Sanwa Electronic Instrument Co 90478 Digital High Response Telemetry System User Manual MT 4S User s Guide indd
Sanwa Electronic Instrument Co Ltd Digital High Response Telemetry System MT 4S User s Guide indd
Contents
- 1. User Manual-1
- 2. User Manual-2
User Manual-2
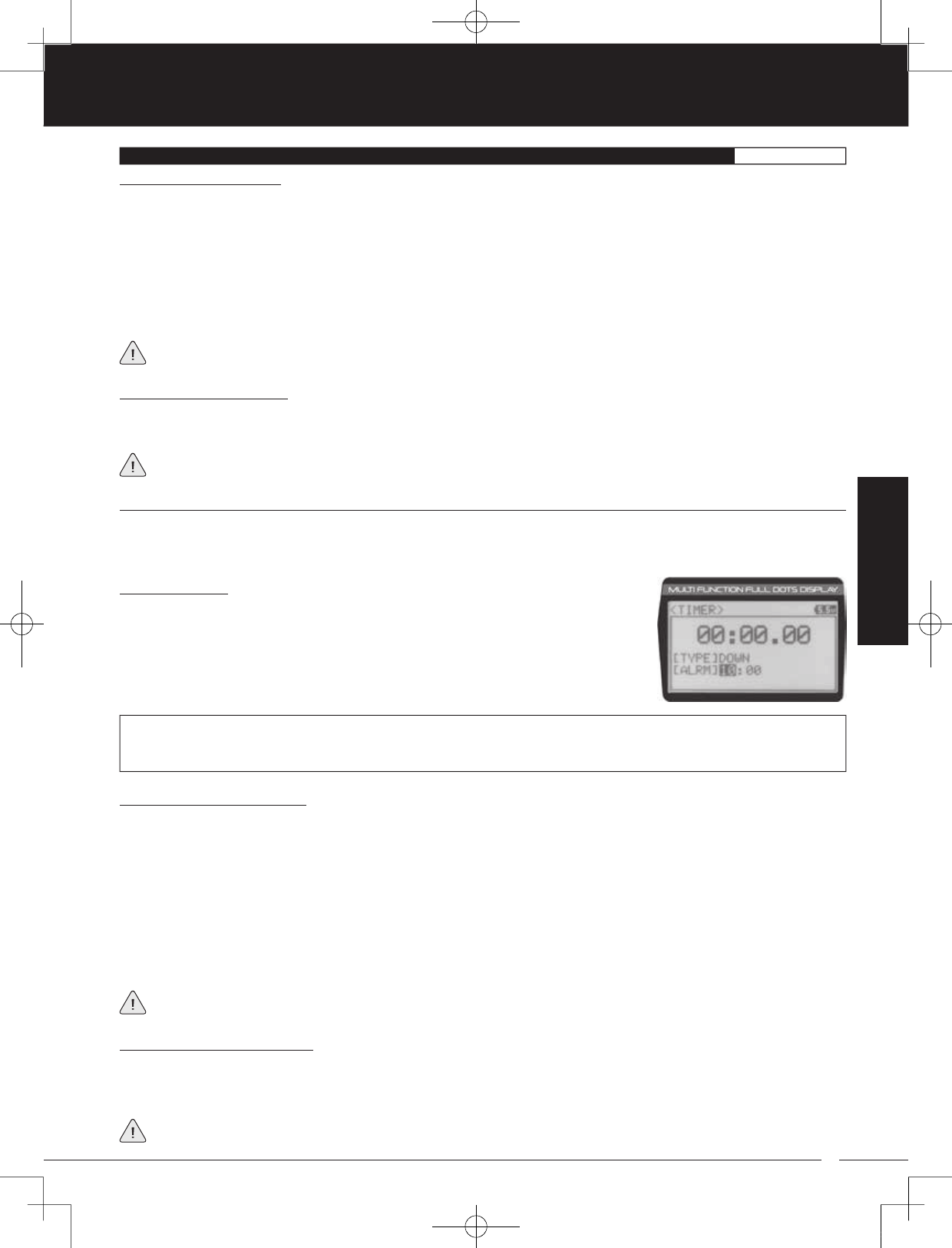
45
TR
TR
TR
90478 2.4GHZ FH4T RADIO SYSTEM USER'S GUIDE
Starting the Interval Timer:
1) In the default configuration, Push-Button Switch Sw2 controls the Interval Timer. Press and HOLD the Push-Button Switch
for 3 seconds. An audible double-tone will sound and INT will flash on the Top Screen indicating the Interval Timer is in
Stand-by.
To start the Interval Timer, press the Push-Button Switch a second time or pull the Throttle Trigger. An audible double-tone will
sound and the Interval Timer will start counting up. Each time the programmed Interval Time elapses, an audible double-tone
will sound and the Interval Timer will restart from zero and the Cumulative Time will be displayed on the Top Screen.
You can manually restart the Interval Timer from zero by pressing the Push-Button Switch while the Interval Timer is running.
If desired, the Timer Function can be assigned to Push-Button Switch Sw1. For more information, see the Key Assignments
section on pages 53 through 58.
Stopping the Interval Timer:
1) To stop the Interval Timer, press and HOLD Push-Button Switch Sw2 for 3 seconds. An audible double-tone will sound
indicating the Interval Timer is stopped and the Cumulative Time will be displayed on the Top Screen and in the TIMER menu.
The Cumulative Time cannot be manually cleared. It will be automatically cleared when the Interval Timer is put in
Stand-by again.
12.TIMER (TRACK TIMERS)PROGRAM
PROGRAM
The Countdown Timer function can be used to notify you of your model’s running time. For example, you can set the
Countdown Timer to alert you when it's time to refuel. When the Countdown Timer expires, a long audible tone will sound and
the Count Up Timer function begins automatically. This allows you to check the time elapsed since the Countdown Timer ran out.
Setting the Alarm:
1) From within the TIMER menu, scroll DOWN to highlight [ALRM] 05.
2) Press the ENTER key, then scroll UP or DOWN to set the desired Alarm Minutes value.
3) To set the Alarm Seconds value, press the ENTER key, then scroll DOWN to highlight 00.
Press the ENTER key a second time, then scroll UP and DOWN to set the desired Alarm
Seconds value.
TIMER ALRM setting range is 00:00 to 99:59. The default setting is 5:00 minutes. An audible tone will sound in 1 second intervals
5 seconds before reaching the Countdown Alarm Time. When the Countdown Alarm Time is reached, a long audible tone
will sound.
Starting the Countdown Timer:
1) In the default configuration, Push-Button Switch Sw2 controls the Countdown Timer. Press and HOLD the Push-Button
Switch for 3 seconds. An audible double-tone will sound and DWN will flash on the Top Screen indicating the Countdown
Timer is in Stand-by.
To start the Countdown Timer, press the Push-Button Switch a second time or pull the Throttle Trigger. An audible
double-tone will sound and the Countdown Timer will start counting down. An audible tone will sound in 1 second intervals
5 seconds before reaching zero. When zero is reached, a long audible tone will sound and the Countdown Timer will begin
counting Up.
You can manually stop the Countdown Timer at any time by pressing the Push-Button Switch. Press the Push-Button Switch
again will start the Countdown Timer from where it was stopped.
If desired, the Timer Function can be assigned to Push-Button Switch Sw1. For more information, see the Key Assignments
section on pages 53 through 58.
Stopping the Countdown Timer:
1) To stop the Countdown Timer, press and HOLD the Push-Button Switch for 3 seconds. An audible double-tone will sound
indicating the Countdown Timer is stopped and either the remaining Countdown Time or elapsed Count Up Time will be
displayed on the Top Screen and in the TIMER menu.
The remaining Countdown Time or Count Up Time cannot be manually cleared. It will be automatically cleared when the
Countdown Timer is put in Stand-by again.
DOWN (Countdown Timer)
MT-4S User's Guide.indd 45 2015/10/27 14:39:05
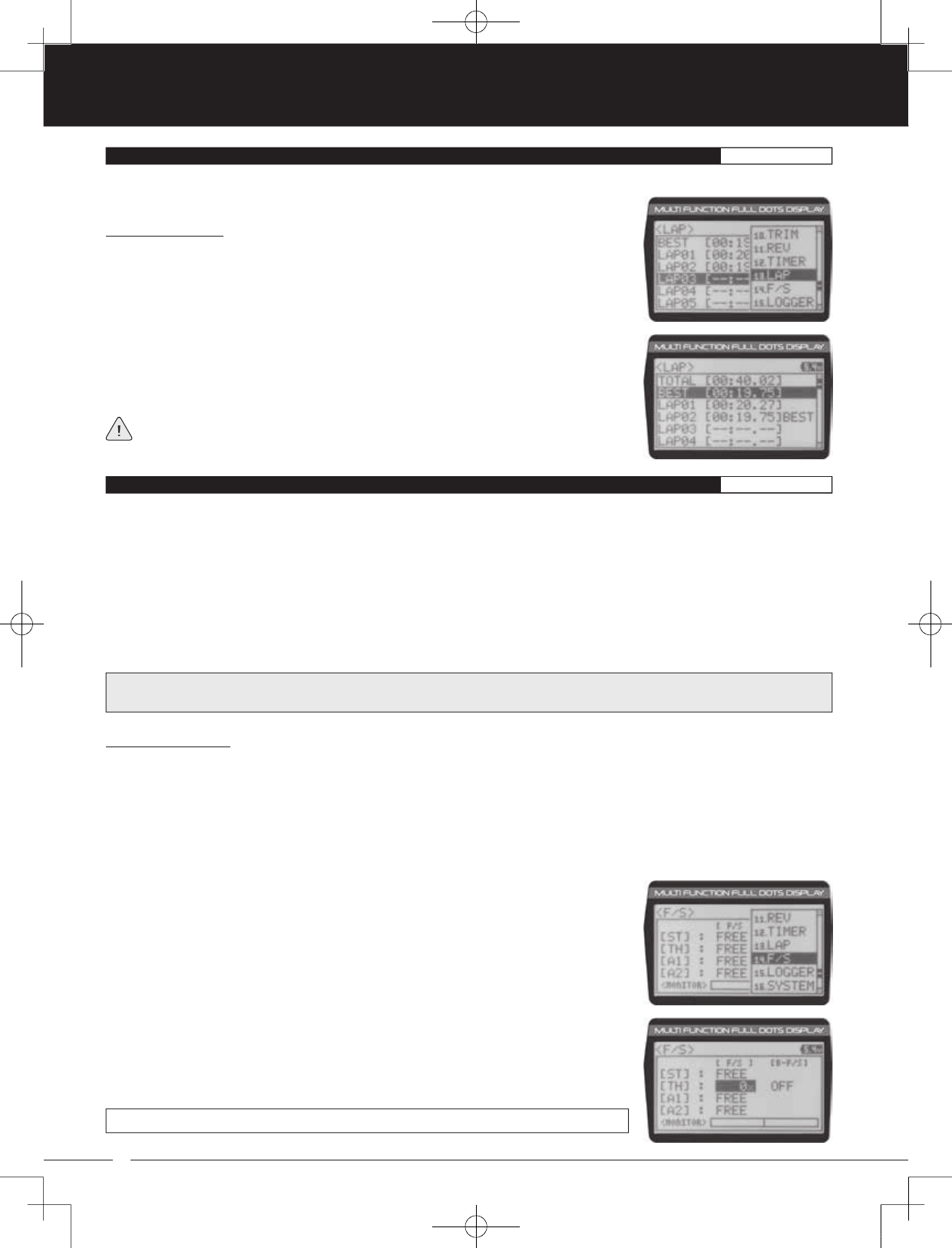
46
90478 2.4GHZ FH4T RADIO SYSTEM USER'S GUIDE
TR
TR
TR
The Lap Times menu displays a total of up to 99 laps that are recorded using the Lap Timer function. Each Lap Time is displayed
along with the Best Lap Time and the Total (Cumulative) Lap Time.
Viewing Lap Times:
1) From the Top Screen, press the ENTER key to open the Programming Menu list.
2) Scroll UP or DOWN to highlight the LAP menu, then press the ENTER key. The LAP menu
will be displayed and the last Lap selected will be highlighted.
3) Scroll UP and DOWN to view the stored Lap Times. Lap Times are stored from the time
you start the Lap Timer to the time you Stop the Lap Timer. The Total (Cumulative) Lap
Time and your Best Lap Time are always displayed at the top of the list.
Lap Times are stored until you restart the Lap Timer function. When the Lap Timer
function is restarted, old Lap Times are cleared and new Lap Times are stored.
The Fail Safe function automatically moves the servos to a predetermined position in the event that the signal between the
transmitter and the receiver is interrupted, whether due to signal degradation or to low transmitter battery. Several different
setting options are available. The Fail Safe function can be set to Hold the servos in the last position they were in when the
signal was lost, or each of the servos can be set to move to a custom position when the signal is lost. For example, the throttle
servo moves to the Brake Side to engage the brakes and stop your model. If you're driving a gas- or glow-powered boat, the
Fail Safe function could be set to lower the throttle to idle and turn the rudder slightly left or right so that the boat will continue
in slow circles.
In addition, a Receiver Battery Voltage Fail Safe function is available which allows you to set a custom voltage that the Receiver
Battery Fail Safe function will Activate at. This is useful if you're using servos with a higher than normal current draw that might
run out of power before the receiver does.
Setting the Fail Safe:
Fail Safe settings can be programmed for each of the four channels individually. In addition, Fail Safe settings are
model-specific, meaning you can have different Fail Safe settings for each Model in memory. Three Fail Safe options
are available for each channel as described below:
FREE - Fail Safe is disabled for this channel. Servos can move freely when the signal is lost.
HOLD - When Fail Safe Activates, the servo will be held in the last position it was in when the signal was lost.
% (PERCENTAGE) - When Fail Safe Activates, the servo will travel to the programmed position when the signal is lost.
IMPORTANT: The Fail Safe function will NOT OPERATE if the receiver loses power. It will operate only if the transmitter and
receiver signal is interrupted or if the transmitter loses power.
1) From the Top Screen, press the ENTER key to open the Programming Menu list.
2) Scroll UP or DOWN to highlight the F/S menu, then press the ENTER key. The F/S menu
will be displayed and [ST]:FREE will be highlighted.
3) Scroll UP or DOWN to highlight the desired channel you would like to change the Fail
Safe option for.
4) Press the ENTER key, then scroll UP or DOWN to choose the desired Fail Safe option for
that channel. If you choose to program a % value, see step 5 below.
F/S setting range is FREE, HOLD, or %. The default setting is FREE.
13.LAP (LAP TIMES)PROGRAM
14.F /S (FAIL SAFE)PROGRAM
MT-4S User's Guide.indd 46 2015/10/27 14:39:06
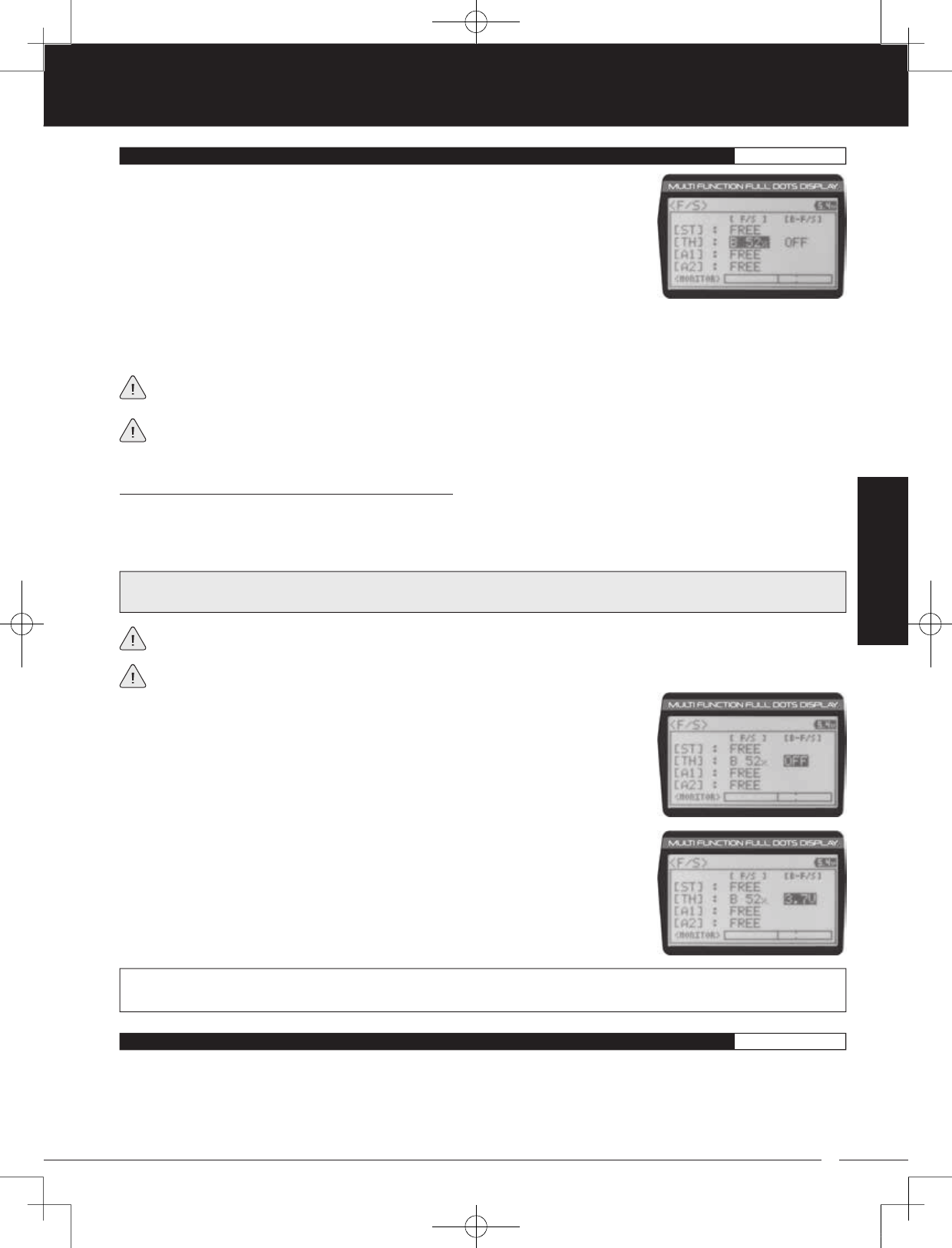
47
TR
TR
TR
90478 2.4GHZ FH4T RADIO SYSTEM USER'S GUIDE
5) To program a Fail Safe percentage value, move the control the amount you want the
servo to move to when the Fail Safe function Activates and HOLD it in that position,
then press and HOLD the ENTER key until an audible tone sounds. The percentage and
direction the servo will travel will be displayed. For example, to set the Throttle Brake to
engage when the Fail Safe function Activates, push the throttle trigger toward the Brake
side the desired amount, HOLD the throttle trigger in that position, then press and HOLD
the ENTER key. The percentage value programmed will be indicated by two hash marks
on the Servo Monitor.
6) Check to ensure your Fail Safe settings are working properly. Make sure that both the transmitter and receiver are turned
ON, then, while someone is holding your model, turn the transmitter OFF. The servos should react correctly based on the
Fail Safe values chosen.
The Fail Safe settings will be retained even if the transmitter loses power or if the transmitter and receiver must be
paired again.
When using an FH2 receiver with your transmitter, these Fail Safe features are not supported. In this case, the Fail Safe
function must be programmed directly through the receiver. For more information, follow the Fail Safe Programming
instructions provided with your FH2 receiver.
14.F /S (FAIL SAFE)PROGRAM
PROGRAM
Setting the Receiver Battery Voltage Fail Safe Function:
The Receiver Battery Voltage Fail Safe function is designed to alert you when your receiver battery requires recharging. This
ensures that the receiver battery's voltage doesn't drop so low that your servos aren't provided adequate voltage to operate
optimally. When Activated, the throttle servo will move to the predetermined position you programmed in step 5 in the Setting the
Fail Safe section above. If this occurs, recharge or replace your receiver batteries.
If FREE or HOLD is chosen for the Throttle channel, you cannot Activate the Receiver Battery Voltage Fail Safe function.
A % value must be chosen for the Throttle channel to be able to program and use the Receiver Battery Fail Safe function.
The Receiver Battery Voltage Fail Safe function works only with FH3 and FH4T receivers.
1) Follow steps 1 through 5 in the Setting the Fail Safe section to program a Throttle Fail
Safe percentage value.
2) From within the F/S menu, press the ENTER key, then scroll DOWN to highlight
[B-F/S] OFF.
3) Press the ENTER key, then scroll UP or DOWN to choose the desired Receiver Battery
Fail Safe Voltage value. Many factors, such as the current draw of your servos and how
many servos you're using, etc., will determine the value to use. A good starting point
would be 3.7V. If it appears your servos are slow or not producing adequate torque what
that Voltage value is reached, Increase the Voltage value.
WARNING: This function is designed for use with glow- or gas-powered Models that use a separate receiver battery pack.
Do NOT use this function with an electric Model that uses the motor battery to power the servos and receiver.
F/S B-F/S setting range for FH4T receivers is OFF and 3.5V to 7.4V. F/S B-F/S setting range for FH3 receivers is OFF and
3.5V to 5.0V. The default setting is OFF regardless of the Modulation Type chosen.
The Telemetry Log function allows you to view a log of the Telemetry Data that is sent from the receiver to the transmitter. You
are able to view Telemetry Data for both Temperature outputs, the RPM output and the receiver's Voltage. This information can
be used to track specific information about your model, such as cylinder head temperature if you're running a nitro-powered
model or battery temperature if you're running an electric model and much more. The interval that Telemetry Data is read and
stored can be adjusted so that Telemetry Data can be stored for up to 90 minutes of use. The Telemetry Log can store 120
different data entries at intervals ranging from 00.1 seconds to 45.9 seconds.
15.LOGGER (TELEMETRY LOG)PROGRAM
MT-4S User's Guide.indd 47 2015/10/27 14:39:06
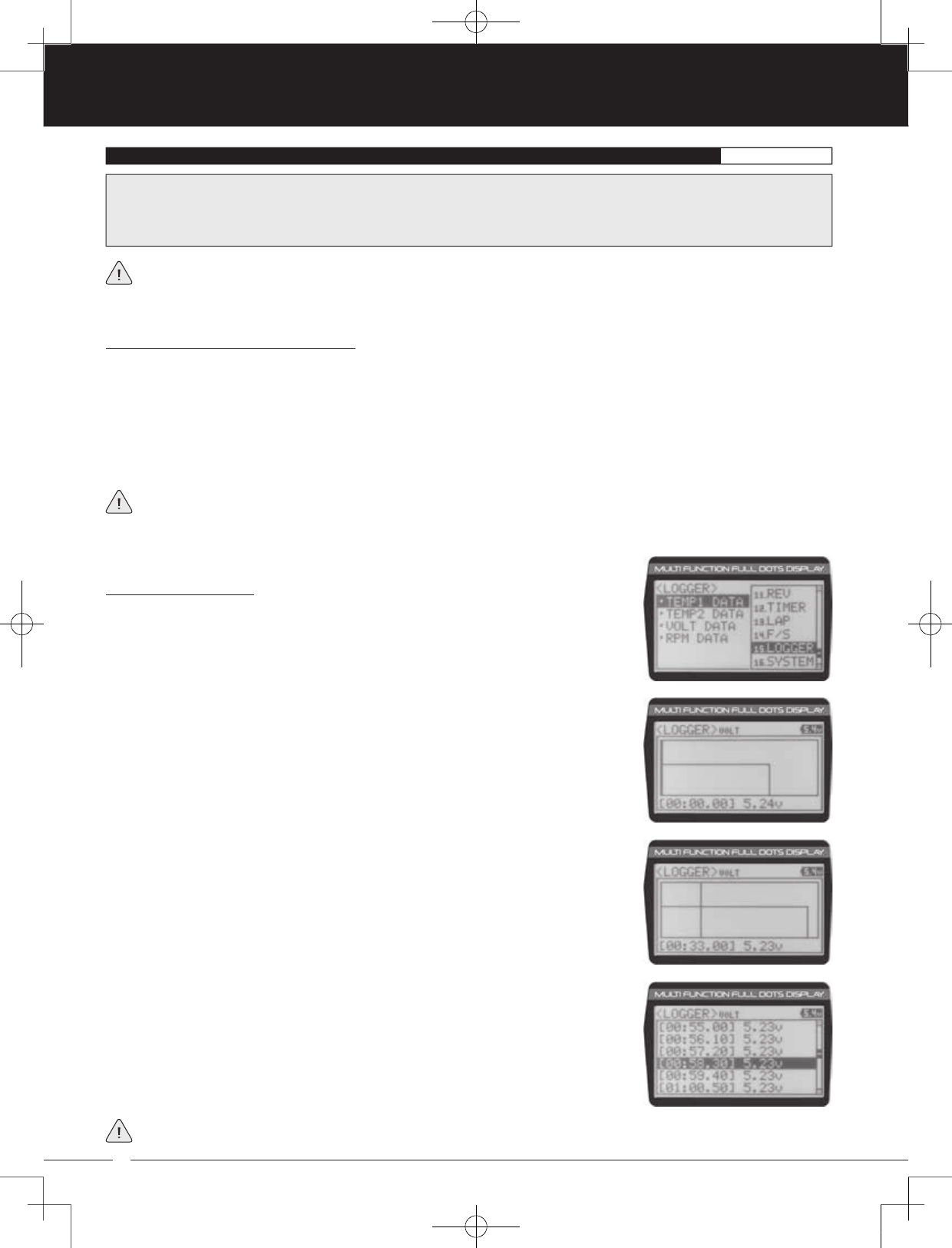
48
90478 2.4GHZ FH4T RADIO SYSTEM USER'S GUIDE
TR
TR
TR
Starting and Stopping the Telemetry Log:
The Telemetry Log function must be Started in order for the transmitter to read and store Telemetry Data from the receiver.
1) In the default configuration, Push-Button Switch Sw1 controls the Telemetry Log. To start the Telemetry Log, press the
Push-Button switch. LED1 (Blue) will flash, indicating the Telemetry Log is storing data. Telemetry Data is stored for all four
Telemetry functions, whether the Telemetry Sensors are hooked up or not.
2) To stop the Telemetry Log, press the Push-Button Switch a second time. If desired, the Telemetry Log Function can be
assigned to Push-Button Switch Sw2. For more information, see the Key Assignments section on pages 53 through 58.
Each time the Telemetry Log is started, any old Telemetry Data is automatically erased. In addition, the Telemetry Log will
stop automatically once the Telemetry Log is filled. The Telemetry Log can store 120 separate entries. If the Log Interval
is set to 00.1 seconds, the Telemetry Log can record for 12 seconds. If the Log Interval is set to 45.1 seconds, the Telemetry Log
can record for 90 minutes. To change the Log Interval value, see the Changing the Telemetry Log Step Value section on page 68.
Viewing Telemetry Data:
1) From the Top Screen, press the ENTER key to open the Programming Menu list.
2) Scroll UP or DOWN to highlight the LOGGER menu, then press the ENTER key. The
LOGGER menu will be displayed and TEMP1 DATA will be highlighted.
3) From within the LOGGER menu, scroll UP or DOWN to highlight the desired Telemetry
Data you would like to view. Choose from TEMP1 DATA, TEMP2 DATA, VOLT DATA or
RPM DATA.
4) Press the ENTER key to open the Telemetry Log.
5) To view the Telemetry Data at a specific point along the graph, scroll UP or DOWN to
move the vertical line right or left. The Telemetry Data for each point the vertical line is at
is displayed at the bottom of the screen.
6) To view all of the Telemetry Data points, press the ENTER key to open the Telemetry
Data List, then scroll DOWN to view all of the recorded Telemetry Data entries.
The Telemetry Log can be started and stopped while viewing Telemetry Data. To start the Telemetry Log, press and HOLD
the ENTER key and to stop the Telemetry Log, press and HOLD the ENTER key a second time.
15.LOGGER (TELEMETRY LOG)PROGRAM
For information about using an optional Telemetry receiver with your 90478 transmitter and installing Telemetry Sensors
into your model, see the Telemetry Connections and Mounting section on pages 69 and 70. In addition, to be able to read
and log Telemetry Data, the Telemetry system must be turned ON. For more information about turning the Telemetry system
ON, see the Telemetry Setting section on pages 67 and 68.
IMPORTANT: Full telemetry support requires the use of an Airtronics 2.4GHz FH4T telemetry-capable surface receiver, such
as the RX-461 or RX-462, along with Airtronics Temperature and RPM Sensors (available separately). The included RX-472
receiver can send Telemetry Data for the voltage of the receiver battery pack only, unless used with the Airtronics Super
Vortex ZERO ESC (available separately) plugged into the BATT/SSL port of the included RX-472 receiver.
MT-4S User's Guide.indd 48 2015/10/27 14:39:07
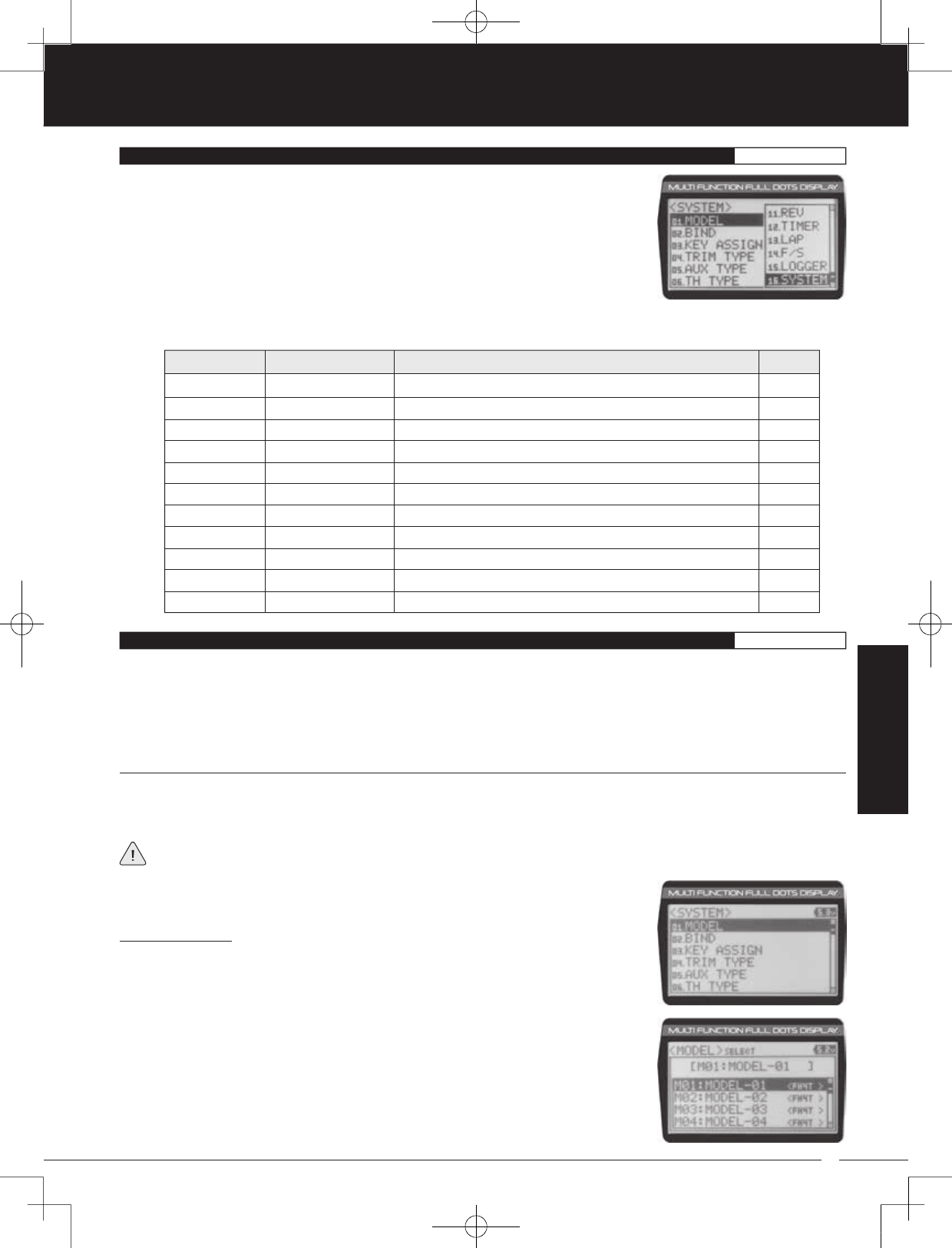
49
TR
TR
TR
90478 2.4GHZ FH4T RADIO SYSTEM USER'S GUIDE
SYSTEM
PG. 49
PG. 52
PG. 53
PG. 59
PG. 59
PG. 60
PG. 61
PG. 61
PG. 62
PG. 63
PG. 68
The different System Menus allow you to program options related directly to the use and
setup of the 90478 transmitter. From changing the Modulation Type, to adjusting LCD
properties and changing Key Assignments to suit your specific setup, it's all here.
1) To access the various System Menus, turn the transmitter ON, then press the ENTER key
(Push-Button Rotary Dial) to open the Programming Menu list. Scroll DOWN to SYSTEM,
then press the ENTER key a second time to open the System Menu. A list of System
Menus will be displayed and the first System Menu will be highlighted.
MENU MENU NAME MENU DESCRIPTION
SYSTEM MENUS
PAGE
SYSTEM MENUS OVERVIEW SYSTEM
2) Use the Push-Button Rotary Dial to scroll UP or DOWN to highlight the desired System Menu, then press the ENTER key to
open the highlighted System Menu.
01.MODEL
02.BIND
03.KEY ASSIGN
04.TRIM TYPE
05.AUX TYPE
06.TH TYPE
07.BUZZER
08.BATTERY
09.LCD
10.TELEMETRY
11.VR ADJUST
Model
Binding
Key Assignments
Servo Trim Type
Auxiliary Type
Throttle Type
Audible Key Tone
Voltage Alarm
Contrast
Telemetry
Variable Rate Adjust
Model Select, Model Naming, Model Copy and Model Clear
Bind, Select Modulation Type and Servo Operating Mode
Assign Functions to the Switches, Rotary Dial and Auxiliary Lever
Change the Servo Trim Type
Choose Auxiliary 1 and Auxiliary 2 Programming Functions
Change the Throttle Servo Travel Proportion
Adjust Audible Key Tone Volume and Tone
Specify Transmitter Battery Low Voltage and Limit Alarms
Adjust LCD Contrast and Backlight Options
Program Telemetry Display Options
Calibrate Steering, Throttle and Auxiliary Lever Controls
The Model menu allows you to select different models using the Model Select function, name your saved models using the
Model Naming function, and copy Programming Data from one model to another, or clear Programming Data from one or
more models using the Model Copy and Model Clear functions. Programming Data for up to 18 different models can be stored
in the transmitter's memory. This allows you to use the transmitter with different models and quickly and easily select the
Programming Data for each of them. In addition, a Model Select Shortcut function is also featured for quick access to the Model
Select (Direct Model) function.
The Model Select function allows you to load the Programming Data for the particular model you wish to drive. The Model Select
menu displays the currently selected model, along with a list of available models that can be selected. The Modulation Type for
each model is also displayed. The transmitter can store Programming Data for up to 18 different models.
When a model is selected and loaded, the Programming Data for that model will be loaded immediately. Modulation
Type, Servo Operating Mode, Key Assignments, Trim Type, Auxiliary Type and Throttle Type options, in addition to all
Programming Menu function options are model-specific.
Selecting a Model:
1) From within the SYSTEM menu, scroll UP or DOWN to highlight the MODEL menu.
2) Press the ENTER key to open the MODEL menu. MODEL SELECT will be highlighted.
3) Press the ENTER key. The MODEL SELECT menu will be displayed and the currently
selected model in the Model Select List will be highlighted.
