HARRIS TR-0058-E Vehicular Repeater Base System (VRBS) User Manual 2
HARRIS CORPORATION Vehicular Repeater Base System (VRBS) 2
HARRIS >
Contents
- 1. Manual 1 rev
- 2. Manual 2 rev
- 3. User Manual 1
- 4. User Manual 2
User Manual 2
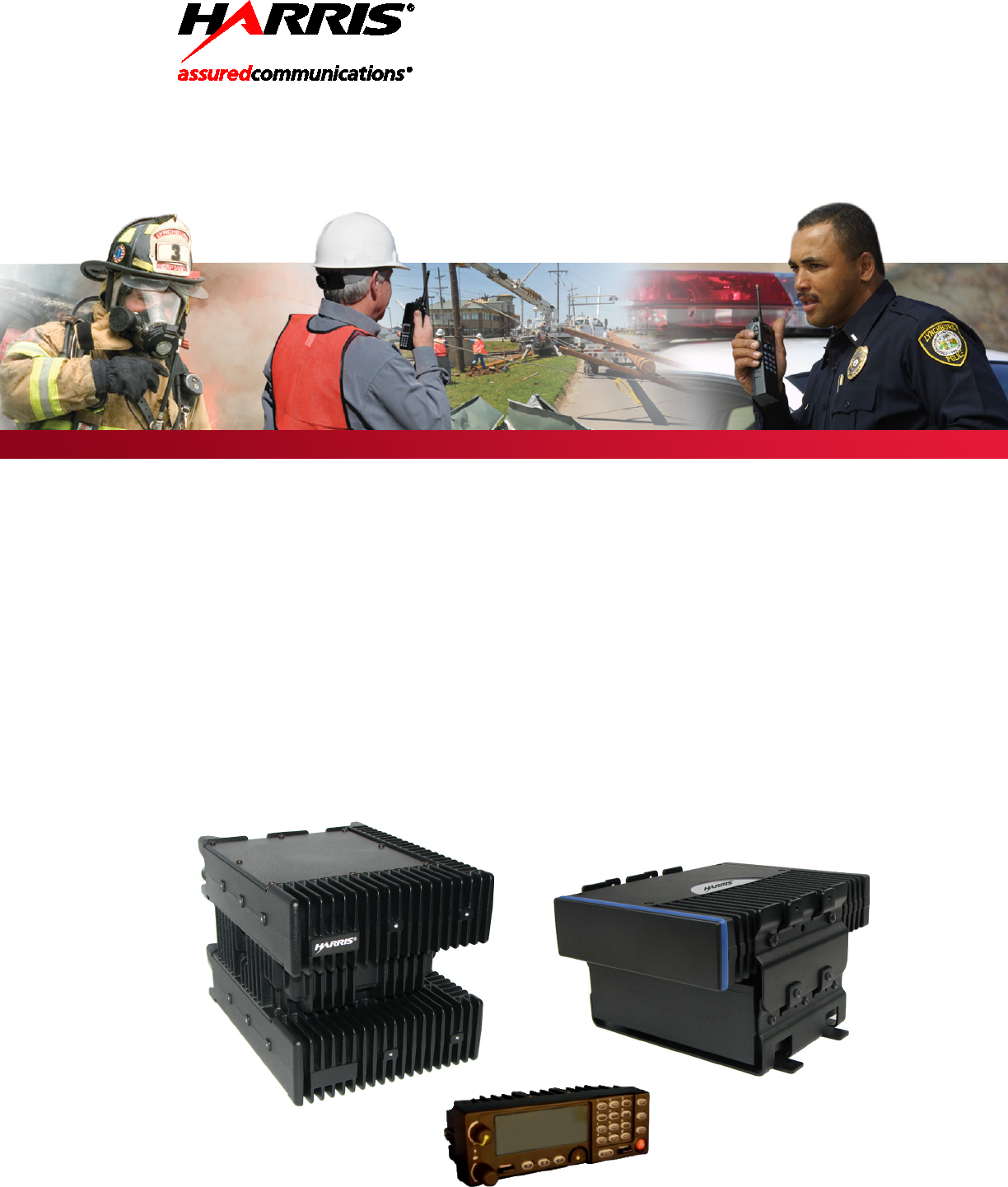
Installation and Product Safety Manual
MM-018337-001
Rev. B, Sep/11
VRS7000 Series
P25 Trunked Cross-Band
Vehicular Repeater Systems
VRS7010, VRS7020, and VRS7030
Includes
VRBS7010, VRBS7020, VRBS7030,
VRMS7010, VRMS7020, VRMS7030
and CH-721 Control Head
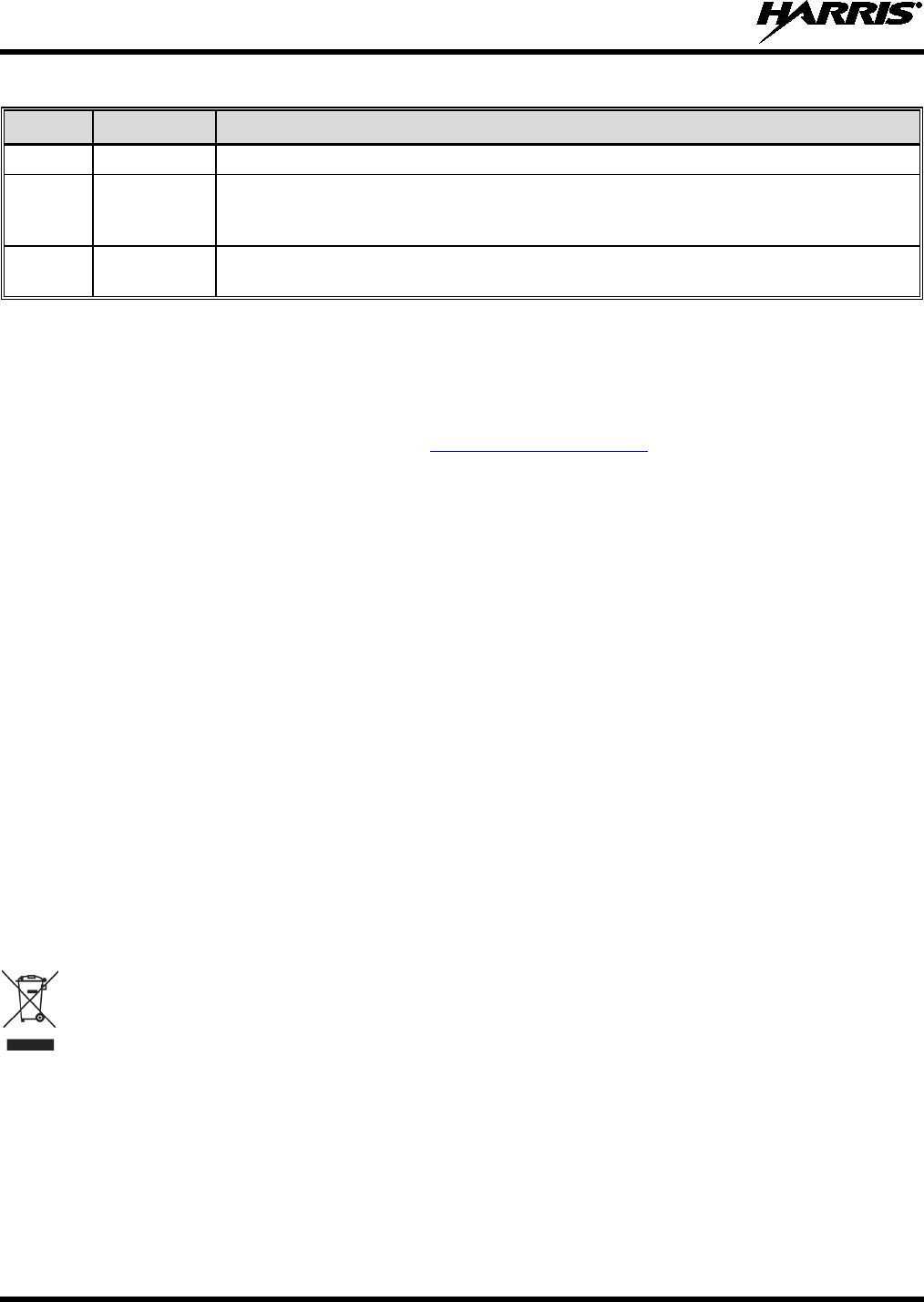
MM-018337-001, Rev. B
2
MANUAL REVISION HISTORY
REV. DATE REASON FOR CHANGE
– Feb/10 Original release.
A Jul/10 Revised antenna part numbers,
introduction, option and accessories tables,
mounting procedures, antenna installation procedures, Interface Cable installation
procedure, and performance test procedures.
B Sep/11 Added VRBS7020, VRBS7030, VRMS7020, and VRM
S7030. Revised optional
cables section.
Harris Corporation, Public Safety and Professional Communications (PSPC) Business, continually evaluates its technical
publications for completeness, technical accuracy, and organization. You can assist in this process by submitting your
comments and suggestions to the following:
Harris Corporation fax your comments to: 1-434-455-6851
PSPC Business or
Technical Publications e-mail us at: PSPC_TechPubs@harris.com
221 Jefferson Ridge Parkway
Lynchburg, VA 24501 ACKNOWLEDGEMENT
This device is made under license under one or more of the following US patents: 4,590,473; 4,636,791; 5,148,482;
5,185,796; 5,271,017; 5,377,229; 4,716,407; 4,972,460; 5,502,767; 5,146,497; 5,164,986; 5,185,795; 5,226,084; 5,247,579;
5,491,772; 5,517,511; 5,630,011; 5,649,050; 5,701,390; 5,715,365; 5,754,974; 5,826,222; 5,870,405; 6,161,089; and
6,199,037 B1. DVSI claims certain rights, including patent rights under aforementioned U.S. patents, and under other U.S.
and foreign patents and patents pending. Any use of this software or technology requires a separate written license from
DVSI. CREDITS
Harris and assuredcommunications are registered trademarks of Harris Corporation.
All other brand and product names are trademarks, registered trademarks, or service marks of their respective holders.
NOTICE!
The material contained herein is subject to U.S. export approval. No export or re-export is permitted without written
approval from the U.S. Government. Rated: EAR99 in accordance with U.S. Dept. of Commerce regulations 15CFR774,
Export Administration Regulations.
Information and descriptions contained herein are the property of Harris Corporation. Such information and descriptions may
not be copied or reproduced by any means, or disseminated or distributed without the express prior written permission of
Harris Corporation, PSPC Business, 221 Jefferson Ridge Parkway, Lynchburg, VA 24501.
Repairs to this equipment should be made only by an authorized service technician or facility designated by the supplier. Any
repairs, alterations or substitutions of recommended parts made by the user to this equipment not approved by the
manufacturer could void the user's authority to operate the equipment in addition to the manufacturer's warranty.
This product conforms to the European Union WEEE Directive 2002/96/EC. Do not dispose of this product in a
public landfill. Take it to a recycling center at the end of its life.
This manual is published by Harris Corporation
without any warranty. Improvements and changes to this manual
necessitated by typographical errors, inaccuracies of current information, or improvements to programs and/or equipment,
may be made by Harris Corporation at a
ny time and without notice. Such changes will be incorporated into new editions of
this manual. No part of this manual may be reproduced or transmitted in any form or by any means, electronic or mechanical,
including photocopying and recording, for any purpose, without the express written permission of Harris Corporation.
Copyright© 2010, 2011, Harris Corporation
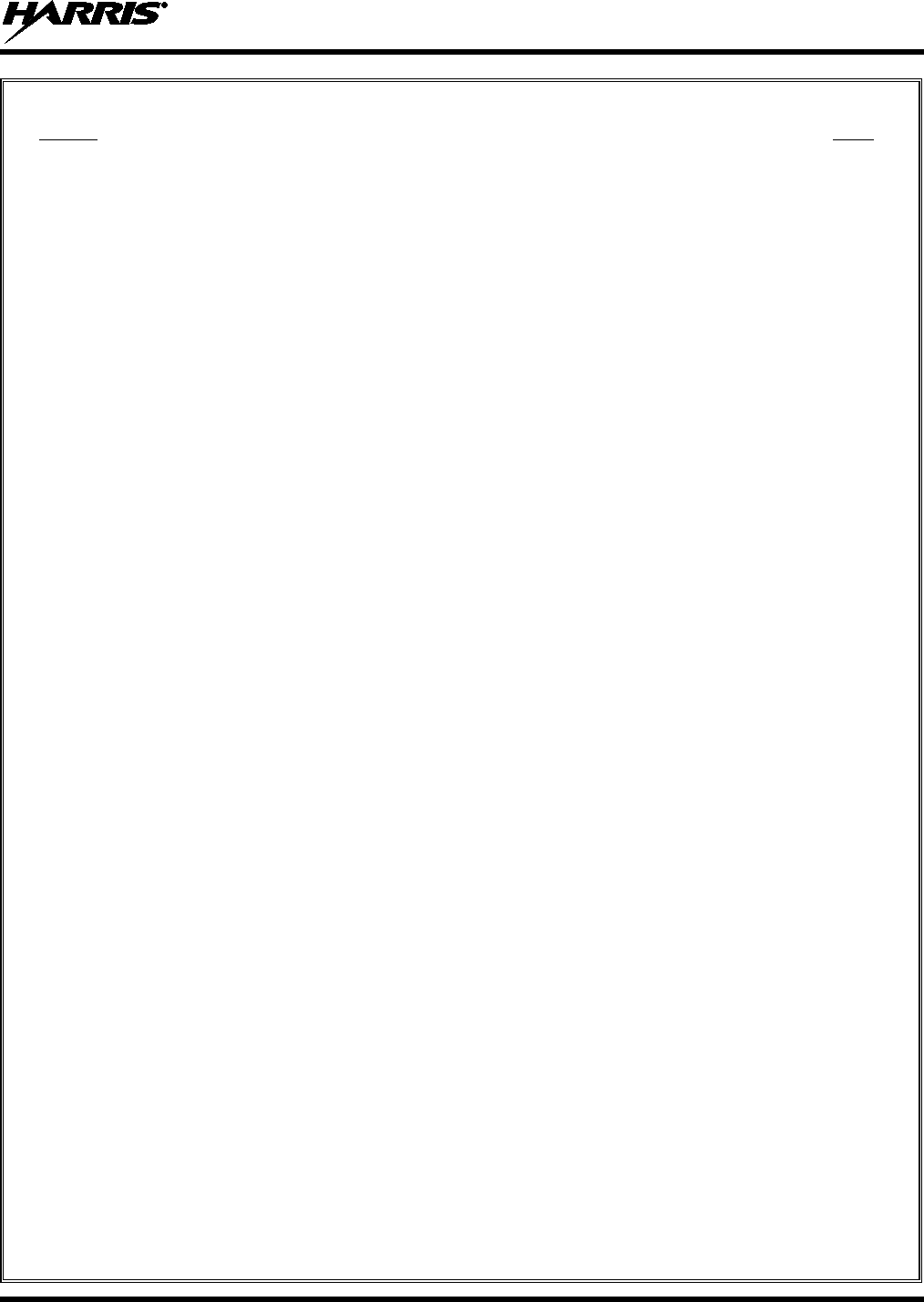
MM-018337-001, Rev. B
3
TABLE OF CONTENTS
Section Page
1 REGULATORY AND SAFETY INFORMATION ................................................................................... 6
1.1 SAFETY SYMBOL CONVENTIONS ................................................................................................. 6
1.2 RF ENERGY EXPOSURE AWARENESS AND CONTROL INFORMATION FOR FCC
OCCUPATIONAL USE REQUIREMENTS ........................................................................................ 6
1.2.1 Federal Communications Commission Regulations ............................................................... 7
1.3 COMPLIANCE WITH RF EXPOSURE STANDARDS ...................................................................... 7
1.3.1 Mobile Antennas .................................................................................................................. 11
1.3.2 Approved Accessories .......................................................................................................... 11
1.3.3 Contact Information .............................................................................................................. 11
1.4 RADIO FREQUENCY INTERFERENCE ......................................................................................... 11
1.4.1 FCC Part 15 .......................................................................................................................... 11
1.4.2 Industry Canada .................................................................................................................... 11
1.5 OCCUPATIONAL SAFETY GUIDELINES AND SAFETY TRAINING INFORMATION ........... 11
1.6 COMMON HAZARDS ...................................................................................................................... 12
1.7 SAFE DRIVING RECOMMENDATIONS ........................................................................................ 13
1.8 OPERATING RULES REGULATIONS ............................................................................................ 13
1.9 OPERATING TIPS ............................................................................................................................. 14
2 SPECIFICATIONS ..................................................................................................................................... 15
2.1 GENERAL .......................................................................................................................................... 15
2.2 REGULATORY ................................................................................................................................. 16
3 INTRODUCTION ....................................................................................................................................... 17
3.1 GENERAL INFORMATION ............................................................................................................. 17
3.1.1 Vehicular Repeater Base System (VRBS) ............................................................................ 17
3.1.2 Vehicular Repeater Mobile System (VRMS) ....................................................................... 18
3.2 OPERATING MODES ....................................................................................................................... 19
3.2.1 Standard Mobile Radio Mode ............................................................................................... 19
3.2.2 Extended Coverage (XCOV) Vehicular Repeater Mode ...................................................... 19
3.3 EQUIPMENT MOUNTING AND CONTROL HEAD ...................................................................... 20
3.4 OPERATING POWER ....................................................................................................................... 20
3.5 RELATED PUBLICATIONS ............................................................................................................. 21
3.6 REPLACEMENT PARTS .................................................................................................................. 21
3.7 TECHNICAL ASSISTANCE ............................................................................................................. 21
4 UNPACKING AND CHECKING THE EQUIPMENT ........................................................................... 22
4.1 MATERIALS...................................................................................................................................... 22
4.2 MATERIAL INSPECTION ................................................................................................................ 23
5 PLANNING THE INSTALLATION ......................................................................................................... 28
5.1 GENERAL INFORMATION ............................................................................................................. 28
5.2 TOOLS REQUIRED ........................................................................................................................... 28
5.3 LOCATING COMPONENTS ............................................................................................................ 31
6 MOUNTING THE RADIO EQUIPMENT ............................................................................................... 32
6.1 INSTALL THE MOUNTING BRACKETS ....................................................................................... 32
6.2 MOUNT THE RADIOS AND FILTER INTO THE BRACKETS ...................................................... 34
7 ANTENNA INSTALLATION ................................................................................................................... 36
7.1 ANTENNA MOUNTING LOCATIONS ........................................................................................... 36
7.1.1 Direct Center or Center-Rear of Rooftop for VRMS Antenna ............................................. 36
7.1.2 Center of Trunk Lid for VRBS Antenna .............................................................................. 36
7.1.3 Rear Deck Lid for GPS Stand-Alone GPS Receive Antenna ............................................... 38
7.2 ANTENNA INSTALLATION PROCEDURES ................................................................................. 39
7.2.1 Installing NMO Antenna Mounts AN-125001-001, -002, -003 and -004 ............................ 39
7.2.2 Installing NMO Magnetic Antenna Mounts AN-125001-007 and AN-125001-008 ............ 42
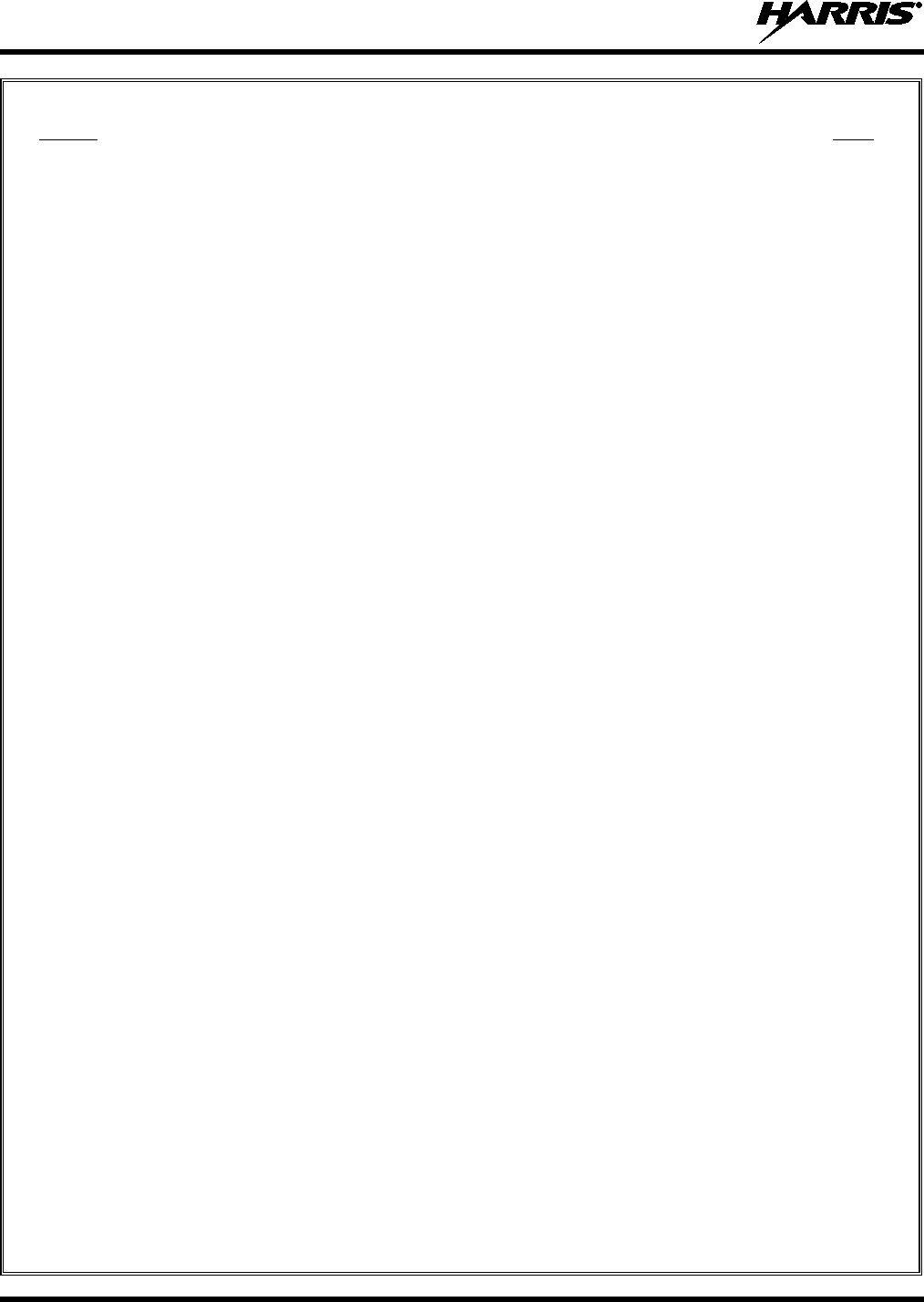
MM-018337-001, Rev. B
4
(Continued)
TABLE OF CONTENTS
Section Page
7.2.3 Installing all Other Antenna Mounts ..................................................................................... 42
7.2.4 Attaching NMO Antenna Elements ...................................................................................... 42
7.2.5 Connecting the Mobile Antennas .......................................................................................... 43
7.2.6 Connect RF Cable Between VRM Radio and 800 MHz Bandpass Filter ............................. 44
7.2.7 Install and Connect GPS Antenna (if Required) ................................................................... 44
8 INTERFACE CABLE INSTALLATION ................................................................................................. 46
8.1 INTERFACE CABLE CA-012349-003 OVERVIEW ........................................................................ 46
8.2 INTERFACE CABLE CA-012349-003 INSTALLATION PROCEDURE ........................................ 49
9 DC POWER INSTALLATION .................................................................................................................. 52
9.1 OVERVIEW OF ON/OFF POWER WIRING CONFIGURATIONS ................................................. 52
9.2 POWER INSTALLATION PROCEDURE ......................................................................................... 53
9.2.1 Radio DC Power Cables and Main Fuse Holders Installation .............................................. 53
10 CONTROL HEAD INSTALLATION ....................................................................................................... 56
10.1 GENERAL INFORMATION ............................................................................................................. 56
10.2 CONTROL HEAD MECHANICAL INSTALLATION ..................................................................... 58
10.2.1 Selecting the Mounting Location .......................................................................................... 58
10.2.2 Using the Standard U-Shaped Mounting Bracket ................................................................. 59
10.2.3 Using the Mounting Pedestal (Optional) .............................................................................. 59
10.3 CAN CONNECTIONS ....................................................................................................................... 60
10.3.1 General Information .............................................................................................................. 60
10.3.2 Make CAN Link Terminations and Cable Connection ......................................................... 60
10.4 CONTROL HEAD POWER CABLE INSTALLATION .................................................................... 61
10.4.1 Install DC Power Cable and Make Power and Ground Connections .................................... 61
10.4.2 Connect DC Power Cable’s White Wire ............................................................................... 62
10.4.3 Using Vehicle Fuse and T-Tap Kit (Optional) Instead of Waterproof Inline Fuse Holder
(Standard) ............................................................................................................................. 64
11 SPEAKER INSTALLATION ..................................................................................................................... 66
12 MICROPHONE ATTACHMENT ............................................................................................................. 66
13 OPTIONAL CABLES ................................................................................................................................. 67
13.1 SERIAL PROGRAMMING CABLE CA-013671-020 ....................................................................... 67
13.2 CH-721 OPTION CABLE CA-011854-001 ........................................................................................ 68
13.3 CH-721 SERIAL PROGRAMMING CABLE CA-104861 ................................................................. 69
14 GPS NMEA-FORMATTED SERIAL DATA CONNECTION ............................................................... 70
15 INITIAL POWER-UP TEST ..................................................................................................................... 71
16 PERFORMANCE TESTS .......................................................................................................................... 72
16.1 REQUIRED TEST EQUIPMENT ...................................................................................................... 73
16.2 VRMS TRANSMITTING INTO A 50-OHM LOAD/TERMINATOR ............................................... 73
16.3 VRMS TRANSMITTING INTO ITS ANTENNA .............................................................................. 75
16.4 VRBS TRANSMITTING INTO A 50-OHM LOAD/TERMINATOR ............................................... 77
16.5 VRBS TRANSMITTING INTO ITS ANTENNA ............................................................................... 78
16.6 TEST PERFORMANCE DATA FORM ............................................................................................. 81
17 COMPLETE THE INSTALLATION ....................................................................................................... 82
18 WARRANTY REGISTRATION ............................................................................................................... 82
19 WARRANTY ............................................................................................................................................... 83
20 WIRING DIAGRAM FOR VRS7000 AND CH-721 ................................................................................ 85
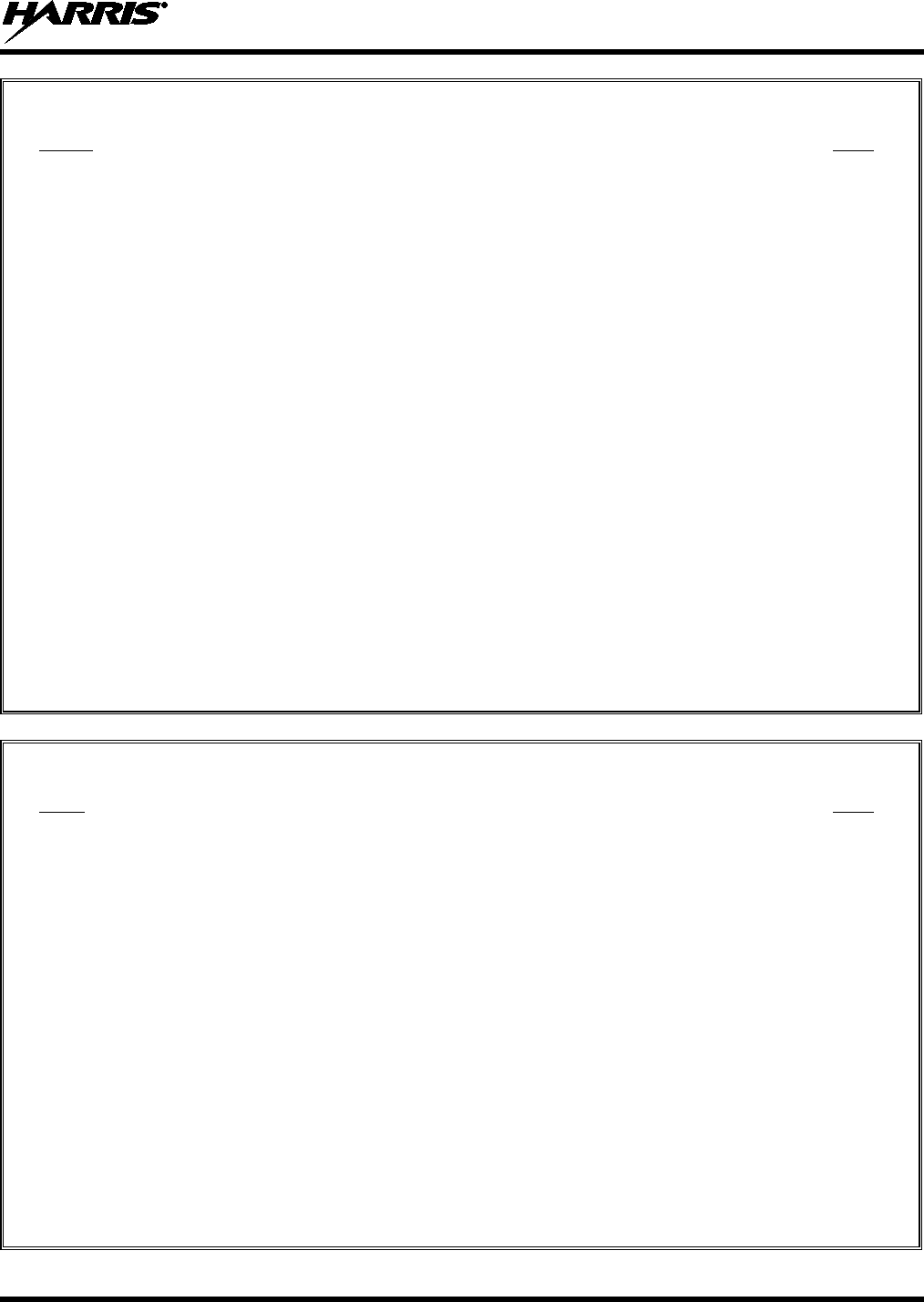
MM-018337-001, Rev. B
5
LIST OF FIGURES
Figure Page
Figure 3-1: Simplified Block Diagram of Extended Network Coverage Mode .................................................. 17
Figure 5-1: Vehicular Repeater Mobile System (VRMS) ................................................................................... 29
Figure 5-2: Vehicular Repeater Base System (VRBS) ......................................................................................... 30
Figure 6-1: Base Bracket (Two Required Per VRS7000 Installation) ................................................................. 33
Figure 6-2: VRMS and VRBS Assembly into Brackets (Exploded Views) ........................................................ 35
Figure 7-1: Required VRMS7010/VRMS7020 Antenna Mounting Locations with Antenna Part Numbers ...... 37
Figure 7-2: Required VRMS7030 Antenna Mounting Locations with Antenna Part Numbers .......................... 38
Figure 7-3: Required VRBS7010/VRBS7020/VRBS7030 Antenna Mounting Locations with Antenna Part
Numbers ...................................................................................................................................... 39
Figure 7-4: Installing a Standard ¾-Inch NMO Antenna Mount (e.g., AN-125001-001 or AN-125001-002) ... 41
Figure 7-5: Installing a Thick-Roof NMO Antenna Mount (e.g., AN-125001-003 or AN-125001-004) ........... 42
Figure 7-6: Crimping Instructions for TNC RF Connector (Actual Size; Dimensions in Inches) ....................... 44
Figure 8-1: Interface Cable CA-012349-003 ....................................................................................................... 46
Figure 10-1: CH-721 System Model Control Head Front Panel ......................................................................... 56
Figure 10-2: CH-721 Rear Panel ......................................................................................................................... 57
Figure 10-3: Standard U-Shaped Control Head Mounting Bracket (Kit Part Number KT-008608) ................... 58
Figure 10-4: Optional Control Head Mounting Pedestal (Part Number MACDOS0012) ................................... 58
Figure 10-5: CAN Cable and Terminator Connections ....................................................................................... 60
Figure 10-6: Contents of Vehicle Fuse and T-Tap Kit FS24473 ......................................................................... 64
Figure 10-7: Attaching T-Tap Terminals to a Switched Power Wire .................................................................. 65
Figure 13-1: Serial Data Cable CA-013671-020 ................................................................................................. 67
Figure 13-2: CH-721 Option Cable CA-011854-001 .......................................................................................... 68
Figure 13-3: Programming Cable CA-104861 .................................................................................................... 69
Figure 16-1: Wattmeter Connections for VRMS7010/VRMS7020/VRMS7030 Antenna Tests ........................ 74
Figure 16-2: Wattmeter Connections for VRBS7010/VRBS7020/VRBS7030 Antenna Tests ........................... 77
LIST OF TABLES
Table Page
Table 1-1: Recommended Minimum Safe Lateral Distance from Transmitting Antenna for Mobile
Radio-to-Network Radio Link (VRMS7010/VRMS7020 Transmit/Receive Antenna) ................ 8
Table 1-2: Recommended Minimum Safe Lateral Distance from Transmitting Antenna for Mobile
Radio-to-Network Radio Link (VRMS7030 Transmit/Receive Antenna)................................... 10
Table 1-3: Recommended Minimum Safe Lateral Distance from Transmitting Antenna for Vehicular
Repeater-to-P25 Radio Link (VRBS7010/VRBS7020/VRBS7030 Transmit/Receive
Antenna) ...................................................................................................................................... 10
Table 4-1: VRS7010 Catalog and Part Numbers ................................................................................................. 22
Table 4-2: VRS7020 Catalog and Part Numbers ................................................................................................. 22
Table 4-3: VRS7030 Catalog and Part Numbers ................................................................................................. 23
Table 4-4: Installation Kit MAMW-NZN8X for VRS7000 and CH-721 ............................................................ 24
Table 4-5: Options and Accessories for VRS7010/VRS7020/VRS7030 ............................................................ 26
Table 4-6: Accessories for CH-721 Control Heads ............................................................................................. 27
Table 8-1: Interface Cable CA-012349-003 Pin-Out/Interconnections ............................................................... 47
Table 8-2: VRS7000-to-VC3000/VC4000 Vehicular Charger Interconnections for Vehicular Repeater
Enable/Disable if using VRMS’s Aux I/O 1 = INP1 (Optional) ................................................. 50
Table 8-3: VRS7000-to-VC3000/VC4000 Vehicular Charger Interconnections for Vehicular Repeater
Enable/Disable if using VRMS’s Aux I/O 2 = INP2 (Optional) ................................................. 51
Table 16-1: Test Equipment Required for Performance Tests ............................................................................ 73
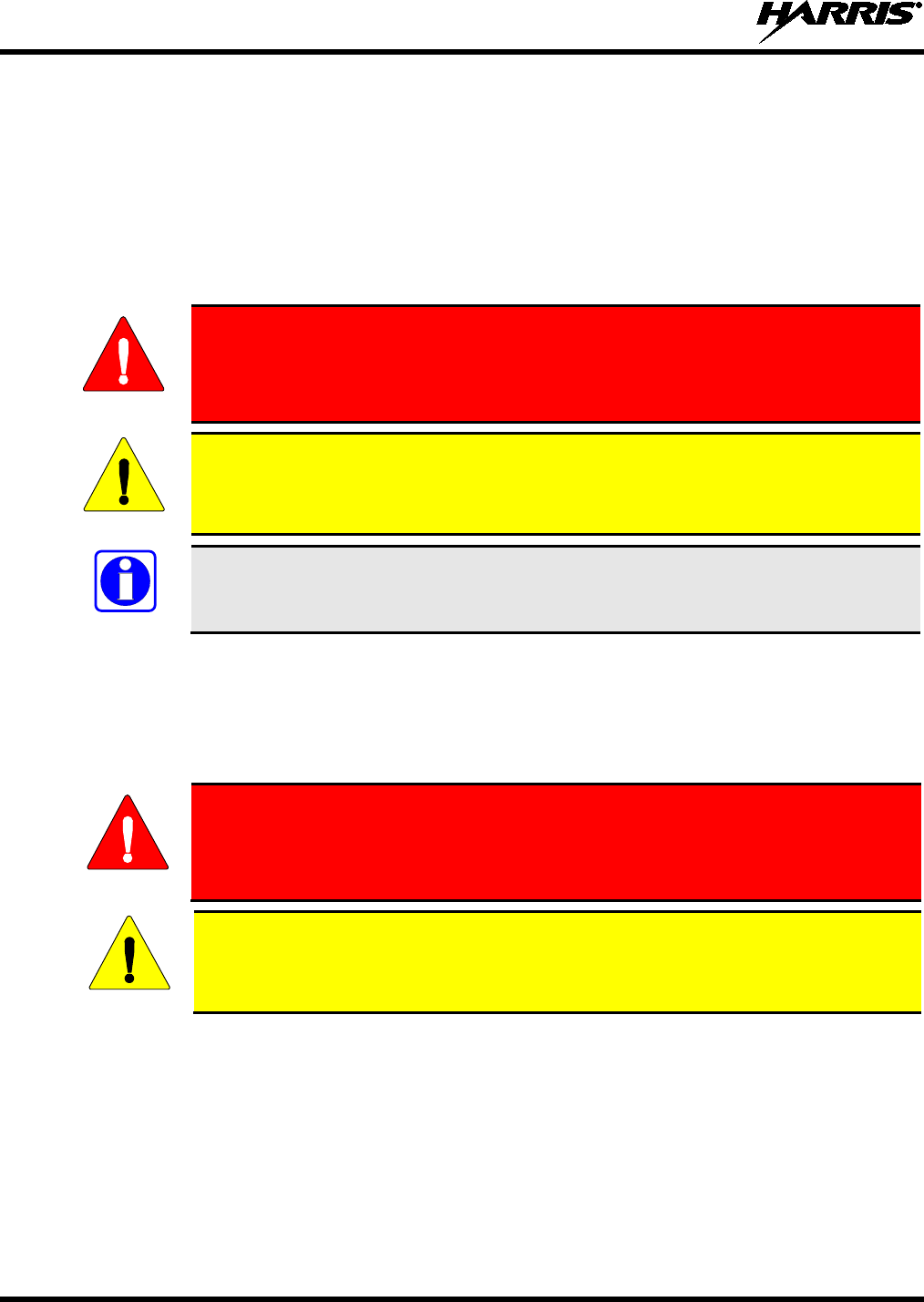
MM-018337-001, Rev. B
6
1 REGULATORY AND SAFETY INFORMATION
1.1 SAFETY SYMBOL CONVENTIONS
The following conventions are used in this manual to alert the user to general safety precautions that must
be observed during all phases of operation, service, and repair of this product. Failure to comply with
these precautions or with specific warnings elsewhere violates safety standards of design, manufacture,
and intended use of the product. Harris assumes no liability for the customer's failure to comply with
these standards.
WARNING
The WARNING symbol calls attention to a procedure, practice, or the like, which,
if not correctly performed or adhered to, could result in personal injury. Do not
proceed beyond a WARNING symbol until the conditions identified are fully
understood or met.
CAUTION
The CAUTION symbol calls attention to an operating procedure, practice, or the like,
which, if not performed correctly or adhered to, could result in damage to the
equipment or severely degrade equipment performance.
NOTE
The NOTE symbol calls attention to supplemental information, which may improve
system performance or clarify a process or procedure.
1.2 RF ENERGY EXPOSURE AWARENESS AND CONTROL
INFORMATION FOR FCC OCCUPATIONAL USE REQUIREMENTS
Before using the mobile two-way radio, read this important RF energy awareness and control
information to ensure compliance with RF exposure guidelines.
WARNING
This radio is intended for use in occupational/controlled conditions, where users
have full knowledge of their exposure and can exercise control over their exposure
to remain below RF exposure limits. This radio is NOT authorized for general
population, consumer, or any other use.
CAUTION
Changes or modifications not expressly approved by Harris
could void the user's
authority to operate the equipment.
This two-way radio uses electromagnetic energy in the radio frequency (RF) spectrum to provide
communications between two or more users over a distance. It uses RF energy or radio waves to send and
receive calls. RF energy is one form of electromagnetic energy. Other forms include, but are not limited
to, electric power, sunlight, and x-rays. RF energy, however, should not be confused with these other
forms of electromagnetic energy, which, when used improperly, can cause biological damage. Very high
levels of x-rays, for example, can damage tissues and genetic material.
Experts in science, engineering, medicine, health, and industry work with organizations to develop
standards for exposure to RF energy. These standards provide recommended levels of RF exposure for
both workers and the general public. These recommended RF exposure levels include substantial margins
of protection. All two-way radios marketed in North America are designed, manufactured, and tested to
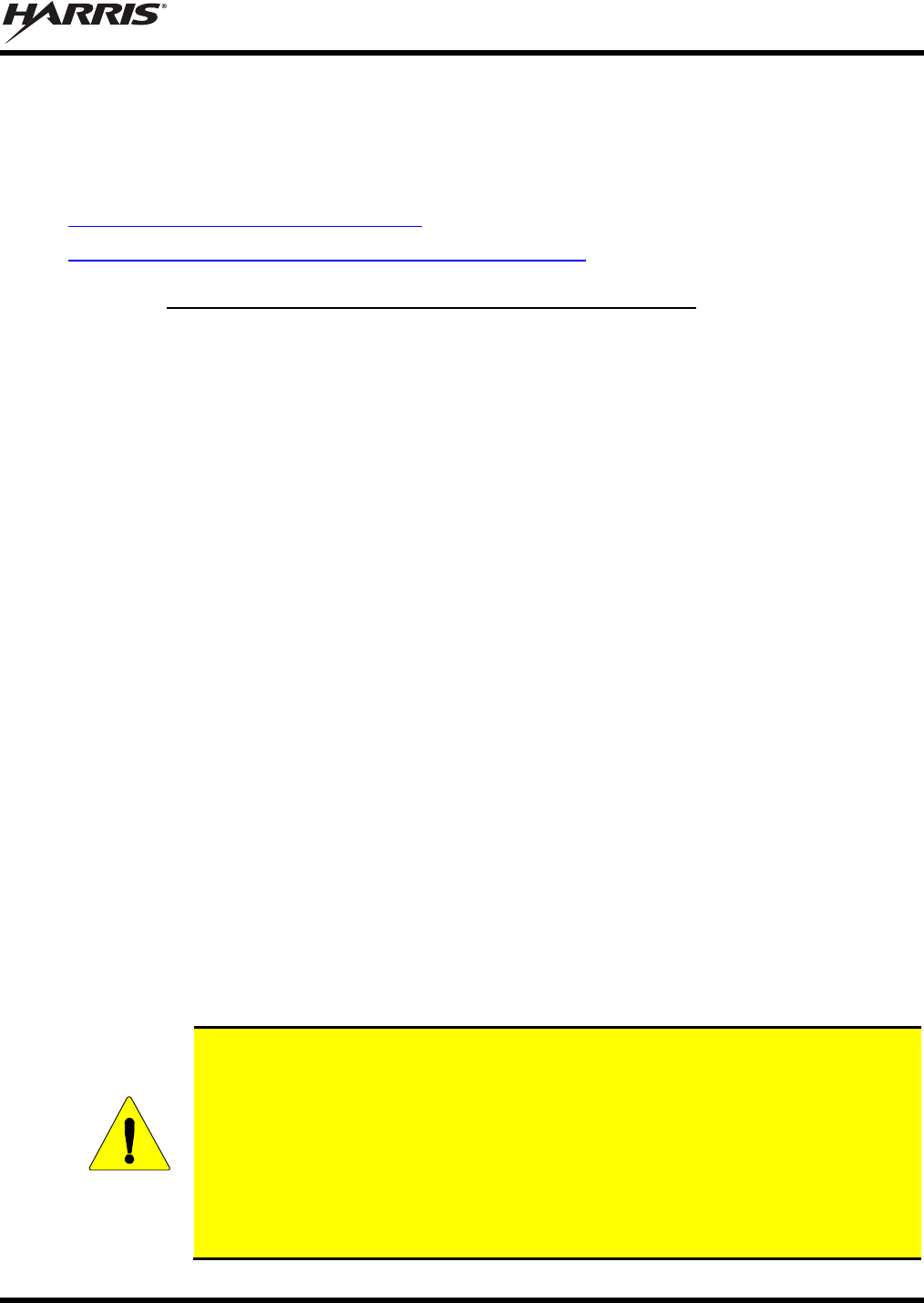
MM-018337-001, Rev. B
7
ensure they meet government-established RF exposure levels. In addition, manufacturers also recommend
specific operating instructions to users of two-way radios. These instructions are important because they
inform users about RF energy exposure and provide simple procedures on how to control it. Please refer
to the following websites for more information on what RF energy exposure is and how to control
exposure to assure compliance with established RF exposure limits:
http://www.fcc.gov/oet/rfsafety/rf-faqs.html
http://www.osha.gov./SLTC/radiofrequencyradiation/index.html
1.2.1 Federal Communications Commission Regulations
Before it was marketed in the United States, the P25 Vehicular Repeater System was tested to ensure
compliance with FCC RF energy exposure limits for mobile two-way radios. When two-way radios are
used as a consequence of employment, the FCC requires users to be fully aware of and able to control
their exposure to meet occupational requirements. Exposure awareness can be facilitated by the use of a
label directing users to specific user awareness information. The radio has an RF exposure product label.
