. When inversion is enabled, an open
circuit input is interpreted as a closed circuit, and a closed circuit input is interpreted as an
open circuit. This feature allows greater flexibility in the attachment of external equipment
to the reader inputs. For example, some proximity sensors indicate presence with an open
circuit. In this instance, command #6941 can enable input inversion so that an open circuit
input indicates a presence. The values for N represent the two inversion options as shown
in Table 7 – 15.
Command Timeout (ms)
6930 0 (always expired)
6931 4
6932 8
6933 12
6934 20
6935 24
6936 32
6937 48
6938 60
6939 92
693A 152
693B 300
693C 452
693D 600
693E 752
693F Infinite (never expires,
factory default)

MPRX Reader
TransCore Proprietary 7–33
Table 7 – 15 Input Inversion Options
Reader response:
Done
695S...S Set Serial Number (Factory Default)
Command #695 assigns the reader serial number according to the format:
695SSSSSS
where SSSSSS is the serial number.
The serial number may contain as many as six uppercase or lowercase ASCII alphanumeric
characters.
Note: The factory-assigned serial number of the reader contains seven characters.
However, to maintain backward compatibility, the reader software allows only six
characters to be entered. When setting the serial number, skip the fourth (middle)
character of the seven-character number shown on the reader product label.
Note: Once assigned, the serial number is preserved during power-down and the
loading of default parameters.
Reader response:
Done
696S...S Store Hardware Configuration String (Factory Default)
Command #696S...S stores hardware configuration information into reader memory.
The hardware configuration string is assigned according to the following format:
696S...S
where S...S is the hardware configuration string that may contain as many as 20
uppercase or lowercase ASCII alphanumeric characters.
Note: Once assigned, configuration information is preserved during power-down and
the loading of default parameters.
Reader response:
Done
Command Option
6940 Disable input inversion (factory default)
6941 Enable input inversion
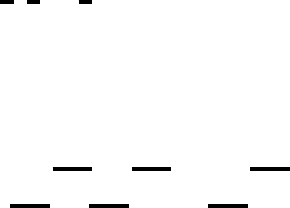
User Guide
TransCore Proprietary
7–34
697 Set User-Programmable Group Select Equals (GSE) Filter
Command #697 sets the user-programmable GSE filter.
The command string is assigned according to the following format:
697 MM AA DDDDDDDDDDDDDDDD
where
MM = The tag uses this mask to determine which of the eight Comparison Data bytes are to
be compared for the Group Select filter.
AA = This field is used by the tag to determine the start address in the tag memory for the
comparison data.
DD…DD = Comparison Data: an 8-byte field (16 characters) used by the tag as the
comparison data for the Group Select filter. The tag compares the data in this field to data
in tag memory beginning at the Start Address to determine if the tag will respond to a reader
Group Select request. Only the bytes having the corresponding bit set in the GSE Mask is
used for this comparison.
As an example, to configure a reader to have only tags with data in byte locations 10, 12,
and 15 (decimal) with hexadecimal values “00,” “01,” and “02,” the following command is
used:
#697 A4 0A 0005014202024133
To understand how the data is interpreted, it is necessary to break down the GSE Mask field,
A4, into binary:
A4 = 1010 0100
This mask equates to the tag comparing the first, third, and sixth bytes of the Comparison
Data to data in the tag beginning at address location 0A (10 decimal).
The Comparison Data field is broken down in bytes with the bytes corresponding to the
mask underlined in bold (for clarification):
Address: 0A 0B 0C 0D 0E 0F 10 11
Data: 00 05 01 42 02 02 41 33
where
0A (10 decimal) must be equal to “00” hexadecimal, the first byte in the Comparison Data
field
0C (12 decimal) must be equal to “01” hexadecimal, the third byte in the Comparison Data
field
0F (15 decimal) must be equal to “02” hexadecimal, the sixth byte in the Comparison Data
field
Reader response:
Done
MPRX Reader
TransCore Proprietary 7–35
Auxiliary Reader Control — Command Group 8
Group 8 commands provide control of reader functions, such as the sense input lines.
8110 Switch on RF Port 0, Fire O Check Tag Address 0 on Check Tag
Pin 0
Command #8110 turns on RF Port 0 and sends the command on Ctag pin 0 to fire o Ctag
address 0.
8111 Switch on RF Port 1, Fire O Check Tag Address 1 on Check Tag
Pin 0
Command #8111 turns on RF Port 1 and sends the command on Ctag pin 0 to fire o Ctag
address 1.
8112 Switch on RF Port 2, Fire O Check Tag Address 0 on Check Tag
Pin 1
Command #8112 turns on RF port2 and sends the command on Ctag pin 1 to fire o Ctag
address 0.
8113 Switch on RF Port 3, Fire O Check Tag Address 1 on Check Tag
Pin 1
Command #8113 turns on RF Port 3 and sends the command on Ctag pin 1 to fire o Ctag
address 1.
8142X Set Check Tag Character on Check Tag Pin 0
Command #8142X sends the command on Ctag pin 0 to set the Ctag character.
8143X Set Check Tag Character on Check Tag Pin 1
Command #8143X sends the command on Ctag pin 1 to set the Ctag character.
8150 Set Check Tag Address to 0 on Check Tag Pin 0
Command #8150 sets the check tag address to 0 on check tag pin 0.
8151 Set Check Tag Address to 1 on Check Tag Pin 0
Command #8151 sets the check tag address to 1 on check tag pin 0.
8152 Set Check Tag Address to 0 on Check Tag Pin 1
Command #8152 sets the check tag address to 0 on check tag pin 1.
8153 Set Check Tag Address to 1 on Check Tag Pin 1
Command #8153 sets the check tag address to 1 on check tag pin 1
User Guide
TransCore Proprietary
7–36
830 Disable Automatic Periodic RF Status Report (Factory Default)
Command #830 is a default set in the factory to disable the automatic periodic RF
status report.
Reader response:
Done
831 Enable Automatic Periodic RF Status Report
Command #831 enables the automatic periodic RF status report. This function sends out
a periodic RF status report if no other message (a tag read) is sent from the reader for a
period of time. This message is the same message that would be sent in response to the
#527 Display RF Status command. Enabling this function is helpful in some sites where
there may not be much tag activity, and the user wants an automatic way to ensure the
communication channel with the reader is still intact. With this function enabled, the host
system will get a message from the reader at least every three minutes.
Reader response:
Done
836 Disable MPRX Mode
Command #836 disables the MPRX mode. Reader
response:
Done
837 Enable MPRX Mode
Command #837 enables the MPRX mode.
Reader response:
Done
836 Disable AI1200 Emulation Mode
Command #842 disables the AI1200 Emulation mode. Reader
response:
Done
837 Enable AI1200 Emulation Mode
Command #843 enables the MPRX mode.
Reader response:
Done
850 MUX RF Port 0 (Factory Default)
Command #850 enables RF Port 0, which disables antenna multiplexing.
Reader response:
Done
MPRX Reader
TransCore Proprietary 7–37
851 MUX Between RF Ports 0 and 1
Command #851 multiplexes between RF ports 0 and 1.
Reader response:
Done
852 MUX Between RF Ports 0, 1, and 2
Command #852 multiplexes between RF ports 0, 1, and 2.
Reader response:
Done
853 MUX Between RF Ports 0, 1, 2, and 3
Command #853 multiplexes between RF ports 0, 1, 2, and 3.
Reader response:
Done
891 MUX Test Mode RF Port 1 Only
Command #891 turns on RF port 1 only for antenna mux testing.
Reader response:
Done
Note: Refer to “MUX Test Modes” on page 7–39 for test operation.
892 MUX Test Mode RF Port 2 Only
Command #892 turns on RF port 2 only for antenna mux testing.
Reader response:
Done
Note: Refer to “MUX Test Modes” on page 7–39 for test operation.
893 MUX Test Mode RF Port 3 Only
Command #893 turns on RF port 3 only for antenna mux testing.
Reader response:
Done
Note: Refer to “MUX Test Modes” on page 7–39 for test operation.
User Guide
TransCore Proprietary
7–38
Check Tag Operation
To enable check tag 0, issue the following commands
#8110 – turn on RF port0, send the command on Ctag pin 0, to fire o Ctag address 0.
#8111 – turn on RF port1, send the command on Ctag pin 0, to fire o Ctag address 1.
#8142X – send the command on Ctag pin 0 to set the Ctag character.
#8150 – send the command on Ctag pin 0 to set the Ctag address to 0.
#8151 – send the command on Ctag pin 0 to set the Ctag address to 1.
To enable check tag 1, issue the following commands
#8112 – turn on RF port2, send the command on Ctag pin 1, to fire o Ctag address 0.
#8113 – turn on RF port3, send the command on Ctag pin 1, to fire o Ctag address 1.
#8143X – send the command on Ctag pin 1 to set the Ctag character.
#8152 – send the command on Ctag pin 1 to set the Ctag address to 0.
#8153 – send the command on Ctag pin 1 to set the Ctag address to 1.
MUX Operational Modes
To enable antenna multiplexing (muxing) operational modes, issue the
following commands
#836/#837 – Disable/enable MPRX mode
#850 – RF port 0 only (factory default)
#851 – mux between RF ports 0 and 1
#852 – mux between RF ports 0, 1, and 2
#853 – mux between RF ports 0, 1, 2, and 3
#552 – Display mux setting. This display message will include “MPRX” if MPRX mode is
enabled (#837).
When MPRX mode is disabled, the reader will continuously step through each port that
has been enabled with #85X, stepping through whichever tag protocols are enabled on
each port, in order. The reader turning RF on will be qualified “RF on by sense” setting.
Command #6401 is used to turn RF on continuously and bypass the RF on by sense.
Sense0 is used for all antennas that are enabled, if RF is turned on by sense, #641.
When MPRX mode is enabled, you must use Sense0 and Sense1 to turn on RF and read
tags. Sense0, when shorted to reader signal ground, will enable tag reads on RF ports 0
and 1 (if enabled with #851) and Sense1 will enable tag reads on Ports 2 and 3 (if enabled
with #853). For example, if commands #837 and #853 have been entered, Sense0 is open,
MPRX Reader
TransCore Proprietary 7–39
Sense1 shorted, and the reader is in data mode, the reader will attempt tag reads toggling
between RF ports 2 and 3 only. Smart muxing, ATA tag data sning, and ATA dwell of two
handshakes per antenna is automatic in MPRX mode.
MUX Test Modes
To enable antenna muxing test modes, issue the following commands
#891 – RF port 1 only
#892 – RF port 2 only
#893 – RF port 3 only
To use these test modes, MPRX mode must be disabled (#836) and muxing must be
disabled (#850). These command modes are not saved to NVM, and will be cleared by
a power cycle of the reader, or by enabling either MPRX mode or muxing. When these
modes are enabled, the reader will continually run through whichever tag protocols have
been enabled, but only on the selected RF port. These test mode commands are qualified
by the RF on by sense settings. Use #6401 to disable RF on by sense, if desired.

Chapter 8
Configuring the MPRX
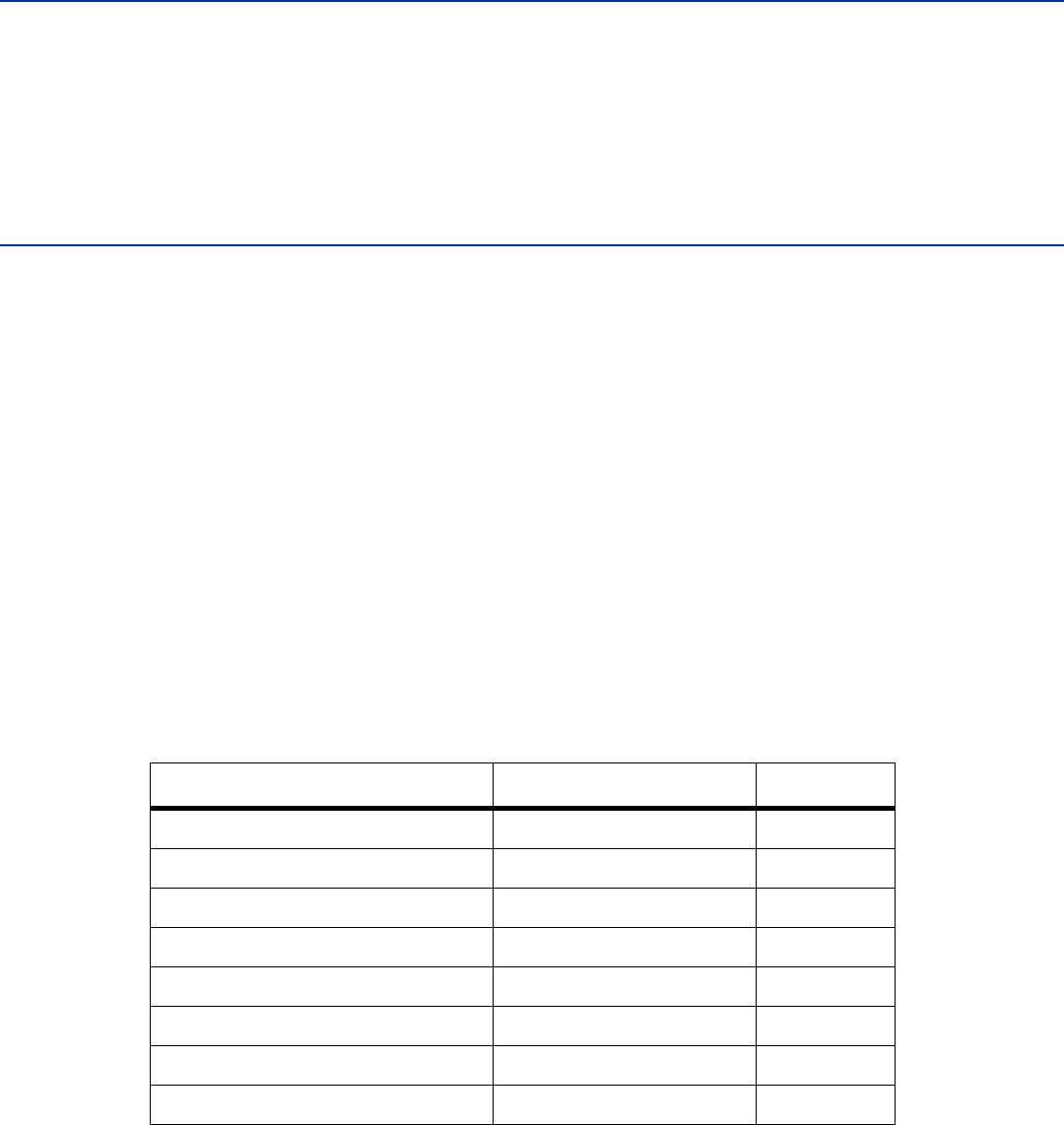
System Guide
TransCore Proprietary
8–2
Chapter 8 Configuring the MPRX
This chapter provides instructions for configuring the Multiprotocol
Reader Extreme (MPRX). The information includes factory configuration
parameter defaults and instructions for using terminal emulation
software to verify and change the MPRX factory configuration defaults.
Configuring the Reader
After installing the MPRX, you need to configure its operating parameters. Terminal settings
should be initially set at 9600 baud, 8 data bits, no parity, 1 stop bit, and no flow control.
Default Operating Parameter Settings
Table 8 – 1 contains the factory default configuration settings for the MPRX operating
parameters. The default configuration settings may not be the correct operating
configuration settings for a specific site. Changes to the configuration settings may have
to be made, depending on the site plan, as described in “Chapter 2 Developing the Site
Plan” on page 2–2 Review the default configurations shown in Table 8 – 1 to determine
which parameters, in addition to operating frequency and operating range, need to be
adjusted. Refer to “Chapter 7 Commands” on page 7–2 for a complete list of parameters
and the corresponding commands.
Note: The dual-protocol MPRX internal timing varies depending on the operative tag
read mode and the type of tag in the read field.
Table 8 – 1 MPRX Default Configuration Settings
Parameter Setting Command
Operating mode Data 00
Baud rate 9600 1005
Stop bits 1 1010
Parity None 1020
Time and date appended Enabled 302
Auxiliary information appended Disabled 310
Unique ID code criteria Separation of 1 ID 4100
Tag translation mode Disabled 452
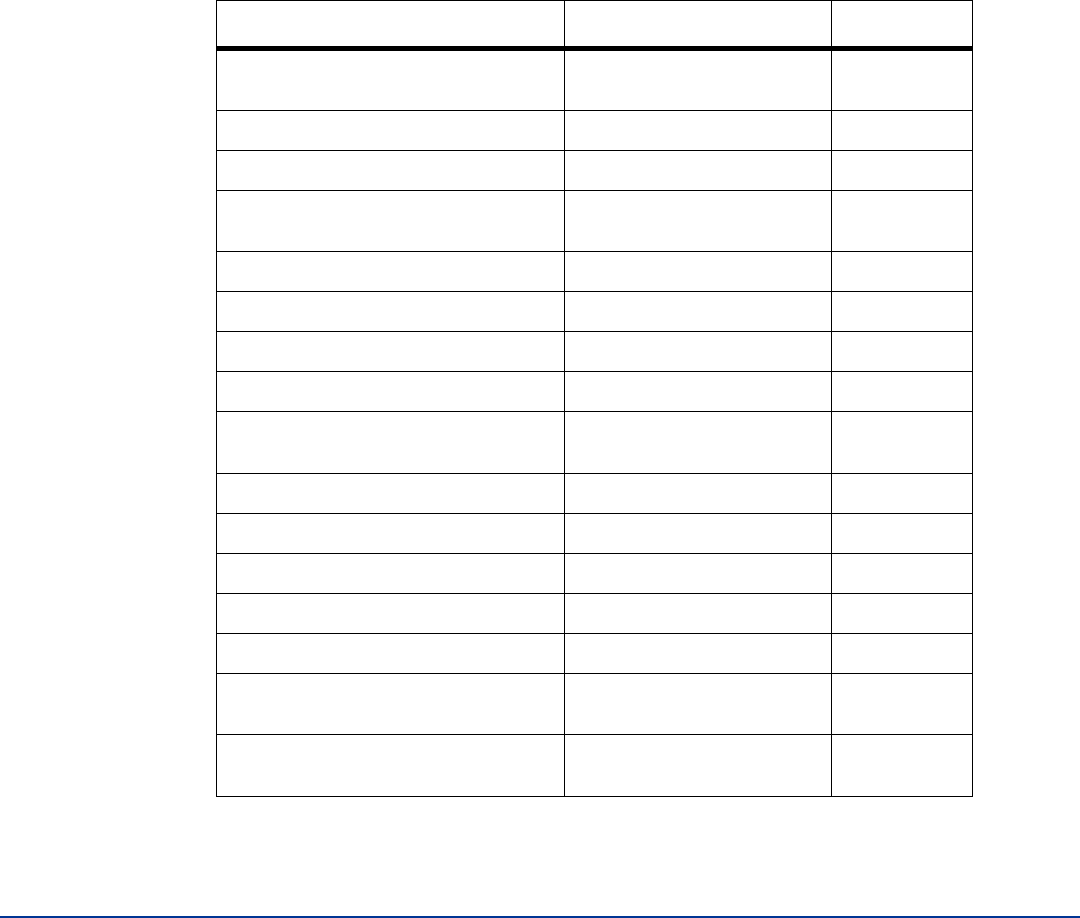
MPRX
TransCore Proprietary 8–3
Parameter Setting Command
SeGo protocol tag initialization
during multi-tag sort
Enabled 456
Reader ID number 00 6000
Communications protocol Basic 610
Error correcting protocol (ECP)
timeout
12.7 sec 612FE
Flow control Software (XON/XOFF) 6141
Echo mode Enabled 6171
ATA operating range Maximum 6431F
RF attenuation Full power 64400
SeGo protocol tag operating
range
Maximum 6451F
Presence without tag reports Disabled 6900
RF-o control Timeout or no presence 6922
RF timeout Never true 693F
Input inversion Disabled 6940
Serial number SSSSSS 695
Store hardware configuration Hardware configuration
not known
696
Automatic periodic RF status
report
Disabled 830
Configuring Parameters with Terminal Emulation
Software
To configure the MPRX using a PC and terminal emulation software to manually enter
MPRX host commands, follow the instructions in the section “Connecting the MPRX to the
Host” on page 4–12 Then, enter the appropriate configuration commands through the
terminal emulation software on the host.
Refer to “Chapter 7 Commands” on page 7–2 for a detailed description of all available
configuration commands.
Starting the Terminal Emulation Software
You can use a PC and any terminal emulation software to enter the host commands to
download flash software, configure reader operating parameters, perform diagnostics,
and retrieve tag data. The following procedures show examples using Hyper Terminal, an
application included with Microsoft Windows. Most terminal emulation applications have a
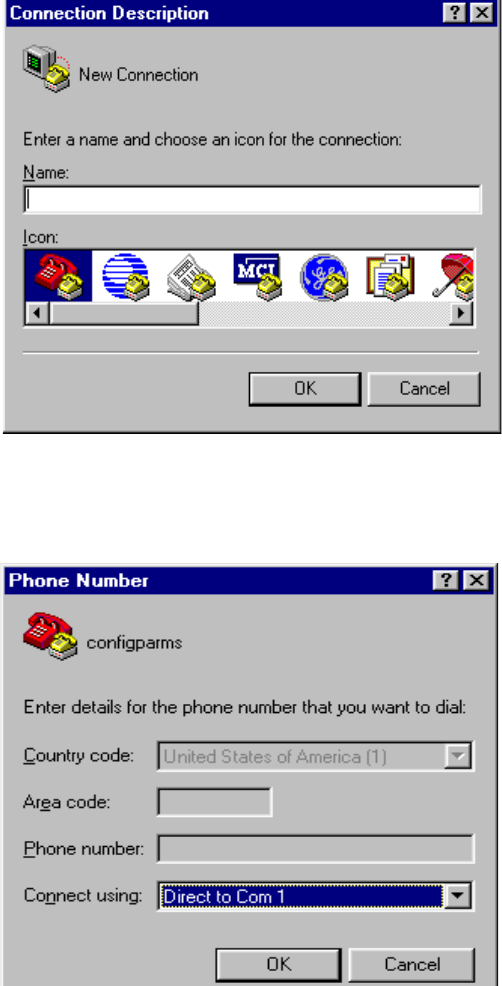
System Guide
TransCore Proprietary
8–4
similar sequence for launching.
To start the terminal emulation software
1. At the command prompt, type your terminal emulation start command; or if using
Windows Hyper Terminal, select:
Programs>Accessories>Hyperterm and press ENTER.
The application displays the Connection Description dialog box as shown in
Figure 8 – 1
Figure 8 – 1 Connection Description Dialog Box
2. Enter a name for the session and click OK. The application displays the Phone Number
dialog box as shown in Figure 8 – 2.
Figure 8 – 2 Phone Number Dialog Box
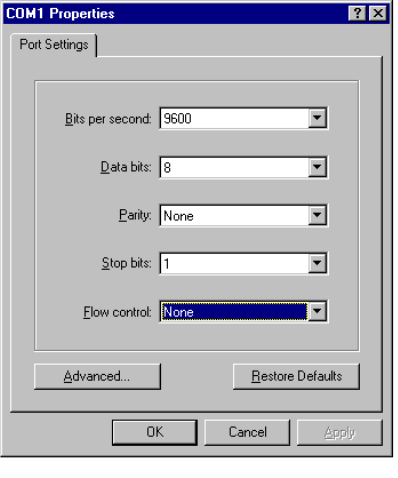
MPRX
TransCore Proprietary 8–5
3. From the Connect using pull-down list, choose the Com 1 option (or whichever com
port on the PC to which the RS-232 cable is attached) and click OK.
The application displays the COM1 Properties dialog box as shown in Figure 8 – 3.
Figure 8 – 3 COM 1 Properties Dialog Box
4. In the pull-down lists on the COM1 Properties dialog box, choose the following values:
• Bits per second: 9600 baud
• Data bits: 8
• Parity: None
• Stop bits: 1
• Flow control: None
Click OK.
The application displays the configparms –Hyper Terminal main screen as shown in
Figure 8 – 4.
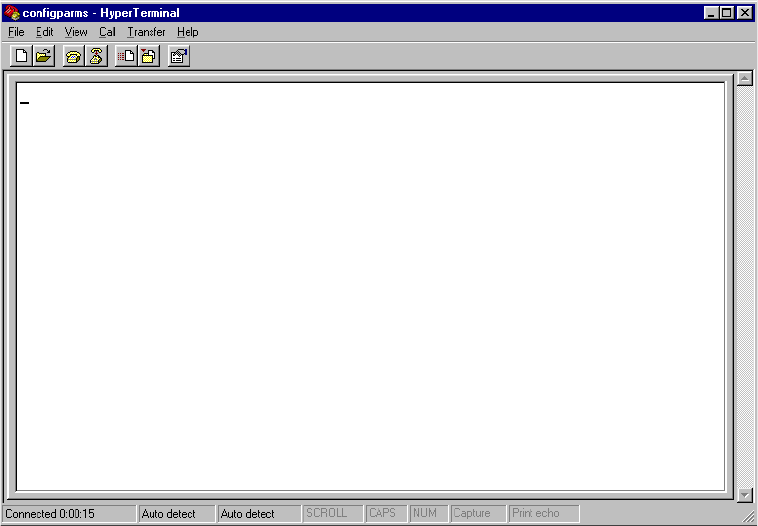
System Guide
TransCore Proprietary
8–6
Figure 8 – 4 Hyper Terminal Main Screen
Verifying Communications
You must verify that the MPRX and the PC or laptop are communicating.
To verify communications
1. Start the terminal emulation application as described in”Starting the Terminal Emulation
Software” on page 8–3.
Note: When testing the MPRX using a laptop computer, TransCore recommends that
you configure laptop communication parameters to match those of the host device to
which the MPRX will be connected after testing and configuration are completed.
2. Cycle the power on the MPRX.
Upon startup, the MPRX transmits a sign-on message, displayed on the terminal
emulation screen as shown in Figure 8 – 5, or a boot ROM failure message.
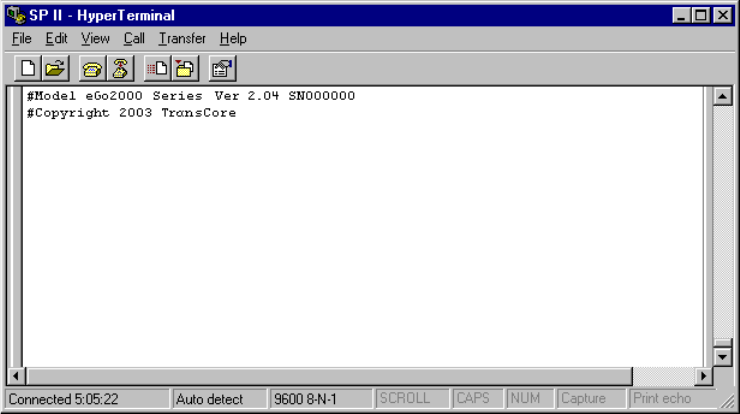
MPRX
TransCore Proprietary 8–7
Figure 8 – 5 Sign-on Message
The sign-on message appears as follows at a baud rate of 38,400 bps:
Model [software version] SNSSSSSS [Copyright notice]
where SSSSSS is the serial number assigned to the MPRX skipping the fourth character
printed on the reader product label.
Serial number 000000 is the default setting and is not a valid number. If this number
appears in the sign-on message, the serial number has not been stored into reader
memory. Contact TransCore Technical Support at 505-856-8007.
If the flash memory checksum is not verifiable, the sign-on message appears as follows:
Model [E4 BOOT] Ver 0.00 A
[Copyright notice]
If the failure message version number equals 0.00 E and no serial number exists, the
flash memory checksum has failed, and the MPRX is operating out of boot ROM. In this
case, the MPRX automatically enters download mode and waits for a new program to be
loaded into the flash memory. Follow the instructions in “Program Download” on page
5–4 .
Communications can also be verified by using the command sequence in Table 8 – 2.
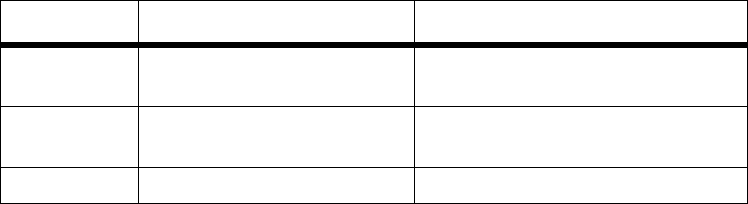
System Guide
TransCore Proprietary
8–8
Table 8 – 2 Command Sequence to Verify Communications
Entry MPRX Response Notes
#01 <CR> #Done <CR/LF> Switches the MPRX to command
mode
#505 <CR> #Model E4 Series Ver
X.XX SN97001P <CR/LF>
Reports the software version
and serial number
#00 <CR> #Done <CR/LF> Returns the MPRX to data mode
3. If a successful sign-on message is not returned, check connections and
communications factors and correct any errors.
To check connections and communications factors
1. Confirm that the MPRX has power.
2. Verify the connections between the PC and the MPRX.
3. Verify the receive (Rx) and transmit (Tx) connections.
4. If using handshaking, verify the request to send (RTS) and clear to send (CTS)
connections.
5. Verify the COM port settings for the MPRX following the instructions in “Serial Port
Communications” on page 8–15 .
Repeat the procedures in “Verifying Communications” on page 8–6.
If you still cannot verify the MPRX and PC communications, contact TransCore Technical
Support.
Verifying Tag Read Capability
After verifying communications between the MPRX and the PC, verify the capability to read
tags. The test tag should match the tag type and protocol of the tags that your system will
be reading.
The polarization of the test tag must be aligned in the same direction as the antenna.
Figure 8 – 6 shows horizontally polarized antenna and tag.
Note: Matching the tag and antenna polarization is critical to obtain optimal system
performance.
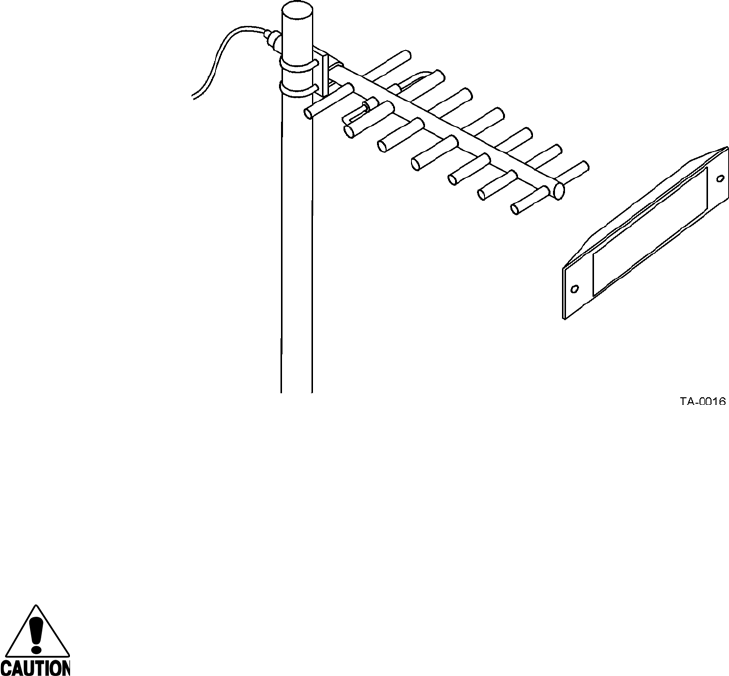
MPRX
TransCore Proprietary 8–9
Figure 8 – 6 Tag and Antenna Orientation (horizontal polarization)
The test tag must be mounted flush against a metal backplane.
Note: The default tag read mode of the reader is the protocol(s) programmed into the
reader. Use only those test tags programmed with the correct protocol(s) for the reader.
Caution
To avoid damage to the MPRX, you must connect the antenna before applying power
to the reader.
To verify tag read capability
1. Once communications are verified, enter the following sequence of commands to turn
on continuous RF:
• #01
• #6401
• #40
• #00
2. Pass one test tag in front of the active MPRX antenna. If the MPRX reads the tag, the
terminal emulation application displays the tag information on the screen as shown in
Figure 8 – 7.
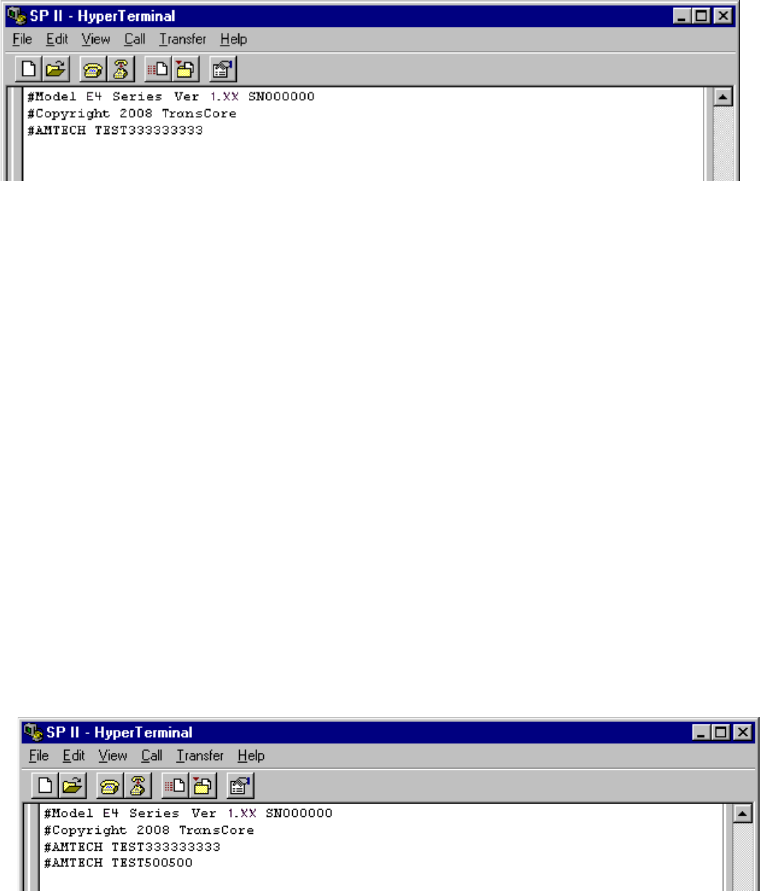
System Guide
TransCore Proprietary
8–10
Figure 8 – 7 Successful Tag Read
If the tag ID is not displayed, perform the following actions:
• Verify that the MPRX is in data mode (command #00 Switch to Data Mode).
• Ensure that the tag you are using is compatible with the MPRX. The MPRX can read
tag types that are compatible with the reader model.
• An MPRX displays the tag read for any tag that is compatible with the reader
programming.
• Using the audible circuit tester as described in “Testing the MPRX Using an Audible
Circuit Tester” on page 4-4, verify that the reader is capable of reading the tag in
the read zone. If it is, the problem is probably in the communications between the
MPRX and the host.
3. Pass a dierent reader-compatible test tag in front of the MPRX antenna.
4. When the MPRX reads the second tag successfully, the terminal emulation application
displays that tag’s information in the main screen below the information for the first tag,
as shown in Figure 8 – 8.
Figure 8 – 8 Second Successful Tag Read
If the read is unsuccessful, perform the following actions:
• Ensure the tag you are using is compatible with the MPRX.
• Using the audible circuit tester as described in “Testing the MPRX Using an Audible
Circuit Tester” on page 4–3, verify that the reader is capable of reading the tag in
the read zone. If it is, the problem is probably in the communications between the
MPRX and the host device.

