Andrew Wireless Innovations Group TFAM1719 Optical wireless distribution system User Manual Manual 2
Andrew Wireless Innovations Group Optical wireless distribution system Manual 2
Contents
- 1. Manual
- 2. Manual 2
Manual 2
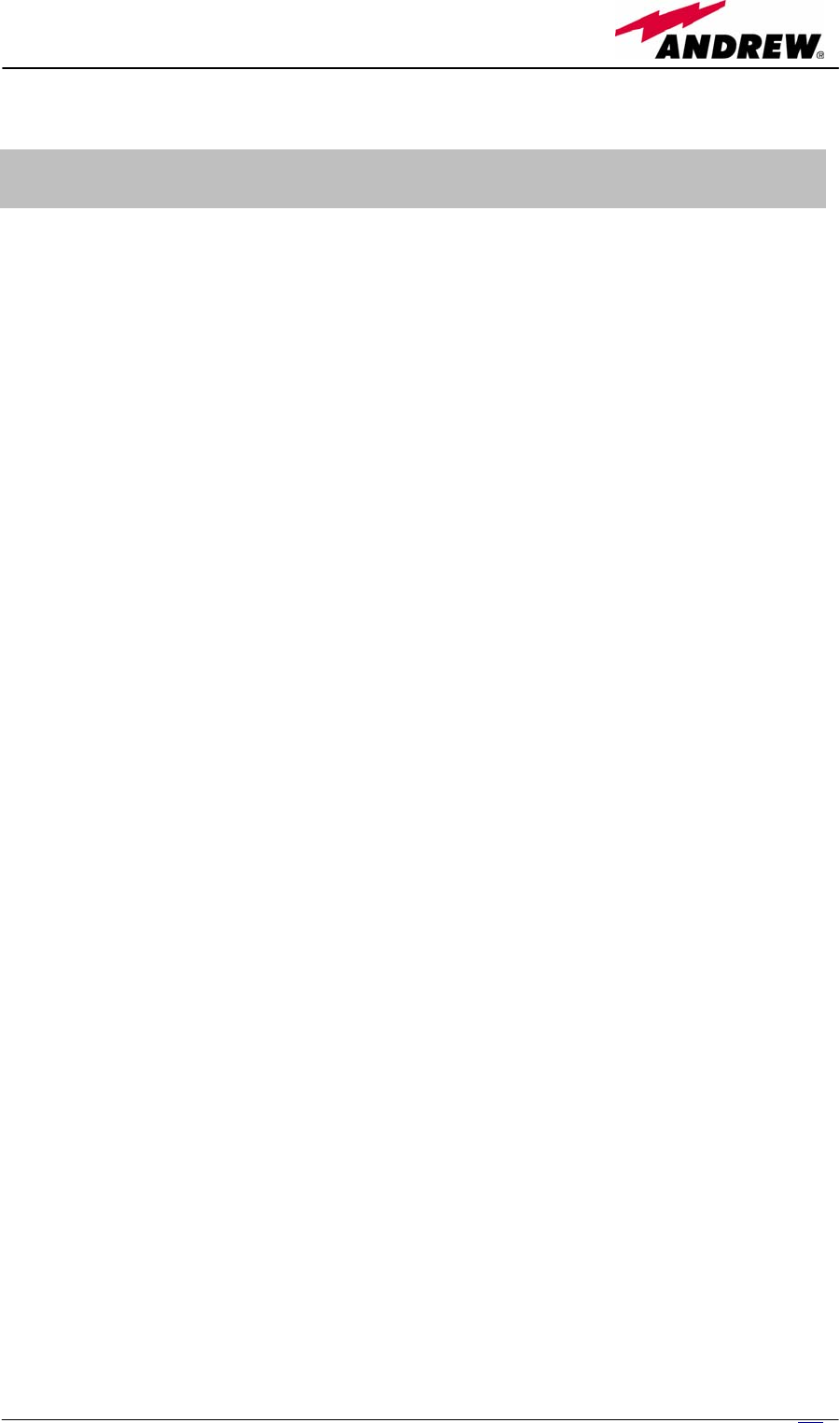
113
MN024-08
5. Rack-based Master Unit
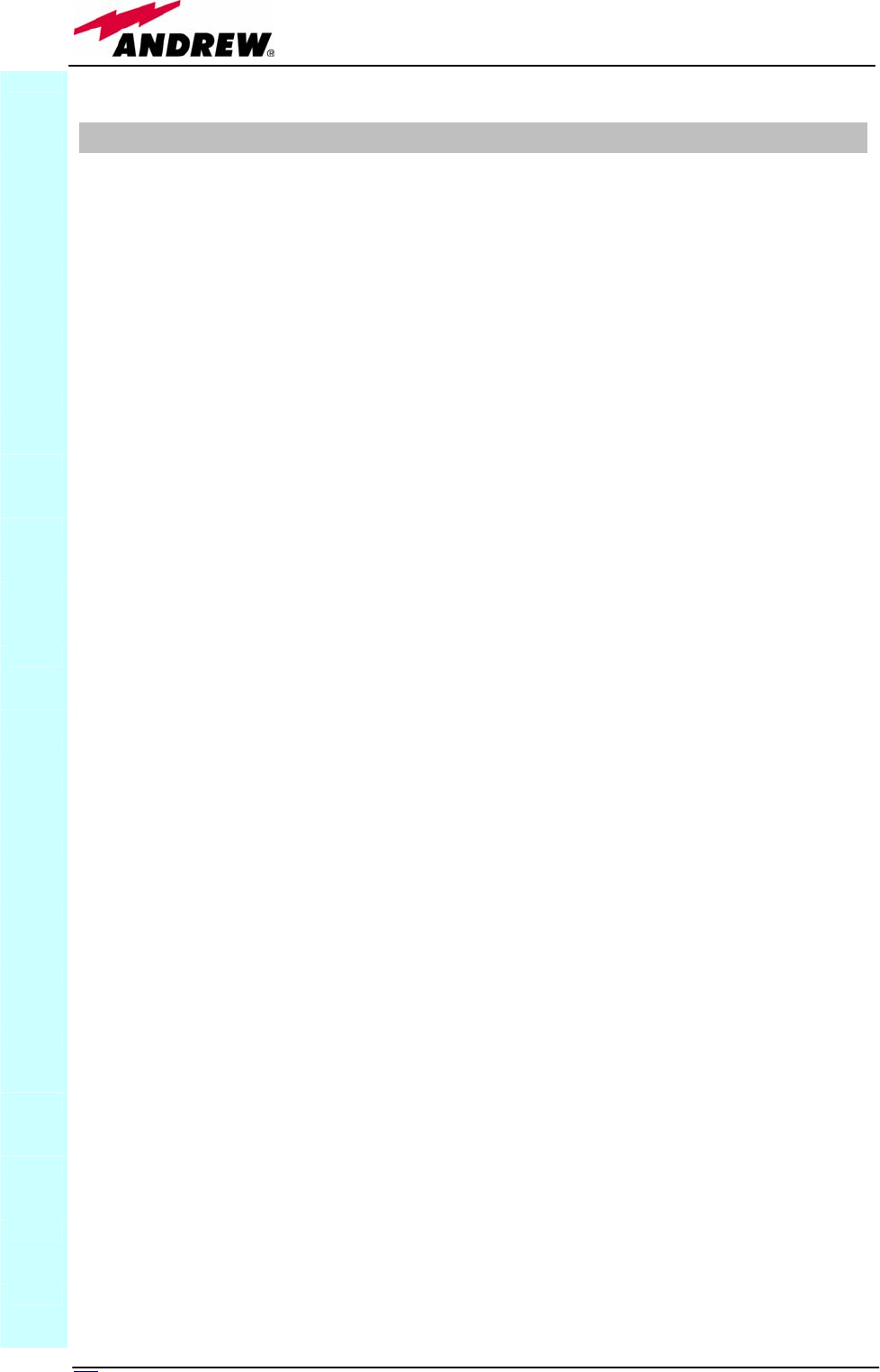
114 User Manual
5.1. TPRNx4 subrack
TPRN
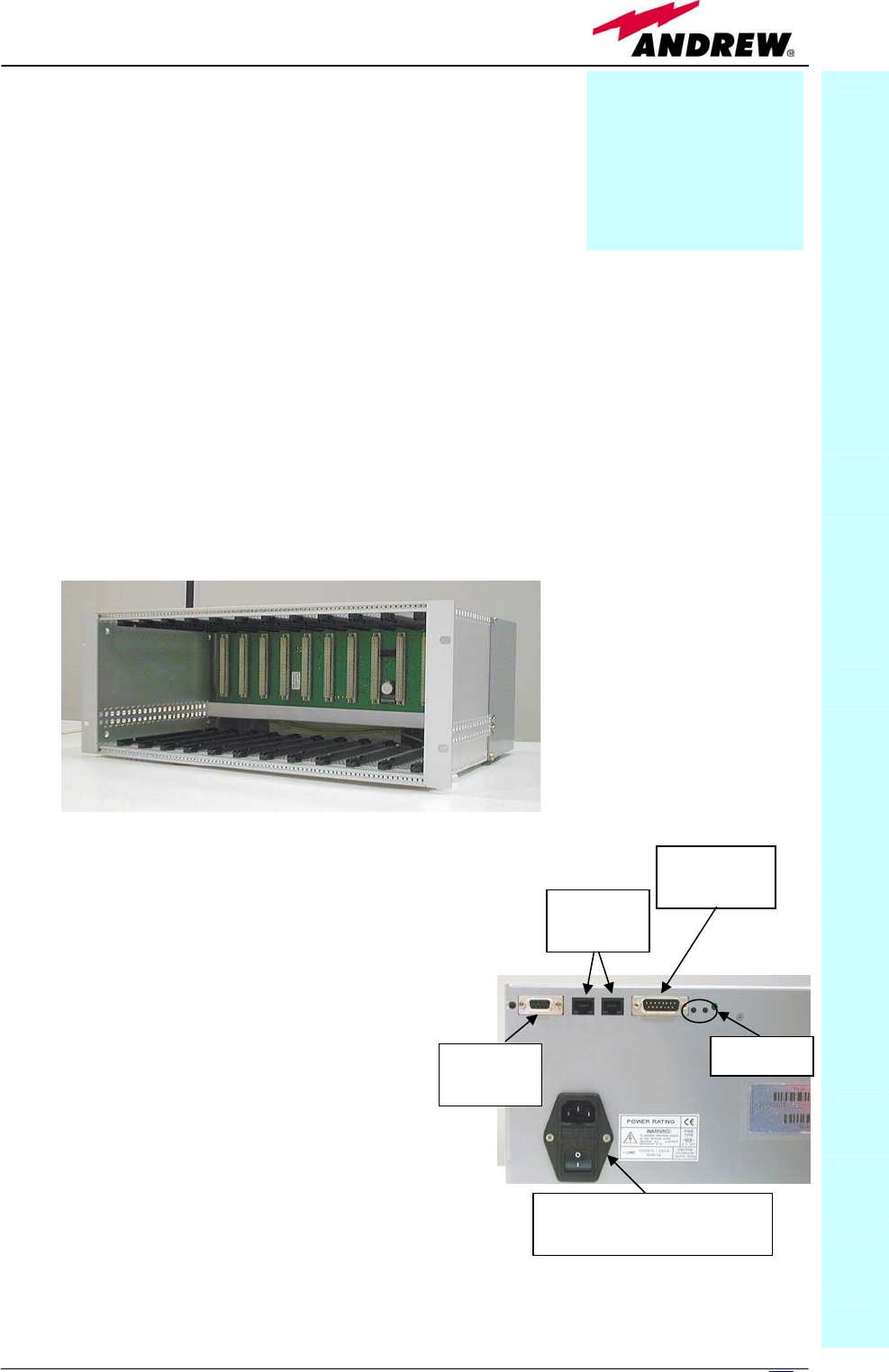
115
MN024-08
Major TPRN features
The TPRNx4 is a 19”subrack where all the Britecell Plus
plug-in modules can be inserted. Britecell Plus
equipment provides a wide variety of these sub-rack
models differentiated by power supply. Each one is
provided with:
• 12 free slots, each with Height=4HE, Width=7TE
• Power supply 220 Vac or -48 Vdc
• Locally or remotely connectable through:
¾ RS232 serial port
¾ RS485 two-wire bus
¾ sub-D 15 pin male-connector
• Internal microcontroller for I2CBUS alarm collection
• Manual reset button, able to re-initialize both the inserted modules and the
TPRN microcontroller
• Manual stand-by button, able to re-initialize the inserted modules, while
keeping the TPRN microcontroller working.
TPRN
Power supply (picture
shows 220Vac version)
RS232
port
RS485
ports
sub D 15
connector
buttons
Fig. 5.1: Front view of the TPRN sub-rack with power
supply and communication ports on the back
Fig. 5.2: Back view of the TPRN sub-
rack with power supply and
communication ports on the back
Module name:
Subrack
TPRNx4
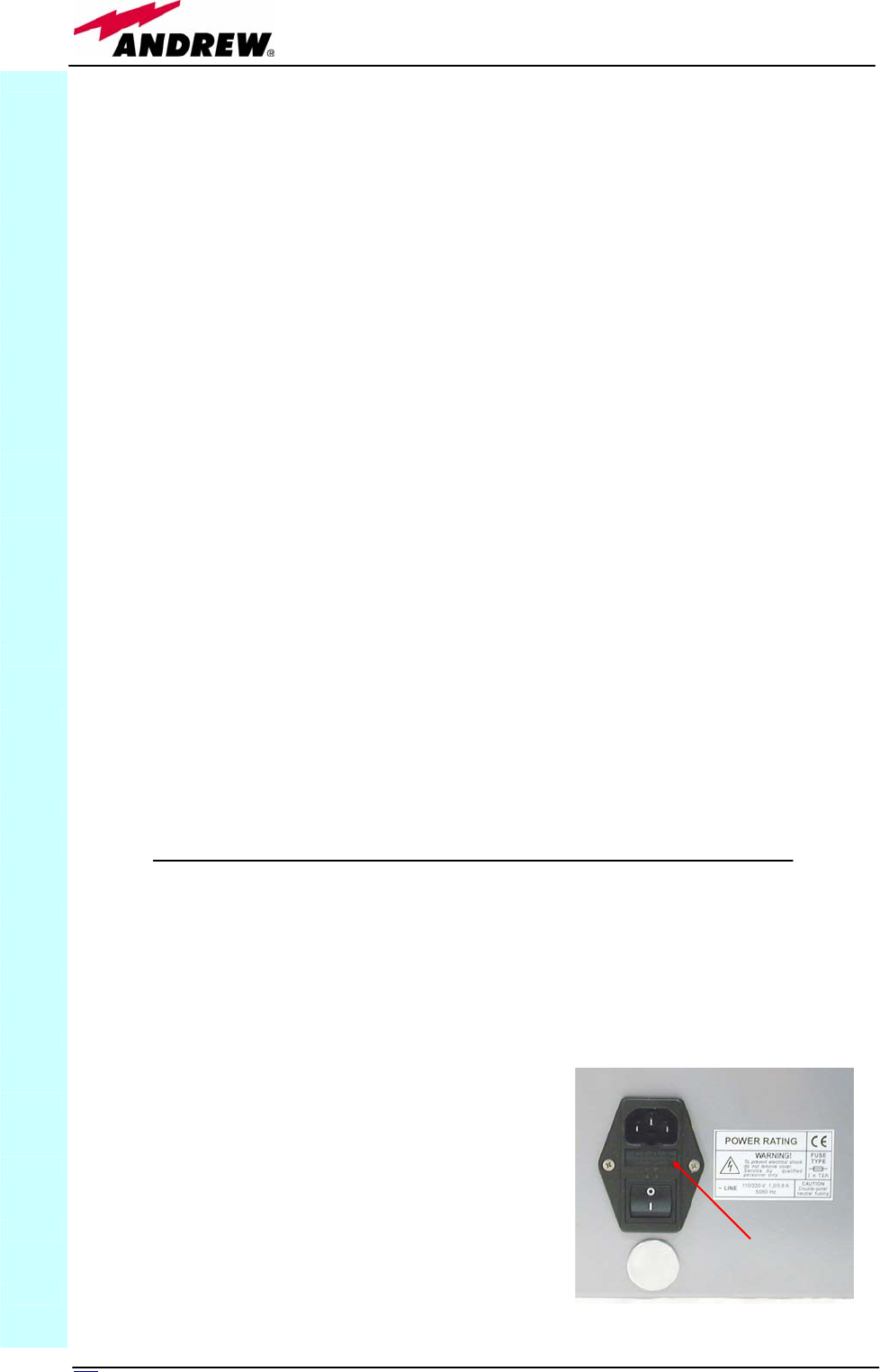
116 User Manual
TPRN models
A brief description of all the available TPRN sub-racks is reported hereinafter.
Passive sub-rack (TPRN04)
• TPRN04 is a passive sub-rack. It does not provide power supply to any
inserted module, and therefore it is designed to host passive modules
only. It can be useful in a multi-sub-rack system, in case the customer
decides to put all the active modules in an active sub-rack, to be chosen
among the following ones.
220 Vac powered sub-racks (TPRN14 / TPRN24)
• TPRN14 is an active sub-rack designed to be fed through 220 Vac
universal mains. Both the connector for 220Vac power supply and the
communication ports are placed on the sub-rack rear. The 220 Vac power
supply is not redundant (ie, no spare adapter is provided).
• TPRN24 is an active sub-rack designed to be fed through 220 Vac
universal mains. Both the connector for 220Vac power and the
communication ports are placed on the sub-rack rear, and the 220 Vac
power supply is redundant: i.e., a spare adapter guarantees the correct
system operations even in case the main 220Vac adapter has a
breakdown.
-48Vdc powered sub-rack (TPRN34)
• TPRN34 is an active sub-rack designed to be fed through –48 Vdc
negative supply. Both the connector for -48Vdc power supply and the
communication ports are placed on the sub-rack rear.
TPRN power supply
All the TPRN models refer to one of the following power supplies.
Universal mains
(85 to 264Vac, 50/60Hz).
This connector is mounted on the TPRN back
panel either for the redundant version or the
simple one. A ground terminal and a couple
of fuses are also included. Fuses have to be
replaced in case they fail (when it happens
the supervision system detects the failure).
TPRN
F
uses
Fig. 5.3: 85 to 264Vac connector
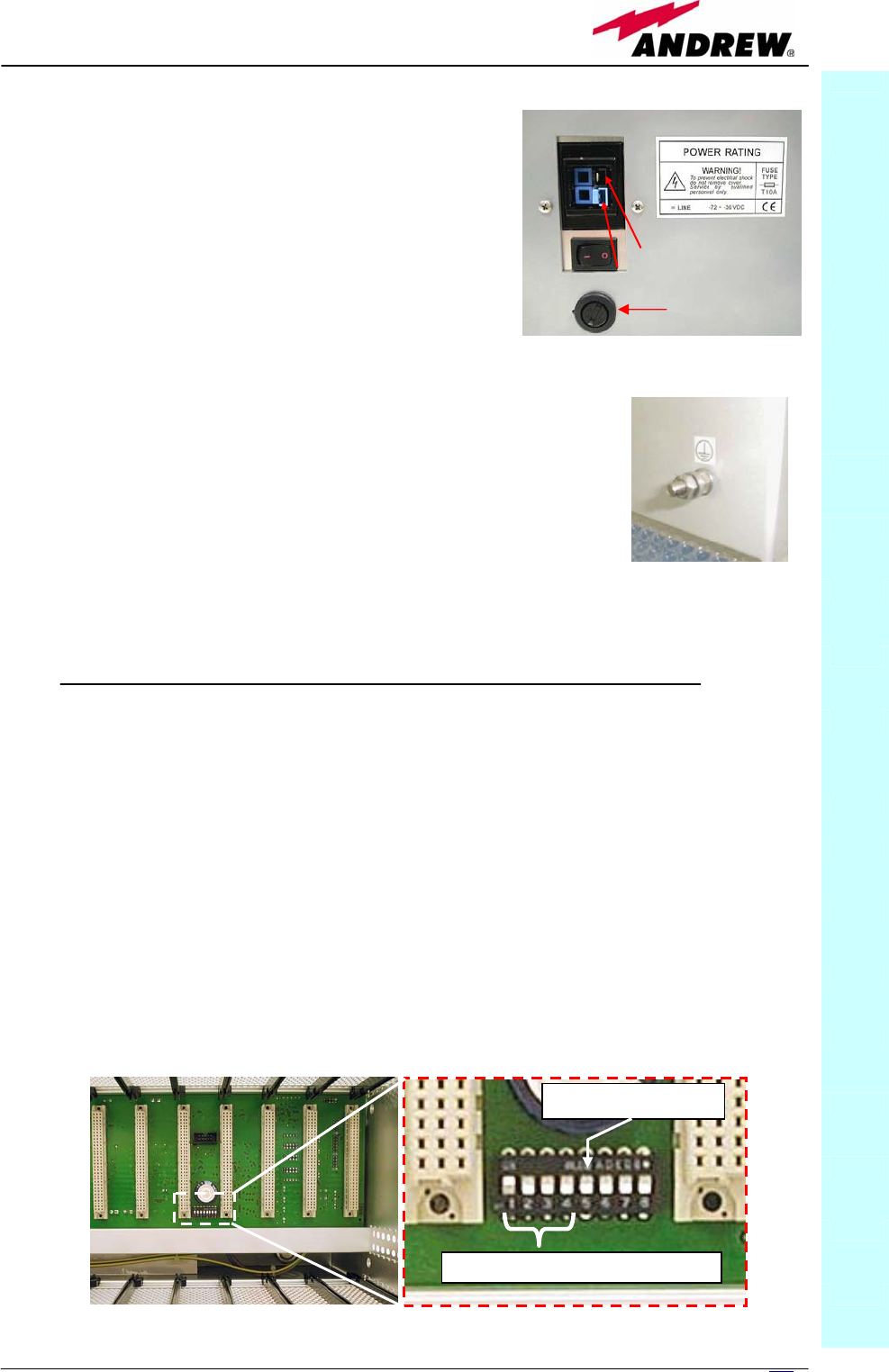
11
7
MN024-08
-48 Vdc
(-72 to -36 Vdc)
This connector is mounted on TPRN back panel.
A fuse is provided underneath the –48 Vdc
connector, and has to be replaced in case it
fails (when it happens the supervision system
detects the failure).
Whatever power supply is chosen (85 to 264 Vac or -72 to -
36 Vdc) an additional external ground terminal is provided
on the TPRN rear (fig. 5.5).
The external power supply (220Vac or -48Vdc) is converted into a +12Vdc
voltage allowing feeding the active modules inserted into the TPRN.
TPRN ports
The TPRN sub-rack is provided with a set of I/0 ports which allows the
connection to any external device.
RS232 serial port
The RS232 serial port can be used to connect the TPRN sub-rack to the
remote supervision unit or to a laptop running LMT software. Please note that
a standard RS232 cable is needed.
The connection baud rate can be set to 9600bps or 19200bps, by properly
setting the dip-switch 5 standing on the interior TPRN backplane (fig. 5.6).
The baud rate setting through dip-switch 5 is shown in table 5.1.
TPRN
Fig. 5.4: -72÷-36Vdc connector
Fig. 5.5: ground terminal on the rear
RS485-addressin
g
di
p
-switches
(
1-4
)
Baud-rate dip-switch (5)
Fig. 5.6: Dip-switches on TPRN backplane.
Fuse
black terminal: 0V
blue terminal:-72 to -36Vdc
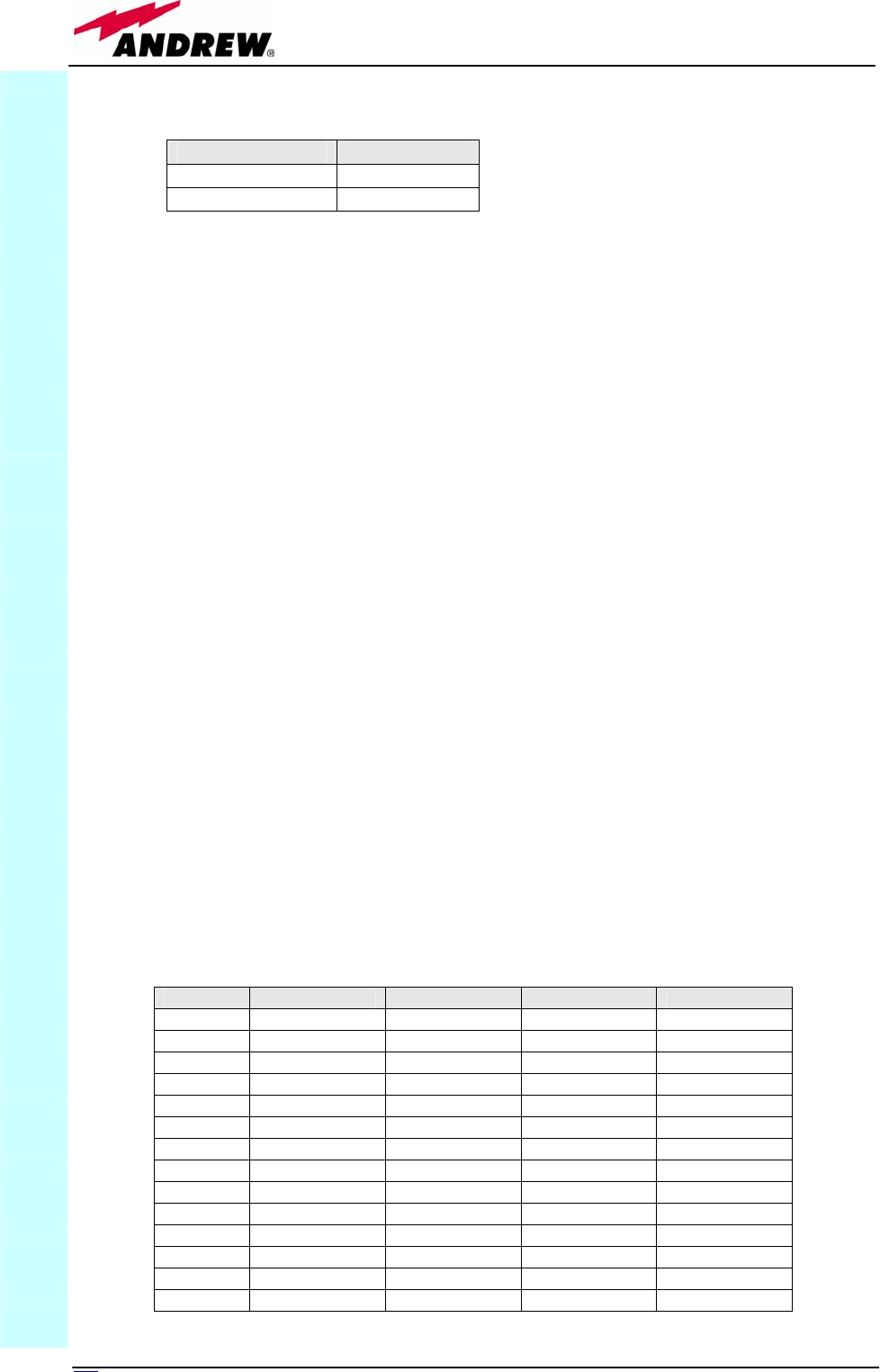
118 User Manual
Whichever baud rate you choose through dip-switch 5, remember that:
• the same RS232 connection speed must be set up on the remote
supervision unit
• the baud rate which is selected through the dip-switch 5 sets the
connection speed for both the RS232 port and the RS485 port as the
TPRN uses both ports with the same rate.
RS485 port
The RS485 port consists of two RJ45 connectors, which can both work as
input or output ports towards a RS485 bus.
This RS485 bus has to be used in order to connect a multi sub-rack system to
the remote supervision unit. In this case:
• the TPRN sub-racks have to be connected one another via RS485 bus
in a daisy chain;
• In order to monitor the whole system, the remote supervision unit has
to be connected to one of the TPRN sub-racks through RS232 port.
Before connecting the TPRN sub-racks belonging to a multi-sub-rack system,
remember to assign an exclusive binary address to each one. This is essential
in order to let the supervision system recognize the different master units
without any conflict.
The binary address assignment can be done through dip-switches 1,2,3,4,
which stand on interior TPRN backplane (see figure 5.6). A list of the
correspondences between the addresses and the dip-switches is provided by
table 5.2: simply note that dip-switch 1 is the least significant binary digit,
while dip-switch 4 is the most significant one.
Address Dip-switch 1 Dip-switch 2 Dip-switch 3 Dip-switch 4
0001 ON OFF OFF OFF
0010 OFF ON OFF OFF
0011 ON ON OFF OFF
0100 OFF OFF ON OFF
0101 ON OFF ON OFF
0110 OFF ON ON OFF
0111 ON ON ON OFF
1000 OFF OFF OFF ON
1001 ON OFF OFF ON
1010 OFF ON OFF ON
1011 ON ON OFF ON
1100 OFF OFF ON ON
1101 ON OFF ON ON
1110 OFF ON ON ON
TPRN
Baud rate [bps] Dip-switch 5
9600 OFF
19200 ON
Table 5.1: Setting RS232 baud
rate throu
g
h di
p
-
switch 5
Table 5.2: Dip-switches address settings
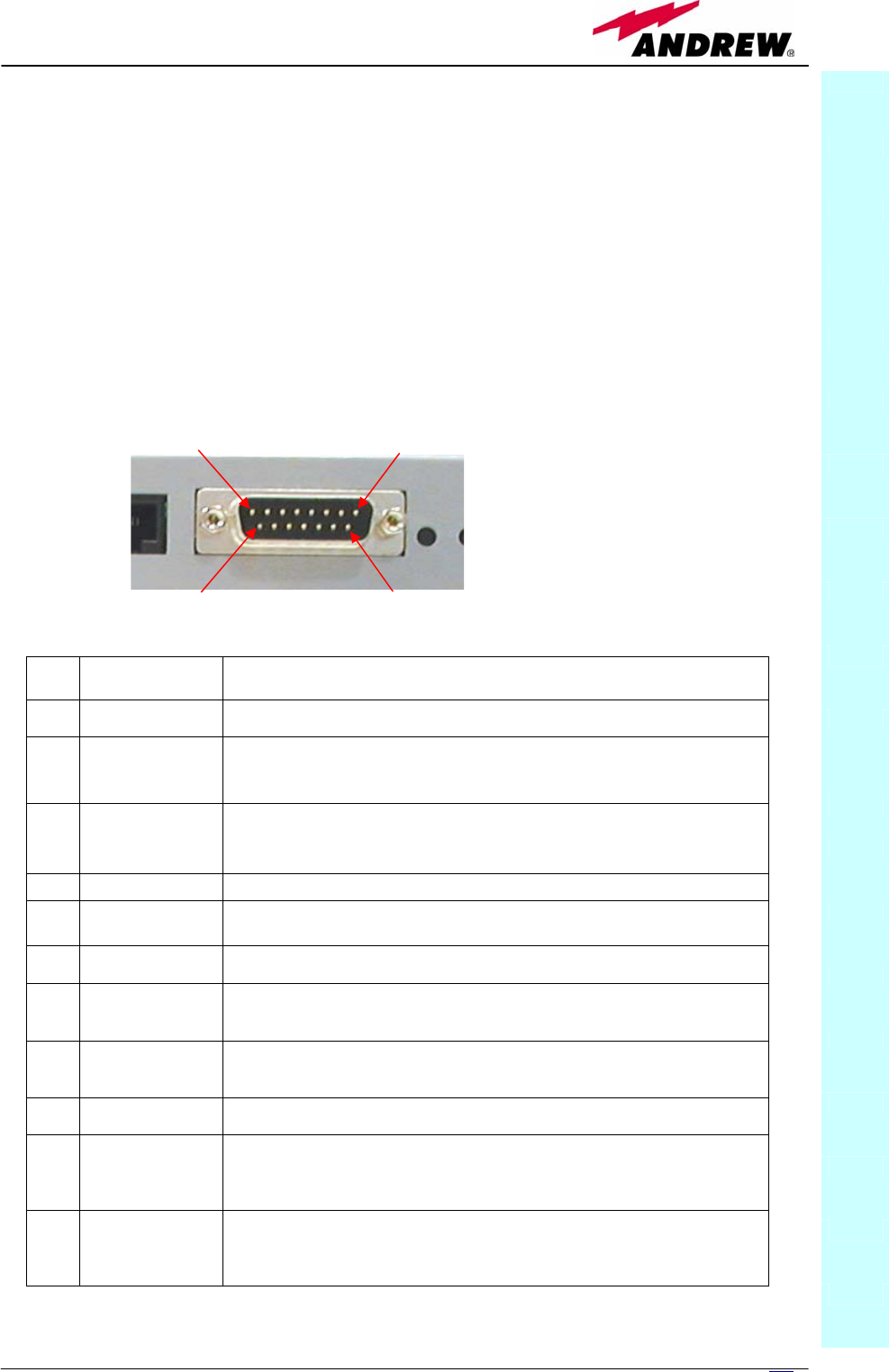
119
MN024-08
The baud rate of the RS485 ports is the same of the RS232 port as per the
dip-switch 5 setting.
Whichever baud rate you choose, remember that:
• the same RS485 connection speed has to be set up on all the
connected device (TPRN sub-racks or TSUN remote supervision unit);
• the baud-rate which is selected through the dip-switch 5 sets the
connection speed for both the RS485 port and the RS232 port.
Sub-D 15 poles male connector
The TPRN sub-rack provides a sub-D 15 poles male connector, shown in fig.
5.7.
PIN Name Meaning
1 Ground It is a ground terminal for digital inputs, i.e. for pin 2, 3, 9, 10.
2 Digital input n.1
(SW assignable)
This port can be used to monitor external equipment status. Once a default
working status has been assigned (through supervision system) to this input port,
any change is detected as a failure signal.
3 Digital input n.2
(SW assignable)
This port can be used to monitor external equipment status. Once a default
working status has been assigned (through supervision system) to this input port,
any change is detected as a failure signal.
4 Disconnected pin No meaning
5,6 Summary of
major alarms
These pins present an open circuit if a major alarm is active on the TPRN sub-
rack or on any module hosted in it.
7,8 Summary of
minor alarms
These pins present an open circuit if a minor alarm is active on the TPRN sub-
rack or on any module hosted in it.
9 Digital input n.3
(SW assignable)
This port can be used to monitor external equipment status. Once a default
working status has been assigned (through supervision system) to this input port,
any change is detected as a failure signal.
10 Digital input n.4
(SW assignable)
This port can be used to monitor external equipment status. Once a default
working status has been assigned (through supervision system) to this input port,
any change is detected as a failure signal.
11 Disconnected pin No meaning
12,13 Digital output n.1
(SW assignable)
These pins are terminals of an output port (output relay 1), which can be driven
through the supervision system. The output port can be set to “open” or “close”
condition. These 2 statuses can be used to pilot any external device connected to
subD-15 connector.
14,15 Digital output n.2
(SW assignable)
These pins are terminals of an output port (output relay 2), which can be driven
through the supervision system. The output port can be set to “open” or “close”
condition. These 2 statuses can be used to pilot any external device connected to
subD-15 connector.
TPRN
PIN 1 PIN 8
PIN 9
PIN 15
Fig. 5.7: sub-D 15 poles
male connector
Tab. 5.3: Functional description of pins provided by sub D male connector.
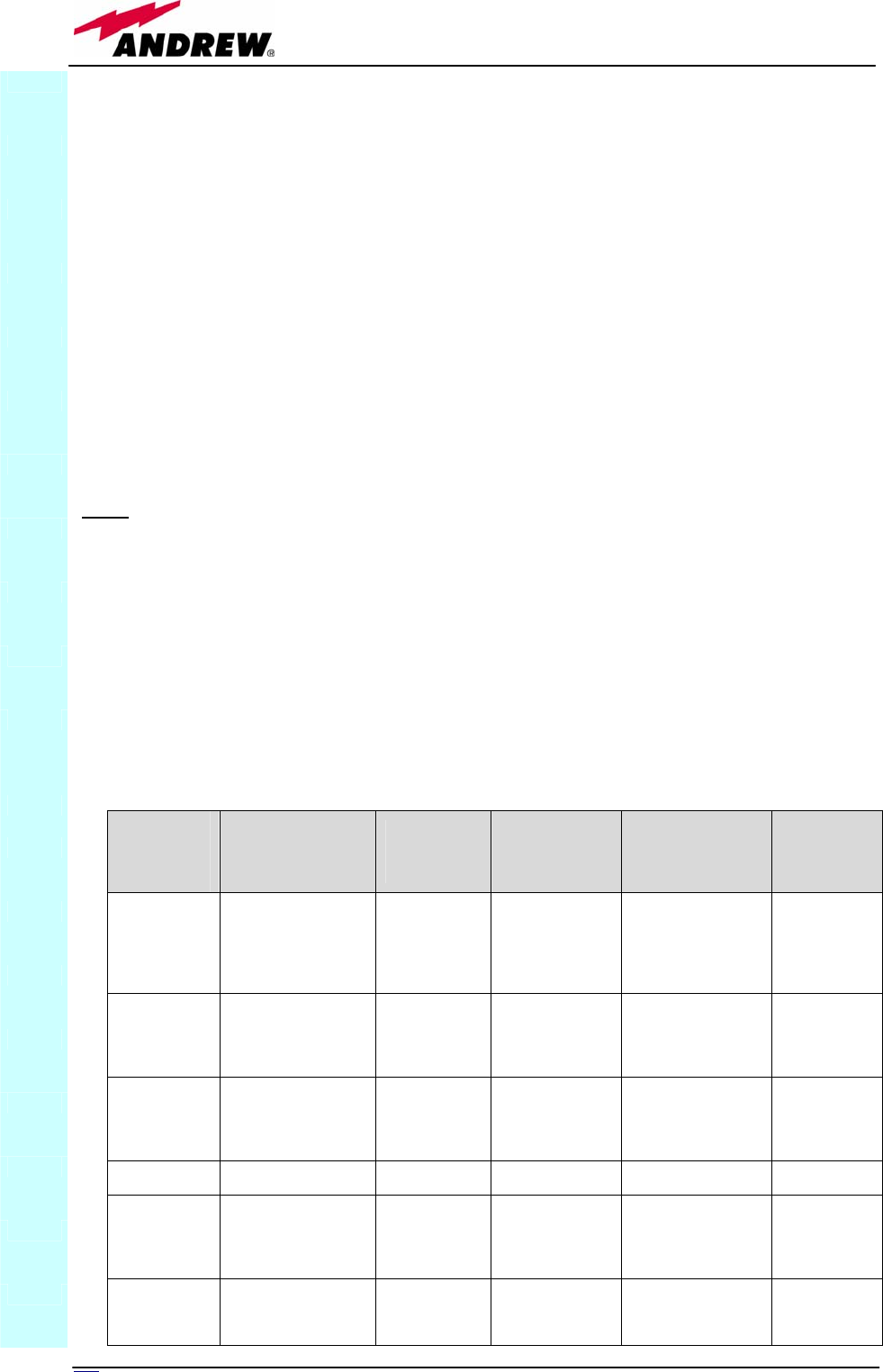
120 User Manual
As highlighted in the previous table, this connector provides:
• 4 opto-isolated input ports which can be used to reveal any failure
condition on external equipment. The default status of these input
ports can be defined through the supervision system. After that, any
change from default status will be revealed as a failure signal.
• a summary of major and minor alarms related to failures detected not
only on the TPRN sub-rack, but also on any active modules hosted by
the TPRN itself.
• 2 relay output ports, which be can used to drive any external device
connected to subD-15 pins adapter. By using the supervision system
each of these output ports can set up on “open” or “close” conditions.
A more detailed description of the meaning and functionality of each pin are
reported in table 8. The pins are numbered from left to right, and from top to
bottom (refer to fig. 18).
Note: The TPRN sub-rack uses I2Cbus standard protocol to collect status and
alarm information from hosted modules. Thanks to that, the alarm summaries
(provided through pins 5-6 and 7-8) report major and minor failures related
not only to TPRN sub-rack but also to any hosted module.
TPRN alarms
A full description of all TPRN alarms is provided by the Supervision system.
The table 4.8 provides a brief description of the TPRN alarms, as they are
reported by the LMT software o
ALARM
CODE
(TSUN
description)
ALARM
DESCRIPTION
ACTIVE
LED
SUPERVISION
PRIORITY
LEVEL
ACTION
RECOMMENDED
RELÉ
PRIORITY
LEVEL
(subrack)
Redundant
supply active
(only for
redundant
power supply
versions)
Backup power supply
activated YELLOW MAJOR Return the unit MINOR
Power Supply
alarm
There is a
degradation on the
power supply
provided to the
boards
RED MAJOR Return the unit MAJOR
I2CBUS bus
error
Internal I2CBUS
communication
malfunction
YELLOW CRITICAL
Check if the fault is
on the unit (see
supervision
system). If not
return the unit
MINOR
Temperature
alarm
Over-temperature
alarm YELLOW MINOR
Check ventilation
and environment MINOR
Aux input
alarm nr0
The device
connected to the
input alarm port 0
caused an alarm
condition
RED CRITICAL
Check the status of
the connected
device
-
Aux input
alarm nr1
The device
connected to the
input alarm port 1
caused an alarm
RED MAJOR
Check the status of
the connected
device
-
TPRN
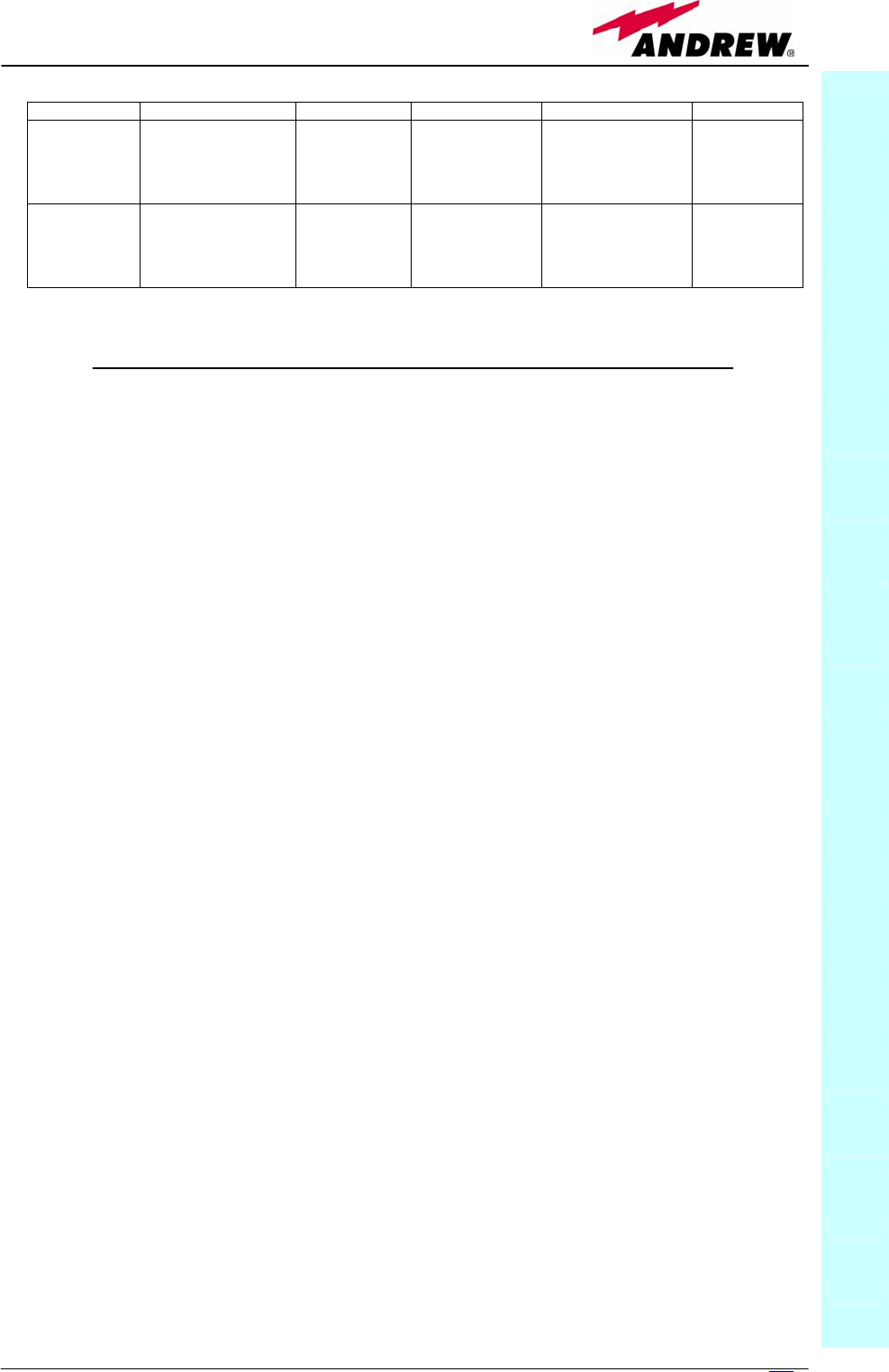
121
MN024-08
condition
Aux input
alarm nr2
The device
connected to the
input alarm port 2
caused an alarm
condition
RED MINOR
Check the status of
the connected
device
-
Aux input
alarm nr3
The device
connected to the
input alarm port 3
caused an alarm
condition
RED WARNING
Check the status of
the connected
device
-
Warning (recommended for system designing and
installing)
Providing a correct heat dissipation
For a correct use of the TPRN sub-rack, it is important to verify that:
• the system is designed in order to put no more than 8 TFLN inside a
TPRN sub-rack. This guarantees a proper heating dissipation for the
system. In case you want to install more than 8 it is important to
provide the sub-rack with a proper ventilation system;
• active and passive modules should be alternated as much as possible
inside the TPRN sub-rack avoiding too many active cards being inserted
close together;
• in case the system consists of more than one TPRN sub-rack, a
minimum distance of 1 HE has to be kept between nearby TPRN sub-
racks to ensure proper heat dissipation. The rack containing the TPRN
sub-racks has to be large enough to guarantee this correct distance
between master units.
Minimizing equipment costs
In order to reduce the cost of Britecell Plus equipment, a multi-sub-rack
system should be designed according to the following guidelines:
• a passive sub-rack (TPRN04) may be used to house only passive
modules;
• an active sub-rack (TPRN14, TPRN24, TPRN34) may be used to sustain
all the active modules, and some of the passive ones (as stated above,
it is advisable to alternate active and passive cards into an active sub-
rack).
TPRN
Tab. 5.4: Description of the alarms of the TPRN subrack
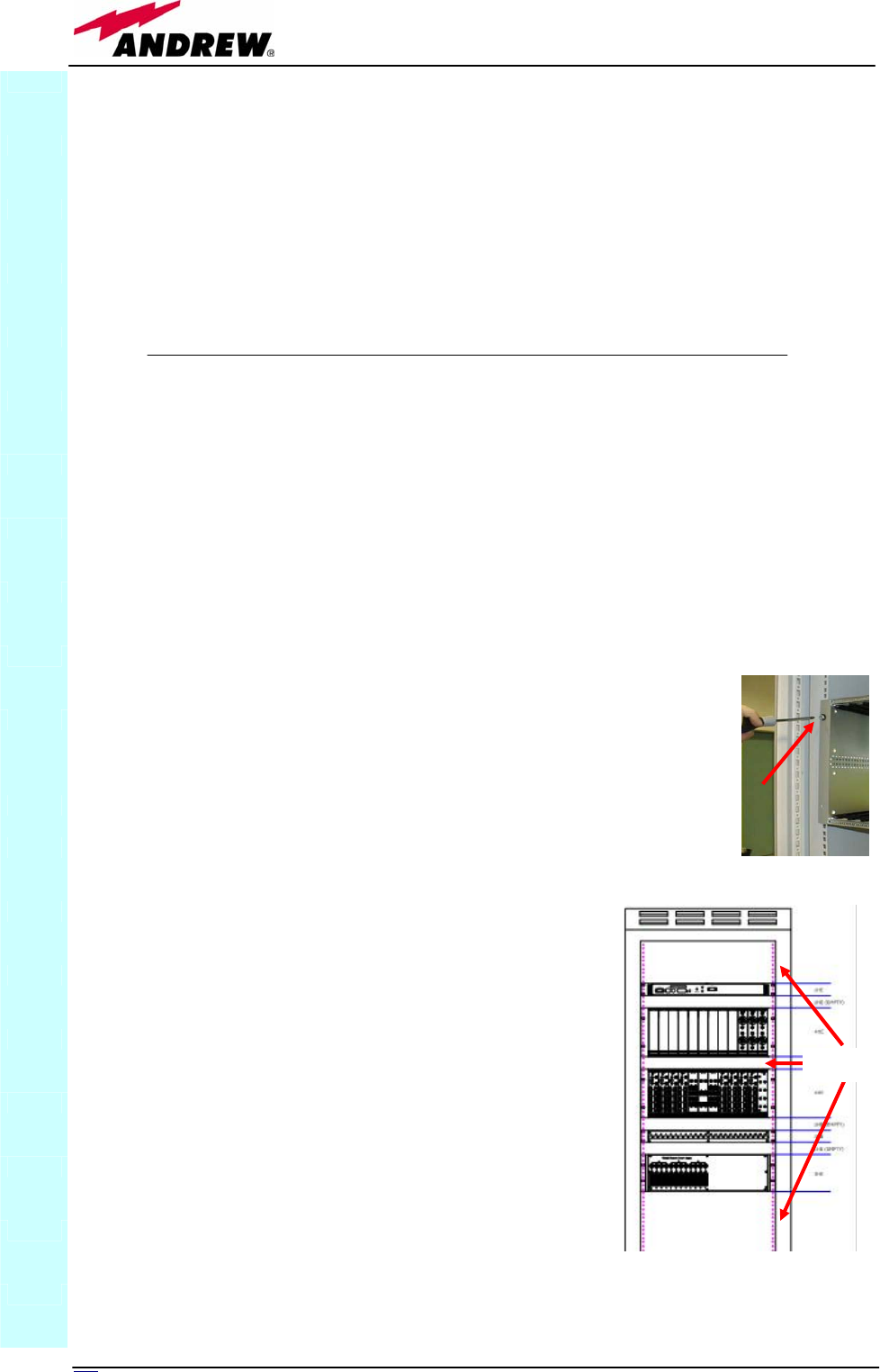
122 User Manual
Setting the dip-switches in a multi sub-rack system
If you are installing a multi-sub-rack system, remember to assign each sub-
rack an exclusive binary address, by properly setting dip-switches 1,2,3,4 on
the interior TPRN backplane (see fig. 5.6 and Tab.5.2). Dip-switch 5 has to be
set on each TPRN sub-rack in order to fix the baud rate for RS485 and RS232
port. Connecting TPRNs through RS485 port is necessary when supervising
the whole multi sub-rack system through the remote supervision unit (to be
set at the same baud rate).
TPRN Installation
The TPRN kit provides:
• 1 TPRN sub-rack
• 1 suitable power cord
• 1 standard RS232 cable (male-female), 2m
• 1 CD Manual
First of all insert the sub-rack into the cabinet and apply 4 screws (not
provided) in order to fix it (fig. 5.8a).
To have a correct TPRN installation, distance between the front
door of the rack and the front side of the TPRN should be at
least 15cm otherwise RF and optical cables can be damaged
when cabinet door is closed.
Leave at least 1HE distance between two subracks
in order to facilitate air circulation.
Leave at least a 1HE free space between the
bottom or the top of the cabinet and the TPRNs.
Connect the ground to the safety ground terminal. Then, connect the power
supply connector to the mains.
TPRN
Fig. 5.8(a): At each front-corner
the subrack is provided with a
screw in order to be fixed to the
1HE
Fig. 5.8(b): Distance between
subracks should be at least 1HE in
order to facilitate air circulation

123
MN024-08
TPRN Start-up
Before switching on the TPRN sub-rack, make sure that:
• all expected modules have been inserted
• the modules have been connected each other by RF jumpers, according
to what has been planned during system design
• every TFLN contained in the Master Unit has been connected to its TFAx
remote units
• each TFAx remote unit has been connected to its coverage antennas
• the remote supervision unit (if present) has been connected/housed
to/into the Master Unit
• different sub-racks have been connected each other via bus RS485 and
each of them have different addresses
• the rack housing the TPRN is large enough to leave a minimum
distance of 1HE between contiguous TPRN sub-racks
Remember that TFAx remote units have to be switched on before relevant
Master Unit.
Once the TPRN sub-rack has been switched on, the system behaviour can be
summarized as per the following steps:
• About 10sec after the TPRN sub-rack has been switched on, all TFLN
modules housed in the TPRN itself begin a “discovery” phase in order
to identify and collect status of the connected TFAx remote units.
While the discovery phase is working (max. 4min. depending on the
system complexity) each TFLN general alarm (i.e., LED “┌┘”) blinks,
whereas the other TFLN LEDs go on showing the detected status.
Do not connect/disconnect any cable or piece of equipment until all
TFLN modules have finished the discovery phase. This may result in
failing the identification of TFAx. Anyway during the discovery phase,
the whole system still works correctly as discovery process aims to
collect information about TFAx but without affecting basic system
functionalities.
TPRN
Fig. 5.8(c) : Power supply and
ground terminals on the rear
side of the TPRN subrack
Power
supply
Ground
terminal
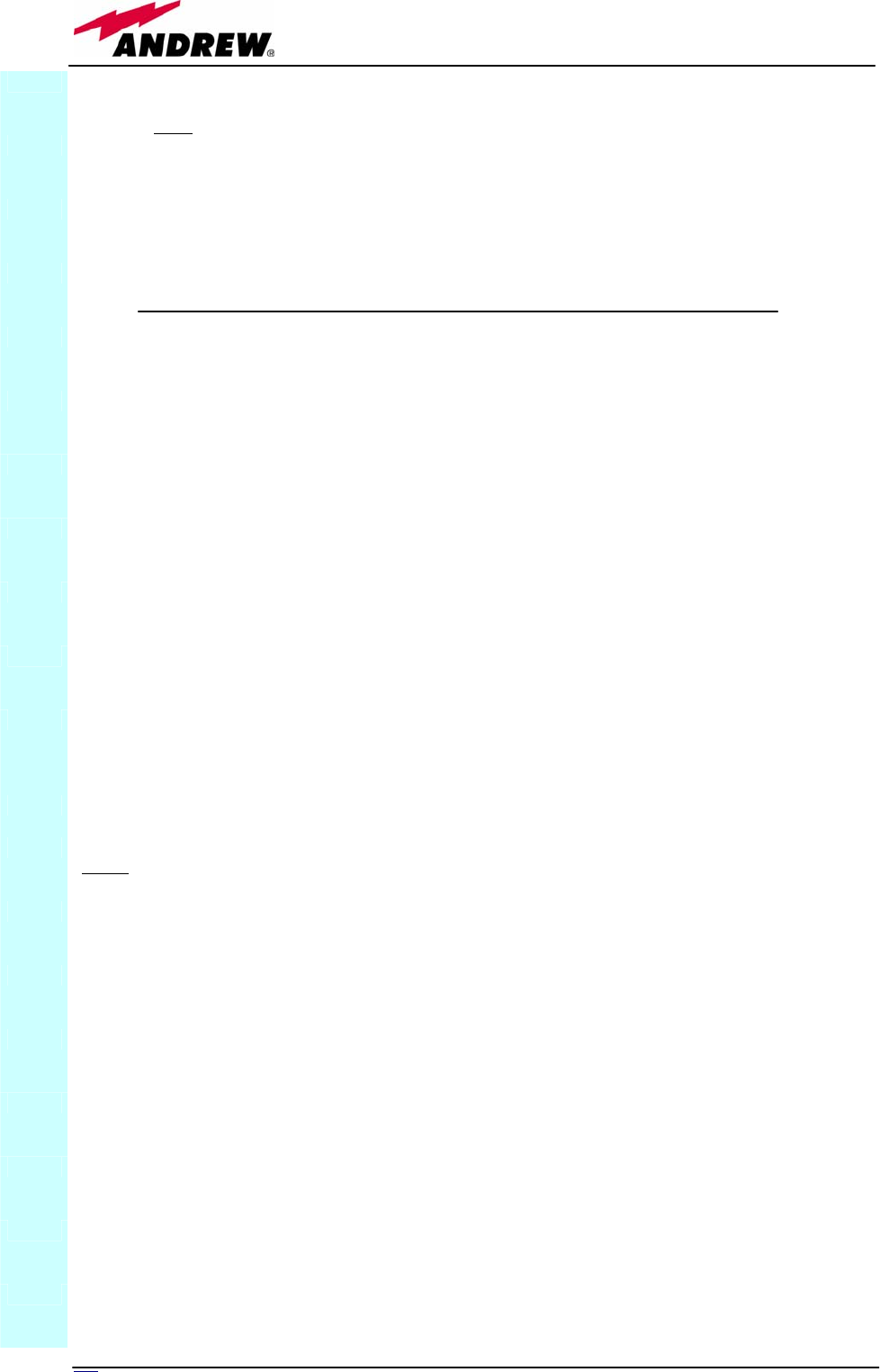
124 User Manual
• O
nce the discovery has finished, the general alarm (i.e. the LED “┌┘”)
on each TFLN panel stops blinking and switches OFF (provided that
the TFLN master optical TRX is not affected by a general failure).
TPRN troubleshooting
In case a TPRN sub-rack shows any problem a more detailed status and
alarm description could be provided through the remote supervision unit.
A complete overview of TPRN alarms is reported in the previous Table 5.4.
The power supply degradation occurs in case the +12Vdc power falls below
an in factory set threshold level. In this case, TPRN automatically turns to
standby mode so that no over-current gets through the circuitry of hosted
modules, thus preserving the system integrity. Once power supply has been
repaired, the TPRN needs to be rebooted. In case the TPRN sub-rack is
equipped with a redundant power supply (TPRN24), a degradation of the
+12 Vdc power results in an automatic switching from main to spare
converter. In case also redundant power supply degrades the TPRN
automatically turns to stand-by mode. Once the power supply has been
repaired the TPRN needs to be rebooted.
I2Cbus alarm occurs when TPRN sub-rack cannot communicate with one or
more hosted module. Each TPRN slot is able to automatically detect the
presence of a module inside the slot. If the module is detected but TPRN is
not able to communicate with it through I2Cbus alarm is activated.
Note: at commissioning remember to mask the unused slots through LMT
software (please refer to the relevant manual for more information) to avoid
not significant alarm being switched on.
In order to carry out a troubleshooting procedure, please check LMT or
supervision system handbooks.
TPRN
Note: in case discovery doesn’t start automatically, check through the LMT or the
remote supervision whether it has been disabled (refer to LMT or remote supervision
system manuals for further information).
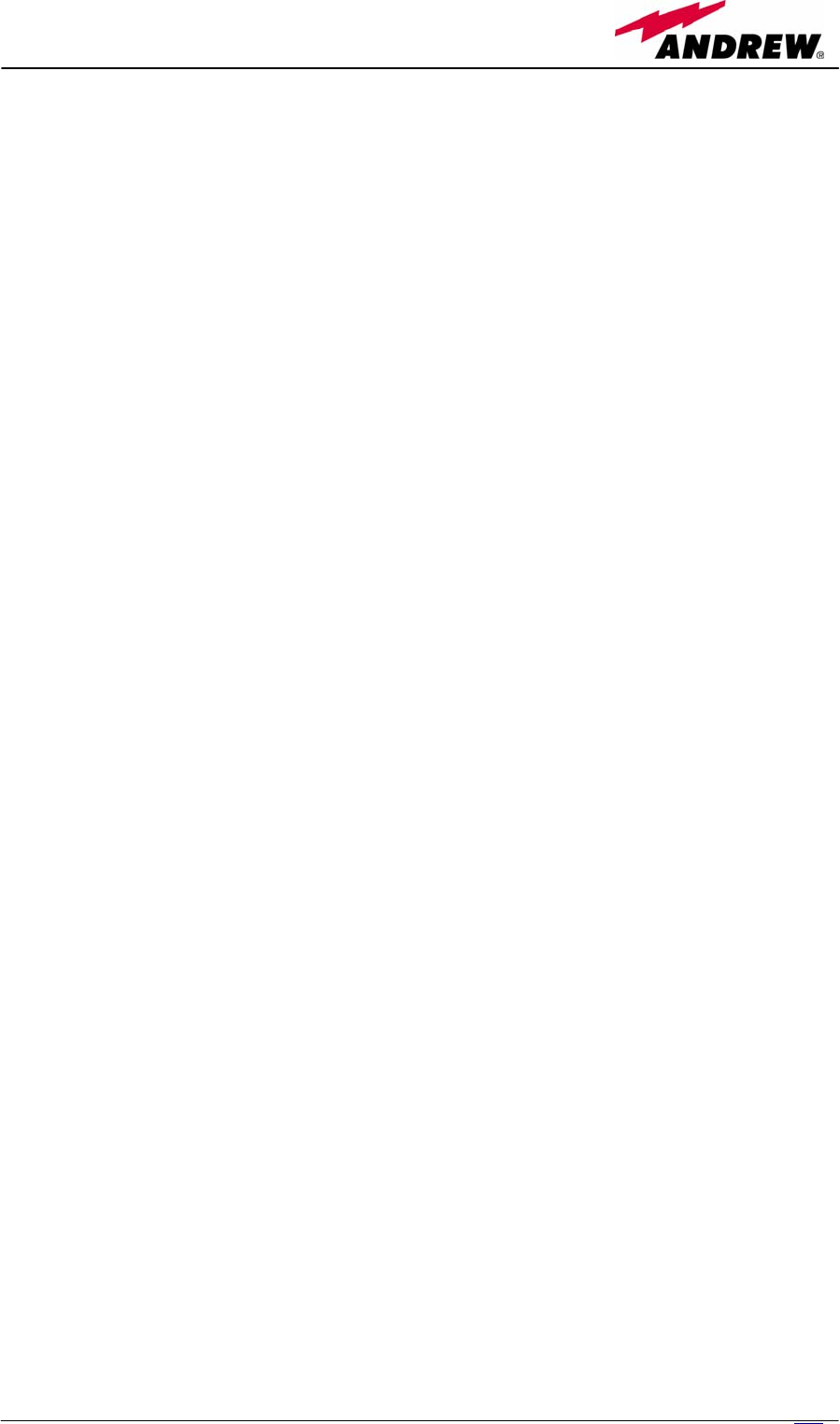
125
MN024-08
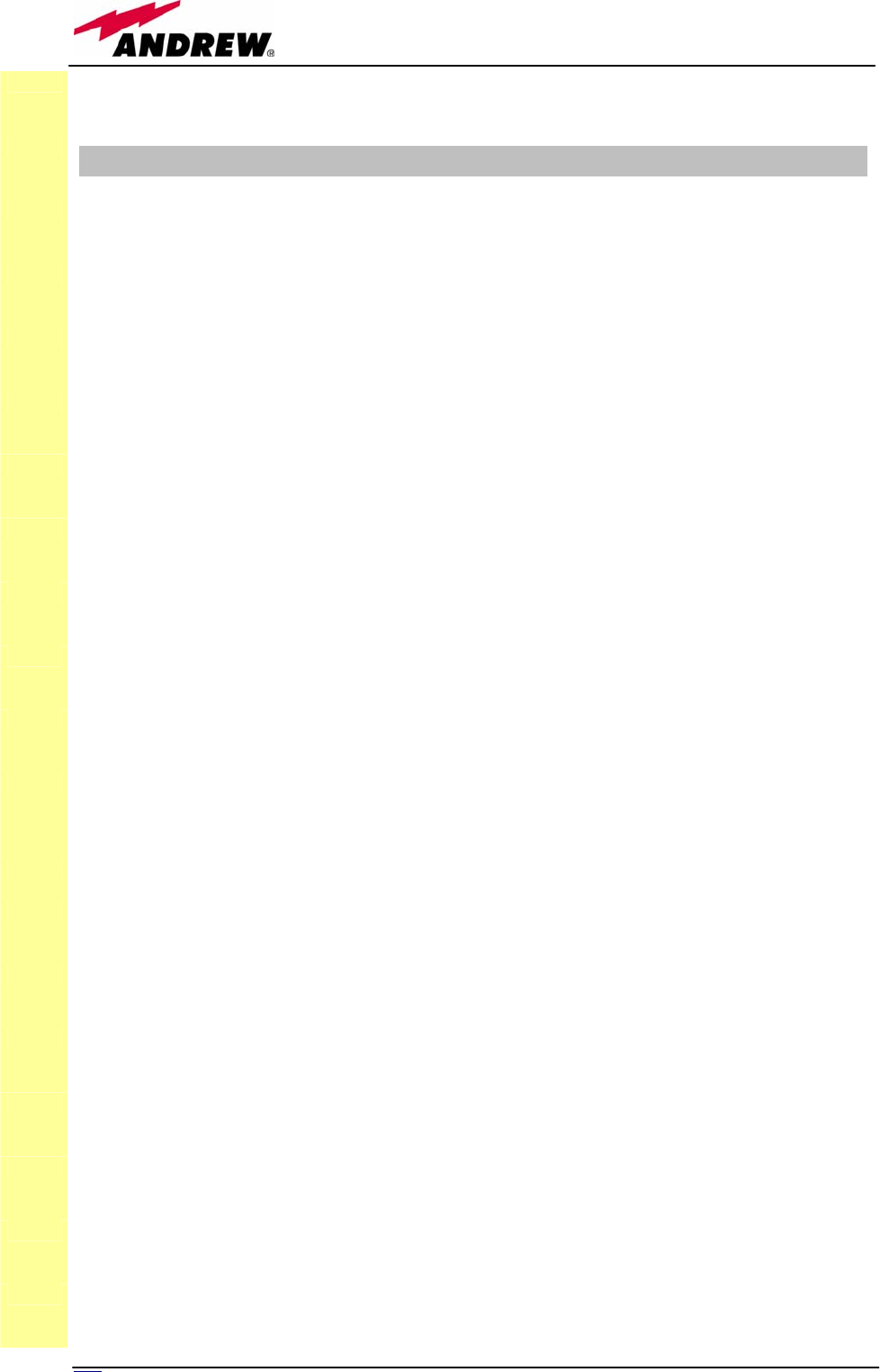
126 User Manual
5.2. Master Optical TRX, TFLN
TFLN
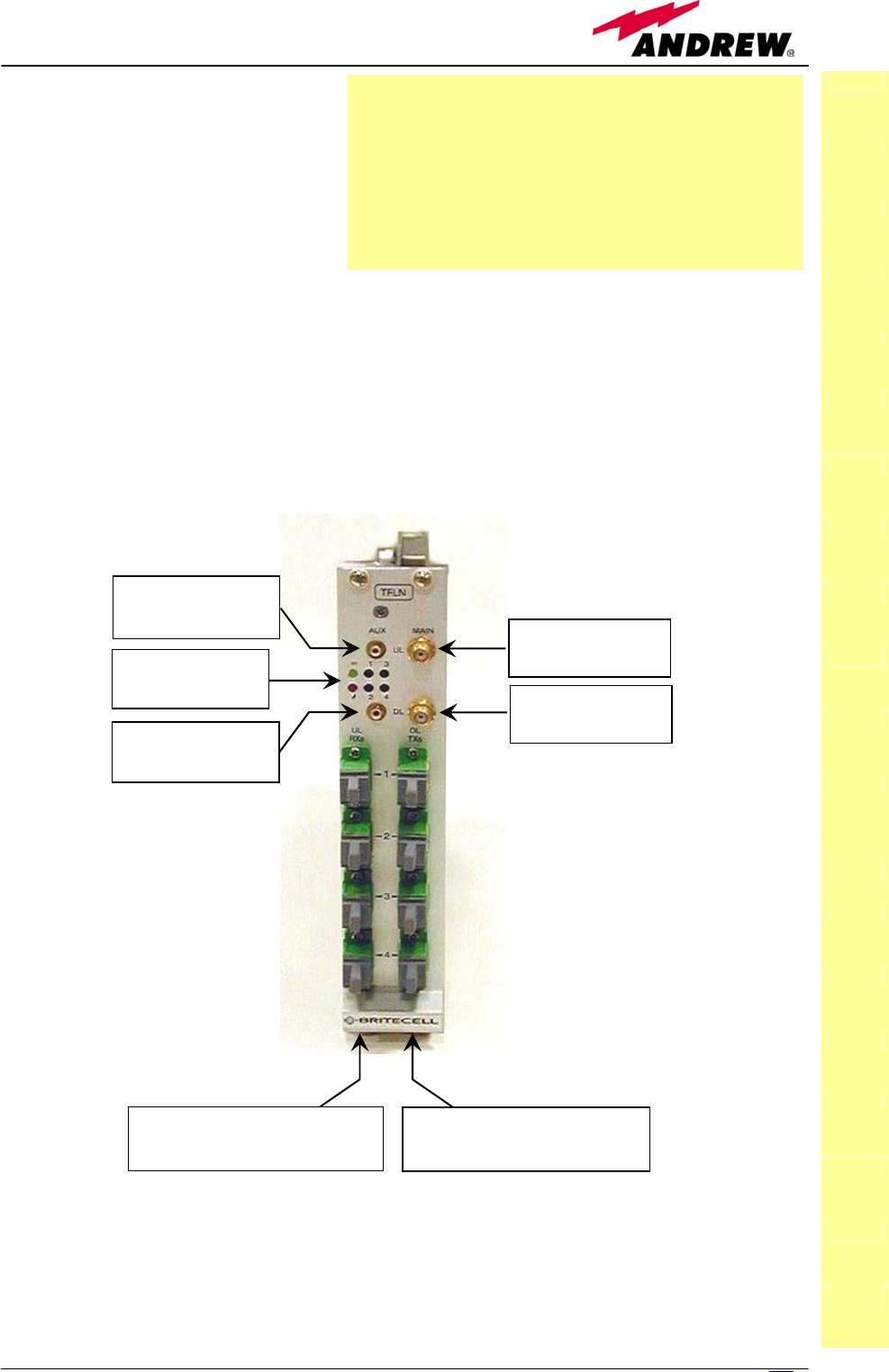
12
7
MN024-08
Main tasks carried out
by the TFLN module
Downlink (DL):
¾ RF-to-optical conversion of
the input RF signal
¾ Optical splitting: input RF
signal is split onto 4 optical outputs
Uplink (UL):
¾ Optical-to-RF conversion of the 4 input optical signals
¾ Automatic Gain Control (AGC) of each converted signal to compensate
optical losses;
¾ RF combining of the 4 adjusted signals into a single RF output
TFLN
Status and
Alarm LED DL RF Main
Input (SMA-f)
UL Optical Fibre
Adapters (SC-APC)
UL RF Main
Output (SMA-f)
DL Optical Fibre
Adapters (SC-APC)
UL RF Auxiliary
Output (SMB-m)
DL RF Auxiliary
Input (SMB-m)
Fig. 5.9 . The TFLN Master Optical TRX
Module name:
Master Optical TRX
TFLN
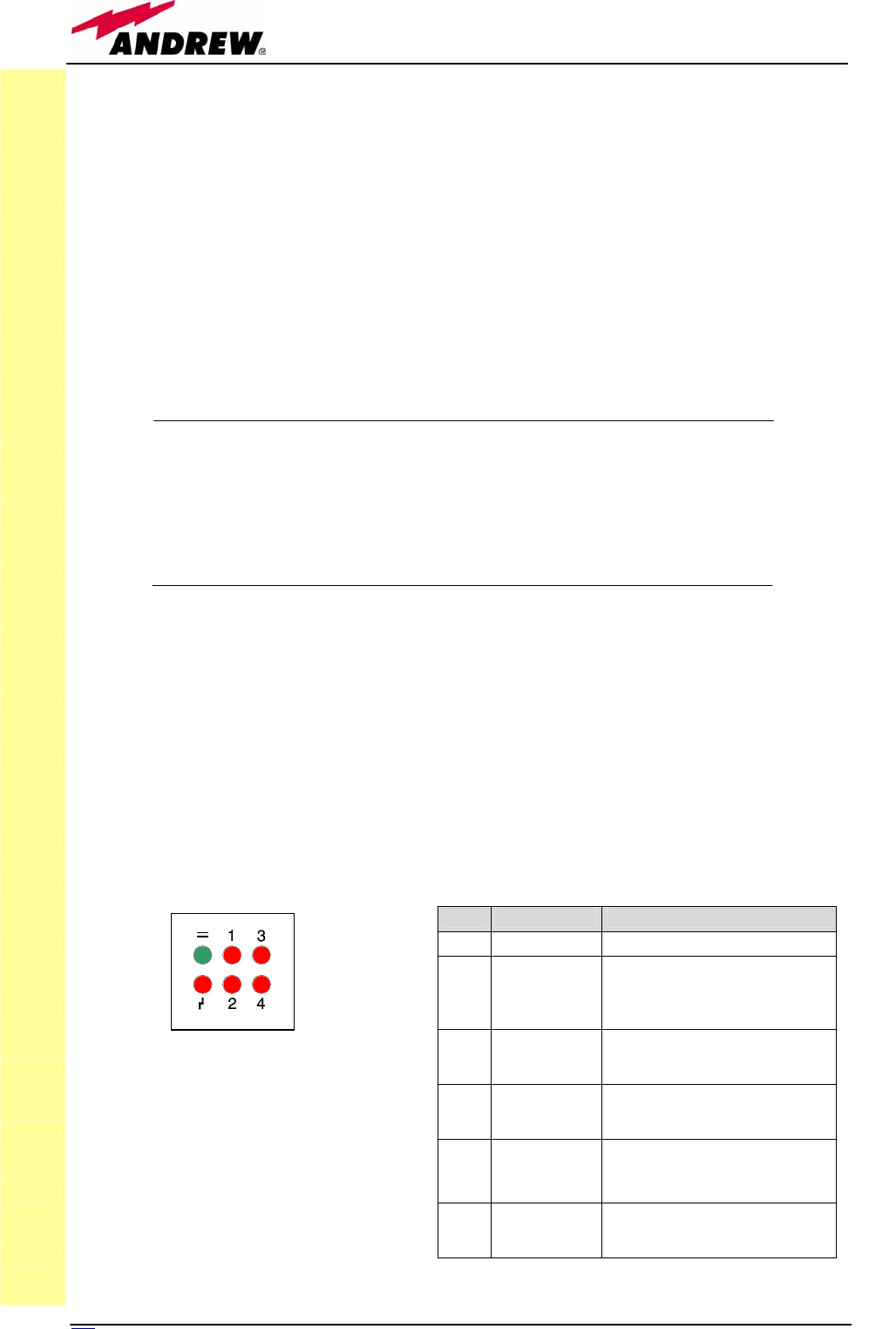
128 User Manual
RF ports
• 1 DL RF input port
• 1 auxiliary DL RF input port
• 1 UL RF output port
• 1 auxiliary UL RF output port
Note: nominal input levels required at RF ports is +10dBm (please refer to
datasheet for further information), as well as RF outputs may require a power
adjustment to fill within the BTS receiving range.
In order to fulfil these requirements, external UL and DL attenuations may be
required (see TBSI module).
Optical ports
• 4 DL optical output ports (SC/APC)
• 4 UL optical input ports (SC/APC)
TFLN visual alarms
The TFLN front panel is provided with 6 LEDs (see on the right), showing
status and alarm information.
