ZTE BTSBI219 cdma2000 Base Transceiver Station User Manual BTSB I219 Installation Manual
ZTE Corporation cdma2000 Base Transceiver Station BTSB I219 Installation Manual
ZTE >
Users Manual
ZXC10-BTSB I2(V1.0)
cdma2000 System
Base Transceiver Station
Installation Manual
ZTE CORPORATION
ZXC10-BTSB I2(V1.0) cdma2000 System Base Transceiver Station
Installation Manual
Manual Version 20050401-R1.0
Product Version V1.0
Copyright © 2005 ZTE Corporation
All rights reserved.
No part of this documentation may be excerpted, reproduced, translated, annotated or
duplicated, in any form or by any means without the prior written permission of ZTE
Corporation.
* * * *
ZTE CORPORATION
ZTE Plaza, Keji Road South, Hi-Tech Industrial Park, Nanshan District, Shenzhen, P.R.China
Website: http://www.zte.com.cn
Postcode: 518057
Customer Support Center: (+86755) 26771900 800-9830-9830
Fax: (+86755) 26770801
Email: support@zte.com.cn
* * * *

FAX: 0086-755-26770160
Suggestions and Feedback
To improve the quality of ZTE product documentation and offer better services to our customers, we hope
you can give us your suggestions and comments on our documentation and fax this form to
+86-755-26770160; or mail to “Marketing center 3rd floor ZTE Plaza, Keji Road South, Hi-Tech Industrial
Park, Nanshan District, Shenzhen, P. R. China”. Our postcode is 518057.
Document name ZXC10-BTSB I2(V1.0) cdma2000 System Base Transceiver Station Installation Manual
Product version V1.0 Document version 20050401-R1.0
Equipment installation time
Your information
Name Company
Postcode Company address
Telephone E-mail
Presentation: How is information presented? (Introductions, procedures, illustrations, others)
F Good F Fair F Average F Poor F Bad
Accessibility: Can you find the information you want? (Table of contents, Index, headings, numbering,
others)
F Good F Fair F Average F Poor F Bad
Your evaluation
of this
documentation
Intelligibility: Can you understand it when you find it? (Language, vocabulary, readability, others)
F Good F Fair F Average F Poor F Bad
Presentation:
Accessibility:
Your su g g e stion s
for improvement
of this
documentation
Intelligibility:
Your other
suggestions on
ZTE product
documentation

FAX: 0086-755-26770160
-i-
Preface
About This Manual
This manual introduces the hardware installation flow and method of the ZXC10
BTSB I2.
It is one of the manuals of the CDMA cellular mobile communication system of ZTE.
This manual is intended to provide basic installation operation guide to the engineering
staff that install the ZXC10 BTSB I2 of ZTE. Operation and maintenance staff of the
equipment can also use it as reference.
Standardized hardware installation is the basis for the normal and stable operation of
the BS and is thus important in the project engineering. To guide the hardware
installation of ZXC10 BTSB I2, this manual is arranged in the order of engineering
installation. This manual first briefs the equipment composition, which enables the
engineering staff to have an overall understanding of the ZXC10 BTSB of ZTE. Then it
details the installation flow of the equipment and the installation check.
How to Use This Manual
This manual comprises 15 chapters:
Chapter 1 Overview of BTS Installation briefs the equipment installation and
commissioning flow, the hardware installation flow and the hardware installation
precautions for the BTS system.
Chapter 2 Installation Preparation introduces the preparations prior to the BTSB
installation, including installation environment check, and preparation for tools,
instruments and technical documentation.
Chapter 3 Unpacking Inspection describes unpacking, acceptance and handover of
the goods.
Chapter 4 Installing the Cabinets describes the installation of the BTSB cabinet, and
the layout, connection and fixing of multiple cabinets.
Chapter 5 Power System Installation describes the installation procedure of the
BTSB power system.
Chapter 6 Installing the Grounding System describes the installation procedure of
the BTSB grounding system.
Chapter 7 Installing the Cabinet Internal Cables introduces the types of BTSB
cabinet internal cables, and describes the installation procedure of them.
Chapter 8 Installing the Trunk Cables describes the installation procedure of the
BTSB trunk cables, and explains how to prepare the E1 cables and how to convert the
75 Ω trunk cables into the 120 Ω trunk cables.
Chapter 9 Installing the Monitoring System introduces the composition of the
monitoring system and describes its installation procedure.
Chapter 10 Installing the Main Antenna Feeder System describes the installation
preparation, the installation flow and the specific installation procedure of the main
antenna feeder system, and explains how to check and test the antenna feeder and how
to conduct waterproof treatment on the connector.
Chapter 11 Installing the GPS Antenna Feeder System describes the installation
preparation, the installation flow and the specific installation procedure of the GPS
antenna feeder system.
Chapter 12 Installing the Board describes the types and functions of boards used in
the BTSB system, and how to install and replace them.
Chapter 13 Hardware Installation Check describes the hardware installation check
requirements of the BTSB system.
Chapter 14 Power-on/Power-off describes the check prior to the BTSB power-on, and
the detailed power-on and power-off operation procedures.
Appendix A gives an abbreviation form.
Conventions
Describing notational conventions, keyboard operation convention, mouse operation
convention and four safety signs.
1. Notational conventions
Angular brackets "<and>" identify names of keys and buttons, and the
information typed by an operator from a terminal. Square brackets "[and]"
indicate a man-machine interface, menu item, data list, or field name. The
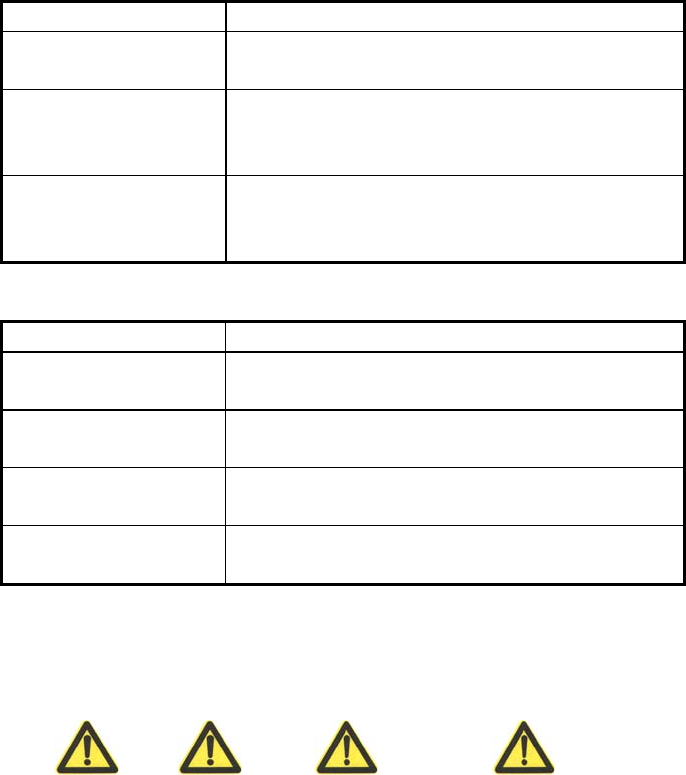
symbol "-->" separates a multi-level menu, e.g., [File --> New --> Folder]
indicates the [Folder] menu item under the [New] submenu of the menu [File].
2. Keyboard operation conventions
Format Description
Character within angular
brackets
Indicating a key or button name, e.g., <Enter>, <Tab>,
<Backspace>, and <a>
<key 1+key 2>
Indicating to hold several keys down at the same time. For
example, <Ctrl+Alt+A> indicates to hold down “Ctrl”, “Alt”
and “A” three keys
<key 1, key 2>
Press Key 1 first. Then release Key 1 and press Key 2. For
example, <Alt, F> indicates to press and release <Alt> key, and
then press <F> key
3. Mouse operation conventions
Format Description
Click Refers to clicking the primary mouse button (usually the left
mouse button) once
Double-click Refers to quickly clicking the primary mouse button (usually the
left mouse button) twice
Right-click Refers to clicking the secondary mouse button (usually the right
mouse button) once
Drag Refers to pressing and holding a mouse button and move the
mouse
4. Signs
Four eye-catching signs are used in this manual to emphasize important and
critical information.
Note,
Caution, Warning, and Danger:
Used to
indicate the precautions during the operation.
Statement: The actual product may differ from what is described in this
manual due to frequent update of ZTE products and fast development of
technologies. Please contact the local ZTE office for the latest updating
information of the product.

FCC & IC STATEMENT
Before using this CDMA ZXC10 BTSB I219 and BTSB I208, read this important RF energy
awareness and control information and operational instructions to ensure compliance with the
FCC and IC RF exposure guidelines.
NOTICE: Working with the equipment while in operation, may expose the technician to RF
electromagnetic fields that exceed FCC rules for human exposure. Visit the FCC website at
www.fcc.gov/oet/rfsafety to learn more about the effects of exposure to RF electromagnetic fields.
Changes or modifications to this unit not expressly approved by the party responsible for
compliance will void the user’s authority to operate the equipment. Any change to the equipment
will void FCC and IC grant.
This equipment has been tested and found to comply with the limits for a Class A digital device,
pursuant to the FCC and IC Rules. This equipment generates, uses and can radiate radio frequency
energy and, if not installed and used in accordance with the instructions, may cause harmful
interference to radio communications. However, there is no guarantee that interference will not
occur in a particular installation.
A PNALE Antenna with a maximum gain of 17dBi is authorized for use with this unit. Outside
antennas must be positioned to observe minimum separation of 2.6M (8.528 feet.) for 800MHz
unit and 1.6M (5.248 feet.) for 1900MHz unit from all users and bystanders. For the protection of
personnel working in the vicinity of outside (uplink) antennas, the following guidelines for
minimum distances between the human body and the antenna must be observed.
The installation of an antenna must be such that, under normal conditions, all personnel cannot
come within 2.6M (8.528 feet.)for 800MHz unit and 1.6M (5.248 feet.) for 1900MHz unit from
the outside antenna. Exceeding this minimum separation will ensure that the worker or bystander
does not receive RF-exposure beyond the Maximum Permissible Exposure according to section
1.1310 i.e. limits for Controlled Exposure.

FAX: 0086-755-26770160
-i-
Contents
1 Overview of BTS Installation.....................................................................................................................i
1.1 Overview........................................................................................................................................1-1
1.2 Hardware Installation Flow............................................................................................................1-4
1.3 Precautions .....................................................................................................................................1-6
2 Installation Preparation..........................................................................................................................2-1
2.1 Installation Environment Inspection ..............................................................................................2-1
2.1.1 Inspection of the Equipment Room Building......................................................................2-1
2.1.2 Inspection of the Indoor Environment ................................................................................ 2-2
2.1.3 Inspection of Power Supply ................................................................................................2-3
2.1.4 Electromagnetic Radiation Protection Requirements..........................................................2-4
2.1.5 Grounding Inspection.......................................................................................................... 2-4
2.1.6 Inspection of the Installation Environment for the Outdoor Antenna Feeder System.........2-5
2.1.7 Safety Inspection.................................................................................................................2-6
2.1.8 Inspection of Corollary Equipment .....................................................................................2-6
2.2 Preparation of Tools and Instruments.............................................................................................2-7
2.3 Preparation of Technical Documents .............................................................................................2-8
3 Unpacking Inspection .............................................................................................................................3-1
3.1 Checking the Goods against the Packing List ................................................................................3-1
3.2 Unpacking the Wooden Box...........................................................................................................3-2
3.2.1 Wooden Box Structure ........................................................................................................3-2
3.2.2 Unpacking ...........................................................................................................................3-2
3.2.3 Inspecting the Rack Outside View ......................................................................................3-3
3.3 Unpacking the Carton ....................................................................................................................3-3
3.3.1 Carton ................................................................................................................................. 3-3
3.3.2 Unpacking........................................................................................................................... 3-4
3.3.3 Inspecting the Boards ......................................................................................................... 3-4
3.4 Goods Acceptance and Handover .................................................................................................. 3-4
4 Installing the Cabinets............................................................................................................................ 4-1
4.1 External Structure of the BTS Cabinet .......................................................................................... 4-1
4.2 Cabinet Layout .............................................................................................................................. 4-2
4.3 Installing a Single BTS Cabinet..................................................................................................... 4-3
4.3.1 Installation Flow of a Single Cabinet.................................................................................. 4-3
4.3.2 Installation Procedure of a Single Cabinet.......................................................................... 4-4
4.4 Connecting and Fixing Multiple Cabinets .....................................................................................4-8
4.5 Cabinet Installation Requirements............................................................................................... 4-10
5 Power Supply System Installation......................................................................................................... 5-1
5.1 Introduction to Power Cables ........................................................................................................ 5-1
5.2 Installation Flow of Power Cables................................................................................................. 5-2
5.3 Cable Installation Procedure.......................................................................................................... 5-2
6 Installing the Grounding System........................................................................................................... 6-1
6.1 Overview of the BTS Grounding System ...................................................................................... 6-1
6.2 Installing the BTS Grounding System ........................................................................................... 6-2
6.2.1 Installing the Outdoor Grounding Copper Bar ................................................................... 6-2
6.2.2 Installing the Feeder Grounding Clip ................................................................................. 6-3
6.2.3 Installing the Indoor Lightning Arrester ............................................................................. 6-6
7 Installing the Cabinet Internal Cables.................................................................................................. 7-1
7.1 Overview of the Internal Cable Installation................................................................................... 7-1
7.1.1 Configuration Types of BTS ............................................................................................... 7-1
7.1.2 Precautions for Installing the RF Cables on the Front Panel .............................................. 7-1
7.2 Installing the Cables for the Single-carrier BTS and the Two-Carrier BTS...................................7-3
7.2.1 Installing the RF Cables for a Single-carrier Single-sector BTS......................................... 7-3
7.2.2 Installing the RF Cables for a Single-carrier Two-sector BTS............................................7-6
7.2.3 Installing the RF Cables for a Single-carrier Three-sector BTS ......................................... 7-9
7.2.4 Installing the RF Cables for a Two-carrier Three-sector BTS...........................................7-14
7.2.5 Connecting the Backplane Signal Cables for the Rack of a Single-carrier or Two-carrier
BTS ............................................................................................................................................7-17
7.3 Installing the Cables for the BTS of Three Carriers and Above...................................................7-17
7.3.1 Installing the RF Cables for a Three-carrier Three-sector BTS ........................................7-18
7.3.2 Installing the RF Cables for a Four-carrier Three-sector BTS ..........................................7-23
7.3.3 Connecting the Jumper Cables Between the Basic Cabinet and the Extended Cabinet....7-28
7.3.4 Connecting the Backplane Signal Cables of the BTS Rack ..............................................7-29
7.4 T1 Cabke ......................................................................................................................................7-31
7.4.1 Functions ...........................................................................................................................7-31
7.4.2 Connection Position of Two Ends, Wiring and Signal Flow Direction of Cable ..............7-31
7.4.3 Function ............................................................................................................................7-32
7.4.4 Connection Positions of Both Ends, Cabling and Signal Flow Direction of Cables.........7-32
8 Installing the Trunk Cables....................................................................................................................8-1
8.1 Installing the Trunk Cables ............................................................................................................8-1
8.2 Preparing the T1 cables..................................................................................................................8-1
9 Installing the Monitoring System ..........................................................................................................9-5
9.1 Composition of the Monitoring System .........................................................................................9-5
9.2 Installing the Monitoring System...................................................................................................9-5
9.2.1 Installing the Indoor Smog Sensor ......................................................................................9-5
9.2.2 Installing the Indoor Temperature/Humidity Sensor........................................................... 9-6
10 Installing the Main Antenna Feeder System.....................................................................................10-1
10.1 Installation Preparation for the Antenna Feeder System ............................................................10-1
10.1.1 Preparations for Installation Staff ................................................................................... 10-2
10.1.2 Installation Environment Inspection ............................................................................... 10-2
10.1.3 Safety Measures Inspection ............................................................................................ 10-3
10.1.4 Preparation of Installation Tools..................................................................................... 10-3
10.2 Structure of the Antenna Feeder System.................................................................................... 10-4
10.3 Installation Content and Flow.................................................................................................... 10-5
10.3.1 Technical Parameters for Antenna Installation ............................................................... 10-6
10.3.2 Antenna Installation Flow............................................................................................... 10-6
10.4 Installing the Antenna Parts ....................................................................................................... 10-7
10.4.1 Determining the Antenna Installation Position ............................................................... 10-7
10.4.2 Handling and Hoisting the Antenna................................................................................ 10-8
10.4.3 Installing and Adjusting the Directional Antenna ........................................................... 10-9
10.4.4 Installing and Adjusting the Omni Antenna.................................................................. 10-12
10.4.5 Connecting and Sealing the Jumper and the Antenna................................................... 10-12
10.4.6 Installing the Feeder Window ....................................................................................... 10-13
10.4.7 Installing the Feeders.................................................................................................... 10-14
10.4.8 Installing the Indoor Jumpers ....................................................................................... 10-25
10.5 Checking and Testing the Antenna Feeders ............................................................................. 10-25
10.6 Waterproof Treatment for the Connectors ............................................................................... 10-25
11 Installing the GPS Antenna Feeder System.......................................................................................11-1
11.1 Installation Preparation for the Antenna Feeder System............................................................ 11-1
11.2 Structure of the Antenna Feeder System.................................................................................... 11-2
11.3 Installation Flow ........................................................................................................................ 11-2
11.4 Installing the Parts ..................................................................................................................... 11-3
11.4.1 Preparing the GPS Coaxial Cable Connectors ................................................................ 11-3
11.4.2 Installing the GPS Lightning Arrester............................................................................. 11-4
12 Installing the Boards .......................................................................................................................... 12-1
12.1 Board Types and Functions of BTS ...........................................................................................12-1
12.2 Introduction to Main BTS Modules ...........................................................................................12-4
12.2.1 RFE Module ....................................................................................................................12-4
12.2.2 HPA .................................................................................................................................12-6
12.2.3 TRX.................................................................................................................................12-8
12.3 Installing and Replacing Boards ..............................................................................................12-10
12.4 Introduction to BDS Plug-in Shelves .......................................................................................12-13
13 Hardware Installation Check.............................................................................................................13-1
13.1 Cabinet Check ............................................................................................................................13-1
13.2 Check of cabling rack................................................................................................................. 13-2
13.3 Laying, Binding and Identification of Cables ............................................................................ 13-2
13.4 Installation Check in terms of power cables and ground wires..................................................13-3
13.5 Check of T1 Cable Installation...................................................................................................13-5
13.6 Sensor Installation Check........................................................................................................... 13-5
13.7 Installation Check of Connections inside a Cabinet................................................................... 13-6
13.8 Installation Check of Indoor 1/2" Jumpers.................................................................................13-6
13.9 Installation and Check of Lightning Arrester.............................................................................13-7
13.10 Installation and Check of Lightning Arrester Rack..................................................................13-7
13.11 Installation and Check of Main Feeder and GPS Feeder..........................................................13-7
13.12 Installation and Check of Feeder Windows and Waterproof Bend of the Main Feeder ...........13-9
13.13 Installation and Check of Three-way Feeder Card.................................................................13-10
13.14 Installation and Check of Outdoor 1/2" Jumpers ...................................................................13-10
13.15 Installation and Check of an Antenna .................................................................................... 13-11
13.16 Check of the Standing Wave Ratio of a Feeder...................................................................... 13-13
13.17 Check of Indoor/Outdoor Environment .................................................................................13-13
14 Power-on/Power-off.............................................................................................................................14-1
14.1 Check before Power-on..............................................................................................................14-1
14.1.1 Check of External Connections of the rack .................................................................... 14-1
14.1.2 Check of Rack Inside...................................................................................................... 14-1
14.2 Power-on Procedures ................................................................................................................. 14-2
14.3 Power-off Procedures ................................................................................................................ 14-3
Appendix A Abbreviations ....................................................................................................................... A-1

FAX: 0086-755-26770160
-i-
List of Figures
Fig. 1.1-1 Overall Structure of the BTSB I2 Rack with the BDS Plug-in Shelf ...............................1-2
Fig. 1.1-2 Schematic Diagram of the BTS Equipment Installation...................................................1-3
Fig. 1.2-1 Hardware Installation Flow ..............................................................................................1-5
Fig. 3.2-1 Structure of the Wooden Box............................................................................................3-2
Fig. 3.3-1 Packing Box of the Module ..............................................................................................3-4
Fig. 4.1-1 Outside View and Dimensions of the Rack ......................................................................4-2
Fig. 4.2-1 Layout of Equipment inside the ZXC10-BTSB I2 Equipment Room..............................4-3
Fig. 4.3-1 Assembly of the BTS Rack Base......................................................................................4-4
Fig. 4.3-2 Fixing the Base with the Rack..........................................................................................4-5
Fig. 4.3-3 Installation Holes of the BTS Rack ..................................................................................4-6
Fig. 4.3-4 Fixing the Rack.................................................................................................................4-7
Fig. 4.3-5 Installing the Rack Baffle Plates....................................................................................... 4-8
Fig. 4.4-1 Enlarged View of the Cable Hole Cover Plate.................................................................. 4-9
Fig. 4.4-2 Assembling the Connecting Bars on the Cabinet Top ......................................................4-9
Fig. 4.4-3 Effect Diagram of Two Cabinets Installed......................................................................4-10
Fig. 5.1-1 BDS Power Cable Installation on BTSB .......................................................................... 5-1
Fig. 5.2-1 Installation Flow of RFS Power .......................................................................................5-2
Fig. 5.3-1 RFS Power Cabling .......................................................................................................... 5-3
Fig. 5.3-2 BDS Power Cabling .........................................................................................................5-3
Fig. 5.3-3 Connection between Busbar and Backplane.....................................................................5-4
Fig. 5.3-4 Connecting Power Cable (1).............................................................................................5-5
Fig. 5.3-5 Connecting Power Cable (2).............................................................................................5-6
Fig. 6.1-1 Wiring for the BTS Ground..............................................................................................6-2
Fig. 6.2-1 Profile of the Grounding Copper Bar............................................................................... 6-3
Fig. 6.2-2 Structure of the Grounding Clip....................................................................................... 6-4
Fig. 6.2-3 Wrapping the Grounding Wire of the Grounding Clip with Waterproof Tape ................. 6-5
Fig. 6.2-4 Installing the Lightning Arrester Frame ........................................................................... 6-7
Fig. 7.1-1 Structure of the RF Cables on the Front Panel of the Rack.............................................. 7-2
Fig. 7.2-1 RF Cable Connection on the Front Panel of the Rack for the Single-carrier Single-sector
BTS...................................................................................................................................................... 7-4
Fig. 7.2-2 Front Panel Wiring for the Rack of the Single-carrier Single-sector BTS with the BDS
Plug-in Shelf........................................................................................................................................ 7-5
Fig. 7.2-3 RF Cable Connection on the Front Panel of the Rack for the Single-carrier Two-sector
BTS...................................................................................................................................................... 7-7
Fig. 7.2-4 Front Panel Wiring for the Rack of the Single-carrier Two-sector BTS with the BDS
Plug-in Shelf........................................................................................................................................ 7-8
Fig. 7.2-5 Circuitry on the Front Panel of the Rack for the Single-carrier Three-sector BTS........ 7-10
Fig. 7.2-6 Front Panel Wiring for the Rack of the Single-carrier Three-sector BTS ...................... 7-11
Fig. 7.2-7 Front Panel Wiring for the Rack of the Single-carrier Three-sector BTS with the
EBDS-HS Part of the EBDS Hybrid Shelf ........................................................................................ 7-12
Fig. 7.2-8 Circuitry on the Front Panel of the Rack for the Two-carrier Three-sector BTS ........... 7-14
Fig. 7.2-9 Front Panel Wiring for the Rack of the Two-carrier Three-sector BTS ......................... 7-15
Fig. 7.3-1 Circuitry on the Front Panel of the Rack for the Three-carrier Three-sector BTS......... 7-19
Fig. 7.3-2 Front Panel Wiring for the Rack of the Three-carrier Three-sector BTS ....................... 7-20
Fig. 7.3-3 Circuitry on the Front Panel of the Rack for the Four-carrier Three-sector BTS........... 7-24
Fig. 7.3-4 Front Panel Wiring for the Rack of the Four-carrier Three-sector BTS......................... 7-25
Fig. 7.3-5 Structure of the LINK Cable .......................................................................................... 7-30
Fig. 7.3-6 LINK Cable Structure .................................................................................................... 7-30
Fig. 7.4-1 100ΩT1 Cable Diagram ................................................................................................. 7-31
Fig. 7.4-1 Terminals of the 100Ω Cable ......................................................................................... 7-33
Fig. 7.4-2 120 Ω Cable ................................................................................................................... 7-34
Fig. 7.4-3 120 Ω T1 Conversion Cable ...........................................................................................7-35
Fig. 7.4-4 BTS Rack-top Interface Board .......................................................................................7-35
Fig. 8.2-1 Assembly Drawing of the CC4Y-J32 Coaxial Cable Connector ...................................... 8-2
Fig. 8.2-2 Coaxial Connector of the DDF.........................................................................................8-3
Fig. 8.2-3 Assembly Drawing of the Coaxial Cable Connector of DDF........................................... 8-4
Fig. 9.2-1 Installing the Smog Sensor Base ......................................................................................9-6
Fig. 9.2-2 Installing the Temperature/Humidity Sensor....................................................................9-7
Fig. 10.2-1 Typical Structure of the Antenna Feeder System of Three-sector BTS ........................10-5
Fig. 10.3-1 Antenna Installation Flow ............................................................................................10-7
Fig. 10.4-1 Hoisting an Antenna .....................................................................................................10-9
Fig. 10.4-2 Installing the Kathrein Antenna.................................................................................. 10-11
Fig. 10.4-3 Adjusting the Pitch Angle of the Antenna ..................................................................10-12
Fig. 10.4-4 Structure of the Feeder Window .................................................................................10-14
Fig. 10.4-5 Structure of a BTS Feeder ..........................................................................................10-15
Fig. 10.4-6 Cutting Tool for the 7/8" Feeder Connector ............................................................... 10-16
Fig. 10.4-7 Cutting the Feeder with a Cutter.................................................................................10-17
Fig. 10.4-8 Checking the Cutting Length of the Feeder................................................................10-17
Fig. 10.4-9 Expand the External Conductor of the Feeder with a Tube Expander........................10-17
Fig. 10.4-10 Connecting the Front Part and the Back Part of the Feeder Connector ....................10-18
Fig. 10.4-11 Fixing the Front Part and the Back Part of the Feeder Connector ............................10-18
Fig. 10.4-12 Hoisting the Feeder to the Tower.............................................................................. 10-21
Fig. 10.4-13 Three-feeder Clip......................................................................................................10-22
Fig. 10.4-14 Method 1 of Introducing Feeders into the Equipment Room ...................................10-23
Fig. 10.4-15 Method 2 of Introducing Feeders into the Equipment Room ...................................10-23
Fig. 10.6-1 Wrap the Waterproof Adhesive Tapes (1)...................................................................10-26
Fig. 10.6-2 Wrap the Waterproof Adhesive Tapes (2)...................................................................10-26
Fig. 10.6-3 Wrap the Waterproof Adhesive Tapes (3)...................................................................10-27
Fig. 11.2-1 Structure of the GPS Antenna Feeder System.............................................................. 11-2
Fig. 11.4-1 Stripping the GPS Coaxial Cable ................................................................................. 11-3
Fig. 11.4-2 Welding the Pins of the GPS Connector....................................................................... 11-3
Fig. 11.4-3 Structure of the N-J7A Cable Assembly....................................................................... 11-4
Fig. 12.2-1 Panel of RFE Modules ................................................................................................. 12-5
Fig. 12.2-2 Structure of the HPA Front Panel ................................................................................. 12-7
Fig. 12.2-3 Structure of the TRX Front Panel................................................................................. 12-9
Fig. 12.3-1 Connectors on the Rear of the Boards and Modules .................................................. 12-11
Fig. 12.3-2 Front Panel of the Boards and Modules ..................................................................... 12-12
Fig. 12.4-1 Slot Diagram of the BDS Plug-in Shelf ..................................................................... 12-13

FAX: 0086-755-26770160
-i-
List of Tables
Table 2.1-1 DC Power Indexes for the Normal Operation of BTS ...................................................2-3
Table 2.1-2 Power Consumption Indexes for the Normal Operation of BTS ...................................2-4
Table 2.2-1 Tools Needed.................................................................................................................. 2-7
Table 2.2-2 Instruments Needed........................................................................................................2-8
Table 7.2-1 Front Panel Wiring of the Rack for the Single-carrier Single-sector BTS .....................7-6
Table 7.2-2 Front Panel Wiring of the Rack for the Single-carrier Two-sector BTS ........................7-9
Table 7.2-3 Front Panel Wiring of the Rack for the Single-carrier Three-sector BTS ....................7-13
Table 7.2-4 Front Panel Wiring of the Rack for the Two-carrier Three-sector BTS .......................7-16
Table 7.3-1 Wiring List of the Front Panel for the 1# Three-carrier BTS Cabinet..........................7-20
Table 7.3-2 Wiring List of the Front Panel for the 1# Four-carrier BTS Cabinet ...........................7-26
Table 7.3-3 Wiring List of the Cables from 1# Multi-carrier BTS Cabinet to 2# Multi-carrier BTS
Cabinet ...............................................................................................................................................7-28
Table 7.3-4 IDs of the LINK Directions..........................................................................................7-30
Table 7.4-1 100ΩT1 Cable Wiring and Signal Flow Direction.......................................................7-31
Table 7.4-1 Identifiers of the Location & Signal Flow Direction at Both Ends of the 100Ω Cable7-33
Table 7.4-2 End B Braiding Pair Sequence of the 120 Ω T1 Conversion Cable.............................7-35
Table 9.2-1 Terminal Connection of the Smog Sensor Cable Connector.......................................... 9-6
Table 9.2-2 Terminal Connection of the Temperature/Humidity Sensor Cable Connector...............9-7
Table 10.4-1 Model and Dimensions of the Feed Window ...........................................................10-14
Table 12.2-1 Description of the Interfaces on the RFE Panel .........................................................12-6
Table 12.2-2 Description of the Interfaces on the HPA Front Panel ...............................................12-8
Table 12.2-3 Description of the TRX RF Interfaces .....................................................................12-10
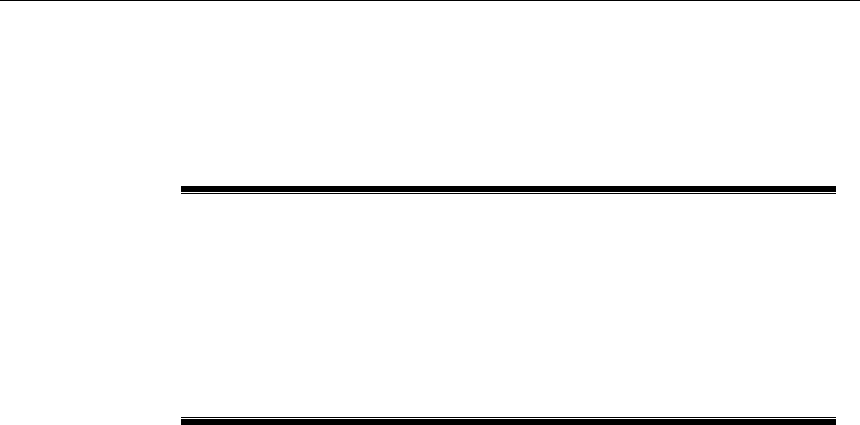
FAX: 0086-755-26770160
1-1
1 Overview of BTS Installation
Summary
This part describes:
● Hardware installation flow of the BTS system;
● Installation precautions of the BTS system.
1.1 Overview
The integrated rack of ZXC10-BTSB comprises five layers each with an insertion box.
From top down, they are the RFE, HPA, power, TRX layer and BDS layers, as shown
in Fig. 1.1-1.
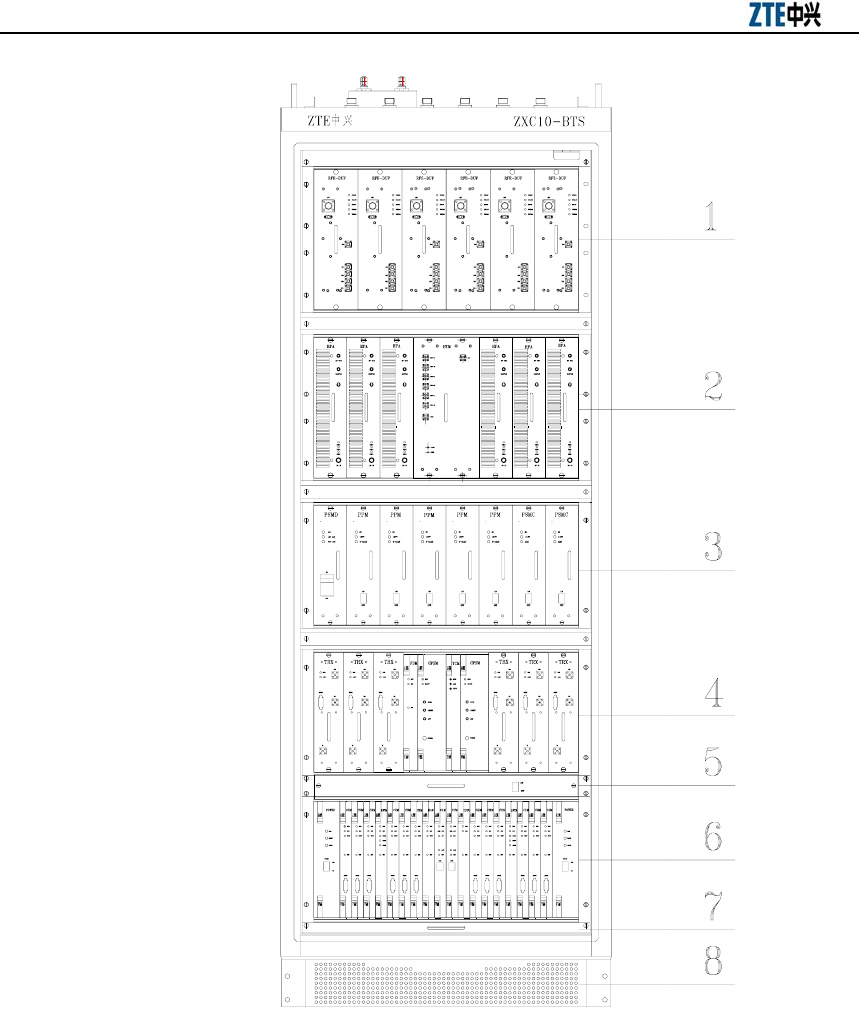
ZXC10-BTS (V5.4) Installation Manual
1-2
1. RFE plug-in shelf base 2. HPA plug-in shelf 3. PSMD/PSMC plug-in shelf 4. TRX plug-in shelf
5. Fan plug-in shelf 6. BDS plug-in shelf 7. Dust filtering plug-in shelf 8. Base
Fig. 1.1-1 Overall Structure of the BTSB I2 Rack with the BDS Plug-in Shelf
The installation of the BTS system comprises the following parts:
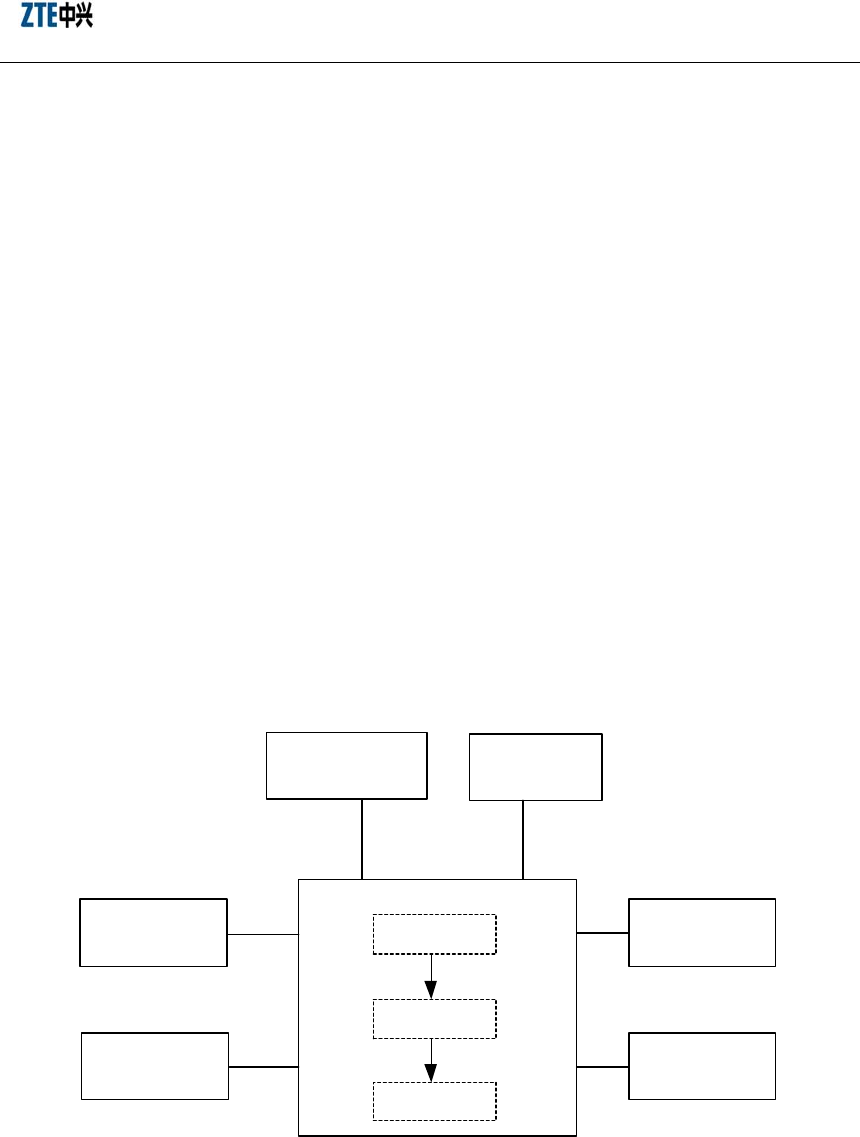
Chapter Error! Style not defined. Err
or! Style not defined.
1-3
1. The installation of the BTS cabinet, including the rack installation, the internal
cable installation, and the board installation and the DIP switch setting;
2. The installation of the power system to provide -48V operating power for the
system;
3. The installation of the grounding system to provide the protection ground for the
parts of the BTS equipment;
4. The installation of the antenna system, including the antenna positioning and
installation, jumper installation, feeder installation, and antenna feeder system
check and test;
5. The installation of the GPS system, including the installation of the GPS and the
feeder;
6. The installation of the trunk cable, including the connection of the cables and the
preparation of the connectors;
7. The installation of the monitoring system, including the installation of the
temperature/humidity sensor and the environment sensor.
BTS system installation is shown in Fig. 1.1-2.
Install the
GPS system
Install the rack
Install the
internal cables
Install the boards
Install the BTS cabinet
Install the
trunk cables
Install the power
supply system
Install the
grounding system
Install the
alarm sy stem
Install the
antenna sy stem
Fig. 1.1-2 Schematic Diagram of the BTS Equipment Installation

ZXC10-BTS (V5.4) Installation Manual
1-4
1.2 Hardware Installation Flow
The normal operation of the ZXC10-BTSB I2 equipment is closely related to the
quality of the installation engineering. The equipment must be installed in a systematic
and standardized way, which helps to remove the equipment stability problems caused
by improper installation and improve the reliability of the system.
This manual focuses on the step-by-step installation method and procedure of the BTS
and its parts. It provides details to enable users to finish the equipment installation.
The indoor installation of the ZXC10-BTS focuses on the rack installation, the indoor
cable preparation and routing. Please follow carefully the steps below:
1. Fix the rack base to the rack;
2. Position the rack;
3. Mark and drill holes for bolts;
4. Fix the cabinet;
5. Install the power cable on the rack top;
6. Install the temperature and humidity sensor on the set top;
7. Install the T1 cable;
8. Install boards and modules inside the rack;
9. Connect the RF cable at the rack front.
The detailed hardware installation flow of the BTS system is as shown in Fig. 1.2-1.
This manual describes the specific installation procedure by chapters according to this
flow.
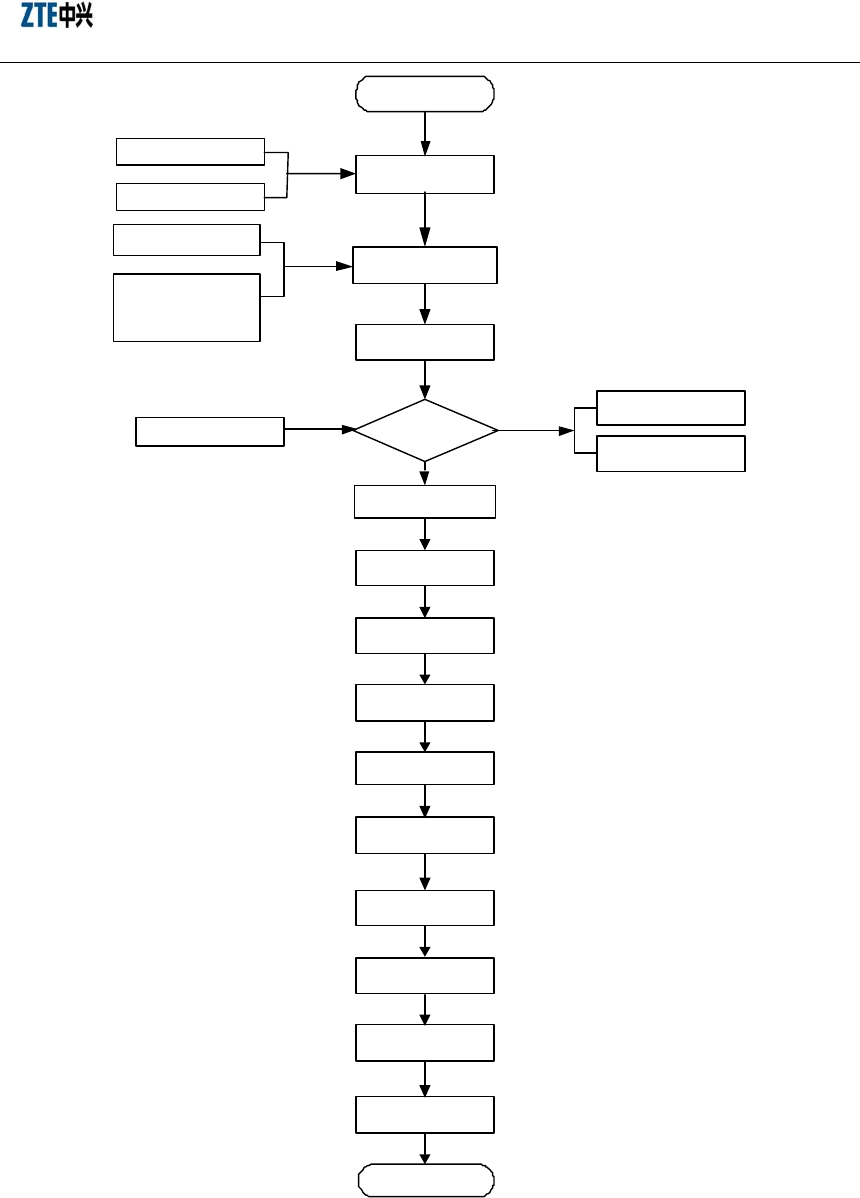
Chapter
Error! Style not defined.
Err
or! Style not defined.
1-5
Survey Report
Project design documents
Environment
Acceptance Report
Cabling racks, power
supply system,
grounding system and
auxiliary facilities
Packing list Check the goods
for consistency
Yes
No
Goods Error
Feedback Form
Goods Replacement
Application Form
Install the power
supply system
Install the cabinets
Install the
grounding system
Install the
internal cables
Install the
monitoring system
Install the main
antenna feeder system
Install the boards
Install the
GPS system
Hardware
installation check
End
Start
Install the
trunk cables
Project installation
preparation
Unpacking Inspection
Check the engineering
conditions
Fig. 1.2-1 Hardware Installation Flow

ZXC10-BTS (V5.4) Installation Manual
1-6
1.3 Precautions
Precautions for the BTS hardware installation:
1. Take careful precautions for the safety of yourself and the equipment during the
installation;
2. Avoid hot plugging/unplugging during module installation;
3. Never install the antenna feeder system in case of lightning;
4. Check whether the lightning arrester is in proper contact before the
thunderstorm season every year. In case any lightning arrester is damaged,
replace it immediately;
5. Lock the cabinet door in time when the cabinet is installed.
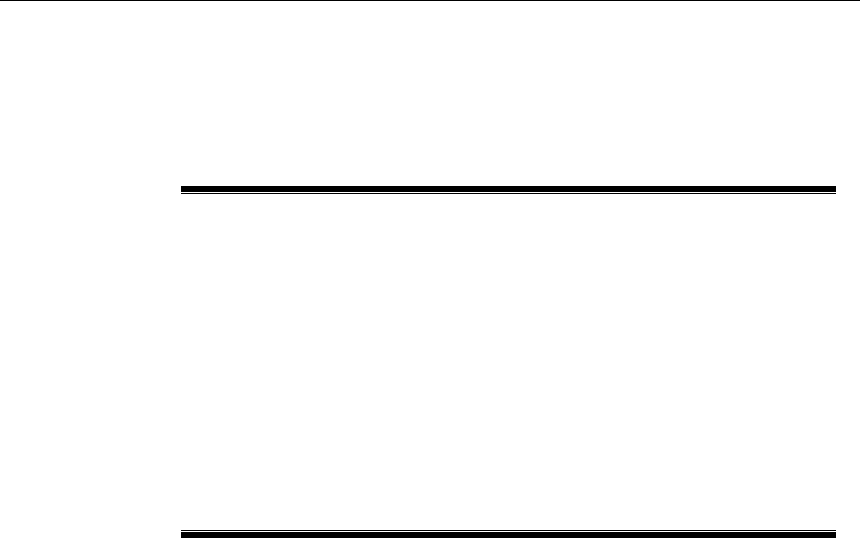
FAX: 0086-755-26770160
2-1
2 Installation Preparation
Summary
This part describes:
● Environment check prior to the BTS installation;
● Tool and instrument preparation prior to the BTS
installation;
● Technical document preparation prior to the BTS
installation.
2.1 Installation Environment Inspection
Conduct the environment inspection prior to the installation. The basic inspection items
are as follows:
Before the project installation, the customer should prepare the equipment room, power
supply and grounding cable, and provide necessary facilities for the project
implementation. The area and height of the equipment room should satisfy the
requirements of the equipment layout. Otherwise, reconstructions are required to
eliminate the hidden dangers in the installation, operation and maintenance of the
equipment.
2.1.1 Inspection of the Equipment Room Building
The items for the equipment room building inspection are as follows:
1. The civil engineering of the equipment room and corridor has been completed,
and the wall is fully dry.
2. The height and width of the doors in the equipment room should not cause any
inconvenience for transporting the equipment. Usually, the height of the main
doors in the equipment room should be no less than 2.2 meters, and the width
should be no less than 1 meter. The net height of the equipment room should be

ZXC10-BTS (V5.4) Installation Manual
2-2
no less than 3 meters. The equipment room should have a sufficient area for the
equipment with extra free space. For ease of operation and maintenance of the
equipment, the space gap for opening the front door should be no less than 1
meter, and the space gap at the rack rear should be no less than 0.8 meter.
3. The equipment room floor can bear the weight over 450kg/m
2
;
4. The wall and ceiling of the equipment room should not chalk or peel off and
should be free of dust accumulation. Fire-retardant materials should be used for
decoration.
5. The shock-proof design of the equipment room should be one degree higher than
the local anti-seismic requirements. Generally, the equipment room should be
able to bear the earthquake of 7 on the Ritcher Scale. Otherwise, shock-proof
reinforcement measures must be adopted for the equipment.
6. Air-conditioning facilities should be provided to maintain desired temperature
and humidity in the equipment room.
7. Lightning screen or lightning arrester should be installed for the places in the
equipment room vulnerable to the lightning. Outdoor metal pipelines should be
grounded when led into the equipment room.
2.1.2 Inspection of the Indoor Environment
The inspection of the indoor equipment room environment covers the inspection of
humidity, temperature, air pressure, antistatic protection, anti-interference requirement,
air conditioning, ventilation, dust proof, rodent proof, fire protection, lighting, and
drainage facilities.
1. Requirements for the ambient temperature and humidity
Operating temperature: -5°C ~ +55°C
Relative humidity: 15% ~ 93%.
2. Requirements for the equipment room floor
The level difference per square meter of the floor should not be more than 2mm.
3. Cleanness
Cleanness is related to the amount of dust and harmful gases in the air. The
equipment room should meet the following cleanness requirements:
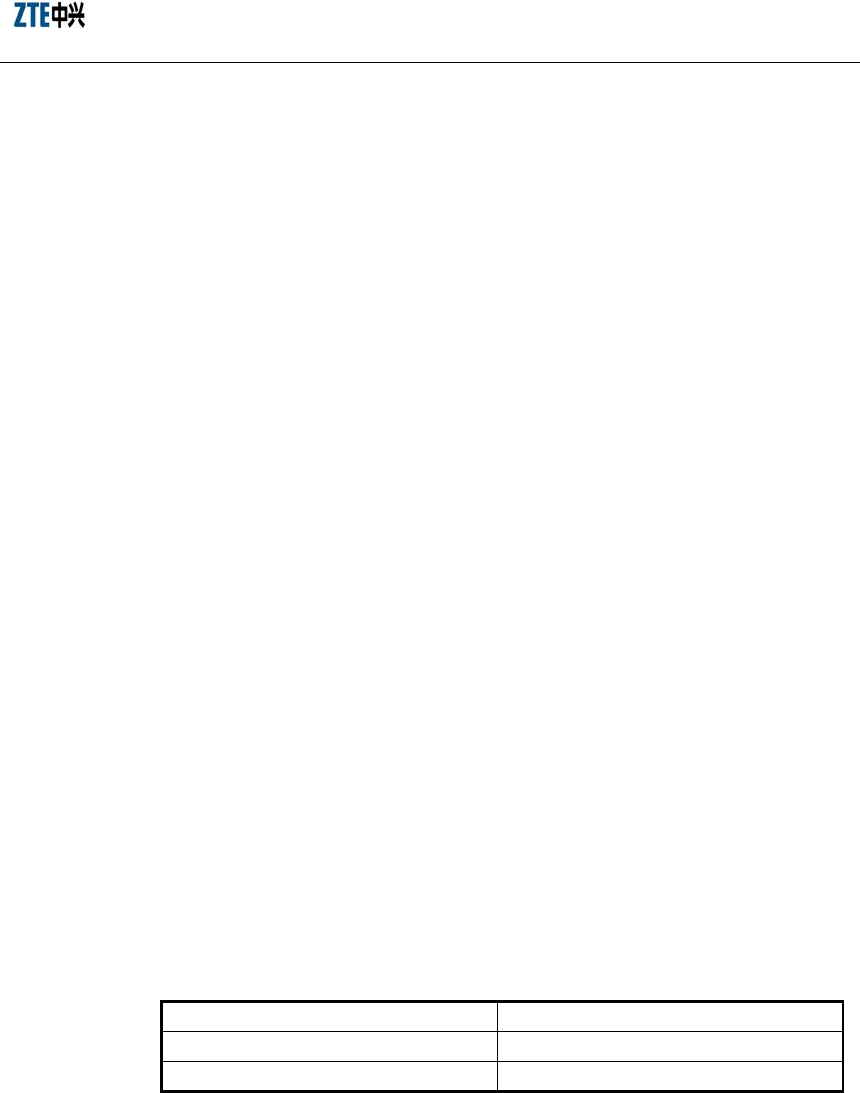
Chapter
Error! Style not defined.
Error! Style not defined.
2-3
● There should be no explosive, conductive, magnetic or corrosive dust in the
equipment room.
● The dust (diameter more than 5µm) density should be no more than 3×10
4
granules/m
3
.
● No corrosive metal or gas that is harmful to insulations, such as SO
2,
NH
3
. in the
equipment rooms.
● The equipment room should be always kept clean, with the doors and windows
properly sealed.
4. Lighting
The equipment room should be equipped with three types of lighting facilities:
common lighting, guaranteed lighting and emergency lighting.
5. Fire-proof requirements
The paint and decoration materials in the equipment room should be fire-proof.
The cabling holes through the wall should be filled with fire-retardant materials.
Fire-fighting devices should be equipped at the appropriate positions.
2.1.3 Inspection of Power Supply
Inspect that the power supply of the equipment room meets the power consumption
requirement of the BTS.
2.1.3.1 Power Supply Range
Please see Table 2.1-1 for the DC power Indexes for the normal operation of
ZXC10-BTSB I2 (supporting 24V DC power).
Table 2.1-1 DC Power Indexes for the Normal Operation of BTS
Item DC Power
Nominal value -48V
Voltage fluctuation range -40~-57V
2.1.3.2 Power Consumption
Power supply and power consumption: The power consumption of ZC10-BTS refers to
the overall power consumption when the operating voltage is -48V and the output
power of each power amplifier is 20W, as shown Table 2.1-2.
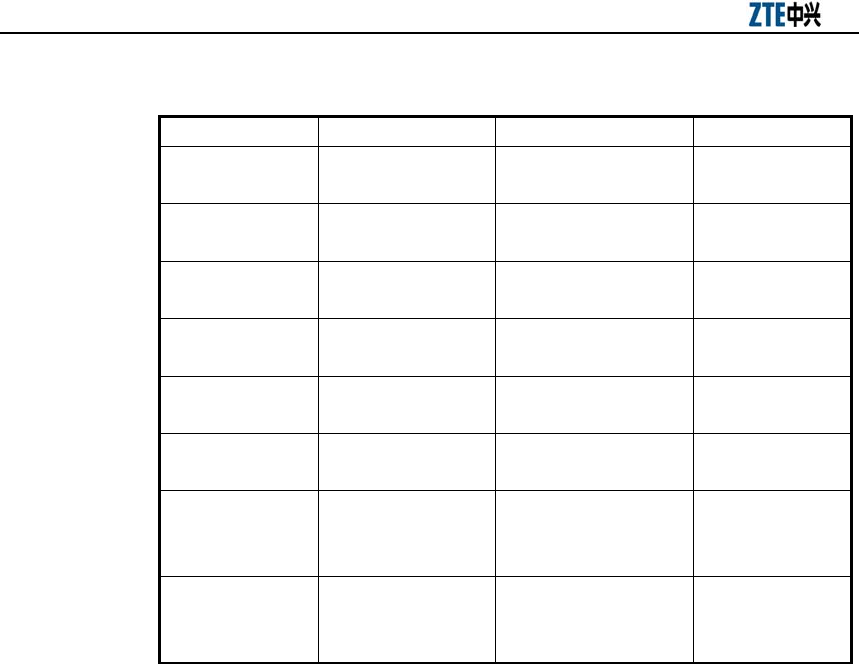
ZXC10-BTS (V5.4) Installation Manual
2-4
Table 2.1-2 Power Consumption Indexes for the Normal Operation of BTS
Configuration Operating Voltage Power Consumption Remarks
Single-carrier
single-sector -48V 850W
Single-carrier
two-sector -48V 1150W
Single-carrier
three-sector -48V 1400W
Two-carrier
single-sector -48V 1100W
Two-carrier
two-sector -48V 1650W
Two-carrier
three-sector -48V 2200W
Three-carrier
three-sector -48V 3600W
Total power
consumption of two
racks
Four-carrier
three-sector -48V 4400W
Total power
consumption of two
racks
2.1.4 Electromagnetic Radiation Protection Requirements
GB8702-88, "Electromagnetic Radiation Protection Regulations" of the People's
Republic of China specifies:
1. Public radiation: For twenty-four hours in a day, the average power density of
electromagnetic radiation (for six consecutive minutes) is < 0.4W/m
2
(30MHz ~
3000MHz).
2. Professional radiation: For eight work hours in a day, the average power density
of electromagnetic radiation (for six consecutive minutes) is < 2W/m
2
(30MHz
~ 3000MHz).
2.1.5 Grounding Inspection
The grounding regulations and resistance requirements (including the lightning
protection requirements) are as follows:
The communication equipment should be well grounded for reliable operation. Good
grounding ensures lightning protection and interference resistance. The grounding

Chapter
Error! Style not defined.
Error! Style not defined.
2-5
cables in the equipment room should be routed in a radiating or flat way. Three
independent grounding cables should be used. The protection ground of the DC power
distribution system, the work ground of the power system and the lightning protection
ground.
The grounding resistance of the BTS should be less than 5Ω. The engineering requires
the grounding resistance to be the smallest possible. The magnitude of grounding
resistance is affected by grounding post resistance, leading wire resistance, contact
resistance between the grounding post and soil, and soil type of. The greatest impact on
grounding resistance comes from soil type. In areas with poor soil conditions, some
resistance-reducing agent (such as propenamide) may be added around the grounding
stake to meet the requirements. Changes in temperature will also cause variations in
resistance. In cold areas, the impact of temperature on the resistance may be reduced
by burying the stake deeply into the ground. Grounding stakes are usually made of
galvanized materials, in proper size. The connection cables from the grounding stake to
the equipment should adopt copper-sheathed wires of good conductivity (core wire
section area less than 50mm
2
, and length as short as possible). If necessary, anti-erosion
protection can be provided to the grounding connection parts to guarantee
low-resistance connection.
The working ground refers to the loop formed through the earth to transmit energy and
information. For instance, the 3-phase AC power supply neutral line ground and the
positive battery ground are both working grounds. This grounding approach can resist
electromagnetic interference and crosstalk.
The protection ground refers to the grounding of the metal shell of the power supply
equipment to prevent hazards to human body due to power leakage.
In addition, the ground for lightning protection should be used to prevent lightning
strike from damaging the equipment and to protect the safety of lives and properties.
2.1.6 Inspection of the Installation Environment for the Outdoor Antenna Feeder
System
1. Check whether the height and the size of the feeder window comply with the
requirements of the BTS equipment and the engineering design drawing.
2. Check the height, weight bearing and grounding of the outdoor cabling rack
against the engineering design.