MPRX
TransCore Proprietary 8–11
Configuring MPRX Parameters
Follow the procedures in this section to configure MPRX parameters using a PC, laptop,
or terminal emulator. The PC or laptop must be connected to and communicating with the
MPRX, and the terminal emulation application must be configured correctly, as described in
the section “Verifying Communications” on page 8-7.
To configure parameters
1. Switch to command mode by typing #01 at the prompt on the terminal emulation
screen, and pressing ENTER.
Note: All MPRX commands are preceded by the start-of-message character (#).
2. To meet requirements of your site, make changes to default operating parameters as
described in the following sections.
The following sections contain procedures to set some of the parameters that are
commonly changed to meet the requirements of a specific site. Procedures are listed in
alphabetical order by parameter.
Appended Tag Data
Use this procedure to set appended tag data parameters using the terminal emulation
application. Refer to “31N Append Auxiliary Information Selection” on page 7-10 for more
information.
To set appended tag data parameters
1. Ensure that the host device is in command mode.
2. Enter command #311 to append auxiliary information or command #310 to have no
auxiliary information appended (factory default). Press ENTER.
ID Separation
The host can select a unique ID separation of one ID or two IDs. The reader default
operation is for a unique ID separation of one ID and a uniqueness timeout of
two minutes. You can disable the uniqueness check using command #40 Transmit All ID
Codes. In this case, every tag ID received is transmitted without regard to uniqueness. You
can reinstate uniqueness checking with commands #4100 or #4101 Select ID Separation.
Note: The MPRX internal timing varies depending on the operative tag read mode and
the type of tag in the read field.
Refer to section “40 Transmit All ID Codes” on page 7–10 “and section “410N Select
Unique ID Code Criteria (Anti-passback Feature)” on page 7–11.
To set ID separation parameters
1. Ensure that the host device is in command mode.
2. Enter command #4100 to select a separation of one ID; enter command #4101 to select
a separation of two IDs. Press ENTER.
System Guide
TransCore Proprietary
8–12
Reports
The MPRX can be configured to transmit presence without tag reports and input status
change reports. A presence without tag report is transmitted in data mode only, and only
if the system has a presence detector. This report is sent if a presence is detected without
the detection of a valid tag ID. Refer to sections “529 Display Presence Input Status” on
page 7–18 and “690N Select Presence Without Tag Report Option” on page 7–30 .
To set presence reporting
1. Ensure that the host device is in command mode.
2. Enter command #529 to display presence input status and press ENTER. P0 indicates
presence without tag reports disabled (factory default), and P1 indicates presence
without tag reports enabled.
3. Enter command #6901 to enable presence without tag reports, or enter command
#6900 to disable presence without tag reports (factory default). Press ENTER.
To set input status change reporting
1. Ensure that the host device is in command mode.
2. Enter command #560 to display input status change report options and press
ENTER.
• E0 = input status change reports disabled (factory default)
• E1 = input status change reports enabled
• M0 = reporting disabled (factory default)
• M1 = changes on input0 reported
• M2 = changes on input1 reported
• M3 = changes on either input reported
Reset Reader
Command #63 Reset Reader resets uniqueness, clears the power fail bit, and transmits
the sign-on message. The reader returns to data mode following the completion of this
command.
Note: This command does not reset any of the configuration parameters.
Refer to “63 Reset Reader” on page 7–25

MPRX
TransCore Proprietary 8–13
To reset the reader
1. Ensure that the host device is in command mode.
2. Enter command #63. Press ENTER.
The terminal emulation screen displays the sign-on message as shown in Figure
8-5 on page 8-8.
Radio Frequency
Caution
The authorized continuous wave (CW) frequency band for the MPRX in the U.S. is
902.25 to 903.75 MHz and 910.00 to 921.50 MHz and the authorized modulated
frequency band for the MPRX in the U.S. is 911.75 to 919.75 MHz. The RF for each
MPRX at the site must be set according to the frequency specified in the FCC site
license. Only trained, authorized installation and maintenance personnel are permitted
by FCC to set the RF.
By using the MPRX an authorized person can set the frequency within the range from 860
to 930 MHz in 0.25 MHz steps. You can set the frequency by using a terminal emulation
program and issuing the frequency command, as discussed in section “647XXX Select RF
Operating Frequency” on page 7–28
Note: For backward compatibility to existing controllers, you can set the RF operating frequency
in 500-kHz steps using command #642NN.
To set the frequency range
1. Ensure that the host device is in command mode.
2. Enter command #647XXX – where XXX is a hexadecimal value from 000 to 118
and press ENTER. Refer to command “647XXX Select RF Operating Frequency” on
page 7-29 for a complete listing of the hexadecimal values and the corresponding
frequencies.
3. To verify that the RF has been changed to the proper setting, type in command
4. #527 to see the current frequency setting.
Caution
Contact TransCore if your application requires a frequency outside of the authorized
frequency range.
RF Transmission
The RF transmission can be controlled by one of the following methods:
• Connecting a presence detector to the SENSE0 circuit
• The host device sending software commands to the MPRX
As a factory default, the MPRX is configured to control the RF power with a presence
detector. Figure 8 – 9 illustrates the methods of controlling RF sense output.
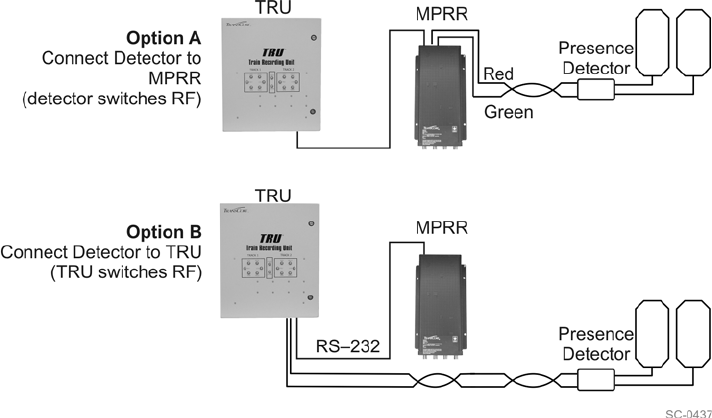
System Guide
TransCore Proprietary
8–14
Figure 8 – 9 MPRX RF Control Options
Presence Detector Controlling RF Transmission
The presence detector can be a loop detector, a track circuit, an infrared sensor, an
ultrasonic sensor, or another presence detection device that is connected to sense input0
to turn on the MPRX RF transmitter. In Figure 8-9, Option A shows a presence detector
controlling the RF transmitter. This operation is ensures that the RF is “on” only when a train
is in the MPRX read zone. Command #641 Select RF-by-Input Control (factory default) must
be enabled.
To set the option of the presence detector controlling the MPRX
• Ensure that the host device is in command mode.
• Enter command #641. Press ENTER.
• Leave the setting on RF-by-input control for normal operation.
Host Controlling RF Transmission
In Figure 8 – 9, Option B shows the host controlling the RF transmitter. This is the most
common implementation.
If the presence detector is connected to the host device, as shown in Option B, commands
#6400 RF O and #6401 RF On sent from the host device turn on and o the MPRX RF
transmitter.
Sense Inputs
The RS–232 configuration used by the MPRX has two sense inputs — SENSE0 and
SENSE1. SENSE0 is used to enable RF on antenna ports 0 and 1 if enabled, and SENSE1
is used to enable RF on antenna ports 2 and 3. The sense input circuits are used to notify
the MPRX of train presence and are designed to be connected to a free- of-voltage dry
contact. The MPRX sense inputs are designed to connect to a dry contact closure.
MPRX
TransCore Proprietary 8–15
You can configure the MPRX to generate input status change reports, which are transmitted
like tag IDs. The host can then respond based on the true/false (closed/open) status of the
sense inputs. Refer to the section “Reports” on page 8–12“.
The following procedures describe how to set sense inputs using the terminal emulation
software. Refer to command “694N Select Input Inversion Option” on page 7–32 for more
information.
To set sense inputs
1. Ensure that the host device is in command mode.
2. Enter command #6940 to disable input inversion (factory default) or command
3. #6941 to enable input inversion, and press ENTER.
Sense Output Device
The sense output is dedicated for testing and set up of the reader. It is defined as the
TAG_LOCK signal and indicates that a valid tag is in the read field.
This sense output is a dry contact that provides a normally open and normally closed
sense output. The relay contacts are rated at 42.2V AC peak (30 Vrms) or 60V DC at 1
A maximum. If controlling an external gate or device requiring high current, an isolation
transformer is required.
Serial Port Communications
The MPRX supports one RS–232 communications port. For the RS–232 communications
specification, the MPRX maintains the following three sets of parameters that aect serial
port communications:
• Port configuration parameters (baud rate, data bits, stop bits, parity)
• Communications protocols (basic, error correcting)
• Flow control scheme (none, software)
The default serial port configuration for each of these three parameters is as follows:
• 9600 baud, 8 data bits, 1 stop bit, no parity
• Basic communications protocol
• Software flow control (XON/XOFF)
You can change these parameters in data mode and command mode operation by
issuing commands with the host device. Use the following procedures to set serial port
communications parameters using the terminal emulation program.
Port Configuration Parameters
Use this procedure to set port configuration parameters using the terminal emulation
program. Refer to sections “100N Select Baud Rate” on page 7–6, “100N Select Baud
Rate” on page 7–6 through “102N Select Parity” on page 7–6
To set baud rate
1. Ensure that the host device is in command mode.

System Guide
TransCore Proprietary
8–16
2. Enter command #100N and press ENTER.
To set stop bits
1. Ensure that the host device is in command mode.
2. Enter command #101N and press ENTER.
To set parity
1. Ensure that the host device is in command mode.
2. Enter command #102N and press ENTER.
Communications Protocol
Use the following procedures to set communications protocol. Refer to sections “610 Select
Basic Communication Protocol (Factory Default)” on page 7–23 through “612NN Select
Error Correcting Protocol Timeout” on page 7–24 for more information.
Caution
Do not switch to ECP (command #611) unless the host is prepared to acknowledge
each reader transmission.
To select a communications protocol
1. Ensure that the host device is in command mode.
2. Enter command #610 to select basic protocol (factory default) or command #611 to
select ECP and press ENTER.
Software Flow Control
The host can enable or disable flow control with command #614N Select Flow Control
Option.
The host can use software control characters (XON/XOFF) to interrupt reader transmissions.
When the reader is configured for software flow control, it stops transmitting if it receives
the XOFF character from the host (host software command 13H). It resumes transmitting
only when it receives the XON character (host software command 11H) from the host. If flow
control is not needed, the reader should be configured for no flow control (#6140 Disable
Flow Control).
Note: TransCore recommends that XON/XOFF flow control be disabled while using the
ECP.
Use the following procedure to set flow control parameters using the terminal emulation
program. Refer to section “614N Select Flow Control Option” on page 7–24 .
To select flow control
1. Ensure that the host device is in command mode.
2. Enter command #6140 to disable flow control, command #6141 to enable software flow
control (factory default) and press ENTER.

MPRX
TransCore Proprietary 8–17
Fine-Tuning and Verifying the Read Zone
If the read zone is too wide or too deep for your application, it can be fine-tuned by
physically adjusting the external antenna mounting orientation, reprogramming the actual
RF power output (#644NN Set RF Attenuation), and/or reprogramming the RF sensitivity
range (#643NN Set ATA Operating Range (Distance) and #645NN Set SeGo Protocol Tag
Operating Range). The combination of these adjustments allows you to confine the read
zone to the area where tagged vehicles pass.
Refer to sections “643NN Select ATA Operating Range (Distance)” on page 7–27 ,
“645NN Set SeGo Protocol Operating Range (Distance)” on page 7–28, and “644NN Set
RF Attenuation” on page 7–27 for more information.
Note: As described in “Marking the Read Zone” on page 4-14, marking the read pattern
using test tags that are hand-carried by a tester gives a general idea of the read
pattern but the pattern may vary somewhat when actual rail assets are read.
Physically Orienting the MPRX Antenna(s)
You can manually adjust the location of the read zone by loosening the antenna(s)
mounting hardware and pointing the antenna in the desired direction. The unit should be
aligned to point directly at the tag as it enters the desired read zone.
Fine-Tuning the Read Zone by Lowering Output Power
You can make the read zone smaller by adjusting the MPRX RF power output from a
maximum of 2 watts to a minimum of 200 milliwatts using command #644NN Set RF
Attenuation.
To adjust the read zone by lowering output power
1. Ensure that your PC is communicating with the MPRX using a terminal emulation
program as described in section “Verifying Communications” on page 8–6.
1. Mark the current read zone as described in section “Marking the Read Zone” on page
4–13.
Caution
Test tags should be compatible with your MPRX. Test tags can be AAR-formatted or
SeGo-protocol tags.
2. Enter command #01 to switch to command mode. You are prompted with #DONE from
the reader and can now enter reader commands.
3. Enter in command #64401 to lower the RF power by 1 dB below 2 watts (default). Press
ENTER.
Note: In the command #644NN, NN can be any hexadecimal value from 00 to 0A.
Settings for attenuation are 1.0 dB increments over a range of 10 dB of attenuation from
the maximum power setting of 2 watts at 0 dB attenuation to a minimum power level
of 200 milliwatts at 10 dB attenuation. Increasing the attenuation lowers the output RF
power.
System Guide
TransCore Proprietary
8–18
4. Switch to data mode by entering command #00 and pressing ENTER.
5. Verify that the read zone has decreased by moving the tag through the desired
read area. If the read zone is still too large, switch to command mode and enter the
command #64402 to lower the output RF power another 1 dB. Continue increasing the
NN value until the read zone matches the desired read zone.
When the desired read zone is established, test the read zone with simulated and real
trac by performing the following procedures:
To test the read zone
1. Ensure that the MPRX is in data mode.
2. With the MPRX running, place one tag behind your back while you hold another tag in
the new read zone. If a valid read, the data from the tag held in the read zone displays
on the PC screen.
3. Switch tags, placing the other tag behind your back and holding the first tag in the read
zone. If a valid read, the data from this tag held in the read zone displays on the PC
screen. If both tags are read, you have successfully adjusted the read range.
4. If one or both tags did not read, follow the suggestions in “Verifying Tag Read
Capability” on page 8–8.
Fine-tuning the Read Zone by Adjusting Sensitivity Range
The MPRX read zone can be fine-tuned by using command #643NN for ATA protocol tag
read mode or #645NN for SeGo protocol tag read mode to reprogram the RF sensitivity
range. Sensitivity range adjustments have less impact on the read pattern than RF power
adjustment, thus RF power adjustment should be used as the main read pattern adjustment
tool. Sensitivity range control may be helpful in stopping some tag reads on the very
edges of the read pattern. To produce a noticeable change in the read pattern, you must
decrease the range sensitivity by more than one increment.
To adjust the read zone by adjusting sensitivity range
1. Ensure that your PC is communicating with the MPRX using a terminal emulation
program as described in “Verifying Communications” on page 8-7.
2. Mark the current read zone as described in “Marking the Read Zone” on page 4–13.
3. Enter command #01 to switch to command mode. You are prompted with #DONE from
the reader and can now enter reader commands.
4. Enter command #64318 or #64518 to decrease the range sensitivity seven increments
below the maximum (default). Press ENTER.
Note: In the command #643NN or #645NN, NN can be any hexadecimal value from 00
to 1F. The reader’s receiver becomes less sensitive to tag signals as the value of NN is
lowered from the maximum sensitivity of 1F to the minimum sensitivity of 00.
5. Verify that the read zone has decreased by moving the tag through the desired
read area. If the read zone is still too large, switch to command mode and enter the
command #64317 or #64517 to decrease the range another increment. Continue
MPRX
TransCore Proprietary 8–19
increasing the NN value until the read zone matches the desired read zone.
When the desired read zone is established, test the read zone with simulated and real
trac by performing the following procedures.
To test the read zone
1. Ensure that the MPRX is in data mode.
2. With the MPRX operating, place one tag behind your back while you hold another
tag in the new read zone. If a valid read, the data from the tag held in the read zone
displays on the host device screen.
3. Switch tags, placing the other tag behind your back and holding the first tag in the read
zone. If a valid read, the data from this tag held in the read zone displays on the host
device screen.
4. If both tags are read, you have successfully adjusted the read range. If one or both tags
did not read, follow the suggestions in “Verifying Tag Read Capability” on page 8–8.

