Nedap N V XQMK2 Anti-Pilferage Device User Manual Manual XQ MK2 2010 1 indd
N. V. Nederlandsche Apparatenfabriek NEDAP Anti-Pilferage Device Manual XQ MK2 2010 1 indd
Contents
- 1. Advertising literature
- 2. User manual
- 3. Installation manual
- 4. Product literature
Installation manual
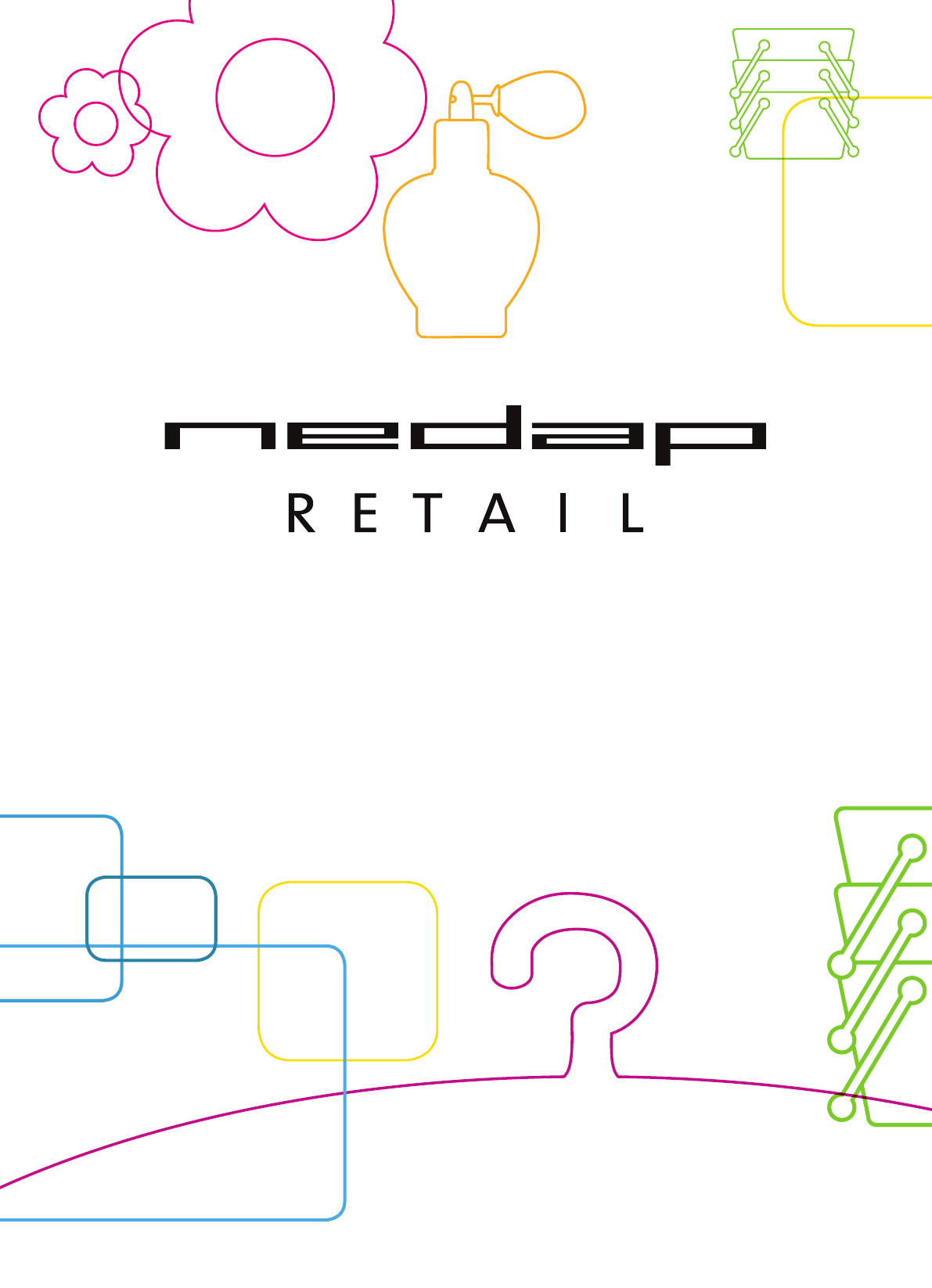
- 1 -
manual
XQ MK2 Electronics
Januari, 2010
PRELIMINARY
Metal Detection Settings Only
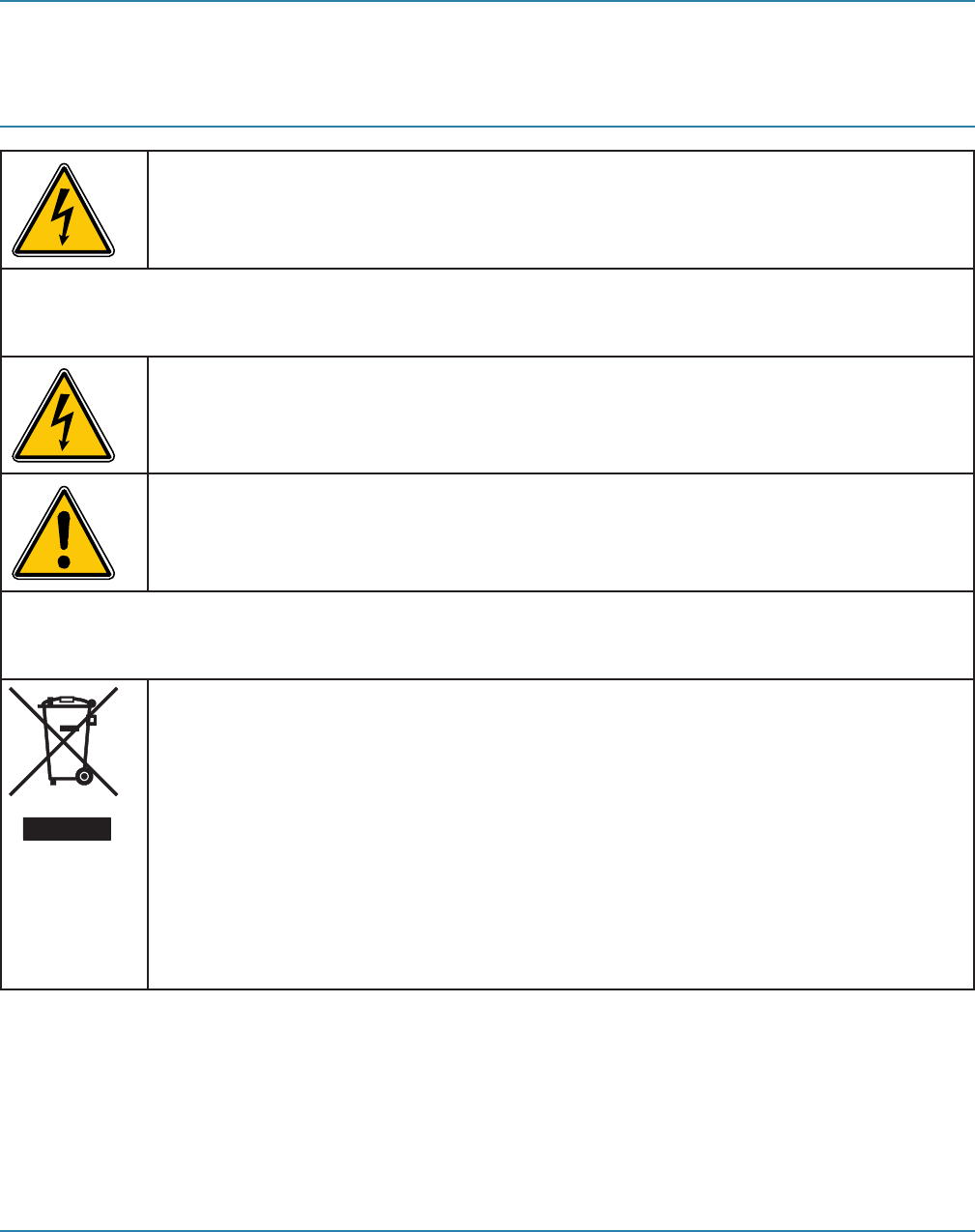
- 2 -
Technical Support
E-Mail : support-rs@nedap.com
Safety precautions
CAUTION - RISK OF ELECTRIC SHOCK - DO NOT OPEN
CAUTION: TO REDUCE THE RISK OF ELECTRICAL SHOCK, DO NOT REMOVE COVER (OR BACK). NO USER-
SERVICEABLE PARTS INSIDE. REFER SERVICING TO QUALIFIED NEDAP SERVICE PERSONNEL.
Lightning ash with an arrowhead, enclosed in a triangle, alerts you to the presence of uninsulated
voltage points inside the product which could cause a serious electrical shock.
An exclamation mark enclosed in a triangle alerts you to important operating and maintenance in-
structions in the documentation provided with the product.
WARNING! To avoid the risk of re or electrical shock, never expose these products to water or operate in a high humid-
ity environment.
EN 50419:2005
EN 50419:2005 This European Standard species a marking
• of electrical and electronic equipment in accordance with Article 11(2) of Directive 2002/96/EC
(WEEE); This is in addition to the marking requirement in Article 10(3) of this Directive which
requires producers to mark electrical and electronic equipment put on the market after 13 August
2005 with a ‘crossed-out wheeled bin’ symbol.
• that applies to electrical and electronic equipment falling under Annex IA of Directive 2002/96/
EC, provided the equipment concerned is not part of another type of equipment that does not fall
within the scope of this Directive. Annex IB of Directive 2002/96/EC contains an indicative list of
the products, which fall under the categories set out in Annex IA of this Directive;
• that serves to clearly identify the producer of the equipment and that the equipment has been put
on the market after 13 August 2005.
© 2009 Nedap Retail Support Netherlands Parallelweg 2d, 7141 DC Groenlo
The software / hardware described in this book / le is furnished under a license agreement and may be used only in ac-
cordance with the terms of the agreement.
Documentation version Manual XQ MK2 2010 1 PRELIMINARY
Copyright Notice
All Rights Reserved. Any technical documentation that is made available by Nedap Retail Support is the copyrighted work of Nedap Retail Support and is owned by Nedap Retail Support.
No warranty The technical documentation is being delivered to you and Nedap Retail Support makes no warranty as to its accuracy or use. Any use of the technical documentation or
the information contained therein is at the risk of the user. Documentation may include technical or other inaccuracies or typographical errors Nedap Retail Support the right to make
changes without prior notice. No part of this publication may be copied without the express written permission of Nedap Retail Support, Parallelweg 2d, 7141 DC Groenlo, Netherlands
Trademarks Nedap, the Nedap logo, Nedap EASi/Net and the Nedap EASi/Net are registered trademarks of Nedap N.V. Groenlo.
Other product names mentioned in this manual may be trademarks or registered trademarks of their respective companies and are hereby acknowledged.
