Enterprise Electronics RANGERX5 Ranger-X5 RADAR User Manual Section 2 Troubleshooting Maintenance Calibration v1 4 DRAFT 002
Enterprise Electronics Corporation Ranger-X5 RADAR Section 2 Troubleshooting Maintenance Calibration v1 4 DRAFT 002
Contents
- 1. User Manual Troubleshooting Maintenance Calibration Part 1
- 2. User Manual Troubleshooting Maintenance Calibration Part 2
- 3. User Manual Overview Theory Part 2
- 4. User Manual Overview Theory Part 1
- 5. User Manual Overview Theory Part 3
- 6. User Manual Overview Theory Part 4
User Manual Troubleshooting Maintenance Calibration Part 1
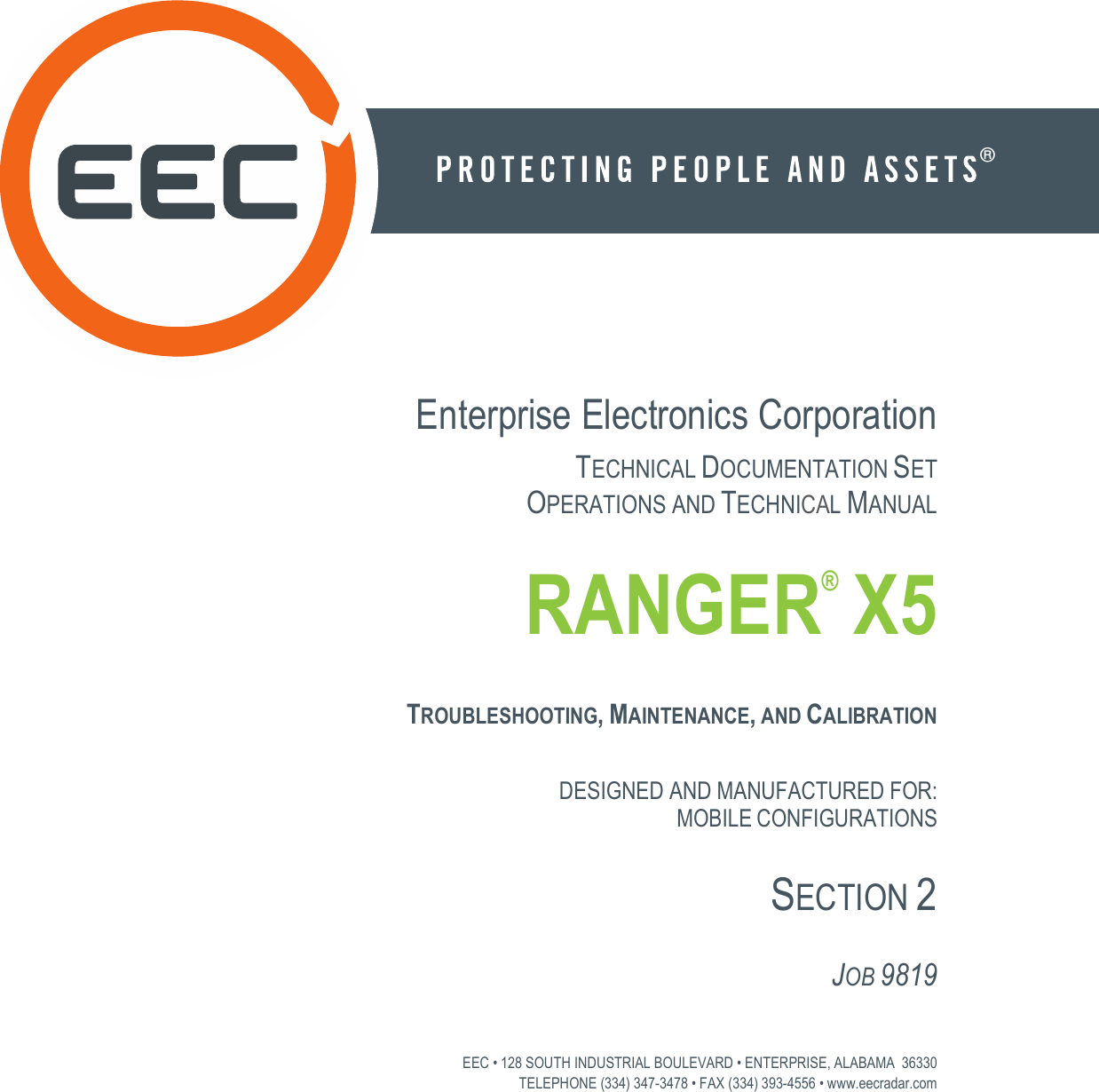
