Digi 50M880 802.11b Wireless Module User Manual DC ME HWR
Digi International Inc 802.11b Wireless Module DC ME HWR
Digi >
Contents
- 1. manual
- 2. user manual
user manual
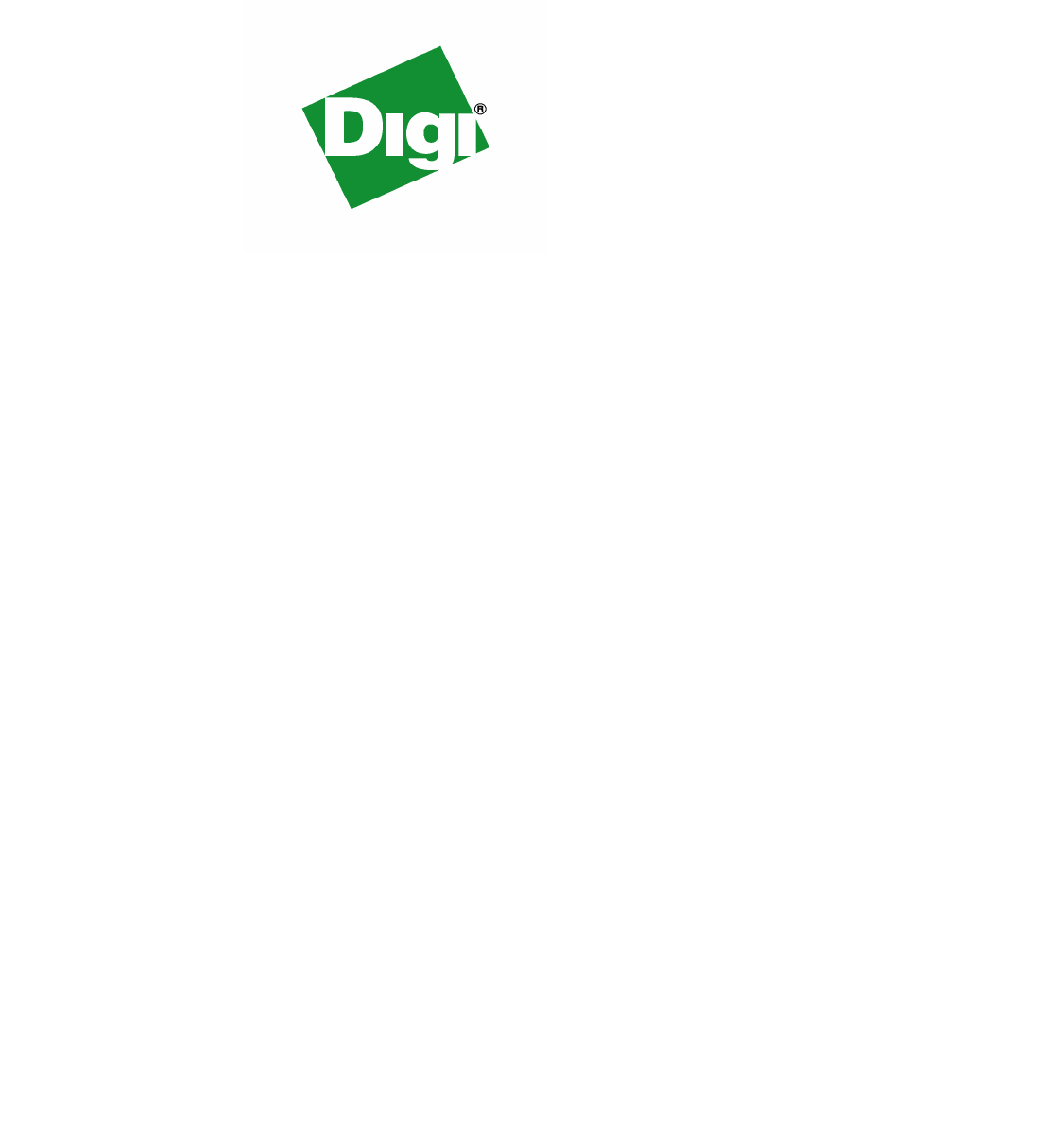
DigiConnectME®&
Digi Connect®Wi‐ME
DigiConnectME®9210
HardwareReference
90000897_F
© Digi International Inc. 2004 -2007. All Rights Reserved.
The Digi logo is a registered trademark of Digi International, Inc.
Connectware and Digi Connect ME and Digi Connect Wi-ME are trademarks of Digi International, Inc.
NetSilicon, NET+Works, NET+OS, and NET+ are trademarks of NetSilicon, Inc.
All other trademarks mentioned in this document are the property of their respective owners.
Information in this document is subject to change without notice and does not represent a commitment on the part of Digi
International.
Digi provides this document “as is,” without warranty of any kind, either expressed or implied, including, but not limited to,
the implied warranties of fitness or merchantability for a particular purpose. Digi may make improvements and/or changes
in this manual or in the product(s) and/or the program(s) described in this manual at any time.
This product could include technical inaccuracies or typographical errors. Changes are periodically made to the information
herein; these changes may be incorporated in new editions of the publication.
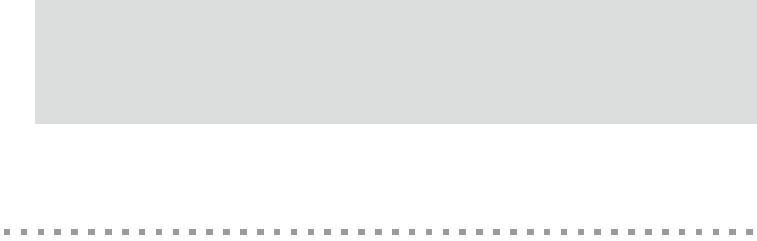
4
Contents
About This Document ................................................................................................................ 6
Related Documentation .................................................................................................... 6
Support Information ......................................................................................................... 7
Chapter 1: About the Digi Connect ME Family of Embedded Modules ......................... 8
Overview .......................................................................................................................... 8
Types of Modules............................................................................................................. 9
Connectors: Power and Device Interface ....................................................................... 11
Connectors: Ethernet Interface....................................................................................... 14
Connectors: Antenna ...................................................................................................... 15
Module LEDs ................................................................................................................. 16
Chapter 2: About the Development Board ....................................................................... 18
Overview ........................................................................................................................18
Basic Description ........................................................................................................... 19
Port Descriptions ............................................................................................................ 22
Connectors and Blocks................................................................................................... 25
Switches.......................................................................................................................... 31
Development Board LEDs ............................................................................................. 32
Power Jack......................................................................................................................35
Test Points ...................................................................................................................... 36
Chapter 3: Programming Considerations......................................................................... 38
Overview ........................................................................................................................38
Module Pinout ................................................................................................................ 39
LEDs............................................................................................................................... 41
Reset ............................................................................................................................... 41
Memory ..........................................................................................................................43

5
Appendix A Module Specifications.................................................................................... 46
Network Interface .......................................................................................................... 46
Serial Interface ............................................................................................................... 47
Data Rates (bps) ............................................................................................................. 47
Flow Control Options..................................................................................................... 47
DC Characteristics ......................................................................................................... 47
Power Management (Connect ME-9210 only) .............................................................. 50
Thermal Specifications .................................................................................................. 51
Mechanical ..................................................................................................................... 53
Bar Code ........................................................................................................................53
Dimensions..................................................................................................................... 53
Recommended PCB Layout........................................................................................... 59
Antenna Information ...................................................................................................... 61
RF Exposure Statement.................................................................................................. 65
Safety Statements........................................................................................................... 65
Appendix B Certifications .................................................................................................. 68
FCC Part 15 Class B ...................................................................................................... 68
Industry Canada ............................................................................................................. 69
Declaration of Conformity ............................................................................................. 70
International EMC Standards......................................................................................... 71
Appendix C Sample Application: PoE Power Supply ..................................................... 74
Appendix D Sample Application: TTL Signals to EIA-232 ............................................ 76
Appendix E Change Log .................................................................................................... 78
Revision F ......................................................................................................................78
Revision E......................................................................................................................78
Revision D......................................................................................................................78
Revision C......................................................................................................................79
Revision B......................................................................................................................79
Revision 90000631_G>90000897_A ............................................................................ 79
Revision G......................................................................................................................79
Revision F ......................................................................................................................80
Revision E......................................................................................................................80
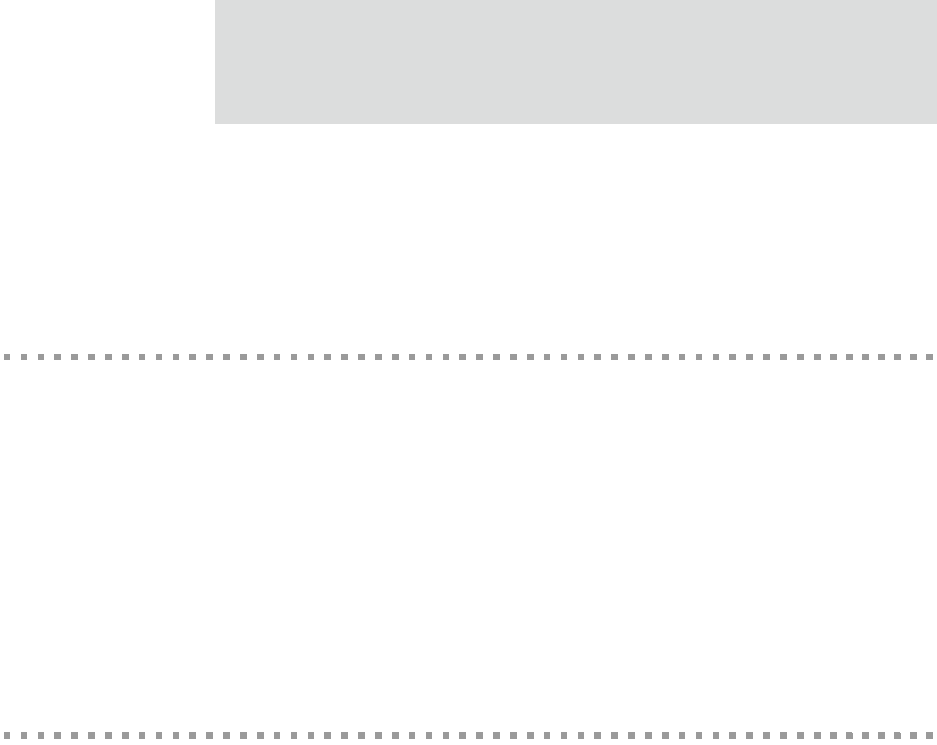
6
••••••••••••••••••••••••••••••••••••••••••••••••••••••••
About This Document
Scope of the Reference Manual
The purpose of this document is to enable developers to integrate the Digi Connect ME,
Digi connect ME 9210, or Digi Connect Wi-ME embedded modules with other devices,
enabling these devices to make use of the module’s rich networking features.
Note:
Unless mentioned specifically by name, the products will be referred to as the
embedded modules or modules. Individual naming is used to differentiate
product specific features. Unless noted otherwise, all Digi Connect ME
related technical information provided in this document also applies to
the Digi Connect ME 9210 module.
Related Documentation
See the NS7520 Hardware Reference for information on the NS7520 chip.
See the NS9210 Hardware Reference for information on the NS9210 chip.
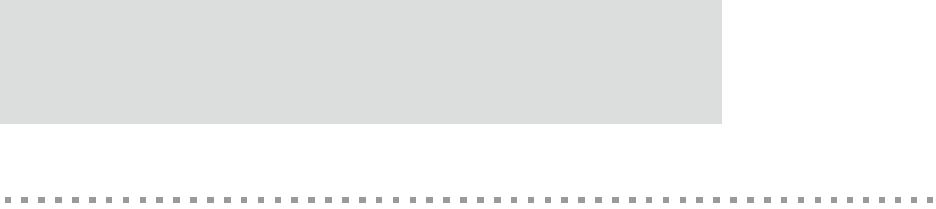
7
Support Information
To get help with a question or technical problem or make comments and recommendations
about Digi products and documentation, use the following contact information.
General Customer Service and Support
Digi International
11001 Bren Road East
Minnetonka, MN 55343
U.S.A.
United States: 1 877-912-3444
Other Locations: 1 952-912-3444
www.digi.com/support/eservice/
eservicelogin.jsp
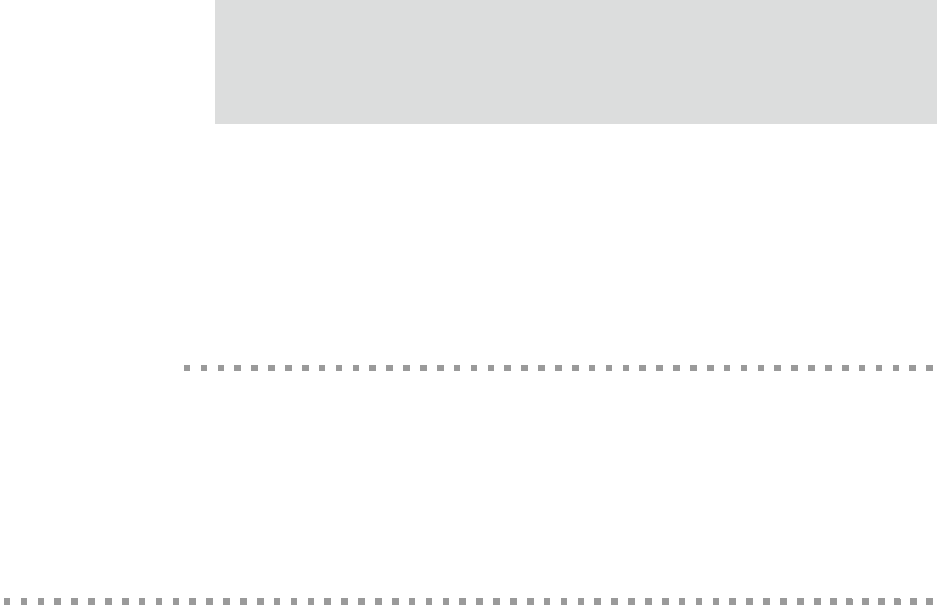
8
About the Digi Connect ME
Family of Embedded
Modules
CHAPTER 1
Overview
The embedded modules provide fully transparent device connectivity over industry-
standard Ethernet connections and allows both equipment manufacturers and systems
integrators to network-enable products at a fraction of the time and cost required to develop
a custom solution. It is a highly flexible and compact single component solution with a
serial port, GPIO, and a robust on-board TCP/IP stack and 10/100 BASE-T Ethernet
support or wireless interface.
Built on Digi's leading 32-bit NET+ARM processor technology, the Digi Connect ME
family of embedded modules offer serial-to-Ethernet functionality through Digi’s Plug-
and-Play Firmware firmware, or the freedom and flexibility of professional embedded
software development provided by the easy-to-use, cost-effective and complete Digi
JumpStart Kits™ for NET+OS and Microsoft .NET Micro Framework.
The Digi Connect ME and Digi Connect Wi-ME modules are utilizing the powerful Digi
NS7520 processor with an ARM7TDMI core running at 55 MHz. They provide integrated
wired or wireless networking and serial device connectivity in a compact connector-style
form factor. The Digi Connect ME 9210 module is the latest, fully form factor and pin
compatible, member of the Digi Connect ME family providing 75 MHz ARM9 core
performance based on the Digi NS9210 processor. In addition to higher performance with
integrated Ethernet connectivity, the Digi Connect ME 9210 offers higher serial data rates,
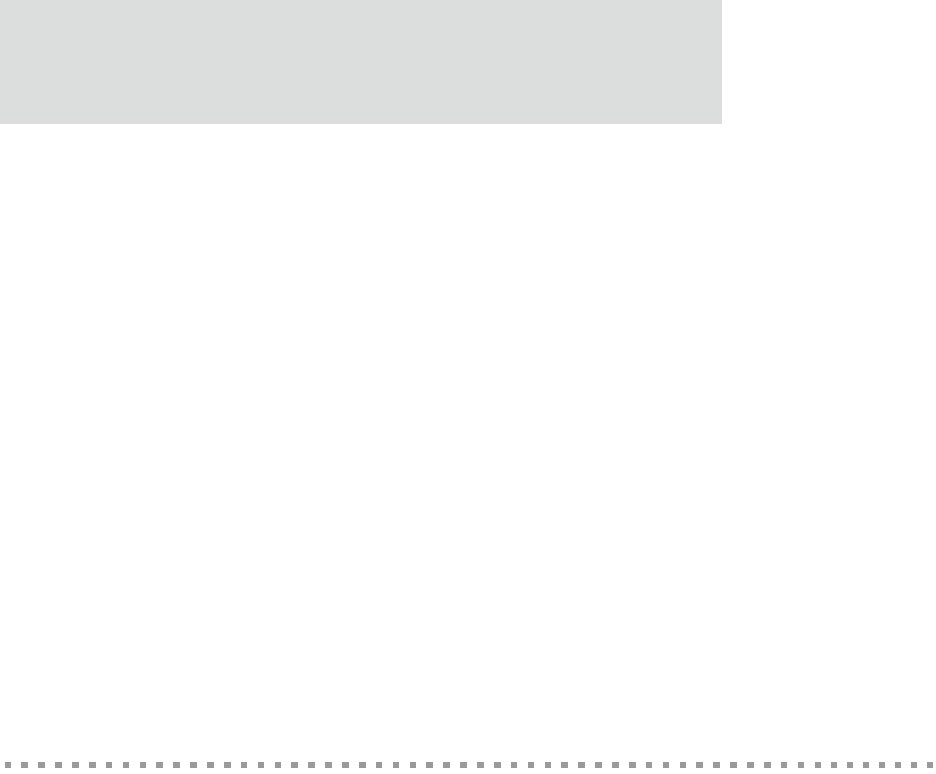
9
SPI functionality, as well as the unique option of application specific interfaces using the
programmable FIMs on the NS9210.
From medical systems to building control and industrial automation, in virtually any
application where embedded device connectivity over Ethernet or wireless connectivity is
needed, embedded modules are the ideal choice, delivering high-performance functionality.
Note:
Unless mentioned specifically by name, the products will be referred to as the
embedded modules or modules. Individual naming is used to differentiate product
specific features. Similarily, information about the Connect ME applies to the
Connect ME 9210 as well unless stated otherwise.
This chapter provides information about the modules hardware and contains the following
topics:
"Types of Modules" on page 9
"Connectors: Antenna" on page 15
"Connectors: Ethernet Interface" on page 14
"Module LEDs" on page 16
Types of Modules
There are two types of modules. One module utilizes Digi Plug-and-Play Firmware, while
the second is customizable with the option to develop a firmware applicaton in .NET MF or
NET+OS. If you are developing your firmware application in NET+OS, you will be using a
module with a JTAG interface.
Note:
JTAG is a commonly used term that is also referred to as IEEE 1149.1, an industry
standard test protocol. JTAG is an abbreviation for the European Joint Test Action
Group, which invented the first versions of the IEEE 1149.1 interface. The JTAG
interface, along with the other development tools, enables you to download, run
and debug programs on the module.
The following figures show the two types of modules.
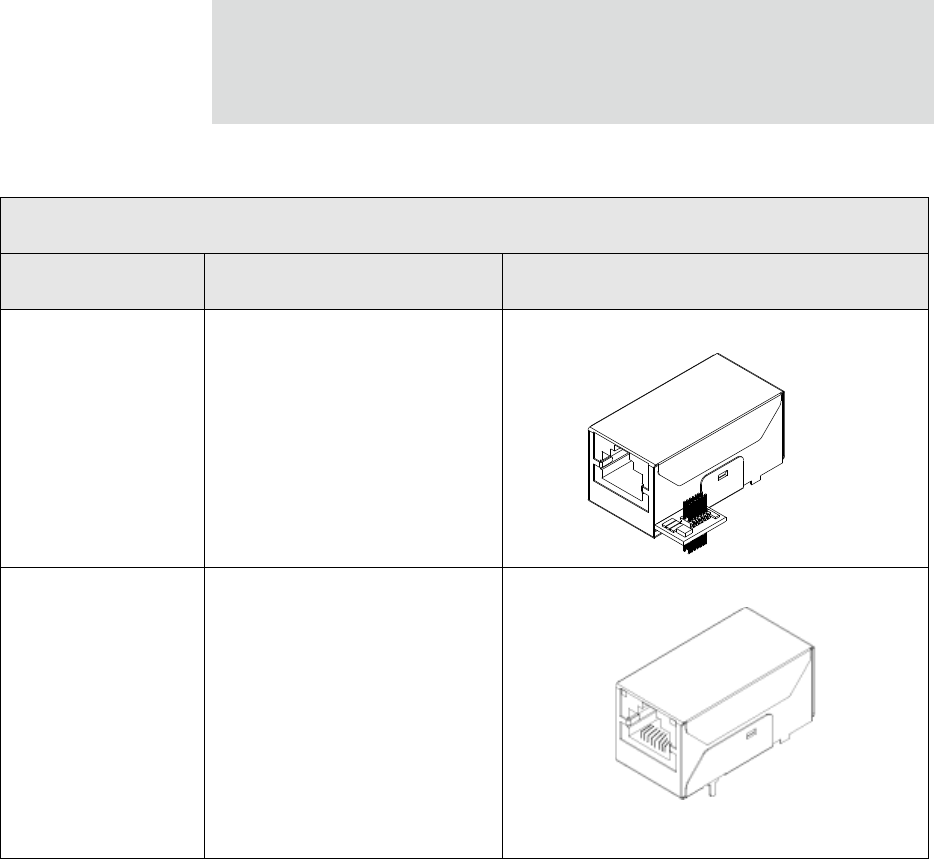
10
Digi Connect ME Modules
Model Description Figure
Digi Connect ME
DC-ME-01T-JT
DC-ME4-01T-JT
Digi Connect ME 9210
DC-ME-Y401-JT
DC-ME-Y402-JT
Used for development
purposes only
JTAG interface
Digi Connect ME
DC-ME-01T-S
DC-ME4-01T-S
DC-ME-01T-C
DC-ME4-01T-C
DC-ME-01T-MF
Digi Connect ME 9210
DC-ME-Y401-C
DC-ME-Y402-C
No JTAG interface
Ordered
independently for use
in your
implementation
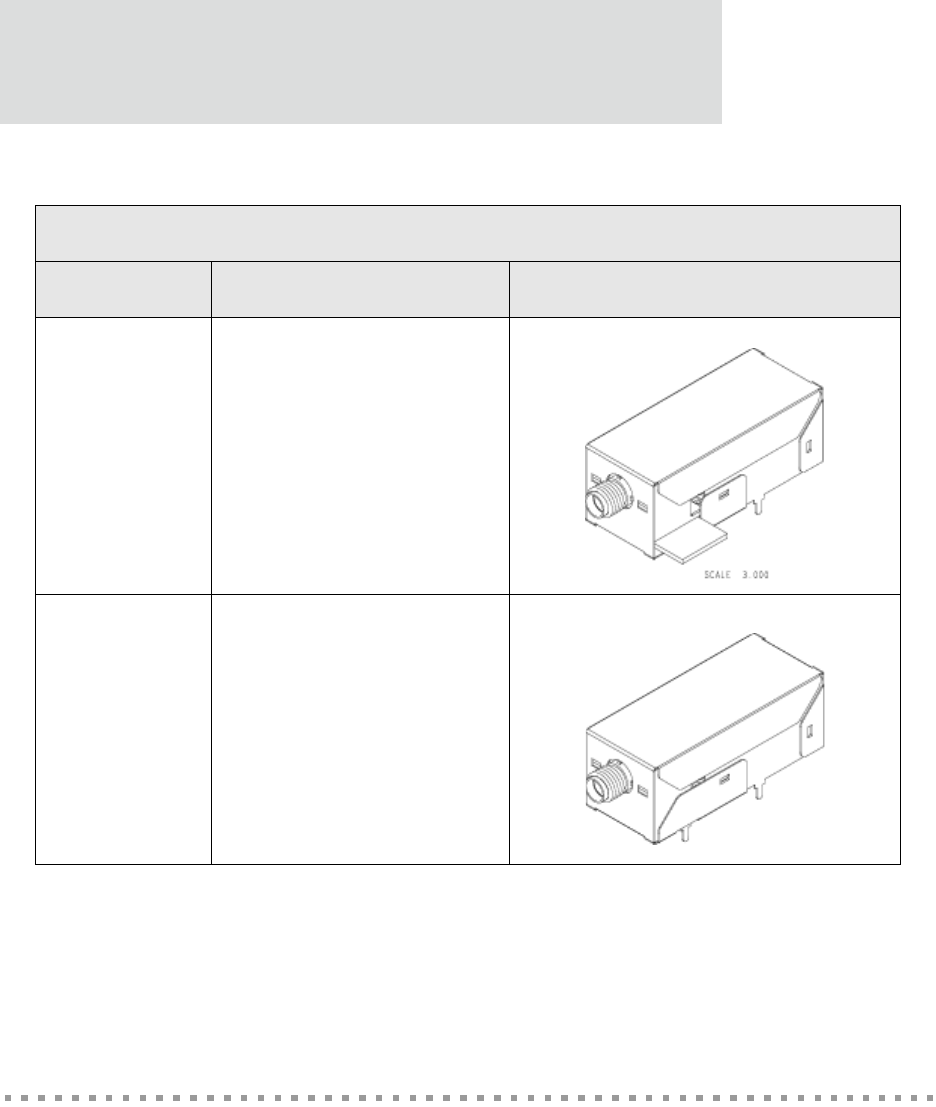
11
Note:
-S: No JTAG for use with Digi Plug-and-Play Firmware
-C: No JTAG for use with custom NET+OS applications
-JT: With JTAG for use with custom firmware development-
-MF: No JTAG for use with Microsoft .NET Micro Framework
Connectors: Power and Device Interface
The module has a 20-pin male connector that supports a serial interface with data rates up
to 230,400 (Digi Connect ME)/ 921,600 bps (Digi Connect ME 9210) and full-modem
Digi Connect Wi-ME Modules
Model Description Figure
DC-WME-01T-JT
Used for development
purposes only
JTAG interface
DC-WME-01T-S
DC-WME-01T-C
No JTAG interface
Ordered
independently for use
in your
implementation.
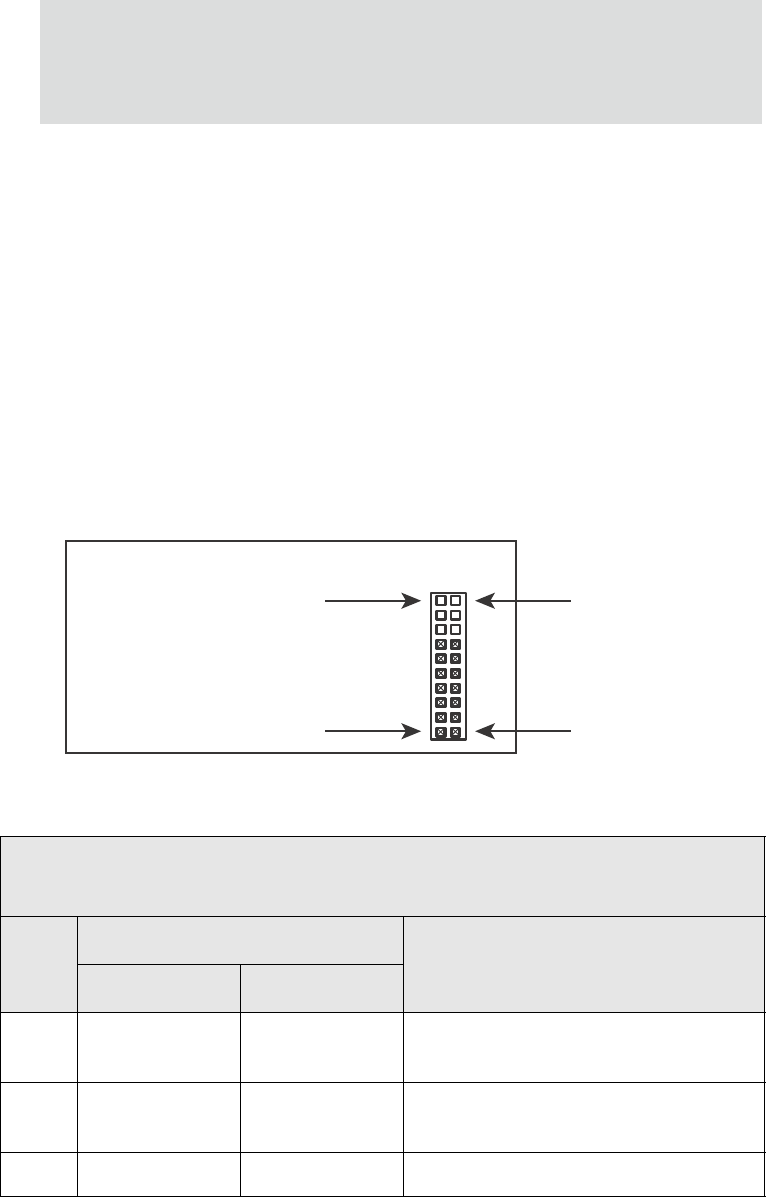
12
control, and GPIO ports. See the following figure for pin orientation and the table for pin
assignments.
