Shinko Electric Co 199909010001 Communication Modem Controller User Manual ROHV Operation Manual
Shinko Electric Co Ltd Communication Modem Controller ROHV Operation Manual
Contents
ROHV Operation Manual
FCC ID : OPO199909010001
KEN72-3699(E)Rev.0
1
CONFIDENTIAL
“SELOHT SOHT-300”
OHT Vehicle Operation Manual
of
SHINKO OHT SYSTEM
Aug.31, 1999(Rev.0)
Shinko Electric Co., LTD
Ise Japan
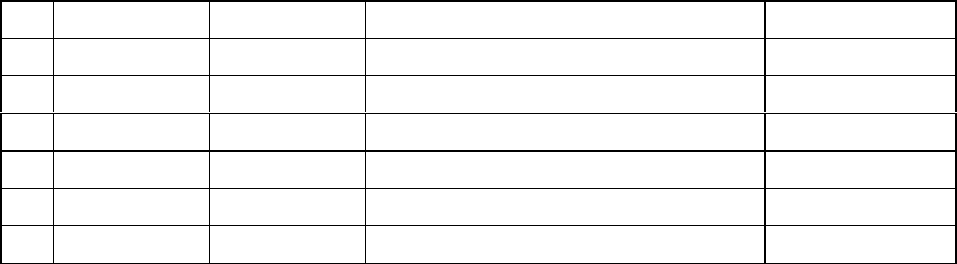
FCC ID : OPO199909010001
KEN72-3699(E)Rev.0
2
Revision Note
# Revision Month/Day/Year Contents Author
#1 Rev.0 Aug.31, 1999 The first edition(Preliminary) Masanao Murata
FCC ID : OPO199909010001
KEN72-3699(E)Rev.0
3
Table of contents
Safety precautions...............................................................................................................................5
(1) General.....................................................................................................................................5
(2) Definitions of Danger and Warning ......................................................................................5
(3) Precautions on use.................................................................................................................6
(4) Storage.....................................................................................................................................7
(5) Transportation.........................................................................................................................7
(6) Installation ...............................................................................................................................7
(7) Operations ...............................................................................................................................8
(8) Maintenance and lnspection..................................................................................................8
1.General...............................................................................................................................................9
1.1 Application..............................................................................................................................9
1.2 Related SEMI document ........................................................................................................9
1.3 Related Rules, Laws ..............................................................................................................9
1.4 Abbreviations .........................................................................................................................9
2.Outline of OHT System and Vehicle .............................................................................................10
2.1 Purpose of OHT....................................................................................................................10
2.2 OHT system ..........................................................................................................................10
2.3 Non-contact power supply..................................................................................................12
2.4 FCC rules...............................................................................................................................13
2.5 FCC Notice and Warning.....................................................................................................14
3.OHT Vehicle.....................................................................................................................................15
3.1 External View of the OHT Vehicle.......................................................................................15
3.2 Name of the parts and function..........................................................................................16
3.3 safety consideration ...........................................................................................................19
3.4 Separation of vehicles and operators................................................................................20
4.Specification ...................................................................................................................................21
4.1General Specification ...........................................................................................................21
4.2 Basic technical specification..............................................................................................22
5Auto Mode and Manual ...................................................................................................................23
5.1 Operation mode of the Vehicle...........................................................................................23
5.2 Auto mode.............................................................................................................................23
5.3 Manual mode ........................................................................................................................23
6Teaching ...........................................................................................................................................24
6.1 Reference.......................................................................................................................24
FCC ID : OPO199909010001
KEN72-3699(E)Rev.0
4
6.2 Two kinds of teaching .........................................................................................................24
7.Move in and move out of the vehicle............................................................................................26
7.1 construction..........................................................................................................................26
7.2 Replacement of the vehicle.................................................................................................26
8. Removal of FOUP from OHV and manual lifting of gripper unit ..............................................29
8.1.Two cases in manual removal of FOUP.............................................................................29
8.2. Two kinds of removal procedures.....................................................................................29
9.MAINTENANCE PLAN ....................................................................................................................33
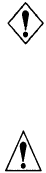
FCC ID : OPO199909010001
KEN72-3699(E)Rev.0
5
Safety precautions
(1) General
Prior to using this product, make sure the “Safety Precautions”, Maintenance Instruction
Manual and other attached documents shall be well read and understood for appropriate
application.
Engage specialists in electrical works.
Don’t improve the product by yourselves.
Be sufficiently proficient with the equipment, the relevant safety knowledge and the
precautions prior to using this product.
In the content of this “Safety Precautions”, items which need to be cautions of out shall
be classified into “Danger” and “Warning”.
(2) Definitions of Danger and Warning
[Note 1] Medium degree of injuries or light injuries refers to injuries, e.g., burns and
electric shock, which do not require hospitalization of or prolonged hospital
visit by the victims. As material losses refers to expanded losses pertaining to
the
damage of property and equipment.
Note that, depending on the situation, the events described under “Warning” may also result
in severe outcome. In either case, make sure that the advice is followed.
After reading, make sure this information shall be kept at places where it can always be read
by users.