01.MODEL (MODEL SELECT, NAMING, COPY AND CLEAR)SYSTEM
MODEL SELECT (Model Select)
MT-4S User's Guide.indd 49 2015/10/27 14:39:07
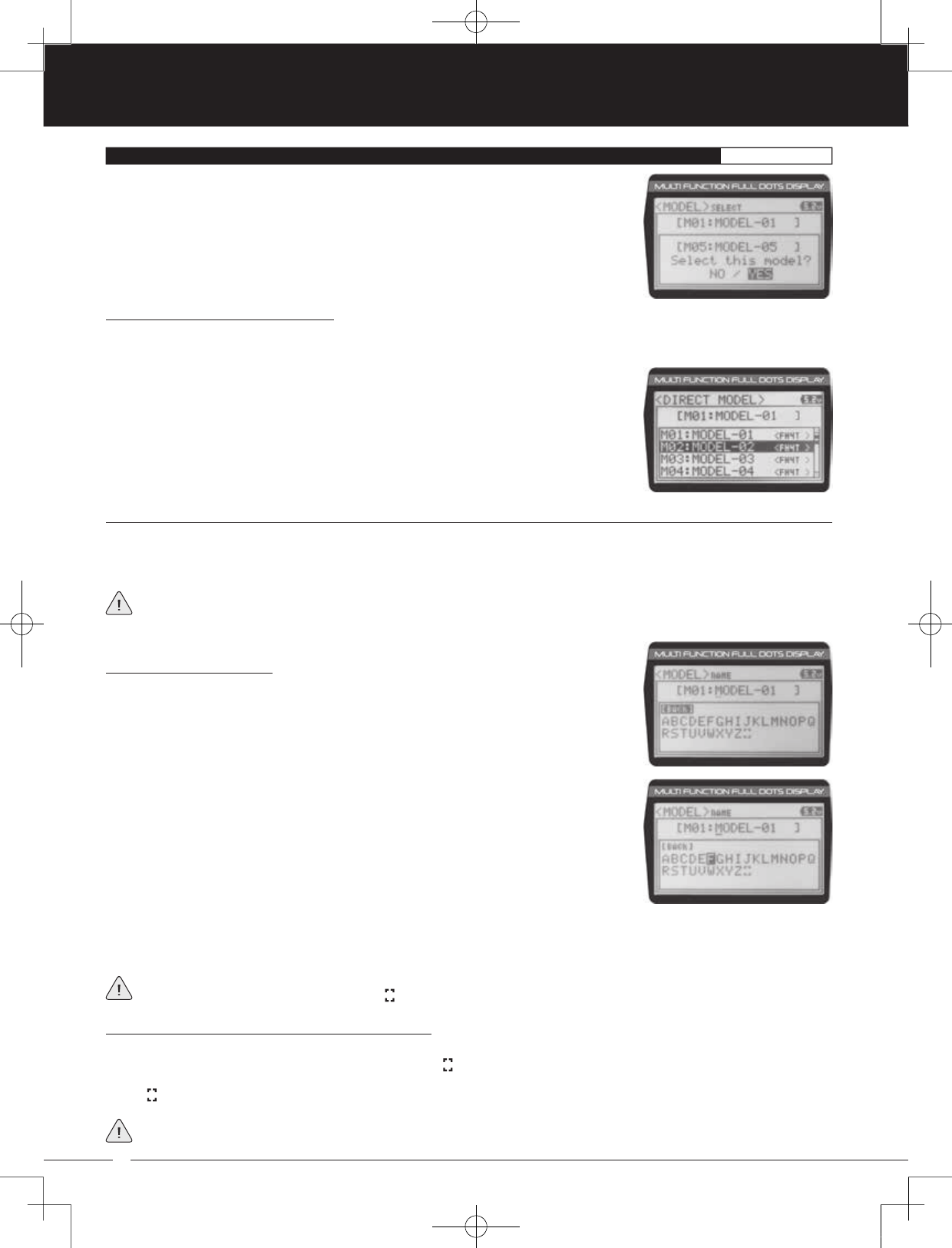
50
90478 2.4GHZ FH4T RADIO SYSTEM USER'S GUIDE
TR
TR
TR
4) Scroll UP or DOWN to highlight the model you would like to select, then press the ENTER
key. Select this model? NO/YES will be displayed.
5) Scroll DOWN to highlight YES, then press the ENTER key. The model that you just
selected will be displayed above the Model Select List and that model's Programming
Data will be loaded.
Model Select Shortcut (Direct Model):
The Model Select Shortcut function allows you to jump directly to the DIRECT MODEL menu when you turn the transmitter ON.
This menu works the same as the MODEL SELECT menu and makes it much quicker select your desired model.
The Model Naming function allows you to name each of the 18 individual models. This makes it easy to keep track of multiple
models. The Model Name can consist of up to 10 letters, numbers, or symbols. Choose from capital letters, lower case letters,
numbers, and various symbols.
A model must be selected before a Model Name can be entered or modified. In the default configuration, M01:MODEL-1
is selected. To enter a Model Name for another model, that model must first be selected using the Model Select function
or the Model Select Shortcut function. For more information, see the Model Select section on pages 49 and 50.
Changing the Model Name:
1) From within the MODEL menu, scroll DOWN to highlight MODEL NAME.
2) Press the ENTER key. The MODEL NAME menu will be displayed, [BACK] will be
highlighted and the underscore will be flashing under the first editable character in the
Model Name.
3) Scroll UP or DOWN to move the underscore to the character you would like change.
4) Press the ENTER key, then scroll UP or DOWN to highlight a character in the Character
List. Press the ENTER key a second time to select the highlighted character. That
character will be displayed and the underscore will move to the next space in the Model
Name.
01.MODEL (MODEL SELECT, NAMING, COPY AND CLEAR)SYSTEM
MODEL NAME (Model Naming)
5) Repeat steps 3 and 4 to enter the rest of the characters. Up to ten characters can be entered. Press the BACK/CANCEL key
to re-gain control of the underscore (the underscore will flash indicating you can scroll UP or DOWN to move it Forward or
Backward).
To select lower case letters, numbers or symbols, continue to scroll UP or DOWN through the various Character Lists. To
add a space in your Model Name, use the icon.
Deleting a Single Character or an Entire Model Name:
1) Scroll UP or DOWN to move the underscore under the character in the Model Name you want to delete. Press the ENTER
key, then scroll UP or DOWN to highlight [BACK] or the icon in the Character List and press the ENTER key. If you want to
delete the entire name, move the underscore to the last character in the name, scroll UP or DOWN to highlight [BACK] or
the icon in the Character List, then repeatedly press the ENTER key.
If you can't move the underscore, press the BACK/CANCEL key to re-gain control of the underscore (the underscore will
flash indicating you can scroll UP or DOWN to move it Forward or Back).
1) Turn the transmitter OFF.
2) Press and HOLD the BACK/CANCEL key, then turn the transmitter ON. The DIRECT
MODEL menu will be displayed. To select a model, follow steps 4 and 5 in the Selecting
a Model section above.
MT-4S User's Guide.indd 50 2015/10/27 14:39:08
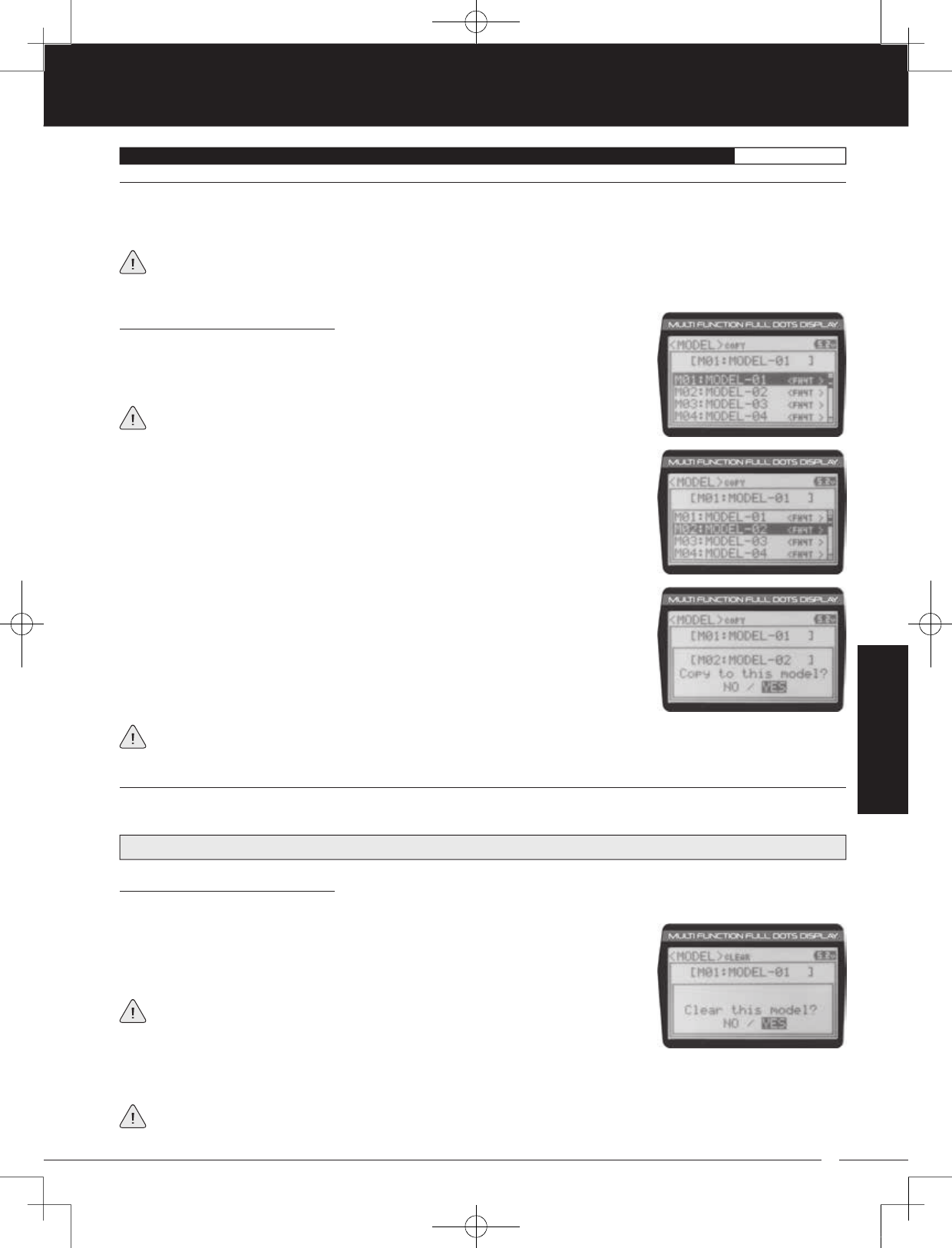
51
TR
TR
TR
90478 2.4GHZ FH4T RADIO SYSTEM USER'S GUIDE
The Model Copy function allows you to copy the Programming Data from one model to another model. For example, if you have
two models that are similar, you can copy the Programming Data from the first model to the second model to use as a base to
start fine-tuning the programming for the second model.
The Model Copy function allows you to copy Programming Data FROM the currently selected model TO any other model
in the Model Copy List. Make sure that prior to using the Model Copy function, you first select and load the desired Model
Programming Data you want to copy FROM, using the Model Select function.
The Model Clear function allows you to Reset model-specific Programming Data for any model back to the factory default
settings.
Clearing Model Programming Data:
1) Using the Model Select function, select the model you would like to Reset the Programming Data for.
WARNING: When the Model Clear function is Executed, all custom Programming Data for that model will be lost!
01.MODEL (MODEL SELECT, NAMING, COPY AND CLEAR)SYSTEM
MODEL COPY (Model Programming Data Copy)
3) Scroll UP or DOWN to highlight the model you would like to copy the Programming
Data TO.
4) Press the ENTER key. Copy to this model? NO/YES will be displayed.
5) Scroll DOWN to highlight YES, then press the ENTER key. After ~3 seconds, Executed
will flash, indicating the Programming Data has been copied to the highlighted model.
All model-specific Programming Data, including the Model Name will be copied to the highlighted model. If you want to
go back and change models or you don't want to copy the Programming Data for any reason, press the BACK/CANCEL key.
Copying Model Programming Data:
1) From within the MODEL menu, scroll DOWN to highlight MODEL COPY.
2) Press the ENTER key. The MODEL COPY menu will be displayed and the first model in
the Model Copy List will be highlighted.
The currently selected model is displayed above the Model Copy List.
MODEL CLEAR (Model Programming Data Reset)
4) Scroll DOWN to highlight YES, then press the ENTER key. After ~3 seconds, Executed will flash, indicating the Programming
Data has been Reset to the default values.
If you want to go back and change models or you don't want to Reset the Programming Data for any reason, press the
BACK/CANCEL key. When Executed, all model-specific Programming Data, including the Model Name, Modulation Type,
Servo Operating Mode, Key Assignments, Trim Type, Auxiliary Type and Throttle Type options will be Reset to the default values.
2) From within the MODEL menu, scroll DOWN to highlight MODEL CLEAR.
3) Press the ENTER key. Clear this model? NO/YES will be displayed.
The currently selected model is displayed at the top of the MODEL CLEAR menu.
SYSTEM
MT-4S User's Guide.indd 51 2015/10/27 14:39:08
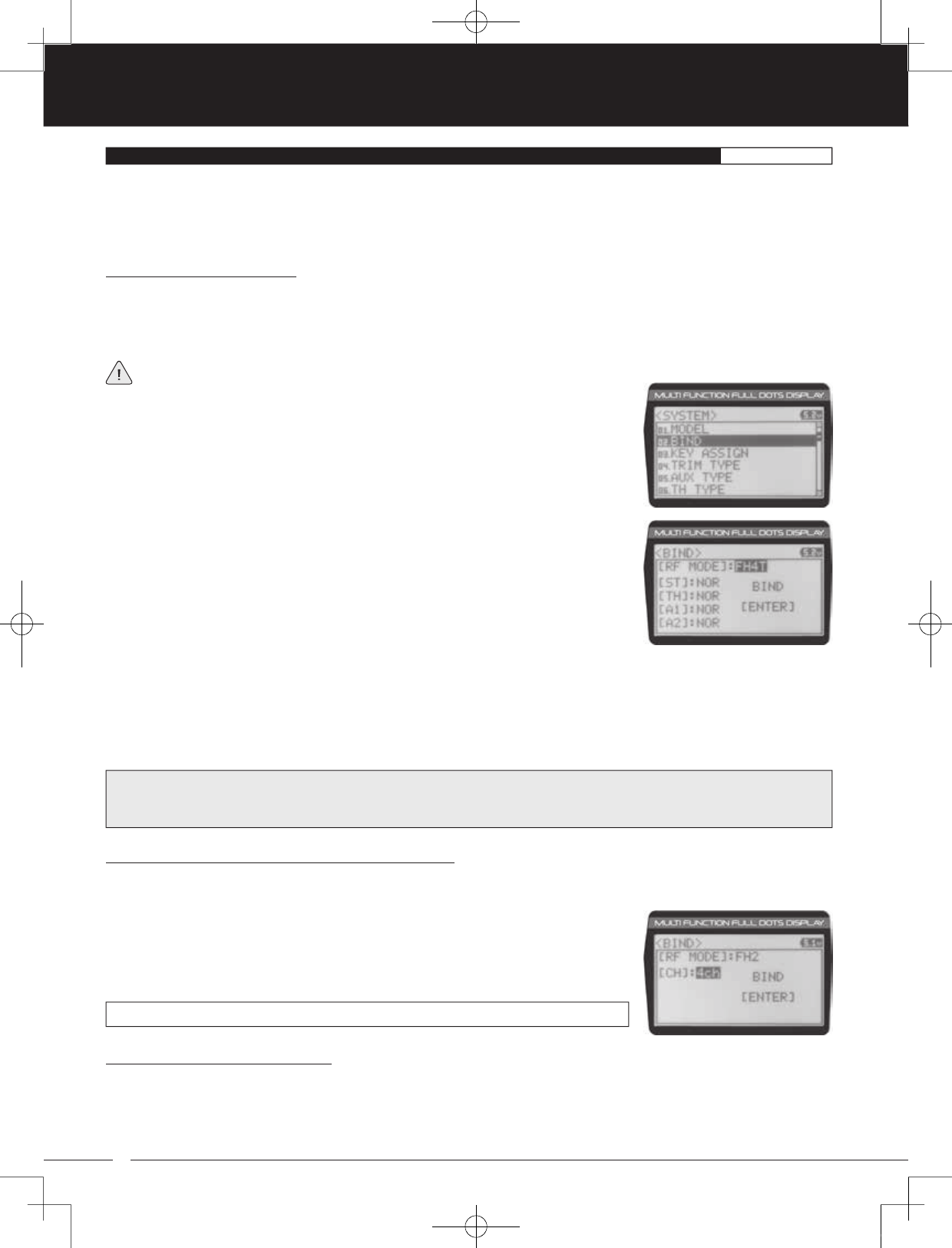
52
90478 2.4GHZ FH4T RADIO SYSTEM USER'S GUIDE
TR
TR
TR
The Binding function allows you to Bind the transmitter and receiver pair. When new, it is necessary to pair the transmitter
and receiver to prevent interference from transmitters operated by other users. This operation is referred to as Binding. Once
the Binding process is complete, the setting is remembered even when the transmitter and receiver are turned OFF. Therefore,
this procedure usually only needs to be done once. In addition, the Modulation Type and Servo Operating Mode can also be
changed to suit your specific setup.
Changing the Modulation Type:
The Modulation Type function allows you to choose the transmitter Modulation Type. The Modulation Type can be changed
to match the receiver you're using. For example, if you wish to use an Airtronics 2.4GHz FH2 receiver with your transmitter,
you would need to change the Modulation Type to FH2 prior to Binding your transmitter and receiver. Modulation Type
is model-specific, meaning that you can have one model use FH4T Modulation and another model use FH2 Modulation, etc.
The Modulation Type must be chosen prior to Binding the transmitter and receiver. Make sure the Modulation Type you
choose matches the Modulation Type of the receiver you're using.
1) From within the SYSTEM menu, scroll UP or DOWN to highlight the BIND menu.
The following Modulation Type options are available:
FH2 - Select this Modulation Type when using an Airtronics 2.4GHz FH2 surface receiver.
FH3 - Select this Modulation Type when using an Airtronics 2.4GHz FH3 receiver.
FH4T - Select this Modulation Type when using an Airtronics 2.4GHz FH4T Telemetry receiver.
FH3F/FH4FT - These Modulation Types are NOT used in North America. They are typically used in France.
2) Press the ENTER key. The BIND menu will be displayed and [RF MODE]:FH4T will be
highlighted.
3) Press the ENTER key, then scroll UP or DOWN to select the desired Modulation Type,
then press the ENTER key a second time. Set to (Modulation Type) NO/YES will be
displayed.
4) Scroll DOWN to highlight YES, then press the ENTER key.
02.BIND (BINDING, MODULATION TYPE AND SERVO OPERATING MODE)SYSTEM
Changing the Channel Mode - FH2 Modulation Type Only:
When the FH2 Modulation Tyep is selected, you can choose to operate the transmitter in either 2-Channel Mode or 4-Channel
Mode. This option is available ONLY when [RF MODE] FH2 is selected.
1) From within the BIND menu, scroll DOWN to highlight [CH]:4ch.
2) Press the ENTER key, then scroll UP or DOWN to choose the desired Channel Mode.
Selecting 2CH will enable 2-channel operation (Steering and Throttle). Selecting 4CH
will enable 4-channel operation (Steering, Throttle, Auxiliary 1 and Auxiliary 2).
BIND CH setting range is 2CH and 4CH. The default setting is 4CH.
IMPORTANT: Not all BIND menu functions are supported by all Modulation Types. Only supported functions will be
displayed once a Modulation Type is chosen. For example, the FH2 Modulation Type does not support the ability to change
the Servo Operating Mode.
Changing the Servo Operating Mode:
The Servo Operating Mode function is used to optimize the radio control system to suit the type of servos you're using in your
model. For example, using the SHR setting with Digital servos will Increase the servo's response time, even above the
manufacturer's stated specification. If you're using Airtronics SRG Digital servos, you can use the SSR setting for the fastest
response time. The combination of using Digital servos and using the correct Servo Operating Mode results in the ultimate feel
and response, making you feel more in control of your model than ever.
MT-4S User's Guide.indd 52 2015/10/27 14:39:09
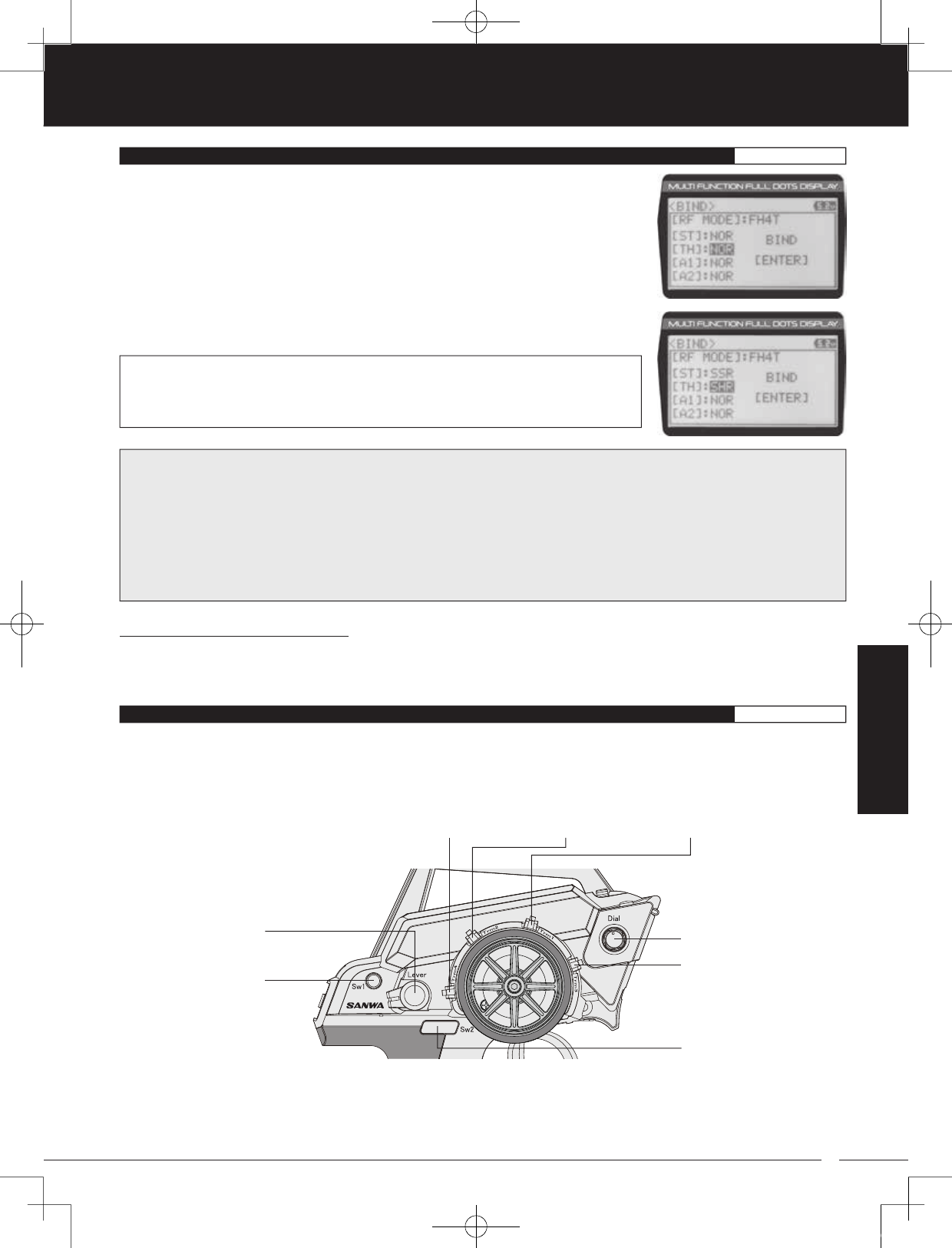
53
TR
TR
TR
90478 2.4GHZ FH4T RADIO SYSTEM USER'S GUIDE
1) From within the BIND menu, scroll UP or DOWN to highlight the desired channel you
would like to change the Servo Operating Mode for. Choose from either [ST]:NOR
(Steering), [TH]:NOR (Throttle), [A1]:NOR (Auxiliary 1) or [A2]:NOR (Auxiliary 2).
02.BIND (BINDING, MODULATION TYPE AND SERVO OPERATING MODE)SYSTEM
IMPORTANT INFORMATION ABOUT SERVO OPERATING MODES:
If you're using Analog servos in your model, DO NOT use SHR or SSR Servo Operating Mode for those channels. Use the
NOR (Normal) Servo Operating Mode with Analog servos. Using SHR or SSR Servo Operating Mode with Analog servos can
result in poor performance or even damage to the servos or the receiver! In some cases, the servo may not operate at all.
Not all ESCs are compatible with SHR or SSR Servo Operating Modes. If your ESC does not operate correctly, change the
Servo Operating Mode to NOR (Normal) for that channel (or channels).
SHR and SSR Servo Operating Modes should only be used with Digital servos. While the SHR Servo Operating Mode can be
used with any brand of Digital servo, the SSR Servo Operating Mode should ONLY be used with Airtronics SRG Digital servos.
2) Press the ENTER key, then scroll UP or DOWN to choose the desired Servo Operating
Mode option for that channel.
SERVO OPERATING MODE setting range is NOR, SHR and SSR. The default setting is
NOR. SSR Operating Mode is not supported when the FH3 or FH3F Modulation Type
is selected. No Servo Operating Modes are supported when the FH2 Modulation Type
is selected.
Binding the Transmitter and Receiver:
To Bind the transmitter and receiver, please see the Transmitter and Receiver Binding section on page 16. Prior to Binding the
transmitter and receiver, make sure to choose the desired Modulation Type that matches the receiver you're using. Servo
Operating Mode can be changed prior to Binding the transmitter and receiver, or after the Binding process.
SYSTEM
Trm1 - Steering Trim
Trm2 - Throttle Trim
Trm3 - Steering Dual Rate
Trm4 - Brake Dual Rate
Sw1 - Telemetry Logger ON/OFF
Sw2 - Timer ON/OFF
Dial Knob - Auxiliary 1 Channel 3
Auxiliary Lever - Auxiliary 2 Channel 4
The Key Assignments function allows you to assign different functions to each of the two Push-Button Switches, the four Trim
Switches, the Dial Knob and the Auxiliary Lever. In addition, the ON/OFF behavior of some Push-Button Switch functions can
be changed. The Key Assignments function also allows you to change the Direction of Travel and the Trim Resolution of the
four Trim Switches and the Rotary Dial. This allows you to fine-tune the movement of the servos when the Trim Switches are
pressed and the Rotary Dial is turned.
03.KEY ASSIGN (KEY ASSIGNMENTS)SYSTEM
Trim Switch
(Trm1)
Dial Knob
Push-Button
Switch (Sw1)
Trim Switch
(Trm2)
Trim Switch (Trm3)
Trim Switch
(Trm4)
Auxiliary Lever
Push-Button
Switch (Sw2)
MT-4S User's Guide.indd 53 2015/10/27 14:39:10
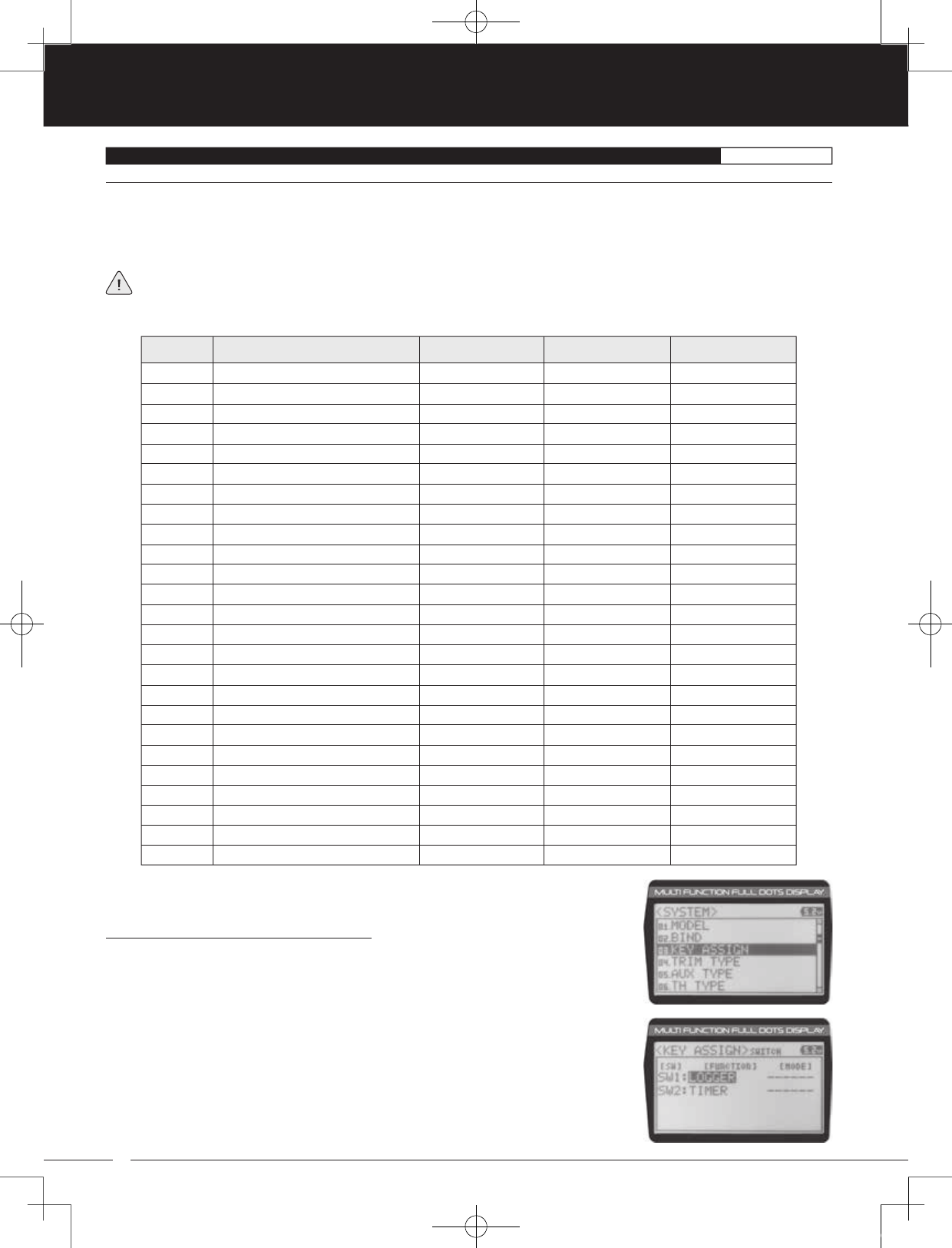
54
90478 2.4GHZ FH4T RADIO SYSTEM USER'S GUIDE
TR
TR
TR
The Key Assignments function allows you to assign the ON/OFF control of various functions to Push-Button Switches Sw1 and
Sw2. This allows you to use the Push-Button Switches to turn functions OFF and ON during use. One function can be assigned
to each Push-Button switch, although both Push-Button Switches can be OFF or ON at the same time. In addition, the ON/OFF
behavior of some Push-Button Switch Key functions can be changed.
When you program a function, that function is ON (Active) by default, unless the function's default ON/OFF value is OFF
as noted in the table below. To toggle the function OFF and ON it must be assigned to a Push-Button Switch.
This table shows the different functions that can be programmed to the two Push-Button Switches:
Changing the Push-Button Switch Function:
1) From within the SYSTEM menu, scroll UP or DOWN to highlight the KEY ASSIGN menu.
03.KEY ASSIGN (KEY ASSIGNMENTS)SYSTEM
SWITCH (Push-Button Switch Key Assignments)
Inhibited
Dual Rate-Steering
Dual Rate-Throttle
Dual Rate-Brake
Curve-Steering
Curve-Steering
Servo Speed-Steering
Servo Speed-Throttle
Anti-Lock Braking
Throttle Offset
Auxiliary 1 Channel 3
Auxiliary 2 Channel 4
Auxiliary 1 CODE1
Auxiliary 1 CODE2
Auxiliary 1 CODE3
Auxiliary 1 CODE4
Auxiliary 1 CODE5
Auxiliary 2 CODE1
Auxiliary 2 CODE2
Auxiliary 2 CODE3
Auxiliary 2 CODE4
Auxiliary 2 CODE5
Timers
Telemetry Clear
Telemetry Logger
Sw2
Sw1
------
ON
ON
ON
ON
ON
ON
ON
ON
ON
ON
ON
ON
ON
ON
ON
ON
ON
ON
ON
ON
ON
OFF
OFF
OFF
OFF
D/R-ST
D/R-TH
D/R-BR
CUR-ST
CUR-TH
SPD-ST
SPD-TH
ALB
OFFSET
AUX1
AUX2
A1CODE1
A1CODE2
A1CODE3
A1CODE4
A1CODE5
A2CODE1
A2CODE2
A2CODE3
A2CODE4
A2CODE5
TIMER
TE-CLR
LOGGER
------
Toggle
Toggle
Toggle
Toggle
Toggle
Toggle
Toggle
Toggle
Toggle
Toggle
Toggle
Toggle
Toggle
Toggle
Toggle
Toggle
Toggle
Toggle
Toggle
Toggle
Toggle
------
------
------
MENU FUNCTION DEFAULT SWITCH DEFAULT MODE DEFAULT ON/OFF
2) Press the ENTER key to open the KEY ASSIGN menu. SWITCH will be highlighted.
3) Press the ENTER key. The SWITCH menu will be displayed and SW1:LOGGER will be
highlighted.
MT-4S User's Guide.indd 54 2015/10/27 14:39:10
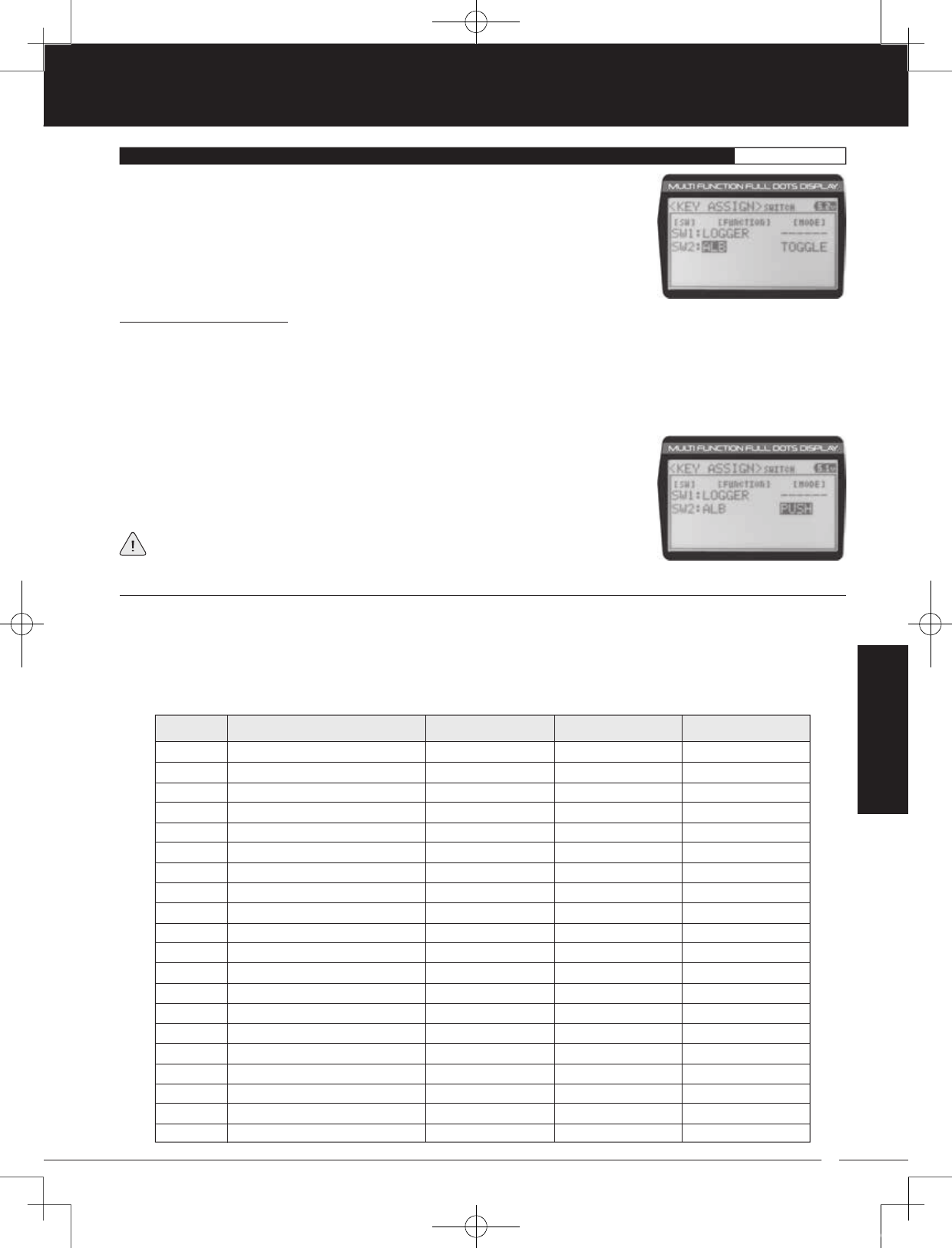
55
TR
TR
TR
90478 2.4GHZ FH4T RADIO SYSTEM USER'S GUIDE
4) Scroll UP or DOWN to highlight the function you would like to change for either SW1
or SW2.
5) Press the ENTER key, then scroll UP or DOWN to choose the desired function for either
SW1 or SW2. A list of functions that can be assigned to the Push-Button Switches is
shown in the table on the previous page.
Changing the Switch Mode:
Some functions allow you to change how the Push-Button Switch operates. The following Switch Modes are available:
TOGGLE - When selected, press the Push-Button Switch to turn the function ON and press the Push-Button Switch a
second time to turn the function OFF. See note on previous page.