Difference in pin assignments/availability
Pin assignments/availability for pins 1 and 2 depend on which module you are using. Pins 1
and 2 are available for Digi Connect ME; these pins are removed for Digi Connect Wi-ME.
The pin assignment table shows the appropriate values.
Power and Device Interface Connector
Power and Device Interface Connector Pin Assignments
Pin
Signal
Description
ME Wi-ME
1 VETH+ — ME: Power Pass-Thru+
Wi-ME: Position Removed
2 VETH- — ME: Power Pass-Thru-
Wi-ME: Position removed
3-6 — — Position removed
00000019
Pi n 2
Pi n 19
Pi n 1
Pi n 20
Module
front
Bot t o m vi ew
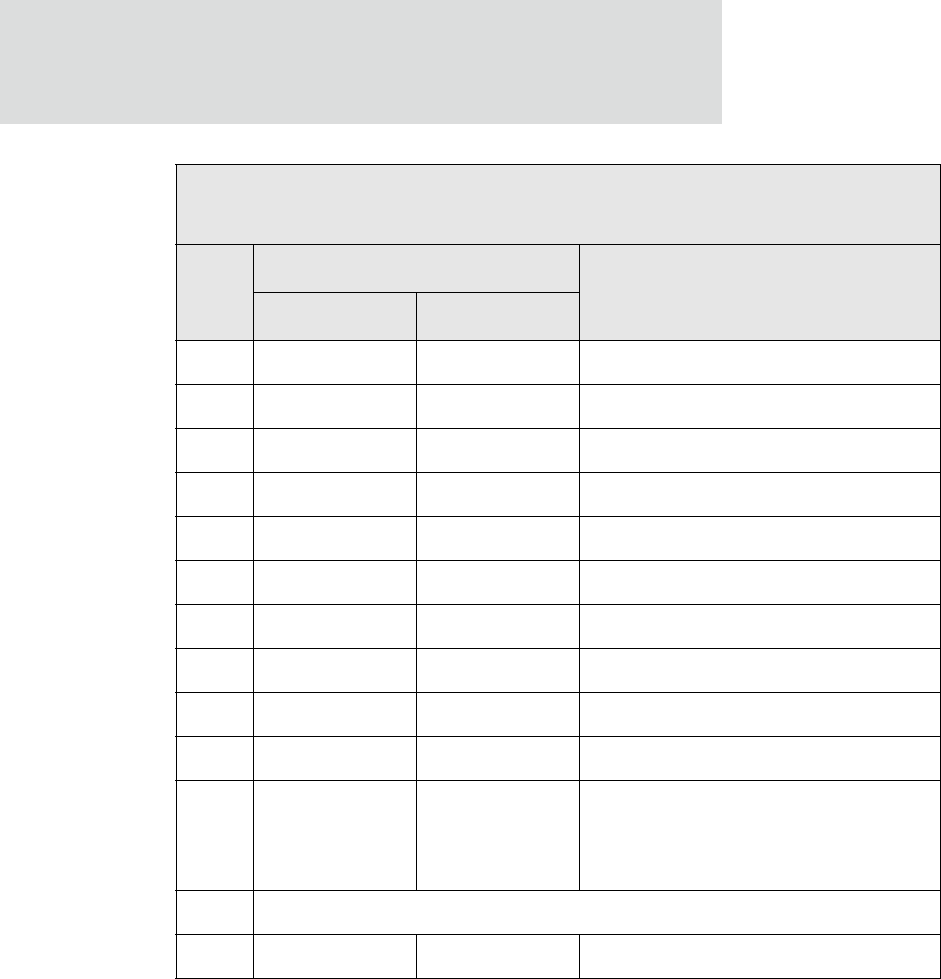
13
Note:
The development board provides connectors for an optional PoE application kit.
Note:
Any pins not used can be left floating.
Note:
See "Module Pinout" on page 39 for detailed IO configuration information.
7 RXD RXD Receive Data (Input)
8 TXD TXD Transmit Data (Output)
9 RTS RTS Request to Send (Output)
10 DTR DTR
Data Terminal Ready (Output)
11 CTS CTS Clear to Send (Input)
12 DSR DSR Data Set Ready (Input)
13 DCD DCD
Data Carrier Detect (Input)
14 /RESET /RESET Reset
15 +3.3V +3.3V Power
16 GND GND Ground
17, 18
Not accessible with Digi Plug-and-Play
Firmware. If using a development kit, see
"Module Pinout" on page 39 for detailed IO
configuration information.
19 Reserved. Do not connect.
20 /INIT /INIT Software Reset
Power and Device Interface Connector Pin Assignments
Pin
Signal
Description
ME Wi-ME
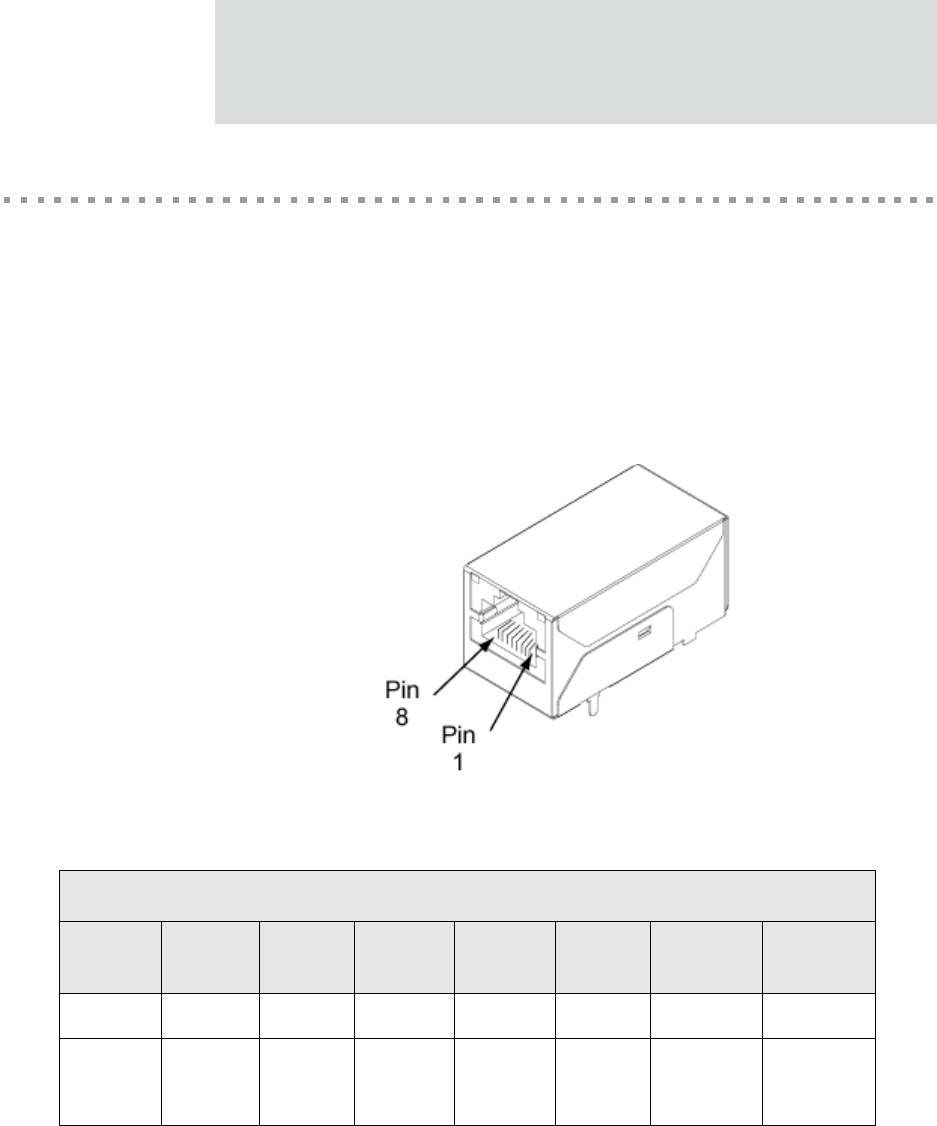
14
Connectors: Ethernet Interface
The Ethernet connector is an 8-wire RJ-45 jack that meets the ISO 8877 requirements for
10/100BASE-T. See the following figure and table for pin orientation and pin assignments.
Note:
Pin orientation and assignments are the same for modules with or without a JTAG
connector.
Ethernet Interface Pin Orientation
Ethernet Interface Pin Assignments
Pin
1
Pin
2
Pin
3
Pin
4
Pin
5
Pin
6
Pin
7
Pin
8
TXD+ TXD- RXD+ EPWR+ EPWR+ RXD- EPWR- EPWR-
Transmit
Data +
Transmit
Data -
Receive
Data +
Power
from
Switch +
Power
from
Switch +
Receive
Data -
Power
from
Switch -
Power
from
Switch -
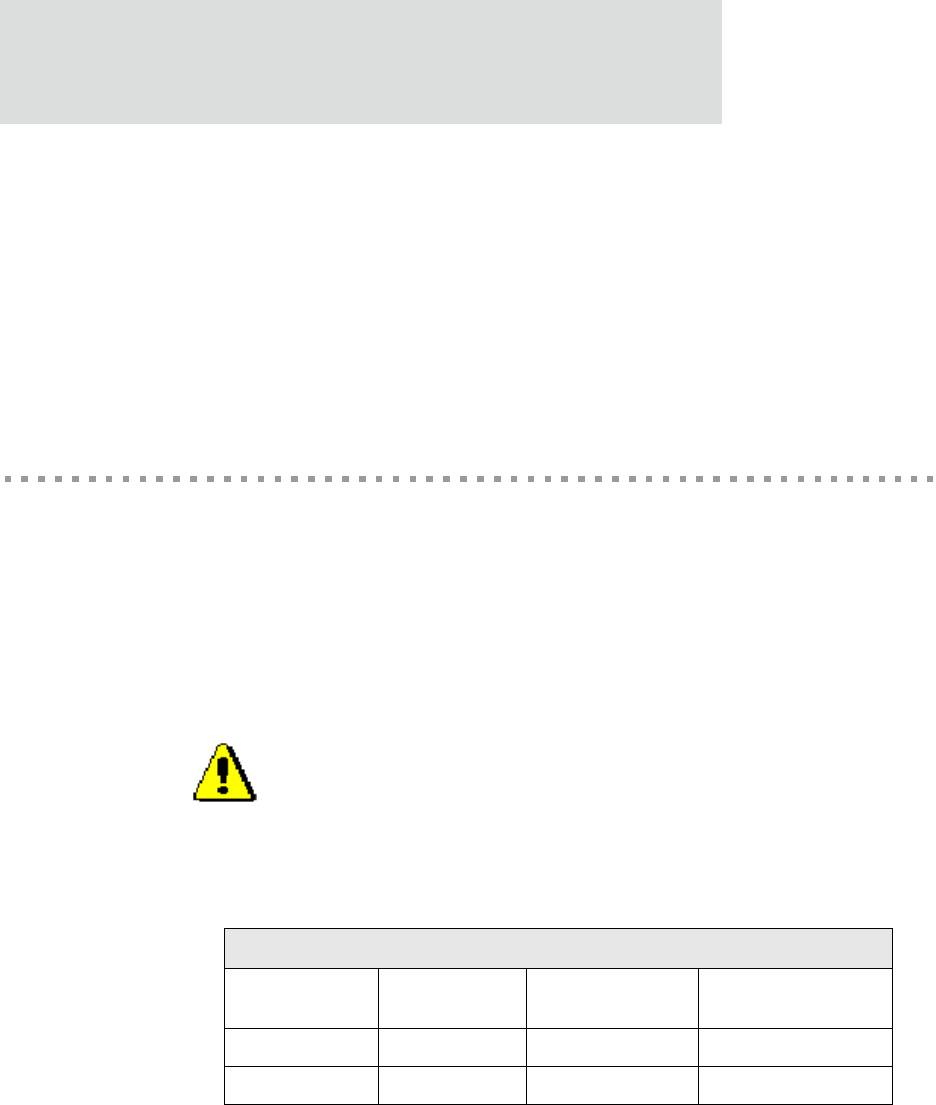
15
Hard Reset
The embedded modules support a hardware reset on pin 14 of the 20-pin header. Pulling
pin 14 low with an open drain driver will force the module into a hard reset state. The
module will remain in the reset state as long and pin 14 is held low and will leave this reset
state ~250mS after pin 14 goes high. Do not actively drive pin 14 high and do not allow the
rise time of the pin 14 to be longer than 100uS. When used with the development board,
this pin is wired to reset button SW4, which means it acts as a hard reset button.
Connectors: Antenna
The Digi Connect Wi-ME is available with 1 RP-SMA connector. The antenna is
connected to the module with a reverse polarity SMA connector (sub-miniature size A).
The antenna only fits on the module one way to ensure a proper connection. Another option
for both signal reception and design flexibility is to use an antenna extension cord to
separate the antenna from the module. This allows the module to fit inside your product but
the antenna to be placed outside the device.
Antenna Specifications
Type Desktop Dipole 30 cm
Antenna Extension Cord
Part number DC-ANT-24DT DG-ANT-20DP-BG DG-EXT-300-RR
Gain 1.8 dBi 2 dBi -.5dB
Caution: This Part 15 radio device operates on a non-interference basis
with other devices operating at this frequency when using the antennae
listed in the Antenna Specification table. Any changes or modification to
user’s authority to operate the device.
the product not expressly approved by Digi International could void the
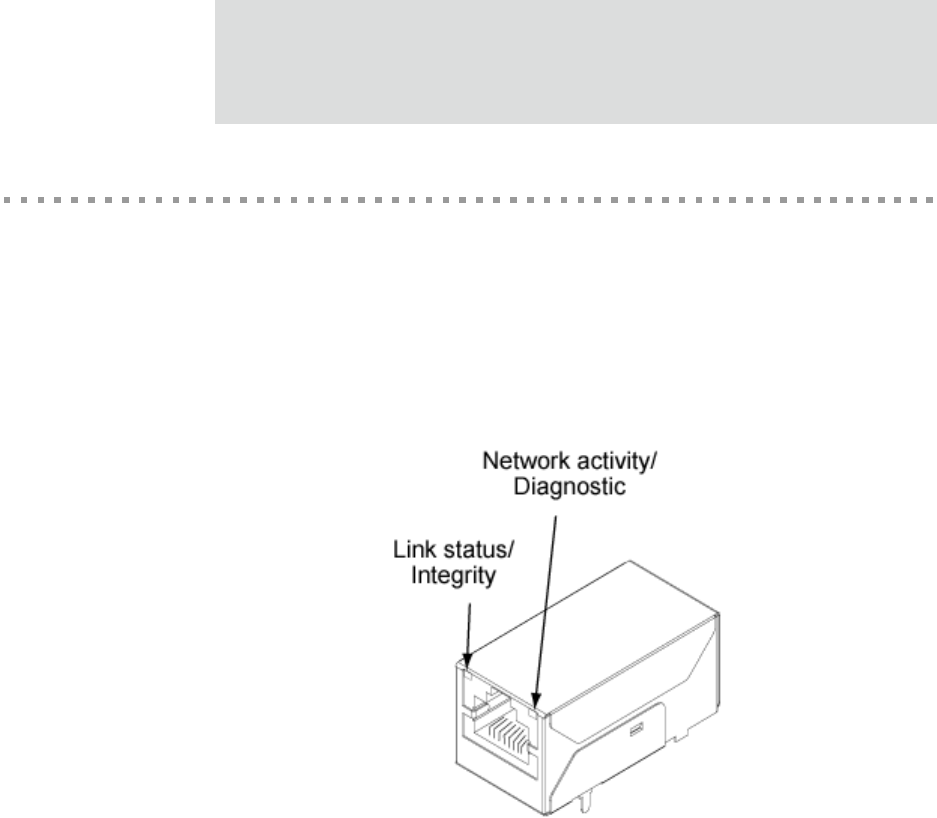
16
Module LEDs
The module has two LEDs that are located near the upper corners of the Ethernet port (see
the following figure). The following table describes the LEDs.
Note:
The LEDs are the same for a module with or without a JTAG connector.
LED Locations
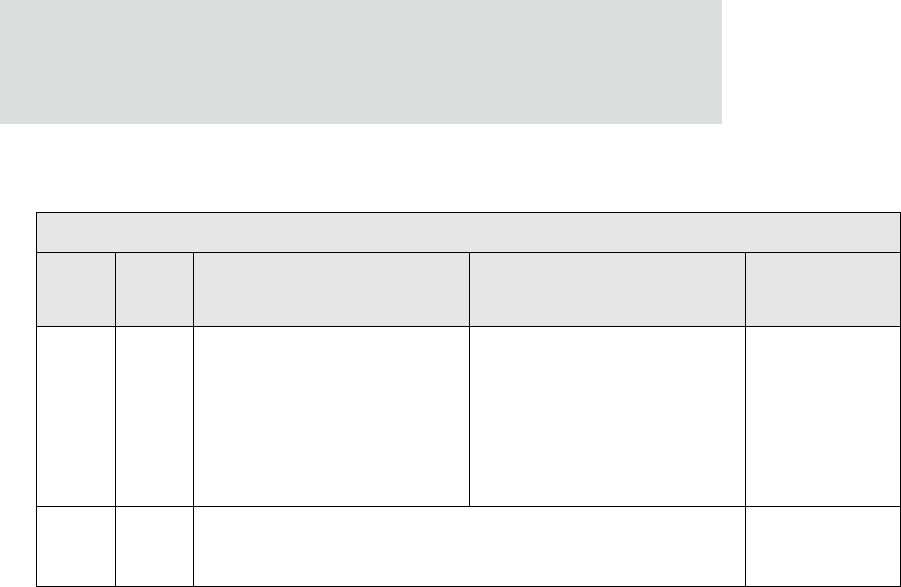
17
LED Behaviors
LED Pin
Header
EM
Digi Plug-and Play Firmware
Digi Connect ME
Digi Plug-and Play Firmware
Digi Connect Wi-ME
Customizable
Modules
Top left
(yellow)
5 (+)
7 (-)
Network link status:
Off - no link has been detected.
On - a link has been detected.
Network link status:
On - unit is associated with an access
point.
Blinking slowly - unit is in ad hoc
mode.
Blinking quickly - unit is scanning
for a network.
Same as Digi Plug-
and Play Firmware
(Network link
status).
Top
right
(green)
1 (+)
3 (-)
Network activity:
Blinking -network data is transmitted or received.
This LED is
software
programmable.
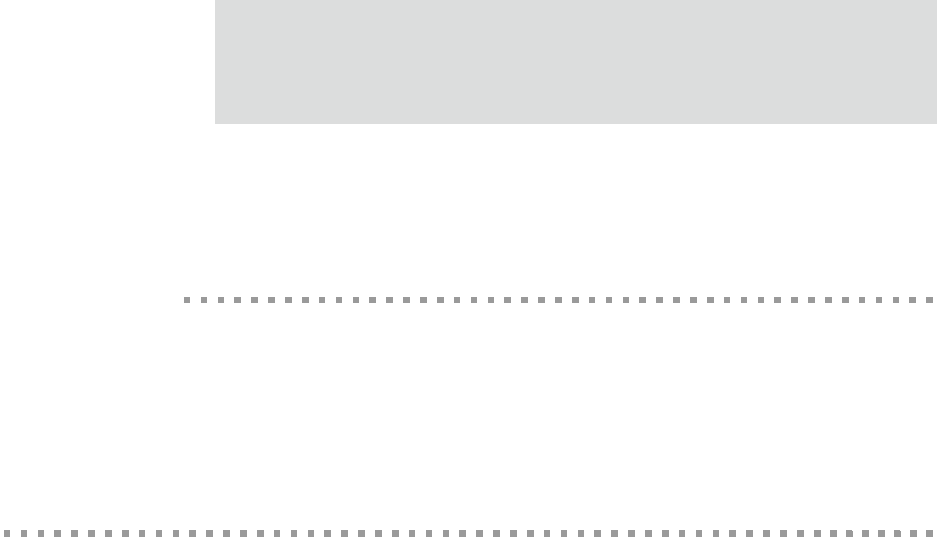
18
About the Development
Board
CHAPTER 2
Overview
The development board is a hardware platform from which you can determine how to
integrate the embedded modules into your design. The board consists of the following main
features:
Socket for connecting the embedded modules
JTAG connection (for use with the development kit only)
GPIO switches
Serial and GPIO ports
Power input
This chapter provides information on development board components and contains the
topics listed below. For more detailed information on the development board, see the
schematic and mechanical drawings on the CD that accompanies your kit. Once you’ve
installed the software that comes with your kit, you can access the schematic from the Start
menu.
"Basic Description" on page 19
"Placement of Module" on page 22
"Connectors and Blocks" on page 25
"Switches" on page 31
"Development Board LEDs" on page 32
"Power Jack" on page 35
"Test Points" on page 36
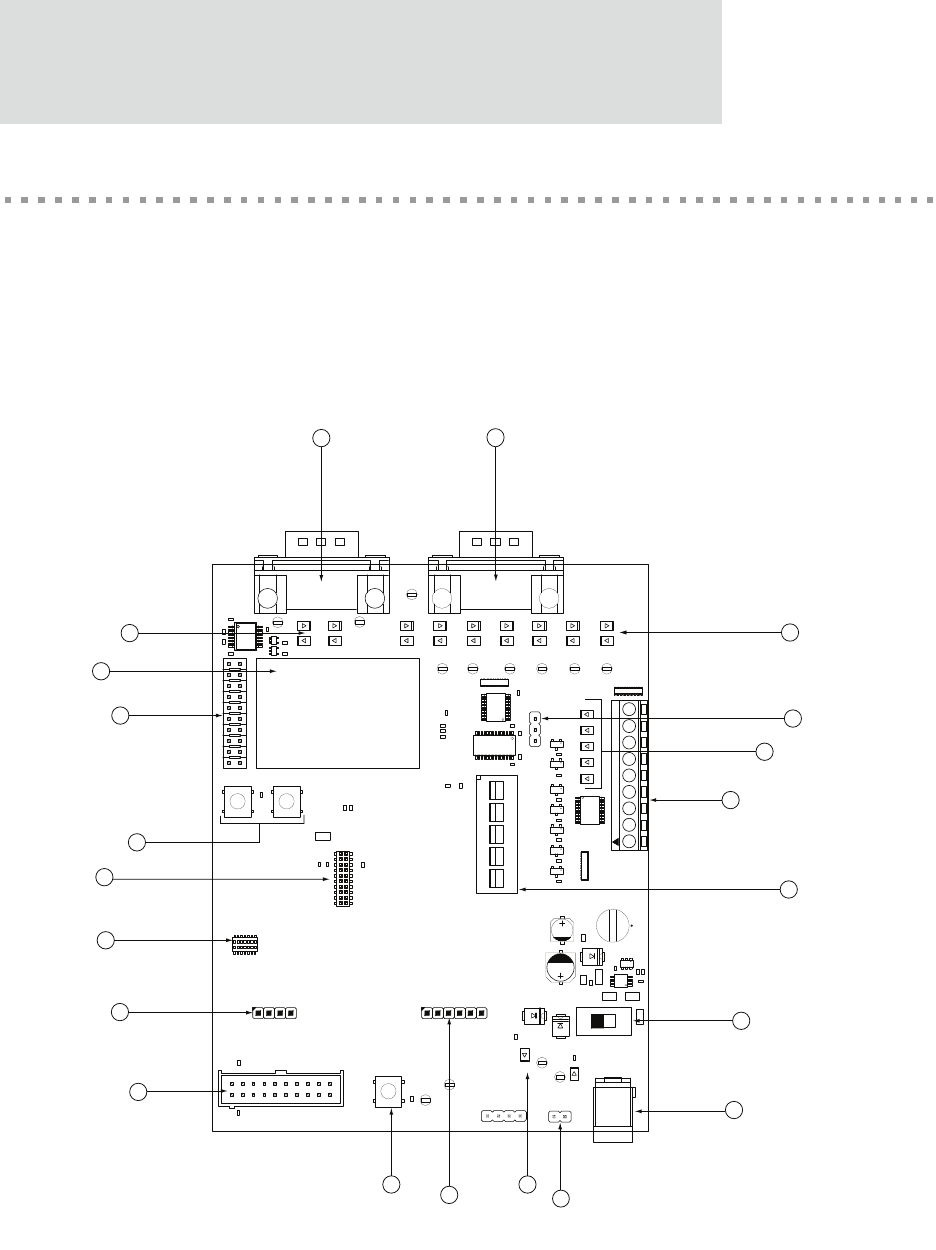
19
TP7TP7 TP8TP8 TP4TP4 TP5TP5 TP10TP10 TP9TP9
TP6TP6
TP3TP3
TP2TP2
L2
P2
U7
P1
C21
R15
D10
C8
C1
R6
U4
CR23
SW4
U5
C12
U3
U6
CR24
D5
P10
R4
C4
R2
P13
RN2
P15
P14
C22
CR18
R13
CR22
CR17
P4
C10
CR12
L1
C15
D9
CR11
C31
R12
U2
CR16
D6
CR21
CR3 CR15
R10
P9
CR6
CR19
U1
R18
CR5
D4
D1
R11
CR8
C29
C24
C19
CR7
VR1
P7
CR10
C14
CR9
C25
CR14
P3
CR13
P12
C9
R7
P8
C27
P5
CR20
P11
D7
C20
C16
SW2
C6
C30
CR25
R17
R16
CR1
C5
R8
C13
CR2
C11
SW5
R1
C7
SW1
C18
D8
R14
RN3
R19
R5
SW3
C2
CR4
C17
C23
D3
R9
D2
RN1
C3
C28
C26
TP11TP11
TP1TP1
TP12TP12
TP13TP13
1
2
3
4
5
6
7
8
9
10
11
12
15
17
16
14 13
19
20
18
21
Basic Description
The development board contains connectors, switches, and LEDs for use while integrating
the embedded module into your design. See the following figure for the location of the
connectors, switches, and LEDs. Additionally, the board provides test points (not shown on
the figure). For more information about test points, see "Test Points" on page 36.
Board Layout and Connector Locations:
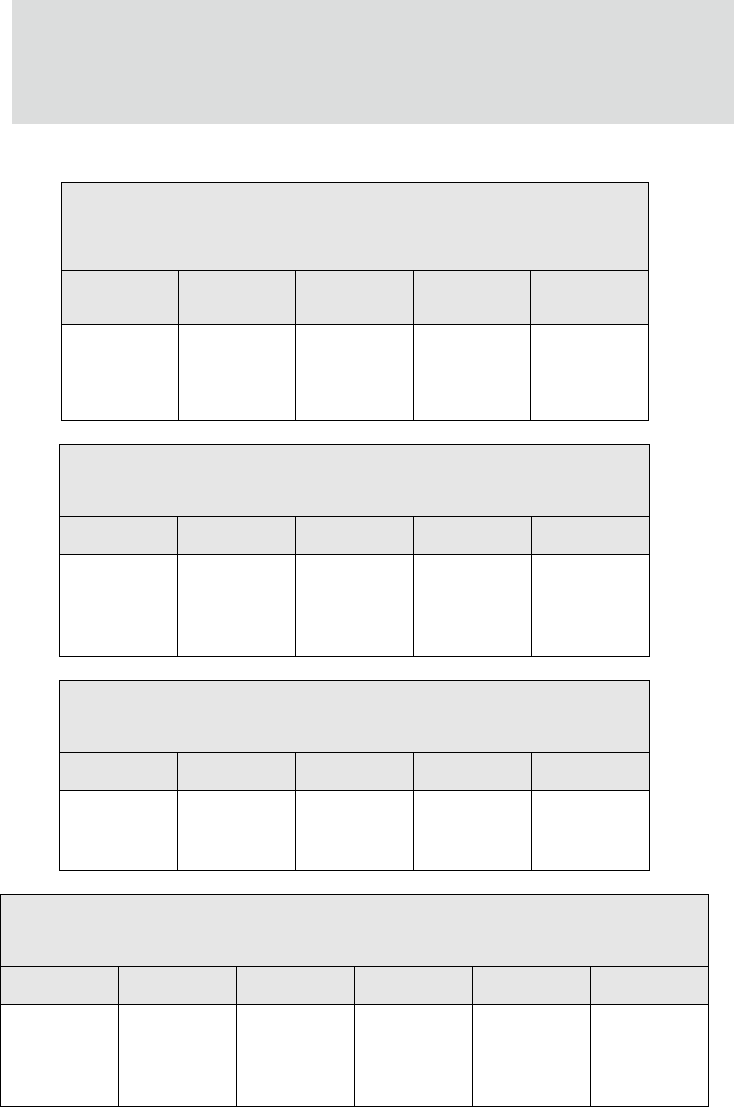
20
Connectors, Switches and LEDs
Board Description Markers 1-5
12345
Secondary
Serial Port, P2
Primary Port
LEDs, CR5 -
CR18
GPIO Switch
Bank, SW3
Prototyping
Area, P4
JTAG
Header, P12
Connectors, Switches and LEDs
Board Description (continued) Markers 6-10
678910
232 Enable
Jumper
Block, P5
Embedded
Module
Connector,
P10
ME JTAG
Connector,
P11
Primary
Serial Port, P1 GPIO Port, P7
Connectors, Switches and LEDs
Board Description (continued) Markers 11-15
11 12 13 14 15
Digital I/O
LEDs, CR19 -
CR23
Logic
Analyzer
header, P3
POE Source
LED, CR24
Reset Switch,
SW4
User
Pushbuttons,
SW1 & SW2
Connectors, Switches and LEDs
Board Description (continued) Markers 16-21
16 17 18 19 20 21
Power Jack,
P15
On/Off
switch, SW5
Secondary
Port LEDs
CR1-CR4
-48V DC
output from
ME module
P13
12V output
from PoE
module P14
Current
Measurement
Option P8

21
"Port Descriptions" on page 22
"Connectors and Blocks" on page 25
"Switches" on page 31
"Development Board LEDs" on page 32
"Power Jack" on page 35
See the following figures for placement of either module onto the development board.