Also, this Installation and Product Safety Manual and the applicable Operator’s Manual include
information and operating instructions required to control RF exposure and to satisfy compliance
requirements.
1.3 COMPLIANCE WITH RF EXPOSURE STANDARDS
The P25 Vehicular Repeater System is designed and tested to comply with a number of national and
international standards and guidelines regarding human exposure to RF electromagnetic energy. This
radio complies with the IEEE and ICNIRP exposure limits for occupational/controlled RF exposure
environment at duty-cycle times of up to 50% (50% transmit, 50% receive) for the VRMS radio
equipment, and up to 100% for the VRBS radio equipment. The radio equipment is authorized by the
FCC for occupational use. In terms of measuring RF energy for compliance with the FCC exposure
guidelines, the radio’s antenna radiates measurable RF energy only while it is transmitting (talking), not
when it is receiving (listening), or in standby mode.
The Vehicular Repeater System complies with the following RF energy exposure standards and
guidelines:
United States Federal Communications Commission (FCC), Code of Federal Regulations; 47 CFR
§ 2 sub-part J.
American National Standards Institute (ANSI)/Institute of Electrical and Electronic Engineers (IEEE)
C95.1-2005.
Institute of Electrical and Electronic Engineers (IEEE) C95.1-2005.
IC Standard RSS-102, Issue 2, 2005: Spectrum Management and Telecommunications Radio
Standards Specification. Radiofrequency Exposure Compliance of Radiocommunication Apparatus
(All Frequency Bands).
CAUTION
Table 1-1 through Table 1-3 list the recommended minimum safe lateral distances for a
controlled environment and for unaware bystanders in an uncontrolled environment,
from transmitting antennas (i.e., monopoles over a ground plane, or dipoles). Table 1-1
and Table 1-2 have the distances for the respective VRMS section of the vehicular
repeater on a per antenna basis. Table 1-3 has the distances for the VRBS section of the
vehicular repeater on a per antenna basis. This data is based upon the mobile radio
installed in a motor vehicle with the radio transmitting at its rated RF power level.
Transmit only when unaware bystanders are at least the uncontrolled recommended
minimum safe lateral distance away from the mobile radio’s transmitting antenna.
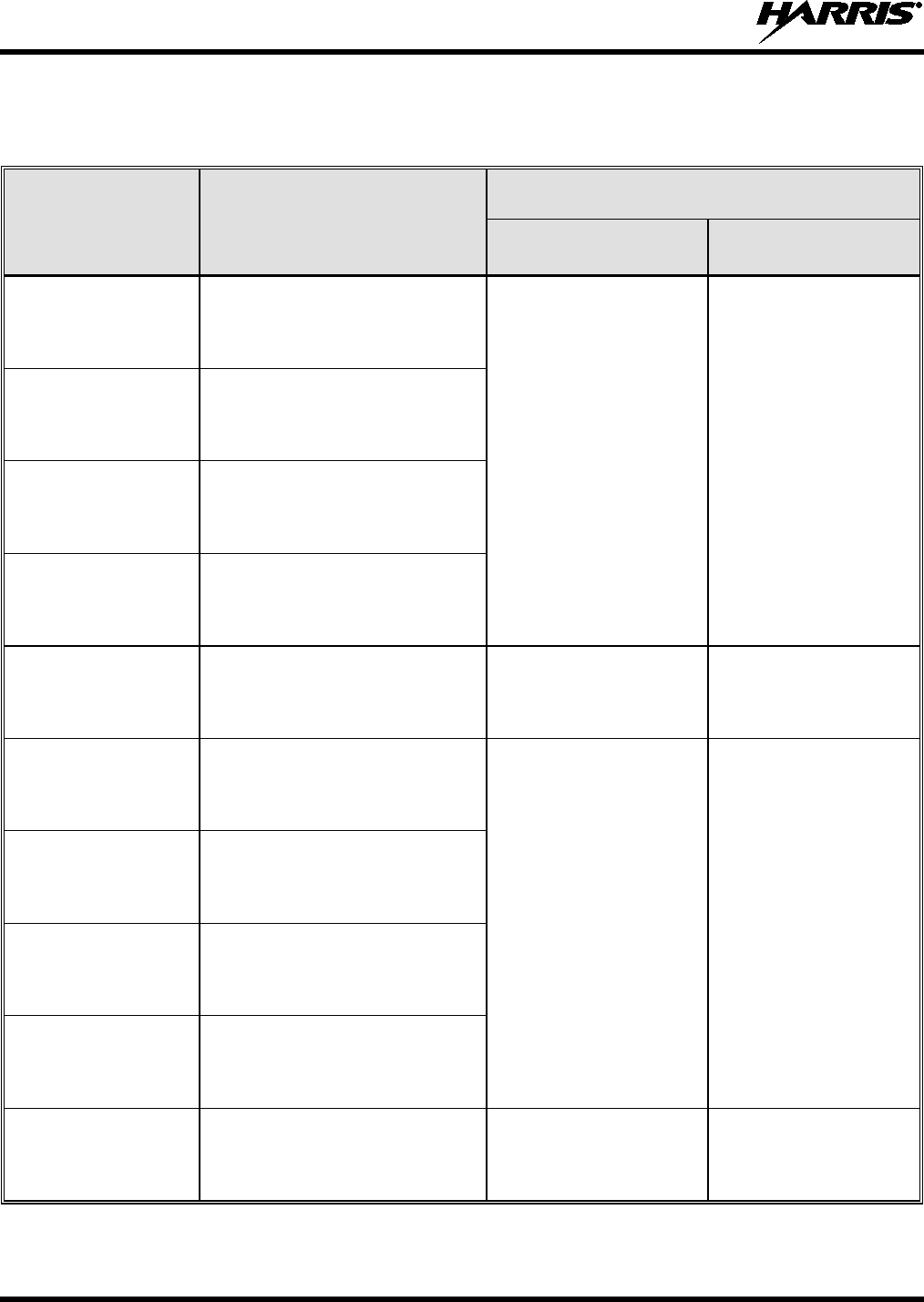
MM-018337-001, Rev. B
8
Table 1-1: Recommended Minimum Safe Lateral Distance
from Transmitting Antenna for Mobile Radio-to-Network Radio Link
(VRMS7010/VRMS7020 Transmit/Receive Antenna)
ANTENNA
PART NUMBER ANTENNA DESCRIPTION
RECOMMENDED MINIMUM LATERAL HUMAN BODY
DISTANCE FROM TRANSMITTING ANTENNA
CONTROLLED
ENVIRONMENT UNCONTROLLED
ENVIRONMENT
AN-125001-002
(mount) with
AN-225001-001
(element)
700/800 MHz Standard
Rooftop-Mount;
3 dBd Gain
9.8 Inches
(25 Centimeters) 21.7 Inches
(55 Centimeters)
AN-125001-002
(mount) with
AN-225001-002
(element)
700/800 MHz Standard
Rooftop-Mount;
Elevated-Feed 3 dBd Gain
AN-125001-002
(mount) with
AN-225001-003
(element)
700/800 MHz Standard
Rooftop-Mount;
Elevated-Feed, No Ground Plane
3 dBd Gain
AN-125001-002
(mount) with
AN-225001-004
(element)
700/800 MHz Standard
Rooftop-Mount;
Low-Profile 2 dBd Gain
AN-125001-002
(mount) with
AN-225001-005
(element)
700/800 MHz Standard
Rooftop-Mount;
5 dBd Gain
11.8 Inches
(30 Centimeters) 23.6 Inches
(60 Centimeters)
AN-125001-004
(mount) with
AN-225001-001
(element)
700/800 MHz Thick
Rooftop-Mount;
3 dBd Gain
9.8 Inches
(25 Centimeters) 21.7 Inches
(55 Centimeters)
AN-125001-004
(mount) with
AN-225001-002
(element)
700/800 MHz Thick
Rooftop-Mount;
Elevated-Feed 3 dBd Gain
AN-125001-004
(mount) with
AN-225001-003
(element)
700/800 MHz Thick
Rooftop-Mount;
Elevated-Feed, No Ground Plane
3 dBd Gain
AN-125001-004
(mount) with
AN-225001-004
(element)
700/800 MHz Thick
Rooftop-Mount;
Low-Profile 2 dBd Gain
AN-125001-004
(mount) with
AN-225001-005
(element)
700/800 MHz Thick
Rooftop-Mount;
5 dBd Gain
11.8 Inches
(30 Centimeters) 23.6 Inches
(60 Centimeters)
(Table Continued on Next Page)
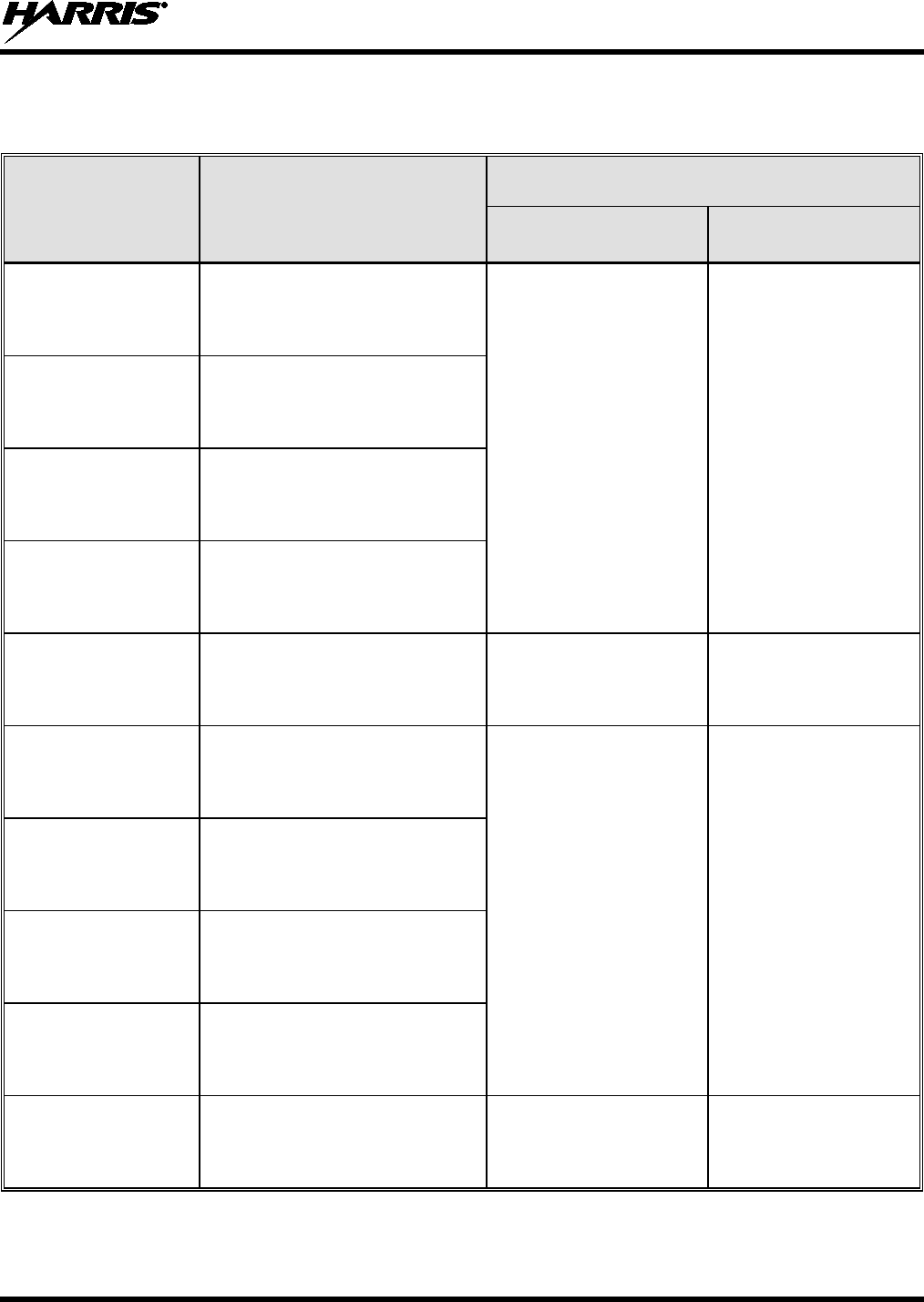
MM-018337-001, Rev. B
9
Table 1-1: Recommended Minimum Safe Lateral Distance
from Transmitting Antenna for Mobile Radio-to-Network Radio Link
(VRMS7010/VRMS7020 Transmit/Receive Antenna)
ANTENNA
PART NUMBER ANTENNA DESCRIPTION
RECOMMENDED MINIMUM LATERAL HUMAN BODY
DISTANCE FROM TRANSMITTING ANTENNA
CONTROLLED
ENVIRONMENT UNCONTROLLED
ENVIRONMENT
AN-125001-006
(mount) with
AN-225001-001
(element)
700/800 MHz GPS Combo
Rooftop-Mount;
3 dBd / 5.15 dBi Gain
9.8 Inches
(25 Centimeters) 21.7 Inches
(55 Centimeters)
AN-125001-006
(mount) with
AN-225001-002
(element)
700/800 MHz GPS Combo
Rooftop-Mount;
Elevated-Feed 3 dBd Gain
AN-125001-006
(mount) with
AN-225001-003
(element)
700/800 MHz GPS Combo
Rooftop-Mount;
Elevated-Feed, No Ground Plane
3 dBd Gain
AN-125001-006
(mount) with
AN-225001-004
(element)
700/800 MHz GPS Combo
Rooftop-Mount;
Low-Profile 2 dBd Gain
AN-125001-006
(mount) with
AN-225001-005
(element)
700/800 MHz GPS Combo
Rooftop-Mount;
5 dBd / 7.15 dBi Gain
11.8 Inches
(30 Centimeters) 23.6 Inches
(60 Centimeters)
AN-125001-008
(mount) with
AN-225001-001
(element)
700/800 MHz Magnetic-Mount;
3 dBd Gain
9.8 Inches
(25 Centimeters) 21.7 Inches
(55 Centimeters)
AN-125001-008
(mount) with
AN-225001-002
(element)
700/800 MHz Magnetic-Mount;
Elevated-Feed 3 dBd Gain
AN-125001-008
(mount) with
AN-225001-003
(element)
700/800 MHz Magnetic-Mount;
Elevated-Feed, No Ground Plane
3 dBd Gain
AN-125001-008
(mount) with
AN-225001-004
(element)
700/800 MHz Magnetic-Mount;
Low-Profile 2 dBd Gain
AN-125001-008
(mount) with
AN-225001-005
(element)
700/800 MHz Magnetic-Mount;
5 dBd Gain 11.8 Inches
(30 Centimeters) 23.6 Inches
(60 Centimeters)
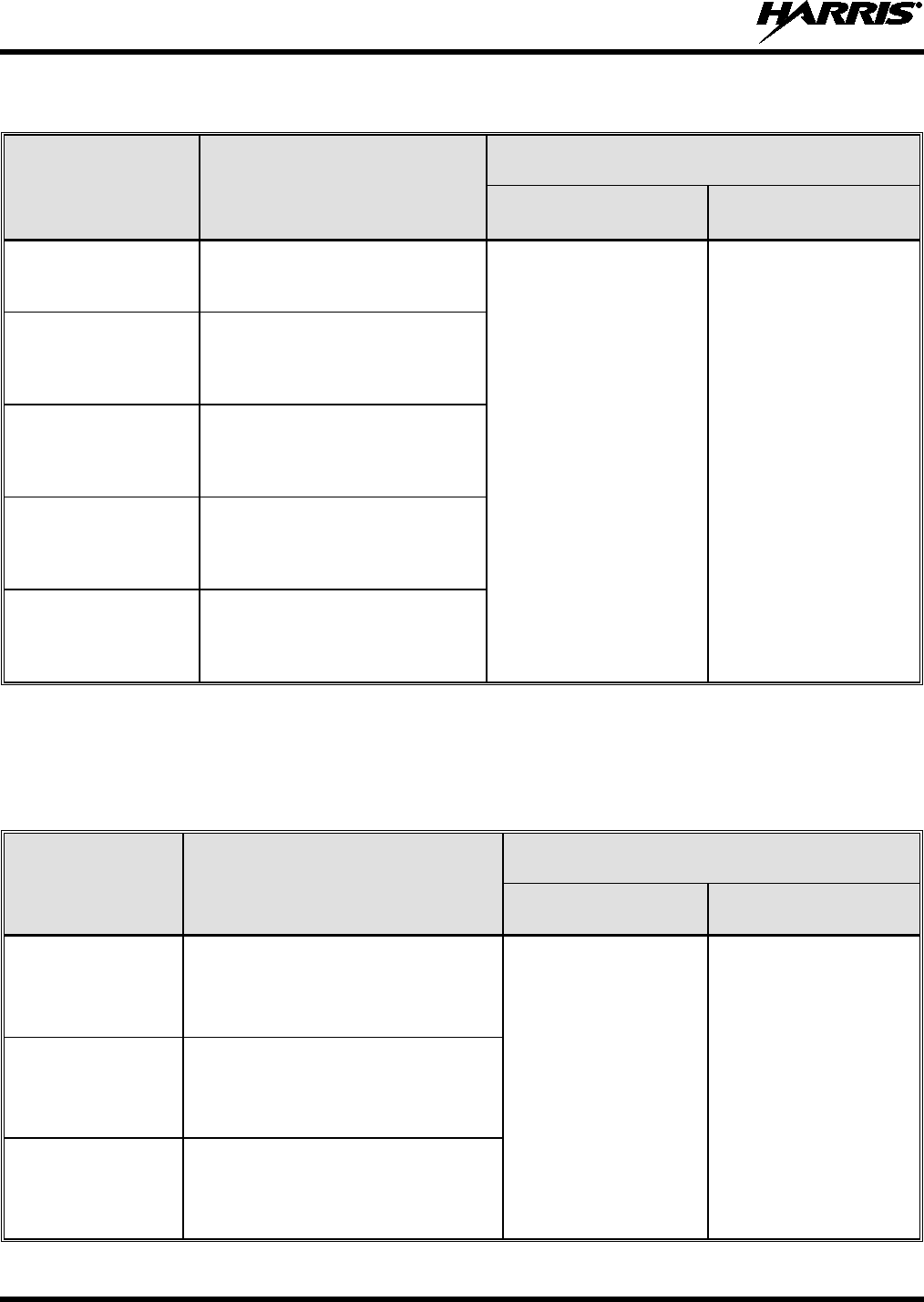
MM-018337-001, Rev. B
10
Table 1-2: Recommended Minimum Safe Lateral Distance from Transmitting Antenna for
Mobile Radio-to-Network Radio Link (VRMS7030 Transmit/Receive Antenna)
ANTENNA
PART NUMBER ANTENNA DESCRIPTION
RECOMMENDED MINIMUM LATERAL HUMAN BODY
DISTANCE FROM TRANSMITTING ANTENNA
CONTROLLED
ENVIRONMENT UNCONTROLLED
ENVIRONMENT
AN102800V1 136 to 941 MHz, ¼-Wavelength*,
Standard Rooftop-Mount;
0 dBd Gain
24.8 Inches
(63 Centimeters) 55.1 Inches
(140 Centimeters)
AN-125001-001
(mount) with
AN-225002-001
(element)
136 to 174 MHz,
Standard Rooftop-Mount;
0 dBd Gain
AN-125001-003
(mount) with
AN-225002-001
(element)
136 to 174 MHz,
Thick Rooftop-Mount;
0 dBd Gain
AN-125001-003
(mount) with
AN-225006-001
(element)
132 to 960 MHz,*
Thick Rooftop-Mount;
0 dBd Gain
AN-125001-007
(mount) with
AN-225002-001
(element)
136 to 174 MHz,
Magnetic-Mount;
0 dBd Gain
* Driven elements of AN102800V1 and AN-225006-001 must be trimmed to proper lengths in order to minimize
antenna system VSWR.
Table 1-3: Recommended Minimum Safe Lateral Distance from Transmitting Antenna for
Vehicular Repeater-to-P25 Radio Link (VRBS7010/VRBS7020/VRBS7030 Transmit/Receive Antenna)
ANTENNA
PART NUMBER ANTENNA DESCRIPTION
RECOMMENDED MINIMUM LATERAL HUMAN
BODY DISTANCE FROM TRANSMITTING ANTENNA
CONTROLLED
ENVIRONMENT UNCONTROLLED
ENVIRONMENT
AN-125001-002
(mount) with
AN-225001-004
(element)
Standard Rooftop-Mount with
Low-Loss Cable and 700/800 MHz
Low-Profile 2 dBd Gain Element
7.9 Inches
(20 Centimeters) 7.9 Inches
(20 Centimeters)
AN-125001-004
(mount) with
AN-225001-004
(element)
Thick Rooftop-Mount with Low-
Loss Cable and 700/800 MHz
Low-Profile 2 dBd Gain Element
AN-125001-008
(mount) with
AN-225001-004
(element)
Magnetic-Mount with Low-Loss
Cable and 700/800 MHz
Low-Profile 2 dBd Gain Element
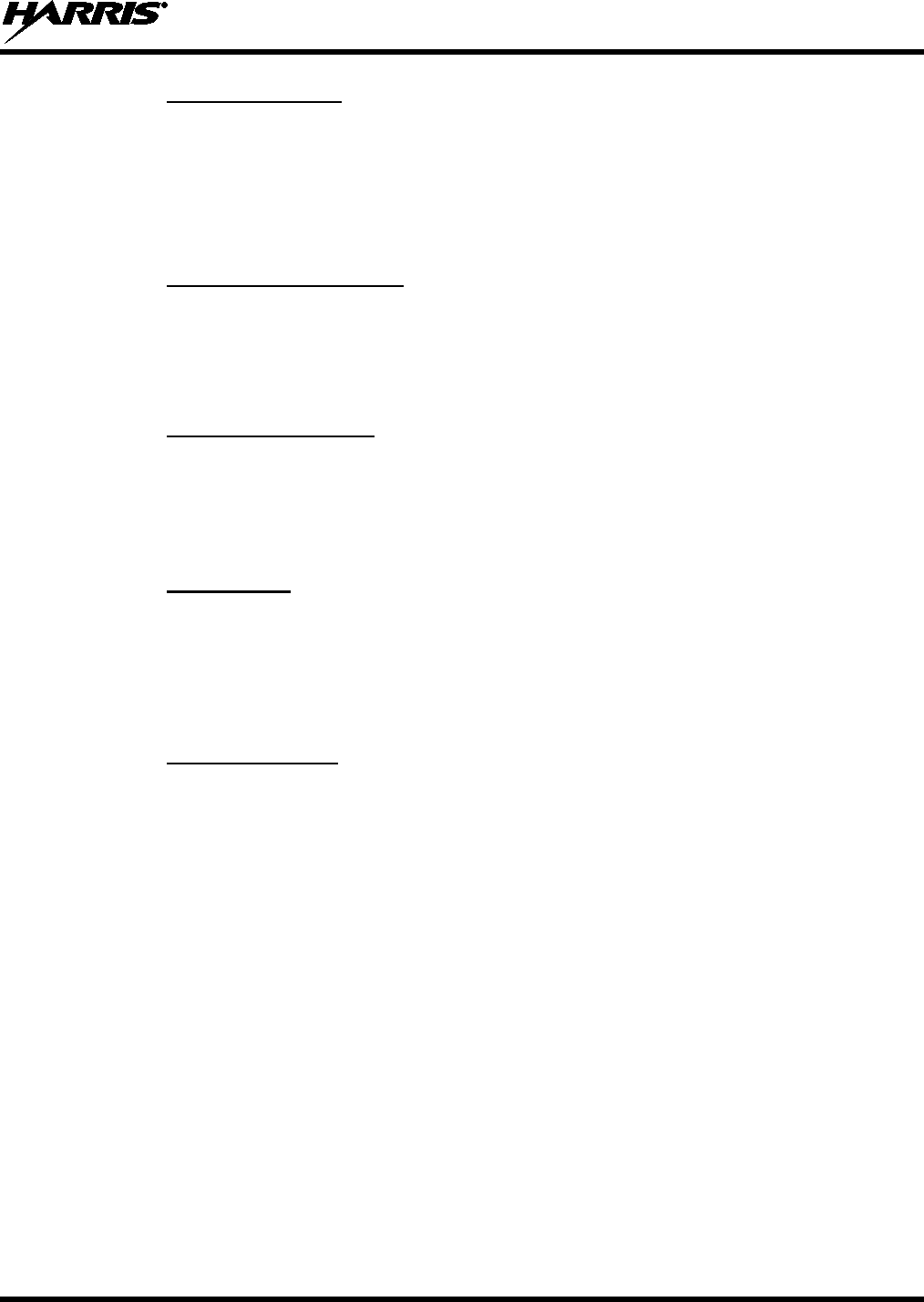
MM-018337-001, Rev. B
11
1.3.1 Mobile Antennas
The antenna(s) for the radios must be installed in accordance with Section 7 in this manual. Installation
guidelines presented in Section 7 are limited to metal-body motor vehicles or vehicles with appropriate
ground planes.
Use only the Harris-approved/supplied antenna(s) or an approved replacement antenna. Unauthorized
antennas, modifications, or attachments can cause the FCC RF exposure limits to be exceeded.
1.3.2 Approved Accessories
The radio has been tested and meets FCC RF guidelines when used with accessories supplied or
designated for use with it. Use of other accessories may not ensure compliance with the FCC’s RF
exposure guidelines, and may violate FCC regulations. For a list of approved accessories refer to Section
4 in this manual (begins on page 22) and/or the Products and Services Catalog.
1.3.3 Contact Information
For additional information on RF exposure and other information, contact Harris using one of the contact
links listed in Section 3.7 on page 21.
1.4 RADIO FREQUENCY INTERFERENCE
1.4.1 FCC Part 15
This device complies with Part 15 of the FCC Rules. Operation is subject to the following two conditions:
1. This device may not cause harmful interference, and
2. This device must accept any interference received, including interference that may cause undesired
operation.
1.4.2 Industry Canada
This device complies with Industry Canada license-exempt RSS standard(s). Operation is subject to the
following two conditions: (1) this device may not cause interference, and (2) this device must accept any
interference, including interference that may cause undesired operation of the device.
Le présent appareil est conforme aux CNR d'Industrie Canada applicables aux appareils radio exempts de
licence. L'exploitation est autorisée aux deux conditions suivantes : (1) l'appareil ne doit pas produire de
brouillage, et (2) l'utilisateur de l'appareil doit accepter tout brouillage radioélectrique subi, même si le
brouillage est susceptible d'en compromettre le fonctionnement.
1.5 OCCUPATIONAL SAFETY GUIDELINES AND SAFETY TRAINING
INFORMATION
To ensure bodily exposure to RF electromagnetic energy is within the FCC allowable limits for
occupational use. Always adhere to the following basic guidelines:
• The push-to-talk button should only be depressed when intending to send a voice message.
• The radio should only be used for necessary work-related communications.
• The radio should only be used by authorized and trained personnel. It should never be operated by
children.
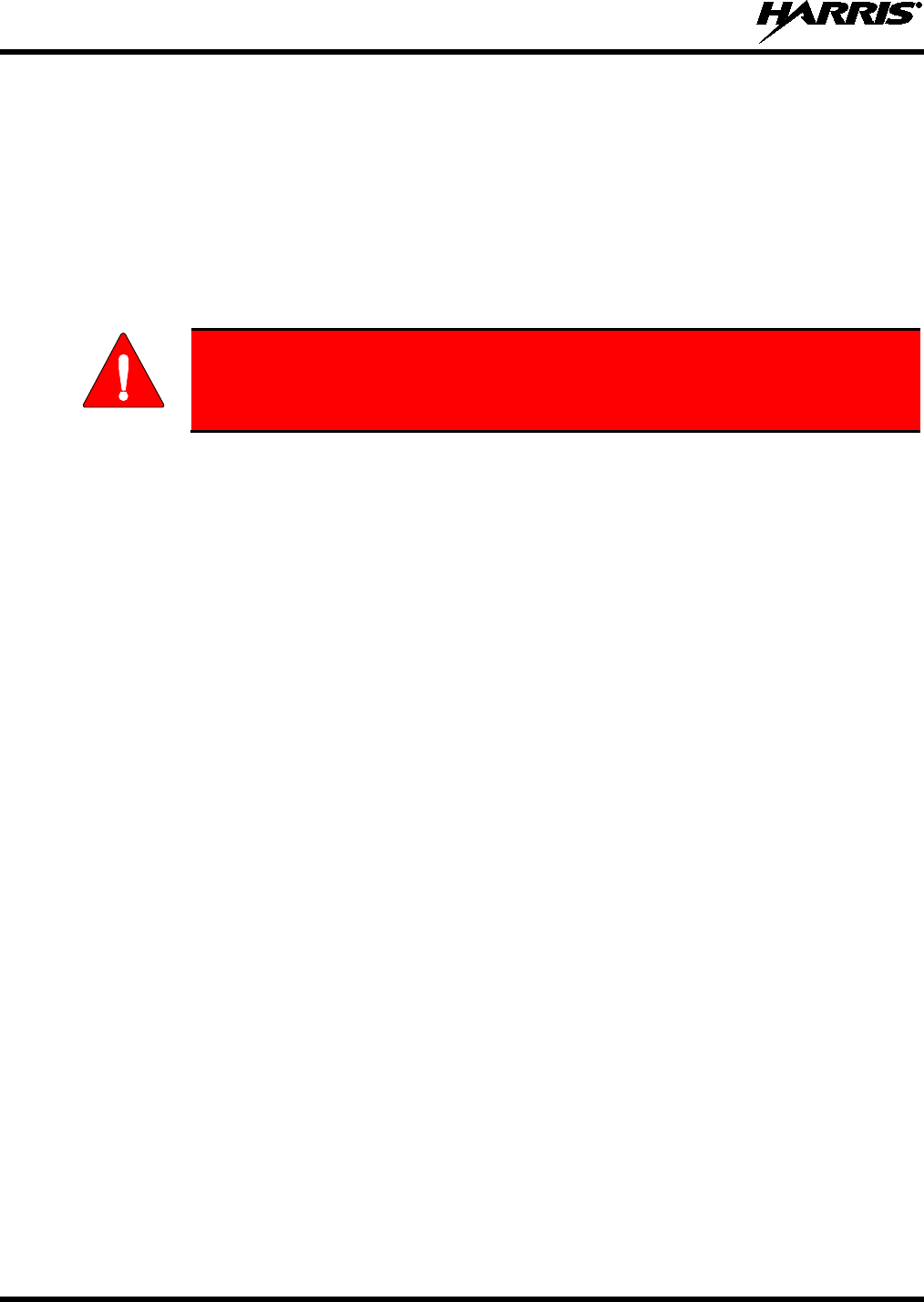
MM-018337-001, Rev. B
12
• Do not attempt any unauthorized modification to the radio. Changes or modifications to the radio may
cause harmful interference and/or cause it to exceed FCC RF exposure limits. Only qualified
personnel should service the radio.
• Always use only Harris-authorized accessories (antennas, control heads, speakers/mics, etc.). Use of
unauthorized accessories can cause the FCC RF exposure compliance requirements to be exceeded.
The information listed above provides the user with information needed to make him or her aware of a RF
exposure, and what to do to assure that this radio operates within the FCC exposure limits of this radio.
1.6 COMMON HAZARDS
WARNING
The operator of any mobile radio should be aware of certain hazards common to
the operation of vehicular radio transmissions. Possible hazards include but are
not limited to:
• Explosive Atmospheres — Just as it is dangerous to fuel a vehicle with its engine running, be sure to
turn the radio OFF while fuelling the vehicle. If the radio is mounted in the trunk of the vehicle, DO
NOT carry containers of fuel in the trunk.
Areas with potentially explosive atmosphere are often, but not always, clearly marked. Turn the radio
OFF when in any area with a potentially explosive atmosphere. It is rare, but not impossible that the
radio or its accessories could generate sparks.
• Interference To Vehicular Electronic Systems — Electronic fuel injection systems, electronic anti-
skid braking systems, electronic cruise control systems, etc., are typical of the types of electronic
devices that can malfunction due to the lack of protection from radio frequency (RF) energy present
when transmitting. If the vehicle contains such equipment, consult the dealer for the make of vehicle
and enlist his aid in determining if such electronic circuits perform normally when the radio is
transmitting.
• Electric Blasting Caps — To prevent accidental detonation of electric blasting caps, DO NOT use
two-way radios within 1000 feet (305 meters) of blasting operations. Always obey the “Turn Off
Two-Way Radios” (or equivalent) signs posted where electric blasting caps are being used. (OSHA
Standard: 1926.900).
• Radio Frequency Energy — To prevent burns or related physical injury from radio frequency
energy, do not operate the transmitter when anyone outside of the vehicle is within the minimum safe
distance from the antenna as specified in Table 1-1/Table 1-2 and Table 1-3. Refer to Section 1.2 for
additional information.
• Vehicles Powered By Liquefied Petroleum (LP) Gas — Radio installation in vehicles powered by
liquefied petroleum gas, where the LP gas container is located in the trunk or other sealed-off space
within the interior of the vehicle, must conform to the National Fire Protection Association standard
NFPA 58. This requires:
The space containing the radio equipment must be isolated and sealed from the space containing
the LP gas container and its fittings.
Outside filling connections must be used for the LP gas container.
The LP gas container space shall be vented to the outside of the vehicle.
• Vehicles Equipped with Airbags — For driver and passenger safety, avoid mounting the radio’s
control head (or any other component) above or near airbag deployment areas. In addition to driver-
side and passenger-side front-impact airbags, some vehicles may also be equipped with side-impact

MM-018337-001, Rev. B
13
airbags. For occupant safety, verify the location of all airbags within the vehicle before installing the
radio equipment.
1.7 SAFE DRIVING RECOMMENDATIONS
The American Automobile Association (AAA) advocates the following key safe driving recommenda-
tions:
• Read the literature on the safe operation of the radio.
• Keep both hands on the steering wheel and the microphone in its hanger whenever the vehicle is in
motion.
• Place calls only when the vehicle is stopped.
• When talking from a moving vehicle is unavoidable, drive in the slower lane. Keep conversations
brief.
• If a conversation requires taking notes or complex thought, stop the vehicle in a safe place and
continue the call.
• Whenever using a mobile radio, exercise caution.
1.8 OPERATING RULES REGULATIONS
Two-way radio systems must be operated in accordance with the rules and regulations of the local,
regional, or national government.
In the United States, this vehicular repeater system must be operated in accordance with the rules and
regulations of the Federal Communications Commission (FCC). Operators of two-way radio equipment,
must be thoroughly familiar with the rules that apply to the particular type of radio operation. Following
these rules helps eliminate confusion, assures the most efficient use of the existing radio channels, and
results in a smoothly functioning radio network.
When using a two-way radio, remember these rules:
• It is a violation of FCC rules to interrupt any distress or emergency message. The radio operates in
much the same way as a telephone “party line.” Therefore, always listen to make sure the channel is
clear before transmitting. Emergency calls have priority over all other messages. If someone is
sending an emergency message – such as reporting a fire or asking for help in an accident, do not
transmit unless assistance can be offered.
• The use of profane or obscene language is prohibited by Federal law.
• It is against the law to send false call letters or false distress or emergency messages. The FCC
requires keeping conversations brief and confined to business. Use coded messages whenever
possible to save on-the-air time.
• Using the radio to send personal messages (except in an emergency) is a violation of FCC rules. Send
only essential messages.
• It is against Federal law to repeat or otherwise make known anything overheard on the radio.
Conversations between others sharing the channel must be regarded as confidential.
• The FCC requires self-identification at certain specific times by means of call letters. Refer to the
rules that apply to the particular type of operation for the proper procedure.
• No changes or adjustments shall be made to the equipment except by an authorized or certified
electronics technician.
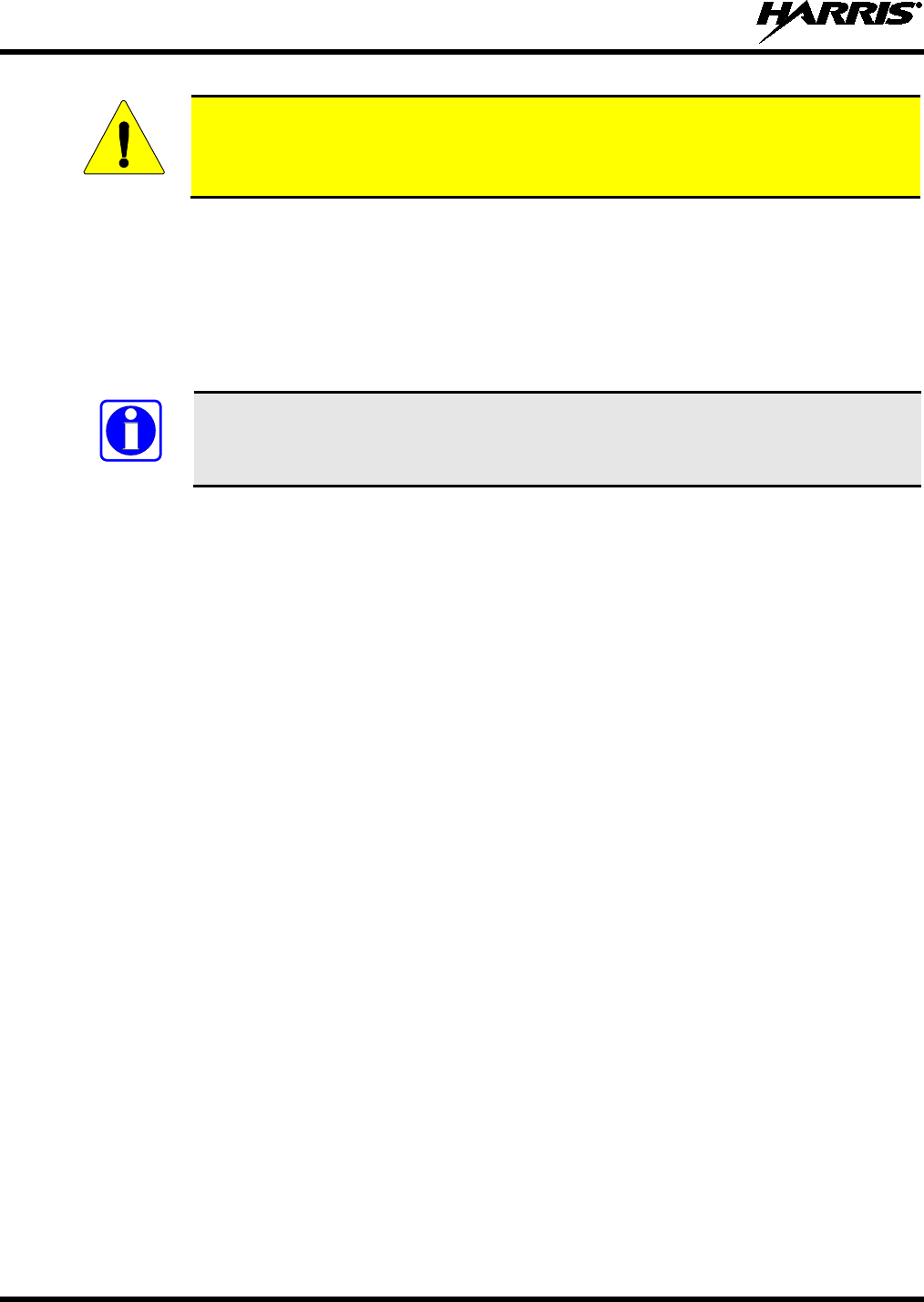
MM-018337-001, Rev. B
14
CAUTION
Under U.S. law, operation of an unlicensed radio transmitter within the jurisdiction of
the United States may be punishable by a fine of up to $10,000, imprisonment for up to
two (2) years, or both.
1.9 OPERATING TIPS
The following conditions tend to reduce the effective range of two-way radios and should be avoided
whenever possible:
• Operating the radio in areas of low terrain, or while under power lines or bridges.
• Obstructions such as mountains and buildings.
NOTE
In areas where transmission or reception is poor, communication improvement may
sometimes be obtained by moving a few yards in another direction, or moving to a
higher elevation.
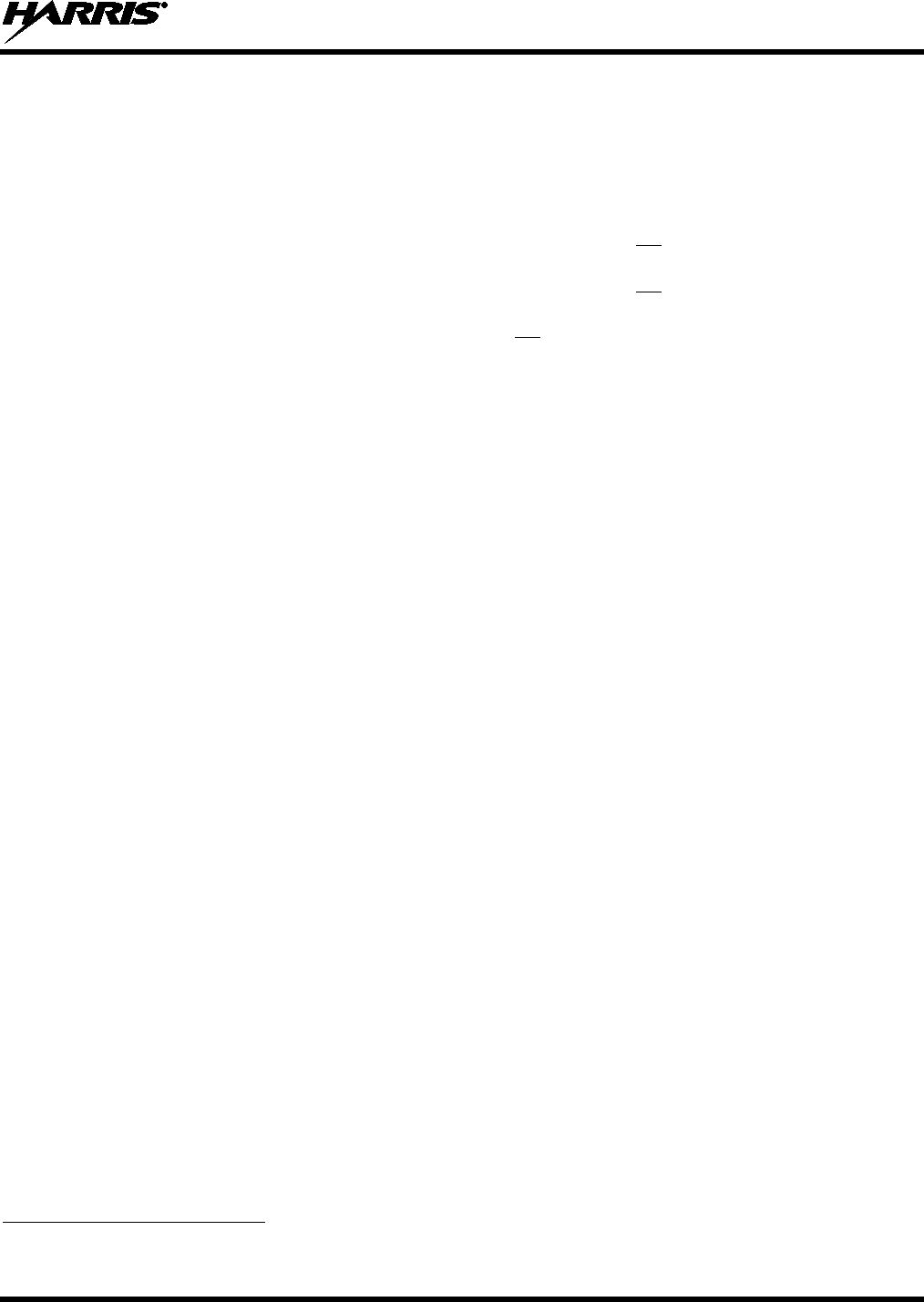
MM-018337-001, Rev. B
15
2 SPECIFICATIONS1
2.1 GENERAL
Dimensions (Height x Width x Depth):
VRMS7010/VRMS7020/VRMS7030: 5.2 x 8.8 x 9.3 inches (13.2 x 22.4 x 23.6 centimeters)
(Includes bracket but not space required for cables)
VRBS7010/VRBS7020/VRBS7030: 7.3 x 8.8 x 9.3 inches (18.5 x 22.4 x 23.6 centimeters)
(Includes bracket but not space required for cables)
Control Head: 2.4 x 6.9 x 3.9 inches (6 x 17.5 x 10 centimeters)
(Does not include bracket and mounting screws)
Weights
VRMS7010/VRMS7020/VRMS7030: 13.6 pounds (6.17 kilograms), less mounting bracket
VRBS7010/VRBS7020/VRBS7030: 13.6 pounds (6.17 kilograms), less mounting bracket
Control Head: 1.25 pounds (0.57 kilograms), less mounting bracket
Mounting Brackets: 1.25 pounds (0.57 kilograms) each
Cable, Interface: 1.25 pounds (0.57 kilograms)
Operating Ambient Temperature Range: -22 to +140° Fahrenheit (-30 to +60° Celsius)
Storage Temperature Range: -40 to +185° Fahrenheit (-40 to +85° Celsius)
Altitude
Operating: 15,000 feet (4572 meters) maximum
Storage/Shipment: 50,000 feet (15,240 meters) maximum
DC Supply Voltage Operating Range
For Full Performance: +13.6 Vdc ±10% (Normal range per TIA-603)
Overall Operating Range: +10.8 to +16.6 Vdc
Continuous without Damage: 0 to +17 Vdc
DC Supply Current, VRS7010/VRS7020/VRS7030
VRMS7010/VRMS7020/VRMS7030
Receive: 1.1 amps maximum
Transmit at 15 Watts Tx Power: 8 amps maximum, 6 amps typical
Transmit at 35 Watts Tx Power: 15 amps maximum, 12 amps typical
Quiescent/Off Current: 2 milliamps maximum
VRBS7010/VRBS7020/VRBS7030
P25 Vehicular Repeater Mode Disabled: 5 milliamps maximum, 2 milliamps typical
P25 Vehicular Repeater Mode Enabled: 6 amps maximum, 5 amps typical
Quiescent/Off Current: 5 milliamps maximum, 2 milliamps typical
DC Supply Current, CH-721 Control Head
With ½-Watt Speaker Output Power: 0.9 amps maximum
With 10-Watts Speaker Output Power: 2.0 amps maximum
With 15-Watts Speaker Output Power: 2.4 amps maximum
Standby Current (Muted): 0.6 amps maximum
Quiescent/Off Current: 100 microamps maximum
1 These specifications are primarily intended for the use of the installation technician. See the appropriate Specifications
Sheet for the complete specifications.
