Rosemount Tank Radar 5401 Radar Level Gauge User Manual Book 5400
Rosemount Tank Radar AB Radar Level Gauge Book 5400
Manual
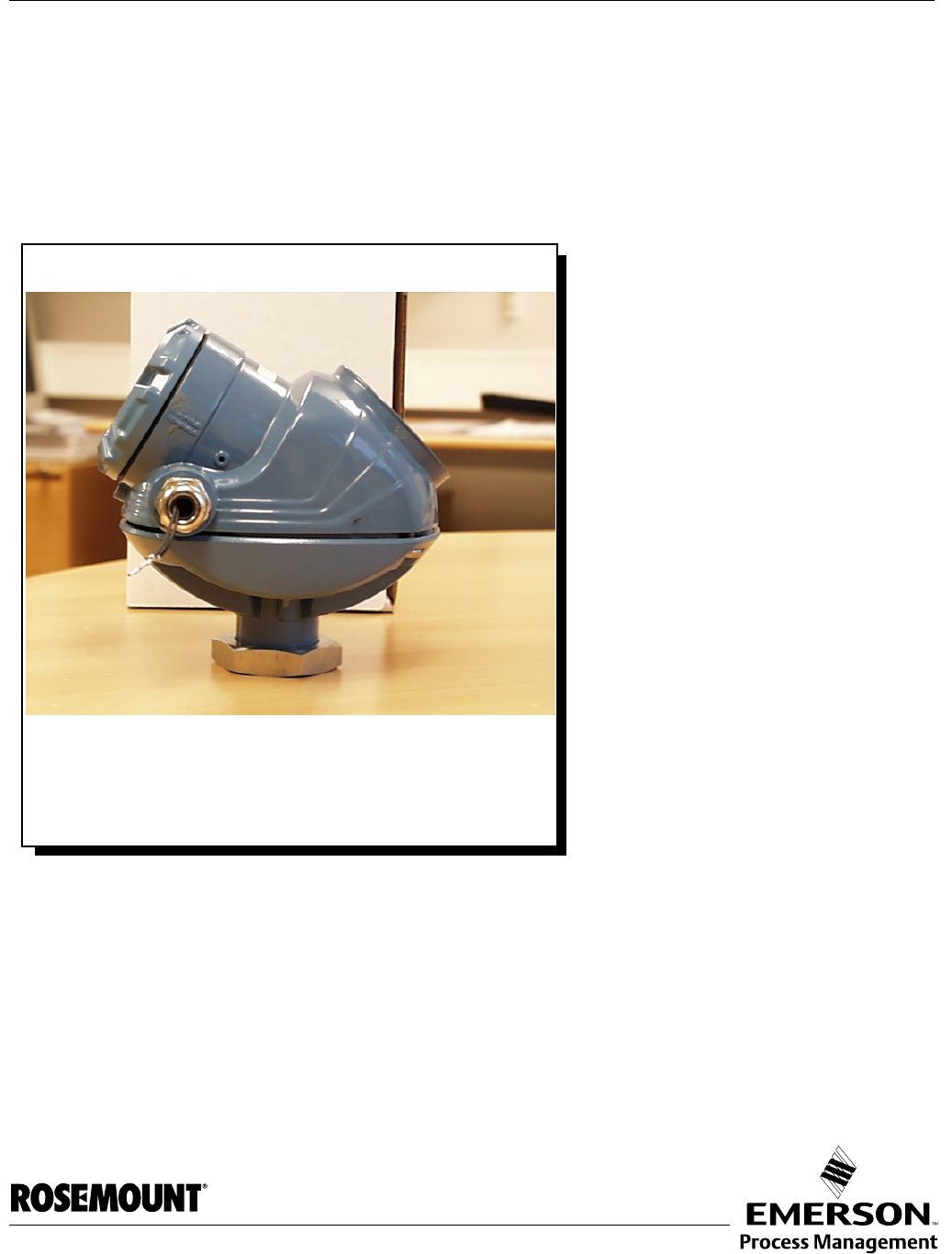
www.rosemount.com
Reference Manual
00809-0100-4026, Rev AA
November 2003
Preliminary copy
Rosemount 5400 Series
Subtitle
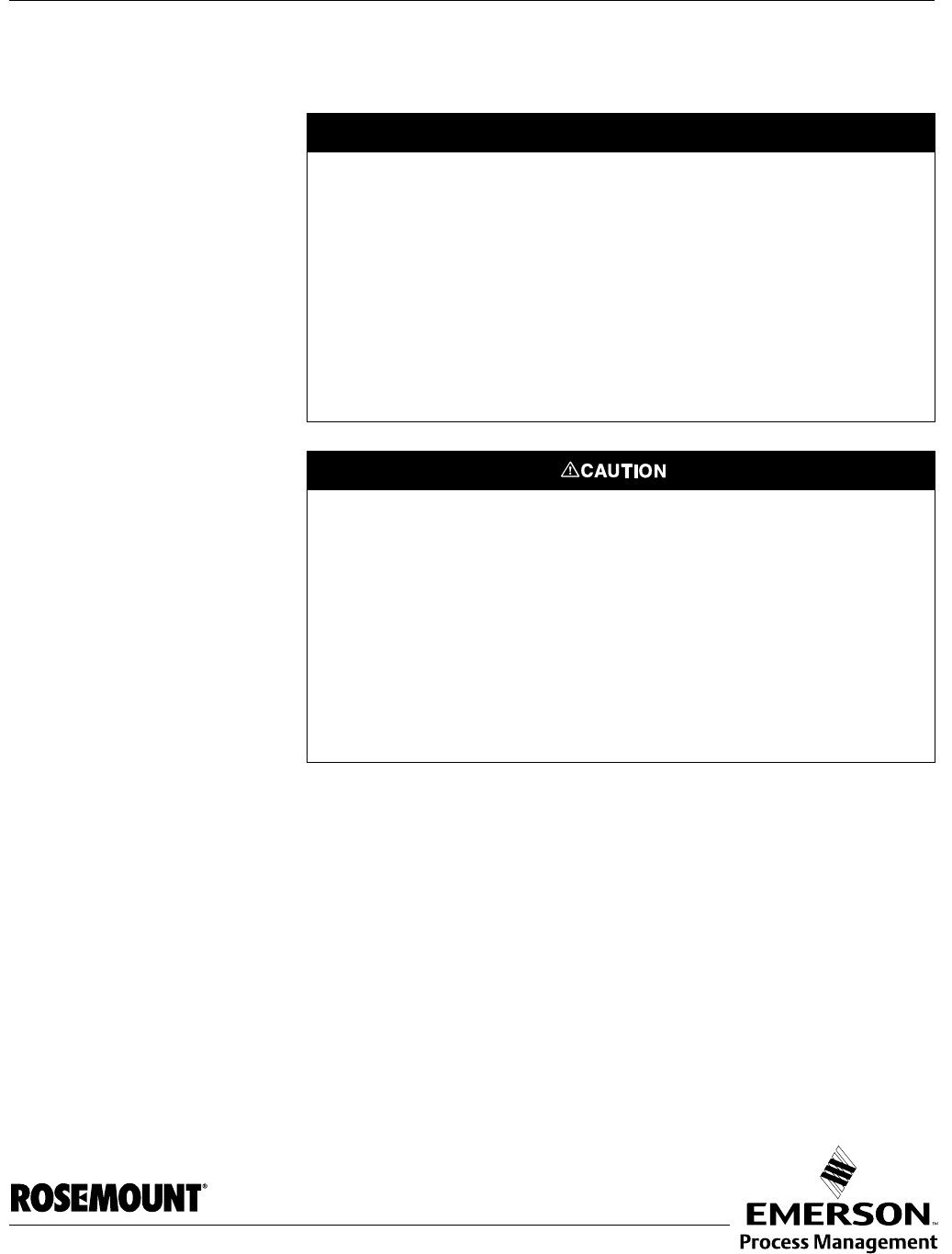
Reference Manual
00809-0100-4026, Rev AA
November 2003 Rosemount 5400 Series
www.rosemount.com
Preliminary copy
Rosemount 5400 Series
Rosemount 5400 Series Radar Transmitter may be protected by one or more U.S. Patents pending and foreign
patents pending.
Rosemount and the Rosemount logotype are registered trademarks of Rosemount Inc.
HART is a registered trademark of the HART Communication Foundation.
Teflon, VITON, and Kalrez are registered trademarks of E.I. du Pont de Nemours & Co.
Asset Management Solutions is a trademark of Emerson Process Management.
Cover Photo: xx
NOTICE
Read this manual before working with the product. For personal and system safety, and for
optimum product performance, make sure you thoroughly understand the contents before
installing, using, or maintaining this product.
Within the United States, Rosemount Inc. has two toll-free assistance numbers.
Customer Central: 1-800-999-9307(7:00 a.m. to 7:00 p.m. CST)
Technical support, quoting, and order-related questions.
North American Response Center:
Equipment service needs.
1-800-654-7768 (24 hours a day – Includes Canada)
For equipment service or support needs outside the United States, contact your local
Rosemount representative.
The products described in this document are NOT designed for nuclear-qualified
applications.
Using non-nuclear qualified products in applications that require nuclear-qualified hardware
or products may cause inaccurate readings.
For information on Rosemount nuclear-qualified products, contact your local Rosemount
Sales Representative.
This product is designed to meet FCC and R&TTE requirements for a non-intentional
radiator.
This device complies with part 15 of the FCC rules. Operation is subject to the following two
conditions: (1) This device may not cause harmful interference, and (2) this device must
accept any interference received, including interference that may cause undesired
operation.
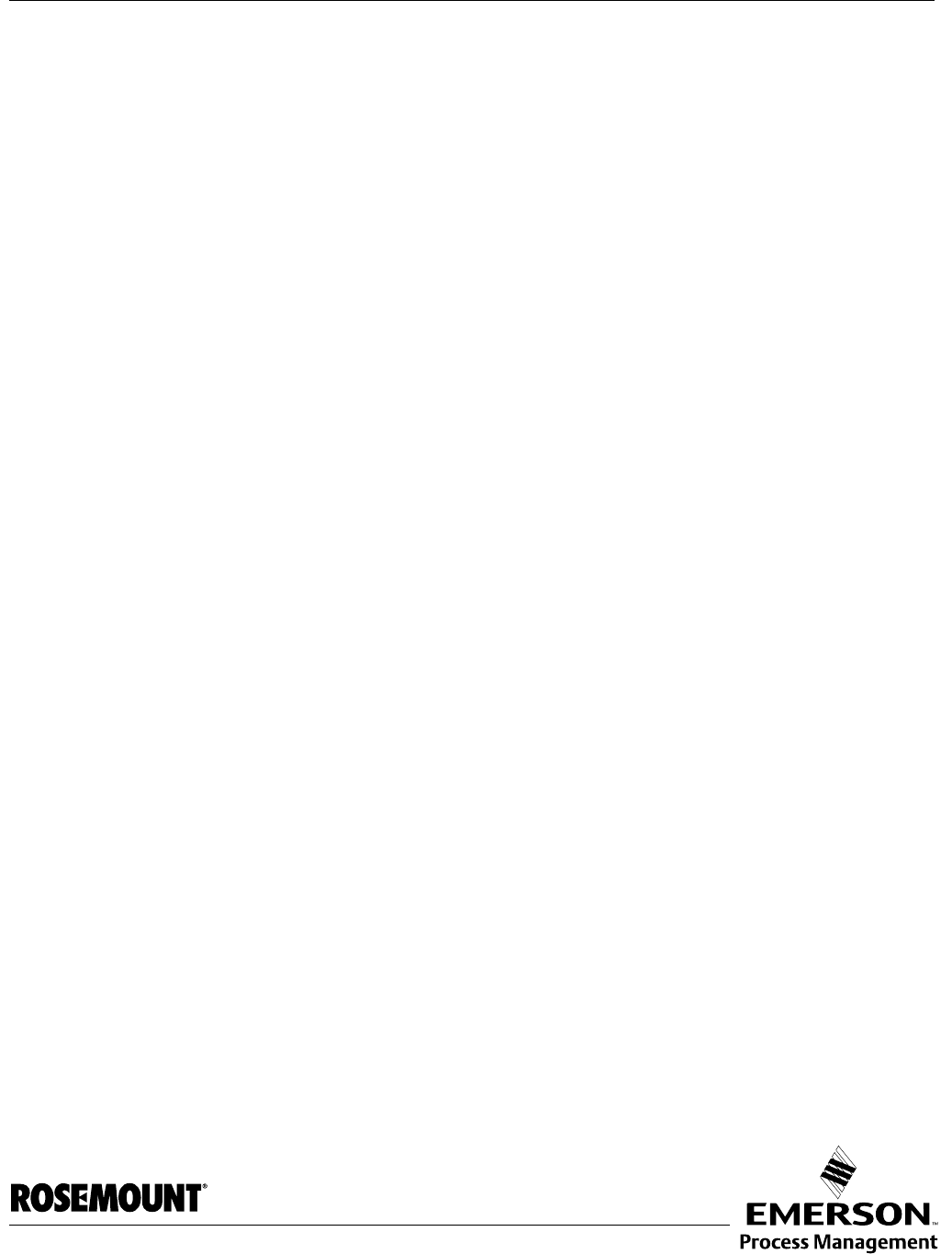
Reference Manual
00809-0100-4026, Rev AA
November 2003 Rosemount 5400 Series
www.rosemount.com
Table of Contents
SECTION 1
Introduction
Safety Messages . . . . . . . . . . . . . . . . . . . . . . . . . . . . . . . . . . . . . . . . . 1-1
Manual Overview . . . . . . . . . . . . . . . . . . . . . . . . . . . . . . . . . . . . . . . . . 1-2
SECTION 2
Transmitter Overview
Theory of Operation. . . . . . . . . . . . . . . . . . . . . . . . . . . . . . . . . . . . . . . 2-1
Components of the transmitter . . . . . . . . . . . . . . . . . . . . . . . . . . . . . . 2-2
System Architecture. . . . . . . . . . . . . . . . . . . . . . . . . . . . . . . . . . . . . . . 2-3
Process Characteristics . . . . . . . . . . . . . . . . . . . . . . . . . . . . . . . . . . . . 2-4
Dielectric constant . . . . . . . . . . . . . . . . . . . . . . . . . . . . . . . . . . . . . 2-4
Foam . . . . . . . . . . . . . . . . . . . . . . . . . . . . . . . . . . . . . . . . . . . . . . . 2-4
Turbulence . . . . . . . . . . . . . . . . . . . . . . . . . . . . . . . . . . . . . . . . . . . 2-4
Temperature/Pressure . . . . . . . . . . . . . . . . . . . . . . . . . . . . . . . . . . 2-4
Vapor . . . . . . . . . . . . . . . . . . . . . . . . . . . . . . . . . . . . . . . . . . . . . . . 2-4
Condensation . . . . . . . . . . . . . . . . . . . . . . . . . . . . . . . . . . . . . . . . . 2-4
Tank Characteristics. . . . . . . . . . . . . . . . . . . . . . . . . . . . . . . . . . . . 2-4
Antenna Selection Guide/Measuring Range . . . . . . . . . . . . . . . . . . . . 2-5
SECTION 3
Installation
Safety messages . . . . . . . . . . . . . . . . . . . . . . . . . . . . . . . . . . . . . . . . . 3-1
Installation Procedure . . . . . . . . . . . . . . . . . . . . . . . . . . . . . . . . . . . . . 3-2
Mounting Considerations . . . . . . . . . . . . . . . . . . . . . . . . . . . . . . . . . . . 3-3
Socket Requirements . . . . . . . . . . . . . . . . . . . . . . . . . . . . . . . . . . . 3-3
Free Space . . . . . . . . . . . . . . . . . . . . . . . . . . . . . . . . . . . . . . . . . . . 3-4
Recommended Mounting Position . . . . . . . . . . . . . . . . . . . . . . . . . 3-5
Beam Width . . . . . . . . . . . . . . . . . . . . . . . . . . . . . . . . . . . . . . . . . . 3-6
Beam Diameter at different distances from flange for 5401 . . . 3-6
Beam Diameter at different distances from flange for 5402 . . . 3-6
Beam angle for 5401 . . . . . . . . . . . . . . . . . . . . . . . . . . . . . . . . . 3-7
Beam angle for 5402 . . . . . . . . . . . . . . . . . . . . . . . . . . . . . . . . . 3-7
Vessel Characteristics . . . . . . . . . . . . . . . . . . . . . . . . . . . . . . . . . . 3-8
Disturbing objects . . . . . . . . . . . . . . . . . . . . . . . . . . . . . . . . . . . . . . 3-8
Mechanical Installation . . . . . . . . . . . . . . . . . . . . . . . . . . . . . . . . . . . . 3-9
Mounting a standard cone antenna . . . . . . . . . . . . . . . . . . . . . . . . 3-9
Mounting in Still Pipes . . . . . . . . . . . . . . . . . . . . . . . . . . . . . . . . . 3-10
Mounting in Bypass Pipes . . . . . . . . . . . . . . . . . . . . . . . . . . . . . . 3-11
Antenna extension . . . . . . . . . . . . . . . . . . . . . . . . . . . . . . . . . . . . 3-12
“Disc Antenna” . . . . . . . . . . . . . . . . . . . . . . . . . . . . . . . . . . . . . . . 3-12
Electrical Installation . . . . . . . . . . . . . . . . . . . . . . . . . . . . . . . . . . . . . 3-13
Cable/conduit entries . . . . . . . . . . . . . . . . . . . . . . . . . . . . . . . . . . 3-13
Grounding. . . . . . . . . . . . . . . . . . . . . . . . . . . . . . . . . . . . . . . . . . . 3-13
Cable Selection . . . . . . . . . . . . . . . . . . . . . . . . . . . . . . . . . . . . . . 3-13
Hazardous Areas . . . . . . . . . . . . . . . . . . . . . . . . . . . . . . . . . . . . . 3-13
Power Requirements . . . . . . . . . . . . . . . . . . . . . . . . . . . . . . . . . . 3-14
Maximum Loop Resistance . . . . . . . . . . . . . . . . . . . . . . . . . . . . . 3-14
Connecting the Transmitter . . . . . . . . . . . . . . . . . . . . . . . . . . . . . 3-15
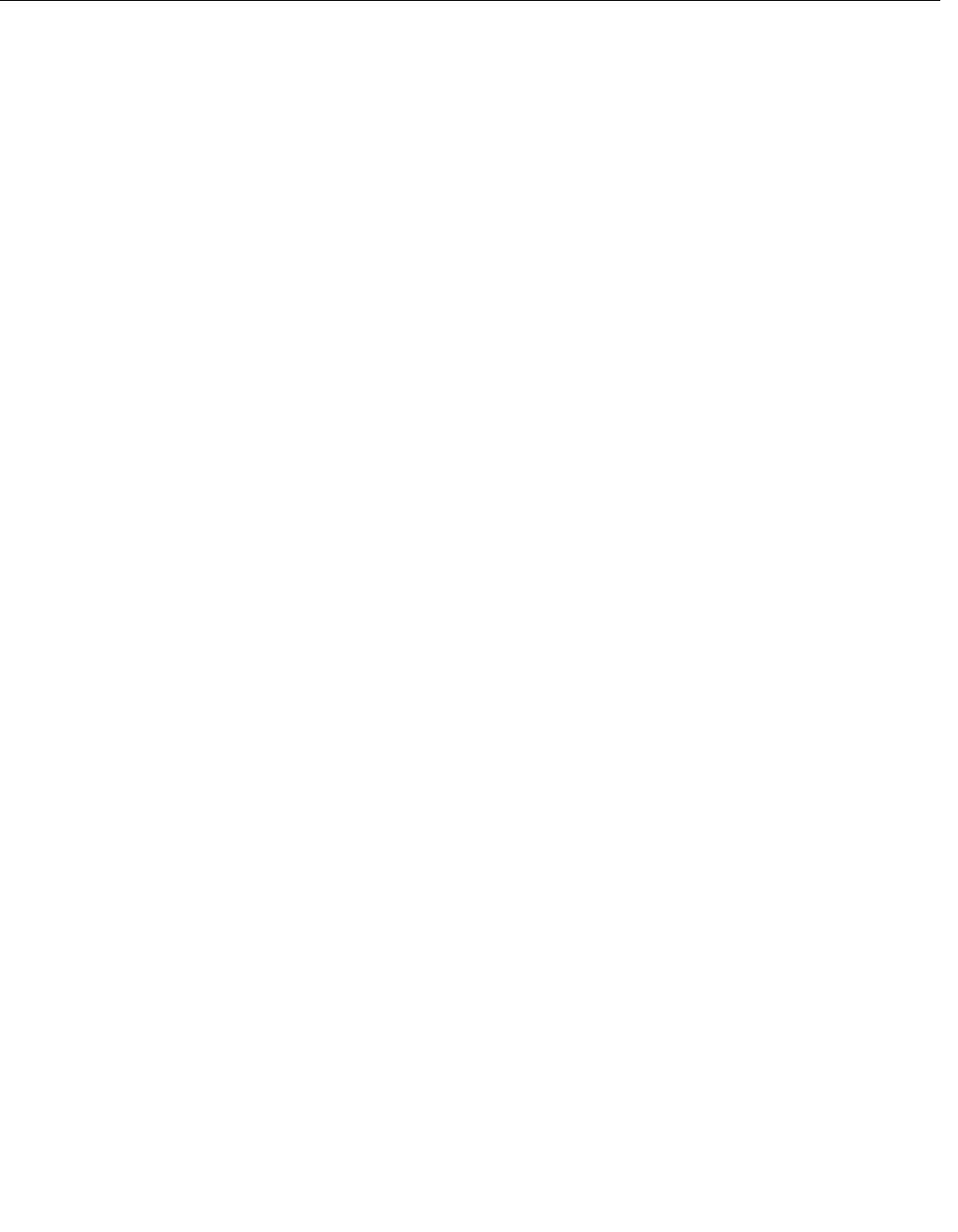
Reference Manual
00809-0100-4026, Rev AA
November 2003
Rosemount 5400 Series
TOC-2
Non-Intrinsically Safe Output . . . . . . . . . . . . . . . . . . . . . . . . . . . . 3-16
Intrinsically Safe Output . . . . . . . . . . . . . . . . . . . . . . . . . . . . . . . . 3-17
IS parameters . . . . . . . . . . . . . . . . . . . . . . . . . . . . . . . . . . . . . 3-17
SECTION 4
Operation
Safety Messages . . . . . . . . . . . . . . . . . . . . . . . . . . . . . . . . . . . . . . . . . 4-1
Display Panel. . . . . . . . . . . . . . . . . . . . . . . . . . . . . . . . . . . . . . . . . . . . 4-2
PC Configuration Software Rosemount Radar Master . . . . . . . . . . . . 4-3
Installing the RRM software . . . . . . . . . . . . . . . . . . . . . . . . . . . . . . 4-3
Specifying the COM Port . . . . . . . . . . . . . . . . . . . . . . . . . . . . . . . . 4-4
To set the COM port buffers . . . . . . . . . . . . . . . . . . . . . . . . . . . 4-4
System Requirements . . . . . . . . . . . . . . . . . . . . . . . . . . . . . . . . . . 4-5
Hardware. . . . . . . . . . . . . . . . . . . . . . . . . . . . . . . . . . . . . . . . . . 4-5
Software . . . . . . . . . . . . . . . . . . . . . . . . . . . . . . . . . . . . . . . . . . 4-5
Help In RRM . . . . . . . . . . . . . . . . . . . . . . . . . . . . . . . . . . . . . . . . . . 4-5
Using the Setup Wizard . . . . . . . . . . . . . . . . . . . . . . . . . . . . . . . . . 4-6
Using the Setup Function . . . . . . . . . . . . . . . . . . . . . . . . . . . . . . . . 4-7
AMS. . . . . . . . . . . . . . . . . . . . . . . . . . . . . . . . . . . . . . . . . . . . . . . . . . . 4-8
Model 275/375 HART Communicator . . . . . . . . . . . . . . . . . . . . . . . . . 4-9
SECTION 5
Configuration/Start-Up
Safety messages . . . . . . . . . . . . . . . . . . . . . . . . . . . . . . . . . . . . . . . . . 5-1
Overview . . . . . . . . . . . . . . . . . . . . . . . . . . . . . . . . . . . . . . . . . . . . . . . 5-2
Basic Configuration . . . . . . . . . . . . . . . . . . . . . . . . . . . . . . . . . . . . 5-2
Echo Tuning . . . . . . . . . . . . . . . . . . . . . . . . . . . . . . . . . . . . . . . . . . 5-2
Advanced Configuration . . . . . . . . . . . . . . . . . . . . . . . . . . . . . . . . . 5-2
Basic Configuration . . . . . . . . . . . . . . . . . . . . . . . . . . . . . . . . . . . . . . . 5-3
Measurement Units . . . . . . . . . . . . . . . . . . . . . . . . . . . . . . . . . . . . 5-3
Display Unit . . . . . . . . . . . . . . . . . . . . . . . . . . . . . . . . . . . . . . . . . . 5-3
Tank Geometry. . . . . . . . . . . . . . . . . . . . . . . . . . . . . . . . . . . . . . . . 5-3
Tank Height . . . . . . . . . . . . . . . . . . . . . . . . . . . . . . . . . . . . . . . . 5-3
Tank Type and Tank Bottom Type . . . . . . . . . . . . . . . . . . . . . . 5-3
Pipe Diameter . . . . . . . . . . . . . . . . . . . . . . . . . . . . . . . . . . . . . . 5-4
Process Conditions. . . . . . . . . . . . . . . . . . . . . . . . . . . . . . . . . . . . . 5-5
Rapid Level Changes . . . . . . . . . . . . . . . . . . . . . . . . . . . . . . . . 5-5
Turbulent Surface . . . . . . . . . . . . . . . . . . . . . . . . . . . . . . . . . . . 5-5
Foam . . . . . . . . . . . . . . . . . . . . . . . . . . . . . . . . . . . . . . . . . . . . . 5-5
Solid Products . . . . . . . . . . . . . . . . . . . . . . . . . . . . . . . . . . . . . . 5-5
Product Dielectric Range. . . . . . . . . . . . . . . . . . . . . . . . . . . . . . 5-5
Volume . . . . . . . . . . . . . . . . . . . . . . . . . . . . . . . . . . . . . . . . . . . . . . 5-5
Analog Output. . . . . . . . . . . . . . . . . . . . . . . . . . . . . . . . . . . . . . . . . 5-6
Output Source/Primary Variable . . . . . . . . . . . . . . . . . . . . . . . . 5-6
Upper/Lower Range Value . . . . . . . . . . . . . . . . . . . . . . . . . . . . 5-6
Alarm Mode . . . . . . . . . . . . . . . . . . . . . . . . . . . . . . . . . . . . . . . . 5-6
Echo Tuning. . . . . . . . . . . . . . . . . . . . . . . . . . . . . . . . . . . . . . . . . . . . . 5-8
Registration of False Echoes . . . . . . . . . . . . . . . . . . . . . . . . . . . . . 5-8
Amplitude Threshold Curve . . . . . . . . . . . . . . . . . . . . . . . . . . . . . . 5-9
Advanced Configuration . . . . . . . . . . . . . . . . . . . . . . . . . . . . . . . . . . 5-10
Advanced Tank Geometry . . . . . . . . . . . . . . . . . . . . . . . . . . . . . . 5-10
Distance Offset (G) . . . . . . . . . . . . . . . . . . . . . . . . . . . . . . . . . 5-10
Minimum Level Offset (C) . . . . . . . . . . . . . . . . . . . . . . . . . . . . 5-10
Hold Off Distance . . . . . . . . . . . . . . . . . . . . . . . . . . . . . . . . . . 5-11
Calibration Distance . . . . . . . . . . . . . . . . . . . . . . . . . . . . . . . . 5-11
Advanced Analog Output Settings . . . . . . . . . . . . . . . . . . . . . . . . 5-11

Reference Manual
00809-0100-4026, Rev AA
November 2003
TOC-3
Rosemount 5400 Series
Antenna Type . . . . . . . . . . . . . . . . . . . . . . . . . . . . . . . . . . . . . . . . 5-12
Tank Connection Length . . . . . . . . . . . . . . . . . . . . . . . . . . . . . . . 5-12
Empty Tank Handling . . . . . . . . . . . . . . . . . . . . . . . . . . . . . . . . . . 5-12
Bottom Echo Visible . . . . . . . . . . . . . . . . . . . . . . . . . . . . . . . . 5-12
Empty Tank Detection Area . . . . . . . . . . . . . . . . . . . . . . . . . . 5-12
Tank Bottom Projection . . . . . . . . . . . . . . . . . . . . . . . . . . . . . . 5-12
Extra Echo. . . . . . . . . . . . . . . . . . . . . . . . . . . . . . . . . . . . . . . . 5-13
Level Alarm is not set when Tank is Empty. . . . . . . . . . . . . . . 5-13
Full Tank Handling . . . . . . . . . . . . . . . . . . . . . . . . . . . . . . . . . . . . 5-13
Level Alarm is Not Set when Tank is Full . . . . . . . . . . . . . . . . 5-13
Full Tank Detection Area. . . . . . . . . . . . . . . . . . . . . . . . . . . . . 5-13
Level above Hold Off Distance Possible . . . . . . . . . . . . . . . . . 5-13
Double Bounce . . . . . . . . . . . . . . . . . . . . . . . . . . . . . . . . . . . . . . . 5-14
Surface Echo Tracking . . . . . . . . . . . . . . . . . . . . . . . . . . . . . . . . . 5-14
Slow Search . . . . . . . . . . . . . . . . . . . . . . . . . . . . . . . . . . . . . . 5-14
Slow Search Speed. . . . . . . . . . . . . . . . . . . . . . . . . . . . . . . . . 5-14
Double Surface . . . . . . . . . . . . . . . . . . . . . . . . . . . . . . . . . . . . 5-14
Upper Product Dielectric Constant . . . . . . . . . . . . . . . . . . . . . 5-14
Select Lower Surface . . . . . . . . . . . . . . . . . . . . . . . . . . . . . . . 5-14
Echo Timeout . . . . . . . . . . . . . . . . . . . . . . . . . . . . . . . . . . . . . 5-14
Close Distance Window . . . . . . . . . . . . . . . . . . . . . . . . . . . . . 5-15
Filter Settings . . . . . . . . . . . . . . . . . . . . . . . . . . . . . . . . . . . . . . . . 5-15
Damping Value . . . . . . . . . . . . . . . . . . . . . . . . . . . . . . . . . . . . 5-15
Activate Jump Filter. . . . . . . . . . . . . . . . . . . . . . . . . . . . . . . . . 5-15
SECTION 6
Service and
Troubleshooting
Safety Messages . . . . . . . . . . . . . . . . . . . . . . . . . . . . . . . . . . . . . . . . . 6-1
Service. . . . . . . . . . . . . . . . . . . . . . . . . . . . . . . . . . . . . . . . . . . . . . . . . 6-2
Analog Output Calibration . . . . . . . . . . . . . . . . . . . . . . . . . . . . . . . 6-2
Viewing Input and Holding Registers . . . . . . . . . . . . . . . . . . . . . . . 6-2
Logging Measurement Data . . . . . . . . . . . . . . . . . . . . . . . . . . . . . . 6-2
Saving the Transmitter Configuration. . . . . . . . . . . . . . . . . . . . . . . 6-2
Diagnostics . . . . . . . . . . . . . . . . . . . . . . . . . . . . . . . . . . . . . . . . . . . 6-3
Using the Spectrum Analyzer . . . . . . . . . . . . . . . . . . . . . . . . . . . . . 6-4
Configuration Report . . . . . . . . . . . . . . . . . . . . . . . . . . . . . . . . . . . 6-5
Surface Search. . . . . . . . . . . . . . . . . . . . . . . . . . . . . . . . . . . . . . . . 6-5
Reset to Factory Settings . . . . . . . . . . . . . . . . . . . . . . . . . . . . . . . . 6-5
Using the Simulation Mode. . . . . . . . . . . . . . . . . . . . . . . . . . . . . . . 6-5
Enable Software Options . . . . . . . . . . . . . . . . . . . . . . . . . . . . . . . . 6-6
Enter Service Mode . . . . . . . . . . . . . . . . . . . . . . . . . . . . . . . . . . . . 6-6
Troubleshooting. . . . . . . . . . . . . . . . . . . . . . . . . . . . . . . . . . . . . . . . . . 6-7
Troubleshooting . . . . . . . . . . . . . . . . . . . . . . . . . . . . . . . . . . . . . . . 6-7
Errors.. . . . . . . . . . . . . . . . . . . . . . . . . . . . . . . . . . . . . . . . . . . . . . . 6-8
Warnings. . . . . . . . . . . . . . . . . . . . . . . . . . . . . . . . . . . . . . . . . . . . . 6-9
Application Errors. . . . . . . . . . . . . . . . . . . . . . . . . . . . . . . . . . . . . 6-10
APPENDIX A
Reference Data
Specifications. . . . . . . . . . . . . . . . . . . . . . . . . . . . . . . . . . . . . . . . . . . . A-1
Dimensional drawings . . . . . . . . . . . . . . . . . . . . . . . . . . . . . . . . . . . . . A-3
Ordering Information . . . . . . . . . . . . . . . . . . . . . . . . . . . . . . . . . . . . . .A-4
Spare Parts . . . . . . . . . . . . . . . . . . . . . . . . . . . . . . . . . . . . . . . . . . . . . A-8
APPENDIX B
Hazardous Approvals
Safety messages . . . . . . . . . . . . . . . . . . . . . . . . . . . . . . . . . . . . . . . . . B-1
European Atex Directive Information . . . . . . . . . . . . . . . . . . . . . . . . . . B-3
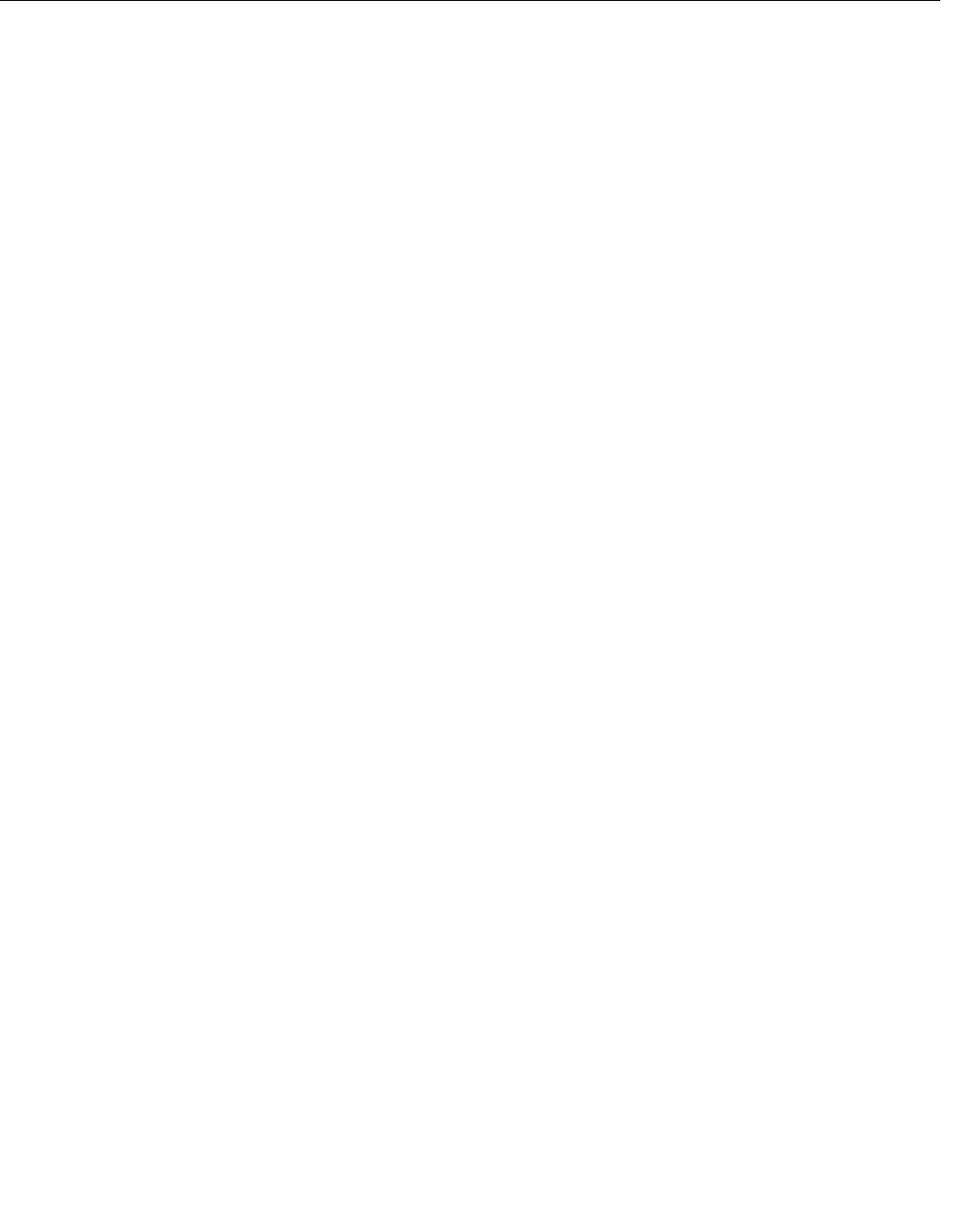
Reference Manual
00809-0100-4026, Rev AA
November 2003
Rosemount 5400 Series
TOC-4
Intrinsic Safety . . . . . . . . . . . . . . . . . . . . . . . . . . . . . . . . . . . . . . . . B-3
Flame Proof . . . . . . . . . . . . . . . . . . . . . . . . . . . . . . . . . . . . . . . . . . B-4
Hazardous Locations Certifications . . . . . . . . . . . . . . . . . . . . . . . . . . . B-5
Factory Mutual (FM) Approvals . . . . . . . . . . . . . . . . . . . . . . . . . . . B-5
Canadian Standards Association (CSA) Approval . . . . . . . . . . . . . B-6
Approval Drawings. . . . . . . . . . . . . . . . . . . . . . . . . . . . . . . . . . . . . . . . B-7
APPENDIX C
HART Communicator
Introduction . . . . . . . . . . . . . . . . . . . . . . . . . . . . . . . . . . . . . . . . . . . . .C-1
Safety Messages . . . . . . . . . . . . . . . . . . . . . . . . . . . . . . . . . . . . . . . . .C-1
Connections. . . . . . . . . . . . . . . . . . . . . . . . . . . . . . . . . . . . . . . . . . . . .C-5
Basic Features. . . . . . . . . . . . . . . . . . . . . . . . . . . . . . . . . . . . . . . . . . .C-6
Action Keys . . . . . . . . . . . . . . . . . . . . . . . . . . . . . . . . . . . . . . . .C-6
ON/OFF Key . . . . . . . . . . . . . . . . . . . . . . . . . . . . . . . . . . . . . . .C-6
Directional Keys . . . . . . . . . . . . . . . . . . . . . . . . . . . . . . . . . . . .C-6
HOT Key . . . . . . . . . . . . . . . . . . . . . . . . . . . . . . . . . . . . . . . . . .C-7
Function Keys . . . . . . . . . . . . . . . . . . . . . . . . . . . . . . . . . . . . . .C-7
Alphanumeric and Shift Keys . . . . . . . . . . . . . . . . . . . . . . . . . .C-7
Menus and Functions . . . . . . . . . . . . . . . . . . . . . . . . . . . . . . . . . . . . .C-8
Main Menu. . . . . . . . . . . . . . . . . . . . . . . . . . . . . . . . . . . . . . . . .C-8
Online Menu . . . . . . . . . . . . . . . . . . . . . . . . . . . . . . . . . . . . . . .C-9
HART Fast Key Feature . . . . . . . . . . . . . . . . . . . . . . . . . . . . . .C-9
Hart Communicator Diagnostic Messages . . . . . . . . . . . . . . . . . . .C-9
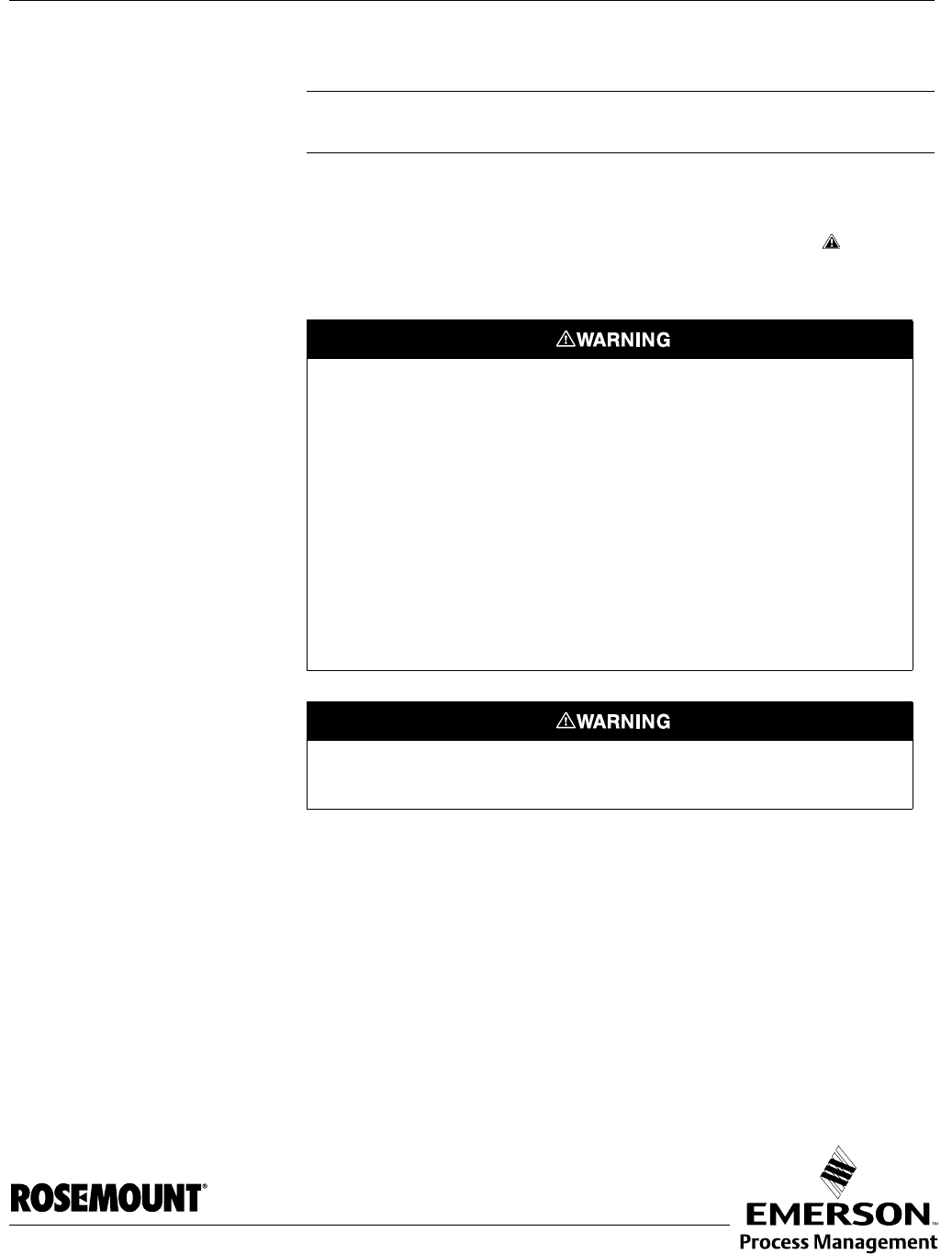
Reference Manual
00809-0100-4026, Rev AA
November 2003 Rosemount 5400 Series
www.rosemount.com
Preliminary copy
Section 1 Introduction
Safety Messages . . . . . . . . . . . . . . . . . . . . . . . . . . . . . . . . . page 1-1
Manual Overview . . . . . . . . . . . . . . . . . . . . . . . . . . . . . . . . page 1-2
SAFETY MESSAGES Procedures and instructions in this manual may require special precautions to
ensure the safety of the personnel performing the operations. Information that
raises potential safety issues is indicated by a warning symbol ( ). Refer to
the saftey messages listed at the beginning of each section before performing
an operation preceded by this symbol.
Failure to follow these installation guidelines could result in death or serious
injury.
• Make sure only qualified personnel perform the installation.
• Use the equipment only as specified in this manual. Failure to do so may
impair the protection provided by the equipment.
Explosions could result in death or serious injury.
• Verify that the operating environment of the transmitter is consistent with the
appropriate hazardous locations certifications.
• Before connecting a HART®-based communicator in an explosive atmosphere,
make sure the instruments in the loop are installed in accordance with
intrinsically safe or non-incendive field wiring practices.
Electrical shock could cause death or serious injury.
• Use extreme caution when making contact with the leads and terminals.
Any substitution of non-recognized parts may jeopardize safety. Repair, e.g. substitution
of components etc., may also jeopardize safety and is under no circumstances allowed.
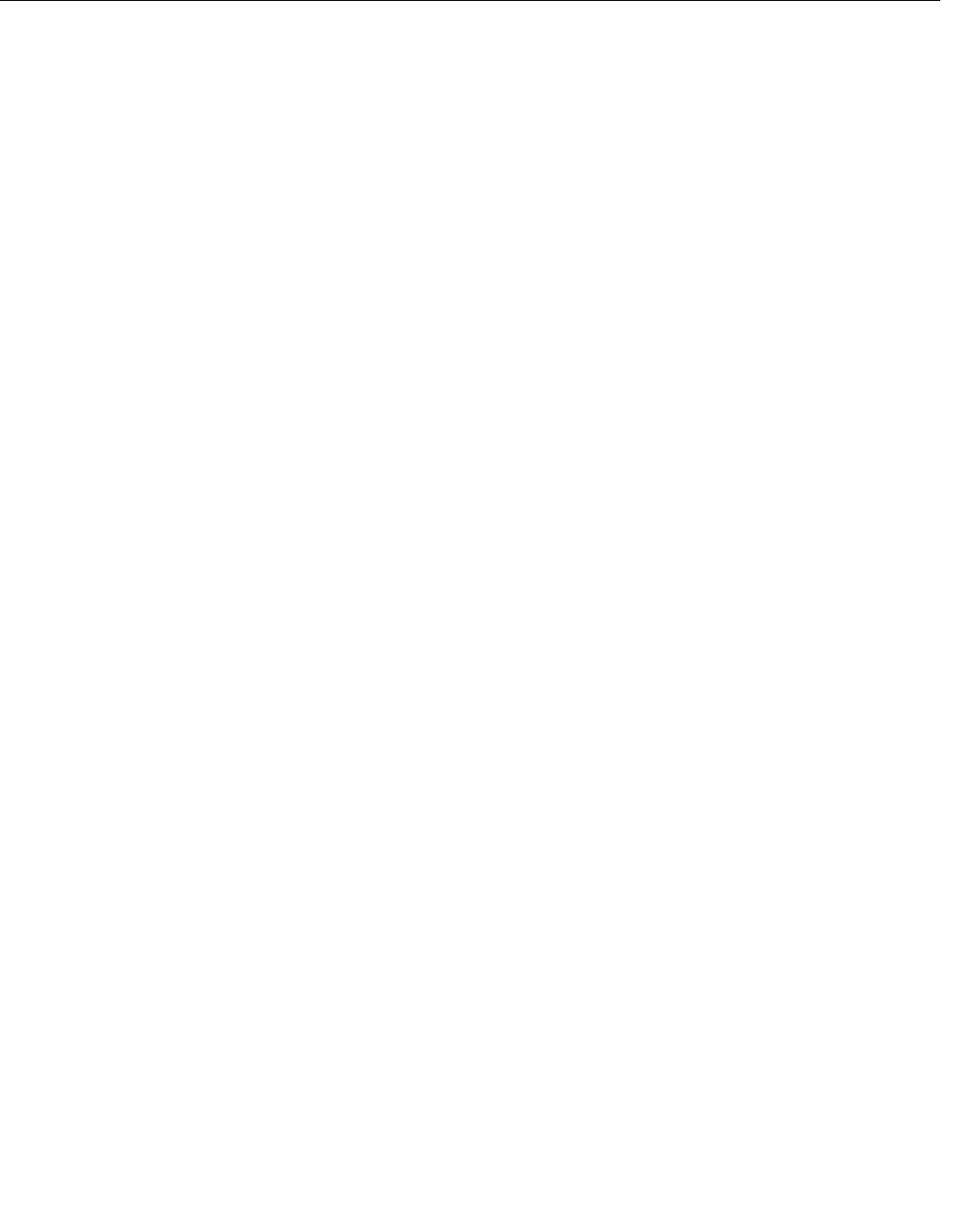
Reference Manual
00809-0100-4026, Rev AA
November 2003
Rosemount 5400 Series
1-2
Preliminary copy
MANUAL OVERVIEW This manual provides installation, configuration and maintenance information
for the Rosemount 5400 Series Radar Transmitter.
Section 2: Transmitter Overview
• Theory of Operation
• Descripton of the transmitter
• Process and vessel characteristics
Section 3: Installation
• Mounting considerations
• Mechanical installation
• Electrical installation
Section 4: Operation
• Display panel
• Configuration tool Rosemount Radar Master
•AMS
• 275/375 communicator
Section 5: Configuration/Start-Up
• Configuration instructions
• Configuration using the HART Communicator
• Configuration using the RCT software
Section 6: Service and Troubleshooting
• Advanced Configuration
• Error and Warning Codes
• Communication Errors
Appendix A: Reference Data
• Specifications
• Ordering Information
Appendix B: Hazardous Approvals
• Examples of labels
• European ATEX Directive information
• FM approvals
• CSA approvals
•Drawings
Appendix C: HART 275/375 Communicator
•Features
• Connections
• Diagnostic messages
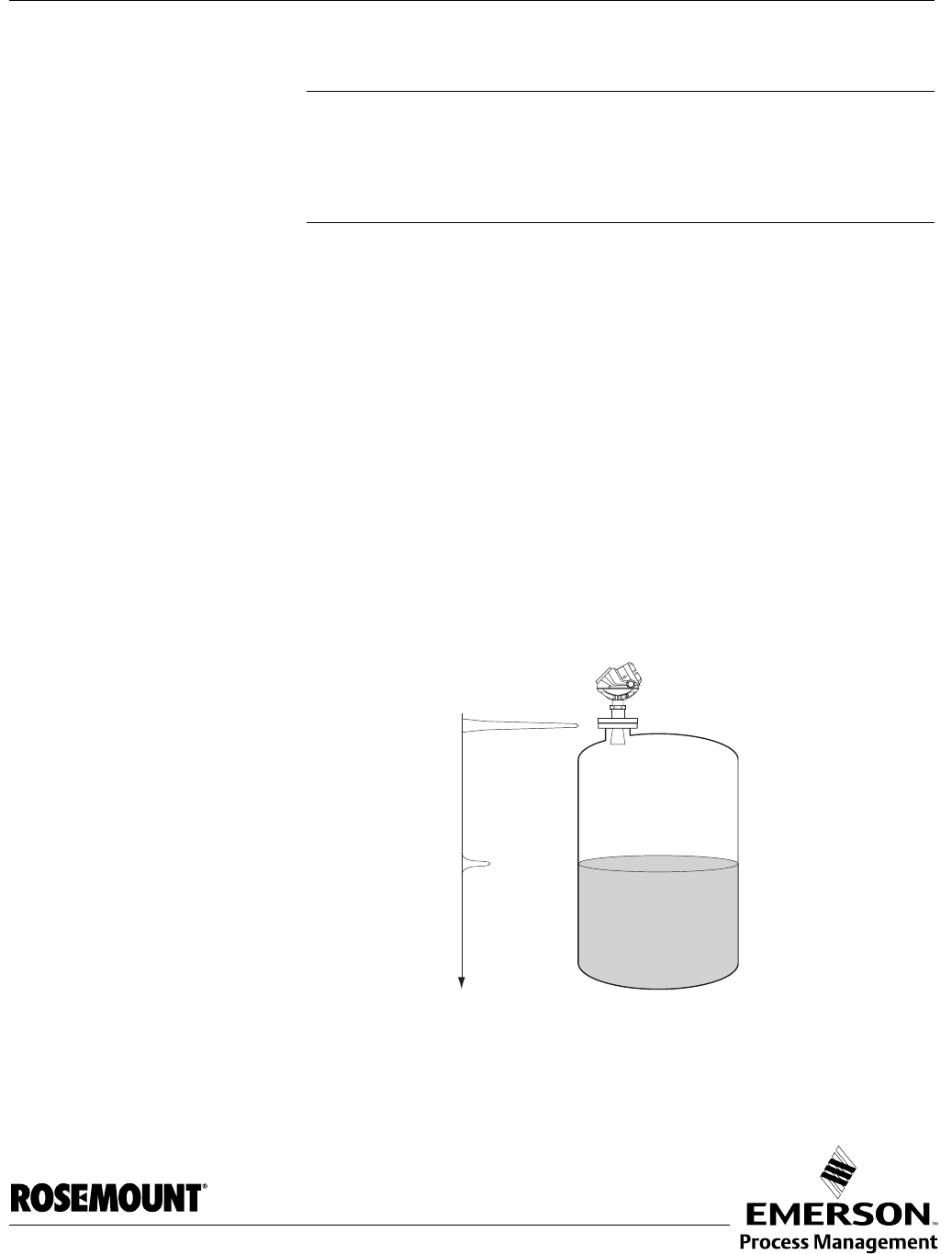
Reference Manual
00809-0100-4026, Rev AA
November 2003 Rosemount 5400 Series
www.rosemount.com
Preliminary copy
Section 2 Transmitter Overview
Theory of Operation . . . . . . . . . . . . . . . . . . . . . . . . . . . . . . page 2-1
Components of the transmitter . . . . . . . . . . . . . . . . . . . . . page 2-2
System Architecture . . . . . . . . . . . . . . . . . . . . . . . . . . . . . . page 2-3
Antenna Selection Guide/Measuring Range . . . . . . . . . . page 2-5
Process Characteristics . . . . . . . . . . . . . . . . . . . . . . . . . . . page 2-4
THEORY OF OPERATION The Rosemount 5400 Series Radar Transmitter is a smart, two-wire
continuous level transmitter that is based on Time Domain Reflectometry
(TDR) principles. A 5400 transmitter is installed at the tank top. It emits short
microwave pulses towards the product surface in the tank. When a pulse
reaches the surface of the material it is measuring, part of the energy is
reflected back to the antenna for subsequent processing by the transmitter
electronics. The time difference between the generated and reflected pulse is
detected by a micro-processor and is converted into a distance from which
the total level or interface level is calculated (see below). The measured
distance is often referred to as the Ullage.
The product level is calculated by using the following relation between tank
height and Ullage:
Level=Tank Height - Ullage.
Figure 2-1. Measurement
principle for the 5400 Series.
TDR_PRINCIPLES(2).EPS
Reference pulse
Level
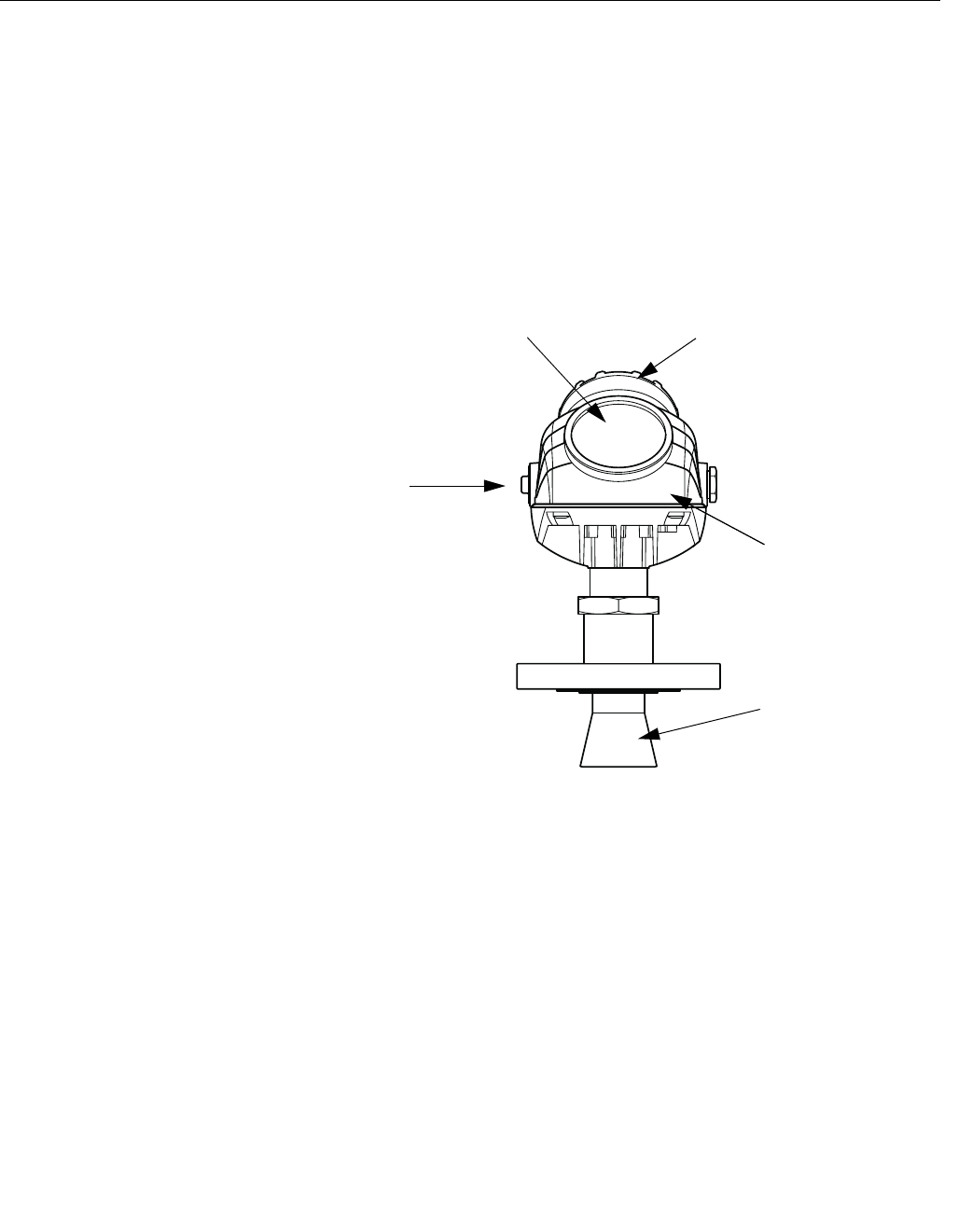
Reference Manual
00809-0100-4026, Rev AA
November 2003
Rosemount 5400 Series
2-2
Preliminary copy
COMPONENTS OF THE
TRANSMITTER
The Rosemount 5400 Series Radar Transmitter has an aluminum transmitter
housing which contains advanced electronics for signal processing.
The radar electronics produces an electromagnetic pulse that is emitted
through the antenna.
There are different antenna types and sizes available for various applications.
Figure 2-2. Transmitter
components.
Radar Electronics
Cable Entry:
½" NPT.
Optional adapters:
M20, PG13.5
TRANSMITTER_COMPONENTS.EPS
Radar Electronics
Antenna
Display Panel Junction Box
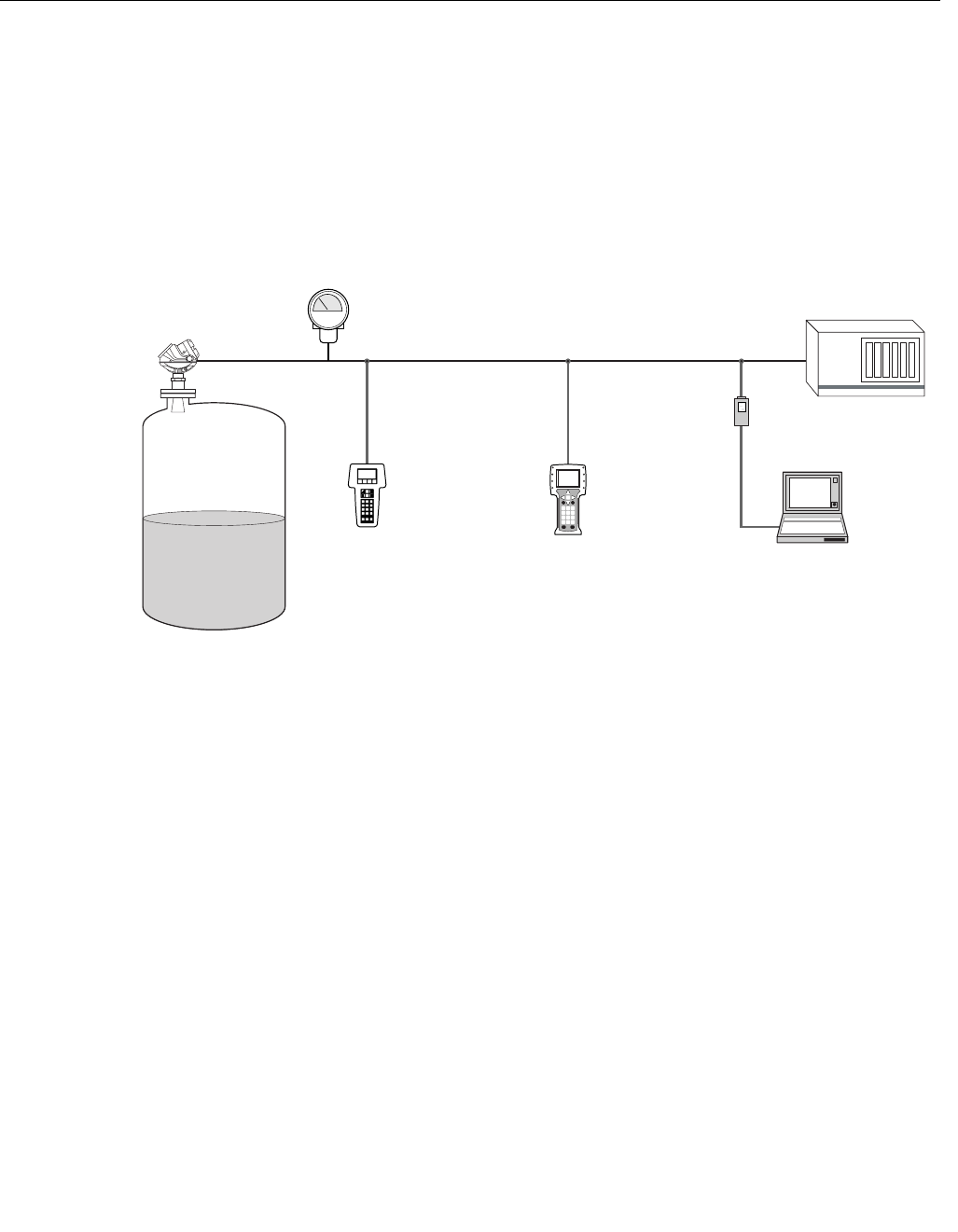
Reference Manual
00809-0100-4026, Rev AA
November 2003
2-3
Rosemount 5400 Series
Preliminary copy
SYSTEM
ARCHITECTURE
The 5400 Series Radar Level Transmitter is a powerful radar level transmitter
suitable for non-contact level measurements in process tanks and other types
of tanks. It is designed for easy installation and maintenance free operation.
The Rosemount 5400 Series Radar Transmitter is loop-powered which
means it uses the same two wires for both power supply and output signal.
The output is a 4-20 mA analog signal superimposed with a digital HART
signal.
Figure 2-3. System Integration
If HART technology is used the Rosemount 5400 Series Radar Transmitter
can easily be configured by using a PC and the Radar Master software
package or via a hand held HART 275/375 Communicator. Radar Master
offers configuration and service capabilities and functions for presentation of
measurement data. The transmitter is also compatible with the AMS™ (Asset
Management Solutions™) software which can be used for configuration.
For stand-alone systems, or as a complement to a PC or a control system,
you can monitor level data using an analog output. As an option, your Model
5400 Radar Level Transmitter can be equipped with an easy-to-use Display
Panel for monitoring measurement data.