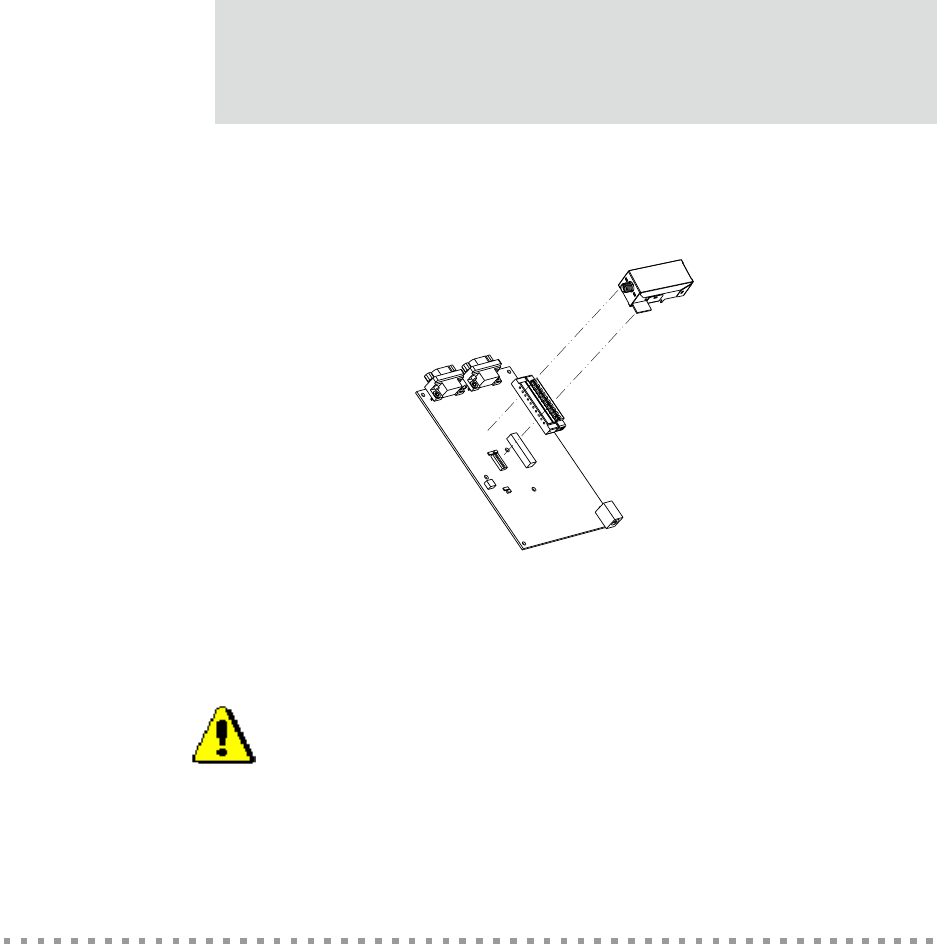
22
Placement of Module
Port Descriptions
The development board provides the following ports:
Primary Serial Port, P1
Secondary Serial Port, P2
GPIO Port, P7
See the figure titled "Board Layout and Connector Locations:" on page 19 for the location
of the ports. The following sections describe the ports.
Caution: When handling the development board, wear a grounding wrist
strap to avoid ESD damage to the board.
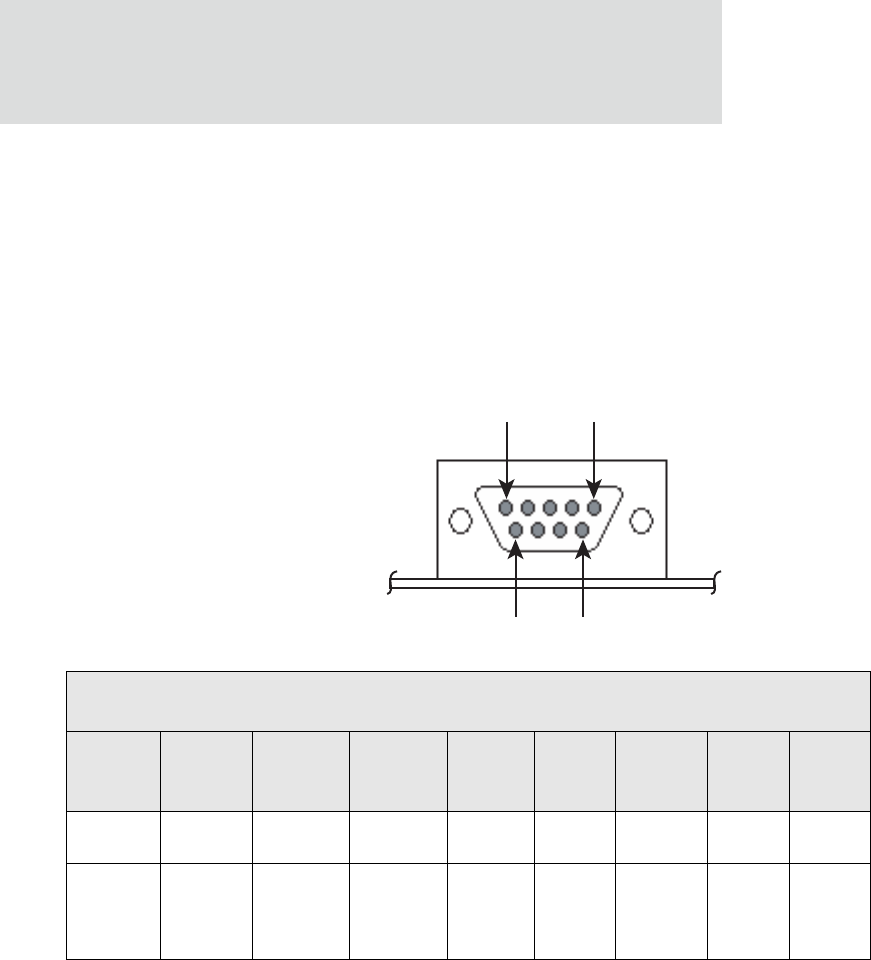
23
Primary Serial Port, P1
The Primary Serial Port is a DB-9 male connector that is labeled as P1 on the development
board. See the following figure for pin orientation; see the following table for pin
assignments.
Primary Serial Port Pin Orientation
Secondary Serial Port, P2
The Secondary Serial Port is a DB-9 male connector that is labeled as P2 on the
development board. The port is used only with the Digi Connect ME modules with JTAG
interfaces for debugging purposes. See the following figure for pin orientation; see the
following table for pin assignments.
Pin 1 Pin 5
Pin 6 Pin 9
Primary Serial Port Pin Assignments
Pin
1
Pin
2
Pin
3
Pin
4
Pin
5
Pin
6
Pin
7
Pin
8
Pin
9
DCD RXD TXD DTR GND DSR RTS CTS —
Data
Carrier
Detect
Receive
Data
Transmit
Data
Data
Terminal
Ready
Signal/
Chassis
Ground
Data Set
Ready
Request
To Send
Clear To
Send
—
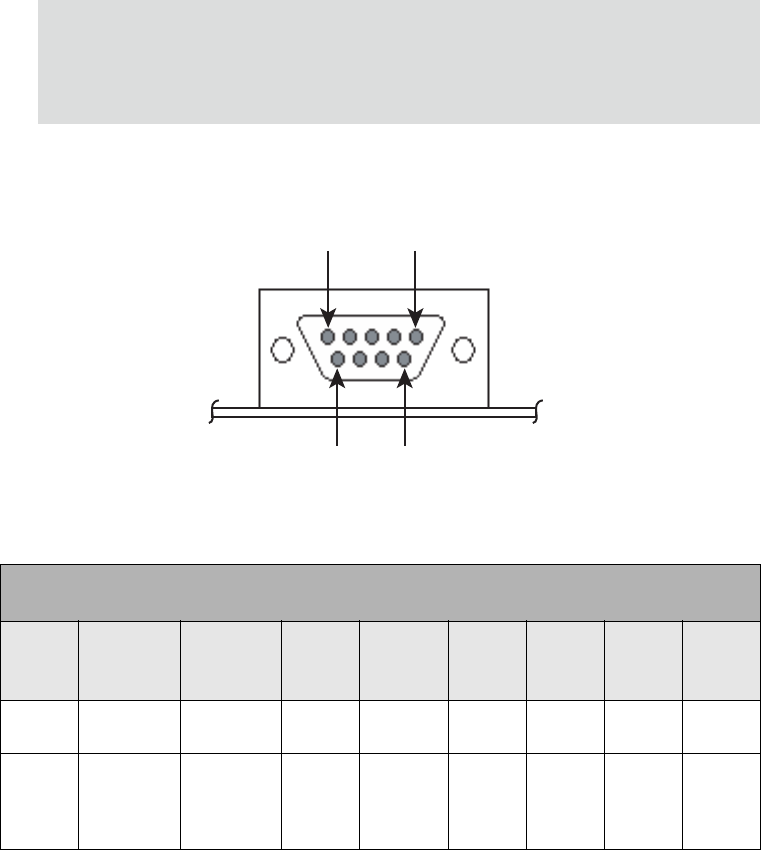
24
Secondary Serial Port Pin Orientation
RS232-Enable Pin Header, P5
When enabled, P5 connects the TTL signals to the RS232 transceiver allowing for RS232
communication on Serial Port 1. When the jumper is removed, the transceiver is no longer
connected and the load is removed from the TTL lines.
GPIO Port, P7
The GPIO port is a 9-pin male right-angle connector that is labeled as P7 on the
development board. See the following figure for pin orientation; see the following tables
for pin assignments. For input and output threshold specifications, see "DC Characteristics"
on page 47.
Secondary Serial Port Pin Assignments
Pin
1
Pin
2
Pin
3
Pin
4
Pin
5
Pin
6
Pin
7
Pin
8
Pin
9
—RXD TXD —GND————
— Receive
Data
Transmit
Data
— Signal/
Chassis
Ground
————
Pin 1 Pin 5
Pin 6 Pin 9
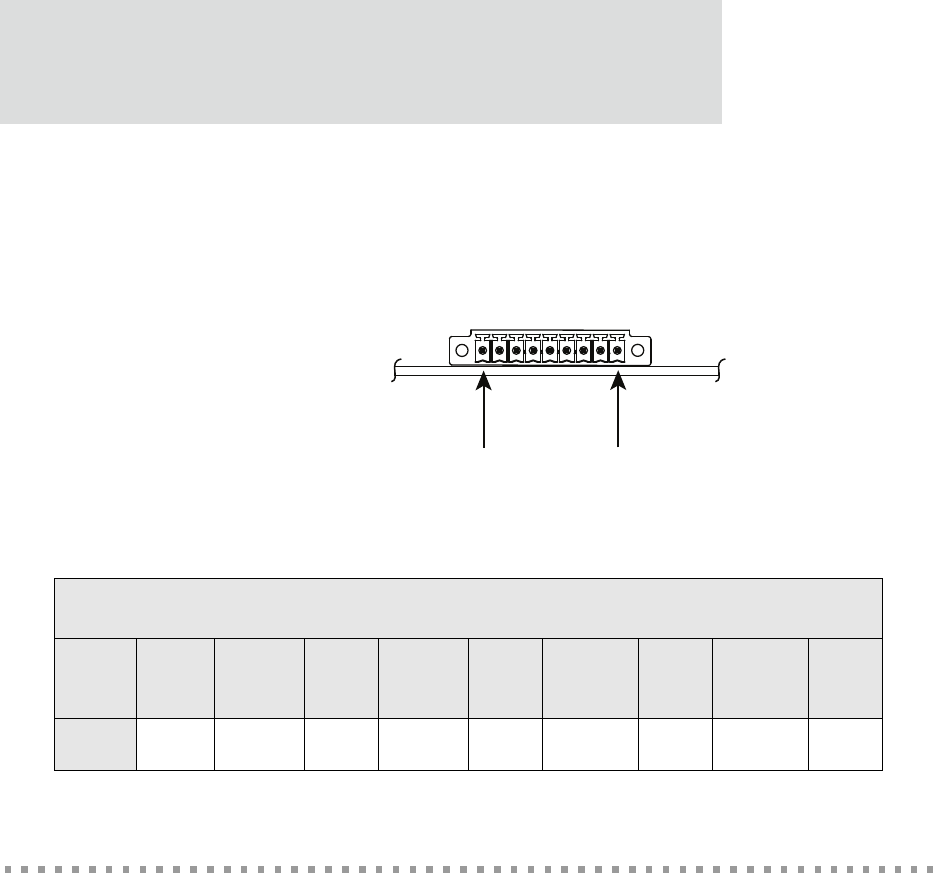
25
Note:
The development board is shipped with a 9-pin screw-flange plug attached to
the GPIO port.
GPIO Port Pin Orientation
Connectors and Blocks
The development board provides the following connectors and blocks:
Embedded Module Connector, P10
The Digi Connect Wi-ME module does not provide pins 1-6
JTAG Debugger Connector, P12.
-48V DC input to PoE module (ME must be connected to a Powering Device
for this feature.), P13
12V DC output from PoE module into Dev Board Power Supply, P14
Logic Analyzer Header, P3
Pin 1 Pin 9
GPIO Port Pin Assignments
Pin
1
Pin
2
Pin
3
Pin
4
Pin
5
Pin
6
Pin
7
Pin
8
Pin
9
Signal GPIO-1 GND GPIO-2 GND GPIO-3 TXD_TTL GPIO-4 RXD_TTL GPIO-5
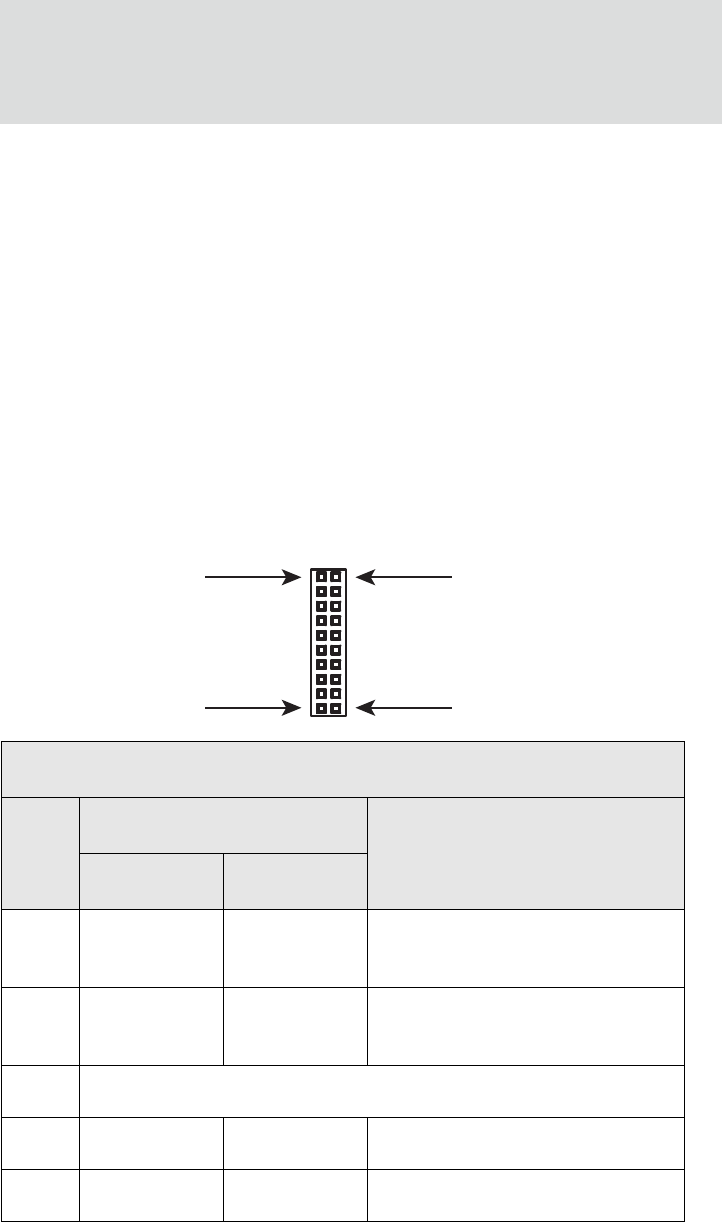
26
See the figure titled "Board Layout and Connector Locations:" on page 19 for the location
of the connectors and blocks. The following sections describe the connectors and blocks.
Embedded Module Connector, P10
The Digi Connect ME embedded module Connector is a 20-pin female vertical header that
is labeled P10 on the development board. See the following figure for pin orientation; see
the following table for pin assignments.
Note:
The figure shows the connector using the same orientation as shown in the
figure titled "Board Layout and Connector Locations:" on page 19.
Embedded Module Connector Pin Orientation
Module Connector Pin Assignments
Pin
Signal
Description
ME Wi-ME
1 VETH+ — ME: Power Pass-Thru +
Wi-ME: Position removed
2VETH- —ME: Power Pass-Thru -
Wi-ME: Position removed
3-6 Position Removed
7RXD RXD Receive Data (Input)
8 TXD TXD Transmit Data (Output)
Pin 20
Pin 1
Pin 19
Pin 2
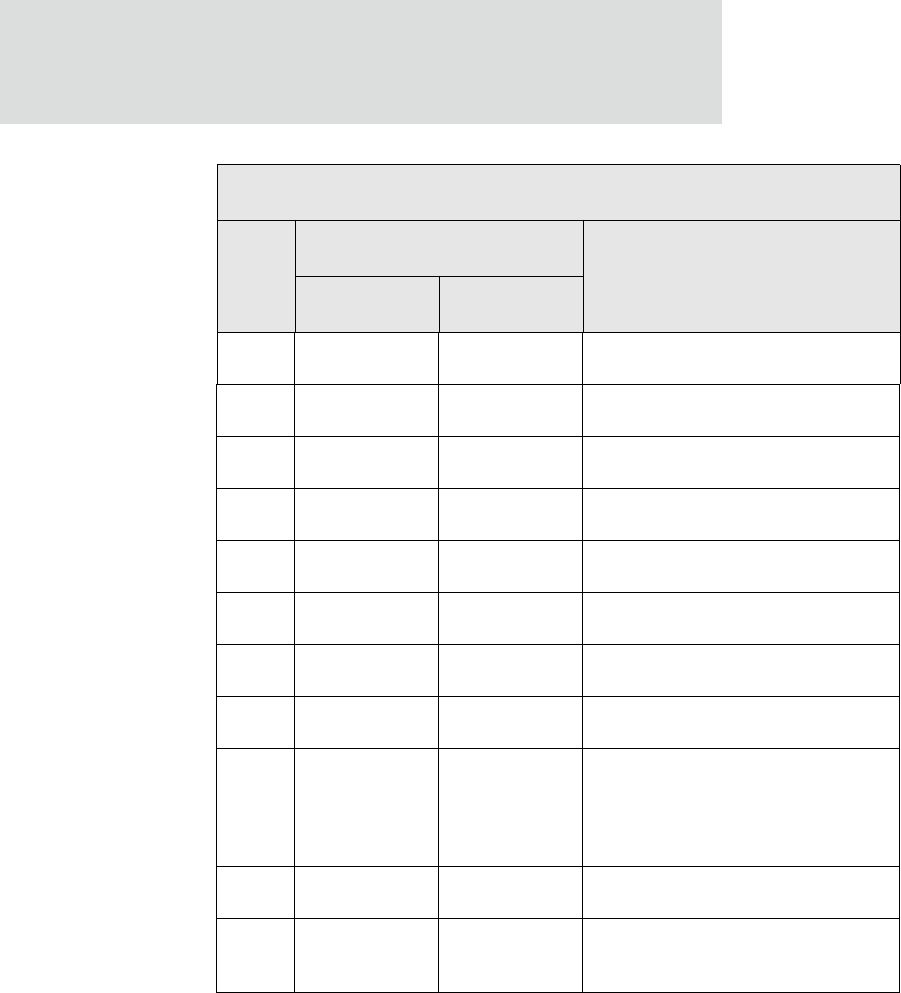
27
Note:
The Digi Connect Wi-ME module does not provide pins 1-6
Note:
See "Module Pinout" on page 39 for detailed IO configuration information.
9RTS RTS Request to Send (Output)
10 DTR DTR Data Terminal Ready (Output)
11 CTS CTS Clear to Send (Input)
12 DSR DSR Data Set Ready (Input)
13 DCD DCD Data Carrier Detect (Input)
14 /RESET /RESET Reset
15 +3.3V +3.3V Power
16 GND GND Ground
17, 18
Not accessible with Digi Plug-and-Play
Firmware. If using a development kit, see
"Module Pinout" on page 39 for detailed
IO configuration information.
19 Reserved
20 /INIT /INIT Digi Plug-and-Play Firmware Software
Reset
Module Connector Pin Assignments
Pin
Signal
Description
ME Wi-ME
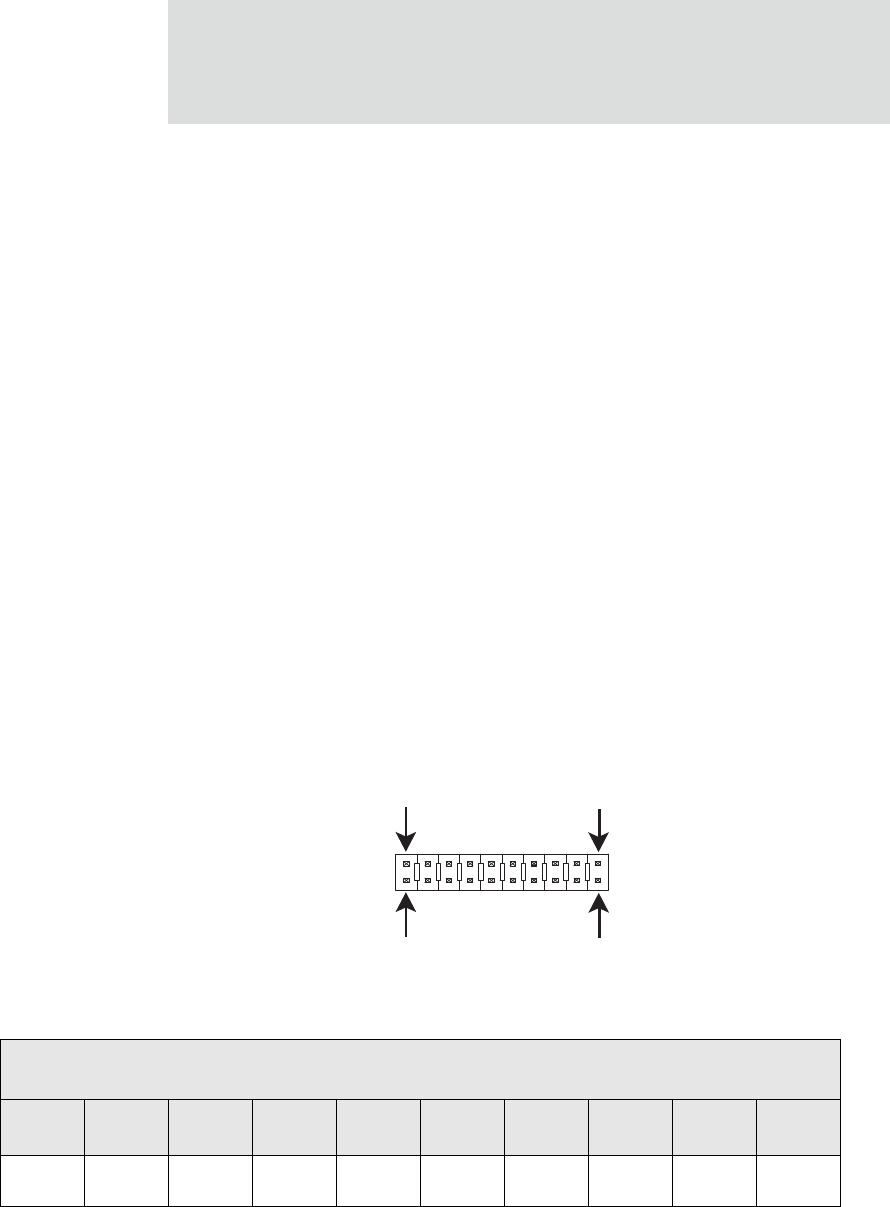
28
Module JTAG Interface Connector, P11
The Module JTAG Interface Connector is a 14-pin female vertical header that is labeled
P11 on the development board. The connector mates with the JTAG connector on the Digi
Connect ME embedded module. The Module JTAG Connector pins are tied to the JTAG
debugger Connector (see “JTAG Debugger Connector, P12”).
Note:
Because there is no direct connection to the Module JTAG Interface
Connector, pin orientation and pin assignments are not described for the
connector.
JTAG Debugger Connector, P12
The JTAG debugger connector is a 20-pin male vertical header that is labeled P12 on the
development board. The connector mates with a JTAG debugger plug (for example, a Digi
JTAG Link). The connector is used with the development kit only. See the following figure
for pin orientation. See the following table for pin assignments.
Note:
The figure shows the connector using the same orientation as shown in the
figure titled "Board Layout and Connector Locations:" on page 19.