ZXC10-BTS (V5.4) Installation Manual
2-6
3. Check the height, weight bearing and grounding of the indoor cabling rack
against the engineering design.
4. Check the height, diameter, weight bearing, wind resistance, grounding,
lightning protection and position of the antenna embracing pole of the BTS on
the roof. Make sure they comply with the BTS equipment requirements and the
engineering design drawing.
5. Check the height, diameter, weight bearing, wind resistance, grounding,
lightning protection and position of the antenna embracing pole of the BTS on
the iron tower. Make sure they comply with the BTS equipment requirements
and the engineering design drawing.
2.1.7 Safety Inspection
Appropriate fire-fighting devices should be equipped in the equipment room, such as a
certain quantity of portable powder fire-extinguishers. As for the large equipment room,
a complete set of automatic fire-fighting system should be equipped. No inflammable
or explosive articles should be placed in the equipment room.
1. Storage of flammable and explosive materials in the equipment room is strictly
prohibited and necessary firefighting equipment must be installed.
2. Different outlets in the equipment room should bear noticeable marks, and
dynamic electricity and lighting electricity should be noticeably differentiated.
3. The equipment room should be far from high-voltage power lines, strong
magnetic fields, strong electric sparks, or other factors that may threaten the
security of the equipment room.
4. Reserved holes in the floors should be covered with safety cover plates.
5. Proper lightning protection facilities should be in place before leading the power
lines and transmission lines into the equipment room.
2.1.8 Inspection of Corollary Equipment
Inspect the following according to configuration requirements specified in the contract:
1. Check whether the external power supply and the power cable connecting the
racks are ready;
2. Check whether the T1 cable connecting the BTS and the BSC is ready.
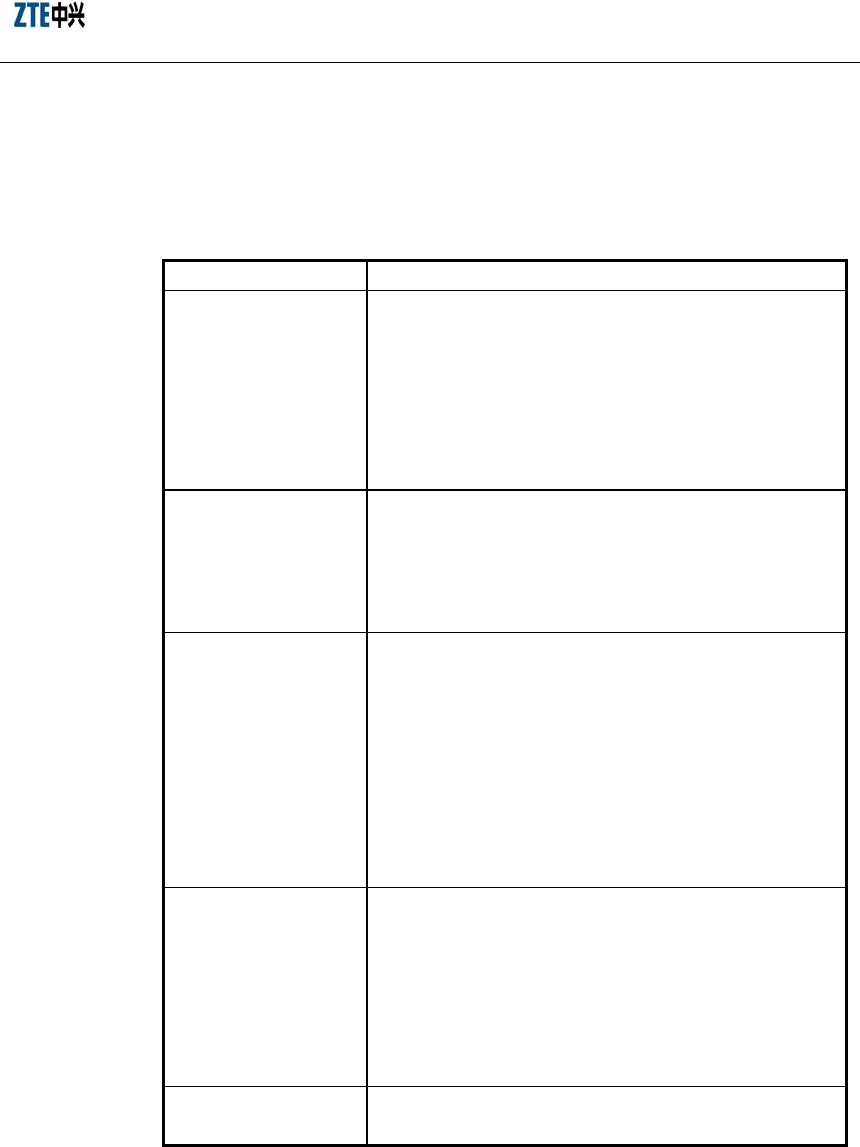
Chapter
Error! Style not defined.
Error! Style not defined.
2-7
2.2 Preparation of Tools and Instruments
A number of tools and instruments are to be used during the BTS installation process.
Prepare the tools and instruments as per Table 2.2-1 and Table 2.2-2.
Table 2.2-1 Tools Needed
Category Name
Special tools
One feeder connector knife
One wire skinner for 100Ω coaxial cables
One crimping pliers for 100Ω coaxial cables
One multi-functional crimping pliers
One multimeter
One SiteMaster VSWR tester
Earth resistance tester
Concrete drilling tools
One electric percussion drill
Several drill bits
One cleaner
One power terminal block (at least three 2-phase sockets and three
3-phase sockets, with the power capacity more than 15A)
General-purpose tools
Philips screwdrivers (4”, 6” and 8” each)
Flathead screwdrivers (4”, 6” and 8” each)
Adjustable wrenches (6”, 8”, 10” and 12” each)
Dual-purpose spanners (17” and 19”)
One set of socket wrench
One 5kg nail hammer
One 300W iron
One 40W iron
One roll of solder wire
Measurement tools
One 50m tape measure
One 5m steel tape
One 400mm level bar
One angle meter
One compass
Level bar
Plumb
Protection tools Antistatic wrist strap
Safety helmet, slip-proof glove
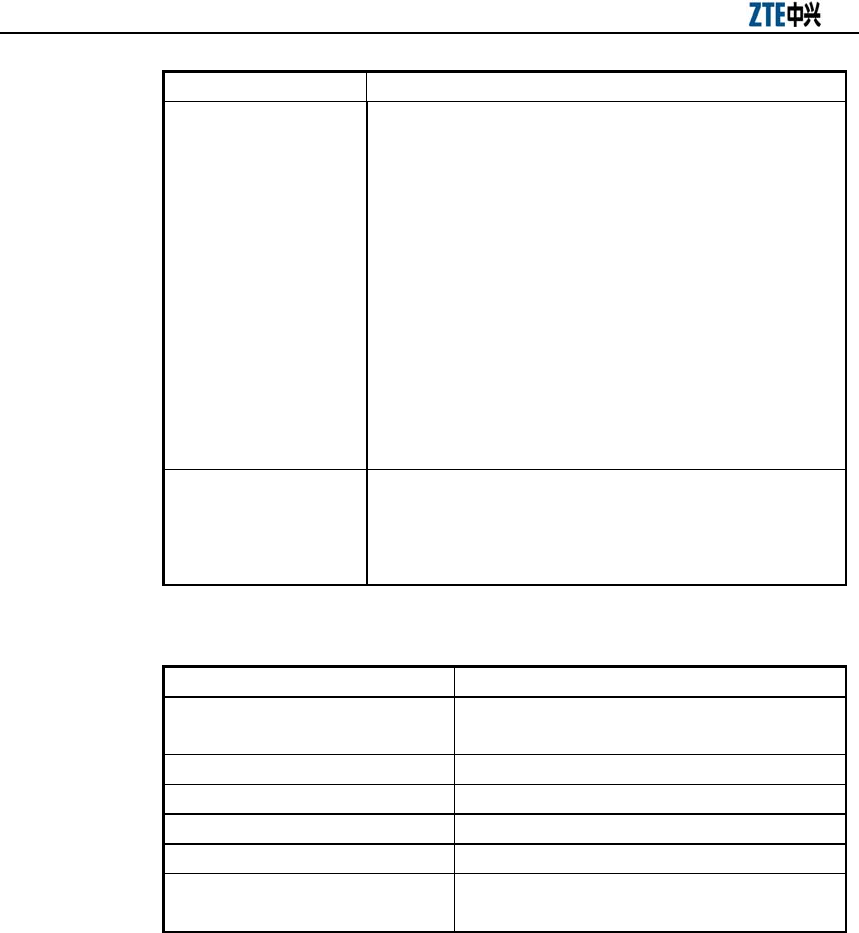
ZXC10-BTS (V5.4) Installation Manual
2-8
Category Name
Small tools
One hacksaw (with several saw blades)
One pair of sharp-nose pliers (8”)
One pair of diagonal pliers (8”)
One pair of slip joint pliers (8")
One pair of vices (8”)
One needle file set (medium sized)
Tweezers
One paintbrush
One pair of scissors
One hot blower
One solder sucker
One pair of hydraulic pliers
Crowbar
Auxiliary tools
Pulley block
Rope
Ladder
Forklift
Table 2.2-2 Instruments Needed
Instrument Name Manufacturer
Spectrum analyzer (needed in some
special cases)
HP
Base station tester SITE MASTER
Test-purpose MS Qualcomm
Compass
Multimeter
Field strength tester (needed in some
special cases)
2.3 Preparation of Technical Documents
The technical documents to be prepared before the commissioning of the equipment
are as follows:
1. Project Survey Report, BTS System Project Design and Engineering Drawing,
and Environment Acceptance Report.
The Project Survey Report should be completed by the engineering staff sent by
the equipment supplier during the onsite survey. If engineering staff cannot

Chapter
Error! Style not defined.
Error! Style not defined.
2-9
conduct the survey in time, he should entrust the equipment user to fill in the
report and mail it back after the survey for the preparation of engineering
materials.
The BTS System Project Design and Engineering Drawing should be completed
by the design party entrusted by the equipment user, and its copy should be
provided by the equipment user to the equipment supplier before equipment
delivery.
The Environment Acceptance Report is used for the first engineering
environment inspection during the project survey. If the environment is found to
fail the inspection, the equipment user is requested to make improvement and
solve the problem. The second environment inspection is conducted before the
engineering starts.
2. ZXC10-BTSB I2 (V1.0) cdma2000 System Base Transceiver Station Installation
Manual; ZXC10-BTSB I2 (V1.0) cdma2000 System Base Transceiver Station
Technical Manual; ZXC10-BTSB I2 (V1.0) cdma2000 System Base Transceiver
Station Hardware Manual; ZXC10-BTSB I2 (V1.0) cdma2000 System Base
Transceiver Station Maintenance Manual.
3. Installation Acceptance Report and Test Acceptance Report.
The Installation Acceptance Report and Test Acceptance Report are the
engineering materials for acceptance after the BTS commissioning. They are
provided by the equipment supplier to the equipment user at the time of delivery.
They should be completed properly after the commissioning of the BTS.
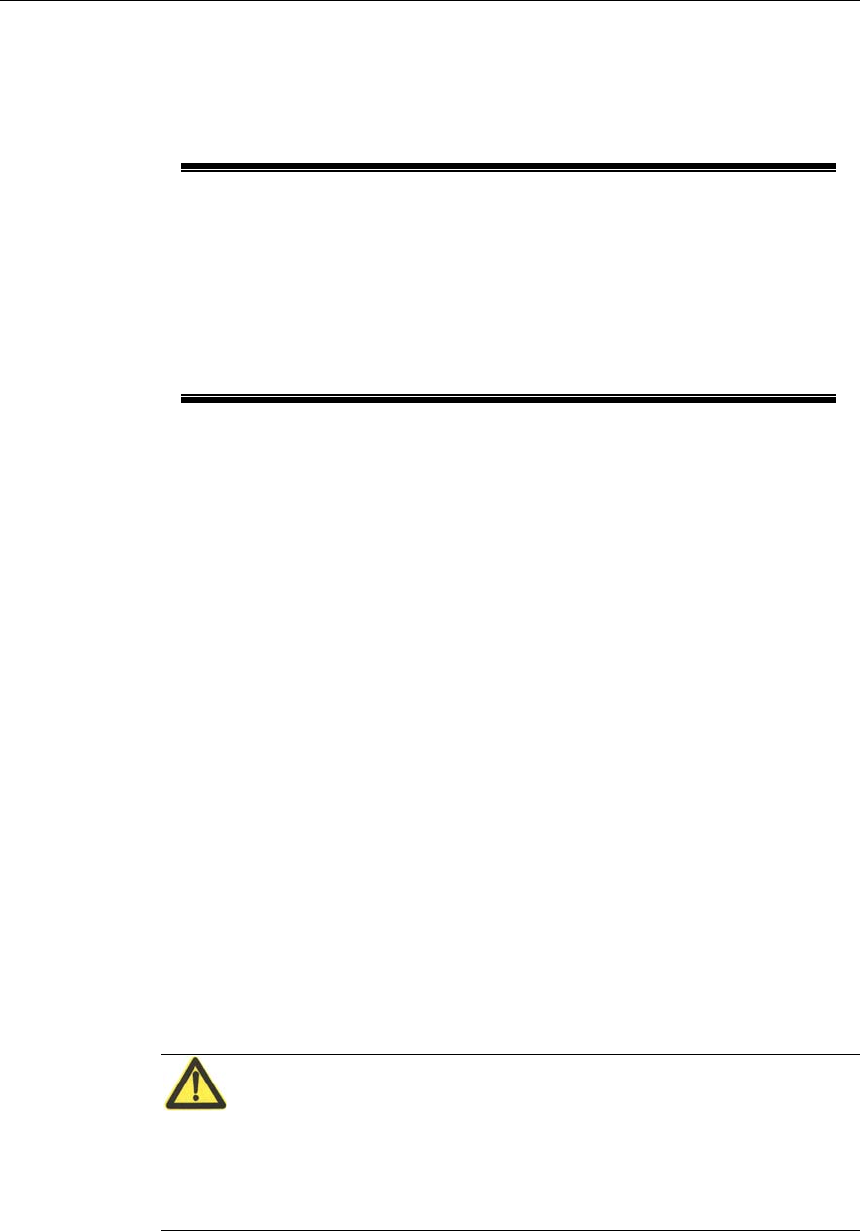
FAX: 0086-755-26770160
3-1
3 Unpacking Inspection
Summary
This part describes:
● Unpacking of the BTS equipment;
● Inspection of the BTS equipment.
3.1 Checking the Goods against the Packing List
1. Check the Delivery Checklist of ZTE Corporation.
2. Unpacking inspection is conducted by the Project Supervising Committee and
representatives from the user. First, check the total number of goods, the
intactness of the packing boxes, and check whether the arrival place is the actual
installation place against the packing list number attached to the packing boxes;
3. If the goods are intact, unpack and inspect the goods. There should be a packing
list in each box, and the engineering supervisor should check the goods against
the packing list. The Unpacking Inspection Report is placed in the packing box
numbered 1#. First open the 1# packing box and take out the Unpacking
Inspection Report. Check the total number of the goods against the inspection
list and record it for filing.
4. During the unpacking inspection process, if there is any short and wrong
shipment or goods damage, you should contact the ZTE headquarters.
5. The packing boxes of ZTE comprise two types: wooden box and carton. Use
different tools to open the boxes accordingly on the site.
Caution:
The ZXC10-BTSB I2 equipment is relatively expensive. During transportation, it
should be well packaged, with clear waterproof and quake-resistant marks. Handle the
equipment with care and protect it from sunshine and rain.
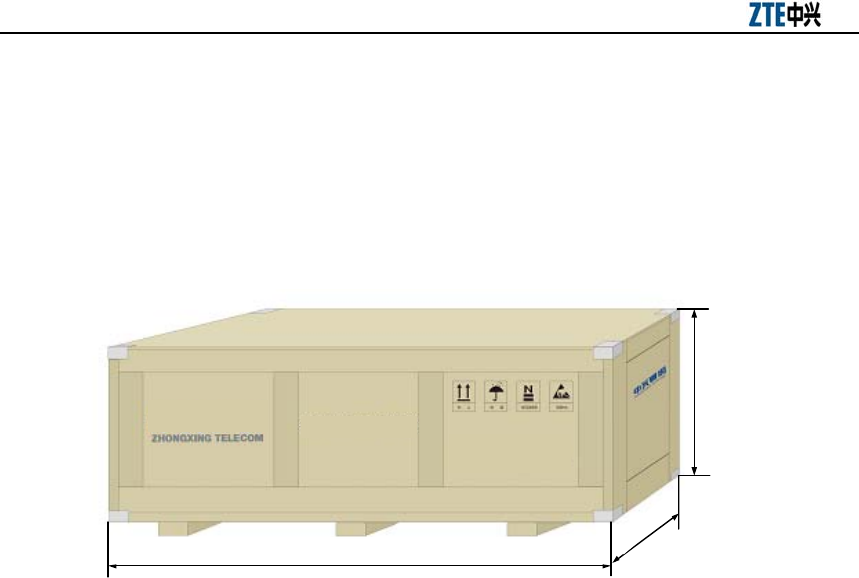
ZXC10-BTS (V5.4) Installation Manual
3-2
3.2 Unpacking the Wooden Box
3.2.1 Wooden Box Structure
The wooden boxes are generally used for packing heavy goods like rack.
The structure of the BTS rack packing box is as shown in Fig. 3.2-1.
2060mm
860mm
860mm
ZXC10-BT S
cabinet
Net weight
Gross weight
Size
Com pany : ZTE CORP ORATION
Fig. 3.2-1 Structure of the Wooden Box
3.2.2 Unpacking
1. Prepare tools such as nail hammer, pliers, flathead screwdrivers, and crowbar;
2. First skin the packing sheet iron. Insert a flat-tip screwdriver into the slit
between the box and the front cover board to make it loose; then insert the
crowbar to unclench the cover board.
3. Keep the box on end and the legs downward, and pull the rack out of the box.
Make sure not to remove the antistatic bag of the rack before pulling the rack
out.
4. Remove the packing adhesive tape of the rack.
Note: The BTS rack is equipped with casters for easy movement. However, you
should control the moving direction with your hands during the move to avoid
damage to the rack or emergencies.

Chapter
Error! Style not define
d.
Error! Style not defined.
3-3
3.2.3 Inspecting the Rack Outside View
Put the rack vertically on the solid ground. The rack should be erected upright without
tilting. Visually there is no dent, bump, scratches, peel, bubbling, stains or other similar
damaged signs. The captive screws should not be loose, missing or misplaced. The
installation slots for plug-in shelves are intact and the slot guide rails are not missing,
damaged or broken. All fittings and accessories required for rack installation are
complete. The labels of installation slots are intact and eligible. The busbar, the exhaust
fan and the installation positions are not damaged or deformed. There is no rack
surface paint flake-off or scratches.
3.3 Unpacking the Carton
3.3.1 Carton
Caution:
1. Avoid taking any circuit board out of the antistatic bags during the unpacking and
acceptance. Do not open the antistatic bags until the board is to be mounted into the
rack. In addition, avoid damaging any antistatic bag and keep it for future use when
storing spare boards and packing the faulty boards for repair.
2. When the equipment is moved from a colder and drier place to a hotter and
damper place, wait for 30 minutes before unpacking the equipment. Otherwise,
moisture may appear on the surface of the equipment and cause damage.
3. Properly recycle the desiccants lest children may eat them by accident. Cartons are
generally used to pack circuit boards and terminal equipment.
The circuit boards are placed in the anti-static protective bags during transportation.
Before unpacking the boards, take proper anti-static protective measures to avoid
damages. In addition, attention should be paid to the ambient temperature. Usually
some desiccant is placed in the anti-static protective bag to absorb moisture and keep
the bag dry.
The packing box of a module is shown in Fig. 3.3-1.
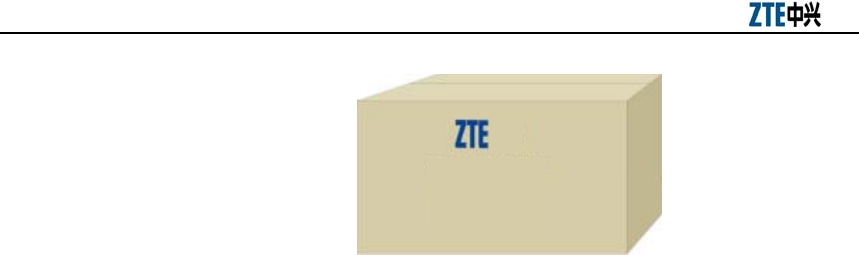
ZXC10-BTS (V5.4) Installation Manual
3-4
ZXC10-BTS Cabinet Component
Net weight :
Gross weight :
Size :
Company: ZT E CORPORAT ION
Fig. 3.3-1 Packing Box of the Module
3.3.2 Unpacking
Take the following steps to unpack a carton:
1. Use the diagonal pliers to cut the straps.
2. Use a paper knife to cut the adhesive tape along the slits on the box covers. Note
that the cut should not be too deep and damage the goods inside.
3. Count the quantity and types of boards inside the carton against the packing list
attached and sign for the acceptance with the customer on site.
3.3.3 Inspecting the Boards
Check the boards against the delivery list and contact the equipment supplier in time if
any incompliance is found.
3.4 Goods Acceptance and Handover
After goods acceptance both parties should sign the Unpacking Inspection Report for
confirmation, after which the goods should be handed over to the customer if they are
to be kept by the customer after acceptance as per the contract terms. Each party should
hold a copy of the Unpacking Inspection Report and the Project Supervisor should
feedback the Acceptance Conclusion of the Report to be archived by the equipment
supplier.
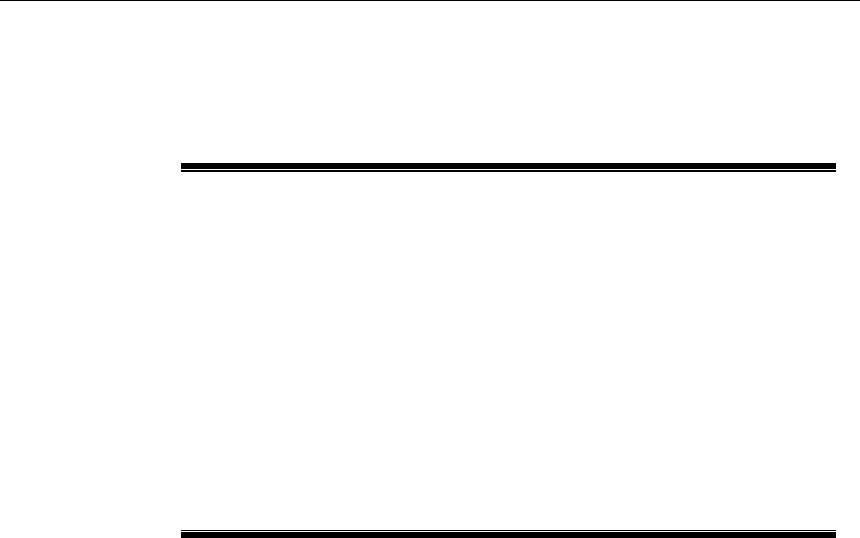
FAX: 0086-755-26770160
4-1
4 Installing the Cabinets
Summary
This part describes:
● External structure of the BTS cabinet;
● Installation procedure of a single BTS cabinet;
● Arrangement of the BTS cabinets;
● Connection and fixation between BTS cabinets;
● Standard of installing the BTS cabinets.
4.1 External Structure of the BTS Cabinet
At present there is only one type of BTS cabinet: Welded cabinet. The BTS rack has a
fully-closed shielded structure, as shown in Fig. 4.1-1.
Dimensions of the rack: 700mm (W) × 600mm (D) × 1800mm (H).
Dimensions of the base: 700mm (W) × 600mm (D) × 100 mm (H).

ZXC10-BTS (V5.4) Installation Manual
4-2
Front door
Base
Fig. 4.1-1 Outside View and Dimensions of the Rack
4.2 Cabinet Layout
The principles of rack layout should be observed in designing the rack installation
positions, since the installation of the ZXC10-BTSB I2 rack needs to satisfy the heat
dissipation and maintenance space requirements. Fig. 4.2-1 shows how to arrange the
equipment inside the equipment room.
1. The rack arrangement should fully take into account the direction from the
feeder to the BTS. The feeder should be as short as possible provided that its
curvature is guaranteed.
2. At least 1m passage should be reserved before the rack.
3. At least 0.8m space should be reserved after the rack for maintenance.
4. Keep a rack position at one side of the rack for future capacity expansion, and
keep the other side at least 0.1m away from the wall.
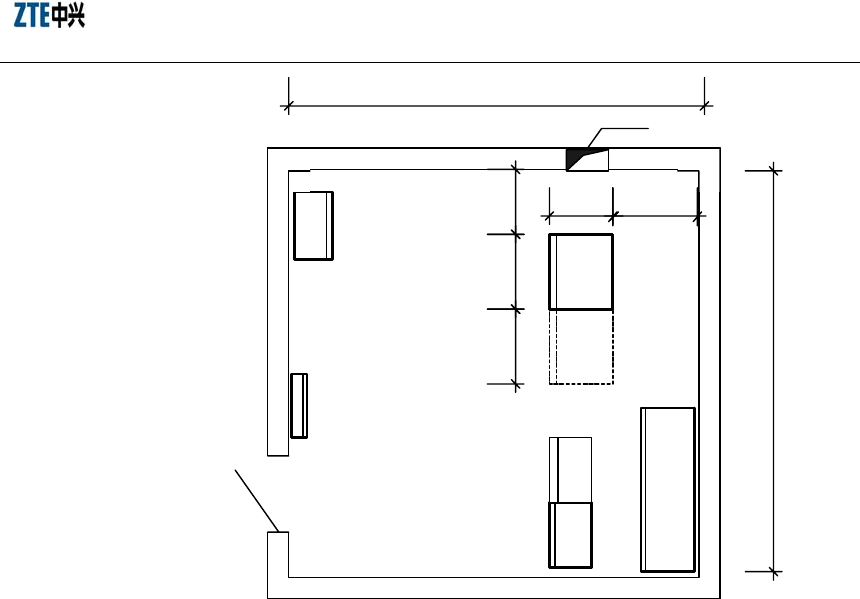
Chapter
Error! Style not defined.
Error! Style not defined.
4-3
4000
4000
AC
Air
conditioner
Storage battery pack
31.4961
23.62227.559127.5591
DC CDMA
BTS
Transmission
equipment
23.622
Feeder hole location
Fig. 4.2-1 Layout of Equipment inside the ZXC10-BTSB I2 Equipment Room
4.3 Installing a Single BTS Cabinet
4.3.1 Installation Flow of a Single Cabinet
The base installation mode is adopted for the BTS cabinet, that is, the cabinet is
installed on the adjustable base provided by ZTE.
When there is no antistatic floor available in the equipment room, the base and the rack
can be mounted directly on the ground. If there is antistatic floor in the equipment
room, angle-steel supports should be prepared by the manufacturers according to the
mounting hole location drawing of the BTS rack and the floor height measured. The
base and rack are then mounted on the support in the same way as fixing the rack onto
the cement ground.
Below is the cabinet installation flow of the ZXC10-BTSB I2, which should to be
strictly followed.
1. Assemble the cabinet base.
2. Marking/positioning.
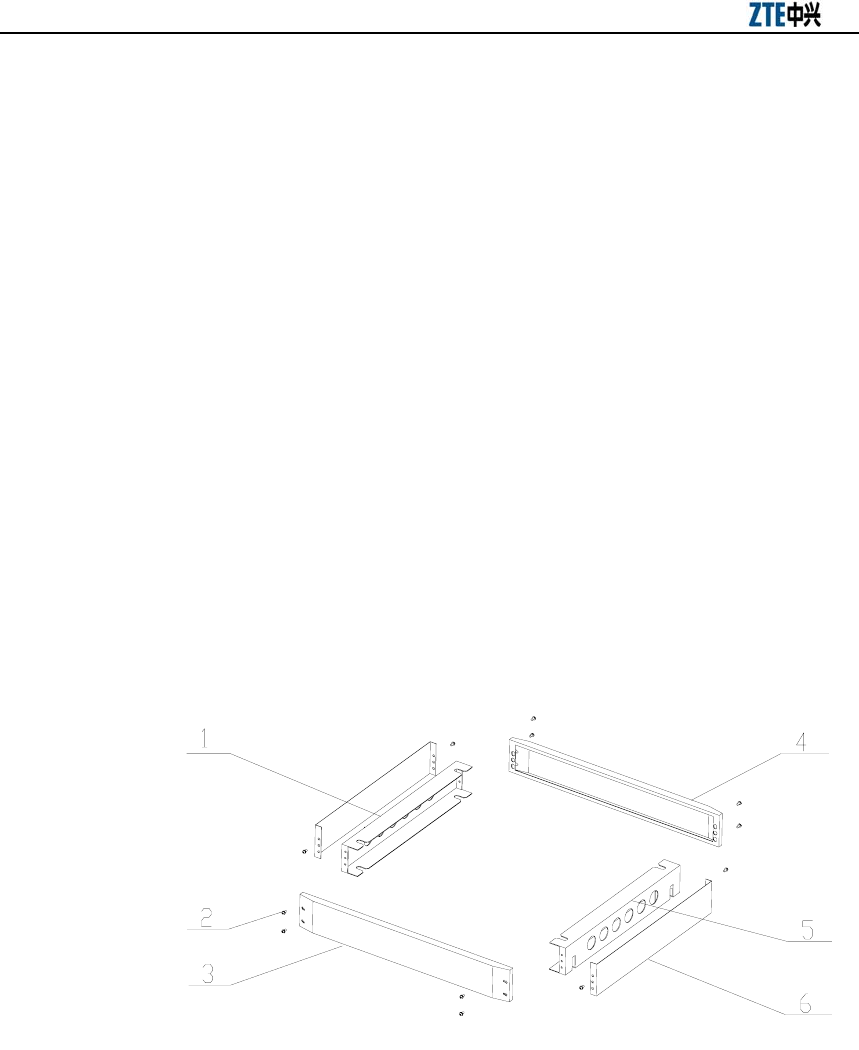
ZXC10-BTS (V5.4) Installation Manual
4-4
3. Drill holes and fix the expansion bolts.
4. Fix the cabinet.
5. Check the cabinet installation.
6. Install the bottom baffles of the cabinet.
4.3.2 Installation Procedure of a Single Cabinet
Below is the procedure of installing a single cabinet on the base.
4.3.2.1 Base Structure
Assemble the rack base:
1. Dimensions of the base
Each base is provided with two supports and four baffle plates. Its dimensions
are:
700mm (W) × 600mm (D) × 100mm (H).
2. Fig. 4.3-1 shows the assembly of the base and its components.
1. Support B 2. Screw M5
×16 3. Front baffle plate 4. Rear baffle plate 5. Support A 6. Side plate
Fig. 4.3-1 Assembly of the BTS Rack Base
4.3.2.2 Fixing the Base
As shown in Fig. 4.3-2, fix the base and the rack in the following procedure:

Chapter
Error! Style not defined.
Error! Style not defined.
4-5
1. Remove the four legs at the bottom of the rack and add a washer to the inner
side of the bolt and nut of each leg, screw the legs back in position and adjust
the leg height of the rack to about 50mm evenly.
2. Lean the rack slight towards one side, insert one support of the base into the gap
between two washers on the legs of the rack, screw tight the two nuts of the legs
and then fix the support at one side of the base with the rack.
3. Lean the rack slightly towards the other side and perform the same operations as
above to fix the support of the base at the other side with the rack.
4. Pay attention to the upper and lower positions of the U-shaped fixing holes on
the base.
Rack
Gask e t
Leg
Base
Fig. 4.3-2 Fixing the Base with the Rack
4.3.2.3 Positioning the Base
First follow the installation engineering design drawing to determine the installation
position of the rack in the equipment room. If there is no such drawing, the rack must
be positioned with the permission of the user. You may mark on the cement floor
according to the dimensions as shown in Fig. 4.3-3, or place the rack in the preset place,
and mark the mounting holes.
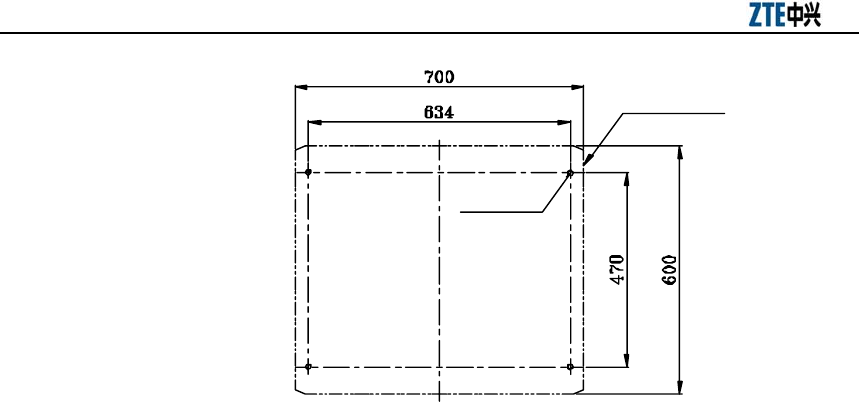
ZXC10-BTS (V5.4) Installation Manual
4-6
Floor area
of the rack
4xM12
anchor bolts
Fig. 4.3-3 Installation Holes of the BTS Rack
Drill holes by taking the following steps:
1. Before drilling, use a sample drill bit to drill a hole at the hole position to help
position the right drill bit. If you use the M12 expansion bolt, you should use the
Φ14 percussion drill bit.
2. The hole depth is the tube length of the expansion bolt plus the length of the bit.
After the hole depth is determined, fix the locating rod of the percussion drill;
3. When drilling, it is recommended that one person drill the holes and the other
clean dust with a cleaner;
4. Put an expansion bolt in the drilled hole and hammer it in with a rubber hammer.
Fix the bolt with its nut and then remove the nut to get ready for the rack
installation. Make sure that the expansion bolt must be securely fixed. If not, the
rack cannot be securely installed.
4.3.2.4 Fixing the Cabinet
Fix the cabinet as follows:
Move the rack mounted with a base gently to the installation position, push the
U-shaped fixing holes on the base into the bolts, and fix the four corners of the rack to
the four bolts with flat washers, spring washers and nuts, as shown in Fig. 4.3-4. Adjust
the legs to keep the rack vertical.

Chapter
Error! Style not defined.
Error! Style not defined.
4-7
M12
anchor bolt
Fig. 4.3-4 Fixing the Rack
4.3.2.5 Rack Installation Check
The rack installation check covers the following aspects:
1. Levelness: Since the floor may be uneven, it is necessary to check the levelness
of the rack after installation. Put the level bar on the level section of the rack
front and side to see if the level vial is centered. If not, it shows the rack is not
installed horizontally. In that case, adjust the legs between the rack and the base
at the four corners of the rack bottom. In the case the floor is uneven and there is
big error, use gaskets to adjust the rack levelness;
2. Verticality: Check the rack verticality with a plumb. The verticality error
between the rack bottom and the rack top should be less than 3mm;
3. Stability: The rack should stand still when you push the upper part of the rack
with your hands;
4. Check the corners in the rack. There should be no metallic scraps or wires left
during the installation, and the rack interior should be clean without any
sundries;
5. All screws are tightened with flat washer and spring washers installed in the
correct sequence.
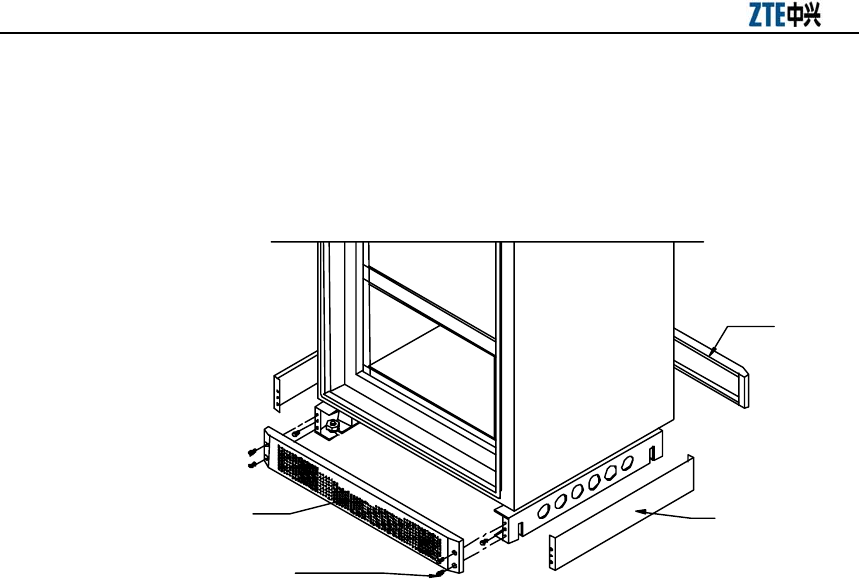
ZXC10-BTS (V5.4) Installation Manual
4-8
4.3.2.6 Installing the Baffle Plate at the Rack Bottom
After the rack is installed, fix the baffle plates on the four sides of the rack bottom.
When installing the baffle plates, install the plates on both sides first and then the plates
on the front and the rear, as shown in Fig. 4.3-5.
Front baffle
M5x16
combination screw
Side p la t e
Rear baffle
Fig. 4.3-5 Installing the Rack Baffle Plates
4.3.2.7 Insulation Test
Conduct the grounding test of the cabinet according to the requirements specified in
Section 2.1.5.
4.4 Connecting and Fixing Multiple Cabinets
This section describes the installation and fixation of multiple cabinets for the
multi-carrier BTS.
When two cabinets are required to be closely placed to each other and keep flush,
remove the cable hole cover plates on the cabinet side panels that contact with each
other for the purpose of cabling, as shown in Fig. 4.4-1.
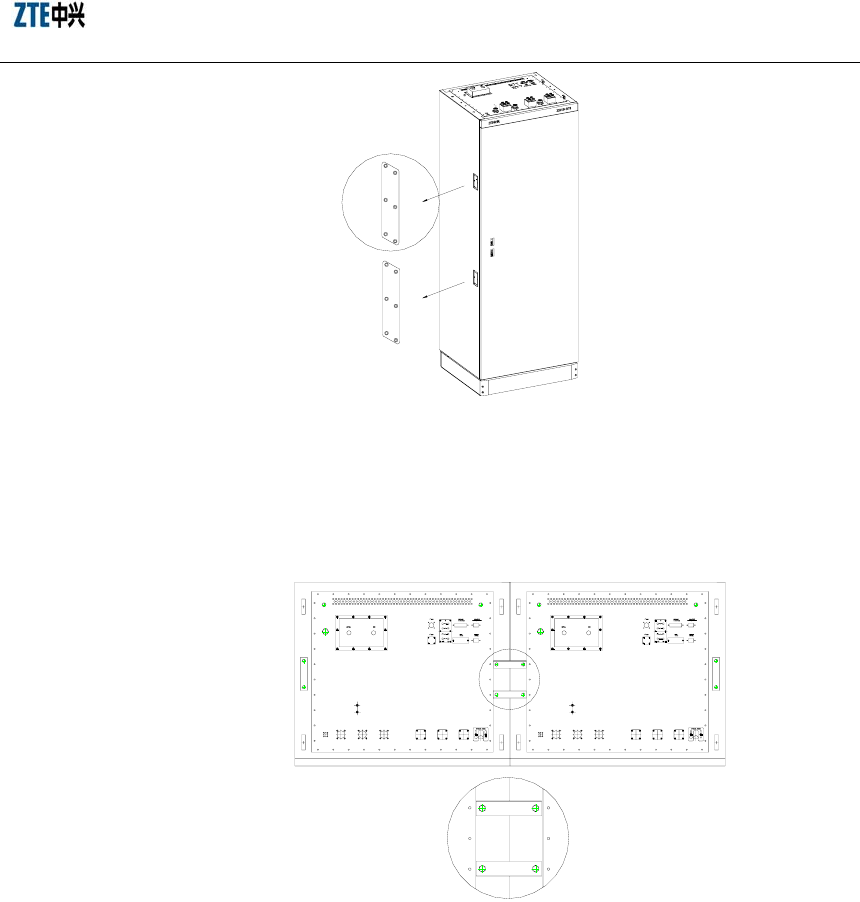
Chapter
Error! Style not defined.
Error! Style not defined.
4-9
Fig. 4.4-1 Enlarged View of the Cable Hole Cover Plate
Next, connect and fix the two cabinets with the connecting bars on the set top, as
shown in Fig. 4.4-2.
Fig. 4.4-2 Assembling the Connecting Bars on the Cabinet Top
When two cabinets are required but they are not to be closely placed to each other, use
the upper cabling mode. For the detailed installation method, please refer to the
assembly diagram of multiple cabinets shown in Fig. 4.4-3.
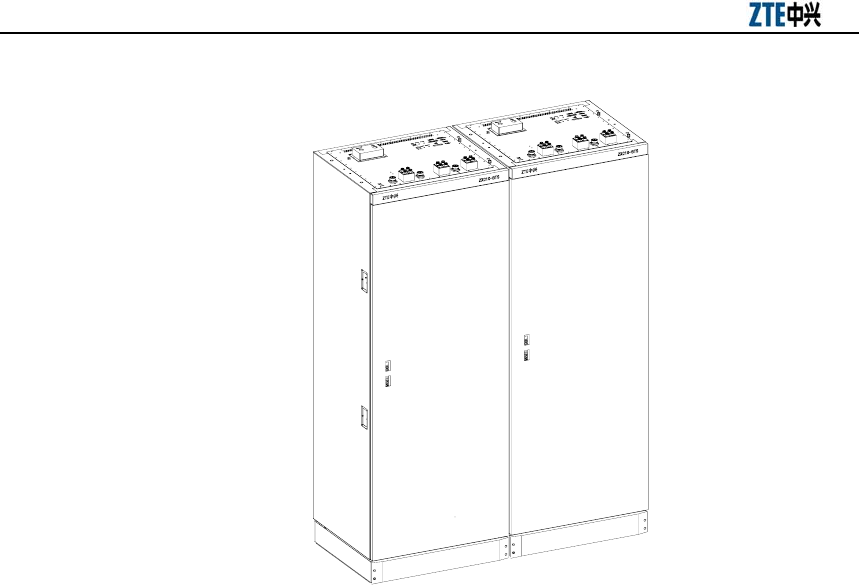
ZXC10-BTS (V5.4) Installation Manual
4-10
Fig. 4.4-3 Effect Diagram of Two Cabinets Installed
4.5 Cabinet Installation Requirements
The installation of the ZXC10-BTSB I2 rack should satisfy the requirements for
equipment heat dissipation and maintenance space. Therefore, the rack installation
position design should meet the rack layout requirements. The cabinet installation
criteria are as follows:
1. The layout of the cabinets should take into consideration the direction from the
feeder to the BTS. The feeder should meet the bending radian requirement and
be as short as possible.
2. There must be an aisle no less than 1m wide in the cabinet front.
3. There must be maintenance room no less than 0.8m in the cabinet rear.
4. A rack space should be reserved at one side of the cabinet for future system
expansion, and the other side is away from the wall at least 0.1m.
5. When the system is expanded to three carriers and four carriers, two cabinets are
required. If they are placed side by side, it is necessary to remove the cable hole
cover plates on the side panel of the cabinets that contact each other to ease the