PUSH - When selected, press and HOLD the Push-Button Switch to turn the function ON. When the Push-Button Switch is
released, the function will be turned OFF.
1) From within the KEY ASSIGN SWITCH menu, scroll DOWN to highlight the MODE you
would like to change for either SW1 or SW2.
2) Press the ENTER key, then scroll UP or DOWN to choose the desired Switch Mode
setting, either TOGGLE or PUSH.
The Switch Mode cannot be changed for all functions. When [MODE] ------, the
Push-Button Switch will act as if it were in Toggle Mode.
The Key Assignments function allows you to assign different functions to Trim Switches Trm1, Trm2, Trm3 and Trm4, the Rotary
Dial and the Auxiliary Lever. This allows you to use the Trim Switches, Rotary Dial and Auxiliary Lever to control those functions
while you're driving. In addition, the Direction of Travel (REV) and the Trim Resolution (Step value) of each Trim Switch and the
Rotary Dial can be changed. The High and Low Travel Limits and the Direction of Travel of the Auxiliary Lever can be changed, too.
This table shows the different functions that can be programmed to the Trim Switches, Rotary Dial and Auxiliary Lever. Table is
continued on the next page.
03.KEY ASSIGN (KEY ASSIGNMENTS)SYSTEM
TRIM, DIAL AND LEVER (Trim Switch, Rotary Dial and Auxiliary Lever Key Assignments)
OFF
TRIM-ST
TRIM-TH
TRIM-A1
TRIM-A2
D/R-ST
D/R-TH
D/R-BR
CU-R-ST
CU-P-ST
CU-R-TH
CU-P-TH
CU-R-BR
CU-P-BR
SP-ST-F
SP-ST-R
SP-TH-F
SP-TH-R
ALB-PO
ALB-ST
MENU FUNCTION DEFAULT SWITCH DEFAULT REVDEFAULT STEP
Inhibited
Trim-Steering
Trim-Throttle
Trim-Auxiliary 1
Trim-Auxiliary 2
Dual Rate-Steering
Dual Rate-Throttle
Dual Rate-Brake
Curve-Rate-Steering
Curve-Point-Steering
Curve-Rate-Throttle
Curve-Point-Throttle
Curve-Rate-Brake
Curve-Point-Brake
Speed-Steering-Forward
Speed-Steering-Return to Neutral
Speed-Throttle-Forward
Speed-Throttle-Return to Neutral
Anti-Lock Braking-Point
Anti-Lock Braking-Stroke
Trm1
Trm2
Trm3
Trm4
------
5
5
1
1
------
NOR
NOR
NOR
NOR
SYSTEM
MT-4S User's Guide.indd 55 2015/10/27 14:39:10
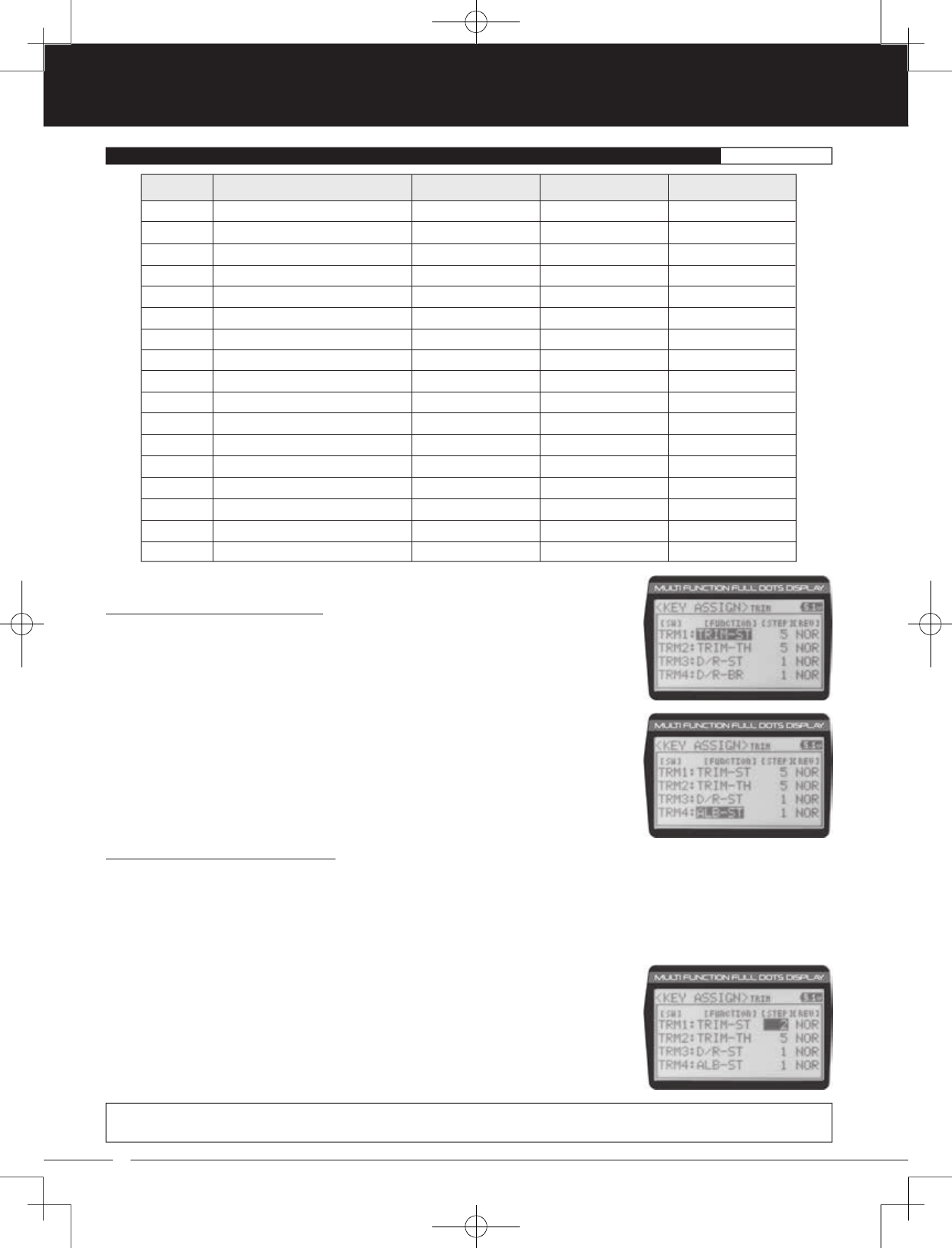
56
90478 2.4GHZ FH4T RADIO SYSTEM USER'S GUIDE
TR
TR
TR
Changing the Trim Switch Function:
1) From within the KEY ASSIGN menu, scroll UP or DOWN to highlight TRIM.
2) Press the ENTER key. The TRIM menu will be displayed and TRM1:TRIM-ST will be
highlighted.
3) Scroll UP or DOWN to highlight the function you would like to change for either TRM1,
TRM2, TRM3 or TRM4.
4) Press the ENTER key, then scroll UP or DOWN to choose the desired function for Trim
Switch Trm1, Trm2, Trm3 or Trm4. A list of functions that can be assigned to the Trim
Switches is shown in the table above and on the previous page.
Changing the Trim Switch Step Value:
The Step function allows you to adjust how far the servos travel when the Trim Switches are pressed. You can increase the
Trim Resolution by decreasing the Step value, so that the servos travel less when you press the Trim Switches. This makes it
possible to fine-tune servo movement extremely accurately.
Alternately, you could decrease the Trim Resolution by increasing the Step values, so that the servos travel more when you
press the Trim Switches. This setting may not be as accurate, although it allows you to command large amounts of servo
travel at a time.
03.KEY ASSIGN (KEY ASSIGNMENTS)SYSTEM
ALB-LG
ALB-HL
ALB-RE
OFFSET
AUX1
AUX2
A1CODE1
A1CODE2
A1CODE3
A1CODE4
A1CODE5
A2CODE1
A2CODE2
A2CODE3
A2CODE4
A2CODE5
INC/DEC
MENU FUNCTION DEFAULT SWITCH DEFAULT REVDEFAULT STEP
Anti-Lock Braking-Lag
Anti-Lock Braking-Hold
Anti-Lock Braking-Release
Throttle Offset
Auxiliary 1 Channel 3
Auxiliary 2 Channel 4
Auxiliary 1 CODE1
Auxiliary 1 CODE2
Auxiliary 1 CODE3
Auxiliary 1 CODE4
Auxiliary 1 CODE5
Auxiliary 2 CODE1
Auxiliary 2 CODE2
Auxiliary 2 CODE3
Auxiliary 2 CODE4
Auxiliary 2 CODE5
Increase/Decrease Values
Rotary Dial
Auxiliary Lever
5
N/A
------
NOR
N/A
------
1) From within the TRIM menu, scroll UP or DOWN to highlight the Step value you would
like to change for either TRM1, TRM2, TRM3 or TRM4.
2) Press the ENTER key, then scroll UP or DOWN to choose the desired Step value for Trim
Switch Trm1, Trm2, Trm3 or Trm4.
TRIM STEP setting range is 1 to 100. The default setting for TRM1 is 5, for TRM2 is 5, for TRM3 is 1 and for TRM4 is 1. The Step
value is a percentage of servo travel.
MT-4S User's Guide.indd 56 2015/10/27 14:39:11
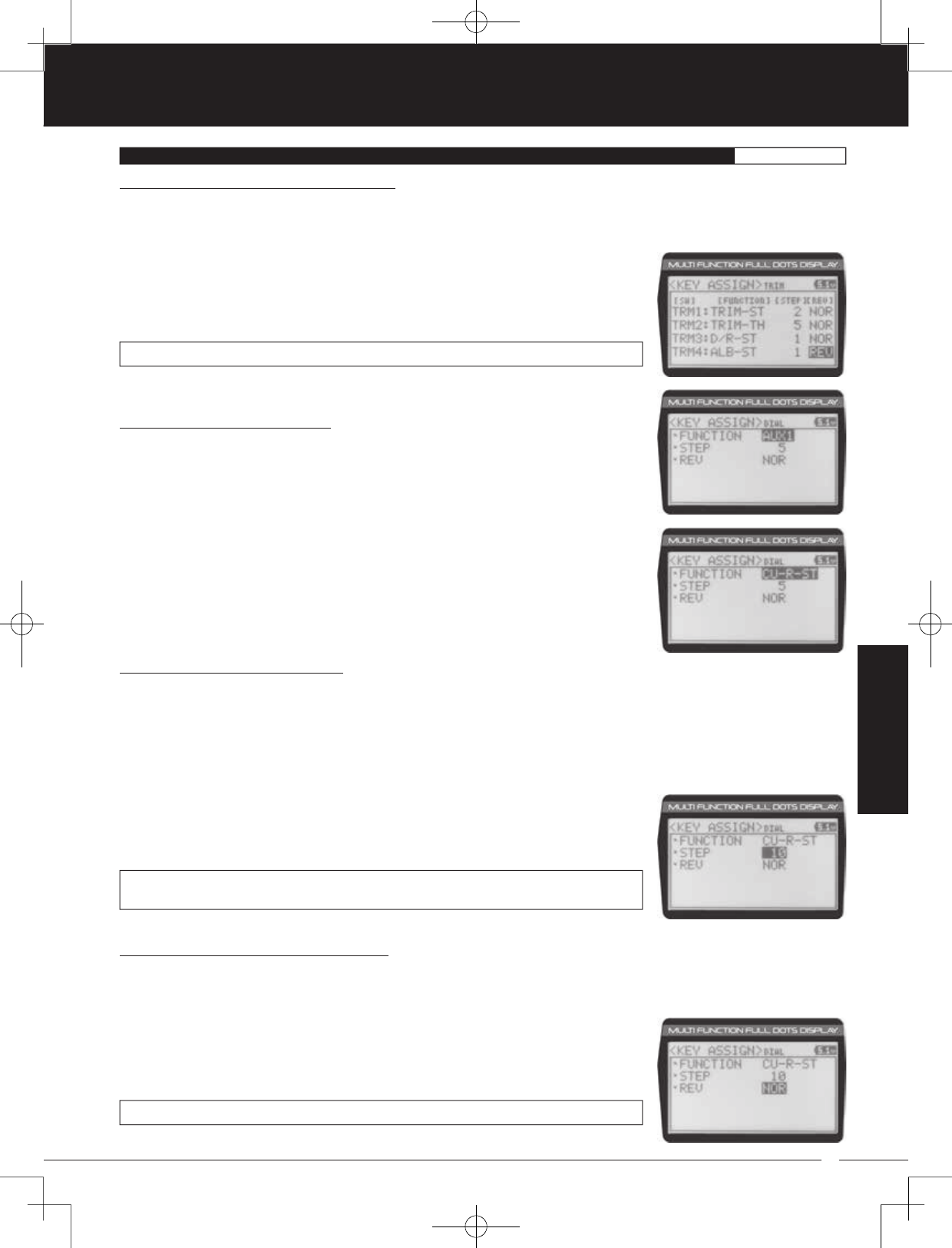
57
TR
TR
TR
90478 2.4GHZ FH4T RADIO SYSTEM USER'S GUIDE
1) From within the TRIM menu, scroll UP or DOWN to highlight the REV value you would
like to change for either TRM1, TRM2, TRM3 or TRM4.
2) Press the ENTER key, then scroll UP or DOWN to choose the desired REV value for Trim
Switch Trm1, Trm2, Trm3 or Trm4.
TRIM REV setting range is NOR and REV. The default setting for all Trim Switches is NOR.
Changing the Rotary Dial Function:
1) From within the KEY ASSIGN menu, scroll UP or DOWN to highlight DIAL.
2) Press the ENTER key. The DIAL menu will be displayed and FUNCTION AUX1 will be
highlighted.
3) Press the ENTER key, then scroll UP or DOWN to choose the desired function for the
Rotary Dial. A list of functions that can be assigned to the Rotary Dial is shown in the
table on pages 55 and 56.
Changing the Rotary Dial Step Value:
The Step function allows you to adjust how far the servo travels when the Rotary Dial is turned. You can increase the Dial
Resolution by decreasing the Step value, so that the servo travels less when you turn the Rotary Dial. This makes it possible to
fine-tune servo movement extremely accurately .
Alternately, you could decrease the Dial Resolution by increasing the Step value, so that the servo travels more when you turn
the Rotary Dial. This setting may not be as accurate, although it allows you to command large amounts of servo travel at
a time.
1) From within the DIAL menu, scroll UP or DOWN to highlight STEP 5.
2) Press the ENTER key, then scroll UP or DOWN to choose the desired Step value for the
Rotary Dial.
DIAL STEP setting range is 1 to 100. The default setting is 5. The Step value is a percentage
of servo travel.
Changing the Trim Switch Direction of Travel:
The direction that the Trim Switches move the servos can be changed from Normal to Reverse. In Normal mode, the Trim
Switches will move the servos toward the High Side when the Trim Switches are pushed Forward. In Reverse mode, the
Trim Switches will move the servos toward the Low Side (the opposite direction) when the Trim Switches are pushed Forward.
03.KEY ASSIGN (KEY ASSIGNMENTS)SYSTEM
Changing the Rotary Dial Direction of Travel:
The direction that the Rotary Dial moves the servo can be changed from Normal to Reverse. In Normal mode, the Rotary Dial
will move the servo toward the High Side when the Rotary Dial is turned clockwise. In Reverse mode, the Rotary Dial will move
the servo toward the Low Side (the opposite direction) when the Rotary Dial is turned clockwise.
1) From within the DIAL menu, scroll UP or DOWN to highlight REV NOR.
2) Press the ENTER key, then scroll UP or DOWN to choose the desired REV value for the
Rotary Dial.
DIAL REV setting range is NOR and REV. The default setting is NOR.
SYSTEM
MT-4S User's Guide.indd 57 2015/10/27 14:39:11
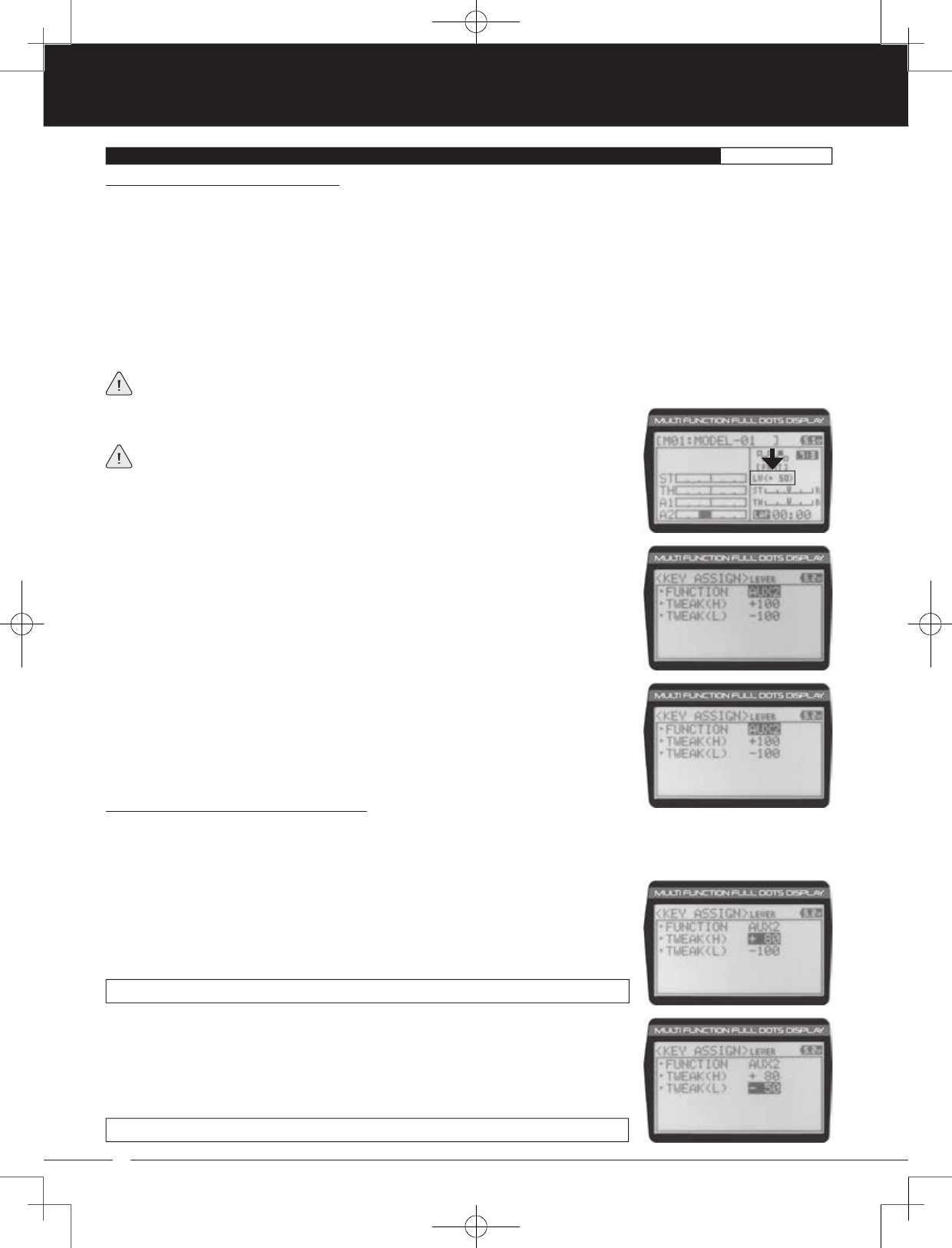
58
90478 2.4GHZ FH4T RADIO SYSTEM USER'S GUIDE
TR
TR
TR
Changing the Auxiliary Lever Function:
In general, the Auxiliary Lever is used to control Auxiliary 1 Channel 3 or Auxiliary 2 Channel 4. Adjusting the High and Low
Tweak values determines how far and in which direction the Auxiliary servo travels when the Auxiliary Lever is moved Up and
Down. For example, if you assign AUX2 to the Auxiliary Lever and adjust the Tweak values to +50 and -50, the Auxiliary 2 servo
will be centered when the Auxiliary Lever is centered and will travel 50% in one direction when the Auxiliary Lever is moved Up
and travel 50% in the other direction when the Auxiliary Lever is moved Down. This allows you to use the Auxiliary Lever like a
2- or 3-position switch.
In addition, the Auxiliary Lever can be used to control the same parameter functions as the Trim Switches and the Rotary Dial.
For example, if you assign TRIM-ST and adjust the Tweak values to +100 and -100, the Auxiliary Lever will control Steering
channel Trim. The direction and amount the Trim moves when you move the Auxiliary Lever Up or Down is dependent on the
Positive and Negative Tweak values.
To control either the Auxiliary 1 or the Auxiliary 2 servos using the Auxiliary Lever, the Auxiliary Type in the AUX TYPE menu
must be either STEP AUX or POINT AUX. For more information, see the Auxiliary Type section on pages 59 and 60.
1) From within the KEY ASSIGN menu, scroll UP or DOWN to highlight LEVER.
2) Press the ENTER key. The LEVER menu will be displayed and FUNCTION AUX2 will be
highlighted.
3) Press the ENTER key, then scroll UP or DOWN to choose the desired function for the
Auxiliary Lever. A list of functions that can be assigned to the Auxiliary Lever is shown in
the table on pages 55 and 56.
When you use the Auxiliary Lever to control a function, such as Steering Dual Rate or
Exponential, the change in values will not be displayed in a pop-up window like they
are when you use the Trim Switches or the Rotary Dial to make the same changes. Instead,
the current position of the Auxiliary Lever is displayed on the Top Screen.
03.KEY ASSIGN (KEY ASSIGNMENTS)SYSTEM
1) From within the LEVER menu, scroll DOWN to highlight TWEAK(H) +100.
2) Press the ENTER key, then scroll UP or DOWN to choose the desired High Side Tweak
value. Increasing the Tweak value will increase servo travel in the High Side direction
and decreasing the Tweak value will decrease servo travel in the High Side direction.
Using a negative value will change the direction of servo travel.
LEVER TWEAK(H) setting range is -100 to +100. The default setting is +100.
Changing the High and Low Tweak Values:
The High and Low Tweak values determine the direction and amount of Auxiliary 1 or Auxiliary 2 servo travel. In addition, the
High and Low Tweak values determine the direction and amount of parameter function changes, such as Steering Trim or the
Anti-Lock Braking Point percentage value.
3) Scroll DOWN to highlight TWEAK(L) -100.
4) Press the ENTER key, then scroll UP or DOWN to choose the desired Low Side Tweak
value. Decreasing the Tweak value will increase servo travel in the Low Side direction
and increasing the Tweak value will decrease servo travel in the Low Side direction. Using
a positive value will change the direction of servo travel.
LEVER TWEAK(L) setting range is -100 to +100. The default setting is -100.
MT-4S User's Guide.indd 58 2015/10/27 14:39:12
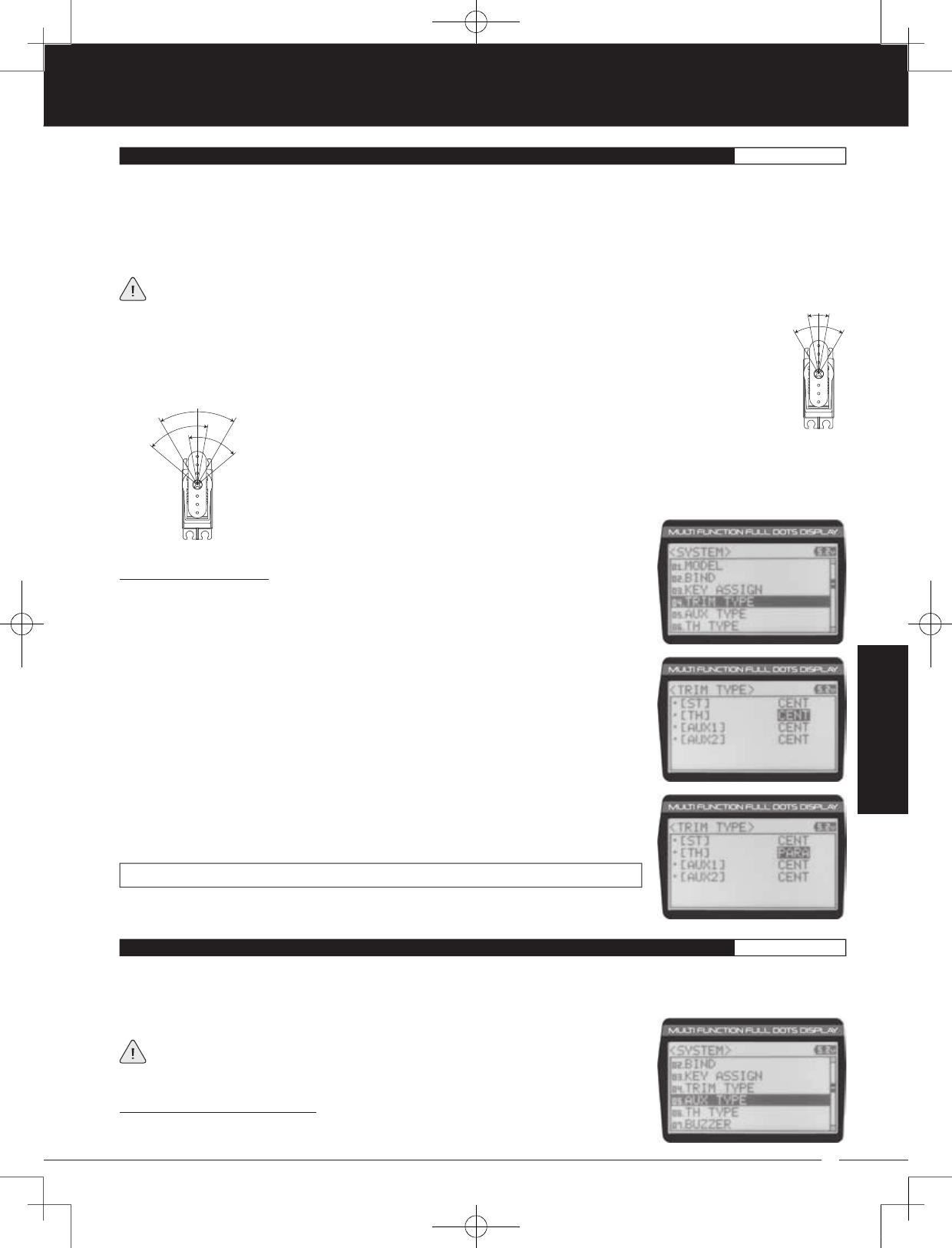
59
TR
TR
TR
90478 2.4GHZ FH4T RADIO SYSTEM USER'S GUIDE
Changing the Trim Type:
1) From within the SYSTEM menu, scroll UP or DOWN to highlight the TRIM TYPE menu.
SYSTEM
04.TRIM TYPE (TRIM TYPE)SYSTEM
The Trim Type function allows you choose the way servo Trim and servo End Point Adjustments interact with each other. When
you apply Trim to a servo, the Neutral Point of the servo shifts toward the High Side or the Low Side. When you do this, the servo
travels less in one direction and more in the other direction because the servo End Points are stationary. In order to balance the
servo travel, you would need to manually readjust the servo End Points. Using the Trim Type function allows you to make the
servo End Points shift toward the High Side or the Low Side when you apply Trim. This maintains balanced servo travel without
the need to manually readjust the servo End Points.
The Trim Type function does not effect servo Sub-Trim. It only effects servo Trim that's input using the Trim Switches, Rotary
Dial or Auxiliary Lever. Servo Sub-Trim, which is different, always uses Parallel Trim.
Two Trim Types are available:
CENTER - When Selected, servo End Points are stationary. In order to balance servo travel, you would need to
manually readjust the servo End Points, if desired.
PARALLEL - When Selected, servo End Points shift toward the High Side or the Low Side automatically
when you apply Trim. This maintains balanced servo travel without the need to manually readjust the
servo End Points.
2) Press the ENTER key. The TRIM TYPE menu will be displayed and [ST] CENT will be
highlighted.
3) Scroll UP or DOWN to highlight the desired channel you would like to change the Trim
Type option for. Choose from either [ST] CENT (Steering), [TH] CENT (Throttle), [AUX1]
CENT (Auxiliary 1) or [AUX2] CENT (Auxiliary 2).
4) Press the ENTER key, then scroll UP or DOWN to choose the desired Trim Type option
for that channel.
TRIM TYPE setting range is CENT and PARA. The default setting for all channels is CENT.
The Auxiliary Type function allows you choose which Auxiliary function is assigned to Auxiliary 1 Channel 3 or Auxiliary 2
Channel 4. One Auxiliary function can be assigned to each Auxiliary Channel and both Auxiliary Channels can be Active and
controlled at the same time using different controls. For example, you can control Auxiliary 1 Channel 3 using the Rotary Dial
and Auxiliary 2 Channel 4 using the Auxiliary Lever.
For details about programming and using each of the Auxiliary functions, in addition
to selecting AUX Type Modes, see the Auxiliary 1 Programming section on pages 27
through 33 or the Auxiliary 2 Programming section on pages 34 through 40.
05.AUX TYPE (AUXILIARY TYPE)SYSTEM
Changing the Auxiliary Function:
1) From within the SYSTEM menu, scroll UP or DOWN to highlight the AUX TYPE menu.
MT-4S User's Guide.indd 59 2015/10/27 14:39:13
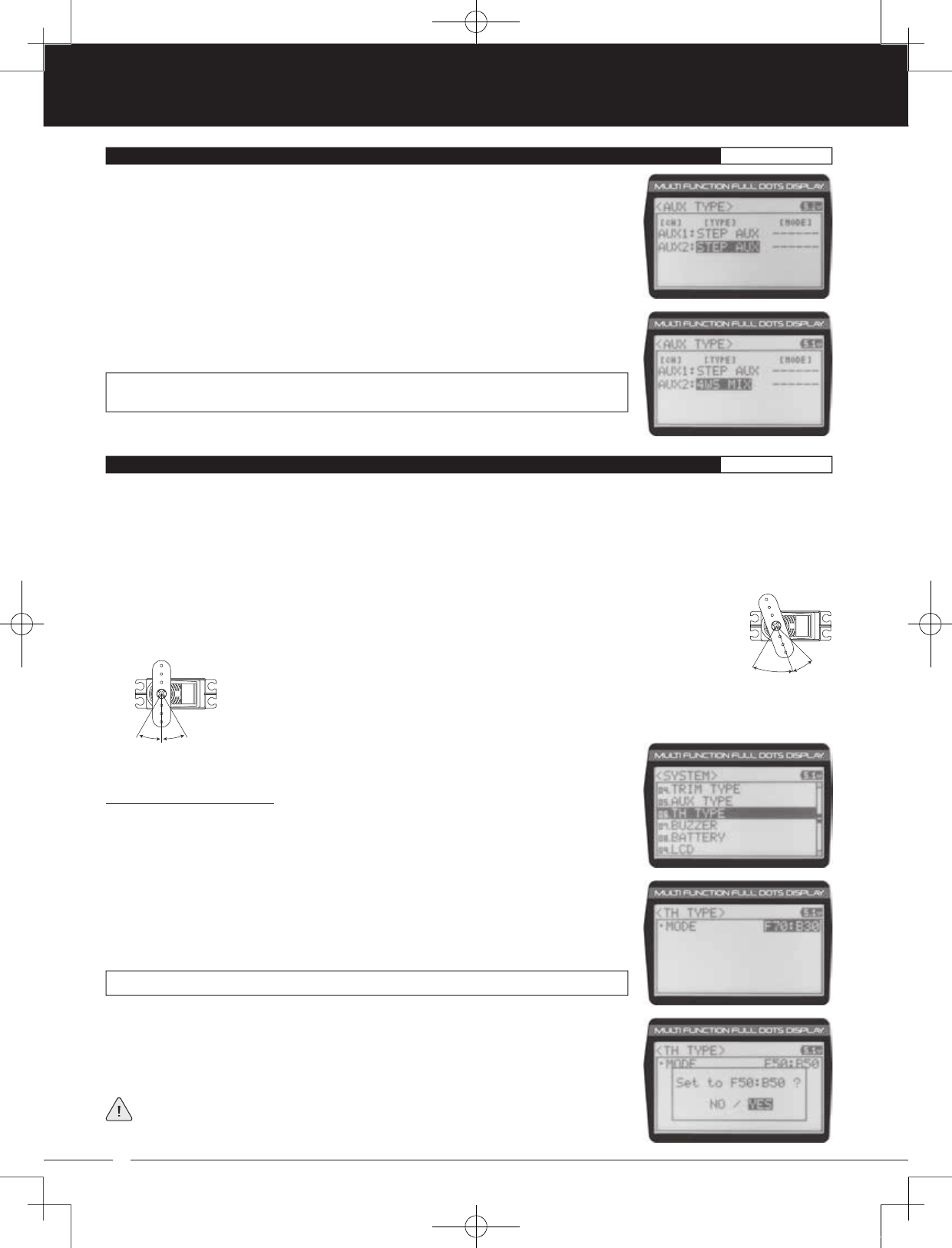
60
90478 2.4GHZ FH4T RADIO SYSTEM USER'S GUIDE
TR
TR
TR
2) Press the ENTER key. The AUX TYPE menu will be displayed and AUX1:STEP AUX will be
highlighted.
3) Scroll UP or DOWN to highlight the desired channel you would like to change the
Auxiliary function for, either AUX1 [TYPE] (Auxiliary 1) or AUX 2 [TYPE] (Auxiliary 2).
4) Press the ENTER key, then scroll UP or DOWN to choose the desired Auxiliary function
to be controlled by that channel.
AUX TYPE setting range is STEP AUX, POINT AUX, 4WS MIX, MOA MIX and AUX MIX. The
default setting for both channels is STEP AUX.
The Throttle Type function allows you to change the proportion between Throttle High Side servo travel and Throttle Brake Side
servo travel. In the default configuration, the Throttle Type is set to F70:B30. This Throttle Type shifts the throttle Neutral Point
toward the Brake Side, resulting in more servo travel toward the High Side and less servo travel toward the Brake Side. Some
users may prefer the proportion between Throttle High Side servo travel and Throttle Brake Side servo travel to be balanced
(F50:B50). The F70:B30 Throttle Type is most common for general use and racing, while the F50:B50 Throttle Type is most
common for Rock Crawling.
Changing the Throttle Type:
1) From within the SYSTEM menu, scroll UP or DOWN to highlight the TH TYPE menu.
2) Press the ENTER key. The TH TYPE menu will be displayed and MODE F70:B30 will be
highlighted.
3) Press the ENTER key, then scroll UP or DOWN to choose the desired Throttle Type
option.
TH TYPE setting range is F70:B30 and F50:B50. The default setting is F70:B30.
05.AUX TYPE (AUXILIARY TYPE)SYSTEM
06.TH TYPE (THROTTLE TYPE)SYSTEM
Two Throttle Types are available:
F70:B30 - When Selected, the Throttle Neutral Point is shifted toward the Brake Side which provides more
High Side servo travel and less Brake Side servo travel. This is most common for general use and racing.
F50:B50 - When Selected, the Throttle Neutral Point is centered, which provides the same amount of
High Side and Brake Side servo travel. This is most common for Rock Crawling.
4) Press the ENTER key. Either Set to F70:B30? NO/YES will be displayed or Set to F50:B50?
NO/YES will be displayed.
5) Scroll DOWN to highlight YES, then press the ENTER key to Activate the chosen Throttle Type.
The current Throttle Type will be displayed on the Top Screen. 7:3 will be displayed
to indicate the current Throttle Type is F70:B30 or 5:5 will be displayed to indicate
the current Throttle Type is F50:B50.
MT-4S User's Guide.indd 60 2015/10/27 14:39:14

61
TR
TR
TR
90478 2.4GHZ FH4T RADIO SYSTEM USER'S GUIDE
The Audible Key Tone function allows you to change the Volume and Tone of the audible sounds that are made when you use
the Trim Switches, Rotary Dial, Auxiliary Lever, Push- Button Rotary Dial and the Timer function. The Volume can be Increased
or Decreased (or Muted) and the Tone can be changed to suit your preference.
Changes made using the Audible Key Tone function also affect the audible sounds that are part of the Timer function.
For example, if you Mute the Audible Key Tones, the sounds that are part of the Timer function will also be Muted.
Transmitter warning alarms, such as the Low Voltage Alert alarm, are unaffected.
SYSTEM
07.BUZZER (AUDIBLE KEY TONE)SYSTEM
Changing the Audible Key Tone Volume:
1) From within the SYSTEM menu, scroll UP or DOWN to highlight the BUZZER menu.
2) Press the ENTER key. The BUZZER menu will be displayed and VOLUME 4 will be
highlighted.
3) Press the ENTER key, then scroll UP or DOWN to choose the desired Volume value.
Increasing the Volume value will increase the Volume of the Audible Key Tones and
decreasing the Volume value will decrease the Volume of the Audible Key Tones.