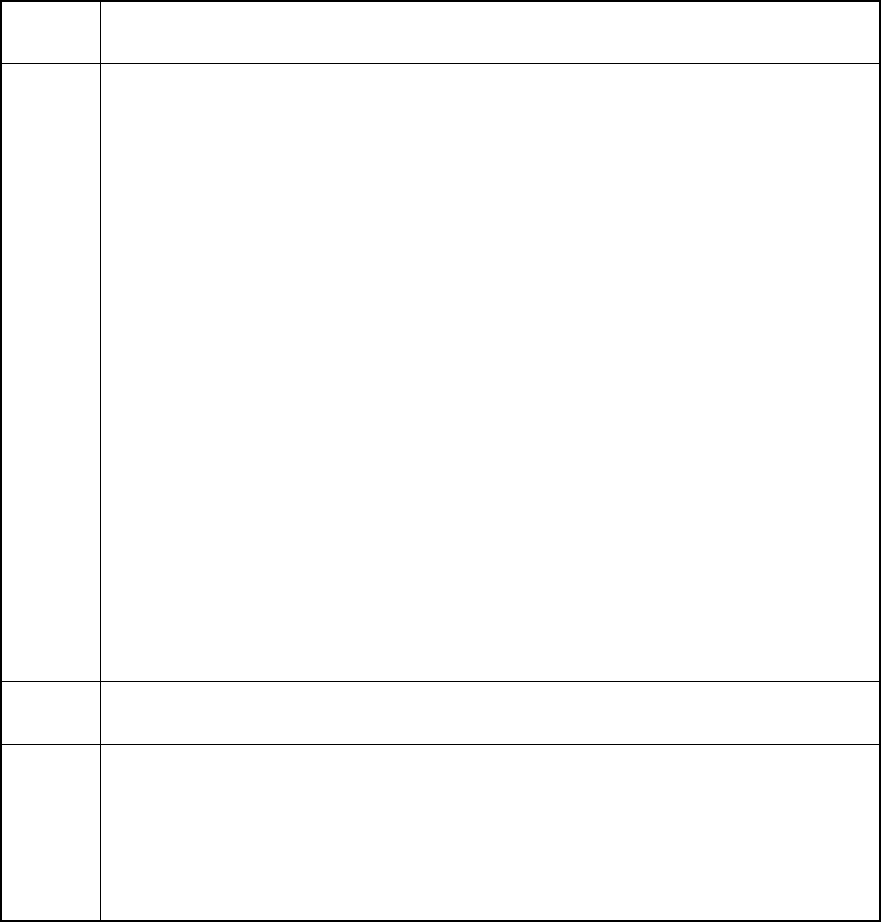
FCC ID : OPO199909010001
KEN72-3699(E)Rev.0
6
(3) Precautions on use
Danger
Follow the following advice strictly to avoid electric shock or burns.
1. Don’t enter the operation area of the vehicle.
Work on the ladder may collide to the vehicle and may cause injury.
2. Don’t touch the vehicle on the track when Power Supply Panel output the
power.
3. Don’t touch the moving parts of the vehicle while it is in operation. Doing
so may cause injuries.
4. Don’t touch and Teaching and maintenance shall be done by a qualified
person.
5. Make sure the earth terminals for the relate equipment shall be grounded.
Not doing so may cause electric shock.
6. Don’t break the cable, impose excessive stress, place heavy weights, or
pinch it between items. Doing so may cause electric shock.
Warning
Don’t use the equipment at locations where water, corrosive atmosphere, or
flammable gas is present, or beside flammable items. Doing so may cause
life and fails.
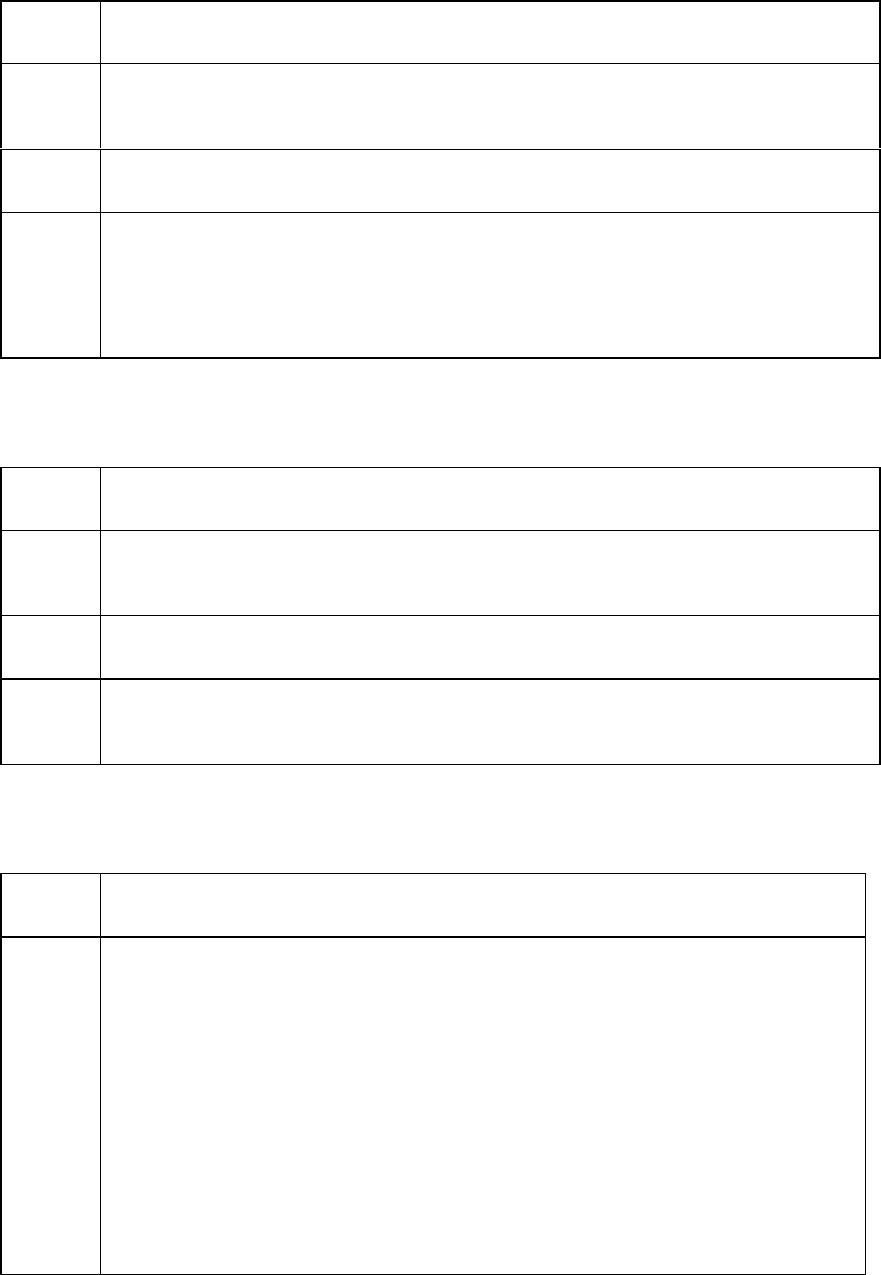
FCC ID : OPO199909010001
KEN72-3699(E)Rev.0
7
(4) Storage
Prohibition
1. Don’t store the equipment at locations where it is subject to rain, water
hazardous gas or liquid.