Digital Printed in the Netherlands
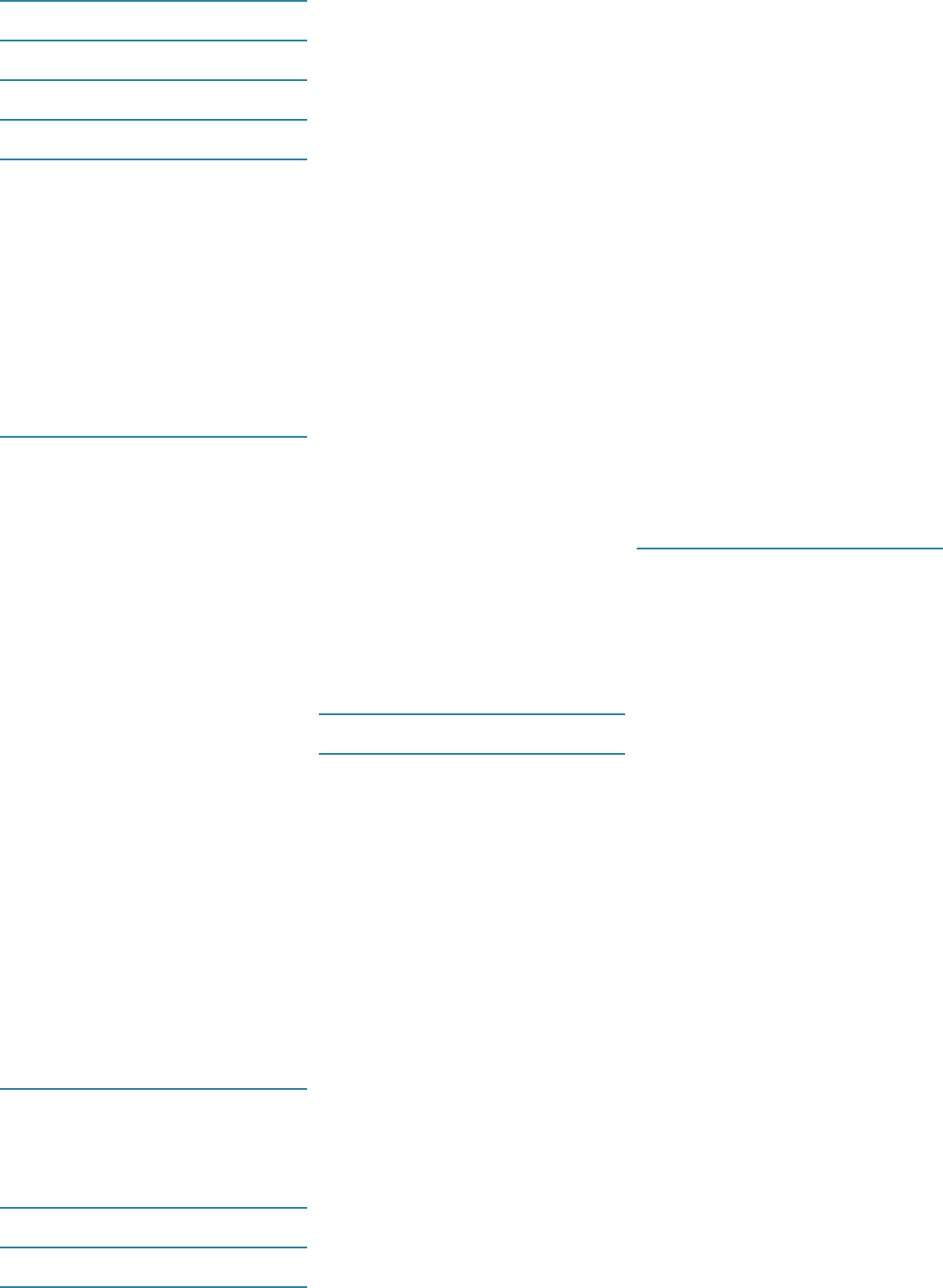
- 3 -
Table of Contents
2 Technical Support
2 Safety precautions
2 Copyright Notice
4 1. Introduction
4 1.1 XQ MK2 RX (R2)
4 1.2 XQ MK2 Tx (T2)
4 1.3 | 4 Watt transmitter
5 1.3.1 Aisle Improvement Module
5 1.4 New Attenuator
5 1.5 Performance Indicator
6 2. Block diagrams
6 2.1 Network communication and
sync
6 2.1.1 Hand-terminal-connection
(K100)
7 2.1.2 Data communication over
coax
7 2.2 Transmitter
7 2.2.1 Anti-deactivation regulation
7 2.2.2 Output multiplexer
7 2.2.3 Tx output power setting
8 2.3 Receiver
8 2.3.1 Input multiplexer
8 2.3.4 Processor
9 2.3.5 Customer counting
9 2.3.6 Test-connectors
9 2.4 Dummy loads
10 3. PCB Components overview
10 3.1 Connector overview XQ TX
12 3.2 Connector overview XQ RX
14 4. Unit address
14 5. Connection to PC / Laptop
15 6. Networking with NCC MK2
15 Overview of necessary NCC’s
15 2 antennas XQ MK2 congura
tion
16 3 antennas XQ MK2 congura
tion
16 4 antennas XQ MK2 congura
tion
17 5 antennas XQ MK2 congura
tion
17 6 antennas XQ MK2 congura
tion
17 7 antennas XQ MK2 congura
tion
18 8 antennas XQ MK2 congura
tion
18 9 antennas XQ MK2 congura
tion
19 10 antennas XQ MK2 congura
tion
19 11-16 antennas XQ MK2 congu
ration
20 30 antennas XQ MK2 congura
tion
21 7. Conguration Manager
22 8. Metal Detection
22 8.1 T2 settings
22 8.1.1 Tx Enable
22 8.1.2 Applicatien Version
22 8.1.3 Bootloader version
22 8.1.4 Sync Period
22 8.1.5 Frequency
22 8.1.6 Current
22 8.1.7 Power
23 8.1.8 Adjusting the transmitter
settings
24 8.2 R2 Settings
24 8.2.1 RxEnable
24 8.2.1 Applicatien Version
24 8.2.2 Bootloader version
24 8.2.3 Sync Period
24 8.2.4 Sync Voltage
24 8.2.5 Frequency
24 8.2.6 Gain
24 8.2.7 Coupling
25 8.3 R2 Alarm
25 8.3.1 Alarm
25 8.3.2 Blocked
25 8.3.3 Sensitivity
25 8.3.4 Threshold
25 8.3.5 Noise level
25 8.3.6 Signal Level
25 8.3.7 Adjusting receiver settings
26 8.4 R2 Scope
27 9. Specications X2
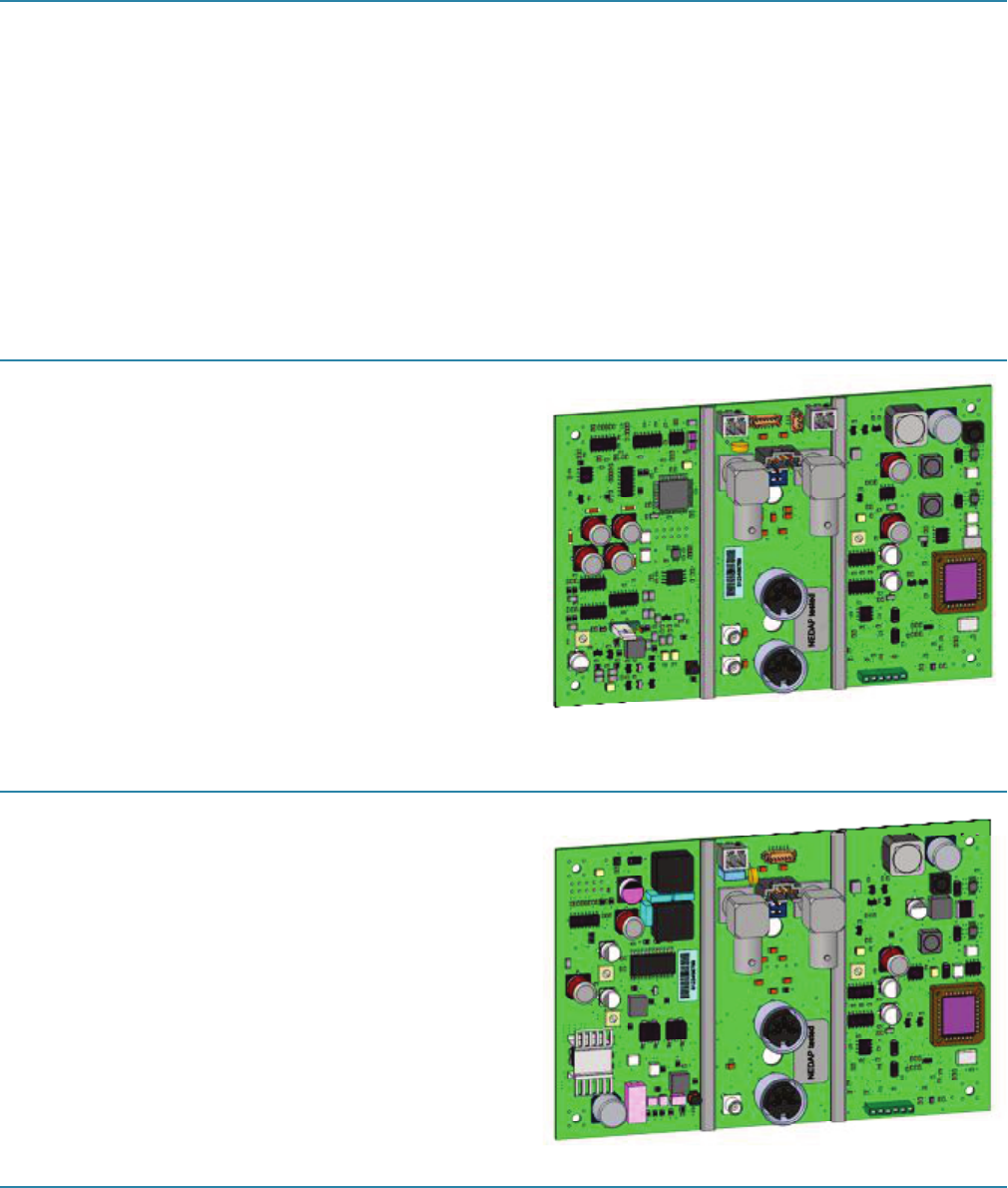
- 4 -
1. Introduction
The XQ MK2 Units are the successors of the XQ series internal OS/T electronics. The complete redesign has many new
features:
• Powerful transmitter (4 watt)
• Attenuator setting can be done for every aisle separately
• Attenuation jumpers are replaced by a rmware setting
• Integral customer counting
• Integral Metal detection, fully (remote) congurable with OS/T congurator
1.1 XQ MK2 RX (R2)
1.2 XQ MK2 Tx (T2)
The Tx units come with a 4 watt transmitter, which can be
switched on with a special functionality module.
1.3 | 4 Watt transmitter
The advantages of the new transmitter are:
• Aisle width between panels can be proximally 10 % more for the same label
OR
• Distance between the panels will be the same and smaller labels can be used
OR
• To suppress interference from other systems
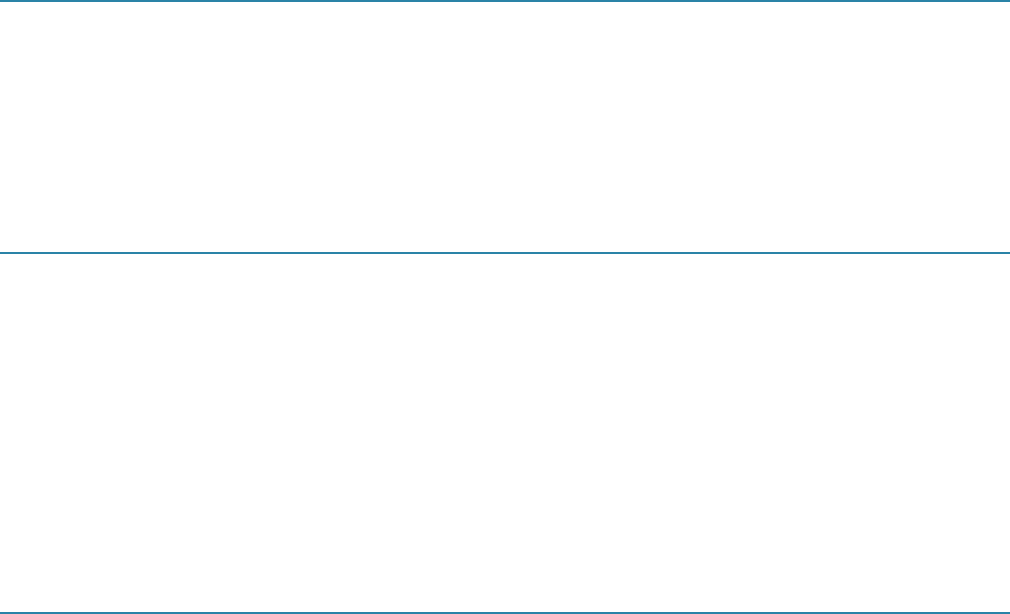
- 5 -
In combination with an AIM module (Aisle Improvement Module) the full features of the transmitter can be used.
1.3.1 The AIM (Aisle Improvement Module)
The module increases the power up to 4Watt.
All antennas suitable for the XQ Mk2 internal units with metal detection will be suitable for 4 Watt (effective power). The
outside of the antenna will be marked with a ‘4W’ addition to the serial label. Inside the antenna the will be a label
“Suitable for 4 W “
1.4 New Attenuator
The advantages for the attenuator are:
• Easy installation
• Additional external attenuators are not necessary anymore
• Hardware jumper settings are replaced through software settings
• Useful for aisles with different aisle width, example system with 2 aisles
• First aisle width is 1.60 meters
• Second aisle width is 1.00 meters
1.5 Performance Indicator
Firmware version 1.8xx and up contains performance indicators. This means that it is possible to actually trace the delivered
system performance.
A Nedap EAS system contains several different signal processing functions, which are mapped to several different hardware
units. For example we have a power supply, a sweep generator, a transmitter, a receiver, and deactivation units. To moni-
tor the performance of the system from bird’s eye view we have to look at and integrate all performance indicators of each
comprising unit. The actual data integration is done off line, in the TOPserver and or Easinet.
For all OST units we need performance indicators:
1. Performance indicator for a power supply.
A measure which indicates in time the actual delivery of good power. In practice as long as the system is working the
power is considered to be good. So this performance is not separately monitored. System uptime is used as indicator.
2. Performance indicator for a sweep generator.
A measure which indicates in time the actual delivery of good sweeps to the system. In practice as long as the system is
working the sweep generator is considered to be good. This performance is not separately monitored. System uptime is
used as indicator.
3. Performance indicator for transmitters.
A measure which indicates in time the actual delivery of good sweeps to the transmitter panel. Interruptions of the
power delivery due to AGC actions are monitored. This is a new performance indicator.
4. Performance indicator for receivers.
A measure which indicates in time the actual reception of clean sweeps from the panel. This is not explicitly monitored.
And a measure which indicates in times the actual level of external noise. This level must contain all detection prohibit-
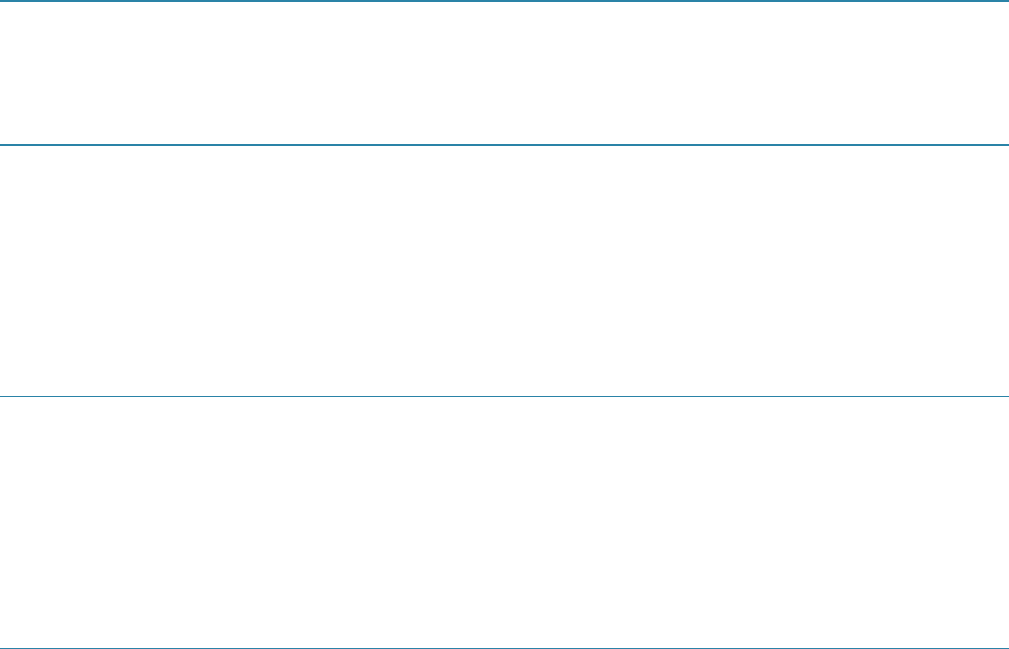
- 6 -
ing signals. This signal is monitored. This is the second new performance indicator.
