HARRIS KRC121106-1 User Manual PubTeX output 1998 12 03 1743
HARRIS CORPORATION PubTeX output 1998 12 03 1743
HARRIS >
Contents
- 1. Instruction maintenance manual
- 2. PDF instruction manual
PDF instruction manual

RBS 884 Micro (1900 MHz) Installation and
Hardware Replacement Manual
EN/LZB 119 3312 R1 1998-11-17 © Ericsson Radio Systems AB 1998 All Rights Reserved

The contents of this document are subject to revision without notice due to
continued progress in methodology, design, and manufacturing.
Ericsson shall have no liability for any error or damages of any kind resulting
from the use of this document.
i00 152-EN/LZB 119 3312 Uae Rev R1 1998-11-17
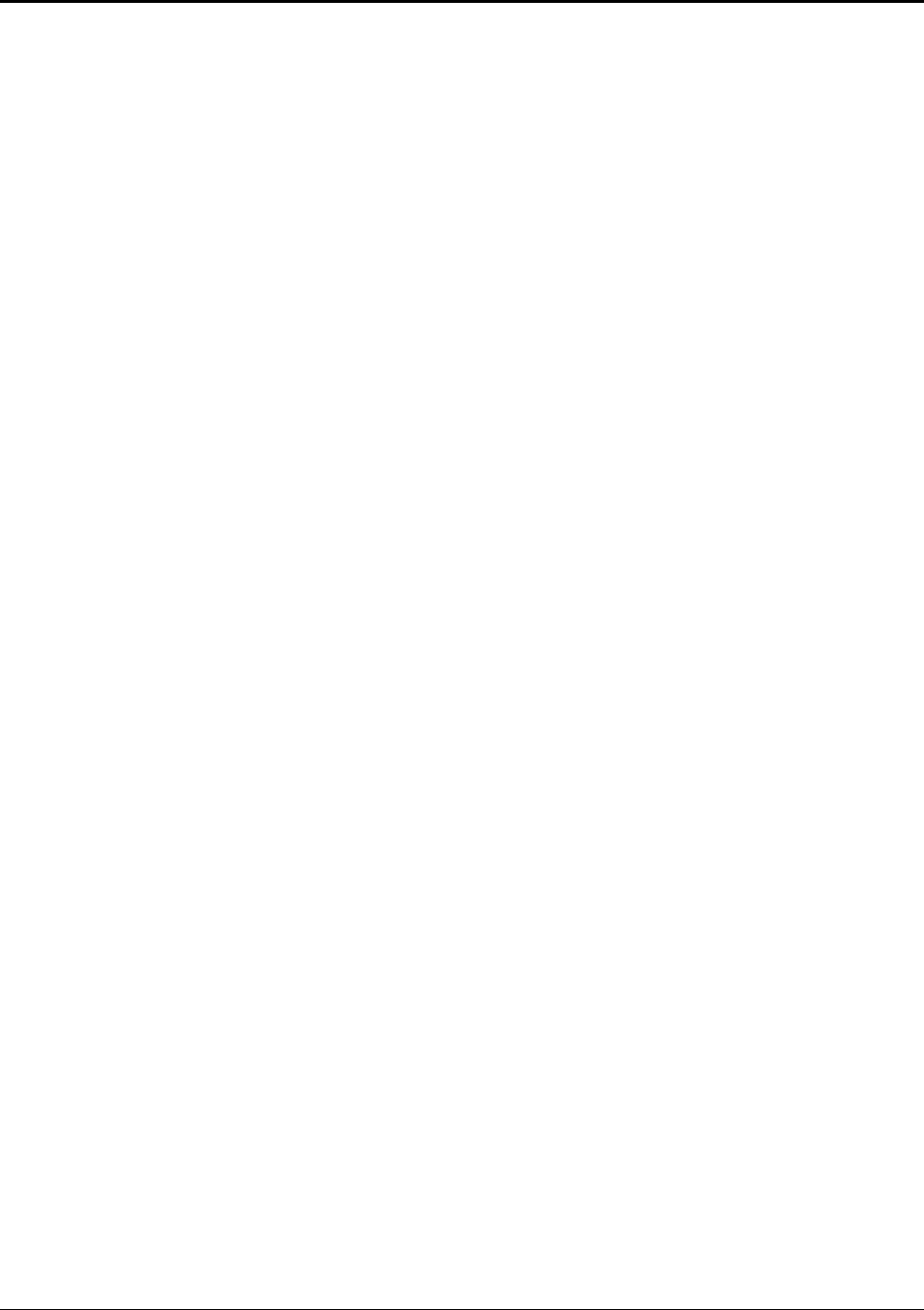
Table of Contents
Part 1 Introduction ...................... 1-1
1 Revision Information ............... 1-1
2 About This Manual ................ 1-1
3 Conventions Used in this Manual ......... 1-2
Part 2 General Product Information .............. 2-1
1 Introduction ................... 2-3
2 Features .................... 2-3
3 Product Lines .................. 2-4
4 Architecture ................... 2-6
Part 3 System Description .................. 3-1
1 Introduction ................... 3-3
2 RBS 884 Micro (1900 MHz) ........... 3-3
3 Installation Configurations ............ 3-18
Part 4 Installation ....................... 4-1
1 Introduction ................... 4-3
2 Safety Considerations .............. 4-3
3 Electrostatic Discharge (ESD) ........... 4-5
4 Tools ...................... 4-6
5 Site Selection .................. 4-7
6 Transportation and Storage ............ 4-8
7 Unpacking .................... 4-9
8 Cabinet Installation ................ 4-12
9 Cable and Power Connections .......... 4-24
10 Setting the Unit Switches ............. 4-39
11 External Alarm Connections ........... 4-50
12 Site Inventory .................. 4-51
13 Equipment Power Up ............... 4-53
14 Cold Start-up .................. 4-56
15 Completing the Installation ............ 4-56
16 LED Indications ................. 4-57
17 Site Expansion .................. 4-62
18 RBS 884 Micro (1900 MHz) Cabinet Repainting . . 4-81
Part 5 Hardware Replacement ................. 5-1
1 Introduction ................... 5-3
2 Safety Considerations .............. 5-3
3 Product Handling and Inspection ......... 5-6
4 General Troubleshooting ............. 5-6
5 Alarm Troubleshooting .............. 5-11
6 RBS Unit Hardware Replacement ......... 5-14
00 152-EN/LZB 119 3312 Uae Rev R1 1998-11-17 ii

Contents
Part 6 Glossary of Terms ................... 6-1
Part 7 Acronyms and Abbreviations .............. 7-1
Appendix A Documentation Overview ................ A-1
Appendix B User Feedback ..................... B-1
Appendix C Internal Cables ..................... C-1
Appendix D Conversion Table ................... D-1
iii 00 152-EN/LZB 119 3312 Uae Rev R1 1998-11-17
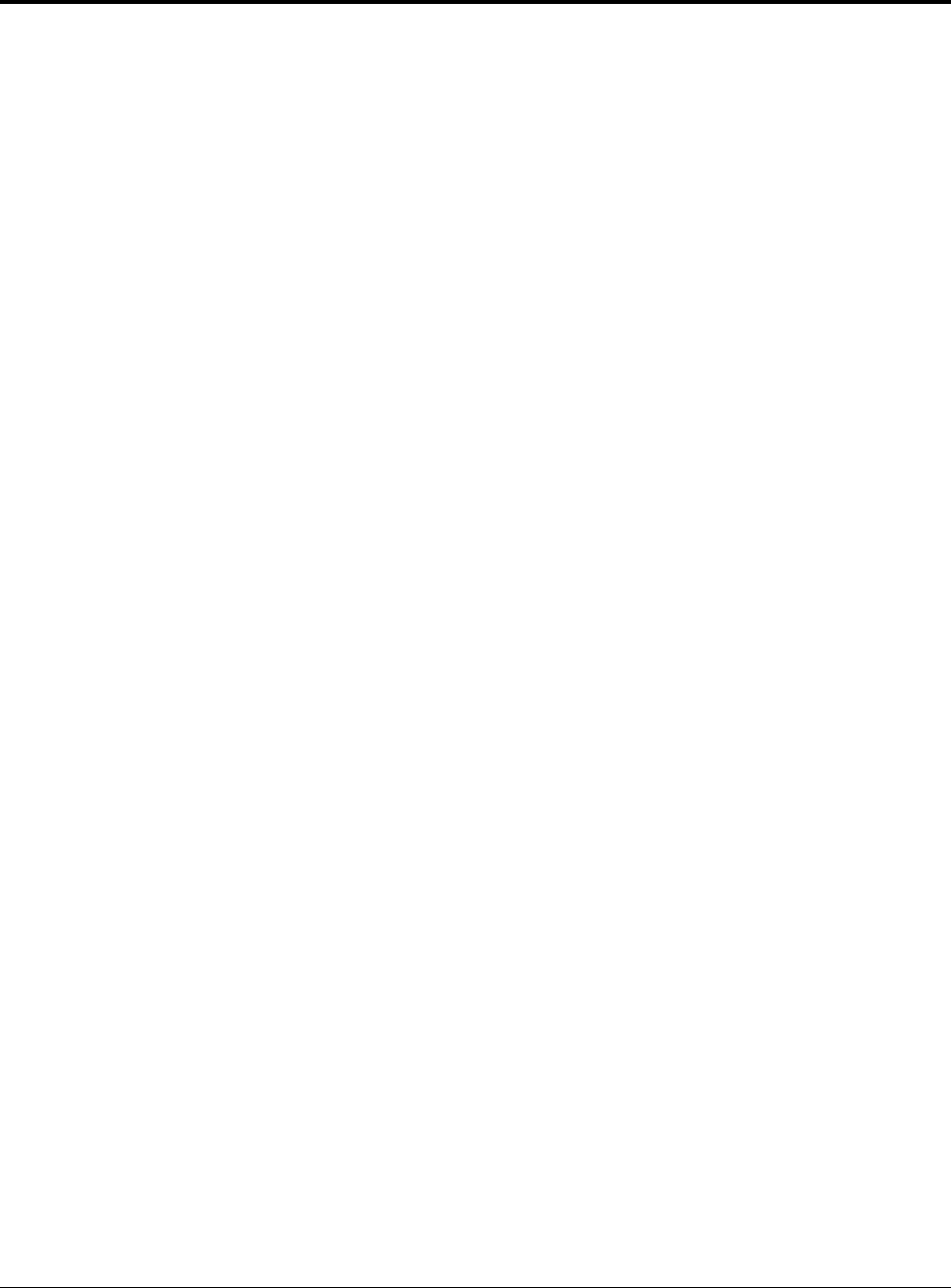
Part 1
Introduction
This part describes the information contained in the manual and the
conventions used in its presentation.
1 Revision Information
This is the first issue of the Installation and Hardware Replacement
Manual (IHRM) for Radio Base Station (RBS) 884 Micro (1900 MHz).
2 About This Manual
This manual contains information required to install, troubleshoot, and
maintain the RBS 884 Micro (1900 MHz) system.
This manual is intended for RBS site installation and site maintenance
personnel.
Before this manual is used to perform any installation or maintenance
activities at a radio base station site, the following actions must be
completed:
•Telephone transmission facilities must be available and tested.
•AC and DC voltage must be available.
•The antenna system must be installed and tested.
•Grounding system must be available.
When the radio base station equipment is installed and tested using the
information in this manual, it will remain powered up and ready for
integration into the network by personnel at the Mobile Switching Center
(MSC).
This manual is divided into the following parts:
•Part 1, Introduction – provides a description of the contents of the
manual and how it can be used.
•Part 2, General Product Information – provides a general description
of an unconfigured base station. Specific Radio Base Station (RBS)
is provided in Part 3, Suystem Description.
0015-EN/LZB 119 3312 Uae Rev A 1998-11-17 1-1

Introduction
•Part 3, System Description – provides a description of the RBS 884
Micro (1900 MHz) equipment hardware and the available
configurations.
•Part 4, Installation – provides procedures for the installation and
powering up the RBS 884 Micro (1900 MHz) system.
•Part 5, Hardware Replacement – provides procedures for
troubleshooting and replacement procedures for critical components
of the RBS 884 Micro (1900 MHz) system.
•Part 6, Glossary of Terms – provides definitions of key terms used in
the manual.
•Part 7, Acronyms and Abbreviations – provides expanded versions of
all of the acronyms and abbreviations used in the manual.
•Appendix A, Document Overview – provides an overview of the
existing customer manuals for RBS 884 products.
•Appendix B, User Feedback – provides information on ordering and
trouble reporting for the RBS 884 customer manuals.
•Appendix C, Internal Cables – provides description of the internal,
factory installed cables within each RBS cabinet.
•Appendix D, Conversion Table – provides table for translating SI
units to American units.
Many of the procedures in this manual require site-specific data from the
Site Installation Documentation relating to the particular radio base station
site. Additional information is available in the RBS 884 Site Engineering
Manual.
The procedures in the manual are intended to be performed in the order
presented.
3 Conventions Used in this Manual
The first time an acronym or abbreviation appears in this manual, the
expanded form is shown, followed by the acronym or abbreviation in
parentheses, for example, Mobile Switching Center (MSC).
The abbreviated form is shown without parentheses when the expanded
form is not used.
A list of acronyms and abbreviations can be found in Part 8.
Names of documents are referred to in italic typeface, for example, Site
Installation Documentation.
1-2 0015-EN/LZB 119 3312 Uae Rev A 1998-11-17
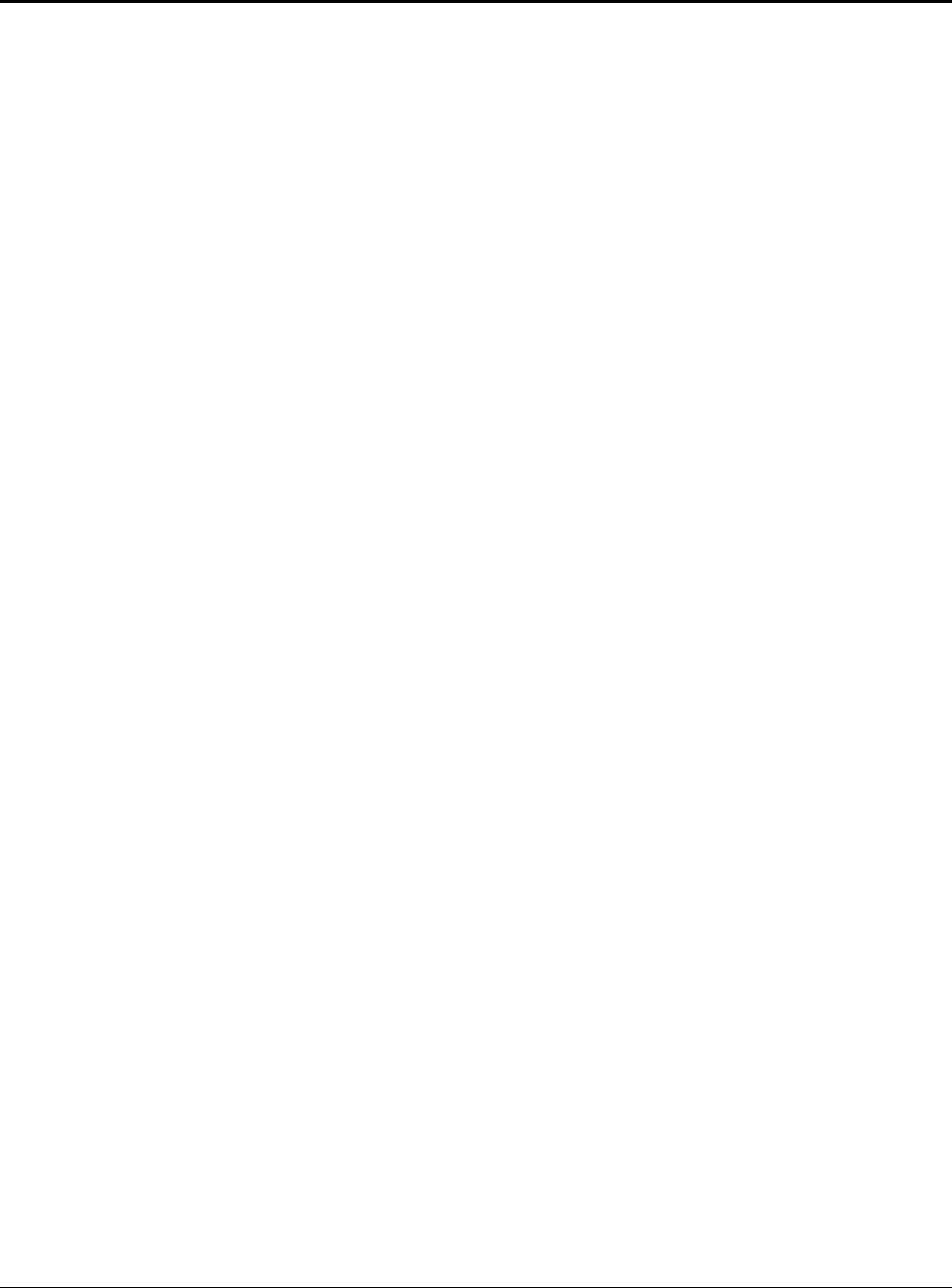
Part 2
General Product Information
1 Introduction .................. 2-3
2 Features .................... 2-3
3 Product Lines .................. 2-4
3.1 RBS 884 Macro ............. 2-4
3.2 RBS 884 Micro .............. 2-5
3.3 RBS 884 Compact ............ 2-6
4 Architecture .................. 2-6
3/1551-EN/LZB 119 3312 Uae Rev A 1998-11-17 2-1
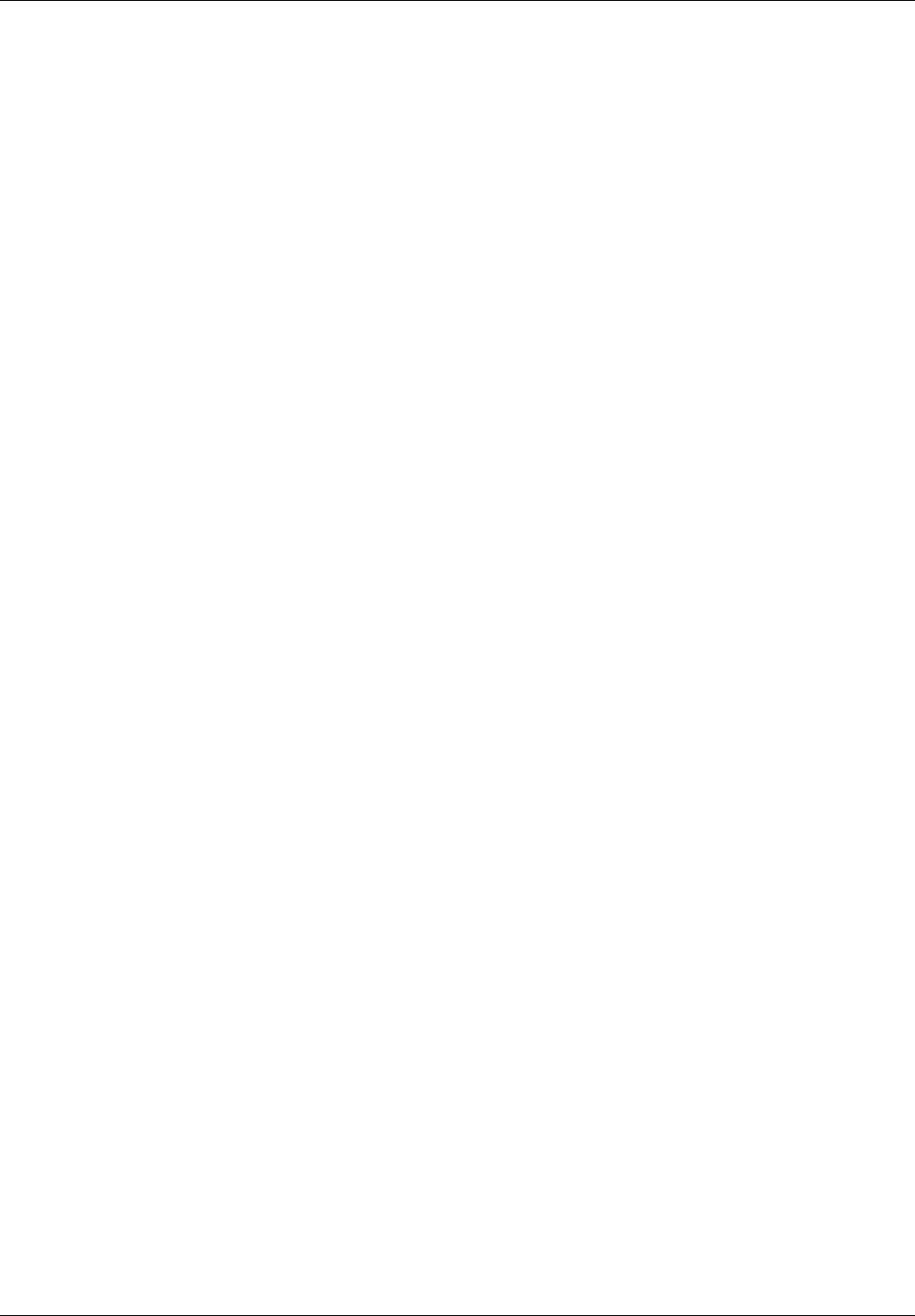
General Product Information
2-2 3/1551-EN/LZB 119 3312 Uae Rev A 1998-11-17
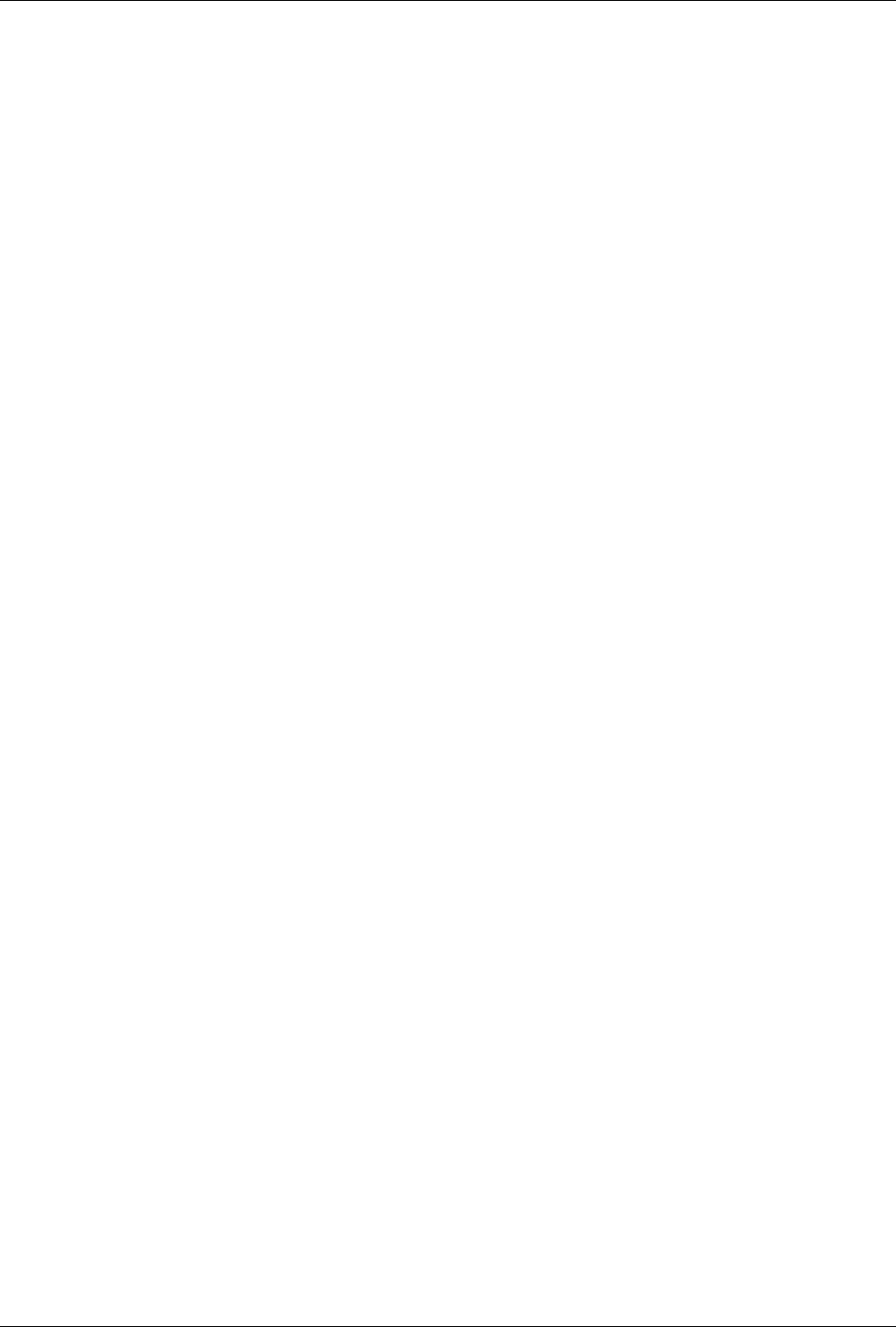
General Product Information
1 Introduction
The General Product Information provides general information on
unconfigured radio base stations. See RBS 884 Site Engineering Manual
for descriptions of the available working base station configurations and
for information on RBS interfaces (for instance, power, transmission, and
antennas).
2 Features
The RBS 884 Series is a series of products in the CMS 8800 family. The
products in the RBS 884 Series are fully featured modular radio base
stations for both the analog AMPS EIA 553 and the digital D-
AMPS EIA IS 136 systems (Advanced Mobile Phone System Electronics
Industry Association 553 system and Digital American Mobile Phone
System Electronics Industry Association Interim Standard 136 system).
A base station in the RBS 884 Series can support one, two, or three cells.
A cell is a defined area covered by one antenna system, and each cell has
one control channel for digital or one for analog, or both. There is one cell
at an omni site, and one to three cells at a sectorized site.
The RBS 884 Series utilizes multi-mode, multi-functional transceivers
(TRXs). The same hardware TRX module can be used for analog and
digital voice, control and monitoring purposes.
The hot repair capability allows replacement of defective units when
power is still applied.
The RBS 884 Series is designed for remote control monitoring allowing
control and fine tuning of all functions and parameters, such as power
output, frequencies, and switching of redundant units from the Mobile
Switching Center (MSC).
A Radio Frequency Test Loop (RFTL) is an optional feature that enables
precise output power settings, Voltage Standing Wave Ratio (VSWR)
alarm, and Receive Signal Strength Indicator (RSSI) test measurements.
The device software is stored in non-volatile memory within the RBS, and
the control part software is downloaded from the MSC, which ensures a
short time to service at power-up.
3/1551-EN/LZB 119 3312 Uae Rev A 1998-11-17 2-3
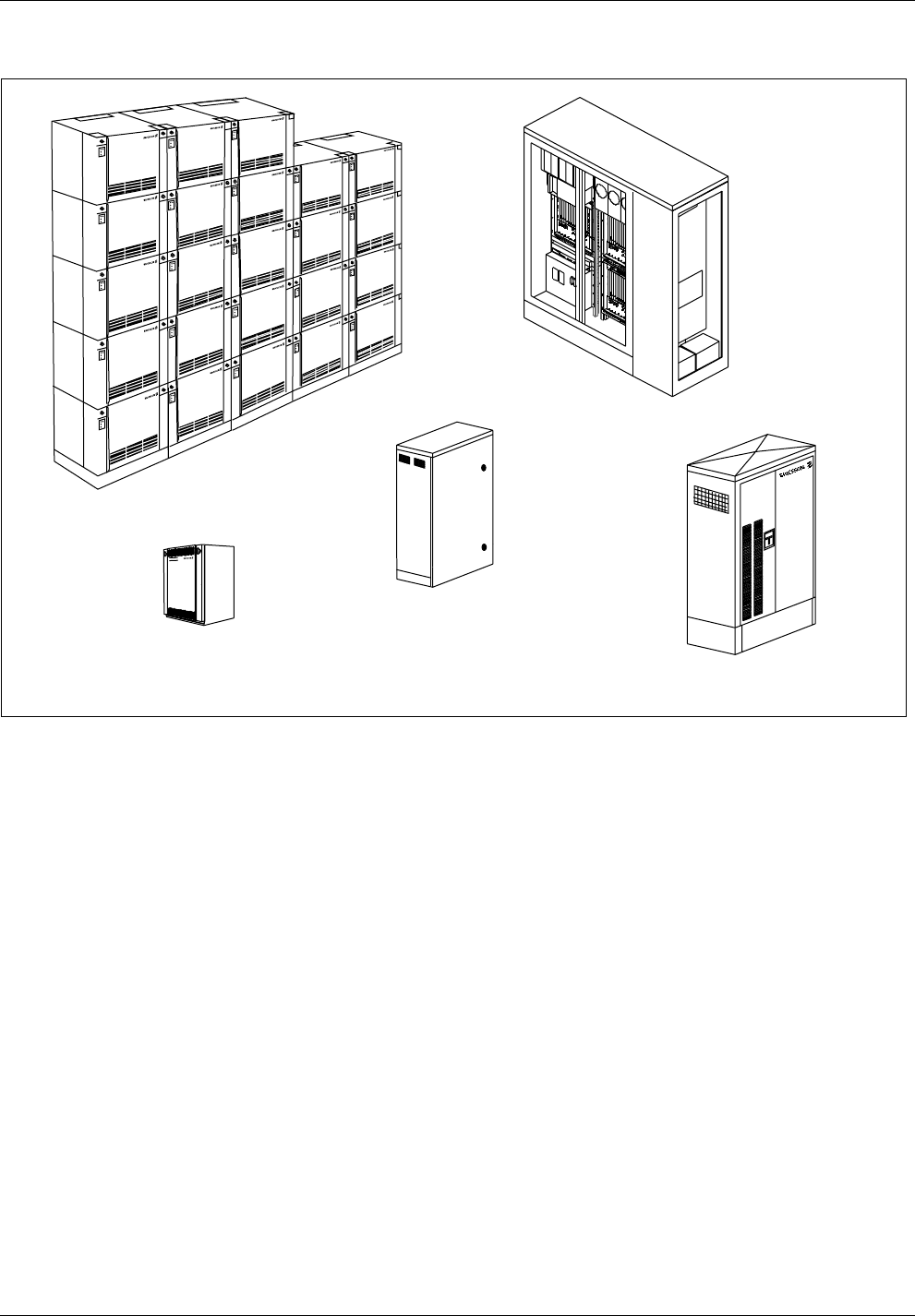
General Product Information
3 Product Lines
RBS 884 RBS 884
RBS 884
RBS 884
RBS 884
RBS 884
RBS 884
RBS 884
RBS 884
RBS 884
RBS 884
RBS 884
RBS 884
RBS 884
RBS 884
RBS 884
RBS 884
RBS 884
RBS 884
RBS 884
RBS 884
RBS 884
RBS 884
RBS 884 Macro
RBS 884
RBS 884 Micro 800 RBS 884 Compact
RBS 884 Outdoor
RBS 884 Micro 1900
Figure 2-1. Product Lines in the RBS 884 Series
The RBS 884 Series includes product lines for macro and micro cells. See
Figure 2-1 on page 2-4.
Note: The maximum number of carriers for each sector stated is the
technical limitation for the defined standard configurations. The
practical usable sector sizes may be limited by the frequency
plan. The capacity of all product lines, with the exception of
the RBS 884 Micro (1900 MHz) is calculated for analog
systems. The capacity of the RBS 884 Micro (1900 MHz) is
calculated for digital systems. See the integration information
in the RBS 884 Operations and Maintenance Manual for
system limitations in digital systems.
3.1 RBS 884 Macro
The macro cell products are intended for normal indoor installations and
are built on-site with a number of cabinets of uniform size and design.
The RBS 884 Macro 800 MHz supports AMPS and digital D-AMPS.
This system operates at 824–894 MHz and provides up to 78 low power or
2-4 3/1551-EN/LZB 119 3312 Uae Rev A 1998-11-17
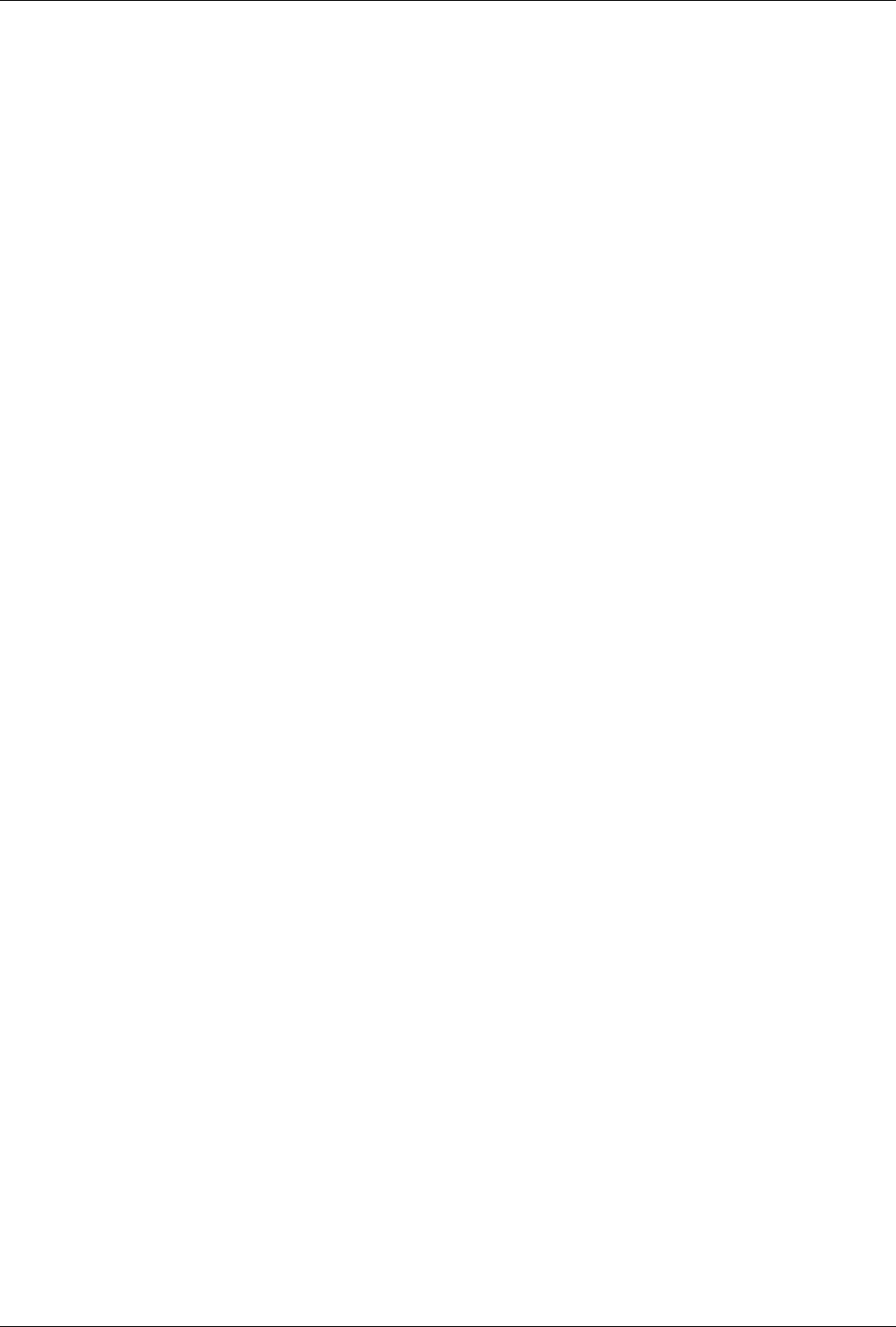
General Product Information
medium power transceivers (3x24 carriers), or up to 96 high power and 6
low power transceivers (3x32 carriers).
The RBS 884 Macro 1900 MHz supports digital D-AMPS and operates at
1850–1990 MHz (A-, B-, or C-band). It provides up to 48 medium power
transceivers (3x15 carriers).
A special configuration, Self Contained Cell Site (SCCS), providing up to
8 transceivers in three sectors (3x7 carriers), can be installed in an outdoor
container.
The RBS 884 Macro DBC (Down Banded Cellular) supports digital D-
AMPS and is applicable to frequencies at 806–860 MHz. Up to 39
medium power transceivers (3x12 carriers) can be used in one installation.
3.2 RBS 884 Micro
The RBS 884 Micro products are used wherever local capacity or coverage
is required.
The RBS 884 Micro 800 MHz is intended for indoor installation, and
typical applications include convention centers, office buildings, parking
areas and tunnels. The RBS 884 Micro comprises one small main cabinet
and two possible expansion cabinets of the same size. It is a completely
functional cell, with a drop and insert transmission interface and RF
equipment built-in. Up to 10 1.5W transceivers can be used in one cabinet
(8 carriers). Up to 30 transceivers can be provided with two auxiliary
cabinets (24 carriers). This gives a total capability of up to 23 analog or
68 digital voice channels (71 with E1 PCM links).
The RBS 884 Micro with Multi Carrier Power Amplifier (MCPA) (800
MHz) supports analog AMPS EIA 553 and digital D-AMPS EIA IS 136
and operates at 824–894 MHz. It is a standard RBS 884 Micro (800 MHz)
equipped with a MCPA for higher output power in one cell. The MCPA is
a separate cabinet mounted below the RBS 884 Micro (800 MHz) cabinet.
Up to three RBS 884 Micro (800 MHz) cabinets and one MCPA can be
mounted in a 19-inch rack cabinet. An RBS 884 Micro with MCPA (800
MHz) can provide up to 23 analog or 68 digital voice channels (71 with
E1 PCM links) in one cell.
The RBS 884 Micro Outdoor (800 MHz) supports analog
AMPS EIA 553 and digital D-AMPS EIA IS 136 and operates at 824–894
MHz. Designed for outdoor use, it is contained in an all-weather steel
enclosure with an environmentally-controlled interior and can be installed
in a wide variety of locations and climatic zones. The RBS 884 Micro
(800 MHz) can be provided with up to 26 transceivers and a total of 24
carriers. This provides a total capacity of up to 23 analog or 68 digital
voice channels (71 with E1 PCM links).
The RBS 884 Micro (1900 MHz) supports digital D-AMPS EIA IS 136
and operates at 1850–1910 MHz. The RBS 884 Micro (1900 MHz) is a
self-contained base station intended primarily for outdoor use. The cabinet
3/1551-EN/LZB 119 3312 Uae Rev A 1998-11-17 2-5

General Product Information
is cooled directly with outdoor air, using a combination of variable speed
blowers and a variable power heater to maintain the cabinet air
temperature within equipment operating limits. Typical applications
include hot spot areas within mature 1900 MHz networks and areas not
covered by the RBS 884 Macro. The RBS 884 Micro (1900 MHz) is
comprised of one small main cabinet and up to two auxiliary primary
cabinets of the same size. The cabinets can be easily mounted on poles, on
the sides of buildings, on rooftops, or on concrete pads. The RBS 884
Micro (1900 MHz) is a complete functional cell, with a drop and insert
transmission interface and built-in RF equipment. Up to 5 transceivers can
be used in one cabinet providing 4 carriers. Up to 15 transceivers can be
used in a three-cabinet installation providing 3x4 carriers. The
three-cabinet installation allows up to 33 digital traffic channels.
The RBS 884 Micro with MCPA is a standard RBS Micro 884 equipped
with a Multi Carrier Power Amplifier (MCPA) for 30 W normal output
power in one cell. The MCPA is a separate cabinet that is smaller than the
RBS 884 Micro cabinet. The cabinets can be wall mounted, and from one
to three cabinets and one MCPA can be mounted in a standard 19-inch or
Telco rack. An RBS 884 Micro with MCPA can provide up to 23 analog
or 68 digital voice channels (71 with E1 PCM links) in one cell.
3.3 RBS 884 Compact
The RBS 884 Compact can be compared to the Micro, but is intended for
outdoor installations. It is contained in an all-weather steel cabinet with an
environmentally-controlled interior and can be installed in a wide variety
of locations and climatic zones. The RBS 884 Compact consists of one
primary cabinet and two possible expansion cabinets of the same size. It is
a completely functional cell with drop and insert transmission interface and
RF equipment built-in. Up to 10 low power transceivers can be used in
one cabinet (8 carriers). Up to 30 transceivers can be provided with two
auxiliary cabinets (24 carriers). This gives a total capability of up to 23
analog or 68 digital voice channels (71 with E1 PCM links).
4 Architecture
The radio base station cabinet contains the equipment needed to control
and handle the communication between the MSC and the mobile stations.
The configuration of equipment in a specific system depends on the
number of sectors, the number of voice channels in each sector, the
transmit power, the frequency band, the number and type of antennas, and
if the site is all analog, mixed analog and digital, or all digital. Figure 2-2
on page 2-7 shows the main connections to and from an RBS.
2-6 3/1551-EN/LZB 119 3312 Uae Rev A 1998-11-17
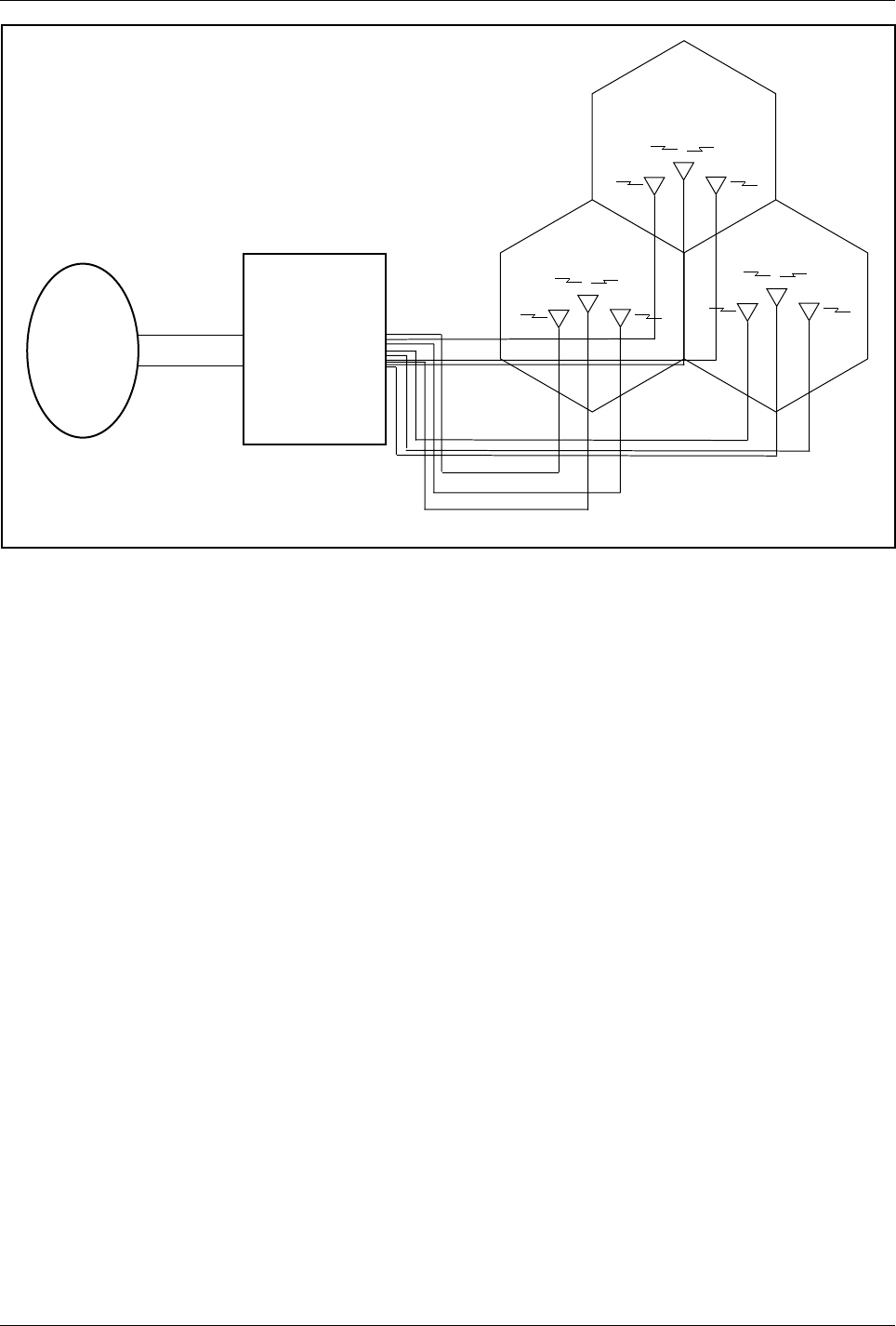
General Product Information
PCM LINK 1
PCM LINK 2
TX
RX RX
TX
RX RX
TX
RX RX
Sector A
Sector B Sector C
Antennas
RBS 884
MSC
Figure 2-2. General Overview of RBS 884 Configuration
The Group Switch (GS) at the MSC is responsible for switching calls
between subscribers. The calls may be between two mobile subscribers or
between a mobile subscriber and a subscriber in the public telephone
network. In the RBS, there are several regional processors, controlled by
and working with the central processor. The regional processors control
the switch and the transceivers in the base station. The switch in the base
station makes sure that the speech signals from the MSC are connected to
the correct transceiver. The transceivers generate radio signals emitted by
the base station antenna to the mobile stations. The semipermanent
connections are set up in the MSC. Each TRX handles three digital speech
channels, but uses only one channel on the PCM link.
Figure 2-3 on page 2-8 shows the logical parts of an RBS.
3/1551-EN/LZB 119 3312 Uae Rev A 1998-11-17 2-7
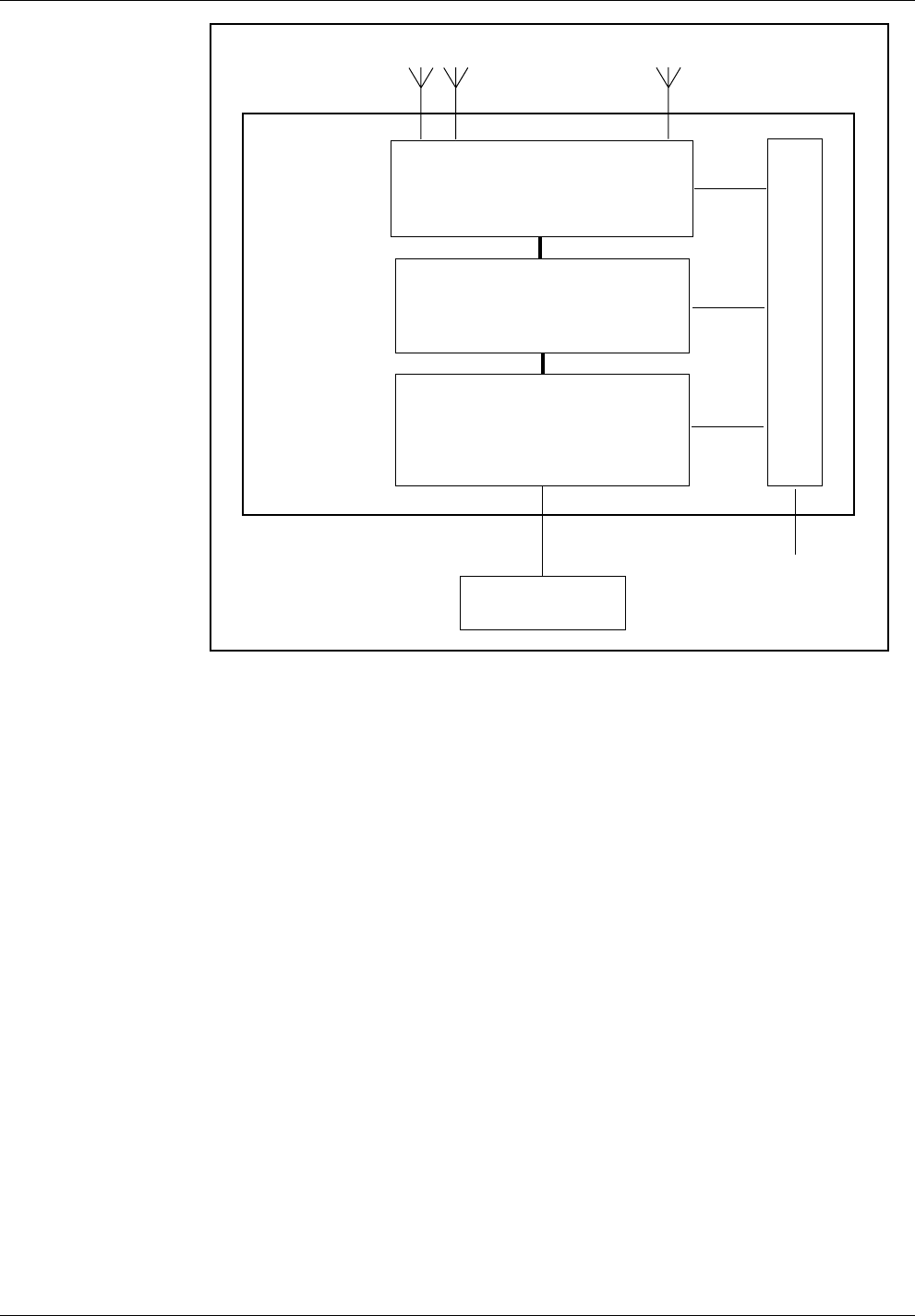
General Product Information
Mobile Switching
Center (MSC)
Control Part
Communicates with MSC and radio
traffic control.
- Remote Multiplexer (terminates PCM link)
- Signal Terminal (decodes control info)
- EMRPs (control TRXs)
Modem Part
Converts speech and data to and from
radio waves.
- Power Splitters for RF input
- Tranceiver Units (TRXs)
Antenna Near Part
- Filter Unit
- Multi-Coupler (Rx amplifier)
- Combiners (one Tx antenna for all carriers)
- Test and calibration
Support Part
Power distribution, fans, external alarms etc.
Rx Tx
T1/E1
PCM Link Power
Radio
Base
Station
(RBS)
Figure 2-3. Block Diagram of a Radio Base Station
The logical parts of the RBS 884 Micro (1900 MHz) are as follows:
•Control Part (COP) – provides communication between the MSC and
the RBS hardware for radio traffic control and statistical data
gathering. In the RBS 884 Macro, the COP consists of Control and
Radio Interface (CRI) cabinet. In Micro and Compact, the COP
consists of the Remote Multiplexer (REMUX), Signaling Terminal
Remote, Micro (STRM), Extension Module Regional Processor,
Micro (EMRPM), and Connection (CONN) boards.
•Modem Part (MOP) – converts digitized speech and data into radio
frequency signals, hosts channel coding and decoding functions, and
performs measurements on radio transmission quality. It is
comprised of transceiver modules (TRXs) in the RBS and voice
coders (TRABs) in the MSC. In the RBS 884 Macro, the MOP
consists of the Transceiver cabinet (TCB) and in the RBS 884 Micro
and Compact, the MOP consists of TRX boards.
2-8 3/1551-EN/LZB 119 3312 Uae Rev A 1998-11-17
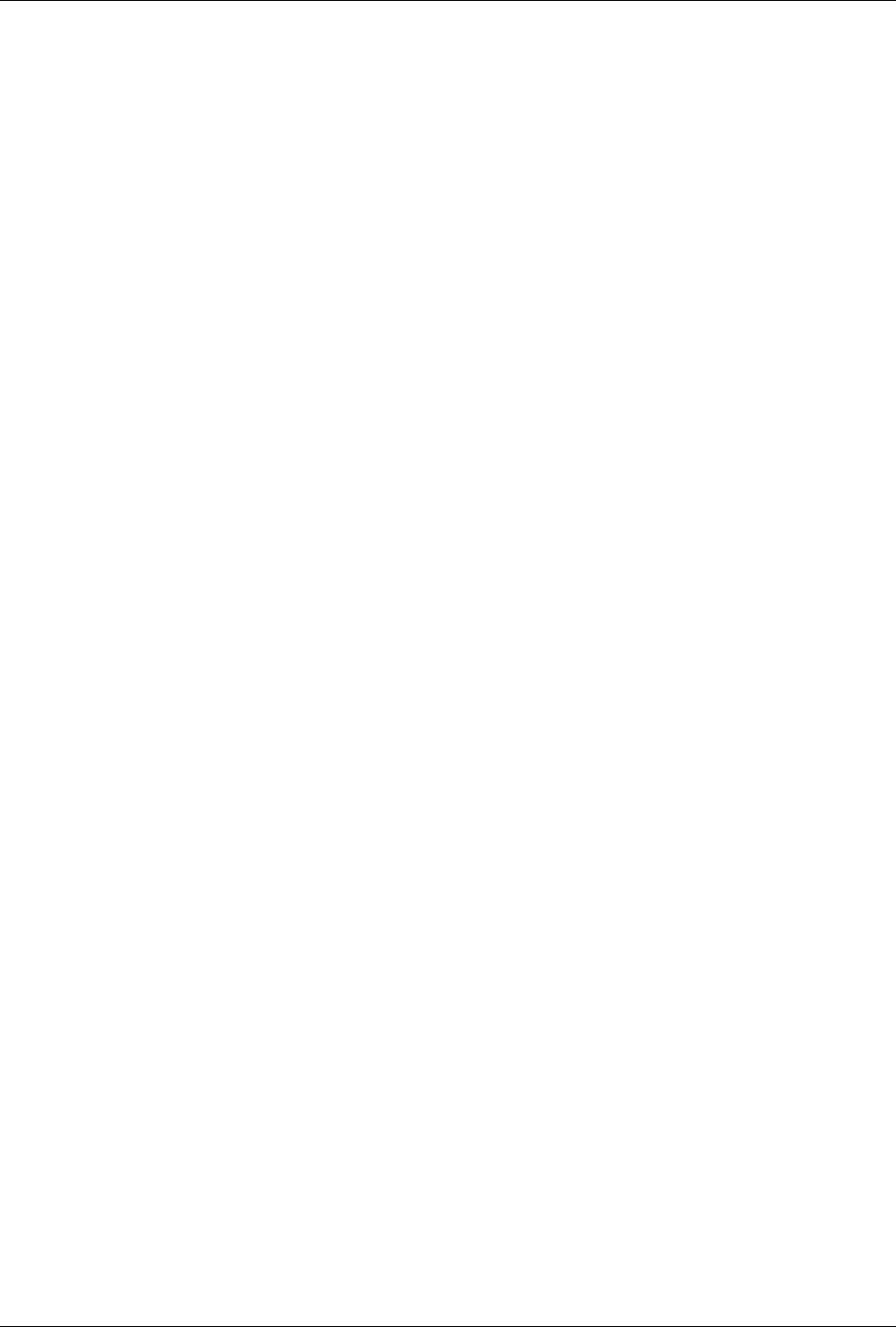
General Product Information
•Antenna Near Part (ANP) – contains components associated with the
RF signal paths, such as auto-tuned combiners, power splitters,
multicouplers, and bandpass filters. In the RBS 884 Macro the ANP
consists of the Antenna Near Part Cabinet (ANPC) and the Auto-
tuned Combiner Cabinet (ATCC). In the RBS 884 Micro (800 MHz)
and in the RBS 884 Compact, it consists of a number of the RFTL,
MC, COMBFILT and CABCOMB boards. In the RBS 884 Micro
(1900 MHz), the ANP, bandpath filters, and Radio Frequency Test
Loop (RFTL) are integrated into a single hardware unit. The
combined ANP/RFTL/Filter unit provides RSSI measurement, output
power measurement and calibration, VSWR supervision, and RF
path testing. The main functions of the ANP are as follows:
– Combine multiple TRX output signals to a single Tx antenna
– Filter TX and RX signals
– Pre-amplify and distribute RX signals
– Protect TRXs from reflected power
– Provide isolation between the TRXs
– Calibrate and supervise the TRXs and associated RF components
•Support Part (SP) – provides general support, such as power supply
and cooling. The components of this part vary significantly between
the product lines.
3/1551-EN/LZB 119 3312 Uae Rev A 1998-11-17 2-9
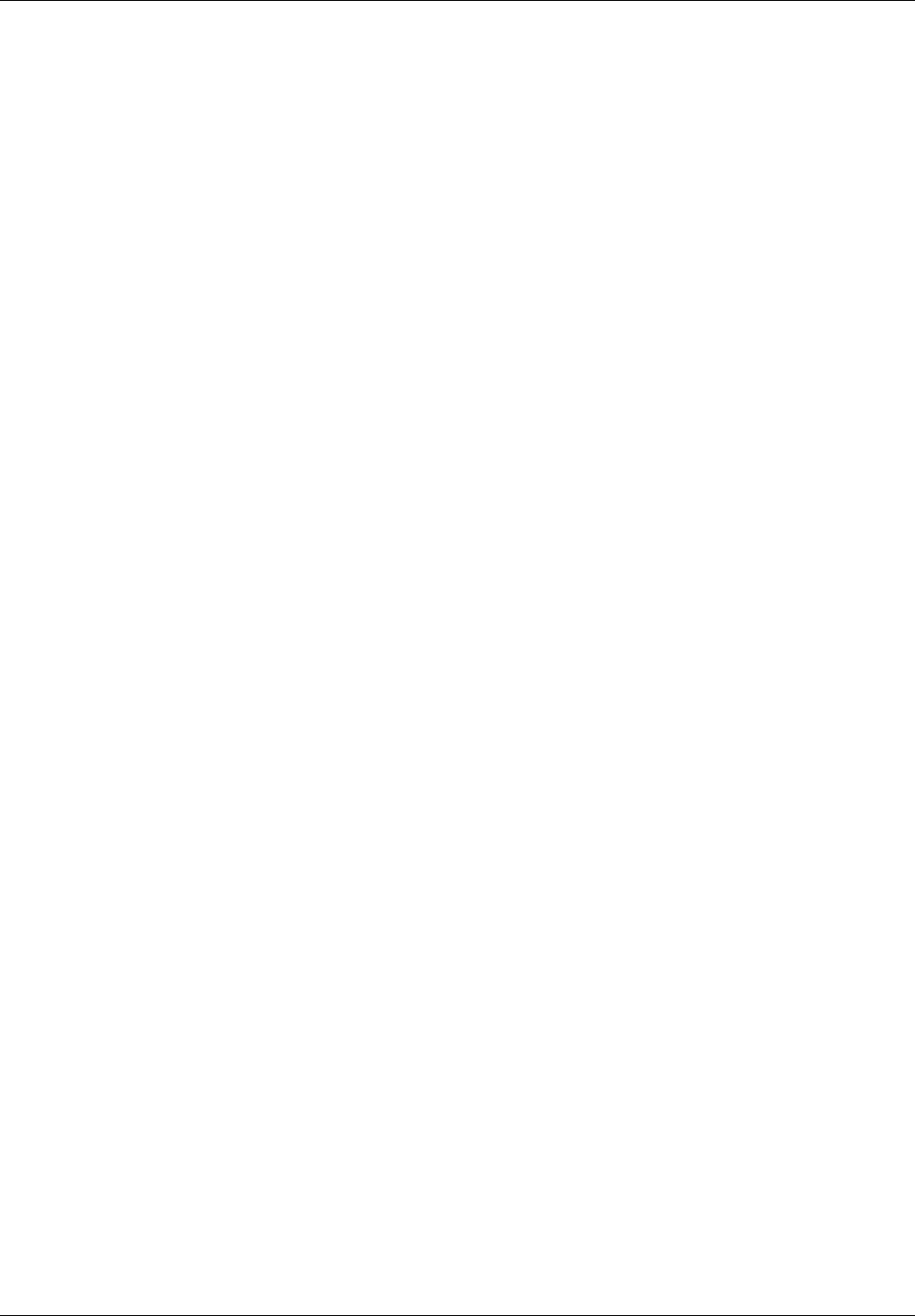
General Product Information
2-10 3/1551-EN/LZB 119 3312 Uae Rev A 1998-11-17
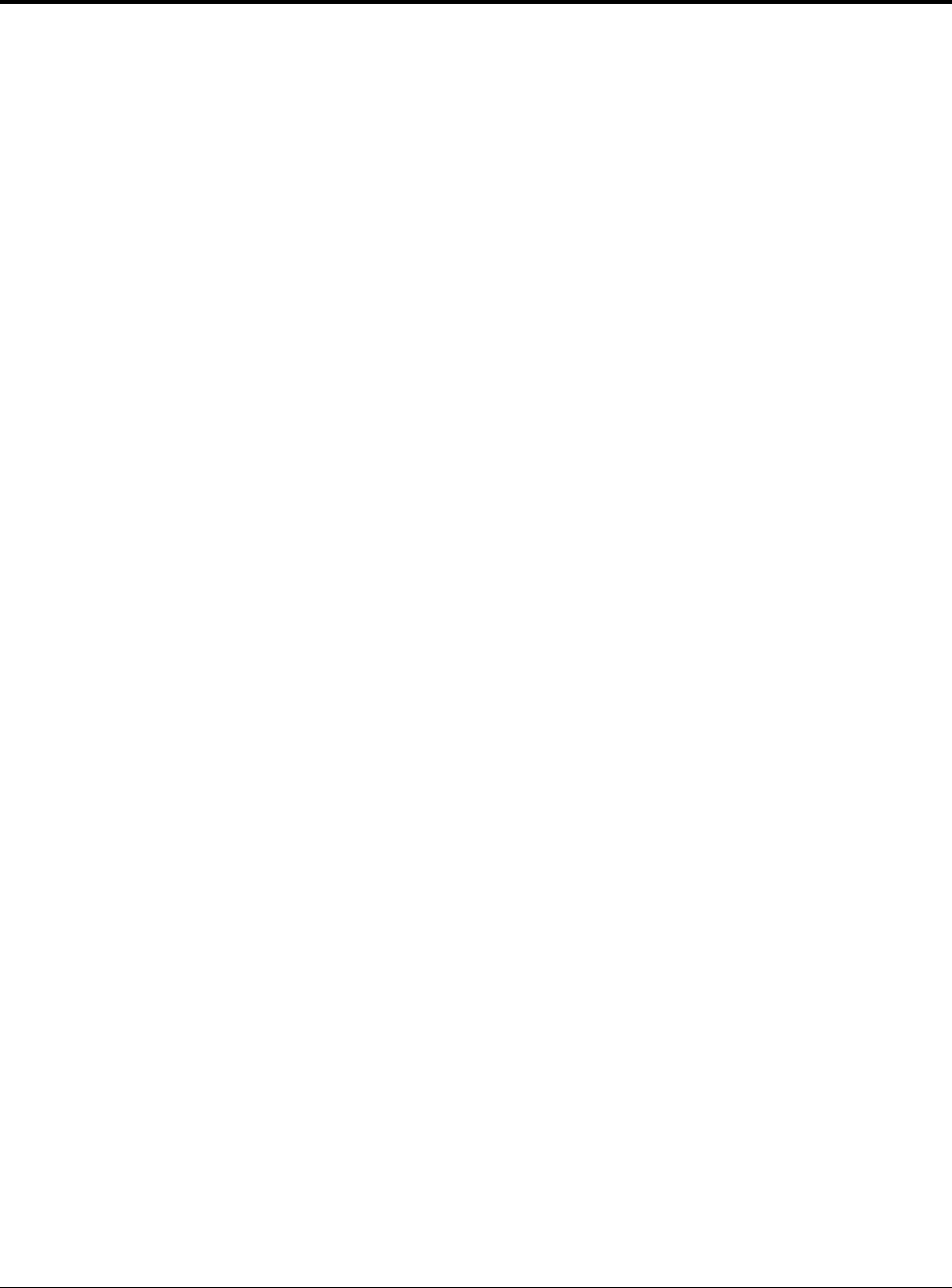
Part 3
System Description
1 Introduction .................. 3-3
2 RBS 884 Micro (1900 MHz) ........... 3-3
2.1 Cabinet Layout .............. 3-3
2.2 Power Distribution Box .......... 3-6
2.3 Equipped Microbase Subrack (EMBS) – Main
Cabinet ................. 3-7
2.4 Equipped Microbase Subrack (EMBS) –
Primary Cabinet ............. 3-11
2.5 Remote Multiplexer (REMUX) ....... 3-13
2.6 Extension Module Regional Processor, Micro
(EMRPM) ................ 3-14
2.7 Transceiver (TRX) ............ 3-15
2.8 Antenna Near Part (ANP)/Radio Frequency
Test Loop (RFTL) ............ 3-16
2.9 Environmental Control Unit ........ 3-17
2.10 Fans ................... 3-17
2.11 Air Filter ................. 3-18
3 Installation Configurations ........... 3-18
3.1 Limitations ................ 3-18
3.2 Standard Configurations RBS 884 Micro (1900
MHz) .................. 3-18
4/1551-EN/LZB 119 3312 Uae Rev A 1998-11-17 3-1
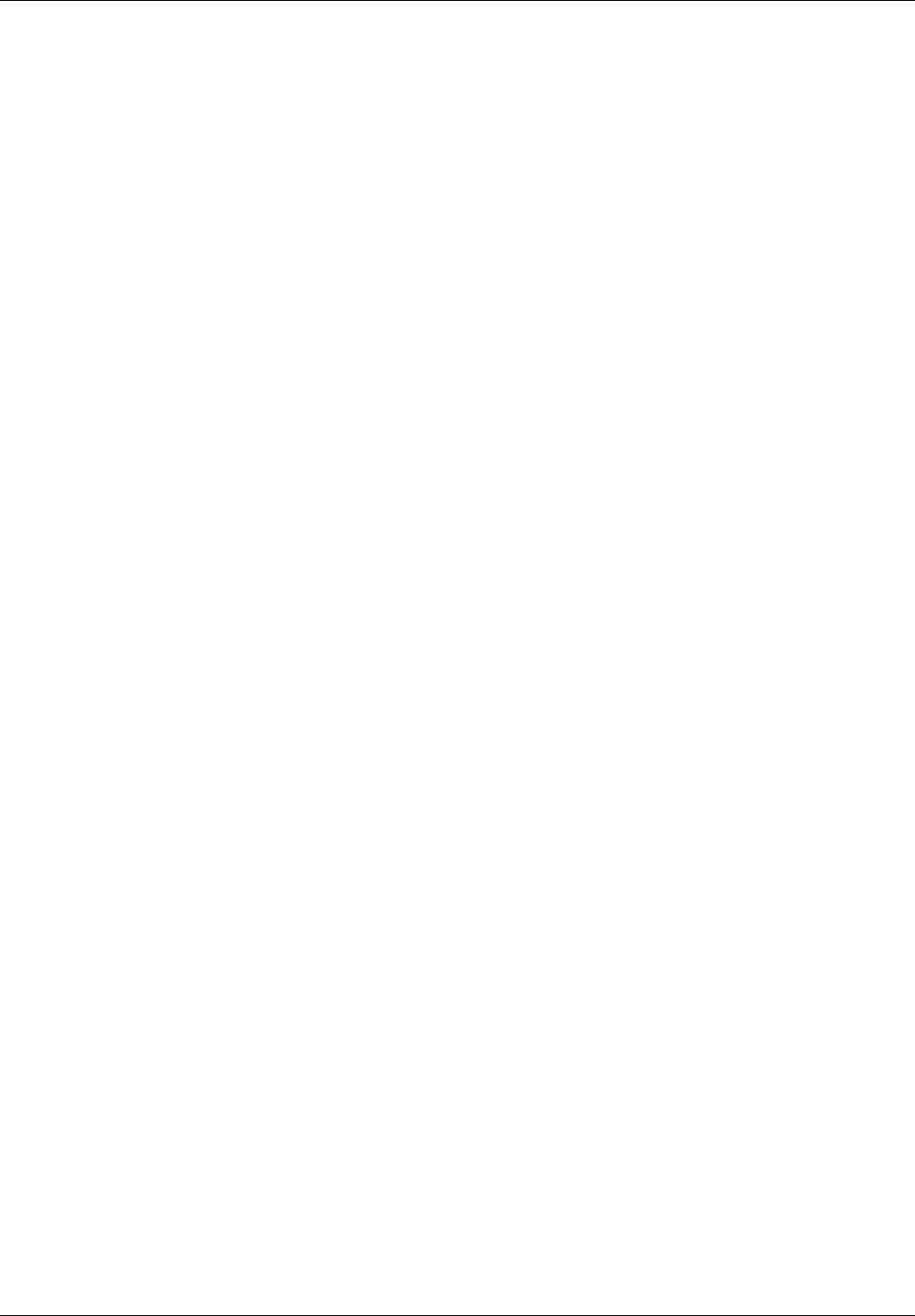
System Descri tion
3-2 4/1551-EN/LZB 119 3312 Uae Rev A 1998-11-17
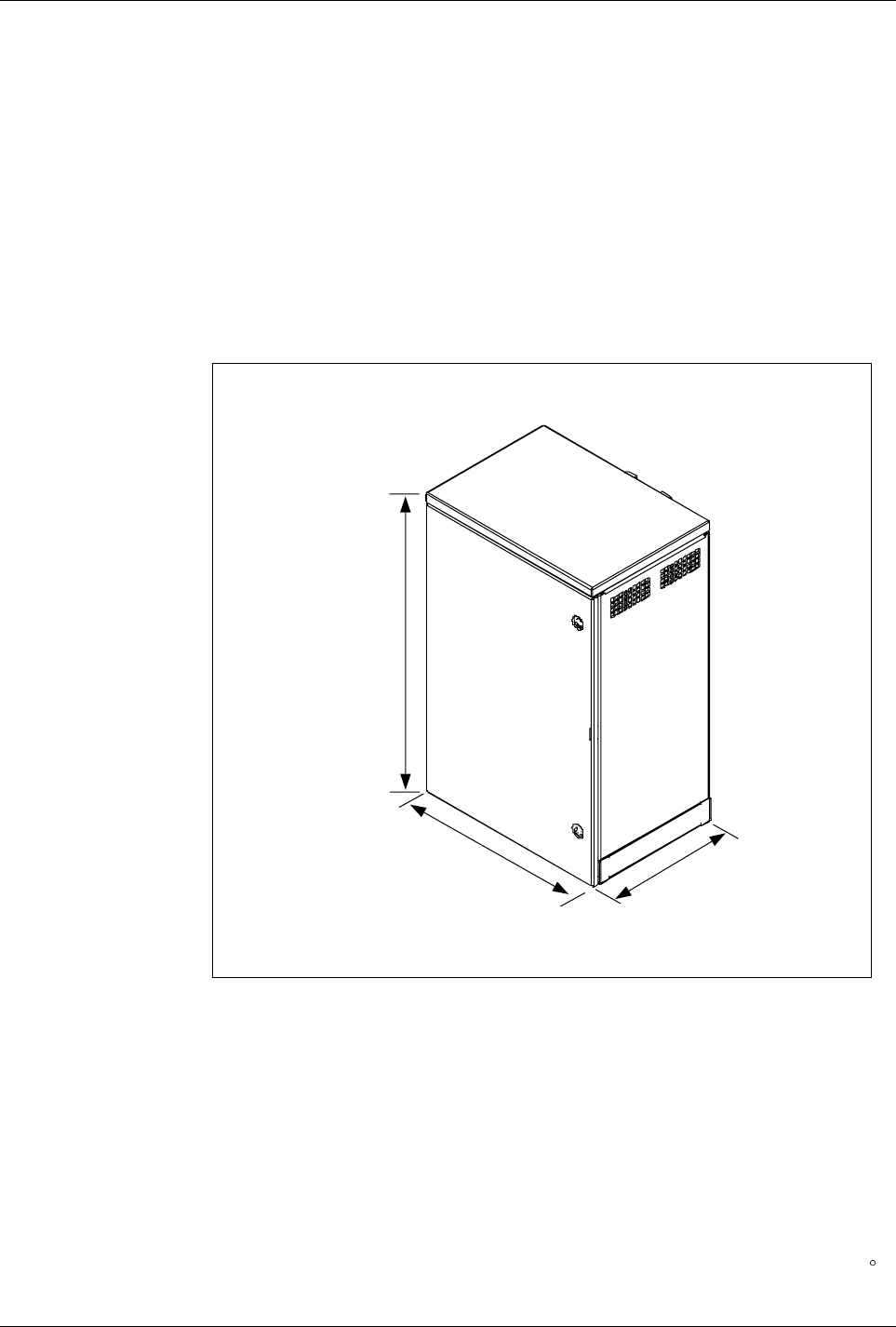
System Descri tion
1 Introduction
The System Description part of this manual describes the RBS 884 Micro
(1900 MHz) equipment hardware and the available configurations.
2 RBS 884 Micro (1900 MHz)
Hardware specifications for the RBS 884 Micro (1900 MHz) are described
in the following sections. Figure 3-1 on page 3-3 is an exterior view of the
cabinet.
95 cm
43 cm
61 cm
Figure 3-1. RBS 884 Micro (1900 MHz) Exterior View of Cabinet
2.1 Cabinet Layout
The RBS 884 Micro (1900 MHz) base station cabinet provides mechanical
support, electrical interconnection, cooling, and environmental protection
for the RBS 884 modules and components. All base station equipment
wiring and cabling are easily accessible from the front of the unit. The
electronic cards and modules plug into the backplanes of the electronics
subrack and the subrack is cooled directly with outside air. The RBS
equipment is protected from the external climatic variations by use of the
environmental control system that supplies the internal modules with 10 C
4/1551-EN/LZB 119 3312 Uae Rev A 1998-11-17 3-3
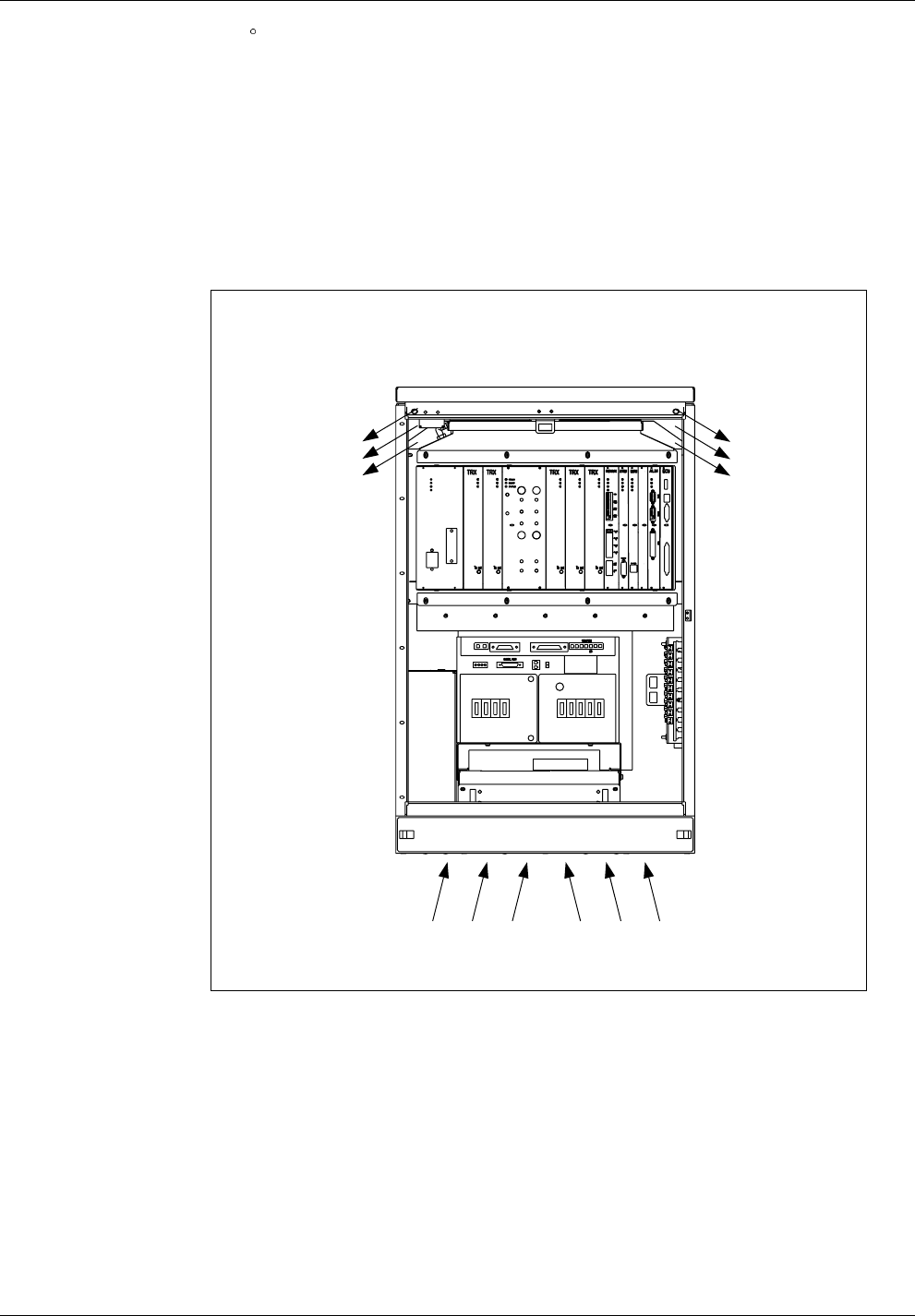
System Descri tion
–45C cooling air during normal operation. Figure 3-2 on page 3-4 shows
the cooling airflow pattern that is established by the environmental control
system. Cabinet siting must allow for adequate airflow space and cable
access and routing space to the bottom of the cabinet.
The RBS 884 Micro (1900 MHz) external cabinet shell is constructed of
aluminum and finished with a polyester powder paint. The exterior of the
cabinet can be refinished by the customer. Refinishing and repainting
information is provided in Part 4 – Installation. The corrosion warranty
does not apply to refinished cabinets.
Air Inlet
Exhaust Exhaust
Figure 3-2. RBS 884 Micro (1900 MHz) With Cooling Airflow Pattern
3-4 4/1551-EN/LZB 119 3312 Uae Rev A 1998-11-17

System Descri tion
The RBS 884 Micro (1900 MHz) is comprised of one main cabinet and up
to two auxiliary primary cabinets, as follows:
•The Main Cabinet is used in all configurations. The Main Cabinet
provides up to four digital TRXs and one Digital Verification
Module (DVER). The four TRXs offer a total of 11 Digital Traffic
Channels (DTCs) and one Dedicated Control Channel (DCCH).
•The Auxiliary Primary Cabinet has a dedicated antenna system and
is used to create an additional sector within an omni cell. The
Auxiliary Primary Cabinet provides up to four digital TRXs and one
DVER device. The four TRXs offer a total of 11 DTCs and one
DCCH. The primary cabinet requires an EMRPM transmission link
connection to the main cabinet.
The RBS 884 Micro (1900 MHz) Main Cabinet contains the following
(see Figure 3-3 on page 3-6):
•Power Distribution Box
•Equipped Microbase Subrack (EMBS)
– Antenna Near Part (ANP) includes the integrated filter unit and
the Radio Frequency Test Loop (RFTL)
– Power Supply Unit (PSU)
– Remote Multiplexer (REMUX)
– Environmental Control Unit (ECU)
– Transceivers (5) (TRX), including 1 Digital Verification Module
(DVER)
– Extension Module Regional Processor, Micro (EMRPM)
– Dummy EMRPM or blank module
– Signaling Terminal Regional, Micro (STRM)
– Alarm Board (ALM)
•Fans (4)
•Heater
•AC surge suppressor
•Backup batteries
•Heater for backup batteries
•PCM surge suppressor units (primary and secondary)
•Antenna connector plate or I/O plate with integral quarter wave
shorting stubs for lightning protection
•Optional air filter
4/1551-EN/LZB 119 3312 Uae Rev A 1998-11-17 3-5
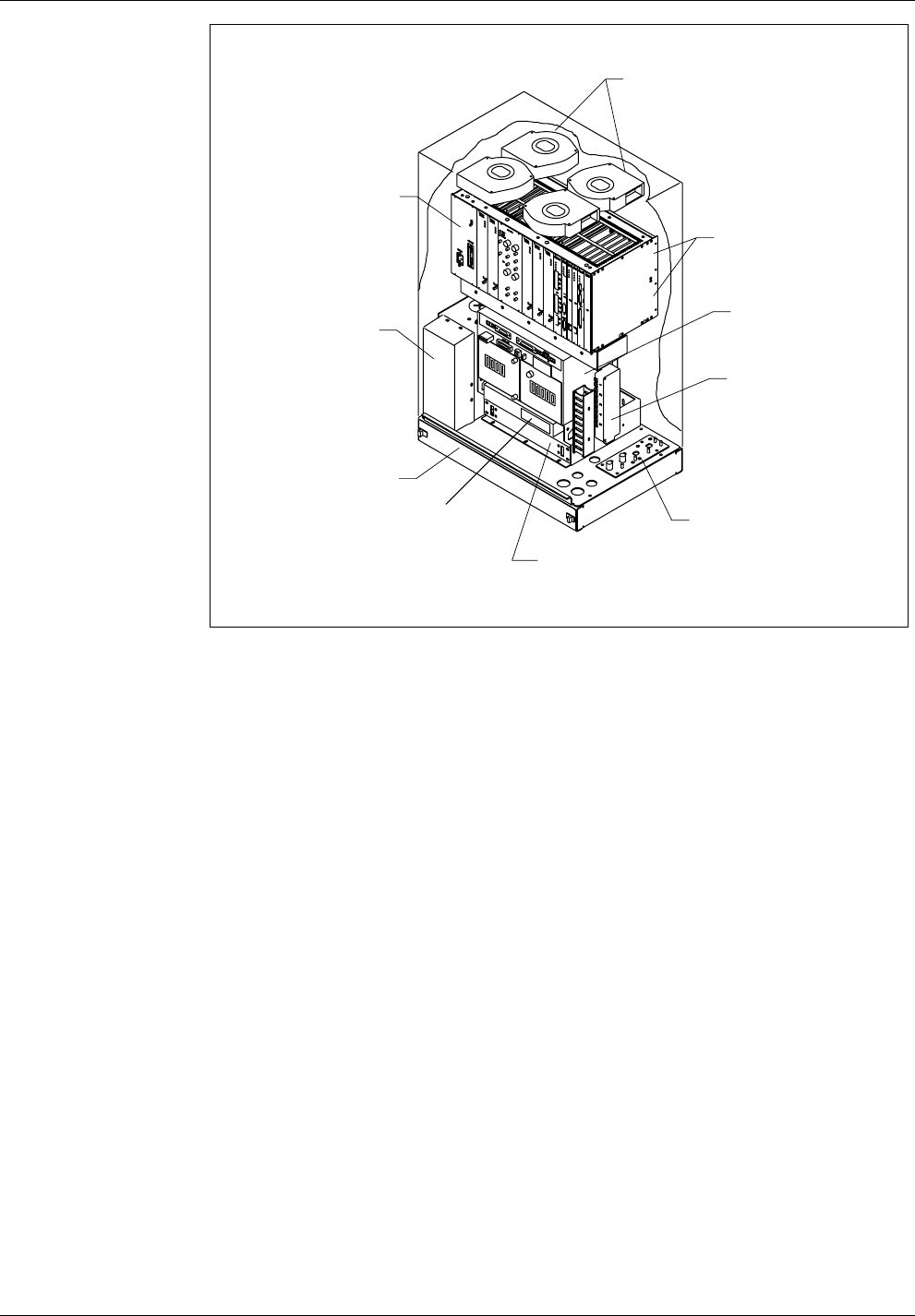
System Descri tion
Subrack
with Plug-In
Modules
Battery
Compartment
(2 Batteries)
Fan Units (4)
Backplanes
AC/DC
Power
Air Filter
Access Panel
Heater
Ground Plate
Primary T1
Surge
Suppressor
Secondary T1
Surge
Suppressor
Figure 3-3. RBS 884 Micro (1900 MHz) Fully-Equipped Cabinet
2.2 Power Distribution Box
The power distribution box supplies the RBS equipment with the AC and
DC supply voltages. See Figure 3-4 on page 3-7
3-6 4/1551-EN/LZB 119 3312 Uae Rev A 1998-11-17
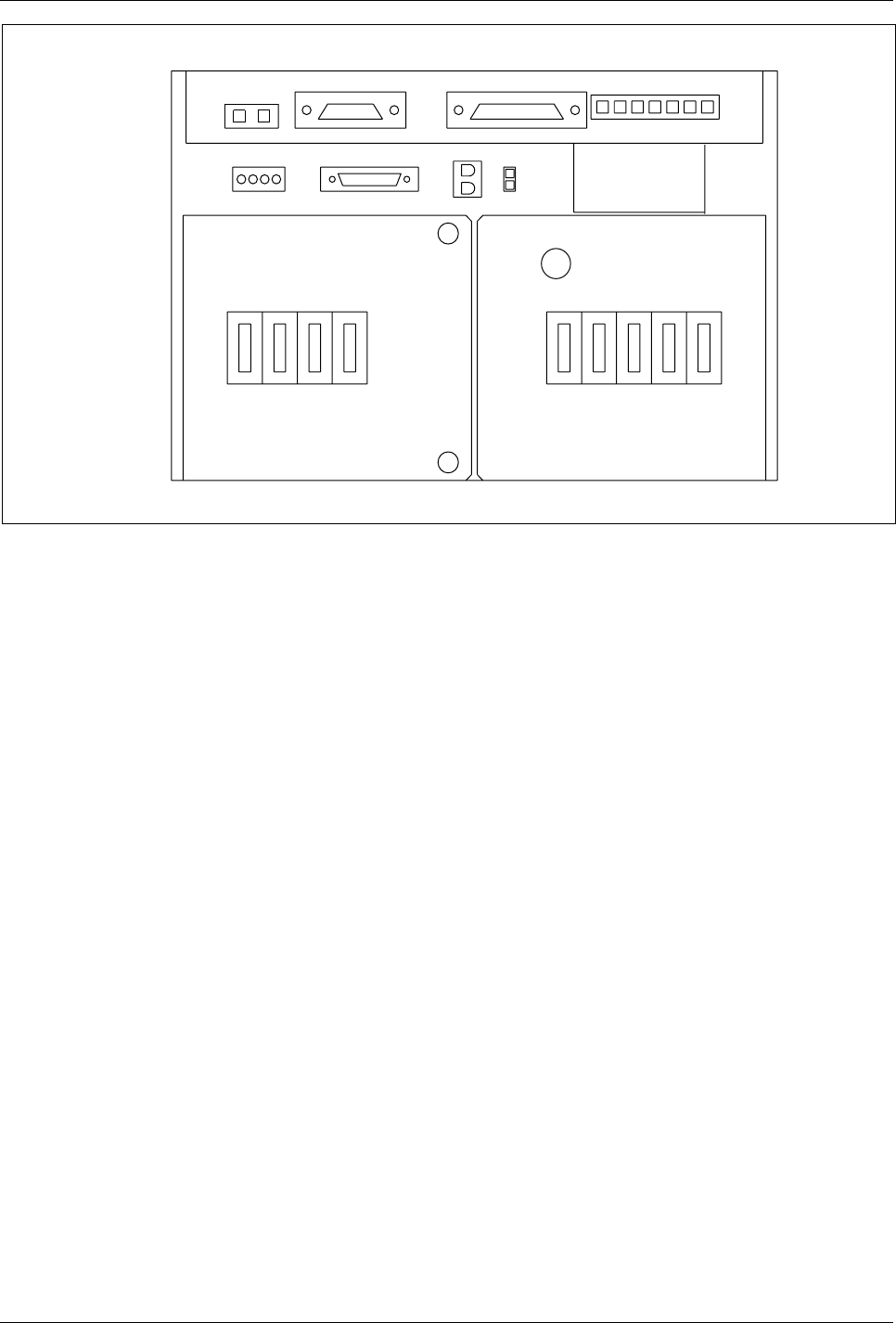
System Descri tion
ALM CABLE ECU CABLE
SUBRK PWR
FAN PWR CSU
SENSORS
AC
CONNECTED
MAIN PSU MAIN
HTR BAT
HTR GFI
OUTLET
BAT ECU CSU FANS
BAT COMP
BAT
ALM DOOR
ALM
ON
OFF
CONVENIENCE
OUTLET
Figure 3-4. RBS 884 Micro (1900 MHz) Power Distribution Box Front Panel
The power distribution box contains the following:
•DC and alarms distribution panel
•DC and AC breakers
•AC mains
•AC surge connection
•Control board with connectors to temperature sensors, alarms, and
the Environmental Control Unit (ECU)
The RBS 884 Micro (1900 MHz) is designed with service breakers to
allow for replacement of the heaters and batteries while the base station
remains powered. The breakers also provide over-current protection. One
main breaker removes power from the entire cabinet.
2.3 Equipped Microbase Subrack (EMBS) – Main Cabinet
The EMBS – Main Cabinet contains the RBS 884 Micro (1900 MHz)
equipment units described in this section. Figure 3-5 on page 3-8 shows
the main cabinet equipment units in their allocated positions. Variable-
speed fans are located in the top of the cabinet and the resulting air flow is
dimensioned to handle a fully-equipped cabinet. The equipment units and
fans are environmentally sealed to protect circuit board traces and
components from direct exposure to outside cooling air.
4/1551-EN/LZB 119 3312 Uae Rev A 1998-11-17 3-7
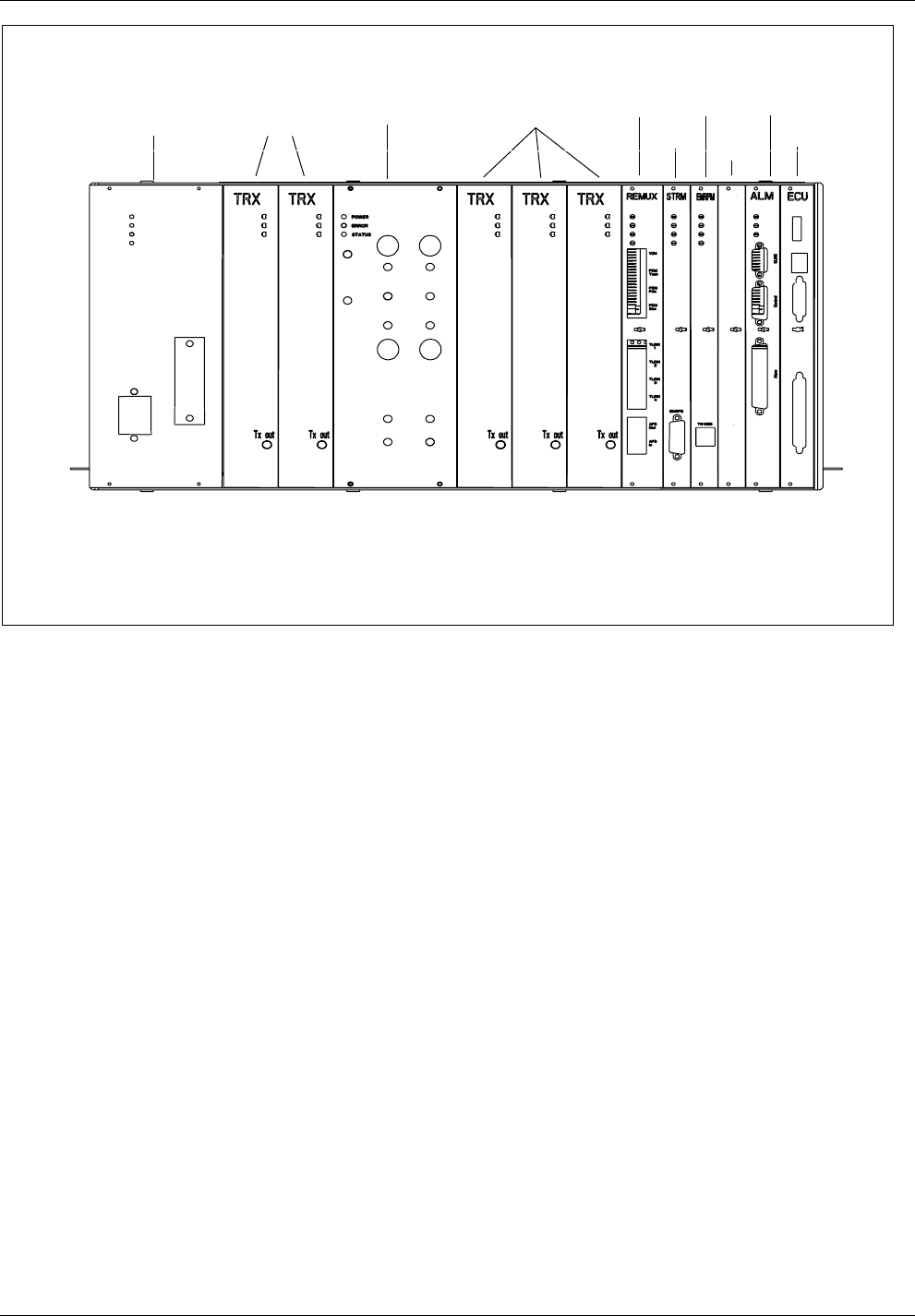
System Descri tion
12 354786 9 11 12 13
Power
Supply
Unit TRX
ANP/RFTL
TRX
REMUX
STRM
EMRPM
BLANK
PANEL
ALM
ECU
ANP/RFTL
PSU
Figure 3-5. RBS 884 Micro (1900 MHz) EMBS Front Panel — Main Cabinet
The equipment units installed in the cabinet are allocated numbered slots,
(slot No.1 to slot No. 13) from left to right, and are dimensioned using
Building Modules (for example, BM = 1/10 in = 2.54 mm) as the unit of
measurement.
3-8 4/1551-EN/LZB 119 3312 Uae Rev A 1998-11-17

System Descri tion
The RBS 884 Micro (1900 MHz) EMBS – Main Cabinet contains the
following:
•Five Transceivers (TRX), including one Digital Verification Module
(DVER) for digital traffic. See Section 2.7 on page 3-15. The five
TRXs are installed as follows:
– Slot 1 (8 BM) – Dedicated Control Channel (DCCH)/Digital
Voice Channel (DVC)
– Slot 2 (8 BM) – DCCH/DVC
– Slot 4 (8 BM) – DCCH/DVC
– Slot 5 (8 BM) – DCCH/DVC
– Slot 6 (8 BM) – DVER
•One Antenna Near Part (ANP) with integrated filter unit and Radio
Frequency Test Loop (RFTL). The ANP is installed in slot 3 (10
BM) The function of the ANP is as follows:
– Supervise the reflected loss of the TX antenna
– Calibrate Receiver Signal Strength Indicator (RSSI)
– Calibrate dynamic power and measurement of output power
– Operate test loop. The measured RF signal from the TX antenna
output is converted to the corresponding RX frequency and is fed
into the receiver at a fixed RF level.
•One Remote Multiplexer (REMUX) to provide T1/E1 PCM line
termination and clock stabilization in the main cabinet. The REMUX
is not included in primary cabinets. The REMUX is installed in slot
7 (12 BM).
•One Signaling Terminal Regional (STRM) to decode control
information and controls the EMRPM control bus. The STRM is not
included in primary cabinets. The STRM is installed in slot 8 (8
BM).
•One Extension Module Regional Processor, Micro (EMRPM) to
provide device control, speech interface to transceivers, alarm
monitoring and a port for computer interface to the Mobile
Switching Center (MSC). The EMRPM is installed in slot 9 (8 BM).
Expansion space for a second EMRPM is available in slot 10.
•One EMRPM Dummy Unit to allow for future expansion for a
second EMRPM. This equipment unit is the same size as the
EMRPM and is used to ensure proper airflow through the unused
subrack slot. The EMRPM Dummy Unit is installed in slot 10 (8
BM).
4/1551-EN/LZB 119 3312 Uae Rev A 1998-11-17 3-9
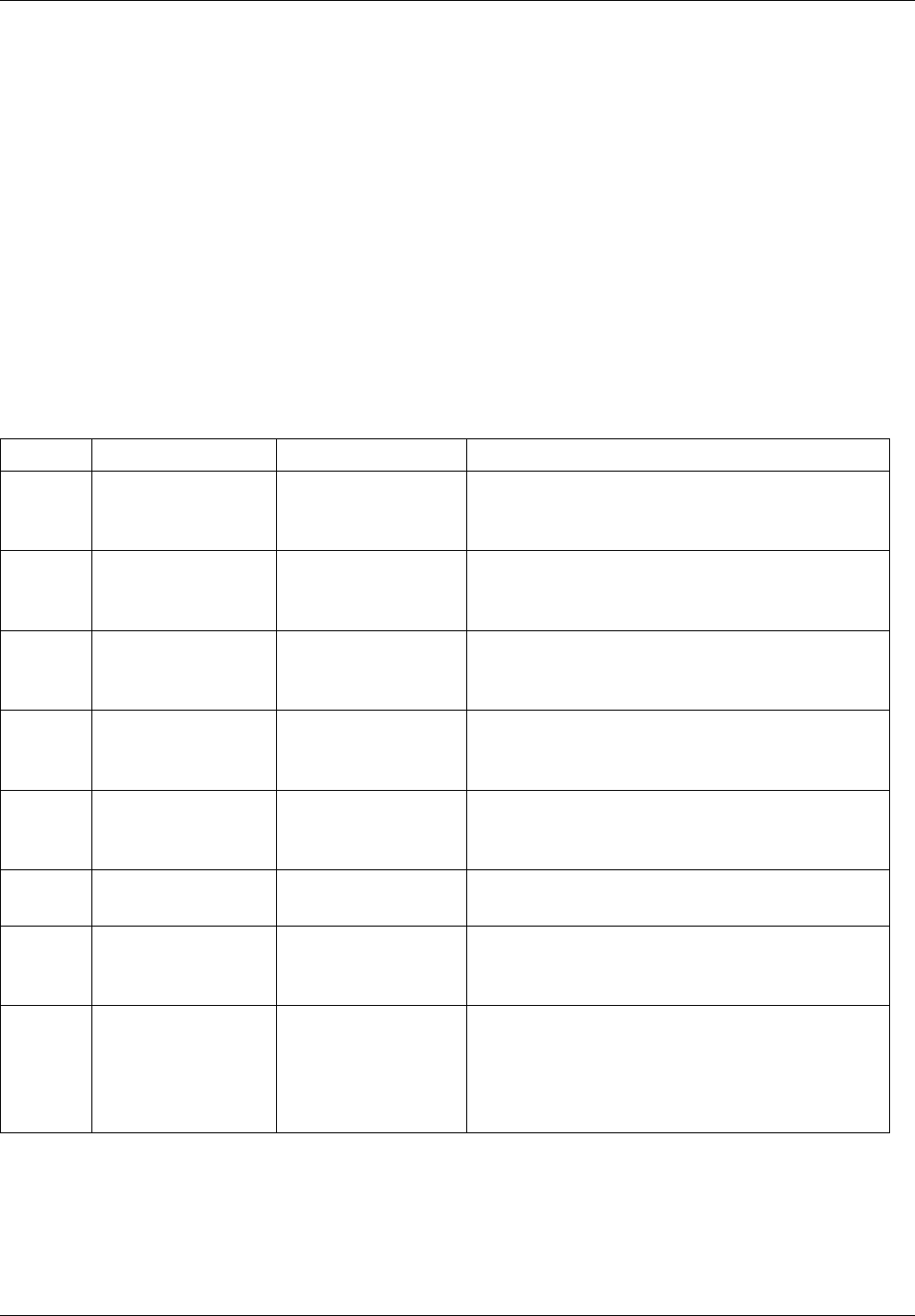
System Descri tion
•One Alarm unit (ALM) to provide maximum connection of 32
external alarms. External alarms are alarms for both internal and
external equipment that are defined as external alarms on the ALM
board. The ALM is installed in slot 11 (10 BM).
•One Environment Control Unit (ECU) to provide temperature
regulation inside the cabinet and provides alarms to the TRXs and
the ALM board. The ECU is installed in slot 12 (10 BM).
Note: Unused TRX slots must be equipped with dummy TRXs or
Radio Matching Units (RMUs). Other unused slots must have
an equipment unit (a blank panel along with a dummy board)
to assure proper airflow and electromagnetic shielding.
See Table 3-1 on page 3-10 for the complete EMBS Main Cabinet
configuration.
Table 3-1. EMBS Configuration for RBS 884 Micro (1900 MHz) Main Cabinet
Slot Name Explanation Comments
1-2 TRX Transceiver The TRXs act as digital voice/control channels.
Slot 1 is recommended for the control channel
TRX.
3ANP/RFTL Antenna Near Part/
Radio Frequency
Test Loop
The ANP provides transmit (TX) and receive
(RX) filtering, low-noise amplifying and RFTL
functionality.
4-5 TRX Transceiver The TRXs act as digital voice/control channels.
Unused TRX slots must contain a dummy TRX
or RMU.
6 TRX Transceiver with
mobile verification
functionality
The TRX in slot 6 is used as a Personal
Communications Services (PCS) or MVER for
uplink measurements.
7REMUX Remote Multiplexer The REMUX provides T1/E1 PCM line
termination and clock stabilization in the main
cabinet.
8STRM Signaling Terminal
Regional Micro
The STRM decodes control information and
controls the EMRPM.
9EMRPM Extension Module
Regional Processor
Micro
The EMRPM controls the TRXs as well as the
REMUX, the ANP/RFTL, and the ALM.
10 Blank
Module
Dummy EMRPM The Blank Module or equipment unit allows for
future expansion for a second EMRPM. This
equipment unit is the same size as the EMRPM
and is used to ensure proper airflow through the
unused subrack slot.
3-10 4/1551-EN/LZB 119 3312 Uae Rev A 1998-11-17
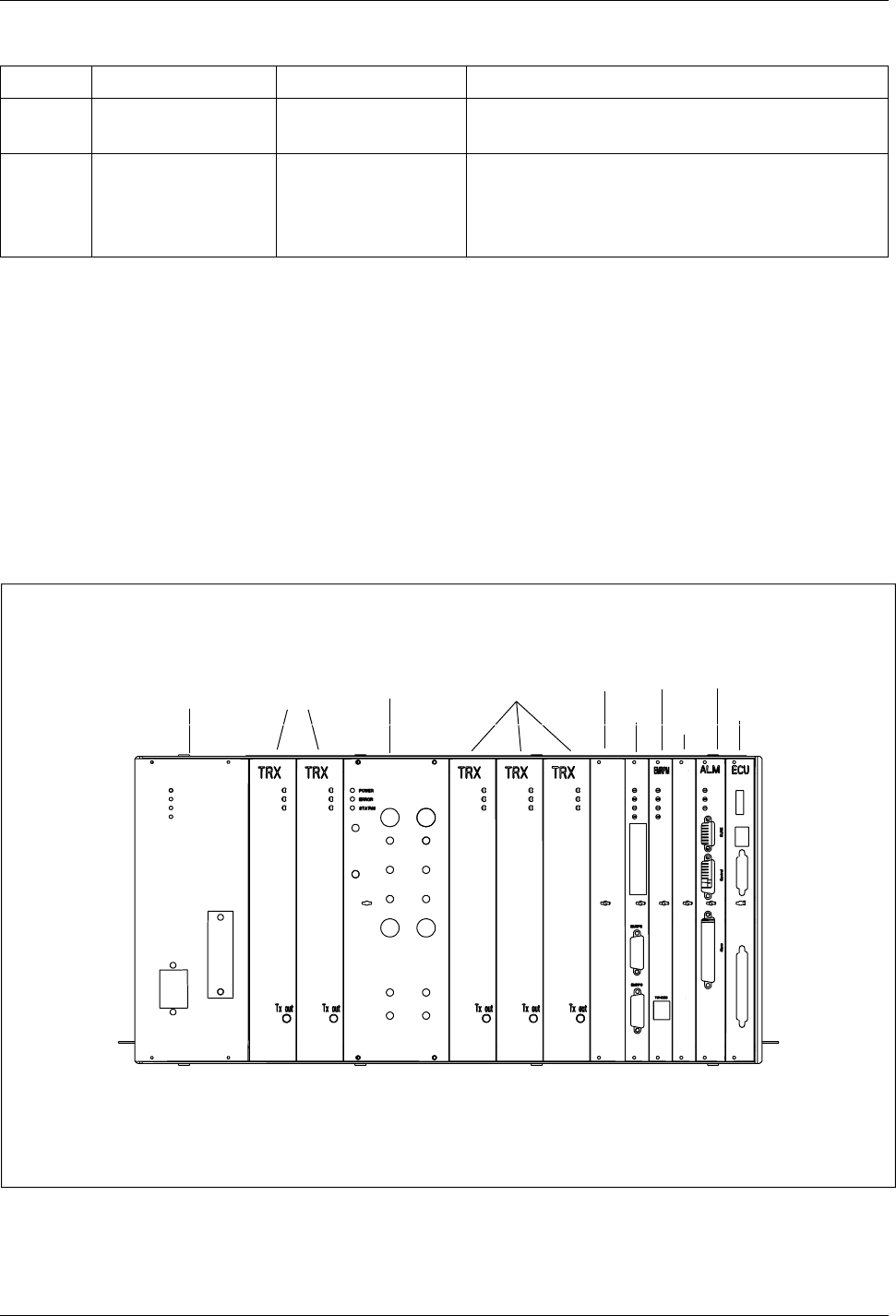
System Descri tion
Table 3-1. EMBS Configuration for RBS 884 Micro (1900 MHz) Main Cabinet (Continued)
Slot Name Explanation Comments
11 ALM Alarm The ALM collects internal and external
equipment alarms.
12 ECU Environmental
Control Unit
The ECU controls temperature regulation inside
the cabinet. The ECU also provides alarms to
the TRXs and the ALM board for fan and heater
failures.
2.4 Equipped Microbase Subrack (EMBS) – Primary Cabinet
The EMBS – Primary Cabinet contains the RBS equipment units described
in this section. Figure 3-6 on page 3-11 shows the primary cabinet units in
their allocated positions. Variable-speed fans are located in the top of the
cabinet and the resulting air flow is dimensioned to handle a
fully-equipped cabinet.
The RBS equipment units and fans are environmentally sealed to protect
circuit board traces and components from direct exposure to outside
cooling air.
12 354786 9 11 12 13
Power
Supply
Unit TRX ANP/RFTL TRX
CONN
EMRPM
BLANK
PANEL
ALM
ECU
BLANK
PANEL
ANP/RFTL
Figure 3-6. RBS 884 Micro (1900 MHz) EMBS Front Panel — Primary Cabinet
4/1551-EN/LZB 119 3312 Uae Rev A 1998-11-17 3-11
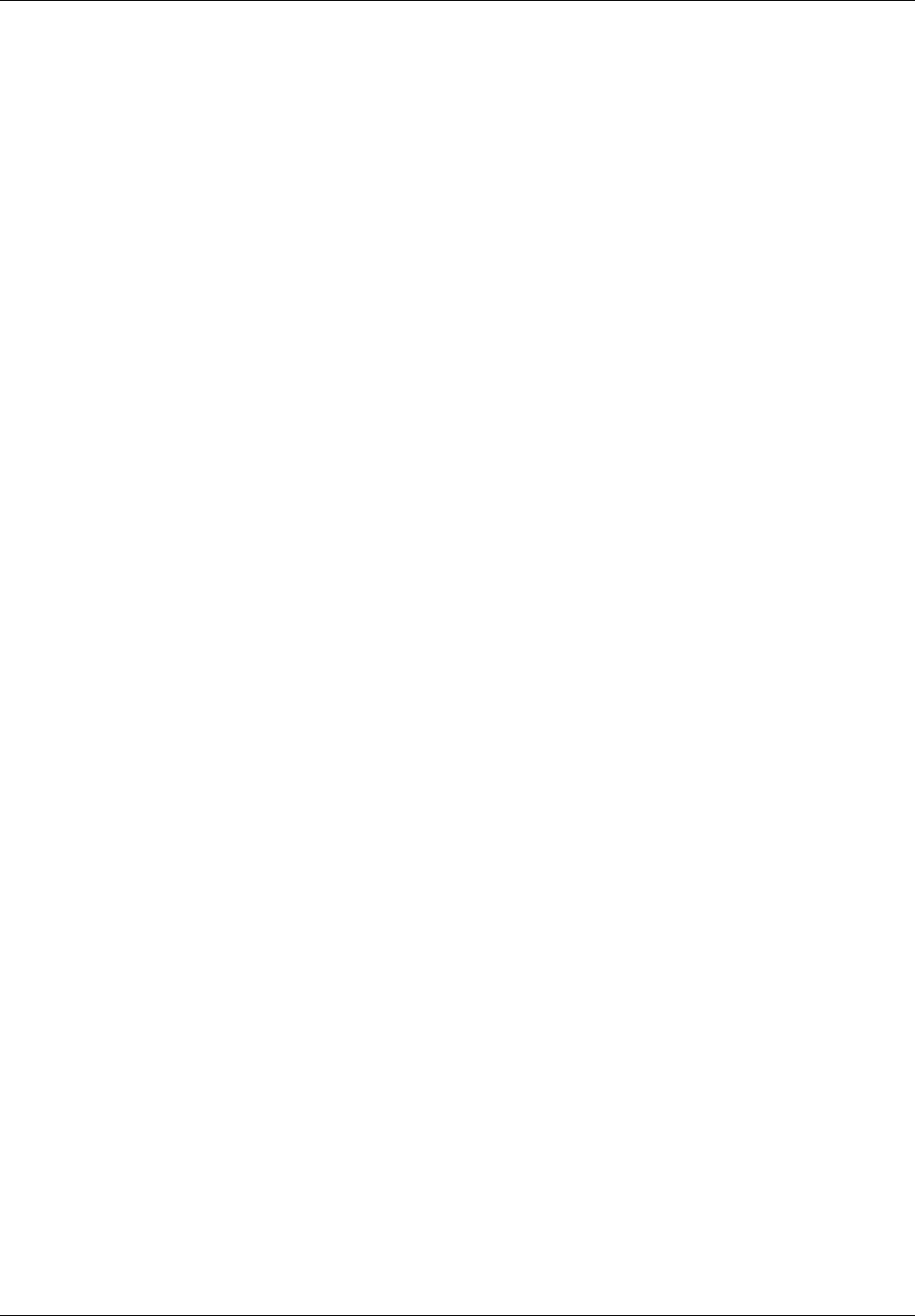
System Descri tion
The RBS 884 Micro (1900 MHz) EMBS – Primary Cabinet contains the
following:
•Five Transceivers (TRX), including one Digital Verification Module
(DVER) for digital traffic. See Section 2.7 on page 3-15. The five
TRXs are installed as follows:
– Slot 1 (8 BM) – DCCH/DVC
– Slot 2 (8 BM) – DCCH/DVC
– Slot 4 (8 BM) – DCCH/DVC
– Slot 5 (8 BM) – DCCH/DVC
– Slot 6 (8 BM) – DVER
•One ANP/RFTL with integrated filter unit. The ANP/RFTL is
installed in slot 3 (10 BM).
•One Blank equipment unit or Dummy REMUX installed in slot 7 (8
BM).
•One Connector (CONN) Unit to relay signals from the REMUX and
STRM units in the main cabinet to the other units in the primary
cabinet. The CONN is installed in slot 8 (8 BM).
•One Extension Module Regional Processor, Micro (EMRPM) to
control the TRX slots 1, 2, 4, 5, and 6. The EMRPM is installed in
slot 9 (8 BM)
•One EMRPM Dummy Unitto allow for future expansion for a second
EMRPM. This equipment unit is the same size as the EMRPM and
is used to ensure proper airflow through the unused subrack slot. The
EMRPM Dummy Unit is installed in slot No.10 (8 BM).
•One Alarm Unit (ALM) to provide a maximum connection of 32
external alarms. External alarms are alarms for both internal and
external equipment that are defined as external alarms on the ALM
board. The ALM is installed in slot 11 (10 BM).
•1 Environment Control Unit (ECU) installed in slot 12 (10 BM).
Note: Unused TRX slots must be equipped with dummy TRXs or
Radio Matching Units (RMU). Other unused slots must have
an equipment unit (a blank panel along with a dummy board)
to assure proper airflow and electromagnetic shielding.
See Table 3-2 on page 3-13 for the complete EMBS – Primary Cabinet
configuration.
3-12 4/1551-EN/LZB 119 3312 Uae Rev A 1998-11-17