LED meaning is reported on the rightward table.
Further information about alarm status is delivered by Britecell Plus
supervision system.
Note: In case the four TFLN optical output ports are not all connected to
remote units, the unused ports must be properly masked at commissioning in
order to avoid spurious alarms (please refer to LMT manual).
TFLN
Label LED colour Meaning
= Green Power supply status OK
┌┘
Red
General TFLN failure, it can be:
- TFLN laser failure
- UL or DL amplifier failure
- TFLN short circuit
1
Red
Low UL optical power received
from remote unit 1 (fault in optical
link 1 or remote unit 1 failure)
2
Red
Low UL optical power received
from remote unit 2 (fault in optical
link 2 or remote unit 2 failure)
3
Red Low UL optical power received
from remote unit 3 (fault in optical
link 3 or remote unit 3 failure)
4
Red
Low UL optical power received
from remote unit 4 (fault in optical
link 4 or remote unit 4 failure)
Fig. 5.10 :LED panel
on TFLN front side
Tab. 5.4: Meanin
g
s of the LEDs on TFLN front
-
side
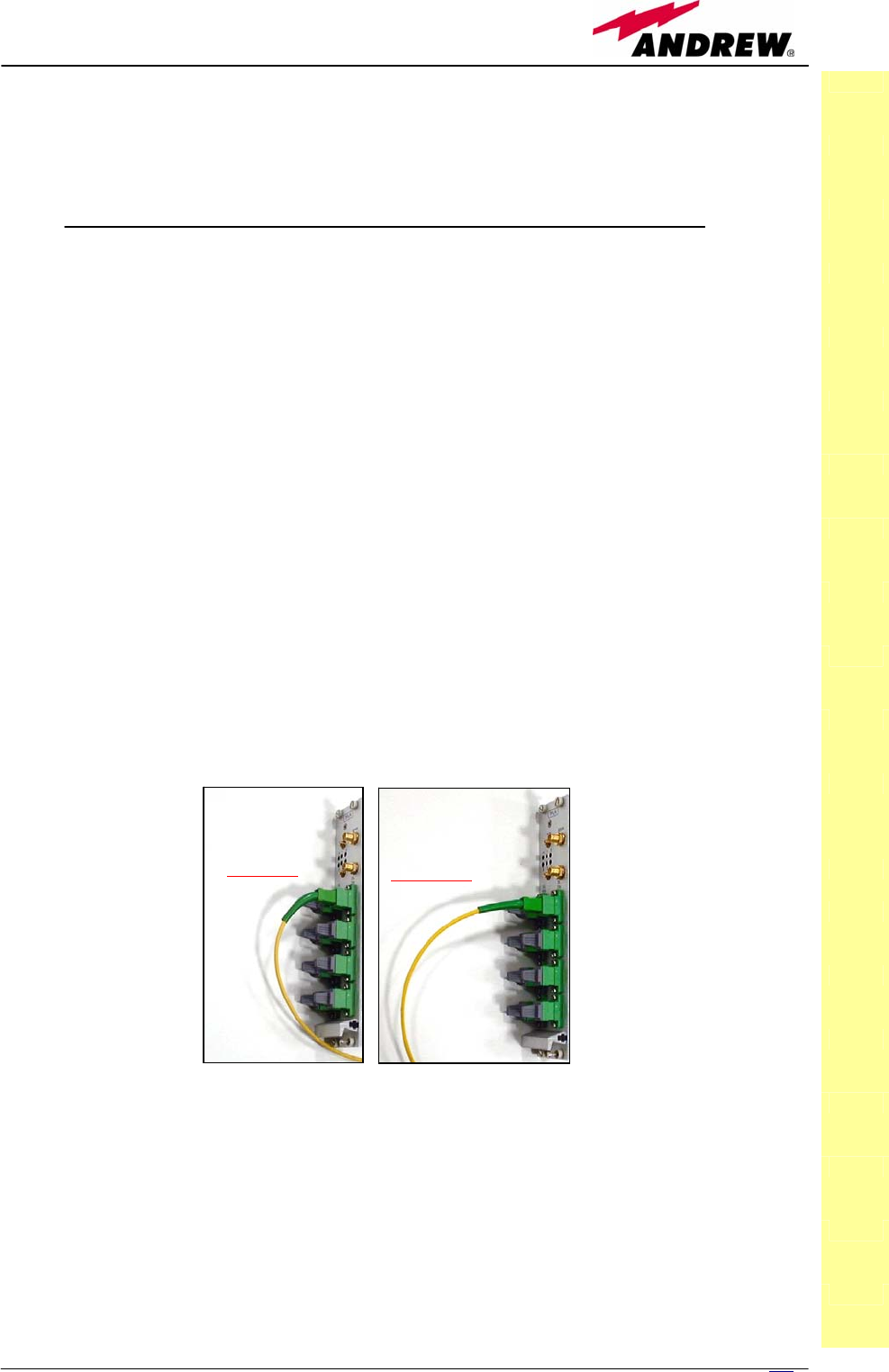
129
MN024-08
TFLN power supply
Each TFLN master optical TRX is supplied by the sub-rack back-plane (12V).
The power consumption of each TFLN master optical TRX is 12W.
Warnings (to be read before the TFLN installation)
Dealing with optical output ports
• The TFLN master optical TRX contains semiconductor lasers. Invisible laser
beams may be emitted from the optical output ports. Do not look towards
the optical ports while equipment is switched on.
Handling optical connections
• When inserting an optical connector, take care to handle it so smoothly
that the optical fibre is not damaged. Optical fibres have to be single-mode
(SM) 9.5/125µm.
• Typically, Britecell Plus equipment is provided with SC-APC optical
connectors. Inserting any other connector will result in severe damages.
• Do not force or stretch the fibre pigtail with radius of curvature less than 5
cm. See fig. 19 for optimal fibre cabling.
• Remove adapter caps only just before making connections. Do not leave
SC-APC adapters open, as they attract dust. Unused SC-APC adapters must
always be covered with their caps.
• Do not touch the adapter tip. Clean it with a proper tissue before inserting
each connector into the sleeve. In case adapter tips need to be better
cleaned, use pure ethyl alcohol
Inserting or removing TFLN modules
• Do not remove or insert any TFLN module into TPRN sub-rack before
having switched off main power supply.
• The TFLN modules must be handled with care, in order to avoid damage to
electrostatic sensitive devices.
• When installing TFLN modules in the sub-rack, take care to alternate active
and passive cards in order to ensure proper heat dissipation.
TFLN
WRONG OPTIMAL
Fig. 5.11: Fibre Optic bending
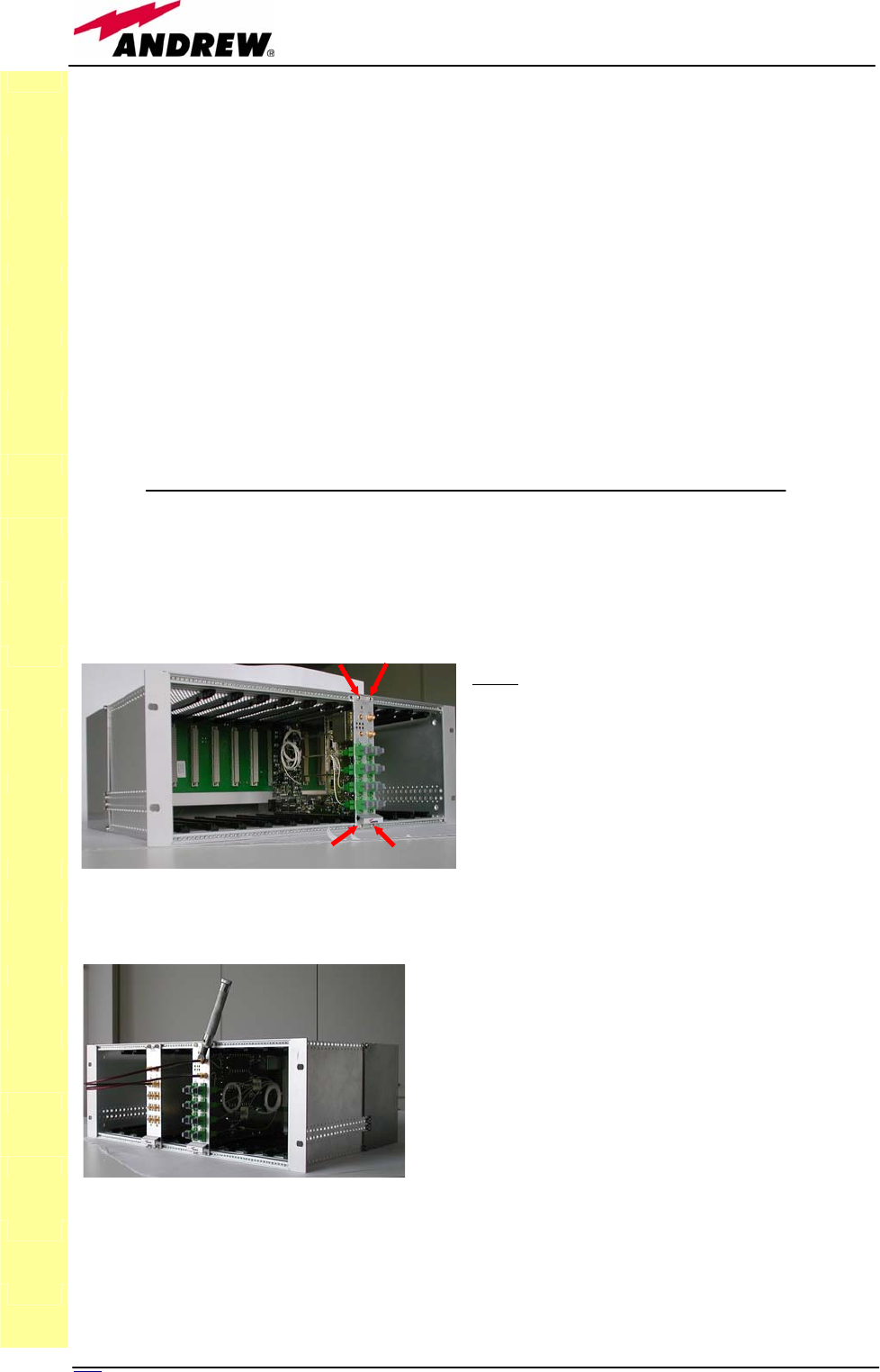
130 User Manual
• In a multi-sub-rack system, remember to assign to each sub-rack a proper
RS485 bus address before installing the modules (please refer to TPRN
section for further details).
TFLN positioning
• In case no ventilation system is installed, do not insert more than 8 TFLN
modules into a sub-rack.
• In case more than 8 TFLN modules have to be housed into a TPRN sub-
rack, it’s advisable to install the TPRN sub-rack inside a rack with forced
ventilation.
• Take care to meet expected requirements on RF ports. An adjustable
attenuator could be necessary when the power coming from the BTS
exceeds the required levels to avoid damages in Britecell Plus circuitry or
increase of spurious emissions.
TFLN installation
The TFLN master optical TRX is housed in a TPRN sub-rack and its dimensions
are 19” width and 4HE height. A TFLN module can be accommodated in any
of these 12 slots.
Note: In case a new TFLN module has
to be installed in a still working Master
Unit, switch off the sub-rack before
inserting the plug-in TFLN module
Firstly, gently insert the TFLN in one of
the 12 available slots, and lock the 4
screws on the front corners.
Then connect the UL and DL RF cable to
the TFLN UL and DL ports, respectively.
Use a specific torque wrench to fix these
RF cables to DL and UL ports.
TFLN
Fig. 5.1
2
: Screws to be fixed at the corners of the TFLN front side
Fig. 5.13: UL and DL RF cables are to be fixed by a torque wrench
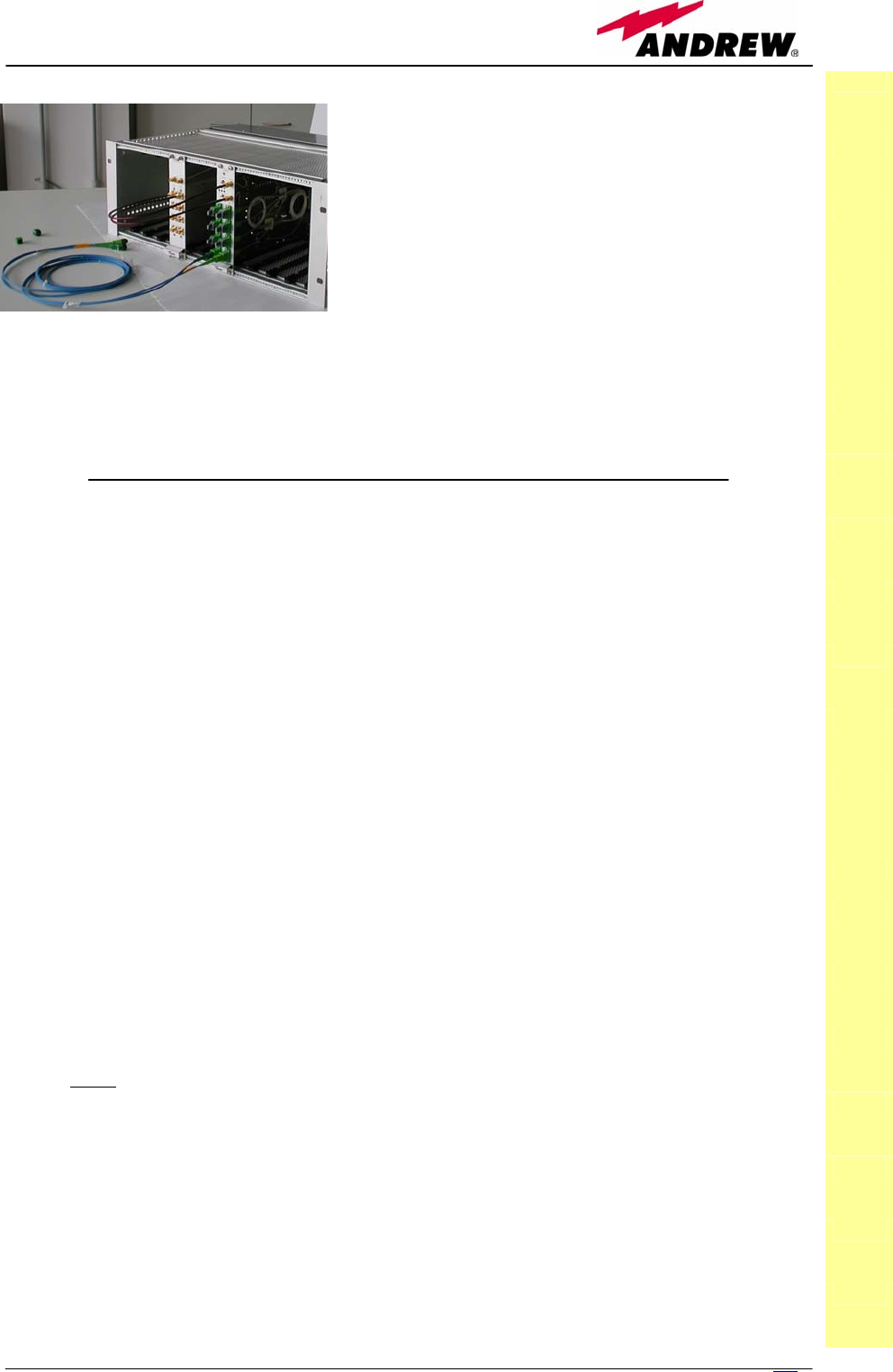
131
MN024-08
Remove the caps from TFLN optical ports
and connect the SC-APC fibre optic cables to
the ports.
UL and DL cables coming from the same
remote unit have to be connected to UL and
DL ports marked by the same number on the
TFLN front panel.
As you switch on the system, carefully refer to the TFLN Start-Up section.
Remember that remote units should be switched on before than the Master
Unit in order to follow a correct Start-Up procedure.
TFLN start-up
Before the Master Unit is switched on, make sure that:
• all expected modules have been inserted into the Master Unit
• the modules have been connected each other by RF jumpers, according to
what planned in the system design
• every TFLN master optical TRX has been connected to relevant remote
units
• each remote unit has been connected to its coverage antennas
• the remote supervision unit, if present, has been connected to the Master
Unit
• different Master Units are connected each other via bus RS485
After that, remember that only when all the remote units are already on, the
Master Unit itself can be turned on.
Once the Master Unit has been switched on, the TFLN behaviour at system
start-up can be summarized as per the following steps:
1. When Master Unit is turns on all the six LEDs upon the TFLN front panel
go on for a couple of seconds. After that, the green LED remains on
(indicating proper power supply) while the other LEDs indicate the
master optical TRX status, according to the following table.
Note: In case unused optical ports of the TFLN have not been masked
through LMT yet, corresponding LEDs will be on. If so, wait for the end
of step 3 (discovery phase) then use LMT to mask them (please refer to
relevant handbook)
2. About 10 seconds after the system has been switched on, TFLN module
begins a “discovery” phase to identify connected remote units. This
operation is necessary to collect all the information to be provided to
the supervision system.
TFLN
Fig. 5.14: Take off the caps and connect the fiber optics cables properl
y
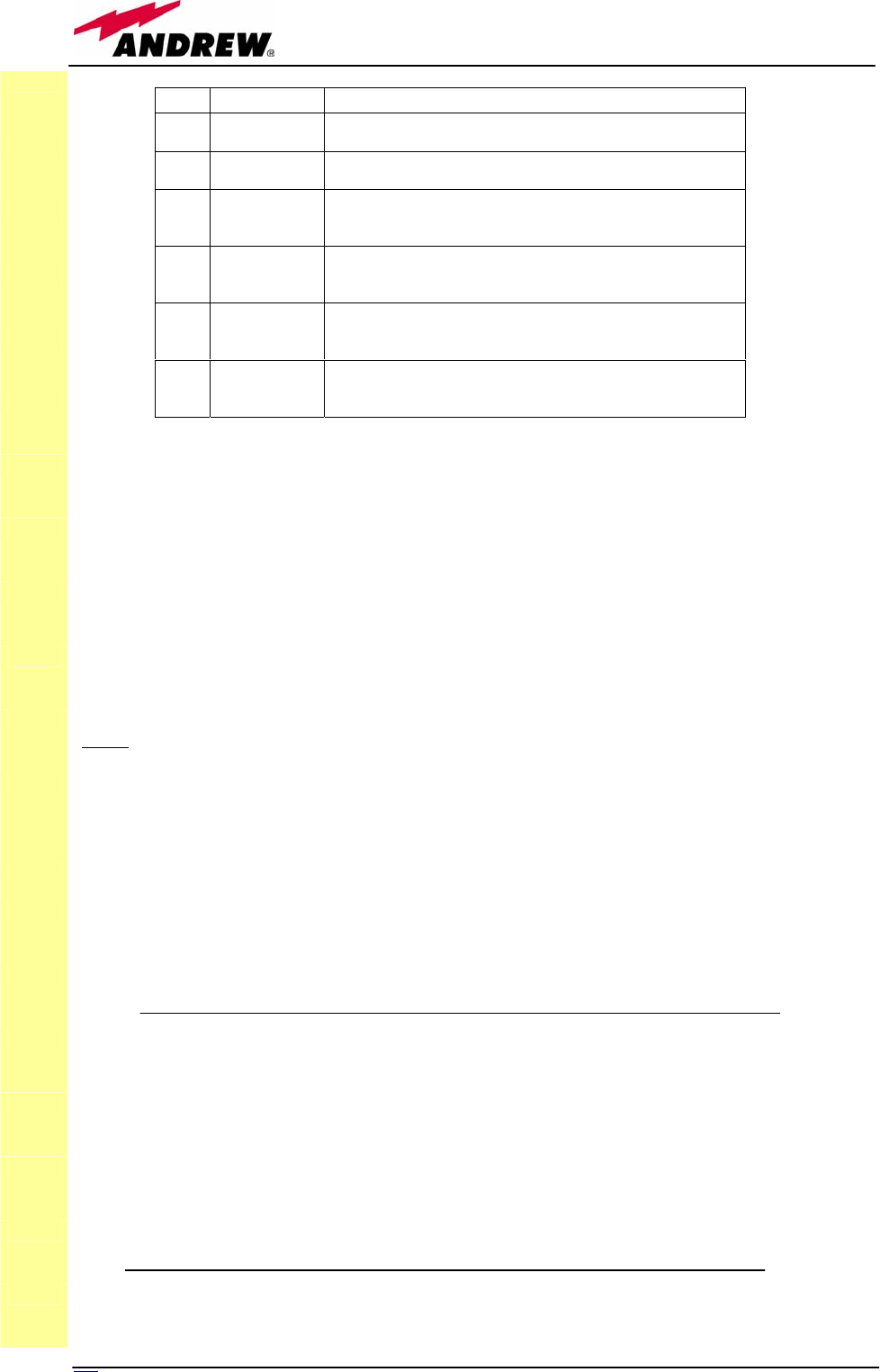
132 User Manual
During the discovery phase the TFLN general alarm (LED ┌┘) blinks while the
other LEDs go on showing previously detected status. Time dedicated to
discovery phase can be at maximum 4min and depends on system
complexity.
Do not connect/disconnect any cable or any piece of equipment during the
discovery phase. This may result in failing the identification of remote units.
Please note that, while the discovery phase is running, the whole system is
working correctly as discovery operations aim only to collect information
about remote units without affecting the system functionalities.
Note: in case discovery doesn’t start automatically, check through the LMT or
the remote supervision whether it has been disabled (refer to LMT or remote
supervision system manuals for further information).
Once the discovery is finished, the TFLN general alarm (LED ┌┘) stops
blinking and switches OFF. The power supply LED (green LED) remains on
while LEDs 1,2,3,4 show either the status of the remote units or the quality of
the UL connections. In case some of these LEDs remain on, check if they refer
to unused optical ports or not. In this case use LMT software to mask it
otherwise if they refer to connected remote units and remain on, please refer
to troubleshooting procedure.
Removing a TFLN module
Switch off the Master Unit power supply, remove the SC-APC optical
connectors, and insert the protection caps into TFLN optical ports. Then
• unscrew the 4 screws and slowly remove the card.
• put the removed TFLN card in its safety box.
• switch on again the Master Unit power supply, and refer to Start Up
section.
Label LED colour Status
= Green ON
(power supply is on)
┌┘ Red OFF
(no major failure affects TFLN operations)
1 Red OFF
(no major failure affects corresponding remote unit or UL
connection)
2 Red OFF
(no major failure affects corresponding remote unit or UL
connection)
3 Red OFF
(no major failure affects corresponding remote unit or UL
connection)
4 Red OFF
(no major failure affects corresponding remote unit or UL
connection)
TFLN
Table 5.5: Status of the TFLN LEDs in full-working conditions
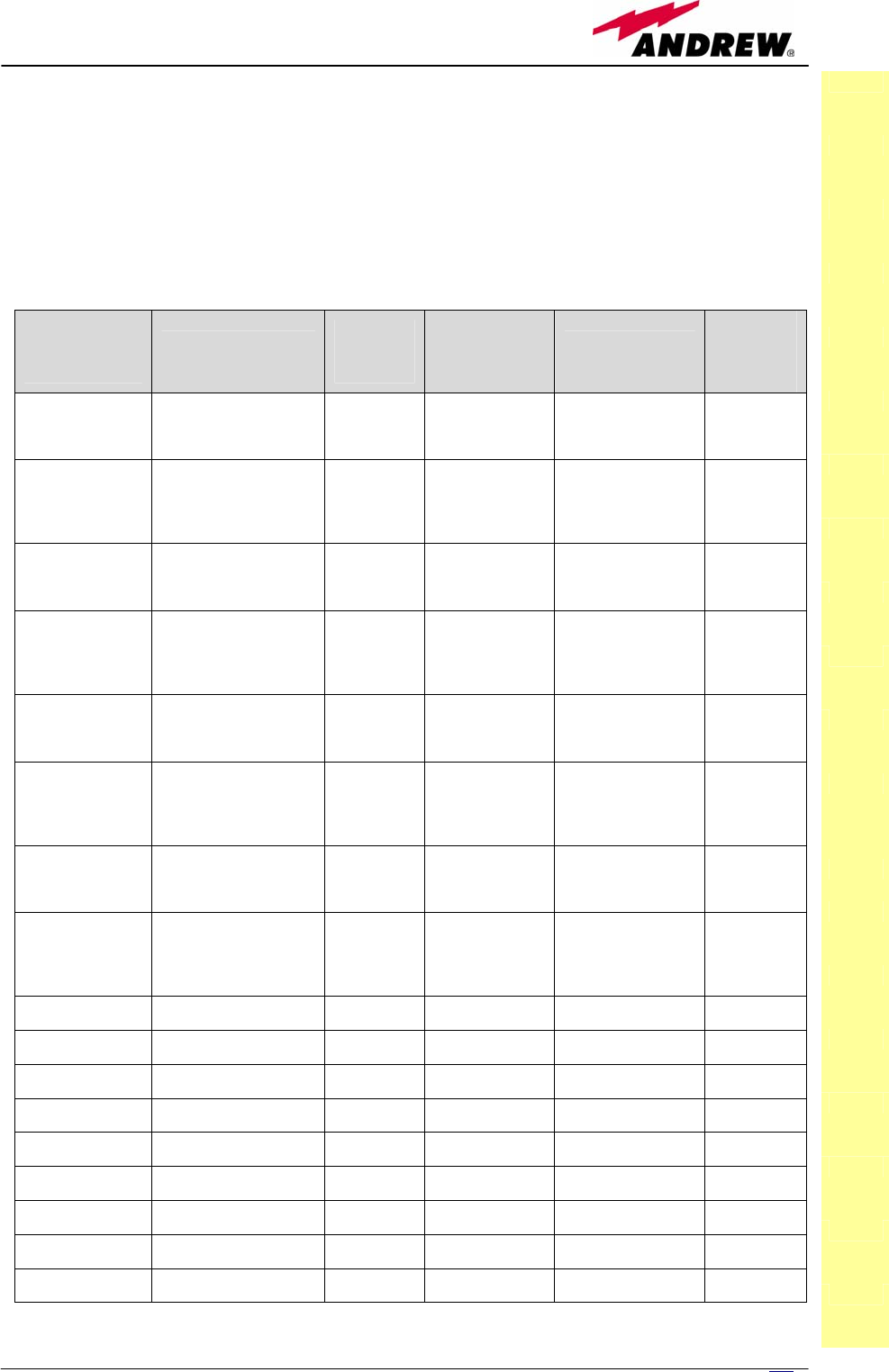
133
MN024-08
TFLN troubleshooting
In case a TFLN master optical TRX has any problem, this will be easily
revealed through LEDs on its front panels otherwise troubleshooting can be
carried out through LMT or supervision system.
LEDs on TFLN front panel detect not only failures of the TFLN board itself but
they also reveals malfunctions located on related remote units.
ALARM CODE
(TSUN
description)
ALARM
DESCRIPTION
ACTIVE
LED
SUPERVISION
PRIORITY
LEVEL
ACTION
RECOMMENDED
RELÉ
PRIORITY
LEVEL
(subrack)
RX1 optical power
fail
The optical power
received on the UL1 is
too low and can’t no
more be compensated
RED
(LED1) CRITICAL
Check the UL1 fibre
and the remote unit
laser status
MAJOR
RX1 AGC out of
range
The optical power
received is under the
allowed 3dB optical
loss but it can be
compensated
NONE MINOR
Clean optical
connectors MINOR
RX2 optical power
fail
The optical power
received on the UL2 is
too low and can’t no
more be compensated
RED
(LED2) CRITICAL
Check the UL2 fibre
and the remote unit
laser status
MAJOR
RX2 AGC out of
range
The optical power
received is under the
allowed 3dB optical
loss but it can be
compensated
NONE MINOR
Clean optical
connectors MINOR
RX3 optical power
fail
The optical power
received on the UL3 is
too low and can’t no
more be compensated
RED
(LED3) CRITICAL
Check the UL3 fibre
and the remote unit
laser status
MAJOR
RX3 AGC out of
range
The optical power
received is under the
allowed 3dB optical
loss but it can be
compensated
NONE MINOR
Clean optical
connectors MINOR
RX4 optical power
fail
The optical power
received on the UL4 is
too low and can’t no
more be compensated
RED
(LED4) CRITICAL
Check the UL4 fibre
and the remote unit
laser status
MAJOR
RX4 AGC out of
range
The optical power
received is under the
allowed 3dB optical
loss but it can be
compensated
NONE MINOR
Clean optical
connectors MINOR
Major Remote
Unit 1 Alarm from RU1 RED
(LED1) - Check remote unit
status MAJOR
Major Remote
Unit 2 Alarm from RU2 RED
(LED2) - Check remote unit
status MAJOR
Major Remote
Unit 3 Alarm from RU3 RED
(LED3) - Check remote unit
status MAJOR
Major Remote
Unit 4 Alarm from RU4 RED
(LED4) - Check remote unit
status MAJOR
DL laser alarm A fault occurs on the
DL laser RED (┌┘) MAJOR Return the unit MAJOR
UL RF alarm HW failure on the UL
RF section RED (┌┘) MAJOR Return the unit MAJOR
DL RF alarm HW failure on the DL
RF section RED (┌┘) CRITICAL Return the unit MAJOR
Board failure
alarm
General failure on
board RED (┌┘) MAJOR Return the unit MAJOR
Temperature
alarm
Over-temperature
alarm NONE MINOR
Check ventilation
and environment MINOR
TFLN
Tab. 5.6: TFLN alarm description
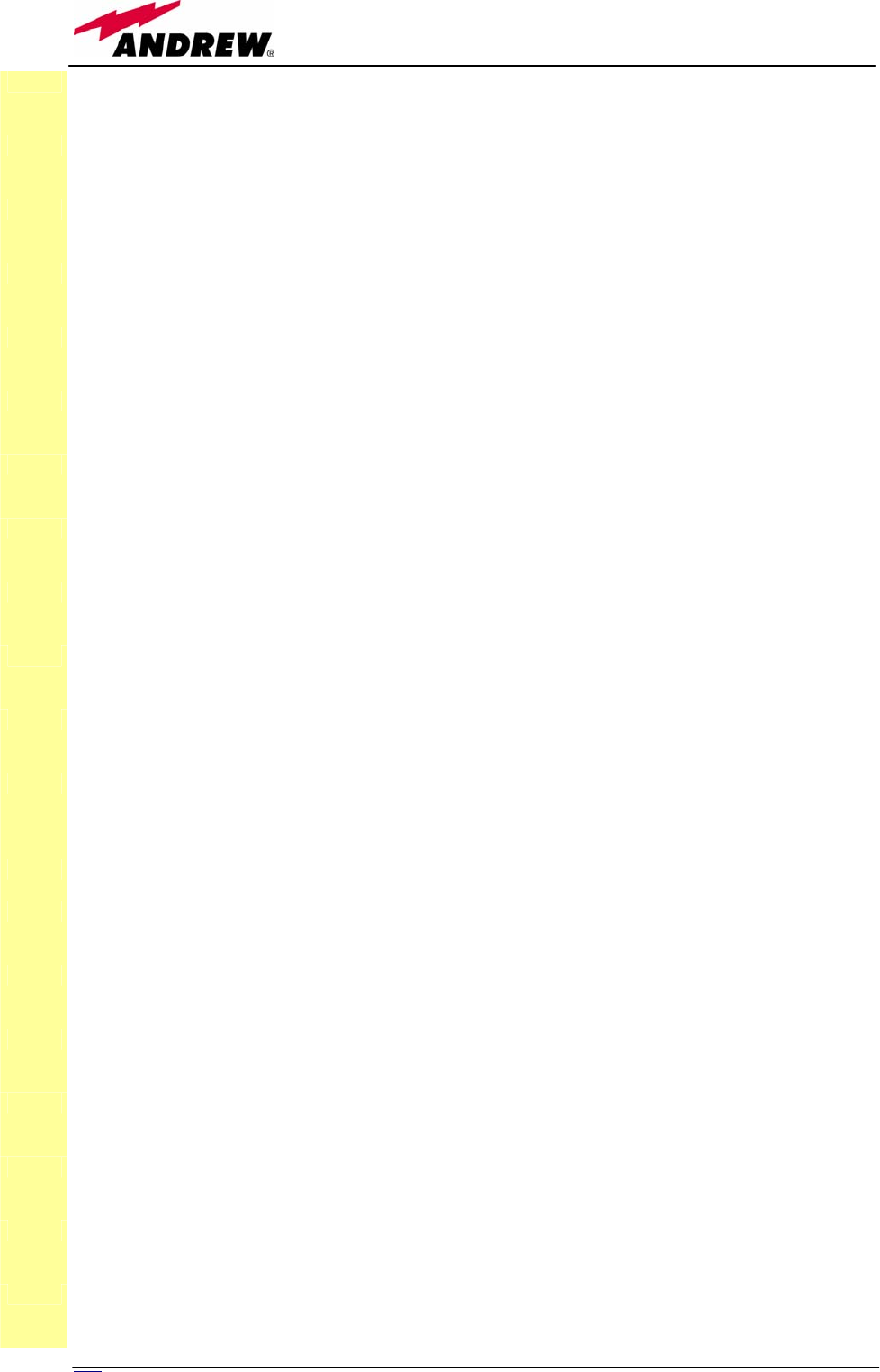
134 User Manual
The previous table reports a brief description of the TFLN alarms, together
with a reference to the corresponding alerted LEDs.
As the table shows, LEDs on the TFLN front panel signal all high priority
alarms while minor alarms, which detect critical situations which should be
checked and tested in order to avoid future possible system faults, are only
revealed by LMT or supervision system.
Each TFLN is provided with an AGC system which compensates optical losses
<3 dB. TFLN LED alarms switch on when the estimated optical losses are
>4dB, the AGC not being able to compensate these losses any more.
One of LEDs 1, 2, 3 or 4 might turn on not only to indicate a high optical loss
detected by TFLN, but also to reveal a remote unit failure. Understanding the
reason why one of LEDs 1, 2, 3 or 4 is on (a remote unit failure, an optical
cable fault or an external equipment malfunction) can be done following the
troubleshooting procedure reported hereinafter.
Quick troubleshooting procedure
(The following procedure is summarized by the flow-chart in fig. 5.15a)
1. In case the TFLN general alarm (LED ┌┘) is on replace the faulty TFLN
master optical TRX with a new one and contact the manufacturer for
assistance.
2. In case one of the LEDs 1, 2, 3 or 4 is on, the corresponding TFLN
adapter might be dirty. Try cleaning it using pure ethyl alcohol. If the
LED is still on go to the corresponding remote unit side and check the
red LED upon TFAx warm side:
a. If it is off, the optical cables or the optical connections are
supposed to have some problem on UL path. Refer to fibre optic
UL troubleshooting for more information (fig. 21).
b. If it is on, refer to remote unit troubleshooting presented in the
previous remote unit section
Fibre optic UL troubleshooting
(The following procedure is summarized by the flow-chart in fig. 5.15b)
1. Check if there is any point where the fibre experiences a small radius of
curvature. In this case, rearrange the optical path in order to avoid
sharp bends (if necessary, replace the optical cable with a longer one). If
this makes the TFLN red LED switch off, troubleshooting has been
successful. Otherwise, follow next steps.
2. Check if the SC-APC connectors are properly installed at both fibre ends
(i.e. TFLN and TFAx ports). If not fix better SC-SPC connectors to
relevant adapters. If this makes the TFLN red LED switch off,
troubleshooting has been successful. Otherwise, follow next steps.
3. Disconnect the optical fibre and clean it at both fibre ends (i.e. TFLN side
and TFAx side) then reconnect the fibre to relevant ports. In case this
makes the TFLN red LED switch off, troubleshooting has been successful.
Otherwise, follow next steps.
4. Disconnect the optical SC-APC connector from TFLN UL port, and
measure the output power POUT(UL) at corresponding fibre end. Then, go
TFLN
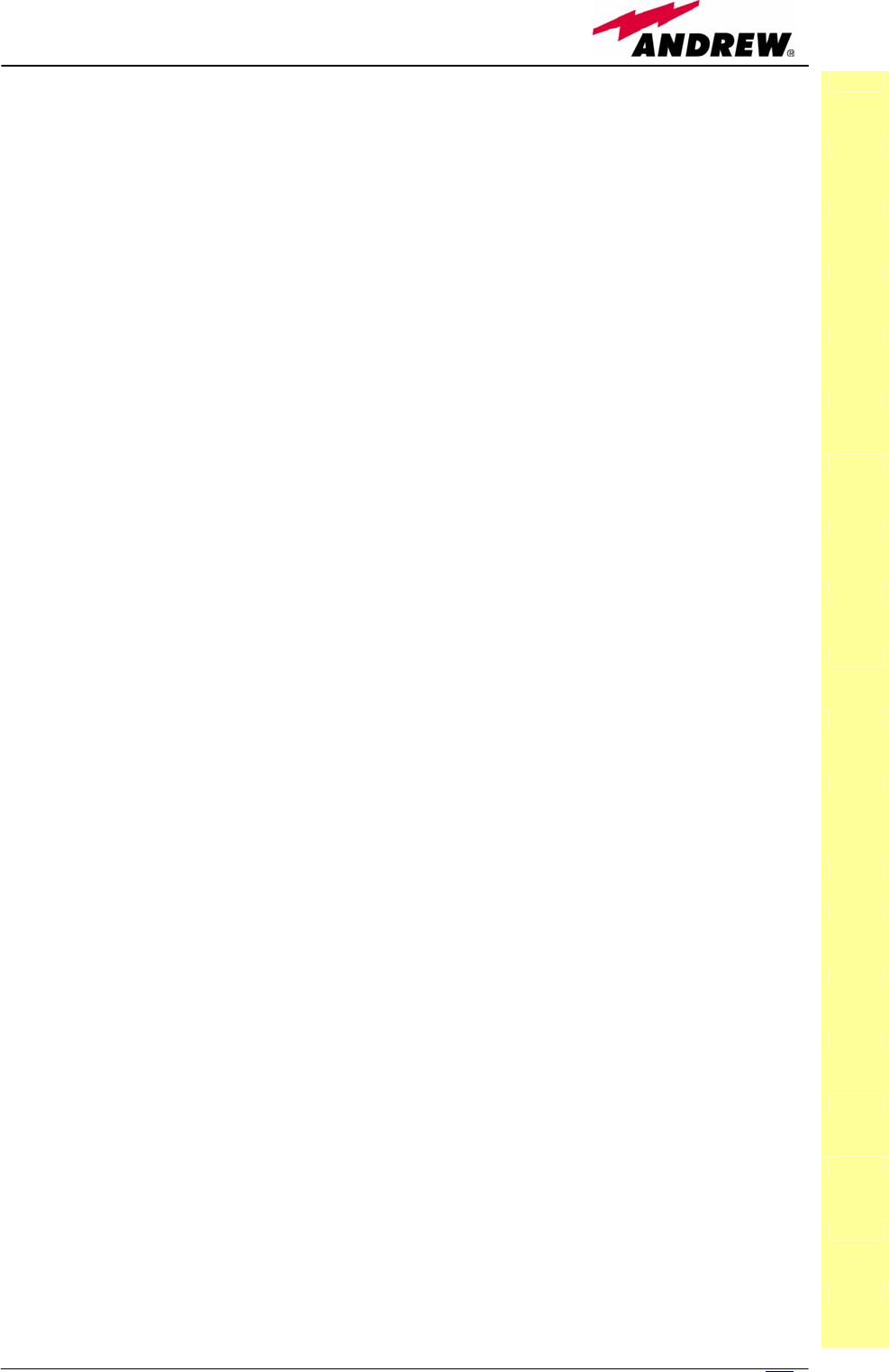
135
MN024-08
to the TFAx side, disconnect the optical SC-APC connector from TFAx UL
port and measure the input power PIN(UL) coming out of the TFAx UL
port.
5. Calculate the UL fibre attenuation AUL as: AUL [dB] = PIN(UL) – POUT(UL)
a. If AUL > 4dB, the fibre optic cable has some problems or cable
path is too long. Replace it.
b. If AUL < 4dB, then TFAx remote unit should be faulty. Before
replacing it, check the TFAx status on supervision system and
contact for assistance
TFLN
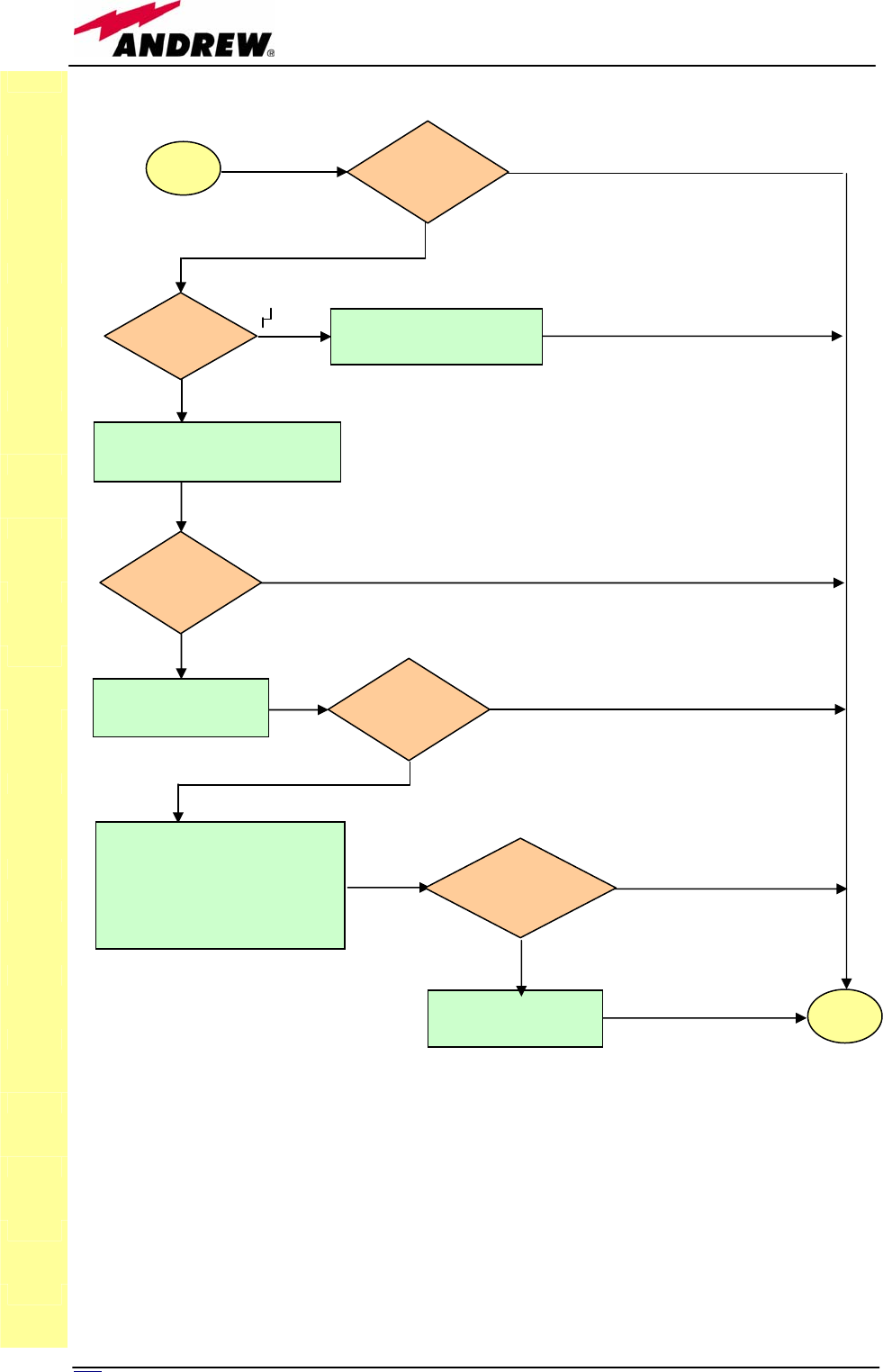
136 User Manual
TFLN
Fig. 5.15 (a): Flow-chart describing the quick troubleshooting procedure
1, 2, 3 or 4
start
Which red
LED is ON? Replace the faulty TFLN
Clean corresponding SC-APC
optical adapter and connector
Yes
Is any red LED
ON upon the
TFLN?
N
o
No
Go to corresponding
remote unit side
No
Yes
Yes
UL optical cables or optical
connections are supposed to
have some problems. Refer to
fibre optic UL troubleshooting
(fig. 5.15b)
No
Refer to remote unit
troubleshooting
Yes
end
Is red LED
upon TFLN
still ON?
Is red LED
upon remote
unit ON?
Is red LED
upon remote
unit still ON?
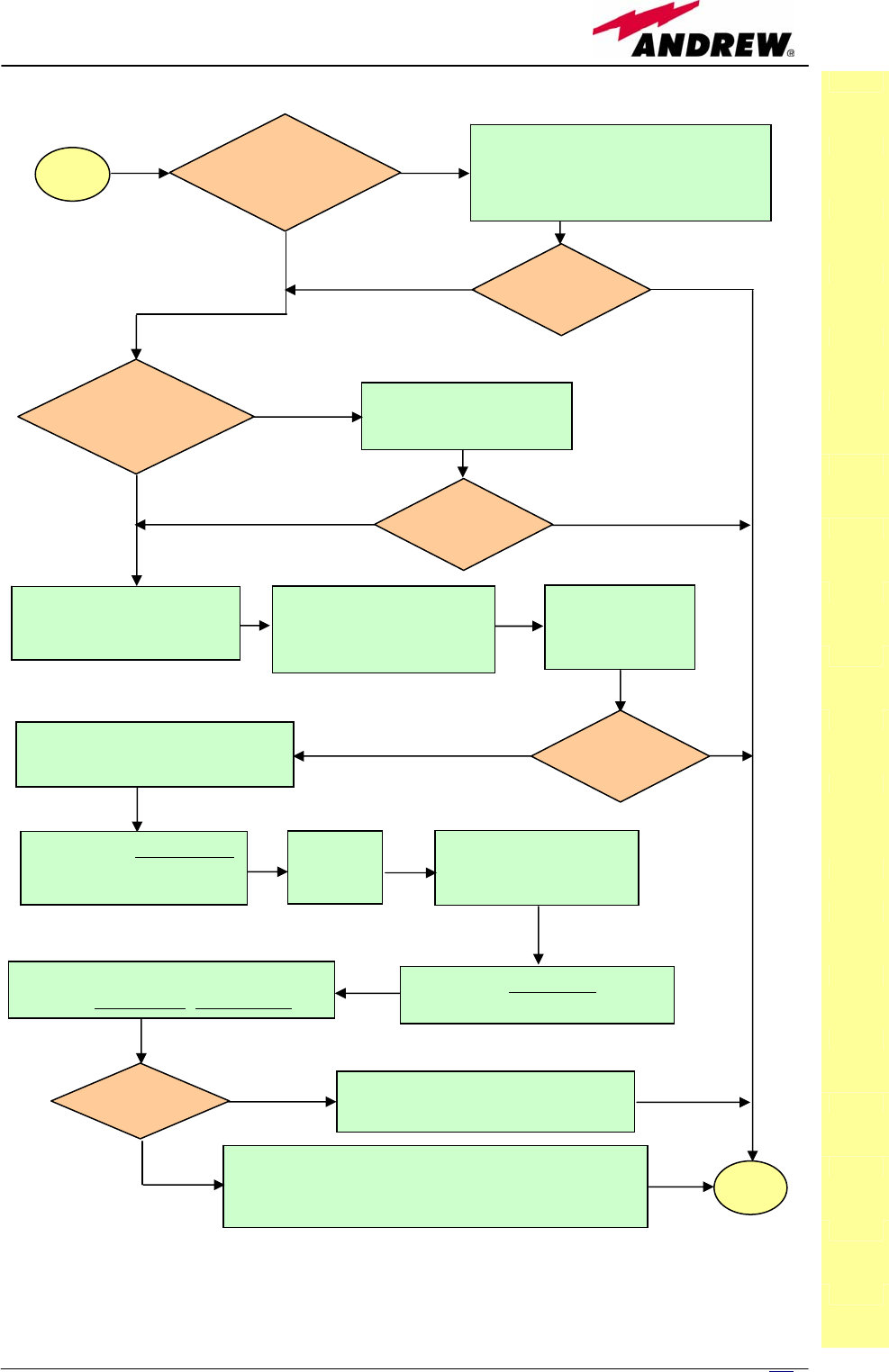
13
7
MN024-08
TFLN
Fig. 5.15 (b): Flow-chart describing the fibre optic UL troubleshooting
start
Is there any small
radius of curvature
of the fibre?
Rearrange the optical path in order to
avoid sharp bends. If necessary
replace the optical cable with a
lon
g
er one.
Is the red LED
upon TFLN still
ON?
Are SC-APC
connectors properly
installed at both fibre
ends?
Fix SC-APC connectors
properly to adapters.
Yes
N
o
N
o
Y
es
No
Y
es
N
o
Y
es
Disconnect the optical SC-APC
connector from TFLN UL port.
Clean the optical SC-APC
p
orts both on TFLN and
TFAx side.
Disconnect the optical fibre
and clean it at both ends.
Re-connect the
fibre to relevant
p
orts.
Measure the output power
at the corresponding fibre
end
Measure the input power entering
the fibre.
Go to the
TFAx
side
Disconnect the optical
SC-APC connector
from TFAx UL
p
ort.
Calculate the UL fibre attenuation:
AUL[dB]=input power - output power
Is AUL > 4dB? Fibre optic cable has some problems.
Replace it.
The TFAx remote unit should be faulty. Before
replacing it, verify its status through supervision
system and contact for assistance. end
No
Y
es
No
Y
es
Is the red LED
upon TFLN still
ON?
Is the red LED
upon TFLN still
ON?
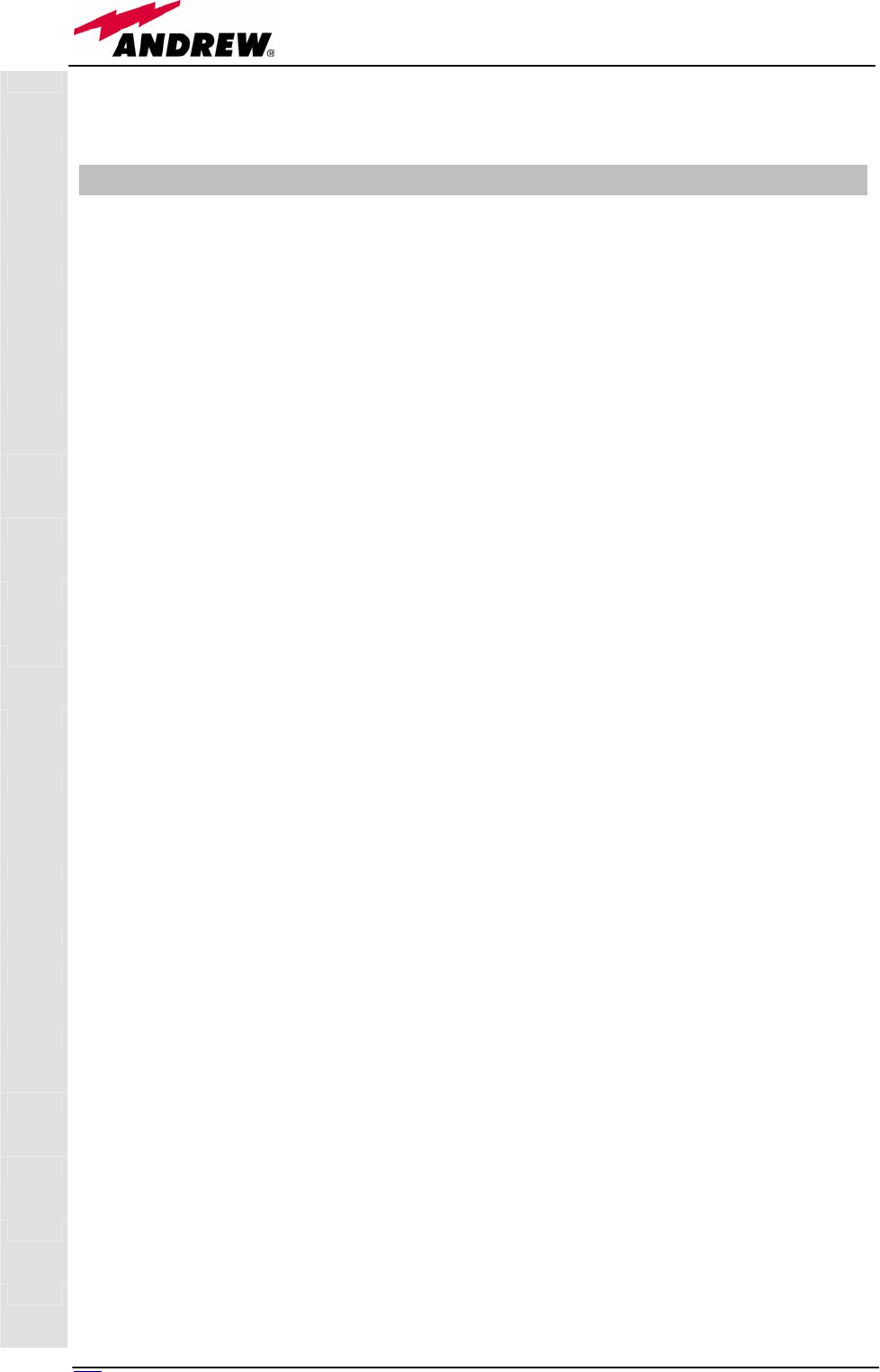
138 User Manual
5.3. Two-way Splitter/Combiner, TLCN2
TLCN2
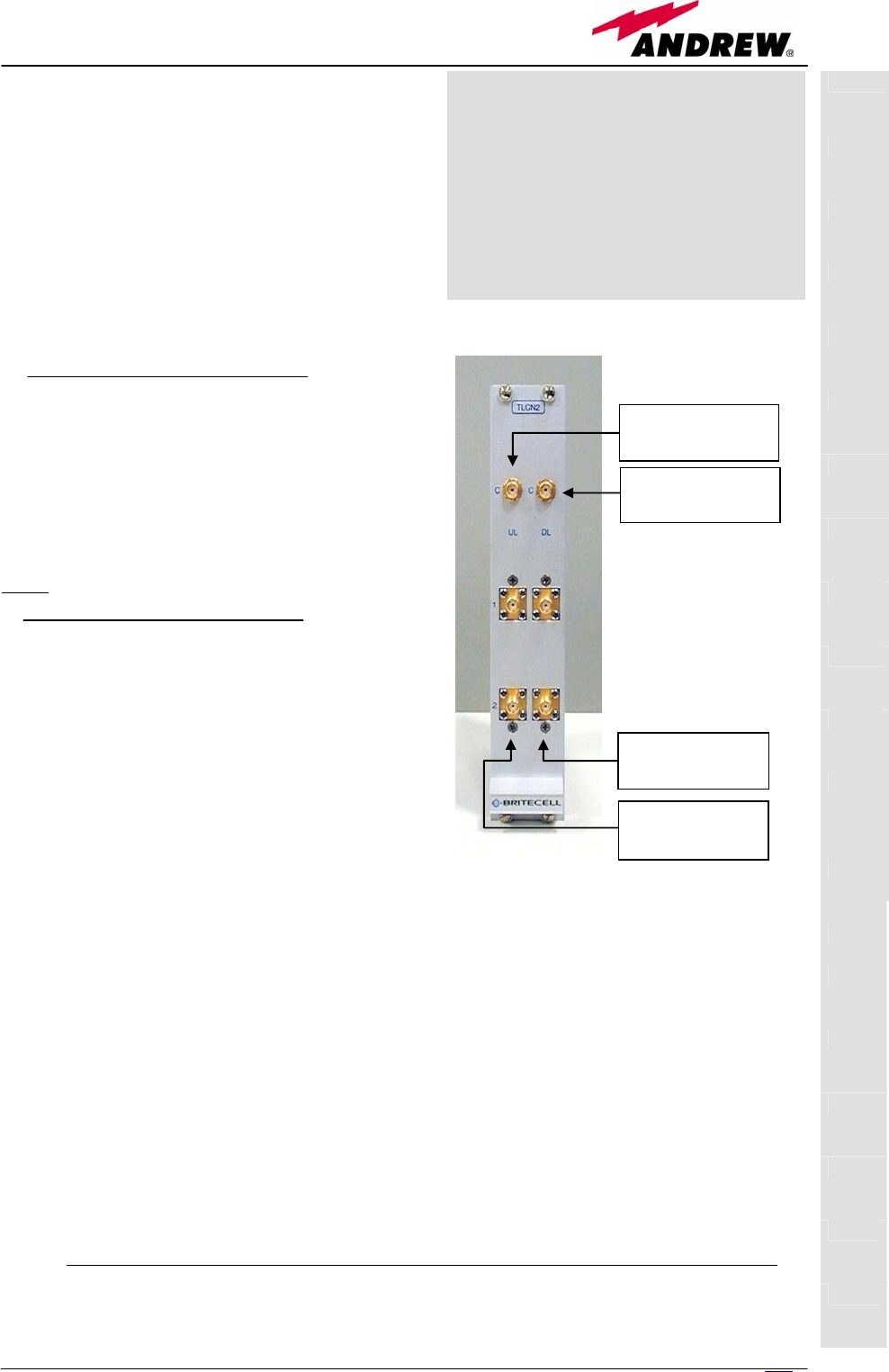
139
MN024-08
Description:
The TLCN2, a bidirectional 2-way
splitter/combiner, provides two identical
combining sections for UL and DL which
can be used:
¾ to combine 2 RF signals into a
common RF output
¾ to split an RF input into 2 RF output
signals
It is a passive wideband module.
RF ports:
• 1 DL common RF port (“C”)
• 2 DL splitted RF ports (“1”,“2”)
• 1 UL common RF port (”C”)
• 2 UL splitted RF ports (“1”,“2”)
Note: each port is bidirectional.
TLCN2 main applications
Main applications of the TLCN2 module are:
• Connecting a donor source to more than
one TFLN master optical TRX, so that:
¾ TLCN2 splits the DL input coming
from a donor source into 2 output
signals entering 2 different TFLN
master optical TRX
¾ TLCN2 combines the UL inputs
coming from 2 TFLN master optical
TRX into 1 common signal entering
the donor source
• Connecting a TFLN master optical TRX to more than one donor source
within the same service, so that:
¾ TLCN2 combines the two DL inputs coming from 2 donor sources into 1
output signal entering the TFLN master optical TRX or a cross band
coupler
¾ TLCN2 splits the UL input coming from TFLN master optical TRX or a
cross band coupler into 2 different output signals entering 2 different
donor sources.
More TLCN2 modules can be used in cascade connections.
TLCN2
DL common RF
p
ort
(
SM
A
-f
)
UL common RF
port (SMA-f)
UL splitted RF
ports (SMA-f)
DL splitted RF
ports (SMA-f)
Fig. 5.16: TLCN2 splitter/combiner
Module name:
2-way splitter/
/combiner
TLCN2

140 User Manual
TLCN2 insertion loss
The TLCN2 insertion loss varies slightly with the frequency bands, as shown in
table 5.7.
When designing the system, remember to take into account the insertion loss
of the TLCN2 if present.
Warnings
The overall input power must not exceed +24dBm
TLCN2 Installation
Since the TLCN2 module doesn’t require any power supply it can be housed
either in an active or a passive TPRN sub-rack.
1. Unpack the kit which includes
1 TLCN2
4 RF jumpers (SMA-m), 2 x 25cm, 2 x 35cm
2. Carefully insert the TLCN2 module in any of the TPRN sub-rack slots and
lock the 4 screws on the front corners.
3. Connect RF cables to UL and DL ports, according to what planned by
designer. Use a specific torque wrench to fix each cable to relevant ports.
4. In case some ports remain unused remember to connect them to a 50 Ω
load (not included)
700-1400MHz 1400-2200MHz 2200-2500MHz
TLCN2 insertion loss 3.7 ± 0.4dB 4.1 ± 0.5dB 4.6 ± 0.4dB
TLCN2
Table 5.7: Insertion loss values within different frequency bands
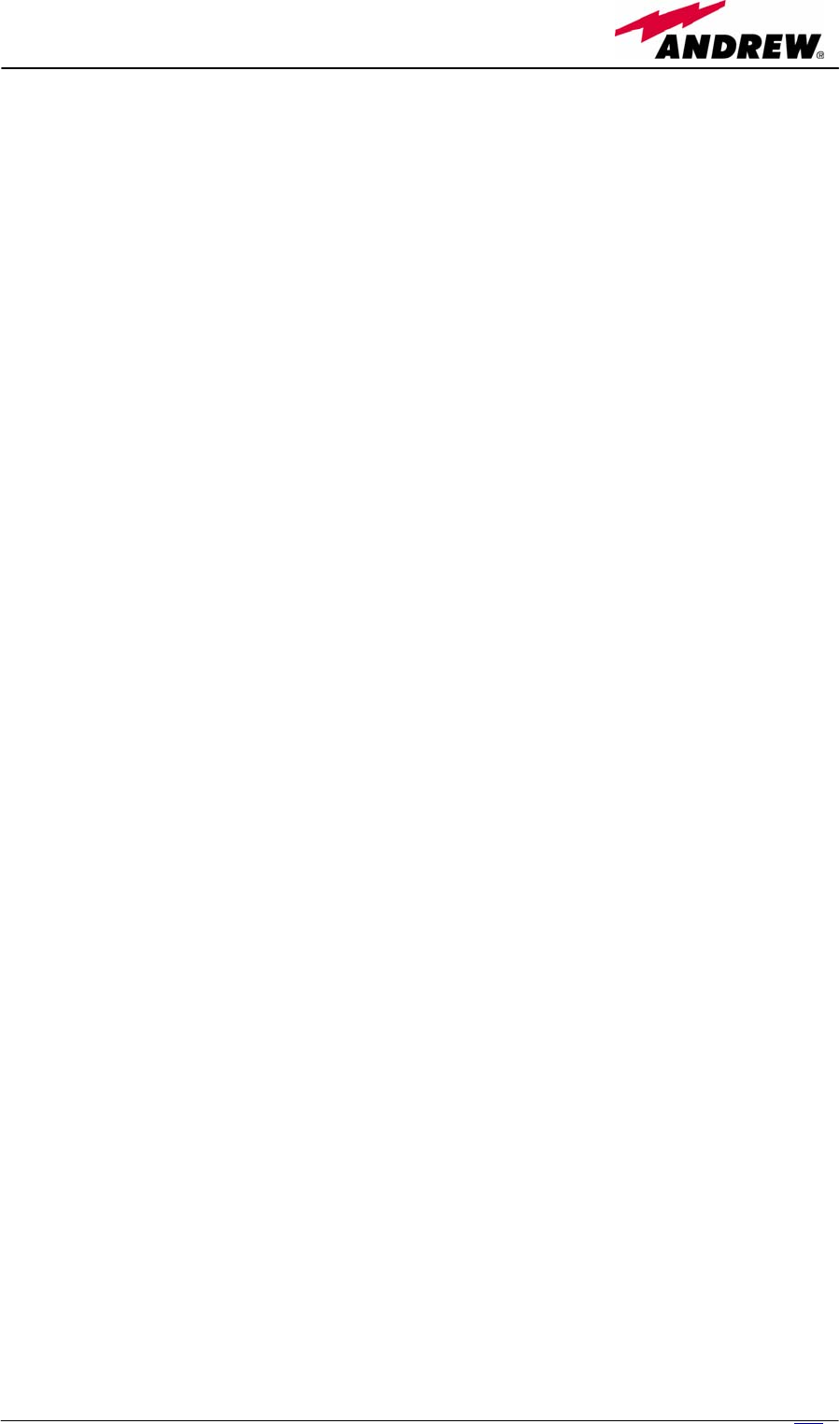
141
MN024-08
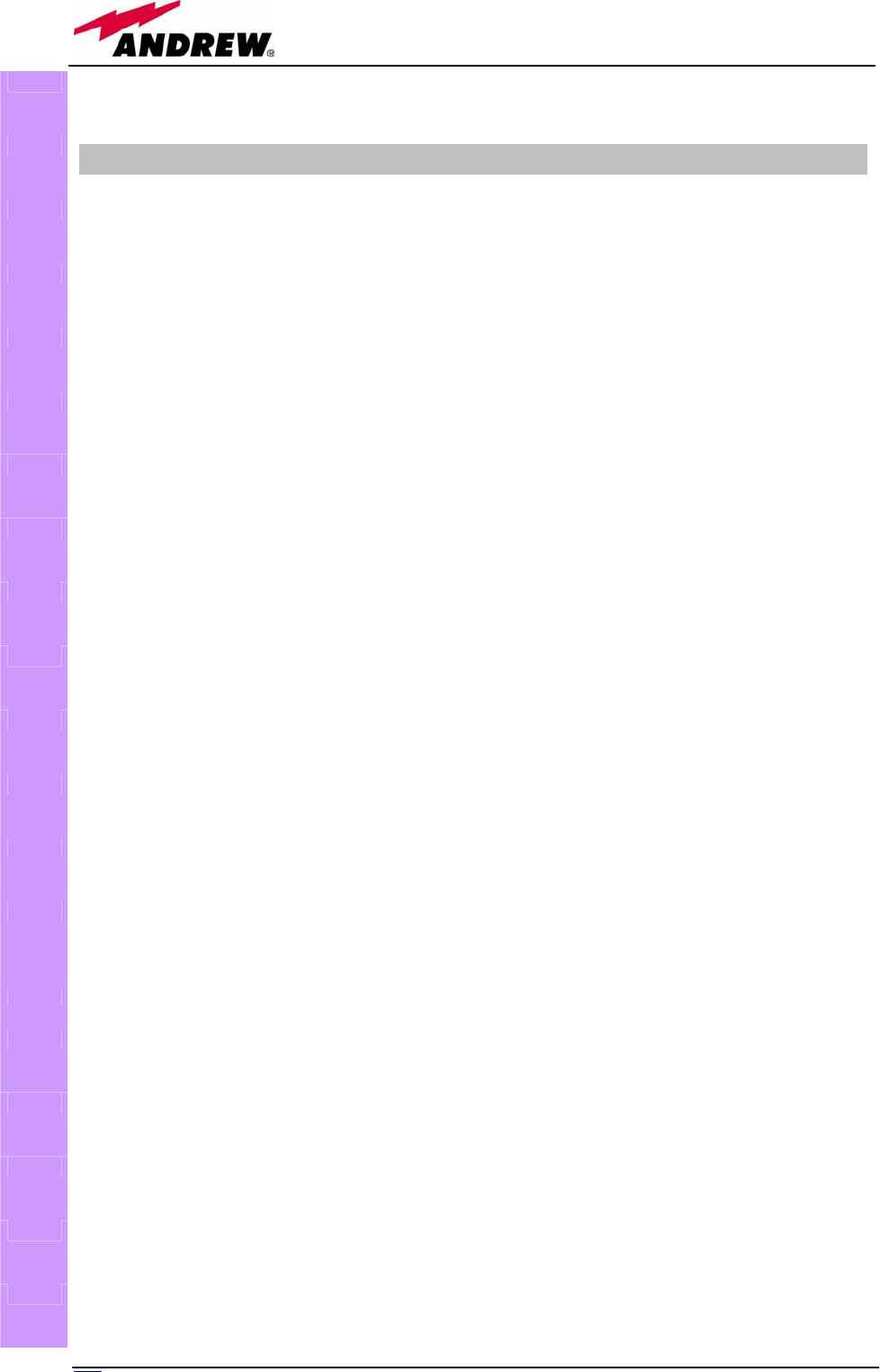
142 User Manual
5.4. Four-way Splitter/Combiner TLCN4
TLCN4
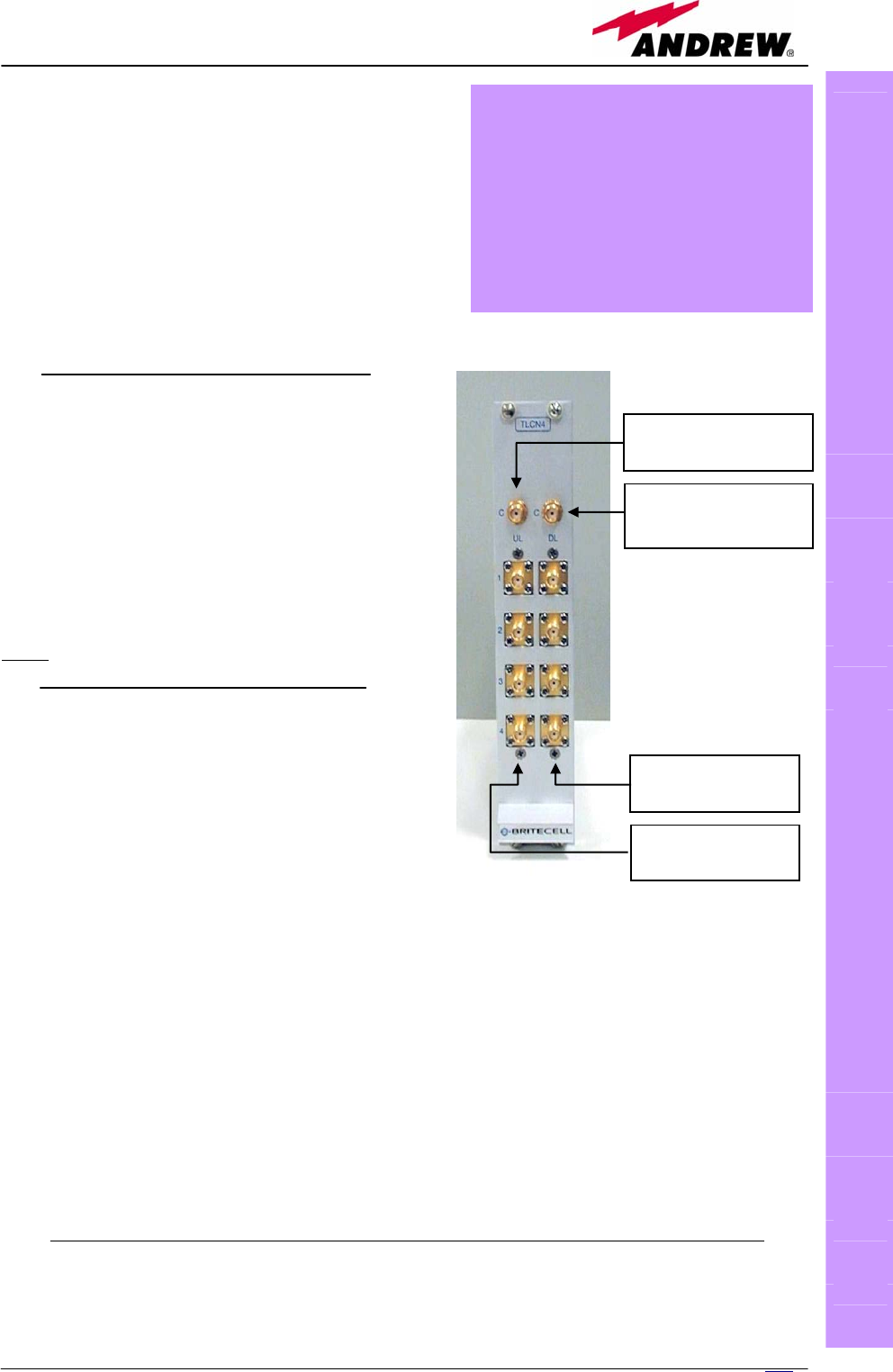
143
MN024-08
Description:
The TLCN4, bidirectional 4-way
splitter/combiner, provides two identical
combining sections for UL and DL which can
be used to:
¾ combine 4 RF signals into a common
RF output
¾ split an RF input into 4 RF output
signals
It is a passive wideband module.
RF ports:
• 1 DL common RF port (“C”)
• 4 DL splitted RF ports (labelled
“1”,“2”,“3”,“4”)
• 1 UL common RF port (”C”)
• 4 UL splitted RF ports (labelled
“1”,“2”,“3”,“4”)
Note: each port is bidirectional.
TLCN4 main applications
Main applications of the TLCN4 module are:
• Connecting a donor source to more than
one TFLN master optical TRX, so that:
¾ TLCN4 splits the DL input coming
from a donor source into 4 output
signals entering 4 different TFLN
master optical TRX
¾ TLCN4 combines the UL inputs
coming from 4 TFLN master optical TRX into 1 common signal
entering the donor source
• Connecting a TFLN master optical TRX to more than one donor source
within the same service, so that:
¾ TLCN4 combines the two DL inputs coming from up to 4 donor
sources into 1 output signal entering the TFLN master optical TRX
¾ TLCN4 splits the UL inputs coming from TFLN master optical TRX into
4 different output signals entering up to 4 different donor sources
More TLCN4 modules can be used in cascade connections.
TLCN4 insertion loss
TLCN4
UL splitted RF
ports
(
SM
A
-f
)
DL splitted RF
ports (SMA-f)
UL common RF
port (SMA-f)
DL common RF
port (SMA-f)
Fig. 5.17: TLCN4 splitter/combiner
Module name:
4-way splitter/
/combiner
TLCN4
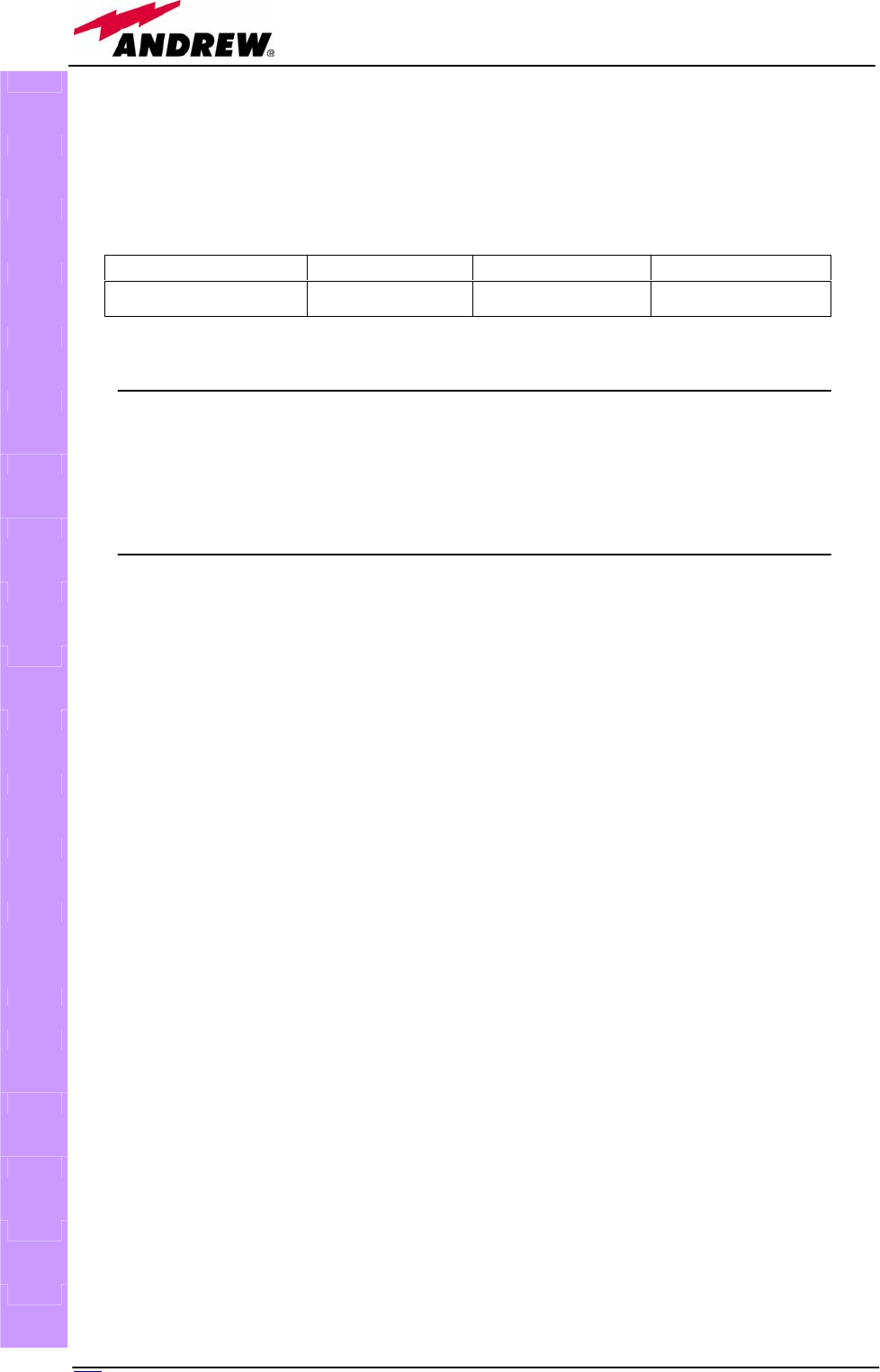
144 User Manual
The TLCN4 insertion losses vary slightly with the frequency bands, as shown
in table 5.8.