Chapter
Error! Style not defined.
Error! Style not defined.
4-11
cabinet internal cabling. Two angle supports should be used on the set top to
connect the two cabinets firmly.
6. When the system is expanded to three carriers and four carriers, two cabinets are
required. If they are not placed close to each other, the upward cabling mode
should be adopted. The specific cabling should comply with the installation
engineering standards.
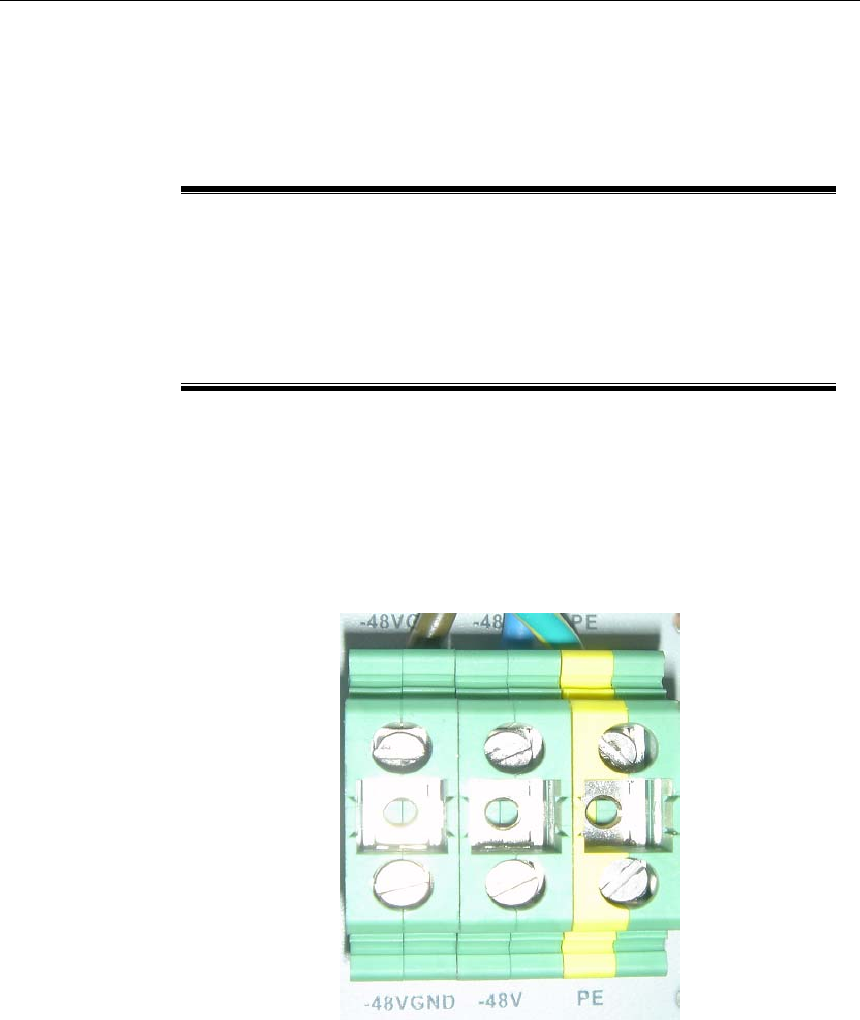
FAX: 0086-755-26770160
5-1
5 Power Supply System Installation
Summary:
z Power cables of BTSB
z Installation method of the BTSB power supply
z Installation procedure of the BTSB power supply
5.1 Introduction to Power Cables
The DC power supply cables consist of the -48V cable (black), grounding cable (blue)
and protection grounding cable (yellow green). The connector of the BDS power cable
on BTSB is shown in Fig. 5.1-1.
Fig. 5.1-1 BDS Power Cable Installation on BTSB
The diameter of the main power cable should be calculated by the actual capacity. The
specifications of the three commonly used BTSB power cables are:
1. Black with the cross section area as 25 mm
2
(working grounding cable).
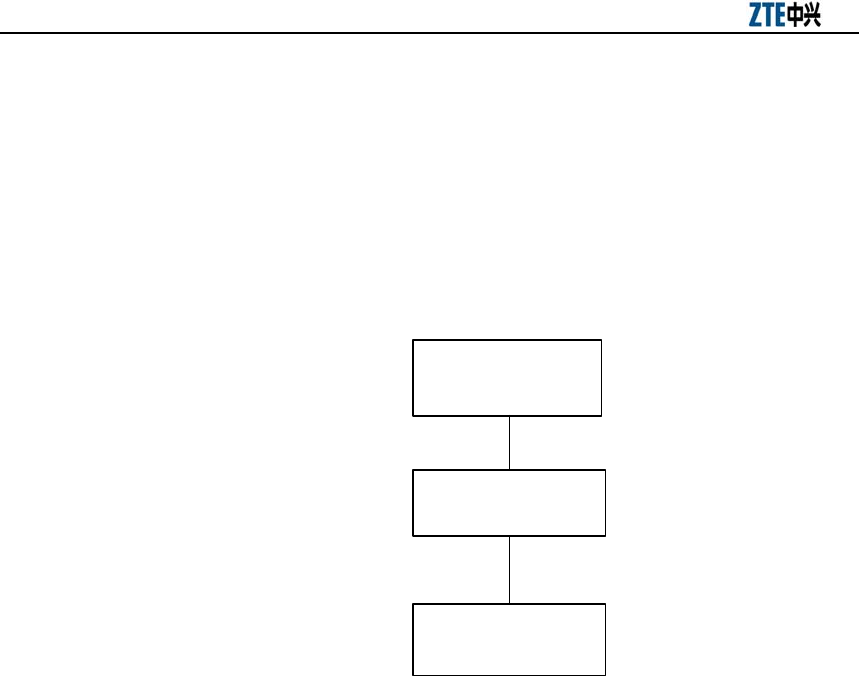
ZXC10-BTS (V5.4) Installation Manual
5-2
2. Blue with the cross section area as 25 mm
2
in section area (-48V).
3. Yellow green with the cross section area as 35 mm
2
(protection grounding
cable).
5.2 Installation Flow of Power Cables
The power cable installation flow is shown in Fig. 5.2-1.
Power cabling in the
cabinet
Power cable
leading from the
distribution frame
Connecting to the filter on
the cabinet
Fig. 5.2-1 Installation Flow of RFS Power
5.3 Cable Installation Procedure
The power supply is led into the filters by the power cables, distributed to the busbars
on the two sides of the cabinet by PD, and then led to the backplane of each plug-in
box by the busbars, As show Fig. 5.3-1.
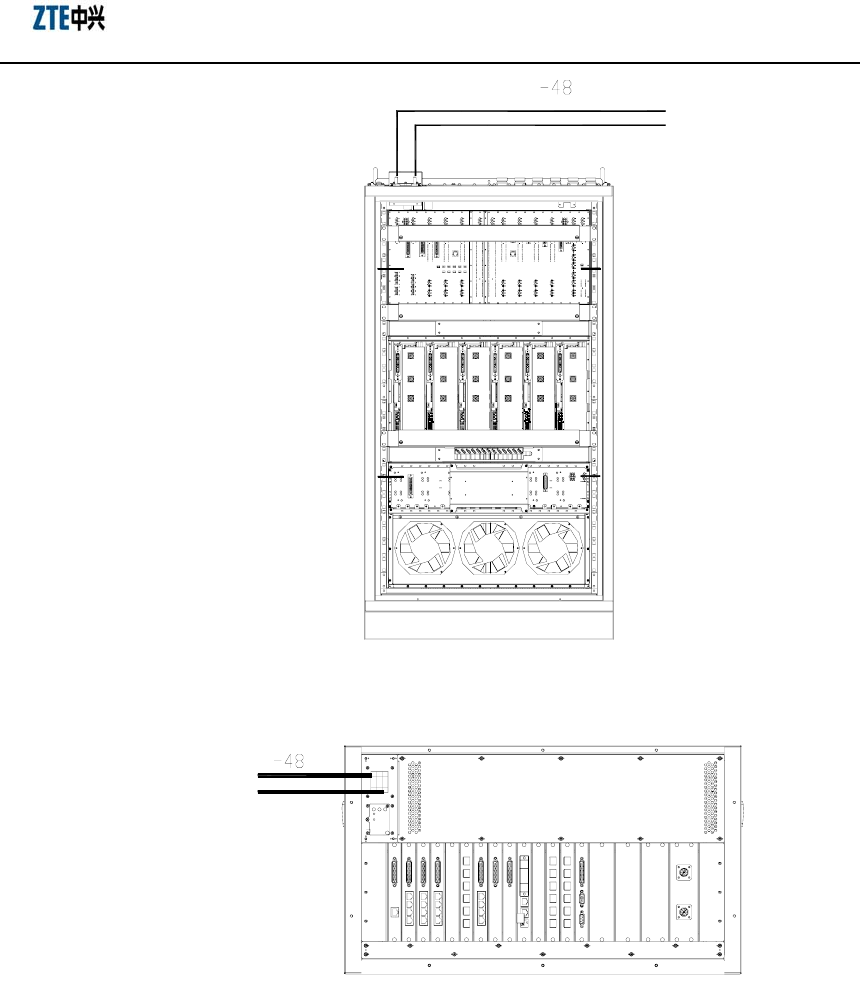
Chapter
Error! Style not defined.
Error!
Style not defined.
5-3
Fig. 5.3-1 RFS Power Cabling
Fig. 5.3-2 BDS Power Cabling
The connection between the busbar and backplane through the -48V power cable is
shown in Fig. 5.3-3.
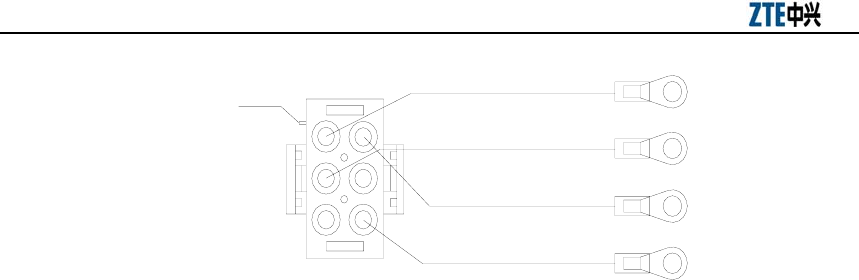
ZXC10-BTS (V5.4) Installation Manual
5-4
1
2
3
4
5
6
6-core power connector
for backplane
Locating key
Lug for busbar
-48V
GNDP
GND
- 48VGND
Blue
Yellow
Black
Black
Fig. 5.3-3 Connection between Busbar and Backplane
End B of the power cable on the busbar usually has been connected before delivery. If
the backplane of the plug-in box has been installed, the End A of the cable has been
connected to the backplane. Only when the equipment capacity is to be expanded or the
backplane is to be replaced, the power cables need to be connected on site.
1. Connection between the DC distribution cabinet and the DC distribution panel
The PE grounding bar of the DC distribution cabinet must be reliably connected
to the protective grounding bar provided by the carrier through the yellow/green
wire with the copper core, plastic insulation layer and the same diameter as the
power cable.
The two -48V terminal blocks of the DC distribution cabinet should be reliably
connected to the -48V DC negative busbars of the active/standby DC
distribution panels respectively. The GND terminal blocks of the DC distribution
cabinet should be reliably connected to the -48V DC positive busbars of the
active/standby DC distribution panels respectively.
If there is no DC distribution cabinet, PE wiring terminals of the cabinets must
be reliably connected with the protective terminal blocks provided by the carrier.
The power cables led out from -48 V and GND wiring terminals of each cabinet
are directly connected to the -48V DC negative busbar and -48V DC positive
busbar of the DC distribution panel.
2. Connection between the DC distribution cabinet and the cabinet
Connect one end of the -48V power cable (blue, 16 mm2) to the -48V wiring
terminal on the filter of the cabinet, and the other end to the -48V busbar of the
DC distribution cabinet.
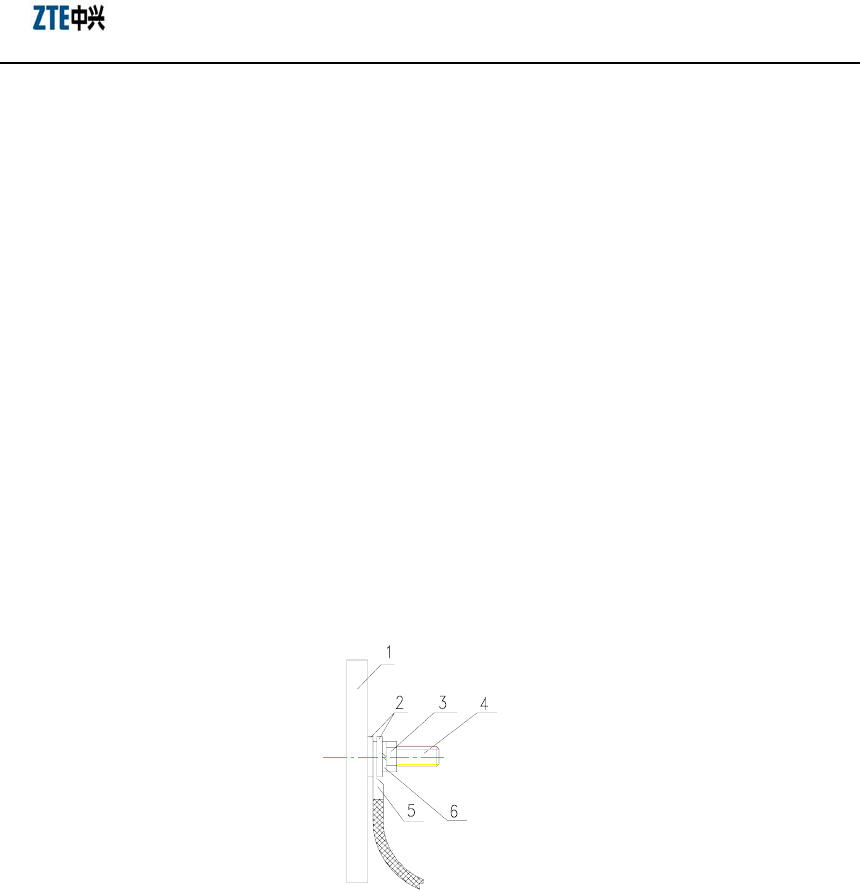
Chapter
Error! Style not defined.
Error!
Style not defined.
5-5
Connect one end of the -48V grounding cable (black, 16 mm2) to the GND
wiring terminal on the filter of the cabinet, and the other end to the GND busbar
of the DC distribution cabinet.
Connect the Protection Earth wire (PE) (yellow green, 25 mm2): one end is
connected to the PE wiring terminal on the P power supply of the cabinet, and
the other end to the PE busbar of the DC distribution cabinet.
3. Intra-module cabinet cascading
In the same module, the GND wiring terminals of each cabinet should be
connected with each other via a shorted cable.
4. Precautions for connecting power cables
While fixing the lug at one end of the DC distribution frame, add the flat washer
and spring washer to make sure that the lug is reliably fixed and that the cable
and wiring bar are in good contact to minimize the contact resistance. For details,
see Fig. 5.3-4.
2-Plain washer
3-Nut
4-Bolt
5-Cable
1-Copper bar
6-Spring washer
Fig. 5.3-4 Connecting Power Cable (1)
When installing lugs, if two or more cables need to be installed on one wiring
post, the lugs should be crossed or installed in a back-to-back way, instead of
being overlapped. If they must be overlapped, they should be bent into 45
o
or
90
o
before installation. Note that the big lug should be put under the small one.
It is recommended to adopt this method in all the places where the lugs need to
be installed. For details, see Fig. 5.3-5.

ZXC10-BTS (V5.4) Installation Manual
5-6
Cross
connection
45º or 50º bending connection Back-to-back
connection
2-Plain washer
3-Nut
4-Bolt
5-Cable
1-Copper bar
6-Spring washer
Fig. 5.3-5 Connecting Power Cable (2)
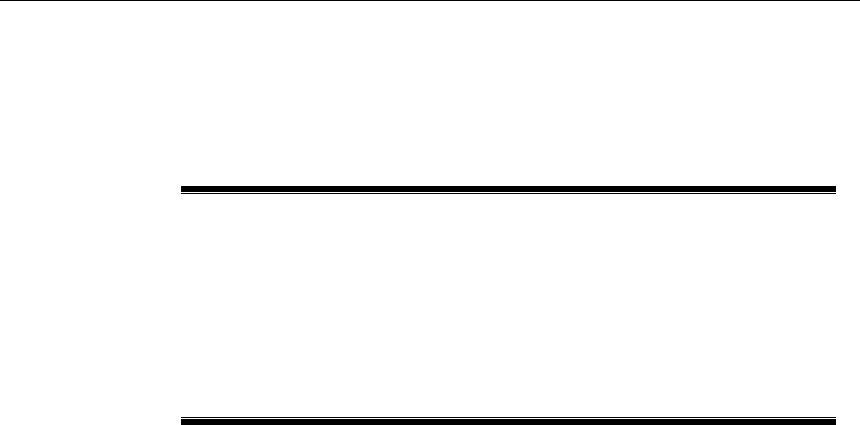
FAX: 0086-755-26770160
6-1
6 Installing the Grounding System
Summary
This part describes:
● Installation method of the BTS grounding system;
● Installation procedure of the BTS grounding system.
6.1 Overview of the BTS Grounding System
The purpose of grounding is to ensure the safety of human body and equipment and to
improve the capability of the equipment to resist electromagnetic interference.
The grounding system consists of indoor part, outdoor part and underground ground
grid of the building.
As to the engineering, the user is responsible for the basic ground grid construction of
the grounding system, the grounding engineering of the iron tower and the building,
and the provision of the connecting point for the indoor and the outdoor grounding
copper bars to connect the ground grid via separate 50mm
2
wires, as shown in Fig.
6.1-1.
The wire of the indoor rack PGND (protection ground) is connected to the indoor
grounding copper bar, as shown in Fig. 6.1-1.
The wire of the BTS rack –48VGND (working ground) is connected to the working
ground terminal of the BTS DC power rack.
To ground the lightning arrester, connect it to the outdoor grounding copper bar with a
wire. And to ground the feeder, connect each feeder to the outdoor grounding copper
bar through a grounding clip before it enters the equipment room, as shown in Fig.
6.1-1.
This section describes the grounding of the BTS equipment and the installation of the
grounding device accessories required for the BTS installation. It covers the
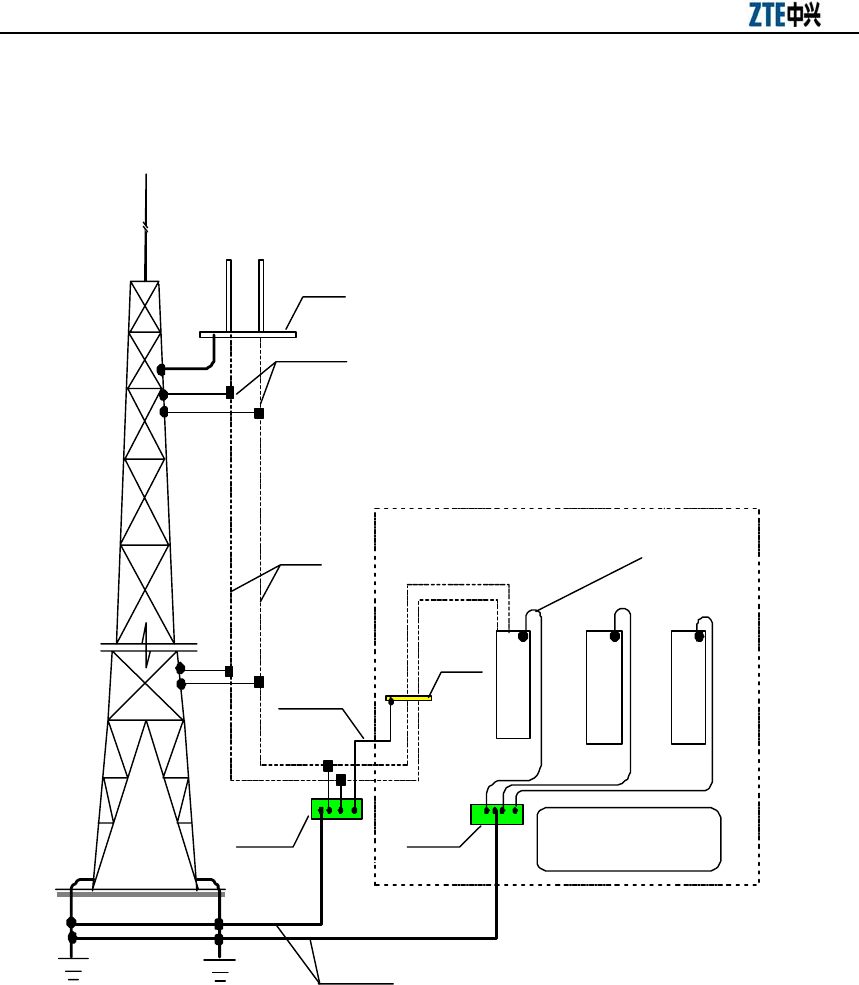
ZXC10-BTS (V5.4) Installation Manual
6-2
installation of the grounding copper bar, the feeder grounding clip and the lightning
arrester.
B
T
S
Grounding
cable 50mm
2
Outdoor
grounding bar
Gr o un din g
cable 35mm
Feeder
grounding clip
Iron tower
platform
U
Feeder
Groun ding cable
of the Lighting
arrester frame
Lightning
arrester frame
DC power frame
Other equipment
2
Indoor
grounding bar
Protection ground of any equipment
(including cabling racks) inside the
equipment room shall be connected
to the indoor grounding bar.
Fig. 6.1-1 Wiring for the BTS Ground
6.2 Installing the BTS Grounding System
6.2.1 Installing the Outdoor Grounding Copper Bar
The outdoor grounding copper bar is used for lightning protection grounding. It is
usually installed on the wall outside the feeder window. The best place for it is right

Chapter
Error! Style not defined.
Error!
Style not defined.
6-3
under the feeder window or on the rainproof wall of the feeder well on the roof top. In
principle, it is better to put it close to the feeder window.
During the practical installation, first determine the installation position of the
grounding copper bar by following the engineering design drawing, and then install the
grounding copper bar on the wall with the expansion bolts. See Fig. 6.2-1 for the
structure of the grounding copper bar.
Fig. 6.2-1 Profile of the Grounding Copper Bar
6.2.2 Installing the Feeder Grounding Clip
Caution:
No installation of grounding clip should be performed in case of any lightning strike,
lest bodily injury may be incurred.
When installing the grounding clip, keep the feeder at the joint of the grounding clip
and the feeder straight.
6.2.2.1 Grounding Principles of Main Feeders
1. Usually, each main feeder should be grounded with grounding clips at least at
three positions: on the tower platform, at the place where the main feeder leaves
the tower for the outdoor cabling rack, and before the cable enters the equipment
room. When the main feeder is over 60m, grounding clips should be added in
the middle of it. Generally, a grounding clip is installed on the feeder every 20m.

ZXC10-BTS (V5.4) Installation Manual
6-4
2. The antenna feeder system, antenna support and new cabling rack installed on
the roof top should be welded to the lightning protection grid of the building.
The feeder should also be grounded at three positions: where it leaves the
antenna embracing pole, where it leaves the roof top, and where it enters the
equipment room.
3. When the main feeder enters the equipment room from the roof top along the
wall, the outdoor cabling ladder provided by the network operator must be
grounded. If not, urge the network operator to finish it as soon as possible.
6.2.2.2 Installing the Grounding Clip
1. Prepare the tools: Paper cutter, flathead screwdrivers, wrench and sharp-nose
pliers.
2. Select a proper installation position for the grounding clip. And cut open the
sheath of the 7/8" feeder to the size of the grounding clip. The structure of the
grounding clip is as shown in Fig. 6.2-2
Grounding end Grounding cable
Feeder
Locking spring plate
of the grounding cable
External copper
core of the feeder
Copper sheet of
the grounding cable
Fig. 6.2-2 Structure of the Grounding Clip
3. Lead the grounding wire of the feeder lightning grounding clip to the ground
grid. No reverse direction is allowed. The angle formed by the grounding wire
and the main feeder should not be more than 15°C. No reverse folding is
allowed.
In the case the antenna feeder system is installed on the tower, the grounding
wire of the grounding clip should be led downward along the tower body.
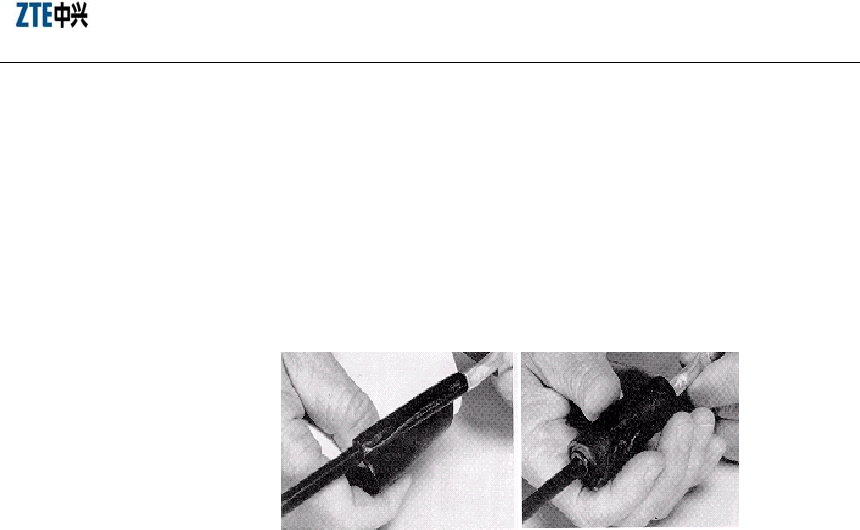
Chapter
Error! Style not defined.
Error!
Style not defined.
6-5
In the case the antenna feeder system is installed on the roof top, the grounding
wire of the grounding clip should be led close to the building lightning
protection grid.
4. Before installing the grounding clip, wrap the grounding wire at the grounding
clip end that is close to the grounding wire copper sheet with the waterproof
adhesive tape, as shown in Fig. 6.2-3. This can improve the sealing effect and
prevent the rain from falling into the feeder interior along the grounding wire.
Fig. 6.2-3 Wrapping the Grounding Wire of the Grounding Clip with Waterproof Tape
5. Clamp the feeder external conductor with the grounding wire copper sheet and
the locking spring plate, so that the grounding wire copper sheet and the feeder
external conductor are fully meshed.
6. Take the following steps to conduct the waterproof treatment to the joint of the
grounding clip and the feeder:
1) First wrap the waterproof adhesive tapes and then wrap the PVC tapes.
2) To wrap the waterproof adhesive tapes, apply them layer by layer from bottom
to top first, then from top to bottom once again, and finally from bottom to top
thrice, that is, wrap three layers of them. During the process, make sure the
upper layer overlaps the lower layer by about half the width of the tapes.
7. The grounding end of the grounding clip can be connected to the main tower
body or the outdoor cabling rack (connected to the lightning protection grid of
the building) on the roof top. Remove paint and oxide within the radius of about
13mm at the connection place, and cover the clean area with antioxidant to
ensure good electric contact. When the grounding end is connected, paint
another coat of antirust paint.
8. Before the main feeder enters the room, the grounding end of the grounding clip
can be connected to the outdoor grounding bar.

ZXC10-BTS (V5.4) Installation Manual
6-6
6.2.3 Installing the Indoor Lightning Arrester
For the wide-band lightning arrester that need not be grounded separately, you may
directly connect it in serial to the place between the main feeder and the indoor set top
jumper. During the installation, the lightning arrester and indoor equipment as the
cabling rack should be insulated.
For the lightning arrester that need be grounded, a lightning arrester frame should be
provided. Please refer to the assembly instructions provided by the supplier for the
assembling of the lightning arrester frame. The installation steps are as follows:
1. Install the lightning arrester on its frame in advance.
During the installation, please note that the connectors at both ends of the
lightning arrester are different: One end is a DIN male connector (DIN-M) and
the other is a DIN female connector (DIN-F). Make sure that the DIN-M
connector of all the lightning arresters installed on the frame are in the same
direction, and the DIN-F connector of all the lightning arresters are in the same
direction. The lightning arrester should be securely installed on the frame and in
close contact with the frame.
2. Fix the assembled lightning arrester to the cabling rack.
Plan the installation position carefully to make both the main feeder and the set
top jumper easily be connected to the lightning arrester and to enable easy
cabling.
The lower part of the lightning arrester frame that is secured to the cabling rack
can be adjusted according to the width of the cabling rack.
When the lightning arrester frame is installed on the cabling rack, make sure that
its DIN-M connector points to the main feeder and its DIN-F connector points to
the connection line from the jumper to the rack.
3. The lightning arrester is installed indoor. Its grounding wire should be connected
to the outdoor grounding copper bar and should not contact with the conductor
of the indoor cabling rack. The lightning arrester frame is insulated from the
cabling rack.
The installation of the lightning arrester frame is as shown in Fig. 6.2-4.

Chapter
Error! Style not defined.
Error!
Style not defined.
6-7
Feeder window
Antenna feeder
lightning arrester
Fixing plate of the
lighting arrester
Lightning
arrester frame
Jumper
Jumper
GPS Lightning
arrester
Insulation
sleeve
Grounding cable of the lightning
arrester frame (to connect the
outdoor grounding bar)
Wall
Antenna
fee d er
GPS feeder
Fig. 6.2-4 Installing the Lightning Arrester Frame
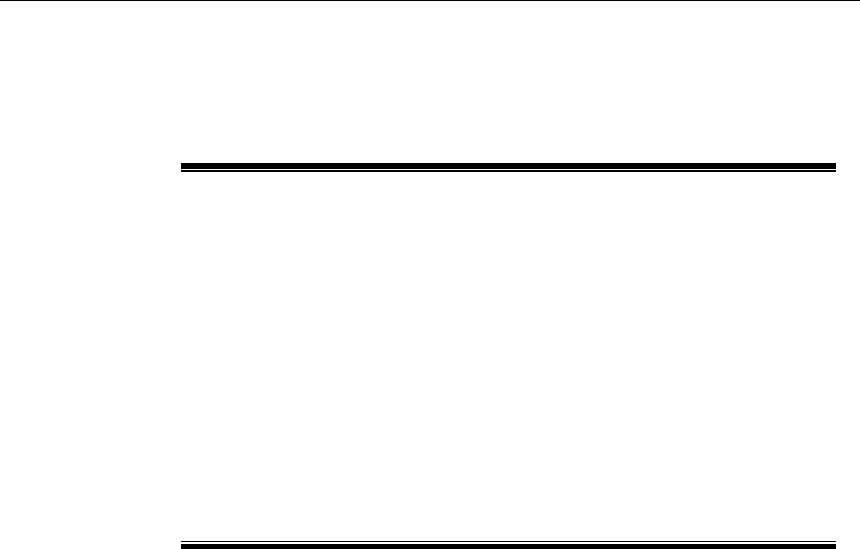
FAX: 0086-755-26770160
7-1
7 Installing the Cabinet Internal Cables
Summary
This part describes:
● Configuration types of BTS and precautions of the
installation of the front panel RF cables;
● Cable installation in BTS single-carrier and two-carrier
configurations;
● Cable installation in BTS three-carrier above
configurations.
7.1 Overview of the Internal Cable Installation
7.1.1 Configuration Types of BTS
A macro BTS can be configured in various ways, e.g., single-carrier three-sector,
two-carrier three-sector and four-carrier three-sector as required by the installation
environment and traffic conditions.
The RFE model varies with the BTS configuration and the number/length of
connection lines configured for the front panel of the rack. The following sections
describe the typical configurations: Single-carrier single-sector, single-carrier
two-sector, single-carrier three-sector, and two-carrier three-sector.
7.1.2 Precautions for Installing the RF Cables on the Front Panel
The front panel of the BTS rack uses RF cables to transmit the uplink and downlink RF
signals between RFE, HPA and TRX. N-type interfaces and SMA interfaces are use.
During the cable installation, make sure to align the cables to the interfaces and screw
them tight.
Generally, the RF cables have been deployed for a new base station and what needs to
do is only take the feeder connectors out of the cabling trough on the front panel and
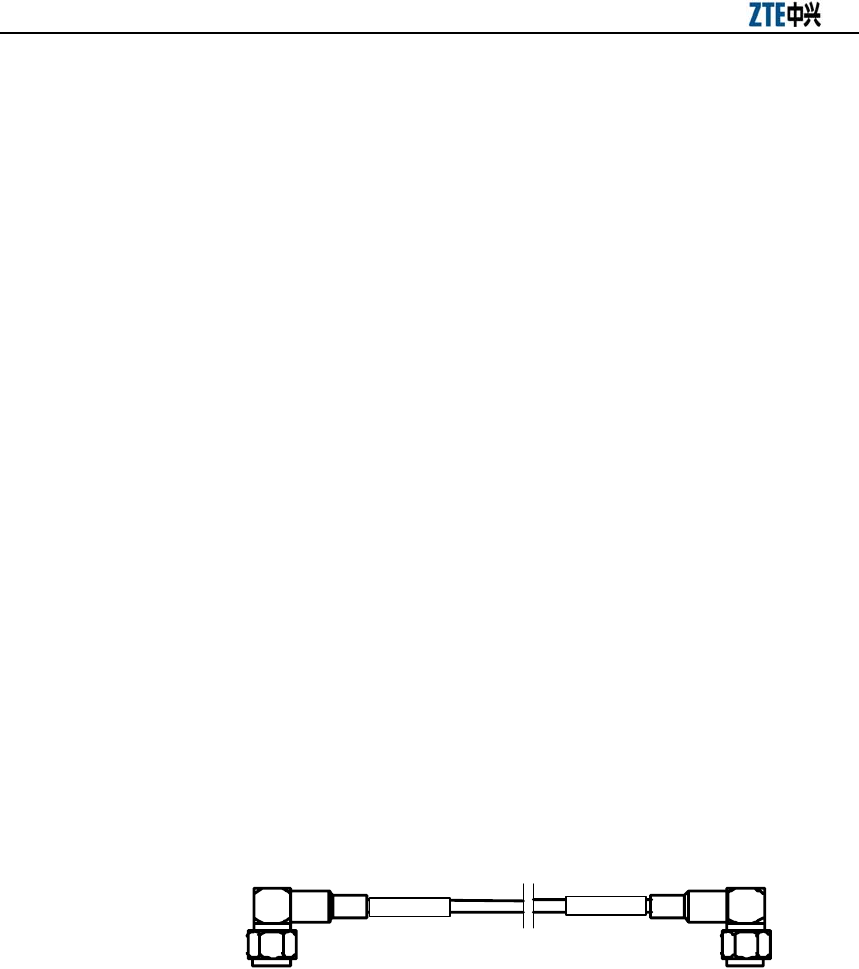
ZXC10-BTS (V5.4) Installation Manual
7-2
connect them to the RF interfaces on the front panel. However, re-cabling is required
for a base station to be expanded in capacity. Note that the RF cables are attached with
labels at both ends. The details are as follows:
1. The upper end (DIN connector) of the 1/2'' feeder from the RF front end to the
rack top has been installed to the rack top before factory delivery, so the onsite
installation only involves its lower end. During the installation, remove
dustproof cap from the lower end (N-type connector) of the feeder, hold the
lower end and slightly push the middle part of the feeder so that the feeder bends
naturally and its lower port aligns to the ANT port on the front panel of RFE,
and then fasten the screw cap. Please be noted that during the installation you
should align both the port and the screw cap to smoothly screw tight the 1/2''
feeder because it is short and has a certain rigidity.
2. Fig. 7.1-1 shows the structure of the RF connection lines between RFE, HPA
and TRX. The cables have all been deployed for the rack before factory delivery
if the base station is newly built. During the installation, open the baffle of the
cabling slot on the front panel and take out the connectors (SMA) and connect
them to the corresponding positions against the labels on the cables. For the
specific content of these labels, please refer to the information about "End A
Direction" and "End B Direction" given in Table 7.2-1, Table 7.2-2, Table 7.2-3
and Table 7.2-4 concerning the "Front Panel Wiring List" of multiple
configurations. Please also be noted that you should check the connectors
against the cable labels once again after installing them.
Label Label
Fig. 7.1-1 Structure of the RF Cables on the Front Panel of the Rack
3. Some additional RFE, HPA and TRX modules are needed for a base station
requiring capacity expansion. The RF cables connecting them need onsite
connection. To do so, you should select the RF connection cables according to
the configuration requirements of the base station to be expanded, deploy the
feeders tidily and bind them securely inside the cabling troughs in accordance
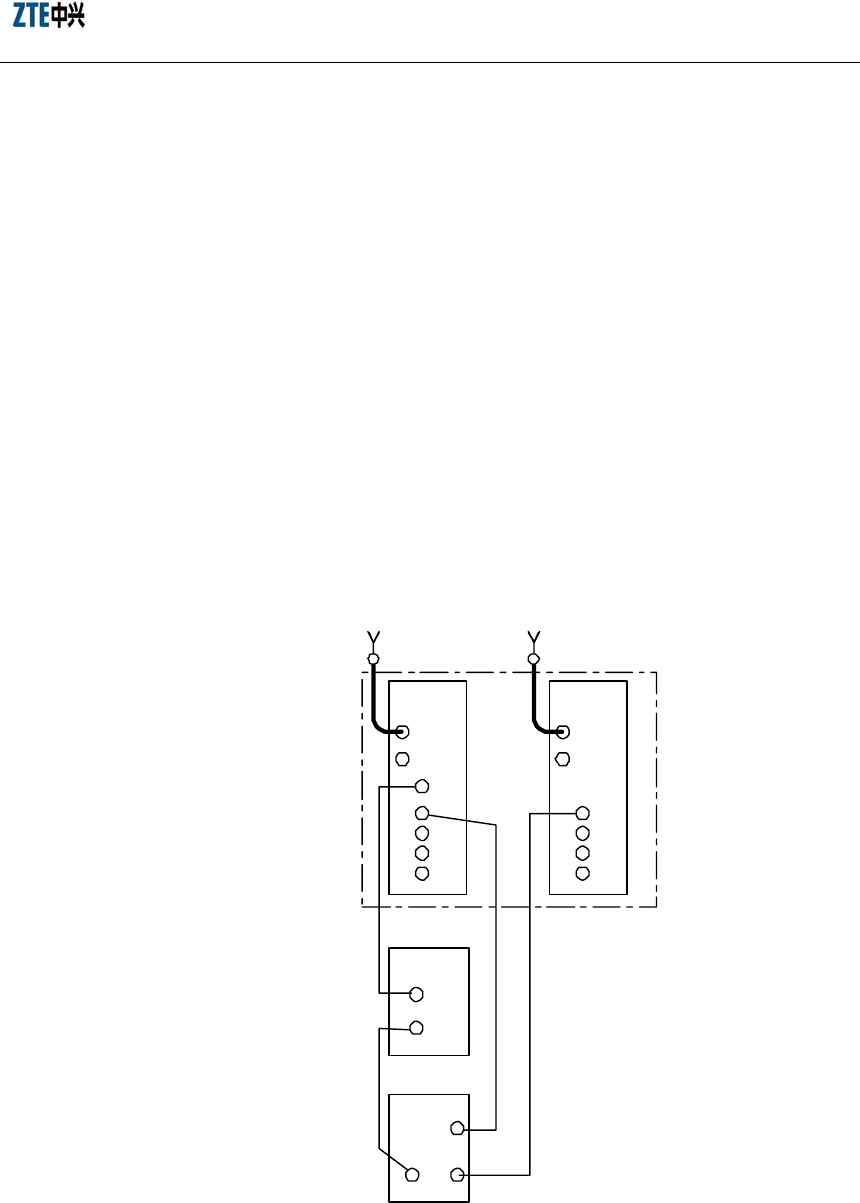
Chapter
Error! Style not defined.
Error! Style
not defined.
7-3
with the route requirements as regulated in the cabling diagram, and then
connect them one by one as instructed by their labels.
4. A load of 50Ω should be matched to each port that does not connect any RF
cable.
5. The cabling should be neat and in order, and no cable should be damaged during
the bundling or cutting of their cable ties.
7.2 Installing the Cables for the Single-carrier BTS and the
Two-Carrier BTS
7.2.1 Installing the RF Cables for a Single-carrier Single-sector BTS
1. Connecting the RF cables
Fig. 7.2-1 shows how to connect the RF cables on the front panel of the rack for
the single-carrier single-sector BTS.
Omni
RFE- DUP
ANT
TEST
HPA
RX1
RX2
RX3
RX4
RFE- DI V
ANT
TEST
RX1
RX2
RX3
RX4
HPA
TRX
RFI N
RFOUT
RX1
RX2TX
Omni

ZXC10-BTS (V5.4) Installation Manual
7-4
Fig. 7.2-1 RF Cable Connection on the Front Panel of the Rack for the Single-carrier Single-sector
BTS
2. Cabling of the front panel
Fig. 7.2-2 shows the wiring of the front panel for the rack of the single-carrier
single-sector BTS.

Chapter
Error! Style not defined.
Error! Style
not defined.
7-5
1/ A 2/A
1/ B 2/ B
3/A 4/ A
3/ B
4/B
5/ A
5/ B
6/ A 7/A
6/B
7/B
8/B
8/A
9/A
9/B
接前门板接地螺柱
10/A
接前门板
接地螺柱
Connected to the
grounding bolt of
the front door
Fig. 7.2-2 Front Panel Wiring for the Rack of the Single-carrier Single-sector BTS with the BDS Plug-in Shelf
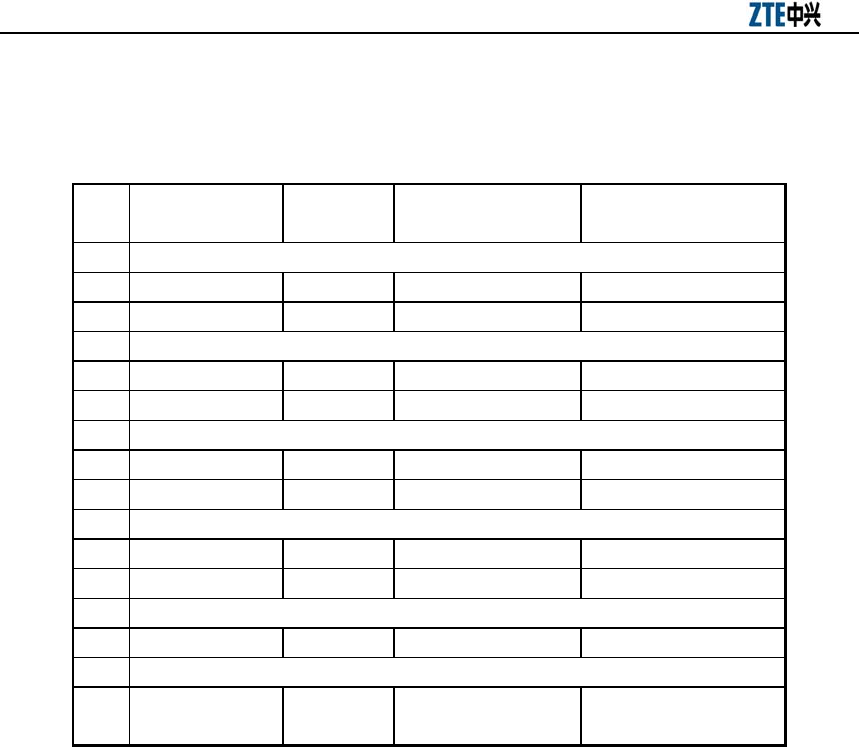
ZXC10-BTS (V5.4) Installation Manual
7-6
3. The wiring of the front panel is further described in Table 7.2-1.
Table 7.2-1 Front Panel Wiring of the Rack for the Single-carrier Single-sector BTS
No. Cable Name and
Code Length (mm) End A Direction End B Direction
RFE RF cables
1 RFE/01-250 (220) 250 (220) BTS-RFE-RFE1-ANT BTS - set top
2 RFE/02-220 220 BTS-RFE-RFE2-ANT BTS - set top
RF03 RF cables
3 RF03/01-530 530 BTS-RFE-RFE1-TEST BTS-HPA-BTM-RFE1
4 RF03/02-460 460 BTS-RFE-RFE2-TEST BTS-HPA-BTM-RFE2
RF01 RF cables
5 RF01/07-1050 1050 BTS-RFE-RFE1-RX1 BTS-TRX-TRX1-RX1
6 RF01/08-1200 1200 BTS-RFE-RFE2-RX1 BTS-TRX-TRX1-RX2
RF06 RF cables
7 RF06/01-260 260 BTS-RFE-RFE1-HPA BTS-HPA-HPA1-RF-OUT
8 RF06/04-800 800 BTS-HPA-HPA1-RF-IN BTS-TRX-TRX1-TX
MS test antenna
9 MS-860 860 BTS-HPA-BTM-ANT BTS - set top
Grounding cables of the door
10 JDX 250 Grounding screw of the
BTS grounding shelf
Grounding screw of the
front door
7.2.2 Installing the RF Cables for a Single-carrier Two-sector BTS
1. Connecting the RF cables
Fig. 7.2-3 shows the circuitry on the front panel of the rack for the single-carrier
two-sector BTS.