BUZZER VOLUME setting range is OFF to 5. The default setting is 4. When OFF is selected, Audible Key Tones will be Muted.
Changing the Tone:
1) From within the BUZZER menu, scroll DOWN to highlight TONE 1.
2) Press the ENTER key, then scroll UP or DOWN to choose the desired Tone value.
Increasing the Tone value will increase the pitch of the Audible Key Tones and decreasing
the Tone value will decrease the pitch of the Audible Key Tones.
BUZZER TONE setting range is 1 to 7. The default setting is 1.
The Voltage Alarm function allows to specify the voltage at which the transmitter Low Voltage Alert and Low Voltage Limit
alarms will sound. This allows you to choose custom voltage settings to match the type of transmitter battery you're using. For
example,if you're using a 6 cell NiMH battery pack or a 2S LiPo battery pack, you can set the Low Voltage Alert alarm and the
Low Voltage Limit alarm voltage values to suit.
This table shows the different Alert and Limit Voltage values we recommend programming.
Changing the Low Voltage Alert Alarm Value:
The Low Voltage Alert alarm will sound to indicate the transmitter batteries are getting low and should be replaced or
recharged. We suggest stopping use as soon as safely possible and replacing or recharging the transmitter batteries. The Low
Voltage Alert alarm will sound each time the transmitter battery voltage decreases by 0.1 volt. To clear this alarm, press the
BACK/CANCEL key or the Push-Button Rotary Dial.
To ensure the safety of your model and your transmitter battery, we suggest using the Alert and Limit Voltage values
shown in the table above. We don't suggest using values lower than recommended.
08.BATTERY (VOLTAGE ALARM)SYSTEM
4.6 Volts
7.0 Volts
7.2 Volts
6.3 Volts
4.4 Volts
6.6 Volts
6.8 Volts
5.8 Volts
BATTERY TYPE ALERT VOLTAGE LIMIT VOLTAGE
4 Cell Alkaline
6 Cell Ni-CD/NiMH
2S LiPo
2S LiFe
MT-4S User's Guide.indd 61 2015/10/27 14:39:14
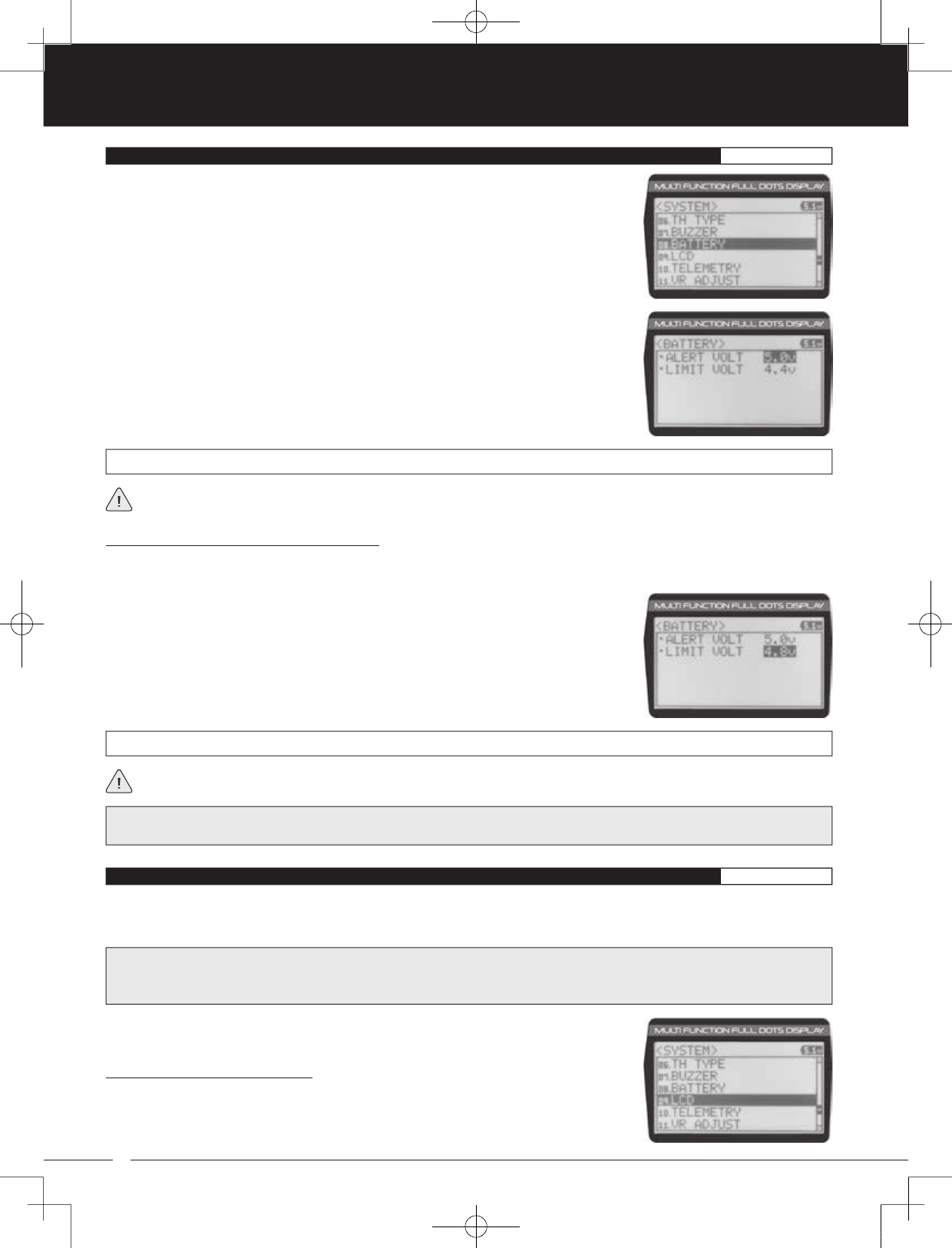
62
90478 2.4GHZ FH4T RADIO SYSTEM USER'S GUIDE
TR
TR
TR
2) Press the ENTER key. The BATTERY menu will be displayed and ALERT VOLT 4.6v will
be highlighted.
3) Press the ENTER key, then scroll UP or DOWN to choose the desired Low Voltage Alert
alarm value. Increasing the Low Voltage Alert alarm value will cause the Low Voltage
Alert alarm to sound at a higher voltage and decreasing the Low Voltage Alert alarm
value will cause the Low Voltage Alert alarm to sound at a lower voltage.
BATTERY ALERT VOLT setting range is 4.1v to 9.0v. The default setting is 4.6v.
The Low Voltage Alert alarm voltage value cannot be set lower than the Low Voltage Limit alarm voltage value.
1) From within the SYSTEM menu, scroll UP or DOWN to highlight the BATTERY menu.
1) From within the BATTERY menu, scroll DOWN to highlight LIMIT VOLT 4.4v.
2) Press the ENTER key, then scroll UP or DOWN to choose the desired Low Voltage Limit
alarm value. Increasing the Low Voltage Limit alarm value will cause the Low Voltage
Limit alarm to sound at a higher voltage and decreasing the Low Voltage Limit alarm
value will cause the Low Voltage Limit alarm to sound at a lower voltage.
Changing the Low Voltage Limit Alarm Value:
The Low Voltage Limit alarm will sound to indicate the transmitter batteries are dangerously low and should be replaced or
recharged right away. The Low Voltage Limit alarm cannot be cancelled. When the Low Voltage Limit alarm sounds, you should
stop use as soon as it's safe, then replace or recharge the transmitter batteries.
BATTERY LIMIT VOLT setting range is 4.0v to 4.9v. The default setting is 4.4v.
WARNING: Continuing to use the transmitter after the Low Voltage Limit alarm sounds can result in loss of control of your
model. When the Low Voltage Alert alarm sounds, stop use as soon as is safe, then replace or recharge the transmitter batteries.
Changing the LCD Contrast Value:
1) From within the SYSTEM menu, scroll UP or DOWN to highlight the LCD menu.
08.BATTERY (VOLTAGE ALARM)SYSTEM
The Low Voltage Limit alarm voltage value cannot be set higher than the Low Voltage Alert alarm voltage value.
09.LCD (LCD CONTRAST AND BACKLIGHT OPTIONS)SYSTEM
The LCD menu allows you change the contrast of the LCD, the Backlight Mode and the Backlight On-Time. Changing the
Contrast settings can make it easier to view the LCD in different lighting conditions and changing the Backlight Mode and
Backlight On-Time affects how the Backlight is turned ON and how long the Backlight stays ON.
IMPORTANT: Leaving the LCD Backlight ON at all times will Increase battery consumption. In addition, Decreasing the
Contrast value near the Lower limit can result in the LCD text becoming impossible to read. Be careful not to set the Contrast
value too low.
MT-4S User's Guide.indd 62 2015/10/27 14:39:15
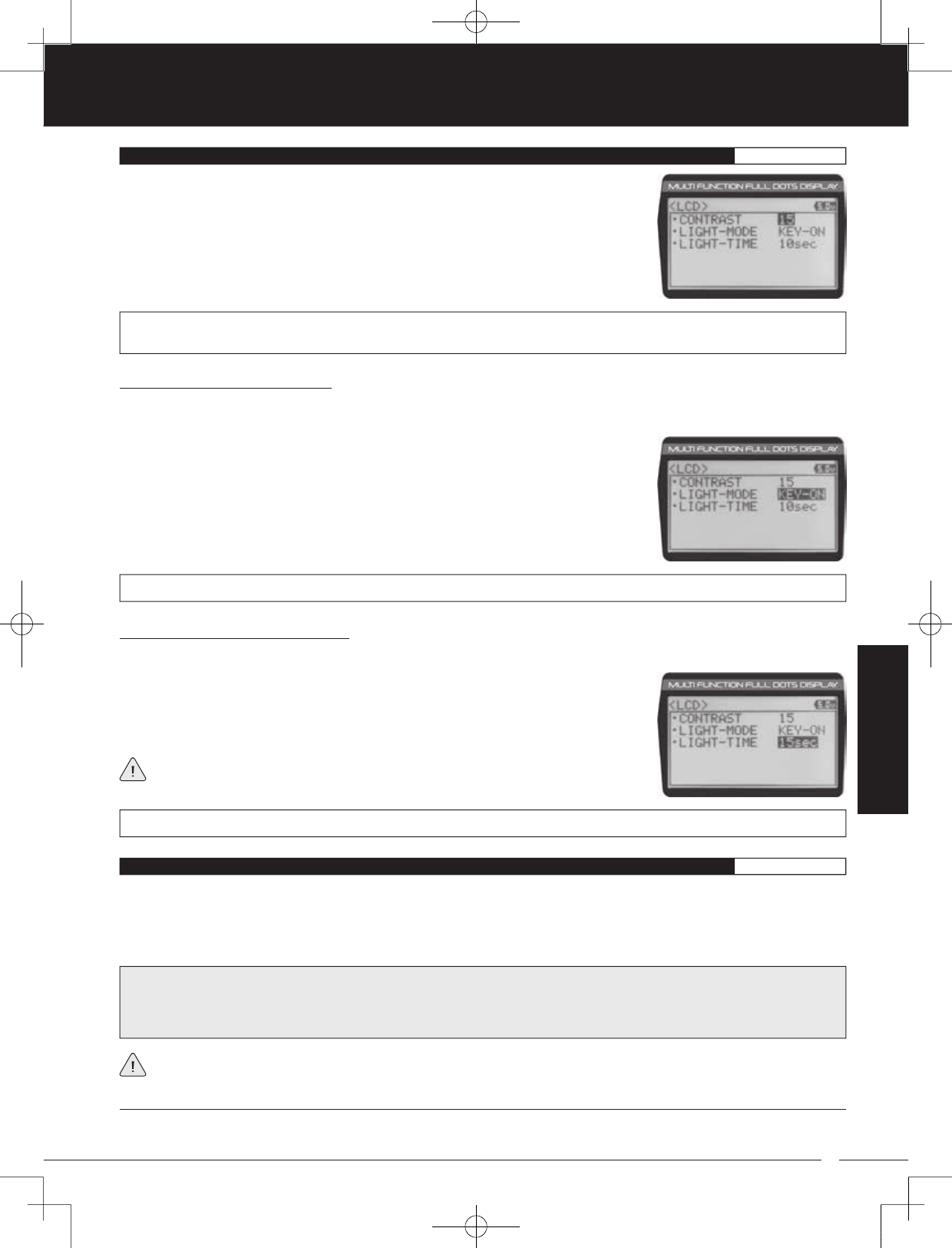
63
TR
TR
TR
90478 2.4GHZ FH4T RADIO SYSTEM USER'S GUIDE
2) Press the ENTER key. The LCD menu will be displayed and CONTRAST 15 will be
highlighted.
3) Press the ENTER key, then scroll UP or DOWN to choose the desired LCD Contrast
value. Increasing the LCD Contrast value will increase the Contrast of the LCD screen
and decreasing the LCD Contrast value will decrease the Contrast of the LCD screen.
LCD CONTRAST setting range is 0 to 30. The default setting is 15. Decreasing the LCD Contrast value too much will make it
impossible to read. We do not suggest using an LCD Contrast value lower than 7.
SYSTEM
09.LCD (LCD CONTRAST AND BACKLIGHT OPTIONS)SYSTEM
Changing the LCD Backlight Mode:
The LCD Backlight Mode option determines how the LCD Backlight operates. When set to OFF, the LCD Backlight will be
turned OFF. When set to KEY-ON, the LCD Backlight will turn ON when a key-press is made. When set to ALWAYS, the LCD
Backlight will stay ON at all times.
LIGHT-MODE setting range is OFF, KEY-ON and ALWAYS. The default setting is KEY-ON.
Changing the LCD Backlight On-Time:
The LCD Backlight On-Time option determines how long the LCD Backlight will stay ON before turning OFF automatically.
LIGHT-TIME setting range is 1 to 30 seconds. The default setting is 10 seconds.
10.TELEMETRY (TELEMETRY DISPLAY OPTIONS)SYSTEM
The Telemetry menu allows you to change different options to configure how the various Telemetry functions are displayed on
the Telemetry Screen and how the Telemetry Logger operates. For example, you are able to change the Telemetry Temperature
reading from Fahrenheit to Celsius, change the values at which Telemetry Sensor alarms sound, change how Speed and RPM
are displayed and much more. In addition, you are also able to change the Telemetry Log Interval to customize how much
Telemetry Data can be stored for review later.
The Temperature 1 and Temperature 2 Settings allow you change how Temperature information is displayed on the Telemetry
Screen and when the Temperature Alert alarm sounds.
For information about using an optional Telemetry receiver with your 90478 transmitter and installing Telemetry
Sensors into your model, see the Telemetry Connections and Mounting section on pages 69 and 70.
IMPORTANT: Full telemetry support requires the use of an Airtronics 2.4GHz FH4T telemetry-capable surface receiver, such
as the RX-461 or RX-462, along with Airtronics Temperature and RPM Sensors (available separately). The included RX-472
receiver can send Telemetry Data for the voltage of the receiver battery pack only, unless used with the Airtronics Super
Vortex ZERO ESC (available separately) plugged into the BATT/SSL port of the included RX-472 receiver.
TEMP1 AND TEMP2 SETTING (Temperature Telemetry Display Options)
1) From within the LCD menu, scroll UP or DOWN to highlight LIGHT-MODE KEY-ON.
2) Press the ENTER key, then scroll UP or DOWN to choose the desired LCD Mode value.
Choose from OFF, KEY-ON or ALWAYS.
1) From within the LCD menu, scroll UP or DOWN to highlight LIGHT-TIME 10sec.
2) Press the ENTER key, then scroll UP or DOWN to choose the desired LCD Time value.
The Time value (in seconds)
If the Backlight Mode is set to ALWAYS or OFF, the LCD Backlight On-Time value
cannot be adjusted.
MT-4S User's Guide.indd 63 2015/10/27 14:39:15
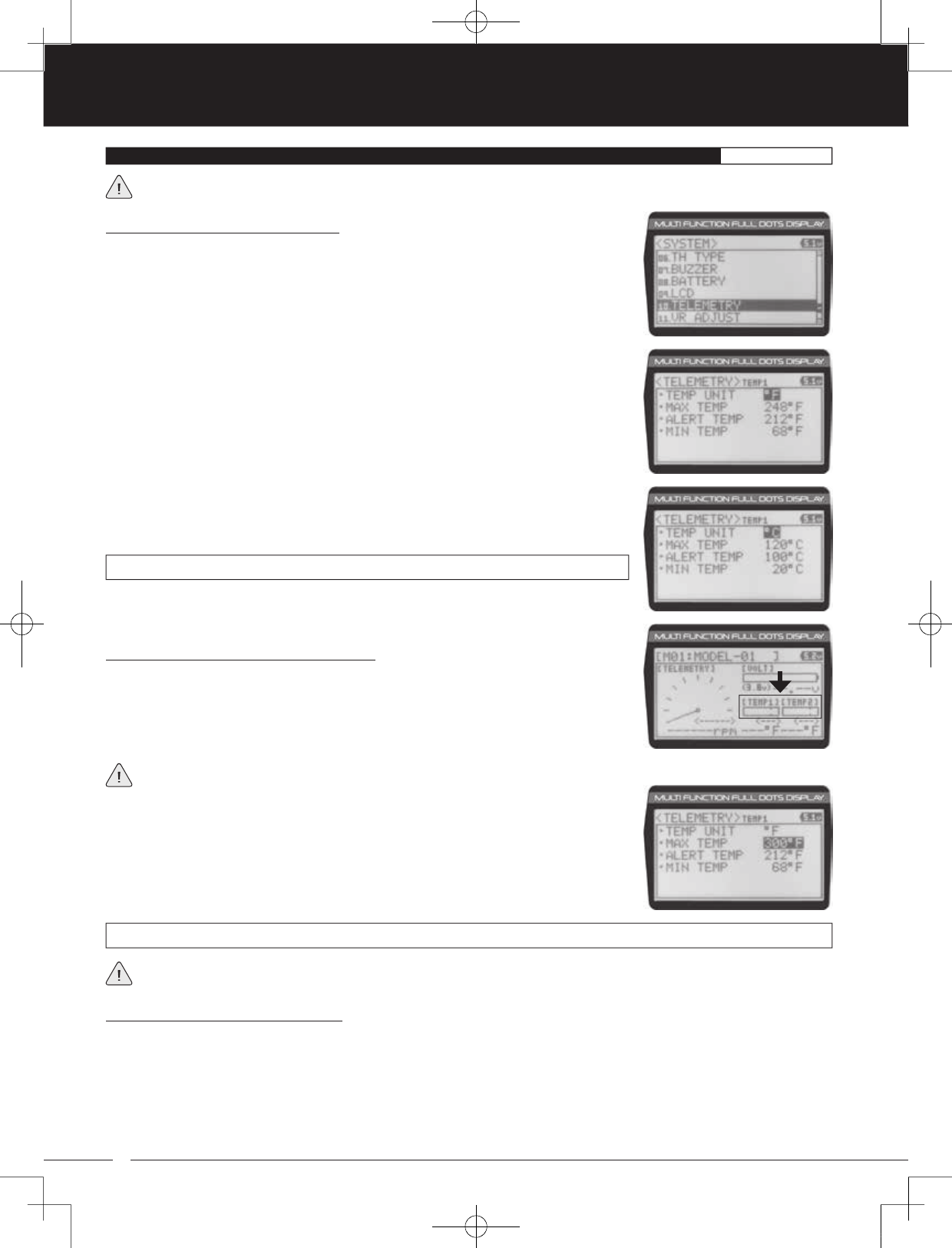
64
90478 2.4GHZ FH4T RADIO SYSTEM USER'S GUIDE
TR
TR
TR
1) From within the TEMP1 or TEMP2 menu, scroll UP or DOWN to highlight MAX TEMP
248ºF (or 120ºC).
2) Press the ENTER key, then scroll UP or DOWN to change the Maximum Temperature
value. The Temperature Display Monitor on the Telemetry Screen will not display
temperature values above the Maximum Temperature value programmed.
Changing the Maximum Temperature Value:
The Maximum Temperature value determines the maximum temperature shown on the
[TEMP1] or [TEMP2] Telemetry Screen Temperature Display Monitors. This allows you to
calibrate each Temperature Display Monitor to match what the Temperatures Sensor is
attached to. This setting does not effect the TEMP1 or TEMP2 Digital Displays.
TELEMETRY MAX TEMP setting range is 68ºF to 302ºF (0ºC to 150ºC). The default setting is 248ºF (120ºC).
The Maximum Temperature value cannot be set lower than the Alert Temperature value or the Minimum Temperature value.
In some cases, you may need to lower the Alert Temperature value prior to lowering the Maximum Temperature value.
Changing the Alert Temperature Value:
The Alert Temperature value determines the temperature at which the Temperature Alert alarm will sound. For example, you
can set an Alert Temperature value for your Nitro engine that will alert you when your engine's cylinder head temperature is
getting too hot.
When the Alert Temperature value is reached, the Temperature Alert alarm will sound and LED2 (Red) will flash. The Temperature
Alert alarm will sound for approximately 5 seconds, however, LED2 will continue to flash until the temperature drops below the
Alert Temperature value. The audible portion of the Temperature Alert alarm can be cleared by pressing the BACK/CANCEL
key or the Push-Button Rotary Dial.
3) Scroll UP or DOWN to highlight TEMP1 SETTING or TEMP2 SETTING.
4) Press the ENTER key. The TEMP1 or TEMP2 menu will be displayed and TEMP UNIT ºF
will be highlighted.
5) Press the ENTER key, then scroll UP or DOWN to change the Temperature Unit to the
desired value.
TELEMETRY TEMP UNIT setting range is ºF and ºC. The default setting is ºF.
10.TELEMETRY (TELEMETRY DISPLAY OPTIONS)SYSTEM
Changing the Temperature Unit Value:
If desired, the Temperature Unit value can be changed from Fahrenheit to Celsius.
1) From within the SYSTEM menu, scroll UP or DOWN to highlight the TELEMETRY menu.
2) Press the ENTER key. The TELEMETRY menu will be displayed and TEMP1 SETTING will
be highlighted.
The tick marks in the Temperature Display Monitors indicate the current temperature relative to the programmed Maximum
and Minimum Temperature values.
This section covers both the TEMP1 and TEMP2 menus, since programming each of them is exactly the same. Choose either
the TEMP1 or the TEMP2 menu depending on which of the two Temperature Sensor Ports you want to make changes to.
MT-4S User's Guide.indd 64 2015/10/27 14:39:16
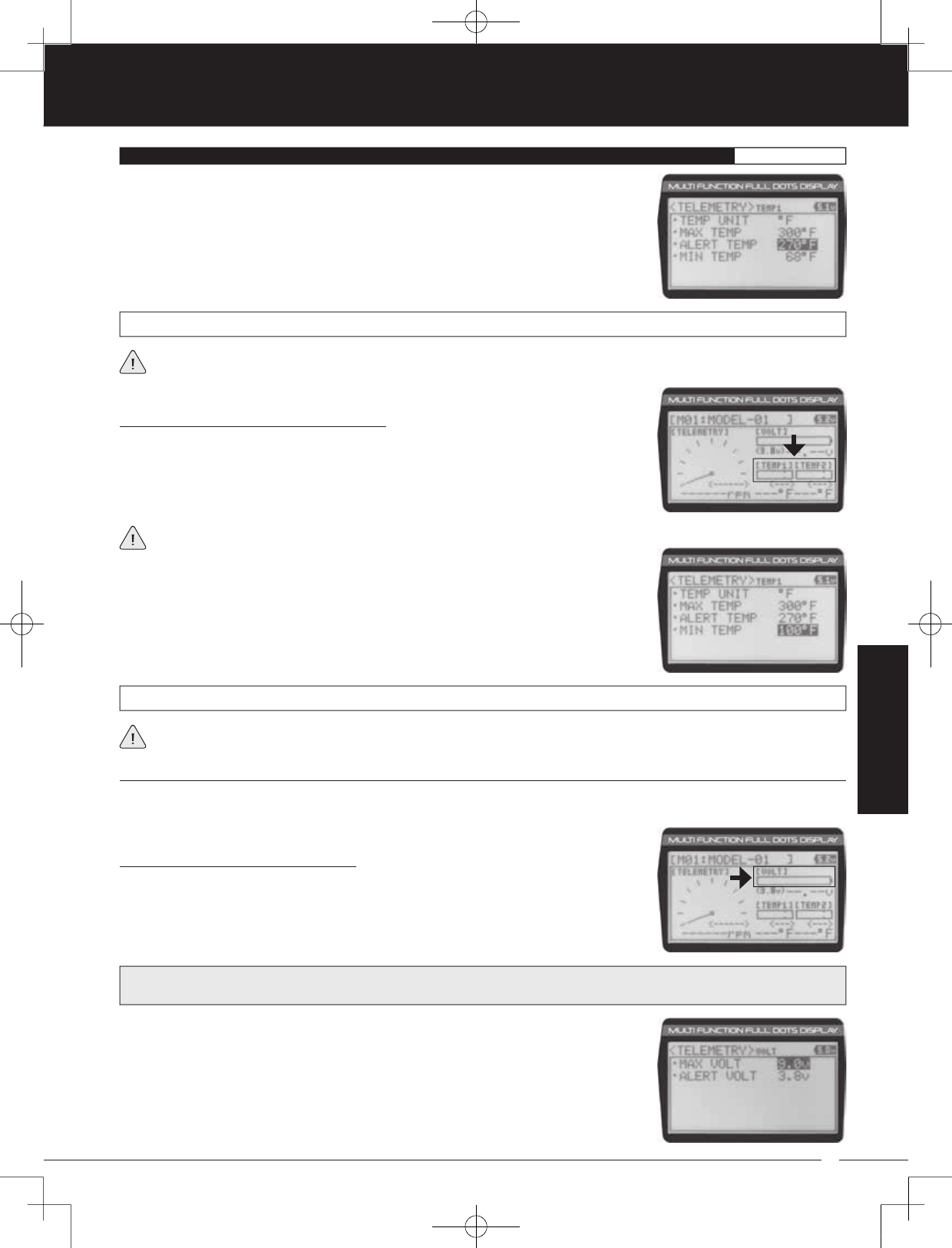
65
TR
TR
TR
90478 2.4GHZ FH4T RADIO SYSTEM USER'S GUIDE
1) From within the TEMP1 or TEMP2 menu, scroll UP or DOWN to highlight ALERT TEMP
212ºF (or 100ºC).
2) Press the ENTER key, then scroll UP or DOWN to change the Alert Temperature value.
The Alert Temperature value is the temperature that the Temperature Alert alarm will
sound at.
TELEMETRY ALERT TEMP setting range is 68ºF to 302ºF (0ºC to 150ºC). The default setting is 212ºF (100ºC).
The Alert Temperature value cannot be set higher than the Maximum Temperature value. In addition, the Alert Temperature
value cannot be set lower than the Minimum Temperature value. In some cases, you may need to lower the Minimum
Temperature value prior to lowering the Alert Temperature value.
Changing the Minimum Temperature Value:
The Minimum Temperature value determines the Minimum temperature shown on the
[TEMP1] or [TEMP2] Telemetry Screen Temperature Display Monitors. This allows you to
calibrate each Temperature Display Monitor to match what the Temperatures Sensor is
attached to. This does not effect the TEMP1 or TEMP2 Digital Displays.
10.TELEMETRY (TELEMETRY DISPLAY OPTIONS)SYSTEM
1) From within the TEMP1 or TEMP2 menu, scroll UP or DOWN to highlight MIN TEMP 68ºF
(or 20ºC).
2) Press the ENTER key, then scroll UP or DOWN to change the Minimum Temperature
value. The Temperature Display Monitor on the Telemetry Screen will not display
temperature values below the Minimum Temperature value programmed.
TELEMETRY MIN TEMP setting range is 32ºF to 302ºF (0ºC to 150ºC). The default setting is 68ºF (20ºC).
The Minimum Temperature value cannot be set higher than the Alert Temperature value or the Maximum Temperature
value. In some cases, you may need to increase these values prior to increasing the Minimum Temperature value.
The tick marks in the Temperature Display Monitors indicate the current temperature relative to the programmed Maximum
and Minimum Temperature values.
The Voltage Setting allows you to change the way receiver battery Voltage information is displayed on the Telemetry Screen
and when the Voltage Alert alarm sounds. For example, you can adjust the Voltage value that the receiver battery Low Voltage
Alert alarm will sound at to match the type of receiver battery you're using.
Changing the Maximum Voltage Value:
The Maximum Voltage value determines the maximum receiver battery Voltage that will
be shown on the [VOLT] Telemetry Screen Display Monitor. This allows you to calibrate the
Voltage Display Monitor to match your model's receiver battery. This setting does not effect
the VOLT Digital Display.
VOLT SETTING (Receiver Battery Voltage Telemetry Display Options)
1) From within the TELEMETRY menu, scroll UP or DOWN to highlight VOLT SETTING.
2) Press the ENTER key. The VOLT menu will be displayed and MAX VOLT 9.0v will be
highlighted.
PRO TIP: We suggest using a value that matches as closely as possible the peaked voltage value of your receiver battery
after it's pulled off your charger.
SYSTEM
MT-4S User's Guide.indd 65 2015/10/27 14:39:16
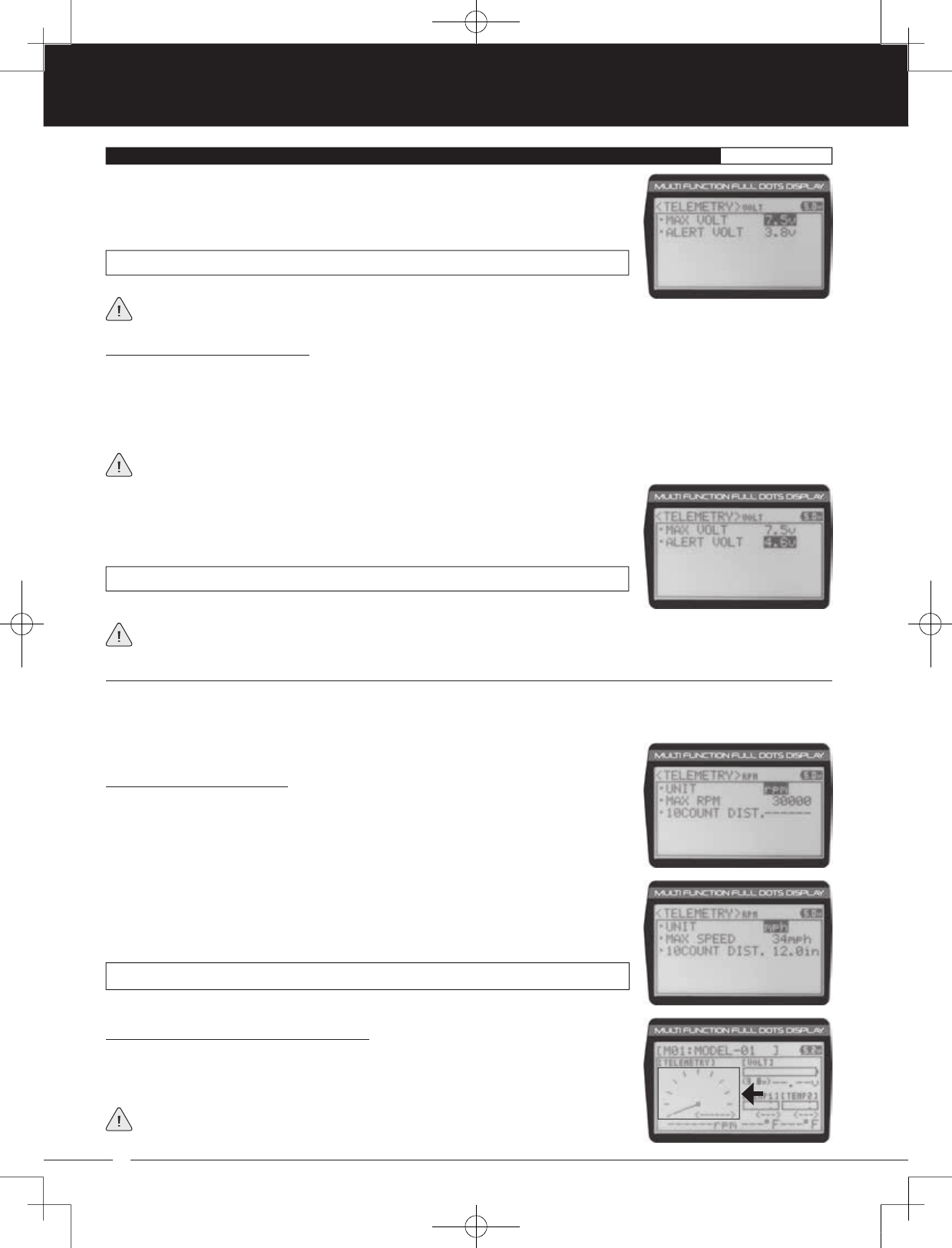
66
90478 2.4GHZ FH4T RADIO SYSTEM USER'S GUIDE
TR
TR
TR
1) From within the VOLT menu, scroll UP or DOWN to highlight ALERT VOLT 3.8v.
2) Press the ENTER key, then scroll UP or DOWN to change the Alert Voltage value. The
Alert Voltage value is the voltage that the Voltage Alert alarm will sound at.
TELEMETRY ALERT VOLT setting range is 3.0v to 9.0v. The default setting is 3.8v.
The Alert Voltage value cannot be set higher than the Maximum Voltage value. In some cases, you may need to raise the
Maximum Voltage value prior to raising the Alert Voltage value.
The RPM Setting allows you to change the way RPM and Speed information is displayed on the Telemetry Screen. For example,
you can choose to display RPMs, MPH or KM/H. The RPM Gauge and the RPM Digital Displays will change from RPM to MPH
or KM/H depending on the RPM Unit value chosen. In addition, if MPH or KM/H is chosen, the RPM sensor can be calibrated
to ensure that the most accurate speed is displayed for your specific model.
Changing the RPM Unit Value:
1) From within the TELEMETRY menu, scroll UP or DOWN to highlight RPM SETTING.
2) Press the ENTER key. The RPM menu will be displayed and UNIT RPM will be highlighted.
3) Press the ENTER key, then scroll UP or DOWN to change the RPM Unit to the desired
value. When RPM is chosen, the Revolutions Per Minute of whatever the RPM Sensor is
attached to will displayed. When MPH or KM/H is chosen, the speed of your model will
be displayed in either Miles Per Hour or Kilometers Per Hour, respectively.
TELEMETRY RPM UNIT setting range is RPM, MPH and KM/H. The default setting is RPM.
Changing the Maximum RPM/Speed Value:
The Maximum RPM/Speed value determines the maximum RPM or Speed value that will
be shown on the Telemetry RPM Gauge. This setting does not effect the RPM or Speed
Digital Display.
The RPM Gauge and RPM/Speed Digital Display names will change from RPM to
MPH or KM/H depending on the RPM Unit value chosen.
10.TELEMETRY (TELEMETRY DISPLAY OPTIONS)SYSTEM
The Maximum Voltage value cannot be set lower than the Alert Voltage value. If
necessary, you may need to lower the Alert Voltage value prior to lowering the Maximum Voltage value.
TELEMETRY MAX VOLT setting range is 3.0v to 9.0v. The default setting is 9.0v.
3) Press the ENTER key, then scroll UP or DOWN to change the Maximum Voltage value.
The Voltage Display Monitor on the Telemetry Screen will not display receiver battery
Voltage values above the Maximum Voltage value programmed.
Changing the Alert Voltage Value:
The Alert Voltage value determines the voltage at which the Voltage Alert alarm will sound. For example, you can set the Alert
Voltage value to alert you to when your model's receiver battery is getting low and needs to be recharged. When the Alert
Voltage value is reached, the Voltage Alert alarm will sound and LED2 (Red) will flash. The Voltage Alert alarm will sound for
approximately 5 seconds, however, LED2 will continue to flash until you recharge the receiver battery. The audible portion of
the Voltage Alert alarm can be cleared by pressing the BACK/CANCEL key or the Push-Button Rotary Dial.
In general, the Alert Voltage value should be high enough to alert you when it's time to recharge your receiver battery, but
not so low that the receiver battery loses power and can no longer control your model.
