Zebra Technologies P100I P100i User Manual 980590 P100iUsersGuide
Zebra Technologies Corporation P100i 980590 P100iUsersGuide
Contents
- 1. User Manual 1 of 2
- 2. User Manual 2 of 2
User Manual 2 of 2
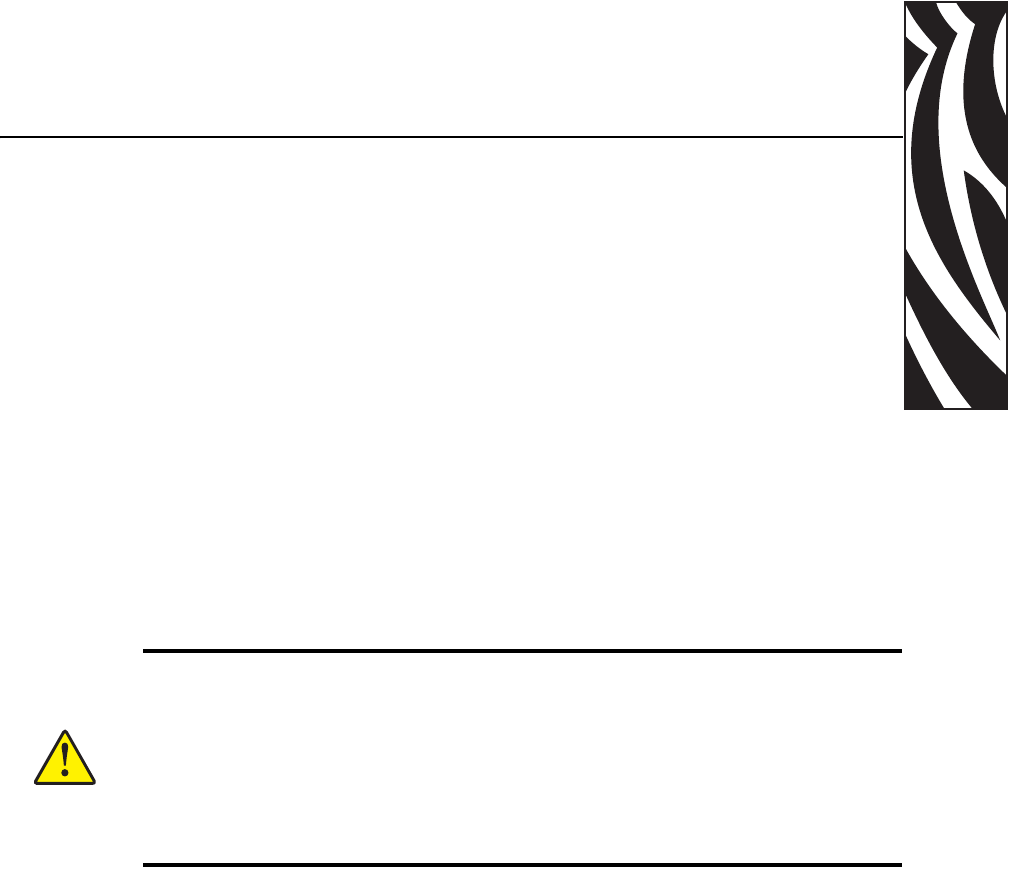
980590-001 Rev. A Draft 1 P100i User’s Manual 37
5
Cleaning
Cleaning System
Your P100i Printer includes a simple cleaning system using Pre-Saturated Cleaning Cards
provided. The regular use of these cards will clean and maintain important parts of your
printer that cannot be reached: including Print Head, the Transport Rollers, and the
Magnetic Encoder Station (optional feature).
When to Clean
After approximately 1000 color cards have been printed, the printer LCD will prompt
CLEAN PRINTER, or when print quality has been degraded.
How to Clean
1. Leave power on.
2. Press and hold the Multi-Function Control Button for 5 seconds.
3. When the cleaning cycle is initiated, the LCD message REMOVE RIBBON THEN
CLOSE LID will display.
N
Caution • PROTECT YOUR FACTORY WARRANTY!
The recommended maintenance procedures must be performed to maintain your
factory warranty. Other than the recommended cleaning procedures described in this
manual, allow only Zebra authorized technicians to service the P100i Printer.
NEVER loosen, tighten, adjust, or bend, etc., a part or cable inside the printer.
NEVER use a high-pressure air compressor to remove particles in the printer.
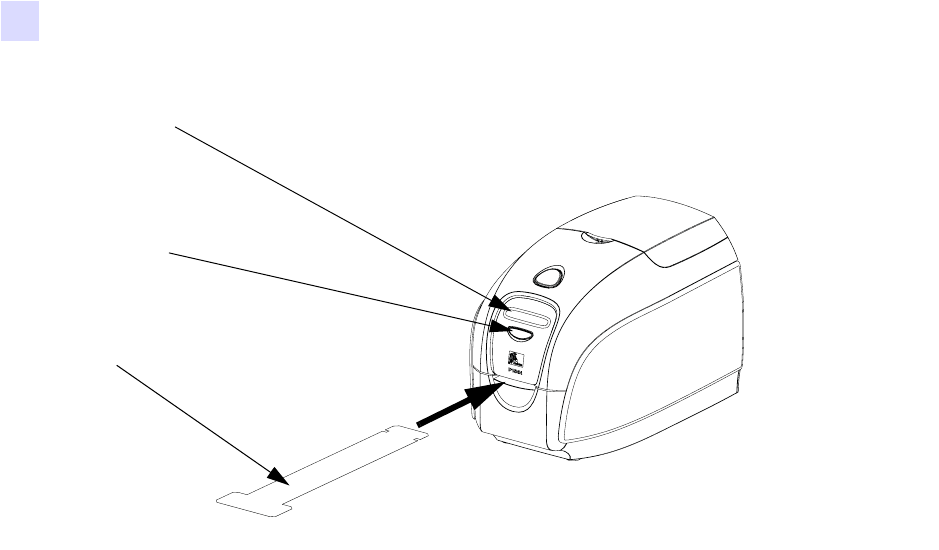
38 P100i User’s Manual 980590-001 Rev. A Draft 1
Cleaning
Cleaning System
4. After the ribbon is removed and the lid is closed, the message EMPTY FEEDER THEN
CLOSE COVER will display.
5. If the lid is opened and closed without removing the ribbon, the REMOVE RIBBON
THEN CLOSE LID message will remain.
6. Once the cover is closed, the firmware will eject any card inside the printer. The message
EJECTING CARD will display.
7. The LCD will then display FEED LONG CLEANING CARD IN EXIT. When the card
sensor registers the presence of the cleaning card, the rollers should take the card into the
printer.
8. When the cleaning process is done, the printer will eject the cleaning card. If the card
sensor still senses the cleaning card, the message REMOVE LONG CLEANING CARD
will display.
9. After the card is removed, the LCD will display READY. You may now reload the ribbon
and continue printing.
Printer Path
Cleaning Card
Multi-Function
Control Button
Multi-Function
LCD Panel
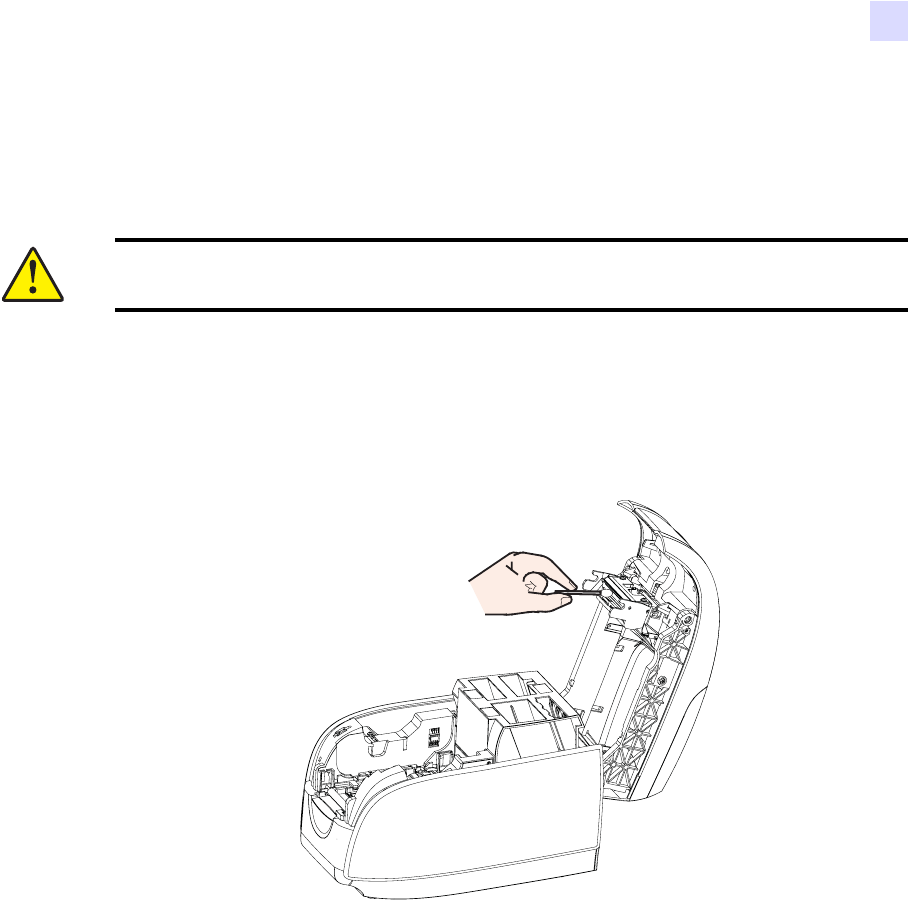
Cleaning
Cleaning the Print Head
980590-001 Rev. A Draft 1 P100i User’s Manual 39
Cleaning the Print Head
Use of the cleaning cards will normally do an adequate job of cleaning the printer. However, a
separate Print head cleaning, using swabs, can remove more stubborn deposits when print
anomalies persist. To avoid deposits, only use foam-tipped swabs.