Mandatory Implementation
1. Store the equipment at locations in not subjected to sun shine. Store it
at predetermined relative humidity and temperature.
0 50 ,90% RH and below, no dew.
(5) Transportation
Warning
1. Don’t carry in a manner except for designated. Doing so may cause
materials loss or injuries.
Mandatory Implementation
1. The equipment may be broken when overloaded. Follow the advice of the
display on the load.
(6) Installation
Warning
1. Don’t climb on top of the equipment or place heavy items on it. Doing so
may cause injuries.
2. Don’t block the air inlet and outlet ports or allow foreign particles to enter them.
Doing so may cause fire.
3. Follow the installation direction strictly as it is so design for dissipation of heat.
fails or fire.
5. Don’t hit the equipment with strong impact. Doing so may cause equipment
fails.
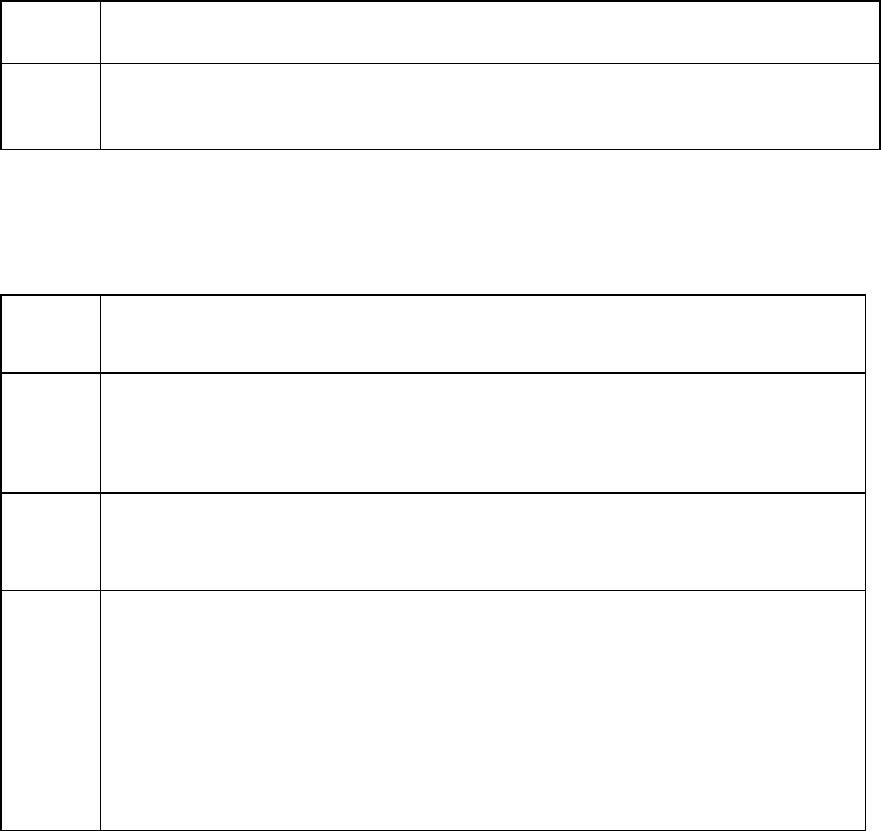
FCC ID : OPO199909010001
KEN72-3699(E)Rev.0
8
(7) Operations
Mandatory Implementation
Install an external emergency circuit so that operations can be immediately stopped
and power cut off when required
(8) Maintenance and lnspection
Prohibition
Don’t engage non-specialist technicians to disassemble and repair the
equipment.
Danger
1. Maintenance of the vehicle shall be done on the ground.
2. Switch off the power and wait for 3 minutes or longer before carrying out
wiring work or inspection. Not doing so may cause electric shock.
(The printed circuit board in the driver applies 300V of high voltage parts)
FCC ID : OPO199909010001
KEN72-3699(E)Rev.0
9
1.General
1.1 Application
This document describes the operation of OHT Vehicle for “SELOHT SOHT-300”, Shinko
OHT(Overhead Hoist Transport) System.
1.2 Related SEMI document
Following documents are parts of the specification:
(1) SEMI E10-0299 (1999) (RAM)
(2) SEMI E15.1-0299 (1999) (LOAD PORT)
(3) SEMI E30-0998 (1998) (GEM)
(4) SEMI Draft 2998 (Future E82-0999 (1999), IBSEM)
(5) SEMI E37.1-96 (1996) (HSMS-SS)
(6) SEMI E47.1-0299 (1999) (FOUP)
(7) SEMI E84-0699 (1999) (Extended P I/O)
1.3 Related Rules, Laws
(1) FCC Part15 Subpart C
(2) FCC Part 18
1.4 Abbreviations
(1) OHT : Overhead Hoist Transport
(2) OHV : Overhead Hoist transport Vehicle
(3) OHVC : Overhead Hoist Vehicle Controller
(4) CMC : Communication Modem Controller
FCC ID : OPO199909010001
KEN72-3699(E)Rev.0
10
2.Outline of OHT System and Vehicle
2.1 Purpose of OHT
OHT is an automated transport system, used in the clean room in a building of the
semiconductor manufacturing factory .
2.2 OHT system
Silicon wafers are transferred from the process tool to process tool kept in a specific carrier
called FOUP (Front Opening Unified Pod) in the clean room.
Top view of a typical OHT system is shown on Fig. 2.1. It is 30 meters x 10 meters size
typically. Fig. 2.2 shows the bird-eye view of the OHT system (example of our DEMO System).
Main device of the system is an OHT Vehicle, which is hung from the OHT track and travels
through the track. OHV has a hoisting mechanism and a FOUP is hoisted down/up to the port of
the process tool. The port is normally called load port. Cross sectional image is shown on
Fig. 2.3.
OHT track is supported from the building ceiling, and OHV is hung from the track.
OHV travels by the linear motor power and the electricity is supplied from the track side by non-
contact power supply system. Non-contact power supply system mainly consists of pick up coil
on OHV side and power cable on the track side.