SYSTEM_5400.EPS
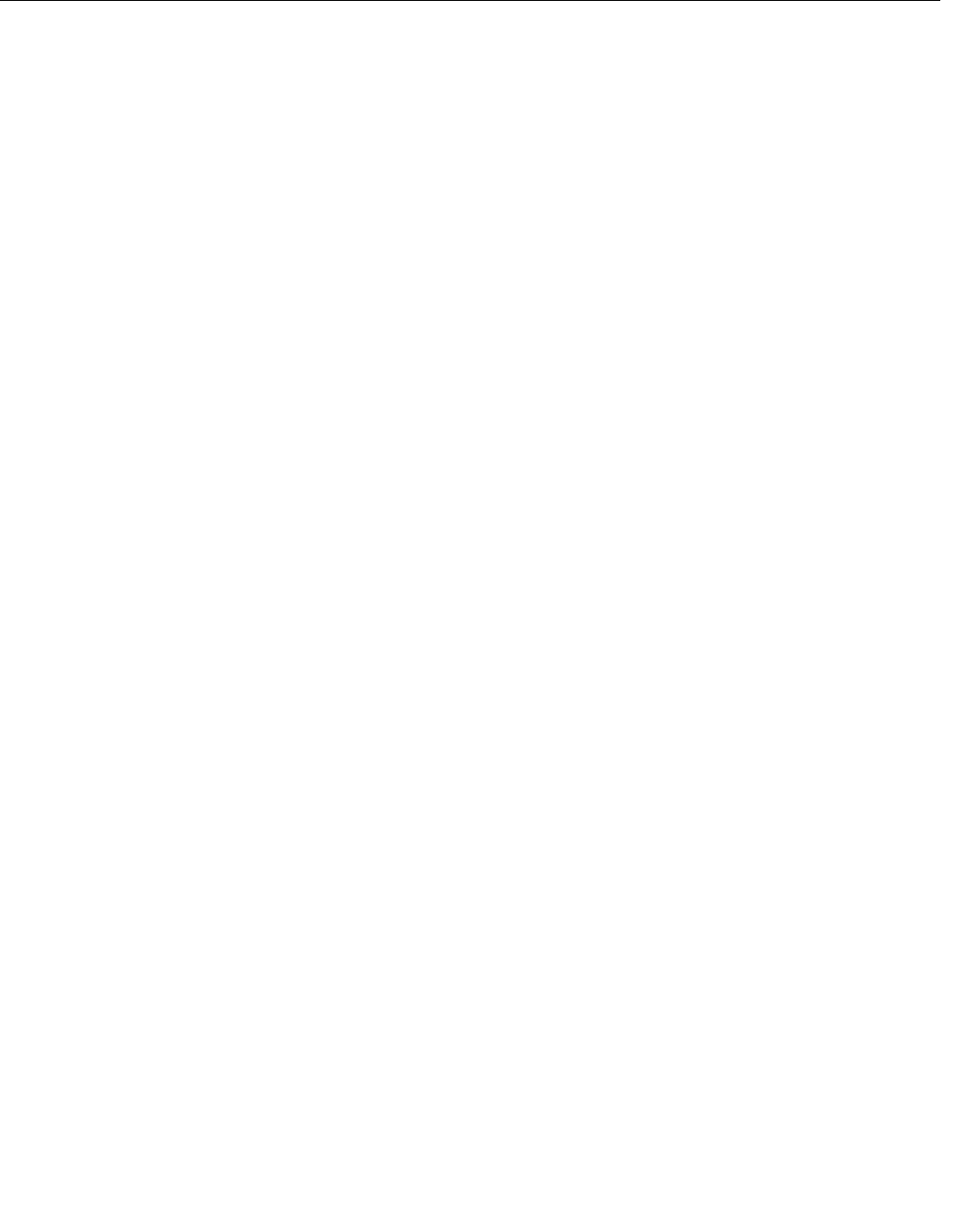
Reference Manual
00809-0100-4026, Rev AA
November 2003
Rosemount 5400 Series
2-4
Preliminary copy
PROCESS
CHARACTERISTICS
Dielectric constant The reflectivity of the product is a key parameter for measurement
performance. A high dielectric constant of the media gives better reflection
and a longer measuring range.
Foam How well the Rosemount 5400 Series Radar Transmitter measures in foamy
applications depends upon the properties of the foam; light and airy or dense
and heavy, high or low dielectrics, etc. If the foam is conductive and creamy
the transmitter will probably measure the surface of the foam. If the foam is
less conductive the microwaves will probably penetrate the foam and
measure the liquid surface.
Stämmer detta för 5400?
Turbulence A calm surface gives better reflection than a turbulent surface. For extremely
turbulent applications the Low Frequency version of the 5400 transmitter is
recommended.
Temperature/Pressure ?
Vapor In some applications, as ammonia, there is heavy vapor above the product
surface that will influence the level measurement. The Rosemount 5400
Series Radar Transmitter can be configured to compensate for the influence
of vapor.
Condensation For applications where condensation may occur the Low Frequency version
of the 5400 transmitter is recommended.
Tank Characteristics The conditions inside the tank have a
significant impact on measurement performance.
For more information see “Vessel Characteristics” on
page 3-8.
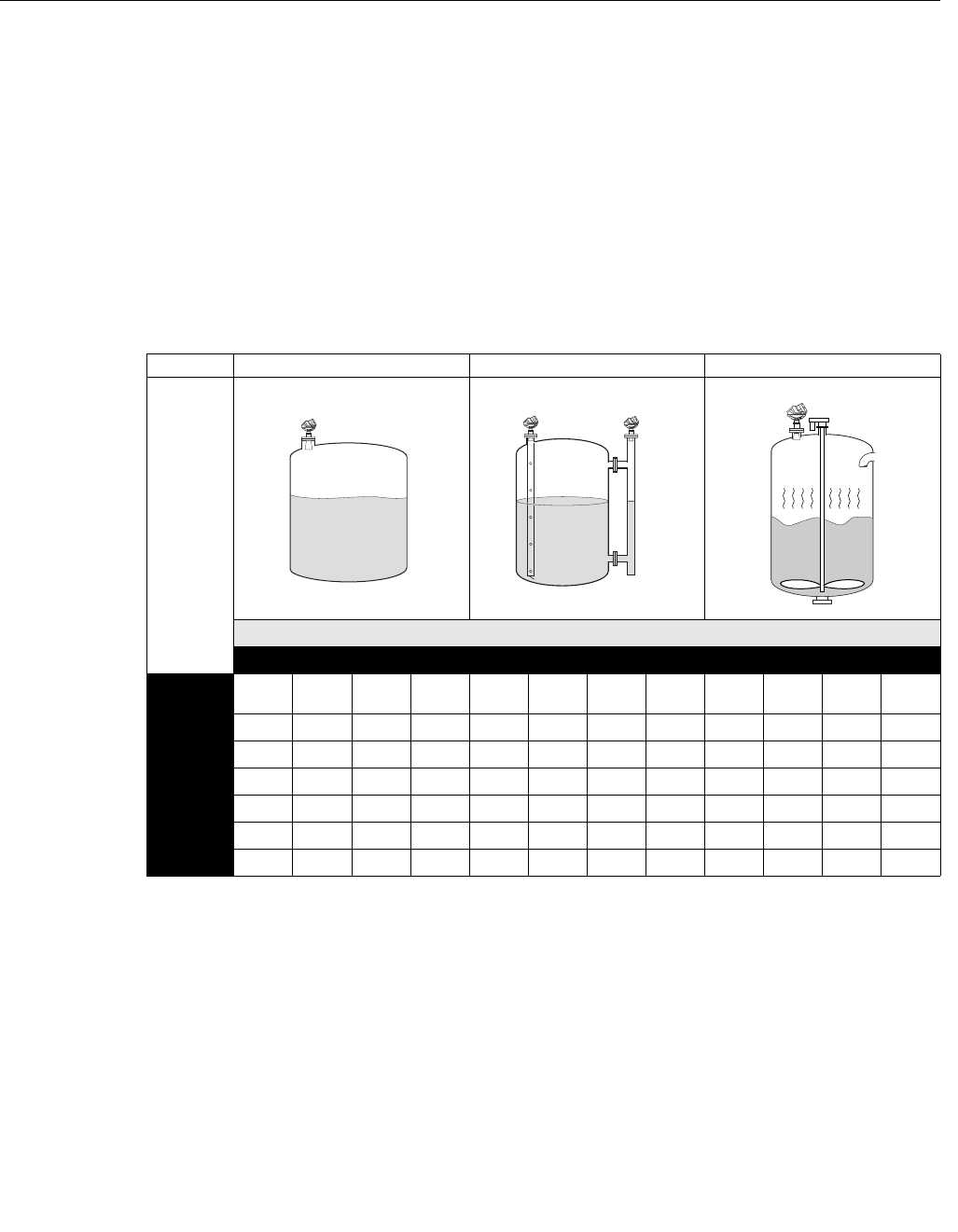
Reference Manual
00809-0100-4026, Rev AA
November 2003
2-5
Rosemount 5400 Series
Preliminary copy
ANTENNA SELECTION
GUIDE/MEASURING
RANGE
The measuring range depends on the antenna type and size, the dielectric
constant (εr) of the liquid and process conditions. For optimum performance,
make sure not to exceed the maximum measuring range values below. The
first table shows values for the high frequency (HF) transmitter and the
second table gives the low frequency (LF) transmitter values.
A: LPG/LNG, ammonia, solids...??? (dielectric constant εr =1.4-1.9).
Pipe installations only?
B: Oil, gasoline and other hydrocarbons, petrochemicals (εr =1.9-4.0)
C: Alcohols, concentrated acids, organic solvents, oil/water mixtures and
acetone (εr =4.0-10.0)
D: Conductive liquids, e.g. water based solutions, dilute acids and alkalis
(εr>10.0)
Storage tank Still Pipe/Bypass Process tank
5401
Antennas
Dielectric Constant
ABCDABCDABCD
Cone, 2 in.
12.5
(42.x)
Cone, 3 in
Cone, 4 in
Cone, 6 in
Cone, 8 in
Disc, 4 in.
Disc, 6 in.
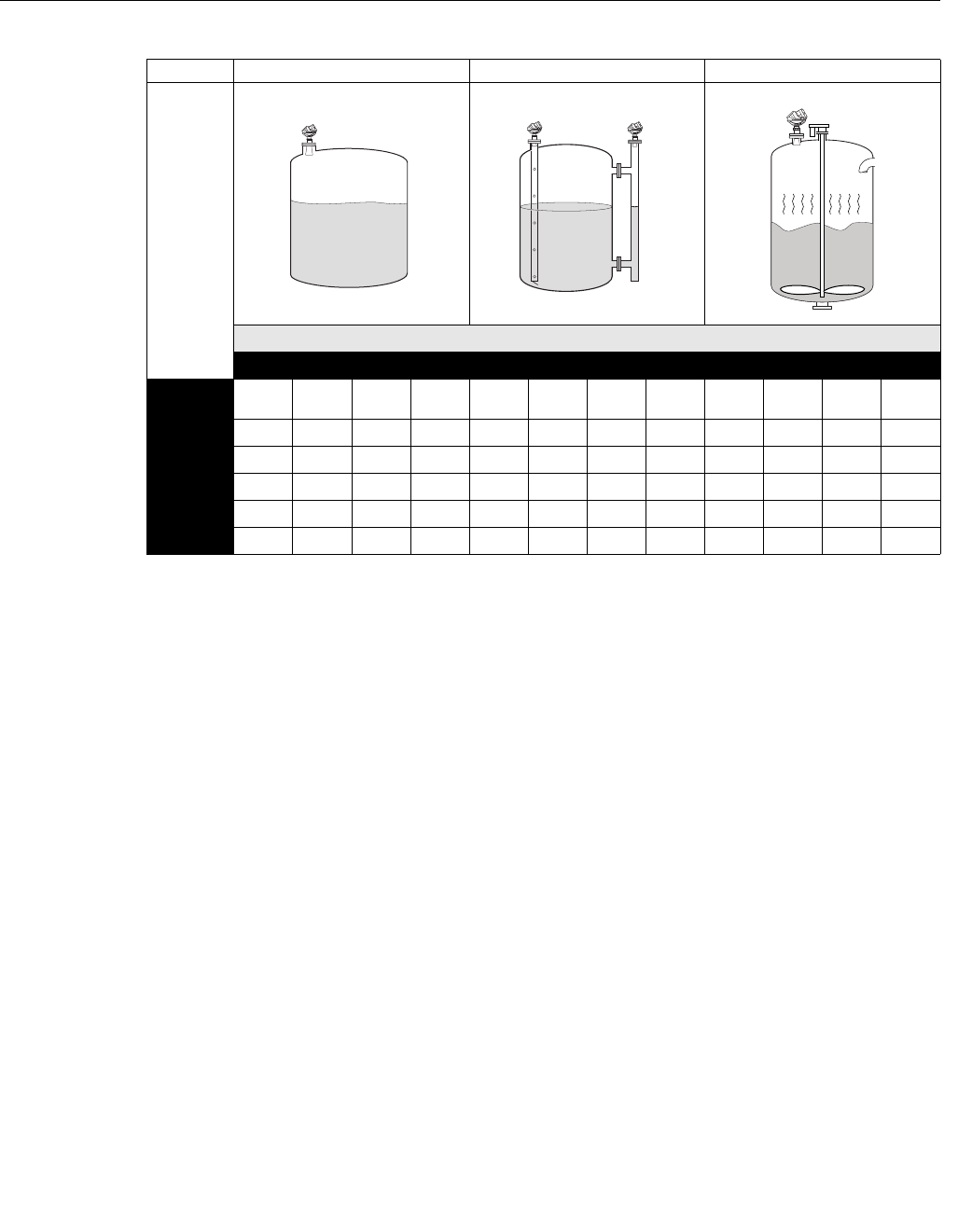
Reference Manual
00809-0100-4026, Rev AA
November 2003
Rosemount 5400 Series
2-6
Preliminary copy
Storage tank Still Pipe/Bypass Process tank
5402
Antennas
Dielectric Constant
ABCDABCDABCD
Cone, 2 in.
12.5
(42.x)
Cone, 3 in
Cone, 4 in
Disc, 2 in.
Disc, 3 in.
Disc, 4 in.
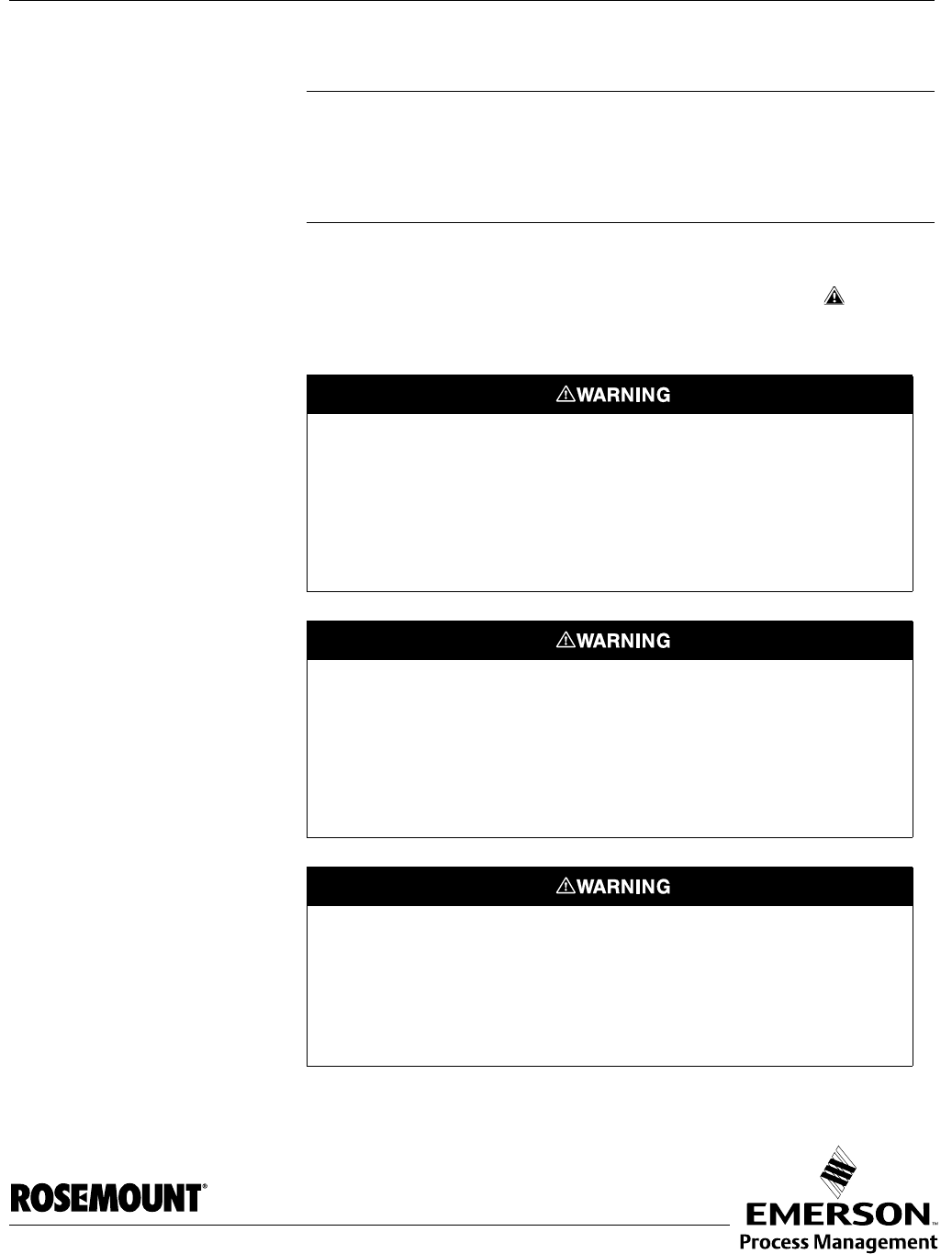
Reference Manual
00809-0100-4026, Rev AA
November 2003 Rosemount 5400 Series
www.rosemount.com
Preliminary copy
Section 3 Installation
Safety messages . . . . . . . . . . . . . . . . . . . . . . . . . . . . . . . . . page 3-1
Installation Procedure . . . . . . . . . . . . . . . . . . . . . . . . . . . . page 3-2
Mounting Considerations . . . . . . . . . . . . . . . . . . . . . . . . . page 3-3
Mechanical Installation . . . . . . . . . . . . . . . . . . . . . . . . . . . page 3-9
Electrical Installation . . . . . . . . . . . . . . . . . . . . . . . . . . . . . page 3-13
SAFETY MESSAGES Procedures and instructions in this section may require special precautions to
ensure the safety of the personnel performing the operations. Information that
raises potential safety issues is indicated by a warning symbol ( ). Please
refer to the following safety messages before performing an operation
preceded by this symbol.
Explosions could result in death or serious injury:
Verify that the operating environment of the transmitter is consistent with the appropriate
hazardous locations certifications.
Before connecting a HART-based communicator in an explosive atmosphere, make
sure the instruments in the loop are installed in accordance with intrinsically safe or
non-incendive field wiring practices.
Do not remove the gauge cover in explosive atmospheres when the circuit is alive.
Failure to follow safe installation and servicing guidelines could result in death or
serious injury:
Make sure only qualified personnel perform the installation.
Use the equipment only as specified in this manual. Failure to do so may impair the
protection provided by the equipment.
Do not perform any service other than those contained in this manual unless you are
qualified.
High voltage that may be present on leads could cause electrical shock:
Avoid contact with leads and terminals.
Make sure the main power to the 5400 transmitter is off and the lines to any other
external power source are disconnected or not powered while wiring the gauge.
To prevent ignition of flammable or combustible atmospheres, disconnect power before
servicing.
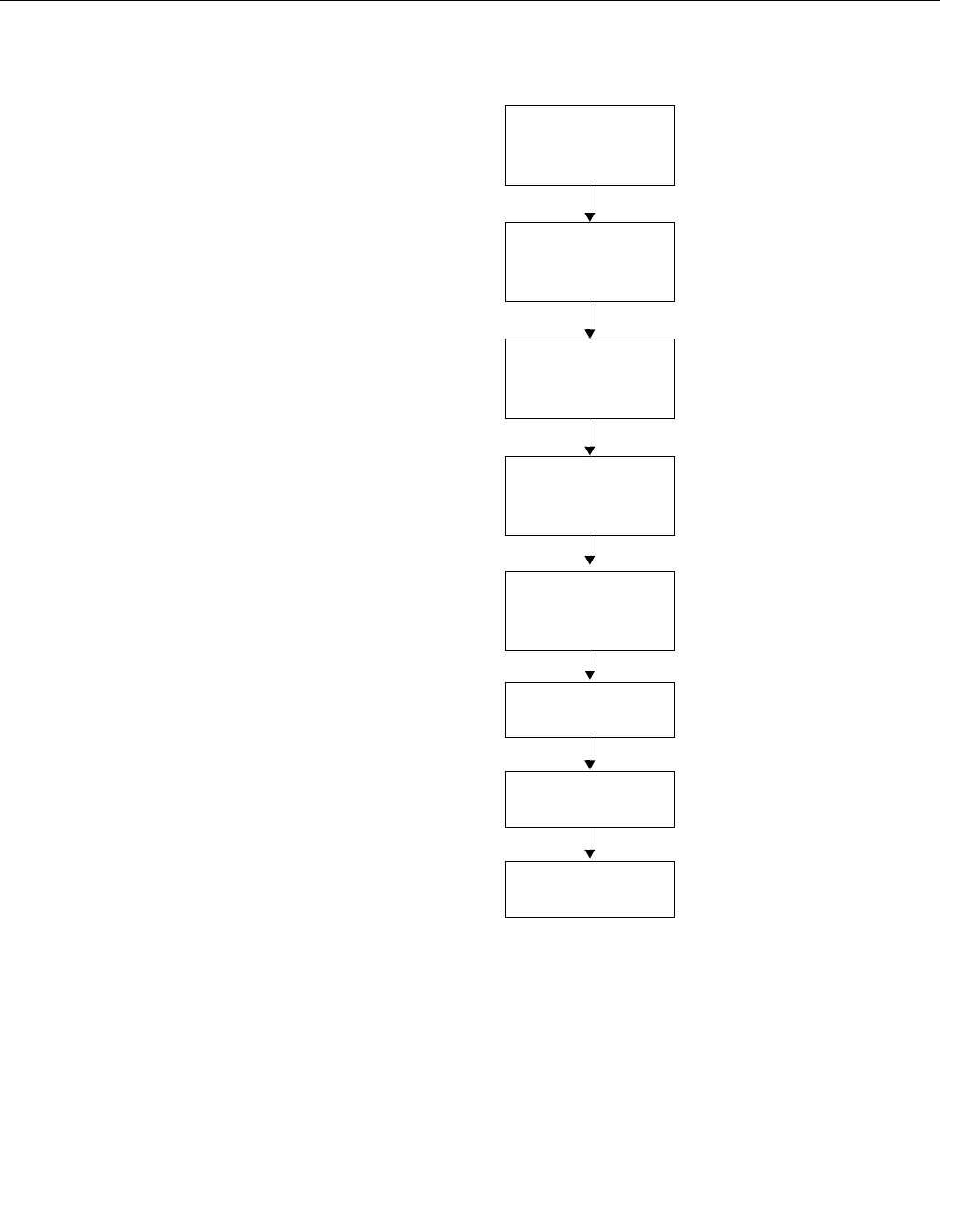
Reference Manual
00809-0100-4026, Rev AA
November 2003
Rosemount 5400 Series
3-2
Preliminary copy
INSTALLATION
PROCEDURE
Follow these steps for proper installation:
Review Installation
Considerations
(see page 3-3)
Check switches for
4-20 mA Alarm Output
(see page xx)
Mount the transmitter
(see page 3-9)
Wire the transmitter
(see page 3-13)
Make sure covers
and cable/conduit
connections are
tight.
Power Up the
transmitter
Configure the
transmitter
(see page 4-1)
Verify measurements
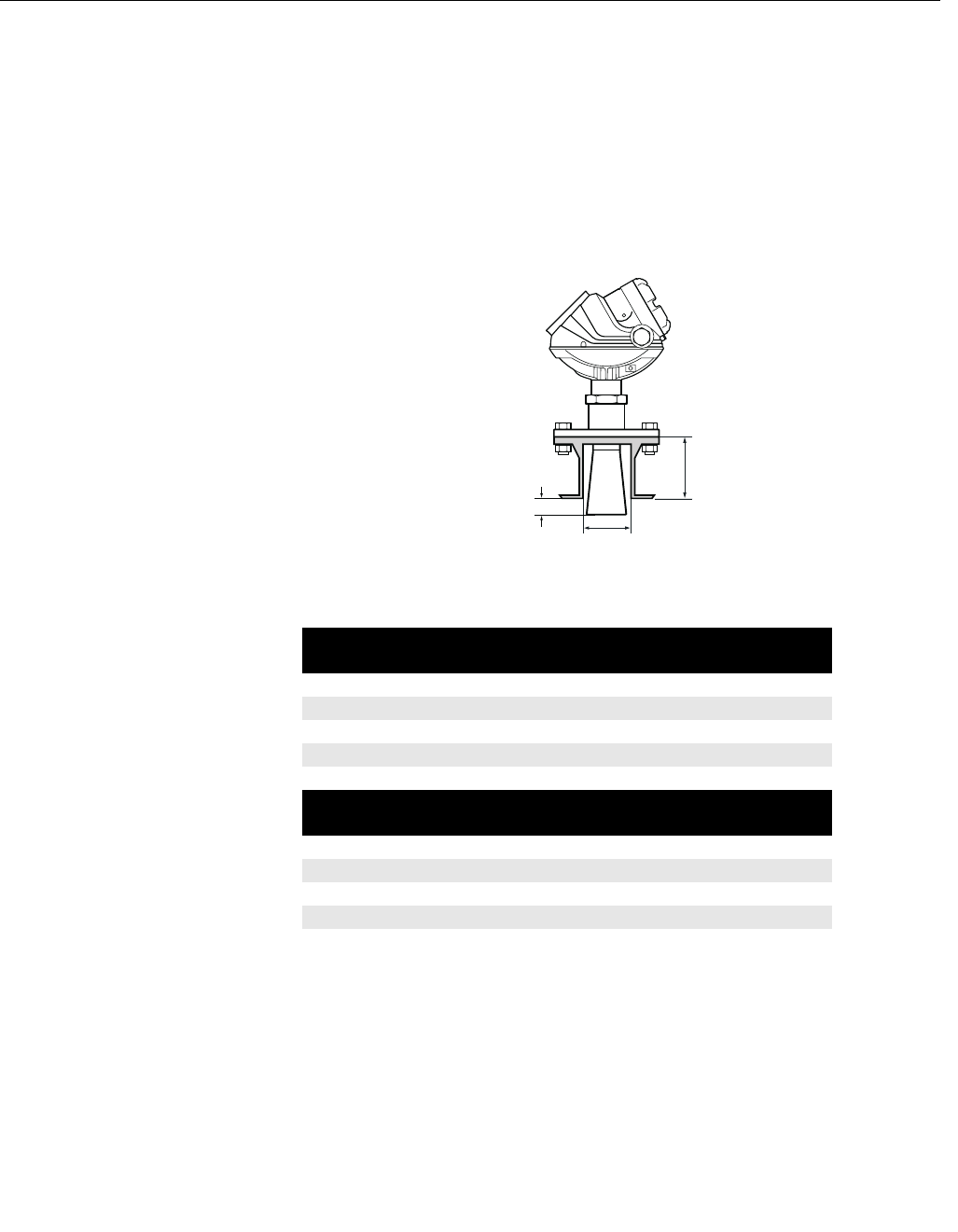
Reference Manual
00809-0100-4026, Rev AA
November 2003
3-3
Rosemount 5400 Series
Preliminary copy
MOUNTING
CONSIDERATIONS
Before you install the Rosemount 5400 Series Radar Transmitter, be sure to
consider specific mounting requirements, vessel characteristics and process
characteristics.
Socket Requirements The 5400 Series is mounted on a nozzle by using appropriate flanges. For
best performance it is recommended that the socket meets the following
requirements:
Figure 3-1. Mounting of the 5400
Series transmitter.
Table 3-1. Requirements on
Socket height and width.
The transmitter should be installed as follows:
• The antenna must be aligned vertically.
• Choose as large antenna diameter as possible. A larger receiving area
concentrates the radar beam and ensures maximum antenna gain.
Increased antenna gain means greater margin for weak surface
echoes. A larger antenna also results in smaller beam angle and
thereby, less interference.
• For best measurement performance, the antenna should stick beneath
the nozzle 0.4 inches (10 mm) or more.
SOCKETREQ.EPS
L
Minimum Diameter
>0.4 inch/
10 mm
5401 Antenna L max (inch/mm) Min. Diameter
(inch/mm)
Cone 4 in. /160 /97
Cone 6i n. /195 /145
Cone 8 in. /280 /193
Disc 4 in.
Disc 6 in.
5402 Antenna L max (inch/mm) Min. Diameter
(inch/mm)
Cone 2 in. /160 /55
Cone 3 in. /160 /72
Cone 4 in. /235 /97
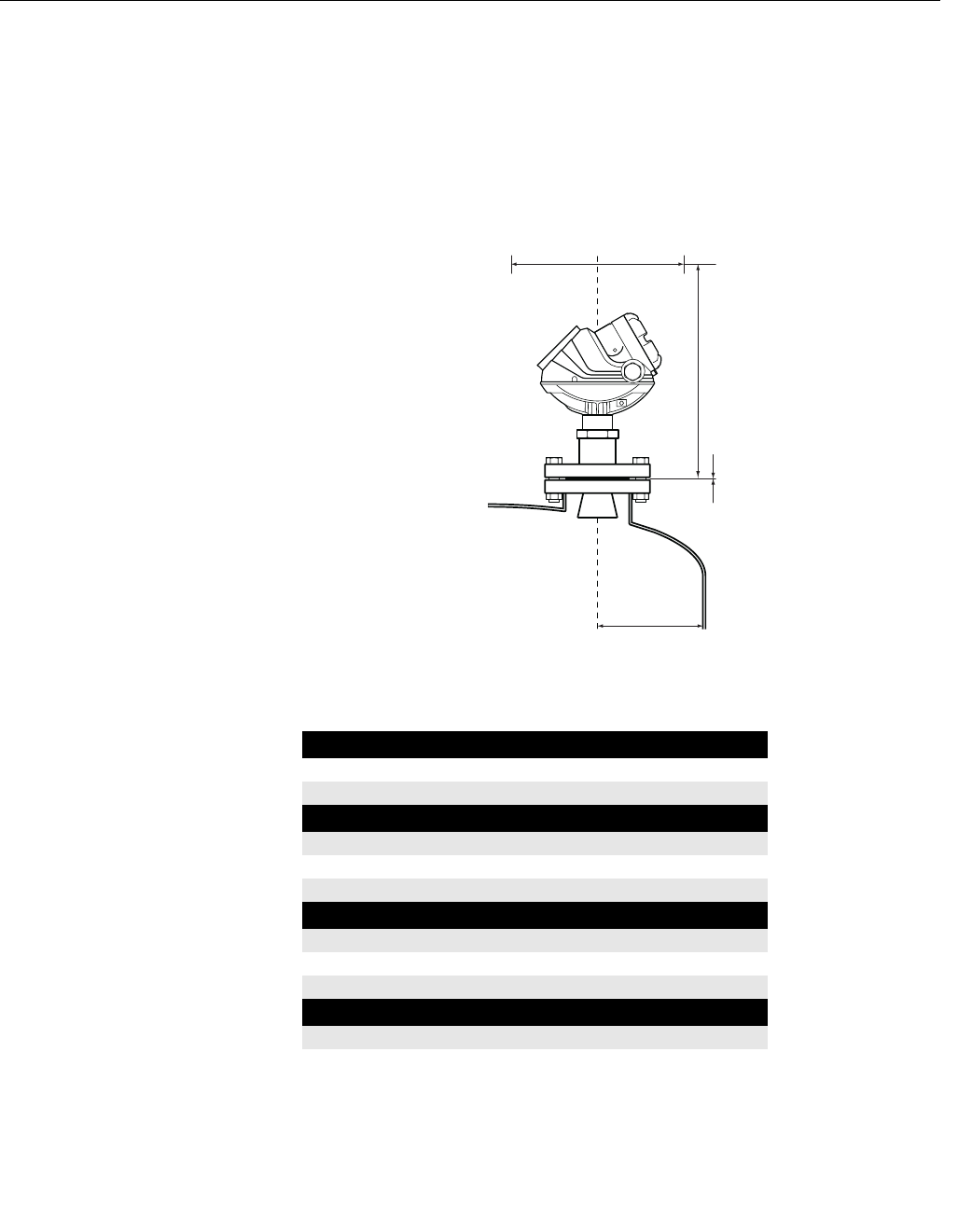
Reference Manual
00809-0100-4026, Rev AA
November 2003
Rosemount 5400 Series
3-4
Preliminary copy
Free Space For easy access to the transmitter make sure that it is mounted with sufficient
service space. For maximum measurement performance the transmitter
should not be mounted too close to the tank wall or other objects in the tank.
If the transmitter is mounted close to a wall, nozzle or other tank obstruction,
noise might appear in the level signal. Therefore the following minimum
clearance, according to the table below, must be maintained:
Figure 3-2. Free space
recommendations.
Table 3-2. Free space
requirements
FREESPACE.EPS
A
B
C
D
A. Service space width Distance (inch/mm)
B. Service space height Distance (inch/mm)
C. Inclination Maximum angle
Cone antenna 2°
D. Minimum distance to tank wall Distance (inch/mm)
Cone antenna 24/600
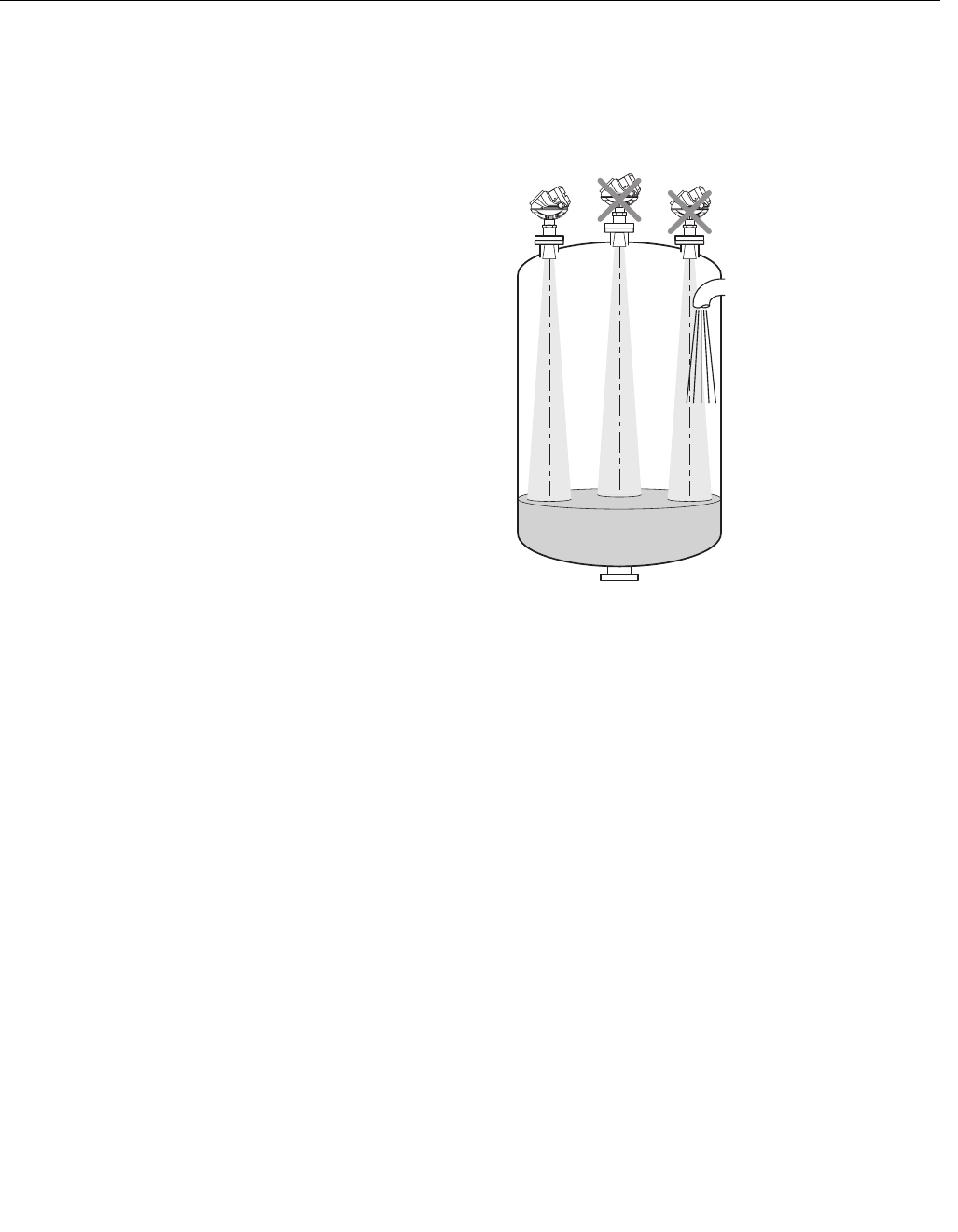
Reference Manual
00809-0100-4026, Rev AA
November 2003
3-5
Rosemount 5400 Series
Preliminary copy
Recommended Mounting
Position
When finding an appropriate mounting position for the transmitter the
conditions of the tank must be carefully considered. The transmitter should be
mounted so that the influence of disturbing objects is reduced to a minimum.
Figure 3-3. It is important to
consider the proper mounting
position.
• Disturbing objects and filling inlets creating turbulence should be kept
at a distance, outside the signal beam (see Figure 3-4 for beam width
information).
• Avoid to install the transmitter at the centre of the tank roof.
• A bridle / still-pipe can be used to avoid interference.
MOUNTING_RESTRICTIONS.EPS
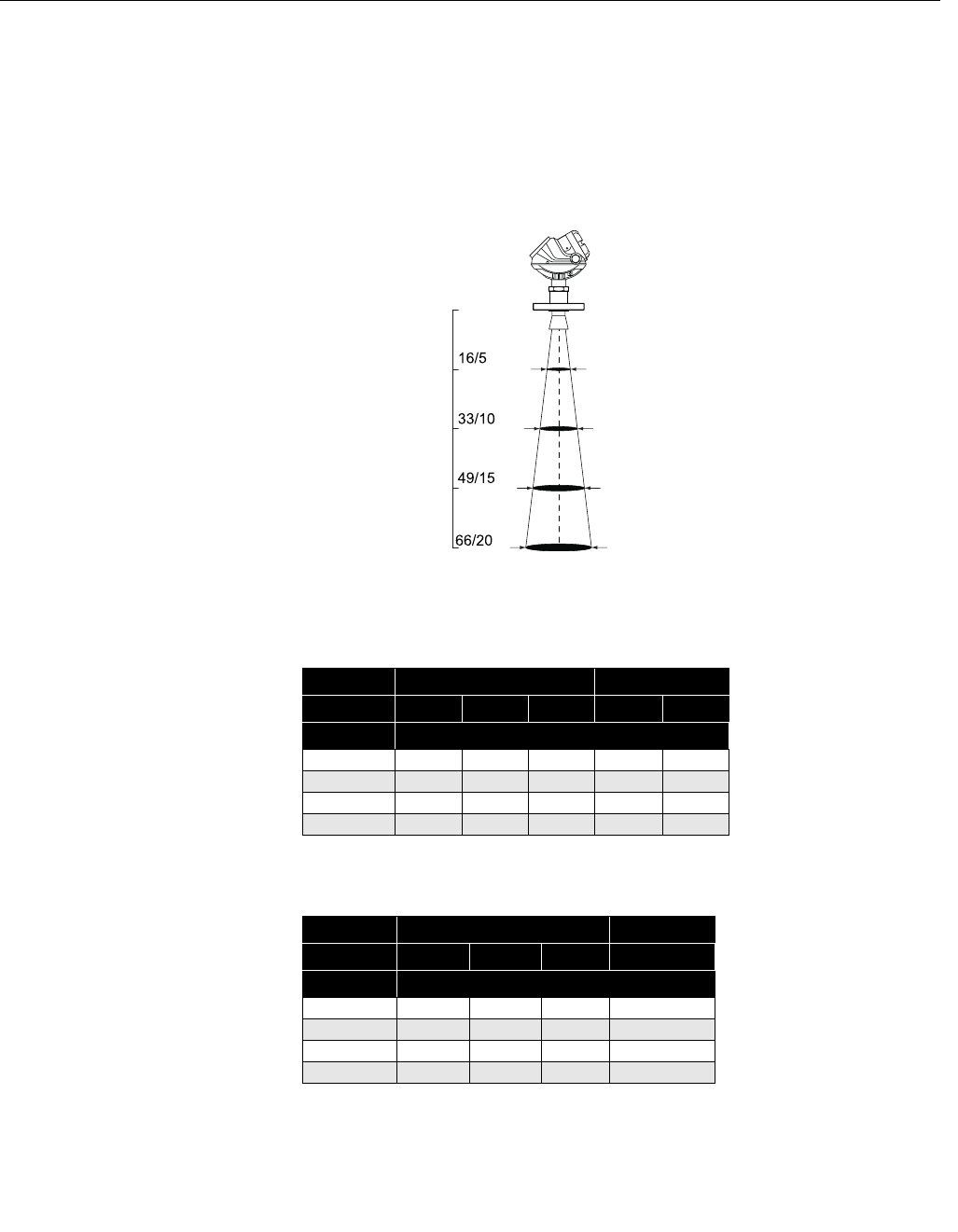
Reference Manual
00809-0100-4026, Rev AA
November 2003
Rosemount 5400 Series
3-6
Preliminary copy
Beam Width • The transmitter should be mounted with as few fittings as possible
within the beam angle.
• The flat tank wall can be located within the antenna beam angle as long
as there is a minimum distance from the transmitter to the tank wall
(see picture for preferred installation).
Figure 3-4. Beam width at
various distances from the
flange.
Beam Diameter at different distances from flange for 5401
Beam Diameter at different distances from flange for 5402
Cone Antenna Disc Antenna
4 in. 6 in. 8 in. 4 in. 6 in.
Distance Beam Diameter, ft (m)
16 ft (5 m) 3,5 21,5 3 2
33 ft (10 m) 74364
49 ft (15 m) 10 64,5 95,5
66 ft (20 m) 13 8 6 12 7,5
Cone Antenna Disc Antenna
2 in. 3 in. 4 in. 2 in.
Distance Beam Diameter, ft (m)
16 ft (5 m) 1,5 1 1 2
33 ft (10 m) 3,5 2,5 1,5 4,5
49 ft (15 m) 53,5 2,5 6,5
66 ft (20 m) 6,5 5 3 9
BEAMWIDTH.EPS
Distance (feet/m)
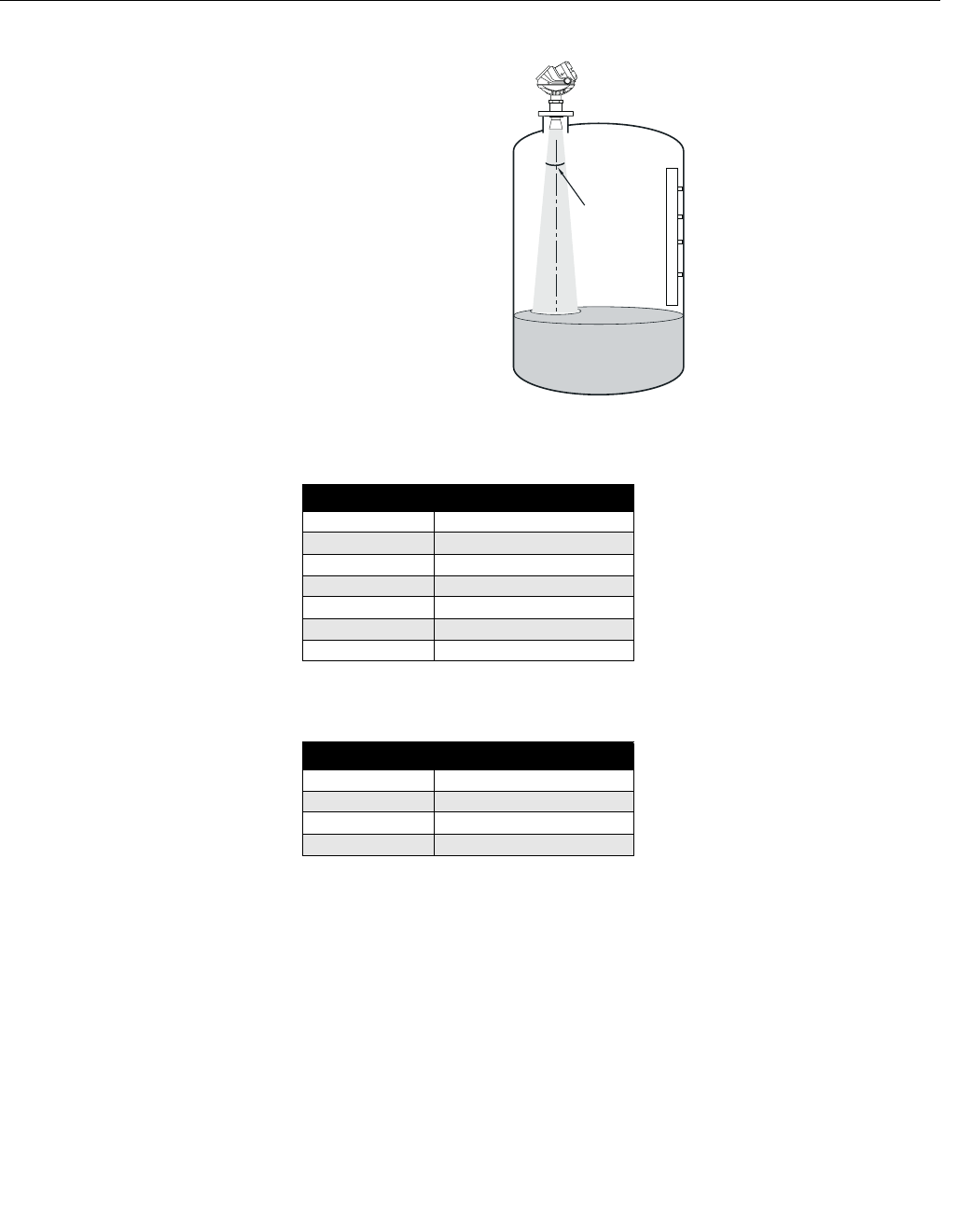
Reference Manual
00809-0100-4026, Rev AA
November 2003
3-7
Rosemount 5400 Series
Preliminary copy
Figure 3-5. Beam angle.
Beam angle for 5401
Beam angle for 5402
Antenna Half Power Beam Width
Cone 2 in. (Still Pipe)
Cone 3 in. (Still Pipe)
Cone 4 in. 37°
Cone 6 in. 23°
Cone 8 in. 17°
Disc 4 in. 34°
Disc 6 in. 21°
Antenna Half Power Beam Width
Cone 2 in. 19°
Cone 3in. 14°
Cone 4in. 9°
Disc 2 in. 25°
Beam Angle
BEAMWIDTH2.EPSS
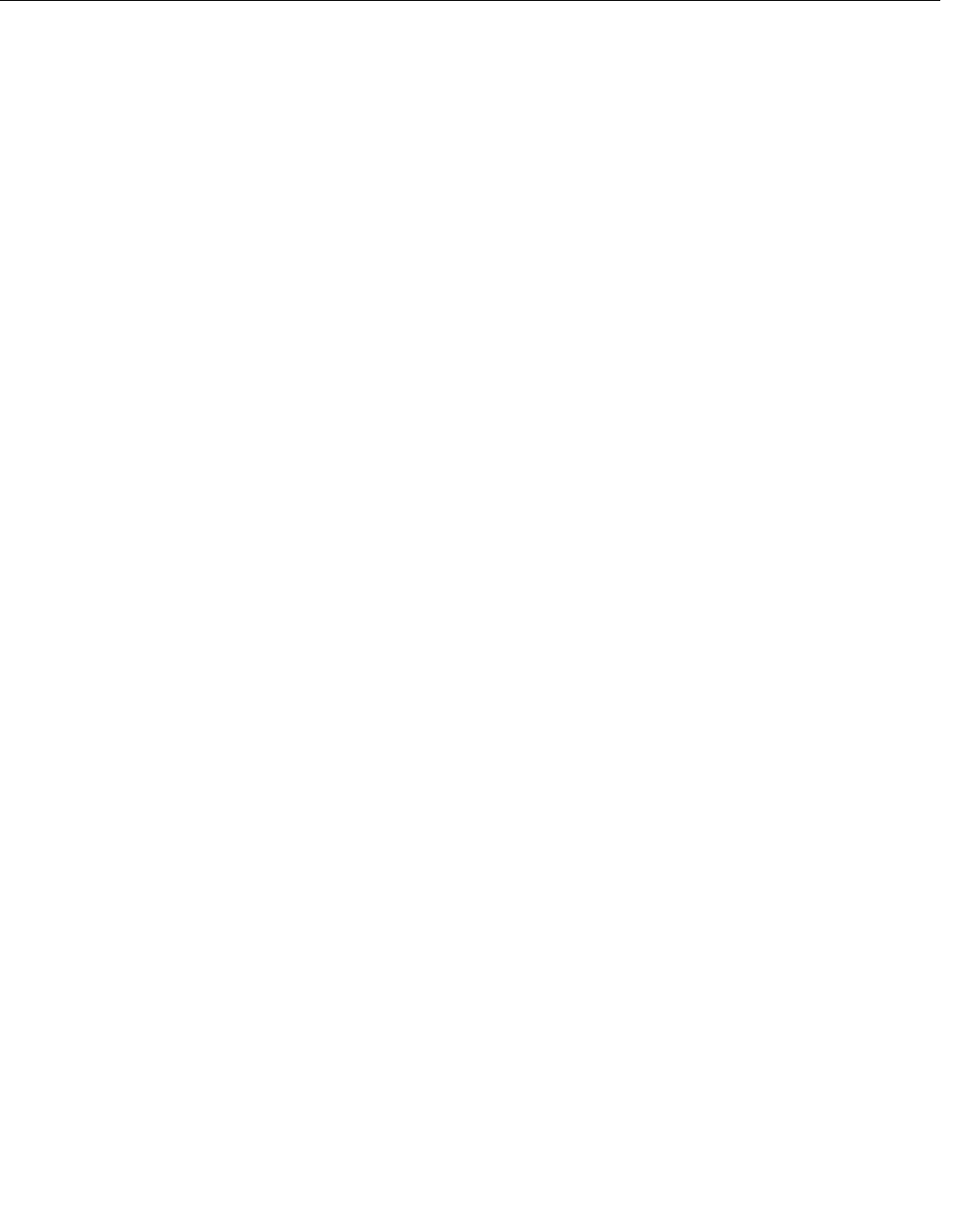
Reference Manual
00809-0100-4026, Rev AA
November 2003
Rosemount 5400 Series
3-8
Preliminary copy
Vessel Characteristics Heating coils, agitators and other objects in the tank may lead to noise in the
measurement signal. Vertical cables causes minimal effect since the radar
signal is scattered rather than directed back to the antenna.
The shape of the tank bottom affects the measurement signal when the
product surface is close to the tank bottom. The 5400 Series has built-in
functions which optimizes measurement performance for various bottom
shapes.
Disturbing objects The 5400 Series transmitter should be mounted so that objects such as
heating coils, ladders etc. are not within the radar signal path. These objects
may cause false echoes resulting in reduced measurement performance.
However, the transmitter has built-in functions designed to reduce the
influence from disturbing objects in case such objects can not be totally
avoided.
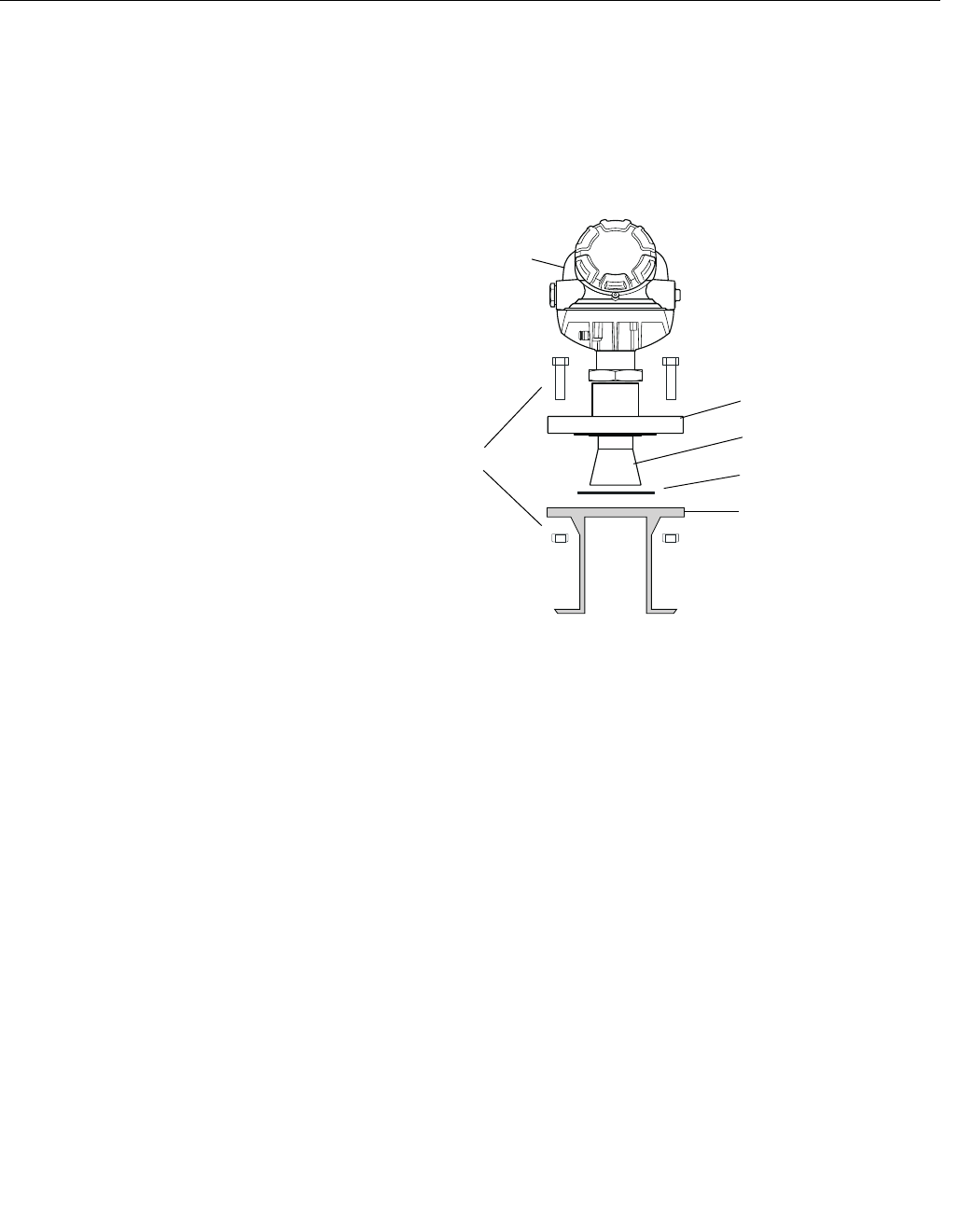
Reference Manual
00809-0100-4026, Rev AA
November 2003
3-9
Rosemount 5400 Series
Preliminary copy
MECHANICAL
INSTALLATION
Mount the transmitter on a nozzle on top of the tank. Make sure only qualified
personnel perform the installation.
Mounting a standard
cone antenna
Figure 3-6. Mounting the 5400
on a tank nozzle.
1. Place a gasket on top of the tank flange.
2. Lower the transmitter with antenna and flange into the tank nozzle.
3. Tighten the bolts and nuts.
Transmitter housing
Bolt/nut
Gasket
Flange
Tank flange
Antenna
MOUNT_TH_FLANGE.EPS
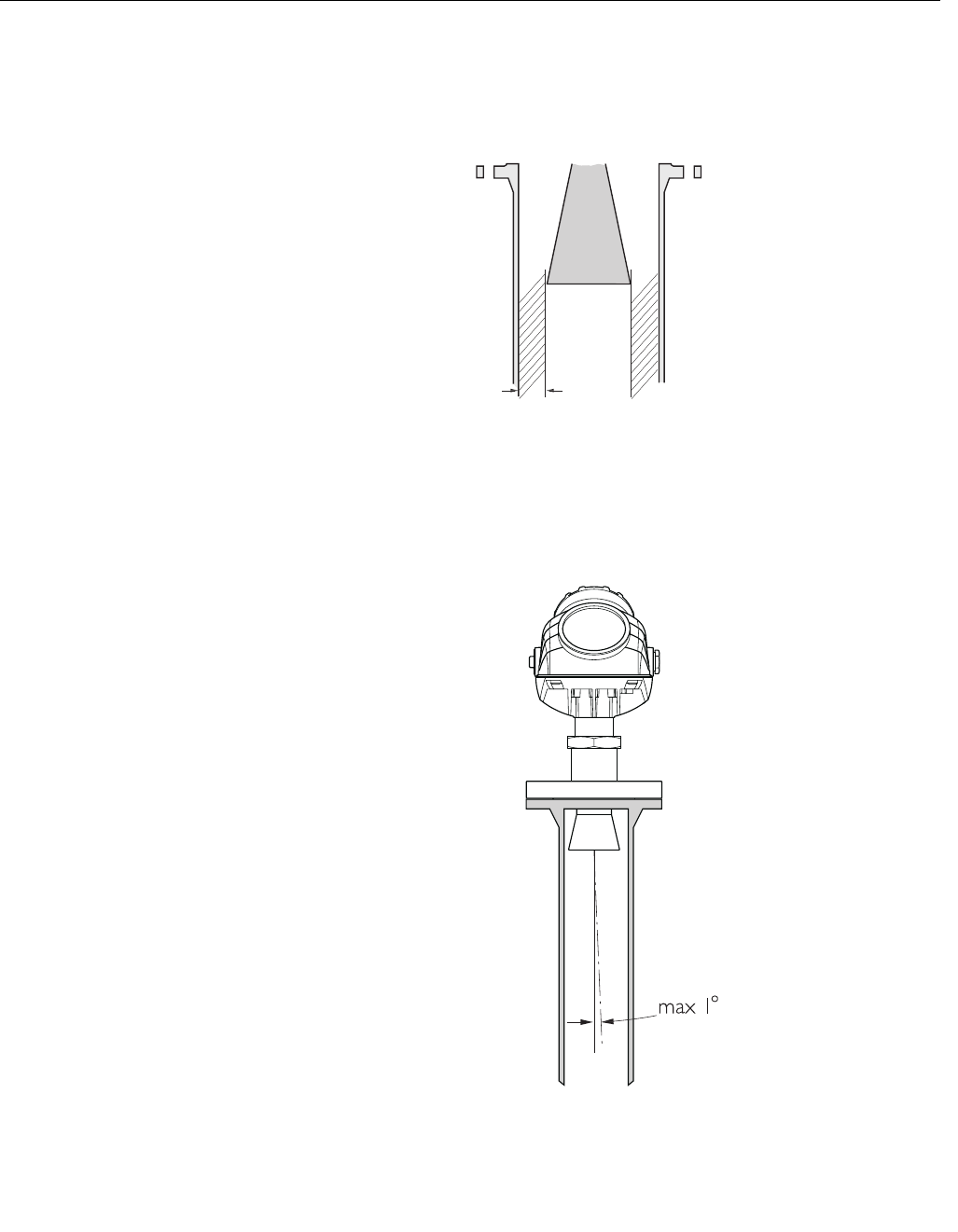
Reference Manual
00809-0100-4026, Rev AA
November 2003
Rosemount 5400 Series
3-10
Preliminary copy
Mounting in Still Pipes Still Pipe mounting is recommended for tanks where surface conditions are
extremely turbulent. The gap between the antenna and the Still Pipe may be
up to 0.4 inch (10 mm).
Figure 3-7. Maximum gap
between antenna and Still pipe.
When the transmitter is mounted in a Still Pipe the inclination should be
within 1°.
Figure 3-8. The transmitter
should be vertically mounted.
STILLPIPE_REQS.EPS
max. 0.4 inch
(10 mm)
STILLPIPE_TANK.EPS
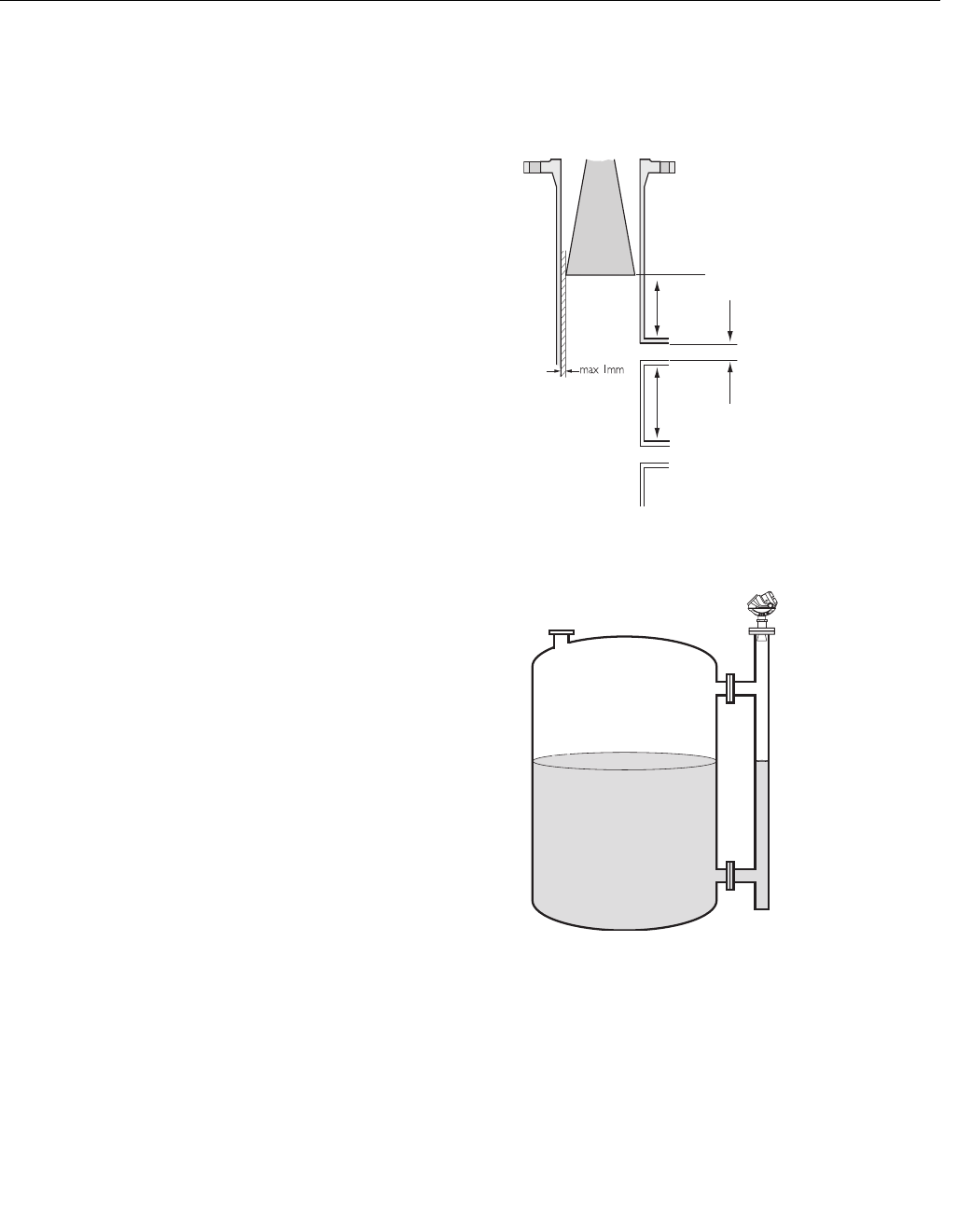
Reference Manual
00809-0100-4026, Rev AA
November 2003
3-11
Rosemount 5400 Series
Preliminary copy
Mounting in Bypass
Pipes
In pipes with inlet pipes in the order of 3 inch or larger the gap between the
pipe and the antenna should be less than 1 mm.
Figure 3-9. Recommended
specifications for bridles with
pipe inlets.
Figure 3-10. Bridle mounting is
recommended for tanks with
turbulent surface conditions.