RPM SETTING (RPM and Speed Telemetry Display Options)
MT-4S User's Guide.indd 66 2015/10/27 14:39:17
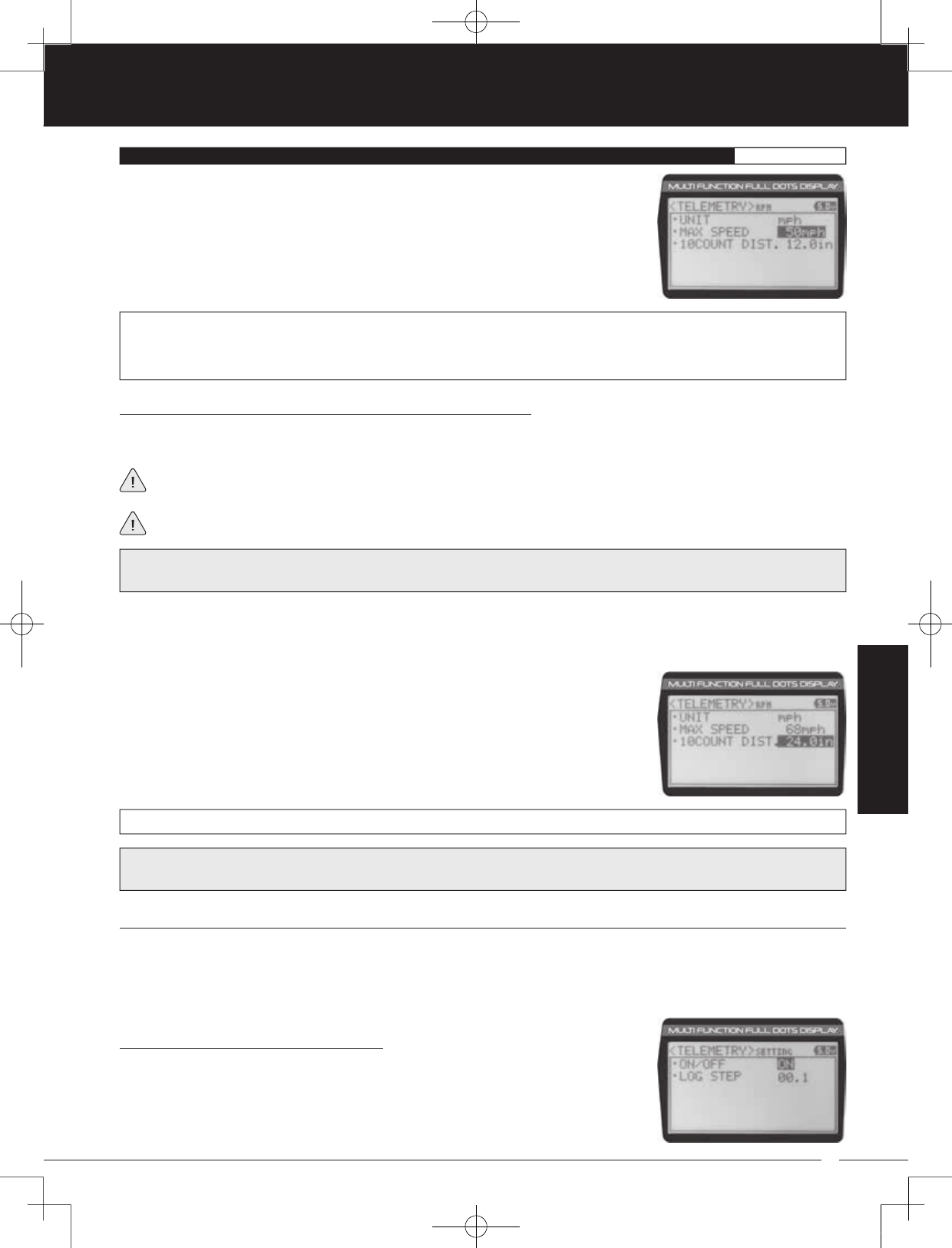
67
TR
TR
TR
90478 2.4GHZ FH4T RADIO SYSTEM USER'S GUIDE
SYSTEM
10.TELEMETRY (TELEMETRY DISPLAY OPTIONS)SYSTEM
1) From within the RPM menu, scroll UP or DOWN to highlight MAX RPM 30000 (or MAX
SPEED 34mph or MAX SPEED 54km/h).
2) Press the ENTER key, then scroll UP or DOWN to change the Maximum RPM or
Maximum Speed value. The RPM Gauge on the Telemetry Screen will not display RPM
or Speed values above the Maximum value programmed.
TELEMETRY MAX RPM setting range is 500 to 127500. The default setting is 30000. TELEMETRY MAX SPEED setting range is
1mph to 335mph (1km/h to 539km/h). The default setting is 34mph (54km/h). The Maximum Speed setting range will vary
based on the 10 Count Distance value programmed when you calibrate the RPM Sensor. For more information, see the
Calibrating the RPM Sensor section on page 67.
3) From within the RPM menu, scroll UP or DOWN to highlight 10COUNT DIST. 12.0in (or
10COUNT DIST. 30cm).
4) Press the ENTER key, then scroll UP or DOWN to change the 10 Count Distance value
to the measurement obtained in step 2 above. For example, if your model traveled 2
feet (61cm) to complete 10 full revolutions, enter 24.0in (61cm).
TELEMETRY 10COUNT DIST setting range is 0.5in to 118.0in (1cm to 300cm). The default setting is 12.0in (30cm).
Calibrating the RPM Sensor - Changing the 10Count Distance Value:
The 10Count Distance value can be changed if you've Selected UNIT MPH or UNIT KM/H. By changing the 10Count Distance
value you are able to calibrate the RPM sensor to read your specific model's actual speed, in either MPH or KM/H.
RPM Sensor calibration is only required if you choose to use the RPM Sensor to display MPH or KM/H. Calibration is
not required if you're displaying RPM.
Prior to calibrating the RPM sensor, you must connect the RPM sensor to your receiver and correctly install the RPM sensor
into your model. For more information, see the Telemetry Connections and Mounting section on pages 69 and 70.
IMPORTANT: When the reflective tape attached to your model's spur gear, pinion gear, etc., crosses the RPM sensor, the
Bind LED on the receiver will flash green once, indicating 1 full revolution. Use this as a guide during the calibration process.
1) With your transmitter and receiver turned ON, and with an Active Telemetry connection, place your model on the ground.
2) Measuring in inches (or centimeters if using KM/H) from where you set your model on the ground, slowly push your
model and measure the distance covered to complete 10 full revolutions of the RPM sensor (the Bind LED on your receiver
will flash green 10 times, indicating 10 full revolutions).
IMPORTANT: Changing the 10Count Distance value will change the Maximum Speed value. After calibration, you should
reset the Maximum Speed value back to the value you chose previously.
TELEMETRY SETTING (Telemetry ON /OFF and Telemetry Log Options)
The Telemetry Setting allows you to choose whether the Telemetry System is turned ON or OFF and change the interval that
Telemetry Data is read and stored.
The interval that Telemetry Data is read and stored can be adjusted so that Telemetry Data can be stored for up to 90 minutes
of use. The Telemetry Log can store 120 different data entries at intervals ranging from 00.1 seconds to 45.9 seconds.
Turning the Telemetry System ON and OFF:
1) From within the TELEMETRY menu, scroll UP or DOWN to highlight TELEMETRY
SETTING.
2) Press the ENTER key. The SETTING menu will be displayed and ON/OFF ON will be
highlighted.
MT-4S User's Guide.indd 67 2015/10/27 14:39:17
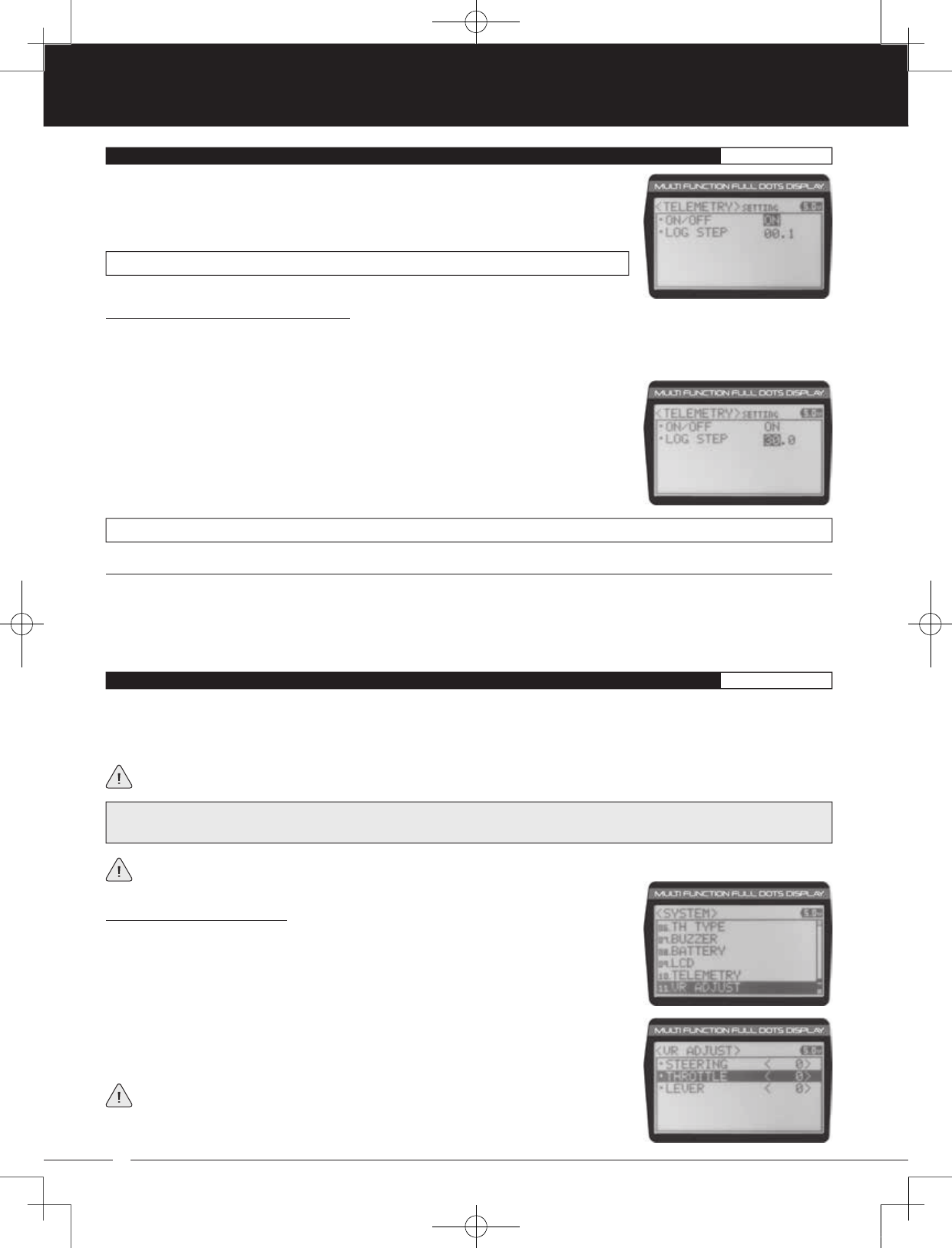
68
90478 2.4GHZ FH4T RADIO SYSTEM USER'S GUIDE
TR
TR
TR
3) Press the ENTER key, then scroll UP or DOWN to change the Telemetry ON/OFF value.
When ON is selected, the Telemetry System is turned ON. When OFF is selected, the
Telemetry System is turned OFF.
TELEMETRY SETTING ON/OFF setting range is ON or OFF. The default setting is ON.
Changing the Telemetry Log Step Value:
The Telemetry Log Step value can be changed to customize how much Telemetry Data and the time interval Telemetry Data
is recorded. The Telemetry Log can store up to 120 separate entries. If the Log Step value is set to 00.1 seconds, the Telemetry
Log can record for 12 seconds. If the Log Step value is set to 45.1 seconds, the Telemetry Log can record for 90 minutes.
TELEMETRY LOG STEP setting range is 00.1 to 45.9. The default setting is 00.1.
1) From within the SETTING menu, scroll UP or DOWN to highlight LOG STEP 00.1.
2) Press the ENTER key, then scroll UP or DOWN to change the Telemetry Log Step value.
Programming a lower Telemetry Log Step value results in narrower, higher resolution
readings, but for a shorter period of time. Programming a higher Telemetry Log Step
value results in broader, lower resolution readings, but for a longer period of time.
Calibrating Control Operation:
1) From within the SYSTEM menu, scroll UP or DOWN to highlight the VR ADJUST menu.
2) Press the ENTER key. The VR ADJUST menu will be displayed and STEERING <0> will be
highlighted.
3) Scroll UP or DOWN to highlight the control you would like to calibrate. Choose from
STEERING <0>, THROTTLE <0> or LEVER <0>.
<0> indicates the current position of the specific channel relative to its specific control.
For example, if the Throttle Trigger is in the Neutral position, but an H or B value is
displayed, the Throttle Channel 2 Neutral position has shifted and should be recalibrated.
The Telemetry Clear function allows you to Reset the High Temperature 1, High Temperature 2 and High RPM values that are
displayed on the Telemetry Screen. The Telemetry Clear function can be assigned to either Push-Button Switch Sw1 or
Push-Button Switch Sw2. When you press the Push-Button Switch the Telemetry Clear function is assigned to, the High
Temperature 1, High Temperature 2 and High RPM values will be Reset the Current values read by the Telemetry Sensors. For
more information see the Push-Button Key Assignments section on pages 53 through 58.
10.TELEMETRY (TELEMETRY DISPLAY OPTIONS)SYSTEM
TE-CLEAR (Telemetry Clear Function)
11.VR ADJUST (VARIABLE RATE ADJUSTMENT)SYSTEM
The Variable Rate Adjustment function allows you to calibrate the operation of the Steering Wheel, Throttle Trigger and Auxiliary
Lever End Points and Neutral positions. Over time, it's possible that the End Points and/or Neutral positions of these controls
may change slightly or you may purposely limit the travel of the Steering Wheel to suit the best feel of the Steering Wheel and
your driving style. Being able to calibrate these controls ensures precise operation at all times and in all conditions.
We recommend using the Variable Rate Adjustment function as part of a periodic maintenance schedule or after adjusting
the Steering Wheel travel as described in the Steering Wheel Travel Adjustment section on page 13.
IMPORTANT: After using the Variable Rate Adjustment function, you should double-check the End Point Adjustments of each
saved Model. If the End Points have moved, they will need to be readjusted using the End Point Adjustment function.
The steps required to calibrate the operation of the Steering Wheel, Throttle Trigger and Auxiliary Lever are the same. The
example shown in this section details calibrating the Throttle Trigger.
MT-4S User's Guide.indd 68 2015/10/27 14:39:18
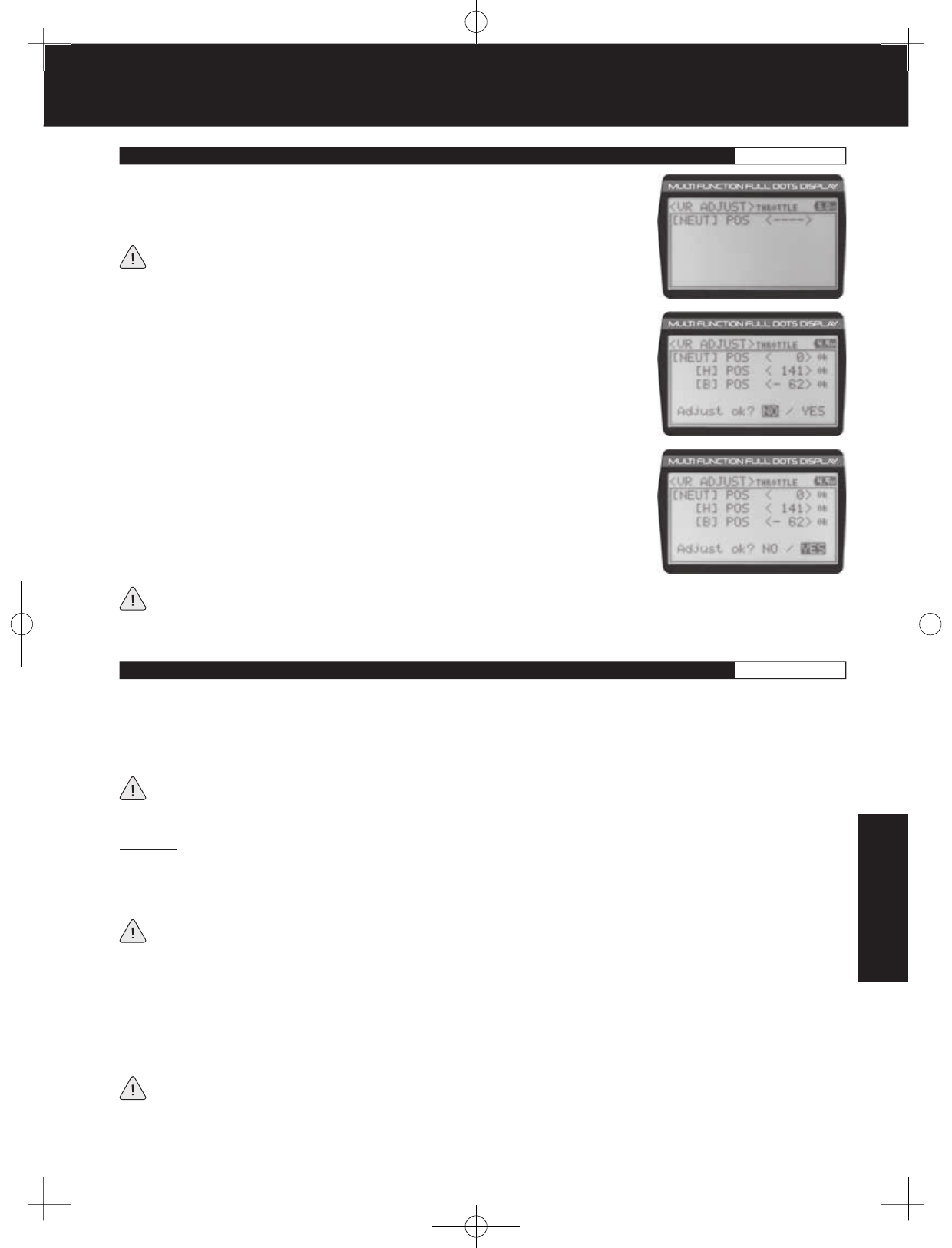
69
TR
TR
TR
90478 2.4GHZ FH4T RADIO SYSTEM USER'S GUIDE
To cancel the calibration process, scroll UP or DOWN to highlight NO, then press the ENTER key. You can then return to
VR ADJUST menu by pressing the BACK/CANCEL key.
8) If desired, repeat steps 3 through 7 to calibrate the remaining controls.
11.VR ADJUST (VARIABLE RATE ADJUSTMENT)SYSTEM
5) Press the ENTER key a second time. A menu with several position indicators will be
displayed.
6) Move the Steering Wheel, Throttle Trigger or Auxiliary Lever all the way in one direction.
Allow the control to return to Neutral, then move the Steering Wheel, Throttle Trigger or
Auxiliary Lever all the way in the opposite direction. A series of values and Adjust ok?
NO/YES will be displayed.
7) Scroll DOWN to highlight YES, then press the ENTER key. Executed will flash, indicating
that the calibration process is complete.
4) With the Steering Wheel, Throttle Trigger or Auxiliary Lever in the Neutral position, press
the ENTER key. [NEUT] POS <-----> will be displayed.
The Auxiliary Lever features a detent to indicate its Neutral position.
REFERENCE
TELEMETRY CONNECTIONS AND MOUNTING REFERENCE
Overview:
The RX-461 and RX-462 receivers each feature two Temperature Sensor Inputs and one RPM Sensor Input, in addition to the
Voltage Sensor built into the receiver. Temperature and RPM Sensors can be installed into your model to give you Temperature
and RPM or Speed feedback in real-time displayed on the transmitter's Telemetry Screen.
The range of the Telemetry System is approximately 260 feet (80 meters), although the range can vary based on many
environmental factors. Use the Telemetry Signal Indicator to determine the quality of the Telemetry Signal.
When used with an Airtronics 2.4GHz FH4T Telemetry-capable surface receiver, such as the RX-461 or RX-462, and up to two
Temperature Sensors and an RPM Sensor (all available separately), Telemetry Data, such as RPM or Speed, Temperature,
and Receiver Voltage can be viewed on the M12 transmitter's Telemetry Screen. This section details connecting the RPM and
Temperature Sensors to the RX-461 and/or RX-462 receiver and how to mount those Sensors into your model. For more
information about the specifics of either receiver, refer to the User's Guide included with your receiver.
For more information about viewing Telemetry Data on the Telemetry Screen, see the TELEMETRY Screen section on
pages 14 and 15. For more information about choosing Telemetry options, see the Telemetry Display Options section on
pages 63 through 68.
Plugging the Telemetry Sensors into the Receiver:
1) Carefully pry up and remove the plastic cover from over the Telemetry Sensor Input Ports on the receiver.
2) Plug the Telemetry Sensor(s) into their respective Input Ports in the receiver. The Temperature Sensor can be plugged into
either the TEMP 1 or the TEMP 2 Input Port and the RPM Sensor is plugged into the RPM Input Port. The Sensor Plugs are
indexed so they can be plugged in only one way.
Make sure to push the Sensor Plugs firmly in place to ensure a good connection. When routing Sensor Wires inside
your model, be careful that they cannot come into contact with any moving parts. The Sensor Wires should be securely
mounted and protected against damage.
In addition, install the dust covers included with your receiver to prevent dirt and debris from getting into any unused Input Ports.
MT-4S User's Guide.indd 69 2015/10/27 14:39:18
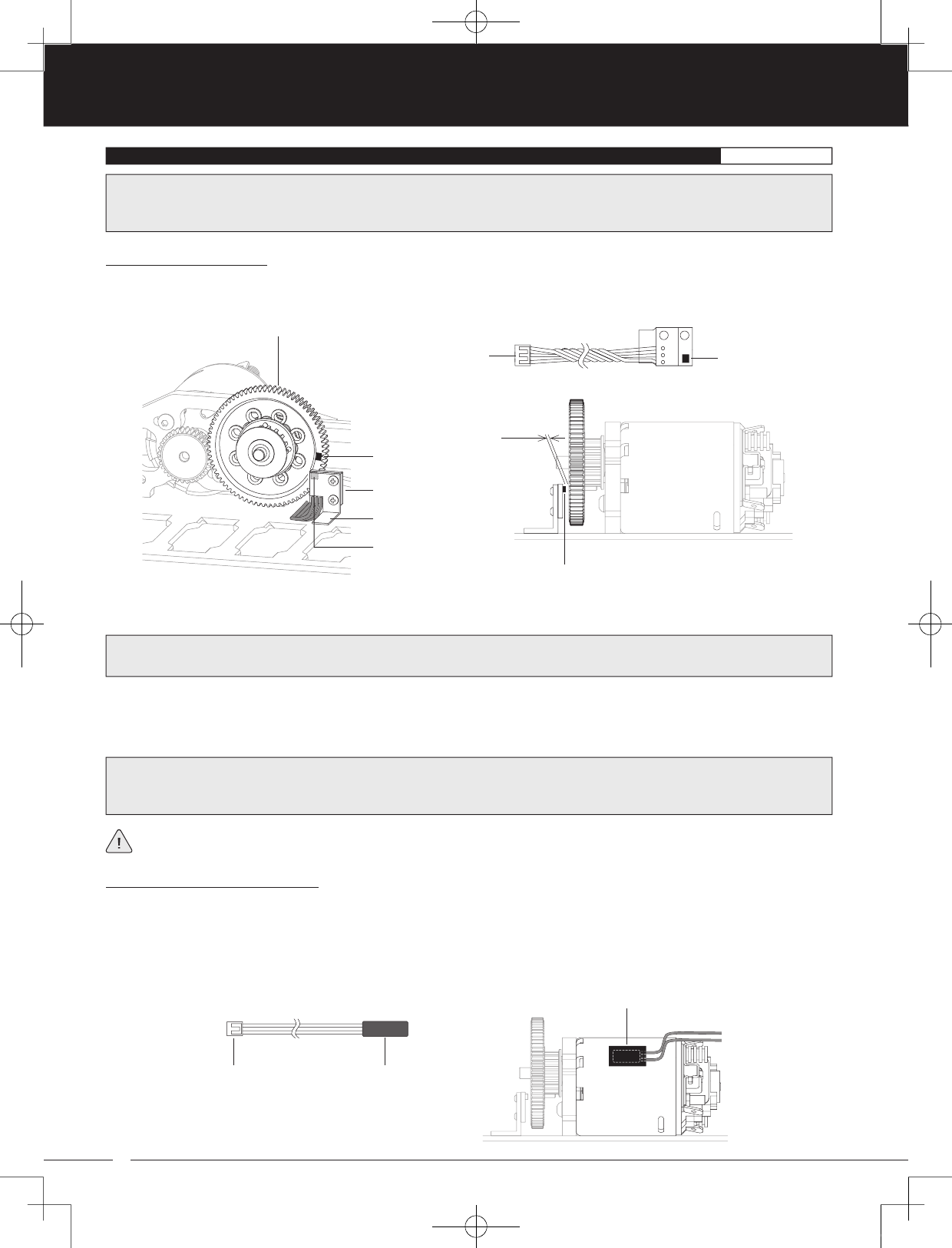
70
90478 2.4GHZ FH4T RADIO SYSTEM USER'S GUIDE
TR
TR
TR
TELEMETRY CONNECTIONS AND MOUNTING REFERENCE
1) Mount the RPM Sensor to an aluminum or ABS angled bracket, then mount the bracket to your model, making sure that it's
held securely in place.
Mounting the RPM Sensor:
The RPM Sensor uses infrared technology to record RPM data from a rotating part, such as a flywheel or a spur gear. One Black
and one White reflective decal is included that is attached to the rotating part so the Sensor Pickup can 'see' it.
Sensor Pickup
Input Plug
Reflective Decal
Angled Bracket
RPM Sensor
Sensor Pickup
Spur Gear or Other Rotating Part
~1mm
Sensor Pickup
Mounting the Temperature Sensor:
1) Secure the Sensor End directly against the part of your engine, motor, battery or other object you want to monitor temperature
readings from, using either a nylon cable tie or high-temperature clear tape. For example, to monitor the cylinder head
temperature of your glow- powered model, the best place to secure the Sensor End is where the bottom of the cylinder head
meets the top of the engine case. The Sensor End can be held in place using a nylon cable tie wrapped around your engine.
To monitor the temperature of your battery pack or electric motor, high-temperature clear tape can be used to secure the
Sensor End to the exact spot you want to monitor.
Sensor EndInput Plug
Attach with
High-Temperature Clear Tape
2) Cut one of the two reflective decals included with the RPM Sensor into an ~2mm diameter and apply it to the rotating part,
so that as the part rotates, the reflective decal passes in Front of the Sensor Pickup. If the rotating part is metallic-colored
(silver, aluminum, chrome, etc.), use the Black reflective decal and if the rotating part is dark-colored (black, blue or another
dark color), use the White reflective decal.
IMPORTANT: For optimal operation, the Sensor Pickup should be positioned approximately 1mm away from the rotating
part (flywheel, spur gear, pinion gear etc.)
After installing the RPM Sensor and connecting it to your receiver, the RPM Sensor must be calibrated. For more information,
see the RPM and Speed Telemetry Display Options section on pages 63 through 68.
IMPORTANT: When installed, it's important that the Sensor Pickup face the rotating part and that the Black or White reflective
decal is positioned so that it passes in Front of the Sensor Pickup. It's also important that the reflective decal contrasts with
the rotating part it's applied to and that the Sensor Pickup is mounted approximately 1mm away from the rotating part.
IMPORTANT: If the Sensor Wires are not long enough for your specific application, you can carefully splice in extra wire of
similar gauge to extend the Sensor Wires to the desired length. Make sure to solder the splices securely together and protect
the splices using heat-shrink tubing.
MT-4S User's Guide.indd 70 2015/10/27 14:39:19
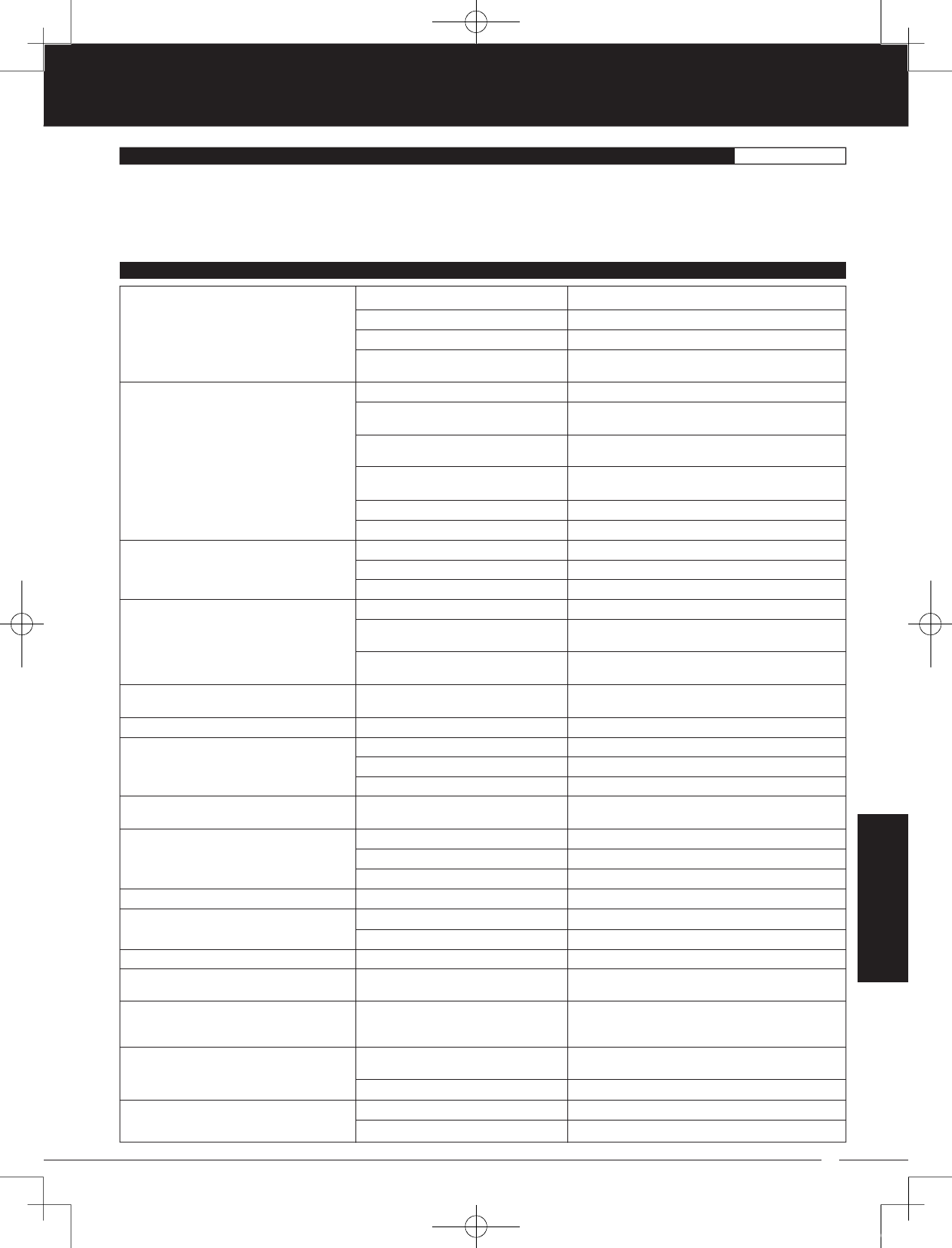
71
TR
TR
TR
90478 2.4GHZ FH4T RADIO SYSTEM USER'S GUIDE
Transmitter does not turn ON
Transmitter will not bind to receiver
Receiver won't power ON
Audible alarm beeps continuously
One or more LEDs flashing
No key-press or Timer function sounds
Servo movement is slow
Servo does not move when using Trim Switch
Inadequate transmitting range
Servo(s) move the wrong direction
Servo Horn(s) not centered
Control linkage(s) bind
Servo moves too much or not enough when
Trim Switch is pressed
Throttle servo moves to programmed position
without input
Can't program Receiver Battery Voltage
Fail Safe
No Telemetry connection
Transmitter batteries installed incorrectly
Battery tray not plugged in
Transmitter batteries are dead
Damage caused by using incorrect
charger or reverse polarity
Modulation Type incorrect
Too much time elapsed after pressing
receiver Bind Button
Attempting to Bind incompatible receiver
Using Electronic Speed control (ESC)
Receiver batteries are dead
Using incorrect Binding procedure
Receiver batteries are dead
Receiver batteries not installed correctly
Loose switch connection
Low transmitter battery voltage
Transmitter left ON 10 minutes or more
without control input
Transmitter battery voltage too high
Indicates transmitter status
Key Tones are Muted
Low receiver battery voltage
Control linkages binding
Using a negative Servo Speed value
Trim is outside of operational range
Low transmitter battery voltage
Low receiver battery voltage
Receiver antenna not mounted correctly
Incorrect Servo Reversing setting
Servo horn not installed correctly
Servo Sub-Trim out of adjustment
To much servo travel
Trim Step resolution requires adjustment
Receiver battery voltage has reached
programmed Receiver Battery Voltage
Fail Safe voltage value
Throttle channel Fail Safe value set to
FREE or HOLD
Using FH2 Reciver
Telemetry System turned OFF
Outside of Telemetry range
Reinstall batteries, observing correct polarity
Plug in battery tray
Replace or recharge transmitter batteries
Contact Airtronics Customer Service
Change Modulation Type to match receiver
Quickly press ENTER key in BIND menu after releasing
receiver Bind Button
Use only Airtronics 2.4GHz FH2, FH3 or FH4T surface
receivers
Disconnect ESC and use dry cell battery for Binding
procedure, then reconnect ESC after Binding
Replace or recharge receiver batteries
Follow Binding procedure carefully
Replace or recharge receiver batteries
Reinstall receiver batteries, observing correct polarity
Double-check all connections including switch
Replace or recharge transmitter batteries
Move Steering Wheel or Throttle Trigger, or press any
key to clear alarm and continue operation
Use transmitter battery whose voltage is 9.6 volts or
less when fully charged
For more information, see LED Condition Indicators
table on page 10.
Increase Key Tone volume in BUZZER menu
Replace or recharge receiver batteries
Adjust control linkages to operate smoothly
Increase Servo Speed value
Center Trim Switches to '0', center the servo horn and
control linkages
Replace or recharge transmitter battery
Replace or recharge receiver batteries
Mount receiver antenna as recommended
Change Servo Reversing setting
Turn servo horn 180º and reinstall
Adjust Servo Sub-Trim to center servo horn
Decrease servo travel using EPA function
Adjust Trim Step resolution
Replace or recharge the receiver batteries
Set Throttle channel Fail Safe to a percentage value
This function is not supported with FH2 receivers
Turn Telemetry System ON
Move transmitter closer to receiver in model
REFERENCE
TROUBLESHOOTING GUIDE REFERENCE
This troubleshooting guide can help you diagnose and solve some of the more common problems that you might encounter
with your radio control system.
If you cannot solve the problem using this troubleshooting guide, please contact Airtronics Customer Service using the information
in the Service and Support section on page 3.