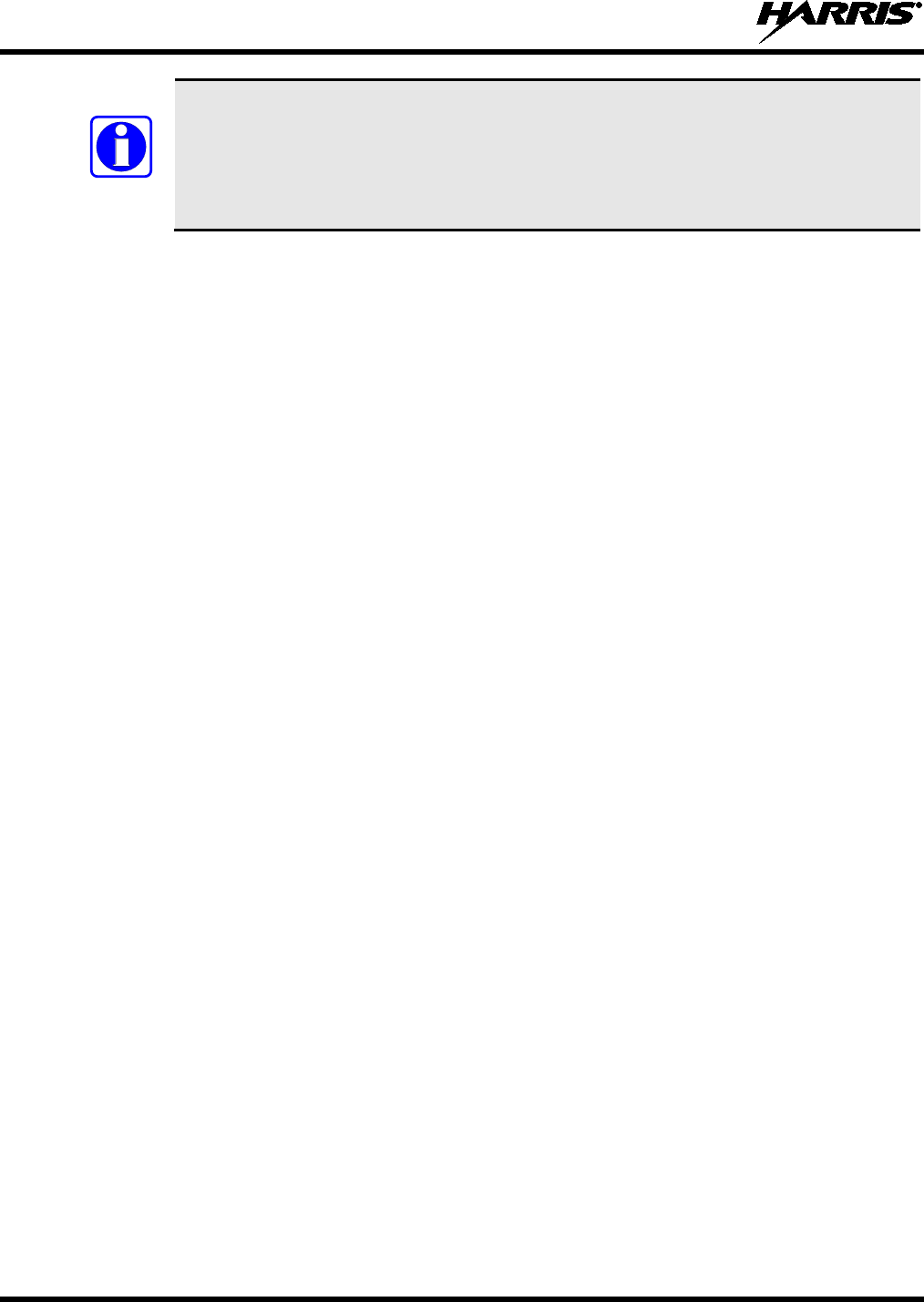
MM-018337-001, Rev. B
16
NOTE
For detailed transceiver-related specifications on the VRMS section of the vehicular
repeater
, refer to the M7300 mobile radio’s installation or maintenance manuals,
publications MM-014763-001 or MM-014718-001 respectively.
For detailed transceiver-related specifications on the VRBS
section of the vehicular
repeater, refer to the products maintenance manual, publication MM-018338-001.
2.2 REGULATORY
FCC Identification Numbers:
VRMS7010 and VRMS7020
(700/800 MHz M7300): OWDTR-0051-E
VRMS7030 (VHF M7300): OWDTR-0055-E
VRBS7010/VRBS7020/VRBS7030: OWDTR-0058-E
Applicable FCC Rules: Part 90 and Part 15
Industry Canada Certifications:
VRMS7010 and VRMS7020
(700/800 MHz M7300): 3636B-0051
VRMS7030 (VHF M7300): 3636B-0055
VRBS7010/VRBS7020/VRBS7030: 3636B-0058
Applicable Industry Canada Rules: RSS-119
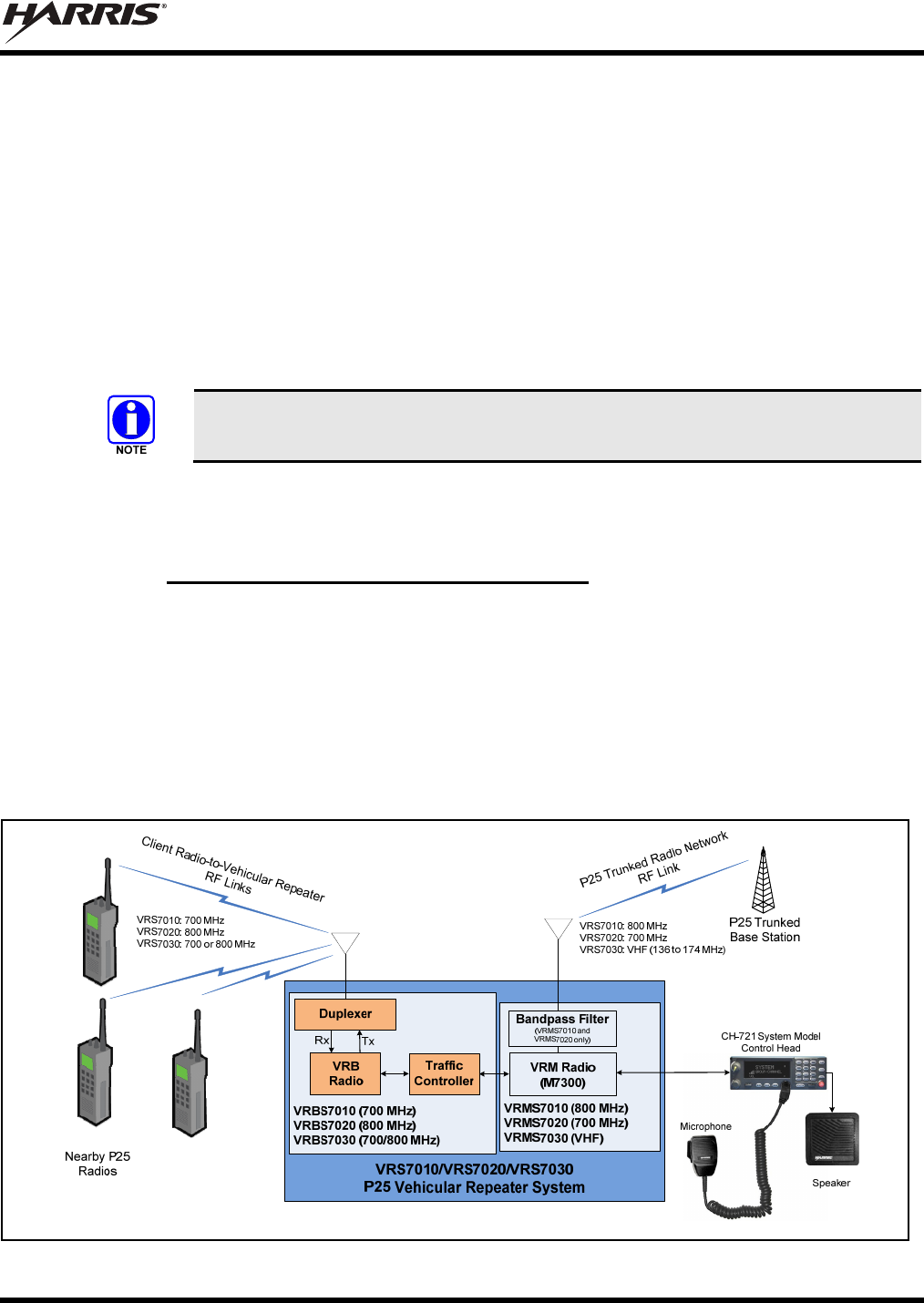
MM-018337-001, Rev. B
17
3 INTRODUCTION
This manual contains product safety and installation-related procedures for the VRS7000 series of
Project 25 (P25) cross-band Vehicular Repeater Systems, together with the CH-721 control head.
Installation procedures cover the mounting and cabling of the equipment, as well as the basic testing of
the mobile radio and control head. An interconnection wiring diagram is included at the rear of this
manual. Important product safety-related information is presented in Section 1.
3.1 GENERAL INFORMATION
The VRS7000 series of P25 cross-band vehicular repeaters includes the three (3) distinctly different P25
Vehicular Repeater Systems: the VRS7010, the VRS7020, and the VRS7030. Each repeater has different
radio frequency bands upon which it operates on. The RF bands are included in Figure 3-1 below.
Henceforth, any reference of “VRS7000” or simply (“VRS”) in this manual applies to
all three (3) P25 vehicular repeater systems, unless otherwise stated.
Each vehicular repeater is a P25 cross-band vehicular repeater for P25 trunked radio networks and a
mobile radio for trunked and conventional radio networks. Each repeater consists of two (2) systems, as
described in the following subsections.
3.1.1 Vehicular Repeater Base System (VRBS)
The system that provides the RF link for nearby P25 radios when the VRS7000 is operating as a P25
vehicular repeater is called the Vehicular Repeater Base System (VRBS). As illustrated in Figure 5-2 on
page 30, the VRBS is formed by a Vehicular Repeater Base (VRB) radio, a Traffic Controller module,
and a duplexer. The VRB radio is the transceiver for the RF link to nearby P25 radios. See Figure 3-1
below. The Traffic Controller section interfaces the VRB radio to the VRM radio. The duplexer allows
the VRB radio to transmit and receive via a single vehicle-mounted antenna.
Within the VRS7010 P25 vehicular repeater, the VRBS is called the VRBS7010. It consists of a dual-
band 700/800 MHz VRB radio that operates in the 700 MHz band, a Traffic Controller, and a 700 MHz
Figure 3-1: Simplified Block Diagram of Extended Network Coverage Mode
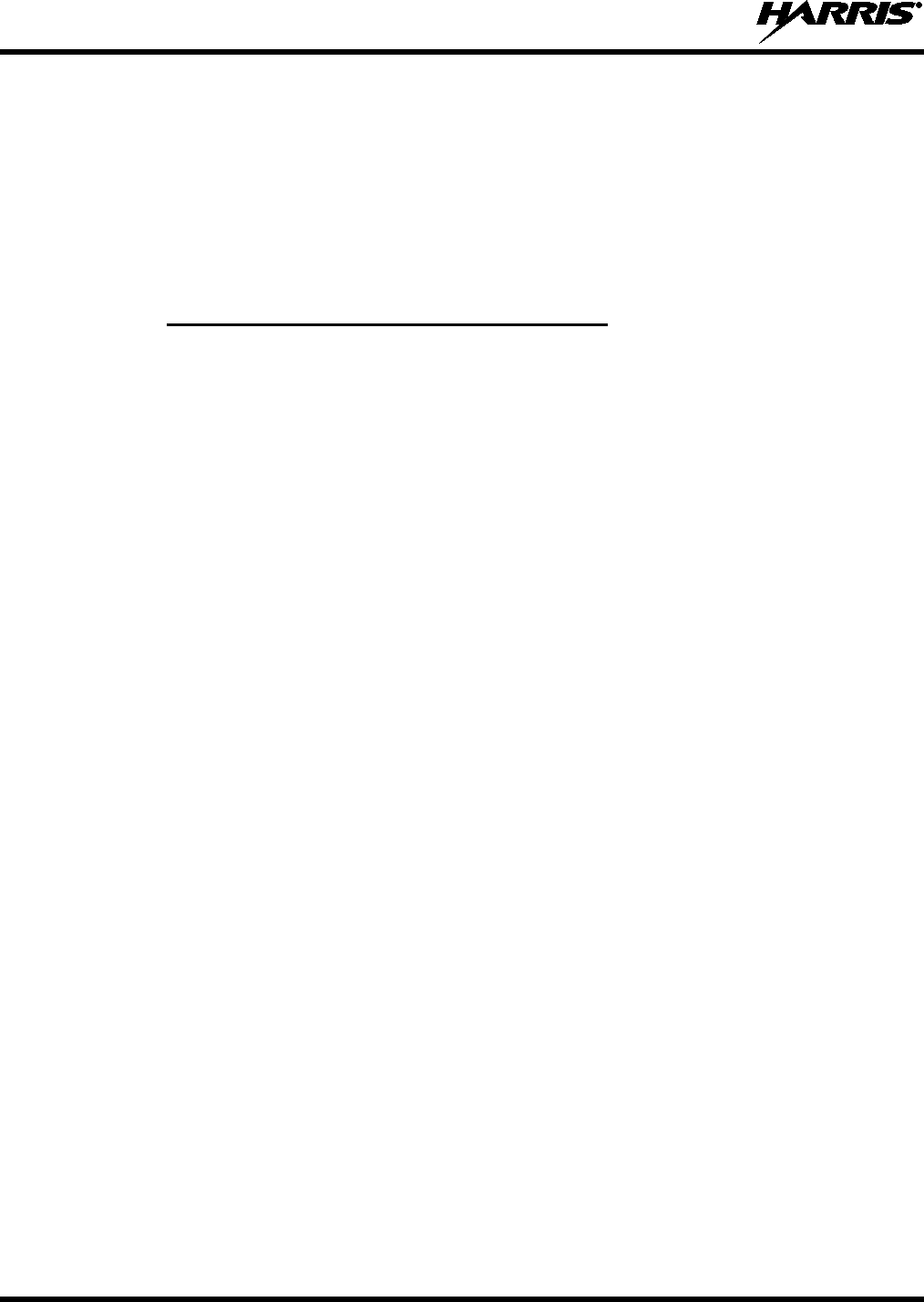
MM-018337-001, Rev. B
18
duplexer. This combination supports the 700 MHz link to portables radios connected to the VRS7010.
Within the VRS7020 P25 vehicular repeater, the VRBS is called the VRBS7020. It consists of a dual-
band 700/800 MHz VRB radio that operates in the 800 MHz band, a Traffic Controller, and an 800 MHz
duplexer. This combination supports the 800 MHz link to portables radios connected to the VRS7020.
Within the VRS7030 P25 vehicular repeater, the VRBS is called the VRBS7030. It consists of a dual-
band 700/800 MHz VRB radio that can operate on either RF band, a Traffic Controller, and a wide-band
700/800 MHz duplexer. This combination supports a 700 MHz or an 800 MHz link to the portables radios
connected to the VRS7030.
3.1.2 Vehicular Repeater Mobile System (VRMS)
The system that provides access to a P25 network is called the Vehicular Repeater Mobile System
(VRMS). The VRMS consists of a remote-mount M7300 mobile radio and a bandpass filter. The M7300
is the Vehicular Repeater Mobile (VRM) radio within the VRMS. The bandpass filter is in series with the
M7300 radio’s antenna port and the vehicle-mounted antenna. This combination provides connectivity to
a trunked or conventional radio network. The M7300 mobile radio (VRM) is a dual-band 700 and
800 MHz mobile radio; however, in this application, only one of the two bands is utilized within a given
VRMS. The VRMS7010/VRMS7020/VRMS7030 is shown in Figure 5-1 on page 29.
Within the VRS7010 vehicular repeater, the VRMS7010’s bandpass filter is an 800 MHz bandpass filter.
Together with the VRM radio, this filter supports the RF link to an 800 MHz P25 trunked radio network.
Within the VRS7020 vehicular repeater, the VRMS7020’s bandpass filter is a 700 MHz bandpass filter.
Together with the VRM radio, this filter supports the RF link to a 700 MHz P25 trunked radio network.
Within the VRS7030 vehicular repeater, the VRMS7030’s bandpass filter is a dual-band 700/800 MHz
bandpass filter. Together with the VRM radio, this filter supports the RF link to a 700 MHz or to an
800 MHz P25 trunked radio network.
When operating as a P25 vehicular repeater, the VRS7000 provides an end-to-end P25 communication
link between nearby P25 trunked radios and a P25 trunked radio network. The VRS7000’s network
extension enables nearby P25 radios to maintain radio communications on a P25 radio network. In this
mode, normal mobile radio communications cannot be accomplished from the radio’s control head. The
radio’s microphone is disabled when it is operating in the P25 vehicular repeater mode.
When it is operating as a mobile radio (i.e., P25 vehicular repeater mode disabled), the VRS7000 supports
communications on P25 trunked and P25 conventional radio systems. As such, the VRS7000’s vehicular
repeater functionality is not available. When the VRS is operating as a mobile radio, the VRBS is
completely powered off and disabled and the VRMS provides half-duplex voice and data
communications. Voice communications are accomplished via the “push-to-talk” (PTT) type microphone
and the speaker connected to the control head.
Installation requires two (2) vehicle-mounted mobile antennas. One combination (“combo”) type mobile
antenna is typically used for the VRMS and its built-in GPS receiver, and another vehicle-mounted
mobile antenna is required for the VRBS. If the VRMS is not connected to a combo-type antenna (i.e., if
the GPS receiver antenna is not integrated into the VRMS transmit/receive antenna) and the VRMS is
equipped with a GPS receiver option, a third vehicle-mounted antenna is required for the GPS receiver
within the VRMS. Antenna installation procedures are included in Section 7 of this manual. A wiring
diagram is shown at the end of this manual.
The radio installation also includes a CH-721 System model control head with a microphone and a
speaker. This equipment provides the interface for the radio’s operator/user. Mounting and installation
accessories complete the mobile radio equipment package. Additional control head information is
included in Section 3.3, and control head installation procedures are included in Section 10 of this
manual.
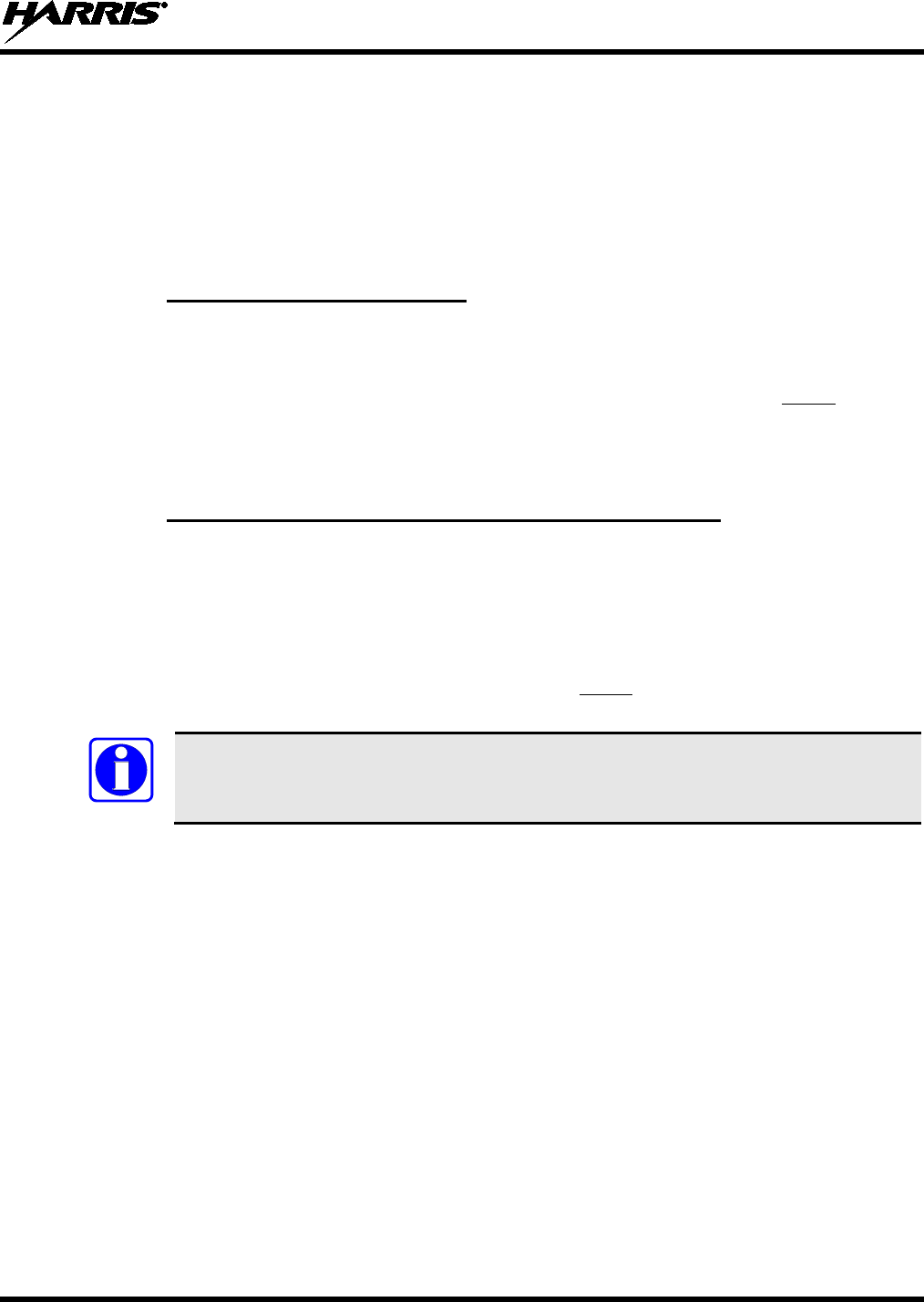
MM-018337-001, Rev. B
19
This radio equipment exceeds many tough environmental specifications included within military standard
MIL-STD-810F, automotive industry standard SAE-J1455, the radio industry standard TIA/EIA-603, and
the radio standard established by the U.S. Forest Service.
3.2 OPERATING MODES
The VRS7000 vehicular repeater with mobile radio has two (2) primary operating modes as described in
the following subsections:
3.2.1 Standard Mobile Radio Mode
When the VRS7000 is operating in the standard mobile radio mode, it functions like a normal mobile
radio. The radio operator uses the interfaces of the connected CH-721 control head (i.e., display, control
buttons/keys, mic and speaker) to control the radio and to communicate with other radio users and
console dispatchers on a trunked or conventional radio network. Nearby P25 radios cannot be linked
through the VRS7000 to the radio network when the VRS7000 is operating in this mode. The VRS7000’s
vehicular repeater functionality is disabled when it is in this operating mode. The VRBS is completely
powered off and disabled.
3.2.2 Extended Coverage (XCOV) Vehicular Repeater Mode
When the VRS7000 is operating in the extended coverage vehicular repeater mode, it provides the
network extension interface that enables nearby P25 radios to access the P25 radio network through the
VRS7000. This mode’s name is typically abbreviated “XCOV vehicular repeater mode,” “XCOV mode”
or simply “VR mode.” Radio coverage for nearby P25 radios is extended because VRS7000’s high-
performance mobile antenna system and higher transmitter output power used to access the P25 network.
See Figure 3-1. When a nearby P25 radio is communicating through the VRS7000, it is considered
“connected” to and a “client” on the VRS7000. The VRS7000 cannot function as a standard mobile radio
when it is operating in this mode.
NOTE
Detailed operating procedures are included in the VRS7000
’s Operator’s Manual,
publication MM-018336-001. See Section 3.5 for additional information.
Typically, the VRS7000 operator places the radio into this mode via a menu selection or preset button
press at the installation’s CH-721 control head. Likewise, the operator can disable this mode via a
CH-721 control head menu selection or preset button press. Alternately, the radio installation may be
wired so this mode can be enabled and disabled by an external switch.
When the VRS7000 is operating in this mode, its VRBS functions like a Voice and Data Over Control
(VDOC) site for the nearby P25 radios. Essentially, the connected P25 radios and the VRBS are linked
together via P25 VDOC protocols on the VRBS RF channel.
When using the XCOV vehicular repeater mode, P25 radios operating through the VRS7000 maintain the
following P25 functions across the two RF links:
• P25 Group Call — Both digital clear voice and digital encrypted voice group calls are supported.
• P25 Individual Call — Unit-to-unit calls between two connected P25 radios, and between a nearby
P25 radio and a radio/console on the P25 radio network are supported.
• P25 User ID — Caller identification information is sent between a connected P25 radio and the P25
radio network.
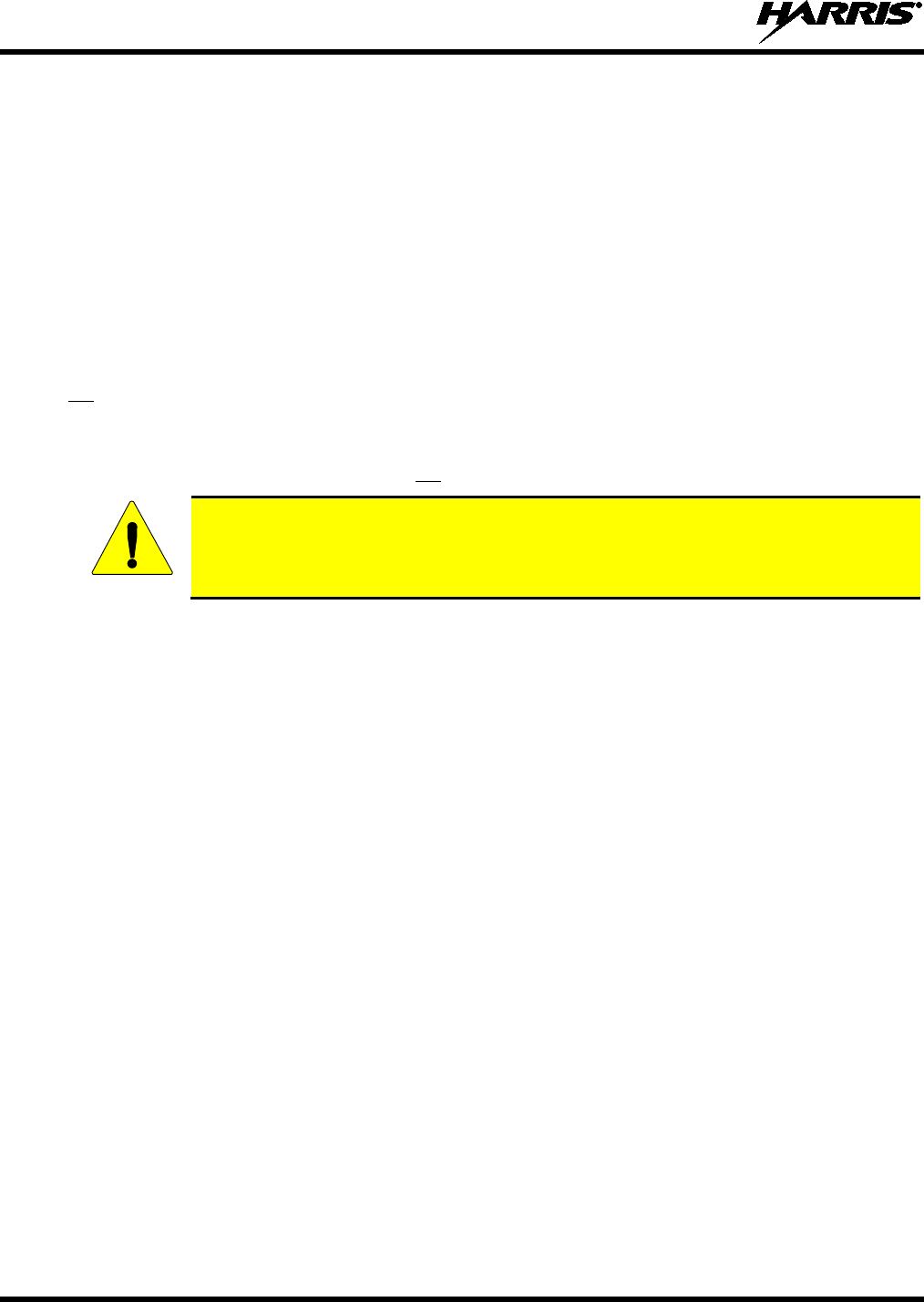
MM-018337-001, Rev. B
20
• P25 Emergency — The link through the VRS7000 provides P25 emergency communications
between the P25 radios connected to the VRS7000 and the P25 radio network.
• P25 System All Call (from Network Only) — A system-wide all-call transmission from the P25
radio network is forwarded to P25 radios connected to the VRS7000.
• Call Grant and Call Queued Tones — A P25 client radio generates call grant and call queued tones
in a similar manner as if it is operating directly on the P25 radio network.
A single VRS7000 allows attachment of up to sixty-four (64) nearby P25 radios. Each radio may
communicate on the same talk group, or on multiple different talk groups (up to sixty-four maximum talk
groups for one talk group per radio). Each connected P25 radio can communicate on the P25 network via
the VRS7000.
When operating in the XCOV vehicular repeater mode, calls transmitted from connected P25 radios are
not routed to the VRS7000’s speaker.
The VRS7000 supports end-to-end Advanced Encryption Standard (AES) encrypted calls. In other words,
if a P25 radio connected to the VRS7000 is transmitting an encrypted call, the VRS7000 simply repeats
the call to the network base station; it does not un-encrypt and then re-encrypt the call.
CAUTION
Limitations of the VRS7000
are described in the product’s operators manual,
publication number MM-018336-001. See Section 3.5 on page 21
for additional
information.
3.3 EQUIPMENT MOUNTING AND CONTROL HEAD
The VRS7000 is designed for remote mounting in a motor vehicle’s trunk, or some other preferably
unoccupied section in a vehicle, such as a fire truck’s equipment shelf. A 3-wire Controller Area Network
(CAN) cable provides radio-to-control head(s) interconnection. One end of the CAN cable connects to a
CAN port on the rear of the VRS7000’s VRMS mobile radio and the other end connects to a CAN port on
the rear of the CH-721 control head. Between the radio and the control head, the CAN link carries
digitized microphone and speaker audio, and controlling data such as button presses and radio messages.
For proper operation, the CAN link must be terminated appropriately on each end.
The CH-721 System model control head provides the user/operator interface for the VRS7000. See Figure
10-2 on page 57. This control head has a large 3-line graphical vacuum-fluorescent display, front panel
controls and buttons for user control of the mobile radio, an internal high-power audio amplifier to drive
an externally-connected speaker, and a front panel microphone connector. It features a 12-key numeric
keypad that provides Dual-Tone Multi-Frequency (DTMF) keypad functionality and easier operator
system/group selection, three (3) preset buttons, and an emergency/home button.
As shown in Figure 10-2 on page 57, the CH-721 System model control head has several connectors
located on its rear panel. These connectors include a DC power connector, two (2) CAN port connectors
used for CAN link interconnections, an external speaker connector, a 9-pin serial port connector for
connecting optional equipment such as a mobile data terminal, and a 25-pin multi-function connector.
3.4 OPERATING POWER
The VRS7000 must be powered by an external +13.6-volt (nominal) DC power source. In mobile
applications, the motor vehicle’s electrical system is utilized as the source of DC power. The VRS7000’s
VRMS and VRBS are separately fused. For detailed specifications, see Section 2 of this manual which
begins on page 15.
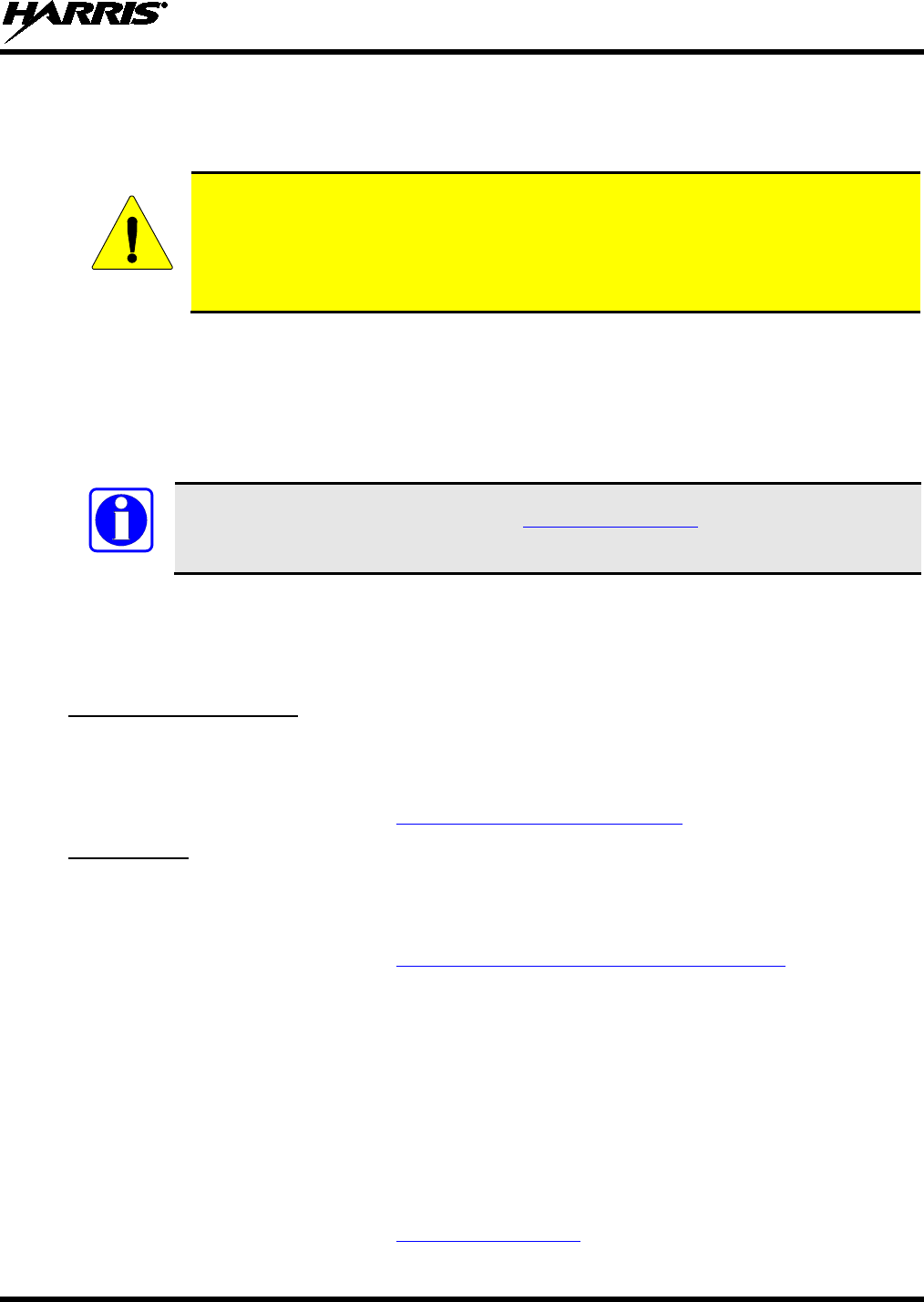
MM-018337-001, Rev. B
21
The control head(s) connected to the radio is also powered by the same DC power source, but fused
separately from the two (2) radios. When the control head is powered-up by the operator, it “wakes up”
the VRM radio by transmitting data to the radio over the CAN link.
CAUTION
Harris recommends the buyer use only a Harris-authorized representative to
install and service this product. The warranties provided to the buyer under the terms
of sale shall be null and void if this product is installed or serviced improperly, and
Harris
shall have no further obligation to the buyer for any damage caused to the
product or to any person or personal property.
3.5 RELATED PUBLICATIONS
The following publications contain additional information about the VRS7000:
•
•
Operator’s Manual:
MM-018336-001
•
Maintenance Manual:
MM-018338-001
NOTE
Publications listed above are available at www.pspc.harris.com via an Information Center
login and Tech Link.
3.6 REPLACEMENT PARTS
Replacement parts can be ordered through the Customer Resource Center. To order replacement parts
through the Customer Resource Center, call, fax or e-mail our ordering system:
United States and Canada:
• Phone Number: 1-800-368-3277 (toll free)
• Fax Number: 1-800-833-7592 (toll free)
• E-mail: PSPC_CustomerFocus@harris.com
International:
• Phone Number: 1-434-455-6403
• Fax Number: 1-434-455-6676
• E-mail: PSPC_InternationalCustomerFocus@harris.com
3.7 TECHNICAL ASSISTANCE
Should the mobile radio or control head require repair, or if there are questions or concerns about the
installation of this equipment, contact the Technical Assistance Center (TAC) using the following
telephone numbers or e-mail address:
• United States and Canada: 1-800-528-7711 (toll free)
• International: 1-434-385-2400
• Fax: 1-434-455-6712
• E-mail: PSPC_tac@harris.com
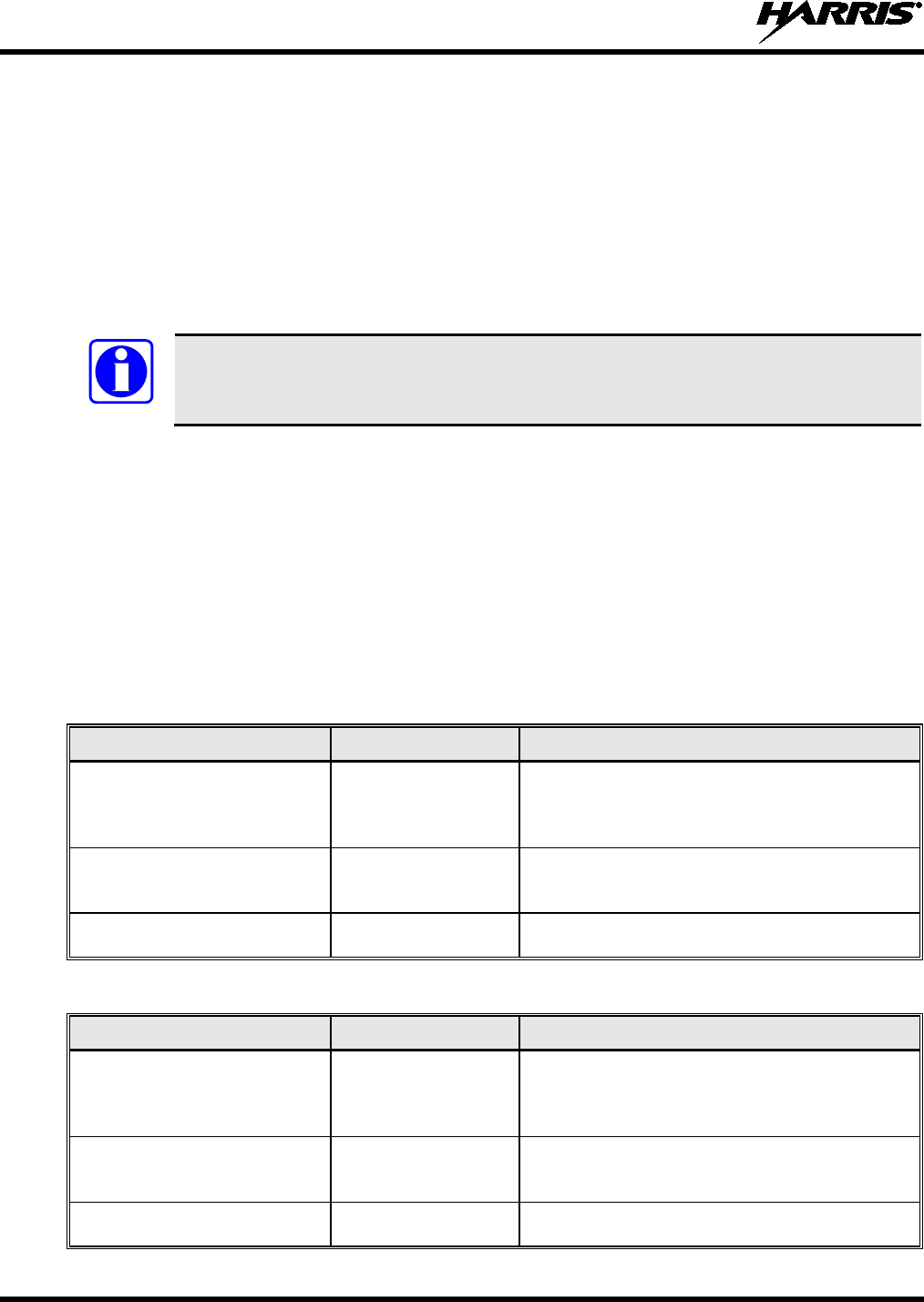
MM-018337-001, Rev. B
22
4 UNPACKING AND CHECKING THE EQUIPMENT
4.1 MATERIALS
A typical set of VRS7010/VRS7020/VRS7030 installation materials includes:
• Vehicular Repeater Mobile System (VRMS7010/VRMS7020/VRMS7030), consists of:
• M7300 Remote-Mount Mobile Radio
• VRM Bandpass Filter (VRMS7010 and VRMS7020 only)
• Vehicular Repeater Base System (VRBS7010/VRBS7020/VRBS7030)
NOTE
For catalog and part numbers, refer to the respective table that follows.