BRIDLE_REQS.EPS
Min. xx
Min. xx
Max. diameter xx
BRIDLE.EPS
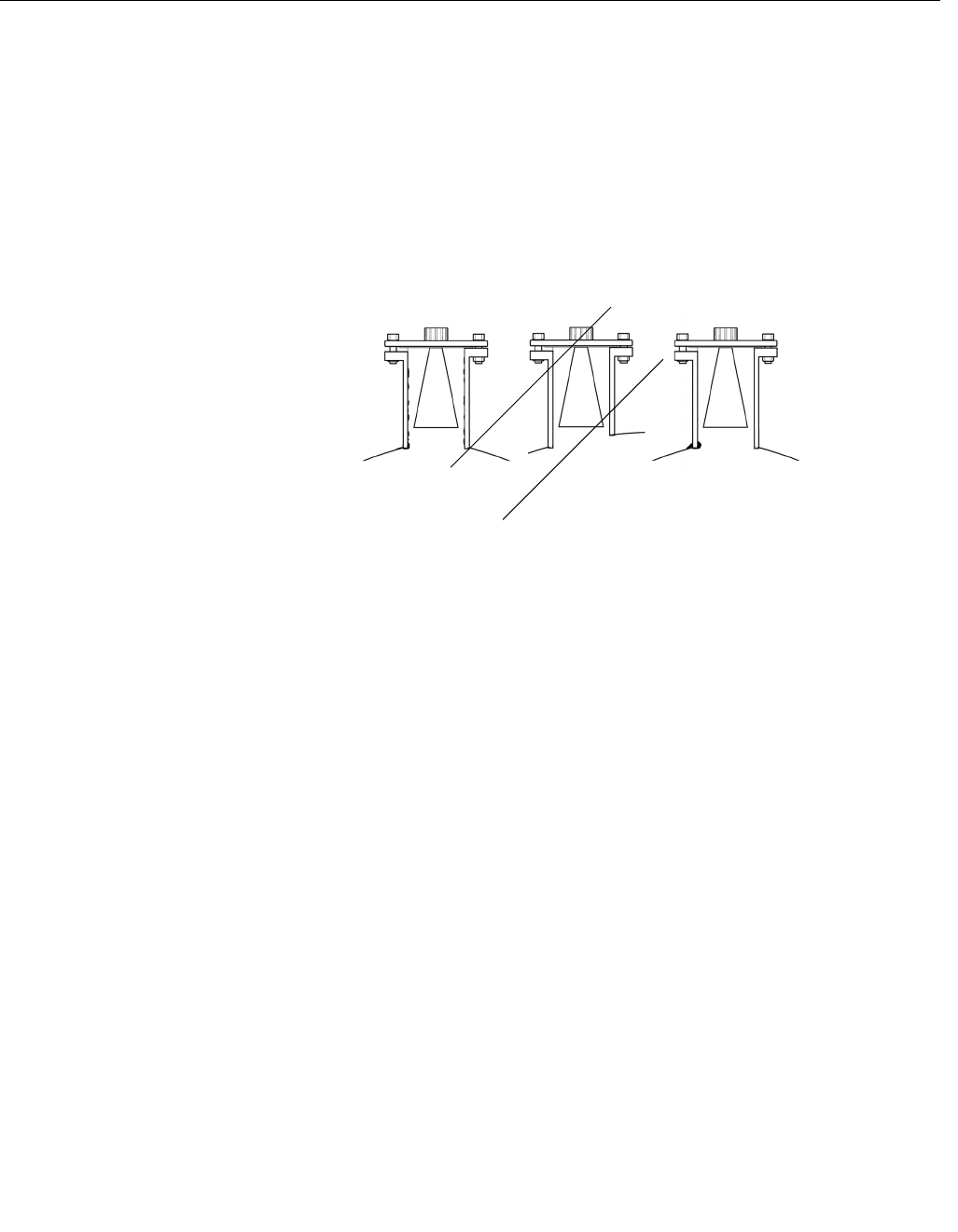
Reference Manual
00809-0100-4026, Rev AA
November 2003
Rosemount 5400 Series
3-12
Preliminary copy
Antenna extension The Extended Cone antenna is suitable for tanks with long nozzles or tanks
where measurements should be avoided in the region close to the nozzle.
Use the Extended Cone antenna if:
• the nozzle is high
• there are disturbing objects close to the tank opening, or
• there is a rough surface at the inside of the nozzle.
Figure 3-11. Typical nozzle
conditions which may decrease
measurement performance.
“Disc Antenna”
Figure 3-12.
BRIDLE_REQS.EPS
DRAFT
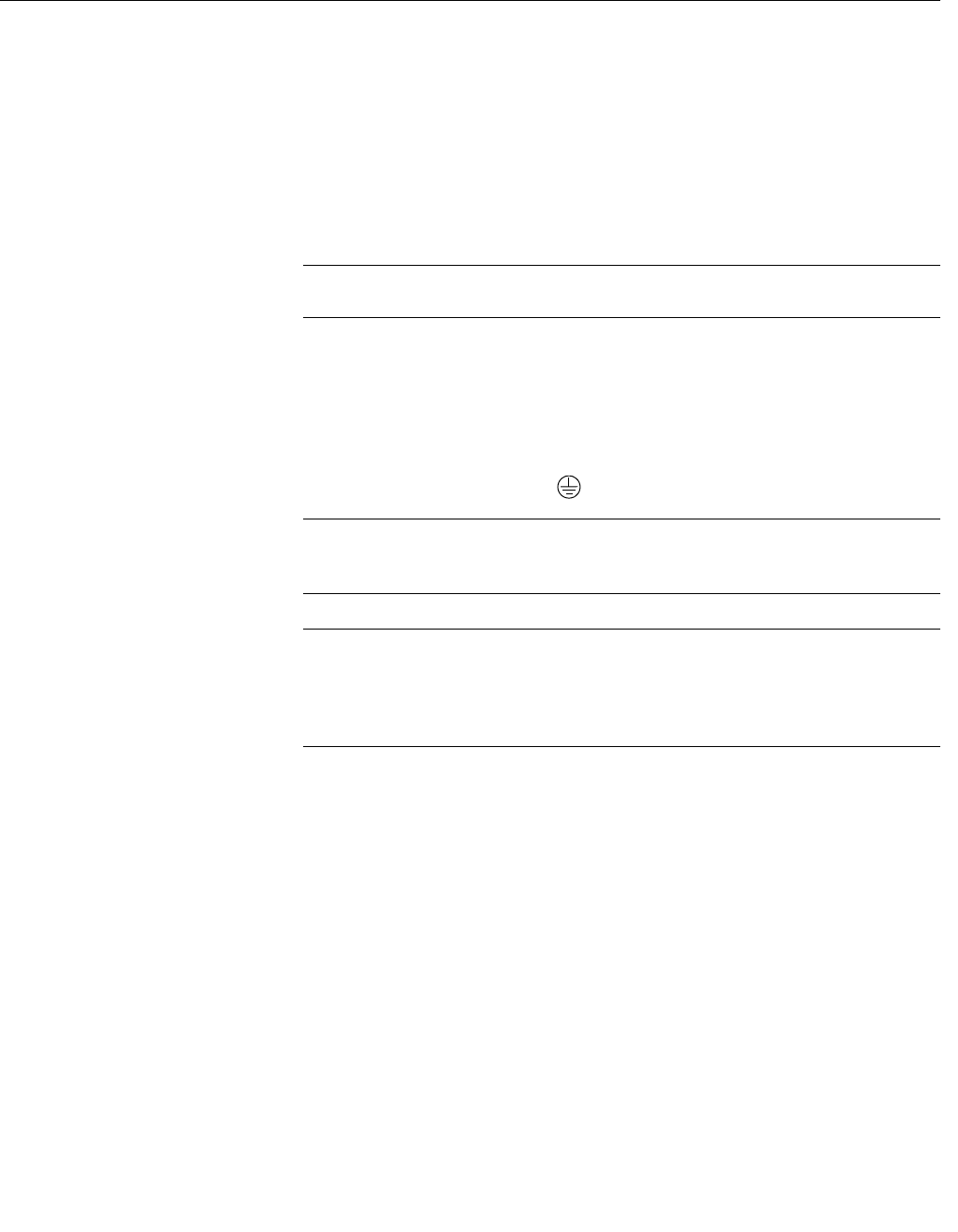
Reference Manual
00809-0100-4026, Rev AA
November 2003
3-13
Rosemount 5400 Series
Preliminary copy
ELECTRICAL
INSTALLATION
Cable/conduit entries The electronics housing has two entries for ½ - 14 NPT. Optional M20×1.5
and PG 13.5 adapters are also available. The connections are made in
accordance with local or plant electrical codes.
Make sure that unused ports are properly sealed to prevent moisture or other
contamination from entering the terminal block compartment of the electronics
housing.
NOTE!
Use the enclosed metal plug to seal the unused port.
Grounding The housing should always be grounded in accordance with national and
local electrical codes. Failure to do so may impair the protection provided by
the equipment. The most effective grounding method is direct connection to
earth ground with minimal impedance. There are two grounding screw
connections provided. One is inside the Field Terminal side of the housing
and the other is located on top of the housing. The internal ground screw is
identified by a ground symbol: .
NOTE!
Grounding the transmitter via threaded conduit connection may not provide
sufficient ground.
NOTE!
In the Explosion proof/Flameproof version the electronics is grounded via the
transmitter housing. After installation and commissioning make sure that no
ground currents exist due to high ground potential differences in the
installation.
Cable Selection Use shielded twisted pair wiring for the Rosemount 5400 Series in order to
comply with EMC regulations. The cables must be suitable for the supply
voltage and approved for use in hazardous areas, where applicable. For
instance, in the U.S., explosion-proof conduits must be used in the vicinity of
the vessel. For the ATEX flame proof approval version of the 5400 Series,
suitable conduits with sealing device or flame proof (EEx d) cable glands must
be used depending on local requirements.
Use 18 AWG to 12 AWG in order to minimize the voltage drop to the
transmitter.
Hazardous Areas When the 5400 transmitter is installed in hazardous area, local regulations
and specifications in applicable certificates must be observed.
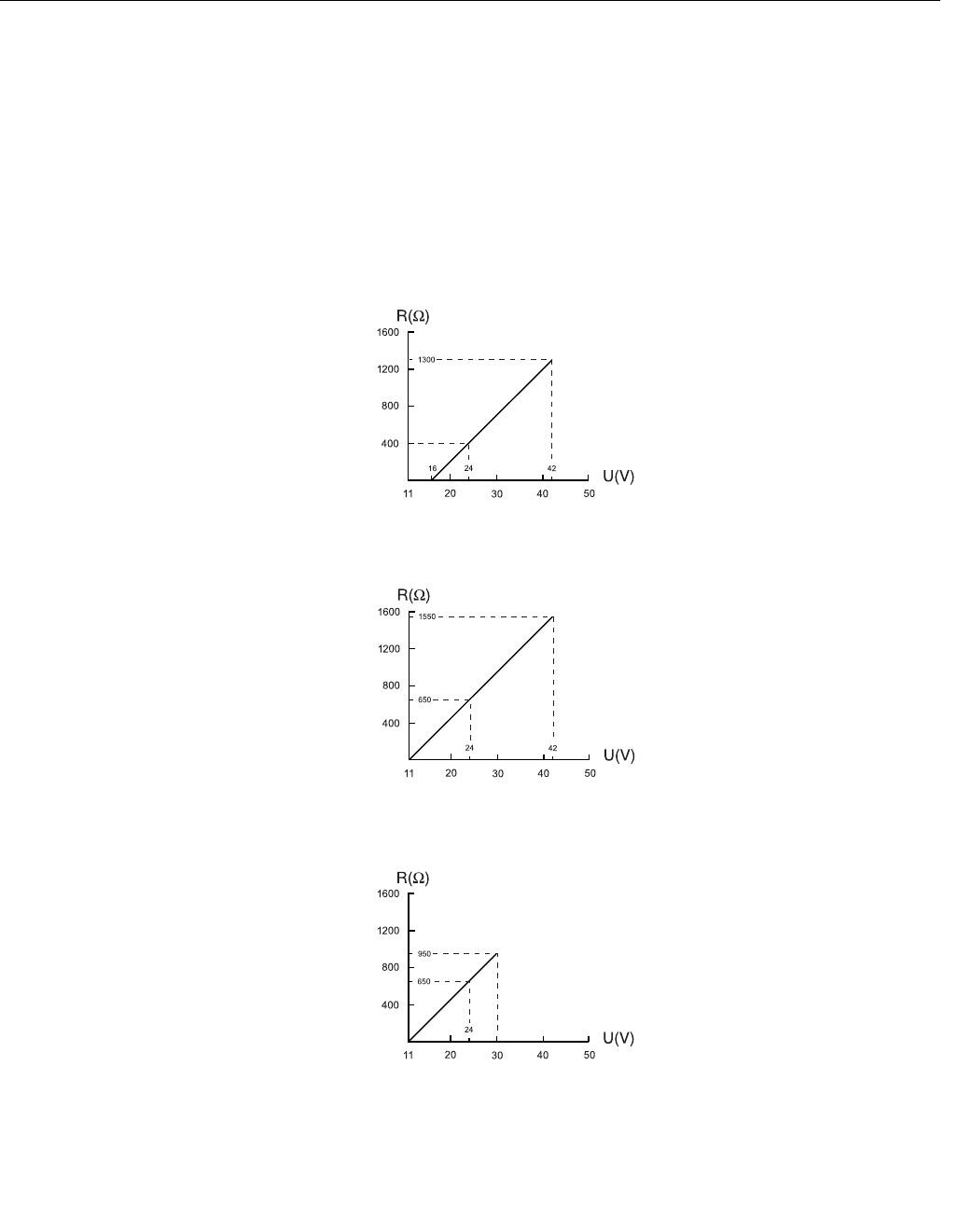
Reference Manual
00809-0100-4026, Rev AA
November 2003
Rosemount 5400 Series
3-14
Preliminary copy
Power Requirements Terminals in the transmitter housing provide connections for signal cables.
The 5400 transmitter operates with power supplies ranging from 15.5 to 45
VDC.
For Intrinsically Safe output the supply voltage must be within xx to xx VDC.
For Explosion Proof/Flame Proof the supply voltage must be within xx to xx
VDC.
Maximum Loop
Resistance
The maximum current loop resistance can be gained from the following
diagrams:
Figure 3-13. Explosion
Proof/Flame Proof installations.
Figure 3-14. Non-hazardous
installations.
Figure 3-15. Intrinsically safe
installations.
DRAFT
MAX_LOAD_EX.EPSMAX_LOAD_NON_INTRINSIC.EP
DRAFT
MAX_LOAD_INTRINSIC.EPS
DRAFT
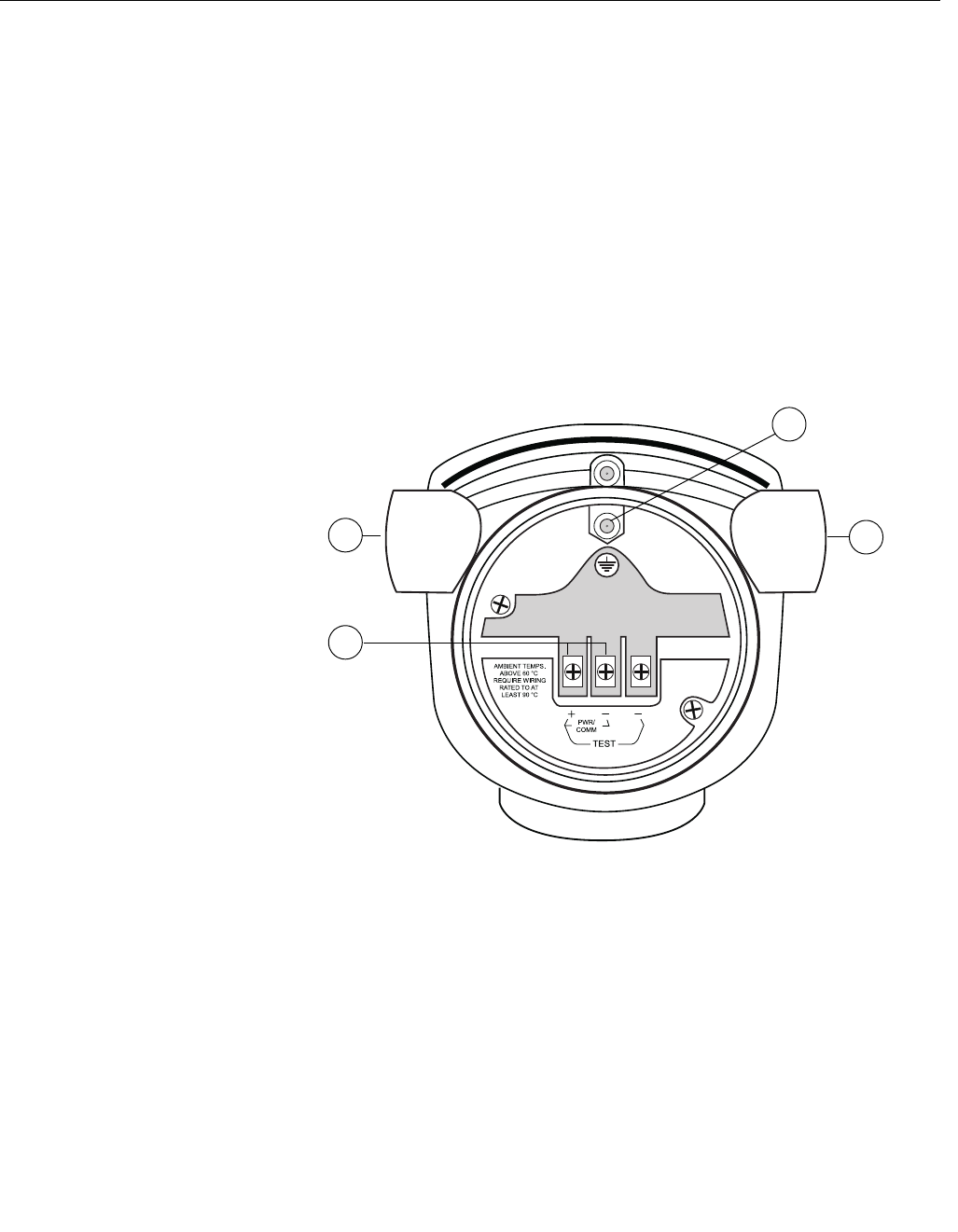
Reference Manual
00809-0100-4026, Rev AA
November 2003
3-15
Rosemount 5400 Series
Preliminary copy
Connecting the
Transmitter
The 5400 Series accepts power supplies ranging from 15.5 VDC to 45 VDC. It
uses 4-20 mA power superimposed with a HART signal.
To connect the transmitter:
1. Make sure that the power supply is disconnected.
2. Remove the cover on the transmitter housing terminal side (see label).
3. Pull the cable through the cable gland/conduit.
4. Connect wires according to Figure 3-17 for non-intrinsically safe output
and according to Figure 3-18 for Intrinsically safe output.
5. Replace the cover and tighten the cable gland.
6. Connect the power supply.
Figure 3-16. Junction box.
1. Cable entry.
2. Ground terminal.
3. Terminal for signal and power supply.
Terminal for signal
and power supply
JUNCTION_BOX.EPS
1
1
3
2
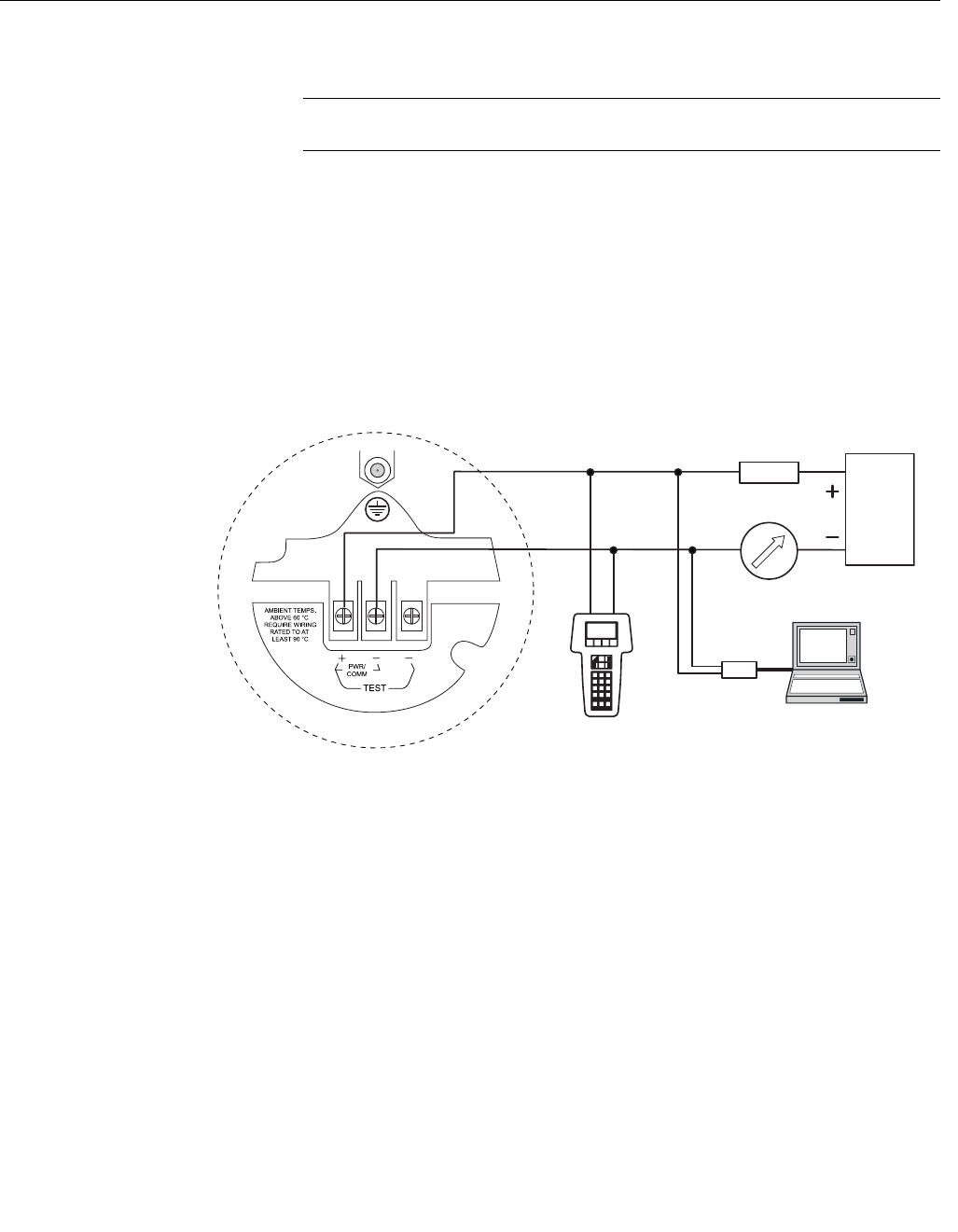
Reference Manual
00809-0100-4026, Rev AA
November 2003
Rosemount 5400 Series
3-16
Preliminary copy
Non-Intrinsically Safe
Output
For non-intrinsically safe installations wire the transmitter as shown in
Figure 3-17.
NOTE!
Make sure that the power supply is off when connecting the transmitter.
The HART 275 Communicator requires a minimum load resistance of 250
Ohm within the loop in order to function properly. For maximum loop
resistance see Figure 3-13 (Explosion/Flame Proof) and Figure 3-14
(Non-hazardous installations).
Figure 3-17. Wiring for
non-intrinsically safe
installations.
Power
supply
WIRING_NON_IS.EPS
HART 275/375
Communicator
Load resistance = 250 Ω
HART Modem
5400 Radar Series Radar Gauge
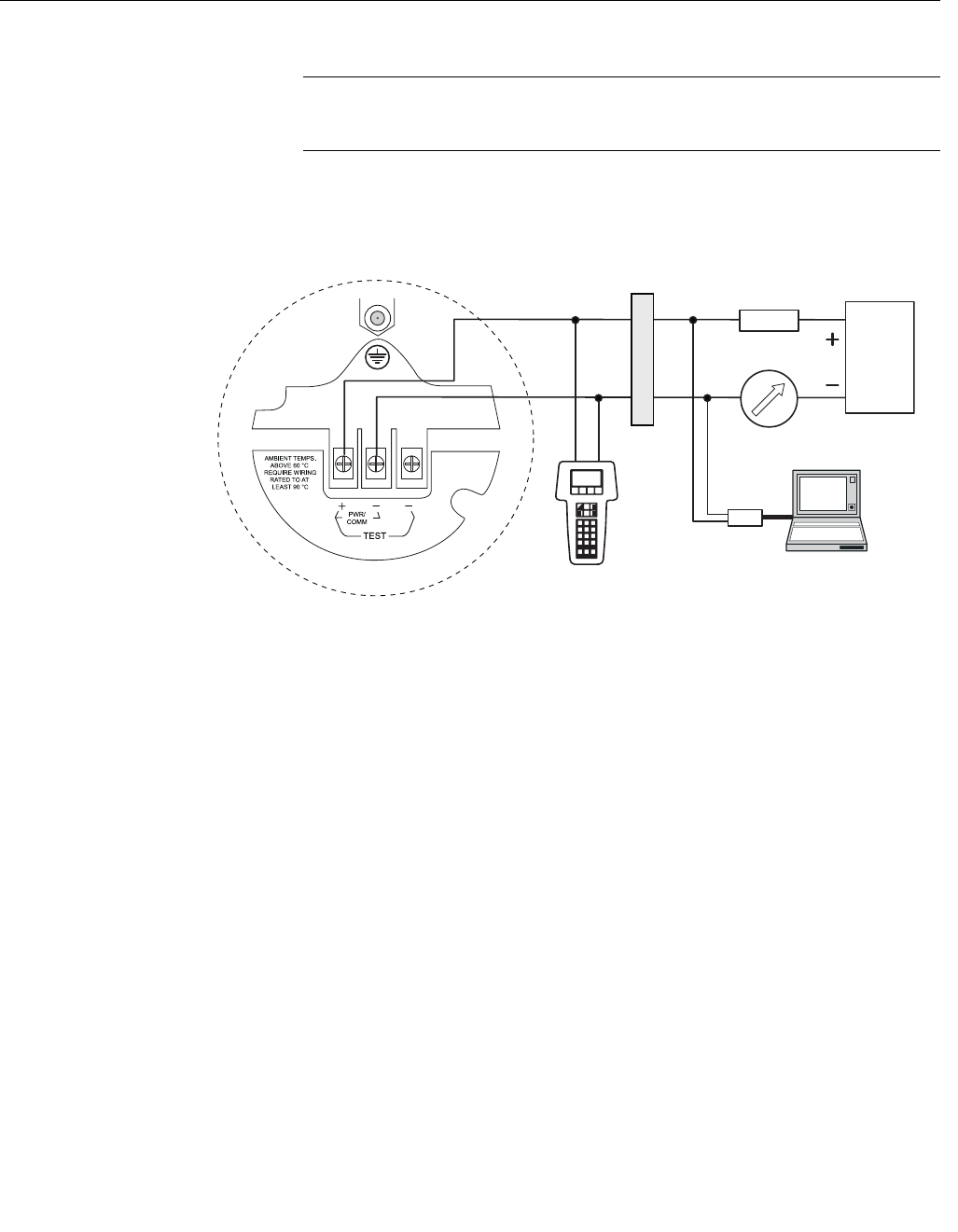
Reference Manual
00809-0100-4026, Rev AA
November 2003
3-17
Rosemount 5400 Series
Preliminary copy
Intrinsically Safe Output For intrinsically safe installations wire the transmitter as shown in Figure 3-18.
NOTE!
Make sure that the instruments in the loop are installed in accordance with
intrinsically safe field wiring practices.
Figure 3-18. Wiring diagram for
intrinsically safe installations
The HART 275 Communicator requires a minimum load resistance within the
loop of 250 Ohm in order to function properly. For maximum load resistance
see Figure 3-15.
The power supply voltage ranges from xx V to xx V.
IS parameters
Ui=30 V.
Ii=130 mA.
Pi=1 W.
Ci=0.
Li=0.
Power
supply
WIRING_IS.EPS
HART 275/375
Communicator
Load resistance = 250 Ω
HART Modem
5400 Radar Series Radar Gauge
Approved IS Barrier
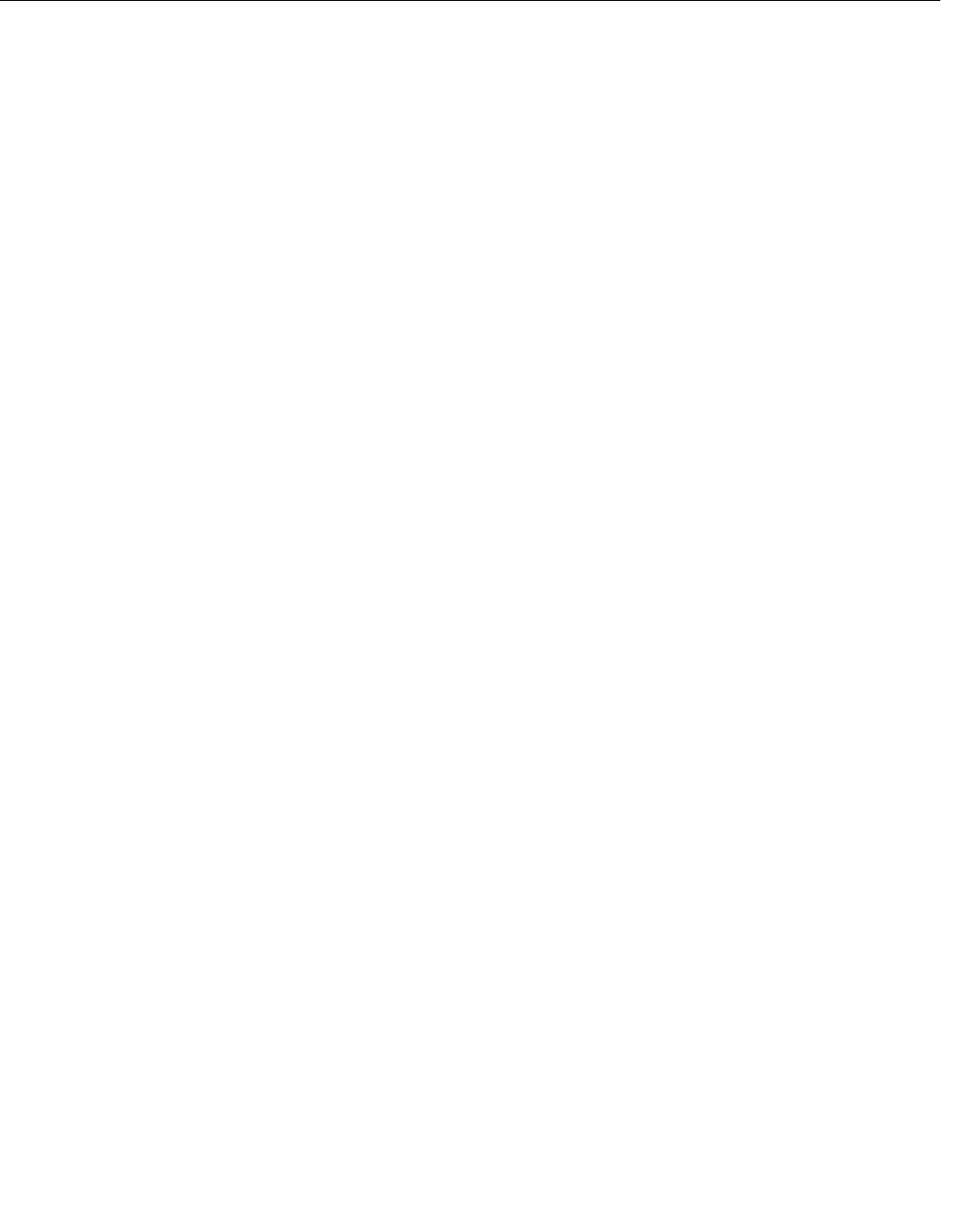
Reference Manual
00809-0100-4026, Rev AA
November 2003
Rosemount 5400 Series
3-18
Preliminary copy
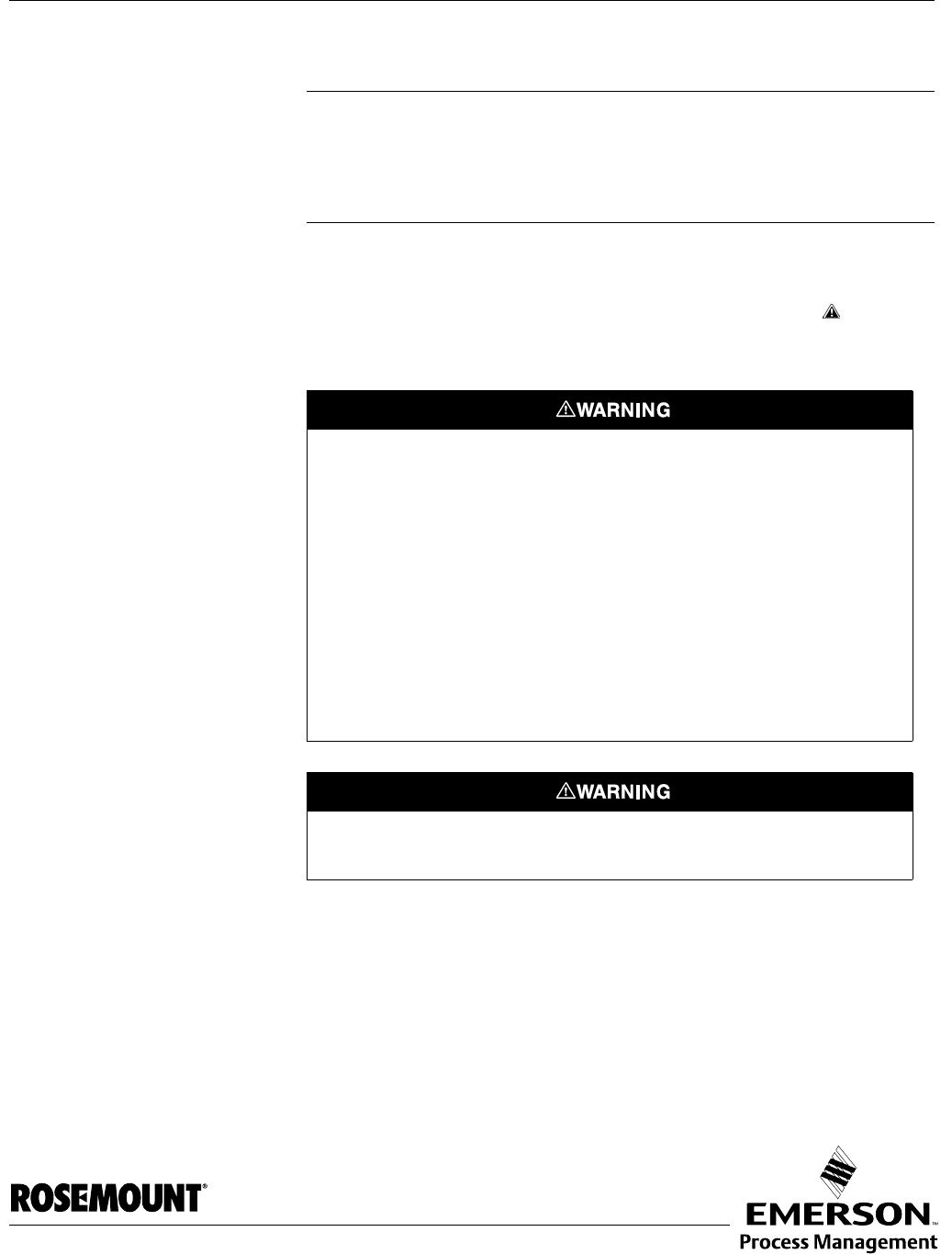
Reference Manual
00809-0100-4026, Rev AA
November 2003 Rosemount 5400 Series
www.rosemount.com
Preliminary copy
Section 4 Operation
Safety Messages . . . . . . . . . . . . . . . . . . . . . . . . . . . . . . . . . page 4-1
Display Panel . . . . . . . . . . . . . . . . . . . . . . . . . . . . . . . . . . . page 4-2
PC Configuration Software Rosemount Radar Master . . page 4-3
AMS . . . . . . . . . . . . . . . . . . . . . . . . . . . . . . . . . . . . . . . . . . . page 4-8
Model 275/375 HART Communicator . . . . . . . . . . . . . . . . page 4-9
SAFETY MESSAGES Procedures and instructions in this manual may require special precautions to
ensure the safety of the personnel performing the operations. Information that
raises potential safety issues is indicated by a warning symbol ( ). Refer to
the safety messages listed at the beginning of each section before performing
an operation preceded by this symbol.
Failure to follow these installation guidelines could result in death or serious
injury.
• Make sure only qualified personnel perform the installation.
• Use the equipment only as specified in this manual. Failure to do so may
impair the protection provided by the equipment.
Explosions could result in death or serious injury.
• Verify that the operating environment of the transmitter is consistent with the
appropriate hazardous locations certifications.
• Before connecting a HART®-based communicator in an explosive atmosphere,
make sure the instruments in the loop are installed in accordance with
intrinsically safe or non-incendive field wiring practices.
Electrical shock could cause death or serious injury.
• Use extreme caution when making contact with the leads and terminals.
Any substitution of non-recognized parts may jeopardize safety. Repair, e.g. substitution
of components etc., may also jeopardize safety and is under no circumstances allowed.
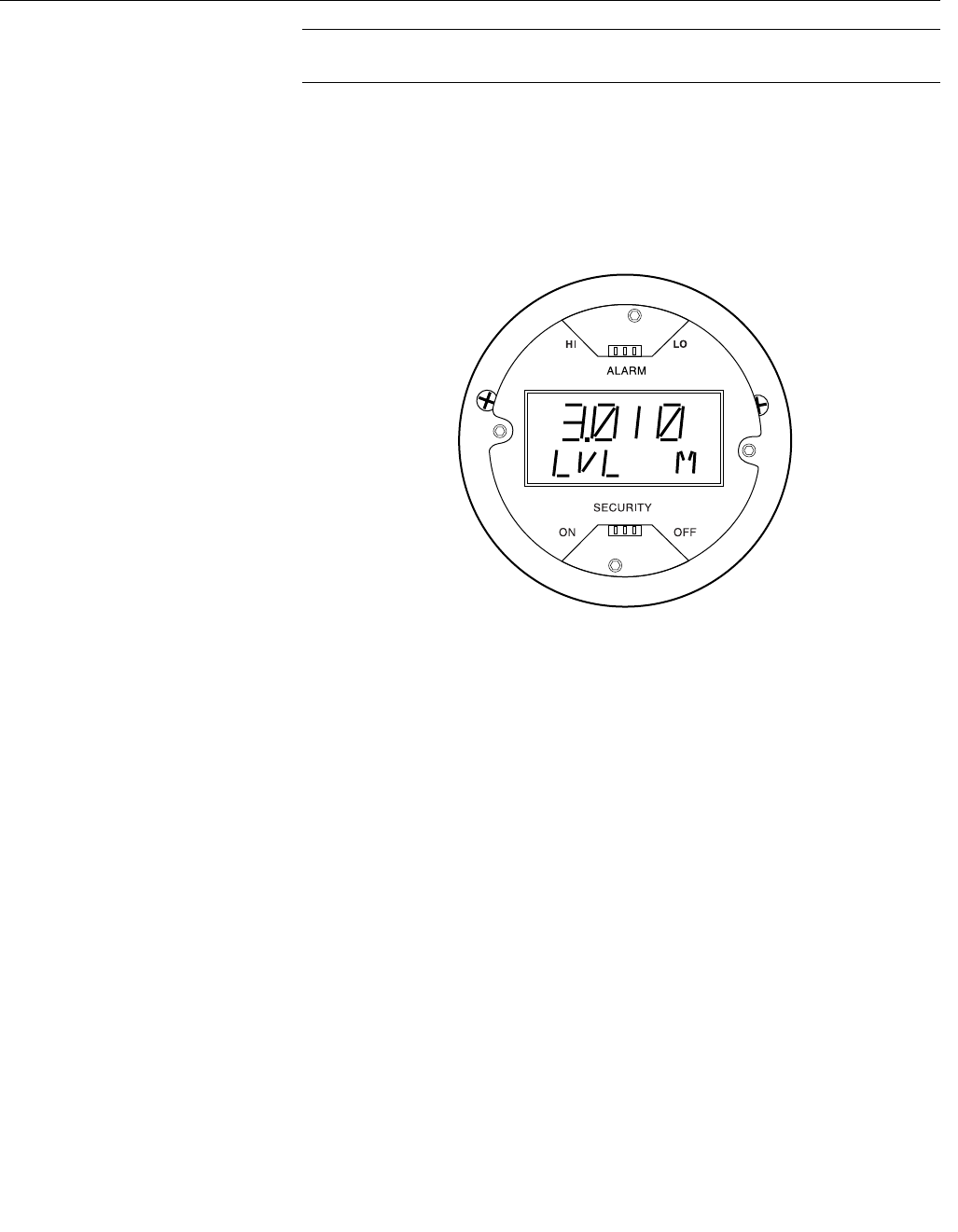
Reference Manual
00809-0100-4026, Rev AA
November 2003
Rosemount 5400 Series
4-2
Preliminary copy
DISPLAY PANEL Description of how the Display Panel is used for
viewing data.
When the transmitter is started the Display Panel presents information such
as antenna type, measurement frequency etc. When the transmitter is up and
running the Display Panel presents Level, Signal Amplitude, Volume and
other measurement data.
Figure 4-1. Display Panel
XXXXXX
Draft
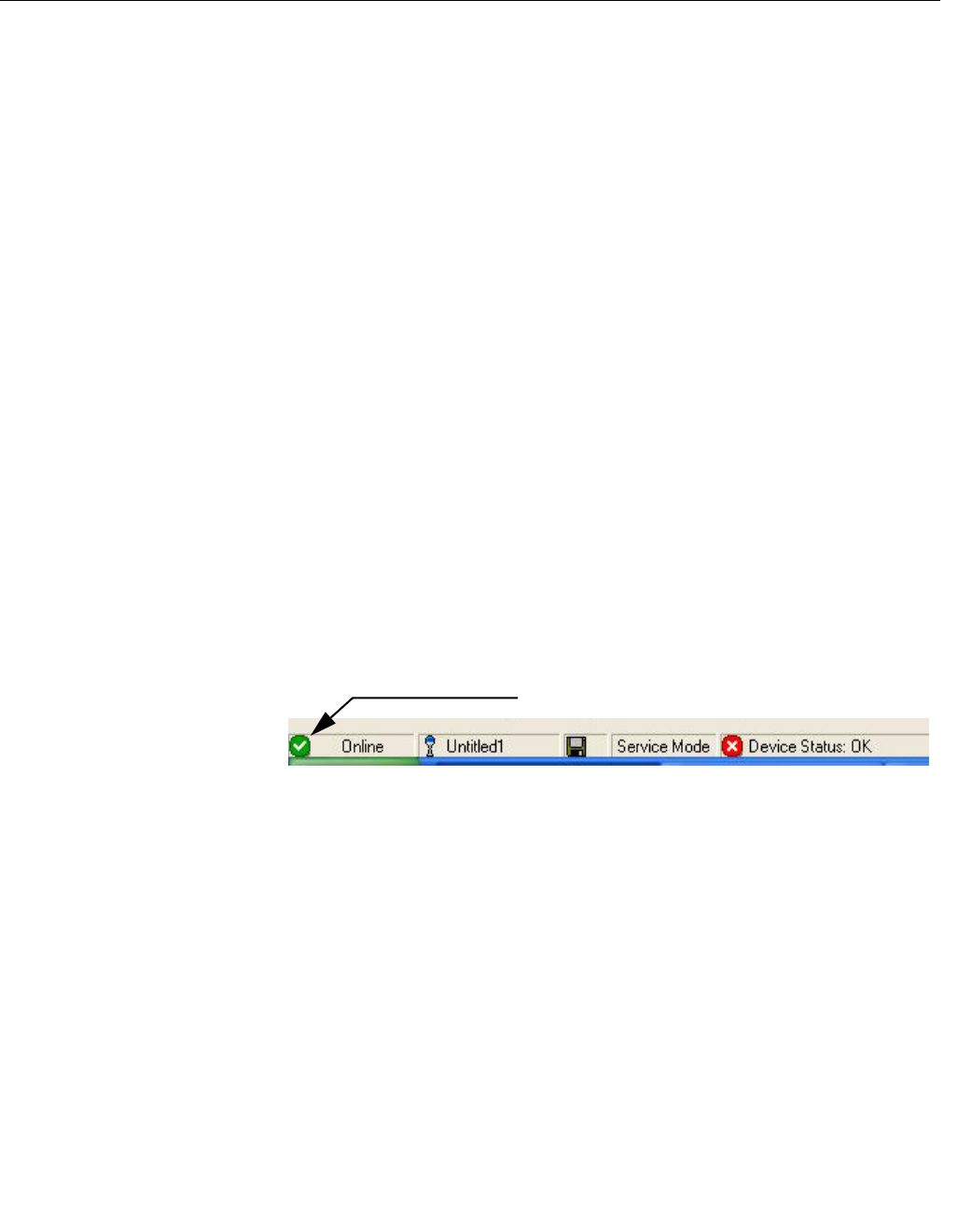
Reference Manual
00809-0100-4026, Rev AA
November 2003
4-3
Rosemount 5400 Series
Preliminary copy
PC CONFIGURATION
SOFTWARE
ROSEMOUNT RADAR
MASTER
The Rosemount Radar Master (RRM) is a user-friendly software tool that
allows you to configure the 5400 transmitter. You can choose either of the
following two methods to configure a 5400 transmitter:
• Start the Wizard for a guided installation if you are un-familiar with the
5400 transmitter.
• Use the Setup function if you are already familiar with the configuration
process or if you just want to change the current settings.
Installing the RRM
software To install the Rosemount Radar Master:
1. Insert the installation CD into your CD-ROM drive.
2. If the installation program is not automatically started, from the windows
Start Bar choose Run and type D:\Setup.exe where D is the CD-ROM
drive.
3. Follow the instructions on the screen.
4. For optimum performance set COM Port Buffers to 1.
To start the RRM:
1. From the Start menu click Programs>Saab Rosemount>Rosemount
Radar Master.
2. In the RRM Status Bar check that RRM communicates with the
transmitter. If communication does not work check that the correct COM
port is connected on the computer and that the COM port is properly
configured, see “Specifying the COM Port” on page 4-4.
RRM communicates
with the devices.
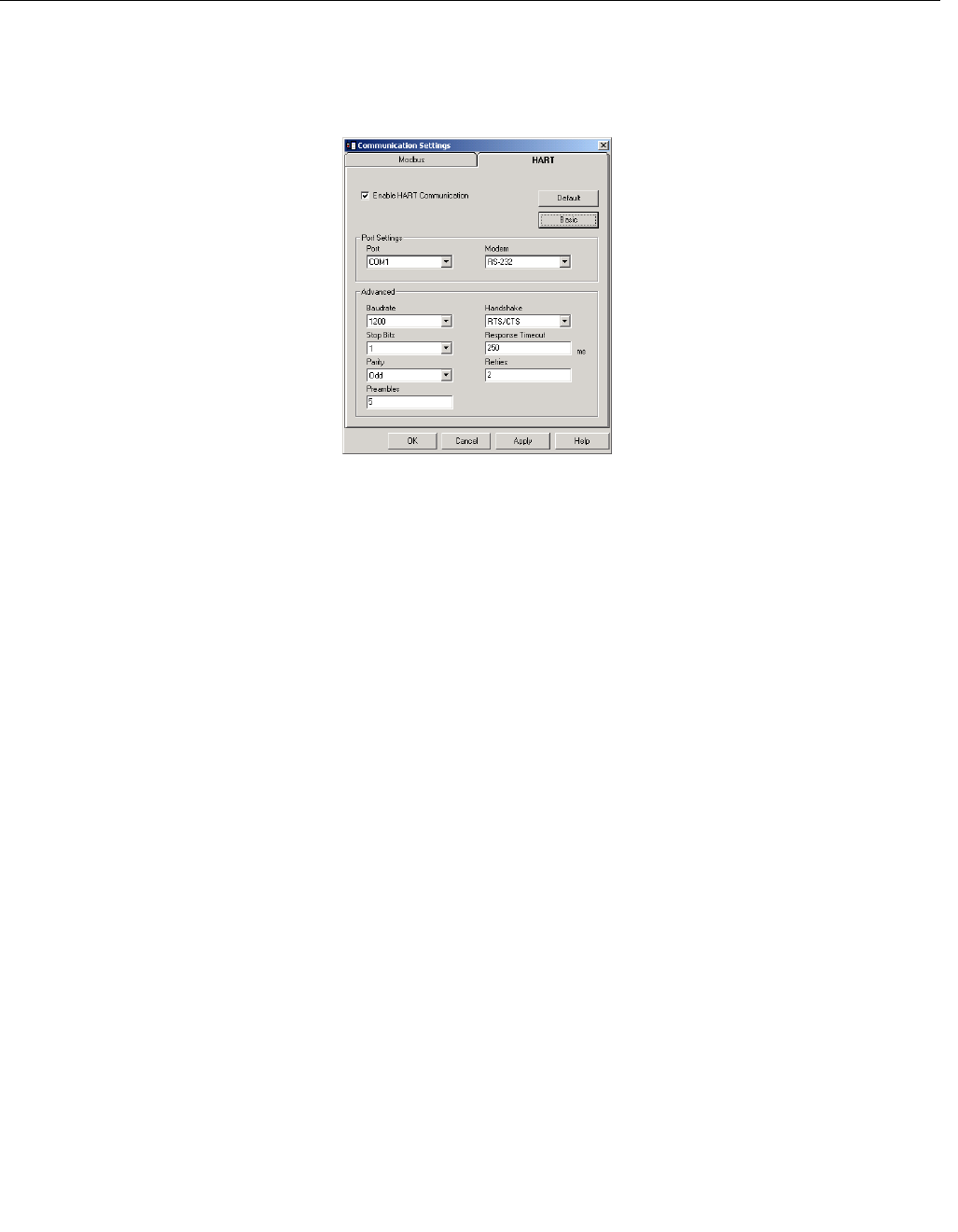
Reference Manual
00809-0100-4026, Rev AA
November 2003
Rosemount 5400 Series
4-4
Preliminary copy
Specifying the COM Port If communication is not established open the Communication Preferences
window and check that the correct COM Port is selected:
1. Select Communication Preferences from the Windows menu.
2. Check which COM port that is connected.
3. Choose the COM Port option that matches the COM Port connected to
the transmitter.
To set the COM port buffers
For Windows 2000 the COM port Receive Buffer and Transfer Buffer need to
be set to 1. To set the COM port buffers do the following:
1. In the MS Windows Control Panel open the System option.
2. Choose the Hardware tab and click the Device Manager button.
3. Expand the Ports node in the tree view.
4. Click the right mouse button on the selected COM port and choose
Properties.
5. Select the Port Settings tab and click the Advanced button.
6. Drag the Receive Buffer and Transfer Buffer slides to 1.
7. Click the OK button.
8. Reboot the computer.
RRM/COMMUNICATIONSETTINGS.BMP
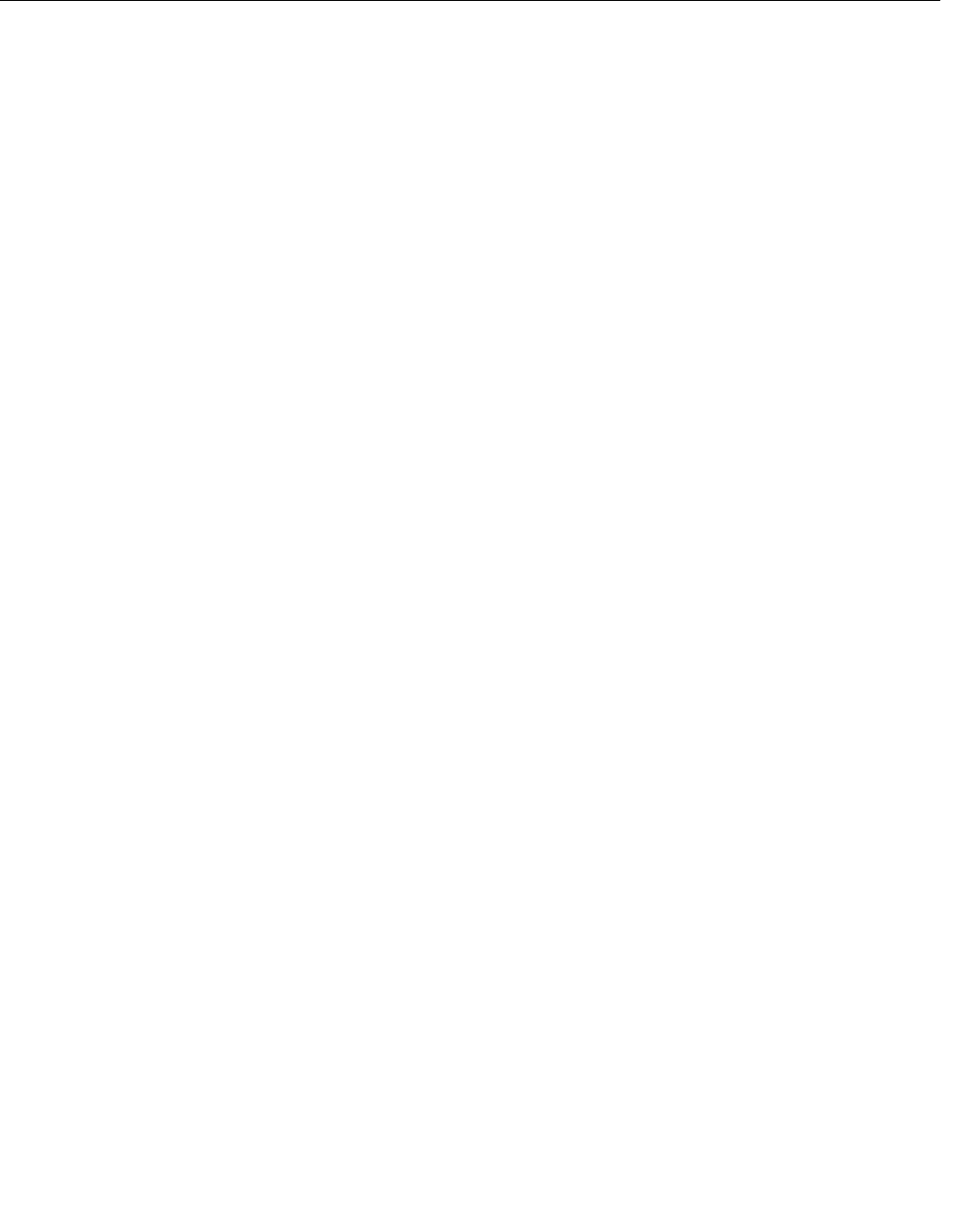
Reference Manual
00809-0100-4026, Rev AA
November 2003
4-5
Rosemount 5400 Series
Preliminary copy
System Requirements Hardware
Processor: Pentium 200MHz
Memory: 64 MB RAM
COM Port: 1 serial COM port
Graphical Card: Screen resolution of 800 x 600. 256 colors.
Hard drive space: 100 MB
Software
Operating Systems supported:
Windows 98 - service pack 3 and above
Windows NT 4 - service pack 6 and above
Windows 2000
Help In RRM Help is accessed by pressing the F1 key or by selecting the Contents option
from the Help menu. If the F1 key is pressed a help text appears with
information about the window that is currently open. If a menu option is
selected a help text appears with information about that particular menu.
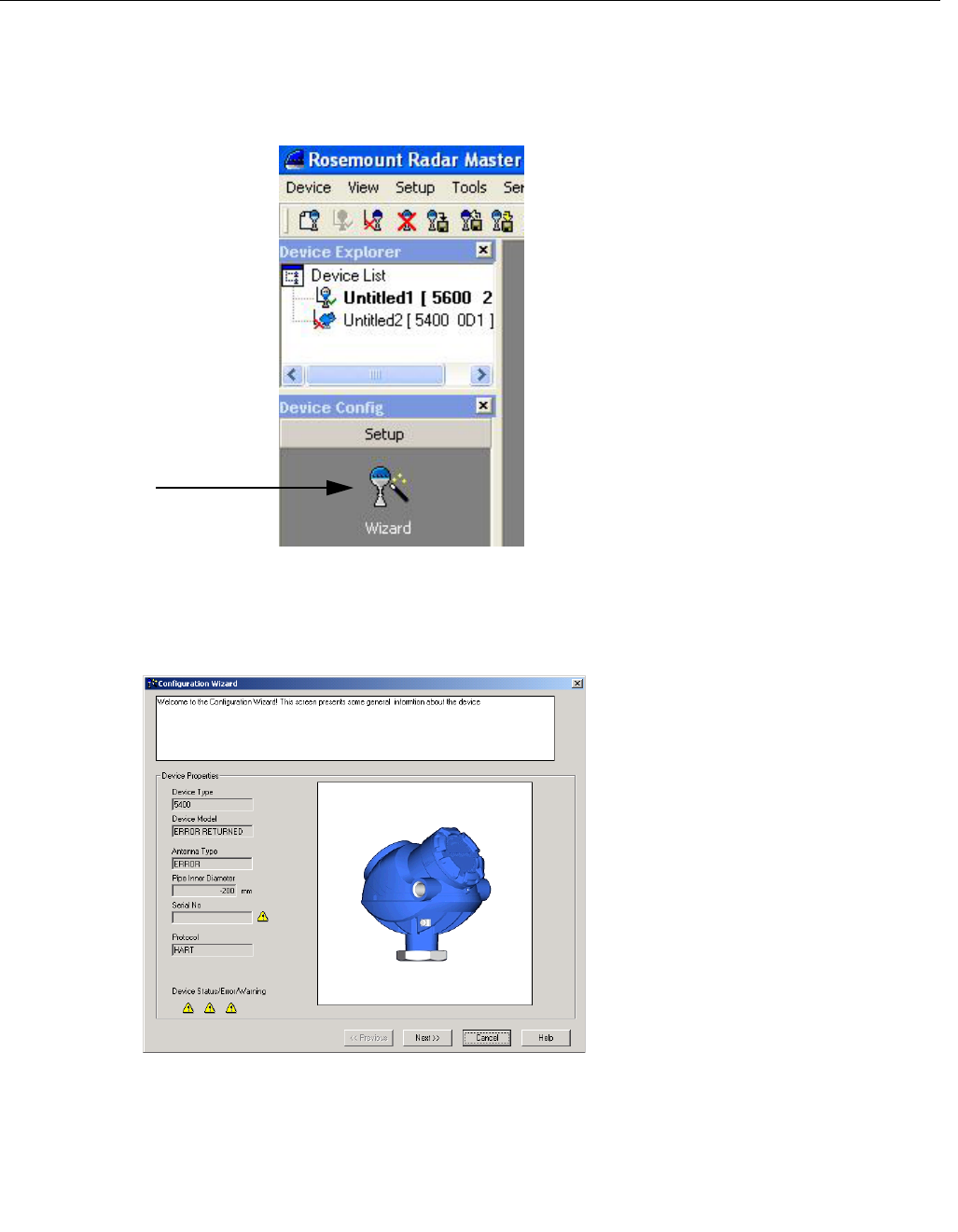
Reference Manual
00809-0100-4026, Rev AA
November 2003
Rosemount 5400 Series
4-6
Preliminary copy
Using the Setup Wizard To install a 5400 transmitter by using the installation Wizard do the following:
Figure 4-2. RRM workspace
Figure 4-3. RRM Wizard
1. Start the RRM software.
2. In the RRM workspace click the
Wizard icon (make sure that the
Basic section is open),
or
choose the View>Wizard menu
option.
Wizard icon
RRM/WIZARDICON.TIF
3. Click the Next button and follow the
instructions. Now you will be guided
through a number of dialogs
allowing you to configure the
transmitter.
RRM/WIZARD.TIF
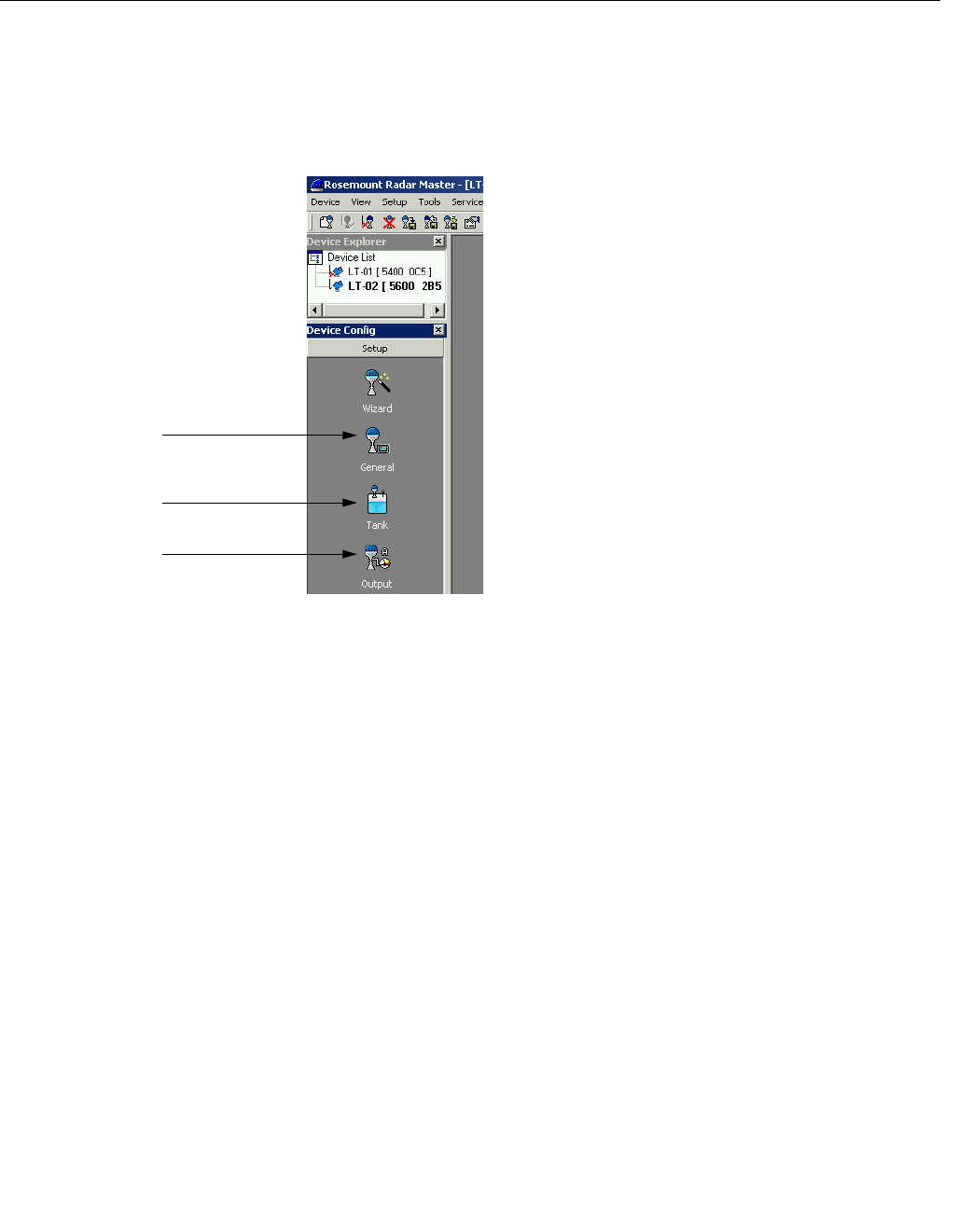
Reference Manual
00809-0100-4026, Rev AA
November 2003
4-7
Rosemount 5400 Series
Preliminary copy
Using the Setup
Function
To install a 5400 transmitter by using the Setup function do the following:
Figure 4-4. RRM workspace
1. Start the RRM software.
2. In the RRM workspace click the
appropriate icon. There are different
icons available for configuration of
Tank Geometry, Analog Output and
general settings such as
measurement units.