JTAG Debugger Connector Pin Orientation
Pin 19 Pin 1
Pin 20 Pin 2
JTAG Debugger Connector Pin Assignments
Pin 1 Pin 2 Pin 3 Pin 4 Pin 5 Pin 6 Pin 7 Pin 8 Pin 9 Pin 10
VCC+ VCC+ /TRST GND TDI GND TMS GND TCK GND
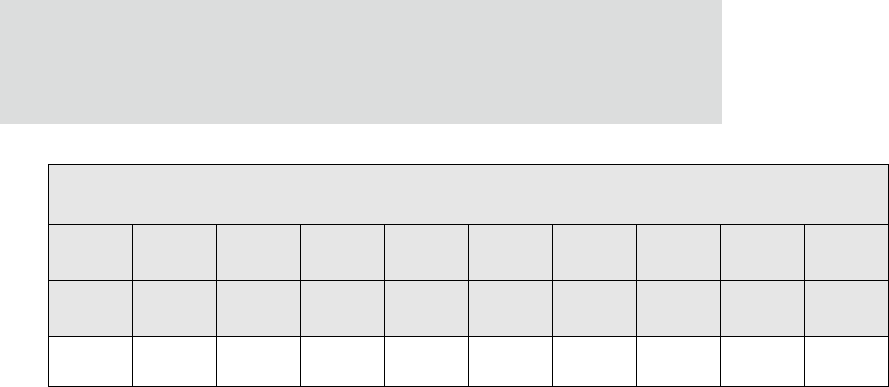
29
Pin 11 Pin 12 Pin 13 Pin 14 Pin 15 Pin 16 Pin 17 Pin 18 Pin 19 Pin 20
RTCK GNO TDO GND /SRST GNO N/A GND N/A GND
JTAG Debugger Connector Pin Assignments
Pin 1 Pin 2 Pin 3 Pin 4 Pin 5 Pin 6 Pin 7 Pin 8 Pin 9 Pin 10
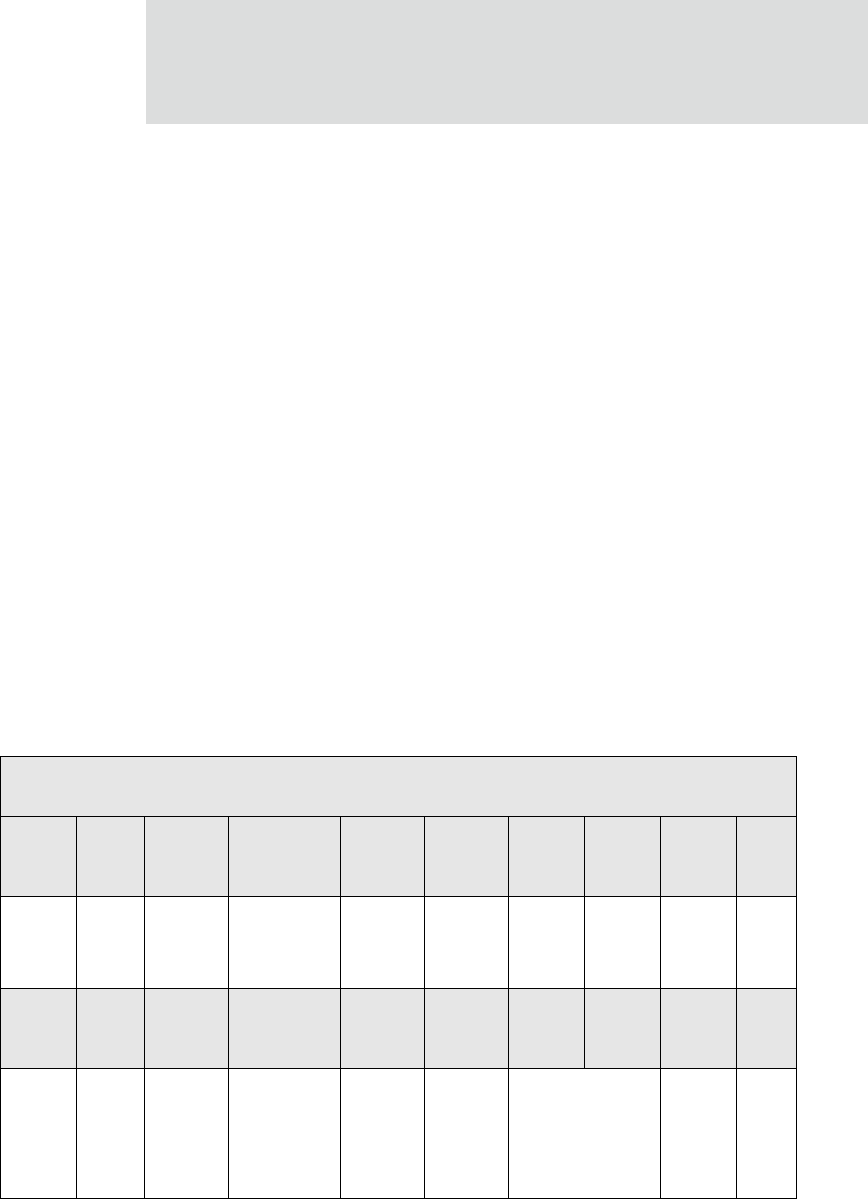
30
Logic Analyzer Header, P3
The Logic Analyzer Header is a 20-pin male vertical header that is labeled P3 on the
development board. The header is for connecting a digital signal analyzer (for example, a
logic analyzer) to the development board. See the following figure for pin orientation; see
the following table for pin assignments.
Note:
The figure shows the connector using the same orientation as shown in the
figure titled "Board Layout and Connector Locations:" on page 19.
Logic Analyzer Header Pin Orientation
Logic Analyzer Header Pin Assignments
Pin
1
Pin
2Pin 3 Pin 4 Pin 5 Pin 6 Pin 7 Pin 8 Pin
9
Pin
10
V_Ether+ V_Ether- Not
Connected Not Connected
Not
Connected
Not
Connected RXD TXD GPIO-4 GPIO-5
Pin
11
Pin
12
Pin
13
Pin
14
Pin
15
Pin
16
Pin
17
Pin
18
Pin
19
Pin
20
GPIO-2 GPIO-3 GPIO-1 /RST 3.3v GND
See "Power and
Device Interface
Connector Pin
Assignments" on
page 12 for details.
Reserved /INIT
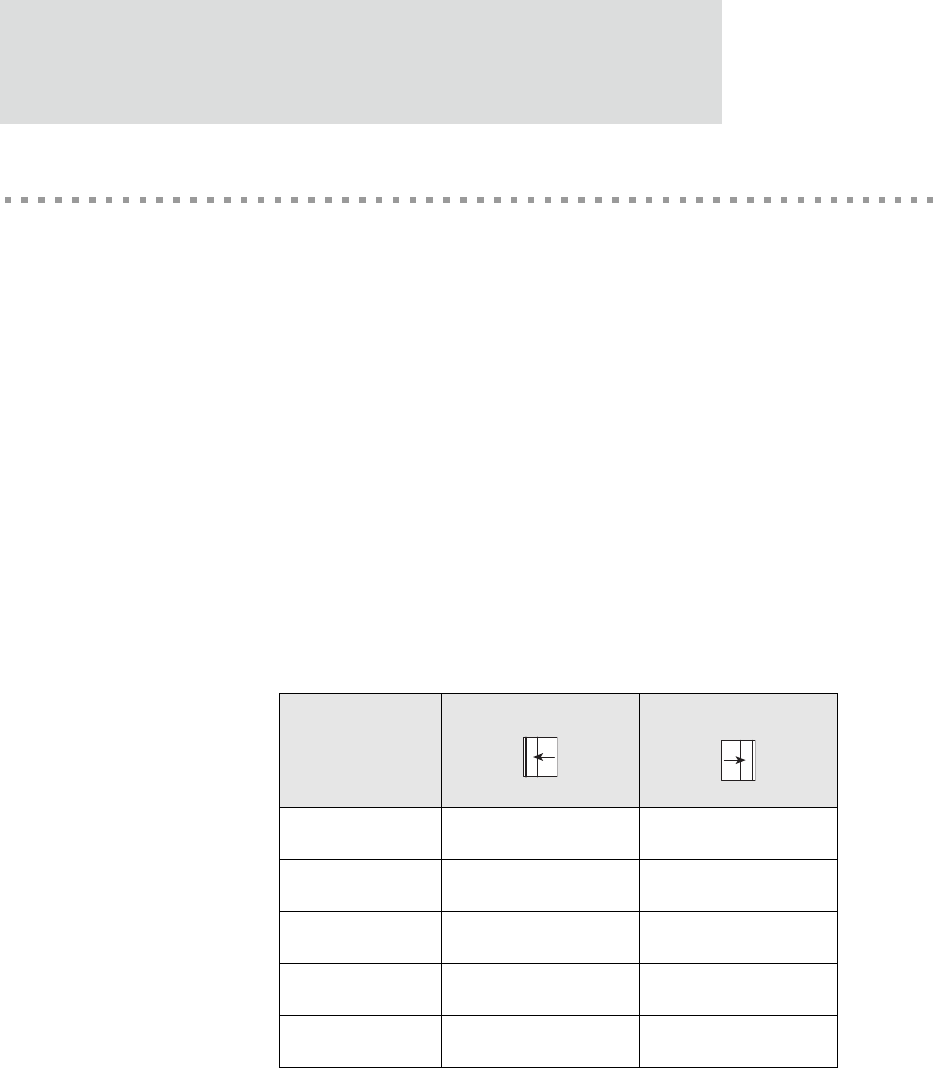
31
Switches
The development board provides the following switches:
GPIO Switch Bank 1, SW3
Reset, SW4
See the figure titled "Board Layout and Connector Locations:" on page 19 for the location
of the switches. The following sections describe the switches.
GPIO Switch Bank 1, SW3
GPIO Switch Bank 1, labeled SW3, is a set of five slide switches that allows the Digi
Connect ME embedded module to use either serial signals or GPIO signals to communicate
with a device.
GPIO Switch Bank 1 Settings
Switch
Number
Left Position Right Position
1 DCD GPIO-1
2 CTS GPIO-2
3 DSR GPIO-3
4 RTS GPIO-4
5 DTR GPIO-5
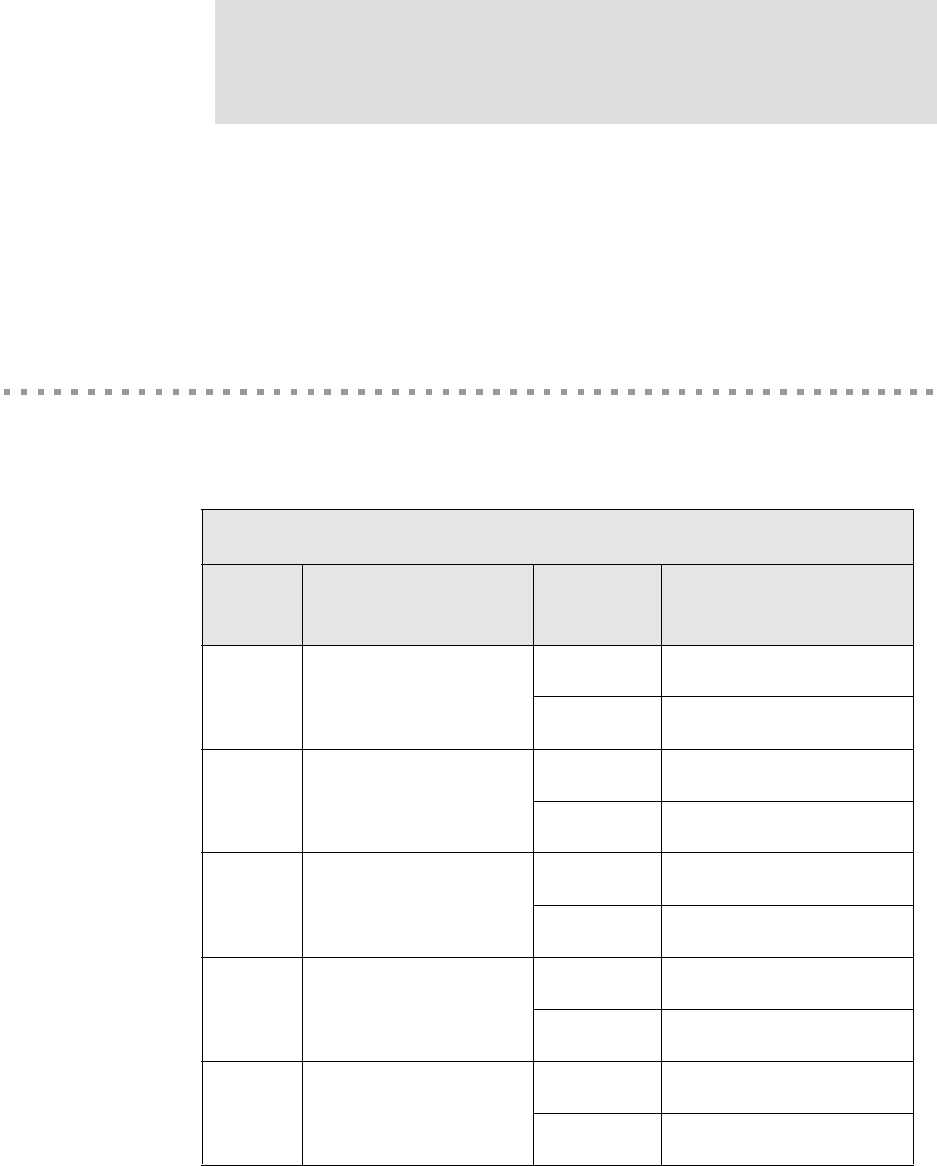
32
Reset, SW4
The Reset switch is a push button switch labeled SW4 on the development board. Pressing
the switch holds the Digi Connect ME embedded module in reset. When the push button is
released, the module reboots.
Development Board LEDs
The development board contains 25 LEDs that are labeled CR1 through CR25. The
following table lists and describes the LEDs.
Development Board LED Descriptions
Board
Label Description
Color or
State
Indication
CR1 TXD, Secondary Serial Port
On Logic 1 on TTL
Off Logic 0 on TTL
CR2 TXD, Secondary Serial Port
On Logic 0 on TTL
Off Logic 1 on TTL
CR3 RXD, Secondary Serial Port
On Logic 1 on TTL
Off Logic 0 on TTL
CR4 RXD,Secondary Serial Port
On Logic 0 on TTL
Off Logic 1 on TTL
CR5 DCD, Primary Serial Port
On Logic 0 on line side
Off Logic 1 on line side
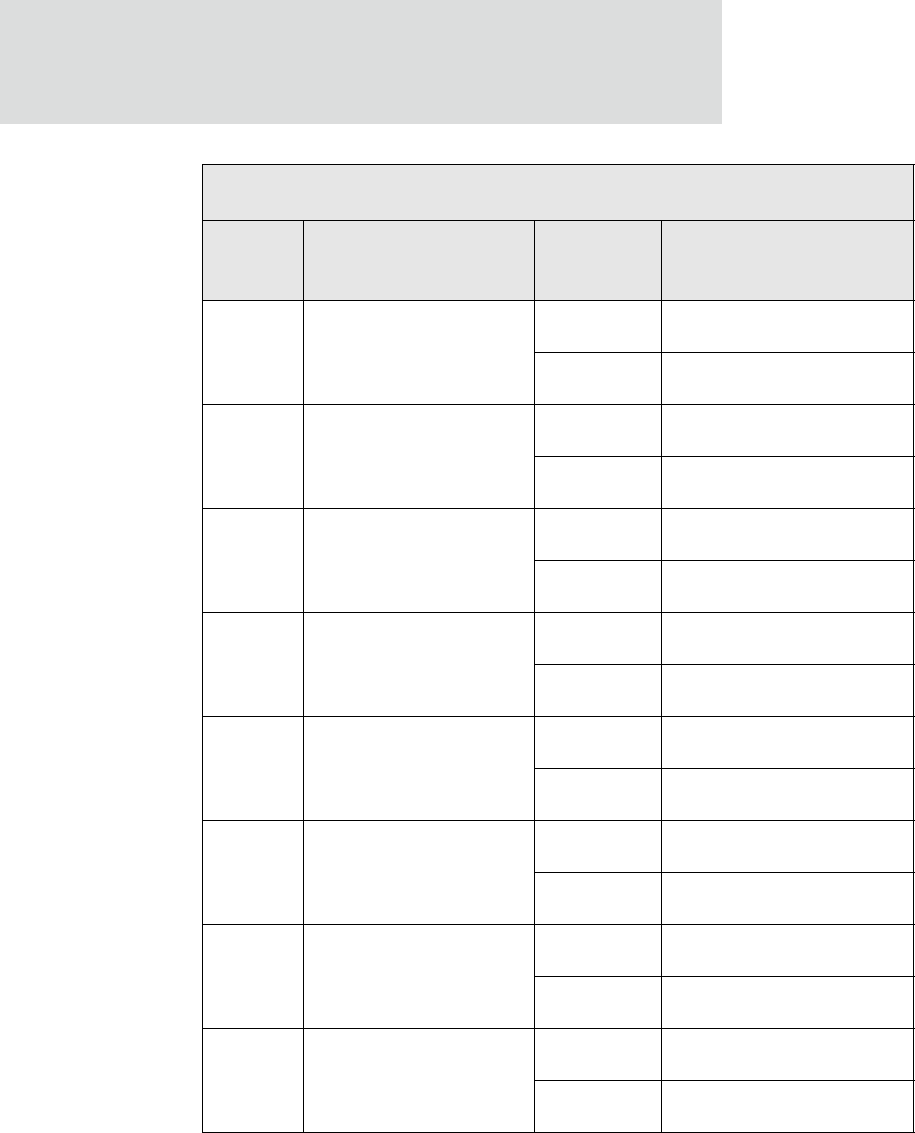
33
CR6 DCD, Primary Serial Port
On Logic 1 on line side
Off Logic 0 on line side
CR7 DSR, Primary Serial Port
On Logic 0 on line side
Off Logic 1 on line side
CR8 DSR, Primary Serial Port
On Logic 1 on line side
Off Logic 0 on line side
CR9 CTS, Primary Serial Port
On Logic 0 on line side
Off Logic 1 on line side
CR10 CTS, Primary Serial Port
On Logic 1 on line side
Off Logic 0 on line side
CR11 RXD, Primary Serial Port
On Logic 0 on line side
Off Logic 1 on line side
CR12 RXD, Primary Serial Port
On Logic 1 on line side
Off Logic 0 on line side
CR13 DTR, Primary Serial Port
On Logic 0 on line side
Off Logic 1on line side
Development Board LED Descriptions
Board
Label Description
Color or
State
Indication
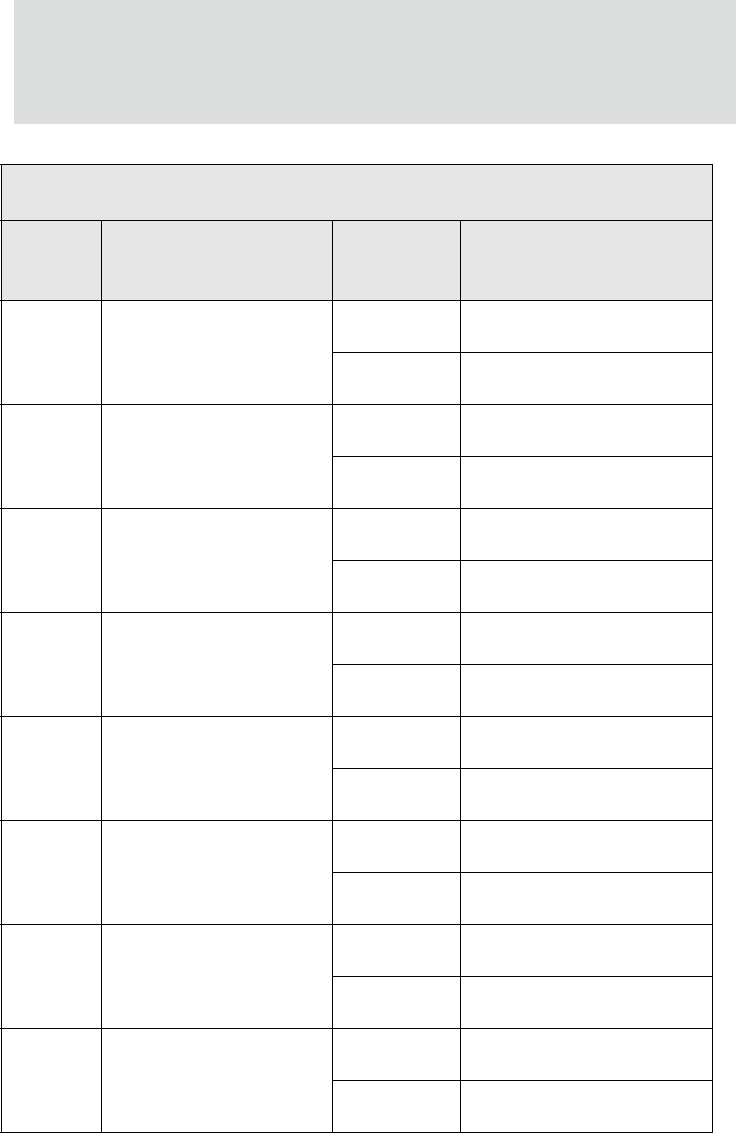
34
CR14 DTR, Primary Serial Port
On Logic 1on line side
Off Logic 0 on line side
CR15 RTS, Primary Serial Port
On Logic 0 on line side
Off Logic 1on line side
CR16 RTS, Primary Serial Port
On Logic 1on line side
Off Logic 0 on line side
CR17 TXD, Primary Serial Port
On Logic 0 on line side
Off Logic 1 on line side
CR18 TXD Primary Serial Port
On Logic 1 on line side
Off Logic 0 on line side
CR19 GPIO 1
On Logic 1
Off Logic 0
CR20 GPIO 2
On Logic 1
Off Logic 0
CR21 GPIO 3
On Logic 1
Off Logic 0
Development Board LED Descriptions
Board
Label Description
Color or
State
Indication
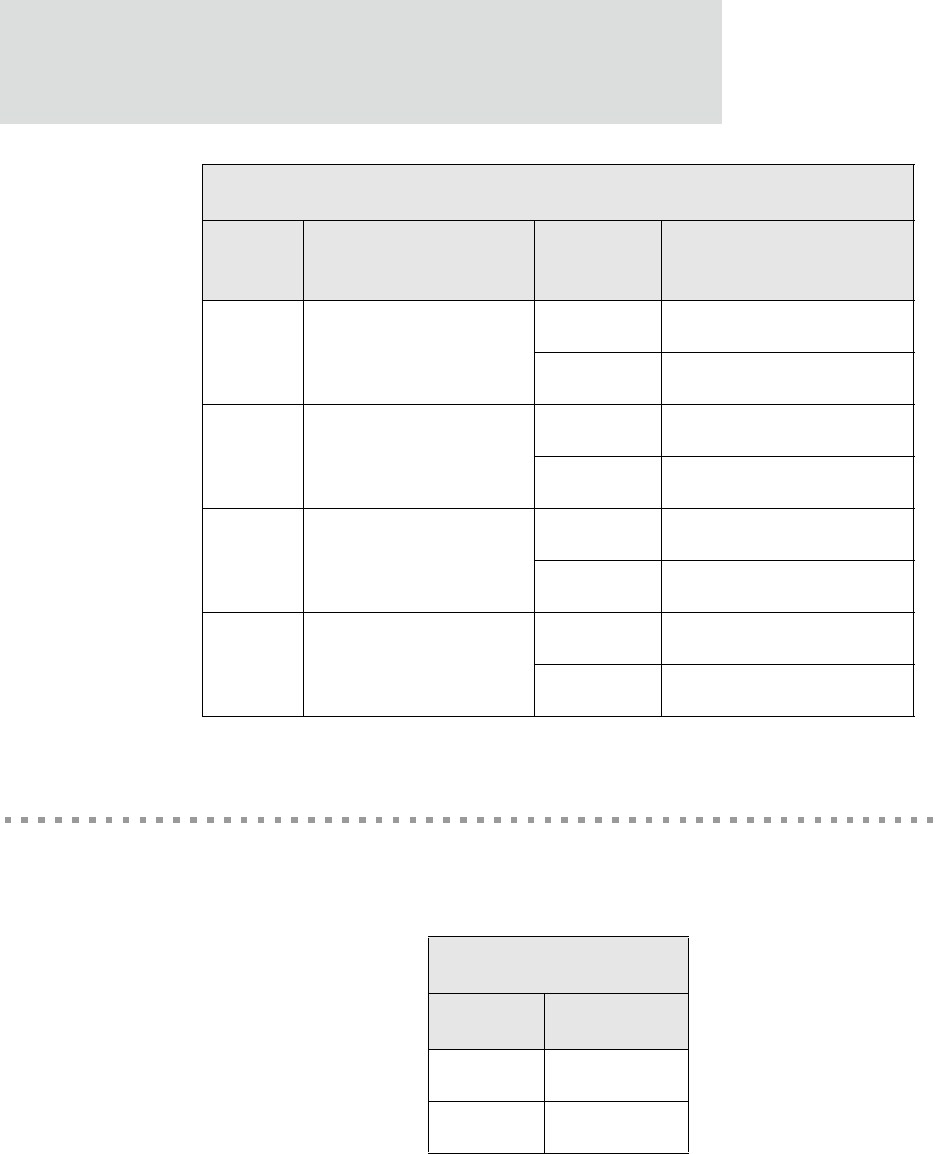
35
Power Jack
The Power Jack is a barrel connector that accepts 9 to 30 VDC +/- 5%. The jack is labeled
as P15 on the development board. The following table shows the polarity of the power jack.
The following figure schematically represents the polarity of the power jack.
CR22 GPIO 4
On Logic 1
Off Logic 0
CR23 GPIO 5
On Logic 1
Off Logic 0
CR24 3.3v LED
On 3.3v present from POE
Off No POE present
CR25 3.3v LED
On 3.3v present
Off No 3.3v present
Development Board LED Descriptions
Board
Label Description
Color or
State
Indication
Power Jack Polarity
Contact Polarity
Center +9 to +30 VDC
Outer Ground
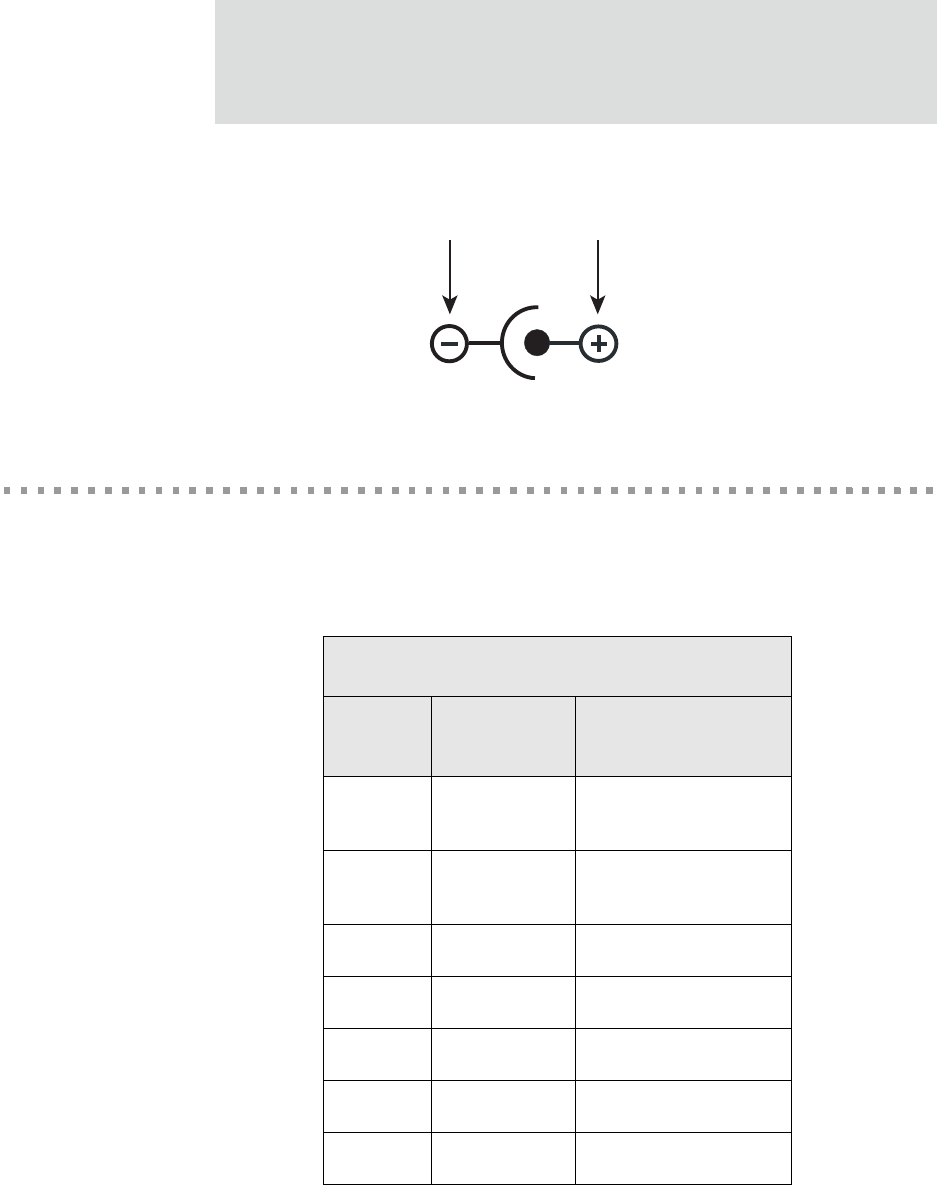
36
Power Jack Polarity, Schematic
Test Points
The development board provides 13 test points that can be identified by a board label . The
test point numbers are in the development board schematic drawings. The following table
lists the test point number, board label, and a brief description of each test point.