With these performance indicators it should be possible to monitor accurately the performance of the system. These
indicators cover the primary detection function. Also the communication is checked continuously of course.
Altogether it is expected that the most frequent occurring disturbances and failures are covered. Some mechanical
failures are not covered, like receiver antennae wire failures. To cover these type of events it is sufcient to look at the
occurrence of label detection events at all. If alarm events occurs one can safely assume that the system is not dead yet.
The most important feature is the logging of EAS detection performance over time. Covered events are downtime due
to power outages, loss of transmit signal due to AGC events, occurrence of alarms, and environmental noise which
degrades the detection performance’s. Of course it is not possible to distinguish between false alarms and true label
alarms, because if that would be possible then all false alarms could be eliminated beforehand.
5. Performance indicator for standalone label deactivation units.
A measure which indicates in time:
• the actual delivery of good power
• the actual delivery of good sweeps to the system
• the actual delivery of good sweeps to the antenna
These parameters are covered by the system uptime indicator.
• the actual reception of clean sweeps from the panel
This parameter is monitored by the receiver (type) performance indicator.
2. Block diagrams
The XQ MK2 Transmitter with integral customer counting and metal detection.
2.1 Network communication and sync
The XQ units are slave-only, they need an RF signal originating from a master output . This could be an NCC, SQ unit or
TDC unit. The RF signal has a frequency of four times 8.2 MHz and sweeps between 30.... 36 MHz.
The RF signal is used to drive the transmitters as well as the receivers. The Coaxial cable between master-output and slave
input is also used to distribute DC power and data-communication
2.1.1 Hand-terminal-connection (K100)
A standard NEDAP RS handheld terminal (HT) may be connected to connector K100. With this HT you can edit the various
local settings. With this terminal all digital settings can be made, even if the network is nonfunctional.
Some settings can only be adjusted by using an OS/T Conguration Manager
Especially the Metal detection settings are only possible with the congurator
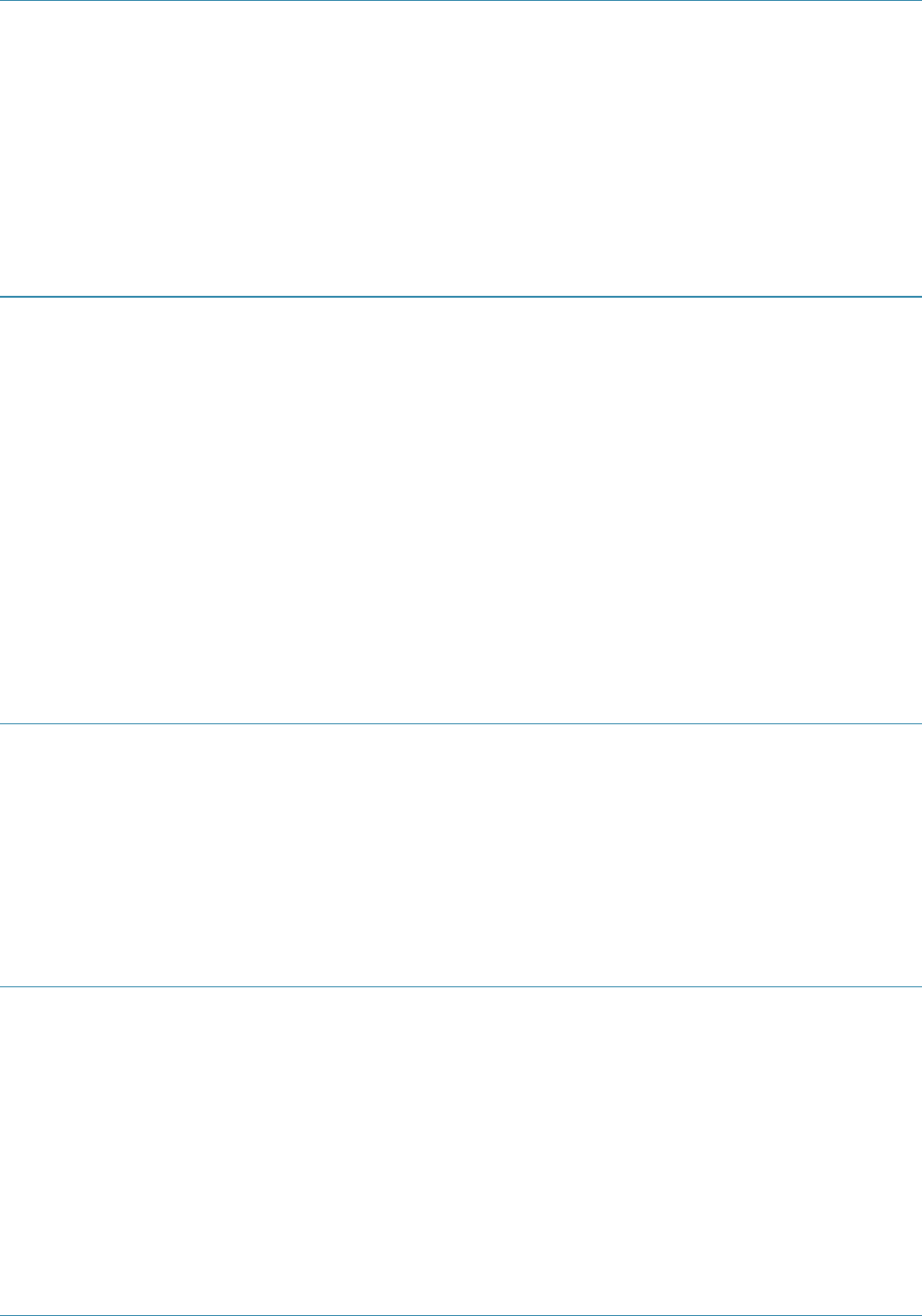
- 7 -
2.1.2 data communication over coax
One of the important features from the OS/T system is the data-com over the coax-cable. With this feature it’s no longer
necessary to use an extra data-cable between the units, which simplies the installation of the system. All the connected
units are interrogated periodically by the master. If there are messages like an alarm on a connected Rx unit, then the mas-
ter unit will process this and takes the necessary action: Sending a command to turn on the lamps on the activated aisle.
The XQ MK2 unit has two slave-sync connectors (K101 and K102) from which the unit can be driven from a NCC-4, SQ, or
TDC unit. DC supply is from the sync-connectors.
2.2 Transmitter
The Transmitter generates an 8.2 MHz RF signal with a maximum power level of 4 Watt to feed the transmitter antenna.
The transmitter receives its RF reference signal and conguration data from the local communication control section.
The start-pulse is distributed as a 1 microsecond break of the RF signal (32 periods) and indicates the start of the 1.6 ms
sweep. All timing of the OS/T-system is related to this start-pulse.
The RF signal (with a 30 till 36 MHz sweep) for the power amplier is divided by for 4 to create the 8.2 MHz transmitter sig-
nal. The power amplier consists of a class D MOSFET driver stage. The square wave output is ltered to achieve a cleaner
carrier. The 50 ohm output impedance is regulated by measuring output current and output voltage and adjusting the drive
signal of the MOSFET power stage accordingly. These two output parameters are measured with a current transformer and
a capacitive voltage divider circuit at the output stage. From these signals a phase control signal and the amplitude control
signal are derived. Both signals can be seen on the test connector. The signals are the feedback to the driver stage.
2.2.1 anti-deactivation regulation
If a RF label comes close to the antenna, it could be deactivated by the transmitter eld. To prevent this phenomenon a tag
detection circuit is used. A tag close to the antenna can be detected by looking at the antenna signal. A resonating tag in
proximity causes a small phase-disturbance in the antenna impedance, which can be seen on the phase control signal of the
transmitter. When in a sweep a tag pulse is found the processor can reduce the transmit power in the next sweep to prevent
deactivation of the tag. After the tag signal disappeared the transmit power is gradually increased to the desired power level.
2.2.2 output multiplexer
The transmitter can feed one antenna. The RF signal is switched during the y-back period of the RF sweep. The multiplexer
is a 1 out of 2 type build with PIN diodes. In the y-back-period the antenna is switched off.
The second output of the multiplexer goes to an internal dummy load. This is used for multiplexing when more than one
aisle is used. The “unused” phases can be dumped in the dummyload.
The antenna-output has his own lamp-control-circuit and can be switched on or off individually. The lamps are controlled
by software. The outputs have open, overload and short-circuit detection. These signals are under processor control.
The lamp control circuit is also used for driving the new-style (two-wire) buzzer.
2.2.3 tx output power setting
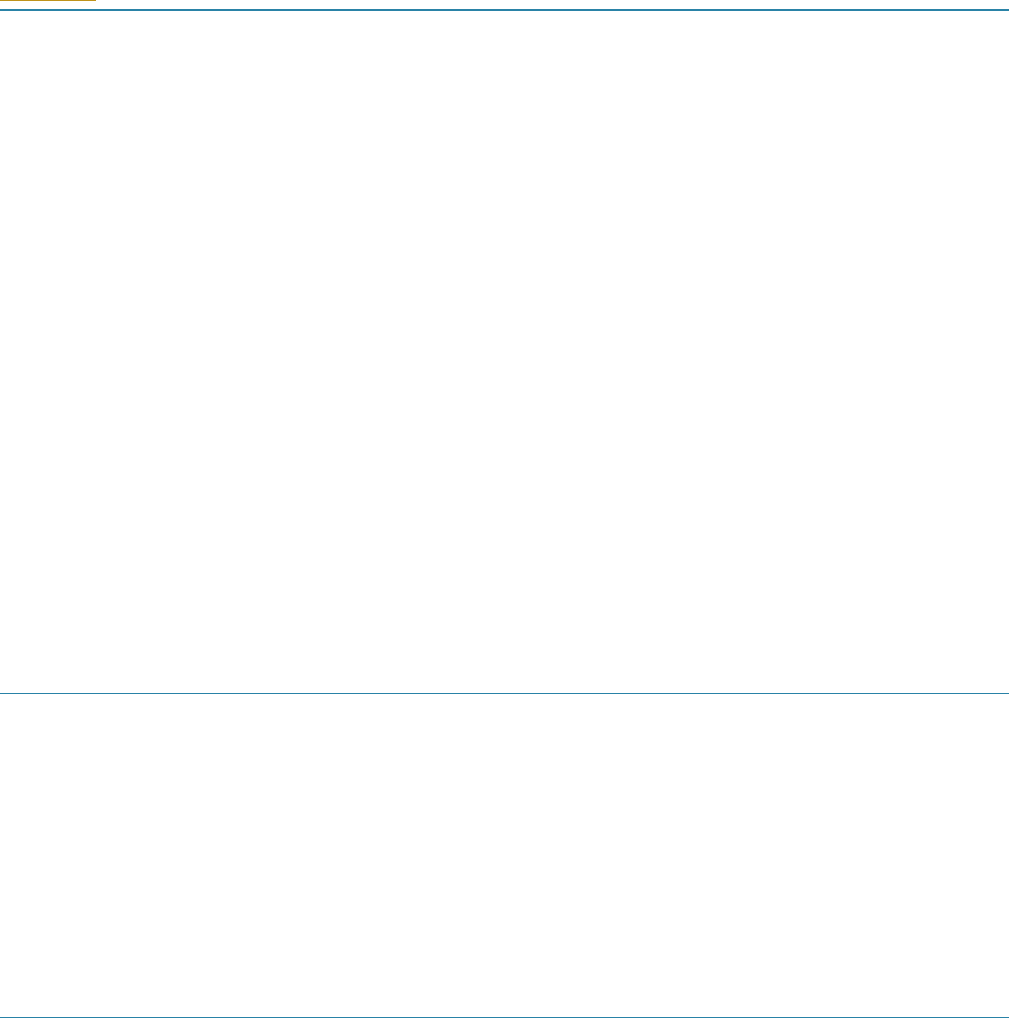
- 8 -
Default power setting is 2 Watts. This is suitable for almost every situation. With large aisle withs (2 meters or more) it can
be usefull to increase the power to 4 watts.
2.3 Receiver
The Receiver detects the tag signals generated by tags in the aisle formed by a transmitter panel and a receiver panel. Even
very small signals can be detected to achieve a very high pick rate. Aided by heavy use of digital signal processing the false
alarm rate is very low, even under difcult noise conditions. The receiver receives its RF reference signal and conguration
data from the local communication control section.
The antenna is connected to K202. Every sweep the antenna canl be connected to the receiver. This is done in the multiplex-
er circuit. After the multiplexer an attenuation stage can be used to reduce the level of direct feed through in case of very
close antenna distance. The attenuator can be selected as 0, -6dB, -12dB and -18dB. The setting is possible with the hand
terminal (under the sensitivity menu) or with the OS/T Conguration Manager.