PROBLEM CAUSE SOLUTION
MT-4S User's Guide.indd 71 2015/10/27 14:39:20
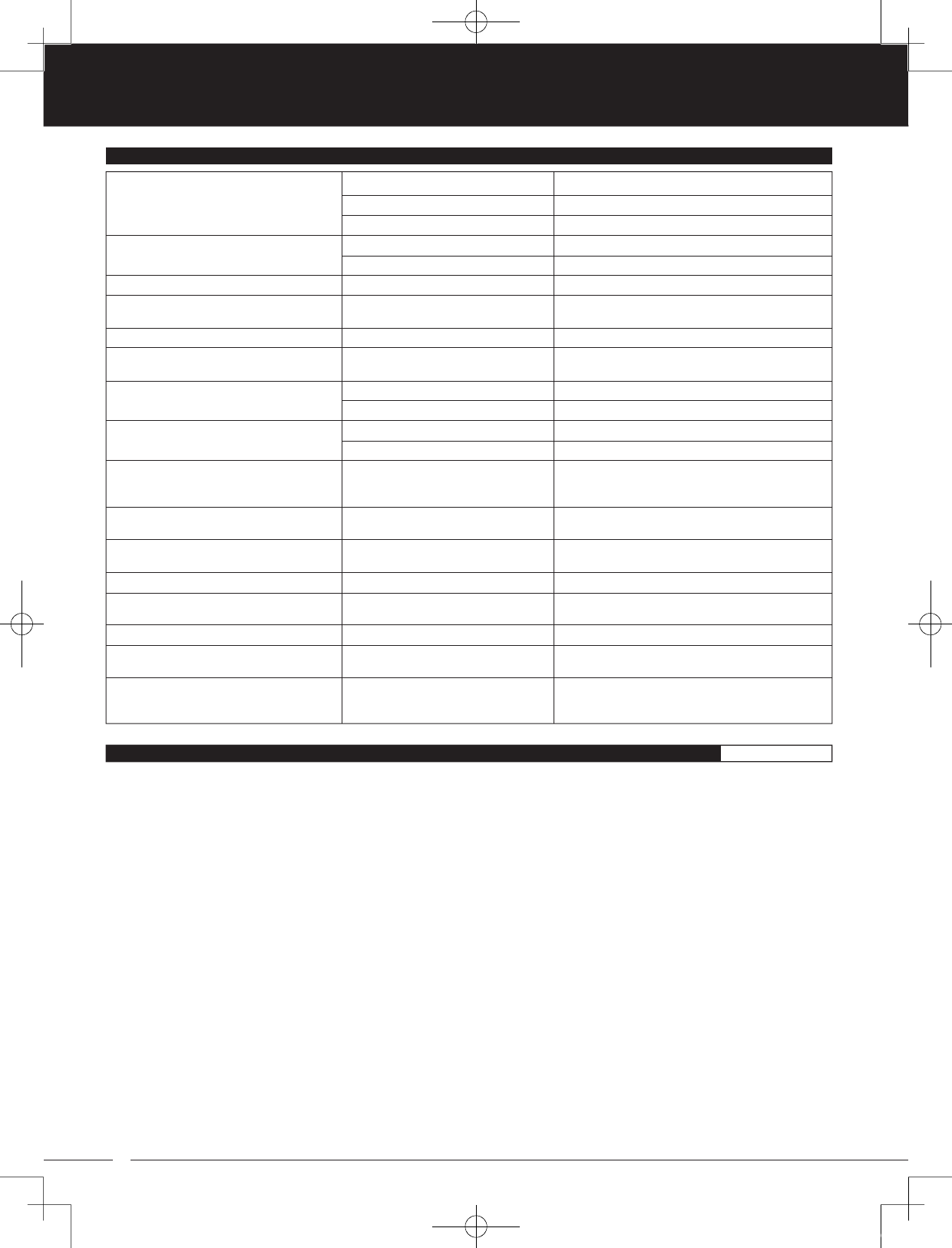
72
90478 2.4GHZ FH4T RADIO SYSTEM USER'S GUIDE
TR
TR
TR
RPM Sensor not functioning
LCD is difficult to read
There is no LCD Backlight
LCD Backlight keeps turning OFF
Throttle servo pulsates
Model veers right or left without control input
Model accelerates without control input
Model seems extremely sensitive to control
input
Servo(s) and/or ESC don't operate at all or
operate erratically
Direction of travel shown on Servo Monitor is
different from control input travel
Can't control underscore when changing
Model Name or User Name
Can't clear Lap Timer
Steering Wheel and/or Throttle Trigger won't
center
Controls don't operate as expected
CODE Auxiliary function does not work
Cannot control Auxiliary functions
Sensor not facing reflective decal
Sensor to far away from rotating part
Not using reflective decal
Contrast setting too high or too low
LCD Backlight is turned OFF
LCD Backlight is turned OFF
LCD LIGHT-MODE is set to Key-On
ABS function is Active
Steering out of trim
Throttle out of trim
Throttle Offset function is Active
Dual Rate value(s) set too high
Controls out of adjustment
Using incorrect Servo Mode setting
This is normal
Cursor is Active in Character Select
screen
This is normal
Spring tension set too loose
Controls out of adjustment
Using incorrect receiver and/or Accessories
Auxiliary Type not selected and/or AUX1 or
AUX2 not assigned to a Trim Switch, Rotary
Dial or Auxiliary Lever
PROBLEM
Mount Sensor so it faces rotating part/reflective decal
Mount Sensor closer to rotating part
Apply contrasting reflective decal to rotating part
Readjust contrast setting
Turn LCD Backlight ON
Set LCD LIGHT-MODE to Key-On or Always
This is normal to save battery power. Increase TIME
value or set LCD LIGHT-MODE to Always
This is normal under Braking with the ABS Active
Use Steering Trim Switch to adjust Steering Trim so
model drives straight
Use Throttle Trim Switch to adjust Throttle Neutral Point
Turn Throttle Offset function OFF
Decrease Dual Rate value(s)
Use the VR Adjust function to calibrate controls
Use correct Servo Mode setting based on the type of
servos you're using in your Model. Use NOR mode for
Throttle channel if using ESC
Direction of travel displayed will vary depending on
Servo Reversing settings
Press BACK key to re-gain control of underscore
Lap Timer will clear when you Start the Lap Timer again
Tighten spring tension
Use the VR Adjust function to calibrate controls
Must use Airtronics or Sanwa receiver and accessories
that support Sanwa Synchronized Link (SSL)
Must first choose Auxiliary Type and ensure AUX1 and/
or AUX2 are assigned to a Trim Switch, Rotary Dial or
Auxiliary Lever
CAUSE SOLUTION
GLOSSARY OF TERMS REFERENCE
Activate: To turn ON a particular function.
Antenna: Transmits the signal from the transmitter to the receiver in the model. Never touch the Antenna during use. Doing so
may result in a weakened RF signal or complete loss of control of your model.
Antenna Reception Wire: The portion of the receiver antenna that receives the transmitter signal. The Antenna Reception Wire
should never be bent or it could be damaged and limit the range of your model .
Anti-Lock Braking: Makes it possible to achieve stable braking even on slippery surfaces. With stable braking, your model is
better able to trace an exact line under braking.
ARC: Adjustable Rate Control (ARC) allows you to vary the amount of servo travel in relation to the movement of the steering
wheel, throttle trigger and auxiliary lever near the Neutral positions to change the way those functions react to control movement.
The position that the Rate can be controlled from is adjustable along the length of control travel.
Audible Key Tone: An audible tone that is emitted from the transmitter each time the Push-Button Rotary Dial, Trim Switch,
Push-Button Switch or Rotary Dial is used.
Auxiliary Lever: The Auxiliary Lever is programmable and will perform a different function depending on what function is
assigned to it. For example, it can be used to control Auxiliary 1 Channel 3 or to control the Servo Speed function. The Auxiliary
Lever features a detent and an audible tone to let you know it's in the Neutral position.
Auxiliary Lever Position Display: Displays the current position of the Auxiliary Lever on the Top Screen.
Auxiliary Mixing: Allows you to Mix either Steering Channel 1 or Throttle Channel 2 to Auxiliary 1 Channel 3 or Auxiliary 2
Channel 4, while maintaining separate Sub-Trim, End Point Adjustments, Servo Reversing and other channel-specific settings.
The Auxiliary Mixing function is used when a custom Mix is necessary.
BACK/CANCEL Key: Returns to the previous menu. Press and HOLD to return to the Top Screen. In addition, cancels certain
warning alarms, such as the Low Voltage Alert alarm.
MT-4S User's Guide.indd 72 2015/10/27 14:39:20
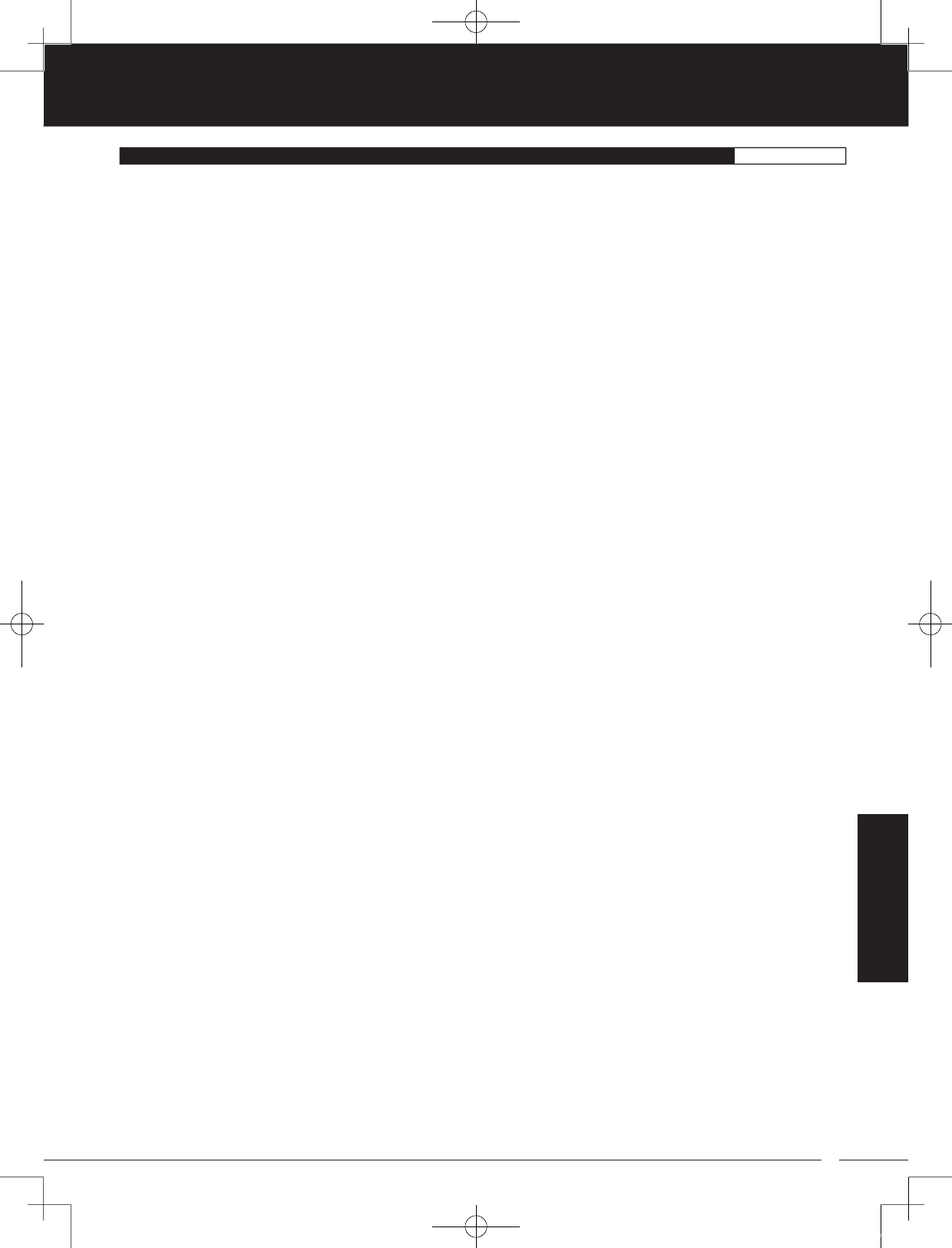
73
TR
TR
TR
90478 2.4GHZ FH4T RADIO SYSTEM USER'S GUIDE
Battery Compartment: Houses the four 'AA' Alkaline cells that power the transmitter. Alternatively, the transmitter can be
powered using four 'AA' NiCd or NiMH rechargeable batteries or a 2S LiPo or 2S LiFe battery pack.
Binding: The act of pairing the transmitter and receiver to prevent interference from transmitters operated by other users. The
transmitter and receiver must be paired so that the two can 'talk' to each other. Once the Binding process is complete, the
setting is remembered even when the transmitter and receiver are turned OFF.
Bind Button: Used in the process of Binding the transmitter and receiver.
Bind LED: Displays the current status of the receiver.
Brake Side: Refers to the throttle trigger stroke that engages the brakes on your model (pushing the throttle trigger).
Burn: Used with the Motor on Axle function (dual ESCs), the front motor is inhibited while keeping full control of the rear motor
during rock crawling.
Center Trim Type: A Trim technology, that when selected, the servo End Points remain stationary when you apply Trim using
the Trim Switches. This can result in unbalanced servo travel. In order to balance servo travel, servo End Points need to be
manually readjusted.
Channel Set: Allows you to make programming changes to each of the four channels without the need to enter each Programming
Menu separately.
Charging Jack: Used for onboard charging of optional NiCd or NiMH batteries. Do not attempt to charge Alkaline batteries.
Only the recommended Airtronics 110v AC charger should be used through the Charging Jack. If using an after-market
Peak-Detection charger or other type of fast charger, the batteries should be removed from the transmitter to avoid damage
to the transmitter circuitry and/or your batteries. Do not attempt to charge a LiPo or LiFe battery pack through the Charging Jack.
Coaxial Cable: The portion of the receiver antenna that extends the Antenna Reception Wire. The Coaxial Cable can be bent
into gentle curves, however, do not bend it acutely, or repeatedly bend it, or the antenna core can be damaged. The Coaxial
Cable should be installed into a nylon tube (antenna tube) and positioned vertically in your model for the best reception.
Code Auxiliary: A function designed for use with future connected products, such as an ESC, whose Programming Parameters
can be changed directly via the transmitter.
Countdown Timer: Used to notify you of your model’s running time. For example, you can set the Countdown Timer to alert you
when it's time to refuel. When the Countdown Timer expires a long audible tone will sound and the Count Up Timer function
begins automatically. This allows you to check the time elapsed since the timer ran out.
Dial Knob: The Dial Knob can rotate 360º and is programmable to perform a different function depending on what function is
assigned to it. For example, it can be used to increase and decrease Programming Values, control a Trim function or control
an Auxiliary Channel.
Dig: Used with the Motor on Axle function (dual ESCs), the rear motor is inhibited while keeping full control of the front motor
during rock crawling.
Digital RPM Display: Displays the current RPM from the RPM Sensor in digital format on the Telemetry Screen.
Digital Temperature Display: Displays the current temperature from the TEMP1 and TEMP2 Temperature Sensors in digital
format on the Telemetry Screen.
Digital Trim Memory: Allows the transmitter to store Trim values in its memory. Any amount of Trim that you set during use
using the Trim Switches is automatically stored in memory for that specific channel and for that specific model. The Trim values
for each model will automatically be loaded when the transmitter is turned ON.
Digital Voltage Indicator: Indicates the current Voltage of the transmitter batteries on both the Top Menu and the Telemetry
Screen.
Dual Rate: The Dual Rate function allows you to change the control authority of the Steering, Throttle High Side and Throttle
Brake Side by changing the amount of servo travel relative to control input. For example, by increasing the Steering Dual Rate,
you can make the steering servo travel more which might prevent your model from pushing during turns. If your model
oversteers during turns, you can reduce the amount of Steering Dual Rate.
End Point Adjustment: Used to adjust the desired amount of servo travel in both directions independently. This makes it possible
to balance servo travel in both directions.
Enter Key: Opens the selected menu or programming option. Press and HOLD to reset the selected programming option to
its default value.
Exponential: Allows you to vary the amount of servo travel in relation to the movement of the steering wheel, throttle trigger
and auxiliary lever near the Neutral positions to change the way those functions react to control movement. The position that
the Rate can be controlled from is fixed.
Fail Safe: Automatically moves the servos to a predetermined position in the event that the signal between the transmitter and
the receiver is interrupted, whether due to signal degradation or low transmitter battery.
FH2 Modulation: Frequency Hopping 2nd generation FHSS technology. FH2 Modulation is used in legacy Airtronics 2.4GHz
FHSS-2 transmitters and receivers, such as the Airtronics M11, M11 FHSS-2, and MX-3FG radio control systems.
GLOSSARY OF TERMS REFERENCE
REFERENCE
MT-4S User's Guide.indd 73 2015/10/27 14:39:20
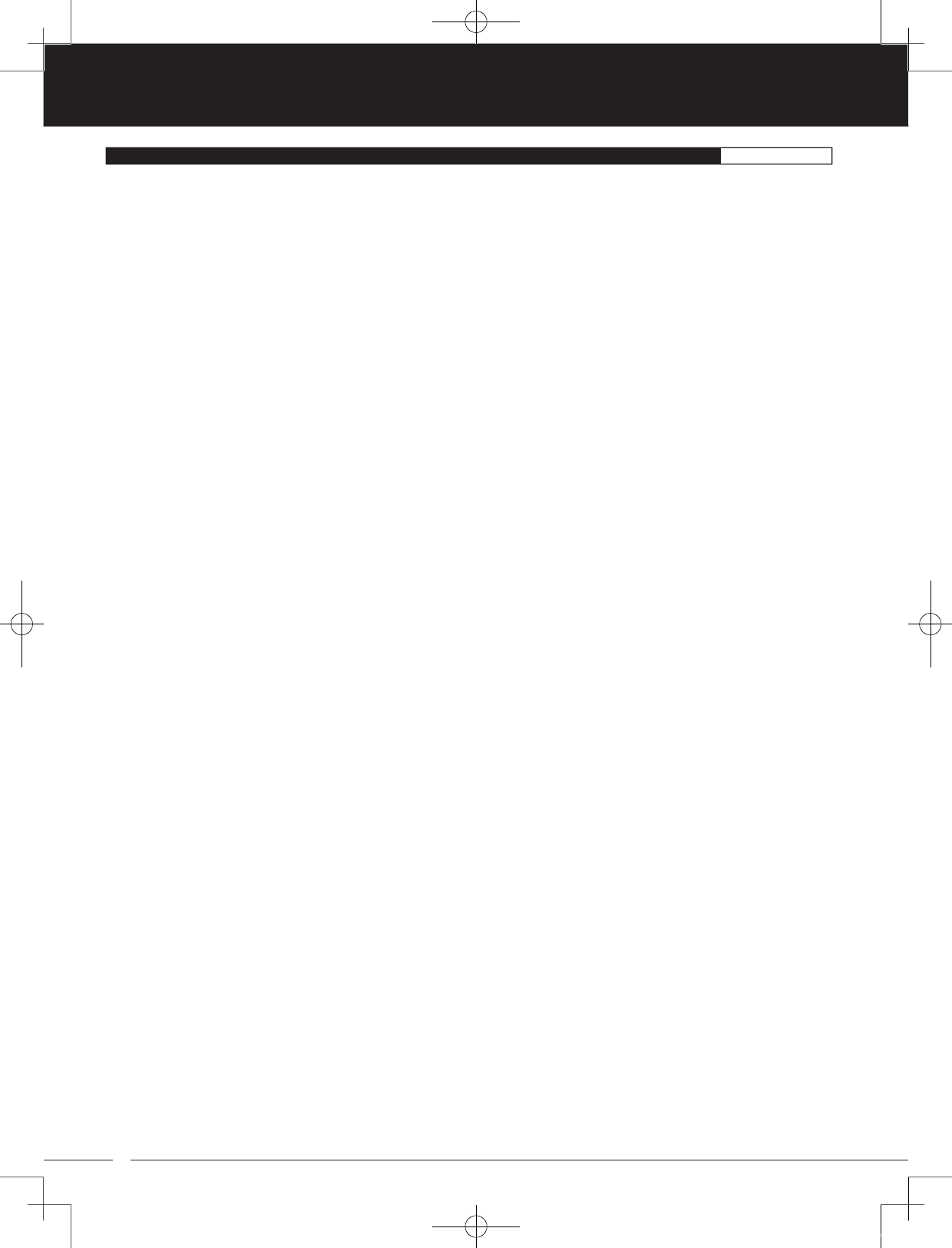
74
90478 2.4GHZ FH4T RADIO SYSTEM USER'S GUIDE
TR
TR
TR
FH3 Modulation: Frequency Hopping 3rd generation FHSS technology. FH3 Modulation is used in new-generation Airtronics
radio control systems, such as the M11X and MX-3X.
FH4T Modulation: Frequency Hopping 4th generation FHSS technology. FH4T Modulation is the latest Airtronics 2.4GHz
frequency modulation and supports Telemetry.
FHSS: Frequency Hopping Spread Spectrum. FHSS is a modulation type which transmits data across the entire frequency
spectrum by transmitting data on different channels at an extremely fast interval.
Four Wheel Steering Mixing: Used to control either the Front or Rear steering independently, or Mix the Front and Rear steering
so that they can be used together. Front or Rear Independent Steering, Parallel Four Wheel Steering and Tandem Four Wheel
Steering options are available.
Goal Time: Used in conjunction with the Lap Timer, the Goal Time is designed to alert you when you reach the maximum
desired elapsed time during your race or during practice.
Grip: The Grip is molded from rubber in an ergonomic shape for increased comfort, control and feel. An optional larger Grip
is included that some users may find feels more comfortable.
High RPM Display: Displays the last highest RPM value on the Telemetry Screen.
High Side: Refers to the throttle trigger stroke that opens the throttle and powers your model (pulling the throttle trigger).
High Temperature Display: Displays the last highest Temperature value on the Telemetry Screen.
Hold Setting: Determines how quickly the Brake moves from the Stroke setting to Neutral when the Anti-Lock Braking function
is Active.
Inactivity Alarm (Power ON Alarm): The Inactivity Alarm will sound if the transmitter is left on for a period of 10 minutes without
any control input from the user. This alarm alerts you to prevent unwanted draining of the transmitter battery. To clear this alarm,
either turn the transmitter OFF or press the BACK/CANCEL key or the Push-Button Rotary Dial.
Inhibit: To deactivate or turn OFF a particular function.
Interval Timer: Notifies you when a set interval elapses while you are driving, giving you an idea of how close you are to your
target time.
KM/H: Kilometers per Hour.
Lag: Controls the amount of delay before the Anti-Lock Brake Activates after reaching the POINT setting.
Lap Timer: Allows you to measure and record times for up to 99 laps. The number of laps completed is displayed in the Timer
menu, and when a lap is completed, the lap time is displayed momentarily on the Top Screen.
Latency: The Response Time between the transmitter and receiver. The lower the Latency value, the faster the Response Time
and the more connected you feel to your model.
LCD Screen: The heart of the programming and display features of the transmitter. All programming and transmitter display
functions are shown on the LCD Screen . The LCD screen features an adjustable backlight and adjustable contrast, making it
easy to view in almost any condition.
LED 1/2: Displays the current signal output status of the transmitter (LED 1 - Blue) and the Telemetry connection (LED 2 - Red).
In addition, one or both LEDs are used to indicate various transmitter conditions. For example, when a Throttle Offset percentage
value is programmed, the blue LED will flash.
Low Voltage Alert Alarm: The Low Voltage Alert alarm will sound when the transmitter batteries reach the Alert Voltage value
programmed in the SYSTEM - ALARM menu. The alarm will sound each time the transmitter battery voltage decreases by 0.1
volt. To clear this alarm, press the BACK/CANCEL key or the Push-Button Rotary Dial.
Low Voltage Limit Alarm: The Low Voltage Limit alarm will sound when the transmitter batteries reach the Limit Voltage value
programmed in the SYSTEM - ALARM menu. This alarm can only be cleared by turning the transmitter OFF and recharging or
replacing the transmitter batteries.
Model Clear: Used to reset the selected model's Programming Data to the default values. All model-specific Programming
Data, including the Model Name and Modulation Type will be Reset to the default values.
Model Naming: Used to name the different models you have saved in the transmitter. This makes it easy to keep track of multiple
models. The Model Name can consist of up to 10 letters, numbers, or symbols. Choose from capital letters, lower case letters,
numbers, and various symbols.
Model Number and Name: Displays the Model Number and Model Name of the currently selected model on both the Top
Screen and the Telemetry Screen.
Model Select: Used to store and retrieve Programming Data for any model 1 through 18. If you have Programming Data stored
for more than one model, using the Model Select function to load the Programming Data for the particular model that you wish
to use. The currently selected Model Number and Model Name is displayed on both the Top Screen and the Telemetry Screen.
Modulation Type Indicator: Indicates the current Modulation Type on the Top Screen that the transmitter is set to.
GLOSSARY OF TERMS REFERENCE
MT-4S User's Guide.indd 74 2015/10/27 14:39:20
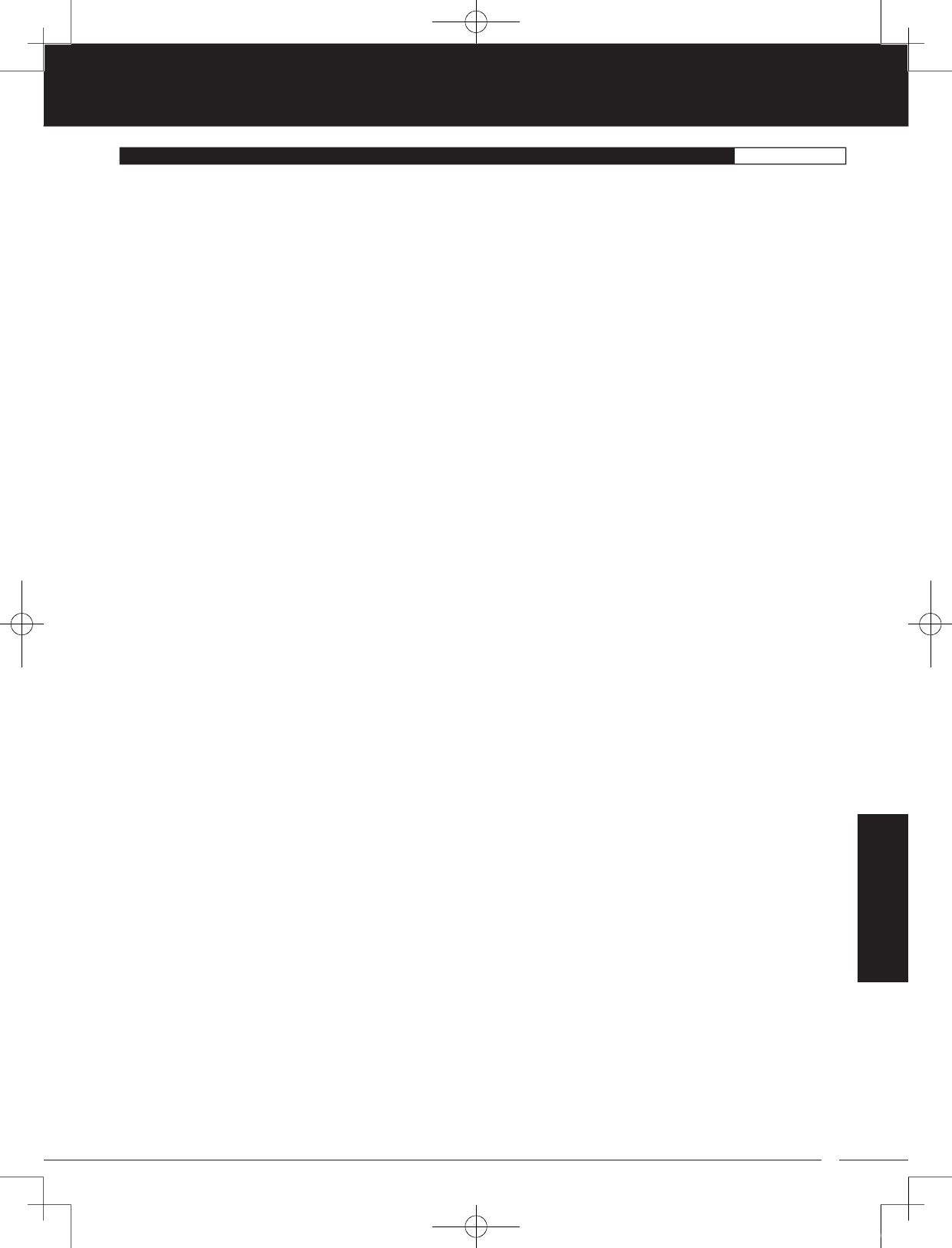
75
TR
TR
TR
90478 2.4GHZ FH4T RADIO SYSTEM USER'S GUIDE
GLOSSARY OF TERMS REFERENCE
Motor on Axle Mixing: Used to control either the Front and Rear throttles together or independently, giving you Dig and Burn
functions. These functions are mostly used in Rock Crawling.
MPH: Miles Per Hour.
Operating Voltage: The safe voltage that the transmitter or receiver can operate within. Exceeding the minimum operating
voltage can result in loss of power to the device(s). Exceeding the maximum operating voltage can result in damage to the
devices(s).
Output Power: The power (in Milliwatts) that your transmitter transmits a signal. Output power is defined by government
guidelines and differs by region.
Over Voltage Alarm: The Over Voltage Alarm will sound if the transmitter battery voltage is greater than 9.6 volts. To clear this
alarm, turn the transmitter OFF and replace the transmitter battery with one that when fully charged does not exceed 9.6 volts.
Parallel (Crab) Steering: Used with Four Wheel Steering, both front and rear wheels pivot right and left together.
Parallel Trim: A Trim technology that when selected, the servo End Points move in equal amounts as the Trim when you use
the Trim Switches. This results in balanced servo travel without the need to manually readjust the End Points.
Point Auxiliary: Used to program Auxiliary Channel 3 or Auxiliary Channel 4 to move the servo to up to 6 different points along
its travel, then cycle through those Points. For example, if your model requires a separate 3-position or more switch to operate
a feature, the Point Auxiliary function can be customized to control this.
Point Setting: Locates the actual point in the servo travel that you want a specific programming setting to occur. This setting
can vary depending on the actual programming setting the Point setting is controlling.
Power Switch: Turns the transmitter ON and OFF.
Push-Button Rotary Dial: The Push-Button Rotary Dial (also referred to as the Up Key, Down Key, or Enter key) is used along
with the BACK/CANCEL Key to facilitate transmitter programming. It allows you to quickly and easily navigate the various
Programming and System Menus and switch between the Top Screen and the Telemetry Screen.
Push-Button Switch: The transmitter features two separate Push-Button Switches in different locations (Sw1 and Sw2). Each
Push-Button Switch is programmable and will perform a different function depending on what function is assigned to it.
Receiver Battery Voltage Fail Safe: Used to set a custom voltage that the Receiver Battery Fail Safe function will Activate at.
When your receiver battery voltage drops to the programmed voltage, the throttle servo will move to the predetermined position
programmed using the Fail Safe function. If this occurs, recharge or replace your receiver batteries.
Receiver Voltage Display: Displays the current voltage of the receiver battery on the Telemetry Screen.
Release Setting: Determines how quickly the Brake moves from Neutral to the percentage value determined by the Stroke
setting when the Anti-Lock Braking function is Active.
RPM: Revolutions Per Minute.
RPM Display Monitor: Displays the current RPM on the Telemetry Screen from the RPM Sensor in graphical format.
Servo Monitor Display: Displays the output levels of the four different channels in bar graph form, allowing you to monitor servo
operation in a virtual manner.
Servo Reversing: Used to electronically switch the direction of servo travel. For example, if you move the steering wheel to the
right, and the steering servo moves to the left, you can use the Servo Reversing function to make the steering servo move to
the left.
Servo Speed: Used to slow down the transit speed of the servos. Servo transit speed can be slowed in both the Forward and
the Return to Center directions.
SHR Servo Operating Mode: Using this setting with Digital servos will increase the servo's response time, even above the
manufacturer's stated specification. Do not use with Analog servos!
SSR Servo Operating Mode: If you're using Airtronics SRG Digital servos, you can use the SSR setting for the fastest response
time. This results in the ultimate feel and response, making you feel more in control of your model than ever. Use only with
Airtronics SRG Digital servos!
Steering Program Indicator: Indicates on the LCD Screen up to four different programming options that are currently
programmed to the Steering channel. The Steering Program Indicator will only be displayed if a Steering channel Programming
Value is programmed.
Steering Trim Display: Displays the current position of the Steering Trim Switch on the Top Screen.
Steering Wheel: Proportionally operates the model's right and left steering control. The Steering Wheel features a foam grip for
increased comfort, control and feel. In addition, the Steering Wheel spring tension and travel limits can be adjusted.
Steering Wheel Tension Adjustment Screw: Used to adjust the spring tension of the steering wheel to best suit the feel of the user.
Step Auxiliary: Allows you to program the Auxiliary 1 servo or Auxiliary 2 servo to move a defined amount when toggled ON
and OFF using a Push-Button Switch.
REFERENCE
MT-4S User's Guide.indd 75 2015/10/27 14:39:20
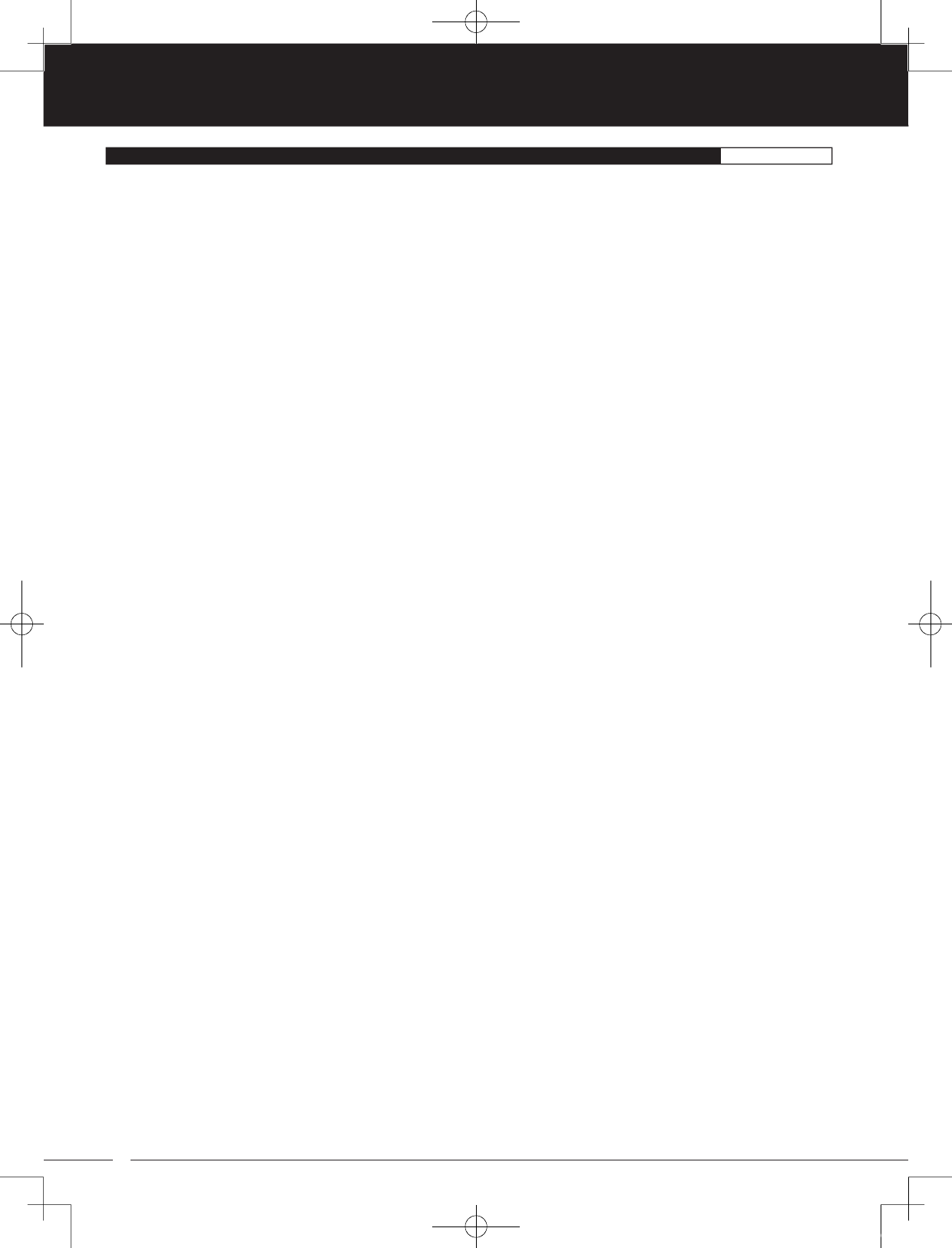
76
90478 2.4GHZ FH4T RADIO SYSTEM USER'S GUIDE
TR
TR
TR
Step Value: A preset amount that the servo will travel when a Trim Switch is pressed once. The step value can be adjusted so
that the servo either moves more or moves less when the Trim Switch is pressed.
Stroke: Determines the amount of Brake that's applied automatically when the Anti-Lock Braking function Activates.
Sub-Trim: Used to correct the Neutral Trim setting for the servos, making it possible to center the Trim switches while ensuring
the servo horns remain centered.
Suppression Capacitor: Primarily used on brushed electric motors, a suppression capacitor helps eliminate electrical noise
that could interfere with the operation of your radio control system.
Tandem Steering: Used with Four Wheel Steering, the front wheels pivot opposite to the rear wheels.
Telemetry: A connection between the receiver and the transmitter that transfers Sensor data from the receiver to the transmitter
that can be viewed in real-time on the Telemetry Screen. Data such as Temperature, Receiver Voltage and RPM or Speed can
be viewed.
Telemetry Signal Indicator: Indicates the current signal strength of the Telemetry connection between the transmitter and
receiver. The Telemetry Signal Indicator will only be displayed when the receiver is turned ON and there is a Telemetry
connection Active.
Temperature Alert Alarm: The Temperature Alert alarm will sound when the TEMP1 and/or TEMP2 temperature reaches the
Alert Temperature value programmed in the SYSTEM - TELEMETRY menu. To clear this alarm, press the BACK/CANCEL key or
the Push-Button Rotary Dial.
Temperature Display Monitor: Displays the current TEMP1 and TEMP2 temperatures in bar graph format on the Telemetry Screen.
Throttle Mode Indicator: Indicates the current Throttle Mode type on the Top Screen.
Throttle Offset: Allows you to shift the Neutral position of the throttle servo, either toward the High Side or the Brake Side. When
used in conjunction with a Push-Button Switch, this function can be used several different ways. For example, if you're driving
a glow- or gas-powered model, you can program the Throttle Offset function to shut down your engine with the press of a
button. In addition, you can program the Throttle Offset function to increase to a steady idle while you're refueling during a race.
Throttle Offset Indicator: Indicates that the Throttle Offset function is programmed. The Throttle Offset Indicator will only be
displayed if a Throttle Offset percentage value is programmed.