Ground +9 to +30 VDC
00000014
Test Point Descriptions
Test
Point
Board Label Description
TP2 TXD TXD-2, Transmit,
Secondary Serial Port
TP3 RXD RXD-2, Receive,
Secondary Serial Port
TP4 CTS CTS, Primary Serial Port
TP5 DTR DTR, Primary Serial Port
TP6 TXD TXD, Primary Serial Port
TP7 RXD RXD, Primary Serial Port
TP8 RTS RTS, Primary Serial Port
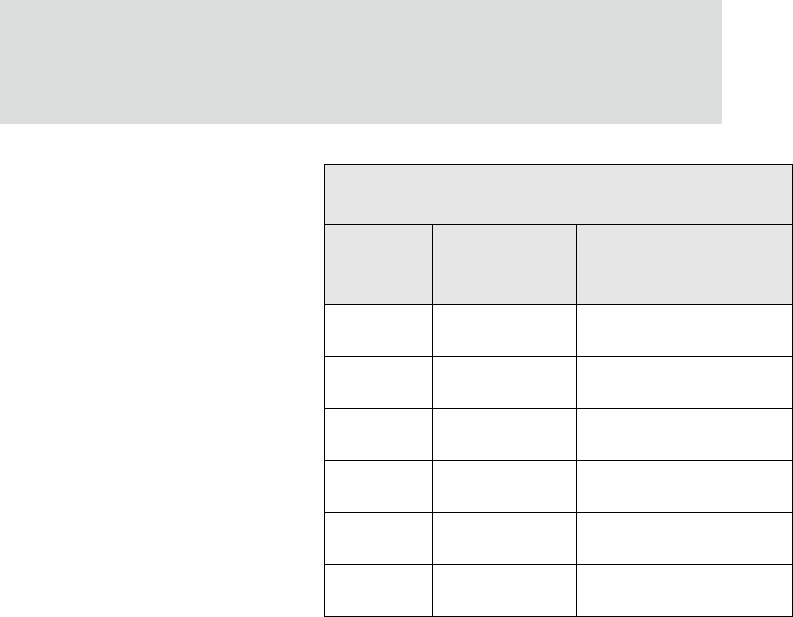
37
TP9 DCD DCD, Primary Serial Port
TP10 DSR DSR, Primary Serial Port
TP12 Reset Reset
TP13 POE 12v POE 12v
TP14 3.3v 3.3v Supply
TP15 GND Ground
Test Point Descriptions
Test
Point
Board Label Description
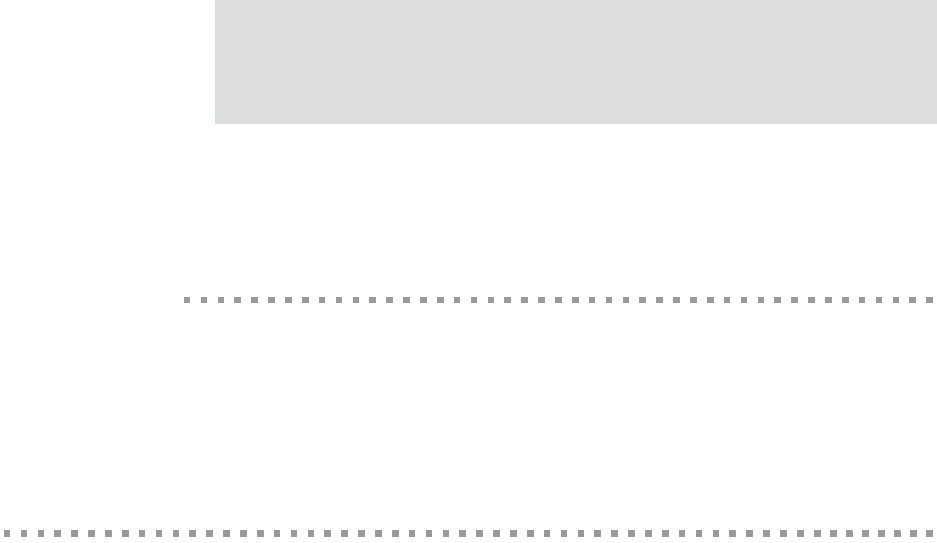
38
Programming Considerations
Programming
Considerations
CHAPTER 3
Overview
This chapter provides information programmers may require to make use of some Digi
Connect ME embedded module hardware resources. It provides programming information
on the following topics for the Digi Connect ME-9210, the Digi Connect ME and the Digi
Connect Wi-ME:
"Module Pinout" on page 39
"LEDs" on page 41
"Reset" on page 41
"Memory" on page 43
"SDRAM" on page 43

Module Pinout
39
Digi Connect ME, Digi Connect Wi-ME & Digi Connect 9210 Hardware Reference
Module Pinout
General Information
The NS7520/NS9210 processors support 16 General Purpose I/O (GPIO) lines, some of
which are reserved for specific functions and some of which can be customized. For Digi
Plug-and-Play Firmware users, see the Digi Connect Family Users Guide for details on
what Pin configurations are available to you.
Module Pinout
The following table provides signal header pinout information for the Digi Connect Me,
Digi Connect Wi-ME and Digi Connect ME 9210 modules. Please refer to the color key
below.
Key
Applies to Digi Connect
ME/Wi-ME modules.
Applies to Digi Connect
ME 9210 modules.
Applies to Digi Connect
ME/Wi-ME and ME 9210
modules.
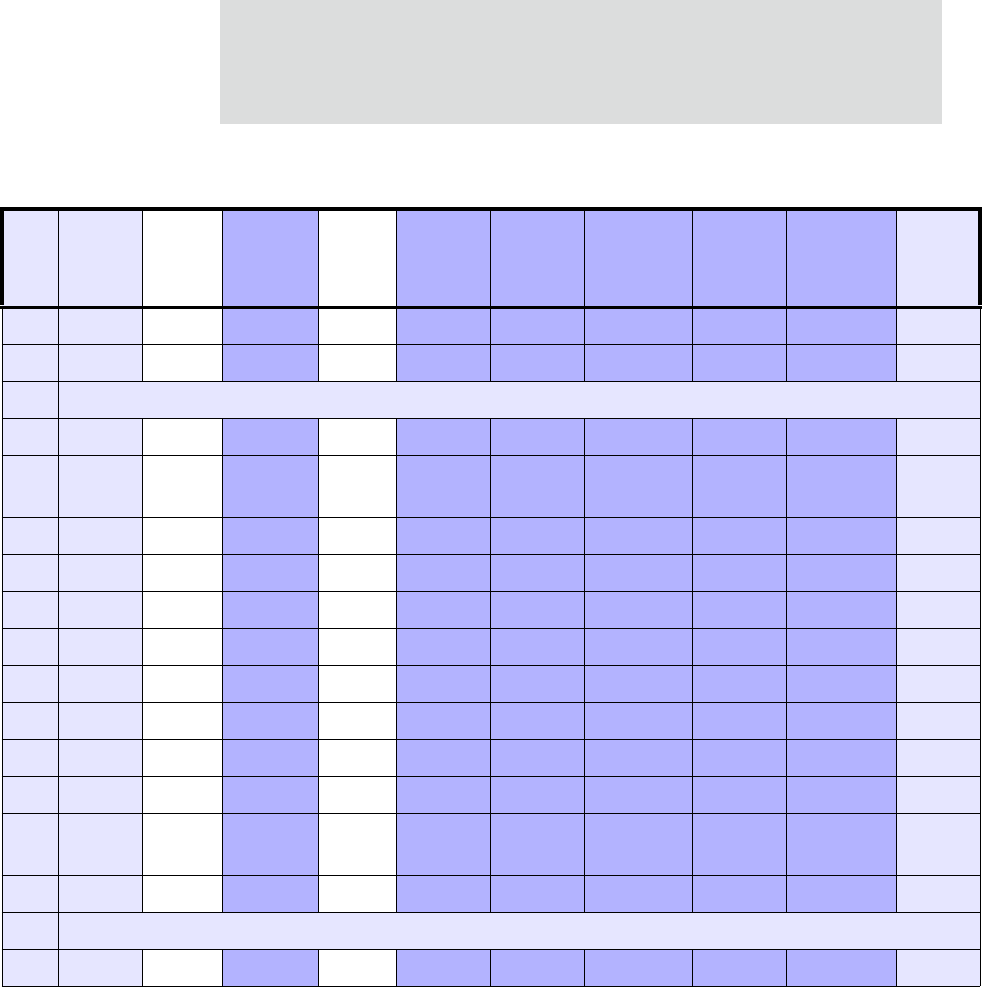
40
Programming Considerations
Note:
A special model of the Digi Connect ME 9210 is required for CAN bus 2.0
support. The CAN bus model does not support the 12C interface. Instead, it
makes GPIO[14] / PIC[0]_CAN_RXD available on pin 17, and GPIO [15]/
PIC[0]_CA_TXD on pin 18. Please contact Digi for availabilty information.
Note:
The Digi Connect Wi-ME module does not provide pins 1-6.
Pin UART
[All]
GPIO
[ME/
Wi-ME]
GPIO
[ME 9210]
Ext
IRQ
[ME/
Wi-ME]
Ext
IRQ
[ME 9210]
I2C
[ME 9210]
SPI
[ME 9210]
FIM
[ME 9210]
Timer
[ME 9210]
Other
[All]
1VETH+
2VETH-
3-6 Positions Removed
7RXD A3 GPIO[3] DATA IN PIC [3]
8TXD A7 GPIO[7] DATA OUT Timer Out 7
Timer In 8
9RTS A5 GPIO[5] 3CLK Timer Out 6
10 DTR A6 GPIO[6] Timer In 7
11 CTS A1 GPIO[1] 0PIC[1]
12 DSR A2 GPIO[2] 1PIC[2]
13 DCD A0 GPIO[0] EN PIC[0]
14 /RST
15 3.3V
16 GND
17 C4 GPIO[12] SDA CLK RESET_
DONE
18 C1 GPIO[9] 1 0 SCL
19 Reserved
20 C5 GPIO [13] CLK Timer Out 9 /INIT
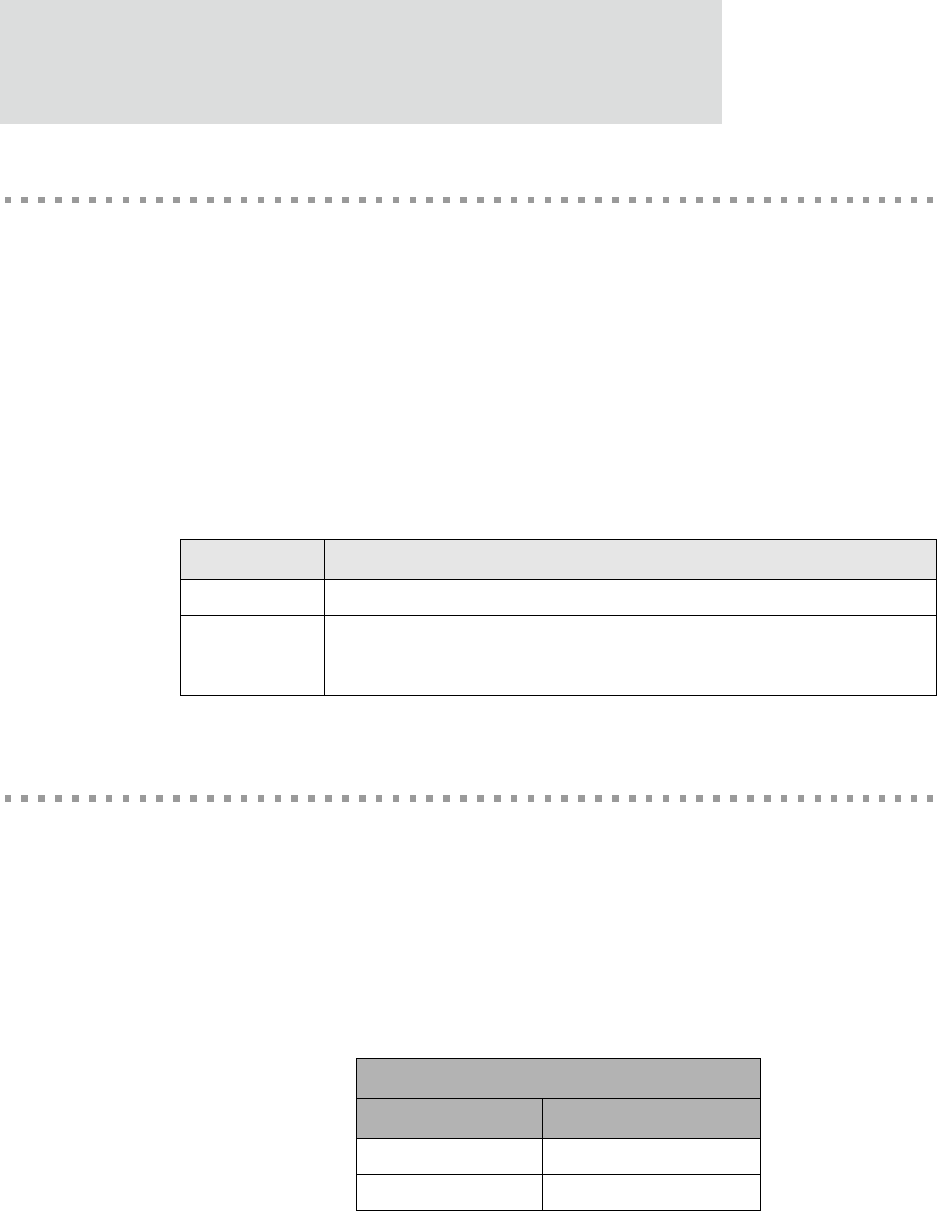
LEDs
41
Digi Connect ME, Digi Connect Wi-ME & Digi Connect 9210 Hardware Reference
LEDs
General Information
The embedded modules have two types of LEDs:
An LED connected directly to GPIO pins on the processor and controlled
directly in software
An LED connected to other hardware components (normally the Ethernet
hardware) and not directly programmable by the operating system
The development kit, by default, correctly configures the GPIO connected to the LED as an
output and then uses this LED to represent Ethernet activity.
Reset
Hard Reset
The embedded module supports a hardware reset via pin 14 of the 20-pin header. The unit
is forced into a hard reset when pulling the pin to ground, or less than 2.88v, for one
microsecond. When plugged into a development board, this pin is wired to the push button
at SW3. As a result, this switch acts as a hard reset button.
LED Description
Yellow This is wired directly to Ethernet hardware and provides an indication of link.
Green
This software-programmable LED is wired to processor GPIO register bit C6/
GPIO[14] and is wired to be lit when low. The default behavior is to blink on
Ethernet activity.
Reset Characteristics
Characteristic Specification
Delay 250 milliseconds (typical)
Threshold 2.88 V
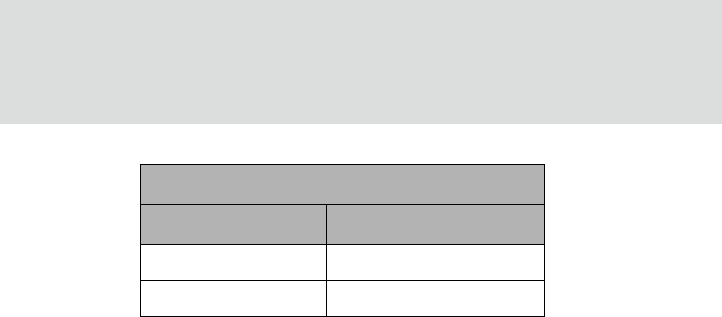
42
Programming Considerations
Minimum Hold Time 1 microsecond pulse
Rise Time 100 microseconds
Reset Characteristics
Characteristic Specification
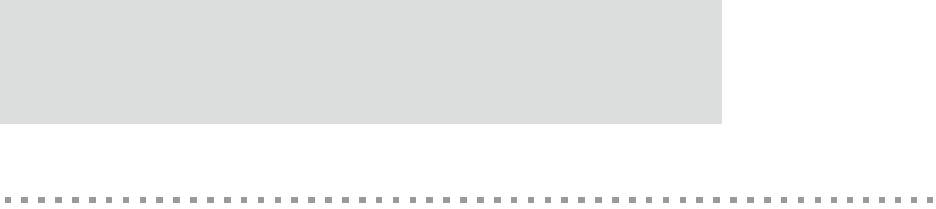
Memory
43
Digi Connect ME, Digi Connect Wi-ME & Digi Connect 9210 Hardware Reference
Memory
Flash
The Digi Connect ME has 2 or 4 MB of flash memory. The Digi Connect Wi-ME has 4 MB
of flash memory.
On the ConnectME/ARM7 family, the flash memory is controlled by chip select 0, located
at 0x02000000.
On the ConnectME-9210/ARM9 family, the flash memory is controlled by chip select 2
(default=st_cs1) and is located at 0x50000000.
SDRAM
The Digi Connect ME and the Digi Connect Wi-ME’s SDRAM is controlled by chip
select 1 and is located at 0x00000000.
The Digi Connect ME 9210’s SDRAM is controlled by chip select 1 (default = dy_cs0)
and is mapped to 0x00000000.
The embedded modules have 8 MB of SDRAM memory.
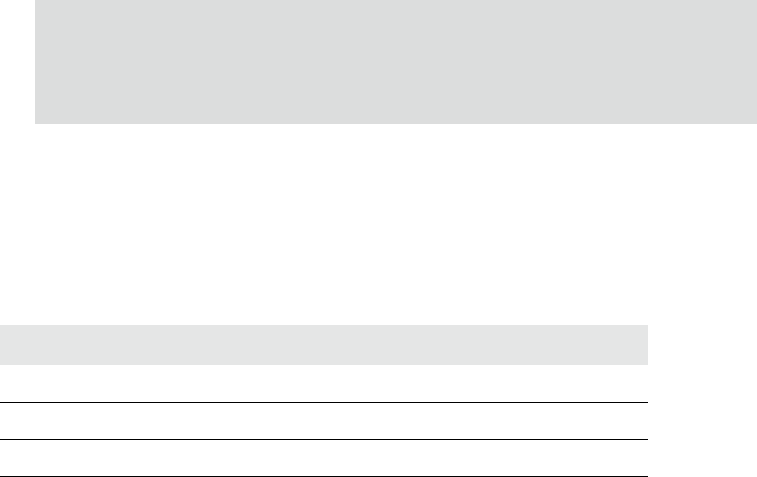
44
Programming Considerations
The following table illustrates typical power consumptions using these power management
mechanisms. These measurements were taken with all Digi NS9210 processor’s I/O clocks
disabled except UART A, UART C, Ethernet MAC, I/O Hub and Memory Clock0 with the
ethernet connected to a 100Mb network, using a standard module plugged into a Digi
JumpStart Kit development board, with nominal voltage applied:
Note 1: This measurement was taken from the R6 current sense resistor using a 0.025 ohm shunt on the
JumpStart Kit development board.
Note 2: This is the default power consumption mode when entering applicationStart(), as measured with the
napsave sample application. The value of the NS9210 Clock Configuration register (A090017C) is 0001200B
hexadecimal.
Note 3: This measurement was produced by selecting the “Clock Scale” menu option in the napsave sample
application.
Note 4: This measurement was produced by selecting the “Deep Sleep/Wakeup with an External IRA” menu
option in the napsave sample application.
Mode Power Consumption1
Normal Operational Mode21.14W (346mA)
Full Clock Scaling Mode3.613W (186mA)
Sleep Mode4.113W (34mA)

Memory
45
Digi Connect ME, Digi Connect Wi-ME & Digi Connect 9210 Hardware Reference
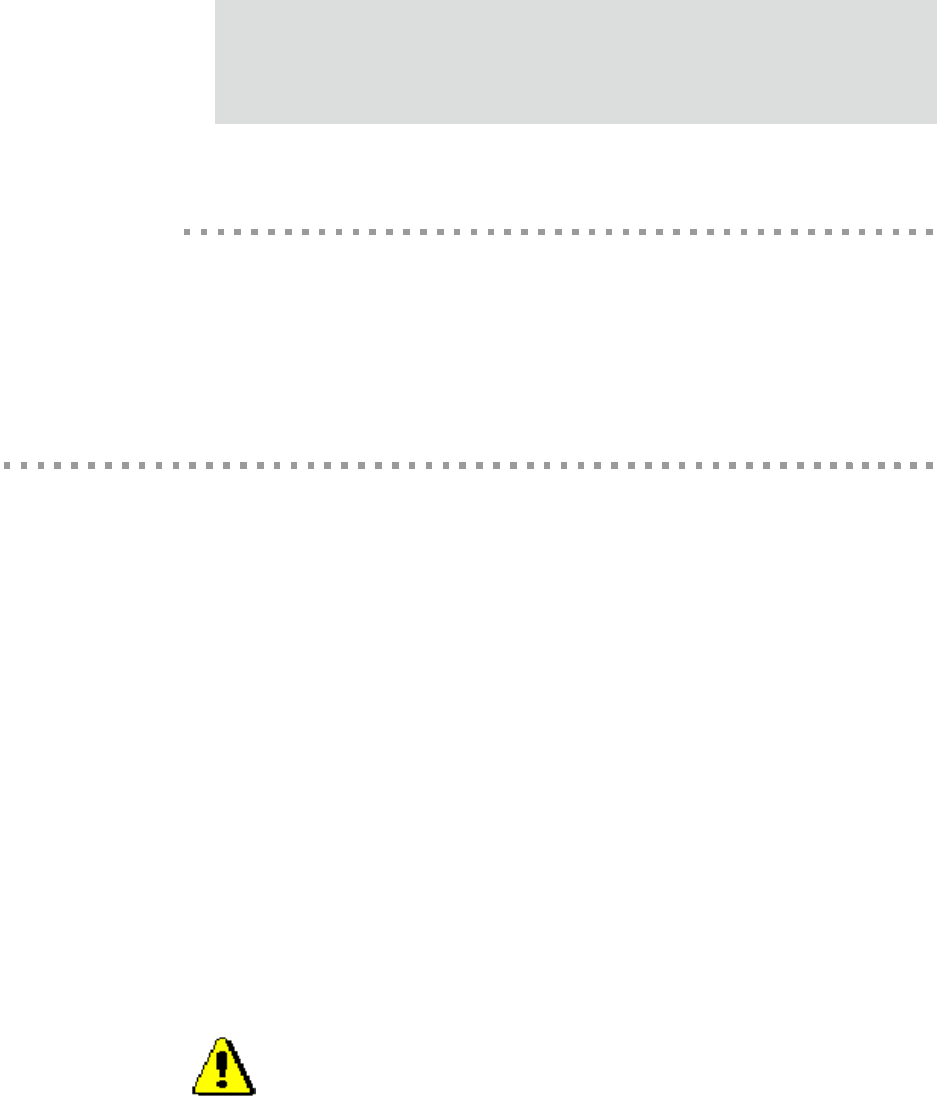
46
Module Specifications
APPENDIX A
Network Interface
Digi Connect ME/ME9210 Digi Connect Wi-ME
Standard: IEEE 802.3
Physical Layer: 10/100Base-T
Data Rate: 10/100Mbps (auto-sensing)
Mode: Half-duplex and full-duplex support
(auto-sensing)
Connector: RJ-45
Standard: IEEE 802.11b
Frequency: 2.4 GHz
Data Rate: Up to 11 Mbps with automatic fallback
Modulation: CCK (11/5 Mbps), DQPSK (2 Mbps),
DBPSK (1 Mbps)
Transmit Power: 16 dBm typical
Receive sensitivity:
– 1Mbps: -92 dBm
– 2Mbps: -89 dBm
– 5.5Mbps: -87 dBm
– 11Mbps: -82 dBm
Antenna Connector: 1 x RP-SMA
Caution: The Digi Connect ME and Digi Connect Wi-ME embedded
modules were designed for use in no clean flux wave soldering processes.
The product is not designed to support draining after a water-wash
process, which can lead to water residue inside the enclosure resulting
from direct entry or condensation after the wash process.
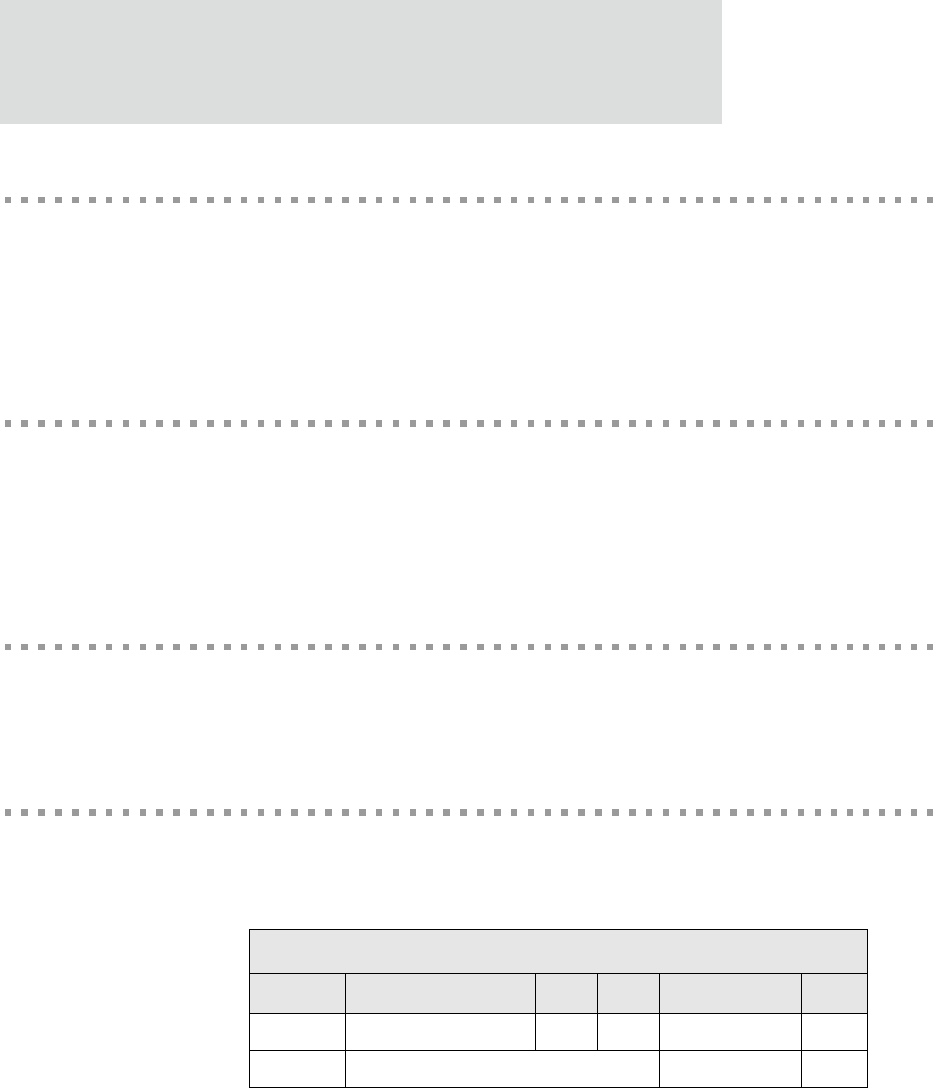
47
Serial Interface
One TTL serial interface (CMOS 3.3v) with full modem control signals (DTR, DSR, DCD,
RTS, CTS). The Connect ME 9210 also supports SPI and FIM-based application specific
interfaces.
Data Rates (bps)
50, 75, 110, 134, 150, 200, 300, 600, 1200, 1800, 2400, 4800, 9600, 14400,19200, 28800,
38400, 57600, 115200, 230400, 460800 (Connect ME 9210 only), 921600 (Connect ME
9210 only)
Flow Control Options
RTS/CTS, XON/XOFF, None
DC Characteristics
The following tables provide DC characteristics for operating conditions, inputs, and
outputs.