Chapter 9
Troubleshooting and Maintenance
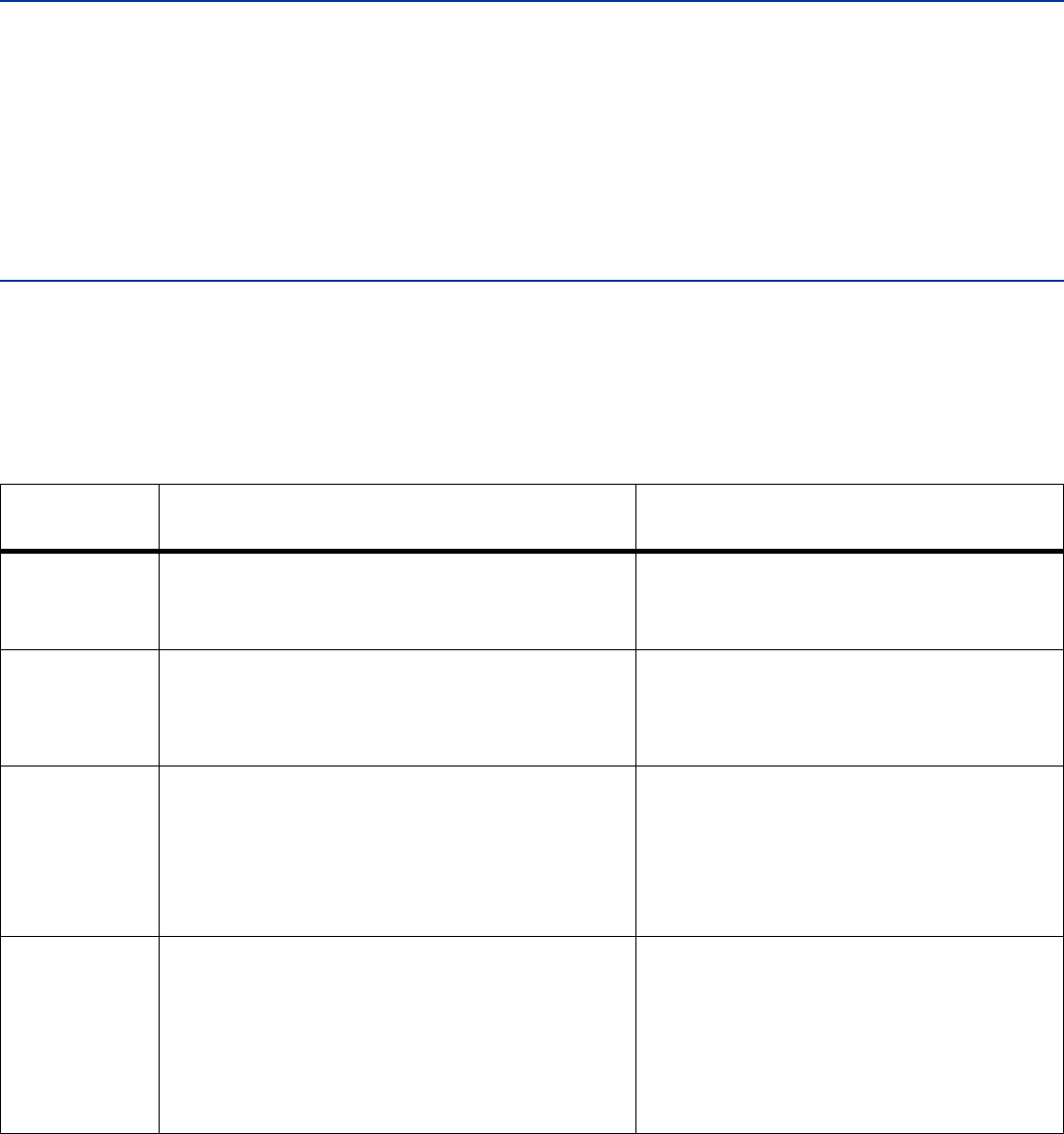
MPRX
TransCore Proprietary 9–1
Chapter 9 Troubleshooting and Maintenance
This chapter contains information for troubleshooting a Multiprotocol
Reader Extreme (MPRX) and performing minimal maintenance checks.
the chapter also includes information for returning products for repair,
technical support, and contact information for providing feedback and
suggestions to TransCore.
Error Messages
The MPRX transmits an error message if a command received from the host is not a
recognized command or if information supplied with the command is incorrect. The reader
sends this message to diagnostic commands if the reader fails the specified test.
Table 9 – 1 contains a list of error messages.
Table 9 – 1 Error Messages
Error
Message
Description Corrective Action
Error06
NVRAM parameters have been lost. The MPRX
will not function properly because the RF
section is shut o until the frequency is reset.
Reset the frequency using command
#647XXX.
Error07
The RF phase locked loop (PLL) has lost
lock and is unable to operate at its intended
frequency. RF output is disabled while the MPRX
attempts to reset the PLL.
Reset the RF frequency. Refer to “Radio
Frequency” on page 8-14 for instructions.
Error08
The RF PLL has successfully regained lock
and has been reset to its proper operating
frequency. The RF section is returned to its state
prior to losing lock (enabled/disabled). Error08
will only be issued after Error07 has been
issued.
No action necessary; the previous error
has been corrected.
ErrorRF1
Warning message that the RF board did not
return an update acknowledge signal
If the reader indicates a single ErrorRF1
event and recovers from the error, no corrective
action is required. You may want to track this
error message if it should occur again. If
the reader indicates repeated ErrorRF1
warning messages then return the reader to
the factory.
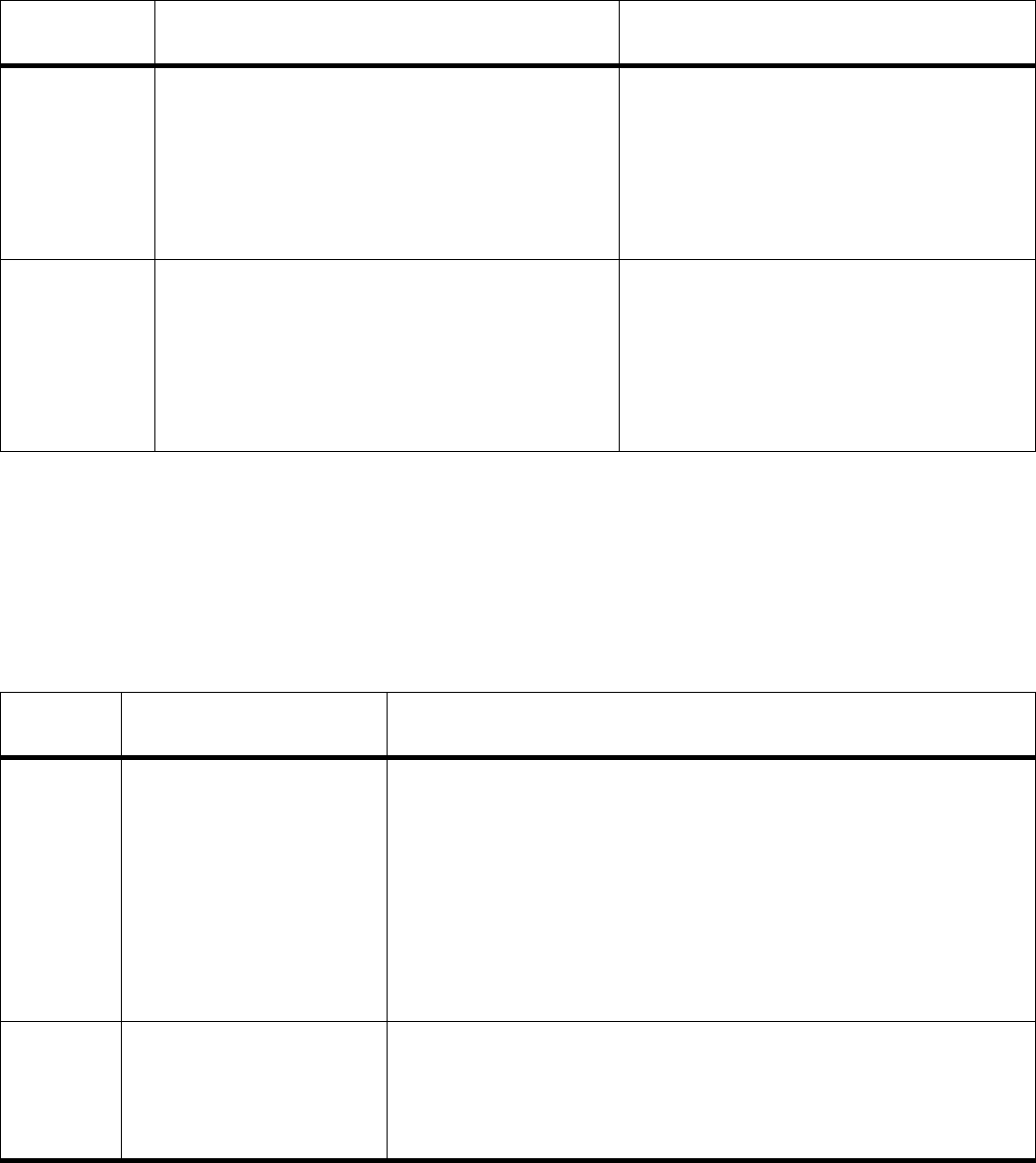
System Guide
TransCore Proprietary
9–2
Error
Message
Description Corrective Action
ErrorRF2 Warning message that the RF module did not
return an INIT DONE signal
If the reader indicates a single ErrorRF2
event and recovers from the error, no corrective
action is required. You may want to track this
error message if it should occur again. If
the reader indicates repeated ErrorRF2
warning messages then return the reader to
the factory.
ErrorRF3 Warning message of unexpected status read,
including status byte, from RF module
If the reader indicates a single ErrorRF3
event and recovers from the error, no corrective
action is required. You may want to track this
error message if it should occur again. If
the reader indicates repeated ErrorRF3
warning messages then return the reader to
the factory.
Troubleshooting
You can use the following table for troubleshooting. Should problems continue, contact
TransCore for return and replacement procedures. If you contact Technical Support, use
the symptom number in Table 9 – 2 to reference the problem that you are having with the
MPRX.
Table 9 – 2 Symptoms and Remedies
Symptom
NumberaSymptom Remedy
1 When performing a quick
test of the MPRX, the buzz
box does not buzz.
Check all your wiring connections and antenna connections and
ensure that your buzz box is functioning.
The wires from the MPRX are grouped in pairs. You could find more
than one red wire, more than one black wire, and so on. You must
connect the correct red and white wire pair to the leads from the
battery.
Verify that RF is on. Using a terminal emulation program, you may
switch to command mode and issue command #527 to determine
RF status. Refer to page 7-18 for more information.
2The baud rate is selected
correctly but nothing
happens.
The MPRX is not communicating with your host device. Check the
power supply to your host device, and check the connections
between the host device and the MPRX. Try reversing the receive
and transmit connections. Also, check the position of the Interface
Selection Switch.
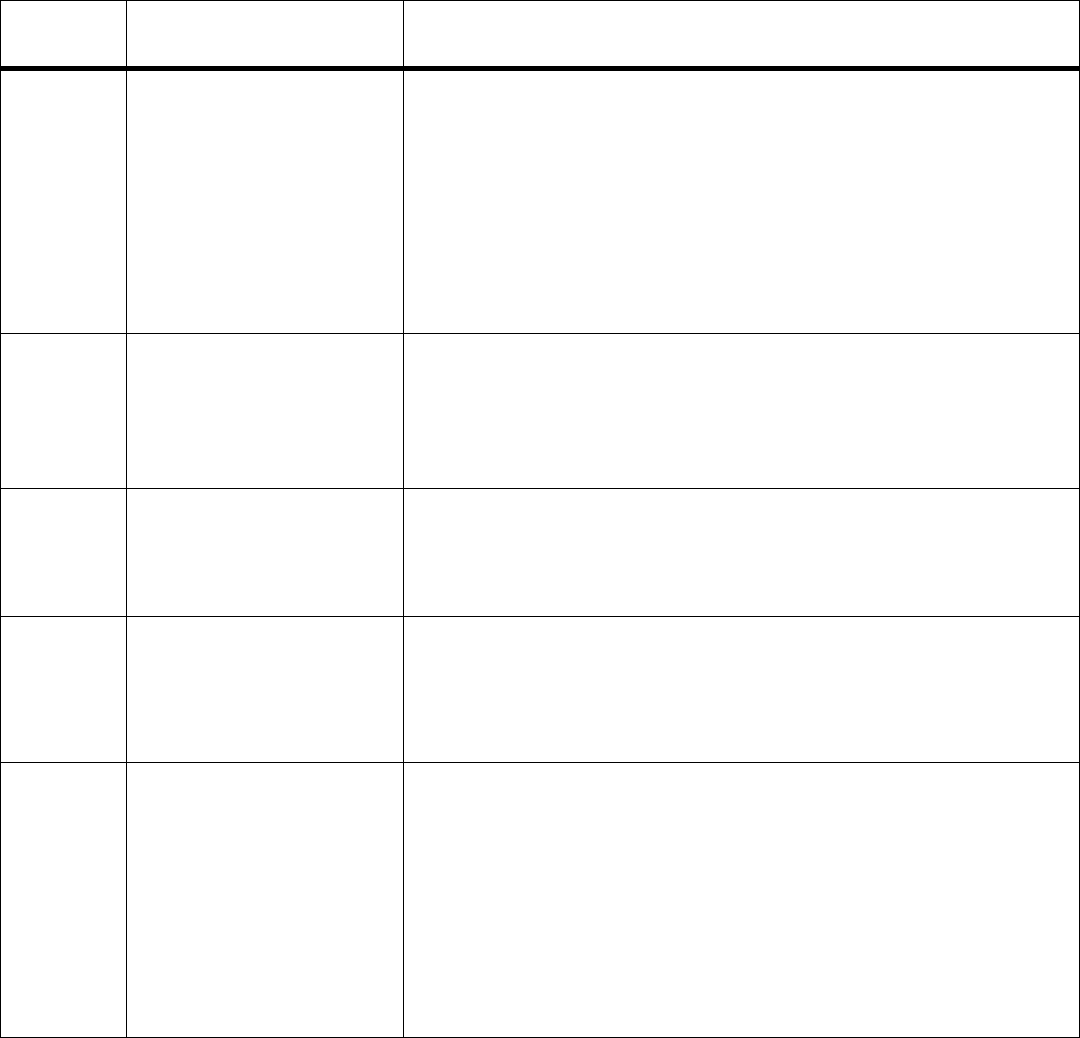
MPRX
TransCore Proprietary 9–3
Symptom
NumberaSymptom Remedy
3When testing the MPRX, all
the wires are connected
correctly but the unit does
not respond.
The MPRX may not have the software loaded inside the unit. Contact
Technical Support as described on page 9-6.
If you are using a terminal emulation program, check that the terminal
emulation setting on the MPRX is VT100.
Check that the MPRX communication cable is connected to the
correct COM port.
Verify that the external antenna is connected correctly.
Also, check the position of the Interface Selection Switch.
4Strange signal responses
come from the MPRX
when tested with the PC.
Ensure that the reader is in the correct interface mode for the test
tag, that is, AAR for an AAR-formatted tag.
Check the system defaults using a terminal emulation program. Both
PC and reader should be set to 9600 baud, 8 bits, 1 stop bit, and no
parity.
5 Nothing happens when
the test tag is passed
in front of the MPRX RF
antenna.
Ensure that the MPRX is powered on
Verify that the reader is set to RF ON (#6401). Verify that the antenna
is connected correctly.
6The MPRX came from
another site and does not
work the way the factory
defaults indicate that it
should.
Dierent commands were probably used to support the other site’s
specific configuration. You can restore the factory defaults by using a
terminal emulation program to switch to command mode and issuing
command #66F Load Default Operating Parameters. All factory
defaults except RF frequency will be restored.
7When connected to a PC
that is running terminal
communications software,
a just-powered up MPRX
displays one of the
following messages:
#Model E4 Series X.XX
SNSSSSSS
#[Copyright notice]
The MPRX works. The software is now loaded. SSSSSS is the
TransCore-assigned serial number for this MPRX. However, if SSSSSS
= 000000, a serial number has never been assigned. If a serial
number has not been assigned to your MPRX, contact TransCore
Technical Support.
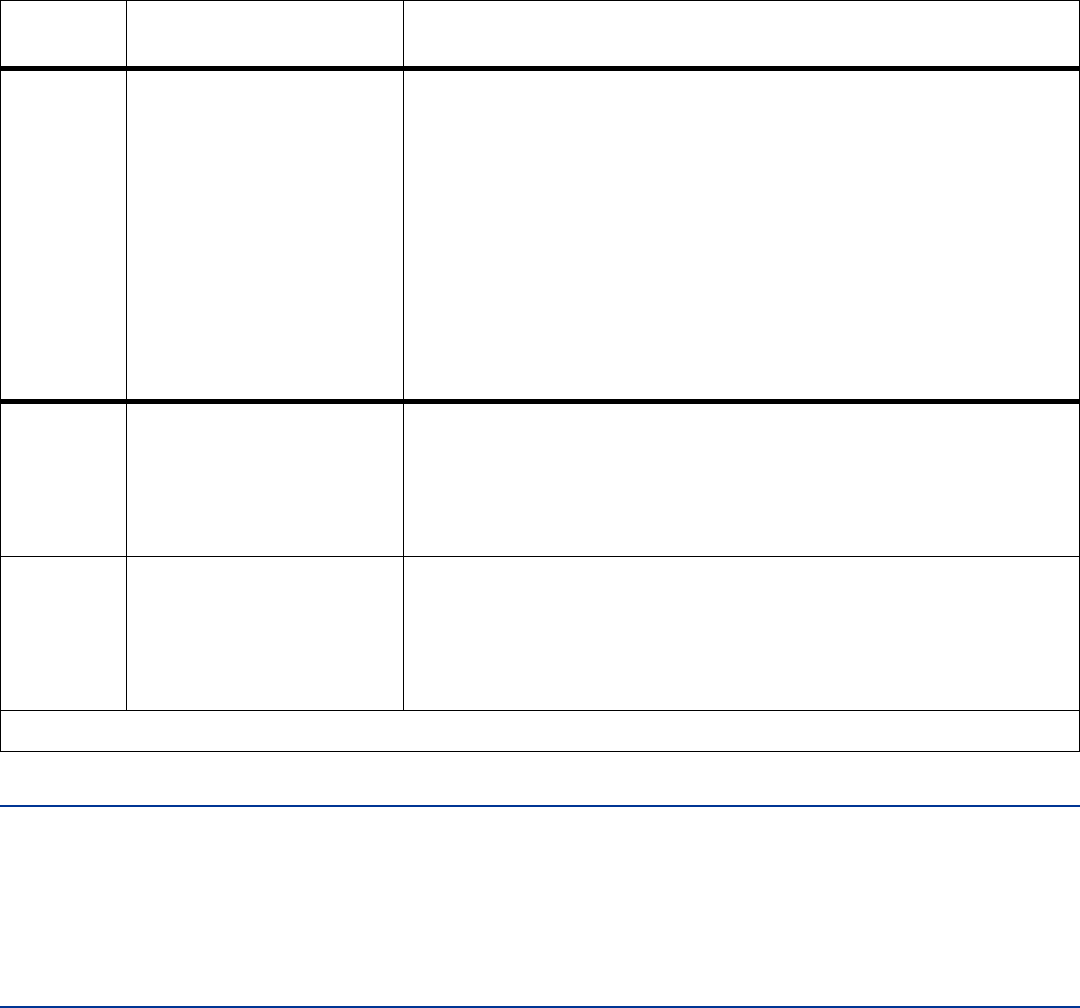
System Guide
TransCore Proprietary
9–4
Symptom
NumberaSymptom Remedy
8The read zone is too
small, even before the RF
power and range control
have been adjusted.
If another MPRX is in the same area, ensure that it is operating on
another frequency that is at least 2 MHz dierent.
Check for possible interference from another nearby RF source:
fluorescent lights, neon signs, high voltage power lines, nearby
cellular telephone, or radio stations. Lights will need to be removed
or shielded. Point the external antenna in a dierent direction to see
if interference comes from only one direction. You may require a
dierent MPRX that uses another frequency.
Verify that the RF power is set to an appropriate value. Verify that
the range adjustment is set to the maximum. Verify that the reader is
getting at least 16V.
9 The perimeter of the read
zone has been defined,
but there is a “hollow” spot
in the center of the zone
that does not read tags.
The angle of the external antenna may need adjustment. Slightly tilt
the external antenna to a dierent angle to change either the length
or width of the read zone.
Check the range control adjustment. Refer to “Radio Frequency” on
page 8–13..
10 The MPRX is reading tags
out of the desired read
zone.
Some interference from other RF or electrical sources may be
occurring. Refer to “Reflection, Refraction, and Diraction of RF
Signals” on page 2–8
Verify that the read zone has been properly set up. Refer to “Fine-
Tuning and Verifying the Read Zone” on page 8–17 .
a Use this number to reference the problem you are having with the MPRX if you contact Transcore for Technical Support.
MPRX Repair
The MPRX is designed for whole-unit replacement and is manufactured with surface-
mounted components. It requires sophisticated testing and repair equipment. All testing
and repairs are performed at TransCore’s factory. Please contact TransCore to obtain a
Return Materials Authorization (RMA) for returning the reader.
Technical Support
Authorized dealers and distributors are responsible for the direct support of all customers.
Authorized dealers and distributors needing support can contact TransCore Technical
Support at (505) 856-8007. Please be prepared to answer a series of questions that are
designed to direct you to the best TransCore support resource available. These questions
will relate to symptoms, configuration, model, and tags used.
Note: End users and facility operators contacting Technical Support will be referred to
the dealer responsible for the system sale.

MPRX
TransCore Proprietary 9–5
Marketing Support
Dealers requiring marketing support may call TransCore Sales Support at 800.923.4824.
System Guide
TransCore Proprietary
9–6

Chapter 10
Interface to Train Recording Unit
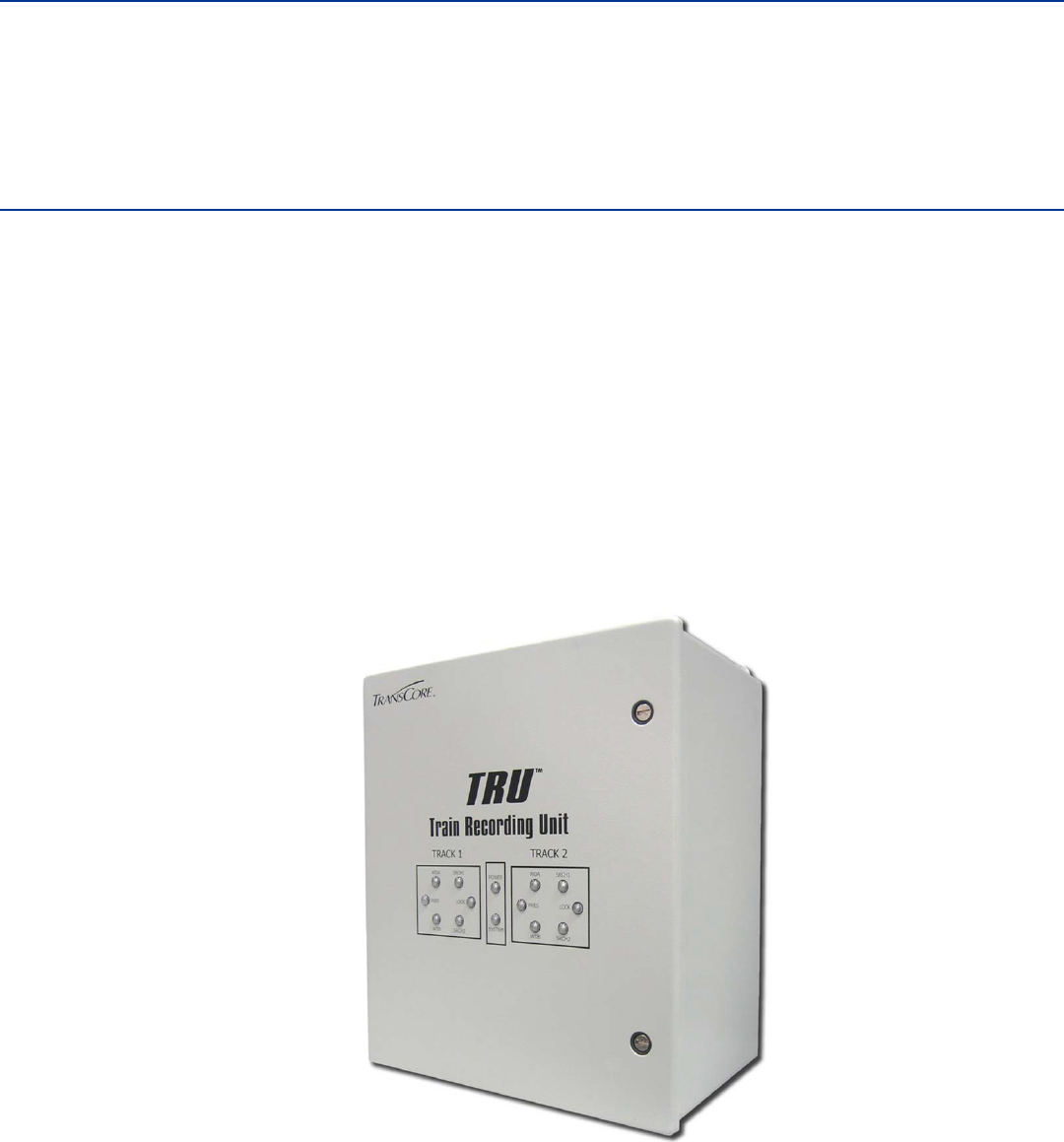
System Guide
TransCore Proprietary
10–2
Chapter 10 Interface to Train Recording Unit
This chapter describes the communication/power interface between
the Multiprotocol Reader Extreme (MPRX) and the Train Recording Unit
(TRU™).
TRU System Overview
The TRU is a system composed of hardware and software that is used at mainline rail
locations in North America. The TRU records detailed information about trains, uses the
information to create “consists” for the trains, and then transmits consist reports to a host
computer system. A train “clean consist” report is a train listing in standing order, where
orientation of tagged equipment is provided, location of untagged equipment is provided,
and car count is accurate. The TRU accommodates normal operating procedures such as
changes in speed and reverse and incorporates intelligence to handle both single and
multi-track locations.
The TRU System hardware includes the TRU “box,” RFID reader(s) or connection for
the Multiprotocol Reader Extreme (MPRX), antennas, wheel detectors, presence loops,
external device interfaces, communications interfaces, and other optional peripherals
(Figure 10 – 1).
Figure 10 – 1 TRU Front Panel Showing Operational LEDs