WORKSPACE_SETUP2.TIF
General
Tank Geometry
Analog Output
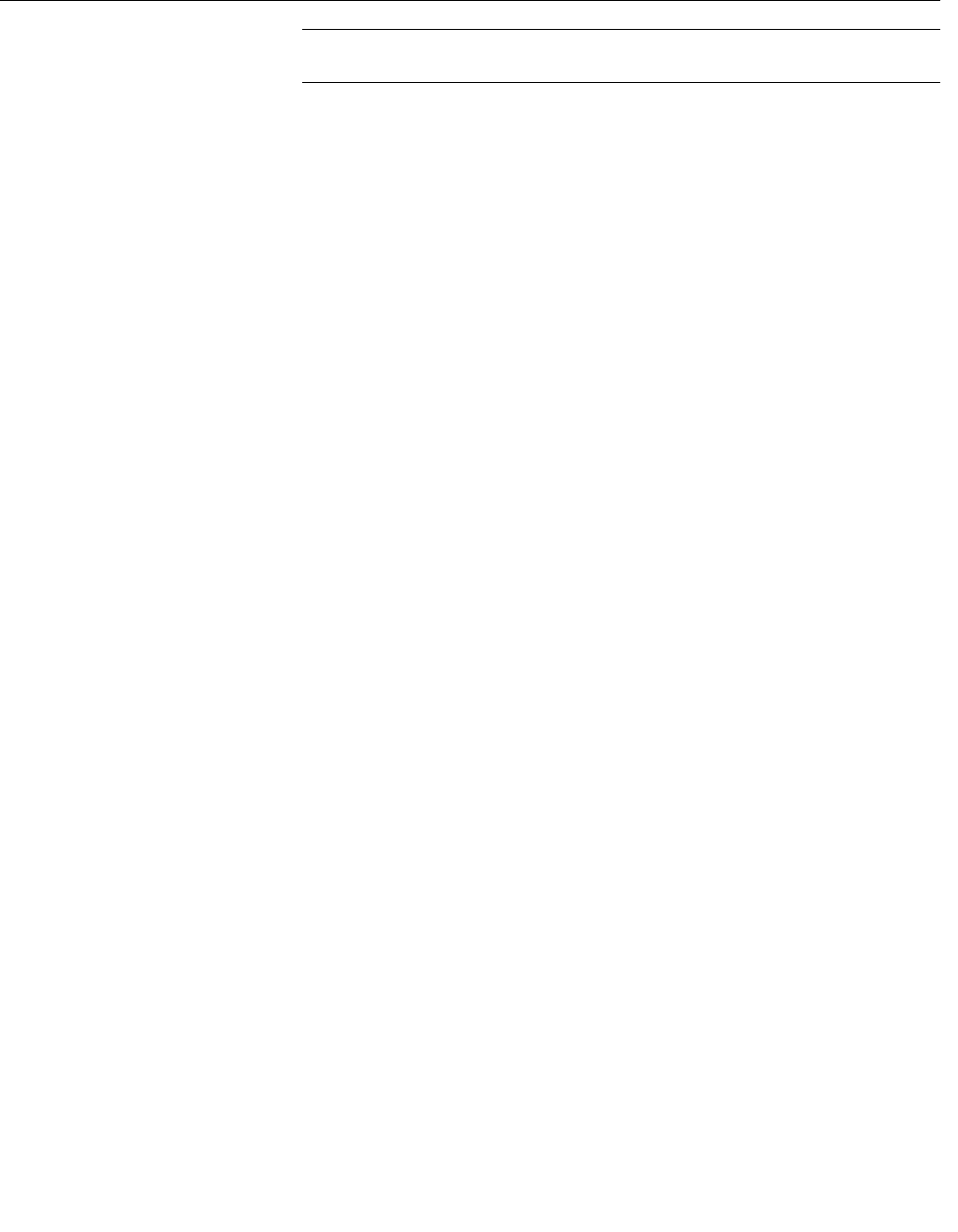
Reference Manual
00809-0100-4026, Rev AA
November 2003
Rosemount 5400 Series
4-8
Preliminary copy
AMS Kort introduktion till hur AMS används för att
konfigurera 5400.
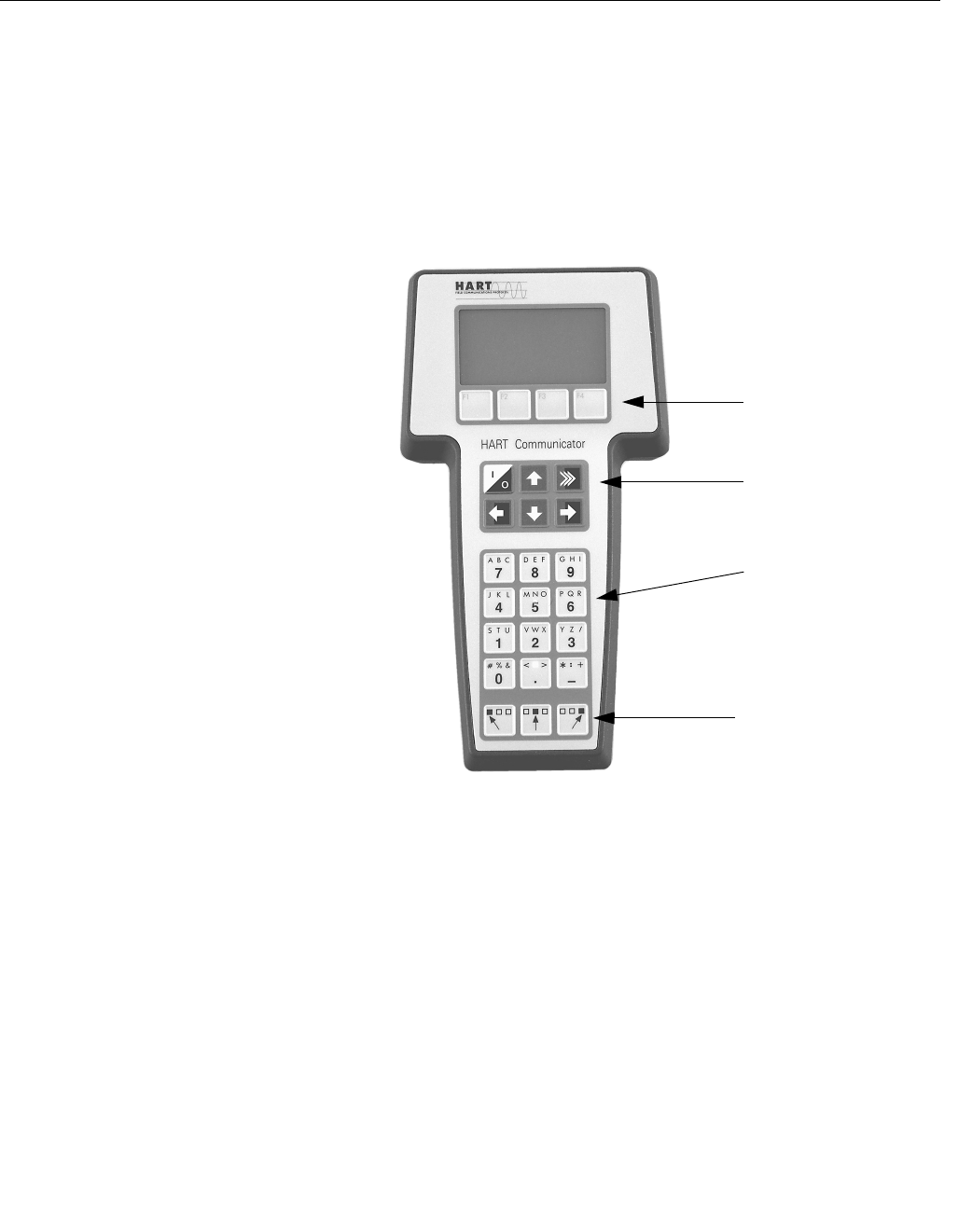
Reference Manual
00809-0100-4026, Rev AA
November 2003
4-9
Rosemount 5400 Series
Preliminary copy
MODEL 275/375 HART
COMMUNICATOR
The 5400 transmitter can be configured by using a HART 275 Communicator.
The menu tree is shown in Figure 4-6 on page 4-10.
Appendix C: HART Communicator provides brief instructions on the use of
the HART Communicator. For information on all the capabilities, refer to the
HART Communicator Product Manual.
Figure 4-5. The HART 275
Communicator.
Function Keys
Action Keys
Alphanumeric Keys
Shift Keys
275
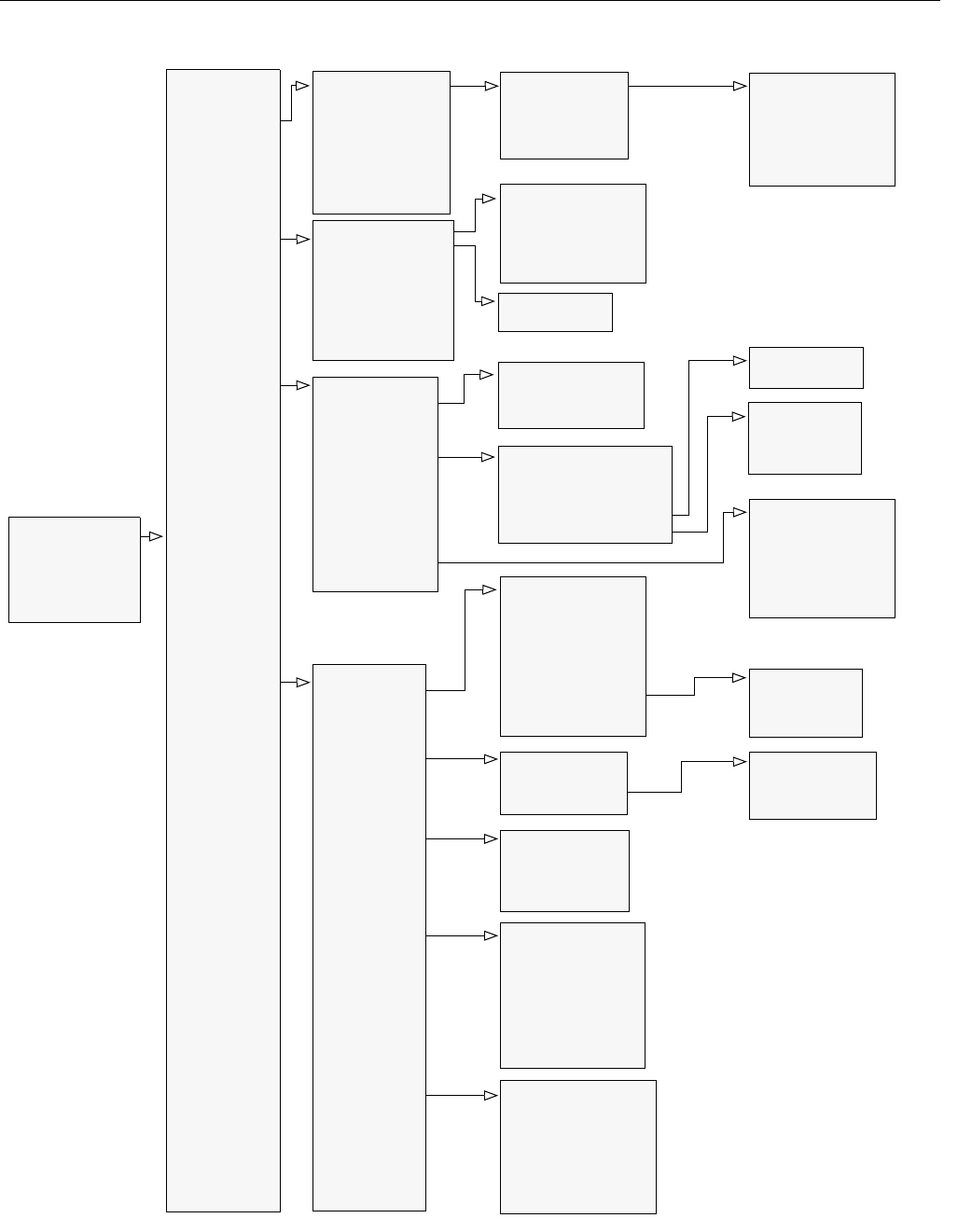
Reference Manual
00809-0100-4026, Rev AA
November 2003
Rosemount 5400 Series
4-10
Preliminary copy
Figure 4-6. HART Communicator Menu Tree
Online Menu
1 DEVICE SETUP
2PV
3AO
4LRV
5URV
1Device
Information
3 HART
4 Echo Tuning
5 Advanced
Tank
1 Variable mapping
2 Level
3 Distance
4 Level Rate
5 Signal Strength
6Volume
7 Internal Temp
1 Diagnostics
2 Simulation
3 Surface Search
4 Set as Empty
5 Restart Device
6 Lock/Unlock Device
7 Factory Settings
8 Trim/Calibrate AO
9 Advanced Service
1 Process
Variables
2Diag/Service
3 Basic Setup
4 Detailed Setup
5 Review Menus
1 Appl Grade Index
2 Measurem Units
3 Guided Setup
1 Distance Units
2 Level Rate Units
3 Volume Units
4 Temperature Units
1 Manufacturer
2 Device Model
3 Serial No
4Tag
5 Descriptor
6 Message
7Date
8 Revision #´s
9 SW versions
- HW Config
1 Poll Address
2Burst Mode
3 Burst Option
4 Num Req Preams
5 Num Resp Preams
1 Antenna Type
2 Pipe Diameter
3TCL
4 Upper Null Zone
5 Min Level Offset
6 Calibration Distance
7 Distance Offset
8 Tank Presentation
1 Found Echoes
2 Regist False Echoes
3 Min Threshold
4 Surface Search
5 Set as Empty
6 Create ATC
7 Add False Echo
8 Remove False Echo
9 Set Min Threshold
1 Variable re-map
2 PV is
3 SV is
4TV is
5QV is
- Level
- Distance
- Level Rate
- Signal Strength
- Volume
- Internal Temp
1 Device Status
2 Device Error
3 Device Warning
4 Measurem Status
5 AO Status
6 Volume Status
2LCD
1 Universal rev
2 Fld dev rev
3 Software rev
4 Hardware rev
1 LCD Variables
2 LCD Language
3 LCD Units
1 Tank Type
2 Tank Bottom Type
3 Tank Height
4 Pipe Diameter
5 Tank Environment
6 Volume
4 Tank Setup
1Simul Mode
2 Simul Distance
1 Distance Units
2 Level Rate Units
3 Volume Unit
4 Temperature Unit
1 Proc Condition
2 Product DC
1 Proc Condition
2 Product DC
1Calc. Method
2 Tank Diameter
3 Tank Length
4 Volume Offset
1PV is
2LRV
3URV
4 Alarm Mode Meas
5 Alarm Mode Fail
6 Disable Lmt Alm
7Damp Value
5AO Setup
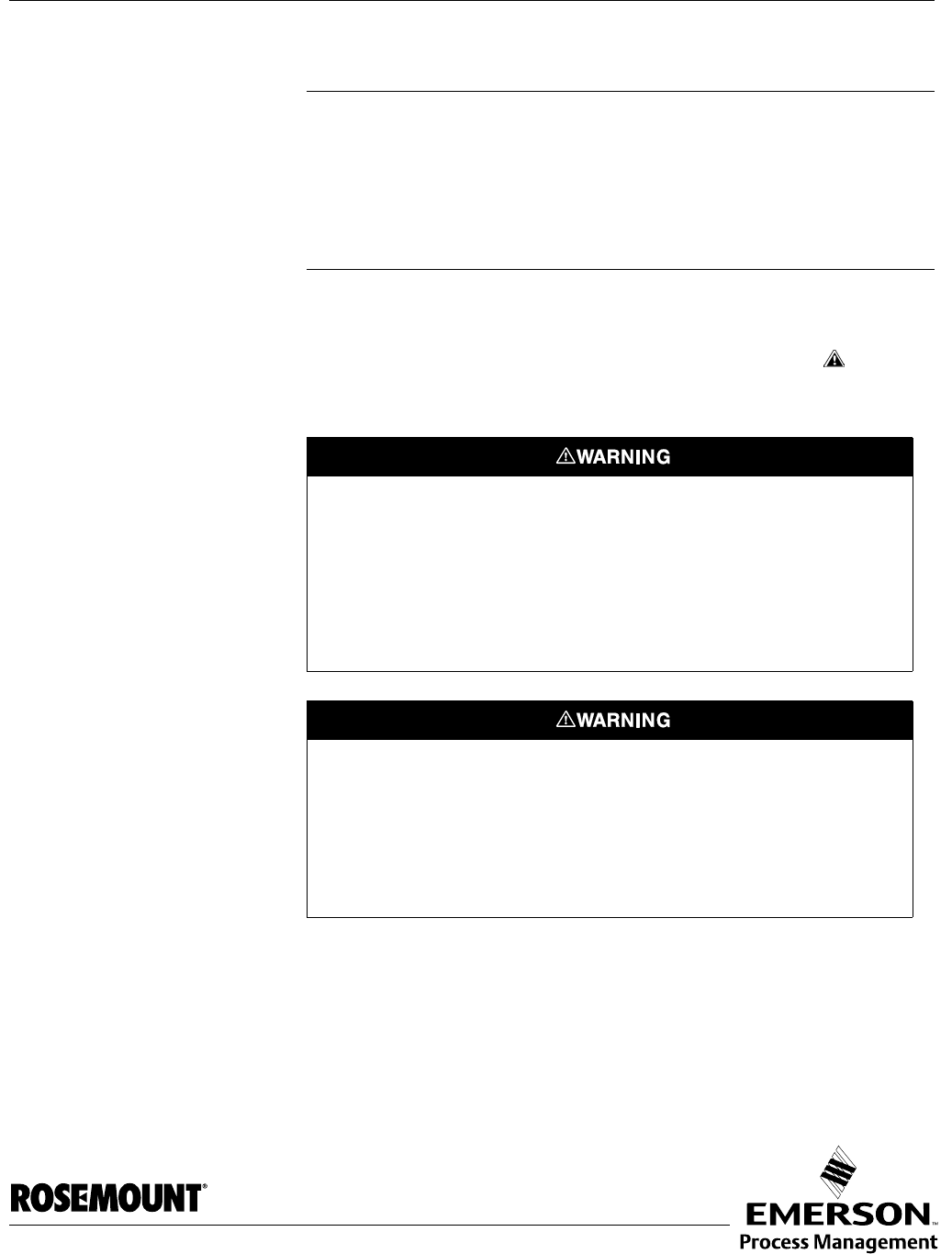
Reference Manual
00809-0100-4026, Rev AA
November 2003 Rosemount 5400 Series
www.rosemount.com
Preliminary copy
Section 5 Configuration/Start-Up
Safety messages . . . . . . . . . . . . . . . . . . . . . . . . . . . . . . . . . page 5-1
Overview . . . . . . . . . . . . . . . . . . . . . . . . . . . . . . . . . . . . . . . page 5-2
Basic Configuration . . . . . . . . . . . . . . . . . . . . . . . . . . . . . . page 5-3
Tank Geometry . . . . . . . . . . . . . . . . . . . . . . . . . . . . . . . . . . page 5-3
Analog Output . . . . . . . . . . . . . . . . . . . . . . . . . . . . . . . . . . . page 5-6
Echo Tuning . . . . . . . . . . . . . . . . . . . . . . . . . . . . . . . . . . . . page 5-8
Advanced Configuration . . . . . . . . . . . . . . . . . . . . . . . . . . page 5-10
SAFETY MESSAGES Procedures and instructions in this section may require special precautions to
ensure the safety of the personnel performing the operations. Information that
raises potential safety issues is indicated by a warning symbol ( ). Refer to
the safety messages listed at the beginning of each section before performing
an operation preceded by this symbol.
Explosions could result in death or serious injury:
Verify that the operating environment of the gauge is consistent with the appropriate
hazardous locations certifications.
Before connecting a HART-based communicator in an explosive atmosphere, make
sure the instruments in the loop are installed in accordance with intrinsically safe or
non-incendive field wiring practices.
Do not remove the gauge cover in explosive atmospheres when the circuit
is alive.
Failure to follow safe installation and servicing guidelines could result in death or
serious injury:
Make sure only qualified personnel perform the installation.
Use the equipment only as specified in this manual. Failure to do so may impair the
protection provided by the equipment.
Do not perform any service other than those contained in this manual unless you are
qualified.
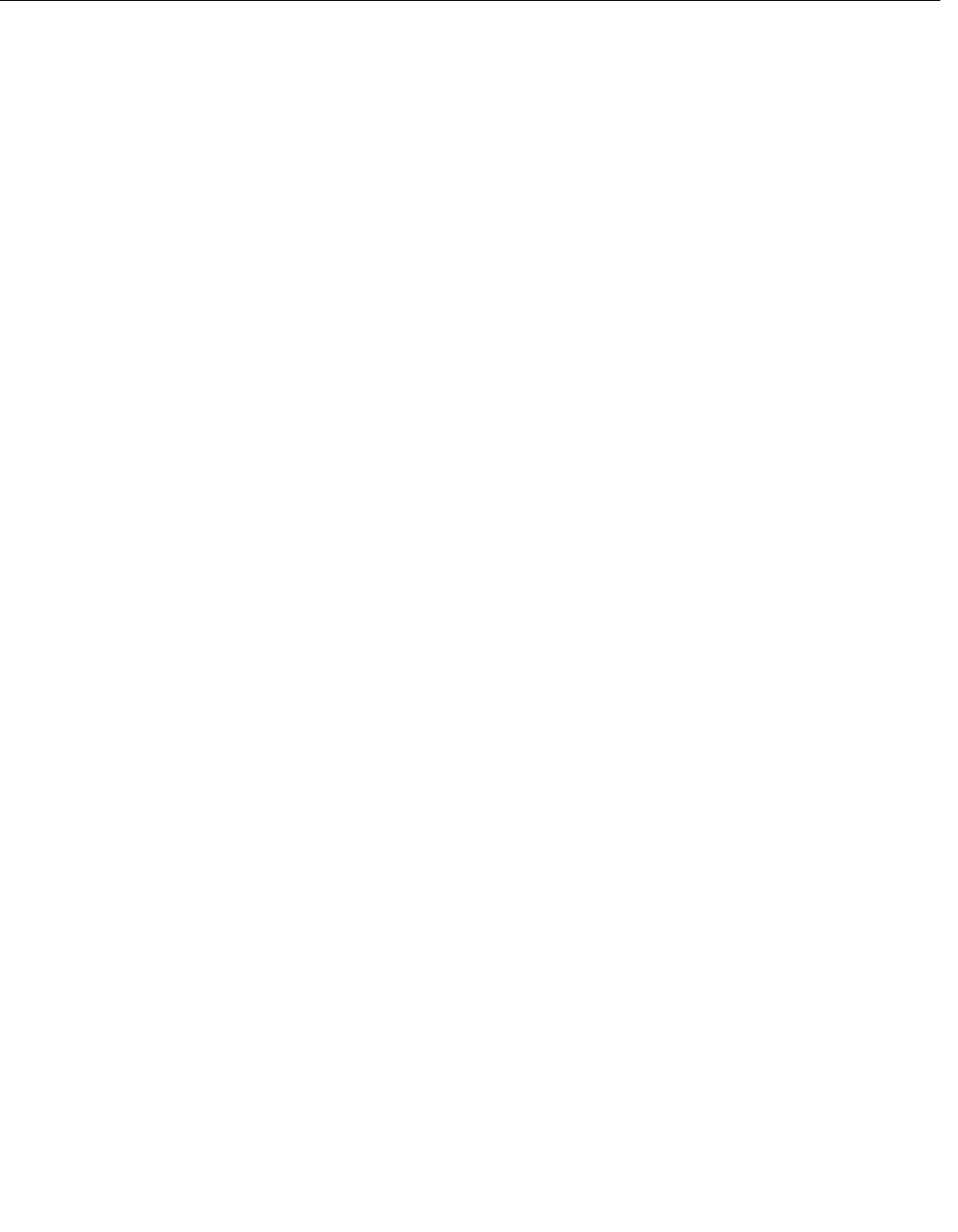
Reference Manual
00809-0100-4026, Rev AA
November 2003
Rosemount 5400 Series
5-2
Preliminary copy
OVERVIEW The Rosemount 5400 transmitter can be pre-configured according to the
ordering specifications in the Configuration Data Sheet.
Basic Configuration The Basic Configuration includes parameters for a standard configuration
which is sufficient in most cases. The Basic Configuration comprises the
following items:
• Measurement Units
• Remote Display Unit
• Tank Configuration
- Tank Geometry
- Environment/Process conditions
- Volume
• Analog Output
Echo Tuning Echo Tuning is used to handle special situations when there are objects in the
tank which cause disturbing echoes. The following tools are available to
handle such situations:
• Amplitude Threshold Curve (ATC)
• False Echo registration
Advanced Configuration For some applications further configuration is needed in addition to the Basic
Configuration. This may be due to the properties of the product or the shape
of the tank. Disturbing objects and turbulent conditions in the tank may also
require that advanced measures are taken.
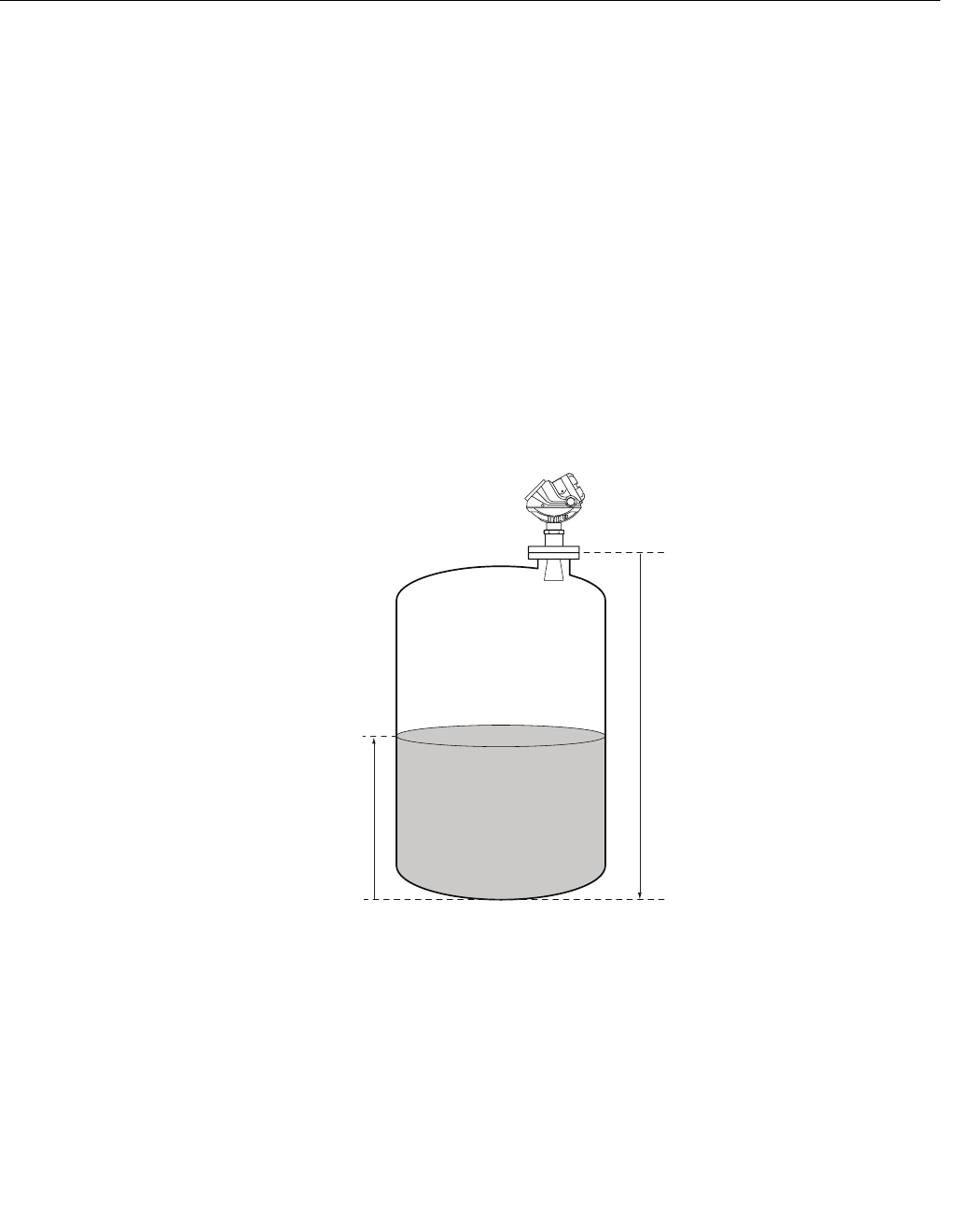
Reference Manual
00809-0100-4026, Rev AA
November 2003
5-3
Rosemount 5400 Series
Preliminary copy
BASIC CONFIGURATION
Measurement Units Specify the measurement units to be used for presentation of Distance, Level
Rate, Volume and Temperature values.
Display Unit Specify the parameters to be presented on the display panel.
Tank Geometry Tank Height
The Tank Height is the distance between the Upper Reference Point and the
Lower Reference Point close to or at the bottom of the tank. The transmitter
measures the distance to the product surface and subtracts this value from
the Reference Gauge Height to determine the level.
Figure 5-1. Tank Geometry
Tank Type and Tank Bottom Type
By defining Tank Type and Tank Bottom Type default values for some
parameters are set. This optimizes the transmitter for a specific combination
of Tank type and Tank Bottom Type. For tank types vertical cylinder and
cubical, all tank bottom types are valid. For tank types Horizontal Cylinder and
Spherical, the parameter Tank Bottom Type is not used. Select Tank Bottom
Type Flat Inclined if the bottom inclination is between 10 and 30 degrees. If
the inclination is less than 10 degrees but there are disturbing objects on the
tank floor (like heating coils) right beneath the transmitter this selection should
also be used.
Tank Height (R)
Product Level
Upper Reference Point
TANKGEOMETRY_STANDARD.EPS
Lower Reference Point
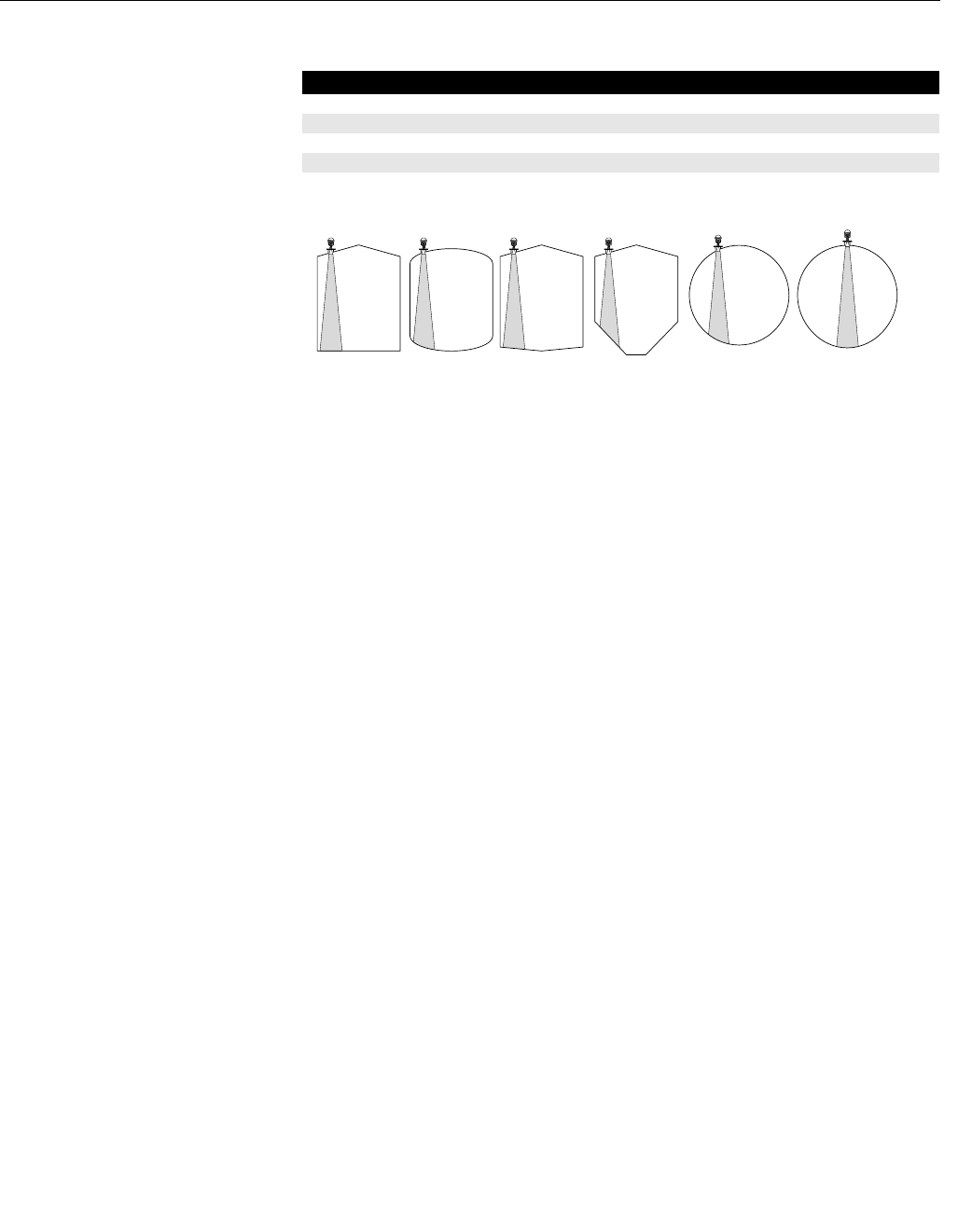
Reference Manual
00809-0100-4026, Rev AA
November 2003
Rosemount 5400 Series
5-4
Preliminary copy
Pipe Diameter
When the transmitter is mounted in a still pipe the inner diameter of the pipe
must be specified. The Pipe Diameter is used to compensate for the lower
microwave propagation speed inside the pipe. An incorrect value will give a
scale factor error. If locally supplied still-pipes are used, make sure the inner
diameter is noted before the pipe is installed.
This option is only available when the transmitter is configured for Antenna
Type Pipe or User Defined.
Table 5-1. Tank Type and Tank Bottom Type
Tank Type Tank Bottom Type
Vertical Cylinder Flat, Dome, Cone, Flat inclined
Horizontal Cylinder Flat, Dome, Cone, Flat inclined
Spherical
Cubical Flat, Dome, Cone, Flat inclined
5600_C_01A.EPS
Flat Dome ConeFlat inclined Spherical Spherical
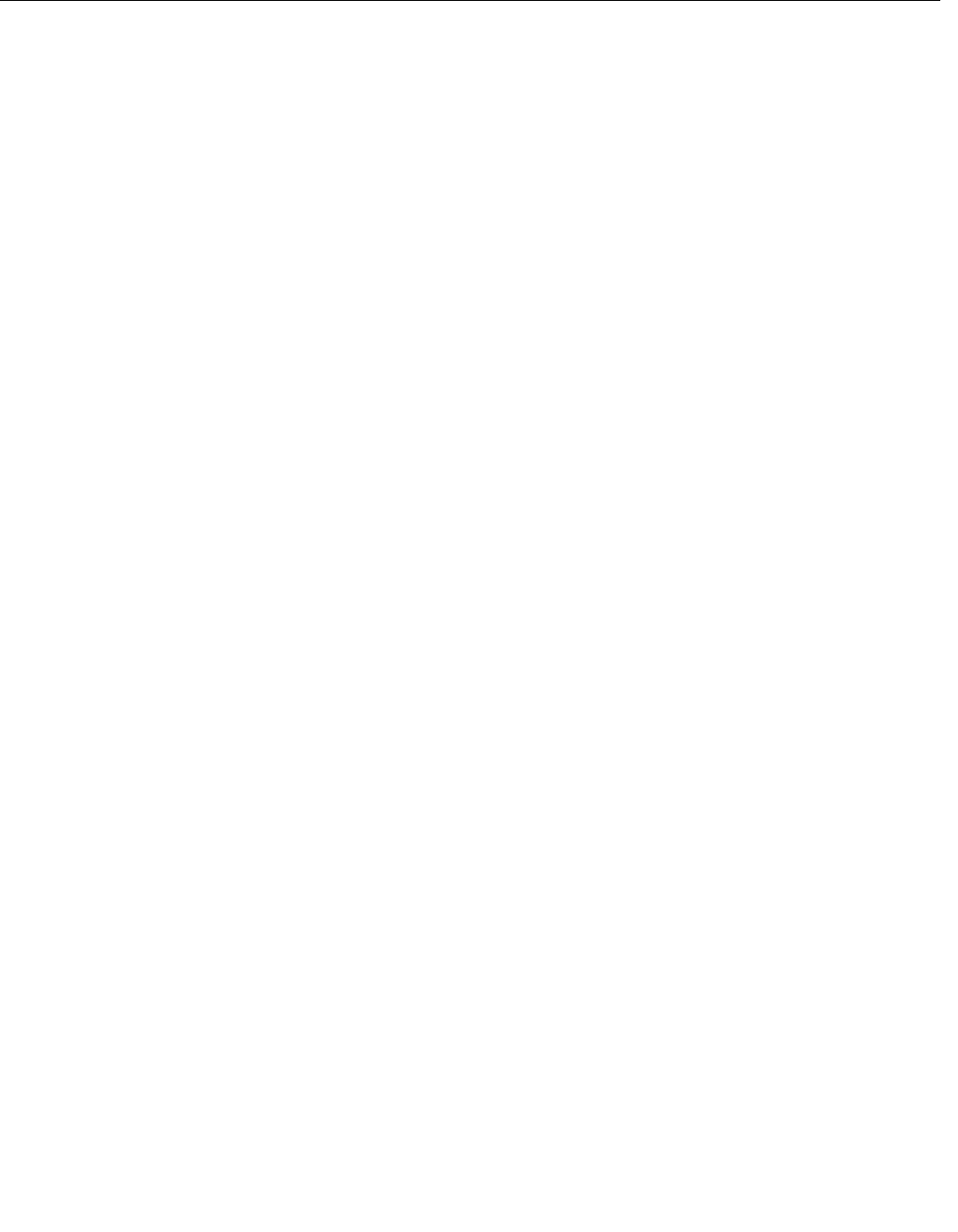
Reference Manual
00809-0100-4026, Rev AA
November 2003
5-5
Rosemount 5400 Series
Preliminary copy
Process Conditions Describe the conditions in your tank according to the Tank Environment
parameters for Process Conditions listed below. For best performance choose
only if applicable and not more than two options.
Rapid Level Changes
Optimize the transmitter for measurement conditions where the level changes
quickly due to filling and emptying of the tank. A standard configured
transmitter is able to track level changes of up to 4 inch/s (100 mm/s). When
the Rapid Level Changes check box is marked, the transmitter can track level
changes of up to 8 inch/s (200 mm/s).
Turbulent Surface
This parameter should be used if the tank shows a turbulent surface. The
reason for the turbulence might be splash loading, agitators, mixers, or boiling
product. Normally the waves in a tank are quite small and cause local rapid
level changes. By setting this parameter the performance of the transmitter
will be improved when there are small and quickly changing amplitudes and
levels.
Foam
Setting this parameter optimizes the gauge for conditions with weak and
varying surface echo amplitudes.
Solid Products
Setting this parameter optimizes the transmitter for solid products, for
example concrete or grains, which are not transparent for radar signals. For
instance, this parameter can be used when the application is a silo with
product buildup.
Product Dielectric Range
The Dielectric Constant is related to the reflectivity of the product. By setting
this parameter measurement performance can be optimized. However, the
transmitter will still be able to perform well even if the actual Dielectric
Constant differs from the configured value.
Volume The Volume Calculation is performed by using a predefined tank shape.
To configure the Model 5400 transmitter for volume calculations you have to
choose a Volume Calculation method.
For volume calculations you can choose one of the standard tank shapes:
Sphere, Horizontal Cylinder, Vertical Cylinder, Horizontal Bullet or Vertical
Bullet.
Enter the following parameters:
• Tank diameter (and the length if it is a horizontal tank).
• Volume Offset: Use this parameter if you do not want zero volume and
zero level to match (for example if you want to include volume below
the zero level.)
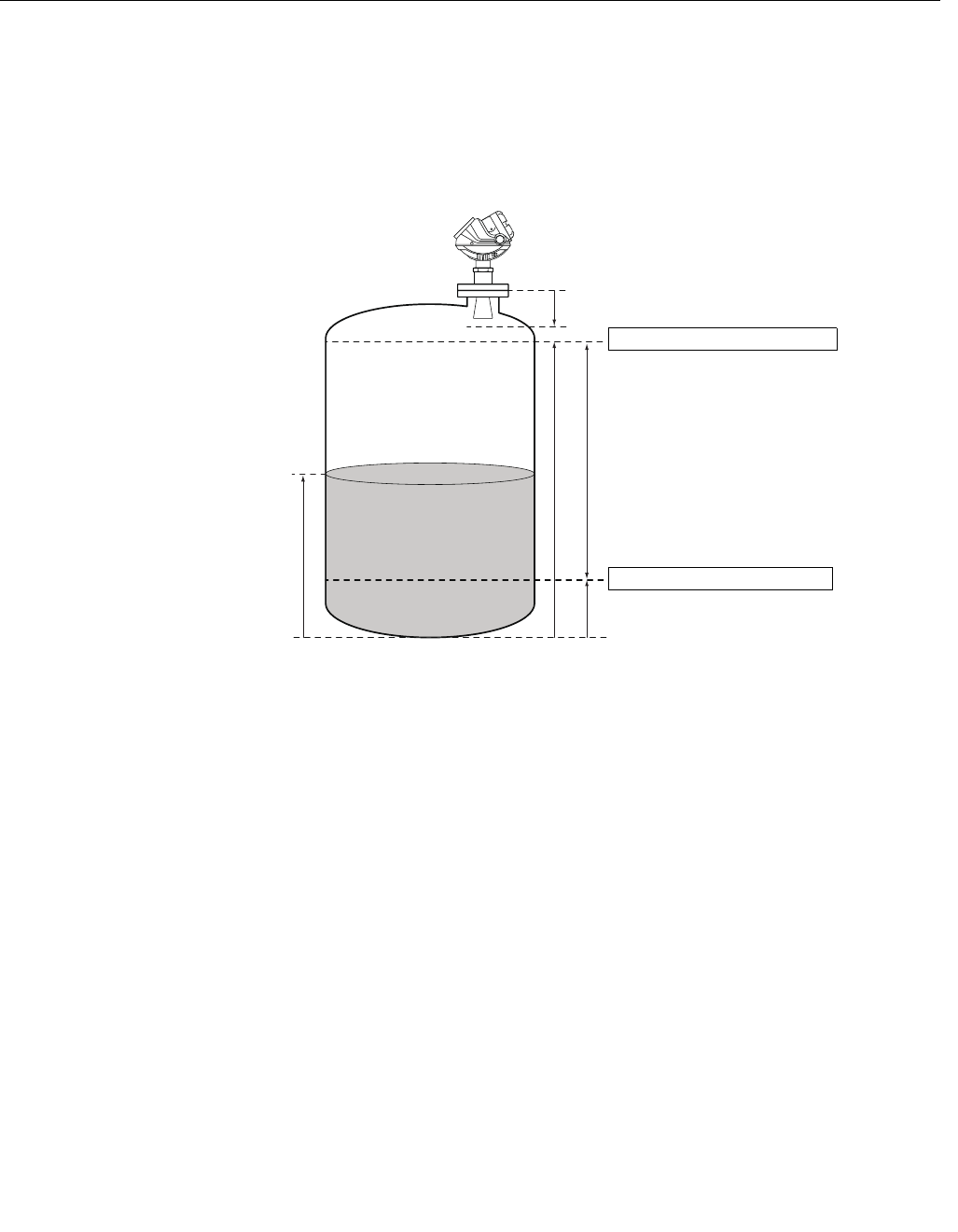
Reference Manual
00809-0100-4026, Rev AA
November 2003
Rosemount 5400 Series
5-6
Preliminary copy
Analog Output The 5400 series has the ability to handle two analog outputs which can be
configured separately.
Figure 5-2. Standard Range
Value settings
Output Source/Primary Variable
Select the source to control the analog output.
Upper/Lower Range Value
Enter the range values that correspond to the analog output values 4 and 20
mA. You can specify any values as long as the Upper Range Value is above
the Lower Range Value. If the measured value goes beyond the
measurement range, the transmitter enters the alarm mode.
The 4 mA Lower Range Value can be set to zero or any level above the Zero
Level.
The 20 mA Upper Range Value should not be within the Hold Off Distance. If
the 20 mA point is within the Hold Off Distance the full range of the analog
output is not used, see “Hold Off Distance” on page 5-11.
Alarm Mode
Choose the desired Alarm Mode. The Alarm Mode specifies the analog output
state when a measurement error occurs or when the measured value is out of
range.
High: the output current is set to 22 mA.
20 mA Upper Range Value (URV)
Product Level
4 mA Lower Range Value (LRV)
Range 0-100 %
ANALOGOUT_SATNDARD.EPS
Zero Level
(Lower Reference Point)
RTG Reference Point
Hold Off Distance
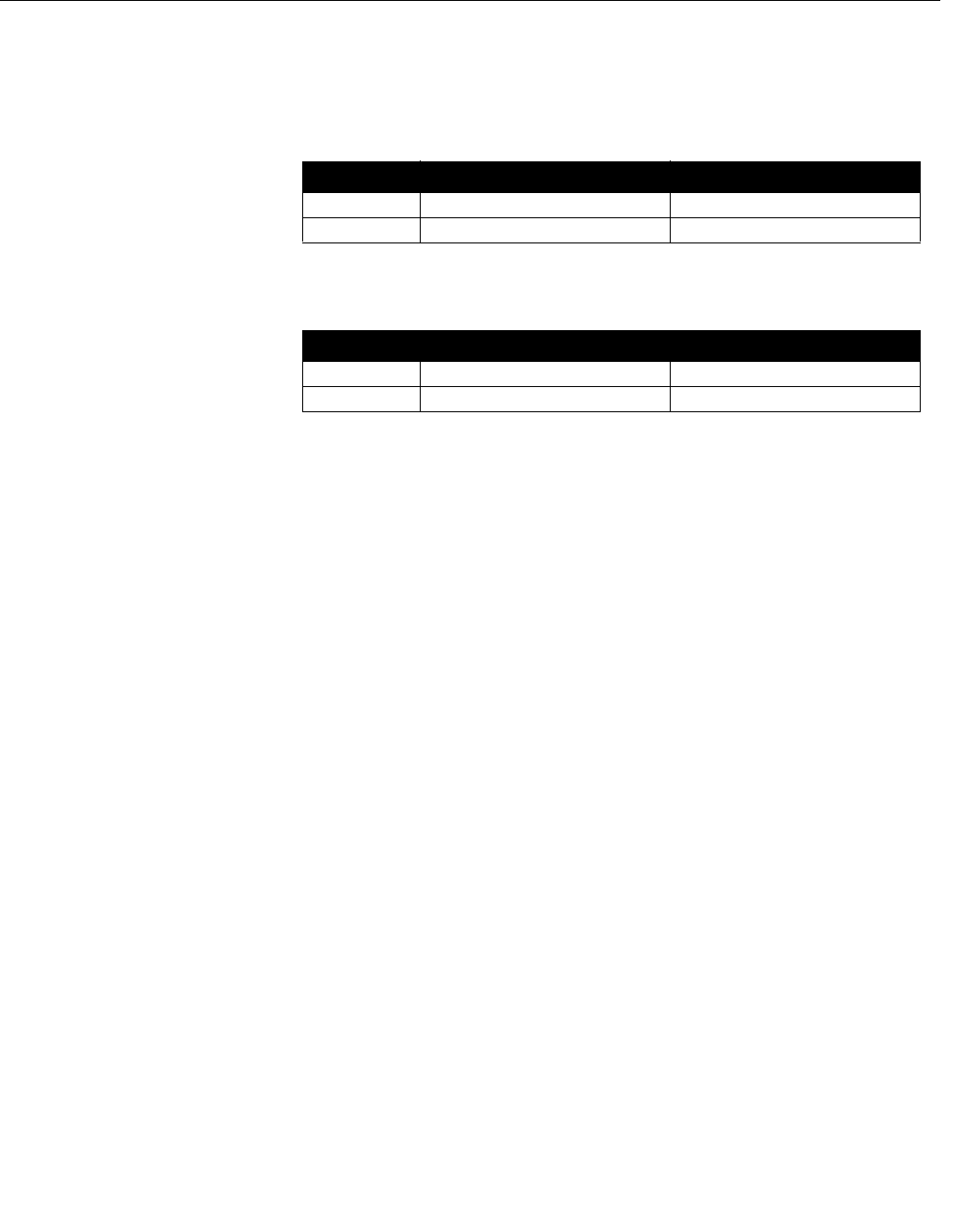
Reference Manual
00809-0100-4026, Rev AA
November 2003
5-7
Rosemount 5400 Series
Preliminary copy
Low: the output current is set to 3.8 mA.
Freeze Current: the output current is set to the present value at the time when
the error occurs.
Table 5-2. Analog Output: Standard Alarm Values vs. Saturation Values
Level 4–20 mA Saturation Values 4–20 mA Alarm Value
Low 3.9 mA 3.75 mA
High 20.8 mA 21.75 mA
Table 5-3. Analog Output: NAMUR-Compliant Alarm Values vs. Saturation
Values
Level 4–20 mA Saturation Values 4–20 mA Alarm Value
Low 3.8 mA 3.6 mA
High 20.5 mA 22.5 mA
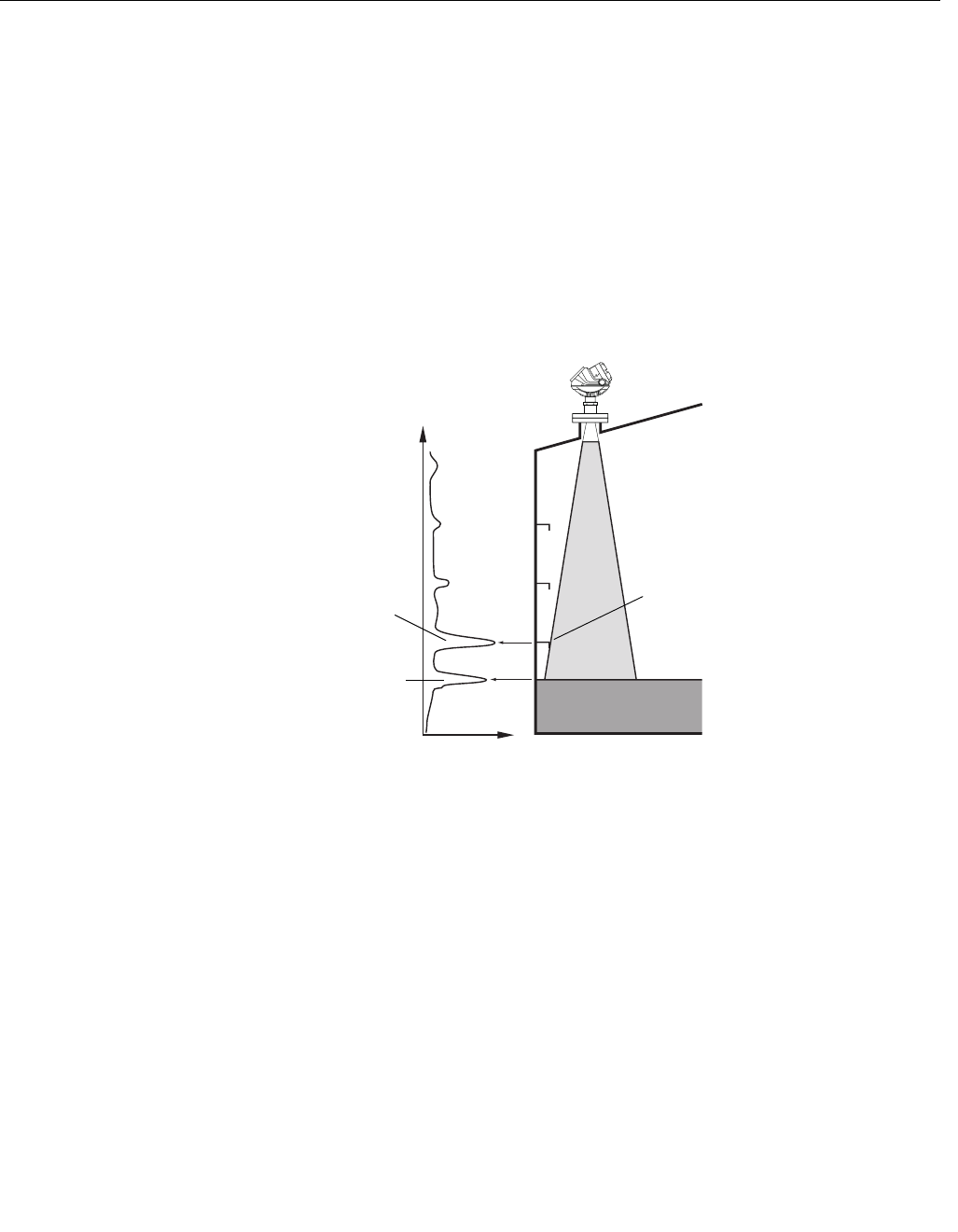
Reference Manual
00809-0100-4026, Rev AA
November 2003
Rosemount 5400 Series
5-8
Preliminary copy
ECHO TUNING There are different methods available for disturbance echo handling with the
Rosemount 5400 Series Transmitter:
• False Echo registration
• Customized Noise Threshold Table (Amplitude Threshold Curve (ATC)
Registration of False
Echoes
The False Echo function is used to improve the performance of the gauge
when the surface is close to a horizontal surface of a stationary object in the
tank. The object causes an echo when it is above the surface. When the
echoes from the surface and the object are close to each other, they might
interfere and cause a decrease in performance.
Figure 5-3.
The False Echo function allows you to register disturbing echoes caused by
objects in the tank in the memory of the gauge. When the surface is passing
by a disturbing object, the gauge can measure with a higher reliability, when
the position of the object is registered. This makes it possible to detect a
product surface close to a disturbance echo even if the surface echo is
weaker than the disturbing echo. See the following recommendations before
you register new interfering echoes:
• Make sure that a correct amplitude threshold is set before you register
any disturbance echoes.
• Keep the number of registered echoes to a minimum.
• Compare the list of interfering echoes with the tank drawing or by
visible inspection of the tank. Note if there are objects like beams,
heating coils, agitators etc. which correspond to the found echoes. Only
register echoes which can be clearly identified as objects in the tank.
• Make sure that the level is stable before you register a disturbance
echo. A fluctuating level may indicate a temporary disturbance which is
not due to an interfering object.
FALSE_ECHOES.EPS
False echo
Surface echo
Disturbing
object
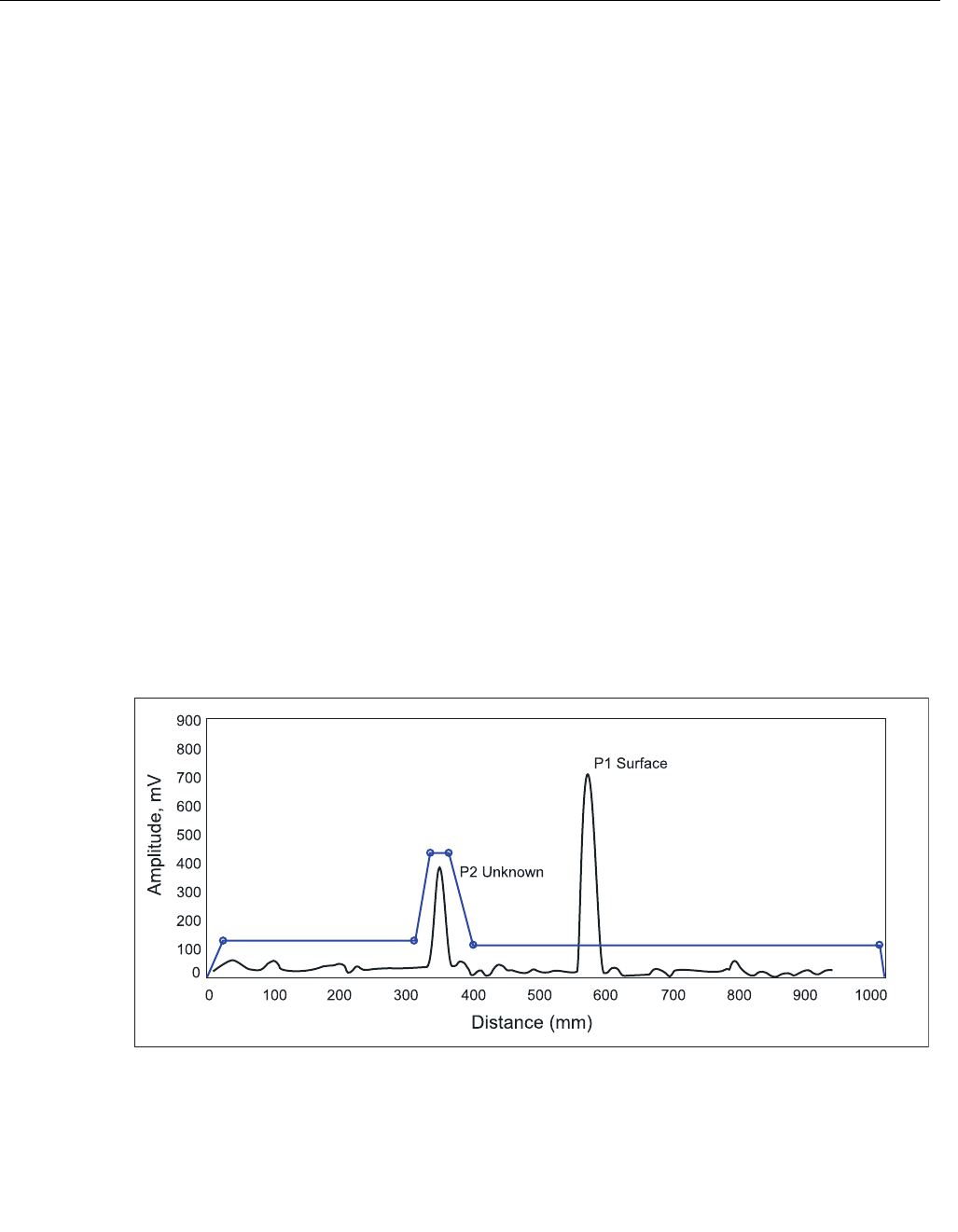
Reference Manual
00809-0100-4026, Rev AA
November 2003
5-9
Rosemount 5400 Series
Preliminary copy
• Do not register a disturbance echo if the amplitude is below the general
amplitude threshold.
• Do not register a disturbance echo if the amplitude is significantly
smaller than the amplitude of the surface echo when the surface is at
the same level as the disturbance. (In some cases weak disturbance
echoes can be filtered out by creating a noise threshold table.
• It may be necessary to register new disturbance echoes at a later stage
when objects have become visible due to surface movement.
Amplitude Threshold
Curve
You can filter out weak disturbing echoes by creating a noise threshold table.
This technique should only be used in special situations, for example at the
bottom of tanks with weak disturbing echoes. In such tanks the transmitter
may lock at disturbances close to the bottom when the tank is empty. Setting
up a noise threshold in this region will guarantee that the transmitter starts
tracking the surface when the tank is filled again. Make sure that the surface
echo amplitude in the bottom region is higher than the noise threshold.
This function can also be used in areas where there occasionally are strong
echoes present, i.e. to block the device from tracking "wall bounce echoes",
moving cleaning gun, wide mixer blades and product mist from spray nozzles.
For those large areas registering a False Echo may not be sufficient.
Furthermore, the ATC-table can be used to remove influence from the tank
nozzle or a still pipe inlet at the top of the tank.
Do not create noise thresholds around echoes which are already registered
as interfering echoes (see “Registration of False Echoes” on page 5-8).
The ATC function is available in the Rosemount Radar Master software.
Figure 5-4.
DRAFT
SPECTRUM_ATC.EPS
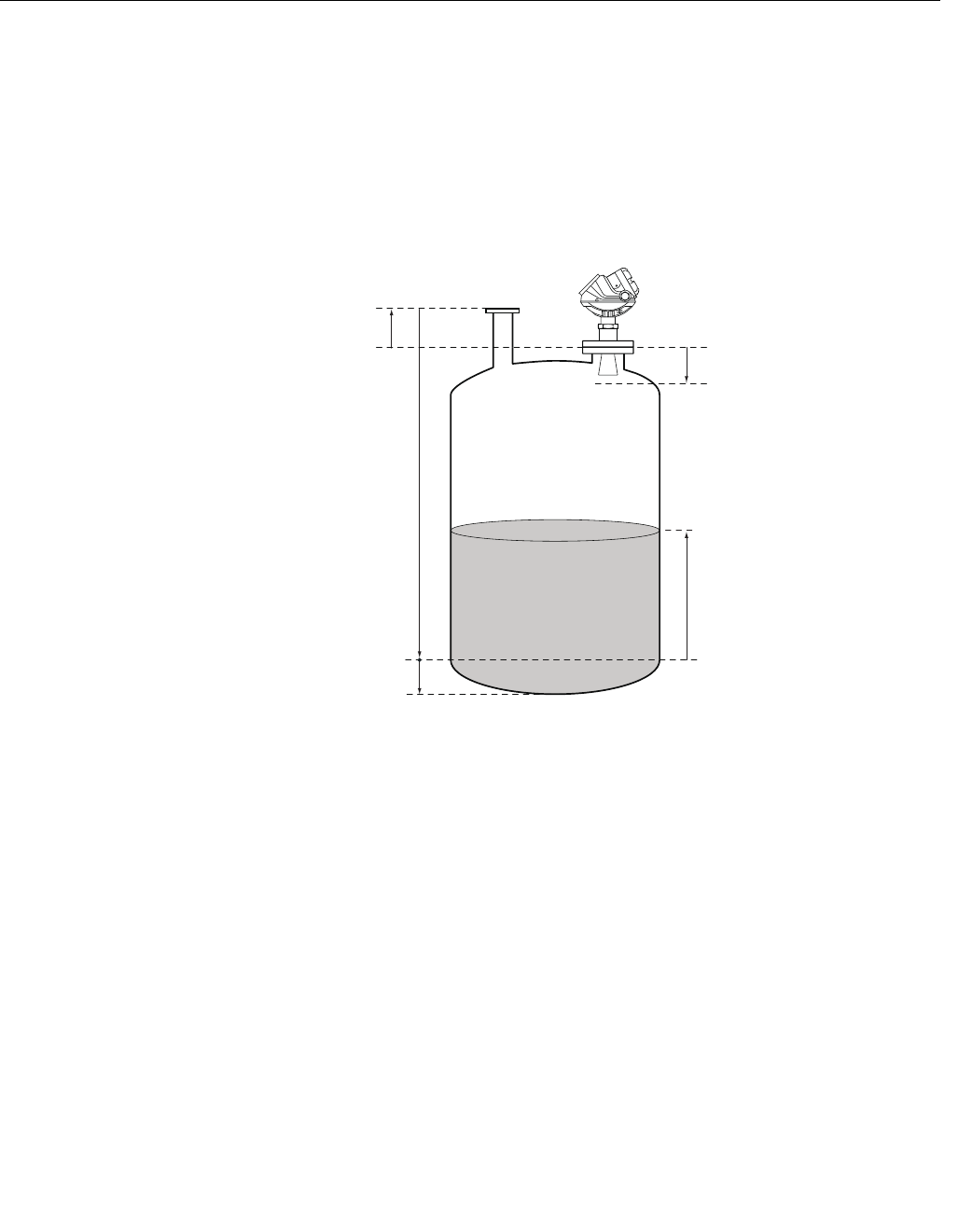
Reference Manual
00809-0100-4026, Rev AA
November 2003
Rosemount 5400 Series
5-10
Preliminary copy
ADVANCED
CONFIGURATION
The advanced transmitter configuration includes settings which can be used
to fine tune the transmitter when standard settings are not sufficient for
optimum performance.
Advanced Tank
Geometry
Figure 5-5. Advanced Tank Geometry
Distance Offset (G)
The Distance Offset is used when the measured level by the gauge should
correspond with the level value obtained by hand-dipping.
The Distance Offset (G) is defined as the distance between the upper
reference point and the flange (the flange is referred to as the Transmitter’s
Reference Point). You can use the Distance Offset to specify your own
reference point at the top of the tank. Set the Distance Offset to zero if you
want the flange as upper reference point. The Distance Offset is defined as
positive if you use an upper reference point above the Transmitter’s
Reference Point.
Minimum Level Offset (C)
The Minimum Level Offset (C) defines a lower null zone which extends the
measurement range beyond the Zero Level Reference Point down to the tank
bottom. The Minimum Level Offset is defined as the distance between the
Zero Level (Tank Level Reference Point) and the minimum accepted level at
the tank bottom. Set the Minimum Level Offset to zero if you use the tank
bottom as Zero Level Reference Point. This case corresponds to the standard
Tank Geometry configuration.