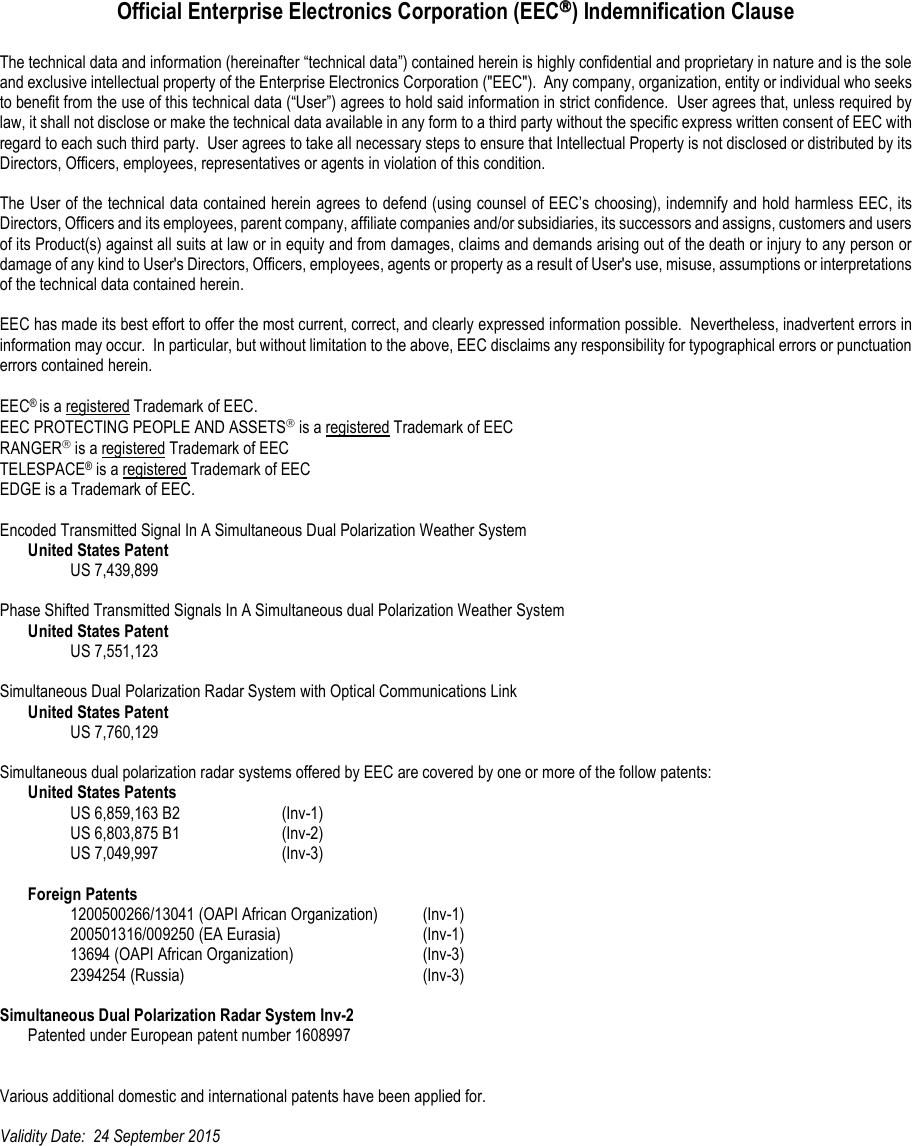
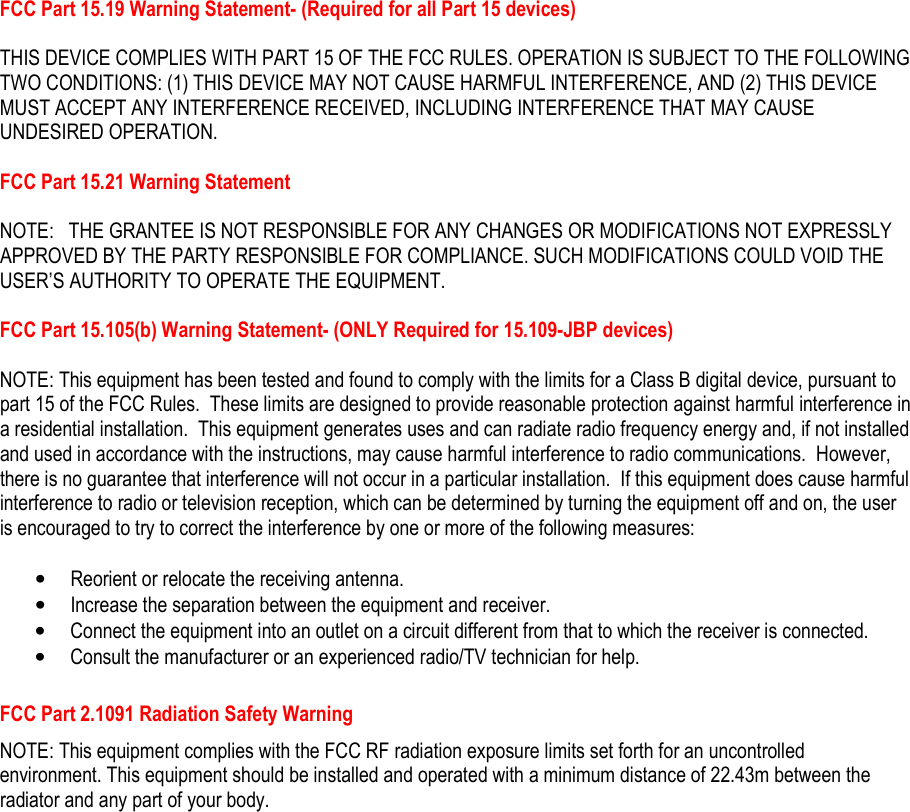
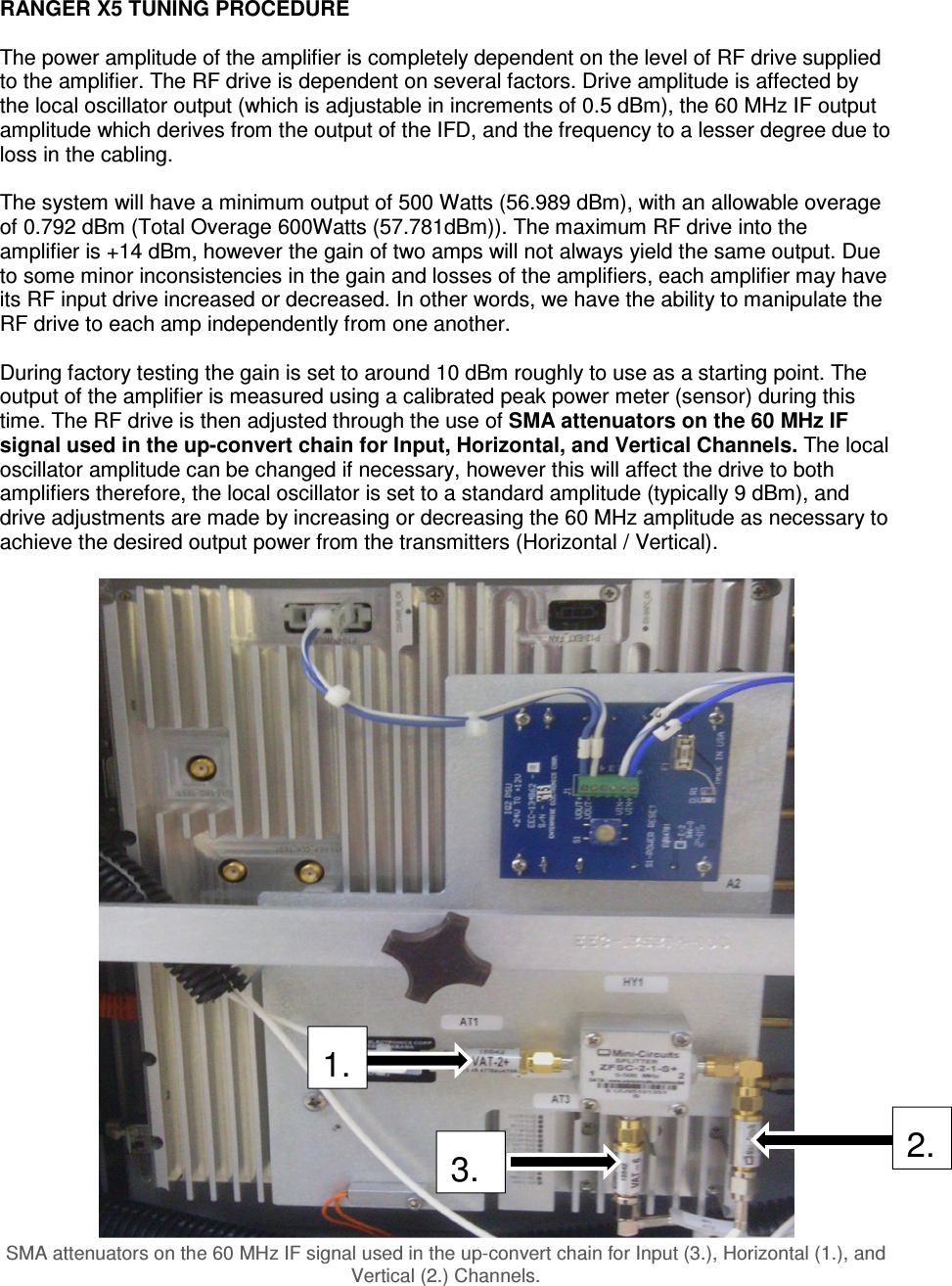
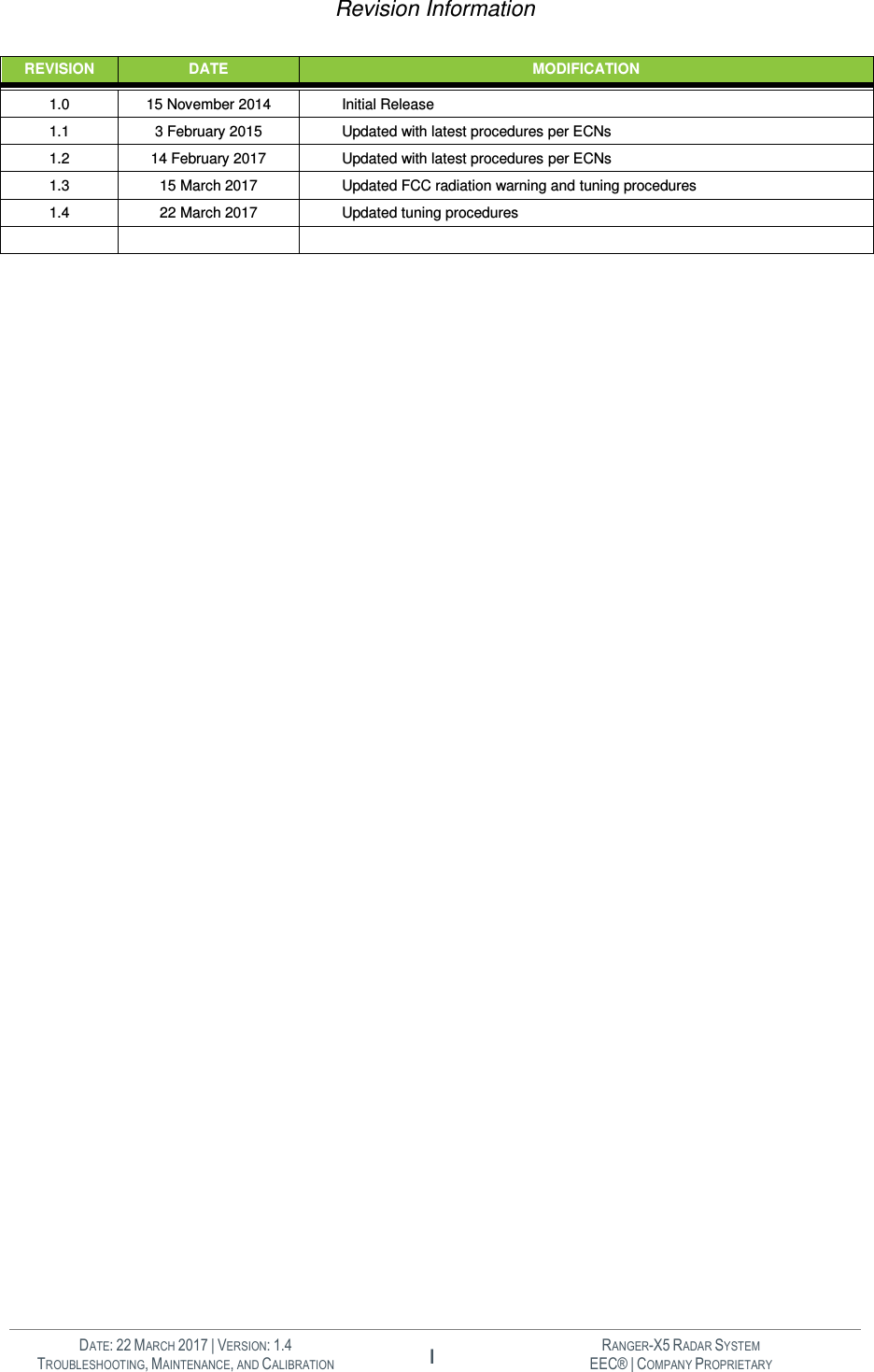
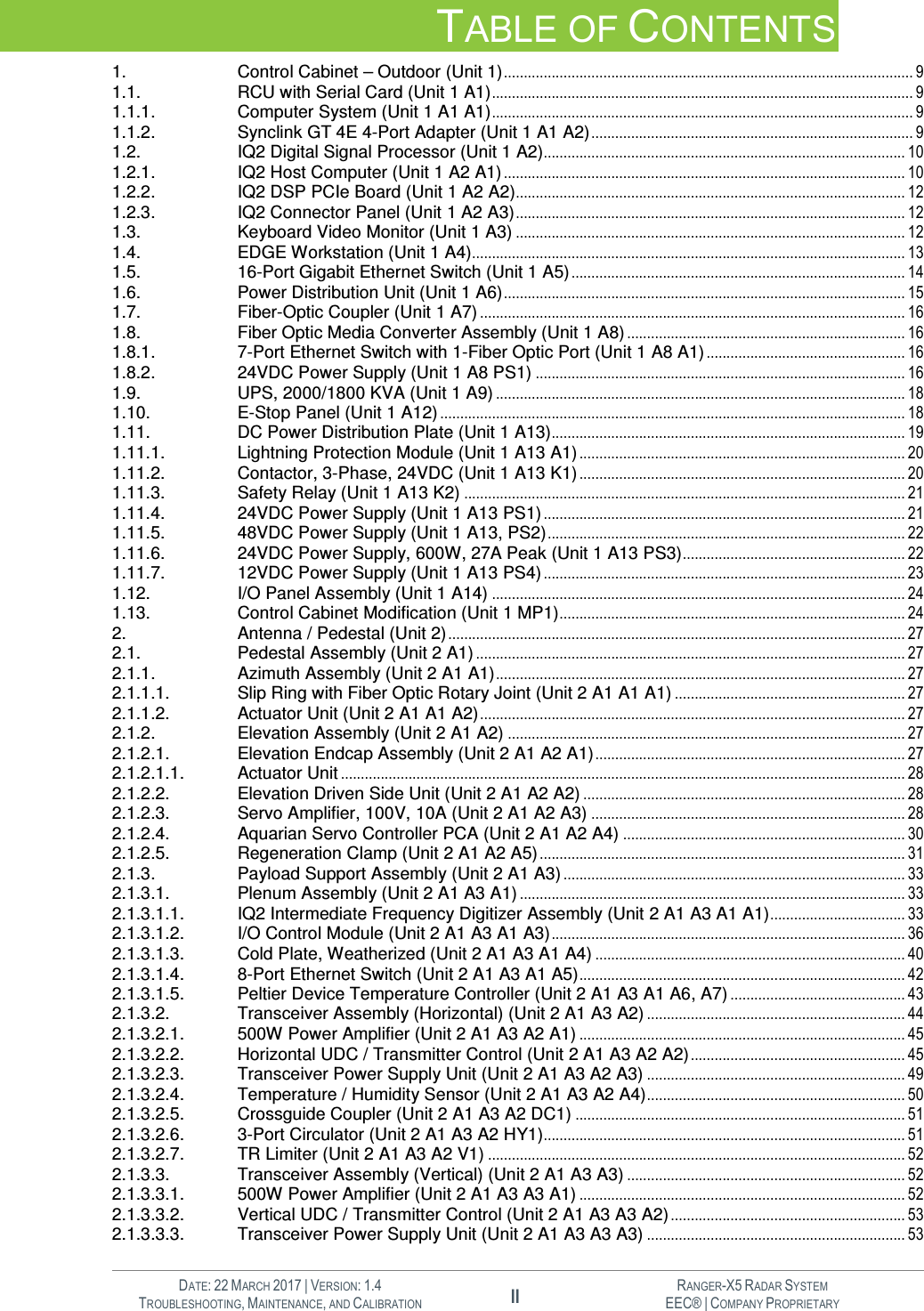
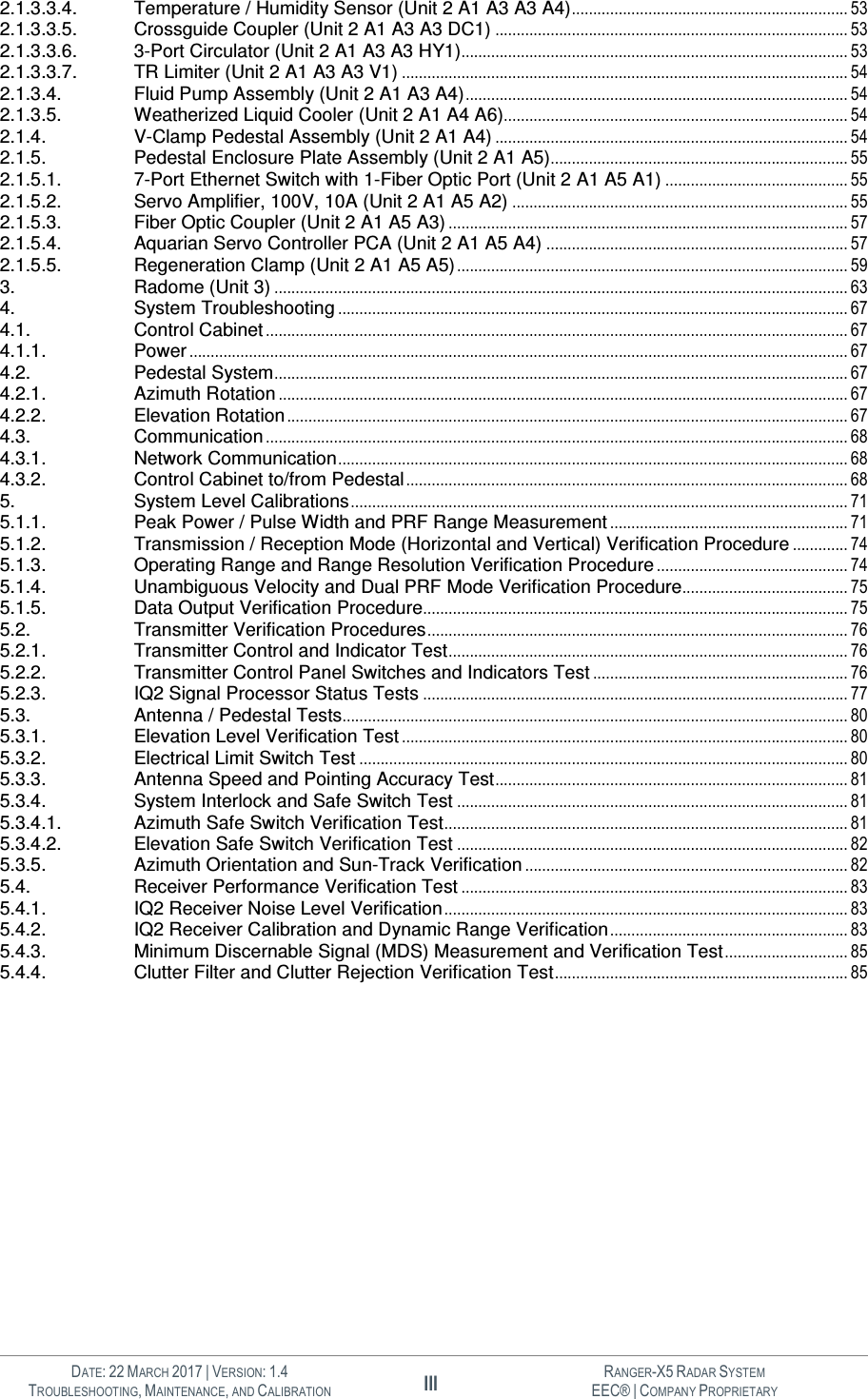
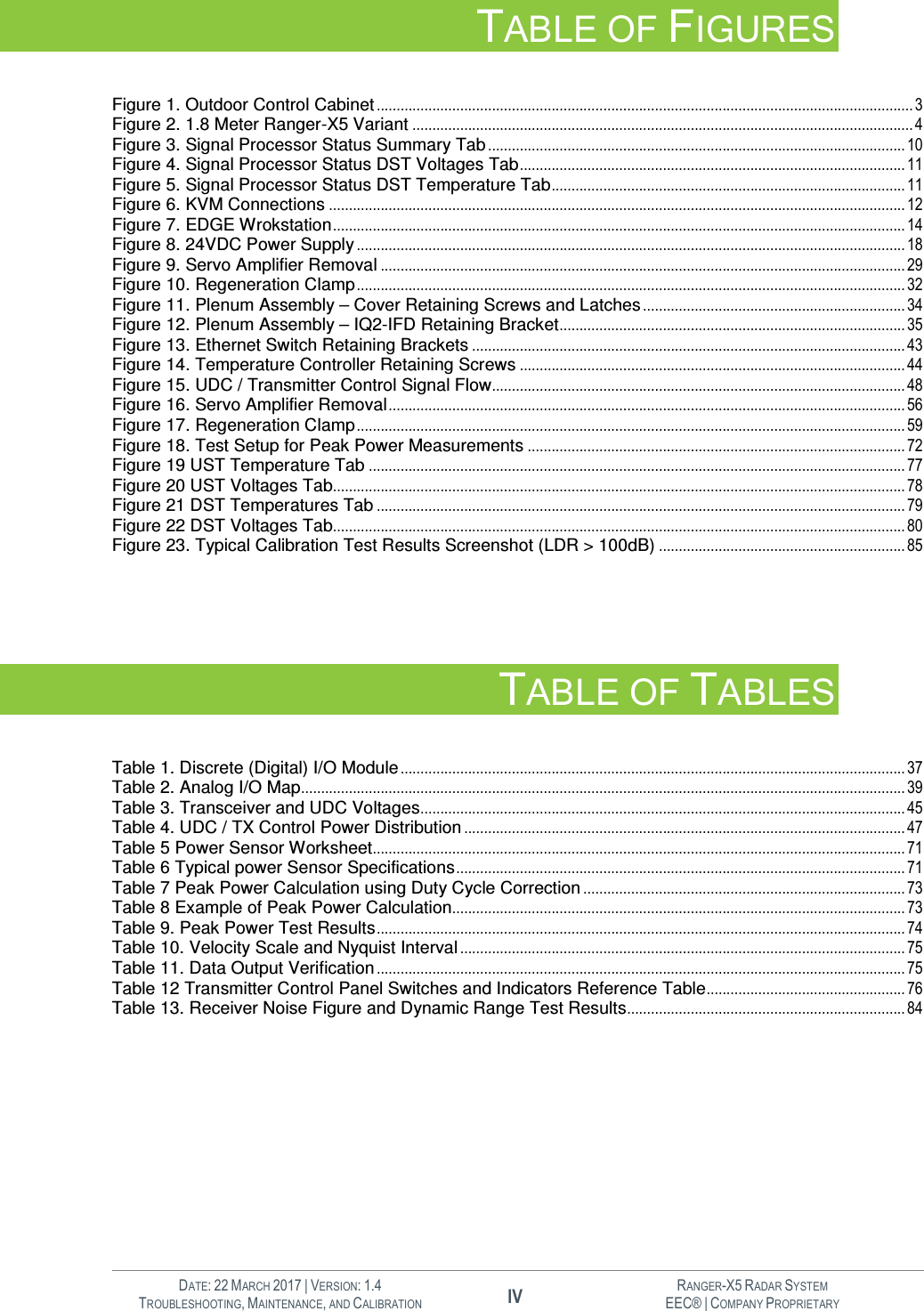
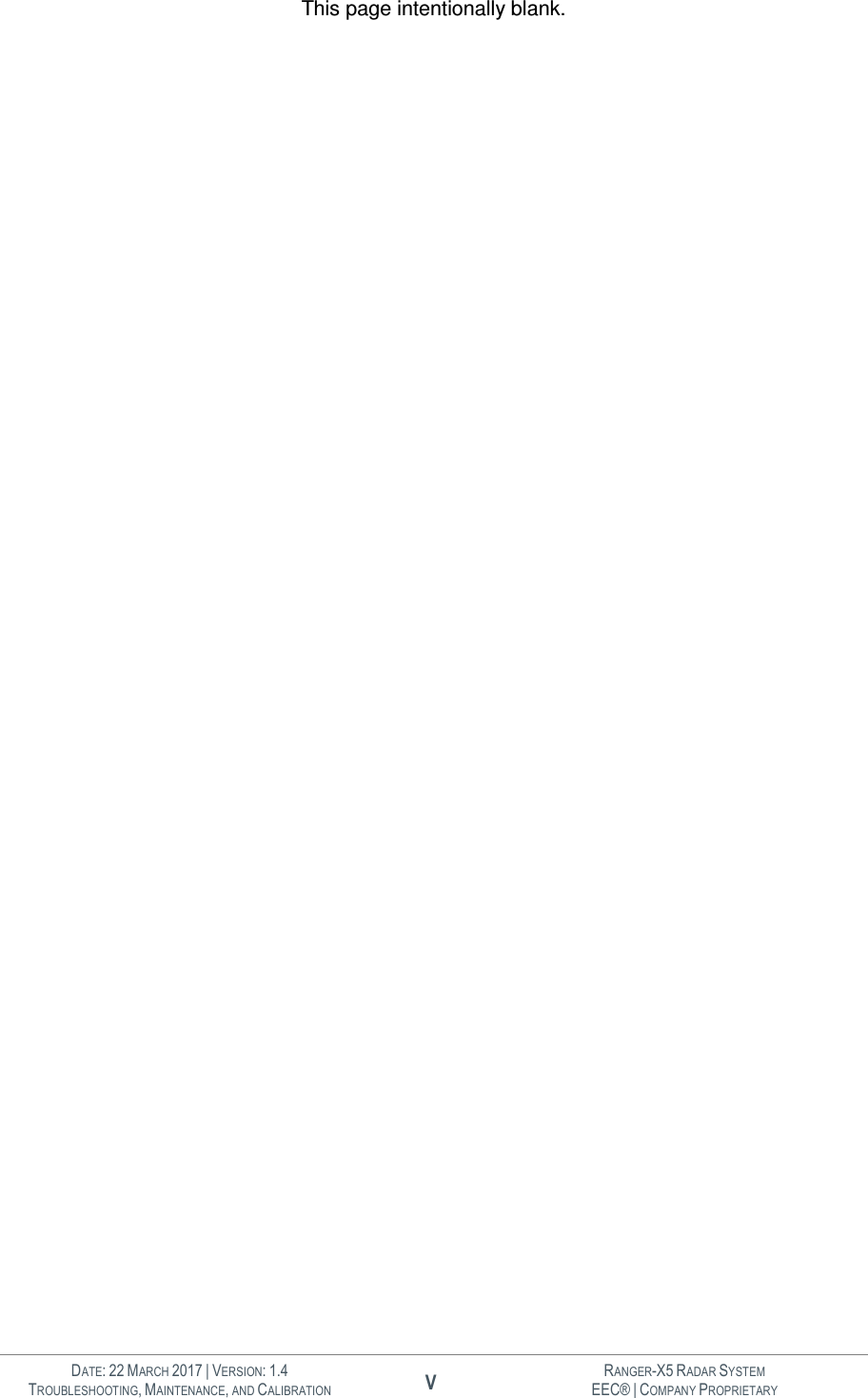