1. Place the printer power switch in the OFF (0) position.
2. Open printer lid by pressing cover release button and open cover fully to reveal the print
head mounted to inside of the cover.
3. Clean Print Head by moving alcohol-moistened swab tip side-to-side across Print Head
elements. Only use moderate force.
4. Allow two to three minutes for the printhead to dry before placing the printer power
switch in the ON ( | ) position.
5. To reorder swabs, reference the P110i Printer Media List.
Caution • Never use a sharp object to scrape deposits from the print head. Permanent
damage to the print head will result
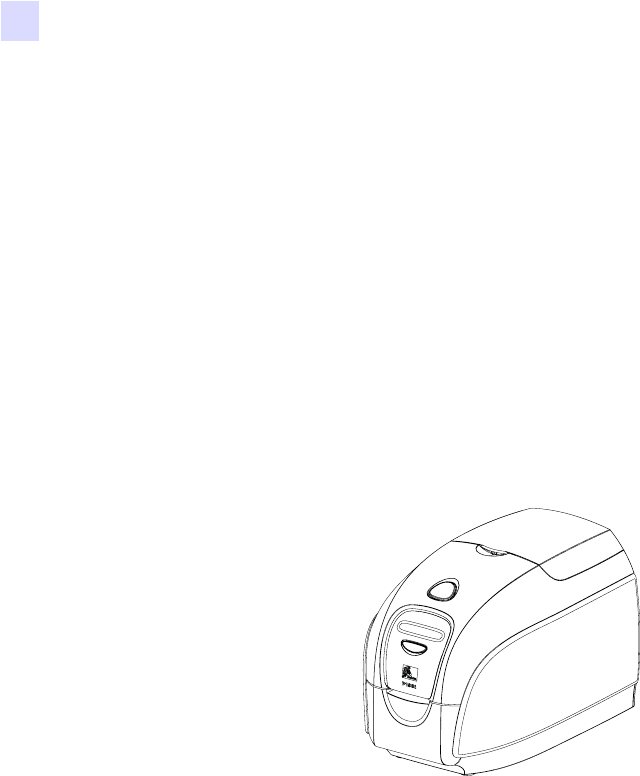
40 P100i User’s Manual 980590-001 Rev. A Draft 1
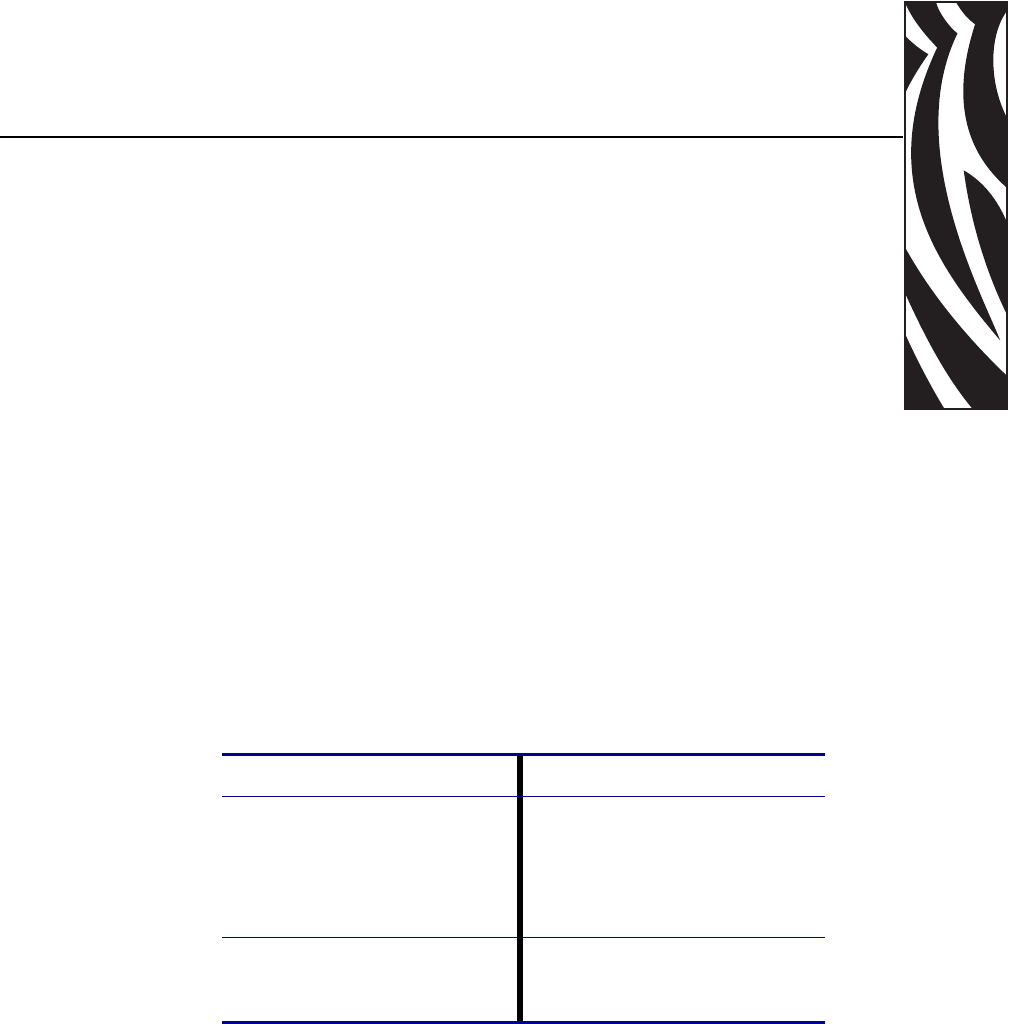
980590-001 Rev. A Draft 1 P100i User’s Manual 41
6
Troubleshooting
Troubleshooting Procedures
The table below offers causes and solutions to symptoms related to improper operation.
Check the table when experiencing any loss of operation or print quality.
Problem / Description Cause / Solution
The LCD Panel displays OUT
OF RIBBON message. 1. Check ribbon. Replace if
defective or entirely used.
Ribbon will automatically
synchronize and printing will
restart with a new card.
The LCD Panel displays PRINT
HEAD OPEN message. 1. Check that Print Head Carriage
is closed and latched. If not, close
and latch it.
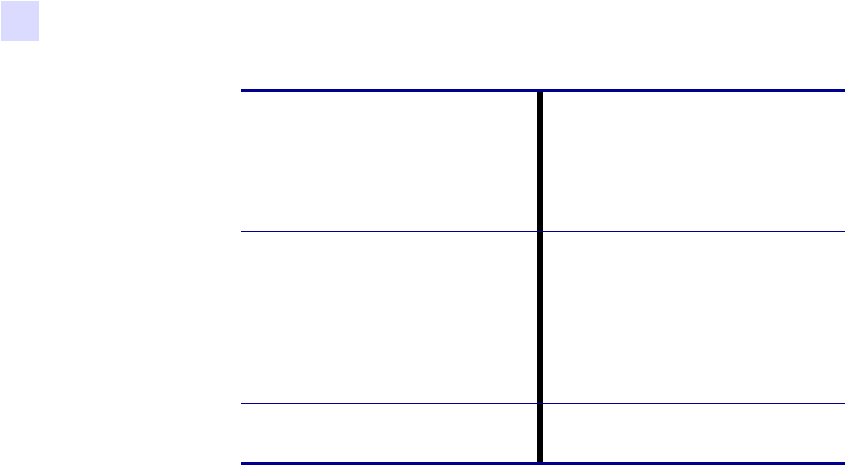
42 P100i User’s Manual 980590-001 Rev. A Draft 1
Troubleshooting
Troubleshooting Procedures
Print Quality Issues
This section will help you resolve print quality problems The print quality is dependent on
several factors. The two most important factors that will increase your print quality are
cleanliness and card stock. To diagnose and fix print quality problems, follow the
troubleshooting procedures below:
The LCD Panel displays
MECHANICAL ERROR
message.