A new feature is the possibility to set the attenuator per phase. The reference RF signal is split in four phases and fed to two
mixers together with antenna input. Each mixer generates a LF signal which is ltered, amplied and muted in the y back
period of the RF carrier. The mute circuitry consists of several stages which are controlled by software. The mixers are fed
with 90 degrees phase shift. The resulting LF signals are further processed by the digital signal processor (DSP).
The DSP uses digital memory to store the past quarter of a second to compare different sweeps and improve on noise level
and other unwanted signals components. The ltered signal after processing can be seen on the scope by looking at the
DAC signal.
2.3.1 input multiplexer
The receiver can process two antenna signals. This means that at most 2 antennas can be connected. The antenna signal
is switched during the y back period of the RF sweep. The multiplexer is a 1 out of 2 type build with PIN diodes. In the y
back period all antennas are switched off.
Antenna input 1 (K202) has his own lamp control circuit and can be switched on or off individually. The lamps are controlled
by software. The outputs have an open, overload, and short circuit detection. These signals are under processor control.
The secondairy antenna input (K201) is only meant for oor antennas and has no lamp/buzzer functionality.
2.3.4 processor
The XQ MK2 series boards (Tx and Rx) have only one processor for RX, TX and Communication control.
The processor has several different tasks. It must maintain the status of the transmitter and receiver and controls several
functions:
• lamp detection
• lamp/lamp overload
• multiplexer
• data communication
• handheld terminal communication
• customer-counting 1x2 inputs
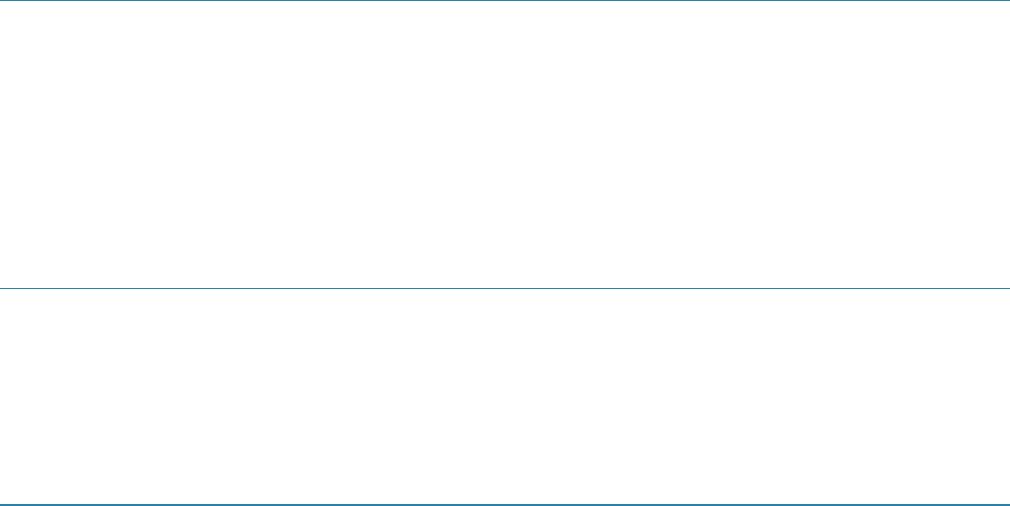
- 9 -
• metal detection
All the processor software and all the settings (including the network address) are contained in ash memory. Software is
downloadable in runtime. A new version can be distributed over the network. After downloading, ashing and verifying a
new version the unit resets and is operational again. This can be done remotely.
2.3.5 customer counting
The XQ MK2 PCB has customer counting on board. Two sensors can be connected to monitor the entrance with direction
sensitivity.
The passage between sensors is shaped and buffered and processed by the processor. In this way incoming and outgoing
label alarms can be counted for separately.
The sensor power output is 12 V dc. It is possible to connect sensor with positive or negative going output signals.
2.3.6 test-connectors
K200: The receiver test-connector shows 3 analogue signals to aid in installing and servicing the receiver section. For easy
external triggering a start pulse is available.
The transmitter test connector shows the analogue signals needed to align and verify the transmitter.
2.4 Dummy loads
Dummy loads are no longer needed for the XQ MK2 PCB’s. Unused channels will be programmed as channel “0”.
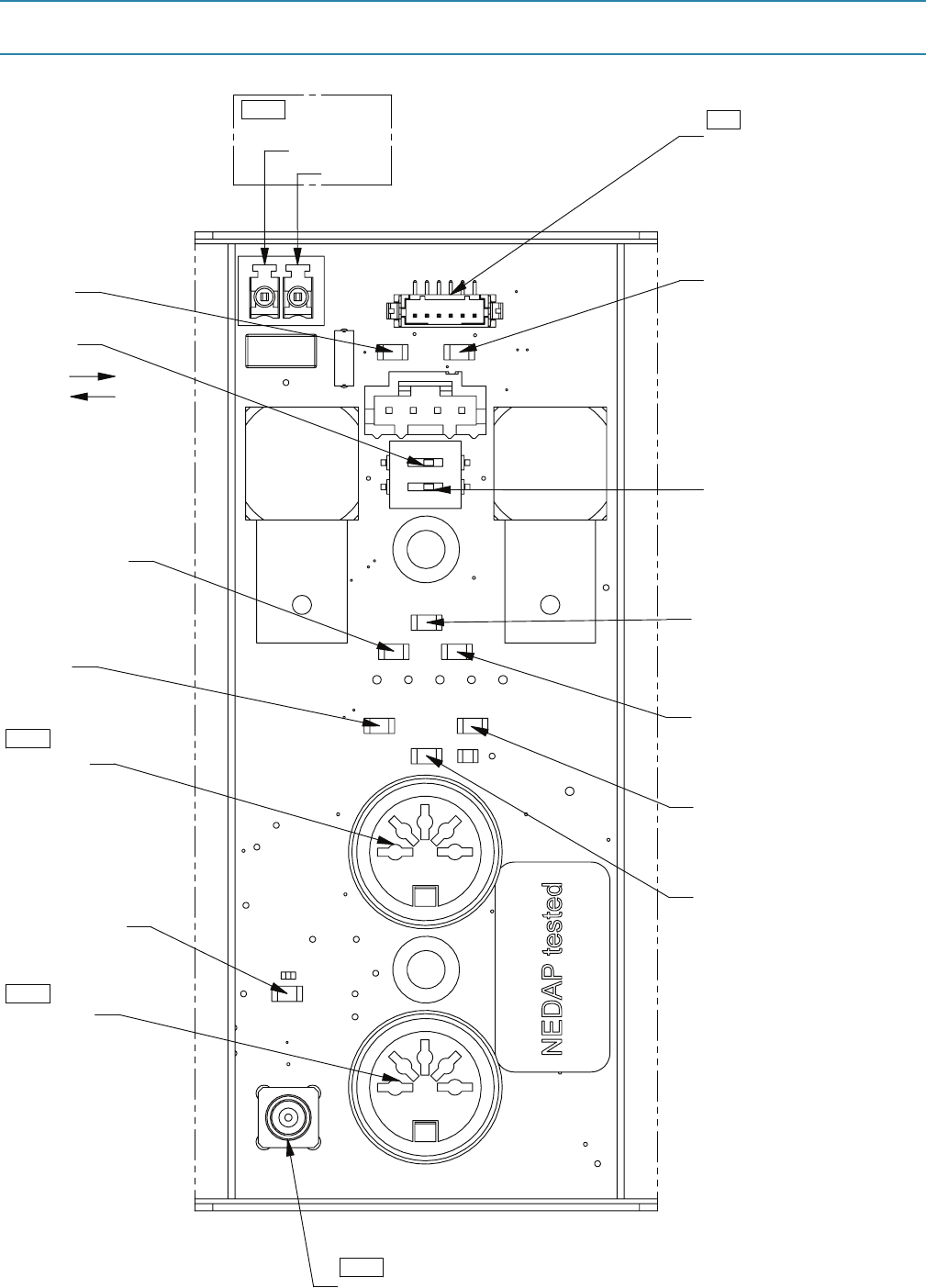
- 10 -
3. PCB Components overview
3.1 Connector overview XQ TX
Antenna (TX out)
Testconn.
Handterm.
Power on (Green)
Metal Detection-error (Red)
Metal Detection ON
(Green)
Lamp (Yellow)
Customer counting
(connector)
50
Ω
(1)
Customer counting 2
(Yellow)
Customer counting 1
(Yellow)
Lamp Overload (Red)
Datacom-error (Red)
Alarm (Yellow)
No function (2)
GND
MD-out
K201
K202
K50
ON
OFF
K200
K100
Metal Detection
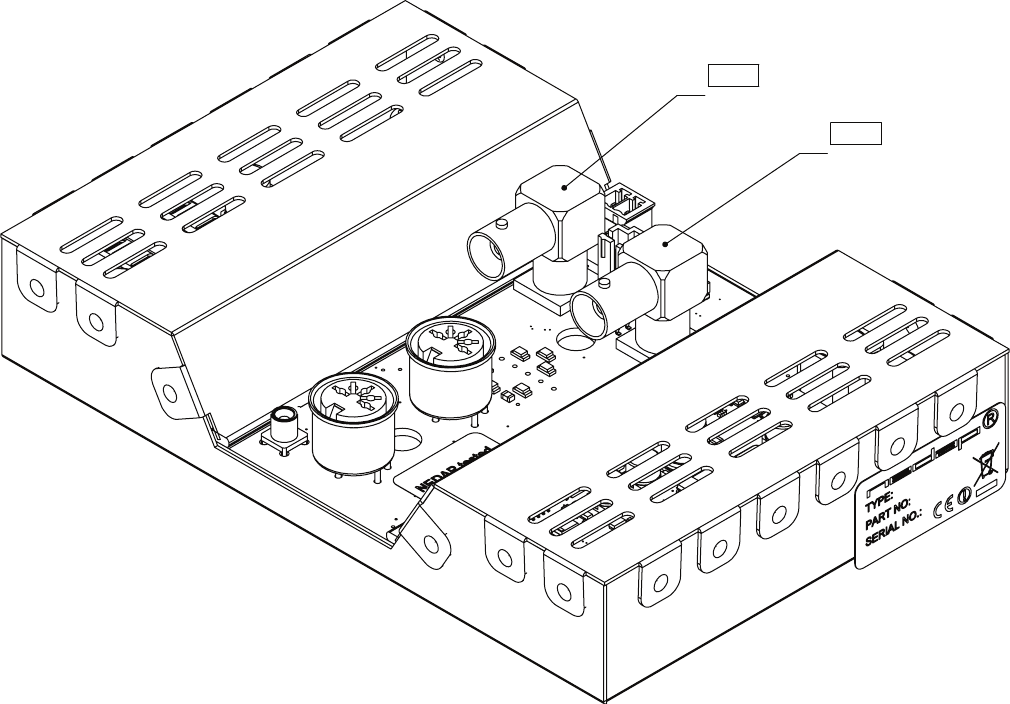
- 11 -
Sync in
Sync out
K101
K102
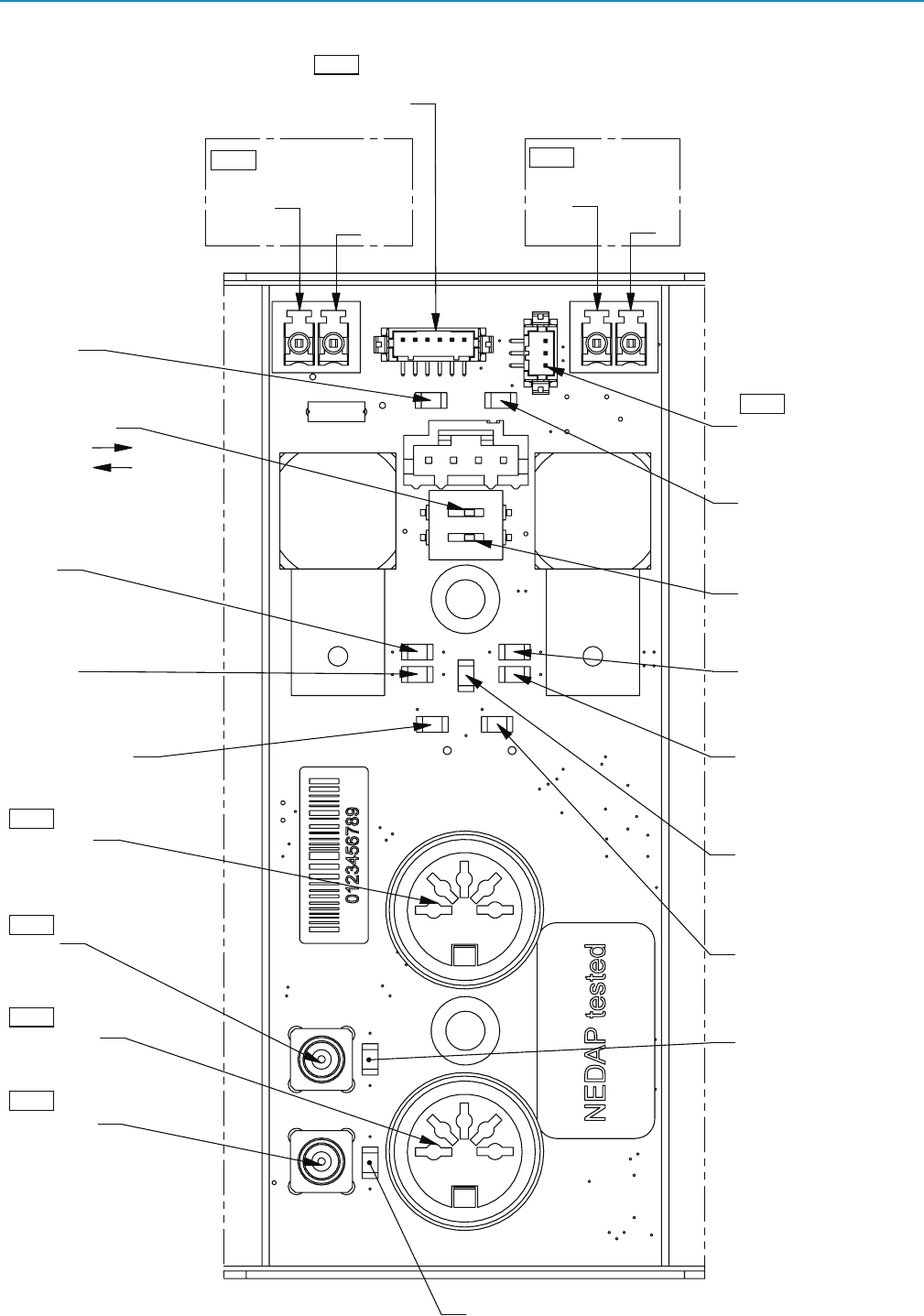
- 12 -
3.2 Connector overview XQ RX
Handterm.