Chapter
Error! Style not defined.
Error! Style
not defined.
7-7
A-ANT
RFE-DUP
ANT
TEST
HPA
RX1
RX2
RX3
RX4
RFE-DIV
ANT
TEST
RX1
RX2
RX3
RX4
A-ANT-DIV
HPA
TRX
RFIN
RFOUT
RX1
RX2
TX
B-ANT
RFE-DUP
ANT
TEST
HPA
RX1
RX2
RX3
RX4
RFE-DIV
ANT
TEST
RX1
RX2
RX3
RX4
B-ANT-DIV
HPA
TRX
RFIN
RFOUT
RX1
RX2TX
Fig. 7.2-3 RF Cable Connection on the Front Panel of the Rack for the Single-carrier Two-sector BTS
2. Cabling of the front panel
Fig. 7.2-4 shows the wiring of the front panel for the rack of the single-carrier
two-sector BTS.
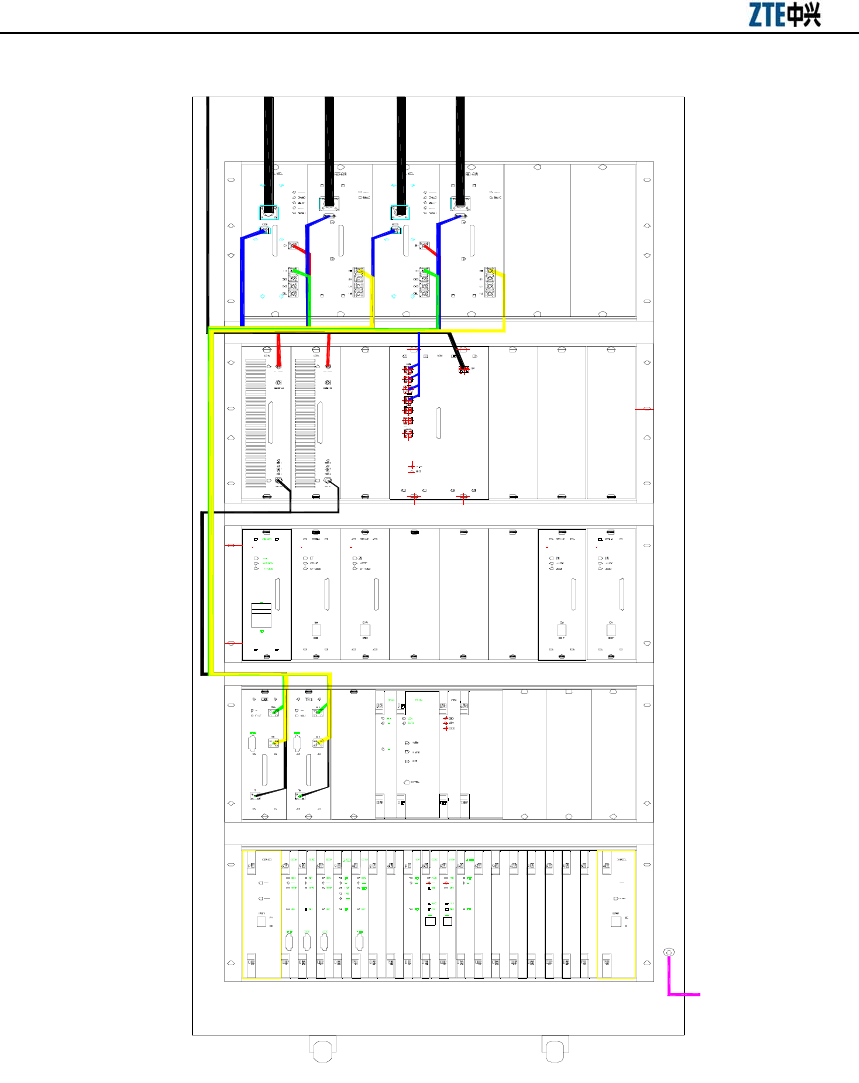
ZXC10-BTS (V5.4) Installation Manual
7-8
1/ A 2/A 3/A 4/A
1/B2/B 3/B4/B
5/A 6/A 7/ A 8/ A
5/ B
6/B
7/B
8/ B
9/A 10/A
9/B 10/B
11/A 12/A 13/A 14 /A
11/B
12/B 13/ B
14/B
15/ B 16/ B
15/A 16/A
17/A
17/B
接前门板接地螺柱
18/A
接前门板
接地螺柱
Connected to the
gro un din g bo lt o f
the front door
Fig. 7.2-4 Front Panel Wiring for the Rack of the Single-carrier Two-sector BTS with the BDS Plug-in Shelf
3. The wiring of the front panel is further described in Table 7.2-2.
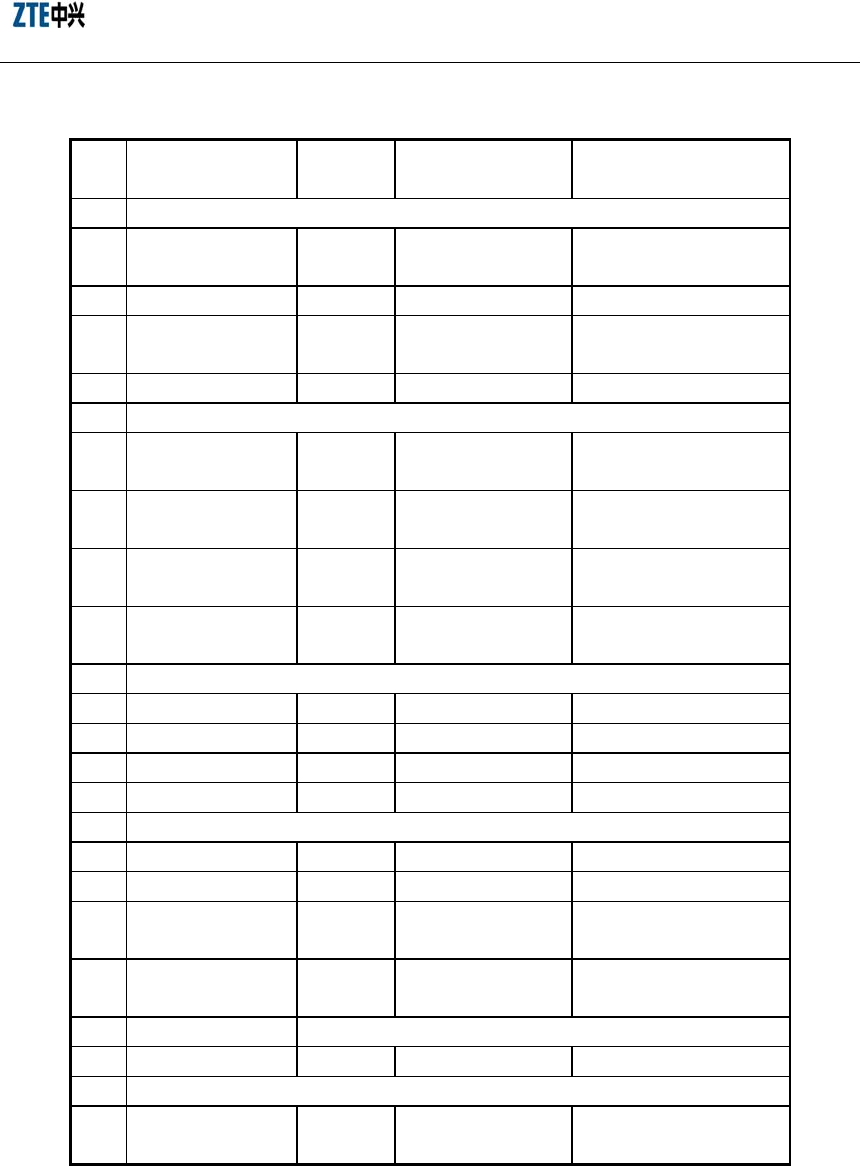
Chapter
Error! Style not defined.
Error! Style
not defined.
7-9
Table 7.2-2 Front Panel Wiring of the Rack for the Single-carrier Two-sector BTS
No. Cable Name and
Code
Length
(mm) End A Direction End B Direction
RFE RF cables
1 RFE/01(02)
-250(220)
250(220) BTS-RFE-RFE1-ANT BTS - set top
2 RFE/02-220 220 BTS-RFE-RFE2-ANT BTS - set top
3 RFE/01(02)
-250(220)
250(220) BTS-RFE-RFE3-ANT BTS - set top
4 RFE/02-220 220 BTS-RFE-RFE4-ANT BTS - set top
RF03 RF cables
5 RF03/01-530 530 BTS-RFE-RFE1-TES
T
BTS-HPA-BTM-RFE1
6 RF03/02-460 460 BTS-RFE-RFE2-TES
T
BTS-HPA-BTM-RFE2
7 RF03/03-380 380 BTS-RFE-RFE3-TES
T
BTS-HPA-BTM-RFE3
8 RF03/04-390 390 BTS-RFE-RFE4-TES
T
BTS-HPA-BTM-RFE4
RF01 RF cables
9 RF01/07-1050 1050 BTS-RFE-RFE1-RX1 BTS-TRX-TRX1-RX1
10 RF01/08-1200 1200 BTS-RFE-RFE2-RX1 BTS-TRX-TRX1-RX2
11 RF01/09-1300 1300 BTS-RFE-RFE3-RX1 BTS-TRX-TRX2-RX1
12 RF01/10-1450 1450 BTS-RFE-RFE4-RX1 BTS-TRX-TRX2-RX2
RF06 RF cables
13 RF06/01-260 260 BTS-RFE-RFE1-HPA BTS-HPA-HPA1-RF-OUT
14 RF06/02-370 370 BTS-RFE-RFE3-HPA BTS-HPA-HPA2-RF-OUT
15 RF06/04-800 800 BTS-HPA-HPA1-RF-I
N
BTS-TRX-TRX1-TX
16 RF06/05-930 930 BTS-HPA-HPA2-RF-I
N
BTS-TRX-TRX2-TX
MS test antenna
17 MS-860 860 BTS-HPA-BTM-ANT BTS - set top
Grounding cables of the door
18 JDX 250 Grounding screw of
the BTS frame
Grounding screw of the front
door
7.2.3 Installing the RF Cables for a Single-carrier Three-sector BTS
1. Connecting the RF cables
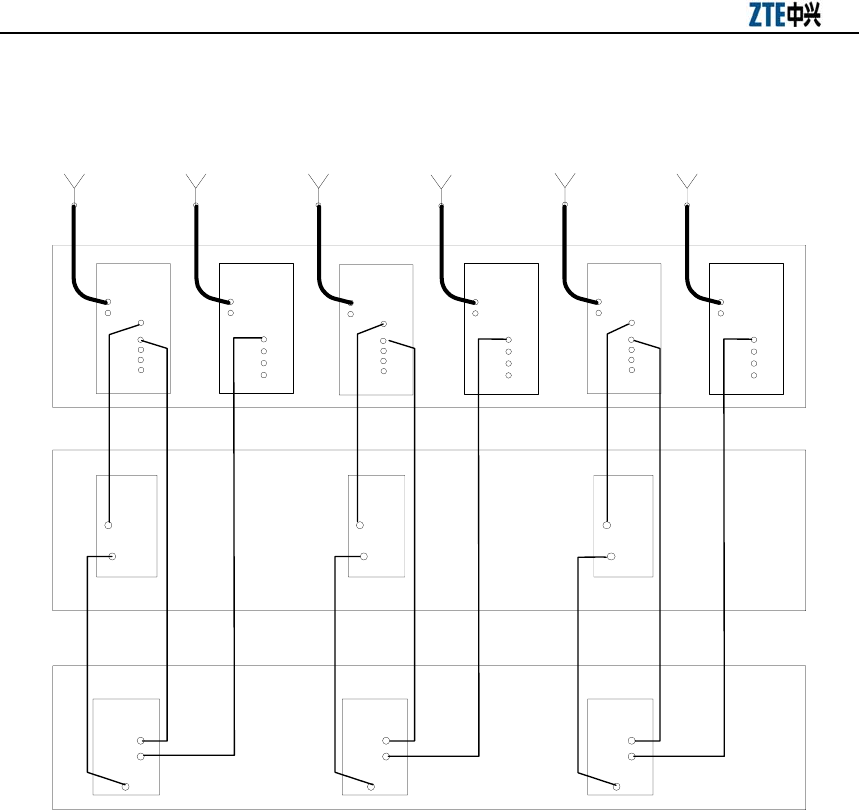
ZXC10-BTS (V5.4) Installation Manual
7-10
Fig. 7.2-5 shows the circuitry on the front panel of the rack for the single-carrier
three-sector BTS.
TX
RX2
TRX
RX1
A-ANT A-ANT B-ANT B-ANT C-ANT C-ANT
TX
RX2
TRX
RX1
TX
RX2
TRX
RX1
RF-OUT
RF-IN
HPA
RF-OUT
RF-IN
HPA
RF-OUT
RF-IN
HPA
RFE-DUP
ANT
TEST HPA
RX2
RX4
RX3
RX1
RFE-DUP
ANT
TEST HPA
RX2
RX4
RX3
RX1
RFE-DIV
TEST
ANT
RX2
RX4
RX3
RX1
RFE-DIV
TEST
ANT
RX2
RX4
RX3
RX1
RFE-DUP
ANT
TEST HPA
RX2
RX4
RX3
RX1
RFE-DIV
TEST
ANT
RX2
RX4
RX3
RX1
Fig. 7.2-5 Circuitry on the Front Panel of the Rack for the Single-carrier Three-sector BTS
2. Cabling of the front panel
Fig. 7.2-6 shows the wiring of the front panel for the rack of the single-carrier
three-sector BTS. Fig. 7.2-7 shows the wiring for the BTS rack with the
EBDS-HS.
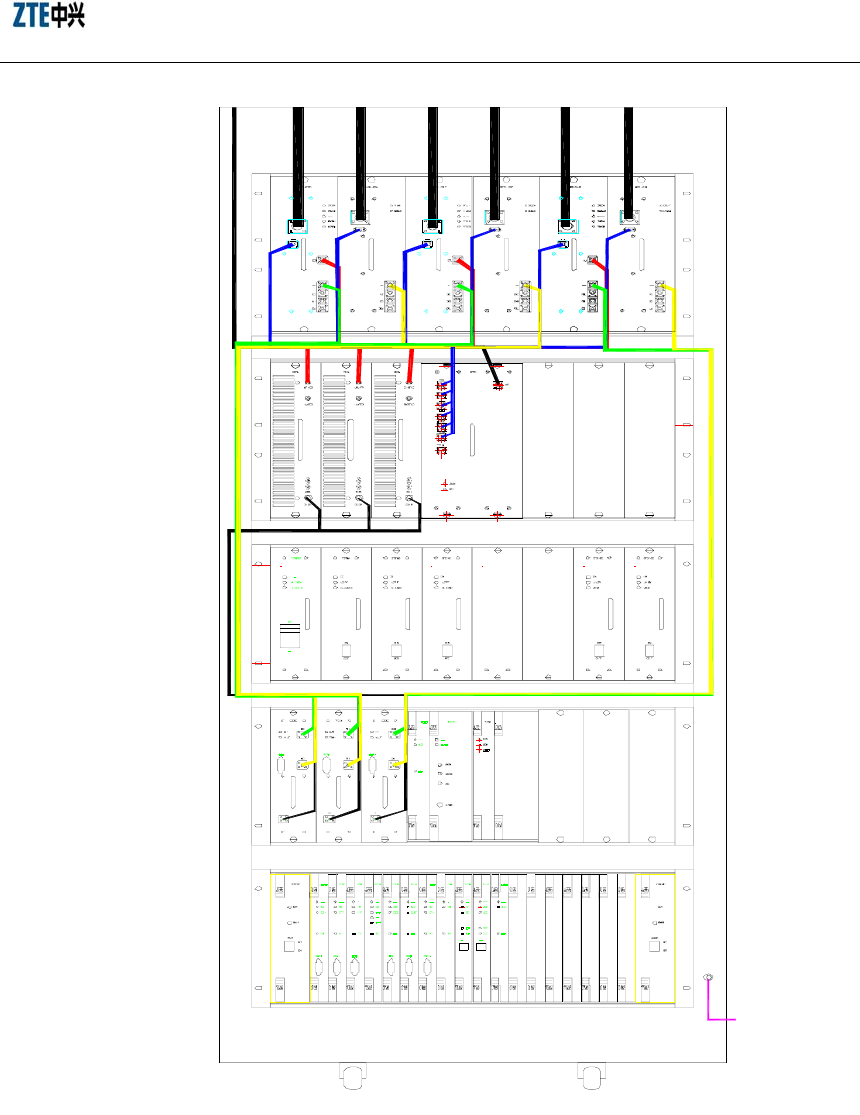
Chapter
Error! Style not defined.
Error! Style
not defined.
7-11
1/A 2/A 3/ A 4/A 5/A 6/ A
1/B 2/B 3/ B 4/B 5/B 6/ B
7/ A 8/ A 9/ A 10/A 11/ A 12/A
7/ B
8/B
9/B
10/B
11/B
12/ B
13/ A 14/ A 15/A
13/B 14/B 15/B
16/A 17/A 18/A 19/A 20/A 21 / A
16/B
17/B 18/ B
19/B
20/B
21/ B
22/ B 23/B 24/B
22/A 23/A 24/A
25/A
25/ B
接前门 板接地螺 柱
26/A
Connected to the
grounding bolt of
the front door
Fig. 7.2-6 Front Panel Wiring for the Rack of the Single-carrier Three-sector BTS
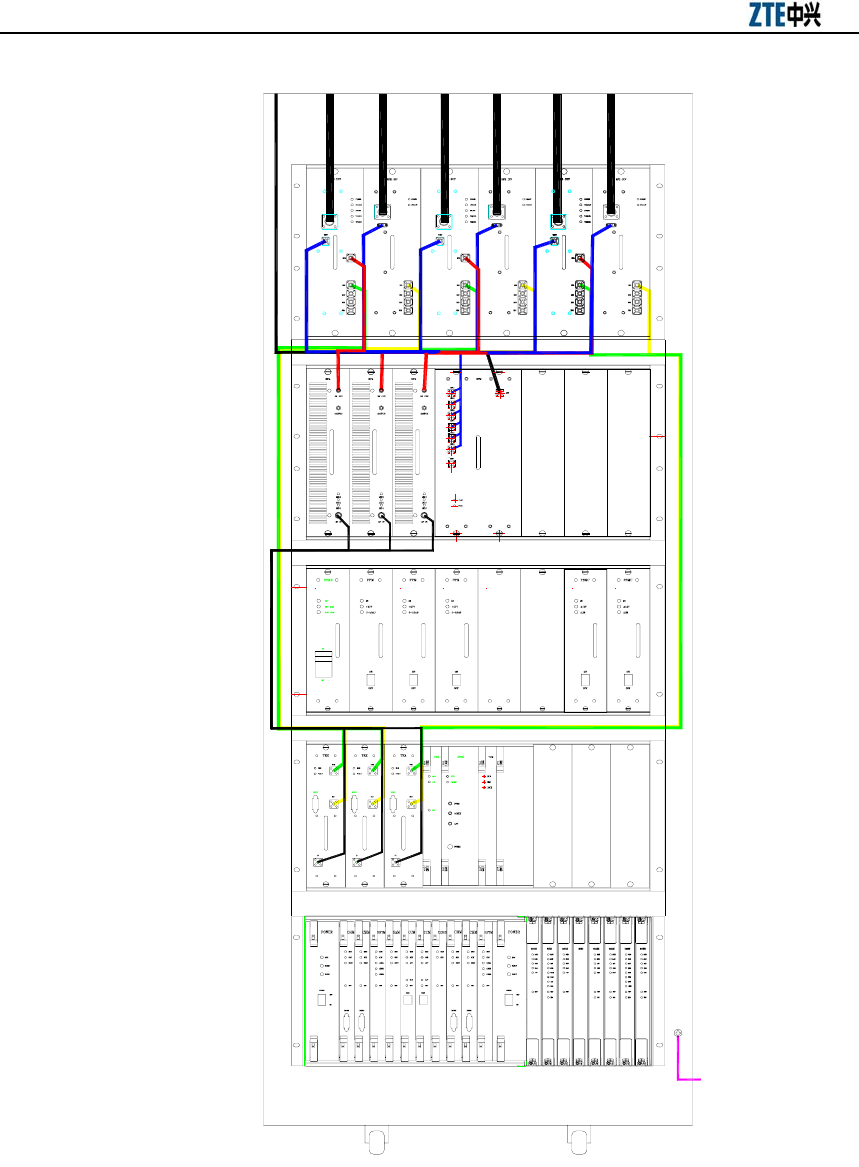
ZXC10-BTS (V5.4) Installation Manual
7-12
接前门板接地螺柱
26/A
18/A
12/B
21/A
19/A 20/A
11/A
14/A
10/A
4/A 5/A
15/A
12/A
6/A
25/B 1/ B 2/B 3/B 5/B
4/B 6/B
23/B
22/B 24/B
19/B
18/B
16/B
17/B 20/B
21/B
23/A
22/A 24/A
14/B
13/B 15/B
16/A 17/A
7/A
1/A
13/A
3/A
8/A 9/ A
2/A
8/B
10/B
11/B
9/B
7/B 25/ A
Connected to
the grounding
bolt of the
front door
Fig. 7.2-7 Front Panel Wiring for the Rack of the Single-carrier Three-sector BTS with the
EBDS-HS Part of the EBDS Hybrid Shelf
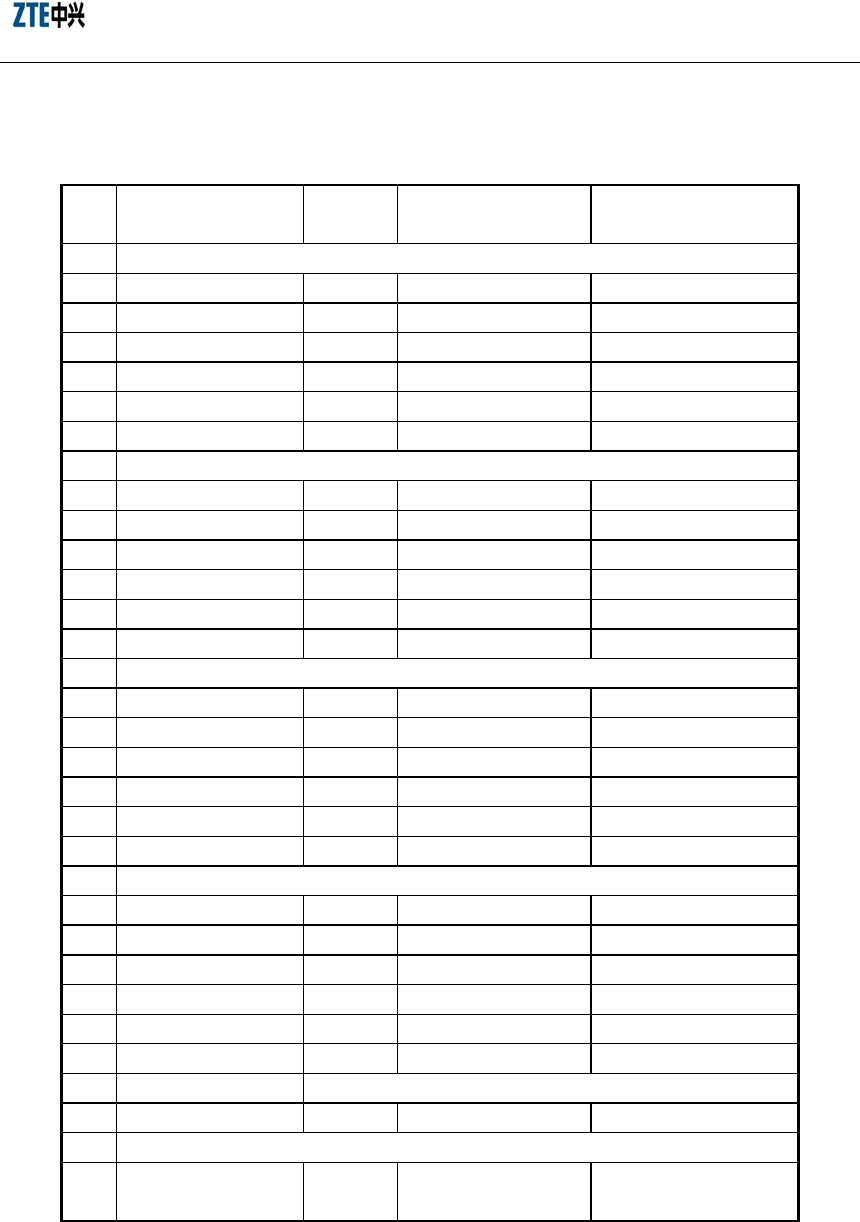
Chapter
Error! Style not defined.
Error! Style
not defined.
7-13
3. The wiring of the front panel is further described in Table 7.2-3.
Table 7.2-3 Front Panel Wiring of the Rack for the Single-carrier Three-sector BTS
No. Cable Name and Code Length
(mm) End A Direction End B Direction
RFE RF cables
1 RFE/01(02) -250(220) 250(220) BTS-RFE-RFE1-ANT BTS - set top
2 RFE/02-220 220 BTS-RFE-RFE2-ANT BTS - set top
3 RFE/01(02) -250(220) 250(220) BTS-RFE-RFE3-ANT BTS - set top
4 RFE/02-220 220 BTS-RFE-RFE4-ANT BTS - set top
5 RFE/01(02) -250(220) 250(220) BTS-RFE-RFE5-ANT BTS - set top
6 RFE/02-220 220 BTS-RFE-RFE6-ANT BTS - set top
RF03 RF cables
7 RF03/01-530 530 BTS-RFE-RFE1-TEST BTS-HPA-BTM-RFE1
8 RF03/02-460 460 BTS-RFE-RFE2-TEST BTS-HPA-BTM-RFE2
9 RF03/03-380 380 BTS-RFE-RFE3-TEST BTS-HPA-BTM-RFE3
10 RF03/04-390 390 BTS-RFE-RFE4-TEST BTS-HPA-BTM-RFE4
11 RF03/05-510 510 BTS-RFE-RFE5-TEST BTS-HPA-BTM-RFE5
12 RF03/06-600 600 BTS-RFE-RFE6-TEST BTS-HPA-BTM-RFE6
RF01 RF cables
13 RF01/07-1050 1050 BTS-RFE-RFE1-RX1 BTS-TRX-TRX1-RX1
14 RF01/08-1200 1200 BTS-RFE-RFE2-RX1 BTS-TRX-TRX1-RX2
15 RF01/09-1300 1300 BTS-RFE-RFE3-RX1 BTS-TRX-TRX2-RX1
16 RF01/10-1450 1450 BTS-RFE-RFE4-RX1 BTS-TRX-TRX2-RX2
17 RF01/11-1400 1400 BTS-RFE-RFE5-RX1 BTS-TRX-TRX3-RX1
18 RF01/12-1370 1370 BTS-RFE-RFE6-RX1 BTS-TRX-TRX3-RX2
RF06 RF cables
19 RF06/01-260 260 BTS-RFE-RFE1-HPA BTS-HPA-HPA1-RF-OUT
20 RF06/02-370 370 BTS-RFE-RFE3-HPA BTS-HPA-HPA2-RF-OUT
21 RF06/03-480 480 BTS-RFE-RFE5-HPA BTS-HPA-HPA3-RF-OUT
22 RF06/04-800 800 BTS-HPA-HPA1-RF-IN BTS-TRX-TRX1-TX
23 RF06/05-930 930 BTS-HPA-HPA2-RF-IN BTS-TRX-TRX2-TX
24 RF06/06-1050 1050 BTS-HPA-HPA3-RF-IN BTS-TRX-TRX3-TX
MS test antenna
25 MS-860 860 BTS-HPA-BTM-ANT BTS - set top
Grounding cables of the door
26 JDX 250 Grounding screw of the
BTS frame
Grounding screw of the
front door
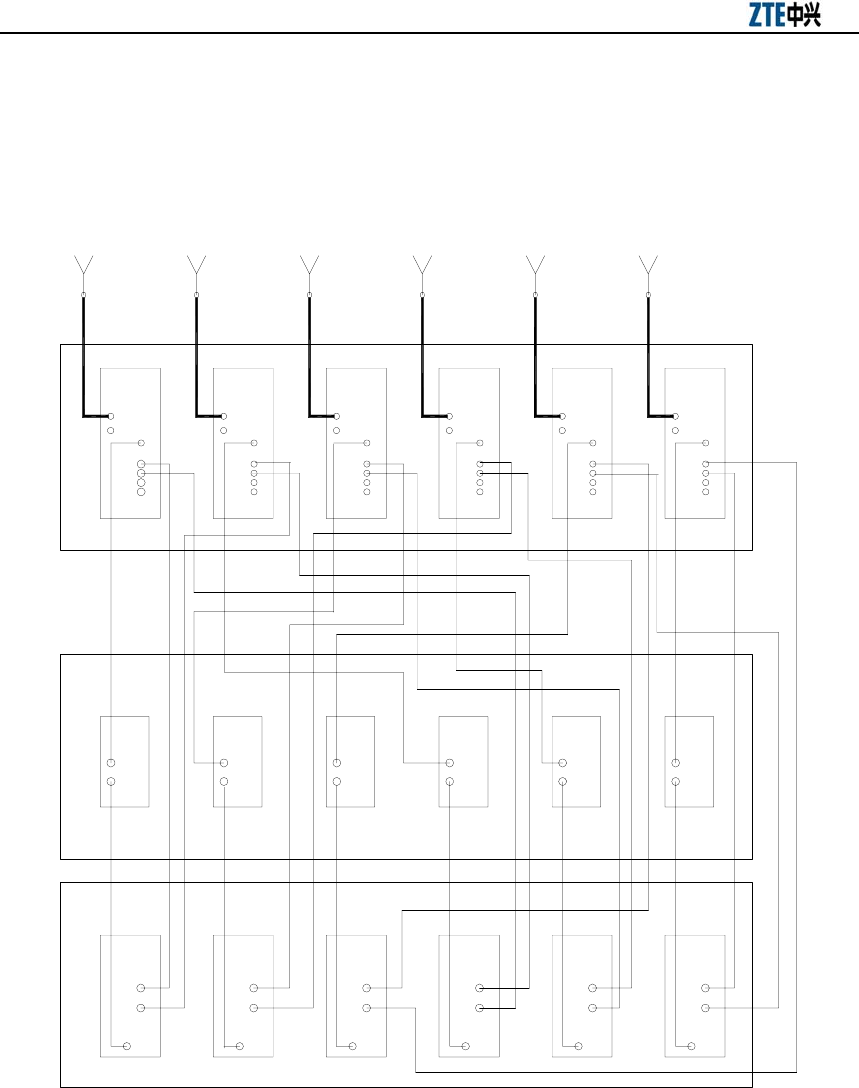
ZXC10-BTS (V5.4) Installation Manual
7-14
7.2.4 Installing the RF Cables for a Two-carrier Three-sector BTS
1. Connecting the RF cables
Fig. 7.2-8 shows the circuitry on the front panel of the rack for the two-carrier
three-sector BTS.
RFOUT
RFI N
HPA
RFOUT
RFI N
HPA
RFOUT
RFI N
HPA
RFOUT
RFI N
HPA
ACBA
TX
RX2
TRX
RX1
TX
RX2
TRX
RX1
TX
RX2
TRX
RX1
TX
RX2
TRX
RX1
f1 f2
RFE- DUP
ANT
TEST HPA
RFE- DUP
ANT
TEST HPA
RFE- DUP
ANT
TEST HPA
RFE- DUP
ANT
TEST HPA
A
f1
ACB
f2
f1:A-ANT f1:B-ANTf2:A-ANT f2:B-ANT
RFOUT
RFI N
HPA
RFOUT
RFI N
HPA
CB
TX
RX2
TRX
RX1
TX
RX2
TRX
RX1
RFE- DUP
ANT
TEST HPA
RFE- DUP
ANT
TEST HPA
CB
f1:C-ANT f2:C-ANT
RX2
RX4
RX3
RX1 RX2
RX4
RX3
RX1 RX2
RX4
RX3
RX1 RX2
RX4
RX3
RX1 RX2
RX4
RX3
RX1 RX2
RX4
RX3
RX1
Fig. 7.2-8 Circuitry on the Front Panel of the Rack for the Two-carrier Three-sector BTS
2. Cabling of the front panel
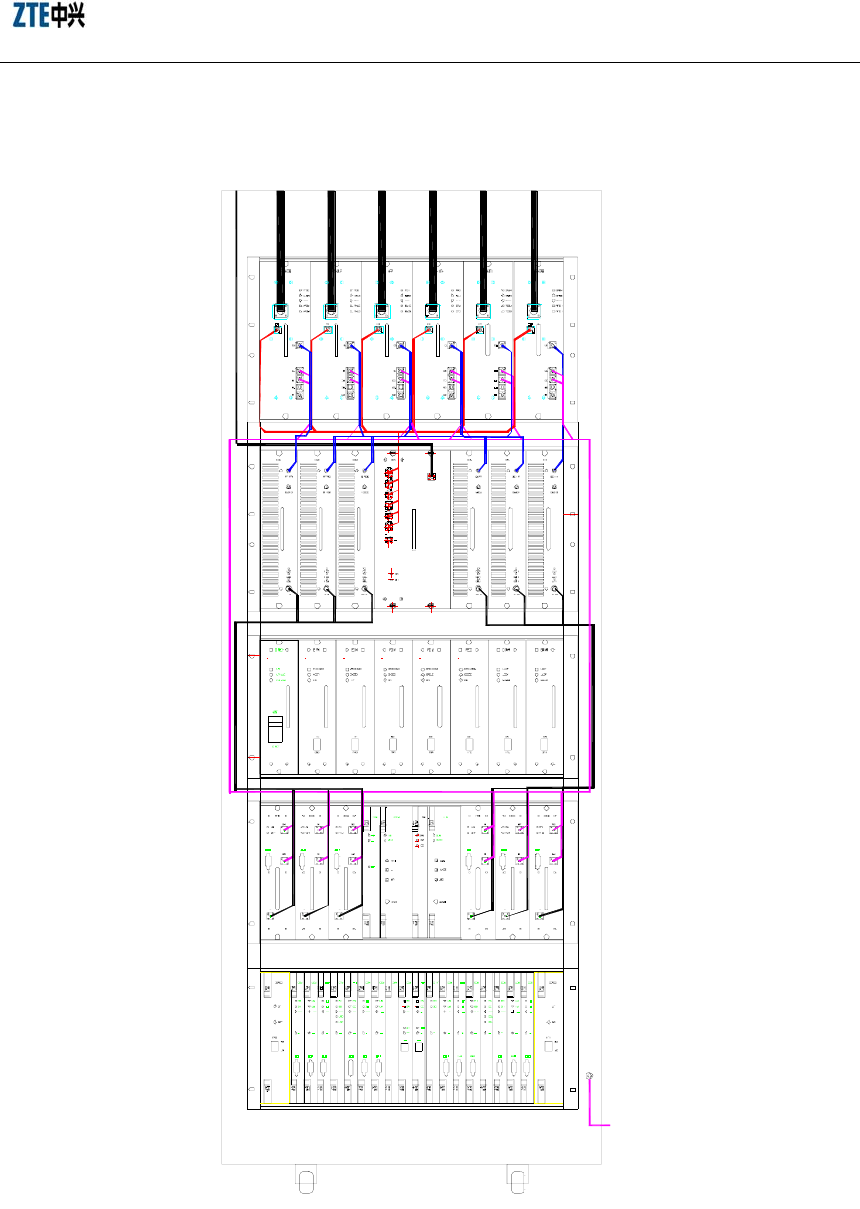
Chapter
Error! Style not defined.
Error! Style
not defined.
7-15
Fig. 7.2-9 shows the wiring of the front panel for the rack of the two-carrier
three-sector BTS.
1/A 2/A 3/A 4/A 5/A 6/A
1/B 2/B 3/ B 4/ B 5/ B 6 / B
7/A 8/A 9/A 10 / A 11/ A 12/A
13/A 14/A 15/A 16/A 17 / A 1 8 /A
13/B 15/B 17/ B 14/B 16/ B 18/B
31/A 32/A 33/A 34/A 35/A 36/A
31/ B 32/B 33/B 34/B 35/B 36/ B
19/B 25/B
20/B 26/B
21/B 27/B
22/B 28/B
23/B 29/B
24/B 30/B
19/A
25/A 22/ A
28/ A
20/ A
26/A 23/ A
29/A
21/ A
27/ A 24/A
30/A
37/A
37/B
38 / A
接前 门板 接地 螺柱
7/B
8/B
9/B
10/B
11/B
12/B
Connected to the
grounding bolt of
the front door
Fig. 7.2-9 Front Panel Wiring for the Rack of the Two-carrier Three-sector BTS

ZXC10-BTS (V5.4) Installation Manual
7-16
3. The wiring of the front panel is further described in Table 7.2-4.
Table 7.2-4 Front Panel Wiring of the Rack for the Two-carrier Three-sector BTS
No. Cable Name and
Code
Length
(mm) End A Direction End B Direction
RFE RF cables
1 RFE/01(02)
-250(220)
250(220) BTS-RFE-RFE1-ANT BTS - set top
2 RFE/01(02)
-250(220)
250(220) BTS-RFE-RFE2-ANT BTS - set top
3 RFE/01(02)
-250(220)
250(220) BTS-RFE-RFE3-ANT BTS - set top
4 RFE/01(02)
-250(220)
250(220) BTS-RFE-RFE4-ANT BTS - set top
5 RFE/01(02)
-250(220)
250(220) BTS-RFE-RFE5-ANT BTS - set top
6 RFE/01(02)
-250(220)
250(220) BTS-RFE-RFE6-ANT BTS - set top
RF03 RF cables
7 RF03/01-530 530 BTS-RFE-RFE1-TEST BTS-HPA-BTM-RFE1
8 RF03/02-460 460 BTS-RFE-RFE2-TEST BTS-HPA-BTM-RFE2
9 RF03/03-380 380 BTS-RFE-RFE3-TEST BTS-HPA-BTM-RFE3
10 RF03/04-390 390 BTS-RFE-RFE4-TEST BTS-HPA-BTM-RFE4
11 RF03/05-510 510 BTS-RFE-RFE5-TEST BTS-HPA-BTM-RFE5
12 RF03/06-600 600 BTS-RFE-RFE6-TEST BTS-HPA-BTM-RFE6
RF01 RF cables
19 RF01/07-1050 1050 BTS-RFE-RFE1-RX1 BTS-TRX-TRX1-RX1
20 RF01/08-1200 1200 BTS-RFE-RFE2-RX1 BTS-TRX-TRX1-RX2
21 RF01/09-1300 1300 BTS-RFE-RFE3-RX1 BTS-TRX-TRX2-RX1
22 RF01/10-1450 1450 BTS-RFE-RFE4-RX1 BTS-TRX-TRX2-RX2
23 RF01/11-1400 1400 BTS-RFE-RFE5-RX1 BTS-TRX-TRX3-RX1
24 RF01/12-1370 1370 BTS-RFE-RFE6-RX1 BTS-TRX-TRX3-RX2
25 RF01/17-1330 1330 BTS-RFE-RFE1-RX2 BTS-TRX-TRX4-RX1
26 RF01/18-1500 1500 BTS-RFE-RFE2-RX2 BTS-TRX-TRX4-RX2
27 RF01/09-1300 1300 BTS-RFE-RFE3-RX2 BTS-TRX-TRX5-RX1
28 RF01/09-1300 1300 BTS-RFE-RFE4-RX2 BTS-TRX-TRX5-RX2
29 RF01/15-1100 1100 BTS-RFE-RFE5-RX2 BTS-TRX-TRX6-RX1
30 RF01/07-1050 1050 BTS-RFE-RFE6-RX2 BTS-TRX-TRX6-RX2
RF06 RF cables
13 RF06/01-260 260 BTS-RFE-RFE1-HPA BTS-HPA-HPA1-RF-OUT
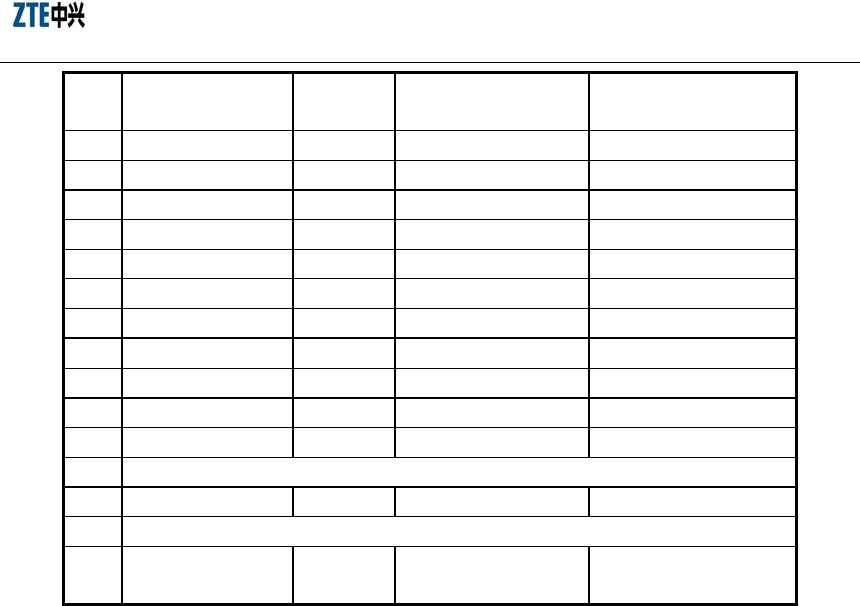
Chapter
Error! Style not defined.
Error! Style
not defined.
7-17
No. Cable Name and
Code
Length
(mm) End A Direction End B Direction
14 RF06/03-480 480 BTS-RFE-RFE2-HPA BTS-HPA-HPA4-RF-OUT
15 RF06/02-370 370 BTS-RFE-RFE3-HPA BTS-HPA-HPA2-RF-OUT
16 RF06/02-370 370 BTS-RFE-RFE4-HPA BTS-HPA-HPA5-RF-OUT
17 RF06/03-480 480 BTS-RFE-RFE5-HPA BTS-HPA-HPA3-RF-OUT
18 RF06/01-260 260 BTS-RFE-RFE6-HPA BTS-HPA-HPA6-RF-OUT
31 RF06/04-800 800 BTS-HPA-HPA1-RF-IN BTS-TRX-TRX1-TX
32 RF06/05-930 930 BTS-HPA-HPA2-RF-IN BTS-TRX-TRX2-TX
33 RF06/06-1050 1050 BTS-HPA-HPA3-RF-IN BTS-TRX-TRX3-TX
34 RF06/06-1050 1050 BTS-HPA-HPA4-RF-IN BTS-TRX-TRX4-TX
35 RF06/05-930 930 BTS-HPA-HPA5-RF-IN BTS-TRX-TRX5-TX
36 RF06/04-800 800 BTS-HPA-HPA6-RF-IN BTS-TRX-TRX6-TX
MS test antenna
37 MS-860 860 BTS-HPA-BTM-ANT BTS - set top
Grounding cables of the door
38 JDX 250 Grounding screw of the
BTS frame
Grounding screw of the
front door
7.2.5 Connecting the Backplane Signal Cables for the Rack of a Single-carrier or
Two-carrier BTS
The internal signal cables at the BTS rack’s backplane are: transit cable from rack top
to GPS antenna of GCM board, T1 transit cable from rack top to DSM board, LVDS
cable, HPA unit cable and BTM cable.
The ZXC10-BTSB I2 backplane cables are ready connected and tested before rack
delivery and it’s unnecessary to lay them over again during installation. For easier
expansion, the backplane cables are already laid out for the configuration of two
carriers and three sectors. For just in case, check if the cables are fast connected before
the rack is powered on. If there is a need to shoot a trouble while commissioning for
expansion purpose, the backplane indications and signal cable labels may be checked
for any connection error or cable problem.
7.3 Installing the Cables for the BTS of Three Carriers and Above
Two BTS cabinets should be combined for the BTSB I2 configuration of three carriers
and above: One basic cabinet (1#) that accommodates the GCM, DCM and SNM
modules, and one extended cabinet (2#).For easier expansion, all backplane cables for
the BTS of three carriers and above are deployed as required by the four-carrier

ZXC10-BTS (V5.4) Installation Manual
7-18
three-sector configuration, while the front panel cabling can be either for three-carrier
three-sector configuration or four-carrier three-sector configuration.
7.3.1 Installing the RF Cables for a Three-carrier Three-sector BTS
1. Connecting the RF cables
Fig. 7.3-1 shows the circuitry on the front panel of the rack for the three-carrier
three-sector BTS.
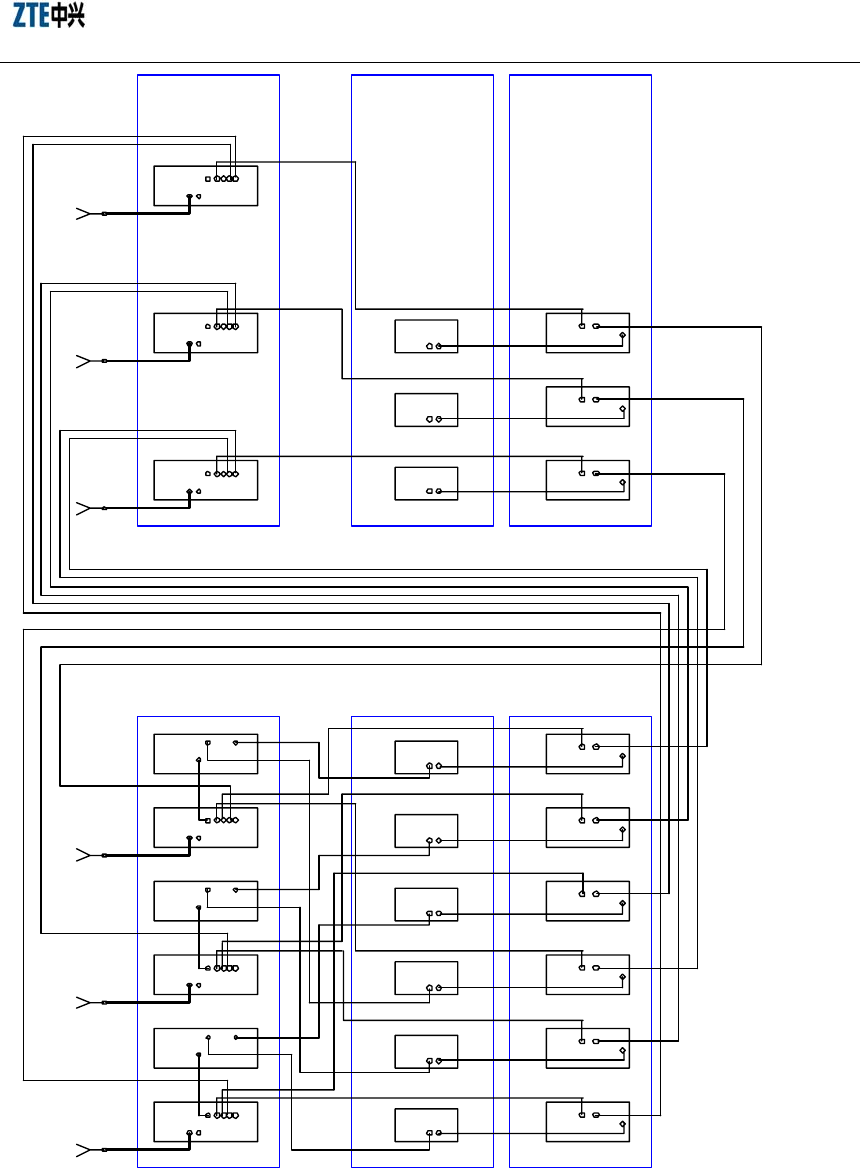
Chapter
Error! Style not defined.
Error! Style
not defined.
7-19
RFOUT
RFI N
HPA
RFOUT
RFIN
HPA
RFOUT
RF I N
HPA
RF OUT
RFI N
HPA
ACBA
TX
RX2
TRX
RX1
TX
RX2
TRX
RX1
TX
RX2
TRX
RX1
TX
RX2
TRX
RX1
f1 f2
RF E- C OM- DUP
ANT
TEST
HPA
RFE-COM
COM
HPA1
RFE-COM-DUP
ANT
TEST
HPA
A
f1
ACB
f2
f1:A-ANT f1:B-ANT
RFOUT
RFI N
HPA
RFOUT
RF I N
HPA
CB
TX
RX2
TRX
RX1
TX
RX2
TRX
RX1
RF E- COM-DUP
ANT
TEST HPA
CB
f1:C-ANT
RX2
RX4
RX3
RX1 HPA2
RFE - C OM
COM
HPA1
HPA2
COM
HPA1
HPA2
RFE-COM
RX2
RX4
RX3
RX1 RX2
RX4
RX3
RX1
RFOUT
RF I N
HPA
RF OUT
RFI N
HPA
RFOUT
RFIN
HPA
CBA
TX
RX 2
TRX
RX 1
TX
RX2
TRX
RX1
TX
RX2
TRX
RX1
f1
RFE - C OM- DUP
ANT
TEST
HPA
RFE- COM-DUP
ANT
TEST
HPA
A
f1
CB
f1:A-ANT f1:B-ANT
RF E- COM-DUP
ANT
TEST HPA
f1:C-ANT
RX2
RX4
RX3
RX1 RX2
RX4
RX3
RX1 RX2
RX4
RX3
RX1
Extended cabinet (No. 2)
Basic cabinet (No. 1)
Fig. 7.3-1 Circuitry on the Front Panel of the Rack for the Three-carrier Three-sector BTS

ZXC10-BTS (V5.4) Installation Manual
7-20
2. Cabling of the front panel
Fig. 7.3-2 shows the wiring of the front panel for the rack of the three-carrier
three-sector BTS.
Wiring of the No. 1 three-carrier BTS Wiring of the No. 2 three-carrier BT S
Connected to the grounding
bolt of the front door
Connected to the grounding
bolt of the front door
Fig. 7.3-2 Front Panel Wiring for the Rack of the Three-carrier Three-sector BTS
3. The wiring of the front panel is further described in Table 7.3-1.
Table 7.3-1 Wiring List of the Front Panel for the 1# Three-carrier BTS Cabinet
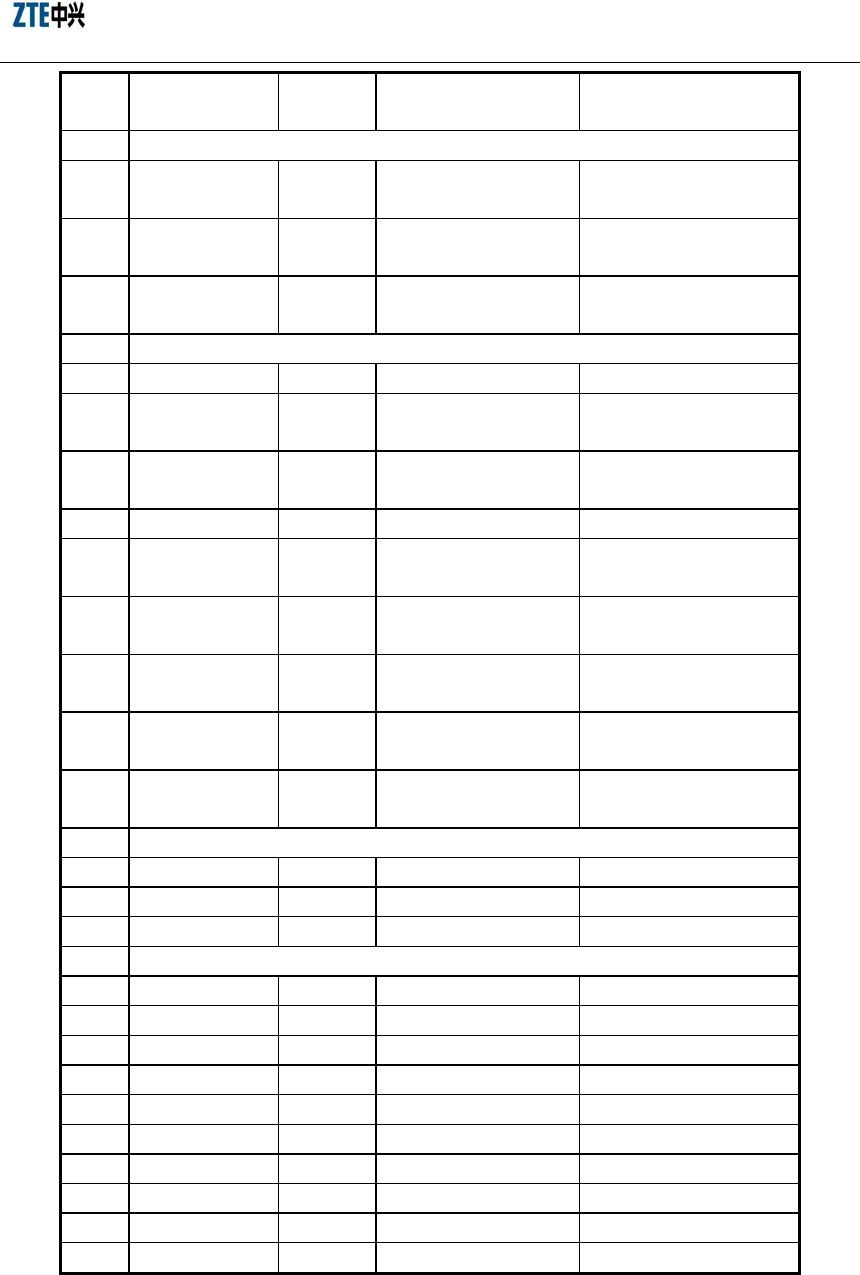
Chapter
Error! Style not defined.
Error! Style
not defined.
7-21
No. Cable Name and
Code
Length
(mm)
End A Direction End B Direction
RFE RF cables
1 RFE/01(02)
-250(220)
250 (220) 1#BTS-RFE-RFE1-ANT 1#BTS – set top ANT1
2 RFE/01(02)
-250(220)
250 (220) 1#BTS-RFE-RFE3-ANT 1#BTS - set top ANT3
3 RFE/01(02)
-250(220)
250 (220) 1#BTS-RFE-RFE5-ANT 1#BTS - set top ANT5
RF08 RF cables
4 RF08/01-850 850 1#BTS-RFE-RFE1-RX3 1#BTS - set top ANT2 - RFE
5 RF08/05-1600 1600 1#BTS-TRX-TRX1-RX2 1#BTS – set top ANT2 -
TRX
6 RF08/08-2000 2000 1#BTS-TRX-TRX4-RX2 1#BTS – set top ANT2 -
TRX
7 RF08/03-1300 1300 1#BTS-RFE-RFE3-RX3 1#BTS - set top ANT4 - RFE
8 RF08/07-1900 1900 1#BTS-TRX-TRX2-RX2 1#BTS – set top ANT4 -
TRX
9 RF08/06-1700 1700 1#BTS-TRX-TRX5-RX2 1#BTS – set top ANT4 -
TRX
10 RF08/02-950 950 1#BTS-RFE-RFE5-RX3 1#BTS – set top ANT6 -
RFE
11 RF08/08-2000 2000 1#BTS-TRX-TRX3-RX2 1#BTS – set top ANT6 -
TRX
12 RF08/04-1450 1450 1#BTS-TRX-TRX6-RX2 1#BTS – set top ANT6 -
TRX
RF07 RF cables
13 RF07 50.5 1#BTS-RFE-RFE1-HPA 1#BTS-RFE-RFE2-COM
14 RF07 50.5 1#BTS-RFE-RFE3-HPA 1#BTS-RFE-RFE4-COM
15 RF07 50.5 1#BTS-RFE-RFE5-HPA 1#BTS-RFE-RFE6-COM
RF06 RF cables
16 RF06/02-370 370 1#BTS-RFE-RFE2-HPA1 1#BTS-HPA-HPA1-RF-OUT
17 RF06/09-400 400 1#BTS-RFE-RFE2-HPA2 1#BTS-HPA-HPA4-RF-OUT
18 RF06/03-480 480 1#BTS-RFE-RFE4-HPA1 1#BTS-HPA-HPA2-RF-OUT
19 RF06/08-320 320 1#BTS-RFE-RFE4-HPA2 1#BTS-HPA-HPA5-RF-OUT
20 RF06/10-600 600 1#BTS-RFE-RFE6-HPA1 1#BTS-HPA-HPA3-RF-OUT
21 RF06/07-180 180 1#BTS-RFE-RFE6-HPA2 1#BTS-HPA-HPA6-RF-OUT
22 RF06/04-800 800 1#BTS-HPA-HPA1-RF-IN 1#BTS-TRX-TRX1-TX
23 RF06/05-930 930 1#BTS-HPA-HPA2-RF-IN 1#BTS-TRX-TRX2-TX
24 RF06/06-1050 1050 1#BTS-HPA-HPA3-RF-IN 1#BTS-TRX-TRX3-TX
25 RF06/06-1050 1050 1#BTS-HPA-HPA4-RF-IN 1#BTS-TRX-TRX4-TX