• CH-721 System Control Head [part number CU23218-0004; catalog number MAMW-CP9F]
• Standard Microphone [part number MC-101616-041; part of catalog number MAMW-MC7Z]
• Installation Kit MAMW-NZN8X for VRS7010/VRS7020/VRS7030 and CH-721 as listed in
Table 4-4
• Two (2) or Three (3) Antennas as listed in Table 4-5
The Installation Kit can be used to install the VRS7000, or individual components may be purchased
separately as needed. Table 4-4 lists the parts included in the kit. Table 4-5 lists part numbers for radio
options and accessories. Table 4-6 includes optional parts available for the CH-721 control head.
Table 4-1: VRS7010 Catalog and Part Numbers
CATALOG NUMBER PART NUMBER DESCRIPTION
MAMW-SDMXX RU-144750-061 Remote-Mount Dual-Band 700/800 MHz
M7300 Mobile Radio (VRM Radio of
VRMS7010)
MAMW-NFL1A FL-017938-010 800 MHz Bandpass Filter
(Bandpass Filter of VRMS7010)
MAMW-VDLXX RU-017933-010 VRBS7010
Table 4-2: VRS7020 Catalog and Part Numbers
CATALOG NUMBER PART NUMBER DESCRIPTION
MAMW-SDMXX RU-144750-061 Remote-Mount Dual-Band 700/800 MHz
M7300 Mobile Radio (VRM Radio of
VRMS7020)
(TBD) FL-017938-020 700 MHz Bandpass Filter
(Bandpass Filter of VRMS7020)
(TBD) RU-017933-020 VRBS7020
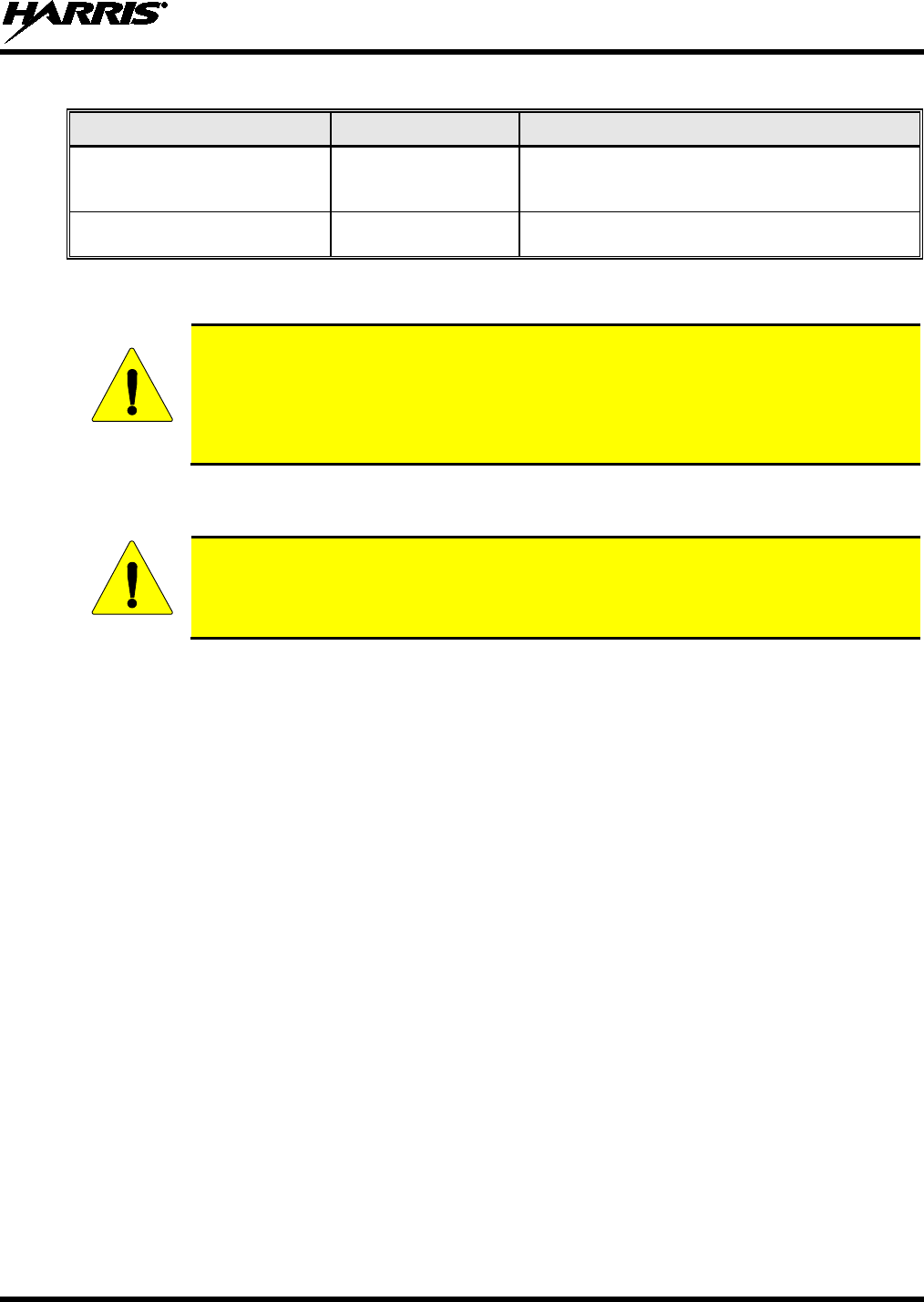
MM-018337-001, Rev. B
23
Table 4-3: VRS7030 Catalog and Part Numbers
CATALOG NUMBER PART NUMBER DESCRIPTION
MAMW-SHMXX RU-144750-041 Remote-Mount 50-Watt VHF M7300 Mobile
Radio (VRM Radio of VRMS7030)
(TBD) RU-017933-030 VRBS7030
4.2 MATERIAL INSPECTION
CAUTION
After removal from the carton, examine the mobile radios, control head and other
components for broken, damaged, loose or missing parts. If any are noted, contact the
Customer Resource Center (see page 21) immediately to discuss and arrange the return
of the equipment to Harris for replacement. Any unauthorized attempts to repair or
modify this equipment will void the warranty and could create a safety hazard.
Upon removing items from the carton and verifying that all equipment is accounted for, proceed with the
installation.
CAUTION
Mounting of the radios, control head, and/or antenna in ways other than those described
in this manual may adversely affect performance, violate FCC rules on RF exposure,
and even damage the unit, posing a potential safety hazard.
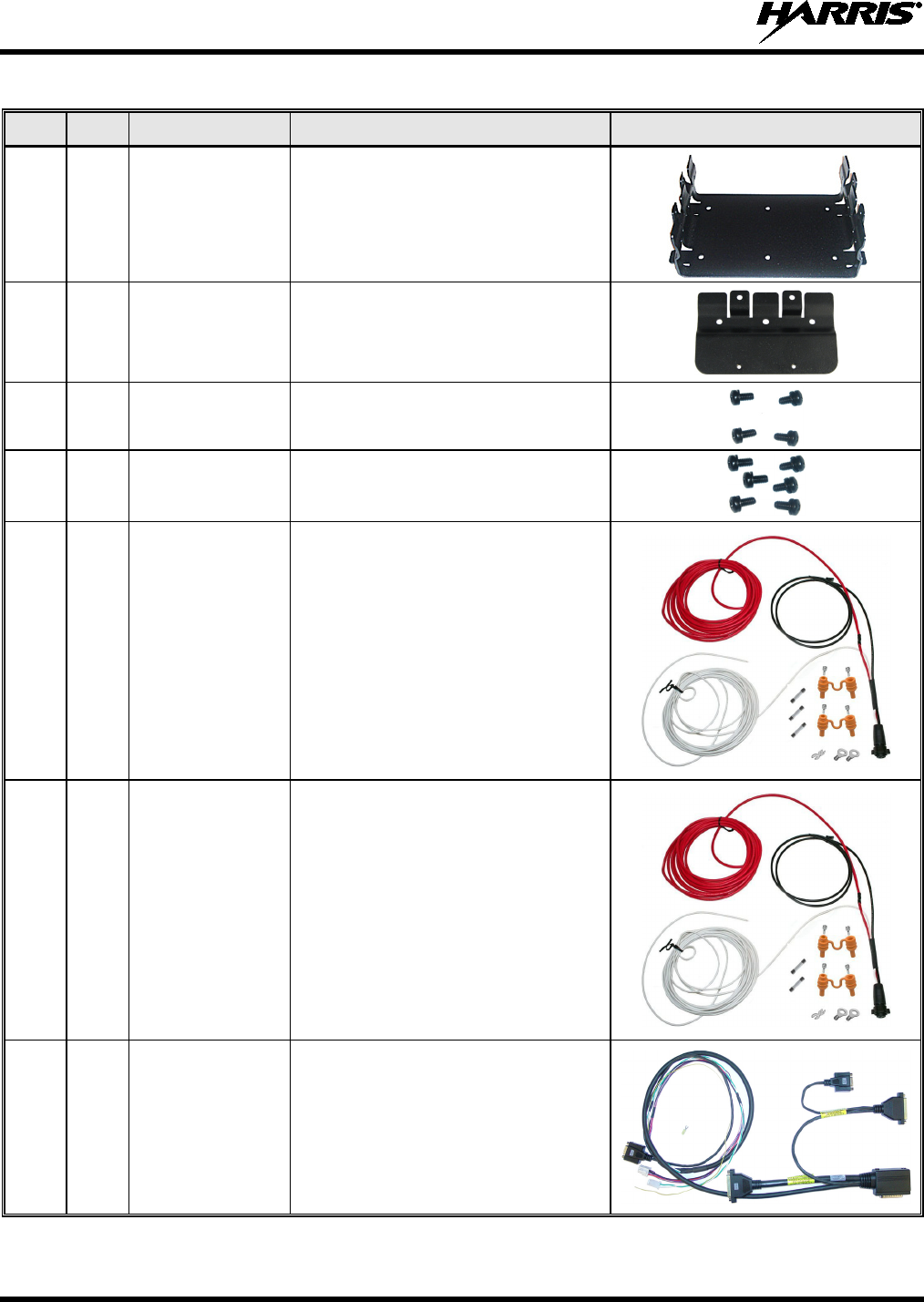
MM-018337-001, Rev. B
24
Table 4-4: Installation Kit MAMW-NZN8X
ITEM QTY. PART NUMBER DESCRIPTION ILLUSTRATION
1 2
1000003678 Bracket, Base.
2 2
FM-018205 Extension Bracket.
3 4
AD00006 Screws: #8-32 Pan-Head (Package
of 4 screws).
4 1
SC-018424 Screws: M5 x 10 mm Philips-Head
SEMS Screws (Package of 6
screws).
5 2
CA-012365-001 Cable, M7200/M7300/M5300 DC
Power. Includes (1) 20-Foot DC
Power Cable with straight connector,
(2) waterproof inline HFB-type fuse
holders, (1) 3-amp AGC fuse, (1)
15-amp AGC fuse, and (1) 20-amp
AGC fuse.
6 1
CA-012616-001 Cable, CH-721 DC Power. Includes
(1) DC Power Cable with straight
connector, (2) waterproof inline HFB-
type fuse holders, (1) 3-amp AGC
fuse, and (1) 5-amp AGC fuse. This
DC Power Cable has a 10-foot
12-AWG red wire (main power input),
a 20-foot white wire (switched power
input), and a 5-foot black wire
(ground).
7 1
CA-012349-003 Cable, VRS7000 Interface.
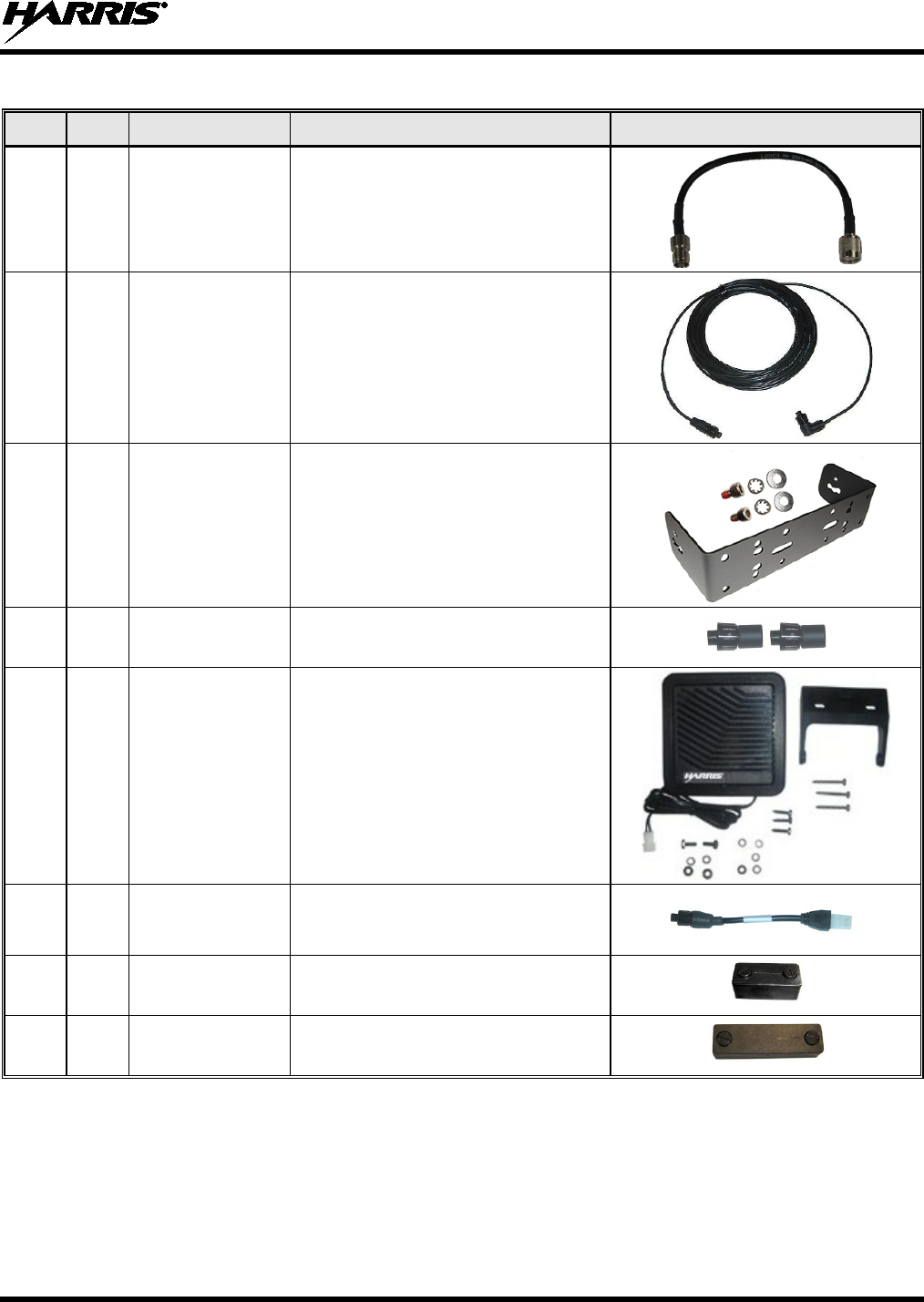
MM-018337-001, Rev. B
25
Table 4-4: Installation Kit MAMW-NZN8X
ITEM QTY. PART NUMBER DESCRIPTION ILLUSTRATION
8 1
CA-018378 Cable, RF; TNC Female to TNC
Male.
9 1
CA-009562-030 Cable, CAN; 30 feet, Right-Angle-to-
Straight Connectors.
10 1
KT-008608 Kit, CH-721 Mounting Bracket.
Includes (1) U-Shaped Mounting
Bracket, (2) ¼-Inch #8-32 stainless-
steel screws, (2) stainless-steel flat
washers and (2) stainless-steel
lockwashers.
11 2
CD-014027-
001
Terminator, CAN; 3-Pin, Straight
Body.
12 1
LS102824V10 Speaker, External Mobile; 20-Watt
(with 4.6-foot cable).
13 1
MAMROS0034-
NN006
Cable, Speaker; 6-Inch, Straight
Connector.
14 1
FM-104859-
001
Cap, Waterproof (For CH-721’s DB-9
serial port connector).
15 1
FM-104859-
002
Cap, Waterproof (For CH-721’s
DB-25 accessory connector).
(Continued)
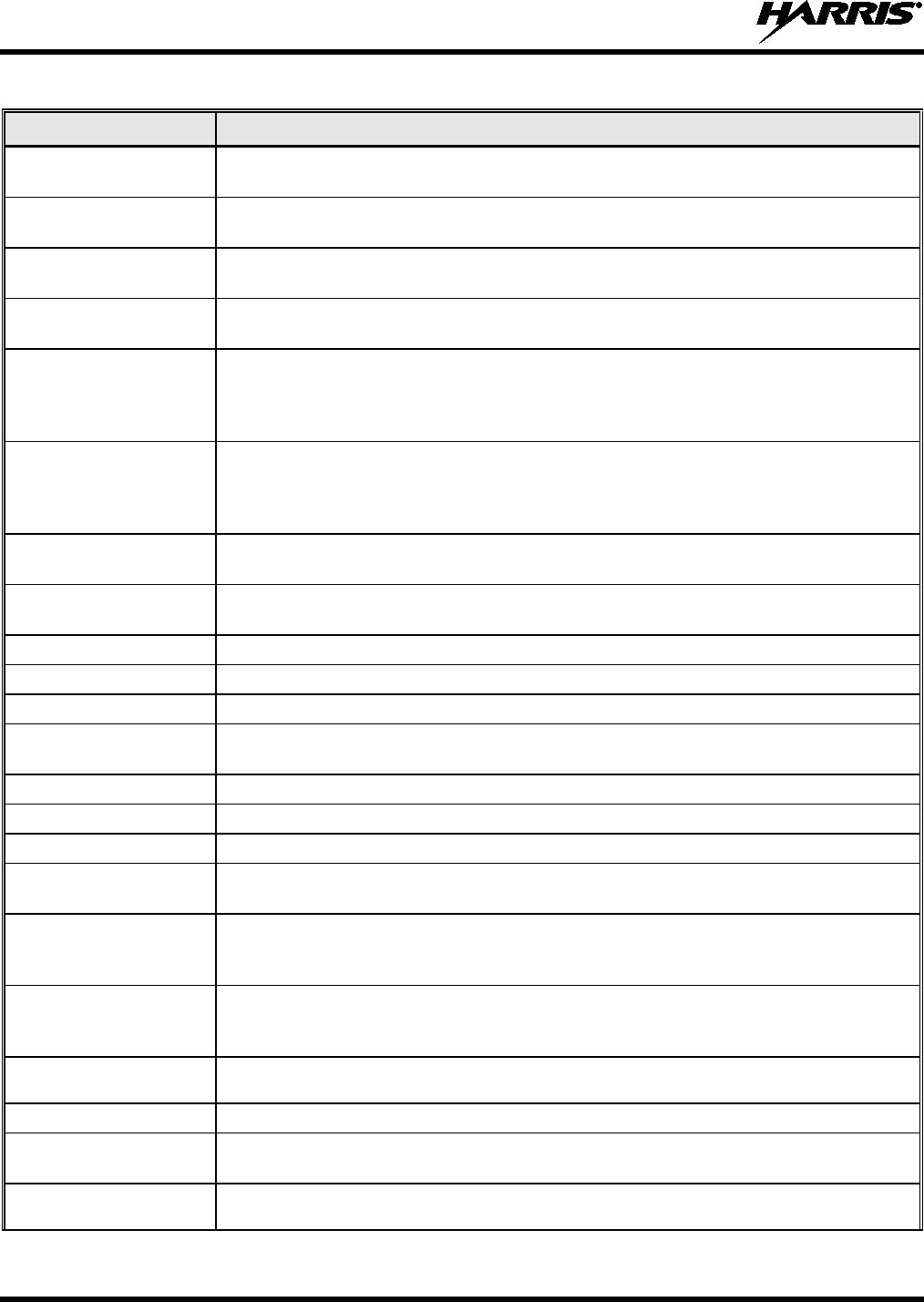
MM-018337-001, Rev. B
26
Table 4-5: Options and Accessories for VRS7010/VRS7020/VRS7030
PART NUMBER DESCRIPTION
AN-125001-001 Antenna Mount: Standard Rooftop, NMO Mounting Base, 15-foot (4.6-meter)
RG-58 A/U (or equivalent) Low-Loss RF Cable, Male TNC RF Connector
AN-125001-002 Antenna Mount: Standard Rooftop, NMO Mounting Base, 15-foot (4.6-meter)
RF-195 (or equivalent) Low-Loss RF Cable, Male TNC RF Connector
AN-125001-003 Antenna Mount: Thick Rooftop, NMO Mounting Base, 15-foot (4.6-meter)
RG-58 A/U (or equivalent) Low-Loss RF Cable, Male TNC RF Connector
AN-125001-004 Antenna Mount: Thick Rooftop, NMO Mounting Base, 15-foot (4.6-meter) RF-195
(or equivalent) Low-Loss RF Cable, Male TNC RF Connector
AN-125001-005 Antenna Mount: GPS Combo Rooftop, NMO Mounting Base, 17-foot (5.1-meter)
RF-195 (or equivalent) Low-Loss RF Cable, Male TNC RF Connector; 17-foot
(5.1-meter) RG174/U (or equivalent) GPS RF Cable with Male SMA RF Connector
(attached); 2.7 to 3.3 Vdc or 4.8 to 5.2 Vdc Bias
AN-125001-006 Antenna Mount: GPS Combo Rooftop, NMO Mounting Base, 17-foot (5.1-meter)
RF-195 (or equivalent) Low-Loss RF Cable, Male TNC RF Connector; 17-foot
(5.1-meter) RG174/U (or equivalent) GPS RF Cable with Male SMA RF Connector
(attached); 2.7 to 3.3 Vdc or 4.8 to 5.2 Vdc Bias
AN-125001-007 Antenna Mount: Magnetic, NMO Mounting Base, 15-foot (4.6-meter) RG-58 A/U (or
equivalent) Low-Loss RF Cable, Male TNC RF Connector
AN-125001-008 Antenna Mount: Magnetic, NMO Mounting Base, 15-foot (4.6-meter) RF-195 (or
equivalent) Low-Loss RF Cable, Male TNC RF Connector
AN-225002-001 Antenna Element: 136 to 174 MHz, 0 dBd Gain, NMO, Factory-Tuned
AN-225001-001 Antenna Element: 700/800 MHz, 3 dBd Gain, NMO, Factory-Tuned
AN-225001-002 Antenna Element: 700/800 MHz, 3 dBd Gain, Elevated-Feed, NMO, Factory-Tuned
AN-225001-003 Antenna Element: 700/800 MHz, 3 dBd Gain, Elevated-Feed No Ground Plane,
NMO, Factory-Tuned
AN-225001-004 Antenna Element: 700/800 MHz, 2 dBd Gain, Low-Profile, NMO, Factory-Tuned
AN-225001-005 Antenna Element: 700/800 MHz, 5 dBd Gain, NMO, Factory-Tuned
AN-225006-001 Antenna Element: 132 to 960 MHz, 0 dBd Gain, NMO, Field-Tuned
AN102800V1 Antenna Kit: 136 to 941 MHz, ¼-Wavelength, Standard Rooftop-Mount 0 dBd Gain,
Field-Tuned
AN-025187-001
(Cat. No. MAMW-NAN5F)
Antenna: GPS Receive-Only, Roof-Mount, 17-foot (5.2-meter) RG174/U (or
equivalent) RF Cable with Male SMA RF Connector (attached); 2.7 to 3.3 Vdc or 4.8
to 5.2 Vdc Bias
AN-025187-003
(Cat. No. MAMW-NAN3L)
Antenna: GPS Receive-Only, Magnetic-Mount, 17-foot (5.2-meter) RG174/U (or
equivalent) RF Cable with Male SMA RF Connector (attached); 2.7 to 3.3 Vdc or 4.8
to 5.2 Vdc Bias
CA-012349-001
(Cat. No. MAMW-NCL8B) Cable, M5300/M7300 Option. See page 46.
CA-013671-020 Cable, Serial Data (20 feet). See page 67.
CN-014756 Connector, RF; TNC Male Crimp-Type for RG58U, RG58A/U and RGU400 Coaxial
Cable
KT-012350-001
(Cat. No. MAMW-NMK5F) Kit, GPS Receiver for M5300/M7300
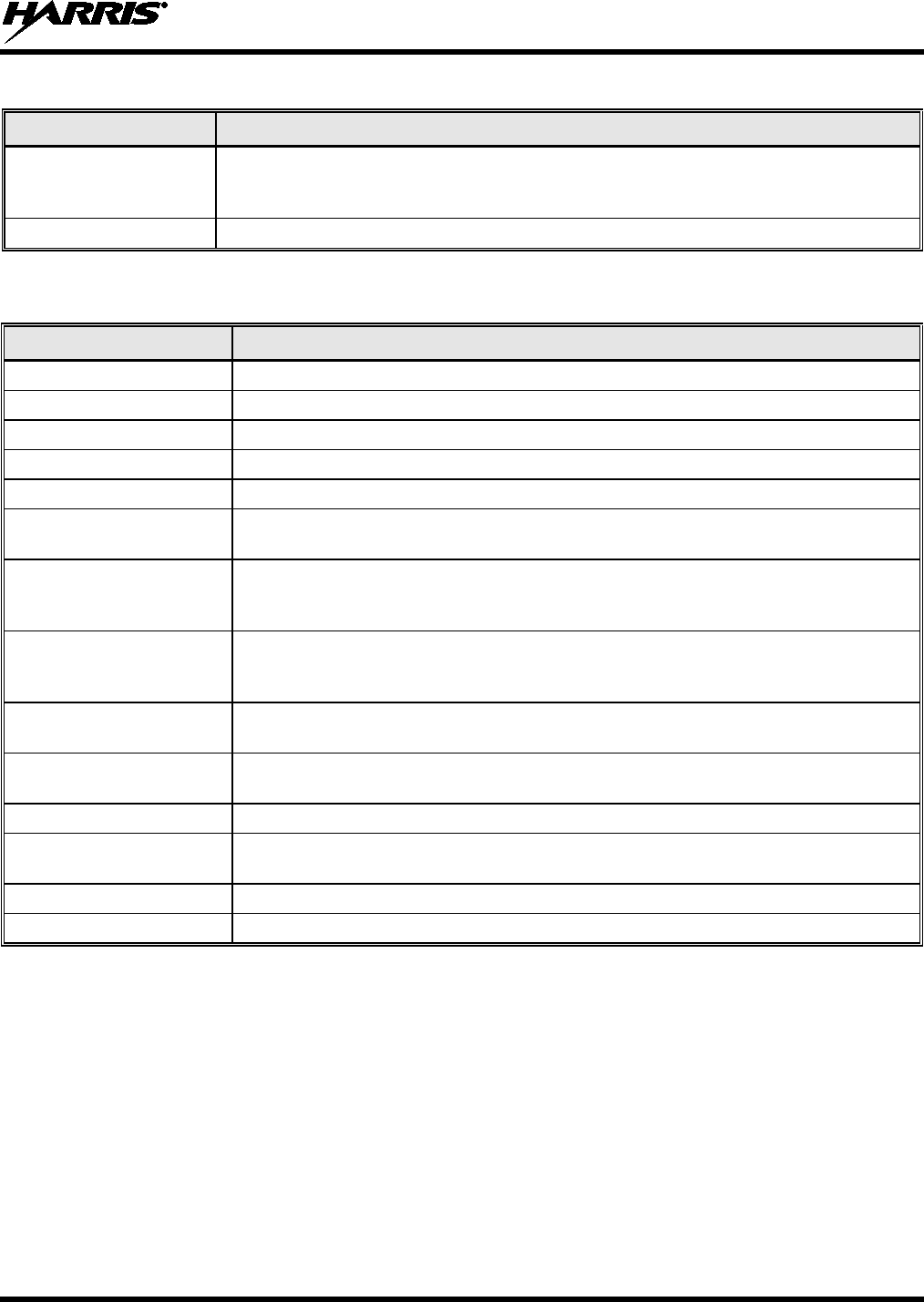
MM-018337-001, Rev. B
27
Table 4-5: Options and Accessories for VRS7010/VRS7020/VRS7030
PART NUMBER DESCRIPTION
KT-015037 Kit, Front-Mount to Remote-Mount Conversion for M5300/M7300 Radio. Includes
CH-721 Conversion Kit, CH-721 Mounting Bracket Kit, CH-721 DC Power Cable,
CAN Cable, CAN Terminator, Speaker Cable, Etc.
CD-014027-001 Terminator, CAN; 3-Pin, Straight Body
Table 4-6: Accessories for CH-721 Control Heads
PART/MODEL NUMBER DESCRIPTION
CA-009562-006 Cable, CAN; 6 feet, Right-Angle-to-Straight Connectors.
CA-009562-030 Cable, CAN; 30 feet, Right-Angle-to-Straight Connectors.
CA-009562-090 Cable, CAN; 90 feet, Right-Angle-to-Straight Connectors.
CA-009562-250 Cable, CAN; 250 feet, Right-Angle-to-Straight Connectors.
CA-011854-001 Cable, CH-721 Option. (Shown in Figure 13-2 on page 68.)
MACDOS0012 Kit, Control Head Pedestal Mounting. Includes Pedestal Mount and Mounting
Screws.
MACDOS0013-CN004 Kit, Speaker; 20-Watt, Straight Connector. (Includes 4-Ohm 20-Watt Speaker
LS102824V10 with 4.6-Foot Cable and 6-Inch Speaker Cable MAMROS0034-
NN006.)
FS24473 Kit, Vehicle Fuse and T-Tap. Includes (1) ATM Fuse Holder, (1) 2-Amp ATM Fuse,
(2) T-Tap Quick-Disconnect Terminals and (1) ¼-Inch Crimp Tab Terminal.
(Contents shown in Figure 10-6 on page 64.)
MC-101616-041 Microphone, Standard with Flush-Mount 90-Degree Connector
(Included with catalog number MAMV-MC7Z)
MC-103334-050 Microphone, Noise-Canceling with Flush-Mount 45-Degree Connector (Included
with catalog number MAMV-NMC9D)
MC-103334-051 Microphone, Noise-Canceling with Flush-Mount 90-Degree Connector
344A4678P1 Microphone Hanger. (Included with catalog numbers MAMV-MC7Z,
MAMV-NMC9C and MAMV-NMC9D.)
MACDOS0010 Terminator, CAN; 3-Pin, Right-Angle Body.
CD-014027-001 Terminator, CAN; 3-Pin, Straight Body.
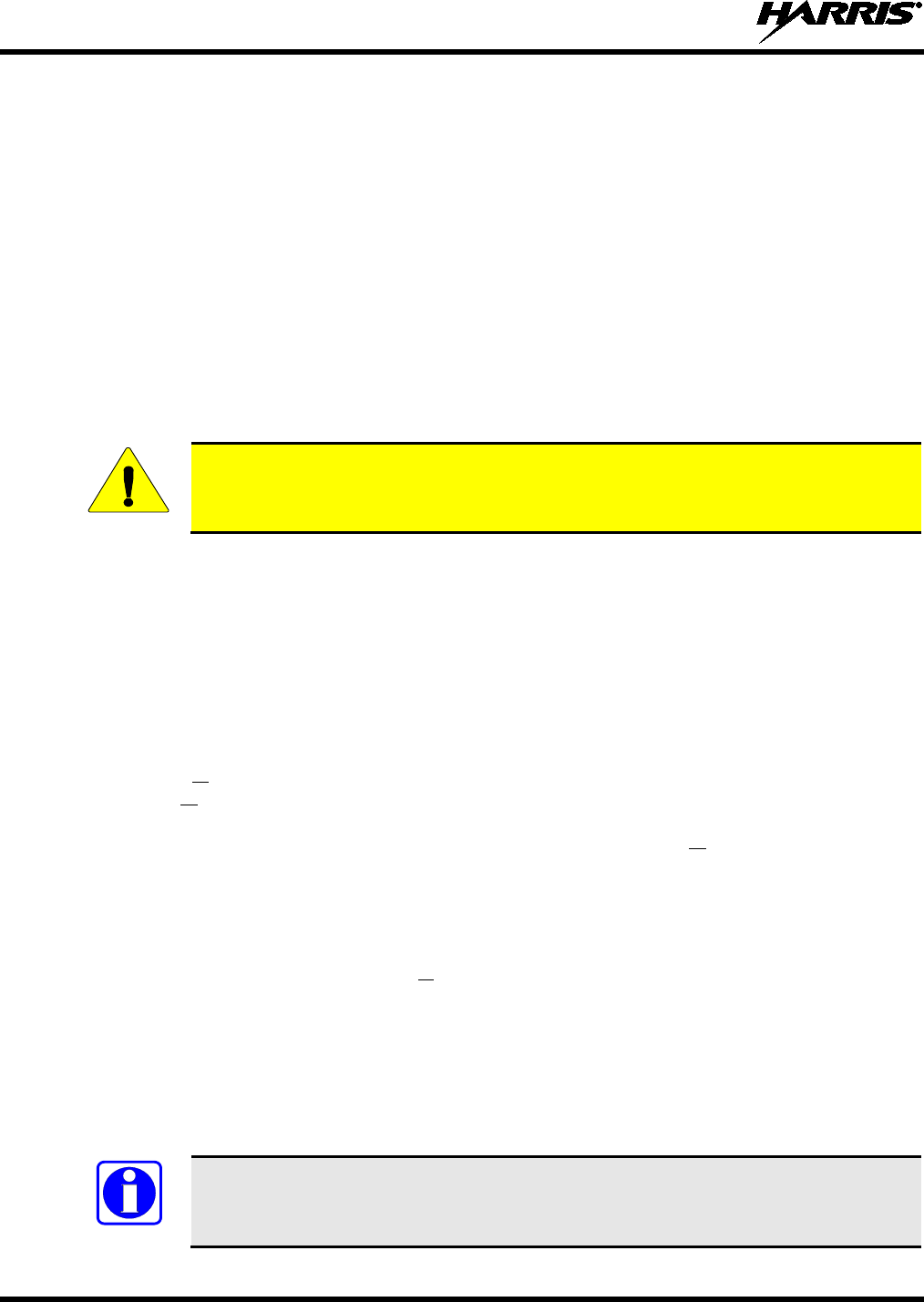
MM-018337-001, Rev. B
28
5 PLANNING THE INSTALLATION
5.1 GENERAL INFORMATION
Before beginning the radio installation, plan it carefully so it will meet the following requirements:
• The installation is safe for the operator and passengers within the vehicle.
• The equipment is installed away from the airbag deployment areas.
• The installation allows for convenient access by the operator, as applicable (i.e., the control head).
• The equipment is protected from water damage.
• The installation is neat and allows easy service access.
• The radio is mounted in a location assuring the vehicle occupant’s safety and out of the way of
passengers and auto mechanics.
• The two (2) transmit/receive antennas can be mounted at least three (3) feet (0.92 meters) apart.
CAUTION
A professional radio installer should perform the installation!
5.2 TOOLS REQUIRED
The following list of equipment is recommended for the installation. Equivalents may be used unless
otherwise specified:
• Non-Insulated Crimp Tool: Thomas & Betts
WT-111-M
• Insulated Terminal Crimp Tool: Klein 1005
• Fuse Holder Crimp Tool: Thomas & Betts –
WT-112M or California Terminal Products
No. 1250 or Channelock No. 909
• 3-Blade Coax Cable Stripper for RG-58
Cable similar to Tyco Electronics 1490490-
1 (includes blades)
• Ratcheting Hex-Crimp Tool for 50-Ohm TNC
and BNC RF Connectors and RG-58 Cable
similar to Tyco Electronics 58433-2 (includes
Crimper 354940-1 and Die Set 58436-1) or
Emerson Network Power 24-9960P
• Non-Metallic Fish Tape, 25-Foot: Klein-
Lite 50156
• Two Pairs of Soft-Jaw Pliers: Tessco
450520 or equivalent
• Flush-Cut and Large Wire Cutters
• Phillips-Head Screwdrivers, #1 and #2
• Flat-Blade Screwdrivers, #1 and #2
• ⅛-Inch Hex Key Wrench (Allen Wrench)
• 5/16-Inch Combination or Open-End Wrench
• Socket and/or Nut Driver Sets
• ¾-Inch Hole Saw with Depth Protection:
Ripley HSK 19 or Antenex HS34
• Clutch-Type (i.e., with torque limit)
Cordless Drill with Drill Bits and Driver
Bits
• Deburring Tool (for ⅜-inch and smaller
holes)
• Tie Wraps: 6-inches or larger
• Various Fasteners (e.g., machine screws and
nuts, Tek screws, etc.)
NOTE
A separate list of test equipment is included in Section 16.1 on page 73.
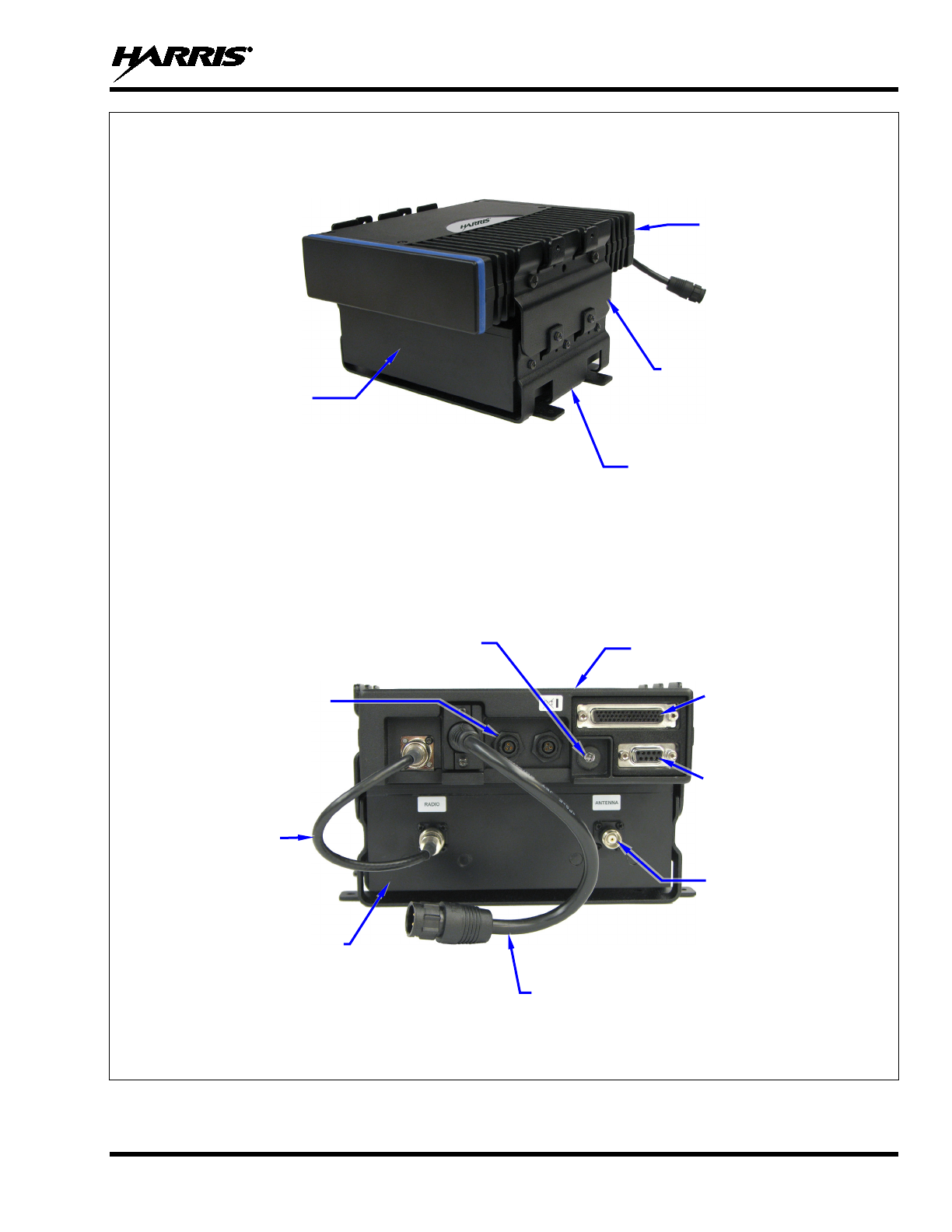
MM-018337-001, Rev. B
29
VRMS7010/VRMS7020/VRMS7030 FRONT-SIDE VEW
VRMS7010/VRMS7020/VRMS7030 REAR VIEW
(Shown Without Any Installation-Related Cables Connected)
Figure 5-1: Vehicular Repeater Mobile System (VRMS)
VRM Radio’s Option
Connector
(Female DB-44)
Bandpass Filter
(VRMS7010 and
VRMS7020 only)
GPS Antenna Cable’s SMA Connector
Bandpass Filter’s
Antenna Connector
(Female TNC)
CAN Port Connectors
(2 Places)
VRM Radio
(M7300)
Bandpass Filter
(VRMS7010 and
VRMS7020 only)
Base Bracket
(included with Installation Kit)
Extension Bracket
(2 places; included with
Installation Kit; used with
VRMS7010 and VRMS7020
only)
RF Cable
(Female TNC
to Male TNC)
VRM Radio (M7300)
VRM Radio’s DC Power Cable
(with 3-Pin Connector)
VRM Radio’s Serial
Port Connector
(Female DB-44)
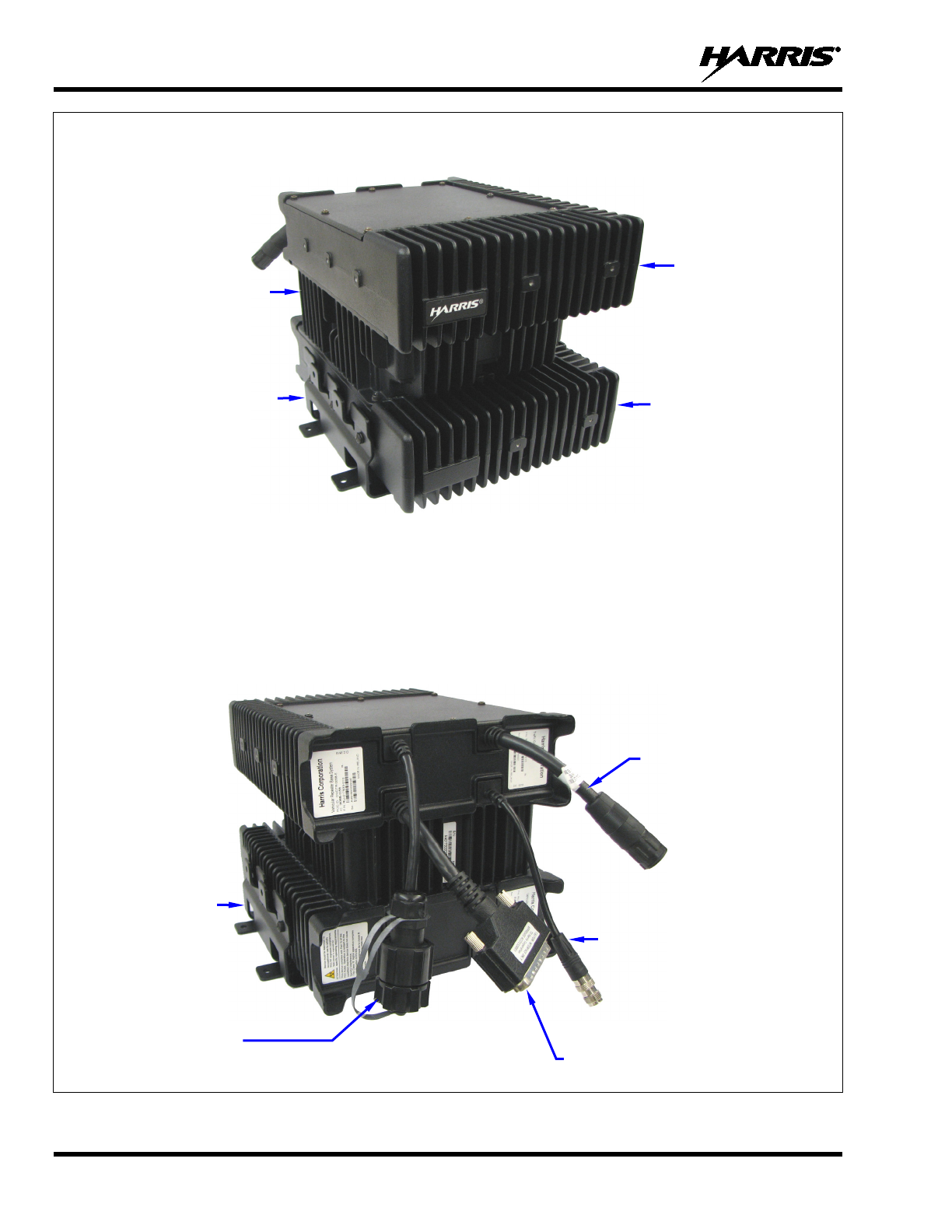
MM-018337-001, Rev. B
30
VRBS7010/VRBS7020/VRBS7030 FRONT-SIDE VIEW
VRBS7010/VRBS7020/VRBS7030 REAR VIEW
(Shown Without Any Installation-Related Cables Connected)
Figure 5-2: Vehicular Repeater Base System (VRBS)
Traffic Controller
Vehicular Repeater
Base (VRB) Radio
Duplexer
DC Power Cable of
VRBS (with 3-Pin
Connector)
Antenna Cable of
VRBS (
with female TNC
connector)
Interface Cable of VRBS7010
(with DB-25 Connector)
Ethernet Cable
(with Sealed RJ-
45
Modular Plug)
Base Bracket
(included with
Installation Kit)
Base Bracket
(included with
Installation Kit)
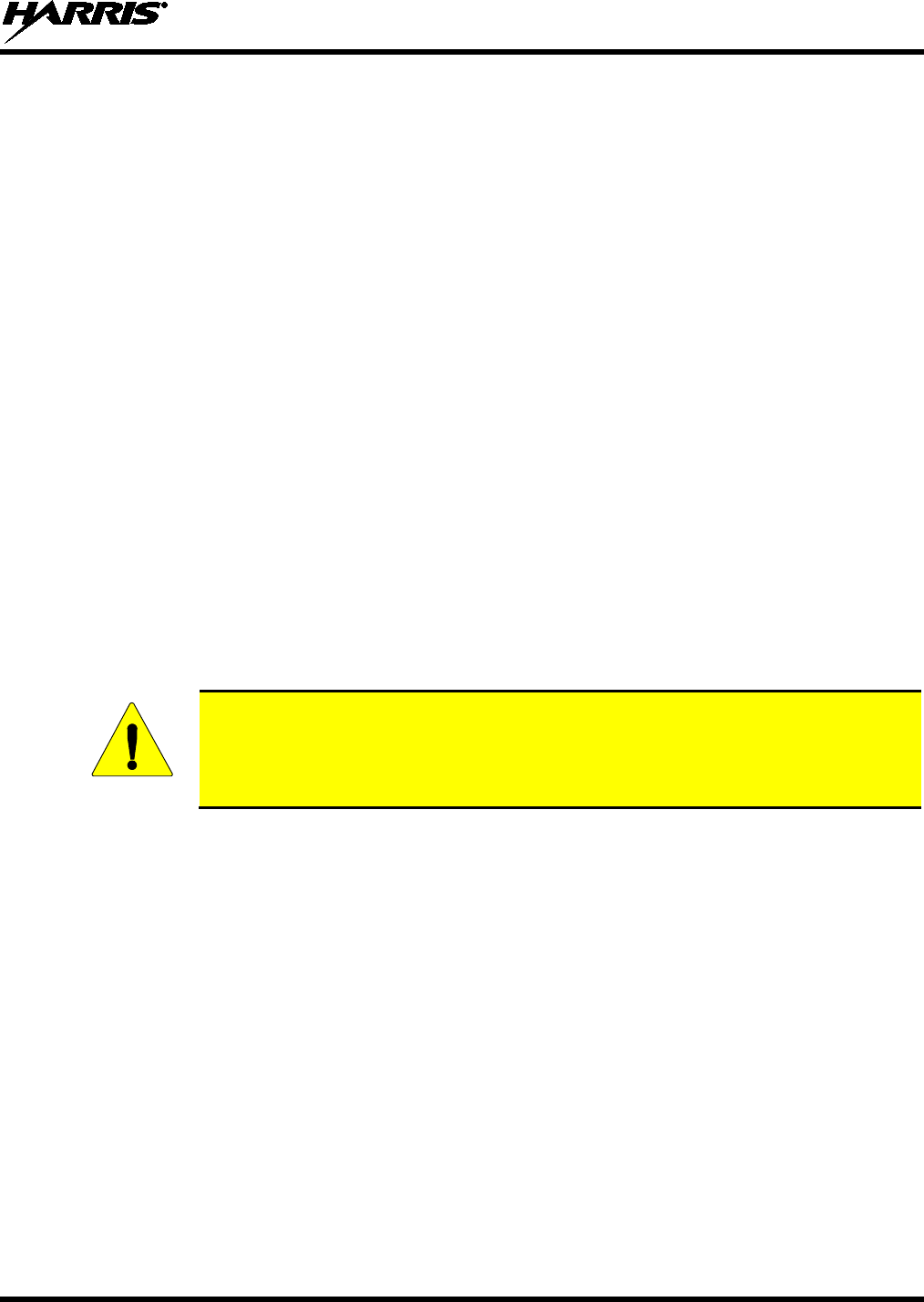
MM-018337-001, Rev. B
31
5.3 LOCATING COMPONENTS
Plan the mounting locations of all components (VRS7000, CH-721, antennas, and cables) and determine
the routes for all wiring and cables. Particularly consider the connection of the control head for planning
purposes.