1. Check that you are using the
correct card type (see Technical
Specifications).
2. Check that ribbon is loaded
correctly.
The LCD Panel displays
ENCODING ERROR message. 1. Check that you are using the
correct magnetic card type (for
low or high coercivity encoding).
2. Verify command syntax.
3. Contact Zebra technical
support.
The LCD Panel displays
CLEAN PRINTER message. 1. Printer cleaning required (see
Chapter 4).
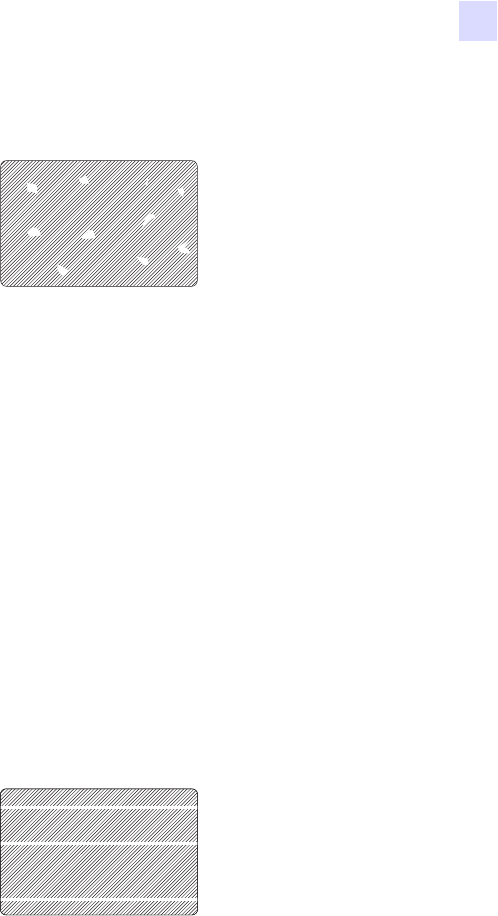
Troubleshooting
Troubleshooting Procedures
980590-001 Rev. A Draft 1 P100i User’s Manual 43
Example • Small spots appear on the printed card with a non-printed area or a different color.
Possible Cause:
• Contamination on the card surface
Solutions:
• Check that cards are stored in a dust free environment
• Use a different supply of cards
Possible Cause:
• Cleaning roller not installed
• Dust inside the printer and/or dirty Cleaning Roller
Solutions:
• Perform a Cleaning of the printer (reference Chapter 5)
• Check that the protective cover was removed from the ribbon cartridge cleaning roller
(reference Chapter 3).
• Replace the cleaning roller located at the front of the printer (reference Appendix B).
Example • There are non-printing horizontal lines (white) on the card surfaces.
Possible Cause:
• Ribbon cartridge is not correctly positioned.
Solutions:
• Ensure that the ribbon is properly rolled onto the ribbon cores of the cartridge and that
there are no wrinkles in the ribbon.
• Replace ribbon cassette.
Possible Cause:
• Print Head is dirty.
Solutions:
• Clean the Print Head
Possible Cause:
• Print Head elements are damaged (e.g., scratched or burnt).
Solutions:
• Call Zebra Customer Service for Print Head replacement information.
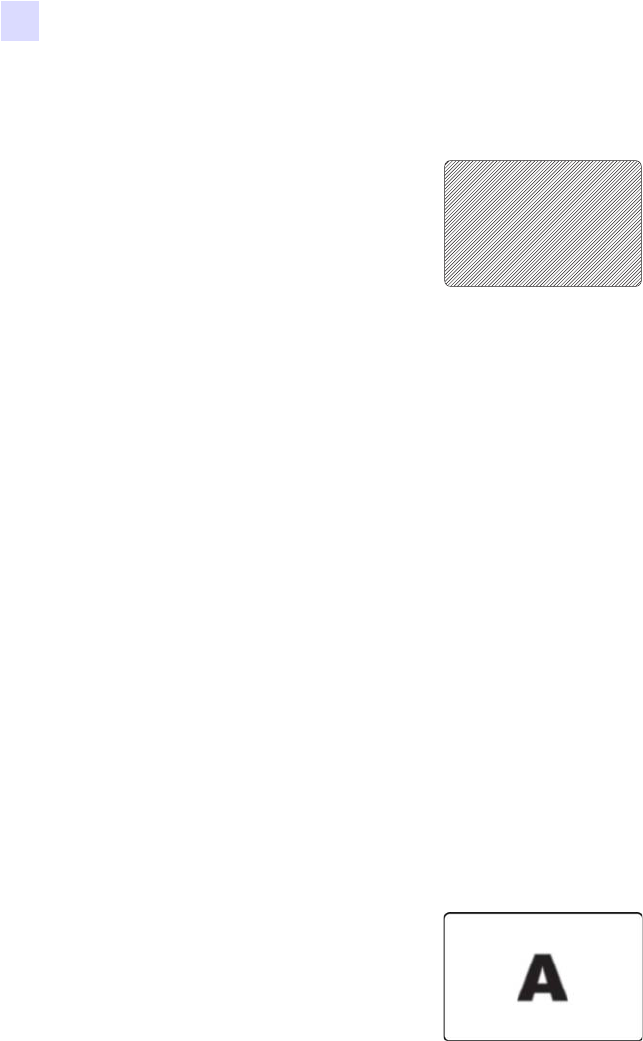
44 P100i User’s Manual 980590-001 Rev. A Draft 1
Troubleshooting
Troubleshooting Procedures
Example • Printing shows very pale or inconsistent results.
Possible Cause:
• Ribbon cartridge have been stored improperly or is damaged.
Solution:
• Change ribbon cartridge and print again.
Possible Cause:
• Cards may not meet specifications
Solution:
• Use a different supply of cards.
Possible Cause:
• Contrast and/or Intensity may be set to values which are too high.
Solution:
• Adjust Contrast and/or Intensity values in software.
Possible Cause:
• Dust or embedded contamination on elements of the Print Head.
Solution:
• Perform a Cleaning of the Print Head (Reference Chapter 4, Cleaning the Print Head)
Example • Printing shows blurry printed image.
Possible Cause:
• Ribbon cartridge may not be correctly positioned.
Solution:
• Check that the ribbon is properly rolled onto the ribbon cores of the cartridge, with no
wrinkles.
• Replace ribbon cartridge, making sure it locks in place, and print again.
Possible Cause:
• Ribbon may not be synchronized on the correct color panel position.
Solution:
• Open lid, then close lid to synchronize ribbon.
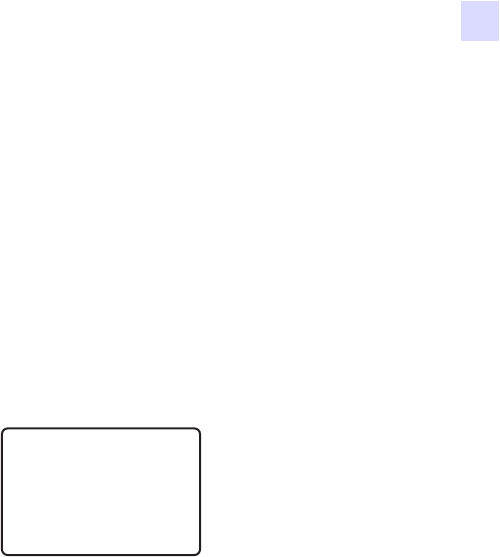
Troubleshooting
Troubleshooting the Ethernet Connection and Adapter
980590-001 Rev. A Draft 1 P100i User’s Manual 45
Possible Cause:
• Cards may not meet specifications.
Solution:
• Use a different supply of cards.
Possible Cause:
• Dust or embedded contamination inside the printer and/or dirty Cleaning Roller.
Solution:
• Clean the Print Head.
• Replace Cleaning Roller.
Example • No printing on the card.
Possible Cause:
• Ribbon cartridge may not be installed in the printer.
Solution:
• Check for ribbon cartridge in the printer.
Possible Cause:
• Cards may not meet specifications.
Solution:
• Use a different supply of cards.
Possible Cause:
• Cable on Print Head may be disconnected.
• Print Head elements may be scratched or burnt.
Solution:
• Call Service for Print Head repair or replacement information.