ZXC10-BTS (V5.4) Installation Manual
7-22
No. Cable Name and
Code
Length
(mm)
End A Direction End B Direction
26 RF06/05-930 930 1#BTS-HPA-HPA5-RF-IN 1#BTS-TRX-TRX5-TX
27 RF06/04-800 800 1#BTS-HPA-HPA6-RF-IN 1#BTS-TRX-TRX6-TX
RF01 RF cables
28 RF01/07-1050 1050 1#BTS-RFE-RFE1-RX1 1#BTS-TRX-TRX1-RX1
29 RF01/17-1330 1330 1#BTS-RFE-RFE1-RX2 1#BTS-TRX-TRX4-RX1
30 RF01/09-1300 1300 1#BTS-RFE-RFE3-RX1 1#BTS-TRX-TRX2-RX1
31 RF01/09-1300 1300 1#BTS-RFE-RFE3-RX2 1#BTS-TRX-TRX5-RX1
32 RF01/11-1400 1400 1#BTS-RFE-RFE5-RX1 1#BTS-TRX-TRX3-RX1
33 RF01/15-1100 1100 1#BTS-RFE-RFE5-RX2 1#BTS-TRX-TRX6-RX1
Grounding cables of the door
34 JDX 250 Grounding screw of the
BTS frame
Grounding screw of the front
door
RFE RF cables
35 RFE/01(02)
-250(220)
250(220) 2#BTS-RFE-RFE1-ANT 2#BTS to set top ANT1
36 RFE/01(02)
-250(220)
250(220) 2#BTS-RFE-RFE3-ANT 2#BTS - set top ANT3
37 RFE/01(02)
-250(220)
250(220) 2#BTS-RFE-RFE5-ANT 2#BTS - set top ANT5
RF08 RF cables
38 RF08/01-850 850 2#BTS-RFE-RFE1-RX3 2#BTS - set top ANT2 - RFE
39 RF08/01-850 850 2#BTS-RFE-RFE1-RX4 2#BTS - set top ANT2 - RFE
40 RF08/05-1600 1600 2#BTS-TRX-TRX1-RX2 2#BTS – set top ANT2 -
TRX
41 RF08/03-1300 1300 2#BTS-RFE-RFE3-RX3 2#BTS - set top ANT4 - RFE
42 RF08/03-1300 1300 2#BTS-RFE-RFE3-RX4 2#BTS - set top ANT4 - RFE
43 RF08/07-1900 1900 2#BTS-TRX-TRX2-RX2 2#BTS – set top ANT4 -
TRX
44 RF08/02-950 950 2#BTS-RFE-RFE5-RX3 2#BTS – set top ANT6 -
RFE
45 RF08/02-950 950 2#BTS-RFE-RFE5-RX4 2#BTS – set top ANT6 -
RFE
46 RF08/08-2000 2000 2#BTS-TRX-TRX3-RX2 2#BTS – set top ANT6 -
TRX
RF06 RF cables
47 RF06/01-260 260 2#BTS-RFE-RFE1-HPA1 2#BTS-HPA-HPA1-RF-OUT
48 RF06/09-400 400 2#BTS-RFE-RFE3-HPA1 2#BTS-HPA-HPA2-RF-OUT
49 RF06/03-480 480 2#BTS-RFE-RFE5-HPA1 2#BTS-HPA-HPA3-RF-OUT
50 RF06/04-800 800 2#BTS-HPA-HPA1-RF-IN 2#BTS-TRX-TRX1-TX
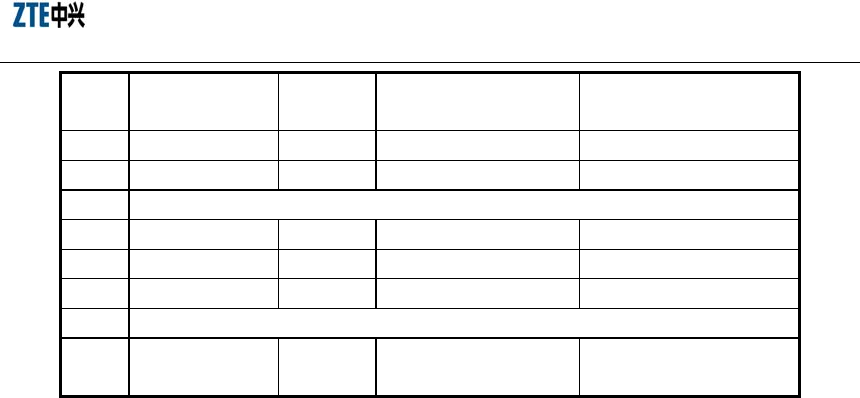
Chapter
Error! Style not defined.
Error! Style
not defined.
7-23
No. Cable Name and
Code
Length
(mm)
End A Direction End B Direction
51 RF06/05-930 930 2#BTS-HPA-HPA2-RF-IN 2#BTS-TRX-TRX2-TX
52 RF06/06-1050 1050 2#BTS-HPA-HPA3-RF-IN 2#BTS-TRX-TRX3-TX
RF01 RF cables
53 RF01/07-1050 1050 2#BTS-RFE-RFE1-RX1 2#BTS-TRX-TRX1-RX1
54 RF01/09-1300 1300 2#BTS-RFE-RFE3-RX1 2#BTS-TRX-TRX2-RX1
55 RF01/20-1600 1600 2#BTS-RFE-RFE5-RX1 2#BTS-TRX-TRX3-RX1
Grounding cables of the door
56 JDX 250 Grounding screw of the
BTS frame
Grounding screw of the front
door
7.3.2 Installing the RF Cables for a Four-carrier Three-sector BTS
1. Connecting the RF cables
Fig. 7.3-3 shows the circuitry on the front panel of the rack for the four-carrier
three-sector BTS.
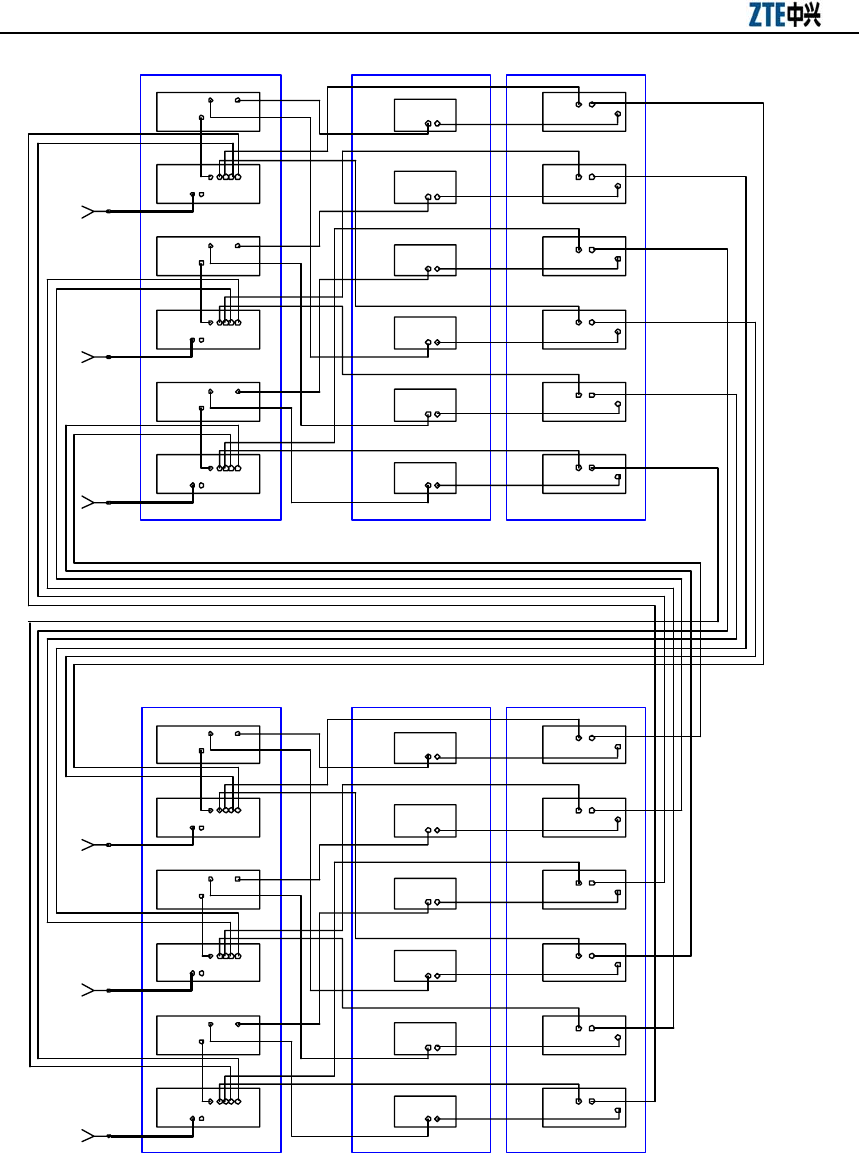
ZXC10-BTS (V5.4) Installation Manual
7-24
RFOUT
RFI N
HPA
RFOUT
RFI N
HPA
RFOUT
RFI N
HPA
RFOUT
RFIN
HPA
ACBA
TX
RX2
TRX
RX1
TX
RX2
TRX
RX1
TX
RX2
TRX
RX1
TX
RX2
TRX
RX1
f1 f2
RFE-COM-DUP
ANT
TEST
HPA
RFE-COM
COM
HPA1
RFE - C OM- DUP
ANT
TEST
HPA
A
f1
ACB
f2
f1: A-ANT f 1:B- ANT
RFOUT
RFI N
HPA
RFOUT
RFI N
HPA
CB
TX
RX2
TRX
RX1
TX
RX2
TRX
RX1
RF E- COM-DUP
ANT
TEST HPA
CB
f1:C-ANT
RX2
RX4
RX3
RX1 HPA2
RFE-COM
COM
HPA1
HPA2
COM
HP A1
HPA2
RF E- C OM
RX2
RX4
RX3
RX1 RX2
RX4
RX3
RX1
RFOUT
RF I N
HPA
RFOUT
RFIN
HPA
RFOUT
RFIN
HPA
RFOUT
RFI N
HPA
ACBA
TX
RX2
TRX
RX1
TX
RX2
TRX
RX1
TX
RX2
TRX
RX1
TX
RX2
TRX
RX1
f1 f2
RFE-COM-DUP
ANT
TEST
HPA
RFE- COM
COM
HPA1
RFE-COM-DUP
ANT
TEST
HPA
A
f1
ACB
f2
f1:A-ANTf1:B-ANT
RFOUT
RFIN
HPA
RFOUT
RF I N
HPA
CB
TX
RX2
TRX
RX1
TX
RX2
TRX
RX1
RF E- C OM-DUP
ANT
TE ST HPA
CB
f1:C-ANT
RX2
RX4
RX3
RX1 HPA2
RF E- COM
COM
HP A1
HPA2
COM
HPA1
HPA2
RFE - C OM
RX2
RX4
RX3
RX1 RX2
RX4
RX3
RX1
Basic cabinet (No. 1)
Extended cabinet (No. 2)
Fig. 7.3-3 Circuitry on the Front Panel of the Rack for the Four-carrier Three-sector BTS
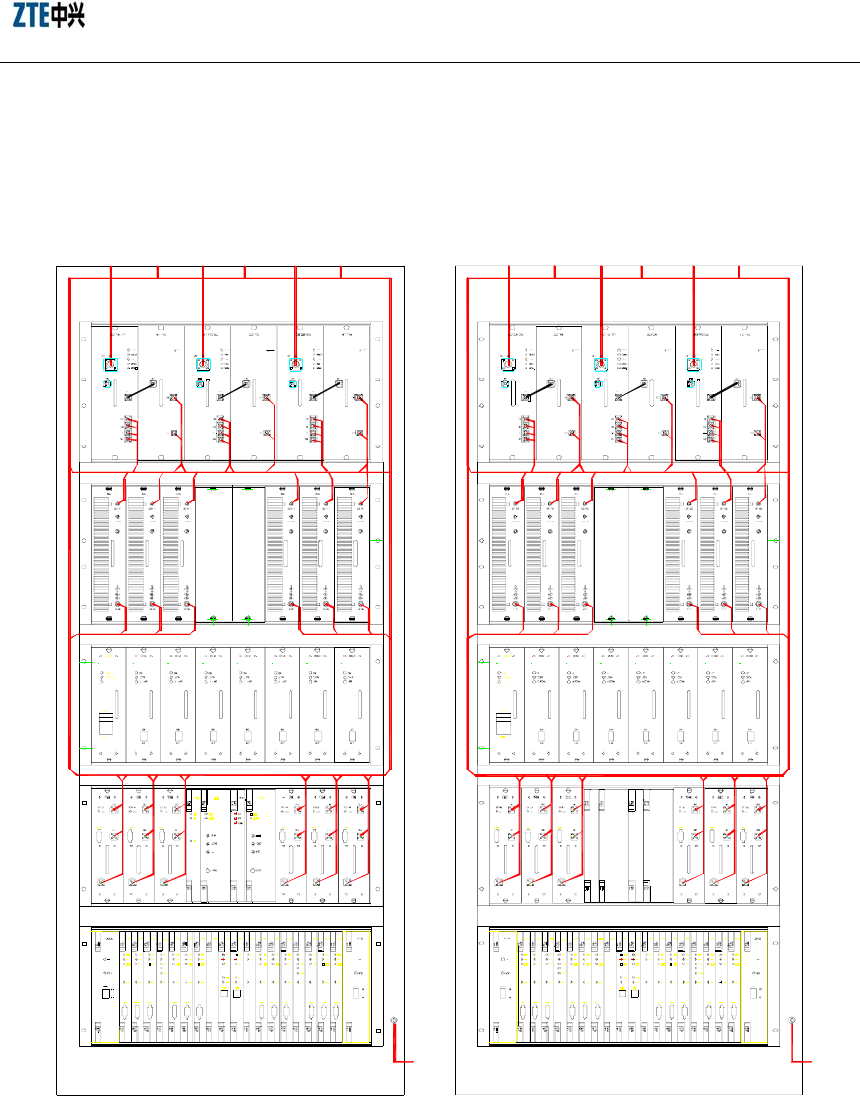
Chapter
Error! Style not defined.
Error! Style
not defined.
7-25
2. Cabling of the front panel
Fig. 7.3-4 shows the wiring of the front panel for the rack of the four-carrier
three-sector BTS.
25/B
6/B
31/B
37/A
15/ B
36/B
30/B
27/B26/ B 29/B28/B
14/B10/B 35/B33/B 32/B
7/ B 11/B
34/ B
25/A
19/B
30/A29/A28/A27/A26/A
24/B23/B21/B 20/B 22/B
16/A
31 / A
4/ A
32 / A
1/A
1/B
24/A
23/A
33/A
20/A 8/A
34/A
19/A
17/A
35/A
12/A
36/A
22/A
21/A
18 / A
17/B
2/A
16/ B
3/ A
18/B
12/B 13/B 14/B 15/B8/B 9/B 10/B 11/ B
4载频1#BTS布线示意图
2/B
4/B 5/B 6/B 7/B
3/B
5/ A 9/A 13/A
74 / A
70/B
63/B
47/B
43/B
62/B
68/B 52/B48/B44/B51/B
65/B64/ B 67/B66/ B
72/ B 69/B 73/ B
71/B
61/B59/B57/B60/B58/B
56/B
62/A 66/A64/A63/A 65/A 67/A
69/A
68/A
42/A
41/A
53/A
38/A
58/A
71/A
70/A
57/A 46/ A
45/A 73/A
72/A
59/A 50/A
49/A 61/A
55/A
56/A
54/A
53/B 54/B
39/A 40/A
60/A
55/B
41/B 42/B 43/B 44/B
38/B
49/B 50/B 51/B 52/B45/B 46/B 47/B 48/B
39/B 40/B
4载频2#BTS布线示意图
前
接
面
板
接
地
螺
钉
前
接
面
板
接
地
螺
钉
Wiring of the No. 1 four-carrier BTS Wiring of the No. 2 four-carrier BTS
Connected to the grounding
bolt of the front door
C
onnected to the grounding
bolt of the front door
Fig. 7.3-4 Front Panel Wiring for the Rack of the Four-carrier Three-sector BTS
3. The wiring of the front panel is further described in Table 7.3-2.
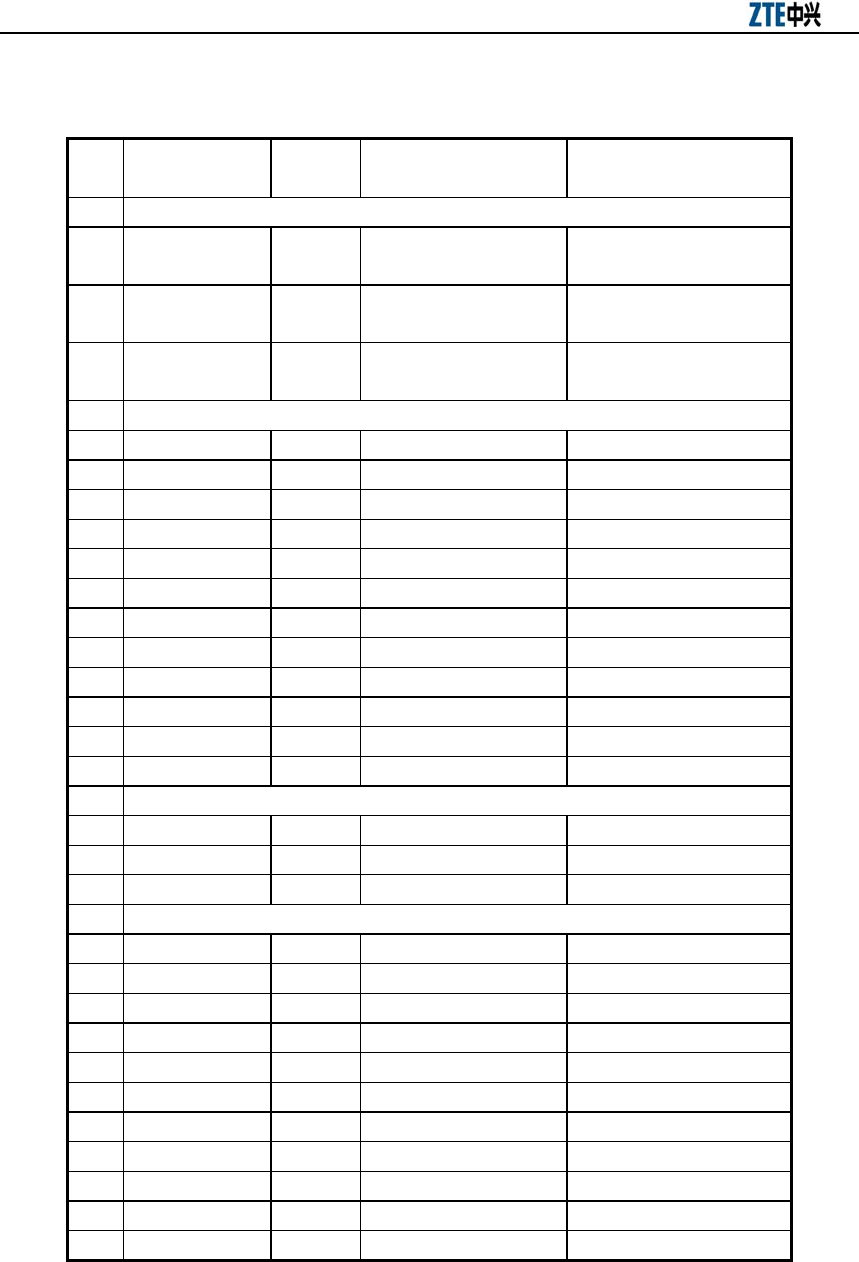
ZXC10-BTS (V5.4) Installation Manual
7-26
Table 7.3-2 Wiring List of the Front Panel for the 1# Four-carrier BTS Cabinet
No. Cable Name and
Code
Length
(mm)
End A Direction End B Direction
RFE RF cables
1 RFE/01(02)
-250(220)
250(220) 1#BTS-RFE-RFE1-ANT 1#BTS – set top ANT1
2 RFE/01(02)
-250(220)
250(220) 1#BTS-RFE-RFE3-ANT 1#BTS - set top ANT3
3 RFE/01(02)
-250(220)
250(220) 1#BTS-RFE-RFE5-ANT 1#BTS - set top ANT5
RF08 RF cables
4 RF08/01-850 850 1#BTS-RFE-RFE1-RX3 1#BTS – set top ANT2 - RFE
5 RF08/01-850 850 1#BTS-RFE-RFE1-RX4 1#BTS – set top ANT2 - RFE
6 RF08/05-1600 1600 1#BTS-TRX-TRX1-RX2 1#BTS – set top ANT2 - TRX
7 RF08/08-2000 2000 1#BTS-TRX-TRX4-RX2 1#BTS – set top ANT2 - TRX
8 RF08/03-1300 1300 1#BTS-RFE-RFE3-RX3 1#BTS - set top ANT4 - RFE
9 RF08/03-1300 1300 1#BTS-RFE-RFE3-RX4 1#BTS - set top ANT4 - RFE
10 RF08/07-1900 1900 1#BTS-TRX-TRX2-RX2 1#BTS – set top ANT4 - TRX
11 RF08/06-1700 1700 1#BTS-TRX-TRX5-RX2 1#BTS – set top ANT4 - TRX
12 RF08/02-950 950 1#BTS-RFE-RFE5-RX3 1#BTS – set top ANT6 - RFE
13 RF08/02-950 950 1#BTS-RFE-RFE5-RX4 1#BTS – set top ANT6 - RFE
14 RF08/08-2000 2000 1#BTS-TRX-TRX3-RX2 1#BTS – set top ANT6 - TRX
15 RF08/04-1450 1450 1#BTS-TRX-TRX6-RX2 1#BTS – set top ANT6 - TRX
RF07 RF cables
16 RF07 50.5 1#BTS-RFE-RFE1-HPA 1#BTS-RFE-RFE2-COM
17 RF07 50.5 1#BTS-RFE-RFE3-HPA 1#BTS-RFE-RFE4-COM
18 RF07 50.5 1#BTS-RFE-RFE5-HPA 1#BTS-RFE-RFE6-COM
RF06 RF cables
19 RF06/02-370 370 1#BTS-RFE-RFE2-HPA1 1#BTS-HPA-HPA1-RF-OUT
20 RF06/09-400 400 1#BTS-RFE-RFE2-HPA2 1#BTS-HPA-HPA4-RF-OUT
21 RF06/03-480 480 1#BTS-RFE-RFE4-HPA1 1#BTS-HPA-HPA2-RF-OUT
22 RF06/08-320 320 1#BTS-RFE-RFE4-HPA2 1#BTS-HPA-HPA5-RF-OUT
23 RF06/10-600 600 1#BTS-RFE-RFE6-HPA1 1#BTS-HPA-HPA3-RF-OUT
24 RF06/07-180 180 1#BTS-RFE-RFE6-HPA2 1#BTS-HPA-HPA6-RF-OUT
25 RF06/04-800 800 1#BTS-HPA-HPA1-RF-IN 1#BTS-TRX-TRX1-TX
26 RF06/05-930 930 1#BTS-HPA-HPA2-RF-IN 1#BTS-TRX-TRX2-TX
27 RF06/06-1050 1050 1#BTS-HPA-HPA3-RF-IN 1#BTS-TRX-TRX3-TX
28 RF06/06-1050 1050 1#BTS-HPA-HPA4-RF-IN 1#BTS-TRX-TRX4-TX
29 RF06/05-930 930 1#BTS-HPA-HPA5-RF-IN 1#BTS-TRX-TRX5-TX
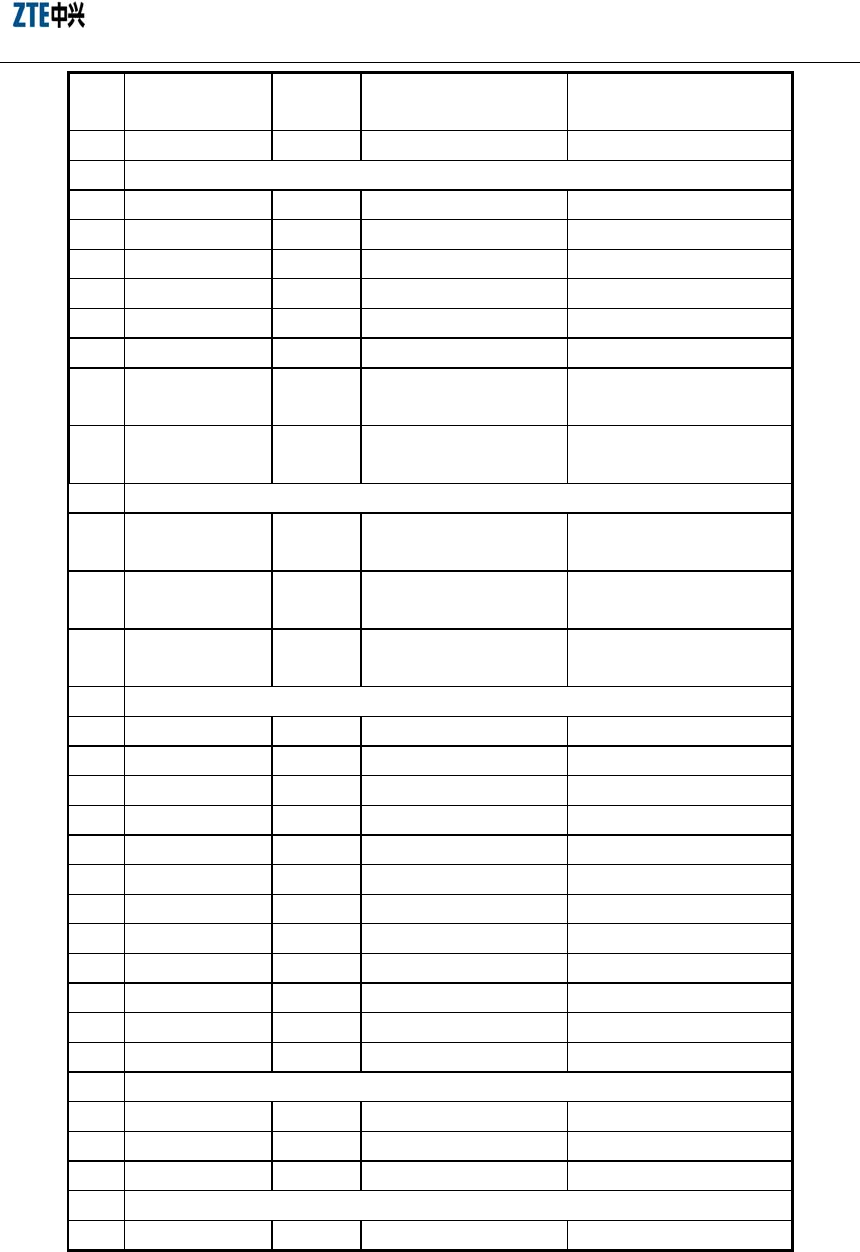
Chapter
Error! Style not defined.
Error! Style
not defined.
7-27
No. Cable Name and
Code
Length
(mm)
End A Direction End B Direction
30 RF06/04-800 800 1#BTS-HPA-HPA6-RF-IN 1#BTS-TRX-TRX6-TX
RF01 RF cables
31 RF01/07-1050 1050 1#BTS-RFE-RFE1-RX1 1#BTS-TRX-TRX1-RX1
32 RF01/17-1330 1330 1#BTS-RFE-RFE1-RX2 1#BTS-TRX-TRX4-RX1
33 RF01/09-1300 1300 1#BTS-RFE-RFE3-RX1 1#BTS-TRX-TRX2-RX1
34 RF01/09-1300 1300 1#BTS-RFE-RFE3-RX2 1#BTS-TRX-TRX5-RX1
35 RF01/11-1400 1400 1#BTS-RFE-RFE5-RX1 1#BTS-TRX-TRX3-RX1
36 RF01/15-1100 1100 1#BTS-RFE-RFE5-RX2 1#BTS-TRX-TRX6-RX1
Grounding cables
of the door
37 JDX 250 Grounding screw of the
BTS frame
Grounding screw of the front
door
RFE RF cables
38 RFE/01(02)
-250(220)
250(220) 2#BTS-RFE-RFE1-ANT 2#BTS - set top ANT1
39 RFE/01(02)
-250(220)
250(220) 2#BTS-RFE-RFE3-ANT 2#BTS - set top ANT3
40 RFE/01(02)
-250(220)
250(220) 2#BTS-RFE-RFE5-ANT 2#BTS - set top ANT5
RF08 RF cables
41 RF08/01-850 850 2#BTS-RFE-RFE1-RX3 2#BTS - set top ANT2 - RFE
42 RF08/01-850 850 2#BTS-RFE-RFE1-RX4 2#BTS - set top ANT2 - RFE
43 RF08/05-1600 1600 2#BTS-TRX-TRX1-RX2 2#BTS – set top ANT2 - TRX
44 RF08/08-2000 2000 2#BTS-TRX-TRX4-RX22 2#BTS – set top ANT2 - TRX
45 RF08/03-1300 1300 2#BTS-RFE-RFE3-RX3 2#BTS - set top ANT4 - RFE
46 RF08/03-1300 1300 2#BTS-RFE-RFE3-RX4 2#BTS - set top ANT4 - RFE
47 RF08/07-1900 1900 2#BTS-TRX-TRX2-RX2 2#BTS – set top ANT4 - TRX
48 RF08/06-1700 1700 2#BTS-TRX-TRX5-RX2 2#BTS – set top ANT4 - TRX
49 RF08/02-950 950 2#BTS-RFE-RFE5-RX3 2#BTS – set top ANT6 - RFE
50 RF08/02-950 950 2#BTS-RFE-RFE5-RX4 2#BTS – set top ANT6 - RFE
51 RF08/08-2000 2000 2#BTS-TRX-TRX3-RX2 2#BTS – set top ANT6 - TRX
52 RF08/04-1450 1450 2#BTS-TRX-TRX6-RX2 2#BTS – set top ANT6 - TRX
RF07 RF cables
53 RF07 50.5 2#BTS-RFE-RFE1-HPA 2#BTS-RFE-RFE2-COM
54 RF07 50.5 2#BTS-RFE-RFE3-HPA 2#BTS-RFE-RFE4-COM
55 RF07 50.5 2#BTS-RFE-RFE5-HPA 2#BTS-RFE-RFE6-COM
RF06 RF cables
56 RF06/02-370 370 2#BTS-RFE-RFE2-HPA1 2#BTS-HPA-HPA1-RF-OUT
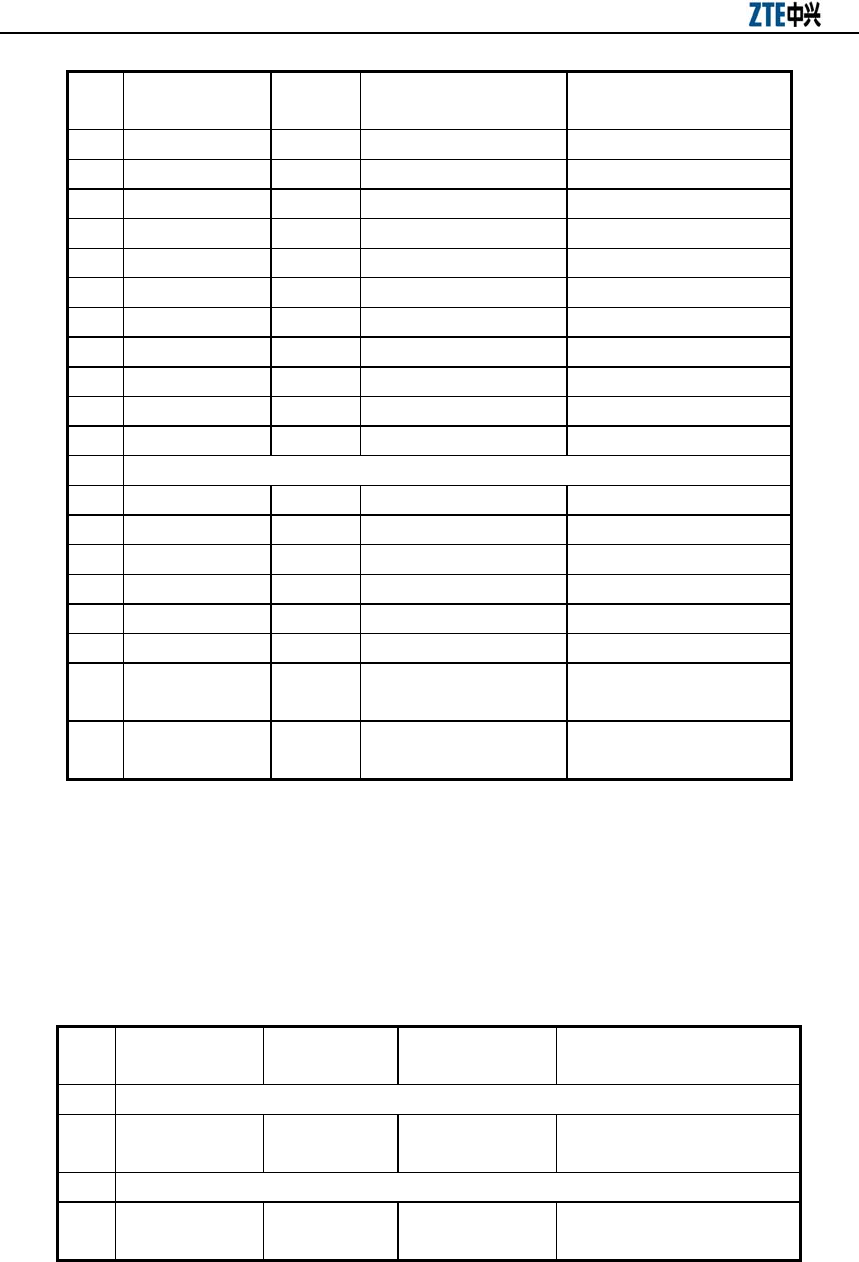
ZXC10-BTS (V5.4) Installation Manual
7-28
No. Cable Name and
Code
Length
(mm)
End A Direction End B Direction
57 RF06/09-400 400 2#BTS-RFE-RFE2-HPA2 2#BTS-HPA-HPA4-RF-OUT
58 RF06/03-480 480 2#BTS-RFE-RFE4-HPA1 2#BTS-HPA-HPA2-RF-OUT
59 RF06/08-320 320 2#BTS-RFE-RFE4-HPA2 2#BTS-HPA-HPA5-RF-OUT
60 RF06/10-600 600 2#BTS-RFE-RFE6-HPA1 2#BTS-HPA-HPA3-RF-OUT
61 RF06/07-180 180 2#BTS-RFE-RFE6-HPA2 2#BTS-HPA-HPA6-RF-OUT
62 RF06/04-800 800 2#BTS-HPA-HPA1-RF-IN 2#BTS-TRX-TRX1-TX
63 RF06/05-930 930 2#BTS-HPA-HPA2-RF-IN 2#BTS-TRX-TRX2-TX
64 RF06/06-1050 1050 2#BTS-HPA-HPA3-RF-IN 2#BTS-TRX-TRX3-TX
65 RF06/06-1050 1050 2#BTS-HPA-HPA4-RF-IN 2#BTS-TRX-TRX4-TX
66 RF06/05-930 930 2#BTS-HPA-HPA5-RF-IN 2#BTS-TRX-TRX5-TX
67 RF06/04-800 800 2#BTS-HPA-HPA6-RF-IN 2#BTS-TRX-TRX6-TX
RF01 RF cables
68 RF01/07-1050 1050 2#BTS-RFE-RFE1-RX1 2#BTS-TRX-TRX1-RX1
69 RF01/17-1330 1330 2#BTS-RFE-RFE1-RX2 2#BTS-TRX-TRX4-RX1
70 RF01/09-1300 1300 2#BTS-RFE-RFE3-RX1 2#BTS-TRX-TRX2-RX1
71 RF01/09-1300 1300 2#BTS-RFE-RFE3-RX2 2#BTS-TRX-TRX5-RX1
72 RF01/11-1400 1400 2#BTS-RFE-RFE5-RX1 2#BTS-TRX-TRX3-RX1
73 RF01/15-1100 1100 2#BTS-RFE-RFE5-RX2 2#BTS-TRX-TRX6-RX1
Grounding cables
of the door
74 JDX 250 Grounding screw of the
BTS frame
Grounding screw of the front
door
7.3.3 Connecting the Jumper Cables Between the Basic Cabinet and the
Extended Cabinet
Table 7.3-3 shows the wiring of the jumper cables between the basic cabinet and the
extended cabinet.
Table 7.3-3 Wiring List of the Cables from 1# Multi-carrier BTS Cabinet to 2# Multi-carrier BTS Cabinet
No. Cable Name and
Code
Length (mm) End A Direction End B Direction
F-LINK-003 cable
1 F-LINK-003 Depends on the
project
1# set top reserved
IO
2# set top reserved IO
10M cable
2 10M cable suite Depends on the
project
1# set top GPS2 2# set top GPS2

Chapter
Error! Style not defined.
Error! Style
not defined.
7-29
No. Cable Name and
Code
Length (mm) End A Direction End B Direction
RF cables
3 RF cable suite Depends on the
project
1#BTS – set top
ANT2 - RFE
2#BTS – set top ANT2 - TRX
4 RF cable suite 1#BTS – set top
ANT2 - RFE
2#BTS – set top ANT2 - TRX
5 RF cable suite 1#BTS – set top
ANT2 - TRX
2#BTS - set top ANT2 - RFE
6 RF cable suite 1#BTS – set top
ANT2 - TRX
2#BTS - set top ANT2 - RFE
7 RF cable suite 1#BTS - set top
ANT4 - RFE
2#BTS – set top ANT4 - TRX
8 RF cable suite 1#BTS - set top
ANT4 - RFE
2#BTS – set top ANT4 - TRX
9 RF cable suite 1#BTS – set top
ANT4 - TRX
2#BTS - set top ANT4 - RFE
10 RF cable suite 1#BTS – set top
ANT4 - TRX
2#BTS - set top ANT4 - RFE
11 RF cable suite 1#BTS – set top
ANT6 - RFE
2#BTS – set top ANT6 - TRX
12 RF cable suite 1#BTS – set top
ANT6 - RFE
2#BTS – set top ANT6 - TRX
13 RF cable suite 1#BTS – set top
ANT6 - TRX
2#BTS – set top ANT6 - RFE
14 RF cable suite 1#BTS – set top
ANT6 - TRX
2#BTS – set top ANT6 - RFE
7.3.4 Connecting the Backplane Signal Cables of the BTS Rack
For three-carrier BTS and four-carrier BTS, the extended rack does not contain the
GCM and the DSM. Therefore, the signal transmission is made from the basic rack to
the extended rack through the rack top jumpers.
1. Connecting the backplane clock cables of the basic rack
Fig. 7.3-5 Structure of the LINK Cable
The structure of the backplane clock cable (LINK cable) in the basic rack is
shown in Fig. 7.3-5.
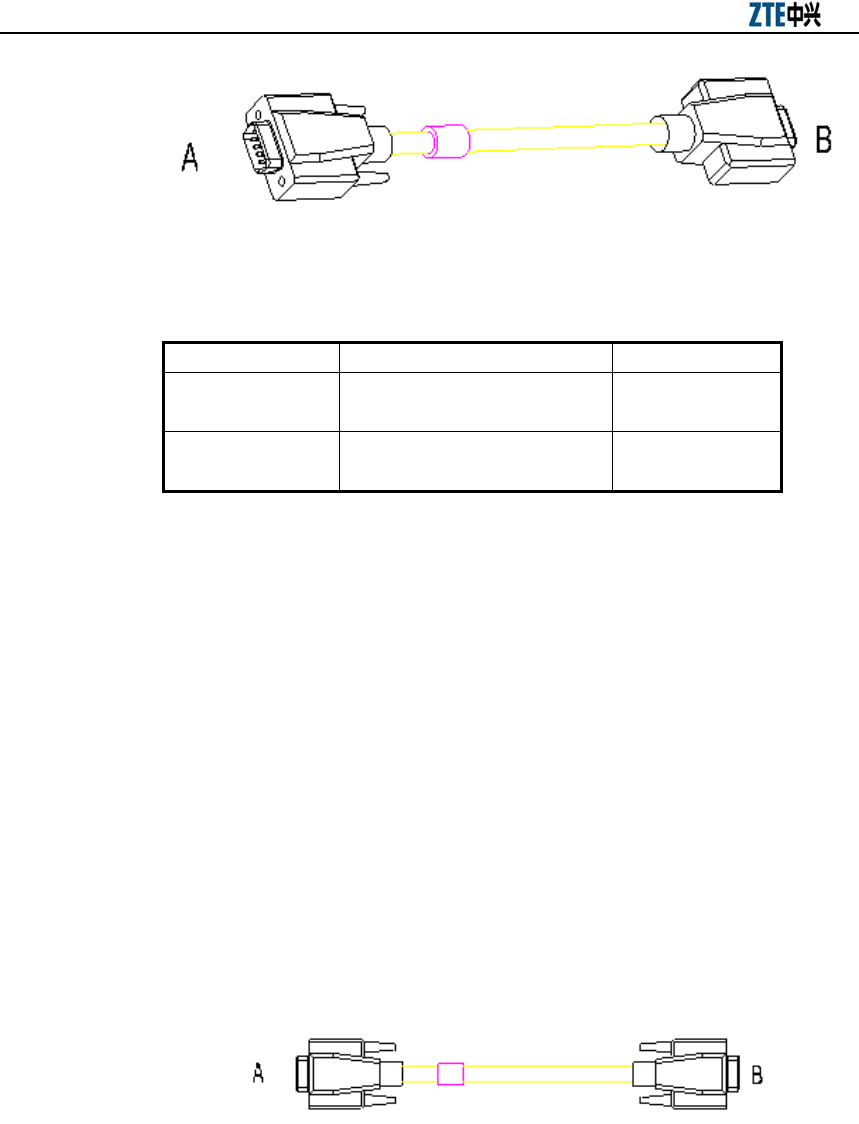
ZXC10-BTS (V5.4) Installation Manual
7-30
Fig. 7.3-5 Structure of the LINK Cable
Table 7.3-4 IDs of the LINK Directions
Cable Name and Code To End A To End B
LINK cable 1#BTS-BBDS4-X70(CLK_MBTS) 1#BTS rack
top-MBDS_SBDS
LINK cable 2#BTS-BBDS4-X70(CLK_SBTS) 2#BTS rack
top-MBDS_SBDS
The LINK cables distribute the IP extension cascade clock and control signals (one for
MBTS output and one for SBTS input) to rack top for cabinet combination purpose.
Definition of signals:
I_30M+_MBTS I_30M-_MBTS: The 30M differential MLVDS digital clock
from MBTS_CDM input to the SBTS rack
I_CHIP+_MBDS I_CHIP-_MBDS: The 16CHIP differential MLVDS clock
from MBDS_GCM output to RIM of SBDS
I_PP2S+_MBDS I_PP2S-_MBDS: The PP2S differential MLVDS clock from
MBDS_GCM output to RIM of SBDS
2. Clock signal jumpers between racks
The structure of the DB9 clock cable LINK between the basic and extended
racks is shown in Fig. 7.3-6.
Fig. 7.3-6 LINK Cable Structure
The backplane LINK cable of the extended multi-carrier rack is the rack top
jumper.
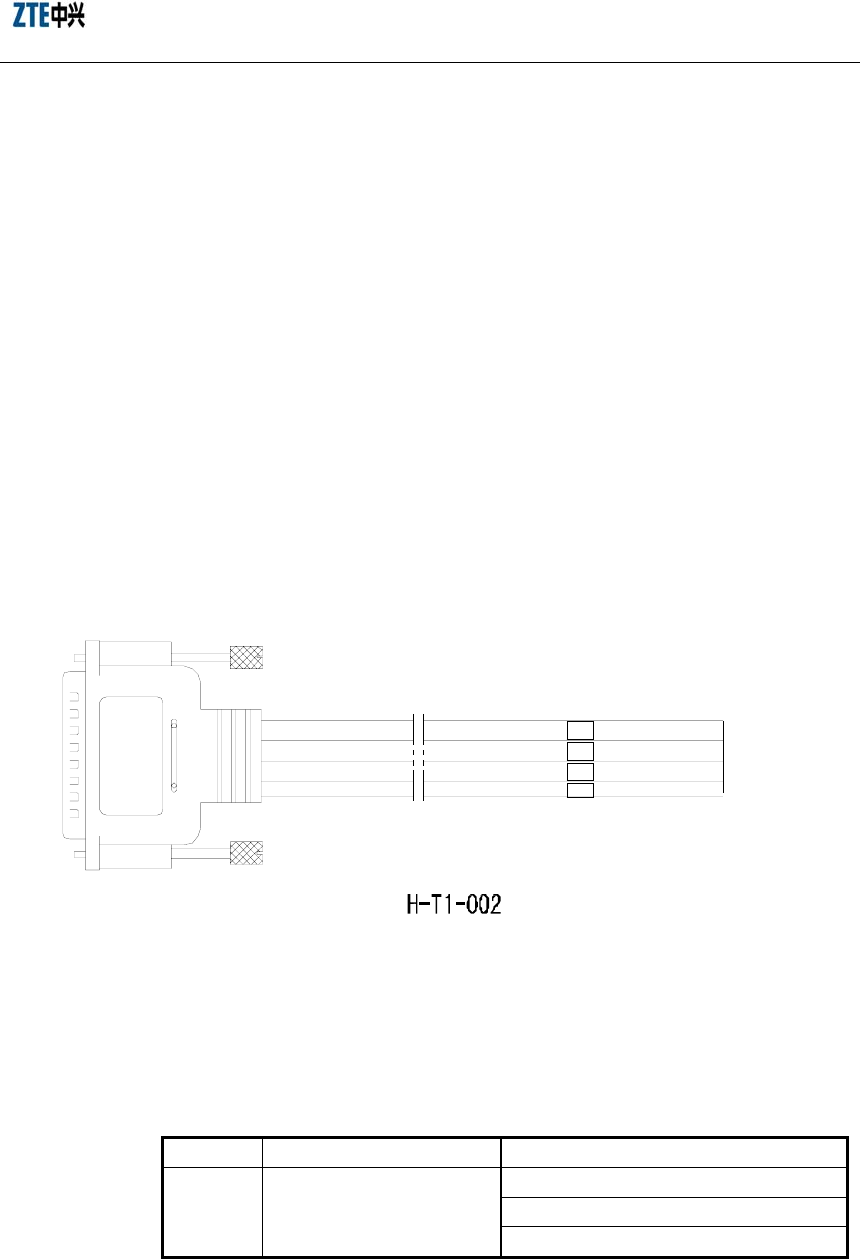
Chapter
Error! Style not defined.
Error! Style
not defined.
7-31
7.4 T1 Cabke
7.4.1 Functions
Abis interface adopts T1 cable as the 100Ω coaxial cable and connects the T1 interface
of board DSM to set top. The characteristic resistance of T1 cable is consistent with the
input and output resistance of the line transceiver set by the transceiver of board T1.
7.4.2 Connection Position of Two Ends, Wiring and Signal Flow Direction of
Cable
One end of the T1 cable is connected with the D-shape 44-core connector on the
backplane of BDS frame, while the other end is fixed on the transfer installation hole
of set top.
When DSM is configured as 100ΩT1, a D-shape 44-core connector is adopted on the
backplane of BDS frame. 8-channel T1 is supported; meanwhile extended 8-channel
T1 is provided. The system supports maximum 16-channel T1.
End A
Fla g
End B1
End B2
End B3
End B4
End B5
End B6
Flag
Flag
Flag
Flag
Fig. 7.4-1 100ΩT1 Cable Diagram
Table 7.4-1 100ΩT1 Cable Wiring and Signal Flow Direction
Serial No. End A Outgoing Direction Flag End B Outgoing Direction Flag
B1:BTS set top-BSC(EXT)_T1_0(IN0)
B2:BTS set top-BSC(EXT)_T1_0(OUT0)
1 BTS-BBDS4-IP_X71
(BSC_T1)
BTS-BBDS4-IP_X76 B3:BTS set top-BSC(EXT)_T1_1(IN1)
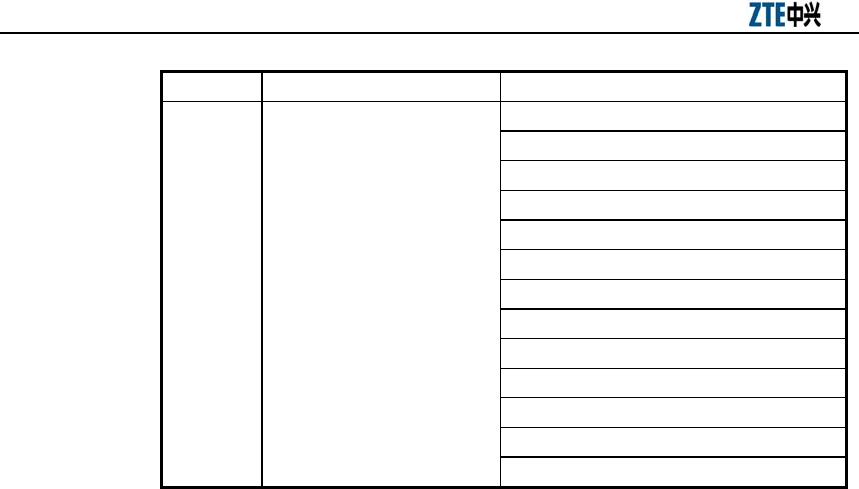
ZXC10-BTS (V5.4) Installation Manual
7-32
Serial No. End A Outgoing Direction Flag End B Outgoing Direction Flag
B4:BTS set top-BSC(EXT)_T1_1(OUT1)
B5:BTS set top- BSC(EXT)_T1_2(IN2)
B6:BTS set top- BSC(EXT)_T1_2(OUT2)
B7:BTS set top- BSC(EXT)_T1_3(IN3)
B8:BTS set top- BSC(EXT)_T1_3(OUT3)
B9:BTS set top- BSC(EXT)_T1_4(IN4)
B10:BTS set top- BSC(EXT)_T1_4(OUT4)
B11:BTS set top- BSC(EXT)_T1_4(IN5)
B12:BTS set top- BSC(EXT)_T1_5(OUT5)
B13:BTS set top- BSC(EXT)_T1_6(IN6)
B14:BTS set top- BSC(EXT)_T1_6(OUT6)
B15:BTS set top- BSC(EXT)_T1_7(IN7)
(EXT_T1)
B16:BTS set top- BSC(EXT)_T1_7(OUT7)
Note: The T1 cable at the extended interface is selected according to the contract. Normally it is not configured.
7.4.3 Function
The T1 cable used at the Abis interface is the 100Ω coaxial cable twisted pair. It
connects the board interfaces to the rack top. The characteristic impedance of the T1
cable is the same as the input/output impedance of the line transceiver set for the
board’s T1 transceiver.
7.4.4 Connection Positions of Both Ends, Cabling and Signal Flow Direction of
Cables
One end of the T1 cable connects to the connector on the backplane of the IP_BDS
shelf, and the other connects to the conversion card at the rack top.
If the 100Ω T1 is used, then the DB44 high-density connector should be employed on
the backplane of the IP_BDS shelf, while the CC4 standard T1 coaxial socket should
be employed to connect the conversion card, as shown in Fig. 7.4-1 and Table 7.4-1.
On the BTS rack top, there are totally 16 T1 interfaces marked as “BSC_IP_T1-0-7”
and “EXT_IP_T1-0-7” (100Ω cable terminals are shown in ). 8 out of the 16 are active
for connecting with the BSC. The rest T1 interfaces are standby or will be used for the
daisy chain configuration of a BTS.
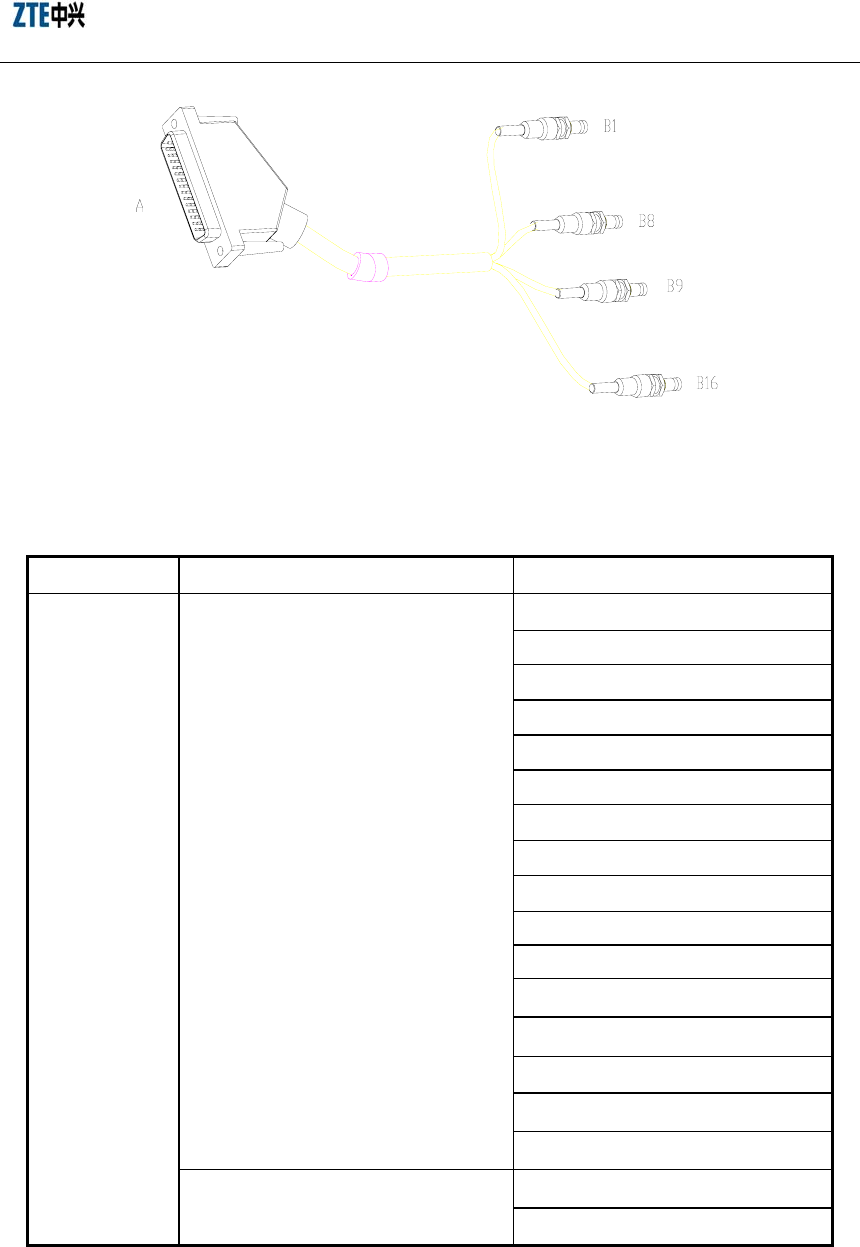
Chapter
Error! Style not defined.
Error! Style
not defined.
7-33
Fig. 7.4-1 Terminals of the 100
Ω
Cable
Table 7.4-1 Identifiers of the Location & Signal Flow Direction at Both Ends of the 100
Ω
Cable
Cable Name End A Direction End B Direction
B1: BSC-IP_T1_0-IN0
B2: BSC-IP_T1_0-OUT0
B3: BSC-IP_T1_1-IN1
B4: BSC-IP_T1_1-OUT1
B5: BSC-IP_T1_2-IN2
B6: BSC-IP_T1_2-OUT2
B7: BSC-IP_T1_3-IN3
B8: BSC-IP_T1_3-OUT3
B9: BSC-IP_T1_4-IN4
B10: BSC-IP_T1_4-OUT4
B11: BSC-IP_T1_5-IN5
B12: BSC-IP_T1_5-OUT5
B13: BSC-IP_T1_6-IN6
B14: BSC-IP_T1_6-OUT6
B15: BSC-IP_T1_7-IN7
A: BTS-BBDS-IP_X71(BSC_E1)
B16:
BSC-IP_T1_7-OUT7
B1: EXT-IP-T1_0-IN0
E1
A: BTS-BBDS-IP_X76(EXT_T1)
B2: EXT-IP T1_0-OUT0
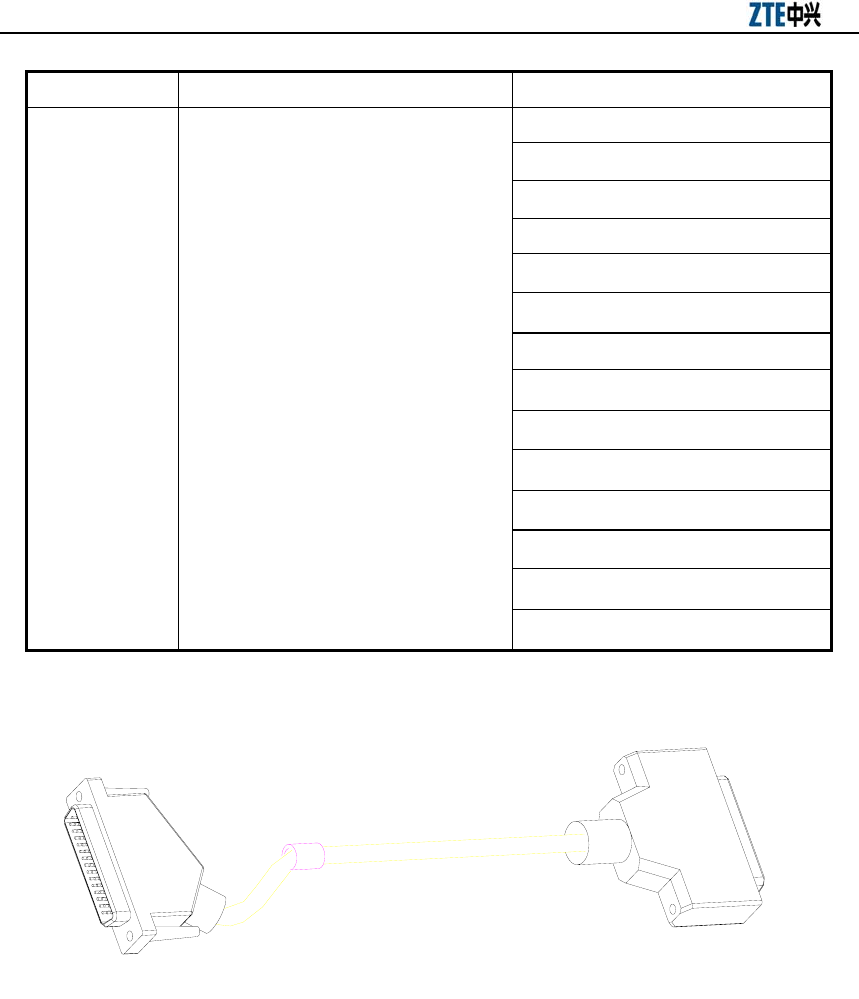
ZXC10-BTS (V5.4) Installation Manual
7-34
Cable Name End A Direction End B Direction
B3: EXT-IP_T1_1-IN1
B4: EXT-IP_T1_1-OUT1
B5: EXT-IP_T1_2-IN2
B6: EXT-IP_T1_2-OUT2
B7: EXT-IP_T1_3-IN3
B8: EXT-IP_T1_3-OUT3
B9: EXT-IP_T1_4-IN4
B10: EXT-IP_T1_4-OUT4
B11: EXT-IP_T1_5-IN5
B12: EXT-IP_T1_5-OUT5
B13: EXT-IP_T1_6-IN6
B14: EXT-IP_T1_6-OUT6
B15: EXT-IP_T1_7-IN7
B16: EXT-IP_T1_7-OUT7
Fig. 7.4-2 120
Ω
Cable