System Descri tion
Table 3-2. EMBS Configuration for RBS 884 Micro (1900 MHz) Primary Cabinet
Slot Name Explanation Comments
1-2 TRX Transmit TRX The TRXs act as digital voice/control channels.
Slot 1 is recommended for the control channel
TRX.
3ANP/RFTL Antenna Near Part/Radio
Frequency Test Loop
The ANP provides transmit (TX) and receive
(RX) filtering, low-noise amplifier and RFTL
functionality.
4-5 TRX Transceiver The TRXs act as digital voice/control channels.
Unused TRX slots must contain a dummy TRX
or RMU.
6 TRX Transceiver with mobile
verification functionality
The TRX in slot 6 acts as a Personal
Communication Services (PCS) or MVER for
uplink measurements.
7Blank
module
Dummy TRX The dummy TRX or RMU ensures proper airflow
through the unused subrack slot.
8CONN Connection Board The CONN board passes TRX signals to the
backplane.
9EMRPM Extension Module
Regional Processor Micro
The EMRPM controls the TRXs as well as the
REMUX, the ANP/RFTL, and the ALM units.
10 Blank
Module
Dummy EMRPM The Blank Module or equipment unit allows for
future expansion for a second EMRPM. This
equipment unit is the same size as the EMRPM
and is used to ensure proper airflow through the
unused subrack slot.
11 ALM Alarm The ALM collects internal and external
equipment alarms.
12 ECU Environmental Control
Unit
The ECU controls temperature regulation inside
the cabinet. The ECU also provides alarms to
the TRXs and the ALM board for fan and heater
failures.
2.5 Remote Multiplexer (REMUX)
The RBS 884 Micro (1900 MHz) contains a REMUX transmission unit for
a 24 channel (T1) or 32 channel (E1) PCM link with the MSC. The
incoming PCM is connected to the PCM Primary (Prim) connector on the
REMUX.
One REMUX unit is installed in slot No. 8 in the main cabinet.
For distances of greater than 200 meters, a customer-supplied Channel
Service Unit (CSU) can be mounted on the shelf above the main cabinet
heater.
Table 3-3 on page 3-14 shows the available REMUX types for T1 and E1
systems.
4/1551-EN/LZB 119 3312 Uae Rev A 1998-11-17 3-13
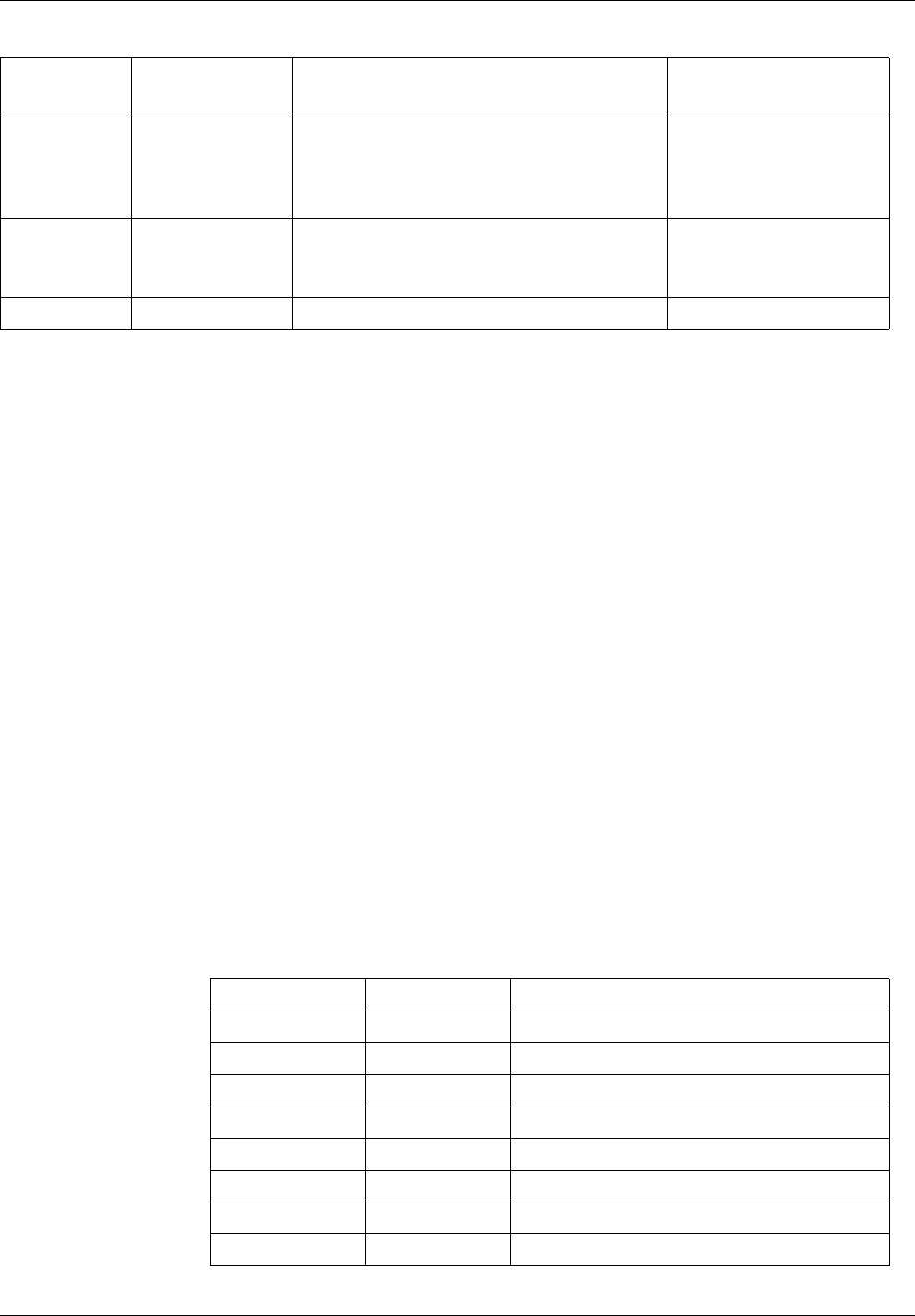
System Descri tion
Table 3-3. PCM System - REMUX
PCM System Type Distance to Nearest Active Device (For
Instance, CSU or Repeater) REMUX
T1 Short Haul
without external
Channel Service
Unit (CSU)
<200 m REMUX 24
T1 Long Haul
with external
CSU
<1800 m REMUX 24
E1 Short Haul <200 m REMUX 32SH
The REMUX switches are preset at the factory according to the
predetermined transmission requirements of the RBS 884 Micro (1900
MHz) site supplied by the site engineer.
The site engineer insures that the installer has access to documented
transmission specifications for the RBS 884 Micro (1900 MHz) site. It is
vital that the site engineer records all PCM line and switching information
in the RBS 884 Site Engineering Manual or other applicable site
installation documents.
2.6 Extension Module Regional Processor, Micro (EMRPM)
Each RBS 884 Micro (1900 MHz) cabinet contains one EMRPM unit
which controls TRX traffic. An extra slot is provided for possible future
expansion for a second EMRPM unit to share the traffic load. Ten devices
can be connected to each EMRPM unit with TLINK connections. These
are numbered TLINK 1 to TLINK 10.
The load capacity of the EMRPM allows up to four of the DVC TLINK
connections for TRXs. The EMRPM is assigned to control the REMUX
and the RFTL.
The incoming time slots are connected in a fixed pattern, as shown in
Table 3-4 on page 3-14.
Table 3-4. RBS 884 Micro (1900 MHz) EMRPM 1
EMRPM TLINK Cabinet slot Function
1 1 TRX
2 2 TRX
3 4 TRX
4 5 TRX
6 6 MVER
7 11 ALM
9 3 ANP
10 7 REMUX
3-14 4/1551-EN/LZB 119 3312 Uae Rev A 1998-11-17
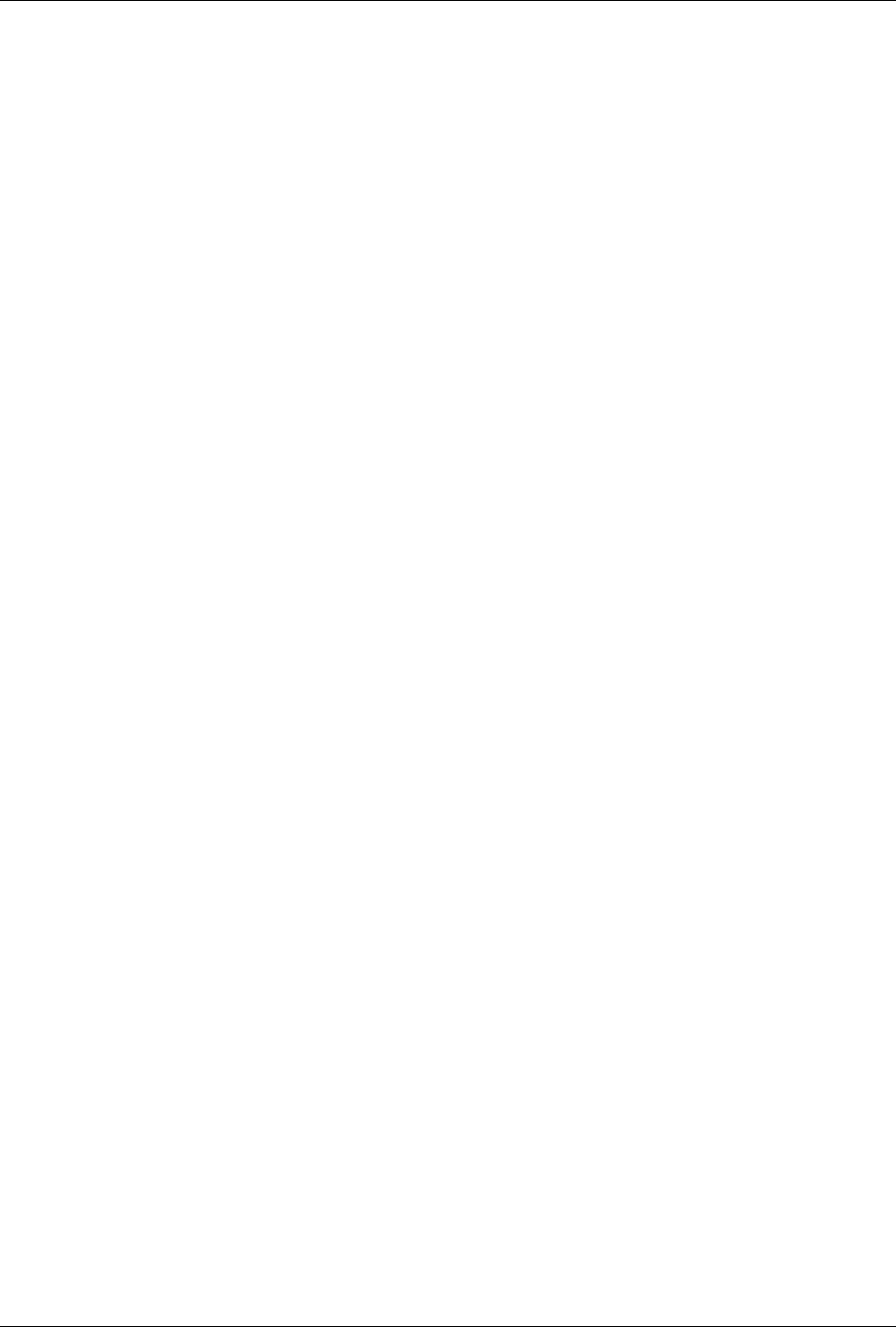
System Descri tion
The addresses of the EMRPM are set using a Double Inline Pack (DIP)
switch on the unit. No address plug is required. The address is dependent
upon the configuration of the RBS site and number of cabinets used.
A computer can be connected to the TW/DEB port at the front of the
EMRPM unit. The interface has the same function as the V24–B3 unit.
2.7 Transceiver (TRX)
The transceiver (TRX) transmits and receives radio signals to and from
mobile stations.
A TRX unit can be remotely configured to support any of the following
channel functions:
•Digital Voice Channel (DVC) – transmits and receives
•Digital Control Channel DCCH) – transmits and receives
•Digital Verification (DVER) Channel – receives only
The selection of transceiver channel function is under software control at
the Mobile Switching Center (MSC). The first time slot may be used for
DCCH and the remaining two time slots for DVCs, or all three time slots
may be used for DVCs.
The TRX provides 33.3 dBm (2.1 W) per carrier at the ANP for the two-
antenna configuration and 36.8 dBm (4.8 W) per carrier at the ANP for the
four-antenna configuration. The dynamic range is 20 dB with 0.2–dB
resolution.
The TRX includes all functionality needed for one RF channel, such as:
•Channel coding and decoding
•Modulation and demodulation
•Power amplification
•Power regulation
•Synchronization
•Diversity combining
•Measurements on received radio signal
•Verification processing (when configured as DVER)
The maximum output power for each TRX is 13.5 W. Note that digital
speech coding takes place in the voice coder units in the MSC and not in
the TRXs. There are 4 TRXs (carriers) for each antenna system that
provide 11 digital voice paths per sector.
Table 3-5 on page 3-16 shows the allocation slots for TRX units in
cabinets that are not fully equipped. In the following table, TRX positions
4/1551-EN/LZB 119 3312 Uae Rev A 1998-11-17 3-15
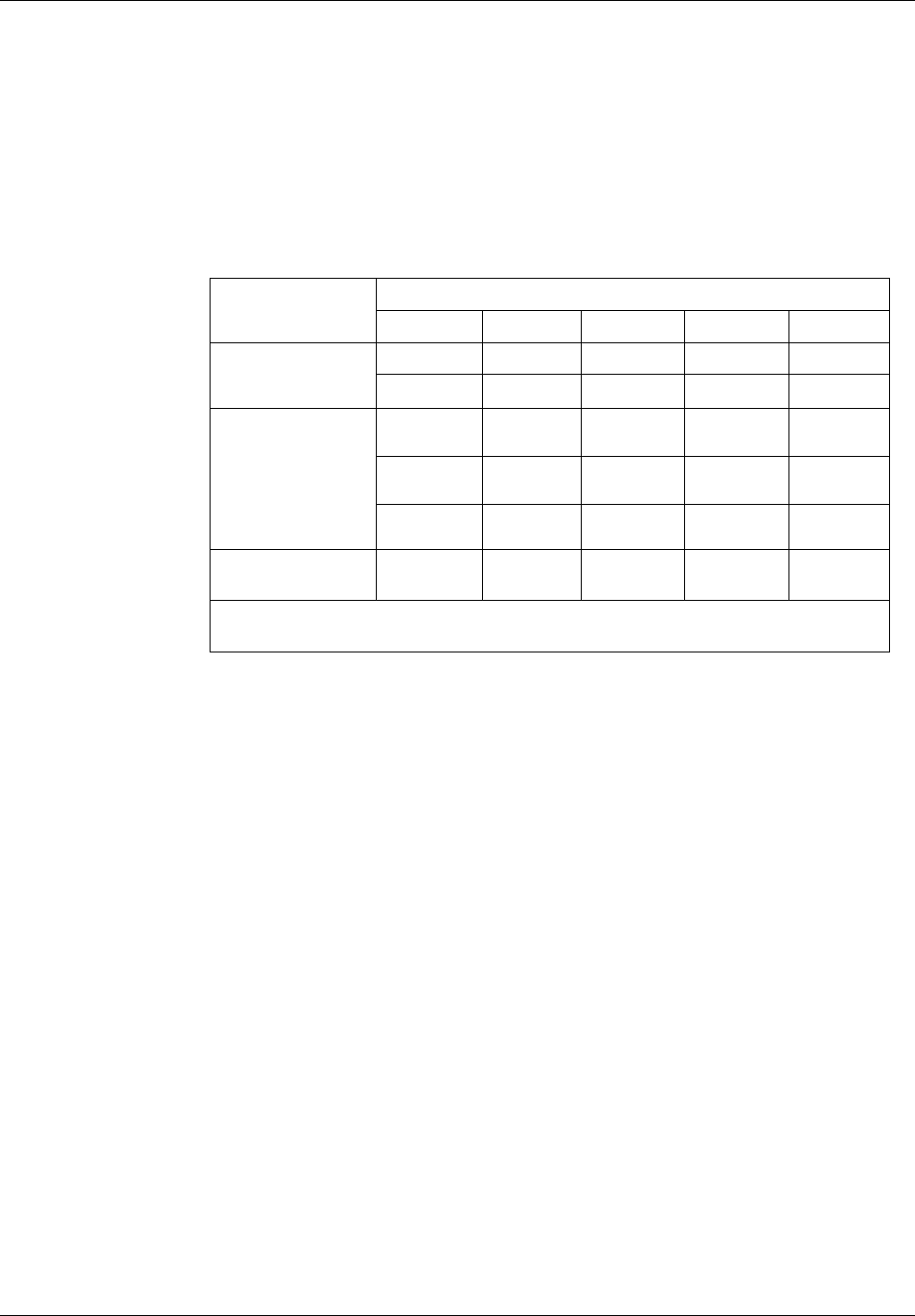
System Descri tion
marked with an asterisk (*), represent factory installed units. All empty
slots must contain an RMU.
Note: The term transceiver or TRX is used in this document to refer
to the hardware unit itself and does not reflect the functionality
of the unit. Subrack position 6 must be equipped with a TRX
that functions as a receiver or Digital Verification Module
(DVER).
Table 3-5. RBS 884 Micro (1900 MHz) TRX Unit Installation – Cabinet Not Fully
Equipped
TRX slot position in cabinet
No. of TRX 1 2 4 5 6 (MVER)
X* X* X*
3X X X*
X* X* X* X*
X X X X*
4
X X X X*
5 X* X* X* X* X*
* Indicates factory installed unit.
The maximum speech traffic capacity for a three cabinet configuration is
33 digital voice channels for both the American standard (T1 environment)
and the International standard (E1 environment).
In cascaded configurations, one PCM time slot for speech is lost for each
additional signaling link.
2.8 Antenna Near Part (ANP)/Radio Frequency Test Loop (RFTL)
The combined Antenna Near Part (ANP), Radio Frequency Test Loop
(RFTL), and integrated filter unit provides combining and splitting of RF
signals to each antenna.
The main functions of the ANP/RFTL are as follows:
•Combine the output signal of the TRXs
•Filter TX and RX signals
•Protect the TRXs from high reflected power
•Pre-amplify and distribute RX signals
•Provide isolation between the TRXs
3-16 4/1551-EN/LZB 119 3312 Uae Rev A 1998-11-17
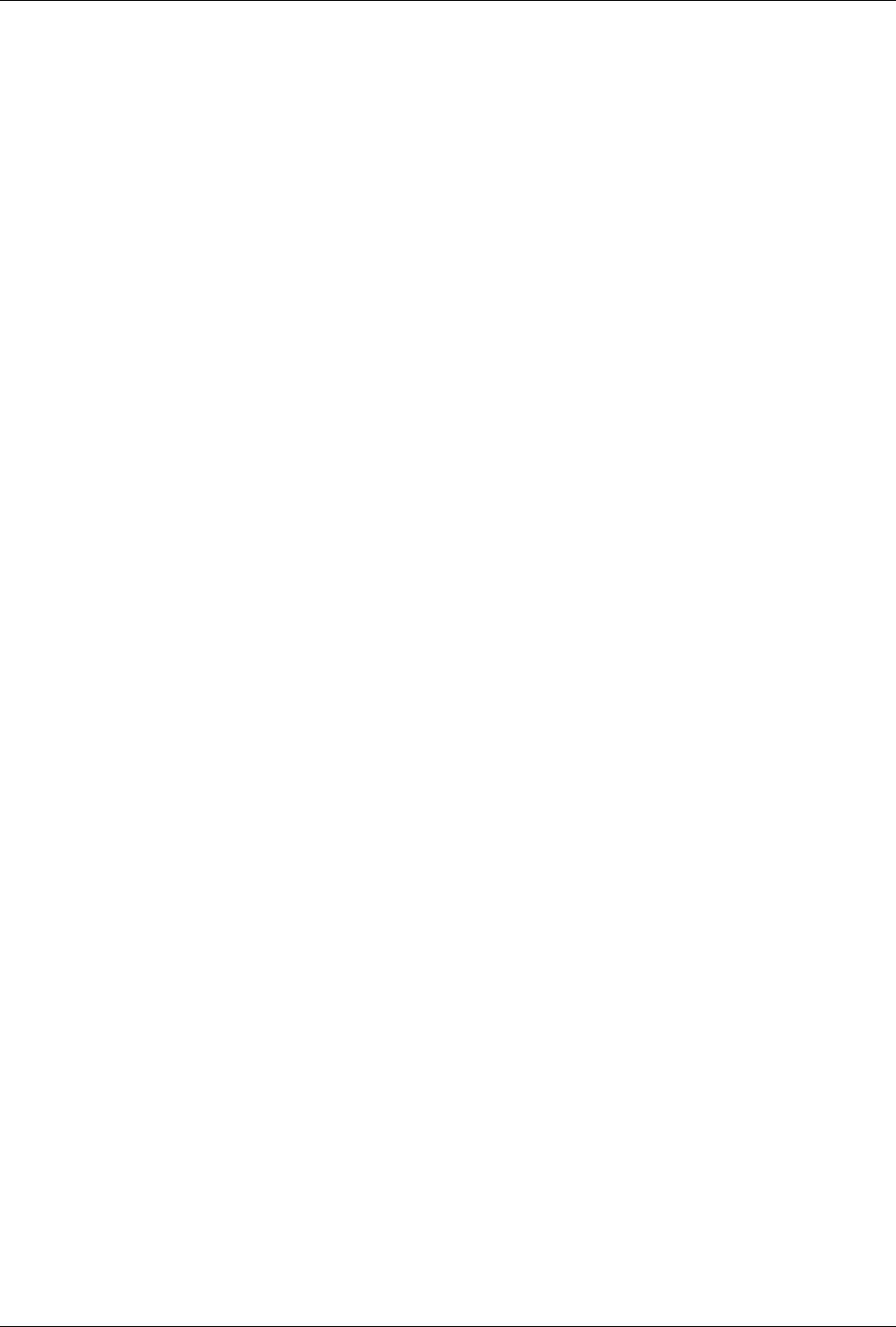
System Descri tion
•Calibrate TRX transmitter and receivers
•Antenna supervision
The ANP, RFTL, and integrated filters are combined in a single ANP/
RFTL assembly and reside in the subrack. The backplane of the subrack
contains a five–way power splitter for each receiver diversity branch. The
ANP/RFTL assembly provides a single signal for each diversity branch
with all splitting performed in the backplane. This design allows all five
TRXs to receive the same signal at the same level.
2.9 Environmental Control Unit
The Environmental Control Unit (ECU) runs a control loop that monitors
the internal cabinet temperature at several different locations. Using these
readings, the ECU maintains the cabinet at an acceptable temperature by
controlling the speed of the fans and the power to the heater. When the
ECU is unable to maintain the cabinet at an acceptable temperature, the
ECU provides alarms to the switch through the EMRPM and ALM boards
and can ultimately remove power from the subrack and shut down the base
station.
2.10 Fans
The RBS 884 Micro (1900 MHz) uses four variable speed-controlled fans
to regulate the temperature of the circuit cards and modules in the cabinet.
The fan control is driven by an open thermal control loop that references
the outside ambient air temperature. The temperature sensor for the fan
control is located in an area that is not affected by solar exposure nor by
power dissipation from the cabinet. The amount of air flow through the
cabinet is limited to that required to maintain the components within their
temperature specifications.
The fans are controlled by the ECU. The ECU is capable of varying the
speed of the fans and can turn off one or more of the fans during low
temperature extremes and during cold temperature start-up. To insure fail-
safe operation, the fans operate at full speed when the thermal sensor
signal is lost.
The fans are modular units and can be easily accessed from the top door
of the RBS 884 Micro (1900 MHz) cabinet. Fan replacement is done with
the fan breaker in the ON position. Base station personnel cycle the fan
breaker off and on to reset the fan alarm after they complete the fan
replacement procedure. Refer to the “Hardware Replacement” part of the
Installation and Hardware Replacement Manual for further information on
the fan replacement procedure.
4/1551-EN/LZB 119 3312 Uae Rev A 1998-11-17 3-17
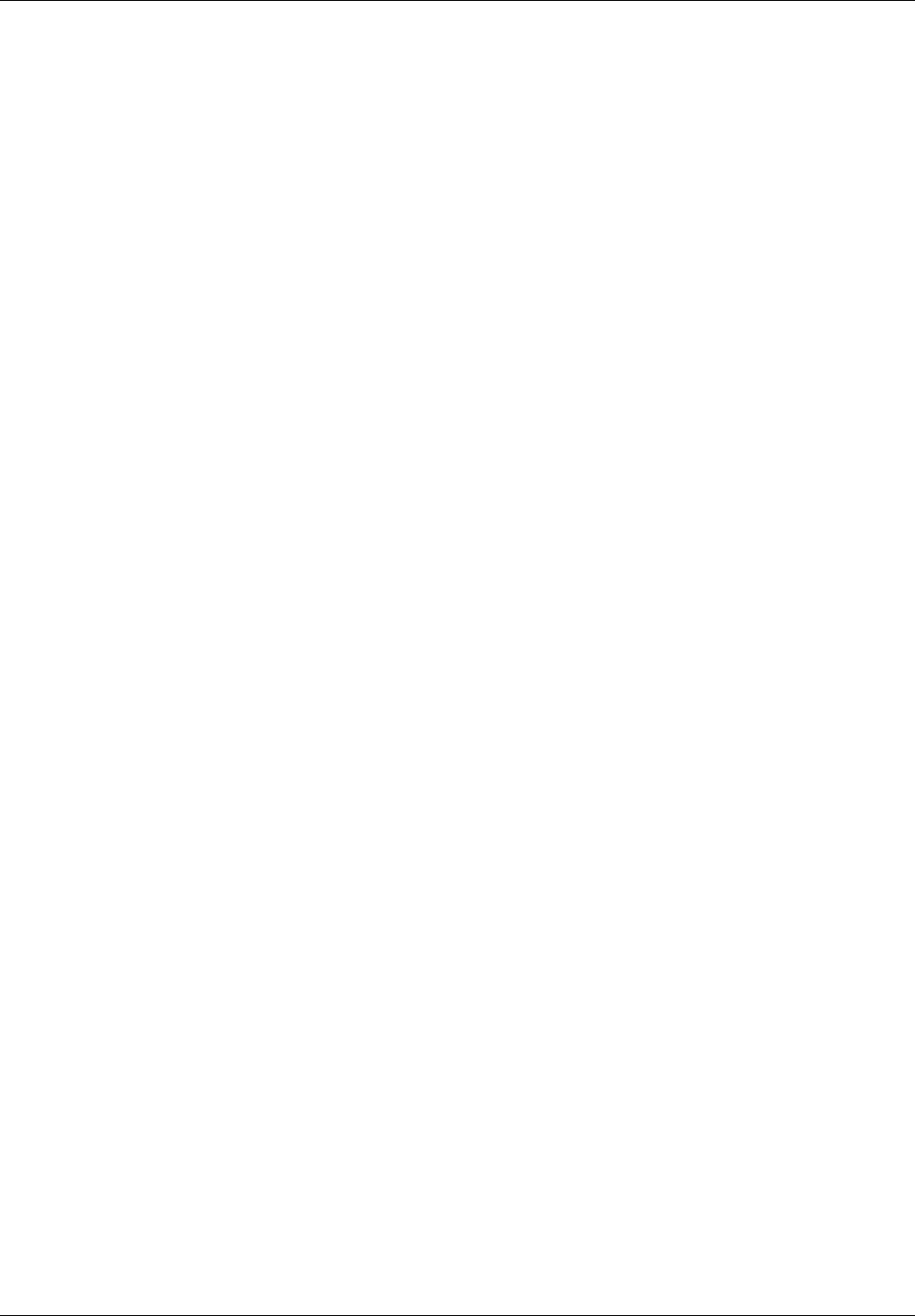
System Descri tion
2.11 Air Filter
The RBS 884 Micro (1900 MHz) cabinet is equipped with a cooling air
intake filter. The lower front panel of the cabinet is removable to gain
access for periodic filter replacement.
3 Installation Configurations
3.1 Limitations
One RBS cabinet can contain up to five TRXs, four of which can be used
for handling speech traffic.
3.2 Standard Configurations RBS 884 Micro (1900 MHz)
The RBS 884 Micro (1900 MHz) cabinets are configured and assembled at
the factory before delivery to the RBS site. It is the responsibility of the
site engineer to dimension the required configuration.
When considering which configuration to choose, dimension the TRX
units. The RBS 884 Micro (1900 MHz) can contain as few as three TRX
units per cabinet. Additional capacity can be added later.
The RBS 884 Micro (1900 MHz) product contains a number of cabinet
configurations depending on the following:
•AC power voltage: 110V 60 Hz or 230V 50 Hz
•Type of transmission: E1 or T1
•Antenna configuration: 2 or 4 antennas
– Two antenna mounting: cabinet-mounted or external
– Four antenna mounting: external
•Frequency band: AD, DBE, or EFC
•Number of TRXs: 3, 4, or 5 (including 1 Digital Verification
[DVER] unit)
The number of cabinets required at the RBS site can be one, two, or three,
depending on the number of TRX units and sectors determined for that
specific RBS site. The 1900 MHz base station cabinet can be configured to
perform as a main or as a primary cabinet by installing the appropriate
equipment units.
The configuration diagrams in this section show cabinets (main, and
primary), PCM input, AC power input, antenna configurations, and
interconnections between cabinets. The cabinets are shown with maximum
equipment installed. The PCM/TLINK/EMRPM, control, and
3-18 4/1551-EN/LZB 119 3312 Uae Rev A 1998-11-17
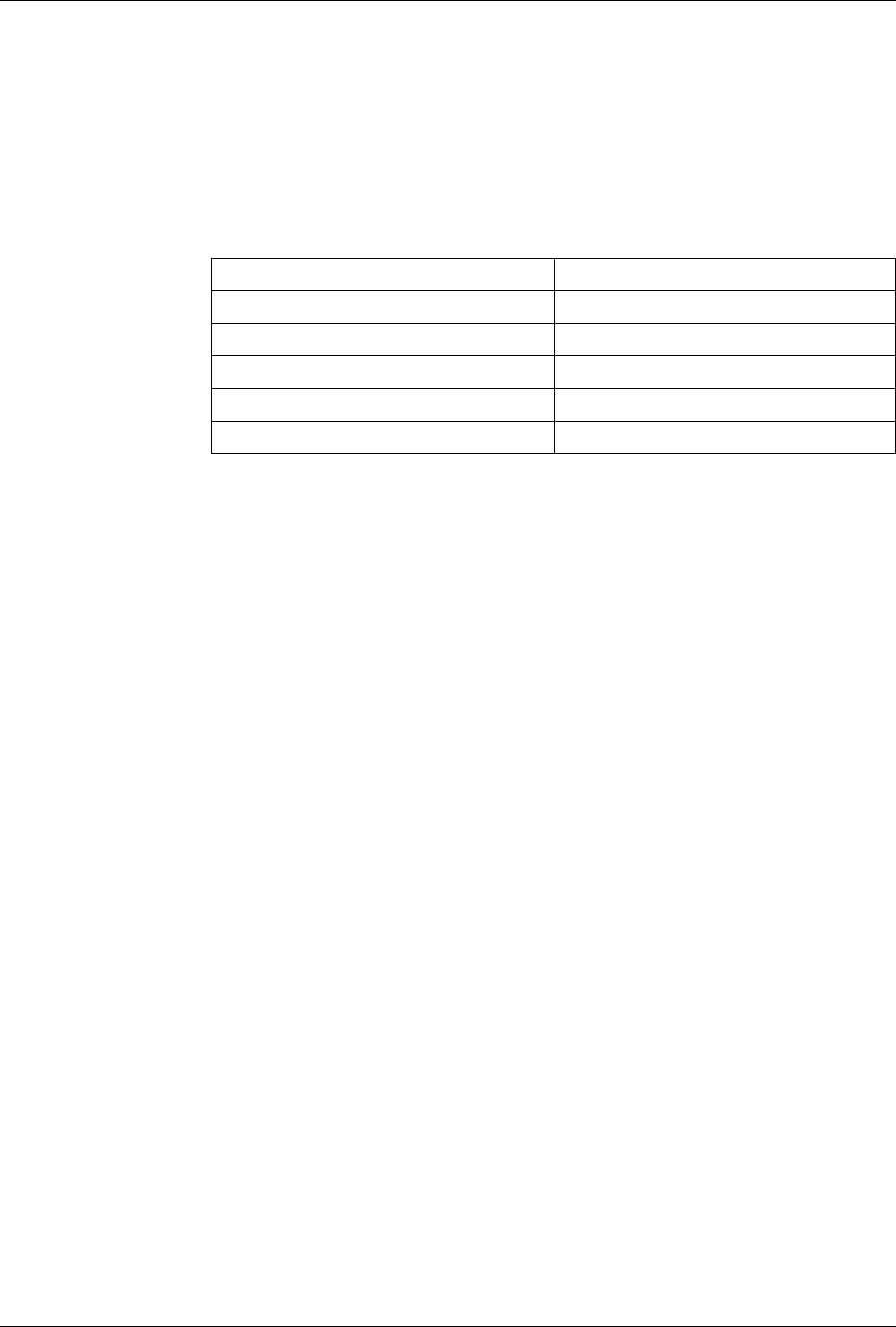
System Descri tion
synchronization interconnections between cabinets are shown as DATA in
the following six configuration diagrams.
Each cabinet requires a separate electrical AC power input supply.
Table 3-6 on page 3-19 provides a list of the antenna and PCM cable
connection points that appear on the underside of the Mounting Base
Connector Plate.
Table 3-6. Mounting Base Connector Plate – External Cables
External Cable Connector Connector Plate Connection
RX/TX ANT A ANT 1
RX/TX ANT B ANT 2
TX ANT C ANT 3
TX ANT D ANT 4
PCM PCM P
The PCM transmission connection from the RBS to the MSC connects
through the PCM lightning protection box that is located below the
subrack in the main cabinet.
Refer to the RF Guidelines for information on reverse isolation and the
output power levels for each configuration.
3.2.1 One-Sector Site
The following cabinet configurations are available for the RBS 884 Micro
(1900 MHz) one-sector site.
3.2.1.1 Single Cabinet - 2 Duplex Filters, 2 TX/RX Antennas
Figure 3-7 on page 3-20 and Figure 3-8 on page 3-20 show one-sector site
configurations. Both of these configurations have a two-antenna ANP with
hybrid combiners and duplex filters connected to an antenna array of two
TX/RX antennas.
The ANP for both the cabinet-mounted antenna and the external antenna is
offered in the following frequency bands:
•AD
•DBE
•EFC
4/1551-EN/LZB 119 3312 Uae Rev A 1998-11-17 3-19
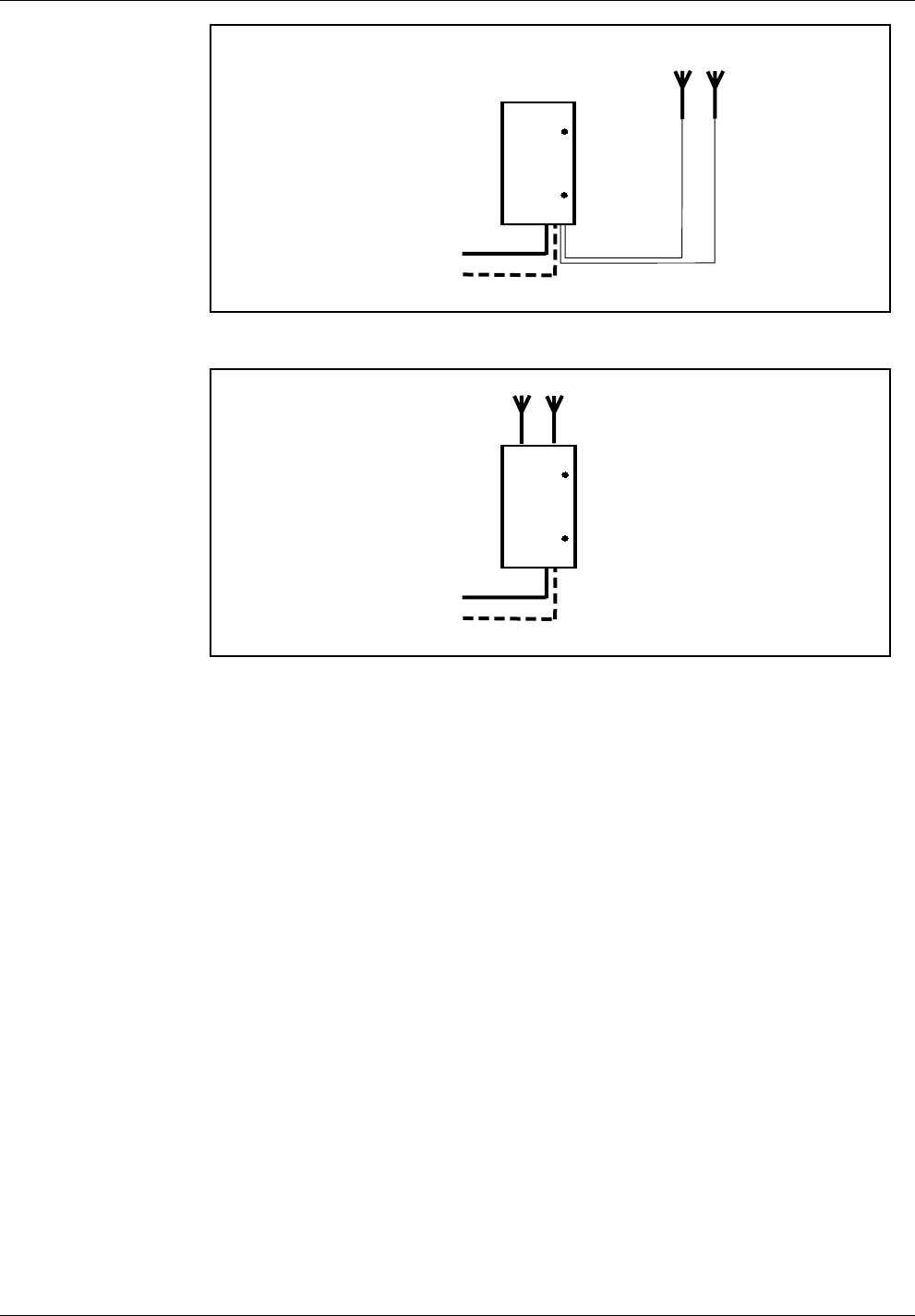
System Descri tion
MAIN
CABINET
AC POWER (110V/230V)
PCM (T1/E1)
●●
TX/RX TX/RX
Two-Antenna
ANP
Figure 3-7. One-Sector Site – One Cabinet with Two External TX/RX Antennas
MAIN
CABINET
AC POWER (110V/230V)
PCM (T1/E1)
●●
TX/RX TX/RX
Two-Antenna
ANP
Figure 3-8. One-Sector Site – One Cabinet with Two Cabinet–Mounted Antennas
The Cabinet-Mounted Antenna Kit can be used to mount two fixed
antennas directly on the cabinet for a totally self-contained base station.
Note: Single sector site expansion is possible with the use of shared
antennas and cell overlays, although RF performance may be
compromised.
3.2.1.2 Single Cabinet — 4 Antennas (2 TX/RX Antennas and 2 TX-Only Antennas)
Figure 3-9 on page 3-21 shows a one-sector site configuration with a four-
antenna ANP connected to an antenna array of two TX-only antennas and
two TX/RX antennas with duplex filters.
The four-antenna ANP is offered in the following frequency bands:
•AD
•DBE
•EFC
3-20 4/1551-EN/LZB 119 3312 Uae Rev A 1998-11-17
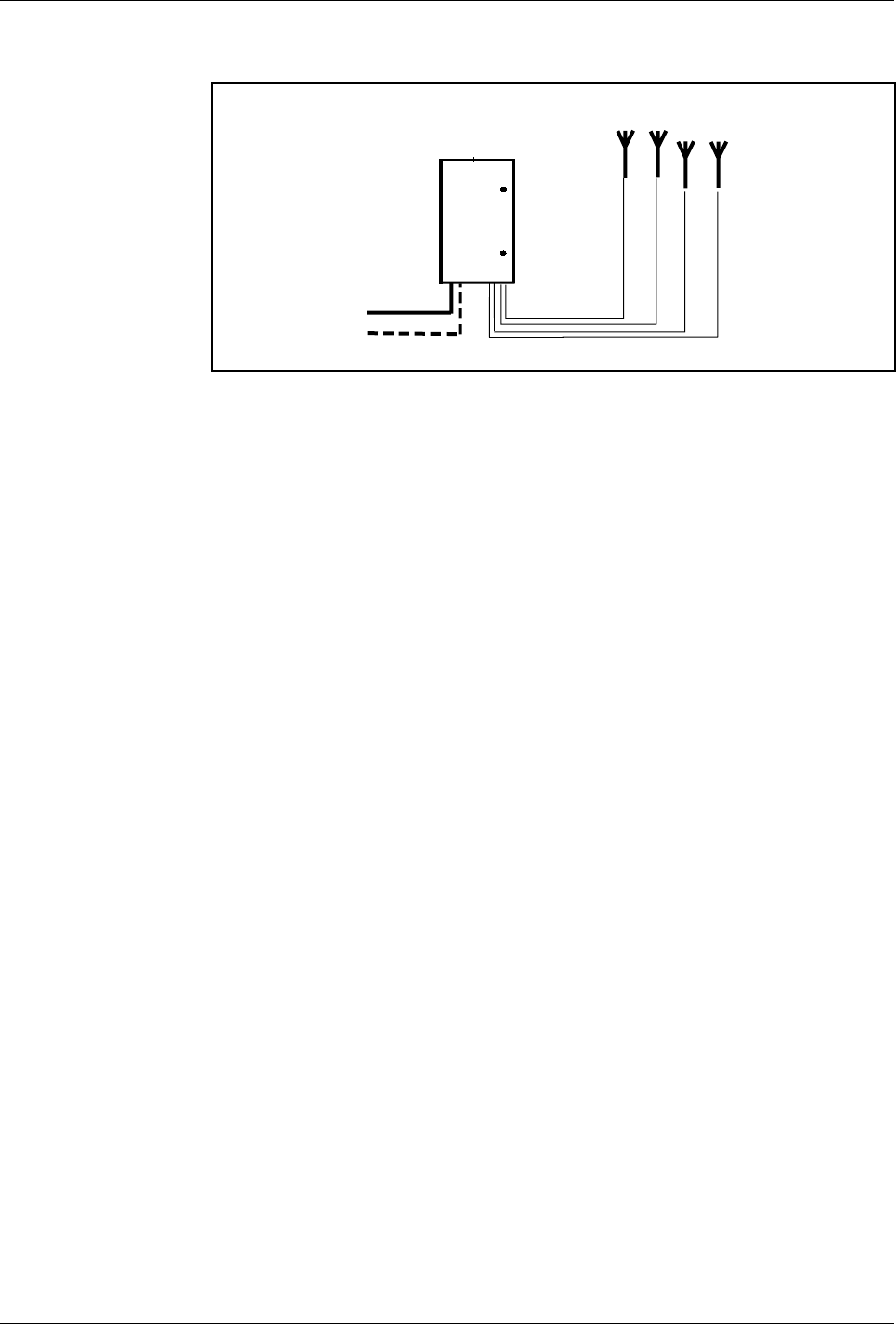
System Descri tion
MAIN
CABINET
AC POWER 110V/230V
PCM (T1/E1)
●●
TX TX/RX
●●
TX/RX TX
Four-Antenna
ANP
Figure 3-9. One-Sector Site – One Cabinet with Four External Antennas
Note: Single sector site expansion is possible with the use of shared
antennas and cell overlays, although RF performance may be
compromised.
3.2.2 Two-Sector Site
The following cabinet configurations are available for the RBS 884 Micro
(1900 MHz) two-sector site.
3.2.2.1 Dual Cabinets — 2 TX/RX Antennas
Figure 3-10 on page 3-22 and Figure 3-11 on page 3-22 show two-sector
site configurations with a main and a primary cabinet. Each cabinet has a
two-antenna ANP with hybrid combiner filters and duplex filters connected
to an antenna array of two TX/RX antennas.
The two-antenna ANP for both the cabinet-mounted antenna and the
external antenna is offered in the following frequency bands:
•AD
•DBE
•EFC
4/1551-EN/LZB 119 3312 Uae Rev A 1998-11-17 3-21
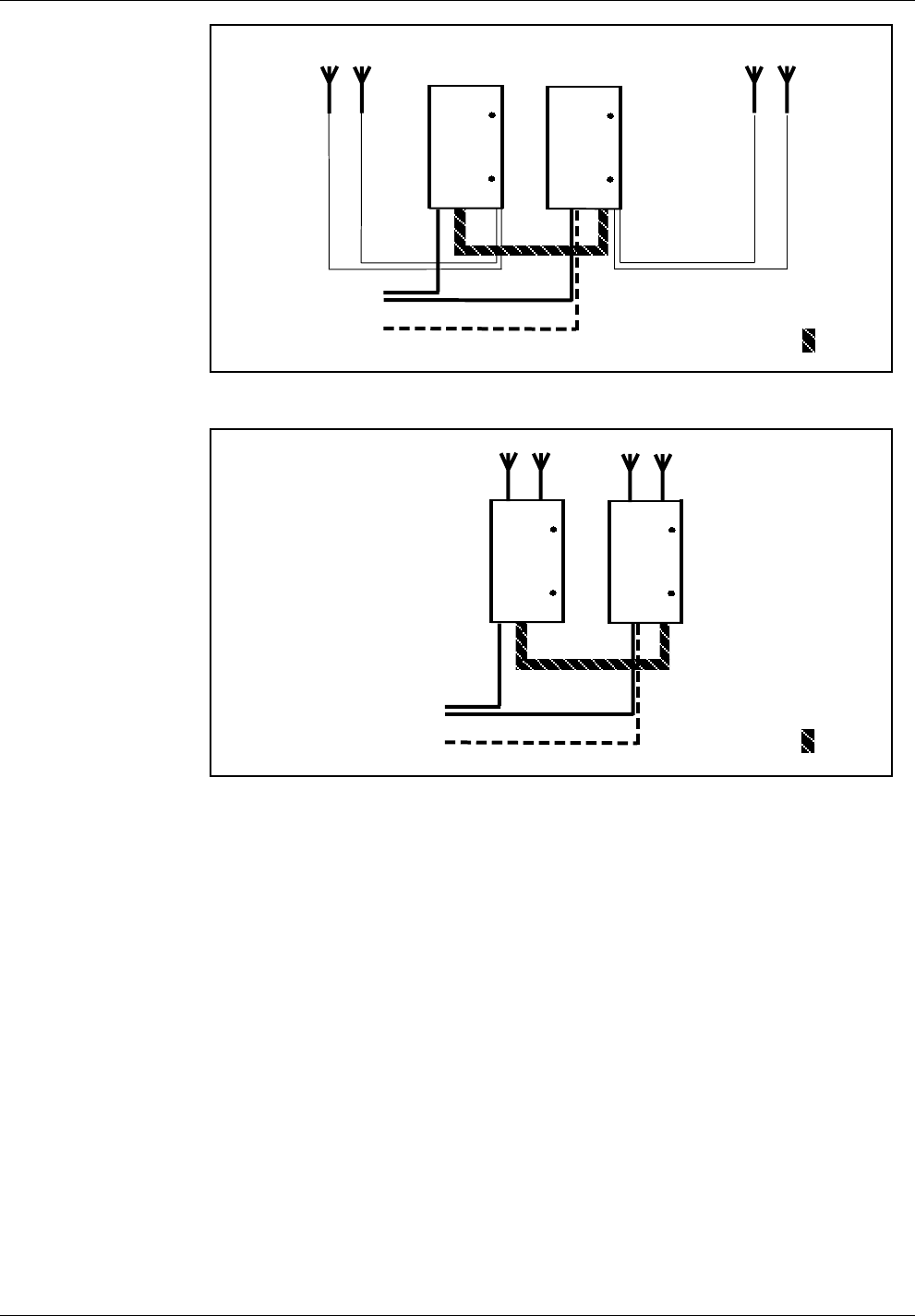
System Descri tion
PRIMARY
CABINET MAIN
CABINET
AC
POWER (110V/230V)
PCM (T1/E1)
●●
TX/RX TX/RX
DATA
●●
TX/RX
TX/RX
Two-Antenna
ANP
Two-Antenna
ANP
Figure 3-10. Two-Sector Site – Each Cabinet with Two External TX/RX Antennas
PRIMARY
CABINET MAIN
CABINET
AC
POWER (110V/230V)
PCM (T1/E1) DATA
●●
●●
TX/RX TX/RX TX/RX TX/RX
Two-Antenna
ANP
Two-Antenna
ANP
Figure 3-11. Two-Sector Site – Each Cabinet with Two Cabinet-Mounted Antennas
The Cabinet-Mounted Antenna Kit can be used to mount two fixed
antennas on each cabinet for a totally self-contained base station site.
3.2.2.2 Dual Cabinets — 4 Antennas (2 TX/RX Antennas and 2 TX-Only Antennas)
Figure 3-12 on page 3-23 shows a two-sector site configuration with a
main and a primary cabinet. Each cabinet has a four-antenna ANP
connected to an antenna array of two TX-only antennas and two TX/RX
antennas with duplex filters.
The four-antenna ANP is offered in the following frequency bands:
•AD
•DBE
•EFC
3-22 4/1551-EN/LZB 119 3312 Uae Rev A 1998-11-17
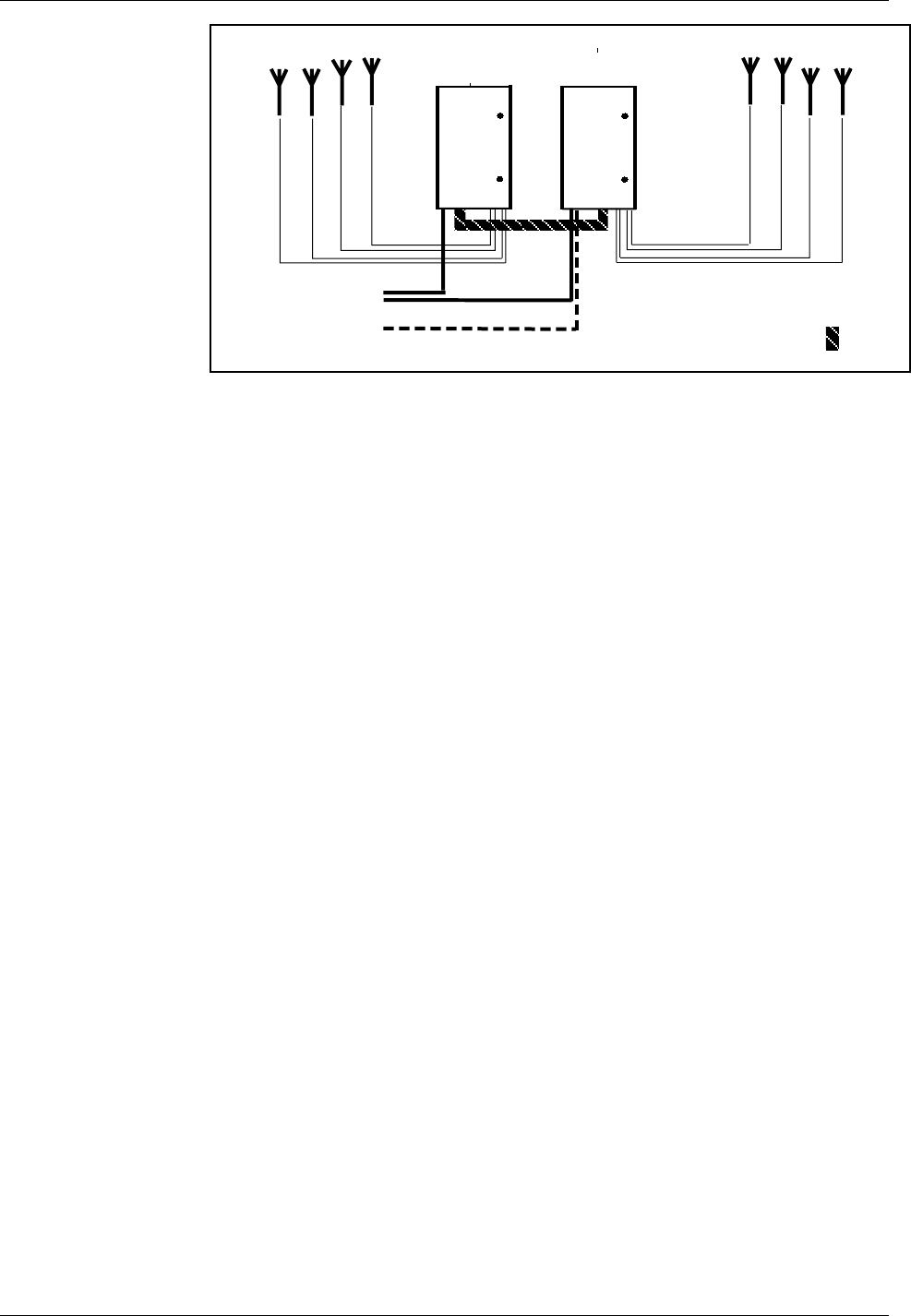
System Descri tion
PRIMARY
CABINET MAIN
CABINET
AC POWER (110V/230V)
PCM (T1/E1)
DATA
●●
TX TX/RX
●●
TX/RX TX
●
TX
TX/RX
●●
TX/RX
TX
●
Four-Antenna
ANP
Four-Antenna
ANP
Figure 3-12. Two-Sector Site – Each Cabinet with Four External Antennas
3.2.3 Three-Sector Site
The following cabinet configurations are available for the RBS 884 Micro
(1900 MHz) in a three-sector site.
3.2.3.1 Triple Cabinets — 2 TX/RX Antennas
Figure 3-13 on page 3-24 and Figure 3-14 on page 3-24 show three-sector
site configurations with a main and two primary cabinets. Each cabinet has
a two-antenna ANP with hybrid combiner filters and duplex filters
connected to an antenna array of two TX/RX antennas. The primary
cabinets are used to provide additional sectors.
The two-antenna ANP for both the cabinet-mounted antenna and the
external antenna is offered in the following frequency bands:
•AD
•DBE
•EFC
4/1551-EN/LZB 119 3312 Uae Rev A 1998-11-17 3-23
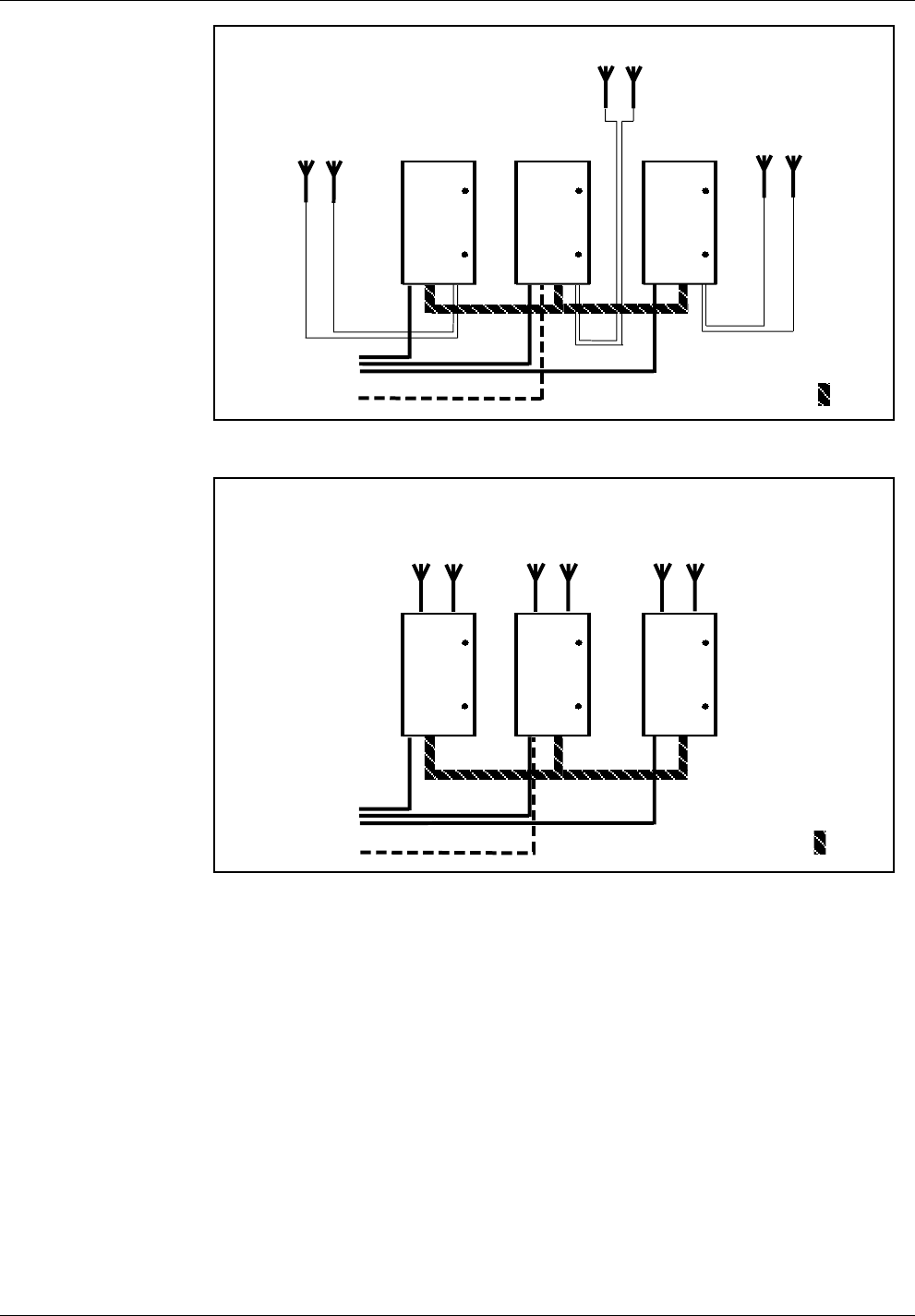
System Descri tion
DATA
PRIMARY 1
CABINET MAIN
CABINET PRIMARY 2
CABINET
AC POWER (110V/230V)
PCM (T1/E1)
●●
●●
TX/RX TX/RX
●●
TX/RX TX/RX TX/RX TX/RX
Two-Antenna
ANP
Two-Antenna
ANP
Two-Antenna
ANP
Figure 3-13. Three-Sector Site – Each Cabinets with Two External TX/RX Antennas
DATA
PRIMARY 1
CABINET MAIN
CABINET PRIMARY 2
CABINET
AC POWER (110V/230V)
PCM (T1/E1)
●●
●●
●●
TX/RX TX/RX TX/RX TX/RX TX/RX TX/RX
Two-Antenna
ANP
Two-Antenna
ANP
Two-Antenna
ANP
Figure 3-14. Three-Sector Site – Each Cabinet with Two Cabinet-Mounted Antennas
The Cabinet-Mounted Antenna Kit can be used to mount two fixed
antennas to each cabinet for a totally self-contained base station site.
3.2.3.2 Triple Cabinets — 4 Antennas (2 TX/RX Antennas, 2 TX-Only Antennas)
Figure 3-15 on page 3-25 shows a three-sector site configuration with one
main and two primary cabinets. Each cabinet has a four-antenna ANP
connected to an antenna array of two TX-only antennas and two TX/RX
antennas with duplex filters.
3-24 4/1551-EN/LZB 119 3312 Uae Rev A 1998-11-17
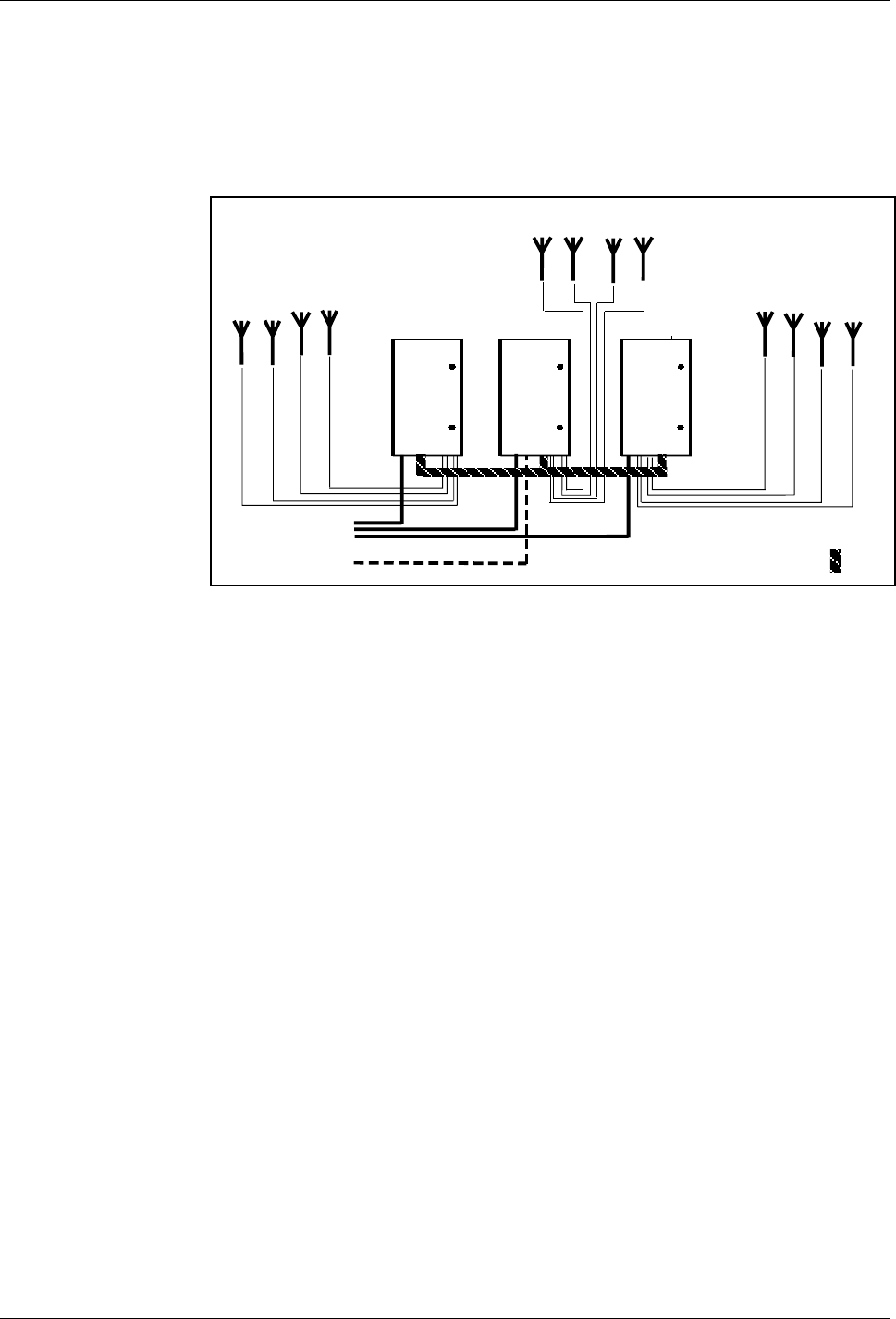
System Descri tion
The four-antenna ANP is offered in the following frequency bands:
•AD
•DBE
•EFC
PRIMARY 1
CABINET MAIN
CABINET PRIMARY 2
CABINET
AC POWER (110V/230V)
PCM (T1/E1)
DATA
●
TX
TX/RX
●●
TX/RX
TX
●
●
TX TX/RX
●●
TX/RX TX
●
TX TX/RX
●●
TX
TX/RX
● ●
Four-Antenna
ANP
Four-Antenna
ANP
Four-Antenna
AN
P
Figure 3-15. Three-Sector Site – Each Cabinet with Four External Antennas
3.2.3.3 Cascade Configurations — RBS 884 Micro (1900 MHz)
RBS 884 Micro (1900 MHz) systems can be connected in a cascading
arrangement (see Figure 3-16 on page 3-26) with a single T1/E1 line in
order to reduce transmission costs. Cascading is used to expand a site and
to create different Radio Cabinet Groups (RCGs) at the same site.
Drop and insert considerations become important when planning the
cascading of an RBS site.
Each Micro (1900 MHz) base station becomes a separate Extension
Module Group (EMG) and has its own control channel (DS0 - 64 kbit/s
channel) on the PCM (T1/E1) transmission cable interconnections.
Additional Control Signaling Link (CLC) extraction timeslots are required
for each additional REMUX introduced to support cascading. This
allocation is determined by the operator or network provider. Each
REMUX will require all switch settings to be checked and reset as
necessary (see the Processes and Procedures part of the RBS 884 Site
Engineering Manual.
To maintain transmission quality, it is recommended that no more than
four RBS 884 Micro (1900 MHz) base stations be cascaded.
4/1551-EN/LZB 119 3312 Uae Rev A 1998-11-17 3-25

System Descri tion
MSC
PCM (T1/E1)
PCM (T1/E1)
PCM (T1/E1)
Base Station 1 Base Station 2 Base Station 3
Figure 3-16. Cascade Configuration
3-26 4/1551-EN/LZB 119 3312 Uae Rev A 1998-11-17
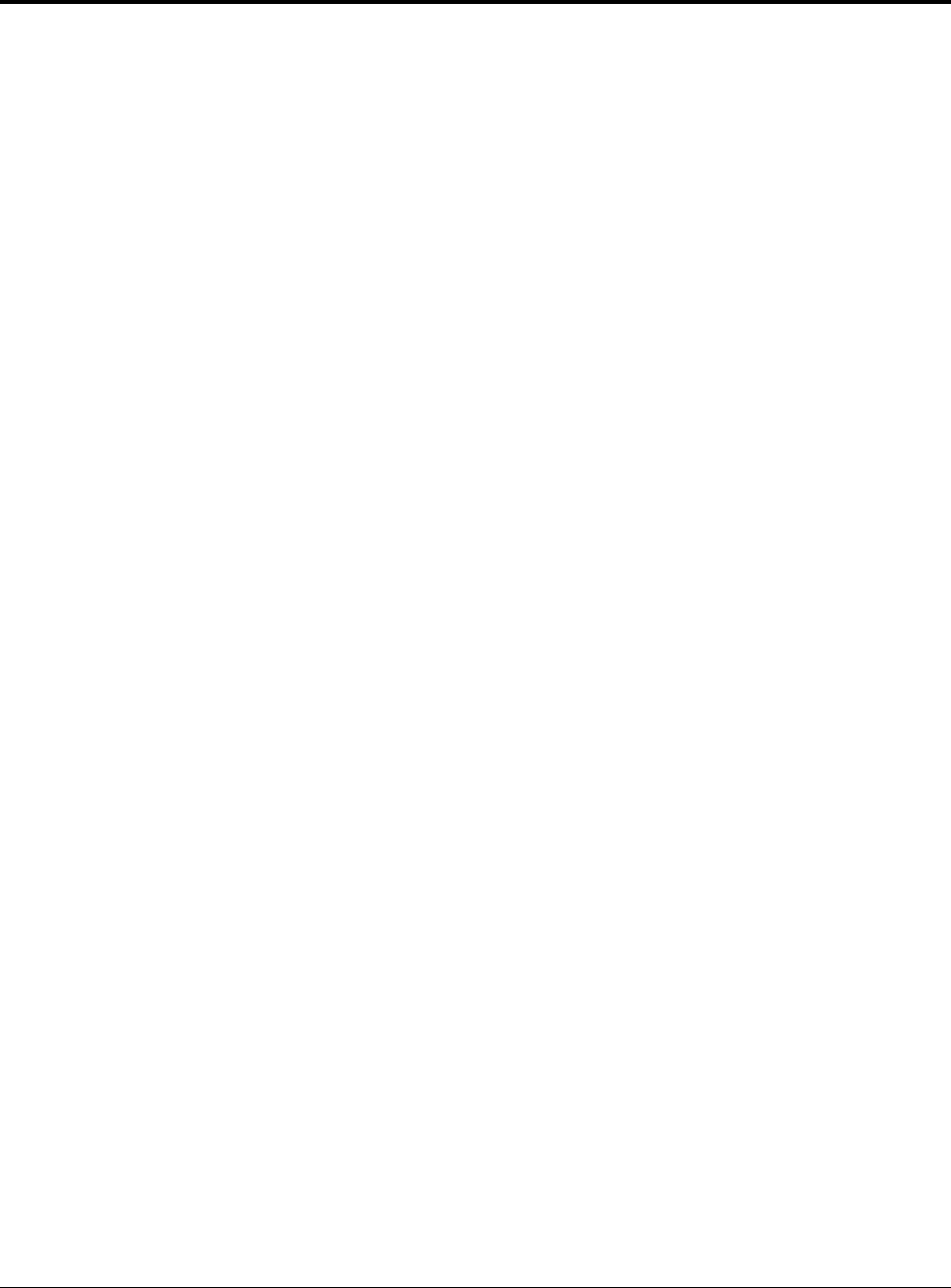
Part 4
Installation
1 Introduction .................. 4-3
2 Safety Considerations ............. 4-3
2.1 Cabinet Grounding ............ 4-3
2.2 Voltage Hazards ............. 4-3
2.3 Radio Frequency Radiation ........ 4-4
2.4 Beryllium Oxide ............. 4-4
2.5 Heavy Loads ............... 4-5
3 Electrostatic Discharge (ESD) .......... 4-5
3.1 Storage and Transport .......... 4-5
3.2 ESD Wrist Strap ............. 4-5
4 Tools ...................... 4-6
5 Site Selection .................. 4-7
5.1 Right-of-Way ............... 4-7
5.2 Public Safety ............... 4-7
5.3 Vulnerability ............... 4-8
5.4 Accessibility ............... 4-8
6 Transportation and Storage ........... 4-8
7 Unpacking ................... 4-9
7.1 Required Tools .............. 4-9
7.2 Unpacking Procedure ........... 4-10
8 Cabinet Installation ............... 4-12
8.1 Required Materials and Tools ....... 4-12
8.2 Installation on a Pad ........... 4-12
8.3 Installation on a Pole ........... 4-15
8.4 Installation on a Wall ........... 4-21
8.5 Installation on a Roof ........... 4-24
9 Cable and Power Connections ......... 4-24
9.1 Grounding ................ 4-24
9.2 Installing Batteries ............ 4-25
9.3 Installing AC Power ............ 4-29
9.4 Cable Installation ............. 4-31
10 Setting the Unit Switches ............ 4-39
10.1 Prerequisites and Tools .......... 4-40
10.2 REMUX Switch Settings ......... 4-41
10.3 EMRPM Switch Settings ......... 4-49
11 External Alarm Connections .......... 4-50
12 Site Inventory .................. 4-51
1/1551-EN/LZB 119 3312 Uae Rev A 1998-11-17 4-1

Installation
12.1 Prerequisites ............... 4-51
12.2 Site Inventory Procedure ......... 4-52
13 Equipment Power Up .............. 4-53
13.1 Prerequisites and Test Equipment ..... 4-53
13.2 Power-Up Procedure ........... 4-54
14 Cold Start-up .................. 4-56
15 Completing the Installation ........... 4-56
15.1 Prerequisites and Tools .......... 4-57
15.2 Installation Completion Procedure ..... 4-57
16 LED Indications ................. 4-57
16.1 PSU LEDs ................ 4-58
16.2 TRX LEDs ................ 4-58
16.3 REMUX LEDs .............. 4-59
16.4 ANP (RFTL) LEDs ............ 4-59
16.5 STRM LEDs ............... 4-60
16.6 ALM LEDs ................ 4-60
16.7 EMRPM LEDs .............. 4-60
16.8 ECU LEDs ................ 4-61
17 Site Expansion ................. 4-62
17.1 Adding TRX Boards ........... 4-62
17.2 Adding Cabinets ............. 4-67
17.3 One-Sector Sites ............. 4-71
17.4 Two-Sector Sites ............. 4-73
17.5 Three Sector Sites ............ 4-76
18 RBS 884 Micro (1900 MHz) Cabinet Repainting . 4-81
18.1 Required Materials and Tools ....... 4-81
18.2 Cabinet Surface Preparation ....... 4-81
18.3 Cabinet Painting ............. 4-82
4-2 1/1551-EN/LZB 119 3312 Uae Rev A 1998-11-17
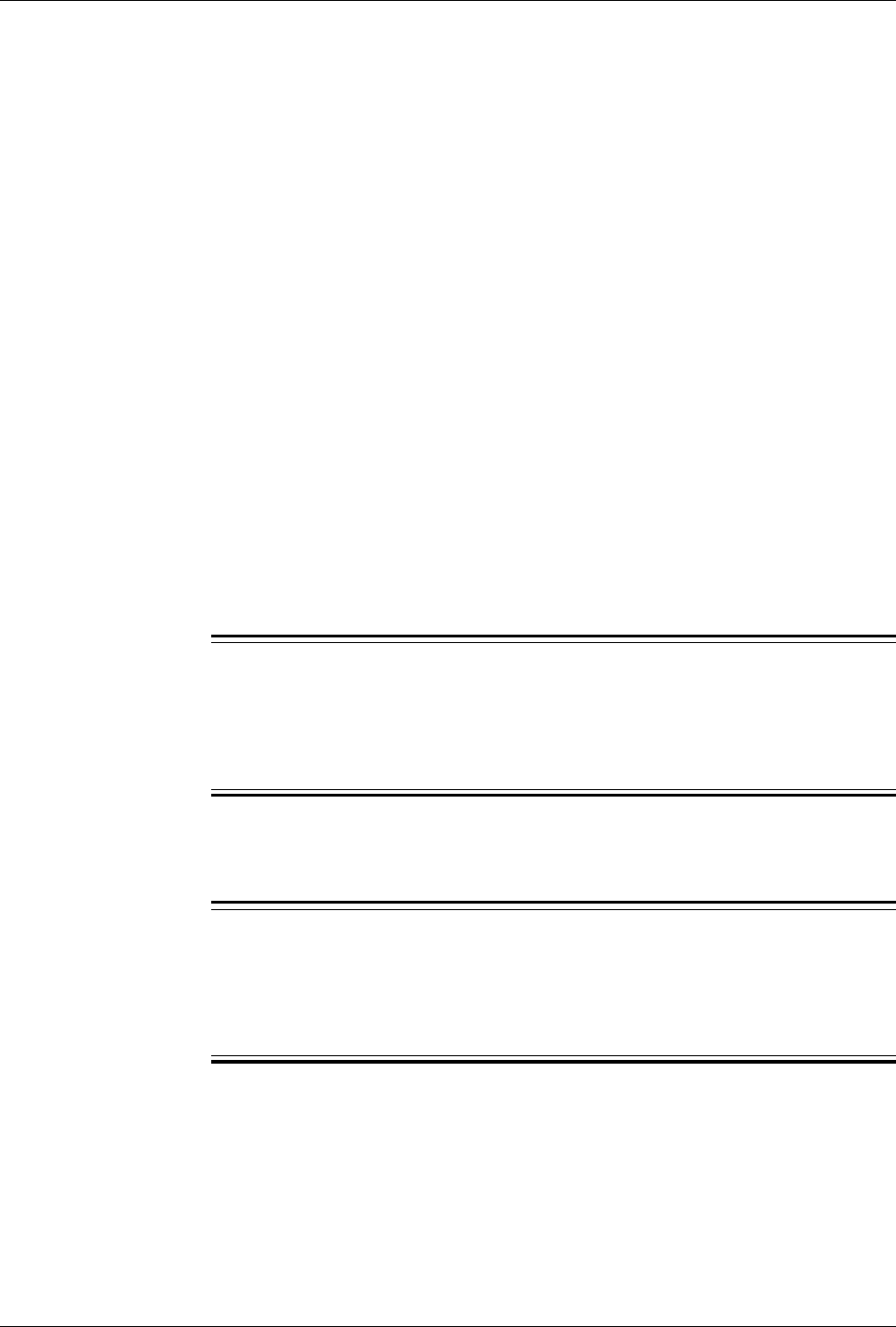
Installation
1 Introduction
This part of the manual contains procedures for unpacking and installing
the RBS 884 Micro (1900 MHz) equipment. Additional procedures are
provided for switch configuration, cable installation, power up, and site
expansion.
The RBS 884 Micro (1900 MHz) cabinet can be installed on a wall, a
pole, or pedestal. The cabinet can also be repainted (refer to Section 18.3
on page 4-82).
2 Safety Considerations
2.1 Cabinet Grounding
This product is Safety Class 1 equipment.
The RBS 884 Micro (1900 MHz) cabinet wiring is based on a single-point
ground system. The cabinet has an external earth-ground stud connection
on the bottom surface of the cabinet shell.
DANGER!
Any interruption of the protective (grounding) conductor or disconnection
of the protective ground terminal will cause a potential shock hazard that
could result in personal injury.
2.2 Voltage Hazards
DANGER!
Voltage in excess of 100V is used in the RBS 884 Micro (1900 MHz).
Observe safety precautions. Contact with voltage as low as 50V can result
in death.
Observe the following safety precautions:
•Do not touch high voltage connections when working on energized
equipment.
•Do not energize equipment before the Power Up procedure in this
manual is performed.
1/1551-EN/LZB 119 3312 Uae Rev A 1998-11-17 4-3
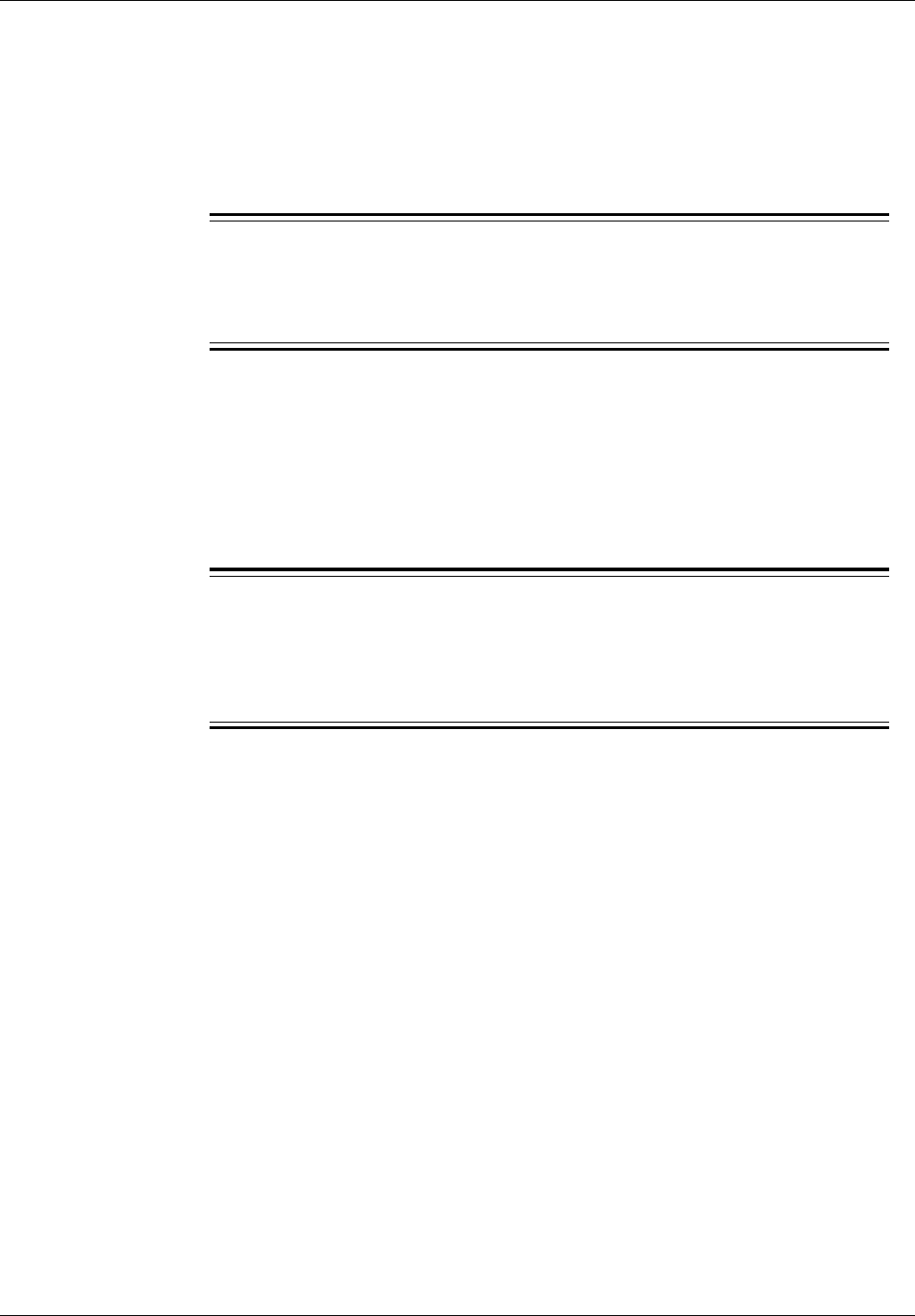
Installation
•Never connect the power cable to the power unit when the unit is
removed from the cabinet.
•Perform all installation and repair procedures in the order presented.
2.3 Radio Frequency Radiation
DANGER!
Radio frequency radiation from an antenna may be a danger to health,
causing severe burns to skin and clothing.
Turn off the transmitters at the MSC prior to working with or near
antennas.
2.4 Beryllium Oxide
Some equipment contains beryllium oxide in ceramic form.
Warning!
Beryllium oxide is poisonous and constitutes a health hazard if present in
finely dispersed form, such as dust or smoke, which can be inhaled. Read
local hazardous chemical regulations before working with beryllium oxide.
Units with components containing beryllium oxide are marked with a
warning label. For detailed information on properties, health and
environmental hazards, refer to the regulations issued by the local
authorities.
The following rules must be obeyed by all persons handling beryllium
oxide:
•Ceramics containing beryllium oxide must not be scraped, filed,
ground, treated with acid, or machined in any other way.
•Compressed air must not be used to clean units containing beryllium
oxide.
•You must always wear protective gloves when handling beryllium
oxide.
•Use wet rags to collect dust and particles from damaged beryllium
oxide components. After use, place the rags in plastic bags and seal
the bags completely.
Scrapped beryllium oxide must be treated as environmentally hazardous
waste. Local authorities enforce regulations, regarding the treatment and
4-4 1/1551-EN/LZB 119 3312 Uae Rev A 1998-11-17
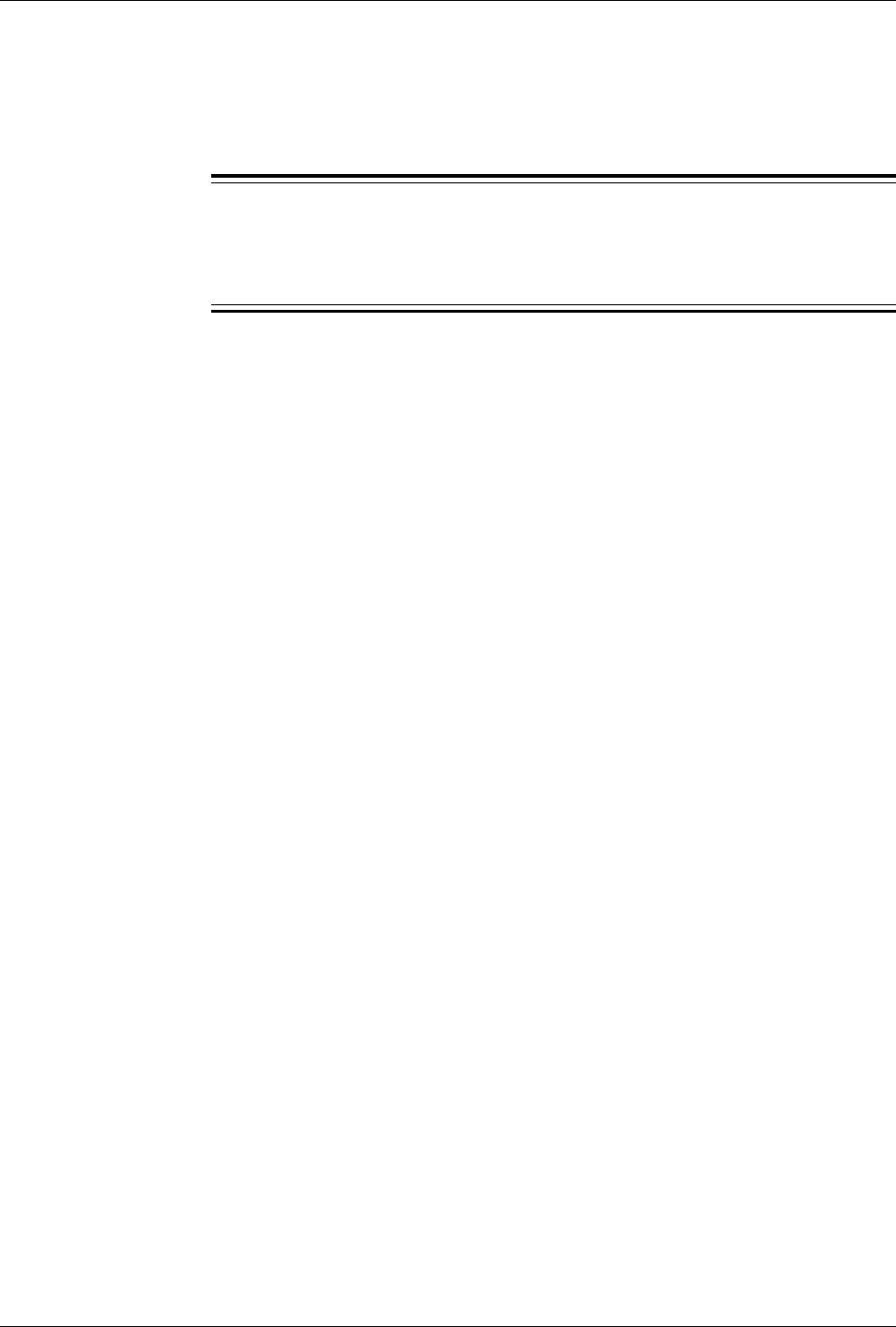
Installation
disposal of environmentally hazardous waste. Investigate the local
regulations that are applicable to you and comply with them.
2.5 Heavy Loads
Warning!
Incorrectly lifting heavy loads can result in severe injury to persons and
damage to the equipment.
A fully equipped RBS 884 Micro (1900 MHz) cabinet weighs 105 kg (230
lbs). Ericsson recommends two persons be present during the maintenance
activities where heavy lifting is required.
3 Electrostatic Discharge (ESD)
The human body acquires static charge in all situations involving
movement. The body rubs against clothes and against a chair when sitting
down, and shoes rub against the floor. The same effect is achieved when
handling ordinary plastic materials.
If the body comes into contact with a grounded integrated circuit (IC)
component, this static charge may cause an electrostatic discharge (ESD)
to take place resulting in damage to the component.
To avoid component damage from ESD, always follow the instructions for
handling sensitive electronic components and circuit boards. Always use
ESD protection equipment when working with such components and
boards.
3.1 Storage and Transport
Store and transport components and circuit boards in their original
packaging.
Alternatively, use a conductive material or special IC carrier that either
short-circuits all contacts and pins, or insulates them from external contact.
3.2 ESD Wrist Strap
When working with circuit boards and cables, an ESD Wrist Strap must be
used to avoid ESD damage. When the strap cable is supplied with an
alligator connector, it can be connected to an unpainted metal part of the
cabinet chassis as shown in Figure 4-1 on page 4-6.
1/1551-EN/LZB 119 3312 Uae Rev A 1998-11-17 4-5
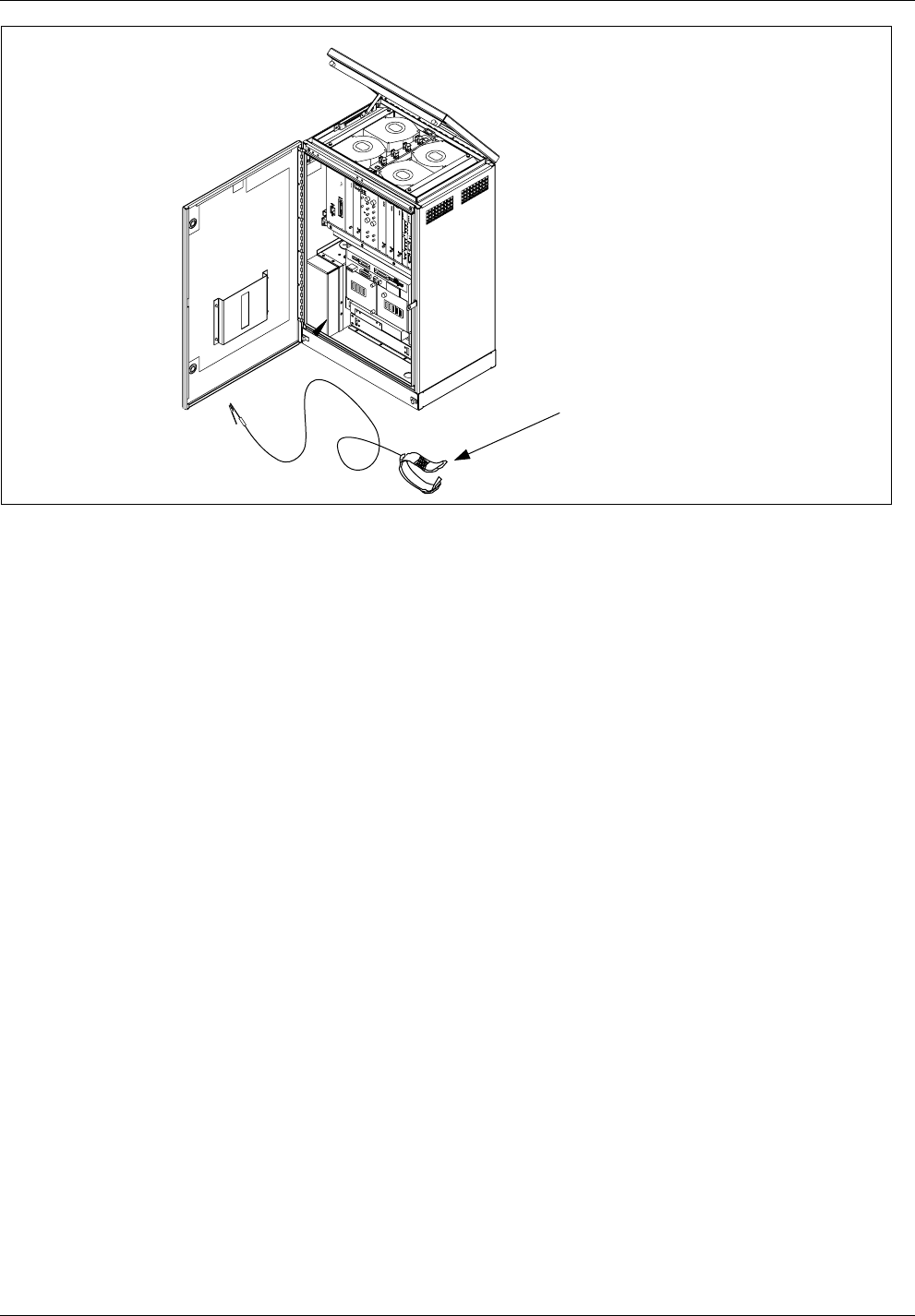
Installation
ESD Wrist Strap
Note: Attach alligator clip to suitable
ground (unpainted surface) in cabinet.
Figure 4-1. ESD Wrist Strap connected to the RBS 884 Micro (1900 MHz) Cabinet
4 Tools
All the tools needed to unpack and install the cabinets, to connect the
grounding cables and braids, to set the switches, to install the cables, and
to perform power up, are shown in Table 4-1 on page 4-7.
4-6 1/1551-EN/LZB 119 3312 Uae Rev A 1998-11-17
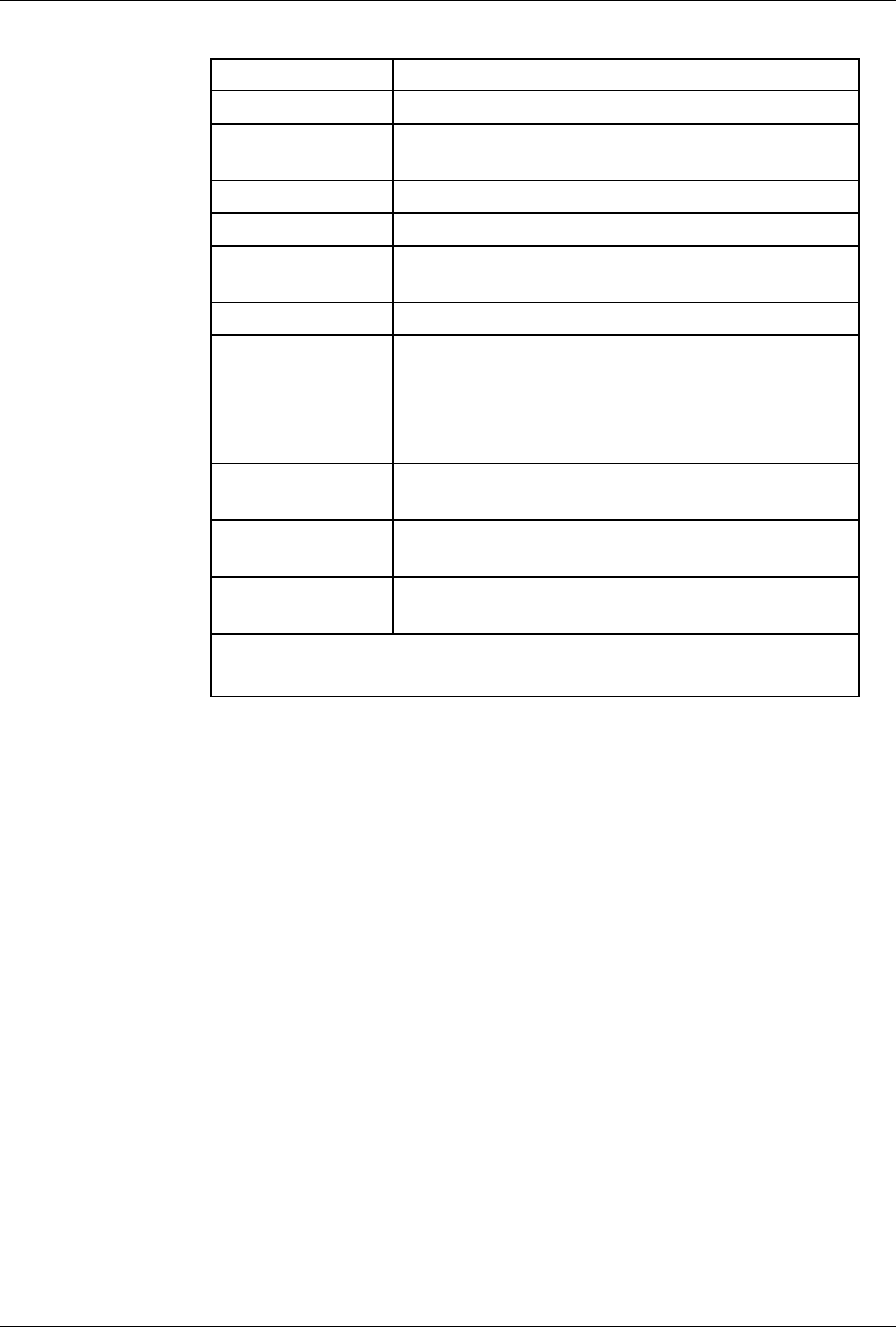
Installation
Table 4-1. Tools List
Product Number Description
N/A Metric Tape Measure1
N/A Horizontal/Vertical Level1
(for wall mounting)
N/A Pen
N/A Drill1
N/A Drill Bit1(appropriate size for use in wall mounting
procedure)
LYB 250 01/14 ESD Wrist Strap and Cable2
LTT 601 82 Torque Wrench set, including:
- Torque Wrench set to torque 0.6 Nm
(to use with the SMA tool or the Torx bit TX10
- Torx bit TX10 (for cabinet unit screws)
- SMA tool (for the coaxial cables)
LTD 117 02 and
LTD 117 14
Unit Extractor Tool (Handle + Button)
N/A AC Voltmeter1
(for checking the line voltage)
N/A Tools for connecting the AC Power Cable to a Line
Power Access Point (if this is the local procedure)
1Included in Tool Kit LTT 601 044/1
2Included in Tool Case LTT 601 84
5 Site Selection
5.1 Right-of-Way
The installing company should acquire the right-of-way from landowners
and obtain permits or other approvals from public authorities before
starting construction.
The RBS 884 Micro (1900 MHz) cabinet should be placed in servitudes,
on dedicated (recorded) easements, or on property owned by the company.
Avoid unrecorded easements.
Rooftop locations require additional considerations and approvals.
5.2 Public Safety
Public safety and street right-of-way should be used only when there is
adequate space to place the cabinet and provide safe working conditions.
1/1551-EN/LZB 119 3312 Uae Rev A 1998-11-17 4-7
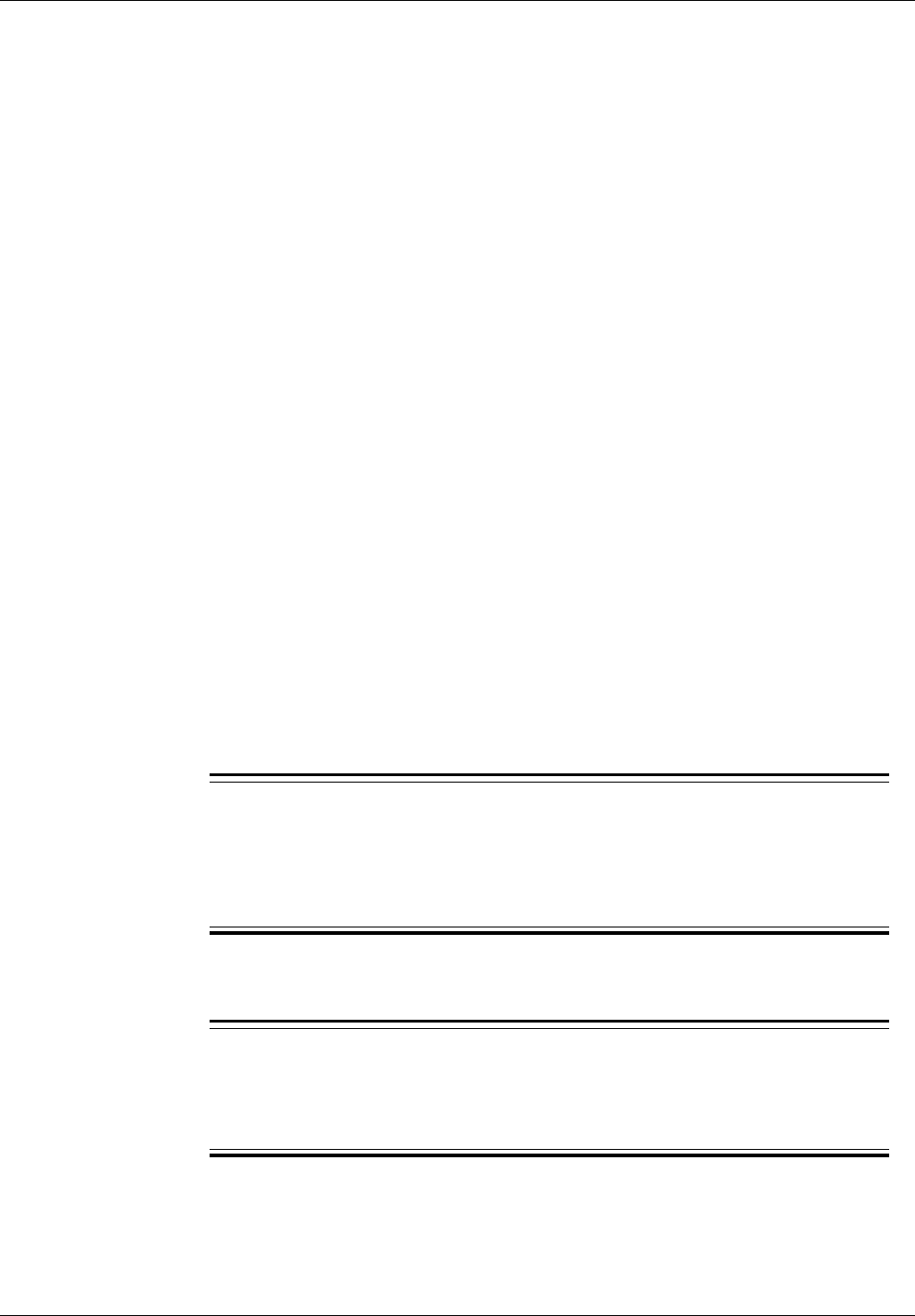
Installation
The cabinet should be placed so that it will not obstruct automobile or
pedestrian traffic.
5.3 Vulnerability
Installation locations should be protected against accidents or vandalism.
Use protective posts when installing cabinets near automobile traffic and
parking areas.
Do not place the cabinets below grade or in flood-prone areas. The cabinet
should always be located on a site above the 100-year flood plain. The site
should not be subject to water runoff or flash flooding during heavy rains.
If an area is subject to frost, the site must be free of heaving.
For pole-mounted cabinets, ensure the pole can support the cabinet weight
(approximately 230 lbs (105 kg).
5.4 Accessibility
For safety, the cabinet should be easily accessible with adequate parking.
Do not install the cabinet within 42.0 inches (1067 mm) of any
obstruction, such as a fence, hedge, or tree.
6 Transportation and Storage
Caution!
Follow all appropriate local transportation, handling, and safety practices
when transporting and storing the cabinet to a staging area or installation
site.
The cabinet is shipped in a wood box on a wood pallet.
Warning!
To avoid possible damage to the cabinet, do not remove the packaging or
pallet from the cabinet until it is at the staging area or installation site.
If the cabinet packaging appears damaged, do not accept the unit or
component from the shipper. Damaged packaging could indicate cabinet or
equipment damage.
4-8 1/1551-EN/LZB 119 3312 Uae Rev A 1998-11-17