Operating Conditions
Symbol Description Min Typ Max Unit
VCC Supply Voltage 3.14 3.3 3.45 V
n/a Power Supply Ripple 40 mVpp
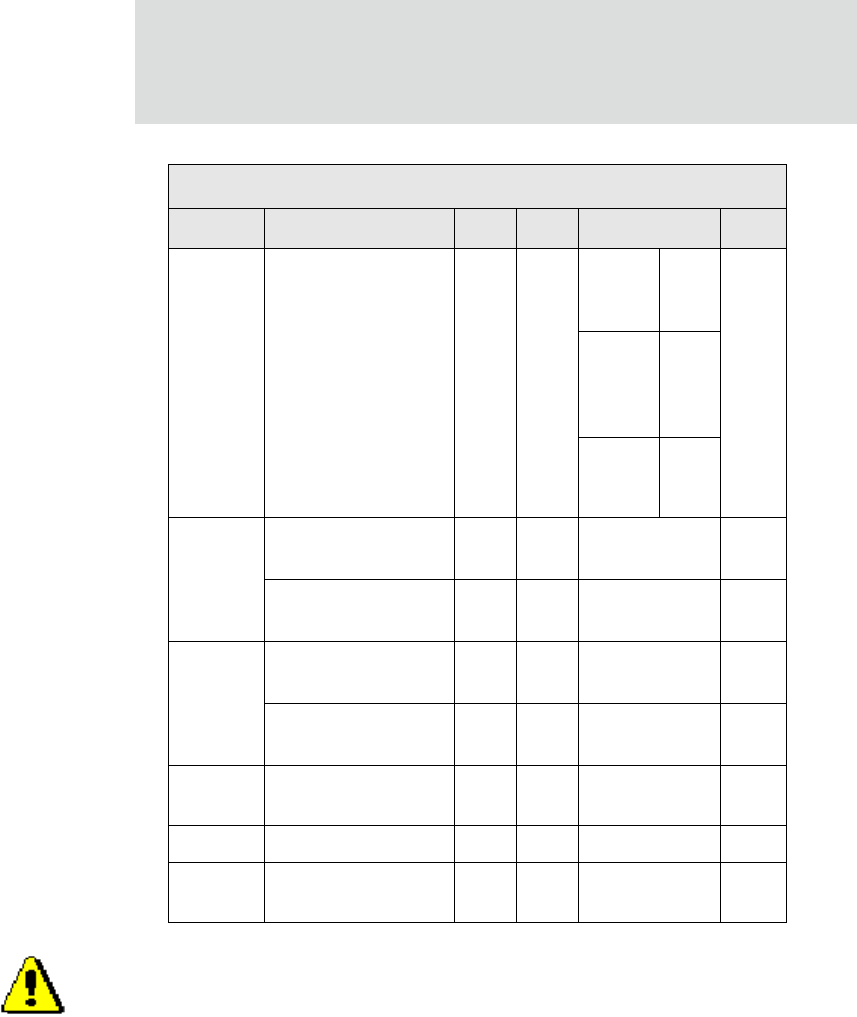
48
Warning: The rise time of the 3.3v power supply must be between 700 μS and 140ms
and the inrush current must be limited to less than 2 A. A rise time outside of these
limits may cause the device to malfunction and give a 3-1-3 diagnostic error.
ICC Supply Current ——
Digi
Connect
ME
270
mA
Digi
Connect
ME
9210
450
Digi
Connect
Wi-ME
400
IIL
Input Current as “0”
(57K pull-up resistor) —— 57 μA
9210
(16K pull up resistor) -10 — 200 μA
IIH
Input Current “1”
(57K pull-up resistor) -10 — 10 μA
9210
(16K pull up resistor) -10 — 10 μA
IOZ
HighZ Leakage
Current -10 — 10 μA
IOD Output Drive Strength — — 2 mA
CIO
Pin Capacitance
(VO=0) —— 4 pF
Operating Conditions
Symbol Description Min Typ Max Unit
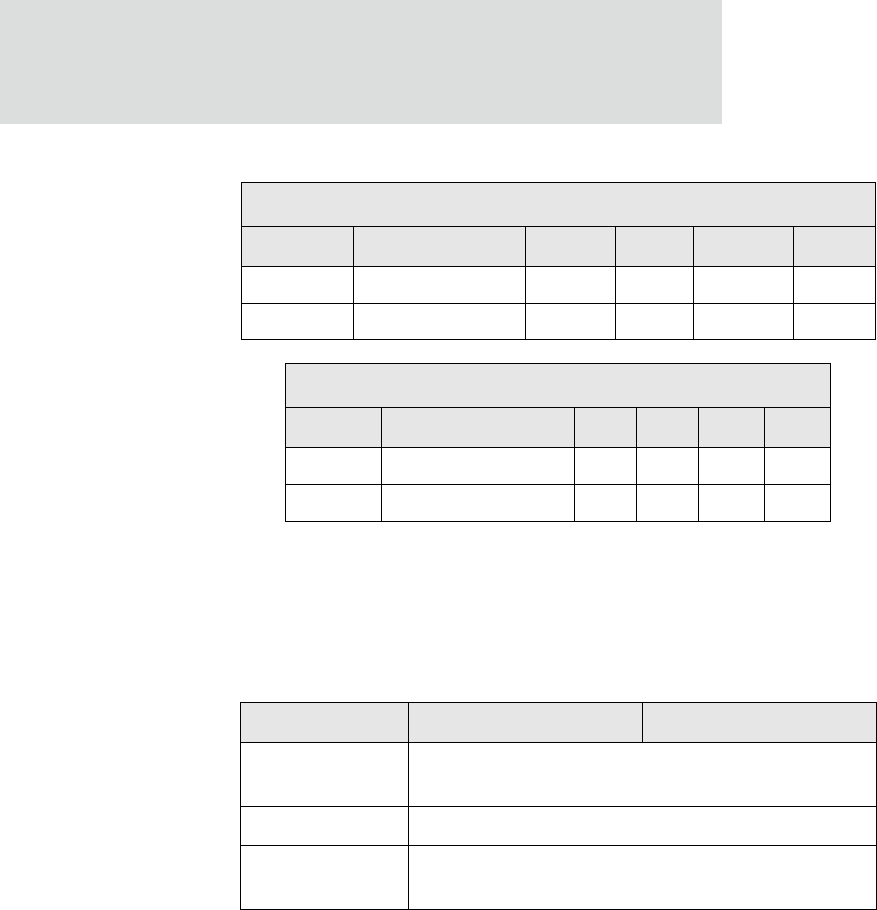
49
Note:
The embedded modules provide an on board supervisor circuit with a 2.88V reset
threshold and an internal 5k pull-up resistor. When VCC falls to the threshold
voltage, a reset pulse is issued, holding the output in active state. When power
rises above 2.88V, the reset remains for approximately 250 ms to allow the system
clock and other circuits to stabilize.
Inputs
Symbol Description Min Typ Max Unit
VIH Input High Voltage 2 — VCC+0.3 V
VIL Input Low Voltage VSS-0.3 — 0.2*VCC V
Outputs
Symbol Description Min Typ Max Unit
VOH Output High Voltage 2.4 — 3.45 V
VOL Output Low Voltage 0 — 0.4 V
Digi Connect ME Digi Connect Wi-ME
Storage
Temperature
-40°F to 257°F
(-40°C to 125°C)
Humidity 5% to 90%
Altitude 12000 feet
(3657.60 meters)
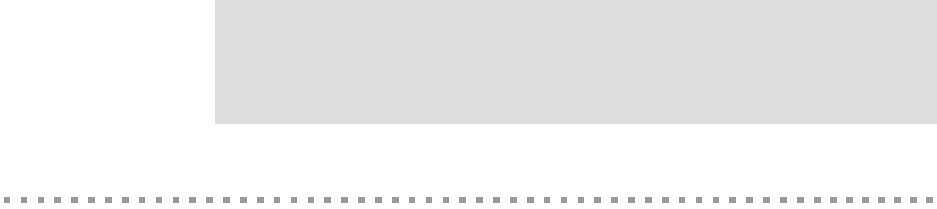
50
Power Management (Connect ME-9210 only)
Using the Digi NET+OS development environment, applications on the Digi Connect ME
9210 are capable of operating the module in several reduced power consumption modes.
These reduced power operating modes utilize the power management mechanisms for the
Digi NS9210 processor for CPU clock scaling and sleep.
In the Clock Scaling mode, the system itself continues to execute instructions, but at a
different clock rate, which can be changed on-the-fly, using Digi’s patented circuitry inside
the NS9210 processor. The clock speed is changed programmatically to lower or raise the
system clock speed, thus reducing or increasing the module’s power footprint, respectively.
Additionally, a Sleep mode is available in which the system stops executing instructions.
Based on the application needs, wake-up triggers can be set up programmatically to
activate the processor back to wherever it left off. In this mode, a drastic power reduction is
realized by reducing the power consumption of the Digi NS9210 processor and the on-
module PHY.
For sample power consumption figures for normal (typical) and power management related
operation of the Digi Connect ME 9210, see below:
3.3VDC @ 346 mA typical (1.14W)
UART and Ethernet activated
Low Speed Idle Mode (approximate)
3.3VDC @ 186 mA (613 mW)
/16 clock scaling, Ethernet activated
Sleep Mode (approximate)
3.3VDC @ 34 mA (113 mW)
Wake-up on EIRQ, Ethernet PHY off
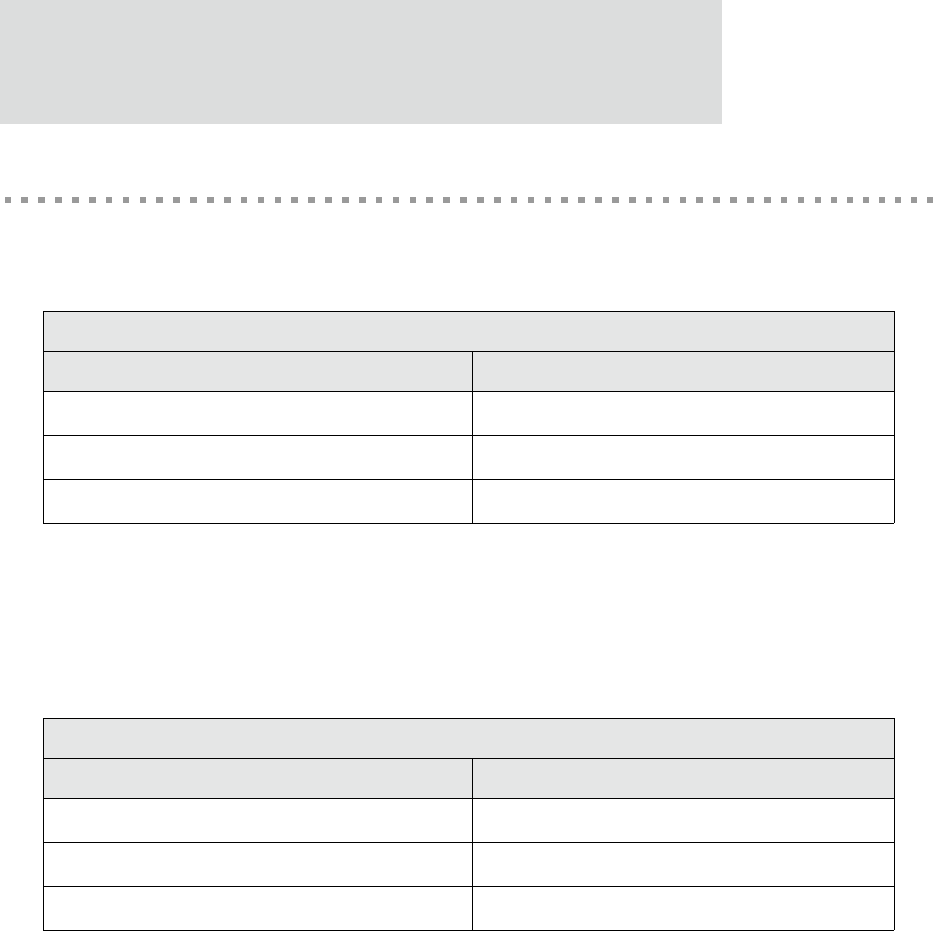
51
Thermal Specifications
The table below shows the standard operating temperature ranges for the entire Digi
Connect ME family of embedded modules.
The lower standard operating temperature ranges are specified without restrictions, except
condensation must not occur.
The upper operating temperature limit depends on the host PCB layout and surrounding
environmental conditions. To simplify the customer’s design process, a maximum case
temperature has been specified.
The maximum case temperature must remain below the maximum, measured at the
location shown in the figure below.
Standard Operating Temperature Ranges
Product Operating Temperature Range
Digi Connect ME -40°C to +85°C
Digi Connect ME 9210 -40°C to +80°C
Digi Connect Wi-ME -30°C to +75°C
Maximum Case Temperature
Product Maximum Case Temperature
Digi Connect ME 96°C
Digi Connect ME 9210 93°C
Digi Connect Wi-ME 85°C
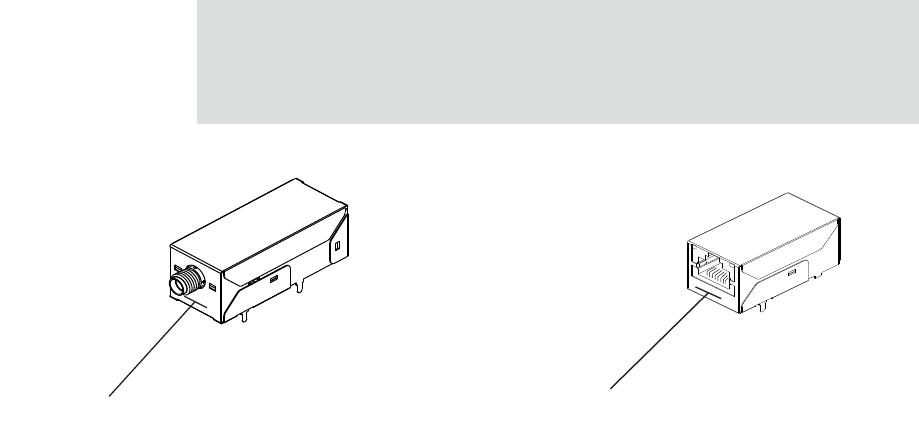
52
Additional Design Recommendations
The following list provides additional design guidance with respect to thermal management
in applications with operating temperatures at the high end or beyond the specified standard
ambient temperature range.
Providing air movement will improve heat dissipation.
The host PCB plays a large part in dissipating the heat generated by the module.
A large copper plane located under the Digi Connect ME 9210 and soldered to
the module’s mounting tabs will improve the heat dissipation capabilities of the
PCB.
If the design allows, added buried PCB planes will also improve heat
dissipation. The copper planes create a larger surface to spread the heat into the
surrounding environment.
Adding a thermal pad or thermal compound, such as Sil-Pad®, Gap Pad® or
Gap Filler products made by the Bergquest Company
(www.bergquistcompany.com), between the host PCB and the underside of the
module will significantly increase the thermal transfer between the module’s
enclosure and the host PCB. Limit the fill area to the folded metal portion of the
module’s underside.
Measure Temperature Here
Measure Temperature Here
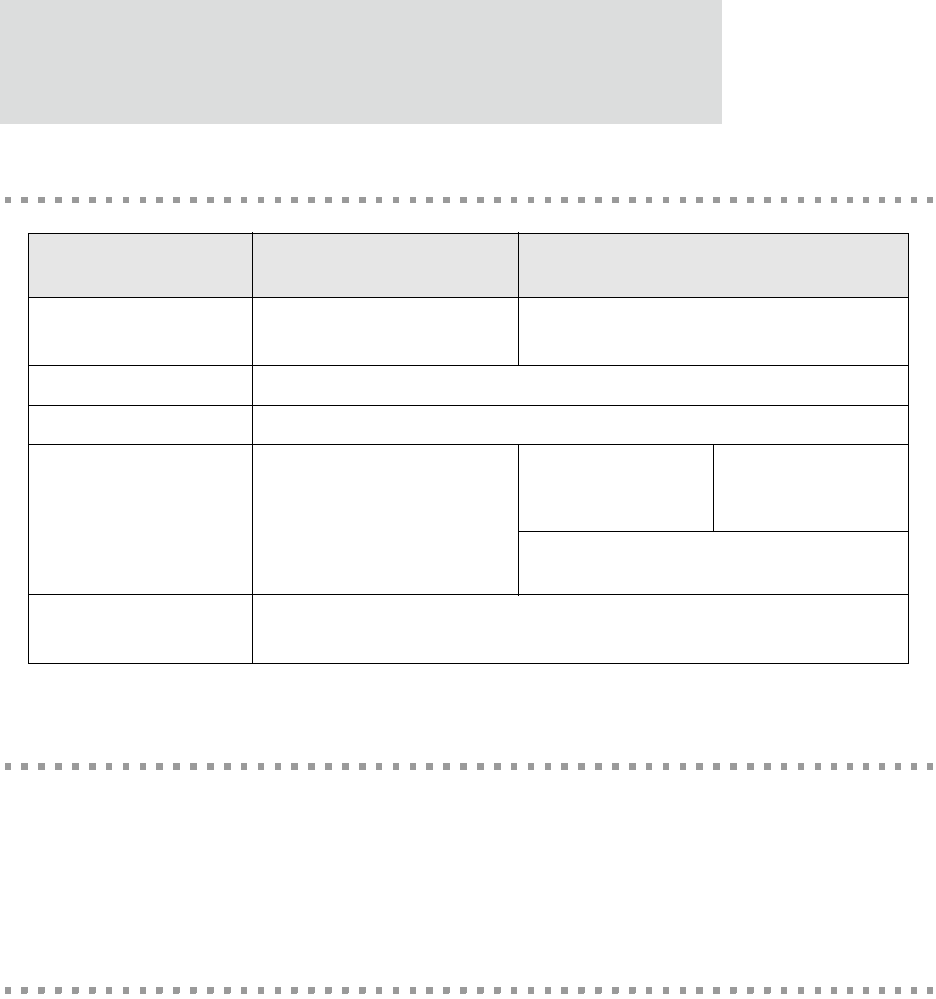
53
Mechanical
Bar Code
The 50m PN is code 3 of 9 (39) and the MAC is code 128. All scanners are set up so if they
read code 3 of 9 they will automatically read 128. The reason for the two different code
types is to maximize the size of the bars within a given space to improved readability.
Dimensions
The following figures show the dimensions of Digi Connect Wi-ME and Digi Connect ME
embedded modules.
Note:
These are the tolerances for the drawings shown on this and the following pages:
Dimensions Digi Connect
ME
Digi Connect
Wi-ME
Length 1.445 in.
(36.703 mm)
1.85 in
(46.99 mm)
Width 0.75 in. (19.05 mm)
Height 0.854 in. (21.69 mm)
Weight .616oz.
17.463g
.696 oz.
19.731 g.
Antenna- .408 oz.
11.567 g
Total - 1.104 oz.
31.298 g
Device/serial
interface connector
20-pin micro header (10-pin double row) with .05-inch (1.27-mm) pitch (Samtec
P/N FTS-110-01-F-DV-TR or similar). Positions 3 through 6 are removed.
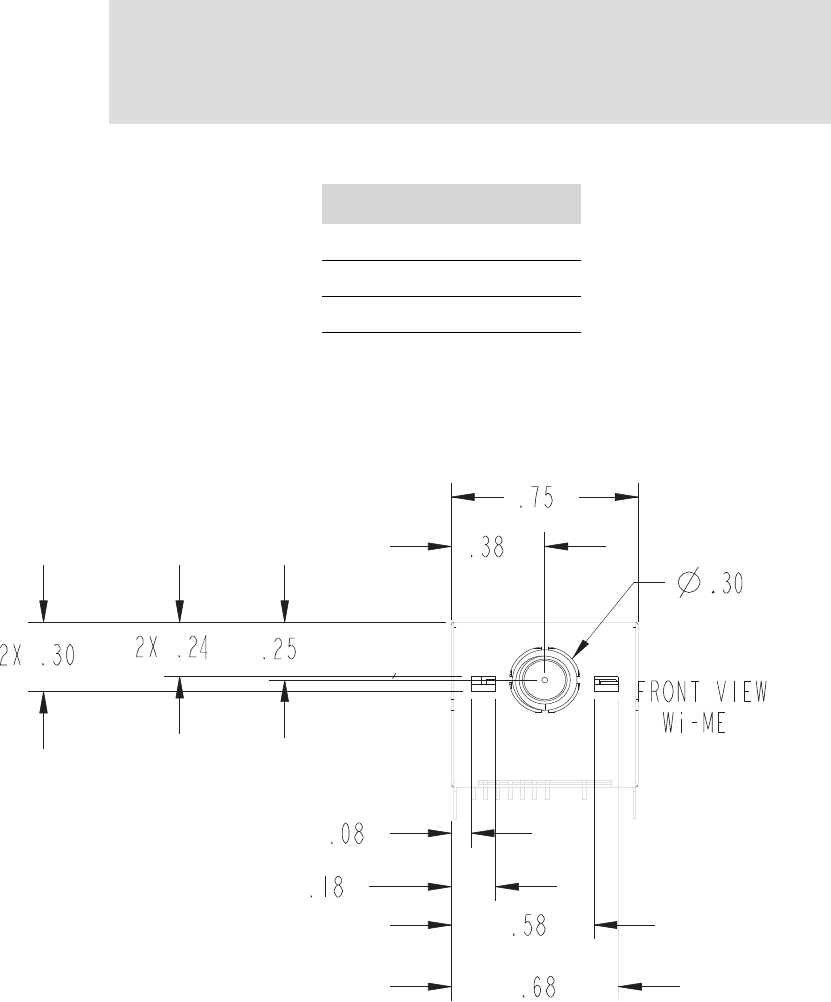
54
Digi Connect Wi-ME Module
Front Wi-ME
Measure Tolerance
.XX ± .02
.XXX ± .010
Angles ± 3°
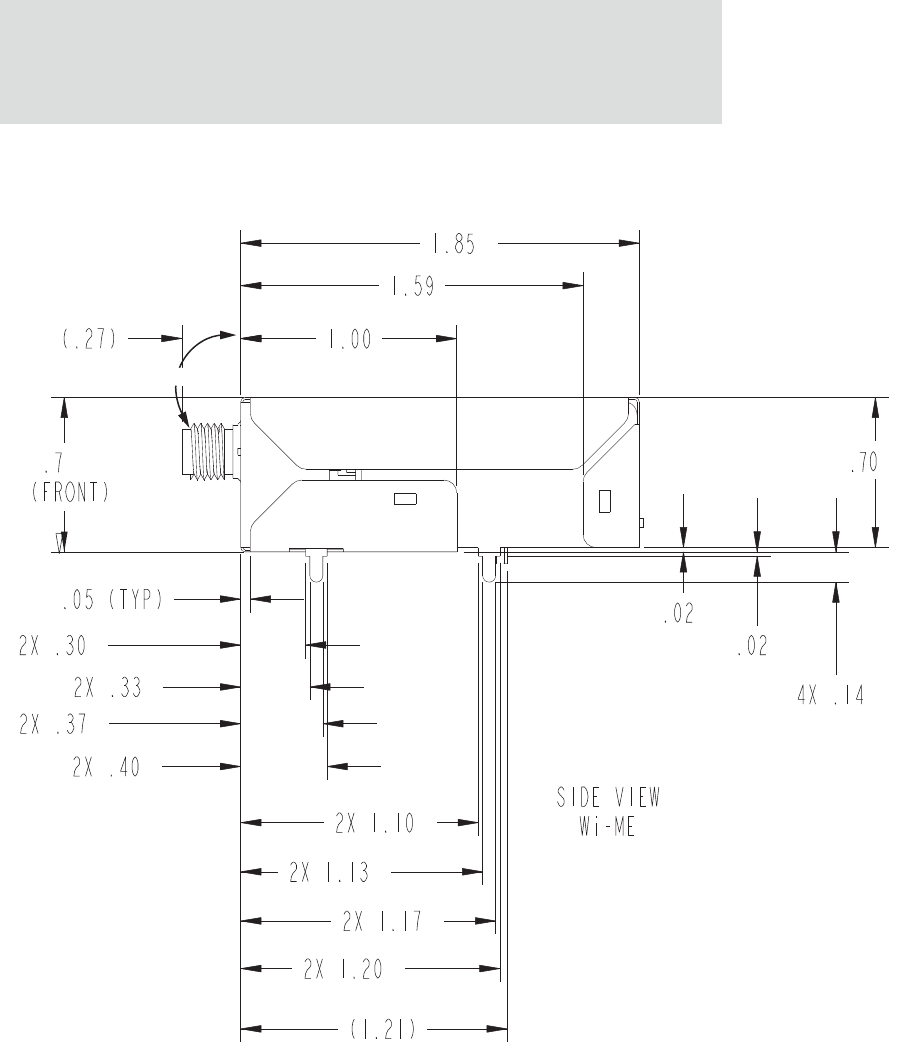
55
Side Wi-ME
90˚ - 5˚
+
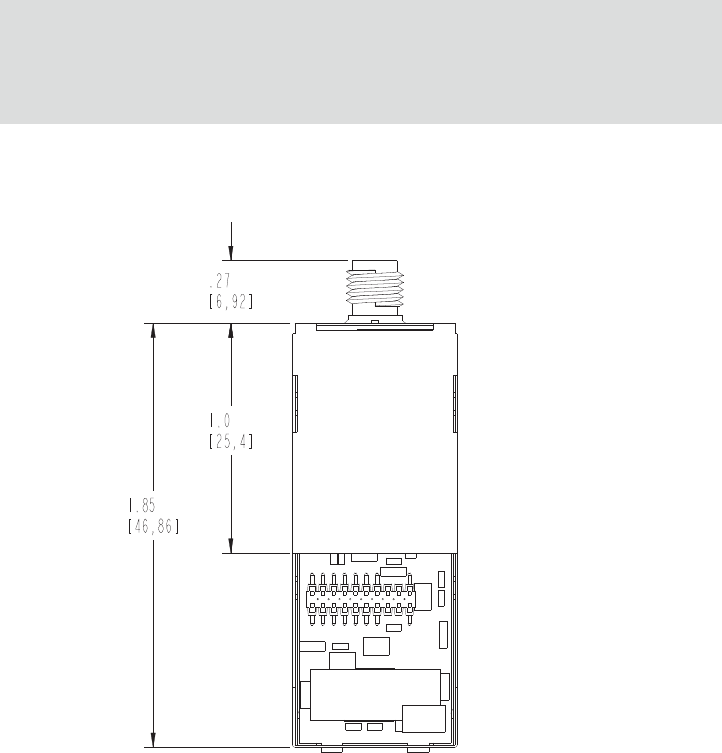
56
Bottom Wi-ME
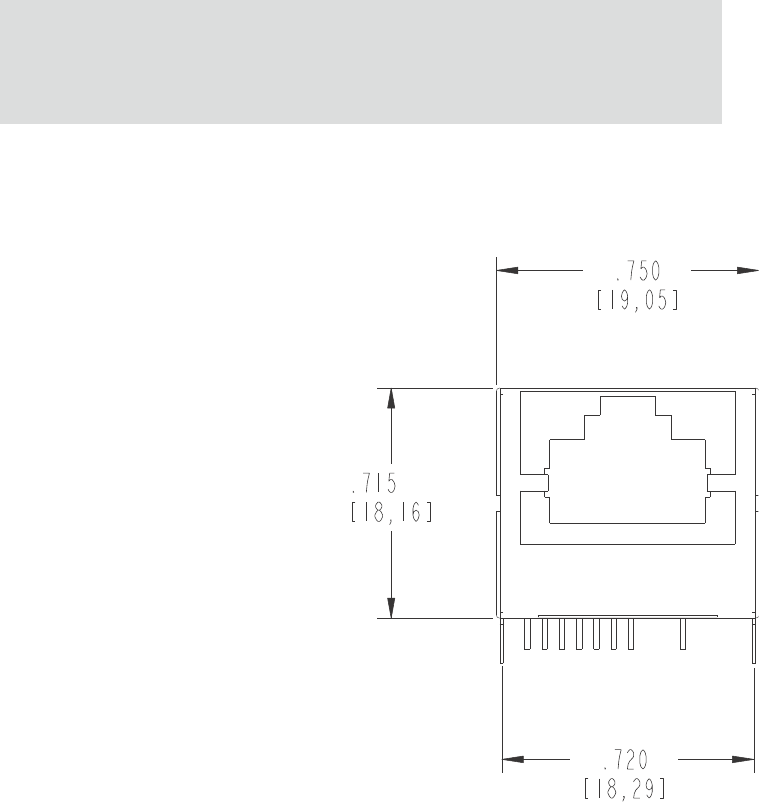
57
Digi Connect ME Module
Front View
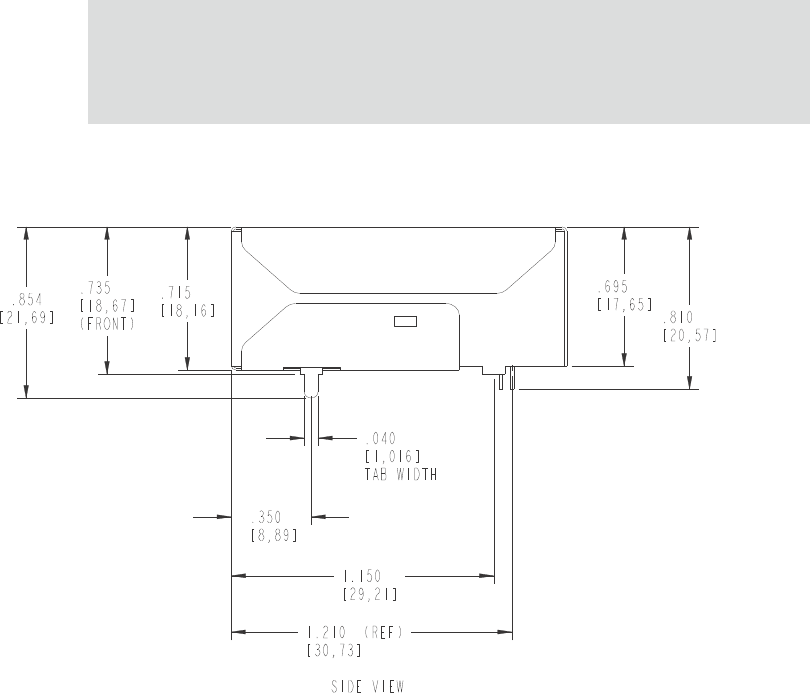
58
Side
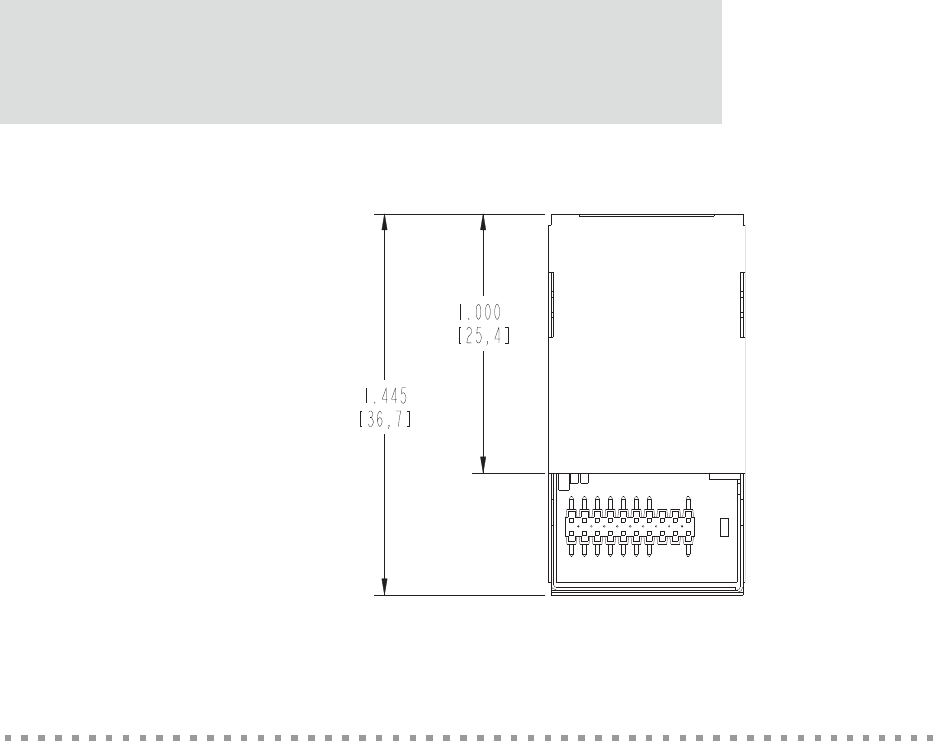
59
Bottom
Recommended PCB Layout
The following figure shows the recommended PCB (printed circuit board) layout of the
Digi Connect Wi-ME and Digi Connect ME. It is strongly recommended that you consider
using the Digi Connect Wi-ME footprint for future flexibility.