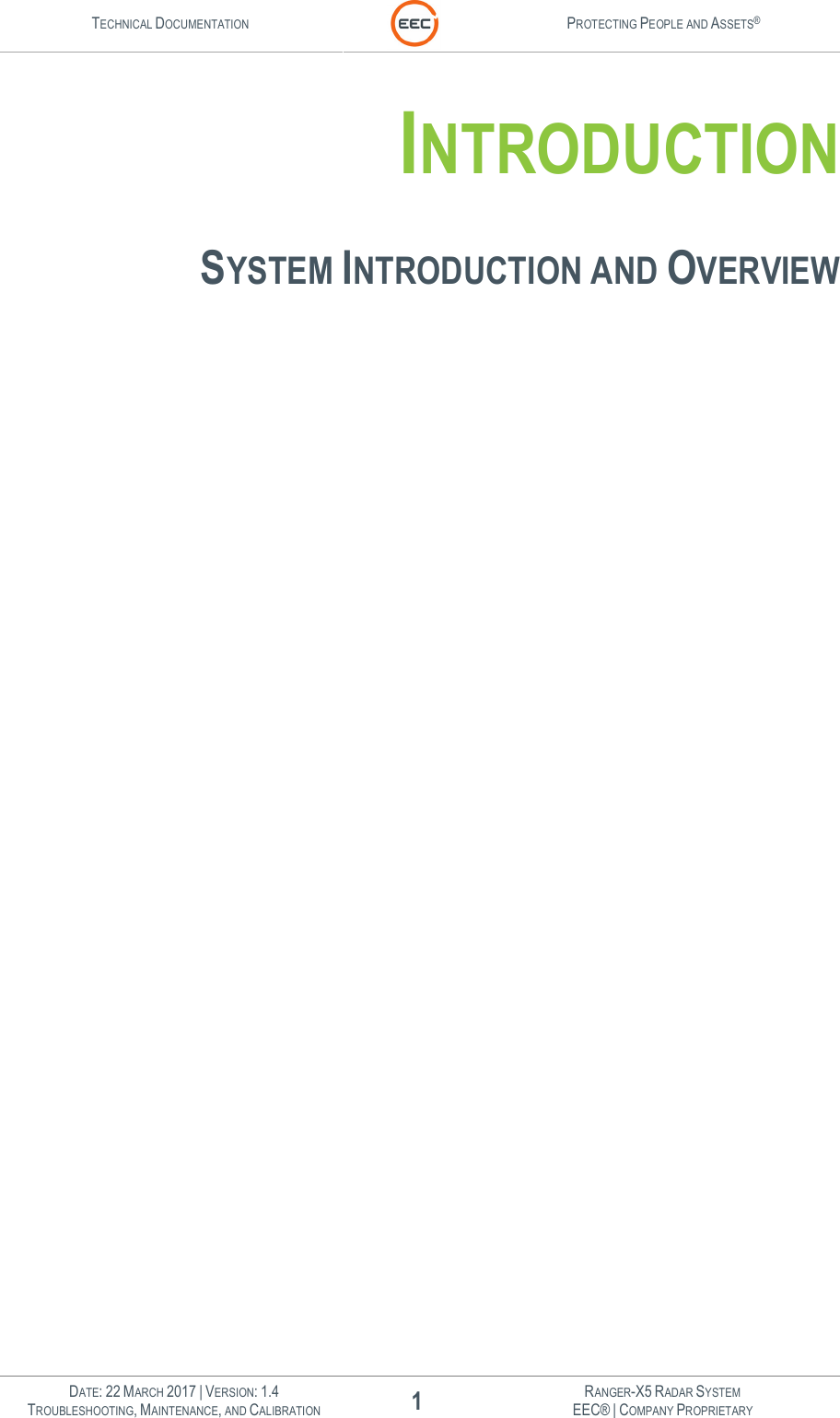
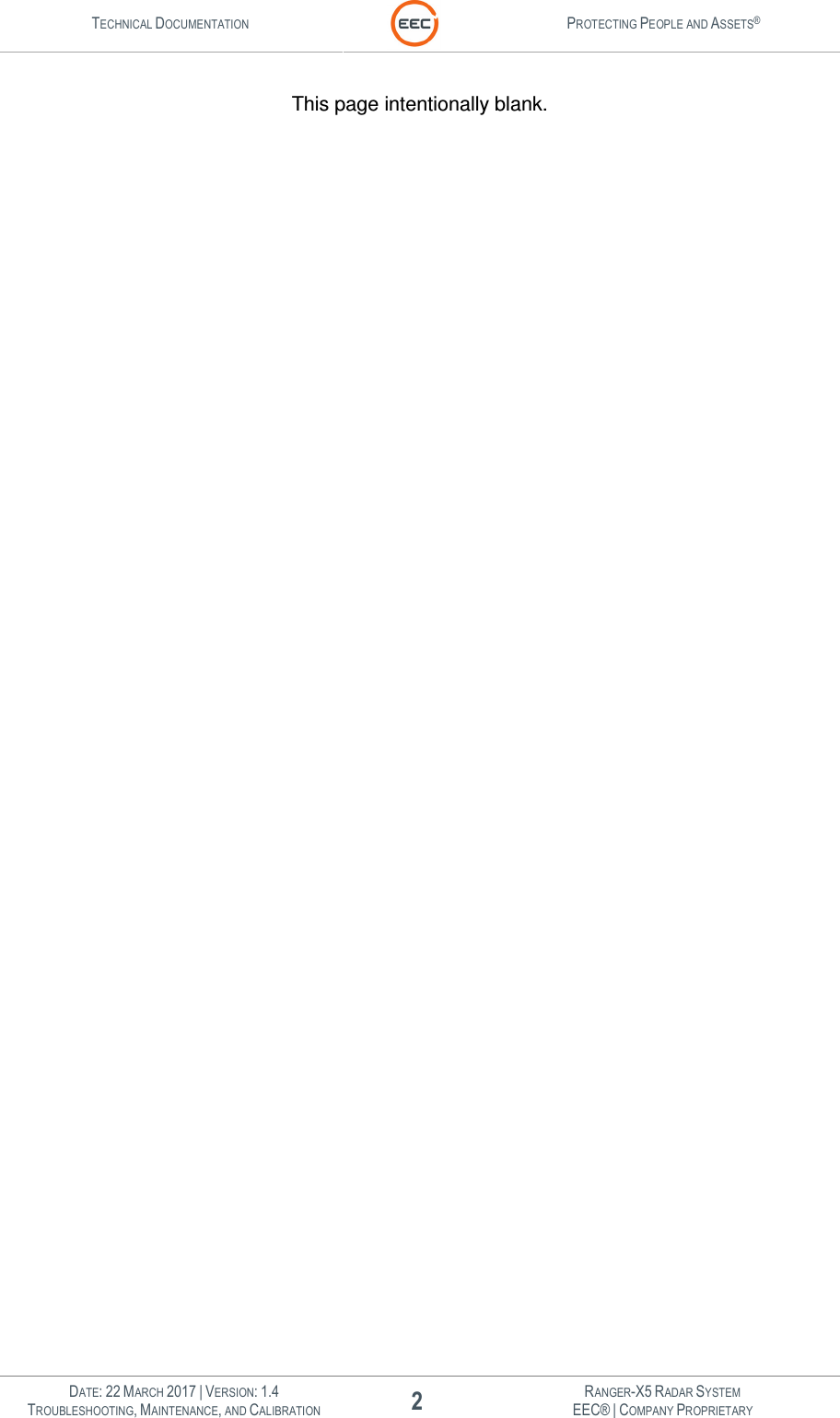
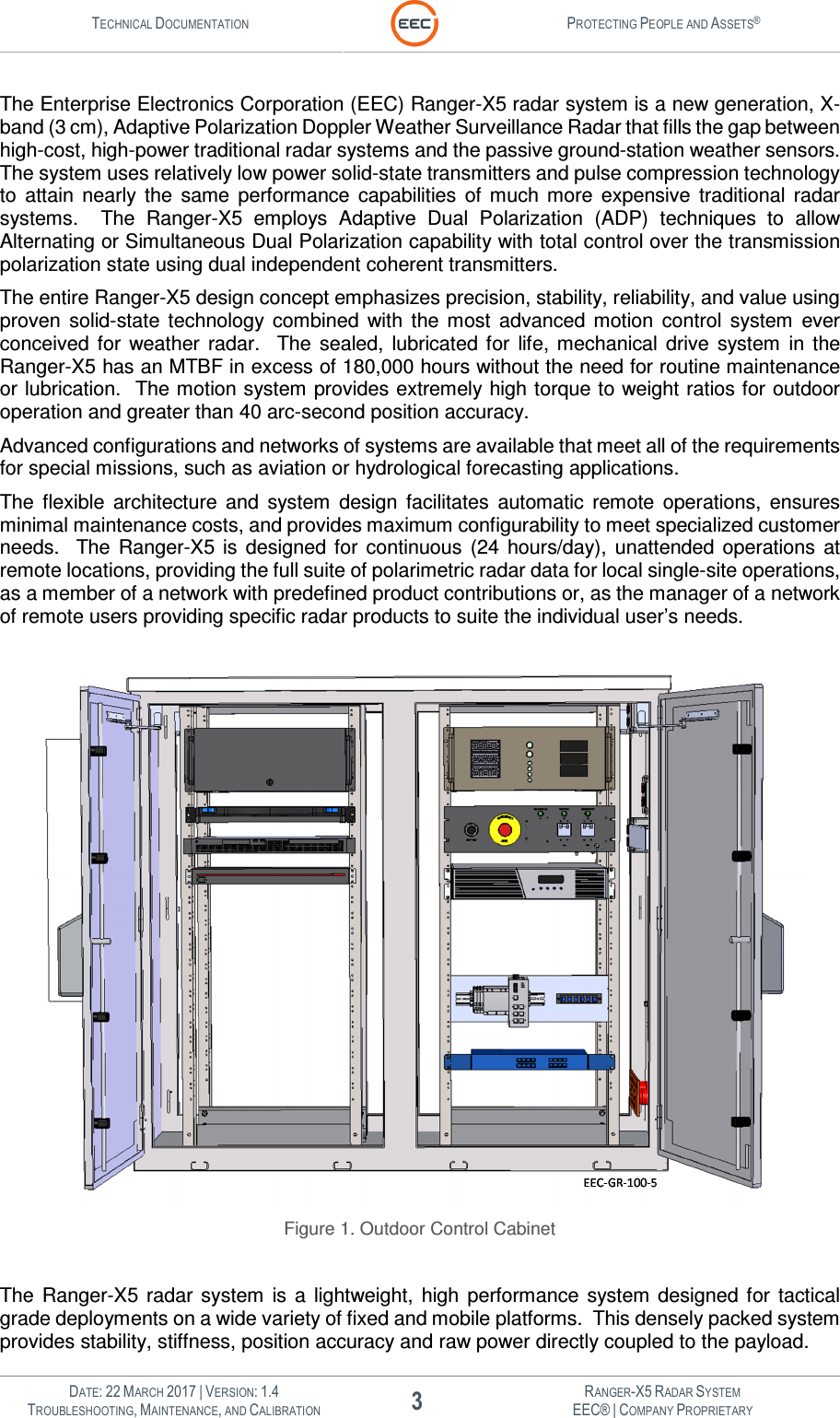
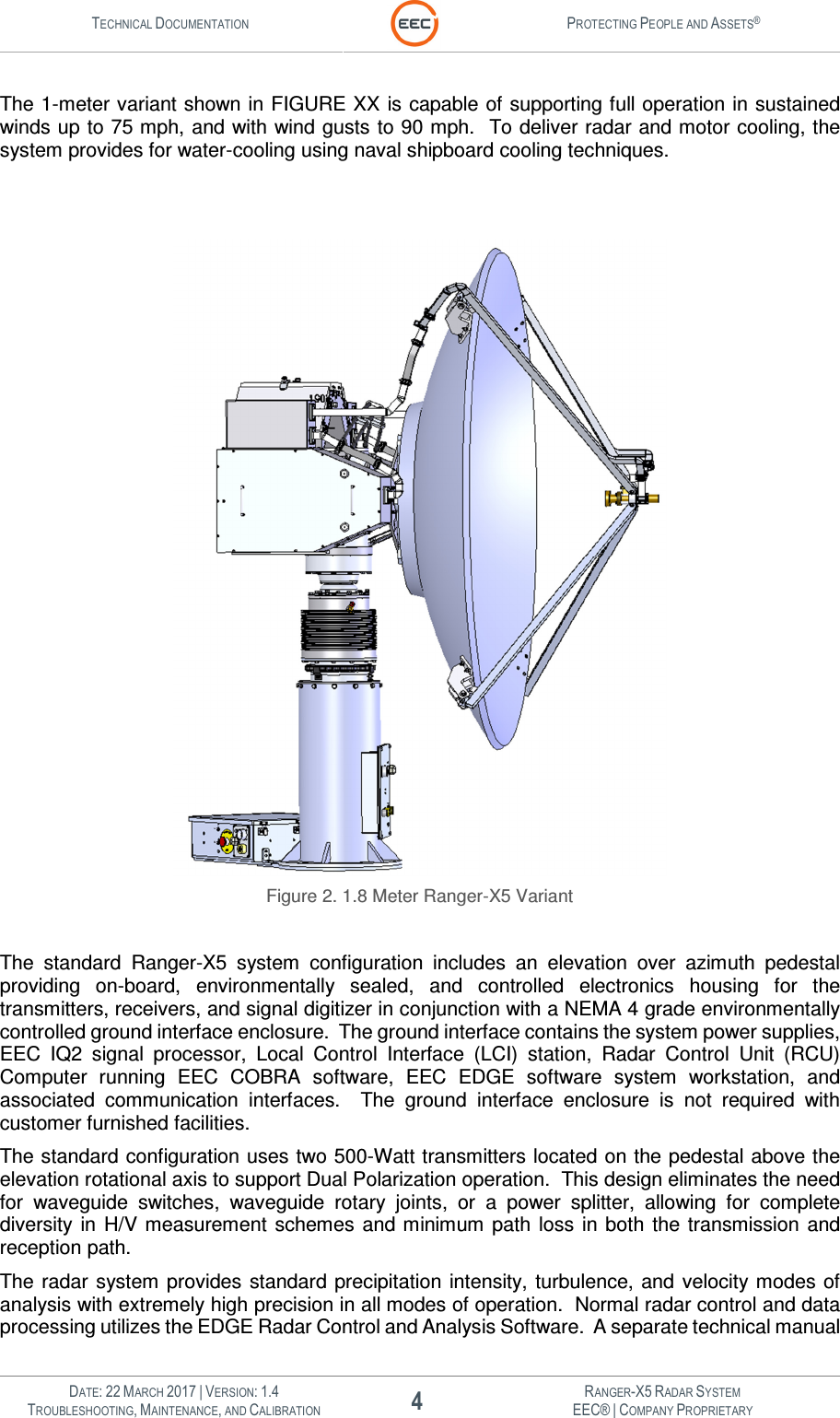
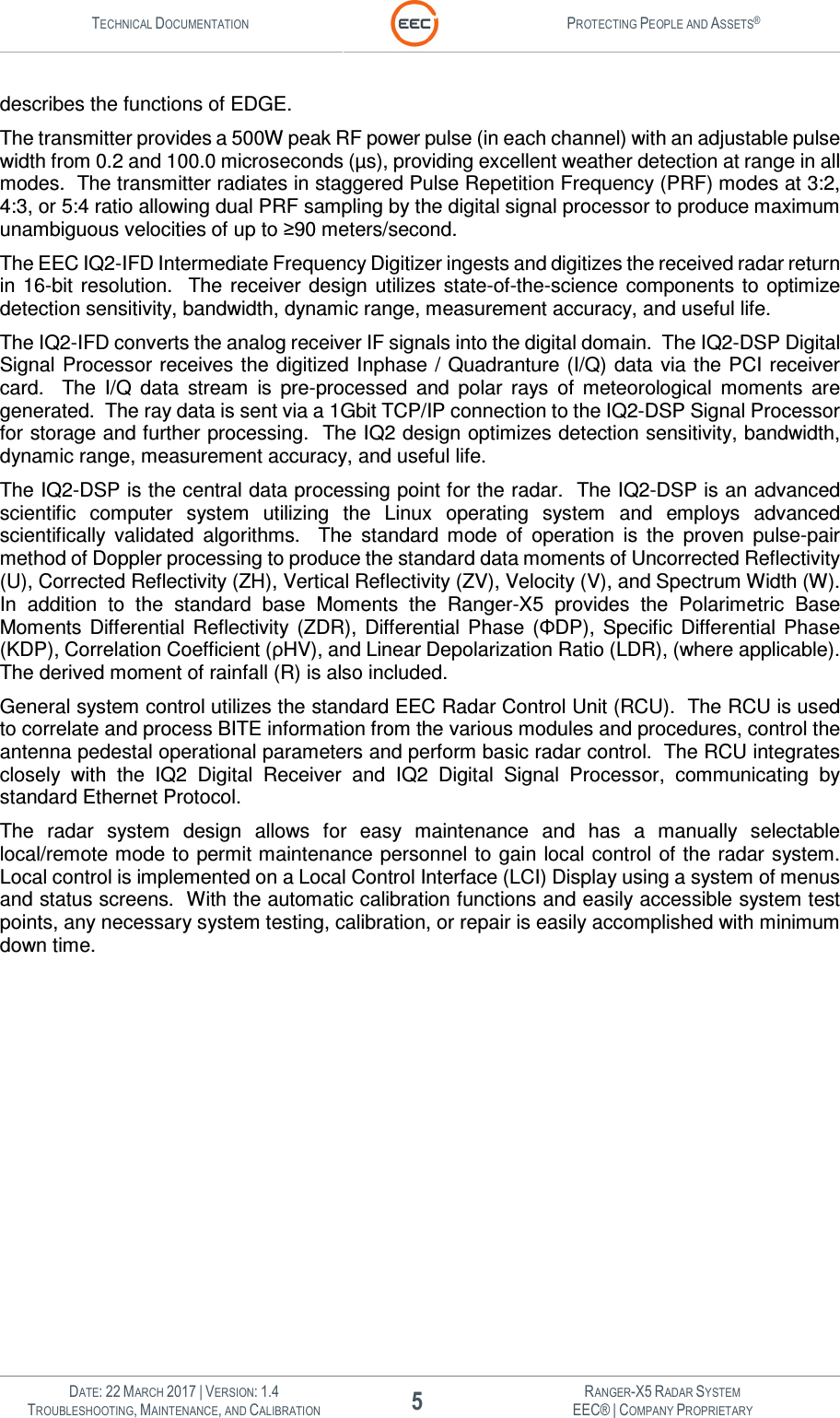
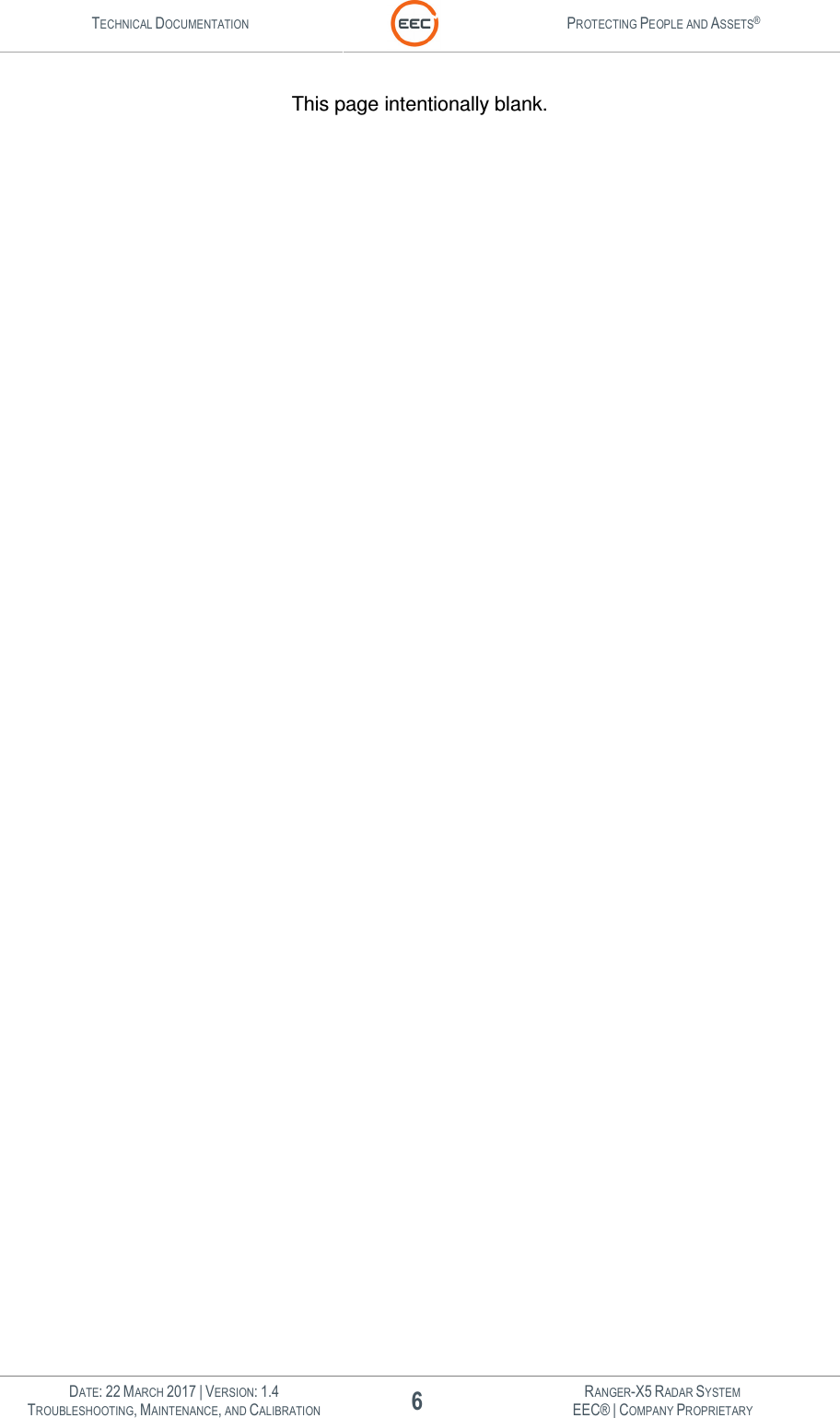
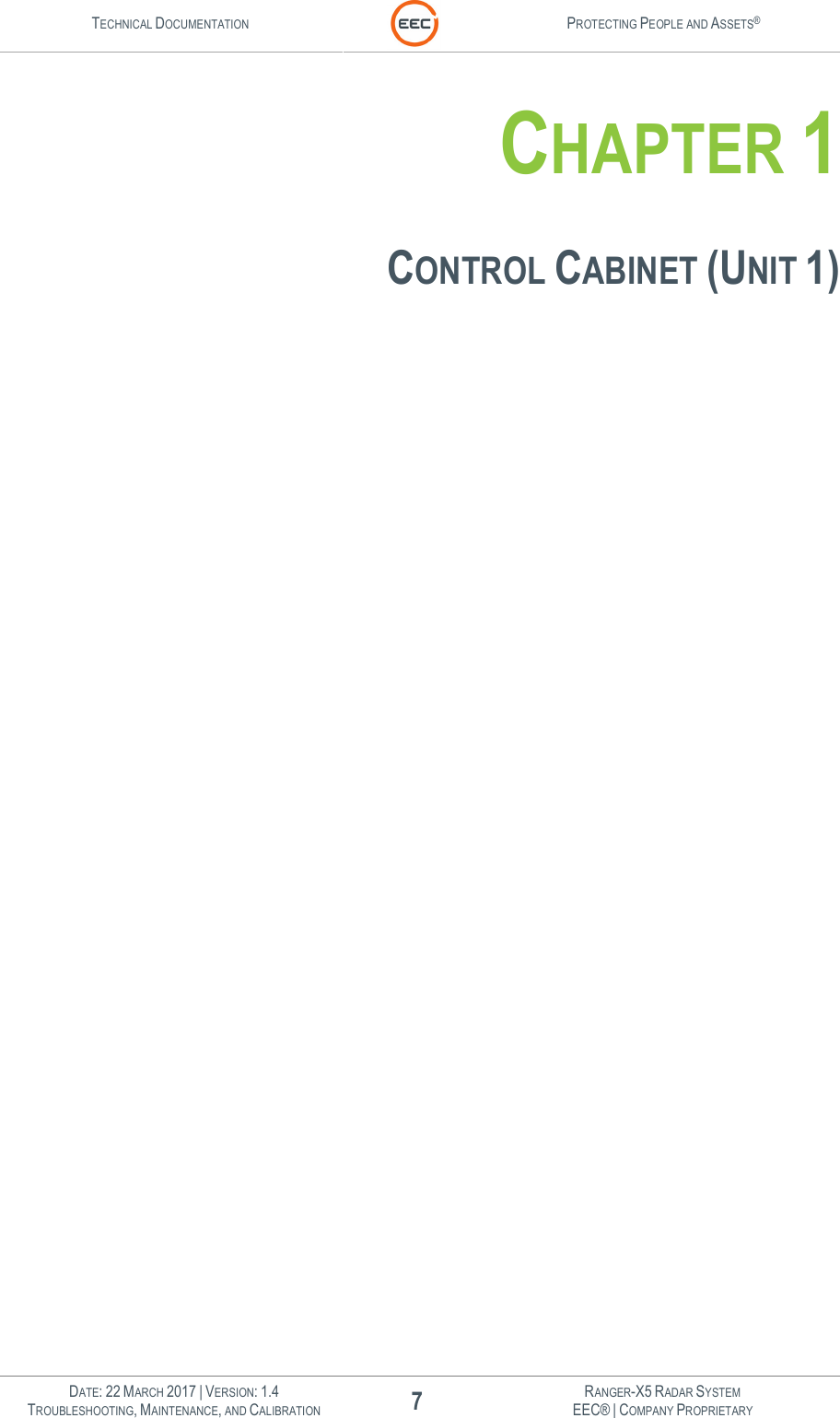
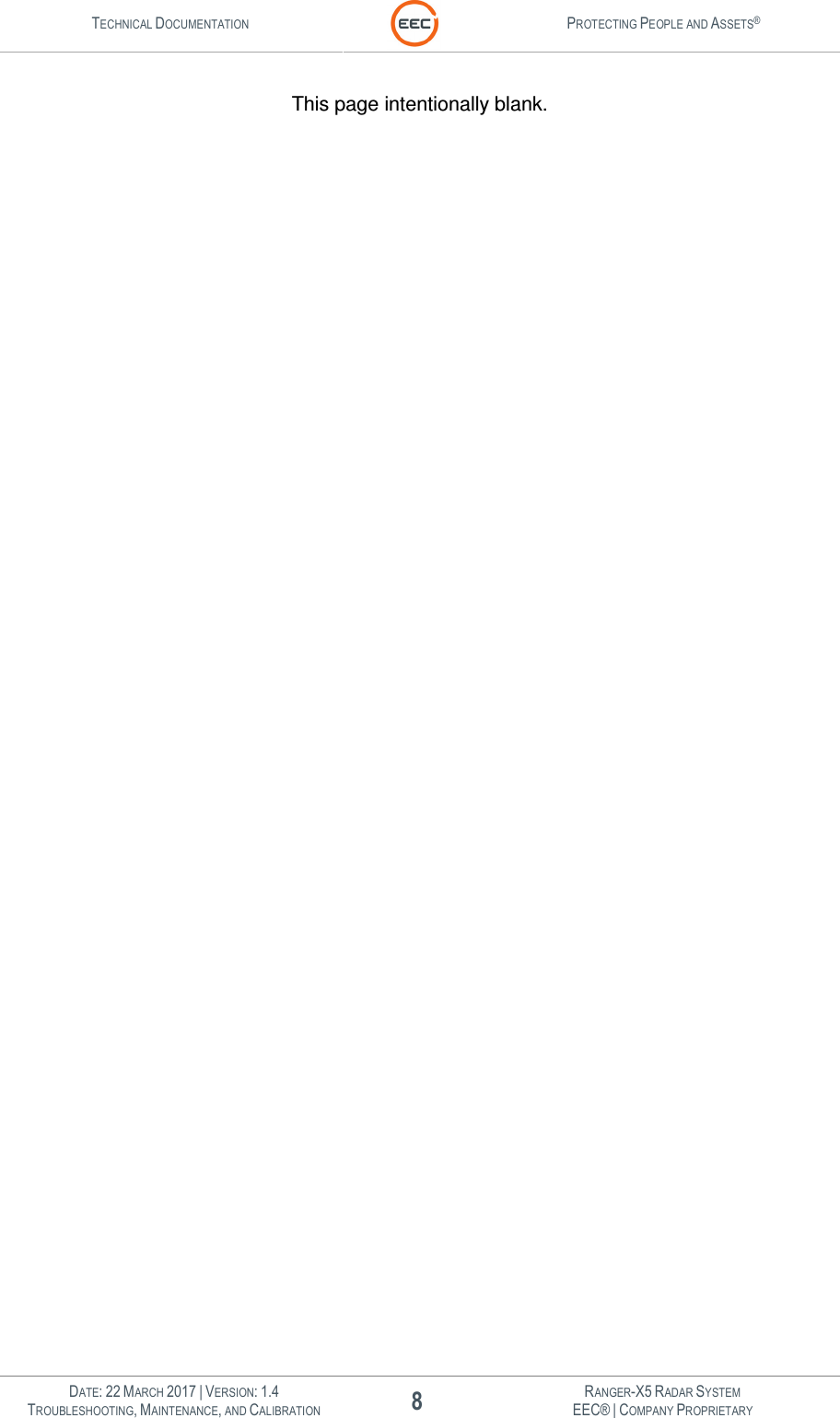