Chapter
Error! Style not defined.
Error! Style
not defined.
7-35
Fig. 7.4-3 120
Ω
T1 Conversion Cable
Table 7.4-2 End B Braiding Pair Sequence of the 120
Ω
T1 Conversion Cable
1(IN0) 2(OUT0) 3(IN1) 4(OUT1) 5(IN2) 6(OUT2) 7(IN3) 8(OUT3)
Blue/1red
Blue/1black
Pink/1red
Pink/1black
Green/1red
Green/1black
Yel low /1 re d
Yellow/1black
Grey/1red
Grey/1black
Blue/2red
Blue/2black
Pink/2red
Pink/2black
Green/2red
Green/2black
9(IN4) 10(OUT4) 11(IN5) 12(OUT5) 13(IN6) 14(OUT6) 15(IN7) 16(OUT7)
End B
Braiding
Pair
Sequence
Yel low /2 re d
Yellow/2black
Grey/2red
Grey/2black
Blue/3red
Blue/3black
Pink/3red
Pink/3black
Green/3red
Green/3black
Yellow/3re d
Yellow/3black
Grey/3red
Grey/3black
Blue/4red
Blue/4black
Note: Blue/1red means there is a red dot identifier on the blue line; while pink/2red means there are 2 red dot identifiers on the pink line.
Fig. 7.4-4 BTS Rack-top Interface Board
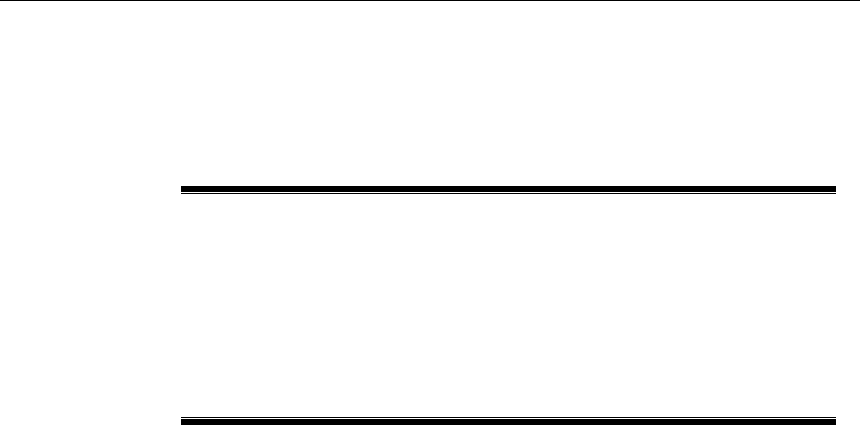
FAX: 0086-755-26770160
8-1
8 Installing the Trunk Cables
Summary
This part describes:
● Installation method of the BTS trunk cables;
● Preparation procedure of the T1 cables.
8.1 Installing the Trunk Cables
The two T1 cable interfaces (marked T1-IN-1 and T1-OUT-1, terminals 13 and 14, on
the BTS rack top are the active interfaces. The other T1 interfaces are standby
interfaces or are used for the daisy chain connection of the BTS.
Follow the method given below in this section to assemble the CC4Y-J32 connector on
the 100Ω coaxial cable and connect the cable end with the CC4Y-J32 connector to the
set top.
According to the transmission equipment or DDF port configured for the BTS, select a
proper coaxial connector and assemble it to the 100Ω coaxial cable to connect with the
related port on the DDF or the transmission equipment. This coaxial connector is
usually configured by the user.
8.2 Preparing the T1 cables
This section describes the preparation of the T1 cables.
1. Making the CC4Y-J32 connector for the T1 cable
The method and procedure to make the connector at the ZXC10-BTSB I2 side is
as shown in Fig. 8.2-1.
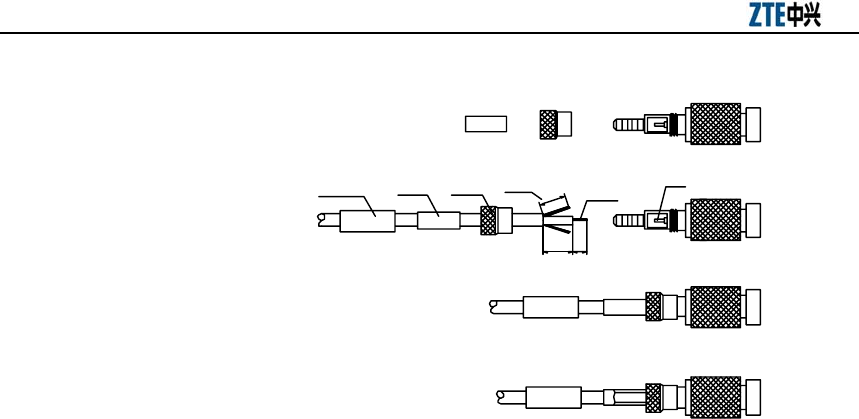
ZXC10-BTS (V5.4) Installation Manual
8-2
7 3
6
Shielded
layer
Part 1
d)
c)
b)
a)
Heat
shrinkable tube
Part 2 Part 3
Part 1 Part 2 Core wire
Leg
Fig. 8.2-1 Assembly Drawing of the CC4Y-J32 Coaxial Cable Connector
1) The plug parts of the CC4Y-J32 RF coaxial connector, as shown in a) of Fig.
8.2-1.
2) As shown in b) of Fig. 8.2-1, slip parts 1 and 2 around the cable, peel one end of
the cable, tin the core wire, and then open the shielding layer forth to help
inserting the plug crimping position.
3) After welding the core wire, screw parts 2 to parts 3, as shown in c) of Fig.
8.2-1.
4) Mount the crimping tube and crimp it with a special tool, as shown in d) of Fig.
8.2-1.
2. Making the coaxial connector plug at the DDF side
The structure of the connector is as shown in Fig. 8.2-2.
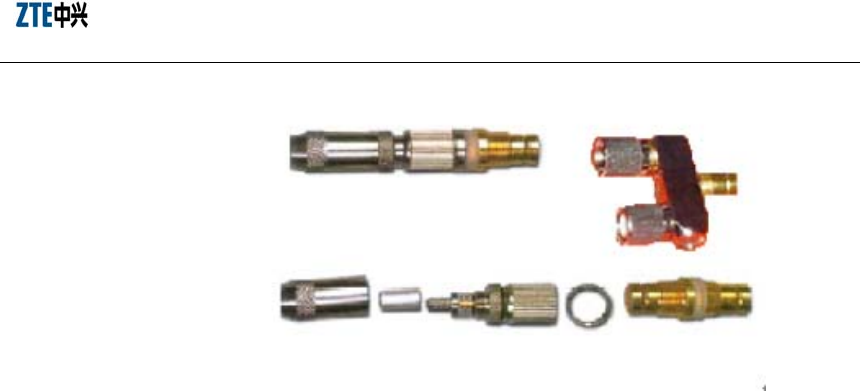
Chapter
Error! Style not defined.
Error!
Style not defined.
8-3
Y-shaped connector
with test probes
Cable connector Socket
Cable connector So ck e t
Fig. 8.2-2 Coaxial Connector of the DDF
Take the following steps to make the connector:
1) Peel the outer jacket of the cable for about 14mm, as shown in a} of Fig. 8.2-3.
2) Slip in sequence the cable connector sheath, the heat-shrink tube and the
crimping tube. Open the shielding net forth with a net opening sleeve (or do it
manually). And then strip the internal insulation layer to expose 3mm of the
internal conductor, as shown in b) of Fig. 8.2-3.
3) As shown in c) of Fig. 8.2-3, insert the internal conductor into the connector.
Note that the core wire must be inserted into the leg at the rear of the internal
conductor. Weld the wire and cut the shielding net neatly to 6mm long.
4) Push the crimping tube and the shielding net to the end of the connector, as
shown in d) of Fig. 8.2-3.
5) As shown in e) of Fig. 8.2-3, crimp the crimping tube into a cube with the
crimping pliers. Note that crimp again in another direction after the first
crimping.
6) As shown in f) of Fig. 8.2-3, slip the heat-shrink tube around the crimped
crimping tube, and heat around it using a hot blower to make it shrink. And then
screw the end sheath.
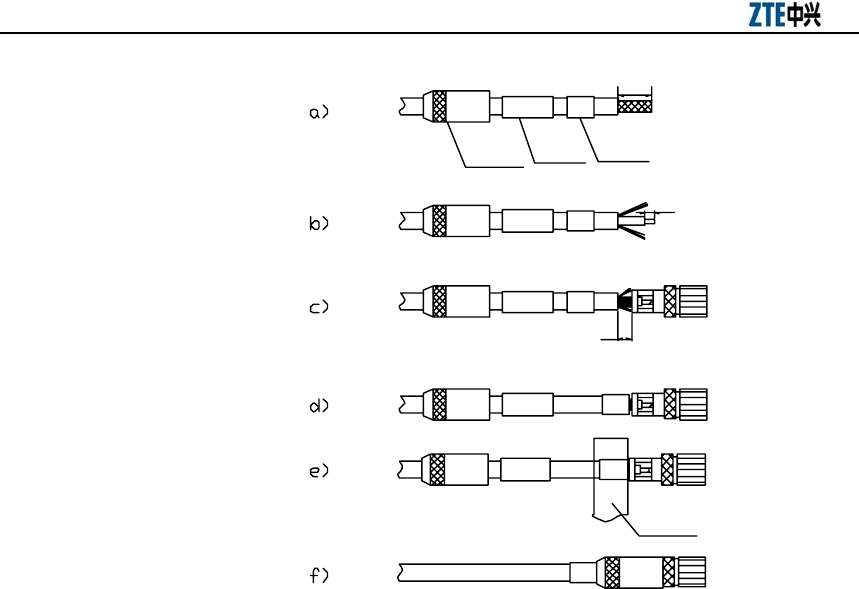
ZXC10-BTS (V5.4) Installation Manual
8-4
Heat
shrinkable
tube
Cable
connector cap
Crimping
pliers
14
3
6
Crimping
tube
Fig. 8.2-3 Assembly Drawing of the Coaxial Cable Connector of DDF
3. Trunk cable test
The internal conductor of the connectors at both ends should be reliably welded
to the internal conductor of the coaxial cable without any dry joint.
The internal conductors of the connectors at both ends have good continuity, and
the external conductors have good continuity. Both the internal conductor and
the external conductor cannot be short-circuited.
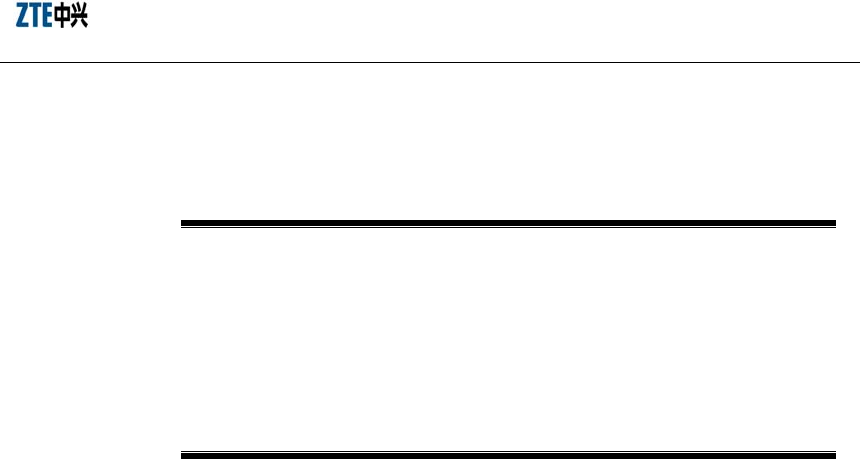
Chapter
Error! Style not defined.
Error!
Style not defined.
9-5
9 Installing the Monitoring System
Summary
This part describes:
● Composition of the monitoring system;
● Installation of the monitoring system.
9.1 Composition of the Monitoring System
The monitoring system consists of the smog sensor and the temperature/humidity
sensor.
9.2 Installing the Monitoring System
9.2.1 Installing the Indoor Smog Sensor
The smog sensor should be installed on the ceiling as close to the rack as possible. The
installation steps are as follows:
1. As shown in b) of Fig. 9.2-1, separate the upper part and the lower part of the
smog sensor;
2. Connect the green and red wires (as shown in a) of Fig. 9.2-1) at end B of the
10m smog sensor cable to the two terminals marked 1 and 3 at the bottom of the
smog sensor (as shown in c) of Fig. 9.2-1);
3. As shown in b) of Fig. 9.2-1, reassemble the upper and lower parts together;
4. Connect the DB25 plug at end A to the DB25 socket on the BTS set top ;
5. The terminal connection of the smog sensor cable connector is described in Table
9.2-1.
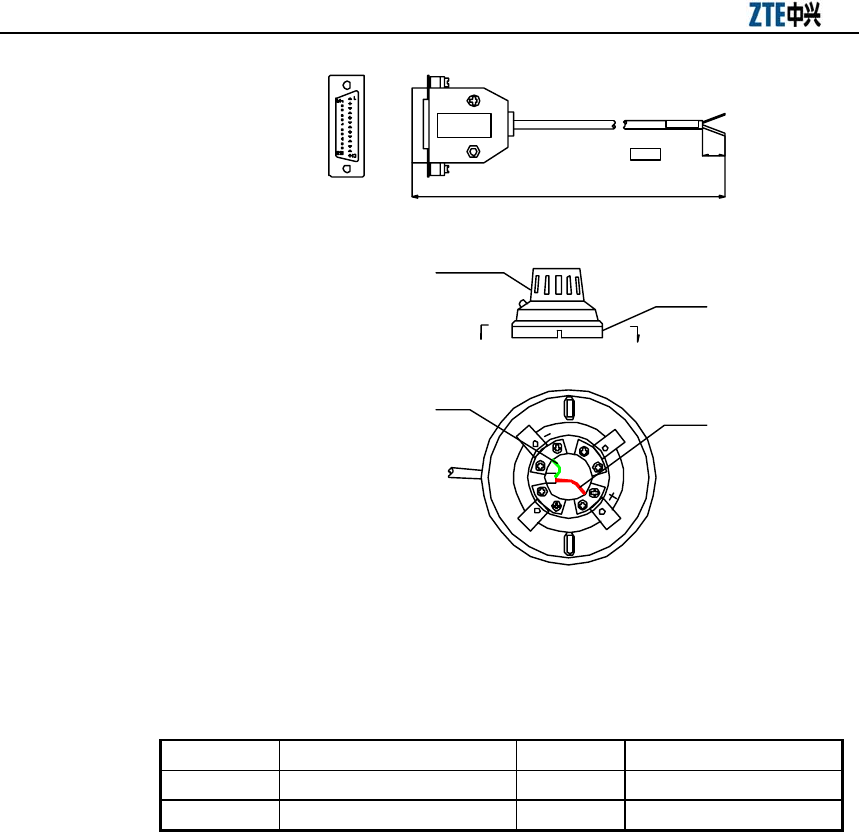
ZXC10-BTS (V5.4) Installation Manual
9-6
B-B
Pinouts of
25-p in male
connector
End A
Green
30
10m
Label
B
B
1
23
4
Upper part of
the smoke sensor
(b)
(a)
(c)
End B
Red
La b e l
Lower part of
the smoke sensor
Green wire
Red wire
Fig. 9.2-1 Installing the Smog Sensor Base
Table 9.2-1 Terminal Connection of the Smog Sensor Cable Connector
Signal 25-pin Male Connector at End A Cable Color Smog Sensor Base at End B
+12V 10 Red 3(+)
-12V 11 Green 1(-)
9.2.2 Installing the Indoor Temperature/Humidity Sensor
The temperature/humidity sensor is mounted on the wall. Select a proper position on
the wall in the equipment room, drill a hole of Φ6, put in a rubber cork, tighten the
captive screw, and finally hang the sensor on the wall through the hole. The dimensions
of the sensor is as shown in b of Fig. 9.2-2.
Both ends of the sensor connection line are DB9 connectors. As shown in a of Fig.
9.2-2, connect the DB9 male connector at end A to the DB9 socket, the
temperature/humidity socket on the BTS set top. And connect the DB9 female
connector at end B to the sensor.
The terminal connection of the cable connector is described in Table 9.2-2.
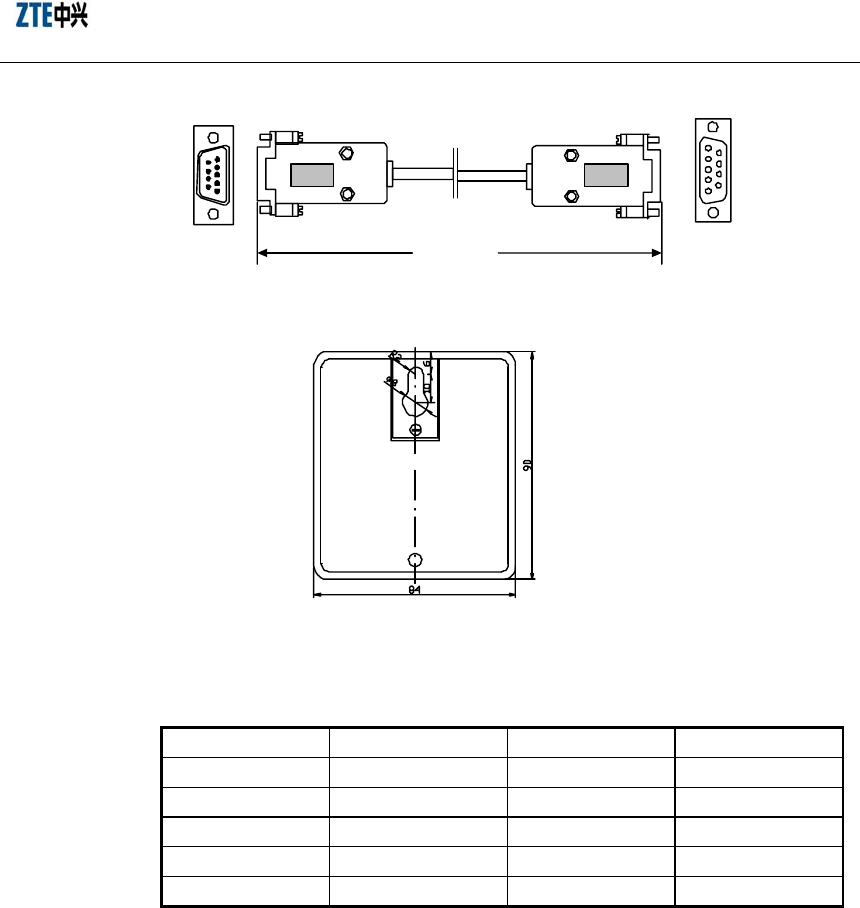
Chapter
Error! Style not defined.
Error!
Style not defined.
9-7
Pinouts of
the DB9 male
connector at
End A
1
6
9 5
End A
Label
End B
1
5
6
9
Label
L=10 m
(a)
(b)
Pinouts of
the DB9 male
connector at
End B
Fig. 9.2-2 Installing the Temperature/Humidity Sensor
Table 9.2-2 Terminal Connection of the Temperature/Humidity Sensor Cable Connector
Signal Pin ID at End A Cable Color Pin ID at End B
HUM 1 White 3
TEMP 7 Blue 4
GND 3 White 1
+5V 8 Orange 5
6 Shielded wire
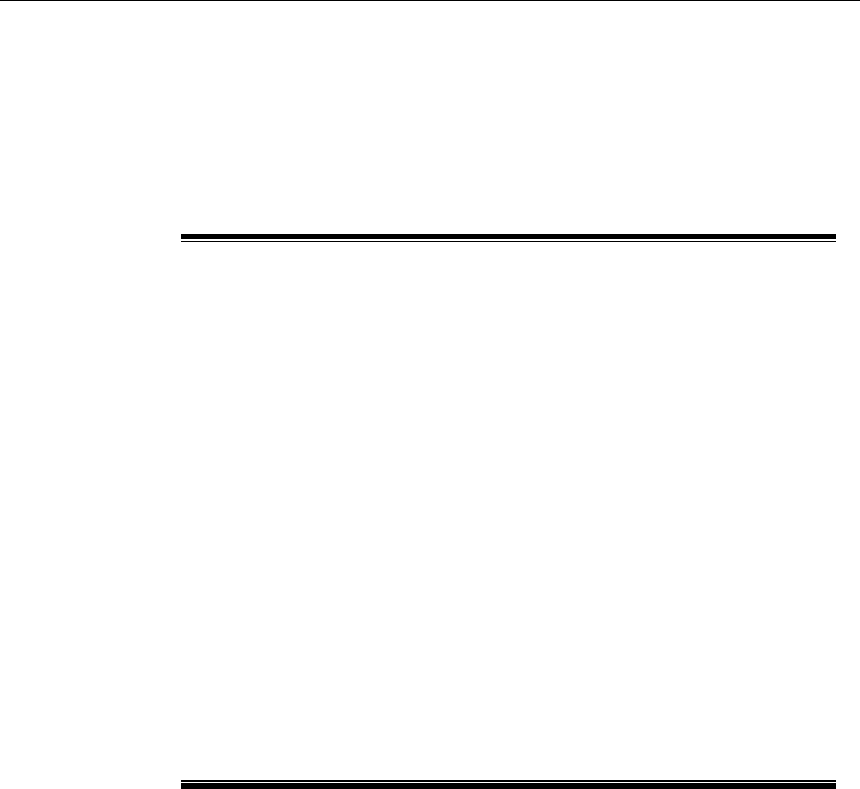
FAX: 0086-755-26770160
10-1
10 Installing the Main Antenna Feeder
System
Summary
This part describes:
● Installation preparation for the BTS main antenna
feeder system;
● Structure of the BTS main antenna feeder system;
● Installation content and flow of the BTS main antenna
feeder system;
● Installation procedure of the parts of the BTS main
antenna feeder system;
● Installation check and test of the antenna feeder
system;
● Waterproof treatment of the connectors.
10.1 Installation Preparation for the Antenna Feeder System
This covers the preparations of staff, safety measures, tools and instruments, and
technical documents, and the installation environment check.
The installation of the antenna feeder equipment is important to the installation of the
BTS equipment. Its construction quality directly affects the operating performance of
the entire BTS system. Most of the BTS installation engineering is the installation of
the antenna feeder equipment that generally takes up 80% of the installation time of the
whole BTS system. The installation of the antenna feeder equipment involves the
installation of the antenna, the jumper, the routing of the main feeder, and the
installation of the lightning protection system and the GPS system. Different antenna
may be used due to different terrain, population density and installation environment.

ZXC10-BTS (V5.4) Installation Manual
10-2
The installation method and procedure differs. In the precondition of quality, the
Installation Supervisor should install the antenna as per the actual situation flexibly and
reasonably by following the BTS engineering design documents and the installation
instructions of the special antenna provided by the manufacturer.
Prior to the installation of the antenna feeder system, inspect the qualification of the
installation staff to work at heights, check and prepare the installation environment, the
installation measures, the installation tools and the antenna feeder to be installed so that
the installation can be carried out successfully.
10.1.1 Preparations for Installation Staff
Generally, the installation of antenna feeder system is supervised by the Installation
Supervisor and carried out by the installation staff.
Requirements for the Installation Supervisor: He should be familiar with the materials,
tools and operation methods used in the antenna feeder installation, and be responsible
for organizing the installation staff and assigning proper tasks (especially working on
the tower) to the staff in the principle of "Safety First". The Installation Supervisor
should fill in the engineering data faithfully.
Requirements for the installation staff: Staff that can conduct the installation
professionally under the instruction of the supervisor. The staff working at heights
should have no acrophobia and be in good health. In addition, he should have the
qualification and certificate for working at heights, observe the requirements for using
the safety tools, have purchased life insurance policy, and should not drink.
10.1.2 Installation Environment Inspection
The environment inspection focuses on the following: The outdoor lightning protection
grounding cable should be in place with the core diameter more than 50mm
2
. The
distance between the antenna lightning arrester, the lightning protection grounding
point, the outdoor cabling rack, and the antenna embracing pole should meet the design
requirement. The strength and the wind-withstanding capability of the embracing pole
should also meet the design requirements. Check the preparation of the compulsory
tools and engineering auxiliary materials. Both parties should negotiate and define the
specific routing of the main feeder.

Chapter Error! Style not defined. Error! Style not de
fined.
10-3
As to the installation of the antenna support, the equipment supplier puts forward
requirements for the antenna structure and dimensions, while the network operator
completes the installation as parts of the equipment room accordingly.
The network operator is also responsible for the installation of the antenna feeder
installation environment such as the outdoor cabling rack, the lightning arrester, the
lightning protection grounding peg, and the outdoor lightning protection grounding
cable. The construction of the wall or the hole on the roof for the feeder window where
the main feeder enters the room involves the infrastructure of the equipment room. It
should be completed as part of the equipment room by the network operator.
10.1.3 Safety Measures Inspection
Caution:
The staff working on the tower must wear the safety belt and must not wear loose
clothes or slippery shoes, while the staff under the tower must wear the safety helmet.
1. Emphasize the safety precautions to the engineering staff.
2. The outdoor engineering of the antenna feeder should be conducted on a fine
day without strong wind.
3. Distinct marks should be set up at the engineering site to keep off people
irrelevant. The staff working under the tower have the obligation to clear the
people irrelevant on-site, especially children, off the site. All the tools and
instruments that might fall off the tower and hurt the personnel under the tower
must be strictly handled. For example, the tools and metal installation parts that
are temporarily not used on the tower should be put in a canvas tool bag. The
bag should be closed once you take out the tool you need.
10.1.4 Preparation of Installation Tools
Installation tools comprise the following:
1. Measurement tools: Compass, multimeter, angle meter, tape;
2. Communication tools: Two MSs;
3. Hoisting tools: Pulley, rope to pull the main feeder;

ZXC10-BTS (V5.4) Installation Manual
10-4
4. Special tools: Main feeder cutter, special tools for preparing main feeder
connectors;
5. General-purpose tools: Adjustable wrench, sharp-nose pliers, diagonal pliers,
electrical knife, file, hacksaw;
6. Safety protection tools: Safety belt (used by engineering staff who step out of
the platform on the tower), safety helmet, safety rope, thick uniform, RF-proof
clothing, canvas tool bag, gloves, multi-purpose power socket;
7. Others: Standing ladder, wooden axle hoisting tool for the main feeder (this can
be borrowed from the local user).
10.2 Structure of the Antenna Feeder System
As shown in Fig. 10.2-1, the antenna feeder system comprises antenna, antenna jumper,
main feeder, lightning arrester, set top jumper, grounding parts and others.
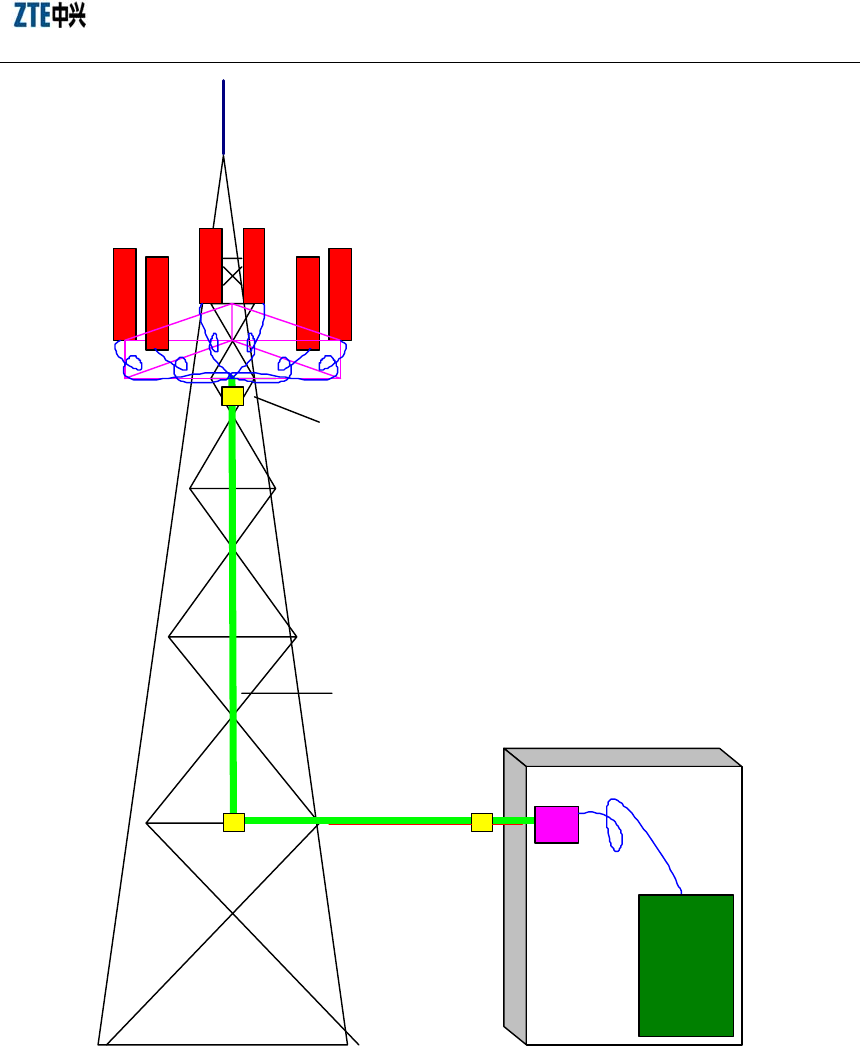
Chapter Error! Style not defined. Error! Style not de
fined.
10-5
Lig h t n in g
arrester
Antenna (6 sets;
directional)
Jumper (1/2''; 6 PCS)
Lightning protection
grounding clip
Main feeder (7/8''; 6 PCS)
BTS
cabinet
Lightning protection
grounding clip
Cabling rack
Lightning protection
grounding clip
Iron tower
Equipment room
Lightning arrester
Jumper (1/2''; 6 PCS)
Fig. 10.2-1 Typical Structure of the Antenna Feeder System of Three-sector BTS
10.3 Installation Content and Flow
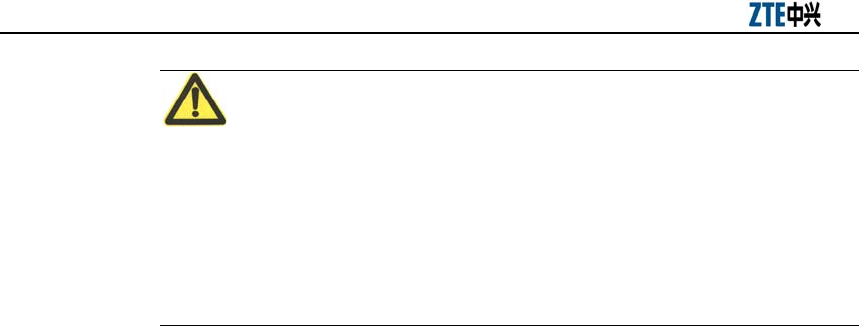
ZXC10-BTS (V5.4) Installation Manual
10-6
Caution:
1. Take careful precautions for the safety of yourself and the equipment during the
whole antenna installation process;
2. When adjusting the antenna that is already working, take certain measures (for
example, wear radiation-shielding clothing), and turn off the high power amplifier to
avoid the direct radiation of the antenna to human body.
10.3.1 Technical Parameters for Antenna Installation
1. Antenna height
It is determined by network planning.
2. Azimuth of antenna
It is determined by network planning.
3. Pitch angle of antenna
It is determined by network planning. Usually 0° ~ 10° adjustable.
4. Antenna direction
It is determined by the azimuth of the antenna. Two antennas in the same sector
should point to the same direction.
5. Distance between diversity antennas
The two antennas in the same sector are diversity receiving antenna to each
other with the same vertical height. The horizontal distance (d) is as large as
possible to satisfy the engineering requirements just by following the formula
below.
d ≥ 10~20λ (or H/d = 11), where d is the horizontal distance between the
diversity antennas, and H is the vertical height from the antenna to the floor. The
diversity distance of the 1900M carrier should be more than 1.5m while that of
the 800M carrier should be more than 3.5m.
10.3.2 Antenna Installation Flow
The antenna installation flow is shown in Fig. 10.3-1.
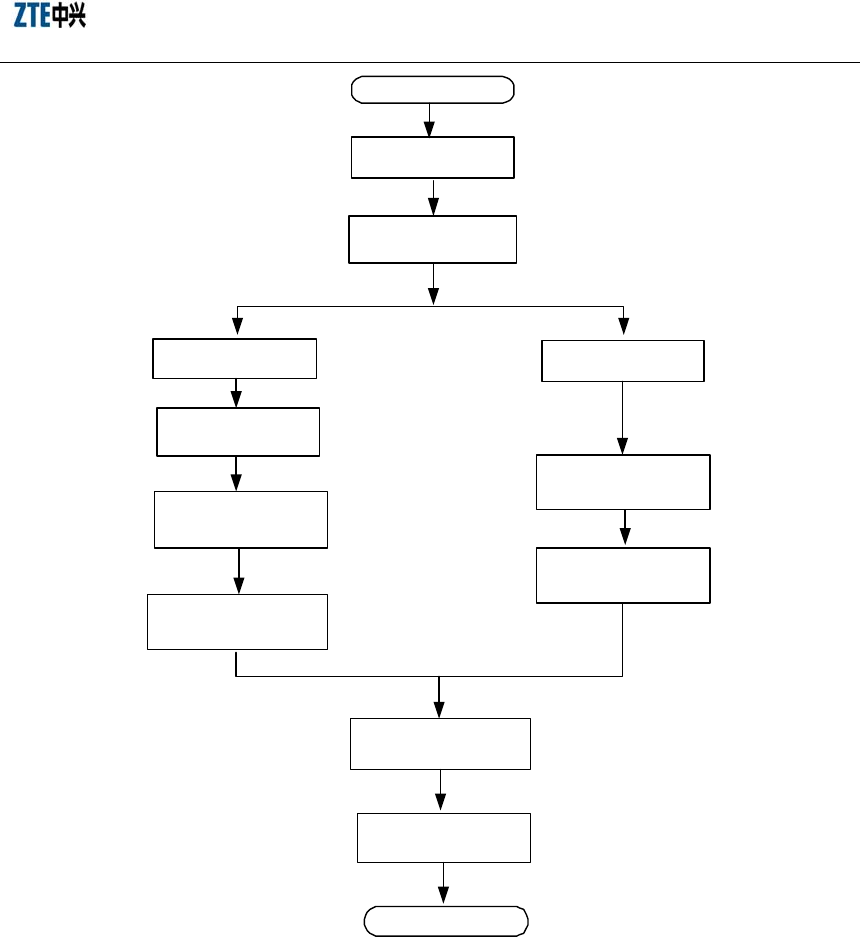
Chapter Error! Style not defined. Error! Style not de
fined.
10-7
St a r t
Directional
antenna
Lift and handle
the antenna
Determine the
installat ion position
Omni antenna
Initial asse m bly of the
installation accessories for
the directional antenna
Initial fixat ion of the
directional antenna
Adjustment of the
direction and pitch angle
of the directional antenna
Initial fixat ion of
the omni antenna
Adjustment of the
vert icalit y of the
omni antenna
Jumper inst allation
and sealing of the
omni antenna
Fixation of the antenna
End
Fig. 10.3-1 Antenna Installation Flow
10.4 Installing the Antenna Parts
10.4.1 Determining the Antenna Installation Position
During the installation, the antenna installation position should be determined
according to the antenna feeder installation drawing among the engineering design
drawing. If the antenna support is installed in a place different as that shown in the
engineering design drawing, second design should be done based on the network
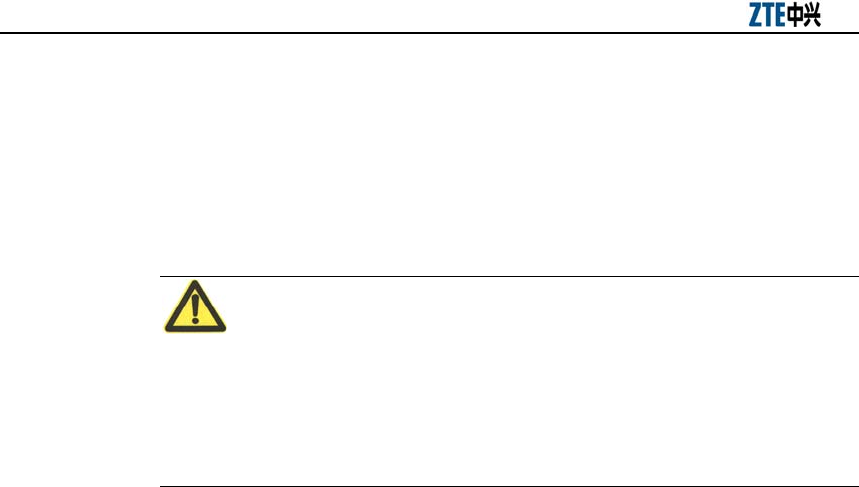
ZXC10-BTS (V5.4) Installation Manual
10-8
coverage requirement of the local BTS, antenna diversity requirement, antenna azimuth
and pitch angle. And design modification solution should be made then after
consultation with the user representative and the design institution, lest the network
coverage after the installation be affected.
10.4.2 Handling and Hoisting the Antenna
Caution:
Personnel both on and under the tower should coordinate to hoist the antenna. During
the hoisting process, the personnel under the tower should pull the antenna away from
the tower body by pulling the rope, lest the antenna be damaged due to crash with the
tower body.
In the case the antenna is to be installed on the tower, use the rope and pulley block to
hoist the antenna, the 3m antenna jumper and all the accessories (such as tools, safety
belts, adhesive tapes and straps) to the tower-top platform and place them in a safe
place. Take corresponding safety measures during the process. Small metal staff as
antenna fixing parts and wrenches should be put in a sealed canvas tool bag before
hoisting, as shown in Fig. 10.4-1.
Both ends of the directional antenna and the omni-antenna should be knotted for easy
coordination of the staff both on and under the tower during the hoisting.
In the case the antenna is to be installed on the roof, move the antenna and the
installation materials to the installation position manually.
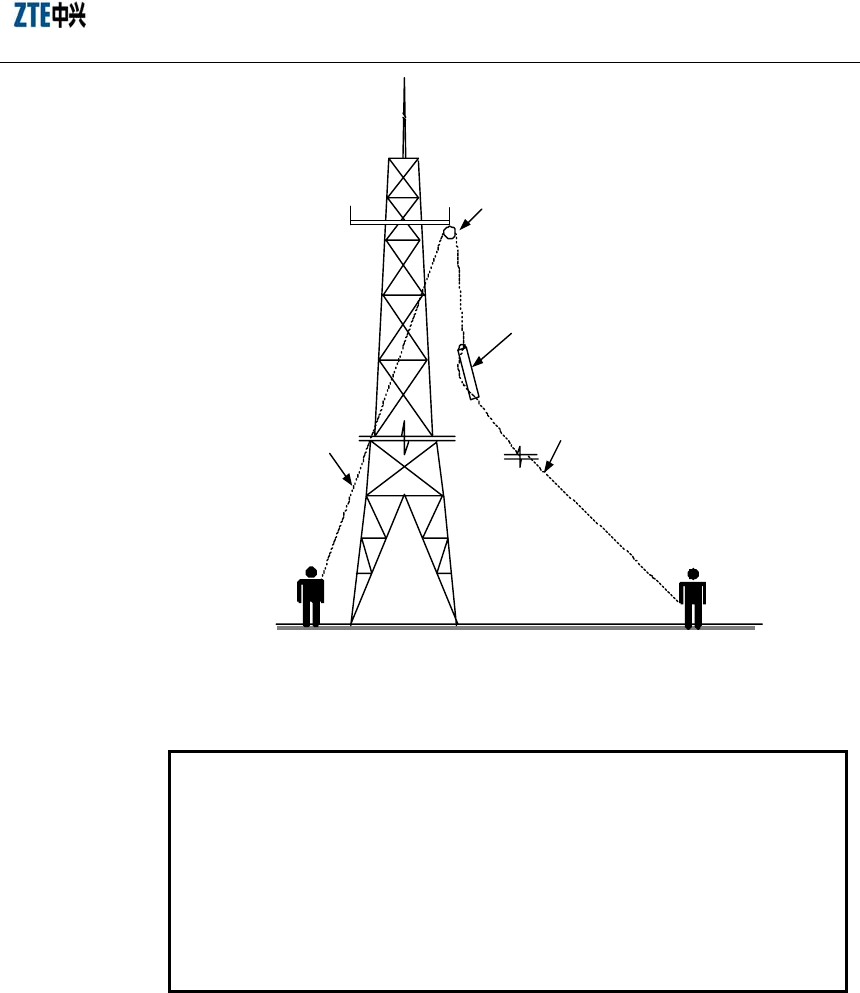
Chapter Error! Style not defined. Error! Style not de
fined.
10-9
Pulley block
Pull-up
rope
Tie the pull-up rope at the upper
and lower ends of the antenna
Pull the antenna away from the
iron tower with this rope to
avoid antenna damage
Fig. 10.4-1 Hoisting an Antenna
10.4.3 Installing and Adjusting the Directional Antenna
Note:
The installation methods of antennas of different models vary from one
manufacturer to another. This section takes the Kathrein antenna as an
example to describe the antenna installation process. Please carefully read
the installation instructions provided along with the antenna during the
installation and install the antenna as per the actual situation.
1. Initial assembly of the directional antenna fittings
The directional antenna has a number of installation fasteners. For example, the
Kathrein antenna has two types of fasteners: 738516 and 737974. Before fixing
the antenna, assemble fastener 737974 to the ends of the antenna, as shown in
Fig. 10.4-2, and then connect fasteners 737974 and 738516. Thus the initial
installation of the directional antenna is complete. All accessories must be
installed with spring and flat washers. Please refer to the instructions attached to

ZXC10-BTS (V5.4) Installation Manual
10-10
the product for descriptions of other fasteners for the antenna of other
manufacturers or of Kathrein.
Usually the antenna fixing accessories and the angle adjustment device
accessories have been installed on the antenna under the tower.
2. Initial fixing of the directional antenna on the antenna embracing pole
Mount the directional antenna installed with clamp accessories on the antenna
embracing pole: The screw should not be too tight that you are unable to adjust
the direction and the pitch angle of the antenna, nor too loose lest the antenna
slip downward.
3. Adjusting the azimuth of the antenna
1) Determine the azimuth of the antenna using a compass. And determine the
installation direction of the directional antenna according to the engineering
design drawing;
2) Turn the antenna slightly to adjust its face direction, as shown in Fig. 10.4-2. At
the same time measure the direction of the antenna with a compass till the error
is within the engineering design requirements (generally not more than 5°);
3) After adjusting the azimuth of the antenna, tighten the fastener 738516.
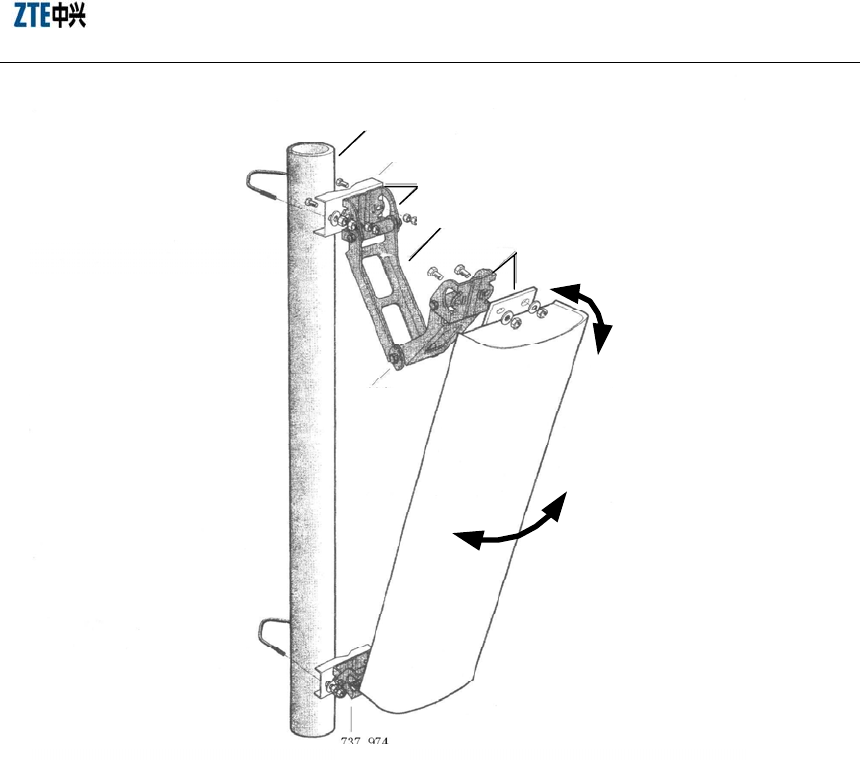
Chapter Error! Style not defined. Error! Style not de
fined.
10-11
Antenna pole f75mm
738 516
737 974
737 974
Connected via a short bolt and fixed with
two nuts for enhanced connection firmness
A short bolt connects the antenna and
the fastener; a sp ring washer and a flat
washer is added here; waterproof gasket
is in the inner circle of the nut
Pull the antenna t op up ward and
downward after initial
installation and fixation to adjust
the pitch angle of the antenna
Kathrein 650
directional
antenna
Pull the antenna leftward and rightward
after initial installation and fixation to
adjust the azimuth of t he antenna
Scale 00~160
Fig. 10.4-2 Installing the Kathrein Antenna
4. Adjusting the pitch angle of the antenna
1) Adjust the pitch angle of the dip meter to the angle required by the engineering
design;
2) Turn the top of the antenna slightly, let go or hold fast the antenna at its top.
Adjust the pitch angle of the antenna till the bead is centered when the adjusted
dip meter is next to the directional antenna, as shown in Fig. 10.4-3;
3) After adjusting the pitch angle of the antenna, tighten the fastener 737974.
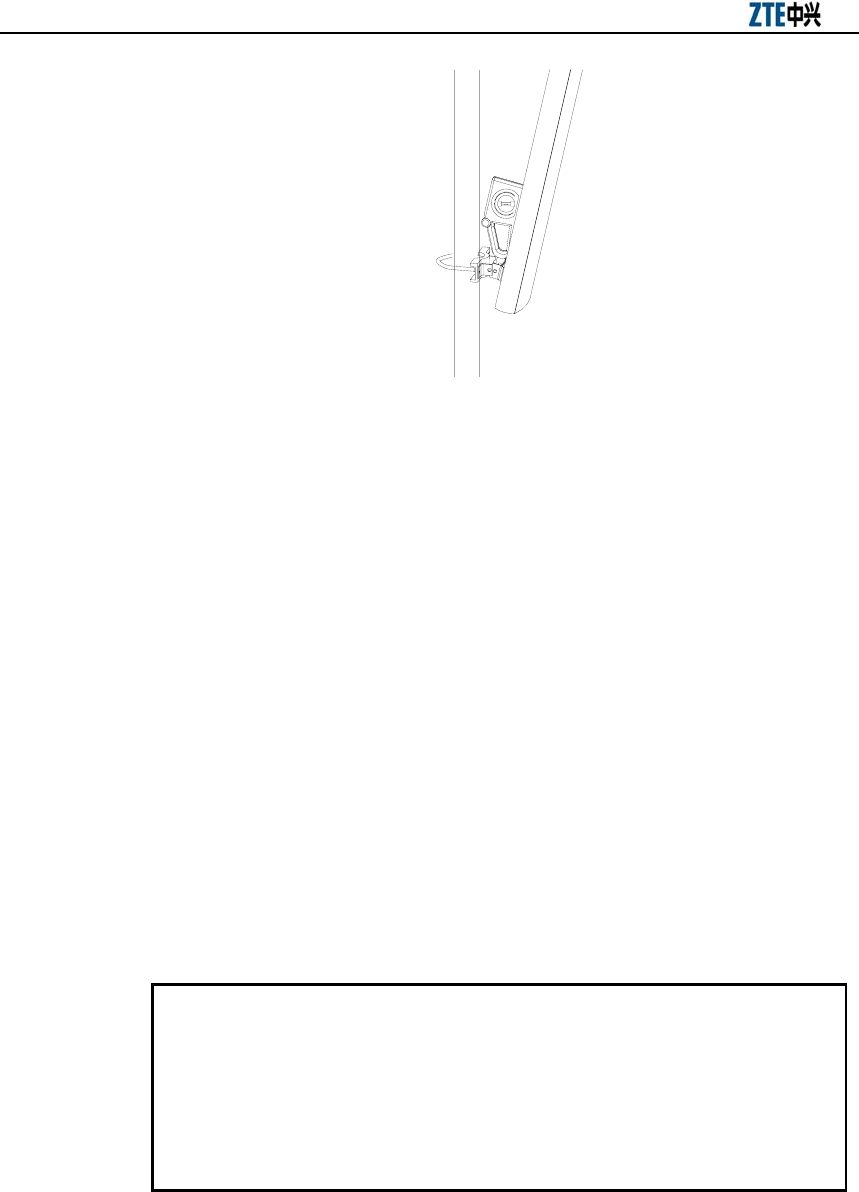
ZXC10-BTS (V5.4) Installation Manual
10-12
Fig. 10.4-3 Adjusting the Pitch Angle of the Antenna
10.4.4 Installing and Adjusting the Omni Antenna
Take the following steps to install the omni antenna:
1. Put the jacket at the antenna lower part close to the support backbone. The top of
the jacket should be flush with or slightly higher than the support top;
2. Fix the jacket at the antenna lower part and the support backbone at two points
with antenna fixing clips. They should be fixed tight enough to bear weight and
withstand wind, and should not be too loose or too tight lest the antenna jacket
be damaged.
3. Check the antenna verticality. The omni antenna must be vertical. Make sure the
antenna is vertical, and then fix it to the antenna embracing pole.
4. Stick the support installed with the antenna out of the tower platform, and adjust
the support to make the antenna vertical.
10.4.5 Connecting and Sealing the Jumper and the Antenna
Note:
The antenna and the jumper can be connected and waterproof treatment can be
conducted on the joint before the antenna is fixed on the embracing pole. This
can reduce the time working at heights and improve the joint connection and
waterproof quality. The installation steps are as follows:
1. Align the connector of the antenna jumper to the antenna interface and screw it
tightly.
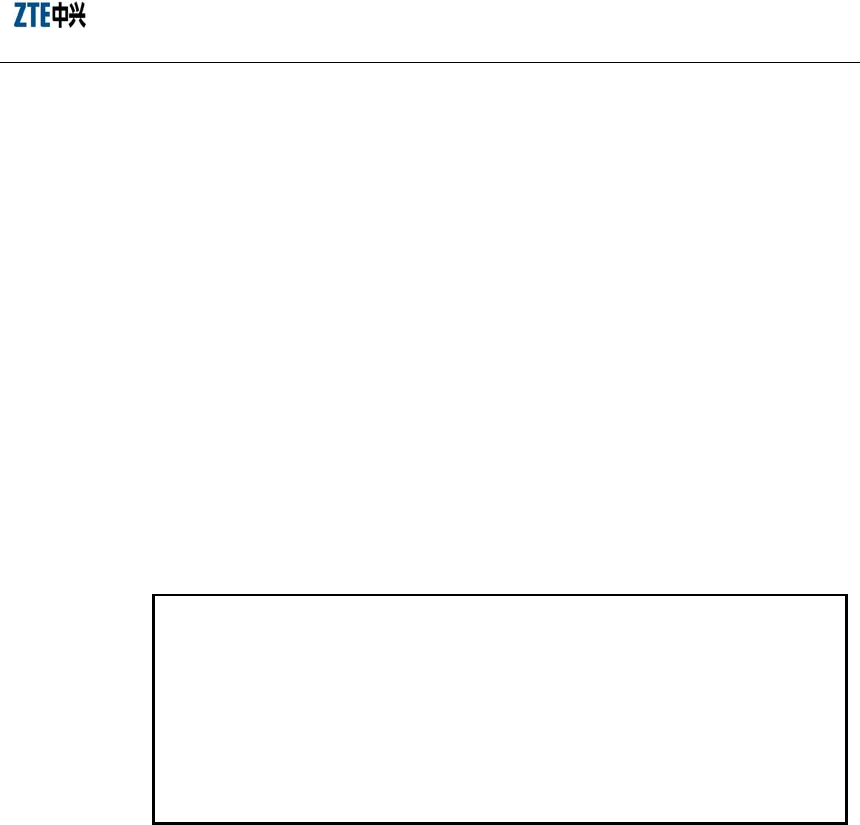
Chapter Error! Style not defined. Error! Style not de
fined.
10-13
2. Perform waterproof treatment to the joint (See section 10.6 "Waterproof
Treatment on Joint" for details):
1) Wrap starting from the root of the antenna joint with waterproof adhesive tape in
the same direction as the fastening direction of the antenna jumper;
2) Stretch the waterproof adhesive tape to double its length, and apply it layer by
layer till it covers about 5cm of the bottom of the feeder joint. During the
process, make sure the upper layer overlaps the lower layer by half the width of
the tape.
3) Grip the tape with hands to make the tape tightly adhered;
4) Apply the PVC tape layer by layer on top of the waterproof adhesive tape.
During the process, make sure the upper layer overlaps the lower layer by half
the width of the tape.
10.4.6 Installing the Feeder Window
Note:
The feeder window provided by ZTE is a four-hole one with the dimensions of
400mm × 400mm. Altogether 12 feeders can go through the feeder window, and
the dimensions of the cavity on the wall can be 300mm × 300mm. If the user
provides a special feeder window, then make the wall cavity according to the
actual dimensions of the feeder window.
The feeder window is usually mounted on the wall outside the equipment room
between the indoor and the outdoor cabling racks.
If the main feeder window is to be installed on the building-top, sealing and waterproof
treatment should be conducted on it. You may use asphalt or glass cement to seal the
feeder window.
The feeder window has four or nine holes and the 4-hole feeder window is as shown in
Fig. 10.4-4. Table 10.4-1 shows the specifications of varying feeder windows. Follow
the steps below to install the feeder window:
1. Determine the installation position of the feeder window as required by the
engineering design drawing;
2. Make a cavity on the wall according to the size of the feeder window;
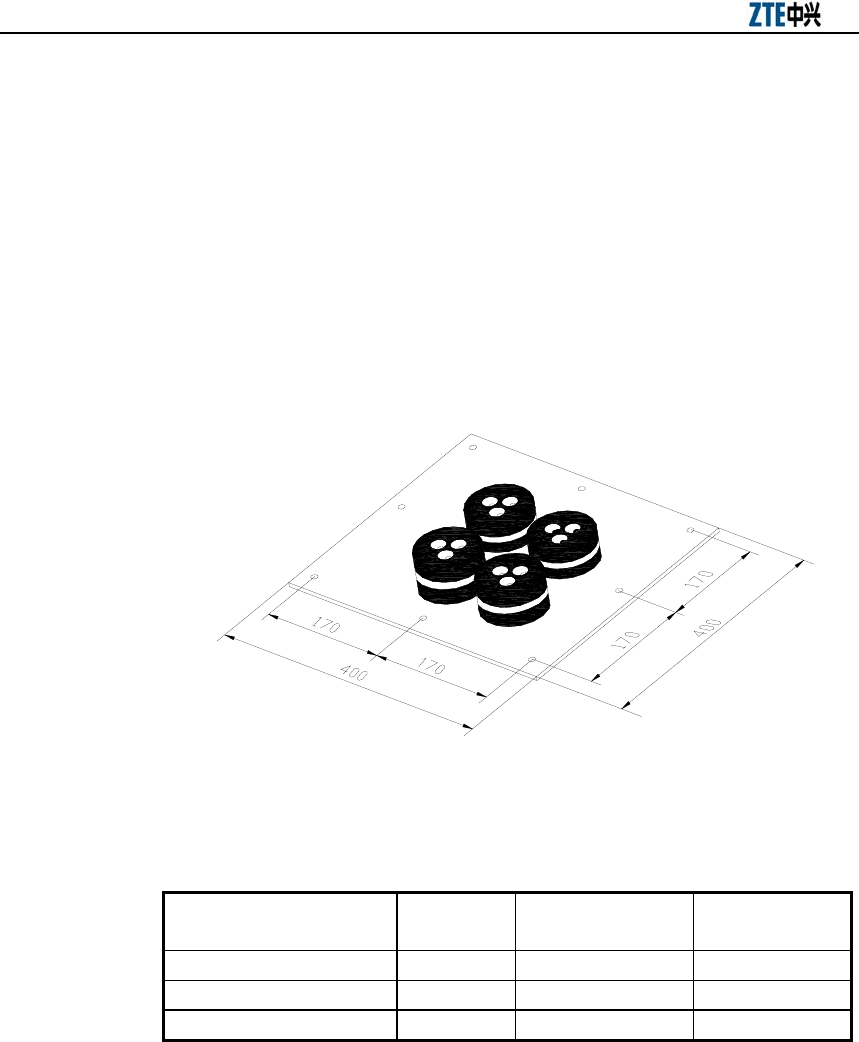
ZXC10-BTS (V5.4) Installation Manual
10-14
3. Drill holes for the expansion bolts using a percussion drill and fix the main
board of the feeder window with expansion bolts;
4. The sealing gasket and sealing tube of the feeder window can be installed when
the main feeder is introduced into the room. See section 10.4.7.6 "Introducing
the Main Feeder into the Equipment Room";
5. For cold areas with sand storms, even if the wall is thick, it is necessary to install
timber baffle plates inside the equipment room to keep warm and keep sands
outside.
Fig. 10.4-4 Structure of the Feeder Window
Table 10.4-1 Model and Dimensions of the Feed Window
Model of feeder window Dimensions Smallest Hole
Required
Preferred Hole
Recommended
4 hole-5/4″ feeder window 400*400 240*240 300*300
9 hole-7/8″feeder window 500*500 360*360 400*400
4 hole-7/8″feeder window 400*400 240*240 280*280
10.4.7 Installing the Feeders
This section only describes the making of the 7/8" feeder connector, the connection and
sealing of the jumper and the main feeder, the connection and sealing of the jumper and
the antenna, and the layout and fixation of the feeder. It contains the following:
1. Determining and measuring the feeder route;