• Determine the customer’s preferences, if any, for location of components. Comply with these
preferences as long as they are consistent with safety recommendations and guidelines presented in
this manual, and other generally accepted professional radio installation practices.
• Nominal dimensions for the VRS7000 and the CH-721 are listed in Section 2.1 of this manual (page
15). These dimensions do not include any clearance space required for cabling, air circulation, access
to mounting hardware, etc. Always plan for and include adequate clearance around the radios.
• The VRMS and the VRBS must be located and mounted within approximately twelve (12) inches of
each other.
• Verify sufficient clearance behind the radios is provided so cables will not be stressed, crushed,
twisted, or bent at severe angles. Also, the front and sides must have clearance for air circulation,
access to mounting hardware, etc.
• Connections at the VRS7000 are made through both “pigtail” type cables exiting the rear of its two
radios, and panel-mount type connectors. This design minimizes the stresses associated with mating
connections and it allows for easy connector mating. However, stresses can still be induced if
adequate service looping is not employed. Connections to the control head is made with connectors
mounted on the rear panel of each head, instead of “pigtail” type cables.
• The VRMS and the VRBS transmit-receive antennas must be located at least three (3) feet (0.92
meters) apart. Refer to Section 7 (page 36) for additional information.
CAUTION
All cables should have a service loop near each connector end. Do not bend the cables
at severe angles near the connector end. Above all, after all components are installed,
verify no cable is under any tension. Failure to do so may lead to damaged cables,
causing intermittent radio operation or complete radio failure.

MM-018337-001, Rev. B
32
6 MOUNTING THE RADIO EQUIPMENT
This section provides details on mounting the VRS7000. The preferred mounting is on top of a firm, flat
surface. See Figure 5-1, Figure 5-2, and refer to the respective wiring diagram at the end of this manual as
necessary. Control head installation procedures are included in Section 10 (page 56) of this manual.
The VRS7000 is relatively heavy, at approximately thirty (30) pounds (13.6 kilograms). Consider this
weight when selecting a mounting surface. Refer to the specifications listed in Section 2.1 (page 15) of
this manual for radio and control head weight specifications.
NOTE
Installation Kit MAMW-NZN8X (contents listed in Table 4-4 on page 24) contains the
set of materials for installing the radio
. Therefore, the following instructions make
repeated reference to this kit. Item numbers given in parenthesis refer to items in the kit.
NOTE
Prior to beginning the installation, verify the VRS7000
has the proper version of
software installed and it has been configured for customer usage.
CAUTION
Though generally mounted in a trunk or remote location, the VRS7000 must be kept
away from heat sources. Mounting it in a location which is out of direct sunlight is
recommended but not required. Adequate ventilation space must be provided to the rear
and side fins. The radio reduces its RF output power when its ambient temperature
exceeds approximately +140o Fahrenheit (+60o Celsius).
WARNING
At a minimum, the mounting surface should be 16-gauge (approximately 1/16-inch
thick) steel sheet metal. Mounting to plastic or other material with low tensile and
shear strength could lead to an unsafe and/or failed mounting condition, turning
the VRS7000 and its base bracket into a projectile during a high-shock incident
such as a motor vehicle accident. If the selected mounting surface does not meet
the minimum 16-gauge steel sheet metal requirement, the surface should be
reinforced with a metal backing plate (not supplied) or it should be reinforced
using some other approved mounting method.
CAUTION
Before drilling holes and/or installing mounting screws, verify these operations will not
damage or interfere with any existing vehicle component
(fuel tank, fuel line,
transmission housing, existing vehicle wiring, etc.). Always check to see how far the
mounting screws will extend below the mounting surface prior to installation. Always
deburr drilled holes before installing screws.
6.1 INSTALL THE MOUNTING BRACKETS
Two (2) identical Base Brackets (Item 1 in Table 4-4) are included with the installation kit. One bracket is
used to mount the VRMS, and the other bracket is used to mount the VRBS. Two (2) Extension Brackets
are also required to mount the VRM radio above its filter. The Extension Brackets basically extend the
height of a Base Bracket to provide a mounting space above the 800 MHz bandpass filter for the VRM
(M7300) mobile radio.
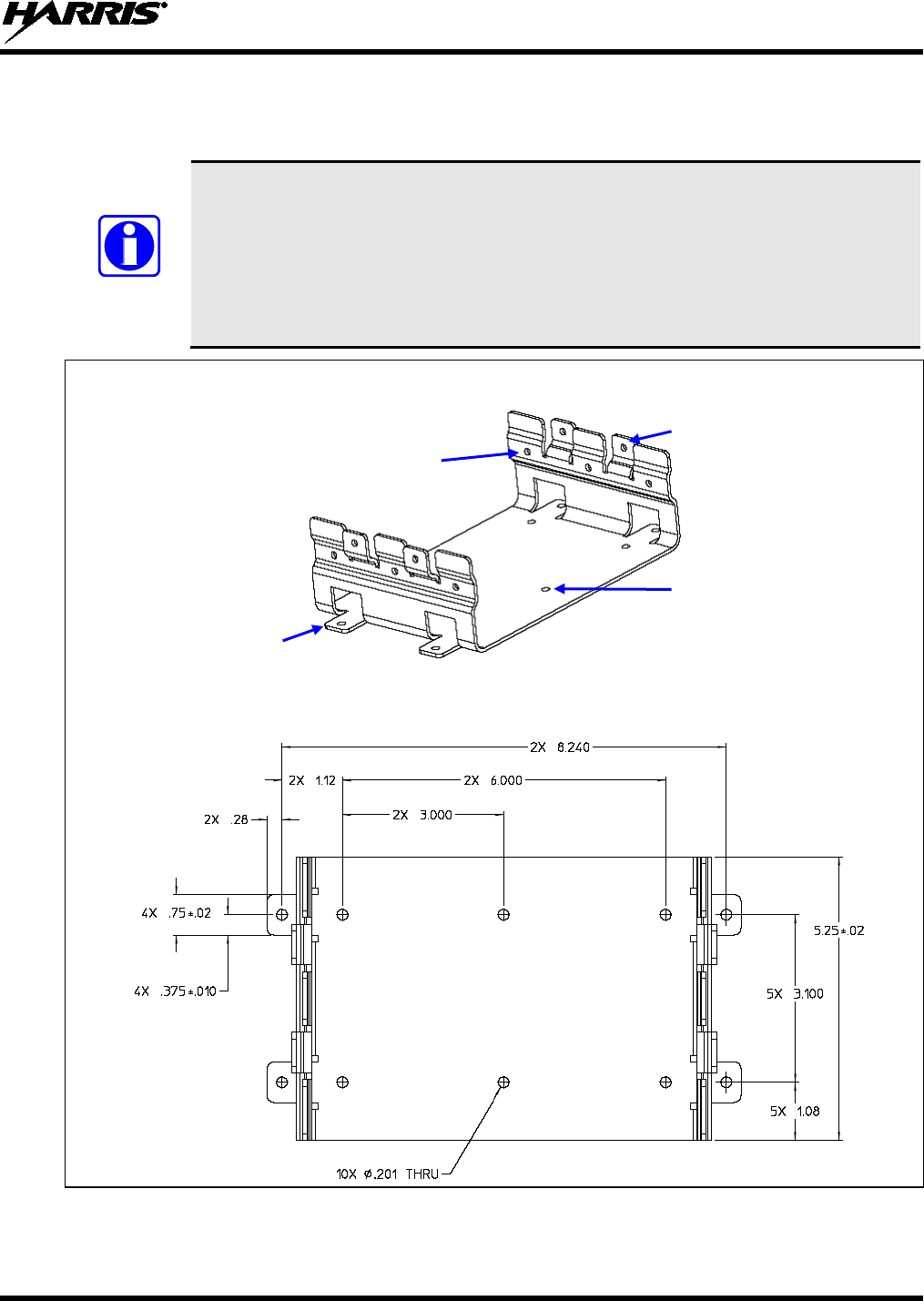
MM-018337-001, Rev. B
33
Typically, both Base Brackets are mounted in the vehicle’s trunk, on the top surface of a trunk tray or the
trunk floor. However, both can be suspended from the trunk’s rear deck if the surface is completely flat,
does not require any shimming and the gauge of deck’s sheet metal is high (16-guage minimum).
NOTE
The section of the cable which interconnects the DB-44 connector on the rear of the
VRMS to the DB-25 connector on the rear of the VRBS is approximately eighteen
(18) inches long. After the radios are secured within mounted brackets, they must be
located so the respective connectors of the cable can mate to the connectors on the rear
of the radios. Typically, both brackets must be mounted within approximately twelve
(12) inches of each. The brackets/radios may be oriented parallel or perpendicular to
each other.
SIDE & TOP VIEW
TOP VIEW WITH SCREW HOLE DIMENSIONS (In Inches)
Figure 6-1: Base Bracket (Two Required Per VRS7000 Installation)
Side Mounting Tabs
(4 places)
Bracket-To-Vehicle
Mount Surface Screw
Holes (10 places)
Bracket-To-Radio/Filter Screw Holes
(6 places, 3 each side)
Four (4) Upper-Most
Holes (2 each side)
Used to Attach
Extension Brackets
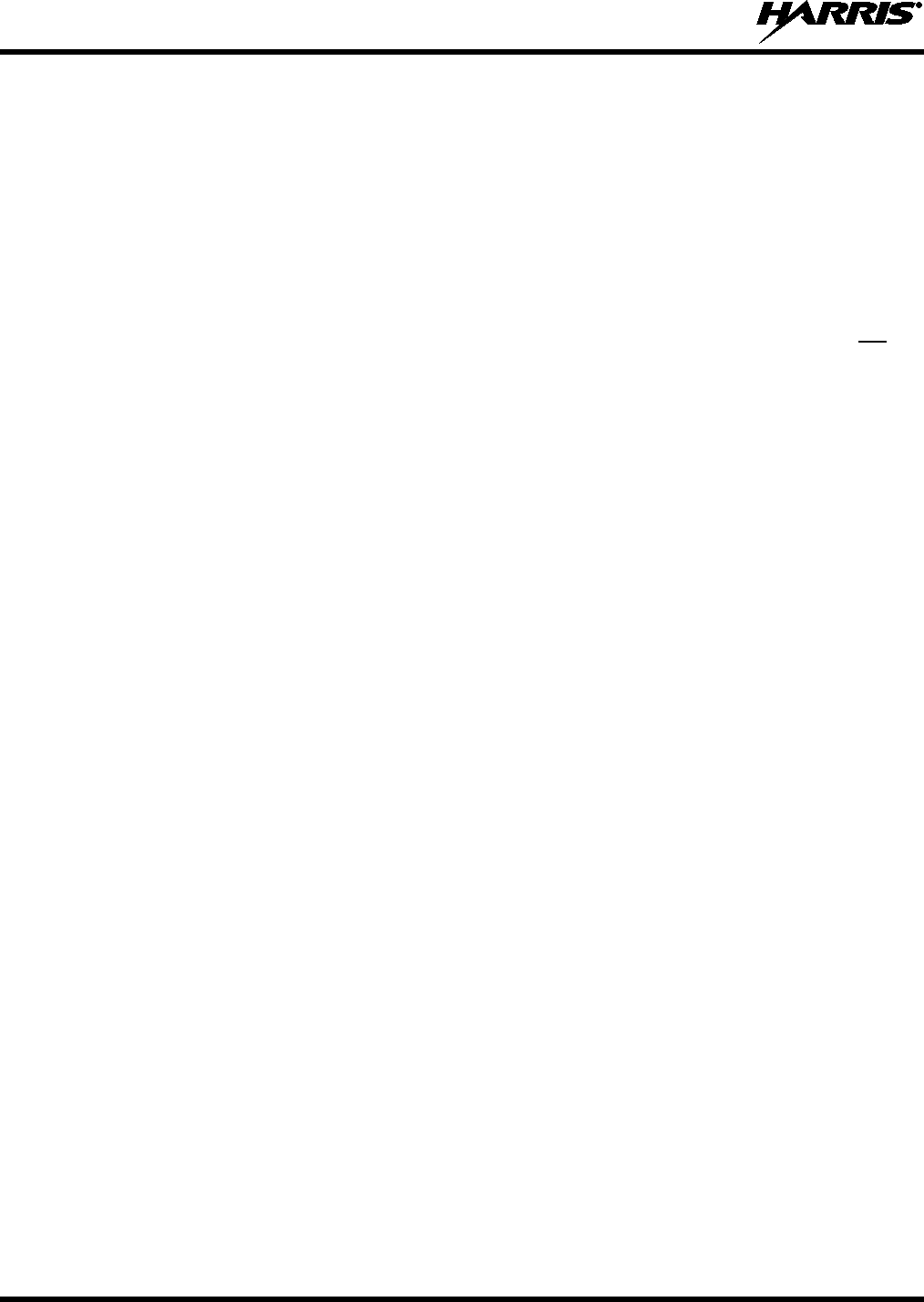
MM-018337-001, Rev. B
34
When installed in a bracket, each radio protrudes several inches from the bracket’s front and back edges.
Therefore, when selecting an exact mounting location, verify sufficient distance at the front and back for
this and additional clearance. A minimum distance of three (3) inches is required from the rear edge of the
bracket; however four (4) inches or more is recommended to improve radio installation and removal ease.
A minimum distance of two (2) inches is recommended from the front edge of each bracket. The bracket
is front/back symmetrical, and left/right symmetrical.
As all installations differ, bracket-to-vehicle mounting screws are not included. The use of #10 stainless-
steel machine screws, stainless-steel flatwashers and stainless-steel self-locking nuts is recommended.
Alternately, #10 stainless-steel self-drilling screws and stainless-steel flatwashers may be used to speed
installation time and/or if the underside of the mounting surface is not easily accessible. Self-drilling
screws such as “TEK” screws do not require drilling of a pilot hole prior to installation. Do not use
common self-threading sheet metal screws because they will loosen over time with vehicle vibrations.
1. Select a location for each Base Bracket—one location for the VRMS’s Base Bracket and one location
for the VRBS’s Base Bracket. As previously stated, both brackets must be mounted within
approximately twelve (12) inches of each other so the section of the cable which interconnects the
two radios will have sufficient length.
2. Using each Base Bracket (Item 1 in Table 4-4) as a template and/or the dimensional information
shown in Figure 6-1, mark and drill mounting holes into the mounting surface for each bracket. At
least six (6) screws per bracket are recommended for proper installation: Four (4) in the screw holes
of a bracket’s side tabs and two (2) in its center-most screw holes. If the installation prevents the
installation of six screws, a minimum of four screws installed in the side tabs’ holes is required, per
bracket.
3. Deburr all newly drilled mounting holes.
4. Set each bracket in place, and install and tighten the mounting screws.
5. Verify both brackets are firmly secured to the mounting surface. A secure mount prevents
unreasonable vibration, which could damage the radio and/or cause its cable connections to loosen.
6. Attach an Extension Bracket to each side of the VRMS’s Base Bracket. Use two #8-32 pan-head
screws per Extension Bracket. These screws are included in the installation kit (Item 3 in Table 4-4).
When tightening the screws, push each Extension Bracket firmly down into the Base Bracket so each
is firm and flush to the other when the screws are tight.
6.2 MOUNT THE RADIOS AND FILTER INTO THE BRACKETS
The radios and the 800 MHz bandpass filter must now be mounted into the brackets in accordance with
this procedure. Exploded view diagrams of each radio stack are shown in Figure 6-2.
1. Slide the 800 MHz bandpass filter into the Base Bracket that has the two (2) attached Extension
Brackets. The two (2) RF connectors must face towards the cabling area of the radio installation.
2. Secure the filter to the Base Bracket using three #8-32 pan-head screws (Item 3 in Table 4-4) per side.
Tighten all six (6) screws with a screwdriver until the lock washers on the screws are fully
compressed and the filter is firm and flush between the sides of the bracket.
3. Slide the M7300 mobile radio between the Extension Brackets, just above the 800 MHz bandpass
filter. The rear of the radio must face towards the cabling area of the radio installation.
4. Secure the M7300 mobile radio to each Extension Bracket using six M5 Philips-head screws (Item 4
in Table 4-4), three (3) screws per radio side. These screws have a captive-type (SEMS) lockwasher.
Tighten all six (6) screws with a screwdriver until the lock washer on each screw is fully compressed,
and the filter is firm and flush between the brackets.
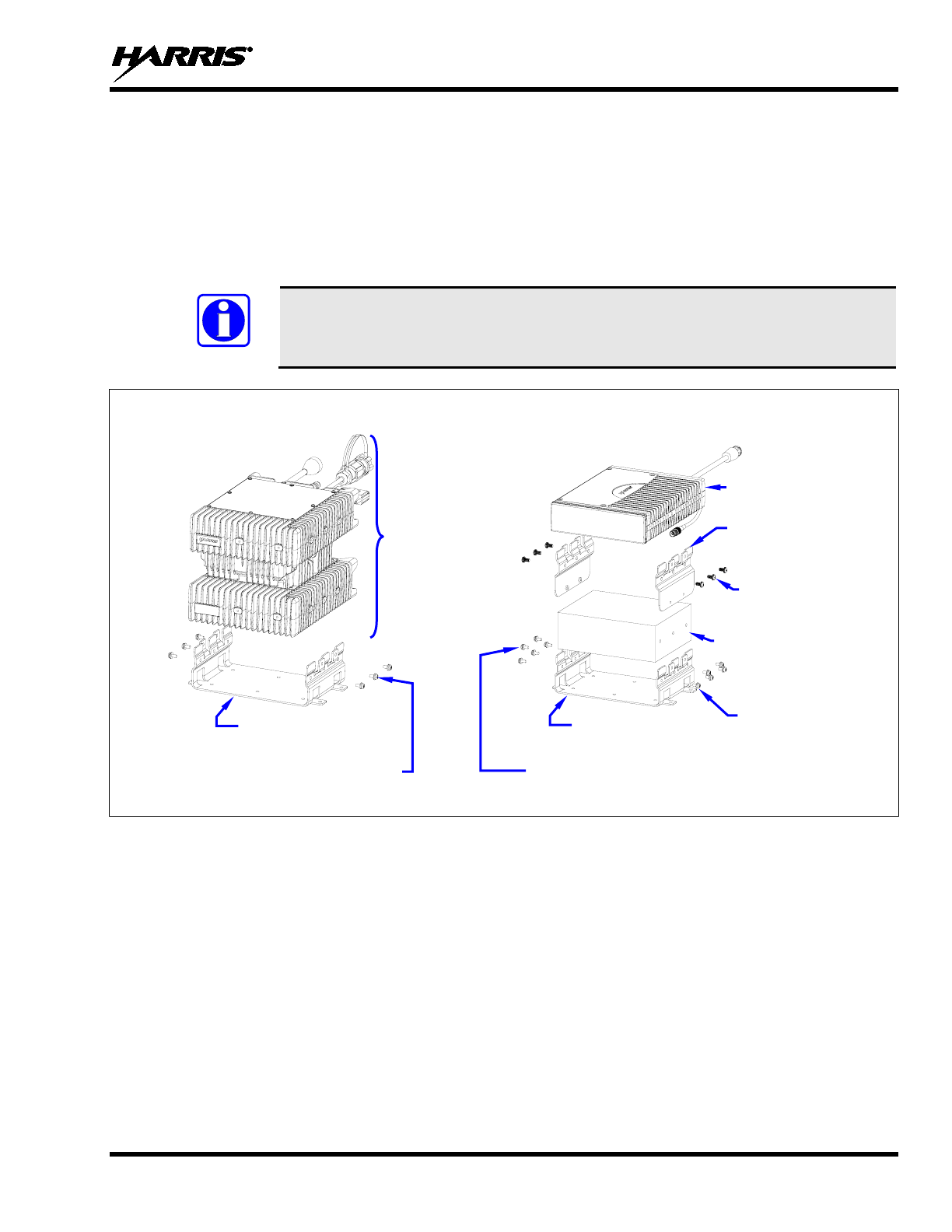
MM-018337-001, Rev. B
35
5. Slide the VRBS into the other Base Bracket. The rear of the radio must face towards the cabling area
of the radio installation.
6. Secure the VRBS to this bracket using three #8-32 pan-head screws (Item 3 in Table 4-4) per side.
Tighten all six (6) screws with a screwdriver until the lock washers on the screws are fully
compressed and the radio is firm and flush between the sides of the brackets.
7. Check the mounting area for proper clearance for cable service looping and for air circulation, plus an
area to secure and stow the excess cable lengths.
NOTE
Proper mounting is one factor that ensures optimal radio performance. An improperly
mounted radio
may experience degradation in the quality of voice and data
communications.
VRBS VRMS
Figure 6-2: VRMS and VRBS Assembly into Brackets (Exploded Views)
VRM Radio
(M7300 Mobile Radio)
Bandpass Filter
Extension Brackets
(2 places)
M5 Philips-Head
Screws (6 places to
secure VRM Radio to
Extension Brackets)
#8-32 Pan-Head
Screws (6 places to
secure Filter to Base
Bracket)
#8-32 Pan-Head Screws
(4 places to secure Extension
Brackets to Base Bracket)
Base Bracket
Base Bracket
VRBS
(Traffic
Controller,
700 MHz
Duplexer,
and
VRB Radio)
#8-32 Pan-Head Screws
(6 places to secure VRBS7010
to Base Bracket)
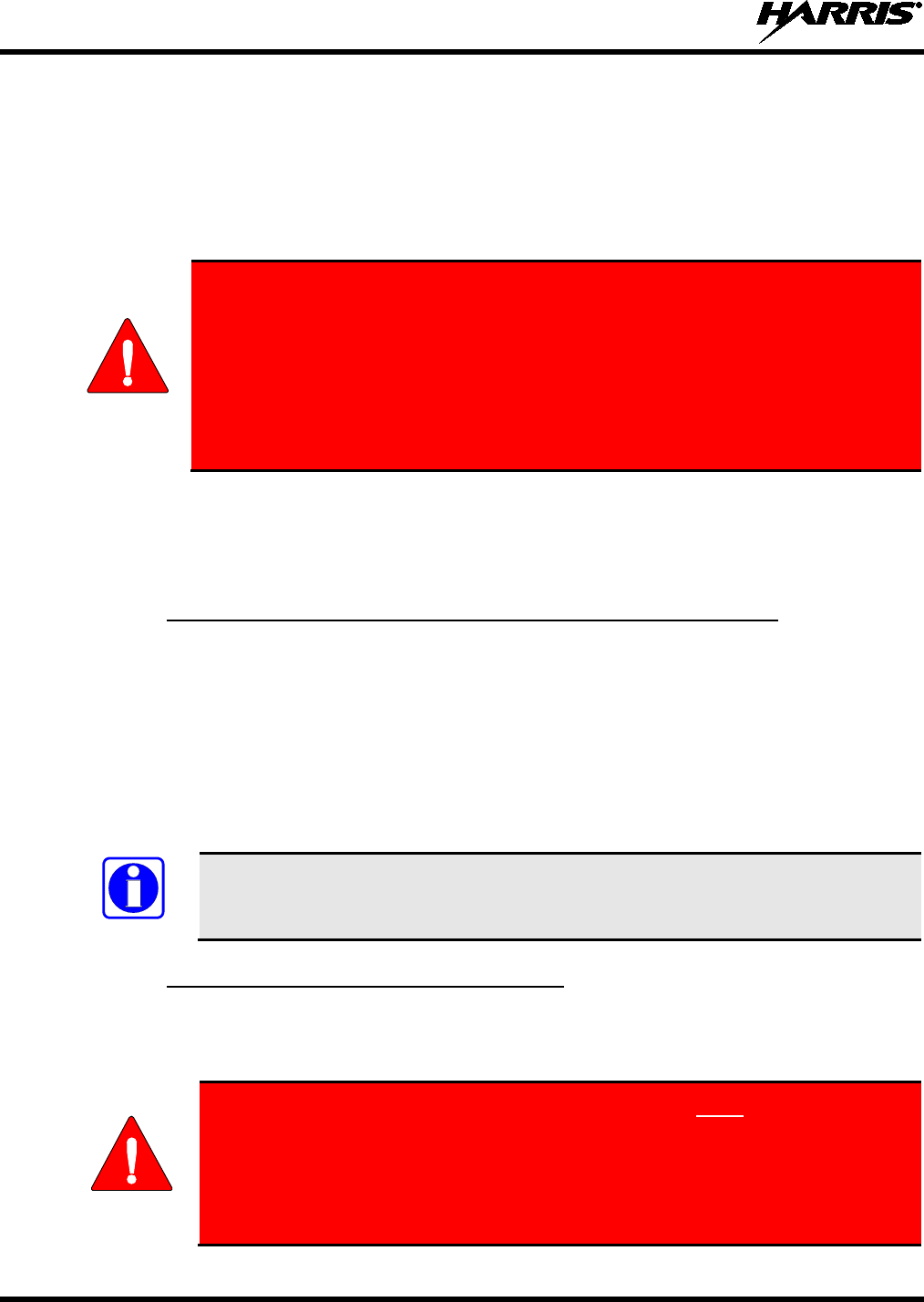
MM-018337-001, Rev. B
36
7 ANTENNA INSTALLATION
7.1 ANTENNA MOUNTING LOCATIONS
The VRMS and the VRBS transmit-receive antennas must be located at least three (3) feet (0.92 meters)
apart. For a standard motor vehicle, the VRMS antenna must be installed at or near the center of the
vehicle’s rooftop, and the VRBS antenna must be installed in the center of the vehicle’s trunk lid.
WARNING
At this time, review all information presented in the
REGULATORY AND
SAFETY INFORMATION section of this manual (begins on page 6). Both
transmit-receive antennas must be installed
in accordance with the guidelines
presented in the REGULATORY AND SAFETY INFORMATION section. In
order to reduce human exposure to radio frequency (RF) electromagnetic energy
during transmit mode, use Table 1-1/Table 1-2 and Table 1-3, and Figure
7-1/Figure 7-2 and Figure 7-3 to determine the best possible antenna mounting
locations
Antennas must be mounted in locations on the vehicle as illustrated and described in this section. Also,
see Table 4-5 for additional information. Always follow manufacturer’s instructions when mounting an
antenna. References to locations through apply to the locations illustrated in Figure 7-1 through
Figure 7-3.
7.1.1 Direct Center or Center-Rear of Rooftop for VRMS Antenna
The center of the vehicle’s roof is the best location for the VRMS antenna (location ). For optimal
performance, the mounting area under the antenna must be flat with a minimum radius of six (6) inches of
metal ground plane. Locating the antenna directly in the center of the roof will minimize human exposure
to RF electromagnetic energy.
If obstructions such as a light bar or another antenna prevent the VRMS antenna from being mounted in
the direct center of the roof, the antenna should be mounted a minimum of one foot away from and behind
the obstruction but in the middle of the roof with respect to the left and right sides of the vehicle (location
).
NOTE
The VRMS and the VRBS transmit-receive antennas must be located at least three (3)
feet (0.92 meters) apart. See Figure 7-1 through Figure 7-3. The radio-end of each
antenna cable must be labeled so each cable is connected to the correct radio.
7.1.2 Center of Trunk Lid for VRBS Antenna
For a standard motor vehicle, the VRBS antenna should be located in the center of the vehicle’s trunk lid
(location ). Locating the antenna directly in the center of the lid will provide the best P25 vehicular
repeater mode improve coverage, and minimize human exposure to RF electromagnetic energy.
WARNING
The antenna cable of Harris-approved antennas should never be cut to a shorter
length. Instead, excess cable must be tied and stowed. This not only prevents the
antenna from radiating above its intended or configured power, but it also allows
for future installation considerations such as a relocation of the mobile radio
within the vehicle. Installations requiring longer cables are to be treated as
custom and separately specified.
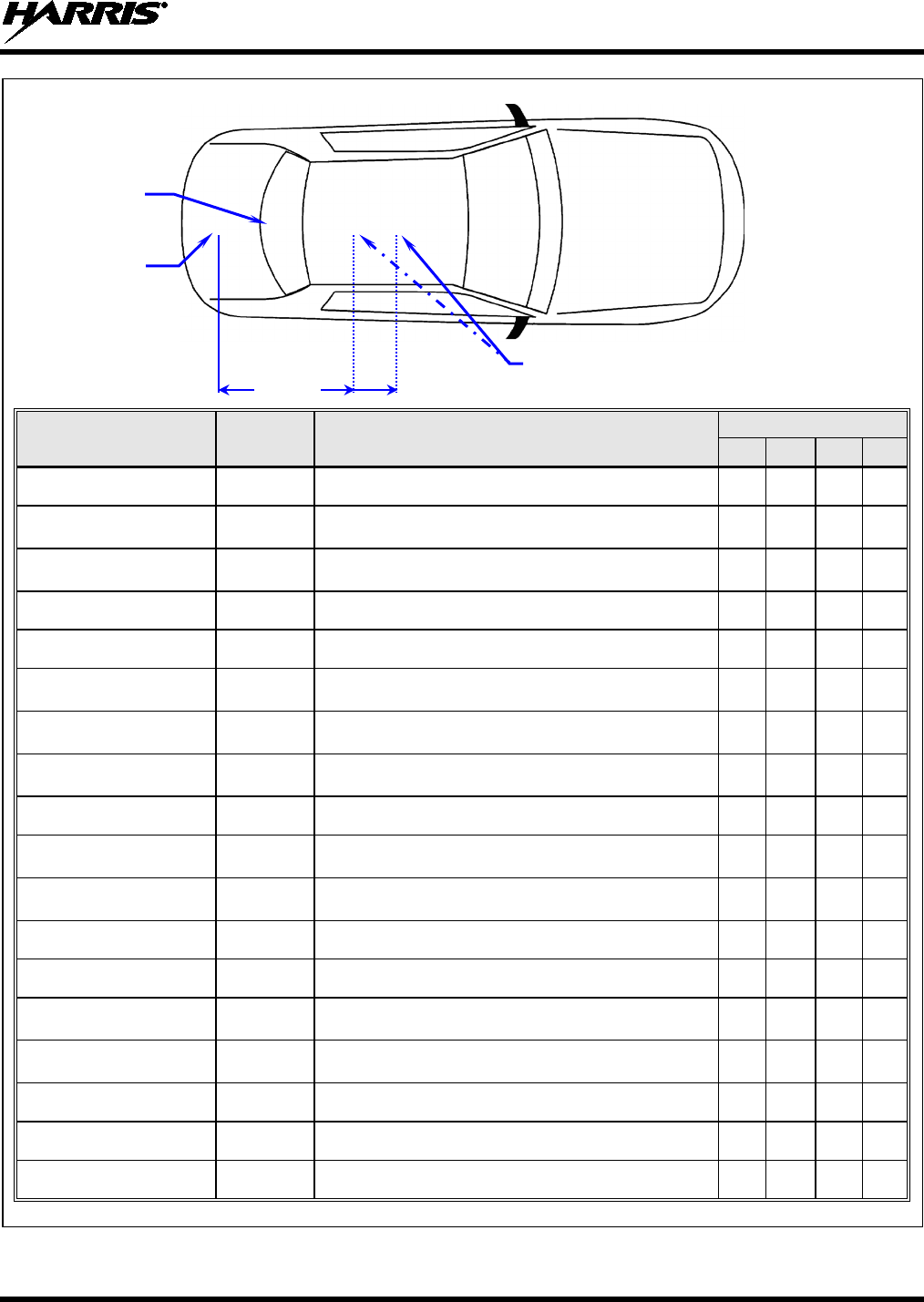
MM-018337-001, Rev. B
37
TOP VIEW OF A TYPICAL VEHICLE
ANTENNA
PART NUMBER FOR
RADIOS ANTENNA DESCRIPTION *
LOCATION
AN-125001-002 (mount) with
AN-225001-001 (element) VRMS7010
VRMS7020 700/800 MHz Standard Rooftop-Mount, 3 dBd Gain
AN-125001-002 (mount) with
AN-225001-002 (element) VRMS7010
VRMS7020 700/800 MHz Standard Rooftop-Mount,
Elevated-Feed, 3 dBd Gain
AN-125001-002 (mount) with
AN-225001-003 (element) VRMS7010
VRMS7020 700/800 MHz Standard Rooftop-Mount,
Elevated-Feed, No Ground Plane, 3 dBd Gain
AN-125001-002 (mount) with
AN-225001-005 (element) VRMS7010
VRMS7020 700/800 MHz Standard Rooftop-Mount, 5 dBd Gain
AN-125001-004 (mount) with
AN-225001-001 (element) VRMS7010
VRMS7020 700/800 MHz Thick Rooftop-Mount, 3 dBd Gain
AN-125001-004 (mount) with
AN-225001-002 (element) VRMS7010
VRMS7020 700/800 MHz Thick Rooftop-Mount,
Elevated-Feed, 3 dBd Gain
AN-125001-004 (mount) with
AN-225001-003 (element) VRMS7010
VRMS7020 700/800 MHz Thick Rooftop-Mount,
Elevated-Feed, No Ground Plane, 3 dBd Gain
AN-125001-004 (mount) with
AN-225001-005 (element) VRMS7010
VRMS7020 700/800 MHz Thick Rooftop-Mount,
Elevated-Feed, 5 dBd Gain
AN-125001-006 (mount) with
AN-225001-001 (element) VRMS7010
VRMS7020 700/800 MHz GPS Combo Rooftop-Mount, 3 dBd Gain
AN-125001-006 (mount) with
AN-225001-002 (element) VRMS7010
VRMS7020 700/800 MHz GPS Combo Rooftop-Mount,
Elevated-Feed, 3 dBd Gain
AN-125001-006 (mount) with
AN-225001-003 (element) VRMS7010
VRMS7020 700/800 MHz GPS Combo Rooftop-Mount,
Elevated-Feed, No Ground Plane, 3 dBd Gain
AN-125001-006 (mount) with
AN-225001-005 (element) VRMS7010
VRMS7020 700/800 MHz GPS Combo Rooftop-Mount, 5 dBd Gain
AN-125001-008 (mount) with
AN-225001-001 (element) VRMS7010
VRMS7020 700/800 MHz Magnetic-Mount, 3 dBd Gain
AN-125001-008 (mount) with
AN-225001-002 (element) VRMS7010
VRMS7020 700/800 MHz Magnetic-Mount,
Elevated-Feed 3 dBd Gain
AN-125001-008 (mount) with
AN-225001-003 (element) VRMS7010
VRMS7020 700/800 MHz Magnetic-Mount,
Elevated-Feed, No Ground Plane, 3 dBd Gain
AN-125001-008 (mount) with
AN-225001-005 (element) VRMS7010
VRMS7020 700/800 MHz Magnetic-Mount, 5 dBd Gain
AN-025187-001 VRMS7010
VRMS7020 GPS Receive Only, Roof-Mount
AN-025187-003 VRMS7010
VRMS7020 GPS Receive Only, Magnetic-Mount
* See Table 4-5 which begins on page 26 for the detailed descriptions.
Figure 7-1: Required VRMS7010/VRMS7020 Antenna Mounting Locations with Antenna Part Numbers
Trunk Lid
Rooftop
Hood
3-Feet
Minimum
Antenna
Separation
VRBS
Antenna
GPS Antenna
(if required;
see text)
VRMS Antenna — Use location (center-most
location) unless an obstruction such as a light
bar or another antenna is nearby. See text.
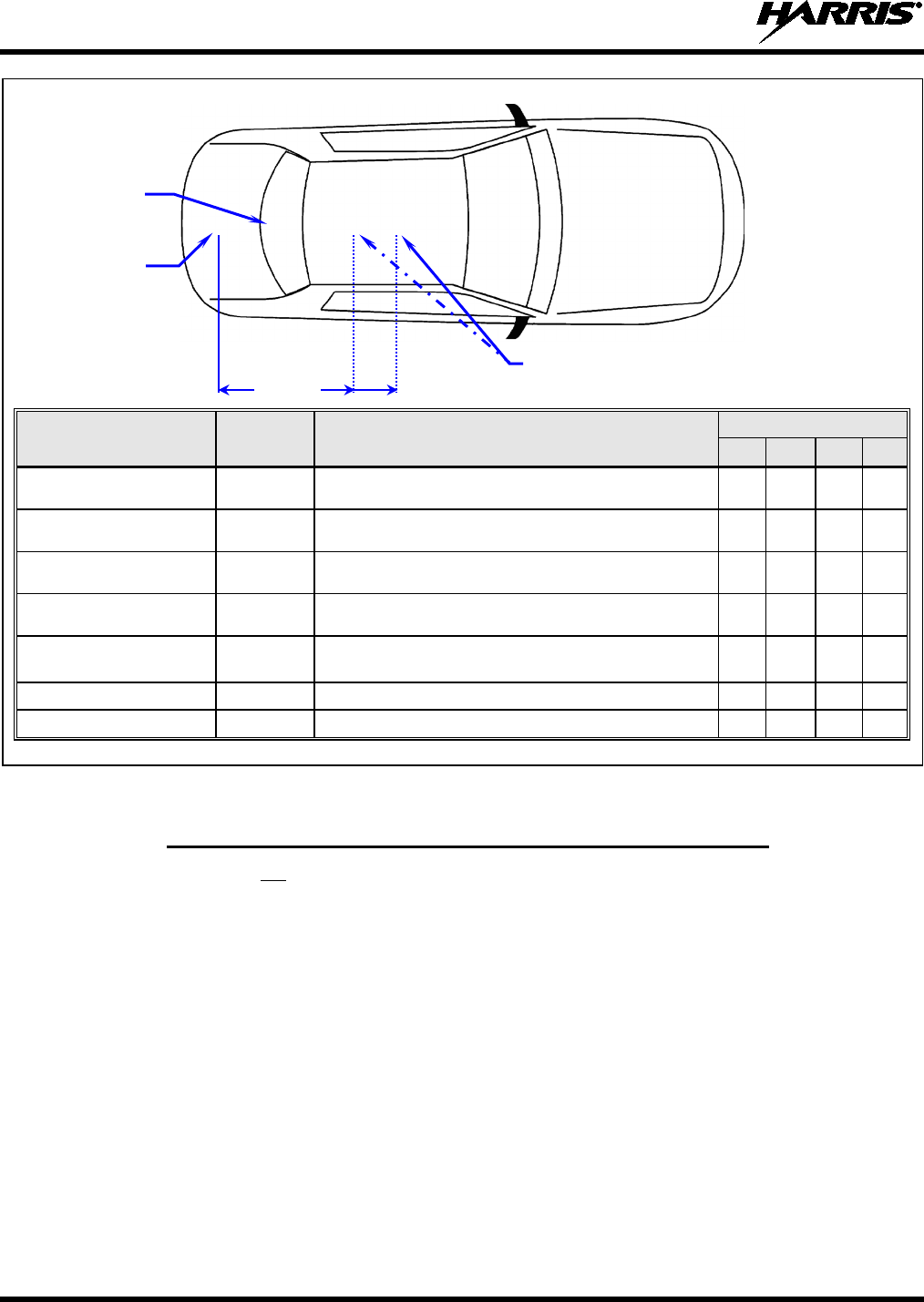
MM-018337-001, Rev. B
38
TOP VIEW OF A TYPICAL VEHICLE
ANTENNA
PART NUMBER FOR
RADIO ANTENNA DESCRIPTION *
LOCATION
AN-125001-001 (mount) with
AN-225002-001 (element) VRMS7030 136 to 174 MHz Standard Rooftop-Mount, 0 dBd Gain
AN-125001-003 (mount) with
AN-225002-001 (element) VRMS7030 136 to 174 MHz Thick Rooftop-Mount, 0 dBd Gain
AN-125001-003 (mount) with
AN-225006-001 (element) VRMS7030 136 to 174 MHz Thick Rooftop-Mount, 0 dBd Gain
AN-125001-007 (mount) with
AN-225002-001 (element) VRMS7030 136 to 174 MHz Magnetic-Mount, 0 dBd Gain
AN102800V1 VRMS7030 136 to 174 MHz Standard Rooftop-Mount,
¼-Wavelength, 0 dBd Gain
AN-025187-001 VRMS7030 GPS Receive Only, Roof-Mount
AN-025187-003 VRMS7030 GPS Receive Only, Magnetic-Mount
* See Table 4-5 which begins on page 26 for the detailed descriptions.