Testconn.
Aux 2
Antenna 1
MD-out
GND
Customer counting 1
(Yellow)
Customer counting 2
(Yellow)
50
Ω (1)
Datacom-error (Red)
Power on (Green)
Lamp (Yellow)
Lamp overload (Red)
Alarm (Yellow)
Metal Detection alarm
(Red)
Metal Detection Blocked
(Yellow)
Antenna 1 active
(Green)
Antenna 2 active
(Green)
Customer counting
(connector)
K106
Keyswitch
K103
-
+
Buzzer
K105
No function (2)
K200
K100
K201
K202
K400
Metal Detection
ON
OFF
Do not use!
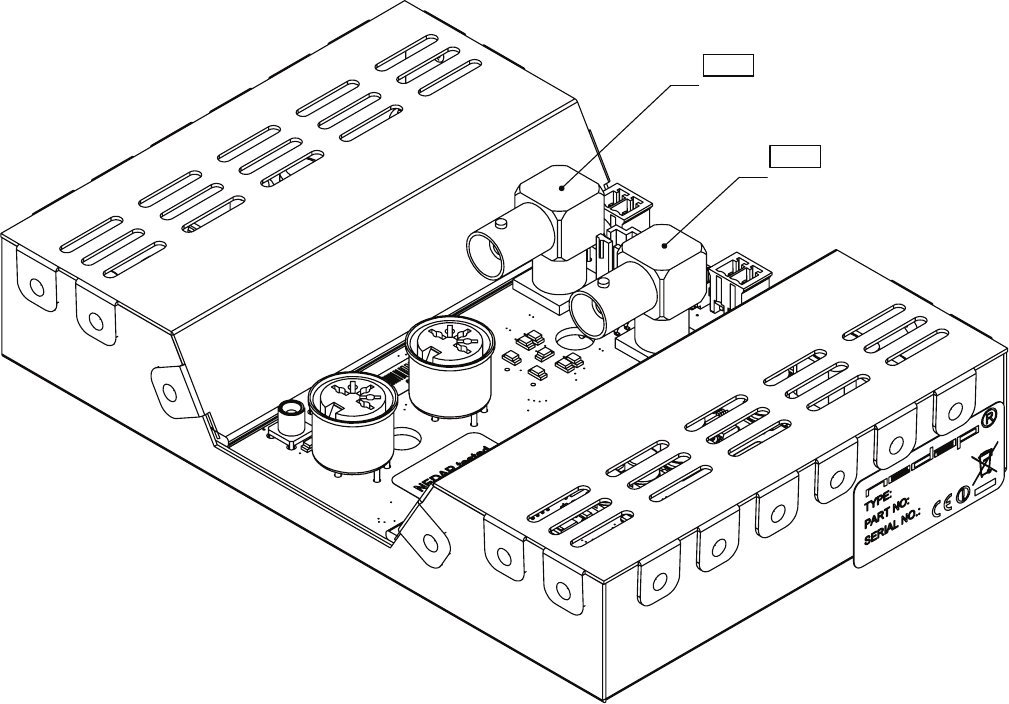
- 13 -
Sync in
Sync out
K101
K102
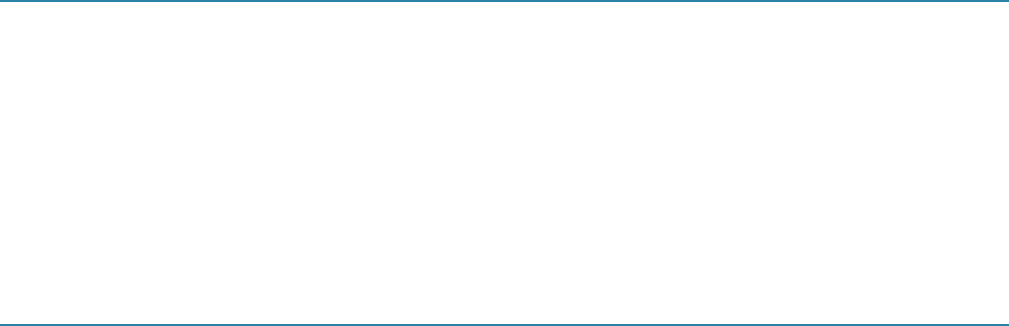
- 14 -
4. Unit address
Each XQ MK2 unit has an unique network address. The address is entered in the master unit to enable data communica-
tion.
The unit address is an 8 digit address; the last four digits will be a xed couple of characters, these characters will be used in
the OS/T Conguration Manager and in the hand held terminal (for instance slave table etc.)
5. Connection to PC / Laptop
The X2 uses a min-usb connector for a direct connection with the Conguration Manager.
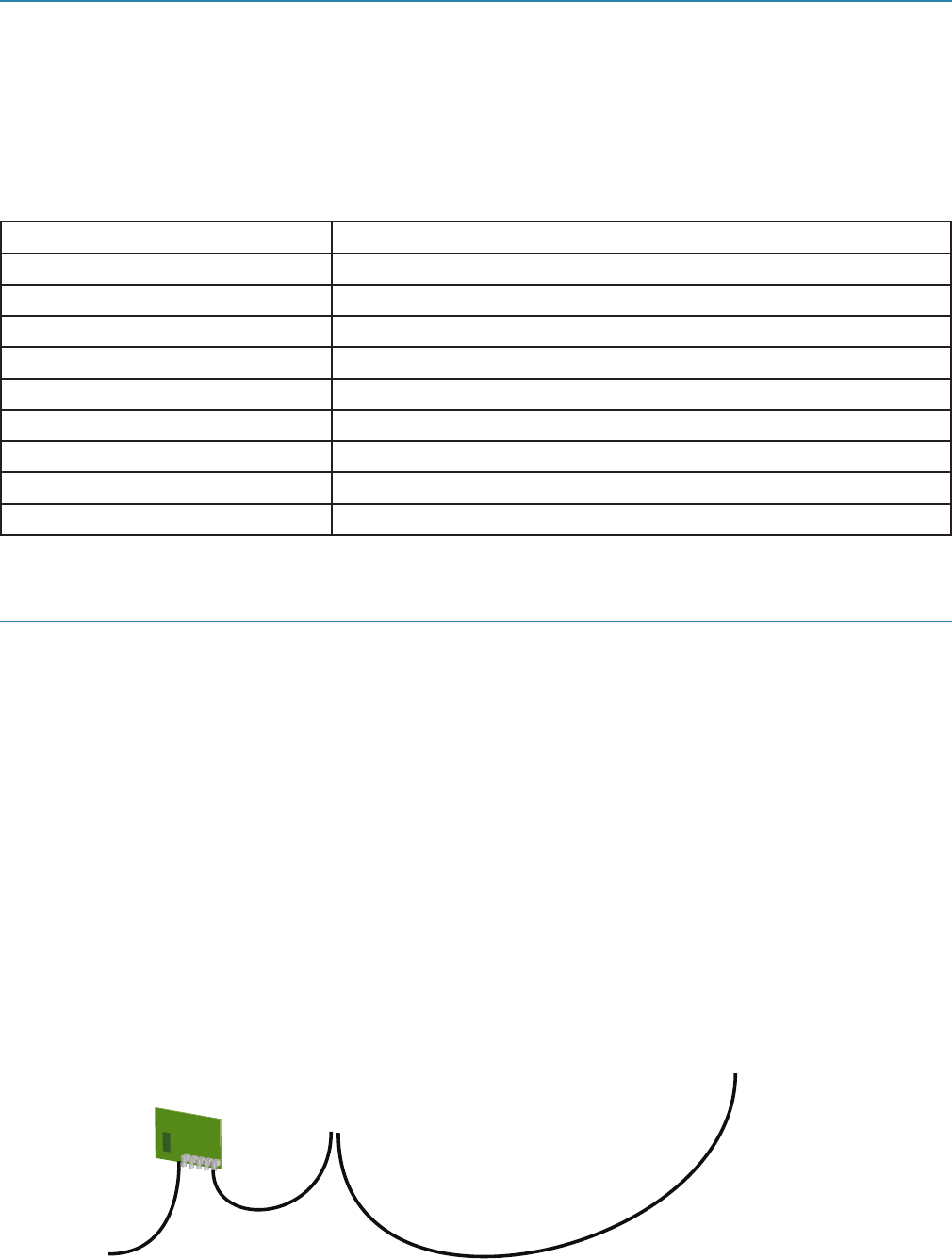
- 15 -
6. Networking with NCC MK2
NCC (networking electronics)
• including power supply
• synchronization of upto 16 antennas (max. 6 antennas per output)
• The NCC MK2 can deliver power for a maximum 10 antennas with XQ MK2 electronics. Iin case of >10 antennas, a
power inserter is needed for the next 10 antennas with XQ MK2 electronics.
Overview of necessary NCC’s and power inserters
Number of antennas Required
1 t/m 10 1 NCC
11 t/m 16 1 NCC + 1 power inserter
17 t/m 26 2 NCC + 1 power inserter
27 t/m 32 2 NCC + 2 power inserter
33 t/m 42 3 NCC + 2 power inserter
43 t/m 48 3 NCC + 3 power inserter
49 t/m 58 4 NCC + 3 power inserter
59 t/m 64 4 NCC + 4 power inserter
etc. etc.