MPRX
TransCore Proprietary 10–3
MPRX to TRU Connection
The MPRX and TRU typically are installed in the same railside hut and are connected by a
communication/power cable. Figure 10 – 2 shows the TRU circular connector port for the
MPRX interface cable.
Figure 10 – 2 TRU-MPRX Communications Interface Cable Port (bottom of TRU)
Figure 10 – 3 shows a graphical representation of the communications interface cable.
10–3
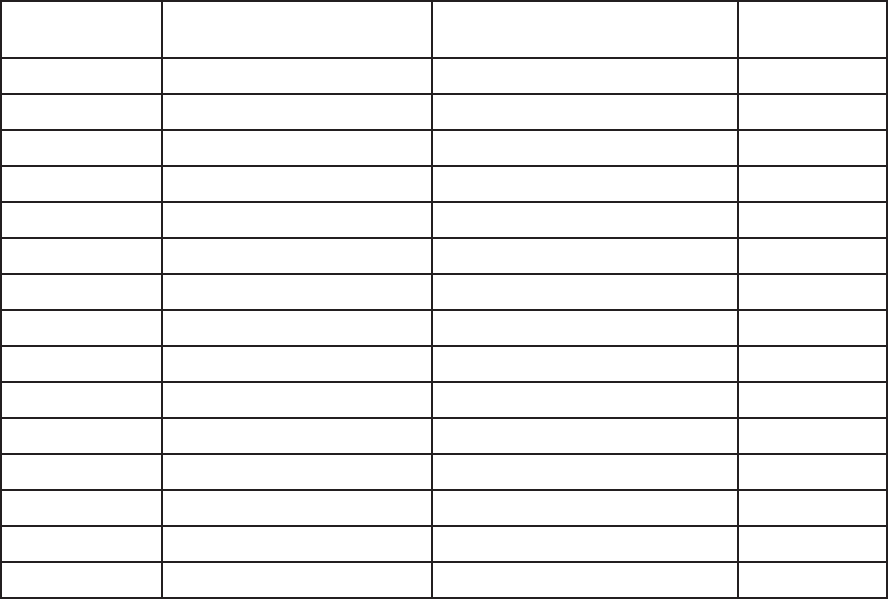
MPRX
TransCore Proprietary 10–5
Table 10 – 1 MPRX-to-TRU Interface Cable Pin and Signal Designations
MPRX Pin Signal Designation Signal Description TRU Pin
1 TXD1 Transmit Data 1 8
2 GND Signal Ground 15
3 LOCK Lock 7
4 GND Signal Ground 14
5 +24RTN +24V Return 6
6 CTS1 Clear to Send 1 13
7 +24RTN +24V Return 5
8RTS1 Request to Send 1 12
9 +24V DC Input Voltage 4
10 GND Signal Ground 11
11 +24V DC Input Voltage 3
12 LOCK_RTN Lock Return 10
13 SENSE_1 Input Sense 1 2
14 RXD1 Receive Data 1 9
15 SENSE_0 Input Sense 0 1

Chapter 11
Check Tag to MPRX Assembly
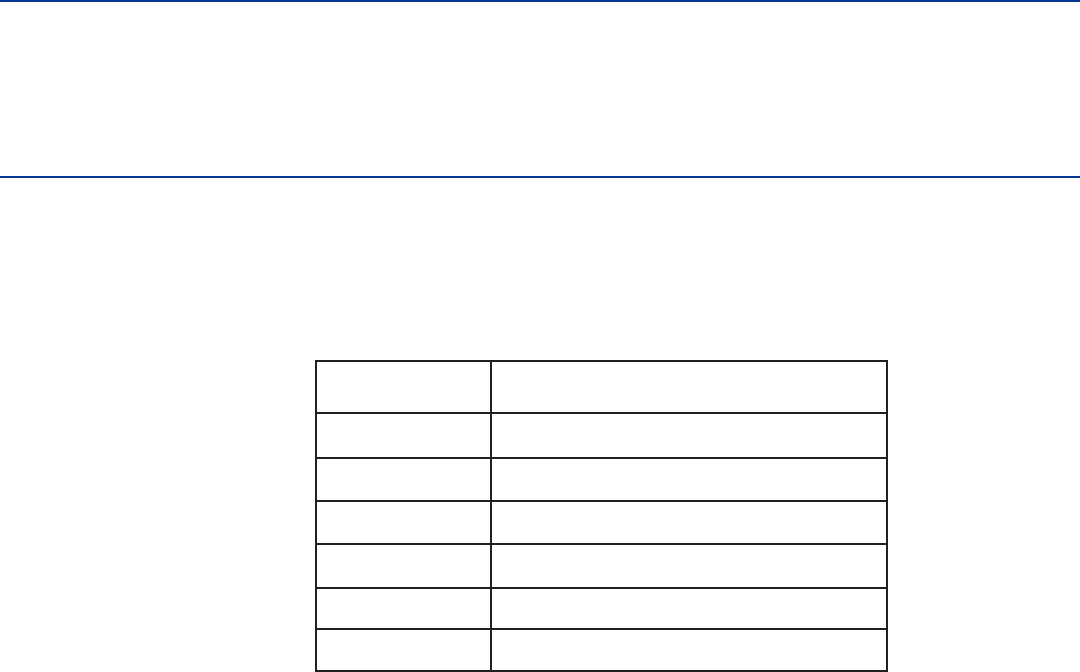
System Guide
TransCore Proprietary
11–2
Chapter 11 AT5720 Check Tag-to-MPRX Assembly
This document describes the procedures to assemble and connect a
check tag assembly to a Multiprotocol Reader Extreme (MPRX).
Required Supplies
Before assembling the check tag antenna kit, make sure you have the necessary
supplies and tools for this task. Check Tag Kit (TransCore P/N 19114-00). Table 11 – 1 lists
the kit parts.
Table 11 – 1 Check Tag Kit Parts List
Quantity Description
1Terminal connector strip (9 position)
2Self-tapping screw
1 Plastic connector housing sleeve
2 Plastic nut cap with rubber insert
1Nylon closing cap
1Check Tag Assembly Instructions
You need the following additional materials and/or tools to complete the installation.
• AT5720 Check Tag(s)
• Jeweler flat-blade screwdriver
• Standard tools (Phillips screwdriver, wire stripper, crescent wrench)
• Multiprotocol Reader Extreme
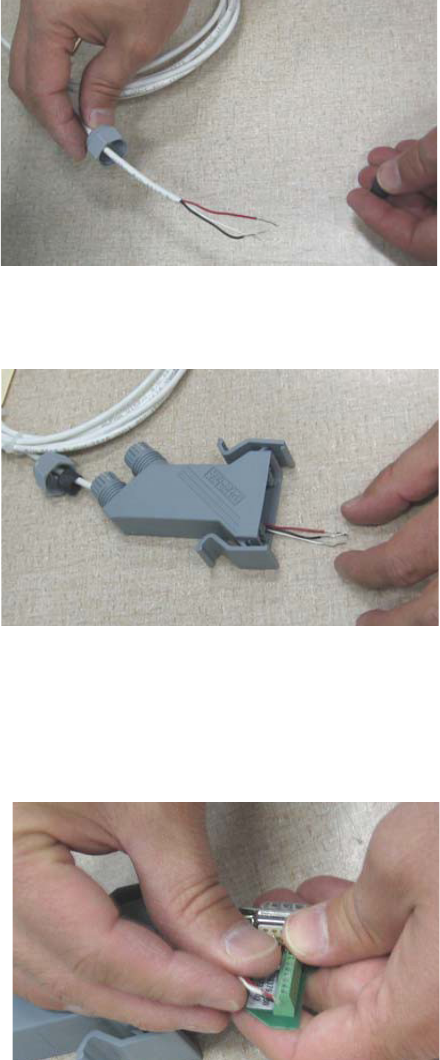
MPRX
• TransCore Proprietary 11–3
To assemble the kit for two check tags
1. Strip the cable insulation to expose the three check tag wires. Strip wire insulation
approximately 1/4 inches to expose bare wire. Slide the plastic nut and rubber grommet
over the wires (Figure 11 – 2).
Figure 11 – 1 Place Nut and Grommet Over Exposed Check Tag Wires
2. Pull the check tag wires through the connector housing (Figure 11 – 3).
Figure 11 – 2 Feed Check Tag Wires through Plastic Housing Connector
3. For Check Tag 0, insert and tighten the check tag wires to the terminal strip as shown in
Figure 11 – 2 and Table 11 – 2.
Figure 11 – 3 Connect Check Tag Wires
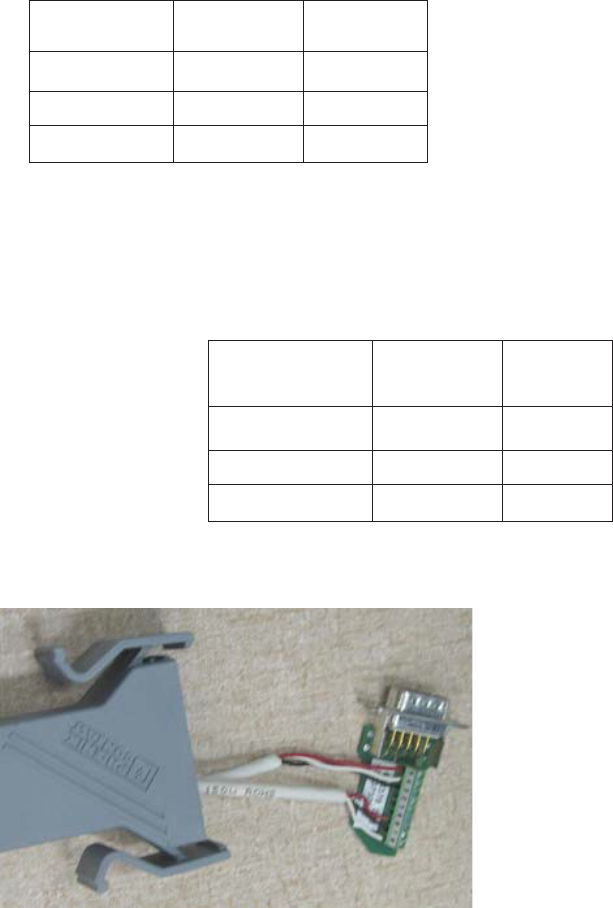
System Guide
TransCore Proprietary
11–4
Table 11 – 2 Check Tag 0 Wire Assignments
4. If connecting two check tags, repeat steps 1 through 3. Connect Check Tag 1 to the
terminal strip as listed in Table 11 – 3.
Table 11 – 3 Check Tag 1 Wire Assignments
Figure 11 – 4 shows both check tags connected to terminal strip.
Figure 11 – 4 Two Check Tag Assemblies Connected to Terminal Strip
5. Insert and tighten the two self-tapping screws to secure the terminal strip (Figure 11 – 5).
Wire Color Pin No.
Ground Black 3
Power Red 4
Data White 5
Wire Color Pin No.
Ground Black 7
Power Red 8
Data White 9
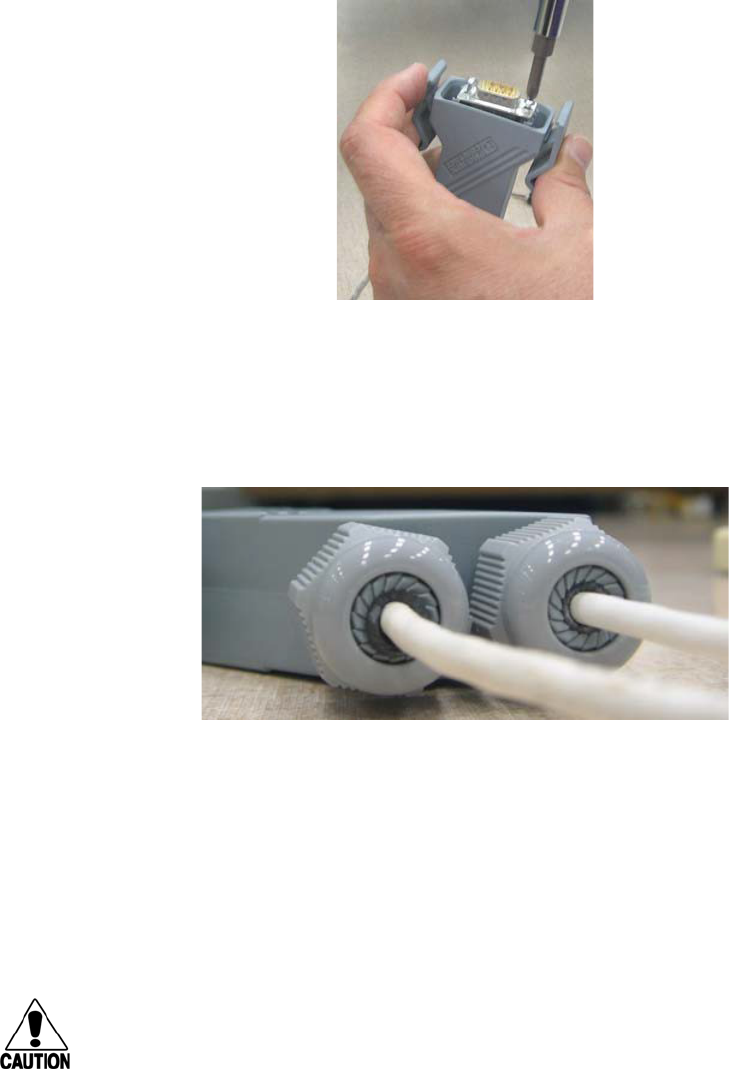
MPRX
• TransCore Proprietary 11–5
Figure 11 – 5 Securing Terminal Strip into Connector Housing
6. To complete the connector assembly, tighten the nuts on the cable end snugly
(Figure 11 – 6).
Figure 11 – 6 Plastic Nuts with Grommets
As the nut is tightened, the connector compresses the grommet around the check tag
cable.
To assemble the kit for one check tag
1. Follow the procedure steps described above in steps 1 through 6, but connect only one
check tag cable.
Caution
If connecting only one check tag, you must insert and secure the nylon closing
cap into the unused terminal connector to protect the terminal strip from possible
contamination.
2. To cover the unused terminal connector, insert the nylon closing cap into the plastic cap
with rubber grommet and tighten snugly (Figure 11 – 7).
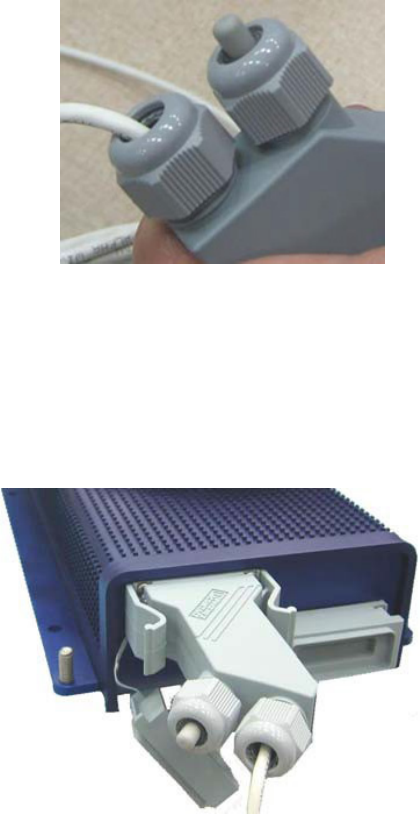
System Guide
TransCore Proprietary
11–6
Figure 11 – 7 Nylon Cap Securely Fastened in Unused Port
To connect the check tag assembly to the MPRX
Remove the dust cover from the Check Tag port of the MPRX and plug in the check tag
cable assembly (signle check tag assembly shown in Figure 11 – 8). Be sure that the two
handles snap into place on the MPRX. This ensures a solid connection.
Figure 11 – 8 Check Tag Assembly Secured to MPRX Port
MPRX
• TransCore Proprietary 11–7

Appendix A
Glossary

System Guide
TransCore Proprietary
A–2
Appendix A Glossary
A
AAR Association of American Railroads
AC alternating current
ACK acknowledge (data valid)
ANSI American National Standards Institute
antenna passive device that converts RF energy into magnetic energy (RF signal)
ASCII American Standard Code for Information Interchange
ASIC application-specic integrated circuit
ATA American Trucking Association
aux auxiliary
AWG AWG (American Wire Gauge) is a U.S. standard set of non-ferrous wire conductor
sizes
B
backscatter portion of an RF signal that is modulated by a tag and radiated back to the reader
baud measure of number of bits per second of a digital signal; for example, 9600 baud =
9600 bits per second
BCKS boot checksum
BCM buer control mode
bps bits per second
byte a binary character; for example, one 8-bit ASCII character
C
check tag tag mounted inside a reader assembly, inside or in close proximity to an external
antenna that is used to check operation of the reader
MPRX
TransCore Proprietary A–3
cmd command
comm communications
command data set that is recognized by the receiving device as intending to elicit a specic
response
conduit exible steel pipe use for electrical wiring
cps characters per second
CR carriage return
CRC cyclic redundancy check
CTRL control
CTS clear to send
D
data information that is processed by a computing device
DC direct current
DIAG diagnostic
E
ECP error correcting protocol
ECPS error correcting protocol status
eGo® Proprietary name for ANSI NCITS 256-2001 and ISO 18000-6B compliant TransCore
products. A registered trademark of TC License, Ltd.
eol end of line
eom end of message
EPROM erasable programmable read-only memory
F
eld physical area/space in which a tag can be read by the reader; also, an element of a data
record/frame. For example, division within a tag’s data frame.
System Guide
TransCore Proprietary
A–4
frames consecutive bits of data in memory that are read and written as a group
frequency bands a range of RF frequencies assigned for transmission by an RF device
H
hex hexadecimal
hexadecimal base 16 numbering system that uses the characters 0 though 9 and A through F to
resent the digits 0 through 16
host device, generally a computer, that is connected to the Multiprotocol Reader Ex-
treme
through the communications port
I
I/O or IO circuits input/output circuits
ID identication; encoded information unique to a particular tag
NCITS American National Standards Institute International Committee for Information
Technology standards
interface connection point for communication with another device
IOST I/O status
ISO International Standardization Organization
L
LF line feed
M
m
meter
MHz megahertz
mode method of operation
MPRX Multiprotocol Reader Extreme
ms millisecond(s)
MPRX
TransCore Proprietary A–5
N
NAK negative acknowledgment (data not valid)
P
passback used to refer to a tag ID that is not passed on to the tag buer
PC personal computer
PCKS EPROM ash checksum
protocol specied convention for the format of data messages communicated between devices
PRST presence status
PWRB power fail bit
R
RAM random access memory
RDID reader ID
read process of acquiring data from a device; for example, from a tag or from computer
memory
reader controlled interrogating device capable of acquiring data from a device; for example,
acquiring and interrupting data from a tag
read zone the physical area in which a tag can be read by the reader
RF radio frequency
RFID radio frequency identication
RFST RF status
ROM read-only memory
RTC real-time clock
RTS request-to-send
S
SCTS status of check tag status
System Guide
TransCore Proprietary
A–6
SeGo Super eGo (SeGo) is a superset of the eGo protocol
SN serial number
som start of message
SSTC input status change reporting options
T
tag small self-contained device acting as an identifying transponder
TRU™ Train Recording Unit
TT tag translation
V
V
volts
Ver version (soware)
W
write process of recording data; for example, writing to computer memory or to a tag’s
memory. Writing writes over (erases) previous data stored at the specied memory
locations.
X
XON/XOFF protocol for controlling the ow of data between computers and other devices on an
asynchronous serial connection. X/ON and X/OFF are signals to turn a transmitter
on or o. e actual signal for X/ON is the same bit conguration as the ASCII Ctrl-Q
keyboard combination (11 hexadecimal). e X/OFF signal is the Ctrl-S character (13
hexadecimal).
MPRX
TransCore Proprietary A–7

Technical Specifications
Appendix B
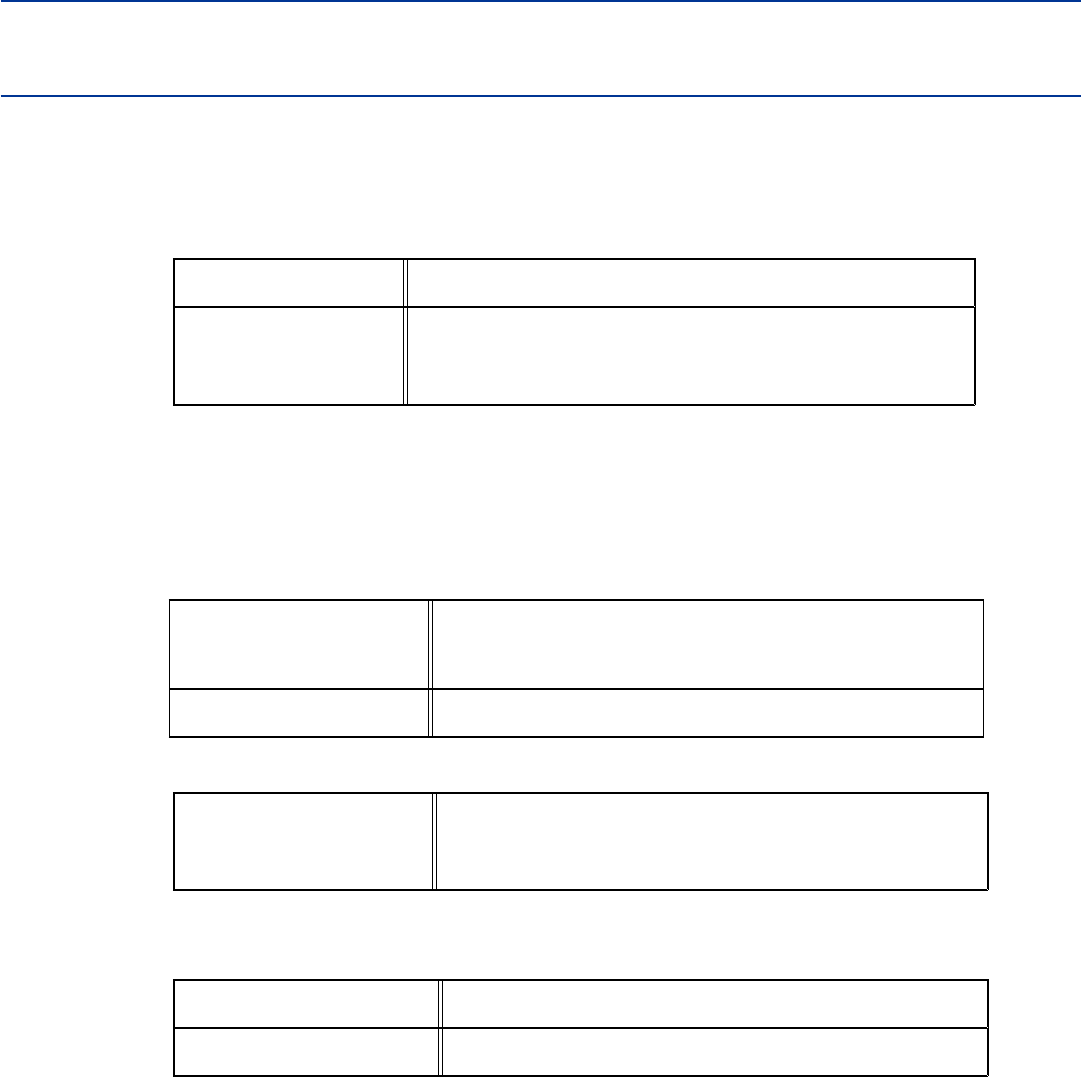
System Guide
TransCore Proprietary
B–2
Appendix B Technical Specifications
Reader Specifications
Communications
a. In the U.S., the authorized continuous wave frequency band is 902.25 to a. 903.75 MHz and 910.00 to 921.50 MHz and the authorized
modulated frequency band for this product is 911.75 to 919.75 MHz.
b. Reading range depends on reader or external antenna configuration, tag type, tag read mode, and operating environment.
Hardware Features
Power Requirements
Physical Attributes
Frequency Selection 860 to 930 MHz capablea
Reading Range
Read performance varies depending on tag, reader, and
external antenna configuration and environment.
Typical read range should be 12 to 17 ft (3.7 to 5.2 m).b
Integrated system with
connectors for external
antennas
RF module, tag decoder, power supply, I/O ports, and
serial communications interface all housed in a single
package.
Case Aluminum (Allodyne)
Input Voltage 12 to 24 VDC (Option)
or
24 to 110VDC (Option)
Size 13 x 5 x 2.49 in. (33 x 7.62 x 6.32 cm)
Weight 5.9 lb (2.6 kg)
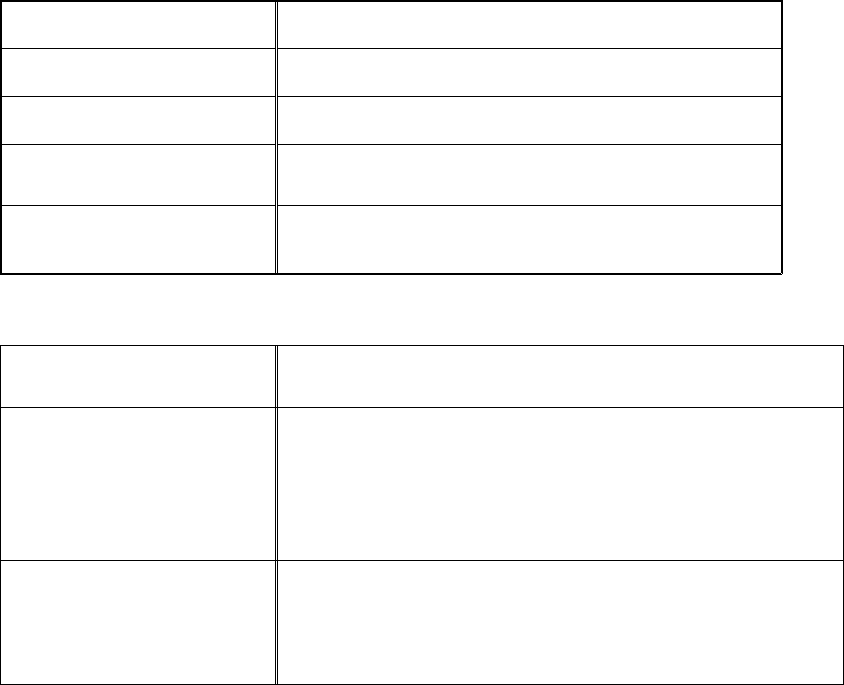
MPRX
TransCore Proprietary B–3
Environmental Parameters
Options
Operating Temperature -40°F to +158°F (-40°C to +70°C)
Humidity 99% condensing
Ingress Protection IP65/IP67 Rated, with appropriate connectors.
Vibration Tolerance The MPRX complies with vibration tolerance limits
specified in AREMA C&S Manual, Part 11.5.1, Class C
Operation Shock
Tolerance
The MPRX complies with shock tolerance limits
specified in AREMA C&S Manual, Part 11.5.1, Class C
Communications
Interface
RS–232, RS-422, Ethernet
Cable Accessory Kits
: MPRX-to-TRU™ cable assembly, 6 ft (1.8 m)
: MPRX-to-TRU cable assembly, 20 ft (6.1 m) 58-7001-003:
MPRX cable assembly, 6 ft (1.8 m), no TRU 58-7001-004
MPRX cable assembly, 20 ft (6.1 m), no TRU
AC/DC Converter
An AC/DC converter is available from TransCore to allow
for connection to 110/220VAC sources. The transformer is
rated -40 to 70C, and will power up to 2 MPRX units. Part
number available upon request.