Chapter Error! Style not defined. Error! Style not de
fined.
10-15
2. Hoisting and cutting the feeder, and labeling the feeder;
3. Making the feeder connector;
4. Distributing and fixing the feeder;
5. Installing the outdoor jumper and conducting waterproof treatment on the joint.
The overall structure of a BTS feeder is as shown in Fig. 10.4-5.
Antenna
jumper
Label
Outdoor part
Feeder
Label
Light nin g arrest er
Cabinet-top
jumper
Indoor part
Fig. 10.4-5 Structure of a BTS Feeder
10.4.7.1 Determining the Feeder Routes
During the engineering installation phase, the layout of the feeder should be
determined according to the feeder wiring drawing among the engineering design
drawings. If the layout of the feeder need be modified as per the practical situation, you
should consult the user representative and try to solve the problem as early as possible.
Please note that the length of the main feeder should be as short as possible.
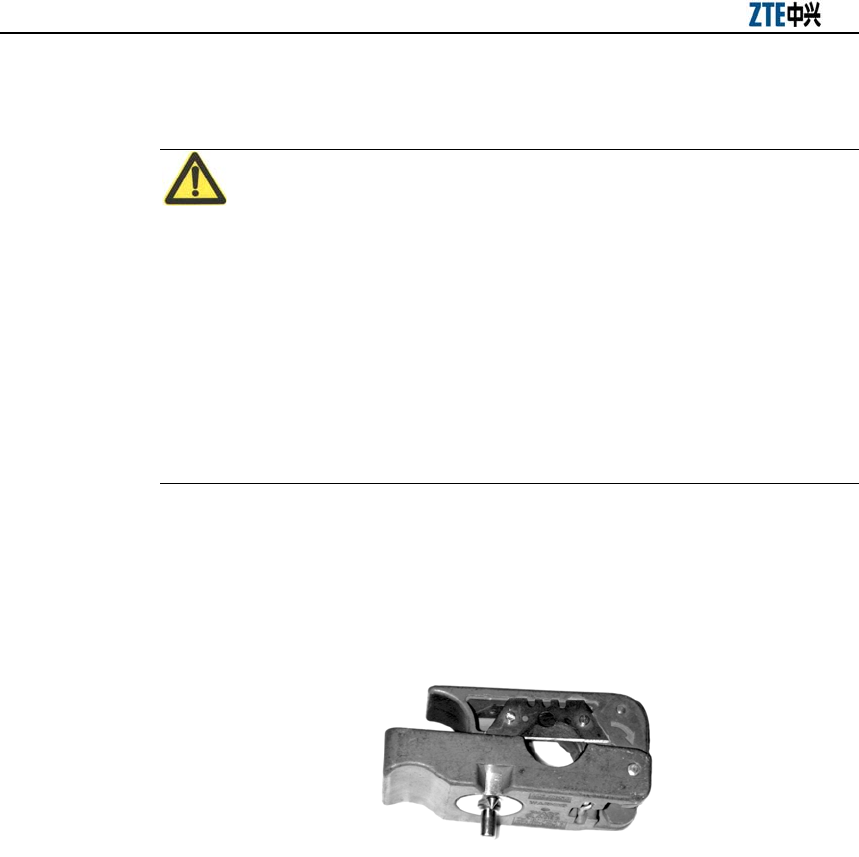
ZXC10-BTS (V5.4) Installation Manual
10-16
10.4.7.2 Preparing the Main Feeder Connectors
Caution:
The preparation of the feeder connector is the most important part in the antenna feeder
installation engineering. The quality of the job directly affects the equipment operation
and the network quality.
Since the cutting tool used is sharp, use it correctly to avoid body injury.
This section takes the Rosenberger 7/8" feeder connector as an example to describe the
preparation process. For the installation of the feeder connector of other specifications
or other manufacturers, please refer to their installation instructions.
Take the 7/8" main feeder connector as an example. The procedure to make the
connector is as follows:
1. The common cutting tool to make the feeder connector is as shown in Fig.
10.4-6.
Fig. 10.4-6 Cutting Tool for the 7/8" Feeder Connector
2. Measure a straight feeder section of about 150mm to be installed with the
connector, and cut and strip the feeder sheath 50mm away from the end using a
safety cutting tool.
3. Put the feeder into the notch of the cutter (EASIAX), leaving a length of four
sheath threads from the main blade. And then close the cutter handles. Since the
position of the cutter is determined according to the threads on the external
copper sheath of the feeder, the main blade should just be aligned to the crest at
the center of a thread of the feeder.
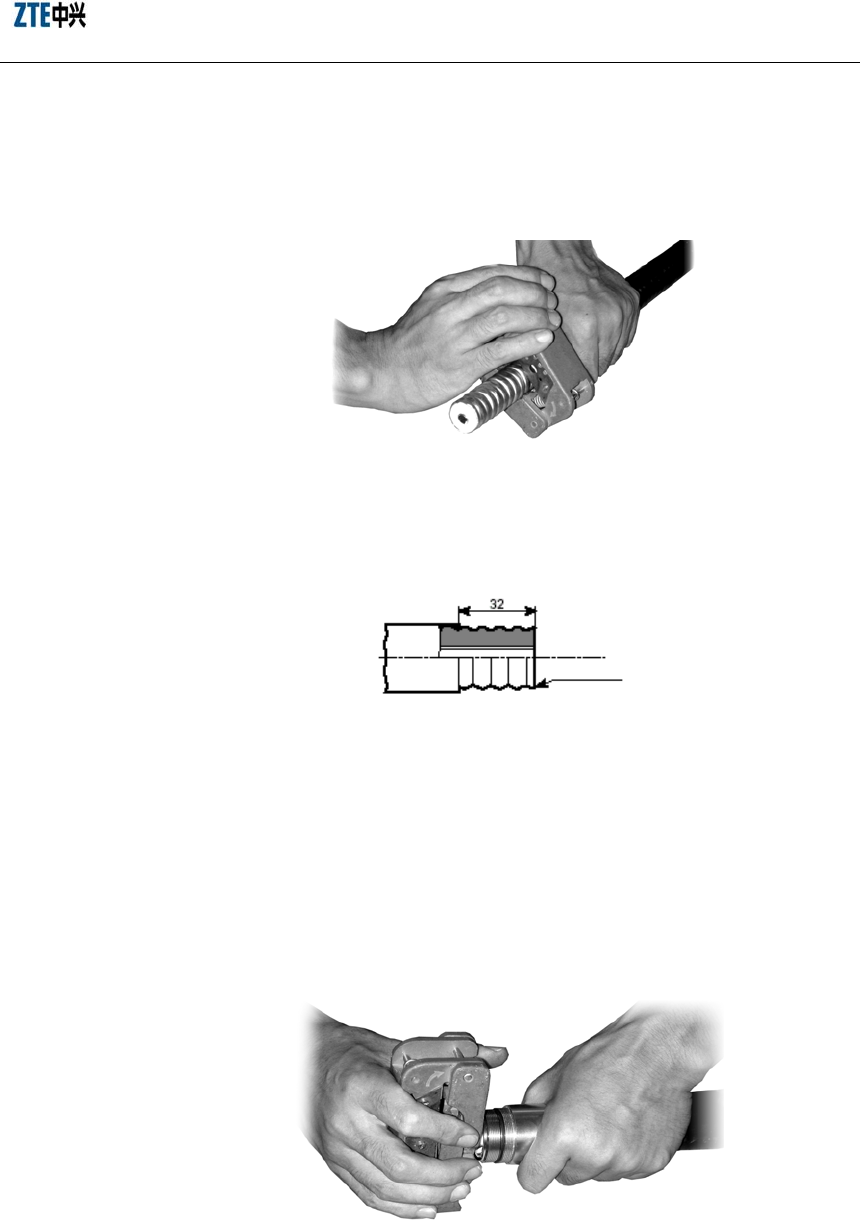
Chapter Error! Style not defined. Error! Style not de
fined.
10-17
4. Turn the cutter in the direction as marked on the cutter till the handles are
completely closed and cut the internal and external copper conductors of the
feeder completely. At the same time, the auxiliary blade of the cutter cuts the
external plastic protection sheath of the feeder, as shown in Fig. 10.4-7.
Fig. 10.4-7 Cutting the Feeder with a Cutter
5. Check the cutting length of the feeder, as shown in Fig. 10.4-8.
Crest position
Fig. 10.4-8 Checking the Cutting Length of the Feeder
6. Separate the front part and back part of the feeder connector, and insert the back
part into the feeder till it contacts with the first corrugation of the feeder.
7. Firmly insert the tube expander of the cutter into the feeder and turn it left and
right to expand the external copper conductor of the feeder, so that it presses
against the back part of the feeder connector, as shown in Fig. 10.4-9.
Fig. 10.4-9 Expand the External Conductor of the Feeder with a Tube Expander
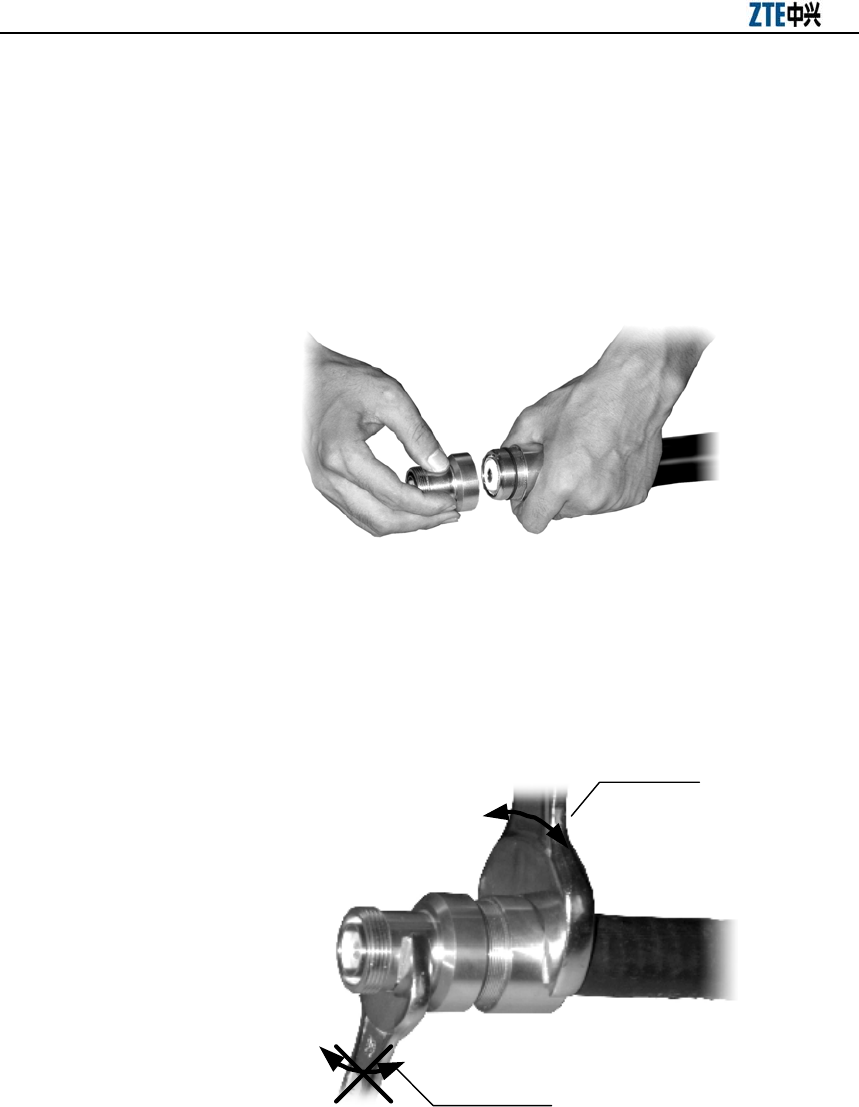
ZXC10-BTS (V5.4) Installation Manual
10-18
8. Check whether there is residual copper scraps. The external copper sheath
should be evenly expanded without burrs. Pull the back part of the feeder
connector outward while keeping it from slipping away from the feeder. If it
does separate from the feeder, make it again.
9. Connect the front part and the back part of the feeder connector, as shown in Fig.
10.4-10.
Fig. 10.4-10 Connecting the Front Part and the Back Part of the Feeder Connector
10. Screw the front part of the feeder connector, and fix it with an appropriate
wrench, so that it does not move against the feeder. Then screw the back part of
the feeder connector with the wrench till it is fixed, as shown in Fig. 10.4-11.
Keep this spanner fixed
Screw this spanner only
Fig. 10.4-11 Fixing the Front Part and the Back Part of the Feeder Connector
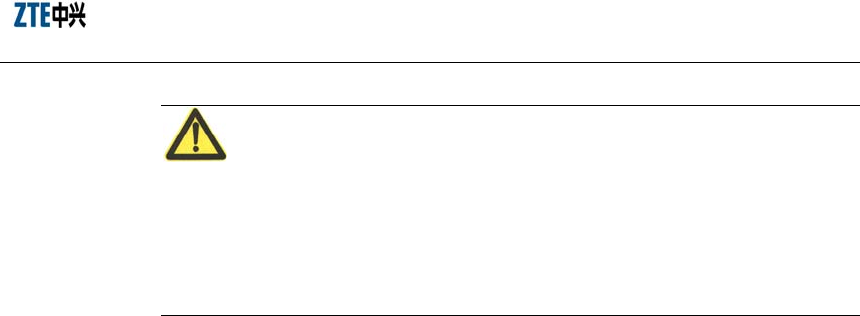
Chapter
Error! Style not defined.
Error! Style not de
fined.
10-19
10.4.7.3 Cutting the Feeders
Caution:
When cutting the main feeder, label it at both ends. Temporary label can also be
attached to the middle of the feeder. All the labels must be consistent. Otherwise, the
feeder may not be correctly connected and the sectors may not correspond to the feeder.
This is crucial!
Usually the feeder is rolled over to the installation site. The length of the main feeder
should be exactly measured again on site according to the final route negotiated with
the user. And the feeder should be cut into sections as required. The cutting steps are as
follows:
1. For the antenna feeder to be installed on the roof
1) Determine the length of the main feeder in each sector again with a tape measure
according to the actual route;
2) Cut the feeder to the length of the measured actual length plus 1m to 2m;
3) After cutting a main feeder, attach the corresponding temporary label to both
ends of the feeder, for example, ANT1, ANT2, ANT3, ANT4, ANT5 and ANT6.
When the feeder is installed, attach the formal label to it.
4) Move the cut feeders to the roof. During the process, take care that the feeders
are not damaged or pressed.
2. For the antenna feeder to be installed on the tower
1) Use roller support, pulley block and hoisting rope to lift one end of the feeder to
the tower top. The personnel under the tower cut the feeder to the length from
the feeder enters the equipment room to the lightning arrester frame plus certain
redundancy. Attach temporary labels to the lower part of the feeder. When the
feeder enters the equipment room, attach the formal label to it.
2) It is better to make the upper connector of the main feeder before hoisting it to
reduce the time that the staff works at heights and to better ensure the
installation quality of the feeder connector.
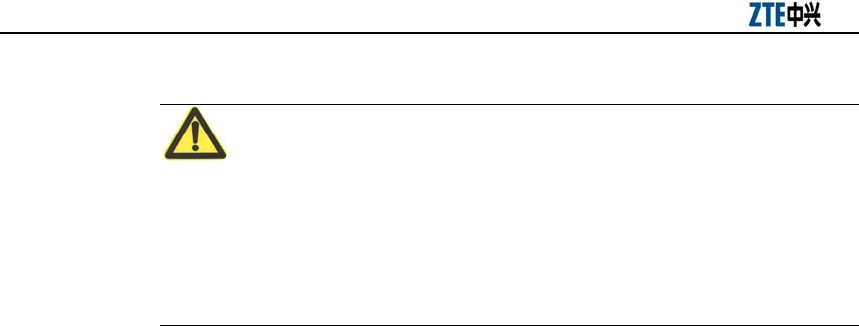
ZXC10-BTS (V5.4) Installation Manual
10-20
10.4.7.4 Hoisting the Main Feeders of the Iron Tower
Caution:
During the hoisting, rough operations are not allowed, lest the sheath of the main
feeder be damaged or scratched. The partial damage of a single main feeder will cause
the whole cable be rejected as useless.
Take precautions for personal safety when hoisting the feeders.
If the main feeder is to be installed on the tower, pulley blocks should be used to hoist
the main feeder, as shown in Fig. 10.4-12. Take the following steps to install the main
feeder:
1. Check again that the main feeder labels attached 0.3m away from both ends of
the main feeder are correct;
2. Wrap the main feeder connector made under the tower with flax (or antistatic
packing bag together with foam) and strap it tightly.
3. Knot and fix the hoisting rope 0.4m and 3.4m away from the feeder connector to
help the staff both on and under the tower pull up the feeder and to prevent the
feeder and its connector from damage caused by their bumping into the tower
during the hoisting process.
4. After the feeder is hoisted to the tower platform, fix the upper end of the cable to
a proper place at several points, lest the cable fall down from the tower.
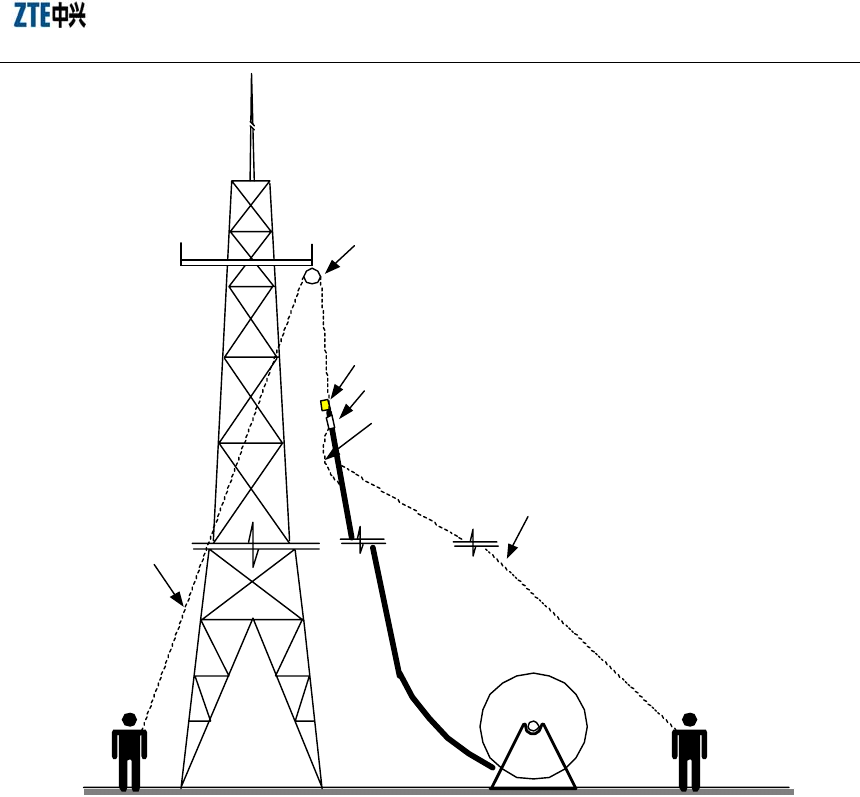
Chapter
Error! Style not defined.
Error! Style not de
fined.
10-21
Pulley block
Feeder head
bandage
Label
Tie the pull-up rope
0.4m and 3.4m away
from the feeder
Pull the feeder away from
the iron tower with this
rope t o avo id damage t o
the feeder or feeder head
Pull-up rope
Fig. 10.4-12 Hoisting the Feeder to the Tower
10.4.7.5 Cabling and Fixing the Main Feeders
1. Cabling principle of the main feeder
● The main feeder that enters the equipment room from the feeder window and is
routed along the indoor cabling rack should be bound neatly without crossing.
● The main feeder that is routed along the indoor cabling rack and the cabling rack
on the tower should have no crossing;
● Make yourself familiar with the routing of the main feeder before cabling it. It is
better to take down its actual route on paper to avoid rework due to crossing the
cable;
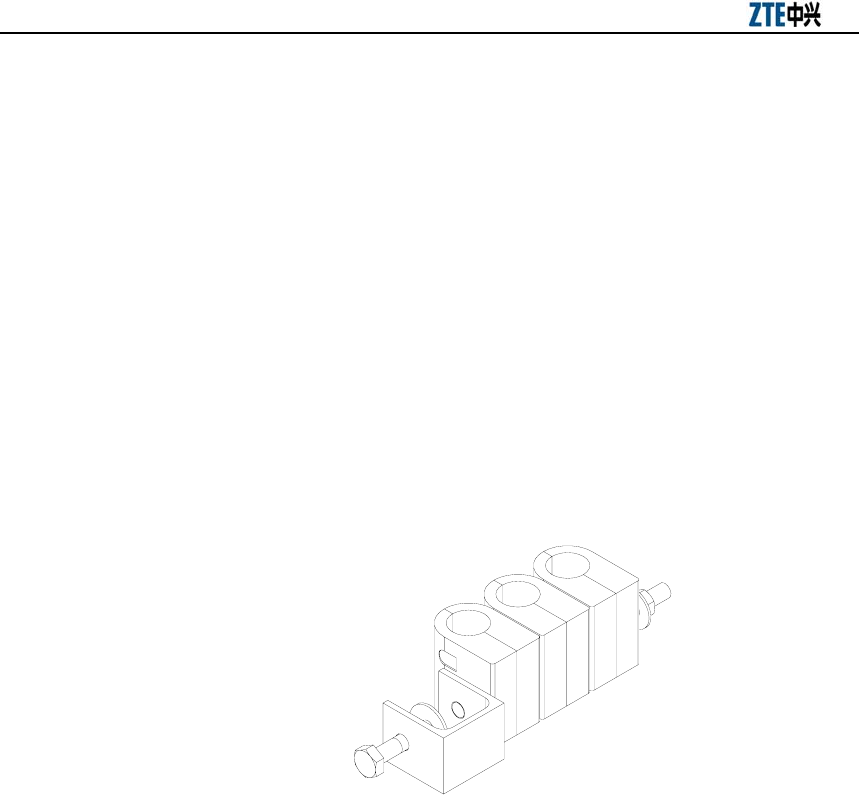
ZXC10-BTS (V5.4) Installation Manual
10-22
● The minimum bending radius of the main feeder should not be less than 20
times the length of the radius of the main feeder. For one-time bending, the
minimum bending radius is 90mm. The minimum bending radius of repeated
bends is 200mm.
● The maximum spacing between the hangers is 1.65m.
2. Cabling procedure of the main feeder
1) Pre-install the three-feeder clips every 1.5 meters (or as per the actual condition
of the iron tower, but no more than 1.65 meters) along the iron tower or cabling
rack. Note that the spacing should be as even as possible and the direction of
installing them should be the same. When installing two rows of feeder clips
inside the same cabling ladder, the two rows should be parallel and arranged
neatly. Fig. 10.4-13 shows the outside view of a three-feeder clip.
Fig. 10.4-13 Three-feeder Clip
2) Sort out the main feeders from the antenna to the equipment room inside.
3) Fix the main feeders from top to bottom and sort them out while attaching the
three-feeder clips. Fasten the feeder clips after smoothing the main feeders. Note
that you should keep the main feeders flat and straight rather than allowing any
bulge between two feeder clips or fixing the feeders at the two ends
simultaneously.
4) Fix the main feeders with three-feeder clips along the outdoor cabling ladders
prepared by the network operator for the main feeders to be routed along the
building top to the equipment room inside.
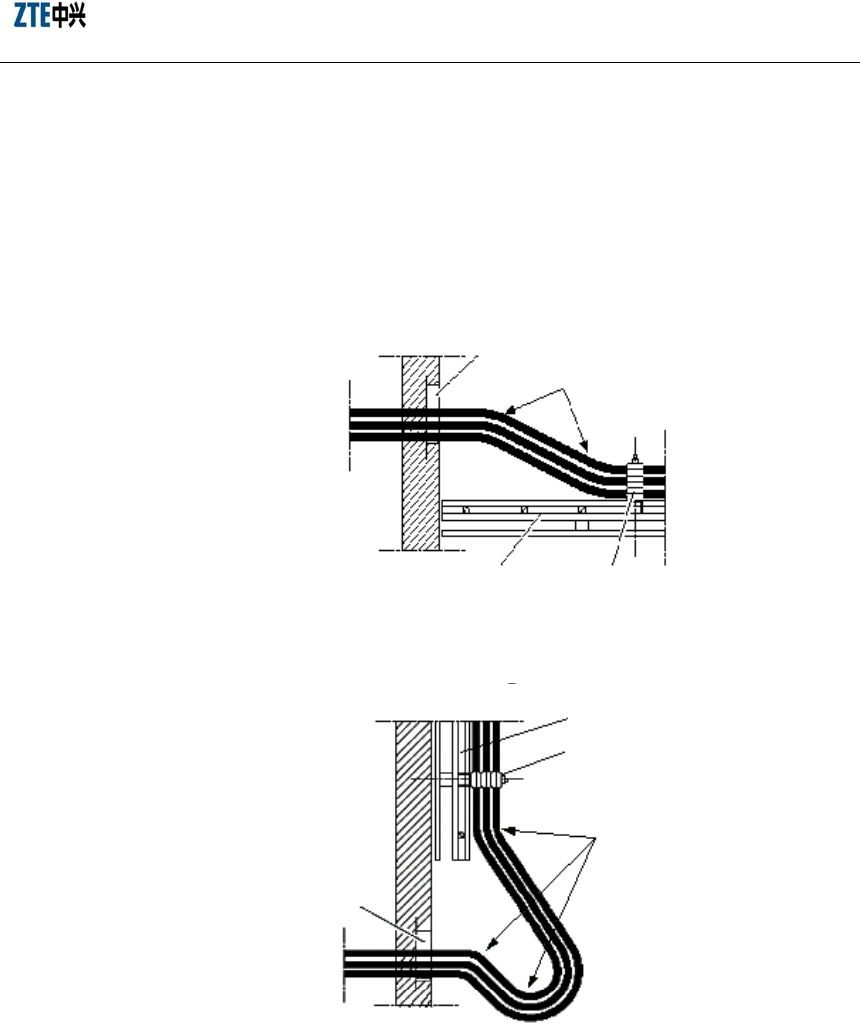
Chapter
Error! Style not defined.
Error! Style not de
fined.
10-23
10.4.7.6 Introducing Main Feeders into the Equipment Room
1. Precautions
● Fig. 10.4-14 and Fig. 10.4-15 illustrate how the common feeders enter the
equipment room. Please ensure that the feeders will not bring any rain into the
equipment room when entering the equipment room. For that purpose, you can
design water curves as necessary.
Feeder window
Bent once with the
minimum diameter
more than 90mm
Indoor Outdoor
Cabling rack Feeder clip
Fig. 10.4-14 Method 1 of Introducing Feeders into the Equipment Room
Indoor
Feeder window
Cabling rack
Feeder clip
Be nt o n ce with the min imu m
di ameter mo re tha n 90mm
Fig. 10.4-15 Method 2 of Introducing Feeders into the Equipment Room
● Use cabling racks both indoors and outdoors to guide the feeders when
introducing them through the feeder window into the equipment room.
2. Installation procedure

ZXC10-BTS (V5.4) Installation Manual
10-24
1) Loosen the fixing hoop from the feeder window to the proper position with
reference to Section 10.4.6, "Installing the Feeder Window", and pull away the
sealing cover of the aperture to thread the feeders.
2) Lead the feeders into the equipment room: Two persons are needed to cooperate
with each other, one indoors and the other outdoors, to introduce the feeders
from the outdoor cabling racks into the indoor cabling racks. During this process,
care should be taken to avoid damaging the indoor equipment or damaging the
feeder due to improper force applied on the outdoor feeder. Fasten the fixing
hoop after pulling the feeders in place.
3) Cut the feeders. Pay attention to the following:
● Check the labels:
Ensure that the temporary labels on the feeders are complete before feeder
cutting and are still attached on the feeders after cutting. This is very important
to avoid feeder chaos.
● Determine the cutting position:
When cutting the feeders, select the cutting position according to the equipment
room conditions (such as the rack installation position, the set top jumper length,
the lightning arrester configuration or the installation position of the lightning
arrester frame), the bending radii of the feeders and the cabling requirements of
the equipment room.
4) Prepare the indoor connectors for the main feeders.
5) Connect the main feeders to the lightning arresters.
If a lightning arrester is not grounded, it should be directly mounted onto the
feeders to ensure proper insulation between the lightning arrester and the cabling
rack.
If a lightning arrester is equipped with a lightning arrester frame, each feeder
should be thoroughly adjusted to ensure the screw threads properly fit in with
the lightning arrester when the main feed and the arrester are connected. For
details, refer to Section 6.2.3, "Installing the Indoor Lightning Arrester".
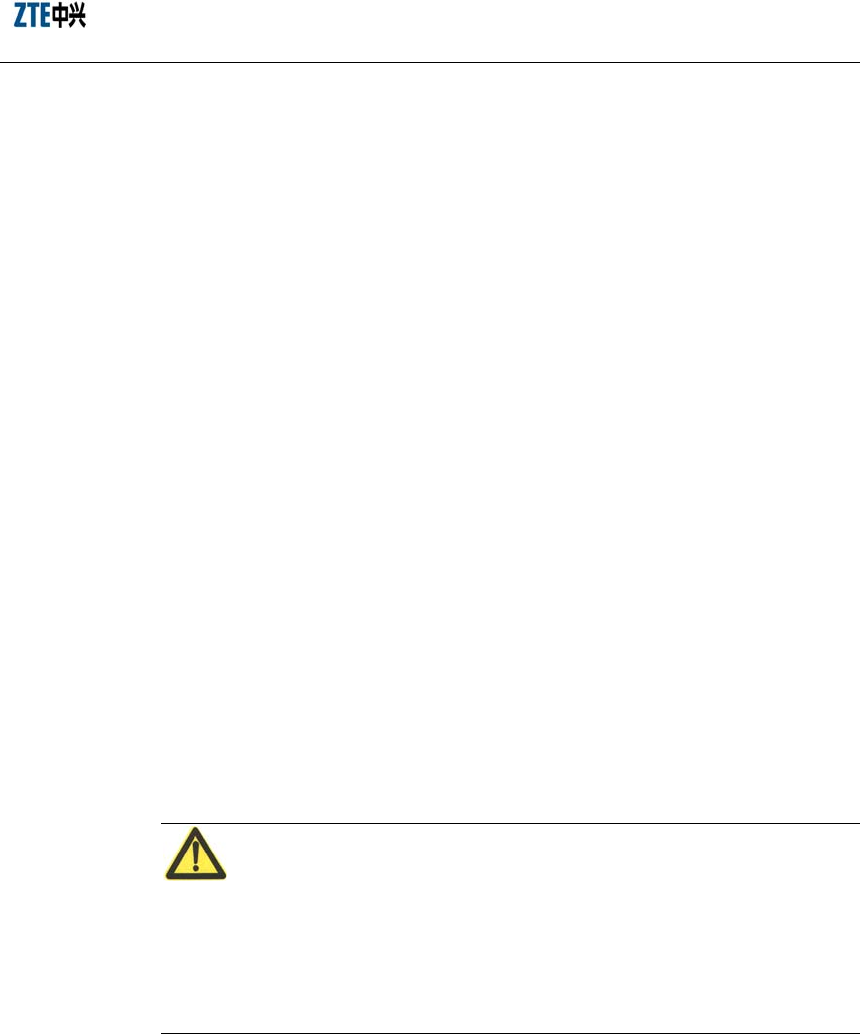
Chapter
Error! Style not defined.
Error! Style not de
fined.
10-25
10.4.8 Installing the Indoor Jumpers
Indoor set top jumpers are used between the lightning arrester connected to the main
feeder and the rack. Usually the finished 2m set top jumpers are used, or the jumpers
can be prepared on site as per the actual length required.
If the 2m finished jumpers are used, they can be directly installed between the lightning
arrester and the rack top.
If the jumpers are prepared on site, 1/2'' feeders should be prepared through cutting
according to the specific length of each jumper. Assemble proper feeder connectors
onto both ends of the feeders according to the feeder connector assembly instructions,
and connect the jumpers between the lightning arrester and rack top.
10.5 Checking and Testing the Antenna Feeders
After installing all the antenna feeders, conduct the SWR test on each of them. The
measured SWR should be less than 1.5 and usually less than 1.3. If this is not satisfied,
check immediately the feeder connectors installed, antenna, feeders and lightning
arresters to find where the problem comes from. For the method of SWR test with
SiteMaster, refer to Appendix G.
10.6 Waterproof Treatment for the Connectors
Caution:
The waterproof sealing for the outdoor jumpers and the feeder grounding clips of the
antenna feeder system is an important part of the antenna feeder installation. It is of
special concern. In the installation process, make sure to use waterproof tapes properly
to ensure the quality of installing the antenna feeder system.
Use 1/2'' jumpers, generally the 3m finished jumpers, between the antenna and main
feeder for transition. Connect the 1/2'' jumper and the feeder and seal their connectors
as follows:
1. Connect and fasten the antenna jumper and the main feeder connector
2. Make waterproof treatment on the connectors in the following steps:
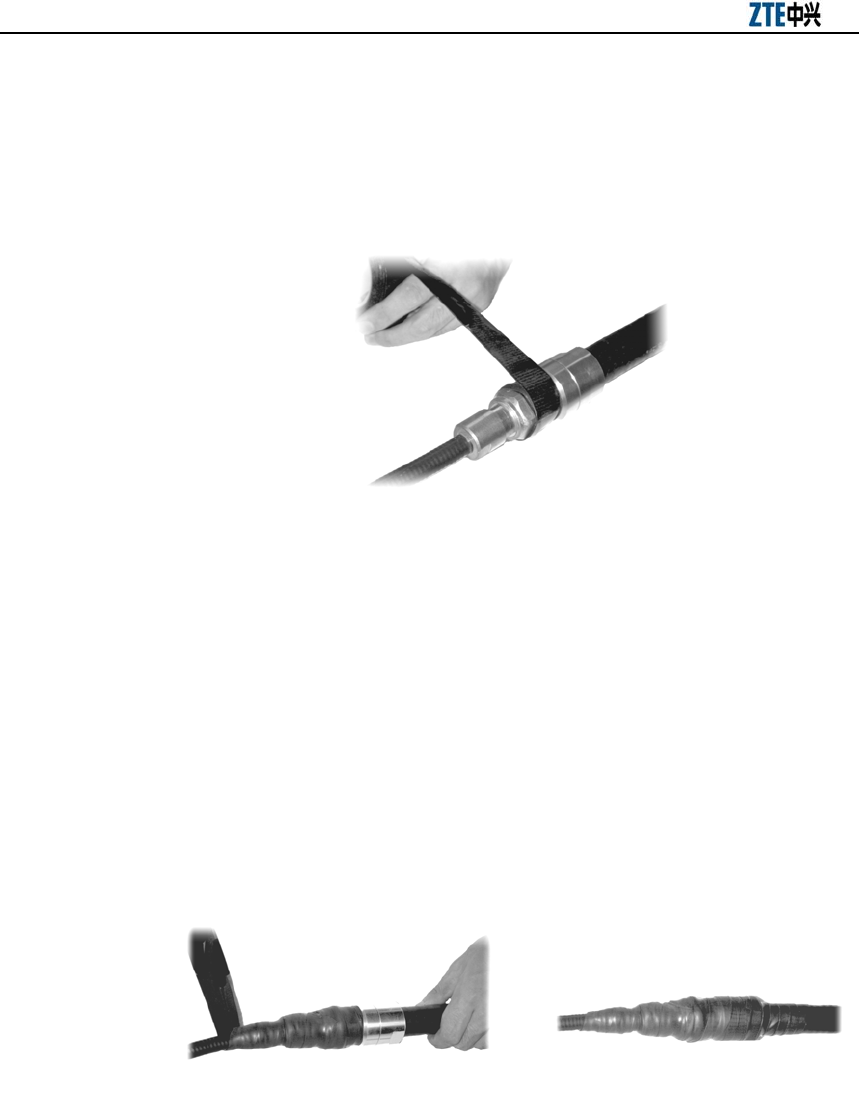
ZXC10-BTS (V5.4) Installation Manual
10-26
1) Cut waterproof adhesive tapes about 200mm long;
2) Wrap the waterproof adhesive tapes from a low position where the connector is
connected and apply them about 200mm long to fill the low-lying parts of the
connector, as shown in Fig. 10.6-1.
Fig. 10.6-1 Wrap the Waterproof Adhesive Tapes (1)
3) Extend the adhesive tapes to double their length when wrapping them. The
direction of wrapping should be the same as the direction of screwing the feeder
connector, lest the feeder connector be loosened during the wrapping process.
4) As shown in Fig. 10.6-2, wrap the adhesive tapes layer by layer and then wrap
them again in the reverse direction. The upper layer covers the lower layer by
about 1/3 to avoid water penetration. Finally, reverse the direction and wrap
them layer by layer again. Apply the tape with three layers without any cut in the
entire process. Wrap the tapes around the feeder connector till they protrude
about 20mm from the feeder connector.
Fig. 10.6-2 Wrap the Waterproof Adhesive Tapes (2)
5) Grip the waterproof adhesive tapes after wrapping them to ensure firm bonding
between the tapes and the feeders/feeder connectors, as shown in Fig. 10.6-3.

Chapter
Error! Style not defined.
Error! Style not de
fined.
10-27
Fig. 10.6-3 Wrap the Waterproof Adhesive Tapes (3)
6) Apply two layers of the PVC tape on top of the waterproof adhesive tape.
During the process, make sure the upper layer overlaps the lower layer by half
the width of the tape.
7) Grip the PVC tapes and the waterproof adhesive tapes to make them tightly
adhered to each other.
8) Tie the two ends of the adhesive tape with straps to prevent it from being aged
or falling off.

FAX: 0086-755-26770160
11-1
11 Installing the GPS Antenna Feeder
System
Summary
This part describes:
● Installation preparation for the GPS antenna feeder
system;
● Structure of the GPS antenna feeder system;
● Installation flow of the GPS antenna feeder system;
● Installation procedure of the parts of the GPS antenna
feeder system;
● Waterproof treatment of the connectors.
11.1 Installation Preparation for the Antenna Feeder System
GPS, as the clock and frequency reference of CDMA, is of great significance.
According to the passive distance measurement principles, GPS antenna receives the
navigation positioning signals from the GPS satellites and demodulates frequency and
clock signals through the GPS signal receiver for use by the related units of the CDMA
base station.
Requirements for the installation of the GPS antenna: The installation position of the
GPS antenna should have a broad view so that the GPS antenna can track satellites as
many as possible. Usually, select a safe place on the roof or at the lower part of the
tower and try to make the GPS feeder short to reduce attenuation.
Requirements for the lightning protection of the GPS antenna: Usually, the GPS
antenna is installed within the 45° lightning protection coverage of the tower. If it is not
within the coverage, the user is required to prepare and install the lightning arrester for
it.
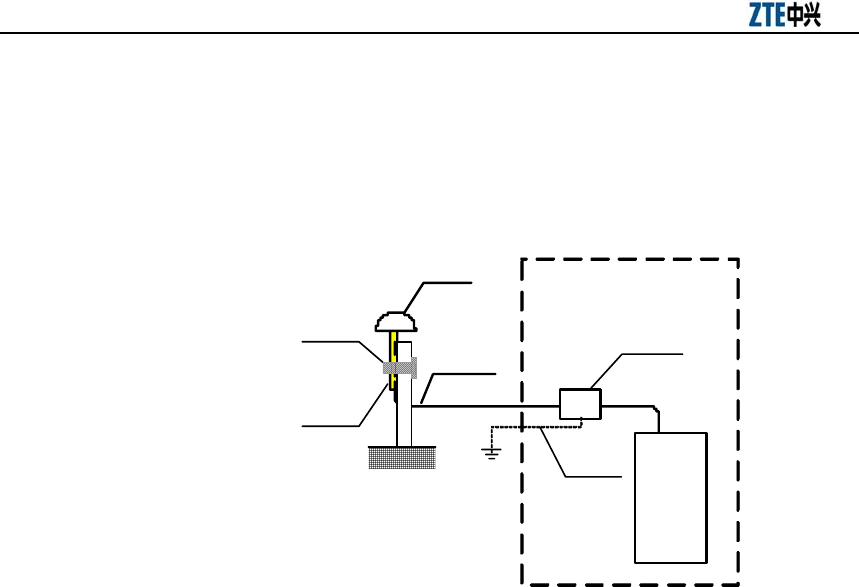
ZXC10-BTS (V5.4) Installation Manual
11-2
Please note that the embracing pole that fixes the GPS antenna must be grounded.
11.2 Structure of the Antenna Feeder System
The structure of the GPS antenna feeder system is as shown in Fig. 11.2-1.
B
T
S
GPS antenna
Coaxial cable
Lightning arrester
Fi xi ng c l i p
Pipe covering
Grounding cable
Fig. 11.2-1
Structure of the GPS Antenna Feeder System
11.3 Installation Flow
Follow the steps below to install the GPS antenna feeder system:
1. According to the preparation of the GPS coaxial cable connector, make the
outdoor connector for the coaxial cable;
2. Thread the connector through the GPS accessory tube and distribute the coaxial
cable from the GPS antenna to the GPS lightning arrester;
3. Screw the outdoor connector of the coaxial cable to the GPS antenna connector;
4. Keep the GPS antenna still while screwing the tube on the GPS antenna;
5. Fix the tube to the embracing pole with a fixing clamp;
6. Cut the coaxial cable according to the installation position of the GPS lightning
arrester, make the indoor connector for the cable, and then connect it to the
lightning arrester. Note that the equipment end and the feeder end of the GPS
lightning arrester must be correctly connected.
7. Distribute the coaxial cable between the GPS lightning arrester and the GPS port
on the BTS equipment.

Chapter
Error! Style not defined.
Error! Style not de
fined.
11-3
11.4 Installing the Parts
11.4.1 Preparing the GPS Coaxial Cable Connectors
1. Stripping
The size of the GPS coaxial cable to be stripped is as shown in Fig. 11.4-1.
6.2 16.7
Fig. 11.4-1 Stripping the GPS Coaxial Cable
2. Welding the core wire
Before welding the core wire, thread the parts with the cable in the sequence as
shown in Fig. 11.4-2. Then weld the cable core wire and the pins. Note that the
cable shielding layer should be open and slipped on the bushing.
Pin Insulating piece Cable shielding
Bushing Pressing tube Nut Cable
Cable core
Tin so lder
Fig. 11.4-2 Welding the Pins of the GPS Connector
3. Parts for Installation
After welding the core wire, put the parts in the sheath. The structure of the
cable assembly is as shown in Fig. 11.4-3.
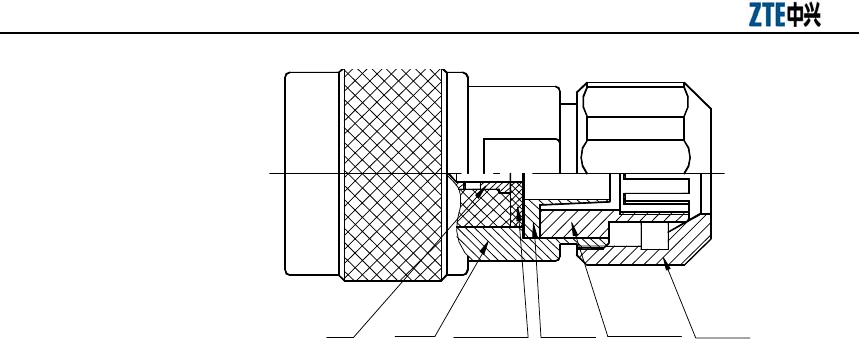
ZXC10-BTS (V5.4) Installation Manual
11-4
Insulating
piece Bushing
Pressing
tube
Shell Nut
Pin
Fig. 11.4-3 Structure of the N-J7A Cable Assembly
11.4.2 Installing the GPS Lightning Arrester
Each GPS system has its own lightning arrester installed between the GPS antenna and
the BTS rack. The lightning arrester should be connected to the outdoor grounding
copper bar via a 6mm
2
grounding cable. For the BTS installed with a lightning arrester
frame, you may fix the GPS lightning arrester onto the frame. In this case, the 6mm
2
grounding cable is unnecessary. Note: The lightning arrester must be connected
correctly.
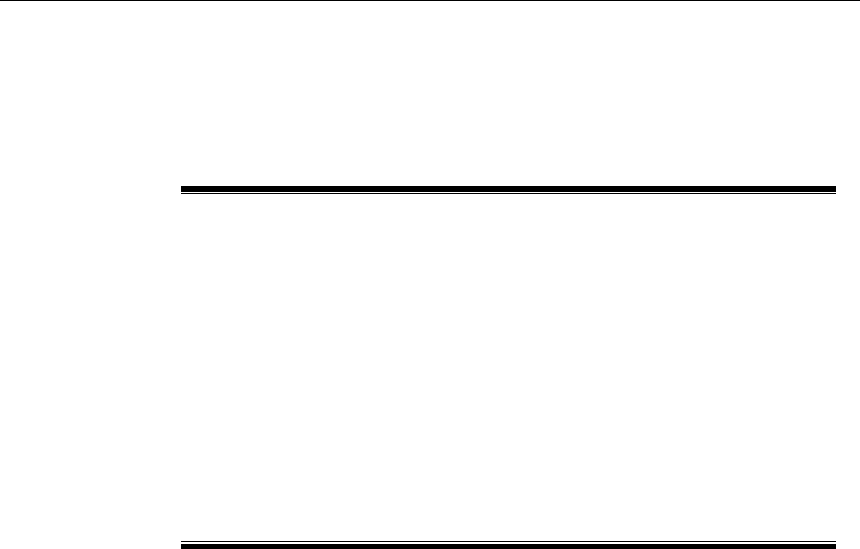
FAX: 0086-755-26770160
12-1
12 Installing the Boards
Summary
This part describes:
● Board types of BTS;
● Installation and replacement methods of the BTS
boards;
● Front panel and interface of some BTS boards;
● Installation sequence of the BTS boards.
12.1 Board Types and Functions of BTS
Modules of the BTS are:
1. DSM
DSM (Data Service Module) lies in the BDS of the BTS. It implements the
trunking, data and signaling processing of Abis interface. It provides 16 E1 lines
externally. Eight are used to connect upstream BSC while other eight to connect
downstream BTS, which support the daisy chain networking mode and can also
function as E1 extension to connect upstream BSC. This board may also connect
to the transmission network to support SDH optical transmission connections.
2. CCM
CCM (Communication Control Module) is the control core for data signaling
routing, signaling processing, resources management and operation/maintenance
of the whole BDS subsystem in BSS.
3. CHM
CHM (Channel Processing Module) conducts modulation and demodulation of
various CDMA channels and implements some power control functions.

ZXC10-BTS (V5.4) Installation Manual
12-2
4. RIM
RIM (Radio Frequency Interface Module) implements the interface between
BDS and RFS. The forward link first sums the baseband data sent from CHM as
per different sectors, multiplexes the summation result, HDLC signaling and
PP2S from GCM, and then sends them to RMM. Then the reverse link receives
the reverse baseband data and HDLC signaling, selects them according to the
signaling sent from CCM, then sends the selected data by broadcasting to the
CHM and the HDLC data to the CCM for processing. RIM lies in the BDS
frame and supports active/standby configuration.
5. SAM
SAM (Site Alarm Module) monitors the running status of the PM and fans, as
well as access control, flood, temperature, humidity, and smog signals. It will
then report the results to the OMC console via CCM. In addition, it provides
RS232 and RS485 interfaces for the connections with external monitoring
devices.
6. GCM
GCM (GPS Control Module) provides reliable and high-stability clock source
for various modules of BTS. The major clocks include TOD (UTC timing
message), system clock (16CHIP and PP2S), circuit clock (2MB and 8K) and
RF reference clock (30M).
7. SNM
SNM lies in the BDS and implements STM-1 downlink and uplink functions for
BTS.
8. CDM
CDM (Clock Distribution Module) distributes the clock of GCM in BTSB to
TRX. The RF reference clock in BTSB is transmitted as the 30M MLVDS clock,
while TRX needs the 10M/12M analog clock. Therefore, CDM is used to
convert the 30M MLVDS clock sent from GCM to TTL signals and generate the
10M/12M analog clock needed by TRX in HIRS through the phase-lock loop.
9. RFE

Chapter
Error! Style not defined.
Error! Style not defined.
12-3
RFE module is the main module connecting the internal system of RFS in the
BTS and the external antenna of the BTS. Its terminal port is the RF port at the
top of the BTS and the test port of the BTS for system testing. It has great
influence on the receiving sensitivity and exit transmitting power of the whole
BTS system.
10. HPA
HPA (High Power Amplifier) amplifies the power of TRX’s forward
transmission signals so that the signals go through the duplex filter of RFE at a
proper power value and then transmitted by antenna into the cell. The CDMA
system requires that HPA should have certain linearity.
11. TRX
TRX is the junction connecting RF and baseband signals. One TRX corresponds
to one sector of one carrier. In the reverse channel, TRX receives the main and
diversity receiving signals of the sector, conducts down conversion, median
frequency filtering, AGC processing and I/Q demodulation on these signals to
convert the received modulated RF signals into baseband I/Q signals. In the
forward channel, TRX conducts I/Q modulation, median frequency filtering and
upward conversion on the baseband I/Q signals to convert them into modulated
RF signals, while also performing TPTL power control.
12. PSMD
PSMB is the main power board of the whole BTS.
13. PSMC
PSMC (±12V power) conducts DC/DC conversion from -48V to ±12V. The
max. output of +12V is 25A and that of -12V is 8A, both providing the RFS
with working power supply in the 1+1 backup mode. This module is also
available with the remote control and teleaction functions.
14. PPM
PPM (27V power board) conducts DC/DC conversion from -48V to +27V. It
has protection functions for input over/under voltage, output over/under voltage,
output over-current, and over-temperature. It employs the
temperature-controlled forced cooling structure and is also available with the
remote control and teleaction functions. Output current of one PPM is 25A.