Troubleshooting the Ethernet Connection and Adapter
Resetting to Factory Defaults
To reset the Ethernet Adapter configuration parameters to the factory defaults, press the
Ethernet Switch
and hold it in while turning the printer power on. Keep the Panel Button pressed until the
Status Indicator light turns green, then release the Ethernet Switch. To print a configuration
card, press and hold the Ethernet Switch until a card starts to print.
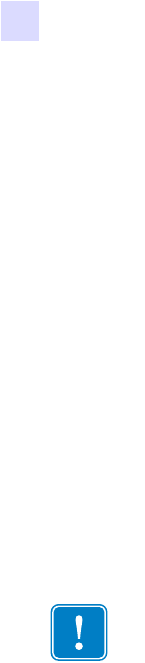
46 P100i User’s Manual 980590-001 Rev. A Draft 1
Troubleshooting
Troubleshooting the Ethernet Connection and Adapter
Ethernet Adapter Status Indicator
A bi-color Status Indicator displays the operational status of the Ethernet Adapter.The
following conditions might occur:
1. During normal operation, the LED is solid green for more than 30 seconds. This indicates
all the hardware is functioning properly and the Ethernet Adapter has detected the
presence of the network. It does not mean the Ethernet Adapter has an IP address or is
attached to a printer queue.
2. If the LED is rapidly flashing green (9 times/sec), the Ethernet Adapter has not detected
the presence of a network cable. To solve the problem:
• Verify that the network cable is appropriate for the network and has an RJ-45
connector.
• Turn the printer power off (O). Remove the network cable from the Ethernet Adapter.
Plug the network cable back in until you hear a positive click. Check the other end of
the cable in the same manner. Turn the printer power on; if the Ethernet Adapter still
does not detect a cable, continue.
• Connect the Ethernet Adapter to a known good network connection. If the Ethernet
Adapter is still unable to detect the network cable, contact Technical Support for
assistance.
3. If the LED is slowly flashing green (1 time/sec), the Ethernet Adapter is trying to print a
job. If the job does not print, check the following:
• Verify that the printer has media and ribbon. If the printer is showing any errors, it is
unlikely that the Ethernet Adapter can send data to the printer. The LED continues to
blink until the printer malfunction is resolved or until the printer is turned off (O).
• Flashing red indicates the Power On Self Test (POST) is in progress.
4. If the LED is solid red for more than 30 seconds, the Ethernet Adapter has failed the
POST. A failed POST can be caused by any of the following:
• The printer attached to the Ethernet Adapter device is malfunctioning. Turn the
printer power off, wait 10 seconds, then turn the printer back on ( | ).
• If the Ethernet Adapter still fails the POST, the Ethernet Adapter has a hardware
problem that can be fixed only by replacing or returning the unit. Contact Technical
Support for repair or replacement information.
5. If the LED is alternately flashing red and green for longer than 2 minutes, the Ethernet
Adapter is in firmware-download mode. This means it is waiting for new firmware data to
be sent before it continues normal functioning. Perform the following:
• If the Ethernet Adapter was purposely put into firmware-download mode, finish the
download with the proper update utility. Contact the Zebra web site at
http://www.zebra.com to download this utility.
• Contact Technical Support for help recovering this unit.
Important • Cables with a rating higher than CAT-6 have not been tested.

Troubleshooting
Troubleshooting the Ethernet Connection and Adapter
980590-001 Rev. A Draft 1 P100i User’s Manual 47
Network Status/Activity Indicator
A bi-color Status/Activity LED indicates network speed, established link, and network
activity.
1. If the LED is off, no link was established.
2. If the LED is solid green, a 100Base link is established.