Figure 7-2: Required VRMS7030 Antenna Mounting Locations with Antenna Part Numbers
7.1.3 Rear Deck Lid for GPS Stand-Alone GPS Receive Antenna
If the VRMS7010 does not use a GPS combination-type antenna and it is equipped with a GPS receiver, a
stand-alone GPS receive antenna must be separately located and mounted. The vehicle’s rear deck lid
(location ) is the recommended mounting location for this case. This locates the GPS antenna inside the
vehicle.
Trunk Lid
Rooftop
Hood
3-Feet
Minimum
Antenna
Separation
VRBS
Antenna
GPS Antenna
(if required;
see text)
VRMS Antenna — Use location (center-most
location) unless an obstruction such as a light
bar or another antenna is nearby. See text.
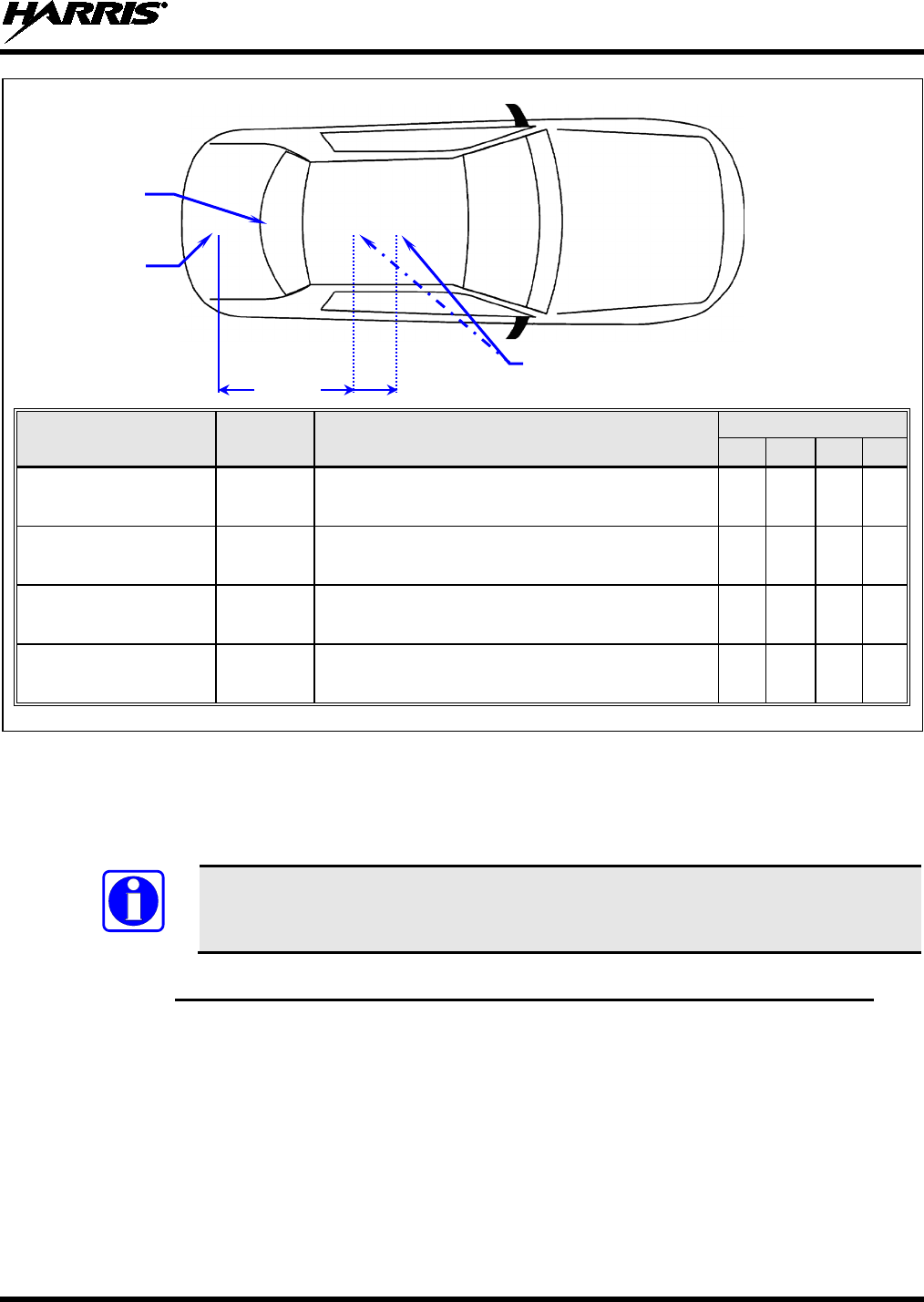
MM-018337-001, Rev. B
39
TOP VIEW OF A TYPICAL VEHICLE
ANTENNA
PART NUMBER FOR
RADIOS ANTENNA DESCRIPTION *
LOCATION
AN-125001-002 (mount) with
AN-225001-004 (element)
VRBS7010
VRBS7020
VRBS7030 700/800 MHz Standard Rooftop-Mount, 2 dBd Gain
AN-125001-004 (mount) with
AN-225001-004 (element)
VRBS7010
VRBS7020
VRBS7030 700/800 MHz Thick Rooftop-Mount, 2 dBd Gain
AN-125001-006 (mount) with
AN-225001-004 (element)
VRBS7010
VRBS7020
VRBS7030 700/800 MHz GPS Combo Rooftop-Mount, 2 dBd Gain
AN-125001-008 (mount) with
AN-225001-004 (element) VRBS7010
VRBS7020
VRBS7030 700/800 MHz Magnetic-Mount, 2 dBd Gain
* See Table 4-5 which begins on page 26 for the detailed descriptions.
Figure 7-3: Required VRBS7010/VRBS7020/VRBS7030
Antenna Mounting Locations with Antenna Part Numbers
7.2 ANTENNA INSTALLATION PROCEDURES
NOTE
Antennas must be installed before completing the radio installation.
7.2.1 Installing NMO Antenna Mounts AN-125001-001, -002, -003 and -004
These NMO style antenna mounts can each be used with several different antenna elements. Only limited
access under the mounting location is typically required. The installation procedure is presented in
Section 7.2.1.3.
7.2.1.1 Standard NMO Antenna Mounts AN-125001-001 and AN-125001-002
These standard ¾-inch NMO antenna mounts require a ¾-inch hole in a relatively flat area of the vehicle
body, with a vehicle metal thickness of between 0.020 and 0.040 inches. AN-125001-002 has a very-low-
loss coax cable (LMR-195 or equivalent).
Trunk Lid
Rooftop
Hood
3-Feet
Minimum
Antenna
Separation
VRBS
Antenna
GPS Antenna
(if required;
see text)
VRMS Antenna
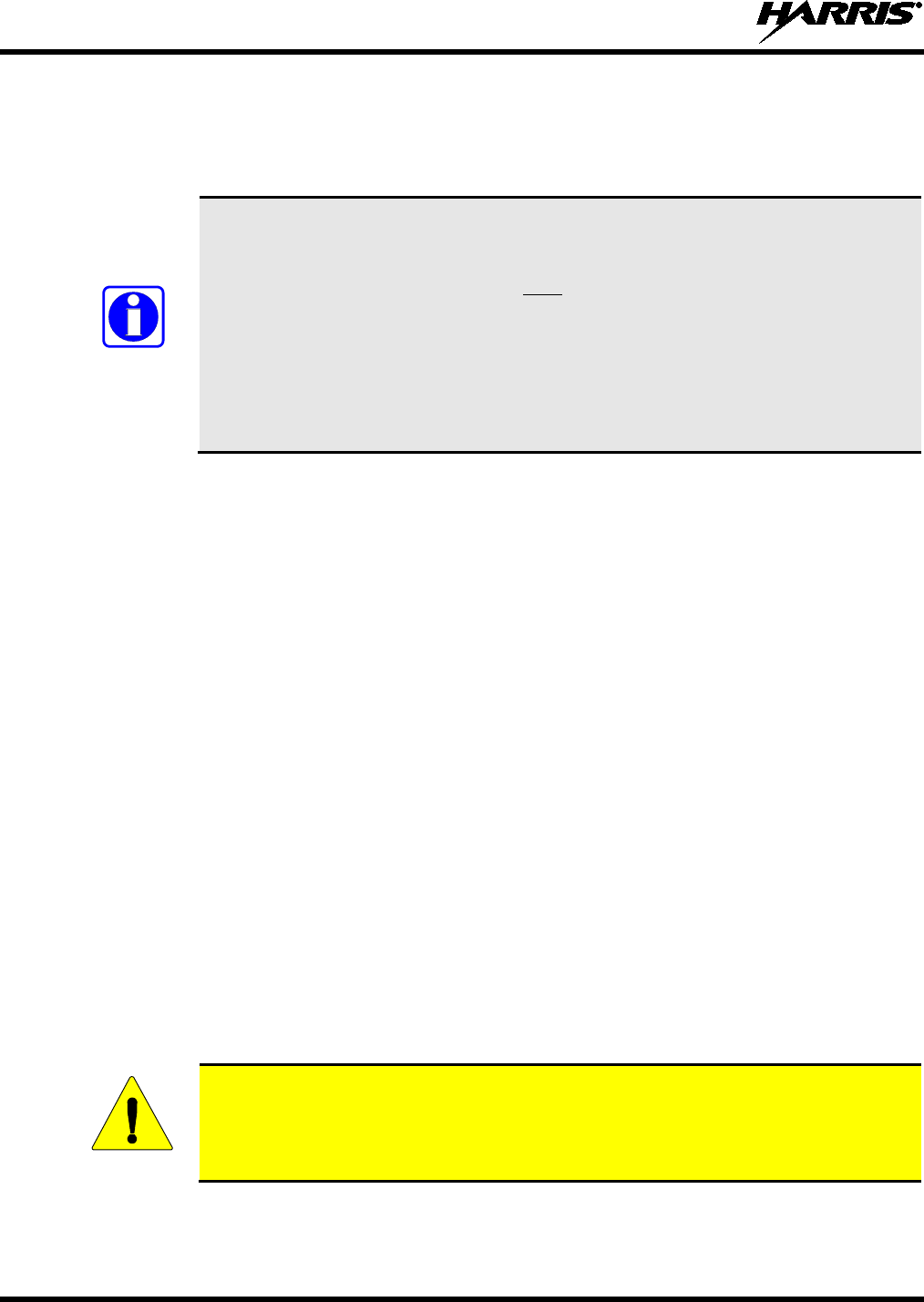
MM-018337-001, Rev. B
40
7.2.1.2 Thick-Roof NMO Antenna Mounts AN-125001-003 and AN-125001-004
Both of these thick-roof NMO antenna mounts use either a ⅜-inch or a ¾-inch mounting hole in a
relatively flat area of the vehicle body, with a vehicle metal thickness of between 0.040 and 0.1875 inches
(3/16-inch maximum thickness). AN-125001-004 has a very-low-loss coax cable (LMR-195 or equivalent).
NOTE
For thick-roof NMO antenna mounts AN-125001-003 or AN-125001-004, using a
⅜-inch mounting
hole will require better access to the underside of the mounting
location than if a ¾-inch hole is used. This is because, in the case of a ⅜-inch hole, the
antenna mount’s bushing assembly must
be inserted from the underside of the
mounting surface.
When using a ¾-inch mounting hole to mount thick-
roof NMO antenna mounts
AN-125001-003 or AN-125001-004, the thickness of the mounting surface must be at
least ⅛-inch (0.125-inch minimum thickness). This requirement is due to the thickness
of the alignment ring used to center the bushing assembly within the ¾-inch mounting
hole.
7.2.1.3 Installation Procedure for Mounts AN-125001-001 through -004
1. Select the antenna mounting location in accordance with the information presented in Sections 1 and
7.1 of this manual. If necessary, contact the Technical Assistance Center for assistance. See page 21
for TAC contact information.
2. Verify no obstructions exist immediately below the respective mounting location on the underside of
the vehicle body, such as vehicle ribbing/body framing, a wiring harness, air bag equipment, etc. Also
verify there is a sufficient access path and clearance for the mount’s coax cable. If there is an
obstruction or insufficient clearance, select another nearby mounting location.
3. Measure and mark the center point of the selected antenna mounting location. Be sure to center the
mark from side-to-side of the vehicle.
4. Obtain a hole saw specifically designed for drilling NMO mounting holes of the required diameter.
(e.g., Antenex/Laird Technologies model HS34 or equivalent for a ¾-inch hole; Antenex/Laird
Technologies model HS38 or equivalent for a ⅜-inch hole).
5. If the vehicle’s headliner panel, carpet, seats, or otherwise, is below the mounting location, move or
remove the headliner panel, etc. as necessary to protect it. Alternately, apply a heat-resistant mask
material (such as a fiberglass mat or thin sheet metal with masked edges) as required to “catch” the
metal shavings and the metal plug (if any) produced by the hole saw. The plug (if any) may be
relatively hot if/when it drops out of the saw upon completion of the hole drilling process. ⅜-inch
diameter hole saws generally produce only shavings, not plugs.
6. With the hole saw and a drill, drill a hole at the marked hole center point. Position the drill square to
(i.e., 90 degrees from) the vehicle mounting surface so paint immediately outside of the perimeter of
the hole is evenly removed.
CAUTION
Excessive use of the hole saw and/or failure to position the drill square with (i.e.,
at a 90-degree angle from) the vehicle mounting surface may result in damage to
the metal mounting surface, in the area immediately outside of the perimeter of
the hole.
7. Ensure the saw removed the paint immediately around the hole as the drilling operation completes. If
not, do so by reinserting the saw completely into the hole and spinning it as required. This allows
proper grounding via the mount’s lock nut on the top of the mounting surface. On the bottom of the
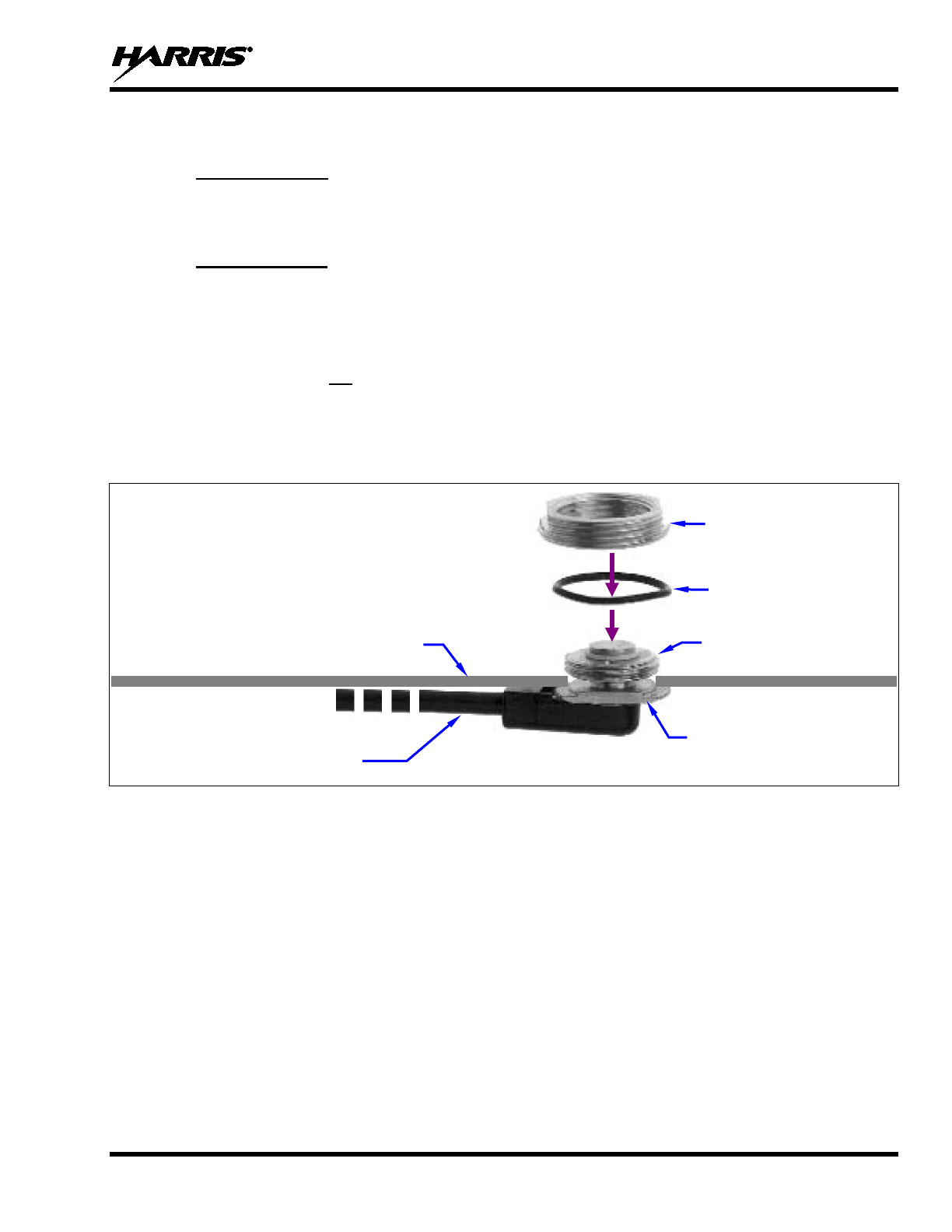
MM-018337-001, Rev. B
41
mounting surface, the “teeth” of the mount’s bushing assembly may not provide a good ground due to
thick vehicle undercoating, thick primer, oxidation/rust, etc.
8. For a ¾-inch hole, feed the unterminated end of the mount’s coax cable into the hole from the top
surface of the vehicle until the mount’s bushing assembly is in position to drop into the hole. The
bushing should be tilted at a slight angle and fed into the hole. The threaded shank of the mount’s
bushing assembly will not fall through a ¾-inch hole.
For a ⅜-inch hole, feed the threaded shank of the mount’s bushing assembly into the hole from the
underside of the mounting surface. Hold it into position until the lock nut is installed.
9. If installing a thick-roof antenna mount (⅜-inch shank) into a ¾-inch hole, place the alignment ring
onto the threaded shank of the mount. This ring has an approximate ¾-inch outside diameter.
10. A tube of synthetic lubricant is included with the antenna mount. Apply this lubricant to the mount’s
rubber O-ring. Do not get any lubricant on the center contact of the mount’s bushing assembly.
11. As illustrated in Figure 7-4 and Figure 7-5, add the O-ring (C) and lock nut (D) to the top of the
mount’s bushing assembly (A). With the O-ring in the groove in the underside of the lock nut, thread
the lock nut onto the bushing assembly. Be sure the O-ring remains in the groove before tightening
the lock nut.
Figure 7-4: Installing a Standard ¾-Inch NMO Antenna Mount
(e.g., AN-125001-001 or AN-125001-002)
Coax Cable
(Partial)
Rubber O-Ring (C)
Vehicle Mounting Surface
(top side)
Bushing Assembly (A)
Lock Nut (D)
Threaded Shank (B)
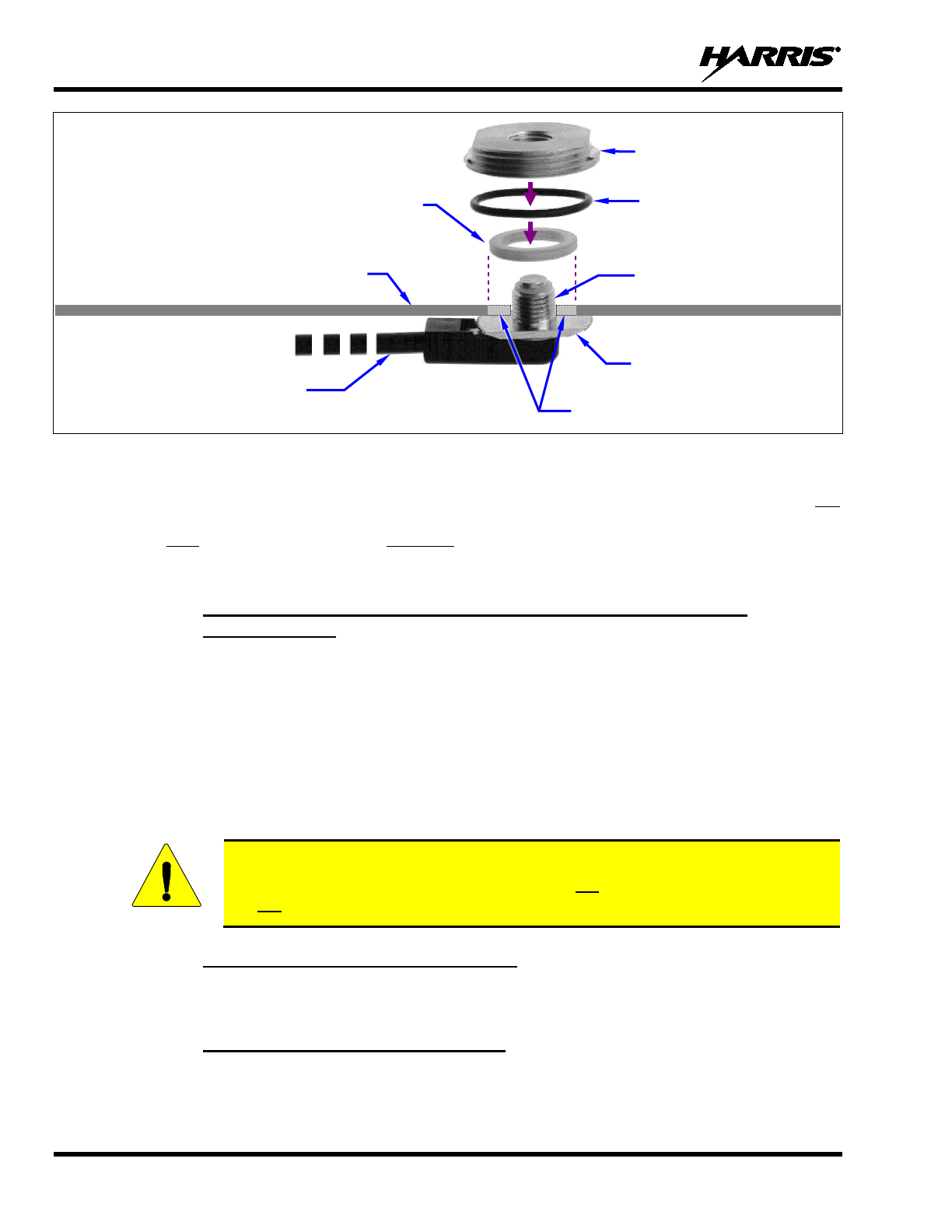
MM-018337-001, Rev. B
42
Figure 7-5: Installing a Thick-Roof NMO Antenna Mount
(e.g., AN-125001-003 or AN-125001-004)
12. Using a 15/16-inch open-end wrench, tighten the lock nut until it fully compresses the O-ring and
makes good contact with the vehicle mounting surface. The groove’s ridges on the bottom of the lock
nut must make full contact with the unpainted metal surface of the vehicle.
13. Install the antenna element per the procedure in Section 7.2.4.
7.2.2 Installing NMO Magnetic Antenna Mounts AN-125001-007 and
AN-125001-008
1. Thoroughly clean the bottom of the magnetic mount and the selected vehicle mounting surface by
removing all dust, dirt, etc.
2. Carefully place the magnet mount onto the metal surface of the vehicle at the selected location. The
coax cable exiting the mount’s base should be orientated towards the point at which it will enter into
the interior of the vehicle. Do not try to reposition it by sliding it on a painted metal surface.
3. Route the mount’s coax cable to the radio location, passing it by the trunk lid’s perimeter gasket, door
perimeter gasket, etc., as necessary.
4. Install the antenna element per the procedure in Section 7.2.4.
CAUTION
To remove a magnetic antenna mount, hold it at the bottom of its base and tilt it at an
angle to release the magnetic attraction force. Do not pull on the mount’s coax cable.
Do not drag the mount across the mounting surface.
7.2.3 Installing all Other Antenna Mounts
For any other type of antenna mount not covered in the previous sections, such as GPS combination
antennas, install the mount in accordance with the installation instructions included with the mount.
7.2.4 Attaching NMO Antenna Elements
1. Clean the top surface of the NMO mount and the surface of the vehicle immediately around the
mount.
Coax Cable
(Partial)
Rubber O-Ring (C)
Vehicle Mounting Surface
(top side)
Bushing Assembly (A)
Lock Nut (D)
Threaded Shank (B)
Alignment Ring
(Used only with ¾-inch mounting hole.
(Extensions shown to illustrate a
⅜-Inch hole vs. a ¾-inch hole.)
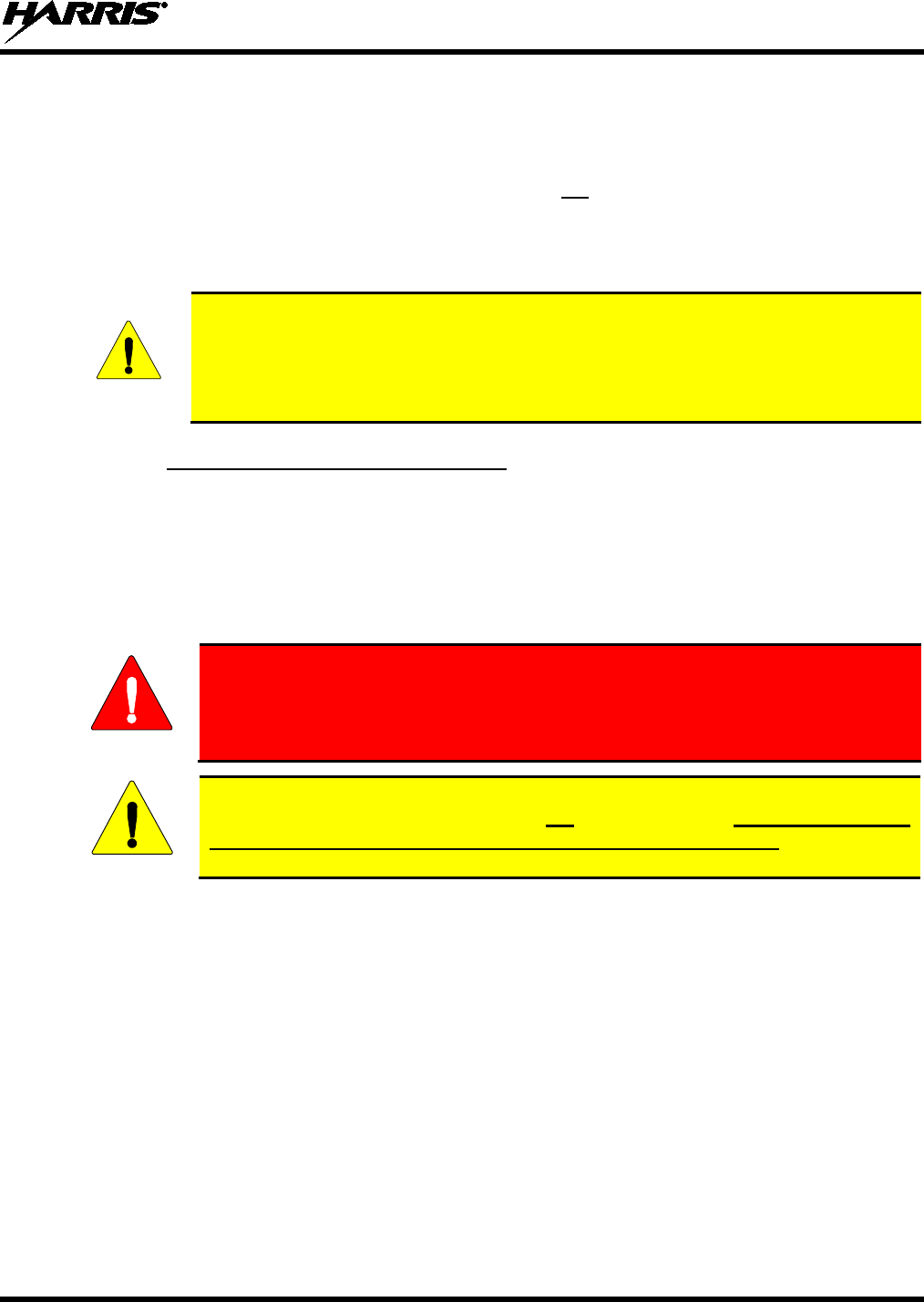
MM-018337-001, Rev. B
43
2. Place the gasket included with the antenna element (not pictured in Figure 7-4 or Figure 7-5) around
the mount and against the surface of the vehicle. If a lubricant or sealant was included with the
gasket, apply it to the gasket before placing the gasket.
3. Apply the antenna element to the top of the mount and tighten it in a clock-wise direction (as viewing
from the top). Use an appropriate wrench if required. Do not over-tighten.
4. Install a placard (not supplied) on the vehicle’s dash panel, in accordance with the following
CAUTION. Place the placard in plain view of the vehicle operator’s position.
5. Continue with the connection procedure presented in the next section.
CAUTION
Before entering any automatic vehicle (“car”) wash equipment, remove the antenna
elements from the antenna mounts, and secure the elements in a safe location inside the
vehicle. This will prevent the wash equipment from damaging the elements and/or
mounts. After exiting the wash equipment, thoroughly dry the top of the mount before
re-installing the elements.
7.2.5 Connecting the Mobile Antennas
1. Label the radio-end of each antenna cable. The cable from the rooftop-mounted antenna (highest of
the two) should be labeled “VRMS Antenna” and the cable from the trunk-mounted antenna (lowest
of the two) should be labeled “VRBS Antenna”
2. Route each antenna cable from the antenna to the rear of the respective radio. Remove headliner
panel, other interior panels, etc., as necessary. Keep each cable out of casual contact areas from
persons within the vehicle. Tie and stow as necessary to protect the cables.
WARNING
Use the full length of coaxial cable included with each antenna. Never cut the
cable to a shorter length, but rather coil any excess. Reducing the length of cable
increases the output power radiated by the antenna, thereby exceeding the
Maximum Permissible Exposure (MPE) allowance regulated by the FCC.
CAUTION
The VRMS and VRBS antennas are not interchangeable. Therefore, label the
radio-end of each cable for future reference, as described in step 1.
3. Using an appropriate crimp tool, crimp the supplied TNC RF connector to the end of each antenna
cable. See Figure 7-6 for crimping instructions.
4. Connect each antenna cable’s TNC plug-type (male) connector to the respective radio’s TNC
receptacle-type (female) RF connector at the rear of the radio. The VRMS antenna cable (labeled
“VRMS Antenna”) must be connected to the “ANTENNA” connector on the rear of the 800 MHz
bandpass filter. The VRMS antenna cable (labeled “VRBS Antenna”) must be connected to the
“pigtail” type antenna cable of the VRBS. Mate the connectors and turn the plug clockwise until
finger-tight.
This will be a temporary connection until the radios and antennas can be tested after the installation is
complete (in accordance with test procedures presented in Section 16). The antennas should be connected
now in case of accidental transmission.
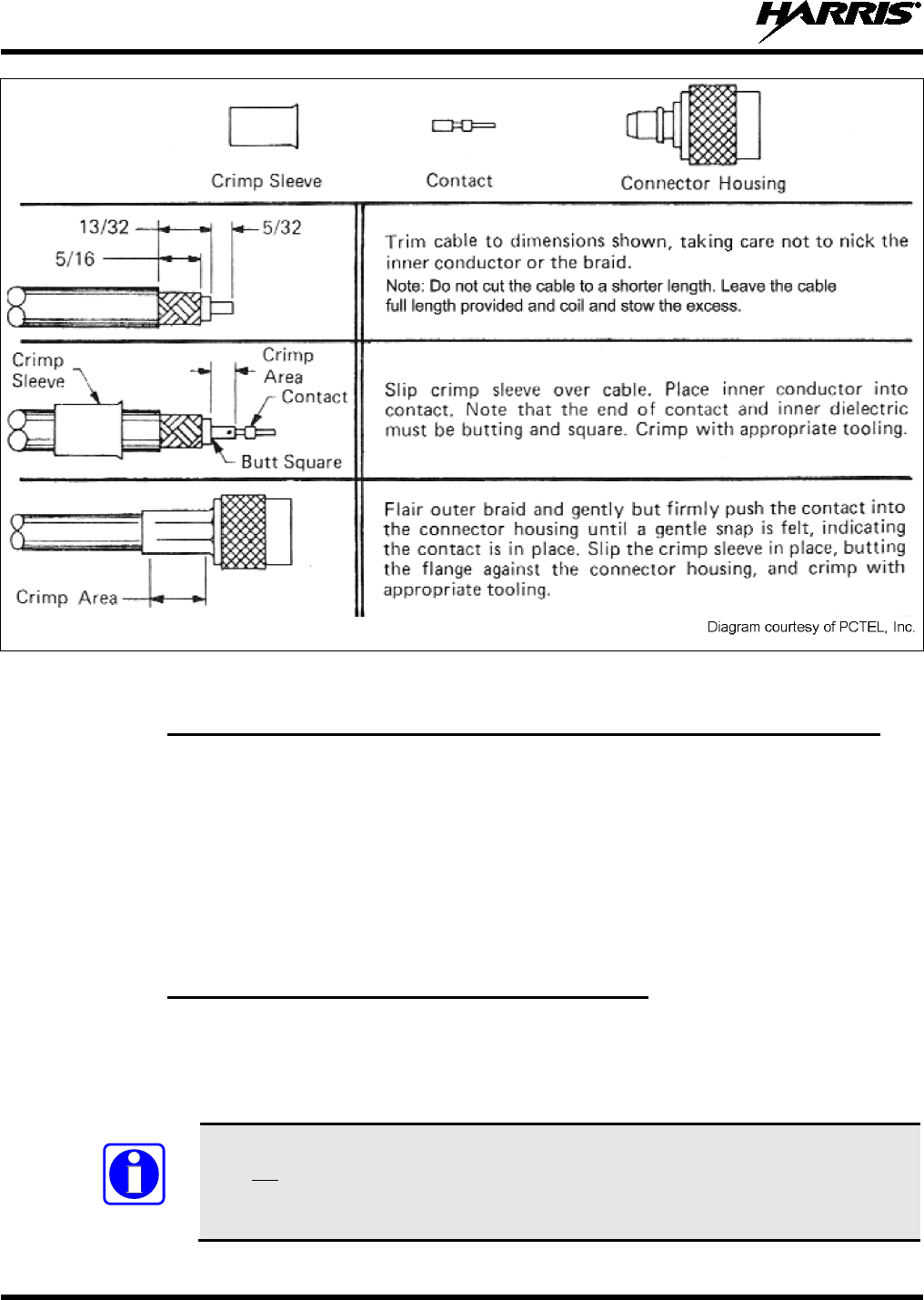
MM-018337-001, Rev. B
44
(VS-AN-025167-010 Rev. A)
Figure 7-6: Crimping Instructions for TNC RF Connector (Actual Size; Dimensions in Inches)
7.2.6 Connect RF Cable Between VRM Radio and 800 MHz Bandpass Filter
An RF cable must be connected between the antenna connector of the M7300 and the 800 MHz bandpass
filter as follows:
1. Obtain RF Cable CA-018378 from the installation kit (item 8 in Table 4-4).
2. Mate the cable’s male TNC connector the radio’s female TNC connector. Do not fully tighten at this
time.
3. Mate the cable’s female TNC connector to the 800 MHz bandpass filter’s male TNC connector.
4. Using a pair of soft-jaw pliers, firmly tighten both of the cable’s TNC connectors. Do not over-tighten.
7.2.7 Install and Connect GPS Antenna (if Required)
The VRMS’s M7300 mobile radio may be equipped with an internal GPS receiver. If so, this receiver
requires connection to an externally-mounted GPS antenna if the GPS functions will be utilized. Some
installations may use a magnetic-mount stand-alone GPS antenna installed separately from the SMR
mobile antenna.
NOTE
Operation in either the standard mobile radio mode or in a vehicular repeater mode
does not require GPS receiver operation. The radio’s GPS receiver is typically used to
support a computer running GPS software connected to the radio via NMEA-formatted
serial data link. Refer to Section 14 for additional information.
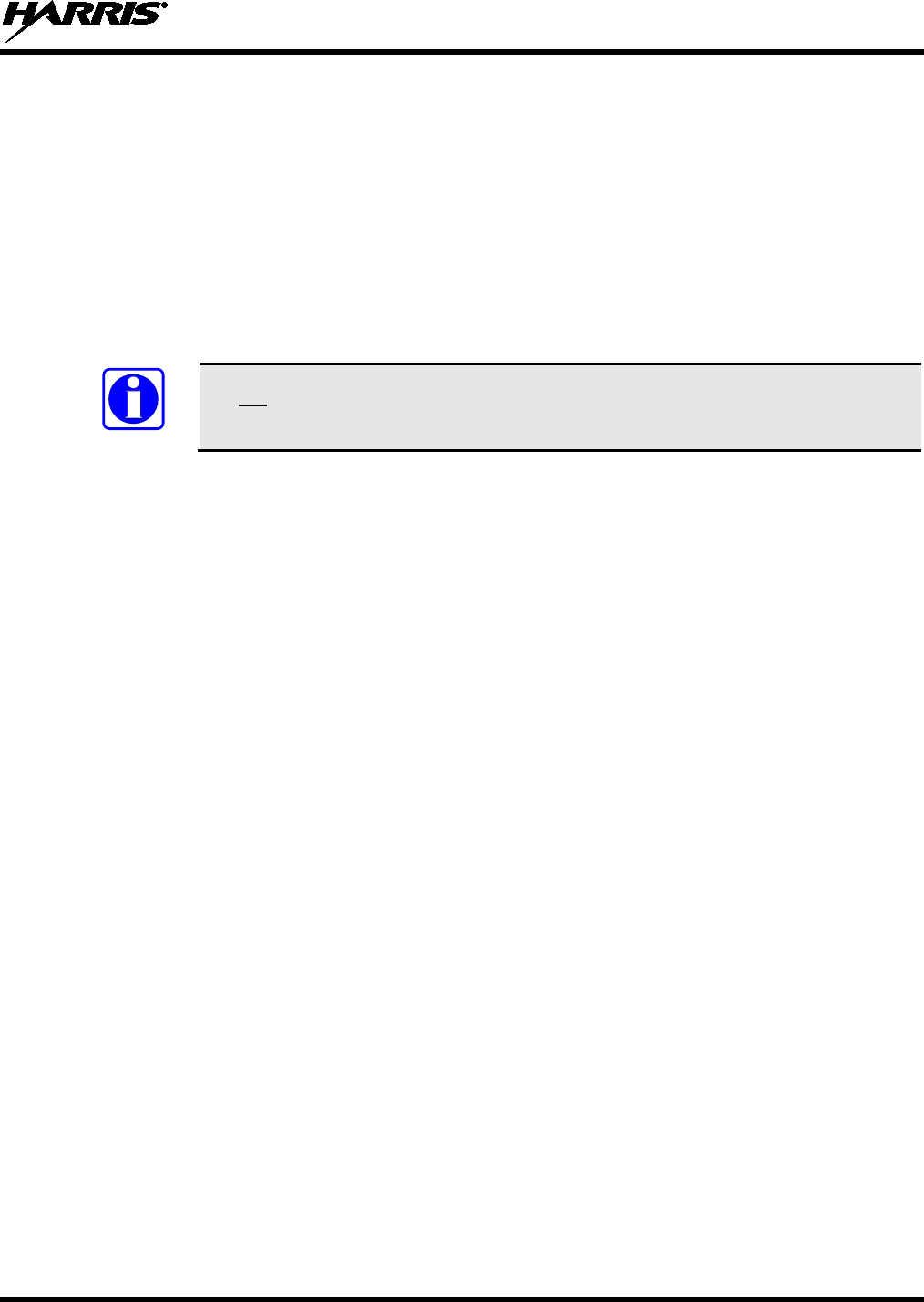
MM-018337-001, Rev. B
45
The following antenna installation procedure is recommended:
1. Once the mounting location is selected, refer to the antenna manufacturer’s mounting and testing
instructions for installation guidance. If necessary, contact the Technical Assistance Center (see page
21 for contact information).
2. Route the cable from the GPS antenna to the rear of the radio. Remove headliner panel, other interior
panels, etc., as necessary. The cable must be kept out of casual contact from persons within the
vehicle.
3. Connect the GPS antenna cable’s SMA plug-type (male) connector to the radio’s SMA receptacle-
type (female) “pigtail” type RF connector at the rear of the radio. Mate the two connectors and turn
the plug clockwise. Tighten using a 5/16-Inch combination or open-end wrenches. Do not over-tighten.
NOTE
Do not alter the length of cable from the GPS antenna. The SMA connector on the end
of the antenna cable is not field-replaceable. Tie and stow excess cable as necessary.
The GPS combo antenna kit includes a GPS antenna built into the base of the mobile antenna. No extra
holes are required for the GPS cable when using this antenna. The antenna must be kept at least six (6)
inches away from any other antenna mounted on the vehicle and have at least six inches of surface ground
plane beneath it.