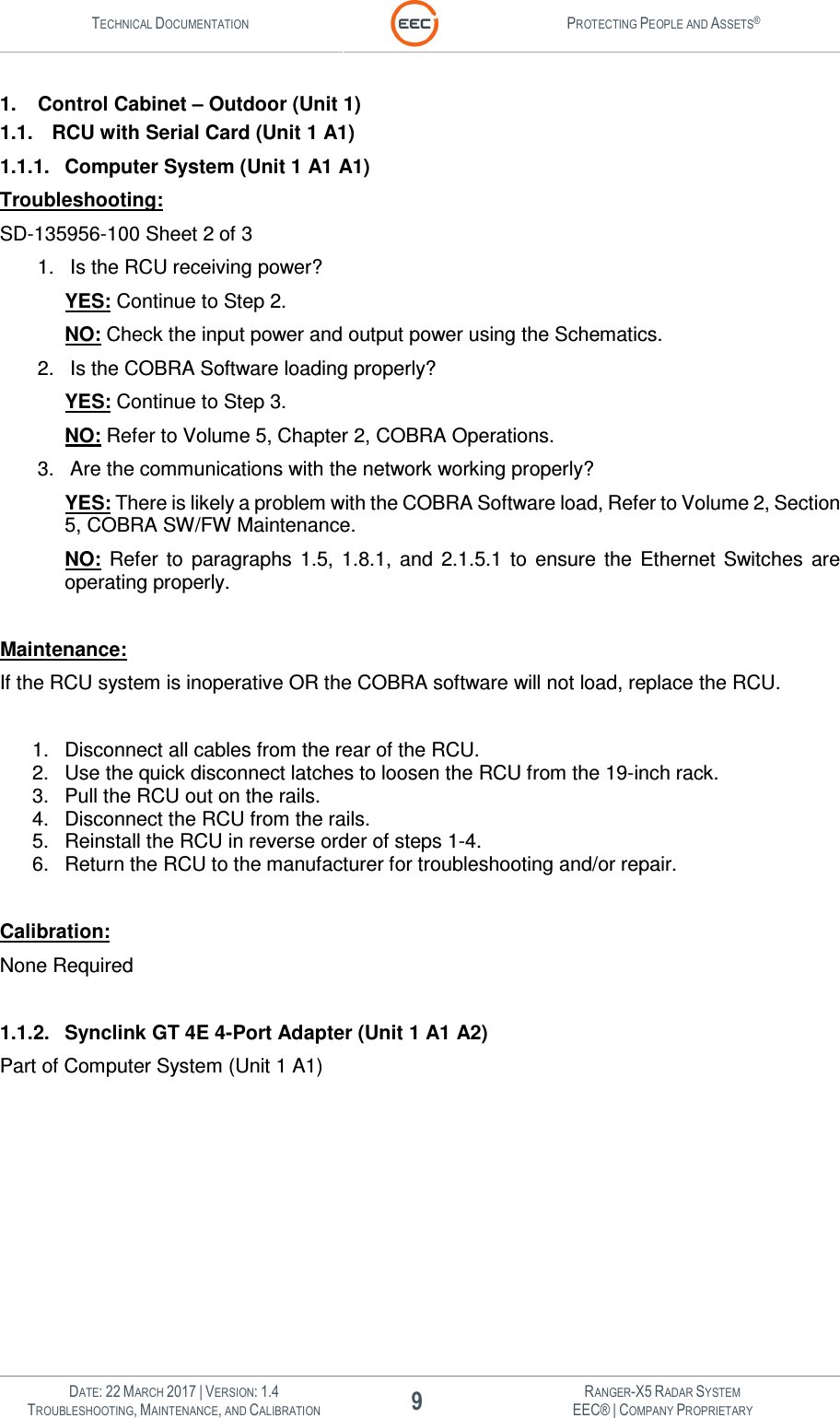
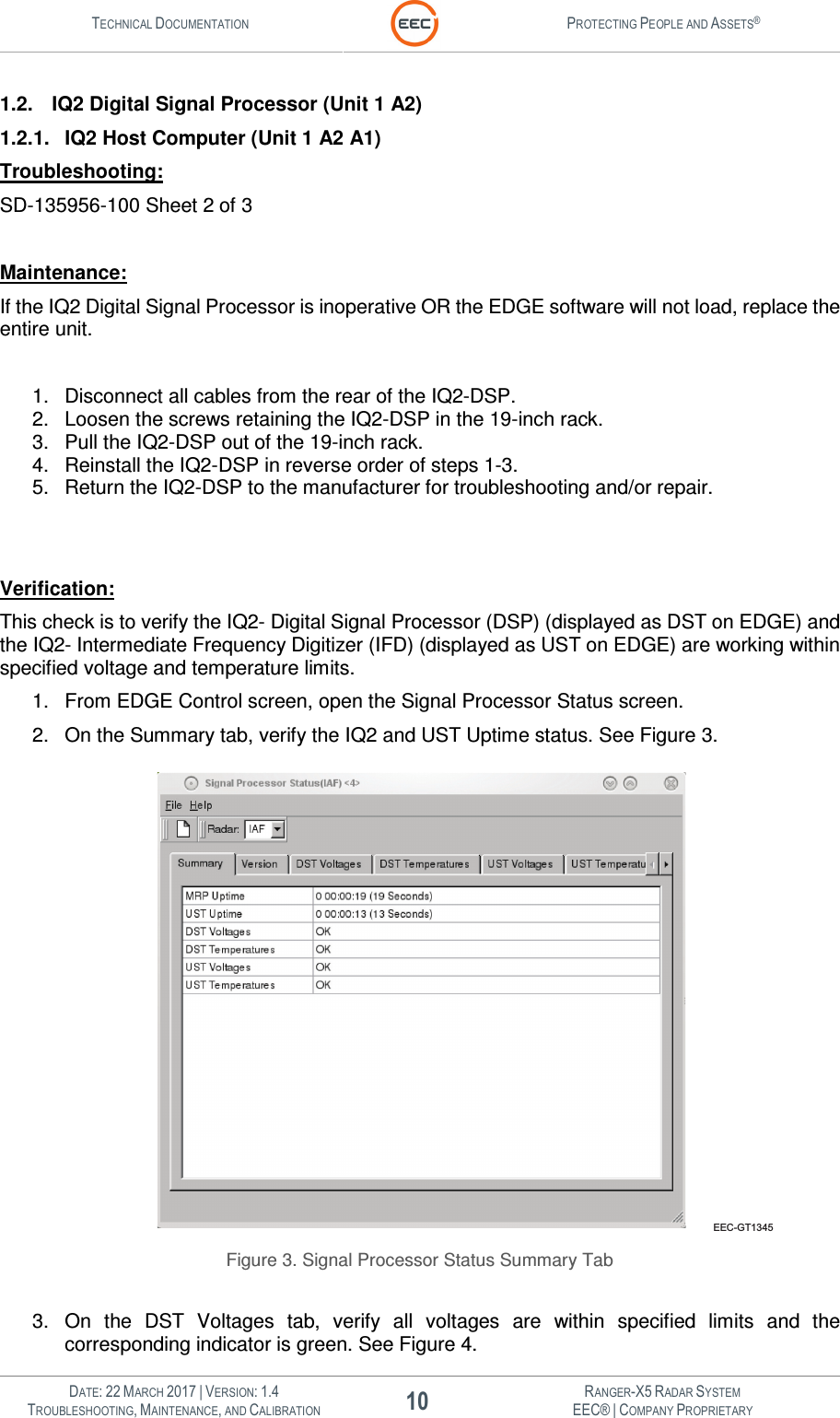
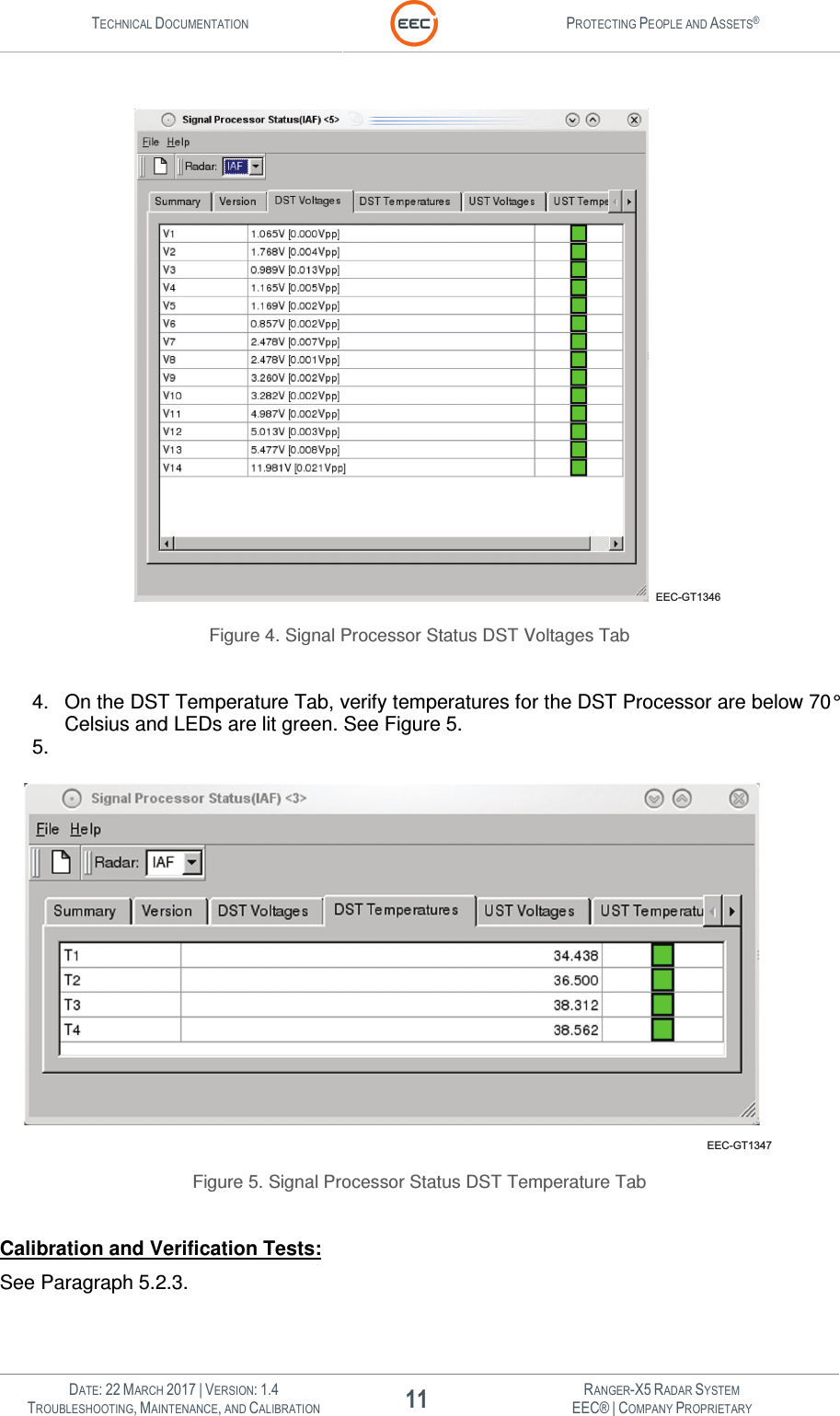
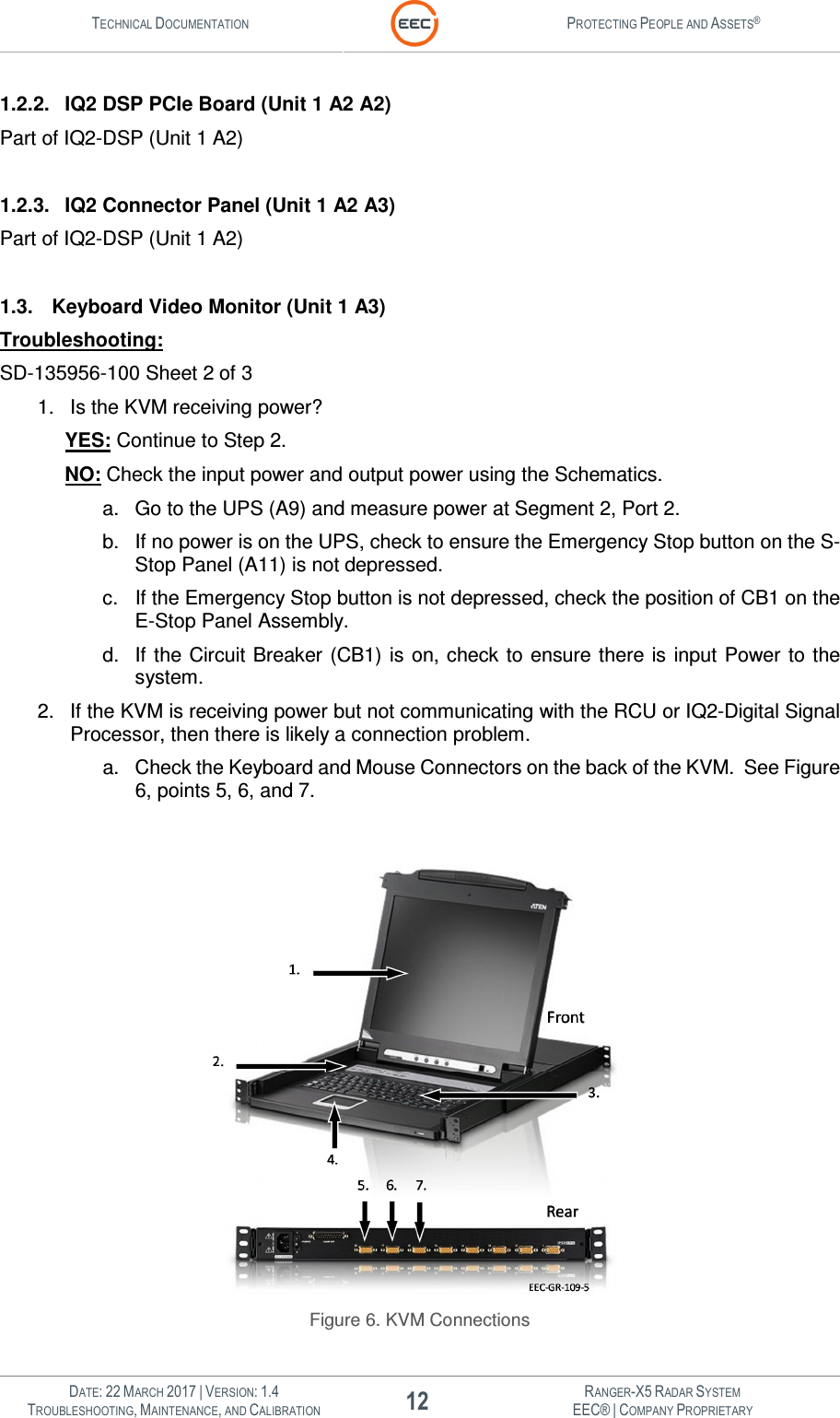
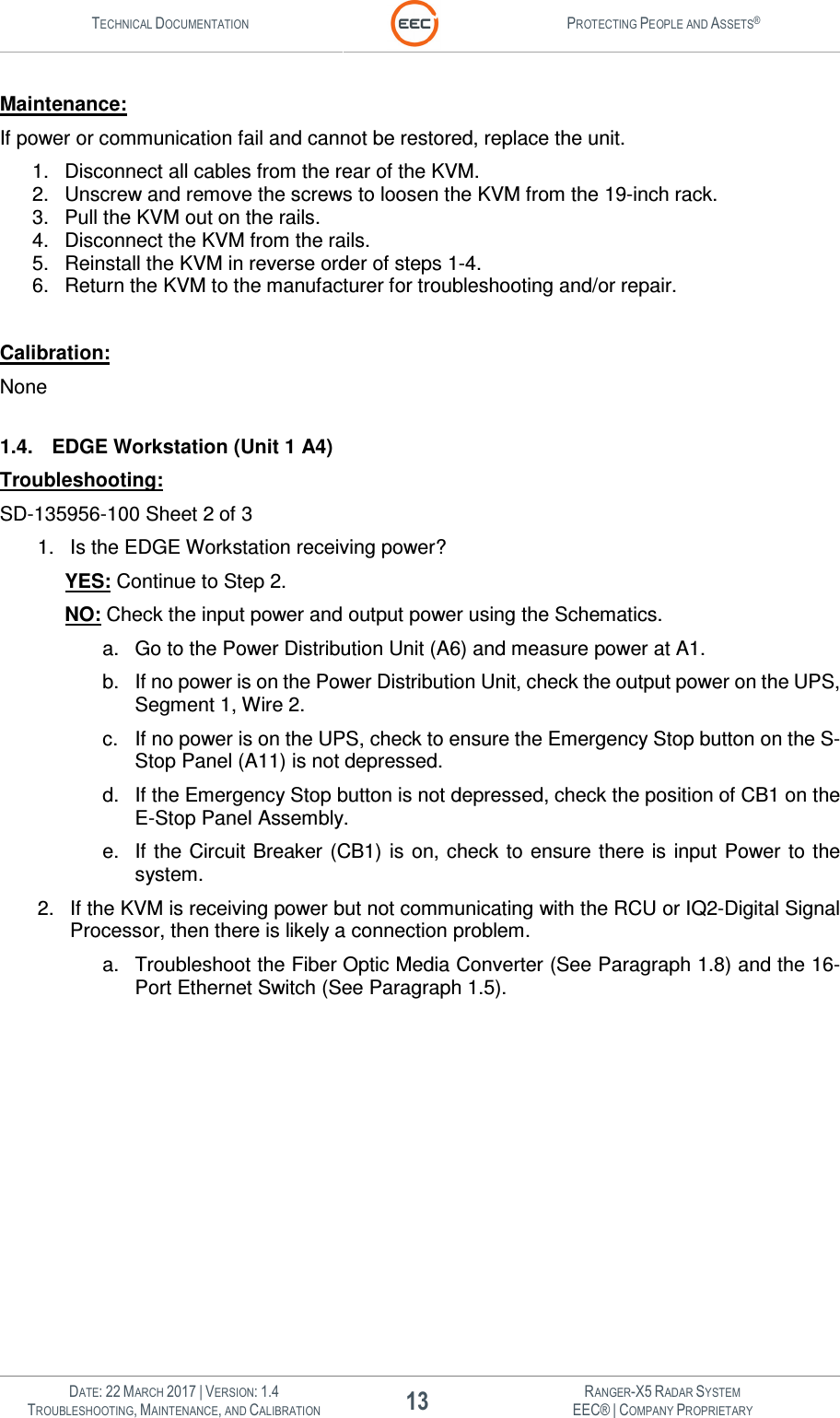
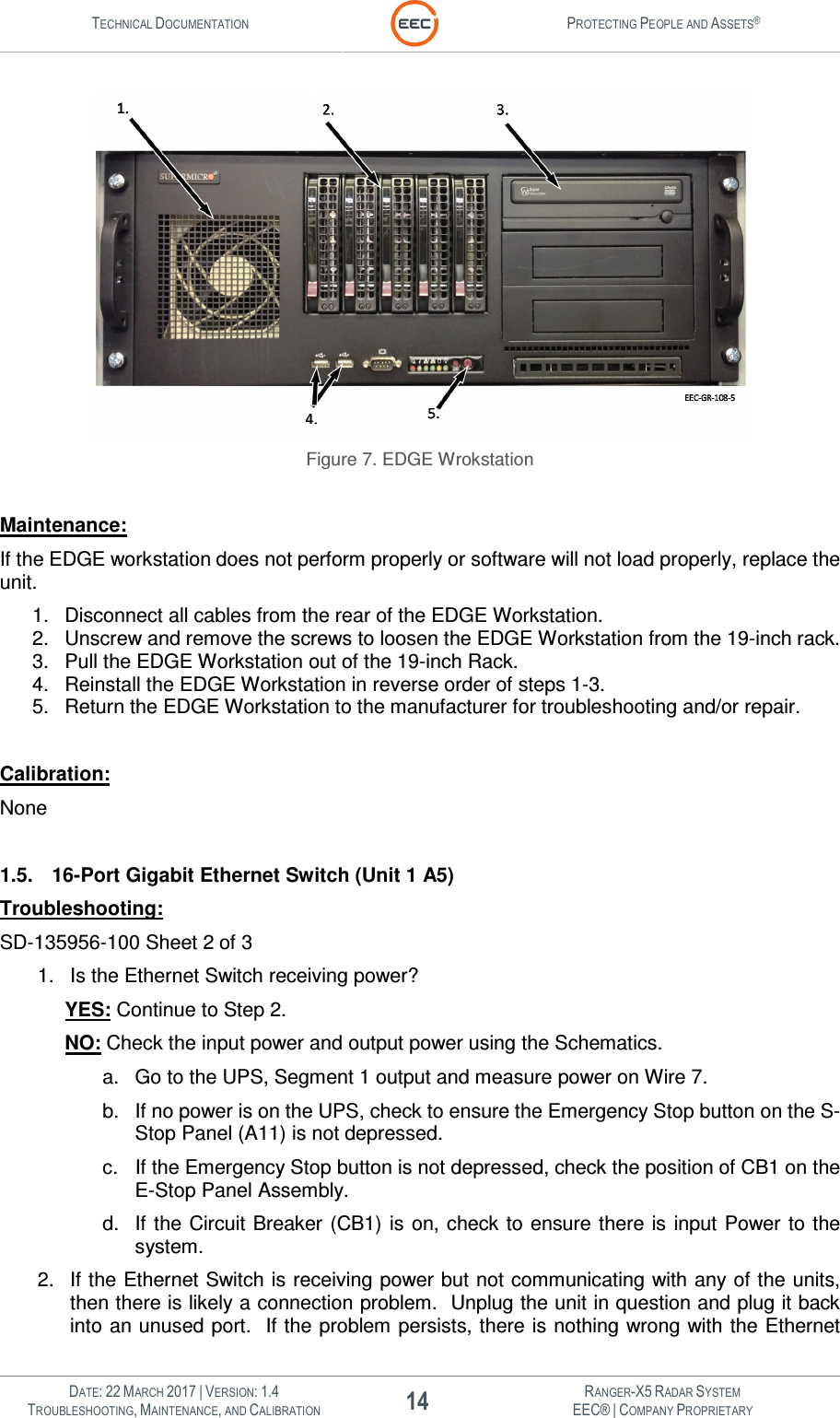
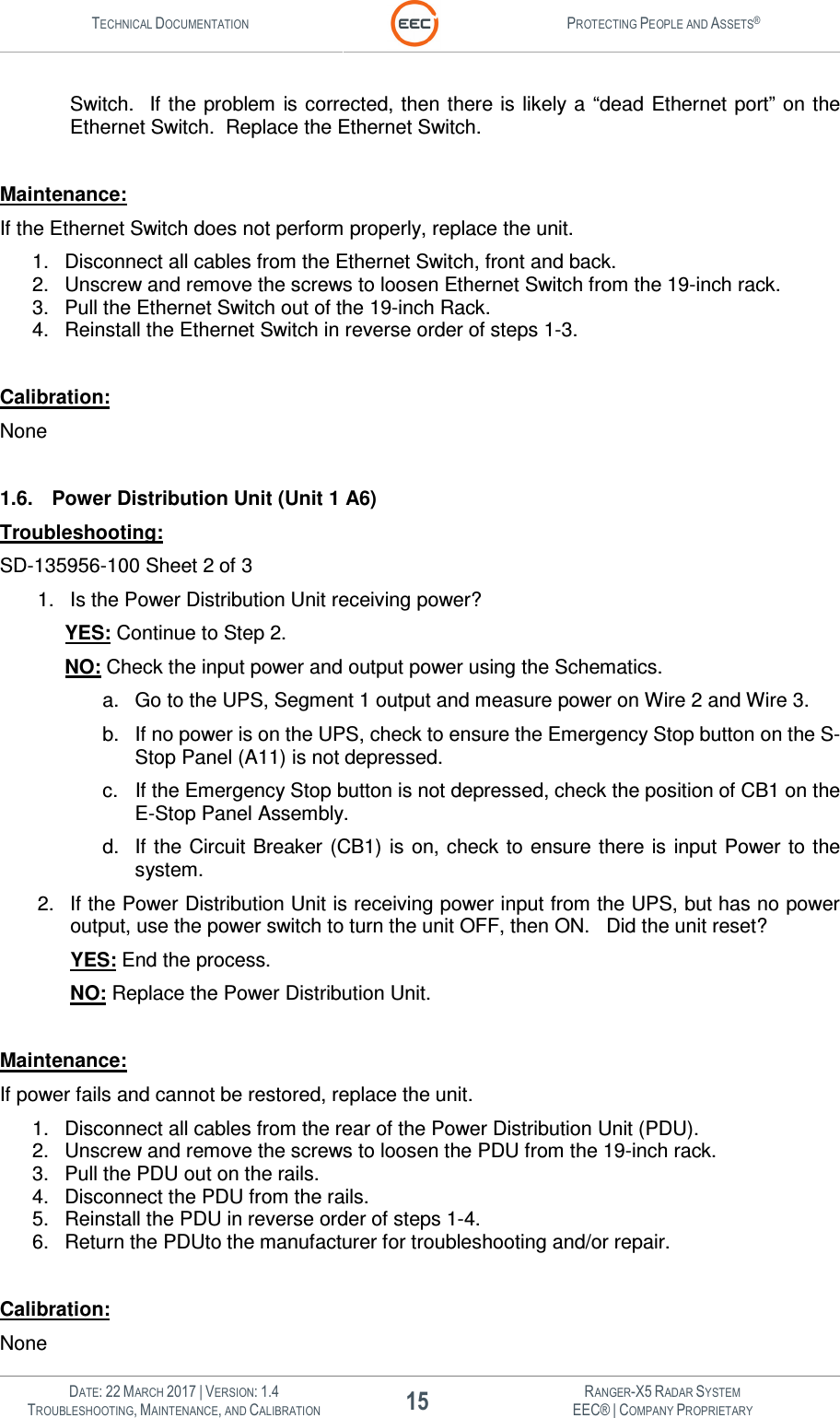
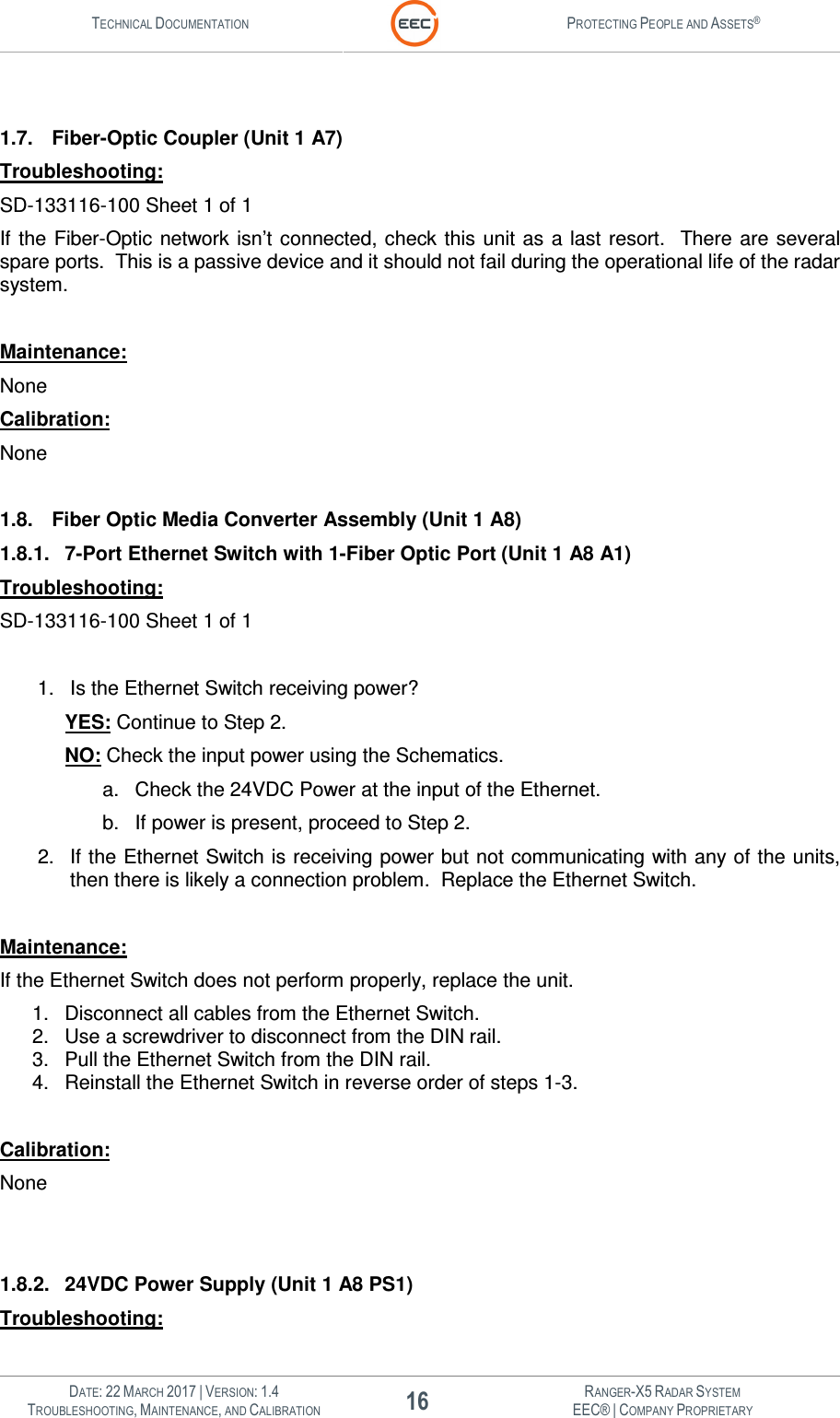