Throttle Program Indicator: Indicates on the LCD Screen up to four different programming options that are currently
programmed to the Throttle channel. The Throttle Program Indicator will only be displayed if a Throttle channel Programming
Value is programmed.
Throttle Trigger: Controls the speed of the model, both forward and backward, or the model's brake. The Throttle Trigger
position, angle and spring tension can all be adjusted.
Throttle Trigger Position Adjustment Indicator: Indicates the current position of the Throttle Trigger. As the throttle trigger
position is adjusted forward or backward, the Throttle Trigger Position Adjustment Indicator will move forward or backward.
Throttle Trigger Position Adjustment Screw: Used to adjust the position of the Throttle Trigger either forward or backward.
Throttle Trigger Tension Adjustment Screw: Used to adjust the spring tension of the throttle trigger to best suit the feel of
the user. Turning the Throttle Trigger Tension Adjustment Screw clockwise increases throttle trigger tension and turning the
Throttle Trigger Tension Adjustment Screw counter-clockwise decreases throttle trigger tension.
Throttle Trim Display: Displays the current position of the Throttle Trim Switch on the Top Screen.
Timer Display: Displays the time of the currently selected Timer on the Top Screen.
Timer Type Indicator: Indicates the current Timer Type selected, either LAP or INT (Interval) on the Top Screen.
Trim Step Resolution: Used to adjust how far the servos travel when the Trim Switches are pressed. You can increase the
resolution, so that the servos travel less when you press the Trim Switches. This makes it possible to fine-tune the settings
extremely accurately. In addition, you could decrease the resolution, so that the servos travel more when you press the Trim
Switches. This setting may not be as accurate, although you can set large amounts of Trim faster.
Trim Switch: The transmitter features four separate Trim Switches positioned around the steering wheel (Trm1, Trm2, Trm3
and Trm4). Each Trim Switch is programmable and will perform a different function depending on what function is assigned
to it. For example, Trm1 and Trm2 can be used to adjust steering and throttle Trim and Trm4 and Trm5 can be used to adjust
Dual Rate and steering EPA.
Variable Rate Adjustment: The Variable Rate Adjustment function allows you to recalibrate the operation of the Steering,
Throttle and Auxiliary Lever End Points and Neutral positions to ensure precise control operation.
Voltage Alert Alarm: The Voltage Alert alarm will sound when the receiver battery in your model reaches the Alert Voltage value
you've programmed in the SYSTEM - TELEMETRY menu. To clear this alarm, press the BACK/CANCEL key or the Push-Button
Rotary Dial.
GLOSSARY OF TERMS REFERENCE
MT-4S User's Guide.indd 76 2015/10/27 14:39:20
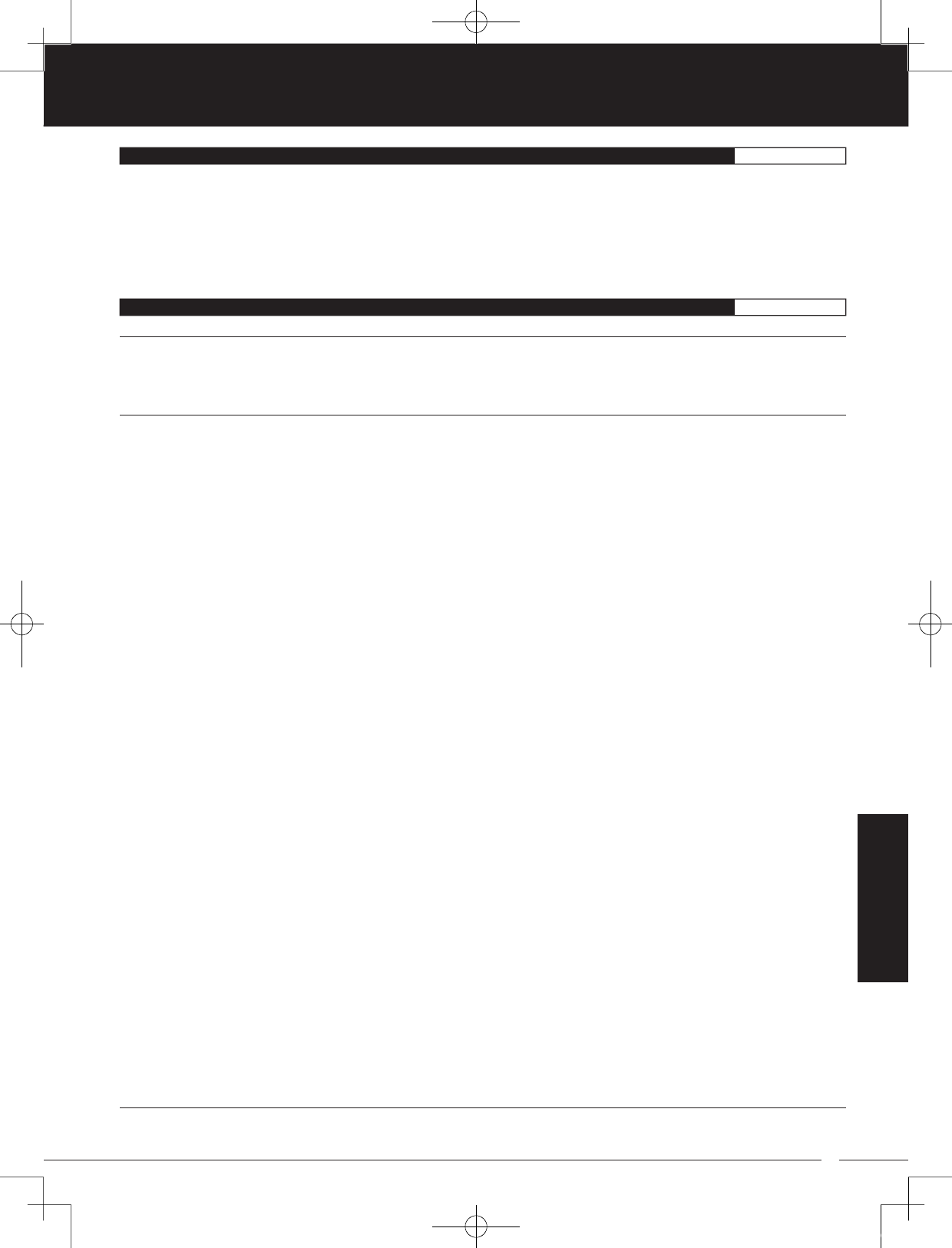
77
TR
TR
TR
90478 2.4GHZ FH4T RADIO SYSTEM USER'S GUIDE
REFERENCE
GLOSSARY OF TERMS REFERENCE
Voltage Alert Indicator: Indicates the currently programmed Voltage value on the Telemetry Screen that the receiver Voltage
Alert alarm will sound at.
Voltage Display Monitor: Displays the current receiver battery voltage on the Telemetry Screen in bar graph format.
Wrist Strap Anchor Slot: Used to attach the wrist strap anchor to the transmitter.
Z-Connector: The type of servo and battery connector used by Airtronics. The Z-Connector is a universal connector which is
electronically compatible with the airborne components of other radio control system manufacturers.
INDEX REFERENCE
Symbols
2.4GHz Frequency Band Precautions 4
2CH Mode, Changing 52
4CH Mode, Changing 52
A
Activate, Definition of 72
Alarms. See Over Voltage Alarm
See Inactivity (Power ON) Alarm
See Low Voltage Alert Alarm
See Low Voltage Limit Alarm
See Temperature Alert Alarm
See Voltage Alert Alarm
Antenna - Receiver, Orientation of 8
Antenna Reception Wire - Receiver, Definition of 9, 75
Antenna Reception Wire - Receiver, Diagram of 8
Antenna - Transmitter, Definition of 8, 72
Antenna - Transmitter, Diagram of 6, 7
Antenna - Transmitter, Orientation of 6
Anti-Lock Braking, Adjusting the Lag Value 26
Anti-Lock Braking, Adjusting the Point Percentage Value 25
Anti-Lock Braking, Adjusting the Release and Hold Values 25
Anti-Lock Braking, Adjusting the Stroke Percentage Value 24
Anti-Lock Braking, Controlling 26
Anti-Lock Braking, Definition of 72
Anti-Lock Braking, Overview 24
ARC (Adjustable Rate Control). See Exponential and ARC Adjustment, Overview
ARC (Adjustable Rate Control), Definition of 72
Audible Key Tone, Overview 61
Audible Key Tone, Changing the Audible Key Tone Volume 61
Audible Key Tone, Changing the Tone 61
Audible Key Tone, Definition of 72
Auxiliary 1 Programming, Function Chart 27
Auxiliary 2 Programming, Function Chart 34
Auxiliary Lever, Definition of 9, 72
Auxiliary Lever, Diagram of 6
Auxiliary Lever Key Assignments, Changing the Auxiliary Lever Function 59
Auxiliary Lever Key Assignments, Changing the High and Low Tweak Values 58
Auxiliary Lever Key Assignments, Overview and Function Table 55, 56
Auxiliary Lever Position Display, Definition of 14, 72
Auxiliary Lever Position Display, Diagram of 14
Auxiliary Mixing, Adjusting the Rate Percentage Value 32, 39
Auxiliary Mixing, Choosing the Auxiliary Mixing Function and the Mixing Type 31, 38
Auxiliary Mixing, Controlling 32, 39
Auxiliary Mixing, Definition of 72
Auxiliary Mixing, Overview 31, 38
Auxiliary Type, Changing the Auxiliary Function 59
Auxiliary Type, Overview 59
B
BACK/CANCEL Key. See also Programming Keys
BACK/CANCEL Key, Diagram of 7
MT-4S User's Guide.indd 77 2015/10/27 14:39:20
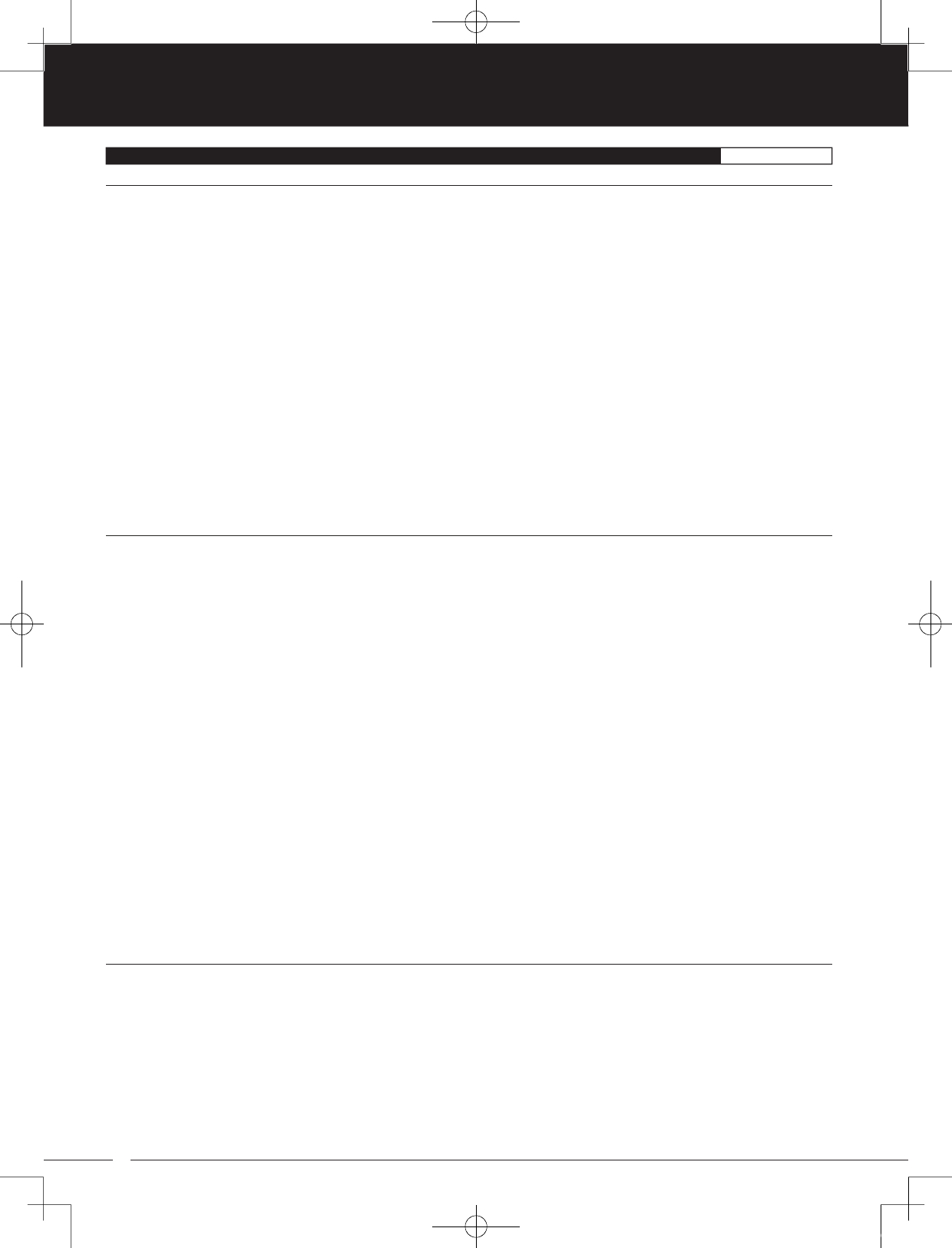
78
90478 2.4GHZ FH4T RADIO SYSTEM USER'S GUIDE
TR
TR
TR
INDEX REFERENCE
B
Battery Compartment, Definition of 9, 73
Battery Compartment, Diagram of 6
Battery Installation. See Transmitter, Battery Installation
Battery Options, Transmitter 5, 11
Battery Plug - Transmitter, Diagram of 11
Battery - Receiver, Installation 8
Bind Button, Definition of 9, 73
Bind Button, Diagram of 8
Binding. See also Transmitter and Receiver Binding
Binding, Changing the Channel Mode (FH2 Modulation Only) 52
Binding, Changing the Modulation Type 52
Binding, Changing the Servo Operating Mode Setting 52
Binding, Definition of 73
Binding, Overview 52
Bind LED. See also Receiver Bind LED Condition Indicator
Bind LED, Definition of 9, 73
Bind LED, Diagram of 8
Brake Side, Definition of 73
Burn. See Motor on Axle Mixing, Changing Motor on Axle Power Distribution Options
Burn, Definition of 73
C
Center Trim. See Trim Type
Center Trim Type, Definition of 73
Channel Mode, Changing the Channel Mode (FH2 Modulation Type Only) 52
Channel Set Menu, Functions List 18
Channel Set Menu, Using 17
Channel Slots. See Receiver Channel Ports
Charging. See Transmitter Battery Charging, Options
Charging Jack, Definition of 9, 73
Charging Jack, Diagram of 7
Coaxial Cable - Receiver, Definition of 9, 73
Coaxial Cable - Receiver, Diagram of 8
Code Auxiliary, Changing the Code Auxiliary Values 33, 40
Code Auxiliary, Changing Code Programming Names 33, 40
Code Auxiliary, Choosing the Code Auxiliary Function 32, 39
Code Auxiliary, Controlling the Code Auxiliary Function 33, 40
Code Auxiliary, Definition of 73
Code Auxiliary, Overview 32, 39
Contrast. See LCD, Changing the Contrast Value
Countdown Timer, Definition of 73
Countdown Timer, Overview 45
Countdown Timer, Setting the Alarm 45
Countdown Timer, Starting the Countdown Timer 45
Countdown Timer, Stopping the Countdown Timer 45
Crab Steering. See Parallel Steering
Curve. See Exponential and ARC Adjustment
D
Dial Knob, Definition of 9, 73
Dial Knob, Diagram of 6, 7
Dig. See Motor on Axle Mixing, Changing Motor on Axle Power Distribution Options
Dig, Definition of 73
Digital RPM Display, Definition of 73
Digital RPM Display, Diagram of 14
Digital Temperature Display, Definition of 73
Digital Temperature Display, Diagram of 14
Digital Temperature Display, Definition of 73
Digital Voltage Indicator, Diagram of 14
Dual Rate, Adjusting the Brake Dual Rate Percentage Value 19
MT-4S User's Guide.indd 78 2015/10/27 14:39:20
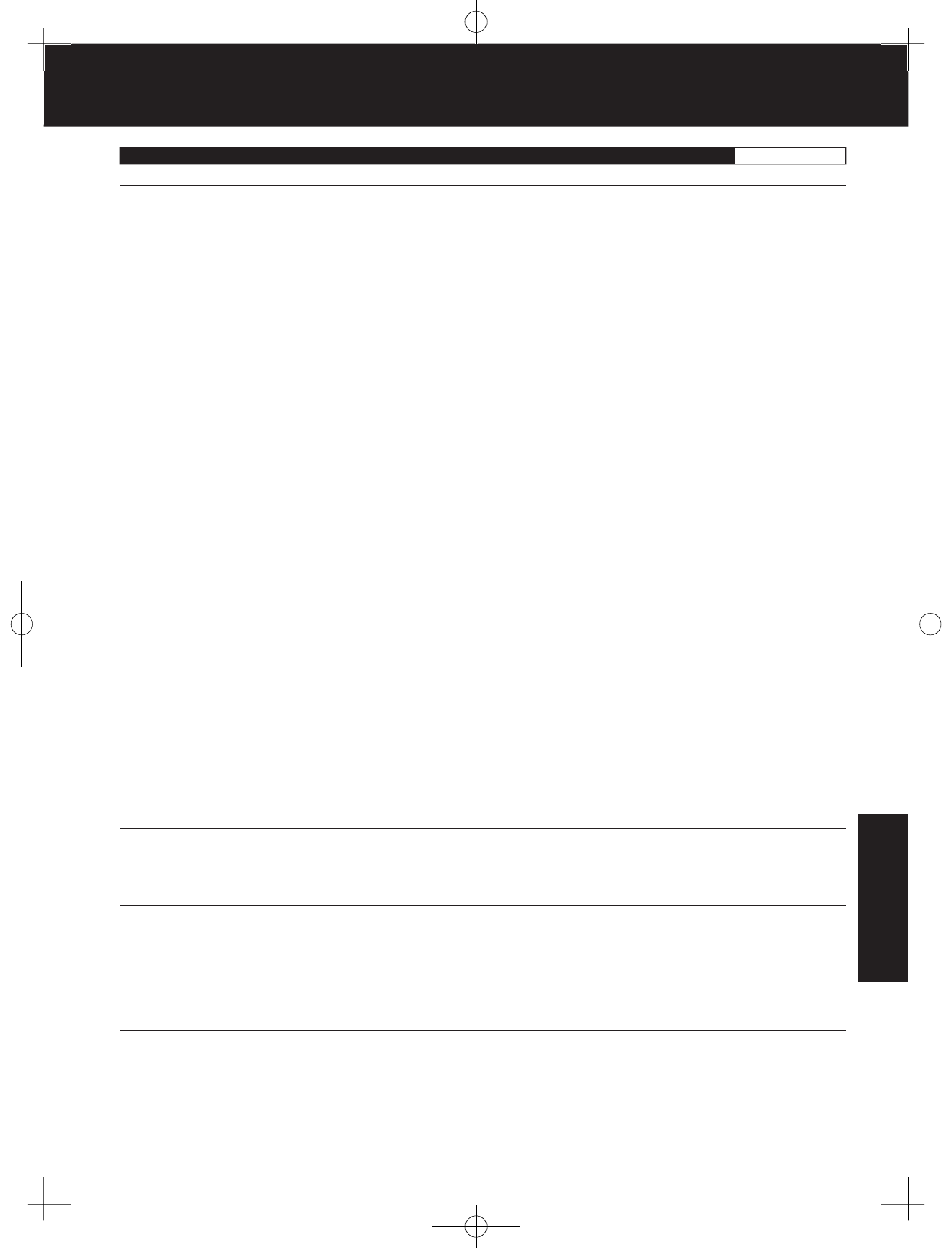
79
TR
TR
TR
90478 2.4GHZ FH4T RADIO SYSTEM USER'S GUIDE
INDEX REFERENCE
D
Dual Rate, Adjusting the Dual Rate Steering Percentage Value 19
Dual Rate, Adjusting the Throttle Dual Rate Percentage Value 19
Dual Rate, Controlling 19
Dual Rate, Overview 18
E
End Point Adjustment, Adjusting the Auxiliary 1 Channel 3 and Auxiliary 2 Channel 4 End Point Adjustment Percentage Values 21
End Point Adjustment, Adjusting the Steering End Point Adjustment Percentage Values 20
End Point Adjustment, Adjusting the Throttle End Point Adjustment Percentage Values 20
End Point Adjustment, Definition of 73
End Point Adjustment, Overview 19
Enter Key. See Programming Keys
Exponential and ARC Adjustment, Adjusting the Point Percentage Value (ARC Only) 22
Exponential and ARC Adjustment, Adjusting the Rate Percentage Value 22
Exponential and ARC Adjustment, Choosing a Channel 22
Exponential and ARC Adjustment, Choosing the Curve Type 22
Exponential and ARC Adjustment, Controlling 22
Exponential and ARC Adjustment, Overview 23
Exponential, Definition of 73
F
Fail Safe, Definition of 73
Fail Safe Limit, Receiver Specification 5
Fail Safe, Overview 46
Fail Safe, Receiver Battery Voltage Fail Safe Function. See Setting the Receiver Battery Voltage Fail Safe Function
Fail Safe, Setting the Fail Safe 46
Fail Safe, Setting the Receiver Battery Voltage Fail Safe Function 47
FCC Compliance Statement 3
Features. See System Features
FH2 Modulation, Definition of 73
FH3 Modulation, Definition of 74
FH4T Modulation, Definition of 74
FHSS, Definition of 74
Four Wheel Steering Mixing, Choosing Four Wheel Steering Mixing Options 29, 36
Four Wheel Steering Mixing, Choosing the Four Wheel Steering Function 29, 36
Four Wheel Steering Mixing, Controlling 30, 38
Four Wheel Steering Mixing, Definition of 74
Four Wheel Steering Mixing, Overview 29, 36
Front Wheel Steering. See Four Wheel Steering Mixing, Choosing Four Wheel Steering Mixing Options
G
Grip, Changing 12
Grip, Definition of 9, 74
Grip, Diagram of 6, 7
H
High RPM Display, Definition of 14, 74
High RPM Display, Diagram of 14
High Side, Definition of 74
High Temperature Display, Definition of 14, 75
High Temperature Display, Diagram of 14
Hold Setting, Definition of 74
I
Inactivity Alarm (Power ON Alarm), Definition of 74
Inactivity (Power ON) Alarm, Overview 10
Inhibit, Definition of 74
Input Voltage. See Nominal Input Voltage, Receiver Specification
See Nominal Input Voltage, Transmitter Specification
Interval Timer, Definition of 74
Interval Timer, Overview 44
REFERENCE
MT-4S User's Guide.indd 79 2015/10/27 14:39:21
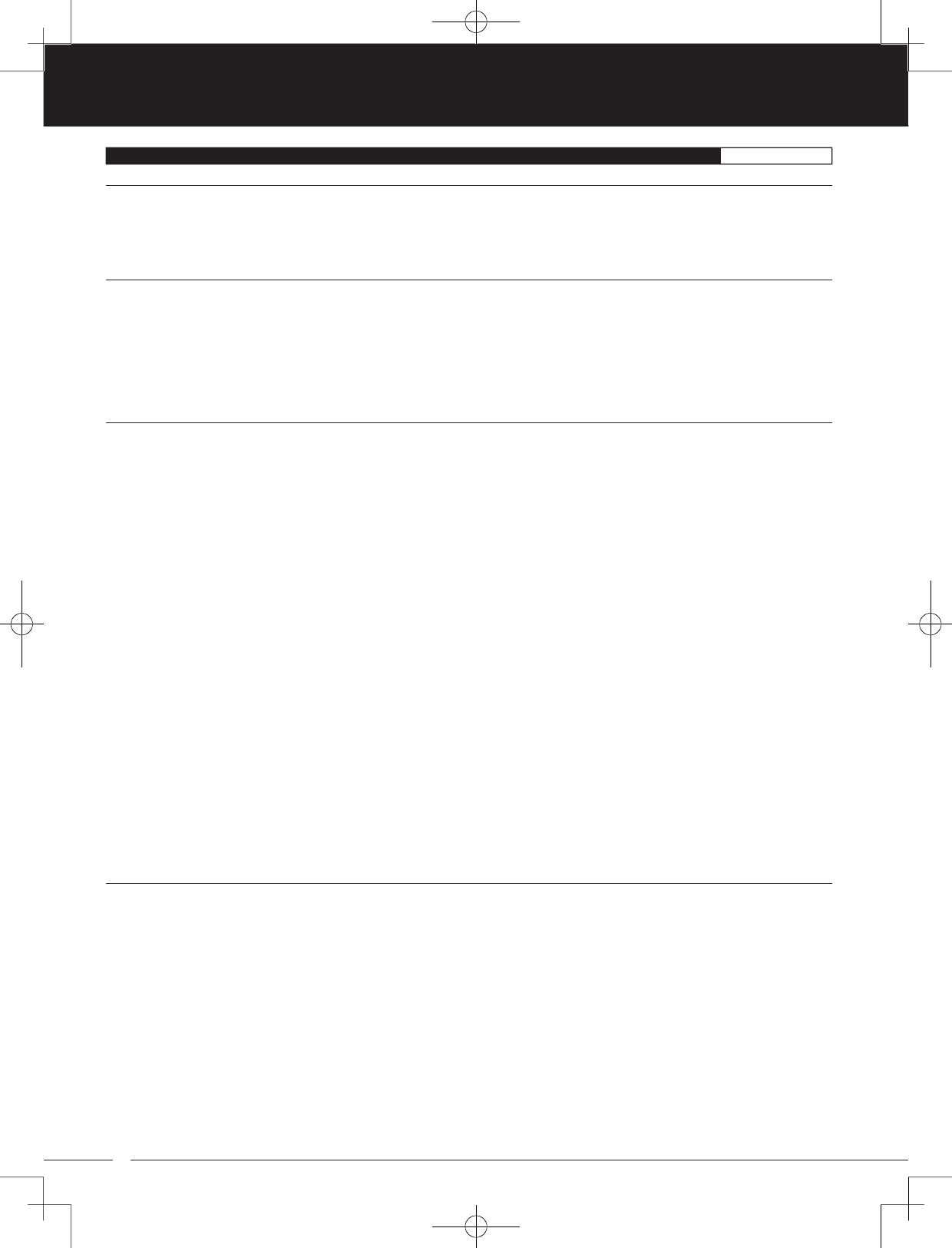
80
90478 2.4GHZ FH4T RADIO SYSTEM USER'S GUIDE
TR
TR
TR
I
Interval Timer, Setting the Alarm (Goal Time) 44
Interval Timer, Setting the Interval Timer (Target Time) 44
Interval Timer, Starting the Interval Timer 45
Interval Timer, Stopping the Interval Timer 45
K
Key Assignments. See Push-Button Switch Key Assignments
See Auxiliary Lever Key Assignments
See Rotary Dial Key Assignments
See Trim Switch Key Assignments
Key Assignments, Diagram of Default Key Assignments 53
Key Tone. See Audible Key Tone
KM/H, Acronym 74
L
Lag, Definition of 74
Lap Timer, Definition of 74
Lap Timer, Overview 43
Lap Timer, Setting the Alarm (Goal Time) 43
Lap Timer, Setting the Interval Timer (Target Time) 43
Lap Timer, Starting the Lap Timer 44
Lap Timer, Stopping the Lap Timer 44
Lap Times, Viewing Lap Times 46
LCD Screen, Changing the Contrast Value 62
LCD Screen, Changing Backlight Mode 63
LCD Screen, Changing the Backlight On-Time 63
LCD Screen, Definition of 9, 74
LCD Screen, Diagram of 7
LED 1/2 Condition Indicators, Overview 10
LED 1/2, Definition of 9, 74
LED 1/2, Diagram of 7
LiPo, LiFe Batteries, Using with Receiver 8
LiPo, LiFe Batteries, Using with Transmitter 11
LiPo, LiFe Batteries, Warnings When Using 11
Low Voltage Alert Alarm, Changing the Low Voltage Alert Alarm Value 61
Low Voltage Alert Alarm, Definition of 74
Low Voltage Alert Alarm, Overview 10
Low Voltage Alert Alarm, Voltage Recommendations Table 61
Low Voltage Limit Alarm, Changing the Low Voltage Limit Alarm Value 62
Low Voltage Limit Alarm, Definition of 74
Low Voltage Limit Alarm, Overview 10
Low Voltage Limit Alarm, Voltage Recommendation Table 61
M
Model Clear, Clearing Model Programming Data 51
Model Clear, Overview 51
Model Copy, Copying Model Programming Data 51
Model Copy, Overview 51
Model Name, Changing the Model Name 50
Model Name, Deleting a Character or an Entire Model Name 50
Model Name, Overview 50
Model Number and Name, Definition of 14, 74
Model Number and Name, Diagram of 14
Model Select, Definition of 74
Model Select, Overview 49
Model Select, Selecting a Model 49
Model Select, Using the Model Select Shortcut Function (Direct Model) 50
Modulation Type, Changing the Modulation Type 52
Modulation Type Indicator, Definition of 14, 74
Modulation Type Indicator, Diagram of 14
INDEX REFERENCE
MT-4S User's Guide.indd 80 2015/10/27 14:39:21
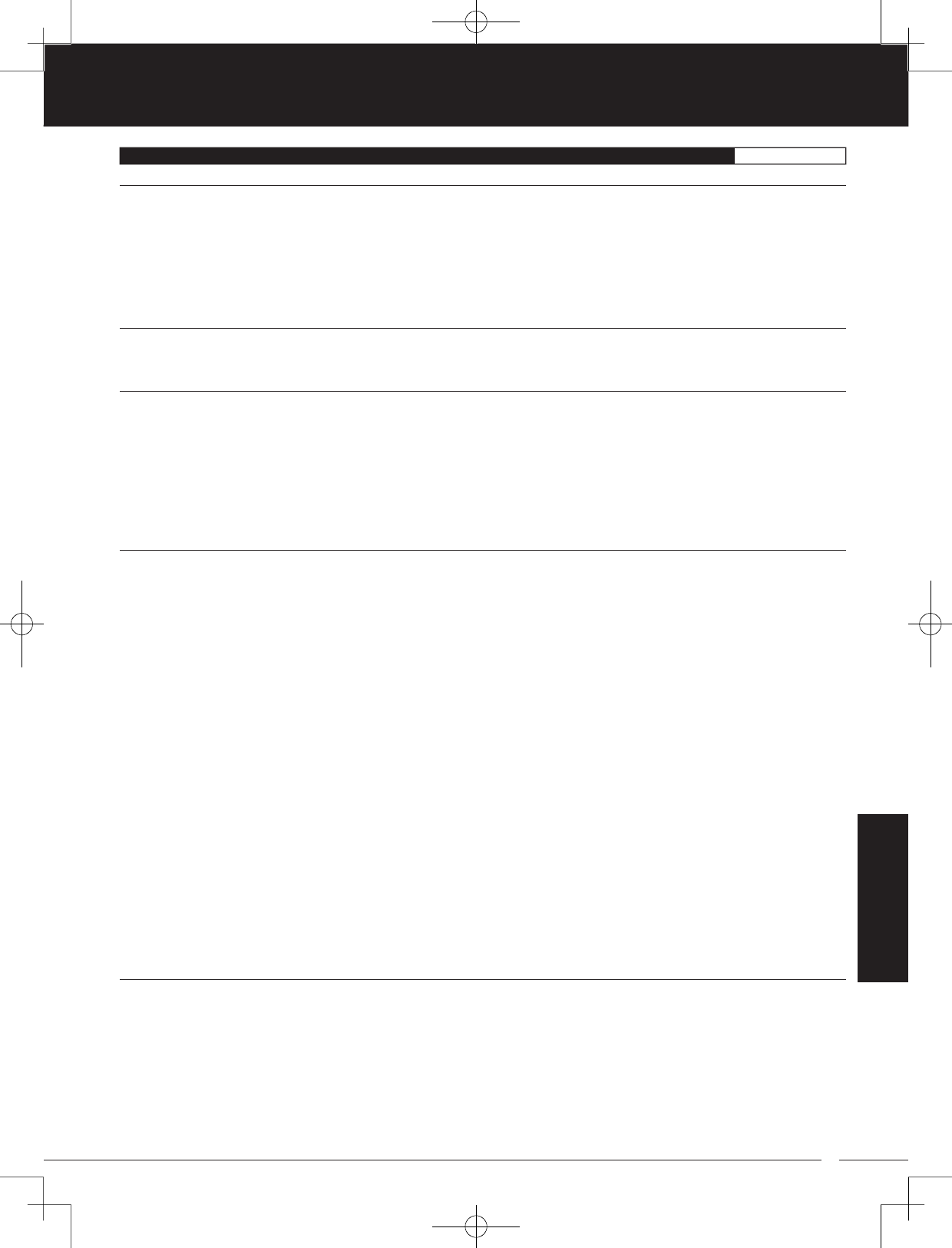
81
TR
TR
TR
90478 2.4GHZ FH4T RADIO SYSTEM USER'S GUIDE
REFERENCE
INDEX REFERENCE
M
Modulation Type, Overview 52
Motor on Axle Mixing, Changing Motor on Axle Power Distribution Options 30, 37