Installation
Always use proper lifting equipment, such as a forklift, to raise the cabinet
and pallet.
Always store the cabinet and battery components in the upright position to
avoid possible damage.
Caution!
Do not stack units for transportation or during storage.
7 Unpacking
The RBS 884 Micro (1900 MHz) cabinet is shipped in a wooden box on a
wood pallet.
7.1 Required Tools
The tools required to unpack the cabinet are shown in Table 4-2 on page
4-9.
Table 4-2. Tools Required to Unpack cabinet
Product Number Description
N/A Tamper resistant wrench (supplied with cabinet)
N/A Socket or adjustable wrench (for pallet bolts)
N/A Hammer
N/A Large flat-blade screwdriver
N/A Small flat pry bar or crow bar
1/1551-EN/LZB 119 3312 Uae Rev A 1998-11-17 4-9
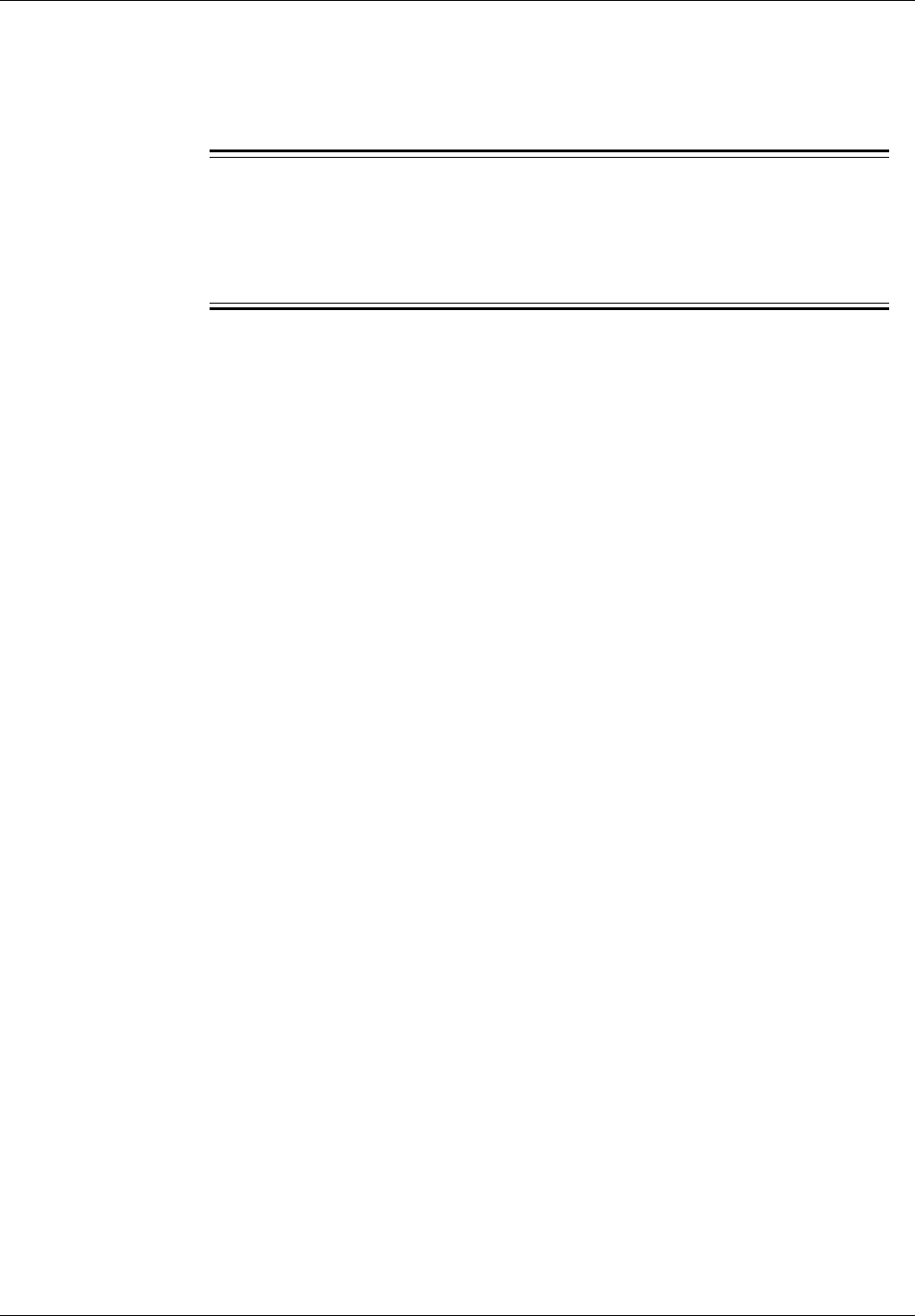
Installation
7.2 Unpacking Procedure
7.2.1 Receiving Materials
Warning!
To avoid damaging the cabinet, do not remove the pallet or wooden box
from the cabinet until the cabinet is transported to a staging or installation
site.
1. After delivery of materials, check the packing slip to verify that all
boxes and crates are received.
2. Inspect all boxes and crates for any visible damage.
3. Report any material shortages or damages to your local logistics
coordinator.
7.2.2 Unpacking
1. Remove all packaging material from around the cabinet and the
pallet.
Note: Do not remove the pallet until the cabinet is ready to be
lifted into the mounting position.
2. Remove the tamper-resistant wrench from the plastic bag taped to
the outside of the Main Cabinet.
3. Use the tamper-resistant wrench to open the doors. Insert the
wrench into a security bolt and turn it 1/4–turn counterclockwise.
Repeat for the other bolt. Open the door.
4. As the door is opened, secure the wind latch at the top of the door.
Open the door until the shoulder slides into the slot at the end of
the bar. To release the wind latch, lift up on the bar.
5. Inspect moving parts, mounting hardware, connectors, and
electronic equipment. If the cabinet or any equipment appears to be
damaged, follow the local procedures or contact the logistics
coordinator.
6. Check the packing slip and verify all parts ordered are received.
7. Remove all packaging and dispose of it according to local practices.
4-10 1/1551-EN/LZB 119 3312 Uae Rev A 1998-11-17
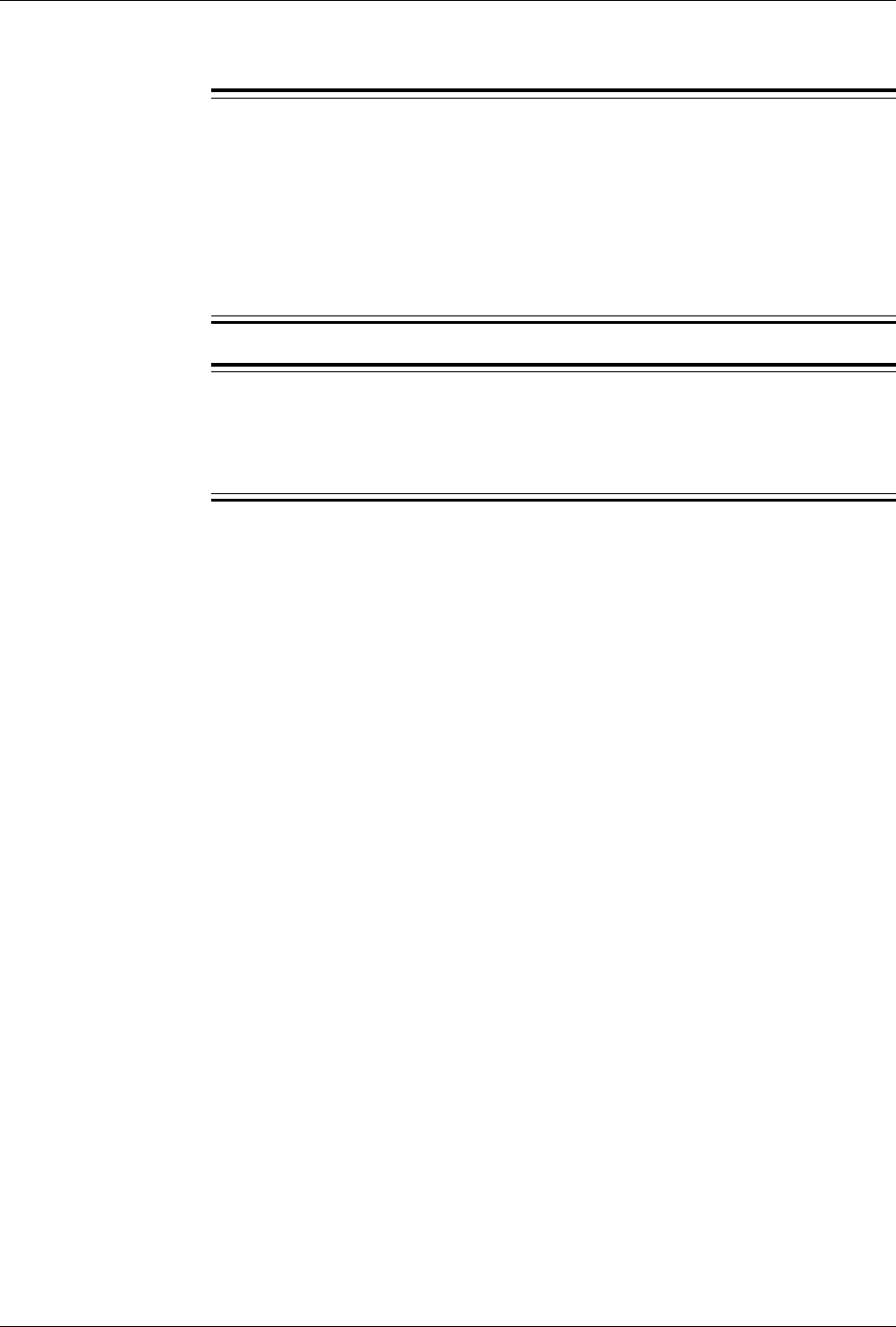
Installation
7.2.3 Lifting the Cabinet
DANGER!
To avoid injury or equipment damage, follow all local safety practices
while lifting the cabinet. Wear all locally recommended safety equipment.
Manual cabinet lifting is not recommended. To avoid injury, use proper
lifting equipment, such as a forklift or crane. Attach any lifting equipment
to lifting ears located on rear of cabinet. Check that there are no
obstructions around cabinet.
Warning!
The RBS 884 Micro (1900 MHz) cabinet will tilt forward when raised by
the lifting ears located on the rear of the cabinet.
Observe the following procedures when lifting the RBS 884 Micro (1900
MHz) cabinet from the pallet:
•Keep bystanders away from work operations at all times.
•Do not lift the cabinet over people. Do not let anyone work, stand,
or pass under a cabinet being lifted.
•All persons working with lifting equipment must wear standard
safety headgear and (when required) gloves.
•When lifting the cabinet and pallet with a forklift, do not damage
cabinet with forks. Lift from the open ends of the pallet.
•For installations where the cabinet will be mounted at higher
locations on a wall or pole, a crane or similar lifting equipment is
recommended. Do not attempt to manually lift cabinet. Follow all
local safety practices.
7.2.4 Removing Cabinet from Pallet
Perform the following steps to remove the cabinet from the pallet:
1. Locate the four pallet mounting bolts. There are four bolts (one in
each corner) in the bottom of the cabinet. Using a socket wrench
or adjustable wrench, remove the four pallet mounting bolts.
2. Secure the cabinet door before moving the cabinet.
1/1551-EN/LZB 119 3312 Uae Rev A 1998-11-17 4-11
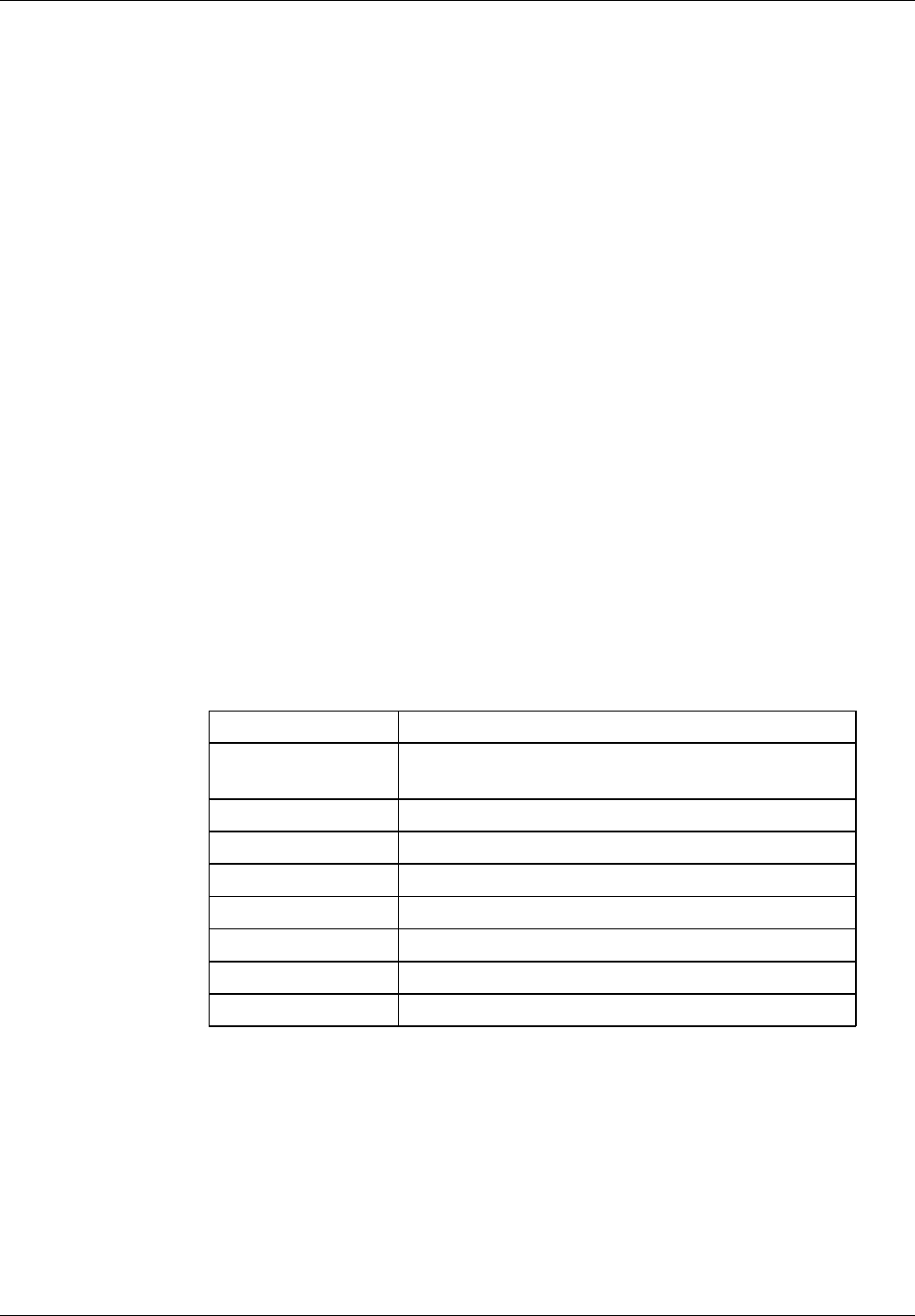
Installation
8 Cabinet Installation
This section describes procedures for installing the RBS 884 Micro (1900
MHz) cabinet on a pad, pole, wall, or roof. Manual cabinet lifting is not
recommended. The RBS 884 Micro (1900 MHz) cabinet requires
mechanical lift assistance for wall or pole mounting. Attach any lift
devices to lifting ears on rear of cabinet. If required, a temporary support
structure can be installed prior to installing the cabinet. Position the
cabinet on the support structure during installation. Do not stand under
cabinet at any time. Follow all safety precautions described in Section
7.2.3 on page 4-11.
8.1 Required Materials and Tools
8.1.1 Materials
Refer to the CMS 8800 Site Materials Catalog for general materials to
install the RBS 884 Micro (1900 MHz) antennas and cables. Cabinet
mounting materials are specified in the individual installation procedures.
8.1.2 Tools
The tools required to mount RBS 884 Micro (1900 MHz) cabinets are
shown in Table 4-3 on page 4-12.
Table 4-3. Tools for Cabinet Installation
Product Number Description
N/A Mechanical lifting equipment capable of supporting
cabinet weight (refer to local safety procedures)
N/A Metric Tape Measure
N/A Horizontal/Vertical Spirit Level
N/A Pen
N/A Drill
N/A Appropriate Size Drill Bit
N/A Socket Wrench
N/A Ratcheting Box Wrench
8.2 Installation on a Pad
The pedestal base mounting kit is used for pad mounting RBS 884 Micro
(1900 MHz) cabinets. The pedestal base mounts on a concrete pad and is
used as the base for the cabinet. A removable front panel allows easy
access for installation of the pedestal, cabinet, and any cables.
4-12 1/1551-EN/LZB 119 3312 Uae Rev A 1998-11-17

Installation
Knock-outs are provided at both ends for routing the cables through the
side walls of the pedestal base to the underside of the cabinet floor. The
knock-outs are not used if the cables enter the pedestal through conduits
from beneath the pad.
Perform the following to install the RBS 884 Micro (1900 MHz) on a pad:
1. Clean all litter from the foundation pad surface.
2. Dress the cable or conduit to avoid interference with the pedestal
base installation.
3. Remove any bolts and washers installed in the concrete anchors. Set
the hardware aside to attach the pedestal base to the pad.
4. Locate the Pedestal Mounting Kit.
5. Place the pedestal base on the concrete pad. Figure 4-2 on page 4-13
illustrates the pedestal base. Align the pedestal base with the screw
anchors that were installed when the concrete pad was poured. If the
screw anchors were not installed at that time, use the pedestal base to
mark the mounting holes for the anchors and drill. See Figure 4-3 on
page 4-14 for the location of the mounting holes on the pedestal base.
Depth
432 mm
(17.0 in)
Height
305 mm
(12.0 in)
Removable front panel
for access to cables
and mounting points
under cabinet Width
610 mm
(24.0 in)
Vents for air entry
into cabinet
Knock-outs for
cable entry/exit
Pedestal Base for Pad Mounting
the RBS 884 Micro (1900 MHz)
cabinet
Figure 4-2. Pedestal Base
1/1551-EN/LZB 119 3312 Uae Rev A 1998-11-17 4-13
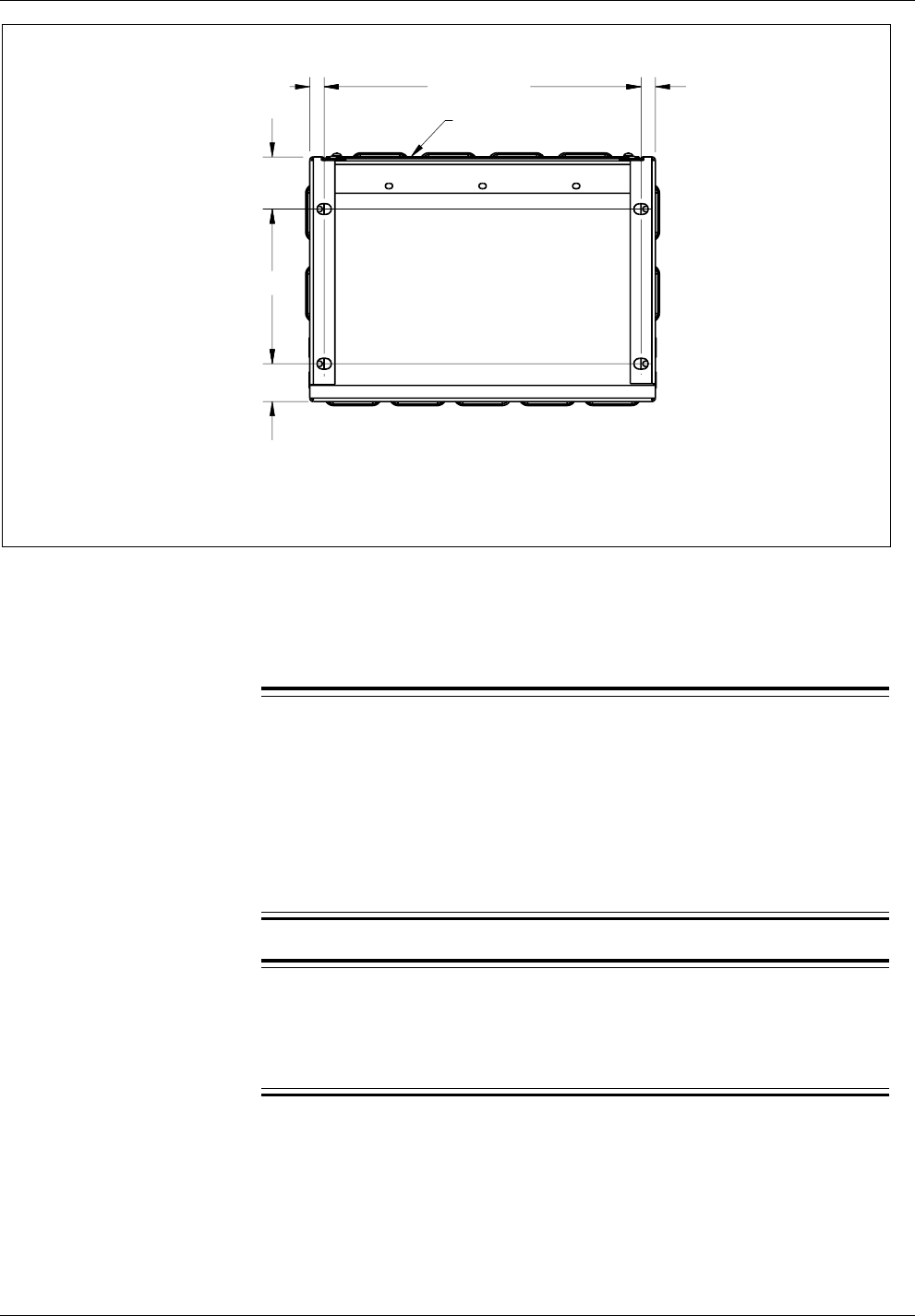
Installation
Bottom view of pedestal base
showing mounting pattern
for securing to concrete pad
Front of Pedestal
10.75 in
(273.05 mm)
2.63 in
(66.80 mm)
3.62 in
(91.95 mm)
1 in
(25.4 mm)
22.00 in
(558.80 mm) 1.00 in
(25.4 mm)
Figure 4-3. Bottom View of Pedestal Mount
6. Attach the pedestal base to the concrete pad and secure with the
appropriate size bolts.
7.
DANGER!
To avoid injury or equipment damage, follow all local safety
practices while lifting the cabinet. Wear all applicable locally
approved safety equipment. Manual cabinet lifting is not
recommended. Use proper lifting equipment. Attach any lifting
devices to lifting ears on rear of cabinet. Keep bystanders away from
work operations at all times.
Warning!
The RBS 884 Micro (1900 MHz) cabinet will tilt forward when
raised by the lifting ears located on the rear of the cabinet.
Place the cabinet onto the pedestal pad mount. Check that the
cabinet is aligned with the pedestal.
4-14 1/1551-EN/LZB 119 3312 Uae Rev A 1998-11-17

Installation
8.
Warning!
Until the mounting hardware secures the cabinet to the pedestal base,
the cabinet is unstable and could fall off the base causing injury or
equipment damage. Make sure the cabinet is safely supported until it
is secured to the pedestal base.
Using the tamper-resistant wrench, remove the front panel on the
pedestal base. Secure the cabinet to the pedestal base using the ten
1/2”-13 bolts, flat washers, and lock washers. Tighten all bolts
securely.
9. If not using cabinet mounted antennas, remove lifting ears from the
cabinet (optional).
10. Install any cabinet mounted antennas.
8.3 Installation on a Pole
Perform the following to install the RBS 884 Micro (1900 MHz) on a pole:
Warning!
For installations where the RBS 884 Micro (1900 MHz) cabinet will be
pole mounted, a crane or similar lifting equipment is required. Ensure the
cabinet is supported by the lifting equipment at all times during the
installation. The cabinet will tilt forward when raised by the lifting ears
located on the rear of the cabinet. Keep bystanders away from the work
area at all times.
1. Locate the Pole-Mount Kit.
2. Identify the mounting bracket, straps, strap tension brackets, and
mounting hardware. A fully assembled Pole Mount is shown in
Figure 4-4 on page 4-16.
1/1551-EN/LZB 119 3312 Uae Rev A 1998-11-17 4-15
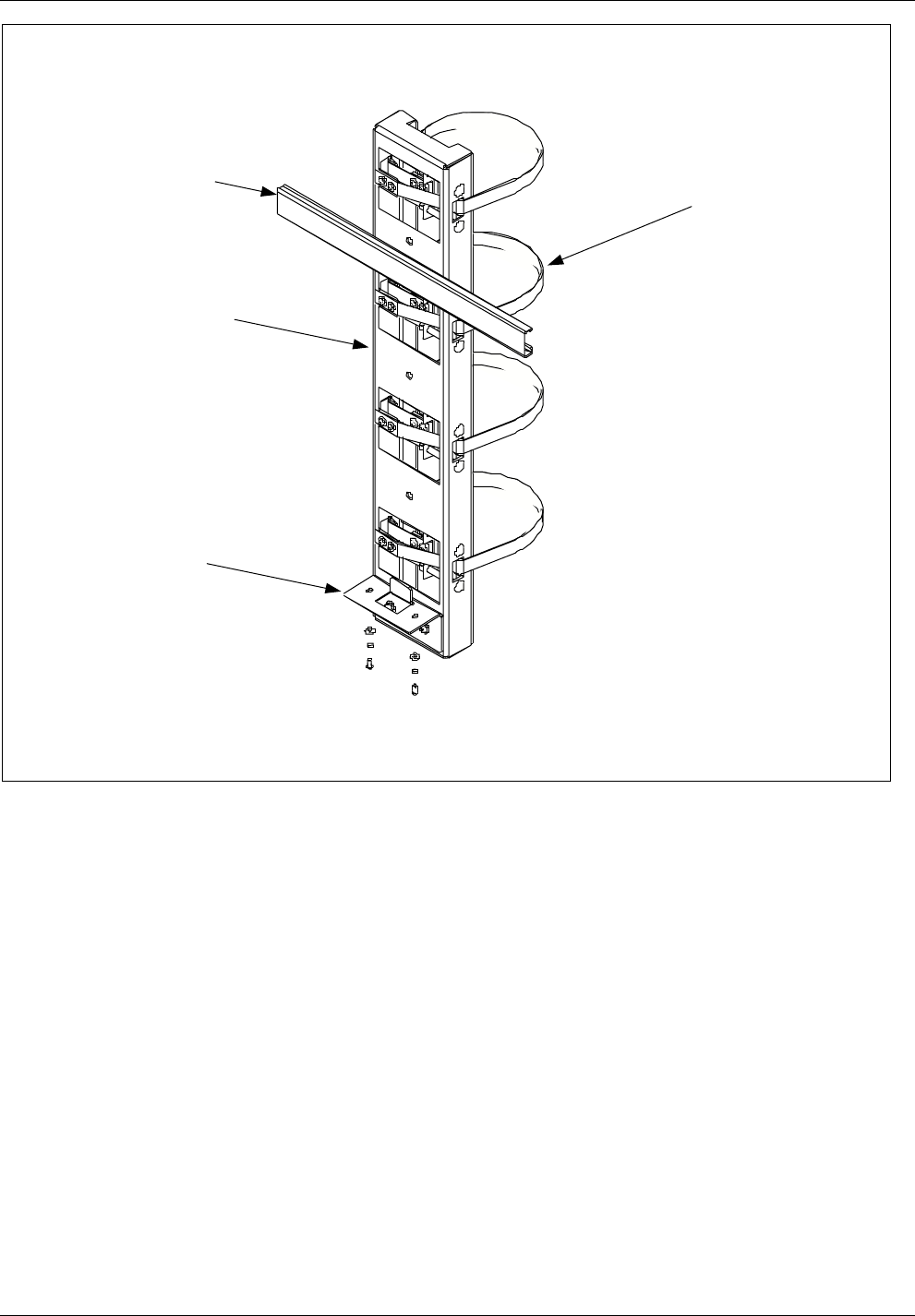
Installation
Mounting Strap
Pole Mount Bracket
L-Bracket
T-Bracket
Figure 4-4. Pole-Mount Assembly
3. Attach the mounting straps to the strap tension brackets using two
screws, two lock washers, and two flat washers. See Figure 4-5 on
page 4-17 for a close-up of the bracket assembly.
4-16 1/1551-EN/LZB 119 3312 Uae Rev A 1998-11-17
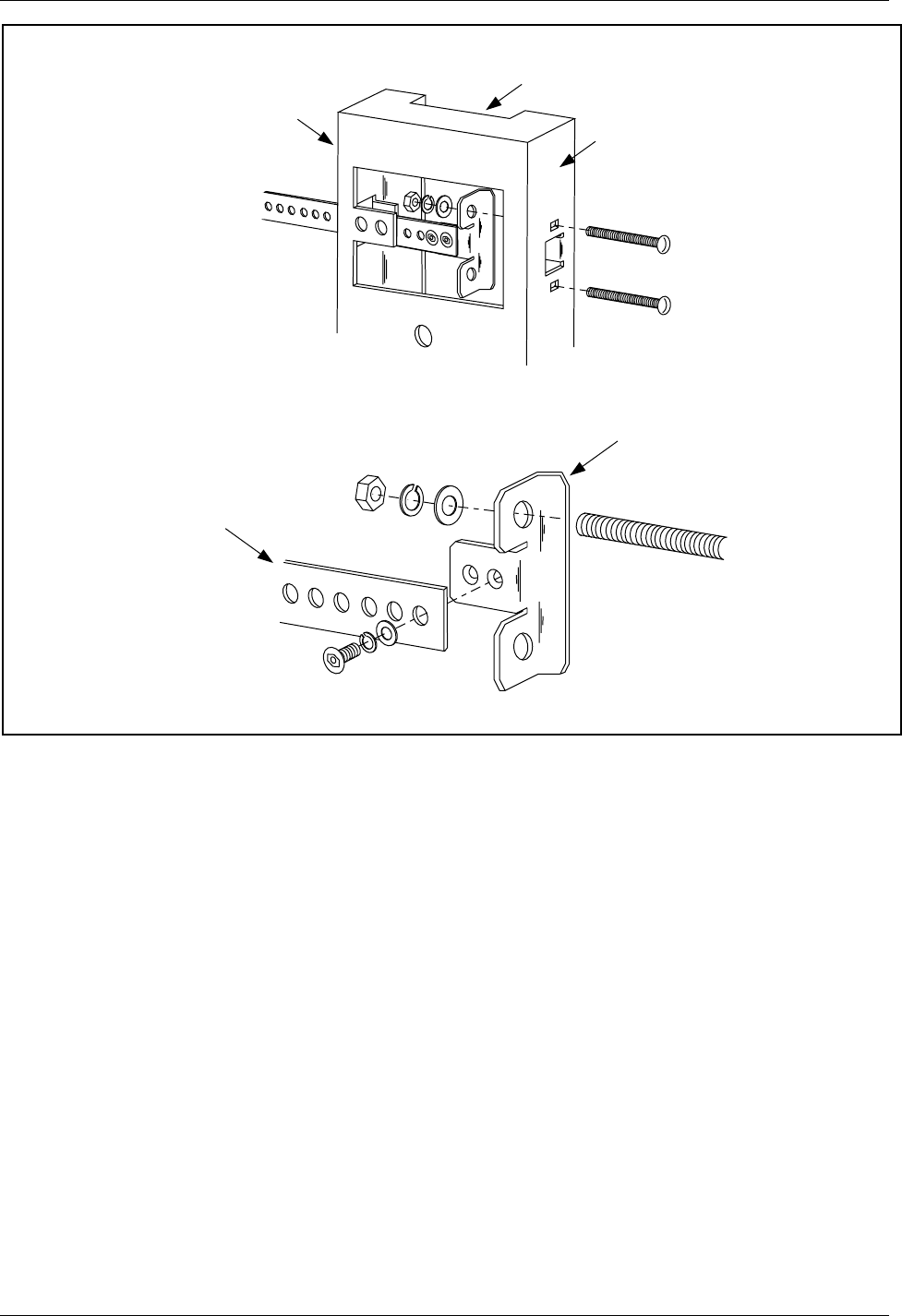
Installation
Pole Mounting Strap
Strap Tension Bracket
Left Side of Mount
Pole Mount
Right Side of Mount
Figure 4-5. Pole-Mount Bracket Assembly
4. Slide the assembled straps through the rear of the bracket and out the
left side holes. Ensure the tension bracket holes are facing the right
side of the bracket. See Figure 4-5 on page 4-17.
5. For each tension bracket, install two carriage bolts through the right
side of the pole-mount bracket and through the strap tension bracket.
6. Slip a washer, a lock washer, and a nut on the ends of the carriage
bolts. Do not tighten nuts on carriage bolts.
7. Place the pole-mount bracket on the pole at the desired height and
wrap mounting straps around the pole.
8. Insert loose end of strap through strap hole on right side of bracket.
Pull strap tight and attach to front strap mounting tab. See Figure
4-6 on page 4-18.
1/1551-EN/LZB 119 3312 Uae Rev A 1998-11-17 4-17
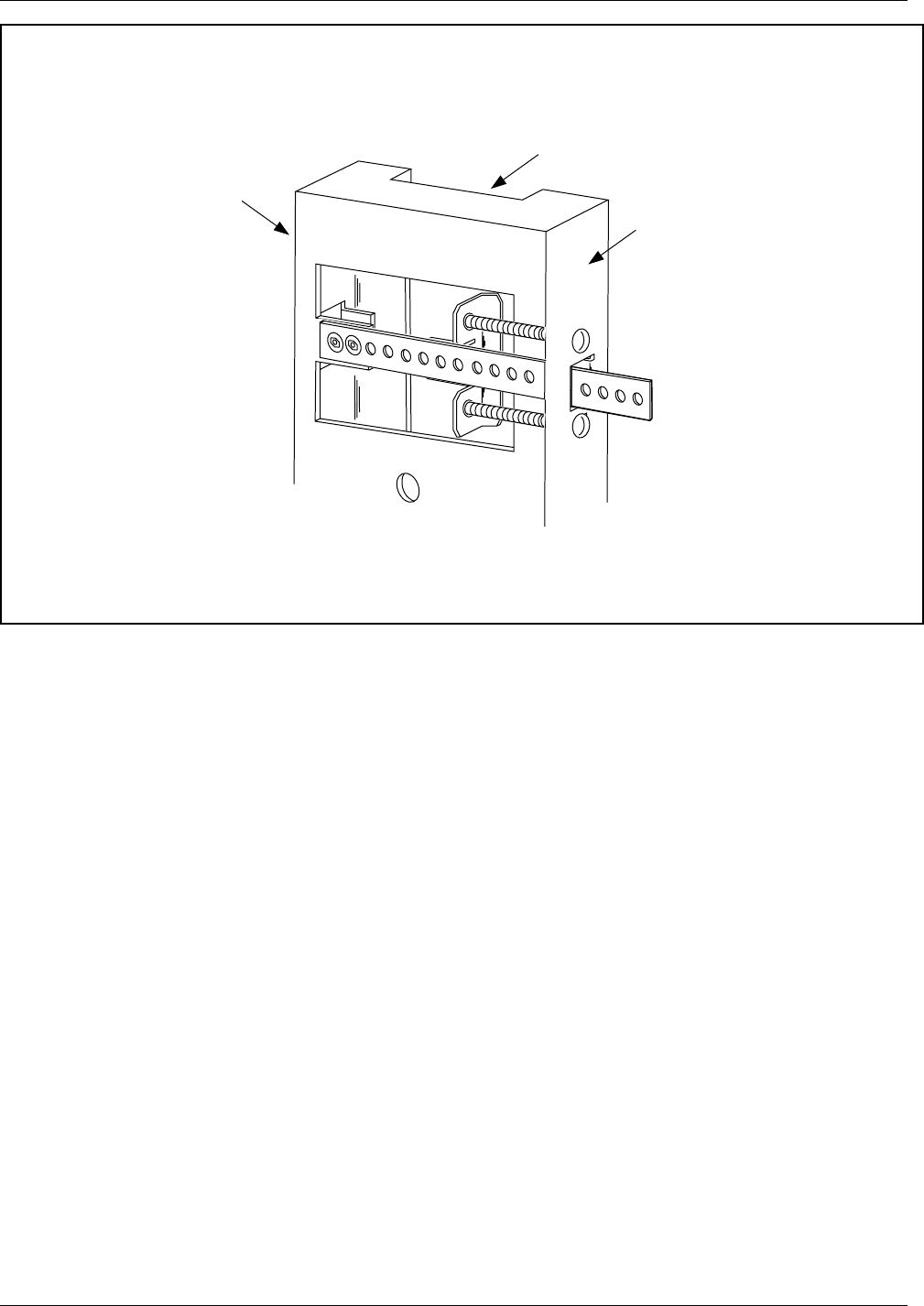
Installation
Left Side of Mount
Pole Mount
Right Side of Mount
Figure 4-6. Pole-Mount Strap Attachment
9. Ensure the bracket is level and tighten the nuts on the carriage bolts
using a ratcheting box wrench. See Figure 4-7 on page 4-19.
Note: If the pole-mount bracket is to be bolted to a pole,
mark and drill holes in the pole prior to lifting
bracket into location. If two or more cabinets are to
be installed, a minimum of 12 inches (305 mm)
clearance must be maintained between cabinets.
4-18 1/1551-EN/LZB 119 3312 Uae Rev A 1998-11-17

Installation
Pole-Mount Assembly
with Straps Pole-Mount Assembly
with Bolts
Figure 4-7. Pole-Mount Assembly Installations
10. Using metal cutting shears or a saw, remove the excess strap.
11. Loosely attach the L-bracket to the pole mount assembly using two
screws, two lock washers, and two flat washers. See Figure 4-4 on
page 4-16 for the position of the L-bracket on the pole mount
assembly.
12. If required, attach the cabinet mounted antenna bracket to the
cabinet. The bracket is installed behind the lifting ears on the rear of
the cabinet.
13. Locate the four mounting bolts (one in each corner) in the base of
the cabinet. Remove the four pallet mounting bolts. Remove the
pallet and dispose in accordance with local practices.
14. Secure the cabinet door before lifting the cabinet.
1/1551-EN/LZB 119 3312 Uae Rev A 1998-11-17 4-19
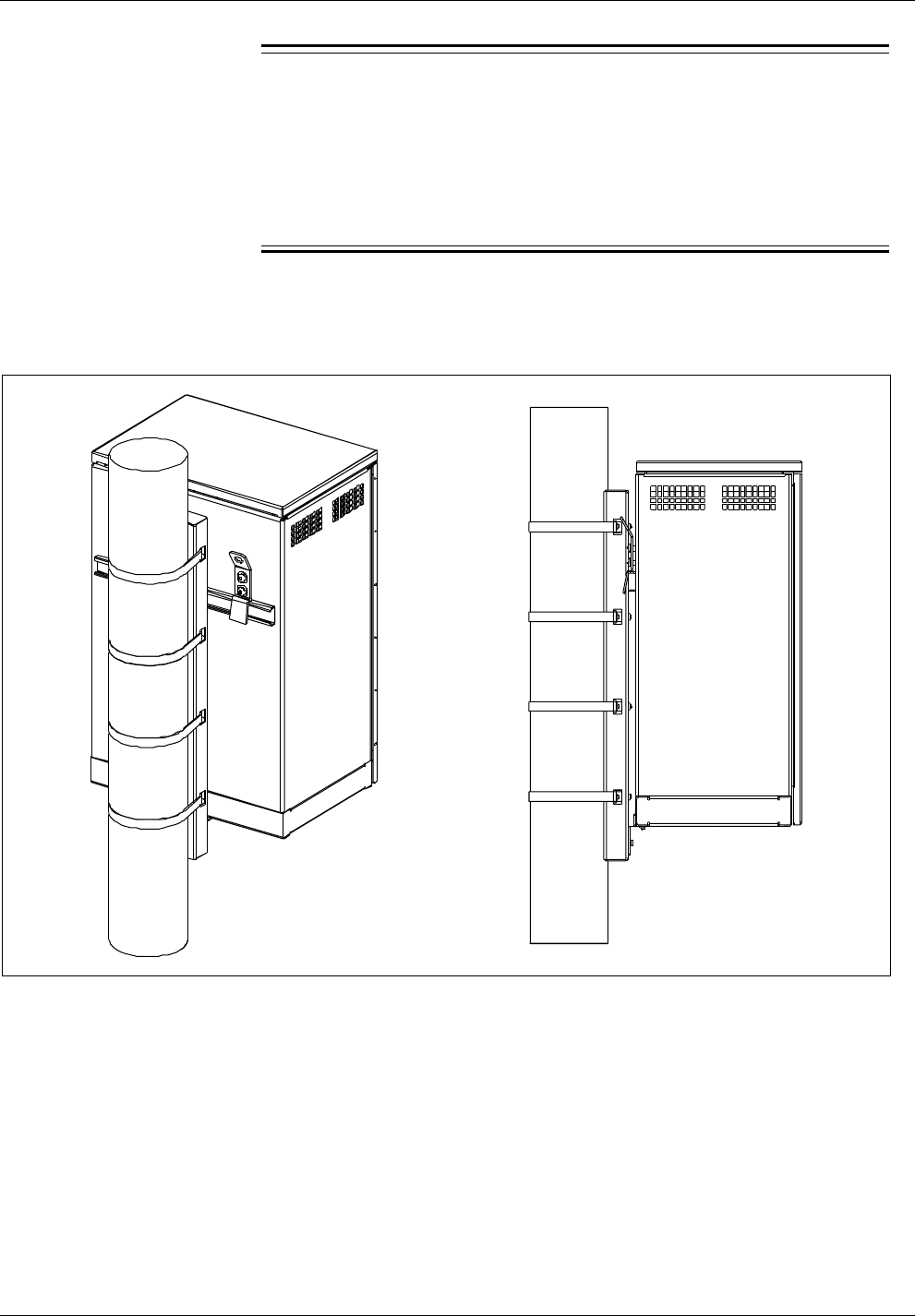
Installation
15.
Warning!
Ensure the cabinet is supported by the lifting equipment at all times
during the installation. The RBS 884 Micro (1900 MHz) cabinet will
tilt forward when raised by the lifting ears located on the rear of the
cabinet. Do not lift the cabinet over people. Do not let anyone work,
stand, or pass under a cabinet while it is being lifted.
Attach the lifting cables or sling to the lifting ears on the mounting
bracket. Carefully lift the cabinet and install the cabinet on the
mounting bracket. See Figure 4-8 on page 4-20.
Figure 4-8. Cabinet Installed on Pole-Mount Assembly
16. If required, adjust cabinet horizontally to align with L-bracket.
17. Attach the L-bracket to the bottom of the cabinet using two screws,
two lock washers, and two flat washers. Tighten all L-Bracket
screws with the tamper-resistant wrench.
18. Install any cabinet mounted antennas to the antenna bracket.
4-20 1/1551-EN/LZB 119 3312 Uae Rev A 1998-11-17
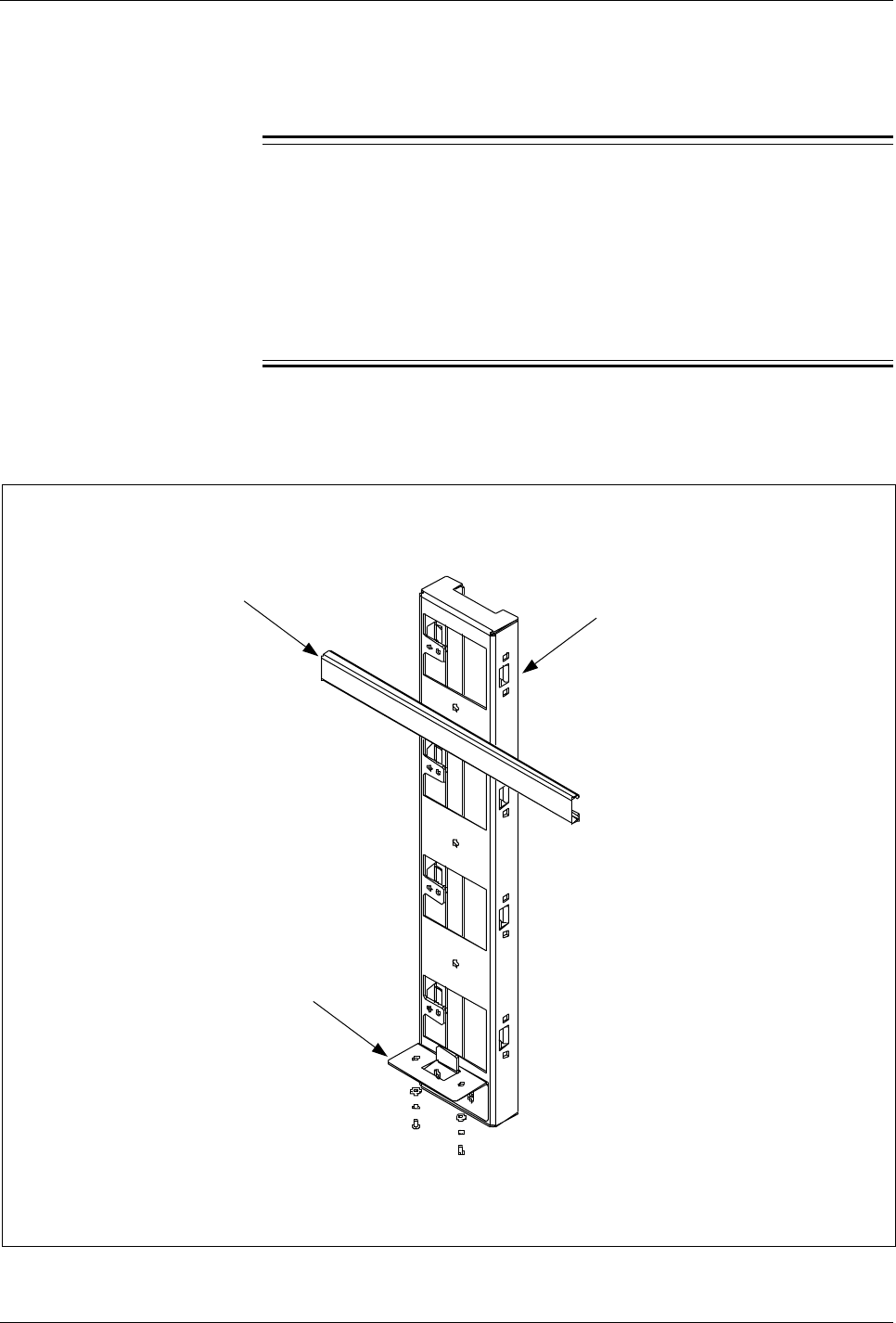
Installation
8.4 Installation on a Wall
Perform the following to install the RBS 884 Micro (1900 MHz) on a wall:
Warning!
Ensure the cabinet is supported by the lifting equipment at all times
during the installation. The RBS 884 Micro (1900 MHz) cabinet will
tilt forward when raised by the lifting ears located on the rear of the
cabinet. A fully configured cabinet weighs over 105 kg (230 lbs).
Ensure the wall can support the cabinet. Reinforce the wall structure
if necessary.
1. Ensure the cabinet is upright
2. Locate the Wall-Mount Kit.
Mounting Bracket
T-Bracket
L-Bracket
Figure 4-9. Wall-Mount Assembly
1/1551-EN/LZB 119 3312 Uae Rev A 1998-11-17 4-21
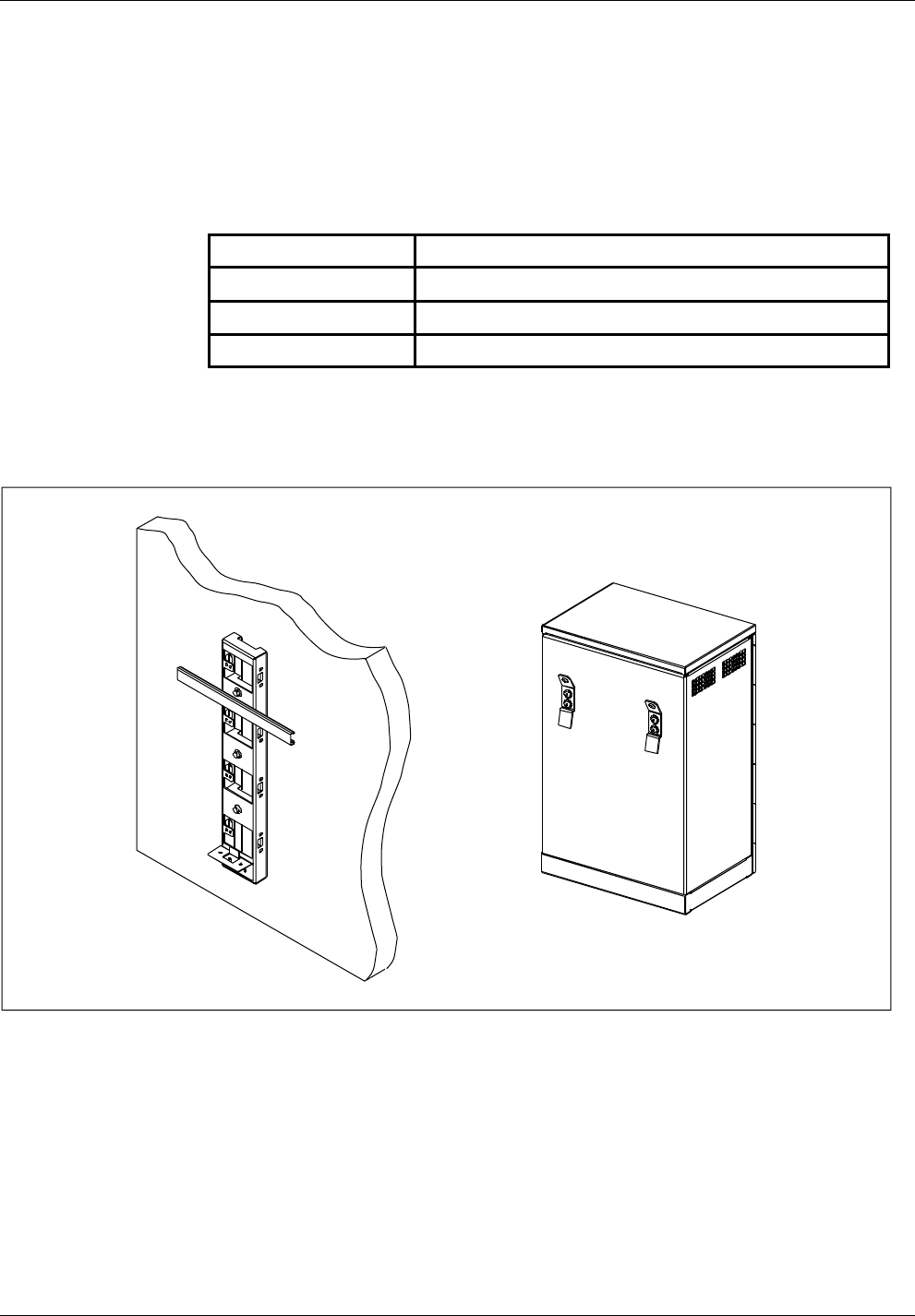
Installation
3. Identify the mounting bracket, and mounting hardware. A fully
assembled Wall Mount Assembly is shown in Figure 4-9 on page
4-21.
4. Locate the place on the wall where the bracket will be mounted and
drill holes appropriate for the length of the anchor to be used. Table
4-4 on page 4-22 is a list of the suggested anchoring hardware.
Table 4-4. Wall Anchors
Type of Wall Recommended Anchor
Masonry 4-1/4-in. x 1-1/4-in. hammer drive anchors
Wood 4-1/2-in. No. 14 RH galvanized wood screws
Hollow Hollow wall mounting not recommended
5. Secure the bracket to the wall using an appropriate anchor. See
Figure 4-10 on page 4-22. Level the bracket before tightening the
bolts.
Figure 4-10. Wall-Mount Assembly Installed on Wall
6. Loosely attach the L-bracket to the wall mount assembly using two
screws, two lock washers, and two flat washers. See Figure 4-9 on
page 4-21 for the position of the L-bracket on the wall mount
assembly.
7. If required, attach the cabinet mounted antenna bracket to the
cabinet. The bracket is installed behind the lifting ears on the rear of
the cabinet.
4-22 1/1551-EN/LZB 119 3312 Uae Rev A 1998-11-17
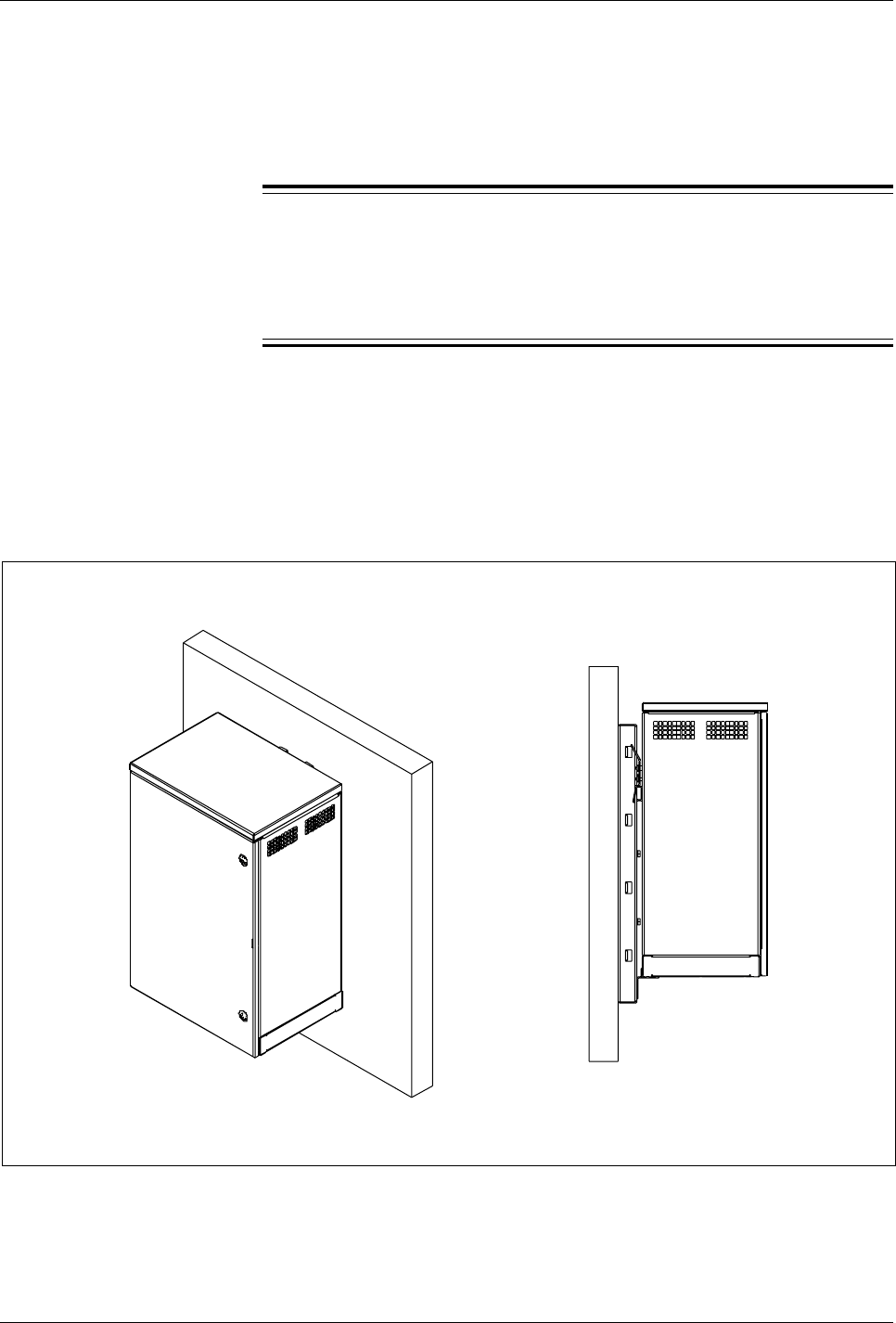
Installation
8. Locate the four mounting bolts (one in each corner) in the base of
the cabinet. Remove the four pallet mounting bolts. Remove the
pallet and dispose of it in accordance with local practices.
9. Secure the cabinet door before lifting the cabinet.
10.
Warning!
A fully configured cabinet weighs 105 kg (230 lbs). Mechanical
lifting equipment is required to lift cabinet into position. Manual
lifting is not recommended.
Lift the cabinet and place it on the cross arm bracket.
11. If required, adjust cabinet horizontally to align with L-bracket.
12. Attach the L-bracket to the bottom of the cabinet using two screws,
two lock washers, and two flat washers. See Figure 4-11 on page
4-23. Tighten all L-Bracket screws with the tamper-resistant wrench.
Figure 4-11. Wall Mounted cabinet
13. Install any cabinet mounted antennas to the antenna bracket.
1/1551-EN/LZB 119 3312 Uae Rev A 1998-11-17 4-23
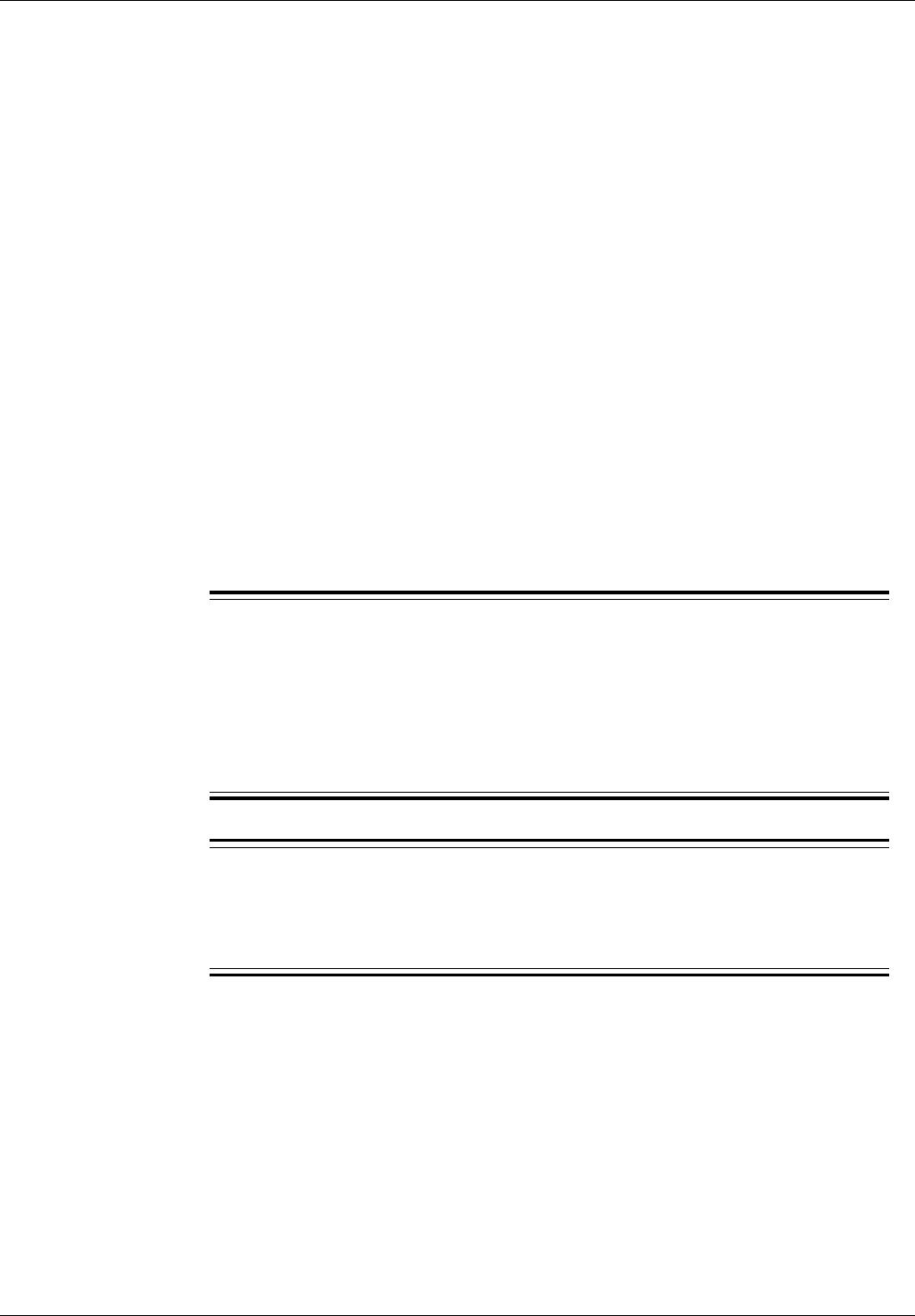
Installation
8.5 Installation on a Roof
Perform the following to install the RBS 884 Micro (1900 MHz) on a roof:
1. Locate the four base mounting bolts (one in each corner) in the
bottom of the cabinets.
2. Remove the four pallet mounting bolts. Remove the pallet and
dispose of in accordance with local practices.
3. Secure the cabinet door before lifting the cabinet.
4. Roof mounted cabinet installations vary depending on the site
configuration and type of roof. Refer to the RBS 884 Site Engineering
Manual for further information on a roof mounted cabinet.
9 Cable and Power Connections
9.1 Grounding
Warning!
Follow all local safety practices, observe all general safety precautions,
and wear all appropriate locally approved safety equipment when
performing any grounding procedures. Perform all required testing before
and after cabinet installation. Only qualified personnel or electricians
should install the ground connections.
Caution!
Ensure all local building codes and National Electrical Code® (NEC) are
met when installing grounding.
Note: Ensure all ground connections are clean and free of oxidation
or rust. Clean all contact surfaces as required.
4-24 1/1551-EN/LZB 119 3312 Uae Rev A 1998-11-17
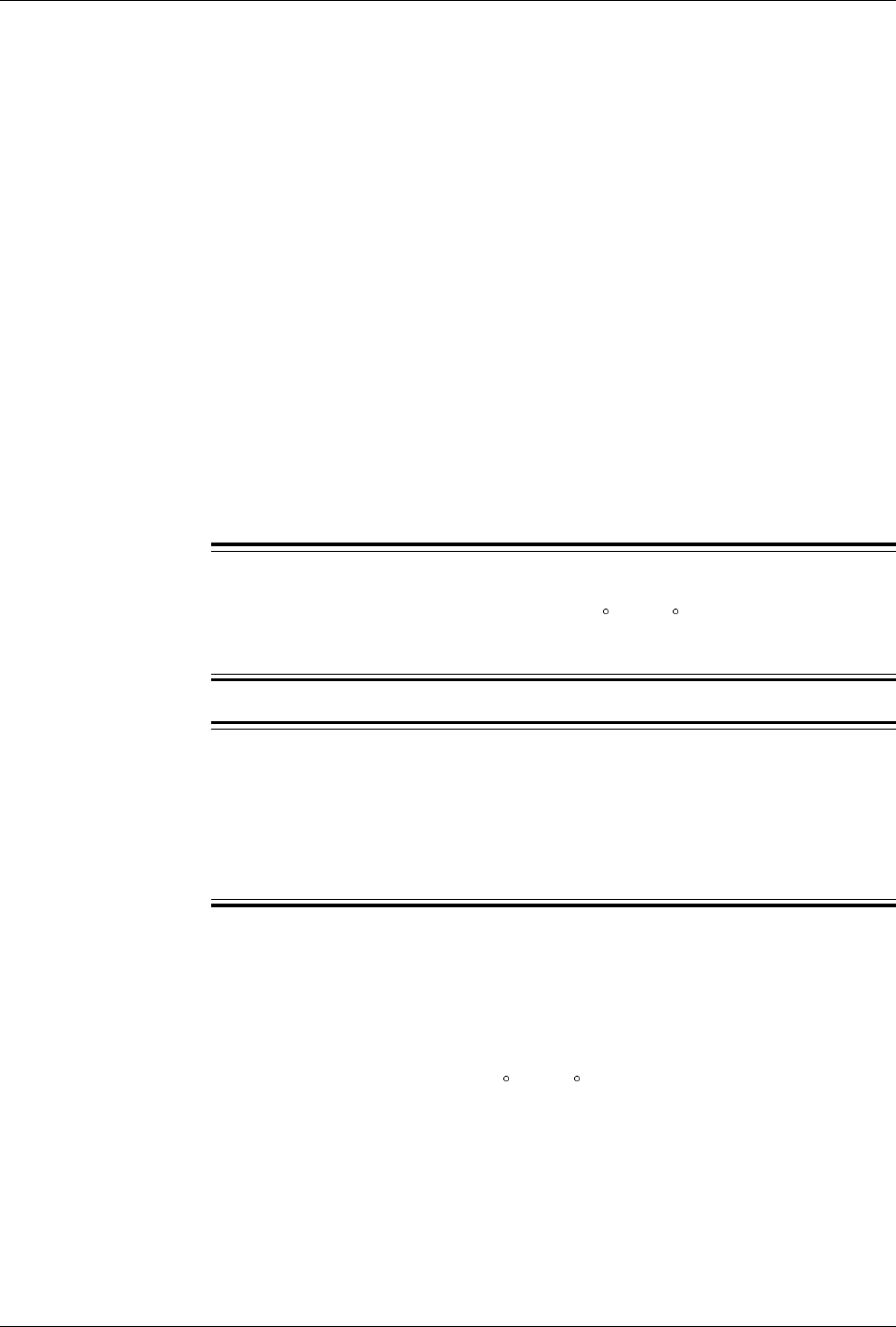
Installation
9.1.1 Perimeter Ground (Pad-Mount only)
1. Before installing cabinet, ensure the ground ring is installed and all
antennas are grounded as described in the RBS 884 Site
Engineering Manual.
2. Install coaxial transmission cable to the RBS 884 Micro (1900
MHz). The 50 ohm cable connects to the lightning surge
suppressors on the earthing plate.
3. Use an ammeter and check to ensure there is no AC or DC current
on cables already terminated to the earth ground point. If current is
present, take steps to isolate circuit and remove current from cables.
9.1.2 Cabinet Ground Cabling
The RBS 884 Micro (1900 MHz) earth ground is connected to an external
grounding lug located on the bottom shell of the cabinet.
9.2 Installing Batteries
DANGER!
Equipment temperatures can reach up to 60 C (140 F). Use extreme caution
when working around the battery enclosure or other internal components.
Warning!
To avoid injury or equipment damage, follow all locally approved safety
practices and wear appropriate safety equipment when working with
batteries. Turn off power to the MAIN circuit breaker (40A) to ensure no
power is supplied to the cabinet.
A +24Vdc battery system is standard with the cabinet for two minutes of
battery reserve. Two 12V batteries are installed in the battery tray in the
lower left area of the cabinet. The batteries are connected in series by a
copper strap.
All batteries are configured with steel cases for applications where
temperatures can reach up to 60 C (140 F).
Perform the following steps to install the batteries into the tray and
connect the batteries to the system:
1/1551-EN/LZB 119 3312 Uae Rev A 1998-11-17 4-25
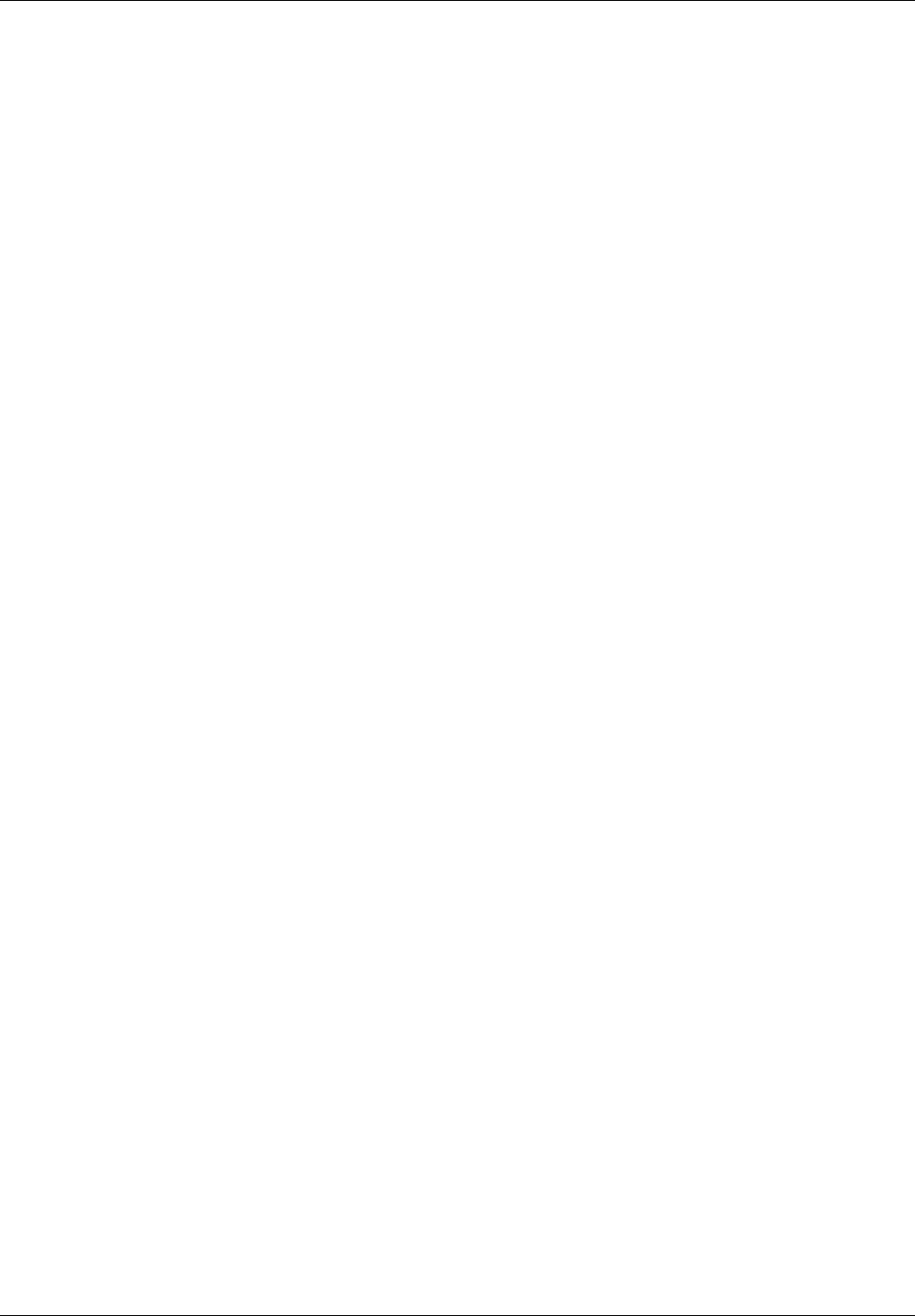
Installation
Note: The DC power supply float voltage is calibrated for +27.0 to
+27.6 Vdc at the batteries. The float is set at the factory and is
not adjusted by the user.
1. Position the BAT circuit breaker on the left side of the AC/DC
Distribution Box to OFF. See Figure 4-12 on page 4-27.
2. Remove the four screws from the battery cover and remove the
cover from the battery compartment.
3. If installed, remove the battery hold-down bracket(s) from left wall
of battery compartment.
4. Remove the battery tray from the battery compartment. Ensure
battery heater remains in position in bottom of compartment.
5. Install the batteries into the battery tray as illustrated in Figure 4-13
on page 4-28. Attach the hold-down bracket to the battery tray.
Note: Torque battery bolts to 50 in-lbs maximum.
6. Connect the center terminals (positive terminal of battery one to
negative terminal of battery two) with the copper strap. Do not
tighten the negative terminal of battery two at this time. See Figure
4-13 on page 4-28
7. Connect the battery cable assembly to the batteries as follows:
– Connect the 8-gauge red cable to the positive terminal (+) of
battery two. See Figure 4-13 on page 4-28.
Note: Ensure that the battery connections will not contact
wall of battery compartment or cover. Reposition
connectors as necessary to provide clearance.
– Connect the 8-gauge black cable to the negative terminal (-) of
battery one.
– Connect one of the 18-gauge white wires labeled POST to the
negative terminal of battery one. Connect the other 18–gauge
white wire to the negative terminal of battery two.
8. Tighten all remaining battery connections.
9. Install the battery tray assembly in the battery compartment.
Ensure the battery cable assembly is not pinched against the battery
compartment. Ensure the battery heater is in proper location under
battery tray.
10. Place the hold-down bracket over the screw on the side wall of the
battery compartment. Secure with a hex nut.
11. Connect the power connector of the battery cable assembly to the
connector at the top of the battery compartment.
12. Connect the Failed Battery Sensor connector.
13. Install the battery cover on the battery compartment with the four
screws.
4-26 1/1551-EN/LZB 119 3312 Uae Rev A 1998-11-17
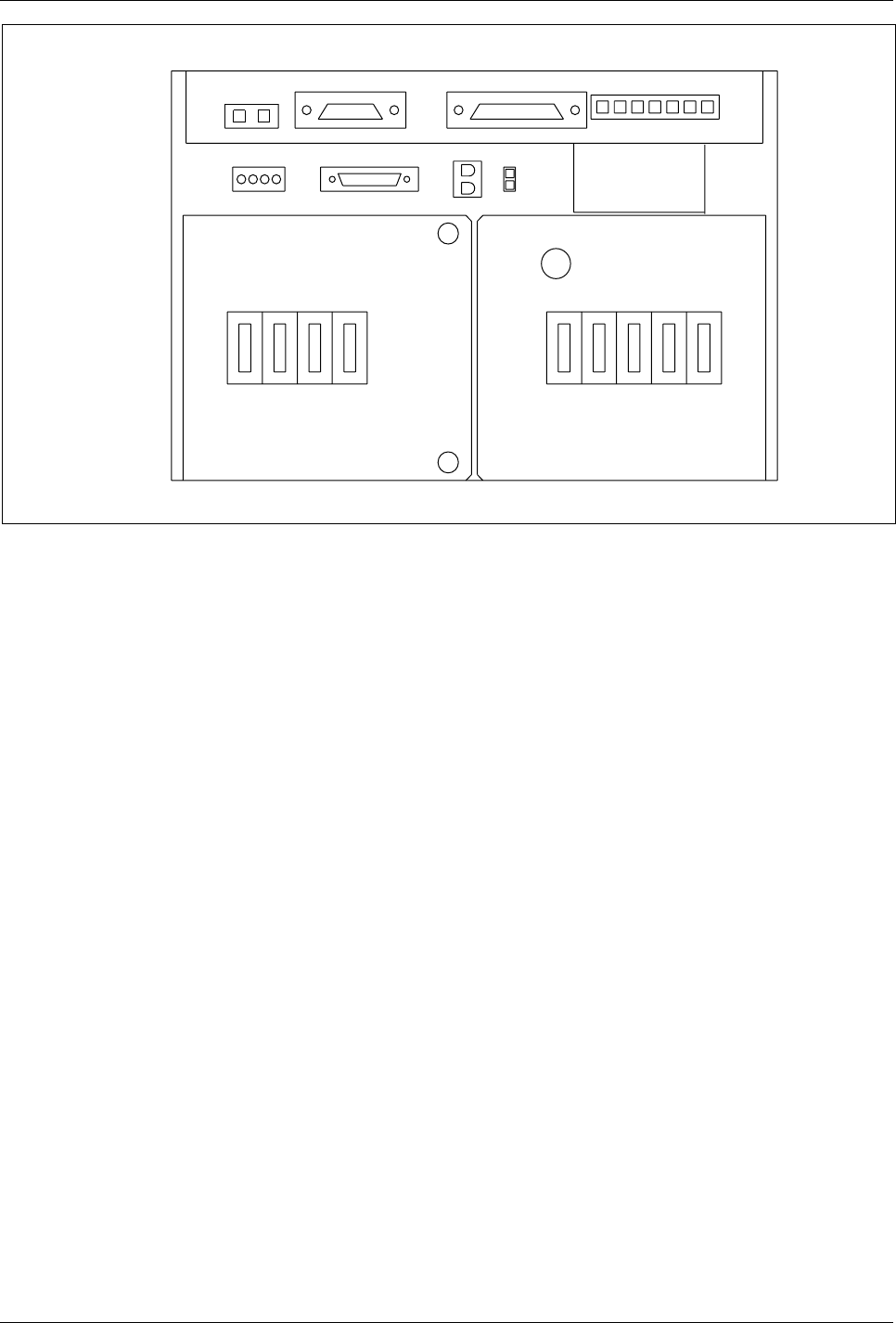
Installation
ALM CABLE ECU CABLE
SUBRK PWR
FAN PWR CSU
SENSORS
AC
CONNECTED
MAIN PSU MAIN
HTR BAT
HTR GFI
OUTLET
BAT ECU CSU FANS
BAT COMP
BAT
ALM DOOR
ALM
ON
OFF
CONVENIENCE
OUTLET
Figure 4-12. AC/DC Distribution Box
1/1551-EN/LZB 119 3312 Uae Rev A 1998-11-17 4-27
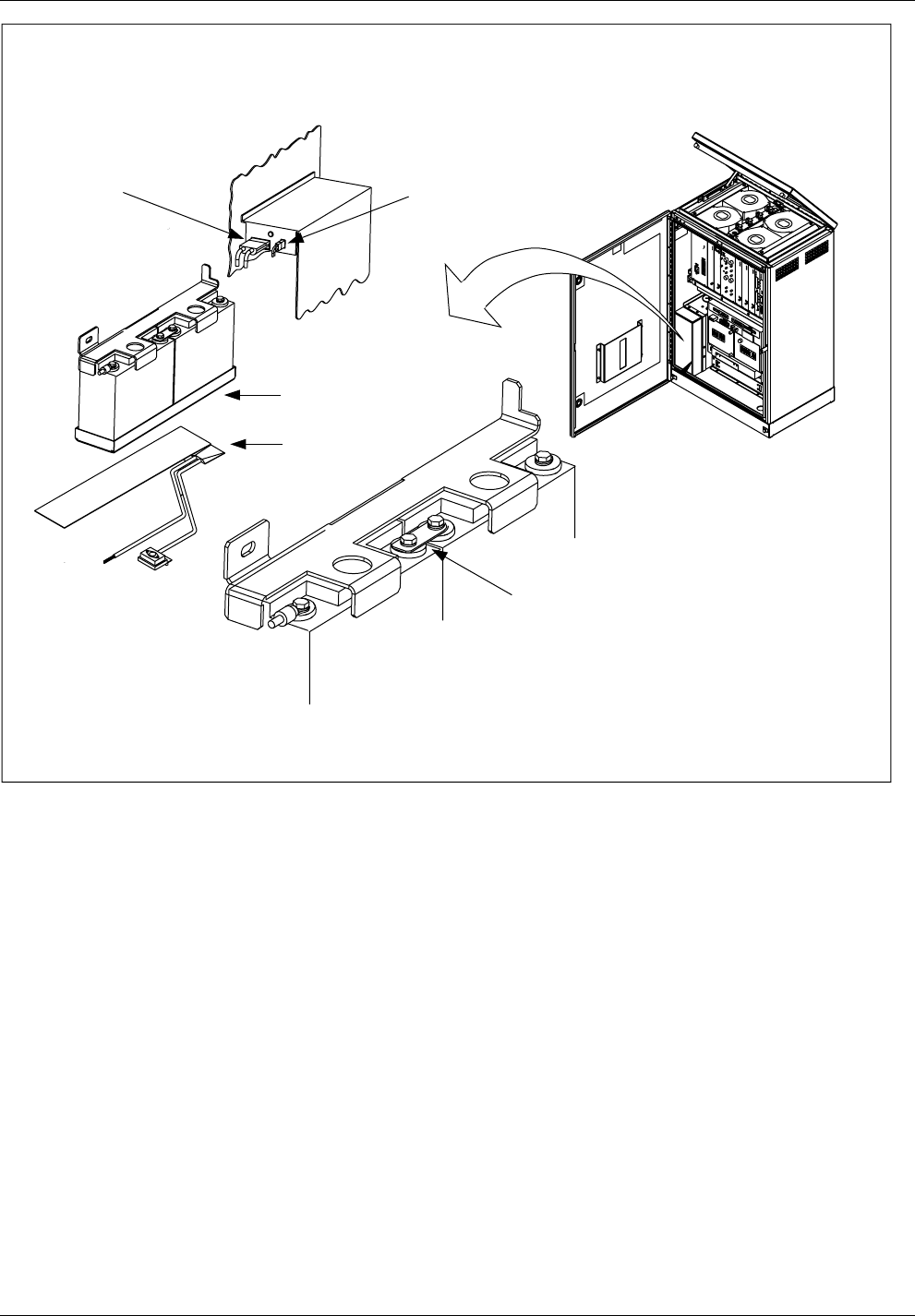
Installation
+
+
-
-
Copper Strap
Battery 1
Battery 2
Battery Tray
Battery Heater
Failed Battery
Sensor Connector
Power Connector
Figure 4-13. Battery Installation in Cabinet
4-28 1/1551-EN/LZB 119 3312 Uae Rev A 1998-11-17