Fig. 2.1 : Top view of a typical OHT system
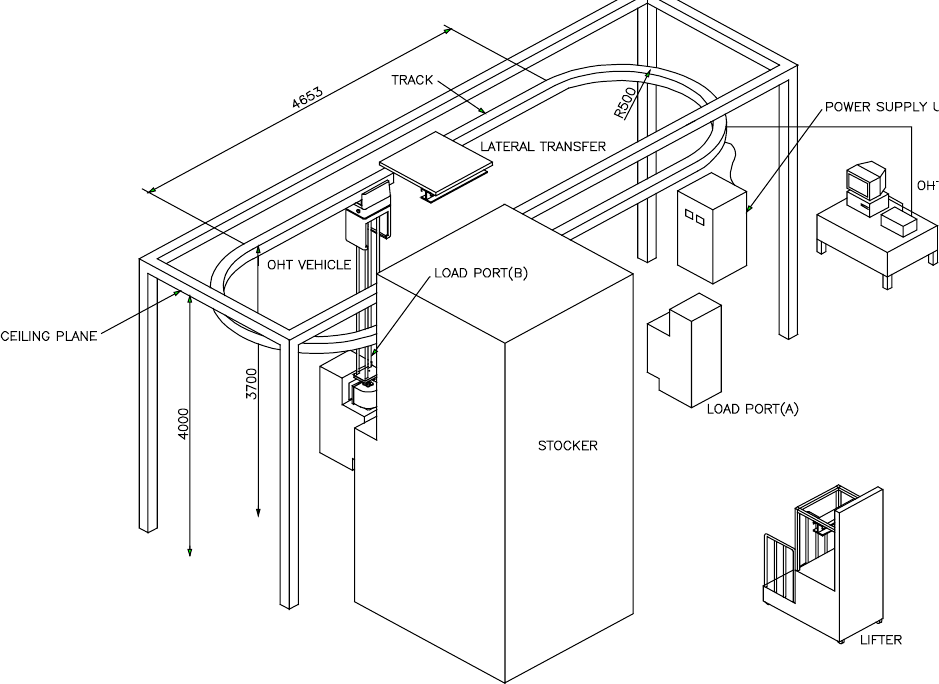
FCC ID : OPO199909010001
KEN72-3699(E)Rev.0
11
Fig.2.2 Bird-eye view of OHT system
Fig. 2.3 Cross sectional image
FCC ID : OPO199909010001
KEN72-3699(E)Rev.0
12
2.3 Non-contact power supply
The principle of non-contact power supply is an electro-magnetic coupling, and it can be
understood as an special style of a transformer, by which electric power is supplied to the OHV.
There is a power cable on the track and alternate current is constantly supplied from the power
supply panel on the ground (Normally it is 400V A.C and 5kW output). Shinko uses 8.66 kHz of
the alternate current for the main power supply. About 300kHz and 350kHz signals are
superposed on the 8.66 kHz main component for realizing the communication between OHV and
ground controller.
FCC ID : OPO199909010001
KEN72-3699(E)Rev.0 13
2.4 FCC rules
Structure of Shinko OHT System & FCC Rules
For OHT system, there are two FCC rules to be applied.
One is part15 subpart C, Intentional radiator portion is applied.
The other is Part 18, Power supply and related components are applied.
See fig. 2.4
Fig.2.4 FCC rules and OHT construction
FCC ID : OPO199909010001
KEN72-3699(E)Rev.0
14
2.5 FCC Notice and Warning
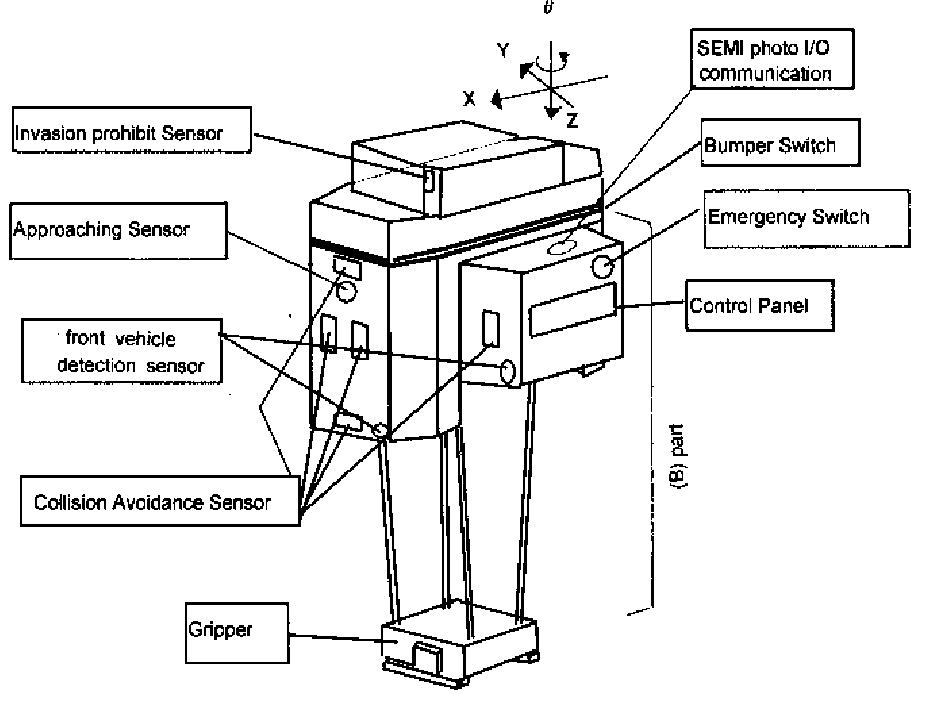
FCC ID : OPO199909010001
KEN72-3699(E)Rev.0
15
3.OHT Vehicle
3.1 External View of the OHT Vehicle
Fig.3.1 shows the outline of the OHT Vehicle
Fig. 3.1 Outline of OHT Vehicle
FCC ID : OPO199909010001
KEN72-3699(E)Rev.0
16
3.2 Name of the parts and function
3.2.1 Vehicle Body
The vehicle consist of X, Y, theta and Z axis. X axis is a traveling of the Vehicle, Y axis is a
lateral shift of the (B) part, theta axis is a rotation of the (B) part, and Z axis is a up/down motion
of the gripper.
Traveling is driven by the linear DC motor. Y, theta axis are driven by brush-less DC motor,
Hoisting axis is driven by AC servo motor. And gripper is driven by brus-hless DC motor.
FFU(Fan Filter Unit) is equipped with the body for keeping the area of the vehicle clean.