When designing the system, remember to take into account the insertion loss
of the TLCN4.
Warnings
The overall input power must not exceed +24dBm
TLCN4 Installation
Since the TLCN4 module doesn’t require any power supply it can be housed
either in an active or a passive TPRN sub-rack.
1. Unpack the kit which include
1 TLCN4
8 RF jumpers (SMA-m), 1 x 18cm, 2 x 23cm, 2 x 28cm, 2 x 33cm,
1 x 36cm
2. Carefully insert the TLCN4 module in any of the TPRN sub-rack slots and
lock the 4 screws on the front corners.
3. Connect RF cables to UL and DL ports, according to what planned by
designer. Use a specific torque wrench to fix each cable to relevant ports.
4. In case some ports remain unused remember to connect them to a 50 Ω
load (not included)
700-1400MHz 1400-2200MHz 2200-2500MHz
TLCN4 insertion loss 7.4 ± 0.4dB 8.0 ± 0.5dB 8.4 ± 0.4dB
TLCN4
Table 5.8: Insertion loss values within different frequency bands

145
MN024-08
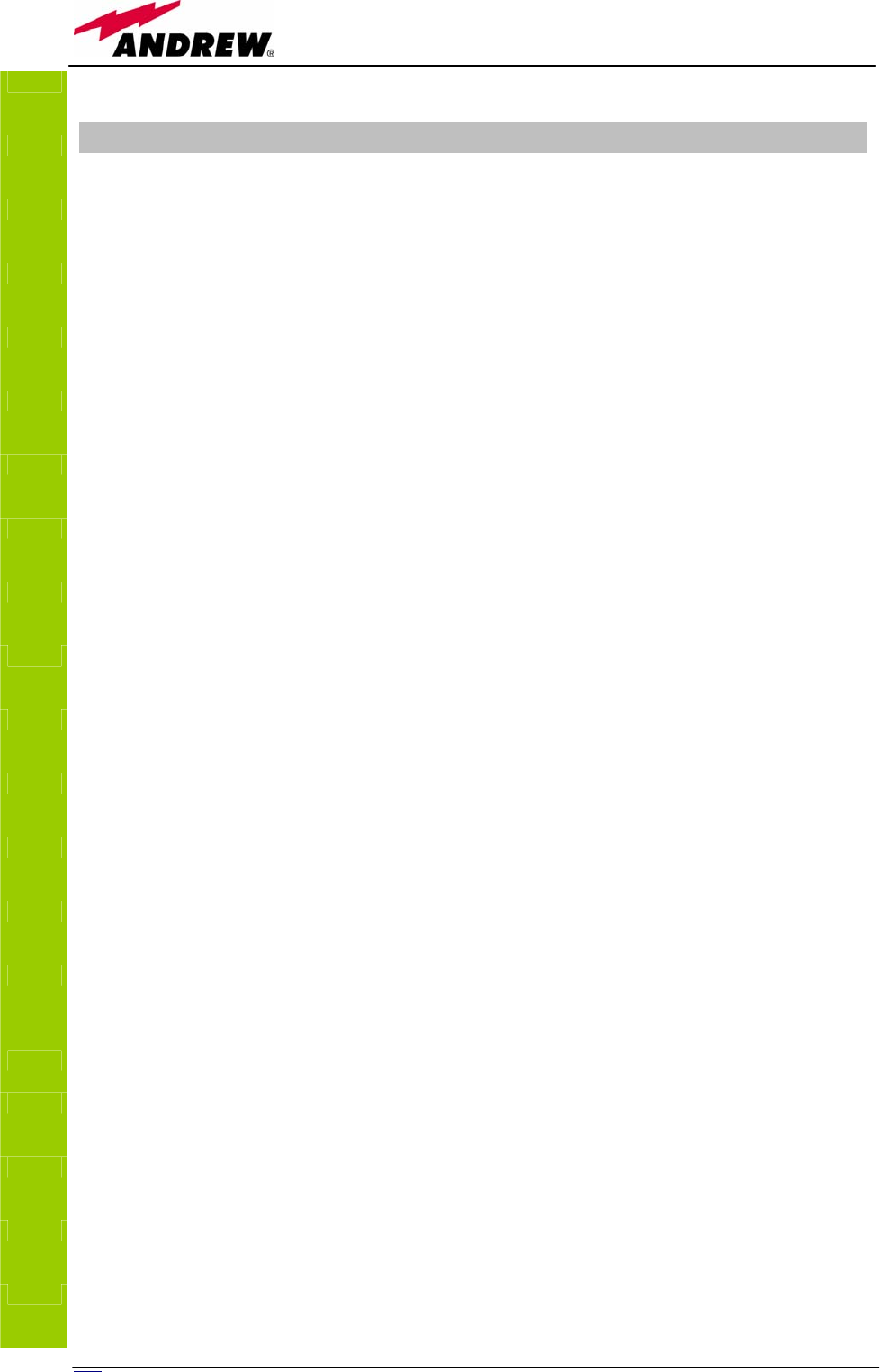
146 User Manual
5.5. RF Dual band Coupler TLDN
TLDN
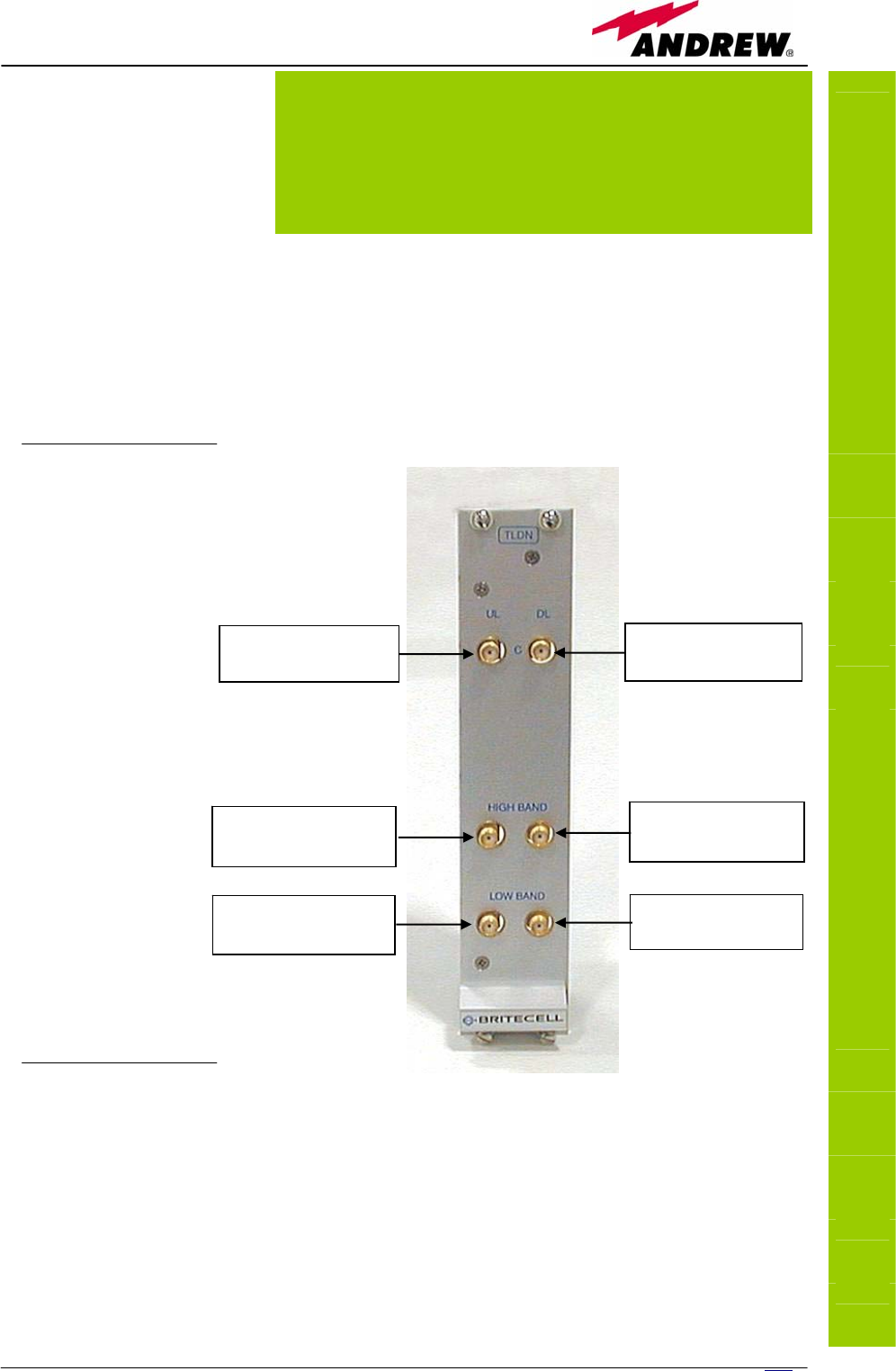
147
MN024-08
Description:
The TLDN is a passive RF
dual band coupler
designed to distribute
signal within the master
unit when coming from
different bands.
Main operations carried out are:
¾ in downlink it combines a low band RF signal (800MHz to 1000MHz) and
a high band RF signal (1700MHz to 2200MHz) into a common RF path
¾ in uplink it filters the composite signal into a low-band (800MHz to
1000MHz) and a high-band (1700MHz to 2200MHz) one.
It is a passive module.
RF ports
• 1 UL common
RF input port
(“C”) for the
combined UL
signal
• 1 UL high-
band RF
output port
• 1 UL low-band
RF output port
• 1 DL common
RF output port
(“C”) for the
combined DL
signal
• 1 DL high-
band RF input
port
• 1 DL low-band
RF input port
TLDN main
applications
Main applications of the TLDN module are:
• Connecting 2 donor sources with different services to one TFLN master
optical TRX in a dual band system, so that:
¾ TLDN combines the DL inputs coming from the 2 different donor
sources (carrying different services) into an output signal entering
the TFLN master optical TRX
TLDN
DL common RF
port (SMA-f)
DL high-band RF
port (SMA-f)
DL low-band RF
p
ort
(
SM
A
-f
)
UL high-band RF
port (SMA-f)
UL low-band RF
port (SMA-f)
UL common RF
port (SMA-f)
Fig. 5.18: The TLDN dual-band coupler
Module name:
RF dual-band coupler
TLDN
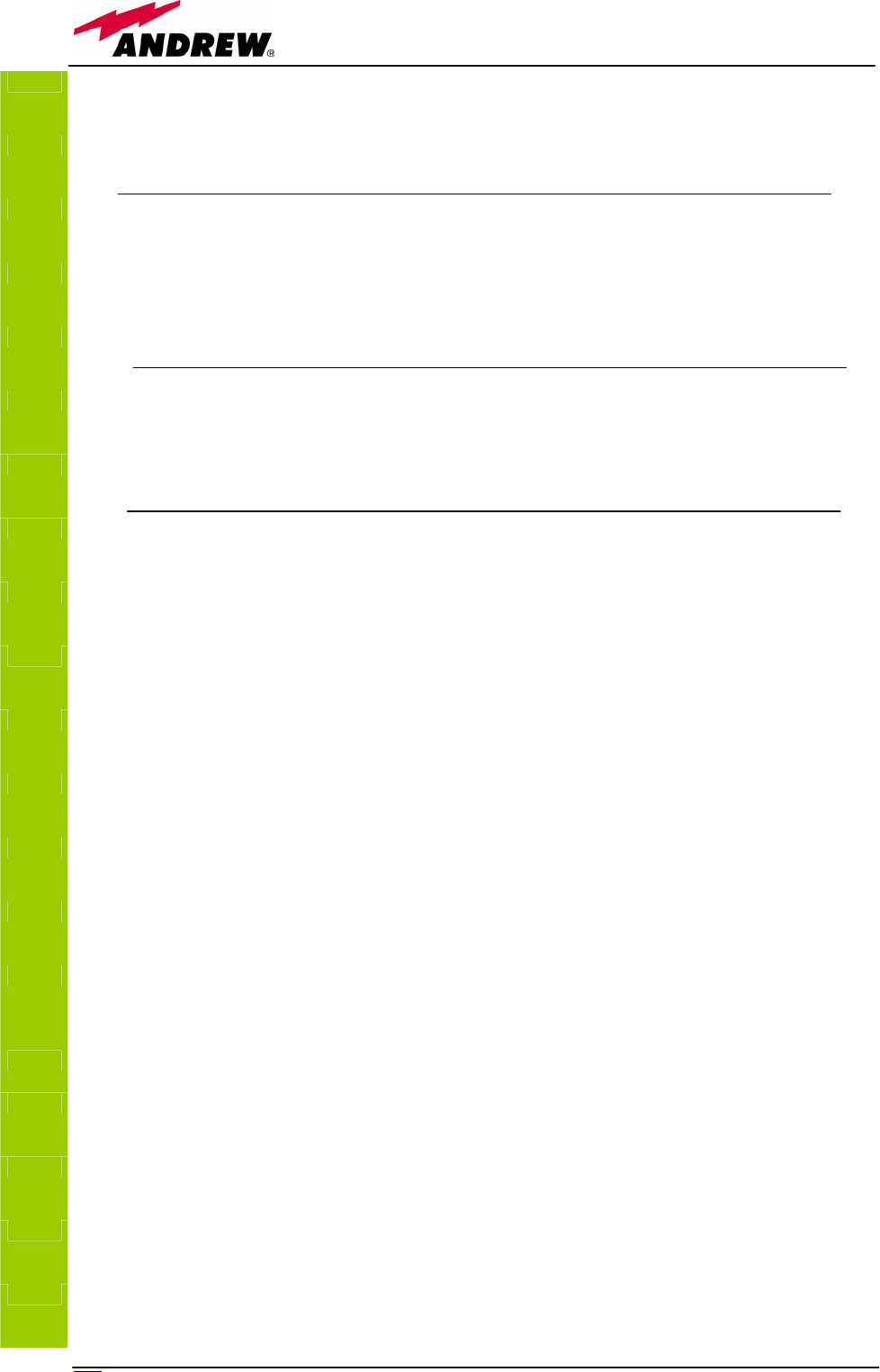
148 User Manual
¾ TLDN filters the UL input coming from a TFLN master optical TRX
into 2 UL outputs entering 2 different donor sources (carrying
different services)
TLDN insertion loss
TLDN insertion loss = 1.0 ± 0.5dB.
When designing the system, remember to take into account the insertion loss
of the TLDN.
Warnings
The overall input power must not exceed +27dBm
TLDN Installation
Since the TLDN module doesn’t require any power supply it can be housed
either in an active or a passive TPRN sub-rack.
1. Unpack the kit which include
1 TLDN
2 RF jumpers (SMA-m), 2 x 40cm
2. Carefully insert the TLDN module in any of the TPRN sub-rack slots and
lock the 4 screws on the front corners.
3. Connect RF cables to UL and DL ports, according to what planned by
designer. Use a specific torque wrench to fix each cable to relevant ports.
TLDN
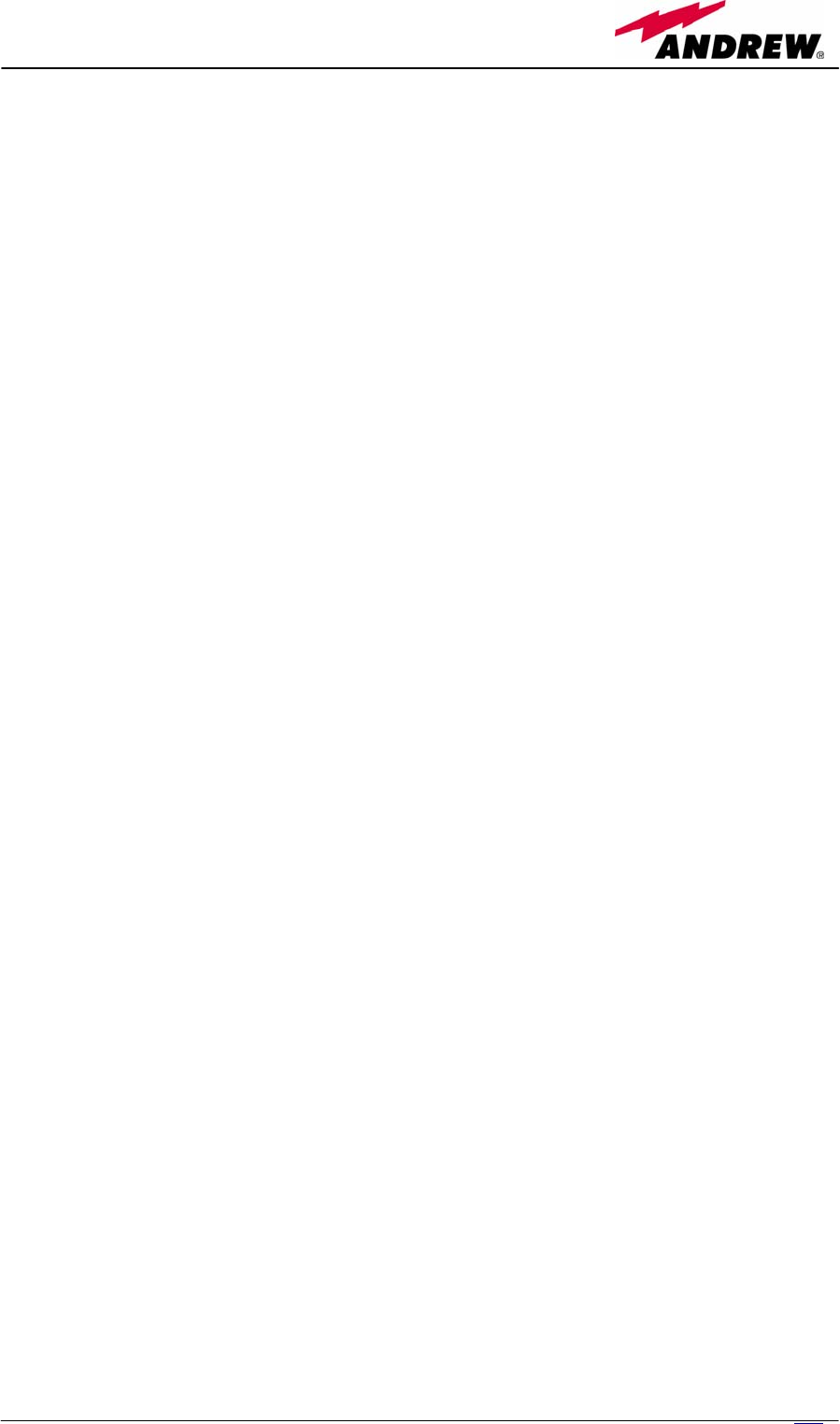
149
MN024-08
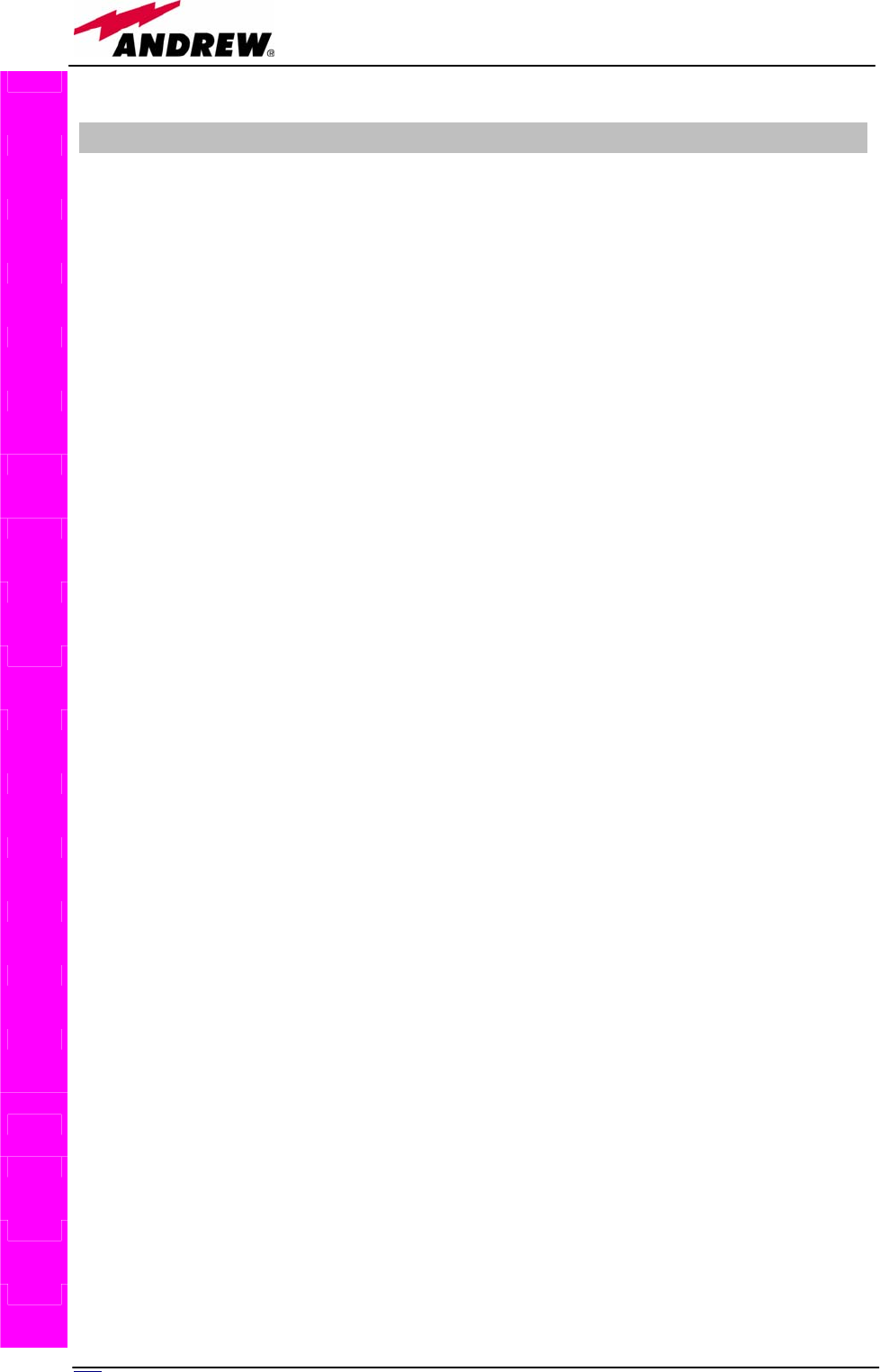
150 User Manual
5.6. RF Tri band Coupler TLTN
TLTN
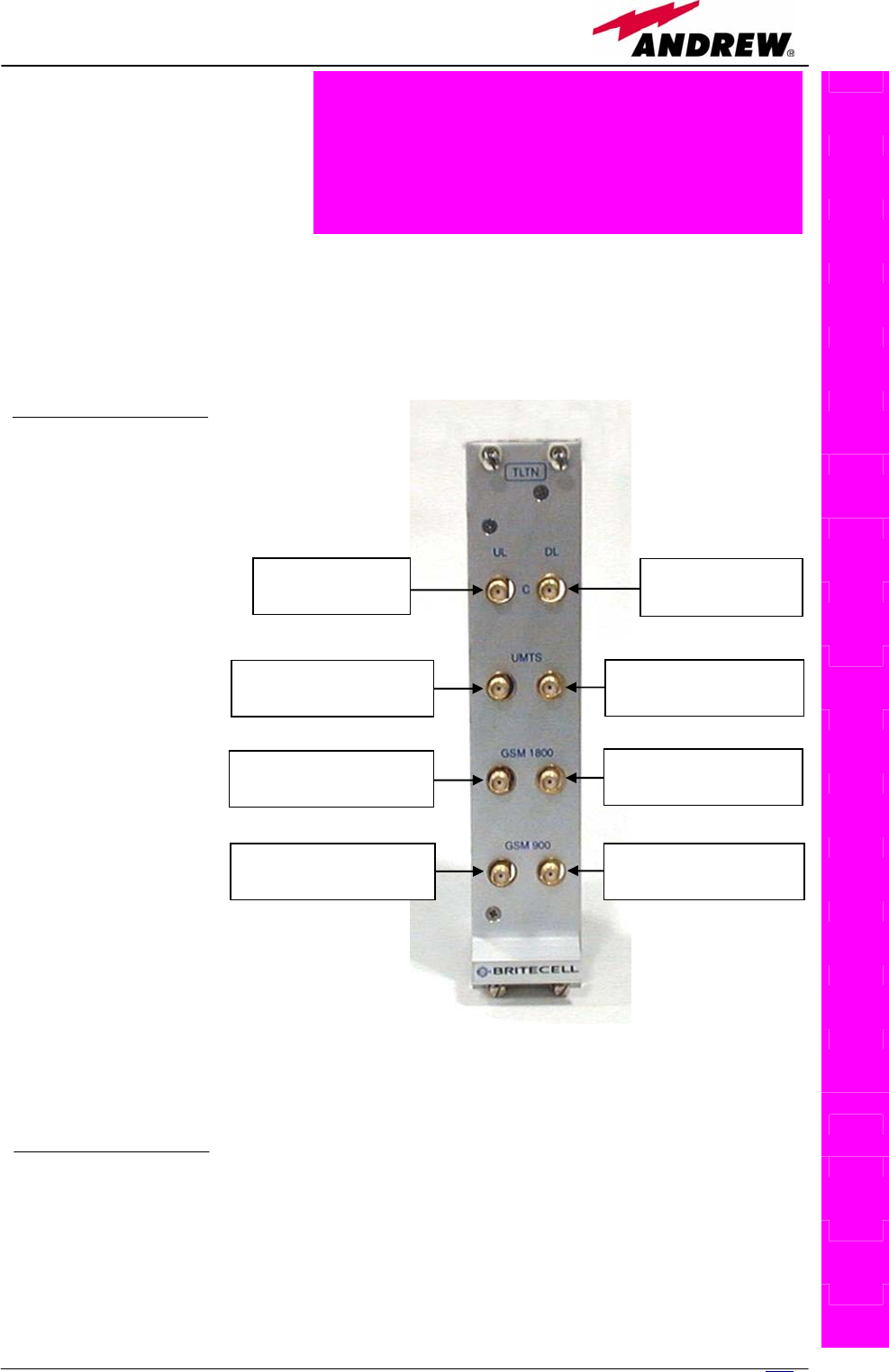
151
MN024-08
Description:
The TLTN is a passive RF tri
band coupler designed to
distribute signal within the
master unit when coming
from different bands.
Main operations carried out are:
¾ in downlink it combines a 800MHz to 1000MHz, a 1700MHz to 2000MHz
signal and a 2000MHz to 2200MHz signal into a single RF path
¾ in uplink it filters a composite signal into a 800MHz to 1000MHz, a
1700MHz to 2000MHz signal and a 2000MHz to 2200MHz one.
It is a passive module.
RF ports
• 1 DL common RF
output port (“C”)
for the combined
DL signal
• 1 DL 2000MHz to
2200MHz RF
input port
• 1 DL 1700MHz to
2000MHz RF
input port
• 1 DL 800MHz to
1000MHz RF
input port
• 1 UL common RF
input port (“C”)
for the combined
UL signal
• 1 UL 2000MHz to
2200MHz RF
output port
• 1 UL 1700MHz to
2000MHz RF
output port
• 1 UL 800MHz to
1000MHz RF
output port
TLTN main applications
Main applications of the TLTN module are:
• Connecting 3 donor sources with different services to one TFLN master
optical TRX in a tri band system, so that:
DL common RF
port (SMA-f)
UL common RF
port (SMA-f)
UL 2000 to 2200MHz
RF port (SMA-f)
UL 1700 to 2000MHz
RF port (SMA-f)
UL 800 to 1000MHz
RF port (SMA-f)
DL 2000 to 2200MHz
RF port (SMA-f)
DL 1700 to 2000MHz
RF port (SMA-f)
DL 800 to 1000MHz
RF port (SMA-f)
Fig. 5.19: The TLTN tri-band coupler
Module name:
RF tri-band coupler
TLTN
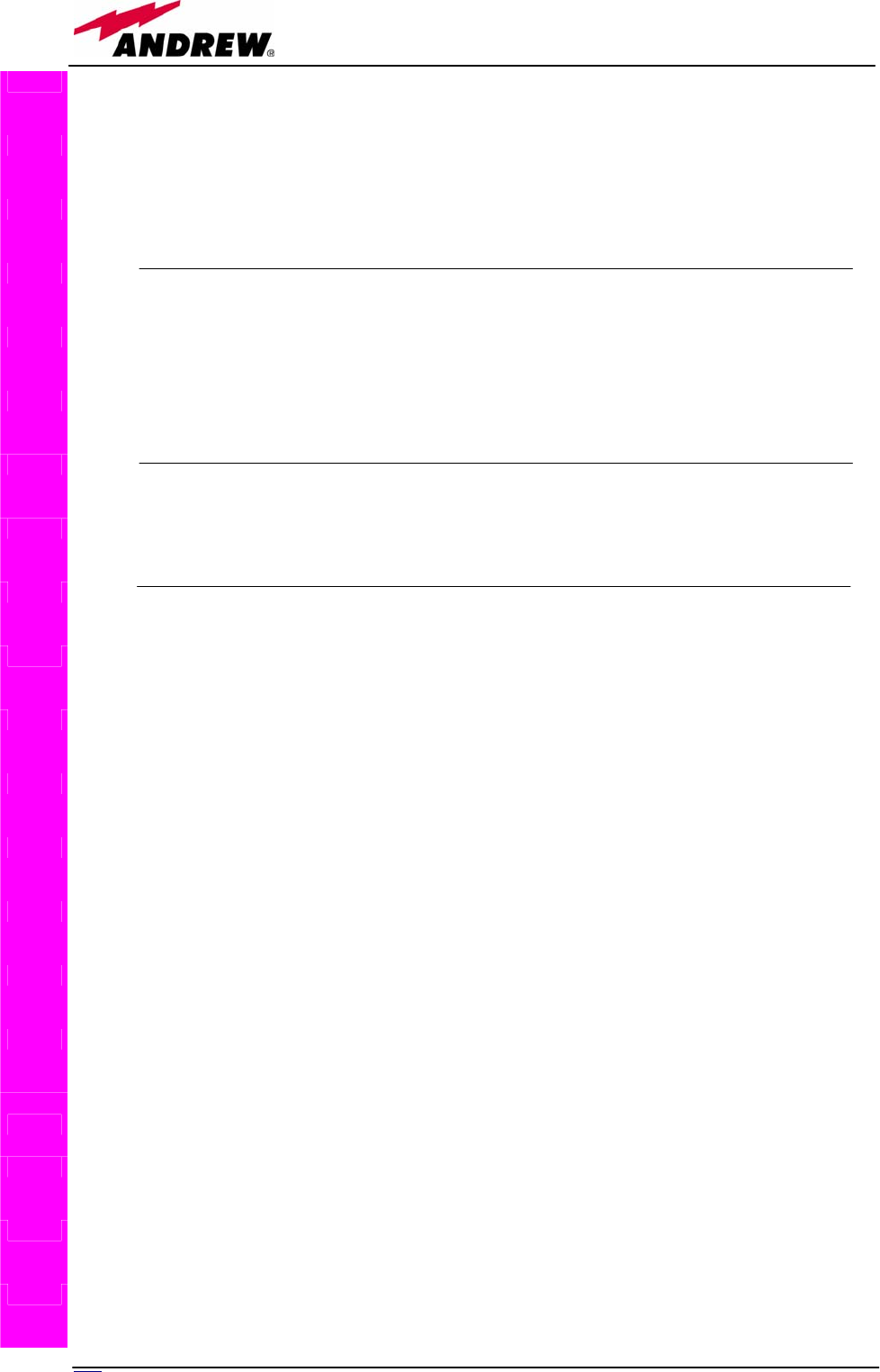
152 User Manual
¾ TLTN combines the DL inputs coming from 3 different donor sources
(carrying different services) into an output signal entering the TFLN
master optical TRX
¾ TLTN filters the UL input coming from the TFLN master optical TRX
into 3 UL outputs entering 3 different donor sources (carrying
different services)
TLTN insertion loss
TLTN insertion loss = 3.0 ± 0.5dB
When designing the system, remember to take into account the insertion loss
of the TLTN.
Warnings
The overall input power must not exceed +27dBm
TLTN Installation
Since the TLTN module doesn’t require any power supply it can be housed
either in an active or a passive TPRN sub-rack.
1. Unpack the kit which include
1 TLTN
2 RF jumpers (SMA-m), 2 x 40cm
2. Carefully insert the TLTN module in any of the TPRN sub-rack slots and lock
the 4 screws on the front corners.
3. Connect RF cables to UL and DL ports, according to what planned by
designer. Use a specific torque wrench to fix each cable to relevant ports.
TLTN
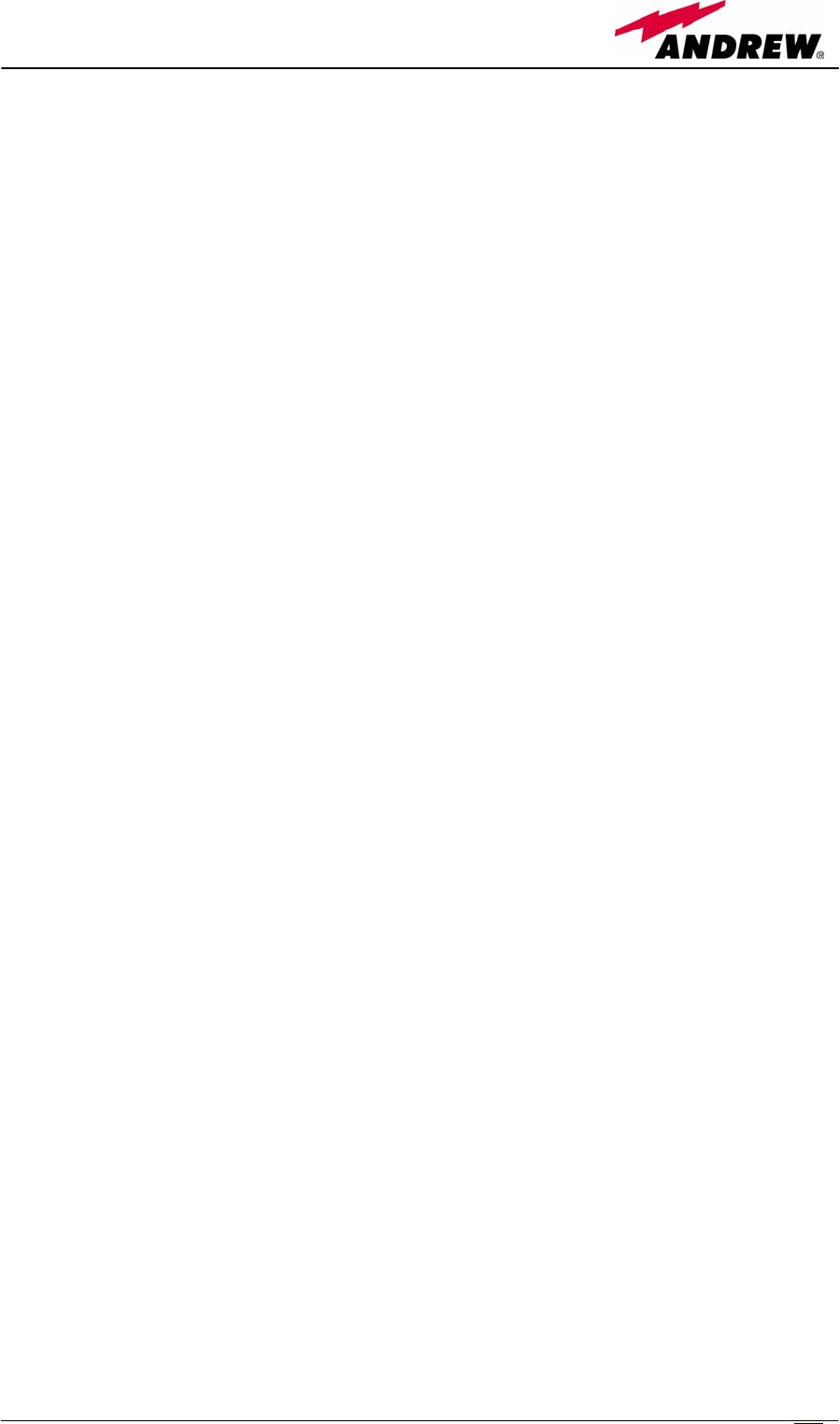
153
MN024-08
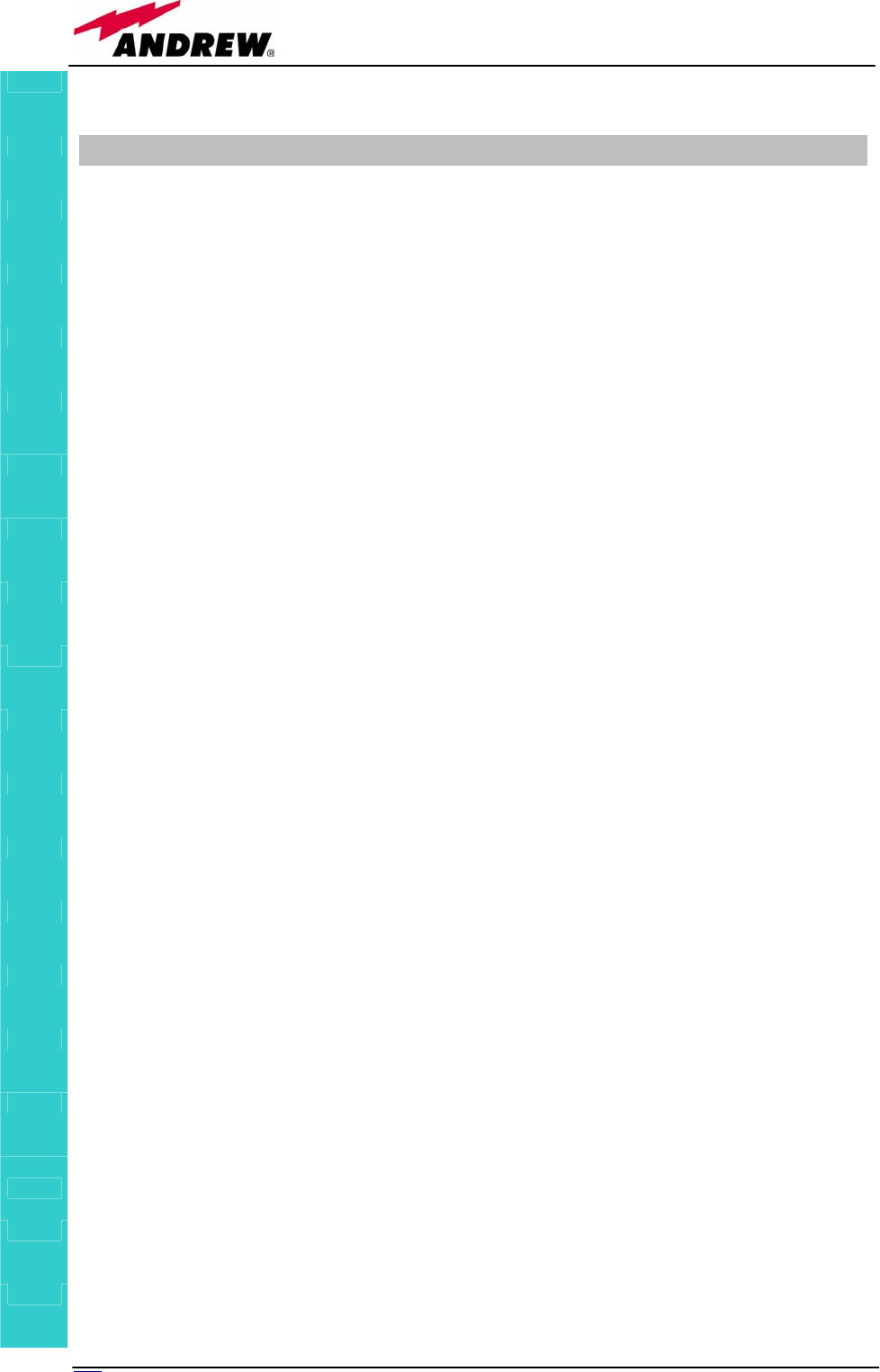
154 User Manual
5.7. RF Duplexer, TDPX
TDPX
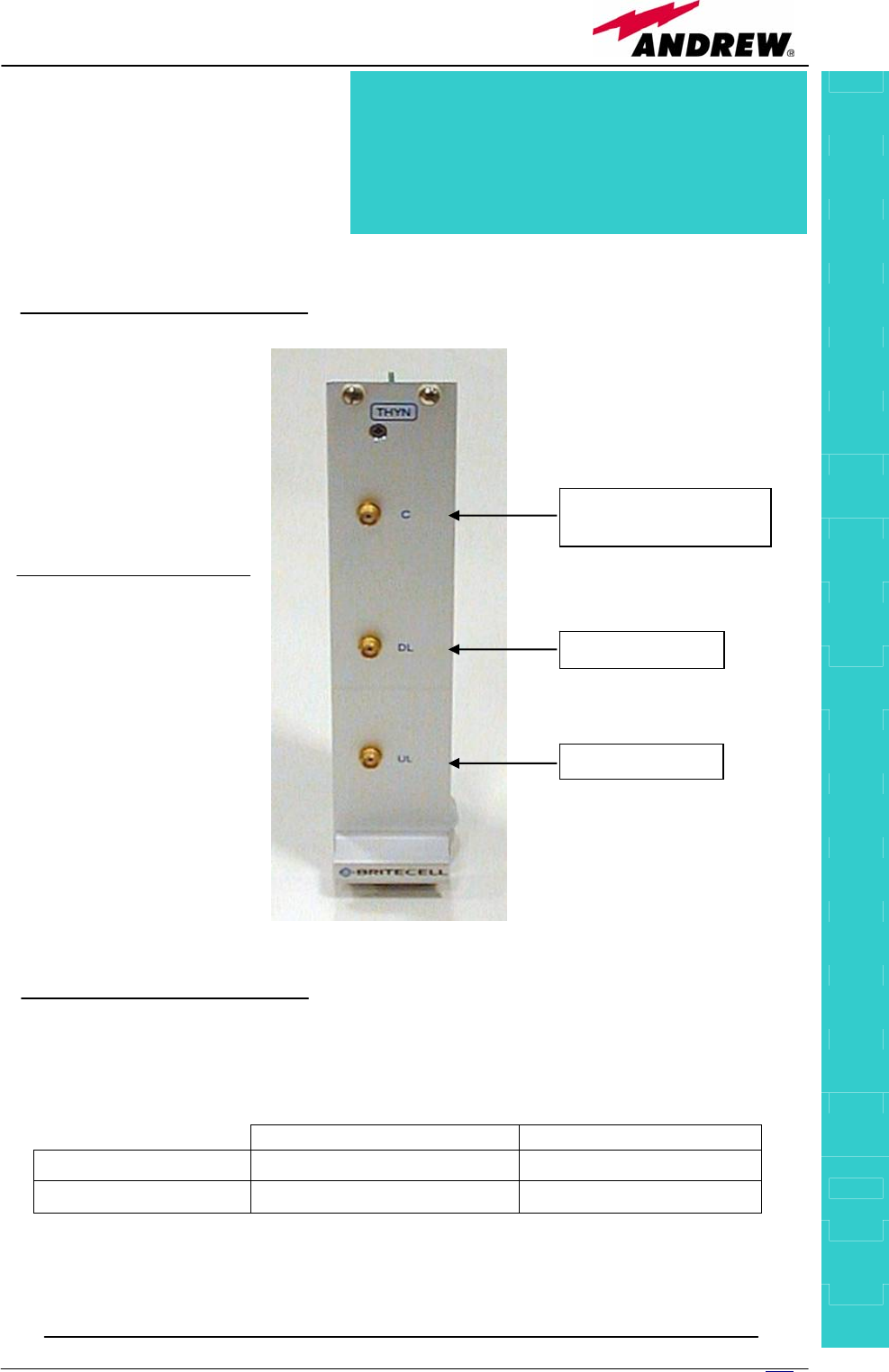
155
MN024-08
Description:
TDPX is a frequency dependent
duplexer that combines downlink
and uplink signals while
maintaining isolation and
stability.
This board has been designed to support where the source is duplexed.
RF ports
• 1 DL RF output
port
• 1 UL RF input port
• 1 common RF port
(“C”) for UL and DL
combined signals
TDPX main
applications
The TDPX main
application is to
connect the duplexed
antenna port of the
donor source to the
Britecell Plus system.
TDPX combines/
/splits the DL and UL
signals coming from
the donor port into
two separated ports
TDPX insertion loss
The TDPX insertion losses are described in table 5.9.
UMTS 2100MHz All other bands
TDPX UL insertion loss 2.0 ± 0.5dB 7.0 ± 0.5dB
TDPX DL insertion loss 2.0 ± 0.5dB 3.3 ± 0.5dB
When designing the system, remember to take into account the insertion
losses of the TDPX.
RF port for combined
UL and DL signals
UL RF port
DL RF port
Table 5.9: Insertion loss values of the TDPX module
Fig. 5.20: The TDPX duplexer
Module name:
RF tri-band coupler
TDP
X
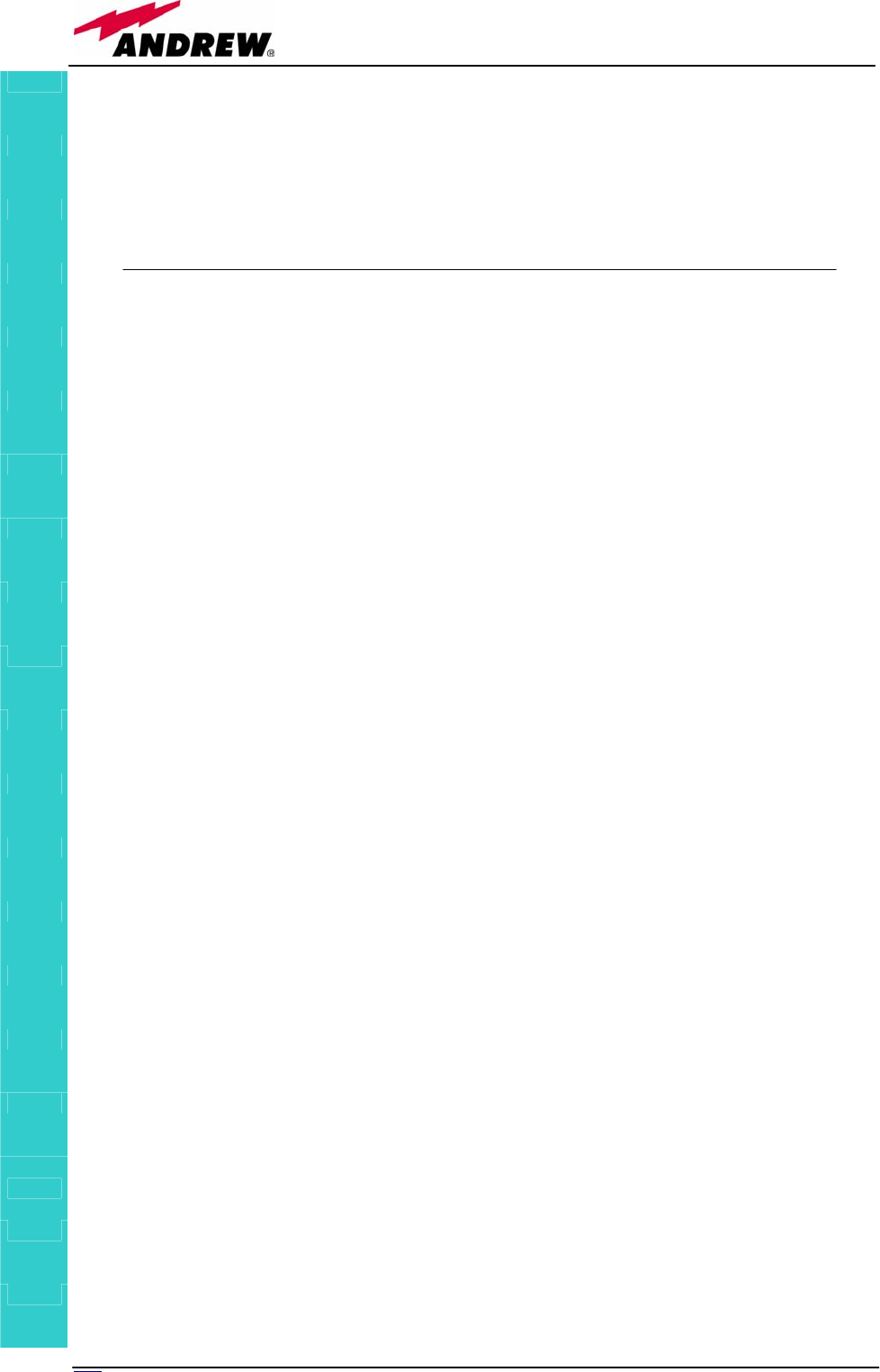
156 User Manual
Warnings
The overall input power must not exceed +30dBm.
As the module is band dependent be sure to choose the right single band
version.
TDPX Installation
Since the TDPX module doesn’t require any power supply it can be housed
either in an active or a passive TPRN sub-rack.
1. Unpack the kit which include
1 TDPX
2 RF jumpers (SMA-m), 2 x 35cm
2. Carefully insert the TDPX module in any of the TPRN sub-rack slots and
lock the 4 screws on the front corners.
3. Connect RF cables to common, UL and DL ports, according to what planned
by designer. Use a specific torque wrench to fix each cable to relevant
ports.
TDPX
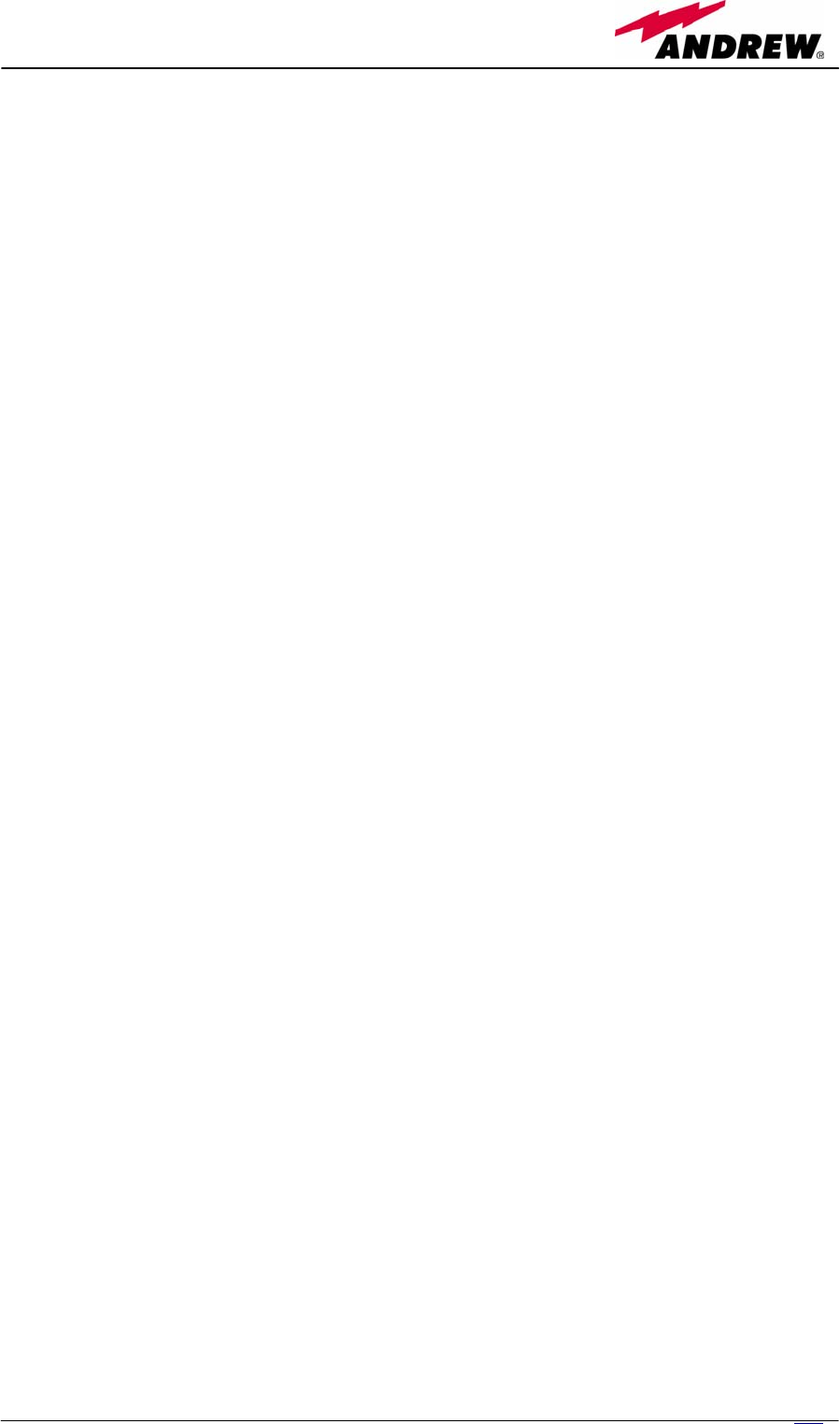
157
MN024-08
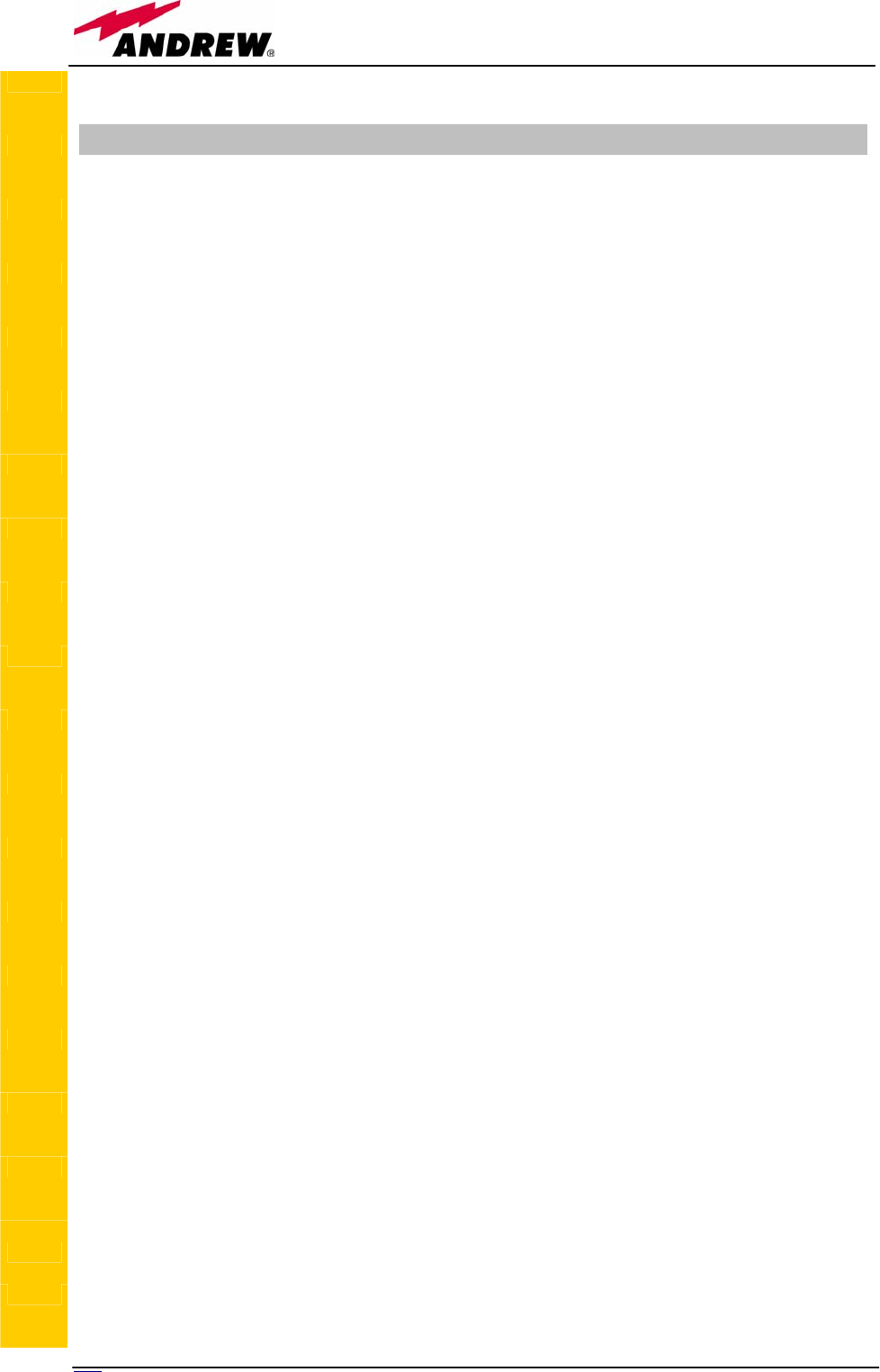
158 User Manual
5.8. Base station Interface TBSI
TBSI
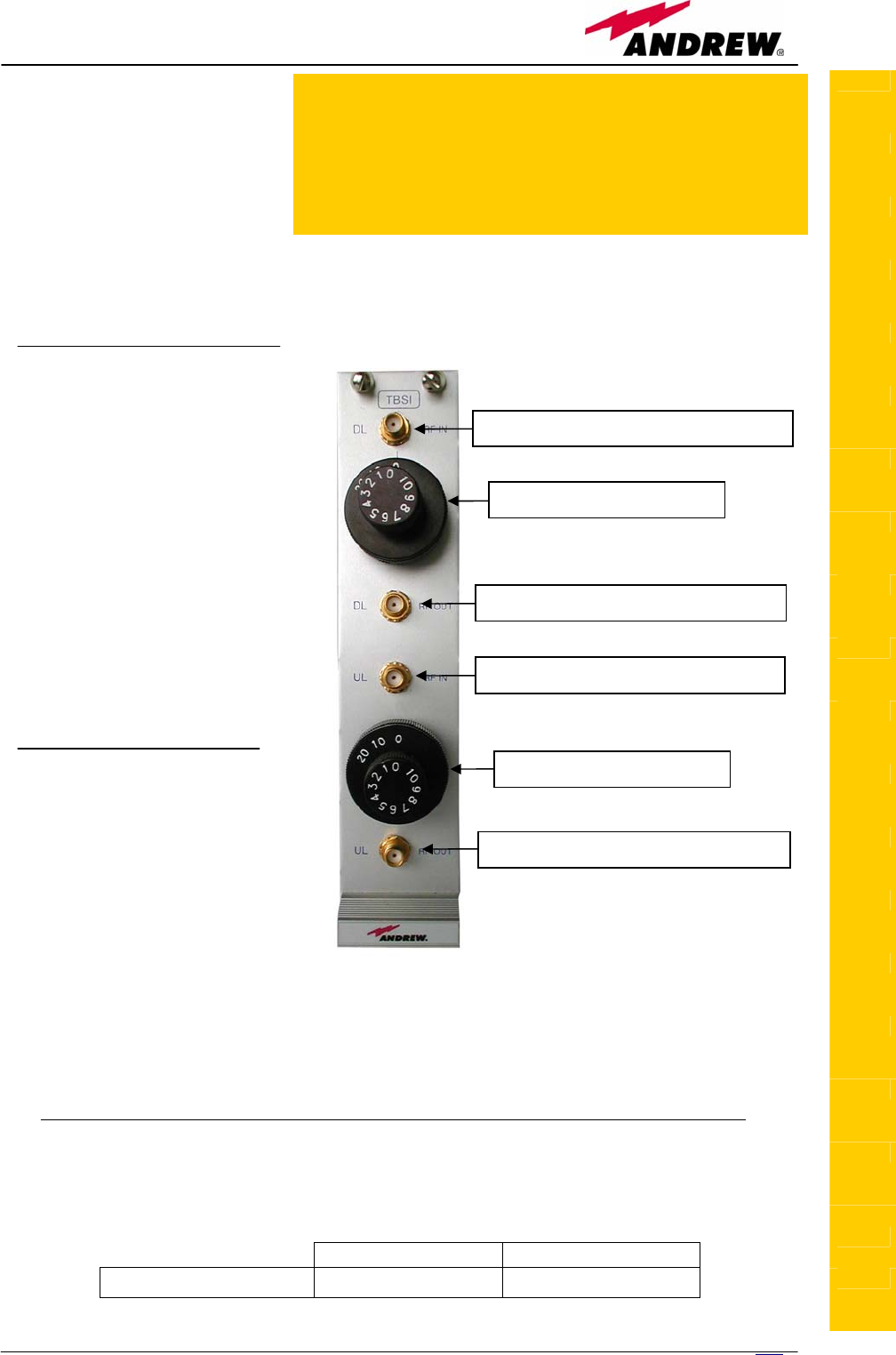
159
MN024-08
Description
The TBSI module adjusts
the signal level between
the donor source and the
Britecell Plus system.
It has 2 independent
variable attenuators to adjust both uplink and downlink separately (please
refer to BriteTool manual to understand how to calculate the right value of
attenuation through BriteTool software)
RF ports
• 1 DL RF input port
• 1 DL RF output port
(attenuated
signal)
• 1 UL RF input port
• 1 UL RF output port
(attenuated signal)
The attenuation required
both on DL and UL can be
properly set through
relevant knobs (30dB
range, 1dB step).
TBSI main
applications
Main applications of the
TBSI module are:
• adjusting RF levels
coming to/from a donor
source:
¾ TBSI adjusts the
DL signal to meet the required power level at TFLN DL RF input
¾ TBSI adjusts the RF UL signal coming from TFLN master optical TRX
in order to meet the desired requirements about blocking level and
receiver sensitivity to the donor source
TBSI insertion loss
The TBSI insertion losses are described in table 5.10:
800MHz to 2000MHz 2000MHz to 2200MHz
TBSI insertion loss < 1dB < 1.3dB
TBSI
DL RF input port (from donor source)
DL attenuation knob
DL RF output port (to master unit)
UL RF input port (from master unit)
UL RF output port (to donor source)
UL attenuation knob
Fig. 5.21: The TBSI base station interface
Table 5.10: Insertion loss values of the TBSI module
Module name:
Base station interface
TBSI
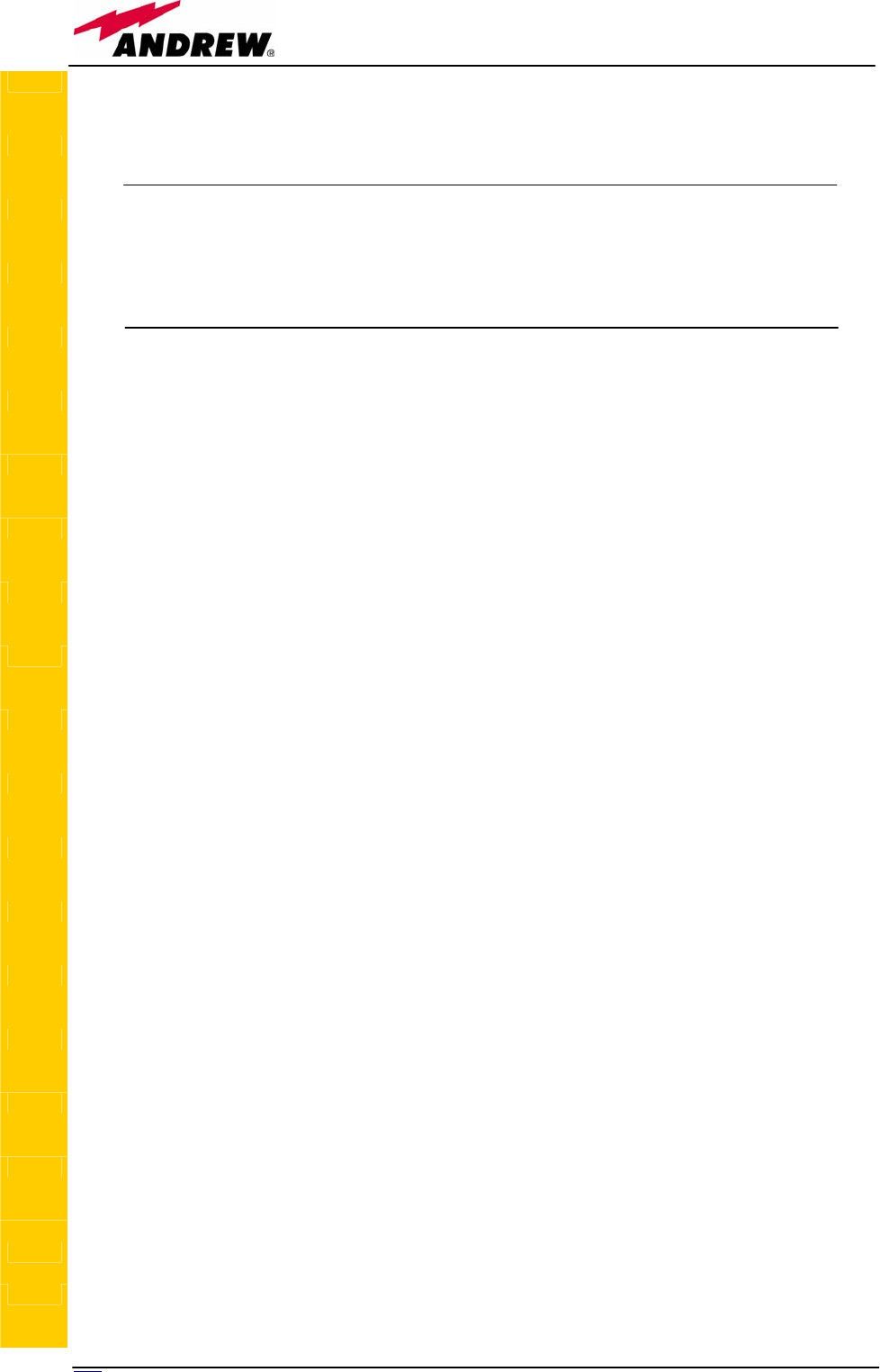
160 User Manual
When designing the system, remember to take into account the insertion loss
of the TBSI.
Warnings
The overall input power must not exceed +30dBm
TBSI Installation
Since the TBSI module doesn’t require any power supply it can be housed
either in an active or a passive TPRN sub-rack.
1. Unpack the kit which include
1 TBSI
2 RF jumpers (SMA-m), 1 x 35cm, 1 x 45cm
2. Carefully insert the TBSI module in any of the TPRN sub-rack slots and
lock the 4 screws on the front corners.
3. Connect RF cables according to what planned by designer. Use a specific
torque wrench to fix each cable to relevant ports.
4. Set proper attenuation values.
TBSI
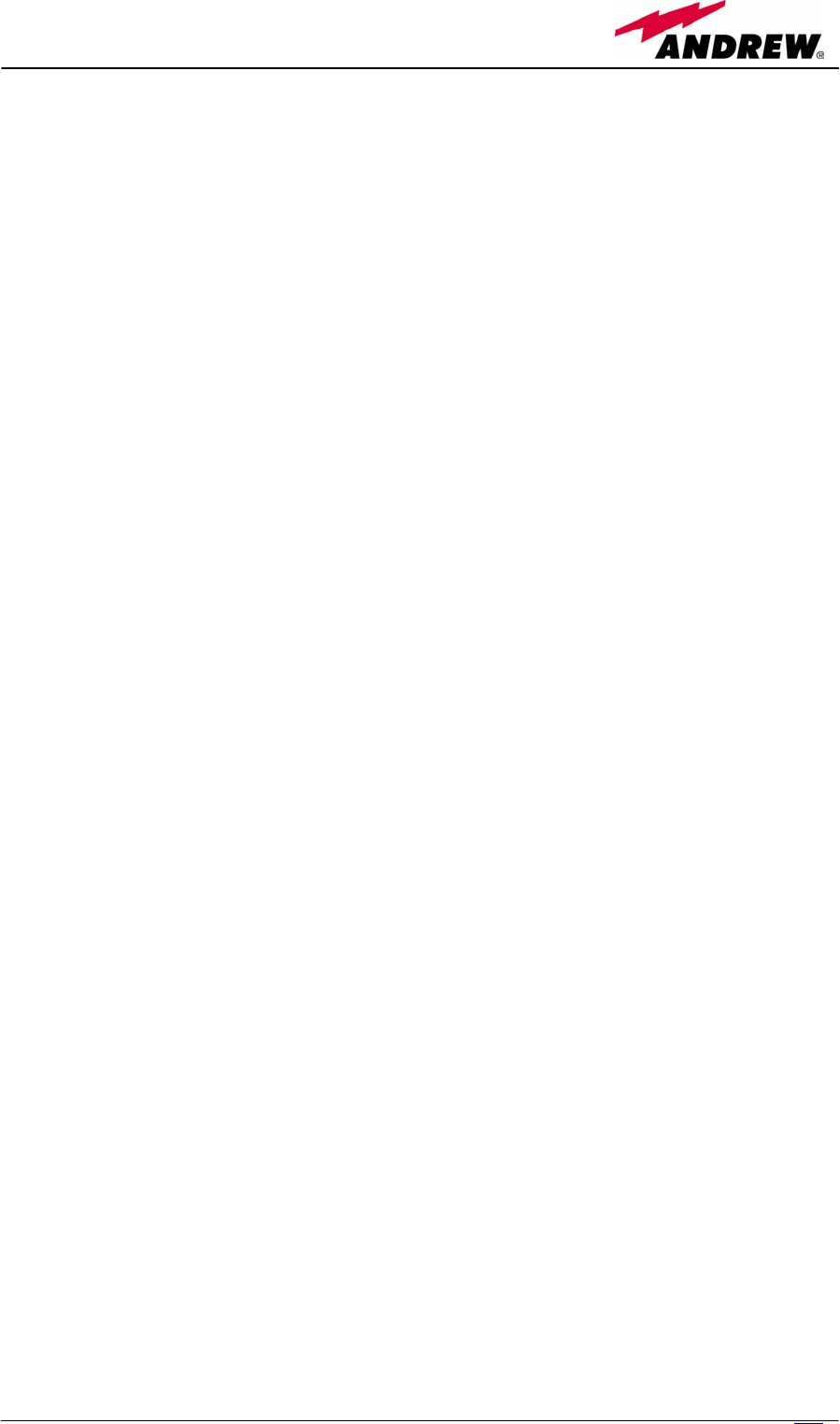
161
MN024-08
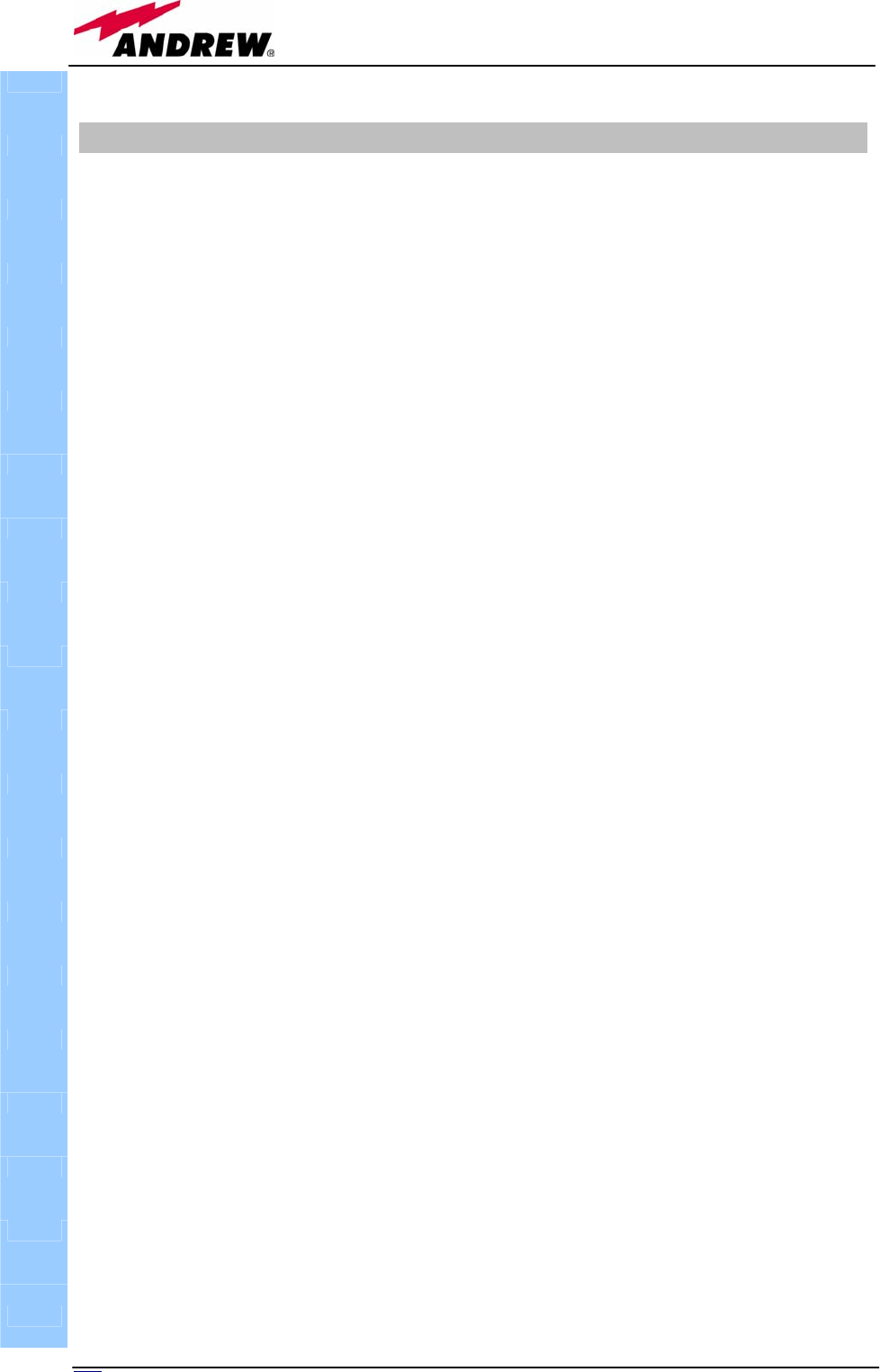
162 User Manual
5.9. Power Limiter TMPx-10
TMPX
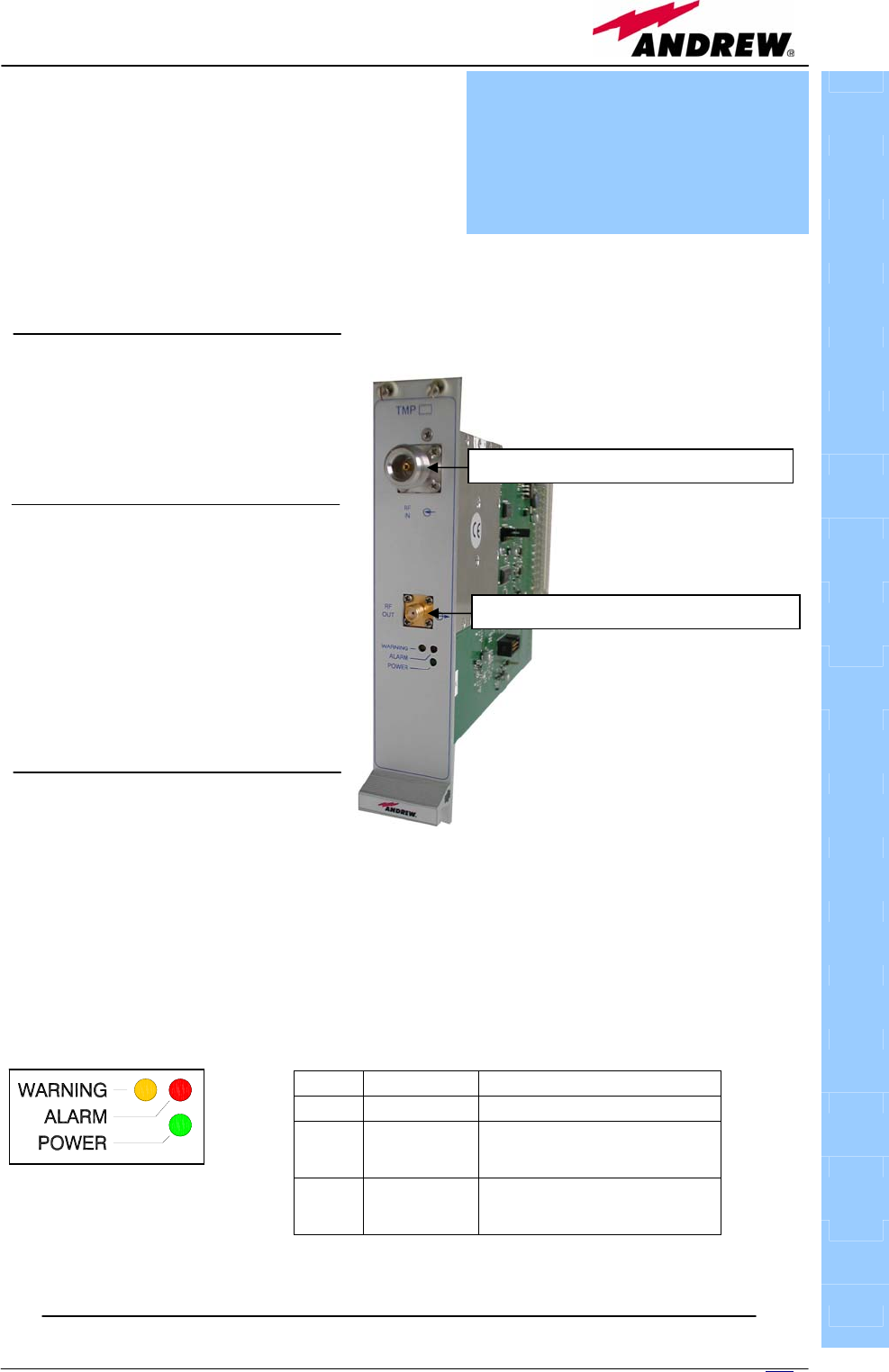
163
MN024-08
Description
The TMPx-10 power limiter monitors the
downlink input power and attenuates it by
10dB above a predetermined set point. The
threshold is programmable through the
supervision system.