3. If the LED is flashing green, a 100Base link is established and network activity has been
detected.
4. If the LED is solid orange, a 10Base link is established.
5. If the LED is flashing orange, a 10Base link was established and network activity has
been detected.
Network activity detected by this LED does not mean the activity is data for the print server.
The activity is all activity on the network seen on the Ethernet Adapter.
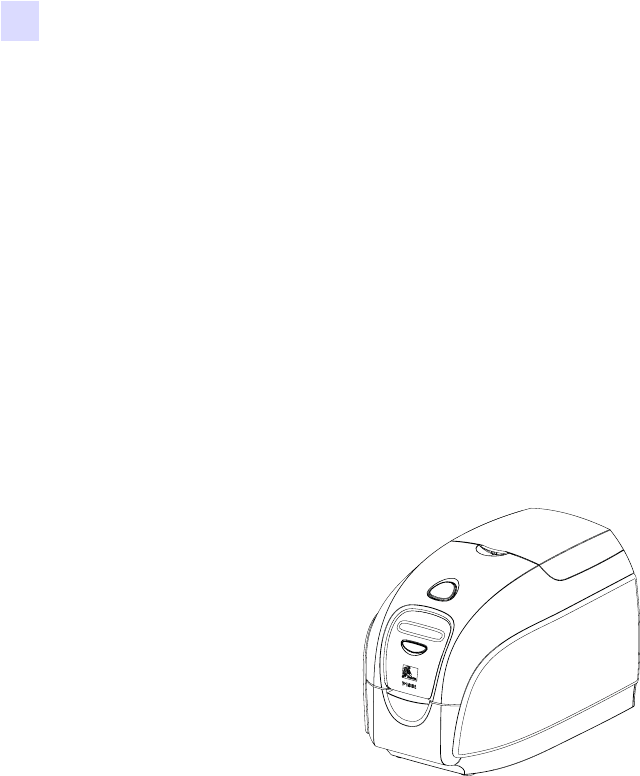
48 P100i User’s Manual 980590-001 Rev. A Draft 1
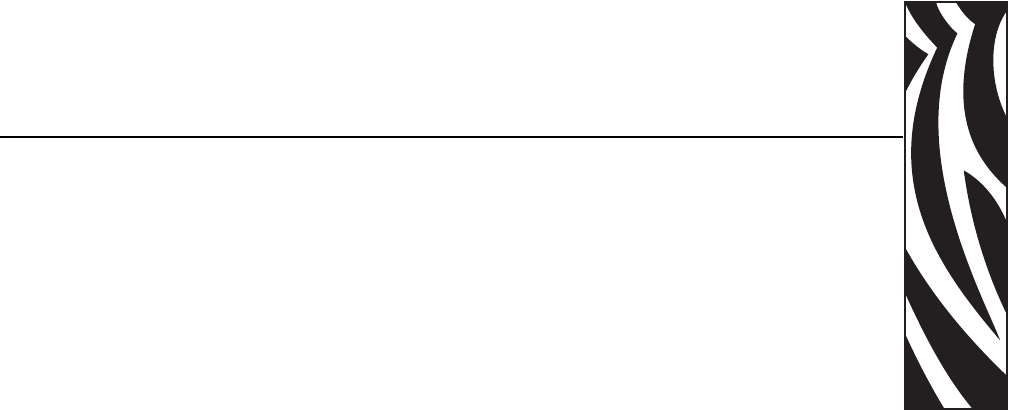
980590-001 Rev. A Draft 1 P100i User’s Manual 49
7
Technical Specifications
General • Load-N-GoTM drop-in ribbon cartridge
• 16-digit LCD display
• Windows® drivers for 2000 and XP
Color Printing • Color dye sublimation or monochrome thermal transfer printing
• 300 dpi (11.8 dots/mm) print resolution
Bar Code • Code 39, Code 128 B & C with & without check digit
• 2 of 5 & 2 of 5 Interleaved
• UPC-A, EAN 8 & EAN 13
• PDF-417 2D bar code and other symbologies can be printed via
Windows drivers
Cards • Types: PVC, PVC Composite
• Card width/length: ISO CR-80-ISO 7810, 2.12" (54mm) x 3.38" (86mm)
• Magnetic Stripe-ISO 7811
• Smart Card-ISO 7816
• Card thickness: 30 mil (.76mm) (+/- 10%)

50 P100i User’s Manual 980590-001 Rev. A Draft 1
Technical Specifications
Ribbon Cartridges
• Load-N-GoTM ribbon cartridge with integrated card-cleaning roller
•i Series technology featuring contact-chip-based ribbon detection
• YMCKO: 200 cards/cartridge
• Monochrome: 1000 cards/cartridge in black or blue; 850 cards/cartridge
white
Interfaces • USB 1.1 (cable included)
• USB 1.1 and built-in Ethernet (optional)
Dimensions • Width: 7.9 in (201mm)
• Depth: 12.9 in (328mm)
• Height: 8.5 in (216mm)
• Weight: 9.5 lbs (4.3kg)
Electrical • 110 ~ 240 Volts AC, 50 ~ 60 Hz (auto switching)
• 8 MB image memory standard
• FCC Class A, CE, UL and CUL approved
Environmental • Operating Temperature: 60°F to 86°F (15°C to 30°C)
• Operating Humidity: 20% to 65% non-condensing
• Storage Temperature: 23°F to 158°F (-5°C to 70°C)
• Storage Humidity: 20% to 70% non-condensing
• Ventilation: Free air
Options • Magnetic encoder (30 mil cards only), 3 track HiCo/LoCo
• Ethernet (10/100 MBps); available at time of order only
•P100i Starter Kit (200 cards and 1 YMCKO ribbon)
• Cleaning Kit (1 cleaning card and 1 cleaning swab)
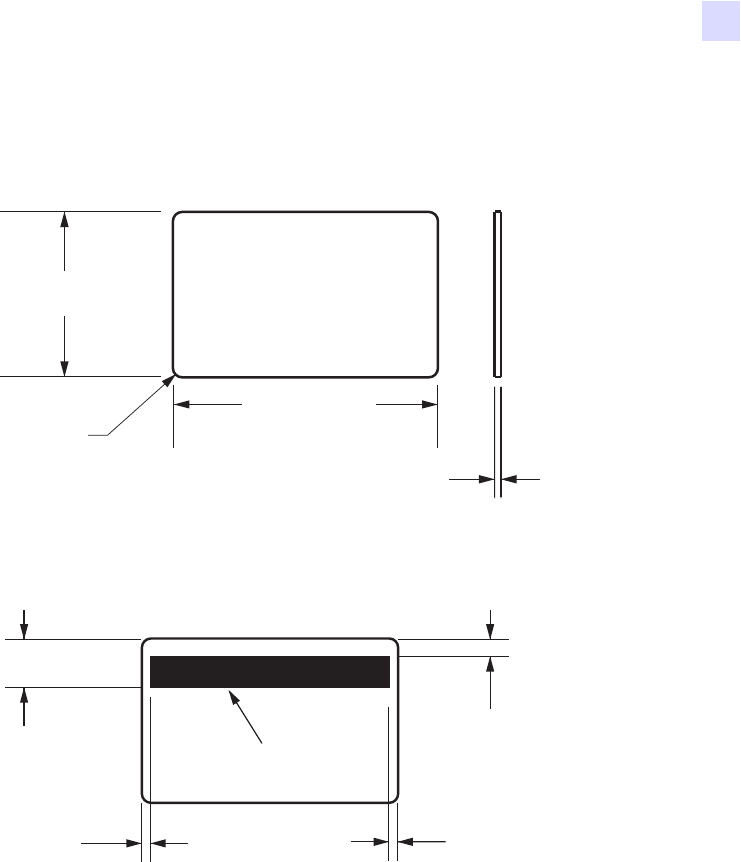
Technical Specifications
Card Dimensions
980590-001 Rev. A Draft 1 P100i User’s Manual 51
Card Dimensions
ISO standard dimensions for plain card
ISO standard dimensions for magnetic stripe card
980504-07-01
2.125 ± 0.002in
(53.98 ± 0.050mm)
Radius
0.125in
(3.18mm)
3.375 ± 0.010in
(85.72 ± 0.25mm)
0.009 ~ 0.034in
(0.23 ~ 0.84mm)
980504-07-02
0.623in (15.82mm) min
0~0.115in (2.92mm) 0~0.115 in (2.92 mm)
MAGNETIC STRIPE
0.218in (5.54mm) max
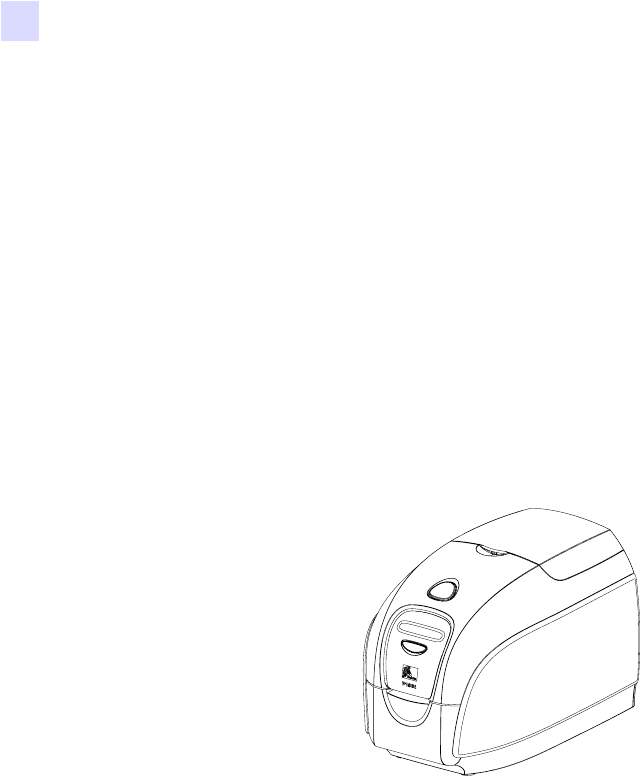
52 P100i User’s Manual 980590-001 Rev. A Draft 1
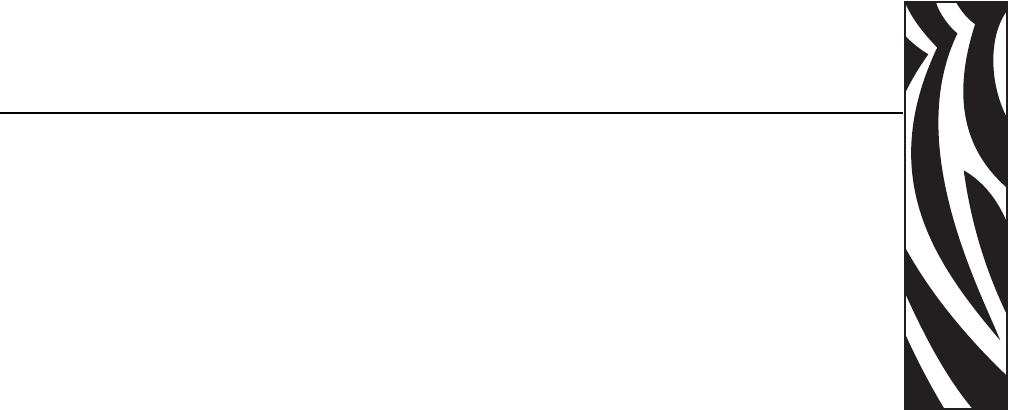
980590-001 Rev. A Draft 1 P100i User’s Manual 53
Appendix A
Magnetic Card Encoder
Magnetic Card Stripe Encoder
This section contains information on the additional operations of the P100i Printers with
Magnetic Card Stripe Encoder.
Introduction
Operation and maintenance requirements for the P100i Printer with the optional magnetic
card stripe encoder. The magnetic encoder can be set for either high or low coercivity.
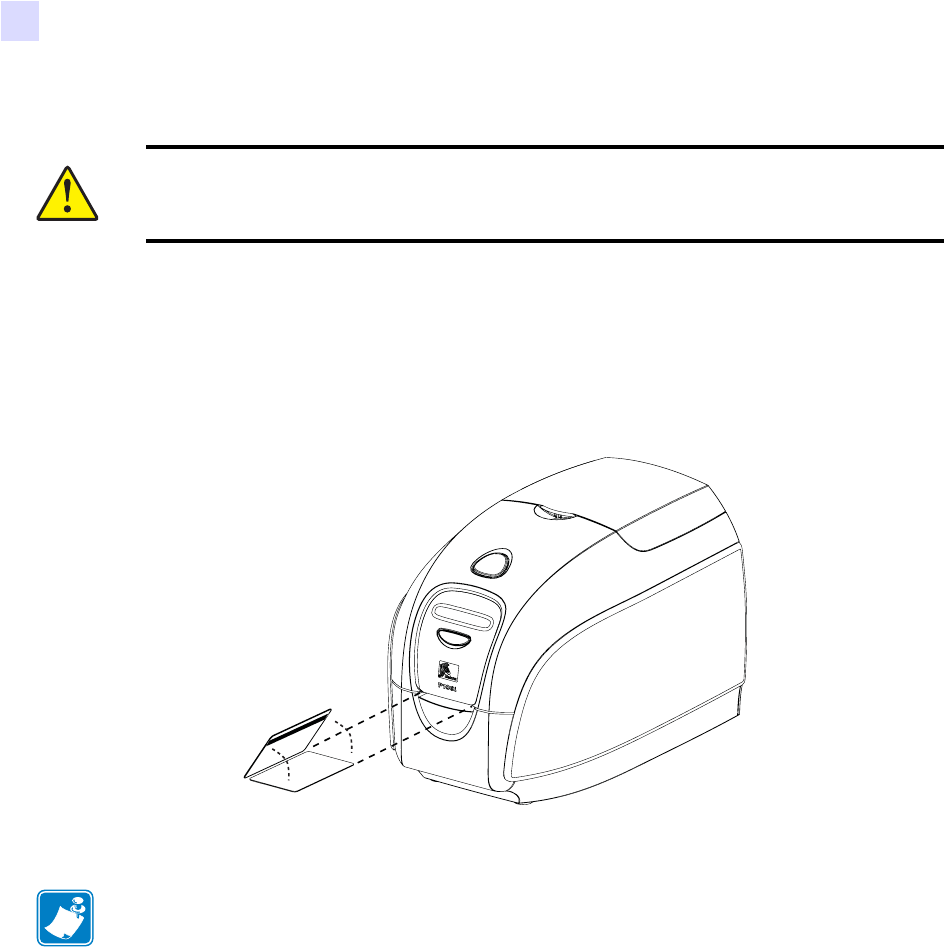
54 P100i User’s Manual 980590-001 Rev. A Draft 1
Magnetic Card Encoder
Introduction
Media Loading Orientation
The magnetic encoder is a factory installed item with the read/write head positioned below or
above the card path, available with HiCo or LoCo encoding.