Wiring Diagram
C
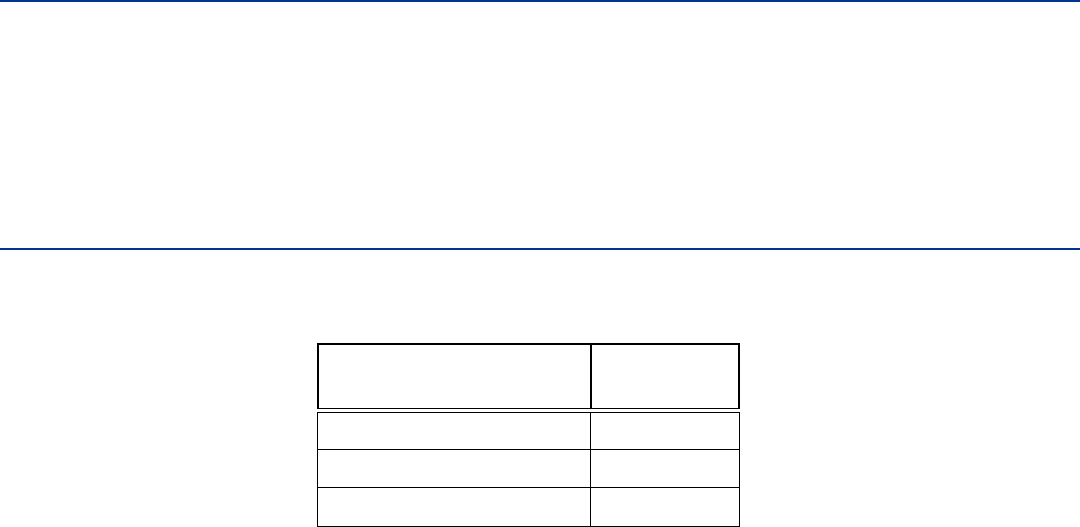
System Guide
TransCore Proprietary
C–2
Appendix C Wiring Information
This appendix contains a graphical representation showing the wiring
connector pin-outs as well as any wiring signal tables used to test
and install the Multiprotocol Reader Extreme (MPRX) for a non-Train
Recording Unit installation.
Communications Interfaces
Table C – 1 lists the interfaces available with the MPRX.
Table C – 1 Communications Interfaces and Conductor Requirements
Table C – 2 lists the MPRX Host Communications Cable Pin Designations. The interface
cable is TransCore P/N (6-foot [1.8-m] cable assembly, no TRU) or (20-foot [6.1-m] cable
assembly, no TRU).
Interface Number of
Conductors
RS–232 3
RS-422 5
Ethernet 4

MPRX
TransCore Proprietary C–3
Table C – 2 MPRX Host Communications Cable Pin Designations
Host Cable
Pair Color Pin Number Name
Pair 1 White 9 SIG_GND
Black 1 RS232 TX
Pair 2 White 10 SIG_GND
Brown 2 RS232 RX
Pair 3 White 12 +V Return
Red 11 +V In
Pair 4 White 12 +V Return
Orange 11 +V In
Pair 5 White 12 +V Return
Yellow 11 +V In
Pair 6 White 3 Lock
Green 4 Lock Return
Pair 7 White 6 RS422 TX-
Blue 5 RS422 TX+
Pair 8 White 8 RS422 RX-
Violet 7 RS422 RX+
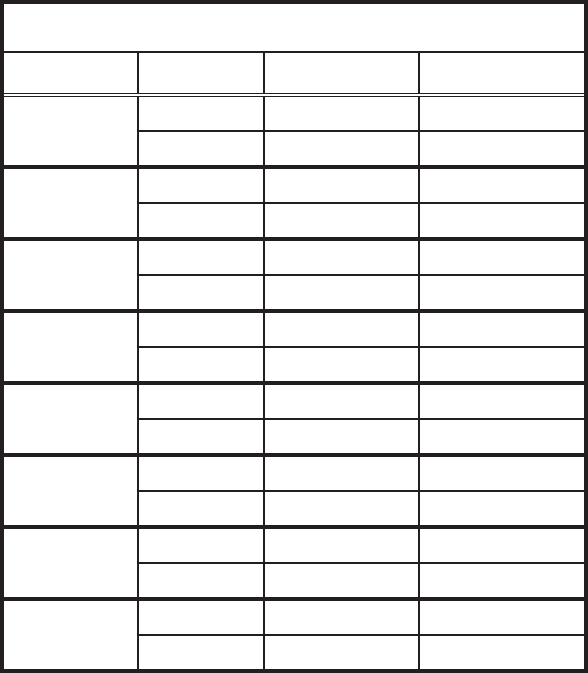
System Guide
TransCore Proprietary
C–4
Table C – 3 lists the MPRX Sense Communications Cable Pin Designations. The interface
cable is TransCore P/N (6-foot [1.8-m] cable assembly, no TRU) or (20-foot [6.1-m] cable
assembly, no TRU).
Table C – 3 MPRX SENSE Communications Cable Pin Designations
Sense Cable
Pair Color Pin Number Name
Pair 1 White 3 I/O GND
Black 7 CTAG 0
Pair 2 White 3 I/O GND
Brown 8 CTAG 1
Pair 3 White 4 I/O GND
Red 1 +12V
Pair 4 White 4 I/O GND
Orange 1 +12V
Pair 5 White 6 OUT 0
Yellow 2 OUT 1
Pair 6 White 11 I/O GND
Green 5 PULSE OUT
Pair 7 White 9 I/O GND
Blue 12 SENSE 0
Pair 8 White 10 I/O GND
Violet 11 SENSE 1

Command Quick Reference
Appendix D
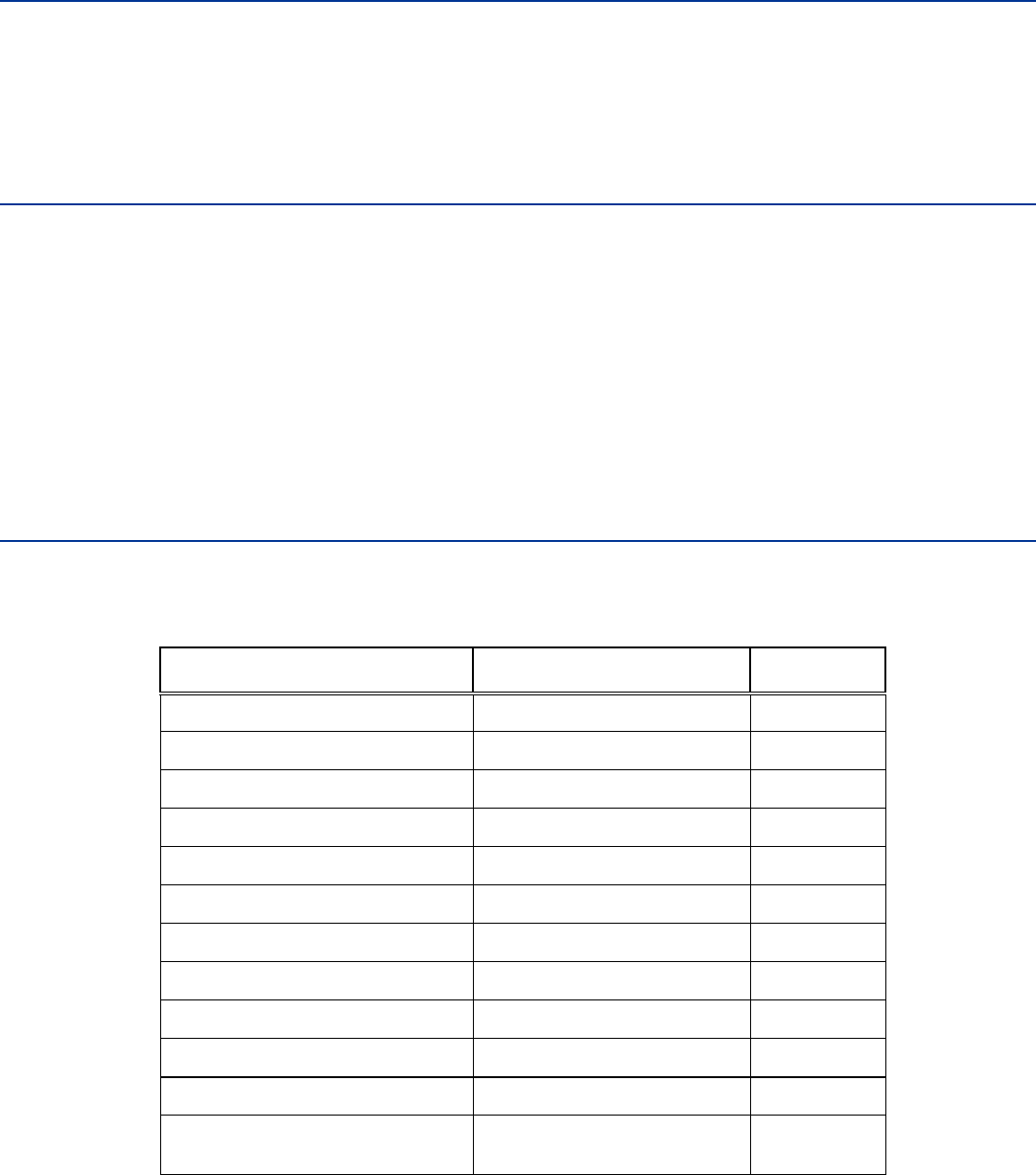
System Guide
TransCore Proprietary
D–2
Appendix D Command Quick Reference
This appendix lists the default configuration settings for the
Multiprotocol Reader Extreme (MPRX) and its commands. Commands
are listed both numerically and alphabetically.
Command Syntax
The command numbers consist of from 2 to 4 hex digits. The letters N or S may follow a
command number. The letter N indicates that part of the command number is variable. The
letter S indicates the requirement for an alphanumeric data string that is to be included
immediately following the command number. Hex digits (0–9, A–F) in either uppercase
or lowercase characters may be used in data strings and for hex digits A–F. For more
information refer to Chapter 5, “This chapter provides software-related information for the
Multiprotocol Reader Extreme (MPRX) System.” on page 5–2.
Table D – 1 lists factory default settings. Table D – 2 lists, in numerical order, all of the
commands available to users. Table D – 3 lists the same commands by command name.
Factory Default Settings
Table D – 1 lists the factory default settings for the MPRX.
Table D – 1 MPRX Default Configuration Settings
Parameter Setting Command
Operating mode Data 00
Baud rate 9600 1005
Stop bits 1 1010
Parity None 1020
Time and data appended Enabled 302
Auxiliary information appended Disabled 310
Unique ID code criteria Separation of 1 ID 4100
Valid ID code criteria Acquisition of 1 ID 4200
Uniqueness time-out 2 minutes 441
Tag translation mode Disabled 452
Multi-tag sort Disabled 454
SeGo protocol tag initialization
during multi-tag sort
Enabled 456
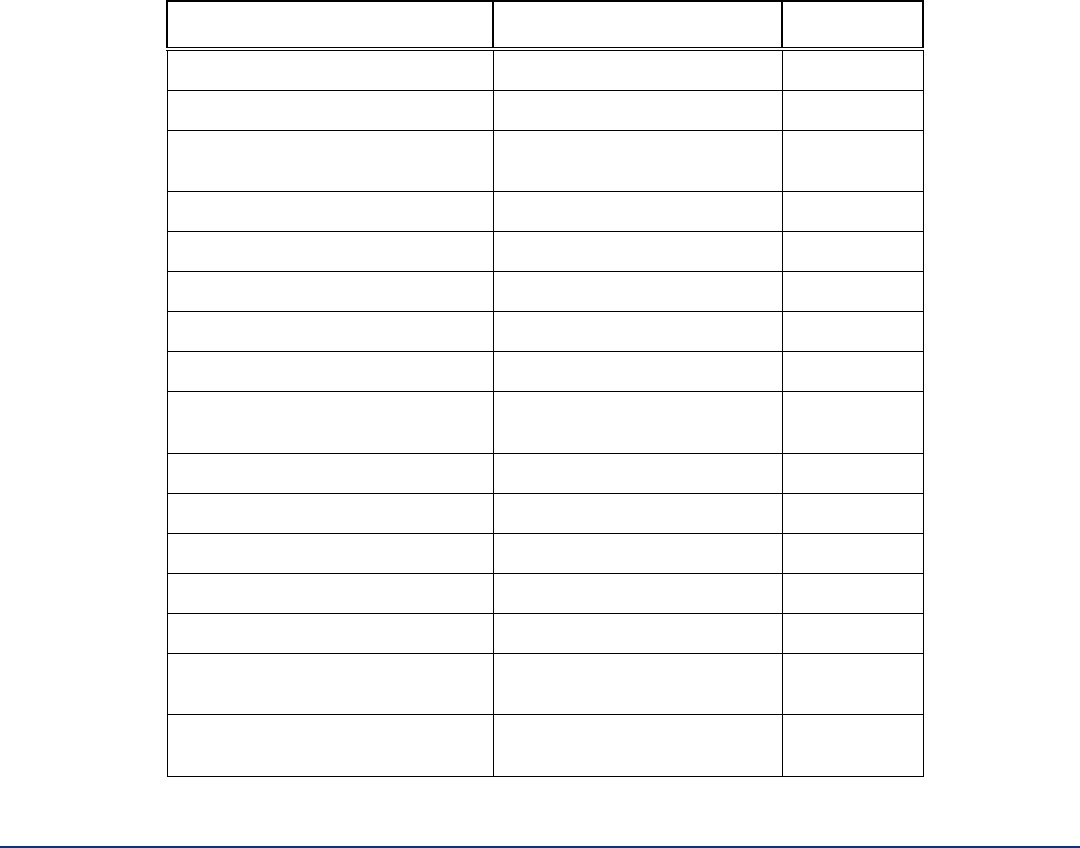
MPRX
TransCore Proprietary D–3
Parameter Setting Command
Reader ID number 00 6000
Communications protocol Basic 610
Error correcting protocol (ECP)
timeout
12.7 sec 612FE
Flow control Software (XON/XOFF) 6141
Echo mode Enabled 6171
RF-by-input control Enabled 641
ATA operating range (distance) Maximum 6431F
RF attenuation Full power 64400
SeGo protocol operating range
(distance)
Maximum 6451F
Presence without tag reports Disabled 6900
RF-o control Timeout or no presence 6922
RF timeout Never true 693F
Input inversion Disabled 6940
Serial number SSSSSS 695
Store hardware configuration Hardware configuration not
known
696
Automatic periodic RF status
report
Disabled 830
Numerical Command List
The following conventions are used in Table D – 2.
Items in bold italics identify factory default settings.
Only the command-related data portion of the reader message is shown.
Refer to Chapter 6, “Chapter 6 Communications Protocols” on page 6–2 ” for the
complete syntax of commands and messages.