Installation
9.3 Installing AC Power
DANGER!
AC power can result in death, injury, or equipment damage. Observe all
safety precautions as specified by local building codes and the National
Electrical Code® (NEC). All procedures should only be performed by
qualified personnel.
DANGER!
Note: The cabinet requires 110V, 60 Hz or 230V, 50 Hz two-wire
plus ground commercial power. All AC equipment from the
service drop to the pad is provided locally. Consult the NEC
and local codes for the correct wire size. Figure 4-14 on page
4-29 shows the location of the AC/DC Distribution Box in the
cabinet.
ALM CABLE ECU CABLE
SUBRK PWR FAN PWR CSU
SENSORS
AC
CONNECTED
MAIN PSU MAIN
HTR BAT
HTR GFI
OUTLET
BAT ECU CSU FANS
BAT COMP
BAT
ALM DOOR
ALM
ON
OFF
Figure 4-14. AC/DC Distribution Box
1/1551-EN/LZB 119 3312 Uae Rev A 1998-11-17 4-29
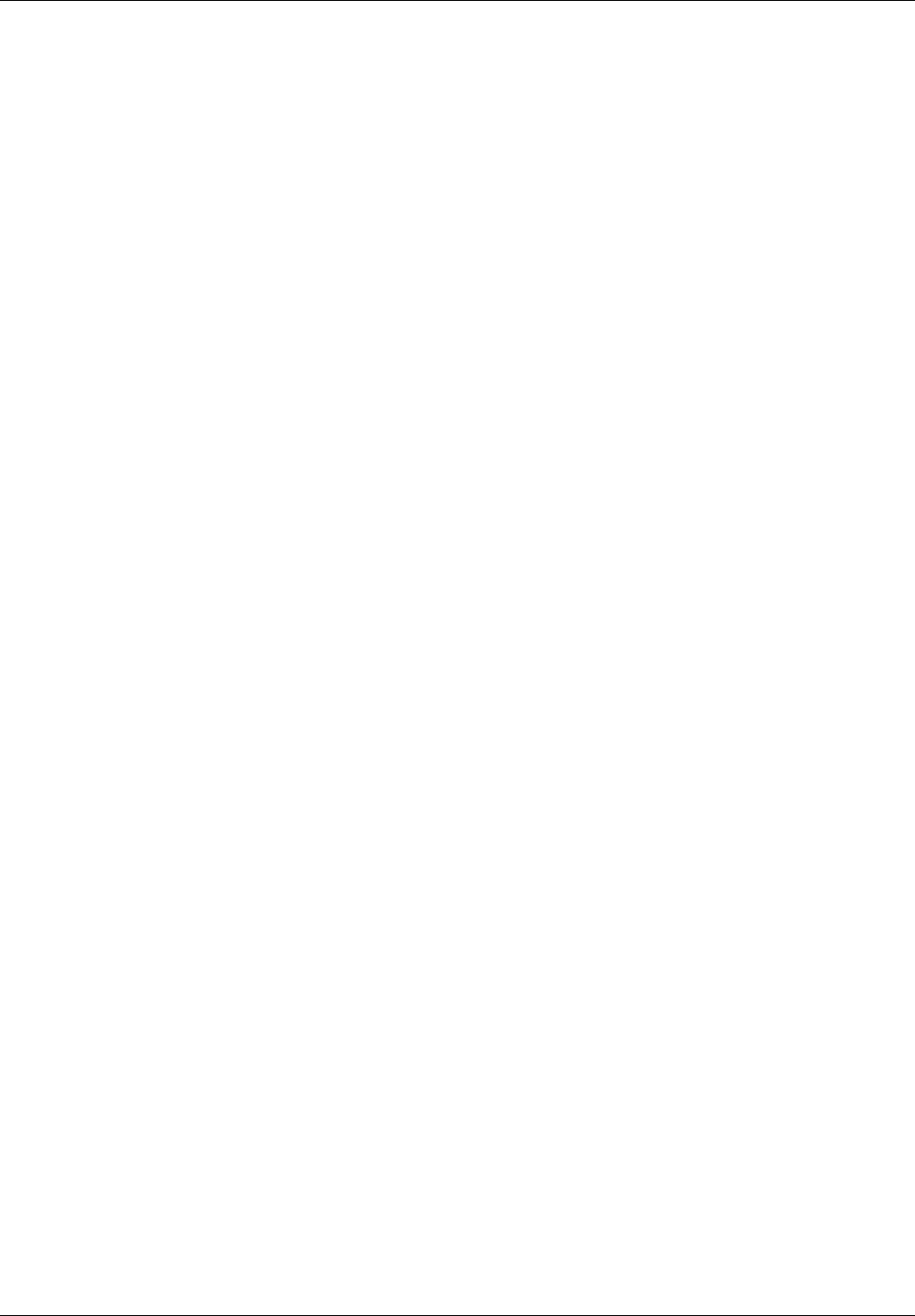
Installation
Before installation, ensure that the AC ground system is installed. The
ground system must be in compliance with local practices and building
codes. Refer to the RBS 884 Site Engineering Manual for more
information.
To install AC power, Perform the following:
1. Open the cabinet and open the AC/DC Distribution Box.
2. The opening in the bottom of the cabinet is sealed with a conduit
fitting to prevent air and water leakage into the cabinet. The conduit
fitting has threads that extend through the bottom of the cabinet.
3. Pull AC and ground wires through conduit into the AC/DC
Distribution Box.
4. Connect ground wire to ground bus inside AC/DC Distribution Box.
5. Connect neutral wire to neutral bus inside AC/DC Distribution Box.
6. Remove clear cover from rear of circuit breakers.
7. Connect the L1 (Line 1) wire to AC main breaker bus (line bus)
inside AC/DC Distribution Box. The minimum recommended wire
size is 8 AWG (type THHN or equivalent.) Refer to Figure 4-15
on page 4-31.
8. Replace clear cover on rear of circuit breakers and close AC/DC
Distribution Box.
9. Bring the external AC conduit up to the bottom of the cabinet and
connect it to the threaded internal AC conduit fitting.
4-30 1/1551-EN/LZB 119 3312 Uae Rev A 1998-11-17
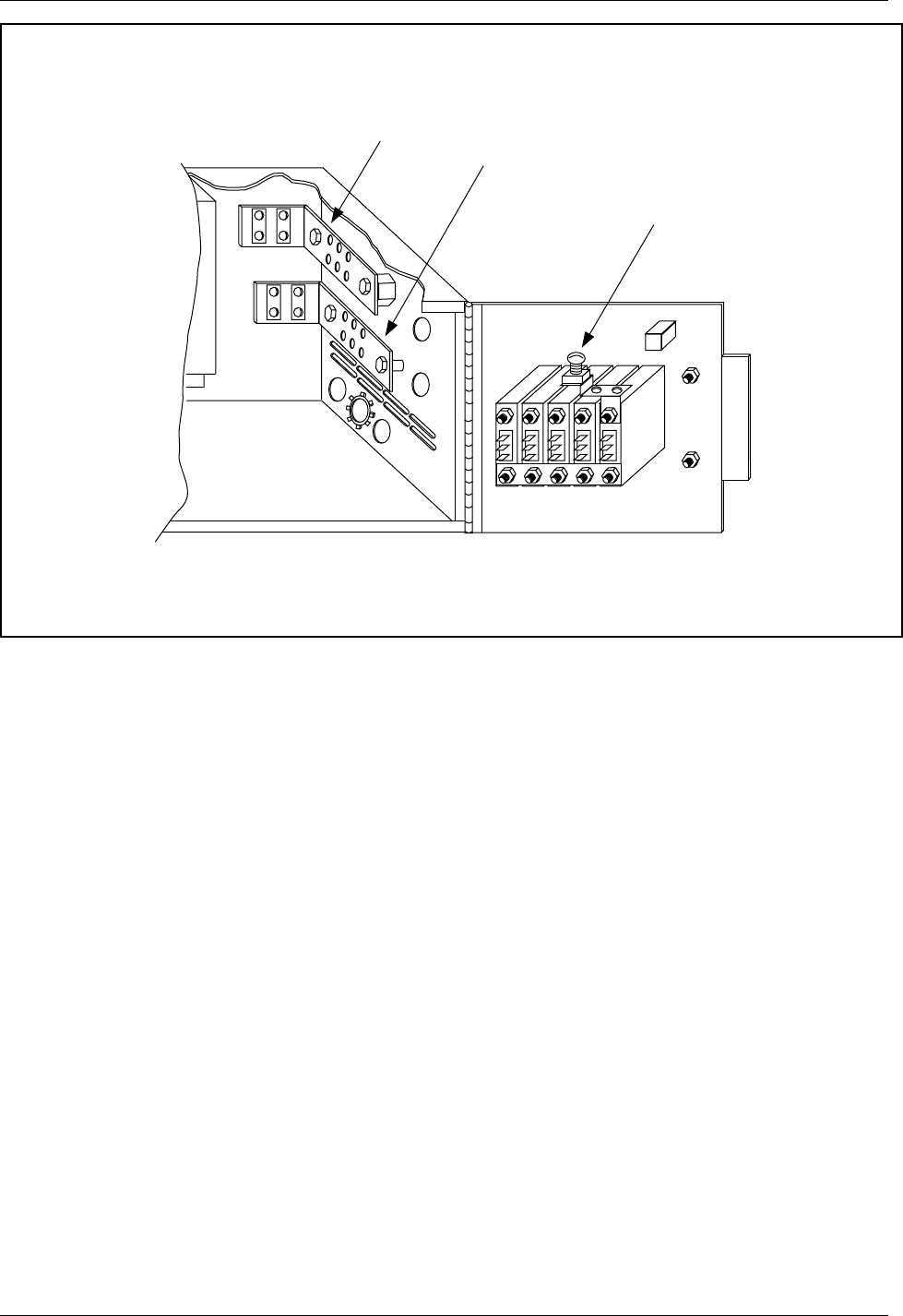
Installation
Neutral Bus
Ground Bus
Line Bus
Figure 4-15. AC/DC Distribution Box
9.4 Cable Installation
Each RBS 884 cabinet arrives on site with internal cables pre-installed.
These cables are described in the Internal Cables appendix in this manual.
This section describes installing external cables in the cabinet. Use the
procedure for one of the following types of installation:
•Pedestal (Pad) Mount, Section 9.4.1 on page 4-32
•Pole Mount, Section 9.4.2 on page 4-38
•Wall Mount, Section 9.4.3 on page 4-39
•Roof Mount, Section 9.4.4 on page 4-39
•Site Expansion, Section 17 on page 4-62
1/1551-EN/LZB 119 3312 Uae Rev A 1998-11-17 4-31
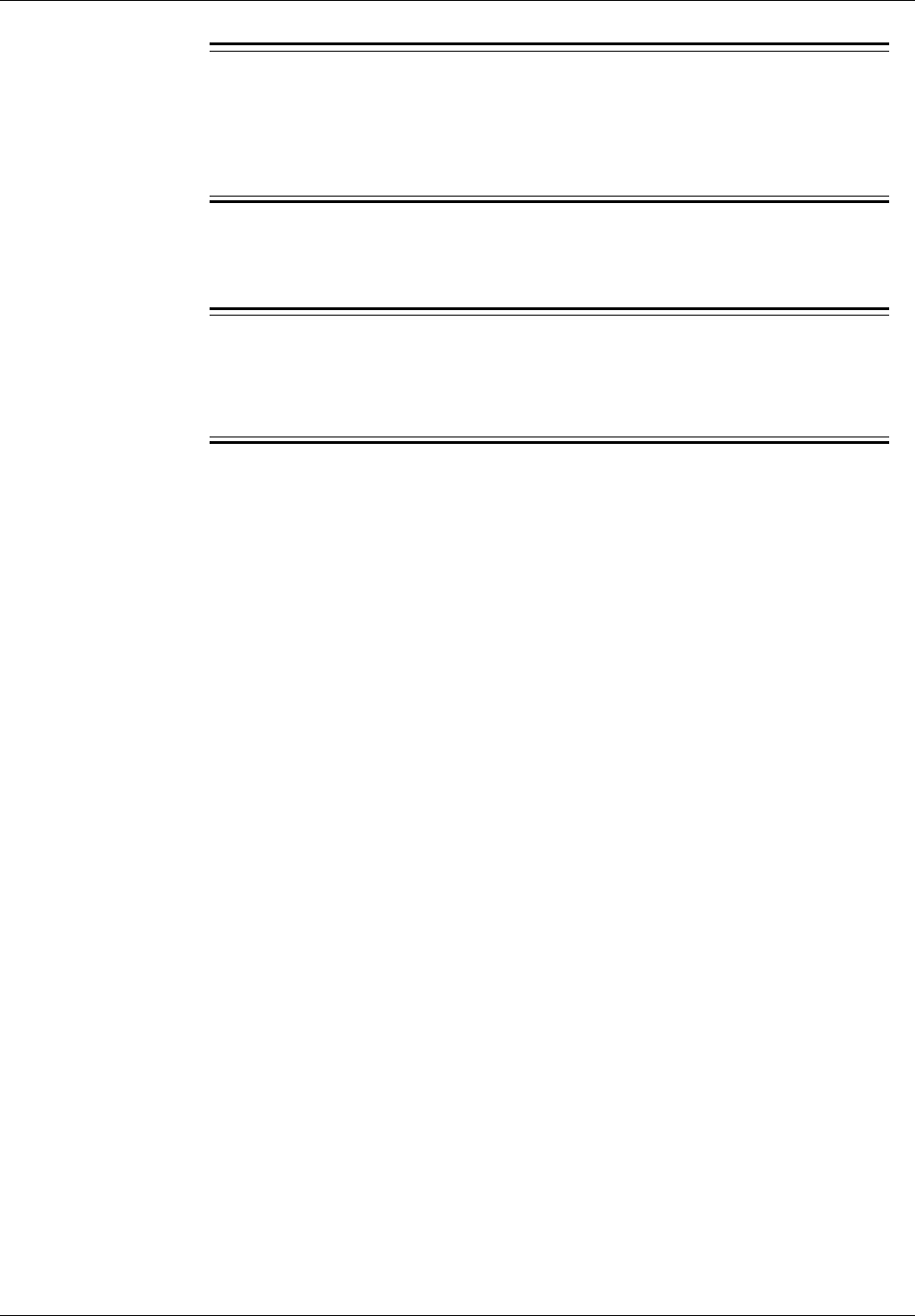
Installation
Caution!
Ensure all site grounding is installed and functioning before installing
cables. Observe all local safety precautions and wear all appropriate
locally approved safety equipment during installation procedures.
9.4.1 Pedestal Mount Cable Installation
Caution!
When installing coaxial cable or cable conduit, follow the minimum
bending radius requirements for the type of cable being installed.
To install cables in a cabinet with a pedestal mount, perform the following:
1. Using a tamper resistant wrench, remove the front panel from the
pedestal base so cables or conduit can be routed to the cabinet. See
Figure 4-17 on page 4-36
Note: This cable installation procedure is for above ground
conduit routing. Refer to the RBS 884 Site Engineering
Manual for information about below ground conduit
routing.
2. Route the T1(E1) conduit into the base of the cabinet. See Figure
4-17 on page 4-36 and Figure 4-18 on page 4-37.
3. Route the antenna cables into the base of the cabinet. See Figure
4-17 on page 4-36 and Figure 4-18 on page 4-37.
Note: When running antenna cables through the pedestal base
knockouts, protect the cables with strain relief
grommets or other appropriate materials.
4. Verify that the AC power conduit and earth ground have been
routed into the base of cabinet. See Figure 4-17 on page 4-36 and
Figure 4-18 on page 4-37.
5. Route the antenna jumper cables into the base of the cabinet and
connect them to the antenna connectors on the bottom of the
earthing plate. See Figure 4-18 on page 4-37.
6. Bond and ground the T1(E1) drop wires according to local
practices before installing them into the cabinet.
4-32 1/1551-EN/LZB 119 3312 Uae Rev A 1998-11-17
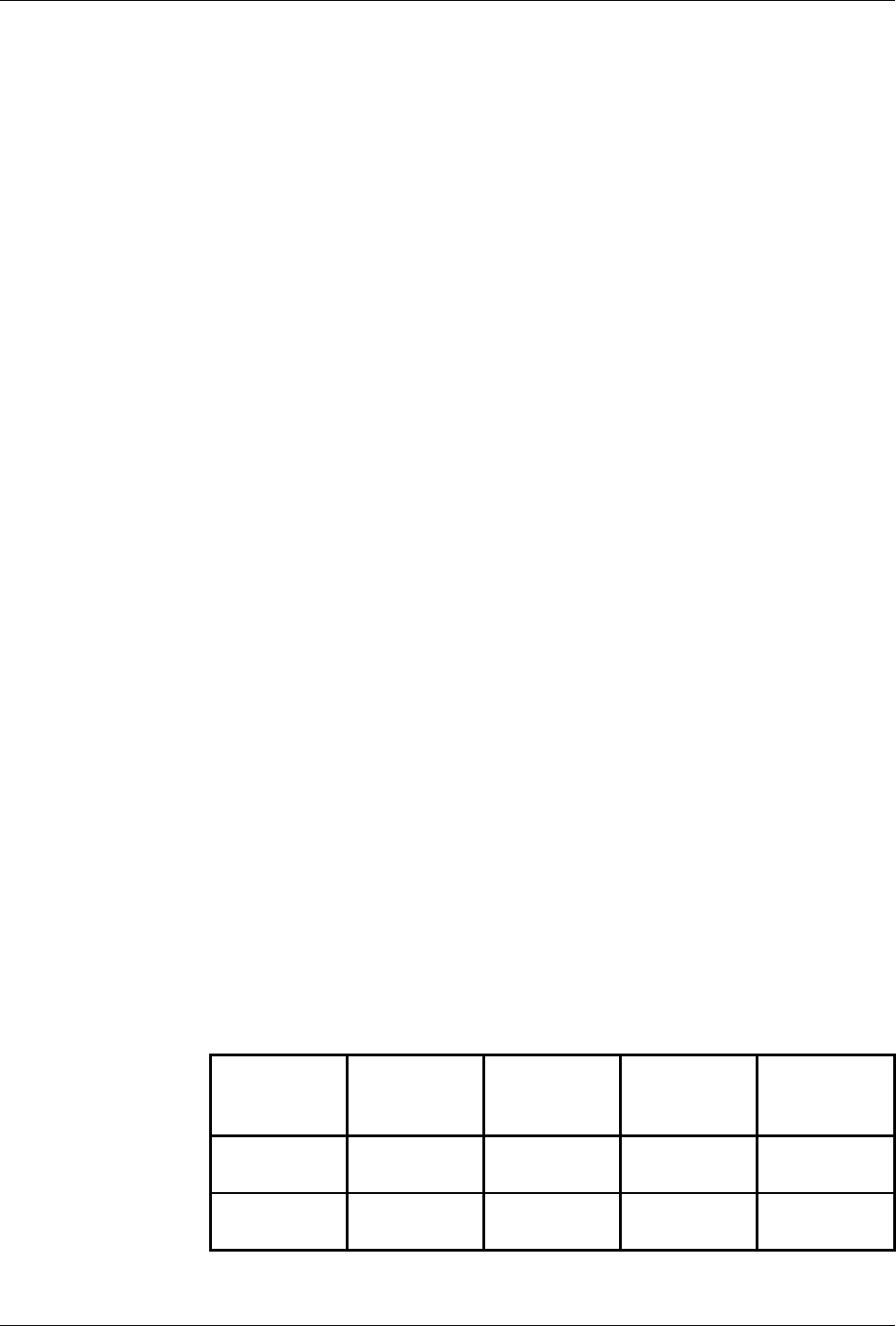
Installation
7. Route the T1(E1) cable through conduit into the base of the
cabinet. Connect cable to the T1(E1) Primary Surge Suppressor
located on the right-hand side of the cabinet. See Figure 4-16 on
page 4-35 for further information on this procedure. See Figure 4-
19 on page 4-38 for a close-up view of the T1(E1) Primary Surge
Suppressor and Table 4-5 on page 4-33 for information on the
input connections. Note that the connector block is grounded to the
I/O plate at the factory.
Note: The hex-nut activators on the T1(E1) Primary Surge
Suppressor block are colored white for tip wires and
orange for ring. The large ports under the activator
clock accommodate 18.5 to 20 AWG wire termination.
The small ports accommodate 22 to 24 AWG wire
termination. Wire stripping or staggering is not needed
when using the T1(E1) Primary Surge Suppressor
block. The Primary Surge Suppressor provides
straight-through access for wire terminations.
8. Trim the ends of the wire. Split the drop leads approximately two
inches. Using a standard 216–type wrench, carefully back off the
activator screw until you feel a stop. The wrench will lift up
approximately 1/4–inch into the open position.
9. Insert the wire into the large or small port on the side of the
activator. Tighten the hex nut on the top of the activator until the
tensions stops. Do not overtighten.
10. If testing or if a talk pair is needed, insert test leads into the hex
nut on the appropriate activator.
11. To reinstall wires, trim the wire ends and split the drop wire leads
approximately two inches and terminate according to the above
procedure.
12. After wiring, keep all activators in the down position for good
housekeeping.
13. After all cables are installed, turn on the AC power.
14. Watch the Power Light Emitting Diodes (LEDs) on each board and
verify the unit is operating properly. Consult the troubleshooting
section in the Hardware Replacement part of this manual for units
that are malfunctioning.
Table 4-5. T1(E1) Input Connections to Primary Surge Suppressor
Terminal No.
REMUX
Connector
Port
T1(E1) Cable T1(E1) Pair
No. Wire
1 (white) PCM/Prim Transmit to
Network
1Tip
1 (orange) PCM/Prim Transmit to
Network
1Ring
1/1551-EN/LZB 119 3312 Uae Rev A 1998-11-17 4-33
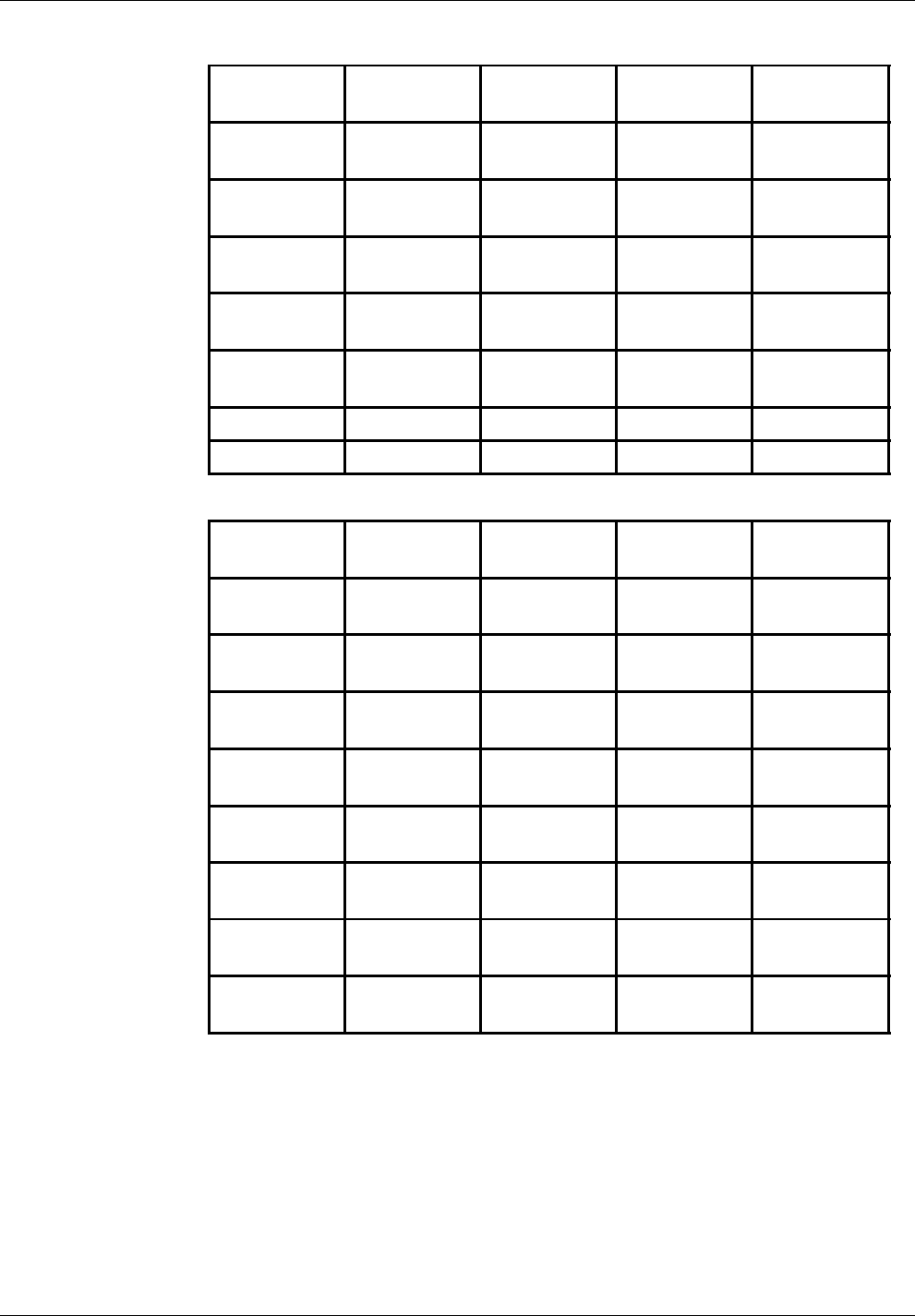
Installation
Table 4-5. T1(E1) Input Connections to Primary Surge Suppressor (Continued)
2 (white) PCM/Prim Receive from
Network
2Tip
2 (orange) PCM/Prim Receive from
Network
2 Ring
3 (white) PCM/Sec Transmit to
Network
1Tip
3 (orange) PCM/Sec Transmit to
Network
1 Ring
4 (white) PCM/Sec Receive from
Network
2Tip
4 (orange) PCM/Sec Receive from
Network
2 Ring
5 (white) Not used
5 (orange) Not used
Table 4-6. T1 Output Connections to Primary Surge Suppressor
RJ45 Conn Pin No. T1(E1) Cable T1(E1) Pair
No. Wire
J1 5Transmit to
Network
1Tip
J1 4Transmit to
Network
1Ring
J1 1 Receive from
Network
2 Ring
J1 2Receive from
Network
2Tip
J2 5Transmit to
Network
1Tip
J2 4Transmit to
Network
1Ring
J2 1Receive from
Network
2Ring
J2 2Receive from
Network
2Tip
4-34 1/1551-EN/LZB 119 3312 Uae Rev A 1998-11-17
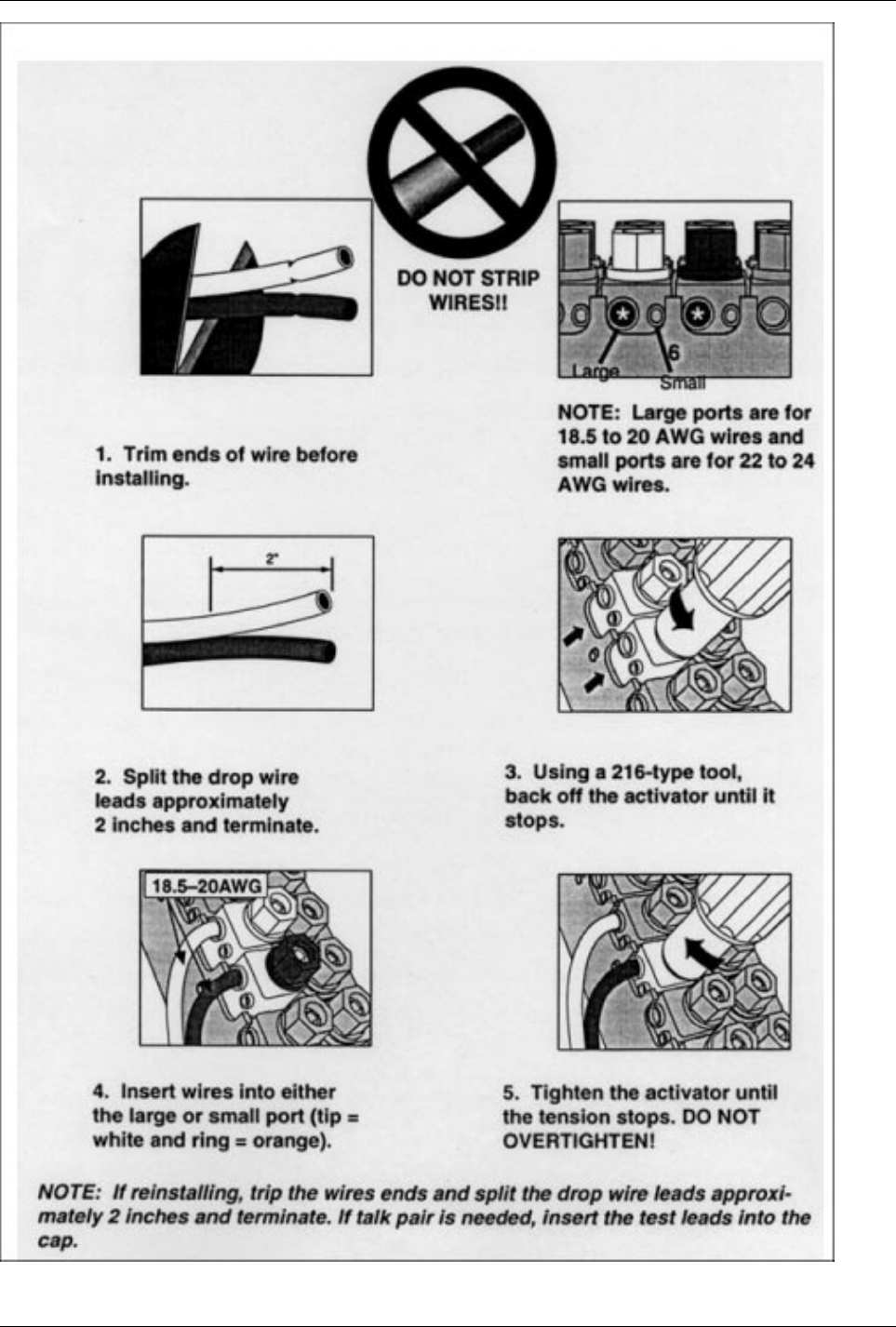
Installation
Figure 4-16. Terminating Wires in T1 Surge Protector
1/1551-EN/LZB 119 3312 Uae Rev A 1998-11-17 4-35
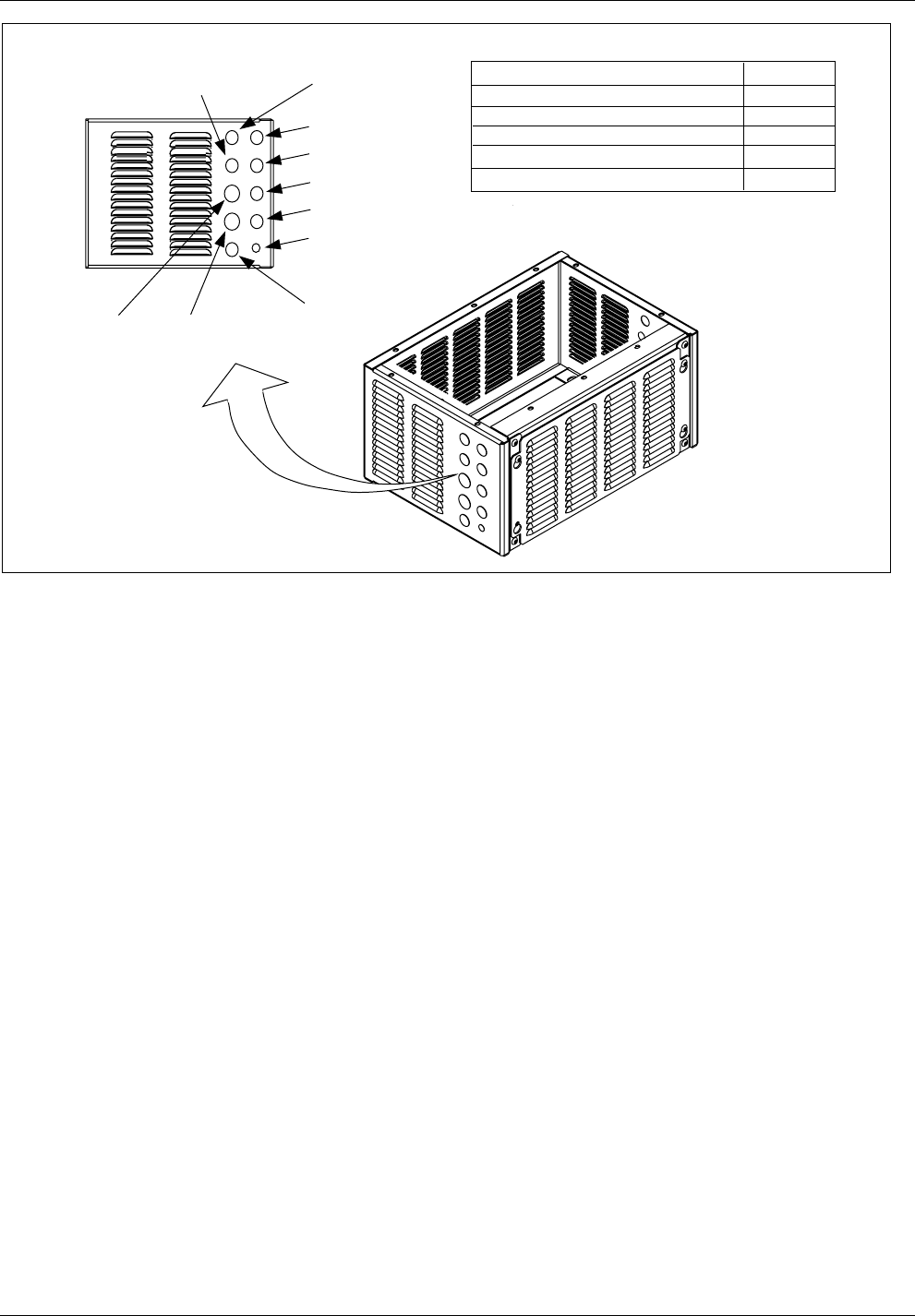
Installation
Antenna 3
Primary 2Primary 1
Antenna 2
Antenna 1
Antenna 4
AC Power
DC Battery
Back-Up
T1(E1) Line
Cabinet
Ground
Right Side
HOLE DIAMETERS
Primary 1 and 2
Antennas
Power
35.05
28.70
28.70
12.70
mm inches
1.38
1.13
1.13
.50
Cabinet Ground
T1(E1) Line
35.05 1.38
Figure 4-17. Pedestal Mount
4-36 1/1551-EN/LZB 119 3312 Uae Rev A 1998-11-17
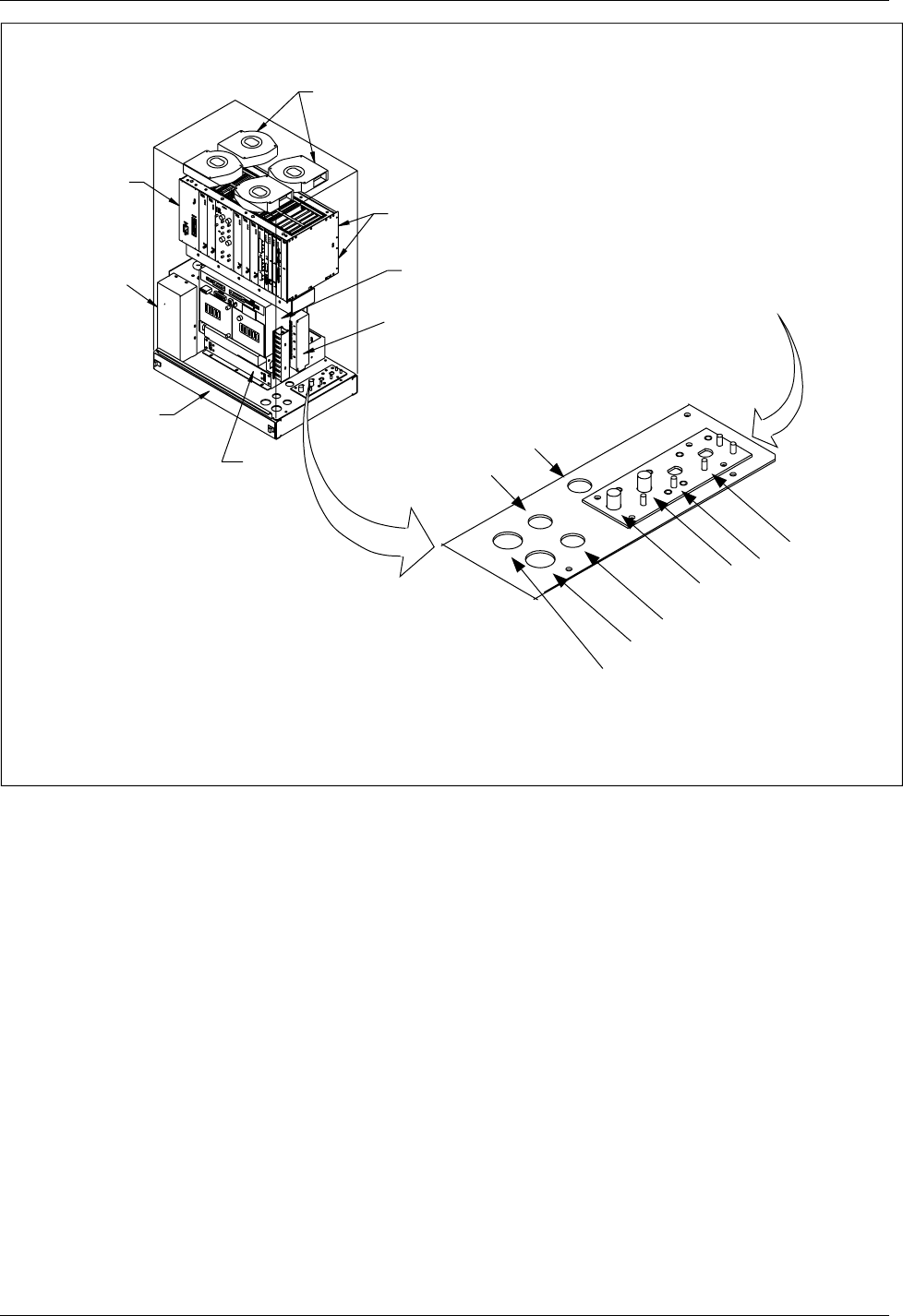
Installation
Antenna 4
Antenna 3
Antenna 2
Antenna 1
AC Power
External
Battery
PCM T1(E1)
Primary 1
Primary 2
Note: Conduit openings in I/O plate fit 3/4" and 1"
liquid-tight flexible conduit.
Battery
Compartment
(2 batteries)
Fans (4)
Backplanes
AC/DC Power
Subrack
with Plug-in
Units
Air Filter
Access Panel
Heater
Primary T1(E1) Surge
Suppressor
Earth ground
connections
below I/O plate
Figure 4-18. Cabinet I/O Plate
1/1551-EN/LZB 119 3312 Uae Rev A 1998-11-17 4-37
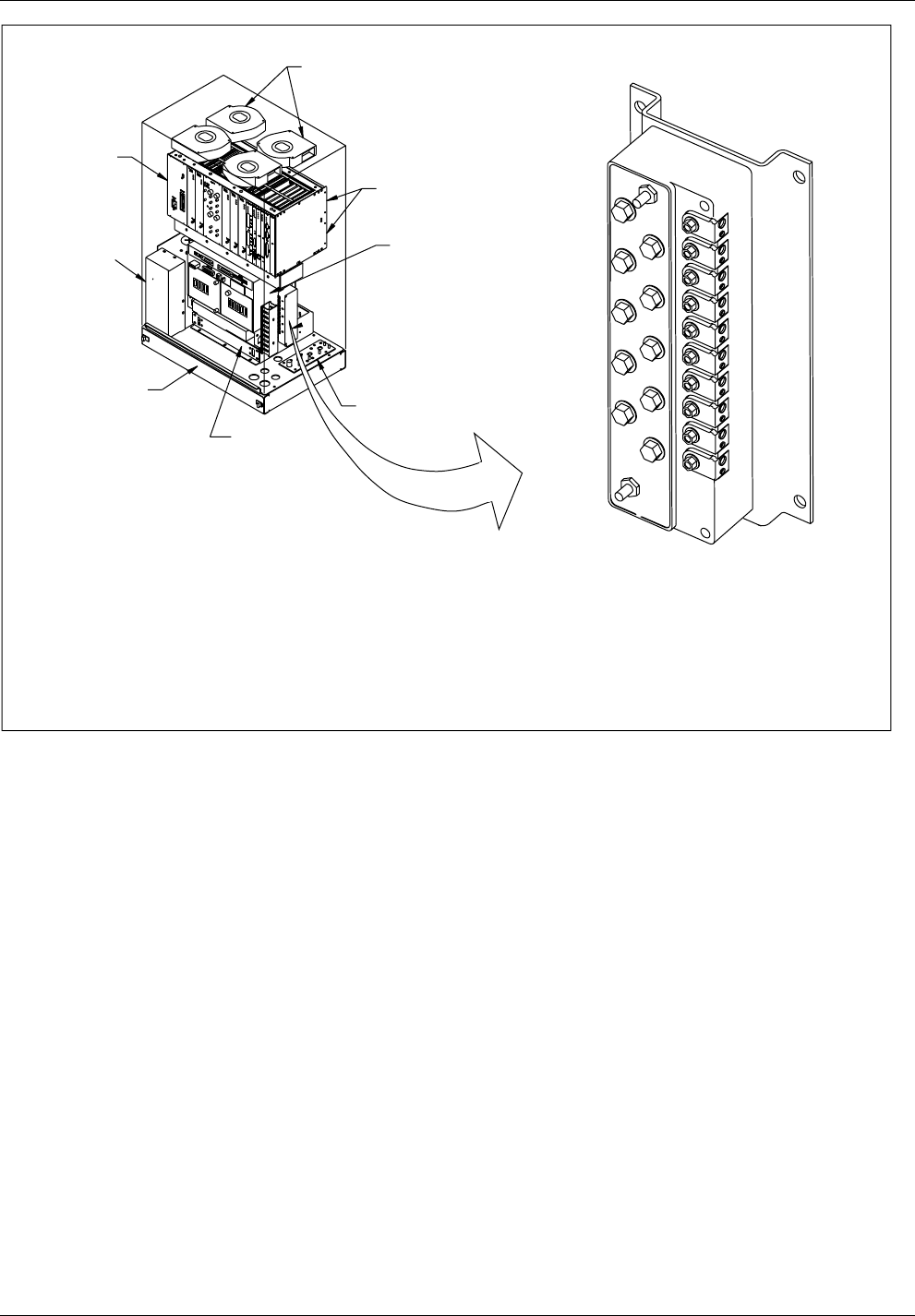
Installation
T1(E1) Primary Surge Suppressor
12345
Battery
Compartment
(2 batteries)
Fans (4)
Backplanes
AC/DC Power
Subrack
with Plug-in
Units
Air Filter
Access Panel
Heater
Ground Plate
Figure 4-19. T1(E1) Primary Surge Suppressor
9.4.2 Pole Mount Cable Installation
1. Route the antenna cable and T1(E1) conduit into bottom of cabinet.
The T1(E1) conduit is terminated at the I/O plate.
2. Slide heat shrink tubing over cable connector and connect the
antenna jumpers to the antenna surge suppressors on I/O plate.
3. Apply heat to heat-shrink tubing to seal connector.
4. Route T1(E1) cables through conduit and connect the cables to the
surge protector. Refer to Table 4-5 on page 4-33.
5. After all cables are installed, turn on the AC power.
6. Watch the LEDs on each board and verify the unit is operating
properly. Consult the Troubleshooting section in the Hardware
Replacement part of this manual for units that are malfunctioning.
4-38 1/1551-EN/LZB 119 3312 Uae Rev A 1998-11-17
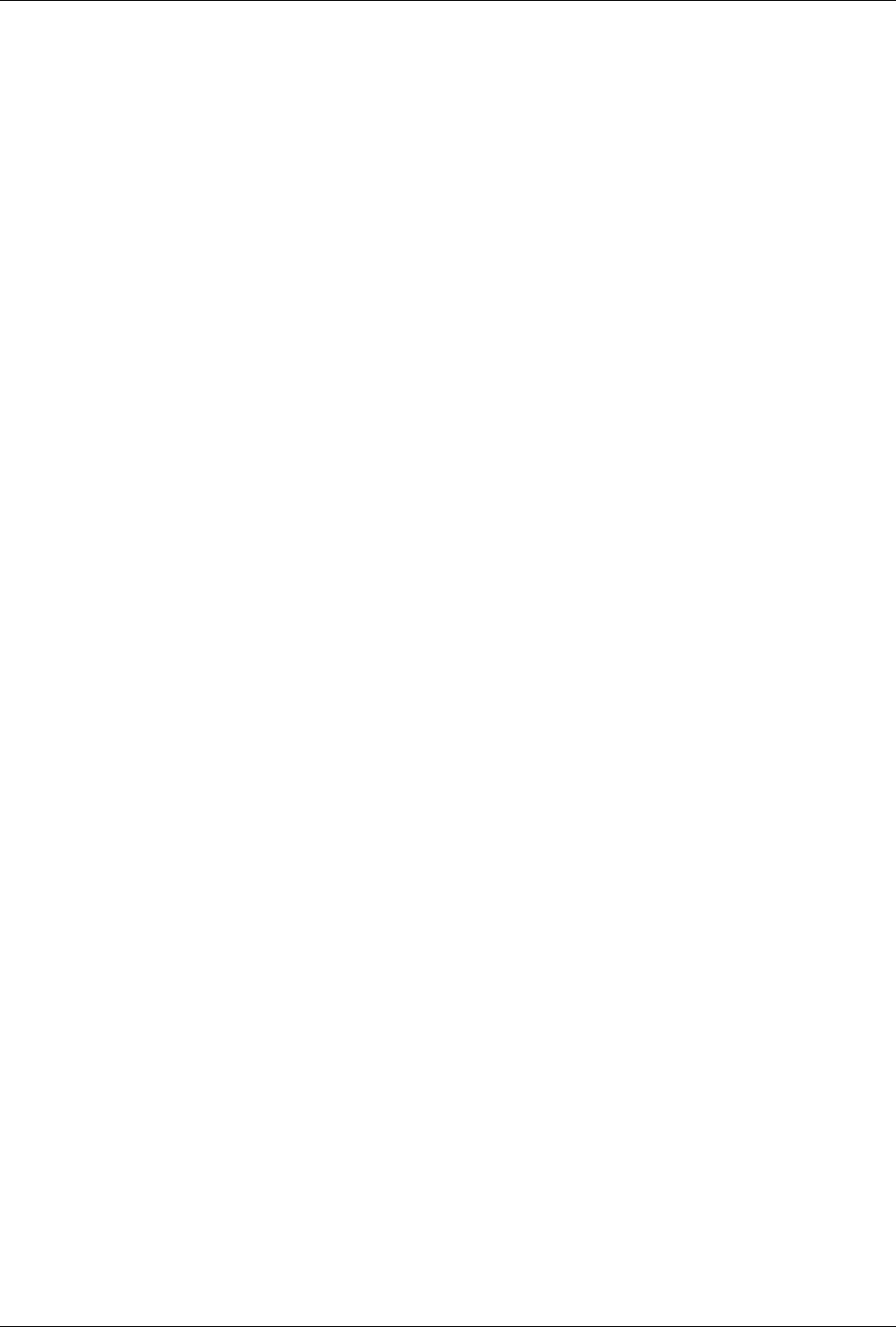
Installation
9.4.3 Wall Mount Cable Installation
1. Route the antenna cable and T1(E1) conduit into bottom of cabinet.
The T1(E1) conduit is terminated at the I/O plate.
2. Slide heat shrink tubing over cable connector and connect the
antenna jumpers to the antenna surge suppressors on I/O plate.
3. Apply heat to heat-shrink tubing to seal connector.
4. Route T1(E1) cables through conduit and connect the cables to the
surge protector. Refer to Table 4-5 on page 4-33.
5. After all cables are installed, turn on the AC power.
6. Watch the LEDs on each board and verify the unit is operating
properly. Consult the Troubleshooting part in the Hardware
Replacement part of this manual that are malfunctioning.
9.4.4 Roof Mount Cable Installation
Cabling of the roof mounted cabinet depends on the type of mounting kit
being used. Any of the three mounting kits, pedestal, pole, or wall, may be
used for the roof mount. Refer to the specific cable installation instructions
in this section for pedestal, pole, or wall mountings.
10 Setting the Unit Switches
Before the RBS 884 Micro (1900 MHz) is powered up, the REMUX and
EMRPM switches must be set. This section describes the procedure for
setting the REMUX and EMRPM switches.
Prior to starting, review electrostatic discharge instructions in Section 3 on
page 4-5.
For information on removing the REMUX or EMRPM, refer to the
Hardware Replacement part of this manual.
The units are shown in Figure 4-20 on page 4-40.
1/1551-EN/LZB 119 3312 Uae Rev A 1998-11-17 4-39

Installation
PCM
Test
TLINK
1
TLINK
2
TLINK
3
TLINK
4
REMUX
Power
Error
V24
PCM
Prim
PCM
Sec
AFS
In
AFS
Out
Status 1
Status 2
Slot for Unit
Extractor Tool
REMUX
Unit EMRPM
Unit
REMUX
Unit
NOTE: Before inserting Unit Extractor Tool,
remove extractor hole plug and set aside. Reinstall
plug after unit removal.
Figure 4-20. Cabinet Units for Switch Settings (Example with a Main Cabinet)
10.1 Prerequisites and Tools
10.1.1 Prerequisites
The following site specific data for setting the switches on the units must be
available in the Configuration Data in the Site Installation Documentation:
•PCM line impedance
•PCM primary line specification (length or attenuation)
•PCM secondary line specification (length or attenuation)
•PCM primary line code and frame mode
•PCM secondary line cascading
•Control Signaling Link (CLC) extraction time slot
•PCM jitter and wander limit
•Frequency
4-40 1/1551-EN/LZB 119 3312 Uae Rev A 1998-11-17
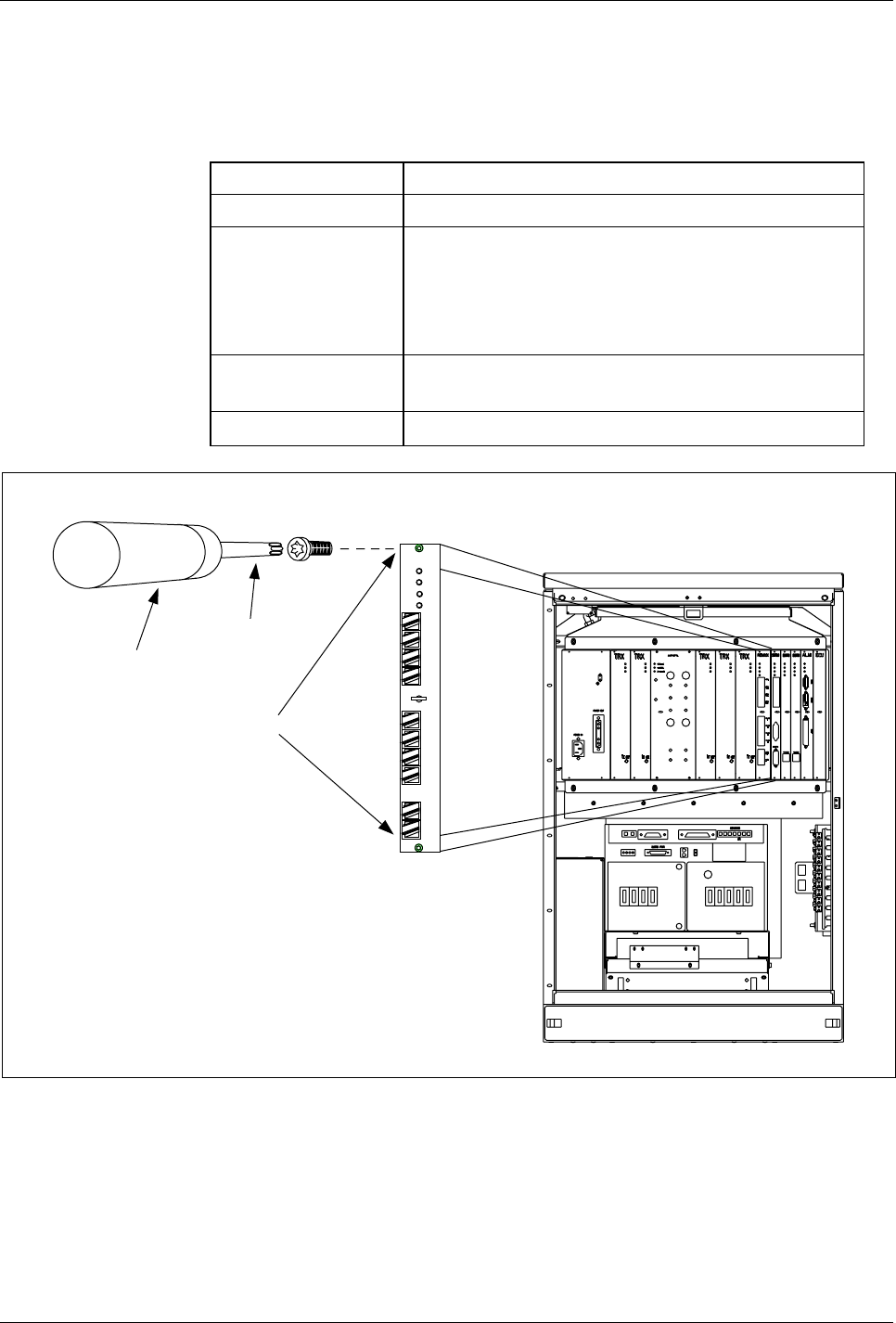
Installation
10.1.2 Tools
The tools shown in Table 4-7 on page 4-41 are required for setting unit
switches.
Table 4-7. Tools for Setting the Unit Switches
Product Number Description
LYB 250 01/14 ESD Wrist Strap and Cable
LTT 601 82 From Torque Wrench set:
-Torque Wrench for torque 0.6 Nm
(to use with the Torx bit TX10)
-Torx bit TX10
(for the unit screws)
LTD 117 02 and
LTD 117 12
Unit Extractor Tool (Handle + Button)
Small screwdriver, pen, or simular tool to set switches
Torx Bit TX10
Torque Wrench
Unit Screws
REMUX
Power
Error
V24
PCM
Prim
PCM
Sec
AFS
In
AFS
Out
Status 1
Status 2
Figure 4-21. Torque Wrench with Torx TX10 Bit
10.2 REMUX Switch Settings
1. Attach the ESD strap to your wrist and connect the free end of the
strap cable to an appropriate ground conductor in the cabinet.
1/1551-EN/LZB 119 3312 Uae Rev A 1998-11-17 4-41
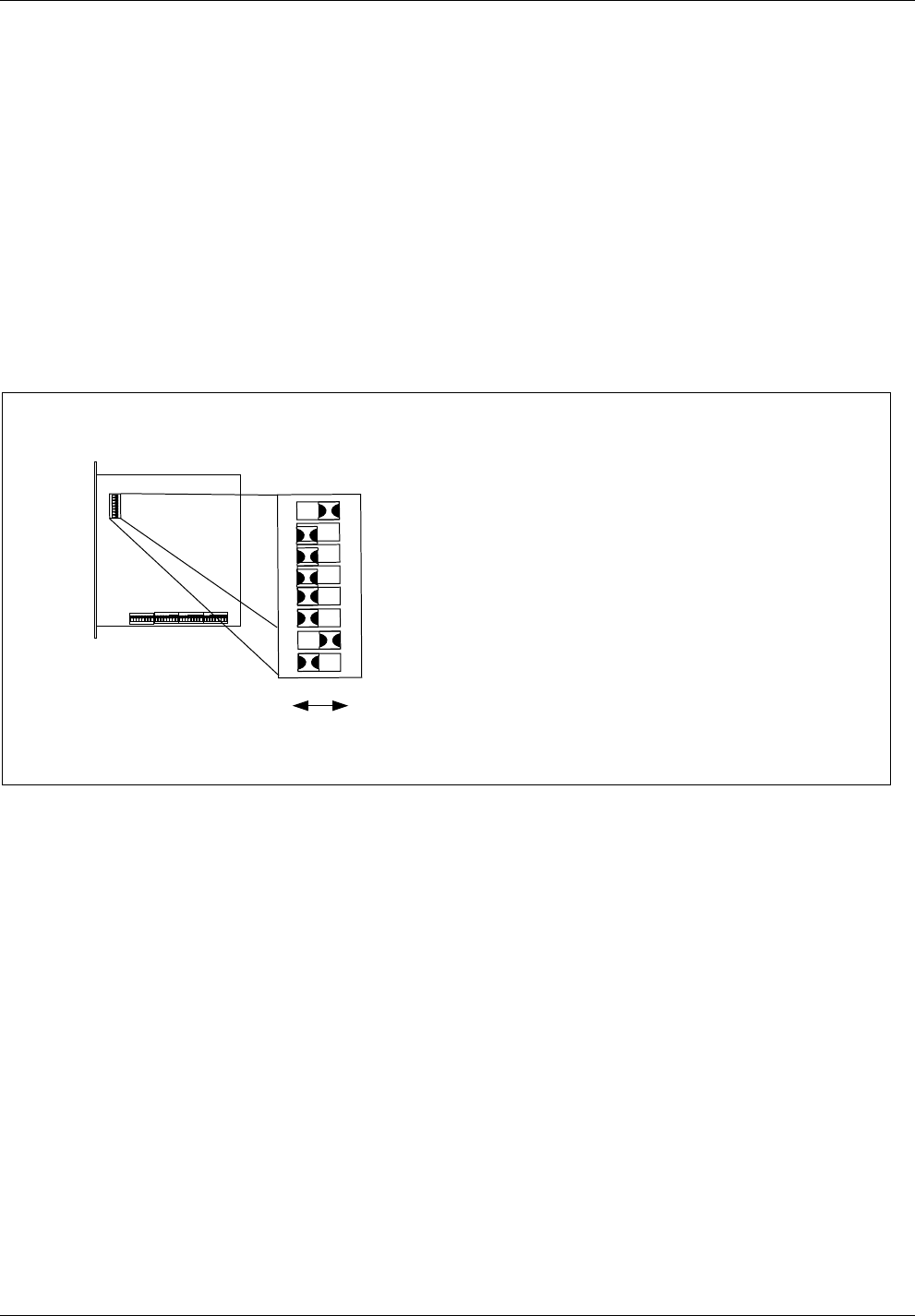
Installation
2. Use the torque wrench with the Torx TX10 to loosen the top and
bottom screws on the front of the REMUX unit.
Note: Do not touch any components or connector pins on
a circuit board.
3. Remove the REMUX unit from the cabinet using the extractor tool
as shown in Figure 4-20 on page 4-40. Save the extractor hole plug
and replace plug after installing the REMUX unit.
4. Locate the eight-pole DIP switch at the top front of the REMUX unit.
5. Set the unit to the PCM line impedance by setting the switches as
shown in Figure 4-22 on page 4-42. The line impedance can be found
in the Configuration Data in the Site Installation Documentation.
12345678
ON
10
Top
12345678
ON
Front Line Impedance Switch Settings (1-8)
75 ohm (E1) 0111 1101
100 ohm (T1) 1011 1110
120 ohm (E1) 0000 0000
REMUX Boards
ROF 367 211/3
ROF 367 211/1
ROF 367 211/3
PCM Line Impedance
Note: This example shows the REMUX set for 100 ohm line impedance (T1)
Figure 4-22. Setting the PCM Line Impedance
6. Locate the 32-pole DIP switch at the bottom of the REMUX unit.
Note: When a DIP switch is in its lower position (with
the REMUX board oriented as shown in Figure
4-22 on page 4-42), the value is 0 (zero).
7. Check with the Configuration Data in the Site Installation
Documentation to determine whether the settings for the PCM
Primary line are decided by the length, attenuation, or impedance of
the line. Set the switches for the appropriate use as follows:
•If line length is used (T1 Short Haul), see Figure 4-23 on
page 4-43.
•If impedance is used (for E1 transmission, and T1 Federal
Communications Commission [FCC] Part 68, Option A), see
Figure 4-24 on page 4-43.
Note: For distances exceeding 40 meters, customer
supplied CSU should be used.
4-42 1/1551-EN/LZB 119 3312 Uae Rev A 1998-11-17
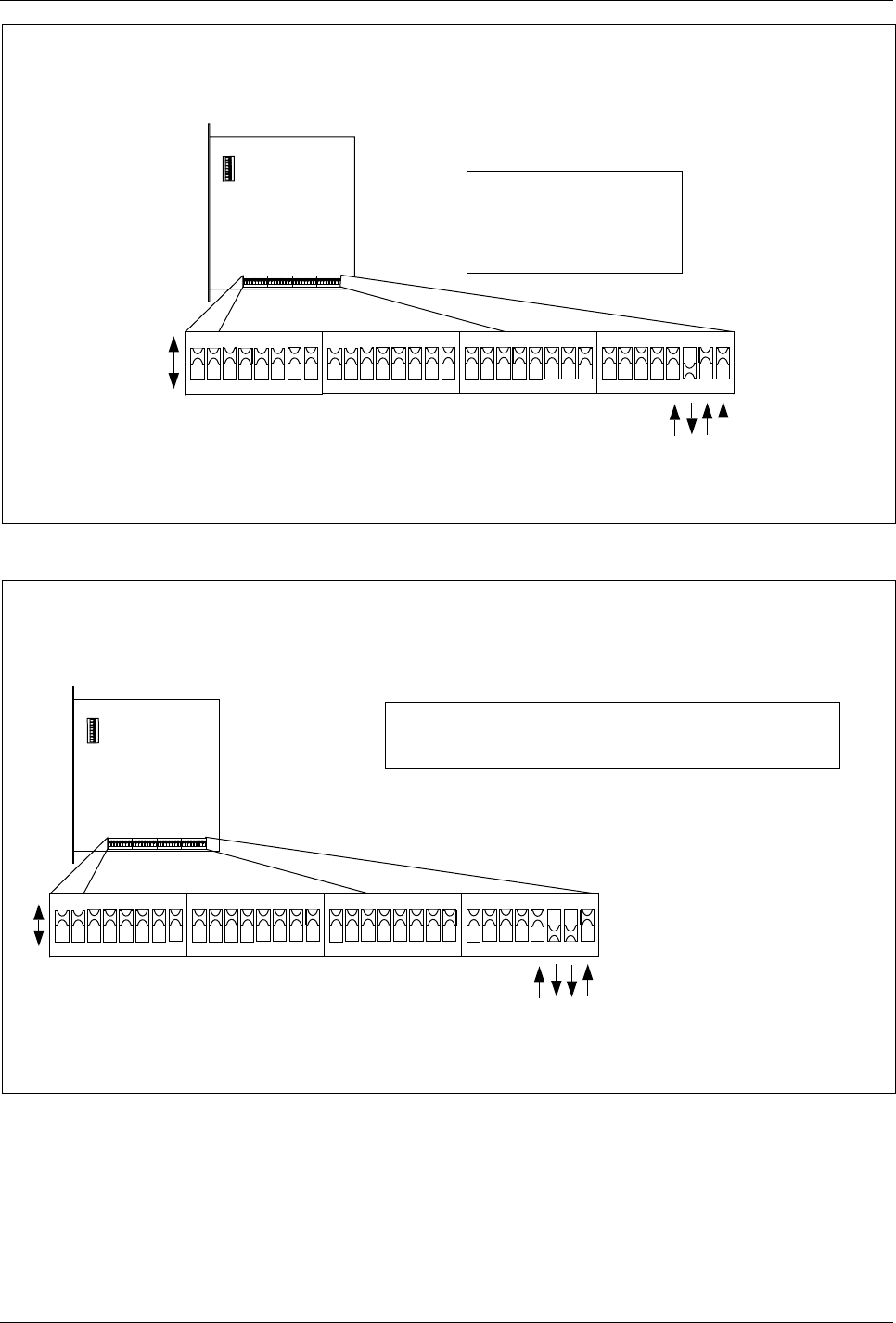
Installation
PCM Primary Line Specification for T1 Short Haul (SH)
Top
12345678
ON
Front
1
0
1 0 1 1
0 to 40 meters => 1011
40 to 80 meters => 1100
80 to 120 meters => 1101
120 to 160 meters => 1110
160 to 200 meters => 1111
Line Length
(REMUX boards ROF 367 211/1, /3)
This example shows the REMUX set for a T1 Short Haul line
up to 40 meters in length, connected to PCM Primary.
Note:
Figure 4-23. Settings for the PCM Primary Line Specification, T1 Short Haul
Note: This example shows the REMUX set for an E1 line with
120 ohm impedance, connected to PCM Primary.
1
0
1 0 0 1
Top
12345678
ON
Front
PCM Primary Line Specification for E1 and T1
75 ohm (E1) => 1000 (ROF 367 211/3)
120 ohm (E1) => 1001 (ROF 367 211/3)
100 ohm (T1 FCC part 68, opt A) => 1010 (ROF 367 211/1)
Line Impedance
Figure 4-24. Settings for the PCM Primary Line Specification, E1 and T1
8. Check with the Configuration Data in the Site Installation
Documentation to determine whether the settings for the PCM
1/1551-EN/LZB 119 3312 Uae Rev A 1998-11-17 4-43
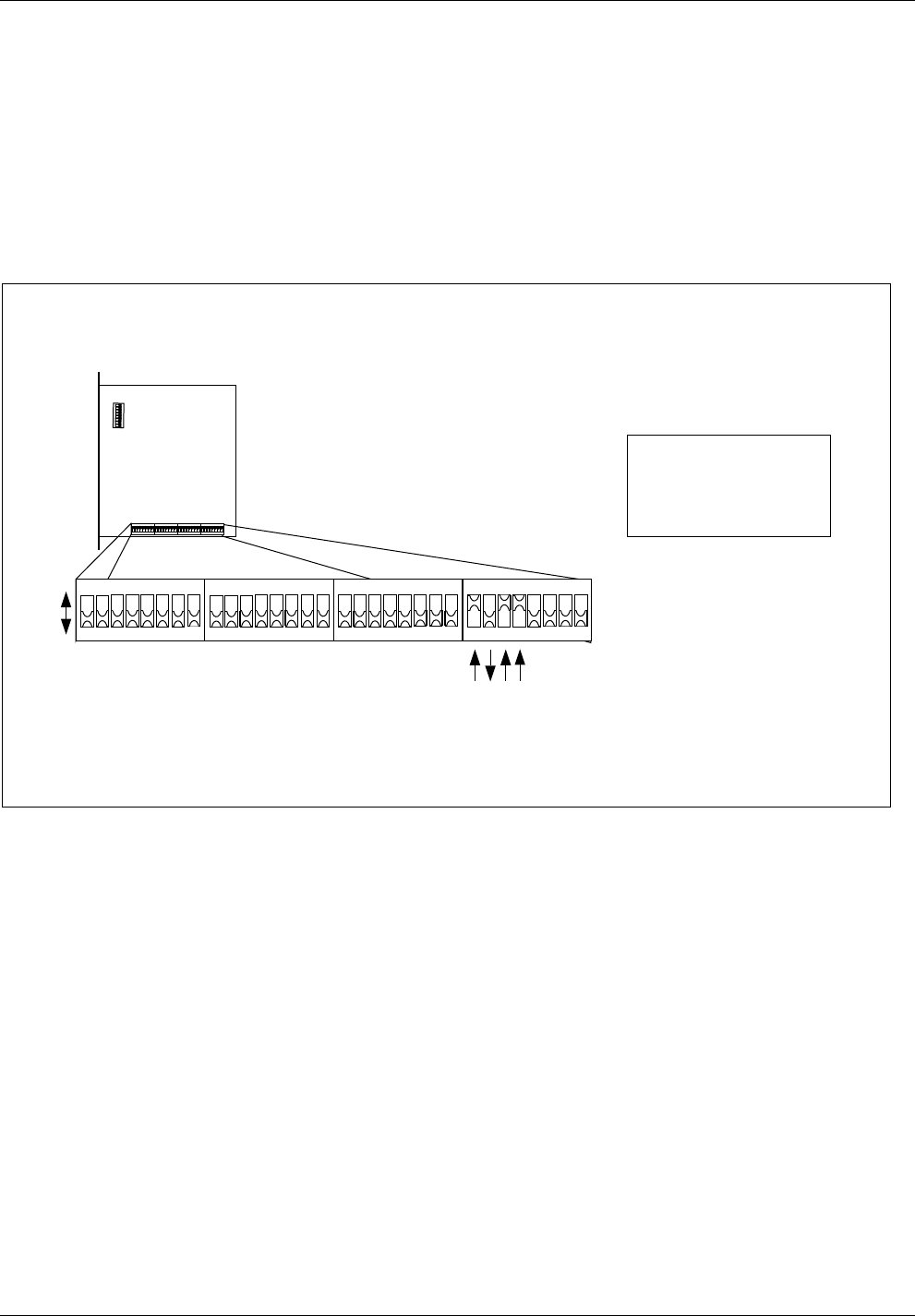
Installation
Secondary line are decided by the length, attenuation, or impedance
of the line. Set the switches for the appropriate use as follows:
•If line length is used (T1 Short Haul), see Figure 4-25 on
page 4-44.
•If impedance is used (for E1 transmission, and T1 FCC Part
68, Option A), see Figure 4-26 on page 4-45.
Note: For distances exceeding 40 meters, customer
supplied CSUs should be used.
1
0
1 0 1 1
Top
12345678
ON
12345678
ON
12345678
ON
12345678
ON
12345678
ON
Front
PCM Secondary Line Specification for T1 Short Haul (SH)
This example shows the REMUX set for a T1 Short Haul line
up to 40 meters in length, connected to PCM Secondary.
Note:
0 to 40 meters => 1011
40 to 80 meters => 1100
80 to 120 meters => 1101
120 to 160 meters => 1110
160 to 200 meters => 1111
Line Length
(for REMUX boards
ROF 367 211/1, /3)
Figure 4-25. Settings for the PCM Secondary Line Specification, T1 Short Haul
4-44 1/1551-EN/LZB 119 3312 Uae Rev A 1998-11-17
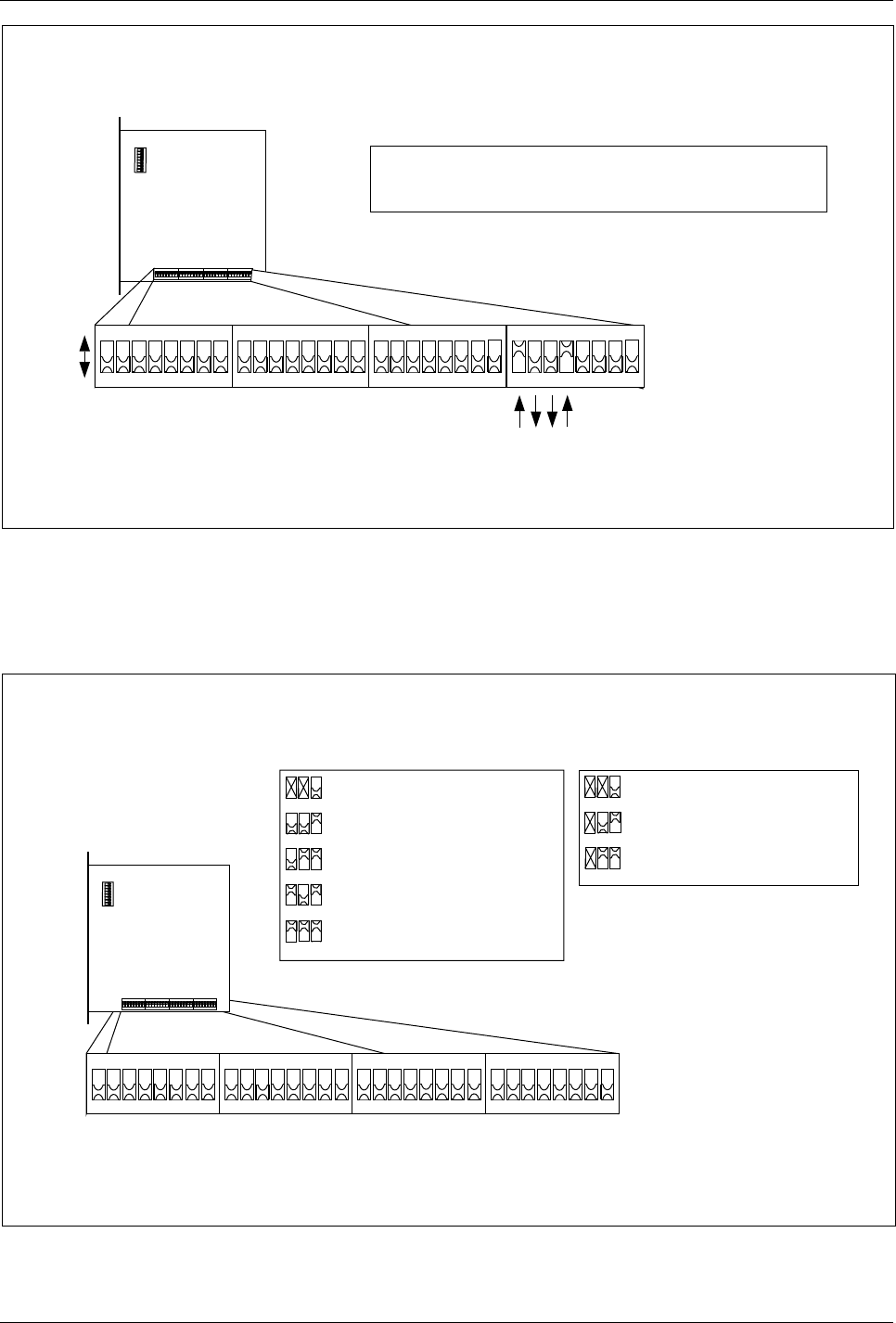
Installation
PCM Seconday Line Specification for E1 and T1
Top
12345678
ON
12345678
ON
12345678
ON
12345678
ON
12345678
ON
Front
1
0
1 0 0 1
Note: The example shows the REMUX set for an E1 line with
120 ohm impedance, connected to PCM Secondary.
Line Impedance
75 ohm (E1)
120 ohm (E1)
100 ohm (T1 FCC part 68, opt A)
=> 1000 (ROF 367 211/3)
=> 1001 (ROF 367 211/3)
=> 1010 (ROF 367 211/1)
Figure 4-26. Settings for the PCM Secondary Line Specification, E1 and T1
9. Set the PCM primary line code and frame mode, as shown in Figure
4-27 on page 4-45, in accordance with the Configuration Data in the
Site Installation Documentation.
PCM Primary Line Code and Frame Mode
Top
12345678
ON
12345678
ON
12345678
ON
12345678
ON
12345678
ON
Front
This example shows the REMUX set for automatic adaptation to line code
and frame mode on the line connected to PCM Primary (T1 or E1).
Note:
= Alternate Mark Inversion (AMI)
and Super Frame
= Bit 8 Zero Substitute (B8ZS)
and Super Frame
= Alternate Mark Inversion (AMI)
and Extended Super Frame
= Bit 8 Zero Substitute (B8ZS)
and Extended Super Frame
= Automatic Adaptation to PCM
(X = 0 or 1)
1
2
4
1
2
4
1
2
4
1
2
4
1
2
4
T1
= Double Frame (DF)
= Cyclic Redundancy Check
(CRC) Multi Frame
= Automatic Adaptation to PCM
(X = 0 or 1)
1
2
4
1
2
4
1
2
4
E1
Figure 4-27. Setting for PCM Primary Line Code and Frame Mode
1/1551-EN/LZB 119 3312 Uae Rev A 1998-11-17 4-45
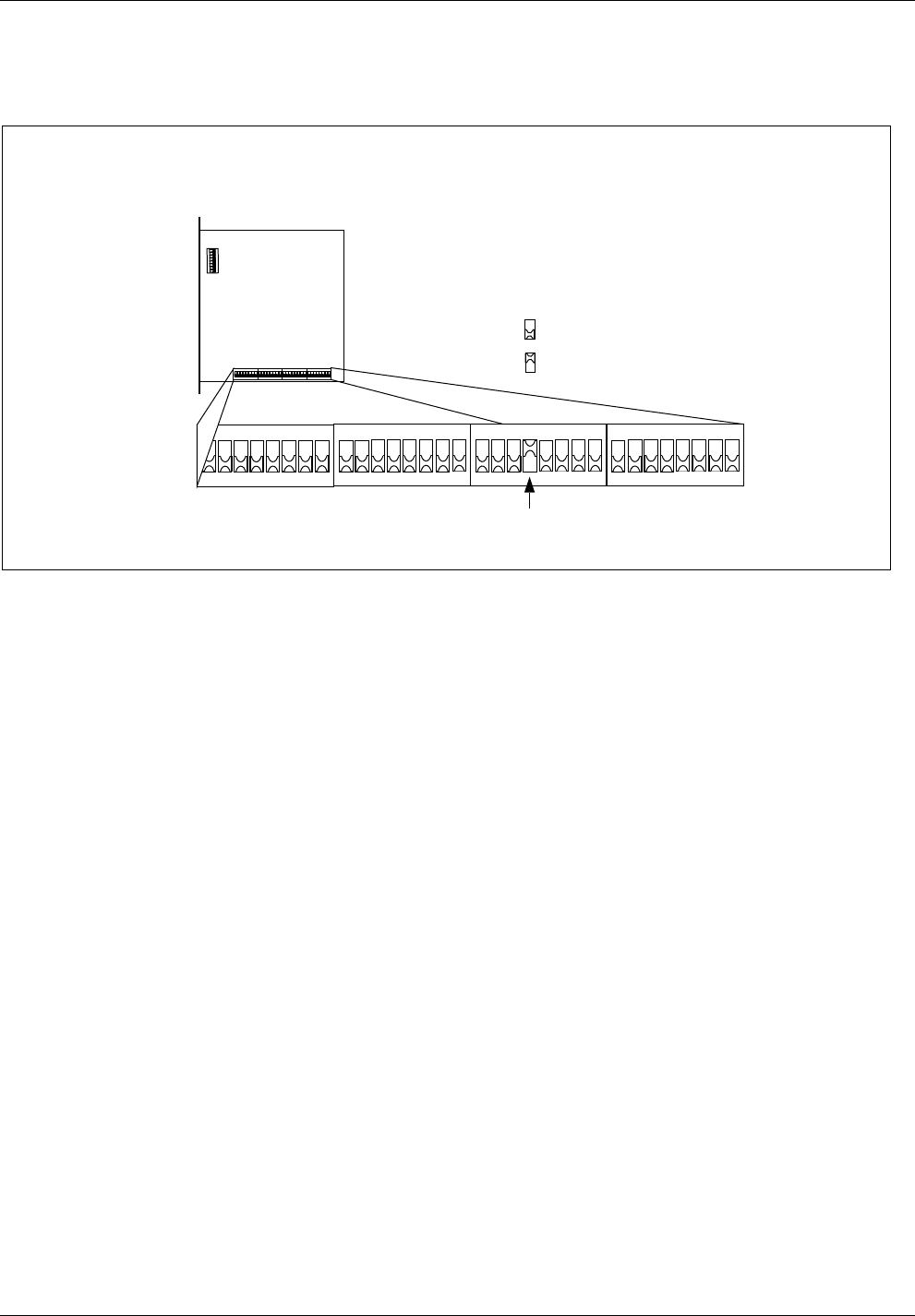
Installation
10. Set the switch to enable or disable the PCM secondary line for
cascading, as shown in Figure 4-28 on page 4-46 in accordance with
the Configuration Data in the Site Installation Documentation.
PCM Secondary Line Cascading
= Cascading enabled
= Cascading disabled
Top
12345678
ON
Front
Note: This example shows the REMUX set to enable the
PCM Secondary line for cascading.
Figure 4-28. Enabling/Disabling the PCM Secondary Line for Cascading
11. For an E1 PCM line, select the timeslot (TS) for Control signaling
Link (CLC) extraction, as shown in Figure 4-29 on page 4-47 in
accordance with the Configuration Data in the Site Installation
Documentation.
4-46 1/1551-EN/LZB 119 3312 Uae Rev A 1998-11-17
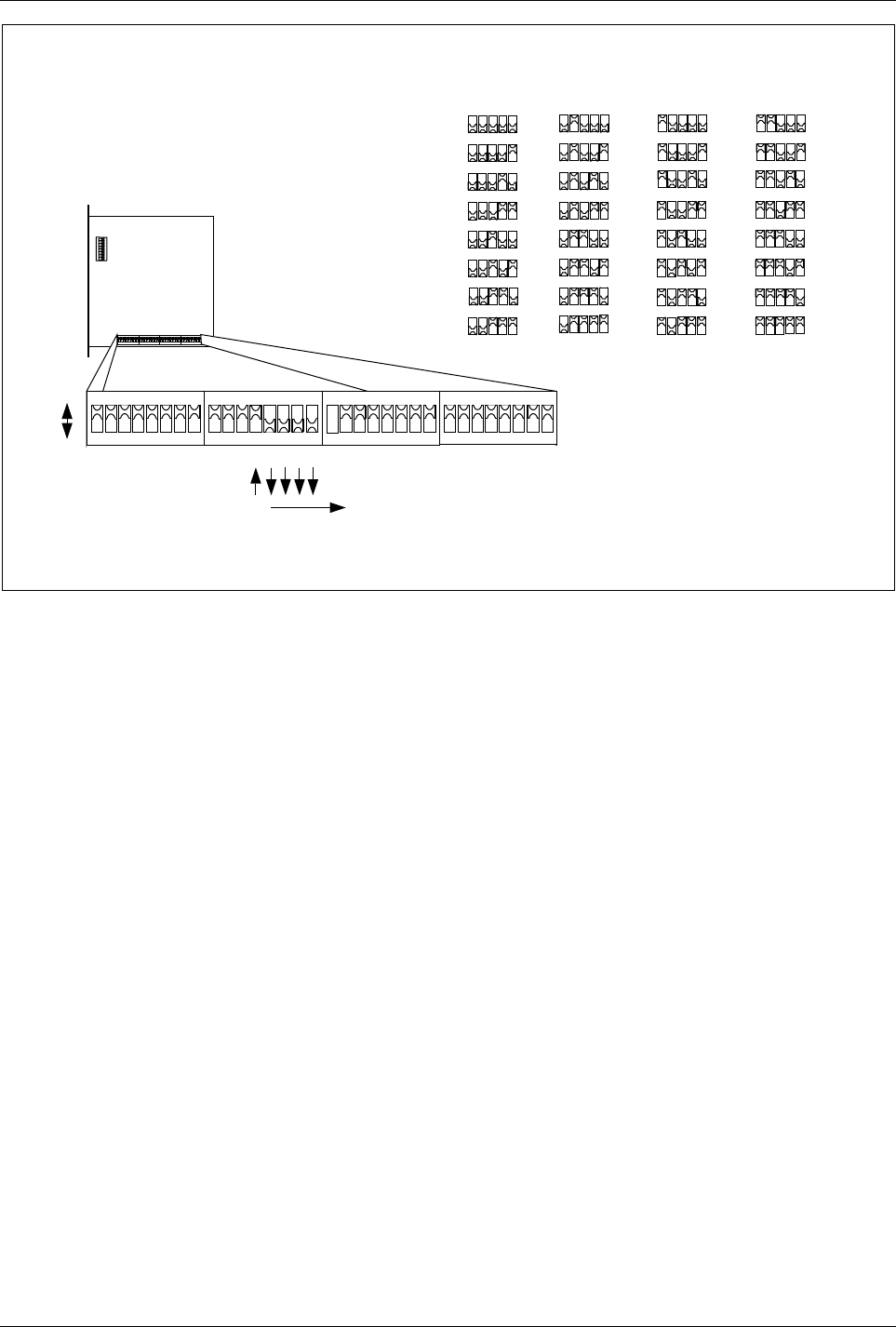
Installation
CLC Extraction Timeslot for E1
1
2
4
16 8
1
2
4
16 8
1
2
4
16 8
1
2
4
16 8
1
2
4
16 8
1
2
4
16 8
1
2
4
16 8
1
2
4
16 8
=TS 0
=TS 1
=TS 2
=TS 3
=TS 4
=TS 5
=TS 6
=TS 7
1
2
4
16 8
1
2
4
16 8
1
2
4
16 8
1
2
4
16 8
1
2
4
16 8
1
2
4
16 8
1
2
4
16 8
1
2
4
16 8
=TS 16
=TS 17
=TS 18
=TS 19
=TS 20
=TS 21
=TS 22
=TS 23
=TS 8
=TS 9
=TS 10
=TS 11
=TS 12
=TS 13
=TS 14
=TS 15
1
2
4
16 8
1
2
4
16 8
1
2
4
16 8
1
2
4
16 8
1
2
4
16 8
1
2
4
16 8
1
2
4
16 8
1
2
4
16 8
1
2
4
16 8
=TS 24
=TS 25
1
2
4
16 8
1
2
4
16 8
=TS 26
1
2
4
16 8
=TS 27
1
2
4
16 8
=TS 28
1
2
4
16 8
=TS 29
1
2
4
16 8
=TS 30
1
2
4
16 8
=TS 31
DIP switch values 0 - 31 = TS 0 - 31
Normal timeslot is TS 16
Top
12345678
ON
Front
Timeslot 16 (TS 16)
16
1
0
1
2
4
16 8
Note: This example shows the selection of timeslot 16 for
CLC extraction (for an E1 line).
Figure 4-29. Setting the CLC Extraction Timeslot for E1
12. For a T1 PCM line, select the timeslot (TS) for Control signaling
Link (CLC) extraction, as shown in Figure 4-30 on page 4-48, in
accordance with the Configuration Data in the Site Installation
Documentation.
1/1551-EN/LZB 119 3312 Uae Rev A 1998-11-17 4-47
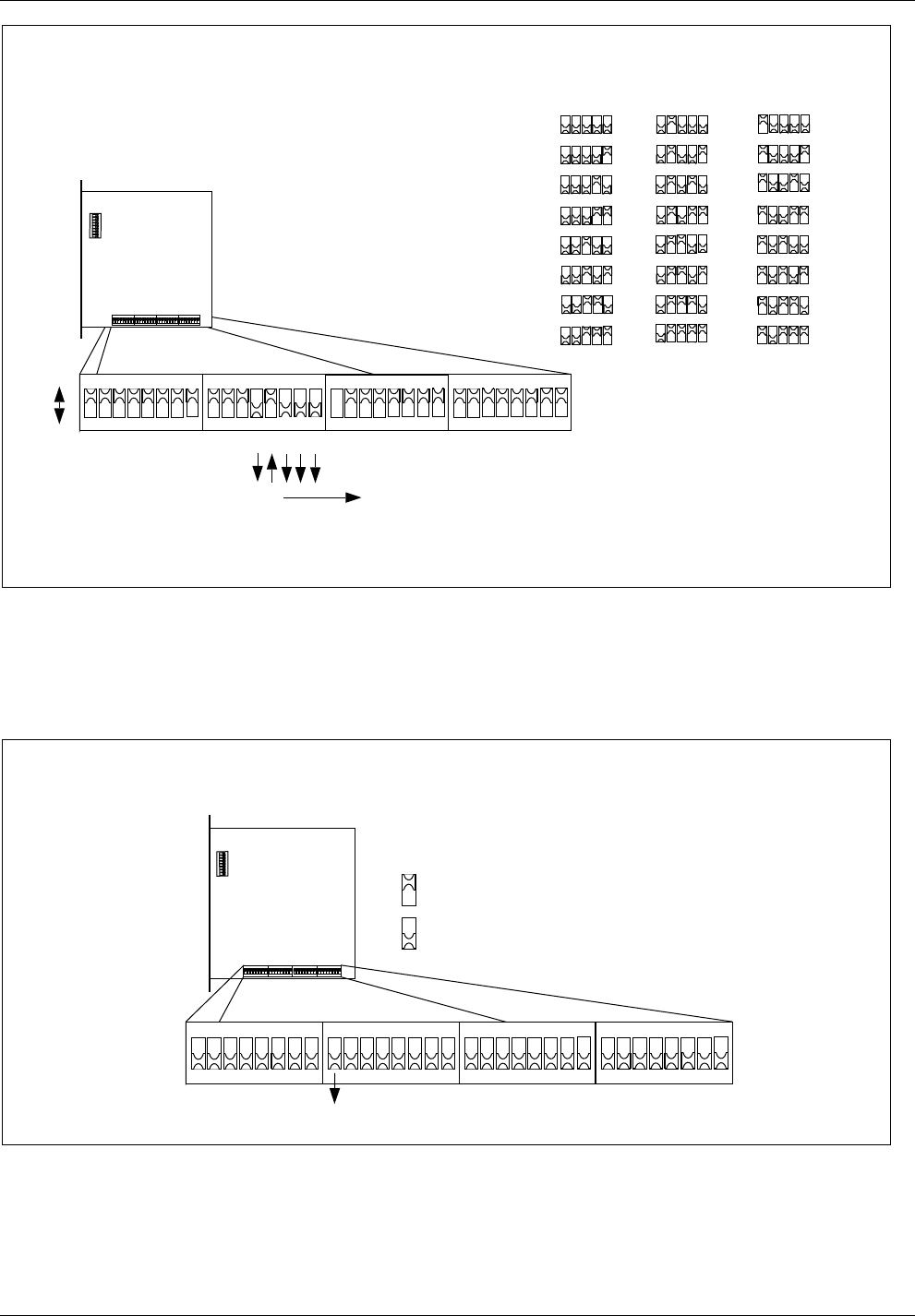
Installation
CLC Extraction Timeslot for T1
1
2
4
16 8
1
2
4
16 8
1
2
4
16 8
1
2
4
16 8
1
2
4
16 8
1
2
4
16 8
1
2
4
16 8
1
2
4
16 8
=TS 1
=TS 2
=TS 3
=TS 4
=TS 5
=TS 6
=TS 7
=TS 8
=TS 17
=TS 18
=TS 19
=TS 20
=TS 21
=TS 22
=TS 23
1
2
4
16 8
1
2
4
16 8
1
2
4
16 8
1
2
4
16 8
1
2
4
16 8
1
2
4
16 8
1
2
4
16 8
1
2
4
16 8
=TS 24
=TS 9
=TS 10
=TS 11
=TS 12
=TS 13
=TS 14
=TS 15
=TS 16
1
2
4
16 8
1
2
4
16 8
1
2
4
16 8
1
2
4
16 8
1
2
4
16 8
1
2
4
16 8
1
2
4
16 8
1
2
4
16 8
Timeslot 9 (TS 9)
8
1
0
1
2
4
16 8
Top
12345678
ON
Front
DIP switch values 0 - 23 = TS 1 - 24
Normal timeslot is TS 9
Note: This example shows the selection of timeslot 9 for
CLC extraction (for a T1 line).
Figure 4-30. Setting the CLC Extraction Timeslot for T1
13. Set the jitter and wander limit for the PCM line for 138 Unit
Intervals (UI), as shown in Figure 4-31 on page 4-48 in accordance
with the Configuration Data in the Site Installation Documentation.
PCM Jitter and Wander Limit
= J/W limit 138 Unit Intervals (UI)
= J/W limit 28 Unit Intervals (UI)
Top
12345678
ON
Front
J/W = 138 UI
Figure 4-31. Setting the PCM Line Jitter and Wander Limit
14. Set the frequency of operation for 1900 MHz as shown in Figure
4-32 on page 4-49.
4-48 1/1551-EN/LZB 119 3312 Uae Rev A 1998-11-17
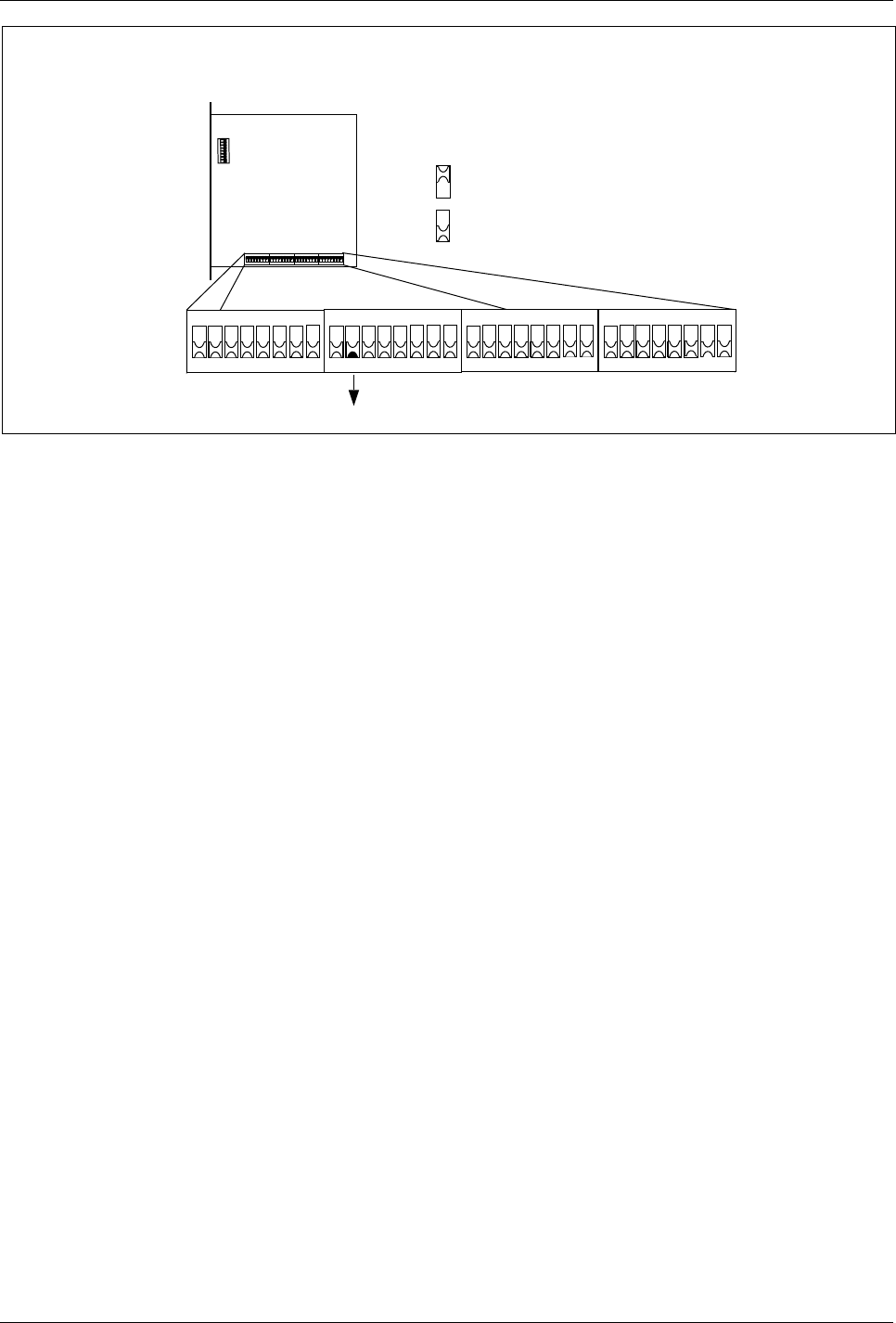
Installation
Frequency Selection
= 1900 MHz
= 800 MHz
Top
12345678
ON
Front
1900 MHz
Figure 4-32. Setting the Frequency of Operation
15. Carefully slide the REMUX unit back into the cabinet following the
guides, and push the unit firmly into the backplane connector.
16. Use the torque wrench with the Torx bit TX10 to tighten the top and
bottom screws on the front to 0.6 Nm.
10.3 EMRPM Switch Settings
1. Keep the ESD strap attached.
2. Use the torque wrench with the Torx bit TX10 to loosen the top and
bottom screws on the front of one of the EMRPM units.
Note: Do not touch any components or connector pins on
a circuit board.
3. Remove the EMRPM unit from the cabinet using the extractor tool.
Save the extractor hole plug and replace plug after installing the
EMRPM unit.
4. Locate the DIP switch and set the EMRPM address, as shown in
Figure 4-33 on page 4-50, depending on which cabinet is being
configured. Set the address as follows:
•Main Cabinet, set the EMRPM unit address to 1.
•Primary Cabinet 1, set the address to 3.
•Primary Cabinet 2, set the address to 5.
1/1551-EN/LZB 119 3312 Uae Rev A 1998-11-17 4-49
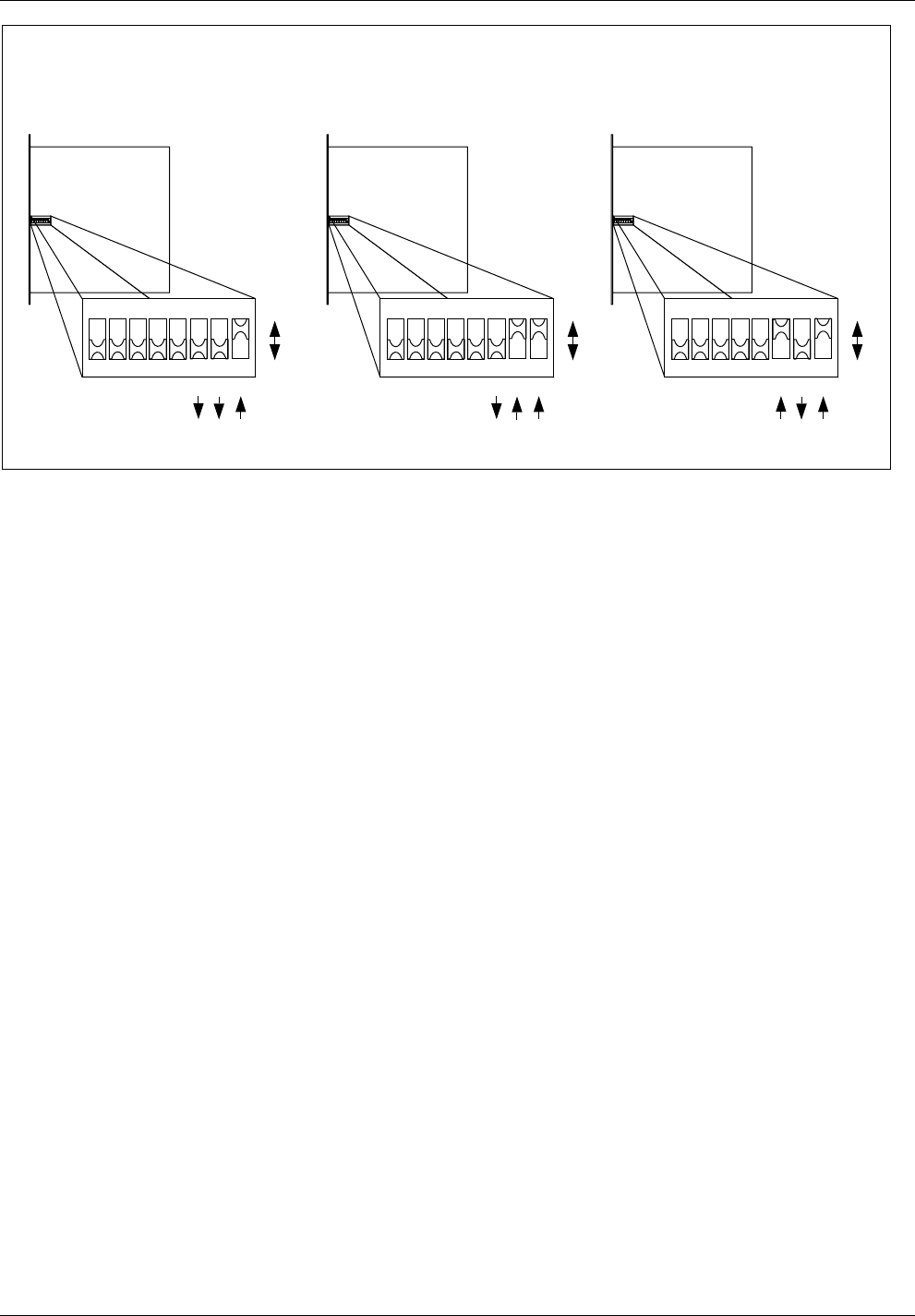
Installation
Main
Cabinet Primary 1
Cabinet Primary 2
Cabinet
Top
1
0
1
2
4
41
+= 5
Top
1
0
1
2
4
1= 1
Top
1
0
1
2
4
1
+= 3
2
Figure 4-33. EMRPM Address Setting
5. Carefully slide the EMRPM unit back into the cabinet following the
guides, and push the unit firmly into the backplane connector.
6. Use the torque wrench with the Torx bit TX10 to tighten the top and
bottom screws on the front.
7. Repeat the same steps for the other EMRPM unit.
11 External Alarm Connections
The RBS 884 Micro (1900 MHz) provides four customer defined external
alarm connections. These connections are available on a terminal block
located on the lower right wall inside the cabinet and connect to the ALM
board. Each alarm is activated by a dry contact closure (either normally
open or normally closed). See Figure 4-34 on page 4-51.
4-50 1/1551-EN/LZB 119 3312 Uae Rev A 1998-11-17
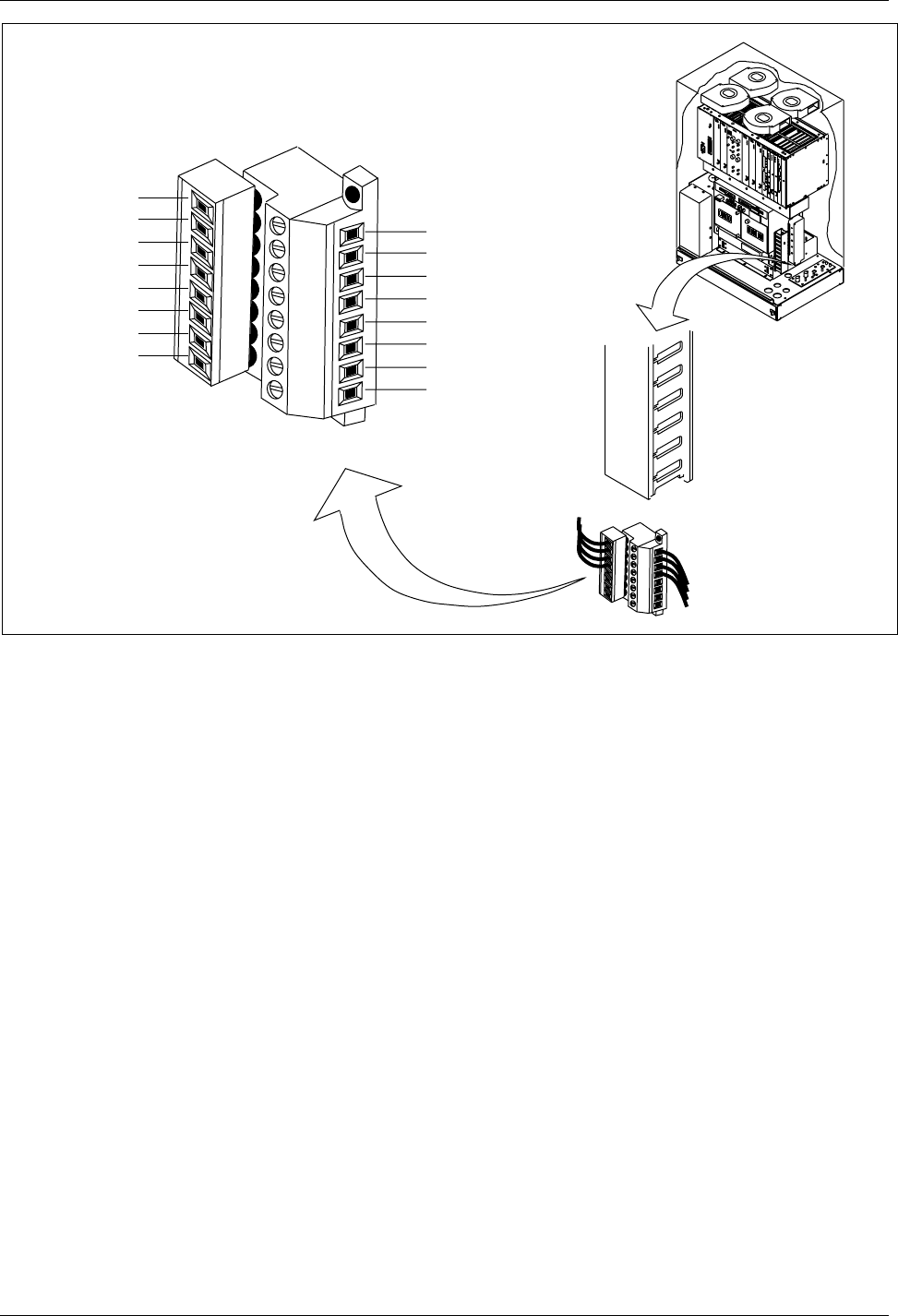
Installation
}
}
}
}
}
}
}
}
Alarm 10
Alarm 11
Alarm 12
Alarm 13
Customer Alarm
Connections
Alarm 10
(pins 11 & 31)
Alarm 11
(pins 12 & 32)
Alarm 12
(pins 13 & 33)
Alarm 13
(pins 14 & 34)
To ALM Board
External Alarm
Terminal Block
is Located on
Lower Right Wall.
Figure 4-34. Customer Defined External Alarm Connection Terminal Block
12 Site Inventory
To facilitate equipment replacement in the RBS cabinets, perform a site
inventory to identify all units delivered, including revision states. This
information is recorded in the Plant Specification found in the Site
Installation Documentation.
12.1 Prerequisites
12.1.1 Prerequisites
Complete the following activities before the site inventory is performed:
•Cabinet mounting, Section 8 on page 4-12
•Grounding, Section 9.1 on page 4-24
•Setting of switches, Section 10 on page 4-39
•Cable installation, Section 9.4 on page 4-31
1/1551-EN/LZB 119 3312 Uae Rev A 1998-11-17 4-51
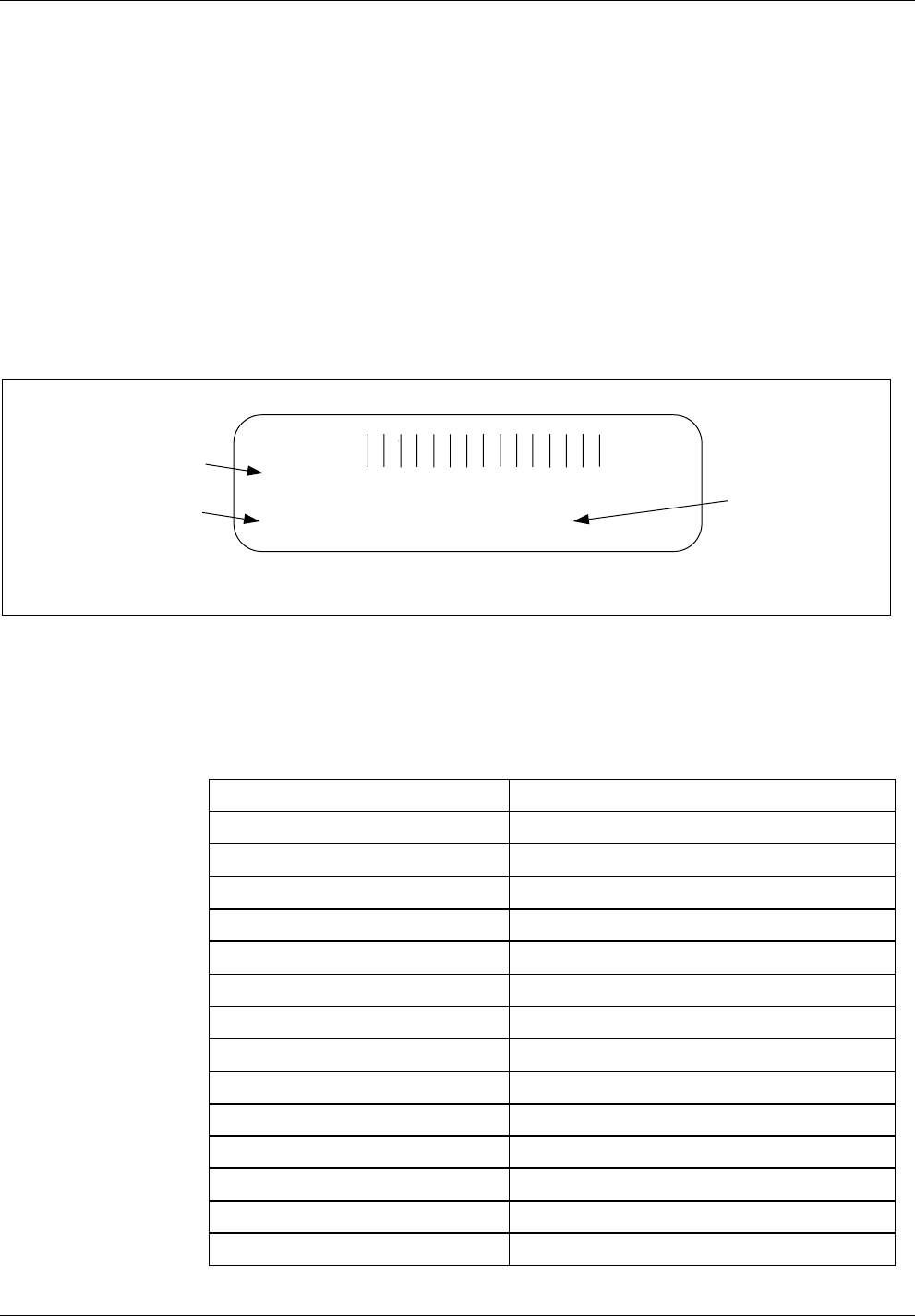
Installation
12.2 Site Inventory Procedure
Site Information
1. Record the name of the site, date, and other relevant information for
each cabinet in the Site Installation Documentation,Plant
Specification, or follow your local procedure.
RBS Cabinet Units
2. Locate the product labels on all of the units in the cabinets. Each
unit has a product label located on its front panel, as shown in Figure
4-35 on page 4-52, indicating its product number and revision state.
A53047P963 99w03 A53
P/ KRC 121 10/4 R1A
Product
Number R-State
Serial
Number
Figure 4-35. Unit Product Label
3. Record the product number, serial number, and R-state for each unit
in each of the cabinets in the Plant Specification (or any other site
inventory list). See Table 4-8 on page 4-52.
Table 4-8. RBS 884 Micro (1900 MHz) Units
Product Number Unit
HRB 102 13 1900 Micro Radio Base Station
ROF 137 2775 ECU Unit
ROA 119 3157/7 ALM
ROF 367 211/1 REMUX - (T1) 24 Channel
ROF 367 211/3 REMUX - (E1) 32 Channel
ROF 367 212/1 CONN
ROF 367 207/1 STRM
ROF 367 210/1 EMRPM
KRC 121 106/1 TRX
KRF 102 115/1 ANP/RFTL (2) Two Antenna (A+D)
KRF 102 115/2 ANP/RFTL (4) Four Antenna (A+D)
KRF 102 115/3 ANP/RFTL (2) Two Antenna (D+B+E)
KRF 102 115/4 ANP/RFTL (4) Four Antenna (D+B+E)
KRF 102 115/5 ANP/RFTL (2) Two Antenna (E+F+C)
4-52 1/1551-EN/LZB 119 3312 Uae Rev A 1998-11-17

Installation
Table 4-8. RBS 884 Micro (1900 MHz) Units (Continued)
Product Number Unit
KRF 102 115/6 ANP/RFTL (4) Four Antenna (E+F+C)
ROF 367 213/1 Dummy EMRPM
ROF 367 216/1 Dummy REMUX
ROF 367 217 Dummy TRX
BKV 301 457 Fan
13 Equipment Power Up
This section describes the procedure for applying AC power to each of the
RBS 884 Micro (1900 MHz) cabinets.
Note: Read the Safety Considerations (Section 2 on page 4-3) before
starting the power up procedure.
13.1 Prerequisites and Test Equipment
13.1.1 Prerequisites
The following activities must be completed for each cabinet before power
can be applied:
•Mounting, Section 8 on page 4-12
•Grounding, Section 9.1 on page 4-24
•Setting of switches, Section 10 on page 4-39
•Cabling, Section 9.4 on page 4-31
•Connecting AC voltage, Section 9.3 on page 4-29
13.1.2 Tools and Test Equipment
The following equipment is required for completing the electrical power
installation and for power-up testing:
•Tools for connecting the AC power cable to a line power access
point, if this is the local procedure
•Multimeter for checking supplied line voltage and polarity for DC
power.
1/1551-EN/LZB 119 3312 Uae Rev A 1998-11-17 4-53