ZXC10-BTS (V5.4) Installation Manual
12-4
When the load exceeds 25A, the board starts limiting current. The HPA is
provided with the working power supply by several 27V PPMs connected in
parallel to work in the N+1 backup mode.
12.2 Introduction to Main BTS Modules
12.2.1 RFE Module
ZTE currently provides two types of RFE (RF Front End) modules. Select the module
according to the BTS configuration as follows:
● RFE-DUP: Applicable to single-carrier BTS and two-carrier BTS;
● RFE-DIV: Diversity RX branch, applicable only to single-carrier BTS.
The panel of the two types of RFE module is as shown in Fig. 12.2-1. All RF interfaces
are located on the front panel, including the interfaces for N connection with the
antenna and the connection to TRX and SMA of HPA.
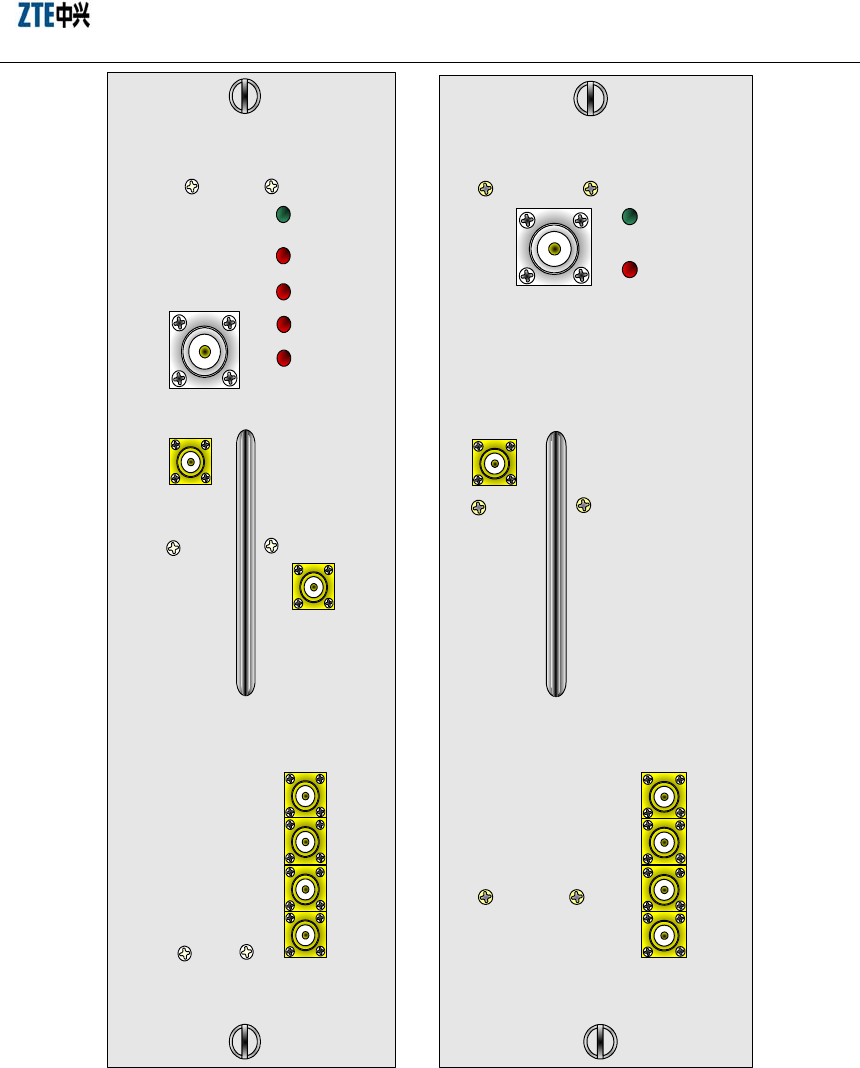
Chapter
Error! Style not defined.
Error! Style not defined.
12-5
PWRON
LNAALM
RFE-DUP
RX1
RX2
RX3
RX4
ANT RFLOW
VSWR15
VSWR30
TEST
HPA
PWRON
LNAALM
RFE- DIV
RX1
RX2
RX3
RX4
ANT
Fig. 12.2-1 Panel of RFE Modules
Description of the interfaces on the RFE panel is given in Table 12.2-1.

ZXC10-BTS (V5.4) Installation Manual
12-6
Table 12.2-1 Description of the Interfaces on the RFE Panel
Name of the
Interface End
Signal To Connector Connection
Mode
ANT TX power signal to the
antenna and RX signal of the
antenna
Cabinet-top antenna
interface
N
connector
1/2" RF cable
HPA Power signal output by HPA RF OUT end of HPA SMA RF cable
RX1 One of the four power
branches of the received
signal amplified by LNA
RX end of TRX of the
first carrier
SMA RF cable
RX2 One of the four power
branches of the received
signal amplified by LNA
RX end of TRX of the
second carrier
SMA RF cable
RX3 One of the four power
branches of the received
signal amplified by LNA
Test interface SMA A 50Ω terminal
load is connected
when the
interface is not in
use.
RX4 One of the four power
branches of the received
signal amplified by LNA
Reserved SMA A 50Ω terminal
load is connected
when the
interface is not in
use.
12.2.2 HPA
The front panel of HPA is as shown in Fig. 12.2-2.
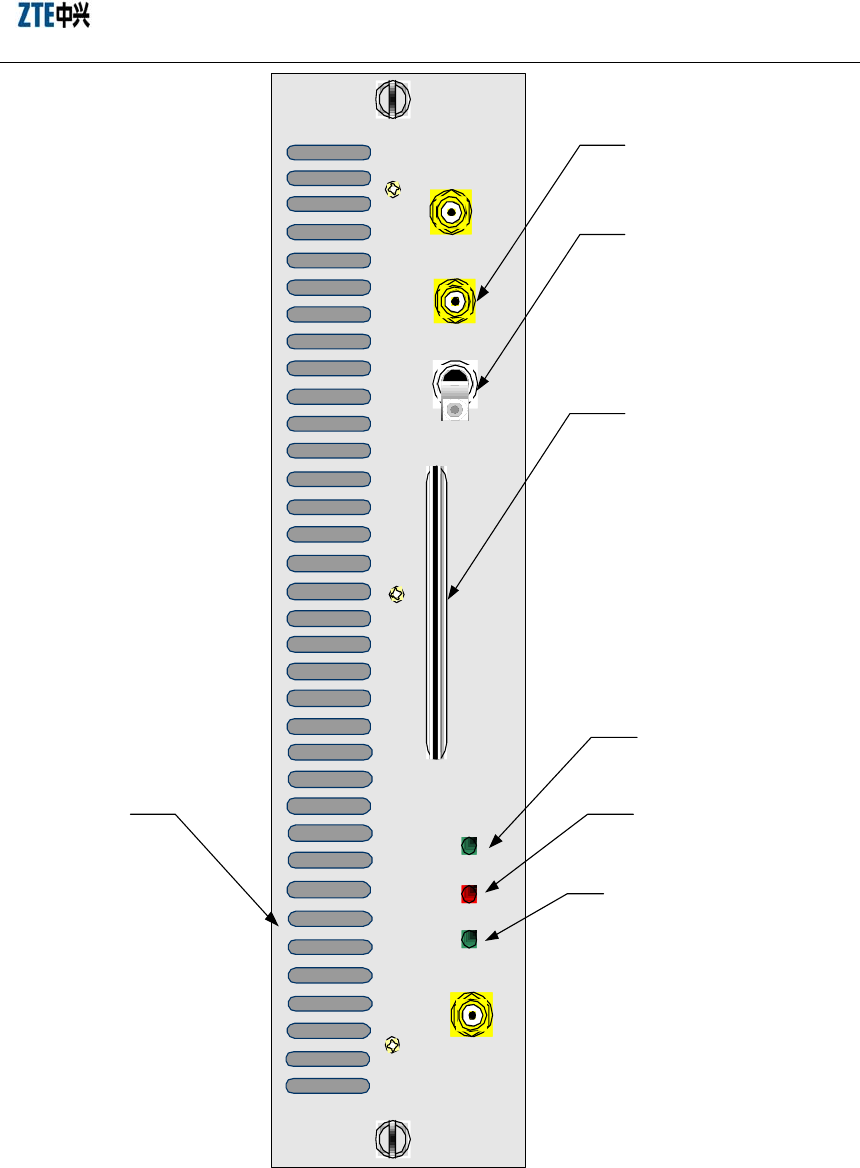
Chapter
Error! Style not defined.
Error! Style not defined.
12-7
PWRON
ALM
HPA
RFON
OFF
RFIN
ON
TEST
RF OUT
Test por t
Power swit ch
Handle
Power indication
VS WR a la rm
Output power alarm
Wind grid
Fig. 12.2-2 Structure of the HPA Front Panel
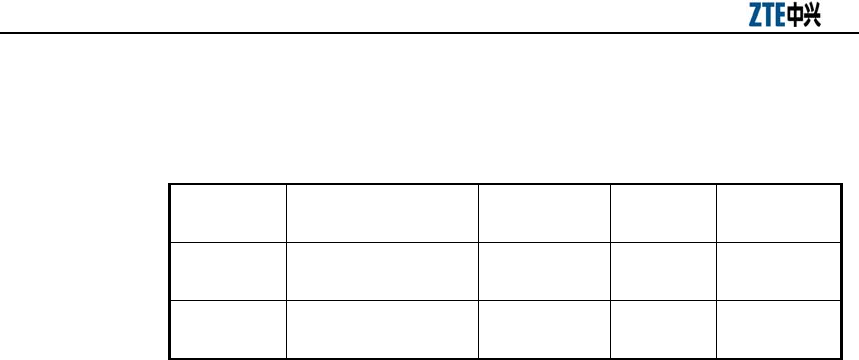
ZXC10-BTS (V5.4) Installation Manual
12-8
Description of the HPA front panel is given in Table 12.2-2.
Table 12.2-2 Description of the Interfaces on the HPA Front Panel
Name of the
Interface End
Signal To Connector Connection
Mode
RF IN Forward TX signal sent
by TRX
TX end of TRX SMA RF cable
RF OUT Amplified forward
power signal
HPA end of
RFE
SMA RF cable
12.2.3 TRX
The structure of the TRX front panel is as shown in Fig. 12.2-3.
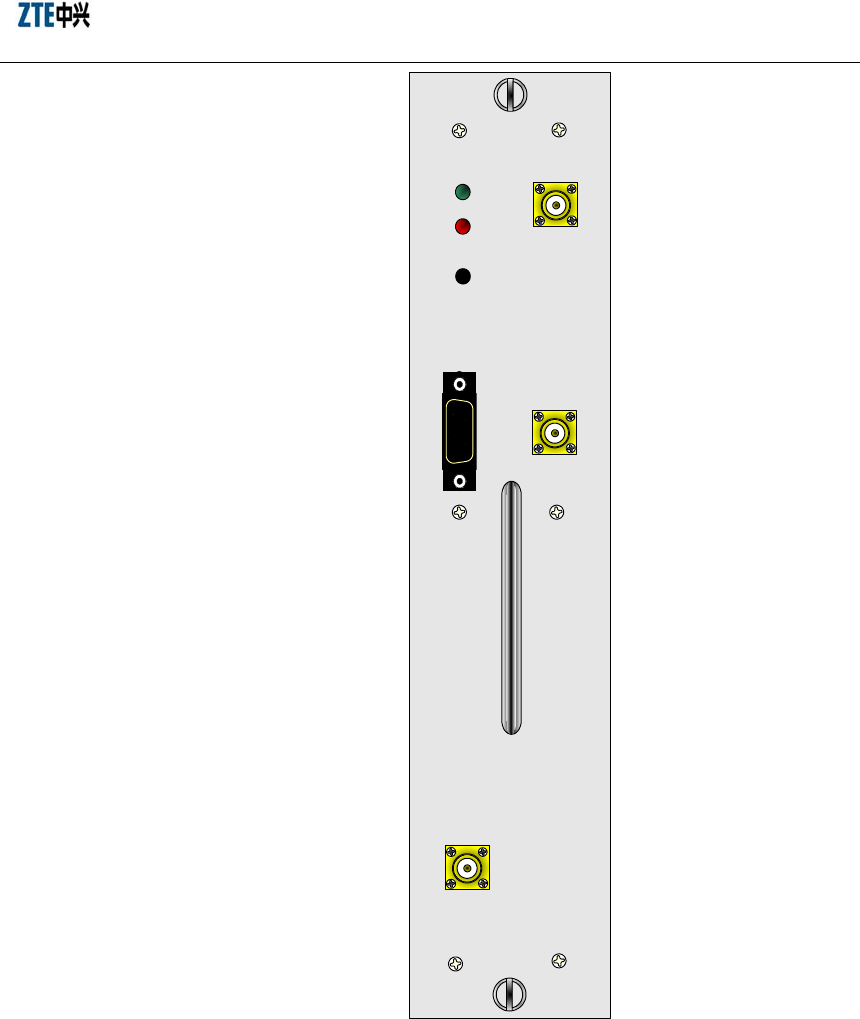
Chapter
Error! Style not defined.
Error! Style not defined.
12-9
RUN
ALM
TRX
TX
RST
RX1
RX2
RS232
Fig. 12.2-3 Structure of the TRX Front Panel
Description of the RF interfaces is given in Table 12.2-3.

ZXC10-BTS (V5.4) Installation Manual
12-10
Table 12.2-3 Description of the TRX RF Interfaces
Name of the
Interface End
Signal To Connector Connection
Mode
TX Forward TX signal
sent by TRX
RF IN end of HPA SMA RF cable
RX1 Reverse RX signal of
RFE
RX output end of a
corresponding RFE
in the same sector
SMA RF cable
RX2 Reverse RX signal of
RFE
RX output end of
another
corresponding RFE
in the same sector
SMA RF cable
12.3 Installing and Replacing Boards
After installing and fastening the BTS rack, the boards and modules can be inserted
into their plug-boxes. Boards and modules in the plug-boxes of the BTS rack can be
inserted both from the front and the rear. Insert them in the correct place during the
installation. Check the socket slot during installation.
1. Structure of the boards and the modules
● Each board and module is installed with connector on its back to connect with
the backplane, as shown in Fig. 12.3-1;
● The board is installed with a panel bar on its front, which has handle on it to
plug/unplug the board.
● There are board name and indicators on the panel bar. The board name indicates
the circuit board type, and the indicators indicate the working status of the board,
as shown in Fig. 12.3-2;
● The circuit boards are vertically inserted into the plug-in shelf in the rack and
connected with one another by the system bus on the backplane.
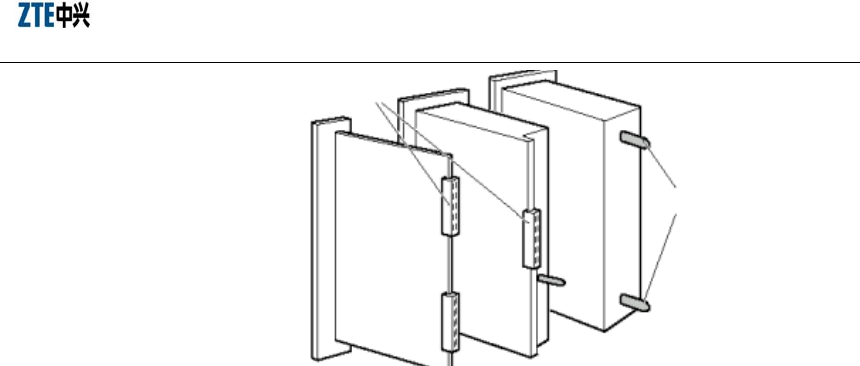
Chapter
Error! Style not defined.
Error! Style not defined.
12-11
Socket connector
Fi xi n
g
pi
n
Fig. 12.3-1 Connectors on the Rear of the Boards and Modules
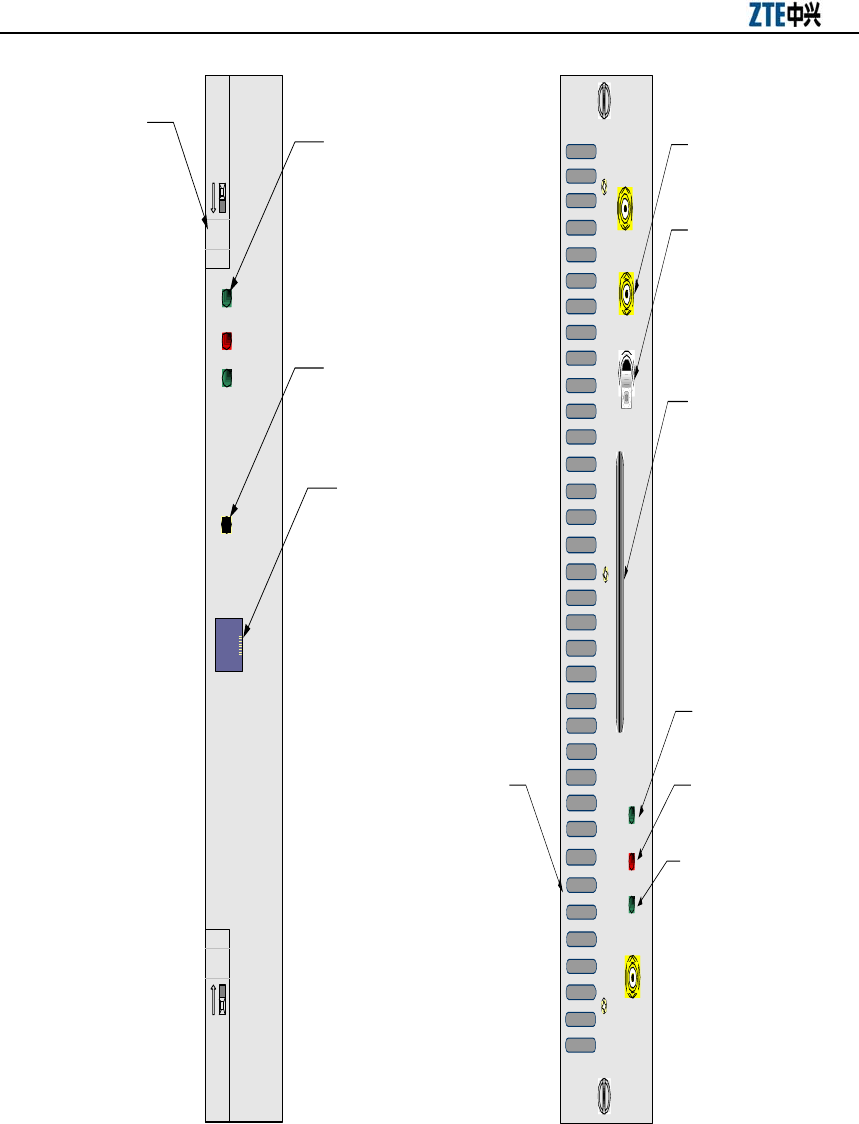
ZXC10-BTS (V5.4) Installation Manual
12-12
RUN
ALM
RST
CHM
TEST
BUSY
Clasper
LED
Reset button
Te st por t
PWRON
ALM
HPA
RFON
OFF
RFIN
ON
TEST
RF OUT
Test port
Power switch
Clasper
Power indication
VSWR alarm
Output power alarm
Wind grid
Fig. 12.3-2 Front Panel of the Boards and Modules
2. Plugging boards and modules

Chapter
Error! Style not defined.
Error! Style not defined.
12-13
1) Be sure to wear the antistatic wrist ring when plugging a board or a module.
2) Take the boards and modules out of the antistatic bags, and check if there is any
parts missing or damaged;
3) Be sure to insert the board to the right place indicated by the board name on the
panel bar;
4) Insert the circuit board vertically along the guide slot till the circuit board cannot
be inserted further, which indicates that the circuit board has been exactly in
place. Never insert the circuit board with extra force, lest the pins on the
backplane be bent or broken.
3. Locking the board
When the board is inserted in place, press down the handle till it clicks, which
indicates that the board is clipped by the spring.
4. Locking the module
When the module is inserted in place, fasten it with the spring nail on the panel.
5. The boards PPM, PSMC, PSMD and HPA in the BTS rack are available with
their own power switches. They should not be plugged until being powered off.
Other boards in the BTS rack (CHM, CCM, CMD, SNM, SAM, DSM, TRX,
RFE and RIM) can be hot plugged.
12.4 Introduction to BDS Plug-in Shelves
The slot diagram of the BDS plug-in shelf is shown in Fig. 12.4-1.
R
I
M
C
H
M
C
H
M
C
C
M
C
C
M
S
N
M
G
C
M
C
D
M
S
A
M
D
S
M
G
C
M
C
H
M
C
H
M
D
S
M
S
N
M
B
I
M
Fig. 12.4-1 Slot Diagram of the BDS Plug-in Shelf
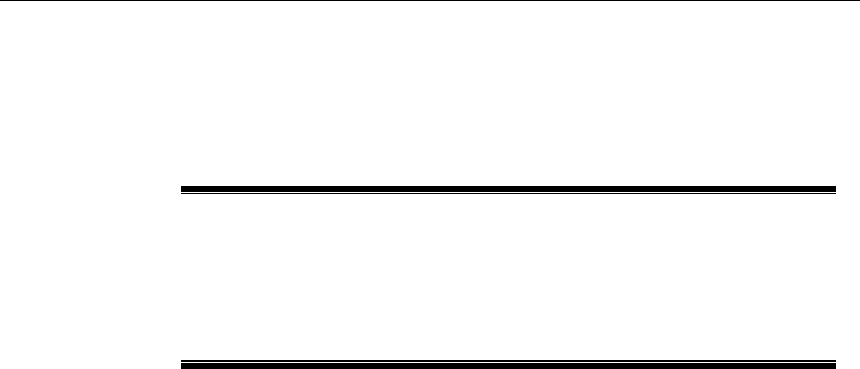
FAX: 0086-755-26770160
13-1
13 Hardware Installation Check
Summary
This part describe the check of the BTS hardware
installation.
After hardware installation is completed in BTS, the installations should be checked
before they are powered on.
13.1 Cabinet Check
An indoor cabinet involves the installation of a BTS rack and other cabinets (such as
DC/AC power cabinets). A cabinet, when installed, should be checked as follows:
1. The rack installation location conforms to the design drawing.
2. A rack, when fixed, should be firmly erected in compliance with the earthquake
proof requirements for an earthquake of magnitude 7 on the Ritcher Scale.
3. The levelness error of a cabinet should be less than 3mm, but its vertical missing
should be no more than 3mm. The gap between two adjacent stands should be
no more than 3mm.
4. The front door of the rack should be flush with the front edges of other
equipment, without any concave or convex.
5. The front of the rack should be at 1m away from the wall, and the rear of the
rack 0.8m away from wall.
6. The parts on the rack should not go off or damaged. The rack should be painted
well and the labels on it should be correct, clear and complete.
7. Check all over the cabinet to make sure that no metal scrap or conducting wire is
left. The cabinet inside is clean and has no sundries.
8. All screws should be tightened with flat washers or spring washers placed
correctly.

ZXC10-BTS (V5.4) Installation Manual
13-2
9. Each stand should be equipped with 4 partition insulators. If installed close to
walls, some of them should be placed between each stand and walls to make a
cabinet and walls insulated.
10. The stand supporter should be consistent with the hole sites of expansion
screws.
11. The upper plane of the conductive floor in the equipment room is no higher than
the lower surface of the stand lest the thermolysis of a stand should be affected.
12. After all cables are laid out, the small cover plates of the wire outlets at the set
top should be pushed forward to cover the wire outlets and prevent rodents
entering the cabinet.
13. In case of a combined cabinet, check whether the cabinets are well arranged and
connecting pieces at the combined set top should be firmly installed.
14. The surface of the integrated equipment should be clean and tidy and the paint
outside it should be in good condition. The identifications should be correct,
clear and complete.
15. The front door of a cabinet must be easily opened or closed.
13.2 Check of cabling rack
In terms of a cabling rack, the hardware installation check is required as follows:
1. The location and height of the cabling rack should meet engineering design
requirements.
2. The flat steel of the cabling rack should be flat and straight, without any
apparent warping or skewness.
3. Each cabling rack should be equipped with a ground wire. All points of
connection should be superior in electrical performance and they are well
connected with the grounding body in the equipment room.
13.3 Laying, Binding and Identification of Cables
As follows are the principles of laying and binding cables:

Chapter
Error! Style not defined.
Error!
Style not defined.
13-3
1. The cables are laid flat and straight, without any apparent fluctuation, skewness,
crossing or jump wire in air. Any remaining length should be curled, bound and
laid in a cable trough.
2. Cables should be bent smoothly and evenly and the outer part of the arc should
be as vertical or horizontal as a direct line.
3. Power cables and signal lines are routed, with over 150mm in between each
other.
4. Both terminals of the cables should be clearly labeled or marked to prevent
connection mistakes.
5. Connector locations should be compact, firm, well-contacted and upright
without broken or bending.
6. After being laid, cables should be trimmed to make them look straight, tidy and
pleasing to the eye, without any crossing.
7. Cable straps should be made tidy and pleasing to the eye. Cable clips should be
evenly spaced, neither too tight nor loose, and go in the same direction.
8. Any excess cable strap should be cut and all indoor cable straps must be cut
from the root, without any tips left.
9. Some residue should be left when all outdoor cable straps are cut after binding.
10. All cable straps must be cut from the root and no tip is left.
11. Each label identifies the uses of a cable and the labels with the same content on
it should be attached on both terminals of the cable.
12. Wrap labels with some cellulose tape to prevent any loosening.
13. All cables, especially main feeders and indoor 1/2" jumpers, should be labeled.
All labels should be arranged in a tidy and beautiful way and go in the same
direction.
13.4 Installation Check in terms of power cables and ground wires
The installation check in terms of power cables and ground wires is required as
follows:

ZXC10-BTS (V5.4) Installation Manual
13-4
1. The power cables and ground wires in the equipment room should be laid in
accordance with engineering design requirements.
2. The PGND protective grounding wire on a BTS rack employs 35mm
2
yellowish
green or yellow copper-core cables and are connected with indoor PGND
grounding copper bars. They should be well contacted and kept firm.
GND/BGND ground wire employs 25mm
2
black copper-core cables and -48V
power cable employs 25mm
2
blue copper-core cables. Both ground wires and
power cables should be laid straight and well connected.
3. An earth bus should be directly connected with an indoor ground wire bus
instead of being connected with any other equipment. The line width of the earth
bus must be more than 50mm
2
.
4. Each grounding point in the grounding copper bar is connected with one piece
of equipment alone.
5. The protective grounding wire and AC neutral line are routed instead of being
placed or used together.
6. AC neutral line in the power room is independently grounded.
7. The indoor ground resistance is less than 5Ω.
8. Each cable is identified clearly and correctly.
9. The ground wire of a power cable, when laid, should be bound separately from
other cables.
10. The remaining length of the ground wire and power cable should be cut off
instead of coiling it up and reserving it.
11. The copper lugs on both terminals of power cables and ground wires should be
soldered or pressed firm.
12. The power cable and ground wire should be of whole material and no connector
is allowed in the middle.
13. The grounding bar should be insulated from walls and the ground wire extends
as short a distance as possible.
14. The primary power supply is correctly connected with the power supply
terminals on the rack.

Chapter
Error! Style not defined.
Error!
Style not defined.
13-5
15. The lifting lug of a power cable should be soldered or pressed firm and upright.
16. The power cable and copper lug must be contacted in a reliable and firm way
and are sealed with an adhesive tape. The copper lug must be connected firmly
with the power cabinet (or the BTS rack).
17. Insulated protective sleeves are well installed on both connecting terminals of
the power supply on the rack top.
18. Power cables, ground wires, trunk lines and RF cables should not be broken or
damaged.
19. The cable labels on both terminals of power cables and ground wires should be
clear and correct.
20. The bare wires at the connecting terminals and lug handle should be tightly
wrapped with insulating tape or put in a heat-shrink tube instead of being
exposed to outside.
21 The connecting terminals should be equipped with flat washers and spring
washers.
13.5 Check of T1 Cable Installation
The installation check of T1 cables involves the following:
1. T1 cable connectors are reliably installed, without any short-circuit or damage.
2. T1 cables are connected correctly and labeled clearly.
3. No T1 connector gets loose. Test with a multimeter whether the connector shell
and ground wire system are well connected. Otherwise, it shows that the ring
flange of the connector and shell are in poor contact.
4. The T1 cables on the set top should reserve some margin length. Do not stress
them in case they cannot be reliably connected with the rack connectors when
the cabling rack vibrates.
5. T1 cable connectors must be connected reliably.
13.6 Sensor Installation Check
Requirements:

ZXC10-BTS (V5.4) Installation Manual
13-6
1. The temperature/humidity sensor is vertically installed and cables are correctly
connected with the set top.
2. The smog sensor is horizontally installed and cables are correctly connected
with the set top.
13.7 Installation Check of Connections inside a Cabinet
The connections inside a cabinet are checked as follows:
1. The RF cables between modules within the rack should be connected in a
correct and reliable way.
2. The screws of all modules within the rack must be rotated to the greatest extent
lest modules and backplanes should not be connected reliably.
3. Any unused connector is screwed on with a matching terminal.
4. The RF cables between TRX, HPA and DUP should be parallel as much as
possible and cannot be extended too tightly. Some residue should be left at the
bending part and connectors connected reliably.
13.8 Installation Check of Indoor 1/2" Jumpers
Indoor 1/2" jumpers involve the following installation check:
1. According to the name plate of the main feeder, use 1/2" jumpers to connect
with the connecting terminals on the rack top.
2. The labels of 1/2" indoor jumpers should be marked with corresponding sectors
and the length of the main feeder.
3. Indoor jumpers should be neither too long nor too short and have beautiful
cabling. They should be bound on the cabling rack in order.
4. The cabling should provide convenience for maintenance and future capacity
expansion.
5. Jumpers should be laid by the layer and sector.
6. There should be 30cm flat and straight where jumpers and a lightning arrester
are connected.

Chapter
Error! Style not defined.
Error!
Style not defined.
13-7
13.9 Installation and Check of Lightning Arrester
The lightning arrester is installed as follows:
1. An RF lightning arrester is connected with the connectors of the feeder on both
terminals and threads should be aligned and tightened.
2. The 6mm
2
yellow ground wire of a GPS lightning arrester must be connected
with an outdoor ground wire bus and is well contacted with outdoor grounding
copper bars.
3. The RF lightning arrester and the GPS lightning arrester should be hung
between two crosspieces of the cabling rack. The lightning arresters should be
insulated from the cabling rack without contact.
13.10 Installation and Check of Lightning Arrester Rack
The lightning arrester is installed as follows:
1. A lightning arrester rack installed should be insulated from the cabling rack.
2. The lightning arrester should be installed on the lightning arrester rack in a firm,
reliable and beautiful way.
3. The grounding copper wire of a lightning arrester rack must be routed to outdoor
grounding copper bars for reliable grounding.
4. When led outdoors, the grounding copper wire of a lightning arrester rack must
be insulated from indoor conductors.
13.11 Installation and Check of Main Feeder and GPS Feeder
The main feeder and GPS feeder are installed as follows:
1. To make a main feeder connector, you have to use a special cutter. The profile of
the main feeder should be flat and smooth. The main feeder has no copper scraps
in its copper tube. The feeder connector should be made normally.
2. 7/8" feeder connector should be tightened with a big spanner and installed in
place to avoid any abnormal standing wave ratio due to false connections and
ensure normal system running.

ZXC10-BTS (V5.4) Installation Manual
13-8
3. The feeder between the tower top and the equipment room should be grounded
in at least three points. The first location is within 1m from the tower up to the
platform. The second is within 1m from the tower to the front of the outdoor
cabling rack. The third is within 1m between the feeder and the feeder window.
The grounding points should be bound firmly with proper waterproof measures.
Where a grounding kit is installed, the outer sheath of a feeder is removed
according to the kit size. When installing the grounding kit, pay attention to
waterproof measures. The terminal of the grounding kit connected with a ground
wire should face downward lest any rainwater should flow into the feeder along
the ground wire.
4. If a tower is above 60m and needs a longer feeder, another feeder grounding clip
should be placed in the middle of the tower.
5. If a feeder is off the tower and routed for above 20m at the building top or on the
cabling rack before going into the room, another grounding clip for lightning
protection should be put at the building top or on the cabling rack.
6. The terminals of the grounding clip of a feeder should be fixed on the steel plate
of a nearby tower.
7. The outdoor grounding copper bar employs a special reliable path to an
underground ground grid. The line width should be more than 50mm
2
.
Otherwise, users should lay connecting cables as soon as possible.
8. For a building without a tower, the antenna feeder ground at the top should be
connected with the nearby lightning protection ground grid on the roof.
9. If the feeder employs a downward cable ladder to go along walls downward
from the building top and enters a room, the cable ladder should be grounded.
10. The ground wire of a feeder should be led from up to down. The separation
angle between the feeder and ground wire should be no more than 15
º
.
11. The cabling of the feeders should be visually appealing without crisscrossing.
They should be well arranged and have no apparent twists and turns. The feeders
entering a room should be tidy, flat, and straight and in the bending of the cables
should be identical. The main feeders are correctly connected and the sectors
concerned are correct too.

Chapter
Error! Style not defined.
Error!
Style not defined.
13-9
12. The minimum bending radius of a feeder should be no less than 20 times the
feeder radius, and the bending radius of the main feeder should be more than
0.3m.
13. The cabling of the main feeders should be planned. When the cabinet front is
parallel to the direction in which a feeder enters a room or the cabinet back is
facing the direction in which a feeder enters a room, the main feeders within a
sector should be arranged as a row. The arrangement order of each row should
be consistent. When the cabinet front faces the direction in which a feeder enters
a room, one sector is arranged as a column and the arrangement order of each
column should be consistent.
14. The feeder connector should have no bare copper sheet. Two name labels should
be bound on both terminals of a feeder to ensure that feeders correspond to
antennas. Write corresponding lengths on a feeder name plate.
15. Avoid any dry joint in soldering GPS core wire.
16. GPS copper core and external outer layer cannot be short-circuited. The core pin
of a feeder connector should be parallel to the external end face of a GPS feeder
connector.
17. GPS feeder connectors should be tightened.
13.12 Installation and Check of Feeder Windows and Waterproof
Bend of the Main Feeder
Feeder windows and waterproof bend of the main feeder are installed as follows:
1. A feeder window is fixed on one indoor wall and the feeder hole bulging on the
feeder window faces outdoors.
2. The glue injection hole on the packing gland on the feeder sealing window
should be sealed upward and luffer boards should be installed on one indoor
walls.
3. When a feeder window is installed at the building top to lead a feeder into the
room, it should be well sealed.
4. When an outdoor feeder enters the equipment room, a waterproof bend must be
made at the outdoor feeder window. The lowest point of the waterproof bend is
required to be 10cm ~20cm lower than the lower edge of the feeder window.

ZXC10-BTS (V5.4) Installation Manual
13-10
5. The minimum bending radius of a feeder should be no more than 20 times the
feeder radius, and the bending radius of the main feeder should be more than
0.3m.
6. The indoor and outdoor parts of a feeder should be both above 0.5m. There
should be 0.3m flat and straight at the lightning protection rack.
13.13 Installation and Check of Three-way Feeder Card
A three-way feeder card is installed as follows:
1. A three-way feeder card should be fixed on an outdoor cabling rack.
2. The intervals between the feeder fixing clips should be even and go in the same
direction.
3. A feeder card every 1.5m should be installed on the main feeder.
13.14 Installation and Check of Outdoor 1/2" Jumpers
Outdoor 1/2" jumpers are installed as follows:
1. Antennas and 1/2" jumpers. The 1/2" jumpers and main feeders should also be
correctly connected. The threads of the connectors should fit in and the
connectors are tightened.
2. The jumper connected with an antenna should be bound along the support
crossbar to the steel frame of the tower.
3. The wrapping requirements between an antenna and 1/2" jumper connector and
the wrapping between a 1/2" jumper and the main feeder connector are as
follows: 1) the connector is wrapped with some waterproof self-adhesive tape; 2)
the waterproof self-adhesive tape at an antenna terminal must be wrapped until
the antenna root; 3) the feeder terminal should be wrapped until 10cm away
from the connector; 4) the waterproof self-adhesive tape is wrapped with an
insulating tape longer than the waterproof self-adhesive tape.
4. At the joint between the jumper and the antennas, they should be parallel to each
other with 30cm in between.
5. The connector is wrapped with a waterproof self-adhesive tape, which must be
extended to an antenna root. Wrap the feeder terminal until 10cm away from the

Chapter
Error! Style not defined.
Error!
Style not defined.
13-11
connector. Wrap the waterproof self-adhesive tape with an insulating tape longer
than the waterproof self-adhesive tape.
6. All outdoor jumper connectors should receive waterproof sealing treatment and
a jumper should be equipped with a waterproof bend.
13.15 Installation and Check of an Antenna
Requirements:
1. An antenna support and a tower should be connected in a reliable and firm way.
2. Check the model of the antenna in use to make sure that it conforms to
networking planning.
3. The hanging height of an antenna refers to the distance between the ground and
the middle of the antenna. It is required that the actual hanging height of an
antenna conforms to network planning, and the antenna should be installed as
designed.
4. The RF antenna and the GPS antenna should be included in the protection area
of a lightning arrester (the area within the downdip of 45º from the lightning
arrester).
5. Measure the azimuth of an antenna. In case of a unipolarization directional
antenna, each antenna should be measured. The actual azimuth of an antenna
conforms to network planning and two antennas within the same sector goes in
the same direction. The azimuth error of the directional antenna is no more than
±5º.
6. Measure the actual mechanical downdip of an antenna with an angulometer. In
case of a unipolarization antenna, each antenna should be measured. An omni
antenna will not be checked and a directional antenna should have the azimuth
error of no more than ±0.5º. The actual mechanical downdip of an antenna
conforms to network planning and two unipolarization antennas have consistent
downdip.
7. The electrically controlled pointer antenna is adjusted with a spanner, and the
electrically controlled digital antenna is controlled with key input in the
equipment room. Note that the control line connected with the antenna is
vulnerable. In the case it is broken, it has to be directly adjusted with a spanner

ZXC10-BTS (V5.4) Installation Manual
13-12
at the antenna terminal. Each of the unipolarization antennas should be
measured. The actual electrically controlled downdip of an antenna conforms to
network planning and two unipolarization antennas should have consistent
downdips. This is not required if it is not an electrically controlled antenna.
8. All antenna poles should be firmly installed and well grounded. All antenna
poles are required to be vertical to the ground and the vertical error should be
less than 2º.In particular, all antennas must be vertical to the ground. Check with
a line hammer to keep the vertical error less than 2º.
9. The receive/transmit horizontal interval of an omni antenna should be no less
than 3.5m.
10. An omni antenna should be at least 1.5m away from the tower while a
directional antenna should be at least 1m away from the tower.
11. The jacket top of an omni antenna should be level to a support or slightly higher
than the support top.
12. When an omni antenna is installed on a roof, the horizontal interval between the
omni antenna and antenna lightning arrester should be no less than 2.5m.
13. An omni antenna installed on a roof should avoid blind area.
14. Check the matching relationship of the main diversity antennas within the
sectors and the set top jumpers on the rack.
15. The diversity distance between two antennas within one sector refers to the
vertical distance between the parallel lines of the two antennas front surfaces. It
is not the distance between two antennas. Diversity distance is irrelevant to
bipolarization antenna. The diversity distance should be 3.5m for 800M system,
1.5m for 1.9G system, and 6.7m for 450M system.
16. The vertical interval between directional antennas within different sectors
installed on the same antenna support should be more than 0.6m.
17. When isolated from an antenna in G network, the vertical separation should be
more than 1m, and the horizontal separation should be more than 2m.
18. GPS antenna should be vertical, secure, in a position as low as possible, and
without barrier. The GPS spatial angle should be more than 90ºC.

Chapter
Error! Style not defined.
Error!
Style not defined.
13-13
19. When there is no tower, the GPS antenna should be installed on the building top
and equipped with a standalone lightning arrester.
13.16 Check of the Standing Wave Ratio of a Feeder
The standing wave ratio of a feeder is checked as follows:
1. Measure the standing wave ratio after antennas and all feeders are installed.
2. The terminal of the indoor 1/2" jumper to the rack is connected with a standing
wave ratio tester for testing. The standing wave ratio should be less than 1.5,
preferably 1.3.
3. Fill in a corresponding vswr value and provide vswr test-chart.
13.17 Check of Indoor/Outdoor Environment
The indoor/outdoor environment is checked as follows:
1. Any outdoor engineering waste should be cleaned. After the installation is over,
the outdoor work site should be recovered to what it was, without any cable
strap, stub, waste paper box, waste cable or waste plastic bag. The whole site
should be clean and tidy.
2. Put away indoor unused materials. The materials to be put in the equipment
room should be kept in order. Keep everything indoor clean and tidy. No
littering is allowed.
3. Under the raised floors at the rack bottom and around the rack, there should be
no cable strap, stub, desiccant and other engineering materials left.
4. The front door, rear door and side plate of the rack should be cleaned without
visible stains caused by hand touching. There should be no dirt inside and
outside the rack (dead angle) and inside the cabinet, there should be no cable
clip or sundries left.
5. There should be no fingerprint or other stains on the cabinet surface.
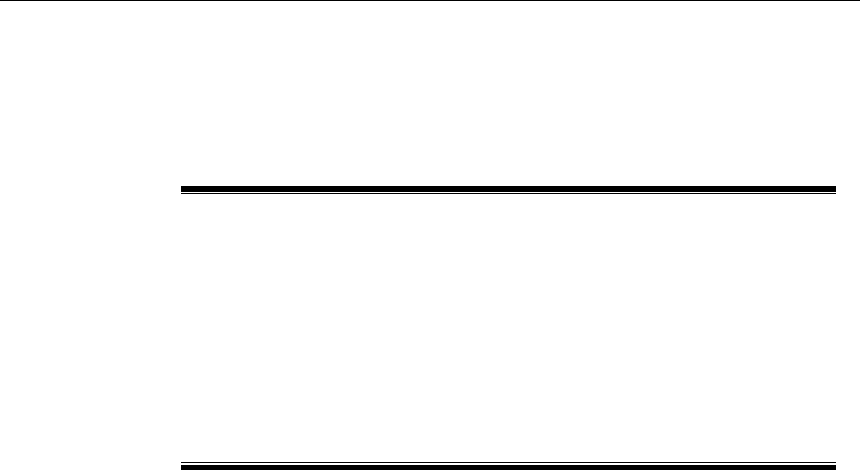
FAX: 0086-755-26770160
14-1
14 Power-on/Power-off
Summary
This part describes:
The check before BTS is powered on;
The power-on procedures of BTS;
The power-off procedures of BTS.
14.1 Check before Power-on
14.1.1 Check of External Connections of the rack
1. Check the power supply cables: check carefully to see whether the power cables
of DC connecting terminals on the set top are correctly connected. Make sure
that the poles are properly connected and screws are tightened.
2. Measure with a multimeter to see whether the voltage input on the DC power
distribution rack is within the allowable range (-40V~-57V). If not, check the
power system in the base station.
3. Make sure that T1 cables are correctly connected without insecure connections.
4. Check the antenna feeder system. Check with a standing wave ratio tester to see
whether the standing wave ratio of the antenna feeder is less than 1.5 (generally
less than 1.3). Feeder connectors should be well assembled and no feeder or
antenna is faulty.
5. Check whether cable labels are attached firmly, correctly and beautifully.
14.1.2 Check of Rack Inside
1. Open the front door of the rack to check whether the RF cables in the rack front
are correctly and firmly connected. Check whether connectors are connected
correctly and firmly according to the cable labels.

ZXC10-BTS (V5.4) Installation Manual
14-2
2. Unscrew 6 screws on the cover plate of the rack back and open it. According to
the cable labels on the back, check the cables for incorrect connections. Also
check the cables on the rack back for loose connections resulting from
loading/unloading, especially the internal cables between T1 cables, internal
connections of GPS and power cable plugs between power supply busbar on the
rack and the boards.
3. Check the DIP switches on the backplane for incorrect setting. According to
actual conditions, check the DIP switches on rear interface backplanes of the
shelves on the rack for incorrect setting. Refer to Appendix F “Description of
DIP Switches on the Backplane in a Base Station”.
14.2 Power-on Procedures
ZXC10-BTSB I2 is initially powered on as follows:
1. Keep boards partially seated in a shelf.
2. Make sure that the power switches of PSMD, PPM, PSMC, PSMB and HPA
inside a BTS rack and the fan layer are off.
3. Turn on the power supply outside the rack. If any abnormality is found, please
shut down the power supply immediately and check it. The rack will not be
powered on until the fault is removed.
4. Plug a PSMD power module into the voltage plane of the rack and turn on the
power switch of the power supply outside the rack. If any abnormality is found,
please immediately shut down the power supply and check it. The rack will not
be powered on until the fault is removed.
5. Turn on the general power switch on the power distribution module (PSMD) on
the rack voltage plane and observe the running of PSMD module. If the
indicator indicates the voltage of -48V, it shows that everything is normal. When
the fan is powered on, the PSMD front panel should give no alarm. If any
abnormality is found, please immediately shut down the power supply and check
it. The rack will not be powered on until the fault is removed.
6. Turn off the PSMD power module switch and plug in turn other power modules
into the rack voltage plane and the BDS layer.

Chapter
Error! Style not define
d.
Error! Style not defined.
14-3
7. Turn on the PSMD power module switch and the turn on one after another other
power module switches into the rack voltage plane and BDS layer. If any
abnormality is found, please immediately shut down the PSMD power supply
and check it. The rack will not be powered on until the fault is removed.
8. Plug all boards into the chassis after all the above power modules are checked. If
any abnormality is found, please immediately shut down the power supply and
check it. The rack will not be powered on until the fault is removed.
9. Finally, turn on in turn the power switches of the HPA. If any abnormality is
found, please immediately shut down the power supply and check it. The rack
will not be powered on until the fault is removed.
At this point the power-on of the BTS rack is completed. By means of the front panel
indicator (Refer to Appendix H) in a base station, observe with the help of the BSC
background controller and test the base station.
Normal power-on procedures of ZXC10-BTSB I2 are as follows:
1. Turn on -48V power switch outside the rack to power the rack, and then Turn on
the PSMD power switch. If any abnormality is found, please immediately shut
down the power supply and check it. The rack will not be powered on until the
fault is removed.
2. Turn on in turn secondary power switches of the plug-in shelf on the voltage
plane inside the rack: first Turn on the PSMC on the voltage plane and PPM
power module switch. Then, turn on the PSMB power module switch at the BDS
layer.
3. Finally, turn on the power switch on HPA board. If any abnormality is found,
please immediately shut down the power supply and check it. The rack will not
be powered on until the fault is removed.
14.3 Power-off Procedures
The power-off procedures of ZXC10-BTSB I2 are the reversed process of power-on,
shown as follows.
1. Turn off the HPA power switch.
2. Turn off the secondary power switches of the shelves of the voltage planes and
the BDS layer: first PSMB and then PSMC.

ZXC10-BTS (V5.4) Installation Manual
14-4
3. Turn off the PSMD power switch on the rack and then the -48V power switch
powering the rack outside.

FAX: 0086-755-26770160
A-1
Appendix A Abbreviations
Abbreviation Full Name
1xEV 1x Evolution
1xEV-DO 1x Evolution Data Only
1xEV-DO High rate packet data
1xEV-DV 1x Evolution Data & Voice
2F3S Two carriers and Three sectors
4F3S Four carriers and Three sectors
A A Interface—the interface of BSC-MSC
AAA Authentication Authorization Accounting
Abis Abis Interface—the interface of BSC--BTS
ATM Asynchronous Transfer Mode
BDS Baseband Digital System
BIM BDS Interface Module
BSC
Base Station Controller
BSS Base Station System
BTM BTS Test Module
BTS Base Transceiver System
CCM Communication Control Module
CDM Clock Distribution Module
CHM Channel Processing Module
CHM-1x Channel Processing Module for cdma2000
DBS Database Subsystem
DSM Data Service Module
EPLD
Electrically Programmable Logic Device
FA Foreign Agent
FER Frame Error Rate
FPGA
Field Programmable Gate Arrays
GCM GPS Control Module
GCM GPS Clock Module
HA Home Agent
HDLC High-level data link control
HDR High Data Rate
HLR Home Location Register
HPA High Power Amplifier
IP Internet Protocol
LNA Low Noise Amplifier
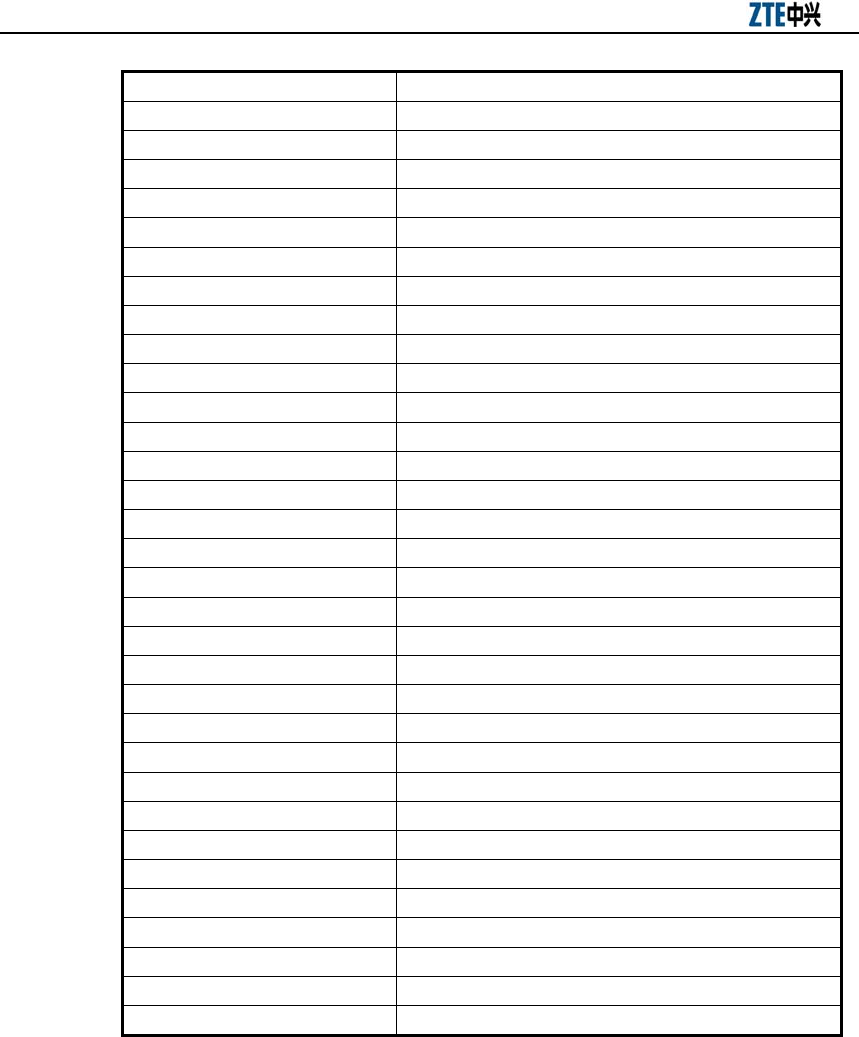
ZXC10-BTS (V5.4) Installation Manual
A-2
Abbreviation Full Name
MAC Media Access Control
MBTS Master BTS
MSC Mobile Switch Center
MTBCF Mean Time Between Criteria Faults
MTBF Mean Time Between Faults
MTTR Mean Time To Recovery
O&M Operations and Maintenance
OMC Operation and Maintenance Center
OSS Operating System Subsystem
OTD
Orthogonal Transmit Diversity
OW Order Wire
PA Power Amplifier
PCF Packet Control Function
PDSN Packet Data Serving Node
PP2S Pulse Per 2 seconds
PPP Point to Point Protocol
RF Radio Frequency
RFS Radio Frequency Subsystem
RIM Radio Interface Module
RRFS Remote RFS
RSSI Received Signal Strength Indicator
RX Receiver
SAM Site Alarm Module
SBTS Slave BTS
SCH Synchronization Channel
SCS System Control Subsystem
SDH Synchronous Digital Hierarchy
SNM SDH Net Module
STS
Space-Time Spreading
TOD Time of Date
TX Transmit
ZXC10-BTSB Type B BTS