TMPx-10 power limiter is available in two versions, one suitable for GSM DL
(800 to 1000MHz or 1800 to 2000MHz) and the other for UMTS 2100MHz DL.
RF ports
• 1 DL RF input port
• 1 DL RF output port
TMP main applications
Main applications of the TMP
module are:
• Check DL RF level coming from
a donor source in order to
protect the system if the level
exceeds a specified threshold.
TMP visual alarms
The TMP front panel is provided
with 3 LEDs (see on the right)
showing status and alarm information
LED meaning is reported on the rightward table.
Further information about alarm status are delivered by Britecell Plus supervision
system
TMPX
Label LED colour Meaning
Power Green Power supply status OK
Alarm Red
It can be:
- TMP power supply alarm
- RF input overdrive
Warning Red
It can be:
- temperature alarm
- no RF signal at the input port
DL RF in
p
ut
p
ort
(
from donor source
)
DL RF out
p
ut
p
ort
(
to master unit
)
Tab. 5.11: Summary of TMP LEDs meaning
Fig. 5.22: The TBSI base station interface
Fig. 5.23: The LED panel
on the TMP front-side
Module name:
Power Limiter
TMPx-10
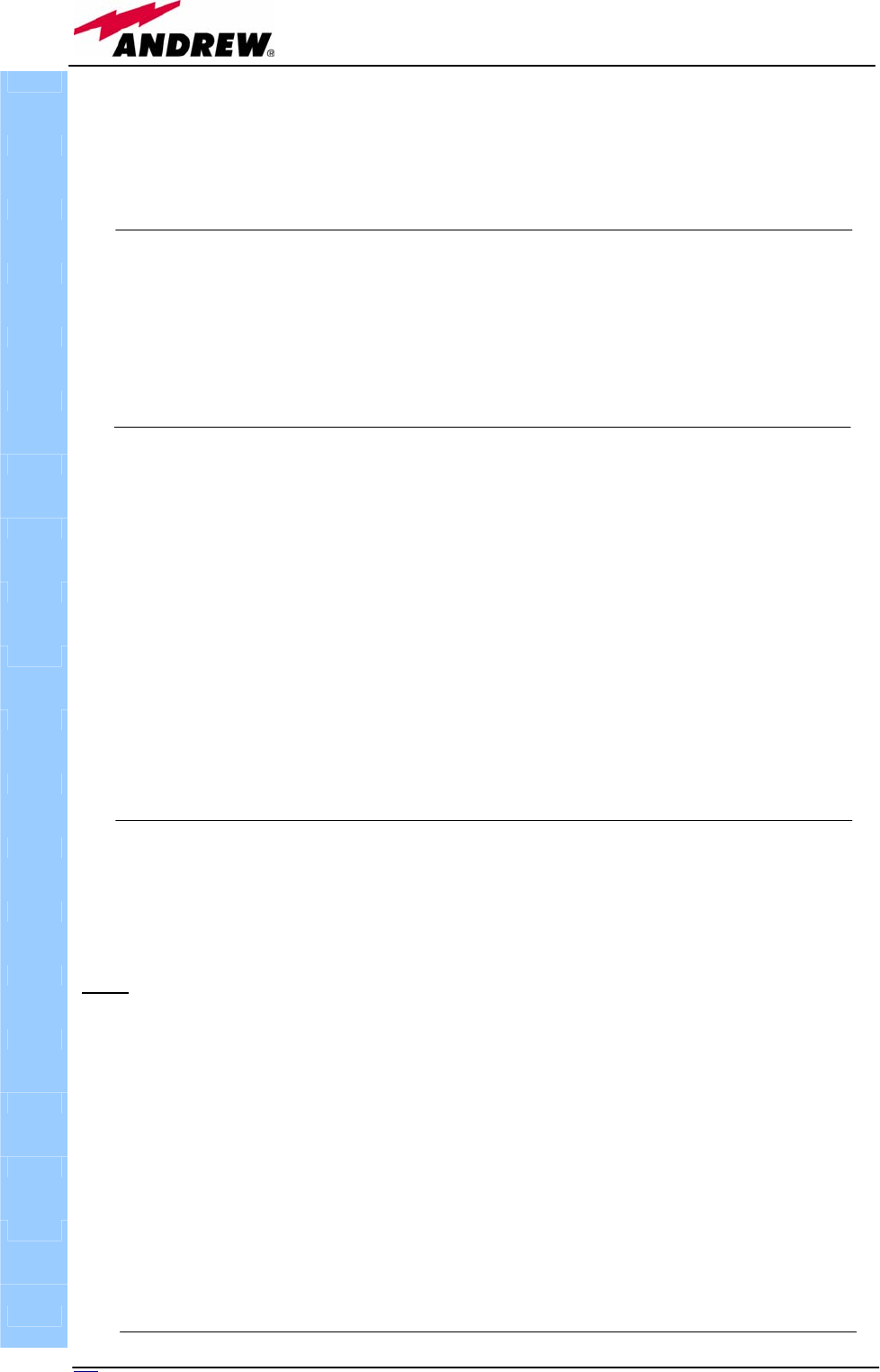
164 User Manual
TMP power supply
Each TMPx-10 power limiter is supplied by the sub-rack back-plane (+12V).
The power consumption of each TMPx-10 is 2W max
TMP insertion loss
TMP insertion loss < 1.7dB.
When designing the system, remember to take into account the insertion loss
of the TMP.
Warnings
The overall input power must not exceed +35dBm.
Inserting or removing TMP modules
• Do not remove or insert any TMP module into TPRN sub-rack before
having switched off main power supply.
• The TMP modules must be handled with care, in order to avoid damage to
electrostatic sensitive devices.
• When installing TMP modules in the sub-rack, take care to alternate active
and passive cards in order to ensure proper heat dissipation.
• In a multi-sub-rack system, remember to assign to each sub-rack a proper
RS485 bus address before installing the modules (please refer to TPRN
section for further details).
TMP installation
The TMP power limiter can be accomodated in any of the 12 slots of a TPRN
active sub-rack.
Note: In case a new TMP module has to be installed in a still working Master
Unit, switch off the sub-rack before inserting the plug-in TMP module
1. Unpack the kit which include
1 TMP
1 RF jumper (SMA-m), 35cm
2. Carefully insert the TMP module in any of the TPRN sub-rack slots and
lock the 4 screws on the front corners.
3. Connect RF cables according to what planned by designer. Use a specific
torque wrench to fix each cable to relevant ports.
4. Switch on the sub-rack. As you switch on the system, carefully refer to
the TFLN Start-up section.
TMPX
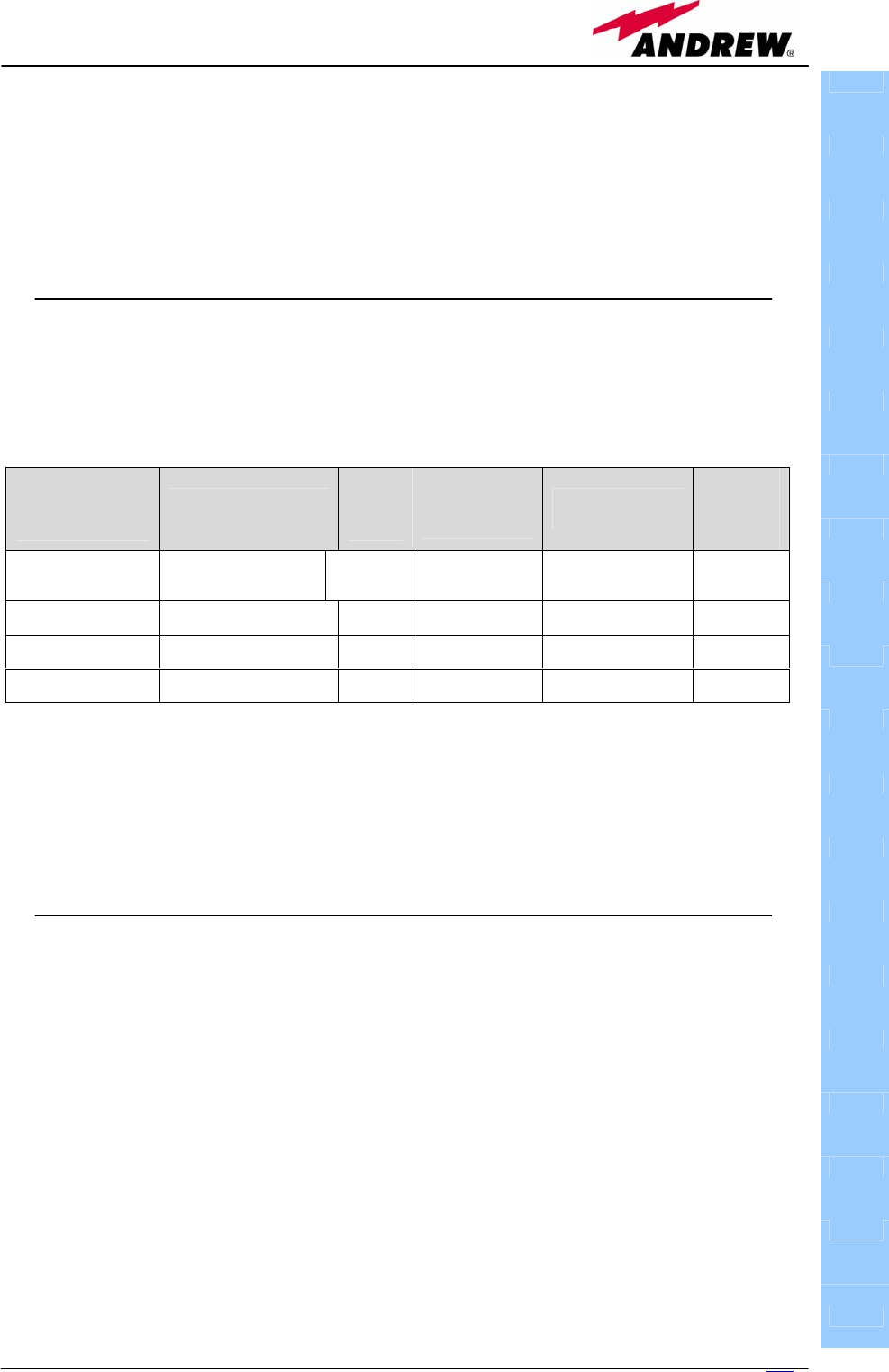
165
MN024-08
Removing a TMP module
Switch off the Master Unit power supply and remove RF jumpers. Then
• unscrew the 4 screws and slowly remove the card.
• put the removed TMP card in its safety box.
• switch on again the Master Unit power supply and refer to TFLN Start-up
section.
TMP troubleshooting
In case a TMP power limiter has any problem, this will be easily revealed
through LEDs on its front panel otherwise troubleshooting can be carried out
through LMT or supervision system.
The previous table reports a brief description of the TMP alarm, together with
a reference to the corresponding alerted LEDs.
Understanding why one LED is on can be done following the troubleshooting
procedure reported hereinafter.
Quick troubleshooting procedure
(The following procedure is summarized by the flow-chart in fig. 22)
1. In case the TMP red led is on and the green led is off there is a problem
on the power supply.
a. Check the TPRN sub-rack and if it is switched off, switch it on.
b. If the sub-rack is switched on, check the backplane power supply
connector to verify if the +12Vdc is provided to the TMP module.
If not there is a fault on the TPRN backplane and you need to
return the sub-rack.
c. Otherwise the TMP power supply section is faulty. Return the
unit.
2. In case the TPM red and green leds are on, the RF level at the input port
has exceeded the specified threshold. Decrease the RF signal or change
the threshold.
3. In case the yellow led is on, check the RF input level
TMPX
ALARM CODE
(TSUN
description)
ALARM
DESCRIPTION
ACTIV
E LED
SUPERVISION
PRIORITY
LEVEL
ACTION
RECOMMENDED
RELÉ
PRIORITY
LEVEL
(subrack)
Power supply alarm
UPS HW failure or
malfunction.
RF is turned OFF
RED MAJOR Return the unit MAJOR
Temperature alarm Over-temperature alarm YELLO
W MINOR Check ventilation
and environment MINOR
RF Input overdrive The input signal has
exceeded the threshold RED WARNING
Check the RF input
signal MAJOR
RF Input No signal No RF signal at the input
port
YELLO
W MINOR Check the RF input
signal MINOR
Tab. 5.12:Description of the TMP alarms

166 User Manual
a. If there isn’t any RF signal at the input, check if the RF cable is
connected at the input port. If it’s connected check the power
coming out from the donor source.
b. Otherwise the temperature range is not within the specified
range, change the temperature range or provide proper air flow.
TMPX
Fig. 5.24: Flow-chart describing the troubleshooting procedure
start
Problem on power supply
Is red
LED ON upon
the TMP?
No
Yes
end
Is green
LED OFF upon
the TMP?
RF level @ input port has
exceeded the threshold.
Check the RF signal.
Yes
Is
TPRN sub-rack
switched on?
Switch on
the sub-rack
Is red
LED ON and
green OFF?
No
Yes
Yes
Check TPRN
backplane
power supply
N
o
Is +12Vdc
provided?
N
o
No
TPRN backplane
is faulty. Return
the TPRN
TMP power supply
section is faulty.
Return the TMP.
No
Is yellow
LED ON upon
the TMP?
No
Yes
Check the RF
input level and
if the RF cable
is connected
Is there
any RF input
level?
No
Yes
Check if the
temperature is
within the
s
p
ecified ran
g
e.

167
MN024-08
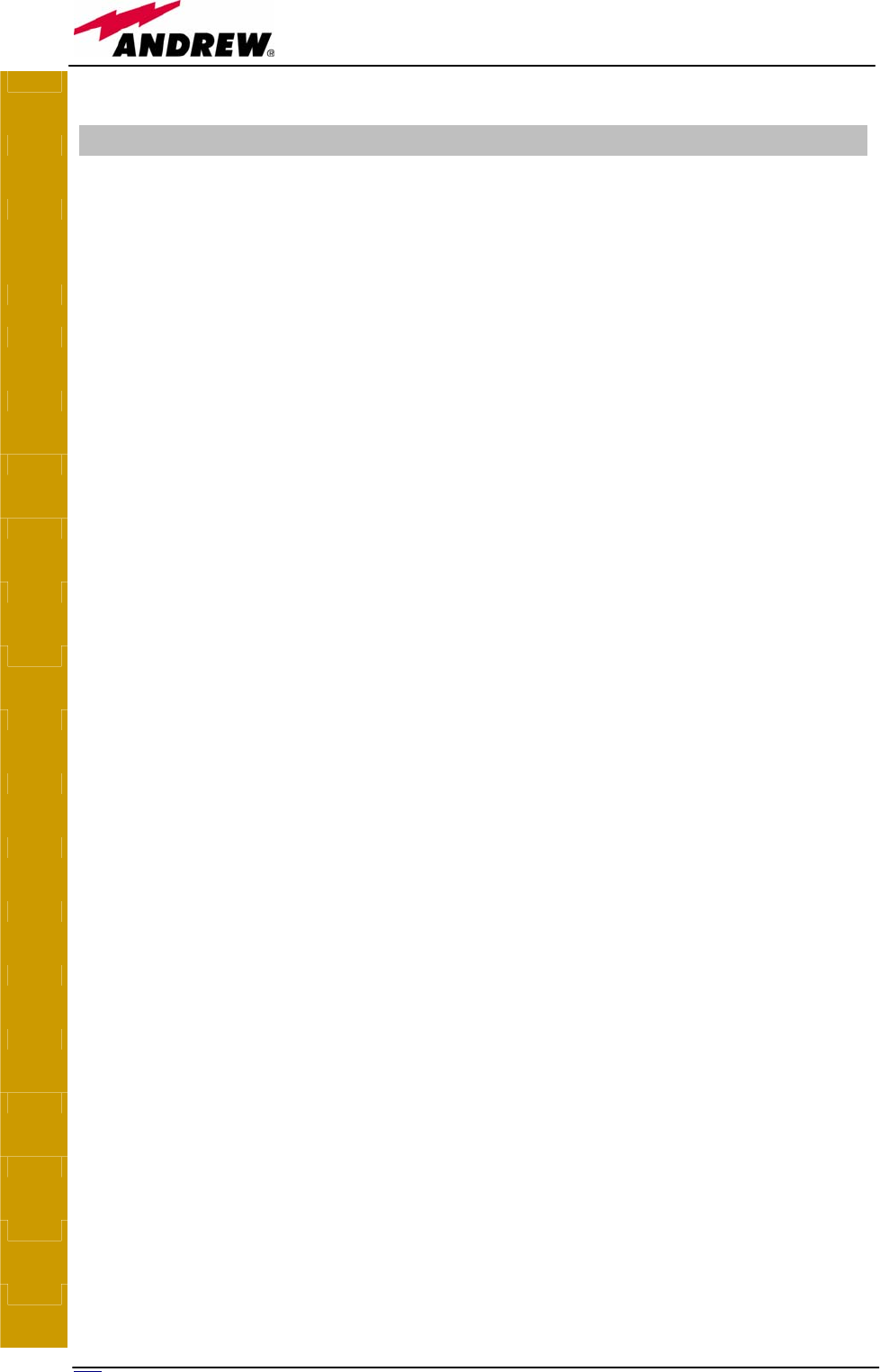
168 User Manual
5.10. Wi-Fi Local Interface, TWLI
TWLI
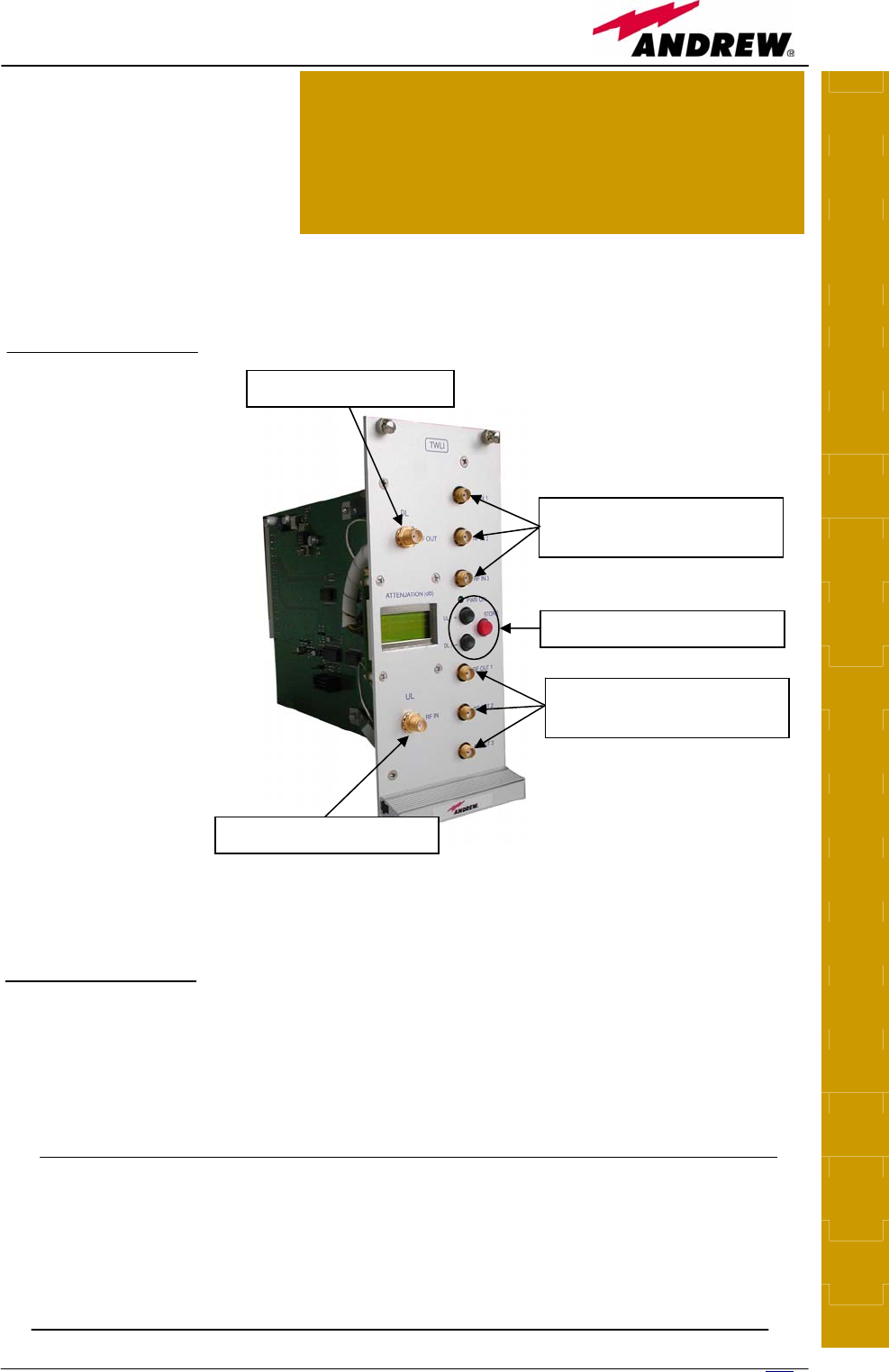
169
MN024-08
Description
Britecell Plus system allows
distributing WLAN service
(802.11b and g) through
the auxiliary channel while
concentrating all the Access
Points together with the central equipment.
The TWLI module allows connecting up to 3 Access Points to one TFLN master
optical TRX and setting up to 4dB attenuation, if needed, on the DL path.
RF ports
• 3 DL RF input
ports receiving
signals from
up to 3
different
Access Points
• 1 DL RF
output port to
the TFLN
auxiliary port
• 1 UL RF input
port from the
TFLN auxiliary
port
• 3 UL RF output
ports sending
signals to up
to 3 different
Access Points
4dB attenuation range is available on the DL path in order to adjust levels
coming from the Access Points.
TWLI main applications
Main applications of the TWLI module are:
• providing to the TFLN the WLAN signals coming from up to 3 Access Points
concentrated on the equipment room.
TWLI power supply
Each TWLI WLAN interface module is supplied by the sub-rack back-plane
(+12V).
The power consumption of each TWLI is 2W max.
TWLI
DL RF input
from Access Points 1 to 3
Attenuation setting buttons
DL RF output to TFLN
UL RF input from TFLN
UL RF output
to Access Points 1 to 3
Fig. 5.25: The TWLI wi-fi
local interface
Module name:
Wi-Fi Local Interface
TWLI
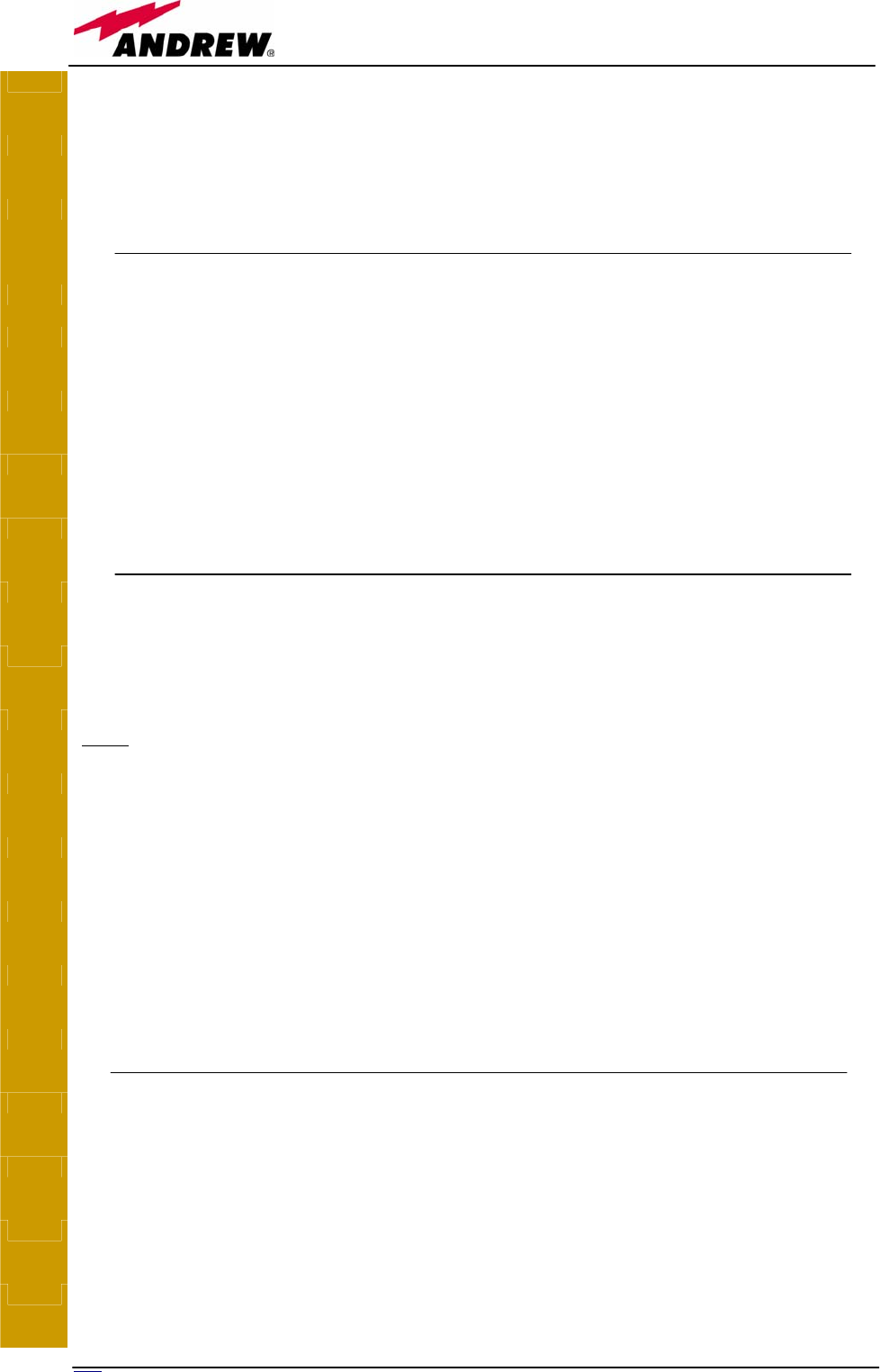
170 User Manual
Warnings
The overall input power must not exceed +19dBm
The TWLI modules must be handled with care, in order to avoid damage to
electrostatic sensitive devices.
Inserting or removing TWLI modules
• Do not remove or insert any TWLI module into TPRN sub-rack before
having switched off main power supply.
• The TWLI modules must be handled with care, in order to avoid damage to
electrostatic sensitive devices.
• When installing TWLI modules in the sub-rack, take care to alternate
active and passive cards in order to ensure proper heat dissipation.
• In a multi-sub-rack system, remember to assign to each sub-rack a proper
RS485 bus address before installing the modules (please refer to TPRN
section for further details).
TWLI installation
The TWLI WLAN local interface can be accomodated in any of the 12 slots of a
TPRN active sub-rack.
Note: In case a new TWLI module has to be installed in a still working Master
Unit, switch off the sub-rack before inserting the plug-in TWLI module
1. Unpack the kit which include
1 TWLI
2 RF jumpers (SMA-m; SMB-f), 2 x 40cm
2. Carefully insert the TWLI module in any of the TPRN sub-rack slots and
lock the 4 screws on the front corners.
3. Connect RF cables according to what planned by designer. Use a specific
torque wrench to fix each cable to relevant ports.
4. Switch on the sub-rack. As you switch on the system, carefully refer to
the TFLN Start-up section.
Removing a TWLI module
Switch off the Master Unit power supply and remove RF jumpers. Then
• unscrew the 4 screws and slowly remove the card.
• put the removed TWLI card in its safety box.
• switch on again the Master Unit power supply and refer to TFLN Start-up
section.
TWLI
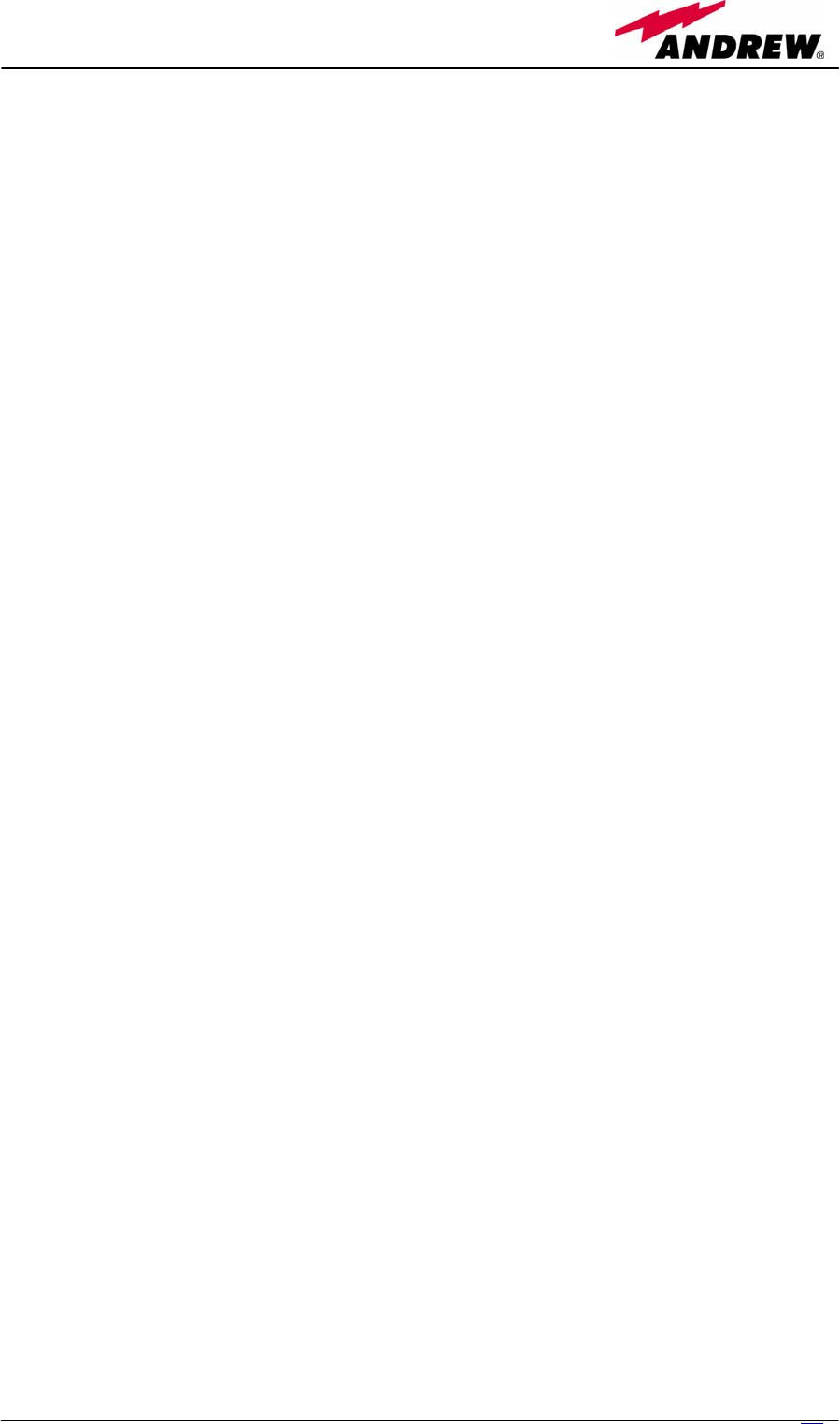
171
MN024-08
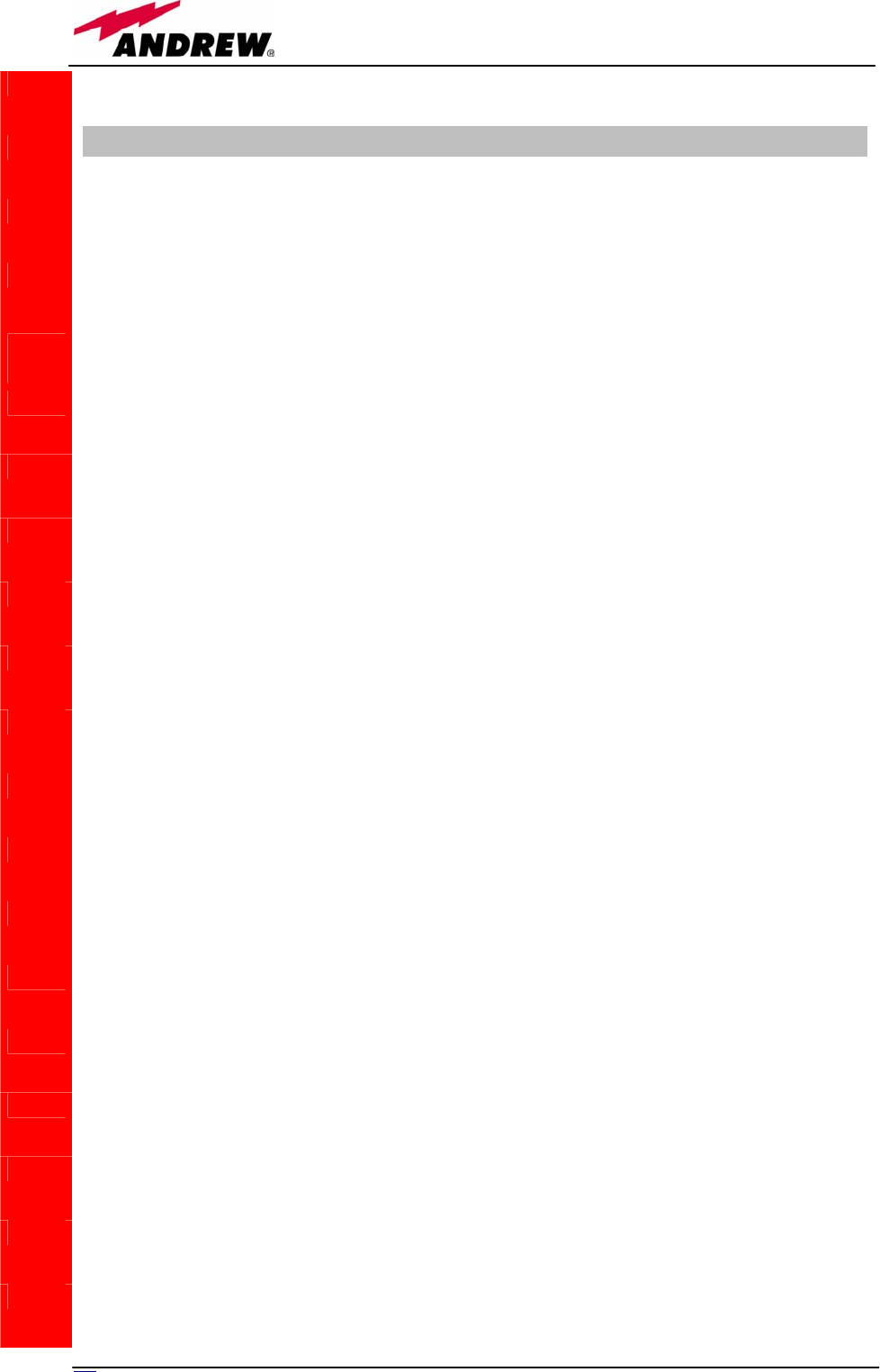
172 User Manual
5.11. Interconnect Link (i-link)
TILx
(intro)
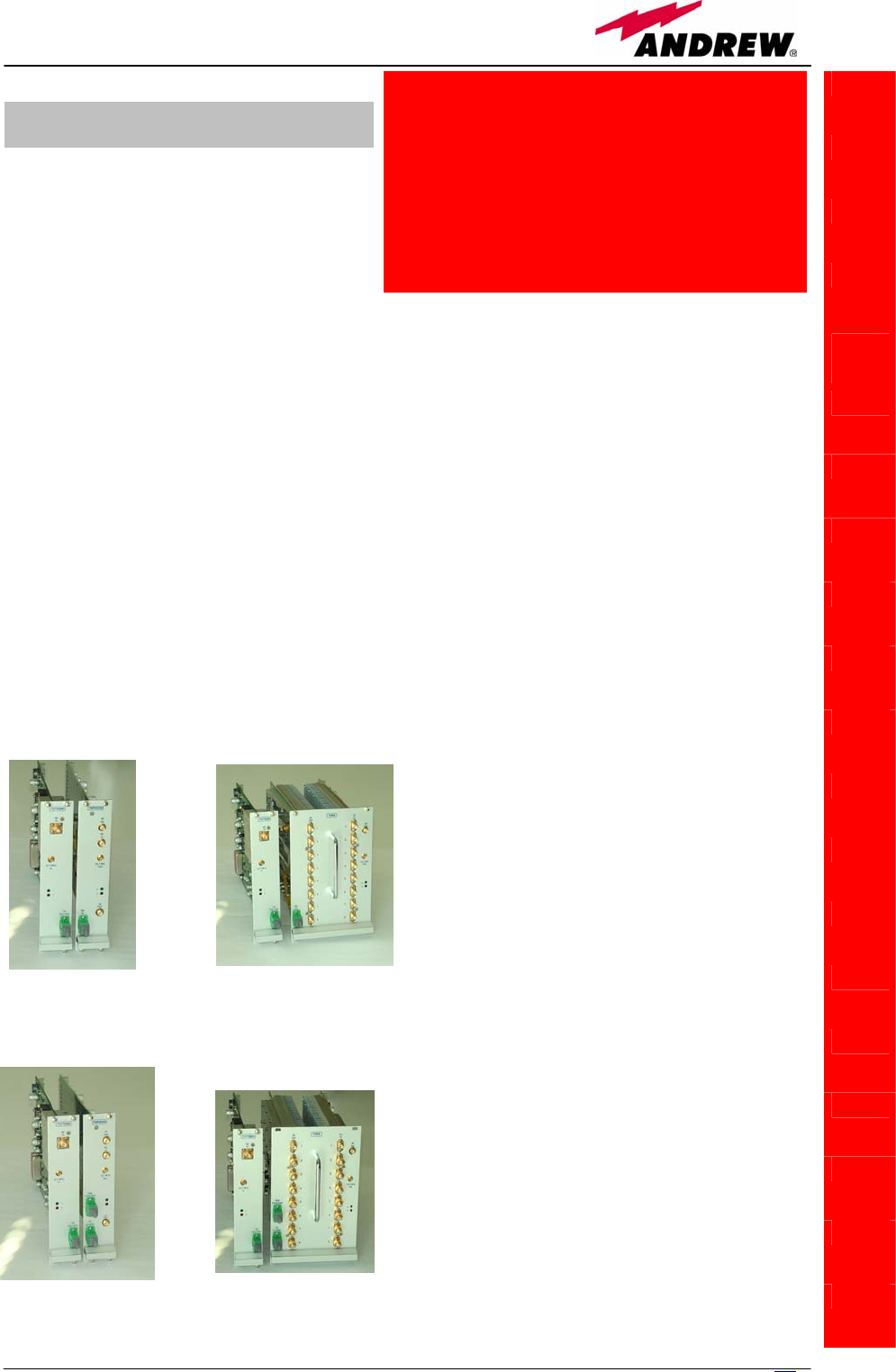
173
MN024-08
the interconnect link is a set of
modules which allows to expand the
system by connecting a second
Britecell Plus subrack station to the
main one, at a distance of up to 20
km. By using more interconnect links at the main station, more Britecell Plus
stations could be connected to the main one, in a star configuration.
Each interconnect link (i-link) is made up by a master-side and by a slave-
side. Both the master side and the slave side are composed by a receiver
module and by a transmitter module (please refer to fig. 5.26, 5.27): the
transmitter modules are identified by the code TDTX, while the receiver
module is identified as TMRX at the master side and as TSRX at the slave side.
The interconnect link is available both in simple version (identified as TILx-HL)
and in WDM version (identified as TILx-HLW). A WDM i-link exploits the same
fibre to transmit both from master to slave and vice-versa (please refer to fig.
5.28b), while the simple link uses a dedicate fiber for the transmission from
master to slave, and a different one for the transmission from slave to master
(please refer to fig. 5.28a).
The following four section will describe in details the i-link modules both in
WDM and not-WDM version.
t
TILx
(intro)
Module name:
Interconnect link
TILx-HL
TILx-HL
W
(a)
(
b
)
(a)
(
b
)
Fig. 5.26: i-link modules: (a)
master side; (b) slave-side.
Fig. 5.27: WDM i-link modules:
(a) master side; (b) slave-side.
5.11.1. Introduction
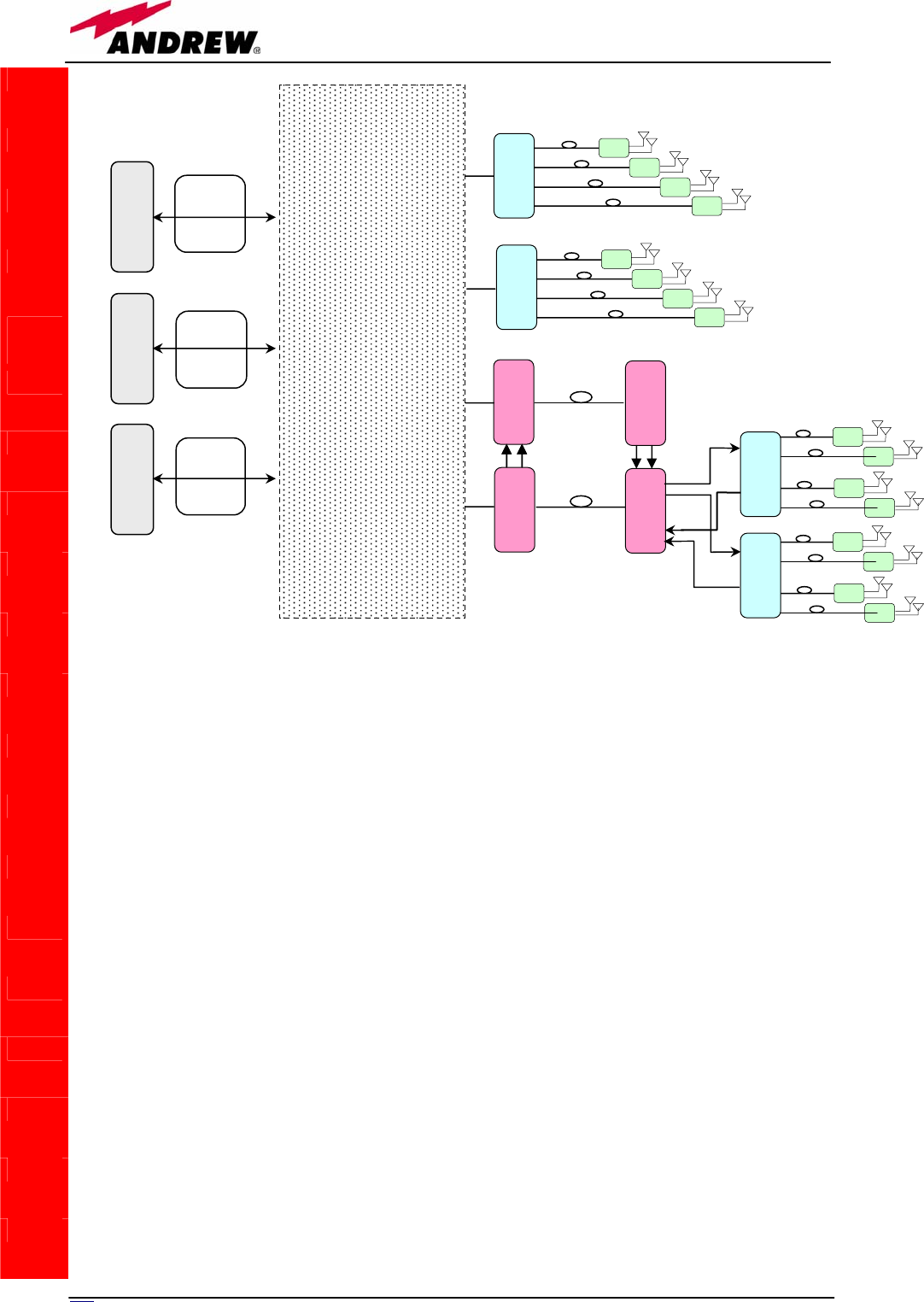
174 User Manual
TILx
(intro)
BTS
INTERFACING
SECTION
+
SPLITTING -
COMBINING
SECTION
TFAx
TFAx
TFAx
TFAx
TFLN
TFLN
TFAx
TFAx
TFAx
TFAx
TFAx
TFAx
TFAx
TFAx
TFLN
TD
T
X
TDTX
TMRX
TSRX
TFLN
TFAx
TFAx
TFAx
TFAx
GSM
900
BTS
GSM
1800
BTS
UMTS
BTS
Fixed
Atten
Fixe
d
Fixed
Atten
Fig. 5.28(a): Block scheme of a Britecell Plus system with a simple i-link
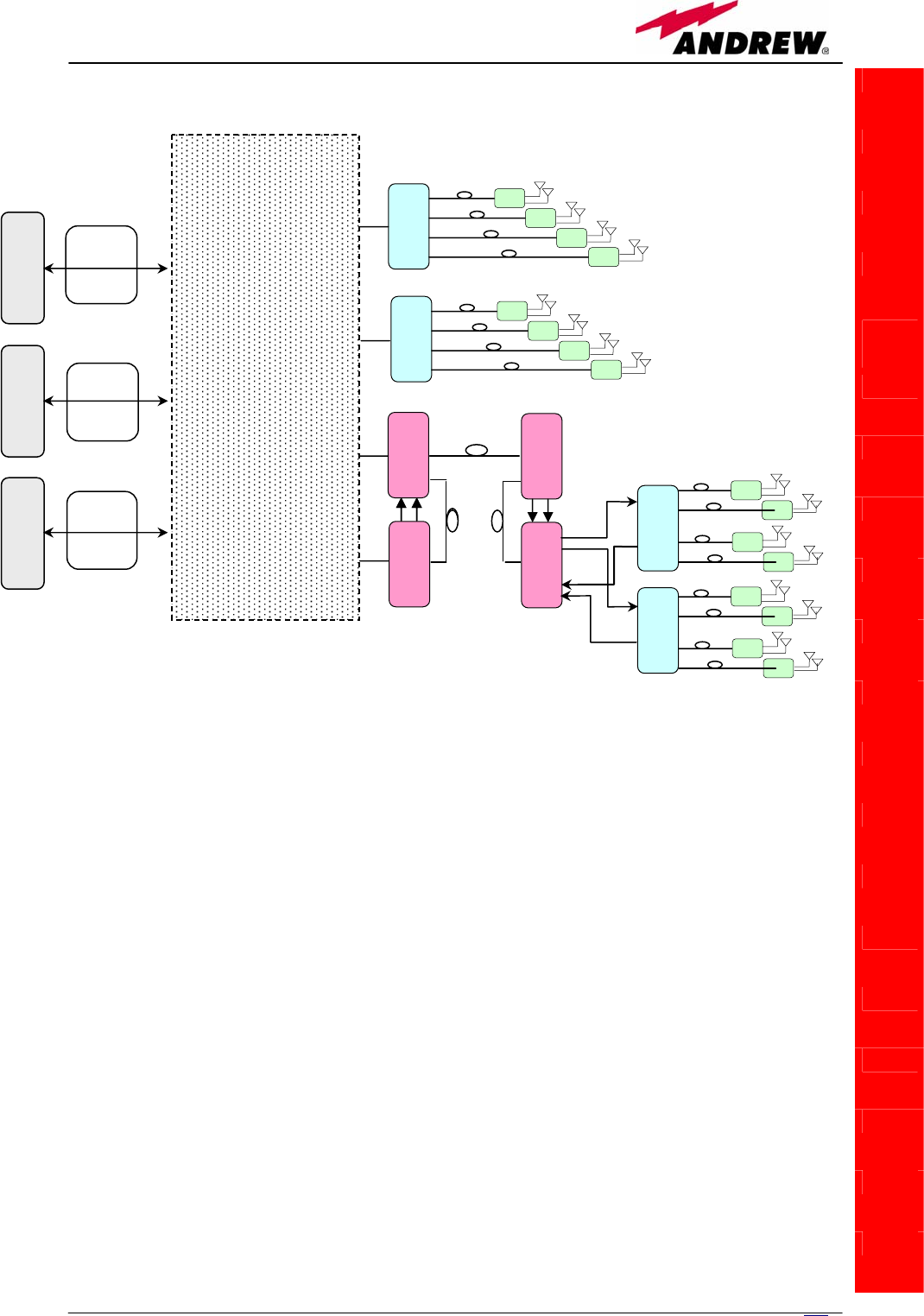
175
MN024-08
TILx
(intro)
Fig. 5.28(b): Block scheme of a Britecell Plus system with a WDM i-link
BTS
INTERFACING
SECTION
+
SPLITTING -
COMBINING
SECTION
TFAx
TFAx
TFAx
TFAx
TFLN
TFLN
TFAx
TFAx
TFAx
TFAx
TFAx
TFAx
TFAx
TFAx
TFLN
TDTX
TDTX
TMRX
TSRX
TFLN
TFAx
TFAx
TFAx
TFAx
GSM
900
BTS
GSM
1800
BTS
UMTS
BTS
Fixed
Atten
Fixe
d
Fixed
Atten
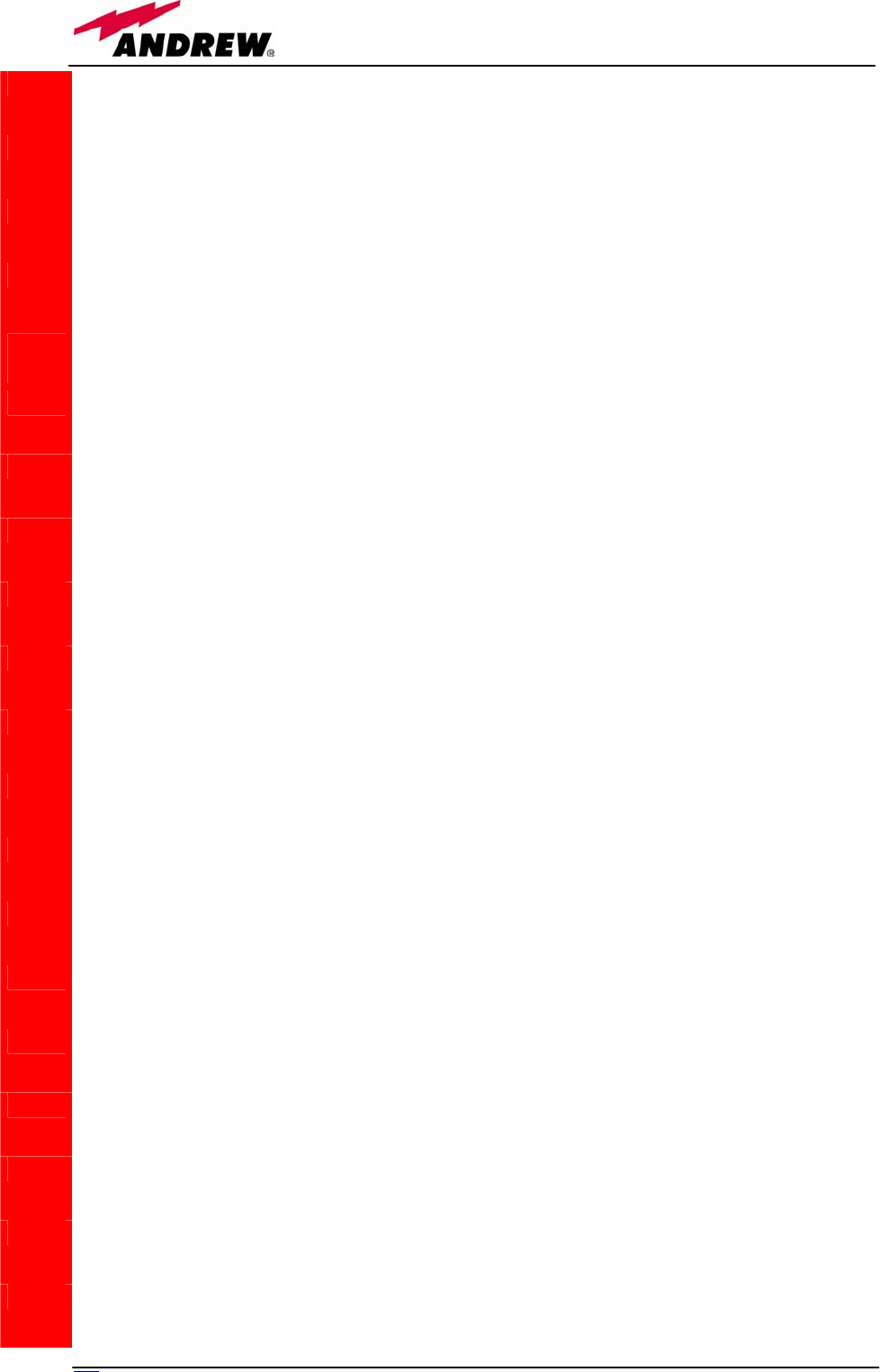
176 User Manual
TILx
(intro)
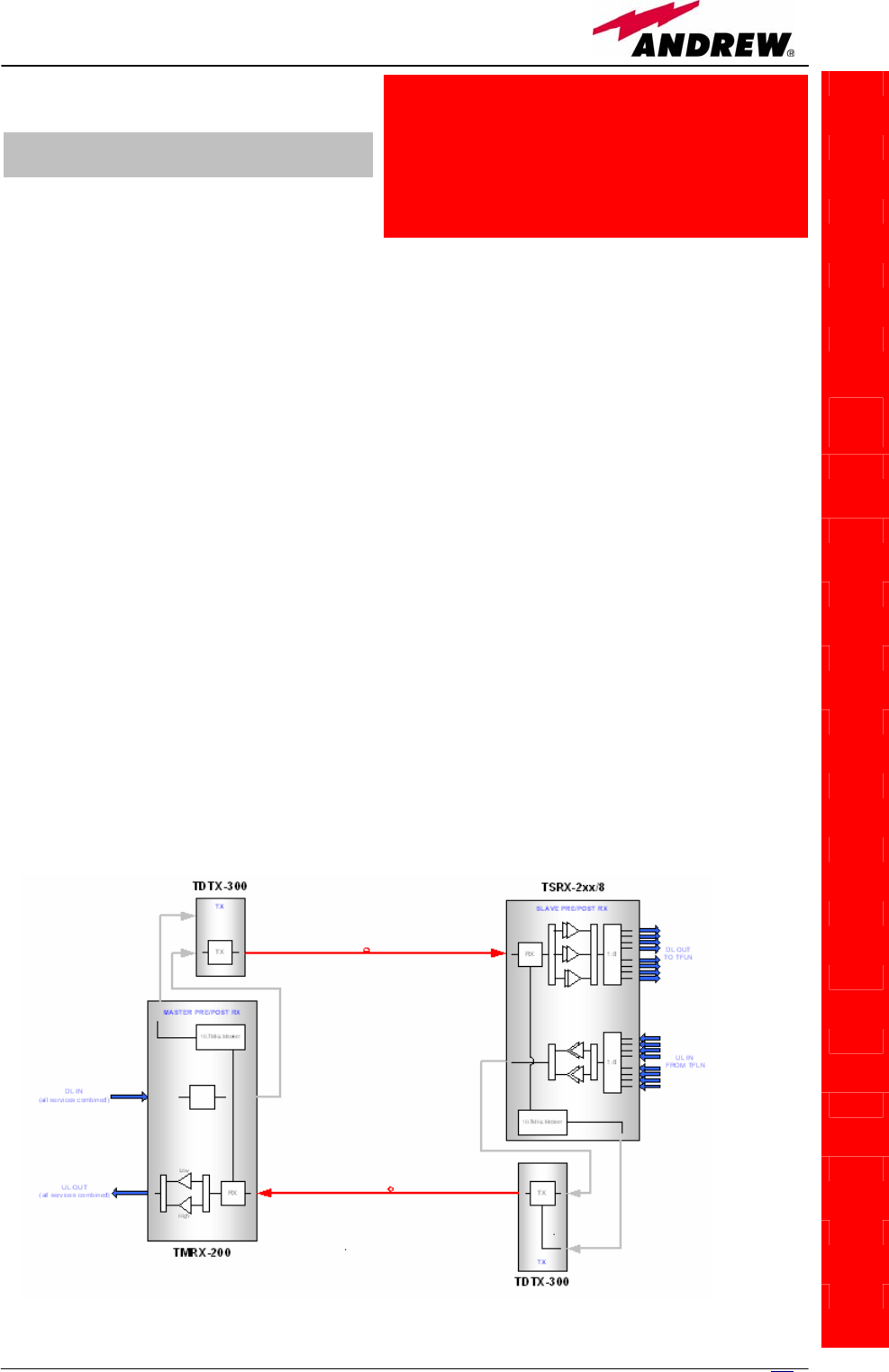
TILx-
-HL
Module name:
Interconnect link
TIL
x
-HL
5.11.2. TILx-HL i-link
Module description:
The TILx interconnect link is a composite module, made up by a transmitter
and a receiver module both on master and on slave side:
• Master side
- TDTX 300 (transmitter module, hosted by 1 subrack slot)
- TMRX 200 (receiver module, hosted by 1 subrack slot)
• Slave side
- TDTX 300 (transmitter module, hosted by 1 subrack slot)
- TSRX 2xx/8 (receiver module, hosted by 3 subrack slots)
The TILx – HL kit is available in EU tri-band version (EGSM 900MHz, GSM
1800MHz, UMTS), in US dual-band version (SMR 800MHz & Cellular 800MHz,
PCS 1900 MHz), and in hybrid version (SMR 800MHz & Cellular 800MHz, GSM
1800MHz, UMTS). These versions just differs in the slave-side receiver TSRX
module, which is the only module whose features vary with the RF
transmitting band.
Block scheme
A scheme of the system, is reported hereinafter, so as describe the
connections between the Interconnect-link modules and to give an insight of
the function of the modules named above.
Fig.5.29 – Interconnect link scheme
177
MN024-08
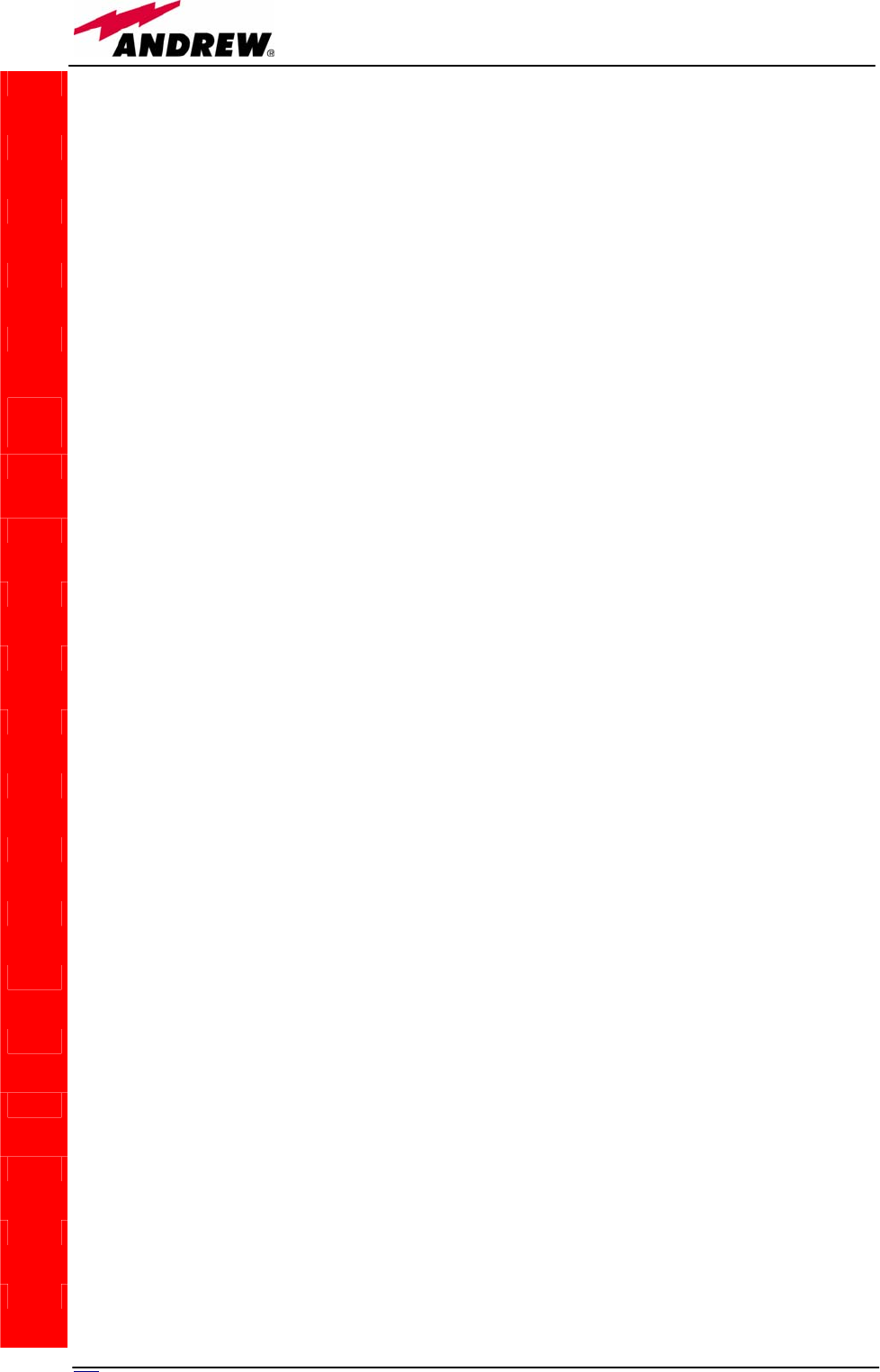
178 User Manual
Main TILx-HL functions:
Downlink:
Uplink:
TILx-
-HL
Master side:
• RF-to-Optical conversion of the signal coming from the
splitting/combining section, and transmission to the slave
i-link modules via fiberoptics cable;
• Modulation and RF-to-Optical conversion of the bus
information, and transmission to the slave i-link modules
via fiberoptics cable (on 1310 nm wavelength);
Slave side
• Optical-to-RF conversion of signal and alarm information,
with Automatic Gain Control (AGC) in order to
compensate the optical losses;
• Distribution of the RF signal to the TFLN optical TRXs, and
demodulation of the bus information
Slave side:
• RF-to-Optical conversion of the signal coming from the
TFLN optical TRXs, and transmission to the master i-link
modules via fiberoptics cable;
• Modulation and RF-to-Optical conversion of the alarm
information, and transmission to the master i-link
modules via fiberoptics cable (on 1310 nm wavelength);
M
aster side:
• Optical-to-RF conversion of signal and alarm information,
with Automatic Gain Control (AGC) in order to
compensate optical losses
• Distribution of the RF signal to the splitting/combining
section, and demodulation of the alarm information
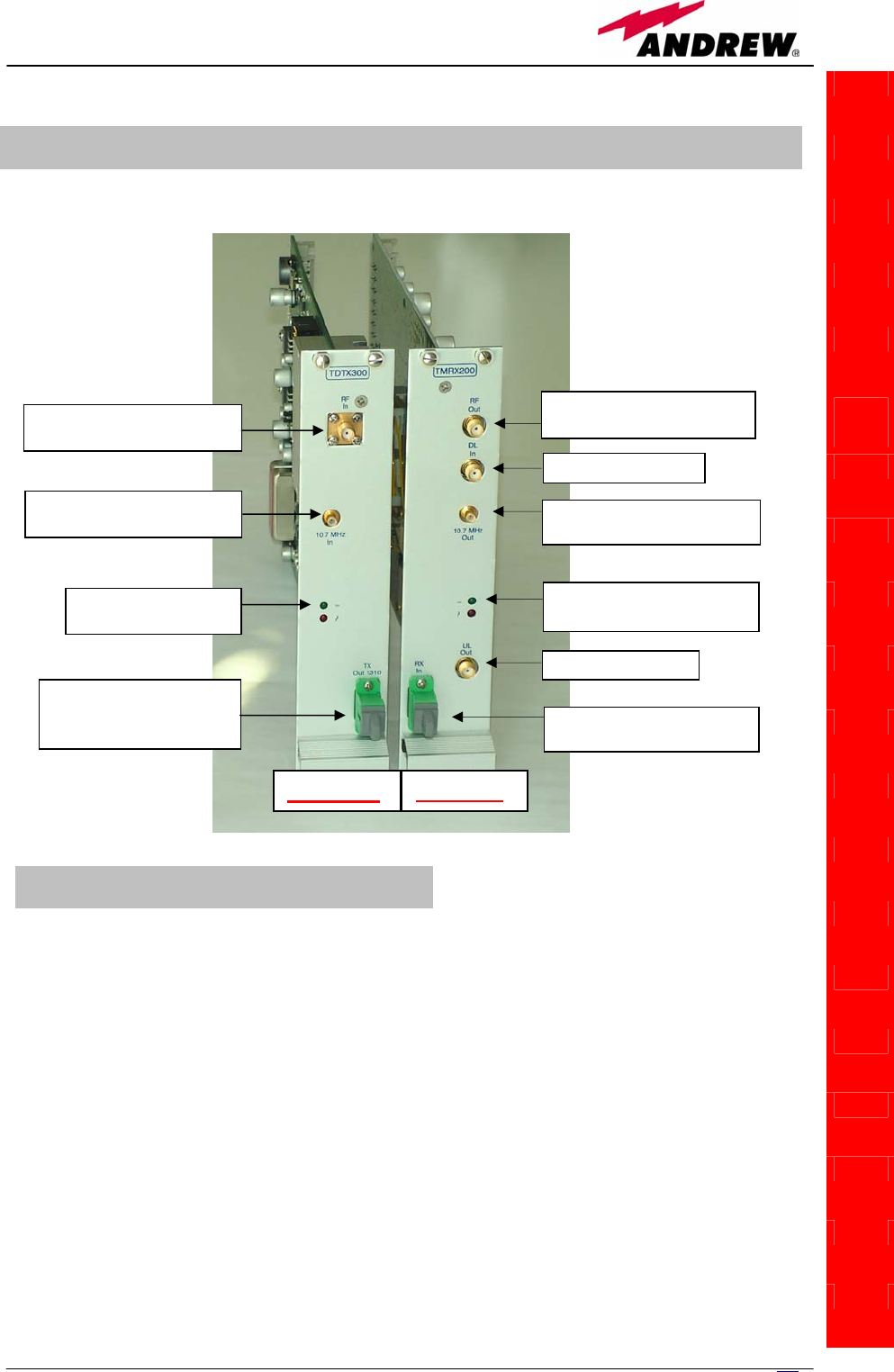
179
MN024-08
TDTX300 transmitter:
TMRX200 receiver:
TILx-
-HL
TILx-HL Master Side: TDTX300 transmitter + TMRX200 receiver
¾ 1 RF output port, to be connected directly to the
RF input port of the TDTX300 adjacent module
¾ 1 alarm output port, to be connected directly to
the alarm input port of the TDTX300 adjacent
module
¾ 1 RF DL port, sent to the passive devices which
interface the Britecell with the BTS
¾ 1 RF UL port, coming from the passive devices
which interface the Britecell with the BTS
¾ 1 RF input port , to be connected directly to the
RF output port of the TMRX200 adjacent module
¾ 1 alarm input port, to be connected directly to
the alarm output port of the TMRX200 adjacent
module
Optical in port connected to
TDTX300 slave
(
SC-APC
)
Optical out port connected to
TSRX 2xx/8 slave(SC-APC)
RF in port connected to
TMRX200 master
(
SMA-f
)
Alarm in port connected to
TMRX200 master
(
SMB-m
)
Alarm out port connected to
TDTX300
m
aste
r
(
SMB-
m
)
RF out port connected to
TDTX300 maste
r
(
SMA-f
)
UL RF
p
ort
(
SMA-f
)
DL RF
p
ort
(
SMA-f
)
GREEN LED: power on
RED LED: ma
j
or alar
m
GREEN LED: power on
RED LED: major alarm
TDTX300 TMRX20
Fig.5.30 – The i-link
master side is made up
by a TDTX300
transmitter and by a
TMRX200 receiver
TILx – HL Master-side: RF ports

180 User Manual
T
DTX300 transmitter:
TMRX200 receiver:
TDTX300 transmitter:
TMRX200 receiver:
TILx-
-HL
Led colour Meaning
Red Optical power failure, wavelength out of
range, power supply failure
Green Power supply OK
Led colour Meaning
Red Power supply failure, modem failure, RF UL
failure, AGC compensation failure
Green Power supply OK
¾ 1 Optical input port, to be connected directly to
the optical output port of the slave-side TDTX300
transmitter
¾ 1 Optical output port, to be connected directly
to the optical input port of the slave-side
TSRX2xx
/
8 receiver
Two control LEDs (one green, one red) are placed on
the TDTX300 front panel. The green LED describes
the power supply status of the TDTX module, while
the red LED describes the major TDTX failure (please
refer to table 5.13)
Two control LEDs (one green, one red) are placed on
the TMRX200 front panel. The green LED describes the
power supply status of the TDTX module, while the red
LED describes the major TMRX failure (please refer to
table 5.14)
TILx – HL Master-side: Optical ports
TILx – HL Master-side: LED Alarms
Table 5.13: Summary of master TDTX300 LEDs meaning
Table 5.14: Summary of TMRX200 LEDs meaning
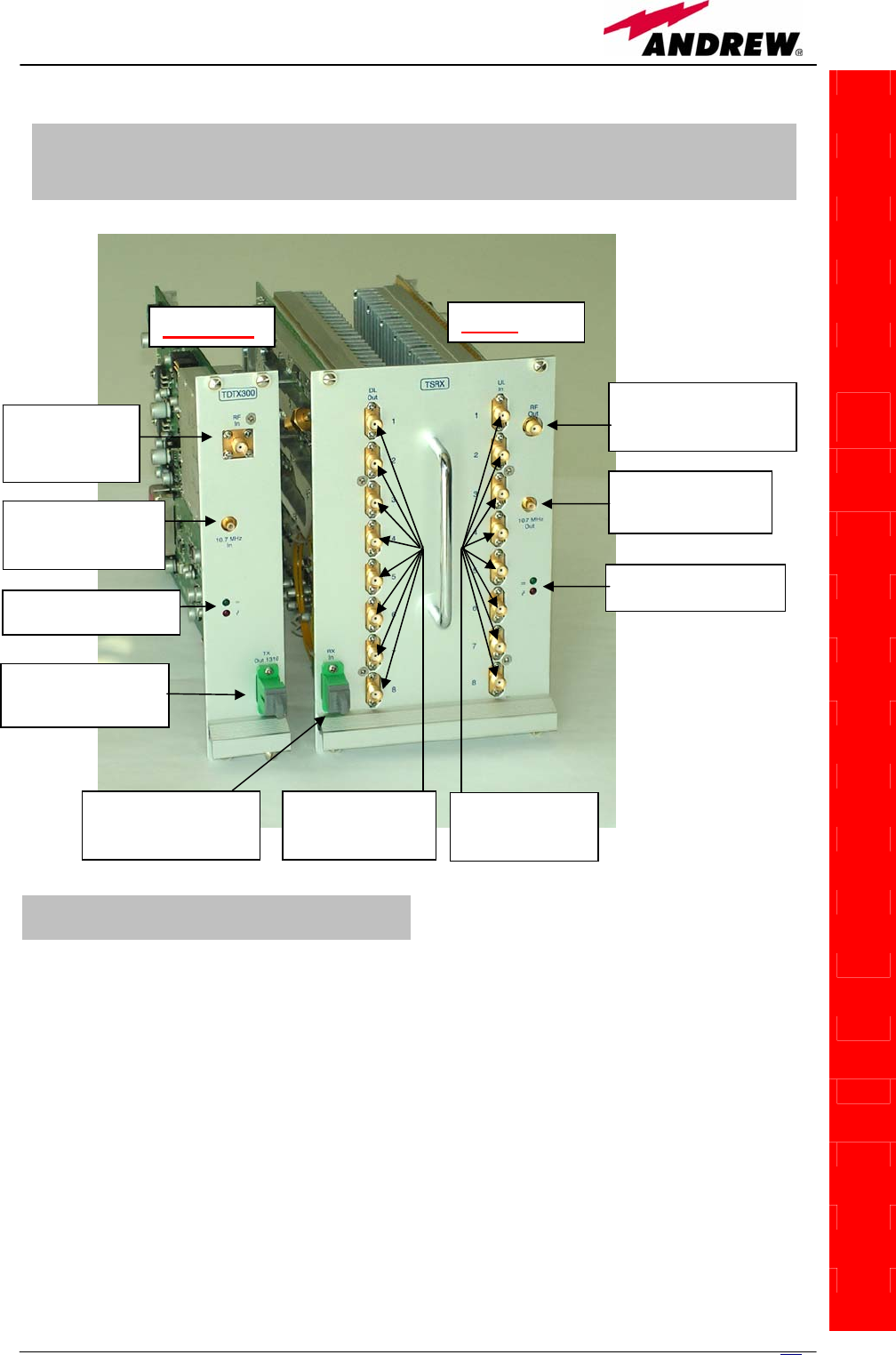
181
MN024-08
TDTX300 transmitter:
TSRX2xx/8 receiver
TILx-
-HL
TILx - HL Slave-Side:
TDTX300 transmitter + TSRX2xx/8 receiver
RF in port
connected to
TSRX2xx/8 slave
(
SMA-f
)
RF out port, connected to
TDTX300 master (SMA-f)
Optical out port ,
connected to TMRX-
200 master (SC-APC)
Optical in port,
connected to TDTX-300
master (SC-APC)
Alarm in port
connected to slave
TSRX2xx/8 (SMB-m)
Alarm out port
connected to master
TDTX300
(
SMB-m
)
GREEN LED: power on
RED LED:ma
j
or alar
m
GREEN LED: power on
RED LED:major alar
m
DL RF ports
connected to TFLN
DL ports (SMA-f)
UL RF ports
connected to TFLN
UL ports (SMA-f)
TDTX300 TSRX
Fig.5.31 – The i-link
master side is made
up by a TDTX300
transmitter and by a
TMRX200 receiver
¾ 1 RF input port , to be connected directly to the
RF output port of the TSRX2xx/8 adjacent
module
¾ 1 alarm input port, to be connected directly to
the alarm output port of the TSRX2xx/8
adjacent module
¾ 1 RF output port, to be connected directly to the
RF input port of the TDTX300 adjacent module
¾ 1 alarm output port, to be connected directly to
the alarm input port of the TDTX300 adjacent
module
¾ 8 RF DL ports, which can feed up to 8 TFLN local
transmitters ;
¾ 8 RF UL ports, which can receive the UL signals
from up to 8 TFLN local transmitters.