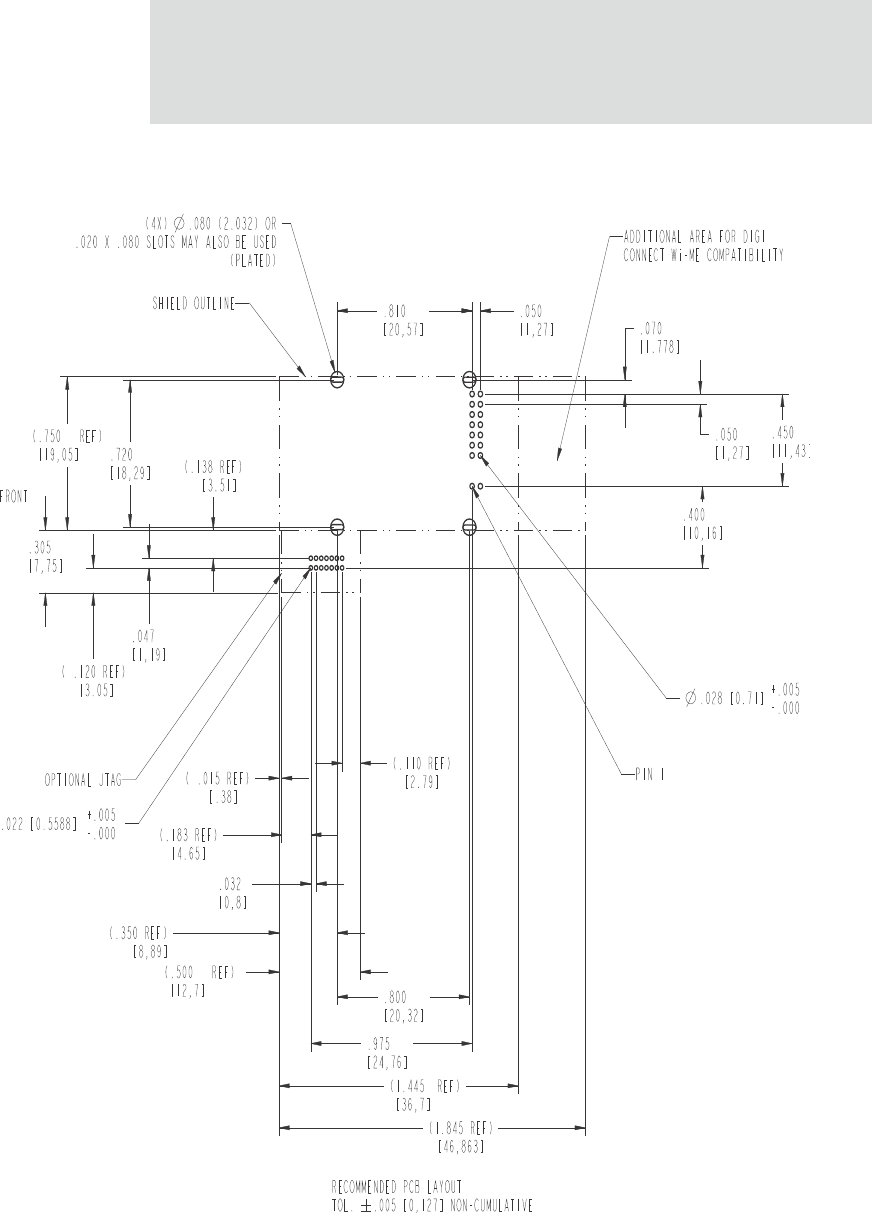
60
Digi Connect ME and Wi-ME
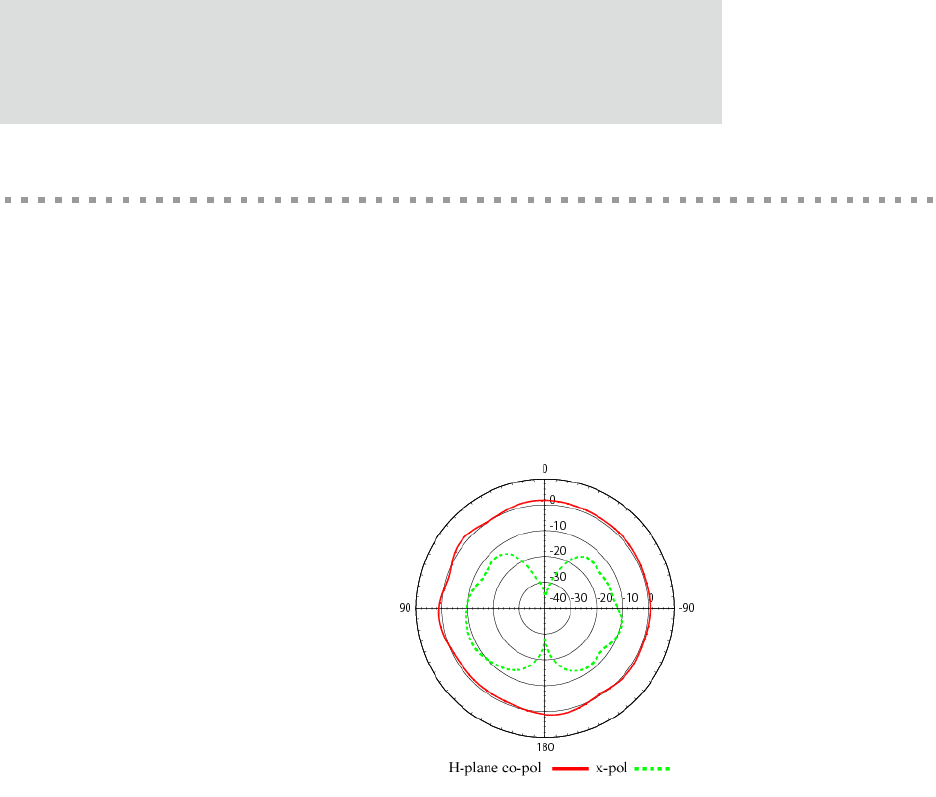
61
Antenna Information
Antenna Strength
The following diagram demonstrates the strength of the signal received by the whip
antenna on both a horizontal and vertical plane. The diagram shows the magnetic field
when the antenna is in a vertical position. The outside line represents the horizontal plane
and the inside dotted line represents the vertical plane.
Radiation Patterns
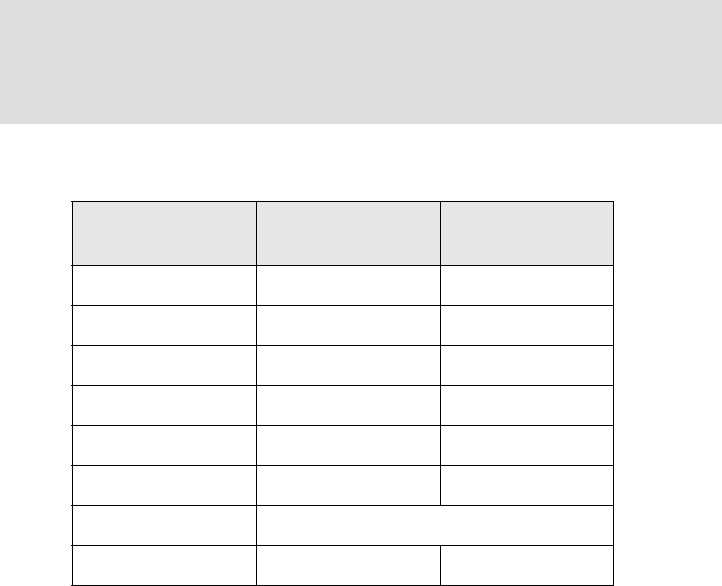
62
Antenna Specifications
Any antenna matching the in-band and out-of-band signal patterns and strengths of the
antenna, whose characteristics are given in the Antenna Description table and the Radiation
Pattern graphic may be used with the Digi Connect Wi-ME.
Antenna
Description Dipole Desktop
Frequency 2.4~2.5 GHz 2.4~2.5 GHz
Power Output 2 W 1 W
DB Gain 2 dBi 1.8 dBi
VSWR < or = 2.0 1.92 max.
Dimension 108.5 x 10.0 mm 105 x4.5 mm
Weight 10.5g 11 g
Connector RP-SMA
Part Number DG-ANT-20DP-BG DC-ANT-24DT
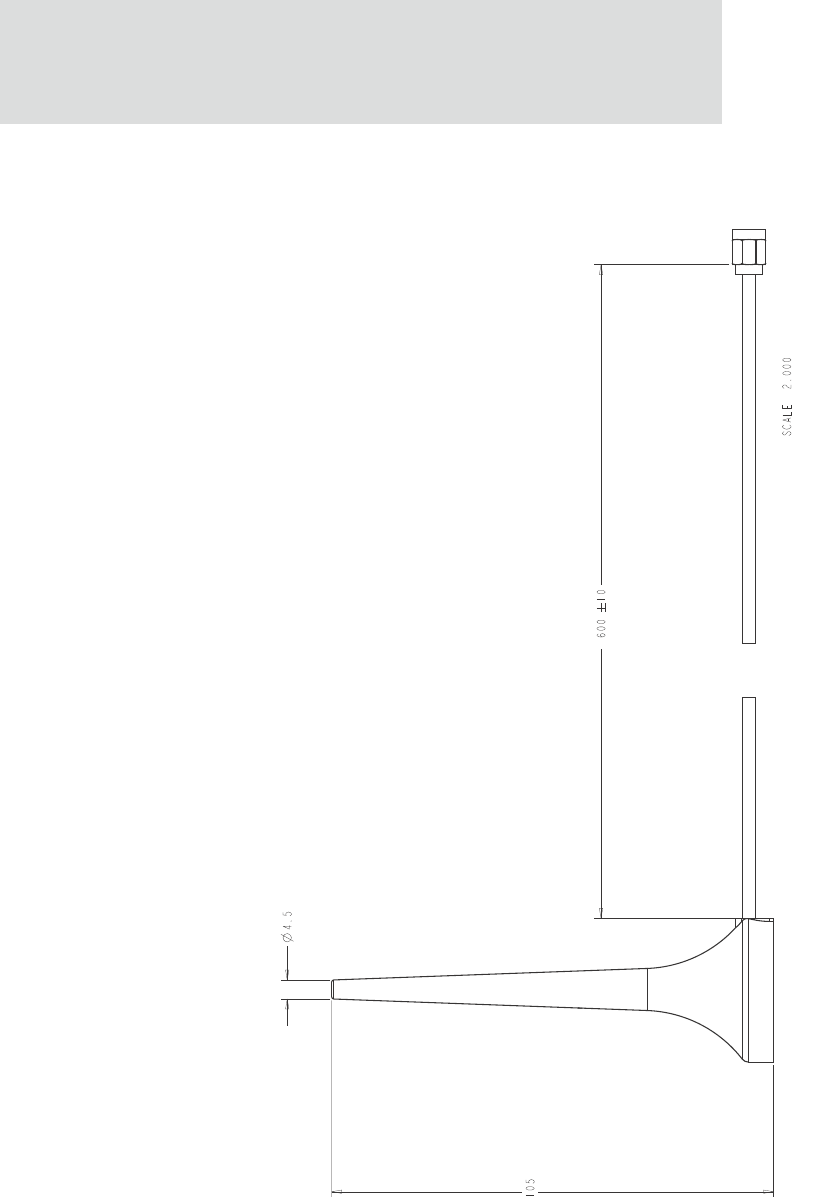
63
Desktop Antenna Dimensions
Unit s: mm
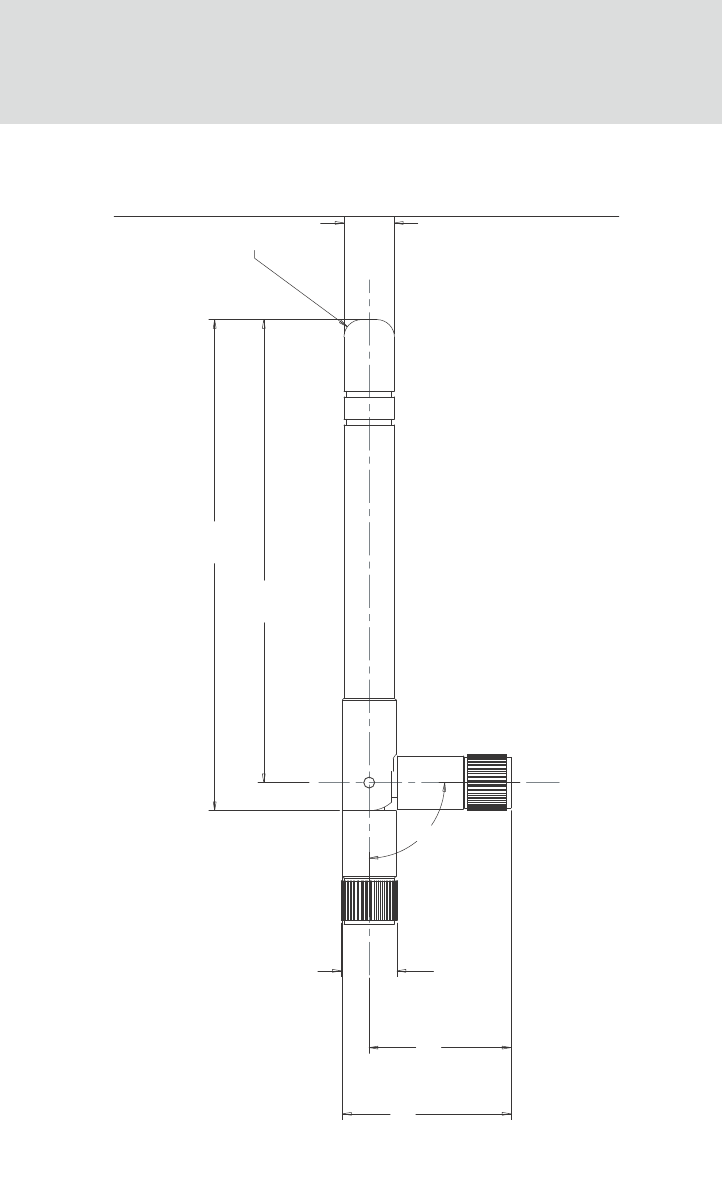
64
Dipole Antenna Dimensions
bOBITRON
SCALE 3.000
UNITS: mm
90.0˚
(9.1)
.360
(88.9)
3.500
(30.5)
1.200
(25.4)
1.010
(83.8)
3.300
(10.1)
.399
R
(3.2)
.125
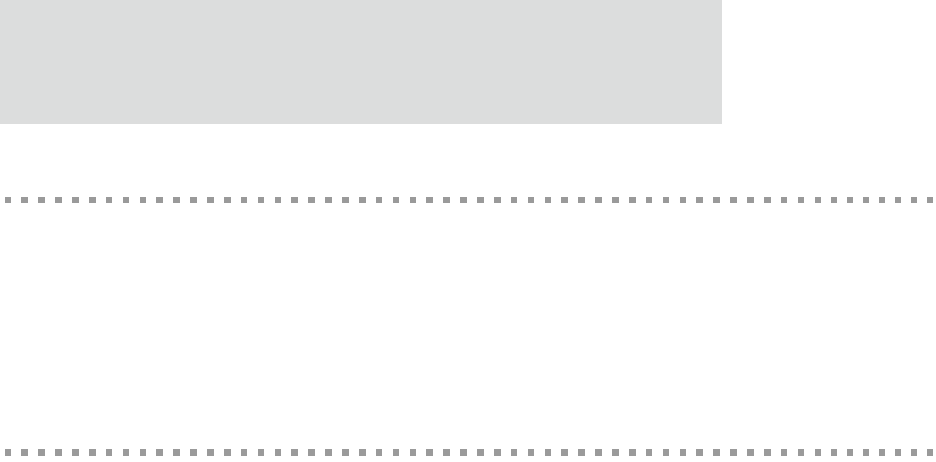
65
RF Exposure Statement
The Digi Connect Wi-ME module complies with the RF exposure limits for humans as
called out in RSS-102. It is exempt from RF evaluation based on its operating frequency of
2.4 GHz, and effective radiated power less than the 3 watt requirement for a mobile device
(>20 cm separation) operating at 2.4 GHz.
Safety Statements
To avoid contact with electrical current:
Never install electrical wiring during an electrical storm.
Never install an ethernet connection in wet locations unless that connector is
specifically designed for wet locations.
Use caution when installing or modifying ethernet lines.
Use a screwdriver and other tools with insulated handles.
You and those around you should wear safety glasses or goggles.
Do not place ethernet wiring or connections in any conduit, outlet or junction
box containing electrical wiring.
Installation of inside wire may bring you close to electrical wire, conduit,
terminals and other electrical facilities. Extreme caution must be used to avoid
electrical shock from such facilities. You must avoid contact with all such
facilities.
Ethernet wiring must be at least 6 feet from bare power wiring or lightning rods
and associated wires, and at least 6 inches from other wire (antenna wires,
doorbell wires, wires from transformers to neon signs), steam or hot water
pipes, and heating ducts.
Do not place an ethernet connection where it would allow a person to use an
ethernet device while in a bathtub, shower, swimming pool, or similar
hazardous location.
Protectors and grounding wire placed by the service provider must not be
connected to, removed, or modified by the customer.

66
Do not touch un-insulated ethernet wiring if lightning is likely!
Do not touch or move the antenna(s) while the unit is transmitting or receiving.
Do not hold any component containing a radio such that the antenna is very
close to or touching any exposed parts of the body, especially the face or eyes,
while transmitting.
Do not operate a portable transmitter near unshielded blasting caps or in an
explosive environment unless it is a type especially qualified for such use
Any external communications wiring you may install needs to be constructed to all
relevant electrical codes. In the United States this is the National Electrical Code Article
800. Contact a licensed electrician for details.

67
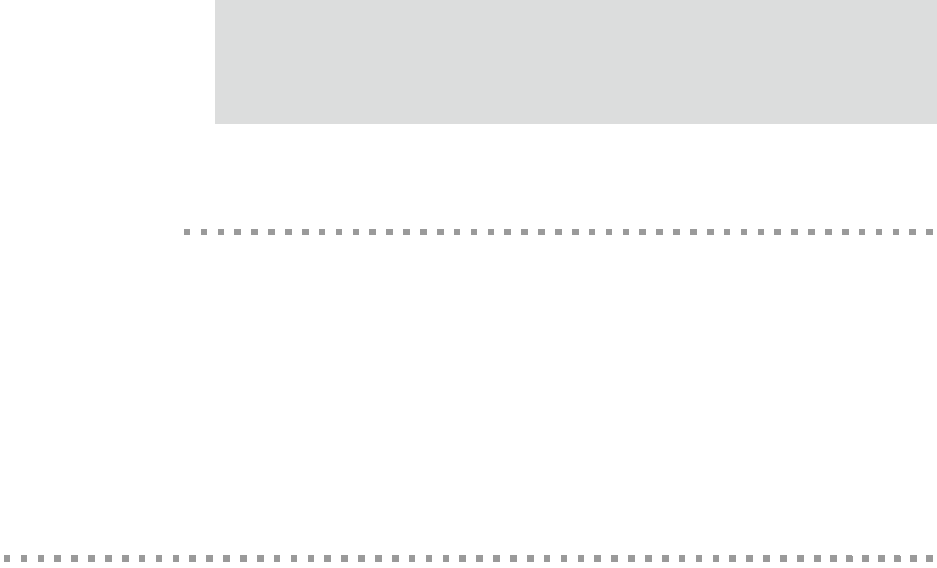
68
Certifications
APPENDIX B
These products comply with the following standards.
FCC Part 15 Class B
Radio Frequency Interference (RFI)(FCC 15.105)
The Digi Connect ME and Digi Connect Wi-ME embedded modules have been tested and
found to comply with the limits for Class B digital devices pursuant to Part 15 Subpart B,
of the FCC Rules. These limits are designed to provide reasonable protection against
harmful interference in a residential environment. This equipment generates, uses, and can
radiate radio frequency energy, and if not installed and used in accordance with the
instruction manual, may cause harmful interference to radio communications. However,
there is no guarantee that interference will not occur in a particular installation. If this
equipment does cause harmful interference to radio or television reception, which can be
determined by turning the equipment off and on, the user is encouraged to try and correct
the interference by one or more of the following measures:
Reorient or relocate the receiving antenna.
Increase the separation between the equipment and the receiver.
Connect the equipment into an outlet on a circuit different from that to which
the receiver is connected.
Consult the dealer or an experienced radio/TV technician for help.
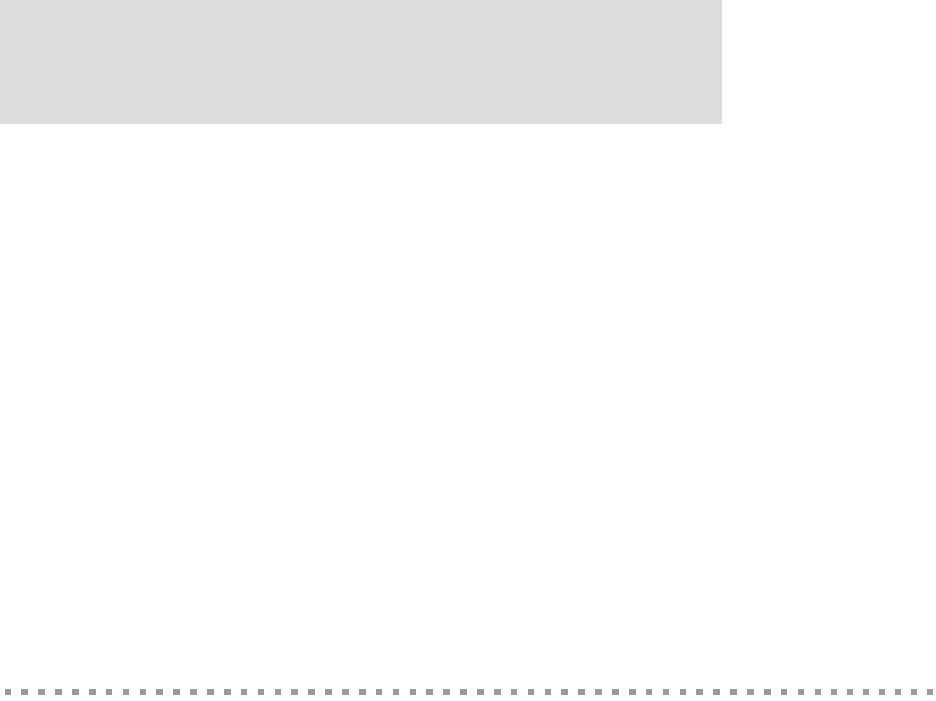
69
Labeling Requirements (FCC 15.19)
This device complies with Part 15 of FCC rules. Operation is subject to the following two
conditions: (1) this device may not cause harmful interference, and (2) this device must
accept any interference received, including interference that may cause undesired
operation.
If the FCC ID is not visible when installed inside another device, then the outside of the
device into which the module is installed must also display a label referring to the enclosed
module FCC ID. This exterior label can use wording such as the following: “Contains
Transmitter Module FCC ID: MCQ-50M880/ IC: 1846A-50M880”.
Modifications (FCC 15.21)
Changes or modifications to this equipment not expressly approved by Digi may void the
user's authority to operate this equipment.
Industry Canada
This digital apparatus does not exceed the Class B limits for radio noise emissions from
digital apparatus set out in the Radio Interference Regulations of the Canadian Department
of Communications.
Le present appareil numerique n'emet pas de bruits radioelectriques depassant les limites
applicables aux appareils numeriques de la class B prescrites dans le Reglement sur le
brouillage radioelectrique edicte par le ministere des Communications du Canada."
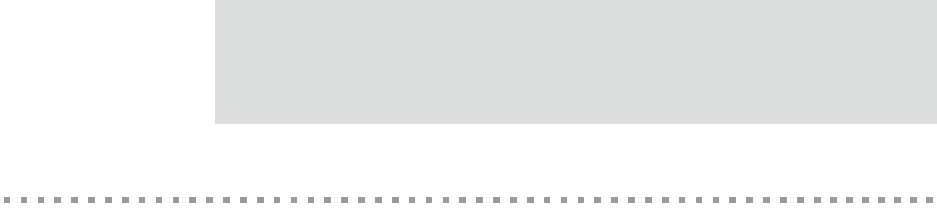
70
Declaration of Conformity
(In accordance with FCC Dockets 96-208 and 95-19)
Digi International declares, that the product:
to which this declaration relates, meets the requirements specified by the Federal
Communications Commission as detailed in the following specifications:
Part 15, Subpart B, for Class B Equipment
FCC Docket 96-208 as it applies to Class B personal
Computers and Peripherals
The product listed above has been tested at an External Test Laboratory certified per FCC
rules and has been found to meet the FCC, Part 15, Class B, Emission Limits.
Documentation is on file and available from the Digi International Homologation
Department.