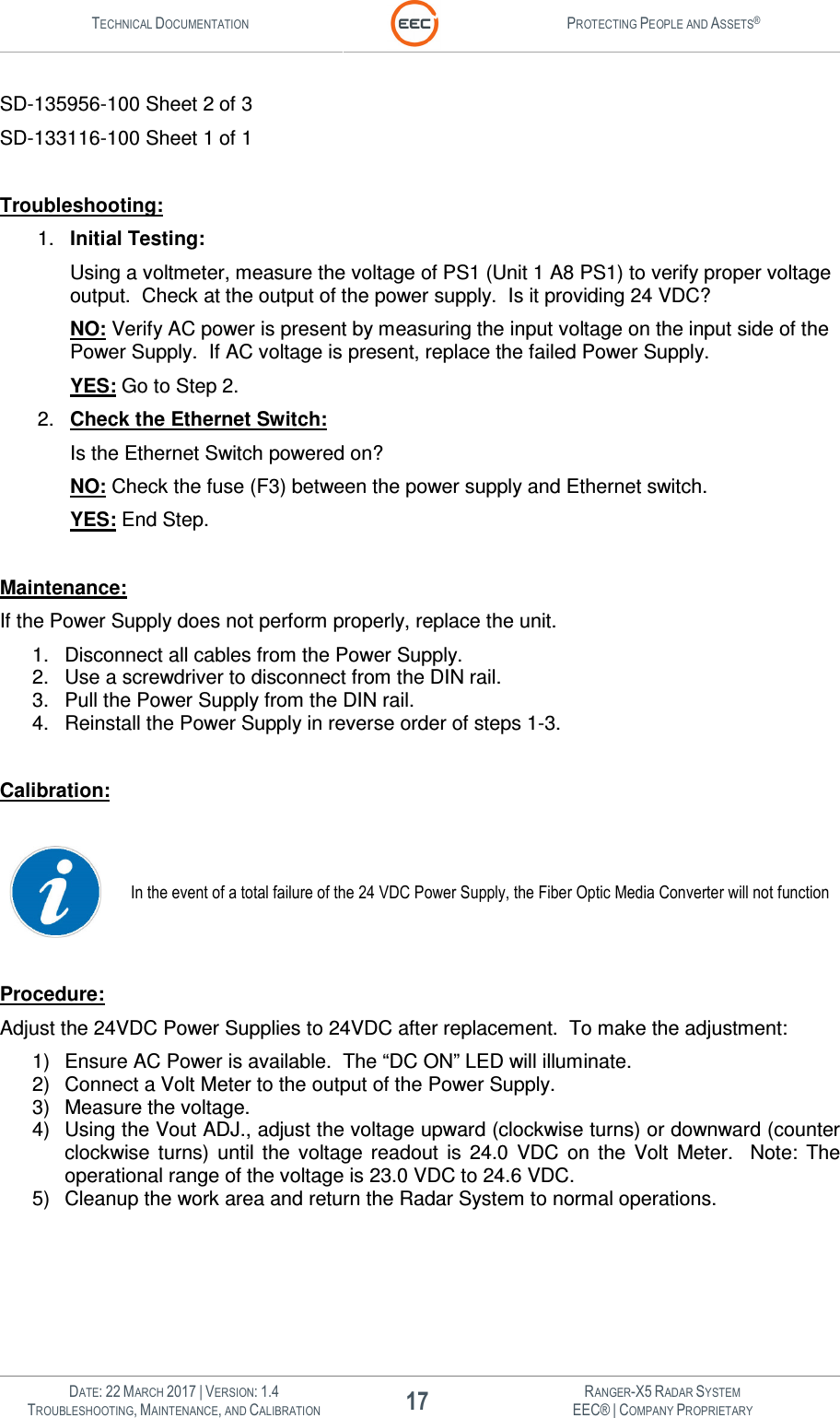
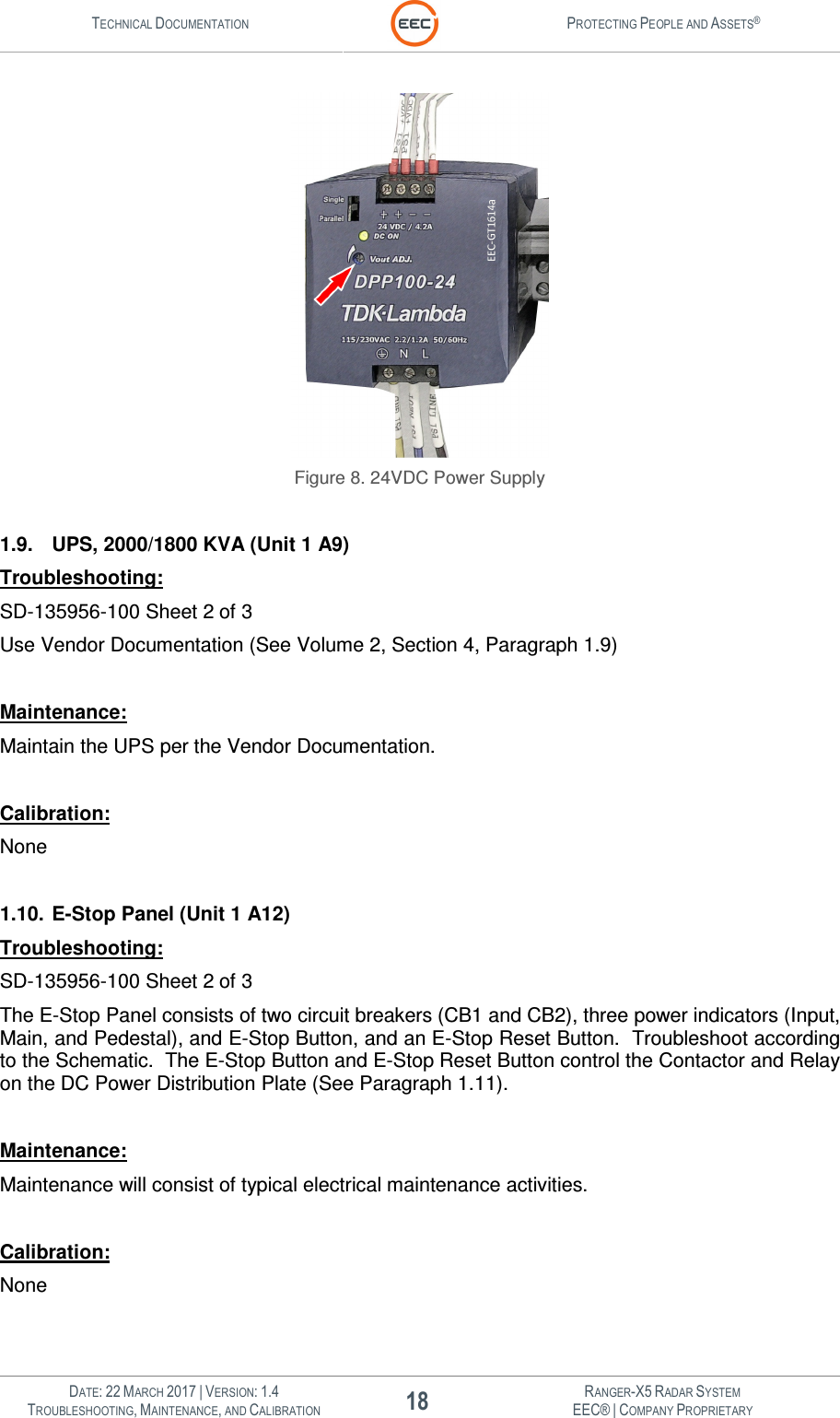
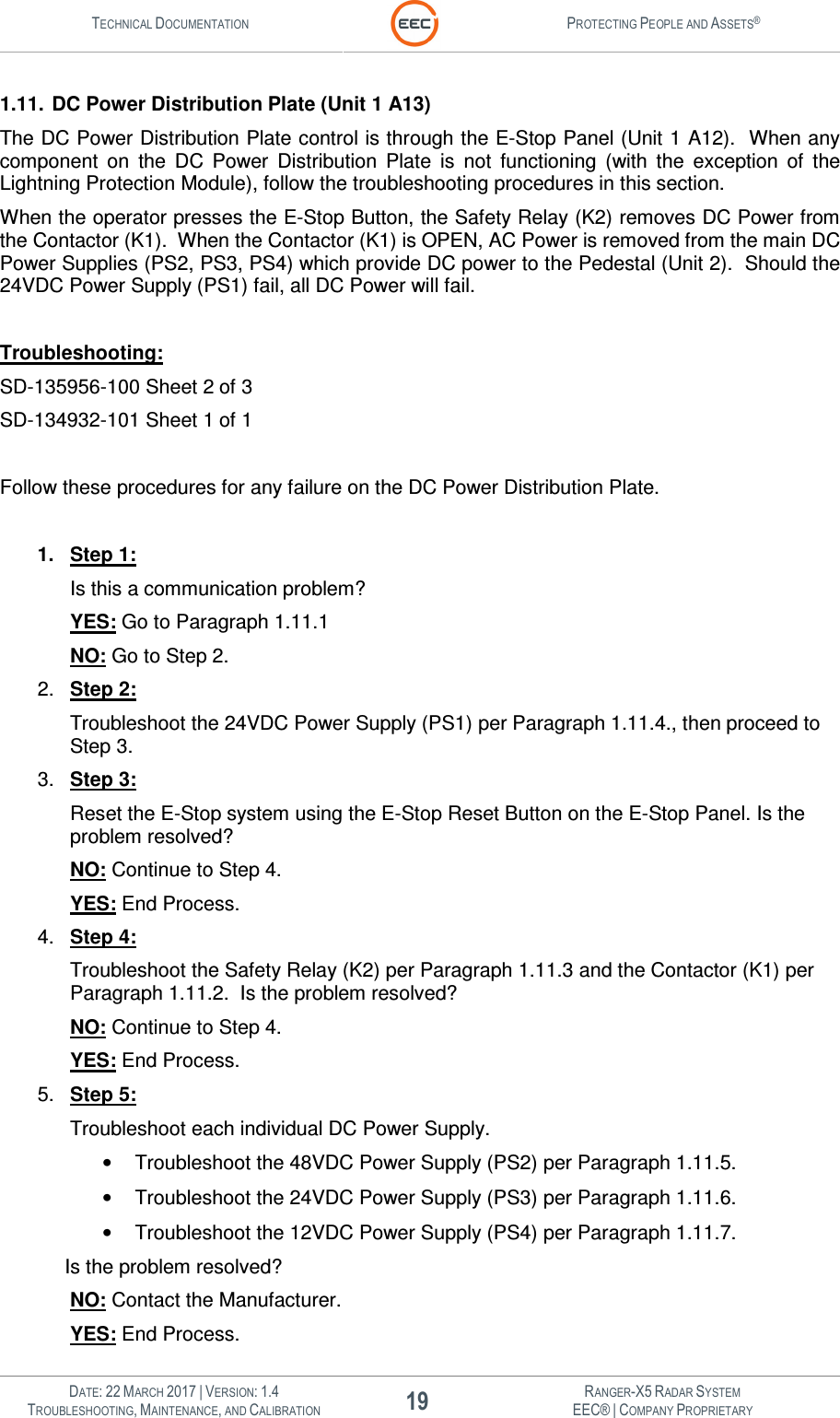
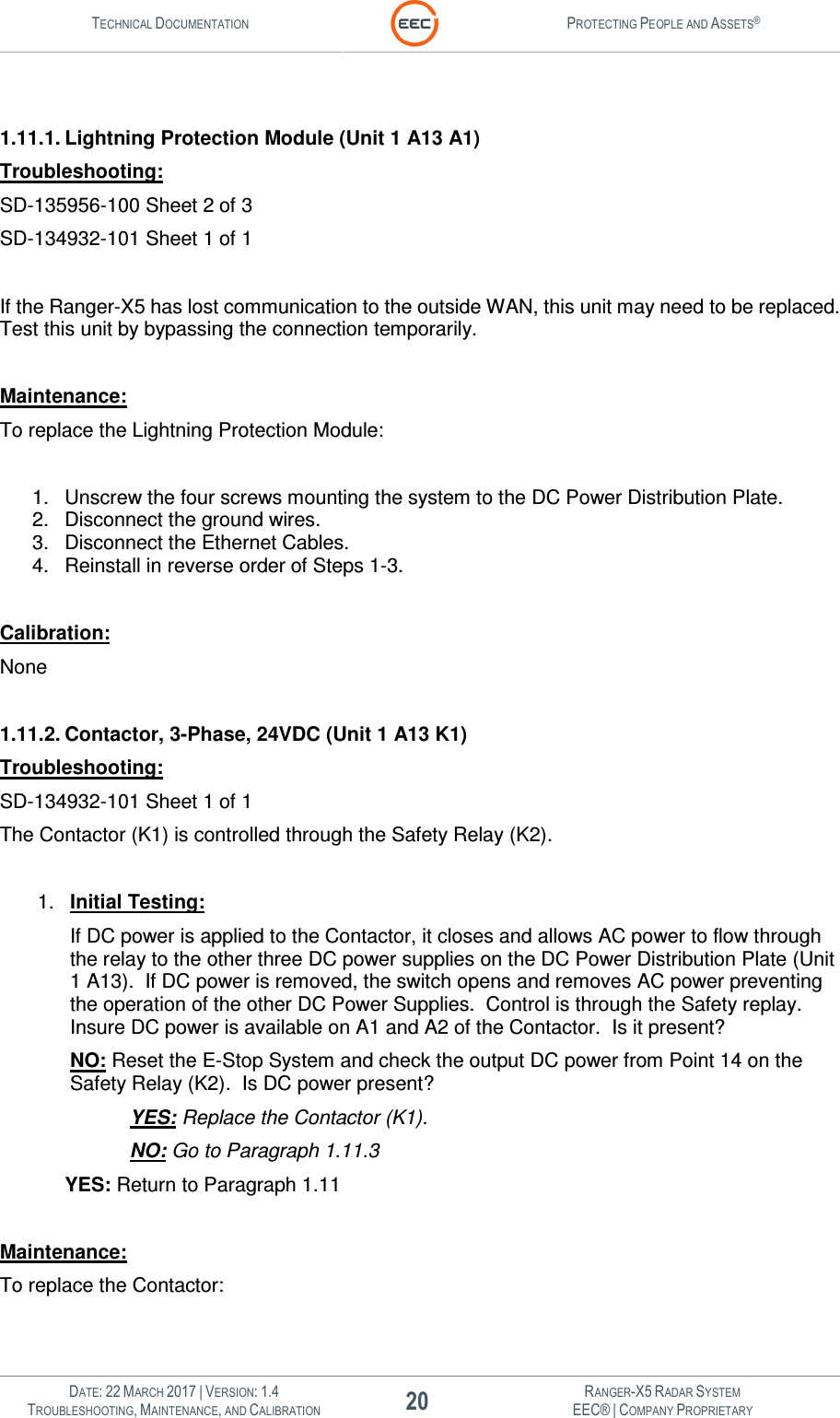
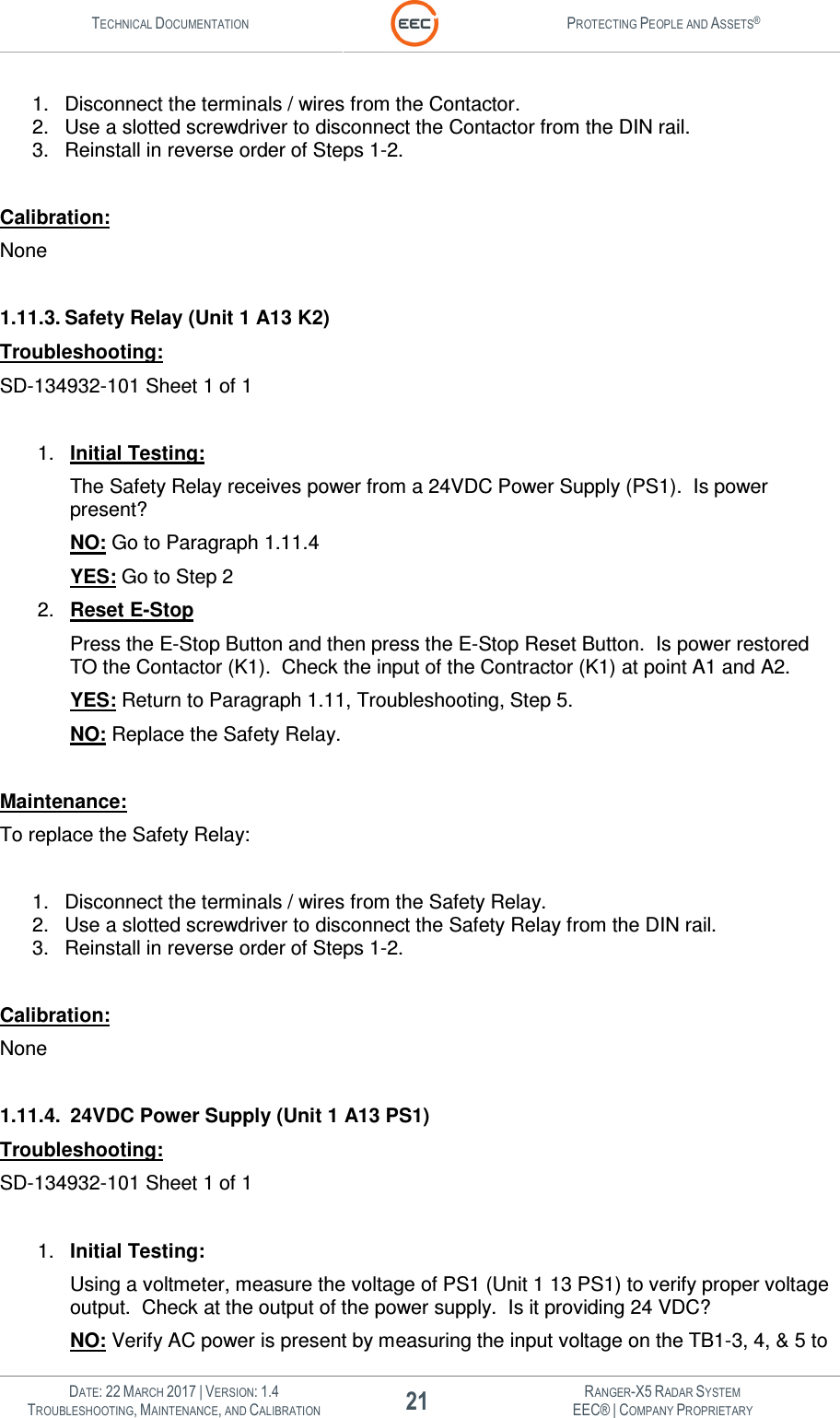

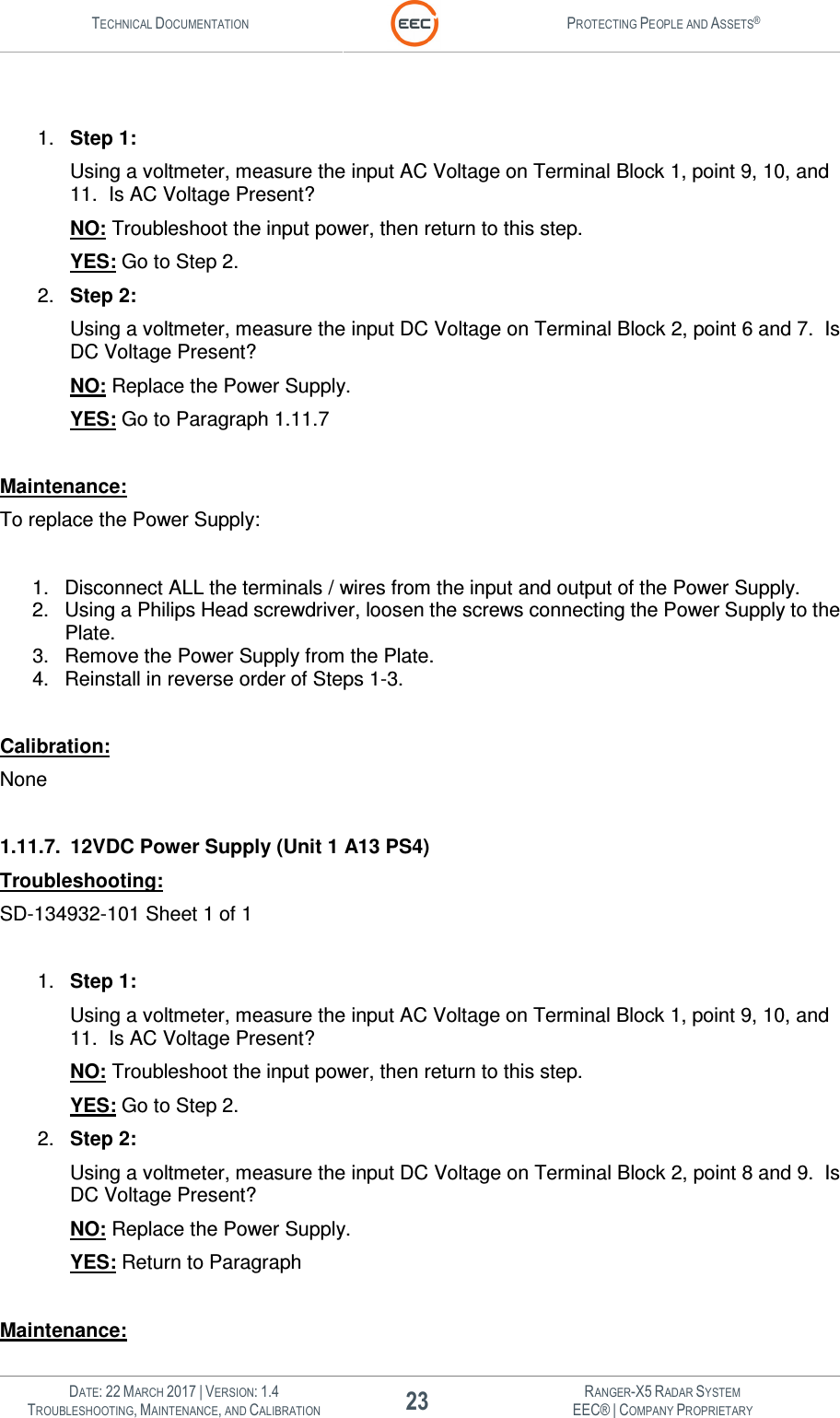
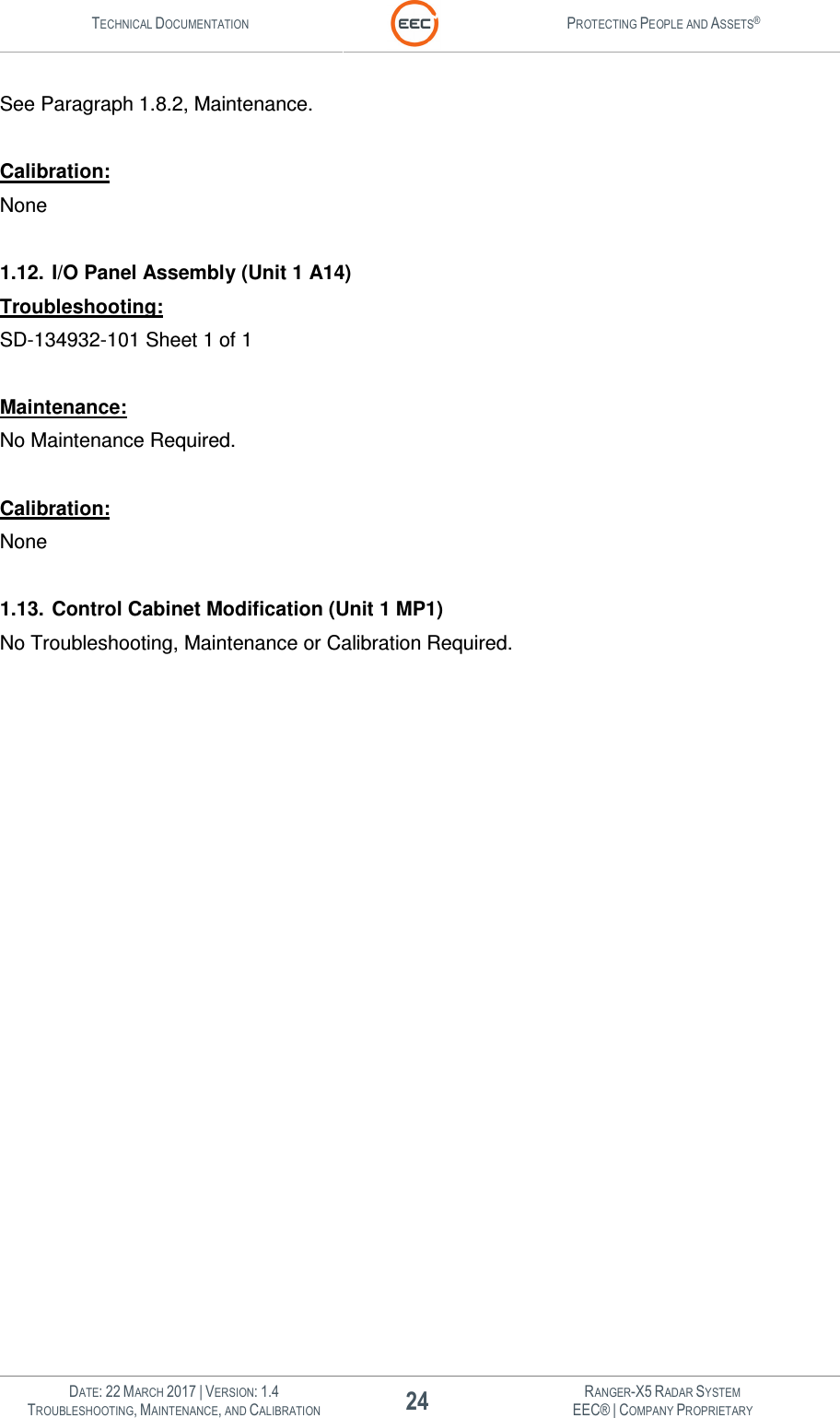