Tank Height (R)
Product Level
Upper Reference Point
Zero Level
(Lower Reference Point)
TANKGEOMETRY_ADVANCED.EPS
Distance Offset (G)
Min LevelOffset (C)
RTG Reference Point
Hold Off Distance
(Upper Range Value)
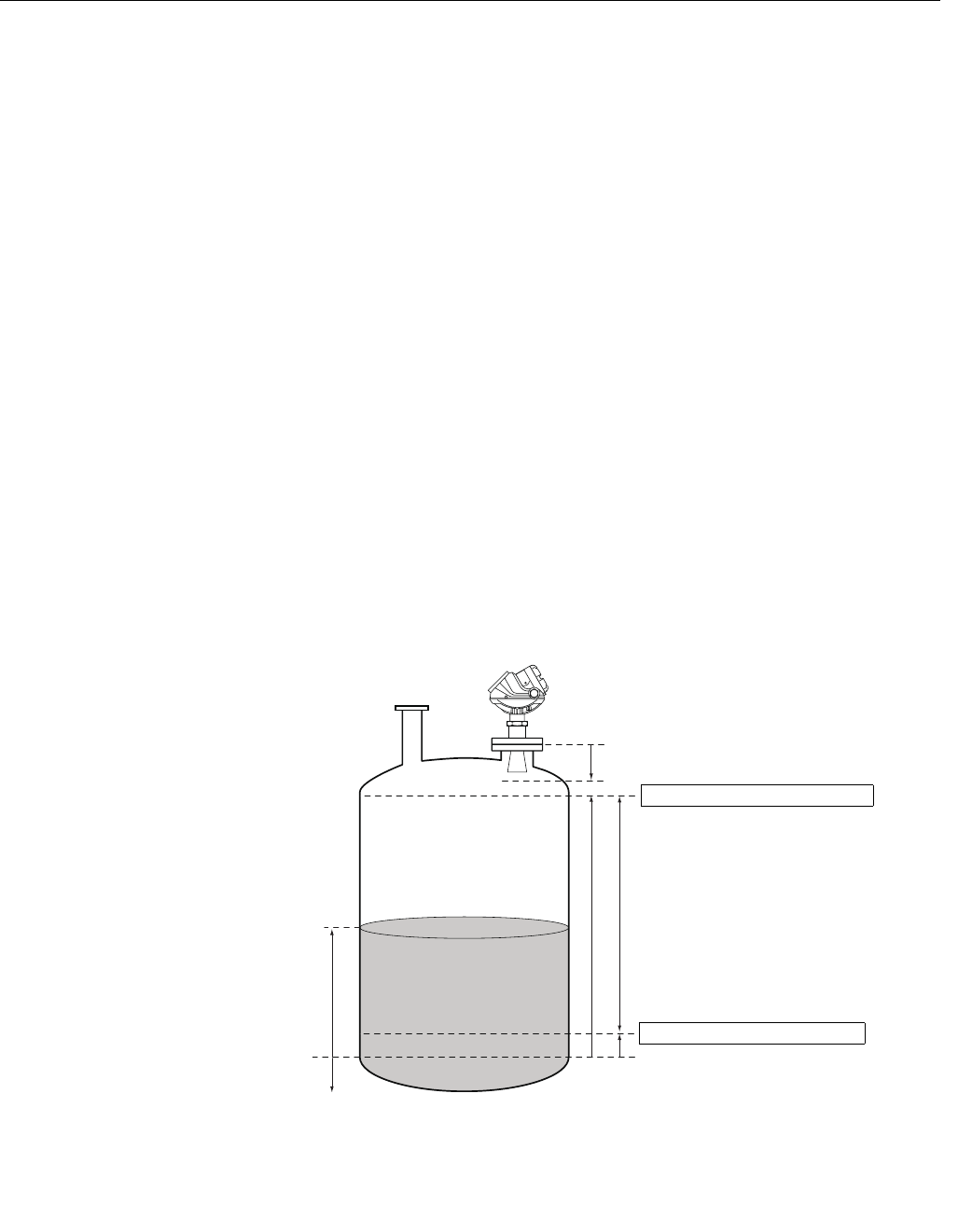
Reference Manual
00809-0100-4026, Rev AA
November 2003
5-11
Rosemount 5400 Series
Preliminary copy
Note that the Tank Height must be measured down to the Zero Level
Reference Point regardless if the Zero Level Reference Point is located at the
tank bottom or at an elevated point as the datum plate.
If the zero level is not defined as the tank bottom and instead is an elevated
point as the datum plate, you need to define the Minimum Level Offset.
Note: The Minimum Level Offset can not be negative.
Hold Off Distance
This parameter should only be changed if there are measurement problems in
the upper part of the tank. Such problems may occur if there are disturbing
objects close to the probe. By increasing the Hold Off Distance the measuring
range is reduced.
Calibration Distance
The Calibration Distance is by default set to zero. It is used to adjust the
transmitter so that measured levels match hand dipped product levels.
Normally a minor adjustment is necessary. There may for example be a
deviation between the actual tank height and the value stored in the
transmitter database.
Advanced Analog Output
Settings
Figure 5-6. Advanced Range
Value settings
20 mA Upper Range Value (URV)
Product Level
4 mA Lower Range Value (LRV)
Range 0-100 %
ANALOGOUT_ADVANCED.EPS
Zero Level
(Lower Reference Point)
RTG Reference Point
Min LevelOffset (C)
Hold Off Distance
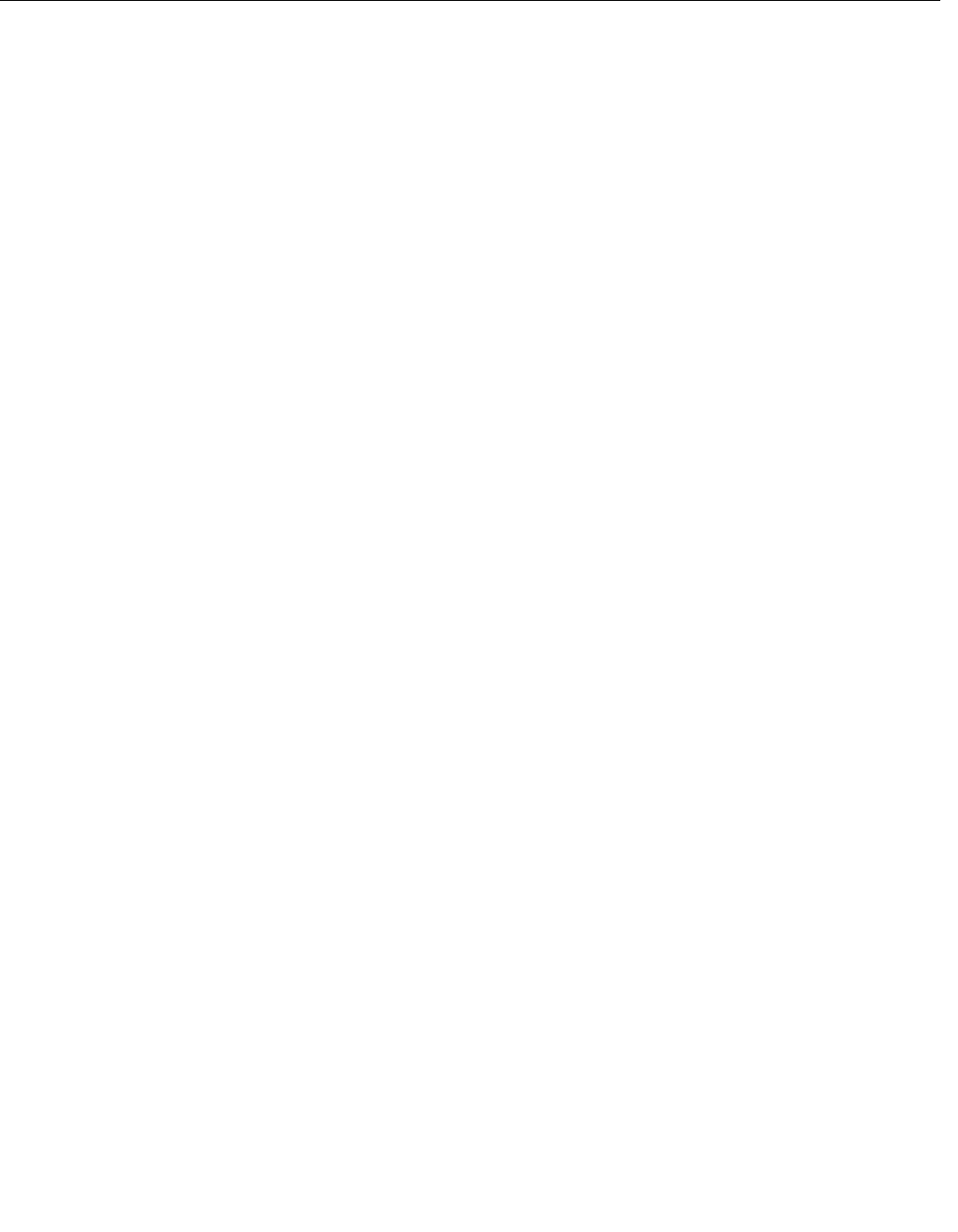
Reference Manual
00809-0100-4026, Rev AA
November 2003
Rosemount 5400 Series
5-12
Preliminary copy
Antenna Type The transmitter is designed to optimize measurement performance for each
available antenna type.
This parameter is pre-configured at factory but may need to be set if a
non-standard antenna is used.
Tank Connection Length The Tank Connection Length (TCL) parameter is adjusted for each antenna
type in order to optimize measurement performance. TCL is set automatically
for standard antennas. For non-standard antennas (antenna type User
Defined) the TCL value needs to be manually adjusted.
Empty Tank Handling The Empty Tank Handling functions handle situations when the surface echo
is close to the tank bottom:
• Tracking weak product echoes
• How to handle lost echoes
If the surface echo is lost the function makes the transmitter present a
zero-level measurement, and an alarm is activated unless this alarm has
been blocked.
Bottom Echo Visible
This parameter is automatically set depending on tank type and tank bottom
type. By setting this parameter the bottom echo will be treated as a
disturbance echo to facilitate tracking of weak surface echoes close to the
tank bottom. If this parameter is not set searching for a lost surface echo is
restricted to a region close to the tank bottom. Only set this parameter if the
bottom echo is visible.
Check if the gauge detects the tank bottom when the tank is empty before
marking the checkbox.
Empty Tank Detection Area
This function is activated by default if you have selected one of the following
Tank Bottom Types: Cone, Dome, Flat Inclined, or Unknown. This function
also requires that the Bottom Echo Visible checkbox is not marked. If it is
marked the function is disabled.
The transmitter will search for the surface echo within the Empty Tank
Detection Area. The Empty Tank Detection Area is calculated as a percentage
of Tank Height (R) + Minimum Level Offset (C) - Distance Offset (G). It has a
lower limit of 400 mm and a higher limit of 1000 mm. Used Empty Tank
Detection
Area is shown in Advanced Setup and can be adjusted manually if required.
Since the transmitter will search for the surface echo in the Empty Tank
Detection Area, it is important that there are no disturbances in this area. If
there are disturbances it may need to be filtered out.
Tank Bottom Projection
This function handles situations close to the tank bottom and may enhance
measurement performance in the tank bottom region. In this region the signal
from the actual tank bottom may in some cases be significantly stronger than
the measurement signal from the product surface.
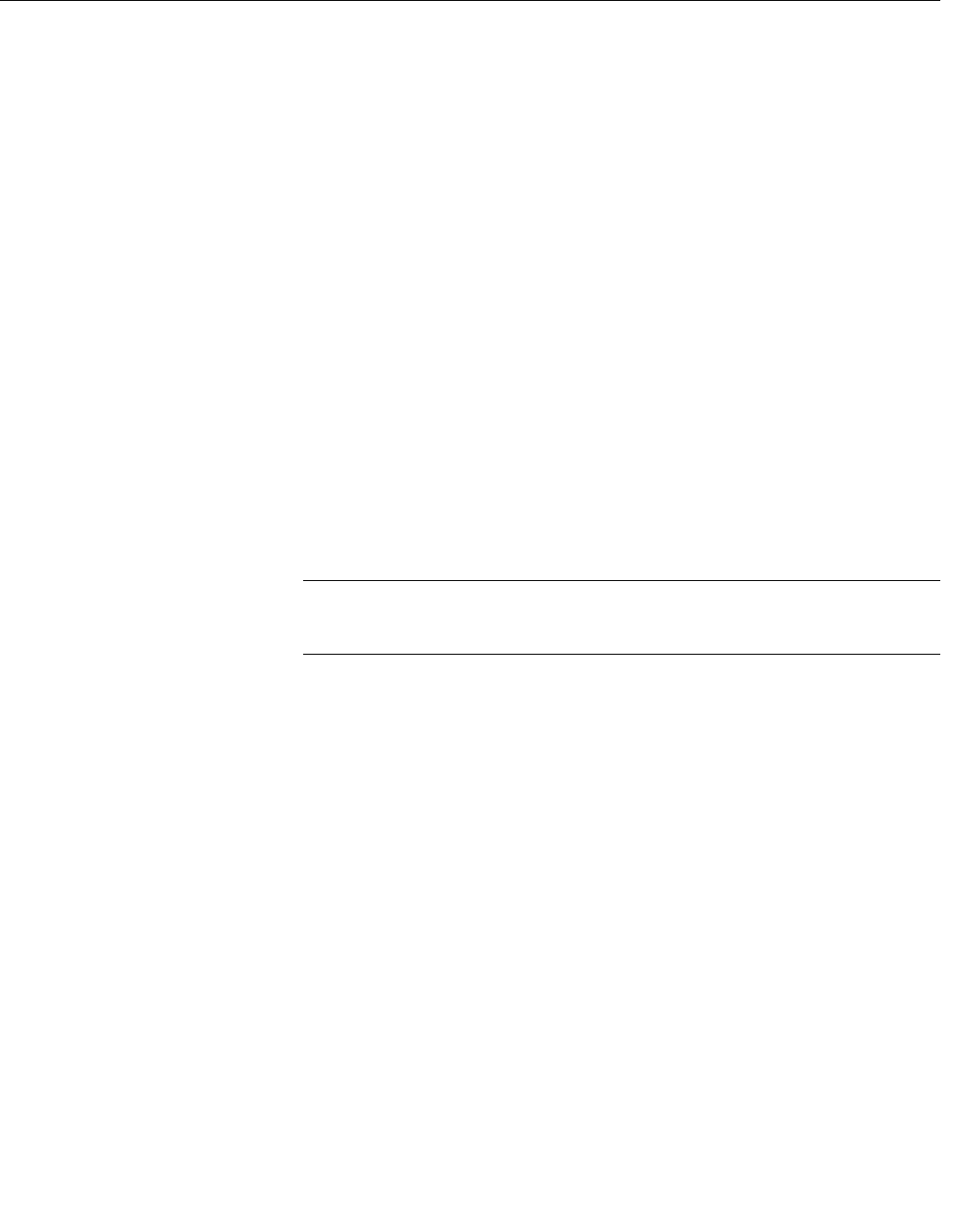
Reference Manual
00809-0100-4026, Rev AA
November 2003
5-13
Rosemount 5400 Series
Preliminary copy
Extra Echo
Extra Echo Detection is used for tanks with domed or conical bottom types
and when no strong echo from the tank bottom exists when the tank is empty.
When the tank is empty an echo beneath the actual tank bottom can
sometimes be seen.
Level Alarm is not set when Tank is Empty
If the echo from the product is lost in an area close to the tank bottom (Empty
Tank Detection Area), the device will enter empty tank state and an alarm is
triggered. (If the device is still able to measure the level, no alarm will be
triggered even if the level is close to the tank bottom.) Two types of alarms are
triggered:
• Invalid Level is set which can be seen in the Diagnostics window (see
Diagnostics)
• The Analog Out for level will go into Alarm Mode (see Output – Analog
Out 1 or Output – Analog Out 2).
Full Tank Handling Level Alarm is Not Set when Tank is Full
If the surface echo is lost close to the top of the tank, the level value will
normally be displayed as “invalid”. Set this parameter to suppress the “invalid”
display.
NOTE
By setting this parameter the analog output will not enter alarm mode for
invalid levels close to the antenna.
Full Tank Detection Area
This parameter defines a range where it is accepted to loose the echo from
the product. If the echo is lost in this range the tank is considered full (the
device enters Full Tank State) and the device will present max level indication.
When the tank is full the device looks in 2 x Full Tank Detection Area for the
product surface. When a new echo is found in this range it is considered to be
the product surface.
Level above Hold Off Distance Possible
Enable the checkbox if the level may rise above the Hold Off Distance (UNZ)
and you want to consider the tank as full in that case. Normally the device will
always be able to track the surface and the product level will never rise that
high. If the checkbox is not enabled and the surface is lost at the top of the
tank the device searches for a surface echo within the whole tank.
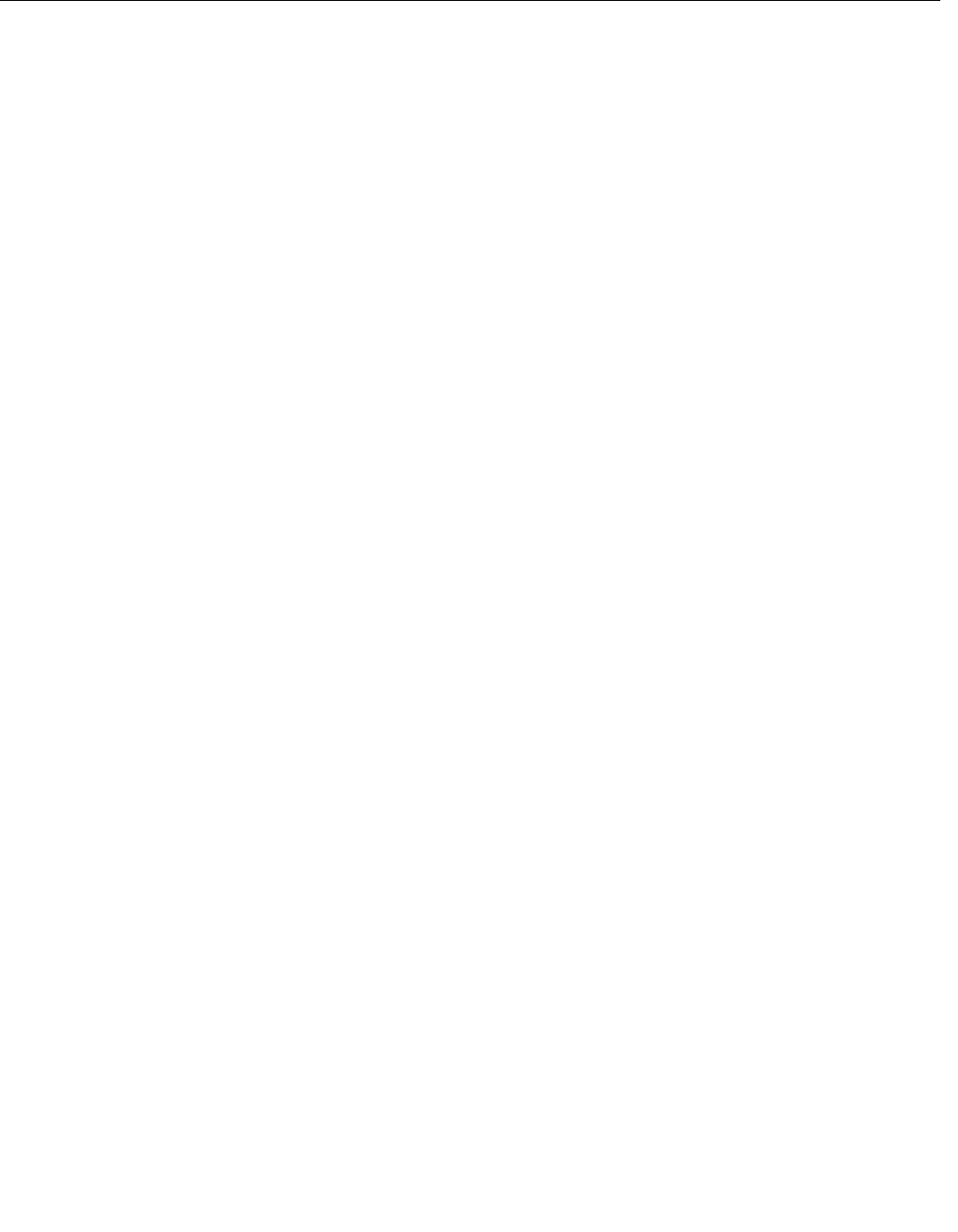
Reference Manual
00809-0100-4026, Rev AA
November 2003
Rosemount 5400 Series
5-14
Preliminary copy
Double Bounce Some radar waves are reflected against the tank roof and back to the surface
before they are detected by the transmitter. Normally, these signals have a
low amplitude and are therefore neglected by the transmitter. For spherical
and horizontal cylinder tanks, in some case the amplitude may be strong
enough to lead the transmitter to interpret the double bounce as the surface
echo. By setting the Double Bounce Possible parameter this type of
measurement situation may be improved. This function should only be used if
the problem of double bounces can not be solved by changing the mechanical
installation.
Surface Echo Tracking Slow Search
This variable controls how to search for the surface if a surface echo is lost.
With this parameter set the transmitter starts searching for the surface at the
last known position, and gradually increases the width of the search region
until the surface is found. If this variable is not set the transmitter searches
through the whole tank. This parameter may typically be used for tanks with
turbulent conditions.
Slow Search Speed
If the surface echo is lost, the transmitter starts to search around the last
known level to find the surface echo again. This parameter indicates how fast
it should expand the search window.
Double Surface
Indicates that there are two liquids or foam in the tank resulting in two
reflecting surfaces. The upper liquid or foam layer must be partly transparent
to the radar signal.
If this function is activated, you can specify which surface to select by using
the Select Lower Surface parameter.
Upper Product Dielectric Constant
This is the dielectric constant for the upper product if there is a Double
Surface situation. A more precise value results in better accuracy for the
lower surface level.
Select Lower Surface
This function should only be used if Double Surface is set. If Select Lower
Surface is set the lower surface will be presented as the product surface. If
not set the upper surface is tracked.
Echo Timeout
Use Echo Timeout to define the time in seconds before the transmitter will
start to search for a surface echo after it has been lost. After an echo has
been lost, the transmitter will not start searching or set Invalid Level until this
time has elapsed.
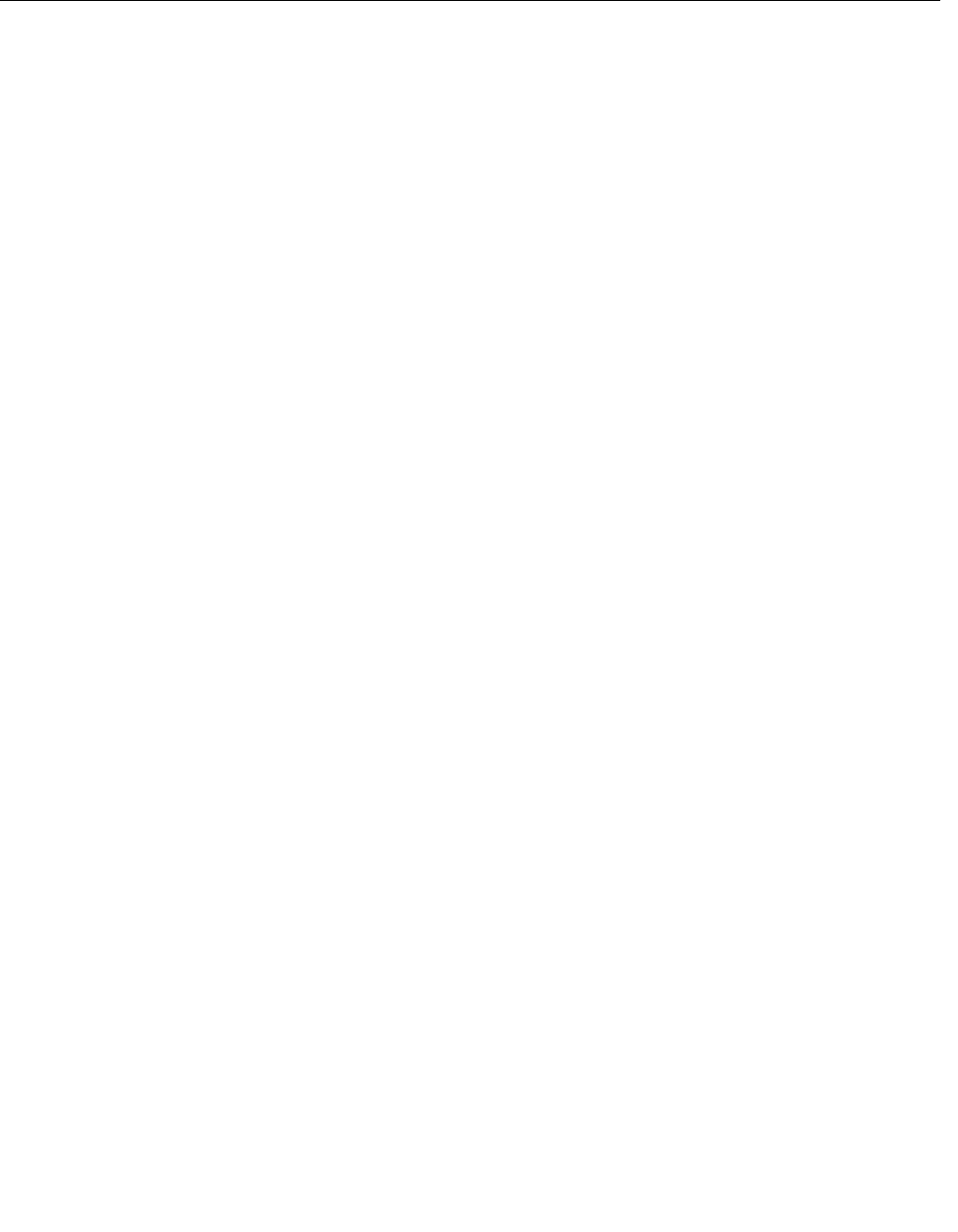
Reference Manual
00809-0100-4026, Rev AA
November 2003
5-15
Rosemount 5400 Series
Preliminary copy
Close Distance Window
This parameter defines a window centered at the current surface position in
which new surface echo candidates can be selected. The size of the window
is ±CloseDist. Echoes outside this window will not be considered as surface
echoes. The transmitter will without delay jump to the strongest echo inside
this window. If there are rapid level changes in the tank, the value of the Close
Distance Window could be increased to prevent the transmitter from missing
level changes. On the other hand, a too large value might cause the
transmitter to select an invalid echo as the surface echo.
Filter Settings Damping Value
The Damping Value defines the level value filtering rate. A low value will give
the new level value by adding a small portion (for instance 1%) of the level
change to the previous level value. A Damping Value setting typically takes
the latest measurement and presents it as the new level. This implies that a
low factor setting makes the level value steady but the gauge reacts slowly to
level changes in the tank. A high factor setting makes the gauge react quickly
to level changes but the level value can be somewhat jumpy.
Activate Jump Filter
If the surface echo is lost and a new surface echo is found, the Jump Filter
tells the transmitter to wait for some time before it jumps to the new echo.
During that time the new echo has to be a valid echo. The Jump Filter does
not use the Distance Filter Factor and can be used in parallel to the Least
Square Filter or the Adaptive Filter. The Jump Filter is typically used for
applications with turbulent surface and makes the echo tracking work
smoother as the level passes the agitator.
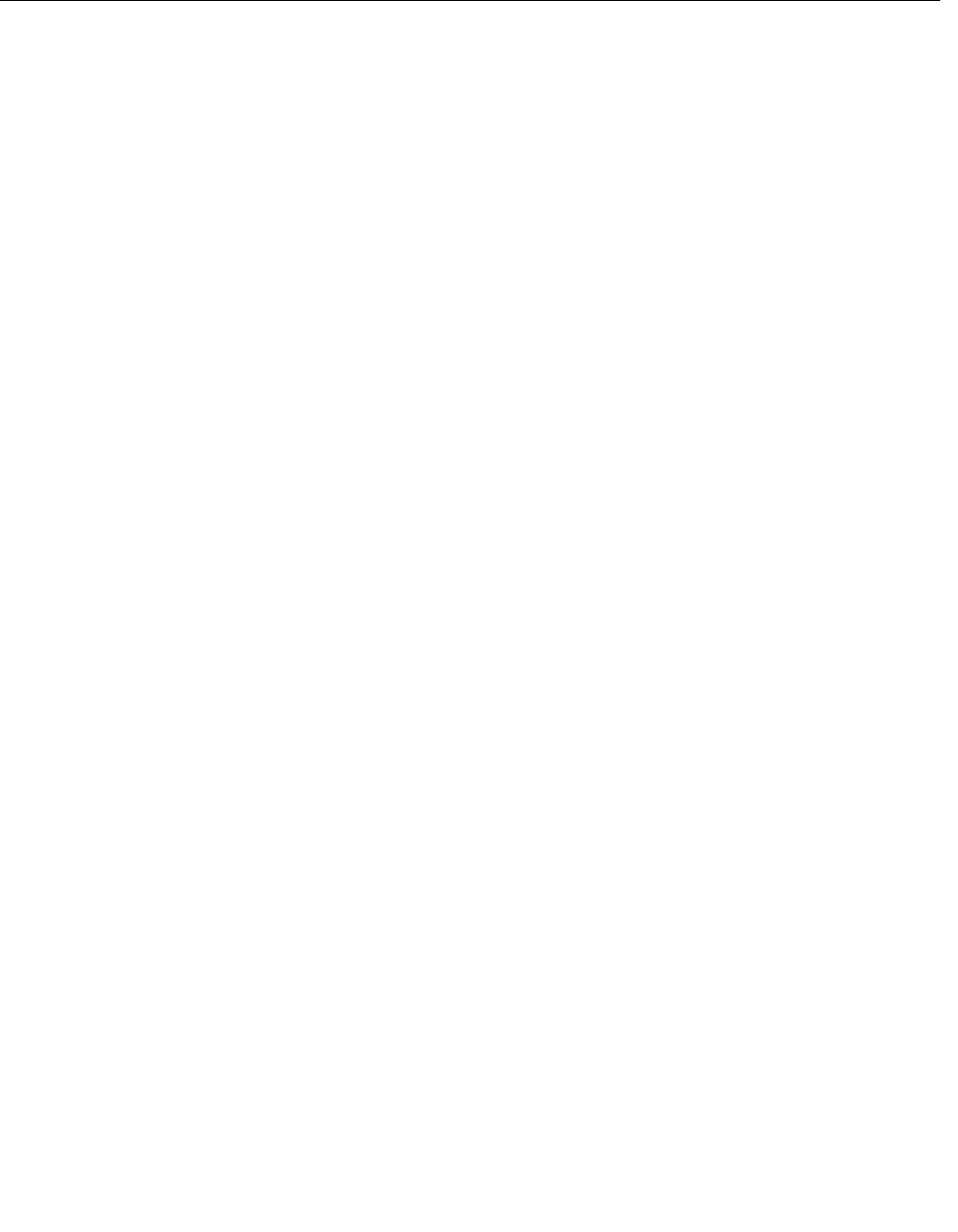
Reference Manual
00809-0100-4026, Rev AA
November 2003
Rosemount 5400 Series
5-16
Preliminary copy
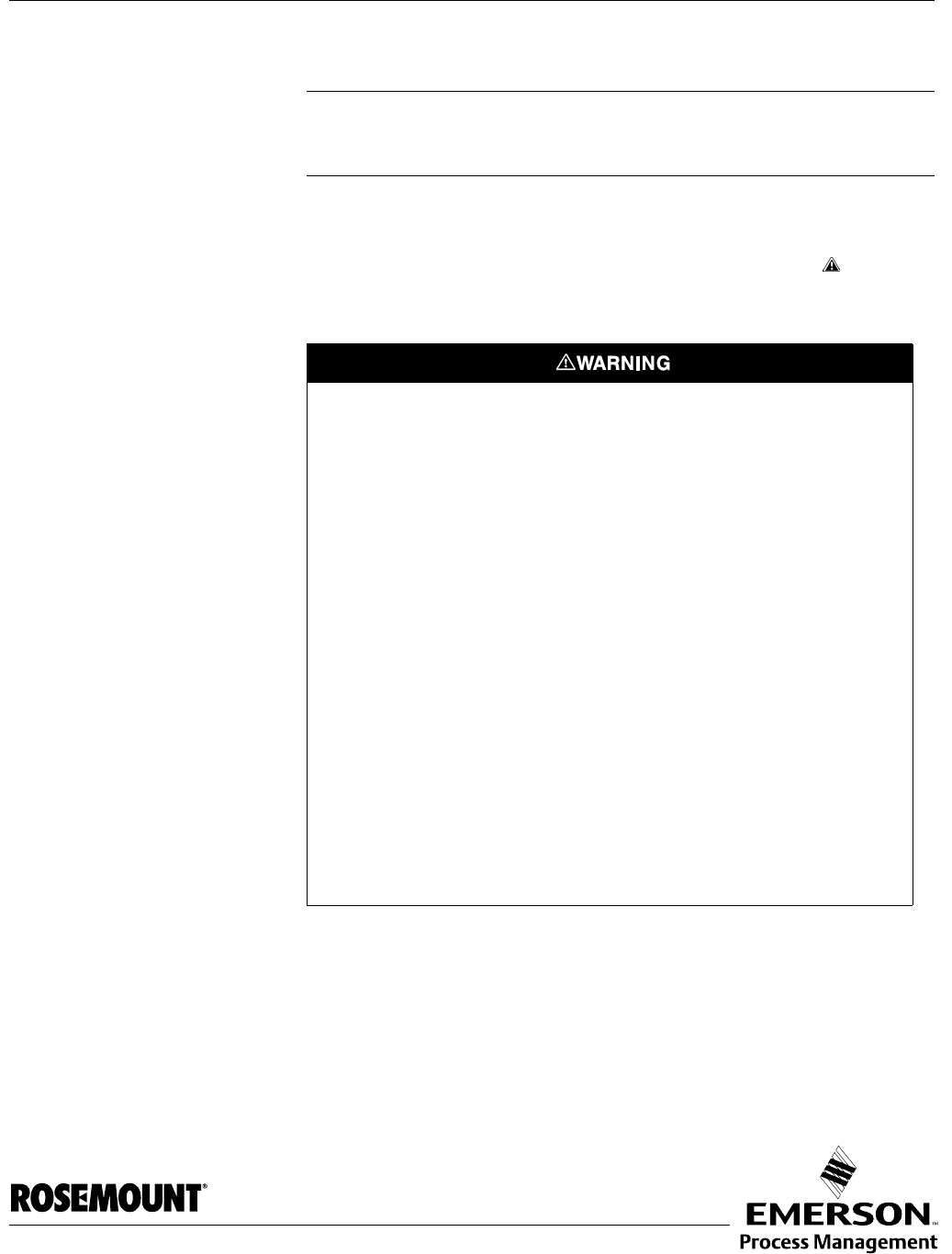
Reference Manual
00809-0100-4026, Rev AA
November 2003 Rosemount 5400 Series
www.rosemount.com
Preliminary copy
Section 6 Service and Troubleshooting
Safety Messages . . . . . . . . . . . . . . . . . . . . . . . . . . . . . . . . . page 6-1
Service . . . . . . . . . . . . . . . . . . . . . . . . . . . . . . . . . . . . . . . . . page 6-2
Troubleshooting . . . . . . . . . . . . . . . . . . . . . . . . . . . . . . . . . page 6-7
SAFETY MESSAGES Procedures and instructions in this manual may require special precautions to
ensure the safety of the personnel performing the operations. Information that
raises potential safety issues is indicated by a warning symbol ( ). Refer to
the saftey messages listed at the beginning of each section before performing
an operation preceded by this symbol.
Failure to follow these installation guidelines could result in death or serious
injury.
• Make sure only qualified personnel perform the installation.
• Use the equipment only as specified in this manual. Failure to do so may
impair the protection provided by the equipment.
Explosions could result in death or serious injury.
• Verify that the operating environment of the transmitter is consistent with the
appropriate hazardous locations certifications.
• Before connecting a HART®-based communicator in an explosive atmosphere,
make sure the instruments in the loop are installed in accordance with
intrinsically safe or non-incendive field wiring practices.
• Any substitution of non-recognized parts may jeopardize safety. Repair, e.g.
substitution of components etc., may also jeopardize safety and is under no
circumstances allowed.
• Substitution of components may impair Intrinsic Safety.
• To prevent ignition of flammable or combustible atmospheres, disconnect
power before servicing.
Electrical shock could cause death or serious injury.
• Use extreme caution when making contact with the leads and terminals.
• To prevent ignition of flammable or combustible atmospheres, disconnect
power before servicing. (Krav från FM?)
• Do not reset circuit breaker unless power has been removed from the
equipment or the area is known to be non-hazardous. (Nonincendive ?)
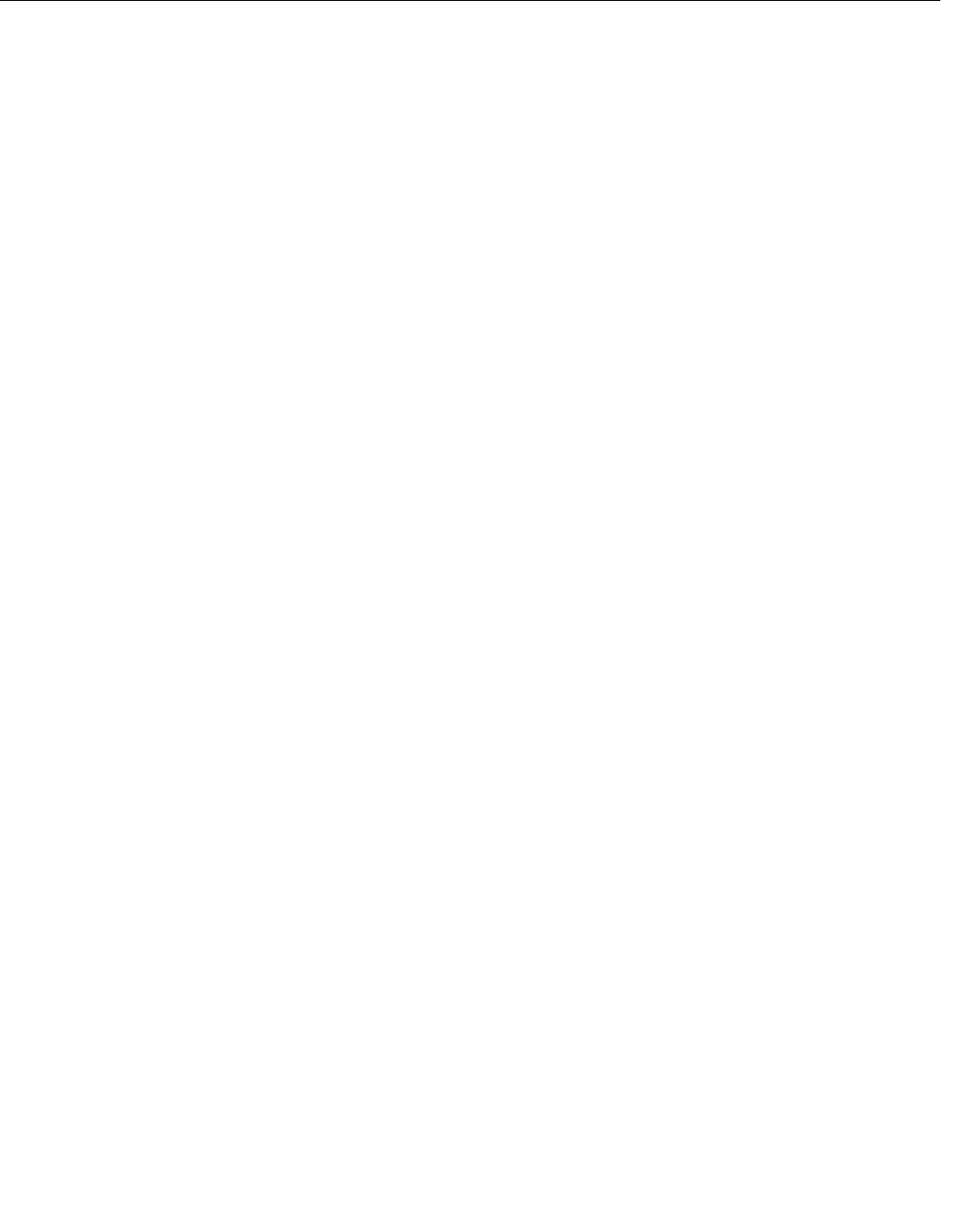
Reference Manual
00809-0100-4026, Rev AA
November 2003
Rosemount 5400 Series
6-2
Preliminary copy
SERVICE The functions mentioned in this section are all available in the Rosemount
Radar Master (RRM) configuration program.
Analog Output
Calibration
Viewing Input and
Holding Registers
Measured data is continuously stored in the Input registers. By viewing the
contents of the Input registers you can check that the device works properly.
The Holding registers store various transmitter parameters used to control the
measurement performance.
By using the RRM program most Holding registers can be edited by simply
typing a new value in the appropriate Value input field. Some holding registers
can be edited in a separate window. In this case you can choose from a list of
options or you can change separate data bits.
Logging Measurement
Data
By using the Log Device Registers function in the RRM software you can log
Input and Holding registers. It is possible to choose from different pre-defined
sets of registers. This function is useful for veryfying that the transmitter works
properly.
Saving the Transmitter
Configuration
Use this RRM option to save the configuration parameters to the configuration
file associated with the device.
If a similar device needs to be installed, parameters in the saved file can be
uploaded directly to the new device.
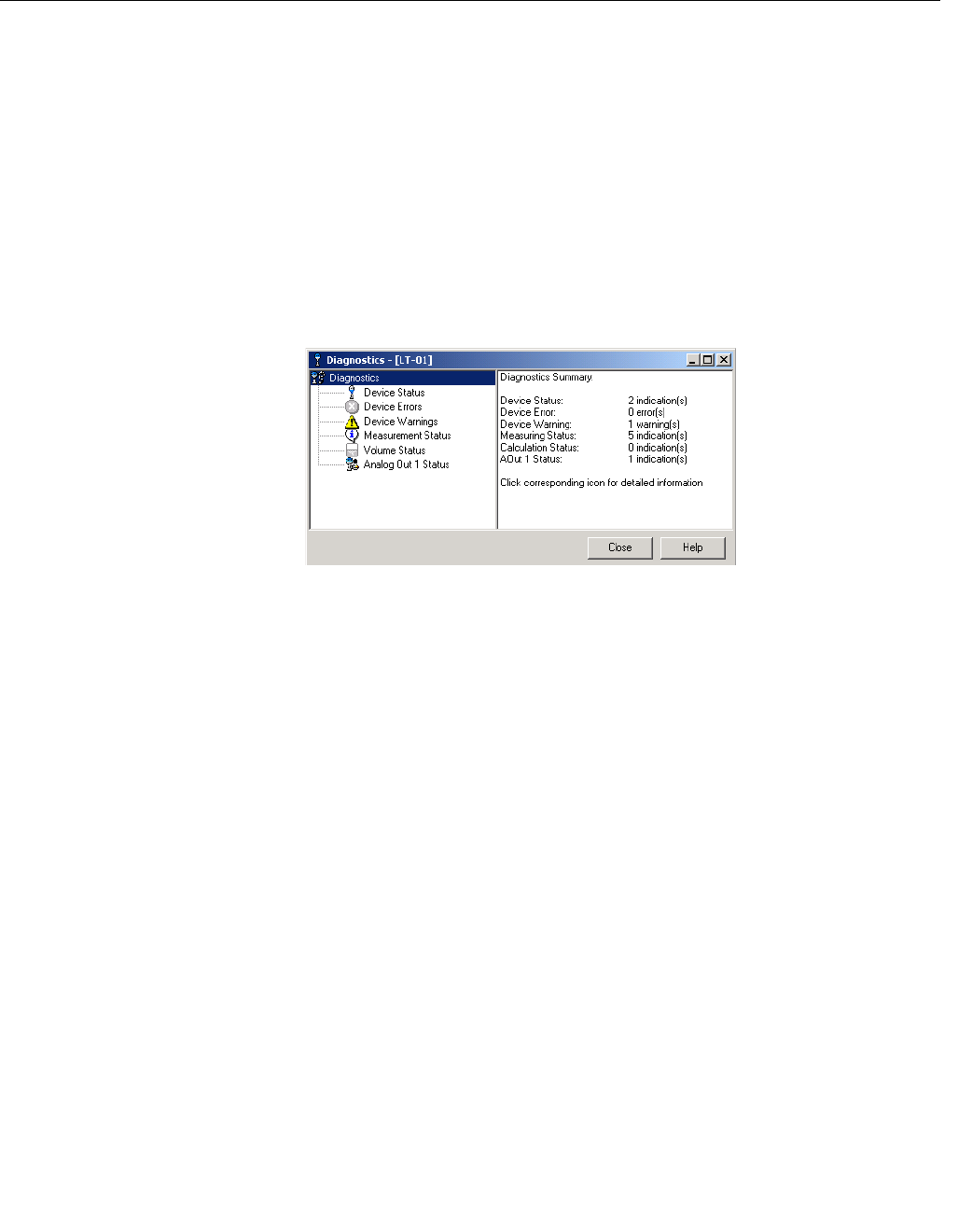
Reference Manual
00809-0100-4026, Rev AA
November 2003
6-3
Rosemount 5400 Series
Preliminary copy
Diagnostics By using the RRM software the following information about the device can be
retrieved:
• device status
• device errors
• device warnings
• measurement status
• volume status
• analog output status
Figure 6-1. The Diagnostics
window in Rosemount Radar
Master.
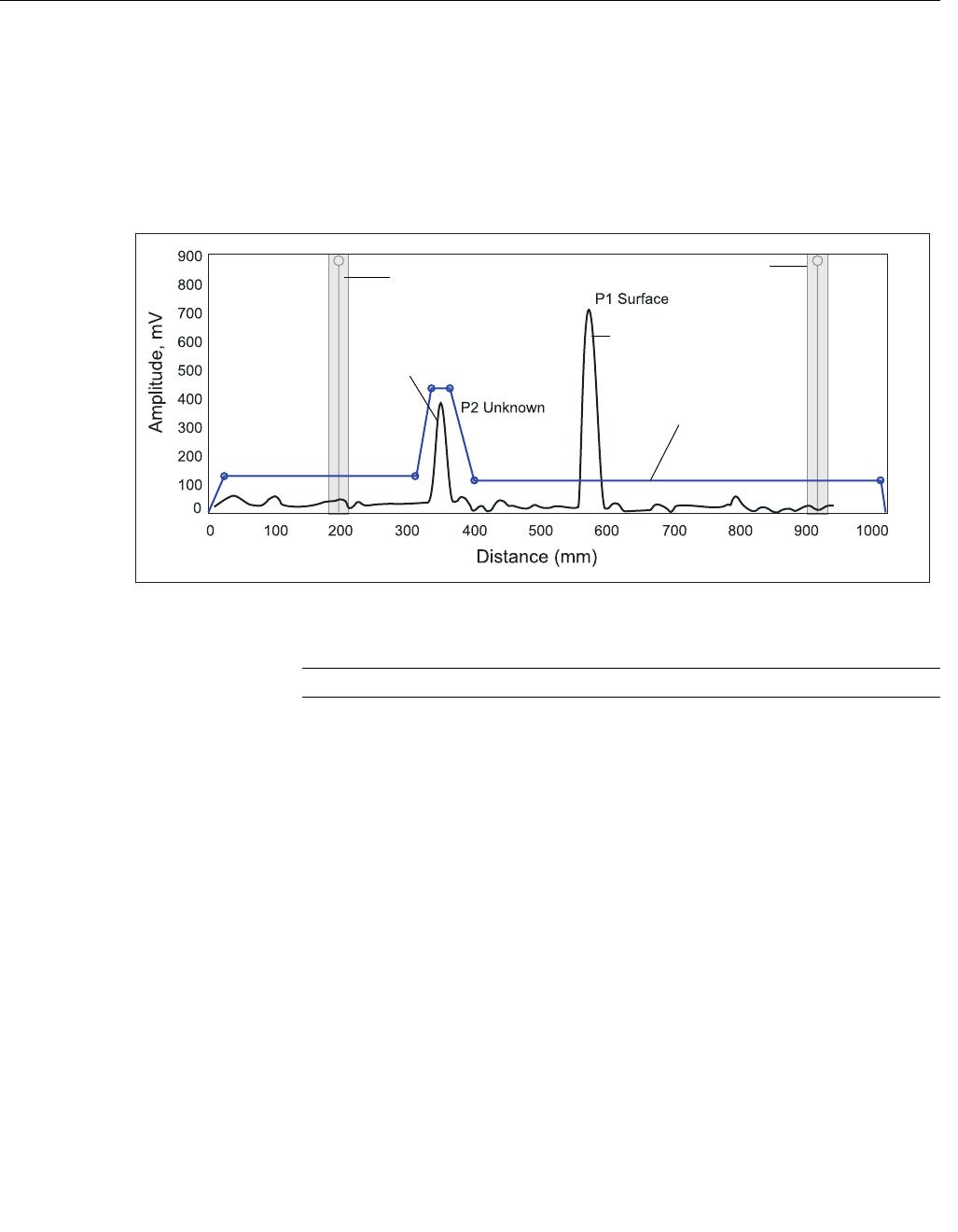
Reference Manual
00809-0100-4026, Rev AA
November 2003
Rosemount 5400 Series
6-4
Preliminary copy
Using the Spectrum
Analyzer
The Spectrum Analyzer in Rosemount Radar Master (RRM) lets you view the
measurement signal amplitude along the tank. Each radar echo is displayed
as a peak in the signal plot. This is a useful tool for obtaining a view of the
tank conditions. The Spectrum Analyzer also lets you register disturbing
echoes and create an Amplitude Threshold Curve (see Section 5: Echo
Tuning for further information).
Figure 6-2.
To be continued...
SPECTRUM.EPS
Amplitude
Threshold Curve
Peak from
product surface
Peak from
disturbing object
Registered
disturbing echo
Registered
disturbing echo
Registered
disturbing echo
Registered
disturbing echo
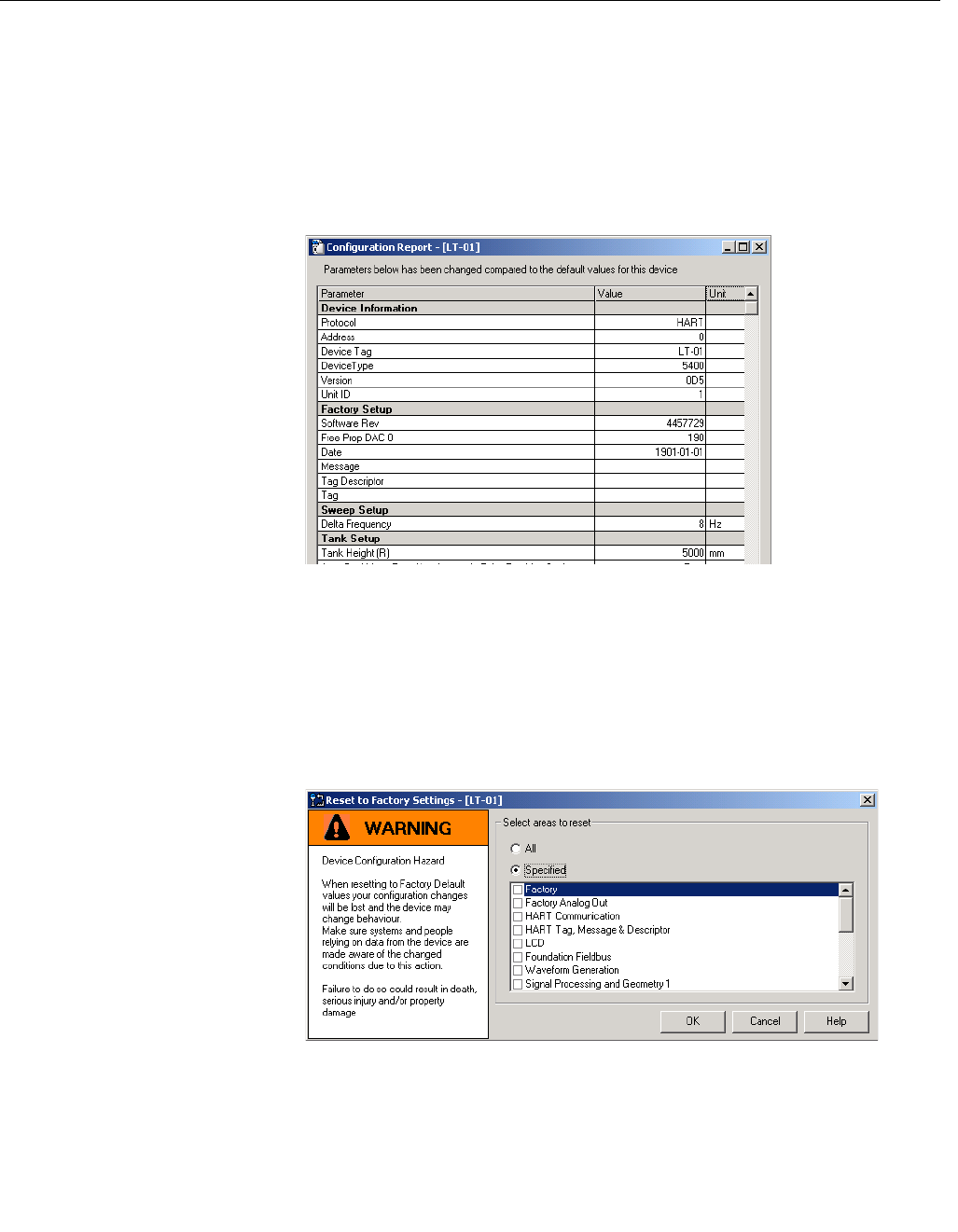
Reference Manual
00809-0100-4026, Rev AA
November 2003
6-5
Rosemount 5400 Series
Preliminary copy
Configuration Report This function in Rosemount Radar Master (RRM) shows what configuration
changes have been done to the transmitter compared to the default
configuration. The report compares a specified backup file with the current
transmitter configuration.
Information on antenna type, software versions, software and hardware
configuration, operation time, error status and unit code is presented.
Figure 6-3. The Configuration
Report window in Rosemount
Radar Master.
Surface Search The Surface Search command triggers a search for the product surface. Use
this function if, for example, the measured level has stuck on a disturbing
object in the tank.
Reset to Factory Settings Resets all or a specific part of the holding registers to factory settings.
Figure 6-4. The Reset to Factory
Settings window in RRM.
Using the Simulation
Mode
This function can be used to simulate measurements and alarms.
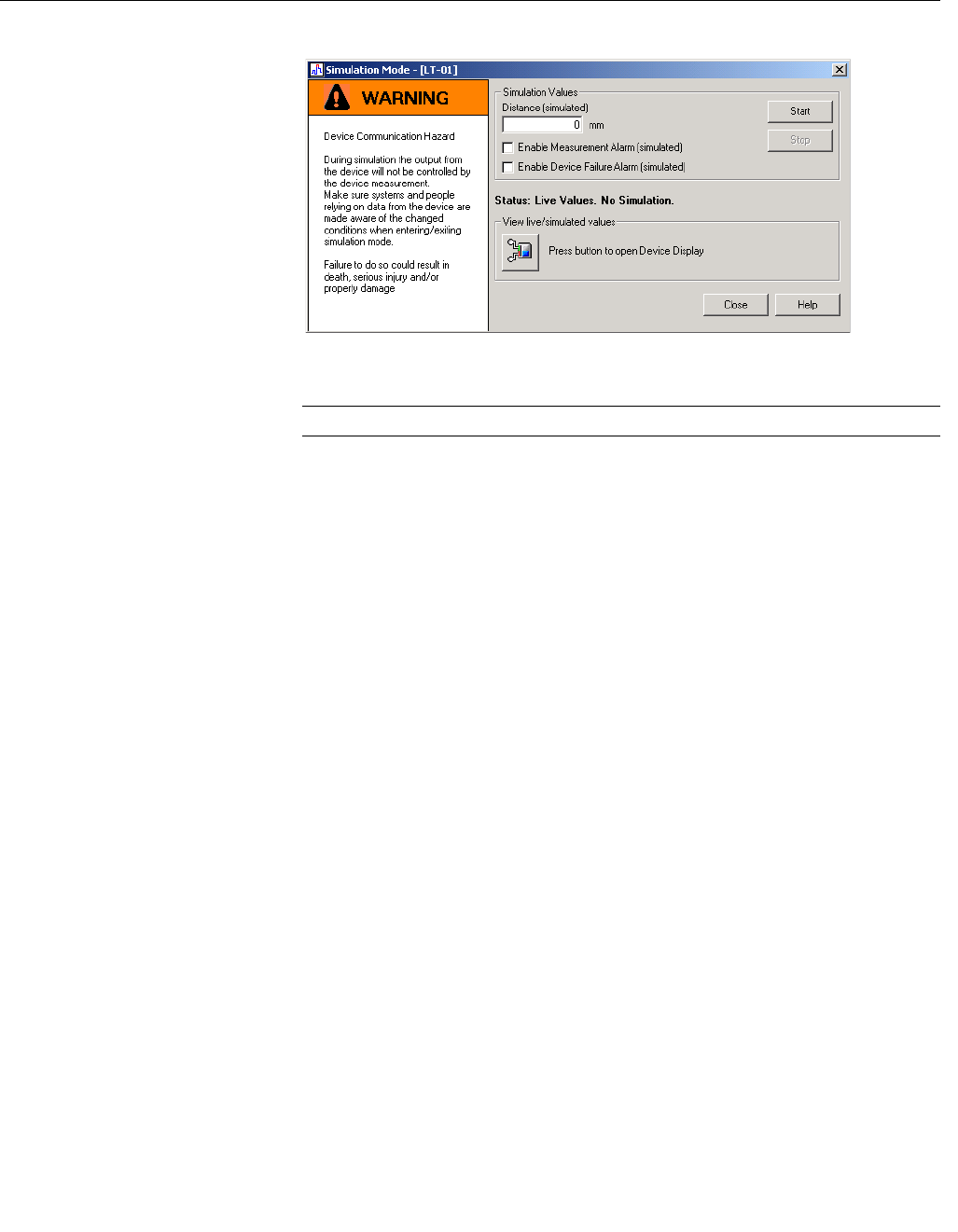
Reference Manual
00809-0100-4026, Rev AA
November 2003
Rosemount 5400 Series
6-6
Preliminary copy
Figure 6-5. The Reset to Factory
Settings window in RRM.
Enable Software Options (Change Start Code)
To be continued...
Enter Service Mode In Rosemount Radar Master (RRM) some useful service functions are
available for the 5400 Series transmitter. By setting RRM into the Service
Mode all the Service menu options in RRM are enabled. The default
password for enabling the Service Mode is “admin”. The password can be
changed by selecting the Change Password option from the Service menu.

Reference Manual
00809-0100-4026, Rev AA
November 2003
6-7
Rosemount 5400 Series
Preliminary copy
TROUBLESHOOTING
Troubleshooting If there is a malfunction despite the absence of diagnostic messages, see
Table 6-1 for information on possible causes.
Table 6-1. Troubleshooting
chart
Symptom Possible cause Action
No level reading • • Check the power supply.
• Check the cables for serial data
communication.
No HART communication. • COM Port configuration does not match
the connected COM Port.
• Cables may be disconnected.
• Wrong HART adderss is used.
• Hardwafe failure.
• Check that correct COM Port is
selected in the HART server (see
“Specifying the COM Port” on
page 4-4).
• Check wiring diagram.
• Verify that the 250 Ohm resistor is in
the loop.
• Check cables.
• Make sure that correct HART short
address is used. Try address=0.
• Check Analog Output current value to
verify that transmitter hardware works.
Analog Out is set in Alarm. Use the command “Read Gauge Status”
in order to check active errors.
P2 is detected but Level is incorrectly
reported as Full or Empty.
Use the command “Read Gauge Status”
and check if the warning “Probe
Immersed” is active. If this is the case
check that:
• the transmitter is configured with
correct probe type,
• the reference pulse (P1) is below
amplitude threshold T4. If not, adjust
T4 to an appropriate value.
Incorrect level reading. • Configuration error.
• Disturbing objects in the tank.
• Check the Reference Gauge Height
parameter.
• Check status information and
diagnostic information.
• Check that the transmitter has not
locked on an interfering object.
Integral display does not work. • Check the display configuration.
• Check loop power.
• Check Display connection.
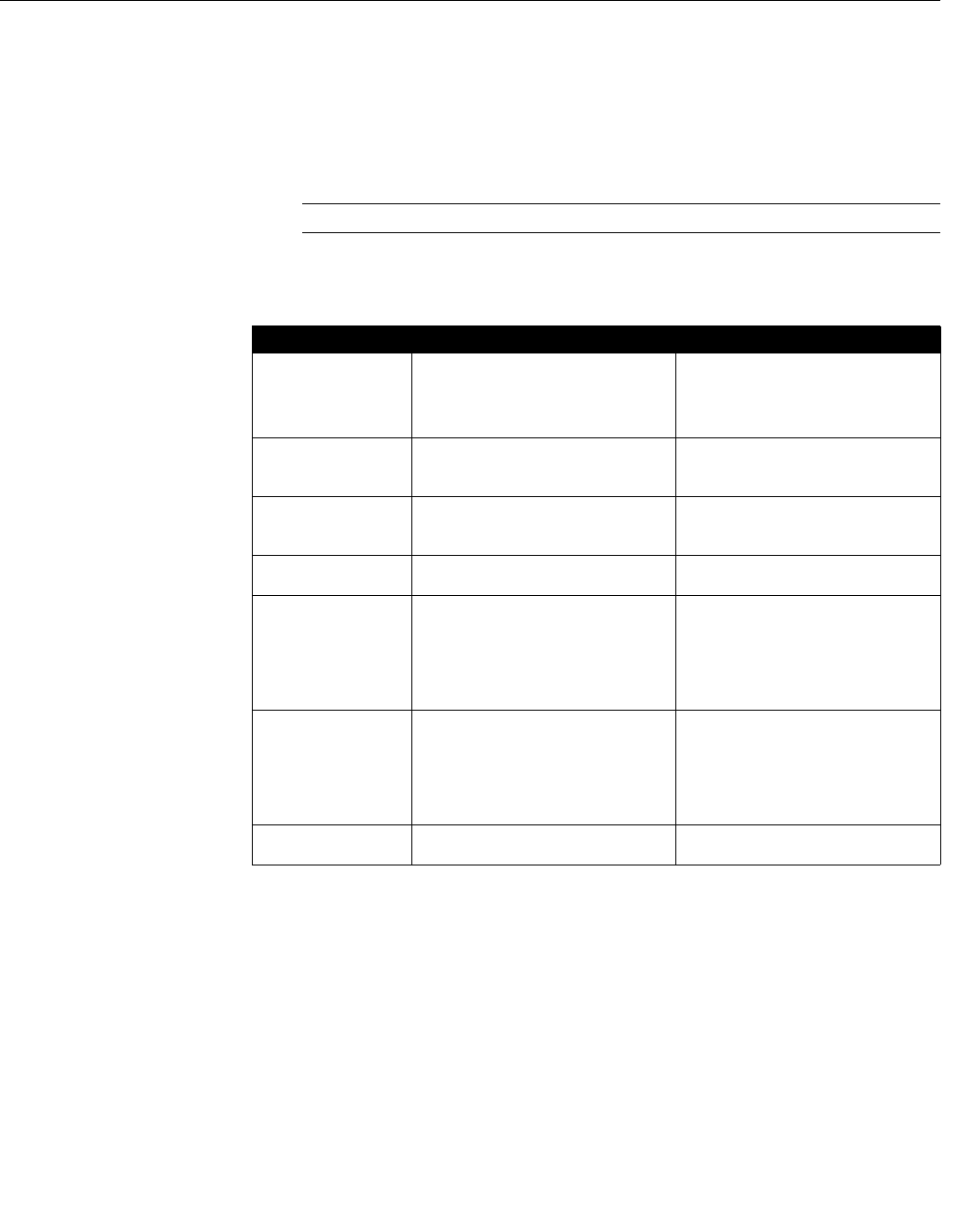
Reference Manual
00809-0100-4026, Rev AA
November 2003
Rosemount 5400 Series
6-8
Preliminary copy
Errors. Table 6-2 is a list of diagnostic messages that may be displayed on the
Integral Display, on the Model 275 HART Communicator, in AMS or by the
Rosemount Radar Master (RRM) software. Errors normally result in Analog
Output alarm.
Errors are indicated in RRM by...
To see the error message do one of the following...
To be continued...
Table 6-2. Error messages.
Message Description Action
Invalid configuration. At least one configuration parameter
is outside allowed range.
NOTE: the default values are used
until the problem is solved.
• Load default database and restart
the transmitter.
• Contact Saab Rosemount service
department if the problem persists.
RAM failure was
detected during
startup test.
The transmitter performs an
immediate reset.
Contact Rosemount service
department.
FPROM failure was
detected during
startup test.
The transmitter performs an
immediate reset.
Contact Rosemount service
department.
Waveform acquisition
failure.
This error is probably caused by
hardware failure.
Contact Rosemount service
department.
EEPROM factory
checksum.
Checksum error in the factory
configuration parameters. Can be
caused by power failure during
configuration or by hardware error.
NOTE: the default values are used
until the problem is solved.
Contact Rosemount service
department.
EEprom user
checksum error.
Caused by error in the User
Configuration parameters. Can be
caused by power failure during
configuration or by hardware error.
NOTE: the default values are used
until the problem is solved
• Load default database and restart
the transmitter.
• Contact Saab Rosemount service
department if the problem persists.
Software error. Contact Rosemount service
department.