Manufacturer's Name: Digi International
Corporate Headquarters: 11001 Bren Road East
Minnetonka MN 55343
Manufacturing Headquarters: 10000 West 76th Street
Eden Prairie MN 55344
Product Name: Digi Connect ME embedded module
Model Number: 50001528-XX
Product Name: Digi Connect Wi-ME embedded module
Model Number: 50000880-XX
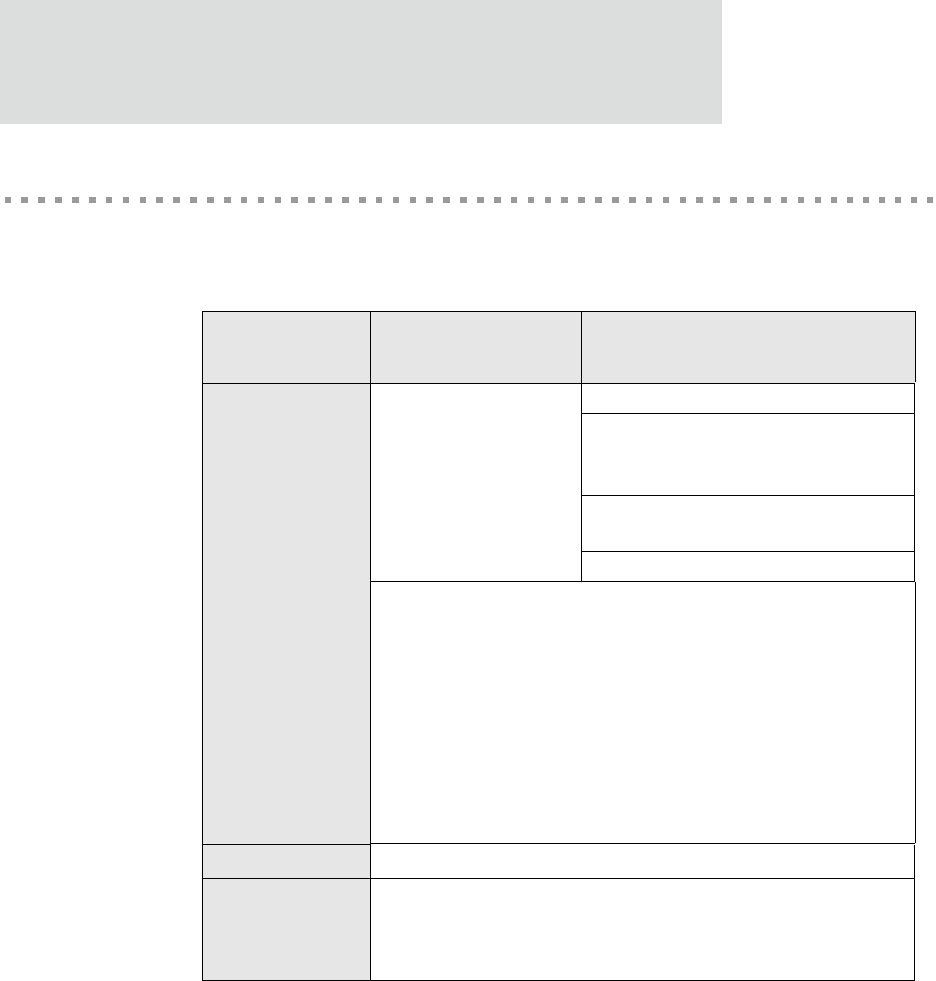
71
International EMC Standards
The Digi Connect ME and Digi Connect Wi-ME embedded modules meet the following
standards:
Standards Digi Connect
ME
Digi Connect
Wi-ME
Emissions
AS/NZS 3548
AS/NZS 3548 CISPR 22
Japan IOH
003NY04115 0000
003GZ04064 0000
FCC Part 15 Subpart C
(FCC ID: MCQ-50M880)
IC RSS 210 (IC:1846A-50M880)
FCC Part 15 Subpart B
ICES-003
EN 55022
EN 61000-4-2
EN 61000-4-3
EN 61000-4-6
EN 301 489-3
EN 300 328
VCCI
Immunity EN 55024
Safety
UL 60950-1
CSA 22.2 No. 60950--1
EN 60950
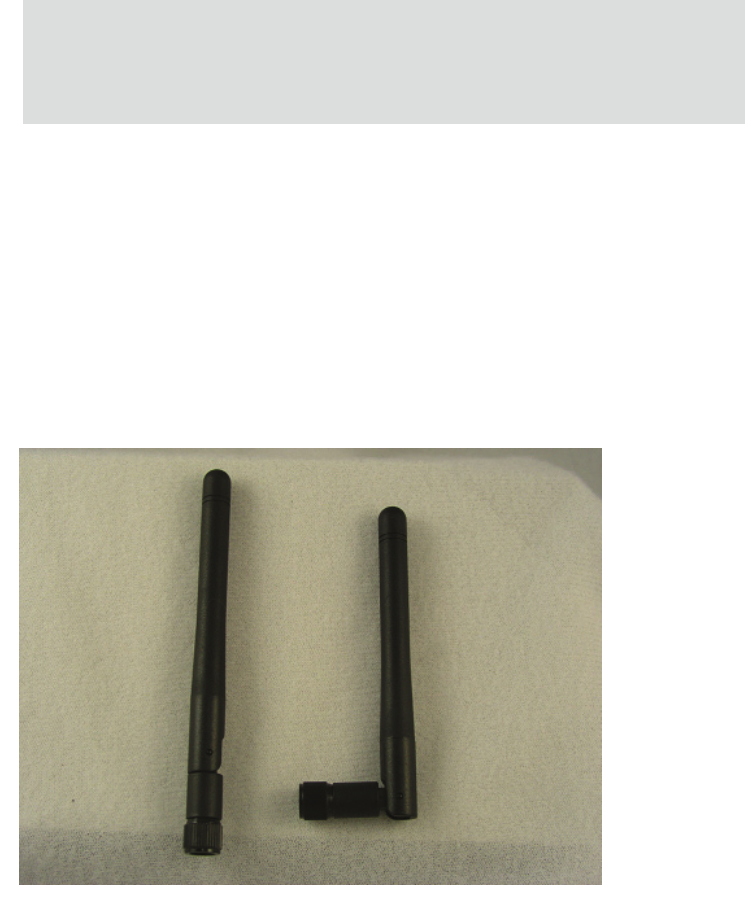
72
Antenna configurations
This device has been designed to operate with the antennas listed below, and having a
maximum gain of [10] dBi. Antennas not included in this list or having a gain greater than
[10] dBi are strictly prohibited for use with this device. The required antenna impedance is
[50] ohms
The following antenna configurations that were tested with the Connect Wi-ME 802.11 b
module.
Digi 29000095, Bobbintron SA-006-1, +2 dBi dipole antenna (RP-SMA)
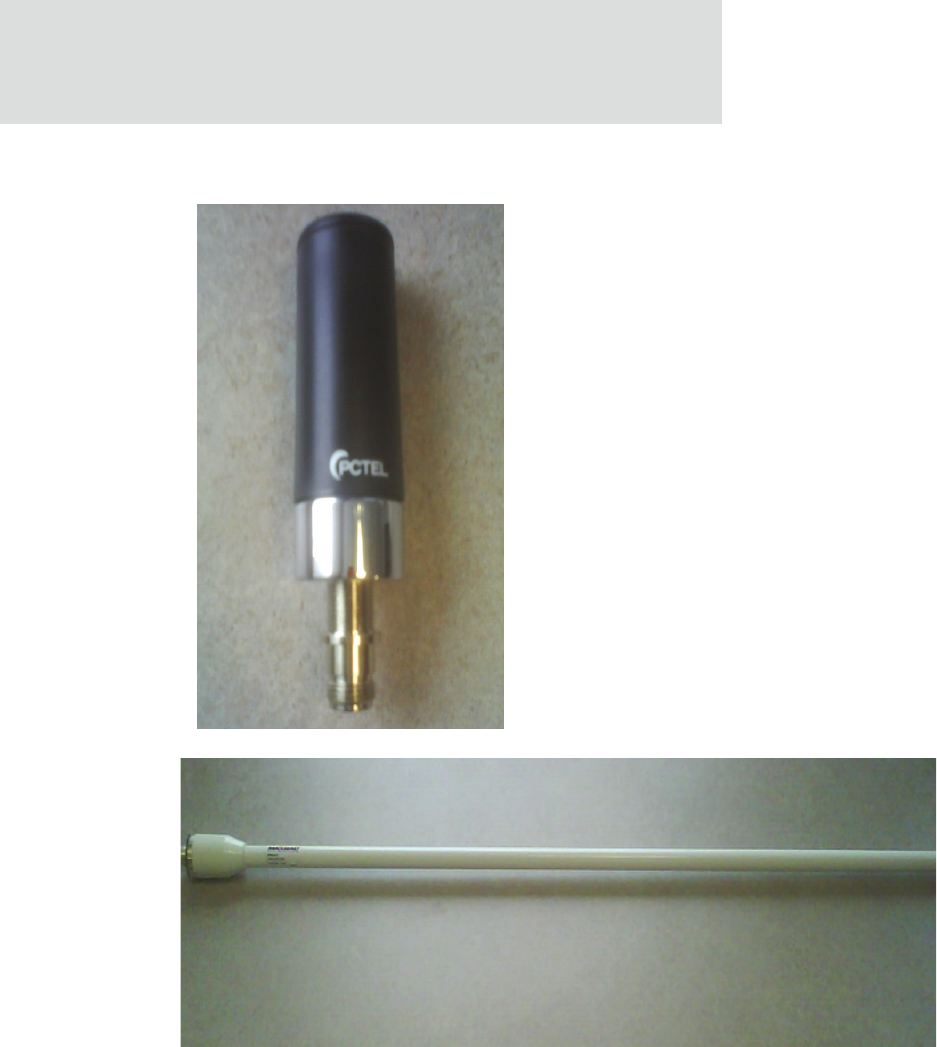
73
PCTEL, MLPV2400NGP, 2.4 GHz, 3dBi gain, no ground place, low profile antenna
MAXRAD, MFB24010, 2.4 GHz, 10 dBi Fiberglass OMNI antenna
To reduce potential radio interference to other users, the antenna type and its gain should be
so chosen that the equivalent isotropically radiated power (e.i.r.p.) is not more than that
permitted for successful communication.
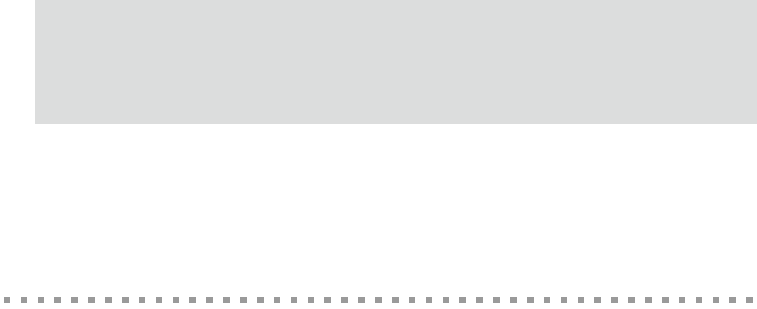
74
Sample Application: PoE
Power Supply
APPENDIX C
The following schematic is an example of PoE Power Supply:
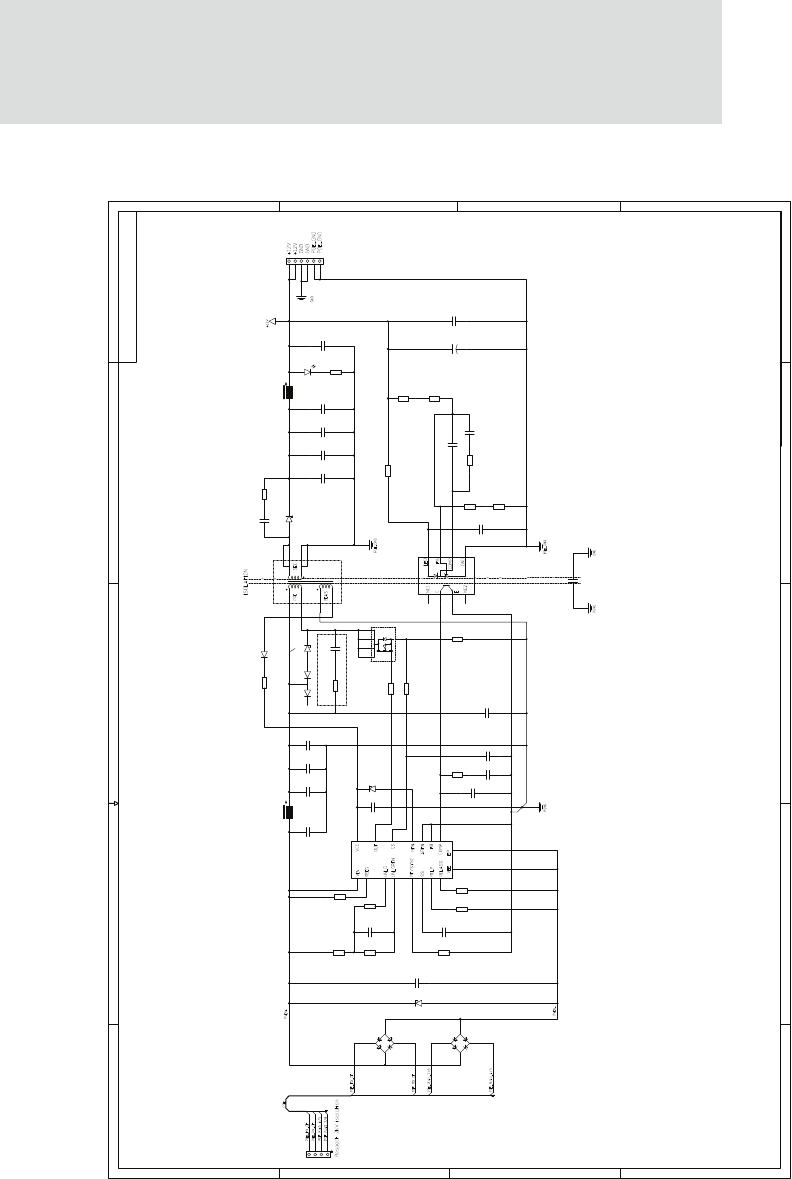
75
5
5
B
A
1234
123
4
C
D
D
C
B
A
MB2S
D1
3
4
2
1
ACAC
POS NEG
MB2S
D2
3
4
2
1
ACAC
POS NEG
LM5070SD
U1
12
13
11
9
3
6
2
14
15
4
5
1
7
10
17
8
16
SMAJ60A-13-F
D3
100n/100V
C2
24K9
R1
1K
R2
220n/100V
C3
33K2
R3
590K
R4
15K
R5
47n/100V
C4
100K
R6
53R6
R7
1K
R8
47n/100V
C5
FOD2741ASDV
4
18
5
7
36
2
U2
47R
R9
100R
R10
1u/10V
C7
18R
R11 LL4148
D4
1n/50V
C6
0R33
R12
3.3u
C9
1n/50V
C10
47n/100V
C11
1u/10V
C12
100n/100V
C15
100n/100V
C16
33R
R17
100n/100V
C20
RED
CR1
10u/10V
C27
10u/10V
C28
10u/10V
C29
1K
R21
1K
R16
10K
R14
0R
R24
56V
D11
D12
3
21
100n/100V
C30
1n/100V
C32
1K
R27
1u/10V
C33
D14
1u/10V
C34
2u2/100V
C36
2u2/100V
C37
2u2/100V
C38
3K3
R28
1K8
R29
4K7
R30
220P/50V
C39
330u/35V
C40
+
4p_R/A_TSM
4
3
2
1
P1
6p_R/A_TSM
6
5
4
3
2
1
P2
4,7uH
L5
4,7uH
L6 SS26
D15
FDC2512
56
21
4
3
U3
T1
C1586-ALD
1
2
3
74
8
9
10
NOT POP
Dual 100V
NC
NC
NC
12V/200mW
60V/2A
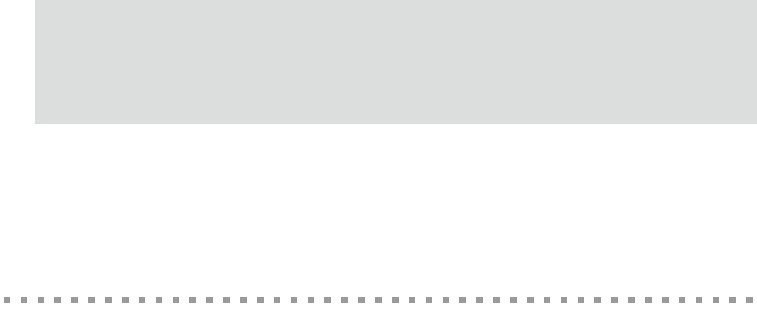
76
Sample Application:
TTL Signals to EIA-232
APPENDIX D
The following schematic is an example of how to convert the modules’s TTL signals to
EIA-232.
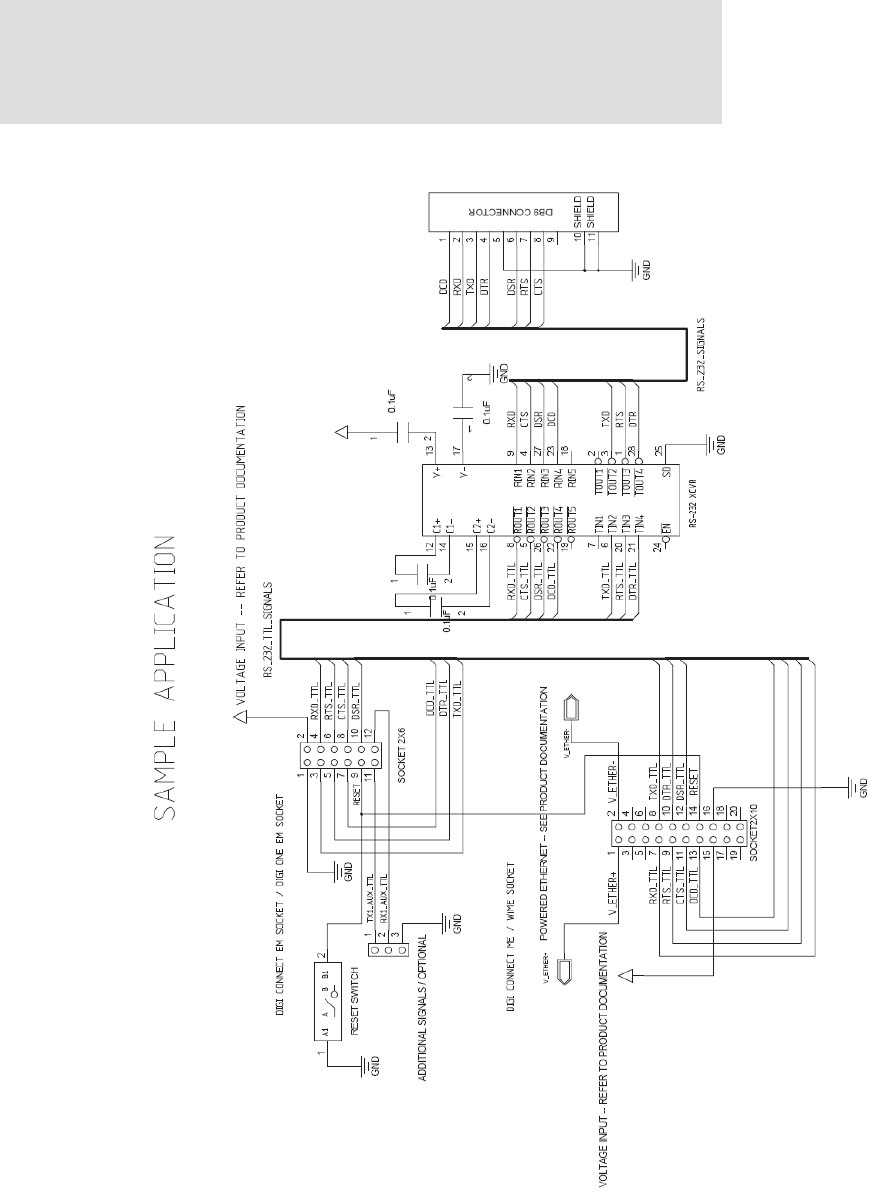
77
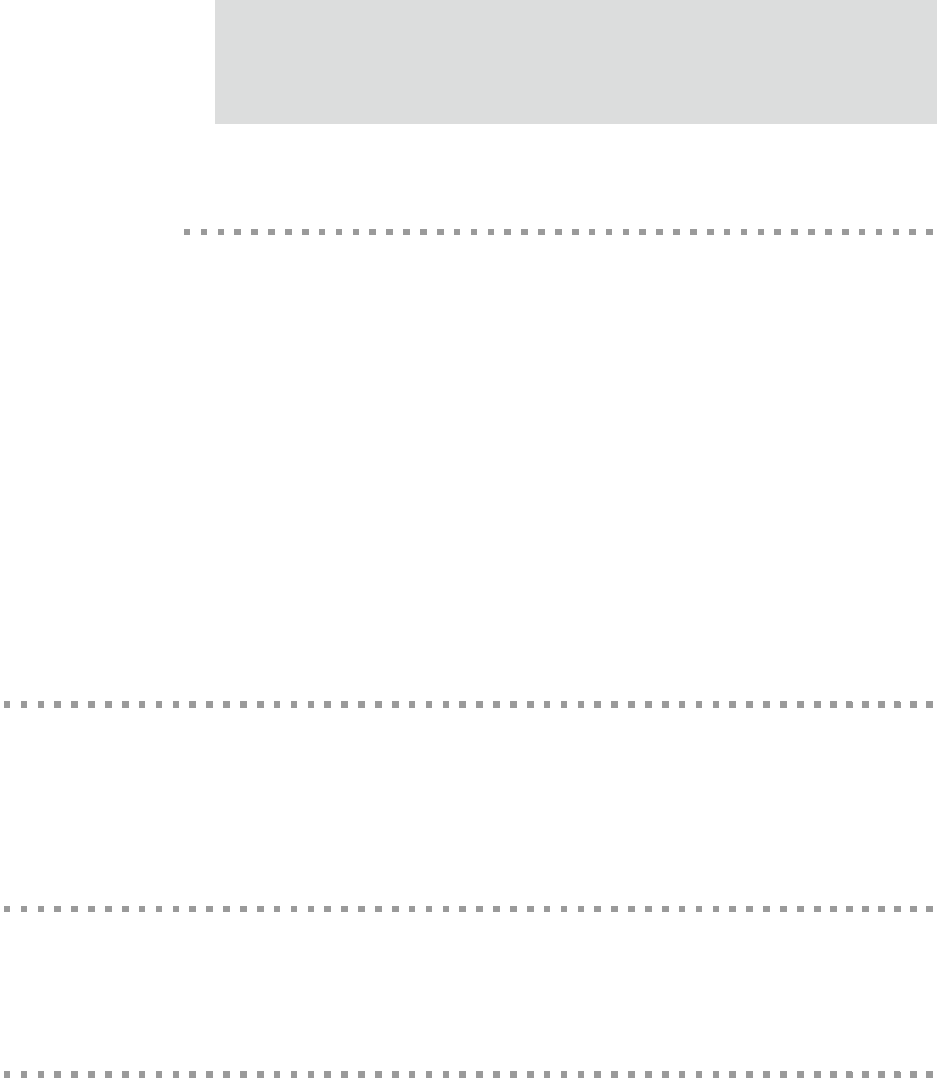
78
Change Log
APPENDIX E
The following changes have been made since the last revision of this document.
Note: As of September 2007, the document number changed from 90000631 to
90000897.
Revision F
Added ME sketch to Thermal Specifications.
Added antenna configurations.
Revision E
Changed schematics in appendix A to reflect correct measurements.
Revision D
Added a new section labeled “Thermal Specifications” to the book. This section outlines
the temperature ranges at which the devices specified can still function properly.
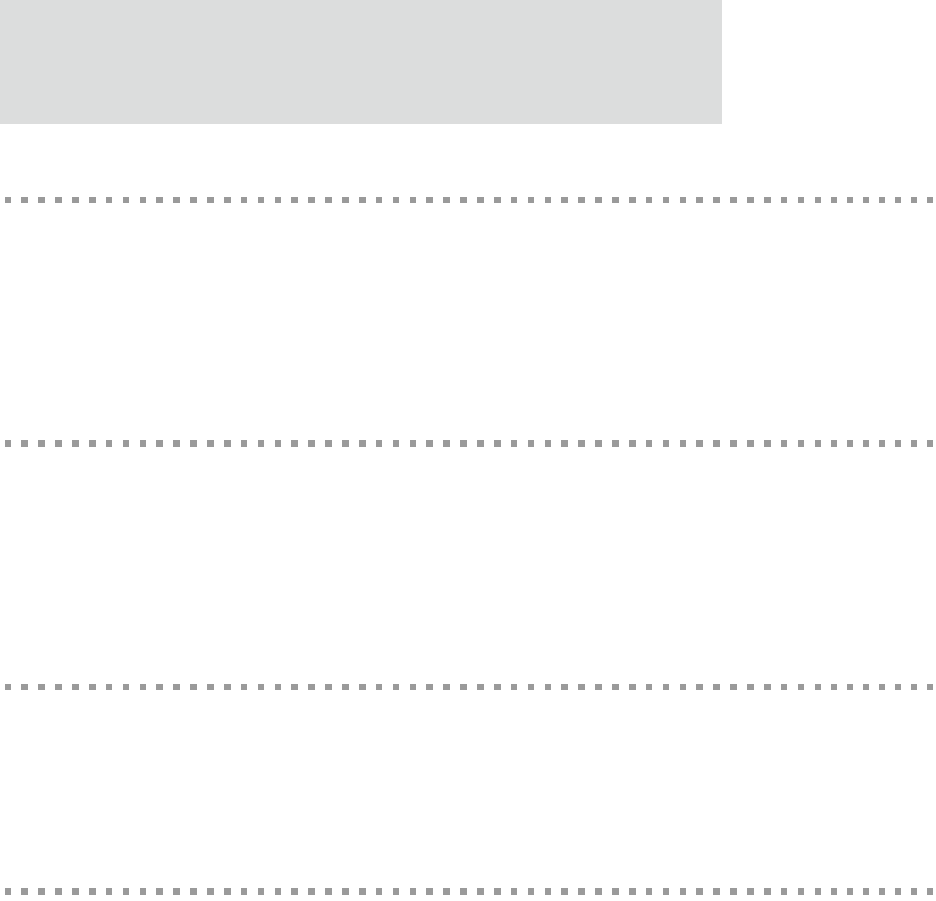
79
Revision C
Updates to schematics in Chapter 2.
Added/revised Module Pin-out table in Chapter 3.
Updated GPIO tables throughout book.
Revision B
Fixed page numbers to make them correspond in PDF form.
Added components to Development Board schematics. (#19 and 20)
Revision 90000631_G>90000897_A
Added Connect ME 9210 related information.
Updated schematics in development board chapter to reflect 9210 changes.
Revision G
Updated the Connectors: power and device interface section to say that pins 1 and 2 on the
connector are available if using Connect ME, not available if using Connect Wi-ME.
Updated the Embedded Module Connector table in Chapter 2 similarly.
Added tolerance information for dimension drawings
Updated Hard Reset section to clarify forcing the unit into hard reset
Updated the ambient (operating) temperature for Connect Wi-ME
Added information regarding reading the bar code
Added P12 Factory reset pin
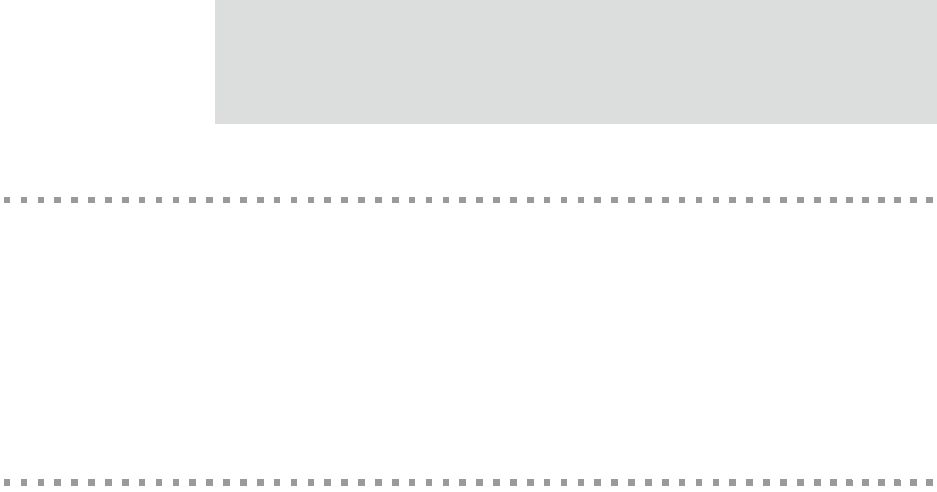
80
Revision F
Updated Antenna drawing
Added product weights
Updated UL labeling description
Updated dimension drawings
Revision E
Added Japan certification
Improve dipole antenna drawing
Corrected imperial pitch measurement
Reformatted tables for easier reading
Added antenna extension cord information
Added more receive sensitivity information
Added Caution for soldering process
Added reset hold times
Added VCC *absolute max* ratings
Combined PCB layouts with improvements

81
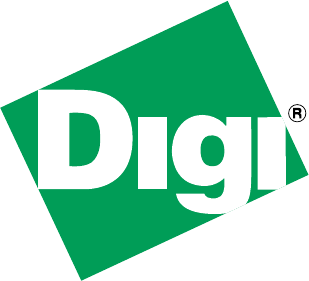