In case of large congurations, we advice you to contact Nedap Retail
2 antennas xQ mK2 configuration
NCC MK2
Power supply
XQ R2
XQ T2
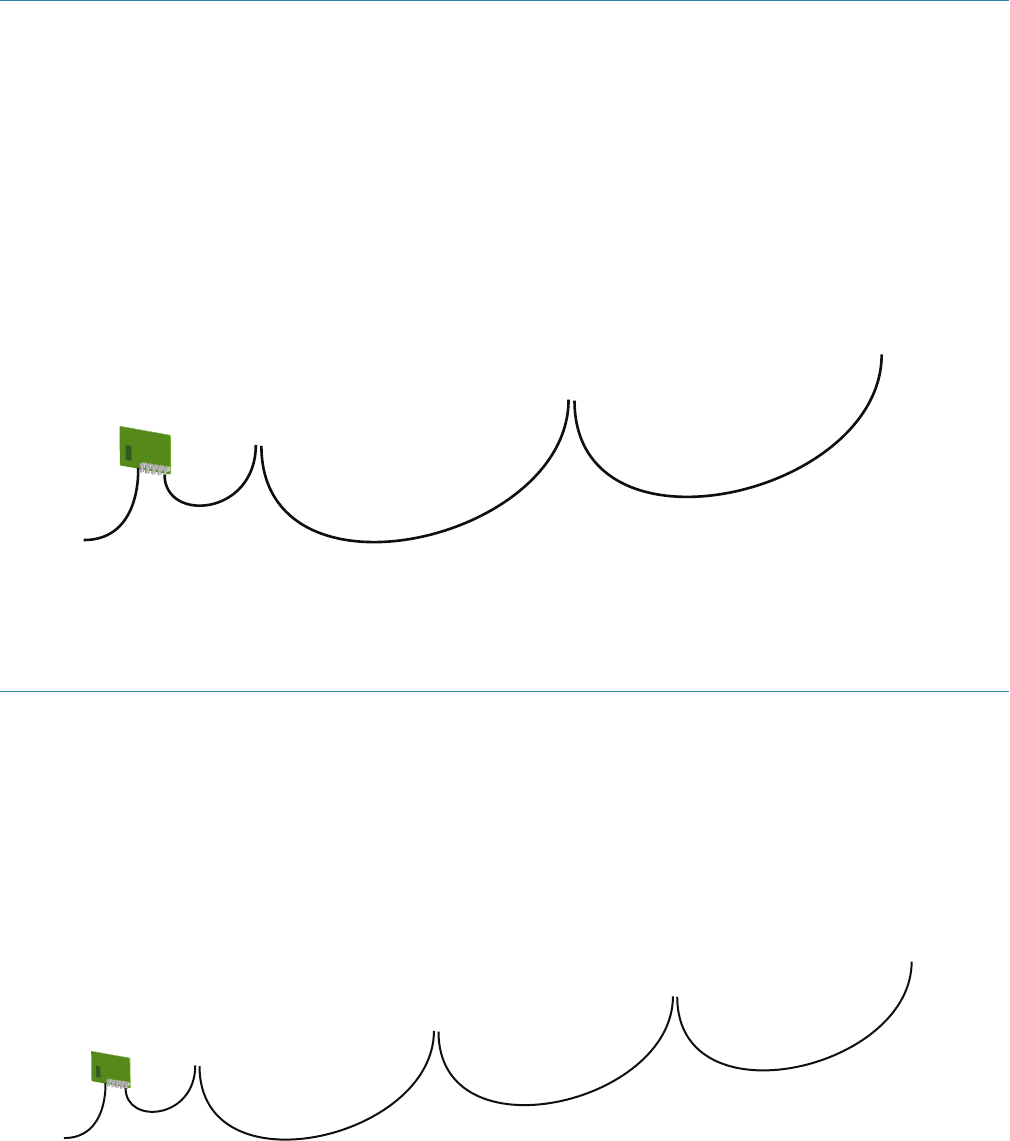
- 16 -
3 antennas xQ mK2 configuration
4 antennas xQ mK2 configuration
NCC MK2
Power supply
XQ R2
XQ T2
XQ R2
NCC MK2
Power supply
XQ R2
XQ T2
XQ R2
XQ T2
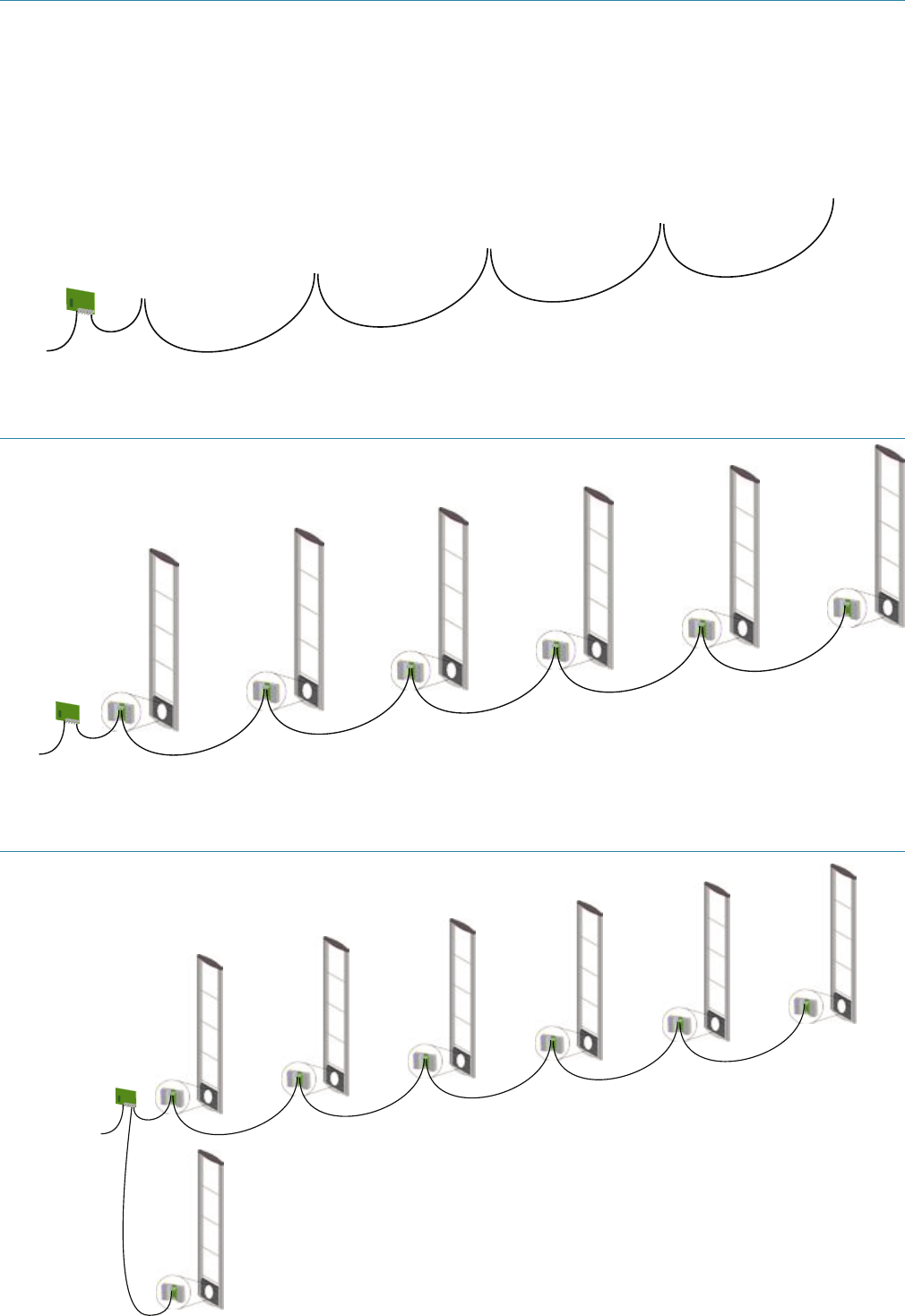
- 17 -
5 antennas xQ mK2 configuration
6 antennas xQ mK2 configuration
7 antennas xQ mK2 configuration
NCC MK2
Power supply
XQ R2
XQ T2
XQ R2
XQ T2
XQ R2
NCC MK2
Power supply
XQ R2
XQ T2
XQ R2
XQ T2
XQ R2
XQ T2
NCC MK2
Power supply
XQ R2
XQ T2
XQ R2
XQ T2
XQ R2
XQ T2
XQ R2
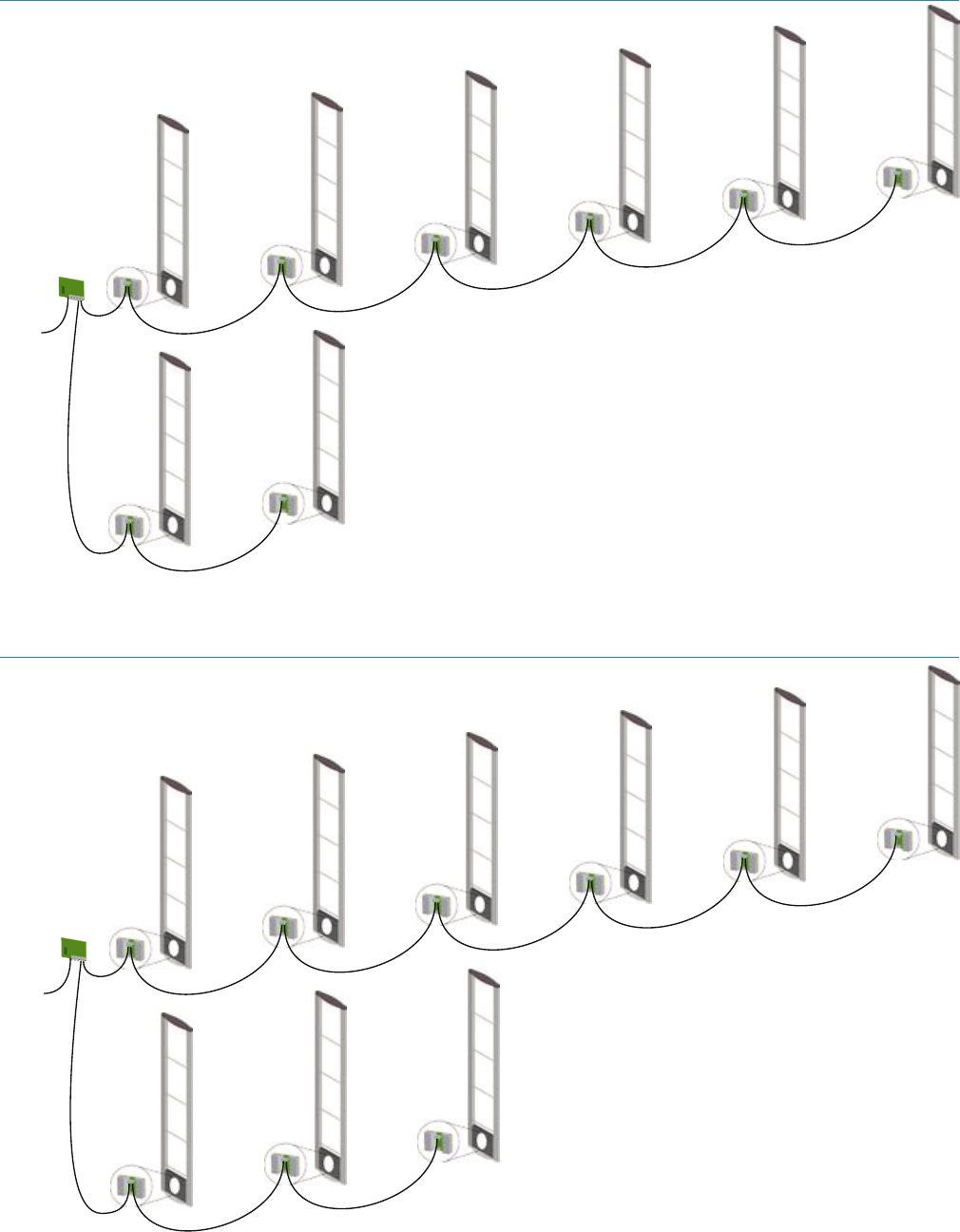
- 18 -
8 antennas xQ mK2 configuration
9 antennas xQ mK2 configuration
NCC MK2
Power supply
XQ R2
XQ T2
XQ R2
XQ T2
XQ R2
XQ T2
XQ R2
XQ T2
NCC MK2
Power supply
XQ R2
XQ T2
XQ R2
XQ T2
XQ R2
XQ T2
XQ R2
XQ T2
XQ R2
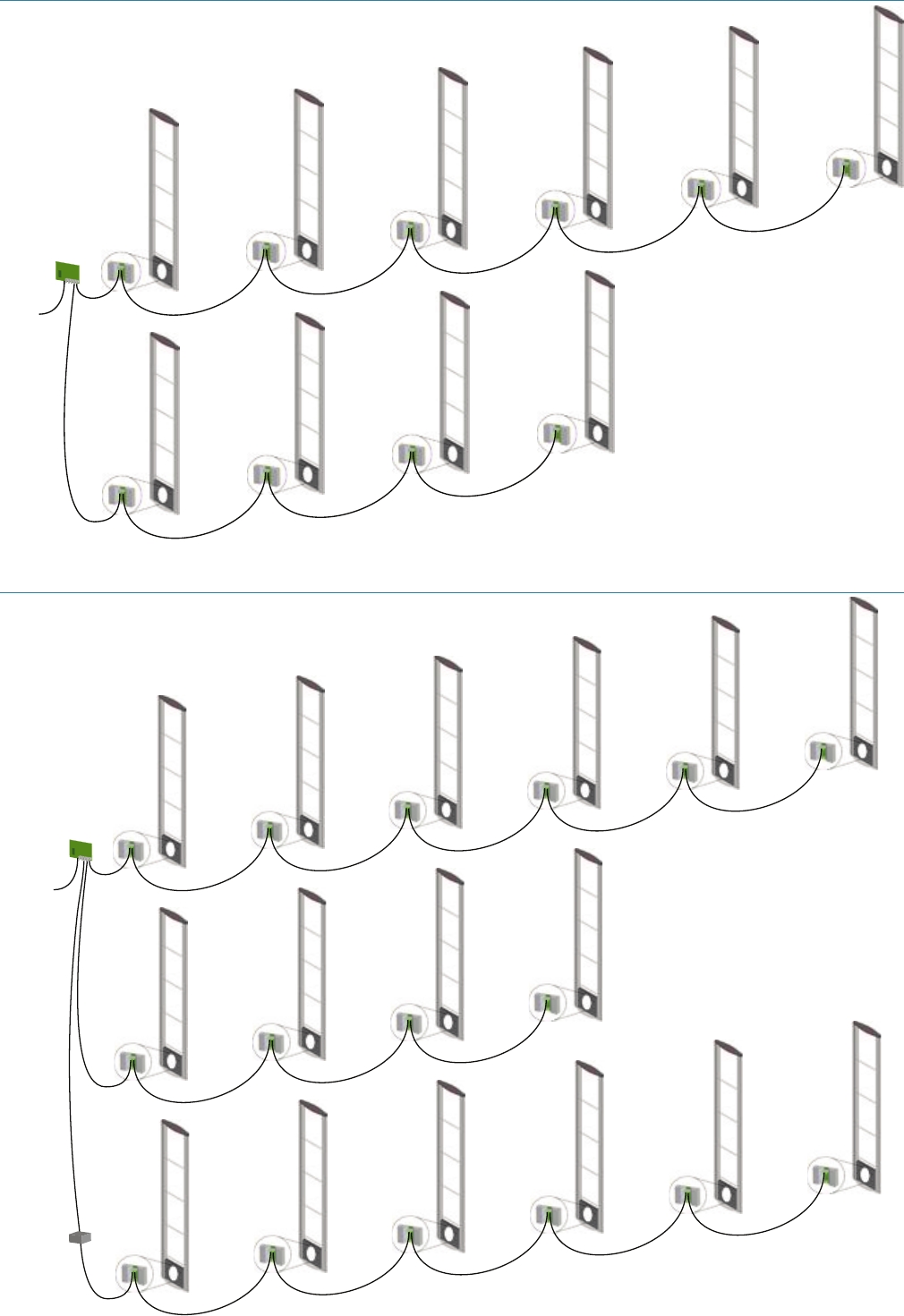
- 19 -
10 antennas xQ mK2 configuration
11-16 antennas xQ mK2 configuration
NCC MK2
Power supply
XQ MK2
Power
Inserter
NCC MK2
Power supply
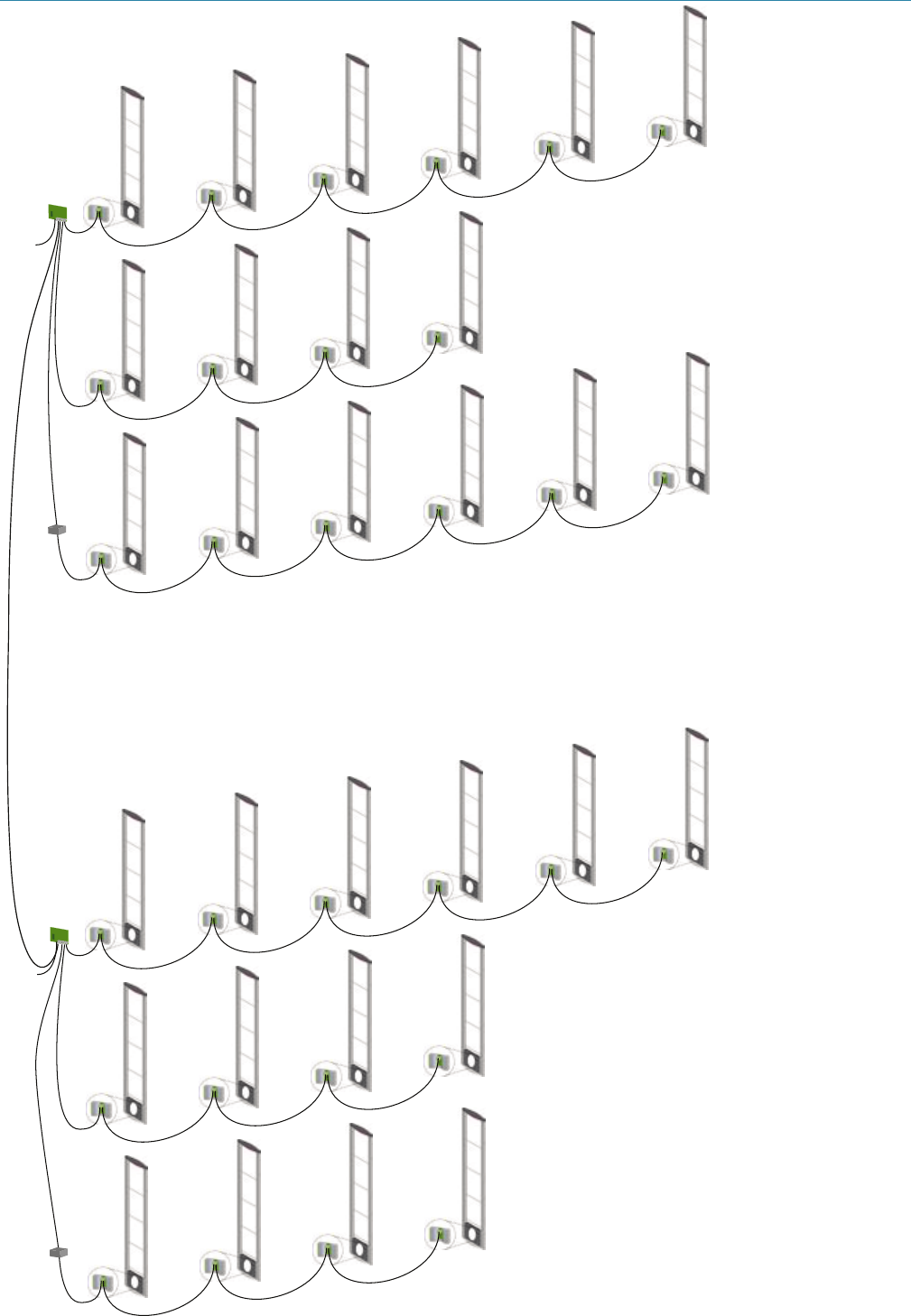
- 20 -
30 antennas xQ mK2 configuration
Power
Inserter
Power
Inserter
NCC MK2
Power supply
NCC MK2
Power supply
XQ R2
XQ T2
XQ R2
XQ T2
XQ R2
XQ T2
XQ R2
XQ T2
XQ R2
XQ T2
XQ R2
XQ T2
XQ R2
XQ T2
XQ R2
XQ T2
XQ R2
XQ T2
XQ R2
XQ T2
XQ R2
XQ T2
XQ R2
XQ T2
XQ R2
XQ T2
XQ R2
XQ T2
XQ R2
XQ T2

- 21 -
7. Conguration Manager
All real-time data displayed in the conguration manager, is a subset from the real data. The data communication is not
showing all data, to limit the load on the data bus.
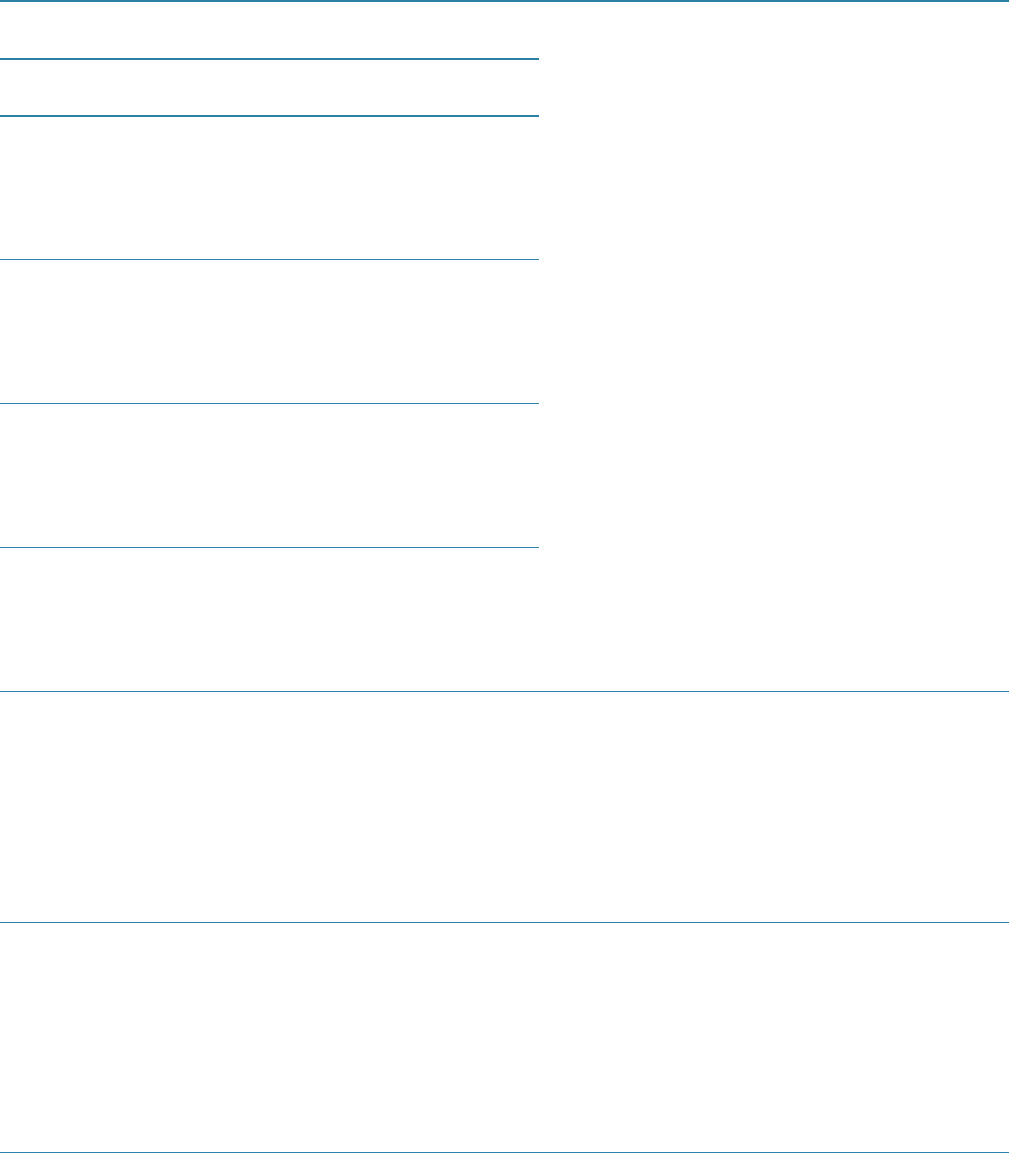
- 22 -
8. Metal Detection
8.1 T2 settings
8.1.1 Tx Enable
Enables or disables the metaldetection transmitter.
Default is disabled.
8.1.2 applicatien version
Firmware version of the metaldetection. This
rmware can be remotely updated.
8.1.3 Bootloader version
Firmware version of the bootloader. This rmware
can only be programmed in the factory.
8.1.4 sync period