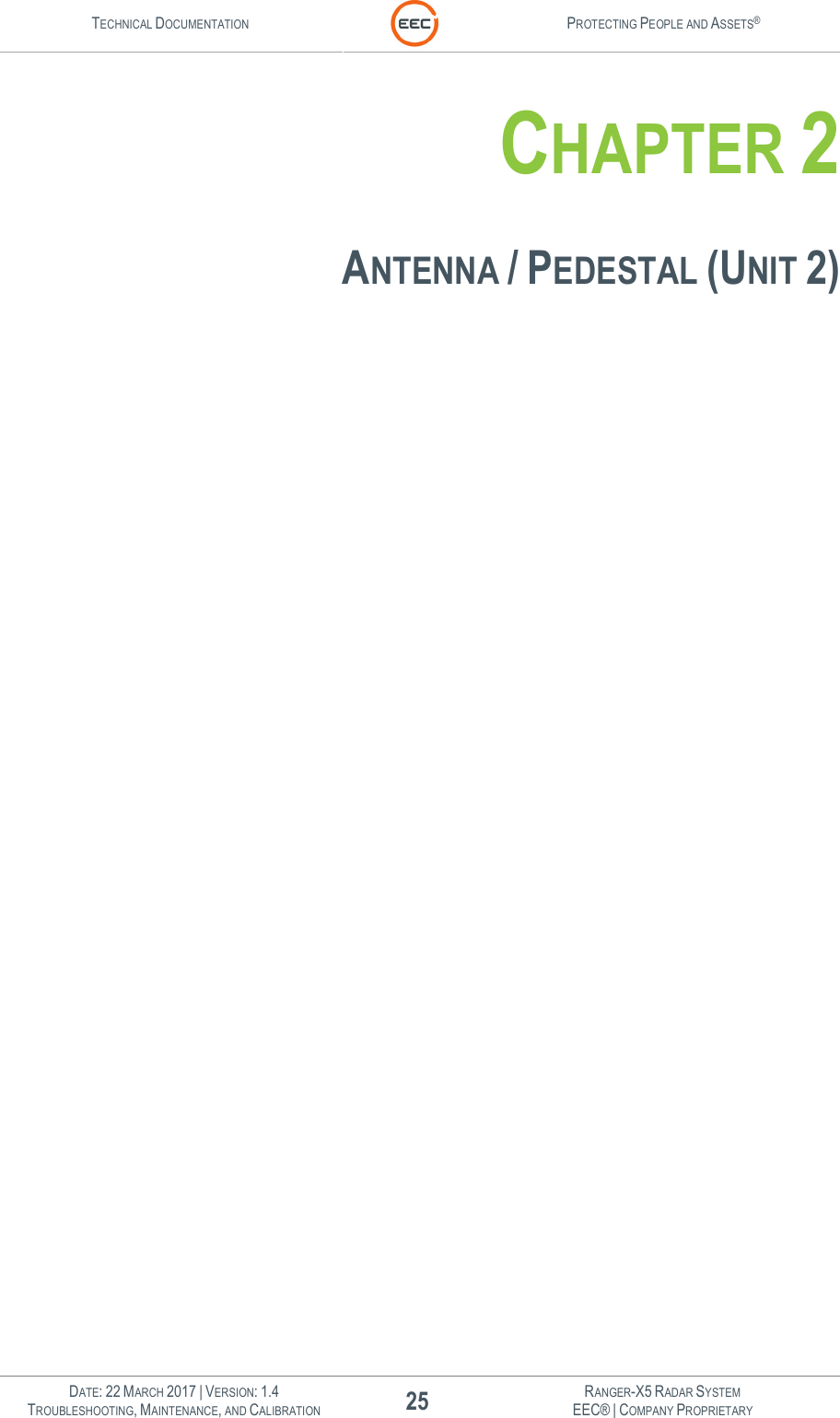
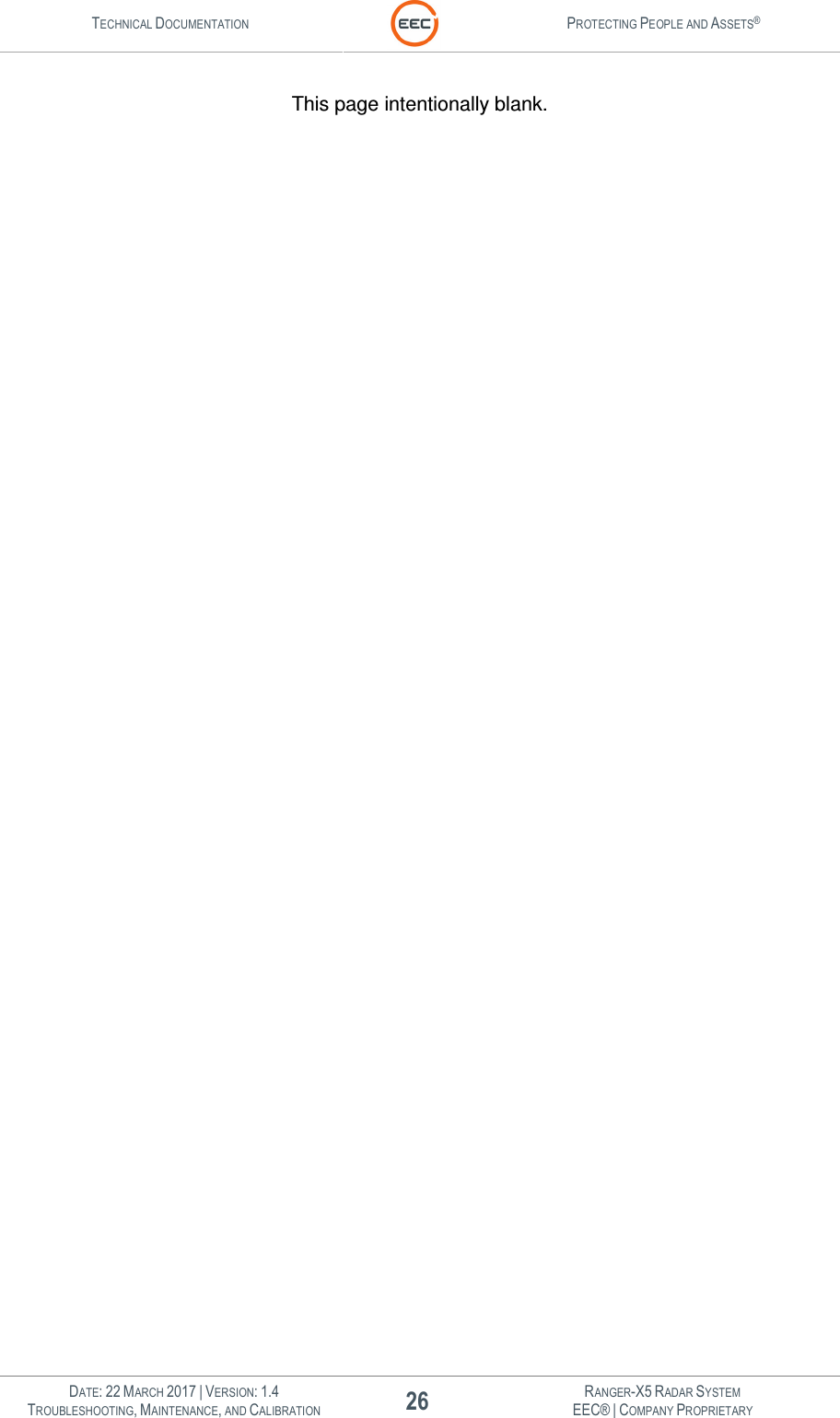
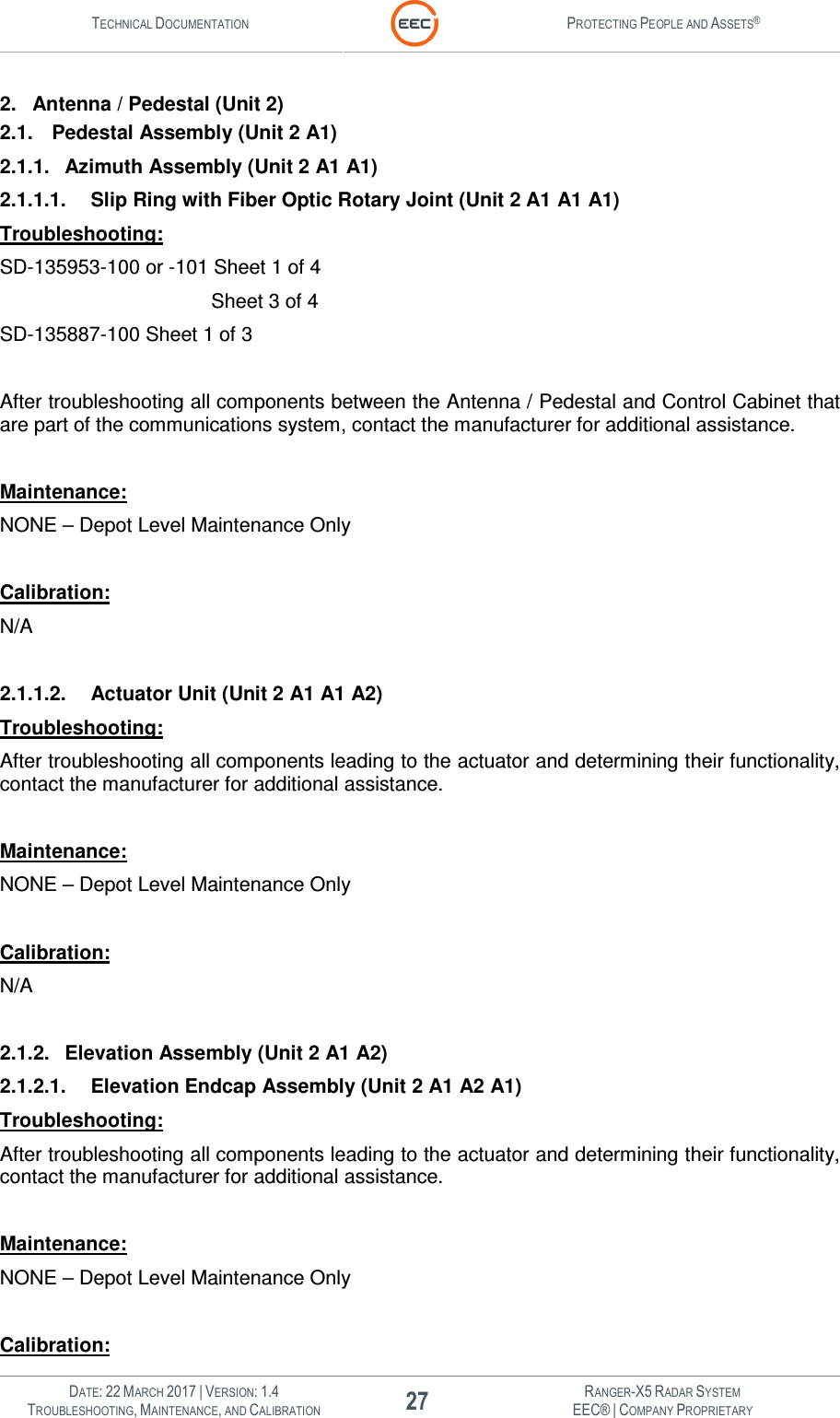
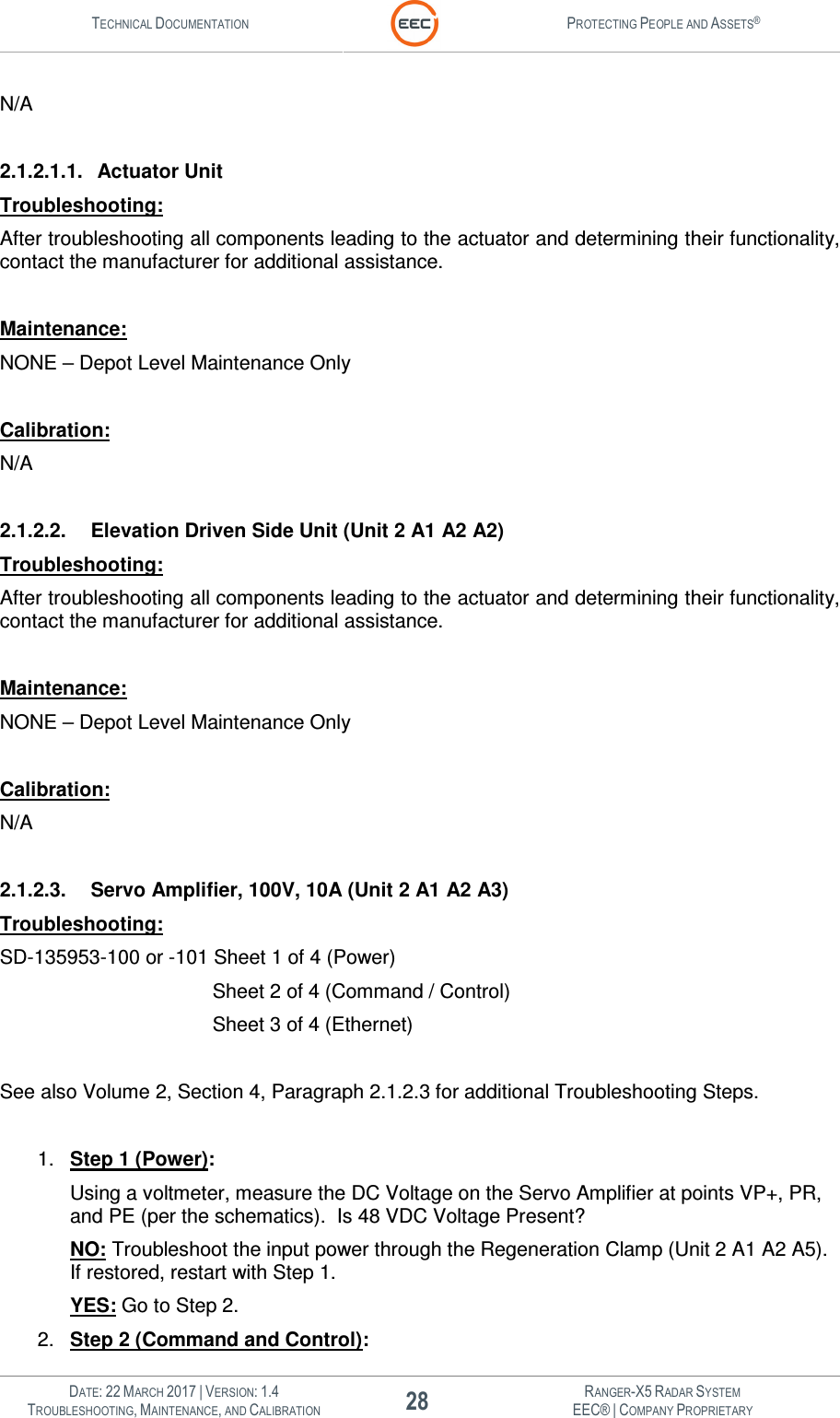
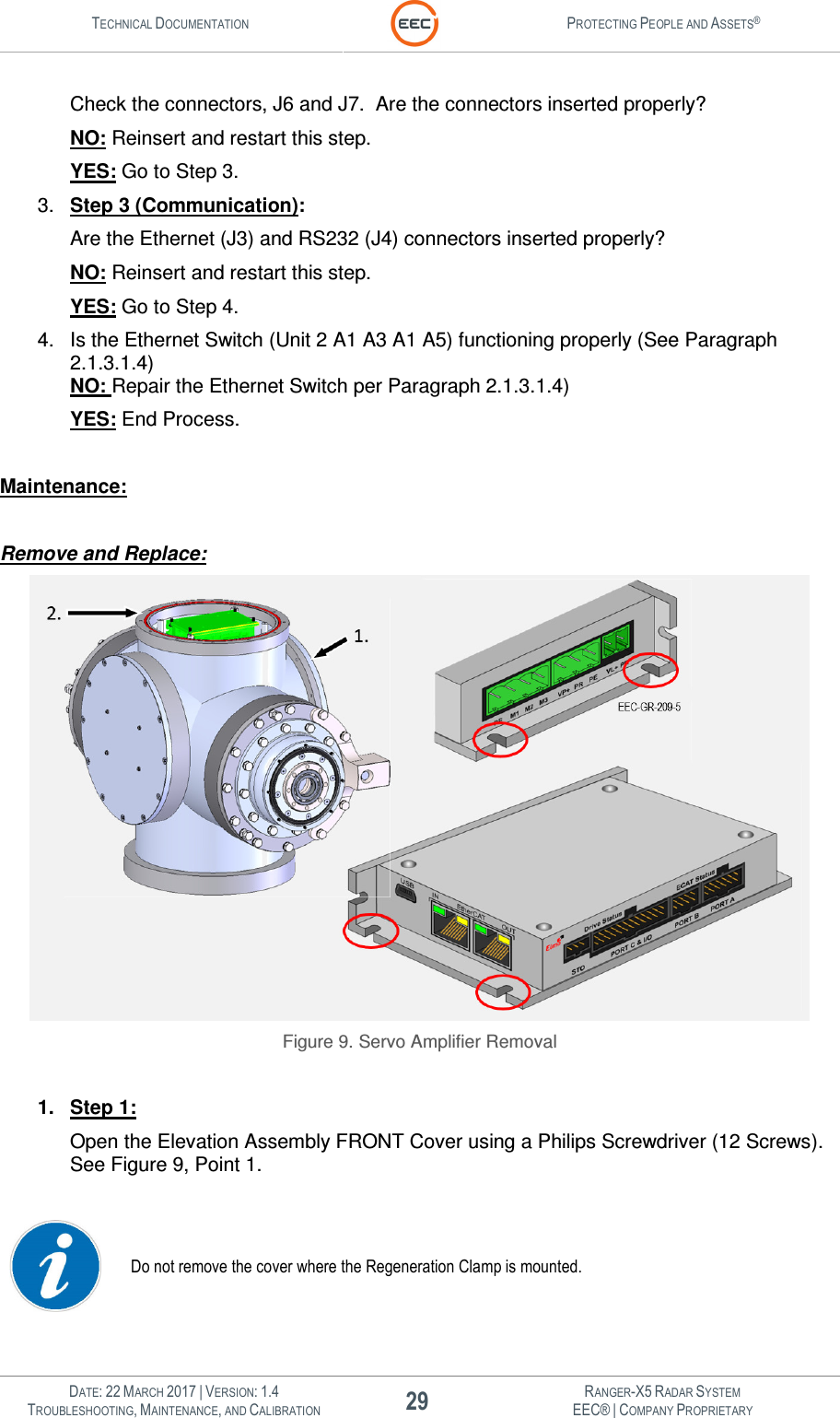
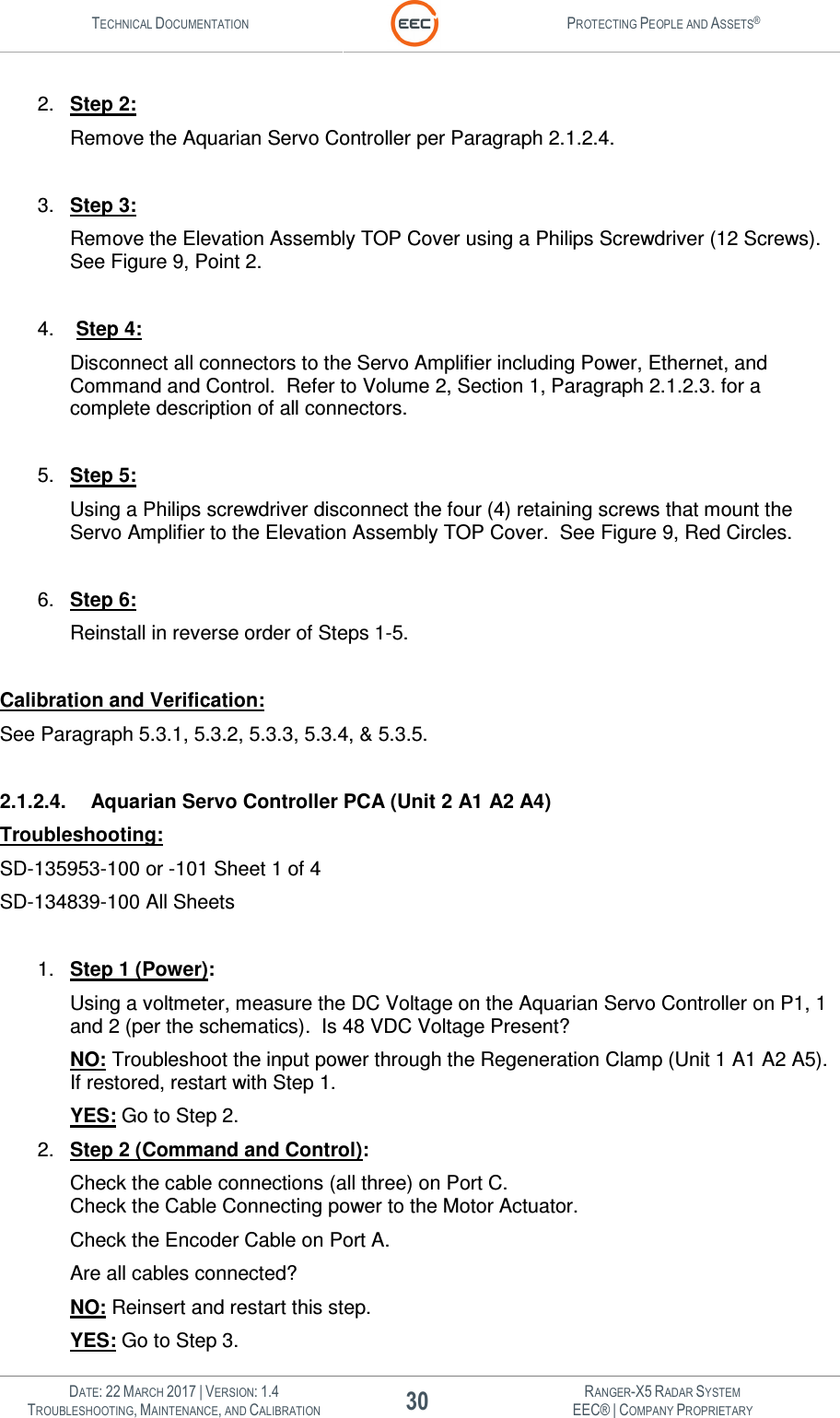
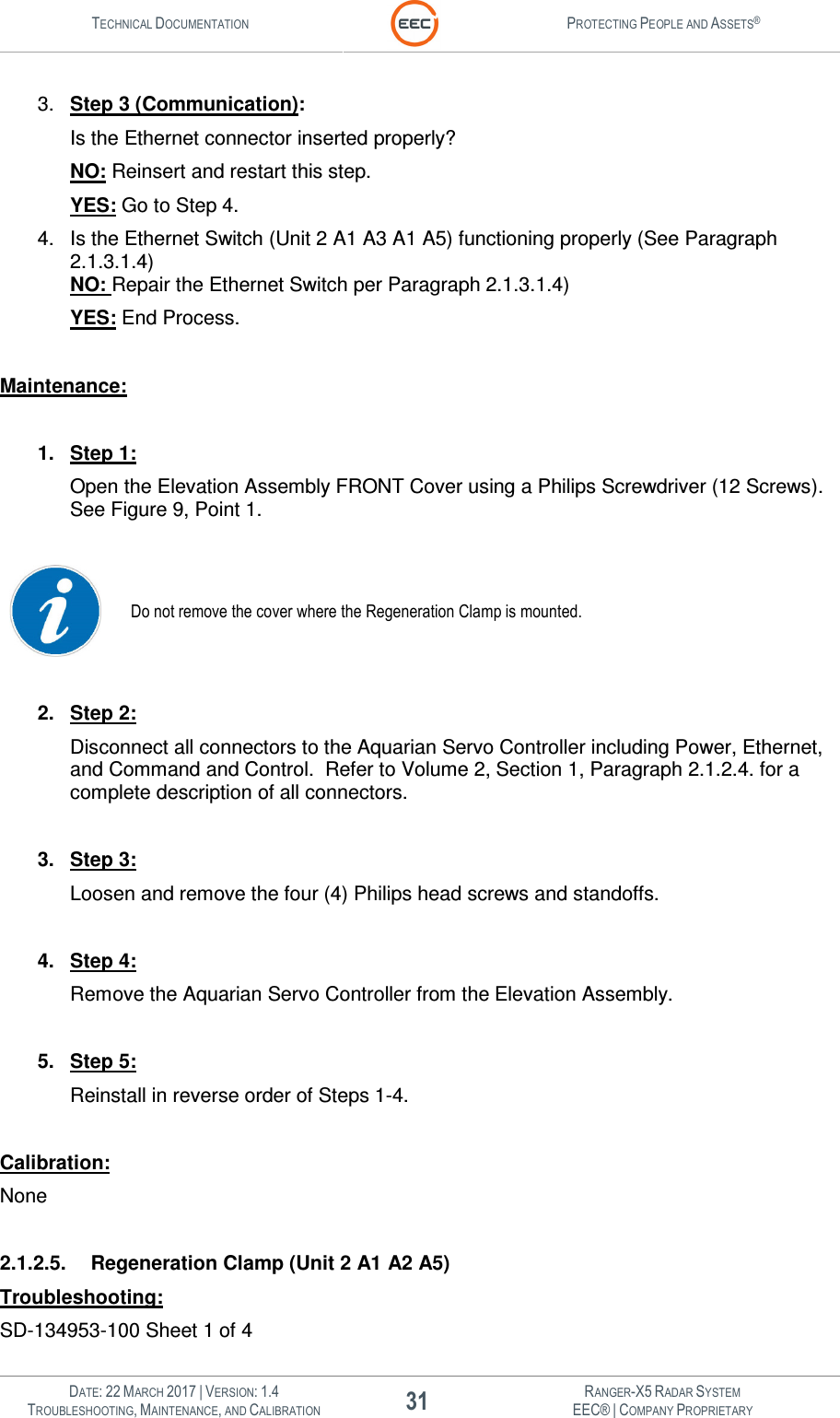
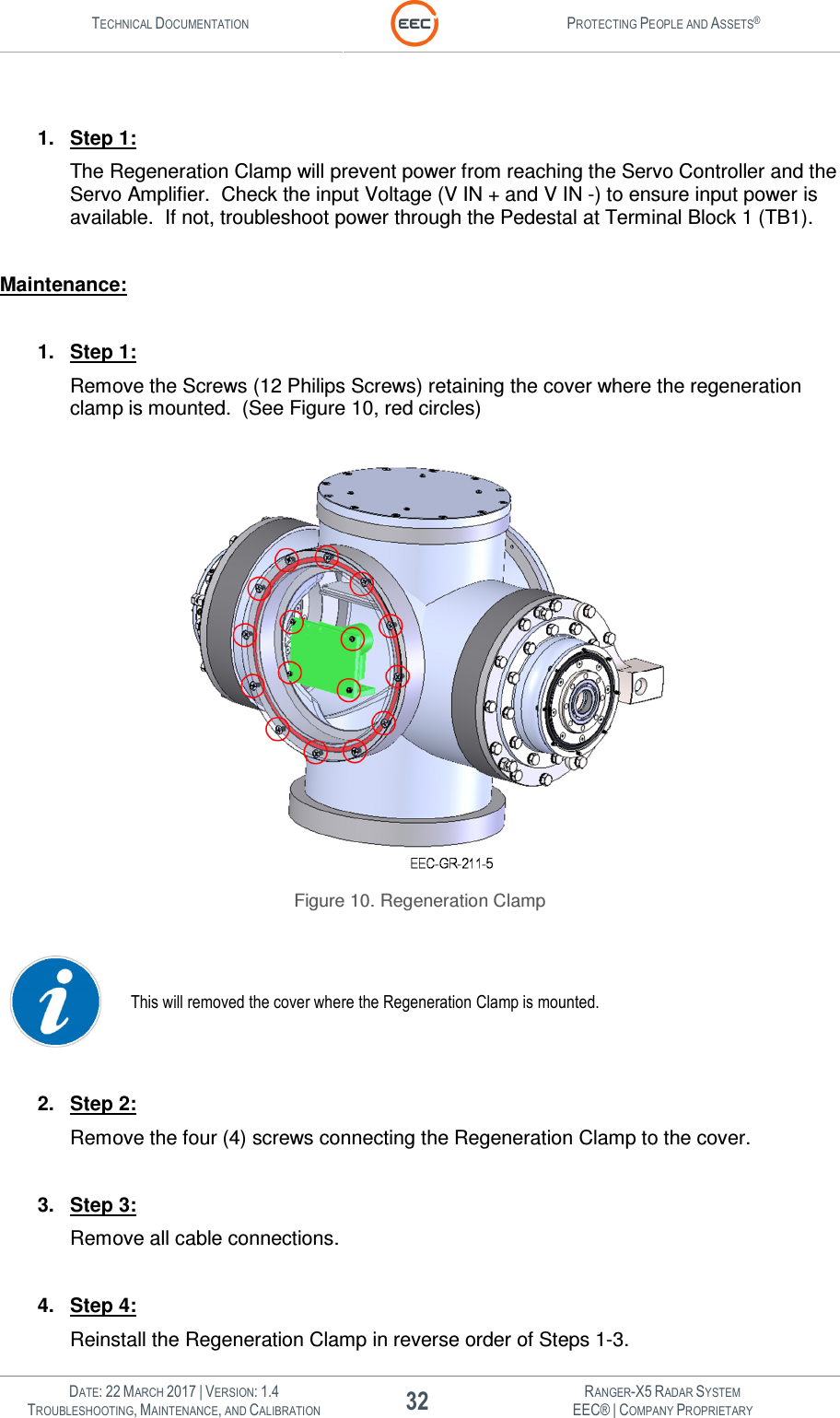