When loading cards with magnetic stripes into the card feeder, please ensure that the magnetic
stripe is toward the right side when facing the printer and down, as shown below.
Magnetic Encoder Cleaning
Use the standard cleaning card process as described in Chapter 4. This cleans the most
important parts of the printer; including the Print Head, Transport Roller, and Magnetic Stripe
Encoder.
Caution • ONLY USE cards that comply with ISO 7810 & 7811 standards for magnetic
stripe cards. The magnetic stripe must be flush to the surface of the card to work properly.
Never use cards which have taped-on magnetic stripes.
Note • Zebra approved HiCo & LoCo PVC cards are available. (Reference P100i printer
Media List.)
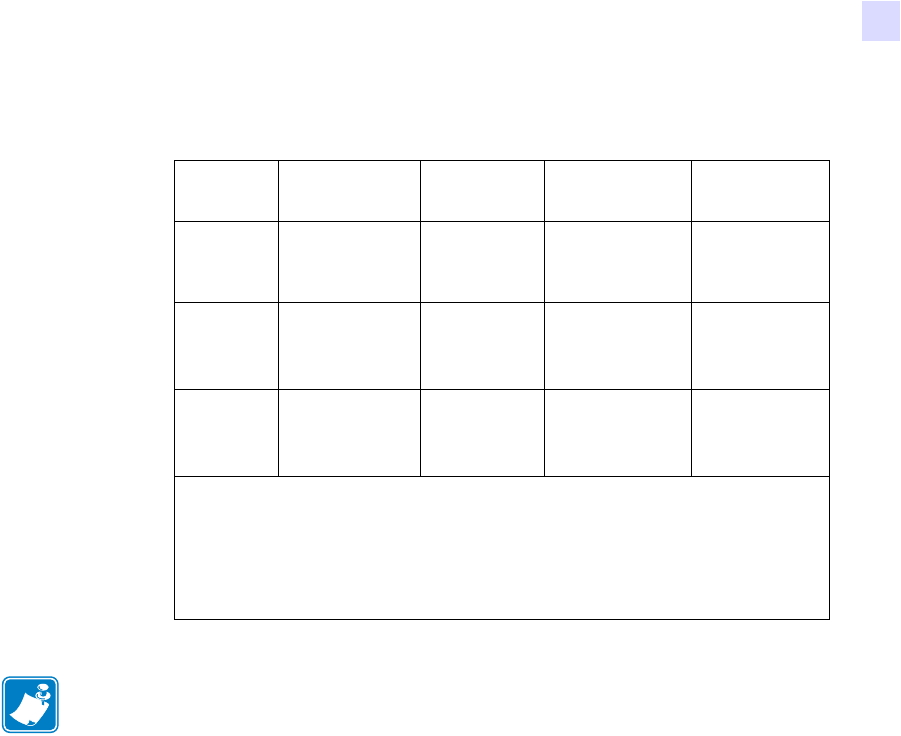
Magnetic Card Encoder
Introduction
980590-001 Rev. A Draft 1 P100i User’s Manual 55
ISO Standard Encoding
Track # Field
Separator Track
Density Valid
Characters # of
characters
1 ^ 210 BPI* Alphanumeri
c (ASCII
20~95†)
79‡
2 = 75 BPI* Numeric
(ASCII
48~62)
40‡
3 = 210 BPI* Numeric
(ASCII
48~62)
107‡
*Bits per inch
†Except the “?” character
‡Including Start, Stop, and LRC characters. Also note that these 3
characters areautomatically managed by the magnetic encoder according
to the ISO Standard Norms.
Note • Refer to the Card Printer Programmer’s Manual for complete programming
information.
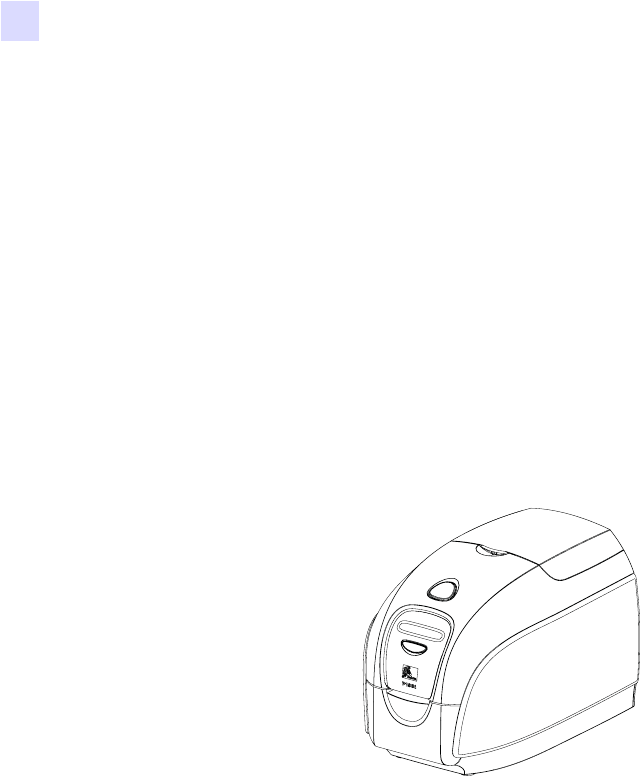
56 P100i User’s Manual 980590-001 Rev. A Draft 1
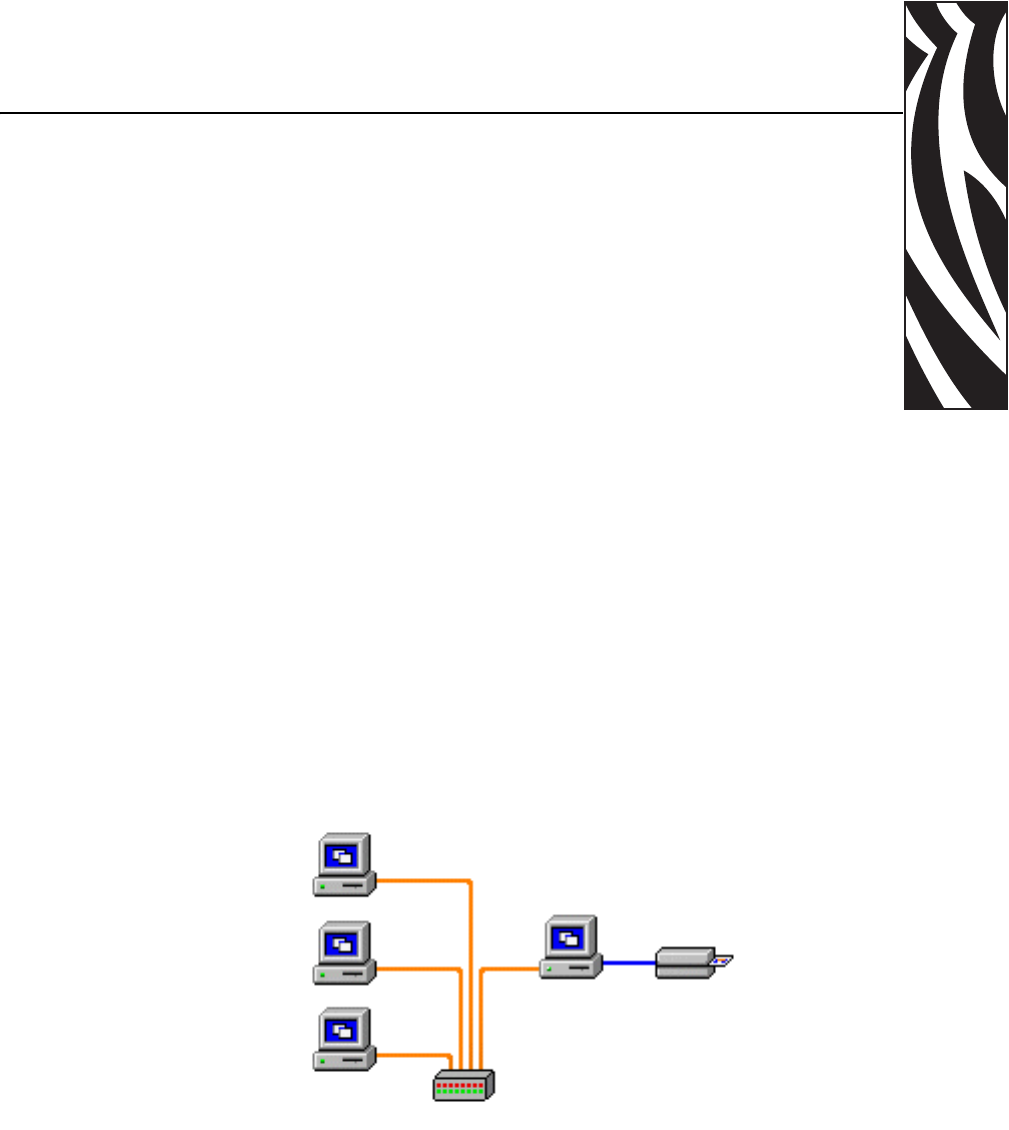
980590-001 Rev. A Draft 1 P100i User’s Manual 57
Appendix B
Connecting to a Network
Card printers can be connected to an Ethernet network in three ways.