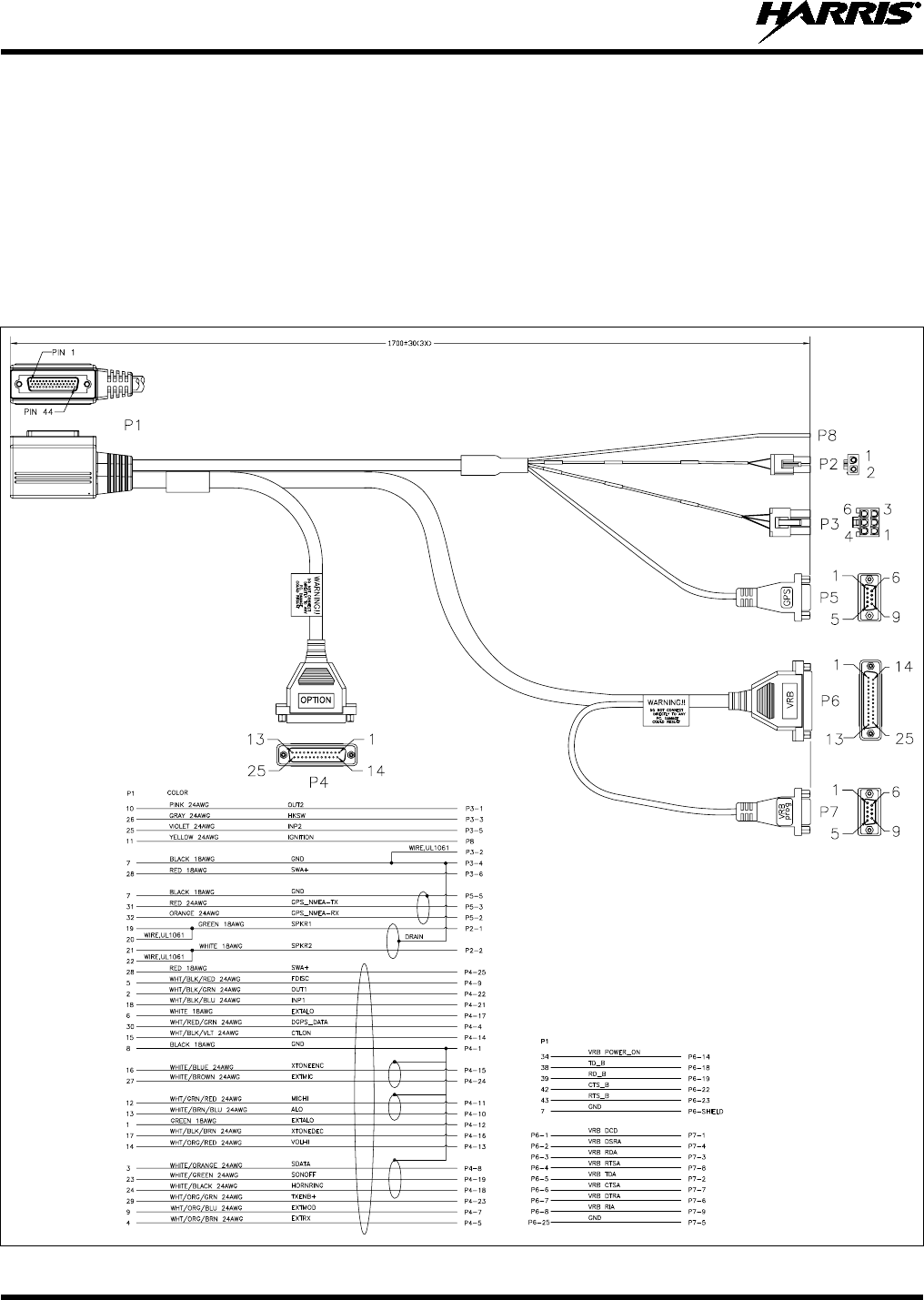
MM-018337-001, Rev. B
46
8 INTERFACE CABLE INSTALLATION
8.1 INTERFACE CABLE CA-012349-003 OVERVIEW
Interface Cable CA-012349-003 interconnects the VRMS to the VRBS. It also provides connections for
optional equipment, if necessary. The cable interconnects the 44-pin I/O connector on the rear of the
VRMS to the 25-pin connector at the rear of the VRBS. For connection of optional equipment, the cable
breaks out into several smaller standardized connectors, allowing straightforward access to external I/O
interfaces provided by the VRMS. The cable is shown in Figure 8-1 below. The cable’s installation
procedure begins on page 49.
MILLIMETERS
(Made From PS-CA-012349 Rev. F)
Figure 8-1: Interface Cable CA-012349-003
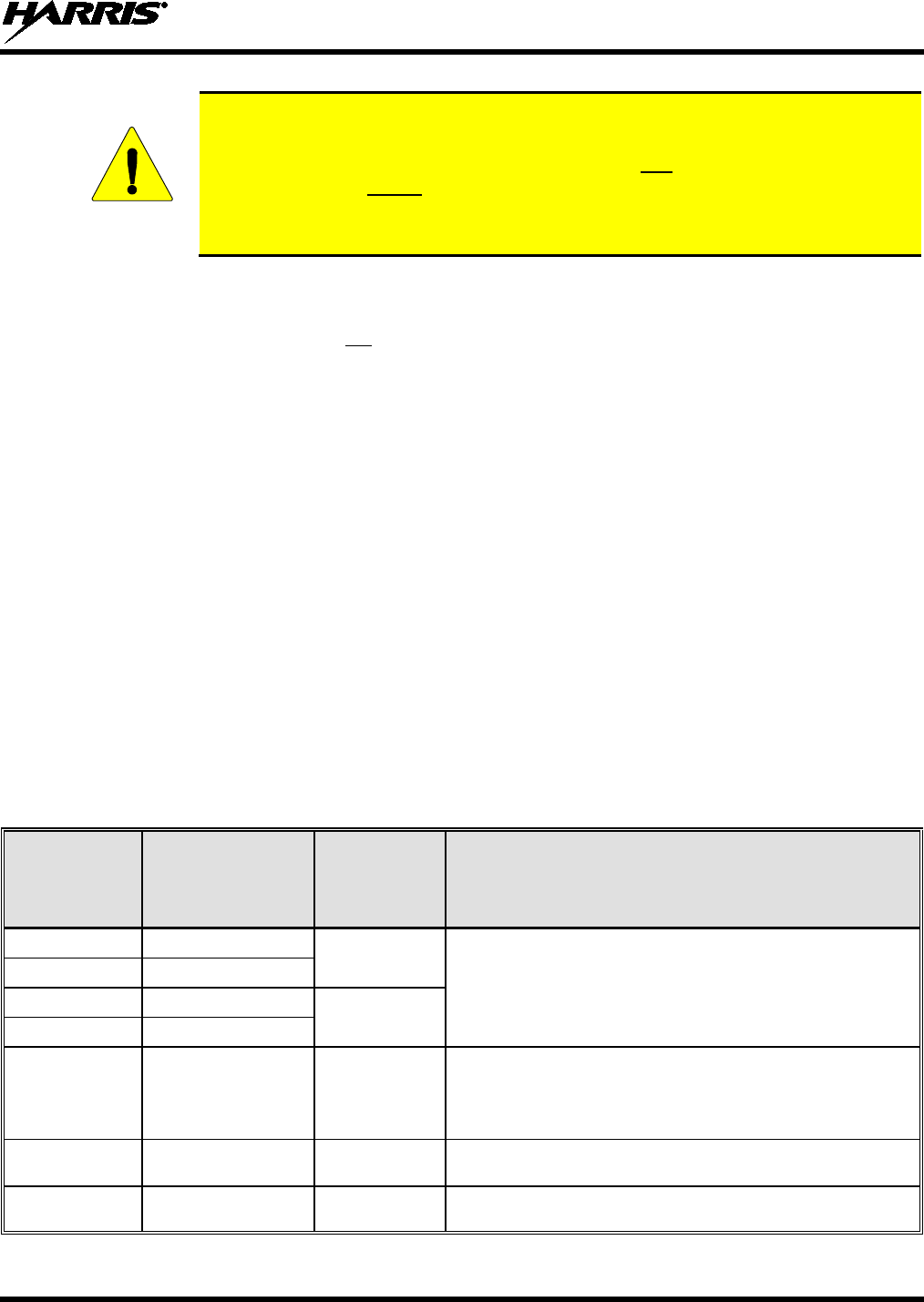
MM-018337-001, Rev. B
47
CAUTION
Observe caution before connecting any external device to the radio via its 44-pin I/O
connector. If an external device has its own DC power source/cable (i.e., if it is
powered separately from the radio), both the radio and the external device must be
properly grounded before connecting the two units and before making a positive (+)
power connection to either unit. Otherwise, fuse(s) inside the radio may fail (open)
and/or other equipment damage could occur.
P1, the cable’s 44-pin D-subminiature (DB-44) connector, mates with the connector on the rear of the
VRMS.
P2, the cable’s 2-pin connector, is not used in this application.
P3, the cable’s 6-pin connector, can be used to connect an external switch used for enabling and disabling
vehicular repeater mode via the radio’s “auxiliary input 2” (i.e., the INP2 digital input). Refer to the
installation procedure in Section 8.2 for the respective connection information. Refer to the maintenance
manual for the respective configuration information. P3 can also used for connecting optional equipment
to the VRS7000.
P4, the cable’s female D-subminiature 25-pin (DB-25) connector, can be used to connect an external
switch used for enabling and disabling vehicular repeater mode via the radio’s “auxiliary input 1” (i.e.,
the INP1 digital input). Refer to the installation procedure in Section 8.2 for the respective connection
information. Refer to the maintenance manual for the respective configuration information. P4 also has
audio and data connections for connection optional equipment to the VRS7000.
P5, the cable’s D-subminiature 9-pin (DB-9) connector, provides (optional) NMEA-formatted GPS serial
data connections for the external computer processing the NMEA-formatted GPS data received by the
GPS receiver within the VRMS (M7300 mobile radio). See Section 14 on page 70 for additional
information.
P6, the cable’s male D-subminiature 25-pin (DB-25) connector, mates to the female 25-pin
D-subminiature connector of the VRBS. These interconnections provide the audio and digital control
paths between the VRMS and the VRBS.
Table 8-1: Interface Cable CA-012349-003 Pin-Out/Interconnections
44-PIN I/O
CABLE
CONNECTOR
P1 PIN
SIGNAL NAME TO/FROM DESCRIPTION
19 SPKR1 P2 pin 1 Speaker Audio Outputs (not used in a VRS7000
installation).
20 SPKR1
21 SPKR2 P2 pin 2
22 SPKR2
10 OUT2 P3 pin 1
Digital Output 2 (open-collector, 500 mA / 30 V maxi-
mum). Use P3 pin 2 for ground.
Configure via the “External Output Control Line 2” in
RPM’s External I/O dialog box.
7 GND P3 pins 2 & 4 Chassis Ground (fused on VRM radio’s
PK Board at
3.15 amps).
26 HKSW P3 pin 3 Digital Input for Hookswitch (default) or for radio
PTT.
Active = Grounded. Inactive = Open. Also see P4 pin 21.
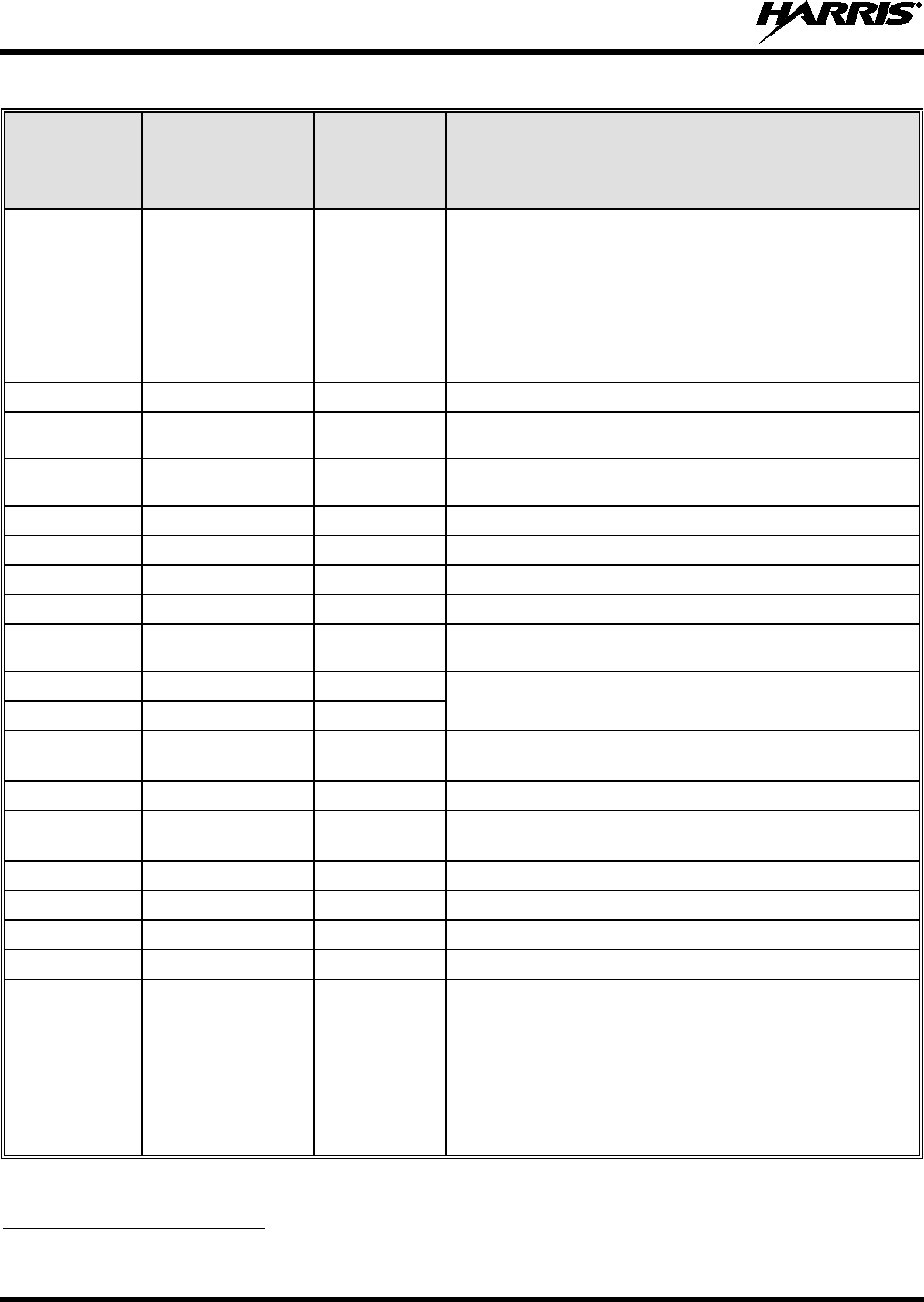
MM-018337-001, Rev. B
48
Table 8-1: Interface Cable CA-012349-003 Pin-Out/Interconnections
44-PIN I/O
CABLE
CONNECTOR
P1 PIN
SIGNAL NAME TO/FROM DESCRIPTION
25 INP2 P3 pin 5
Digital Input 2. Active/Enable = Grounded. Inactive/-
Disable = Open. Use P3 pin 4 for ground.
For use as a
vehicular repeater enable/disable input controlled by an
external switch, configure by using “Auxiliary Input 2
” in
RPM’s P25 Vehicular Repeater Options dialog box.
Refer
to Section 8.2 in this manual, and
the configuration
information presented in the VRS7000
maintenance
manual for additional information.
28 SWA+ P3 pin 6 Switched A+ DC Power Output (not normally used).
8 GND P4 pin 1 Chassis ground (fused on VRM radio’s
PK Board at
3-amps).
30 DGPS_DATA P4 pin 4 NMEA-Formatted GPS
Receiver Module DGPS
Correction Data Serial Data Input.
4 EXTRX P4 pin 5 External Rx Audio Input (not normally used).
9 EXTMOD P4 pin 7 External Tx Audio Input (not normally used).
3 SDATA P4 pin 8 See footnote 2.
5 FDISC P4 pin 9 Buffered Discriminator Audio Output (not normally used).
13 ALO P4 pin 10 Audio Ground/Reference
(fused on VRM radio’s PK
Board at 3.15 amps).
12 MICHI P4 pin 11 See footnote 2.
1 EXTALO P4 pin 12
14 VOLHI P4 pin 13
Volume High Audio Output (not muted; not normally
used).
15 CTLON P4 pin 14 Control-On Digital Input (not used).
16 XTONEENC P4 pin 15 External Tone Encode Audio
Input (default) or Auxiliary
Mic Audio Input. Also see P4 pin 24.
17 XTONEDEC P4 pin 16 External Tone Decode Audio Output.
6 EXTALO P4 pin 17 Reference/Ground for external audio.
24 HORNRING P4 pin 18 See footnote 2.
23 SONOFF P4 pin 19 See footnote 2.
18 INP1 P4 pin 21
Digital Input 1. Active/Enable = Grounded. Inactive/-
Disable = Open. Use P4 pin 1 for ground.
For use as a
vehicular repea
ter enable/disable input controlled by an
external switch, configure by using “Auxiliary Input 1
” in
RPM’s P25 Vehicular Repeater Options dialog box.
Refer
to Section 8.2 in this manual, and
the configuration
information presented in the VRS7000
maintenance
manual for additional information.
2 This pin on the radio’s DB-44 connector is typically not used. Use the respective pin on the CH-721 Option Cable’s female
DB-25 pin connector. Refer to the installation manual for additional information.

MM-018337-001, Rev. B
49
Table 8-1: Interface Cable CA-012349-003 Pin-Out/Interconnections
44-PIN I/O
CABLE
CONNECTOR
P1 PIN
SIGNAL NAME TO/FROM DESCRIPTION
2 OUT1 P4 pin 22
Digital Output 1 (open-collector, 500 mA / 30 V maxi-
mum). Use P4 pin 1 for ground.
C
onfigure via the “External Output Control Line 1” in
Radio Personality Manager’s (RPM’s
) External I/O dialog
Box.
29 TXENB+ P4 pin 23 Transmit Enable B+ Output (open-
collector). Active/Radio
Transmitting = Grounded
. Inactive/Not Transmitting =
Open. (not normally used).
27 EXTMIC P4 pin 24 External/Auxiliary Mic Audio Input. Use P4 pin 17
for
ground. Also see P4 pin 15.
28 SWA+ P4 pin 25 Switched A+ DC Power Output (not normally used).
32 GPS_NMEA_RX P5 pin 2 NMEA-Formatted GPS
Receiver Position Data Serial
Data Output.
31 GPS_NMEA_TX P5 pin 3 NMEA-Formatted GPS Receiver Module Initializ
ation
Data Serial Data Input.
7 GND P5 pin 5 Ground for GPS Serial Data Signals (fused on
VRM
radio’s PK Board at 3.15 amps).
11 IGNITION (no
connection) Unused/Spare ignition sense input
34 VRB_POWER_ON P6 pin 14
When a vehicular repeater mode is enabl
ed, a logic output
from the VRM (i.e., M7300 mobile radio) pulls this logic line
high (greater than 2 volts). This turns on the VRBS via a
high-
current DC switch circuit located on the I/O Board
within the VRBS. When a vehicular repeater mode is
disabled,
the logic output from the VRM remains in a low
state, keeping the VRBS powered off.
38 TD_B P6 pin 18
Asynchronous serial data interface between VRM (i.e.,
M7300 mobile radio) and Traffic Controller in VRBS.
These interface lines transfer digitized audio
and control
data messages between the VRM and the Traffic
Controller.
39 RD_B P6 pin 19
42 CTS_B P6 pin 22
43 RTS_B P6 pin 23
33, 35, 36, 37,
40, 41, 44 (no connection) — These connections of the VRM radio’s DB-
44 connector
are not used in the VRS7000 application.
8.2 INTERFACE CABLE CA-012349-003 INSTALLATION PROCEDURE
Follow this procedure to install the Interface Cable:
1. Obtain Interface Cable CA-012349-003. It is included in the installation kit.
2. Mate the cable’s male 44-pin D-subminiature (DB-44) connector to the female 44-pin D-subminiature
connector on the rear of the VRMS. Using a screwdriver, tighten the two jackscrews securely.
3. Mate the cable’s male D-subminiature 25-pin (DB-25) connector (labeled VRB) to the VRBS’s
female 25-pin D-subminiature connector. Using a screwdriver, tighten the two jackscrews securely.
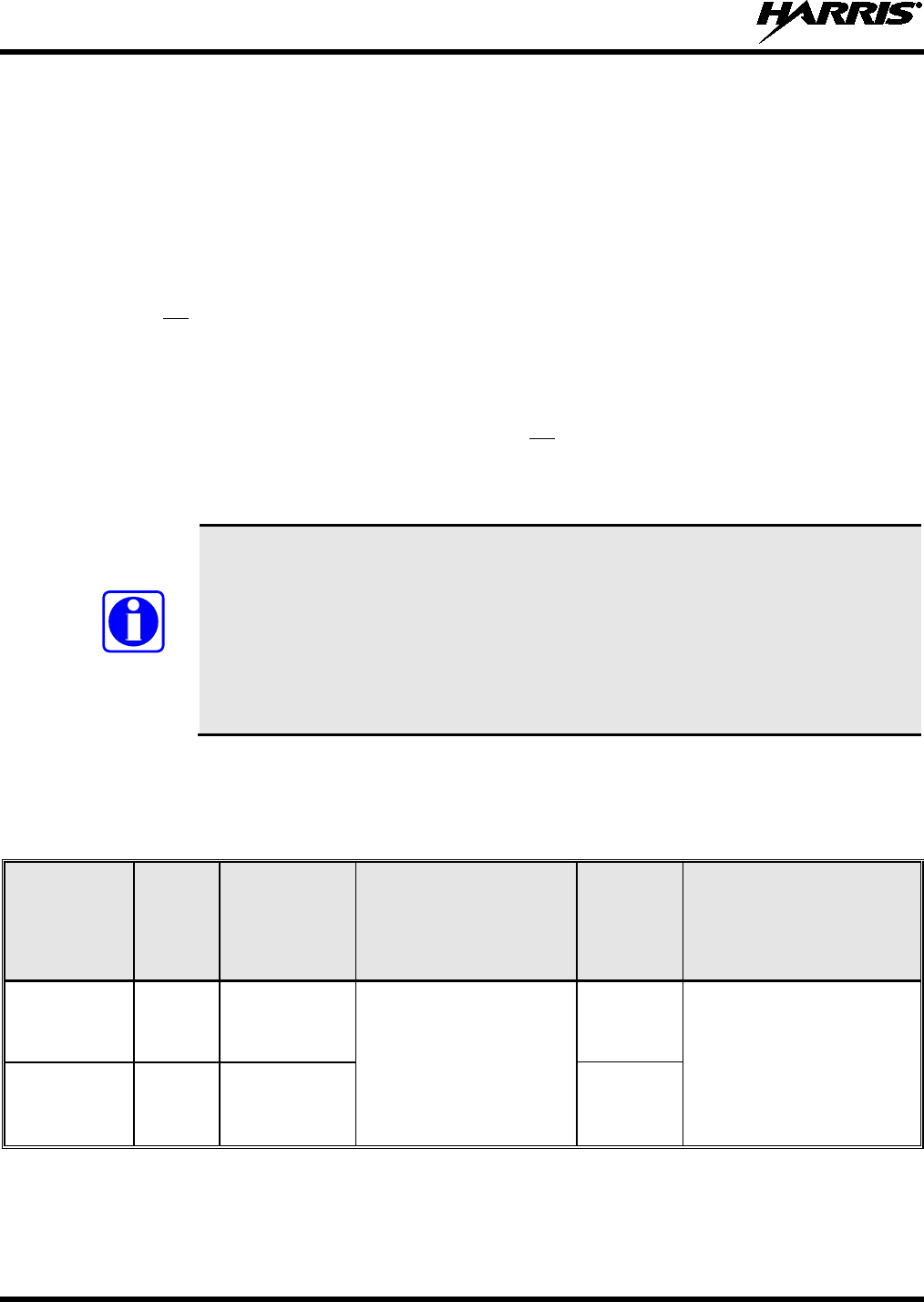
MM-018337-001, Rev. B
50
4. The VRS7000’s configuration may require connection to an external switch to enable and disable
vehicular repeater mode (with or without a corresponding control head button press action). Consult
with the radio system administration personnel as necessary, to determine the configuration of the
“VR Enable Method.” In this case, either digital input INP1 (“Aux I/O 1” in RPM) or digital input
INP2 (“Aux I/O 2” in RPM) of the VRMS (i.e., M7300 mobile radio) must be wired to an external
single-pole switch as follows:
a. If the “VR Enable Method” is configured for “Keypad and Aux I/O 1” or just “Aux I/O 1,”
wire an appropriate switch between connector P4 pin 1 (ground) and pin 21 (digital input INP1).
P4 is the cable’s 25-pin option connector. The required connector to mate to P4, switch, and wire
are not supplied. The use of 18-AWG wire is recommended.
b. If the “VR Enable Method” is configured for “Keypad and Aux I/O 2” or just “Aux I/O 2,”
wire an appropriate switch between connector P3 pin 4 (ground) and pin 5 (digital input INP2).
P3 is the cable’s 6-pin connector. A connector to mate to P3 with six terminals (Molex part
numbers 39-01-2066 and 39-01-0061) is supplied with the Interface Cable when it ships from the
factory. The required switch and wire are not supplied. The use of 18-AWG wire is
recommended.
c. Mount the switch in an appropriate location and placard it appropriately (e.g., “Vehicular
Repeater Enable/Disable.”
NOTE
If the digital input providing the vehicular repeater enable/disable function must be
controlled by an external device such as a portable radio’s vehicular charger, substitute
external switch connections for connections to the device’s vehicular repeater switched
output. In this case, be sure to connect the ground of the VRSM (P4 pin 1 if using
INP1; P3 pin 4 if using INP2) to the ground of the external device, and connect the
digital input of the VRMS (P4 pin 21 if using INP1; P3 pin 5 if using INP2) to the
switched output of the external device. Interconnections for the VC3000 and VC4000
Vehicular Chargers are presented in Table 8-2 and Table 8-3.
5. Tie and stow the cable and all wiring.
Connection information for NMEA-formatted GPS serial data is included in Section 14 on page 70.
Table 8-2: VRS7000-to-VC3000/VC4000 Vehicular Charger Interconnections for
Vehicular Repeater Enable/Disable if using VRMS’s Aux I/O 1 = INP1 (Optional)
VRMS 44-PIN
I/O CABLE
CONNECTOR
PIN
SIGNAL
NAME
INTERFACE
CABLE
CA-012349-
003’s 25-PIN
OPTION
CONNECTOR
RECOMMENDED
CONNECTOR AND
TERMINALS FOR
MATING TO P4
VC3000/-
VC4000’s
5-PIN
CONNEC-
TOR PIN
RECOMMENDED
CONNECTOR AND
TERMINALS FOR MATING
TO VC3000/VC4000’s 5-PIN
CONNECTOR
18 INP1 P4 pin 21 Tyco Electronics
1658659-1 Connector
(includes Shielded
Enclosure and
Jackscrews) and Tyco
Electronics 1-745267-0
Contacts (Pins)
4
(“Repeater”) Molex 39-01-4051
Connector and Molex
39-00-0158 Contacts
(Both are provided with the
VC3000/VC4000’s
installation kit.)
8 GND P4 pin 1 5
(“SW Gnd”)
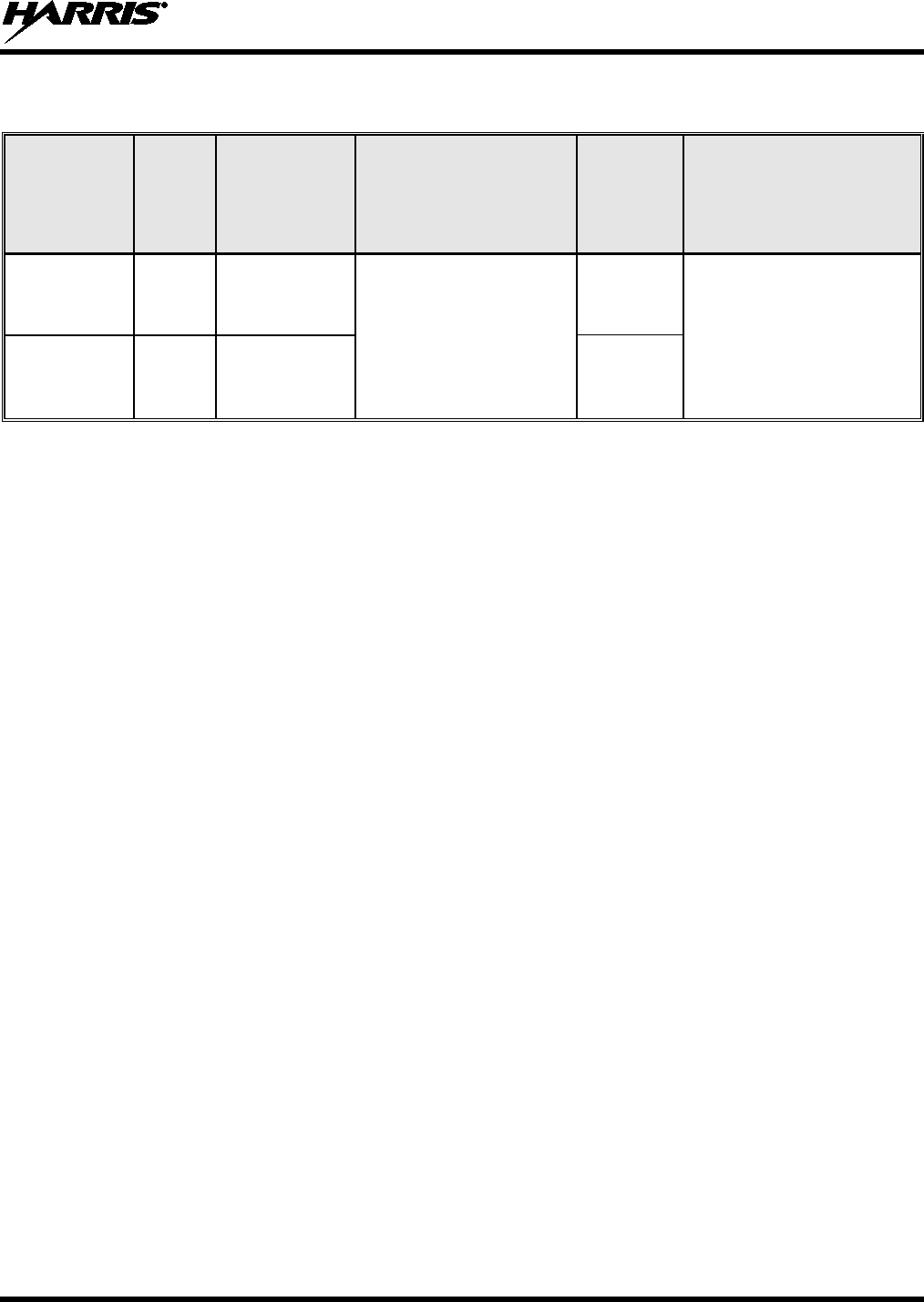
MM-018337-001, Rev. B
51
Table 8-3: VRS7000-to-VC3000/VC4000 Vehicular Charger Interconnections for
Vehicular Repeater Enable/Disable if using VRMS’s Aux I/O 2 = INP2 (Optional)
VRMS 44-PIN
I/O CABLE
CONNECTOR
PIN
SIGNAL
NAME
INTERFACE
CABLE
CA-012349-
003’s 25-PIN
OPTION
CONNECTOR
RECOMMENDED
CONNECTOR AND
TERMINALS FOR
MATING TO P3
VC3000/-
VC4000’s
5-PIN
CONNEC-
TOR PIN
RECOMMENDED
CONNECTOR AND
TERMINALS FOR MATING
TO VC3000’S 5-PIN
CONNECTOR
25 INP2 P3 pin 5 Molex 39-01-2066
Connector and Molex
39-01-0061 Contacts
(Both are provided with
Interface Cable
CA-012349-003)
4
(“Repeater”) Molex 39-01-4051
Connector and Molex
39-00-0158 Contacts
(Both are provided with the
VC3000/VC4000’s
installation kit.)
7 GND P3 pin 4 5
(“SW Gnd”)
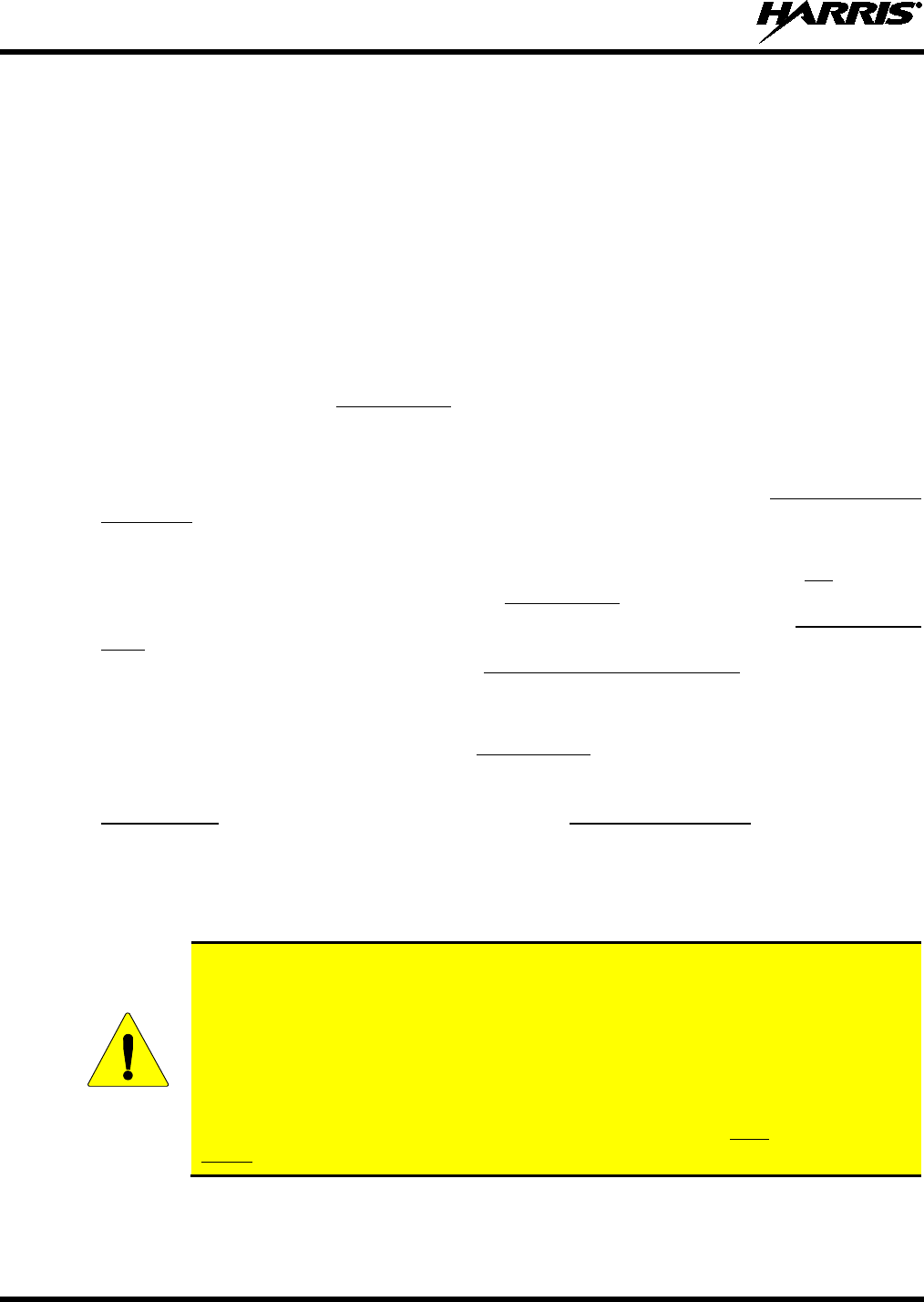
MM-018337-001, Rev. B
52
9 DC POWER INSTALLATION
Refer to the wiring diagram at the end of this manual as necessary when performing wiring procedures
presented in this section.
9.1 OVERVIEW OF ON/OFF POWER WIRING CONFIGURATIONS
Radio on/off power control is accomplished by the control head. When the control head is turned on, it
“wakes-up” the VRMS via data activity on the CAN link. The VRMS automatically powers-up the VRBS
when the P25 vehicular repeater mode is enabled. The following power wiring configurations are
supported:
• Radio turns on and off automatically with vehicle’s ignition switch/key — This configuration
allows the on/off state of the vehicle’s ignition switch/key to control the on/off power state of the
radio. The white wire of the control head’s DC Power Cable is connected to a fused switched power
source, typically identified as vehicle “Accessory” power. This source must switch on (up to positive
(+) battery voltage potential) when the vehicle’s ignition switch/key turns on, and it must switch off
(to near zero volts) when the ignition switch/key turns off. The required fuse rating is 3 amperes.
When using this configuration, the CH-721 control head’s on/off/volume control must be left in the
on position for automatic power-up/down to function properly.
• Radio turns on and off with a manual switch — This configuration is used when, for example, the
radio must remain on even when the ignition key must be removed from the vehicle and a separate
on/off switch is acceptable. The white wire of the control head’s DC Power Cable is connected to one
side of a manually-controlled switch, and the other side of this switch is connected to unswitched and
fused vehicle power. The required fuse rating is 3 amperes. When using this configuration, the
CH-721 control head’s on/off/volume control must be left in the on position for automatic power-
up/down to function properly.
• Radio turns on with control head’s on/off/volume control (“hot wired”) — This configuration
allows radio on/off power control only via the control head’s on/off/volume control. It may be desired
if, for example, the radio must remain on even when the ignition key must be removed from the
vehicle and a separate on/off switch is not desired and/or not acceptable. The white wire of the
control head’s DC Power Cable must be connected to unswitched and fused vehicle power. The
required fuse rating is 3 amperes.
The VRMS, the VRBS, and the control head require separately-fused main DC power. This is the red
wire of each DC power cable. The switch power source to the control head is also separately fused. This
is the white wire of the control head’s DC power cable. In-line type fuses and fuse holders are utilized.
CAUTION
Any DC input power
provided to the radio shall be no higher or lower than
13.6 volts DC ±10%. The DC input power should be free and clear of any AC noise or
DC spikes above 18 volts. If the vehicle cannot meet these requirements, then DC
conditioning will be required before any DC power is connected to the radio. This
includes conditioning for both the radio’s main DC power input lead and for its
switched ignition sense power input. DC conditioning can be accomplished by a noise
filter or DC isolation equipment such as Harris part number FL-018314-001 or FL-
018314-002, or similar units with equal specifications. The fuse must be placed in-line
before any noise filter. Contact TAC for additional information.
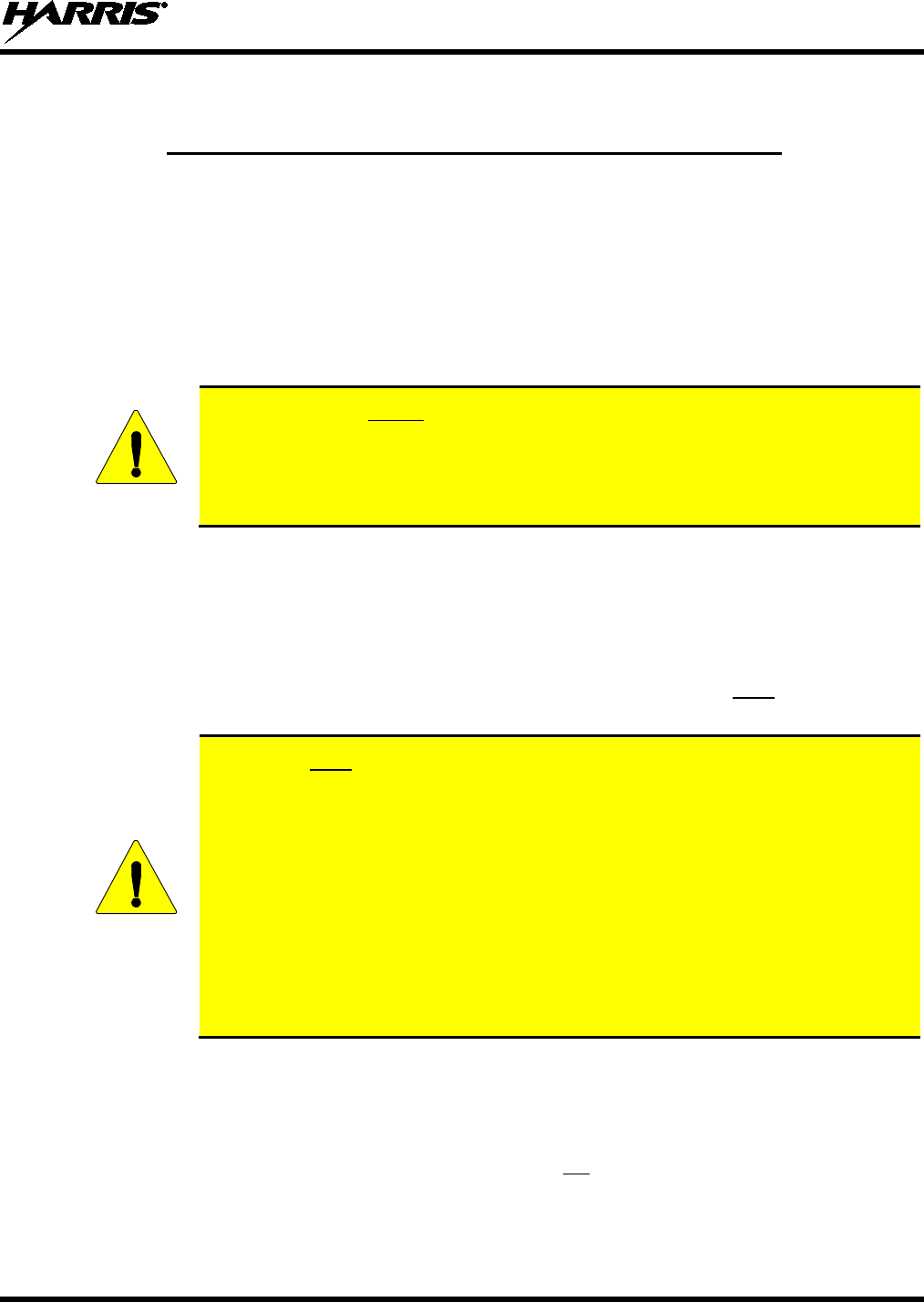
MM-018337-001, Rev. B
53
9.2 POWER INSTALLATION PROCEDURE
9.2.1 Radio DC Power Cables and Main Fuse Holders Installation
Each radio DC power cable has a 3-pin connector, a 20-foot red wire for the main power connection, a
20-foot white wire which is not used/not connected in this application, and a 4-foot black wire for the
ground connection. Each cable is supplied with AGC-type waterproof fuse holders, AGC-type fuses, and
non-insulated ring terminals. The following installation procedures are recommended:
9.2.1.1 Black Wire Connections (Ground Wires)
1. Obtain two (2) DC Power Cables, part number CA-012365-001. These cables are included in the
installation kit.
CAUTION
Do not confuse the radios’ DC Power Cables which each has a 10-AWG red wire with
the control head’s DC Power Cable which has a 12-AWG red wire. The radios require
much more DC operating current than the control head. Therefore, each radio requires
the larger size (10-AWG) wire. Control head DC Power Cable installation procedures
are included in Section 10 of this manual.
2. Connect one DC Power Cable to the VRMS by mating its 3-pin connector to the VRMS’s 3-pin DC
power cable connector. Visually align the key and firmly push and turn the outer locking ring
clockwise until it stops. A click will be sensed to confirm proper mating.
3. Connect the other DC Power Cable to the VRBS using the same connection method.
4. Prepare to connect both cables’ black wires to vehicle ground by locating an area of vehicle
metal within approximately three (3) feet of the two radios. This surface must have a solid and
stable connection to vehicle ground (i.e., battery ground).
CAUTION
The radios must have a solid and stable ground connection to vehicle ground. If
there is no well-grounded metal surface within approximately three (3) feet of the
radios, a metal grounding strap or a heavy-
gauge wire (with proper wire
terminals) must be added between the metal surface and a solid and stable vehicle
grounding point, preferably near the battery. Some vehicles are equipped with a
high-current DC power access point (a vehicle option) that provides high-current
power and ground studs, typically in the vehicle’s trunk area. In this case, the
ground stud of the power access point can be considered a good vehicle ground,
and used as such. Metal surfaces should be stripped of all paint and dirt to expose
bare metal before attaching a grounding strap or wire terminal. To make all
ground connections, the use of stainless-steel hardware with machine-screw
threads, shelf-locking nuts and washers is recommended.
5. Strip the area of any paint or dirt to expose a bare metal surface, approximately ¾-inch square.
6. Drill a hole in the approximate center of the bare metal surface, and deburr it. A ⅜-inch non-
insulated ring terminal is supplied with each cable to make the ground connection. Therefore, hole
diameter should be appropriate for the utilized grounding screw/bolt size and type used to connect the
ring terminals to the bare metal surface. This hardware is not supplied.
7. Cut the two (2) black wires to the required length plus some additional length for service loops in
each wire, then strip insulation back approximately ¼-inch.