System Guide
TransCore Proprietary
D–4
Table D – 2 MPRX Commands Listed Numerically
Number Command Name Reader Message
00 Switch to data mode Done
01 Switch to command mode Done
1002 Set baud rate = 1200 baud Done
1003 Set baud rate = 2400 baud Done
1004 Set baud rate = 4800 baud Done
1005 Set baud rate = 9600 baud Done
1006 Set baud rate = 19.2 K baud Done
1007 Set baud rate = 38.4 K baud Done
1010 Use one stop bit Done
1011 Use two stop bits Done
1020 Disable parity Done
1021 Select even parity Done
1022 Select odd parity Done
20 Set time Done
21 Set date Done
22 Display time and date Time and date
300 No time and date appended Done
302 Time and date appended Done
310 Disable aux info append Done
311 Enable aux info append Done
40 Transmit all IDs Done
4100 Select one ID separation Done
4101 Select two ID separation Done
4102 Select three ID separation Done
4103 Select four ID separation Done
4200 Select 1 valid ID code Done
4201 Select 2 valid ID codes Done
4202 Select 3 valid ID codes Done
4203 Select 4 valid ID codes Done
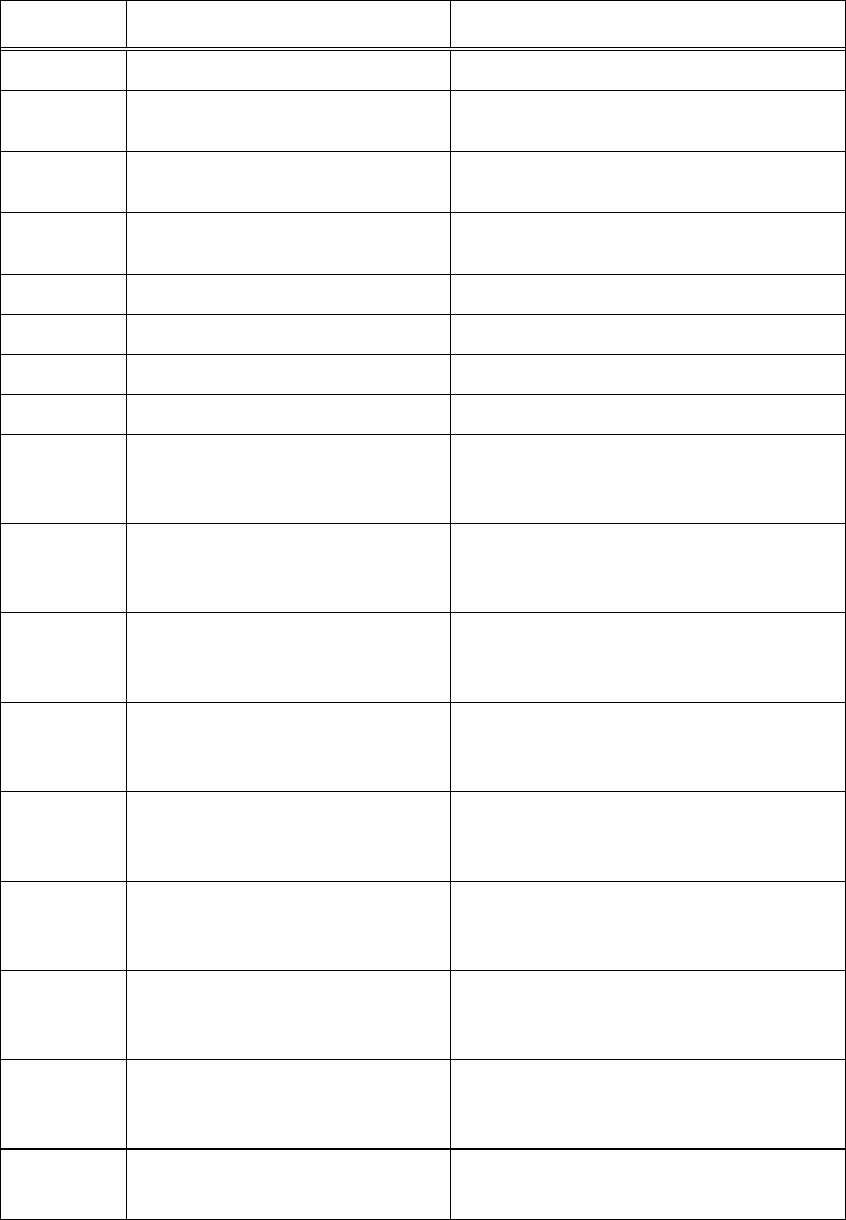
MPRX
TransCore Proprietary D–5
Number Command Name Reader Message
440 Reset uniqueness Done
441 Set uniqueness time-out to 2
minutes
Done
442 Set uniqueness time-out to 15
seconds
Done
443 Set uniqueness time-out to 30
seconds
Done
452 Disable tag translation mode Done
453 Enable tag translation mode Done
454 Disable multi-tag sort Done
455 Enable multi-tag sort Done
456 Enable SeGo protocol tag
initialization during multi-tag
sort
Done
457 Disable SeGo protocol tag
initialization during multi-tag
sort
Done
480 Disable ATA Done if MPRX model supports this
tag protocol. Error if tag protocol is
unsupported.
481 Enable ATA Done if MPRX model supports this
tag protocol. Error if tag protocol is
unsupported.
484 Disable SeGo Done if MPRX model supports this
tag protocol. Error if tag protocol is
unsupported.
485 Enable SeGo Done if MPRX model supports this
tag protocol. Error if tag protocol is
unsupported.
488 Disable eATA Done if MPRX model supports this
tag protocol. Error if tag protocol is
unsupported.
489 Enable eATA Done if MPRX model supports this
tag protocol. Error if tag protocol is
unsupported.
505 Display version Model [model]
Ver [version no.] SN [serial no.]
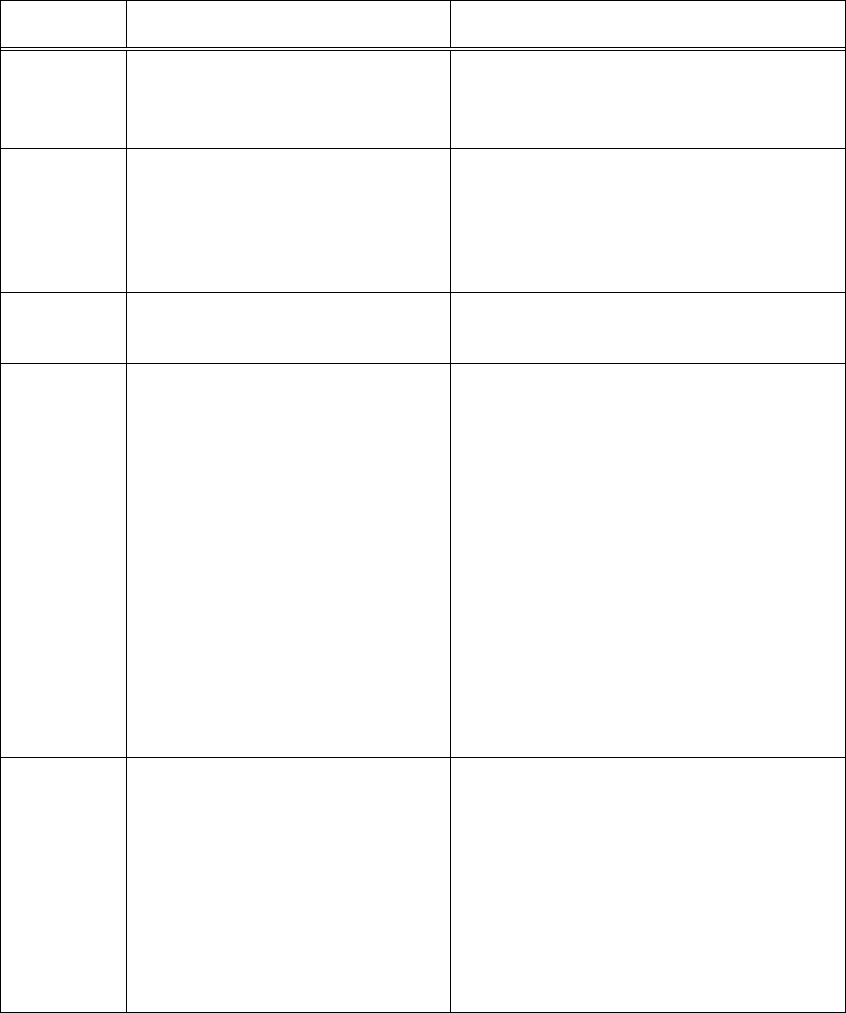
System Guide
TransCore Proprietary
D–6
Number Command Name Reader Message
506 Display hardware configuration
information
S...S
S...S = ASCII string (maximum length of
20 characters)
520 Display power fail bit PWRB Px R0
P0 = no power fail has occurred
P1 = power fail has occurred
R0 = not applicable to the MPRX
521 Display reader ID number RDID xx
xx = 00–FF
522 Display comm port parameters MAIN Bx Sx Px D0
B2 = 1200
B3 = 2400
B4 = 4800
B5 = 9600
B6 = 19.2
B7 = 38.4
S0 = one stop bit S1 = two stop bits P0
= no parity
P1 = even P2 = odd
D0 = EOL delay of 0 ms
524 Display appended info status IDAP T0 D0 Xx
T0 = time not appended
T1 = time appended
D0 = date not appended
D1 = date appended
X0 = aux info not appended
X1 = aux info appended
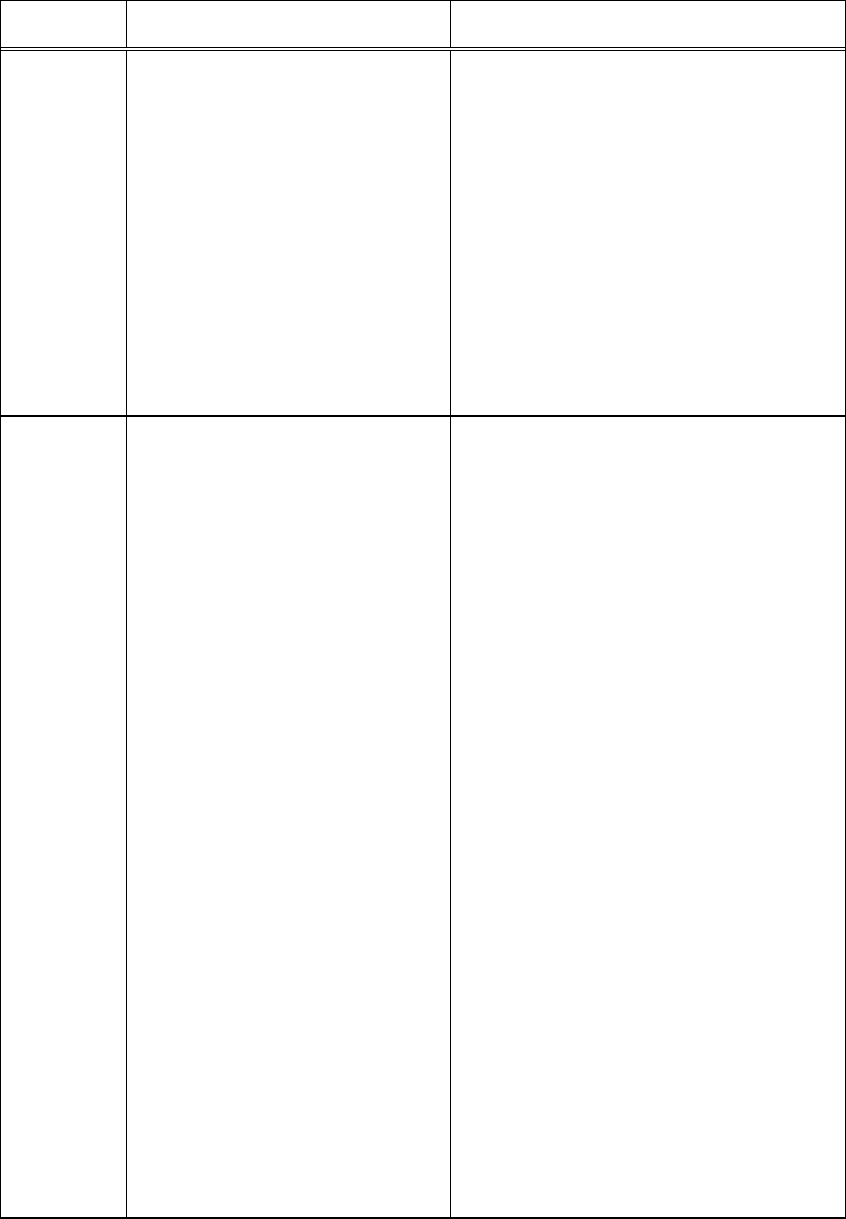
MPRX
TransCore Proprietary D–7
Number Command Name Reader Message
525 Display comm protocol ECPS Px Txx Xx S0
P0 = basic
P1 = ECP
P2 = data Inquiry
Txx = ECP timeout
ms = 50 * xx
FF = disabled ECP timeout
X0 = no flow control
X1 = software flow control
S0 = som character is #
527 Display RF status RFST Cx Ox Tx Fxxx Rxx Gxx
Axx I04
C0 = RF controlled by host
C1 = RF-by-presence sensor
O0 = RF o
O1 = RF on
T1 = uniqueness timeout of 2 min
T2 = uniqueness timeout of 15 sec
T3 = uniqueness timeout of 30 sec
Fxxx = RF output frequency,
xxx = 000 to 118
Rxx = Tag decoder range (distance) for
ATA tags, 00 to 1F hexadecimal range
value
Gxx = Tag decoder range (distance) for
eGo Plus Tags, 00 to 1F hexadecimal
range value Axx = RF power
attenuation, 00 max to 0A min (10 dB
less than max)
I04 = fixed
Note: If you enter RF settings using
command #642NN, the display command
for RF output frequency, F is “Fxx” and
indicates use of the backward-compatible
frequency entry method.
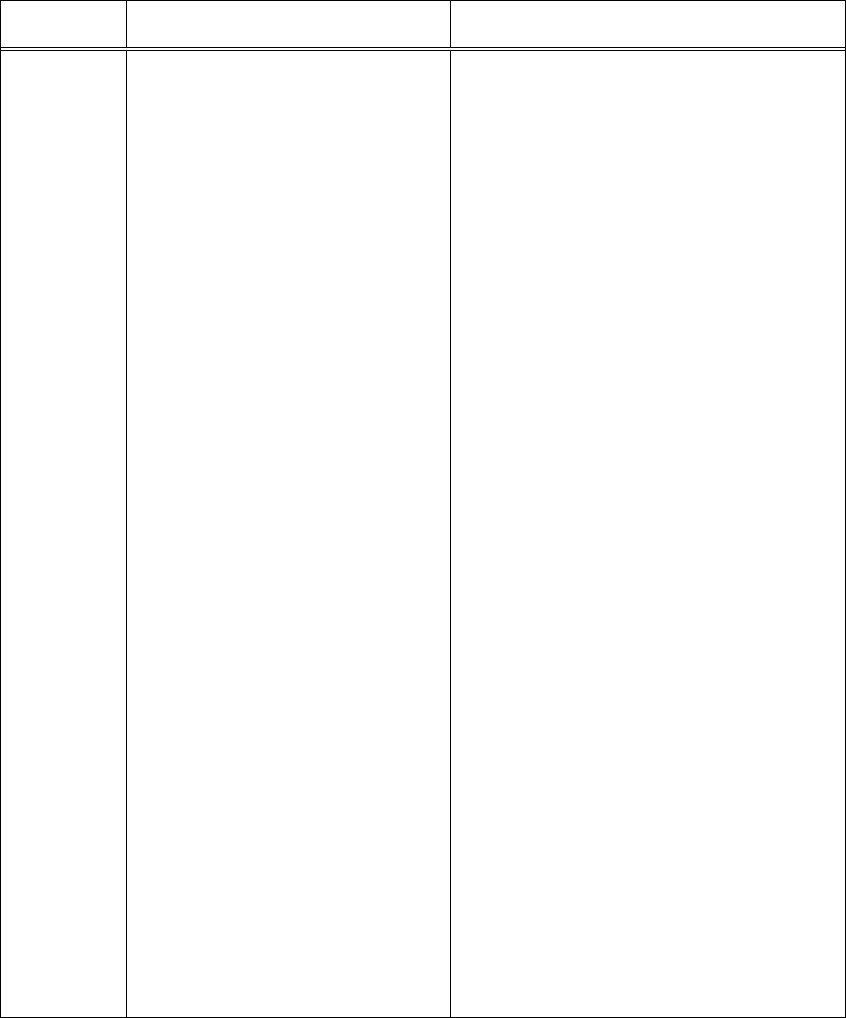
System Guide
TransCore Proprietary
D–8
Number Command Name Reader Message
529 Display presence input status PRST Px D0 Ax Tx Ix
P0 = disable presence w/o tag reports
P1 = enable presence w/o tag reports
D0 = min presence true period of 0 ms
A0 = RF o on timeout
A1 = RF o on timeout or tag A2 = RF
o on timeout or no presence
T0: RF timeout of 0 ms (always expired)
T1: RF timeout of 4 ms
T2: RF timeout of 8 ms
T3: RF timeout of 12 ms
T4: RF timeout of 20 ms
T5: RF timeout of 24 ms
T6: RF timeout of 32 ms
T7: RF timeout of 48 ms
T8: RF timeout of 60 ms
T9: RF timeout of 92 ms
TA: RF timeout of 152 ms
TB: RF timeout of 300 ms
TC: RF timeout of 452 ms
TD: RF timeout of 600 ms
TE: RF timeout of 752 ms
TF: RF timeout infinite, never expires
(factory default)
I0 = Input inversion disabled (factory
default)
I1 = Input inversion enabled
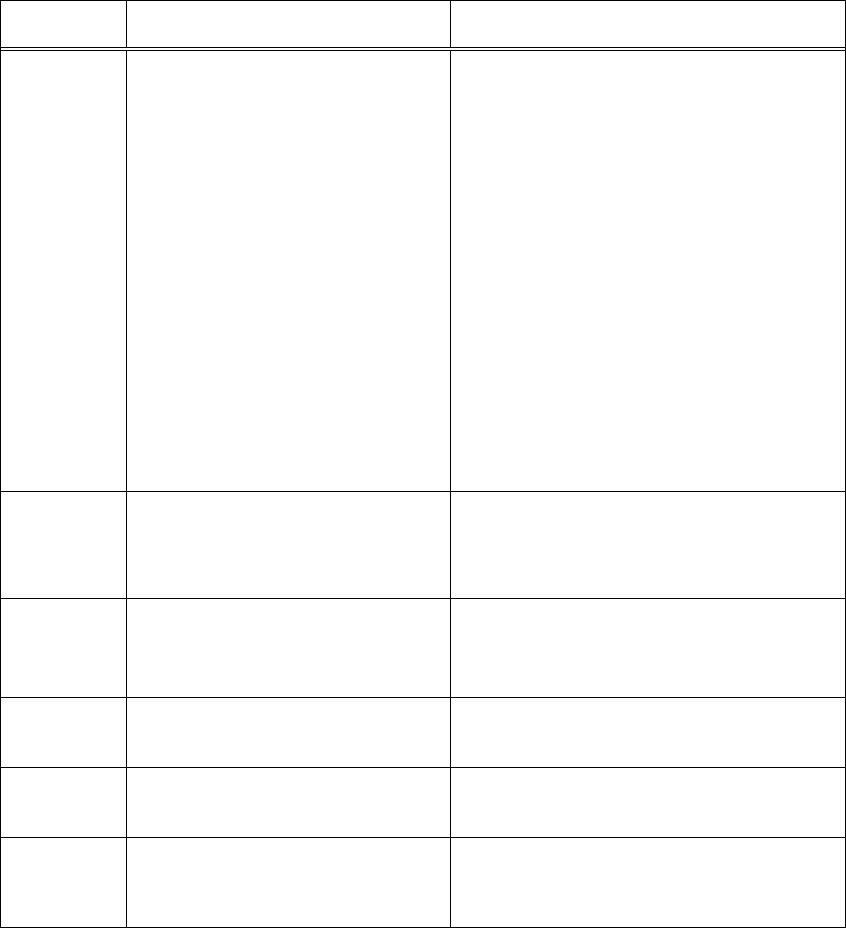
MPRX
TransCore Proprietary D–9
Number Command Name Reader Message
530 Display RF0 filter status RF0S Ux V0
U0 = one ID separation (factory default)
U1 = two ID separation
U2 = transmit all IDs
U3 = buer all IDs
V0 = valid ID code criteria of one
acquisition (factory default)
V1 = valid ID code criteria of two
acquisitions
V2 = valid ID code criteria of three
acquisitions
V3 = valid ID code criteria of four
acquisitions
534 Display tag translation mode
status
TT <0 to 1>
0 = tag translation mode disabled
1 = tag translation mode enabled
537 Display echo status ECHO x
0 = disabled (factory default) 1 =
enabled
540 Display flash checksum PCKS I0000 Exxxx
xxxx = 4-byte ASCII checksum
543 Display boot checksum BCKS xxxx
xxxx = 4-byte ASCII checksum
549 Get user-programmable group
select equals (GSE) filter data
The response data is formatted
similar to the data in the configuration
command.
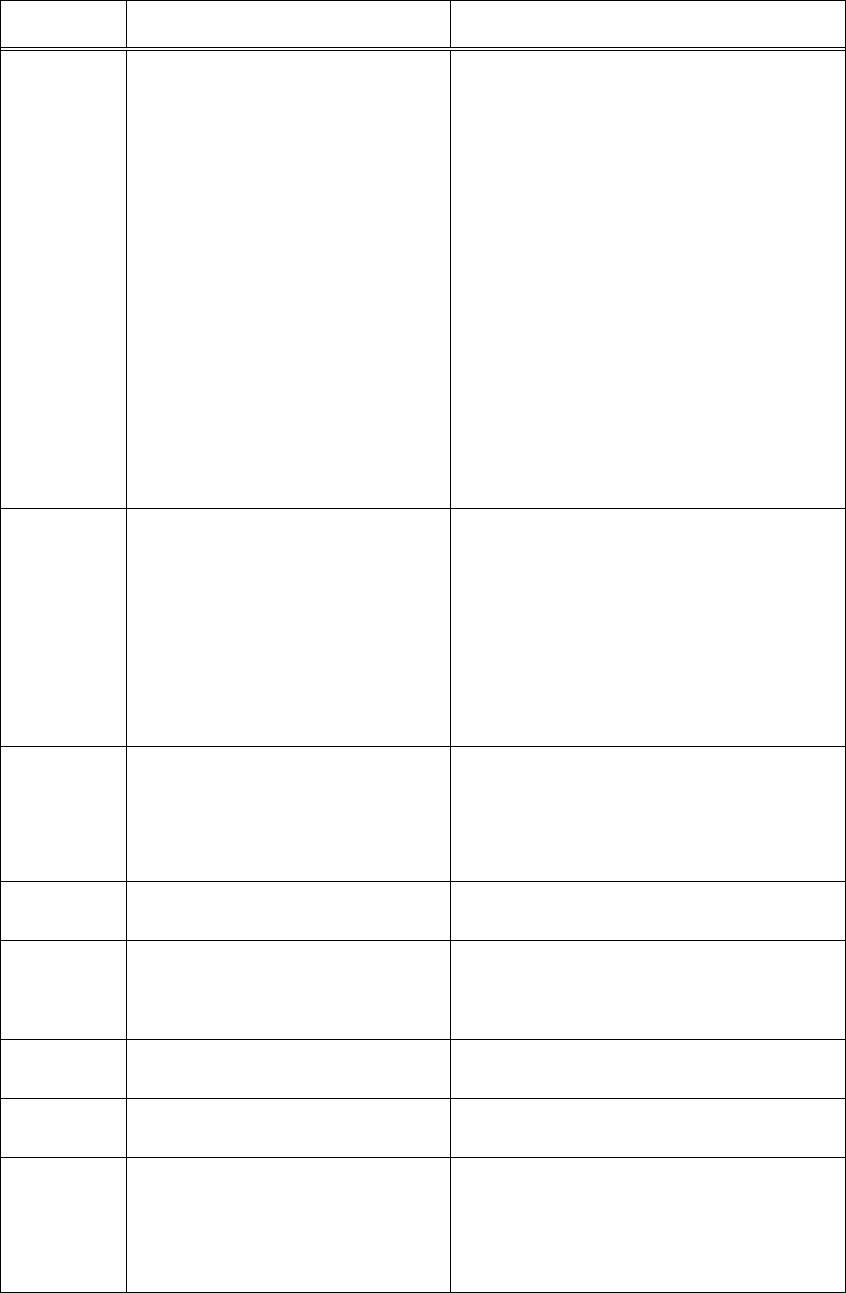
System Guide
TransCore Proprietary
D–10
Number Command Name Reader Message
552 Request sensor status change Reader response:
MUX x<0 to 3> <MPRX>
where
x = 0 antenna multiplexing disabled, RF
on port 0 only
x = 1 antenna multiplexing between RF
ports 0 and 1 when sense0 active
x = 2 antenna multiplexing between RF
ports 0 and 1 when sense0 active and
RF port 2 when sense1 active
x = 3 antenna multiplexing between RF
ports 0 and 1 when sense0 active and
RF ports 2 and 3 when sense1 active
MPRX = MPRX mode selected
560 Display input status change SSTC Ex Mx
E0 = status change reports disabled
E1 = status change reports enabled
M0 = no reporting
M1 = report change on input0 M2 =
report change on input1 M3 = report
change on either input
570 Display operating mode status ATA:<E, D> eGo:<I, F, D> SeGo:<I, F, D>
IAG:<E, D> Sort:<E, D>
I = ID (64 bits) E = Enabled
F = Full transaction (eATA) D = Disabled
577 Report buered handshakes XX = number of handshakes
60NN Set reader ID number NN =
00–FF
(00 = factory default)
Done
610 Select basic protocol Done
611 Select ECP protocol Done
612NN Set ECP timeout
NN = 01–FE (1–255)
timeout = 50 ms * NN (if NN =
FF, timeout is disabled)
Done
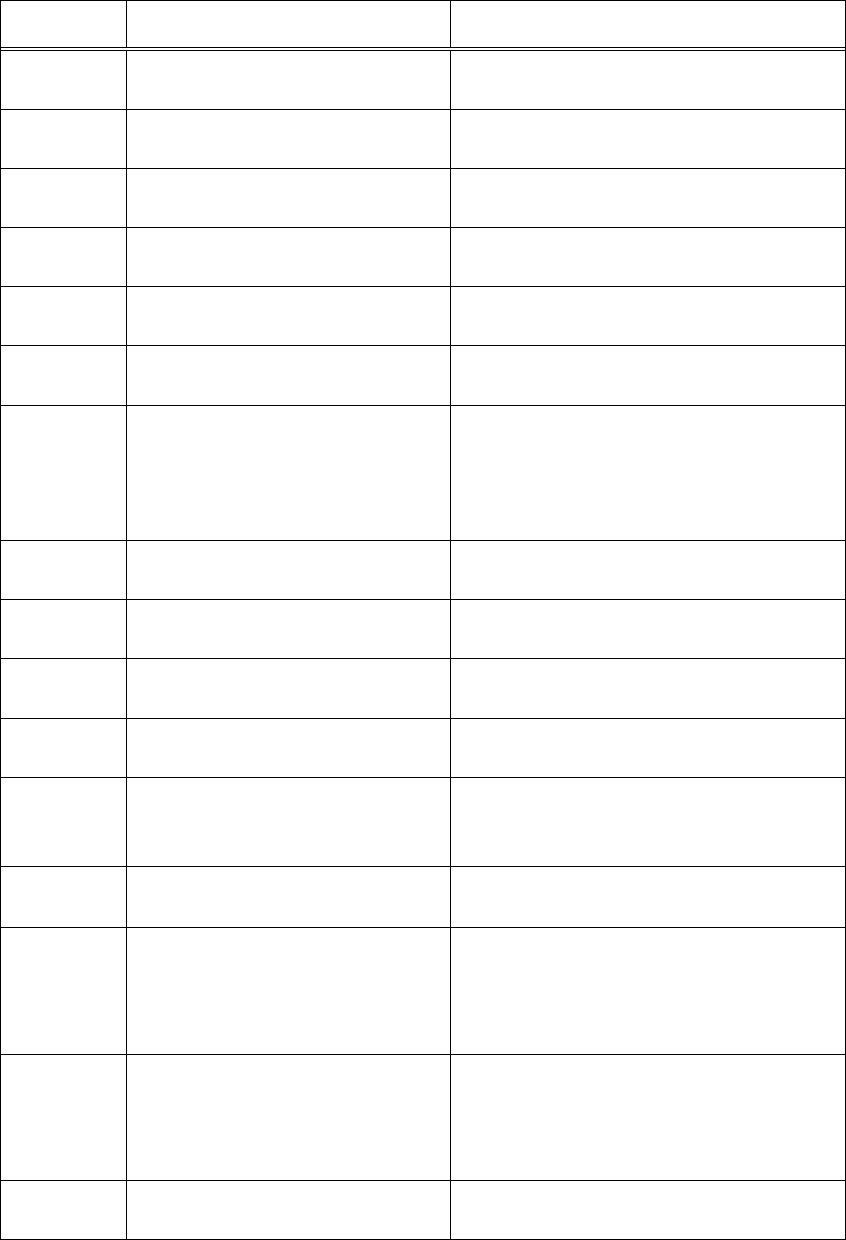
MPRX
TransCore Proprietary D–11
Number Command Name Reader Message
612FE Set ECP timeout = 12.7 sec Done
613 Enable data inquiry protocol Done
6140 Disable flow control Done
6141 Enable software flow control Done
6170 Disable echo Done
6171 Enable echo Done
63 Reset reader Model [model]
Ver [version no.] SN [serial no.]
Copyright [date]
TransCore
6400 Turn o RF Done
6401 Turn on RF Done
641 Select RF-by-input control Done
642NN Select RF operating frequency Done
643NN Set ATA operating range
(distance) NN = 00 (shortest) to
1F (longest) 1F = default
Done
644NN Set RF attenuation NN = 00 to
0A
Done
645NN Set SeGo protocol operating
range (distance)
NN = 00 (shortest) to 1F
(longest)
Done
647XXX Select RF operating frequency
from 860 to 930 in 250 kHz
steps
XXX = 000 - 118 (hexadecimal)
Done
65 Reset power fail bit Done
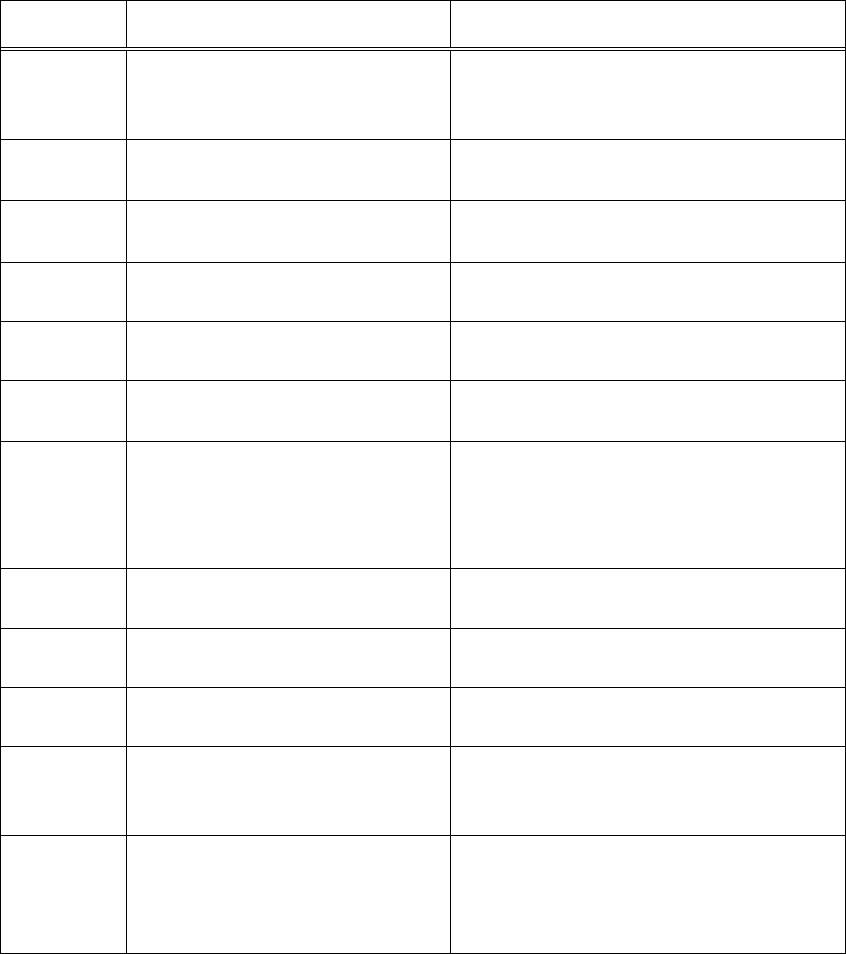
System Guide
TransCore Proprietary
D–12
Number Command Name Reader Message
66F Load default operating
parameters (except RF
operating frequency)
Done
6900 Disable presence without tag
reports
Done
6901 Enable presence without tag
reports
Done
6920 Turn RF o on timeout Done
6921 Turn RF o on timeout/tag Done
6922 Turn RF o on timeout/no
presence
Done
693N Set RF timeout N = 0–F
(always expired, 4,8,12,20,24,
32,48,60,92,152, 300,452,
600,752, infinite)
Done
693F Set RF timeout = infinite Done
6940 Disable input inversion Done
6941 Enable input inversion Done
695S...S Set serial number S...S =
ASCII string (maximum length
of 6 characters)
Done
696S...S Store hardware configuration
string S...S = ASCII string
(maximum length of 20
characters)
Done
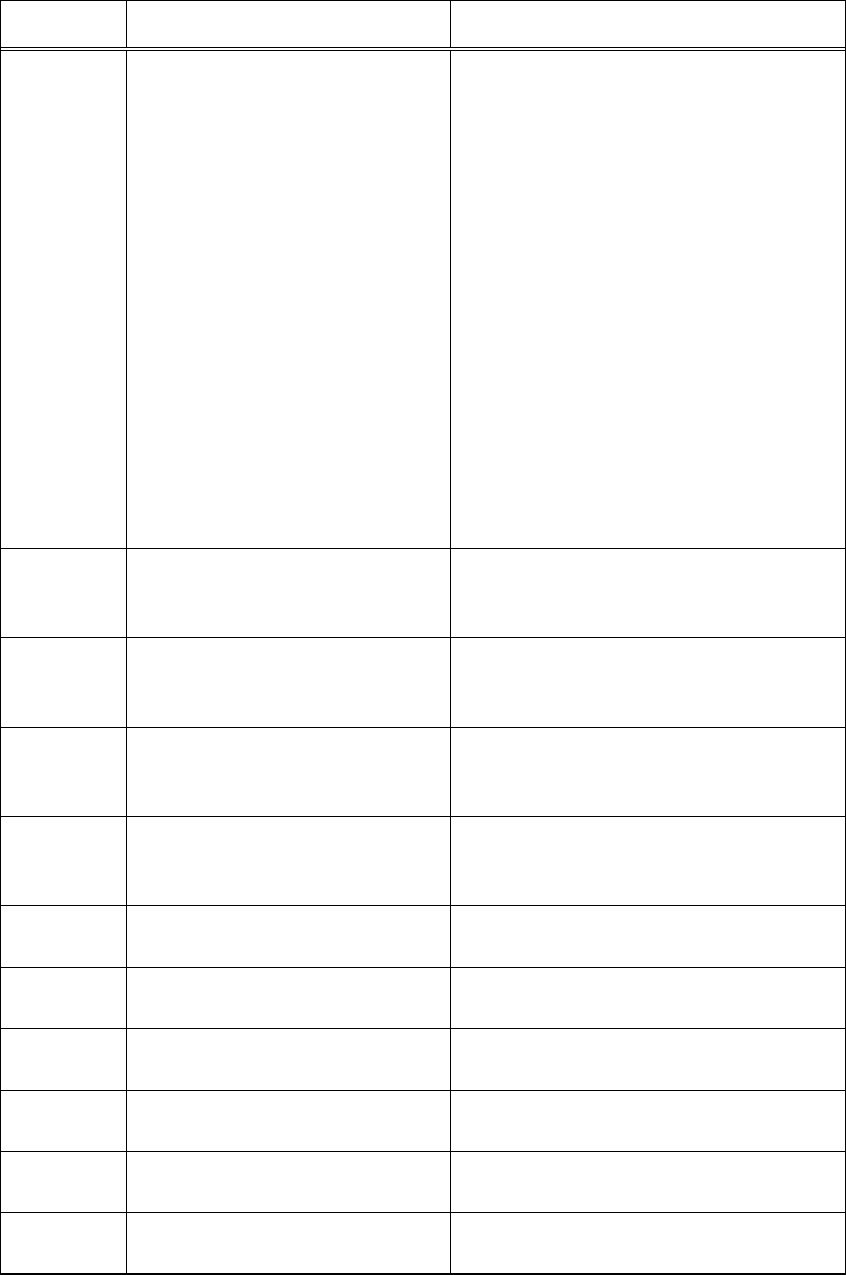
MPRX
TransCore Proprietary D–13
Number Command Name Reader Message
697 Set user-programmable group
select equals (GSE) filter
697 MM AA
DDDDDDDDDDDDDDDD
where
MM = determines which of the
eight comparison data bytes
are to be compared for the
Group Select filter
AA = determines the start
address in the tag memory for
the comparison data
D...D = 8-byte field (16
characters) used by the tag as
the comparison data for the
group select filter
Done
8110 Switch on RF port 0, fire o
check tag address 0 on check
tag pin 0
Done
8111 Switch on RF port 1, fire o
check tag address 1 on check
tag pin 0
Done
8112 Switch on RF port 2, fire o
check tag address 0 on check
tag pin 1
Done
8113 Switch on RF port 3, fire o
check tag address 1 on check
tag pin 1
Done
8142X Set check tag character on
check tag pin 0
Done
8143X Set check tag character on
check tag pin 1
Done
8150 Set check tag address to 0 on
check tag pin 0
Done
8151 Set check tag address to 1 on
check tag pin 0
Done
8152 Set check tag address to 0 on
check tag pin 1
Done
8153 Set check tag address to 1 on
check tag pin 1
Done
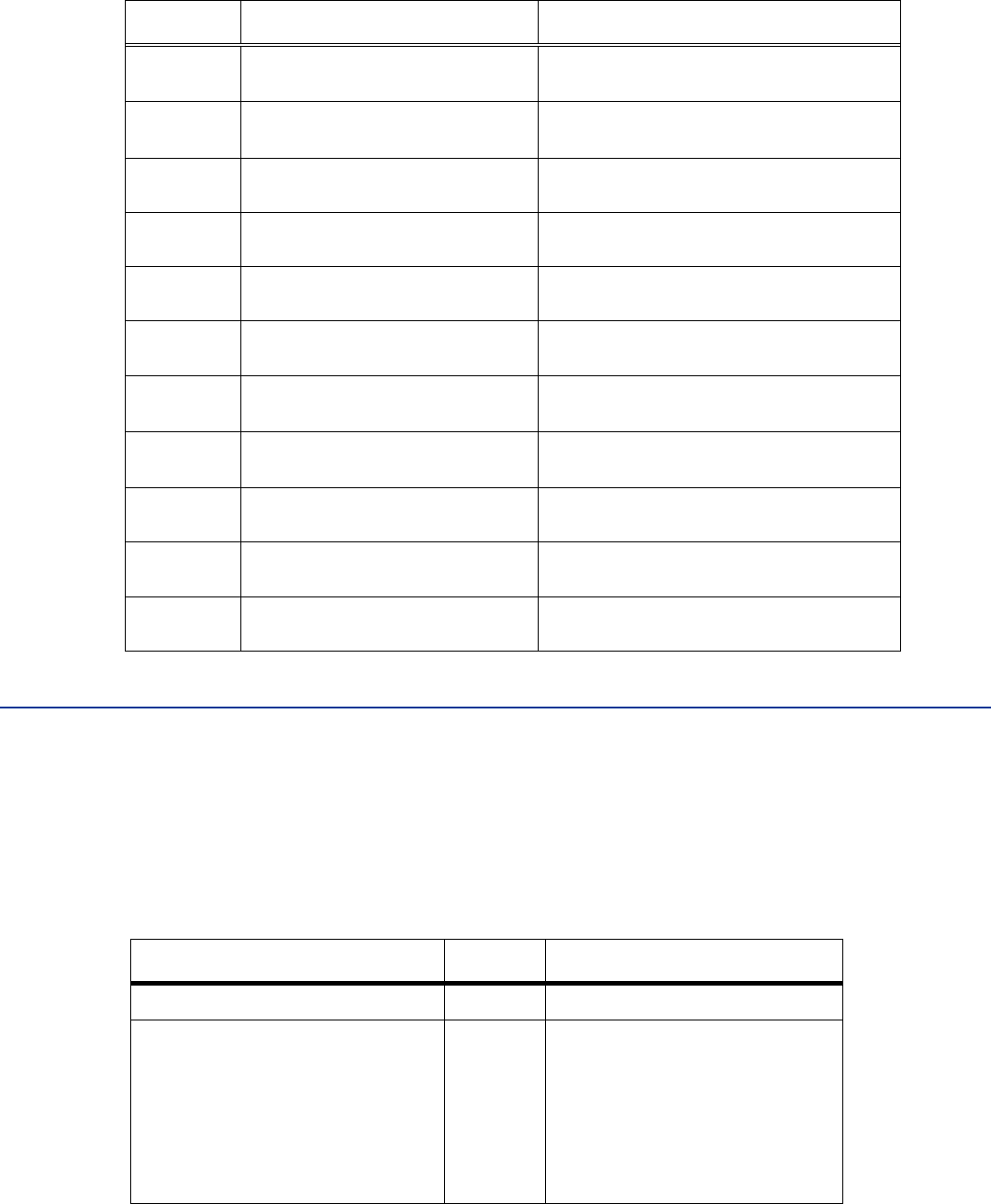
System Guide
TransCore Proprietary
D–14
Number Command Name Reader Message
830 Disable automatic periodic RF
status report
Done
831 Enable automatic periodic RF
status report
Done
836 Disable MPRX mode Done
837 Enable MPRX mode Done