3.2.2 Gripper
The gripper is a mechanism for gripping the FOUP. It is hung from the body with four belts.
The power of the gripper is supplied from the body with the metal wire in the belts.
3.2.3 Bumper Switch
Bumper switch is a contact tape switch attached around the vehicle body. If it touch the
obstacle, the power source of the traveling motor is cut.
3.2.4 Emergency Switch
Emergency stop button is equipped. BY pushing this button, the power source of every servo
motor Is cut off and movement of the vehicle will be stopped.
3.2.5 Look Forward Sensor
Each vehicle has a sensor system monitoring the envelope of its traveling area. By this system,
obstacles in front of the vehicle is detected and the collision will be avoided.
FCC ID : OPO199909010001
KEN72-3699(E)Rev.0
17
3.2.6 Control panel
Fig. 3.2 Is a outline of the control panel. The meaning of LED indicator and Switches are
as follows.
Fig. 3.2 Control panel
(1)LED Indicator
A: Reserved : status of the software(servo)
B: Reserved : status of the software(servo)
C: Rx data : turn on when data received
D: Tx data : turn on when data transmitted
E: Gripper close : turn on when close LS is on
F: Gripper open : turn on when open LS is on
G: Falling protection arm out : turn on when arm is out
H: Falling protection arm in : turn on when arm is inside
I: Detection of collision avoidance sensor (long range) :
turn on when collision avoidance sensor(long range) activated
J: Detection of collision avoidance sensor(short range) :
turn on when collision avoidance sensor(short range) activated
K: Detection of Invasion prohibition sensor
turn on when invasion prohibition sensor activated
L: Detection of approaching sensor
turn on when approaching sensor activated
M: Error of speed settling : speed command of the software is over the designed value
N: Detection of FOUP falling : FOUP is putting on the falling protection arm
O: Reserved : status of the software
P: Reserved : status of the software
Q: Reserved : status of the software
FCC ID : OPO199909010001
KEN72-3699(E)Rev.0
18
(2) 7 segment LED
It indicate the status of the vehicle
(3) Switches
R: Mode switch(Key switch)
Manu : Set while Maintenance
Auto : mode controlled by OHVC
change to local mode by OHVC and controlled by Remote Control Box
Local : Remote Control Box
S: CPU reset : Reset of CPU board.
T: Err Reset : Reset of Latch circuit of the error.
U: E84 on/off : On/off a SEMI photo I/O communication.
V: MD on/off : On/off a Melody sound of the vehicle.
FCC ID : OPO199909010001
KEN72-3699(E)Rev.0
19
3.3 safety consideration
3.3.1 EMO ( Emergency Power OFF) on Power Supply Panel
EMO switch is installed on the front surface of Power Supply Panel. By pressing this button,
power supply to all the vehicle in that system (generally in the bay) will be suddenly stopped
and all the vehicles will be suddenly stopped (stopped within three seconds at worst).
Same function EMO switches can be added to the system optionally. Shinko will supply the
predetermined quantity of EMO switches and the installation (fixing in adequate position) in the
bay shall be done by customer.
(Remarks)
Fixing position of EMO switch shall be decided by customer considering the FAB operation.
According the SEMI S8 and other standards, the EMO position shall be between 81 cm to 165
cm in height if the operators are standing position in work.
3.3.2 P I/O interlock with manufacturing tool
Shinko system is fully compliant with SEMI E84 in P I/O hand shaking. If ES (Emergency Stop)
signal from passive side (manufacturing tool) is activated, hoisting movement of the
corresponding vehicle will be suddenly stopped.
3.3.3 Estop(Emergency Stop) on Vehicle
Estop button is installed on each vehicle. By pushing this button, vehicle movement (traveling
and hoisting gripping) will be suddenly stopped.
3.3.4 Look forward sensor (Envelope sensor)
There are many kinds of sensors in front of the Vehicle. These sensors are collision avoidance
sensor, front vehicle detection sensor, approaching sensor, invasion prohibit sensor.
Collision detection sensors detect the obstacles and vehicle exist in front of the vehicle .
These sensors detect the object in 2 stale (Long range and short range).
Long range output is settled to detect about the distance in 3000mm. If it activated, the vehicle
changes the speed to middle speed.
Short range output is settled to detect about the distance in 1500mm . when all the short range
sensor are activated, and the front vehicle detection sensor is detecting, then the vehicle
changes to creep speed. Otherwise Vehicle will stop.
Approaching sensor is settled to detect the object in distance of 150-200mm. If this sensor
detect, the vehicle will stop.
3.3.5 Fall protection arm
Each vehicle has fall protection arms, which tries to protect the FOUP in vehicle and traveling
position falling in the case of FOUP breakage.
FCC ID : OPO199909010001
KEN72-3699(E)Rev.0
20
3.3.6 Bumper Switch
Bumper switch is a contact tape switch attached around the vehicle body. If it touch the
obstacle, the power source of the traveling motor is cut. For safety, two bumper switches are
equipped in parallel.
3.3.7 Look down sensor
Each vehicle can be optionally added a look down sensor, which detects the obstacles
between the vehicle and the load port.
(It is under development, not yet completed.)
3.3.8 Invasion prohibit sensor
Invasion prohibit sensor of the vehicle is a receiver and it operate make a pair to ground side
sensor(transmitter). If this sensor detect the signal of ground side sensor, vehicle stop. And
this signal is removed, the vehicle start to travel.
3.4 Separation of vehicles and operators
Even the Shinko system has the safety system offering above, it is strictly expected to
customer for considering the separation of vehicles and operators, such as adding partition or
doors on the load port , or inhibit the operators moving into the bay.
FCC ID : OPO199909010001
KEN72-3699(E)Rev.0
21
4.Specification
4.1General Specification
4.1.1. Transport carrier
(1) Name : 300mm wafer FOUP
(2) Type :
(3) Manufacturer :
(4) Material : Compliant with SEMI E47.1-0299 (1999)
(5) Color : Compliant with SEMI E47.1-0299 (1999)
(6) Weight : 8.7 kgf (Max., including 25 wafers)
(7) Dimension : 430mm (W) x 356 mm (L) x 338 mm (H)
(8) Outline shape : Compliant with SEMI E47.1-0299 (1999)
4.1.2 Transport unit
(1) 1 FOUP / 1 vehicle
4.1.3 Environment condition
(1) Cleanliness : Class 100 (0.2 um)
(2) Temperature : 23 Degrees Celsius
(3) Humidity : %
(4) Corrosive gas : Nil
(5) Floor surface : Punching plate
(6) Ceiling Material : ULPA filter
(7) Ceiling height : 12 feet
(8) Required strength of the ceiling height
Refer to YDM-12075 for Customer specific condition.