Printer Sharing
In printer sharing, the printer is connected locally to the host computer and configured to
be shared to other client computers. Client computers connect to the printer over the
network through the host computer.
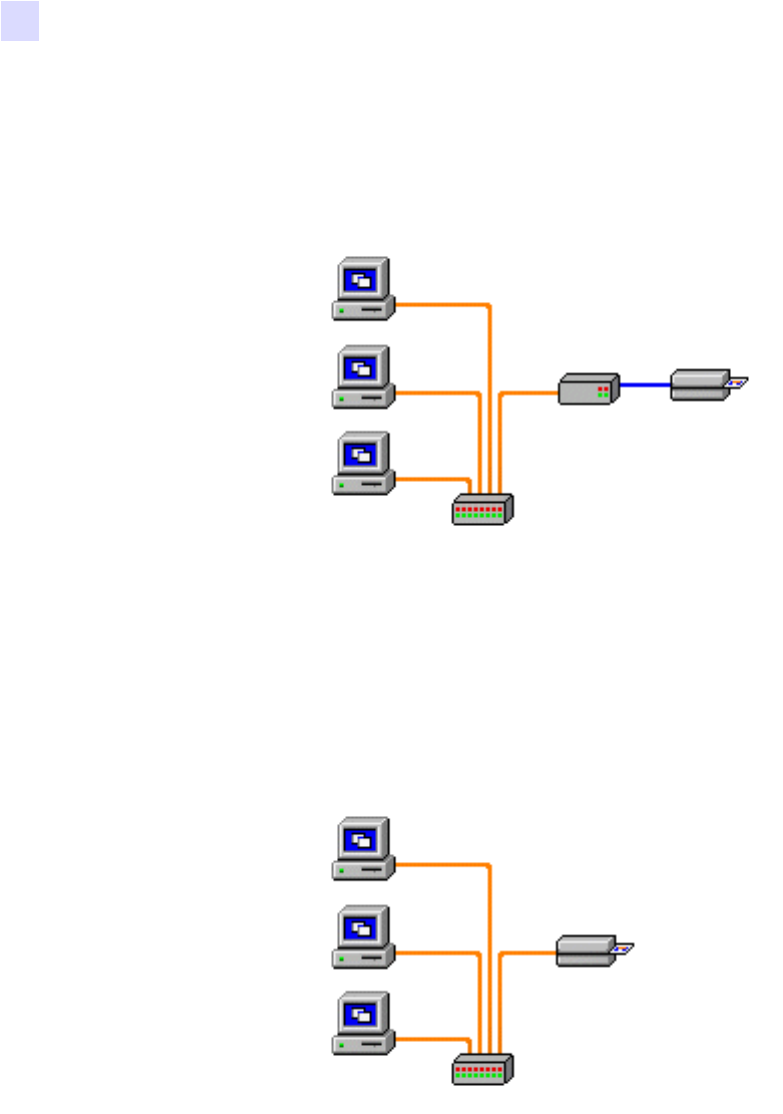
58 P100i User’s Manual 980590-001 Rev. A Draft 1
Connecting to a Network
External Print Server
External Print Server
A stand alone device that acts as a server on the network specifically for receiving print jobs
and passing them to the printer. Client computers connect to the print server over a network.
Internal Print Server
Similar to an external print server, except the print server is integrated into the printer. This
removes the need for a separate power supply and separate device drivers. This is the simplest
way to network a printer.
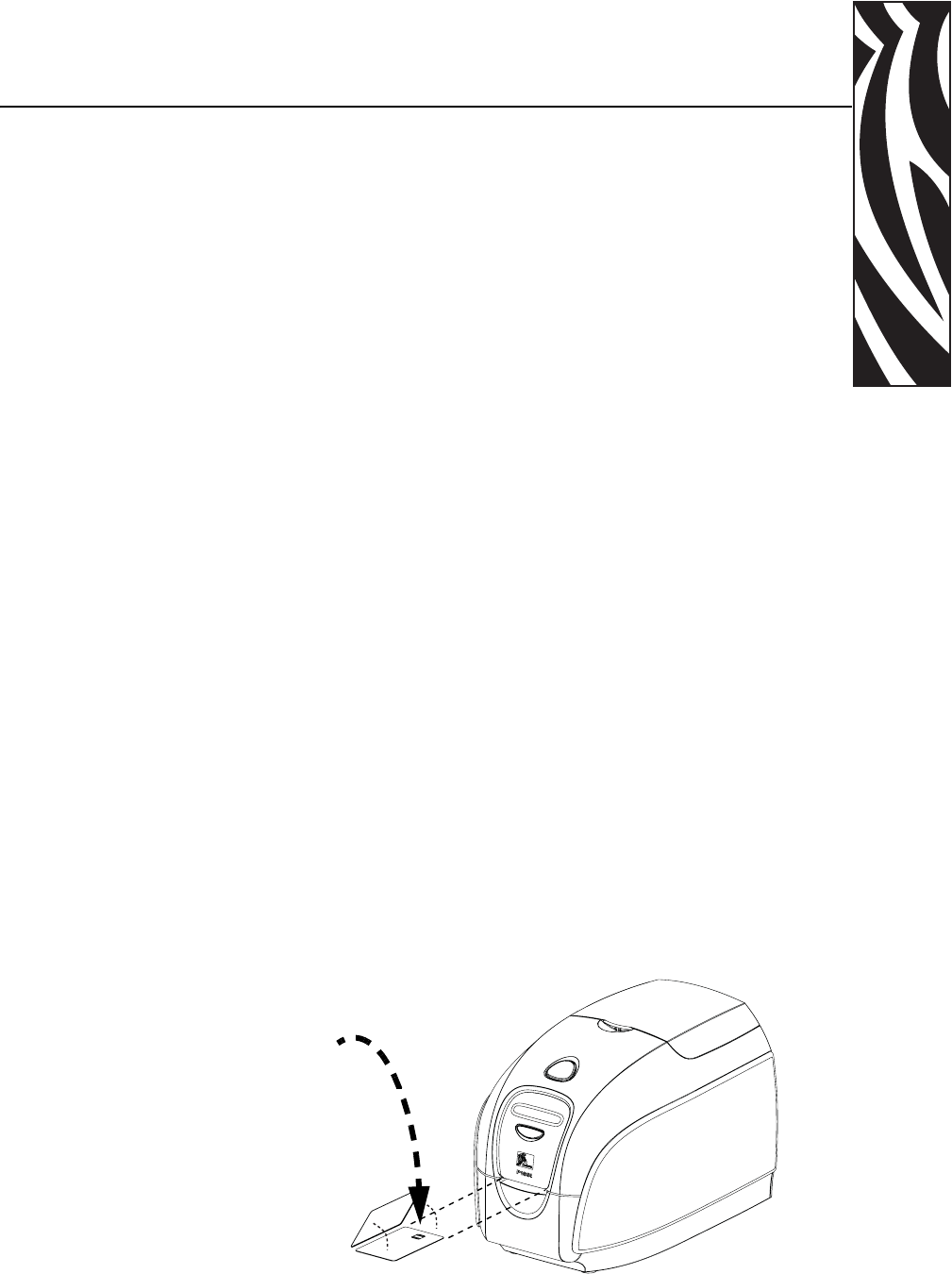
980590-001 Rev. A Draft 1 P100i User’s Manual 59
Appendix C
Smart Card Contact Station
This section contains information on the additional operations of a P100i Printer equipped
with the optional Smart Card Contact Station.