Installation
13.2 Power-Up Procedure
AC Power Connection
1. Verify the AC CONNECTED lamp on the front panel of the AC/DC
distribution box is ON.
2. Position the following circuit breakers on the front panel of the AC/
DC distribution box to ON in the following sequence (see Figure
4-36 on page 4-54 for the location of the circuit breakers).
•Main
•PSU
•ECU
•FANS
ALM CABLE ECU CABLE
SUBRK PWR FAN PWR CSU
SENSORS
AC
CONNECTED
MAIN PSU MAIN
HTR BAT
HTR GFI
OUTLET
BAT ECU CSU FANS
BAT COMP
BAT
ALM DOOR
ALM
ON
OFF
Figure 4-36. Cabinet Circuit Breakers on AC/DC Distribution Box
3. After the above circuit breakers are on, the fans will start up fast and
drop back to a normal operating speed. Observe that for about 20
seconds after power-up, the red Error LEDs on all units in the
subrack flash at 3 Hz as the units perform internal self-tests.
4-54 1/1551-EN/LZB 119 3312 Uae Rev A 1998-11-17
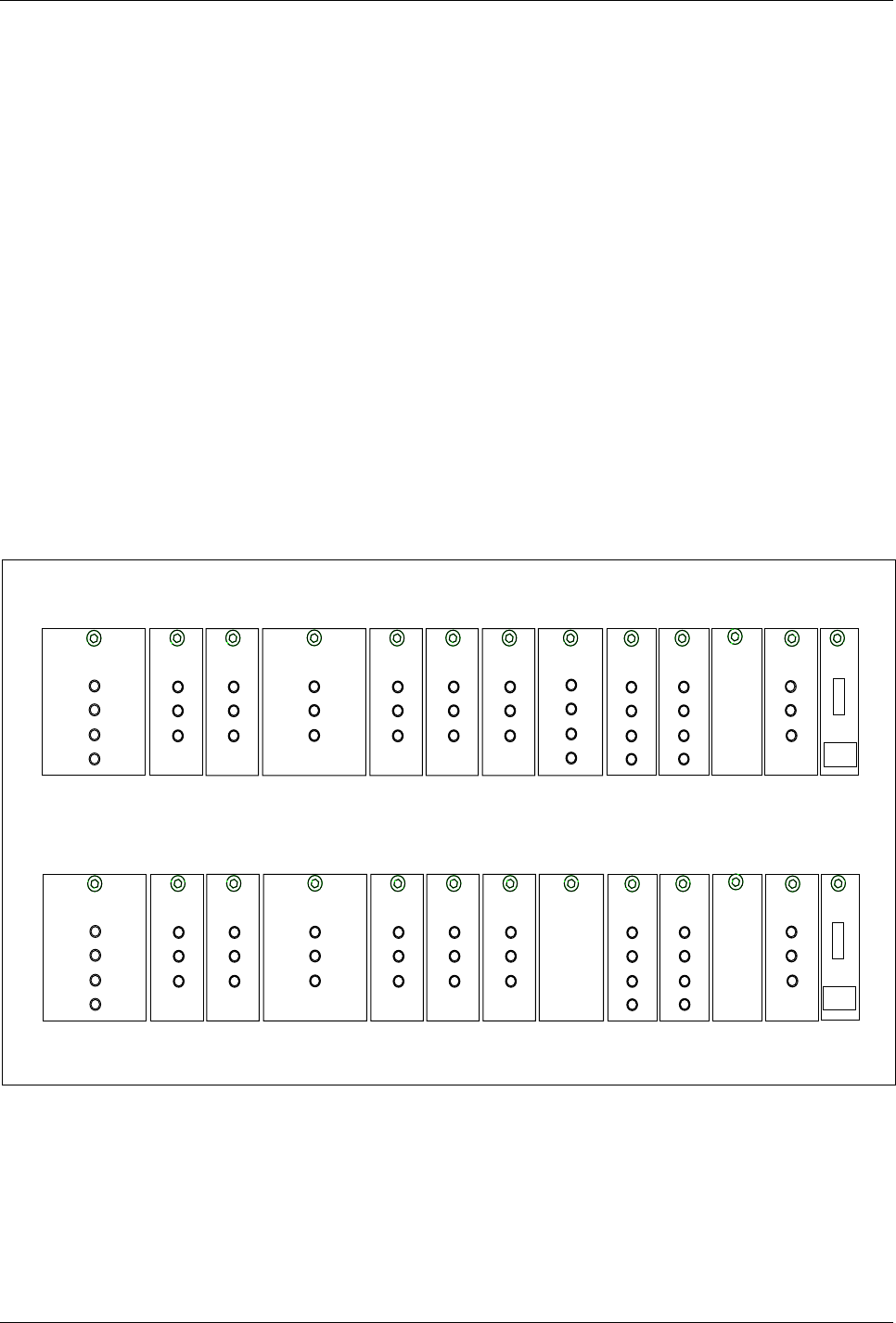
Installation
4. Position the remainder of the circuit breakers to ON as follows:
•BAT
•MAIN HTR
•BAT HTR
•CSU (if customer-supplied CSU equipment is installed)
Note: Do not turn on the GFI OUTLET circuit breaker
unless performing maintenance on the
equipment.
Power-Up Test
5. After 20 seconds, verify that all fans at the top of the cabinet are
running. If not, refer to the "Troubleshooting" section in the
Installation and Hardware Replacement Manual for information on
detecting faulty units.
6. Check that the green LED on each of the units in the cabinet is on
(see Figure 4-37 on page 4-55).
Main Cabinet
Primary Cabinet
TRX
Power
Error
Status
REMUX
Power
Error
Status 1
Status 2
Power
Error
Status 1
EMRPM
Status 2
ALM
Power
Error
Status
TRX
Power
Error
Status
TRX
Power
Error
Status
TRX
Power
Error
Status
TRX
Power
Error
Status
ANP/RFTL
Power
Error
Status
Power
Error
Status 1
Status 2
STRM
PSU
AC Main
DC Output
Current Limit
ECU
00
TRX
Power
Error
Status
Power
Error
Status 1
EMRPM
Status 2
ALM
Power
Error
Status
TRX
Power
Error
Status
TRX
Power
Error
Status
TRX
Power
Error
Status
TRX
Power
Error
Status
ANP/RFTL
Power
Error
Status
Power
Error
Status 1
Status 2
CONN
PSU
AC Main
DC Output
Current Limit
ECU
00
Figure 4-37. The Green Power LEDs and Red Error LEDs
7. If any of the green Power LEDs are off, replace the unit in
accordance with the “Hardware Replacement” part of the Installation
and Hardware Replacement Manual.
8. Check that none of the red Error LEDs is on (see Figure 4-37 on
page 4-55).
1/1551-EN/LZB 119 3312 Uae Rev A 1998-11-17 4-55
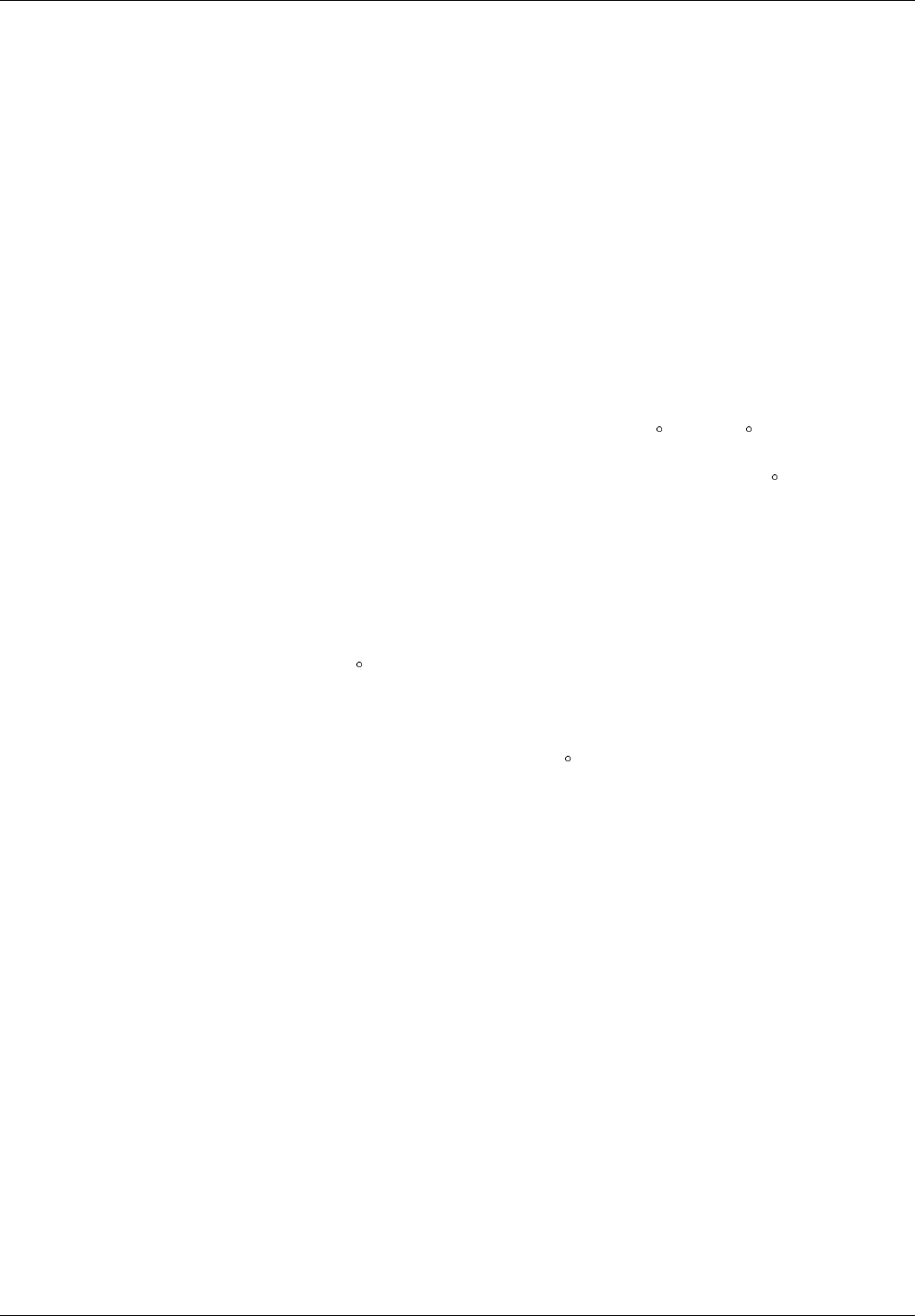
Installation
9. If any of the red Error LEDs are on or flashing continuously, replace
the unit in accordance with the “Hardware Replacement” part of the
Installation and Hardware Replacement Manual.
10. Repeat Step 1 on page 4-54 to Step 9 on page 4-56 for each cabinet.
11. Inform the MSC operator that the unit has been replaced and is ready
to be tested.
14 Cold Start-up
During an AC power-on event, the ECU checks the temperature of the
equipment before allowing DC power to be distributed to the rest of the
equipment. The ECU prohibits the equipment from operating when its
temperature is outside the safe function limits (-5 C to +50 C). The cold-
start mode is used when AC is first applied and the subrack thermal mass
temperature is below the subrack inlet temperature limit of 10 C.
If a cold start-up condition exists, heaters are activated to warm the cabinet
temperature. The heater is controlled by a variable voltage from the ECU
(5Vdc to 12Vdc) to provide 80 to 1600 watts of variable heat.
During the warm-up period, the fans operate at 20% of full flow
circulating the heated air trough the cabinet. When the subrack thermal
mass reaches 10 C, the ECU applies power to the Subrack Power Bus.
The warm-up time from AC power-on until the equipment reaches
operational temperature varies with the initial equipment temperature. At
an initial equipment temperature of -35 C, the warm-up can take
approximately 55 minutes.
The ECU does not generate any alarms to the MSC during a cold start-up.
The ECU Cold Start error code (C0) does appear on the ECU LED display.
15 Completing the Installation
This section describes the general housekeeping duties required to
complete the installation.
4-56 1/1551-EN/LZB 119 3312 Uae Rev A 1998-11-17
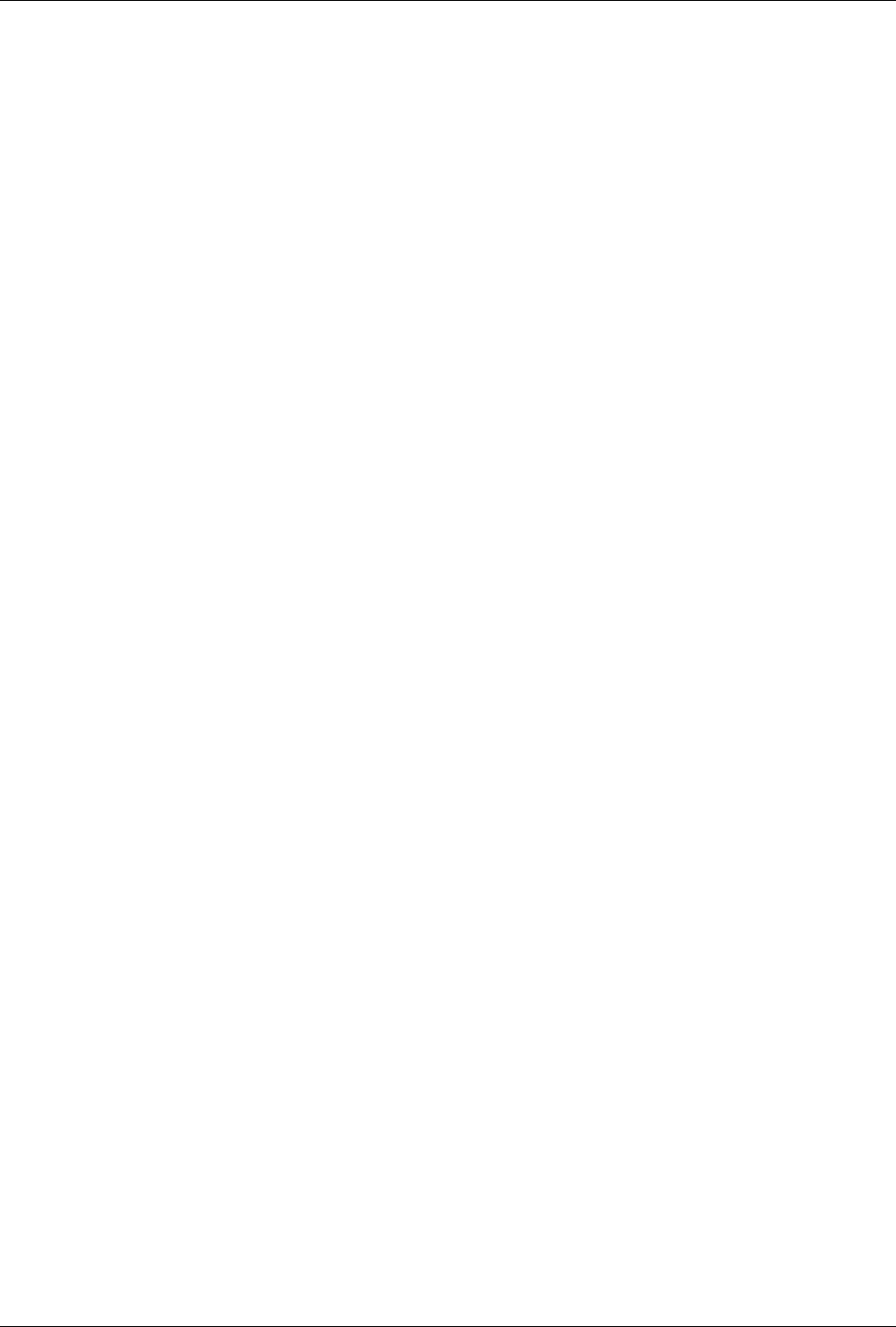
Installation
15.1 Prerequisites and Tools
15.1.1 Prerequisites
The Installation Completion Procedure can be completed only after the
equipment has been successfully powered up in accordance with Section
13 on page 4-53.
15.1.2 Tools
A tie-wrap tool is required to complete the “Installation Completion
Procedure.”
15.2 Installation Completion Procedure
This procedure describes the general housekeeping duties required to
complete the base station installation.
General housekeeping
1. Verify that all cables, except antenna and ground, enter the cabinet
through conduit. The conduit must be terminated at the bottom of
the cabinet at the locations shown in Figure 4-18 on page 4-37.
2. Secure internal cables in cable trays.
3. Trim any tie-wrap ends to within 1/8” of the wrap.
4. Verify that all activators on the Primary T1/E1 Surge Protector are in
the down position.
5. Recycle the packing materials in accordance with the local
regulations.
16 LED Indications
Active devices are equipped with Light Emitting Diodes (LEDs) to
indicate the status of the device. Refer to Figure 4-38 on page 4-58 for the
location of LEDs on a TRX unit.
In general:
•Green LEDs indicate the power is on.
•Red LEDs indicate an error has occurred (a red LED that is on,
indicates that an unspecified error has occurred in that unit).
•Yellow LEDs show operational status.
1/1551-EN/LZB 119 3312 Uae Rev A 1998-11-17 4-57
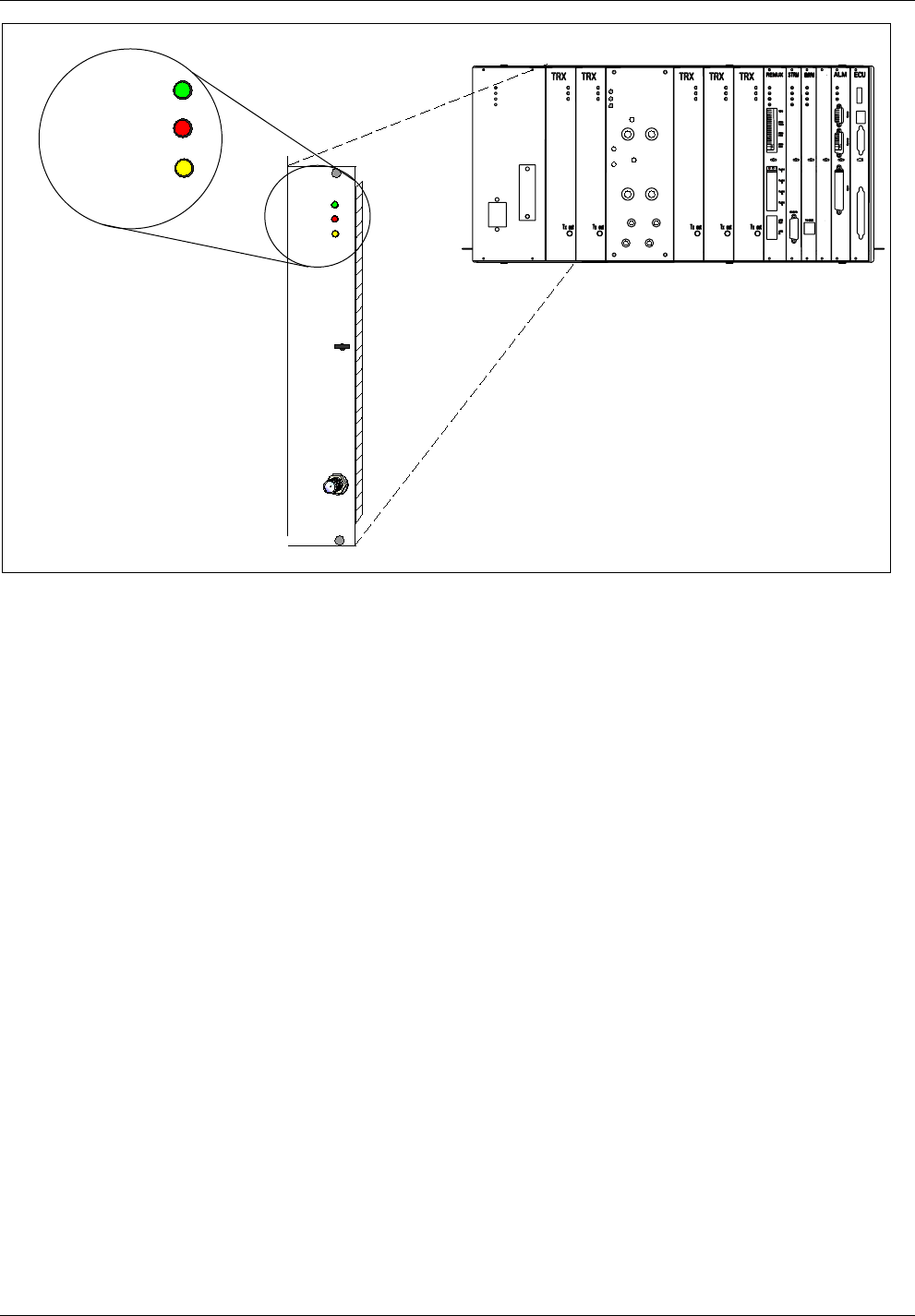
Installation
✚
Tx out
POWER
ERROR
STATUS
✚
TRX
1900
POWER
ERROR
STATUS
TX 2
TX 1
TX 4
TX 3
RX/TX
ANT A RX/TX
ANT B
TX ANT C TX ANT D
Power
Error
Status
ANP/RFTL
Figure 4-38. LED on a TRX
16.1 PSU LEDs
In the RBS 884 Micro (1900 MHz) PSU unit, four LED indicators are
provided for the following:
•PSU
•AC Mains
•DC Output
•Current Limit
Note: During battery charging, the Current Limit LED will be on.
This is a normal indication.
16.2 TRX LEDs
In the RBS 884 Micro (1900 MHz) TRX units, three LED indicators are
provided for the following:
•Red Error LED
ON: Indicates an error or fault with the TRX
FLASH 3 Hz: Power-up test
FLASH: Communication with EMRPM is lost
4-58 1/1551-EN/LZB 119 3312 Uae Rev A 1998-11-17
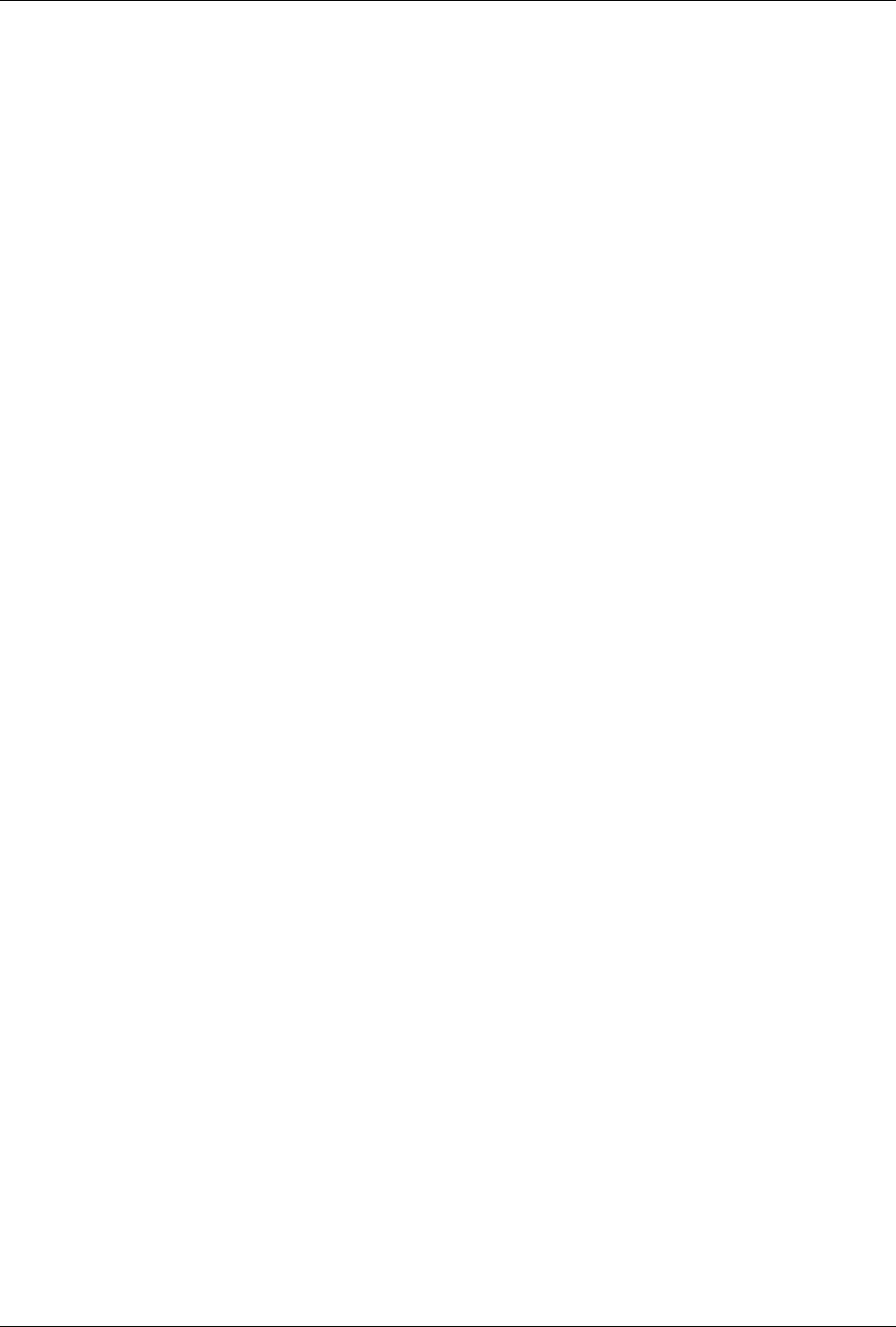
Installation
•Yellow Status LED
OFF: No PCM signal is present on the primary interface
FLASHING: Indicates TRX(s) are on (33% duty cycle =1 timeslot,
66% duty cycle=2 timeslot, 99% duty cycle=3 timeslot)
•Green Power LED
ON: Indicates the TRX is powered on
16.3 REMUX LEDs
In the RBS 884 Micro 1900 REMUX unit, four LED indicators are
provided for the following:
•Red Error LED
ON: Indicates an error or fault with the TRX
FLASH 3 Hz: Power-up test
FLASH: Communication with EMRPM/S is lost
•Yellow Status LEDs (2)
OFF: No PCM signal is present on the primary interface
FLASH 3 Hz: Primary PCM interface is not operable
FLASH 15 Hz: Primary PCM interface is operable
•Green Power LED
ON: Indicates the REMUX is powered on
16.4 ANP (RFTL) LEDs
In the RBS 884 Micro (1900 MHz) ANP (RFTL) unit, three LED
indicators are provided for the following:
•Red Error LED
ON: Indicates an error or fault with the ANP (RFTL)
•Yellow Status LED
OFF: No PCM signal is present on the primary interface
•Green Power LED
ON: Indicates the ANP (RFTL) is powered
1/1551-EN/LZB 119 3312 Uae Rev A 1998-11-17 4-59
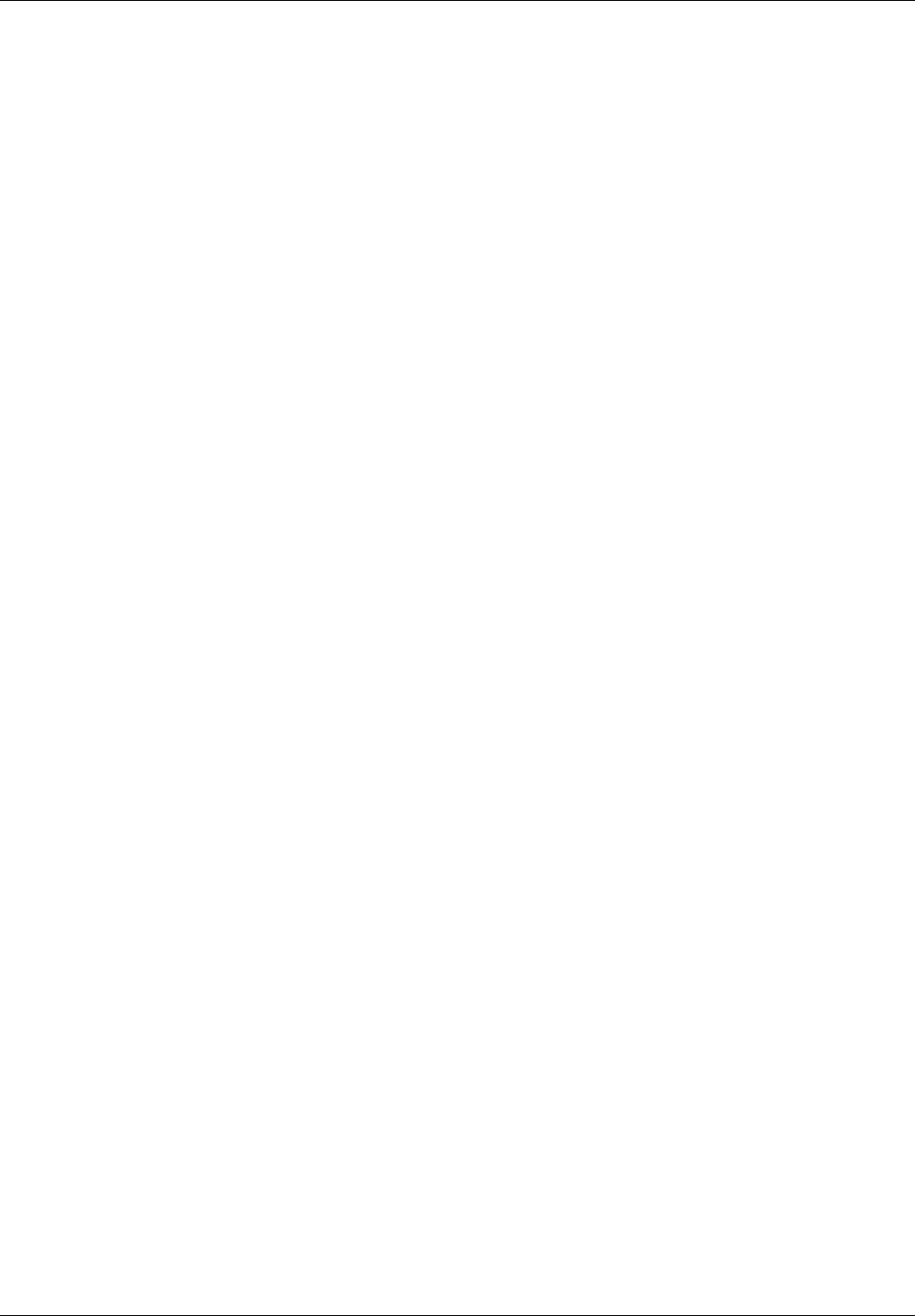
Installation
16.5 STRM LEDs
In the RBS 884 Micro (1900 MHz) STRM unit, two LED indicators are
provided for the following:
•Yellow Status LED
FLASHING 8 Hz: Blocked
FLASHING 1 Hz: Deblocked
FLASHING Two blinks-pause-two blinks: Signaling Terminal
Central (STC) communication not working
•Green Power LED
ON: Indicates the STRM is powered on
16.6 ALM LEDs
In the RBS 884 Micro (1900 MHz) ALM unit, three LED indicators are
provided for the following:
•Red Error LED
ON: Indicates an error or fault with the TRX
FLASH 3 Hz: Power-up test
FLASH: Communication with EMRPM/S is lost
•Yellow Status LED
OFF: No PCM signal present on the primary interface
•Green Power LED
ON: Indicates the TRX is powered on
16.7 EMRPM LEDs
In the RBS 884 Micro (1900 MHz) EMRPM unit, four LED indicators are
provided for the following:
•Red Error LED
ON: Indicates an error or fault with the EMRPM
•Yellow Status 1 LED
OFF: Turned off by APZ at EMRPM reset
ON: Turned on when EMRPM is started
FLASHING: Starts to blink when traffic is pending and is set to ON
when there is no traffic
4-60 1/1551-EN/LZB 119 3312 Uae Rev A 1998-11-17
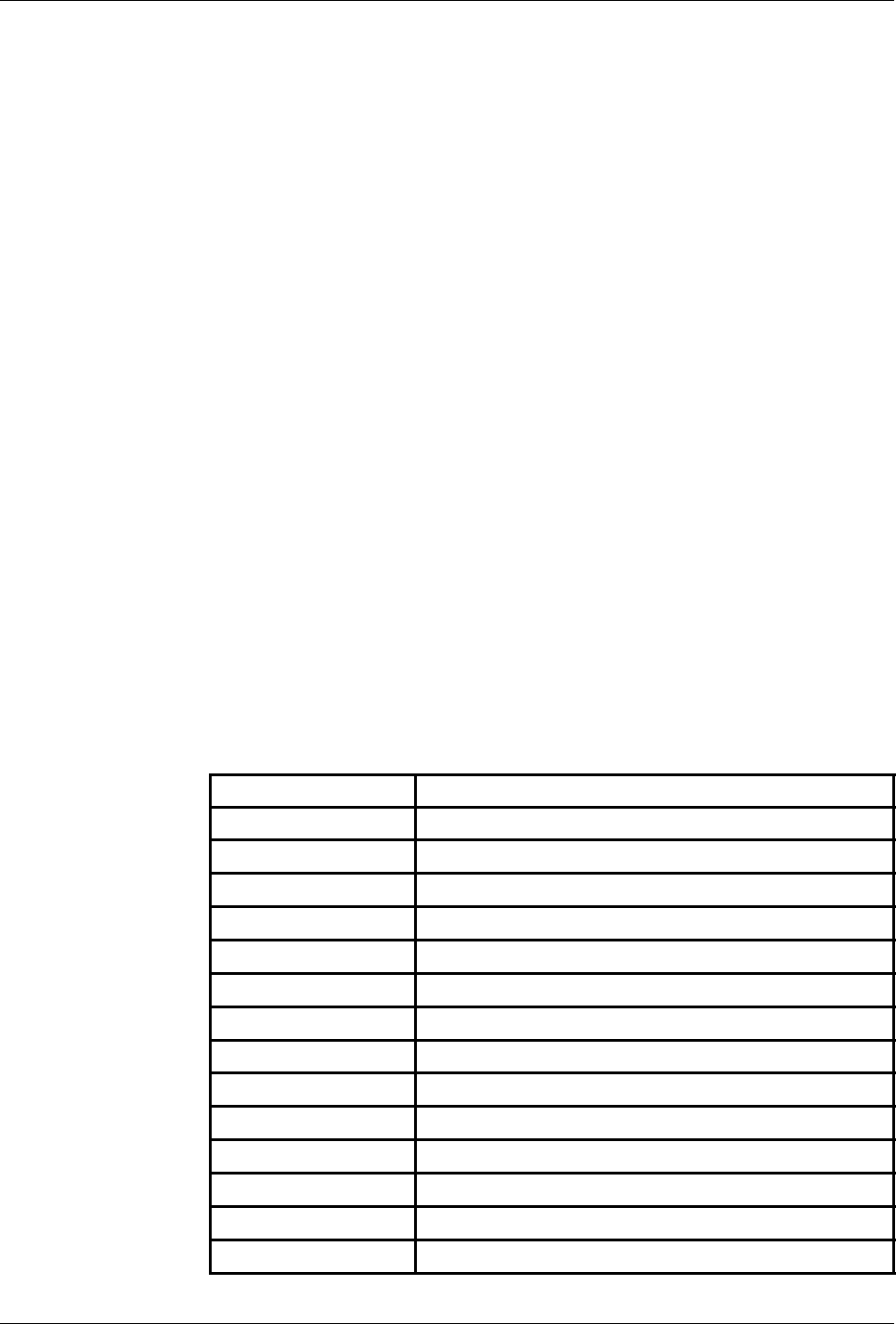
Installation
•Yellow Status 2 LED
OFF: Turned off by APZ at EMRPM reset, at restart, and when all
devices are blocked
ON: Turned on when at least one device is deblocked but all
individuals are blocked
FLASHING: Indicates at least one deblocked individual
•Green Power LED
ON: Indicates the EMRPM is powered on
16.8 ECU LEDs
The ECU in the RBS 884 Micro (1900 MHz) provides interfaces to the
following cabinet equipment:
•Main DC Power Bus Disconnect Relay
•Temperature Sensors
•PSU
•Main Heater
•ALM
Two seven-segment displays on the front of the ECU provide error codes
to indicate equipment failure alarms and ALM status (see Table 4-9 on
page 4-61).
Table 4-9. ECU Error Codes
Error Code Description
A0 Temperature shutdown alarm
A1 Single fan alarm
A2 Multiple fan alarm
A3 Main heater alarm
A4 PSU failure alarm
A5 Battery temperature alarm
F1 Fan #1 failure
F2 Fan #2 failure
F3 Fan #3 failure
F4 Fan #4 failure
FF Fan test
S1 Ambient Temperature Sensor failure
S2 Inlet Temperature Sensor failure
S3 Subrack Temperature Sensor failure
1/1551-EN/LZB 119 3312 Uae Rev A 1998-11-17 4-61
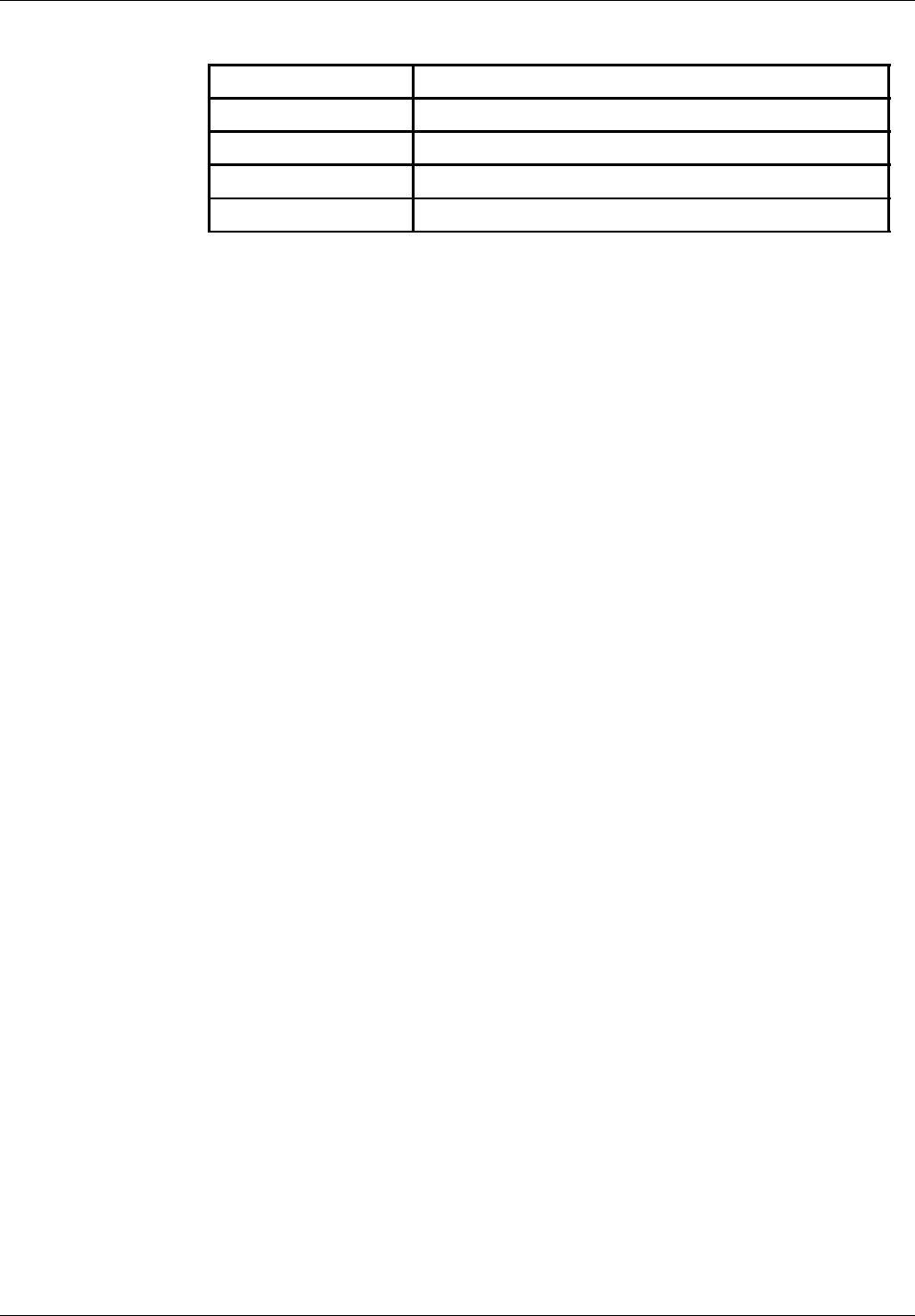
Installation
Table 4-9. ECU Error Codes (Continued)
S4 Exhaust Temperature Sensor failure
S5 Battery Compartment Temperature Sensor failure
S6 Inlet 2 (backup) Temperature Sensor failure
C0 Cold start
C1 Cold start timeout > 30 minutes
17 Site Expansion
An RBS 884 Micro (1900 MHz) can be expanded by adding the following:
•TRXs to one or more of the cabinets (see Section 17.1 on page 4-62).
•One or two Primary Cabinets (see Section 17.2 on page 4-67).
After completing the site expansion, fill in the Site Inventory list in the Site
Installation Documentation. Note the date and the R-state of the new units.
This section also provides additional cabling information for the following
configurations:
•One-sector sites, one cabinet with two antennas
•One-sector sites, one cabinet with four antennas
•Two-sector sites, two cabinets with two antennas per cabinet
•Two-sector sites, two cabinets with four antennas per cabinet
•Three-sector sites, three cabinets with two antennas per cabinet
•Three-sector sites, three cabinets with four antennas per cabinet
17.1 Adding TRX Boards
To increase call handling capacity within a sector, replace the base
station’s RMUs with TRXs.
Note: Other options for single-sector site expansion are not supported
by the RBS 884 Micro (1900 MHz).
17.1.1 Tools
The tools required for adding TRXs to a cabinet are shown in Table 4-10
on page 4-63, Figure 4-39 on page 4-63, Figure 4-40 on page 4-64, and
Figure 4-41 on page 4-64.
4-62 1/1551-EN/LZB 119 3312 Uae Rev A 1998-11-17
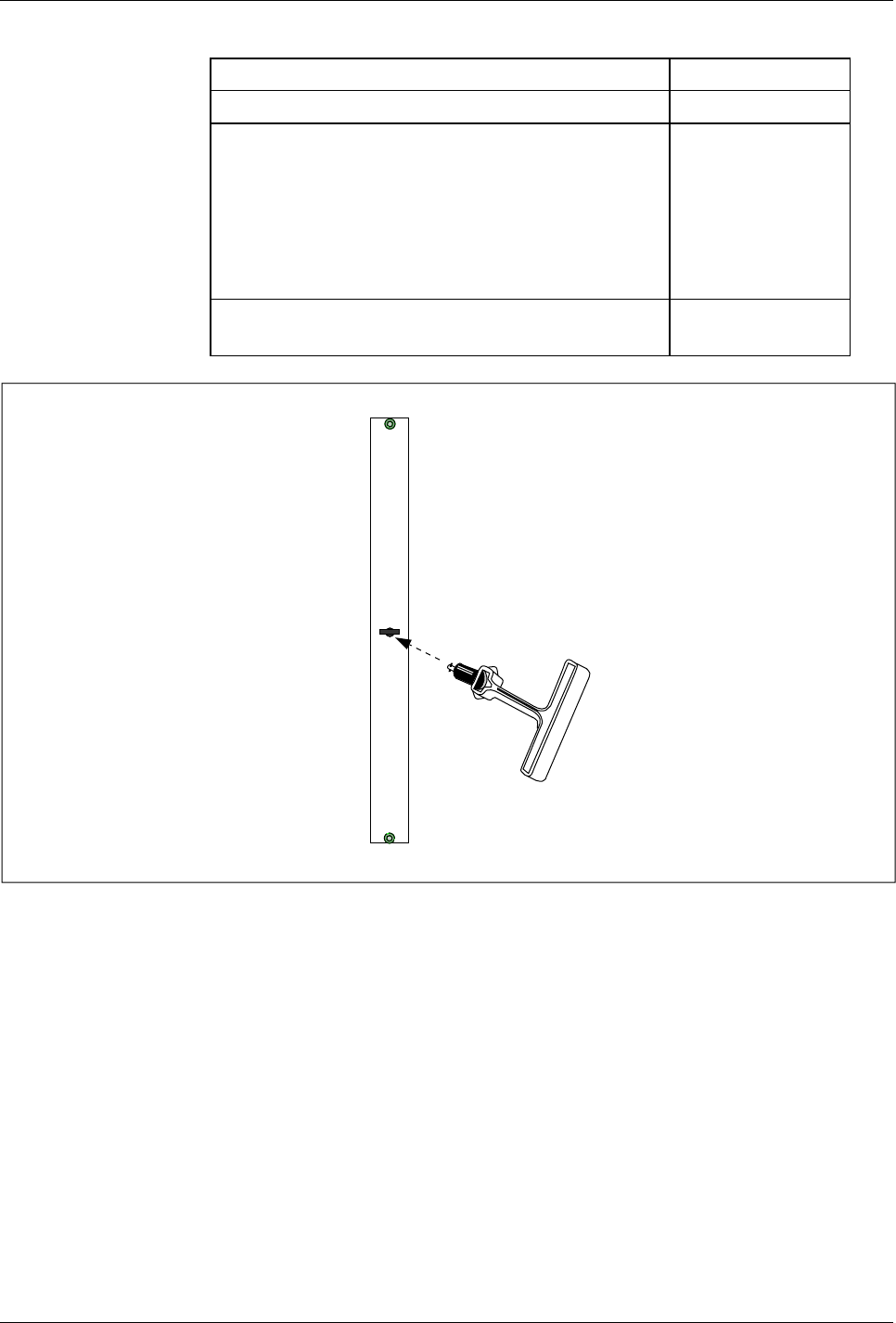
Installation
Table 4-10. Tools for Adding TRXs
Description Product Number
ESD Wrist Strap and Cable LYB 250 01/14
Torque Wrench set including:
- Torque Wrench for torque 0.6 Nm
(to use with the SMA tool and the torx bit TX10
- Torx bit TX10
(for circuit board screws)
- SMA tool
(for the coaxial cables)
LTT 601 82
Unit Extractor Tool (Handle and Button) LTD 117 02 and
LTD 117 14
RMU
Figure 4-39. Unit Extractor Tool (extracting an RMU)
1/1551-EN/LZB 119 3312 Uae Rev A 1998-11-17 4-63

Installation
Torx Bit
TX10
Torque Wrench
Unit Screws
Power
Error
Status
Tx out
TRX
Figure 4-40. Torque Wrench with Torx TX10
Torque Wrench SMA Tool
SMA Connector
Figure 4-41. Torque Wrench with SMA Tool
4-64 1/1551-EN/LZB 119 3312 Uae Rev A 1998-11-17
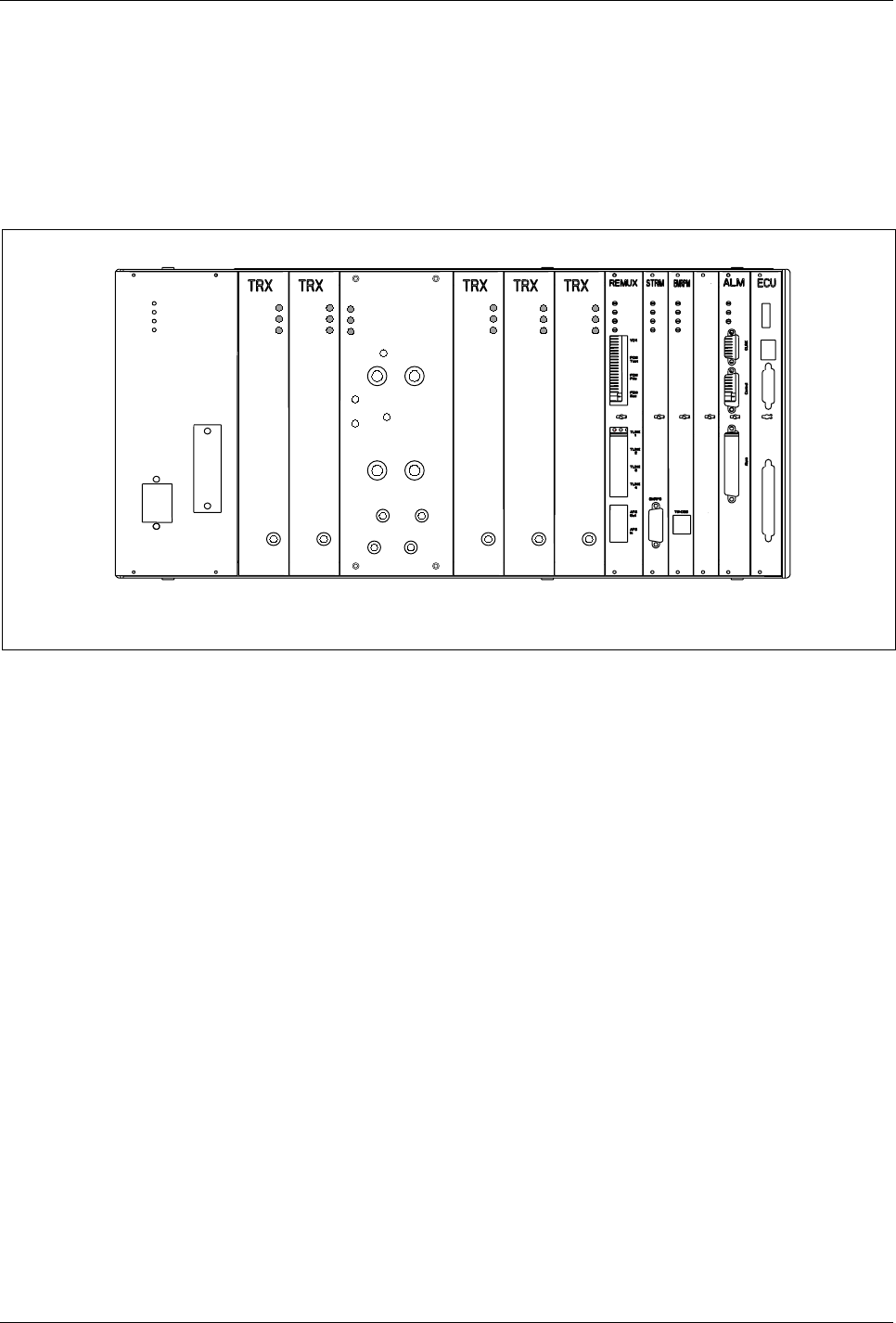
Installation
17.1.2 TRX Positions
See Figure 4-42 on page 4-65 for TRX positions. TRXs are added to the
cabinet in the following positions.
•Third TRX in slot 4
•Fourth TRX in slot 5
12 3 54786 9 11 12 13
Power
Error
Status
Power
Error
Status
Power
Error
Status
Power
Error
Status
Power
Error
Status
Tx out Tx out Tx out Tx out Tx out
TX 2
TX 1
TX 4
TX 3
RX/TX
ANT A RX/TX
ANT B
TX ANT C TX ANT D
Power
Error
Status
ANP/RFTL
PSU
Figure 4-42. Unit Positions
17.1.3 Installation Procedure
Perform the following procedure to install a TRX unit.
1. Attach the ESD strap to your wrist and connect the free end of the
strap cable to an appropriate ground conductor in the cabinet.
See Section 3 on page 4-5 for more information about ESD.
2. Remove the first RMU (dummy TRX).
Use the torque wrench with the Torx bit TX10 to loosen the
screws, and the unit extractor tool to pull the blank panel out.
3. Carefully slide the TRX into the cabinet following the guides. Push
it firmly into the backplane connector.
4. Use the torque wrench with the Torx bit TX10 to tighten the
screws on the front.
Turn the torque wrench until it slides to tighten screws to 0.6 Nm.
5. Check that the green power LED on the unit is on and the red error
LED is off. If this is not the case, refer to the "Troubleshooting"
section in the Installation and Hardware Replacement Manual for
information on detecting faulty units.
1/1551-EN/LZB 119 3312 Uae Rev A 1998-11-17 4-65
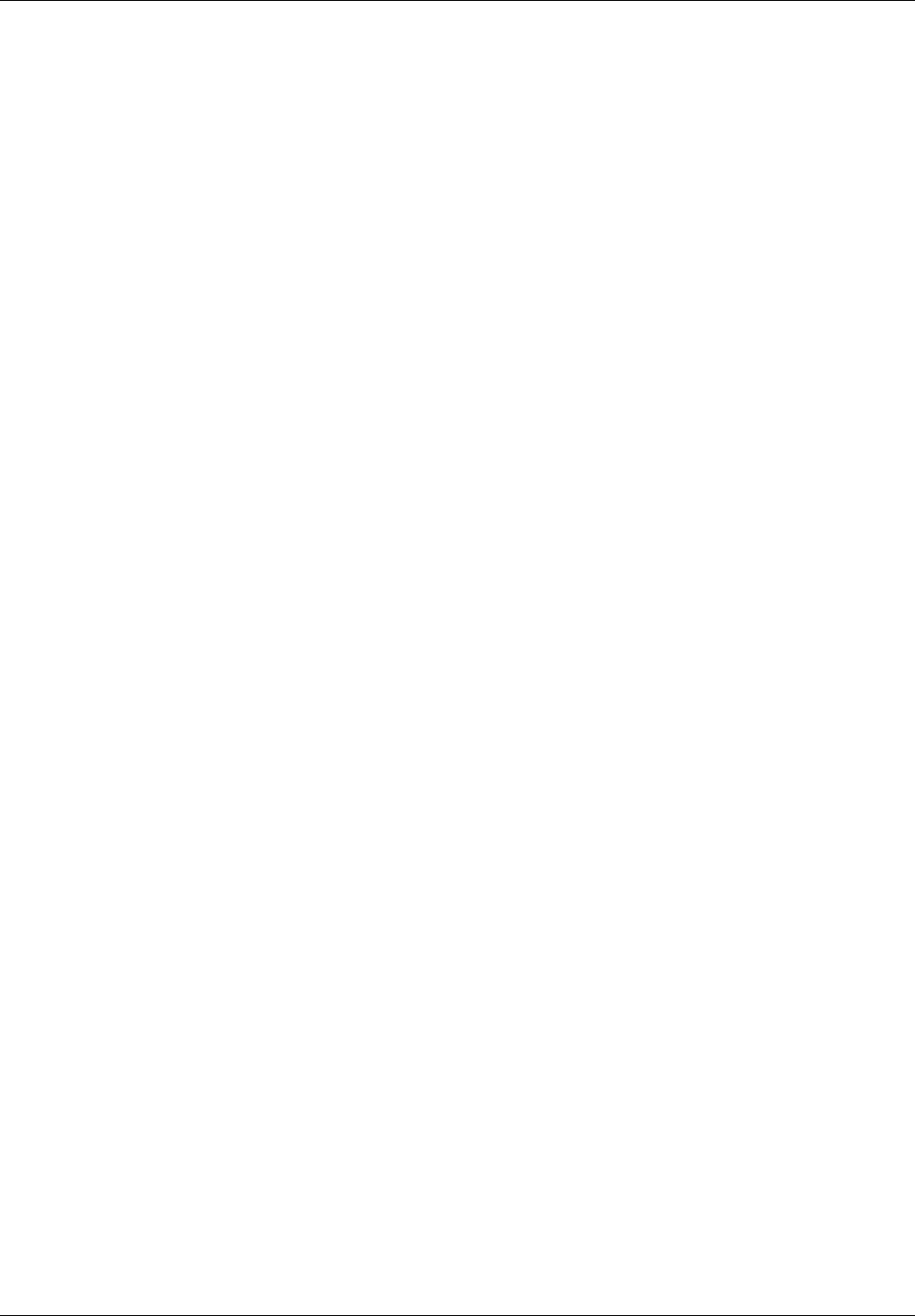
Installation
6. The cables are installed as shown in Figure 4-43 on page 4-67.
Choose the appropriate example in the figure (depending on the
number of antennas connected to the cabinet).
When attaching the cable connector to the connector on the unit,
hand-tighten as much as possible. Thereafter, fully tighten using
the torque wrench with the SMA tool.
Turn the torque wrench until it slides to tighten connector to 0.6
Nm.
7. Follow the same procedure for all other TRXs to be installed.
8. Inform the MSC operator that the installation is complete.
4-66 1/1551-EN/LZB 119 3312 Uae Rev A 1998-11-17
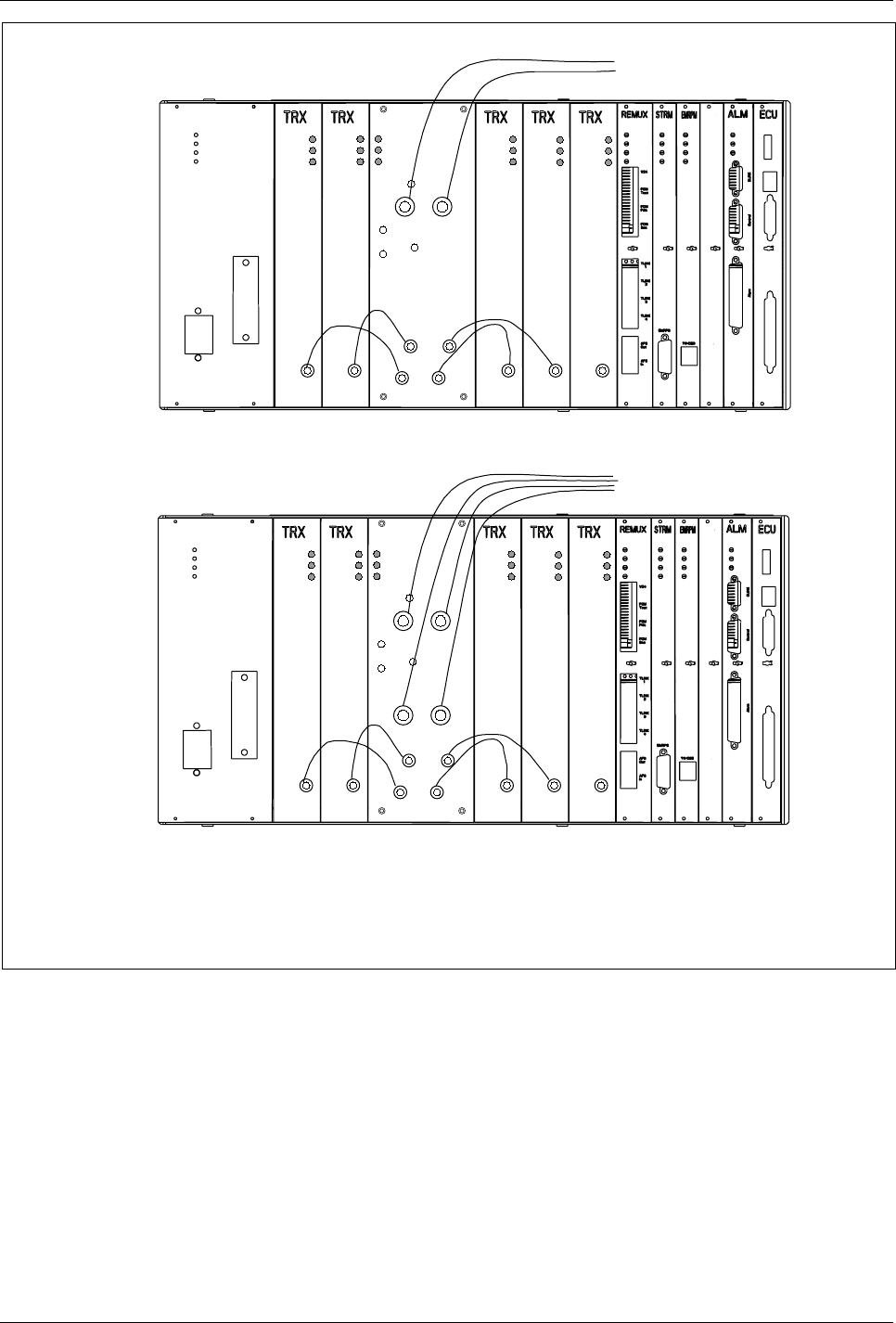
Installation
Note: The TRX board in position 6 is used as a Digital Verification Module (DVER)
Cabinets illustrated are Main Cabinets, although the cabling is the same for Primary Cabinets.
Cabinet using Two Antennas
Cabinet using Four Antennas
Power
Error
Status
Power
Error
Status
Power
Error
Status
Power
Error
Status
Power
Error
Status
Tx out Tx out Tx out Tx out Tx out
To antenna terminals
on I/O connector plate
Pos. 6
Power
Error
Status
Power
Error
Status
Power
Error
Status
Power
Error
Status
Power
Error
Status
Tx out Tx out Tx out Tx out Tx out
To antenna terminals
on I/O connector plate
Pos. 6
TX 2
TX 1
TX 4
TX 3
RX/TX
ANT A RX/TX
ANT B
Power
Error
Status
ANP/RFTL
TX 2
TX 1
TX 4
TX 3
RX/TX
ANT A RX/TX
ANT B
TX ANT C TX ANT D
Power
Error
Status
ANP/RFTL
PSU
PSU
Figure 4-43. TRX Cable Connections for Cabinets with Antennas
17.2 Adding Cabinets
A radio base station is expanded to a two-sector site by adding a Primary
cabinet to the Main cabinet. The radio base station is expanded to a three-
sector site by adding an additional Primary cabinet. Two or three cabinets
that occupy the same site location and serve separate sectors are referred to
1/1551-EN/LZB 119 3312 Uae Rev A 1998-11-17 4-67
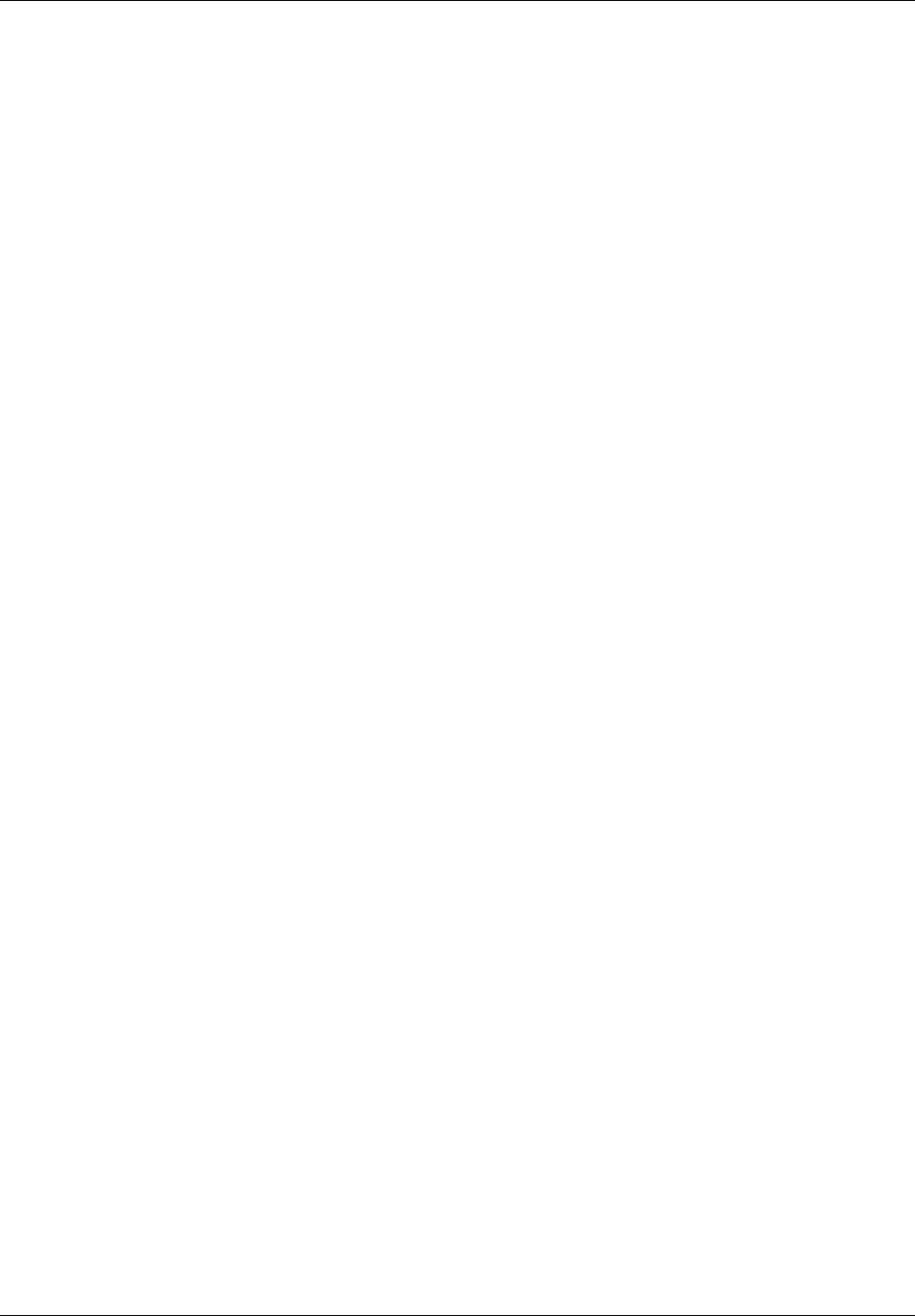
Installation
as collocated cabinets. Collocated cabinets are connected together with the
following cables:
•EMRPM Bus (EMRPB). The EMRPB cables are daisy chained from
the Main cabinet to the Primary 1 cabinet and then to the Primary 2
cabinet.
•TLINKS. Two TLINKS are run directly from the Main cabinet to
each of the Primary cabinets.
•Air Frame Synchronization (AFS). The AFS cable is daisy chained
from the Main cabinet to the Primary 1 cabinet and then to the
Primary 2 cabinet.
These cables are run in liquid tight flexible conduit from the floor of one
cabinet to the floor of the next cabinet. The Main and Primary cabinets
have two 1 3/8 inch (33 mm) diameter knockouts for 1 inch (25 mm)
diameter conduit. Both cabinet cable entries are located on the bottom
surface of the cabinet in the front right corner.
Note: All cables routed into and through the pedestal mounting base
should be encased in liquid tight flexible conduit. Do not
terminate the liquid tight flexible conduit at the pedestal base
knockouts.
A diagram of cable routing for collocated cabinets is shown in Figure 4-44
on page 4-69.
4-68 1/1551-EN/LZB 119 3312 Uae Rev A 1998-11-17

Installation
MAIN
CABINET
PRIMARY
CABINET 1
PRIMARY
CABINET 2
RX/TX Antenna
RX/TX Antenna
TX Antenna
TX Antenna
TW/BSTI
Alarms
AC Power
External Battery
RX/TX Antenna
RX/TX Antenna
TX Antenna
TX Antenna
TW/BSTI
Alarms
AC Power
External Battery
RX/TX Antenna
RX/TX Antenna
TX Antenna
TX Antenna
TW/BSTI
Alarms
AC Power
External Battery
PCM to/from MSC
PCM to/from other site
A
F
S
A
F
S
E
M
R
P
B
E
M
R
P
B
T
L
I
N
K
T
L
I
N
K
AFS
Figure 4-44. RBS 884 Micro (1900 MHz) Cable Routing for Collocated Cabinets
Use the Extension Cable Set (NTM 201 1807) for each collocated cabinet.
The Extension Cable Set is customer assembled. The cable set contains
the following:
•AFS Cable (six meters) with RJ45 connectors
•TLINK Cable (six meters) with RJ45 connectors
•EMRPB Cable (six meters)
•Two Insulation Displacement Connection (IDC) connectors
•Two IDC connector backshells
•T-Handle Connector Tool (for seating wires) See Section 17.2.2 on
page 4-70 for information on how to use the T-Handle Connector
tool.
The EMRPB cable transfers control data between the STRM in the Main
cabinet and the CONN in the Primary cabinet. See Table 4-11 on page
4-70 and Figure 4-45 on page 4-71 for cable connector assembly.
1/1551-EN/LZB 119 3312 Uae Rev A 1998-11-17 4-69
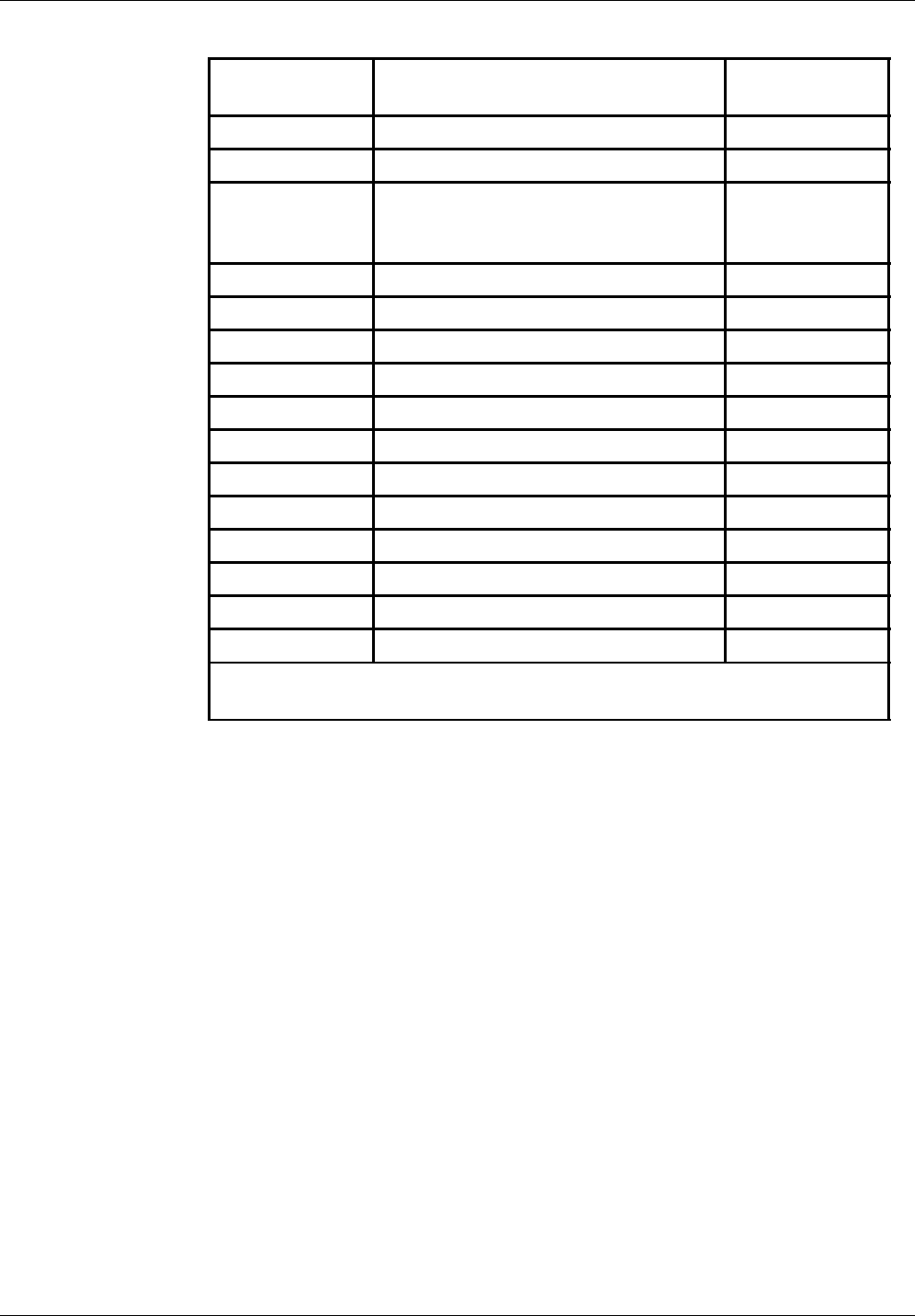
Installation
Table 4-11. Extension Cable Connector Signals and Pin Connections
Connector A
(Pin No.) Signal Connector B
(Pin No.)
1 CLKM+ (Transmit clock from STRM) 1
2 DATAM+ (Transmit data from STRM) 2
3
DATAM+ (Transmit data from
STRM)BLO+ (Blocking Signal from
STRM)
3
4BSB+ (Bus standby signal from STRM) 4
5CLKS+ (Receive clock to STRM) 5
6 DATAS+ (Receive Data to STRM) 6
7Not Connected 7
8GND 8
9CLKM- (Transmit clock from STRM) 9
10 DATAM- (Transmit data from STRM) 10
11 DATAM- (Transmit data from STRM) 11
12 BSB- (Bus standby signal from STRM) 12
13 CLKS- (Receive clock to STRM) 13
14 DATAS- (Receive Data to STRM) 14
15 Not Connected 15
NOTE: To ensure adequate shielding, clamp the cable braid and shield between
backshell halves during assembly.
17.2.1 Required Materials and Tools
17.2.1.1 Materials
The Extension Cabinet Cable Set — NTM 201 1807 is used to connect
collocated cabinets.
Install the cables in the order they appear in the table enclosed with each
cable kit.
17.2.1.2 Tools
The T-Handle connector tool that is supplied with the Extension Cabinet
Cable Set is the only tool required for intercabinet cabling. Refer to Section
17.2.2 on page 4-70 for information on the T-Handle connector tool
17.2.2 Using the T-Handle Connector Tool
The following procedure explains how to use the T-Handle connector tool
to insert individual, unstripped wires into the IDC connectors. The T-
4-70 1/1551-EN/LZB 119 3312 Uae Rev A 1998-11-17
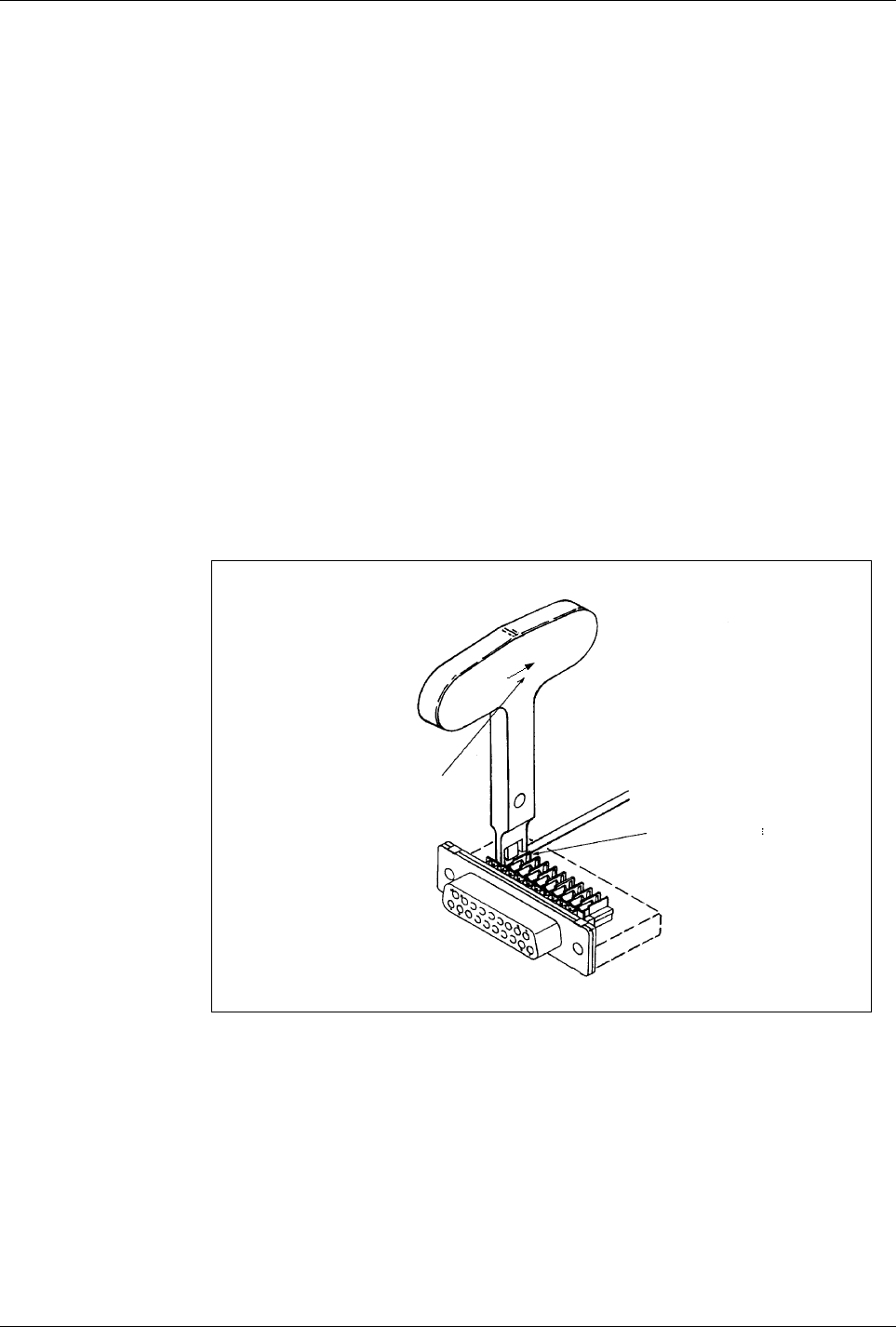
Installation
Handle connector tool features a blade that is used to push the wire
squarely into the contact and to crimp the wire insulation area, thus
providing a reliable connection.
1. Support the wire termination side of the IDC connector on a block
or other suitable flat surface and position the IDC connector so that
the wire termination area of the contacts face upward.
2. Position the unstripped wire over the desired contact with the wire
butting against the plastic shoulder and not extending past it.
3. Place the tool on the wire as shown in Figure 4-45 on page 4-71.
Make sure that the arrow on the tool handle points toward the wire
termination side of the IDC connector.
4. Press straight down on the tool handle to insert the wire.
Note: To avoid damage to the tool, the wire, or the contact,
do not apply pressure at an angle, and do not use
excessive pressure.
5. Remove the tool and inspect the contact for proper wire insertion.
Repeat the procedure if necessary.
Cabling wires
Arrow faces wire
side of connector
Tool positioned on wire
Figure 4-45. Cable Assembly with Cable Connector Tool
17.3 One-Sector Sites
Before beginning the installation, attach the ESD strap to your wrist and
connect the free end of the strap cable to an appropriate ground conductor
in the cabinet.
The following cabinet configurations are examples of fully configured sites.
1/1551-EN/LZB 119 3312 Uae Rev A 1998-11-17 4-71
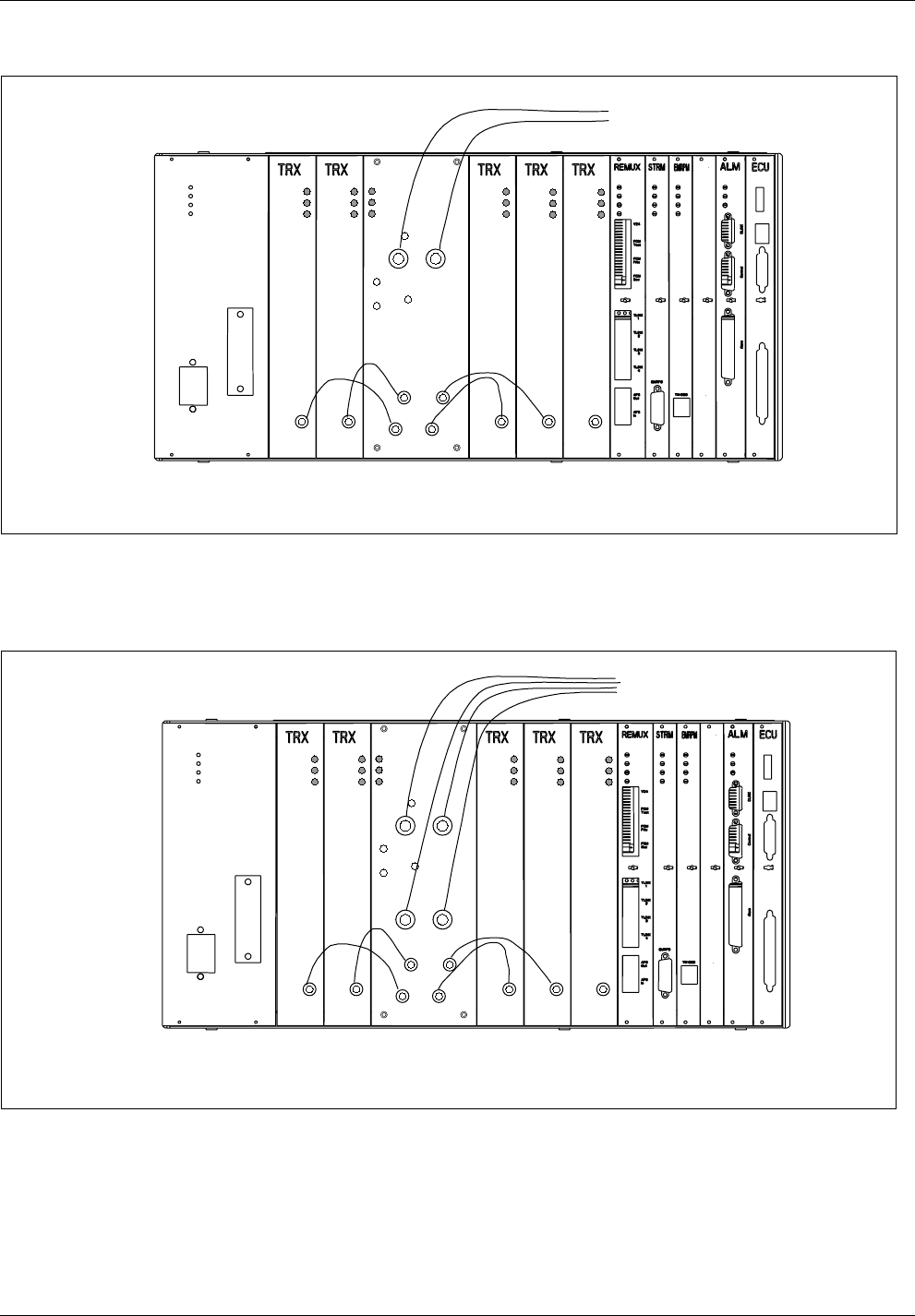
Installation
17.3.1 One-Sector Sites, One Cabinet with Two Antennas
Power
Error
Status
Power
Error
Status
Power
Error
Status
Power
Error
Status
Power
Error
Status
Tx out Tx out Tx out Tx out Tx out
To antenna terminals
on I/O connector plate
Note: The TRX board in position 6 is used for DVER
Pos. 6
TX 2
TX 1
TX 4
TX 3
RX/TX
ANT A RX/TX
ANT B
Power
Error
Status
ANP/RFTL
PSU
Figure 4-46. One-Sector Site, One Cabinet with Two Antennas
17.3.2 One-Sector Sites, One Cabinet with Four Antennas
Note: The TRX board in position 6 is used for DVER
Power
Error
Status
Power
Error
Status
Power
Error
Status
Power
Error
Status
Power
Error
Status
Tx out Tx out Tx out Tx out Tx out
Pos. 6
To antenna terminals
on I/O connector plate
TX 2
TX 1
TX 4
TX 3
RX/TX
ANT A RX/TX
ANT B
TX ANT C TX ANT D
Power
Error
Status
ANP/RFTL
PSU
Figure 4-47. One-Sector Site, One Cabinet with Four Antennas
4-72 1/1551-EN/LZB 119 3312 Uae Rev A 1998-11-17
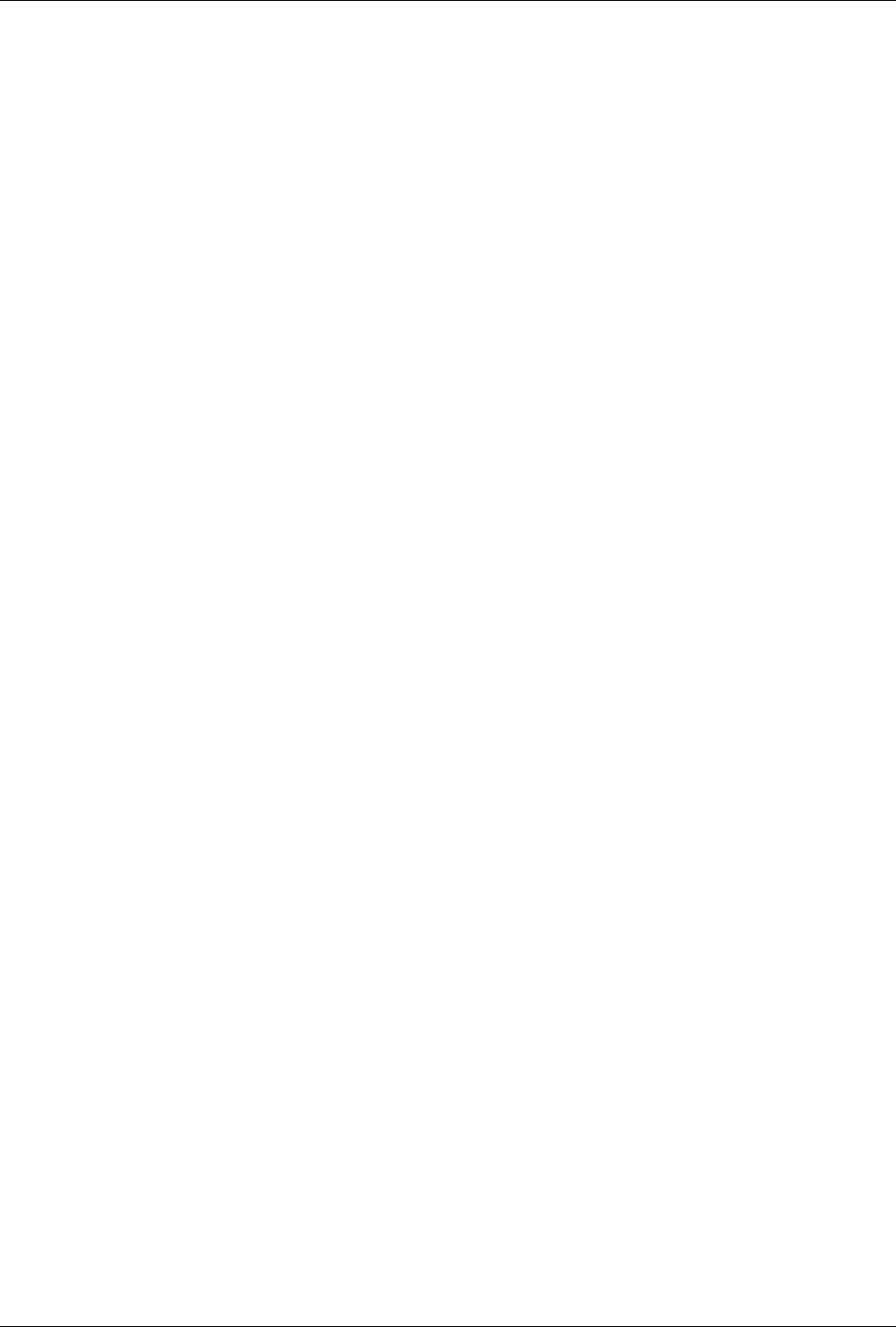
Installation
17.4 Two-Sector Sites
Before beginning the installation, attach the ESD strap to your wrist and
connect the free end of the strap cable to an appropriate ground conductor
in the cabinet.
EMRPB, TLINK, and AFS Cables are routed between cabinets using 1”
liquid-tight, flexible conduit. Conduit is run from the floor of the Main
cabinet to the floor of the Primary cabinet.
Note: Route the EMRPB cable through the conduit and use the
connector tool (see Figure 4-45 on page 4-71) to terminate to
an IDC connector. The signal and pin connections for the IDC
connector are shown in Table 4-11 on page 4-70.
17.4.1 Two-Sector Site, Each Cabinet with Two Antennas
Use the following steps to cable the Main and Primary cabinets in a two-
sector site using two antennas. Use the cables in the Extension Cabinet
Cable Set (NTM 201 1807). See Figure 4-48 on page 4-74 for placement
of cables.
1. Connect a cable from the AFS OUT connector on the REMUX
board in the Main cabinet to the External AFS IN connector on the
CONN board in the Primary cabinet.
2. Connect a cable from the TLINK 1 Interface connector on the
REMUX board in the Main cabinet to the TLINK 1 Interface
connector on the CONN board in the Primary cabinet.
3. Connect a cable from the EMRPB interface connector on the
STRM board in the Main cabinet to the top EMRPB interface
connector on the CONN board in the Primary cabinet.
4. Insert a termination plug (RVN991200012) in the bottom EMRPB
interface connector on the CONN board.
1/1551-EN/LZB 119 3312 Uae Rev A 1998-11-17 4-73
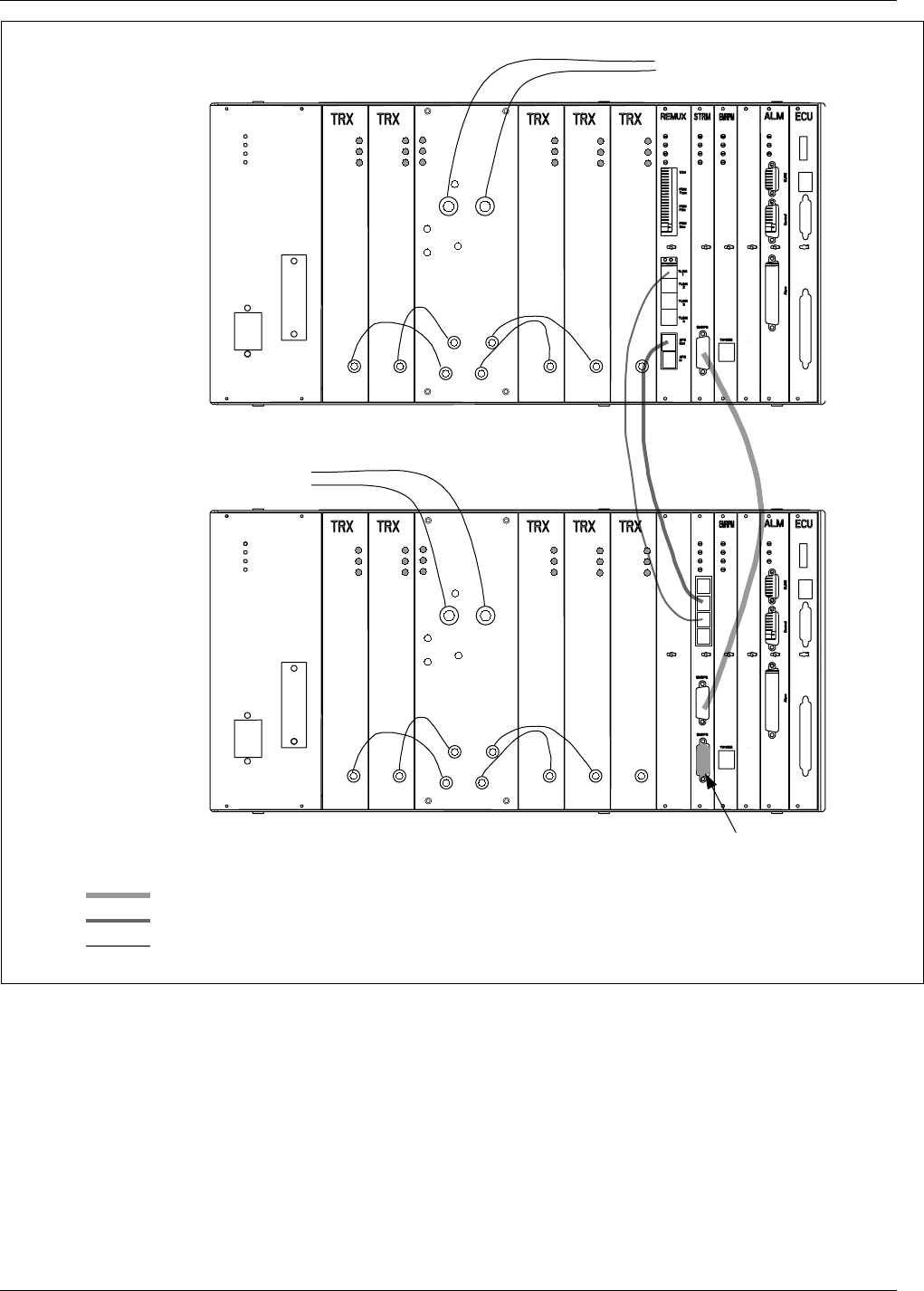
Installation
Note: The TRX board in position 6 is used for DVER
EMRPB
AFS
TLINK
Power
Error
Status
Power
Error
Status
Power
Error
Status
Power
Error
Status
Power
Error
Status
Tx out Tx out Tx out Tx out Tx out
To antenna terminals
on I/O connector plate
Main
Cabinet
Terminator
Power
Error
Status
Power
Error
Status
Power
Error
Status
Power
Error
Status
Power
Error
Status
Tx out Tx out Tx out Tx out Tx out
Primary
Cabinet
To antenna terminals
on I/O connector plate
TX 2
TX 1
TX 4
TX 3
RX/TX
ANT A RX/TX
ANT B
Power
Error
Status
ANP/RFTL
TX 2
TX 1
TX 4
TX 3
RX/TX
ANT A RX/TX
ANT B
Power
Error
Status
ANP/RFTL
PSU
PSU
Figure 4-48. Two-Sector Site, Each Cabinet with Two Antennas
4-74 1/1551-EN/LZB 119 3312 Uae Rev A 1998-11-17
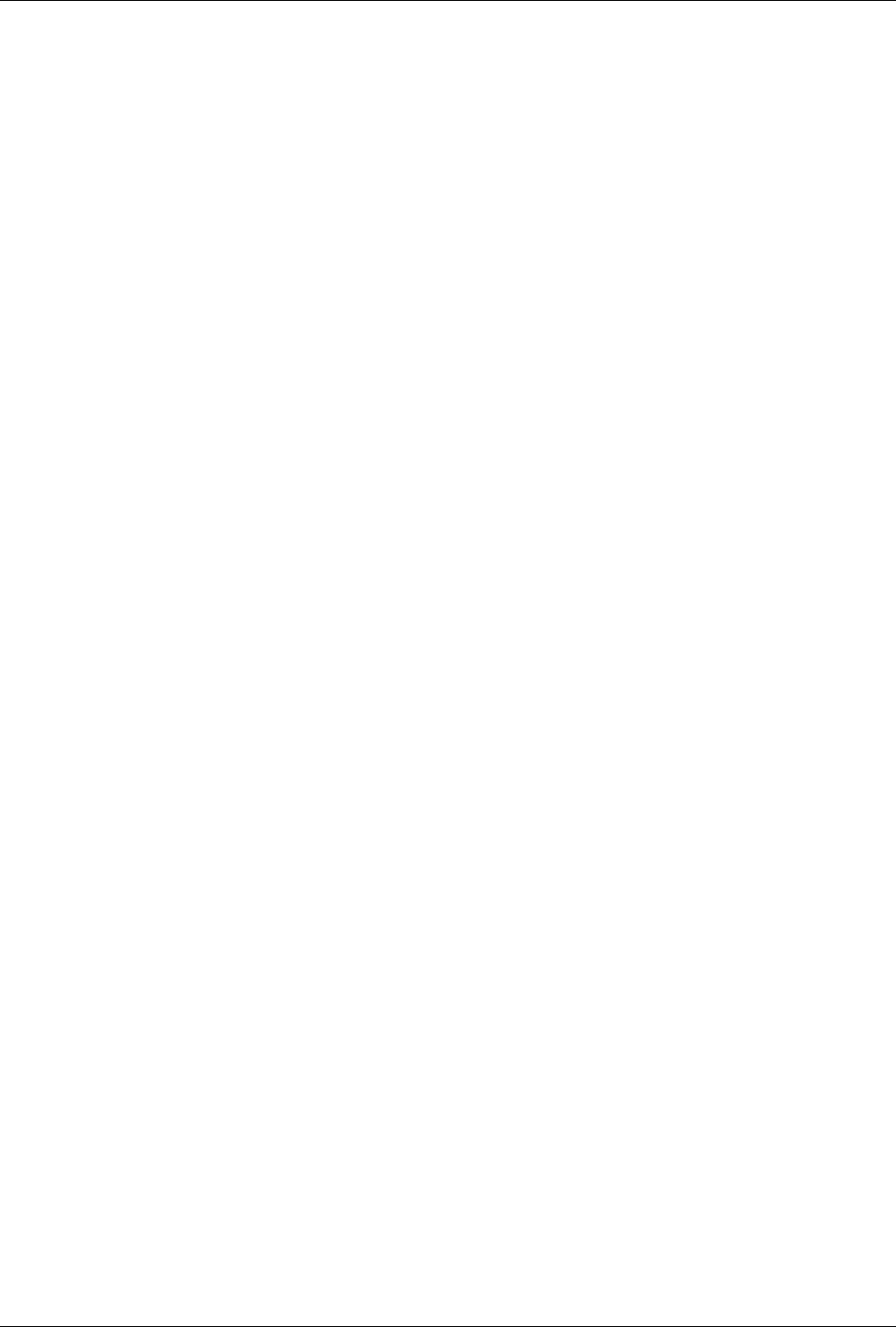
Installation
17.4.2 Two-Sector Site, Each Cabinet with Four Antennas
Use the following steps to cable the Main and Primary cabinets in a two-
sector site using four antennas. Use the cables in the Extension Cable Set
(NTM 201 1807). See Figure 4-49 on page 4-76 for placement of cables.
1. Connect a cable from the TLINK 1 Interface connector on the
REMUX board in the Main cabinet to the TLINK 1 Interface
connector on the CONN board in the Primary cabinet.
2. Connect a cable from the External AFS OUT connector on the
REMUX board in the Main cabinet to the External AFS IN
connector on the CONN board in the Primary cabinet.
3. Connect a cable from the EMRPB interface connector on the
STRM board in the Main cabinet to the top EMRPB interface
connector on the CONN board in the Primary cabinet.
4. Insert a termination plug (RVN991200012) in the bottom EMRPB
interface connector on the CONN board.
1/1551-EN/LZB 119 3312 Uae Rev A 1998-11-17 4-75
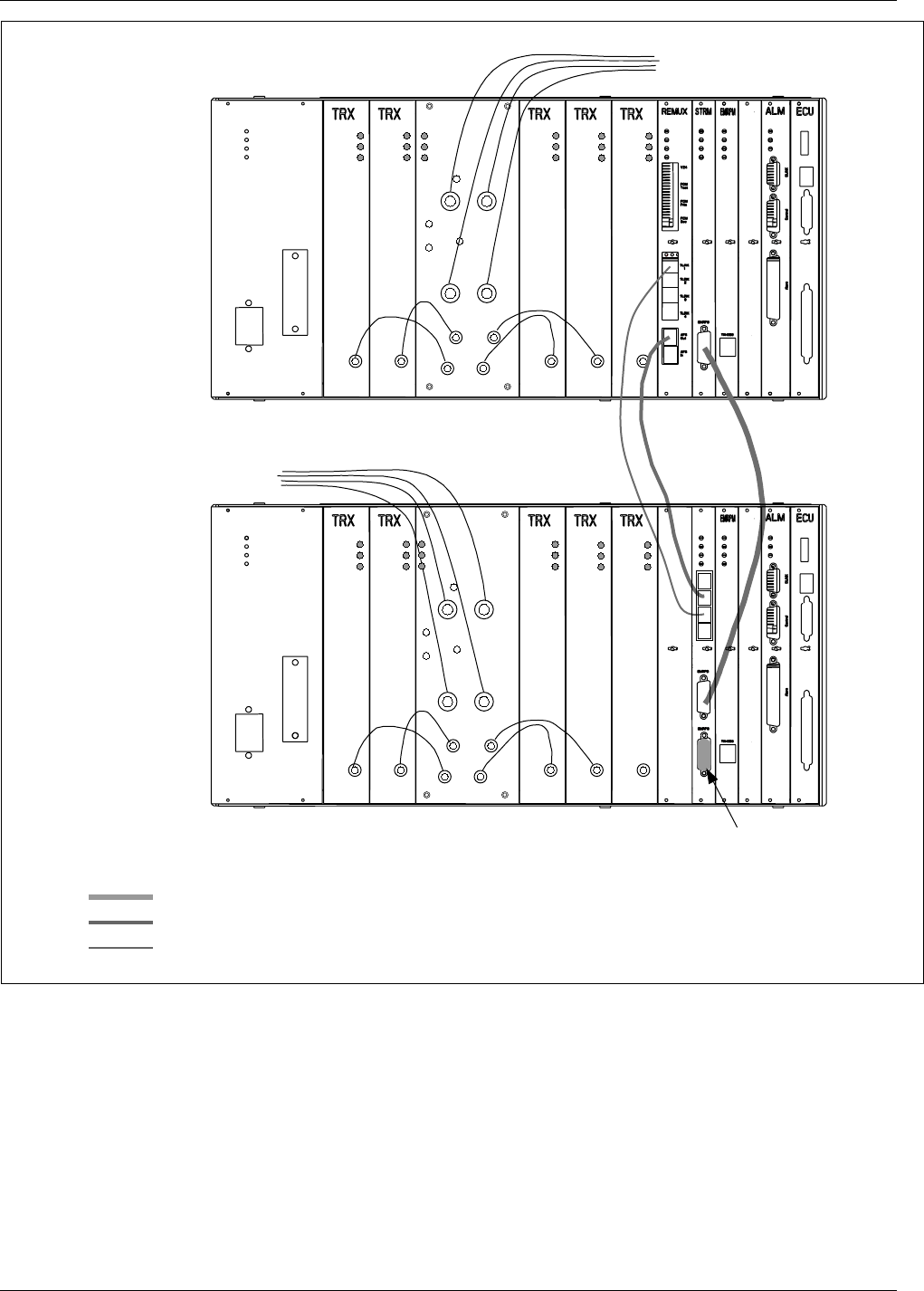
Installation
Power
Error
Status
Power
Error
Status
Power
Error
Status
Power
Error
Status
Power
Error
Status
Tx out Tx out Tx out Tx out Tx out
To antenna terminals
on I/O connector plate
Main
Cabinet
Note: The TRX board in position 6 is used for DVER
EMRPB
AFS
TLINK
Power
Error
Status
Tx out
Power
Error
Status
Power
Error
Status
Power
Error
Status
Power
Error
Status
Tx out Tx out Tx out Tx out
Terminator
Primary
Cabinet
To antenna terminals
on I/O connector plate
TX 2
TX 1
TX 4
TX 3
RX/TX
ANT A RX/TX
ANT B
TX ANT C TX ANT D
Power
Error
Status
ANP/RFTL
TX 2
TX 1
TX 4
TX 3
RX/TX
ANT A RX/TX
ANT B
TX ANT C TX ANT D
Power
Error
Status
ANP/RFTL
PSU
PSU
Figure 4-49. Two-Sector Site, Each Cabinet with Four Antennas
17.5 Three Sector Sites
Before you begin the installation, attach the ESD strap to your wrist and
connect the free end of the strap cable to an appropriate ground conductor
in the cabinet.
4-76 1/1551-EN/LZB 119 3312 Uae Rev A 1998-11-17

Installation
EMRPB, TLINK, and AFS Cables are routed between cabinets using 1”
liquid-tight, flexible conduit. Conduit is run from the floor of the Main
cabinet to the floor of the Primary cabinet.
Note: Route the EMRPB cable through the conduit and use the
connector tool (see Figure 4-45 on page 4-71) to terminate to
an IDC connector per Table 4-11 on page 4-70.
17.5.1 Three-Sector Site, Each Cabinet with Two Antennas
Use the following steps to cable the Main, Primary 1, and Primary 2
cabinets in a three-sector site using two antennas. Use the cables in the
Extension Cable Set (NTM 201 1807). See Figure 4-50 on page 4-78 for
placement of cables.
1. Connect a cable from the TLINK 1 Interface connector on the
REMUX board in the Main cabinet to the TLINK 1 Interface
connector on the CONN board in the Primary 1 cabinet.
2. Connect a cable from the TLINK 3 Interface connector on the
REMUX board in the Main cabinet to the TLINK 1 Interface
connector on the CONN board in the Primary 2 cabinet.
3. Connect a cable from the External AFS OUT connector on the
REMUX board in the Main cabinet to the External AFS IN
connector on the CONN board in the Primary 1 cabinet.
4. Connect a cable from the External AFS OUT connector on the
CONN board in the Primary 1 cabinet to the External AFS IN
connector on the CONN board in the Primary 2 cabinet.
5. Connect a cable from the EMRPB interface connector on the
STRM board in the Main cabinet to the top EMRPB interface
connector on the CONN board in the Primary 1 cabinet.
6. Connect a cable from the bottom EMRPB interface connector on
the CONN board in the Primary 1 cabinet to the top EMRPB
interface connector on the CONN board in the Primary 2 cabinet.
7. Insert a termination plug (RVN991200012) in the bottom EMRPB
interface connector on the CONN board in the Primary 2 cabinet.
1/1551-EN/LZB 119 3312 Uae Rev A 1998-11-17 4-77
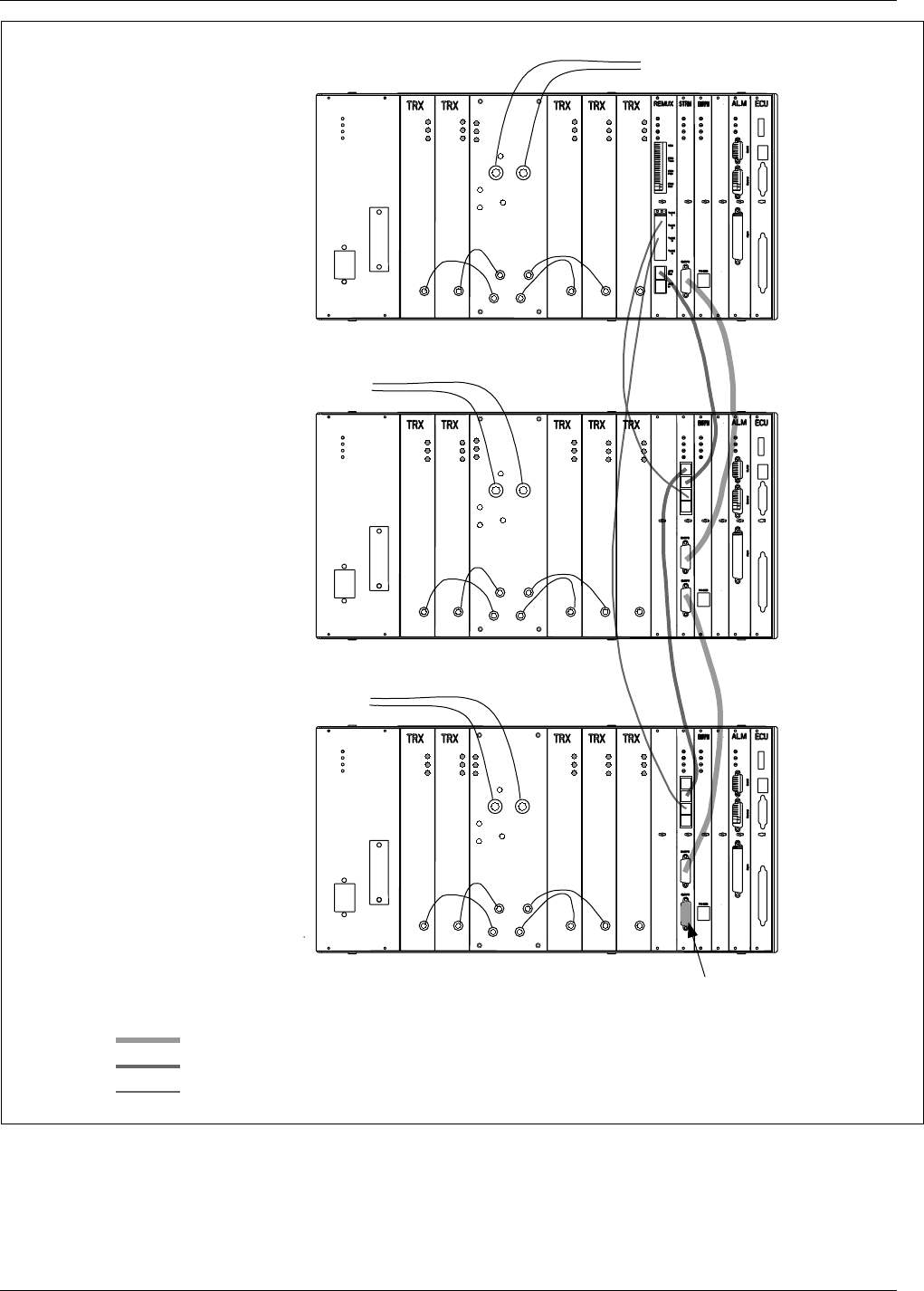
Installation
Note: The TRX board in position 6 is used for DVER
EMRPB
AFS
TLINK
Terminator
Main
Cabinet
Power
Error
Status
Power
Error
Status
Power
Error
Status
Power
Error
Status
Power
Error
Status
Tx out Tx out Tx out Tx out Tx out
To antenna terminals
on I/O connector plate
Pos
. 6
Primary 1
Cabinet
Power
Error
Status
Power
Error
Status
Power
Error
Status
Power
Error
Status
Power
Error
Status
Tx out Tx out Tx out Tx out Tx out
To antenna terminals
on I/O connector plate
Pos
. 6
Primary 2
Cabinet
Power
Error
Status
Power
Error
Status
Power
Error
Status
Power
Error
Status
Power
Error
Status
Tx out Tx out Tx out Tx out Tx out
To antenna terminals
on I/O connector plate
Pos
. 6
TX 2
TX 1
TX 4
TX 3
RX/TX
ANT A RX/TX
ANT B
Power
Error
Status
ANP/RFTL
TX 2
TX 1
TX 4
TX 3
RX/TX
ANT A RX/TX
ANT B
Power
Error
Status
ANP/RFTL
TX 2
TX 1
TX 4
TX 3
RX/TX
ANT A RX/TX
ANT B
Power
Error
Status
ANP/RFTL
PSU
PSU
PSU
Figure 4-50. Three-Sector Site, Each Cabinet with Two Antennas
4-78 1/1551-EN/LZB 119 3312 Uae Rev A 1998-11-17
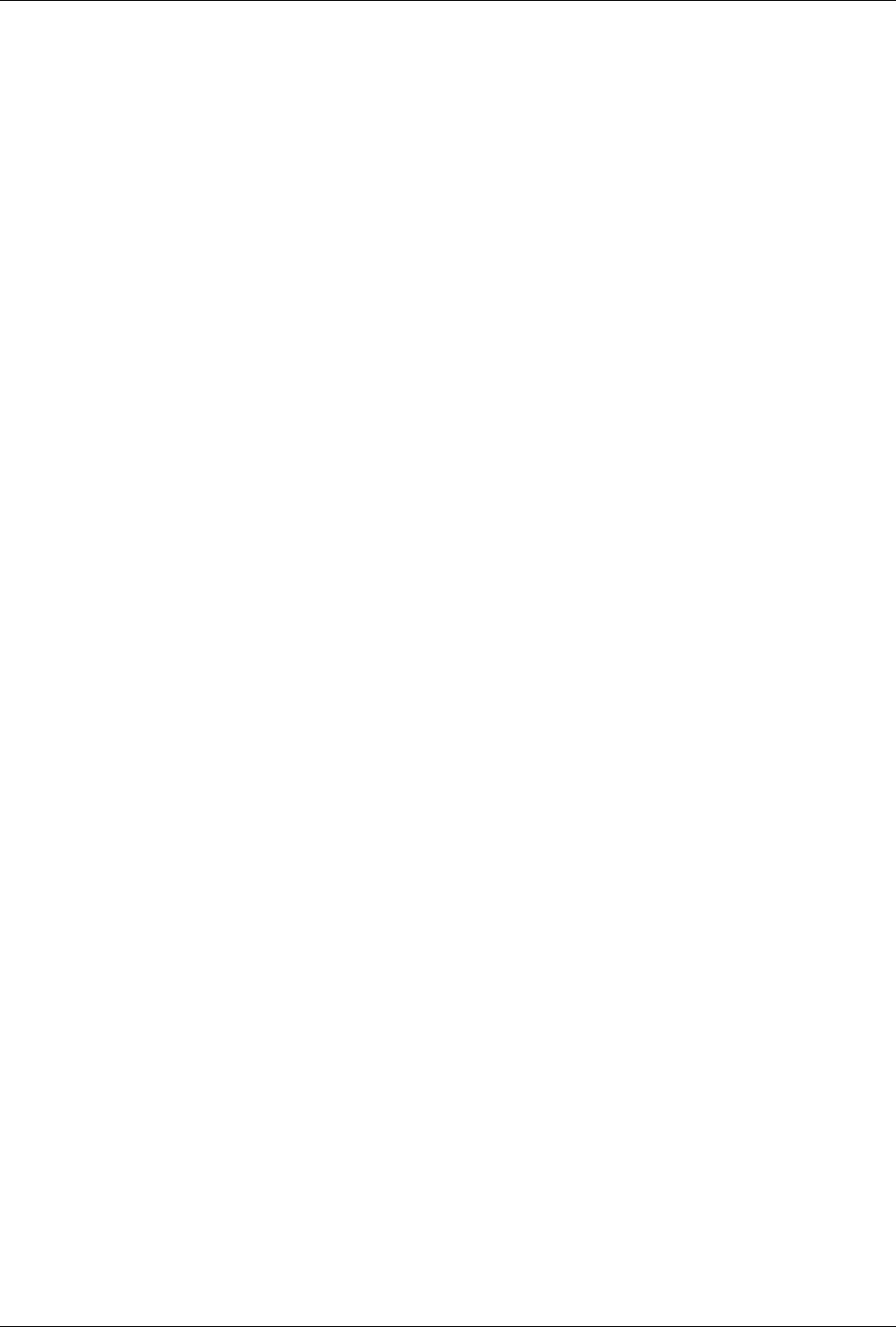
Installation
17.5.2 Three-Sector Site, Each Cabinet with Four Antennas
Use the following steps to cable the Main, Primary 1, and Primary 2
cabinets in a three-sector site using four antennas. Use the cables in the
Extension Cable Set (NTM 201 1807). See Figure 4-51 on page 4-80 for
placement of cables.
1. Connect a cable from the TLINK 1 Interface connector on the
REMUX board in the Main cabinet to the TLINK 1 Interface
connector on the CONN board in the Primary 1 cabinet.
2. Connect a cable from the TLINK 3 Interface connector on the
REMUX board in the Main cabinet to the TLINK 1 Interface
connector on the CONN board in the Primary 2 cabinet.
3. Connect a cable from the External AFS OUT connector on the
REMUX board in the Main cabinet to the External AFS IN
connector on the CONN board in the Primary 1 cabinet.
4. Connect a cable from the External AFS OUT connector on the
CONN board in the Primary 1 cabinet to the External AFS IN
connector on the CONN board in the Primary 2 cabinet.
5. Connect a cable from the EMRPB interface connector on the
STRM board in the Main cabinet to the top EMRPB interface
connector on the CONN board in the Primary 1 cabinet.
6. Connect a cable from the bottom EMRPB interface connector on
the CONN board in the Primary 1 cabinet to the top EMRPB
interface connector on the CONN board in the Primary 2 cabinet.
7. Insert a termination plug (RVN991200012) in the bottom EMRPB
interface connector on the CONN board in the Primary 2 cabinet.
1/1551-EN/LZB 119 3312 Uae Rev A 1998-11-17 4-79