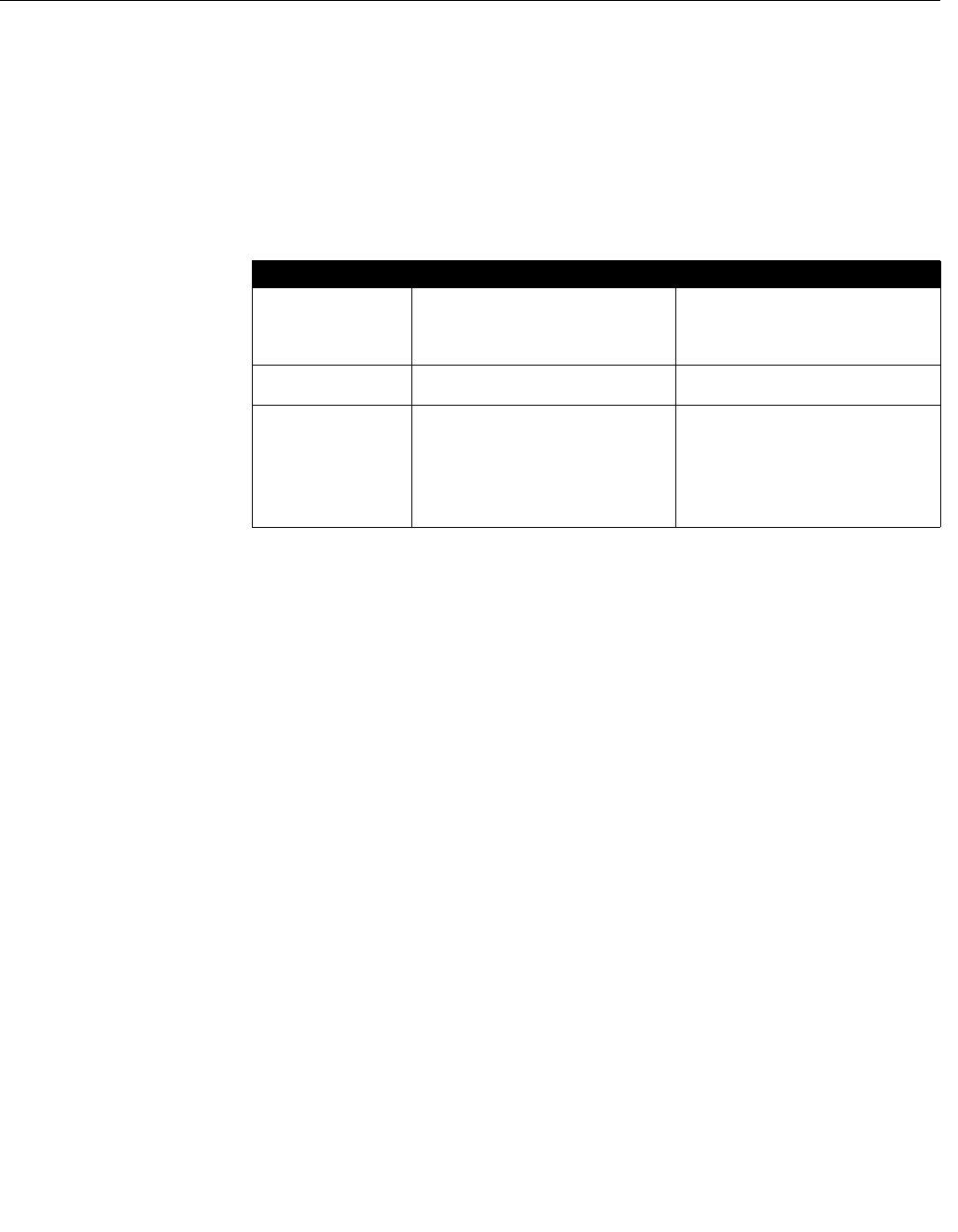
Reference Manual
00809-0100-4026, Rev AA
November 2003
Rosemount 5400 Series
6-9
Preliminary copy
Warnings. Table 6-3 is a list of diagnostic messages that may be displayed on the
Integral Display, on the Model 275 HART Communicator or by the Rosemount
Radar Master (RRM) software. Warnings are less serious than errors and in
most cases do not result in Analog Output alarms.
Warnings are indicated by...
To see the warning message do one of the following...
Table 6-3. Warning messages.
Message Description Action
No level pulse is
found.
Possible cause:
• Wrong threshold level T2.
• Liquid level in Dead Zone or
below probe end.
• View the waveform plot and
check amplitude threshold T2.
Internal temperature
out of range.
-40 ºC<Internal Temperature<85 ºC. Contact Rosemount service
department.
Volume computation
warning. • Volume configuration error.
• Strapping table error.
• Check that correct tank type is
selected for volume configuration.
• Check that tank dimensions for
volume are correct.
• If strapping table is used, check the
level vs. volume points.
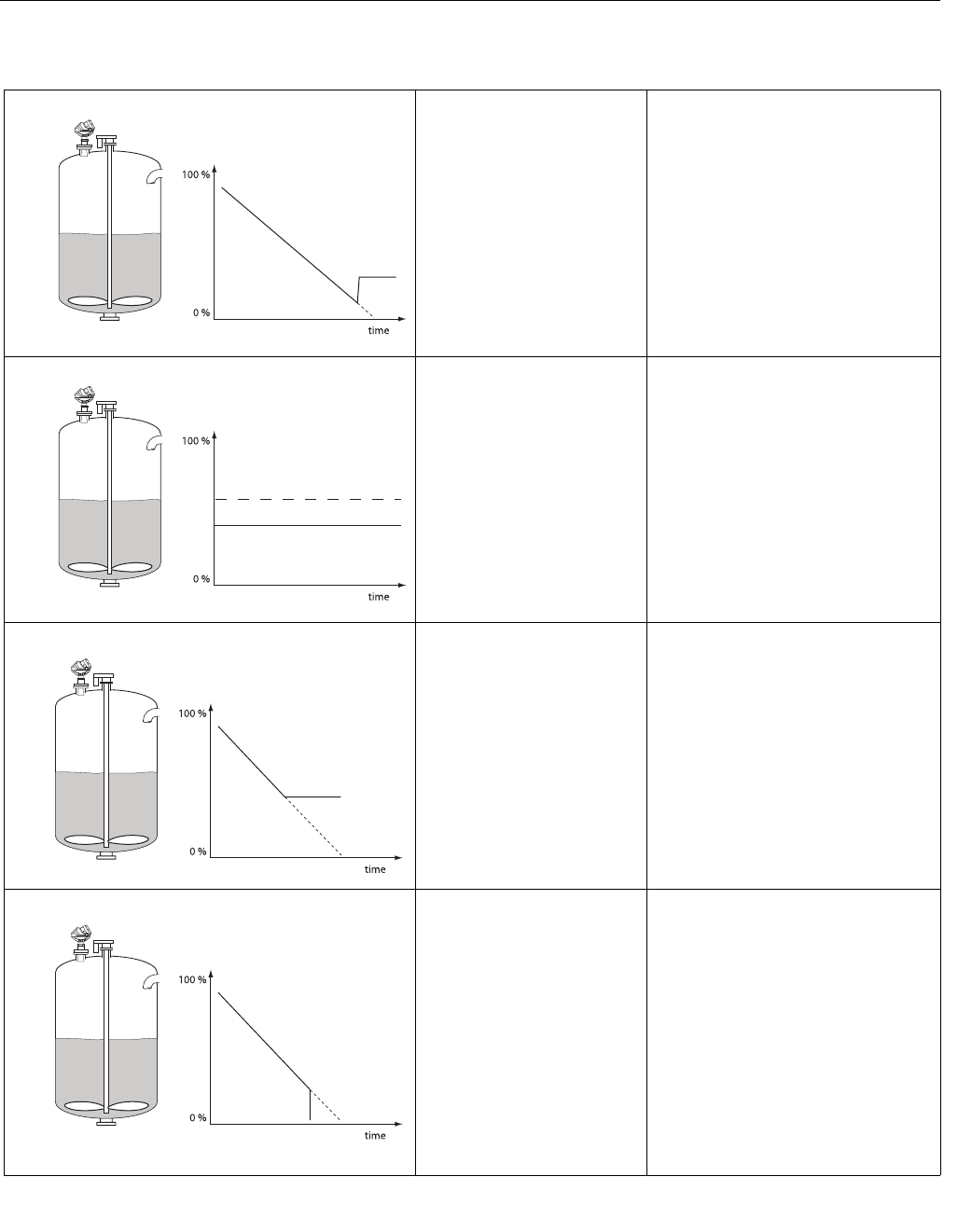
Reference Manual
00809-0100-4026, Rev AA
November 2003
Rosemount 5400 Series
6-10
Preliminary copy
Application Errors.
Level jumps to a higher level
near the bottom of the tank.
May be caused by sloping tank bottom.
Action:
• Make sure that parameter Bottom
always visible is not set.
• Increase parameter Empty Tank
Detection Area if measurement in this
region is not crucial.
• Increase the CFAR threshold value.
Incorrect Level. Action:
Check tank geometry configuration.
Measured value gets stuck. May be caused by disturbing object in the
tank
Action:
• Remove disturbing object.
• Move tha transmitter to another
position.
• Use the Echo Tuning function in RRM
to register the false echo that causes
the transmitter to lock on the wrong
level.
Measured value drops to empty
tank.
May be caused by strong echoes from the
tank bottom when product is slightly
transparent.
Action:
• Make sure that parameter Bottom
always visible is set.
APPLICATION_ERROR_1.EPSAPPLICATION_ERROR_2.EPSAPPLICATION_ERROR_3.EPSAPPLICATION_ERROR_EMPTY.EPS
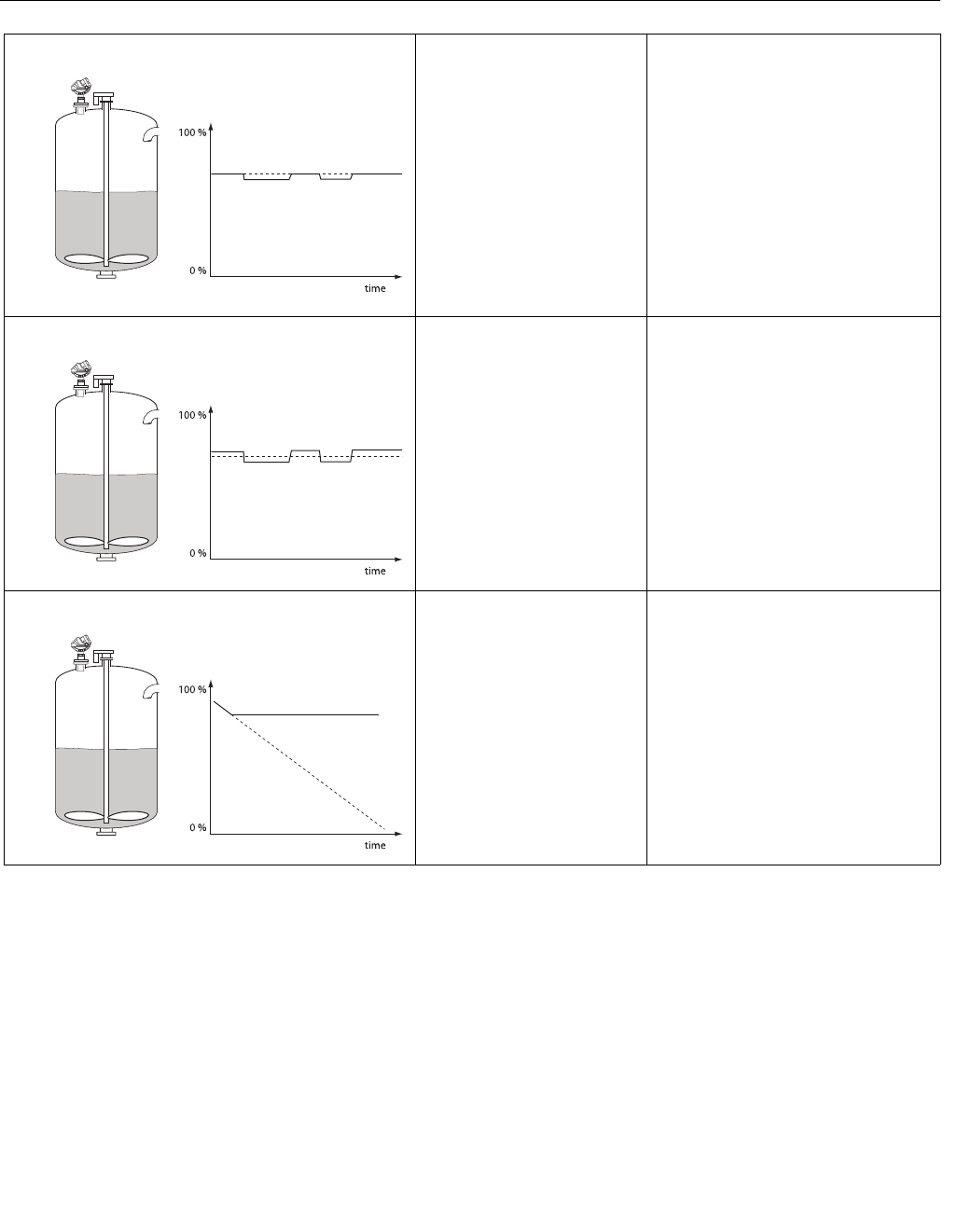
Reference Manual
00809-0100-4026, Rev AA
November 2003
Rosemount 5400 Series
6-11
Preliminary copy
Measured level jumps to a lower
value.
May be caused by:
• Radar echo bouncing off from the
surface to the tank roof and back to
the surface.
• Product with very high reflectivity that
causing very strong echoes.
• Two products layered in the tank.
Action:
• Move the transmitter away from the
center of the tank roof.
• Enable the Double Bounce function.
• Enable the Double Surface function
Measured level oscillates around
a steady value.
May be caused by:
• Foam on the product surface.
• Turbulent product surface.
Action:
• Enable the Tank Environment Foam
parameter.
• Enable the Tank Environment
Turbulent Surface parameter.
Measured level gets stuck near
the top of the tank.
May be caused by:
• Antenna tip ends inside the tank
nozzle.
• Disturbing objects near the antenna.
Action:
• Cut the nozzle.
• Increase the Hold Off distance.
APPLICATION_ERROR_JUMPLOW.EPSAPPLICATION_ERROR_AROUNDSTABLE.EPS
APPLICATION_ERROR_TOP.EPS
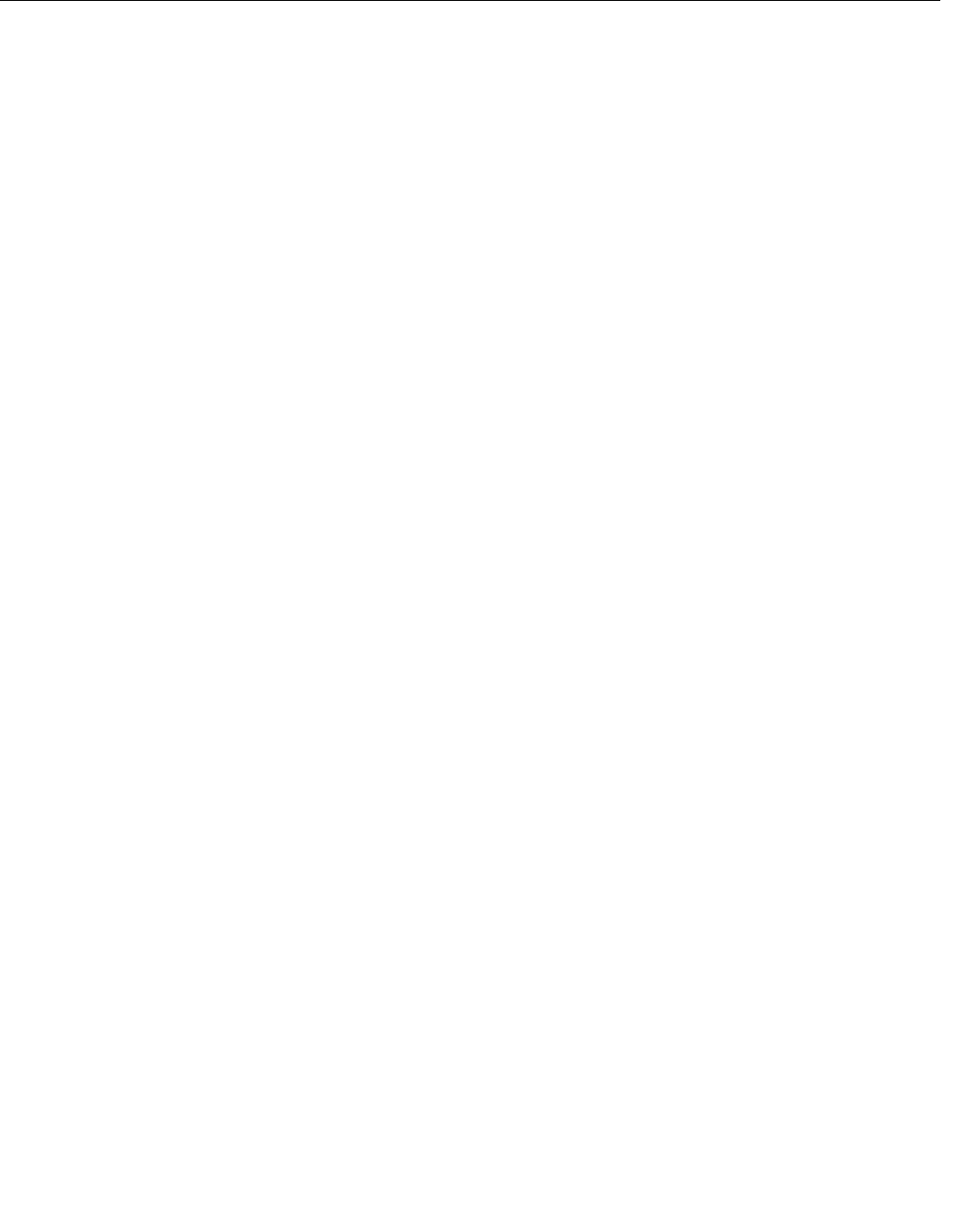
Reference Manual
00809-0100-4026, Rev AA
November 2003
Rosemount 5400 Series
6-12
Preliminary copy
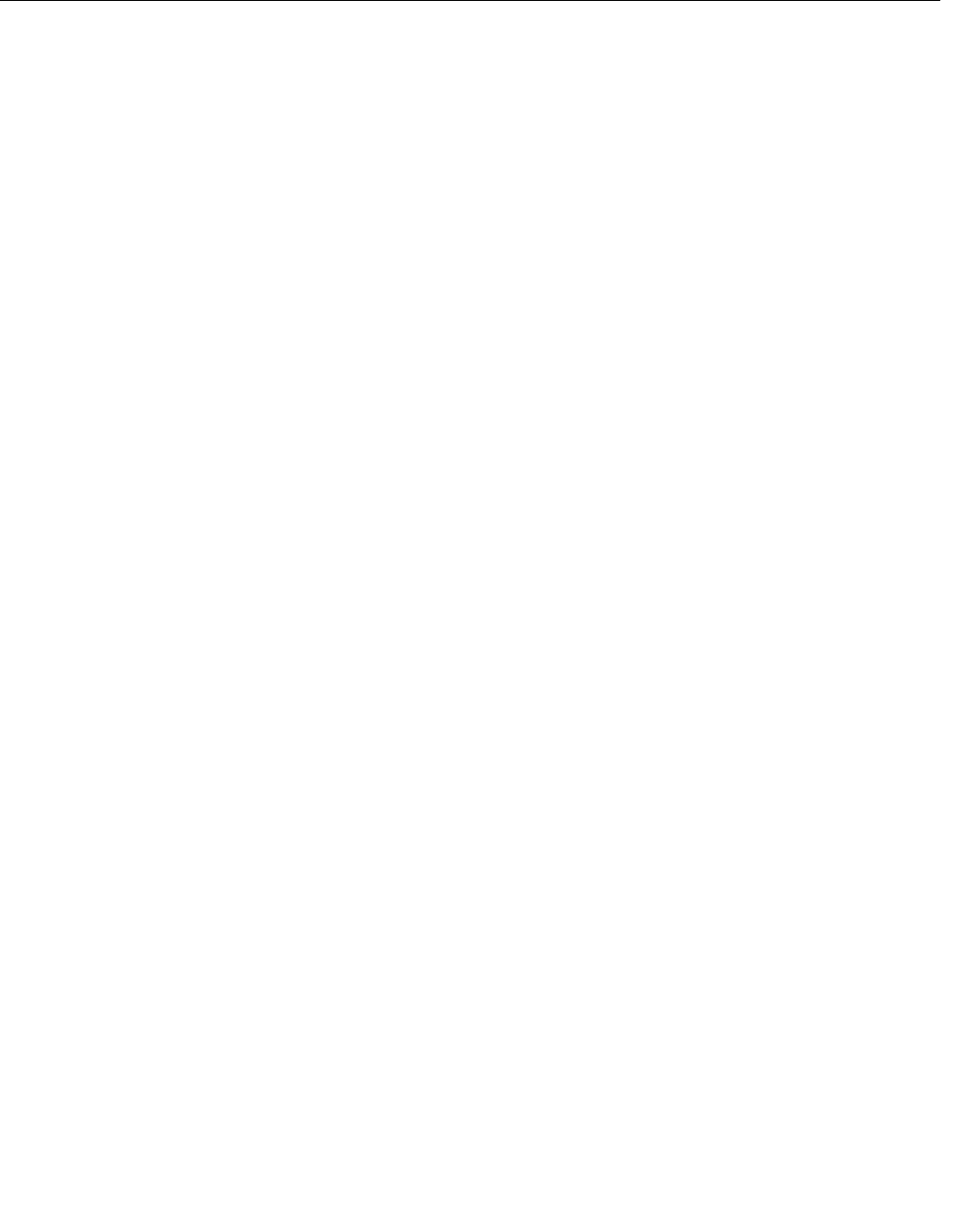
Reference Manual
00809-0100-4026, Rev AA
November 2003
6-13
Rosemount 5400 Series
Preliminary copy
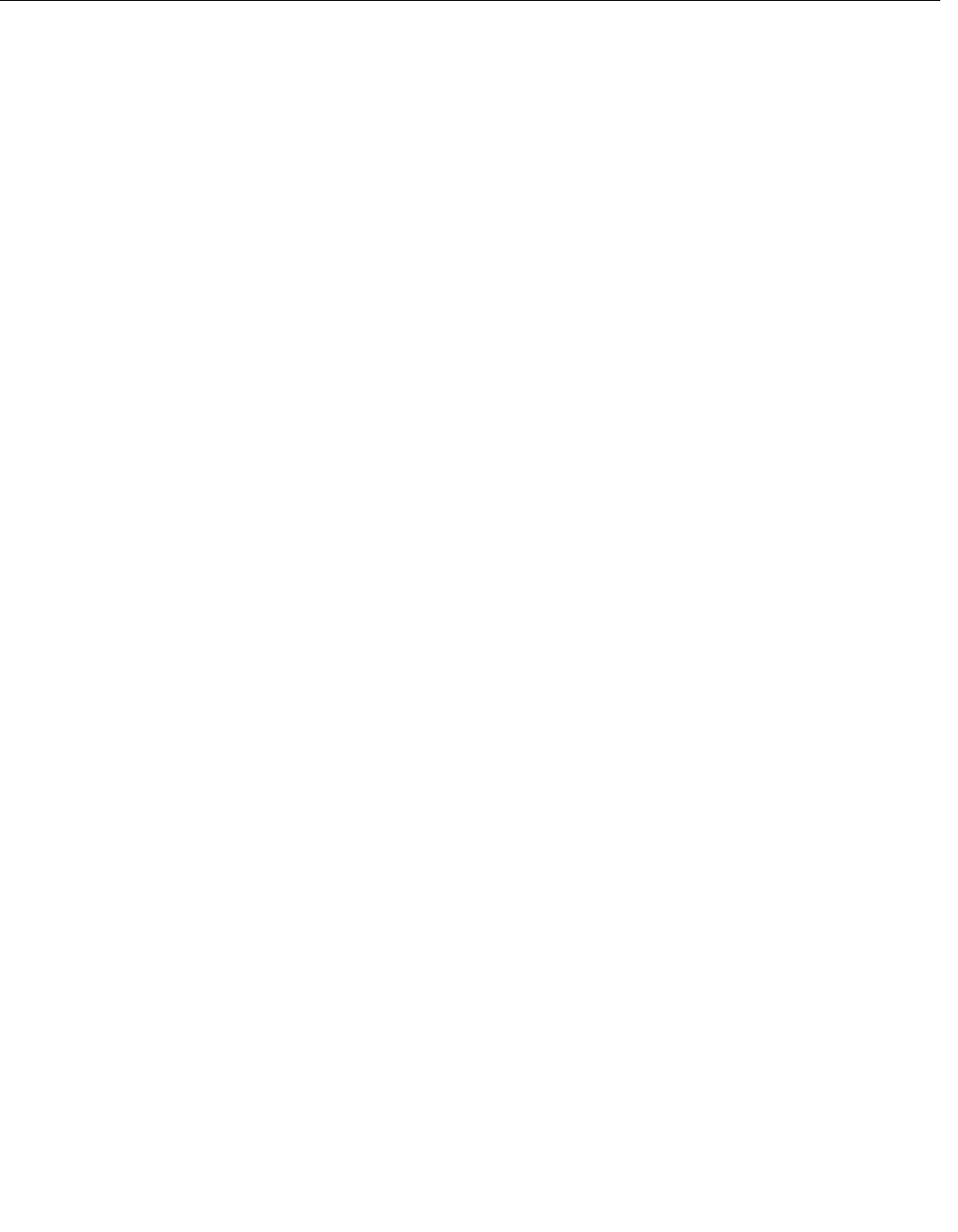
Reference Manual
00809-0100-4026, Rev AA
November 2003
Rosemount 5400 Series
6-14
Preliminary copy
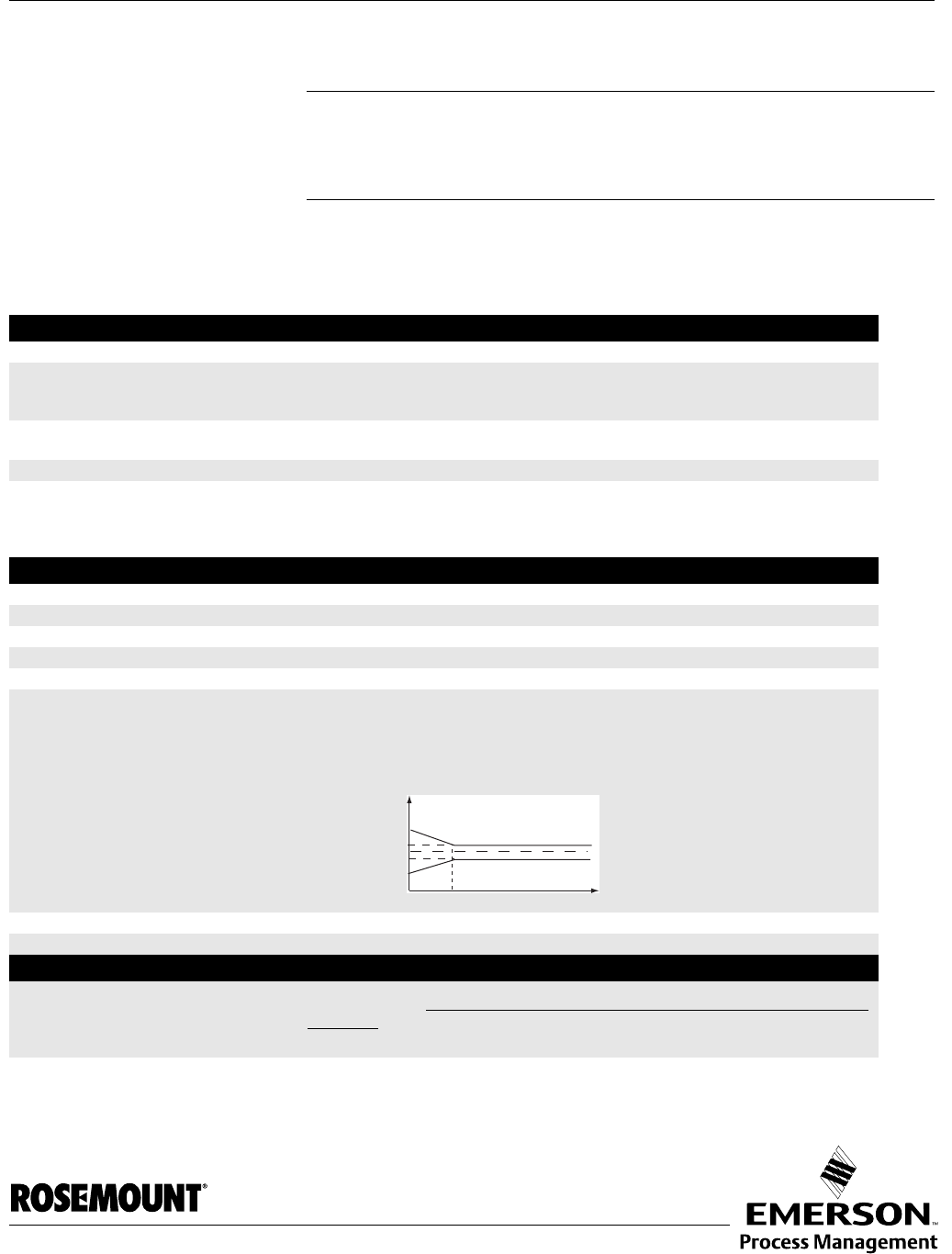
Reference Manual
00809-0100-4026, Rev AA
November 2003 Rosemount 5400 Series
www.rosemount.com
Preliminary copy
Appendix A Reference Data
Specifications . . . . . . . . . . . . . . . . . . . . . . . . . . . . . . . . . . . page A-1
Dimensional drawings . . . . . . . . . . . . . . . . . . . . . . . . . . . . page A-3
Ordering Information . . . . . . . . . . . . . . . . . . . . . . . . . . . . . page A-4
Spare Parts . . . . . . . . . . . . . . . . . . . . . . . . . . . . . . . . . . . . . page A-8
SPECIFICATIONS
General
Product Rosemount 5400 Series Radar Level Transmitter.
Measurement Principle Pulsed, free propagating radar.
5401: ~6 GHz
5402: ~26 GHz
Reference Conditions Free space reflection from flat metal plate, ambient temperature and pressure,
minimum damping
Microwave Output Power TBD
Beam Angle 5401: 2, 3, 4, 6, 8 in. cone
5401: 6, 8 in. disc
5402: 2, 3, 4 in. cone
5402: 2, 3, 4 in. disc
Measuring Performance
Instrument Accuracy ± 0.1 in. (± 3 mm)
Resolution 0.04 in. (1 mm)
Repeatability ± 0.04 in. (± 1 mm) at 5 m distance.
Ambient Temperature Effect ± 0.005 % of measured distance per 50°F (10°C)
Update Interval 1 per second.
Measuring Range 0-98.4 ft (0-30 m) from antenna tip, measured from mounting flange face???Kan man
ange ett nedre samt ett övre värde för samtliga antenner (då får man med övre dödzon,
eller vad vi väljer att kalla denna parameter för, per automatik). See Measuring range
for details. Near zone accuracy?. Olika 5401/5402/cone/disc/storlekar. Hur presentera?
Level Rate 10 mm/s as default, adjustable to 200 mm/s.
MTBF > 80 years @ 77°F (25°C).
Display / Configuration
Integral Display The 6-digit local intregal display can toggle between all process variables (level,
distance, volume, internal temperature, peak amplitudes, percentage of range, analog
current out) and has 15 mm digit size. It also shows diagnostics and error information.
Note! The display cannot be used for configuration purposes.
Accuracy, inches (mm)
Distance, ft (m)
in. (10/30 mm)
in. (mm)
ft (0.5 m) ft (20 m)
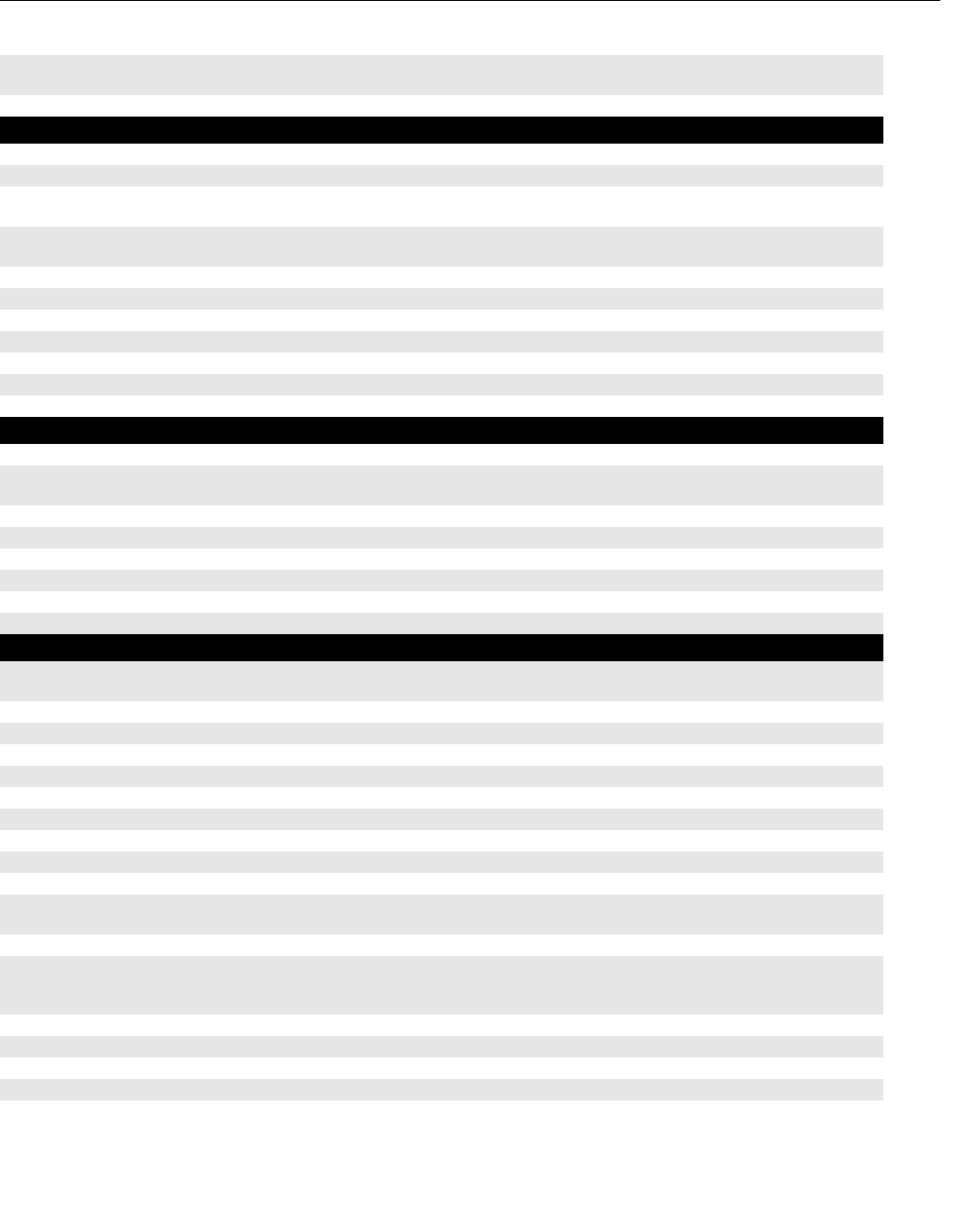
Reference Manual
00809-0100-4026, Rev AA
November 2003
Rosemount 5400 Series
A-2
Preliminary copy
Output Variables Level, Distance and Volume
Output Units Level and Distance: ft, inch, m, cm or mm
Volume: ft3, inch3, US gals, Imp gals, barrels, yd3, m3 or liters
Configuration Tools RRM, HART 275 / 375, AMS
Electric
Power Supply Loop-powered (2-wire), 11-42 VDC
Power Consumption TBD
Output Alternative 1: HART® + 4-20 mA current loop (non-IS or IS option)
Alternative 2: Foundation fieldbus (optional IS version)
Signal on Alarm Standard: Low=3.75 mA, High=21.75 mA
Namur NE43: Low=3.6 mA, High=22.5 mA
Linearity TBD.
Temperature Drift TBD, sid 41?
Output Impedance TBD
External Loop Resistance See diagrams on page 12
IS Parameters See “Hazardous Locations Certifications” on page 13
Cable Entry M20x1.5, 1/2 in
Output Cabling 18-12 AWG?.
Mechanical
Antennas 2, 3, 4, 6, 8 in. See “Antennas” on page 7, pageA-4 and A-6.
Antenna Material Exposed to Tank
Atmosphere
316 / 316L SST, Teflon (PTFE or equivalent) and O-ring material (see “Ordering
Information” on page 15 and A-6)
Housing / Enclosure Polyurethane-covered Aluminum
Dimensions See “Dimensional Drawings” on page 14.
Height above flange TBD
Weight, excl. flange TBD
Flanges / Threads See “Ordering Information” on page 15 and A-6.
Nozzle Height Up to 20 in. (500 mm)
Environment
Ambient Temperature -40°F to 176°F (-40°C to 80°C). For the LCD display, the temperature range is -4°F to
130°F (-20°C to 55°C)
Storage Temperature -58°F to 194°F (-50°C to 90°C)
Process Temperature -40°F to 392°F (-40°C to 200°C)
Process Pressure Full vacuum to 580 psig (-1 bar to 40 bar) at 302°F (150°C)
Humidity 0 - 100% Relative Humidity, 100 % Relative Humidity at 176°F (80°C)
Factory Sealed Yes.
Ingress Protection NEMA 4X, IP65, 66, 67
EU Directive compliance CE mark, 93/68/EEC (complies with applicable directives: R&TTE, EMC, ATEX)
ATEX directive 94/9/EC
Overfill Protection Approval WHG overfill protection
Telecommunication (FCC and R&TTE) FCC part 15 (1998) subpart B and R&TTE (EU directive 1999/5/EC). Considered to be
an unintentional radiator under the Part 15 rules.
Vibration Resistance According to IACS UR E10
Electromagnetic Compatibility Emission and Immunity:
EMC directive 89/336/EEC (CISPR16 Class A level) and NAMUR recommendations
NE21, closed metal tanks.???
EMI/RFI in addition to requirements for CE mark NAMUR????
Transient / Built-in Lightning Protection Complies with IEEE 587 Category B transient protection and IEEE 472 surge protection
Pressure Equipment Directive (PED) Compliance.
Ordinary Location FM 3810 Compliance.
Boiler Approval CSA B51-97 Compliance.
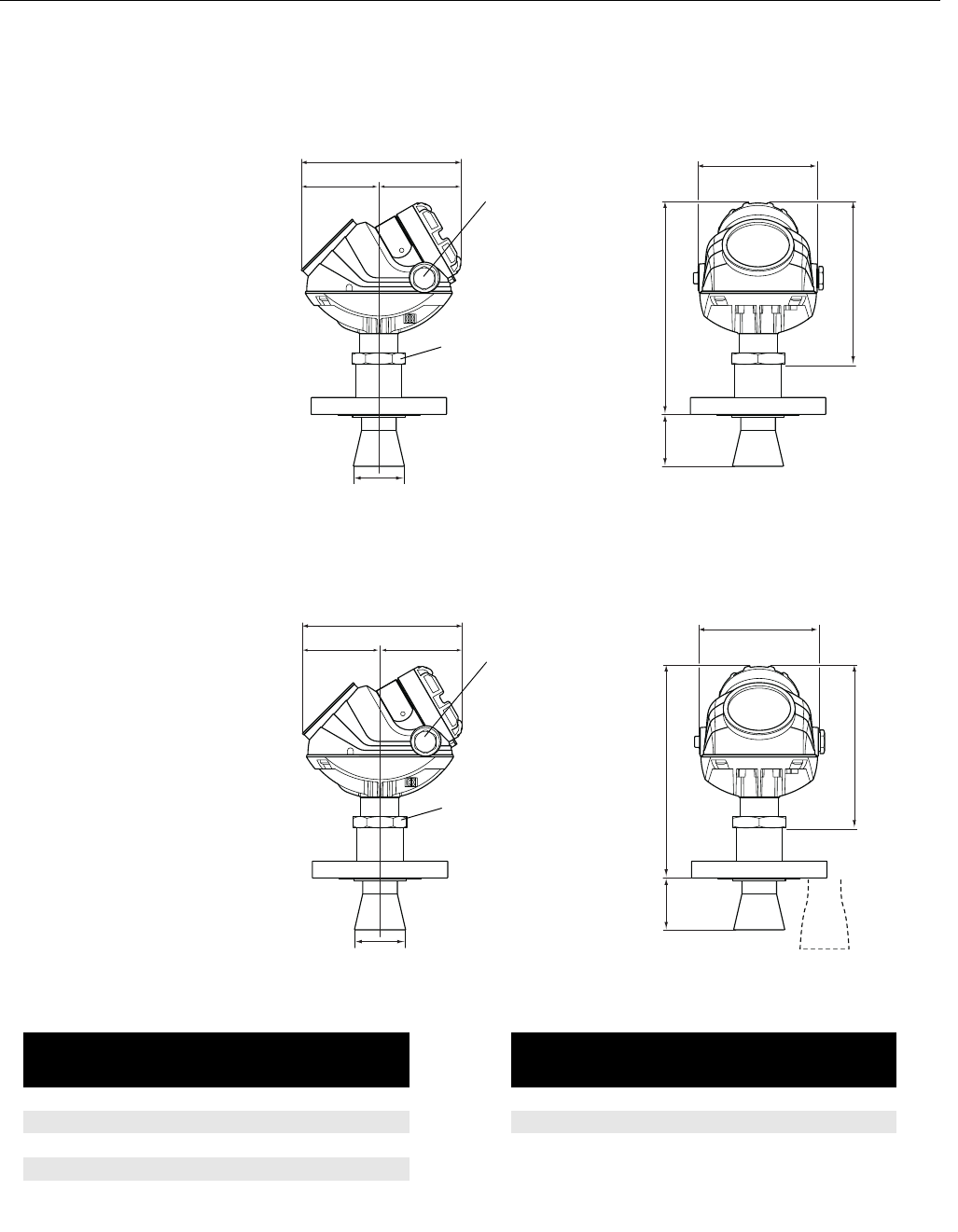
Reference Manual
00809-0100-4026, Rev AA
November 2003
A-3
Rosemount 5400 Series
Preliminary copy
DIMENSIONAL
DRAWINGS
Figure A-1. Dimensions of 5401
Series transmitter Low
Frequency version with cone
antenna.
Figure A-2. Dimensions of 5402
Series transmitter High
Frequency version with cone
antenna.
DIMENSIONS_LF.EPS
B
A
xx
½ - 14 NPT
Optional
adapters:
M20x1.5
PG13.5
xx
xx xx
xx xx
s60
DIMENSIONS_HF.EPS
B
A
xx
½ - 14 NPT
Optional
adapters:
M20x1.5
PG13.5
xx
xx
xx
xx xx
s60
5401
Cone size (inch) A B
2 100 (4.0)
3
4
6
8
5402
Cone size (inch) A B
2 100 (4.0)
3
4
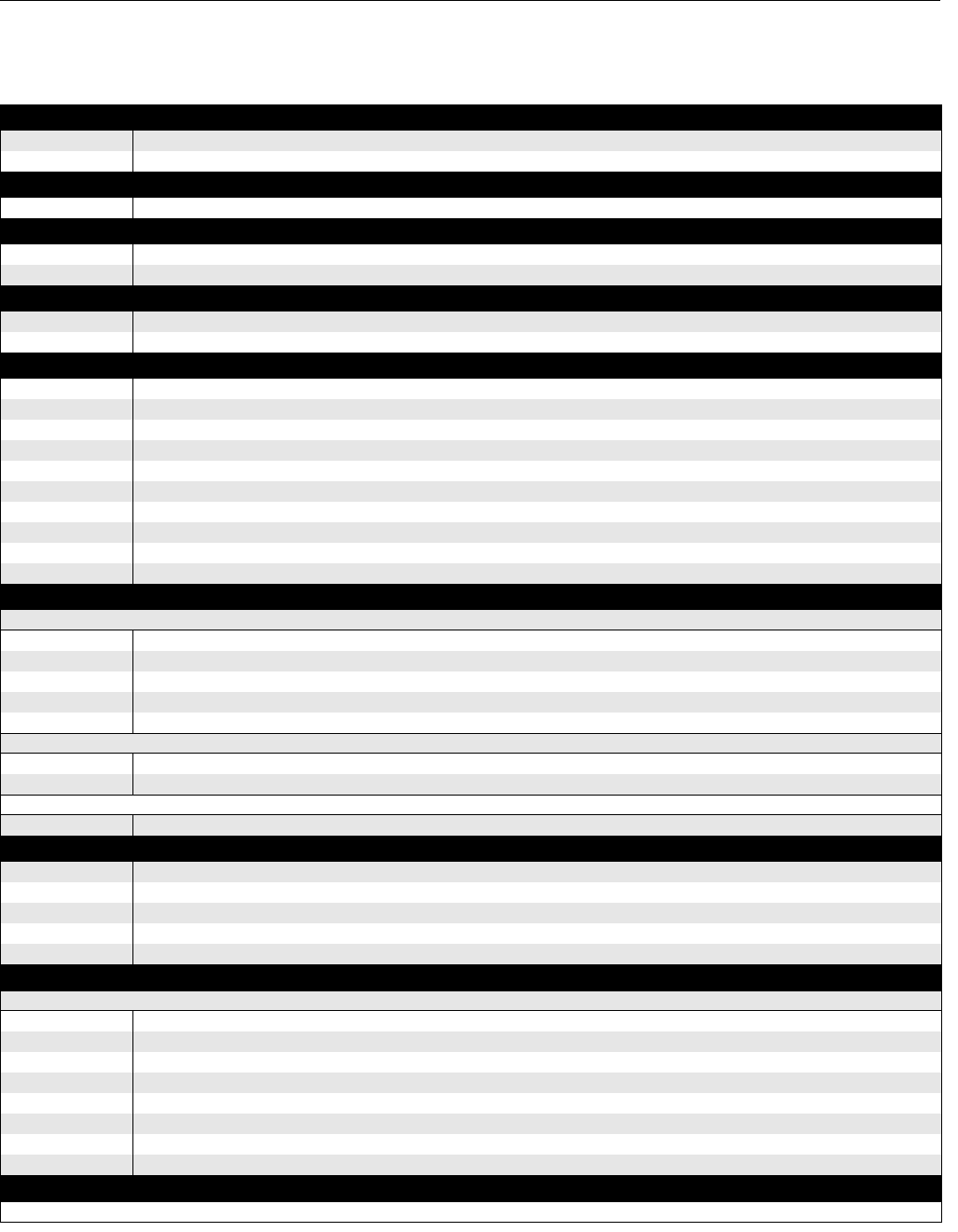
Reference Manual
00809-0100-4026, Rev AA
November 2003
Rosemount 5400 Series
A-4
Preliminary copy
ORDERING INFORMATION
Model Code for Rosemount 5401, Low Frequency (C-band)
Model Product Description
5401 Low frequency version
Code Housing Material
APolyurethane-covered Aluminum
Code Signal Output
H4-20 mA with HART® communication
F FOUNDATION™ fieldbus (AI block only)
Code Conduit / Cable Threads
11/2 inch - 14 NPT
2M20 x 1.5 adapter
Code Product Certifications
NA No Hazardous Locations Certifications
E1 ATEX Flameproof
I1 ATEX Intrinsic Safety
IA ATEX FISCO Intrinsic Safety (requires FOUNDATION™ fieldbus Signal Output)
E5 FM Explosion Proof
I5 FM Intrinsic Safety and Non-incendive
IE FM FISCO Intrinsic Safety (requires FOUNDATION™ fieldbus Signal Output)
E6 CSA Explosion Proof
I6 CSA Intrinsic Safety
IF CSA FISCO Intrinsic Safety (requires FOUNDATION™ fieldbus Signal Output)
Code Antenna - Size and Material
Cone Antennas
2S 2 in. DN 50, 316 / 316 L SST (EN 1.4404) (pipe installations only)
3S 3 in. DN 80, 316 / 316 L SST (EN 1.4404) (pipe installations only)
4S 4 in. DN 100, 316 / 316 L SST (EN 1.4404)
6S 6 in. DN 150, 316 / 316 L SST (EN 1.4404)
8S 8 in. DN 200, 316 / 316 L SST (EN 1.4404)
PTFE Disc Antennas
4P 4 in. PTFE, DN 100, 316 / 316 L SST (EN 1.4404)
6P 6 in. PTFE, DN 150, 316 / 316 L SST (EN 1.4404)
Other Antennas
XX Customer specific
Code Tank Sealing
PV PTFE with Viton o-rings
PK PTFE with Kalrez 6375 o-rings
PE PTFE with EPDM o-rings
PB PTFE with Buna-N o-rings
PD PTFE disc antenna (o-rings not needed) (only for disc antenna)
Code Process Connection and Material
ANSI Flanges
AA 2 inch, 150 lbs, 316 / 316 L SST (EN 1.4404)
AB 2 inch, 300 lbs, 316 / 316 L SST (EN 1.4404)
BA 3 inch, 150lbs, 316 / 316 L SST (EN 1.4404)
BB 3 inch, 300 lbs, 316 / 316 L SST (EN 1.4404)
CA 4 inch, 150 lbs, 316 / 316 L SST (EN 1.4404)
CB 4 inch, 300 lbs, 316 / 316 L SST (EN 1.4404)
DA 6 inch, 150 lbs, 316 / 316 L SST (EN 1.4404)
EA 8 inch, 150 lbs, 316 / 316 L SST (EN 1.4404)
Code Process Connection and Material, continued (5401)
DIN Flanges
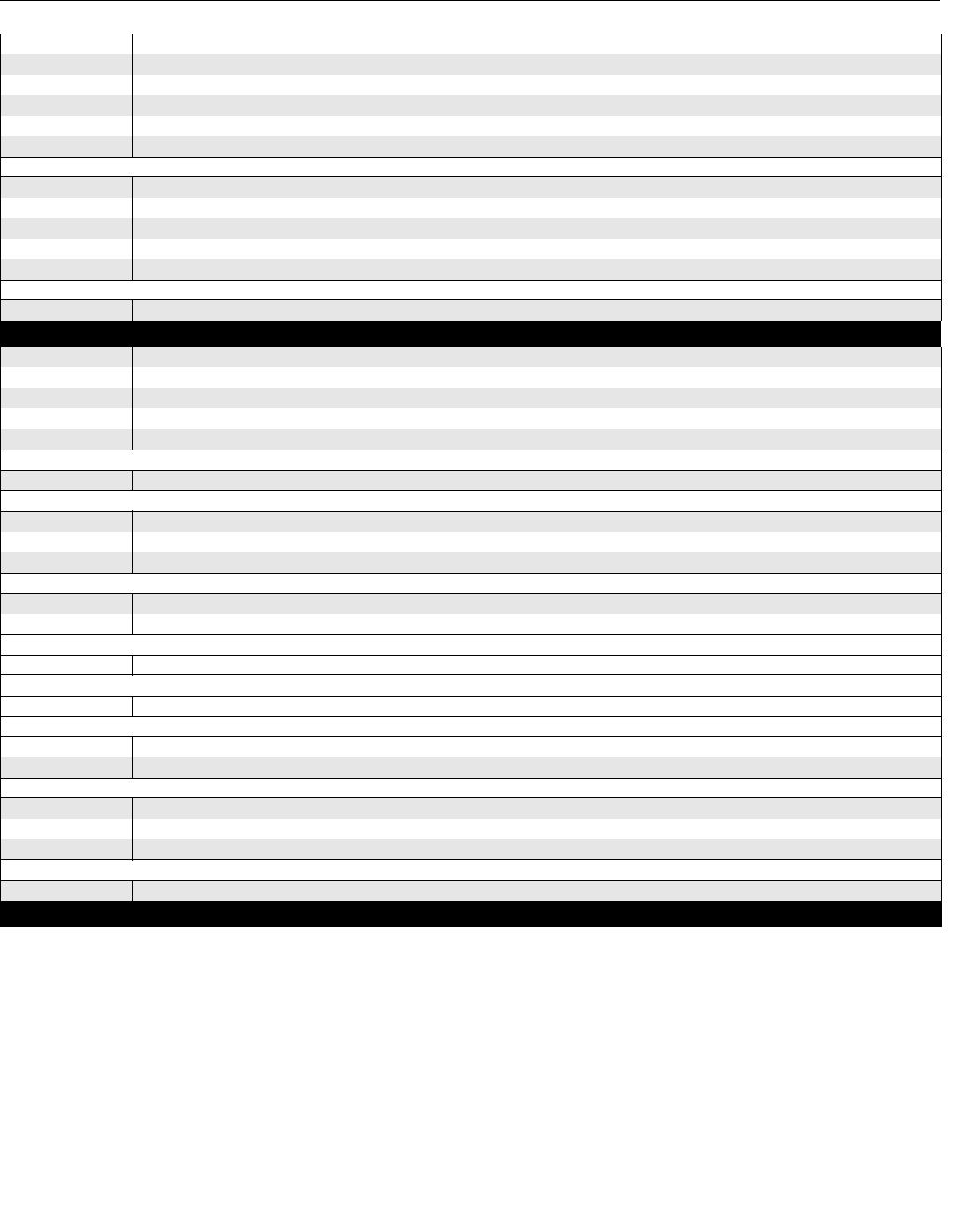
Reference Manual
00809-0100-4026, Rev AA
November 2003
A-5
Rosemount 5400 Series
Preliminary copy
HB DN 50 PN 40, 316 / 316 L SST (EN 1.4404)
IB DN 80 PN 40, 316 / 316 L SST (EN 1.4404)
JA DN 100 PN 16, 316 / 316 L SST (EN 1.4404)
JB DN 100 PN 40, 316 / 316 L SST (EN 1.4404)
KA DN 150 PN 16, 316 / 316 L SST (EN 1.4404)
LA DN 200 PN 16, 316 / 316 L SST (EN 1.4404)
JIS Flanges
TA 10 K 50 A, 316 / 316 L SST (EN 1.4404)
UA 10 K 80 A, 316 / 316 L SST (EN 1.4404)
VA 10 K 100 A, 316 / 316 L SST (EN 1.4404)
YA 10 K 150 A, 316 / 316 L SST (EN 1.4404)
ZA 10 K 200 A, 316 / 316 L SST (EN 1.4404)
Other Flanges
XX Customer specific
Code Options
M1 Integral digital display
BT Bar Code Tag with tag number and purchase order number
T1 Transient Protection Terminal Block (standard with FISCO)
SP Weather Protection Shield
GS Guaranteed start-up at -58°F (-50°F)
Software Configuration
C1 Factory configuration (CDS required with order)
Alarm Limit Configuration
C4 NAMUR alarm and saturation levels, high alarm
C5 NAMUR alarm and saturation levels, low alarm
C8 Low alarm(1) (standard Rosemount alarm and saturation levels)
Special Certificates
Q4 Calibration Data Certificate
Q8 Material Traceability Certification per EN 10204 3.1B(2)
Special Procedures
P1 Hydrostatic testing
Overfill
U1 Overfill protection according to German WHG/TÜV
Plantweb Functionality
A1 Regulatory Control: PID. (Requires FOUNDATION™ fieldbus)
D1 Diagnostics suite
Antenna Extensions
S1 100 mm, 316 / 316 L SST (EN 1.4404)
S2 200 mm, 316 / 316 L SST (EN 1.4404)
S3 300 mm, 316 / 316 L SST (EN 1.4404)
Customer Special
XX Special option
Typical Model Number: 5401 A F 1 IA 4P PD CA - M1 C1 A1
(1) Standard alarm setting is freeze (high)??????
(2) Option available for pressure retaining wetted parts.
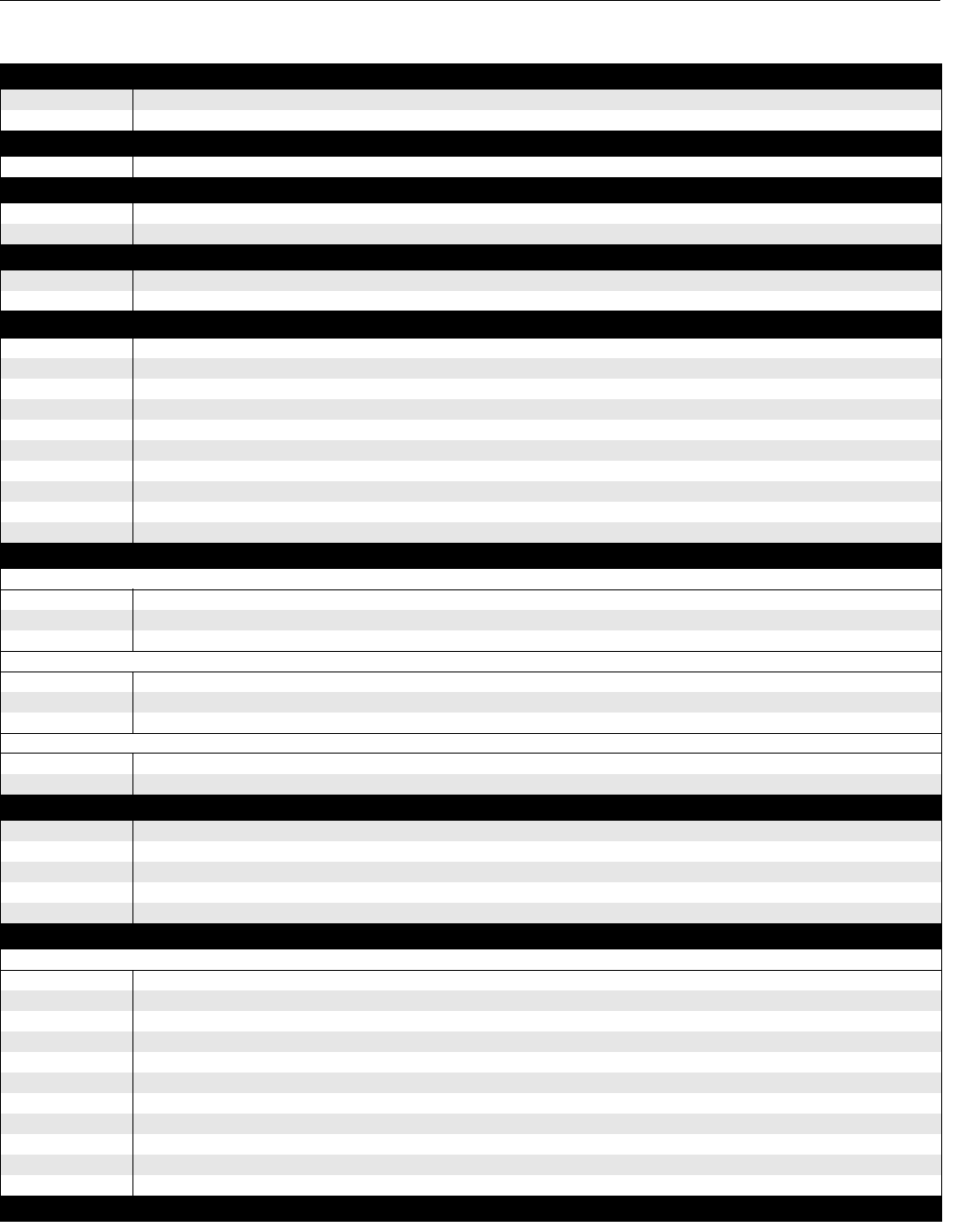
Reference Manual
00809-0100-4026, Rev AA
November 2003
Rosemount 5400 Series
A-6
Preliminary copy
Model Code for Rosemount 5402, High Frequency (K-band)
Model Product Description
5402 High frequency version
Code Housing Material
APolyurethane-covered Aluminum
Code Signal Output
H4-20 mA with HART® communication
F FOUNDATION™ fieldbus (AI block only)
Code Conduit / Cable Threads
11/2 inch - 14 NPT
2M20 x 1.5 adapter
Code Product Certifications
NA No Hazardous Locations Certifications
E1 ATEX Flameproof
I1 ATEX Intrinsic Safety
IA ATEX FISCO Intrinsic Safety (requires FOUNDATION™ fieldbus Signal Output)
E5 FM Explosion Proof
I5 FM Intrinsic Safety and Non-incendive
IE FM FISCO Intrinsic Safety (requires FOUNDATION™ fieldbus Signal Output)
E6 CSA Explosion Proof
I6 CSA Intrinsic Safety
IF CSA FISCO Intrinsic Safety (requires FOUNDATION™ fieldbus Signal Output)
Code Antenna - Size and Material
Cone Antennas
2S 2 in. DN 50, 316 / 316 L SST (EN 1.4404) (pipe installations only)
3S 3 in. DN 80, 316 / 316 L SST (EN 1.4404) (pipe installations only)
4S 4 in. DN 100, 316 / 316 L SST (EN 1.4404)
PTFE Disc Antennas
2P 2 in. PTFE, DN 50, 316 / 316 L SST (EN 1.4404)
3P 3 in. PTFE, DN 80, 316 / 316 L SST (EN 1.4404)
4P 4 in. PTFE, DN 100, 316 / 316 L SST (EN 1.4404)
Other Antennas
XX Customer specific
Code Tank Sealing
PV PTFE with Viton o-rings
PK PTFE with Kalrez 6375 o-rings
PE PTFE with EPDM o-rings
PB PTFE with Buna-N o-rings
PD PTFE disc antenna (o-rings not needed) (only for disc antenna)
Code Process Connection and Material
ANSI Flanges
AA 2 inch, 150 lbs, 316 / 316 L SST (EN 1.4404)
AB 2 inch, 300 lbs, 316 / 316 L SST (EN 1.4404)
BA 3 inch, 150lbs, 316 / 316 L SST (EN 1.4404)
BB 3 inch, 300 lbs, 316 / 316 L SST (EN 1.4404)
CA 4 inch, 150 lbs, 316 / 316 L SST (EN 1.4404)
CB 4 inch, 300 lbs, 316 / 316 L SST (EN 1.4404)
DA 6 inch, 150 lbs, 316 / 316 L SST (EN 1.4404)
EA 8 inch, 150 lbs, 316 / 316 L SST (EN 1.4404)
IB DN 80 PN 40, 316 / 316 L SST (EN 1.4404)
JA DN 100 PN 16, 316 / 316 L SST (EN 1.4404)
JB DN 100 PN 40, 316 / 316 L SST (EN 1.4404)
Code Process Connection and Material, continued (5402)
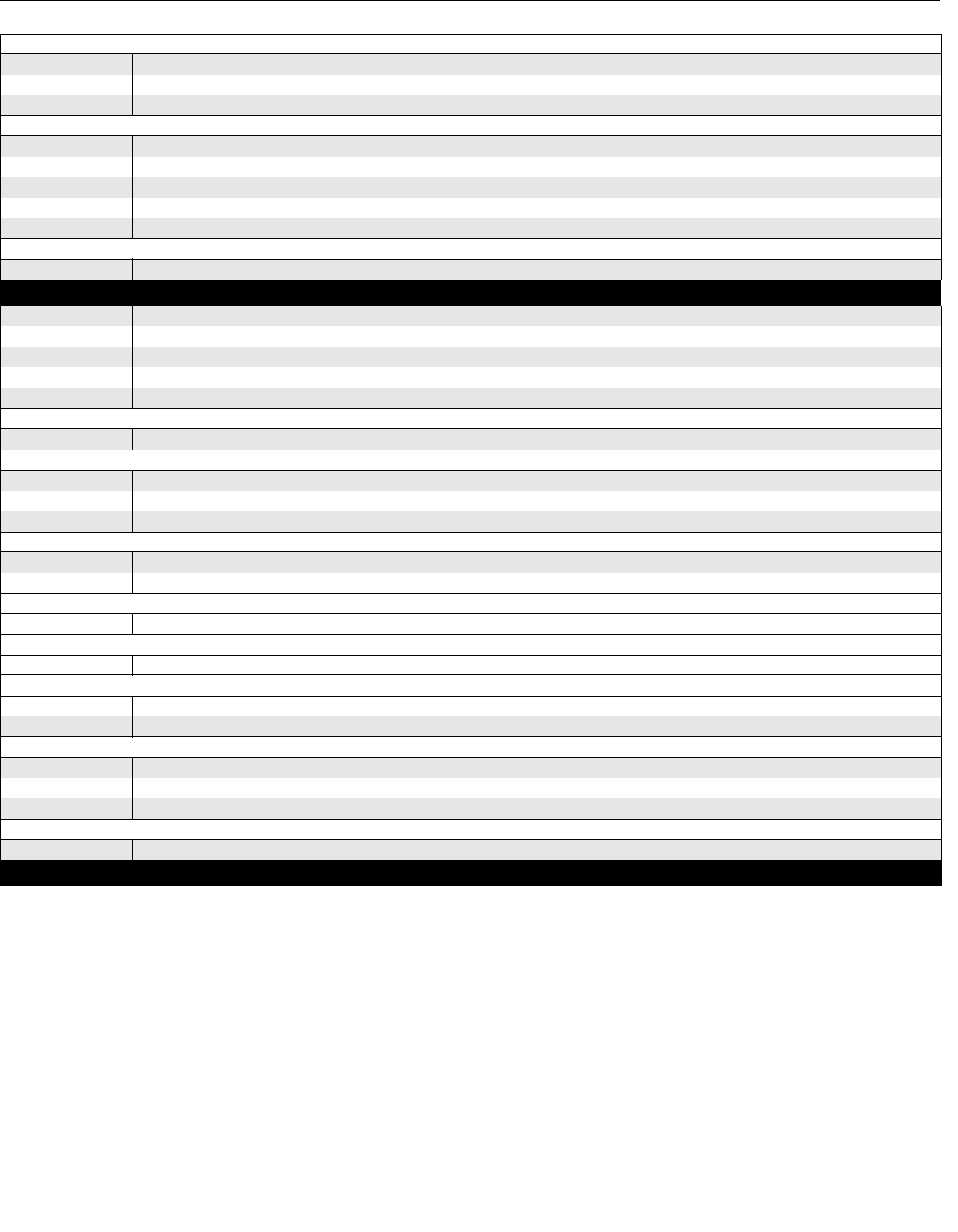
Reference Manual
00809-0100-4026, Rev AA
November 2003
A-7
Rosemount 5400 Series
Preliminary copy
DIN Flanges
HB DN 50 PN 40, 316 / 316 L SST (EN 1.4404)
KA DN 150 PN 16, 316 / 316 L SST (EN 1.4404)
LA DN 200 PN 16, 316 / 316 L SST (EN 1.4404)
JIS Flanges
TA 10 K 50 A, 316 / 316 L SST (EN 1.4404)
UA 10 K 80 A, 316 / 316 L SST (EN 1.4404)
VA 10 K 100 A, 316 / 316 L SST (EN 1.4404)
YA 10 K 150 A, 316 / 316 L SST (EN 1.4404)
ZA 10 K 200 A, 316 / 316 L SST (EN 1.4404)
Other Flanges
XX Customer specific
Code Options
M1 Integral digital display
BT Bar Code Tag with tag number and purchase order number
T1 Transient Protection Terminal Block (standard with FISCO)
SP Weather Protection Shield
GS Guaranteed start-up at -58°F (-50°F)
Software Configuration
C1 Factory configuration (CDS required with order)
Alarm Limit Configuration
C4 NAMUR alarm and saturation levels, high alarm
C5 NAMUR alarm and saturation levels, low alarm
C8 Low alarm(1) (standard Rosemount alarm and saturation levels)
Special Certificates
Q4 Calibration Data Certificate
Q8 Material Traceability Certification per EN 10204 3.1B(2)
Special Procedures
P1 Hydrostatic testing
Overfill
U1 Overfill protection according to German WHG/TÜV
Plantweb Functionality
A1 Regulatory Control: PID. (Requires FOUNDATION™ fieldbus)
D1 Diagnostics suite
Antenna Extensions
S1 100 mm, 316 / 316 L SST (EN 1.4404)
S2 200 mm, 316 / 316 L SST (EN 1.4404)
S3 300 mm, 316 / 316 L SST (EN 1.4404)
Customer Special
XX Special option
Typical Model Number: 5401 A F 1 IA 4P PD CA - M1 C1 A1
(1) Standard alarm setting is freeze (high)??????