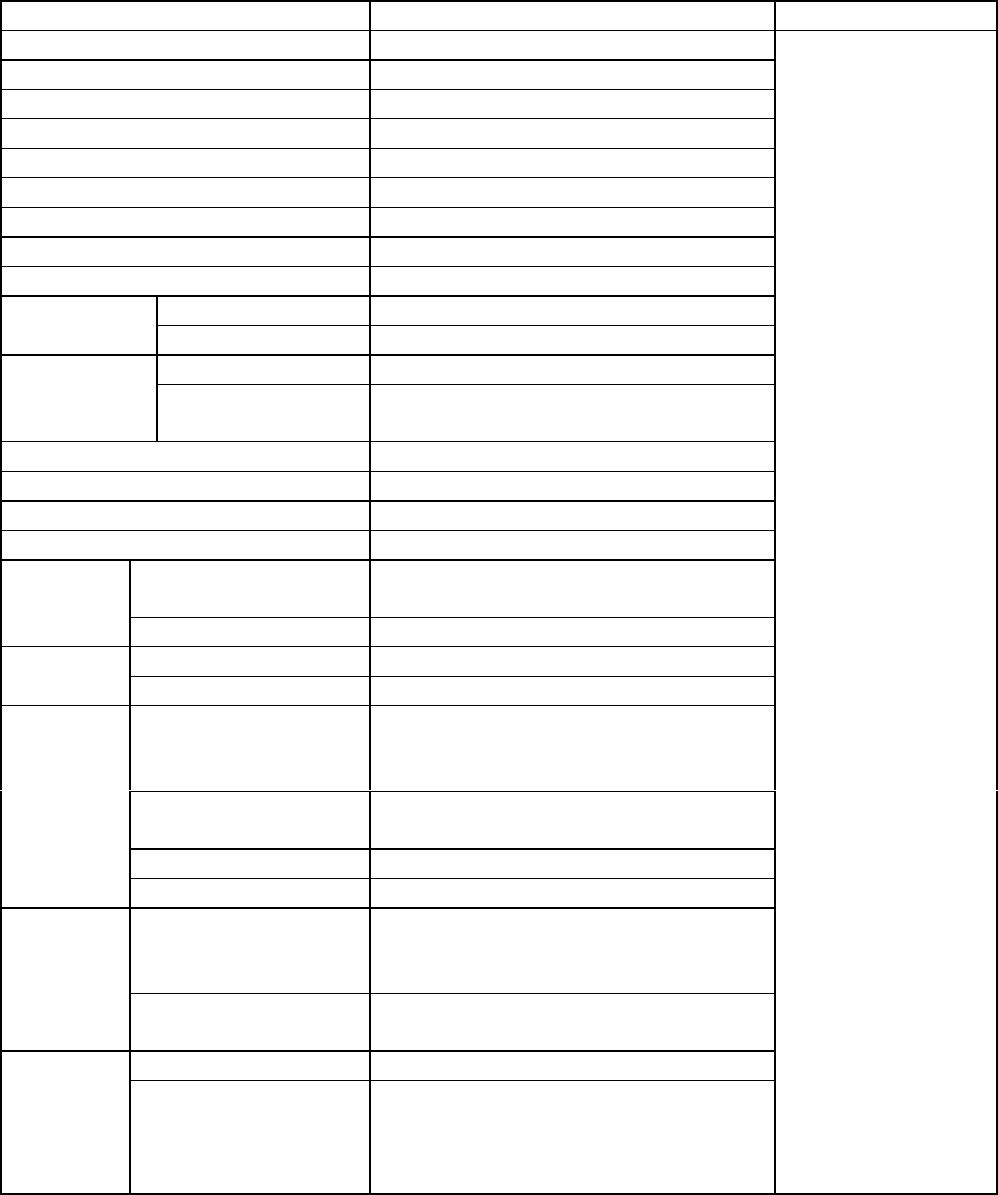
FCC ID : OPO199909010001
KEN72-3699(E)Rev.0
22
4.2 Basic technical specification
ITEM SPECIFICATION REMARKS
Track structure One loop
Driven method LDM (Linear Direct-currency Motor)
Max. payload (kg-F) 10
Running speed, at straight (m/s) Max. 1.5
Running speed, at curve (m/s) 0.5
Running acceleration (m/s2)1.0
Hoisting speed (m/s) 1.0
Hoisting acceleration (m/s2)1.0
Hoist stroke (m) Max. 2.2
Carrier position Horizontal X,Y(mm) +/- 1
repeatability Height (mm) +/- 1
Vehicle stop Lateral(mm) +/- 30
position
compensation
Rotational (degree)
(horizontal space)
+/- 10
Cleanliness Less than CLASS 100 (0.2um)
Track radius (mm/r) 500 (at the center)
Carrier vibration 0.5G
Power supply to Vehicle Non-contact , electro-magnetic coupling
Communi
-cation
Controller to vehicle Power line communication continuous, all area
Vehicle to Load port P I/O (E23, E84)
Track & Material Aluminum & Stainless Steel
support Cross section of track 267.5 (W) x 161 (H)
Vehicle
structure
Frame material Steel(surface finishing)
Stainless steel & aluminum plate
Anti flammable plastic
Gripper Stainless steel & aluminum plate
Anti flammable plastic
Weight (kg) 80
Outline dimension (mm) 490(W) x 675(L) x 892(H)
Power supply
panel
INPUT/OUTPUT INPUT : AC208 V (three phase)
OUTPUT: (AC300V to 400V) , 8.66kHz, 5kW
(Standard)
Optional large power
unit can be offered.