850 MUX RF port 0 Done
851 MUX between RF ports 0 and 1 Done
852 MUX between RF ports 0, 1, and
2
Done
853 MUX between RF ports 0, 1, 2, and
3
Done
891 MUX test mode RF port 1 only Done
892 MUX test mode RF port 2 only Done
893 MUX test mode RF port 3 only Done
Alphabetical Command List
The following conventions are used in Table D – 3:
Items in bold italics identify factory default settings.
Only the command-related data portion of the reader message is shown.
Refer to Chapter 7, “Chapter 7 Commands” on page 7–2 for the complete syntax of
commands and messages.
Table D – 3 MPRX Commands Listed Alphabetically
Command Name Code Reader Message
All IDs transmit 40 Done
Appended info status display 524 IDAP T0 D0 Xx
T0 = time not appended
T1 = time appended
D0 = date not appended
D1 = date appended
X0 = aux info not appended
X1 = aux info appended
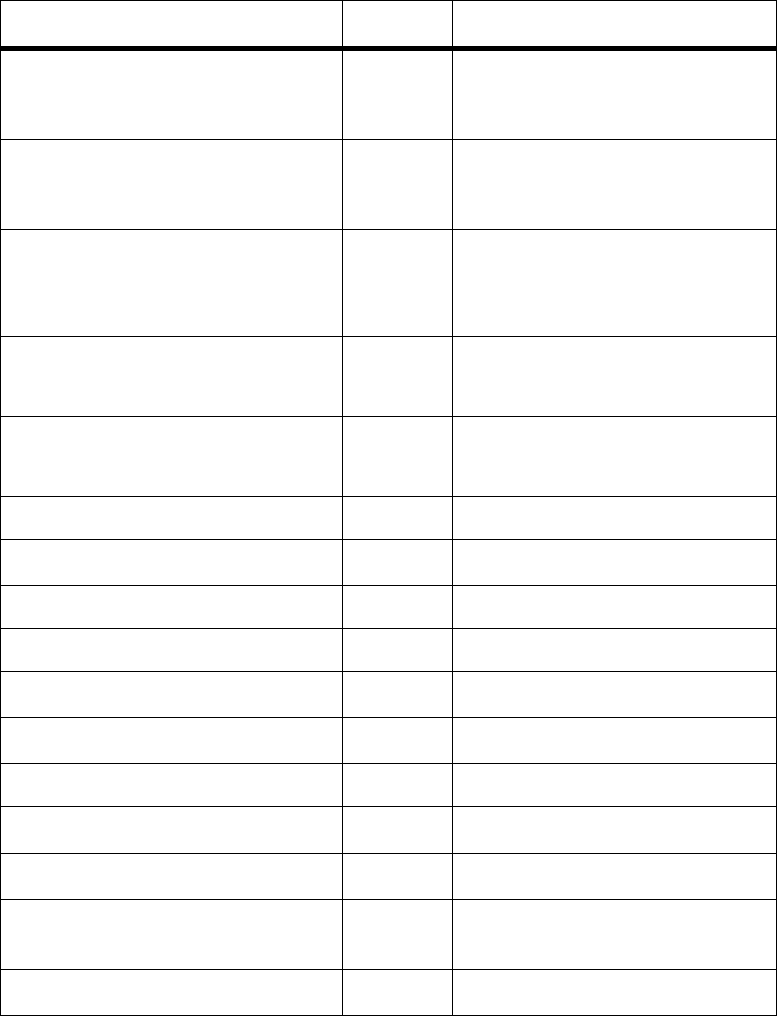
MPRX
TransCore Proprietary D–15
Command Name Code Reader Message
ATA disable 480 Done if MPRX model supports
this tag protocol. Error if tag
protocol is unsupported.
ATA enable 481 Done if MPRX model supports
this tag protocol. Error if tag
protocol is unsupported.
ATA operating range set
NN = 00 (shortest) to 1F (longest)
1F = default
643NN Done
Automatic periodic RF status
report disable
830 Done
Automatic periodic RF status
report enable
831 Done
Aux info append disable 310 Done
Aux info append enable 311 Done
Basic protocol select 610 Done
Baud rate = 1200 baud set 1002 Done
Baud rate = 19.2 K baud set 1006 Done
Baud rate = 2400 baud set 1003 Done
Baud rate = 38.4 K baud set 1007 Done
Baud rate = 4800 baud set 1004 Done
Baud rate = 9600 baud set 1005 Done
Boot checksum display 543 BCKS xxxx
xxxx = 4-byte ASCII checksum
Buered handshake report 577 XX = number of handshakes
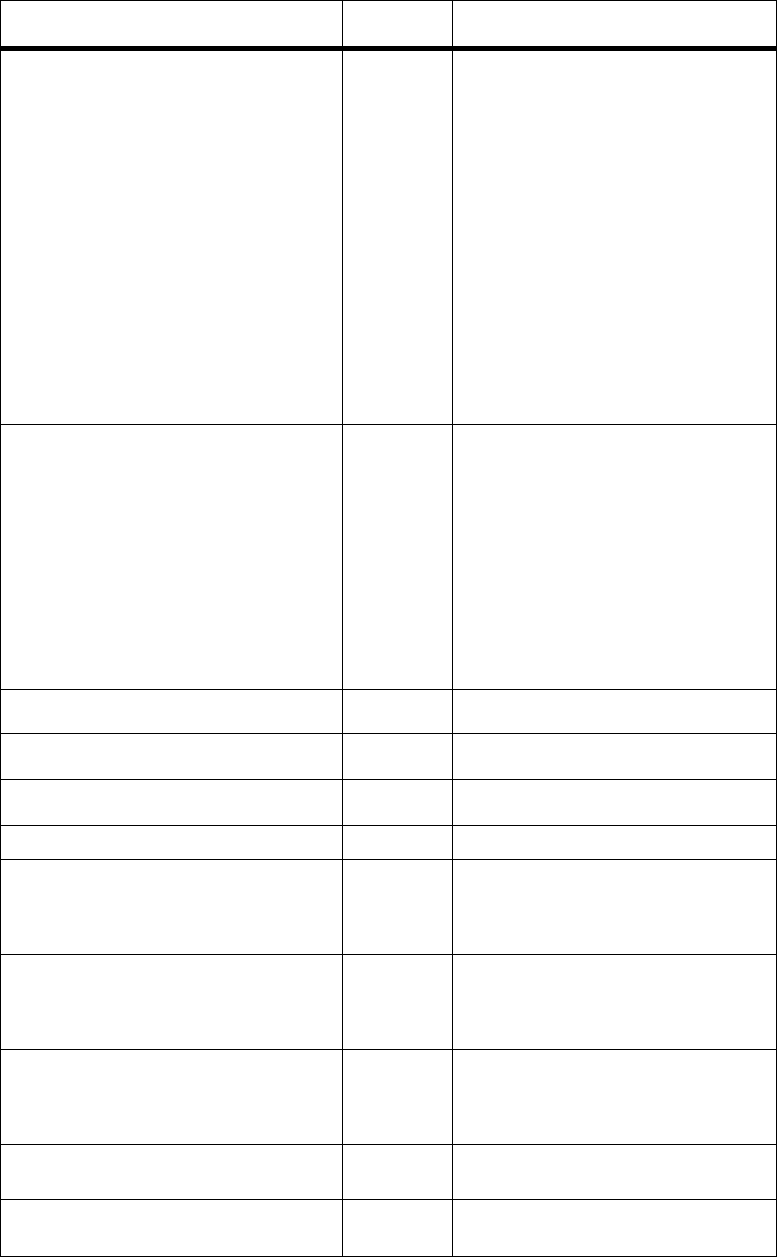
System Guide
TransCore Proprietary
D–16
Command Name Code Reader Message
Comm port parameters display 522 MAIN Bx Sx Px D0 B0 = 110
B1 = 300
B2 = 1200
B3 = 2400
B4 = 4800
B5 = 9600
B6 = 19.2
B7 = 38.4
S0 = one stop bit S1 = two stop
bits P0 = no parity
P1 = even P2 = odd
D0 = EOL delay of 0 ms
Comm protocol display 525 ECPS Px Txx Xx S0 P0 = basic
P1 = ECP
P2 = data inquiry Txx = ECP
timeout ms = 50 * xx
TFF = disabled ECP timeout X0
= no flow control
X1 = software flow control S0 =
SOM character is #
Command mode switch 01 Done
Data inquiry protocol enable 613 Done
Data mode switch 00 Done
Date set 21 Done
Default operating parameters
load (except RF operating
frequency)
66F Done
eATA disable 488 Done if MPRX model supports
this tag protocol. Error if tag
protocol is unsupported.
eATA enable 489 Done if MPRX model supports
this tag protocol. Error if tag
protocol is unsupported.
Echo disable 6170 Done
Echo enable 6171 Done
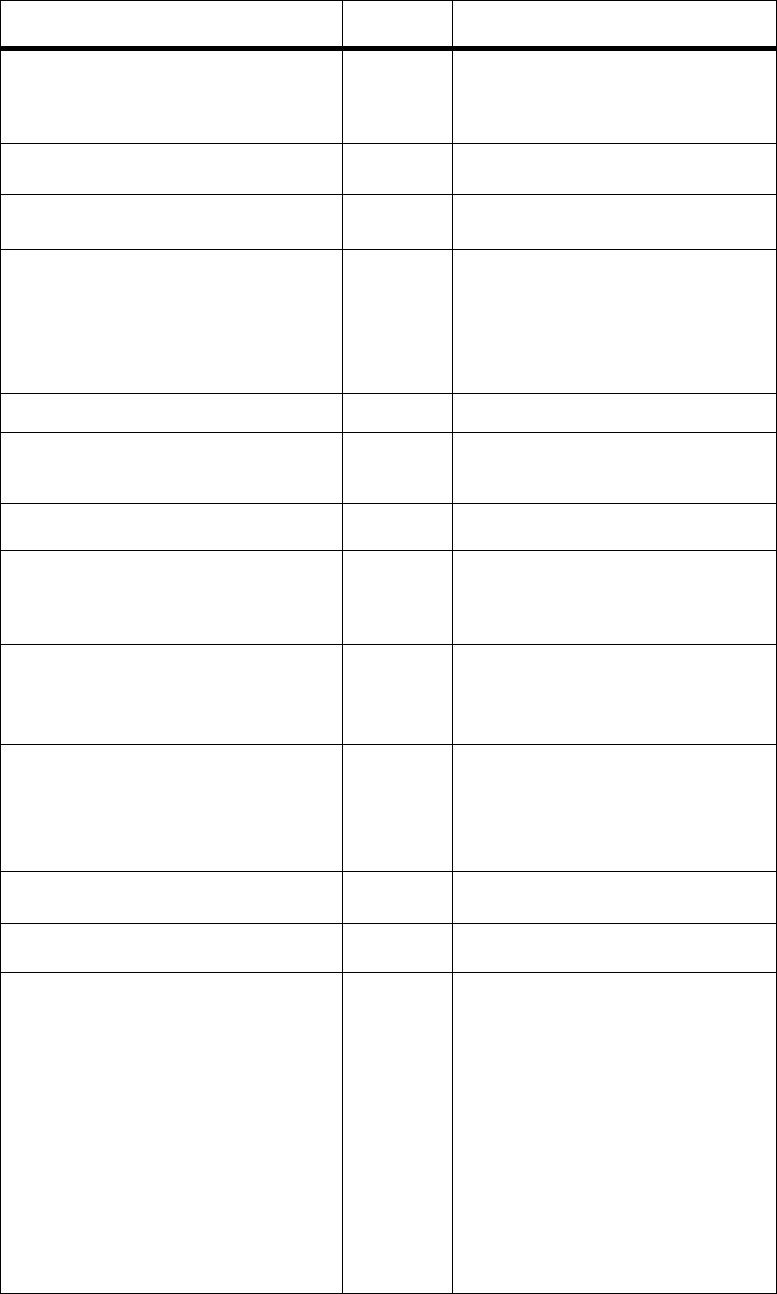
MPRX
TransCore Proprietary D–17
Command Name Code Reader Message
Echo status display 537 ECHO x
0 = disabled
1 = enabled
ECP protocol select 611 Done
ECP timeout set = 12.7 sec 612FE Done
ECP timeout set
NN = 01–FE (1–255)
timeout = 50 ms * NN
(if NN = FF, timeout is disabled)
612NN Done
Even parity select 1021 Done
Flash checksum display 540 PCKS I0000 Exxxx
xxxx = 4-byte ASCII checksum
Flow control disable 6140 Done
Get user-programmable group
select equals (GSE) filter data
549 The response data is formatted
similar to the data in the
configuration command.
Hardware configuration
information display
506 S...S
S...S = ASCII string (maximum
length of 20 characters)
Hardware configuration string
store
S...S = ASCII string (maximum
length of 20 characters)
696S...S Done
Input inversion disable 6940 Done
Input inversion enable 6941 Done
Input status change display 560 SSTC Ex Mx
E0 = status change reports
disabled
E1 = status change reports
enabled
M0 = no reporting
M1 = report change on input0
M2 = report change on input1
M3 = report change on either
input
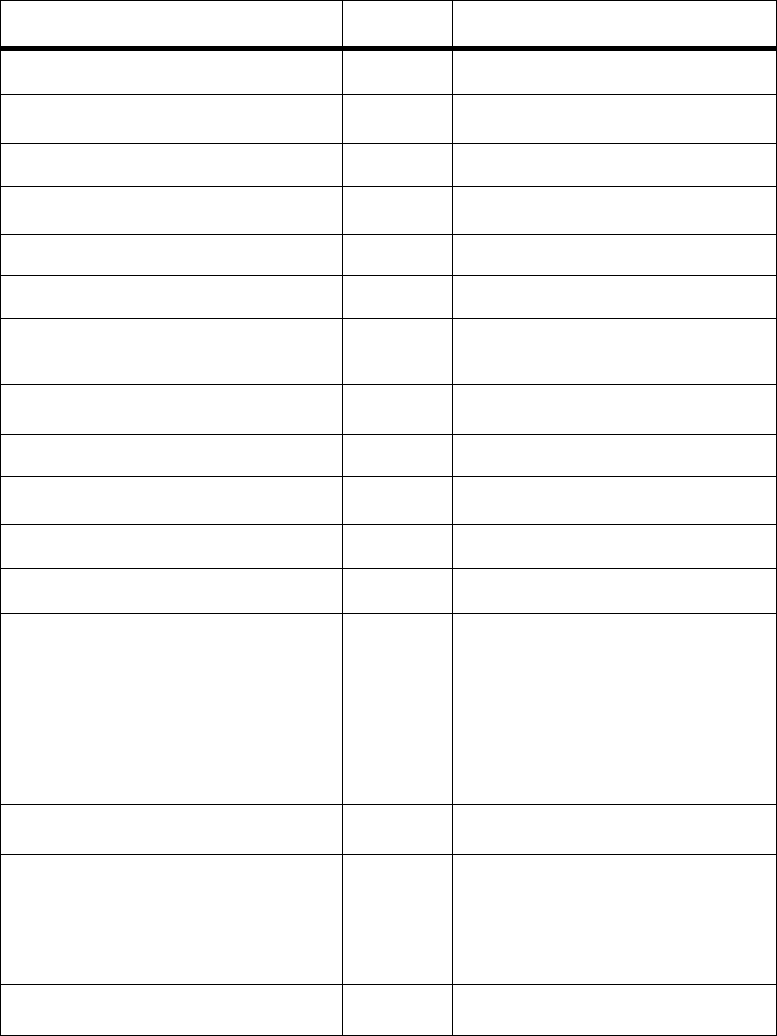
System Guide
TransCore Proprietary
D–18
Command Name Code Reader Message
MPRX mode disable 836 Done
MPRX mode enable 837 Done
Multi-tag sort disable 454 Done
Multi-tag sort enable 455 Done
MUX RF port 0 850 Done
MUX between RF ports 0 and 1 851 Done
MUX between RF ports 0, 1, and 2 852 Done
MUX between RF ports 0, 1, 2, and 3
853 Done
MUX test mode RF port 1 only 891 Done
MUX test mode RF port 2 only 892 Done
MUX test mode RF port 3 only 893 Done
Odd parity select 1022 Done
Operating mode status display 570 ATA:<E, D> eGo:<I, F, D>
SeGo:<I, F, D> IAG:<E, D>
Sort:<E, D>
I = ID (64 bits) E = Enabled
F = Full transaction (eATA) D =
Disabled
Parity disable 1020 Done
Power fail bit display 520 PWRB Px R0
P0 = no power fail has
occurred P1 = power fail has
occurred R0 = not applicable
Power fail bit reset 65 Done
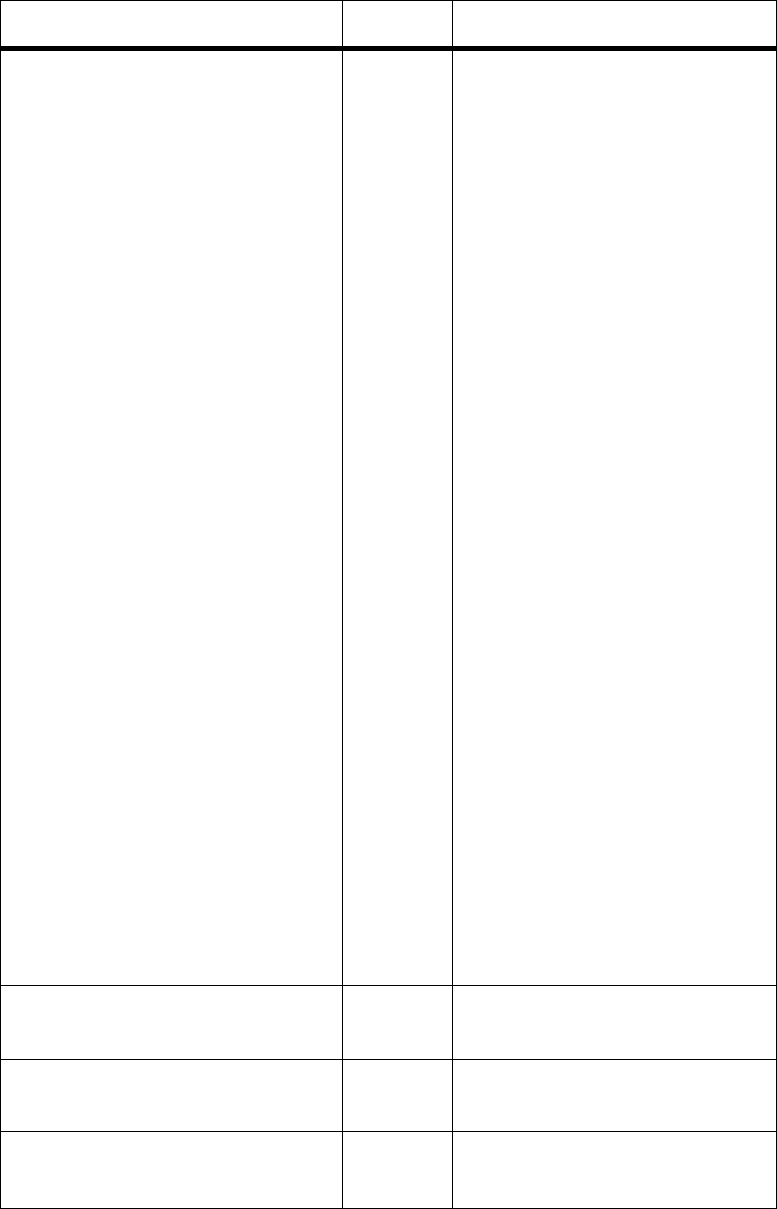
MPRX
TransCore Proprietary D–19
Command Name Code Reader Message
Presence input status display 529 PRST Px D0 Ax Tx Ix
P0 = disable presence w/o tag
reports
P1 = enable presence w/o tag
reports
D0 = min presence true period
of 0 ms
A0 = RF o on timeout
A1 = RF o on timeout or tag
A2 = RF o on timeout or no
presence
T0: RF timeout of 0 ms (always
expired)
T1: RF timeout of 4 ms T2: RF
timeout of 8 ms T3: RF timeout
of 12 ms T4: RF timeout of
20 ms T5: RF timeout of 24
ms T6: RF timeout of 32 ms
T7: RF timeout of 48 ms T8:
RF timeout of 60 ms T9: RF
timeout of 92 ms TA: RF timeout
of 152 ms TB: RF timeout of
300 ms TC: RF timeout of 452
ms TD: RF timeout of 600 ms
TE: RF timeout of 752 ms
TF: RF timeout infinite, never
expires (factory default)
I0 = Input inversion disabled
(factory default)
I1 = Input inversion enabled
Presence without tag reports
disable
6900 Done
Presence without tag reports
enable
6901 Done
Reader ID number display 521 RDID xx
xx = 00–FF
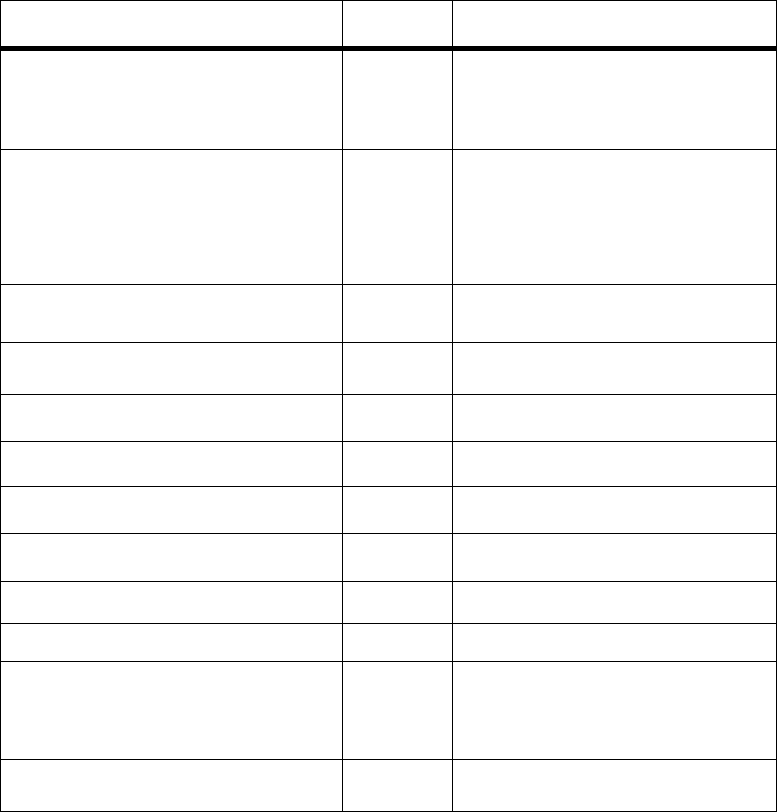
System Guide
TransCore Proprietary
D–20
Command Name Code Reader Message
Reader ID number set NN = 00-
FF
(00 = factory default)
60NN Done
Reader reset 63 Model [model]
Ver [version no.] SN [serial no.]
Copyright [date]
TransCore
Report changes both 823 Done
RF attenuation set NN = 00 to 0A 644NN Done
RF o on timeout 6920 Done
RF o on timeout/no presence 6922 Done
RF o on timeout/tag 6921 Done
RF turn o 6400 Done
RF turn on 6401 Done
RF on by input control 641 Done
RF operating frequency from 860
to 930 in 250 kHz steps select
XXX = 000 - 118 (hexadecimal)
647XXX Done
RF operating frequency select 642NN Done
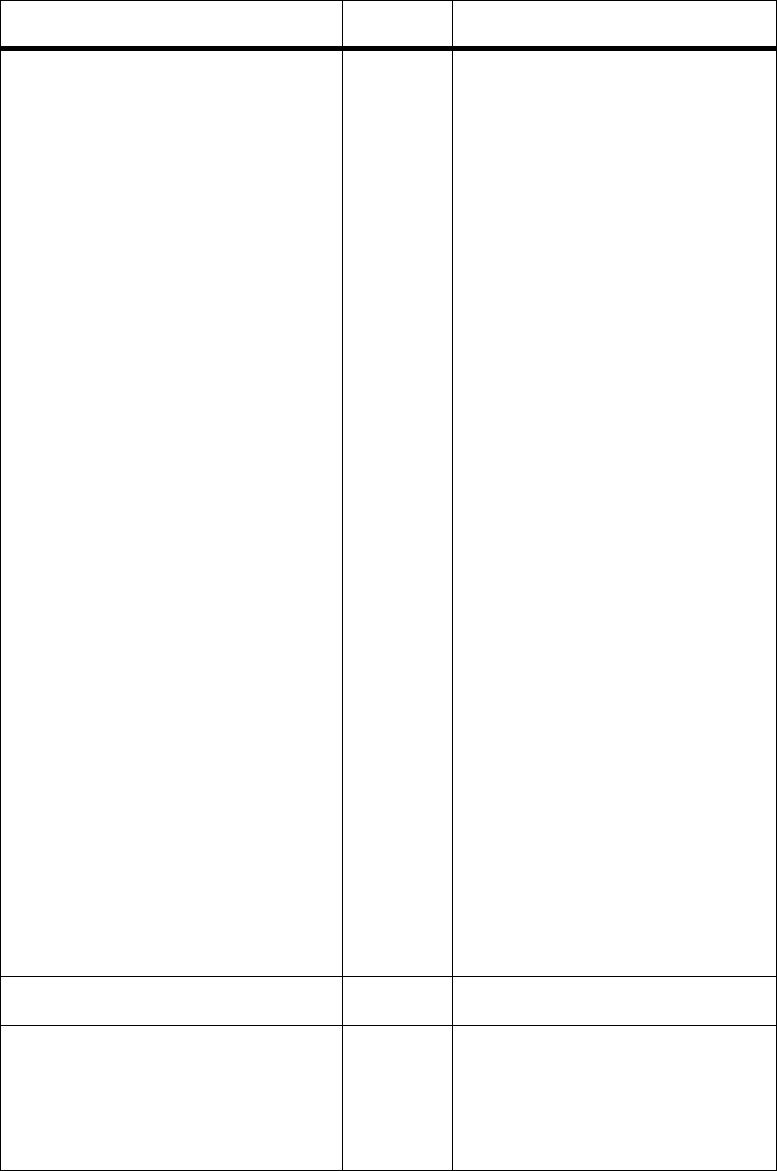
MPRX
TransCore Proprietary D–21
Command Name Code Reader Message
RF status display 527 RFST Cx Ox Tx Fxxx Rxx Gxx
Axx I04
C0 = RF controlled by host C1
= RF-by-presence sensor O0 =
RF o
O1 = RF on
T1 = uniqueness timeout of 2
min T2 = uniqueness timeout of
15 sec
T3 = uniqueness timeout of 30
sec
Fxxx = RF output frequency, xxx
= 000 to 118
Rxx = Tag decoder range
(distance) for ATA tags, 00 to 1F
hexadecimal range value
Gxx = Tag decoder range
(distance) for eGo Plus Tags, 00
to 1F hexadecimal range value
Axx = RF power attenuation, 00
max to 0A min (10 dB less than
max)
I04 = fixed
If you enter RF settings
using command #642NN,
the display command for RF
output frequency, F is “Fxx” and
indicates use of the backward-
compatible frequency entry
method.
RF timeout = innite set 693F Done
RF timeout set N = 0–F
(always expired, 4,8,12,20,24,32,
48,60,92,152,300,452,600,752
ms, infinite)
693N Done
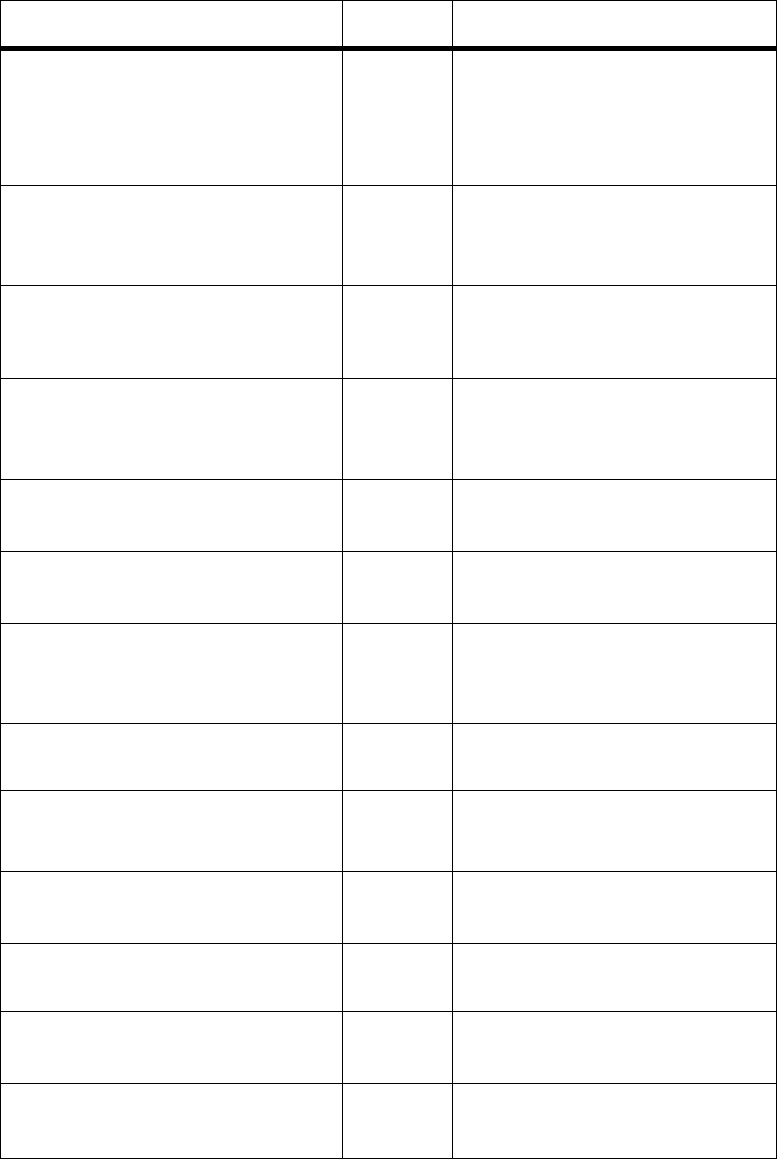
System Guide
TransCore Proprietary
D–22
Command Name Code Reader Message
RF0 filter status display 530 RF0S Ux V0
U0 = one ID separation U1 =
two ID
U2 = transmit all
SeGo disable 484 Done if MPRX model supports
this tag protocol. Error if tag
protocol is unsupported.
SeGo enable 485 Done if MPRX model supports
this tag protocol. Error if tag
protocol is unsupported.
SeGo protocol operating range
set NN = 00 (shortest) to 1F
(longest)
645NN Done
SeGo protocol tag initialization
during multi-tag sort
456 Done
SeGo protocol tag initialization
during multi-tag sort disable
457 Done
Serial number set S...S = ASCII
string (maximum length of 6
characters)
695S...S Done
Set check tag character on check
tag pin 0
8142X Done
Set check tag character on check
tag pin 1
8143X Done
Set check tag address to 0 on
check tag pin 0
8150 Done
Set check tag address to 1 on
check tag pin 0
8151 Done
Set check tag address to 0 on
check tag pin 1
8152 Done
Set check tag address to 1 on
check tag pin 1
8153 Done
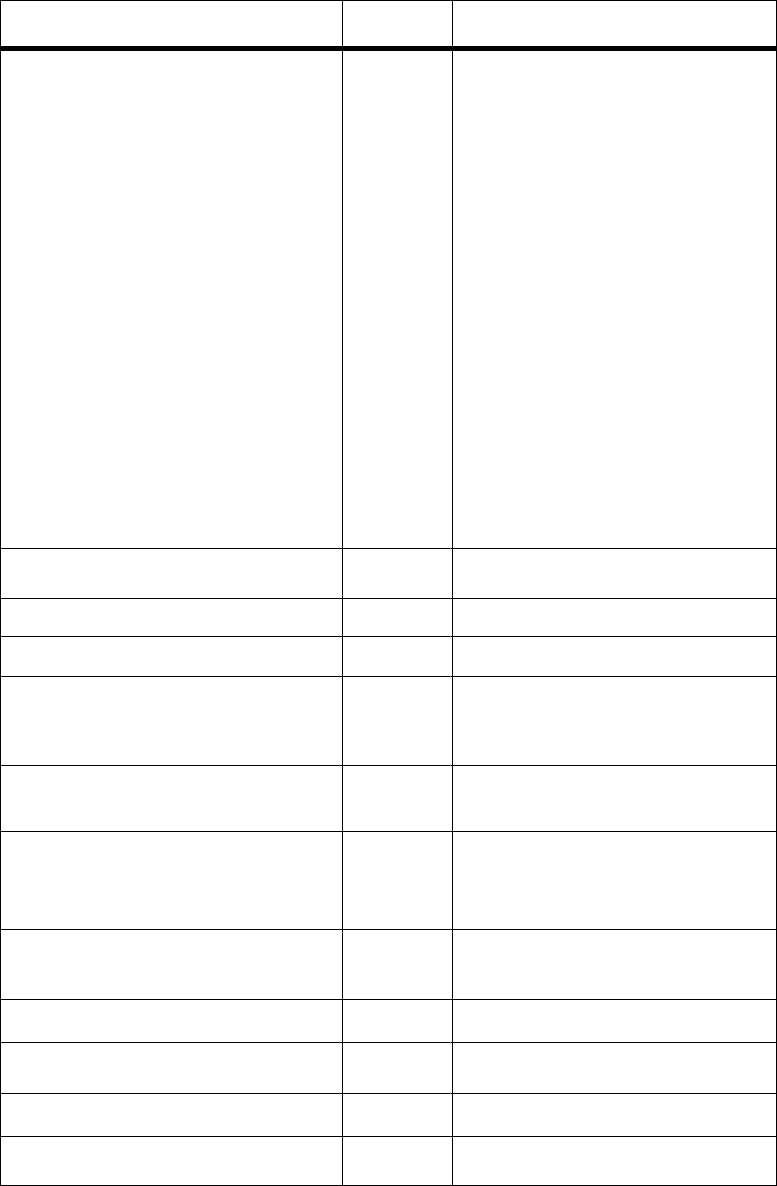
MPRX
TransCore Proprietary D–23
Command Name Code Reader Message
Set user-programmable group
select equals (GSE) filter
697 MM AA
DDDDDDDDDDDDDDDD
where
MM = determines which of the
eight comparison data bytes are
to be compared for the Group
Select filter
AA = determines the start
address in the tag memory for
the comparison data
D...D = 8-byte field (16 characters)
used by the tag as the
comparison data for the group
select filter
697 Done
Software flow control enable 6141 Done
Stop bit use one 1010 Done
Stop bit use two 1011 Done
Switch on RF port 0, fire o
check tag address 0 on check
tag pin 0
8110 Done
Switch on RF port 1, fire o check
tag address 1 on check tag pin 0
8111 Done
Switch on RF port 2, fire o
check tag address 0 on check
tag pin 1
8112 Done
Switch on RF port 3, fire o check
tag address 1 on check tag pin 1
8113 Done
Tag ID separation select four 4103 Done
Tag ID separation select one 4100 Done
Tag ID separation select three 4102 Done
Tag ID separation select two 4101 Done
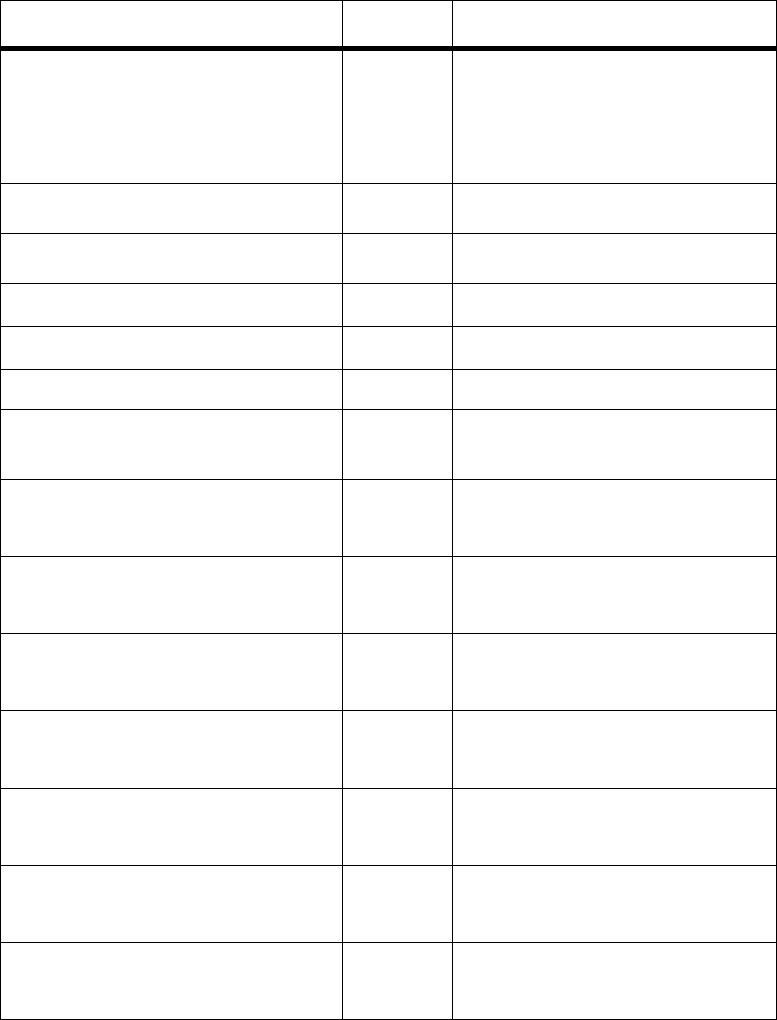
System Guide
TransCore Proprietary
D–24
Command Name Code Reader Message
Tag translation mode status
display
534 TT <0 to 1>
0 = tag translation mode
disabled
1 = tag translation mode
enabled
Time and date appended 302 Done
Time and date display 22 Time and date
Time and date not appended 300 Done
Time set 20 Done
Uniqueness reset 440 Done
Uniqueness time-out set to 2
minutes
441 Done
Uniqueness time-out set to 15
seconds
442 Done
Uniqueness time-out set to 30
seconds
443 Done
Valid ID code select four 4203 Done
Valid ID code select one 4200 Done
Valid ID code select three 4202 Done
Valid ID code select two 4201 Done
Version display 505 Model [model]
Ver [ver no.] SN [serial no.]
MPRX
TransCore Proprietary D–25