The measured period time of the OST sync pulse
(Sweep setting 0 1 2 3).
8.1.5 freQuency
The required metal detection frequency. In the future the range will be limited from 120..130
kHz. Now the range is from 100..150kHz for testing the PLL and lters. In the eld only use the
range of 120..130kHz.
The Frequency is only an indication. The actually generated frequency is calculated from the
measured period time of the sync pulse.
8.1.6 current
An indication of the mean current drawn by the Tx Transmitter stage. The amount of current
drawn depends very much on the frequency that is set, the type of antenna in use and the
tolerance in the ltering components used.
Therefore this is only a very rough indication. The current in the Tx transmitter stage is also
limited by hardware.
8.1.7 power
The output power of the transmitter output stage. Low and high power are available. Step
between Low and High is 6dB. The High power setting does not give any advantage in the
sense of increased metaldetection sensitivity. High Power is ony needed at extreme distances
between the panels and in Panels where the Antenna PCB is in the center of the antenna like
EQ45 and D50. These antenna’s give half the eld compared with antenna’s with their PCB at
the end of the eight antenna . Current coming from the center will ow equally in both loops of
the eight loop.
In an antenna with antenna PCB at the end of the eight loop The High power setting could be
used when there is extreme environmental noise.
When this is the case it is better to use another frequency setting.

- 23 -
8.1.8 adjusting tHe transmitter settings
• Check the Tx Enable box to enable the transmitter
• Adjust the frequency (Default 125kHz will be ok normally)
• Adjust the Power Setting (Default Low is preferred)
• Save the metaldetection settings by pushing the Metaldetection Save button. In the future
this button will be combined with the save & close button
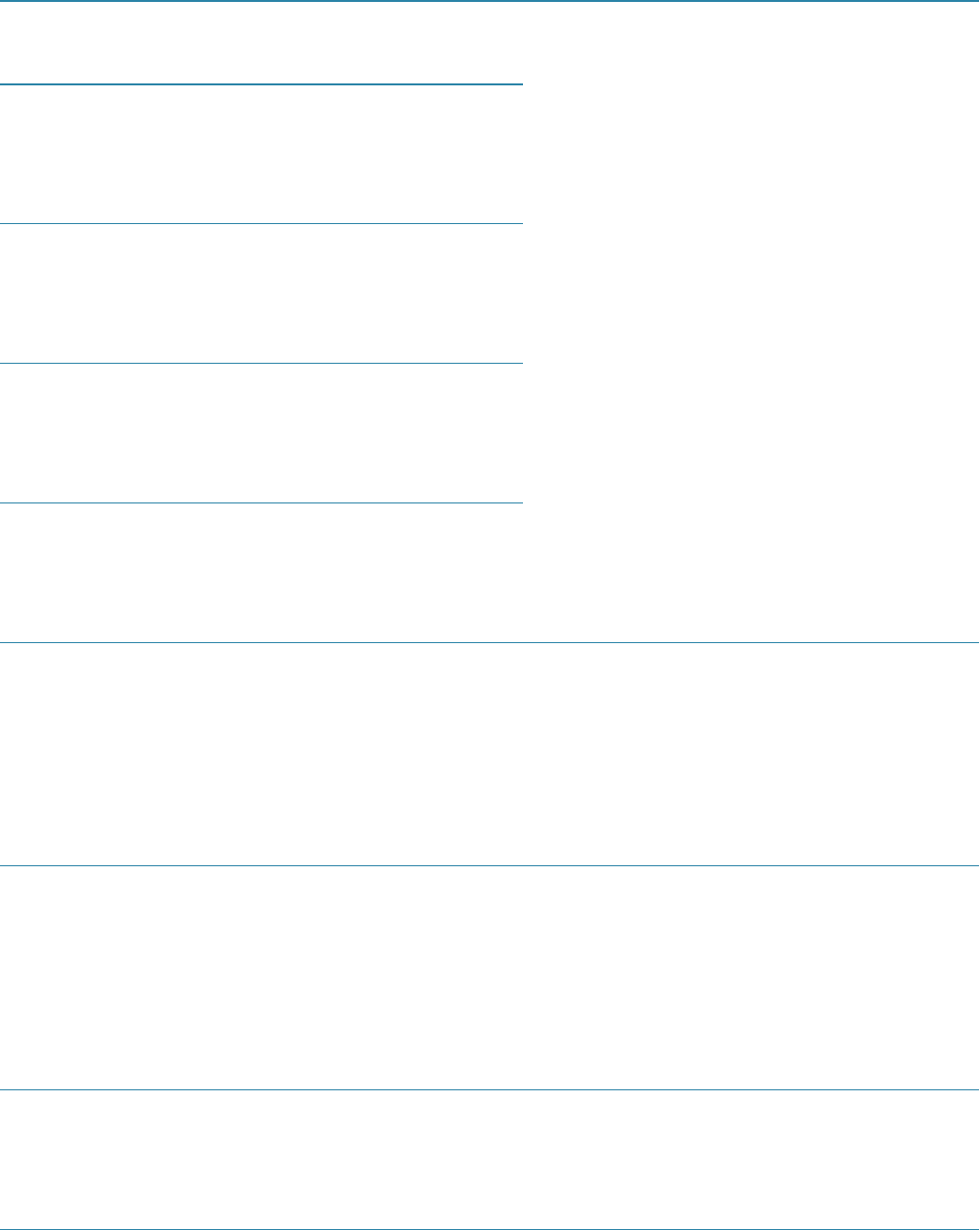
- 24 -
8.2 R2 Settings
8.2.1 RxEnable
Enables or disables the metaldetection receiver.