Installation
Note: The TRX board in position 6 is used for DVER
Main Cabinet
Primary 1
Cabinet
Primary 2
Cabinet
EMRPB
AFS
TLINK
Power
Error
Status
Power
Error
Status
Power
Error
Status
Power
Error
Status
Power
Error
Status
Tx out Tx out Tx out Tx out Tx out
Power
Error
Status
Tx out
Power
Error
Status
Power
Error
Status
Power
Error
Status
Power
Error
Status
Tx out Tx out Tx out Tx out
Power
Error
Status
Tx out
Power
Error
Status
Power
Error
Status
Power
Error
Status
Power
Error
Status
Tx out Tx out Tx out Tx out
Pos
. 6
Terminator
To antenna terminals
on I/O connector plate
To antenna terminals
on I/O connector plate
To antenna terminals
on I/O connector plate
Pos
. 6
Pos
. 6
TX 2
TX 1
TX 4
TX 3
RX/TX
ANT A RX/TX
ANT B
TX ANT C TX ANT D
Power
Error
Status
ANP/RFTL
TX 2
TX 1
TX 4
TX 3
RX/TX
ANT A RX/TX
ANT B
TX ANT C TX ANT D
Power
Error
Status
ANP/RFTL
TX 2
TX 1
TX 4
TX 3
RX/TX
ANT A RX/TX
ANT B
TX ANT C TX ANT D
Power
Error
Status
ANP/RFTL
PSU
PSU
PSU
Figure 4-51. Three-Sector Site, Each Cabinet with Four Antennas
4-80 1/1551-EN/LZB 119 3312 Uae Rev A 1998-11-17
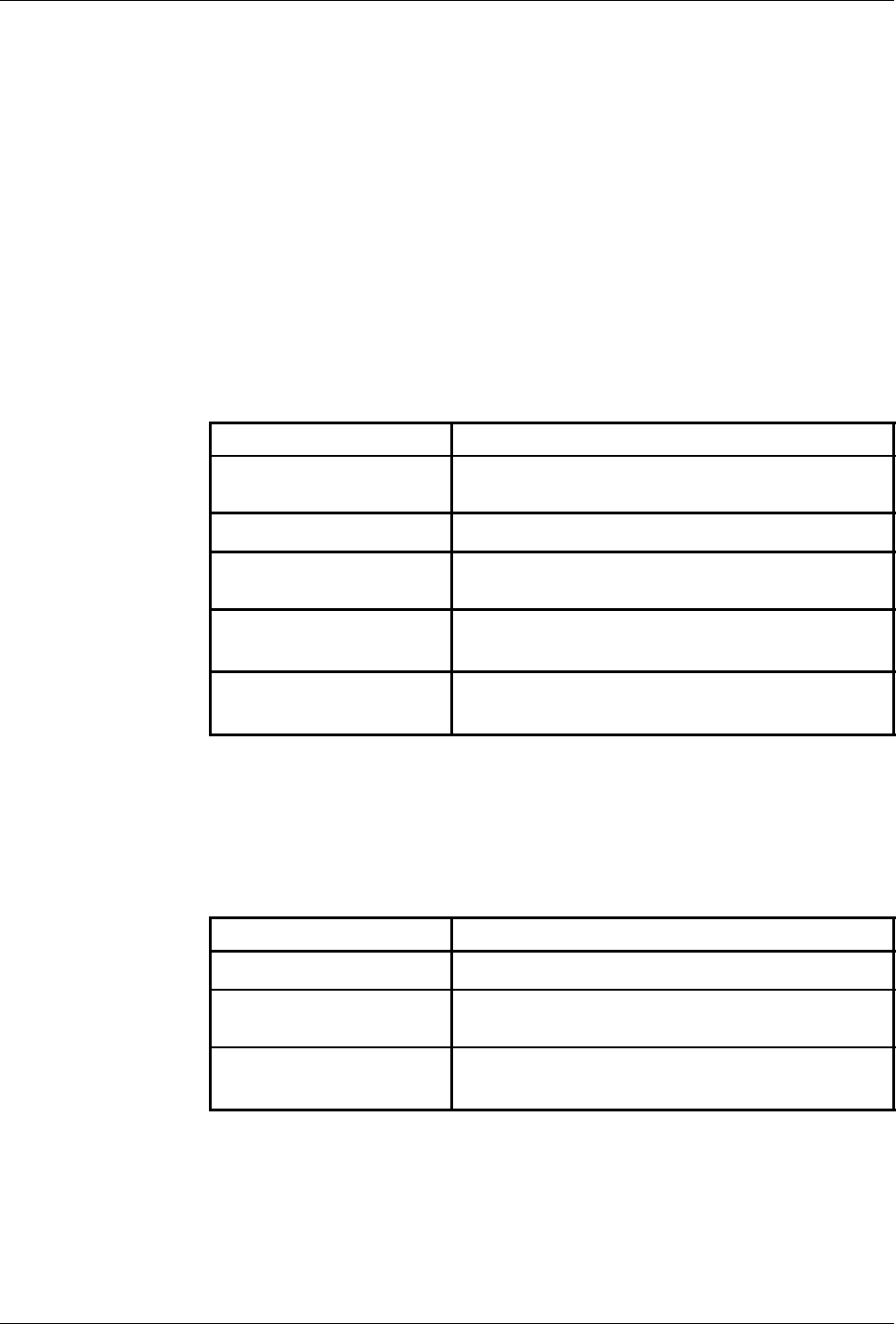
Installation
18 RBS 884 Micro (1900 MHz) Cabinet Repainting
This section provides instructions for repainting RBS 884 Micro (1900
MHz) cabinets. The instructions are intended as general recommendations
only and may not be suitable in all applications.
18.1 Required Materials and Tools
18.1.1 Materials
Prior to repainting the cabinet, obtain all materials listed in Table 4-12 on
page 4-81
Table 4-12. Cabinet Repainting Materials
Part Number Description
Refer to Paint
Manufacturer
Two-component polyurethane coating (paint chip
required for color matching)
N/A 80 grit (or finer) Sandpaper (for orbital sander)
N/A 120 grit (or finer) Sandpaper (for finish sanding)
N/A Tack Cloth
N/A Masking Tape
18.1.2 Tools
Prior to repainting the cabinet, obtain all tools listed in Table 4-13 on page
4-81
Table 4-13. Cabinet Repainting Tools
Part Number Description
N/A Orbital Sander
N/A Paint Spraying Equipment
N/A Sanding Blocks (as required)
18.2 Cabinet Surface Preparation
Prior to repainting the RBS 884 Micro (1900 MHz) cabinet, prepare the
cabinet surface as outlined in the following steps:
1/1551-EN/LZB 119 3312 Uae Rev A 1998-11-17 4-81
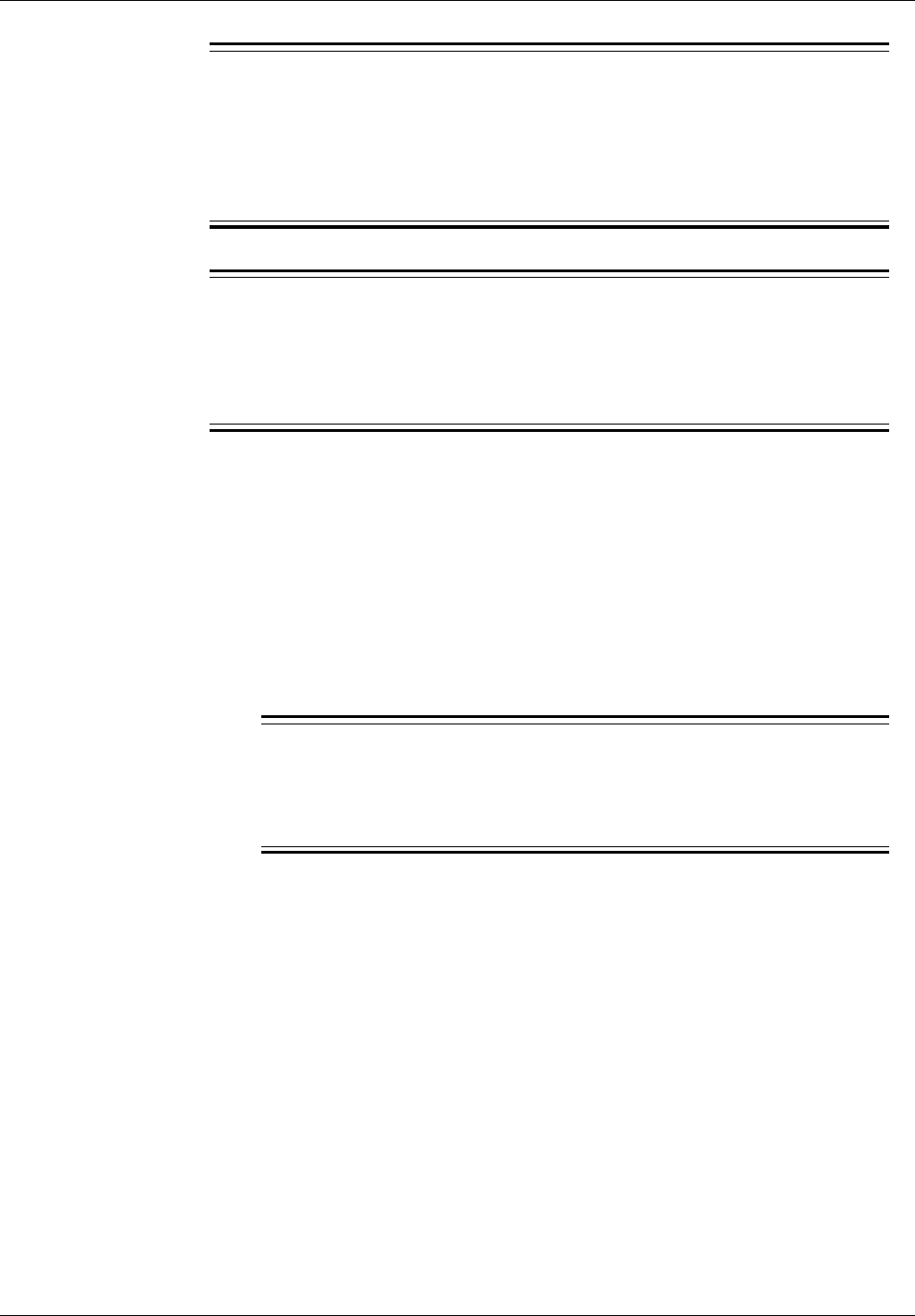
Installation
DANGER!
Paint, paint dust, and paint refinishing chemicals can be hazardous to your
health and result in injury or damage to equipment. Do not breathe paint
fumes or paint dust. Wear protective breathing equipment and work only
in well ventilated areas. Follow all local safety practices.
Caution!
Sanding the surface of the RBS 884 Micro (1900 MHz) cabinet may result
in reduced corrosion resistance. Also, use of a darker paint color will
degrade the thermal performance of the cabinet.
1. Using an orbital sander with 80 grit or finer sandpaper, lightly sand
all surfaces to be painted.
2. Blow off any excess sanding dust with compressed air.
3. Using a tack cloth, wipe down all surfaces.
4. If scratches or imperfections are visible in the surface, lightly sand
surfaces again using 120 grit or finer sandpaper.
5.
Caution!
To ensure proper paint adhesion, all paint dust and any other loose
material must be removed from the cabinet surface.
Using a tack cloth, wipe down all surfaces.
6. Mask all areas that are not to be painted, including hinges and door
hardware.
18.3 Cabinet Painting
To apply the primer and finish paint to the cabinet, perform the following
steps:
Applying Primer Paint to Cabinet
1. Using appropriate paint spraying equipment, apply primer to all areas
to be painted.
4-82 1/1551-EN/LZB 119 3312 Uae Rev A 1998-11-17
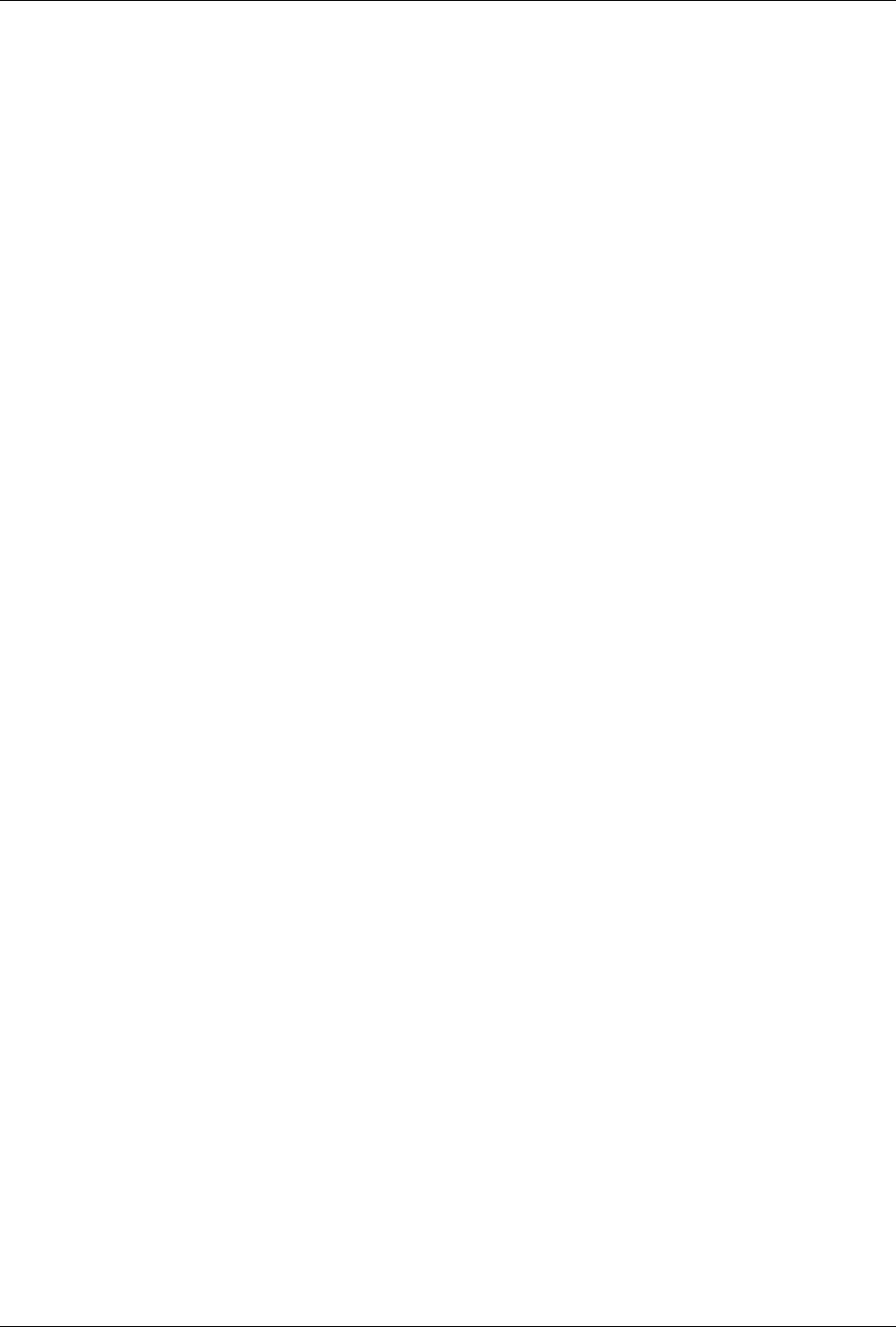
Installation
2. Allow primer to dry for a minimum of 30 minutes.
Note: Paint drying times vary according to environmental
conditions such as temperature and humidity. Refer
to the paint manufacturer’s specifications for drying
times.
3. When primer is dry, feather sand the edges of the primed areas.
4. Wipe all surfaces clean with a tack cloth. Ensure surface is free of
all dust and debris.
Applying Finish Paint to Cabinet
5. Prepare finish paint as specified by the paint manufacturer.
Note: The finish paint is a two-part polyurethane coating
(paint and catalyst) that hardens with age. Painting
time is limited after mixing. Refer to the paint
manufacturer’s specifications for working life of the
mixed paint.
6. Using appropriate paint spraying equipment, apply the finish paint to
all areas to be painted.
7. Allow paint to dry and apply one or more additional coats.
8. Allow painted cabinet to dry for a minimum of 24 hours (48 hours
recommended) before handling or removing any masking.
9. After 24 to 48 hours, carefully remove masking from hinges and
door hardware.
Note: Two-component polyurethane paint includes a
catalyst that causes the paint to harden and become
more durable with age. Within the first 48 hours
after application, the paint is soft and scuffs easily.
Use care to not scuff or mar the surface.
1/1551-EN/LZB 119 3312 Uae Rev A 1998-11-17 4-83
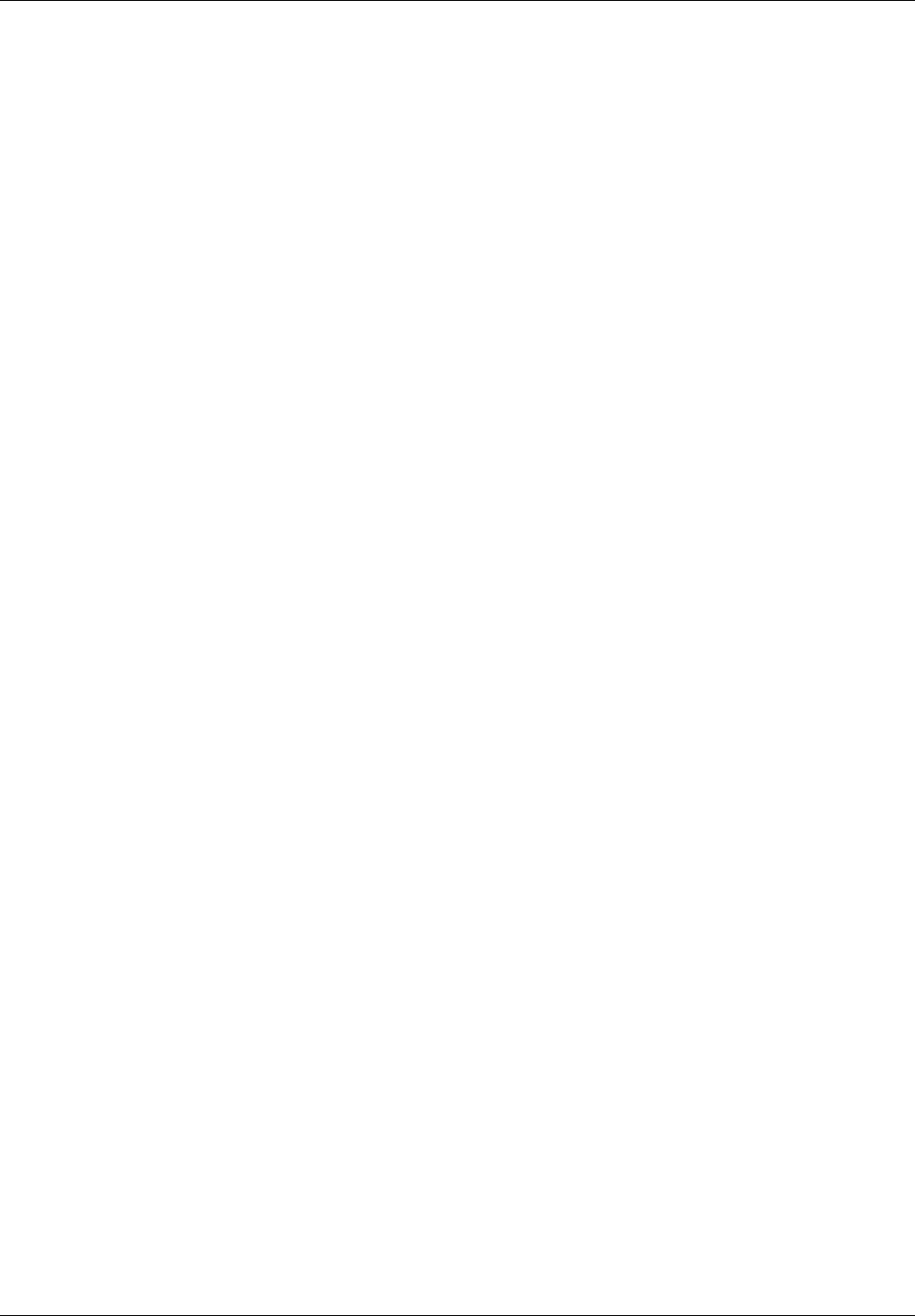
Installation
4-84 1/1551-EN/LZB 119 3312 Uae Rev A 1998-11-17
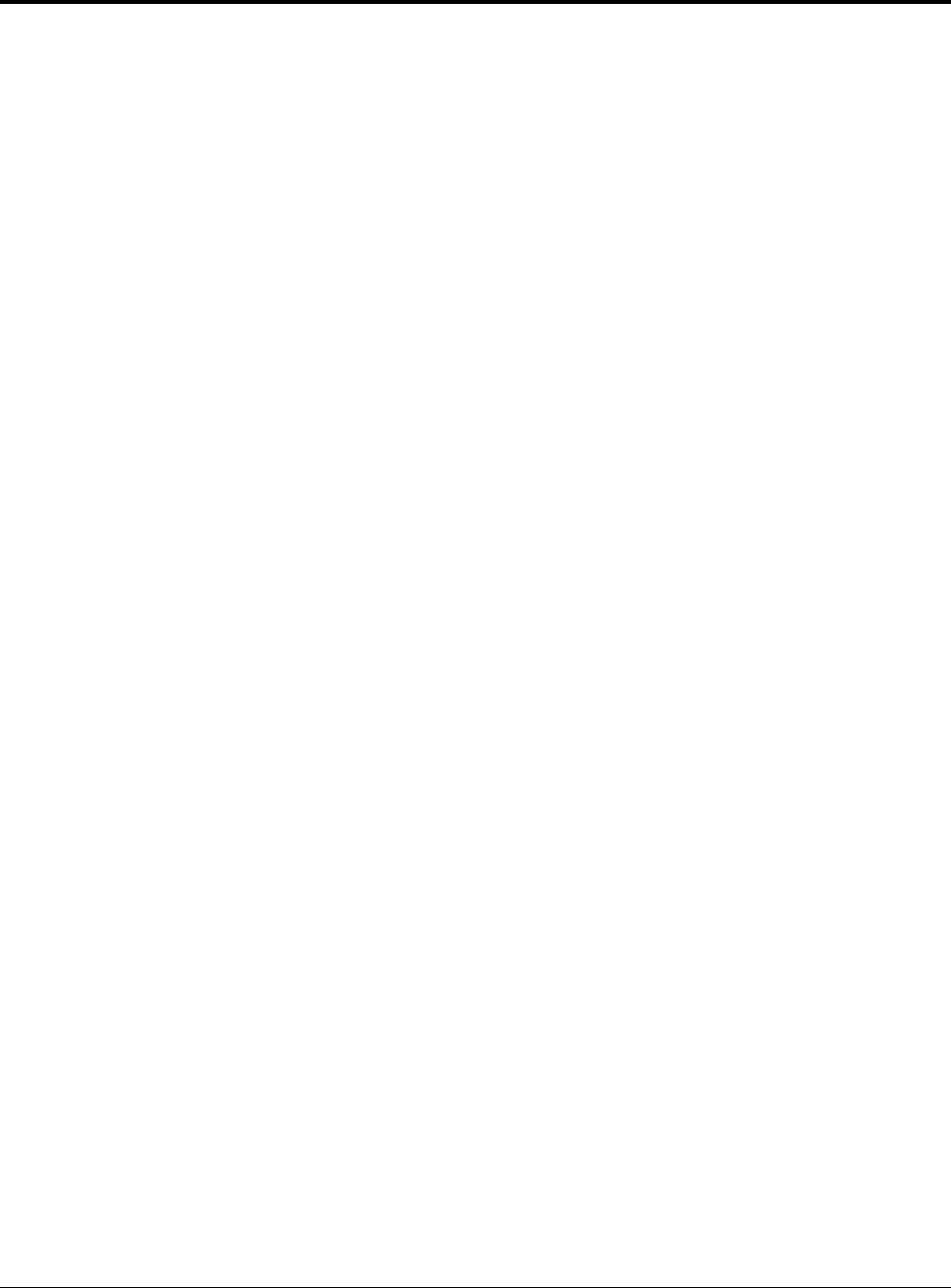
Part 5
Hardware Replacement
1 Introduction .................. 5-3
2 Safety Considerations ............. 5-3
2.1 Grounding of the RBS Cabinets ...... 5-3
2.2 Voltage Hazards ............. 5-4
2.3 Radio Frequency Radiation ........ 5-4
2.4 Beryllium Oxide ............. 5-4
2.5 Heavy Loads ............... 5-5
3 Product Handling and Inspection ........ 5-6
4 General Troubleshooting ............ 5-6
4.1 Prerequisites and Tools .......... 5-6
4.2 Troubleshooting Procedure for RBS 884 Micro
(1900 MHz) Cabinets ........... 5-7
5 Alarm Troubleshooting ............. 5-11
6 RBS Unit Hardware Replacement ........ 5-14
6.1 Prerequisites and Tools .......... 5-15
6.2 Power Supply Unit (PSU) Replacement . . 5-18
6.3 Remote Multiplexer (REMUX) Unit
Replacement ............... 5-21
6.4 Signal Terminal Receiver, Micro (STRM) Unit
Replacement ............... 5-24
6.5 Connector (CONN) Unit Replacement . . . 5-26
6.6 Extension Module Regional Processor
(EMRPM) Unit Replacement ....... 5-28
6.7 Transceiver (TRX) Unit Replacement . . . 5-31
6.8 Antenna Near Part (ANP)/Radio Frequency
Test Loop (RFTL) Unit Replacement .... 5-33
6.9 Alarm (ALM) Unit Replacement ...... 5-35
6.10 Environmental Control Unit (ECU)
Replacement ............... 5-37
6.11 Fan Replacement ............ 5-39
6.12 Main Heater Assembly Replacement .... 5-42
6.13 Battery Heater Replacement ....... 5-45
6.14 Battery Replacement ........... 5-48
6.15 AC Surge Suppressor Replacement .... 5-52
6.16 Pulse Code Modulation (PCM) (T1/E1) Primary
Surge Suppressor Replacement ...... 5-55
6.17 Pulse Code Modulation (PCM) T1(E1)
Secondary Surge Suppressor Replacement 5-56
6.18 Air Filter Replacement .......... 5-58
2/1551-EN/LZB 119 3312 Uae Rev A 1998-11-17 5-1
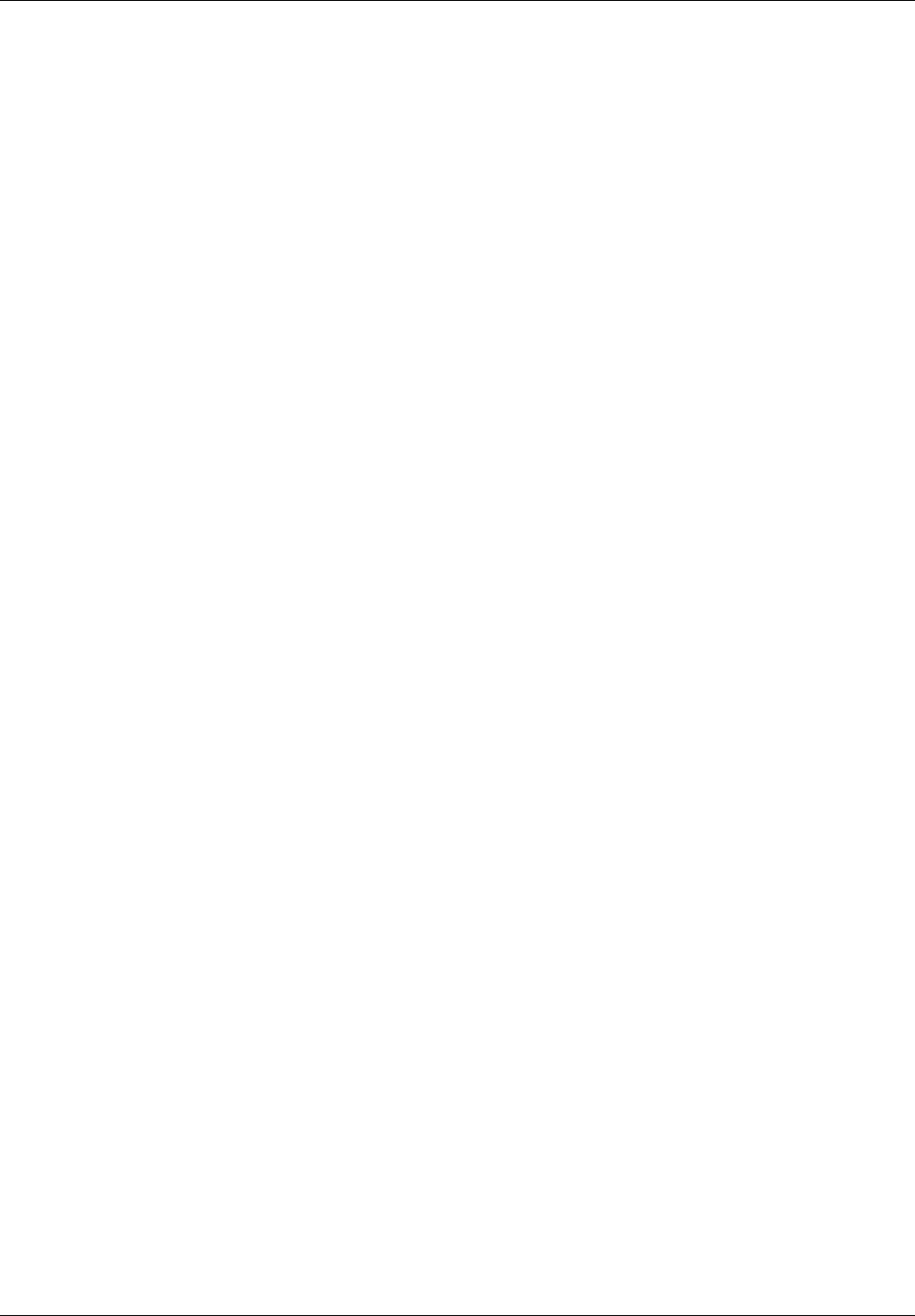
Hardware Re lacement
5-2 2/1551-EN/LZB 119 3312 Uae Rev A 1998-11-17

Hardware Re lacement
1 Introduction
This part of the manual lists procedures for basic troubleshooting and
hardware replacement of faulty items of equipment, such as cabinet units
or cables.
The use of the procedures by a site maintenance technician may depend on
instructions from the MSC personnel who are able to determine the status
of the RBS site equipment from the MSC.
The site maintenance technician may be asked to replace a particular unit
using the procedure in Section 6 on page 5-14, or to follow the
troubleshooting procedure in Section 4 on page 5-6 for determining a
faulty unit. The troubleshooting procedure is also used if failures occur
during the power-up procedure.
2 Safety Considerations
2.1 Grounding of the RBS Cabinets
This product is Safety Class 1 equipment.
The RBS cabinets must be connected to the AC power through a grounded
power cable, with the ground wire firmly connected to an electrical ground
(safety ground) at the power outlet.
2/1551-EN/LZB 119 3312 Uae Rev A 1998-11-17 5-3

Hardware Re lacement
DANGER!
Any interruption of the protective (grounding) conductor, or disconnection
of the protective ground terminal will cause a potential shock hazard that
could result in personal injury.
2.2 Voltage Hazards
DANGER!
Voltage in excess of 100V is used in the RBS 884 Micro (1900 MHz).
Observe safety precautions. Contact with voltage as low as 50V can result
in death.
Observe the following safety precautions:
•Do not touch high voltage connections when working on energized
equipment.
•Do not energize equipment before the Power Up procedure in this
manual is performed.
•Never connect the power cable to the power unit when the unit is
removed from the cabinet.
•Perform all installation and repair procedures in the order presented.
•Keep one hand away from the equipment, if the nature of the
maintenance permits, to reduce the possibility of current flowing
through vital body organs.
Note: The power cable serves as the only power disconnection device
for the cabinet.
2.3 Radio Frequency Radiation
DANGER!
Radio frequency radiation from an antenna may be a danger to health,
causing severe burns to skin and clothing.
All transmitters must be disabled prior to working with or near antennas.
2.4 Beryllium Oxide
Some equipment contains beryllium oxide in ceramic form.
5-4 2/1551-EN/LZB 119 3312 Uae Rev A 1998-11-17
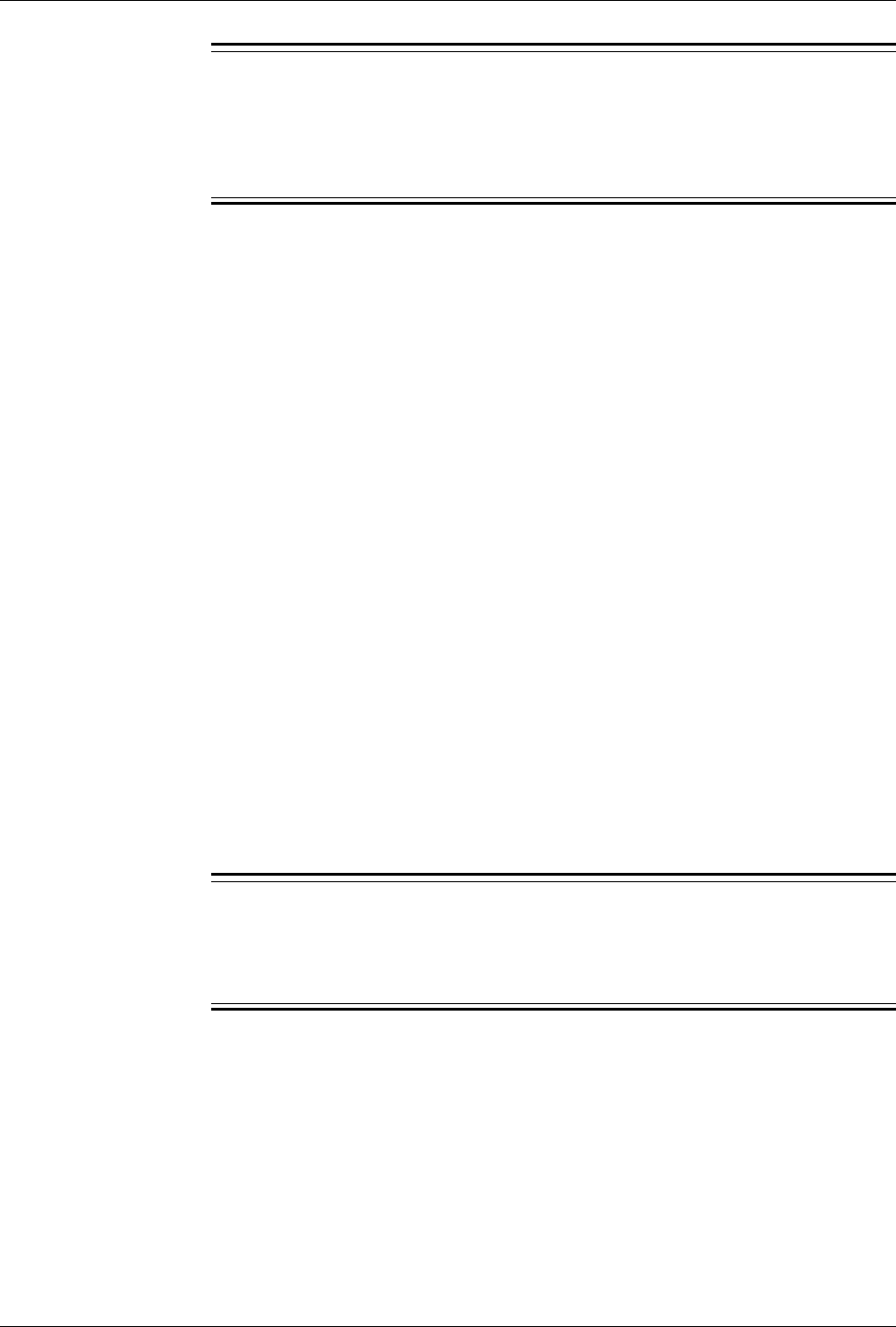
Hardware Re lacement
DANGER!
Beryllium oxide is poisonous and constitutes a health hazard if present in
finely dispersed form, such as dust or smoke, which can be inhaled. Read
local hazardous chemical regulations before working with beryllium oxide.
Units with components containing beryllium oxide are marked with a
warning label. For detailed information on properties, health and
environmental hazards, refer to the regulations issued by the local
authorities.
The following rules must be obeyed by all persons handling beryllium
oxide:
•Ceramics containing beryllium oxide must not be scraped, filed,
ground, treated with acid, or machined in any other way.
•Compressed air must not be used to clean units containing beryllium
oxide.
•Always wear protective gloves when handling beryllium oxide.
•Use wet rags to collect dust and particles from damaged beryllium
oxide components. After use, place the rags in plastic bags and seal
the bags completely.
Scrapped beryllium oxide must be treated as environmentally hazardous
waste. Local authorities enforce regulations regarding the treatment and
disposal of environmentally hazardous waste. Comply with all applicable
local regulations.
2.5 Heavy Loads
Warning!
Incorrectly lifting heavy loads can result in severe injury to persons and
damage to the equipment.
A fully equipped RBS 884 Micro (1900 MHz) cabinet weighs 105 kg (230
lbs). Ericsson recommends two persons be present during the maintenance
activities where heavy lifting is required.
2/1551-EN/LZB 119 3312 Uae Rev A 1998-11-17 5-5

Hardware Re lacement
3 Product Handling and Inspection
Components may be damaged because of ESD. Read the “Electrostatic
Discharge” section in the Installation and Hardware Replacement Manual
for information and directions.
A hardware replacement unit must always be kept in its original packaging
until it is installed on a site.
The unit must not be exposed to wide variations in temperature, to direct
sunshine, or to high levels of humidity, such as may occur if the unit is
left in a closed vehicle.
When handling circuits boards, do not touch any components or connector
pins.
If the packing material is damaged, inspect the unit immediately. If the
unit appears to be damaged, follow local procedures or return it to the
local service center for repair or hardware replacement.
A faulty unit must always be accompanied by a completed Repair Traveler
Note, with written information concerning the circumstances of the
suspected fault. A Repair Traveler Note is a tie-on tag, which can be
attached to the unit.
4 General Troubleshooting
Operational status of the RBS equipment is indicated by LEDs mounted on
the front of the units plugged into the cabinets.
In general, green LEDs are used for power status, red LEDs are used for
error status, and yellow LEDs are used to indicate other types of
operational status.
The procedure in this section is used to determine faulty units by visual
inspection of the LEDs and other means. If the procedure does not result
in the detection of a faulty unit, the MSC must be informed in order to
determine if a problem at the site is still indicated at the MSC.
4.1 Prerequisites and Tools
4.1.1 Prerequisites
The troubleshooting procedure in this section is intended to be followed if
an RBS unit fault is detected during the power-up procedure, or at the
request of the MSC as a result of an RBS site equipment error indication
at the MSC.
5-6 2/1551-EN/LZB 119 3312 Uae Rev A 1998-11-17

Hardware Re lacement
4.1.2 Tools
Tools required to troubleshoot the RBS 884 Micro (1900 MHz) are shown
in Table 5-1 on page 5-7.
Table 5-1. Tools List
Product Number Description
Pen
LYB 250 01/14 ESD Wrist Strap and Cable2
LTD 117 02 and
LTD 117 14
Unit Extractor Tool (Handle + Button)
N/A AC or AC/DC Voltmeter1
(for checking the line voltage)
1Included in Tool Kit LTT 601 044/1
2Included in Tool Case LTT 601 84
4.2 Troubleshooting Procedure for RBS 884 Micro (1900 MHz)
Cabinets
To troubleshoot the RBS 884 Micro (1900 MHz), perform the following:
Cabinet Access
1. Unlock the door latches as shown in Figure 5-1 on page 5-7
Figure 5-1. Unlocking the RBS Cabinet Door
2/1551-EN/LZB 119 3312 Uae Rev A 1998-11-17 5-7
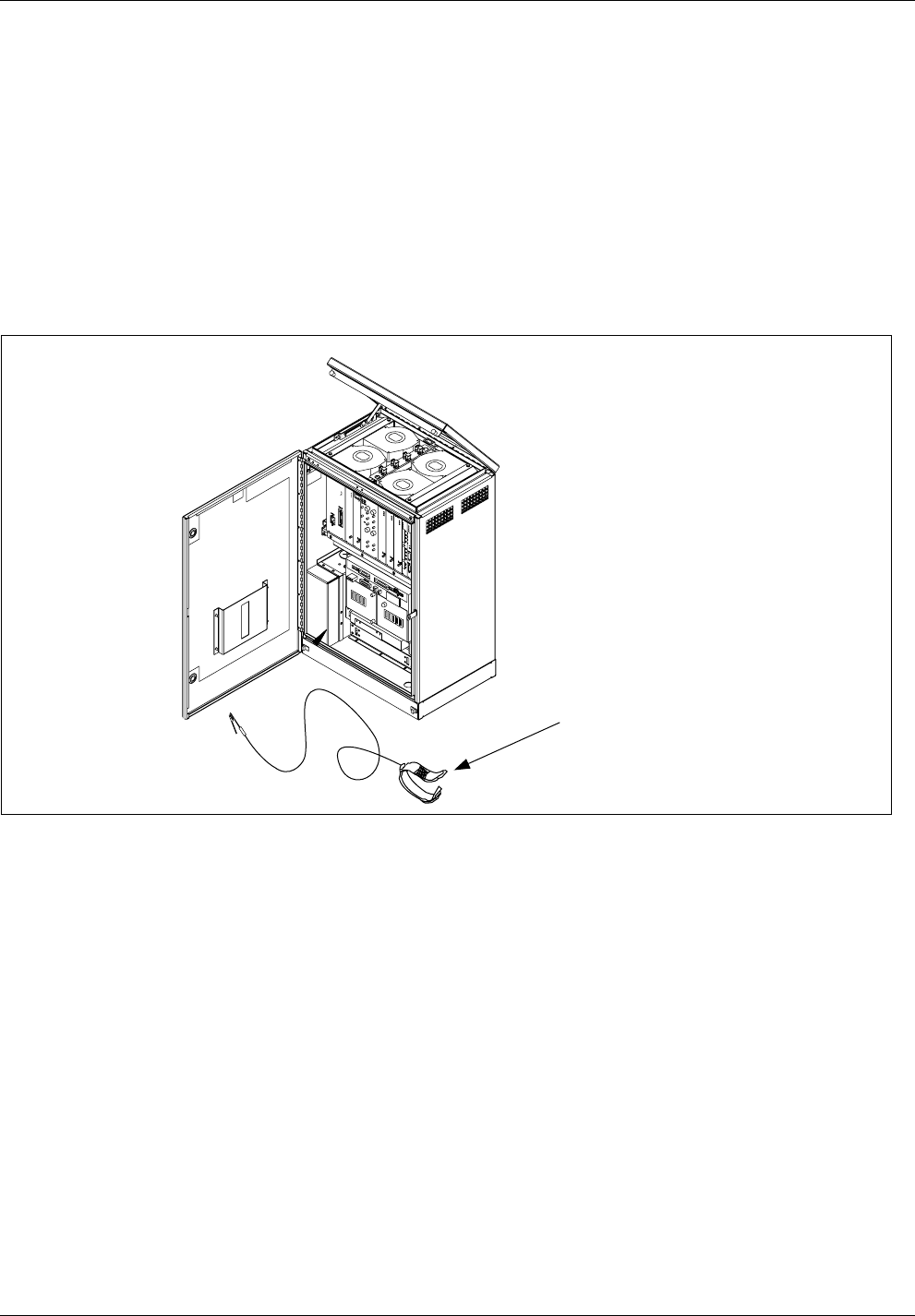
Hardware Re lacement
2. Open the cabinet door and secure the wind latch at the top of the
door. Open the door until the shoulder slides into the slot at the end
of the bar.
3. Disable the intrusion alarm by pulling out the black pin at the top of
the door frame.
4. To release the wind latch, lift up on the bar and close the door.
5. Attach the ESD strap and connect the alligator clip to a suitable
ground on the cabinet chassis. Do not attach to a painted or coated
surface. See Figure 5-2 on page 5-8.
ESD Wrist Strap
Note: Attach alligator clip to suitable
ground (unpainted surface) in cabinet.
Figure 5-2. Opening the RBS Cabinet and Attaching the ESD Strap
Troubleshooting Flowchart
6. Follow the flowchart shown in Figure 5-3 on page 5-9 or Figure 5-4
on page 5-10 to identify a unit suspected to be faulty.
5-8 2/1551-EN/LZB 119 3312 Uae Rev A 1998-11-17

Hardware Re lacement
AC Power Troubleshooting
PSU OK
AC OK
DC OUTPUT ON
PSU CURRENT LIMIT
PSU LEDs
PSU OK
LED
on?
PSU
DC
OUTPUT ON
LED
on?
PSU
AC OK
LED
on?
No
Yes
AC
MAIN
breaker
on?
Turn AC MAIN
Breaker on.
No
Yes
No
Reset PSU circuit
breaker
and check
AC power cable.
PSU
AC OK
LED
on?
No
Replace PSU.
Refer to
Power Unit (PSU)
Replacement Section.
Report to MSC
Replace PSU.
Refer to
Power Unit (PSU)
Replacement Section.
Report to MSC
Yes
Yes
Refer to DC Power
Troubleshooting
Start
Yes
No
AC
CONNECTED
indicator
on?
Verify incoming
AC power
is OK
Yes
No
AC
CONNECTED
indicator
on?
Report to MSC
Replace PSU.
Refer to
Power Unit (PSU)
Replacement Section.
Report to MSC
No
Yes
Figure 5-3. Troubleshooting Flowchart for AC Power Connection
2/1551-EN/LZB 119 3312 Uae Rev A 1998-11-17 5-9
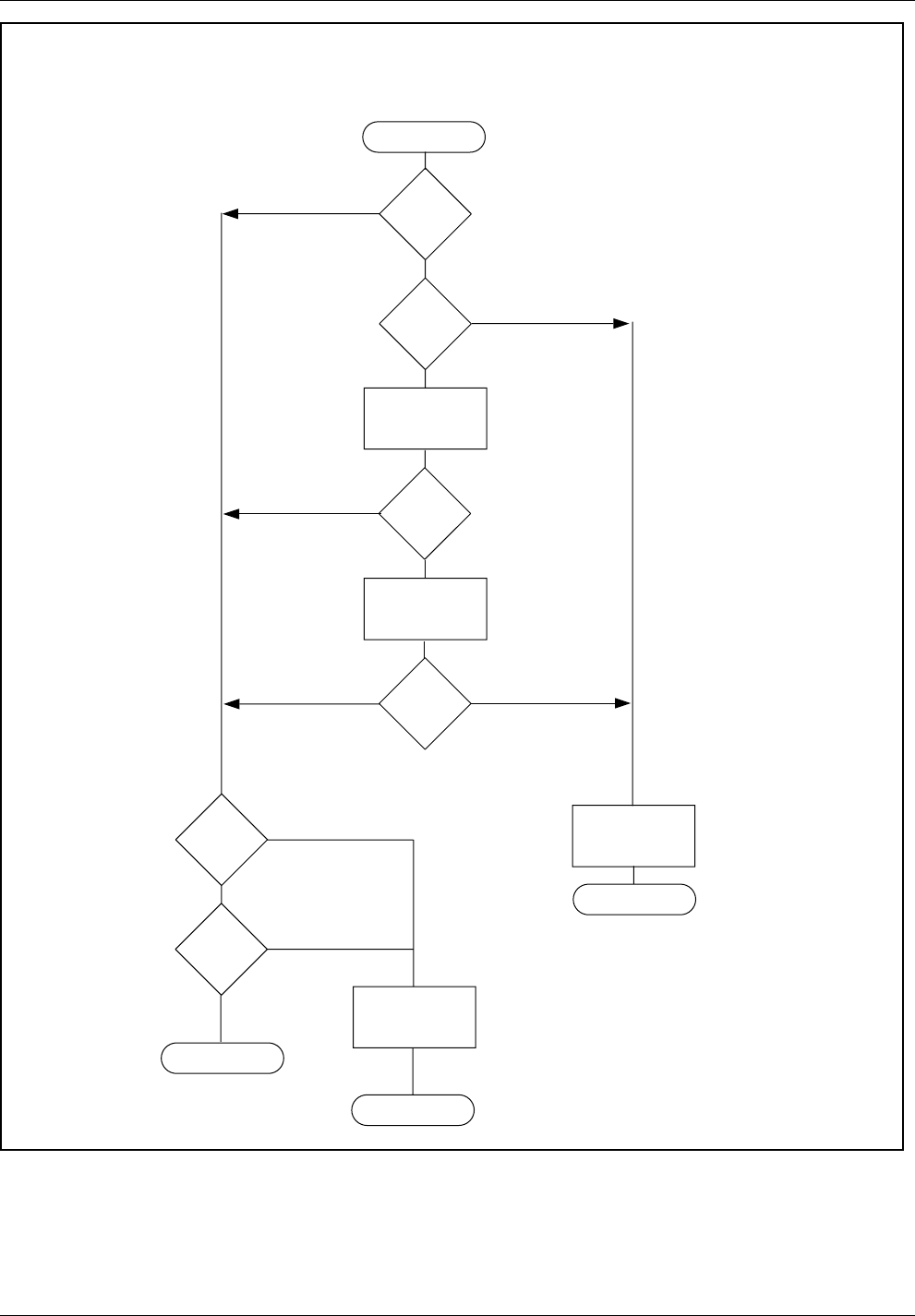
Hardware Re lacement
Start
Fan
airflow
OK?
No
Replace Fan.
Refer to the
Fan Replacement
section.
Report to MSC
Reset Fan breaker
and check fan power
cable
Ensure DC
power available
from power cable
Fan
airflow
OK?
Yes
Fan
Failure Code
on
ECU?
No
Fan
airflow
OK?
Yes
Error Codes
on
ECU?
Replace suspect unit.
Refer to the
Unit Replacement
Section.
All unit
red LEDs
off?
Report to MSC
Yes No
No
No
Yes
Yes
No
DC Power Troubleshooting
Report to MSC
Yes
Figure 5-4. Troubleshooting Flowchart for DC Power Connection
5-10 2/1551-EN/LZB 119 3312 Uae Rev A 1998-11-17
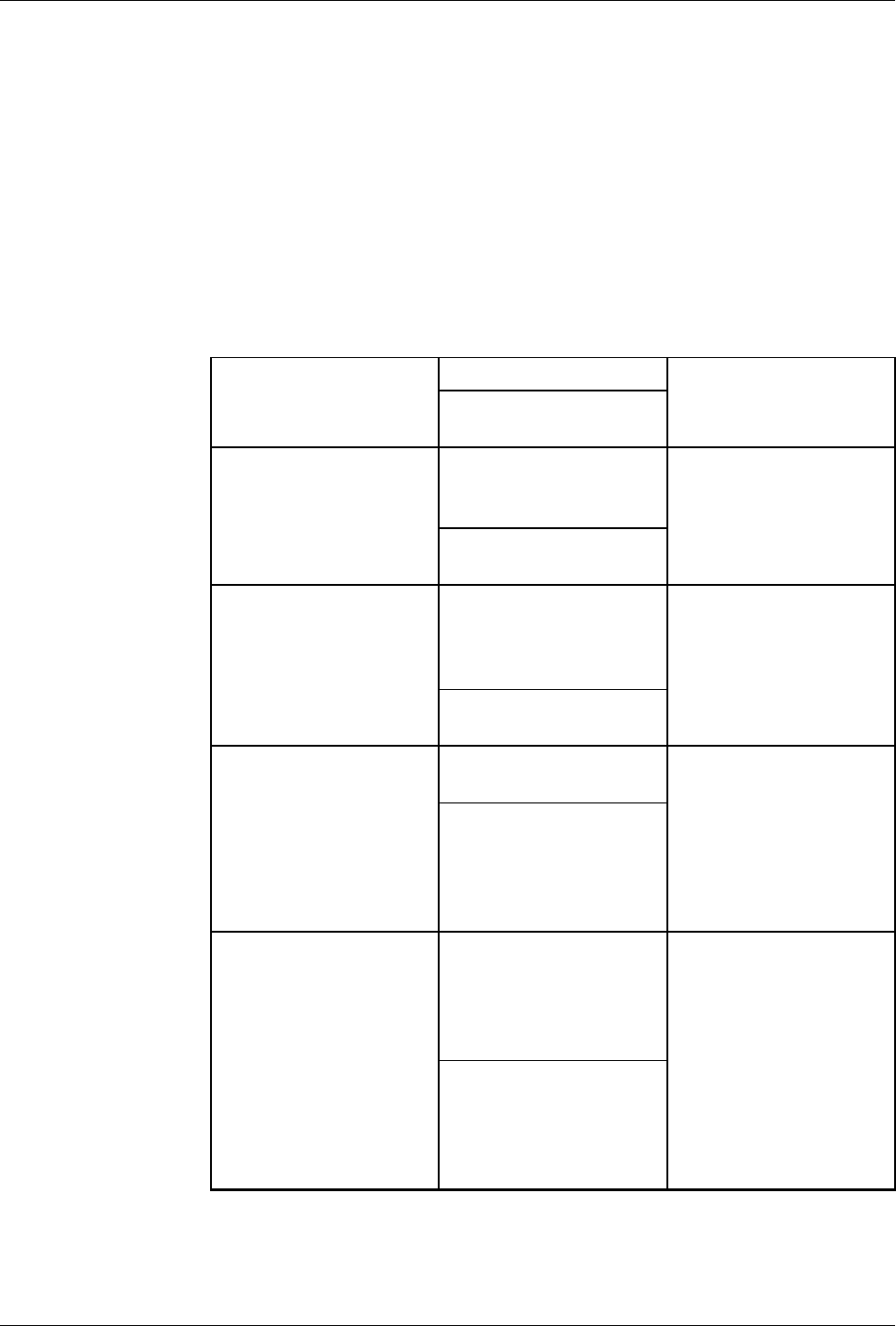
Hardware Re lacement
7. If Troubleshooting procedures have been performed as part of a
power-up procedure, return to the appropriate section and complete
the power-up procedure.
5 Alarm Troubleshooting
Refer to Table 5-2 on page 5-11 for RBS 884 Micro (1900 MHz) alarm
conditions and corrective actions. For alarm routing, refer to both Table
5-2 on page 5-11 and Figure 5-5 on page 5-14.
Table 5-2. Alarm Troubleshooting
Condition
Alarm Name Alarm Source/Routing Corrective Action/
Alarm Clearing
Fan not within ±25% of
set speed (checked once
per second)
Single Fan Alarm
From ECU/TRXs by way
of backplane
Reset fan breaker
Two or more fans not
within ±25% of set speed
(checked once per
second)
Multi-Fan Alarm
From ECU/TRXs by way
of backplane
Reset fan breaker
AC Mains ≤minimum
PSU voltage requirement
AC Mains Failure Alarm
From PSU by way of AC/
DC Distribution Box by
way of cable to ECU by
way of cable to EMRPM
by way of backplane
Self clears when AC
Mains voltage is
adequate to power PSU
AC Mains > 100 Vac and
DC Out < 24 Vdc
and
Output Current < 1A
PSU Failure Alarm
From PSU by way of AC/
DC Distribution Box by
way of cable to ECU by
way of cable to EMRPM
through backplane
Self clears (trigger
conditions not valid) after
PSU power is within
specification
2/1551-EN/LZB 119 3312 Uae Rev A 1998-11-17 5-11
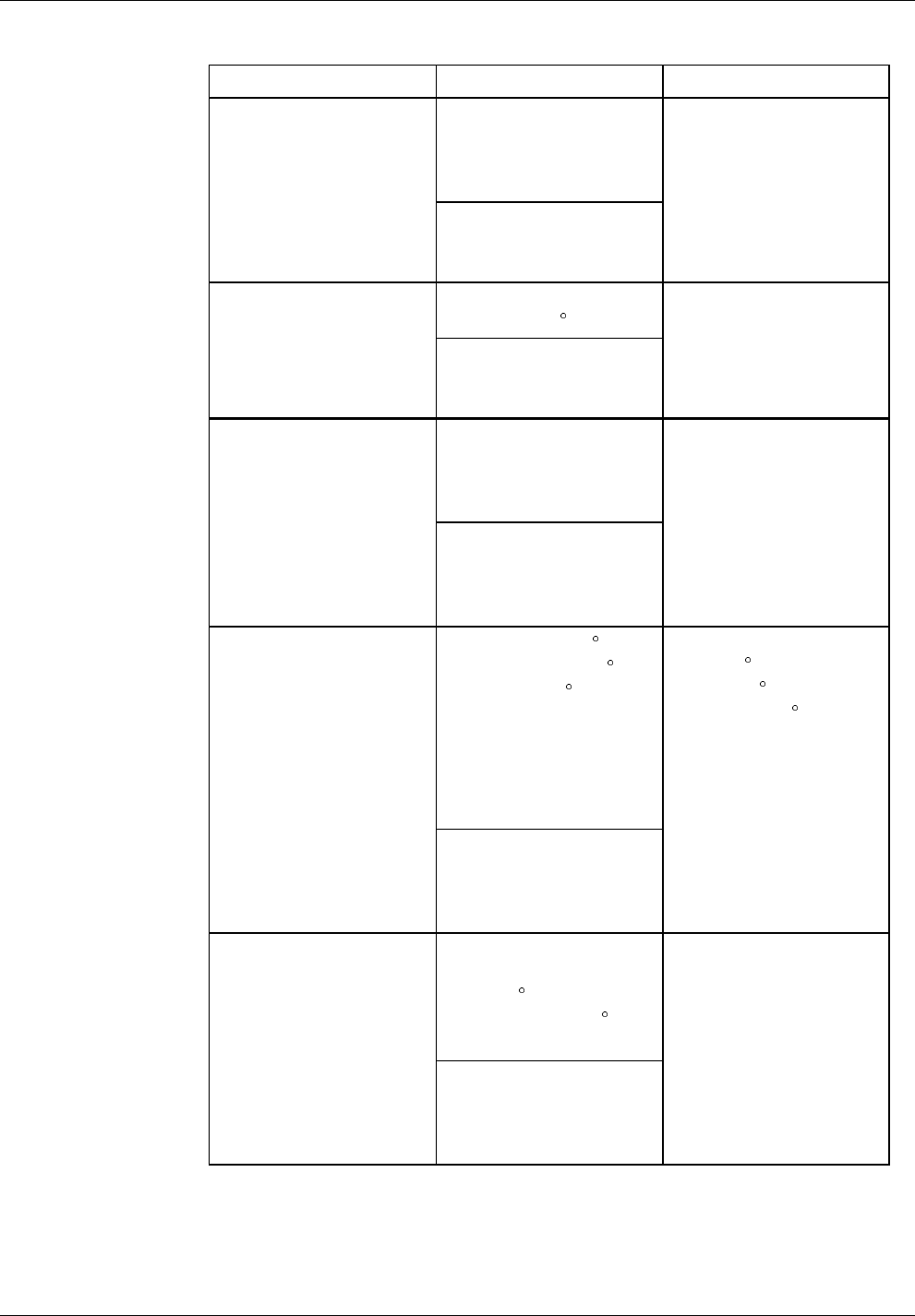
Hardware Re lacement
Table 5-2. Alarm Troubleshooting (Continued)
Condition
DCBus Voltage < 22.9
VDC; disconnects
Battery when < 20.9
VDC
Low Voltage Disconnect
Alarm
From AC/DC Distribution
Box to ALM through
cable
Self Clears
Temperature of Battery
Terminal > 70
Battery Thermal Alarm
From AC/DC Distribution
Box to ALM through
cable
Self clears
One or more temperature
sensors shorted or open
(checked once per
second)
Temperature Sensor
Failure Alarm
From ECU to AC/DC
Distribution Box through
cable to ALM through
cable
Self clears
Subrack Inlet ≤-6 Cor
Subrack Inlet ≥+51 Cor
Exhaust ≥+62 C. After
alarm generation, there
is a six-second delay
before subrack is
disconnected (checked
once per second).
Temperature Shutdown
Alarm
From ECU to AC/DC
Distribution Box through
cable to ALM through
cable
Self clears if Subrack
Inlet ≥-4 C and Subrack
Inlet ≤+49 C and
Exhaust ≤+60 C
Ten-minute delay
(warning) if ambient
temp ≤0C and Subrack
Inlet < ambient + 5 C for
ten minutes
Main Heater Failure
Alarm
From ECU to AC/DC
Distribution Box through
cable to ALM through
cable
Reset Main Heater
breaker
5-12 2/1551-EN/LZB 119 3312 Uae Rev A 1998-11-17
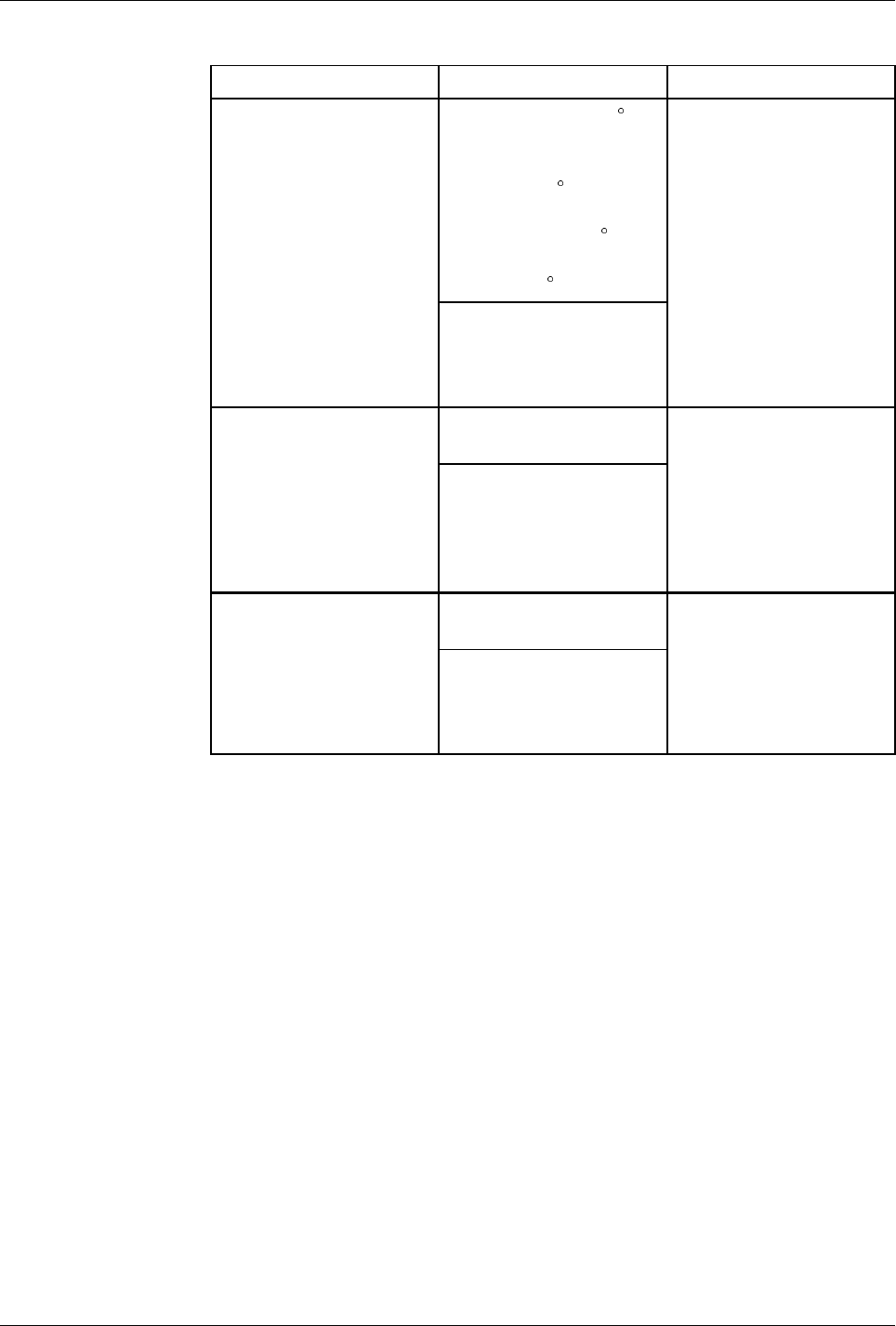
Hardware Re lacement
Table 5-2. Alarm Troubleshooting (Continued)
Condition
Ambient temp > +15 C
and Battery
Compartment >
ambient + 10 C
or
Ambient temp < -5 C and
Battery Compartment <
ambient + 5 C
Battery Compartment
Temperature Alarm
From ECU to AC/DC
Distribution Box through
cable to ALM through
cable
Self clears when
temperature returns to
within specifications
AC Surge
No AC Power = alarm
AC Surge Suppressor
Alarm
From AC Surge
Suppressor through
cable to AC/DC
Distribution Box through
cable to ALM
Self clears if AC Surge
Suppressor is not
damaged
Top or Front Door is
Open
Door Alarm
From Switches through
cable to AC/DC
Distribution Box through
cable to ALM
Self clears when both
doors closed
2/1551-EN/LZB 119 3312 Uae Rev A 1998-11-17 5-13
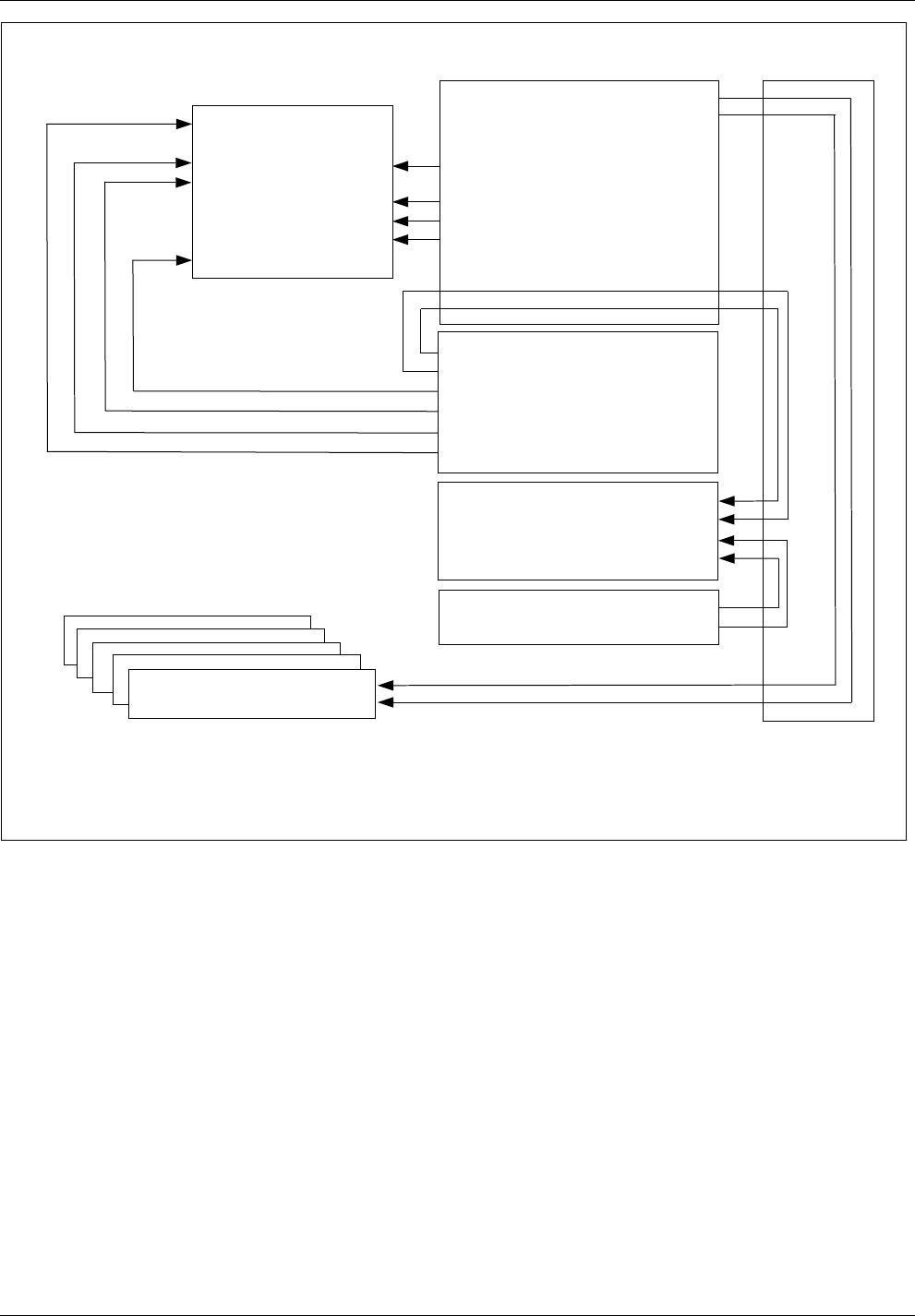
Hardware Re lacement
External Alarm 0 (APT)
External Alarm 3 (APT)
External Alarm 4 (APT)
External Alarm 5 (APT)
External Alarm 6 (APT)
External Alarm 7 (APT)
External Alarm 8 (APT)
External Alarm 9 (APT)
Single Fan Alarm
Multiple Fan Alarm
Temperature Shutdown Alarm
Main Heater Alarm
Battery Comp. Temp. Alarm
Temp. Sensor Failure Alarm
AC Mains Failure Alarm
PSU Failure Alarm
Battery Thermal Discon. Alarm
Low Voltage Disconnect Alarm
Door Alarm
Surge Suppressor Alarm
MC-B Alarm
MC-A Alarm
ANP
AC Alarm (Alarm 3 - APT/Printout)
DC Alarm (Alarm 2 - APT/Printout)
MC-A Alarm (Alarm 1 - APT OBS)
MC-B Alarm (Alarm 0 - APT OBS)
EMRPM
ECU
ALM
Backplane
Distribution Box
Fan Alarm 1 (Malfunction Log)
Fan Alarm 2 (Malfunction Log)
Note: When both fan alarms are
sent, APT alarm is generated.
Figure 5-5. RBS 884 Micro (1900 MHz) Alarm Routing
6 RBS Unit Hardware Replacement
When a suspected faulty unit is identified either by indications at the MSC
or by the troubleshooting procedures in Section 4 on page 5-6, follow the
appropriate procedure in this section to replace the unit.
Hardware replacement procedures are provided for the following devices:
•Power Supply Unit (PSU)
•Remote Multiplexer (REMUX) Unit
•Signal Terminal Receiver, Micro (STRM) Unit
5-14 2/1551-EN/LZB 119 3312 Uae Rev A 1998-11-17

Hardware Re lacement
•Connector (CONN) Unit
•Extension Module Regional Processor, micro (EMRPM) Unit
•Transceiver (TRX) Unit
•Antenna Near Part (ANP)/Radio Frequency Test Loop (RFTL) Unit
•Alarm (ALM) Unit
•Environmental Control Unit (ECU)
•Fans
•Main Heater
•Battery Heater
•Batteries
•AC Surge Suppressor
•Pulse Code Modulation (PCM) (T1/E1) Primary Surge Suppressor
•Pulse Code Modulation (PCM) (T1/E1) Secondary Surge Suppressor
•Air Filter
6.1 Prerequisites and Tools
6.1.1 Prerequisites
Before a faulty unit is replaced, the hardware replacement unit must be
available and must have the same or higher R-state number (R-state letters
do not matter).
When units other than the PSU are replaced, suitable blank panels (8M,
10M, or 12M) or dummy TRXs (RMUs) must be available in case the
hardware replacement takes an extended amount of time. The blank panels
ensure proper cooling and EMC shielding.
6.1.2 Tools
The tools required for unit hardware replacement are shown in Table 5-3
on page 5-16, Figure 5-6 on page 5-16, Figure 5-7 on page 5-17 and
Figure 5-8 on page 5-17. Additionally, an ESD bag is required for the unit
suspected to be faulty (other type of bag can be used for fan and power
units).
2/1551-EN/LZB 119 3312 Uae Rev A 1998-11-17 5-15

Hardware Re lacement
Table 5-3. Tools for RBS Unit Hardware Replacement
Product Number Description
LYB 250 01/14 ESD Wrist Strap and Cable
LTT 601 82 Torque Wrench set including:
- Torque Wrench 0.6 Nm
- Torx bit T10 for circuit board screws
- SMA tool for the coaxial cables
LSA 126 11/10 Torx driver TX10
LTD 117 02 and
LTD 117 14
Unit Extractor Tool (Handle and Button)
N/A Small Screwdriver or Pen (to set switches)
N/A Repair Traveler Note
PCM
Test
TLINK
1
TLINK
2
TLINK
3
TLINK
4
REMUX
Power
Error
V24
PCM
Prim
PCM
Sec
AFS
In
AFS
Out
Status 1
Status 2
NOTE: Before removing any unit, remove and save
the extractor hole plug. Replace plug after installing
or replacing unit.
TX 2
TX 1
TX 4
TX 3
RX/TX
ANT A RX/TX
ANT B
TX ANT C TX ANT D
Power
Error
Status
ANP/RFTL
Figure 5-6. Unit Extractor Tool (Example with the REMUX Unit)
5-16 2/1551-EN/LZB 119 3312 Uae Rev A 1998-11-17
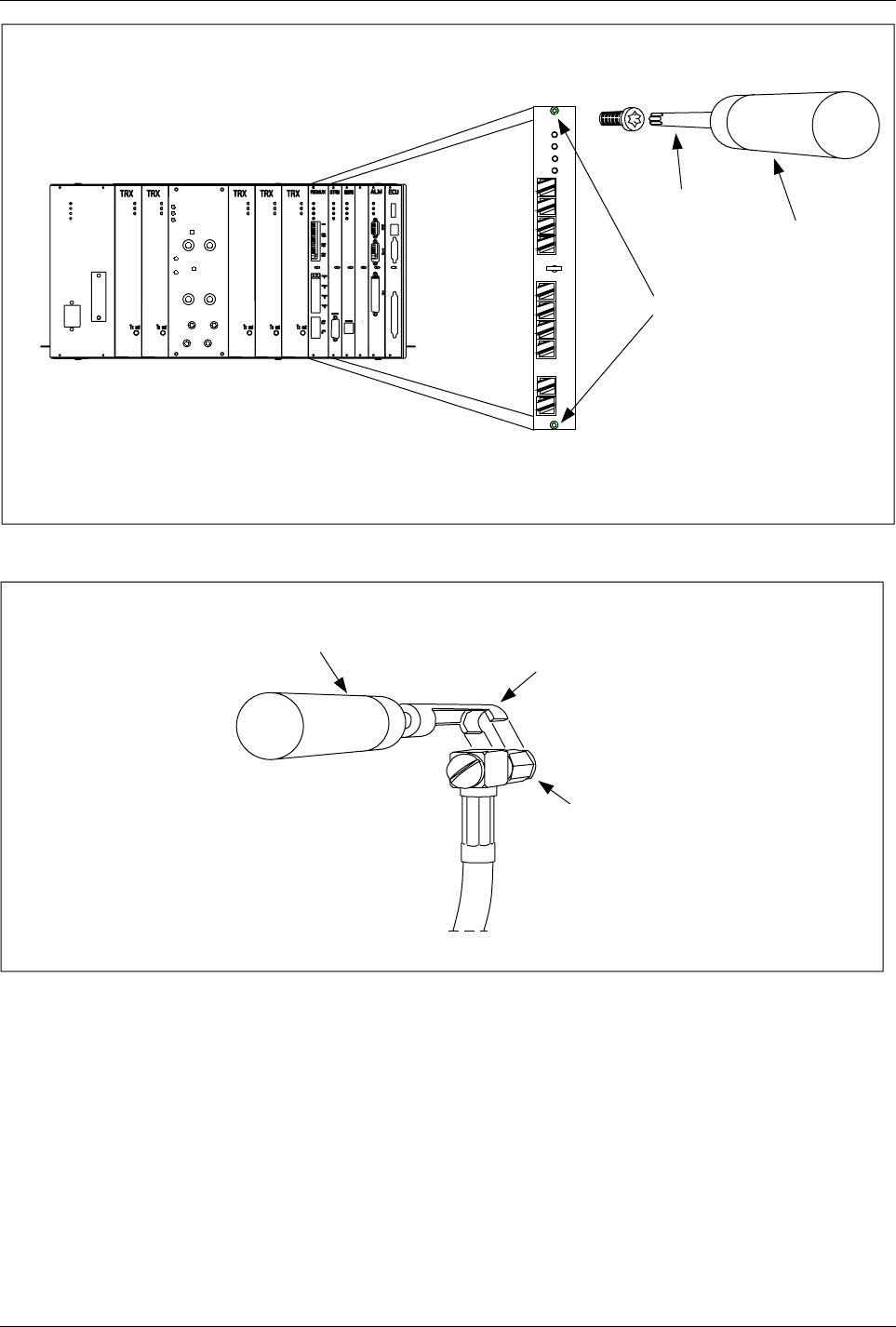
Hardware Re lacement
Torx Bit T10
Torque Wrench
Unit Screws
PCM
Test
TLINK
1
TLINK
2
TLINK
3
TLINK
4
REMUX
Power
Error
V24
PCM
Prim
PCM
Sec
AFS
In
AFS
Out
Status 1
Status 2
TX 2
TX 1
TX 4
TX 3
RX/TX
ANT A RX/TX
ANT B
TX ANT C TX ANT D
Power
Error
Status
ANP/RFTL
Figure 5-7. Torque Wrench with Torx Bit TX10 (Example with the REMUX Unit)
Torque Wrench
SMA Tool
SMA Connector
Figure 5-8. Torque Wrench with SMA Tool
2/1551-EN/LZB 119 3312 Uae Rev A 1998-11-17 5-17
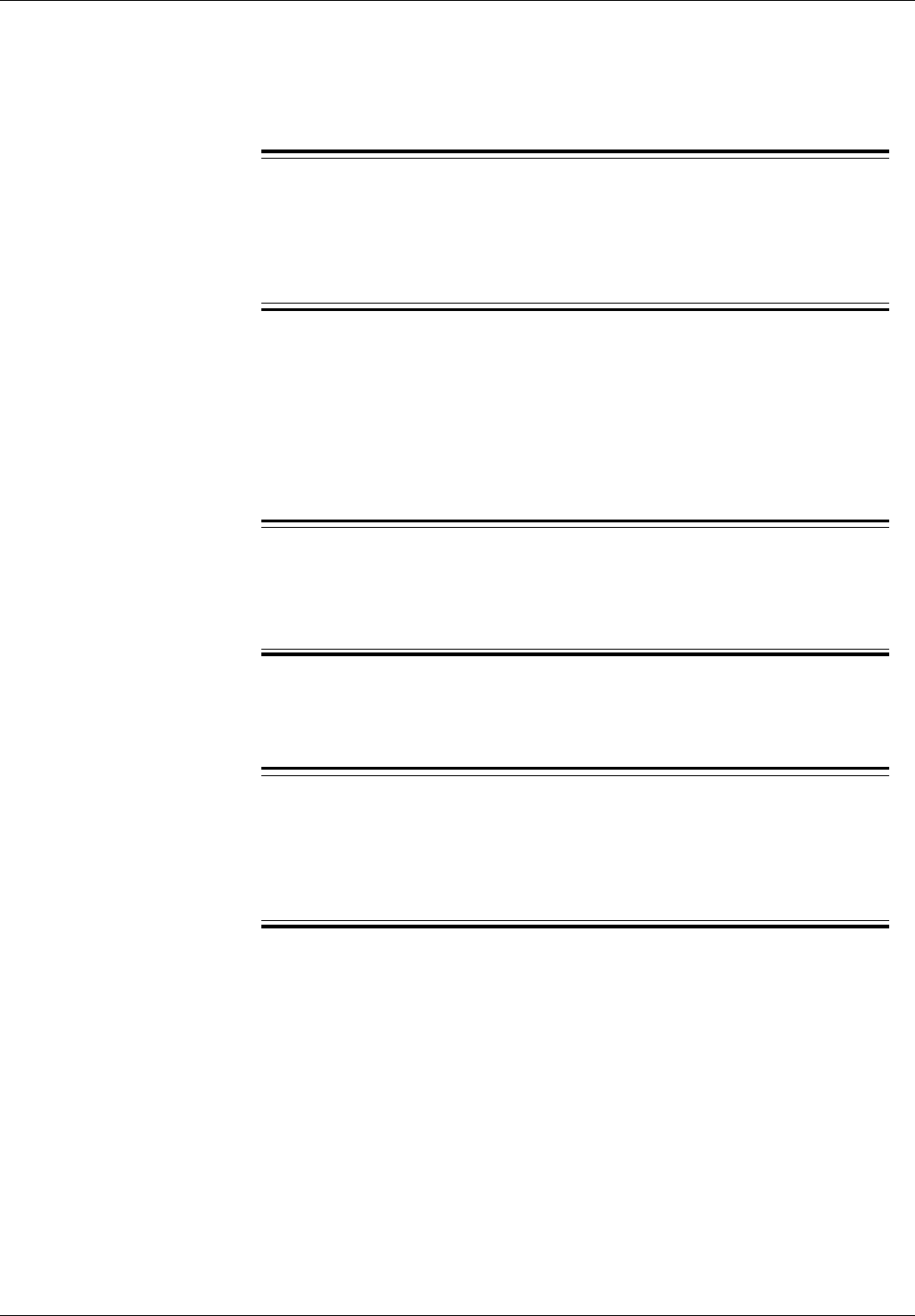
Hardware Re lacement
6.2 Power Supply Unit (PSU) Replacement
Unit Removal
Warning!
The following procedure will disable the RBS 884 Micro (1900
MHz). The unit will be out of service during the procedure. Contact
the MSC before performing the following procedure.
1. Obtain permission from the MSC operator to replace the unit. RBS
units must be blocked at the MSC before replacement.
2. Open the cabinet door and secure the wind latch at the top of the
door. Open the door until the shoulder slides into the slot at the end
of the bar.
3.
Warning!
A unit must never be replaced by another unit with a lower R-state
number.
Ensure the PSU is the same type as the unit to be replaced, and that
it has the same or higher R-state number.
4.
Warning!
Verify all TRX status LEDs (see Figure 5-9 on page 5-19) in the
cabinet are off. If the main cabinet power unit is to be changed, all
TRX status LEDs in all cabinets have to be checked.
If any TRX status LEDs are on or flashing, contact the MSC operator.
5-18 2/1551-EN/LZB 119 3312 Uae Rev A 1998-11-17
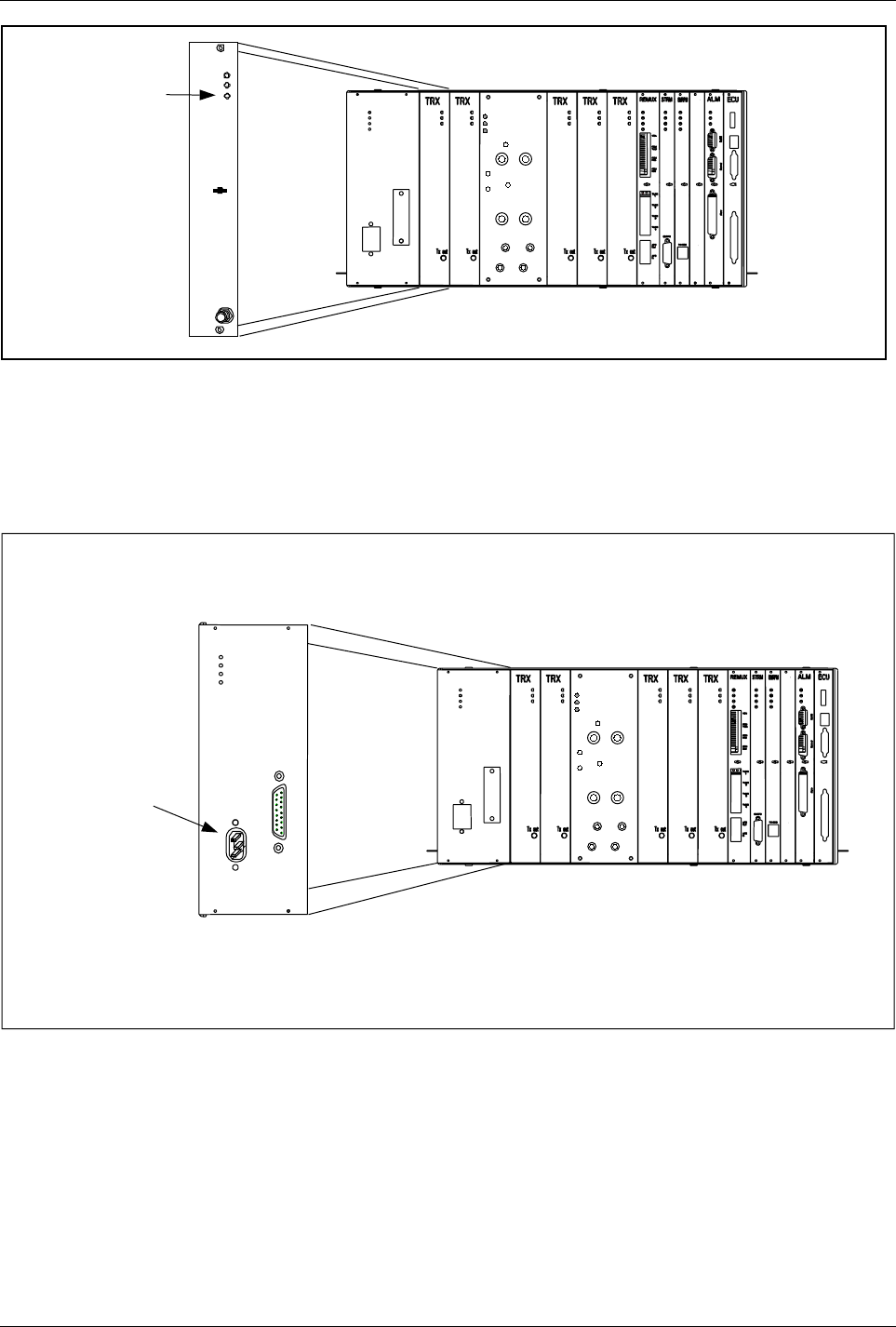
Hardware Re lacement
Status LED
Tx Out
Power
Error
Status
1900M
TRX
TX 2
TX 1
TX 4
TX 3
RX/TX
ANT A RX/TX
ANT B
TX ANT C TX ANT D
Power
Error
Status
ANP/RFTL
PSU
Figure 5-9. A TRX Unit
5. Attach the ESD strap to your wrist and connect the free end of the
strap cable to an appropriate ground conductor in the cabinet.
6. Locate the PSU shown in Figure 5-10 on page 5-19.
AC Power
Connector TX 2
TX 1
TX 4
TX 3
RX/TX
ANT A RX/TX
ANT B
TX ANT C TX ANT D
Power
Error
Status
ANP/RFTL
PSU
PSU
Figure 5-10. The Power Unit
7. Power down the RBS cabinet by turning the PSU and AC Mains
circuit breakers OFF.
8. Disconnect the AC Power connector.
9. Disconnect the DC Power connector.
2/1551-EN/LZB 119 3312 Uae Rev A 1998-11-17 5-19

Hardware Re lacement
10. Use the torque wrench with the Torx bit TX10 to loosen the screws
on the front of the unit.
11. Pull the unit out, and place it in a bag.
Unit Hardware Replacement
12. Remove the replacement PSU from its packaging and carefully slide
the unit into the cabinet in place of the old unit.
13. Use the torque wrench with a Torx bit TX10 to tighten the screws on
the front to 0.6 Nm.
14. Reconnect the AC and DC Power connectors.
15. Follow the procedure for powering up the cabinet in the “Equipment
Power Up” section in the Installation and Hardware Replacement
Manual.
16. Inform the MSC operator that the unit has been replaced and is ready
to be tested.
17. Remove the ESD strap cable from the cabinet, and detach it from
your wrist.
18. Update the Plant Specification in the Site Installation Documentation
concerning the new PSU. Use the comments field to note the date of
hardware replacement and the new R-state number.
19. Close the cabinet door.
Unit Repair
20. Complete the Repair Traveler Note and attach it to the PSU
suspected to be faulty.
21. Pack the PSU in the packing material from the new unit and return it
to your local service center.
5-20 2/1551-EN/LZB 119 3312 Uae Rev A 1998-11-17
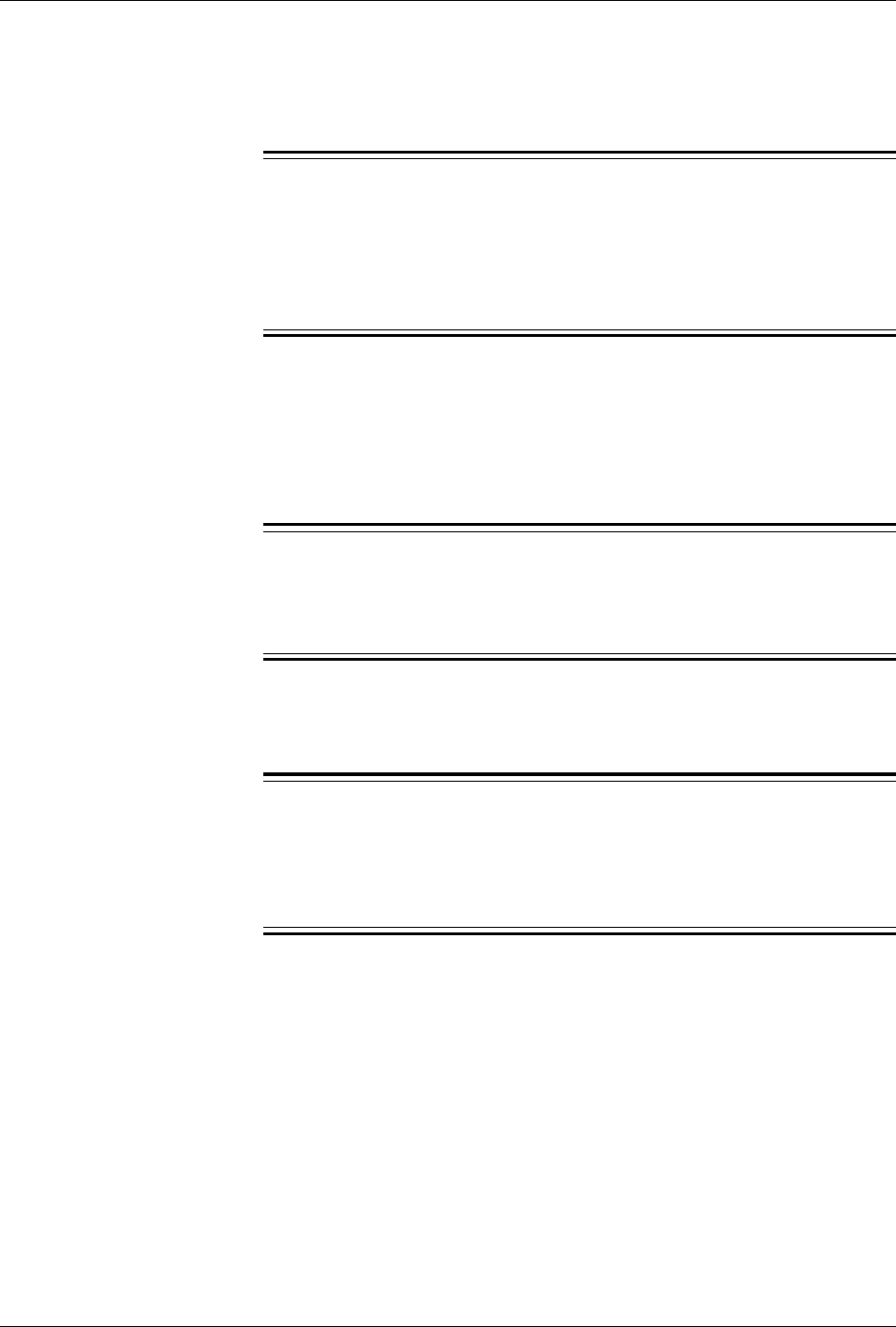
Hardware Re lacement
6.3 Remote Multiplexer (REMUX) Unit Replacement
Unit Removal
Warning!
The following procedure will disable the RBS 884 Micro (1900
MHz). The unit will be out of service during the procedure. Contact
the MSC before performing the following procedure. This procedure
will also disable any additional sectors and cascaded RBS systems.
1. Obtain permission from the MSC operator to replace the REMUX.
2. Open the cabinet door and secure the wind latch at the top of the
door. Open the door until the shoulder slides into the slot at the end
of the bar.
3.
Warning!
A unit must never be replaced by another unit with a lower R-state
number.
Check that the REMUX is the same type as the unit to be replaced,
and that it has the same or higher R-state.
4.
Warning!
Check that the REMUX status LEDs (see Figure 5-11 on page 5-22)
and all TRX status LEDs (see Figure 5-9 on page 5-19) in all
cabinets are OFF.
If any of the mentioned status LEDs are on or flashing, contact MSC
operator.
2/1551-EN/LZB 119 3312 Uae Rev A 1998-11-17 5-21

Hardware Re lacement
PCM
Test
TLINK
1
TLINK
2
TLINK
3
TLINK
4
REMUX
Power
Error
V24
PCM
Prim
PCM
Sec
AFS
In
AFS
Out
Status 1
Status 2
TX 2
TX 1
TX 4
TX 3
RX/TX
ANT A RX/TX
ANT B
TX ANT C TX ANT D
Power
Error
Status
ANP/RFTL
PSU
Figure 5-11. The REMUX Unit
5. Attach the ESD strap to your wrist and connect the free end of the
strap cable to an appropriate ground conductor in the cabinet.
6. Make a note of the cables connected to the REMUX.
7. Disconnect the cables from the REMUX.
8. Use the torque wrench with the Torx bit TX10 to loosen the screws
on the front of the unit.
9.
Warning!
The slot in the cabinet must not be left empty for an extended period
of time. If there is any delay in installing the REMUX, then a blank
panel (Blank 12M) must be screwed into the slot position (or the old
unit left in position).
Pull out the REMUX, using the extractor tool, and place it in an
ESD bag. Save the extractor hole plug. Replace the plug after
installing or replacing the unit.
Unit Hardware Replacement
10. Remove the replacement REMUX from its ESD bag and set its
switches to match those on the old unit. The switch settings are
described in the “Setting the Unit Switches” section in the
Installation and Hardware Replacement Manual.
11. Carefully slide the replacement unit into the cabinet. Push the unit
firmly into the backplane connector.
5-22 2/1551-EN/LZB 119 3312 Uae Rev A 1998-11-17

Hardware Re lacement
12. Use the torque wrench with the Torx bit TX10 to tighten the screws
on the front to 0.6 Nm.
13. Check that the green power LED on the unit is on and the red error
LED is off. If this is not the case, refer to the troubleshooting
procedures in Section 4 on page 5-6 for detection of units suspected
to be faulty.
14. Connect the cables that were disconnected in Step 7 on page 5-22 to
the unit. For cable connections, refer to the External Cable
Installation section in the “Installation” part of the Installation and
Hardware Replacement Manual. Additional information can be
found in “Appendix C” of the Installation and Hardware
Replacement Manual.
15. The REMUX requires approximately 20 minutes to synchronize. If
the RBS 884 Micro (1900 MHz) does not become operational after
20 minutes, issue a software repair command to the STRM. The
command is RECEI.
16. Inform the MSC operator that the REMUX has been replaced and is
ready to be tested.
17. Remove the ESD strap cable from the cabinet, and detach it from
your wrist.
18. Update the Plant Specification in the Site Installation Documentation
concerning the new unit. Use the comments field to note the date of
the hardware replacement and new R-state.
19. Close the cabinet door.
Unit Repair
20. Complete the Repair Traveler Note and attach it to the REMUX
suspected to be faulty.
21. Pack the REMUX in the packing material from the new unit and
return it to the local service center.
2/1551-EN/LZB 119 3312 Uae Rev A 1998-11-17 5-23
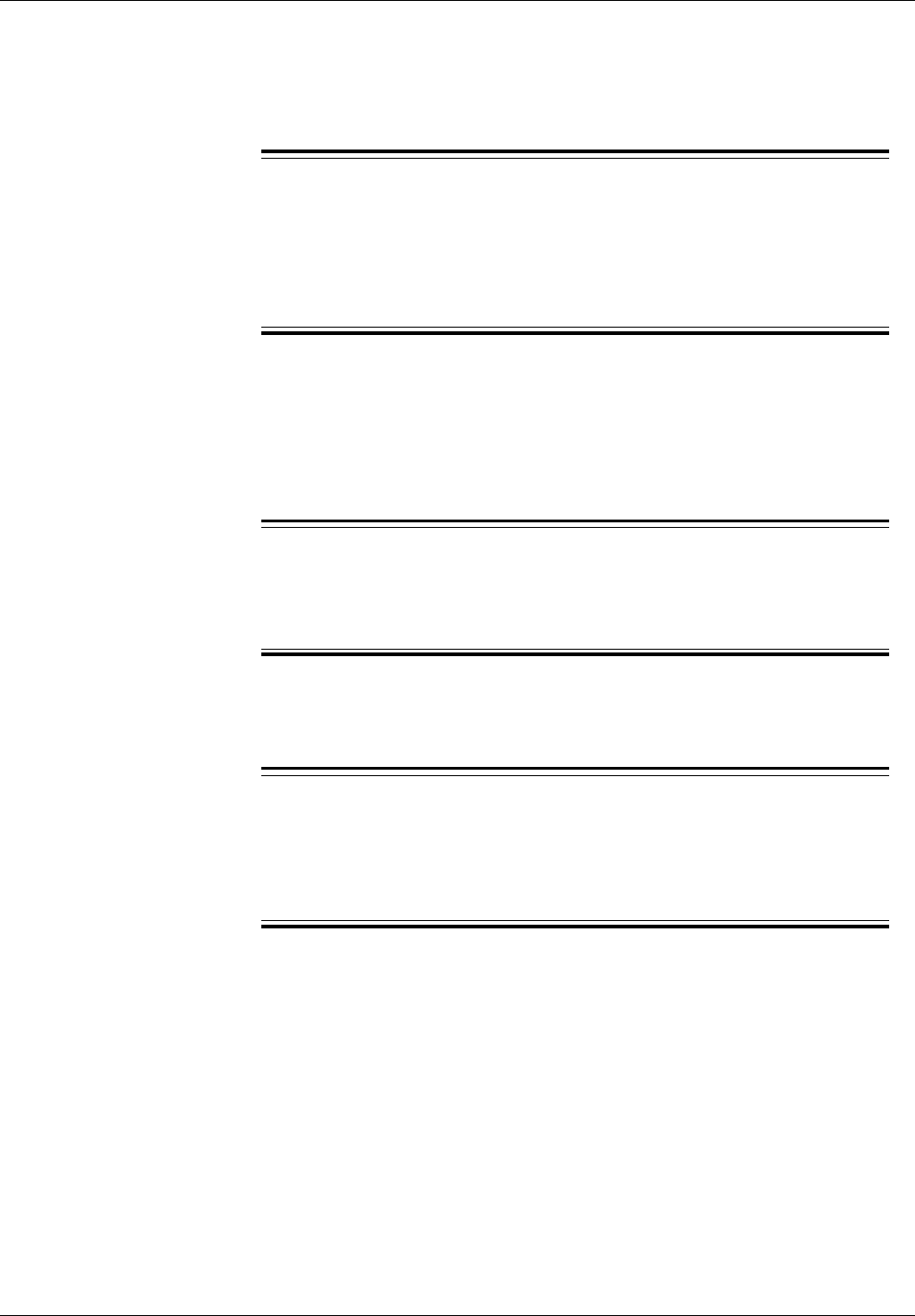
Hardware Re lacement
6.4 Signal Terminal Receiver, Micro (STRM) Unit Replacement
Unit Removal
Warning!
The following procedure will disable the RBS 884 Micro (1900
MHz). The unit will be out of service during the procedure. Contact
the MSC before performing the following procedure. This procedure
will also disable any additional sectors and cascaded RBS systems.
1. Obtain permission from the MSC operator to replace the unit.
2. Open the cabinet door and secure the wind latch at the top of the
door. Open the door until the shoulder slides into the slot at the end
of the bar.
3.
Warning!
A unit must never be replaced by another unit with a lower R-state
number.
Check that the replacement STRM is the same type as the unit to be
replaced, and that it has the same or higher R-state number.
4.
Warning!
Check that the STRM status LEDs (see Figure 5-12 on page 5-25)
and all TRX status LEDs (see Figure 5-9 on page 5-19) in all
cabinets are OFF.
If any of the mentioned status LEDs are on or flashing, contact the
MSC operator.
5-24 2/1551-EN/LZB 119 3312 Uae Rev A 1998-11-17