(2) Option available for pressure retaining wetted parts.
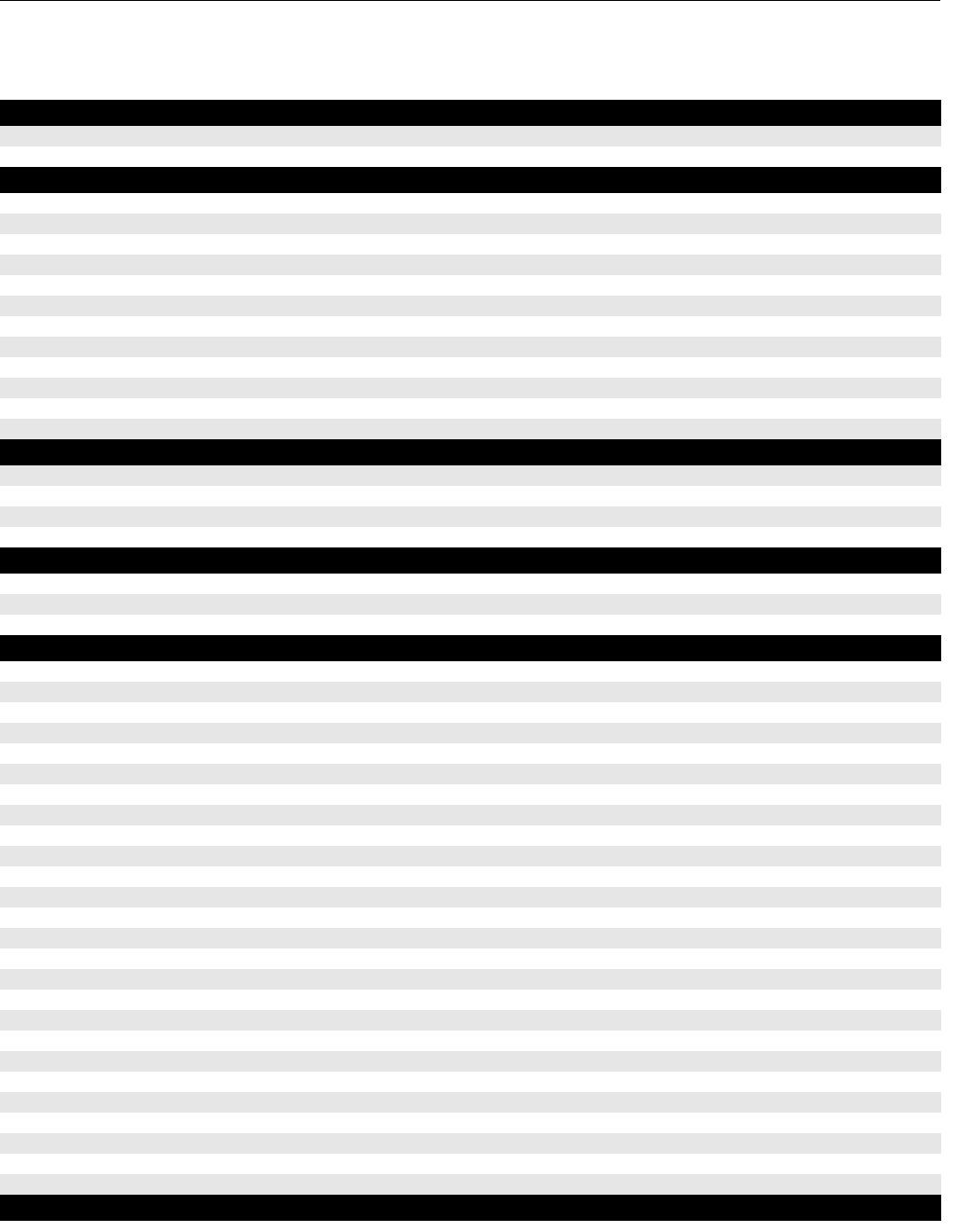
Reference Manual
00809-0100-4026, Rev AA
November 2003
Rosemount 5400 Series
A-8
Preliminary copy
SPARE PARTS
Spare parts list Transmitter head Model 5401/5402
Model Product Description
5401HF High frequency version, 26 GHz
5401LF Low frequency version, 6 GHz
Code Cone Antenna - Size and Material
Stainless Steel 316L (1.4...)
2S 2 in. DN 50 (pipe installations only)
3S 3 in. DN 80 (pipe installations only)
4S 4 in. DN 100
6S 6 in. DN 150 (only available for 5401LF)
8S 8 in. DN 200 (only available for 5401LF)
Hastelloy (HC..)
2H 2 in. DN 50 (pipe installations only)
3H 3 in. DN 80 (pipe installations only)
4H 4 in. DN 100
6H 6 in. DN 150 (only available for 5401LF)
8H 8 in. DN 200 (only available for 5401LF)
Code Antenna Extensions (delivered in same material as antenna)
XX No antenna extension
X1 100 mm
X2 200 mm
X3 300 mm
Code Tank Sealing
PV PTFE with Viton o-rings
PK PTFE with Kalrez o-rings
PE PTFE with EPDM o-rings
Code Flange Process Connection
ANSI Flanges
AA 2 inch, 150 lbs
AB 2 inch, 300 lbs
AC 2 inch, 600 lbs
BA 3 inch, 150lbs
BB 3 inch, 300 lbs
BC 3 inch, 600 lbs
CA 4 inch, 150 lbs
CB 4 inch, 300 lbs
CC 4 inch, 600 lbs
DA 6 inch, 150 lbs
DB 6 inch, 300 lbs
DC 6 inch, 600 lbs
EA 8 inch, 150 lbs
EB 8 inch, 300 lbs
EC 8 inch, 600 lbs
DIN Flanges
HA DN 50 PN 16
HB DN 50 PN 40
HC DN 50 PN 64
IA DN 80 PN 16
IB DN 80 PN 40
ÏC DN 80 PN 64
JA DN 100 PN 16
JB DN 100 PN 40
JC DN 100 PN 64
Code Flange Process Connection
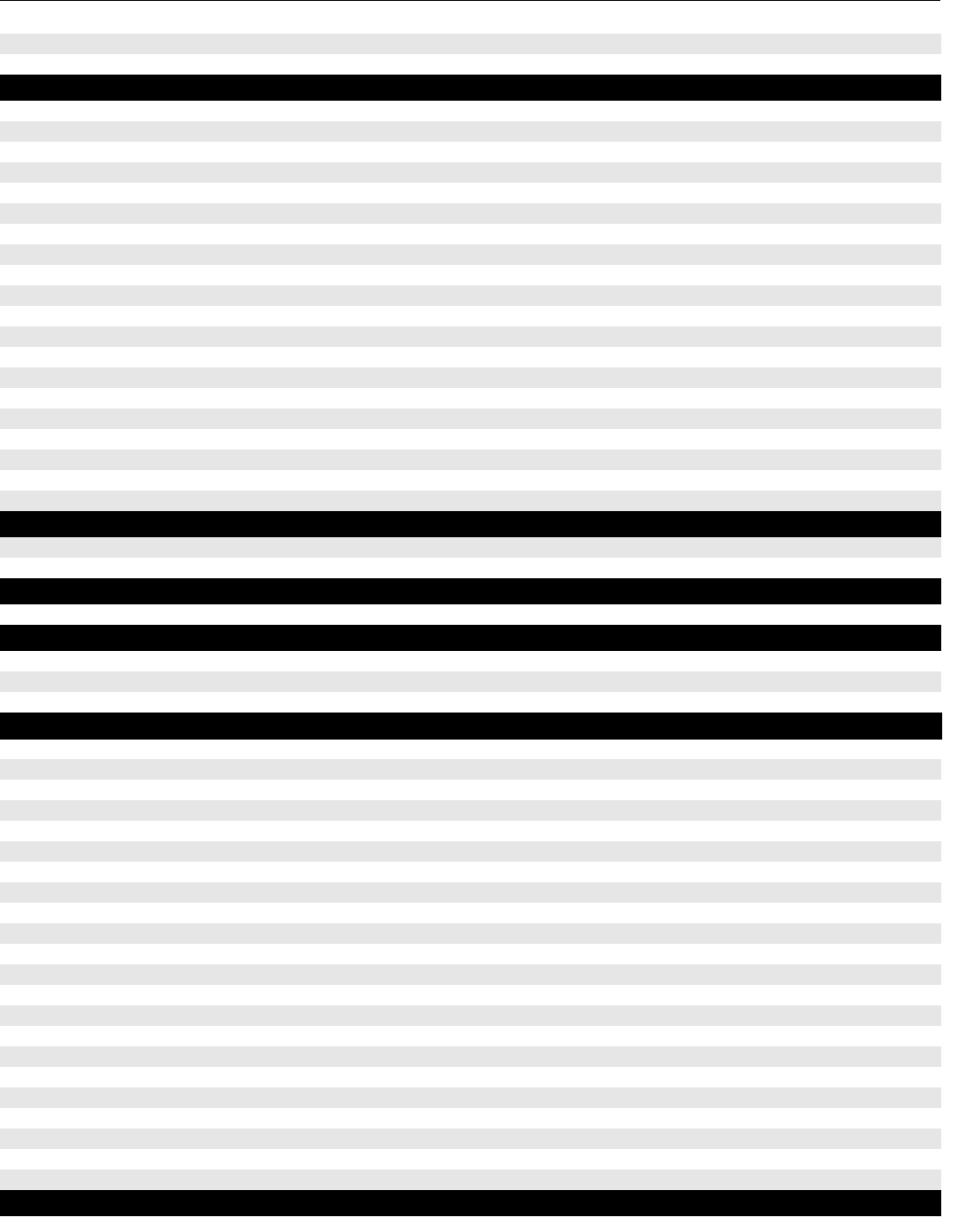
Reference Manual
00809-0100-4026, Rev AA
November 2003
A-9
Rosemount 5400 Series
Preliminary copy
KA DN 150 PN 16
KB DN 150 PN 40
Code Flange Process Connection, continued
DC DN 150 PN 64
EA DN 200 PN 16
EB DN 200 PN 40
EC DN 200 PN 64
JIS Flanges
PA
PB
PC
QA
QB
QC
RA
RB
RC
SA
SB
SC
TA
TB
TC
Code Signal Output
H4-20 mA with HART® communication
FFieldbus Foundation
Code Housing Material
APolyurethane-covered Aluminum
Code Conduit / Cable Threads
11/2 inch - 14 NPT
2M20 x 1.5 adapter
3PG 13.5 adapter
Code Product Certifications
NA No Hazardous Locations Certifications
E1 ATEX Flameproof
E4 JIS Flameproof
E5 FM Explosion Proof
E6 CSA Explosion Proof
E7 SAA Flameproof
E? GOSStandart Flameproof
E? GP (China) Flameproof
I1 ATEX Intrinsic Safety
I4 JIS Intrinsic Safety
I5 FM Intrinsic Safety and Non-incendive
I6 CSA Intrinsic Safety
I7 SAA Intrinsic Safety
I? GOSStandart Intrinsic Safety
I? GP (China) Intrinsic Safety
IA ATEX FISCO Intrinsic Safety (requires Fieldbus Foundation Signal Output)
ID JIS FISCO Intrinsic Safety (requires Fieldbus Foundation Signal Output)
IE FM FISCO Intrinsic Safety (requires Fieldbus Foundation Signal Output)
IF CSA FISCO Intrinsic Safety (requires Fieldbus Foundation Signal Output)
IG SAA FISCO Intrinsic Safety (requires Fieldbus Foundation Signal Output)
?? Overfill protection according to German WHG/TÜV
?? Telecom certification for non-metal tanks
Typical Model Number: 5401LF 2S XX PV AA H A 1 E1 M1 ?? C1
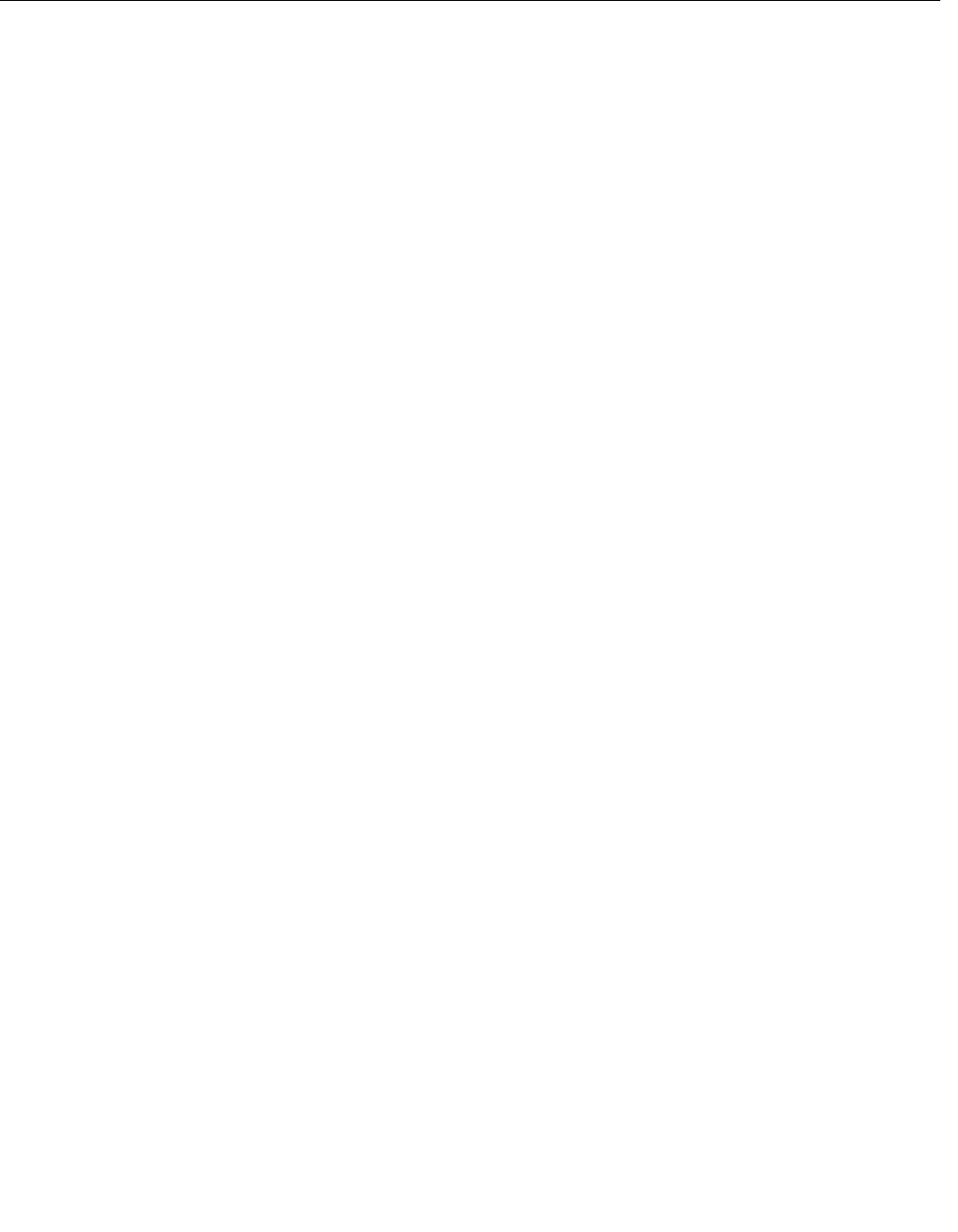
Reference Manual
00809-0100-4026, Rev AA
November 2003
Rosemount 5400 Series
A-10
Preliminary copy
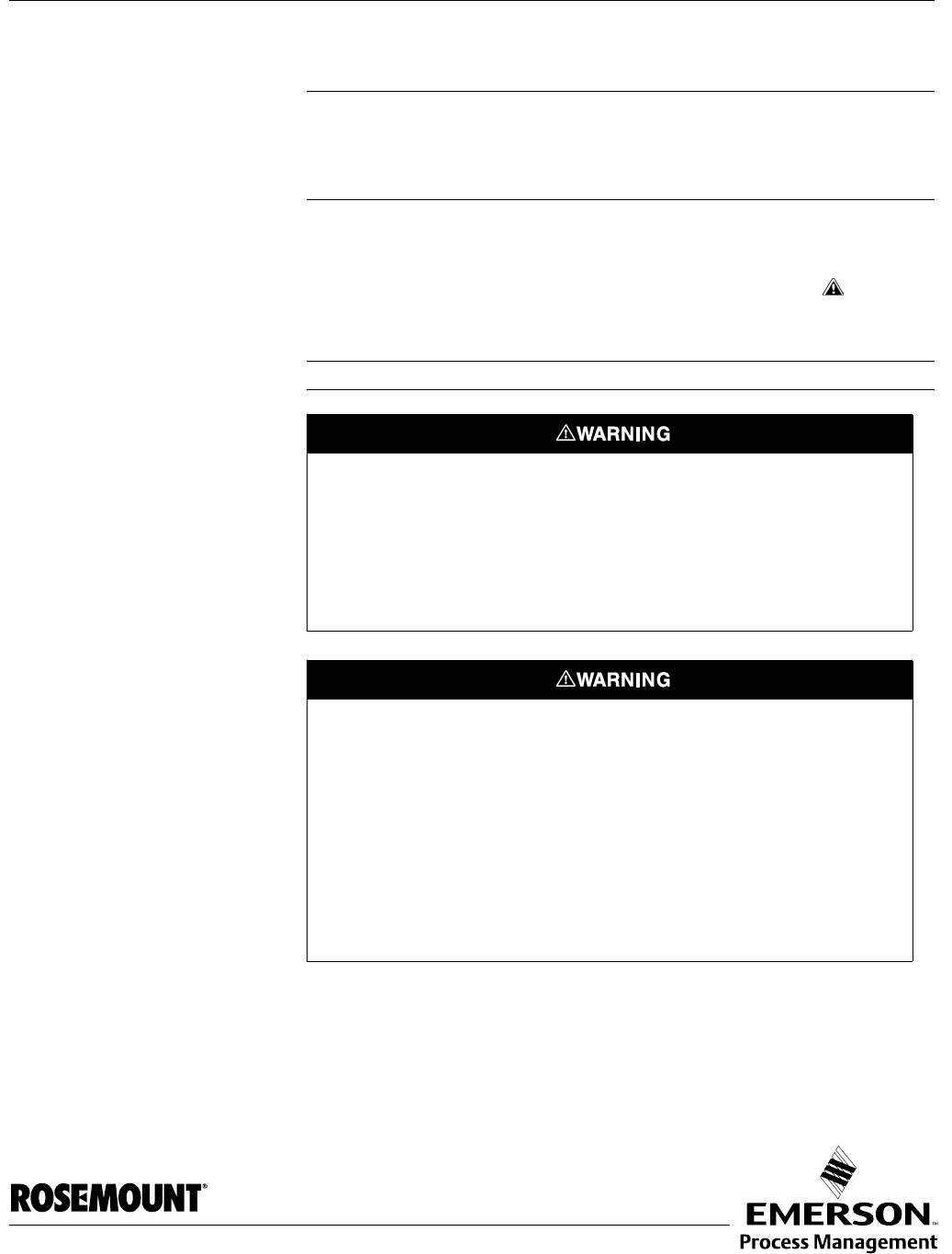
Reference Manual
00809-0100-xx, Rev AA
November 2003 Rosemount 5400
www.rosemount.com
Preliminary copy
Appendix B Hazardous Approvals
Safety messages . . . . . . . . . . . . . . . . . . . . . . . . . . . . . . . . . page B-1
European Atex Directive Information . . . . . . . . . . . . . . . . page B-3
Hazardous Locations Certifications . . . . . . . . . . . . . . . . . page B-5
Approval Drawings . . . . . . . . . . . . . . . . . . . . . . . . . . . . . . . page B-7
SAFETY MESSAGES Procedures and instructions in this section may require special precautions to
ensure the safety of the personnel performing the operations. Information that
raises potential safety issues is indicated by a warning symbol ( ). Please
refer to the following safety messages before performing an operation
preceded by this symbol.
Explosions could result in death or serious injury:
Verify that the operating environment of the gauge is consistent with the appropriate
hazardous locations certifications.
Before connecting a HART-based communicator in an explosive atmosphere, make
sure the instruments in the loop are installed in accordance with intrinsically safe or
non-incendive field wiring practices.
Do not remove the gauge cover in explosive atmospheres when the circuit is alive.
Failure to follow safe installation and servicing guidelines could result in death or
serious injury:
Make sure the transmitter is installed by qualified personnel and in accordance with
applicable code of practice.
Use the equipment only as specified in this manual. Failure to do so may impair the
protection provided by the equipment.
Do not perform any service other than those contained in this manual unless you are
qualified.
Substitution of components may impair Intrinsic Safety.
To prevent ignition of flammable or combustible atmospheres, disconnect power before
servicing.
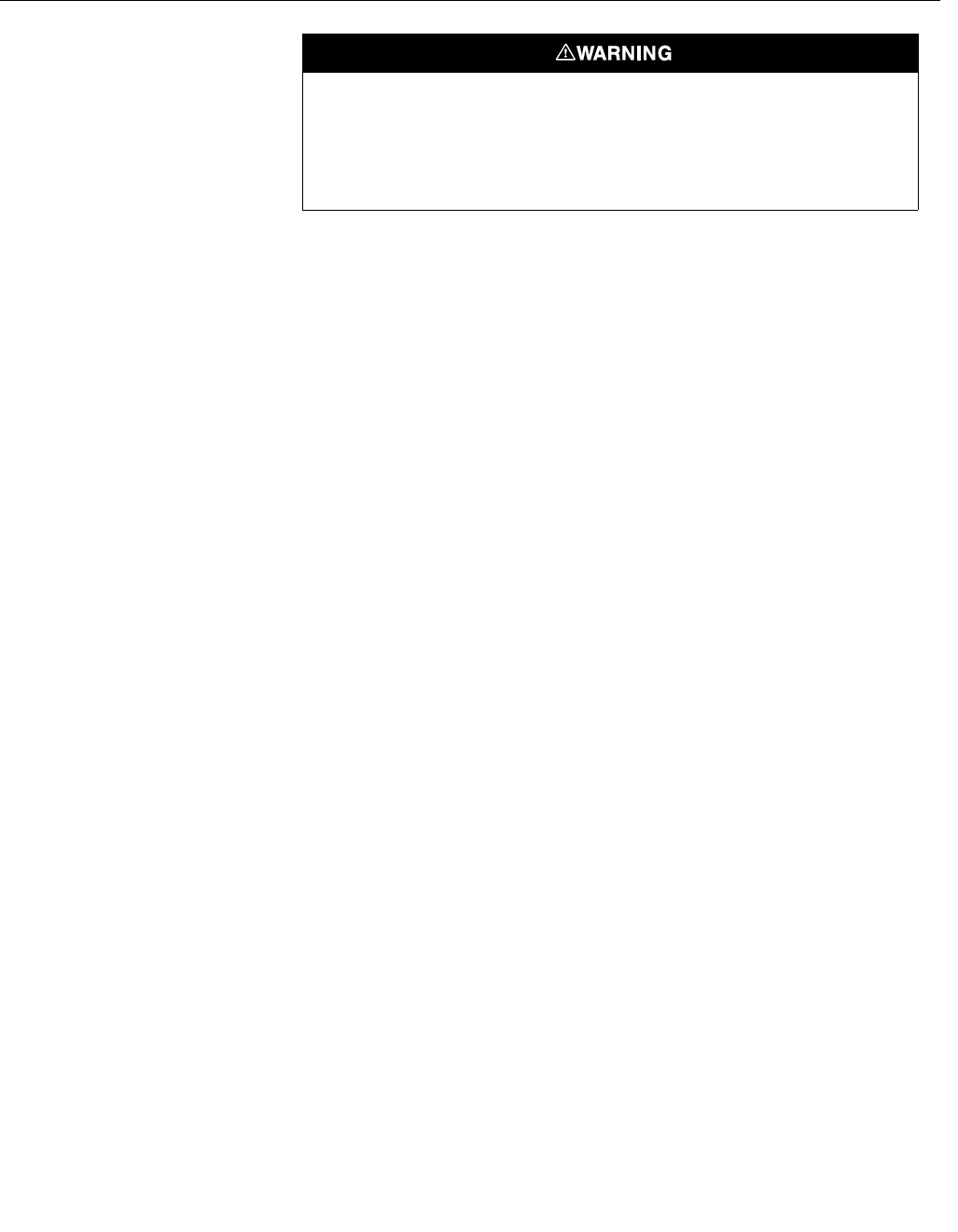
Reference Manual
00809-0100-xx, Rev AA
November 2003
Rosemount 5400
B-2
Preliminary copy
High voltage that may be present on leads could cause electrical shock:
Avoid contact with leads and terminals.
Make sure the main power to the Radar Transmitter is off and the lines to any other
external power source are disconnected or not powered while wiring
the gauge.
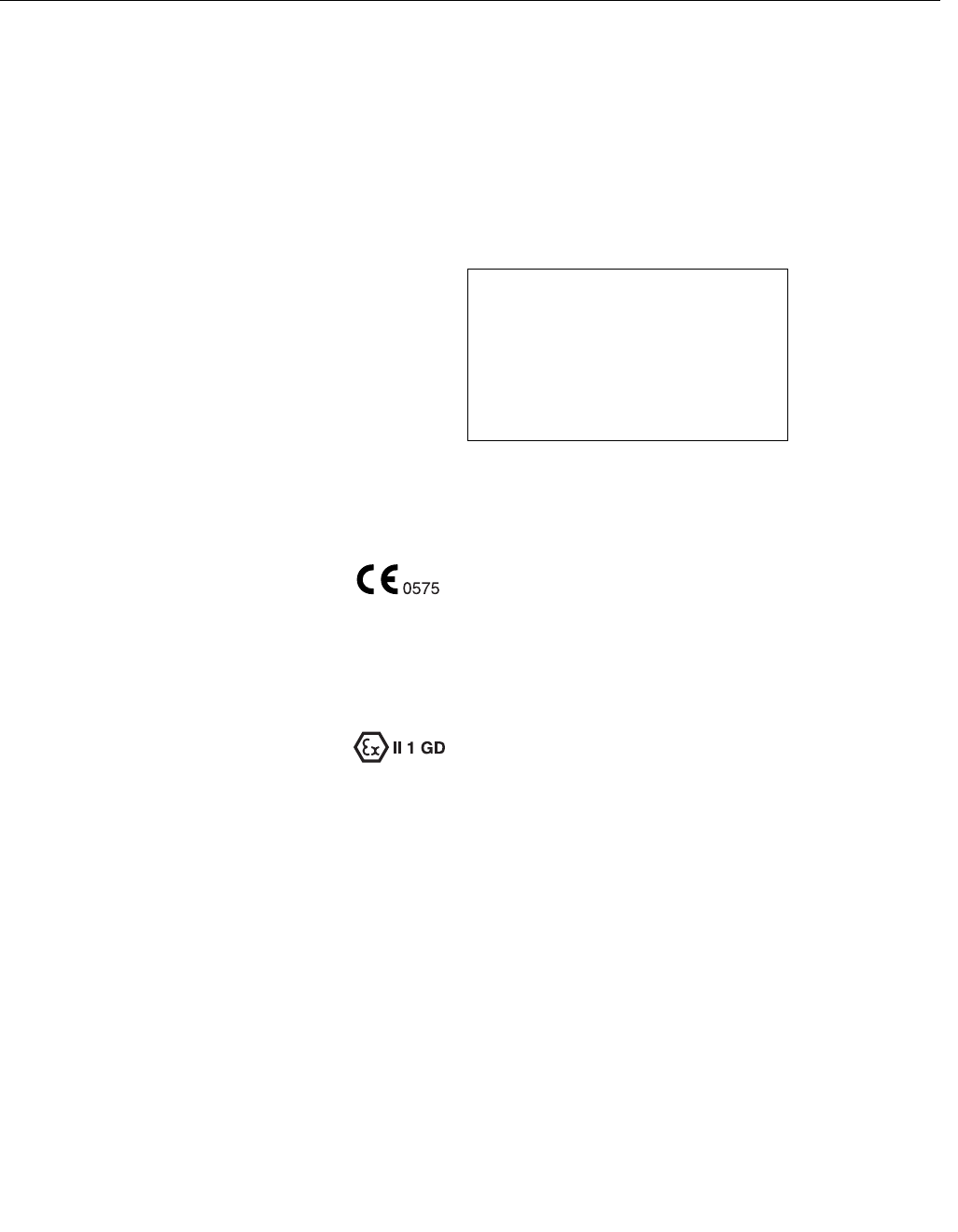
Reference Manual
00809-0100-xx, Rev AA
November 2003
B-3
Rosemount 5400
Preliminary copy
EUROPEAN ATEX
DIRECTIVE
INFORMATION
Intrinsic Safety The Rosemount 5400 Series Transmitter that has the following label attached
has been certified to comply with Directive 94/9/EC of the European
Parliament and the Council as published in the Official Journal of the
European Communities No. L 100/1 on 19-April-1994.
Figure B-1. Approval Label
ATEX (KEMA) and Name Plate
The following information is provided as part of the label of the transmitter:
• Name and address of the manufacturer (Rosemount).
• CE Conformity Marking
• Complete model number
• The serial number of the device
• Year of construction
• Marking for explosion protection:
• EEx ia IIC T4 (-40 °C ≤ Ta ≤ +70 °C)
Ui=xx V
Ii=xx mA
Pi=x W
Ci=x, Li=x
• xx ATEX certificate number:
Label
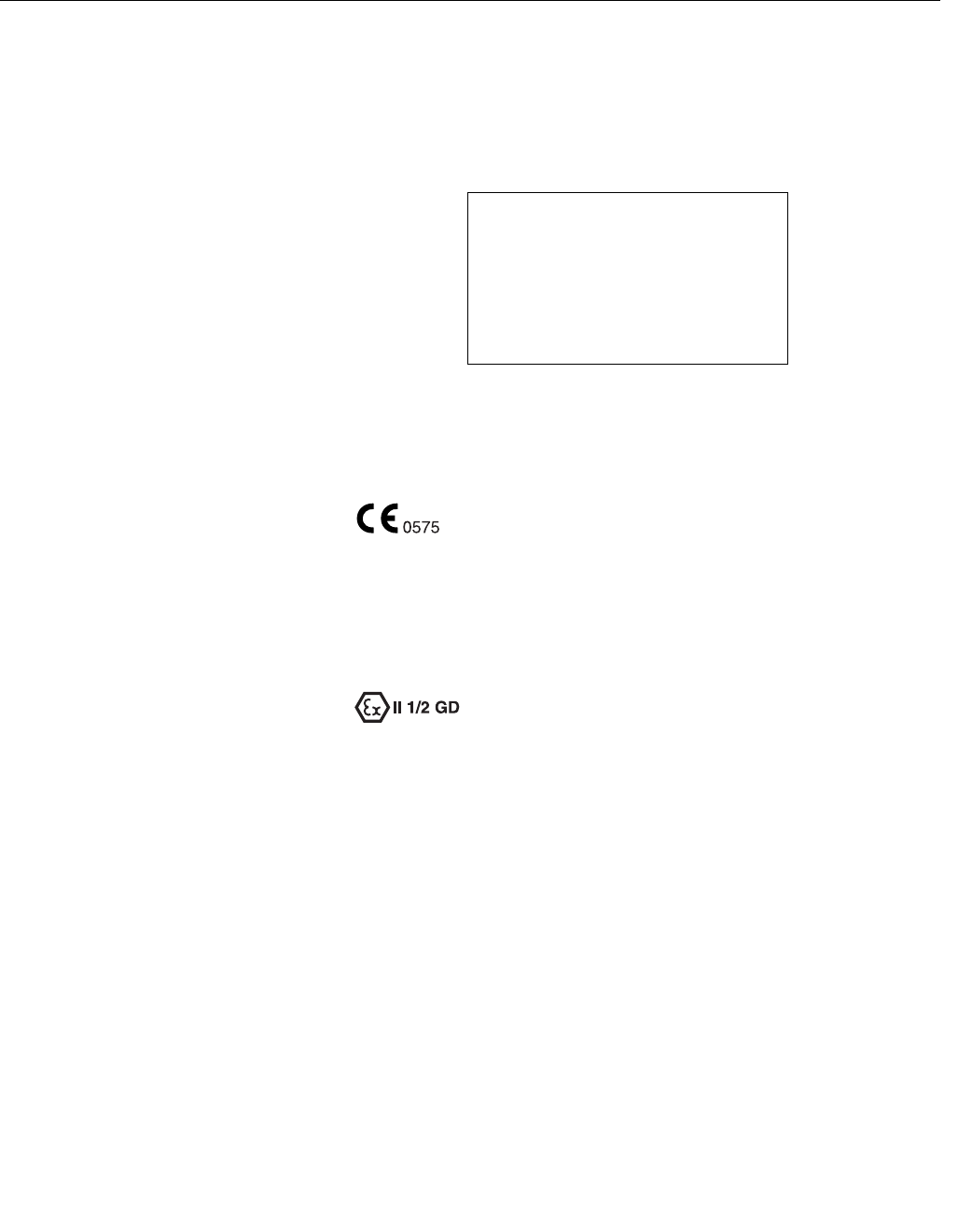
Reference Manual
00809-0100-xx, Rev AA
November 2003
Rosemount 5400
B-4
Preliminary copy
Flame Proof The Rosemount 5400 Series Transmitter that has the following label attached
has been certified to comply with Directive 94/9/EC of the European
Parliament and the Council as published in the Official Journal of the
European Communities No. L 100/1 on 19-April-1994.
Figure B-2. Approval Label
ATEX (KEMA) and Name Plate
The following information is provided as part of the label of the transmitter:
• Name and address of the manufacturer (Rosemount).
• CE Conformity Marking
• Complete model number
• The serial number of the device
• Year of construction
• Marking for explosion protection:
• EEx d[ia]ia IIC T4 (-40 °C<Ta< +70 °C)
• KEMA ATEX certificate number: KEMA 01ATEXyyyy
Label
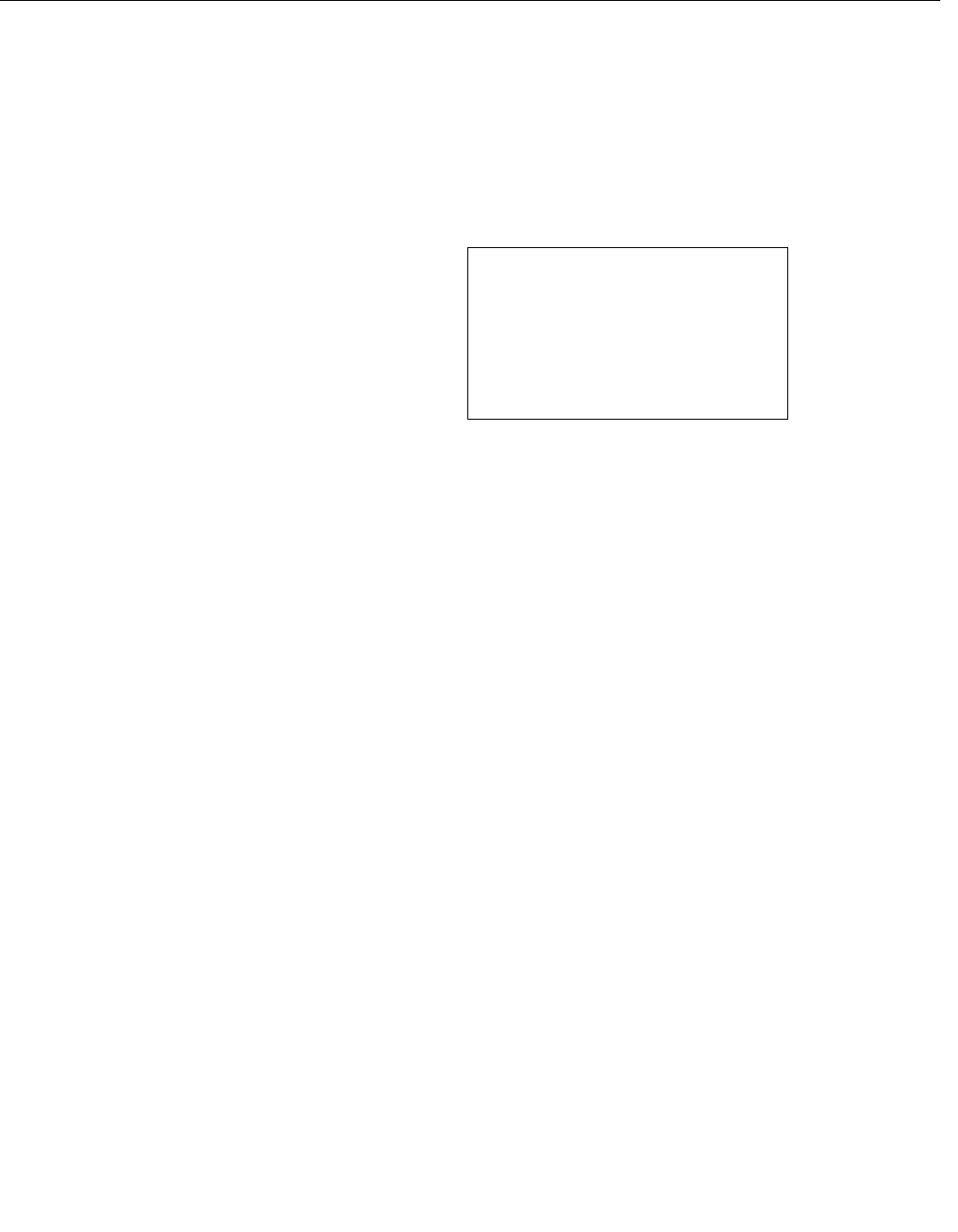
Reference Manual
00809-0100-xx, Rev AA
November 2003
B-5
Rosemount 5400
Preliminary copy
HAZARDOUS
LOCATIONS
CERTIFICATIONS
The Rosemount 5400 Series Transmitters that have the following labels
attached have been certified to comply with the requirements of the approval
agencies noted.
Factory Mutual (FM)
Approvals
Figure B-3. Approval Labels
Factory Mutual (FM)
E5 Explosion-Proof for Class I, Division 1, Groups A, B, C and D.
Dust-Ignition proof for Class II/III, Division 1, Groups E, F and G; with
intrinsically safe connections to Class I, II, III, Div 1, Groups A, B, C, D,
E, F and G.
Temperature class T4 @+70 °C.
Ambient temperature limits: -40°C to + 70°C
Factory Sealed.
I5 Intrinsically Safe for Class I, II, III, Division 1, Groups A, B, C, D
and G.
Intrinsically Safe for Class I, Zone 0, AEX ia IIC T4 Ta=70°C.
Temperature code T4 at 70°C max ambient.
Control Drawing: xxx.
Non-incendive for Class I, Division 2, Groups A, B, C and D.
Suitable for Class II, III, Division 2, Groups F and G.
Non-incendive maximum operating parameters: 42 V, 25 mA.
Temperature code T4 at 70°C max ambient.
Label
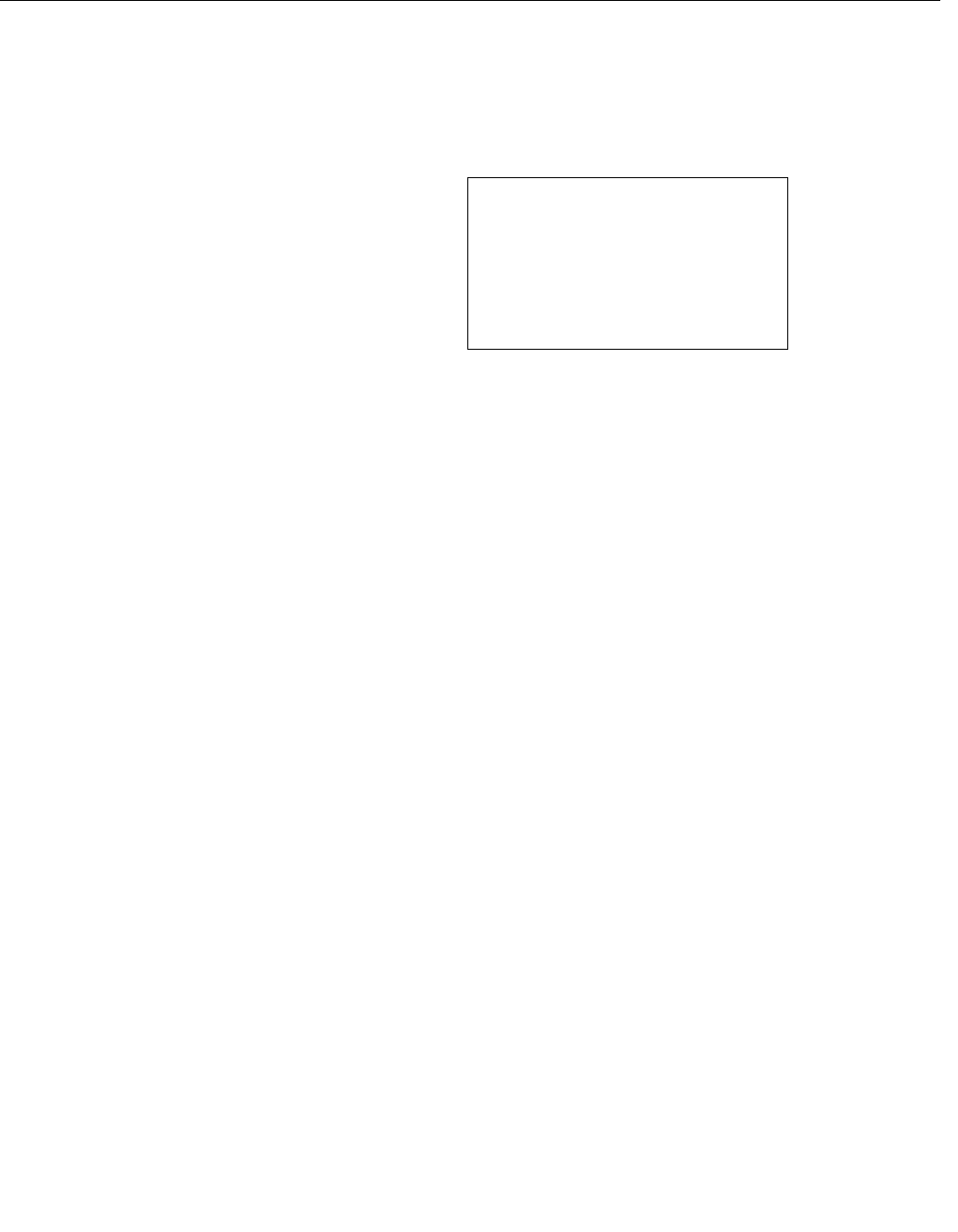
Reference Manual
00809-0100-xx, Rev AA
November 2003
Rosemount 5400
B-6
Preliminary copy
Canadian Standards
Association (CSA)
Approval
Cert. no. xxxx.
Figure B-4. Approval Label
Canadian Standards Association
(CSA)
E6 Explosion-Proof for Class I, Division 1, Groups C and D.
Dust Ignition Proof for Class II, Div. 1 and 2, Groups E, F and G.
Dust-Ignition proof for Class III, Division 1, Hazardous Locations
[Ex ia IIC T4] Ex ia IIC T4.
Ambient temperature limits: -40°C to + 70°C.
Factory Sealed.
I6 Intrinsically Safe: Ex ia IIC T4.
Intrinsically Safe for Class I, Division 1, Groups A, B, C and D.
Temperature code T4.
Control Drawing: xxxx.
Non-incendive for Class III, Division 1, Hazardous Locations.
Non-incendive for Class I, Division 2, Groups A, B, C and D.
Ambient temperature limits: -40 °C to + 70 °C.
Label
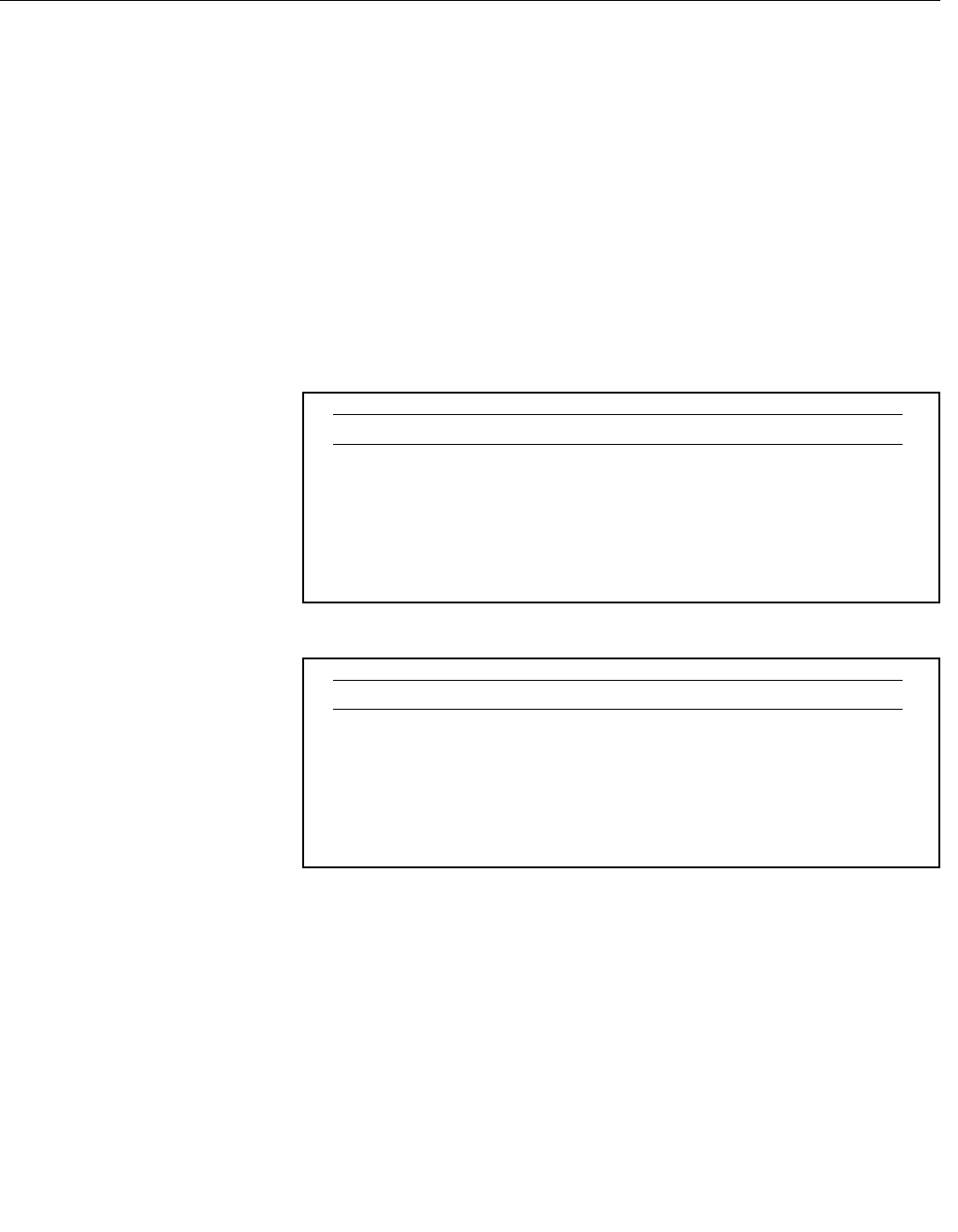
Reference Manual
00809-0100-xx, Rev AA
November 2003
B-7
Rosemount 5400
Preliminary copy
APPROVAL DRAWINGS This section contains Factory Mutual installation drawings and Canadian
Standards installation drawings. You must follow the installation guidelines
presented in order to maintain certified ratings for installed transmitters.
This section contains the following drawings:
Saab Rosemount drawing 91500xx-xxx, Issue 1:
System Control Drawing for hazardous location installation of intrinsically safe
FM approved apparatus.
Saab Rosemount drawing 91500xx-xxx, Issue 1:
System Control Drawing for hazardous location installation of CSA approved
apparatus.
Figure B-5. System Control
Drawing for hazardous location
installation of intrinsically safe
FM approved apparatus.
Figure B-6. System Control
Drawing for hazardous location
installation of CSA approved
apparatus.
System Control Drawing
System Control Drawing
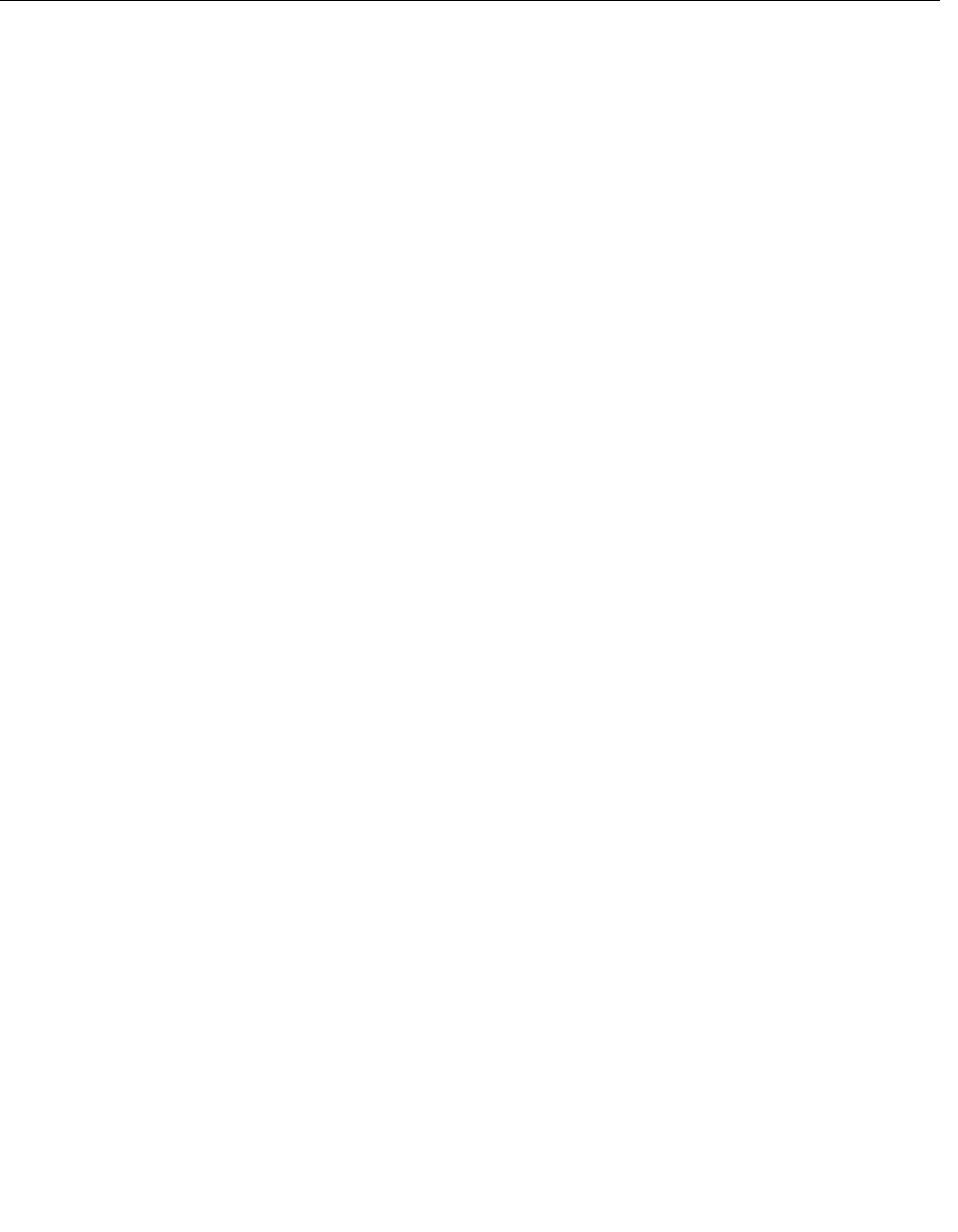
Reference Manual
00809-0100-xx, Rev AA
November 2003
Rosemount 5400
B-8
Preliminary copy
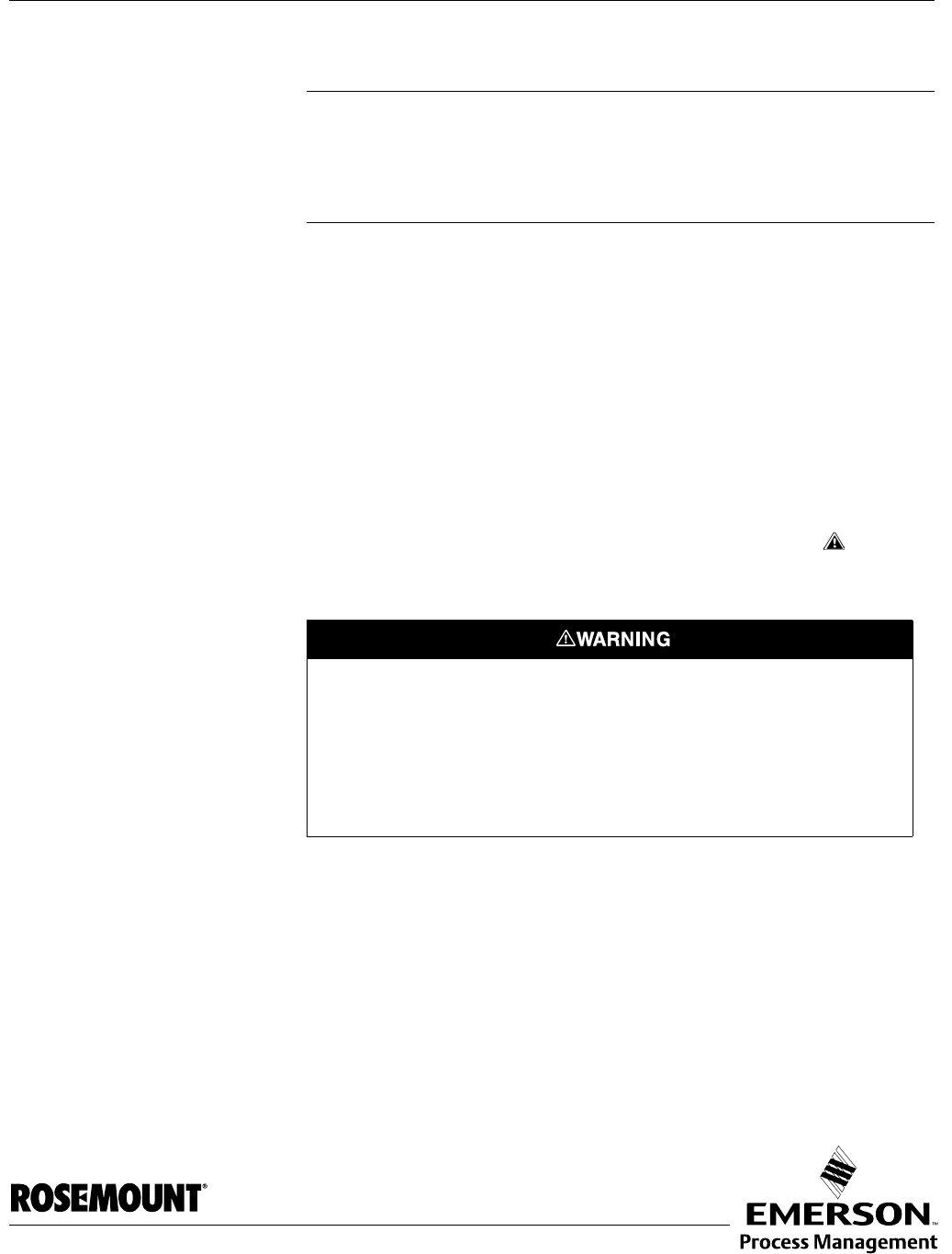
Reference Manual
00809-0100-xx, Rev AA
November 2003 Rosemount 5400 Series
www.rosemount.com
Appendix C HART Communicator
Introduction . . . . . . . . . . . . . . . . . . . . . . . . . . . . . . . . . . . . . page C-1
Safety Messages . . . . . . . . . . . . . . . . . . . . . . . . . . . . . . . . . page C-1
Connections . . . . . . . . . . . . . . . . . . . . . . . . . . . . . . . . . . . . page C-5
Basic Features . . . . . . . . . . . . . . . . . . . . . . . . . . . . . . . . . . page C-6
Menus and Functions . . . . . . . . . . . . . . . . . . . . . . . . . . . . . page C-8
INTRODUCTION This appendix provides an introduction to using the HART Communicator with
the Rosemount Model 5400 transmitter, including the HART Communicator
keypad, connections, menu structure and Fast Key sequence features.
The HART Communicator manual provides detailed instructions on the use
and features of the HART Communicator. This brief summary will familiarize
you with the HART Communicator but is not meant to replace the HART
Communicator manual. For information on all the capababilities of the HART
Communicator, refer to the HART Communicator Product Manual (document
00809-0100-4275).
SAFETY MESSAGES Procedures and instructions in this section may require special precautions to
ensure the safety of the personnel performing the operations. Information that
raises potential safety issues is indicated by a warning symbol ( ). Please
refer to the following safety messages before performing an operation
preceded by this symbol.
Explosions could result in death or serious injury:
Verify that the operating environment of the gauge is consistent with the appropriate
hazardous locations certifications.
Before connecting a HART-based communicator in an explosive atmosphere, make
sure the instruments in the loop are installed in accordance with intrinsically safe or
non-incendive field wiring practices.
Do not remove the gauge cover in explosive atmospheres when the circuit is alive.
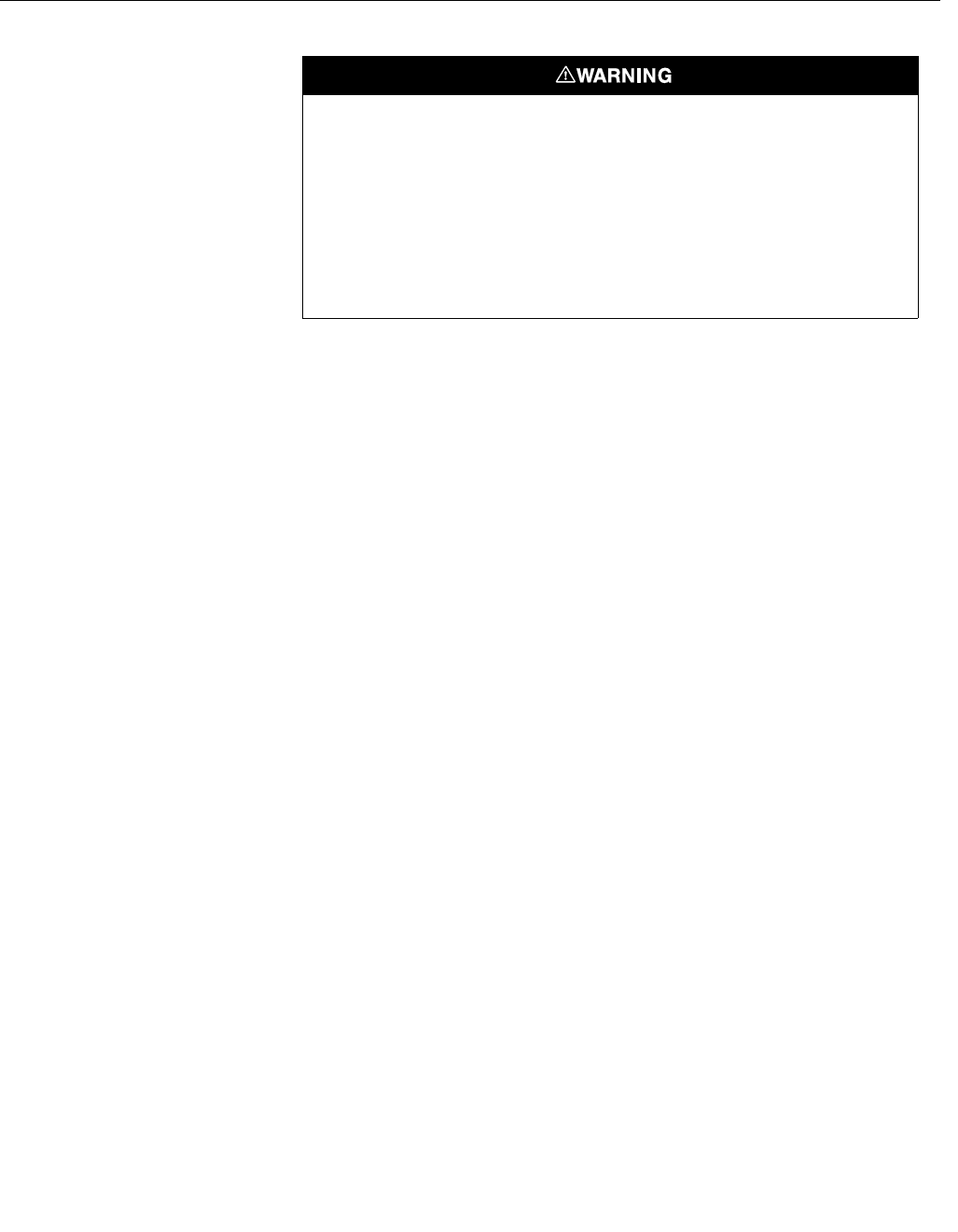
Reference Manual
00809-0100-xx, Rev AA
November 2003
Rosemount 5400 Series
C-2
Failure to follow safe installation and servicing guidelines could result in death or
serious injury:
Make sure only qualified personnel perform the installation.
Use the equipment only as specified in this manual. Failure to do so may impair the
protection provided by the equipment.
Do not perform any service other than those contained in this manual unless you are
qualified.
As a matter of routine, the Model 3300 transmitter and all other equipment in your
tank should be shut off prior to entering the tank.