Default is disabled.
8.2.1 applicatien version
Firmware version of the metaldetection. This
rmware can be remotely updated.
8.2.2 Bootloader version
Firmware version of the bootloader. This rmware
can only be programmed in the factory.
8.2.3 sync period
The measured period time of the ost sync pulse
(Sweep setting 0 1 2 3).
8.2.4 sync voltage
This is the measured voltage at the output of the phase-correction integrator. The Phase-
correction will adjust the phase error caused by phaseshift through the air (little) and phaseshift
caused by the receivers input lter (much and depending on the frequecy that is set). The
Voltage that is displayed is only an indication and does not always have to be the same with
the same frequency setting. In a correct working system it wil be stable.
8.2.5 freQuency
The required metal detection frequency. In the future the range will be limited from 120..130
kHz. Now the range is from 100..150kHz for testing the PLL and lters. In the eld only use the
range of 120..130kHz.
The Frequency is only an indication. The actually generated frequency is calculated from the
measured period time of the sync pulse.
8.2.6 gain
This is the gain of the preamplier stage. It wil inuence the direct coupling as well as the
metaldetection signal equally.
8.2.7 coupling
The measured direct coupling at the receiver Mixer (Vtop). The direct coupling has to be
200mV minimal. When the coupling is less than 200mV the Phase correction integrator does
not function propery. The receiver will be blocked by the software and generate no alarms.
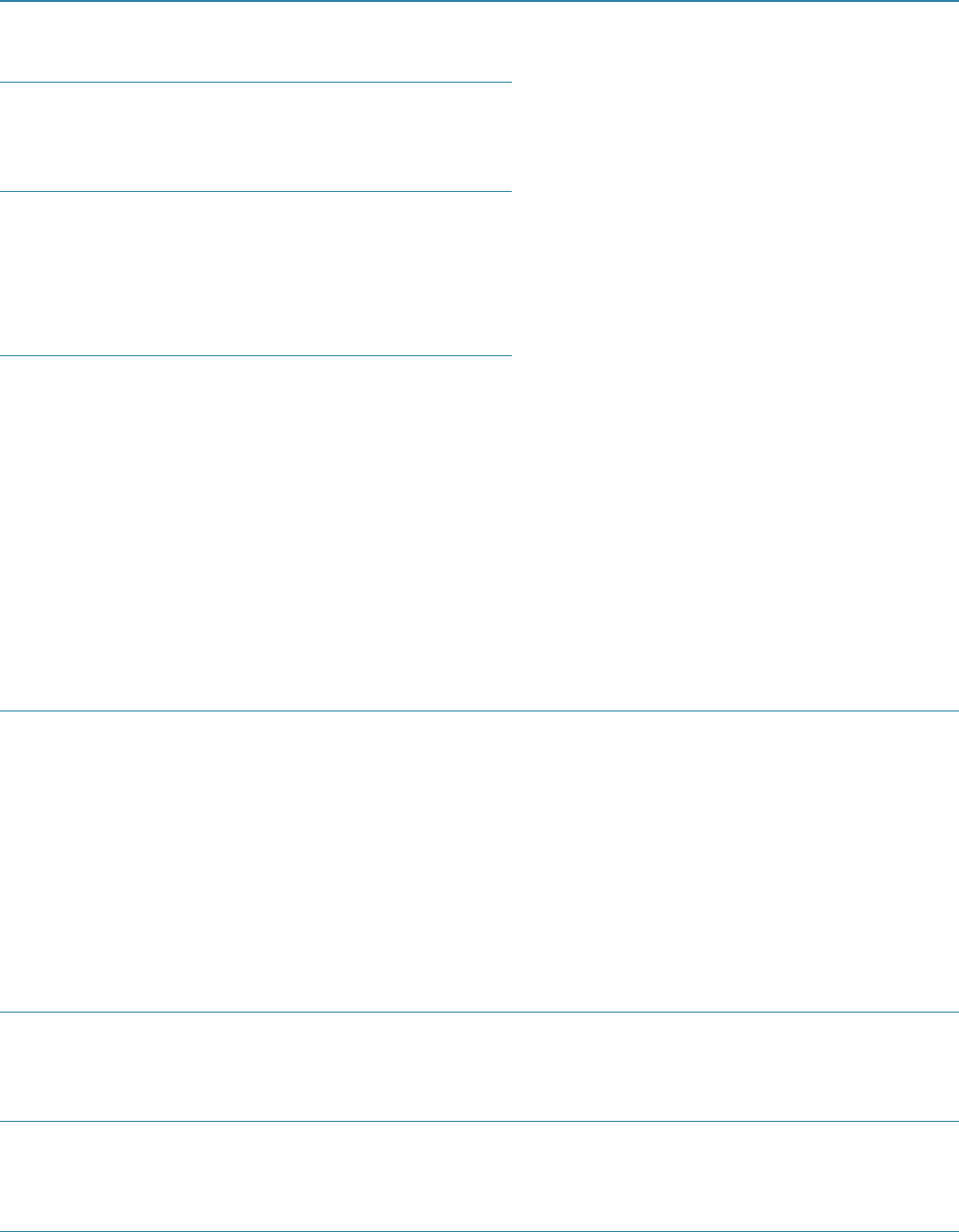
- 25 -
8.3 R2 Alarm
8.3.1 alarm
Indicates if there is a metal detection alarm.
8.3.2 BlocKed
Indicates if the reiceiver is blocked. This happens
after a reboot and if the direct coupling runs below
200mV.
8.3.3 sensitivity
The Sensitivity together with the Threshold give
the Threshold for the Metaldetection alarm. The
Sensitivity is related to the direct couping. Large
Direct coupling gives us a large metal signal. For
alarming the Metal signal has to be a Sensitivity
(dB) amount of the direct coupling.
By relating to the direct couling the distance of
antenna’s and the power setting have no inuence
on the calcutated alarm threshold. (This is not totally correct yet but will be in the near future).
Good setting of the sensitivity is about 10..20dB.
8.3.4 tHresHold
This setting determines by what factor the measured Noise is multiplied and the alarm
threshold is raised.
Noise is caused by Rx and Tx Pll jitter and noise picked up from the environment. Noise is
measured continuously and dynamically increases the Alarm threshold.
A lot of noise results in a less sensitive system.
By decreasing the Noise Threshold the system becomes more sensitive but the probability of
false alarm is increased.
Good setting for the Noise threshold is 3..9dB.
8.3.5 noise level
Indication of the measured noise.
8.3.6 signal level
Indication of the measured Metal signal
8.3.7 adjusting receiver settings
Check Rx Enable to enable the receiver.
Adjust the frequency so that it is the same as the transmitters frequency
Adjust the Gain until the direct coupling indicator is in the green area.
Green is ok but preferably about 1000mV.
Wait until the receiver is recovered from changing the settings. When it is recovered On the
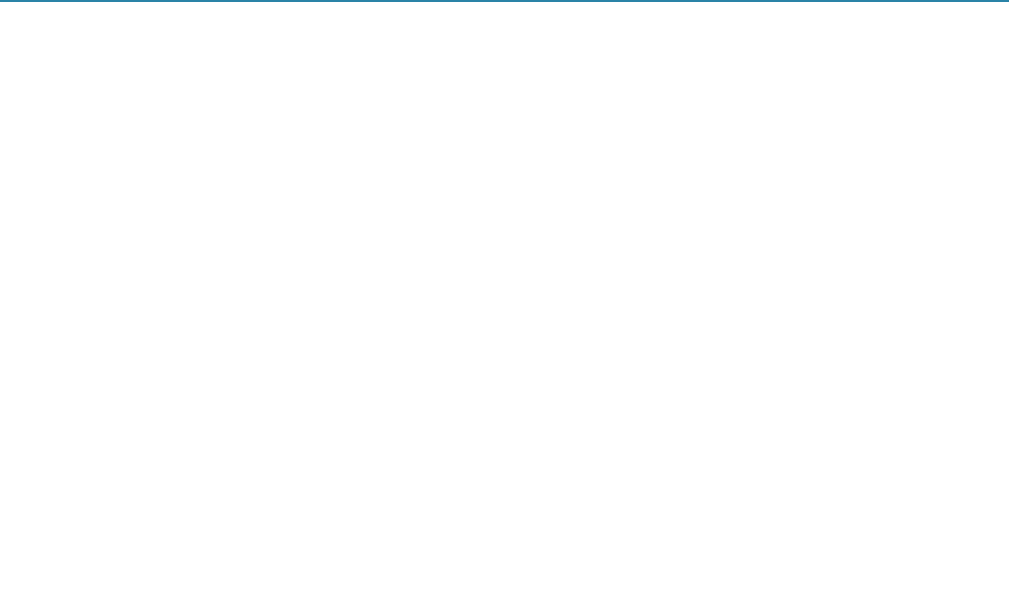
- 26 -
Alarm Tab you will see that the Noise level is Low (about -54dB).
Adjust the sensitivity to the required sensitivity.
Save the metaldetection settings by pushing the Metaldetection Save button.
In the future this button will be combined with the save & close button.
8.4 R2 Scope
This scope displays the Metal signal that is
measured. It gives a good indication of what is
happening in the system.

- 27 -
9. Specications X2
Frequency : 8.2 MHz
Antenna Connections : 1x 50 Ohm BNC Transceiver connector
Synchronization : 1x input 50 Ohm BNC
1x output 50 Ohm BNC
Weight : 3 kg
Temperature range : 0°C …+40°C
Power Supply : 30~33V DC, 400mA
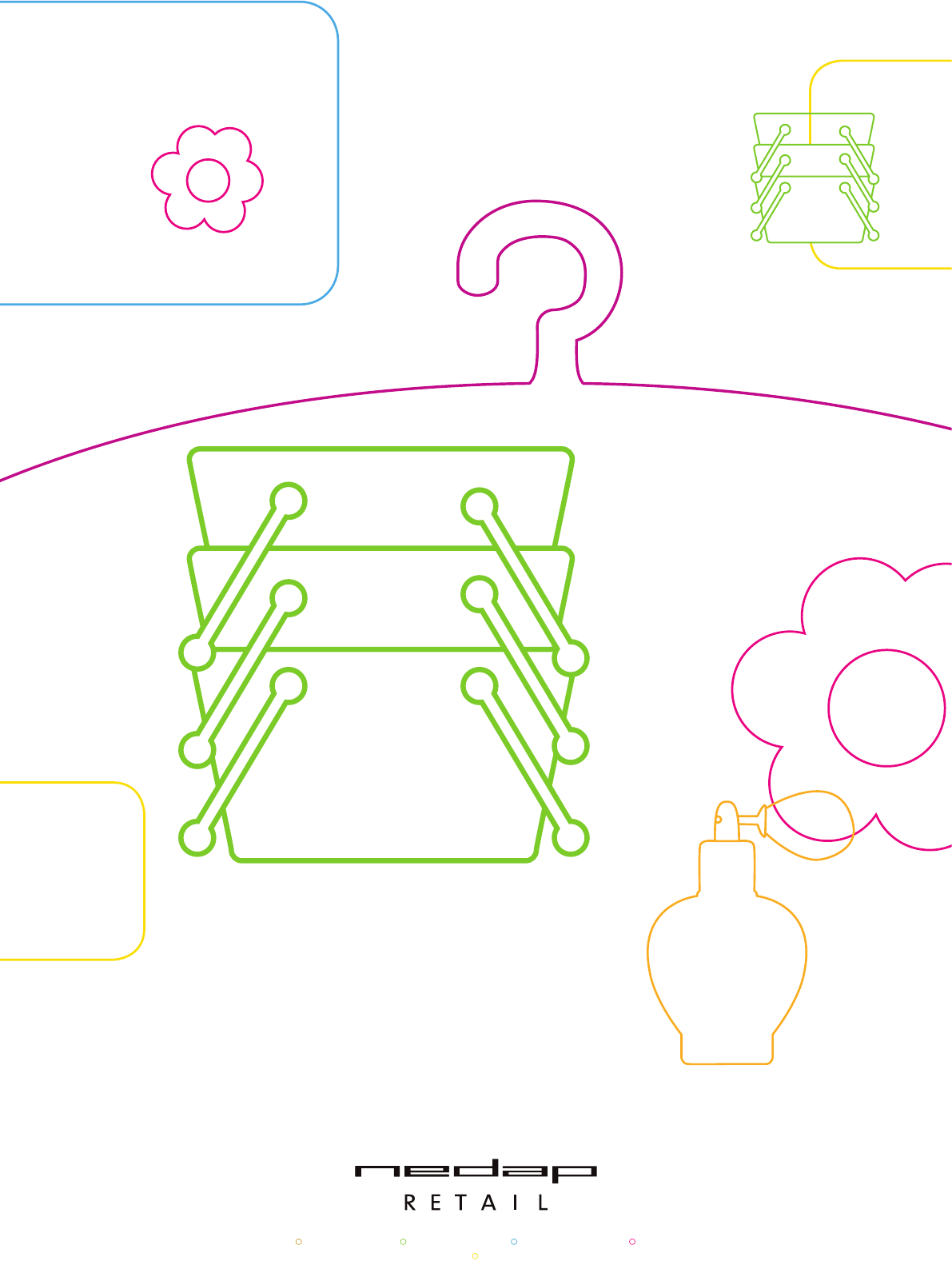
- 28 -
parallelweg 2d 7141 dc groenlo the netherlands t +31 (0) 544 47 15 55 f +31 (0) 544 46 58 14
e info-rs@nedap.com www.nedapretail.com