Motor on Axle Mixing, Choosing the Motor on Axle Mixing Function 30, 37
Motor on Axle Mixing, Controlling 31, 38
Motor on Axle Mixing, Definition of 75
Motor on Axle Mixing, Overview 30, 37
MPH, Acronym 75
N
Nominal Input Voltage, Receiver Specification 5
Nominal Input Voltage, Transmitter Specification 5
O
Offset. See Throttle Offset, Overview
Operating Voltage, Definition of 75
Operating Voltage Range, Receiver Specification 5
Operating Voltage Range, Transmitter Specification 5
Output Power, Definition of 75
Output Power, Transmitter Specification 5
Over Voltage Alarm, Definition of 75
Over Voltage Alarm, Overview 10
P
Packaging 2
Parallel Steering. See Four Wheel Steering Mixing, Choosing Four Wheel Steering Mixing Options
Parallel Steering, Definition of 75
Parallel Trim. See Trim Type
Parallel Trim, Definition of 75
Point Auxiliary, Adjusting the Point Auxiliary Values 28, 35
Point Auxiliary, Choosing the Point Auxiliary Function and the Number of Points 28, 35
Point Auxiliary, Controlling 28, 35
Point Auxiliary, Definition of 75
Point Auxiliary, Overview 28, 35
Point Setting, Definition of 75
Power Switch, Definition of 9, 75
Power Switch, Diagram of 6, 7
Precautions, Receiver 4. See also Receiver Precautions
Precautions, Transmitter 4. See also Transmitter Precautions
Programming Keys, Overview and Functions 15
Programming Menus, Overview with Programming Menus Table 17
Push-Button Rotary Dial. See also Programming Keys, Overview
Push-Button Rotary Dial, Definition of 9, 75
Push-Button Rotary Dial, Diagram of 7
Push-Button Switch, Definition of 9, 75
Push-Button Switches, Diagram of 6
Push-Button Switch Key Assignments, Changing the Push-Button Switch Function 54
Push-Button Switch Key Assignments, Changing the Switch Mode 55
Push-Button Switch Key Assignments, Overview and Function Table 54
R
Rear Wheel Steering. See Four Wheel Steering Mixing, Choosing Four Wheel Steering Mixing Options
Receiver Antenna Wire Routing Diagram 8
Receiver Battery Voltage Fail Safe, Definition of 75
Receiver Battery Voltage Fail Safe Function. See Fail Safe, Setting the Receiver Battery Voltage Fail Safe Function
Receiver Bind LED Condition Indicator Table 8
Receiver Channel Ports, Diagram of 8
Receiver Connections and Mounting 8
Receiver Features Diagram 8
Receiver Input Voltage Specification 5
Receiver Precautions 4
MT-4S User's Guide.indd 81 2015/10/27 14:39:21
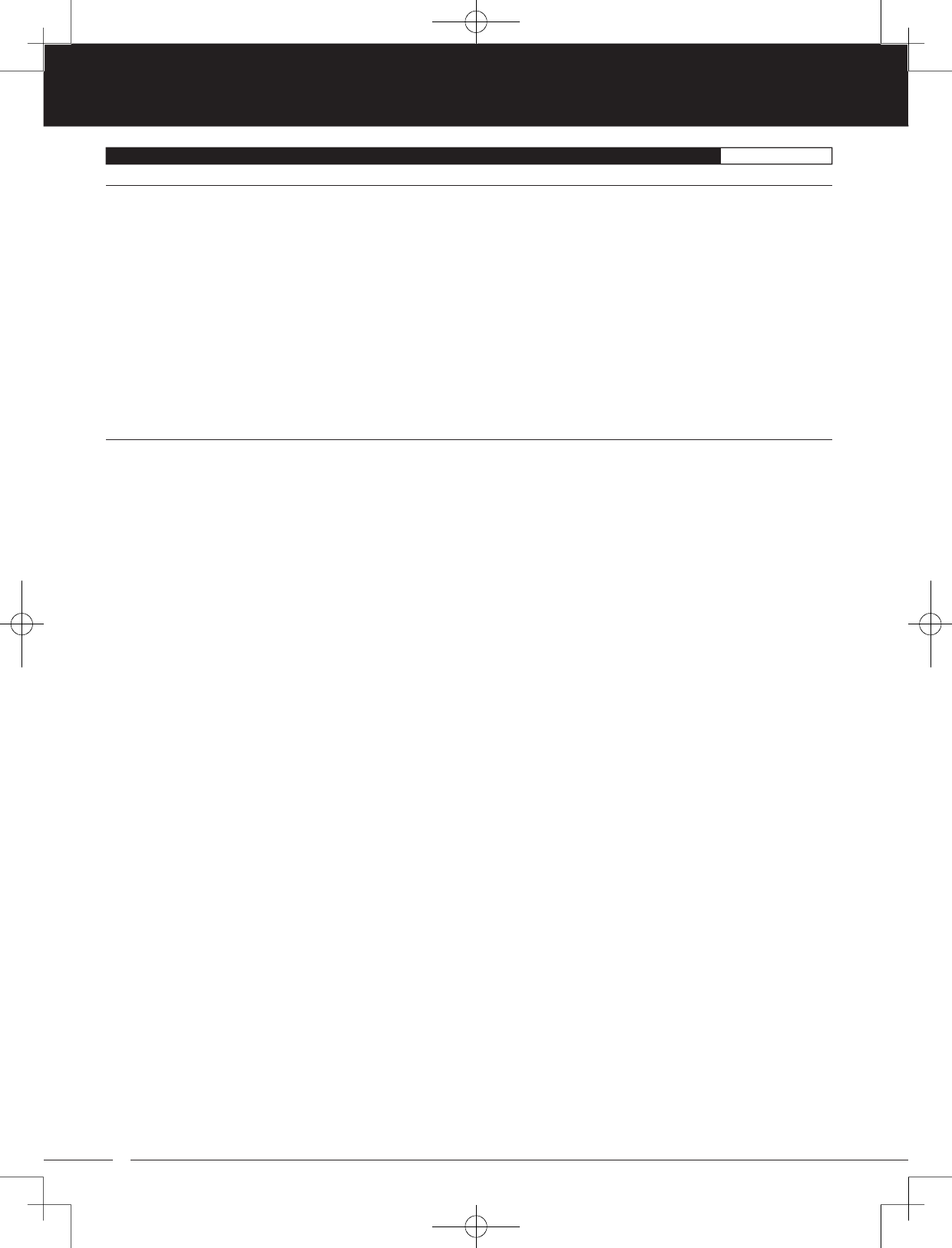
82
90478 2.4GHZ FH4T RADIO SYSTEM USER'S GUIDE
TR
TR
TR
INDEX REFERENCE
R
Receiver Specifications 5
Receiver, Using 7.4 Volt Servos 8
Receiver Voltage Display, Definition of 15, 75
Receiver Voltage Display, Diagram of 14
Release, Definition of 75
RF Exposure Statement 3
Rotary Dial Key Assignments, Changing the Rotary Dial Direction of Travel 57
Rotary Dial Key Assignments, Changing the Rotary Dial Function 57
Rotary Dial Key Assignments, Changing the Rotary Dial Step Value 57
Rotary Dial Key Assignments, Overview and Function Table 55
RPM, Acronym 75
RPM Display Monitor, Definition of 15, 75
RPM Display Monitor, Diagram of 14
RPM Sensor, Calibrating the RPM Sensor 67
S
Safety 3
Servo Connectors, Overview 9
Servo Operating Mode, Changing the Servo Operating Mode Setting 52
Servo Operating Mode, Overview 52
Servo Monitor Display, Definition of 15, 75
Servo Monitor Display, Diagram of 14
Servo Recommendations 5
Servo Reversing, Changing the Servo Reversing Values 42
Servo Reversing, Definition of 75
Servo Reversing, Overview 42
Servo Speed, Adjusting the Forward Speed Value 23
Servo Speed, Adjusting the Return to Neutral Speed Value 24
Servo Speed, Controlling 24
Servo Speed, Definition of 75
Servo Speed, Overview 23
Servo Sub-Trim. See Trim and Servo Sub-Trim, Overview
Servo Sub-Trim, Definition of 75
Servos, Using 7.4 Volt. See Receiver, Using 7.4 Volt Servos
Servos, Using Analog, SHR or SRG Digital. See Changing the Servo Operating Mode Setting
SHR Servo Operating Mode. See Servo Operating Mode, Changing the Servo Operating Mode Setting
SHR Servo Operating Mode, Definition of 75
Specifications, Transmitter and Receiver 5
SSR Servo Operating Mode. See Servo Operating Mode, Changing the Servo Operating Mode Setting
SSR Servo Operating Mode, Definition of 75
Steering Mixing. See Auxiliary Mixing, Overview
Steering Program Indicator, Definition of 15, 75
Steering Program Indicator, Diagram of 14
Steering Trim Display, Definition of 15, 75
Steering Trim Display, Diagram of 14
Steering Wheel, Definition of 9, 75
Steering Wheel, Diagram of 6
Steering Wheel Spring Tension, Changing 13
Steering Wheel Tension Adjustment Screw, Definition of 9, 75
Steering Wheel Tension Adjustment Screw, Diagram of 6
Steering Wheel Travel, Changing 13
Step Auxiliary, Adjusting the Step Auxiliary Value 27
Step Auxiliary, Choosing the Step Auxiliary Function 27
Step Auxiliary, Controlling 27
Step Auxiliary, Definition of 75
Step Auxiliary, Overview 27
Step Value, Definition of 76
Stroke, Definition of 76
Sub-Trim. See Trim and Servo Sub-Trim, Overview
Suppression Capacitor. See Receiver Precautions
MT-4S User's Guide.indd 82 2015/10/27 14:39:21
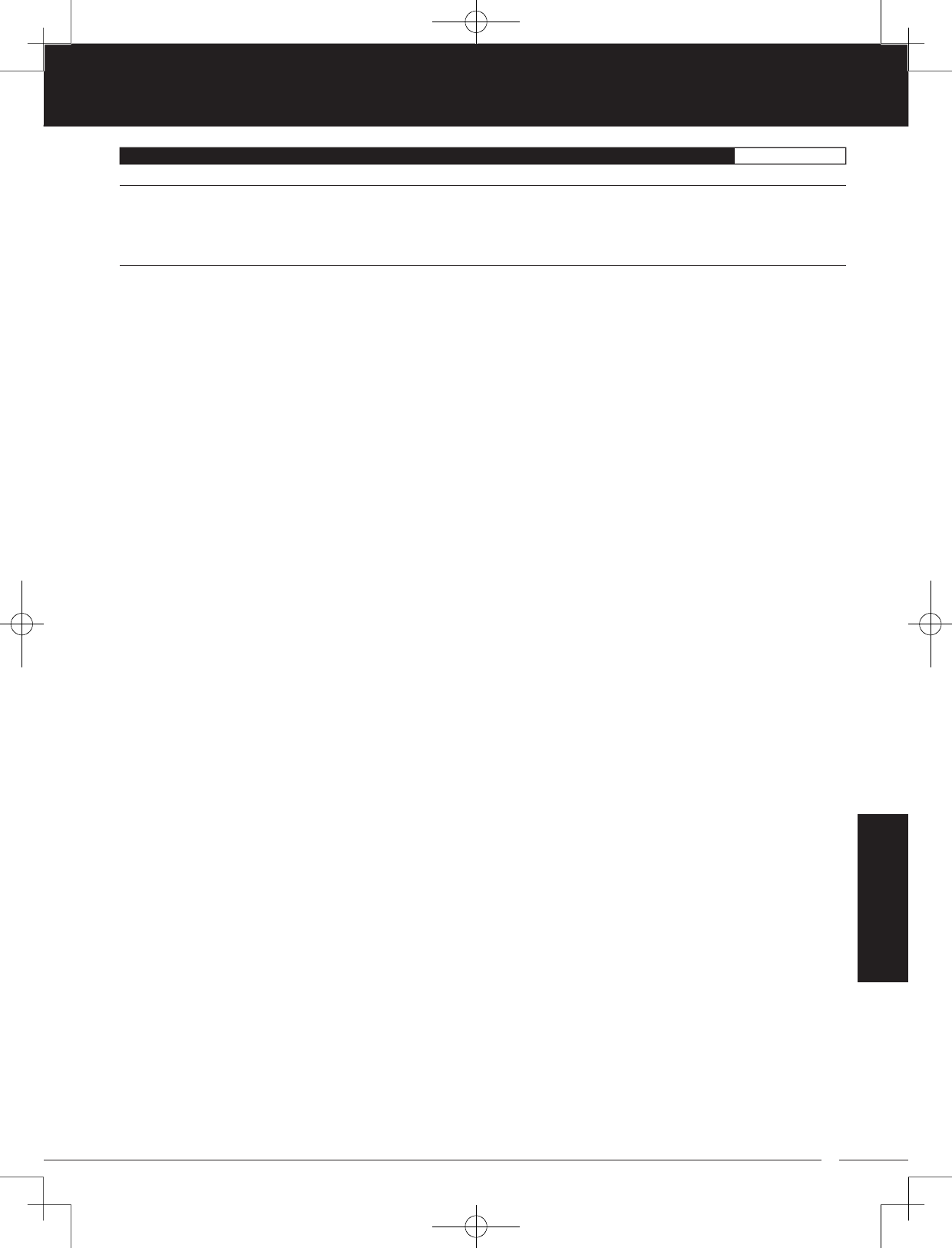
83
TR
TR
TR
90478 2.4GHZ FH4T RADIO SYSTEM USER'S GUIDE
REFERENCE
INDEX REFERENCE
S
Suppression Capacitor, Definition of 76
System Features 5
System Menus, Overview with System Menus Table 49
T
Tandem Steering. See Four Wheel Steering Mixing, Choosing Four Wheel Steering Mixing Options
Tandem Steering, Definition of 76
Telemetry, Calibrating the RPM Sensor 67
Telemetry Clear Function, Overview and Using 68
Telemetry Data. See Telemetry Log, Viewing Telemetry Data
Telemetry, Definition of 76
Telemetry Log, Changing the Telemetry Log Step Value 68
Telemetry Log, Overview 47
Telemetry Log, Starting and Stopping the Telemetry Log 48
Telemetry Log, Viewing Telemetry Data 48
Telemetry, Mounting the RPM Sensor 70
Telemetry, Mounting the Temperature Sensor 70
Telemetry, Overview 63
Telemetry RPM Display, Changing the Maximum RPM/Speed Value 66
Telemetry RPM Display, Changing the RPM Unit Value 66
Telemetry RPM Sensor, Diagram of 70
Telemetry Screen, Overview 14
Telemetry Sensors, Connecting to Receiver 69
Telemetry Sensors, Overview 69
Telemetry Signal Indicator, Definition of 15, 76
Telemetry Signal Indicator, Diagram of 14
Telemetry Temperature Display, Changing the Alert Temperature Value 64
Telemetry Temperature Display, Changing the Maximum Temperature Value 64
Telemetry Temperature Display, Changing the Minimum Temperature Value 65
Telemetry Temperature Display, Changing the Temperature Unit Value 64
Telemetry Temperature Sensor, Diagram of 70
Telemetry, Turning ON and OFF 67
Telemetry Voltage Display, Changing the Alert Voltage Value 66
Telemetry Voltage Display, Changing the Maximum Voltage Value 65
Temperature Alert Alarm, Definition of 76
Temperature Alert Alarm, Overview 10
Temperature Display Monitor, Definition of 15, 76
Temperature Display Monitor, Diagram of 14
Temperature Sensor, Mounting the Temperature Sensor 70
Throttle Mixing. See Auxiliary Mixing, Overview
Throttle Mode Indicator, Diagram of 14
Throttle Mode Indicator, Definition of 15, 76
Throttle Offset, Adjusting the Throttle Offset Position Percentage Value 26
Throttle Offset, Controlling 26
Throttle Offset, Definition of 76
Throttle Offset Indicator, Definition of 15, 76
Throttle Offset Indicator, Diagram of 14
Throttle Offset, Overview 26
Throttle Offset, Turning the Throttle Offset Function ON or OFF 26
Throttle Program Indicator, Diagram of 14
Throttle Program Indicator, Definition of 15, 76
Throttle Trigger Angle Adjustment, Changing 12
Throttle Trigger, Definition of 9, 76
Throttle Trigger, Diagram of 6
Throttle Trigger Position Adjustment, Changing 12
Throttle Trigger Position Adjustment Indicator, Definition of 9, 76
Throttle Trigger Position Adjustment Indicator, Diagram of 7
Throttle Trigger Position Adjustment Screw, Definition of 9, 76
Throttle Trigger Position Adjustment Screw, Diagram of 6
MT-4S User's Guide.indd 83 2015/10/27 14:39:21
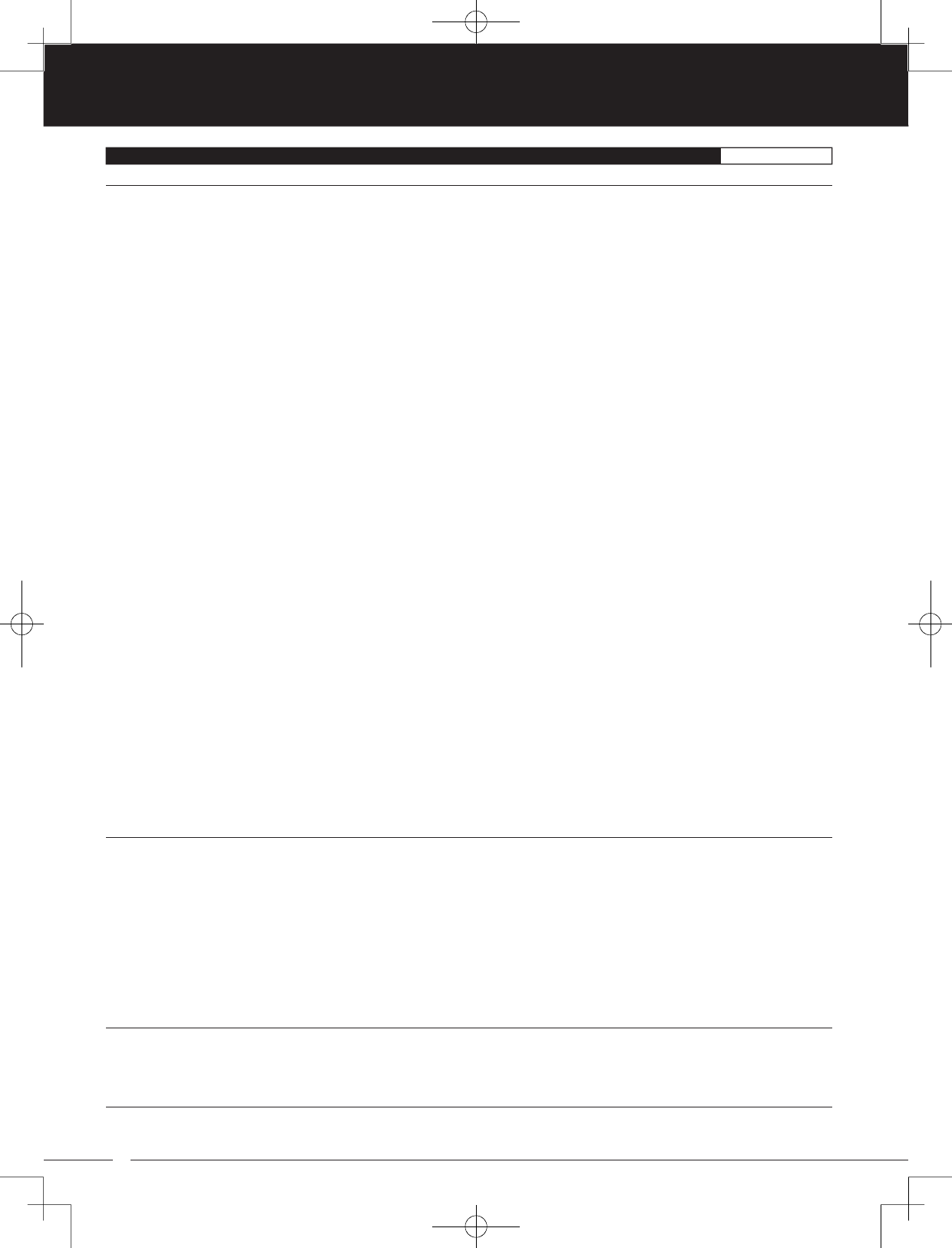
84
90478 2.4GHZ FH4T RADIO SYSTEM USER'S GUIDE
TR
TR
TR
INDEX REFERENCE
T
Throttle Trigger Spring Tension, Changing 13
Throttle Trigger Tension Adjustment Screw, Definition of 9, 76
Throttle Trigger Tension Adjustment Screw, Diagram of 6
Throttle Trim Display, Definition of 15, 76
Throttle Trim Display, Diagram of 14
Throttle Type, Changing the Throttle Type 60
Throttle Type, Overview 60
Timer Display, Diagram of 14
Timer Type Indicator, Definition of 15, 76
Timer Type Indicator, Diagram of 14
Top screen, Overview 14
Track Timers. See Lap Timer, Overview
See Interval Timer, Overview
See Countdown Timer, Overview
Track Timers, Choosing the Timer Type 43
Track Timers, Overview 43
Transmitter and Receiver Binding 16
Transmitter Battery Charging Options 11
Transmitter Battery Holder Connector, Diagram of 11
Transmitter Battery Installation 11
Transmitter Overview Diagrams 6, 7
Transmitter Input Voltage, Specification 5
Transmitter Precautions 4
Transmitter Specifications 5
Transmitter, Battery Options 11
Trim and Servo Sub-Trim, Adjusting the Servo Sub-Trim Values 41
Trim and Servo Sub-Trim, Adjusting the Trim Values 41
Trim and Servo Sub-Trim, Controlling the Trim Function 42
Trim and Servo Sub-Trim, Overview 41
Trim Step Resolution, Definition of 76
Trim Switch, Definition of 9, 76
Trim Switches, Diagram of 6, 7
Trim Switch Key Assignments, Overview with Functions Table 55
Trim Switch Key Assignments, Changing the Trim Switch Direction of Travel 57
Trim Switch Key Assignments, Changing the Trim Switch Function 56
Trim Switch Key Assignments, Changing the Trim Switch Step Value 56
Trim Type, Changing the Trim Type 59
Trim Type, Overview 59
Troubleshooting Guide 71
V
Variable Rate Adjustment, Calibrating Control Operation 68
Variable Rate Adjustment, Definition of 76
Variable Rate Adjustment, Overview 68
Voltage Alert Alarm, Definition of 76
Voltage Alert Alarm, Overview 10
Voltage Alert Indicator, Definition of 15, 77
Voltage Alert Indicator, Diagram of 14
Voltage Display Monitor, Definition of 15, 77
Voltage Display Monitor, Diagram of 14
Voltage Indicator. See also Digital Voltage Indicator
W
Wrist Strap Anchor, Installing 13
Wrist Strap Anchor Slot, Definition of 9, 77
Wrist Strap Anchor Slot, Diagram of 6, 7
Z
Z-Connector. See Servo Connectors, Overview
Z-Connector, Definition of 77
MT-4S User's Guide.indd 84 2015/10/27 14:39:21
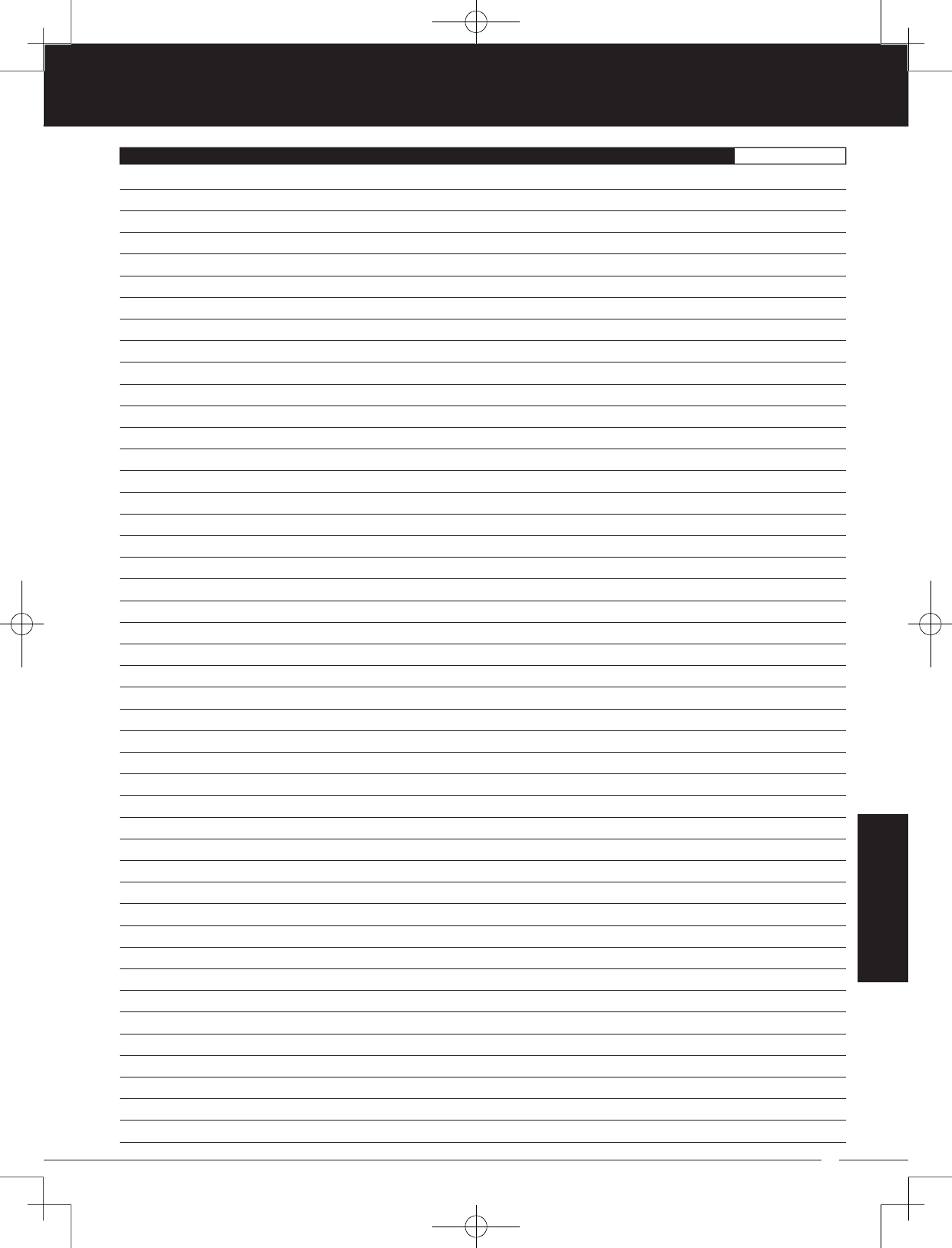
85
TR
TR
TR
90478 2.4GHZ FH4T RADIO SYSTEM USER'S GUIDE
REFERENCE
NOTES REFERENCE
MT-4S User's Guide.indd 85 2015/10/27 14:39:21
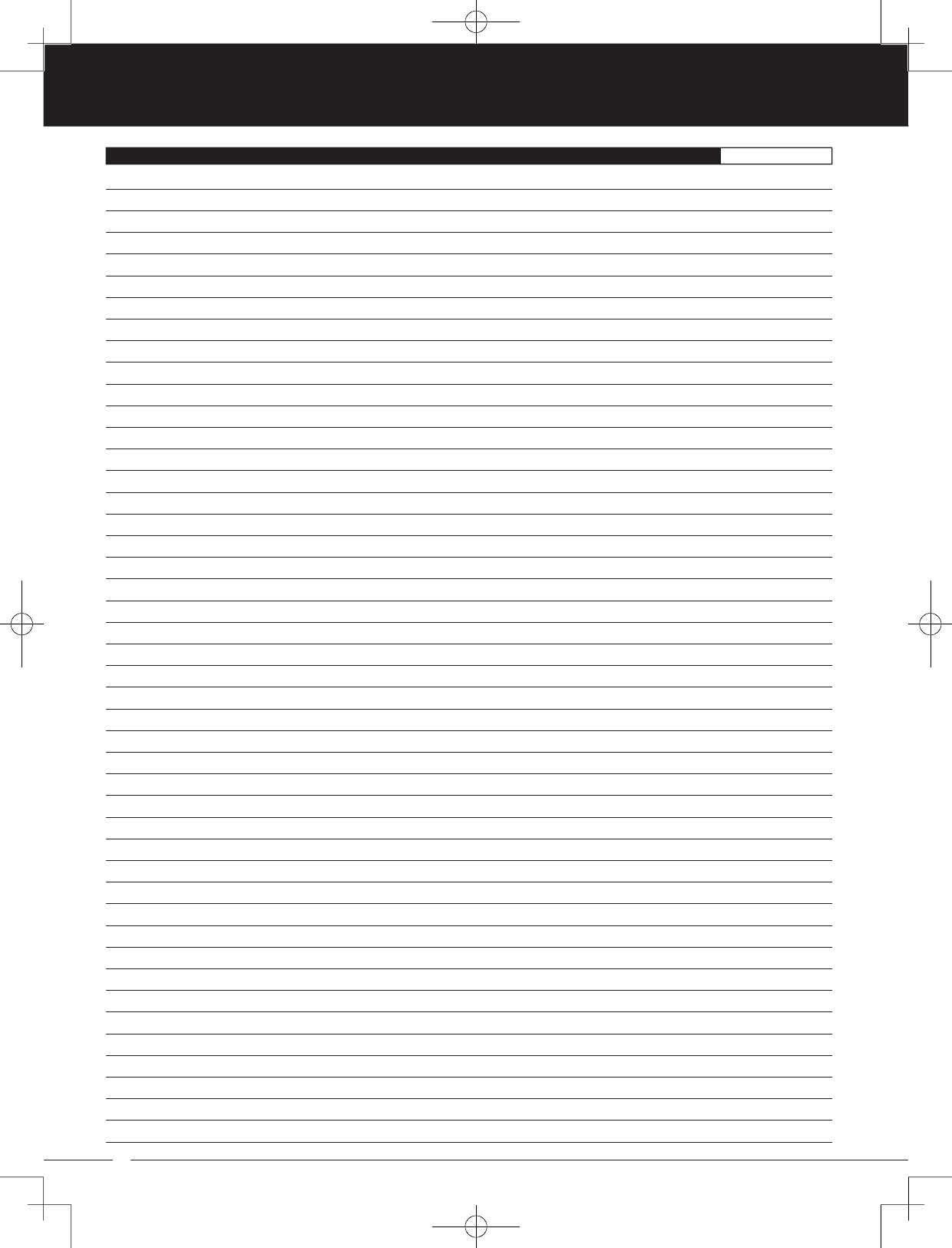
86
90478 2.4GHZ FH4T RADIO SYSTEM USER'S GUIDE
TR
TR
TR
NOTES REFERENCE
MT-4S User's Guide.indd 86 2015/10/27 14:39:21
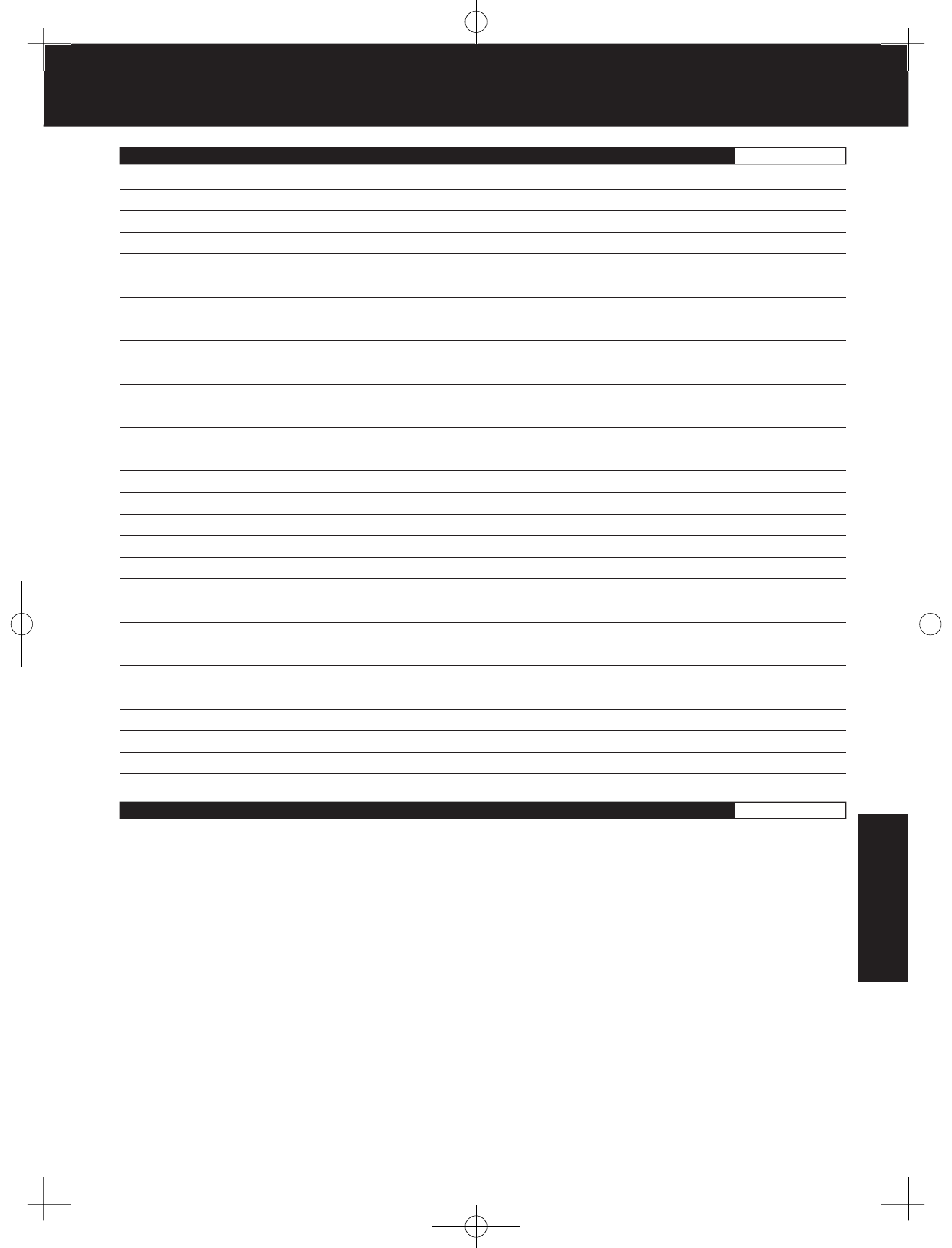
87
TR
TR
TR
90478 2.4GHZ FH4T RADIO SYSTEM USER'S GUIDE
WARRANTY AND LIABILITY INFORMATION REFERENCE
Airtronics guarantees this product to be free from defects in both material and workmanship at the time of purchase. Global
Services will repair or replace at our discretion, equipment determined to be defective, otherwise, the user is responsible for
any charges for the repair or replacement of the equipment in question. This warranty does not cover cosmetic damage
caused by the user, nor does it cover damage caused by misuse, modification, negligence, abuse, improper connections,
acts of God or damage caused by alterations by unauthorized persons. This warranty only applies to the original purchaser and
requires proof of purchase to redeem. This warranty does not cover components purchased by the user that were not part of
this original product. This warranty does not cover typical wear and tear from use.
Airtronics shall not be liable for any damage resulting from the use of this product. As Airtronics has no control over the use,
setup, modification or misuse of this product, no liability shall be assumed nor accepted for any resulting damage or injury. By
the act of using this product, the user accepts all resulting liability.
In no case shall Airtronics’s liability exceed the original cost of the purchased product.
Some states do not allow the exclusion or limitation of incidental or consequential damages, or allow limitations on how long
an implied warranty lasts, so the above limitations may not apply to you. This warranty gives you specific legal rights, and you
may have other rights which vary from state to state.
Crash damage will not be covered under warranty. Do not request warranty service for a crash-damaged product.
This warranty covers product purchase in North America. For warranty information and service for products purchased
outside of North America, contact your local Airtronics or Sanwa agent.
NOTES REFERENCE
REFERENCE
MT-4S User's Guide.indd 87 2015/10/27 14:39:21
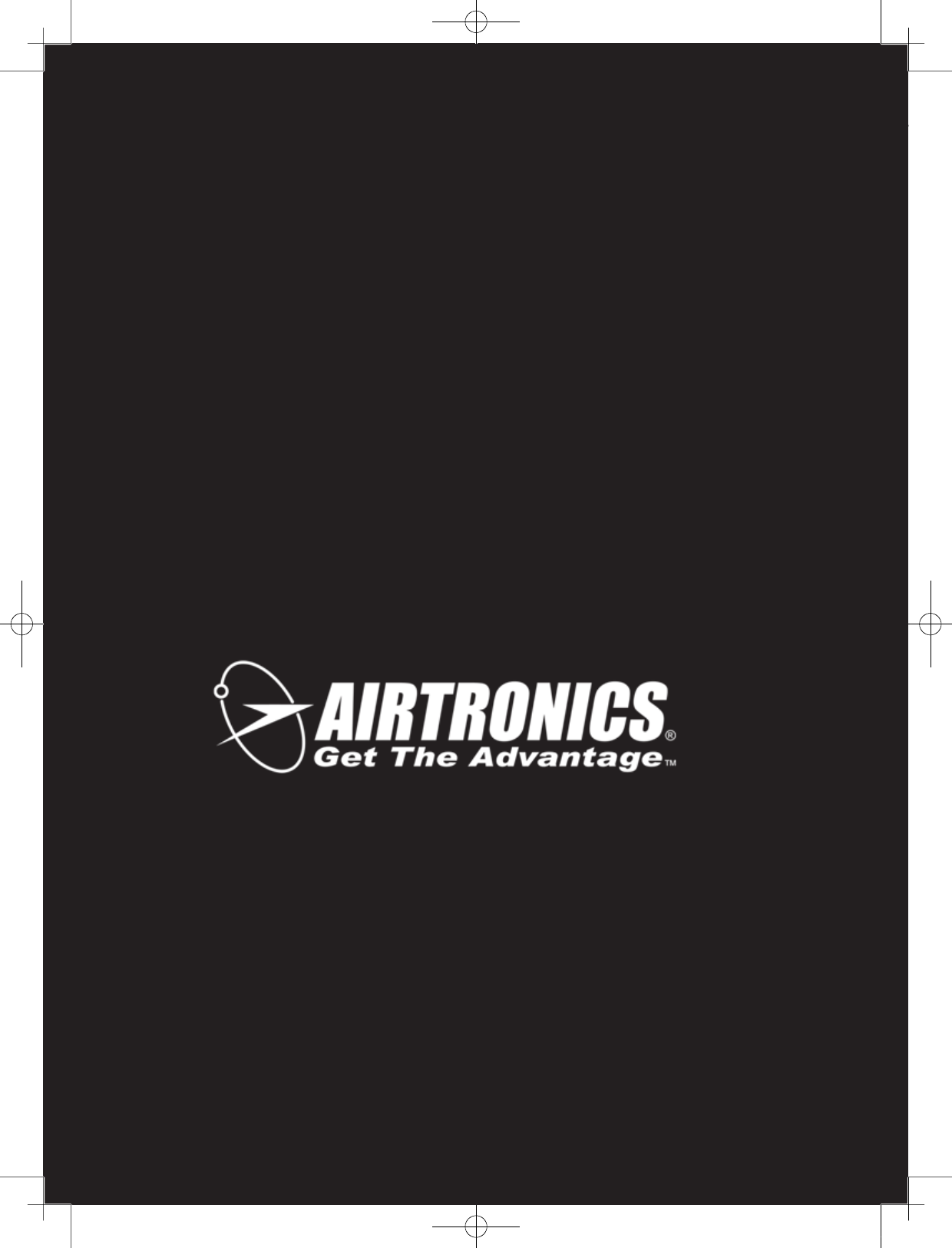
88
90478 2.4GHZ FH4T RADIO SYSTEM USER'S GUIDE
TR
TR
TR
Airtronics is Imported Exclusively in North America by:
Global Hobby Distributors
18480 Bandilier Circle
Fountain Valley, CA 92708
Telephone: (714) 963-0329
Fax: (714) 964-6236
Email: service@airtronics.net
http://globalservices.globalhobby.com
http://www.airtronics.net
Features and Specifications are Subject to Change Without Notice.
All contents © 2013 Airtronics, Inc.
All Rights Reserved. Revision 1 01.13.2014 670A14482A
MT-4S User's Guide.indd 88 2015/10/27 14:39:23