(Normal one) Outline dimension &
structure
500(W) x 500(D) x 1600(H)
Air-cooling, Steel plate enclosure
(Output voltage
depends on Demand)
Controller Hardware PC/AT compatible Window NT PC
(OHVC) Software O/S : Window NT 4.0
HOST I/F : IBSEM compatible
(based on SEMI E30.4-0699)
Communication : HSMS (Ethernet)
Table 4.1 Technical specification
FCC ID : OPO199909010001
KEN72-3699(E)Rev.0
23
5Auto Mode and Manual
5.1 Operation mode of the Vehicle
Operation mode of the Vehicle is shown in Fig. 5.1
Fig. 5.1 Operation mode of the Vehicle
5.2 Auto mode
(assumption : Vehicle has already moved in the OHT main track)
(1) Change the key switch of the control panel to “Auto”
(2) Send a entry command from OHVC
--- The vehicle start to run in order to search position ID(Bar Code Label)
If the vehicle searched BCL, the vehicle stop at that position.
(3)Control by the OHVC
After then, the vehicle will be controlled by the OHVC.
5.3 Manual mode
In this mode, the vehicle is controlled by the remote control box.
There are two method to inter this mode.
(1) Change the key switch of the control panel to “Local”
(2) Send a message to change “Local” from OHVC
As to the operation of the remote control box, refer to the “operation manual of the remote
control box”
FCC ID : OPO199909010001
KEN72-3699(E)Rev.0
24
6Teaching
6.1 Reference
(1) Teaching manual (KEN72 - 3644(E)
(2) Remote control box specification (KEN72-3501(E))
(3) Remote control box operation manual (KEN72-3502(E))
6.2 Two kinds of teaching
There are two ways of teaching methods
(1) Manual teaching
In this, teaching is carried out by moving the vehicle. Vehicle is operated by teaching operator
with remote control box.
The image of Manual teaching is shown in Fig. 6.1
(2) semi-auto teaching
Set a target LED to the bottom of the gripper, and set a PSD(Position Detecting Device) to the
load port.
The gripper goes down to closely above the FOUP height. The PSD see the LED and
know the displacement between FOUP center and load port FOUP center.
The PSD send a message to the vehicle to correct the position. The vehicle move to the gripper
to displacement makes to zero. The vehicle memorize this information as a position data of
teaching.
Above procedure is controlled by Personal computer for teaching.
The image of Semi-auto teaching is shown in Fig. 6.2
In detail, refer to the Teaching manual
FCC ID : OPO199909010001
KEN72-3699(E)Rev.0 25
Fig. 6.1 Image of Manual teaching Fig. 6.2 Image of Semi-auto teaching
FCC ID : OPO199909010001
KEN72-3699(E)Rev.0
26
7.Move in and move out of the vehicle
Move in and move out of the vehicle to the OHT Track is done by using Maintenance Lifter and
Shifter.
7.1 construction
Construction of the Maintenance Shifter & Lifter is shown in Fig. 7.1
7.2 Replacement of the vehicle
Move in of the vehicle
(1) The back up vehicle is loaded in the work bench. Move the back up vehicle to the
maintenance lifter and shifter.
(2) Connect a connector of the operation panel to the ground side connector.
(3) Down the lifter trail and tie up to the track of the working bench with a cramp.
(4) Shift the vehicle to the lifter from working bench by human power.
(5) Remove a cramp, and up the lifter with a buck up vehicle.
(6) (Stop the host controlled operation).
(7) Turn off the output of Power Supply Panel.
(8) Do a lateral shift, then do a longitudinal shift, and then joint the shifter rail to the
lifter rail.
(9) Shift the vehicle to the shifter from a lifter by human power.
(10) Do a lateral shift, then shift the vehicle to the main track.
(11) Turn on the Power Supply Panel.
(12) Down load the Data copy from OHVC to vehicle
(13) (Start the host controlled operation)
(14) Disconnect the connector of the operation panel
Move out of the vehicle
(1) Move and stop the vehicle on the shifter rail.
If vehicle is troubled and can not travel by it’s self, turn off the power of Power Supply
Panel and human push the vehicle with his hand.
(2) Connect a connector of the operation panel to the ground side connector.
(3) (Stop the host controlled operation)
(4) Turn off the Power Supply Panel.
(5) Do a lateral shift, then do a longitudinal shift, and then joint the shifter rail to the
lifter rail.
FCC ID : OPO199909010001
KEN72-3699(E)Rev.0
27
(6) Shift the vehicle to the lifter from the shifter by human power.
(7) Do a longitudinal shift, then do a lateral shift, and return to the main track.
(8) Turn on the Power Supply Panel.
(9) (Start the host controlled operation).
(10) Down the lift and tie up to the track of the working bench with a cramp.
(11) Shift the vehicle to the working bench from the lifter by human power.
(12) Remove a cramp and up the lifter.
(14) Disconnect the connector of the operation panel.
Warning
Don’t do vehicle move in/out with FOUP loaded
Don’t enter the working area of the vehicle move in/out
FCC ID : OPO199909010001
KEN72-3699(E)Rev.0 28
Fig. 7.1 Construction of Maintenance Shifter & Lifter
FCC ID : OPO199909010001
KEN72-3699(E)Rev.0
29
8. Removal of FOUP from OHV and manual
lifting of gripper unit
8.1.Two cases in manual removal of FOUP
There are two cases in manual removal of FOUP. They are case1 and case 2 below.
(case1) Power Supply Panel is on and remote control box can control OHV gripper.
(case2) Power Supply Panel is off and OHV is not supplied the power.
8.2. Two kinds of removal procedures
There are two kinds of removal procedures according to the position of gripper unit.
8.2.1 Position A : Hoisting belts extended long and gripper unit is not in the OHV body
(Fig. 8.1)
Procedure is as follows;
(1) Support the FOUP
(2) Open the gripper
(3) Lift the gripper unit
(Case 1)
Open the gripper and Lift the gripper unit
--- It can be realized by remote control box.
(Case 2)
(1) Open the gripper and Lift the gripper unit ---By human power
(2) Lift the gripper unit is realized by attaching the handle to OHV and
turning it.
8.2. 2. Position B : Hoisting belts don’t extended long and the gripper unit is in the OHV
body (Fig. 8.2)
In this case, the gripper is in the OHV body with gripper closed and gripper can not
open.
So, going down the gripper unit is necessary at first.