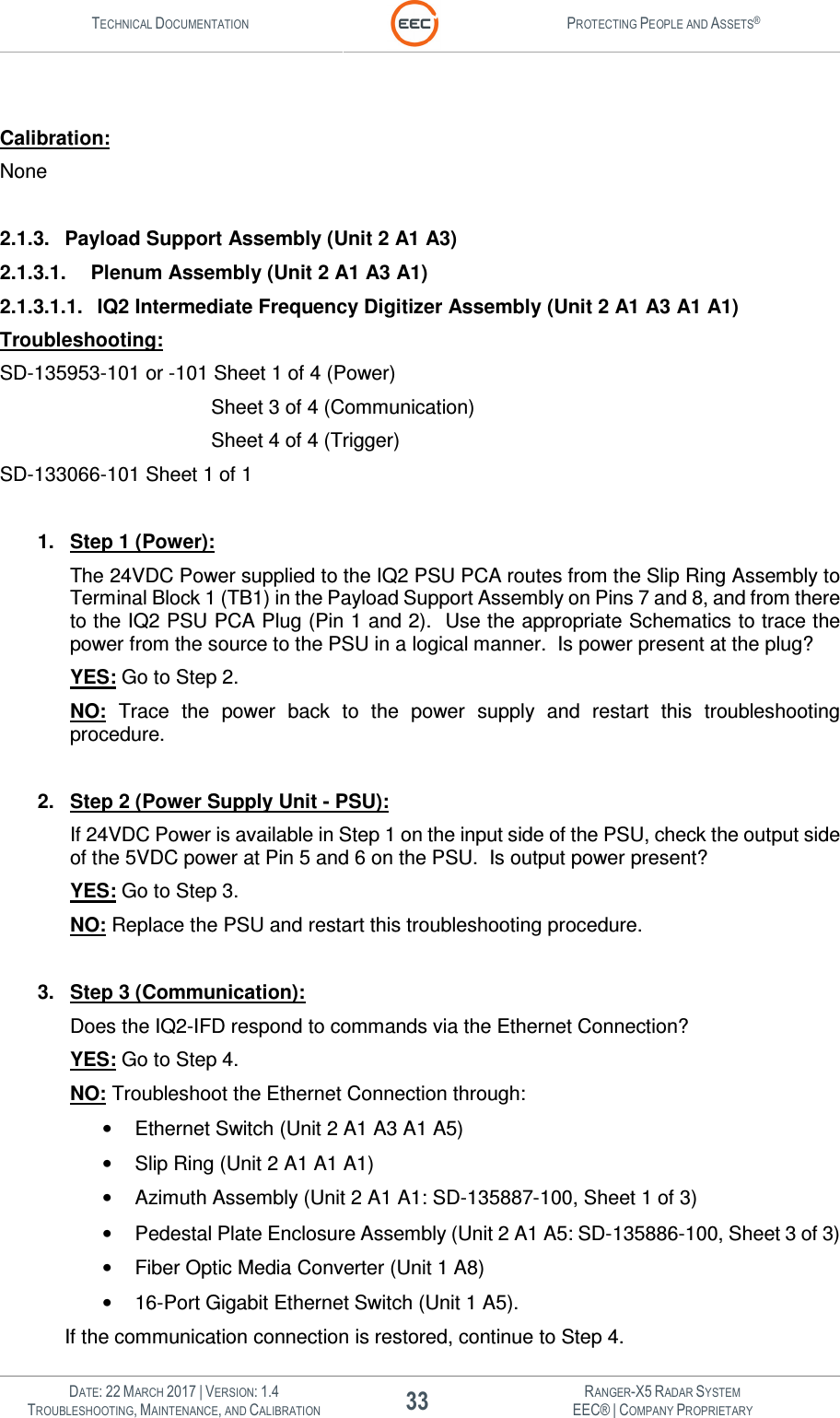
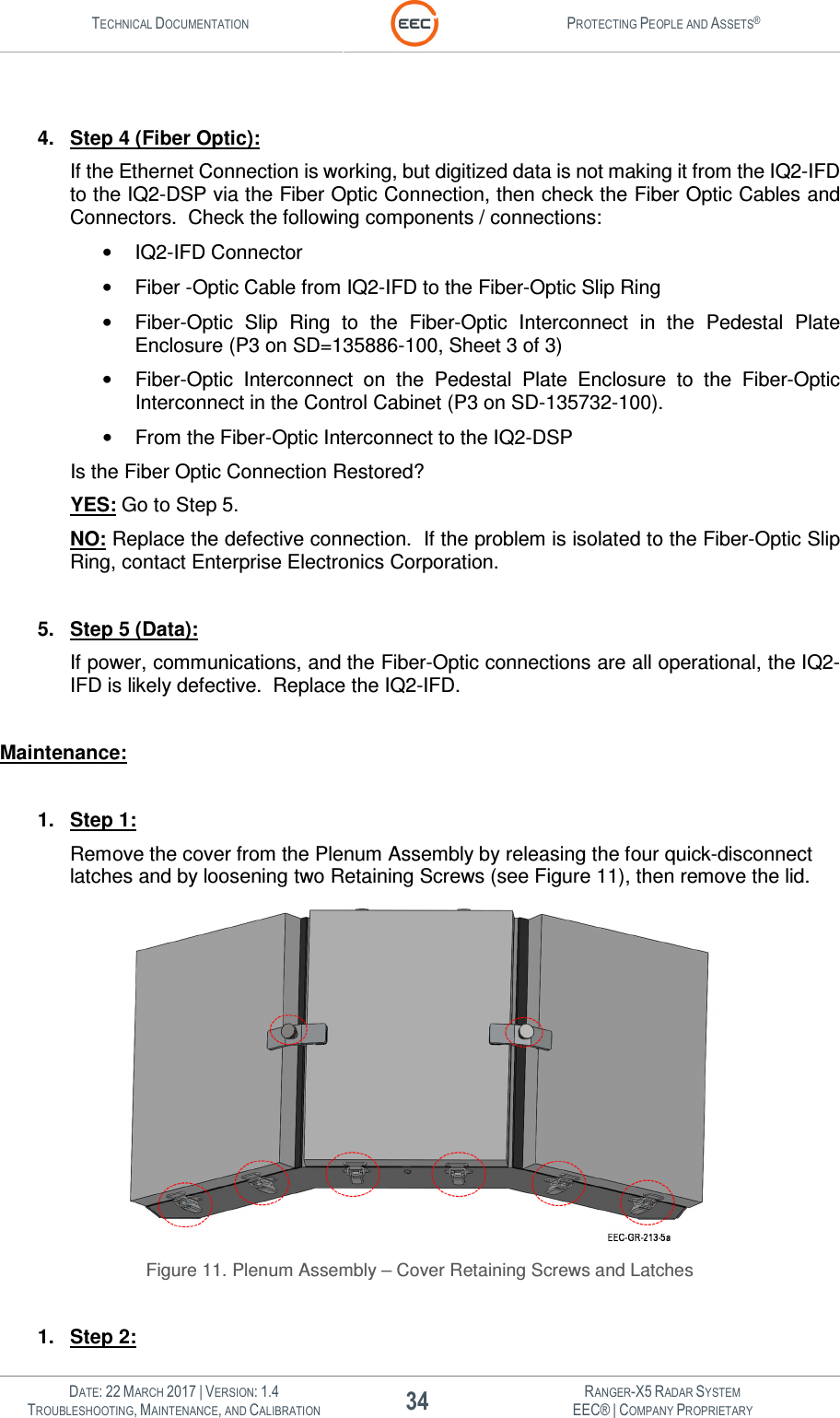
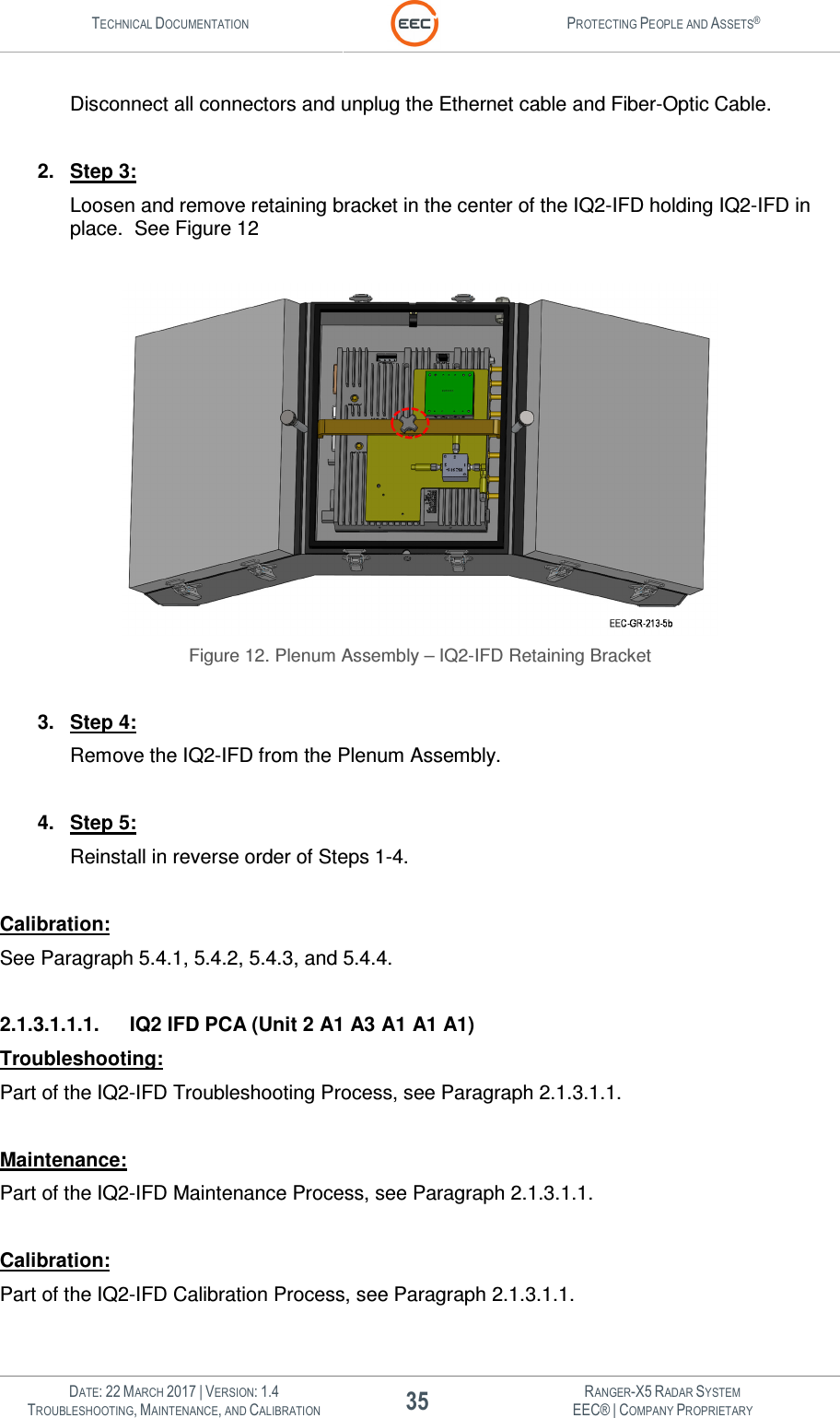
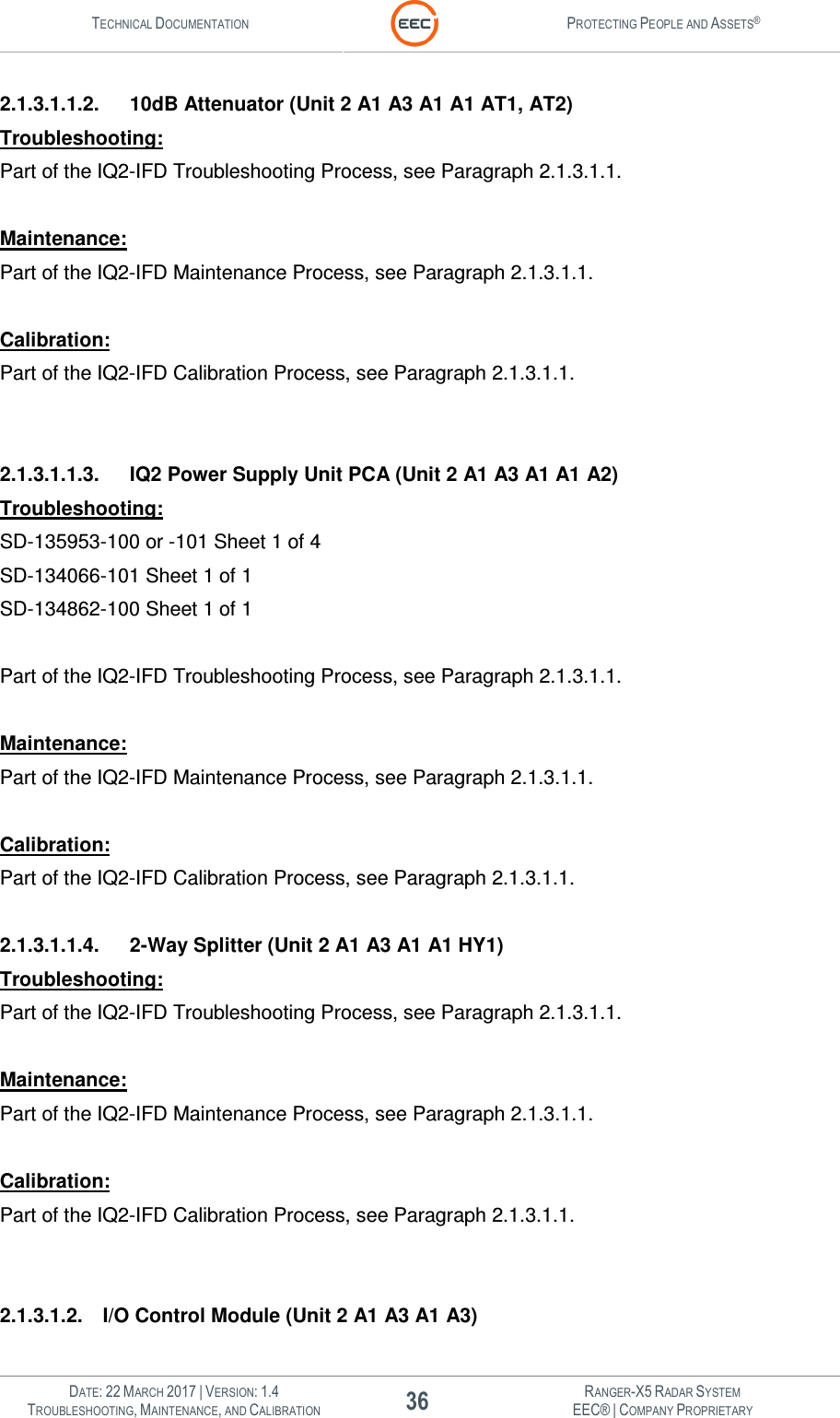
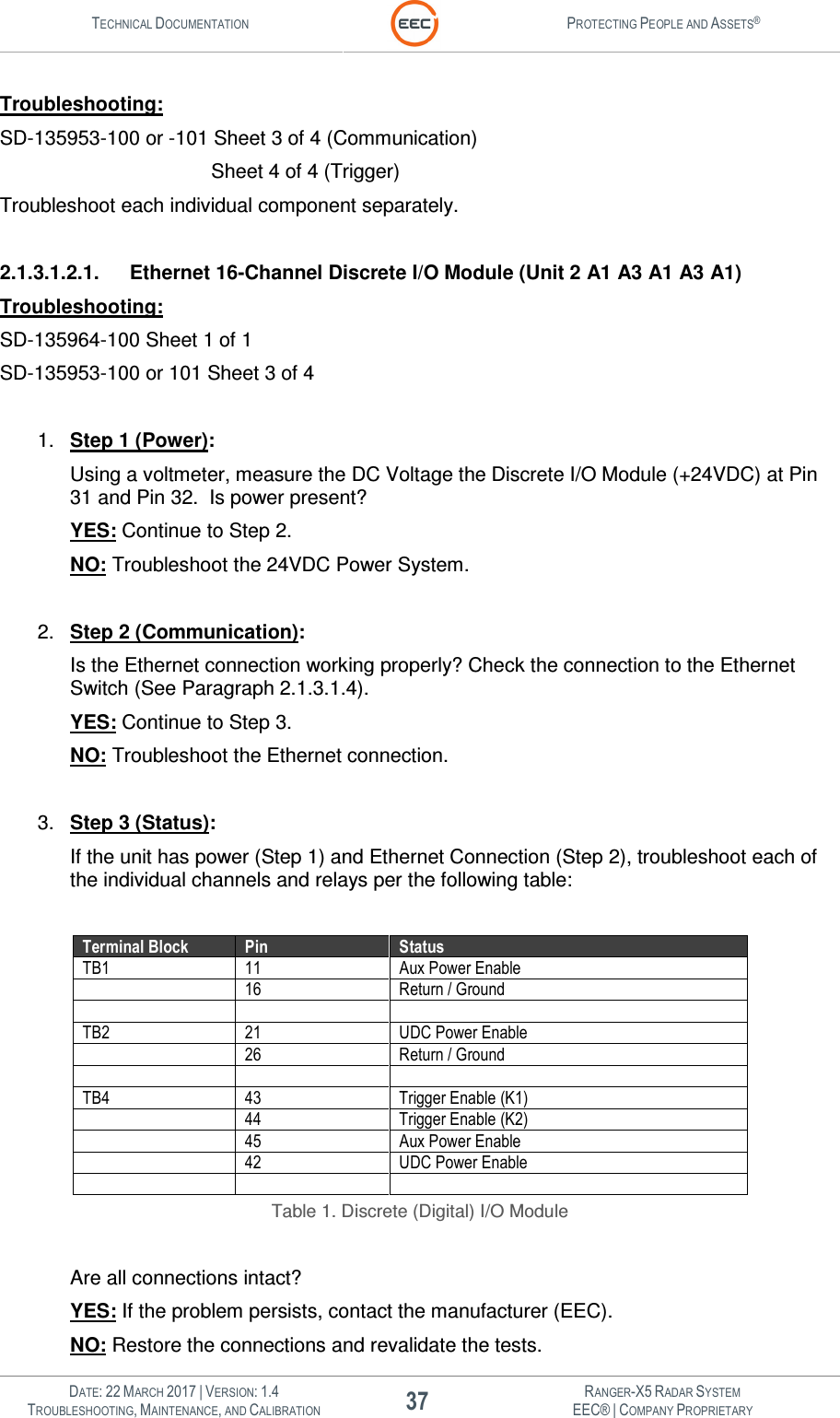
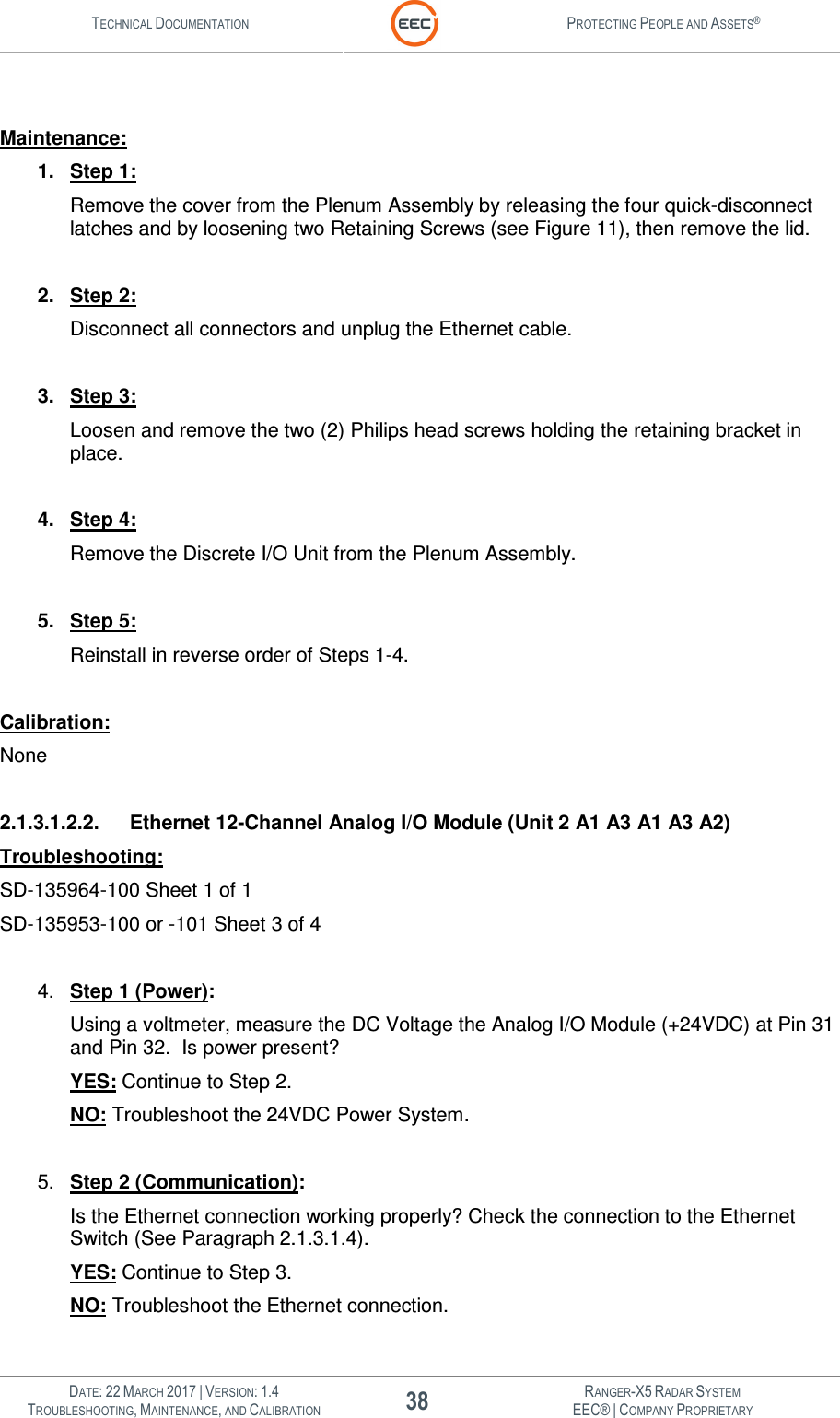
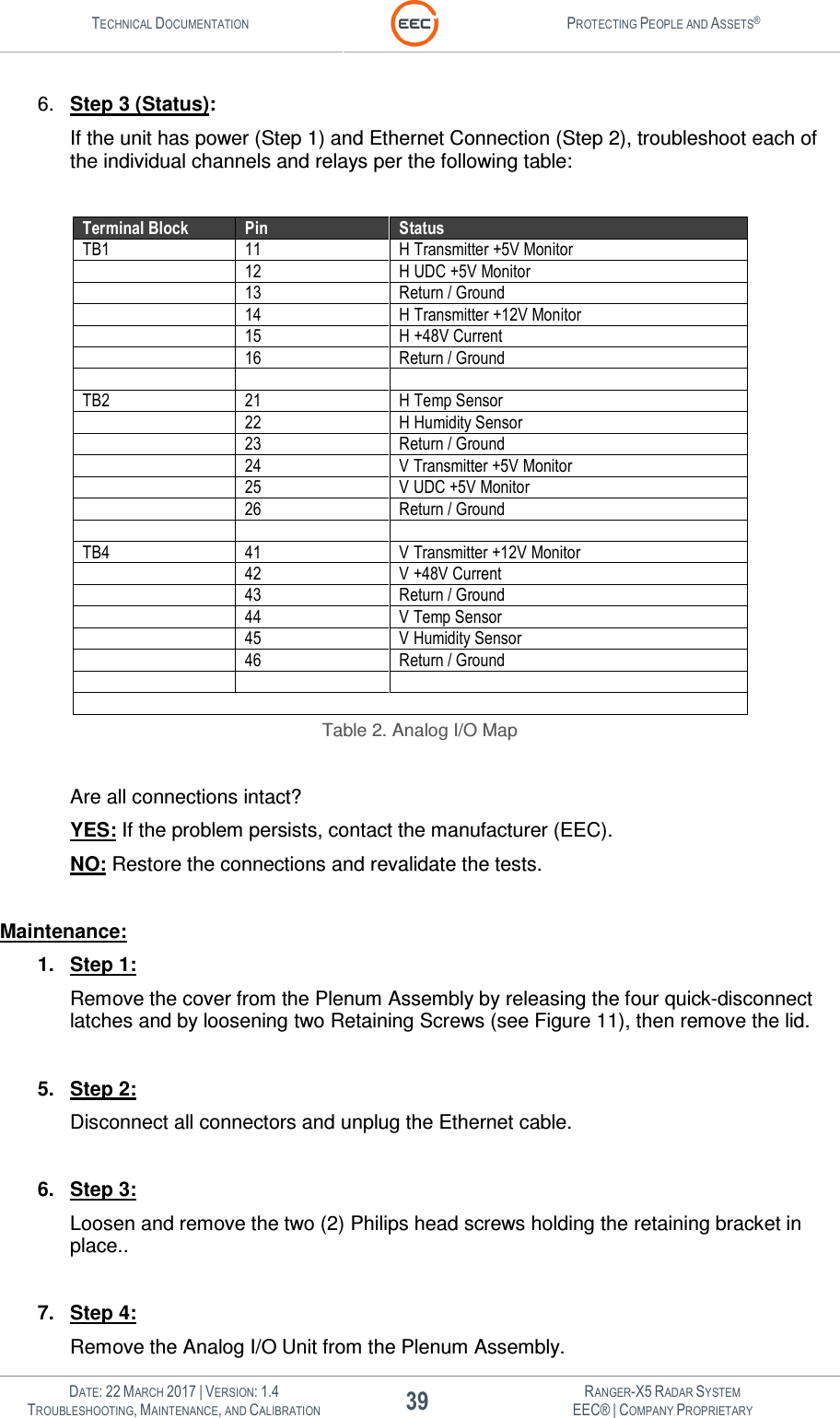
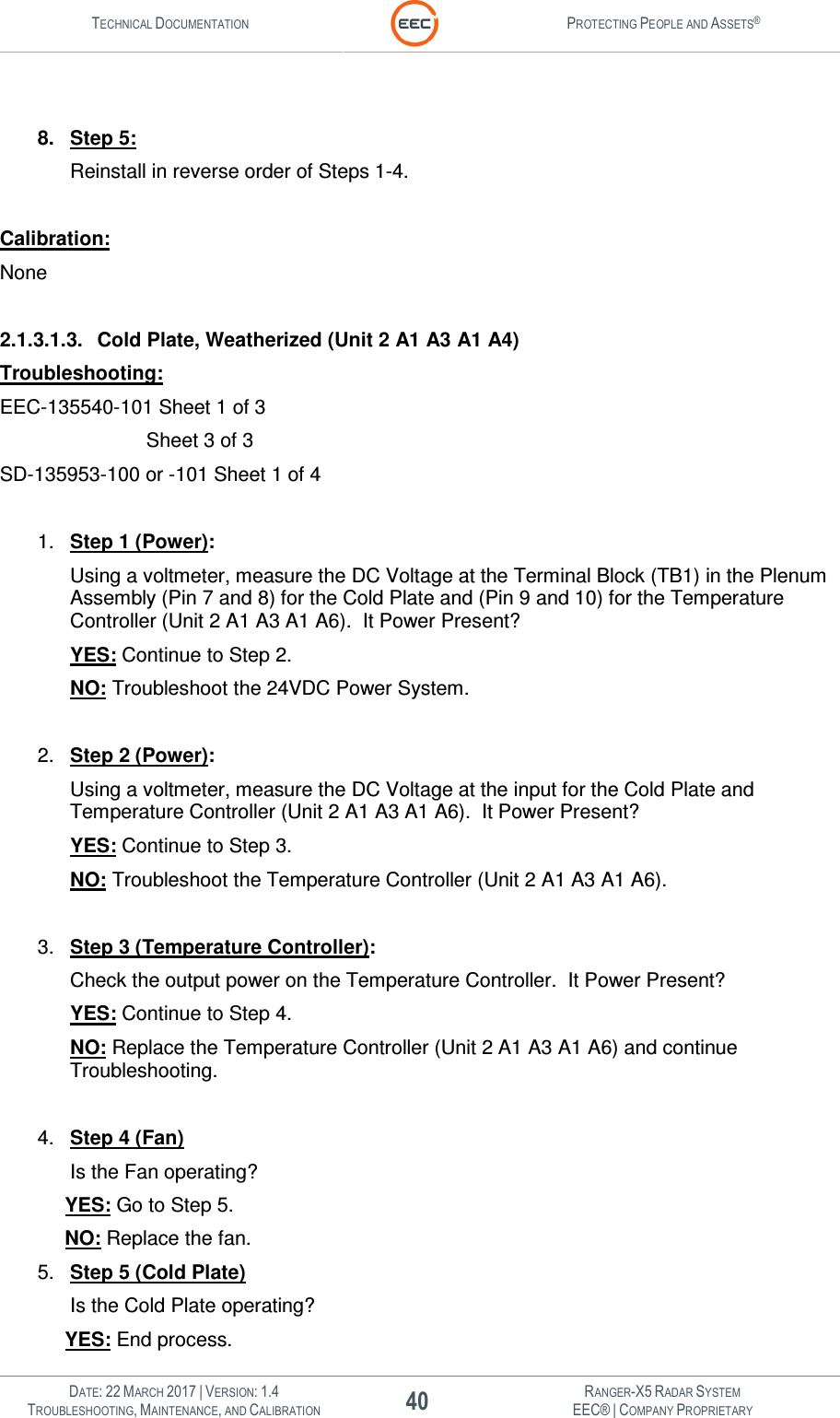