TILx – HL Slave-side: RF ports
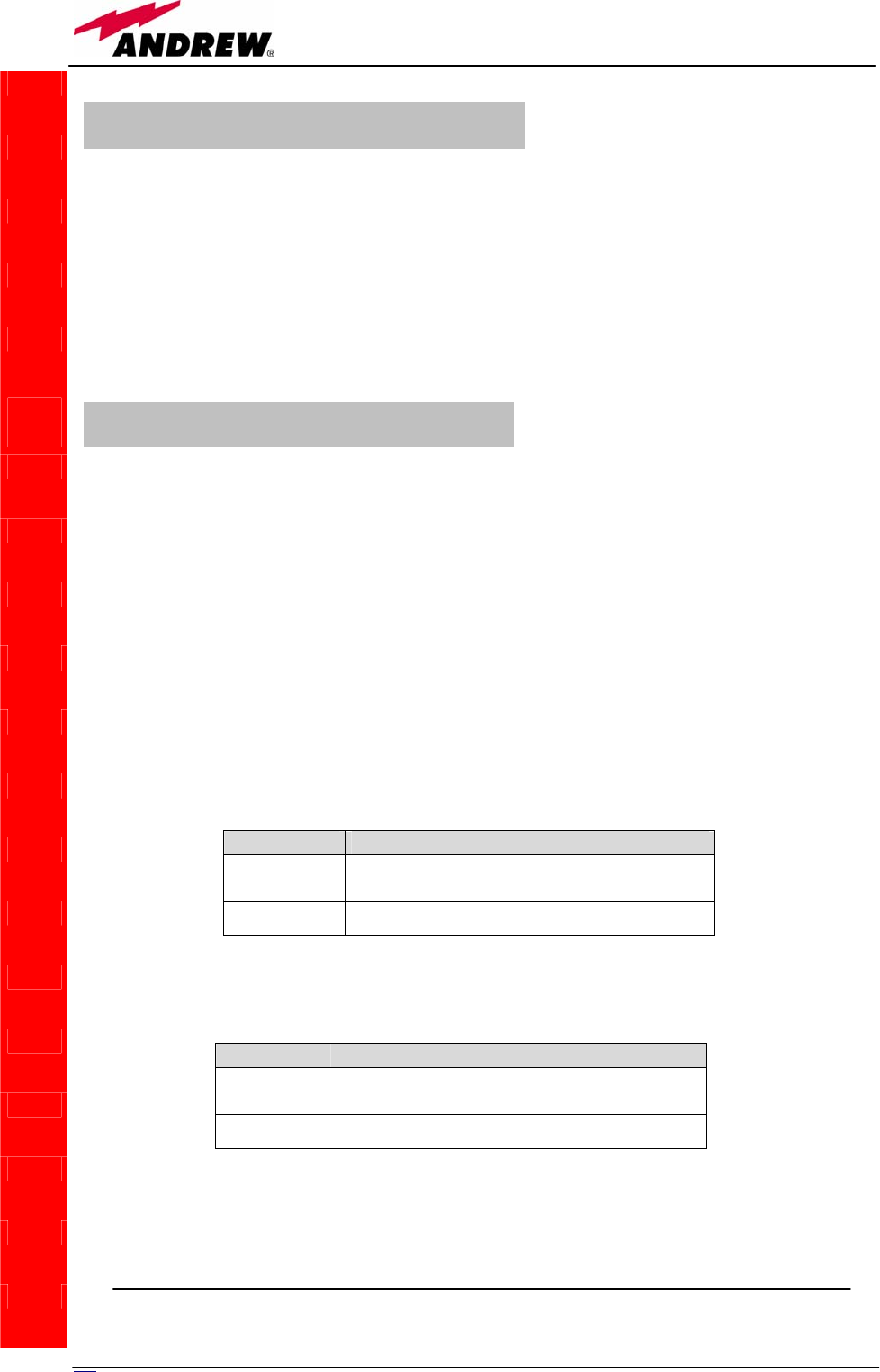
182 User Manual
TDTX 300 transmitter:
TSRX2xx/8 receiver:
TDTX300 transmitter:
TSRX2xx/8 receiver:
TILx-
-HL
Led colour Meaning
Red Optical power failure, wavelength out of
range, power supply failure
Green Power supply OK
Led colour Meaning
Red Power supply failure, modem failure, RF UL
and DL failure, AGC compensation failure
Green Power supply OK
¾ 1 Optical input port, to be connected directly
to the optical output port of the master-side
TDTX300 transmitter
¾ 1 Optical output port, to be connected directly
to the optical input port of the master-side
TMRX200 receiver
Table 5.15: Summary of slave TDTX300 LEDs meaning
Two control LEDs (one green, one red) are placed
on the TDTX300 front panel. The green LED
describes the power supply status of the TDTX
module, while the red LED describes the major
TDTX failure.
Two control LEDs (one green, one red) are placed
on the TSRX2xx/8 front panel. The green LED
describes the power supply status of the TSRX
module, while the red LED describes the major
TSRX failure.
TILx -HL Slave-side: Optical ports
TILx – HL Slave-side: LED Alarms
Table 5.16: Summary of TSRX2xx/8 LEDs meaning
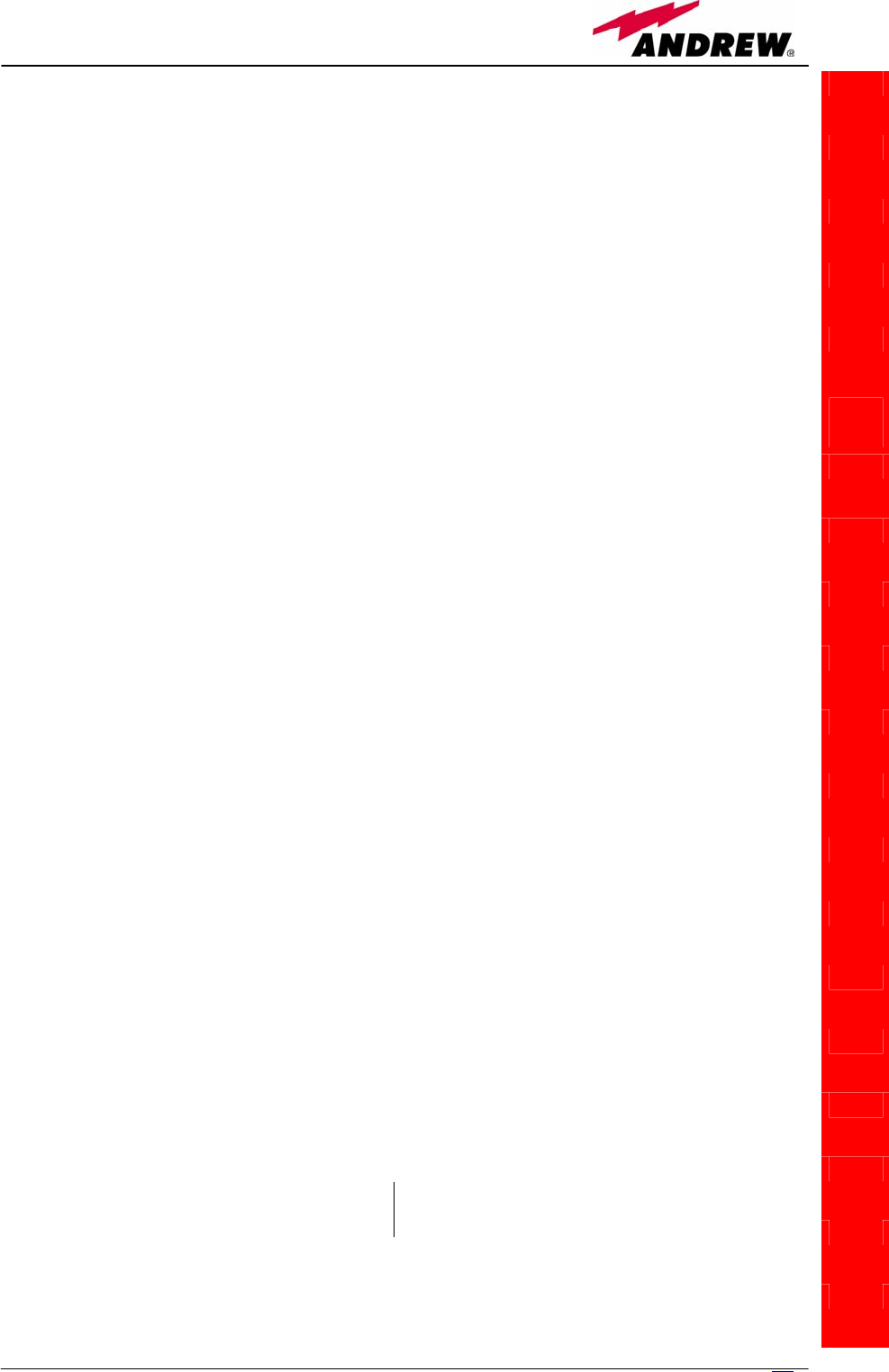
183
MN024-08
Warnings (to be read before the TILx – HL installation)
Dealing with optical output ports
• The TDTX modules (both on master and on slave side) contain
semiconductor lasers. Invisible laser beams may be emitted from the
optical output ports. Do not look towards the optical ports while equipment
is switched on.
Handling optical connections
• When inserting an optical connector, take care to handle it so smoothly
that the optical fibre is not damaged. Optical fibres have to be single-mode
(SM) 9.5/125µm.
• Typically, Britecell Plus equipment is provided with SC-APC optical
connectors. Inserting any other connector will result in severe damages.
• Do not force or stretch the fibre pigtail with radius of curvature less than 5
cm.
• Remove adapter caps only just before making connections. Do not leave
SC-APC adapters open, as they attract dust. Unused SC-APC adapters must
always be covered with their caps.
• Do not touch the adapter tip. Clean it with a proper tissue before inserting
each connector into the sleeve. In case adapter tips need to be better
cleaned, use pure ethyl alcohol
Inserting or removing TDTX, TMRX, TSRX modules
• Do not remove or insert any module into TPRN sub-rack before having
switched off main power supply.
• Modules must be handled with care, in order to avoid damage to
electrostatic sensitive devices.
• When installing the modules in the sub-rack, take care to alternate active
and passive cards in order to ensure proper heat dissipation.
• In a multi-sub-rack system, remember to assign to each sub-rack a proper
RS485 bus address before installing the modules (please refer to TPRN
section for further details).
Placing the TILx -HL modules inside the subrack
• The i-link modules at slave side should be installed in the middle of the
slave subrack, or at least they should have no more than 4 TFLN modules
both on the right side and on the left side of the TSRX 2xx/8 module. This
requirement is advised in order to allow connection between the TSRX
module and all the TFLN transmitters (see fig. 5.33)
TILx – HL installation
Both on master side and on slave side, the i-link modules are to be housed
into a TPRN active sub-rack.
TILx-
-HL
Master Cable Installation Kit:
• 1 SMA-Male/SMA-Male RF jumpers
• 1 SMB-Female/SMB-Female RF jumper
Slave Cable Installation Kit:
• 17 SMA-Male/SMA-Male RF jumpers
• 1 SMB-Female/SMB-Female RF jumper
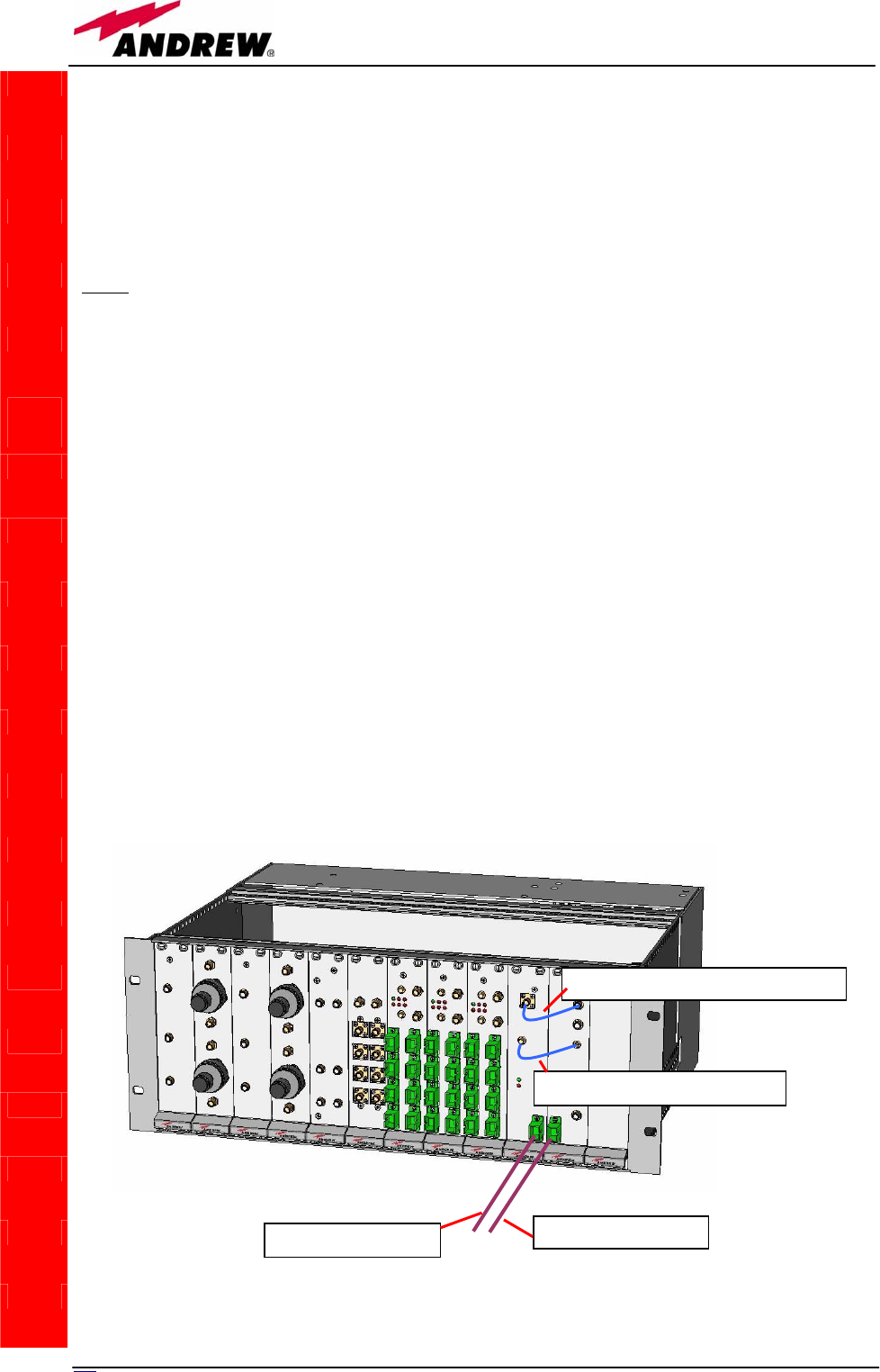
184 User Manual
On the master-side station, the i-link modules are to be housed into 2
adjiacent slots, chosen among the 12 available ones in the subrack.
On the slave-side subrack, the i-link modules are to be housed into 4
adjiacent slots: moreover, due to the particular cabling they require, these 4
adjiacent slots should be placed in mid-subrack, so that no more than 4 TFLN
local units stay on each side of the i-link modules (as shown in fig. 5.33).
Note: If the i-link modules are to be installed in an already working Master
Unit, switch off the sub-racks before inserting the modules.
Before inserting the boards into the TPRNx4 subracks, make sure to set
proper RS485 addresses. A basic rule of the Britecell installation is that 2
subracks belonging to the same Master Unit should always have different
RS485 addresses (please refer to “TPRN Installation” section): since the
interconnect-link basically provides an extension of the Master Unit bus, any
subrack on the i-link master-side should also have a RS485 address different
from any subrack on the i-link slave side.
Please refer to “TPRNx4 Installation” section for more information on setting
the RS485 address.
Firstly, carefully insert the TMRX200 and the TDTX300 boards in 2 adjacent
slots of the Master side subrack. Lock the 4 screws on the corners of each
boards.
Use the provided SMA-m RF jumper in order to connect the RF Out Port of the
TMRX200 module to the RF In Port of the adjacent TDTX300 module. Use the
SMB-f jumper to connect the 10.7MHz ports of the two boards. Fix these RF
jumpers to the RF ports through a proper torque wrench (not included).
Remove the protection cap from the optical ports of the 2 modules on the
master side.
Take a SC-APC fiber, clean the fibre termination, and connect it to the optical
TILx-
-HL
R
F
j
um
p
er
(
S
MA-m / SMA-m
)
RF jumper (SMB-f / SMB-f)
Fig. 5.32: TILx-HL master side
DL optical cable
UL optical
cable
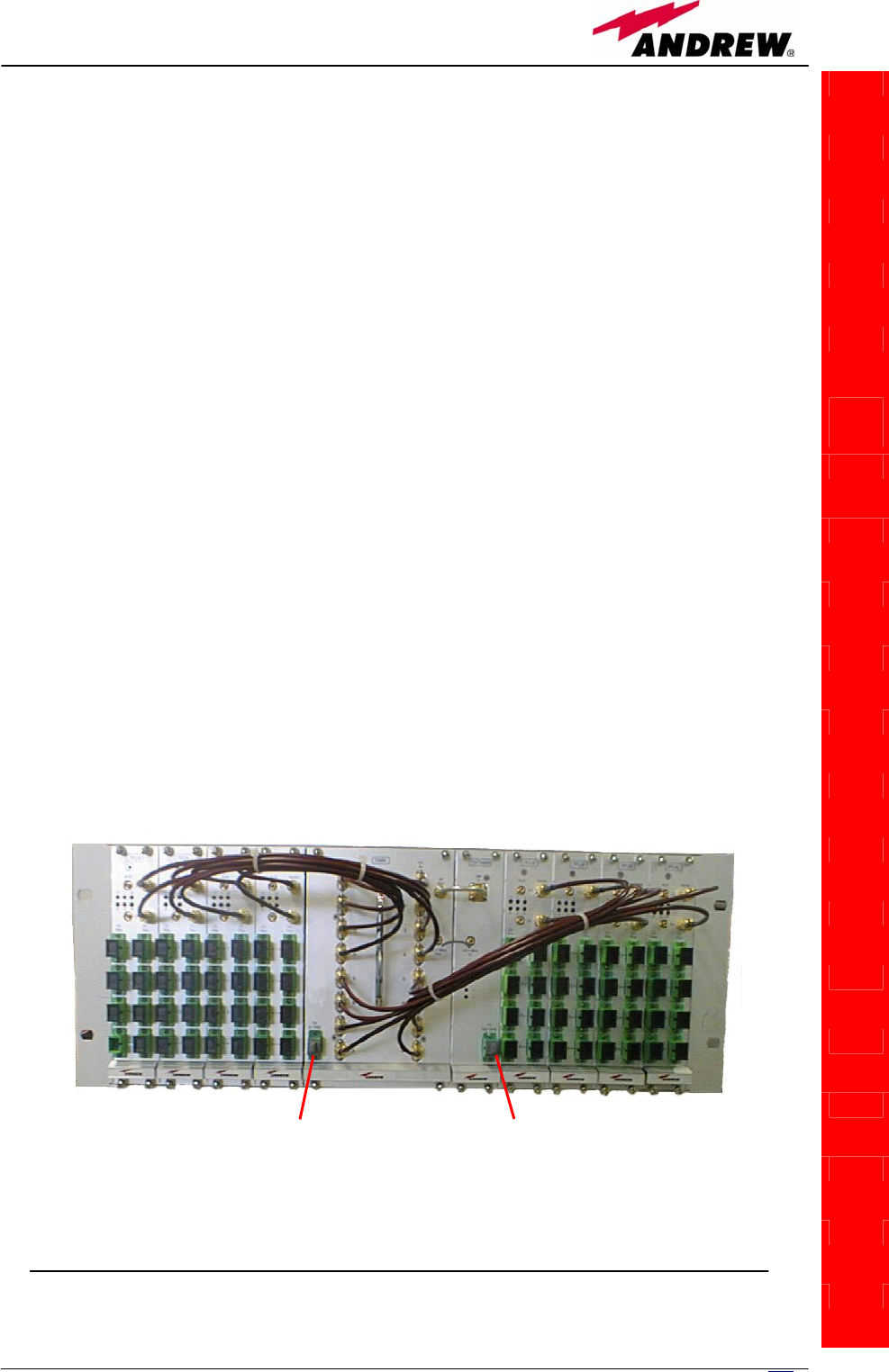
185
MN024-08
out port of the master-side TDTX300 module. (This fiber shall be directly
connected to the optical in port of the TSRX2xx/8 module on the slave-side
subrack)
Take a SC-APC fiber, clean the fibre termination, and connect it to the optical
in port of the TMRX200 module (This fiber shall be directly connected to the
optical out port of the TDTX300 on the slave-side subrack)
Carefully insert the TSRX2xx/8 and the TDTX300 boards in 4 adjacent slots of
the Master side subrack. As already explained, take care not to have more
than 4 TFLN modules on each side of the i-link pieces. Lock the 4 screws on
the corners of each boards.
Use the provided SMA-m RF jumper in order to connect the RF Out Port of the
TSRX2xx/8 module to the RF In Port of the adjacent TDTX300 module. Use the
SMB-f jumper to connect the 10.7MHz ports of the two boards.
Use the longer RF jumpers (included) to connect each pair of TSRX UL and DL
ports to the corresponding UL and DL ports of each TFLN module mounted on
slave-side subrack. If less than 8 TFLNs are used at slave-side, make sure to
mask the TSRX-2xx/8 unused DL and UL ports by SMA loads (not provided).
Remove the protection cap from the optical ports of the 2 modules on the
slave side.
Take a SC-APC fibre, clean the fibre termination, and connect it to the optical
out port of the master-side TDTX300 module. This fiber has to be directly
connected to the optical in port of the TMRX200 module of the master-side
subrack. Use a specific torque wrench to fix the RF cables to the RF ports.
Take a SC-APC fiber, clean the fibre termination, and connect it to the optical
in port of the TSRX200 module. This fiber has to be directly connected to the
optical out port of the TDTX300 on the master-side subrack.
As you switch on the system, carefully refer to the “TILx-HL start-up” section.
TILx-
-HL
Fig. 5.33: TILx-HL slave side
DL o
p
tical cable UL o
p
tical cable
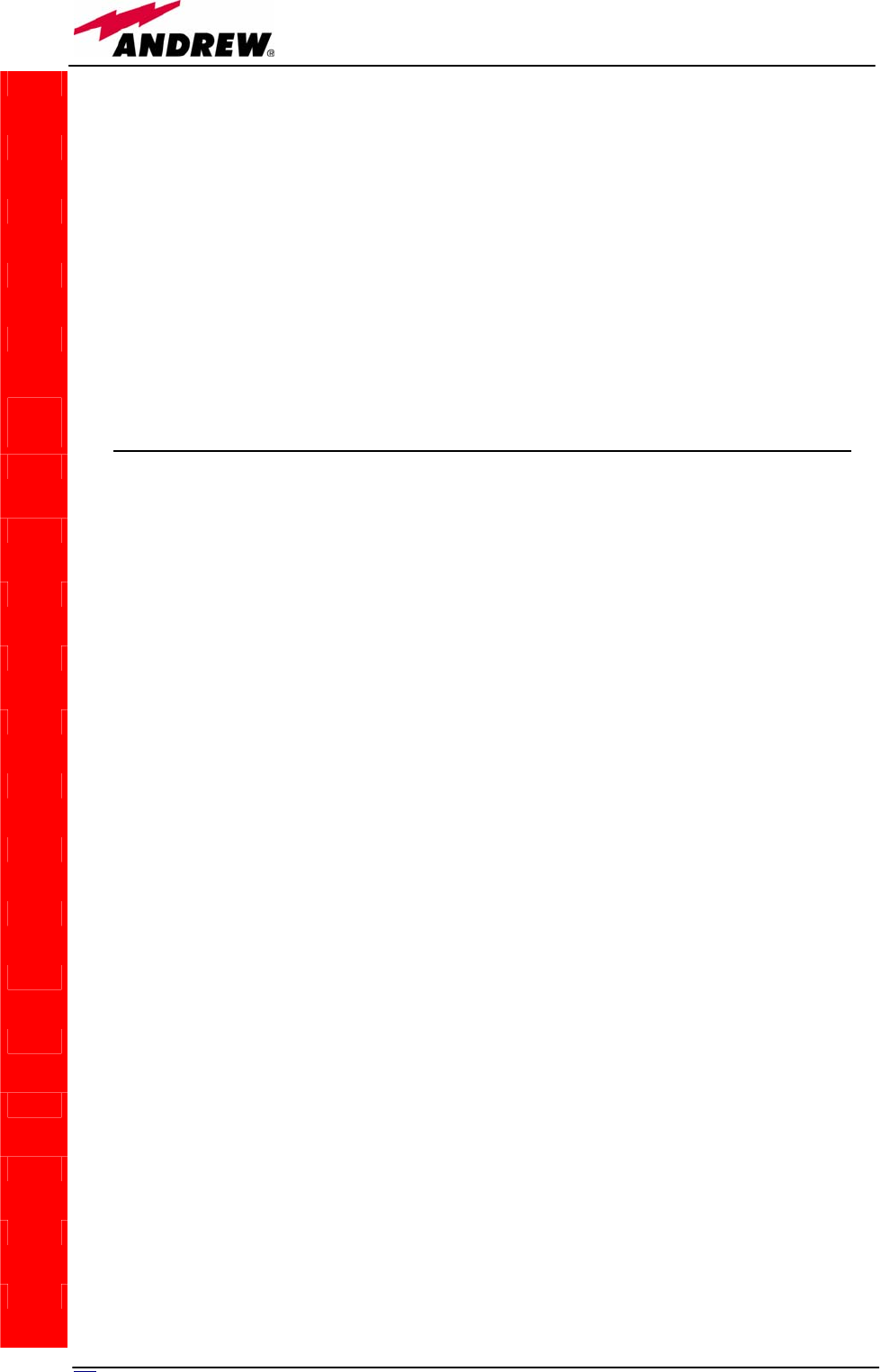
18
6
User Manual
Removing a TILx - HL module
To remove an i-link module, firstly switch off the TPRNx4 subrack which
houses the module.
Remove the fibers and the RF jumpers connected to the i-link module which is
going to be removed. Insert the caps on the optical ports which has just been
disconnected.
Unscrew the 4 screws at the corners of the i-link module which is going to
removed, and slowly remove the card.
Put the card in its safety box
TILx – HL start-up
Before both the master-side station and the slave-side station(s) are switched
on, make sure that:
• all expected modules have been inserted into the Master Unit
• the modules have been connected each other by RF jumpers, according to
what planned in the system design
• the i-link master modules have been connected to the relevant slave side
modules through fiberoptics cables;
• every TFLN master optical TRX has been connected to relevant remote
units
• each remote unit has been connected to its coverage antennas
• the remote supervision unit, if present, has been connected to the Master
Unit
• both on the master-side and on slave-side stations, the different subracks
are connected each other via bus RS485
After that, remember that all remote units have to be switched on before the
master-side and the slave-side subracks. When all the remote units are on,
the different subracks (at master-side and slave-side) can be switched on.
Once all the active subracks have been switched on, the behaviour of the
different i-link modules can be summarized as follows:
o All the LEDs on the different i-link modules (both on master side and on
slave side) turn on for a couple of seconds;
o After that, all the green LEDs on the different modules remain ON (thus
indicating proper power supply), while the red LEDs switch off as soon as
the master-side and the slave-side detect each other;
o During normal working operations, the LEDs on the front panels of the
TILx modules should behave according to what described in table 5.13,
5.14, 5.15, 5.16;
o Once all the master-side and slave-side subracks have been switched
on, the system should begin to work correctly. Anyway, in order that the
i-link modules are recognized by the supervision management system, it
is necessary that the system carries out the discovery phase (please
refer to Supervision System Manual for more details). During this phase,
TILx-
-HL
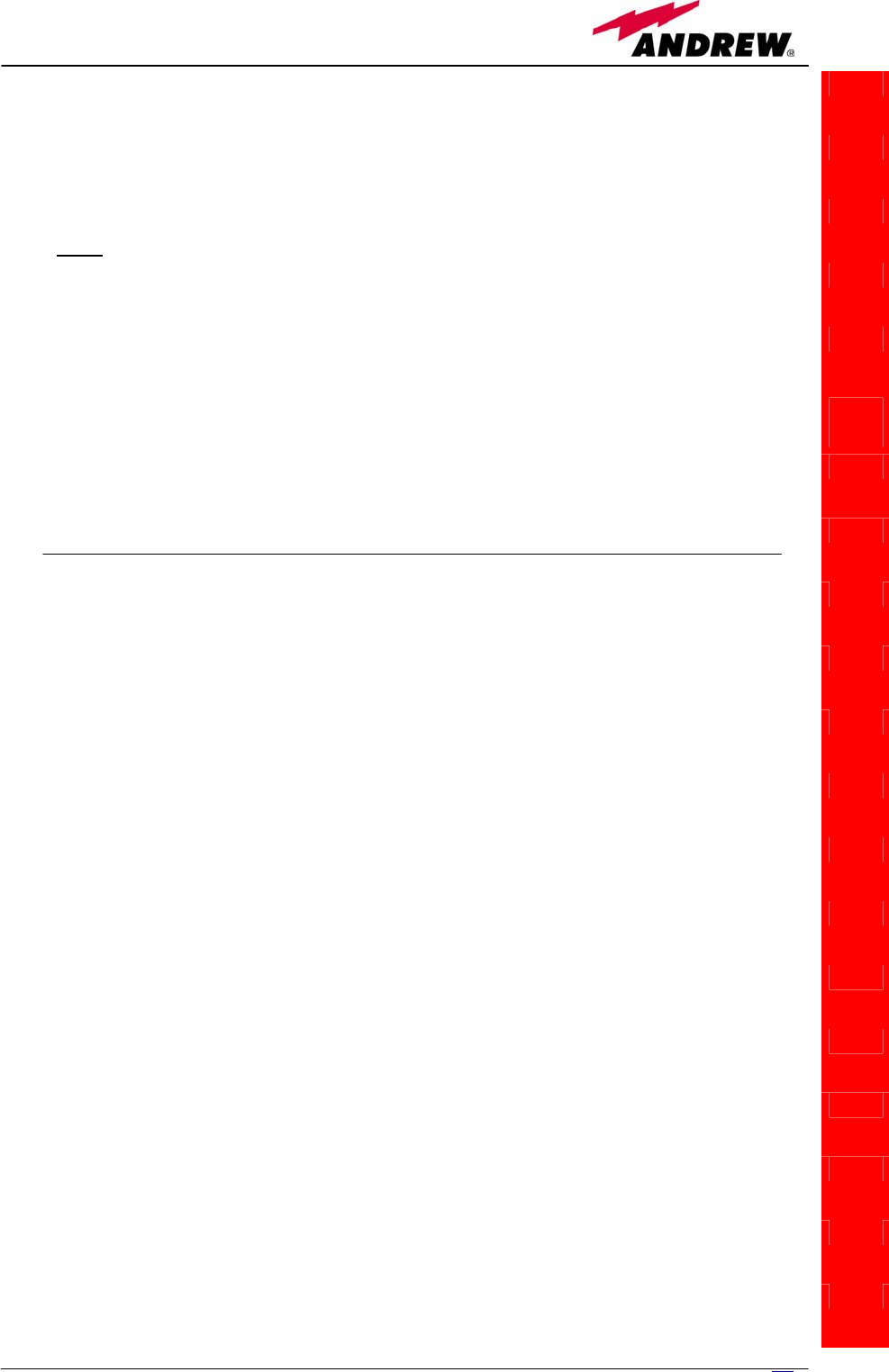
18
7
MN024-08
whose duration depends on the system complexity and which can last at
max. 4min, the TFLN LEDs ┌┘ blink. Do not connect/disconnect any
cable or any piece of equipment during the discovery phase! This
may result in failing the identification of some equipment.
o Finally, please note that the receiver module TSRX2xx/8 has only one
connection with the subrack backplane, so that the LMT software and the
supervision system will detect it as a 1-slot card. More in details, only the
slot which hosts the TSRX LED alarms is recognized by LMT or
supervision. The other 2 slots hosting the TSRX receiver are therefore to
be masked through the LMT or the Supervision System Interface (please
refer to the relevant user manuals) in order to avoid fictitious alarm
notifications.
TILx – HL troubleshooting
Faults on the i-link modules can be revealed:
• by LEDs on the front panels of the modules themselves
• by the LMT software running on a PC connected to a master side or a slave-
side subrack via RS232 port;
• by the supervision system interface managed by the remote supervision
unit, usually placed conveniently on the master-side.
Both LMT and supervision system provide full information about the device
causing the alarm. As a consequence, troubleshooting procedure can be very
immediate when failure detection is directly carried out through LMT or
supervision system.
The tables 5.17, 5.18, 5.19 reports a brief description of alarm related to the
different i-link modules, together with a reference to corresponding alerted
LEDs and to possible recovery actions.
As shown by these tables, the LEDs show only the alarms concerning the
board where they are housed: so, a red LED which is switched on at TSRX
front side reveals an alarm affecting the TSRX module itself (it does not deals
with the alarms affecting the other module of the i-link slave-side, which is an
TDTX300, and whose alarms will be detected by its own LEDs). Moreover,
these tables show that the LEDs reveals only major alarms, whereas the minor
alarms (i.e. the low priority ones) are revealed only by the LMT software or
through the TSUN supervision system. The minor alarms usually detect critical
situations which should be checked so as to avoid future possibile system
faults.
Although any alarm detected by a LED on the i-link modules should be verified
through LMT or supervision software when an accurate check is needed, some
ordinary maintenance procedures could be carried out quickly following the
instructions described hereinafter
TILx-
-HL
Note: in case discovery doesn’t start automatically, check through the
LMT or the remote supervision whether it has been disabled (refer to
LMT or remote supervision system manuals for further information).
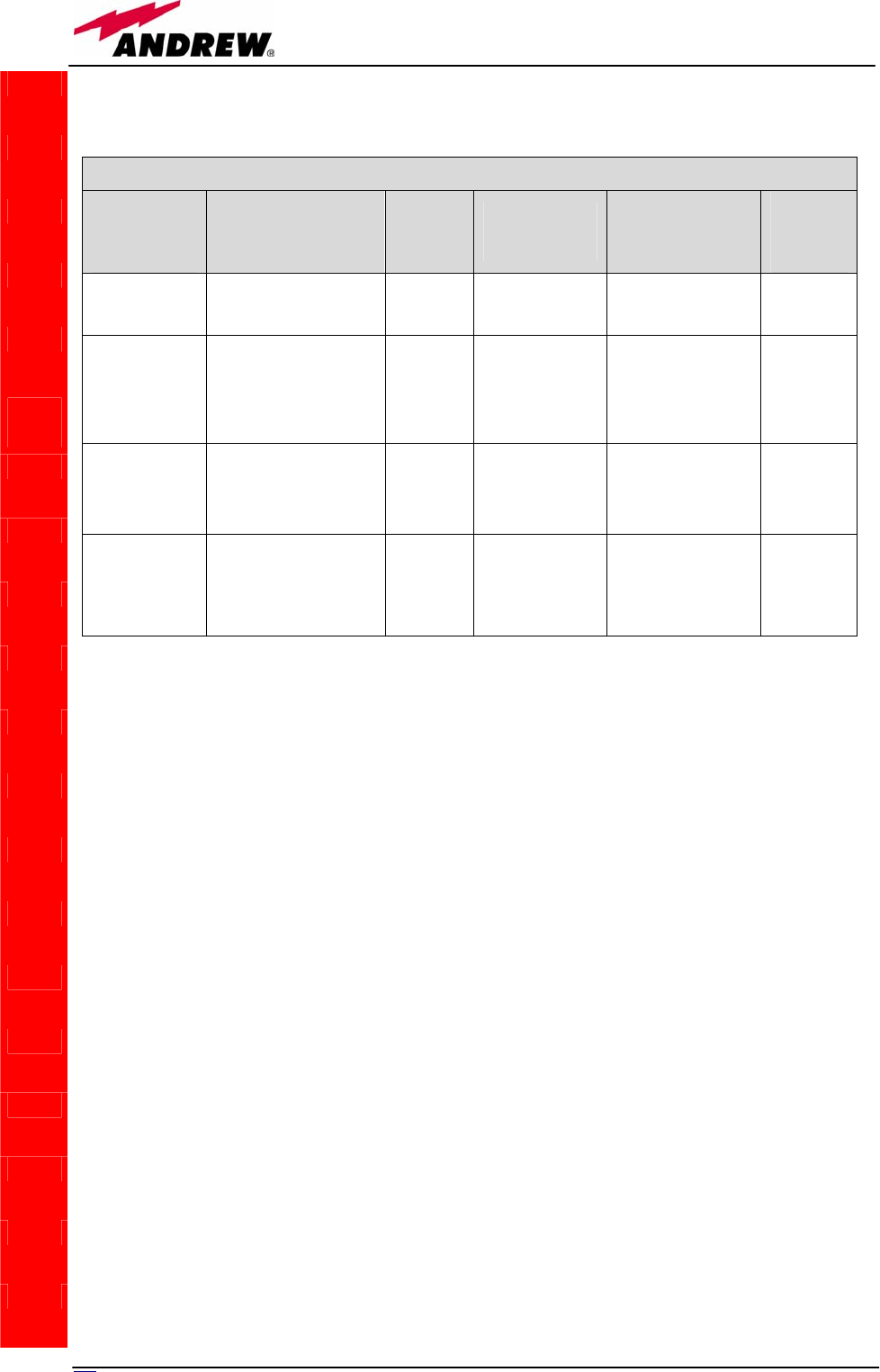
188 User Manual
TILx-
-HL
TDTX 300 (master side or slave side)
ALARM
CODE
(TSUN
description)
ALARM
DESCRIPTION
ACTIVE
LED
SUPERVISION
PRIORITY
LEVEL
ACTION
RECOMMENDED
RELÉ
PRIORITY
LEVEL
(subrack)
Vcc alarm
There is a degradation on
the power supply provided
by the backplane
RED MAJOR Return the unit MAJOR
Optical power
<1dB
The received optical power
experiences a degradation
which is near to the AGC
working threshold (but it
can still compensate
losses)
NONE MINOR
Check the optical loss /
AGC status on the
TSRX or TMRX
module at the other
side of the
imterconnect link
MINOR
Optical power
<3dB
The transmitted optical
power experiences a
degradation which can no
more be compensated by
the AGC.
RED MINOR Return the unit MAJOR
Temperature
Alarm
Over-temperature alarm
(lower than 0° C or higher
than 65° C)
NONE WARNING
Check the subracks
ventilation; verify the
environmental
conditions involving
heating and air
circulation
MINOR
Table 5.17: Description of TDTX300 alarms, as they are described by the LMT
software or by the suspervision interface
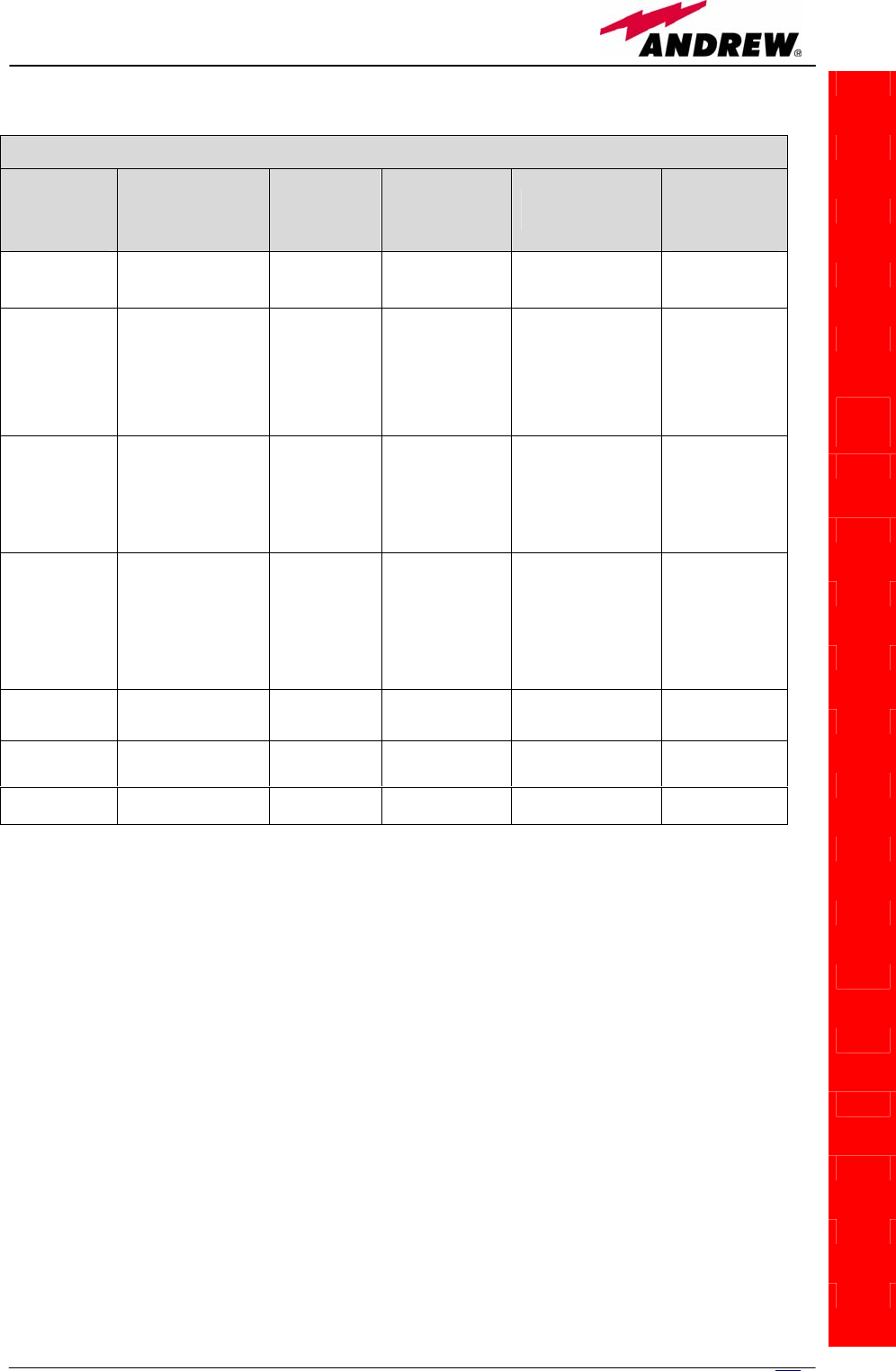
189
MN024-08
TMRX 200
ALARM
CODE
(TSUN
description)
ALARM
DESCRIPTION
ACTIVE
LED
SUPERVISION
PRIORITY
LEVEL
ACTION
RECOMMENDED
RELÉ
PRIORITY
LEVEL
(subrack)
Power supply
alarm
There is a degradation
in power supply
distribution
RED MAJOR Return the unit MAJOR
RX1 AGC out
of range
The received optical
power experiences a
degradation which is
near to the AGC
working threshold (but
it can still compensate
losses)
NONE WARNING
Check the optical loss
/ AGC status on the
TSRX or TMRX
module at the other
side of the
imterconnect link
MINOR
RX1 Optical
power fail
The transmitted
optical power
experiences a
degradation which can
no more be
compensated by the
AGC
RED MAJOR Return the unit MAJOR
Temperature
alarm
Over-temperature
alarm NONE WARNING
Check the subrack
and cabinet
ventilation, verify the
environmental
conditions involving
heating and air
circulation
MINOR
FSK modem
alarm
HW problem on the
10.7 MHz FSK
modem
RED CRITICAL Return the unit MAJOR
UL RF alarm UL hardware failure RED MAJOR Return the unit MAJOR
Current Fail Overcurrent alarm RED MAJOR Return the unit MAJOR
TILx-
-HL
Table 5.18: Description of TMRX200 alarms, as they are described by the LMT
software or by the suspervision interface
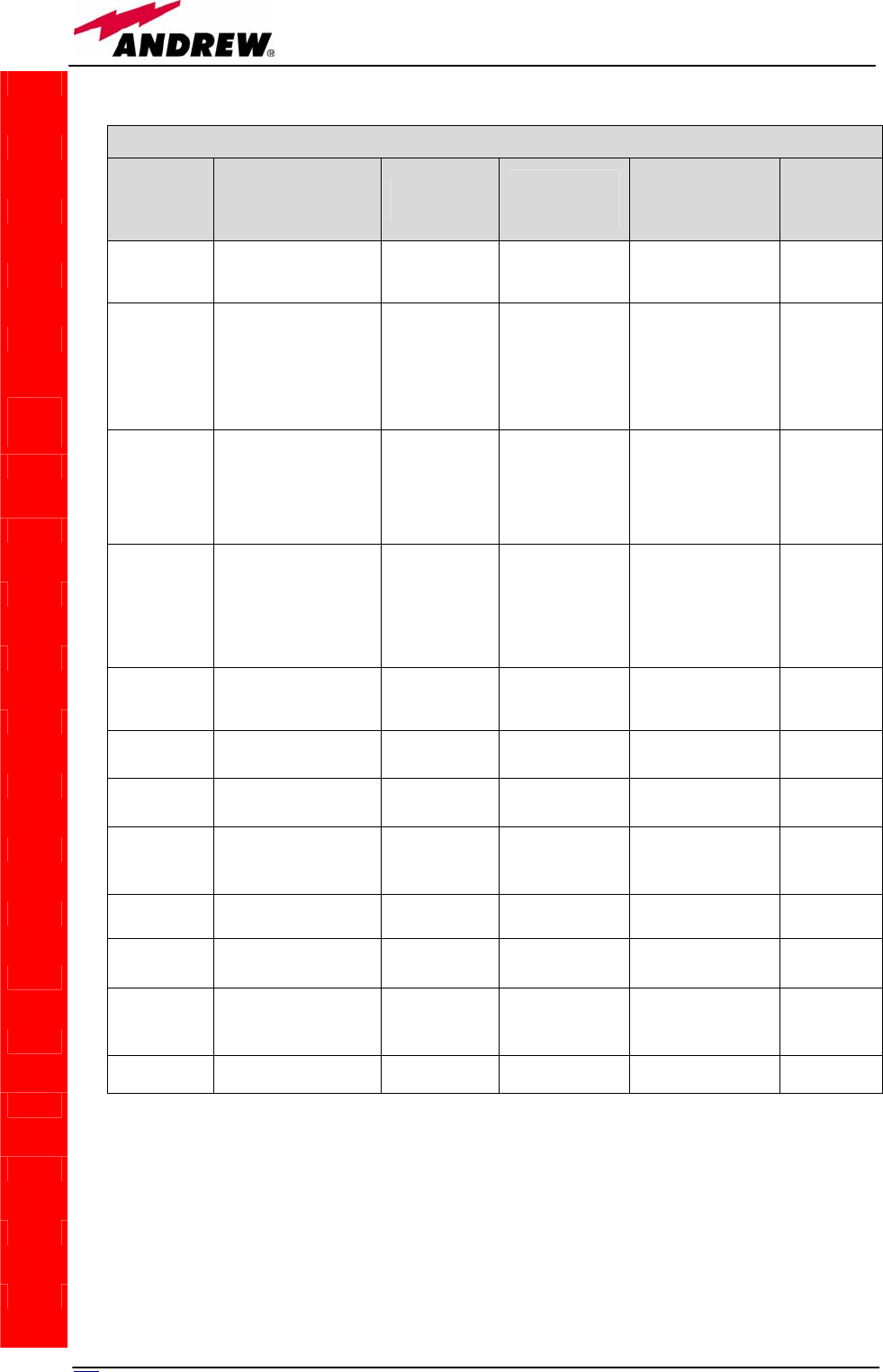
190 User Manual
TSRX 2xx/8
ALARM
CODE
(TSUN
description)
ALARM
DESCRIPTION ACTIVE LED
SUPERVISION
PRIORITY
LEVEL
ACTION
RECOMMENDED
RELÉ
PRIORITY
LEVEL
(subrack)
Power supply
alarm
There is a degradation in
power supply distribution RED MAJOR Return the unit MAJOR
RX1 AGC out
of range
The received optical
power experiences a
degradation which is
near to the AGC working
threshold (but it can still
compensate losses)
NONE WARNING
Check the optical loss
/ AGC status on the
TSRX or TMRX
module at the other
side of the
interconnect link
MINOR
RX1 Optical
power fail
The transmitted optical
power experiences a
degradation which can
no more be compensated
by the AGC
RED MAJOR Return the unit MAJOR
Temperature
alarm Over-temperature alarm NONE WARNING
Check the subrack and
cabinet ventilation,
verify the
environmental
conditions involving
heating and air
circulation
MINOR
FSK modem
alarm
HW problem on the 10.7
MHz FSK
modulator/demodulator
RED CRITICAL Return the unit MAJOR
DL Low band
RF alarm
HW failure on the DL
RF low band RED CRITICAL Return the unit MAJOR
DL High band
RF alarm
HW failure on the DL
RF high band RED CRITICAL Return the unit MAJOR
DL UMTS RF
alarm
(only on TSRX
247/8 version)
HW failure on the DL
RF UMTS band RED CRITICAL Return the unit MAJOR
UL Low-band
RF Alarm
HW failure on the UL
RF low band RED CRITICAL Return the unit MAJOR
UL High-band
RF Alarm
HW failure on the UL
RF high band RED CRITICAL Return the unit MAJOR
UL UMTS RF
alarm
(only on TSRX
247/8 version)
HW failure on the UL
UMTS band RED CRITICAL Return the unit MAJOR
Current Fail Overcurrent alarm RED MAJOR Return the unit MAJOR
TDTX-300 module troubleshooting
The TDTX module is an optical transmitter whose alarm status cannot be influenced by dirt
optical adapters or by some problems in fiberoptics cables towards the opposite i-link side. If the
red light is switched on in the TDTX front panel, please check if you have connected properly the
TILx-
-HL
Table 5.19: Description of TSRX2xx/8 alarms, as they are described by the LMT
software or by the suspervision interface

191
MN024-08
RF jumper. If the RF connection proves to be ok and the red LED keep on switching on, please
contact the manufacturer.
TMRX-200 module troubleshooting
Ordinary troubleshooting procedures which can be carried out on TMRX-200 module first involve
a check of the optical adapter status and of the fiberoptics cable. If the alarm status still persists, a
reboot of both the TMRX-200 module and of the TSRX-2xx/8 module can be performed so as to
re-inizialize the link.
Quick TMRX-200 troubleshooting procedure
(The following procedure is summarized by the flow-chart in fig. 5.34a)
In case the red LED is ON, please follow these steps:
1. Clean the optical adapter
2. If the problem still persists, refer to the TMRX/TSRX fiber optic troubleshooting so as to
check if the optical cable or optical connection has any problem on DL path
3. If previous actions didn’t make the LED switch off, a reboot of both the TMRX-200 module
and of the TSRX-2xx/8 module (on the slave-side) could be performed so as to re-inizialize
the link.
4. If the red LED still remains on, please check the alarm status by the LMT or the
supervision unit in order to better understand the problem and its possible solution.
TMRX/TSRX fiber optic troubleshooting
(The following procedure is summarized by the flow-chart in fig. 5.34b)
1. Check if there is any point where fibre experiences a short radius of
curvature. In this case, rearrange the optical path in order to avoid sharp
bends (if necessary, replace the optical cable with a longer one). If TMRX
(TSRX) red LED switches off, troubleshooting has been successfully
carried out. Otherwise, follow next steps.
2. Check if SC-APC connectors are properly installed at both fibre ends. In
case they are not, fix more firmly the SC-SPC connectors to their
adapters. If the TMRX (TSRX) red LED switches off, troubleshooting has
been successful. Otherwise, follow next steps.
3. Disconnect the optical fibre and clean it better at both ends, then clean
also the relevant SC-APC adapters. Re-connect the fibre to relevant ports
after cleaning. If it doesn’t make TMRX (TSRX) red LED switch off, follow
next steps.
4. Disconnect the fiber from the TMRX (TSRX) port, and measure the power
Pout which comes out from the fiber. Then, go to the module where the
other end of the fiber is connected (it can be either on the slave side and
on the master side, depending on the fiber or on the jumper you are
verifying), disconnect it and measure the input power Pin coming out of
the port. Calculate the fibre attenuation A due to the fiberoptics cable: Af
[dB] = Pin – Pout
a. If ADL > 10 dB, then the fibre optic cable has some problems. Replace it with a new one.
b. If ADL < 10 dB troubleshooting procedure has not identified the problem. Refer to
supervision system or contact the manufacturer for assistance.
TILx-
-HL
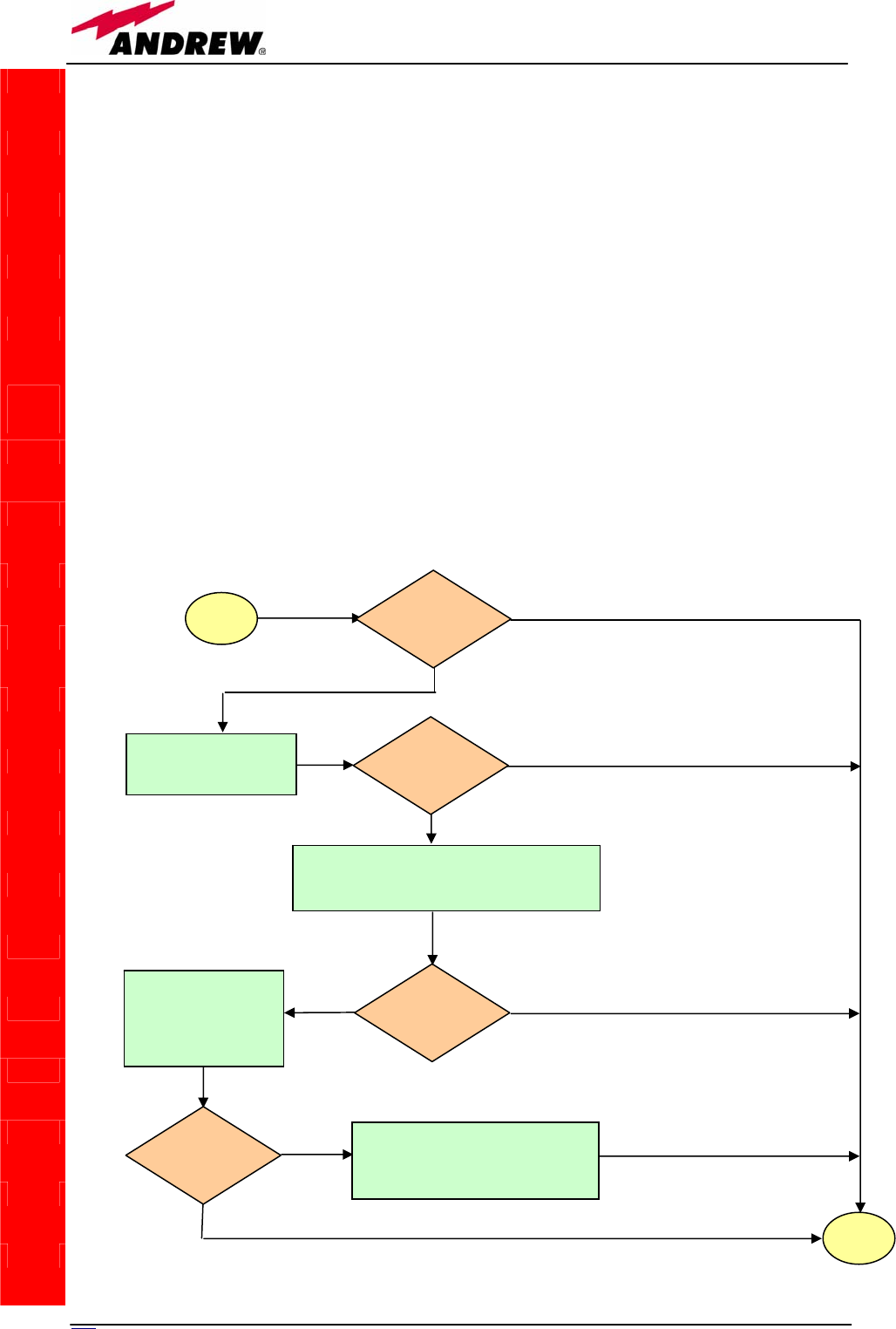
192 User Manual
TSRX-2xx/8 module troubleshooting
Ordinary troubleshooting procedures which can be carried out on TMRX-200 module first involve
a check of the optical adapters status and of the fiberoptics cables. If the alarm status still persists,
a reboot of both the TMRX-200 module and of the TSRX-2xx/8 module can be performed so as to
verify if the problem depends on a failed modem connectivity.
Quick TSRX-2xx/8 troubleshooting procedure
(The following procedure is summarized by the flow-chart in fig. 5.34c)
In case the red LED is ON, please follow these steps:
1. Clean the optical adapter
2. If the problem still persists, refer to the fibre optic DL troubleshooting so as to check if the
optical cable or optical connection has any problem on DL path
3. If previous actions didn’t make the LED switch off, a reboot of both the TSRX-2xx/8
module and of the TMRX-200 module (on the master side) could be performed so as to test
modem connectivity.
4. If the red LED still remains on, please check the alarm status by the LMT or the supervision
unit in order to better understand the problem and its possible solution.
TILx-
-HL
sta
r
t
Is the red LED
ON upon the
TMRX 200?
Yes
No
Clean the SC-APC
optical adapter and
connecto
r
No
Yes
end
Is red LED upon
TMRX 200
still ON?
Optical cable or optical connections may have
some problems. Refer to TMRX/TSRX fiberoptic
troubleshooting (fig. 5.34c)
Yes
Is red LED upon
TMRX 200
still ON?
No
Reboot both the
TMRX-200 module
(on i-link slave side)
and the TMRX-200
(on i-link master-side)
Is red LED upon
TMRX 200
still ON?
Quick troubleshooting procedure has
not identified the problem. Refer to
supervision system or contact the
manufacture
r
Yes
No
Fig. 5.34(a): Flow-chart describing the quick TMRX200 troubleshooting.
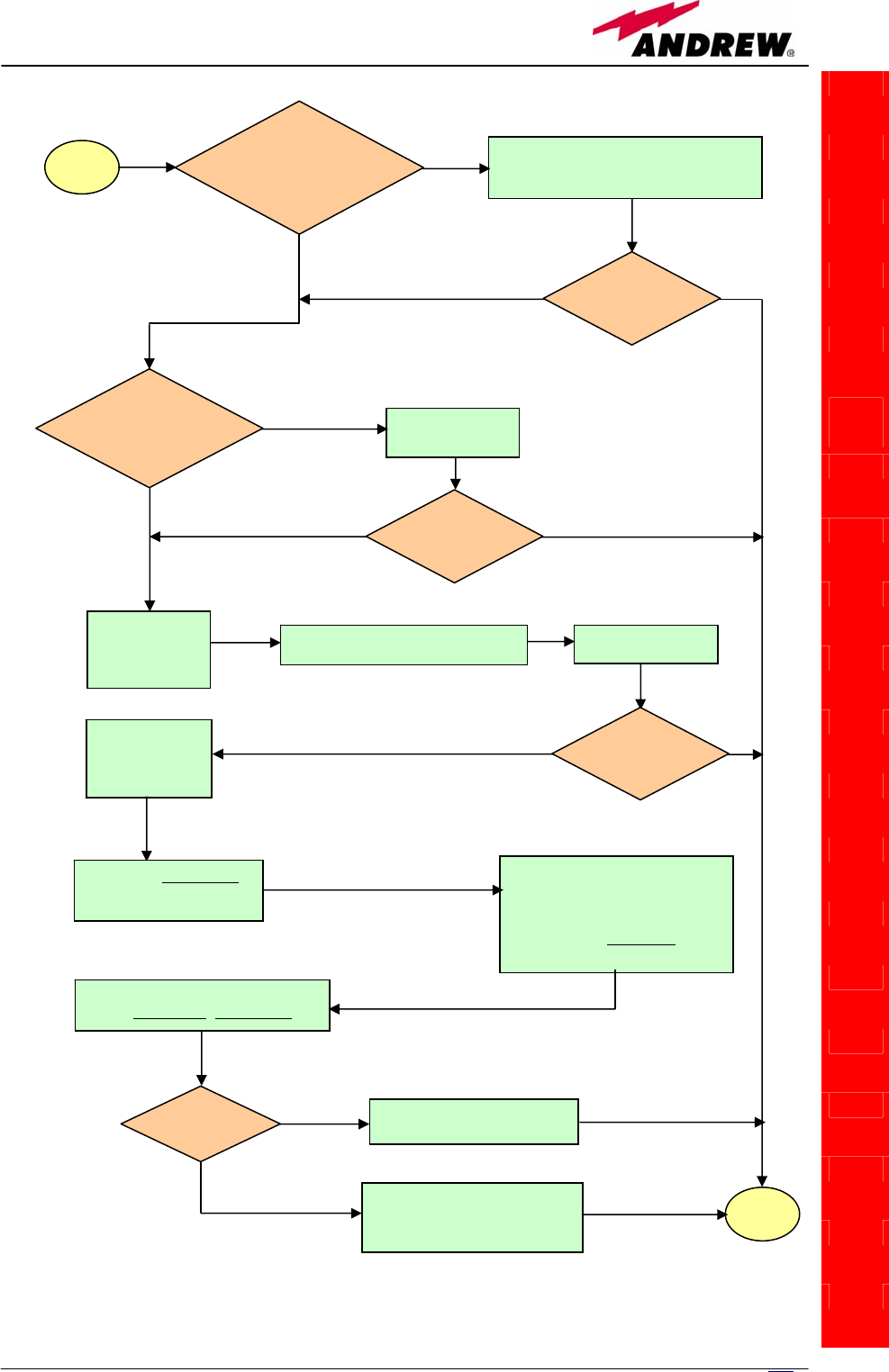
193
MN024-08
TILx-
-HL
start
Is there any point
where the fibre
experiences a small
radius of curvature?
Rearrange the optical path to avoid sharp
bends. If necessary replace the optical
cable with a lon
g
er one.
Is red LED
upon TMRX/TSRX
still ON?
Are SC-APC
connectors properly
installed at both fibre ends? Fix better SC-
APC connectors
Yes
No
No
Yes
No
Yes
No
Yes
Disconnect the
optical SC-APC
connector from
TMRX/TSRX
Clean the optical SC-APC ports
corresponding to both the fiber ends
Disconnect the
fiber optic cable
and clean it at
b
oth ends.
Reconnect the fibre
to relevant ports
Measure the output power
at corresponding fibre end.
Connect the adap
ter again
Go to the module where the other
end of the fiber is connected,
disconnect the corresponding SC-
APC connector , and measure the
corresponding input power. Then
connect the adapter again.
Calculate fibre attenuation
A[dB]=input power - output power
Is A > 10dB? Fibre optic cable has some
p
roblems. Re
p
lace it.
Quick troubleshooting procedure
has not identified any problem
on the fiber optics cable
end
No
Yes
No
Yes
Is red LED
upon TMRX/TSRX
ON?
Is red LED
upon TMRX/TSRX
still ON?
Fig. 5.34(b): Flow-chart describing the TMRX/TSRX fiberoptic troubleshooting.
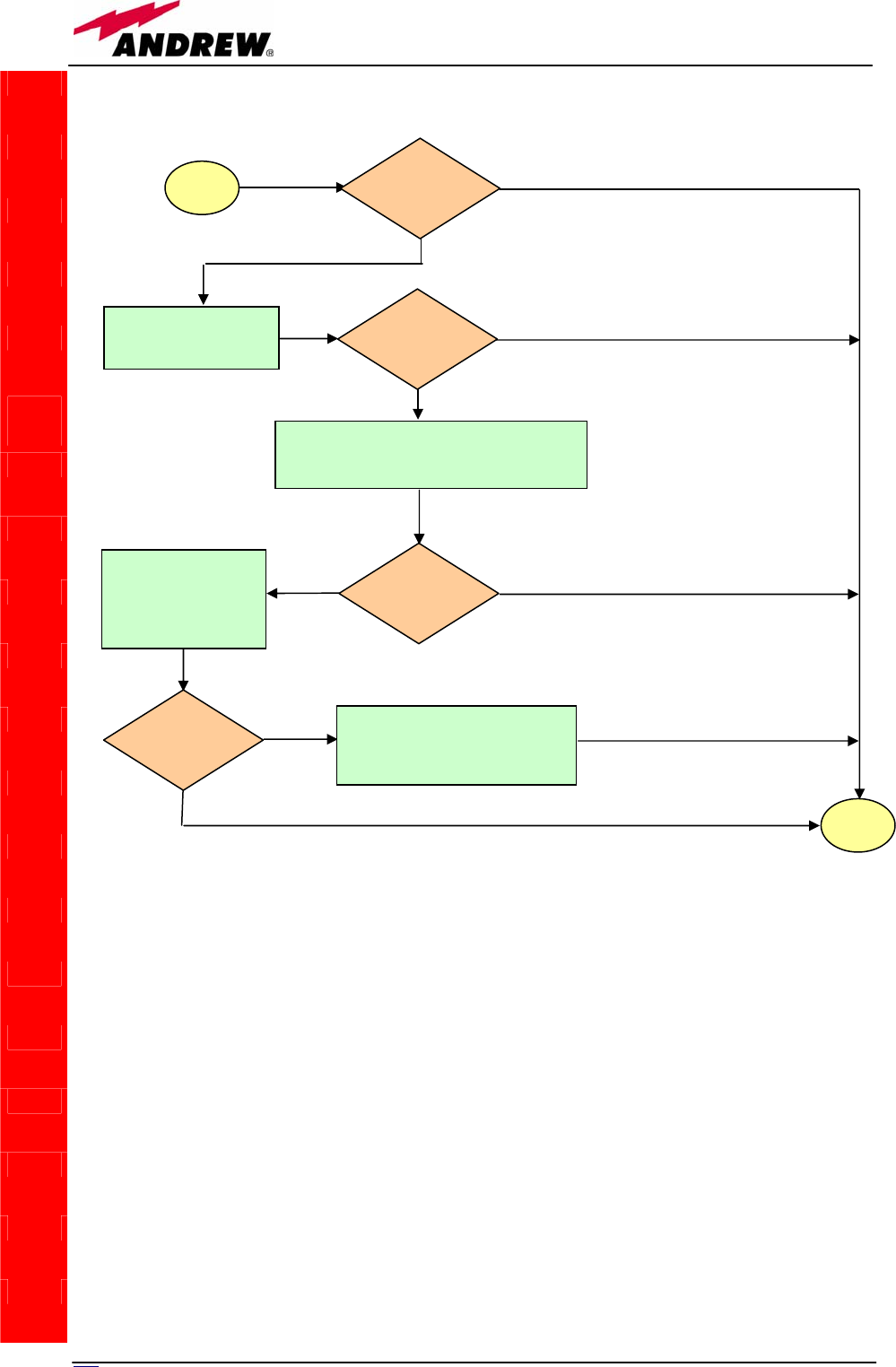
194 User Manual
TILx-
-HL
Fig. 5.34(c): Flow-chart describing the quick TSRX2xx/8 troubleshooting.
sta
r
t
Is the red LED
ON upon the
TSRX 2xx/8?
Yes
No
Clean the SC-APC
optical adapter and
connecto
r
No
Yes
end
Is red LED upon
TSRX 2xx/8
still ON?
Optical cable or optical connections may have
some problems. Refer to TMRX/TSRX
fiberoptic troubleshooting (fig. 5.34c)
Yes
Is red LED upon
TSRX 2xx/8
still ON?
No
Reboot both the
TSRX-2xx/8 module
(on i-link slave side)
and the TMRX-200
(on i-link master-side)
Is red LED upon
TSRX 2xx/8
still ON?
Quick troubleshooting procedure
has not identified the problem.
Refer to supervision system or
contact the manufacture
r
Yes
No
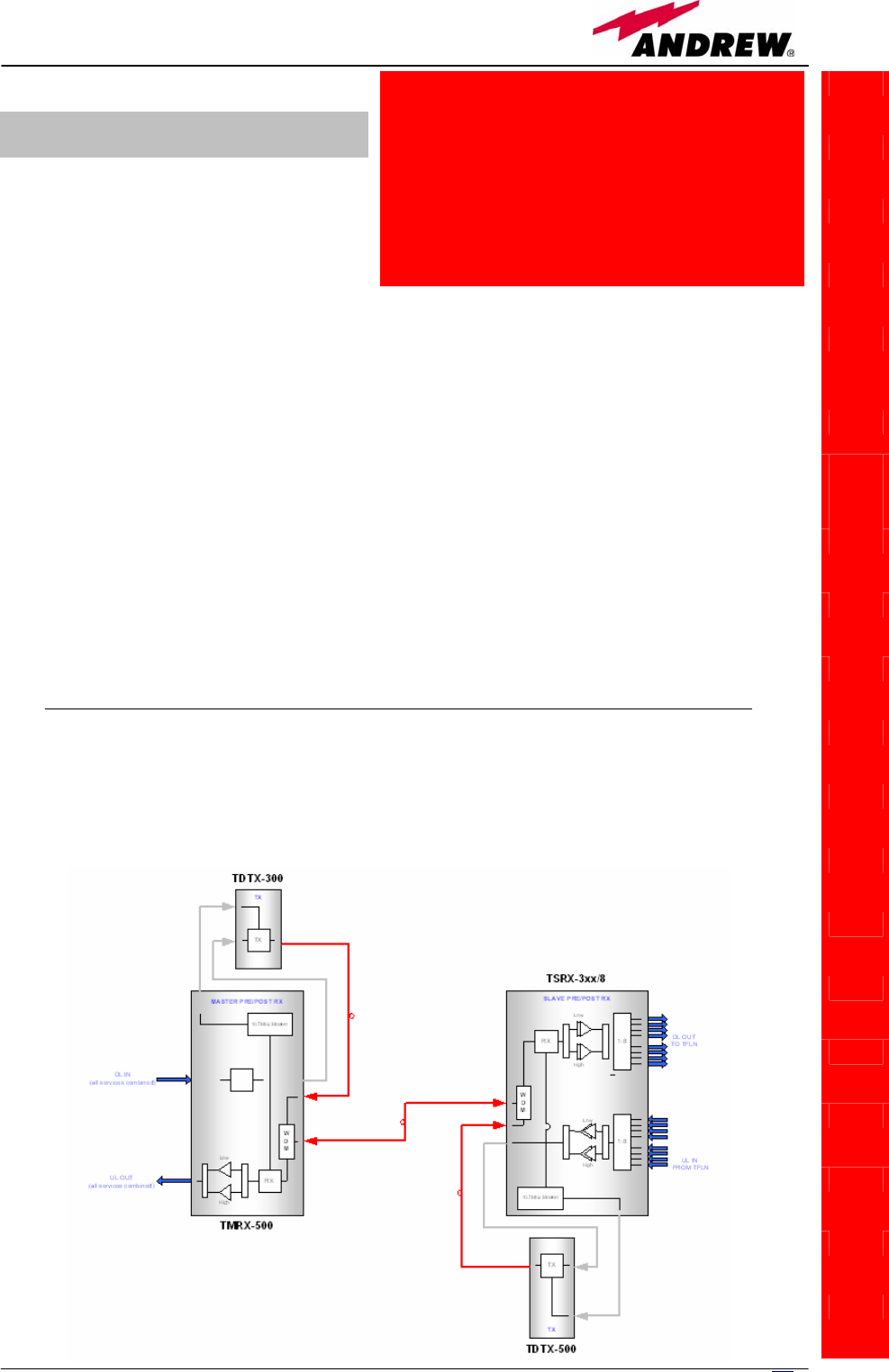
TILx-
-
HLW
Module name:
WDM interconnect
link
TIL
x
-HL
W
5.11.3. TILx-HLW i-link
Module description:
The WDM interconnect link is a
composite module, made up by a
transmitter and a receiver module
both on master and on slave side:
• Master side
-TDTX-300 (transmitter module, hosted by 1 subrack slot)
-TMRX-500 (receiver module, hosted by 1 subrack slot)
• Slave side
-TDTX-500 (transmitter module, hosted by 1 subrack slot)
-TMRX-3xx/8 (receiver module, hosted by 3 subrack slots)
The TILx – HLW kit is available in EU tri-band version (EGSM 900MHz, GSM
1800MHz, UMTS), in US dual-band version (SMR 800MHz & Cellular 800MHz,
PCS 1900 MHz), and in hybrid version (SMR 800MHz & Cellular 800MHz, GSM
1800MHz, UMTS). These versions just differs in the slave-side receiver TSRX
module, which is the only module whose features vary with the RF
transmitting band.