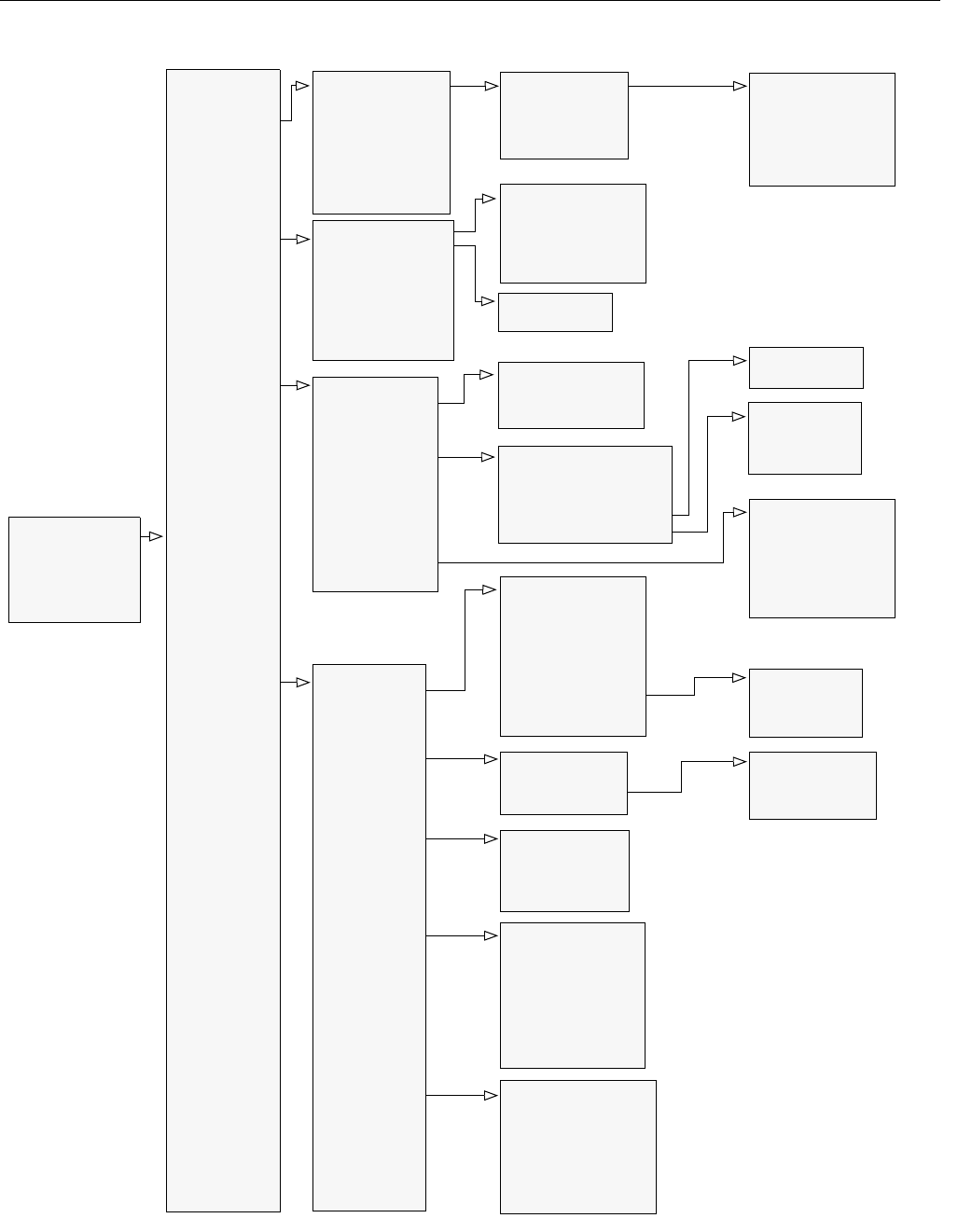
Reference Manual
00809-0100-xx, Rev AA
November 2003
C-3
Rosemount 5400 Series
Figure C-1. HART Communicator Tree
Online Menu
1 DEVICE SETUP
2PV
3AO
4LRV
5URV
1Device
Information
3 HART
4 Echo Tuning
5 Advanced
Tank
1 Variable mapping
2 Level
3 Distance
4 Level Rate
5 Signal Strength
6Volume
7 Internal Temp
1 Diagnostics
2 Simulation
3 Surface Search
4 Set as Empty
5 Restart Device
6 Lock/Unlock Device
7 Factory Settings
8 Trim/Calibrate AO
9 Advanced Service
1 Process
Variables
2Diag/Service
3 Basic Setup
4 Detailed Setup
5 Review Menus
1 Appl Grade Index
2 Measurem Units
3 Guided Setup
1 Distance Units
2 Level Rate Units
3 Volume Units
4 Temperature Units
1 Manufacturer
2 Device Model
3 Serial No
4Tag
5 Descriptor
6 Message
7Date
8 Revision #´s
9 SW versions
- HW Config
1 Poll Address
2Burst Mode
3 Burst Option
4 Num Req Preams
5 Num Resp Preams
1 Antenna Type
2 Pipe Diameter
3TCL
4 Upper Null Zone
5 Min Level Offset
6 Calibration Distance
7 Distance Offset
8 Tank Presentation
1 Found Echoes
2 Regist False Echoes
3 Min Threshold
4 Surface Search
5 Set as Empty
6 Create ATC
7 Add False Echo
8 Remove False Echo
9 Set Min Threshold
1 Variable re-map
2 PV is
3 SV is
4TV is
5QV is
- Level
- Distance
- Level Rate
- Signal Strength
- Volume
- Internal Temp
1 Device Status
2 Device Error
3 Device Warning
4 Measurem Status
5 AO Status
6 Volume Status
2LCD
1 Universal rev
2 Fld dev rev
3 Software rev
4 Hardware rev
1 LCD Variables
2 LCD Language
3 LCD Units
1 Tank Type
2 Tank Bottom Type
3 Tank Height
4 Pipe Diameter
5 Tank Environment
6 Volume
4 Tank Setup
1Simul Mode
2 Simul Distance
1 Distance Units
2 Level Rate Units
3 Volume Unit
4 Temperature Unit
1 Proc Condition
2 Product DC
1 Proc Condition
2 Product DC
1Calc. Method
2 Tank Diameter
3 Tank Length
4 Volume Offset
1PV is
2LRV
3URV
4 Alarm Mode Meas
5 Alarm Mode Fail
6 Disable Lmt Alm
7Damp Value
5AO Setup
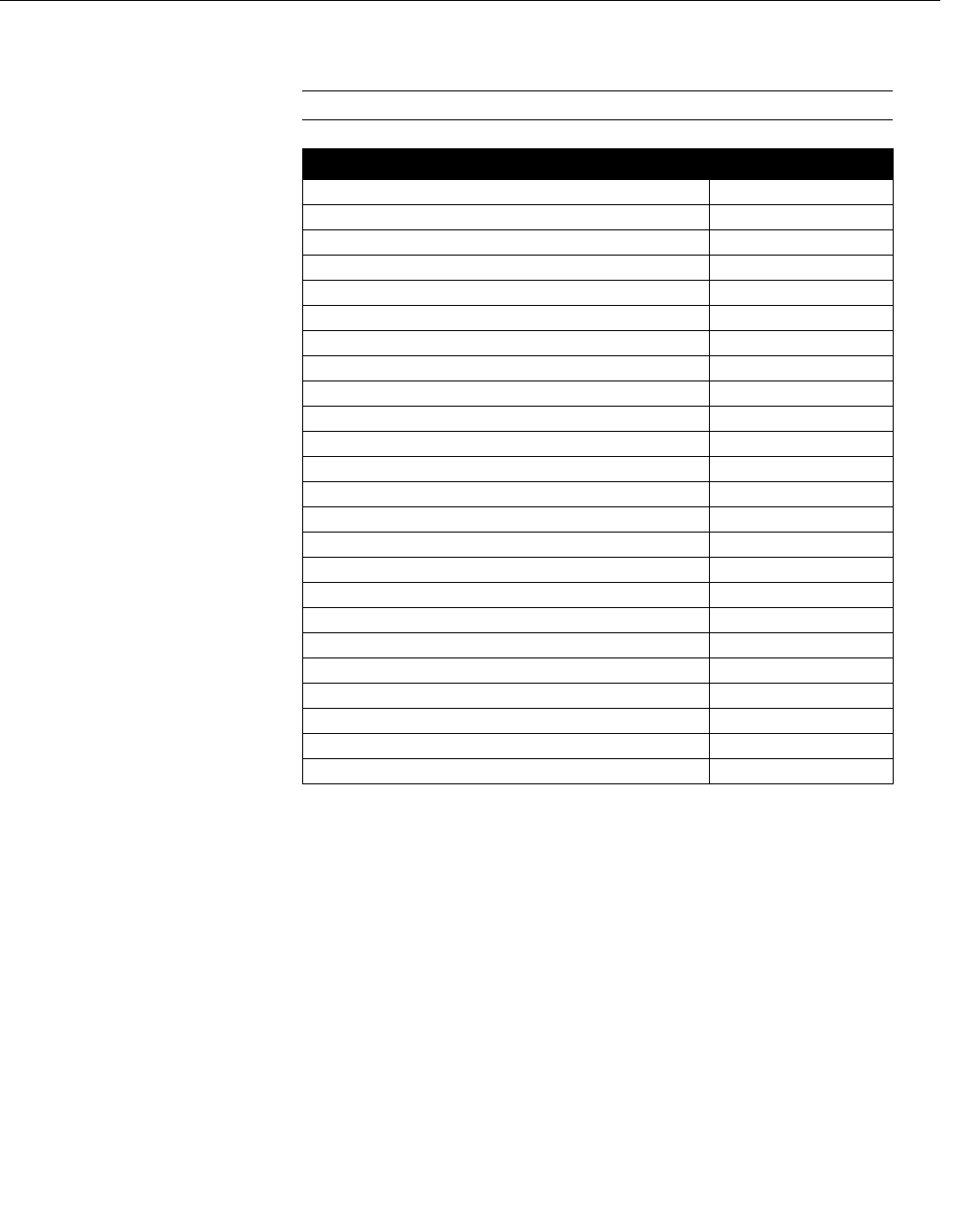
Reference Manual
00809-0100-xx, Rev AA
November 2003
Rosemount 5400 Series
C-4
Table C-1. HART Fast Key Sequences
Ska anpassas till 5400!
Function HART Fast Key
Device Information 1, 4, 1
Display Language 1, 4, 2, 2
Display Variables 1, 4, 2, 1
Level Units 1, 3, 2, 1
Loop Test 1, 2, 2
Lower Range Value (LRV) (4 mA) 1, 3, 3
Master Reset 1, 2, 1, 2
Measurement Mode 1, 3, 9
Poll Address 1, 4, 5, 2, 1
Primary Variable 1, 1, 1, 1
Antenna Type 1, 4, 5, 1
Product Dielectric 1, 3, 8
Range Values 1, 3, 3, 2
Reference Gauge Height 1, 3, 4
Strapping Table 1, 4, 3, 4
Tag 1, 3, 1
Tank Type 1, 4, 3, 1
Tank Diameter 1, 4, 3, 2
Temperature Units 1, 3, 2, 3
Upper Null Zone 1, 4, 4, 5
Upper Range Value (URV) (20 mA) 1, 3, 3
Vapor Dielectric 1, 3, 7
Variable Remapping 1, 1, 1, 1
Volume Units 1, 3, 2, 2
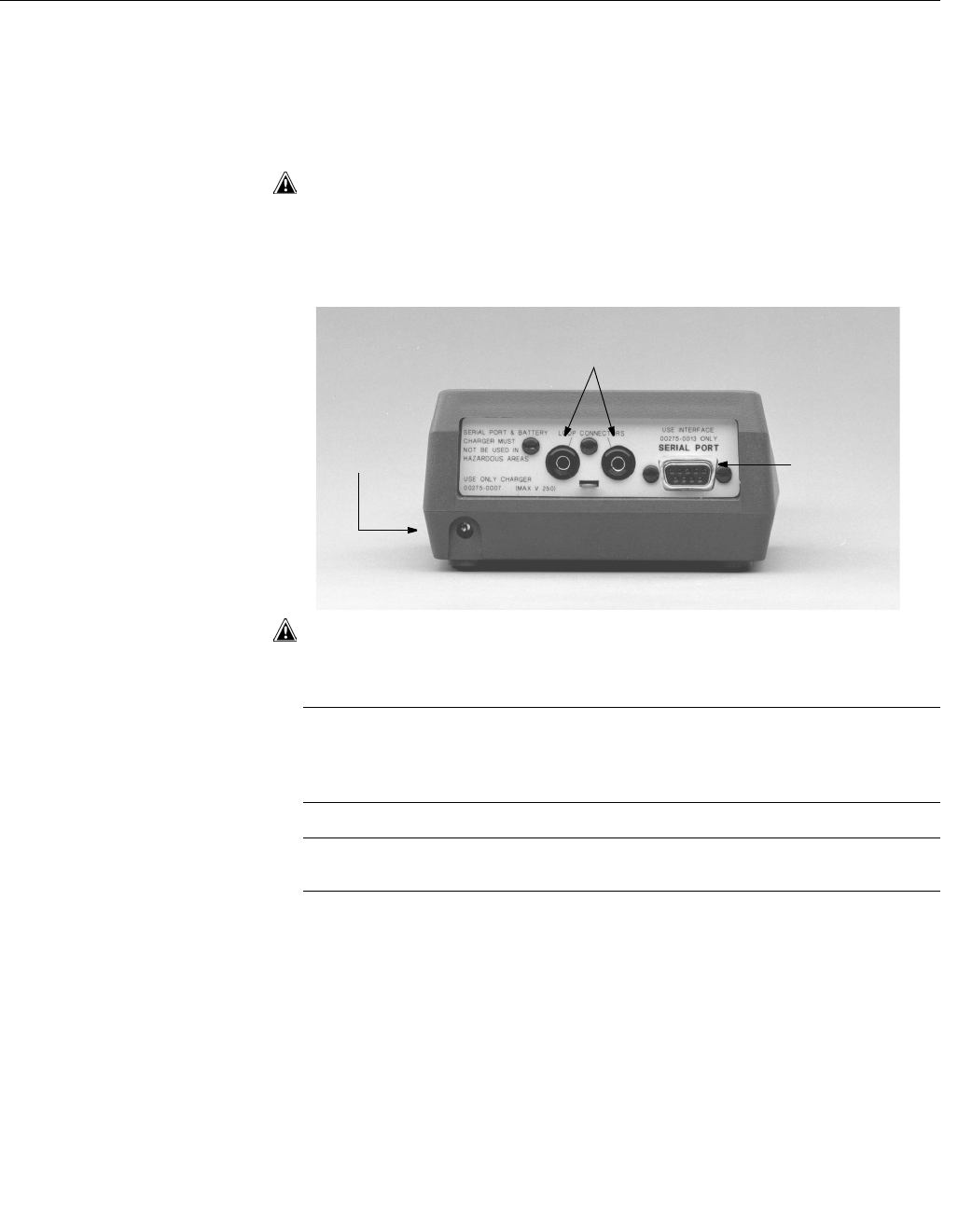
Reference Manual
00809-0100-xx, Rev AA
November 2003
C-5
Rosemount 5400 Series
CONNECTIONS The HART Communicator exchanges information with the 5400 Series
transmitters from the control room, the instrument site, or any wiring
termination point in the loop. The HART Communicator should be connected
in parallel with the transmitter. Use the loop connection ports on the rear panel
of the HART Communicator (see Figure C-2). The connections are
non-polarized.
Do not make connections to the serial port or NiCad recharger pack in an
explosive atmosphere.
Figure C-2. Rear connection
panel with Optional NiCad
Recharger Jack
Before connecting the HART Communicator in an explosive atmosphere,
make sure the instruments in the loop are installed in accordance with
intrinsically safe or non-incendive field wiring practices.
NOTE
The HART Communicator needs a minimum of 250 ohms resistance in the
loop to function properly. The HART Communicator does not measure loop
current directly.
NOTE
Loop must be broken to insert the 250 ohm load resistor.
Loop Connection Ports
Optional NiCad
Recharger Jack Serial Port
008AB
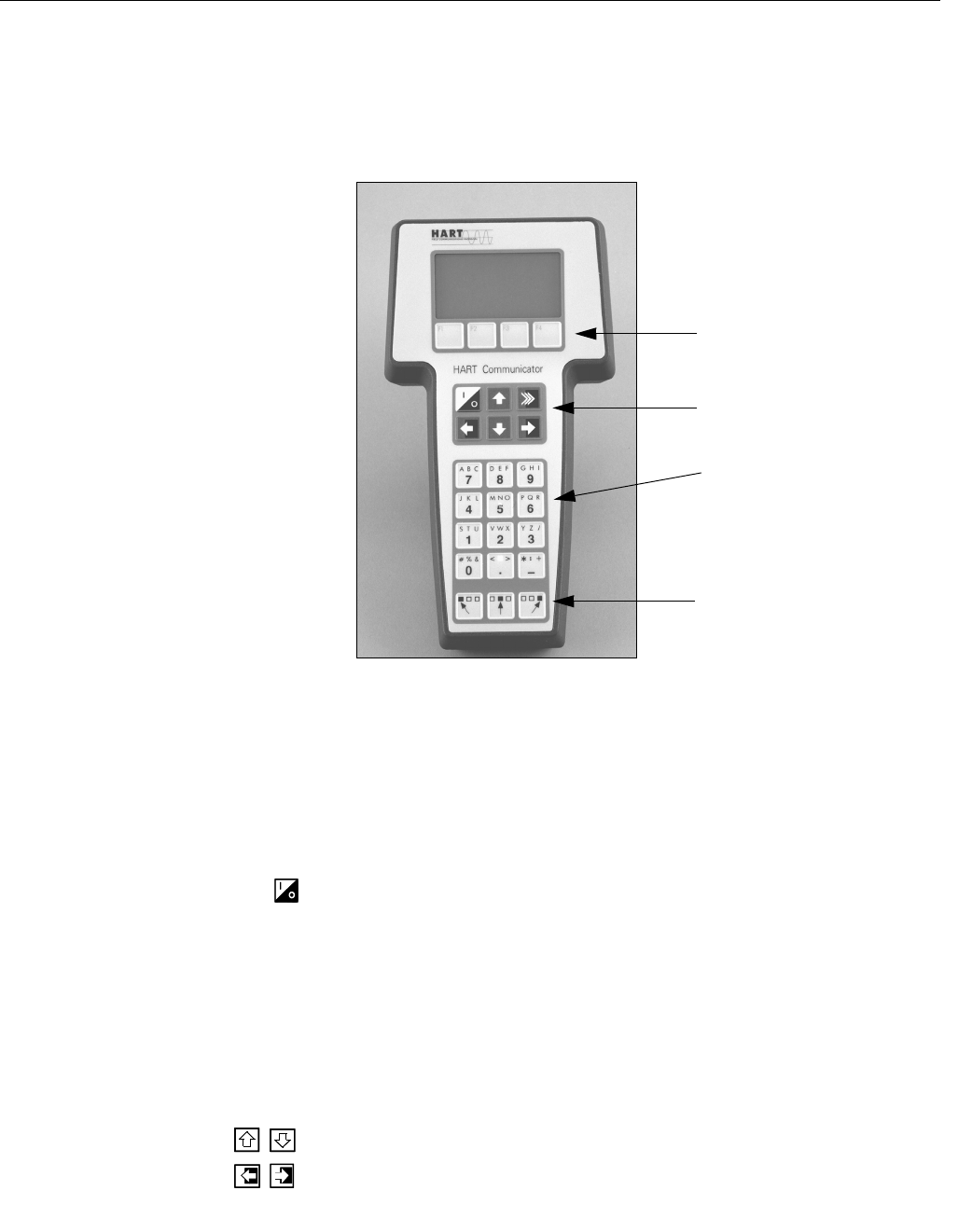
Reference Manual
00809-0100-xx, Rev AA
November 2003
Rosemount 5400 Series
C-6
BASIC FEATURES The keys of the HART Communicator include action keys, function keys,
alphanumeric keys, and shift keys.
Figure C-3. 275 HART
Communicator
Action Keys
As shown in Figure C-3, the action keys are the six blue, white, and black
keys located above the alphanumeric keys. The function of each key is
described as follows
ON/OFF Key
Use this key to power the HART Communicator. When the communicator is
turned on, it searches for a gauge on the 4–20 mA loop. If a device is not
found, the communicator displays the message, “No Device Found. Press
OK.”
If a HART-compatible device is found, the communicator displays the Online
Menu with device ID and tag.
If a HART-compatible device is found, the communicator displays the Online
Menu with device ID and tag.
Directional Keys
Use these keys to move the cursor up, down, left, or right. The right arrow key
also selects menu options, and the left arrow key returns to the previous
menu.
Function Keys
Action Keys
Alphanumeric Keys
Shift Keys
011AB
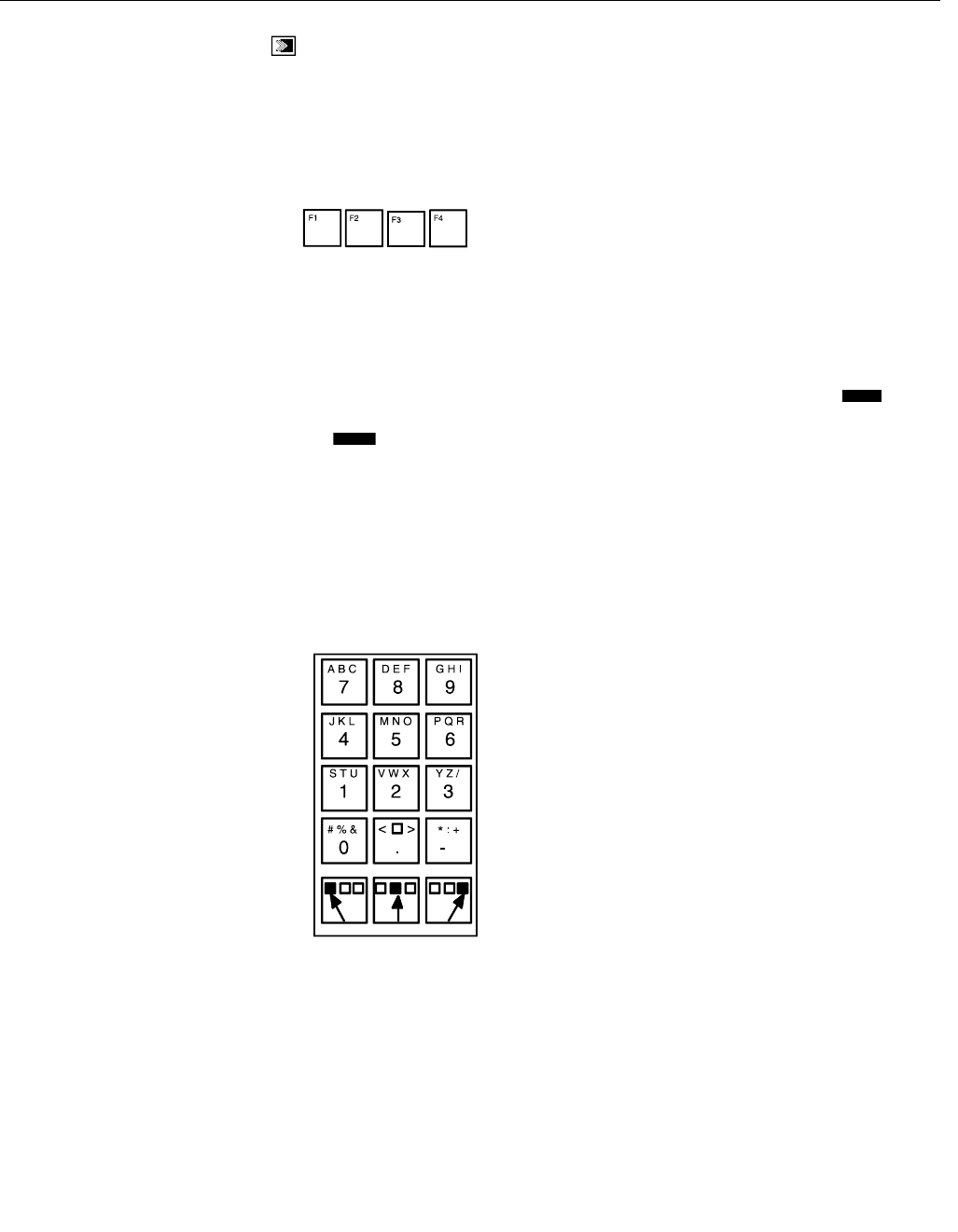
Reference Manual
00809-0100-xx, Rev AA
November 2003
C-7
Rosemount 5400 Series
HOT Key
Use this key to quickly access important, user-defined options when
connected to a HART-compatible device. Pressing the Hot Key turns
the HART Communicator on and displays the Hot Key Menu.
See Customizing the Hot Key Menu in the HART Communicator manual for
more information.
Function Keys
Use the four software-defined function keys, located below the LCD, to
perform software functions. On any given menu, the label appearing above a
function key indicates the function of that key for the
current menu.
As you move among menus, different function key labels appear over the four
keys. For example, in menus providing access to online help, the label
may appear above the F1 key. In menus providing access to the Home Menu,
the label may appear above the F3 key. Press the key to activate the
function. See the HART Communicator manual for details on specific
Function Key definitions.
Alphanumeric and Shift Keys
The Alphanumeric keys perform two functions: fast selection of menu options
(refer to HART Fast Key Feature in this section) and data entry.
Figure C-4. HART
Communicator Alphanumeric
and Shift Keys
Some menus require data entry. Use the Alphanumeric and Shift keys to enter
all alphanumeric information into the HART Communicator. If you press an
Alphanumeric key alone from within an edit menu, the bold character in the
center of the key appears. These large characters include the numbers zero
through nine, the decimal point (.), and the dash symbol (–).
To enter an alphabetic character:
1. Press the Shift key that corresponds to the position on the Alphanumeric
key of the letter you want.
2. Press the Alphanumeric key.
HELP
HOME
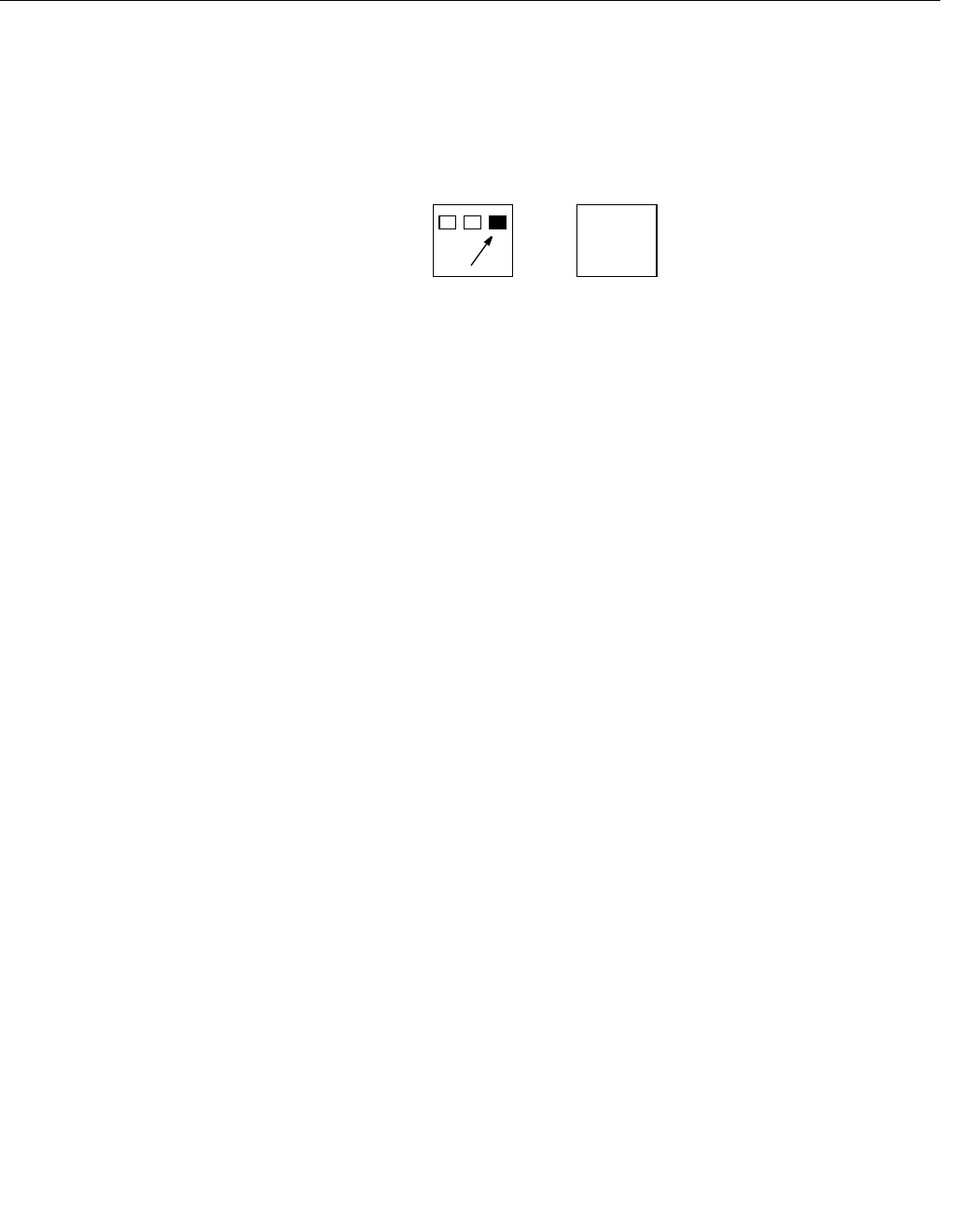
Reference Manual
00809-0100-xx, Rev AA
November 2003
Rosemount 5400 Series
C-8
For example, to enter the letter R, first press the right Shift key, then the “6”
key (see Figure C-5). Do not press these keys simultaneously, but one after
the other.
Figure C-5. Data Entry Key
Sequence
MENUS AND
FUNCTIONS
The HART Communicator is a menu driven system. Each screen provides a
menu of options that can be selected or provides direction for input of data,
warnings, messages, or other instructions.
Main Menu
When the HART Communicator is turned on, one of two menus appears: the
Online Menu or the Main Menu.
If the HART Communicator is connected to an operating loop, the
communicator finds the device and displays the Online Menu.
If it is not connected to a loop, the communicator indicates that no device was
found. When you press OK (F4), it displays the Main Menu.
The Main Menu provides the following options:
•Offline – The Offline option provides access to offline configuration data
and simulation functions.
•Online – The Online option checks for a device and if it finds one,
brings up the Online Menu. Online communication with the 3300 Series
Transmitter automatically loads the current gauge data to the HART
Communicator.
•Transfer – The Transfer option provides access to options for
transferring data either from the HART Communicator (memory) to the
3300 Series Transmitter (device) or vice versa. Transfer is used to
move offline data from the HART Communicator to the gauge, or to
retrieve data from a gauge for offline revision.
•Frequency Device – The Frequency Device option displays the
frequency output and corresponding pressure output of
current-to-pressure transmitters.
•Utility – The Utility option provides access to the contrast control for the
HART Communicator LCD screen and to the autopoll setting used in
multidrop applications.
To select an option from the menu, you can use the up and down
arrow keys and the select (right arrow) key or you can simply press
the corresponding number on the alphanumeric keypad to “fast select” the
option.
6
P Q R
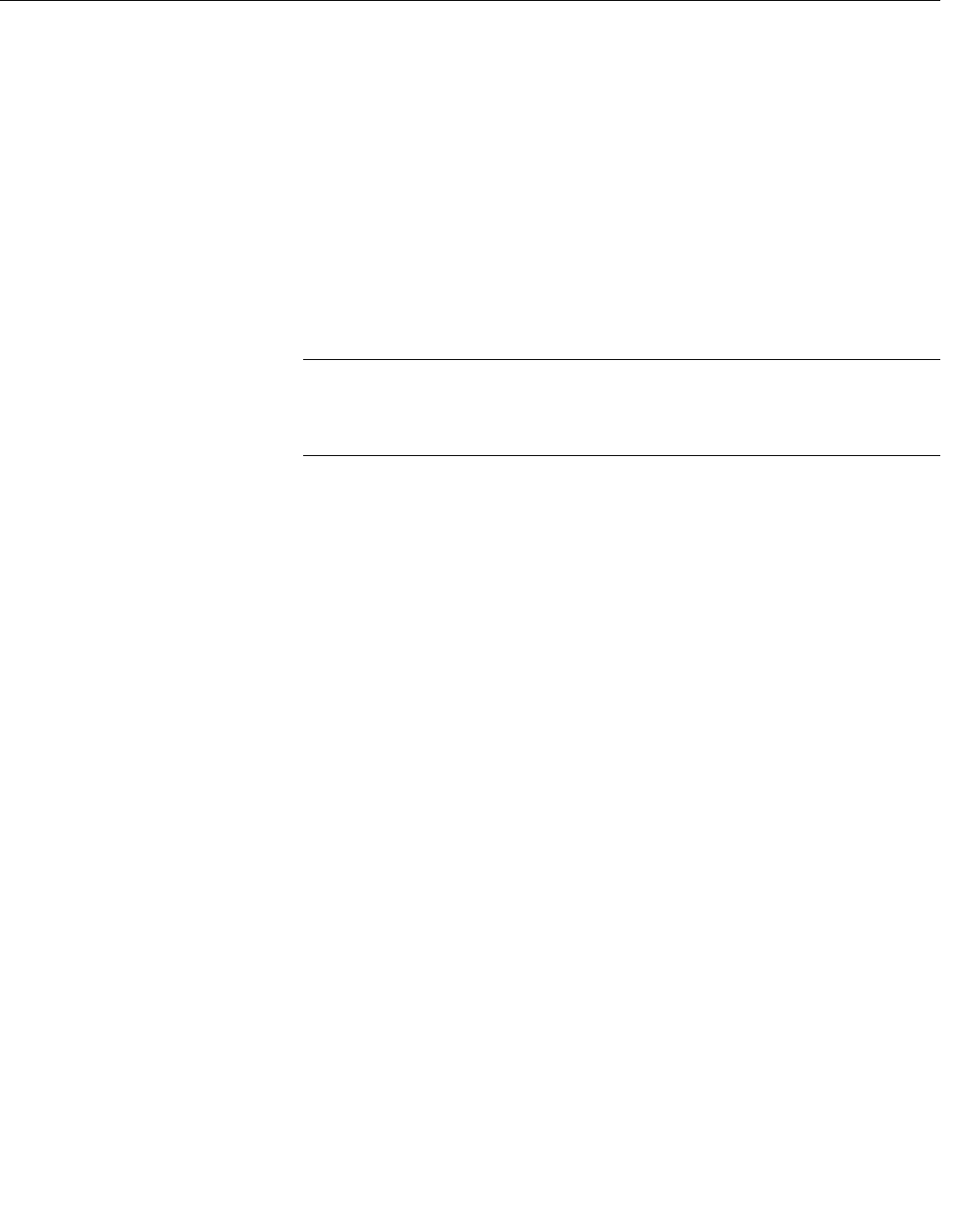
Reference Manual
00809-0100-xx, Rev AA
November 2003
C-9
Rosemount 5400 Series
After selecting a Main Menu option, the HART Communicator provides the
information you need to complete the operation. If further details are required,
consult the HART Communicator manual.
Online Menu
The Online Menu can be selected from the Main Menu or it appears
automatically if the HART Communicator is connected to an active
loop and can detect an operating 3300 transmitter.
Online mode is used for direct evaluation of a particular meter,
re-configuration, changing parameters, maintenance, and other functions.
When configuration variables are reset in online mode, the new
settings are not activated until the data is sent to the gauge. Press SEND (F2)
when it is activated to update the process variables of the 3300 transmitter.
NOTE
The Main Menu can be accessed from the Online Menu. Press the left arrow
action key to deactivate the online communication with the gauge and to
activate the Main Menu options.
HART Fast Key Feature
The HART Fast Key feature provides quick online access to gauge variables
and functions. Instead of stepping your way through the menu structure using
the Action Keys, you can press a HART
Fast Key sequence to move from the Online Menu to the desired variable or
function. On-screen instructions guide you through the
rest of the screens.
The HART Fast Key sequences are made up of the series of numbers
corresponding to the individual options in each step of the menu structure. For
example, from the Online Menu you can change the Date. Following the
menu structure, you would:
1. Press 1 to reach Device Setup.
2. Press 4 for Detailed Setup.
3. Press 1 for Device Information.
4. Press 5 for Date.
So, the corresponding HART Fast Key sequence is 1, 4, 1, 5.
HART Fast Keys are operational only from the Online Menu. If you use them
consistently, you return to the Online Menu by pressing HOME (F3) when it is
available. If you do not start at the Online Menu, the HART Fast Keys will not
function properly.
Use Table C-1, an alphabetical listing of online functions, to find the
corresponding HART Fast Keys. These codes are applicable only to the 3300
Series and the HART Communicator.
Hart Communicator
Diagnostic Messages
The following table is a list of messages used by the HART Communicator
and their corresponding descriptions.
Variable parameters within the text of a message are indicated with <variable
label>.
Reference to the name of another message is identified by <message>.

Reference Manual
00809-0100-xx, Rev AA
November 2003
Rosemount 5400 Series
C-10
Table C-2. HART Communicator Diagnostic Messages
Message Description
Add item for ALL device types or
only for this ONE device type.
Asks the user whether the hot key item being added should be added for all device types or only for
the type of device that is connected.
Command Not Implemented The connected device does not support this function.
Communication Error Either a device sends back a response indicating that the message it received was unintelligible, or
the HC cannot understand the response from the device.
Configuration memory not
compatible with connected
device
The configuration stored in memory is incompatible with the device to which a transfer has been
requested.
Device Busy The connected device is busy performing another task.
Device Disconnected Device fails to respond to a command.
Device write protected Device is in write-protect mode. Data can not be written.
Device write protected.
Do you still want to shut off?
Device is in write-protect mode. Press YES to turn the HC off and lose the unsent data.
Display value of variable on
hotkey menu?
Asks whether the value of the variable should be displayed adjacent to its label on the hotkey menu if
the item being added to the hotkey menu is a variable.
Download data from
configuration memory to device
Prompts user to press SEND softkey to initiate a memory to device transfer.
Exceed field width Indicates that the field width for the current arithmetic variable exceeds the device-specified
description edit format.
Exceed precision Indicates that the precision for the current arithmetic variable exceeds the device-specified
description edit format.
Field device has malfunctioned
due to a Hardware Error or
Failure
The 3300 transmitter may simply be configured incorrectly (20 mA point in upper Null Zone, etc.)
Verify the configuration.
Ignore next 50 occurrences
of status?
Asked after displaying device status. Softkey answer determines whether next 50 occurrences of
device status will be ignored or displayed.
Illegal character An invalid character for the variable type was entered.
Illegal date The day portion of the date is invalid.
Illegal month The month portion of the date is invalid.
Illegal year The year portion of the date is invalid.
Incomplete exponent The exponent of a scientific notation floating point variable is incomplete.
Incomplete field The value entered is not complete for the variable type.
Looking for a device Polling for multidropped devices at addresses 1–15.
Mark as read only variable on
hotkey menu?
Asks whether the user should be allowed to edit the variable from the hotkey menu if the item being
added to the hotkey menu is a variable.
No device configuration in
configuration memory
There is no configuration saved in memory available to re-configure offline or transfer to a device.
No Device Found Poll of address zero fails to find a device, or poll of all addresses fails to find a device if auto-poll is
enabled.
No hotkey menu available for
this device.
There is no menu named “hotkey” defined in the device description for this device.
No offline devices available. There are no device descriptions available to be used to configure a device offline.
No simulation devices available. There are no device descriptions available to simulate a device.
No UPLOAD_VARIABLES in ddl
for this device
There is no menu named “upload_variables” defined in the device description for this device. This
menu is required for offline configuration.
No Valid Items The selected menu or edit display contains no valid items.
OFF KEY DISABLED Appears when the user attempts to turn the HC off before sending modified data or before
completing a method.
Online device disconnected with
unsent data. RETRY or OK to
lose data.
There is unsent data for a previously connected device. Press RETRY to send data, or press OK to
disconnect and lose unsent data.
Out of memory for hotkey
configuration. Delete
unnecessary items.
There is no more memory available to store additional hotkey items. Unnecessary items should be
deleted to make space available.
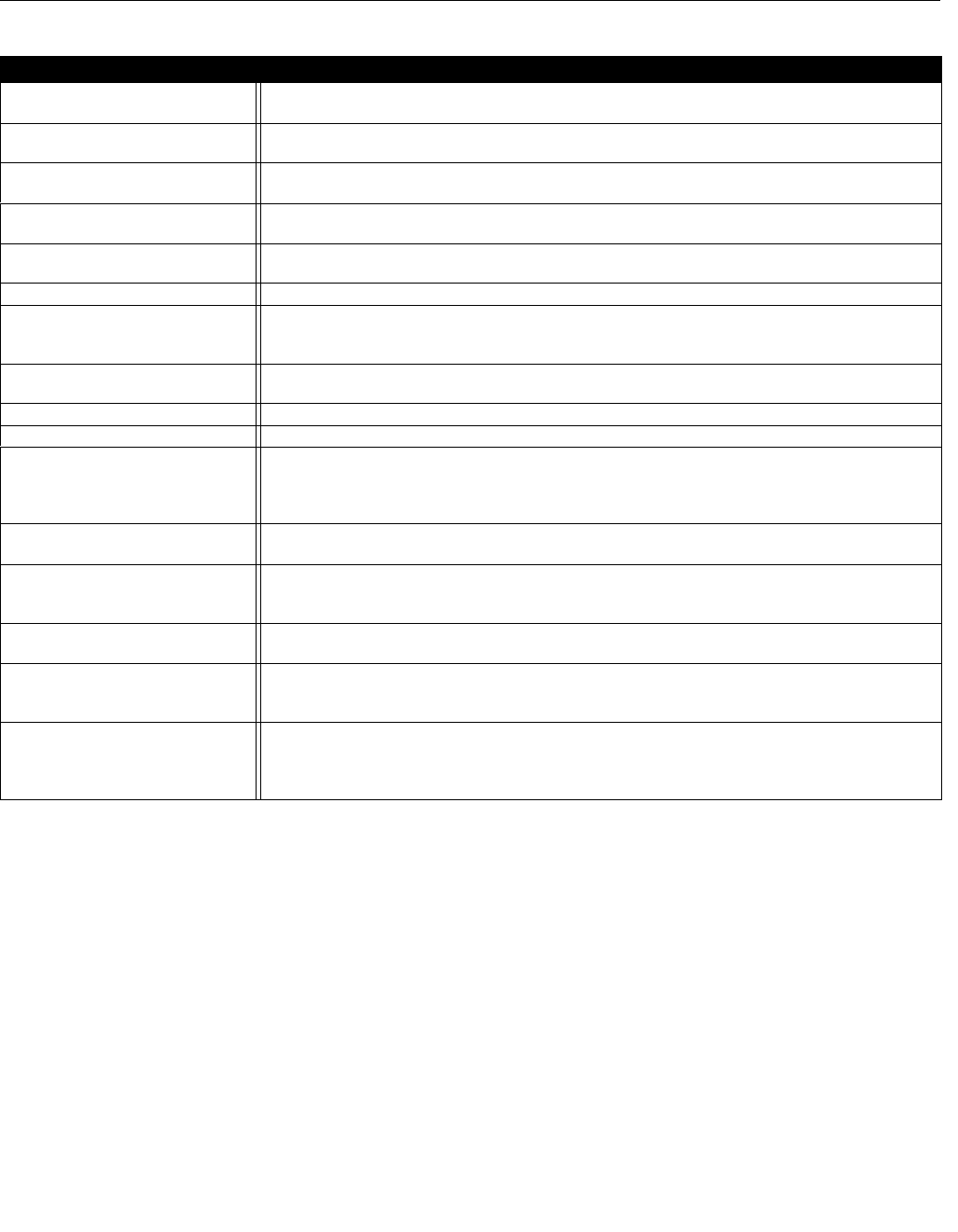
Reference Manual
00809-0100-xx, Rev AA
November 2003
C-11
Rosemount 5400 Series
Overwrite existing
configuration memory
Requests permission to overwrite existing configuration either by a device-to-memory transfer or by
an offline configuration. User answers using the softkeys.
Press OK... Press the OK softkey. This message usually appears after an error message from the application or
as a result of HART communications.
Restore device value? The edited value that was sent to a device was not properly implemented. Restoring the device value
returns the variable to its original value.
Save data from device to
configuration memory
Prompts user to press SAVE softkey to initiate a device-to-memory transfer.
Saving data to
configuration memory.
Data is being transferred from a device to configuration memory.
Sending data to device. Data is being transferred from configuration memory to a device.
There are write only variables
which have not been edited.
Please edit them.
There are write-only variables which have not been set by the user. These variables should be set or
invalid values may be sent to the device.
There is unsent data. Send it
before shutting off?
Press YES to send unsent data and turn the HC off. Press NO to turn the HC off and lose the unsent
data.
Too few data bytes received Command returns fewer data bytes than expected as determined by the device description.
Transmitter Fault Device returns a command response indicating a fault with the connected device.
Units for <variable label> has
changed. Unit must be sent
before editing, or invalid data will
be sent.
The engineering units for this variable have been edited. Send engineering units to the device before
editing this variable.
Unsent data to online device.
SEND or LOSE data
There is unsent data for a previously connected device which must be sent or thrown away before
connecting to another device.
Use up/down arrows to change
contrast. Press DONE when
done.
Gives direction to change the contrast of the HC display.
Value out of range The user-entered value is either not within the range for the given type and size of variable or not
within the min/max specified by the device.
<message> occurred
reading/writing <variable label>
Either a read/write command indicates too few data bytes received, transmitter fault, invalid response
code, invalid response command, invalid reply data field, or failed pre- or post-read method; or a
response code of any class other than SUCCESS is returned reading a particular variable.
<variable label> has an unknown
value. Unit must be sent before
editing, or invalid data will be
sent.
A variable related to this variable has been edited. Send related variable to the device before editing
this variable.
Table C-2. HART Communicator Diagnostic Messages
Message Description
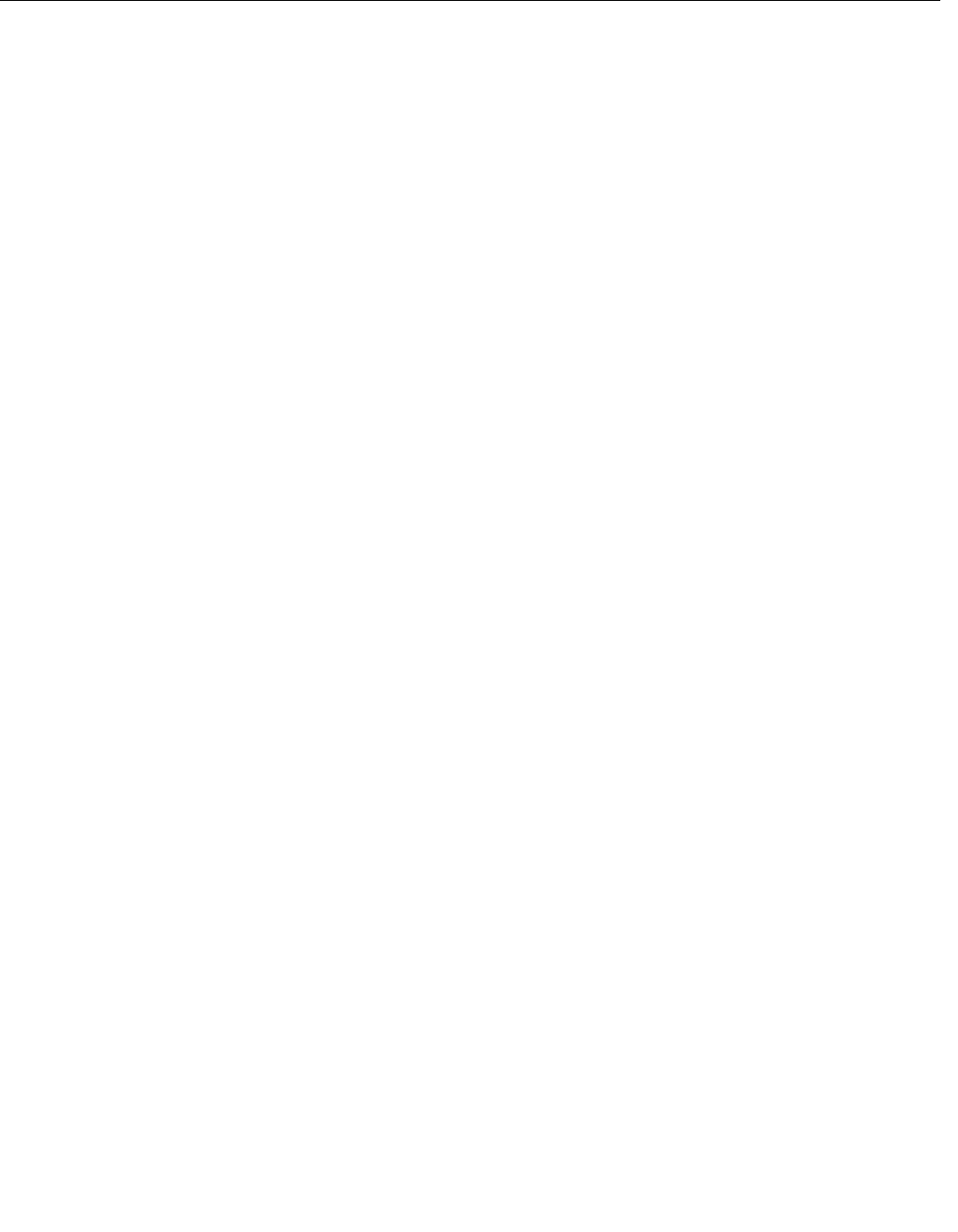
Reference Manual
00809-0100-xx, Rev AA
November 2003
Rosemount 5400 Series
C-12
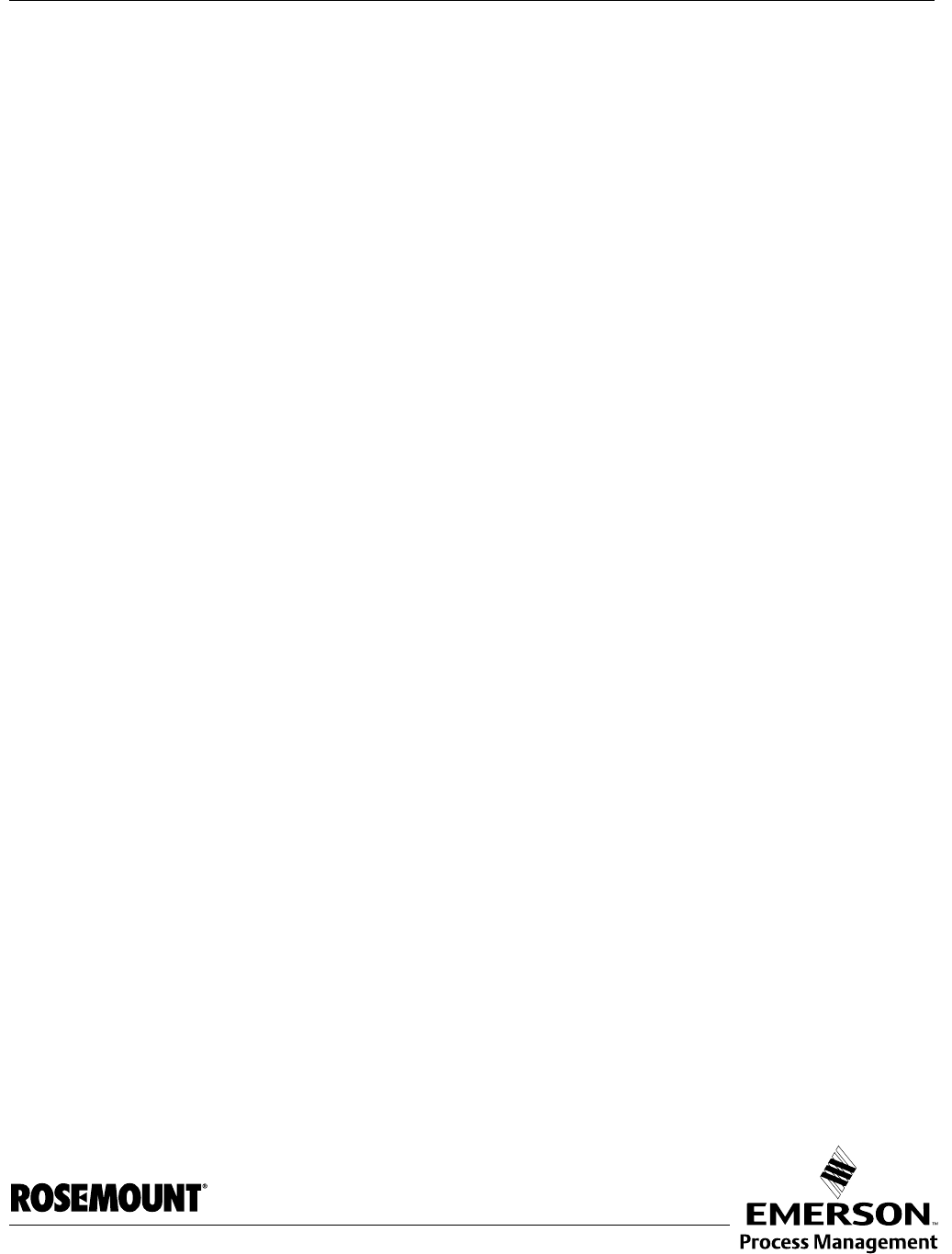
Reference Manual
00809-0100-xx, Rev AA
November 2003 Rosemount 5400 Series
www.rosemount.com
Index
Numerics
4 and 20 mA Points . . . . . . . 4-10
A
Action Keys
Up Arrow Key . . . . . . . . . C-6
Analog Output
alarm values . . . . . . . . . . 5-7
saturation values . . . . . . . 5-7
Approval Drawings . . . . . . . . . B-7
Approvals . . . . . . . . . . . . . . . B-1
Atex . . . . . . . . . . . . . . . . . . . B-3
C
Cable Selection . . . . . . . . . . 3-13
Cable/conduit entries . . . . . . 3-13
Canadian Standards Association
approval . . . . . . . . . . . . . B-6
system control drawing . . B-7
COM Port . . . . . . . . . . . . . . . 4-4
E
Electrical installation . . . . . . . 3-13
connecting the transmitter 3-15
Intrinsically Safe Output . 3-17
Non-Intrinsically Safe Output 3-16
European ATEX Directive Information
B-3
F
Factory Mutual
approval . . . . . . . . . . . . . B-5
system control drawing . . B-7
Fast Key Feature . . . . . . . . . . C-8
Fast Key Sequence Table . . . . C-4
Foam . . . . . . . . . . . . . . . . . . 2-4
Function Keys . . . . . . . . . . . . C-7
Functions . . . . . . . . . . . . . . . C-8
G
Grounding . . . . . . . . . . . . . . 3-13
H
HART Communicator
alphanumeric keys . . . . . C-7
connecting . . . . . . . . . . . C-5
connections and hardware C-5
fast key feature . . . . . . . . C-8
fast key sequence table . . C-4
function keys . . . . . . . . . C-7
functions . . . . . . . . . . . . C-8
main menu . . . . . . . . . . . C-8
menus . . . . . . . . . . . . . . C-8
menus and functions . . . . C-8
online menu . . . . . . . . . . C-9
shift keys . . . . . . . . . . . . C-7
Hazardous Locations Certifications
B-5
I
Installation
cable selection . . . . . . . 3-13
cable/conduit entries . . . 3-13
Free Space . . . . . . . . . . 3-4
grounding . . . . . . . . . . 3-13
mounting considerations . 3-3
power requirements . . . 3-14
procedure . . . . . . . . . . . 3-2
recommended mounting position
3-5
M
Maximum load resistance 3-16, 3-17
Menus . . . . . . . . . . . . . . . . . C-8
N
NAMUR-Compliant Alarm . . . 5-7
P
Power Requirements . . . . . . 3-14
R
RCT
COM Port . . . . . . . . . . . 4-4
Setup . . . . . . . . . . . . . . 4-7
Wizard . . . . . . . . . . . . . . 4-6
Recommended mounting position 3-5
S
Shift Keys . . . . . . . . . . . . . . C-7
T
Time Domain Reflectometry . . .2-1
Transmitter housing . . . . . . . .2-2
Troubleshooting . . . . . . . . . . .6-7
V
Vapor . . . . . . . . . . . . . . . . . .2-4
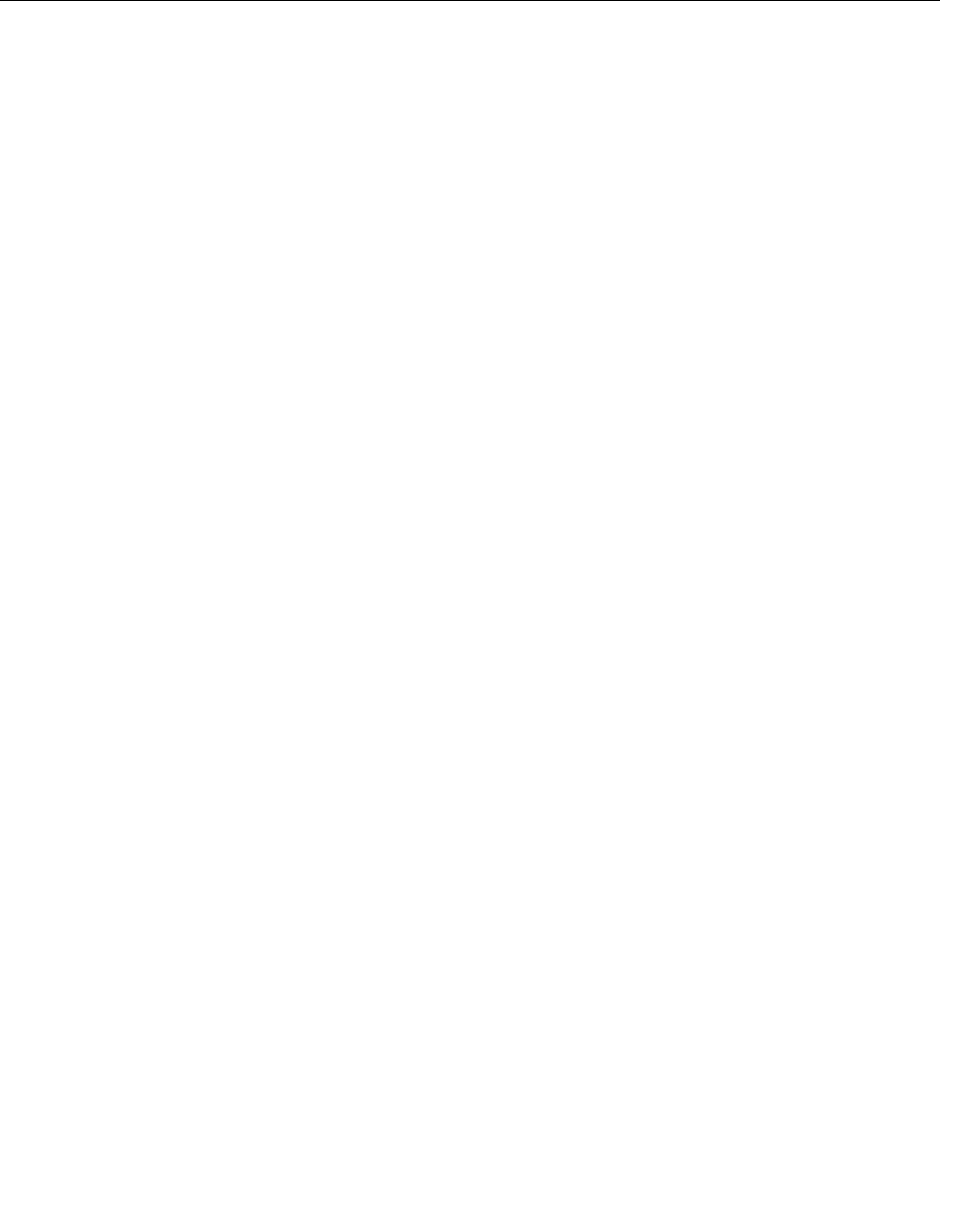
Reference Manual
00809-0100-xx, Rev AA
November 2003
Rosemount 5400 Series
Index-2
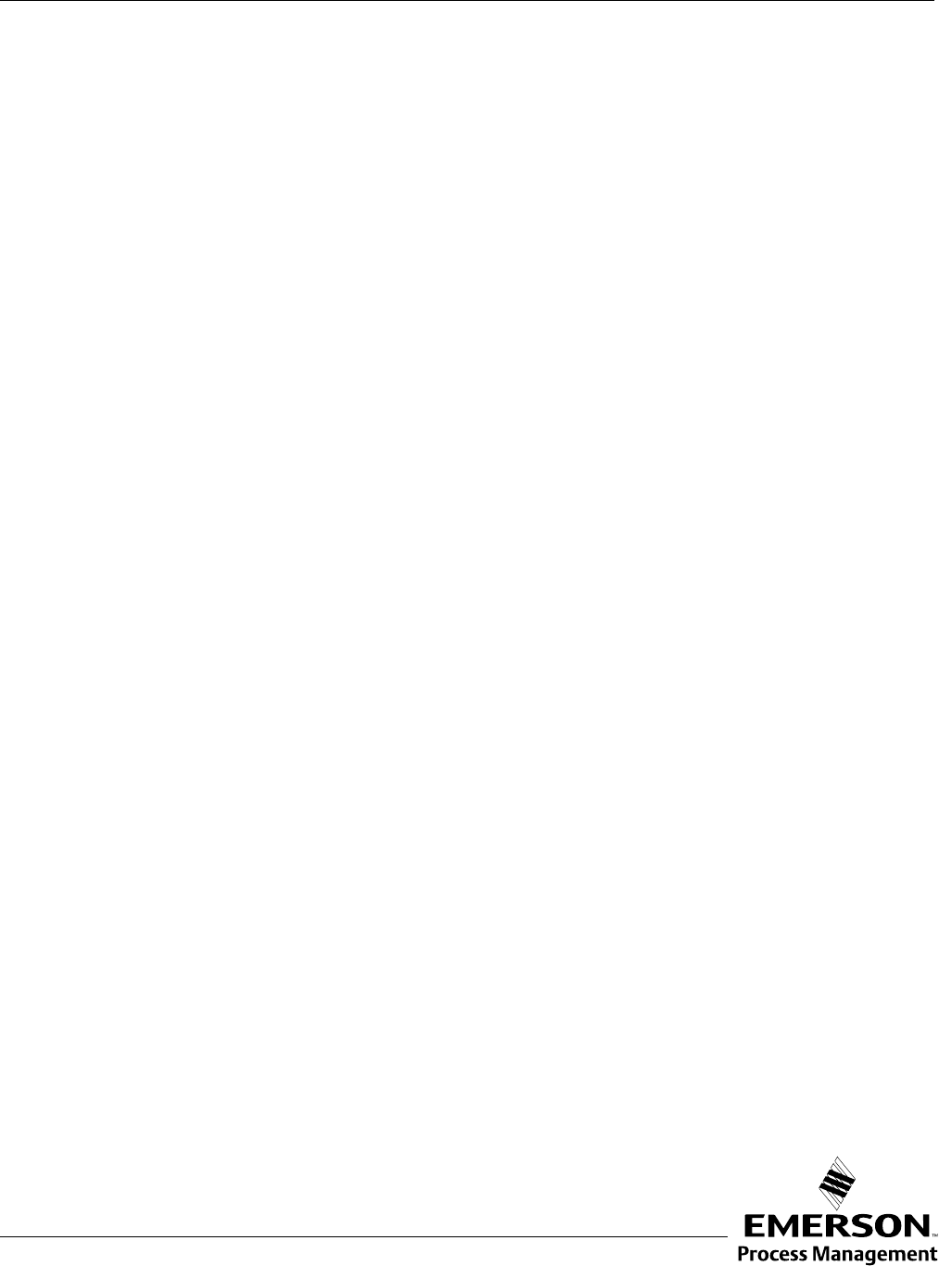
Reference Manual
00809-0100-4026, Rev AA
November 2003 Rosemount 5400 Series
Emerson Process Management
© 2003 Rosemount Inc. All rights reserved.
00000
Rosemount and the Rosemount logotype are registered trademarks of Rosemount Inc.
PlantWeb is a registered trademark of one of the Emerson Process Management group of companies.
Teflon, VITON, and Kalrez are registered trademarks of E.I. du Pont de Nemours & Co.
Asset Management Solutions is a trademark of Emerson Process Management.
All other marks are the property of their respective owners.
Rosemount Inc.
8200 Market Boulevard
Chanhassen, MN 55317 USA
T (U.S.) 1-800-999-9307
T (International) (952) 906-8888
F (952) 949-7001
www.rosemount.com
Fischer-Rosemount Limited
Heath Place
Bognor Regis
West Sussex PO22 9SH
England
Tel 44 (1243) 863121
Fax 44 (1243) 867554
Fischer-Rosemount
Singapore Pte Ltd.
1 Pandan Crescent
Singapore 128461
Tel (65) 777-8211
Fax (65) 777-0947
AP.RMT-Specialist@emersonprocess.com