Hardware Re lacement
Status LEDs
STRM
Power
Error
Status 1
EMRPB
Status 2
OUT
TX 2
TX 1
TX 4
TX 3
RX/TX
ANT A RX/TX
ANT B
TX ANT C TX ANT D
Power
Error
Status
ANP/RFTL
PSU
Figure 5-12. The STRM Unit
5. Attach the ESD strap to your wrist and connect the free end of the
strap cable to an appropriate ground conductor in the cabinet.
6. Disconnect the cable or terminator from the STRM.
7. Use the torque wrench with the Torx bit TX10 to loosen the screws
on the front of the STRM.
8.
Warning!
The slot in the cabinet must not be left empty for an extended period
of time. If there is any delay in installing the STRM, a blank panel
(Blank 8M) must be screwed into the slot position.
Pull out the unit, using the extractor tool, and place it in an ESD
bag. Save the extractor hole plug. Replace the plug after installing
or replacing the unit.
Hardware Replacement Unit
9. Remove the replacement STRM from its ESD bag.
10. Carefully slide the replacement unit into the cabinet in place of the
old unit. Push the unit firmly into the backplane connector.
11. Use the torque wrench with the Torx bit TX10 to tighten the screws
on the front to 0.6 Nm.
12. Check that the green power LED on the unit is on and the red error
LED is off. If this is not the case, refer to the troubleshooting
procedures in Section 4 on page 5-6 for detection of units suspected
to be faulty.
13. Reconnect the STRM cable or terminator.
2/1551-EN/LZB 119 3312 Uae Rev A 1998-11-17 5-25
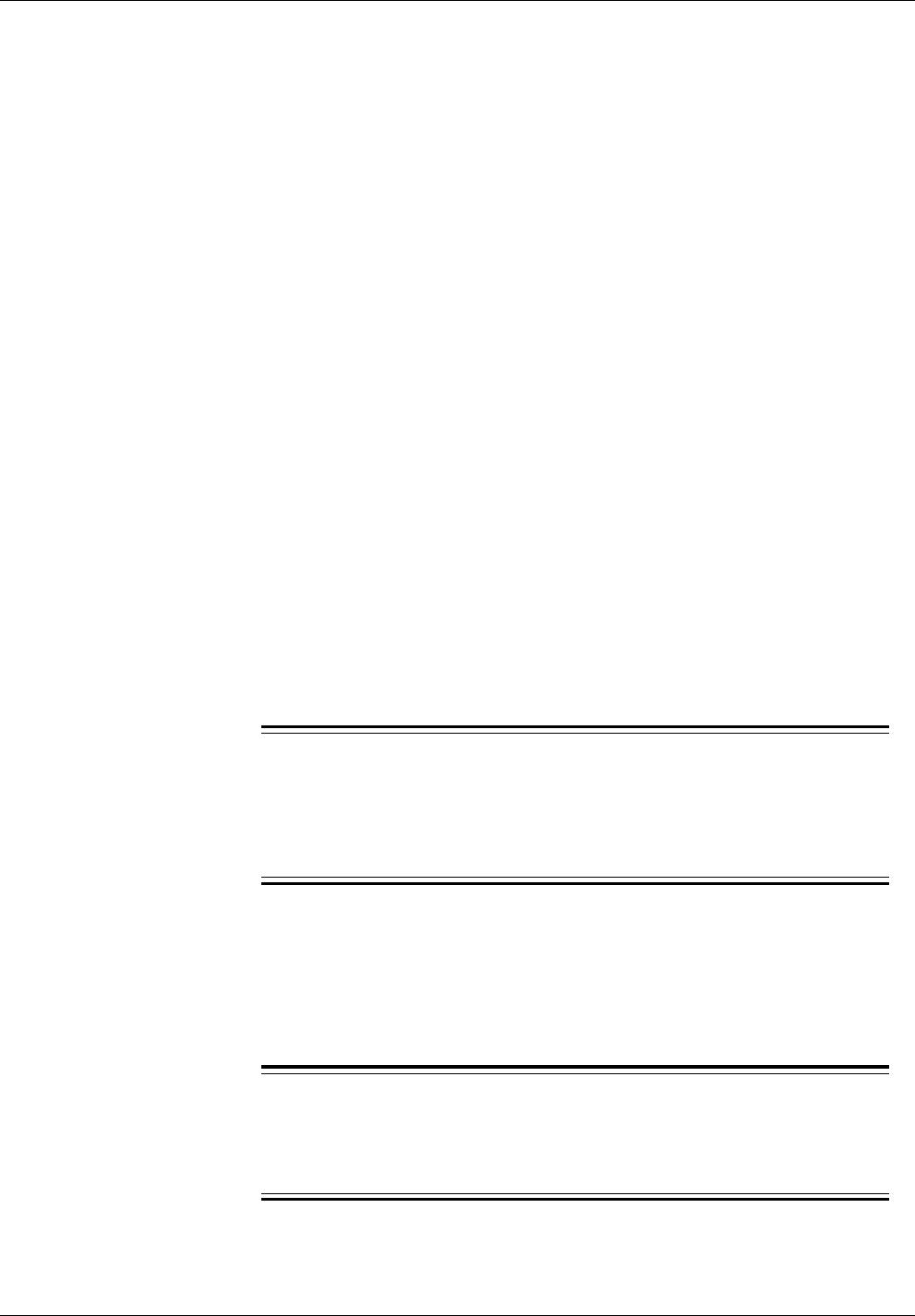
Hardware Re lacement
14. If the RBS 884 Micro (1900 MHz) does not become operational,
cycle the power to the cabinet to reload the software.
15. Inform the MSC operator that the STRM has been replaced and is
ready to be tested.
16. Remove the ESD strap cable from the cabinet, and detach it from
your wrist.
17. Update the Plant Specification in the Site Installation Documentation
concerning the new STRM. Use the comments field to note the date
of the hardware replacement and new R-state.
18. Close the cabinet door.
Unit Repair
19. Complete the Repair Traveler Note and attach it to the STRM
suspected to be faulty.
20. Pack the STRM in the packing material from the new unit and return
it to the local service center.
6.5 Connector (CONN) Unit Replacement
Unit Removal
Warning!
The following procedure will disable the RBS 884 Micro (1900
MHz). The unit will be out of service during the procedure. Contact
the MSC before performing the following procedure.
1. Obtain permission from the MSC operator to replace the CONN unit.
2. Open the cabinet door and secure the wind latch at the top of the
door. Open the door until the shoulder slides into the slot at the end
of the bar.
3.
Warning!
A unit must never be replaced by another unit with a lower R-state
number.
Check that the replacement CONN unit is the same type as the unit
to be replaced, and that it has the same or higher R-state number.
5-26 2/1551-EN/LZB 119 3312 Uae Rev A 1998-11-17
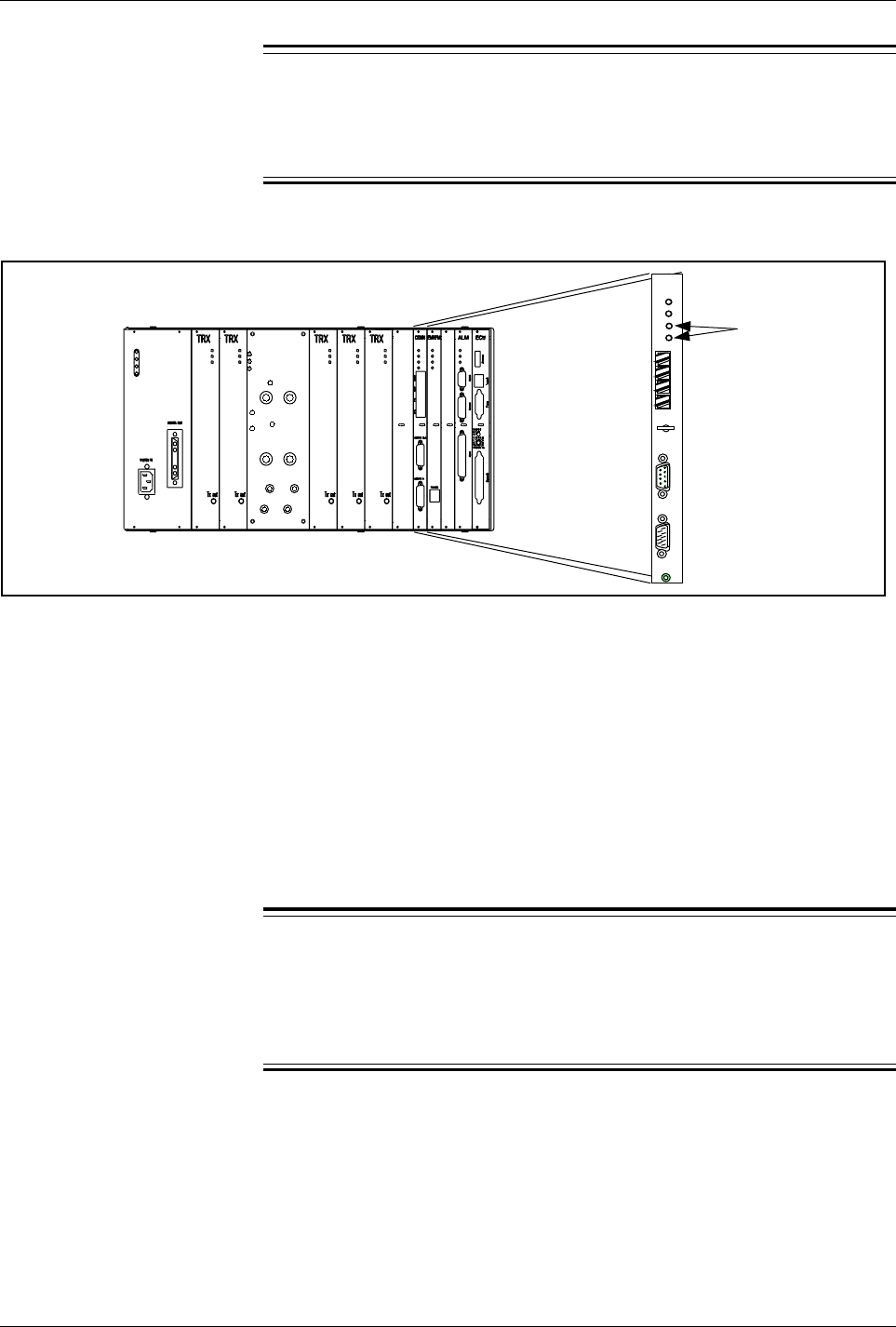
Hardware Re lacement
4.
Warning!
Check that all TRX status LEDs (see Figure 5-9 on page 5-19) in the
relevant cabinet are OFF.
If they are on or flashing, contact the MSC operator.
Power
Error
Status 2
IN
OUT
EMRPB
AFS
Out
AFS
In
TL 1
TL 2
Status 1
CONN
Status LEDs
TX 2
TX 1
TX 4
TX 3
RX/TX
ANT A RX/TX
ANT B
TX ANT C TX ANT D
Power
Error
Status
ANP/RFTL
PSU
Figure 5-13. The CONN Unit
5. Attach the ESD strap to your wrist and connect the free end of the
strap cable to an appropriate ground conductor in the cabinet.
6. Make a note of the cables connected to the CONN unit.
7. Disconnect the cables from the CONN unit.
8. Use the torque wrench with the Torx bit TX10 to loosen the screws
on the front of the CONN unit.
9.
Warning!
The slot in the cabinet must not be left empty for an extended period
of time. If there is any delay in installing the CONN unit, a blank
panel (Blank 8M) must be screwed into the slot position.
Pull out the CONN unit, using the extractor tool, and place it in an
ESD bag. Save the extractor hole plug. Replace the plug after
installing or replacing the unit.
Hardware Replacement Unit
10. Remove the replacement CONN unit from its ESD bag.
2/1551-EN/LZB 119 3312 Uae Rev A 1998-11-17 5-27
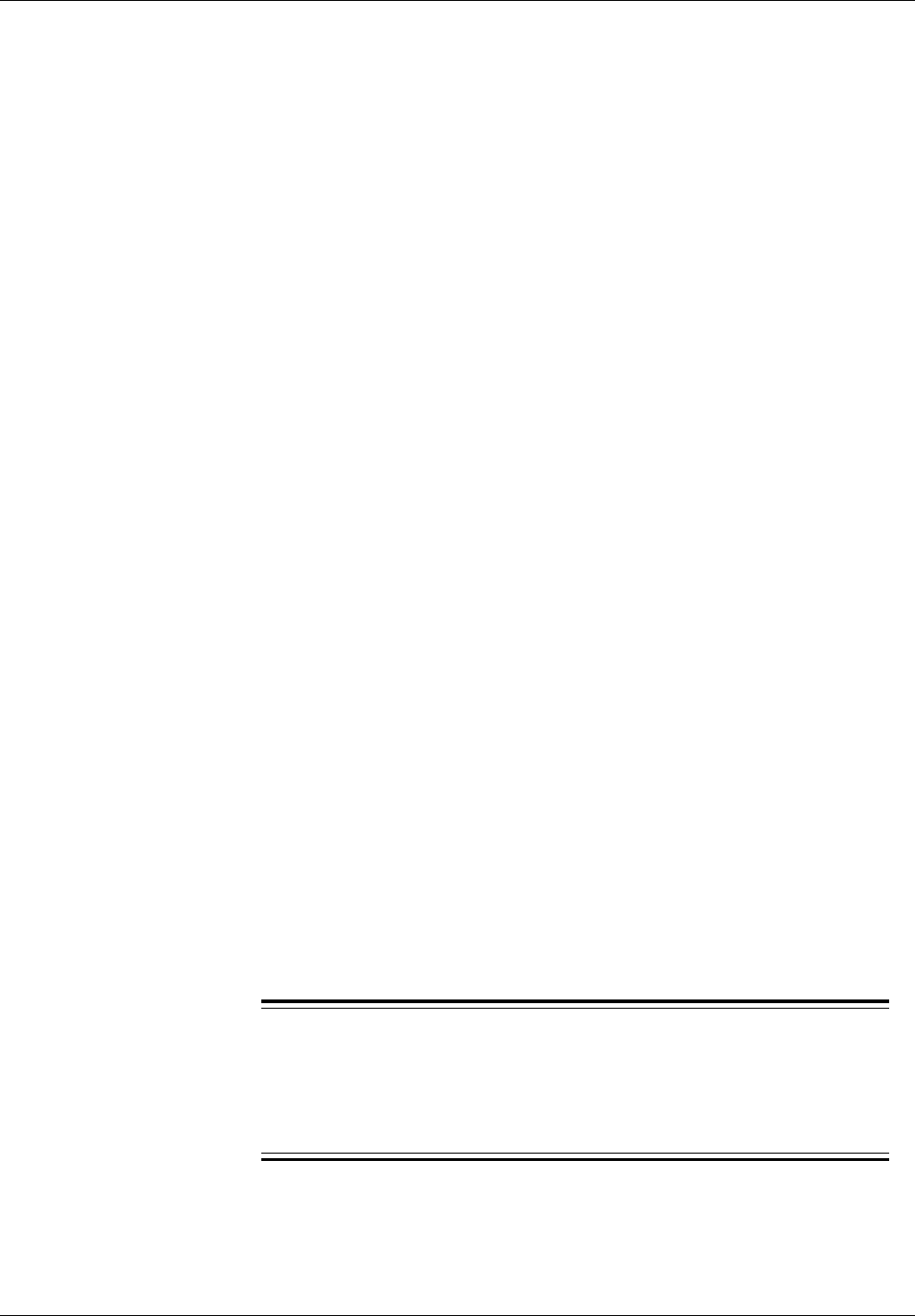
Hardware Re lacement
11. Carefully slide the replacement unit into the cabinet. Push the unit
firmly into the backplane connector.
12. Use the torque wrench with the Torx bit TX10 to tighten the screws
on the front to 0.6 Nm.
13. Check that the green power LED on the unit is on and the red error
LED is off. If this is not the case, refer to the troubleshooting
procedures in Section 4 on page 5-6 for detection of units suspected
to be faulty.
14. Reconnect the CONN unit cables.
15. Inform the MSC operator that the CONN unit has been replaced and
is ready to be tested.
16. Remove the ESD strap cable from the cabinet, and detach it from
your wrist.
17. Update the Plant Specification in the Site Installation Documentation
concerning the new CONN unit. Use the comments field to note the
date of hardware replacement and new R-state.
18. Close the cabinet door.
Unit Repair
19. Complete the Repair Traveler Note and attach it to the CONN unit
suspected to be faulty.
20. Pack the unit in the packing material from the new unit and return it
to the local service center.
6.6 Extension Module Regional Processor (EMRPM) Unit
Replacement
Unit Removal
Warning!
The following procedure will disable the RBS 884 Micro (1900
MHz). The unit will be out of service during the procedure. Contact
the MSC before performing the following procedure.
1. Obtain permission from the MSC operator to replace the EMRPM
unit.
5-28 2/1551-EN/LZB 119 3312 Uae Rev A 1998-11-17
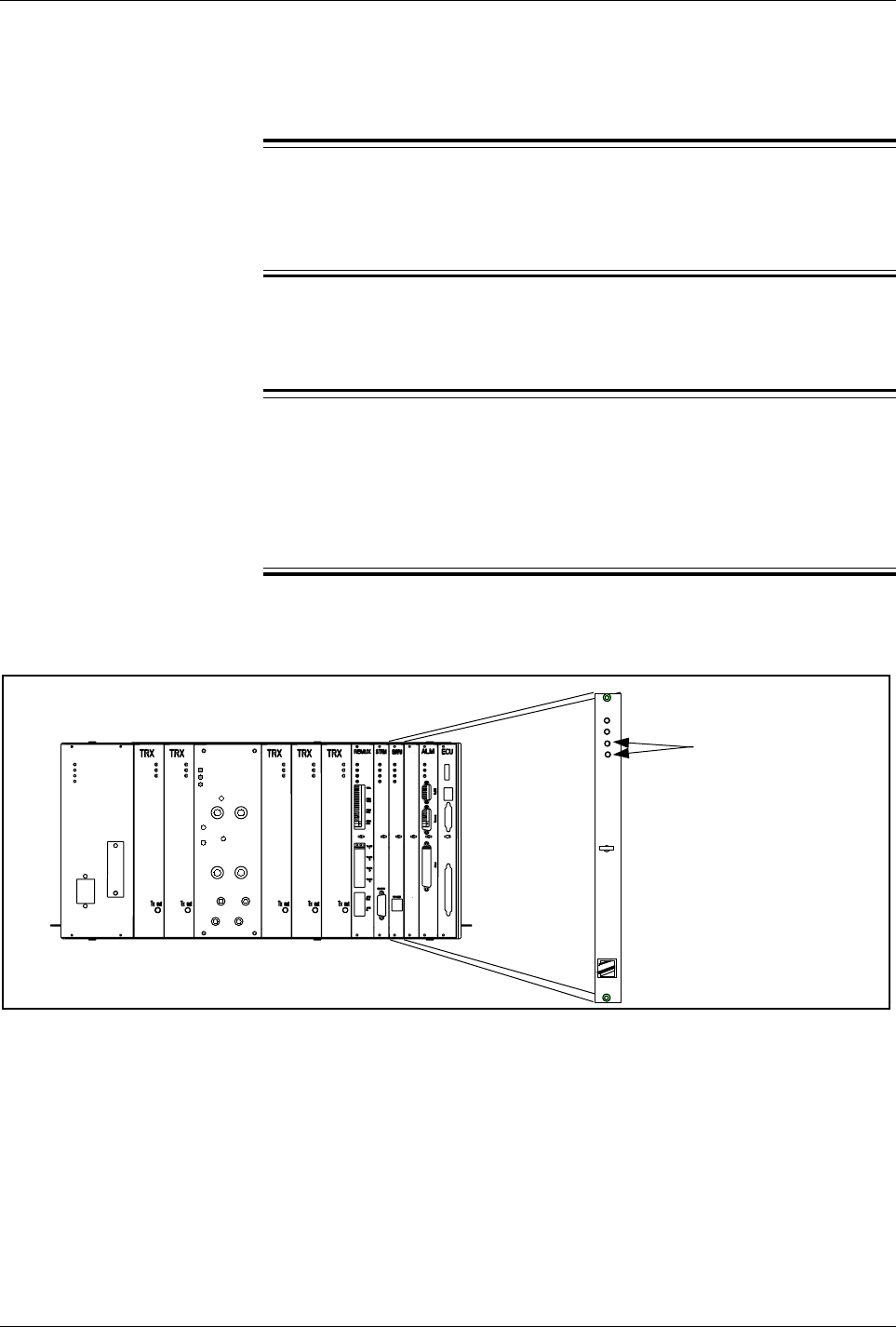
Hardware Re lacement
2. Open the cabinet door and secure the wind latch at the top of the
door. Open the door until the shoulder slides into the slot at the end
of the bar.
3.
Warning!
A unit must never be replaced by another unit with a lower R-state
number.
Check that the replacement EMRPM unit is the same type as the unit
to be replaced, and that it has the same or higher R-state number.
4.
Warning!
Check that the EMRPM status LEDs (see Figure 5-14 on page 5-29)
and all TRX status (see Figure 5-9 on page 5-19) in the relevant
cabinet are OFF. If any main cabinet EMRPM is to be changed, all
TRX status LEDs in all cabinets have to be checked.
If any of the mentioned status LEDs are on or flashing, contact the
MSC operator.
Status LEDs
Power
Error
Status 1
Status 2
TW/DEB
TX 2
TX 1
TX 4
TX 3
RX/TX
ANT A RX/TX
ANT B
TX ANT C TX ANT D
Power
Error
Status
ANP/RFTL
PSU
Figure 5-14. An EMRPM Unit
5. Attach the ESD strap to your wrist and connect the free end of the
strap cable to an appropriate ground conductor in the cabinet.
6. Disconnect the cables from the unit.
7. Use the torque wrench with the Torx bit TX10 to loosen the screws
on the front of the unit.
2/1551-EN/LZB 119 3312 Uae Rev A 1998-11-17 5-29
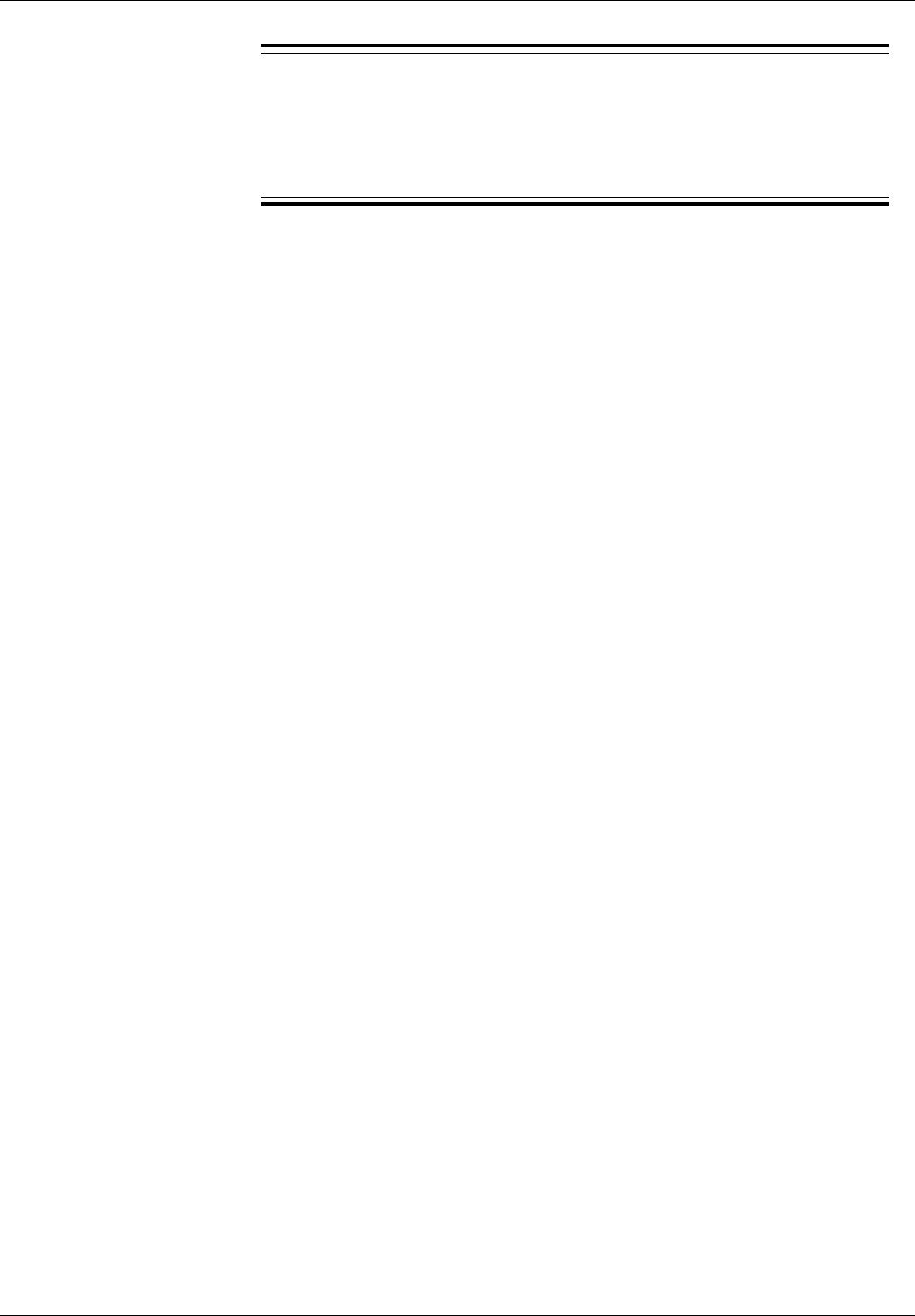
Hardware Re lacement
8.
Warning!
The slot in the cabinet must not be left empty for an extended period
of time. If there is any delay in installing the EMRPM unit, a blank
panel (Blank 8M) must be screwed into the slot position.
Pull out the unit, using the extractor tool, and place it in an ESD
bag. Save the extractor hole plug. Replace the plug after installing
or replacing the unit.
Unit hardware replacement
9. Remove the replacement EMRPM unit from its ESD bag and set the
address switches to match those on the old unit. EMRPM address
switch settings are described in the Setting the Unit Switches section
of the “Installation” part of the Installation and Hardware
Replacement Manual.
10. Carefully slide the replacement EMRPM unit into the cabinet. Push
the unit firmly into the backplane connector.
11. Use the torque wrench with the Torx bit TX10 or TX8 to tighten the
screws on the front to 0.6 Nm.
12. Check that the green power LED on the unit is on and the red error
LED is off. If not, refer to the troubleshooting procedures in Section
4 on page 5-6 for detection of units suspected to be faulty.
13. If the RBS 884 Micro (1900 MHz) does not become operational after
five to eight minutes, cycle the power to the cabinet to reload the
software.
14. Inform the MSC operator that the EMRPM has been replaced and is
ready to be tested.
15. Remove the ESD strap cable from the cabinet, and detach it from
your wrist.
16. Update the Plant Specification in the Site Installation Documentation
concerning the new unit. Use the comments field to note the date of
the hardware replacement and new R-state.
17. Close the cabinet door.
Unit Repair
18. Complete the Repair Traveler Note and attach it to the unit suspected
to be faulty.
5-30 2/1551-EN/LZB 119 3312 Uae Rev A 1998-11-17
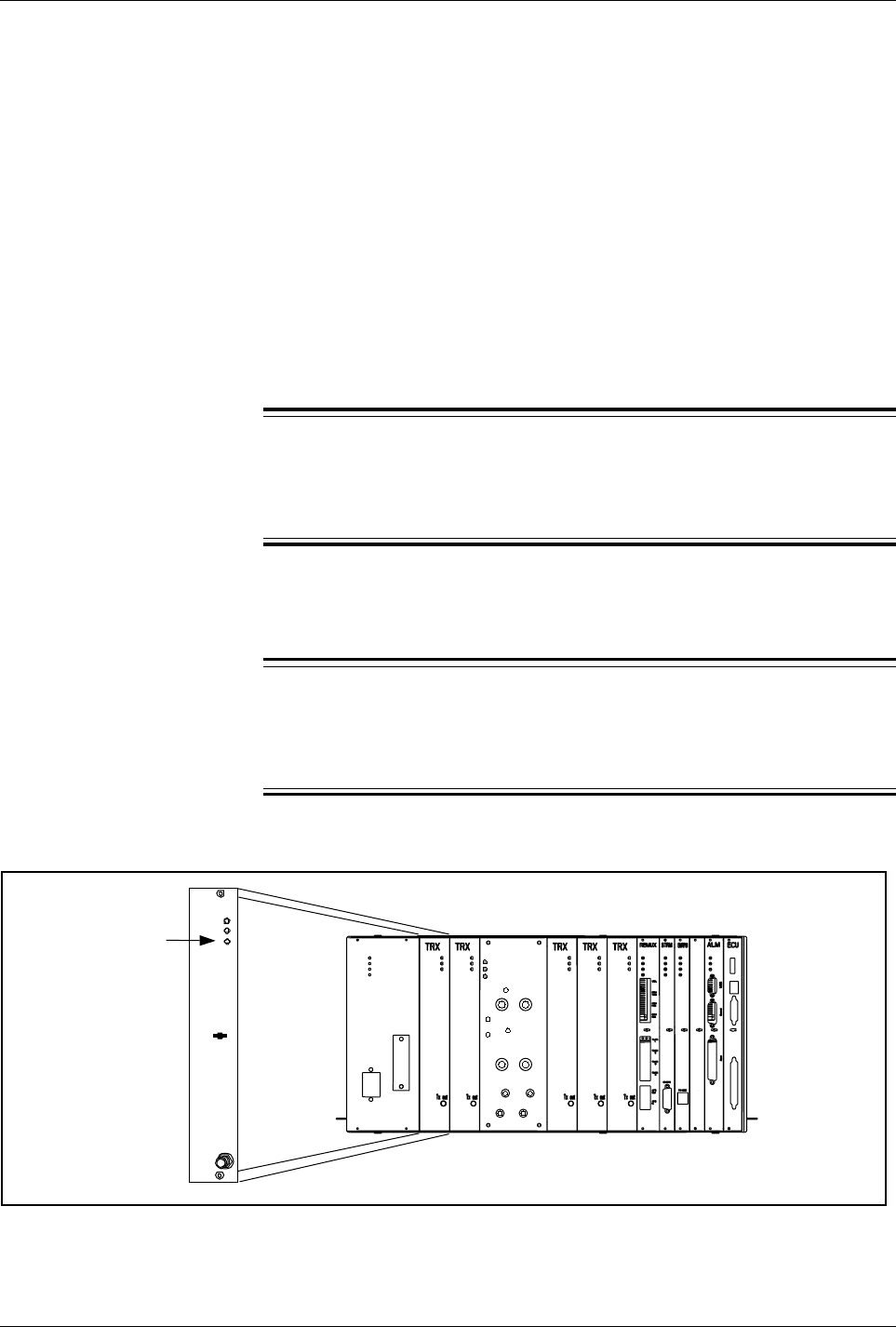
Hardware Re lacement
19. Pack the unit in the packing material from the new unit and return it
to the local service center.
6.7 Transceiver (TRX) Unit Replacement
Unit Removal
1. Obtain permission from the MSC operator to replace the TRX.
2. Open the cabinet door and secure the wind latch at the top of the
door. Open the door until the shoulder slides into the slot at the end
of the bar.
3.
Warning!
A unit must never be replaced by another unit with a lower R-state
number.
Check that the replacement TRX is the same type as the unit to be
replaced, and that it has the same or higher R-state number.
4.
Warning!
Check that the status LED on the TRX to be replaced (see Figure
5-15 on page 5-31) is OFF.
If it is on or flashing, contact the MSC operator.
Status LED
Tx Out
Power
Error
Status
1900M
TRX
TX 2
TX 1
TX 4
TX 3
RX/TX
ANT A RX/TX
ANT B
TX ANT C TX ANT D
Power
Error
Status
ANP/RFTL
PSU
Figure 5-15. A TRX Unit
2/1551-EN/LZB 119 3312 Uae Rev A 1998-11-17 5-31

Hardware Re lacement
5. Manually block the TRX to be replaced. This assures that any calls
are handed off to another TRX.
6. Attach the ESD strap to your wrist and connect the free end of the
strap cable to an appropriate ground conductor in the cabinet.
7. Disconnect the cable from the TRX, using the torque wrench with
the SMA tool.
8. Use the torque wrench with the Torx bit TX10 to loosen the screws
on the front of the unit.
9.
Warning!
The slot in the cabinet must not be left empty for an extended period
of time. If there is any delay in installing the hardware replacement
unit, an RMU (dummy TRX) must be installed or the old TRX left
in position.
Pull out the TRX, using the extractor tool, and place it in an ESD
bag. Save the extractor hole plug. Replace the plug after installing
or replacing the TRX.
Unit Hardware Replacement
10. Remove the replacement TRX from its ESD bag.
11. Carefully slide the replacement unit into the cabinet in place of the
old unit. Push the unit firmly into the backplane connector.
12. Use the torque wrench with the Torx bit TX10 to tighten the screws
on the front to 0.6 Nm.
13. Check that the green power LED on the unit is on and the red error
LED is off. If not, refer to the troubleshooting procedures in Section
4 on page 5-6 for detection of units suspected to be faulty.
14. Reconnect the TRX cable. Hand tighten the cable and then use the
torque wrench with the SMA tool to tightened to 0.6 Nm.
15. Manually deblock the TRX.
16. Inform the MSC operator that the TRX has been replaced and is
ready to be tested.
17. Remove the ESD strap cable from the cabinet, and detach it from
your wrist.
18. Update the Plant Specification in the Site Installation Documentation
concerning the new TRX. Use the comments field to note the date of
the hardware replacement and new R-state.
5-32 2/1551-EN/LZB 119 3312 Uae Rev A 1998-11-17

Hardware Re lacement
19. Close the cabinet door.
Unit Repair
20. Complete the Repair Traveler Note and attach it to the TRX
suspected to be faulty.
21. Pack the unit in the packing material from the new unit and return it
to your local service center.
Note: TRX components contain beryllium oxide. Return
the TRX to the local service center for proper
disposal.
6.8 Antenna Near Part (ANP)/Radio Frequency Test Loop (RFTL) Unit
Replacement
Unit Removal
Warning!
The following procedure will disable the RBS 884 Micro (1900
MHz). The unit will be out of service during the procedure. Contact
the MSC before performing the following procedure.
1. Obtain permission from the MSC operator to replace the ANP/RFTL.
2. Open the cabinet door and secure the wind latch at the top of the
door. Open the door until the shoulder slides into the slot at the end
of the bar.
3.
Warning!
A unit must never be replaced by another unit with a lower R-state
number.
Check that the replacement ANP/RFTL unit is the same type as the
unit to be replaced, and that it has the same or higher R-state number.
4.
Warning!
Check that the status LED on the unit to be replaced (see Figure
5-16 on page 5-34) is OFF.
2/1551-EN/LZB 119 3312 Uae Rev A 1998-11-17 5-33
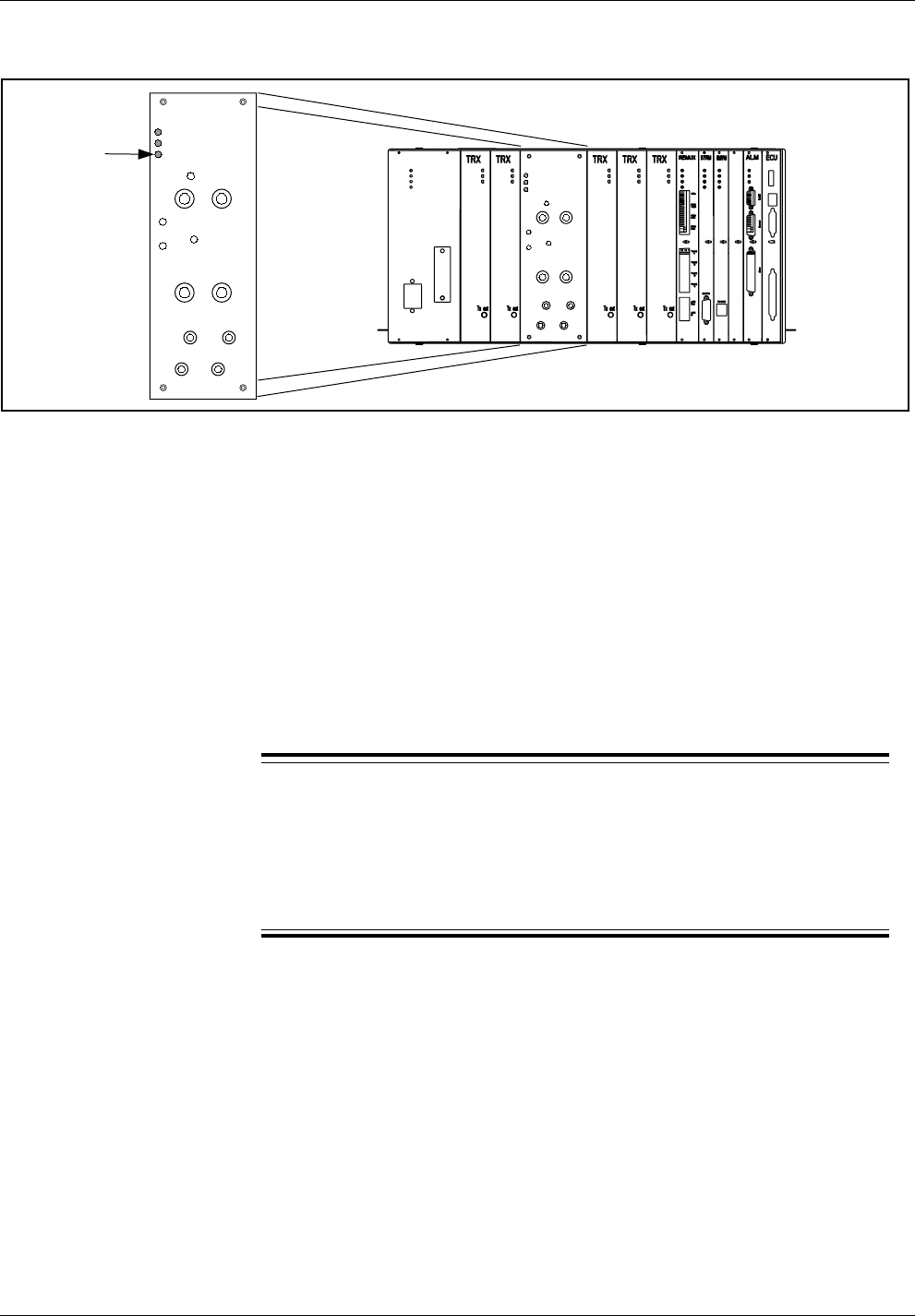
Hardware Re lacement
If it is on or flashing, contact the MSC operator.
Status LED
TX 2
TX 1
TX 4
TX 3
RX/TX
ANT A RX/TX
ANT B
TX ANT C TX ANT D
Power
Error
Status
ANP/RFTL
TX 2
TX 1
TX 4
TX 3
RX/TX
ANT A RX/TX
ANT B
TX ANT C TX ANT D
Power
Error
Status
ANP/RFTL
PSU
Figure 5-16. The ANP/RFTL Unit
5. Attach the ESD strap to your wrist and connect the free end of the
strap cable to an appropriate ground conductor in the cabinet.
6. Make a note of the cables connected to the ANP/RFTL.
7. Disconnect the cables from the ANP/RFTL. Disconnect antenna
cables by hand. Use the torque wrench with the SMA tool for other
cables.
8. Use the torque wrench with the Torx bit TX10 or TX8 to loosen the
screws on the front of the ANP/RFTL.
9.
Warning!
The slot in the cabinet must not be left empty for an extended period
of time. If there is any delay in installing the replacement ANP/
RFTL unit, leave the old unit in the slot until the replacement unit is
available.
Using the extractor tool, remove the ANP/RFTL and place it in an
ESD bag. Save the extractor hole plug. Replace the plug after
installing or replacing unit.
Unit Hardware Replacement
10. Remove the replacement ANP/RFTL from its ESD bag.
11. Carefully slide the replacement unit into the cabinet. Push the unit
firmly into the backplane connectors.
12. Use the torque wrench with the Torx bit TX10 to tighten the screws
on the front to 0.6 Nm.
5-34 2/1551-EN/LZB 119 3312 Uae Rev A 1998-11-17

Hardware Re lacement
13. Check that the green power LED on the ANP/RFTL is on and the
red error LED is off. If not, refer to the troubleshooting procedures
in Section 4 on page 5-6 for detection of units suspected to be faulty.
14. Reconnect the ANP/RFTL cables. Hand tighten all cables. Do not
use the torque wrench on TNC connectors. On non-TNC connectors,
use the torque wrench with the SMA tool to tightened to 0.6 Nm.
For cable connections, refer to the “External Cable Installation”
section in the Installation and Hardware Replacement Manual.
Additional information can be found in “Appendix C” of the
Installation and Hardware Replacement Manual.
15. Inform the MSC operator that the ANP/RFTL has been replaced and
is ready to be tested.
16. Remove the ESD strap cable from the cabinet, and detach it from
your wrist.
17. Update the Plant Specification in the Site Installation Documentation
concerning the new unit. Use the comments field to note the date of
hardware replacement and new R-state.
18. Close the cabinet door.
Unit Repair
19. Complete the Repair Traveler Note and attach it to the unit suspected
to be faulty.
20. Pack the unit in the packing material from the new unit and return it
to the local service center.
6.9 Alarm (ALM) Unit Replacement
Unit Removal
1. Obtain permission from the MSC operator to replace the ALM unit.
2. Open the cabinet door and secure the wind latch at the top of the
door. Open the door until the shoulder slides into the slot at the end
of the bar.
3.
Warning!
A unit must never be replaced by another unit with a lower R-state
number.
2/1551-EN/LZB 119 3312 Uae Rev A 1998-11-17 5-35

Hardware Re lacement
Check that the replacement ALM unit is the same type as the unit to
be replaced, and that it has the same or higher R-state number.
4.
Warning!
Check that the status LED on the ALM unit (see Figure 5-17 on
page 5-36) is OFF.
If it is on or flashing, contact the MSC operator.
Status LED
ALM
Power
Error
Status
CLINK
Control
Alarm
TX 2
TX 1
TX 4
TX 3
RX/TX
ANT A RX/TX
ANT B
TX ANT C TX ANT D
Power
Error
Status
ANP/RFTL
PSU
Figure 5-17. The Alarm Unit
5. Attach the ESD strap to your wrist and connect the free end of the
strap cable to an appropriate ground conductor in the cabinet.
6. Make a note of the cables connected to the unit.
7. Disconnect the cables from the unit.
8. Use the torque wrench with the Torx bit TX10 to loosen the screws
on the front of the unit.
Note: All external alarms are disabled when the ALM
unit is blocked.
9.
Warning!
The slot in the cabinet must not be left empty for an extended period
of time. If there is any delay in installing the replacement ALM unit,
a blank panel (Blank 10M) must be installed in the slot position.
Using the extractor tool, remove the ALM unit and place it in an
ESD bag. Save the extractor hole plug. Replace the plug after
installing or replacing unit.
5-36 2/1551-EN/LZB 119 3312 Uae Rev A 1998-11-17
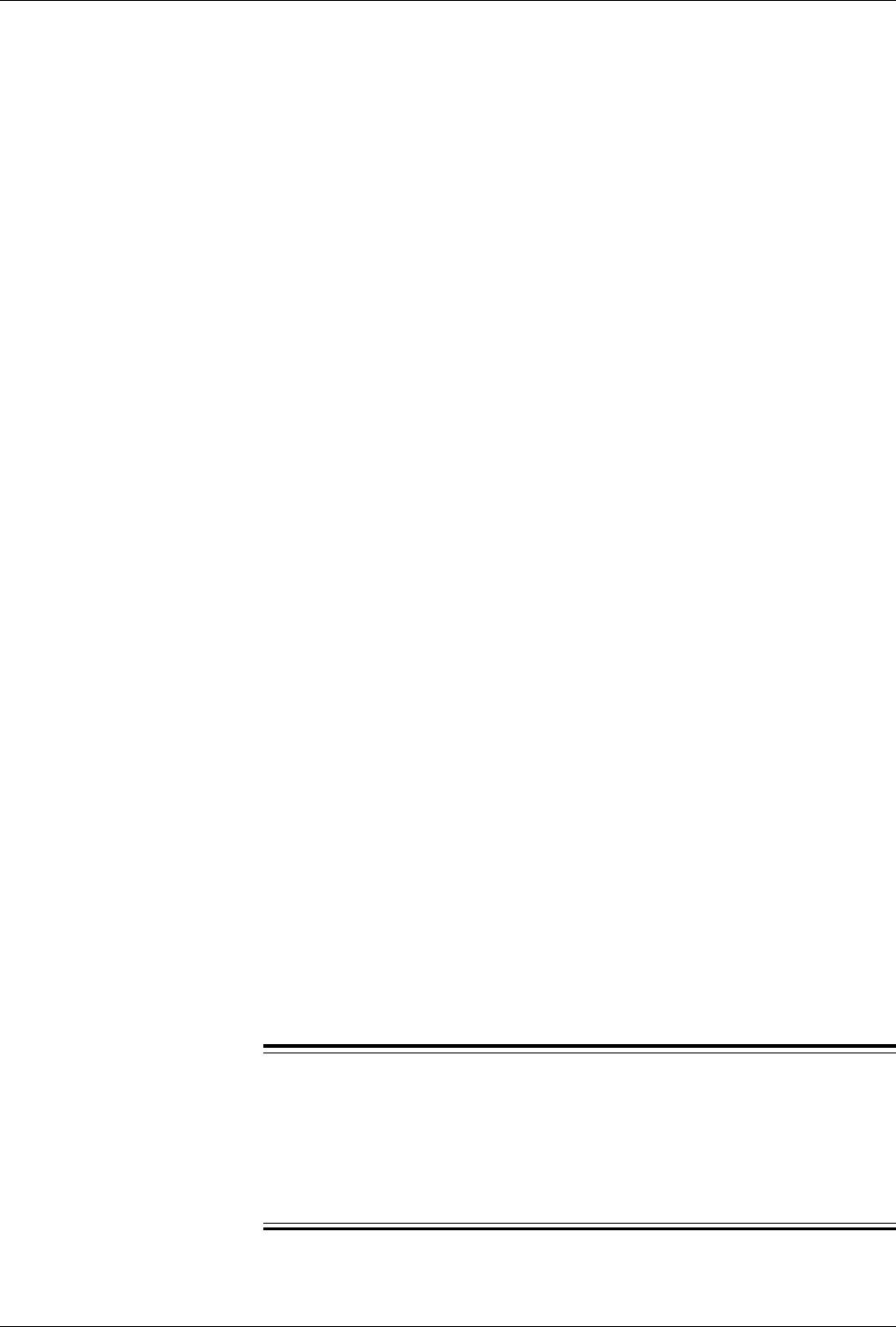
Hardware Re lacement
Unit Hardware Replacement
10. Remove the replacement ALM unit from its ESD bag.
11. Carefully slide the replacement ALM unit into the cabinet. Push the
unit firmly into the backplane connector.
12. Use the torque wrench with the Torx bit TX10 to tighten the screws
on the front to 0.6 Nm.
13. Check that the green power LED on the unit is on and the red error
LED is off. If not, refer to the troubleshooting procedures in Section
4 on page 5-6 for detection of units suspected to be faulty.
14. Reconnect the ALM cables.
15. Inform the MSC operator that the ALM has been replaced and is
ready to be tested.
16. Remove the ESD strap cable from the cabinet, and detach it from
your wrist.
17. Update the Plant Specification in the Site Installation Documentation
concerning the new ALM unit. Use the comments field to note the
date of hardware replacement and new R-state.
18. Close the cabinet door.
Unit Repair
19. Complete the Repair Traveler Note and attach it to the ALM unit
suspected to be faulty.
20. Pack the ALM unit in the packing material from the new unit and
return it to your local service center.
6.10 Environmental Control Unit (ECU) Replacement
Unit Removal
Warning!
The following procedure will disable the RBS 884 Micro (1900
MHz). The base station will be out of service during the procedure.
Contact the MSC before performing the following procedure. Inform
the MSC operator that the base station will be disabled.
1. Obtain permission from the MSC operator to replace the ECU unit.
2/1551-EN/LZB 119 3312 Uae Rev A 1998-11-17 5-37
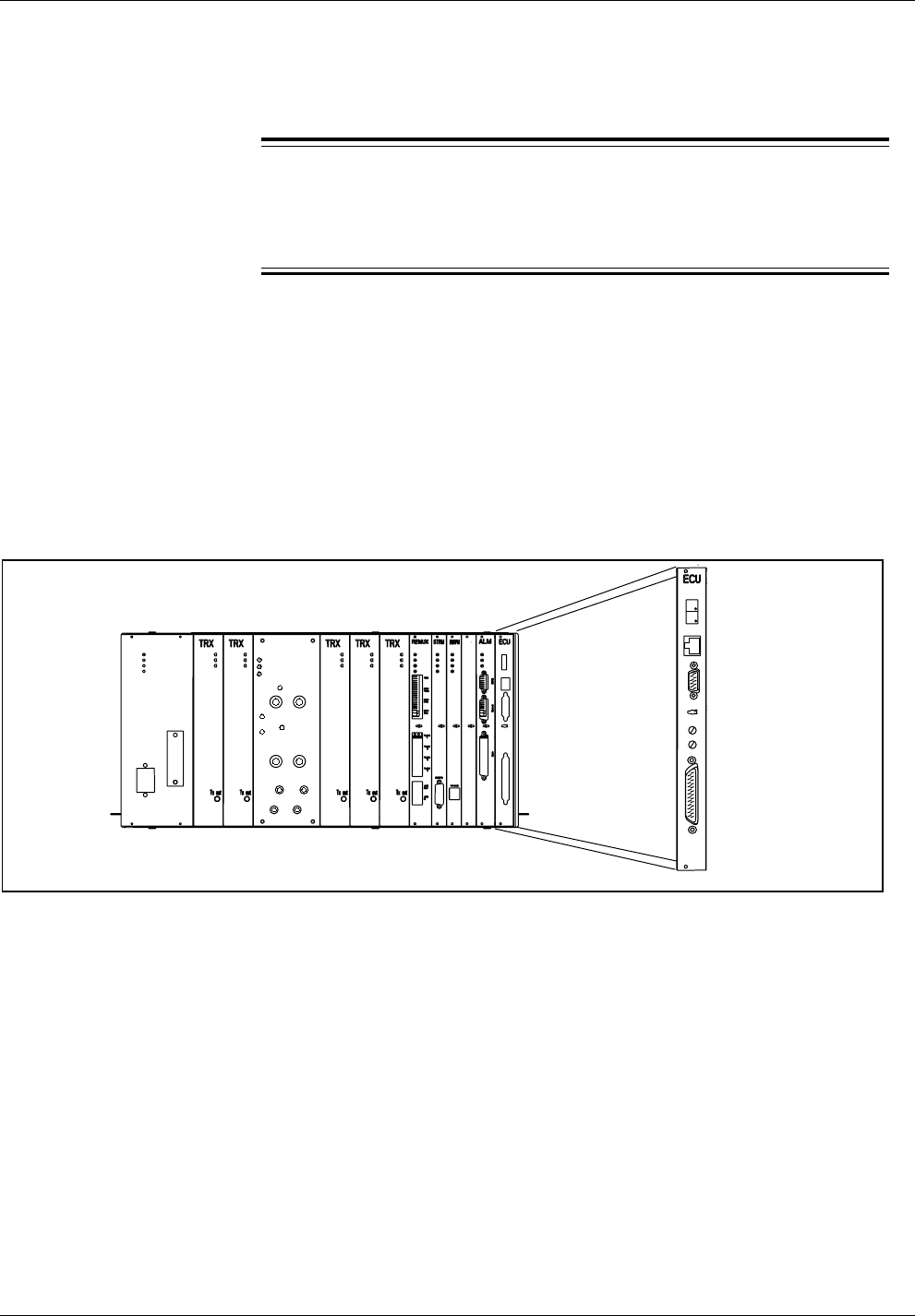
Hardware Re lacement
2. Open the cabinet door and secure the wind latch at the top of the
door. Open the door until the shoulder slides into the slot at the end
of the bar.
3.
Warning!
A unit must never be replaced by another unit with a lower R-state
number.
Check that the replacement ECU unit is the same type as the unit to
be replaced, and that it has the same or higher R-state number.
4. Attach the ESD strap to your wrist and connect the free end of the
strap cable to an appropriate ground conductor in the cabinet.
5. Turn off the ECU circuit breaker.
6. Make a note of the cables connected to the ECU unit. Refer to
Figure 5-18 on page 5-38).
TX 2
TX 1
TX 4
TX 3
RX/TX
ANT A RX/TX
ANT B
TX ANT C TX ANT D
Power
Error
Status
ANP/RFTL
PSU
Figure 5-18. Environmental Control Unit (ECU)
7. Disconnect the cables from the ECU unit.
Note: When cables are disconnected from the ECU, the
system assumes the ECU has failed. As a result, all
fans will be powered on at full speed. This is
normal.
8. Use the torque wrench with the Torx bit TX10 to loosen the screws
on the front of the ECU unit.
9. Using the extractor tool, remove the ECU unit and place it in an ESD
bag. If required, remove the handle of the extractor tool. Save the
extractor hole plug. Replace the plug after installing or replacing unit.
5-38 2/1551-EN/LZB 119 3312 Uae Rev A 1998-11-17
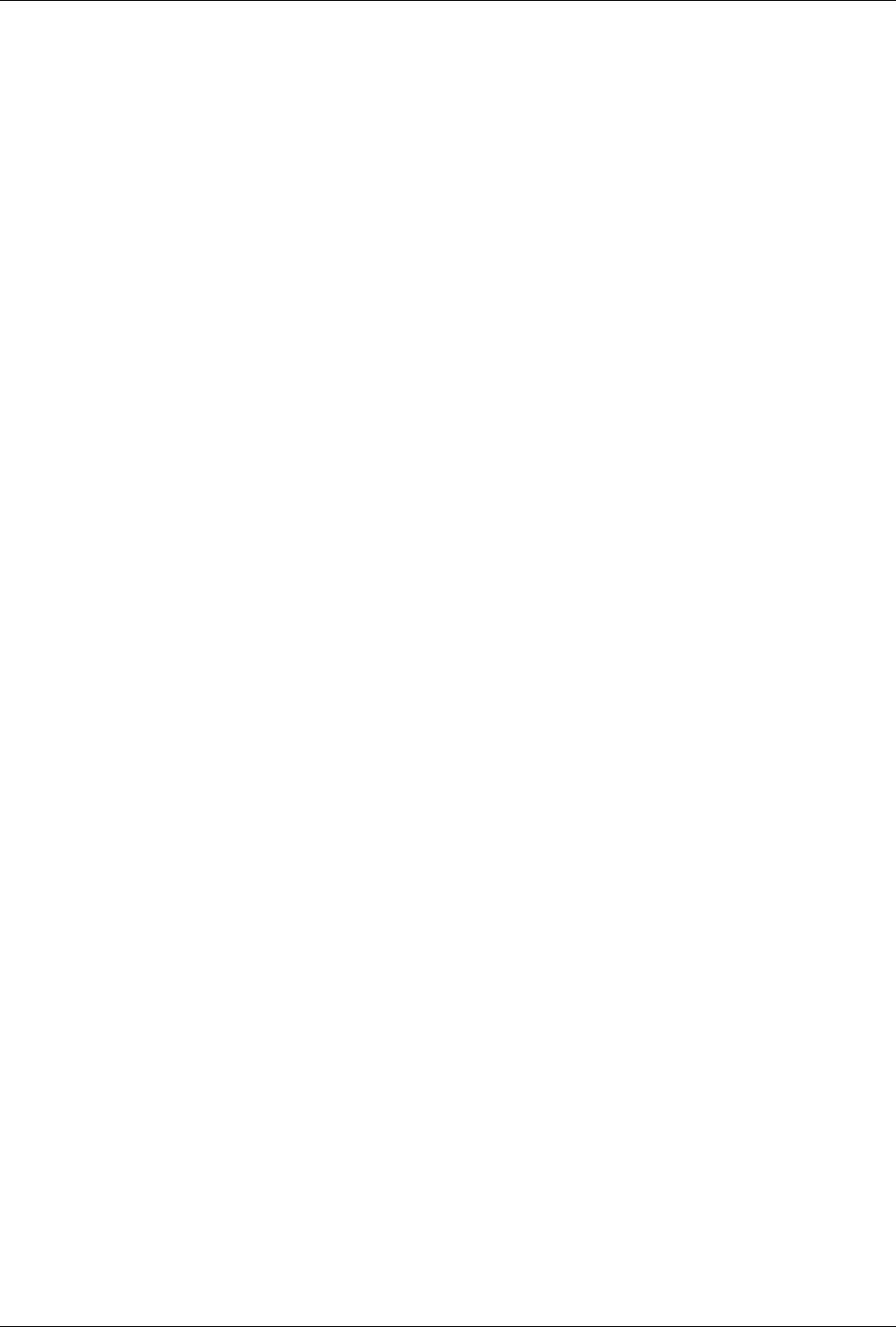
Hardware Re lacement
Unit Hardware Replacement
10. Remove the replacement ECU unit from its ESD bag.
11. Carefully slide the replacement ECU unit into the cabinet. Push the
unit firmly into the backplane connector.
12. Use the torque wrench with the Torx bit TX10 to tighten the screws
on the front. Turn the torque wrench until it slides to tighten to 0.6
Nm.
13. Reconnect the ECU cables.
14. Turn on the ECU circuit breaker.
15. After fan test is complete, verify the decimal points located in the
two-digit display are illuminated. If not, refer to the troubleshooting
procedures in Section 4 on page 5-6 for detection of units suspected
to be faulty.
16. After ECU replacement, block and deblock all units in the RBS 884
Micro (1900 MHz) cabinet.
17. Remove the ESD strap cable from the cabinet, and detach it from
your wrist.
18. Update the Plant Specification in the Site Installation Documentation
concerning the new ECU unit. Use the comments field to note the
date of hardware replacement, and new R-state.
19. Close the cabinet door.
20. Inform the MSC operator that the ECU unit has been replaced.
Unit Repair
21. Complete the Repair Traveler Note and attach it to the ECU unit
suspected to be faulty.
22. Pack the ECU unit in the packing material from the new unit and
return it to the local service center.
6.11 Fan Replacement
Unit Removal
1. Obtain permission from the MSC operator to replace the Fan unit.
2. Open the cabinet door and secure the wind latch at the top of the
door. Open the door until the shoulder slides into the slot at the end
of the bar.
2/1551-EN/LZB 119 3312 Uae Rev A 1998-11-17 5-39
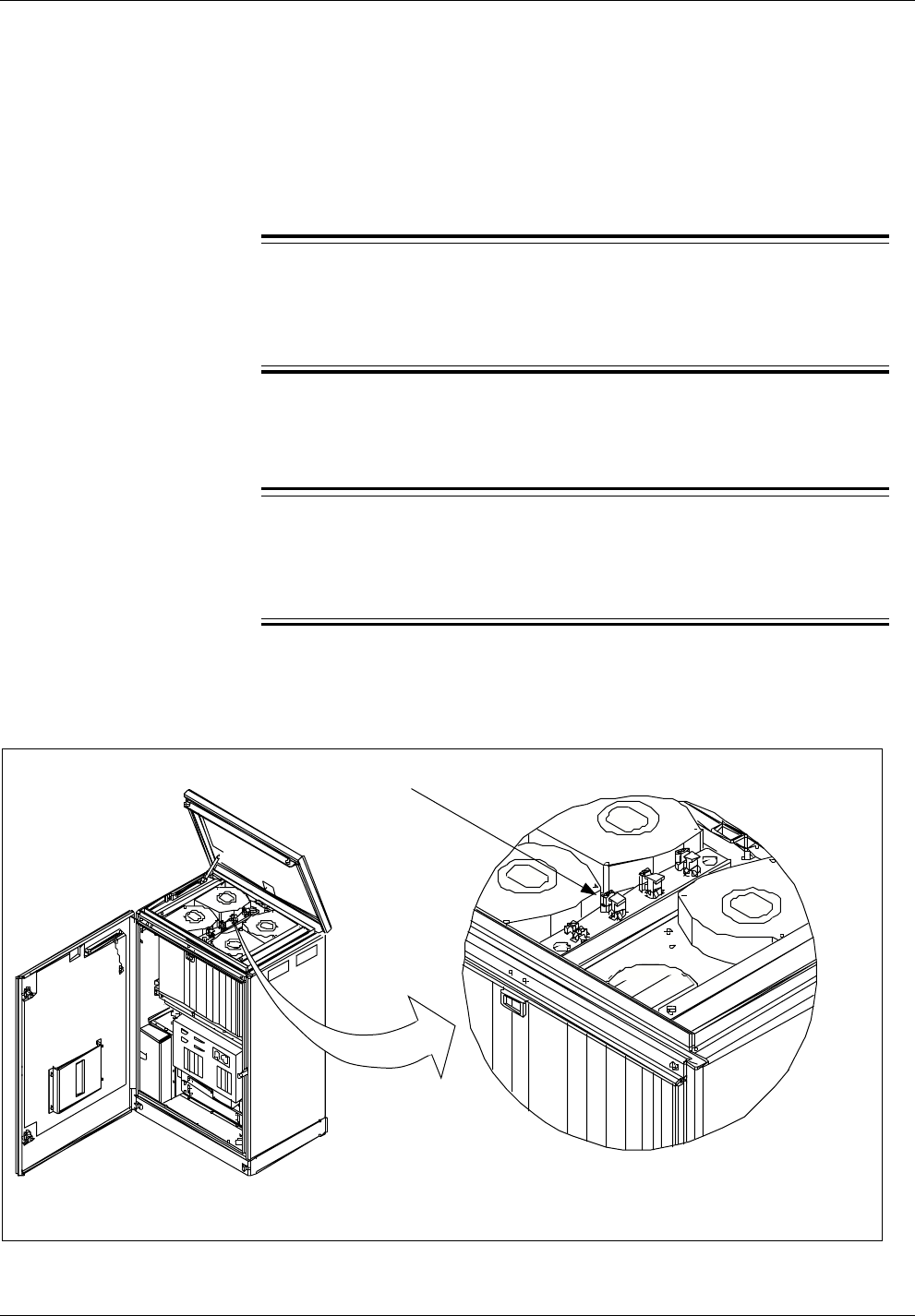
Hardware Re lacement
3. Pull out the two plungers in the lid and fully lift lid. Lower lid
slightly while pushing the support brace towards the rear of the
cabinet. The support brace should engage the mating bracket and
lock the lid in position.
4. Identify the failed Fan unit. The code displayed on the front of the
ECU indicates which Fan has failed.
5.
Warning!
A unit must never be replaced by another unit with a lower R-state
number.
Check that the replacement Fan unit is the same type as the unit to
be replaced, and that it has the same or higher R-state number.
6.
Warning!
The remaining steps in this procedure must be performed as quickly
as possible in order to avoid overheating the cabinet.
Disconnect the cable from the Fan unit.
7. Disconnect the three-wire connector. See Figure 5-19 on page 5-40.
Fan Connectors
Figure 5-19. The Fan Unit
5-40 2/1551-EN/LZB 119 3312 Uae Rev A 1998-11-17

Hardware Re lacement
8. Disconnect the two-wire connector.
9. Remove the tie wraps securing the Fan wiring.
10. Remove the three screws that secure the Fan unit to the cabinet
frame.
11. Remove the Fan unit.
Unit Hardware Replacement
12. Remove the replacement Fan unit from any packing material.
13. Install new Fan unit and replace three mounting screws.
14. Replace tie wraps if required.
15. Reconnect the two-wire Fan connector.
16. Reconnect the three-wire Fan connector.
17. Cycle the Fan breaker (turn off and turn on) to reset the Fan alarm.
The Fan start-up sequence will be initiated.
18. If the new Fan does not start, refer to the troubleshooting procedures
in Section 4 on page 5-6 for detection of units suspected to be faulty.
19. Close the lid by disengaging the support brace. Press down firmly on
the lid until the two plungers engage the slots on the cabinet. Press
the plungers toward rear of cabinet to lock lid.
20. Update the Plant Specification in the Site Installation Documentation
concerning the new Fan unit. Use the comments field to note the
date of hardware replacement and new R-state.
21. Close the cabinet door.
22. Inform the MSC operator that the Fan has been replaced.
Unit Repair
23. Complete the Repair Traveler Note and attach it to the Fan unit
suspected to be faulty.
24. Pack the Fan unit in the packing material from the new unit and
return it to your local service center.
2/1551-EN/LZB 119 3312 Uae Rev A 1998-11-17 5-41

Hardware Re lacement
6.12 Main Heater Assembly Replacement
Warning!
The following procedure will disable the RBS 884 Micro (1900 MHz).
The unit will be out of service during the procedure. Contact the MSC
operator before performing the following procedure.
Unit Removal
1. Obtain permission from the MSC operator to replace the Main
Heater Assembly.
2. Open the cabinet door and secure the wind latch at the top of the
door. Open the door until the shoulder slides into the slot at the end
of the bar.
3. Place the MAIN HTR circuit breaker on the right side of the AC/DC
Distribution Box in the OFF position. See Figure 5-20 on page 5-42.
ALM CABLE ECU CABLE
SUBRK PWR FAN PWR CSU
SENSORS
AC
CONNECTED
MAIN PSU MAIN
HTR BAT
HTR GFI
OUTLET
BAT ECU CSU FANS
BAT COMP
BAT
ALM DOOR
ALM
ON
OFF
Figure 5-20. AC/DC Distribution Box
4. Locate the Main Heater Assembly. See Figure 5-21 on page 5-43.
5-42 2/1551-EN/LZB 119 3312 Uae Rev A 1998-11-17
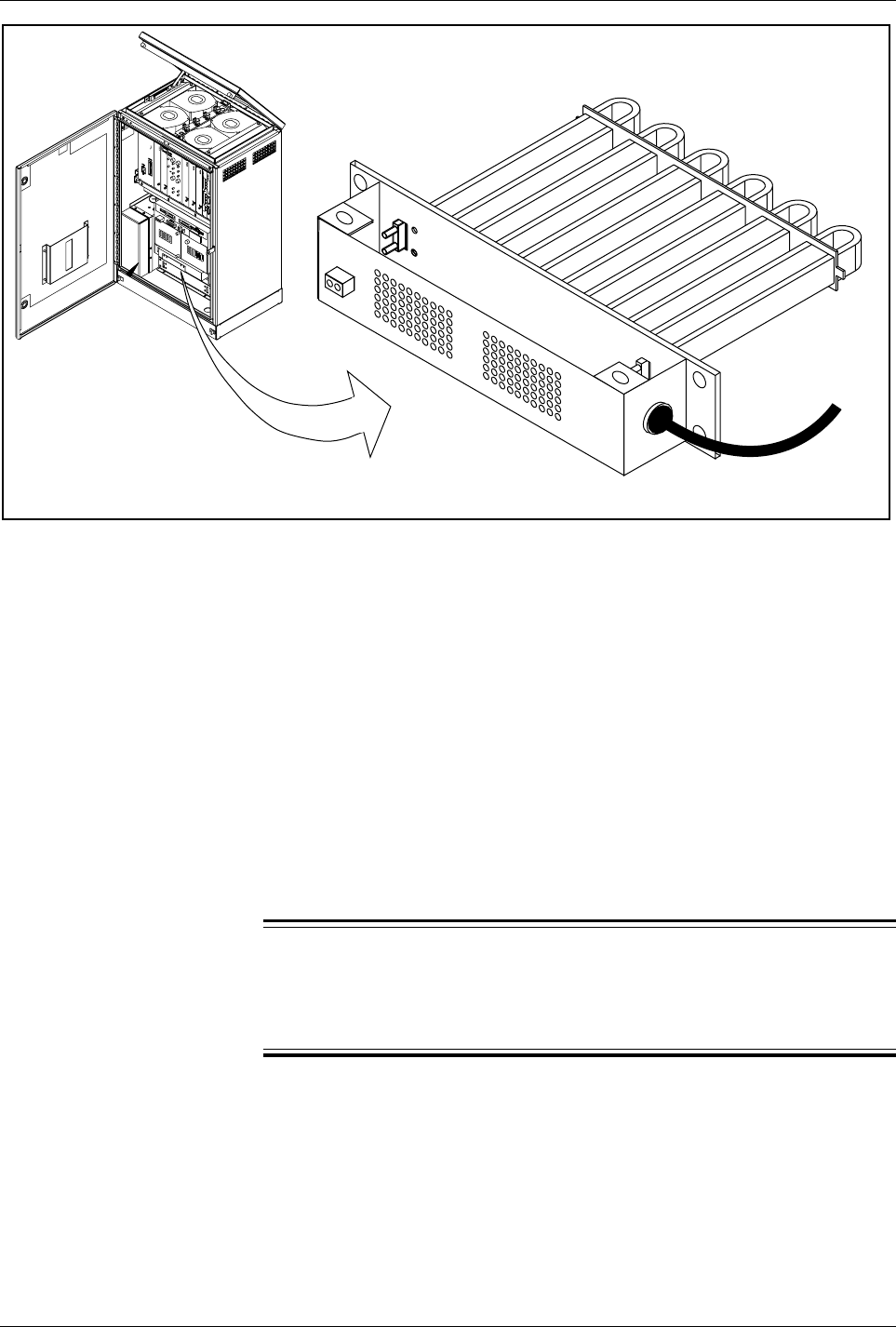
Hardware Re lacement
Figure 5-21. Subrack Heater
5. Check that the Main Heater Assembly is the same type as the
assembly to be replaced.
6. Unplug the control wires from the front of the Main Heater
Assembly.
7. Remove the two screws located on the top of the perforated
assembly cover. Remove the cover and retain for installation on
replacement assembly.
8. Remove the mounting screws located on each side of the Main
Heater Assembly (two per side). Pull the assembly out four to six
centimeters.
9.
DANGER!
Use a voltmeter to verify the unit is NOT energized. Do not assume
power is OFF.
Locate the heater power cable on the right side of the assembly.
Follow cable into the Main Heater Assembly and locate the black,
white, and green power wires.
Note: If required, remove any ties or clamps securing
power wires.
10. Disconnect the black, white, and green power wires. If needed,
record wire position and connections.
2/1551-EN/LZB 119 3312 Uae Rev A 1998-11-17 5-43
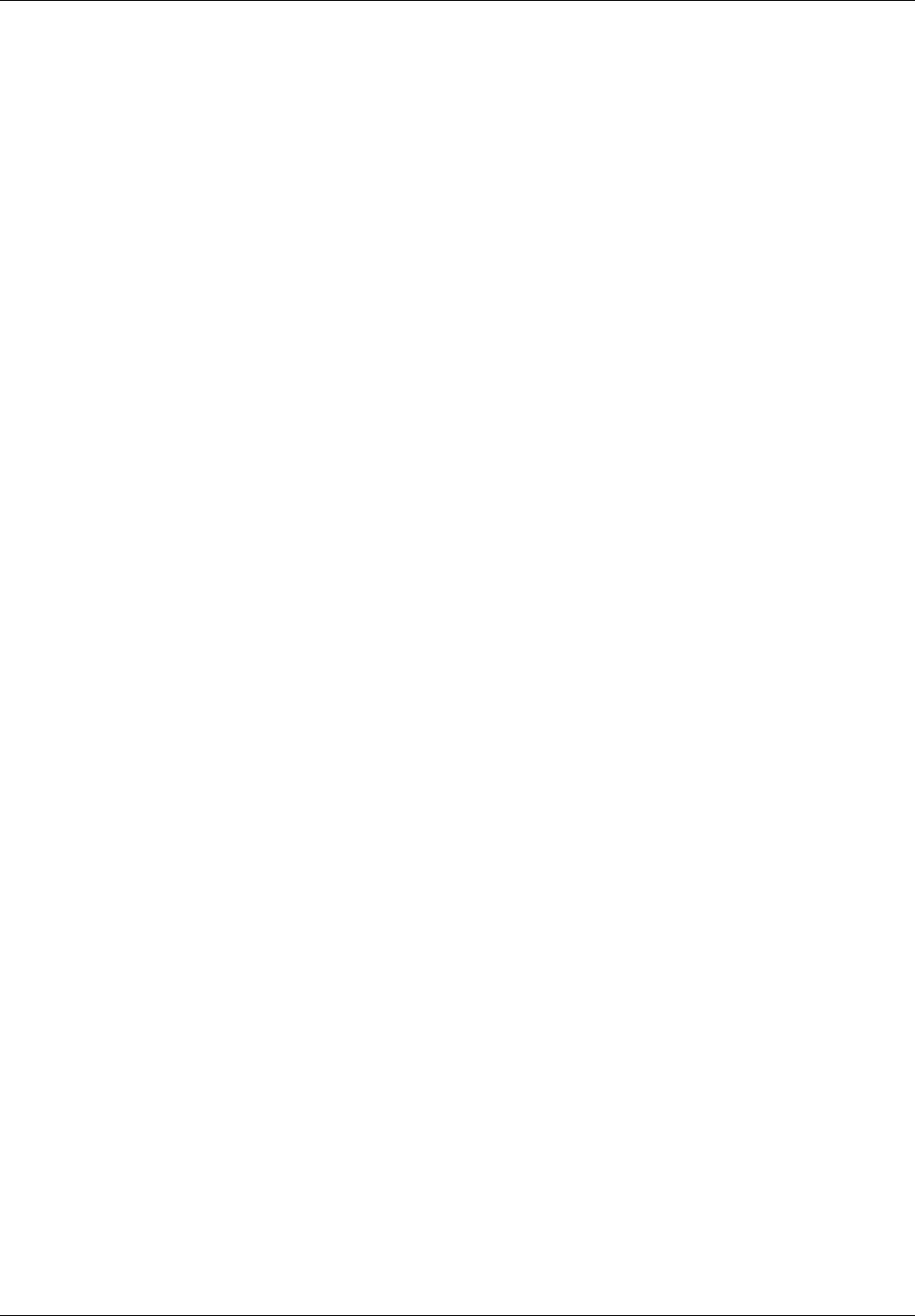
Hardware Re lacement
11. Remove the strain relief and remove the power cable from the heater
assembly. Remove the Main Heater Assembly from the cabinet.
Unit Hardware Replacement
12. Remove the replacement Main Heater Assembly from any packing
material.
13. Remove the two screws located on the top of the perforated
assembly cover. Remove the cover.
14. Insert the replacement assembly approximately eight to ten
centimeters into cabinet opening.
15. Insert power cable through right side of the assembly.
16. Reconnect the black, white, and green power wires. The black wire
connects to the solid-state relay terminal (2). The white wire
connects to 1L1 and 1L2 with a wire nut. The green wire connects
to the heater assembly ground.
17. Replace the top cover and tighten screws.
18. Push the Main Heater Assembly all the way into the cabinet opening
and replace the mounting screws (two per side).
19. Reconnect the control wires to the front of the Main Heater
Assembly.
20. Place the MAIN HTR circuit breaker on the right side of the AC/
DC Distribution Box in the ON position.
21. Update the Plant Specification in the Site Installation Documentation
concerning the new assembly. Use the comments field to note the
date of the hardware replacement and new R-state.
22. Close the cabinet door.
23. Inform the MSC operator that the Main Heater Assembly has been
replaced.
Unit Repair
24. Complete the Repair Traveler Note and attach it to the unit suspected
to be faulty.
25. Pack the assembly in the packing material from the new assembly
and return it to the local service center.
5-44 2/1551-EN/LZB 119 3312 Uae Rev A 1998-11-17
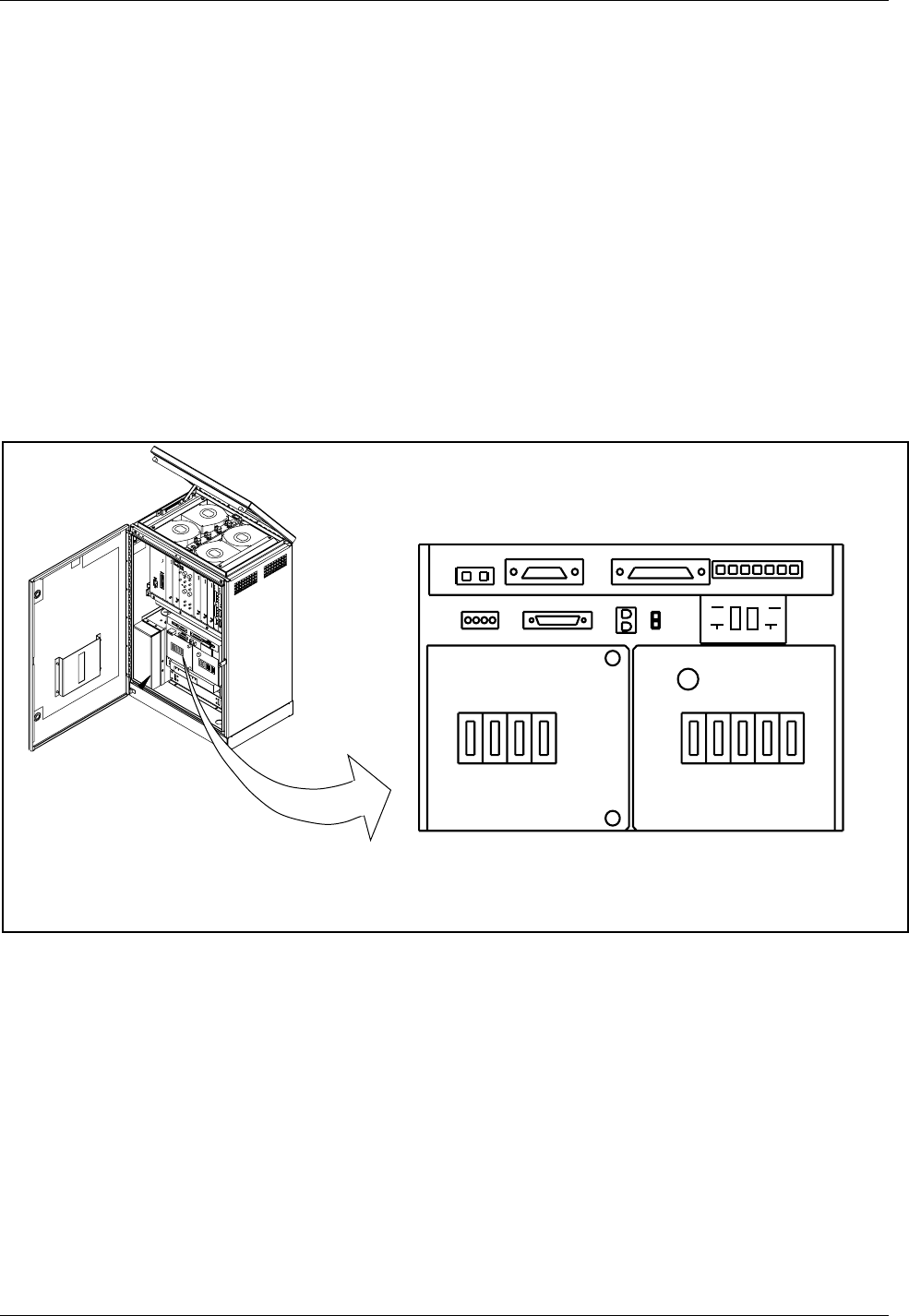
Hardware Re lacement
6.13 Battery Heater Replacement
Unit Removal
1. Obtain permission from the MSC operator to replace the Battery
Heater.
2. Open the cabinet door and secure the wind latch at the top of the
door. Open the door until the shoulder slides into the slot at the end
of the bar.
3. Place the BAT circuit breaker on the left side of the AC/DC
Distribution Box in the OFF position. See Figure 5-22 on page 5-45.
4. Place the BAT HTR circuit breaker on the right side of the AC/DC
Distribution Box in the OFF position. See Figure 5-22 on page 5-45.
ALM CABLE ECU CABLE
SUBRK PWR FAN PWR CSU
SENSORS
AC
CONNECTED
MAIN PSU MAIN
HTR BAT
HTR GFI
OUTLET
BAT ECU CSU FANS
BAT COMP
BAT
ALM DOOR
ALM
ON
OFF
Figure 5-22. AC/DC Distribution Box
5. Locate the battery compartment and Battery Heater under the battery
tray. See Figure 5-23 on page 5-46.
2/1551-EN/LZB 119 3312 Uae Rev A 1998-11-17 5-45
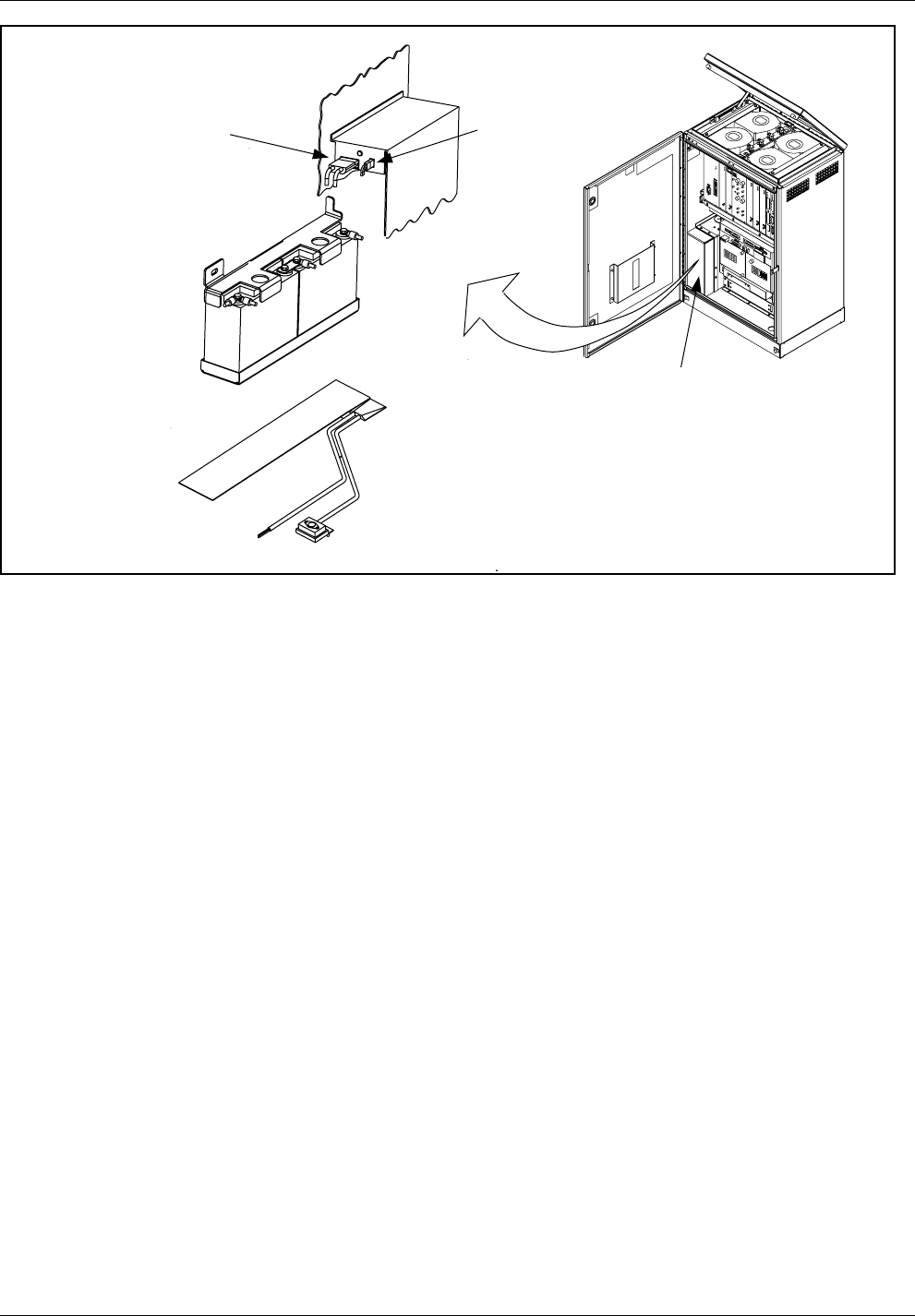
Hardware Re lacement
Battery
Compartment
Failed Battery
Sensor connector
Power Connector
Figure 5-23. Location of Battery Compartment and Battery Heater
6. Remove the four screws from the battery cover and remove the cover
from the battery compartment.
7. Disconnect the Failed Battery Sensor connector. See Figure 5-24 on
page 5-47.
5-46 2/1551-EN/LZB 119 3312 Uae Rev A 1998-11-17
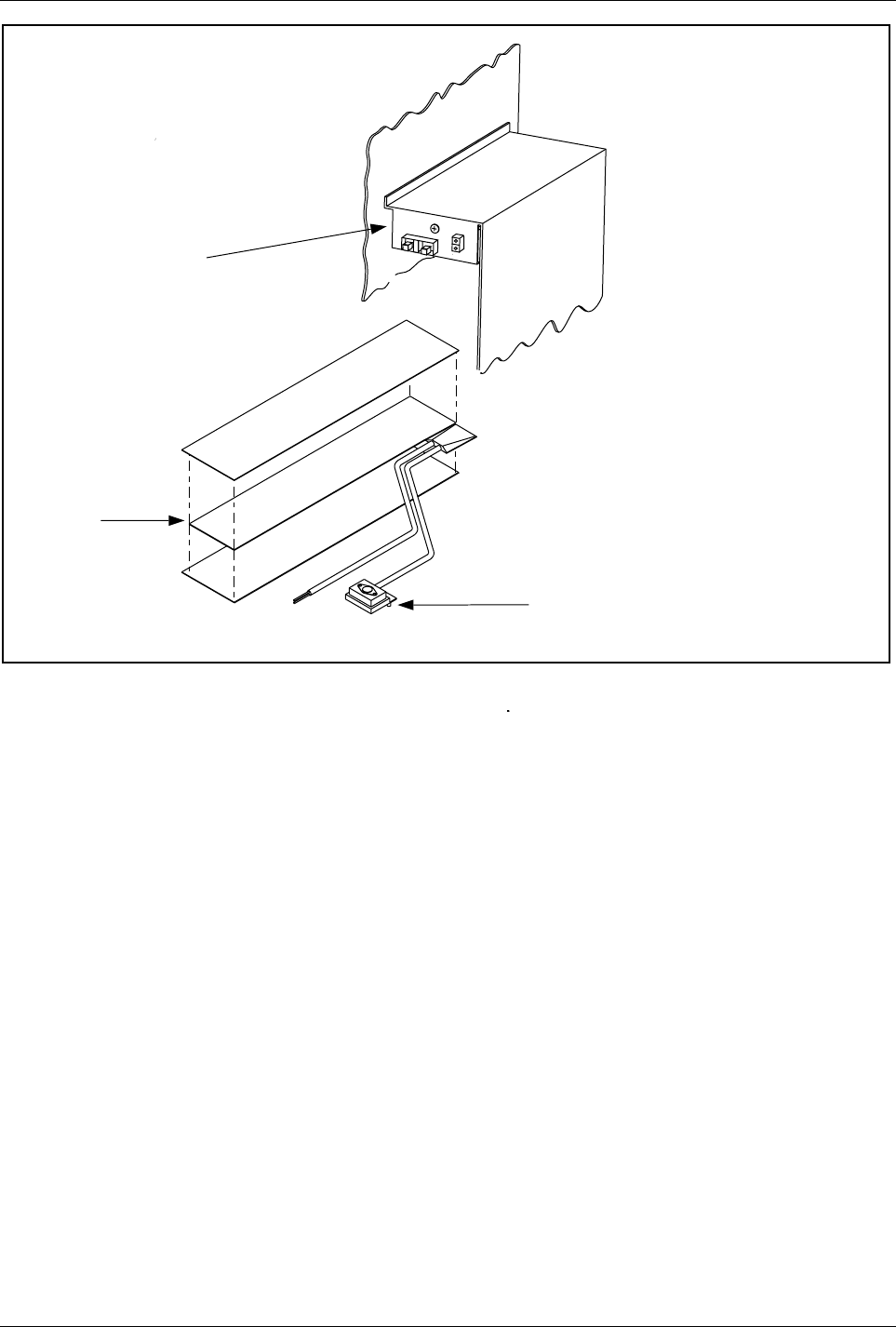
Hardware Re lacement
Heater Assembly
Electrical Connections
Located Inside
Enclosure
Thermostat
Heater
Figure 5-24. Battery Heater Assembly
8. Disconnect the power connector of the battery cable assembly from
the connector at the top of the battery compartment.
9. Remove the hex nut on the hold-down bracket on the side wall of
the battery compartment. Remove the hold down bracket.
10. Remove the battery tray with the batteries from the battery
compartment.
11. Remove the screw on the front of the wiring enclosure located above
the battery compartment. Support the enclosure.
12. Pull the enclosure down and locate the two screws securing the
battery heater thermostat to the bottom of the enclosure.
13. Remove the thermostat nuts and thermostat.
14. Remove the two heater power wires from the terminal strip inside
the enclosure. Remove the strain relief and pull the wires through
the bottom of the enclosure.
15. Remove the Battery Heater from the cabinet.
2/1551-EN/LZB 119 3312 Uae Rev A 1998-11-17 5-47
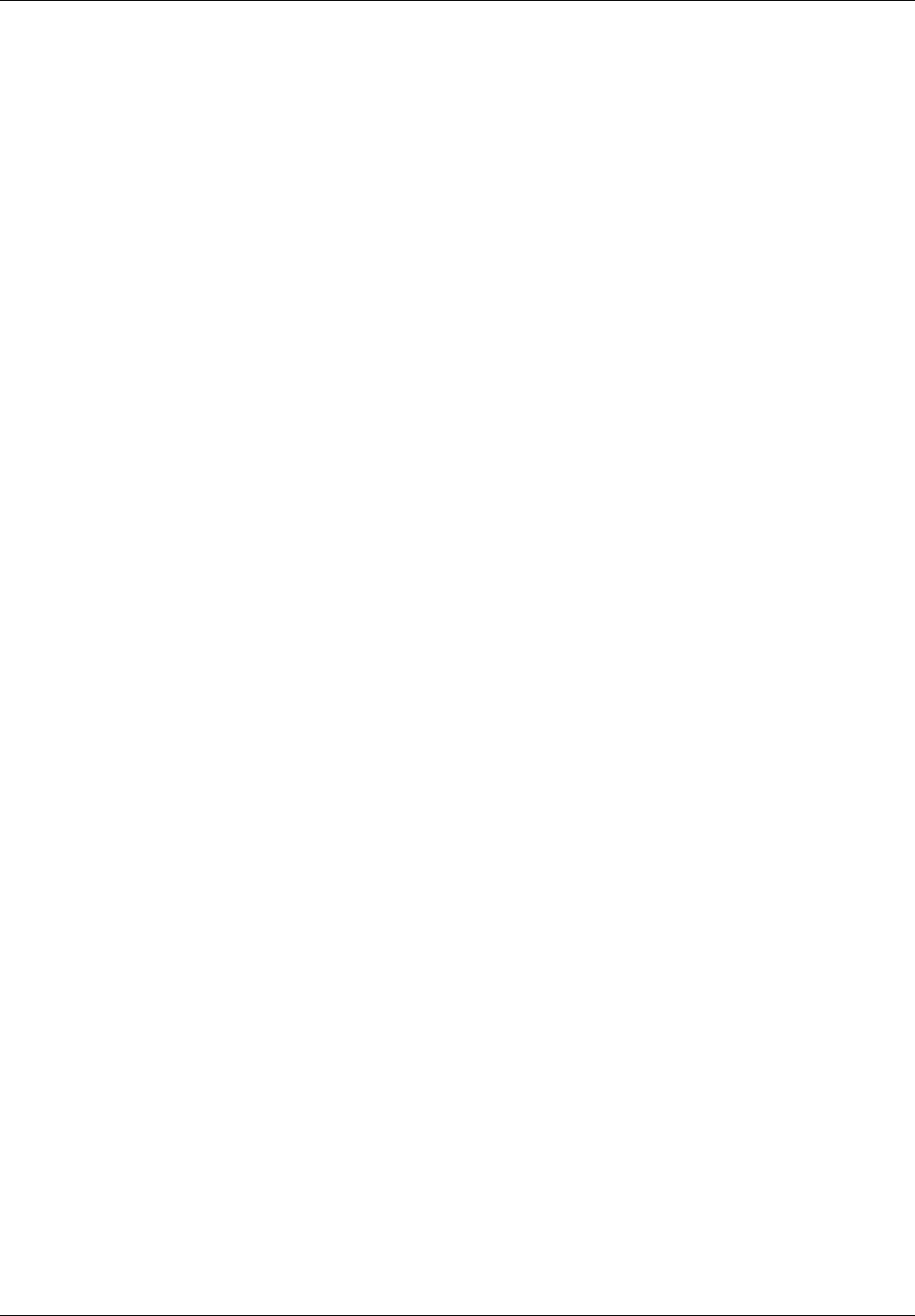
Hardware Re lacement
Unit Hardware Replacement
16. Remove any packing material from the replacement Battery Heater.
17. Push the two heater power wires through the strain relief and the
bottom of the enclosure. Connect the wires to the terminal strip.
18. Secure the thermostat to the bottom of the enclosure.
19. Raise the enclosure and slide the pins into the holes. Secure the
enclosure to the top of the battery compartment.
20. Install the battery tray.
21. Install the hold-down bracket and the hex nut on the side wall of the
battery compartment.
22. Reconnect the power connector of the battery cable assembly to the
connector at the top of the battery compartment.
23. Reconnect the Failed Battery Sensor connector.
24. Replace the battery compartment cover.
25. Place the BAT circuit breaker on the left side of the AC/DC
Distribution Box in the ON position.
26. Place the BAT HTR circuit breaker on the right side of the AC/DC
Distribution Box in the ON position.
27. Update the Plant Specification in the Site Installation Documentation
concerning the new Battery Heater. Use the comments field to note
the date of the hardware replacement and new R-state.
28. Close the cabinet door.
29. Inform the MSC operator that the battery heater has been replaced.
Unit Repair
30. Complete the Repair Traveler Note and attach it to the Battery
Heater suspected to be faulty.
31. Pack the Battery Heater in the packing material from the new heater
and return it to the local service center.
6.14 Battery Replacement
Unit Removal
1. Obtain permission from the MSC operator to replace the Battery.
5-48 2/1551-EN/LZB 119 3312 Uae Rev A 1998-11-17
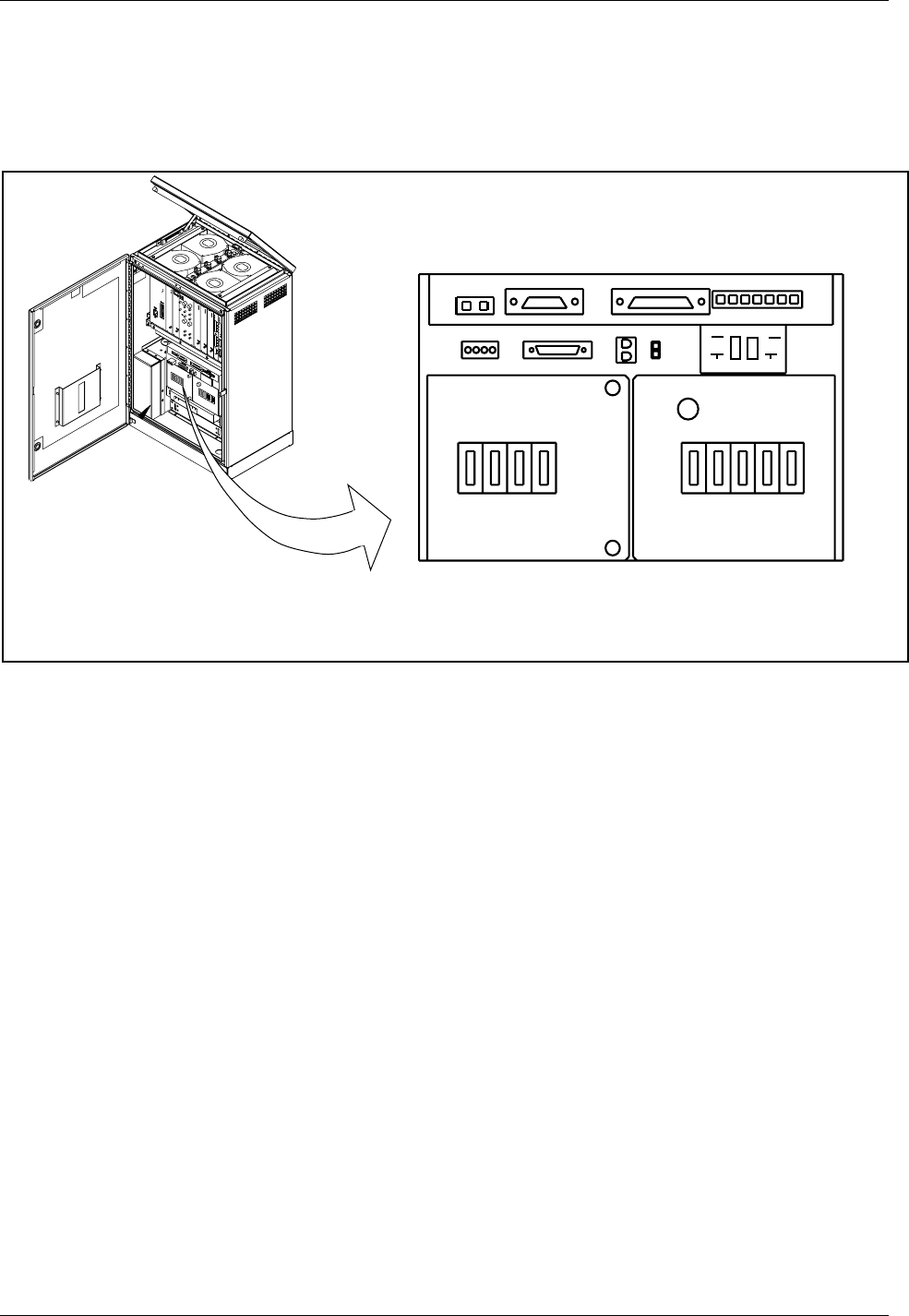
Hardware Re lacement
2. Open the cabinet door as described in the steps beginning with Step
1 on page 5-7.
3. Place the BAT circuit breaker on the left side of the AC/DC
Distribution Box in the OFF position. See Figure 5-25 on page 5-49.
ALM CABLE ECU CABLE
SUBRK PWR FAN PWR CSU
SENSORS
AC
CONNECTED
MAIN PSU MAIN
HTR BAT
HTR GFI
OUTLET
BAT ECU CSU FANS
BAT COMP
BAT
ALM DOOR
ALM
ON
OFF
Figure 5-25. AC/DC Distribution Box
4. Locate the battery compartment. See Figure 5-26 on page 5-50.
2/1551-EN/LZB 119 3312 Uae Rev A 1998-11-17 5-49
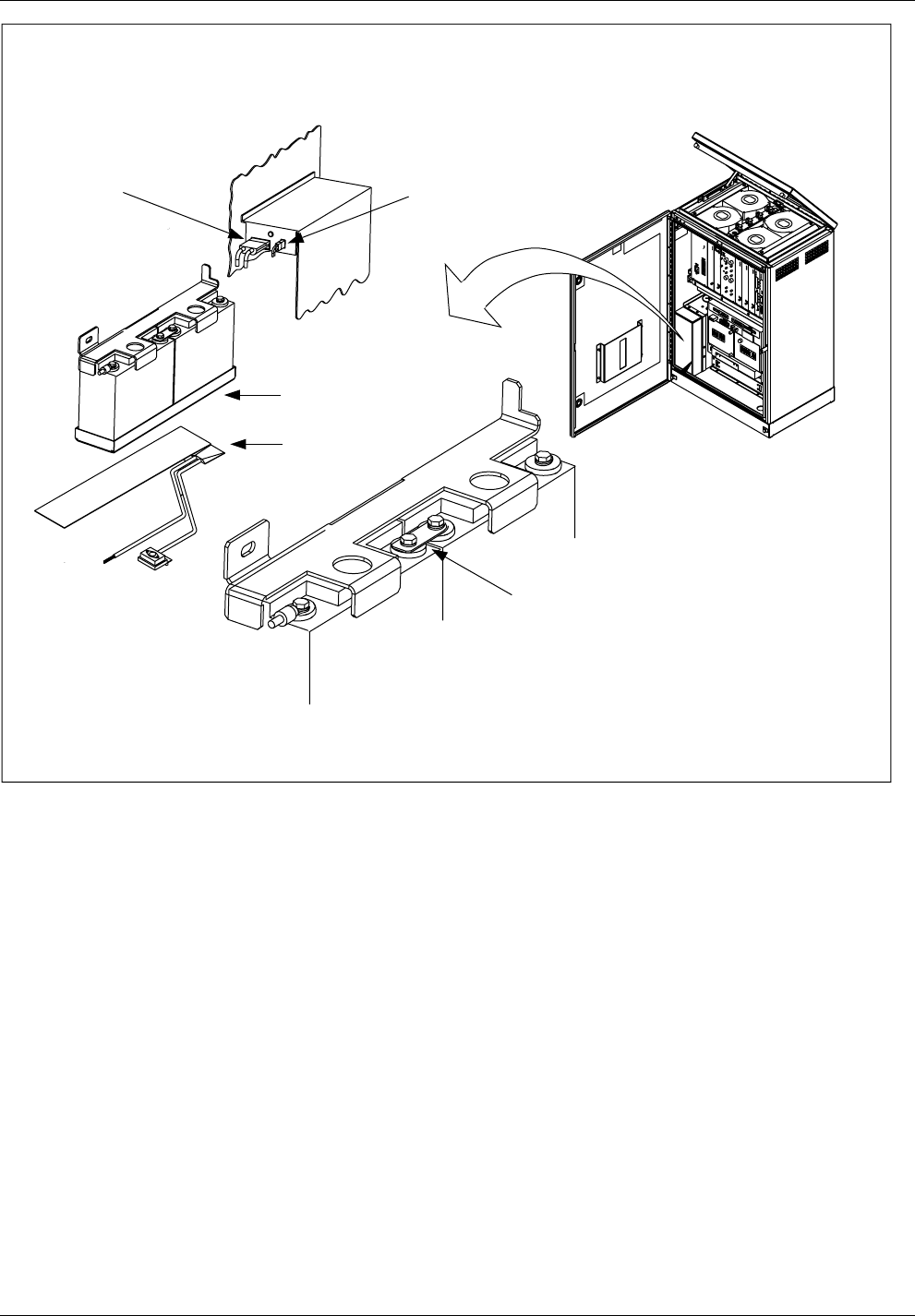
Hardware Re lacement
+
+
-
-
Copper Strap
Battery 1
Battery 2
Battery Tray
Battery Heater
Failed Battery
Sensor Connector
Power Connector
Figure 5-26. aBattery Assembly
5. Remove the four hex head bolts from the battery cover and remove
the cover from the battery compartment.
6. Disconnect the Failed Battery Sensor connector. Refer to Figure
5-24 on page 5-47.
7. Disconnect the power connector of the battery cable assembly from
the connector at the top of the battery compartment.
8. Remove the hex nut on the hold-down bracket on the side wall of
the battery compartment. Remove the hold down bracket.
9. Remove the battery tray with the batteries from the battery
compartment.
10. Disconnect the 8-gauge red cable from the positive terminal (+) of
battery 2.
5-50 2/1551-EN/LZB 119 3312 Uae Rev A 1998-11-17
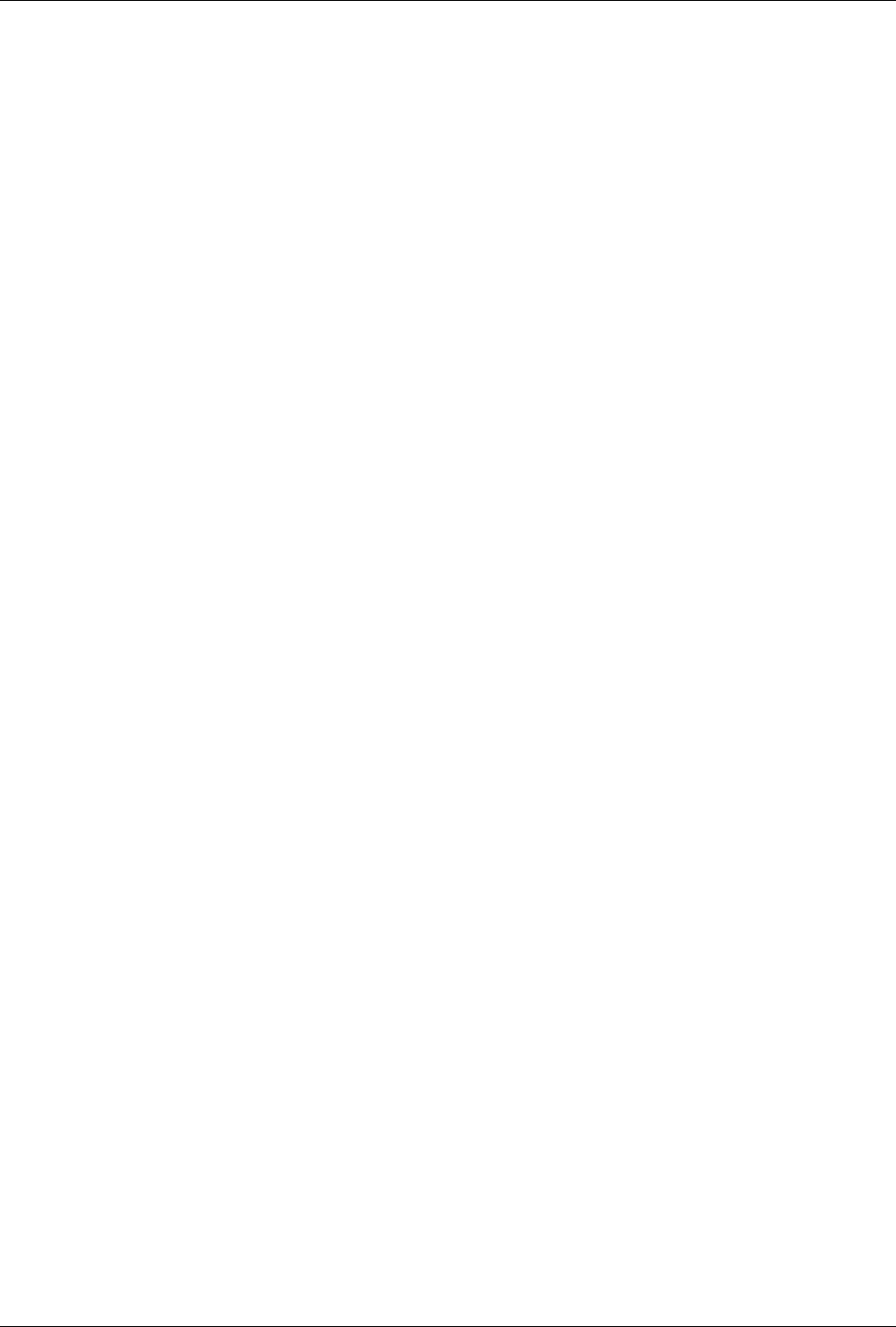
Hardware Re lacement
11. Disconnect the 8-gauge black cable from the negative terminal (-) of
battery 1.
12. Disconnect one of the 18-gauge white wires labeled POST from the
negative terminal (-) of battery 1. Disconnect the other 18-gauge
white wire from the negative terminal (-) of battery 2.
13. Remove the copper strap connecting the center terminals (positive
terminal of battery 1 to negative terminal of battery 2).
14. Remove the batteries from the battery tray.
15. Dispose of old batteries properly.
Unit Hardware Replacement
16. Remove the replacement batteries from the packing material.
17. Install the batteries into the battery tray as illustrated in Figure 5-24
on page 5-47. Place the hold-down bracket on the batteries.
18. Connect the center terminals (positive terminal of battery 1 to
negative terminal of battery 2) with the copper strap. Do not tighten
the negative terminal of battery 2 at this time.
19. Connect one of the 18-gauge white wires labeled POST to the
negative terminal of battery 1. Connect the other 18-gauge white
wire to the negative terminal of battery 2.
20. Connect the 8-gauge black cable to the negative terminal (-) of
battery 1.
21. Connect the 8-gauge red cable to the positive terminal (+) of battery
2.
Note: Ensure the terminals are placed inward, toward the
back of the battery. Torque all bolts to 50 in-lbs.
22. Install the battery tray with the batteries in the battery compartment.
Make sure the battery cable assembly is not pinched against the
battery compartment.
23. Place the hold-down bracket over the screw on the side wall of the
battery compartment. Secure with a hex nut.
24. Connect the power connector of the battery cable assembly to the
connector at the top of the battery compartment.
25. Connect the Failed Battery Sensor connector.
26. Replace the battery cover on the battery compartment.
27. Place the BATT circuit breaker on the left side of the AC/DC
Distribution Box in the ON position.
2/1551-EN/LZB 119 3312 Uae Rev A 1998-11-17 5-51
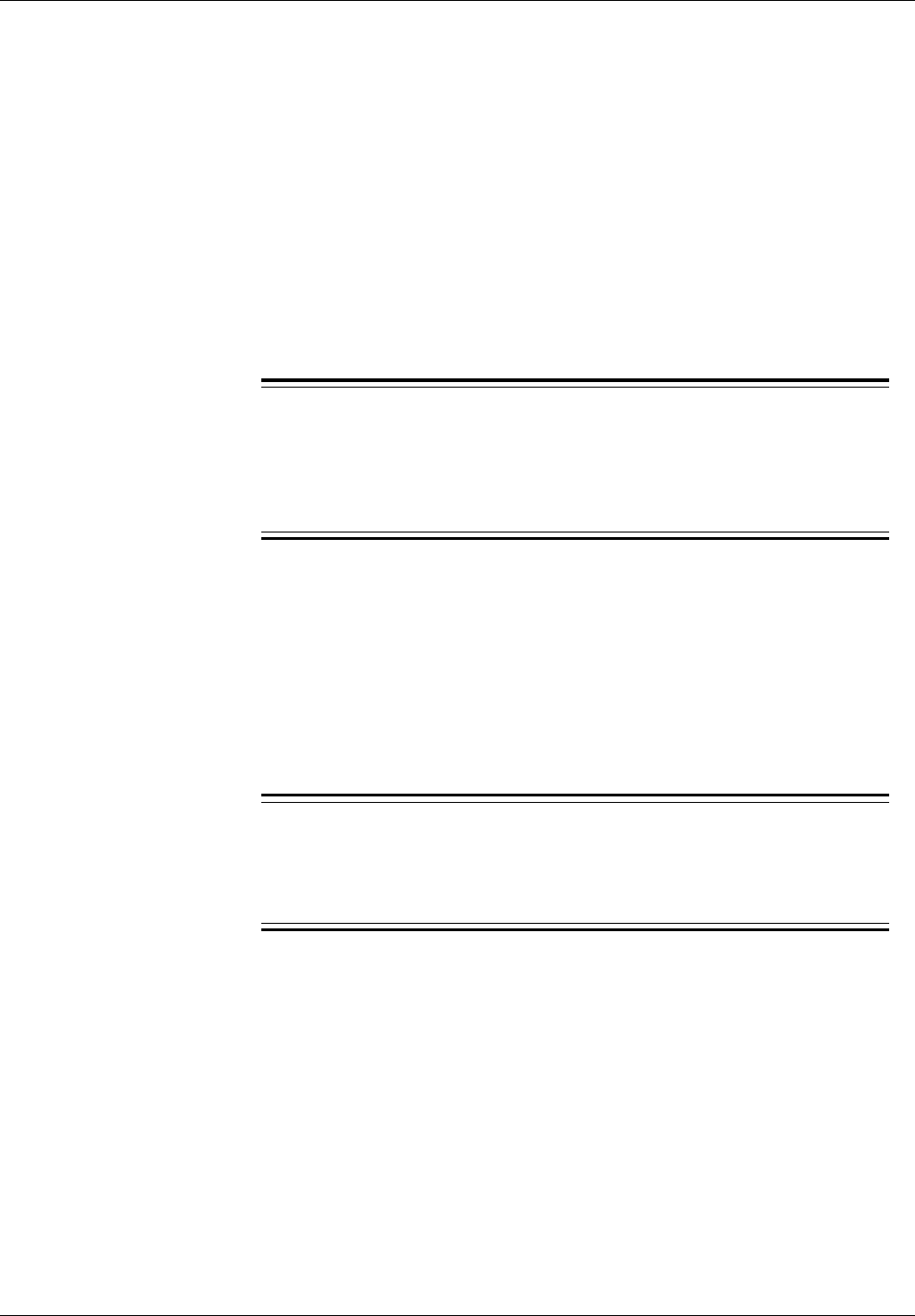
Hardware Re lacement
28. Update the Plant Specification in the Site Installation Documentation
concerning the new battery. Use the comments field to note the date
of the hardware replacement and new R-state.
29. Close the cabinet door.
30. Inform the MSC operator that the internal battery has been replaced.
6.15 AC Surge Suppressor Replacement
Unit Removal
Warning!
The following procedure will disable the RBS 884 Micro (1900
MHz). The unit will be out of service during the procedure. Contact
the MSC before performing the following procedure.
1. Obtain permission from the MSC operator to replace the AC Surge
Suppressor.
2. Open the cabinet door and secure the wind latch at the top of the
door. Open the door until the shoulder slides into the slot at the end
of the bar.
3. Disconnect all power to the RBS 884 Micro (1900 MHz) cabinet.
4.
Warning!
Verify all power is removed from the cabinet. Verify the AC
CONNECTED indicator light is OFF.
Place the MAIN circuit breaker on the right side of the AC/DC
Distribution Box in the OFF position. See Figure 5-27 on page 5-53.
5-52 2/1551-EN/LZB 119 3312 Uae Rev A 1998-11-17