Procedure is as follows
(1) Go down the gripper unit outside of OHV
(2) Support the FOUP
(3) Open the gripper
(4)Lift the gripper unit
FCC ID : OPO199909010001
KEN72-3699(E)Rev.0
30
(Case 1)
Down the gripper, open the gripper and lift the gripper unit ---By the
remote control box.
(Case 2)
Detailed procedure is as follows
(1) Connect the external power supply unit to the OHV
(2) Push the FOUP falling protection unit inside as necessary by
human power
(3) Support the FOUP
(4) Push the brake release switch on the external power supply unit
and go down the gripper unit
(5) Open the gripper by human power
(6) Attach the handle to the OHV and turn it and lift the gripper unit
as necessary.
.
FCC ID : OPO199909010001
KEN72-3699(E)Rev.0 31
Fig. 8.1 Manual removal of FOUP from OHV and manual lifting of gripper unit (Position A)
FCC ID : OPO199909010001
KEN72-3699(E)Rev.0 32
Fig.8.2 Manual removal of FOUP from OHV and manual lifting of gripper unit (Position B)
FCC ID : OPO199909010001
KEN72-3699
33
9.MAINTENANCE PLAN
9.1 General
This chapter describes the maintenance plan of Shinko OHT system.
9.2 Maintenance plan
It consists of following four category;
(1) Daily check (during the normal operation)
(2) Semi-annual maintenance
(3) Every one year maintenance
(4) Every two years maintenance
9.2.1 Daily check
It is not a maintenance but a daily check during the normal operation. By the experience of daily
operation, abnormal noise or vibration can be detected. Important check points are as follows:
(1) Vehicle
(1-a) Be careful at the movement of each axis (i.e. X-axis (running), Y-theta-axis, and Z-
axis(up-down) ). If abnormal noise or vibration might be happened, it should be
recorded and it simply increased, maintenance shall be rescheduled.
(1-b) See the surface (such as cover, connection point), and check whether there is a dirt or
tear.
(1-c) See the surface of the hoisting belts, and check whether there is a dirt or wound.
(2) Rail
(2-a) Listen to the sound of rail and vehicle when it travels on the joint portion of the rail.
(3) Power Supply Panel
(3-a) See the ampere-meter and it’s value is within the predetermined value range.
FCC ID : OPO199909010001
KEN72-3699
34
9.2.2 Semi-annual maintenance
(1) Vehicle
A vehicle shall be removed from the rail and open the outside cover and check and do the
following items;
(1-a) Check the looseness of the bolts and screws. If it is loosen re-tighten them. Important
points are running mechanism, Y-theta axis movement parts, support of the hoisting
mechanism.
(1-b) Check the connector of all the cables. If it is loosen, re-tighten it.
(1-c) Check the surface of the rollers (running, guide and encoder) to see the wear, tear, dirt,
scratch, etc.
(1-d) Check the function of main sensors and indicators such as beam sensor for
measurement of front area, 7 segments LED. In this test, external power supply shall
be connected to the vehicle.
(1-e) See the hoisting belt and check the scratch and tear of the belt and the wire in the belt.
(1-f) Check the function of Estop, bumper switch, Fall protection sensor. Operate each by
connecting the external power supply unit.
(1-g) See the finger of Gripper unit and check whether there is a dirt or tear. See the gripper
operation keeps horizontal accuracy.
Above maintenance can be done one vehicle by one vehicle and the system operation can
be continued. Actual maintenance time for one vehicle will be 30 minutes.
(2) Rail
Stop the host controlled operation and switch off the Power Supply Panel and check the rail
by approaching to very near to the rail. See and touch the touch position of vehicle rollers
and non-contact power supply cables. If scratch or big tear is found, it shall be replaced.
See the bolts of rail support and joint of rails. If it becomes loose, re-tighten them.
Actual system stop time will be 30 minutes.
(3) Power supply Panel
Stop the host controlled operation and switch off the Power Supply Panel and open the door
of power supply unit. Re-tighten the bolts and screws. After recovery of power supply Panel
, Estop shall be test operated.
EMO of the OHT system also shall be tested.
Actual system stop time will be 20 minutes. Maintenance item (2) above and (3) will be
continuously done.
(4) Maintenance shifter and lifter
By removing and installing a vehicle, check the noise and vibration of shifter and lifter at
work is existing or not.
FCC ID : OPO199909010001
KEN72-3699
35
9.2.3 Every one year maintenance
(1) Vehicle
A vehicle shall be removed from the rail and open the cover and check and do the following
items;
(1-a) Same items with 9.2.2 (1) semi-annual maintenance.
(1-b) Grease-up the gear portion (Y-theta axis, Z-axis, Protection arm).
(1-c) Check the surface of Lens and wipe if it becomes dirty. Check the iris and focus is
correct (same with predetermined value).
(1-d) Do the test operation of each pendant switch.
Actual maintenance time for one vehicle will be 60 minutes
(2) Rail
Same with9.2.2 (2) Semi-annual maintenance.
(3) Power supply unit
Same with 9.2.2 (3) Semi-annual maintenance.
(4) Shifter and maintenance lifter
Same with 9.2.2 (4) Semi-annual maintenance.
FCC ID : OPO199909010001
KEN72-3699
36
9.2.4 Every two year maintenance
(1) Vehicle
A vehicle shall be removed from the rail and open the outside cover and check and do the
following items;
(1-a) Same items with 9.2.2 (1) semi-annual maintenance.
(1-b) Replace the memory back-up battery.
(1-c) Replace the hoisting belts (all four belts).
(1-d) Replace the FFU (Fan Filter Unit).
As for the replacement of memory back-up battery and FFU unit, it will not be necessary for
replacing all of them. By studying the tendency of damage, replacing time period will be
examined.
Actual maintenance time for one vehicle will be 90 minutes
(2) Rail
Same with 9.2.2 (2) Semi-annual maintenance.
(3) Power supply Panel
(3-a) Same action with 9.2.2 (3) Semi-annual maintenance, and
(3-b) Replace the Fan unit.
As for the replacement of Fan unit, it will not be necessary for replacing all of them. By
studying the tendency of damage, replacing time period will be examined.
(4) Shifter and maintenance lifter
Same with 9.2.2 (4) Semi-annual maintenance.
FCC ID : OPO199909010001
KEN72-3699
37
Fig. 9.1 Outline of Shinko OHT SYSTEM