Block scheme
A scheme of the system, is reported hereinafter, so as describe the
connections between the Interconnect-link modules and to give an insight of
the function of the modules named above.
Fig.5.35 – Scheme of the
WDM interconnect link
195
MN024-08
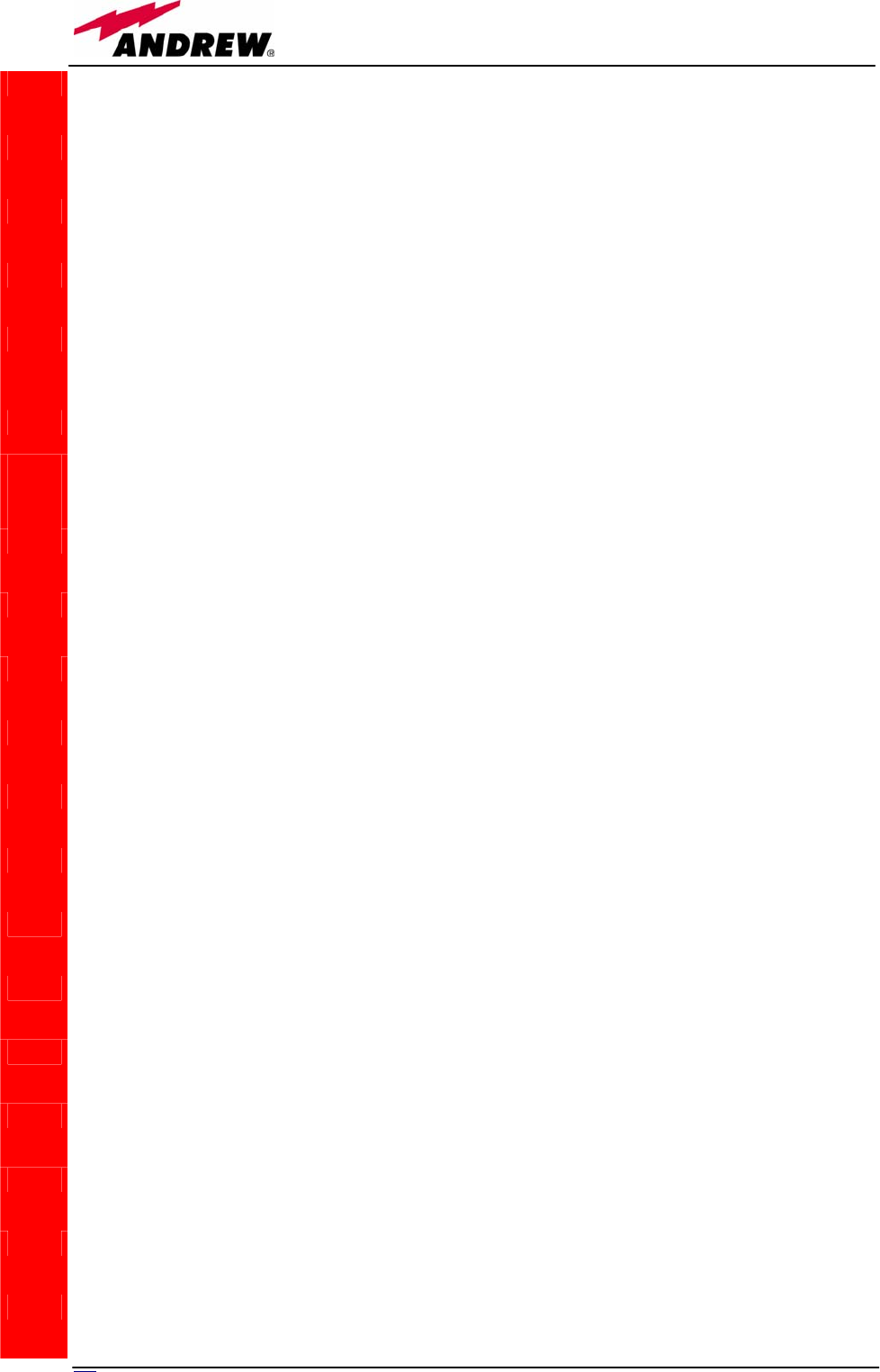
19
6
User Manual
Main TILx-HLW functions:
Downlink:
Uplink:
TILx-
-
HLW
Master side:
• RF-to-Optical conversion of the signal coming from the
splitting/combining section, and transmission to the slave
i-link modules via fiberoptics cable;
• Modulation and RF-to-Optical conversion of the bus
information, and transmission to the slave i-link modules
via fiberoptics cable (on 1310 nm wavelength);
Slave side
• Optical-to-RF conversion of signal and alarm information,
with Automatic Gain Control (AGC) in order to
compensate the optical losses;
• Distribution of the RF signal to the TFLN optical TRXs, and
demodulation of the bus information
Slave side:
• RF-to-Optical conversion of the signal coming from the
TFLN optical TRXs, and transmission to the master i-link
modules via fiberoptics cable;
• Modulation and RF-to-Optical conversion of the alarm
information, and transmission to the master i-link
modules via fiberoptics cable (on 1310 nm wavelength);
• Optical-to-RF conversion of signal and alarm information,
with Automatic Gain Control (AGC) in order to
compensate optical losses
• Distribution of the RF signal to the splitting/combining
section, and demodulation of the alarm information
Master side:
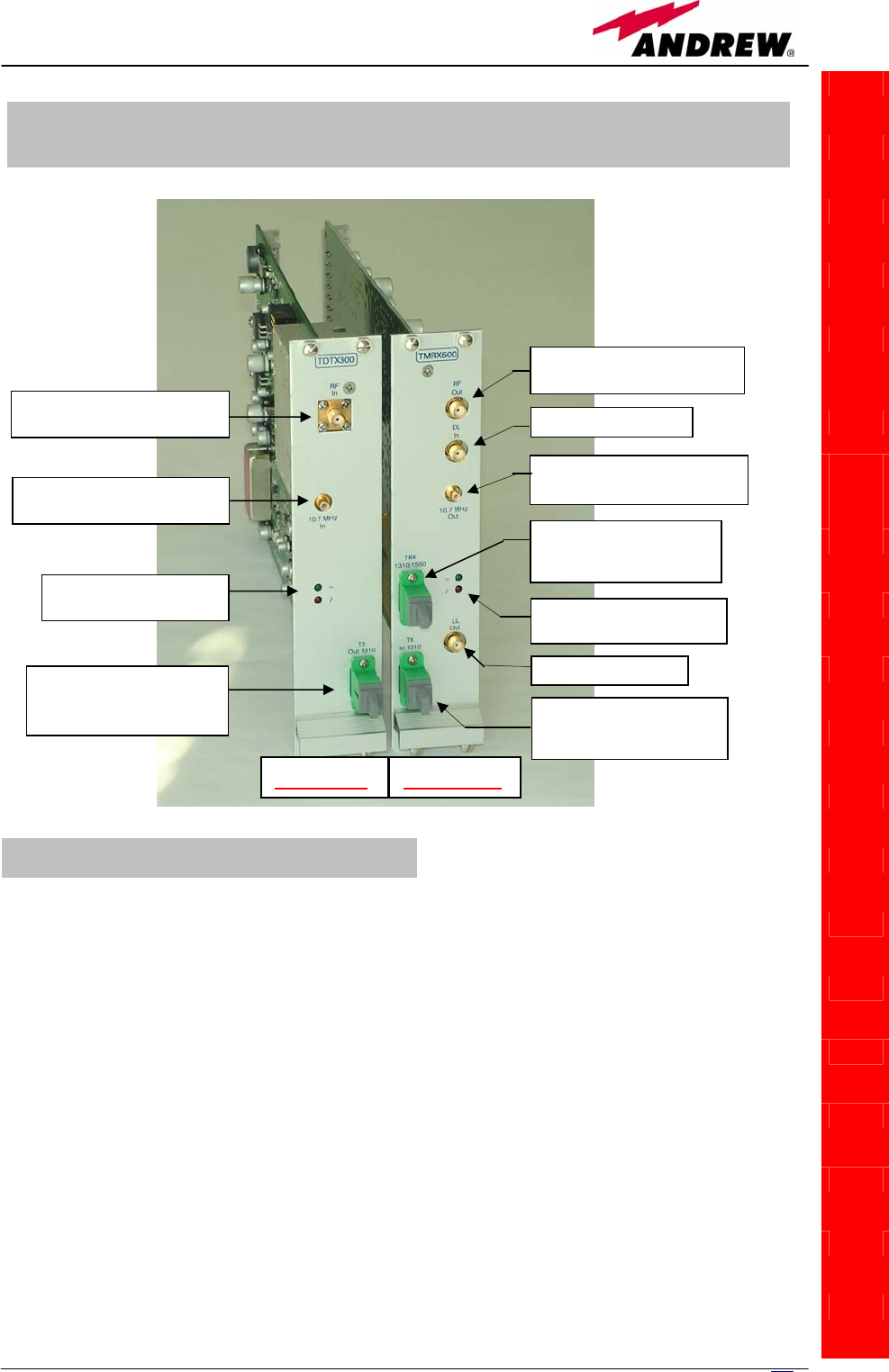
197
MN024-08
TDTX300 transmitter
TMRX500 receiver
TILx-
-
HLW
¾ 1 RF input port , to be connected directly to the RF
output port of the TMRX500 adjacent module
¾ 1 alarm input port, to be connected directly to the
alarm output port of the TMRX500 adjacent module
TILx-HLW Master Side:
TDTX300 transmitter + TMRX500 receiver
Optical port connected to
slave TSRX3xx/8 (SC-
APC
)
Optical port connected to
TMRX 500 master (SC-APC)
RF port connected to TMRX500
maste
r
(
SMA-f
)
Alarm in port connected to
TMRX500 master
(
SMB-m
)
Alarm out port connected to
TDTX300 master (SMB-m)
RF port connected to TDTX300
maste
r
(
SMA-f
)
UL RF
p
ort
(
SMA-f
)
DL RF
p
ort
(
SMA-f
)
GREEN LED: power on
RED LED: ma
j
or alar
m
GREEN LED: power on
RED LED: ma
j
o
r
alar
m
TDTX300 TMRX500
Optical port connected to
TDTX300 master (SC-APC)
¾ 1 RF output port, to be connected directly to the RF
input port of the TDTX300 adjacent module
¾ 1 alarm output port, to be connected directly to the
alarm input port of the TDTX300 adjacent module
¾ 1 RF DL port, sent to the passive devices which
interface the Britecell with the BTS
¾ 1 RF UL port, coming from the passive devices which
interface the Britecell with the BTS
Fig. 5.36: WDM i-link
master side is made
up by a TDTX300
transmitter and by a
TMRX500 receiver
TILx-HLW Master-side: RF ports
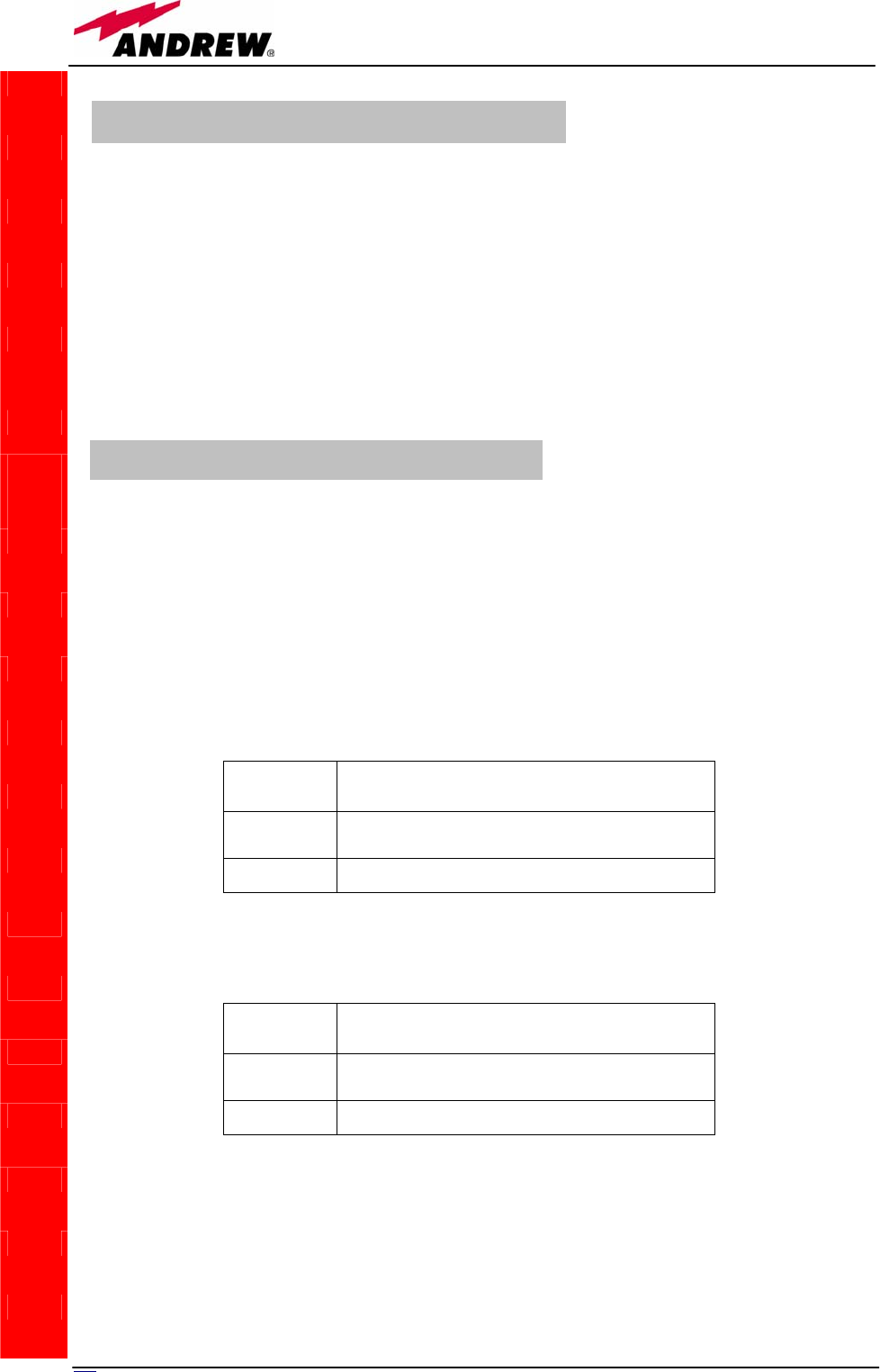
198 User Manual
TDTX300 transmitter:
TMRX500 receiver:
TDTX300 transmitter:
TMRX500 receiver
TILx-
-
HLW
Led
colour Meaning
Red Optical power failure, wavelength out of
range, power supply failure
Green Power supply OK
Led
colour Meaning
Red Power supply failure, modem failure, RF UL
failure, AGC compensation failure
Green Power supply OK
¾ 1 input port (1310 in), to be connected directly to the
optical output port of the master-side TDTX300
transmitter
¾ 1 WDM TRX port (1310/1550), to be connected to the
TSRX3xx/8 module on the slave side
¾ 1 output port (1310 out), to be connected directly
to the optical input port of the master-side
TMRX500 receiver
Two control LEDs (one green, one red) are placed on
the TDTX300 front panel. The green LED describes
the power supply status of the TDTX module, while
the red LED describes the major TDTX failure.
Two control LEDs (one green, one red) are placed on the
T
MRX500 front panel. The green LED describes the power
supply status of the TDTX module, while the red LED
describes the major TMRX failure.
Table 5.20. Summary of TDTX300 LEDs meaning
Table 5.21 summary of TMRX500 LEDs meaning
TILx-HLW Master-side: Optical ports
TILx-HLW Master-side: LED Alarms
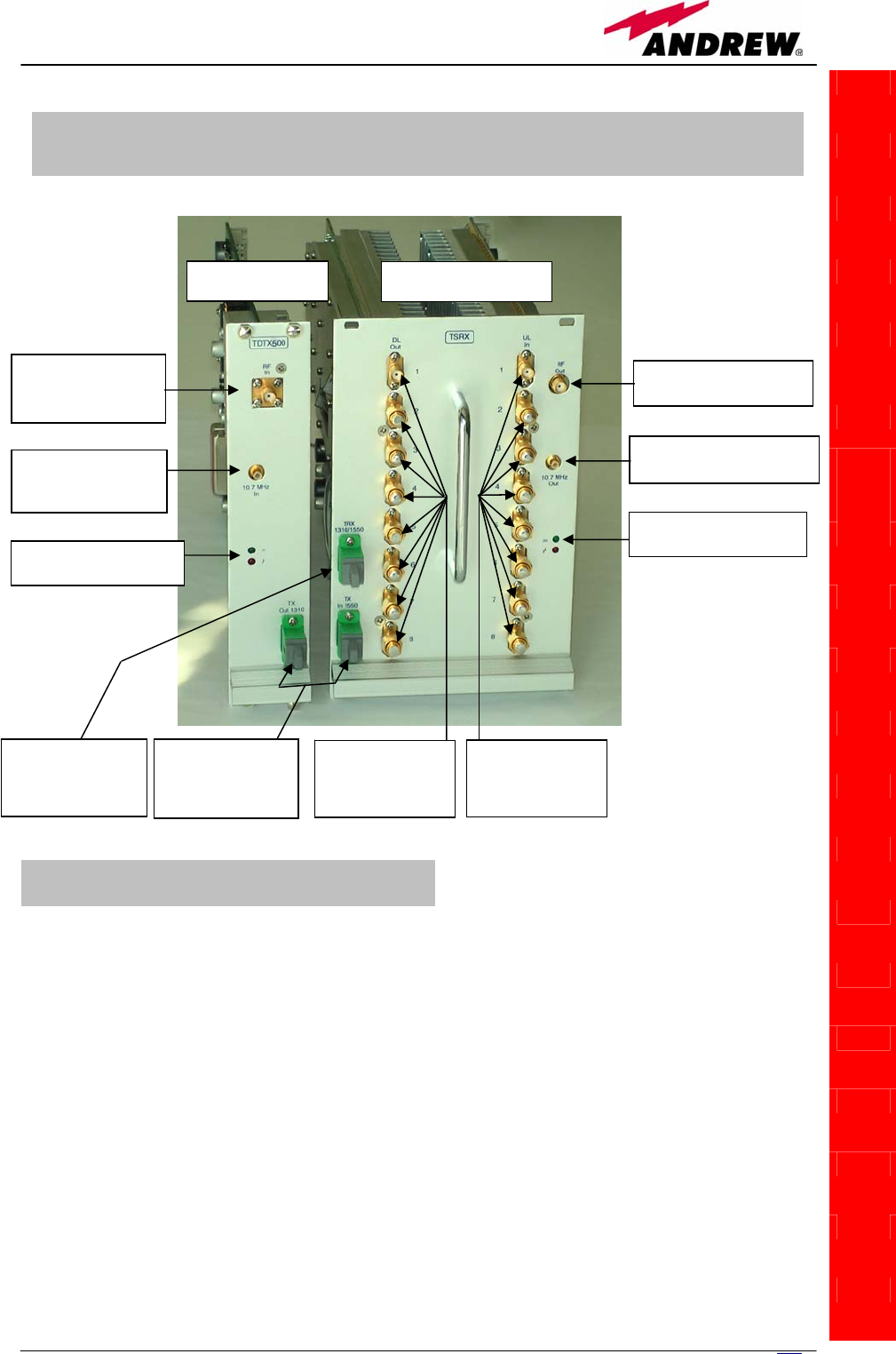
199
MN024-08
TDTX500 transmitter:
TSRX 3xx/8 receiver
TILx-
-
HLW
¾ 1 RF output port, to be connected directly to the RF
input port of the TDTX300 adjacent module
¾ 1 alarm output port, to be connected directly to the
alarm input port of the TDTX300 adjacent module
¾ 8 RF DL ports, which can feed up to 8 TFLN local
transmitters ;
¾ 8 RF UL ports, which can receive the UL signals from
up to 8 TFLN local transmitters.
¾ 1 RF input port , to be connected directly to the RF
output port of the TSRX3xx/8 adjacent module
¾ 1 alarm input port, to be connected directly to the
alarm out
p
ut
p
ort of the TSRX3xx/8 ad
j
acent
TILx-HLW Slave-Side:
TDTX500 transmitter + TSRX3xx/8 receiver
WDM I-link Slave-side: RF ports
RF port connected to
TSRX3xx/8 slave
(SMA-f)
RF Rx port from
TDTX500 slave
(
SMA-f
)
Optical port to be
connected to
TMRX-500 master
(
SC-APC
)
Optical ports to
connect each other
by the fiber optic
j
um
p
e
r
RF port connected to
TSRX3xx/8 slave
(
SMB-m
)
RF Rx port from TDTX500
slave (SMB-m)
GREEN LED: pwr on
RED LED:ma
j
or alar
m
GREEN LED: power on
RED LED:ma
j
or alar
m
DL ports connected
to TFLN DL ports
(SMA-f)
UL ports connected
to TFLN UL ports
(SMA-f)
TDTX 500 TSRX 3xx/8
Fig.5.37: the WDM
i-link master side is
made up by a
TDTX500
transmitter and by a
TSRX3xx receiver
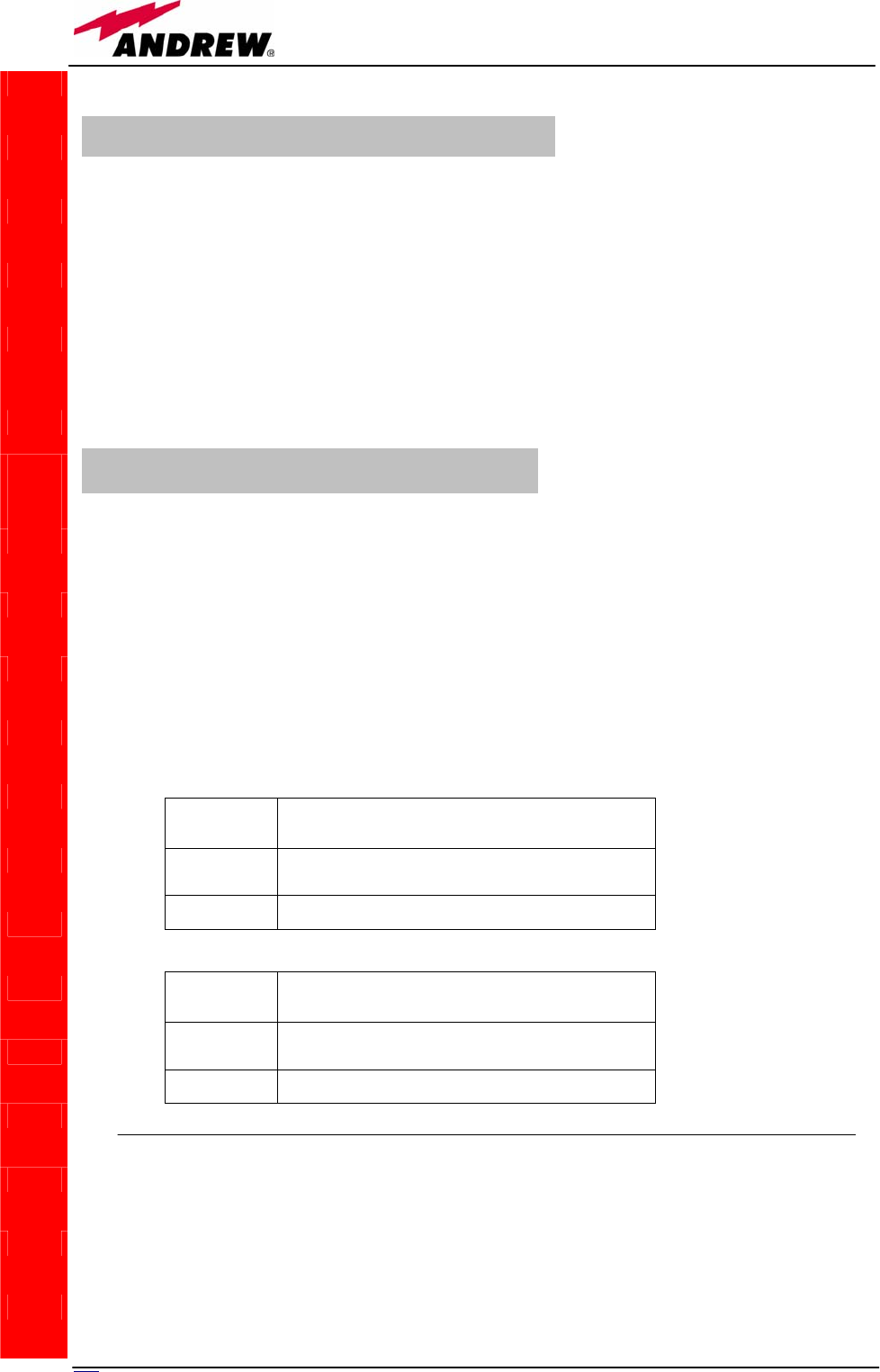
200 User Manual
TDTX 500 transmitter:
TSRX 3xx/8 receiver:
TDTX500 transmitter:
TSRX 3xx/8 receiver
Warnings (to be read before the TILx-HLW
installation)
Dealing with optical output ports
• The TDTX modules (both on master and on slave side) contain
semiconductor lasers. Invisible laser beams may be emitted from the
TILx-
-
HLW
Led
colour Meaning
Red Optical power failure, wavelength out of
range, power supply failure
Green Power supply OK
Led
colour Meaning
Red Power supply failure, modem failure, RF UL
and DL failure, AGC compensation failure
Green Power supply OK
¾ 1 input port(1550 in), to be connected directly to
the optical output port of the slave-side TDTX500
transmitter
¾ 1 WDM TRX port (1310/1550nm), to be connected
to the TMRX500 module on the master side
¾ 1 output port (1550 out), to be connected directly to
the optical input port of the slave-side TSRX 3xx/8
receiver
Two control LEDs (one green, one red) are placed on the
TDTX300 front panel. The green LED describes the power
supply status of the TDTX module, while the red LED
describes the major TDTX failure.
Two control LEDs (one green, one red) are placed on
the TSRX3xx/8 front panel. The green LED describes
the power supply status of the TDTX module, while the
red LED describes the major TSRX failure.
WDM I-link Slave-side: Optical ports
WDM I-link Slave-side: LED Alarms
Table 5.23:
Summary of
TSRX3xx/8 LEDs
meaning
Table 5.22:
Summary of
TDTX500 LEDs
meaning
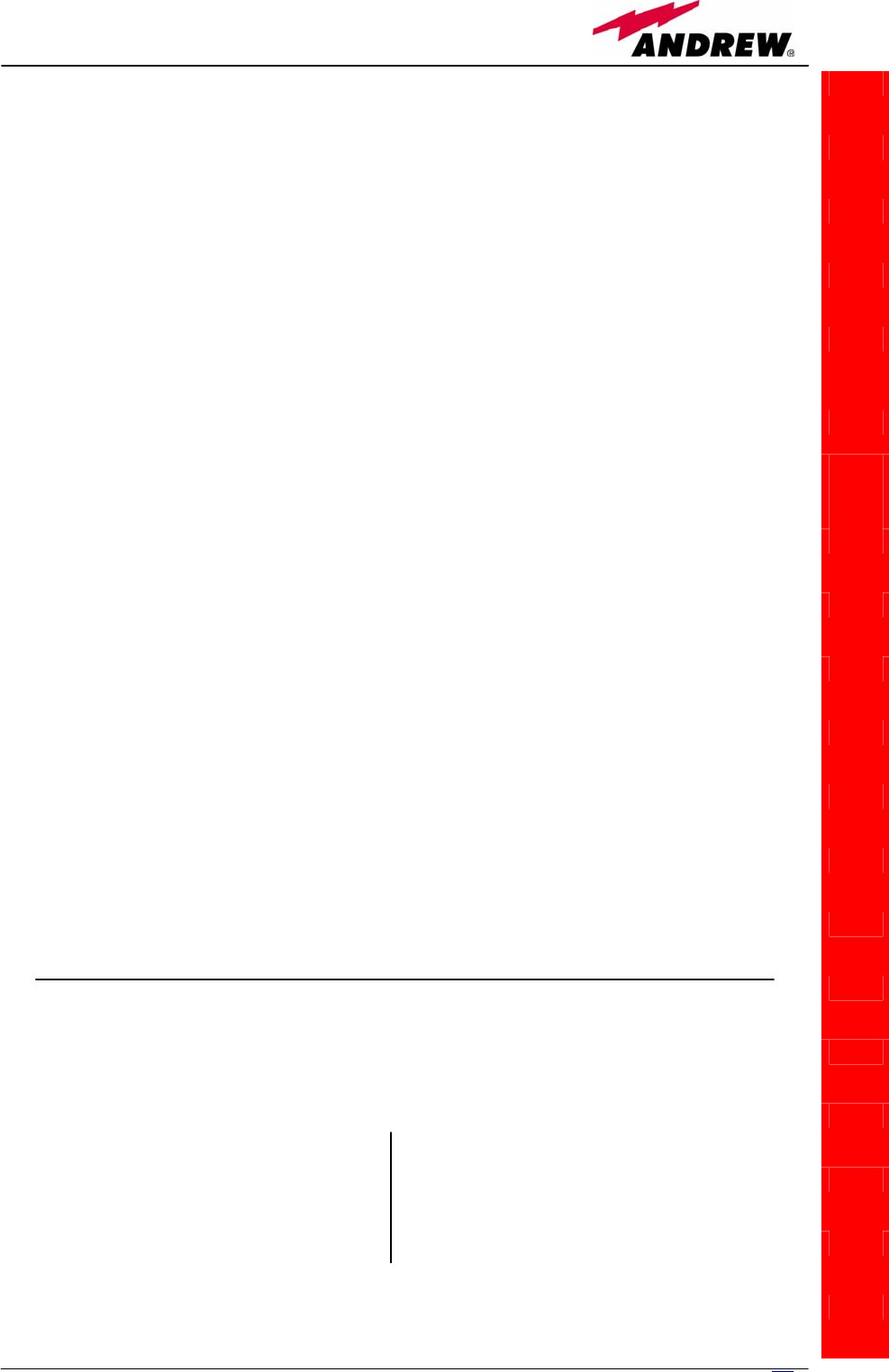
201
MN024-08
optical output ports. Do not look towards the optical ports while equipment
is switched on.
•
Handling optical connections
• When inserting an optical connector, take care to handle it so smoothly
that the optical fibre is not damaged. Optical fibres have to be single-mode
(SM) 9.5/125µm.
• Typically, Britecell Plus equipment is provided with SC-APC optical
connectors. Inserting any other connector will result in severe damages.
• Do not force or stretch the fibre pigtail with radius of curvature less than 5
cm.
• Remove adapter caps only just before making connections. Do not leave
SC-APC adapters open, as they attract dust. Unused SC-APC adapters must
always be covered with their caps.
• Do not touch the adapter tip. Clean it with a proper tissue before inserting
each connector into the sleeve. In case adapter tips need to be better
cleaned, use pure ethyl alcohol
Inserting or removing TDTX, TMRX, TSRX modules
• Do not remove or insert any module into TPRN sub-rack before having
switched off main power supply.
• Modules must be handled with care, in order to avoid damage to
electrostatic sensitive devices.
• When installing the modules in the sub-rack, take care to alternate active
and passive cards in order to ensure proper heat dissipation.
• In a multi-sub-rack system, remember to assign to each sub-rack a proper
RS485 bus address before installing the modules (please refer to TPRN
section for further details).
Positioning the TILx-HLW modules inside the subrack
• The i-link modules at slave side should be installed in the middle of the
slave subrack, or at least they should have no more than 4 TFLN modules
both on the right side and on the left side of the TSRX 3xx/8 module. This
requirement is advised in order to allow connection between the TSRX
module and all the TFLN transmitters (see fig. 5.39)
TILx-HLW installation
The TILx-HLW modules are provided with:
Both on master side and on slave side, the WDM i-link modules are to be
housed into a TPRN active sub-rack.
TILx-
-
HLW
Master Cable Installation Kit:
• 1 SMA-Male/SMA-Male RF
jumpers
• 1 SMB-Female/SMB-Female RF
jumper
• 1 Fiber Optic Jumper
Slave Cable Installation Kit:
• 17 SMA-Male/SMA-Male RF
jumpers
• 1 SMB-Female/SMB-Female RF
jumper
• 1 Fiber Optic Jumper
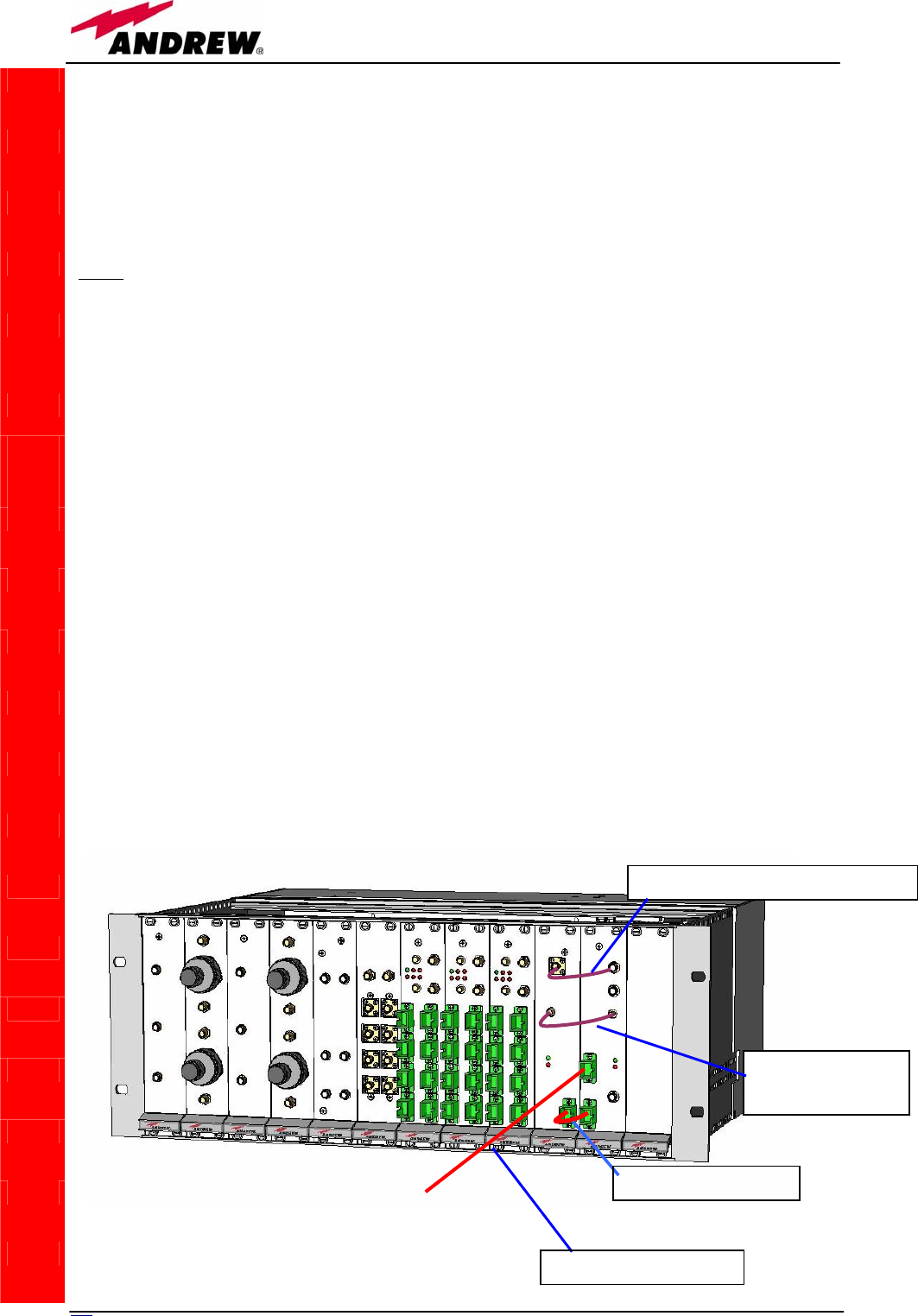
202 User Manual
On the master-side station, the WDM i-link modules are to be housed into 2
adjiacent slots, chosen among the 12 available ones in the subrack.
On the slave-side subrack, the WDM i-link modules are to be housed into 4
adjiacent slots: moreover, due to the particular cabling they require, these 4
adjiacent slots should be placed in mid-subrack, so that no more than 4 TFLN
local units stay on each side of the WDM i-link modules (see fig. 5.39).
Note: If the TILx-HLW modules are to be installed in an already working
Master Unit, switch off the sub-racks before inserting the modules.
Before inserting the boards into the TPRNx4 subracks, make sure to set
proper RS485 addresses. A basic rule of the Britecell installation is that 2
subracks belonging to the same Master Unit should always have different
RS485 addresses (please refer to “TPRN Installation” section): since the
interconnect-link basically provides an extension of the Master Unit bus, any
subrack on the i-link master-side should also have a RS485 address different
from any subrack on the i-link slave side.
Please refer to “TPRNx4 Installation” section for more information on setting
the RS485 address.
Firstly, carefully insert the TMRX-500 and the TDTX-300 boards in 2 adjacent
slots of the Master side subrack. Lock the 4 screws on the corners of each
boards.
Use the provided SMA-m RF jumper in order to connect the RF Out Port of the
TMRX500 module to the RF In Port of the adjacent TDTX300 module. Use the
SMB-f jumper to connect the 10.7MHz ports of the two boards. Fix these RF
jumpers to the RF ports through a proper torque wrench (not included).
Remove the protection cap from the optical ports of the 2 modules on the
master side.
Take the optical jumper, clean the fibre connectors, and use it to connect the
1310 output port of the TDTX 300 and the 1310 input port of the TMRX500
TILx-
-
HLW
Fig. 5.38: TILx-HLW master side
RF
j
um
p
er
(
S
MA-m / SMA-m
)
RF jumper
(SMB-f / SMB-f)
UL/DL o
p
tical cable
o
p
tical
j
um
p
er
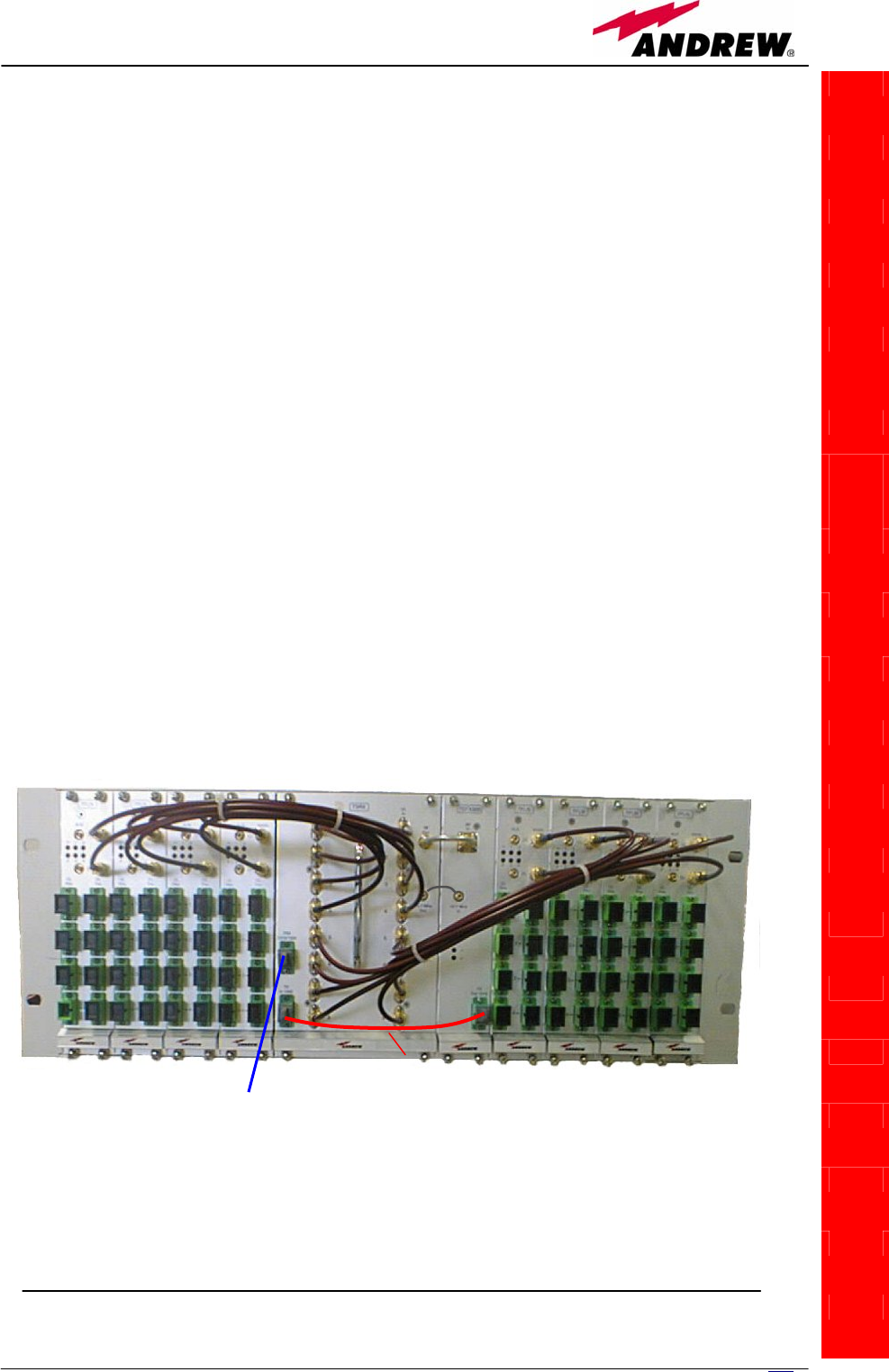
203
MN024-08
module.
Take a SC-APC fiber, clean the fibre termination, and connect it to the
1310/1550 TRX port of the TMRX 500 module (This fiber shall be directly
connected to the 1310/1550 TRX port of the TSRX 3xx/8 on the slave-side
subrack)
Carefully insert the TSRX-3xx/8 and the TDTX-500 boards in 4 adjacent slots
of the Master side subrack. As already explained, take care not to have more
than 4 TFLN modules on each side of the i-link pieces. Lock the 4 screws on
the corners of each boards.
Use the provided SMA-m RF jumper in order to connect the RF Out Port of the
TSRX 3xx/8 module to the RF In Port of the adjacent TDTX500 module. Use
the SMB-f jumper to connect the 10.7MHz ports of the two boards.
Use the longer RF jumpers (included) to connect each pair of TSRX UL and DL
ports to the corresponding UL and DL ports of each TFLN module mounted on
slave-side subrack. If less than 8 TFLNs are used at slave-side, make sure to
mask the TSRX-3xx/8 unused DL and UL ports by SMA loads (not provided).
Remove the protection cap from the optical ports of the 2 modules on the
slave side.
Take the optical jumper, clean the fibre connectors, and use it to connect the
1550 output port of the TDTX500 and the 1550 input port of the TSRX3xx/8
module.
Connect the 1310/1550 TRX port of the TSRX3xx/8 module to the fiberoptics
cable coming from the 1310/1550 TRX port of the TMRX500 module on the
master-side.
As you switch on the system, carefully refer to the “TILx-HLW start-up”
section.
TILx-
-
HLW
Fig. 5.39: TILx-HLW slave side
UL/DL optical
cable Optical
jumper
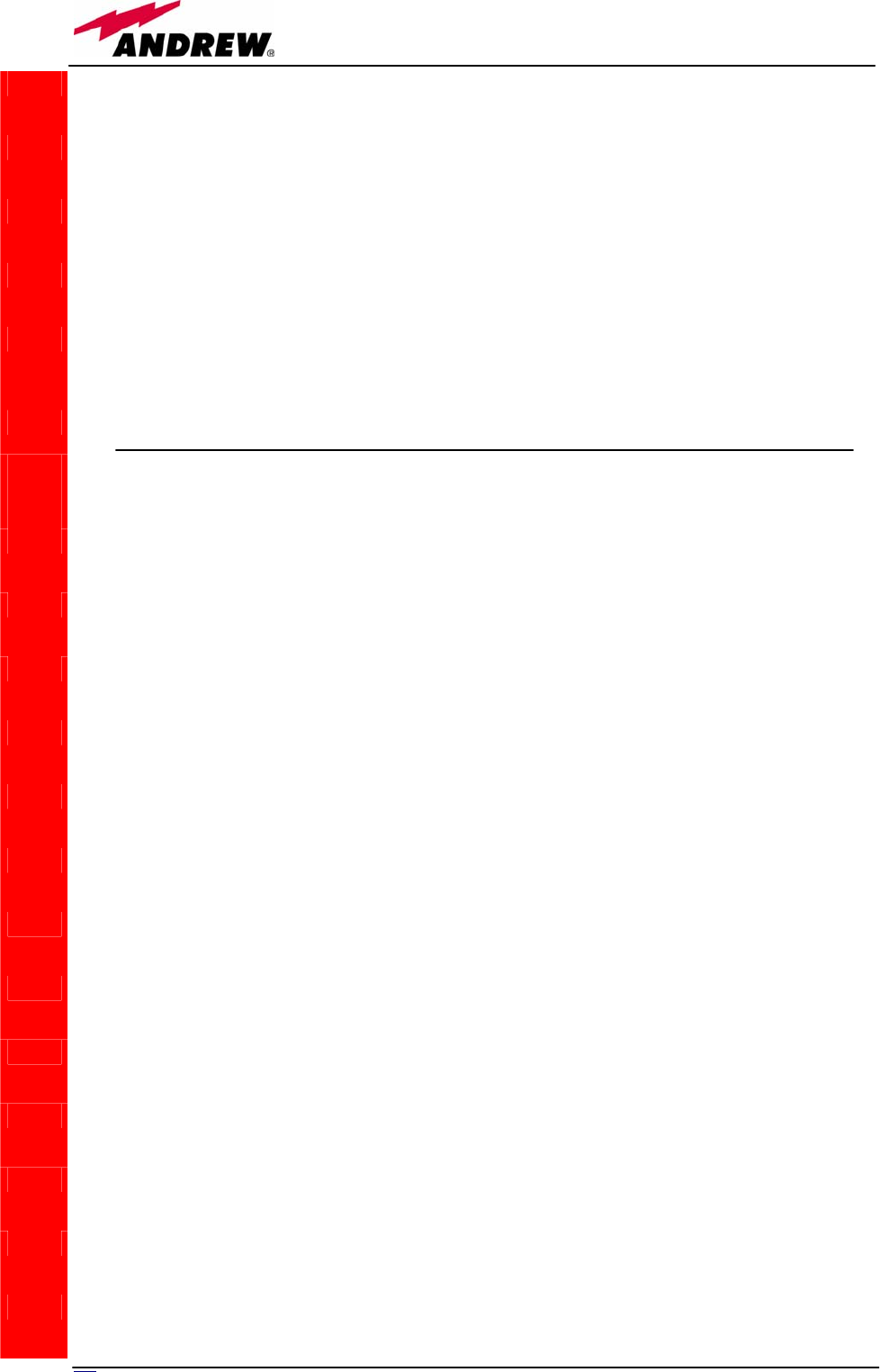
204 User Manual
Removing a TILx-HLW module
To remove a TILx-HLW module, firstly switch off the TPRNx4 subrack which
houses the module.
Remove the fibers and the RF jumpers connected to the WDM i-link module
which is going to be removed. Insert the caps on the optical ports which has
just been disconnected.
Unscrew the 4 screws at the corners of the WDM i-link module which is going
to removed, and slowly remove the card.
Put the card in its safety box
TILx-WDM start-up
Before both the master side station and the slave-side stations are switched
on, make sure that:
• all expected modules have been inserted into the Master Unit
• the modules have been connected each other by RF jumpers, according to
what planned in the system design
• the TILx-HLW master modules have been connected to the relevant TILx-
HLW slave modules through fiberoptics cables;
• every TFLN master optical TRX has been connected to relevant remote
units
• each remote unit has been connected to its coverage antennas
• the remote supervision unit, if present, has been connected to the Master
Unit
• both on the master-side and on slave-side stations, different subracks are
connected each other via bus RS485
After that, remember that only when all the remote units are already on, the
different subracks composing the Master Unit can be switched on. Once all
the active subracks have been switched on, the behaviour of the different i-
link modules can be summarized as follows:
o All the LEDs on the different TILx-HLW modules (both on master side
and on slave side) turn on for a couple of seconds;
o After that, all the green LEDs on the different modules remain ON (thus
indicating proper power supply), while the red LEDs switch off as soon as
the master-side and the slave-side detect each other;
o During normal working operations, the status of the LED should be the
one described in table 3.
o Once all the master-side and slave-side subracks have been switched
on, the system should begin to work correctly. Anyway, in order that the
i-link modules are recognized by the supervision management system, it
is necessary that the system carries out the discovery phase (please
refer to Supervision System Manual for more details). During this phase,
whose duration depends on the system complexity and which can last at
max. 4min, the TFLN LEDs ┌┘ blink. Do not connect/disconnect any
TILx-
-
HLW
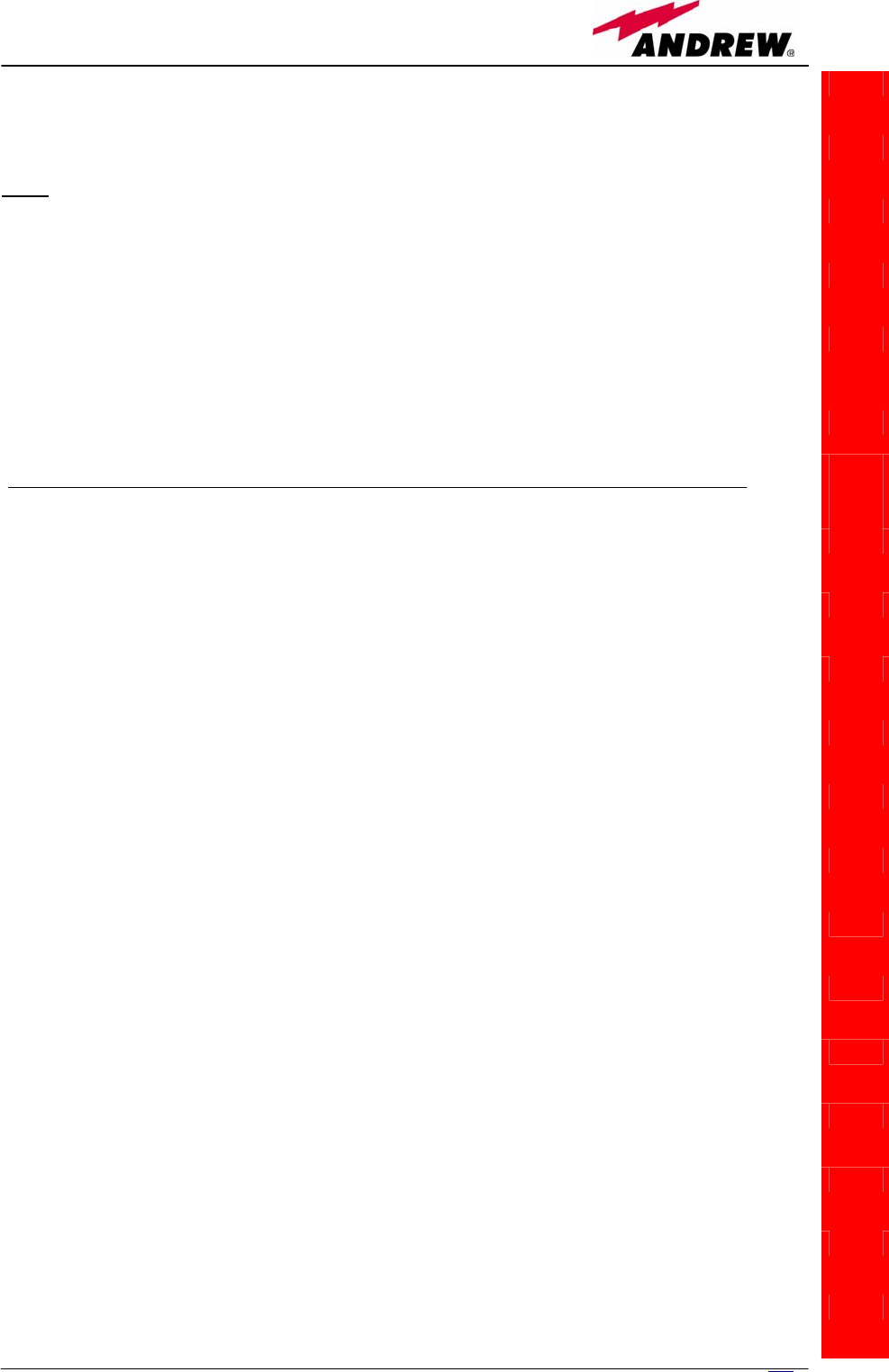
205
MN024-08
cable or any piece of equipment during the discovery phase! This
may result in failing the identification of some equipment.
Note: in case discovery doesn’t start automatically, check through the LMT or
the remote supervision whether it has been disabled (refer to LMT or remote
supervision system manuals for further information).
o Finally, please note that the receiver module TSRX3xx/8 has only one
connection with the subrack backplane, so that the LMT software and the
supervision system will detect it as a 1-slot card. More in details, only the
slot which hosts the TSRX LED alarms is recognized by LMT or
supervision. The other 2 slots hosting the TSRX receiver are therefore to
be masked through the LMT or the Supervision System Interface (please
refer to the relevant user manuals) in order to avoid fictitious alarm
notifications.
TILx-HLW troubleshooting
Faults on the i-link modules can be revealed:
• by LEDs on the front panels of the modules themselves
• by the LMT software running on a PC connected to a master side or a slave-
side subrack via RS232 port;
• by the supervision system interface managed by the remote supervision
unit, usually placed conveniently on the master-side.
Both LMT and supervision system provide full information about the device
causing the alarm. As a consequence, troubleshooting procedure can be very
immediate when failure detection is directly carried out through LMT or
supervision system.
The tables 5.24, 5.25, 5.26, 5.27 report a brief description of alarm related to
the different i-link modules, together with a reference to corresponding alerted
LEDs and to possible recovery actions.
TILx-
-
HLW
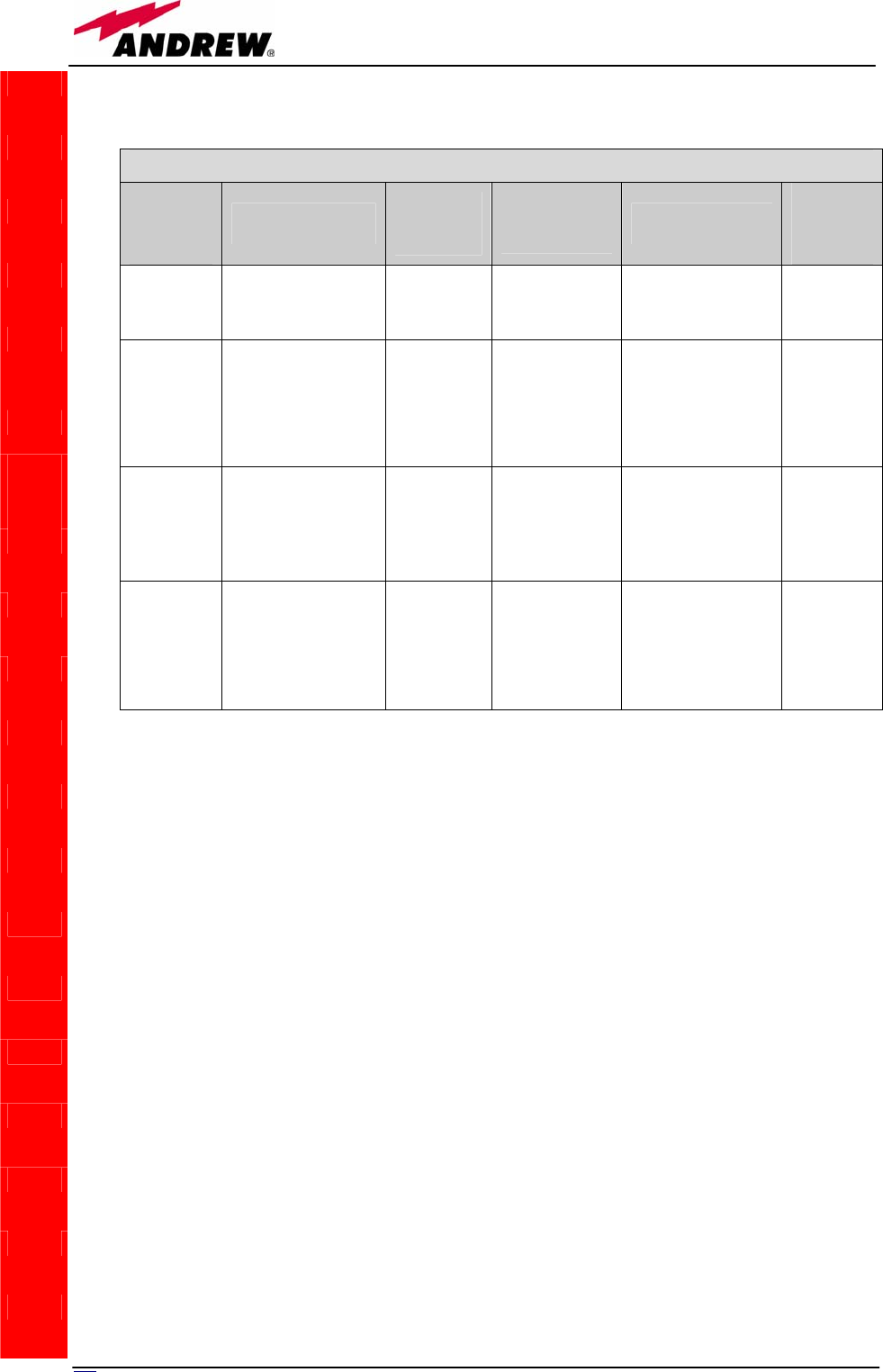
20
6
User Manual
TDTX300 (master side)
ALARM
CODE
(TSUN
description)
ALARM
DESCRIPTION
ACTIVE
LED
SUPERVISION
PRIORITY
LEVEL
ACTION
RECOMMENDED
RELÉ
PRIORITY
LEVEL
(subrack)
Vcc alarm
There is a degradation
on the power supply
provided by the
backplane
RED MAJOR Return the unit MAJOR
Optical
Power
< 1dB
The received optical
power experiences a
degradation which is
near to the AGC
working threshold (but it
can still compensate
losses)
NONE MINOR
Check the optical loss /
AGC status on the
TSRX or TMRX
module at the other side
of the imterconnect link
MINOR
Optical power
< 3 dB
The transmitted optical
power experiences a
degradation which can
no more be compensated
by the AGC.
RED MAJOR Return the unit MAJOR
Temperature
Alarm Over-temperature alarm NONE WARNING
Check the subrack and
cabinet ventilation,
verify the
environmental
conditions involving
heating and air
circulation
MINOR
TILx-
-
HLW
Table 5.24: Description of the TDTX300 alarms, as they are described by the LMT
software or by the supervisione interface
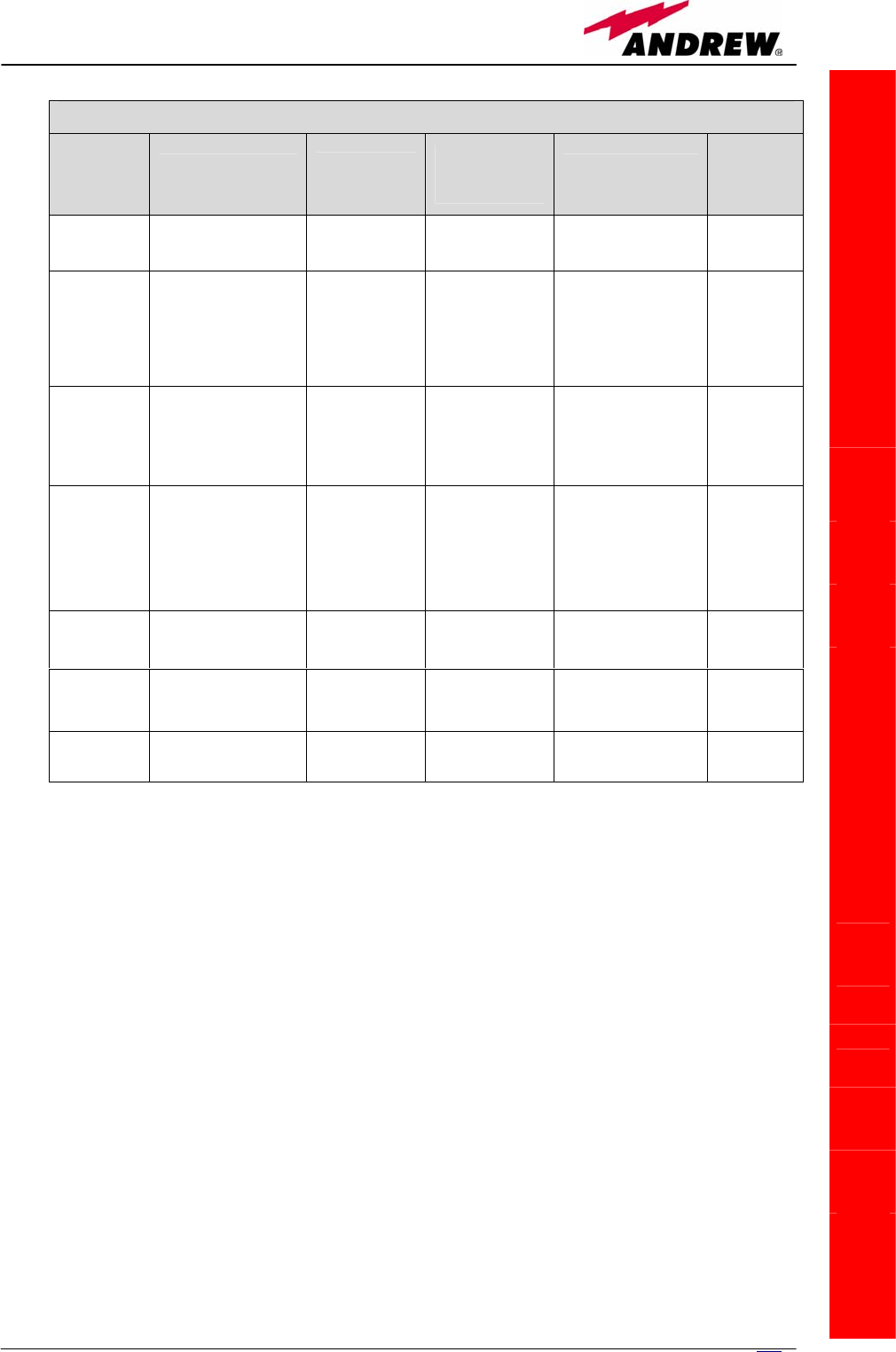
207
MN024-08
TMRX500 (master side)
ALARM
CODE
(TSUN
description)
ALARM
DESCRIPTION ACTIVE LED
SUPERVISION
PRIORITY
LEVEL
ACTION
RECOMMENDED
RELÉ
PRIORITY
LEVEL
(subrack)
Power supply
alarm
There is a degradation
in power supply
distribution
RED MAJOR Return the unit MAJOR
AGC out of
range
The received optical
power experiences a
degradation which is
near to the AGC
working threshold (but
it can still compensate
losses)
NONE WARNING
Check the optical loss /
AGC status on the
TSRX or TMRX
module at the other
side of the
imterconnect link
MINOR
Optical power
fail
The transmitted optical
power experiences a
degradation which can
no more be
compensated by the
AGC
RED MAJOR Return the unit MAJOR
Temperature
alarm Over-temperature alarm NONE WARNING
Check the subrack and
cabinet ventilation,
verify the
environmental
conditions involving
heating and air
circulation
MINOR
FSK modem
alarm
HW problem on the
10.7 MHz FSK
modulator/ demodulator
RED CRITICAL Return the unit MAJOR
UL RF alarm UL Hardware failure RED MAJOR Return the unit MAJOR
Current Fail Overcurrent alarm RED MAJOR Return the unit MAJOR
TILx-
-
HLW
Table 5.25: Description of the TMRX500 alarms, as they are described by the LMT software or by
the supervisione interface
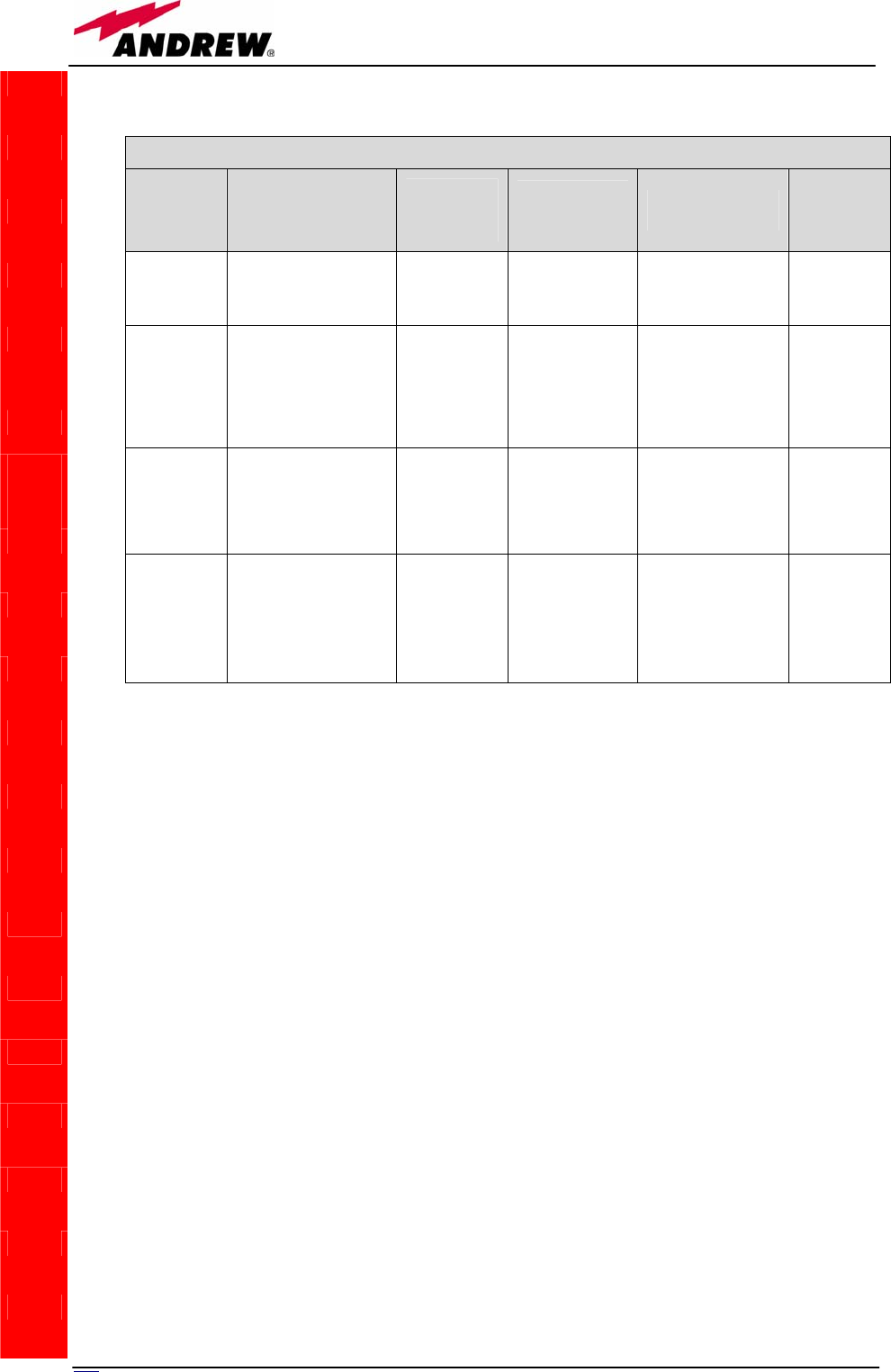
208 User Manual
TDTX500 (slave side)
ALARM
CODE
(TSUN
description)
ALARM
DESCRIPTION
ACTIVE
LED
SUPERVISION
PRIORITY
LEVEL
ACTION
RECOMMENDED
RELÉ
PRIORITY
LEVEL
(subrack)
Vcc alarm
There is a degradation on
the power supply
provided by the
backplane
RED MAJOR Return the unit MAJOR
Optical power
< 1 dB
The received optical
power experiences a
degradation which is near
to the AGC working
threshold (but it can still
compensate losses)
NONE MINOR
Check the optical loss
/ AGC status on the
TSRX or TMRX
module at the other
side of the
imterconnect link
MINOR
Optical power
< 3 dB
The transmitted optical
power experiences a
degradation which can no
more be compensated by
the AGC.