Hardware Re lacement
ALM CABLE ECU CABLE
SUBRK PWR FAN PWR CSU
SENSORS
AC
CONNECTED
MAIN PSU MAIN
HTR BAT
HTR GFI
OUTLET
BAT ECU CSU FANS
BAT COMP
BAT
ALM DOOR
ALM
ON
OFF
Figure 5-27. AC/DC Distribution Box
5. Open the front of the AC/DC Distribution Box and locate the AC
Surge Suppressor on the back wall. See Figure 5-28 on page 5-53.
AC Surge Suppressor
Located on Rear Wall of
AC/DC Control Enclosure
PROTECTEDPOW
ERO
N
LINE
NEUTRAL
Figure 5-28. AC Surge Suppressor Assembly
6. Verify the LEDs on the front of the AC Surge Suppressor are off.
2/1551-EN/LZB 119 3312 Uae Rev A 1998-11-17 5-53

Hardware Re lacement
7. Disconnect the LINE and NEUTRAL wires from the front of the
surge suppressor.
8. Remove the nuts securing the AC Surge Suppressor to rear wall.
Remove the AC Surge Suppressor.
Unit Hardware Replacement
9. Remove any packing material from the replacement AC Surge
Suppressor.
10. Install new AC Surge Suppressor to rear wall of AC/DC Distribution
Box.
11. Reconnect the LINE and NEUTRAL wires to the front of the surge
suppressor.
12. Place the MAIN circuit breaker on the right side of the AC/DC
Distribution Box in the ON position.
13. Verify the LEDs on the front of the AC Surge Suppressor are on.
14. Close the AC/DC Distribution Box.
15. Update the Plant Specification in the Site Installation Documentation
concerning the new unit. Use the comments field to note the date of
the hardware replacement and new R-state.
16. Close the cabinet door.
17. Inform the MSC operator that the AC Surge Suppressor has been
replaced.
Unit Repair
18. Complete the Repair Traveler Note and attach it to the unit suspected
to be faulty.
19. Pack the unit in the packing material from the new unit and return it
to the local service center.
5-54 2/1551-EN/LZB 119 3312 Uae Rev A 1998-11-17
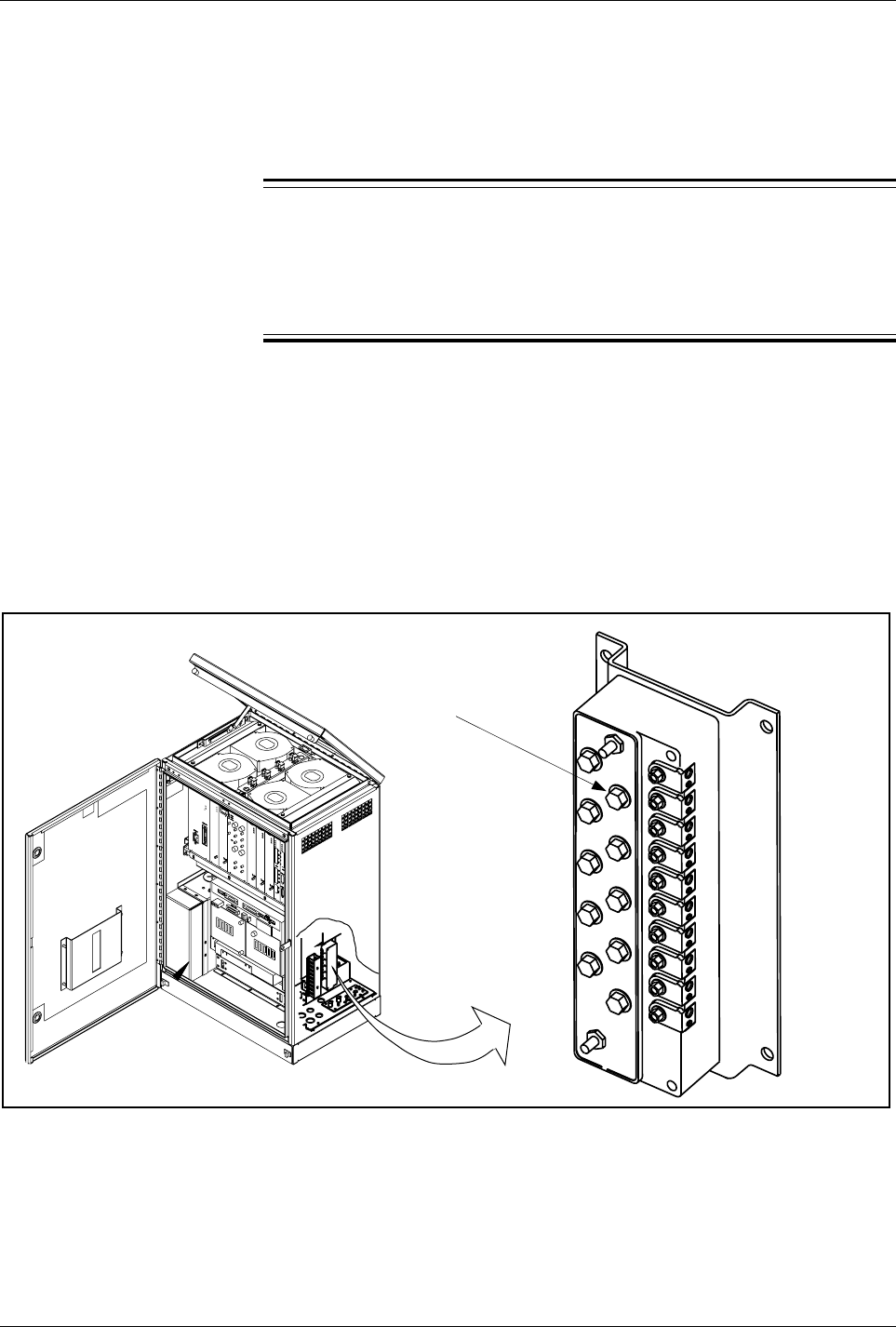
Hardware Re lacement
6.16 Pulse Code Modulation (PCM) (T1/E1) Primary Surge Suppressor
Replacement
Unit Removal
Warning!
The following procedure will disable the RBS 884 Micro (1900
MHz). The unit will be out of service during the procedure. Contact
the MSC before performing the following procedure.
1. Obtain permission from the MSC operator to replace the PCM
Primary Surge Suppressor.
2. Open the cabinet door and secure the wind latch at the top of the
door. Open the door until the shoulder slides into the slot at the end
of the bar.
3. Locate the PCM Primary Surge Suppressor on the right inside wall
of cabinet. See Figure 5-29 on page 5-55.
12345
Located on Right Inside Wall
T1(E1) PCM Primary Surge
Suppressor Tube (10)
Figure 5-29. T1(E1) Primary Surge Suppressor
4. Remove the T1(E1) cable wires from the PCM Primary Surge
Suppressor. Record the position of the wires.
5. Remove the four nuts securing the PCM Primary Surge Suppressor
to the cabinet. Remove the unit from the cabinet.
2/1551-EN/LZB 119 3312 Uae Rev A 1998-11-17 5-55
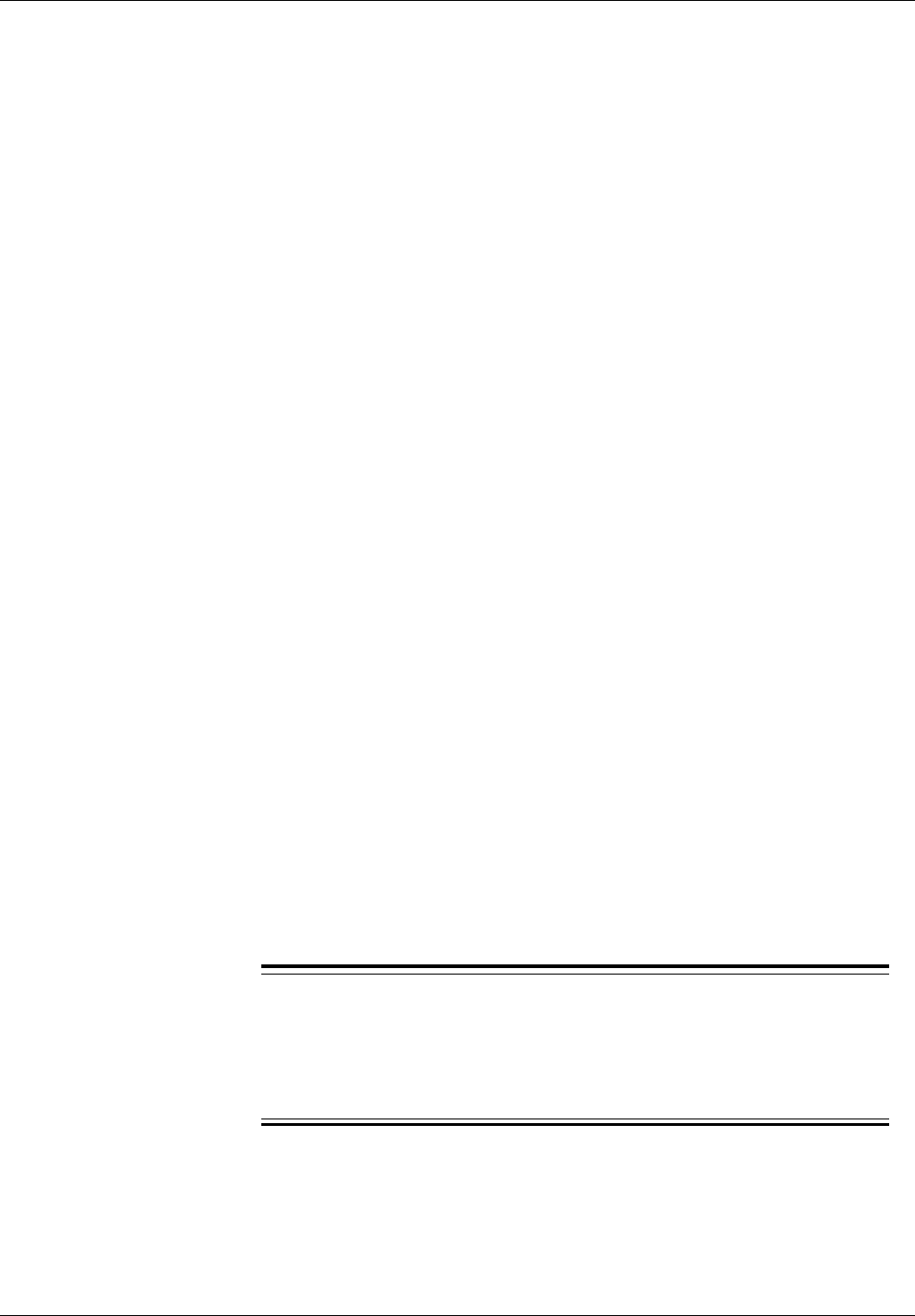
Hardware Re lacement
Unit Hardware Replacement
6. Remove the replacement PCM Primary Surge Suppressor.
7. Install the replacement unit in the cabinet.
8. Connect the T1(E1) cable wires into the large and small activator
ports (tip=white and ring=orange).
Note: Large ports are for 18.5 to 20 AWG wires and
small ports are for 22 to 24 AWG wires.
9. Using a 216–type tool, tighten the activator until the tension stops.
Do Not Overtighten.
10. Update the Plant Specification in the Site Installation Documentation
concerning the new unit. Use the comments field to note the date of
the hardware replacement, and new R-state.
11. Close the cabinet door.
12. Inform the MSC operator that the PCM Primary Surge Suppressor
has been replaced.
Unit Repair
13. Complete the Repair Traveler Note and attach it to the unit suspected
to be faulty.
14. Pack the PCM Primary Surge Suppressor in the packing material
from the new unit and return it to your local service center.
6.17 Pulse Code Modulation (PCM) T1(E1) Secondary Surge
Suppressor Replacement
Unit Removal
Warning!
The following procedure will disable the RBS 884 Micro (1900
MHz). The unit will be out of service during the procedure. Contact
the MSC before performing the following procedure.
1. Obtain permission from the MSC operator to replace the unit.
2. Open the cabinet door and secure the wind latch at the top of the
door. Open the door until the shoulder slides into the slot at the end
of the bar.
5-56 2/1551-EN/LZB 119 3312 Uae Rev A 1998-11-17

Hardware Re lacement
3. Locate the PCM Secondary Surge Suppressor. See Figure 5-30 on
page 5-57.
PCM T1(E1) Secondary Surge
Suppressor is Located Below
the AC/DC Box
Suppressor #2
(Optional)
Suppressor #1
Ground Wire
(to Gnd Plate)
PCM T1(E1) Shielded Cable
(From: Equipment To: Subrack
REMUX "PCM PRIM")
PCM T1(E1) Shielded Cable
(From: Equipment To: Subrack
REMUX "PCM SEC")
PCM T1(E1) Shielded Cable
(From: Line To: PSSI-J2)
PCM T1(E1) Shielded Cable
(From: Line To: PSSI-J1)
Figure 5-30. PCM T1(E1) Secondary Surge Suppressor Assembly
4. Remove the T1(E1) cables from the PCM Secondary Surge
Suppressor. Record position of cables if required.
5. Remove the ground wire.
6. Remove the two mounting screws (or nuts) and remove the PCM
Secondary Surge Suppressor from the cabinet.
Unit Hardware Replacement
7. Install the replacement PCM Secondary Surge Suppressor in cabinet
and replace two mounting screws.
8. Connect T1(E1) cables and ground wire.
9. Update the Plant Specification in the Site Installation Documentation
concerning the new unit. Use the comments field to note the date of
the hardware replacement and new R-state.
10. Close the cabinet door.
11. Inform the MSC operator that the PCM Secondary Surge Suppressor
has been replaced.
2/1551-EN/LZB 119 3312 Uae Rev A 1998-11-17 5-57
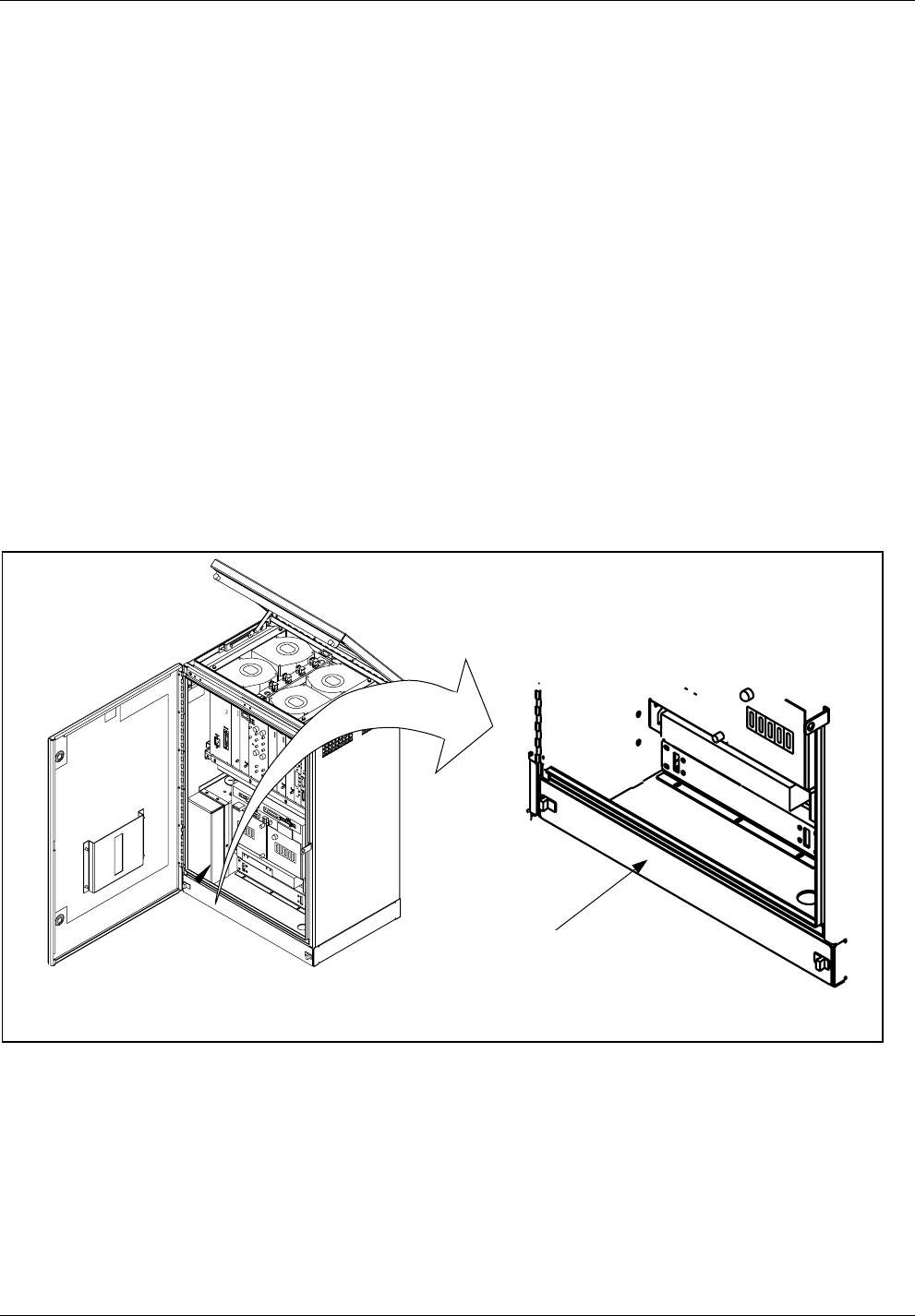
Hardware Re lacement
Unit Repair
12. Complete the Repair Traveler Note and attach it to the unit suspected
to be faulty.
13. Pack the PCM Secondary Surge Suppressor in the packing material
from the new unit and return it to the local service center.
6.18 Air Filter Replacement
Unit Removal
1. Obtain permission from the MSC operator to replace the Air Filter.
2. Open the cabinet door and secure the wind latch at the top of the
door. Open the door until the shoulder slides into the slot at the end
of the bar.
3. Locate the lower air filter cover. See Figure 5-31 on page 5-58.
Air Filter Located Behind
Cover Plate
Figure 5-31. Air Filter Location
4. If equipped with slide latches, grasp the slide latches and move
outward. If equipped with screws, remove the screws. Remove the
cover and set aside.
5. Locate the Air Filter and slide outward.
Note: Use care when removing Air Filter. Ensure that no
dust or debris from the Air Filter enters the cabinet.
5-58 2/1551-EN/LZB 119 3312 Uae Rev A 1998-11-17

Hardware Re lacement
6. Dispose of the old Air Filter properly.
Unit Hardware Replacement
7. Remove the replacement Air Filter and note air flow directional
arrows on side of the filter.
8. Install the new Air Filter with directional air flow arrows pointed up.
9. Replace the front cover and slide the latches inward to secure the
cover.
10. Update the Plant Specification in the Site Installation Documentation
concerning the new unit: use the comments field to note the date of
hardware replacement, and new R-state.
11. Close the cabinet door.
12. Inform the MSC operator that the Air Filter has been replaced.
2/1551-EN/LZB 119 3312 Uae Rev A 1998-11-17 5-59
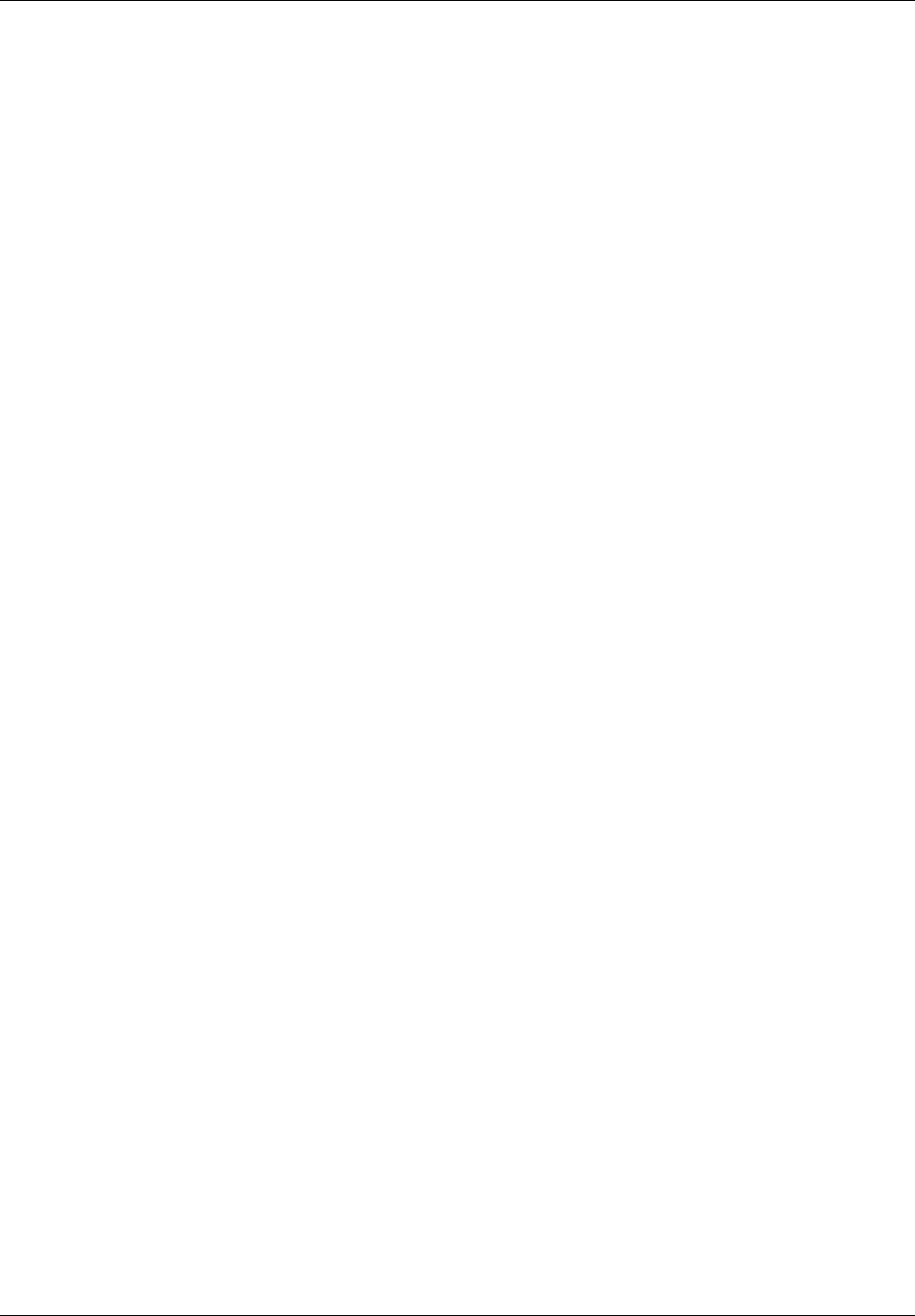
Hardware Re lacement
5-60 2/1551-EN/LZB 119 3312 Uae Rev A 1998-11-17

Part 6
Glossary of Terms
Auxiliary Cabinet Any extra RBS cabinet besides the main RBS
cabinet. It is connected to the main cabinet (no
direct connection with the MSC).
Cascading Connecting another radio base station to a first
one, thus using a common PCM line to the MSC.
Dummy TRX A blank panel with an empty box behind, to be
placed in unused TRX positions to ensure proper
cooling and EMC shielding.
E1 Connection The European standard for 2.048 Mbit/s PCM
connections, carrying 32 independent 64 kbit/s
channels (DS0s) numbered 0–31.
Main Cabinet The Main Cabinet is directly connected to an
MSC by a PCM link. The cabinet always has an
antenna system.
Mobile Switching
Center The Mobile Switching Center handles all
connections and disconnections of calls to a
mobile station (MS) and serves as the interface
between the mobile network and the Public
Switched Telephone Network (PSTN).
Primary Cabinet The Primary Cabinet is used to create an
additional sector within an omni cell.
T1 Connection The American standard for 1.544 Mbit/s PCM
connections carrying 24 independent 64 kbit/s
channels (DS0s) numbered 1–24.
1/0033-EN/LZB 119 3312 Uae Rev A 1998-11-17 6-1
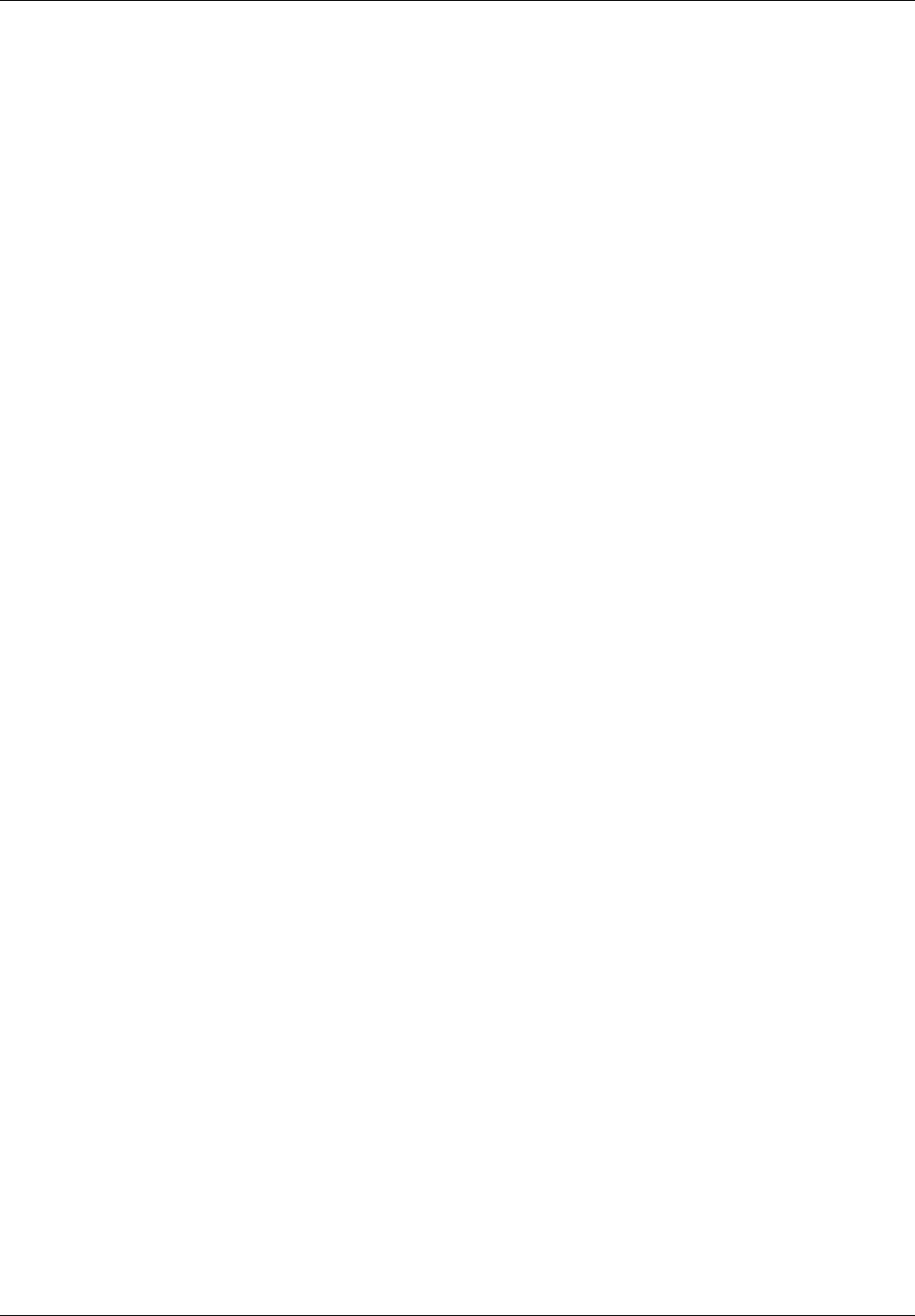
Glossary of Terms
6-2 1/0033-EN/LZB 119 3312 Uae Rev A 1998-11-17

Part 7
Acronyms and Abbreviations
AC Alternating Current
ALM Alarm (Module for RBS)
AMPS Advanced Mobile Phone Service
ANP Antenna Near Part
ATC Autotuned Combiner
ATCC Autotuned Combiner Cabinet
B8ZS Bit 8 Zero Substitute
CABCOMB Cabinet Combiner
CLC Control Signaling Link
COMBFILT Combiner Filter
CONN Connection Board
COP Control Part
CRC Cyclic Redundancy Check
CRI Control and Radio Interface
CSU Channel Service Unit
D-AMPS Digital Advanced Mobile Phone Service
DBC Down Banded Cellular
DC Directional Coupler
DCCH Digital Control Channel
DS0 Digital Signal Level 0
DTC Digital Traffic Channel
DVER Digital Verification Module
ECU Environmental Control Unit
EMBS Equipped Micro base Subrack
EMC Electromagnetic Compatibility
EMRP Extension Module Regional Processor
EMRPM EMRP for Micro Base
ESD Electrostatic Discharge
FCC Federal Communications Commission
GS Group Switch
IC Integrated Circuit
IHRM Installation and Hardware Replacement Manual
LED Light Emitting Diode
MC MultiCoupler
MCPA MultiCarrier Power Amplifier
2/0033-EN/LZB 119 3312 Uae Rev A 1998-11-17 7-1
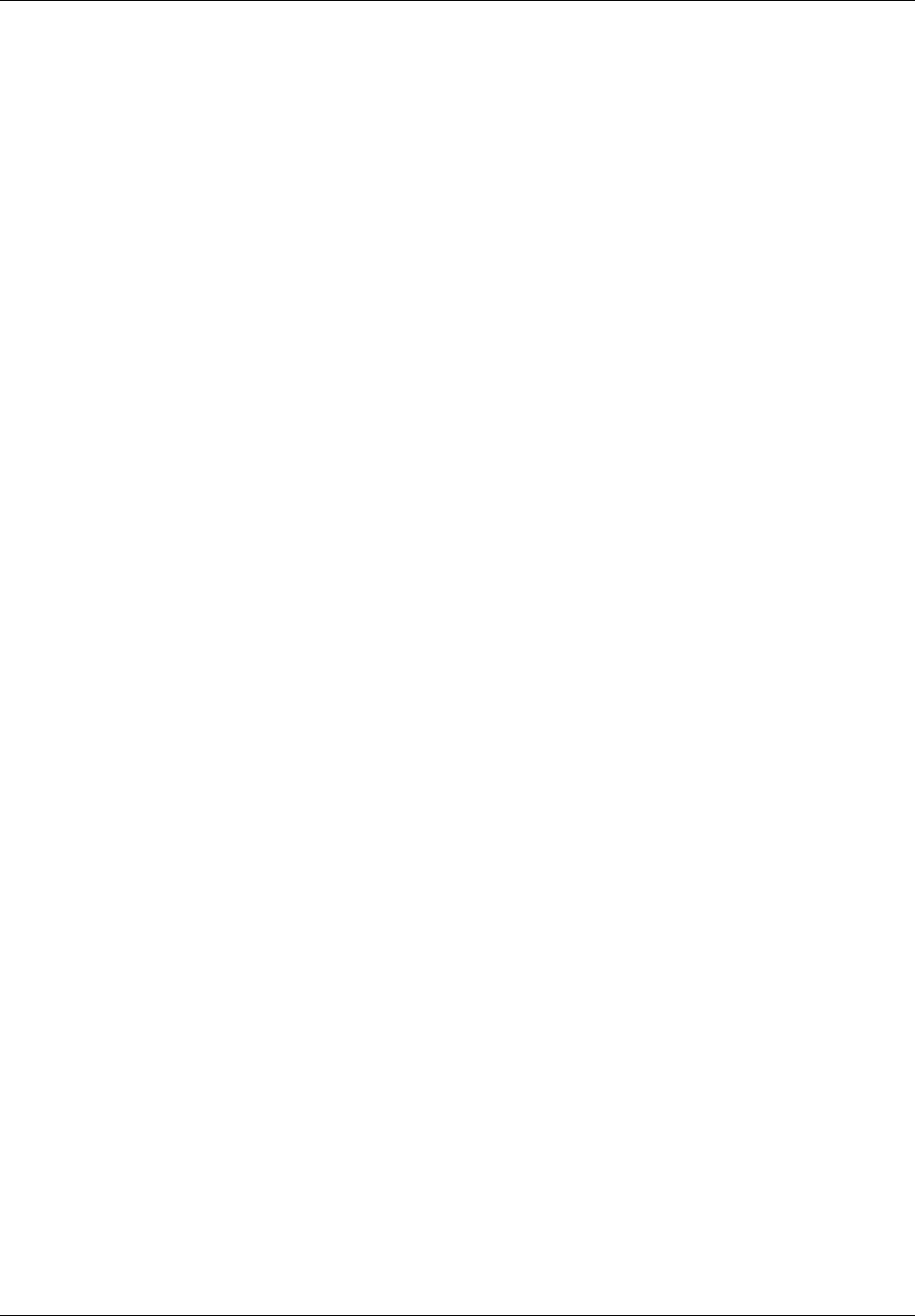
Acronyms and Abbreviations
MOP Modem Part
MSC Mobile Switching Center
MVER Mobile Verification Module
PCB Printed Circuit Board
PCM Pulse Code Modulation
PSU Power Supply
RBS Radio Base Station
RCG Radio Cabinet Group
REMUX Remote Multiplexor: Interfacing Board for the RBS
RF Radio Frequency
RFTL Radio Frequency Test Loop
RMU Radio Matching Unit
RSSI Received Signal Strength Indicator
RX Receiver
SCCS Self-Contained Cell Site
SP Signalling Point (SS7)
SP Support Processor (MSC)
STC Signaling Terminal Central
STR Signaling Terminal Regional
STRM Signal Terminal Remote
TCB Transceiver Cabinet
TLINK Transmission Link
TRAB Transcode Rate Adapter Board
TRX Transceiverm (Module for RBS)
TS Time slot
TX Transmitter
VSWR Voltage Standing Wave Radio
7-2 2/0033-EN/LZB 119 3312 Uae Rev A 1998-11-17
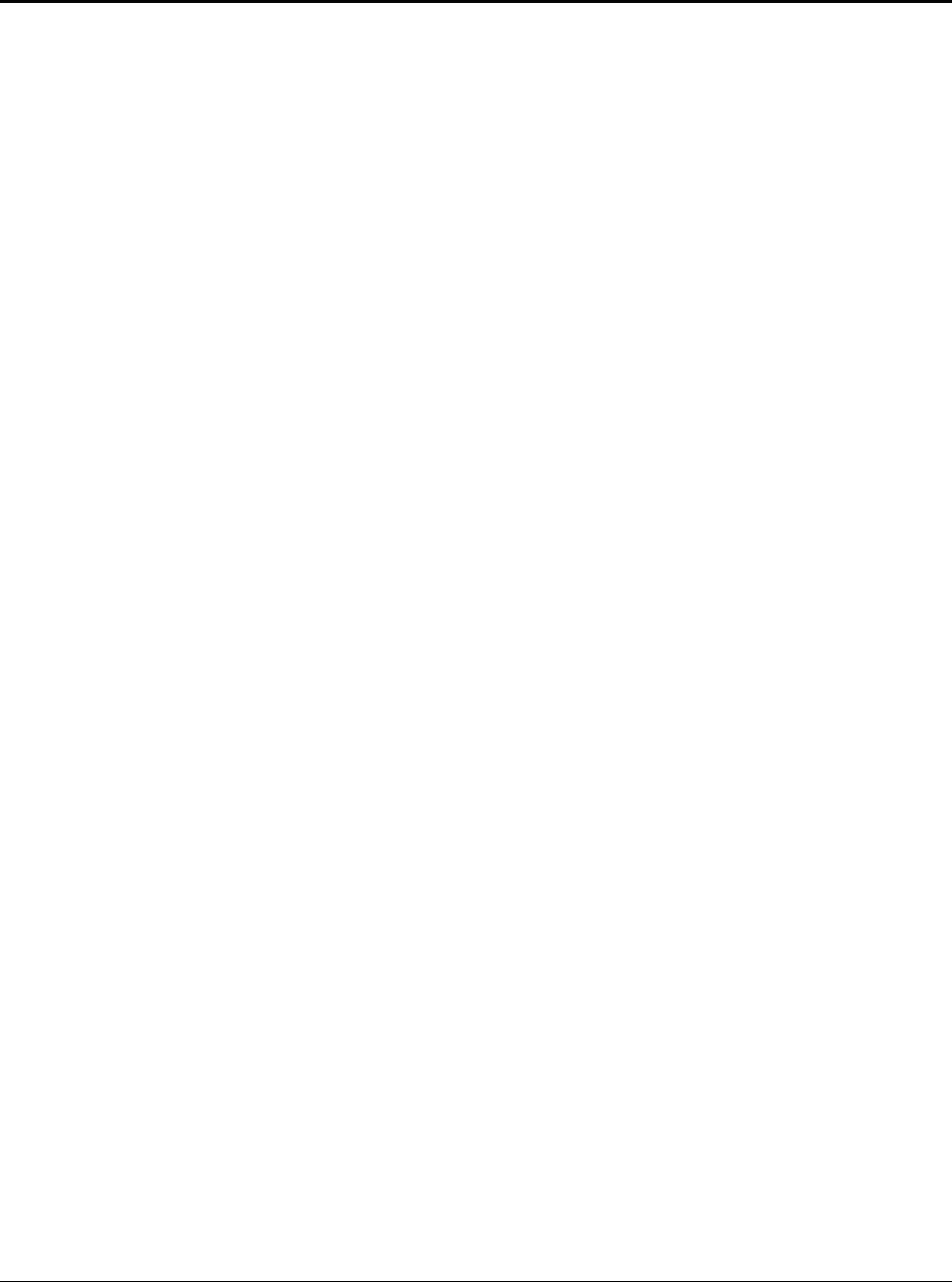
Appendix A
Documentation Overview
1 Introduction .................. A-3
2 RBS 884 Customer Manuals .......... A-3
5/1551-EN/LZB 119 3312 Uae Rev A 1998-11-17 A-1
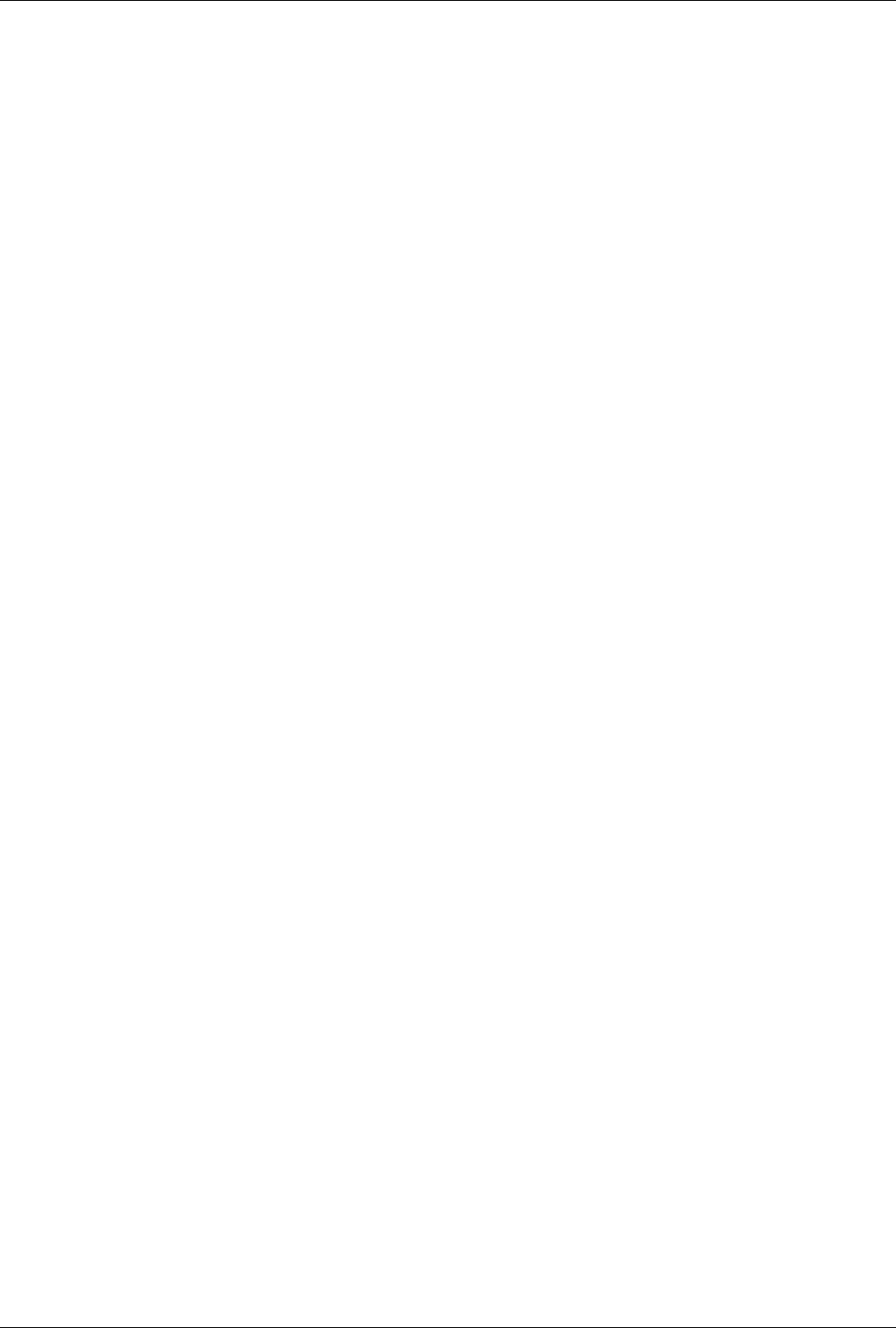
A endix A
A-2 5/1551-EN/LZB 119 3312 Uae Rev A 1998-11-17

A endix A
1 Introduction
This appendix provides an overview of the existing customer manuals for
RBS 884, the work procedures covered by the manuals, and the
recommended use of the manuals.
2 RBS 884 Customer Manuals
The customer manuals for RBS 884 cover the work procedures for Radio
Network Design, Radio Site Engineering, Data Transcript, Installation and
Test, Customer System Test, and Maintenance (see Figure A-1 on page
A-3).
RF Module Site Engineering
Manual Installation and Hardware
Replacement Manual Operations and
Maintenance Manual
Job Procedures
Installation
and
Test
Operations and
Maintenance Manual
Integration Guidelines
Figure A-1. RBS 884 Customer Manuals Related to Work Procedures
Use the RF Modules to plan and dimension a cellular network based on the
Ericsson Cellular Telephone System. Engineer the sites using the RBS 884
Site Engineering Manual, and create a data transcript using the RBS
Integration Guidelines.
Install and test the sites using the General Installation Instructions and the
Installation and Hardware Replacement Manual. These manuals cover
5/1551-EN/LZB 119 3312 Uae Rev A 1998-11-17 A-3
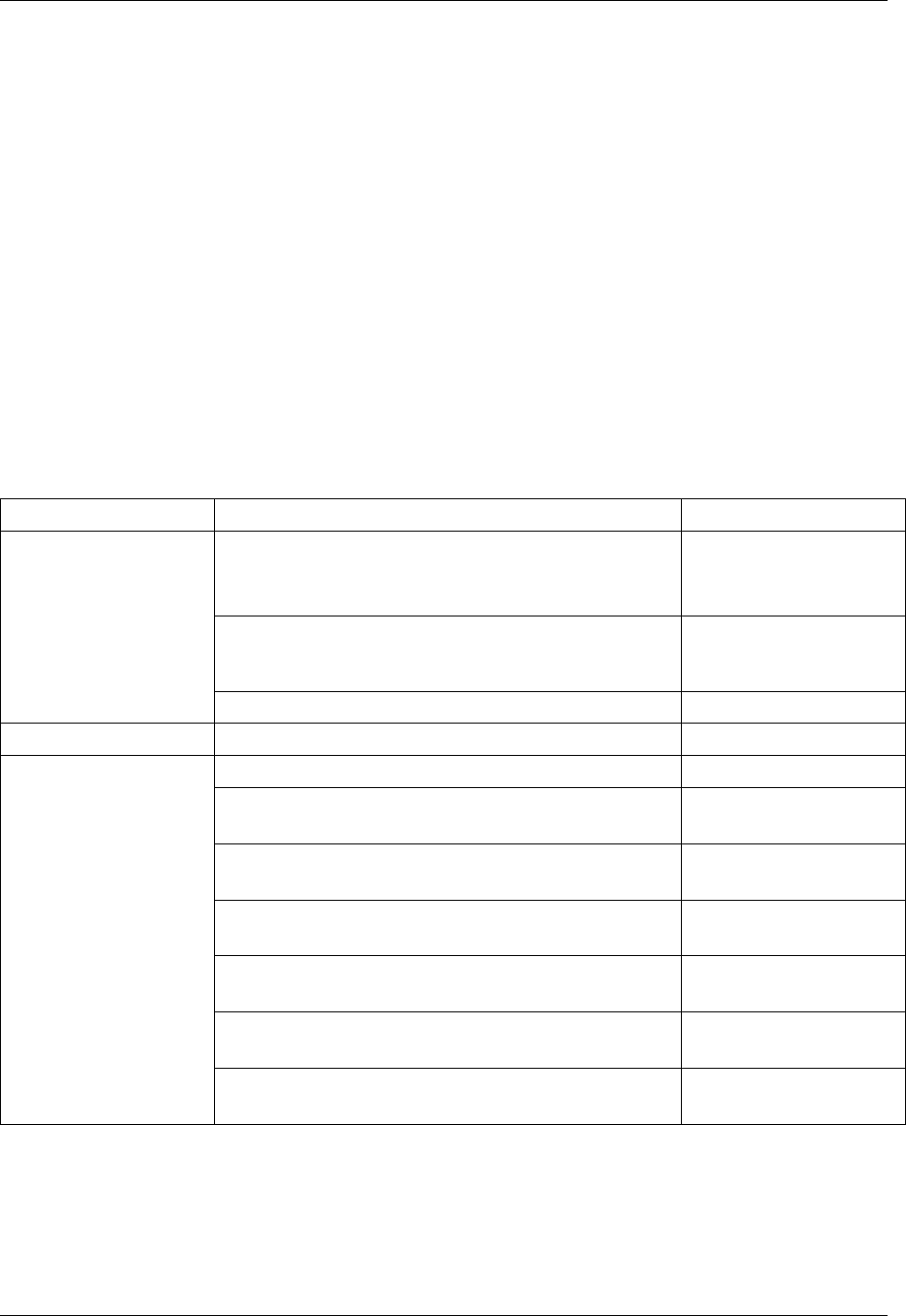
A endix A
installation of new base stations, replacement of hardware, and extension
of existing base stations. There is one manual for each type of RBS:
•RBS 884 Macro Installation and Hardware Replacement Manual (one
manual for each frequency band)
•RBS 884 Micro Installation and Hardware Replacement Manual (one
manual for each frequency band)
•RBS 884 Compact Installation and Maintenance Manual
Test the sites using the Installation and Hardware Replacement Manual
and the Job Procedures. Commission the sites and test the cellular
network using the Job Procedures and the RBS Integration Guidelines.
Use the Job Procedures during operation and maintenance from the
Mobile Switching Center (MSC). Use the Parts Catalog to identify
replaceable RBS parts, and use the Installation and Hardware Replacement
Manual for RBS hardware replacement and hardware extensions.
Table A-1. RBS 884 Customer Manuals
Manual Type Customer Manual Product Number
RF Engineering RF Module - CMS 8800 EN/LZB 119 3278
RF Module - DBC EN/LZB 119 2888
RF Module - Fixed Cellular Telephony EN/LZB 119 3277
Site Engineering RBS 884 Series Site Engineering Manual EN/LZB 119 2855
Installation General Installation Instructions EN/LZB 119 3342
RBS 884 Macro 800 MHz Installation and Hardware
Replacement Manual EN/LZB 119 3307
RBS 884 Macro 1900 MHz Installation and Hardware
Replacement Manual EN/LZB 119 3308
RBS 884 DBC Installation and Hardware Replacement
Manual EN/LZB 119 3309
RBS 884 Micro (800 MHz) Installation and Hardware
Replacement Manual EN/LZB 119 3311
RBS 884 Micro (1900 MHz) Installation and Hardware
Replacement Manual EN/LZB 119 3312
RBS 884 Compact Installation and Maintenance
Manual EN/LZB 119 2224
A-4 5/1551-EN/LZB 119 3312 Uae Rev A 1998-11-17
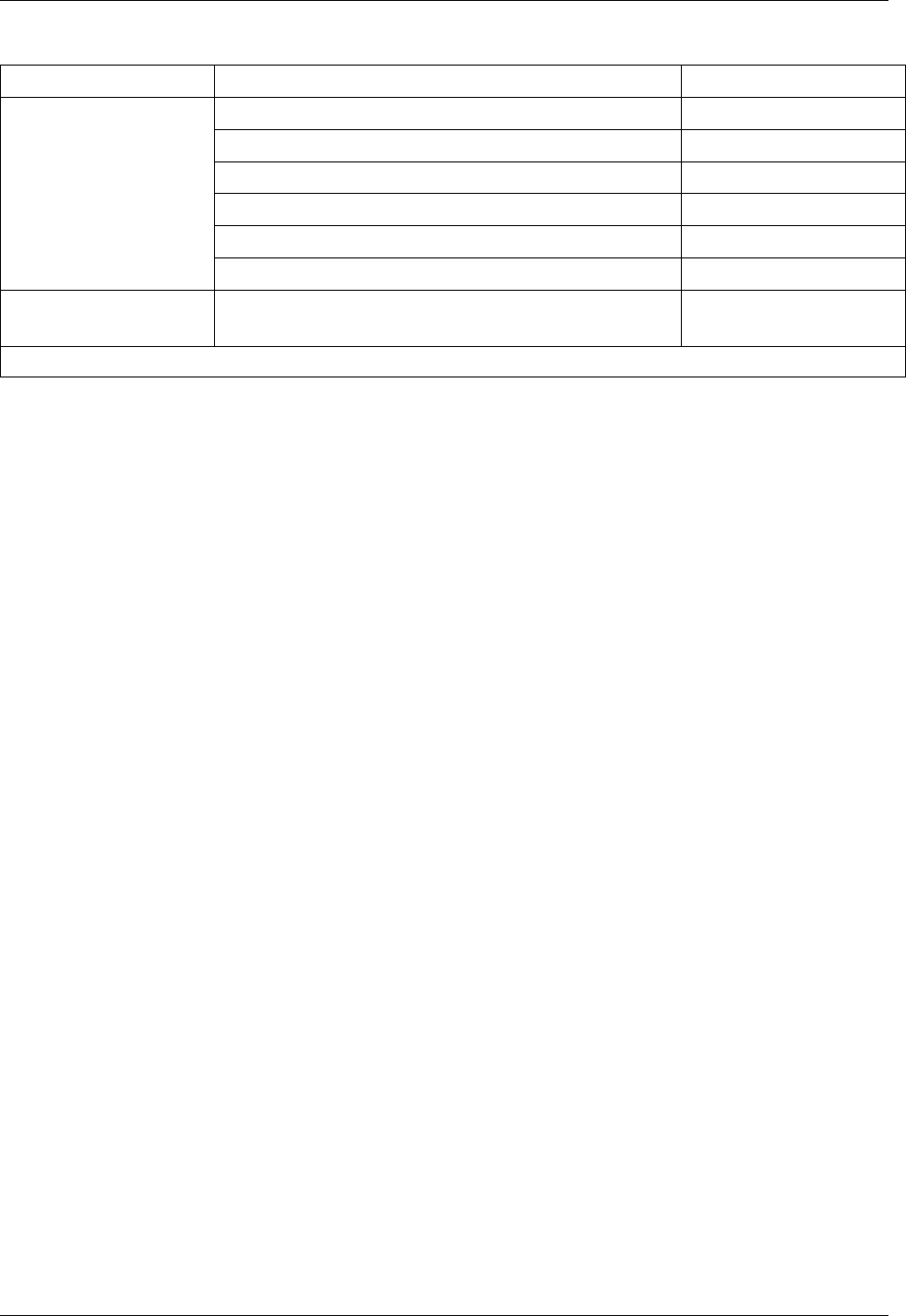
A endix A
Table A-1. RBS 884 Customer Manuals (Continued)
Manual Type Customer Manual Product Number
Parts Catalog RBS 884 Macro 800 MHz Parts Catalog EN/LZB 119 2453
RBS 884 Macro 1900 MHz Parts Catalog EN/LZB 119 2784
RBS 884 DBC Parts Catalog EN/LZB 119 2857
RBS 884 Micro (800 MHz) Parts Catalog EN/LZB 119 2454
RBS 884 Micro (1900 MHz) Parts Catalog EN/LZB 119 3320
RBS 884 Compact Parts Catalog EN/LZB 119 2455
Operation and
Maintenance
RBS 884 Series Operations and Maintenance Manual
CMS 8800 Version 4.0 1LZY 213 1045
1Available on CD-ROM only
The Job Procedures and the Integration Guidelines are available as part of
the RBS 884 Operations and Maintenance Manual.
5/1551-EN/LZB 119 3312 Uae Rev A 1998-11-17 A-5
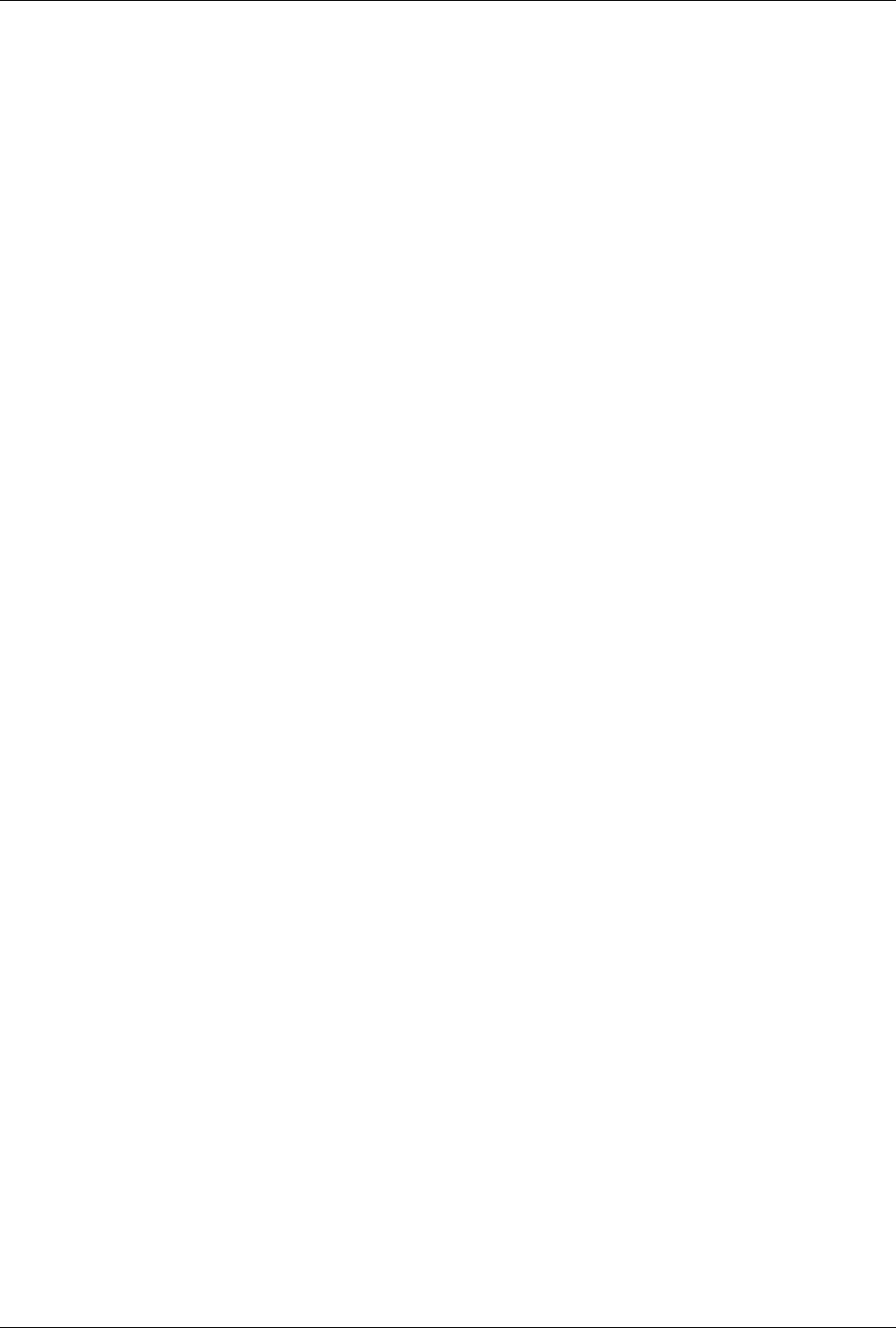
A endix A
A-6 5/1551-EN/LZB 119 3312 Uae Rev A 1998-11-17
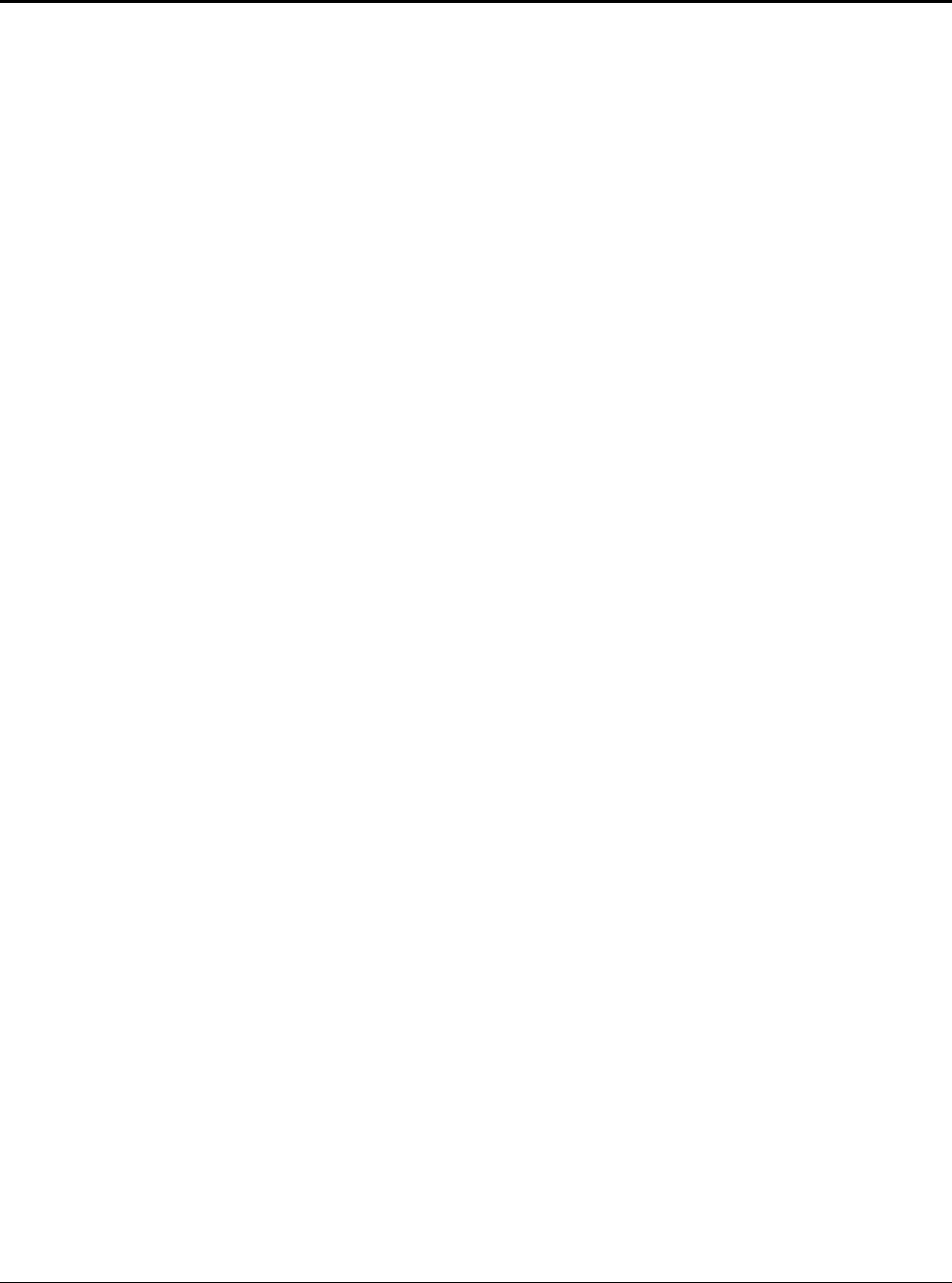
Appendix B
User Feedback
1 Introduction .................. B-3
2 Ordering of Customer Manuals ......... B-3
3 Problem Solving ................ B-3
4 Trouble Reporting ............... B-3
6/1551-EN/LZB 119 3312 Uae Rev A 1998-11-17 B-1
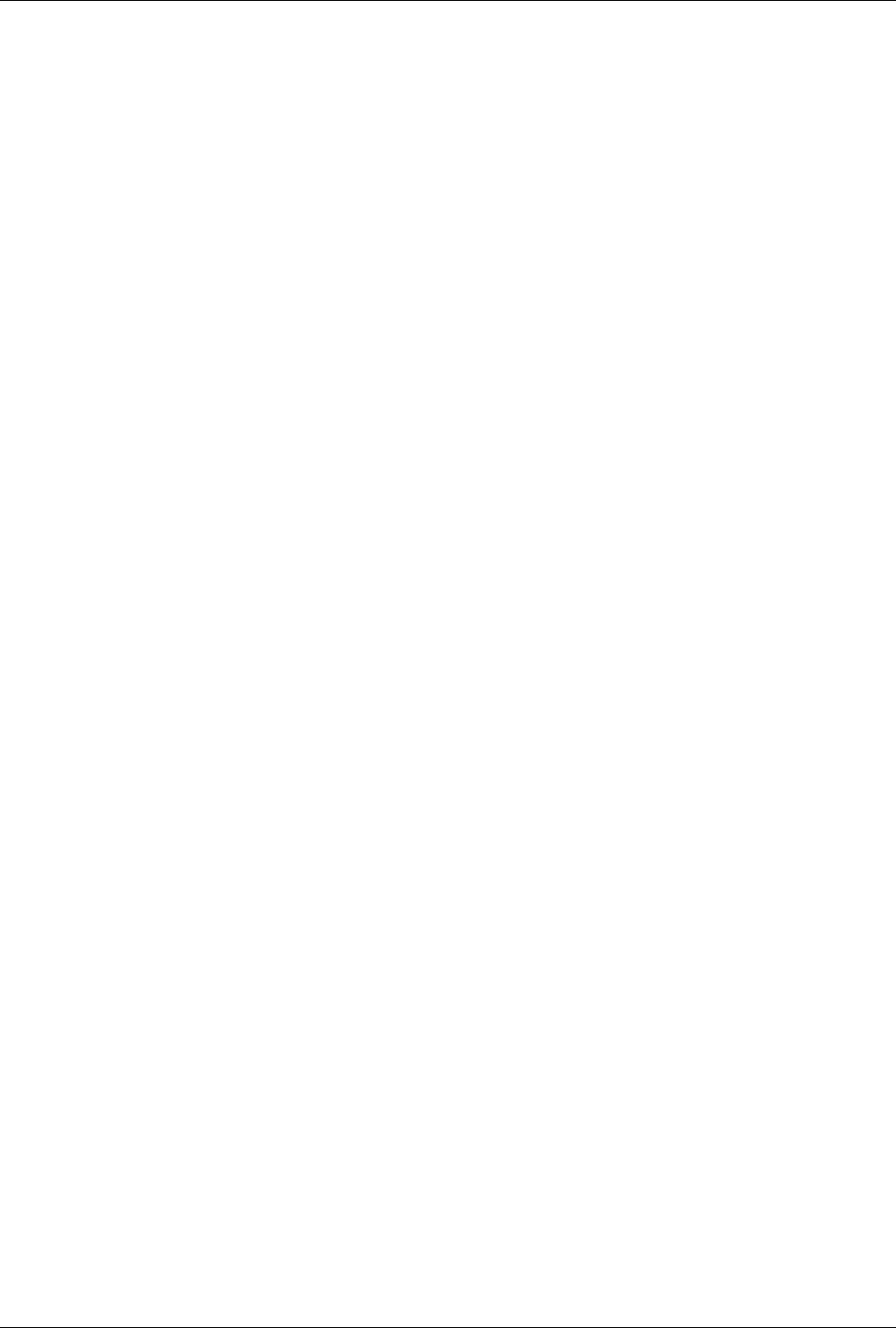
A endix B
B-2 6/1551-EN/LZB 119 3312 Uae Rev A 1998-11-17
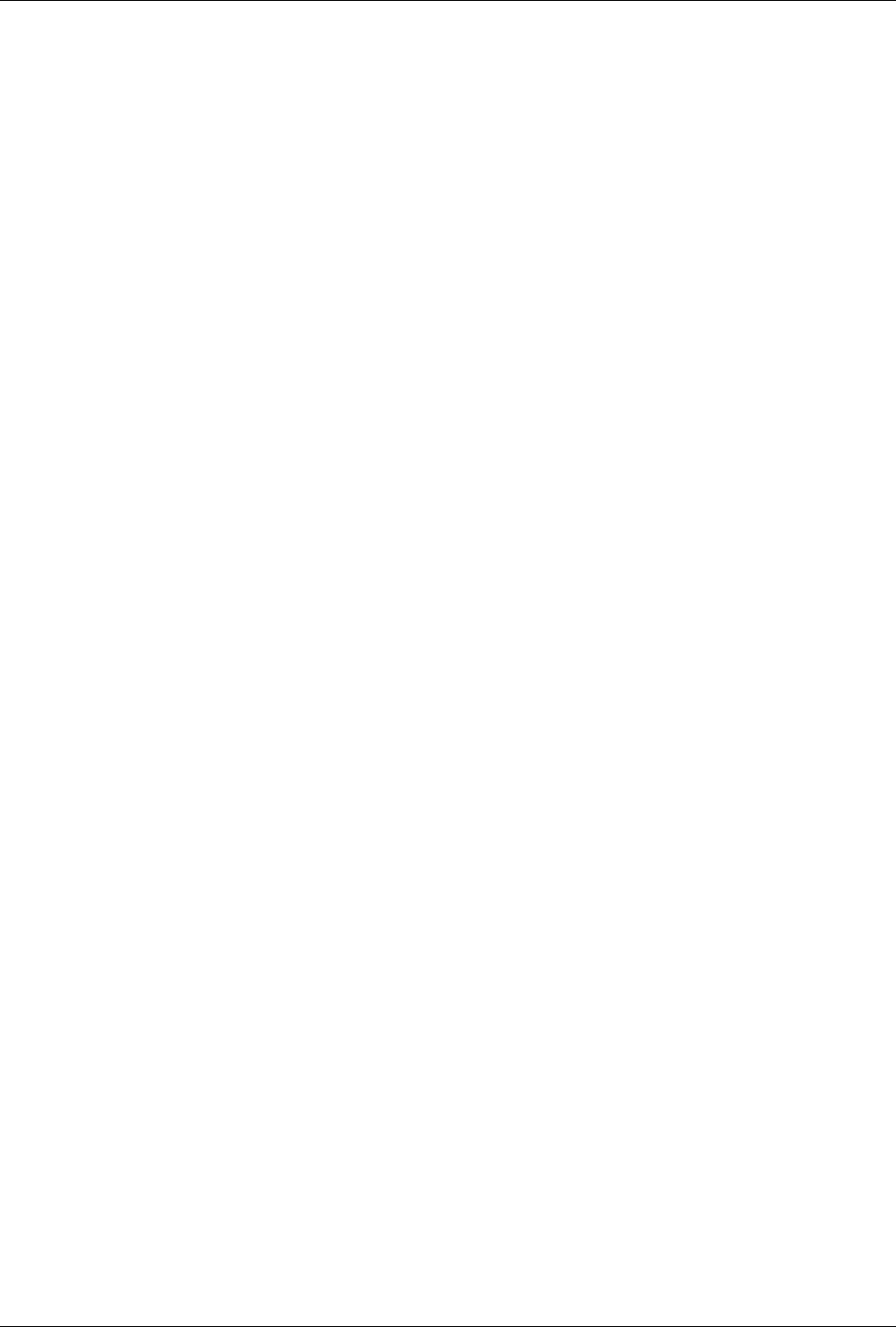
A endix B
1 Introduction
This appendix provides information on ordering and trouble reporting for
the RBS 884 customer manuals.
2 Ordering of Customer Manuals
For ordering of RBS 884 customer manuals, please contact your Ericsson
account manager.
3 Problem Solving
If you have any problems with a radio base station in the RBS 884 series
that can not be solved by reading the manuals, please contact your nearest
Ericsson Technical Assistance Center (TAC).
4 Trouble Reporting
Please report any errors found in this manual to:
Ericsson Radio Systems, AR/SO
S-164 80 Stockholm
Sweden
or
e-mail: era.erarimpl@memo.ericsson.se
send e-mail as “Mime Compliant” (7–bits)
6/1551-EN/LZB 119 3312 Uae Rev A 1998-11-17 B-3
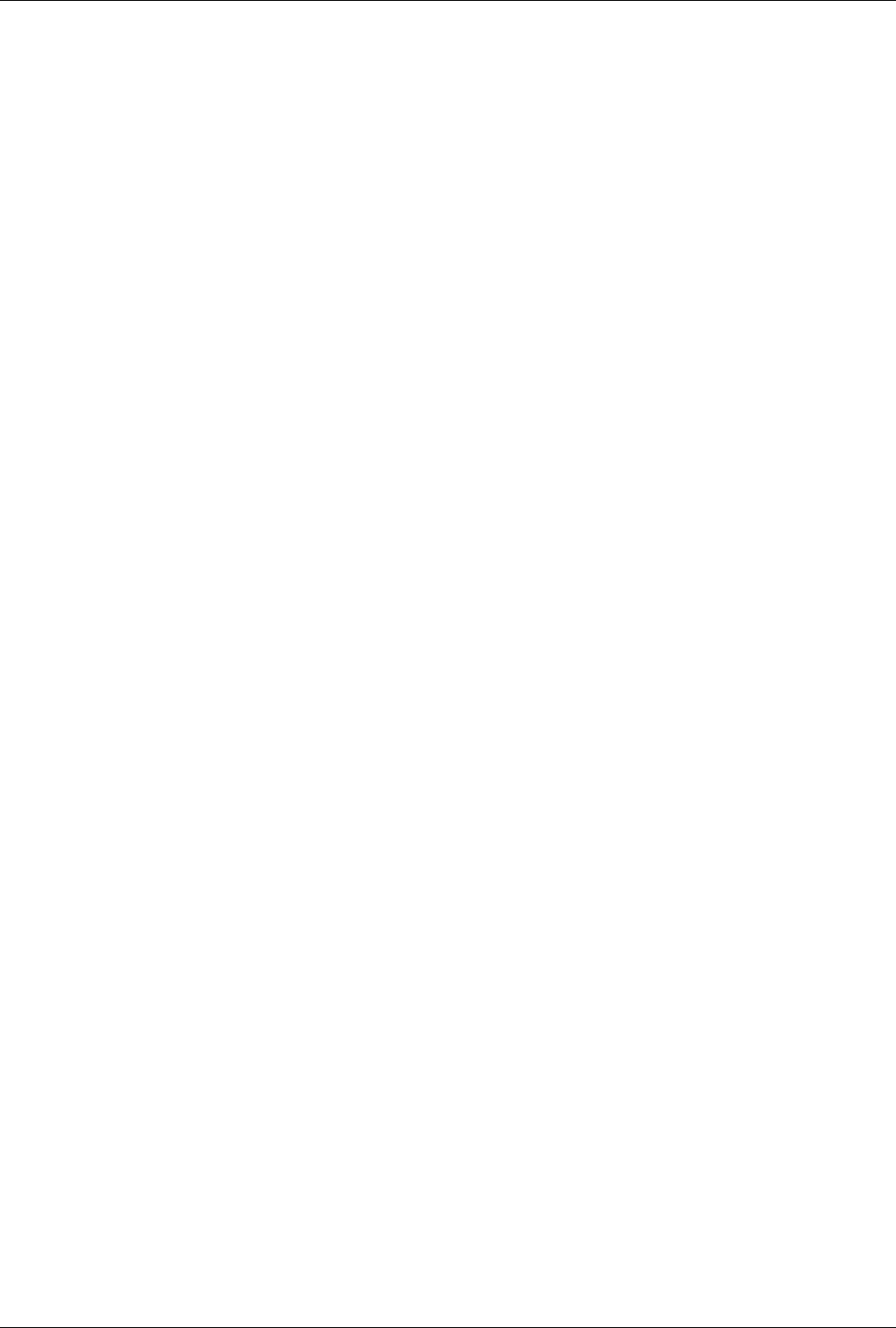
A endix B
B-4 6/1551-EN/LZB 119 3312 Uae Rev A 1998-11-17
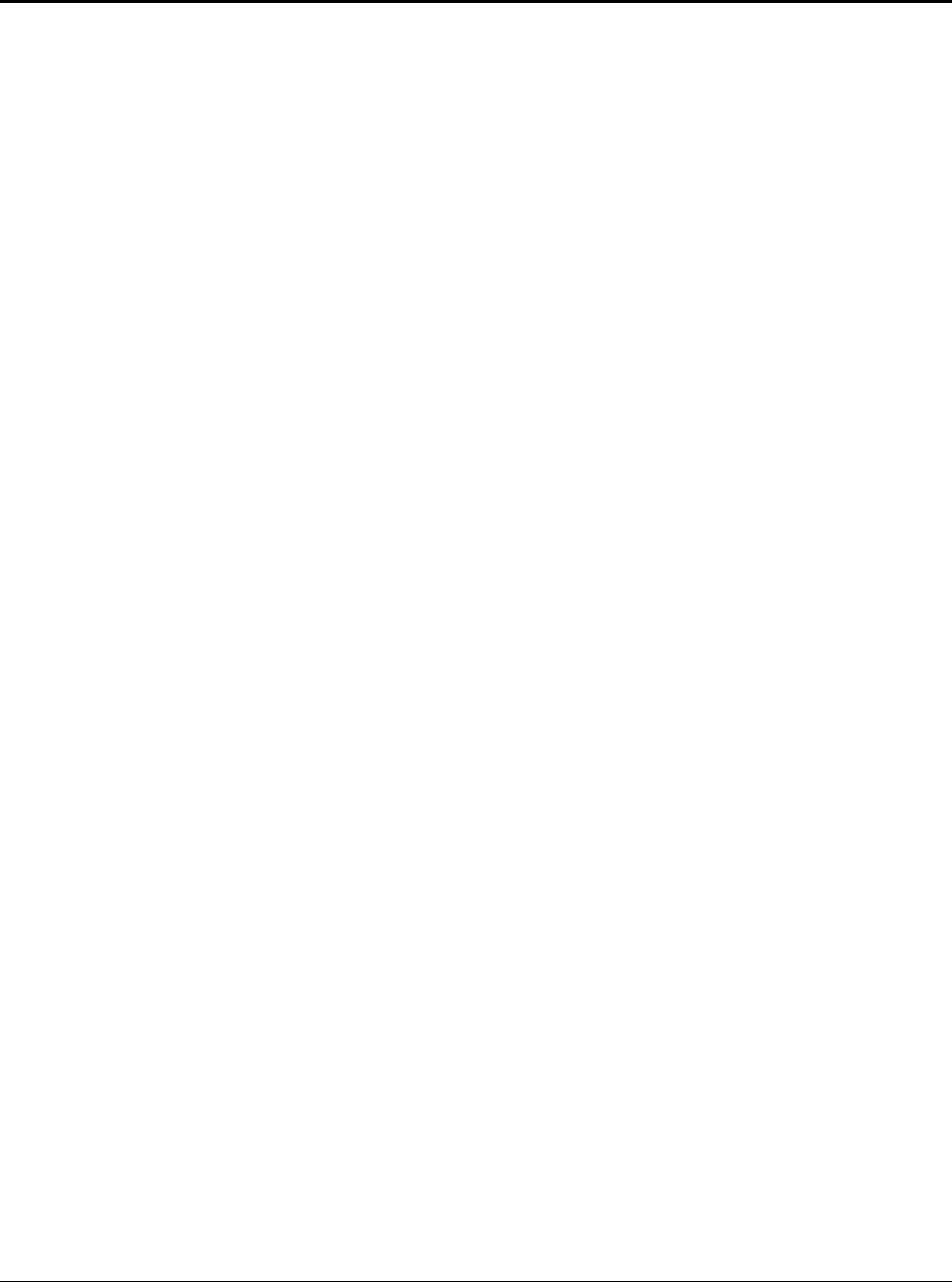
Appendix C
Internal Cables
1 Introduction .................. C-3
2 One-Sector Sites ................ C-3
3 Two-Sector Sites ................ C-5
4 Three-Sector Sites ............... C-7
5 Transceivers (TRXs) .............. C-9
7/1551-EN/LZB 119 3311 Uae Rev A 1998-11-17 C-1
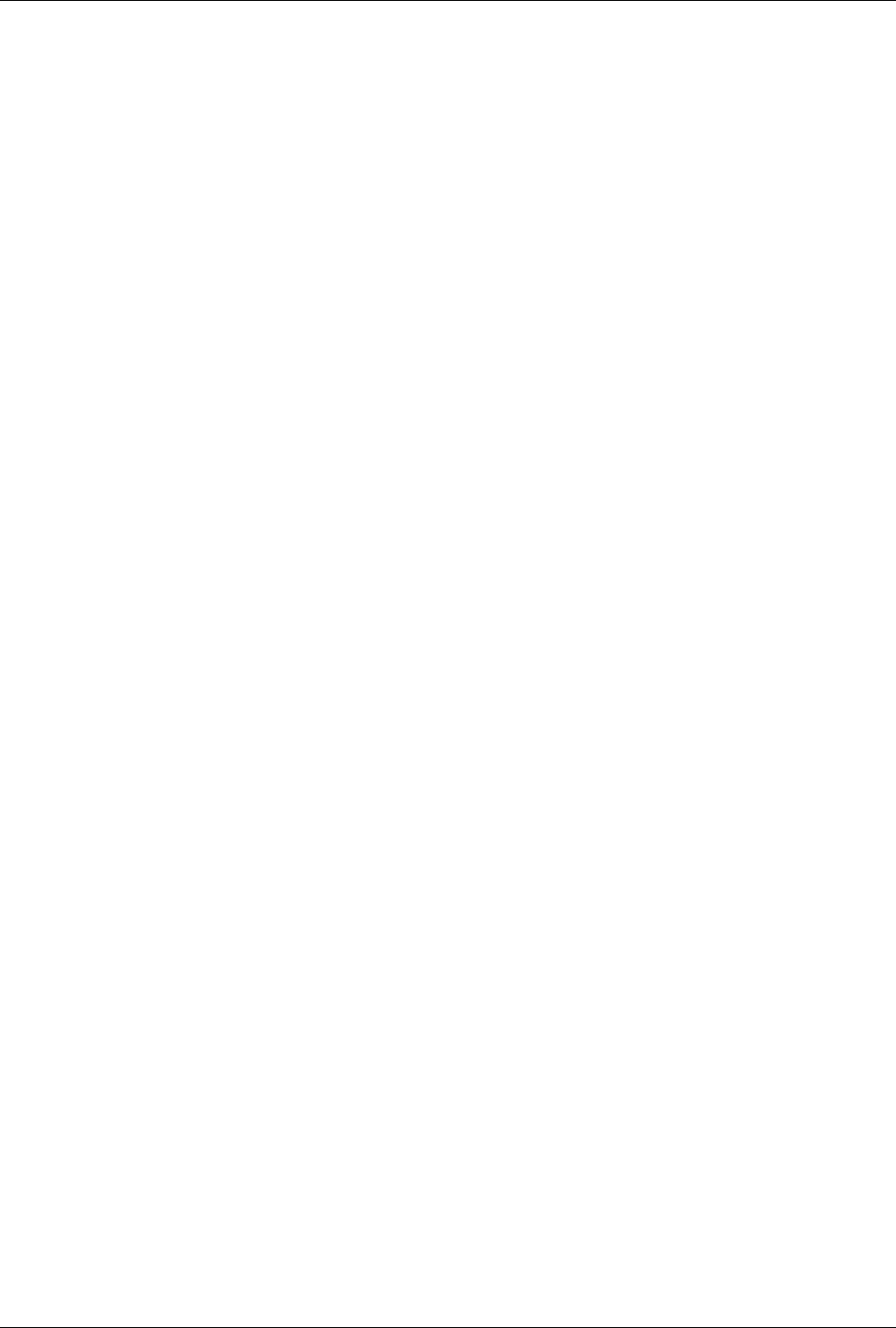
A endix C
C-2 7/1551-EN/LZB 119 3311 Uae Rev A 1998-11-17

A endix C
1 Introduction
This appendix describes the internal cabling within each RBS cabinet.
All internal cables are installed at the factory.
The configuration diagrams in this section show cabinets (Main and
Primary), antenna configurations, and interconnections between cabinets.
The cabinets are shown with maximum equipment installed.
2 One-Sector Sites
Power
Error
Status
RX/TX
ANT 1 RX/TX
ANT 2
TX IN 1
TX IN 2
TX IN 3
TX IN 4
Power
Error
Status
Power
Error
Status
Power
Error
Status
Power
Error
Status
Power
Error
Status
Tx out Tx out Tx out Tx out Tx out
To antenna terminals
on I/O connector plate
Note: The TRX board in position 6 is used as DVER
Pos. 6
Figure C-1. One-Sector Site, One Cabinet with Two Antennas
7/1551-EN/LZB 119 3311 Uae Rev A 1998-11-17 C-3
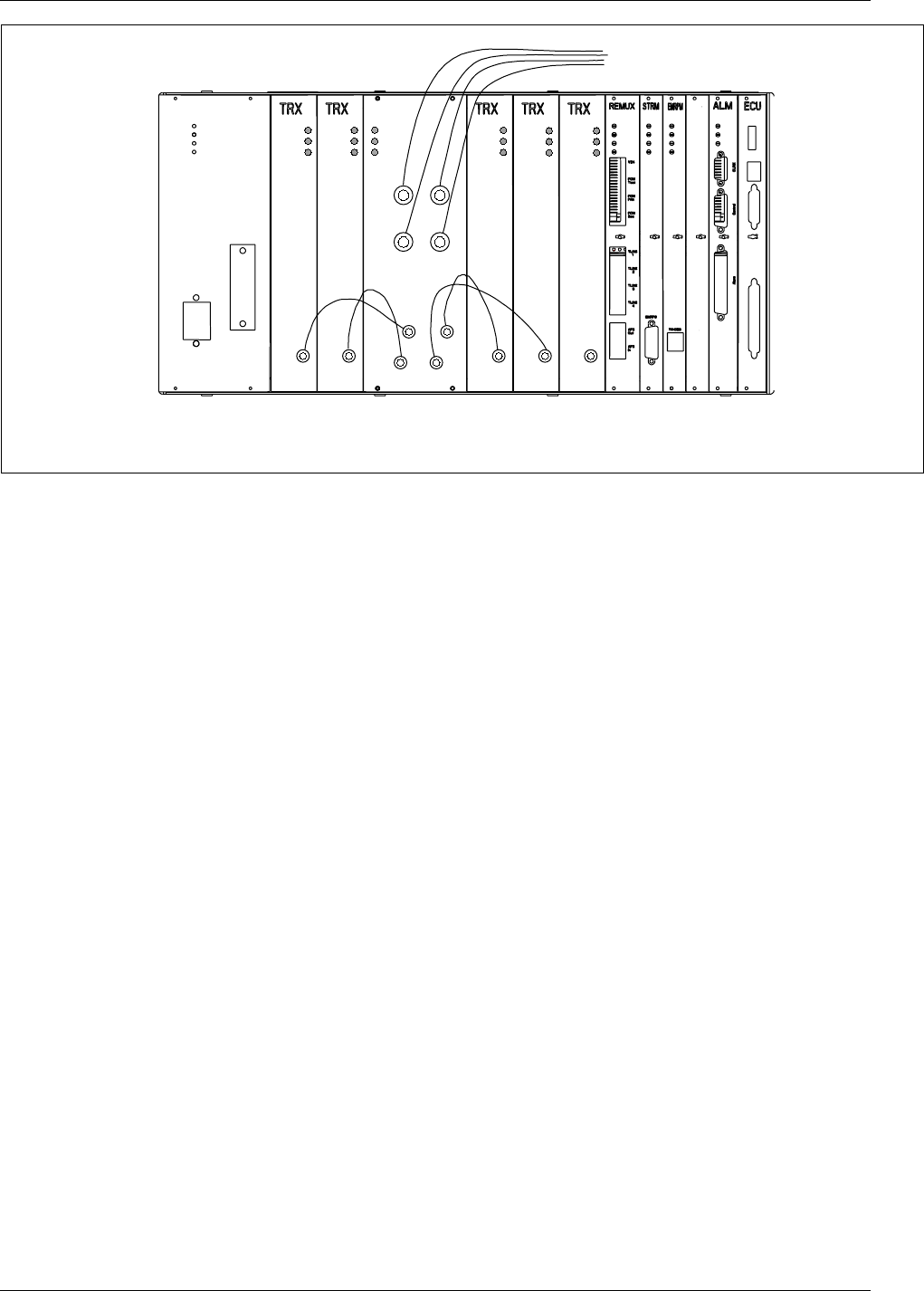
A endix C
Note: The TRX board in position 6 is used for DVER
Power
Error
Status
Power
Error
Status
Power
Error
Status
Power
Error
Status
Power
Error
Status
Tx out Tx out Tx out Tx out Tx out
Power
Error
Status
TX IN 1
TX IN 2
TX IN 3
TX IN 4
RX/TX
ANT 1 RX/TX
ANT 2
RX/TX
ANT 3 RX/TX
ANT 4
Pos. 6
To antenna terminals
on I/O connector plate
Figure C-2. One-Sector Site, One Cabinet with Four Antennas
C-4 7/1551-EN/LZB 119 3311 Uae Rev A 1998-11-17
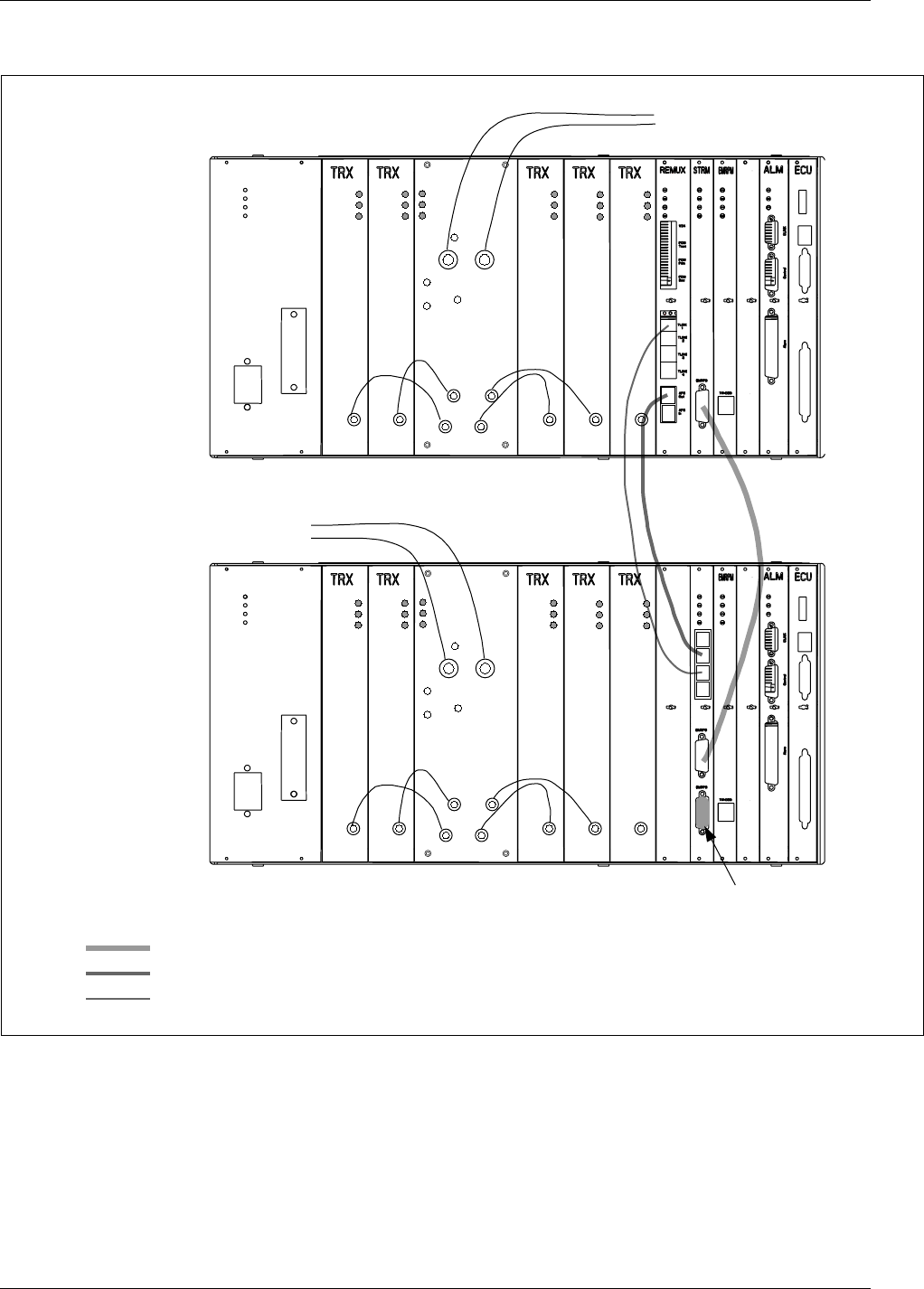
A endix C
3 Two-Sector Sites
Note: The TRX board in position 6 is used for DVER
EMRPB
AFS
TLINK
Power
Error
Status
Power
Error
Status
Power
Error
Status
Power
Error
Status
Power
Error
Status
Tx out Tx out Tx out Tx out Tx out
To antenna terminals
on I/O connector plate
Main
Cabinet
Terminator
Power
Error
Status
Power
Error
Status
Power
Error
Status
Power
Error
Status
Power
Error
Status
Tx out Tx out Tx out Tx out Tx out
Primary
Cabinet
To antenna terminals
on I/O connector plate
TX 2
TX 1
TX 4
TX 3
RX/TX
ANT A RX/TX
ANT B
Power
Error
Status
ANP/RFTL
TX 2
TX 1
TX 4
TX 3
RX/TX
ANT A RX/TX
ANT B
Power
Error
Status
ANP/RFTL
PSU
PSU
Figure C-3. Two-Sector Site, Two Cabinets, Each Cabinet with two Antennas
7/1551-EN/LZB 119 3311 Uae Rev A 1998-11-17 C-5

A endix C
Power
Error
Status
Power
Error
Status
Power
Error
Status
Power
Error
Status
Power
Error
Status
Tx out Tx out Tx out Tx out Tx out
To antenna terminals
on I/O connector plate
Main
Cabinet
Note: The TRX board in position 6 is used for DVER
EMRPB
AFS
TLINK
Power
Error
Status
Tx out
Power
Error
Status
Power
Error
Status
Power
Error
Status
Power
Error
Status
Tx out Tx out Tx out Tx out
Terminator
Primary
Cabinet
To antenna terminals
on I/O connector plate
TX 2
TX 1
TX 4
TX 3
RX/TX
ANT A RX/TX
ANT B
TX ANT C TX ANT D
Power
Error
Status
ANP/RFTL
TX 2
TX 1
TX 4
TX 3
RX/TX
ANT A RX/TX
ANT B
TX ANT C TX ANT D
Power
Error
Status
ANP/RFTL
PSU
PSU
Figure C-4. Two-Sector Site, Two Cabinets, Each Cabinet with Four Antennas
C-6 7/1551-EN/LZB 119 3311 Uae Rev A 1998-11-17
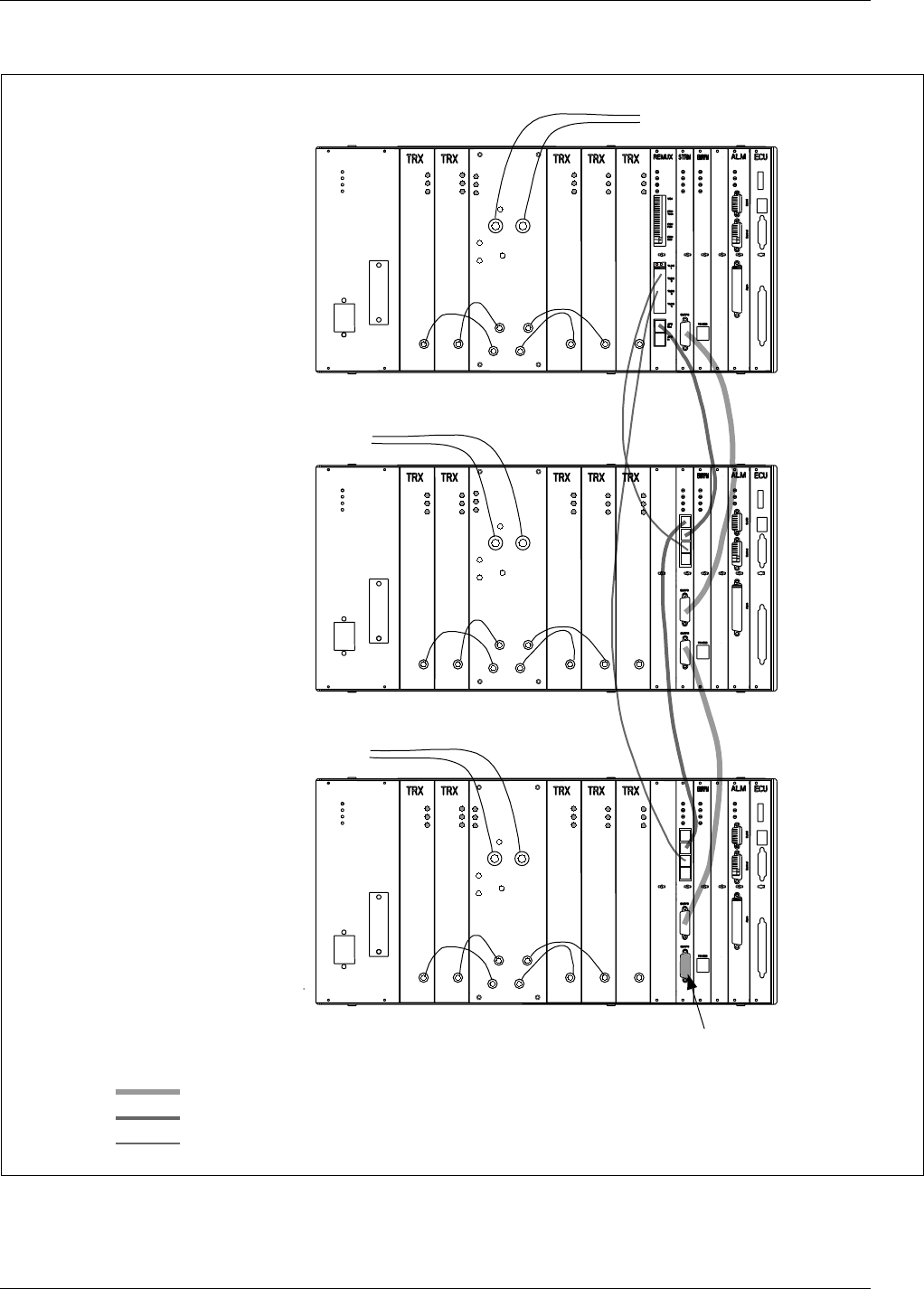
A endix C
4 Three-Sector Sites
Note: The TRX board in position 6 is used for DVER
EMRPB
AFS
TLINK
Terminator
Main
Cabinet
Power
Error
Status
Power
Error
Status
Power
Error
Status
Power
Error
Status
Power
Error
Status
Tx out Tx out Tx out Tx out Tx out
To antenna terminals
on I/O connector plate
Pos
. 6
Primary 1
Cabinet
Power
Error
Status
Power
Error
Status
Power
Error
Status
Power
Error
Status
Power
Error
Status
Tx out Tx out Tx out Tx out Tx out
To antenna terminals
on I/O connector plate
Pos
. 6
Primary 2
Cabinet
Power
Error
Status
Power
Error
Status
Power
Error
Status
Power
Error
Status
Power
Error
Status
Tx out Tx out Tx out Tx out Tx out
To antenna terminals
on I/O connector plate
Pos
. 6
TX 2
TX 1
TX 4
TX 3
RX/TX
ANT A RX/TX
ANT B
Power
Error
Status
ANP/RFTL
TX 2
TX 1
TX 4
TX 3
RX/TX
ANT A RX/TX
ANT B
Power
Error
Status
ANP/RFTL
TX 2
TX 1
TX 4
TX 3
RX/TX
ANT A RX/TX
ANT B
Power
Error
Status
ANP/RFTL
PSU
PSU
PSU
Figure C-5. Three-Sector Site, Each Cabinet with Two Antennas
7/1551-EN/LZB 119 3311 Uae Rev A 1998-11-17 C-7

A endix C
Note: The TRX board in position 6 is used for DVER
Main Cabinet
Primary 1
Cabinet
Primary 2
Cabinet
EMRPB
AFS
TLINK
Power
Error
Status
Power
Error
Status
Power
Error
Status
Power
Error
Status
Power
Error
Status
Tx out Tx out Tx out Tx out Tx out
Power
Error
Status
Tx out
Power
Error
Status
Power
Error
Status
Power
Error
Status
Power
Error
Status
Tx out Tx out Tx out Tx out
Power
Error
Status
Tx out
Power
Error
Status
Power
Error
Status
Power
Error
Status
Power
Error
Status
Tx out Tx out Tx out Tx out
Pos
. 6
Terminator
To antenna terminals
on I/O connector plate
To antenna terminals
on I/O connector plate
To antenna terminals
on I/O connector plate
Pos
. 6
Pos
. 6
TX 2
TX 1
TX 4
TX 3
RX/TX
ANT A RX/TX
ANT B
TX ANT C TX ANT D
Power
Error
Status
ANP/RFTL
TX 2
TX 1
TX 4
TX 3
RX/TX
ANT A RX/TX
ANT B
TX ANT C TX ANT D
Power
Error
Status
ANP/RFTL
TX 2
TX 1
TX 4
TX 3
RX/TX
ANT A RX/TX
ANT B
TX ANT C TX ANT D
Power
Error
Status
ANP/RFTL
PSU
PSU
PSU
Figure C-6. Three-Sector Site, Each Cabinet with Four Antennas
C-8 7/1551-EN/LZB 119 3311 Uae Rev A 1998-11-17

A endix C
5 Transceivers (TRXs)
The transceiver cables (RPM 513 977/00185) are installed as shown in
Figure C-7 on page C-9.
Note: The TRX board in position 6 is used for MVER
Cabinets illustrated are Main Cabinets, but the cabling is the same for Primary Cabinets.
Cabinet using Four Antennas Pos. 6