Compatible Tag Information
E
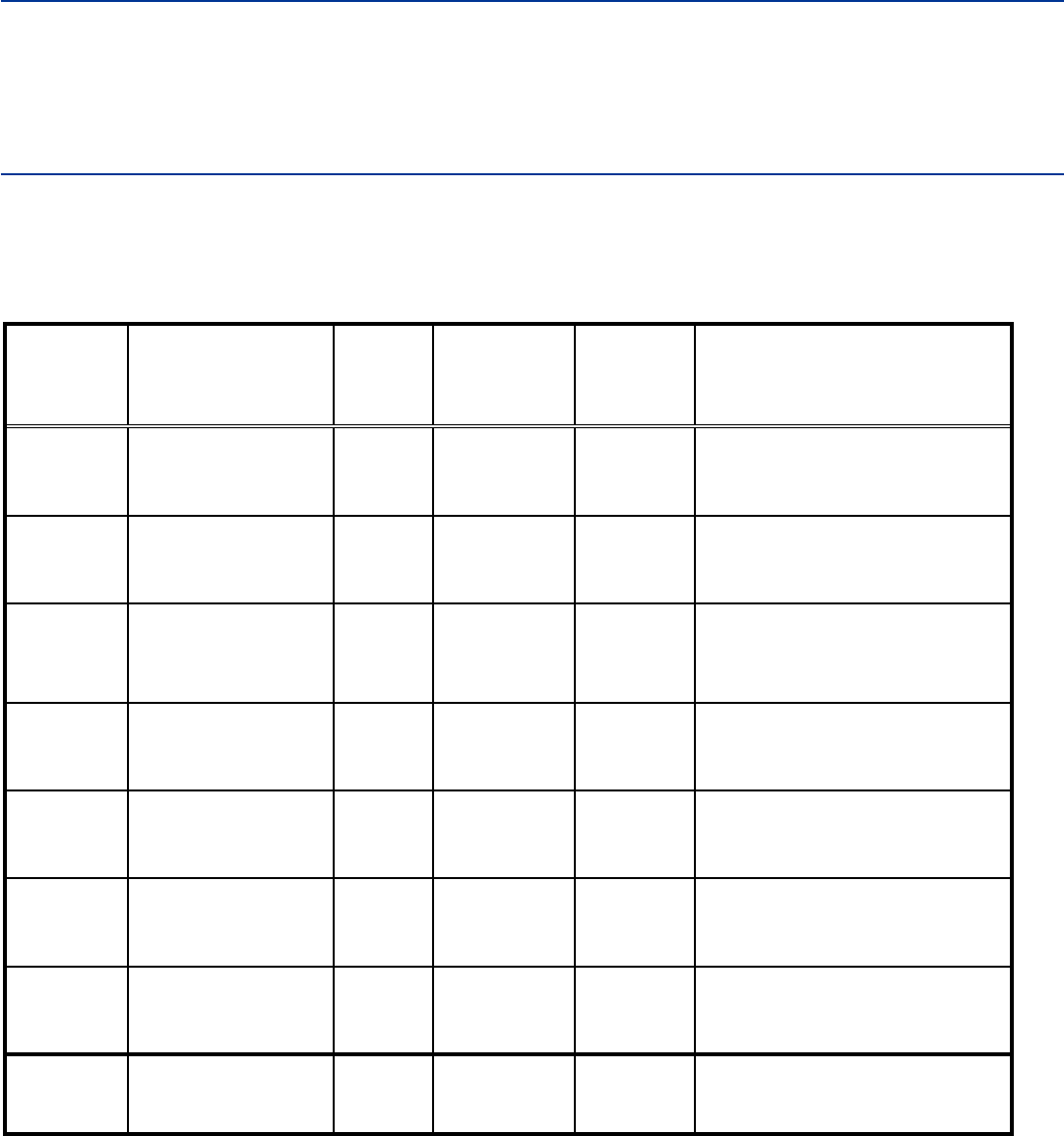
System Guide
TransCore Proprietary
E–2
Appendix E Compatible Tag Information
This appendix gives helpful information about the tags that are
compatible with the Multiprotocol Reader Extreme (MPRX).
Tag Configurations
Table E – 1 lists the TransCore Super eGo® (SeGo) protocol tags that are compatible with
the MPRX.
Table E – 1 SeGo Protocol Tags
Tag Model
Number Tag Type Power
Source
Number of
6-bit ASCII
Charactersa
Number
of 128-Bit
Framesa
Special Features
AT5120 Rail Beam 20 1
860 to 880 MHz frequency,
chemical resistant case, metal
external install
AT5118 Rail Beam 20 1
915 MHz frequency, high-
temperature chemical-resistant
case, metal external install
AT5133 Transportation Beam 20 1
915 MHz frequency, high-
temperature chemical-resistant
case, metal external install
AT5412 Transportation Beam 10 1/2
915 MHz frequency, high-
temperature chemical-resistant
case, metal external install
AT5413 Rail Beam 20 1
915 MHz frequency, high-
temperature chemical-resistant
case, metal external install
AT5414 Transportation 8-year
battery 10 1/2
Multifrequency, high-
temperature chemical-resistant
case, metal external install
AT5415 Transportation Beam 10 1/2
915 MHz frequency, high-
temperature chemical-resistant
case, metal external install
AT5549 Rail 10-year
battery 20 1 915 MHz frequency; water-
resistant, metal external install
a. These fields apply to eATA-programmed tags only. Contact TransCore for information regarding tags programmed with these
features.
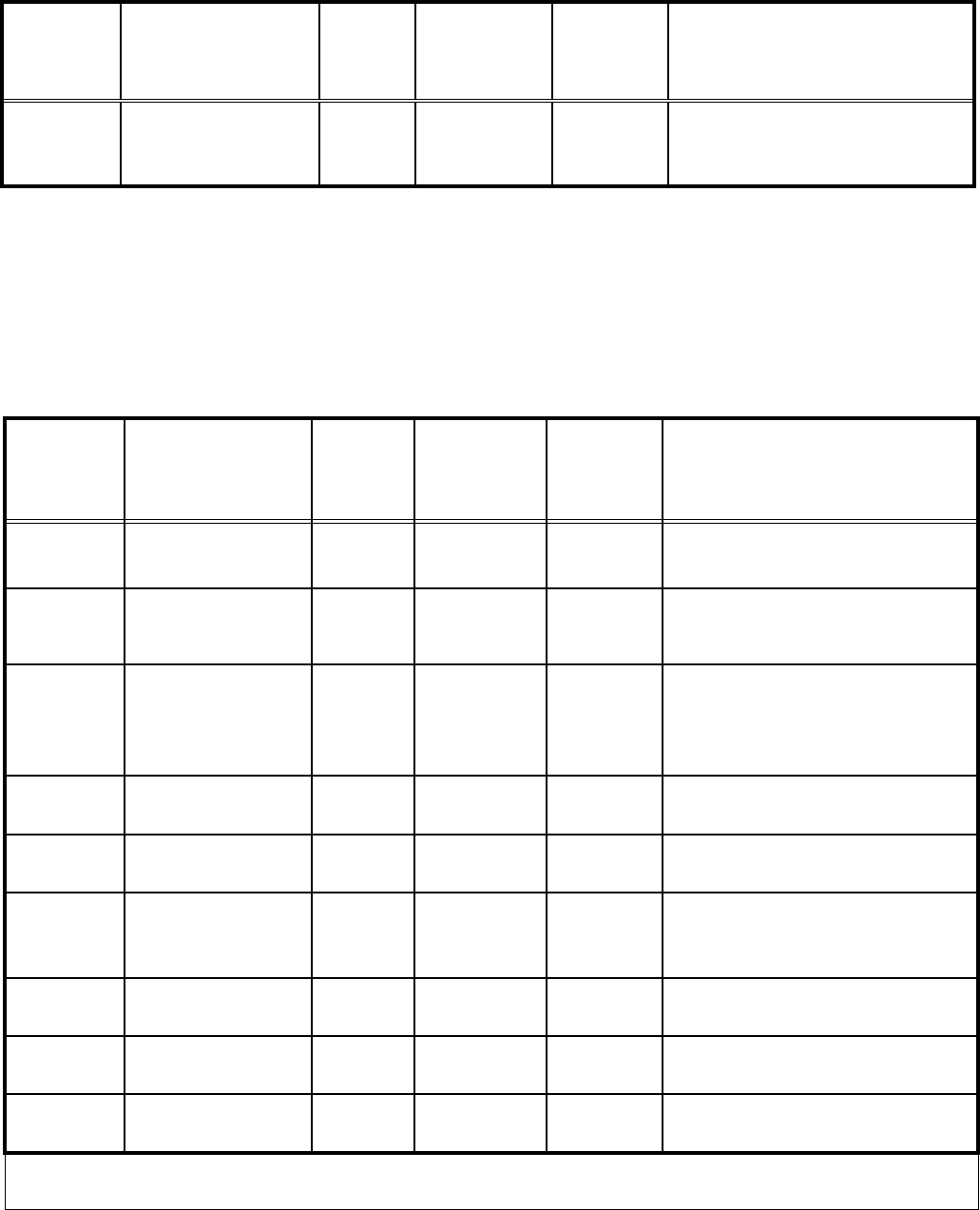
MPRX
TransCore Proprietary E–3
Table E – 2 lists most AAR-formatted tag models that are compatible with the MPRX.
Table E – 2 AAR-formatted Tags
Tag Model
Number Tag Type Power
Source
Number of
6-Bit ASCII
Characters
Number
of 128-Bit
Frames
Special Features
AT5110 Transportation Beam 20 1 915 MHz frequency, metal
external install
AT5112 Access control,
transportation
Beam 10 1/2 915 MHz frequency, metal
external install
AT5114 Access control,
transportation
10-yr
battery
10 1/2 Multifrequency, metal external
install
AT5117 Rail External 10 1/2 915 MHz frequency; weather
resistant, metal external install
AT5119 Rail External 10 1/2 915 MHz frequency; weather
resistant, metal external install
AT5125 Transportation Beam 20 1 915 MHz frequency; high-
temperature chemical-resistant
case, metal external install
AT5510 Transportation 10-yr
battery
20 1 Multifrequency, metal external
install
AT5704 Transportation External 4608 256 Multifrequency, dynamic tag,
metal external install
AT5707 Transportation 8-yr
battery
40a 2 915 MHz frequency, dynamic
tag, metal external install
If desired, in place of 40 six-bit ASCII characters, the AT5707 can support up to 34 seven-bit ASCII characters.
Tag Model
Number Tag Type Power
Source
Number of
6-bit ASCII
Charactersa
Number
of 128-Bit
Framesa
Special Features
AT5910 Transportation 8-year
battery 20 1
Multifrequency, high-
temperature chemical-resistant
case, metal external install
a. These fields apply to eATA-programmed tags only. Contact TransCore for information regarding tags programmed with these
features.

System Guide
TransCore Proprietary
E–4
Tag Data Formats
Tags are programmed at the TransCore factory with the tag model number, date of
manufacture, and data format. Contact TransCore for special order entry procedures for the
format that applies to your system. The following tag data formats can be used:
• 10-character alphanumeric ASCII — Four alphanumeric characters are fixed and can be
used to identify either the dealer or the user. The remaining six positions are numeric
and should be unique for each tag issued. For example, the entry ACME000001 might
be specified as the first tag on the order entry form from ACME Rail Lines.
• 20-character alphanumeric ASCII — Four alphanumeric characters are typically fixed
and the remaining 16 positions are numbered sequentially.
• AAR/ISO — For requirements for this format, refer to ISO 10374 and the most recent
version of Association of American Railroads Standard for Automatic Equipment
Identification.
MPRX
TransCore Proprietary E–5