RED MAJOR Return the unit MAJOR
Temperature
Alarm Over-temperature alarm NONE WARNING
Check the subrack and
cabinet ventilation,
verify the
environmental
conditions involving
heating and air
circulation
MINOR
TILx-
-
HLW
Table 5.26: Description of the TDTX500 alarms, as they are described by the LMT
software or by the supervisione interface
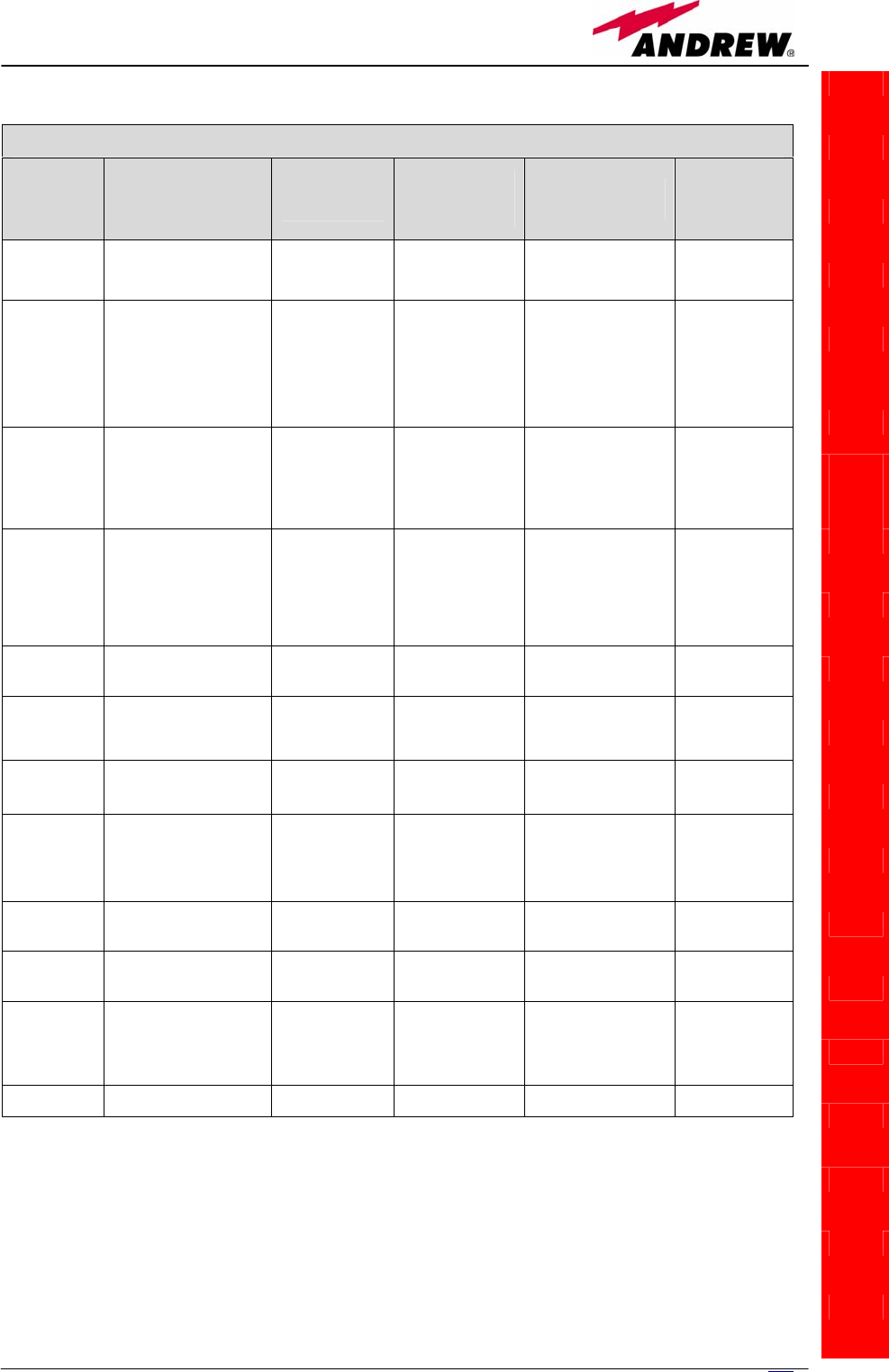
209
MN024-08
TSRX3xx/8 (slave side)
ALARM
CODE
(TSUN
description)
ALARM
DESCRIPTION ACTIVE LED
SUPERVISION
PRIORITY
LEVEL
ACTION
RECOMMENDED
RELÉ
PRIORITY
LEVEL
(subrack)
Power supply
alarm
There is a degradation in
power supply distribution RED MAJOR Return the unit MAJOR
AGC out of
range
The received optical
power experiences a
degradation which is
near to the AGC working
threshold (but it can still
compensate losses)
NONE WARNING
Check the optical loss
/ AGC status on the
TSRX or TMRX
module at the other
side of the
interconnect link
MINOR
Optical power
fail
The transmitted optical
power experiences a
degradation which can
no more be compensated
by the AGC
RED MAJOR Return the unit MAJOR
Temperature
alarm Over-temperature alarm NONE WARNING
Check the subrack and
cabinet ventilation,
verify the
environmental
conditions involving
heating and air
circulation
MINOR
FSK modem
alarm
HW problem on the 10.7
MHz FSK
modulator/demodulator
RED CRITICAL Return the unit MAJOR
DL Low band
RF alarm
HW failure on the DL
RF low band RED MAJOR Return the unit MAJOR
DL High
band RF
alarm
HW failure on the DL
RF high band RED MAJOR Return the unit MAJOR
DL UMTS
RF alarm
(only on
TSRX 347/8
version)
HW failure on the DL
RF UMTS band RED MAJOR Return the unit MAJOR
UL Low band
RF alarm
HW failure on the UL
RF low band RED MAJOR Return the unit MAJOR
UL High
band RF
alarm
HW failure on the UL
RF high band RED MAJOR Return the unit MAJOR
UL UMTS
RF alarm
(only on
TSRX 347/8
version)
HW failure on the UL
RF UMTS band RED MAJOR Return the unit MAJOR
Current Fail Overcurrent alarm RED MAJOR Return the unit MAJOR
TILx-
-
HLW
Table 5.27: Description of the TSRX3xx/8 alarms, as they are described by the LMT
software or by the supervisione interface
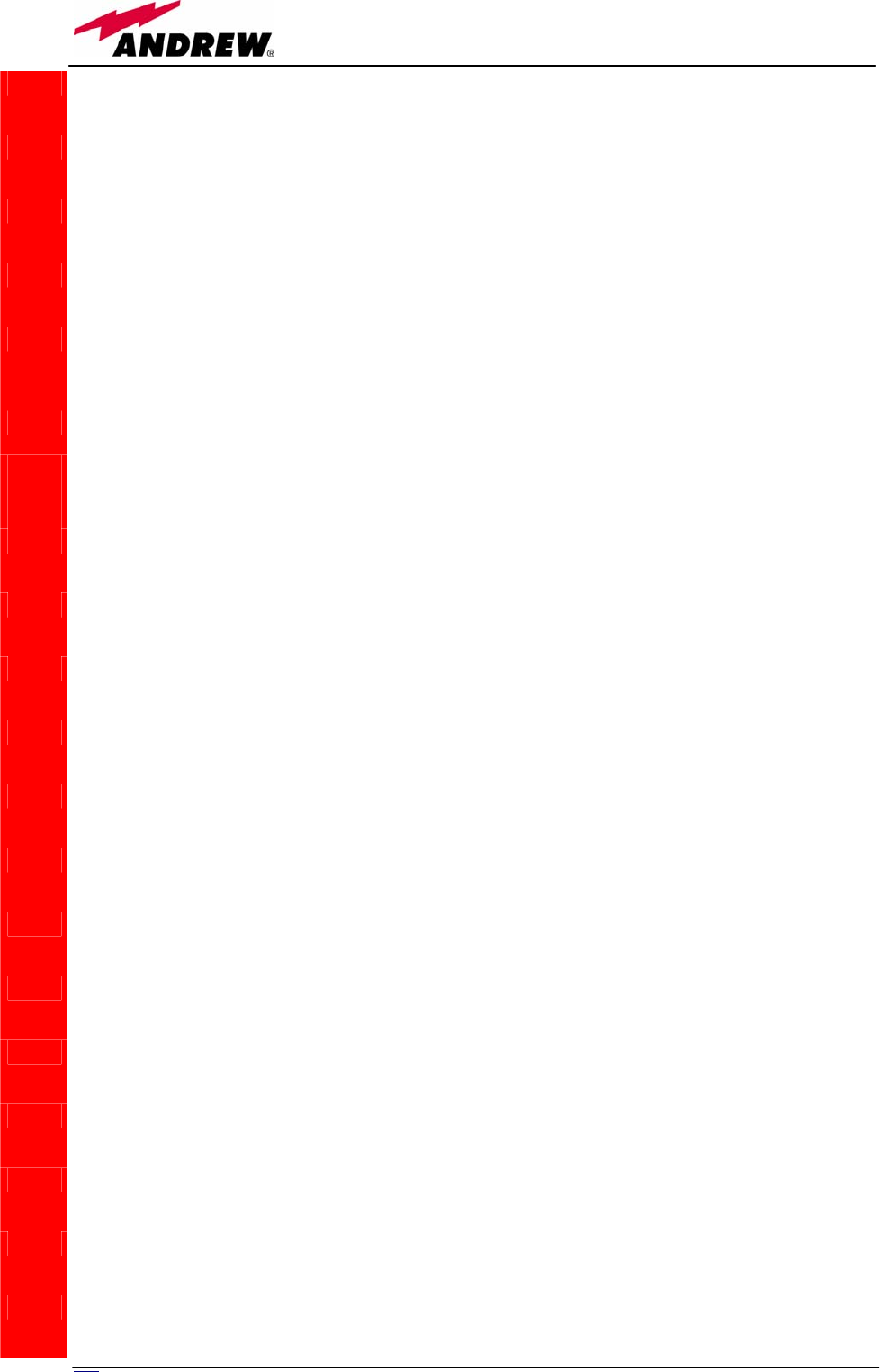
210 User Manual
As shown by these tables, the LEDs show only the alarms concerning the
board where they are housed: so, a red LED which is switched on at TSRX
front side reveals an alarm affecting the TSRX module itself (it does not deals
with the alarms affecting the other module of the i-link slave-side, which is an
TDTX300, and whose alarms will be detected by its own LEDs). Moreover,
these tables show that the LEDs reveals only major alarms, whereas the
minor alarms (i.e. the low priority ones) are revealed only by the LMT
software or through the TSUN supervision system. The minor alarms usually
detect critical situations which should be checked so as to avoid future
possibile system faults.
Although any alarm detected by a LED on the i-link modules should be
verified through LMT or supervision software when an accurate check is
needed, some ordinary maintenance procedures could be carried out quickly
following the instructions described hereinafter.
TDTX300 and TDTX500 troubleshooting
The TDTX modules are basically two optical transmitters whose alarm status
cannot be influenced by dirt optical adapters or by some problems in
fiberoptics cables. If any red light is switched on in a TDTX front panel, please
check if you have connected properly the RF jumpers. If the RF connections
prove to be ok and the red LED keeps on switching on, please contact the
manufacturer.
TMRX500 module troubleshooting
Ordinary troubleshooting procedures which can be carried out on TMRX500
module first involve a check of the optical adapters status and of the
fiberoptics cables. If the alarm status still persists, a reboot of both the
TMRX500 module and of the TSRX3xx/8 module can be performed so as to
re-inizialize the link.
Quick TMRX-500 troubleshooting procedure
(The following procedure is summarized by the flow-chart in fig. 5.40b)
In case the red LED is ON, please follow these steps:
1. Clean the optical adapter
2. If the problem still persists, refer to TMRX/TSRX fiber optical
troubleshooting so as to check if the optical connectors and, the optical
cable and the optical jumpers have some problems.
3. If previous actions didn’t make the LED switch off, a reboot of both the
TMRX500 module and of the TSRX3xx/8 module (on the slave-side) could
be performed so as to test modem connectivity.
4. If the red LED still remains on, please check the alarm status by the LMT or
the supervision unit in order to better understand the problem and its
possible solution.
TILx-
-
HLW
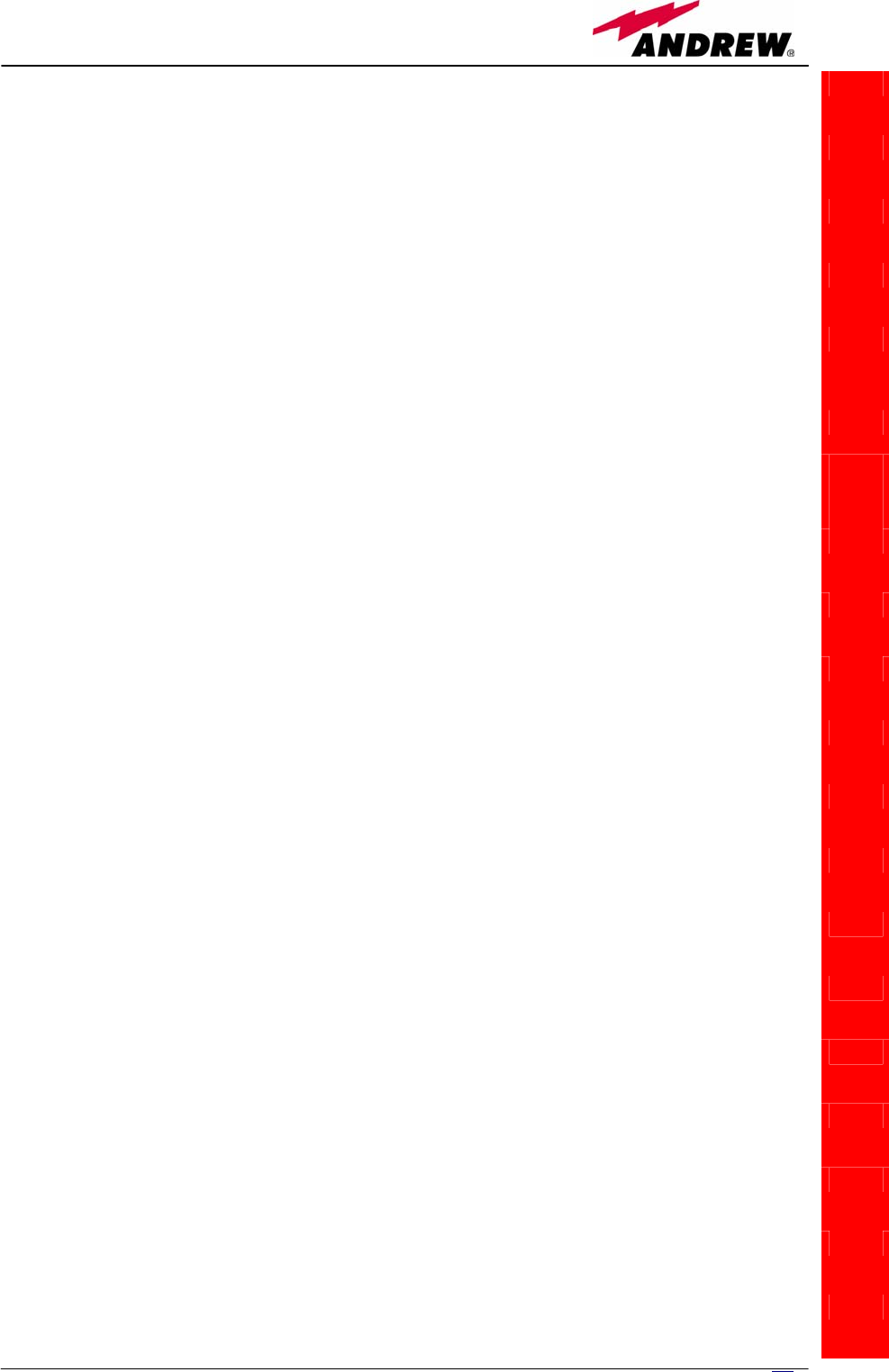
211
MN024-08
TMRX/TSRX fibre optic troubleshooting
(The following procedure is summarized by the flow-chart in fig. 5.40b)
1. Check if there is any point where fibre experiences a short radius of
curvature. In this case, rearrange the optical path in order to avoid sharp
bends (if necessary, replace the optical cable with a longer one). If TMRX
(TSRX) red LED switches off, troubleshooting has been successfully
carried out. Otherwise, follow next steps.
2. Check if SC-APC connectors are properly installed at both fibre ends. In
case they are not, fix more firmly the SC-SPC connectors to their
adapters. If the TMRX (TSRX) red LED switches off, troubleshooting has
been successful. Otherwise, follow next steps.
3. Disconnect the optical fibre and clean it better at both ends, then clean
also the relevant SC-APC adapters. Re-connect the fibre to relevant ports
after cleaning. If it doesn’t make TMRX (TSRX) red LED switch off, follow
next steps.
4. Disconnect the fiber from the TMRX (TSRX) port, and measure the power
Pout which comes out from the fiber. Then, go to the module where the
other end of the fiber is connected (it can be either on the slave side and
on the master side, depending on the fiber or on the jumper you are
verifying), disconnect it and measure the input power Pin coming out of
the port. Calculate the fibre attenuation A due to the fiberoptics cable: Af
[dB] = Pin – Pout
a. If Af > 10 dB, then the fibre optic cable has some problems. Replace it
with a new one.
b. If Af < 10 dB troubleshooting procedure has not identified the
problem. Refer to supervision system or contact the manufacturer for
assistance.
TSRX3xx/8 module troubleshooting
Ordinary troubleshooting procedures which can be carried out on TMRX200
module first involve a check of the optical adapters status and of the
fiberoptics cables. If the alarm status still persists, a reboot of both the TMRX-
500 module and of the TSRX3xx/8 module can be performed so as to re-
inizialize the link.
Quick TSRX3xx/8 troubleshooting procedure
In case the red LED is ON, please follow these steps:
1. Clean the optical adapter
2. If the problem still persists, refer to the fibre optic troubleshooting so as to
check if the optical cable or optical connection has any problem.
3. If previous actions didn’t make the LED switch off, a reboot of both the
TSRX3xx/8 module and of the TMRX500 module (on the master side) could
be performed so as to test modem connectivity.
4. If the red LED still remains on, please check the alarm status by the LMT or
the supervision unit in order to better understand the problem and its
possible solution.
TILx-
-
HLW
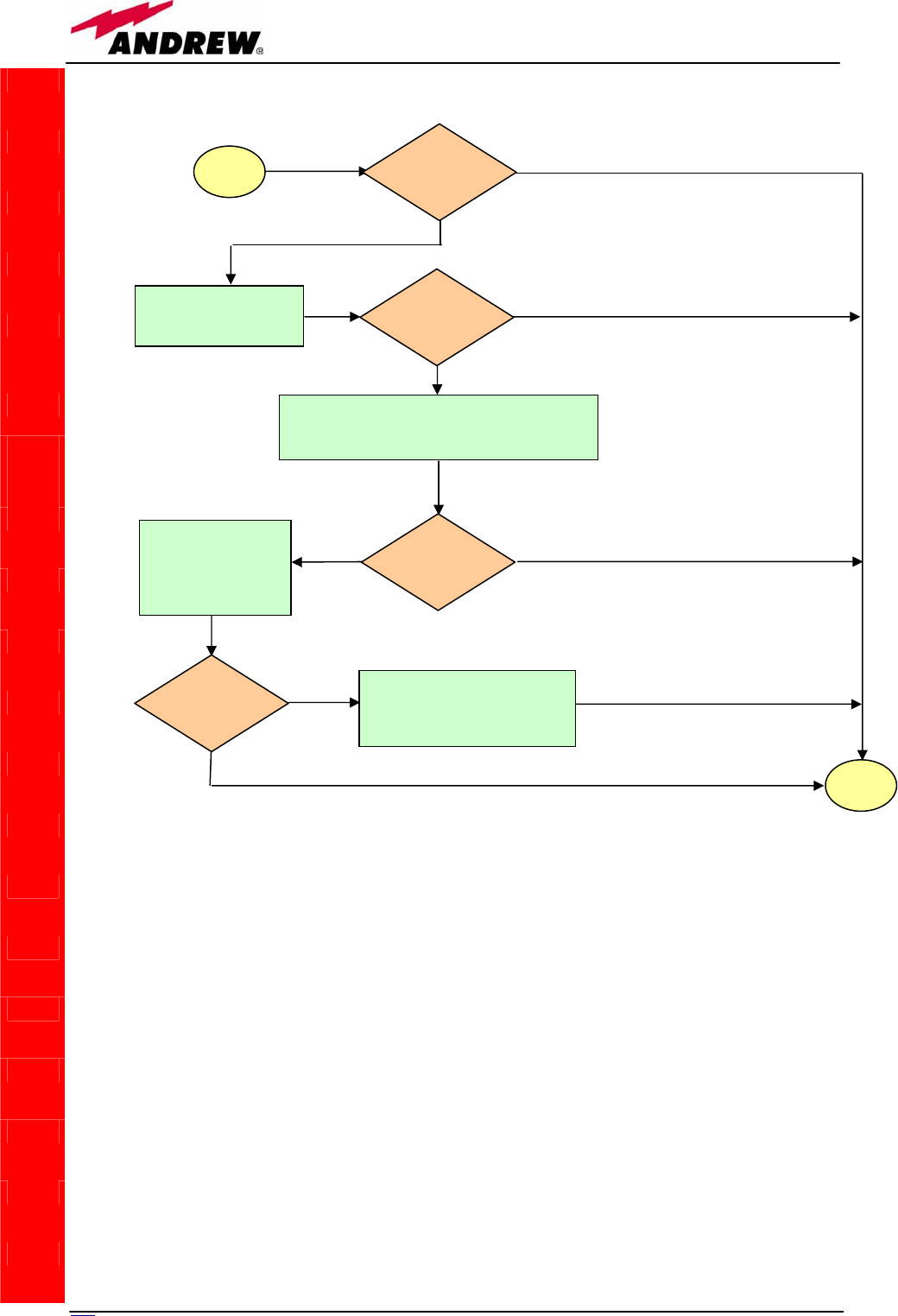
212 User Manual
TILx-
-
HLW
Fig. 5.40a: Flow-chart describing the quick TMRX500 troubleshooting.
sta
r
t
Is the red LED
ON upon the
TMRX 500?
Yes
No
Clean the SC-APC
optical adapter and
connecto
r
No
Yes
end
Is red LED upon
TMRX 500 still
ON?
Optical cable, optical jumper or optical connections
may have some problems. Refer to TMRX/TSRX
fiberoptic troubleshooting (fig. 5.40b)
Yes Is red LED upon
TMRX 500 still
ON?
No
Reboot both the
TMRX 500 module
(on i-link master side)
and the TSRX-347/8
(on i-link slave-side)
Is red LED upon
TMRX 500 still
ON?
Quick troubleshooting procedure
has not identified the problem.
Refer to supervision system or
contact the manufacture
r
Yes
No
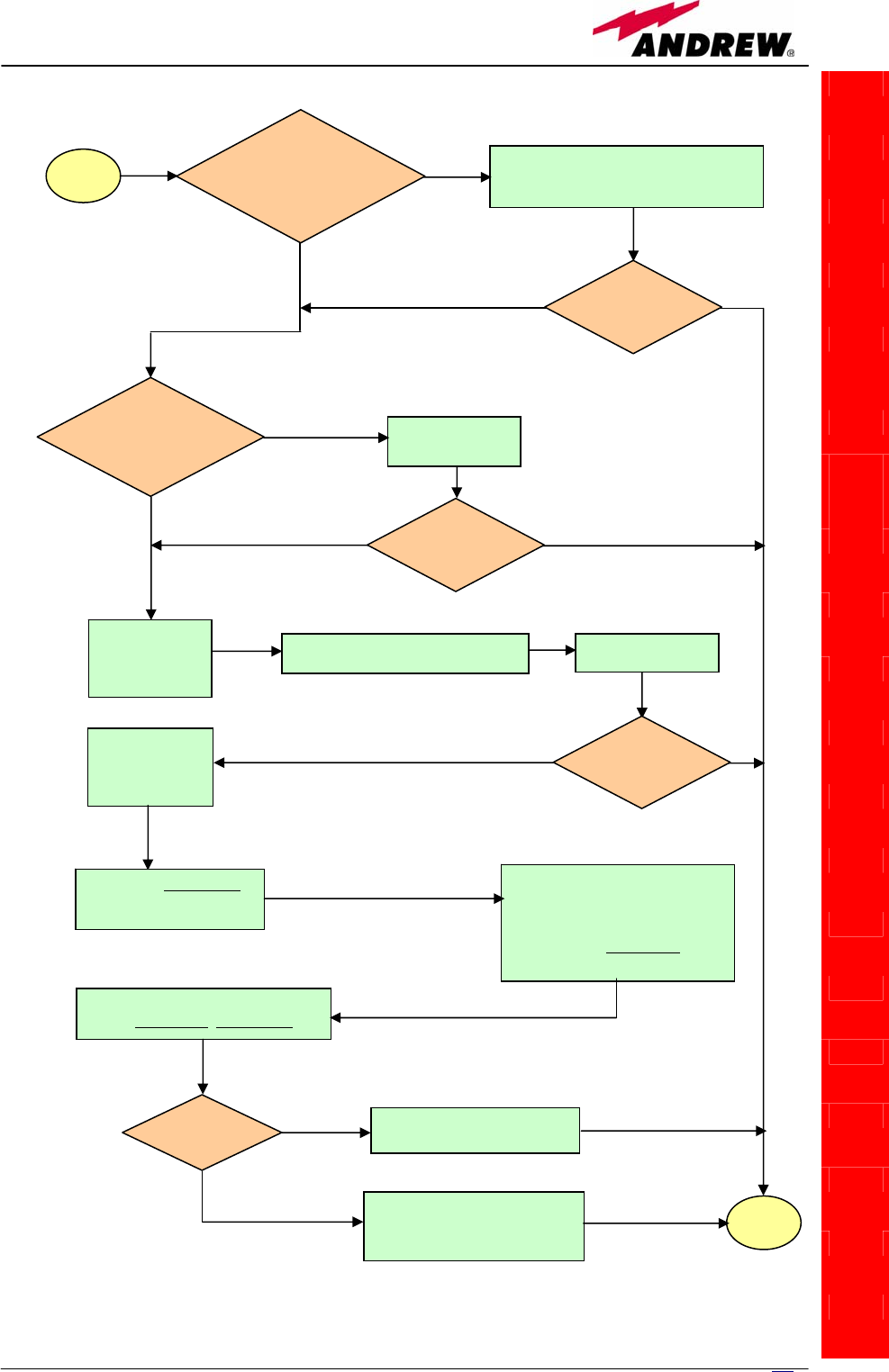
213
MN024-08
TILx-
-
HLW
Fig. 5.40b: Flow-chart describing the TMRX/TSRX fiberoptic troubleshooting.
start
Is there any point
where the fibre
experiences a small
radius of curvature?
Rearrange the optical path to avoid sharp
bends. If necessary replace the optical
cable with a lon
g
er one.
Is red LED
upon TMRX/TSRX
still ON?
Are SC-APC
connectors properly
installed at both fibre ends? Fix better SC-
APC connectors
Yes
No
No
Yes
No
Yes
No
Yes
Disconnect the
optical SC-APC
connector from
TMRX/TSRX
Clean the optical SC-APC ports
corresponding to both the fiber ends
Disconnect the
fiber optic cable
and clean it at
b
oth ends.
Reconnect the fibre
to relevant ports
Measure the output power
at corresponding fibre end.
Connect the adapter again
Go to the module where the other
end of the fiber is connected,
disconnect the corresponding SC-
APC connector , and measure the
corresponding input power. Then
connect the adapter again.
Calculate fibre attenuation
A[dB]=input power - output power
Is A > 10dB? Fibre optic cable has some
p
roblems. Re
p
lace it.
Quick troubleshooting procedure
has not identified any problem
on the fiber optics cable
end
No
Yes
No
Yes
Is red LED
upon TMRX/TSRX
ON?
Is red LED
upon TMRX/TSRX
still ON?
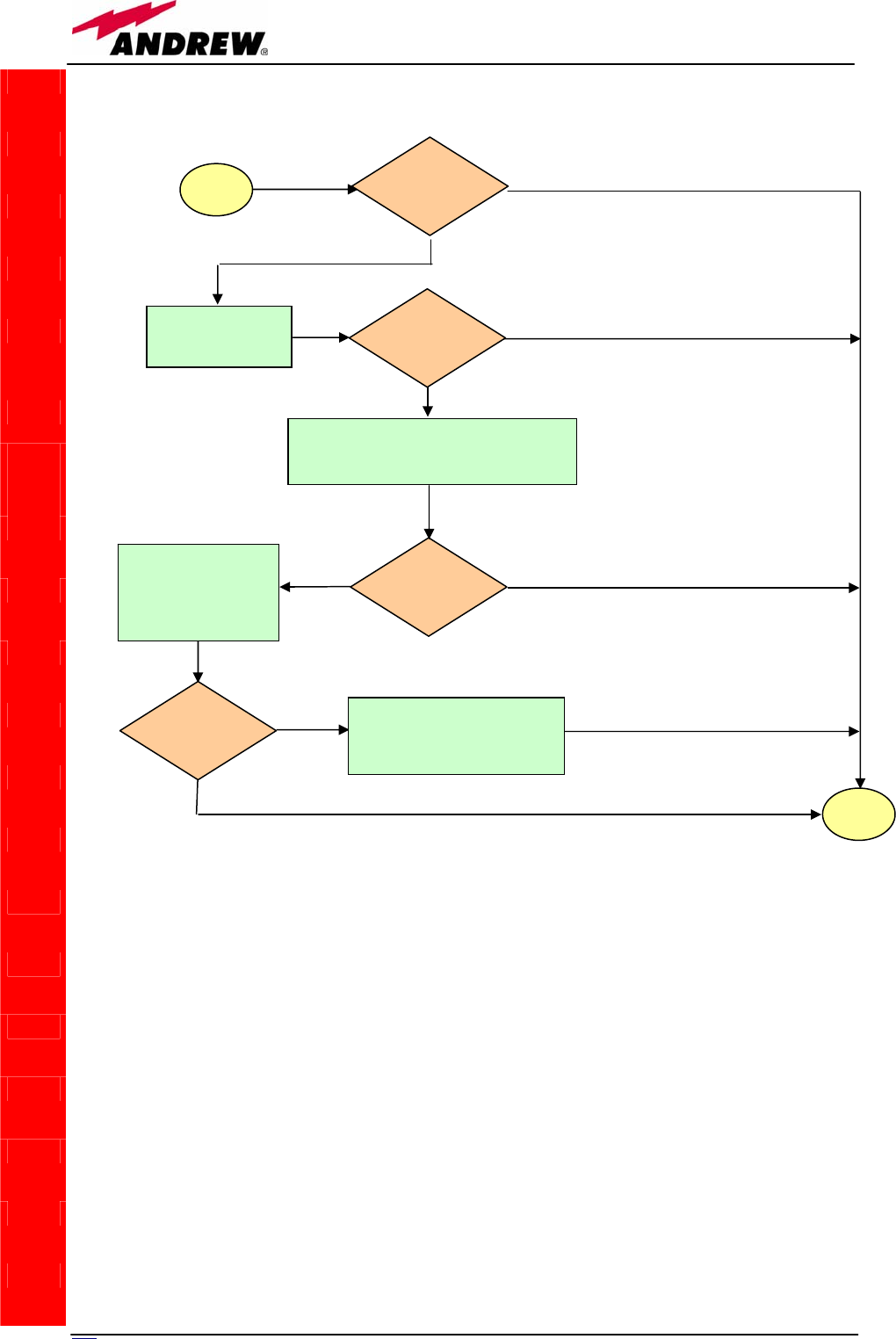
214 User Manual
TILx-
-
HLW
sta
r
t
Is the red LED
ON upon the
TSRX 2xx/8?
Yes
No
Clean the SC-APC
optical adapter and
connecto
r
No
Yes
end
Is red LED upon
TSRX 2xx/8
still ON?
Optical cable or optical connections may have
some problems. Refer to TMRX-TSRX
fiberoptic troubleshooting (fig.5.40b)
Yes Is red LED upon
TSRX 2xx/8
still ON?
No
Reboot both the
TSRX-2xx/8 module
(on i-link slave side)
and the TMRX-200
(on i-link master-side)
Is red LED upon
TSRX 2xx/8
still ON?
Quick troubleshooting procedure
has not identified the problem.
Refer to supervision system or
contact the manufacture
r
Yes
No
Fig. 5.40c: Flow-chart describing the quick TSRX3xx/8 troubleshooting.
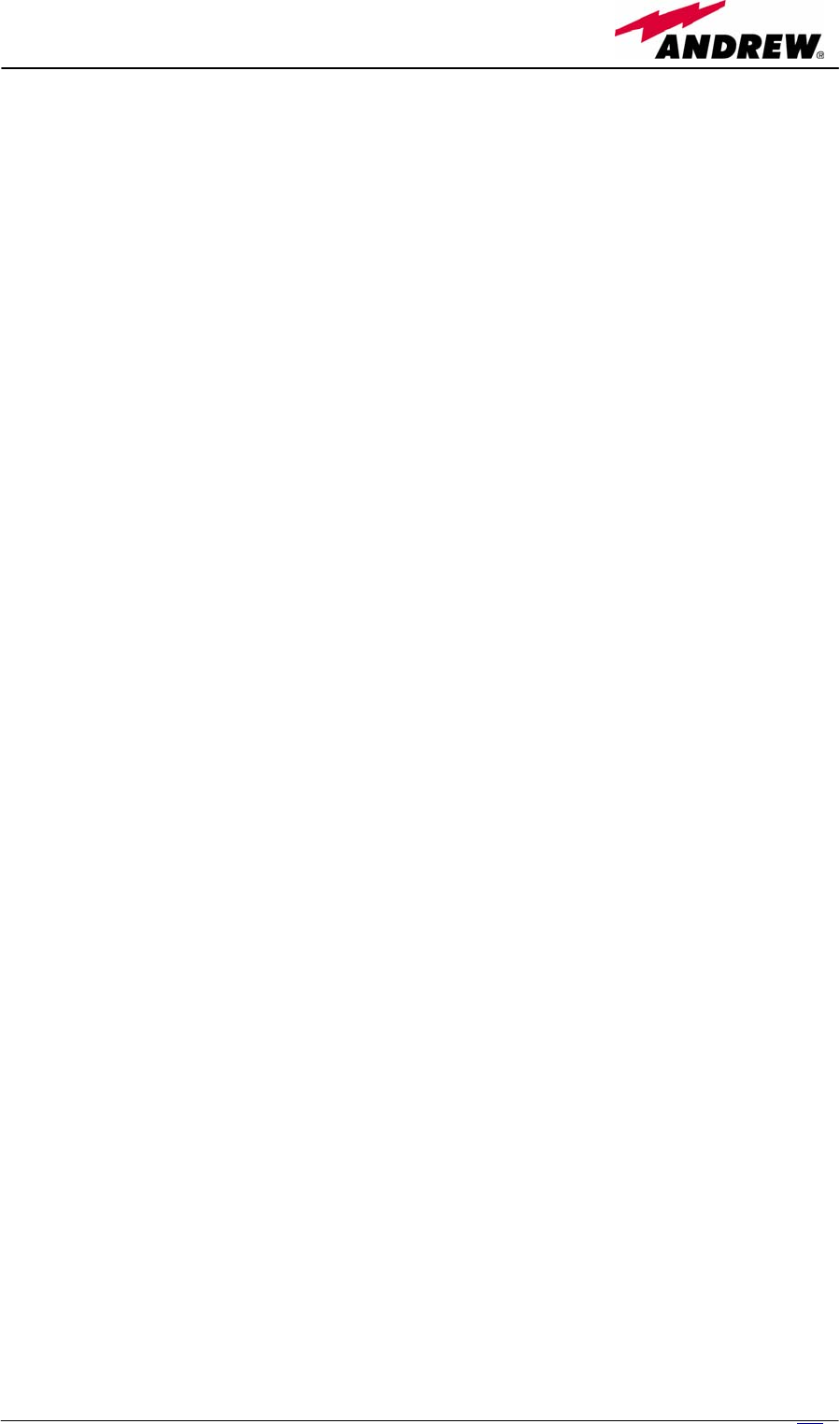
215
MN024-08
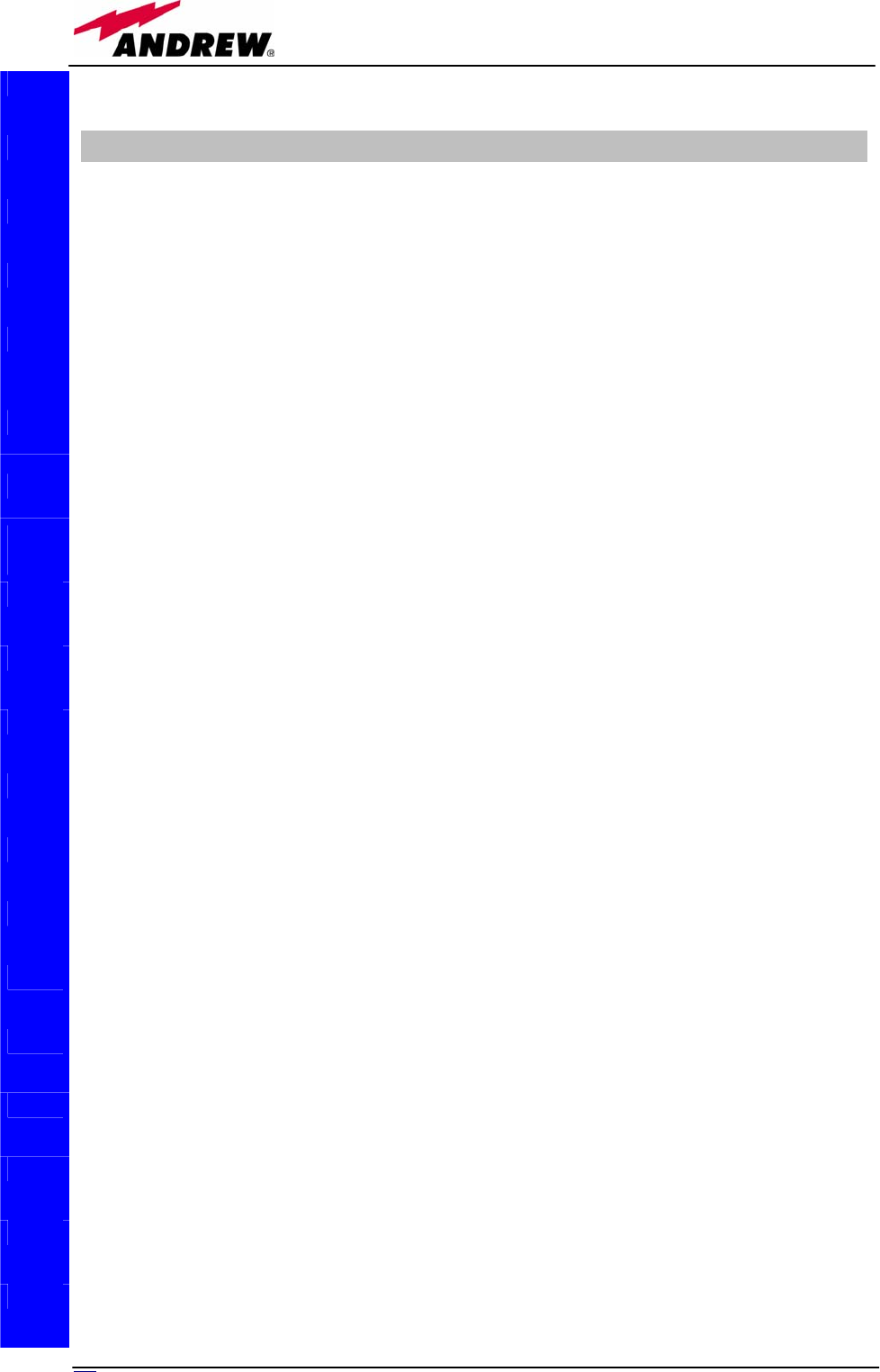
21
6
User Manual
5.11. Remote Supply TRS/TRSN
TRS
TRSN
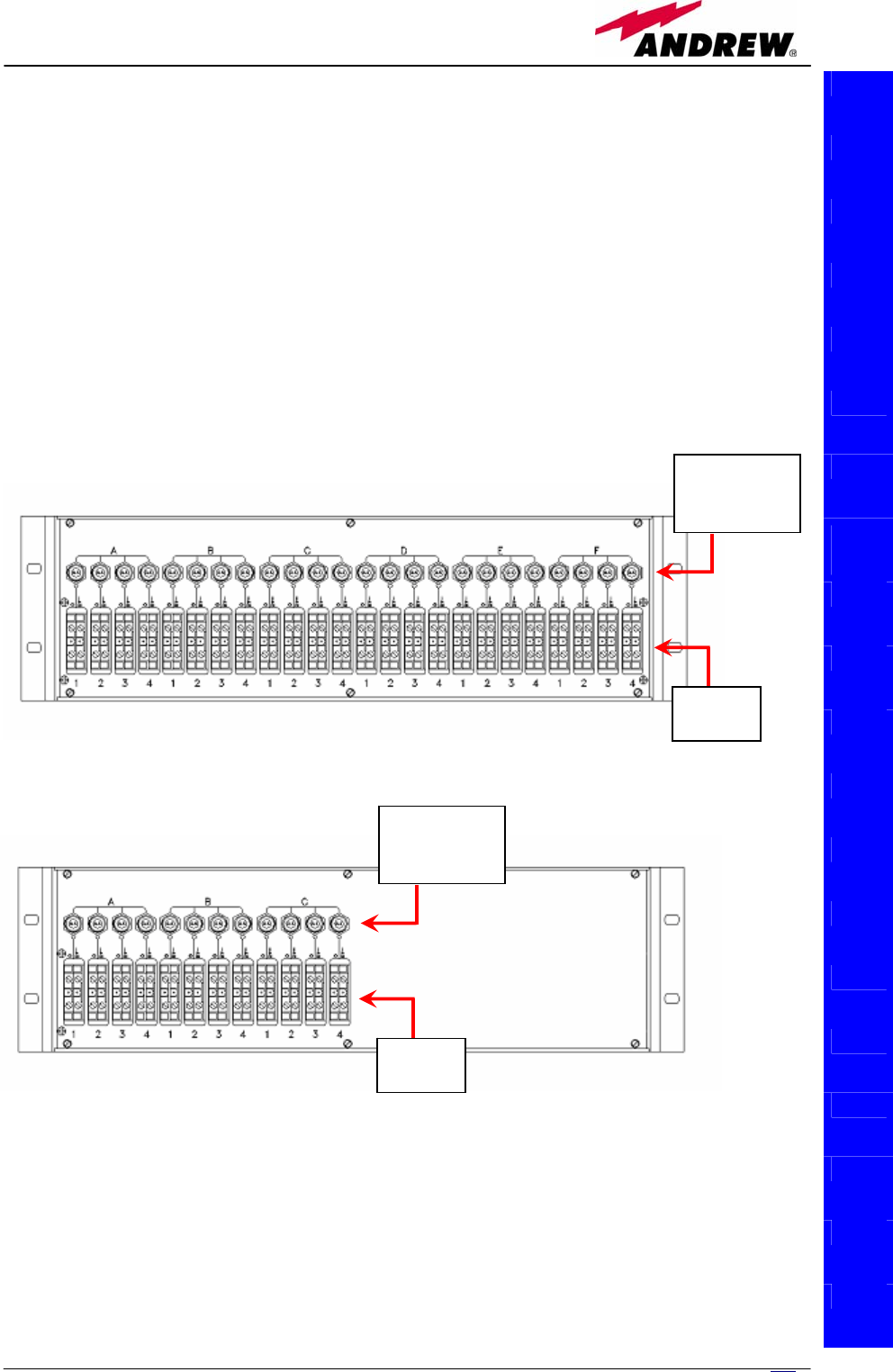
217
MN024-08
The TRS/TRSN is a sub-rack unit which provides remote supply to up to 24
remote units, by means of dedicated outputs with short-circuit protection
switches.
It is available in 2 versions. The TRSN version is able to supply 1 A per port
and it can feed all remote units. The TRS version is able to supply 0.5A per
port: it can feed only single and dual band TFAN remote units, as well as the
TFAM20 one.
The TRS/TRSN unit provides DC power supply to the remote units through
standard AWG14/16 copper lines. Maximum allowed distances depend on the
section of these copper lines, on the remote unit current consumption, and on
the voltage range.
TRS
TRSN
(
a
)
(
b
)
Fig. 5.41. (a) Front panel of a TRSN or a TRS sub-rack provided with 24 power supply
outputs. (b) Front panel of a TRSN sub-rack provided with 12 power supply outputs.
Short-circuit
protection
switches
Power
out
p
uts
Short-circuit
protection
switches
Power
outputs
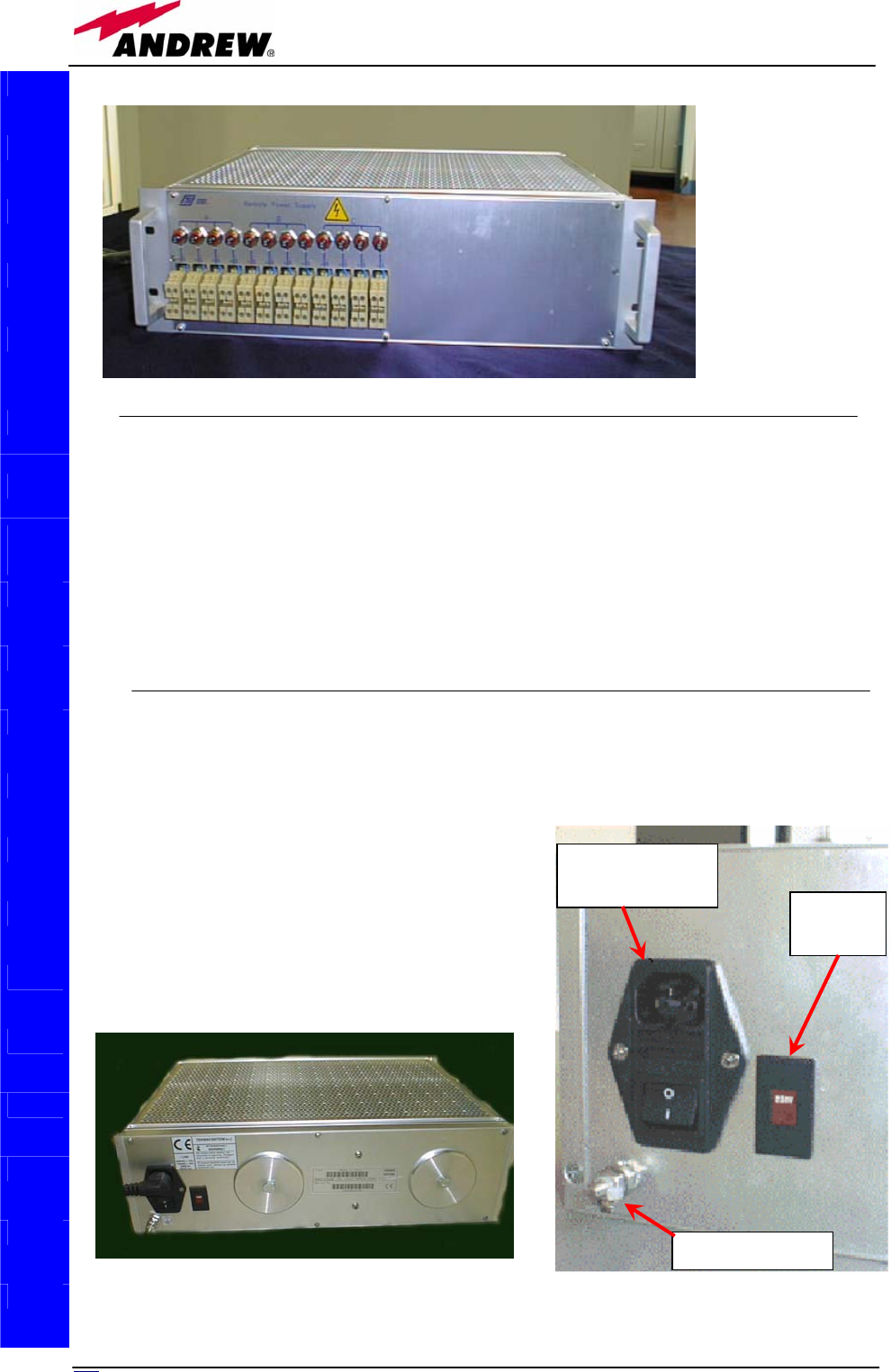
218 User Manual
Ports
The TRSN version (suitable to all types of remote units) is available with
• 12 supply outputs
• 24 supply outputs
It can supply 1 A per port.
The TRS version (suitable to single and dual band TFAN remote units and to
TFAM20) is available with 24 supply outputs. It can supply 0.5 A per port.
Power supply
Both the TRS and the TRSN subracks can be feeded either by 115 Vac mains
or by 230 Vac mains (50/60Hz). The proper
feeding voltage has to be selected through a
voltage selector which is placed on the back
panel, near the mains connector .
Thanks to the active distribution system
(please refer to the electrical scheme in fig.
5.45a), a -48 Vdc power supply be conveyed
to the remote units connected to the output
ports.
TRS
TRSN
Fig. 5.42. Picture
of 12- output
TRSN subrack.
Voltage
selecto
r
Ground screw
Mains
connector and
Fig. 5.43. Picture of the rear side of the TRS/TRSN subrack feeded by 115Vac-230Vac mains (a).
Mains connector, fuse, voltage selector and ground screw on the TRS/TRSN rear panel(b).
(a) (b)
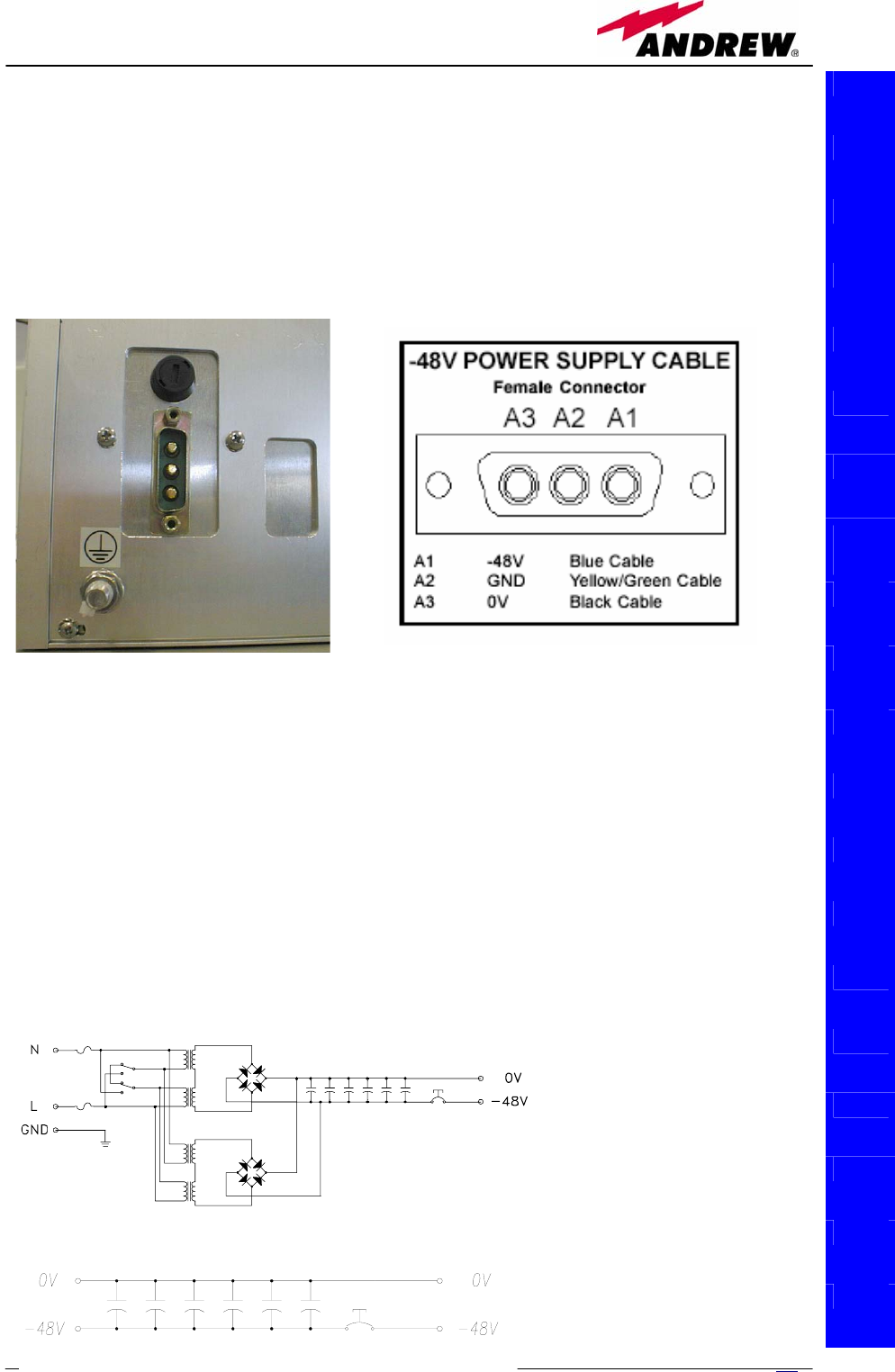
219
MN024-08
The TRSN subrack is also available in passive version TRSNx-3, which can be
feeded by direct current (–72 to –36 Vdc). In this case, the -48 Vdc current is
conveyed to the remote units thanks to a passive distribution system (please
refer to fig. 5.45b).
Please read carefully the cabling instructions in order to connect the provided
power cable to the poles of the -48 Vdc connector properly (see fig.5.44b).
Ground terminals are part of the power supply connectors. External grounding
terminals (screw) are also available (see fig. 5.43a,b)
Mains connectors also house the following fuses:
• 250V, 4A delayed type for the active version (feeded by 115 Vac mains
or by 230 Vac mains)
• -48V, 15A delayed type for the passive version (feeded by -48 Vdc
supply)
TRS
TRSN
Fig. 5.44. (a): Power supply connector, fuse, voltage selector and ground screw on the the rear
side of the TRSN subrack feeded by -48 Vdc current TRS/TRSN rear panel. (b) Cabling
instructions for the -48 Vdc connector
(b)
(a)
(
a
)
Fig. 5.45.
(a) Active distribution system used
by a TRS/TRSN subrack feeded by
115Vac-230Vac mains
(b) Passive distribution system used
by a TRSN subrack feeded by a -48
Vdc power supply,
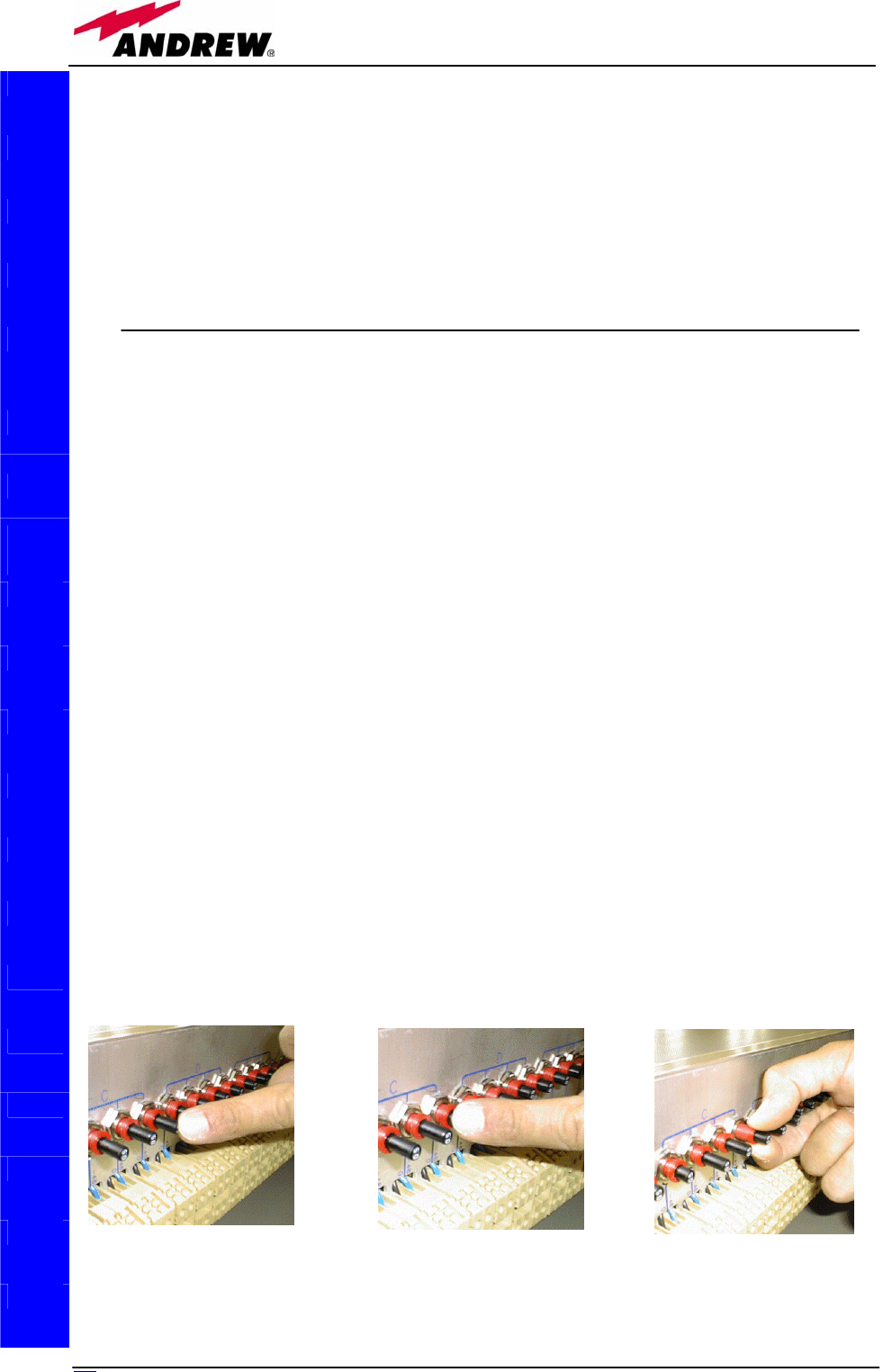
220 User Manual
Warnings
• Caution: do not open the unit before disconnecting the mains. Internal
assemblies can be accessed by qualified personnel only.
• Do not connect supply outputs to remote units before switching off the
unit or disconnecting the mains.
Being a DC supply provided, a wrong connection can damage the remote
unit. Verify the proper polarity before switching on the equipment
TRS/TRSN installation
The TRS/TRSN sub-rack should be placed as close as possible to the TPRN to
allow an easy cabling in case of mixed fibre-copper cables. If the sub-rack
mounting location is not provided with a good air circulation, leave at least
one unit free between sub-racks.
The kit includes
• 1 TRS/TRSN
• 1 power cable
To install the TRS/TRSN remote supply unit follow next steps:
1. Fix the TRS/TRSN sub-rack to the cabinet with 4 screws
2. During the installation phase don’t connect the power cable to the main
power line and don’t switch on the TRS/TRSN
3. Set the switch in accordance with your main power line (115 Vac or 230
Vac) for universal mains option. In case of negative supply option (-48
Vdc), no switch is provided. Then connect the ground screw.
4. Before connecting the wires from TRS/TRSN to the remote units, open all
the fuses pulling the red circle then connect electrical wires for the remote
units (5.46c)
5. When all electrical wires have been connected and the system is ready to
start, connect the power cable, switch on the TRS/TRSN. Push one fuse at
a time (5.46b).
Each remote unit can be switched on/off by the relevant switch. The Pictures
5.46 below show how to do it.
TRS
TRSN
Fig. 5.46 Short circuit protection switches. (a): OFF position . (b): ON position: push down the
black button. (c): Pull out the red collar in order to switch off.
(
a
)
(
b
)
(
c
)

221
MN024-08
If a surge or an overloading condition occur the switch automatically jump into
an OFF position.
TRS/TRSN behaviour at start-up
• Check if power supply voltage selector is in the correct position (115 or 230
Vac). In passive distribution version this selector is not present.
• Have all the switches in off position
• Check the connection polarity is not wrong
• Power on the TRS/TRSN unit through the back general switch
• Power on each remote unit through the front panel switches
• Check if the remote units shows the proper green supply led on
TRS/TRSN troubleshooting
If the remote unit doesn't appear to be properly supplied:
• Check the fuses on the rear panel
• Check the voltage at the front panel screw connectors: nominal value
without load is -59Vdc, nominal value with full load is -48Vdc. If those
values are exceeded by 10% check if the mains are within the allowed
limits. In passive distribution version, the output voltage depends on the
supply source.
• Check the voltage at the remote side it should be in the range -36 to -72
Vdc that is the maximum allowed range admitted by the remote units.
If the protection switch jump always in OFF position
• Check if there is any short on the line
• Check if the remote unit shows the nominal current power consumption
• Check if there was any long period overshooting related to the mains
supply.
If the fuses blow up after a power-on with all the front switches on, there
should be a too high initial peak current transient: check the proper fuse
(delayed type) or substitute with an higher current fuse (i.e. 6A or 10A). If the
problem still persists check the proper ground /mains connection.
TRS
TRSN
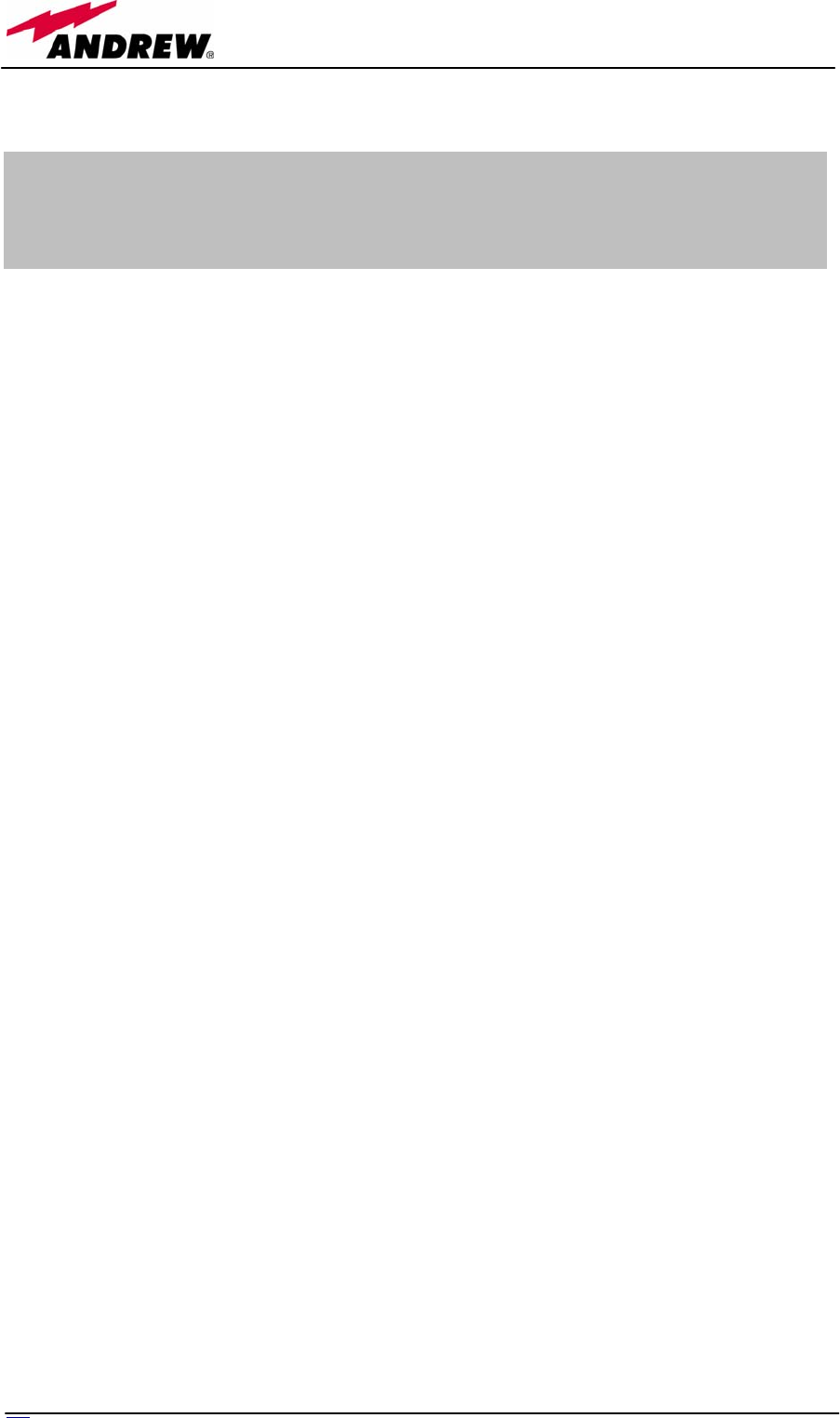
222 User Manual
6. Warning
and Safety Requirements
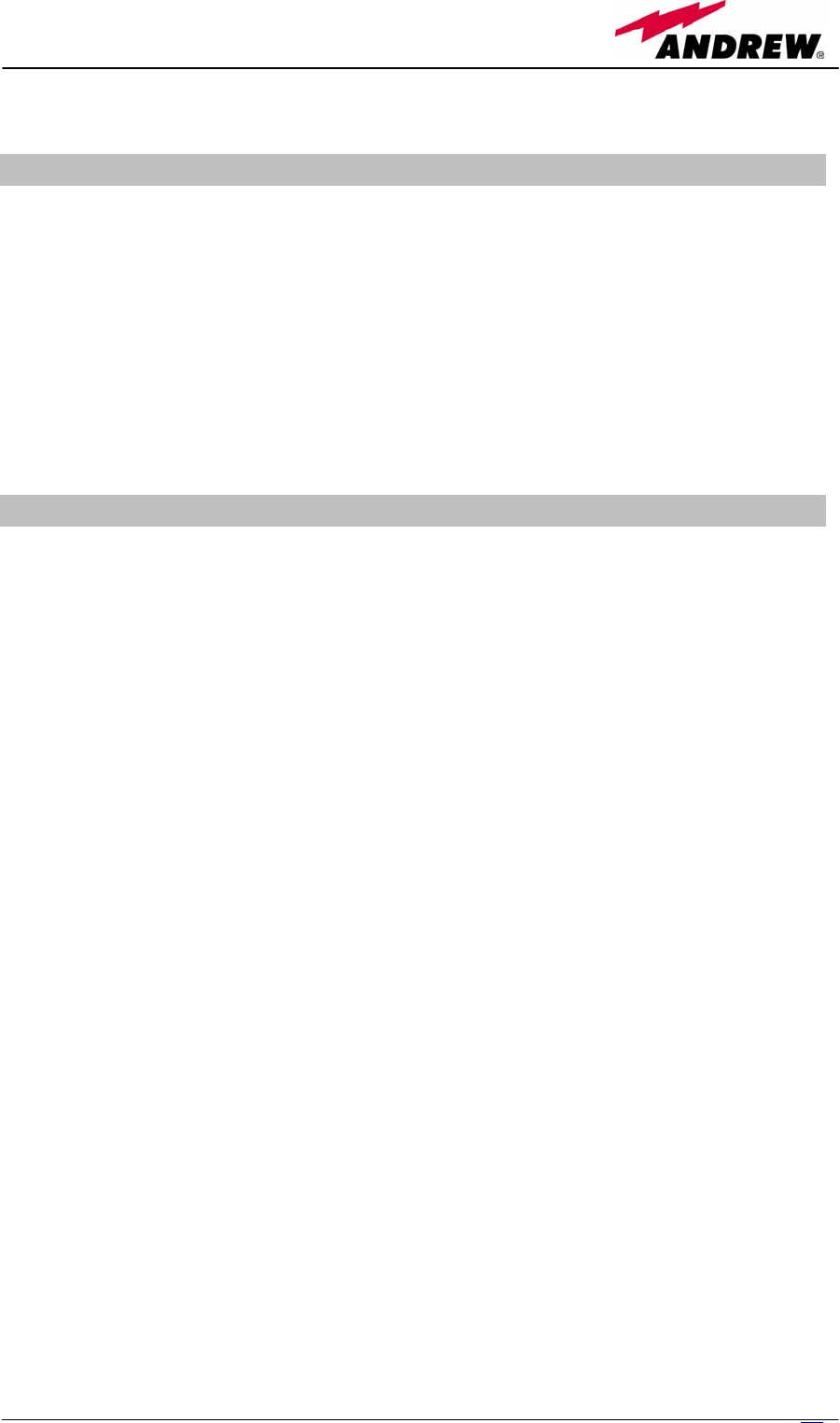
223
MN024-08
6.1. Environmental Conditions
This equipment is designed to be installed in indoor environments.
Operating temperature: +5 to +40°C (for all the pieces of equipment,
except remote units case L)
-20 to +50°C (only for remote units case L)
Do not install in corrosive atmosphere or in critical environmental conditions
such as hazardous classified areas (1).
6.2. Installation Site Features
A trained technician should carry out the installation of the master unit. Since
the system is designed for indoor installation, the master unit should be
installed in a dry and suitable location where:
• no explosion risks is present;
• the environment is not classified as a high-risk one in case of fire;
• suspended particles are not to be found in great concentration;
• the environment is not subject to any traffic which could cause crash
damages;
• the site is properly located with respect to the ergonomic positioning of the
working environments;
• the system is placed in a private room, protected against any possible
violation;
• do not install the system in direct sunlight or in place where water may
drop on the device (for example under air-conditioning equipment).
• the site must be accessible by maintenance personnel;
• the site must be dry, with low humidity;
• the site must guarantee proper space for cables and natural ventilation to
the system;
• 2 meters must be kept between the rack and any heating opening.
The remote units should be mounted in reasonable locations as well:
• do not install remote units inside heating or conditioning;
• do not install remote units inside cable pipeline or fire-prevention site (fire
escape, lift tunnels, emergency exits, which have to guarantee defined
safety standards);
• keep into consideration that the temperature in the upper part of a room is
higher than at 2 meter height. For false ceiling installation of case-A and
case-B remote units, verify that the environment temperatures do not
exceed allowed limits;
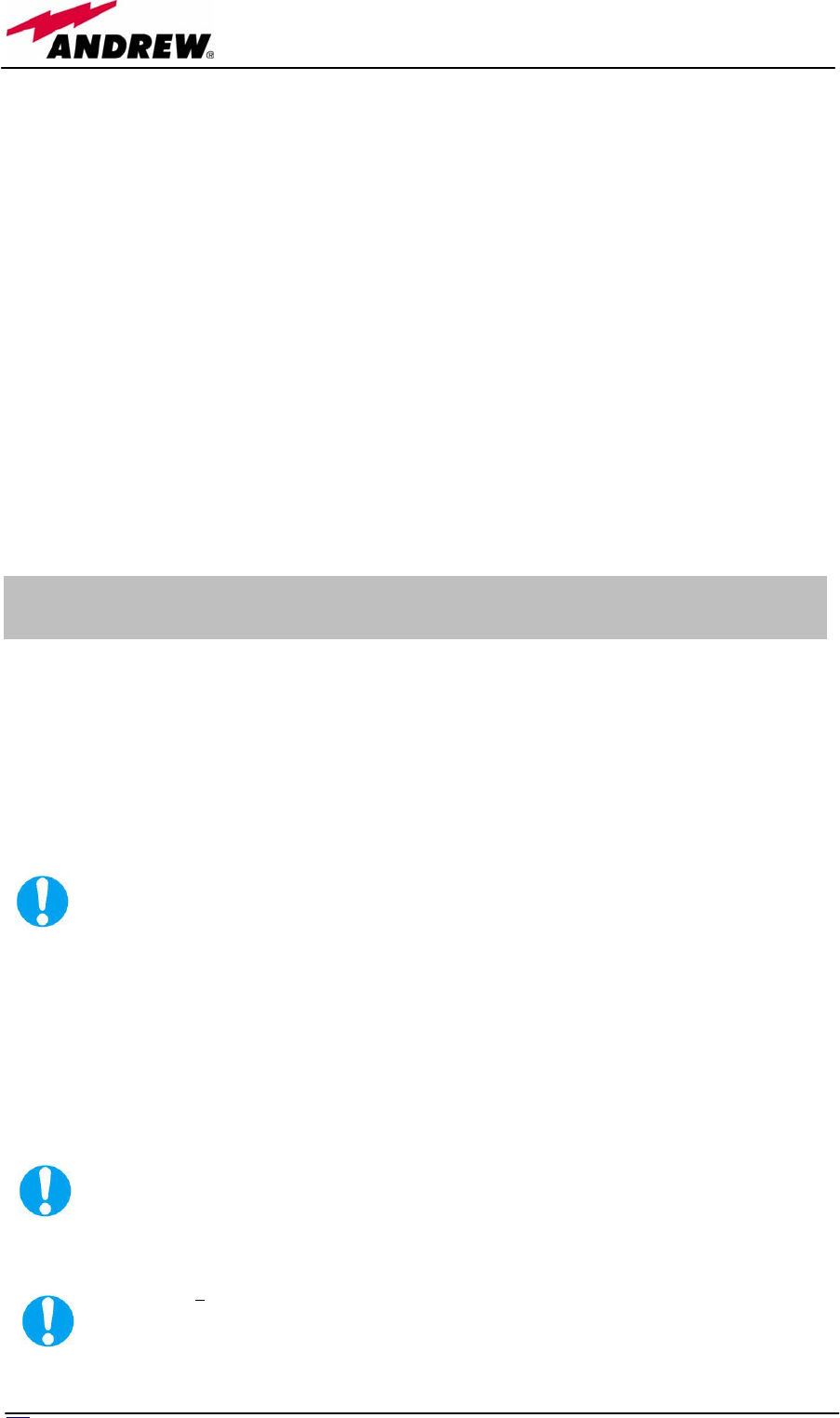
224 User Manual
• each remote unit requires its own power and a connection to the mains can
be needed;
• keep into consideration that each remote unit transmits RF signal and
safety volume must be respected (refer to country regulations for safety
volume magnitude);
• remote units must be mounted according to what specified in the relevant
installations instructions;
• Weight and dimensions of case-L and case-F remote units should be
carefully considered when choosing the installation site and positioning.
During any installation step, please consider the potential risk of any
equipment drop off
• When choosing the installation site and position, please consider that any
remote units must be accessible for tests and maintenance.
(1) Hazardous locations are those areas "where fire or explosion hazards may
exist due to flammable gases or vapours, flammable liquids, combustible dust,
or ignitable fibres or flyings"
6.3. Safety and Precautions
during Installation or maintenance
During installation the following means and tools will be needed:
Typical electrician tools:
cross-point screwdriver, scissors, pliers, nippers, drill and bits, screws for
fixing remote units to the wall.
Typical means:
proper ladder, scaffolding or air platform for installation of remote units.
CAUTION: some modules are electrostatic-sensitive devices;
electrostatic discharges are caused by direct contact or by an
electrostatic field. If a charged body approaches an electrically
conducting surface, the acquired potential is discharged. An
equalising current can than flow in the associated circuitry and
generate permanently damaging voltages by induction.
The human body should be grounded at the same potential as
the component or equipment being handled. A wrist strap creates
an equipotential electrical connection between the object and the
human.
CAUTION: Do not paint or otherwise coat Britecell Plus
equipment.
CAUTION: Great caution should always be used when installing any
equipment at a height upper than 2 meters. Personnel who are
installing this equipment should be informed about the possible risks
and safety measures when elevated.
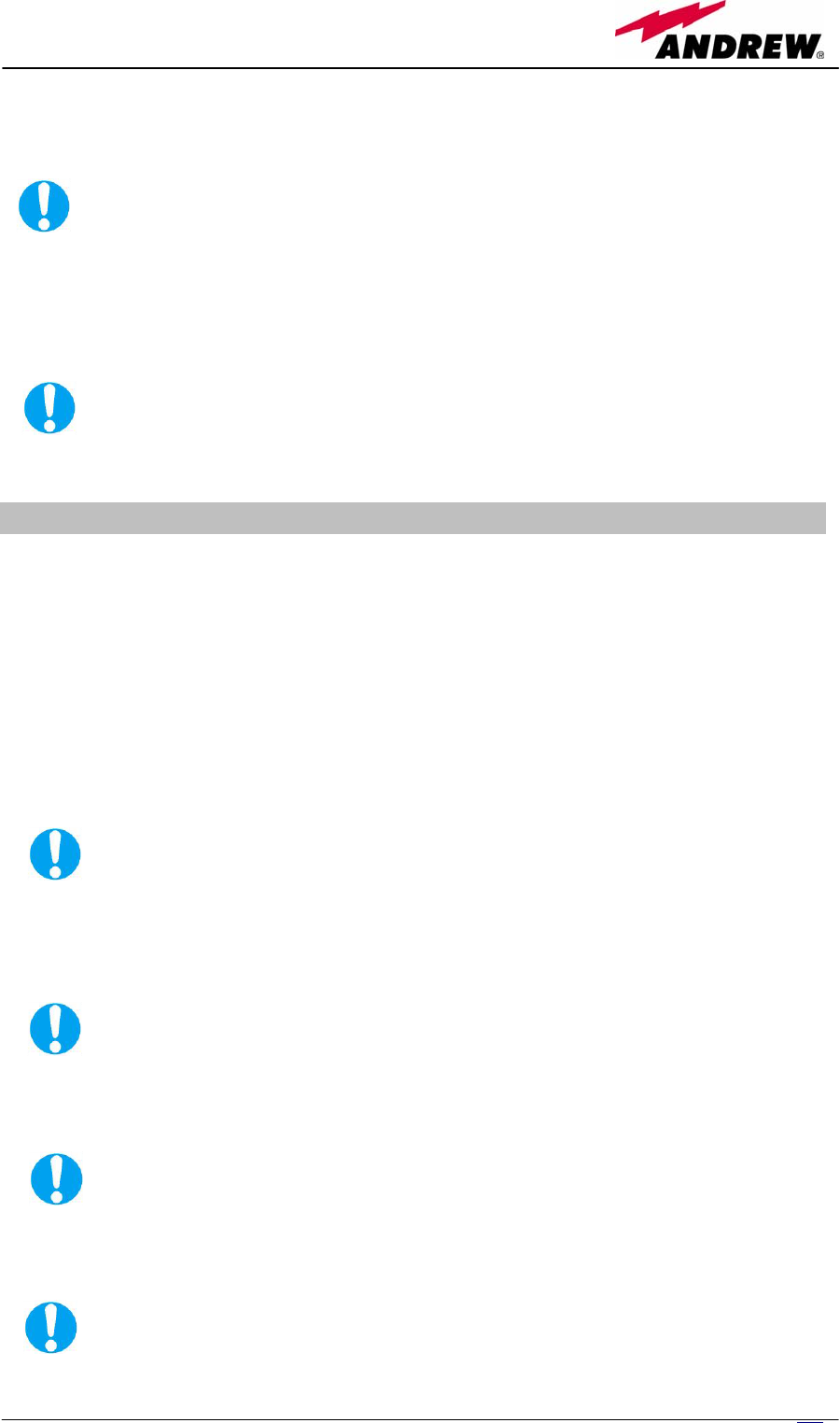
225
MN024-08
CAUTION: Case-F and Case-L remote units are provided with
some door panels which have to be managed with care during
installation or maintenance operations.. Always switch off the
remote while working with the panel opened. When closing the
panels, take care not to leave any tool inside the equipment, not
to hurt your fingers, and not to trap clothes, bracelets, chains, or
long hair.