Introduction
Smart Cards can have a built-in microcomputer and/or memory to store fingerprints, voice
recognition patterns, medical records, and other such data. The printer may be equipped
with an optional contact station for programming Smart Cards (ISO 7816). This printer
model responds to commands that position the card at the contact station, where the printer
connects to the contacts on the Smart Card. All other printer operations remain the same as
the standard models.
Media Loading Orientation
Orient the cards with the gold-plated Smart Card contacts at the top surface of the card and
nearer the card entry slot.
Smart
Card
Contacts
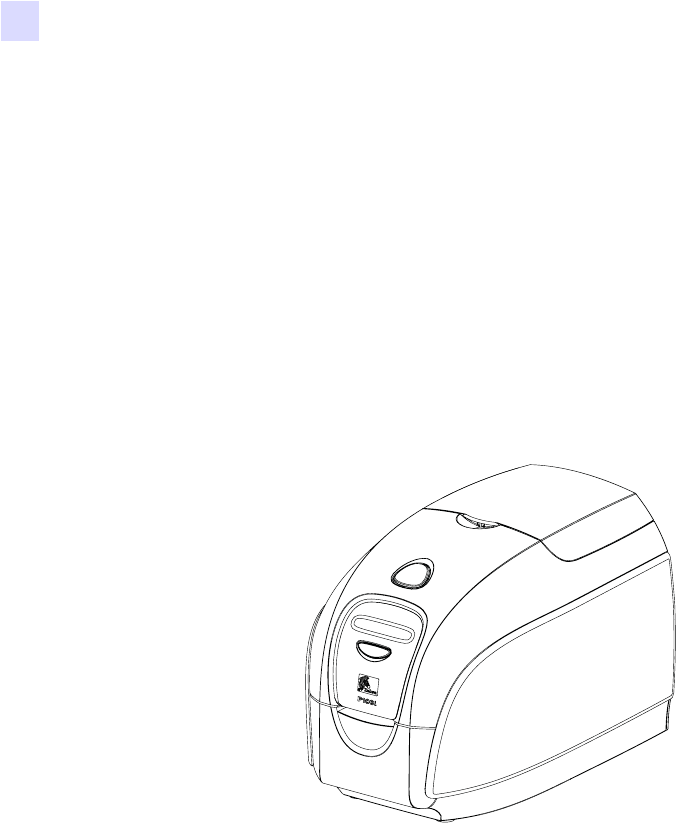
60 P100i User’s Manual 980590-001 Rev. A Draft 1
Smart Card Contact Station
Media Loading Orientation
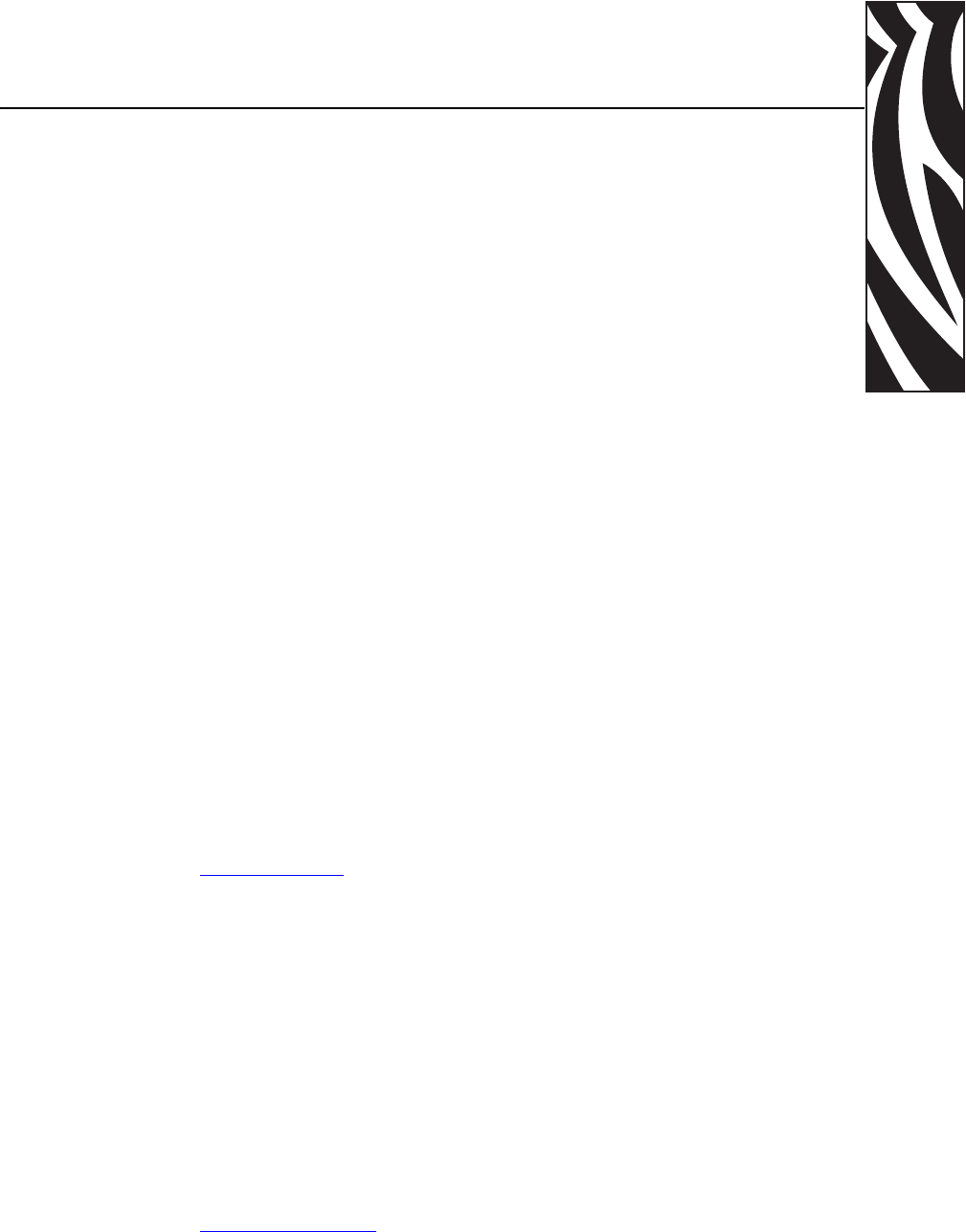
980590-001 Rev. A Draft 1 P100i User’s Manual 61
Appendix D
Worldwide Sales & Support
Sales and Support Locations
North America:
Zebra Technologies Card Printer Solutions
1001 Flynn Road
Camarillo, CA 93012-8706 USA
Phone: + 1 (805) 579 1800
Fax: + 1 (805) 579 1808
Toll free in US: (800) 452-4056
e-mail: cards@zebra.com
Europe, Middle East, and Africa:
Zebra Technologies Card Printer Solutions
The Valley Centre, Gordon Road
High Wycombe
Buckinghamshire HP13 6EQ
United Kingdom
Phone: + 44 (0) 870 241 1527
Fax: + 44 (0) 870 241 0765
e-mail: eurosales@zebra.com
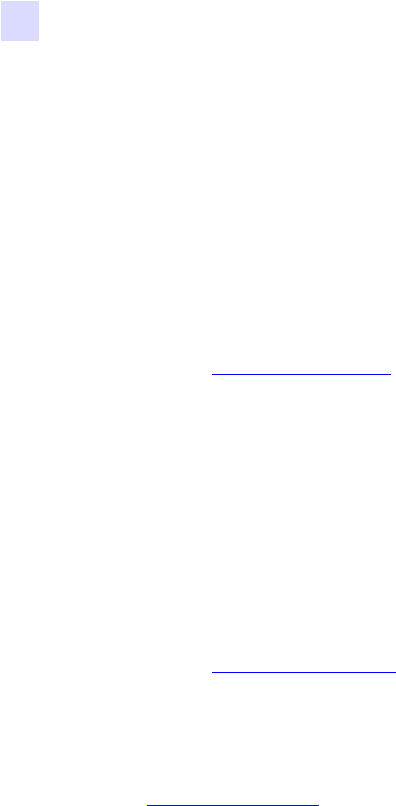
62 P100i User’s Manual 980590-001 Rev. A Draft 1
Worldwide Sales & Support
Website
Asia Pacific:
Zebra Technologies Card Printer Solutions
120 Robinson Road
#06-01 Parakou Building
Singapore 068913
Phone: + 65 6858 0722
Fax: + 65 6885 0836
e-mail: asiasales@zebra.com
Latin America:
Zebra Technologies Card Printer Solutions
9800 NW 41st Street, Suite 220
Doral, FL 33178 USA
Phone: + 1 (305) 558 3100
Fax: + 1 (305) 558-8485
e-mail: latinsales@zebra.com
Website
www.zebracard.com