Never remove the cover from a TFAx remote unit or from a TPRN
subrack when the power supply is ON.
6.4. Power Supply Connection
Power connection has to be carried out following all necessary precautions:
• it must be properly made according to the due diligence rules (ex.: EN
rules, IEC rules, etc.);
• in accordance with the rules for safety against direct or indirect contacts;
• in accordance with the rules for safety against the over current (short
circuit, overloading);
• in accordance with the rules for safety against over voltage;
• connection is to be carried out by proper and competent staff
CAUTION
In North America this equipment is to be installed in accordance
to National Electric Code (NEC) ANSI/NFPA 70 and Canadian
Electric Code (CEC) Part 1, C22.1.
CAUTION
Do not remove or insert any module into the TPRN sub-rack
without prior switching power supply off.
CAUTION
Do not connect AC power until you have verified that the line
voltage is correct.
Do not remove the plastic cover of the external power supply
adapter.
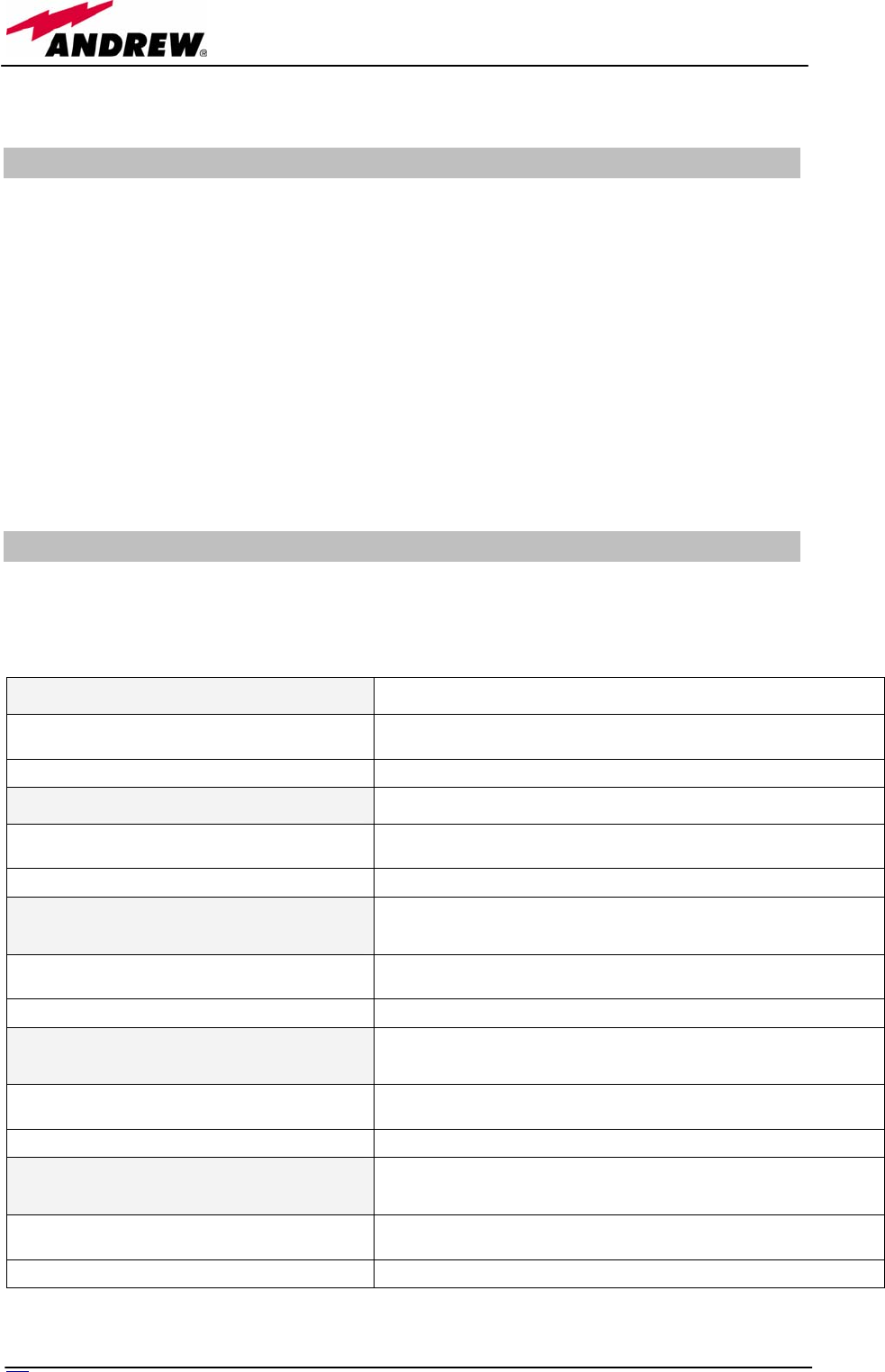
22
6
User Manual
6.5. Safety and Precautions for Lasers
The optical transmitter used in Britecell Plus contains a laser which has a
power level that is not dangerous for health. However it is classified as class 1
equipment (in accordance to EN60825). It is nevertheless prudent in the
installation phase to observe the following rules:
• Never look directly inside the optic connector exit of the transmitters when
it is switched on. The wavelength of the laser is not visible to the human
eye, which means that long-term damage will not be immediately known.
• When working with the optical connectors, check at each end that both
transmitting lasers are switched off.
6.6. Health and Safety Warnings
Antenna installation must conform within the following guidelines to meet FCC
RF exposure limits, otherwise an environmental evaluation is required if:
Broadband PCS (subpart E):
Non building mounted antennas: Height above ground level to lowest point of antenna< 10m Radio (Part 24) and total
power of all channels > 2000 W ERP (3280 W EIRP)
Building-mounted antennas: Total power all channels>2000W ERP (3280W EIRP)
Narrowband PCS (subpart D):
Non-building-mounted antennas: Height above ground level to lowest point of antenna < 10m Radio (Part 24) and
total power of all channels > 1000 W ERP (1640 W EIRP).
Building-mounted antennas: Total power of all channels > 1000 W ERP (1640 W EIRP).
Cellular Radiotelephone Service (Part 22,
subpart H):
Non-building-mounted antennas: Height above ground level to lowest point of antenna < 10m Radio (Part 22) and
total power of all channels > 1000 W ERP (1640 W EIRP).
Building-mounted antennas: Total power of all channels > 1000 W ERP (1640 W EIRP).
Paging and Radiotelephone Service (Part
22, subpart E):
Non-building-mounted antennas: Height above ground level to lowest point of antenna < 10m Radio (Part 22) and
total power of all channels > 1000 W ERP (1640 W EIRP).
Building-mounted antennas: Total power of all channels > 1000 W ERP (1640 W EIRP).
Private Land Mobile Radio\Specialized
Mobile Radio (Part 90):
Non-building-mounted antennas: Height above ground level to lowest point of antenna < 10m Radio (Part 90) and
total power of all channels > 1000 W ERP (1640 W EIRP).
Building-mounted antennas: Total power of all channels > 1000 W ERP (1640 W EIRP).
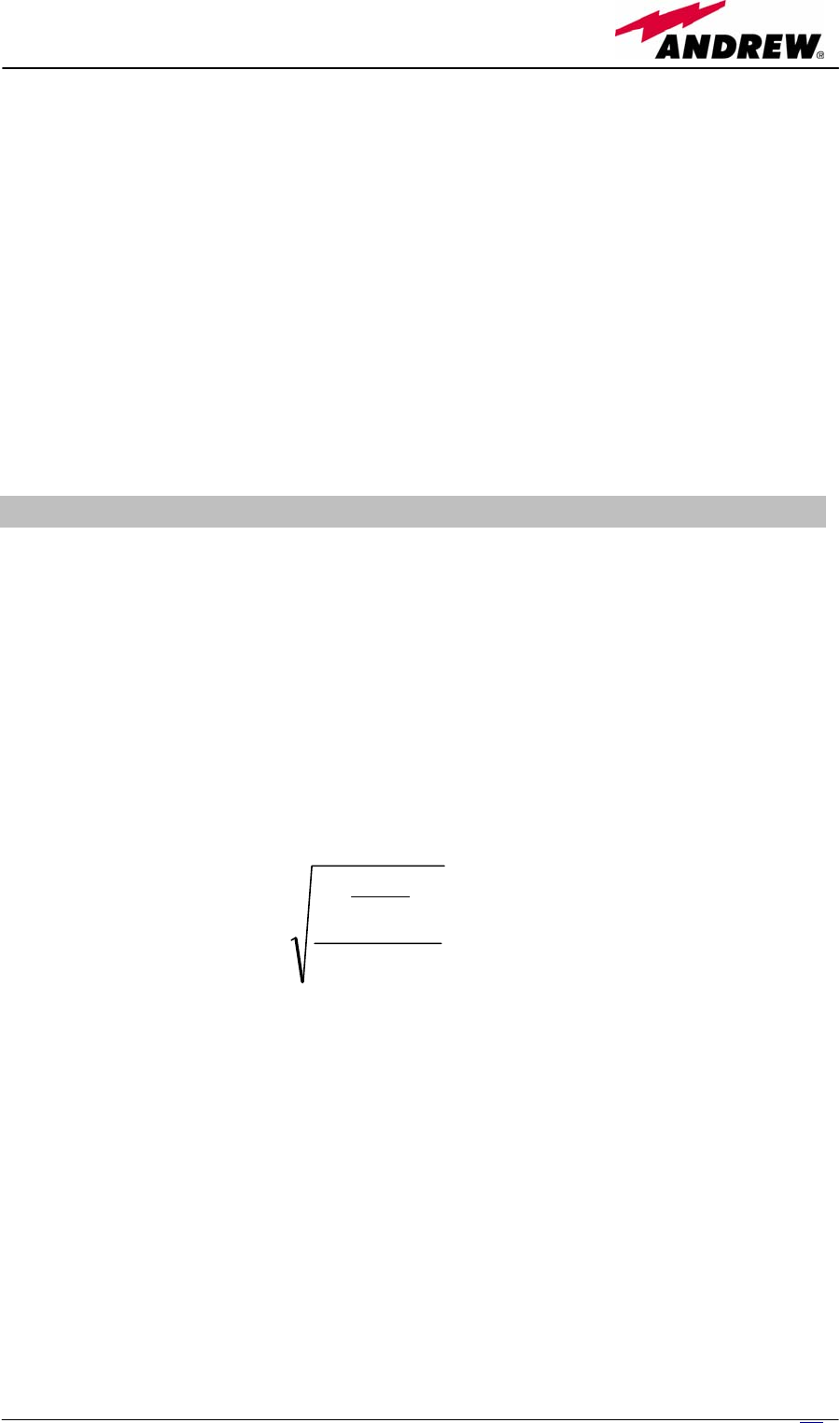
227
MN024-08
To meet RSS Canadian standards the following guidelines has to be taken into
account:
• The manufacturer rated output power of the equipment is for single carrier
operation. For situations in which multiple carrier signals are present, the
rating would have to be reduced by 3.5dB especially when the output
signal is re-radiated and can cause interference to adjacent band users.
This power reduction is to be by means of input power or gain reduction
and not by an attenuator at the output of the device.
• To satisfy RF exposure requirements, the antenna(s) used for the system
must be installed to provide a separation distance of at least 20cm from all
people and the highest antenna gain which can be used is 12dBi.
6.7. Electromagnetic Fields and RF Power
Britecell Plus system generates electromagnetic radiation, which can
exceed safety levels in the immediate vicinity of the antenna.
The most widely accepted standards are those developed by the
International Commission on Non-Ionizing Radiation Protection (ICNIRP)
and the Institute of Electrical and Electronics Engineers (IEEE).
Formula for minimum safety distances
The formula for calculating the minimum safety distances uses the
specifications of a particular antenna that could be driven by TFAx.
()
S
P
r
LG
π
4
10 10
min
−
= (6.1)
This equation includes the following factors:
• G is the antenna gain (in dB) compared to isotropic
radiating antenna;
• P is the RF power that is present at the antenna connector
(in W);
• L is the total loss (in dB) between the TFAx remote unit
output port and the antenna input port;
• S is the maximum allowed power density in air (in W/m2).
Its values should be calculated according to the limit
exposures to time-varying and magnetic fieds. The
reference values are reported in ICNIRP guidelines, unless
otherwise specified by specific regulations.
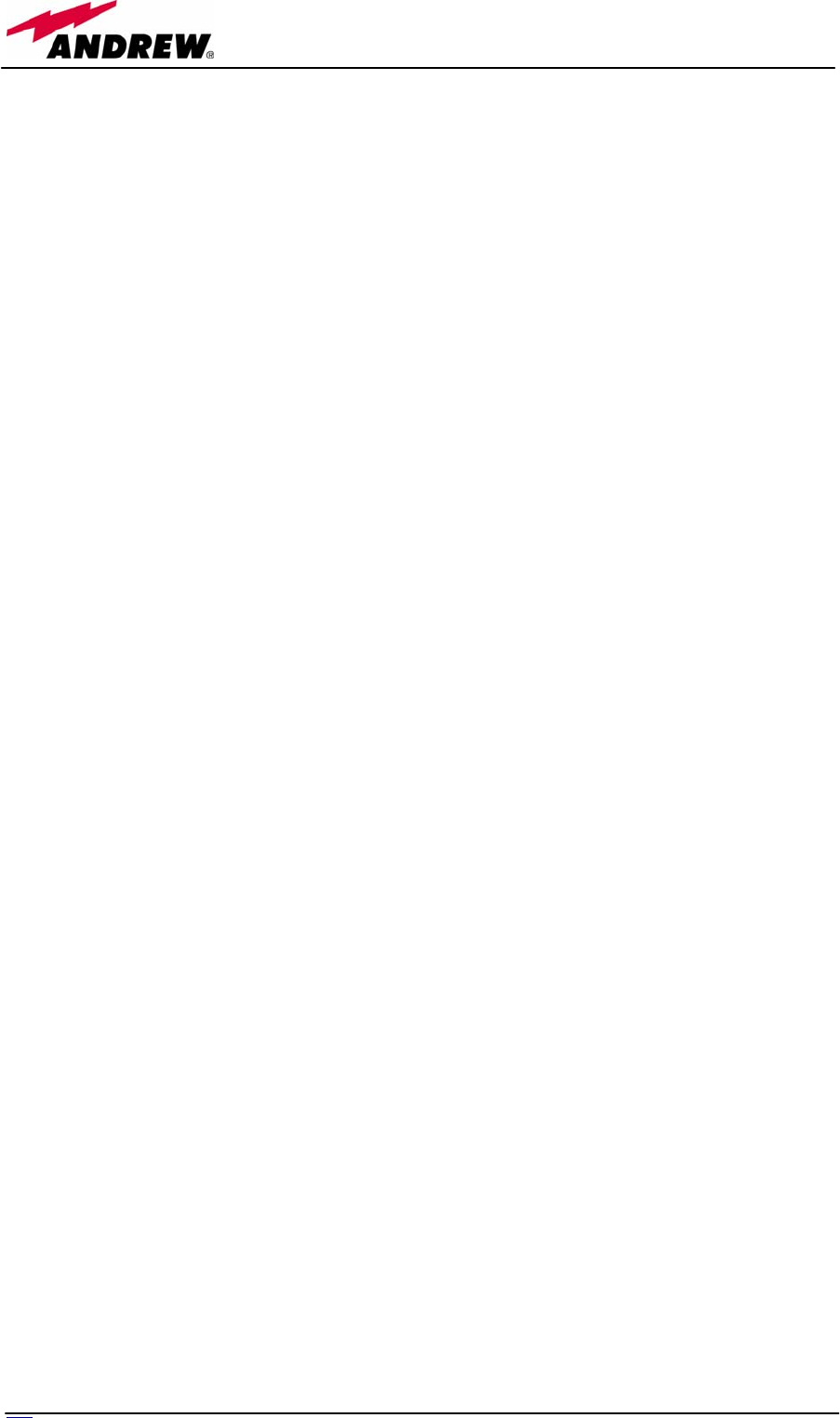
228 User Manual
(please note that, if regulations only define the maximum electrical field
strength and the maximum magnetic field strength, the allowed power
density can be obtained as: S= E2/377= B2·377, where 377 is the
characteristics impedance of the empty space).
Example 1. Let’s suppose to use a High Power TFAH20 to distribute CDMA
signals through a directional antenna, feeded by a 2-metre length RG223
cable (no splitters used). Let’s suppose the antenna gain is 7 dB.
Let’s assume, moreover, that the maximum allowed power density we have to
comply with is: S = 10 W m-2
(typical ICNIRP reference level for general public exposure to time-varying
electric and magnetic fields).
By reading the Britecell bulletin, we know that the output power P at the
TFAH20 antenna port is 37 dBm (=5.012 W). By reading the cable specs, we
get that RG223 cable losses can be estimated as 0.55 dB/m. Total losses
between the TFAH20 output port and the antenna input port can therefore be
estimated as follows:
L = 0.55 (dB/m) x 2 (m) = 1.1 dB
By replacing the above values of G, L, P, S parameters inside the relation 6.1,
we therefore get the the following minimum safety distance from the antenna:
rmin = { 10 · exp [ (7 - 1.1) / 10 ] · 5.012} / (4·π·10) } · exp (-1/2) = 0.394 m
Example 2. Let’s suppose to use a Low Power TFAM85/19 through a
directional antenna, feeded by a 5 -metre length RG223 cable with a 2-way
splitter. Let’s suppose that the antenna Gain is 7 dB and that our Britecell
system distributes one Cellular800 carrier and one PCS 1900.
Let’s assume that the maximum allowed power density we have to comply
with is: S = 50 W·m2
(typical ICNIRP reference level for occupational exposure to time-varying
electric and magnetic fields)
By reading the Britecell bulletin, we know that the output power per carrier at
the TFAM antenna port is 21 dBm (=0.126 W) for the Cellular 850 MHz
frequency band, and 20 dBm (0.1 W) in the PCS 1900 MHz frequency band.
The total output power at the antenna port is therefore P = 0.126 + 0.1 =
0.226 W.
Let’s assume that the splitter insertion losses are 3.5 dB. By reading the cable
specs, we get that RG223 cable losses can be estimated as 0.55 dB/m. Total
losses between the TFAM85/19 output port and antenna input port can
therefore be estimated as follows:
L = 0.55 (dB/m) x 5 (m) + 3.5 = 5.25 dB
By replacing the above values of G, L, P, S parameters inside the relation 6.1,
we therefore get the the following minimum safety distances from the
antenna:
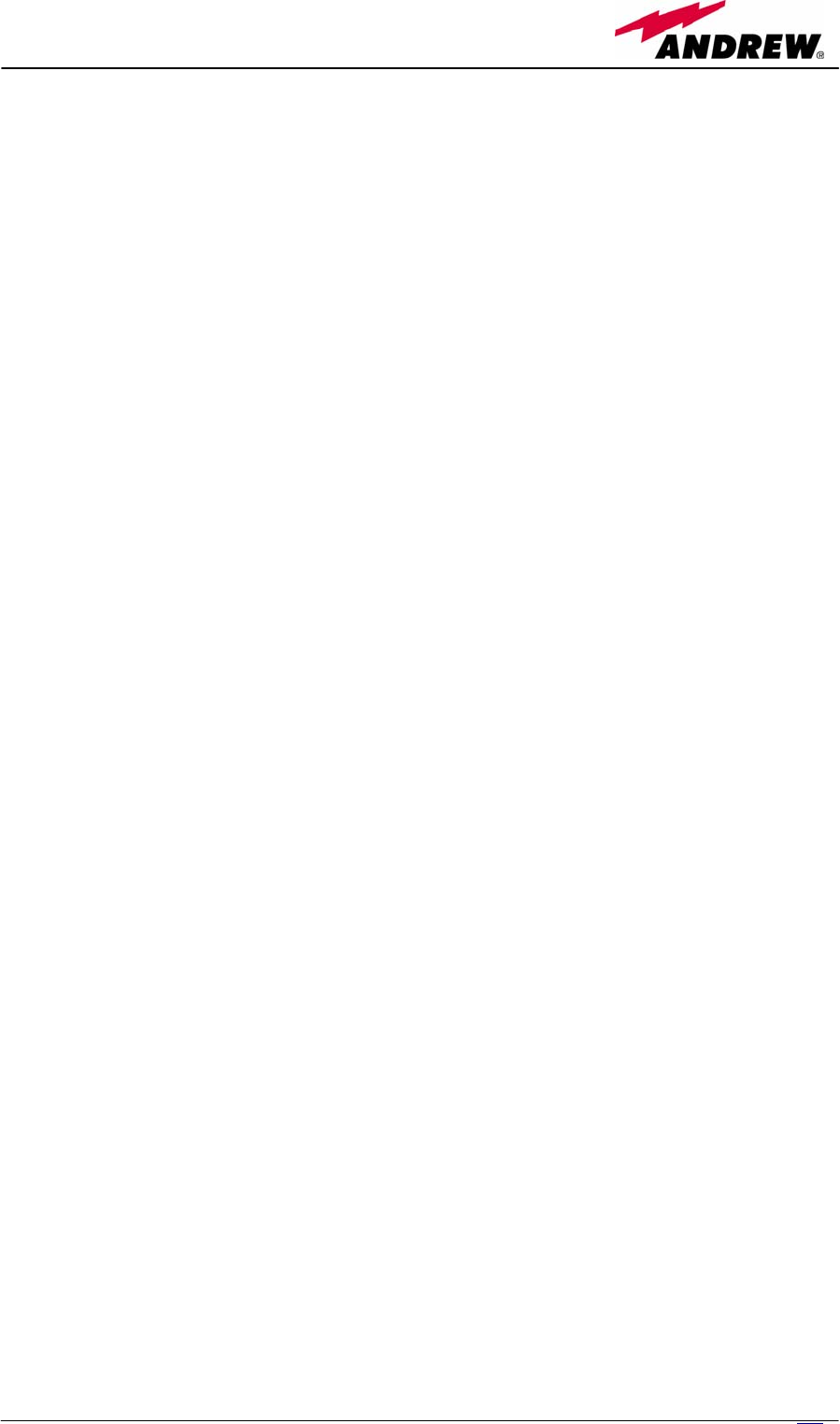
229
MN024-08
rmin = { 10 · exp [ (7 - 5.25) / 10 ] · 0.226} / (4·π·50) } · exp (-1/2) = 0.023
m
Example 3. Let’s suppose to have a Low Power TFAM90/20 connected to an
omnidirectional antenna through a 20-metre length ½” cable (no splitters
used). Let’s suppose that the antenna Gain is 7 dB and that our Britecell
system distributes two GSM900 carriers and one UMTS2100 carrier.
Moreover, let’s assume that the maximum allowed electrical field strength is:
E = 6 V m
(typical Italian reference level for exposure to time-varying electric and
magnetic fields). The corresponding value of the maximum allowed power
density is:
S = E2 /377 = 0.1 W/m2
By reading the Britecell bulletin, we get that the output power at the TFAM
antenna port is 14 dBm/carrier (=0.025 W) for a 2-carrier GSM900 MHz
distribution, and 17 dBm (0.05 W) for 1 WCDMA carrier.
The 900 MHz and 2100 MHz output powers at the remote unit ports are:
P900MHz,TFAx = 0.025W+0.025W=0.05W (for 900MHz signals)
P2100MHz,TFAx= 0.05W (for 2100MHz signals)
Let’s assume that the ½” cable losses are 0.07 dB/m in the 900 MHz band and
0.18 dB/m in the 2100 MHz band; the total losses between the TFAM90/20
output port and the antenna input ports can therefore be estimated as follows:
L900MHz = 0.07 (dB/m) x 10 (m) = 0.7 dB on 900MHz signals
L2100MHz=0.18 (dB/m) x 10 (m) =1.8 dB on 2100MHz signals
The term “10 exp (G-L/10) P” which appears inside the relation 6.1 should
therefore be calculated apart for each frequence, and then added in order to
calculate the composite contribution:
P900MHz, ant = 10 exp[(7-0.7)/10]· 0.05 = 0.213 W
P2100MHz,ant = 10 exp[(7-1.8)/10]·0.05 = 0.165 W
Pcomposite= P900MHz, ant + P2100MHz,ant= 0.378W
By dividing the total power through (4·π·S) and taking the square root
according to the relation 6.1, we therefore get the the following minimum
safety distances from the antenna:
rmin = { Pcomposite /(4·π·0.1)} · exp (-1/2) = 0.54 m
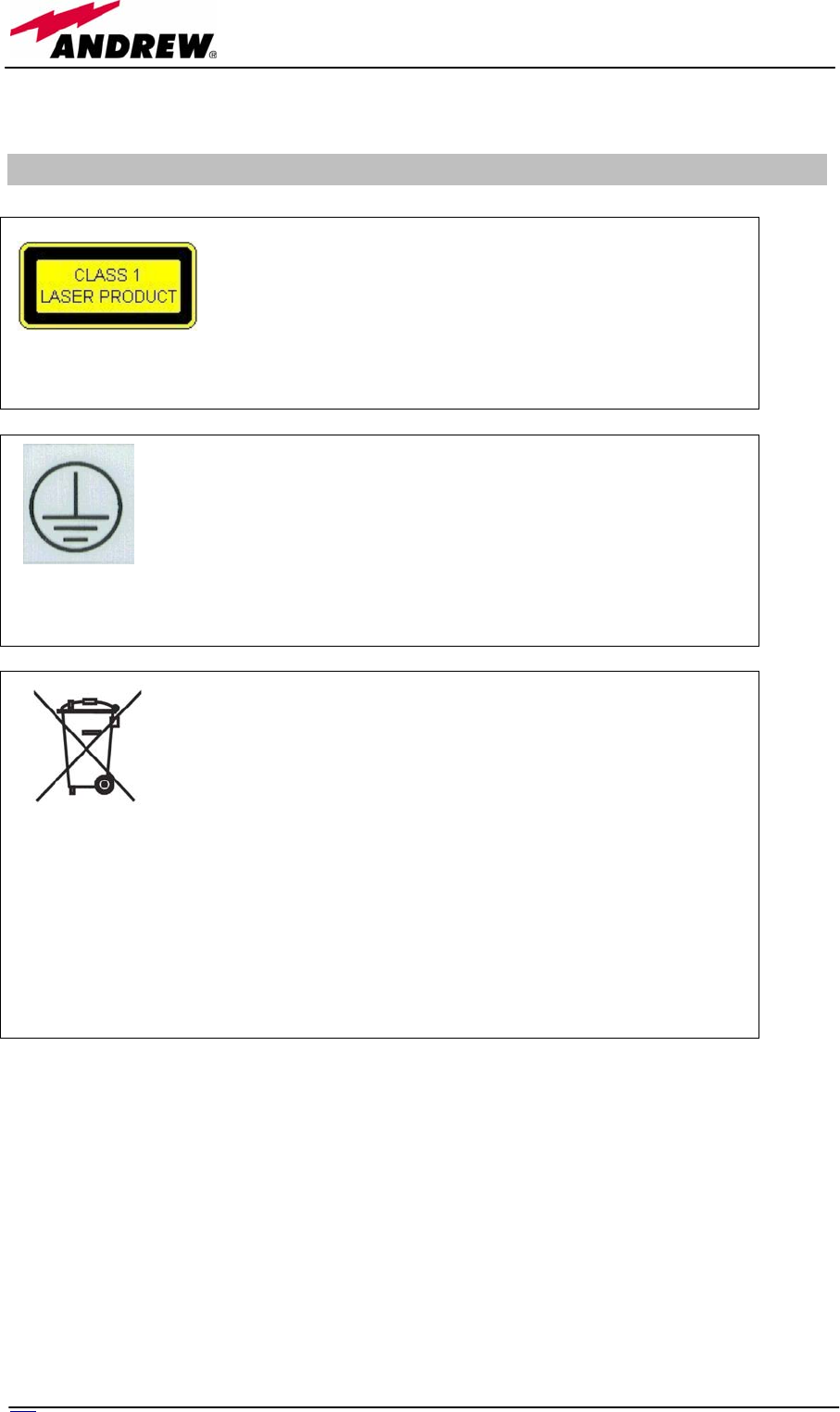
230 User Manual
6.8. Warning Labels
CLASS 1 laser product
GROUND - Use this terminal for a safety
ground connection of the equipment.
When this equipment is no longer used,
please do not throw it into a trush container
as unsorted municipal waste. Waste electrical
electronic equipment (WEEE) must be
collected apart and disposed of according to
the European Directives 2002/96/EC and
2003/108/EC. In order to comply with the
proper WEEE disposal, it is suggested that
you contact the manufacturer. Any failure to
comply with the above regulations will be
punished through fines
Please refer to Appendix B for further details
about the equipment disposal
Fig. 6.1:
Laser safety Label
Fig. 6.2:
Ground Label
Fig. 6.3:
WEEE Identification Label
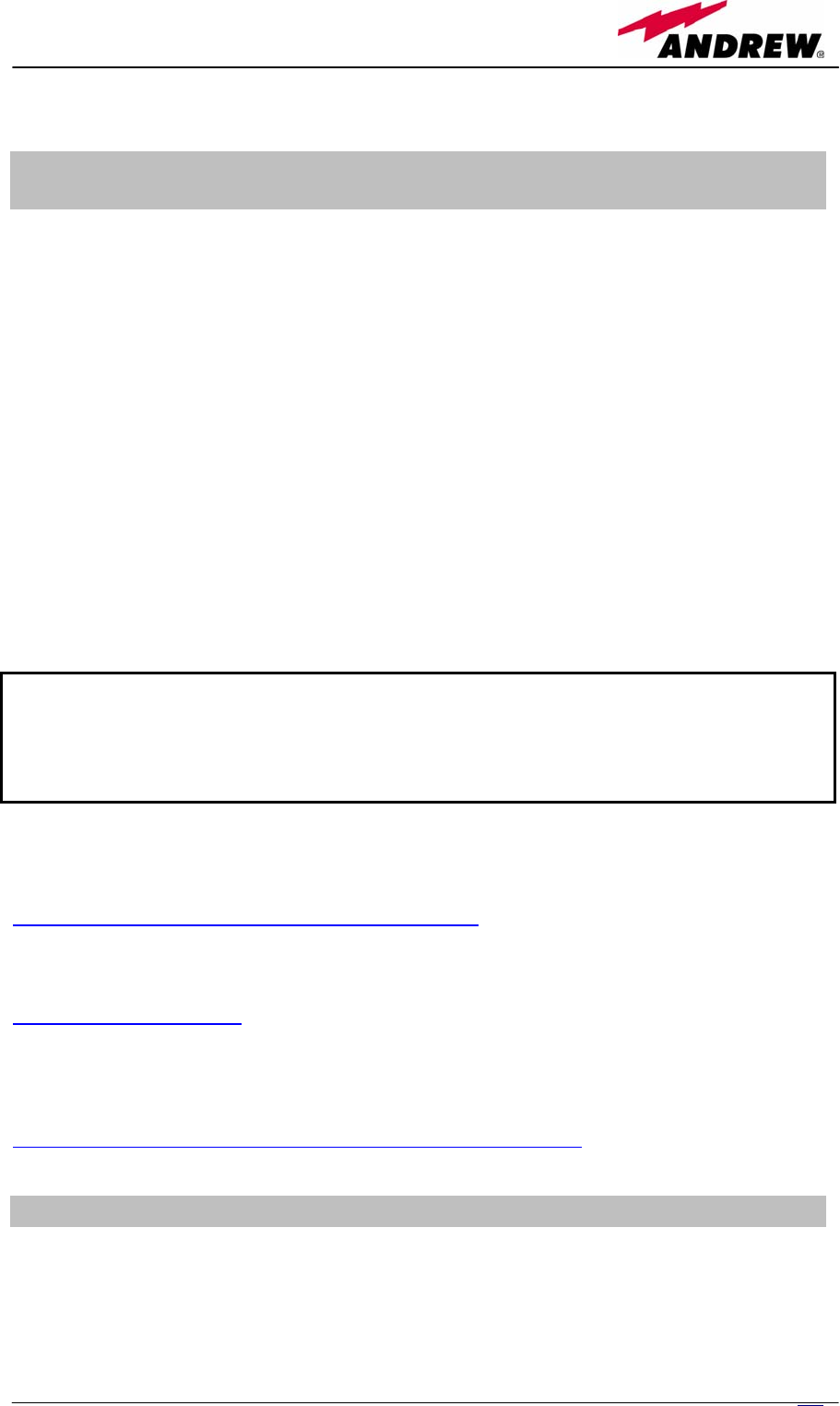
231
MN024-08
7. TECHNICAL SUPPORT
Andrew Corporation offers technical support by providing these 24-Hour call
services:
North America (toll free) to U.S.A.
Telephone 1-800-255-1479
Fax 1-800-349-5444
Any Location (International) to U.S.A.
Telephone + 1(708) 349-3300
Fax + 1 (708) 349-5410
Britecell Plus is developed by:
Andrew Wireless Systems Srl
Via Pier De Crescenzi 40
48018 Faenza, Italy
Tel: +39.0546.697111
Fax: +39.0546.682768
Useful information about the product are available on the dedicated pages of
Andrew’s website:
http://www.andrew.com/products/inbuilding/
For further information about the product, please write to:
Britecell@Andrew.com
In order to address us any question, comment or suggestion, you can also go
to following page of the Andrew’s website:
http://www.andrew.com/contactus/contact.aspx?ct=11
7.1. Returning equipment
Before returning some equipment to the manufacturer for repairing or
replacing, the customer should give prior notice to the manufacturer and ask
the Return Material Authorisation (RMA request).
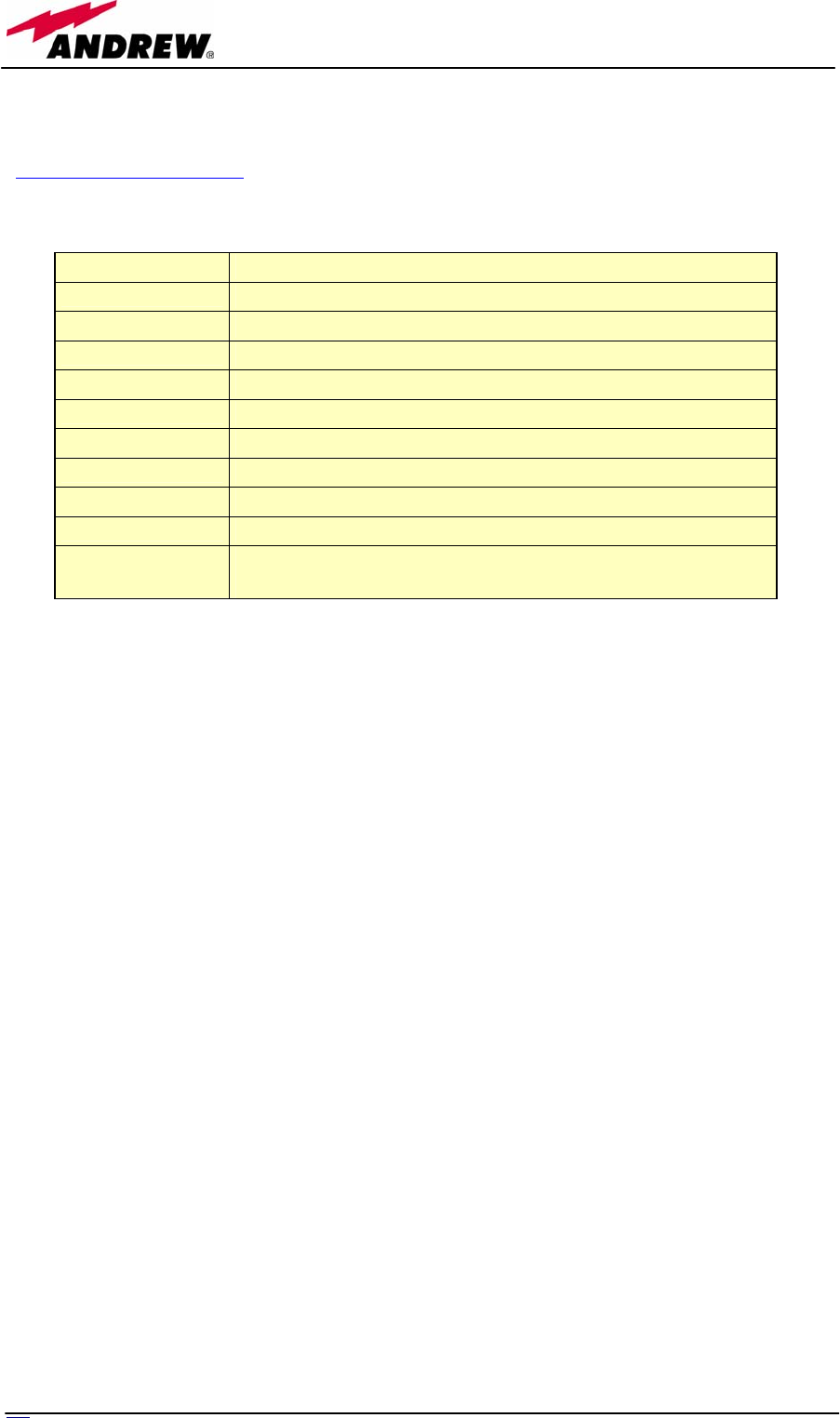
232 User Manual
Before sending any piece of equipment to the manufacturer, you must send us
the following RMA request form via fax (+39 0546 682768) or via e-mail
(britecell@andrew.com).
RMA REQUEST FORM
1Please refer to the serial label
Upon accepting your RMA request, the manufacturer will assign you a unique
RMA code. You will therefore be able to return the equipment to the
manufacturer. Please remember that:
• each piece of equipment must be packaged with care before shipment;
• a copy of the RMA request form must be enclosed inside the returning
equipment packaging, with the clear indication of the RMA code you
received from the manufacturer.
The returned pieces can be repaired (when possible) or replaced (when no
repairing can be carried out). These operations can be performed under
warranty (please see the warranty conditions specified in the sales contract) or
out-of-warranty. In the latter case, we will send you a quotation for equipment
repairing or replacement.
When returning the repaired or replaced equipment, the manufacturer will
issue a check report, which will included in the packaging together with the
returned pieces. The customer will be informed about any corrective actions
suggested by quality assurance.
Company name
Address
Contact person
Invoice number
Delivery note
N°. of pieces
Model1
Serial Number1
Lot1
Year1
Description of the
Failure/defect
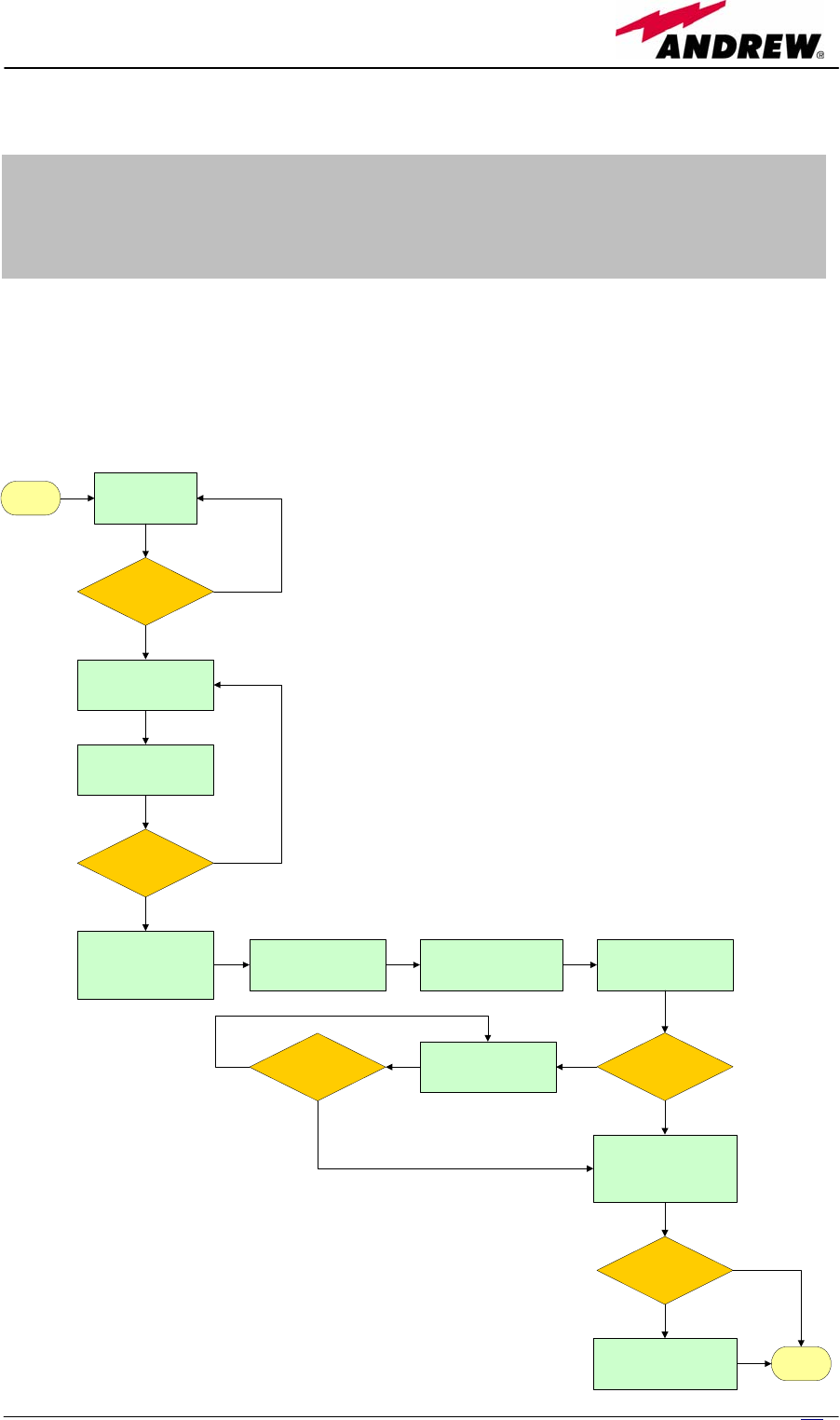
233
MN024-08
Appendix A:
System Commissioning
The following flow charts want to be a quick reference for Britecell Plus®
system installation and commissioning.
The first flow chart (see Fig. A.1) highlights the main steps for system
installation and commissioning starting from the equipment unpacking up to
the check of the coverage and call quality.
Fig. A.1: Flow-chart describing main
installation and commissioning steps
START UNPACK THE
EQUIPMENT
ARE THERE
ANY
BOXES LEFT?
YES
NO
INSTALL AND CABLE
MASTER UNIT
INSTALL AND CABLE
REMOTE UNITS
(see flow chart in Fig. 29)
EVERYTHING
COMPLETED?
YES
NO
CALCULATE
ATTENUATION VALUE
USING BRITETOOL
(see Britetool Manual)
SET DL AND UL
ATTENUATION START UP THE SYSTEM
(see flow-chart in Fig. 30)
IS SYSTEM
WORKING
PROPERLY?
YES
NO
GO THROUGH
TROUBLESHOOTING
PROCEDURE
IS NOW
WORKING
PROPERLY?
DO THE WALK TEST TO
VERIFY COVERAGE (DL)
AND MAKE A CALL TO
VERIFY ITS QUALITY (UL)
YES
NO
IS
COVERAGE
AND CALL QUALITY
OK?
YES
NO
CHECK DL LEVEL WITH A
SPECTRUM ANALYSER
CHECK THE DESIGN AND
CHANGE IT IF
NECESSARY END
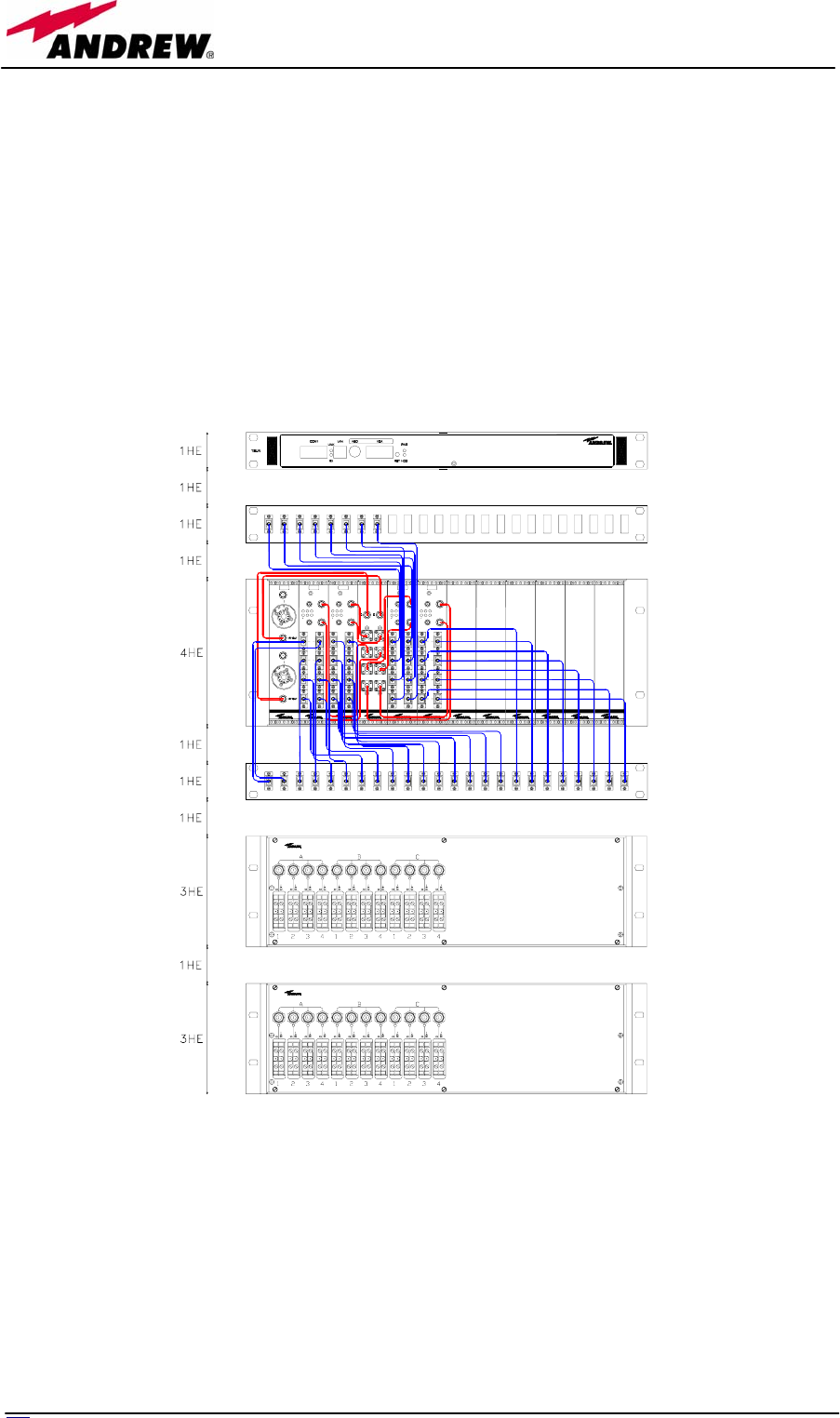
234 User Manual
The previous flow chart contains the following cross references:
• the master unit installation and cabling is described in more details in
the flow chart in figure A.3. It takes care of the flow of actions from the
sub-rack mounting on the cabinet up to the settings and connections
needed in case a remote supervision has to be considered.
An example of system layout at master unit side is presented in figure
A.2 for a configuration consisting in 1 sector with 4 TFLN master optical
TRXs.
For more details about TSUNx configuration and start-up refer to the
Remote Supervision manual.
• once the whole system has been installed, the attenuation on the base
station interface has to be defined in order to set up the performances.
Use the Britetool Software to calculate the required attenuation values
for uplink and downlink. Refer to Britetool manual for more information
on how to use it.
• the system start-up is described in more details in the flow chart in
figure A.4. It takes care of the flow of actions from the remote and
UL
UL
DL
RF IN
DL
TBSI
RF IN
AUX MAIN
UL
DL
13
24
=
TFLN
1
2
3
4
UL DL
RXs TXs
AUX MAIN
UL
DL
13
24
=
TFLN
1
2
3
4
UL DL
RXs TXs
AUX MAIN
UL
DL
13
24
=
TFLN
1
2
3
4
UL DL
RXs TXs
AUX MAIN
UL
DL
13
24
=
TFLN
1
2
3
4
UL DL
RXs TXs
UL DL
1
2
3
4
Fig. A.2: Cabinet layout for a 1 sector with 4 TFLN master optical TRXs configuration
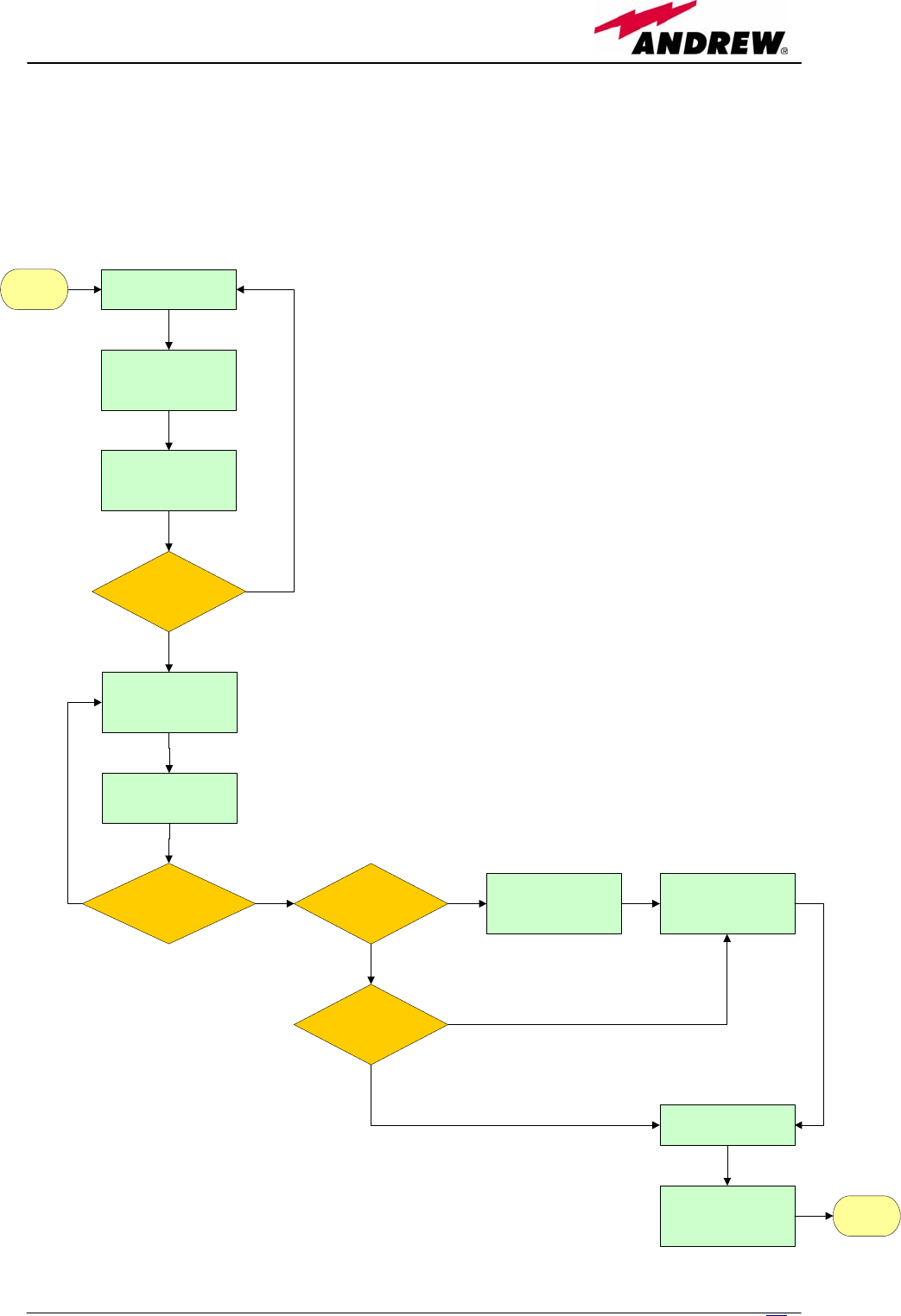
235
MN024-08
master unit switch on and discovery up to the system configuration
through LMT Software and/or remote supervision system.
For more details on how to use LMT and about TSUNx configuration and
start-up refer to relevant manuals.
• in case the system is not working properly, refer to the troubleshooting
procedures reported into relevant sections.
START MOUNT THE SUBRACK
INTO THE CABINET
SET THE SUBRACK
BAUD RATE
(THE SAME FOR ALL)
(see Fig. 16 and Tab. 6)
SET THE SUBRACK
ADDRESS
(DIFFERENT FOR EACH)
(see Fig. 16 and Tab. 7)
IS THERE ANY
OTHER SUBRACK?
YES
NO
INSERT ALL THE
BOARDS INTO THE
SUBRACK ACCORDING
TO DESIGN
CONNECT THE BOARDS
USING RF CABLE KITS
PROVIDED
ARE ALL
BOARDS INSERTED AND
CONNECTED?
NO YES IS THERE A
TSUN1 OR TSUN3
DEVICE?
YES CONNECT TSUNx COM2
PORT TO ONE
SUBRACK RS232 PORT
NO
IS THERE A
TSUN6 DEVICE?
NO
YES
CONNECT SUBRACKS
IN A DAISY CHAIN
USING RS485 PORTS
CONNECT THE
POWER CABLES
SWITCH ON THE
SUBRACK ONLY AFTER
HAVING CONNECTED
THE REMOTE UNITS
END
Fig. A.3: Flow-chart describing master unit installation and
cabling steps
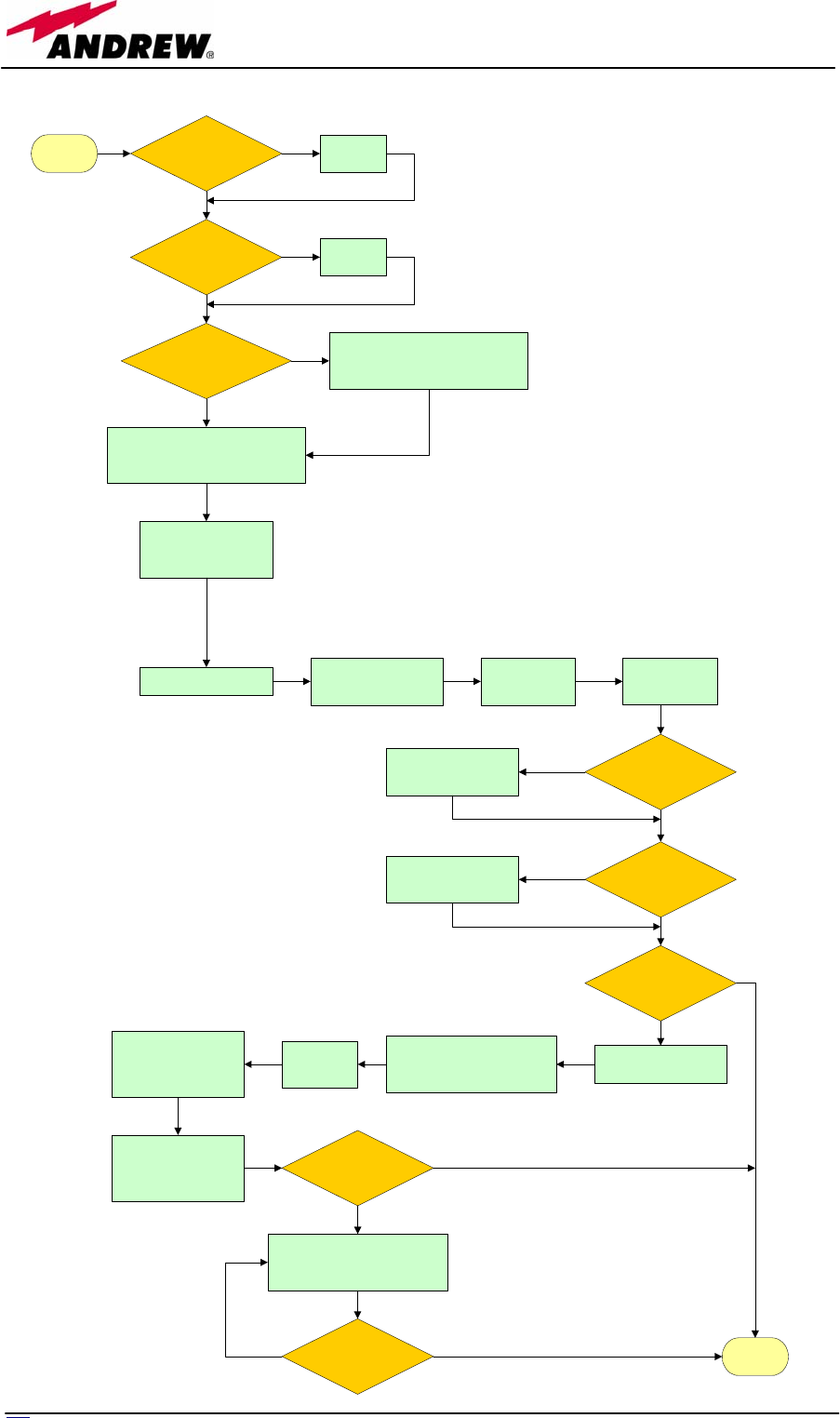
23
6
User Manual
START ARE ALL
REMOTE UNITS
SWITCHED ON?
YES
NO SWITCH
THEM ON
ARE ALL
SUBRACKS SWITCHED
ON?
NO SWITCH
THEM ON
YES
WAIT UNTIL
DISCOVERY IS FINISHED
(TFLN general alarm LED stop blinking)
CONNECT A LAPTOP
TO THE RS232
SUBRACK PORT
RUN LMT SELECT
QUICK CONFIGURATION
MENU
MASK
SLOTS
(see LMT manual)
IS MASTER UNIT
WORKING
PROPERLY?
YES
NO
FOLLOW
TROUBLESHOOTING
PROCEDURE
ARE
REMOTE UNITS
WORKING
PROPERLY?
YES
NO
FOLLOW
TROUBLESHOOTING
PROCEDURE
IS SUPERVISION
SYSTEM INCLUDED?
YES
CONNECT THE LAPTOP
TO TSUNx LAN PORT
OPEN AN INTERNET BROWSER
AND TYPE DEFAULT ADDRESS
(see Remote Supervision manual)
LOGIN
ACCESS
CONFIGURATION MENU
AND REBOOT TO APPLY
CHANGES
NO
ACCESS
CONNECTIVITY MENU
AND RUN SYSTEM
DISCOVERY
IS SUPERVISION
SYSTEM WORKING?
YES
NO
CHECK FOR CONFIGURATION
AND RUN SYSTEM DISCOVERY
AGAIN
IS SUPERVISION
SYSTEM NOW
WORKING?
NO YES END
HAS DISCOVERY
STARTED?
(TFLN general alarm LED blinking)
NO
YES
ENABLE IT THROUGH THE LMT OR
REMOTE SUPERVISION SYSTEM
(see relevant manuals)
MASK
TFA
(see LMT manual)
Fig. A.4: Flow-chart describing
system start-up steps
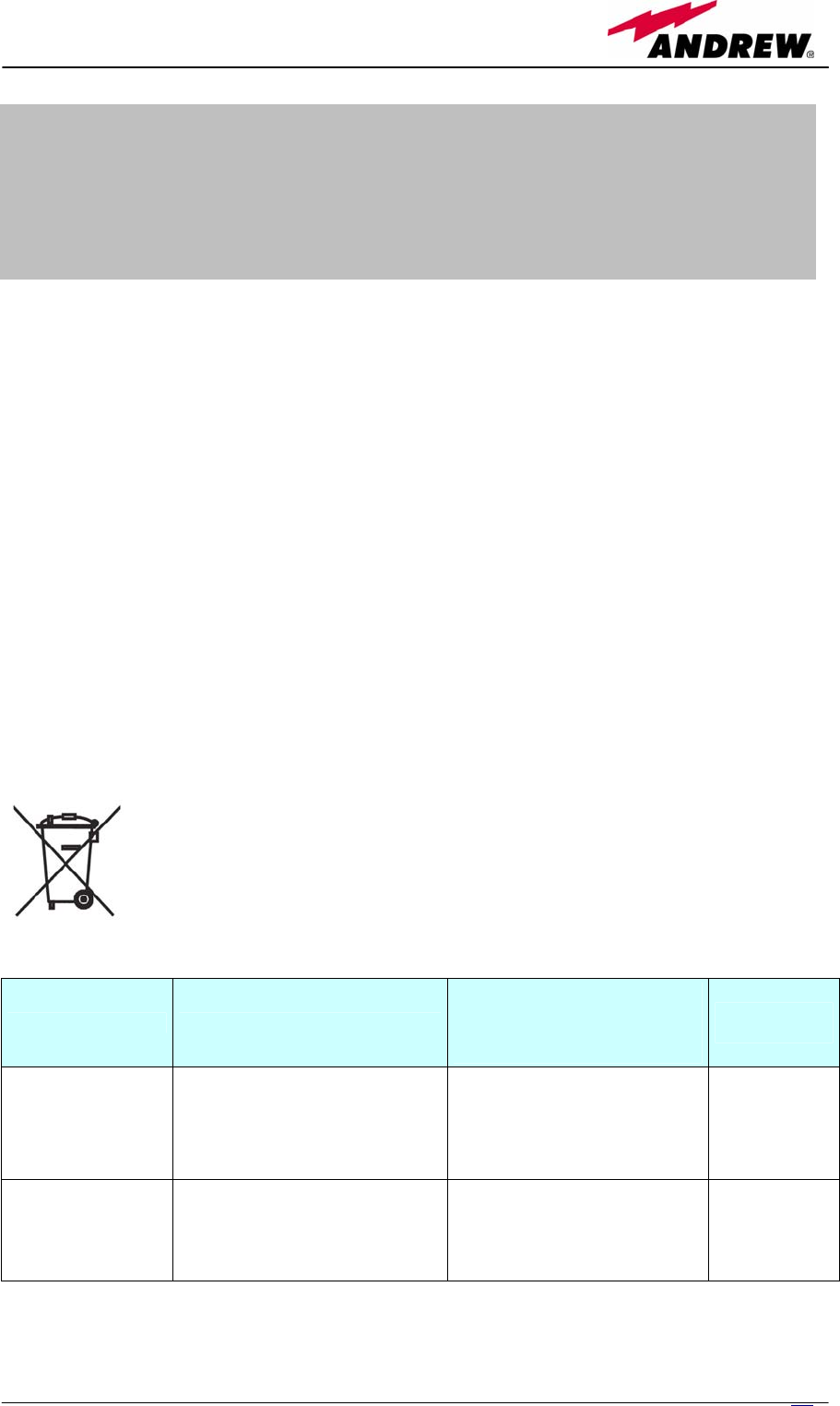
23
7
MN024-08
Appendix B:
EU Guidelines
for WEEE disposal
All Britecell Plus products are properly labelled (please refer to fig. B.1) so as
to inform the customer that no piece of equipment should be treated as
unsorted municipal waste. Within the EU boundariers, any Britecell Plus
equipment which is no longer used should be treated and disposed of
according to European Directives 2002/96/EC and 2003/108/EC. The above
regulations state that Waste Electric Electronic Equipment (WEEE) have to be
disposed of by authorised centers with proper license for WEEE treatment.
The customer can decide to dispose of the unused equipment only if he owns a
WEEE disposal licence. Otherwise, he should contact the manufacturer or any
center which is authorised for WEEE treatment. Any failure to comply with the
above regulations will be punished through a penalty whose amount and terms
are set by each EU Member State.
The information reported hereinafter (table B.1) are aimed to provide the
costumer and/or the WEEE treatment center with any information about
recycling and disposing of the Britecell Plus equipment. These guidelines fall
within Andrew’s efforts to increase re-use, recycling and other forms of
recovery, leading to a reduction in the amount of waste going to landfill or
incineration.
Products Recyclable materials
Wastes to be disposed of
by approved companies
(licensees for European
Waste No. 160216)
Hazardous
materials
TFAx Case A
TFAx Case B
• Alluminium (external case)
• Metal (RF connectors,
screws, bottom cover)
• Plastic (optical connectors
and adapters)
• cables, fiberoptics cables,
internal circuit boards
• psu, inlet (for any TFAx
Case A, except TFAM20)
• None
TPSN Power
Supply
• Plastic (external case; inlet
and plug in the 220 Vac
version)
• Metals (wall bearing;
screws)
• Cables, internal circuit
board
• Electrolytic
capacitors
Fig. B.1: WEEE Identification Label
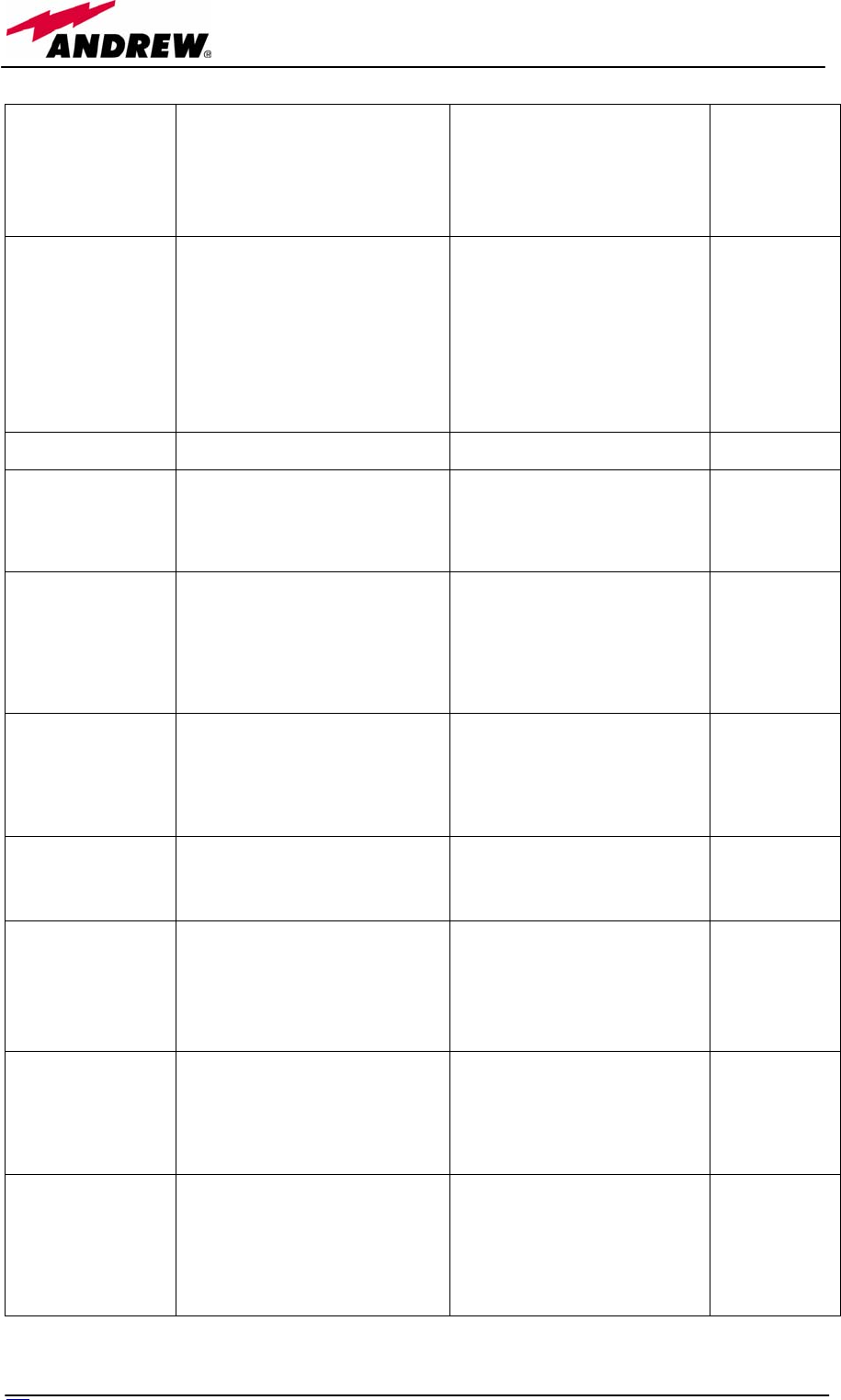
238 User Manual
TFAH Case F • Alluminium (external case)
• Metal (RF connectors,
screws, cavity filters)
• Plastic (optical connectors
and adapters ; power
connector; )
• cables, fiberoptics cables,
internal circuit boards,
psu, inlet
• None
TFAH Case L • Alluminium (external case;
wall-fixing plates; pipe
connection and PG 13,5 ;
strain reliefs)
• Metal (RF connectors,
screws, cavity filters)
• Plastic (optical connectors
and adapters ; power
connector; )
• cables, fiberoptics cables,
internal circuit boards,
psu, inlet
• None
TKA installation kit • Alluminium (wall bearing) • None • None
TPRN • Alluminium (external case)
• Metal (screws, bottom
cover)
• Plastic (black guides
housing the modules)
• cables, internal circuit
boards, psu, inlet
• None
TFLN • Alluminium (front panel)
• Metal (RF connectors,
screws)
• Plastic (optical connectors
and adapters ; side
protections of the electronic
board)
• cables, fiberoptics cables,
internal circuit board
• None
TFLF • Metal (RF connectors,
screws)
• Plastic (optical connectors
and adapters ; side
protections of the electronic
board)
• cables, fiberoptics cables,
internal circuit board
• None
TLCN2, TLCN4,
TLDN,TLTN, TDPX,
TMP
• Alluminium (front panel)
• Metal (RF connectors,
screws)
• cables, internal circuit
board
• None
TBSI • Alluminium (front panel)
• Metal (RF connectors,
screws)
• Plastic (handles on the
TBSI front panel)
• cables, internal circuit
board
• None
TWLI • Alluminium (front panel)
• Metal (RF connectors,
screws)
• Plastic (buttons on the front
panel)
• cables, internal circuit
board
• None
TILx • Alluminium (front panel)
• Metal (RF connectors,
screws)
• Plastic (optical connectors
and adapters ; side
protections of the electronic
board)
• cables, fiberoptics cables,
internal circuit boards
• None
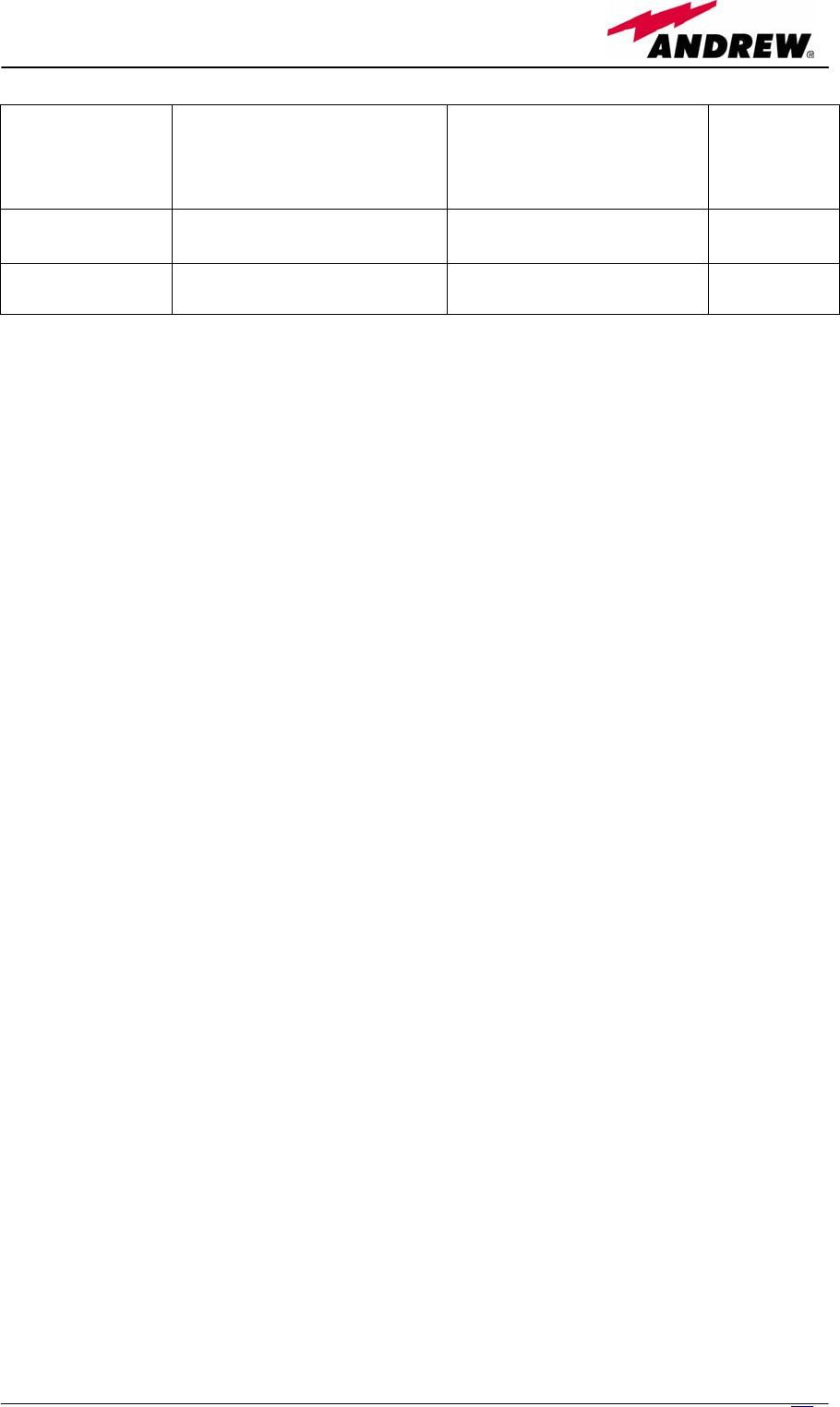
239
MN024-08
TRS / TRSN • Alluminium (external case)
• Metal (screws)
• Copper (Transformers
model with active
distributions)
• cables, internal circuits,
circuit breakers
• None
TSUN 6 • Alluminium (front panel)
• Metal (screws)
• Internal circuit board • None
TSUN 1 / TSUN 3 • Metal (screws, external
case)
• Internal circuit board,
psu, inlet
• None
Table B.1. Guidelines on recycling and disposing of Britecell Plus electrical and electronic equipment