8. Crimp a ⅜-inch non-insulated ring terminal (supplied with the cable) to the end of each black wire.
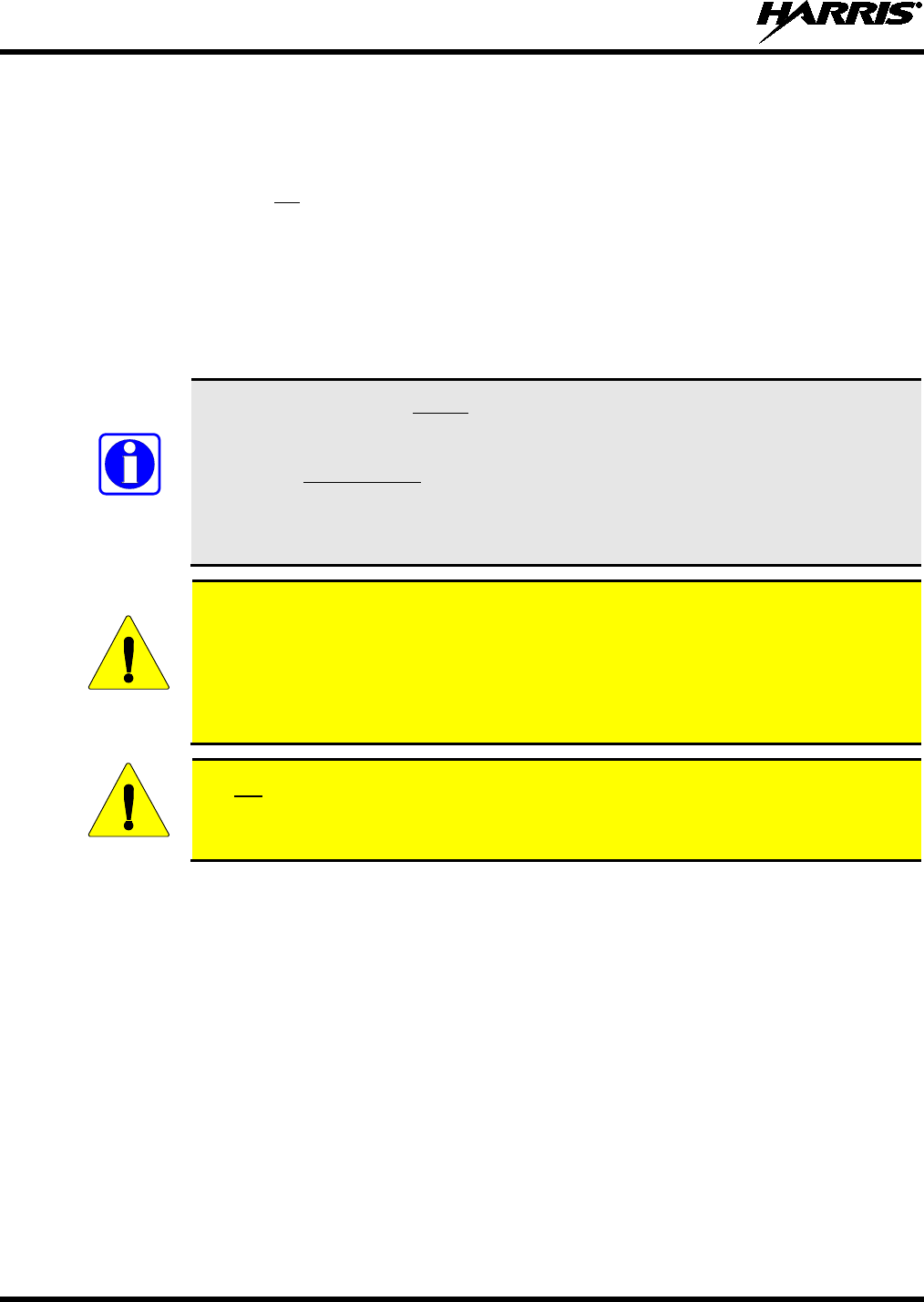
MM-018337-001, Rev. B
54
9. Attach the two (2) ring terminals with black wires to the bare metal surface using stainless-steel self-
locking hardware (i.e., machine screws with washers and locking nuts) or other appropriate hardware
to ensure a reliable terminal-to-metal contact. Tighten securely.
10. Apply an approved paint or rust-inhibitor over the remaining exposed bare metal surface and around
the ring terminal. Do not use an acid-based sealant.
9.2.1.2 R ed Wires and Main Fus e Holder Connections (R adios ’ Main Power Wires )
1. Continue installation of two (2) DC Power Cables by routing their 20-foot 10-AWG red wires to the
location of the vehicle’s battery (or its main DC bus bar or stud). Route the wires through channels in
the vehicle to the location of the battery. Remove interior panels, door kick panels, etc., as necessary.
Protect the wires from possible chafing where necessary. Tie and stow it as necessary.
NOTE
The white wire of both radios’ DC Power Cables require no electrical connection.
Rather than be cut from the two cables, it is recommended that these wires be routed up
to the vehicle’s fuse box, coiled, labeled, and stowed for possible future use. The white
wire of the control head’s DC Power Cable is the radio installation’s ignition sense
input for on/off power control of both the control head and radio. Radio on/off power
control is accomplished by the control head. The control head “wakes-up” the VRMS
via data activity on the CAN link.
CAUTION
Plan the routing of the two 10-AWG red wires carefully, using an existing access hole
in the vehicle’s firewall if possible. Alternately, drill a new hole approximately 3/8-inch
in diameter and install a small rubber grommet to protect the wires from chafing on the
hole’s sharp metal edge.
To prevent fumes from entering the passenger
compartment, this hole/grommet/wire combination must also be sealed with a
silicon-based sealer before completing the installation.
CAUTION
Do not install any wiring or fuse
holder over or in the near vicinity of the vehicle’s
engine. Excessive engine heat can cause permanent damage to these components and
can lead to intermittent electrical connection to the battery.
2. Obtain two (2) waterproof inline fuse holders (HFB type) included with the DC Power Cables.
3. Observe and abide by the following WARNING!
4. Cut the red wires to the required lengths for connection to the battery’s positive (+) battery terminal
(or the main DC bus bar or stud).
5. Prepare to splice the two (2) inline fuse holders into the red wires by cutting the red wires again, at
approximately three (3) to six (6) inches from each end.
6. Strip all wire ends back approximately ⅜-inch each, place a fuse holder shell on each wire, and
securely crimp a fuse holder terminal to each wire end. Before crimping, verify fuse holder shells are
oriented in the correct directions (i.e., with each large end towards the wire end).
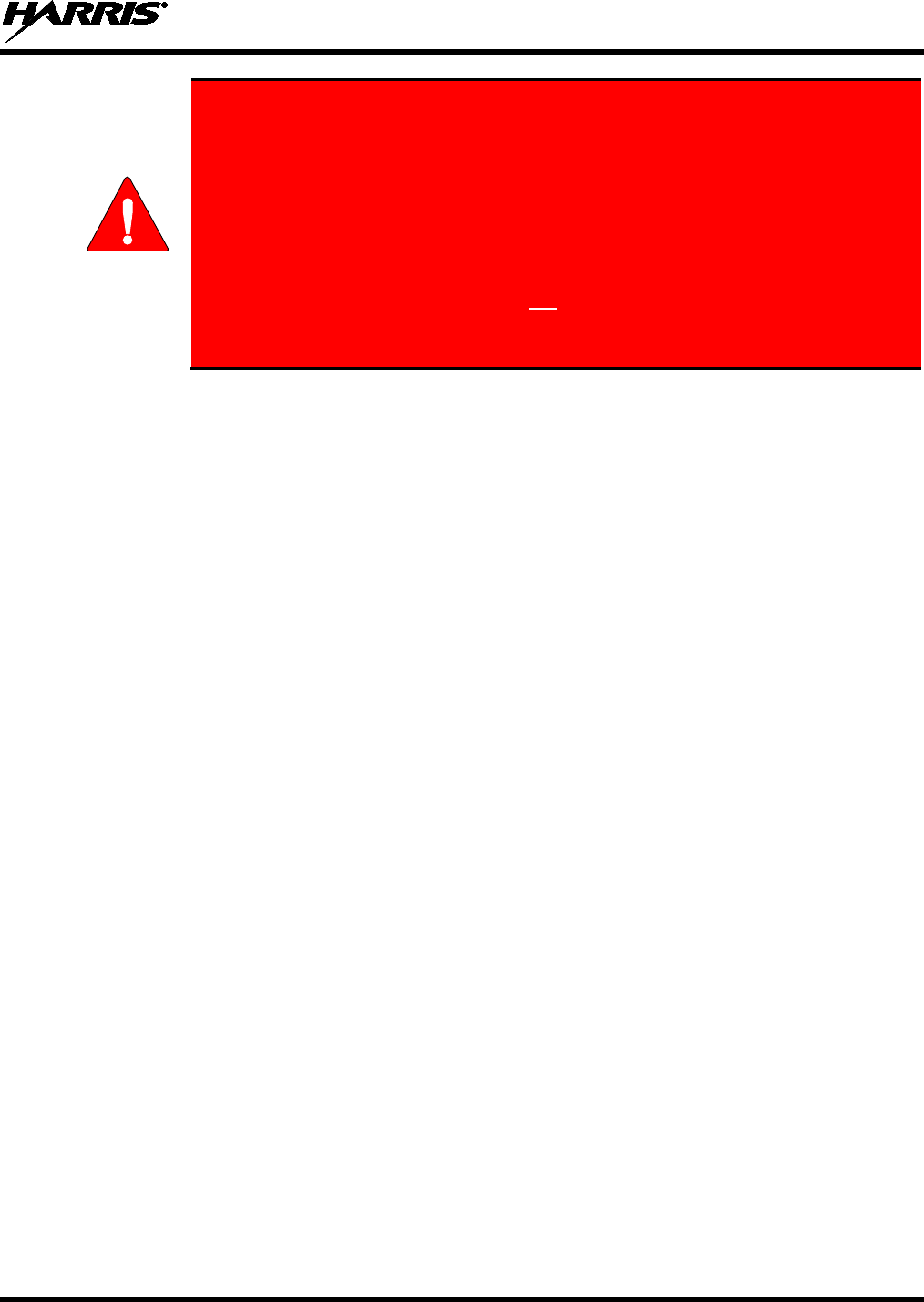
MM-018337-001, Rev. B
55
WARNING
Before making connections to the battery’s positive post, carefully disconnect the
battery’s negative (ground) cable(s). This will prevent tools or other metallic
objects which come in contact with the battery’s positive terminal from shorting to
vehicle ground, causing sparks or even a fire or an explosion! When disconnecting
the negative cable(s), cover/insulate the positive post(s) if it is not already so a tool
cannot short between the posts. Some vehicles, such as those with diesel engines
have more than one battery; in this case, disconnect the negative cables at all
batteries.
Radio and control head fuses should not be installed until all wiring is complete.
This will prevent the radio from powering up prematurely and/or causing an in-
rush of current that could lead to shorting of the battery, sparks, or even fire.
7. Label each fuse holder and red wire appropriately (e.g., “VRMS: 15-AMP FUSE” and “VRBS:
15-AMP FUSE”).
8. Do NOT install fuses into the fuse holders at this time.
9. Crimp an appropriate electrical terminal to each short red wire. A ⅜-inch ring terminal is included
with each cable for this purpose, but another terminal type (not supplied) may be used if required.
10. Connect both ring terminals directly to the battery’s positive post, or if present, to a stud on the
battery’s main/non-switched power distribution terminal block.
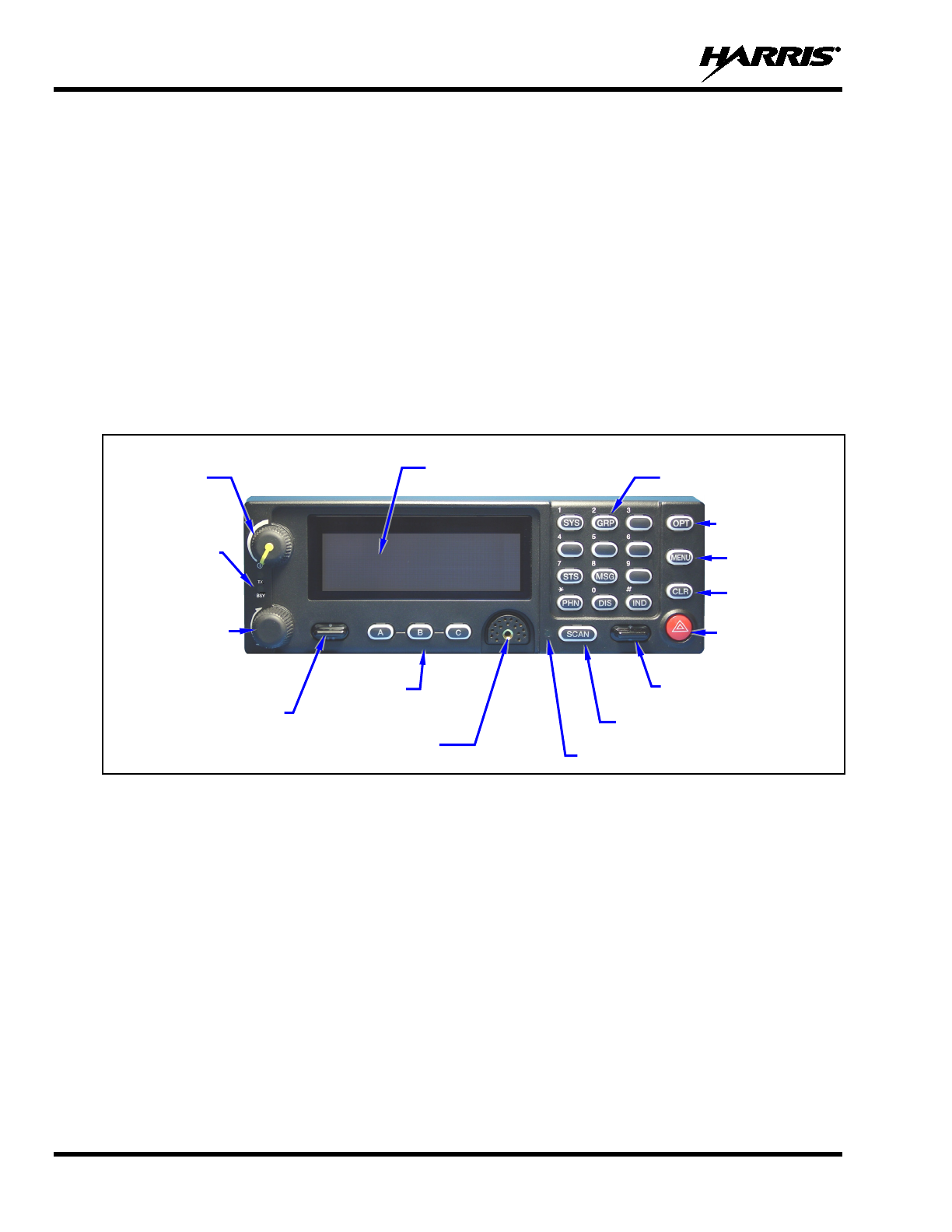
MM-018337-001, Rev. B
56
10 CONTROL HEAD INSTALLATION
10.1 GENERAL INFORMATION
Since the VRS7000 is a remote-mount mobile radio, it must be connected to a control head to provide the
operator-to-radio interface. The CH-721 System model control head is used with the VRS7000.
The front panel of the CH-721 System mode control head is shown in Figure 10-1. This control head has
a large 3-line graphical vacuum-fluorescent display, front panel controls and buttons for user control of
the mobile radio, an internal high-power audio amplifier to drive an externally-connected speaker, and a
front panel microphone connector. It features a 12-key numeric keypad that provides Dual-Tone Multi-
Frequency (DTMF) keypad functionality and easier operator system/group selection, three (3) preset
buttons, and an emergency/home button. Other front panel components include a microphone connector
and LED-type indicators. One LED indicator is the busy indicator that lights when the radio is receiving a
call and one is the transmitter-enabled indicator that lights when the radio is transmitting. The front panel
also has an ambient light sensor for automatic display dimming.
Figure 10-1: CH-721 System Model Control Head Front Panel
Figure 10-2 illustrates the control head’s rear panel. Connectors on the rear panel include two (2) CAN
port connectors, a speaker audio (output) connector and a 25-pin D-subminiature (DB-25) accessory
connector, and a 9-pin D-subminiature (DB-9) serial port connector. The DB-25 accessory connector is
used for connection of optional equipment to the control head, such as a siren/light control system. The
DB-9 serial port connector is typically only used during programming performed at the factory.
Clear Button
Menu Button
Option Button
On/Off/
Volume
Control
System/Group
Knob
Transmit
and Busy
Indicators
•/•• Ramp Control
Preset
Buttons
3-Line Graphical Vacuum
Fluorescent Display
Microphone Connector
+/- Ramp Control
Ambient Light-Level Sensor
Scan On/Off Button
12-Key Keypad
Emergency/
Home Button
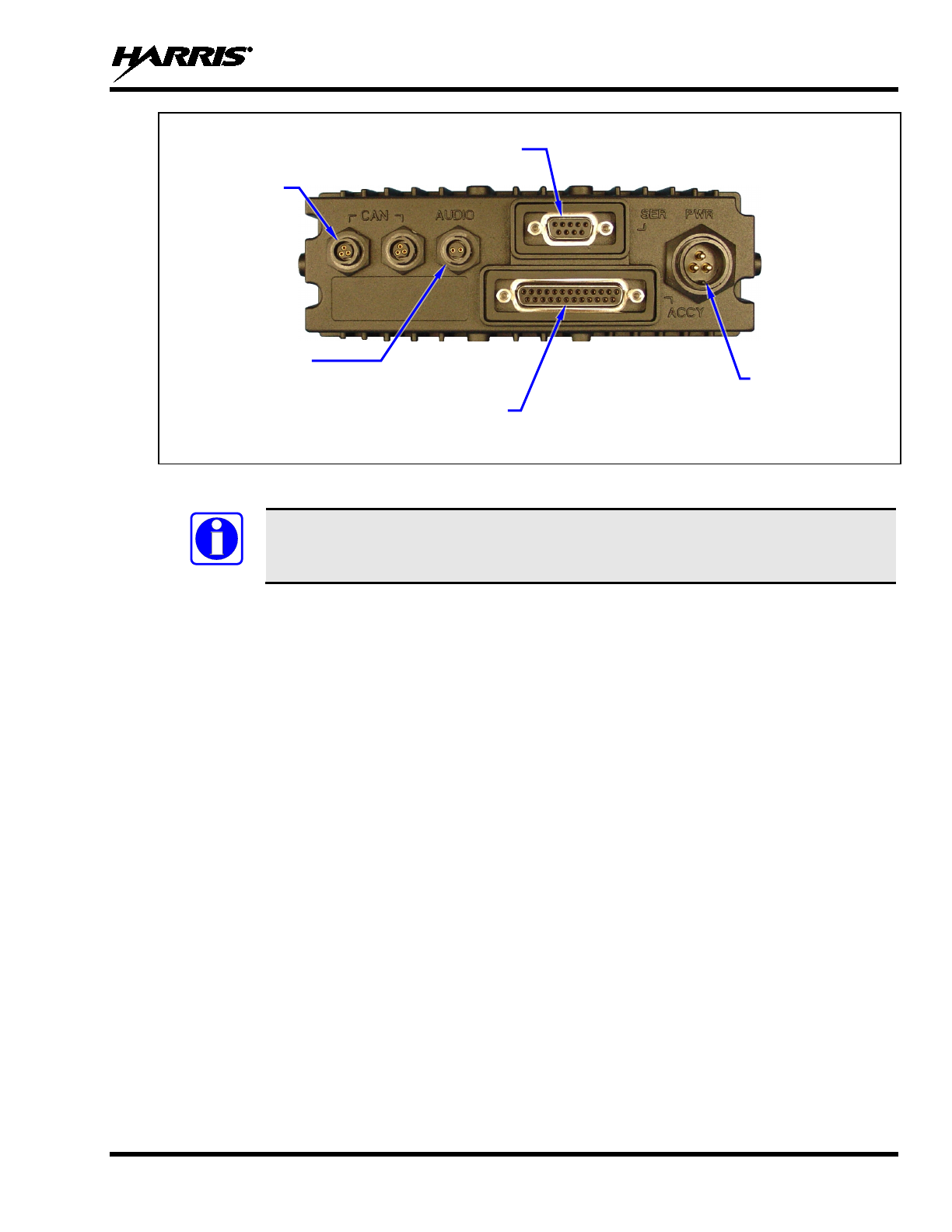
MM-018337-001, Rev. B
57
Figure 10-2: CH-721 Rear Panel
NOTE
Prior to installing the control head, verify it has the proper software version installed and
verify it has been properly configured for customer use.
CAN Port
Connectors
(2 places)
Speaker Audio
Connector
Serial Port Connector
(DB-9)
DC Power
Connector
Accessory Connector
(DB-25)
Note: Serial and Accessory connectors are
shown without waterproof covers.
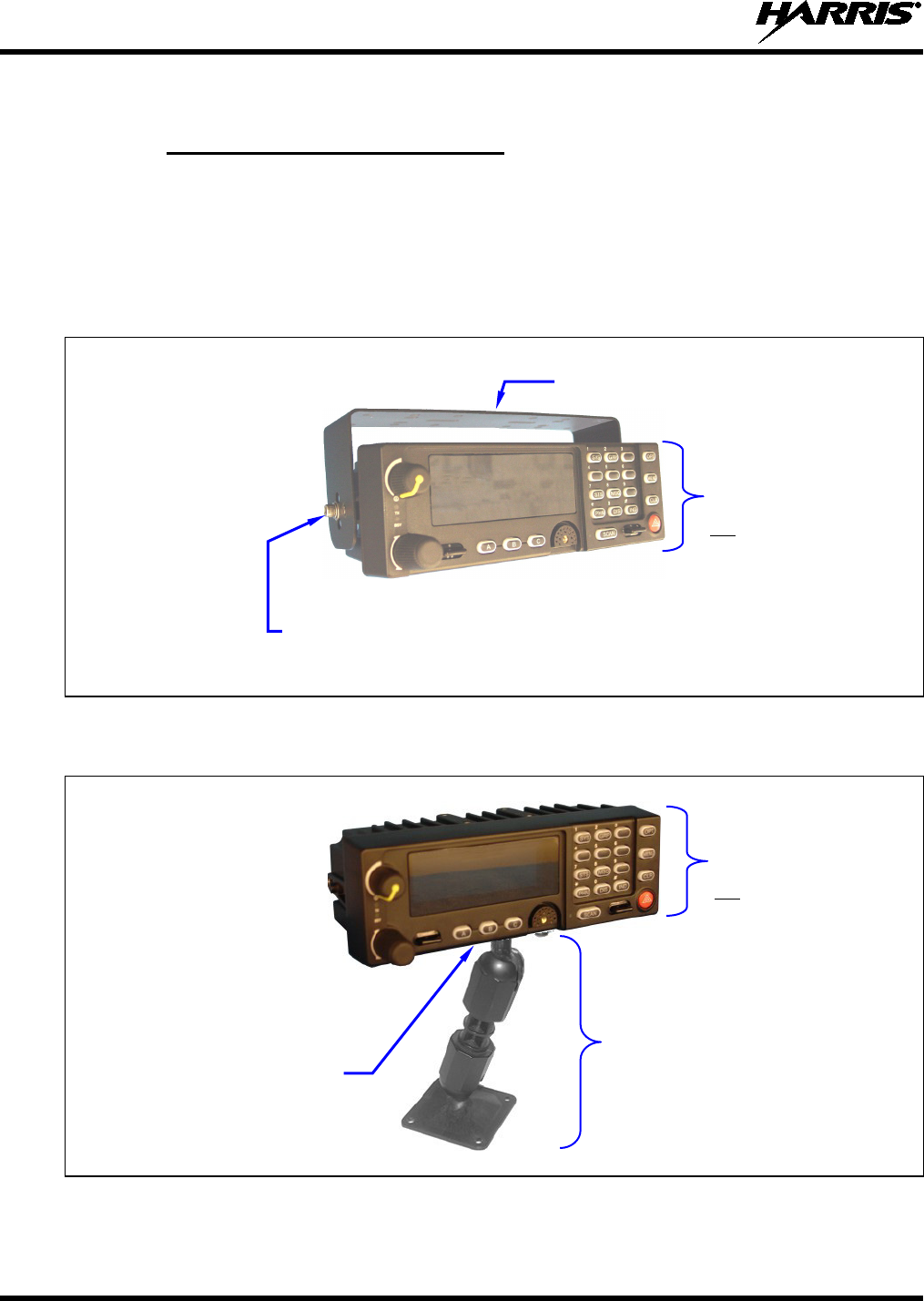
MM-018337-001, Rev. B
58
10.2 CONTROL HEAD MECHANICAL INSTALLATION
10.2.1 Selecting the Mounting Location
When selecting a location for the CH-721 control head, first observe the safety and operator-convenience
related information presented in Section 5.1 on page 28. Also always consider and include clearance for
the microphone’s connector that must mate to the mic connector on the front panel of the head, and
clearance for the connectors/cables that must mate to the connectors on the rear panel of the head. The
CH-721 control head can be mounted under or on top of a mounting surface (typically the vehicle’s dash)
as space permits using either the standard U-shaped mounting bracket or the optional mounting pedestal.
Figure 10-3: Standard U-Shaped Control Head Mounting Bracket (Kit Part Number KT-008608)
Figure 10-4: Optional Control Head Mounting Pedestal (Part Number MACDOS0012)
Mounting Bracket
(Shown positioned above control head)
Control Head Mounting
Pedestal MACDOS0012
(Pedestal can be attached to the
bottom of the head, as shown, or it
can be attached to the top of the
head.)
Bracket shown
attached to a CH-721
System model
control head (Head is
not included with
Mounting Bracket Kit.)
Pedestal shown
attached to a CH-721
System model
control head (Head is
not included with
Mounting Pedestal.)
Socket-Head Cap (Allen) Screw, Lockwasher and Flat
Washer; 2 places each side (Included with kit)
#8-32 Pan-Head Screw; 4
places
(Included with
Mounting Pedestal)
For a “hanging” control head
installation, the pedestal can
be attached to the top of the
head via threaded holes in
the top of the head’s case.
This figure shows the
pedestal attache
d to the
bottom of the control head via
threaded holes in the bottom
of the case.
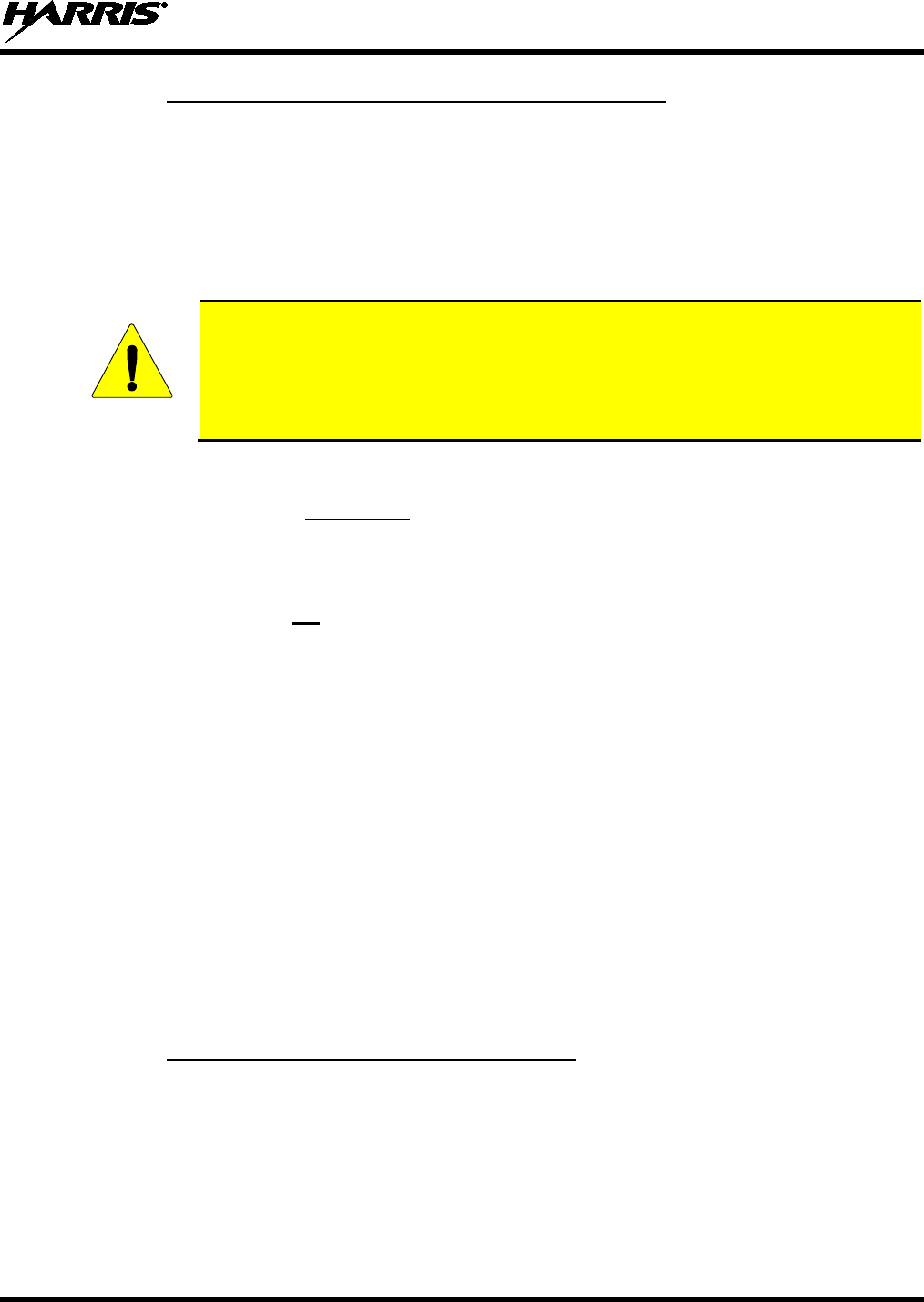
MM-018337-001, Rev. B
59
10.2.2 Using the Standard U-Shaped Mounting Bracket
If the standard U-shaped Mounting Bracket will be used to mount the control head, the following
mounting procedure is recommended. This bracket is included with the Mounting Bracket Kit listed in
Table 4-4 (on page 24).
1. Using the Mounting Bracket as a template, mark and drill mounting holes into the mounting
surface as required. The round and elliptical holes in the bracket’s vehicle mounting surface are
symmetrical so forward/backwards positioning is not important during this step. However,
positioning is important in the next step.
CAUTION
When drilling holes, be careful to avoid damaging some vital part of the vehicle (fuel
tank, transmission housing, etc.). Always check to see how far the mounting screws
will extend below the mounting surface prior to installation. After drilling pilot holes,
remove all metal shavings from them (i.e., deburr the holes) before placing the bracket
and installing the mounting screws.
2. Postion the bracket at the mounting surface so the two round holes in its two side “ears” are
nearest to the normal location of the operator (typically towards the rear of the vehicle) and the
two slotted holes are farthest from the normal location of the operator (typically towards the front
of the vehicle).
3. Install and tighten the mounting screws. Screws for mounting the bracket to the mounting
vehicle’s surface are not included, as all installations differ. Self-tapping screws are
recommended. Do not use common self-threading sheet metal screws because they will loosen
over time with vehicle vibrations.
4. Verify the bracket is held firmly to the mounting surface. Firm mounting prevents unreasonable
vibration, which could damage the control head and/or cause its cable connections to loosen.
5. Slide the control head into the bracket, placing the two pegs protruding from its left and right
sides into the respective round holes in the bracket’s two side “ears.”
6. In each side “ear” of the mounting bracket, start a #8-32 socket-head cap (Allen) head screw with
a lockwasher and a flat washer by inserting the screw through the slotted hole in the bracket and
then into the threaded hole in the side of the control head. This hardware is included with
Mounting Bracket Kit. The lockwasher should be adjacent to the screw head and the flat washer
should be adjacent to the bracket. Turn each screw clockwise as observed from the head of the
screw.
7. The control head can be positioned at various angles for best display viewing at the normal
position of the operator. As necessary, turn it on the pegs to a good position and tighten both
screws using an 1/8-inch hex key (Allen) wrench until the control head is held firmly in place. Do
not over-tighten.
10.2.3 Using the Mounting Pedestal (Optional)
An optional Mounting Pedestal, part number MACDOS0012, may be purchased separately to replace the
standard U-shaped Mounting Bracket. This pedestal can be attached to the bottom of the control head as
shown in Figure 10-4 and then mounted to a mounting surface below the two. It can also be attached to
the top of the head and then mounted to a mounting surface above the two.
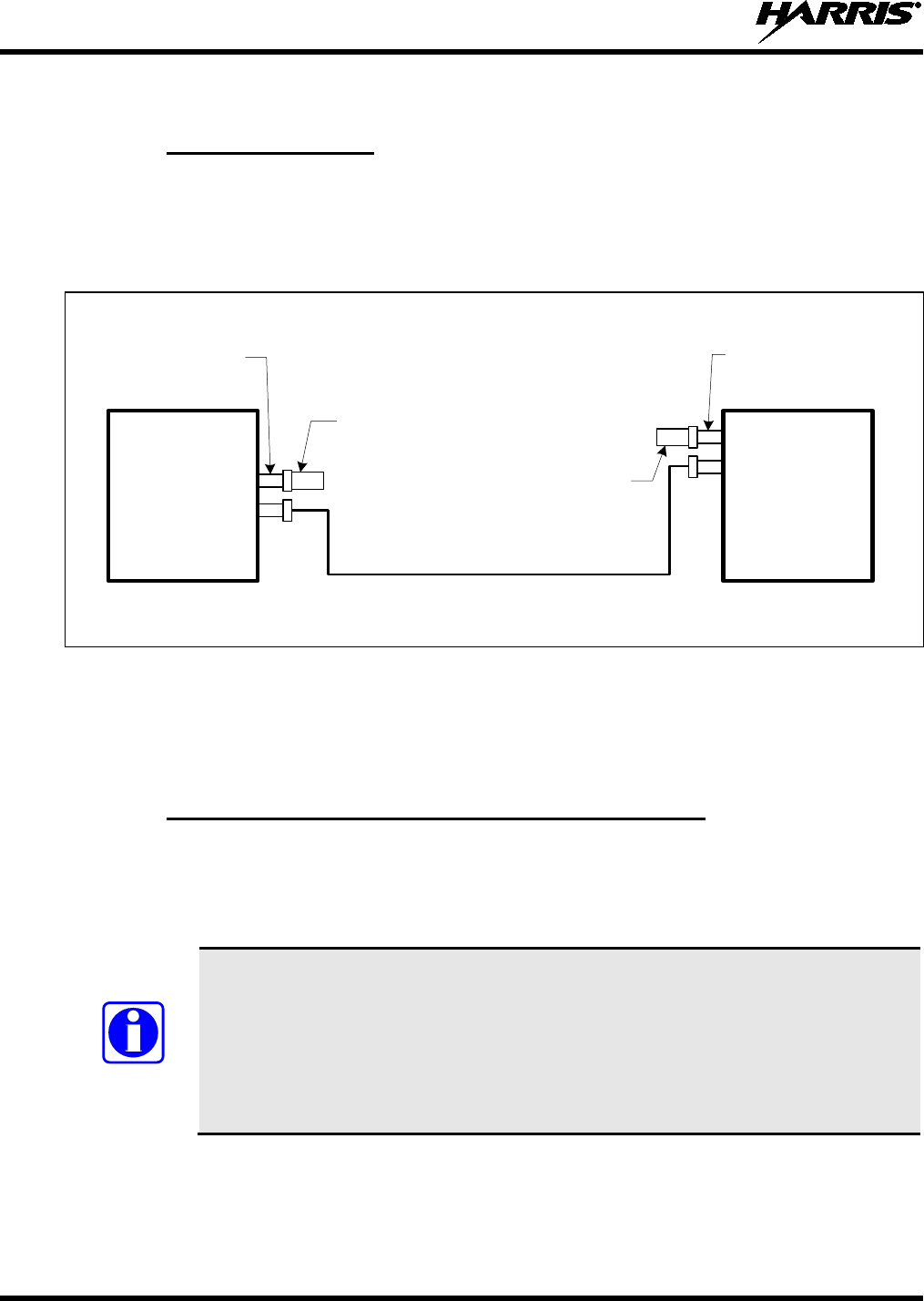
MM-018337-001, Rev. B
60
10.3 CAN CONNECTIONS
10.3.1 General Information
The installation requires a CAN cable between every two “CAN devices” and CAN terminators on each
end of the CAN link. The VRS7000’s VRMS is considered a CAN device, and each CH-721 control head
in the installation is also considered a CAN device. Figure 10-5 illustrates CAN cable and CAN
terminator connections. Because CAN devices do not have internal terminators, the CAN link must be
terminated at both ends via a CAN terminator.
CAN Terminator CD-014027-001
(for radio end)
CH-721
Control
Head
CAN Cable CA-009562-nnn
(where nnn specifies cable length in feet)
CAN Terminator CD-014027-001
(for control head end)
CAN
3-Pin CAN Port
Connectors on
Rear of Radio
(2 places)
CAN
CAN
VRM
(M7300
Mobile
Radio)
CAN
3-Pin CAN Port
Connectors on Rear
of Control Head
(2 places)
For Available CAN Cable Lengths and Respective Part Numbers, see Table 4-6 on page 27
Figure 10-5: CAN Cable and Terminator Connections
Both the VRMS and the control head have two CAN ports. Figure 5-1 on page 29 shows the radio’s two
CAN port connectors, which are located on cable side of the I/O cable’s DB-44 connector. Figure 10-2 on
page 57 shows the two ports on the control head’s rear panel.
10.3.2 Make CAN Link Terminations and Cable Connection
Follow this procedure to complete CAN cable connections:
1. Connect the CAN Terminator (Item 11 listed in Table 4-4 on page 24) onto either one of the two
smaller 3-pin connectors on the rear of the CH-721. This action makes the CAN termination at the
control head end of the CAN link.
NOTE
When mating any CAN connection (terminators and cables), visually align the
¾-moon-
shaped keys of the connectors, and then gently push and turn the outer
locking ring of the plug (male) connector clockwise until it stops. A mild click will be
sensed to confirm proper mating. Without visual alignment as a guide, it is possible
with excessive force to mate the CAN connectors improperly. Damage to the
connector(s) may result. Therefore, visual alignment is recommended when mating
CAN connectors.
2. Route the CAN Cable (Item 9 listed in Table 4-4) through the vehicle’s interior wire/cable channeling
to the VRMS. Remove interior panels, door kick panels, etc., as necessary. Protect the cable from
possible chafing as necessary.
3. Attach the CAN Cable’s connector to one of the two CAN port connectors on the VRMS’s I/O cable.
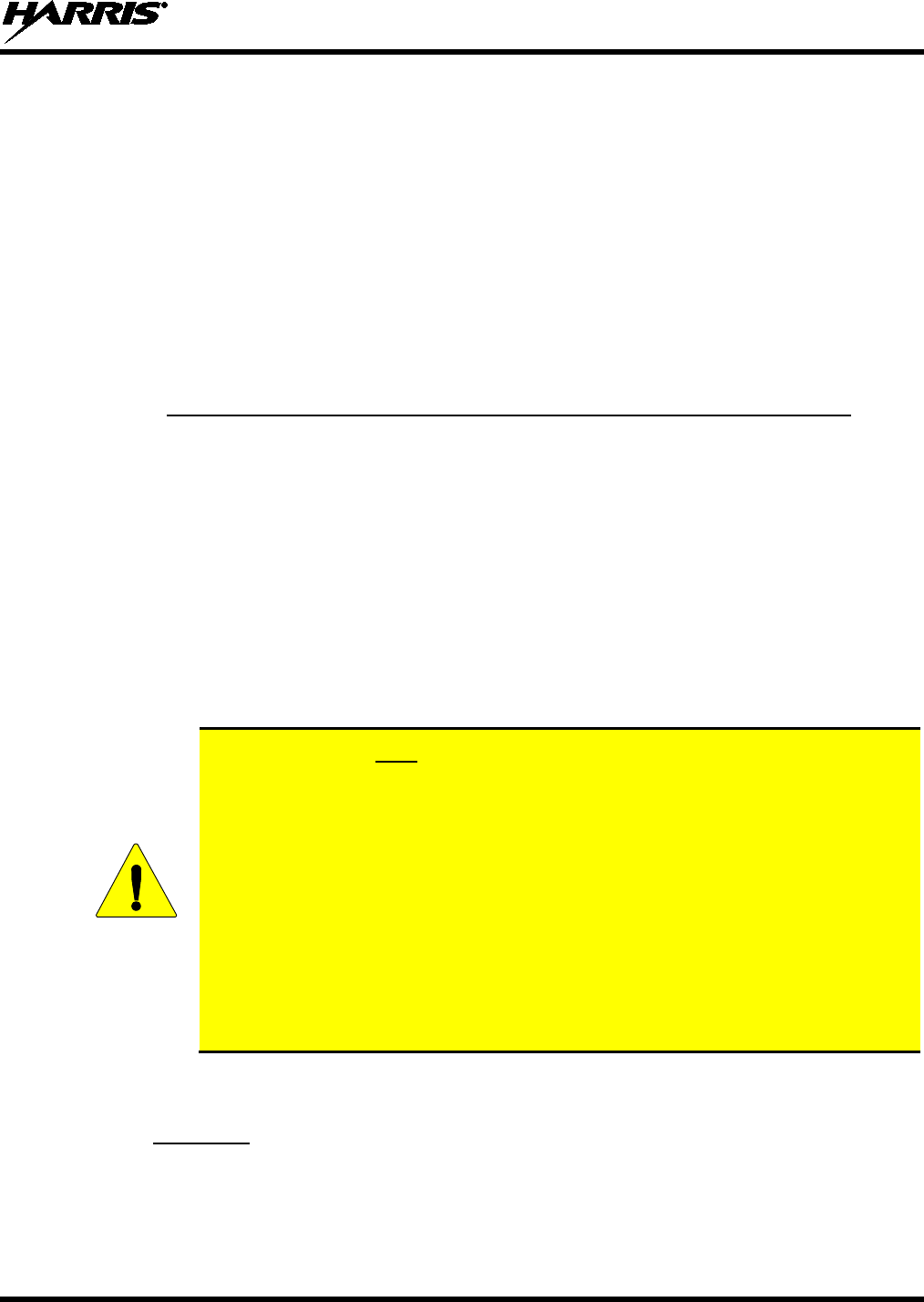
MM-018337-001, Rev. B
61
4. Connect the other end of the CAN Cable to the open CAN port connector at the rear of the control
head.
5. Connect the CAN Terminator (Item 11 in Table 4-4) onto either one of the two smaller 3-pin
connectors on the VRMS’s I/O cable. This action makes the CAN termination at the radio end of the
CAN link.
6. Loop, tie and stow the excess cable as necessary.
10.4 CONTROL HEAD POWER CABLE INSTALLATION
Plan the route of the control head’s DC Power Cable carefully. Do not route the cable where it will be
damaged by heat sources or by casual contact, and protect it from wire chafe per standard installation
methods. The following procedures are recommended:
10.4.1 Install DC Power Cable and Make Power and Ground Connections
1. Connect the control head’s DC Power Cable (Item 6 listed in Table 4-4 on page 24) to the large 3-pin
connector at the rear of the head. Visually align the key and gently push and turn the outer locking
ring clockwise until it stops. A click will be sensed to confirm proper mating.
2. At the back of the control head, locate a nearby section of vehicle chassis ground and strip this area of
any paint or dirt to expose a bare metal surface.
3. Cut the black wire of the control head’s DC Power Cable to the required length, plus a service loop of
at least six (6) inches, then strip it and crimp a ⅜-inch ring terminal to it. Two (2) ring terminals of
this type are included with the cable.
4. Drill a hole as necessary and attach this ring terminal to chassis ground. Use stainless-steel self-
locking hardware (i.e., machine screws with washers and locking nuts) or other appropriate hardware
to ensure a reliable terminal-to-metal contact. Tighten securely.
CAUTION
The control head must have a solid and stable ground connection to vehicle
ground. If there is no well-grounded metal surface within approximately four (4)
feet of the control head, the DC Power Cable’s black wire should be extended to a
solid and stable vehicle grounding point, preferably near the battery. Some
vehicles are equipped with a high-current DC power access point (option) that
provides high-current power and ground studs, typically in the vehicle’s trunk
area. In this case, the ground stud of the power access point can be considered a
good vehicle ground, and used as such. Metal surfaces should be stripped of all
paint and dirt to expose bare metal before attaching a ground wire. To make all
ground connections, the use of stainless-steel hardware with machine-screw
threads, shelf-locking nuts and washers is recommended. To extend the length of
the ground wire, use at least 12-
AWG wire and approved wire splicing
techniques.
5. At the back of the control head, tie and stow the cable as necessary.
6. For the positive 12-volt DC main power source connection, route the cable’s red wire to the location
of an unswitched 12-volt DC power source, typically near the vehicle’s battery. Remove interior
panels, door kick panels, etc. Protect the wire from possible chafing as necessary. This is the control
head’s main DC power source.
7. Obtain one of the waterproof inline fuse holders (HFB-type) included with the control head’s DC
Power Cable.
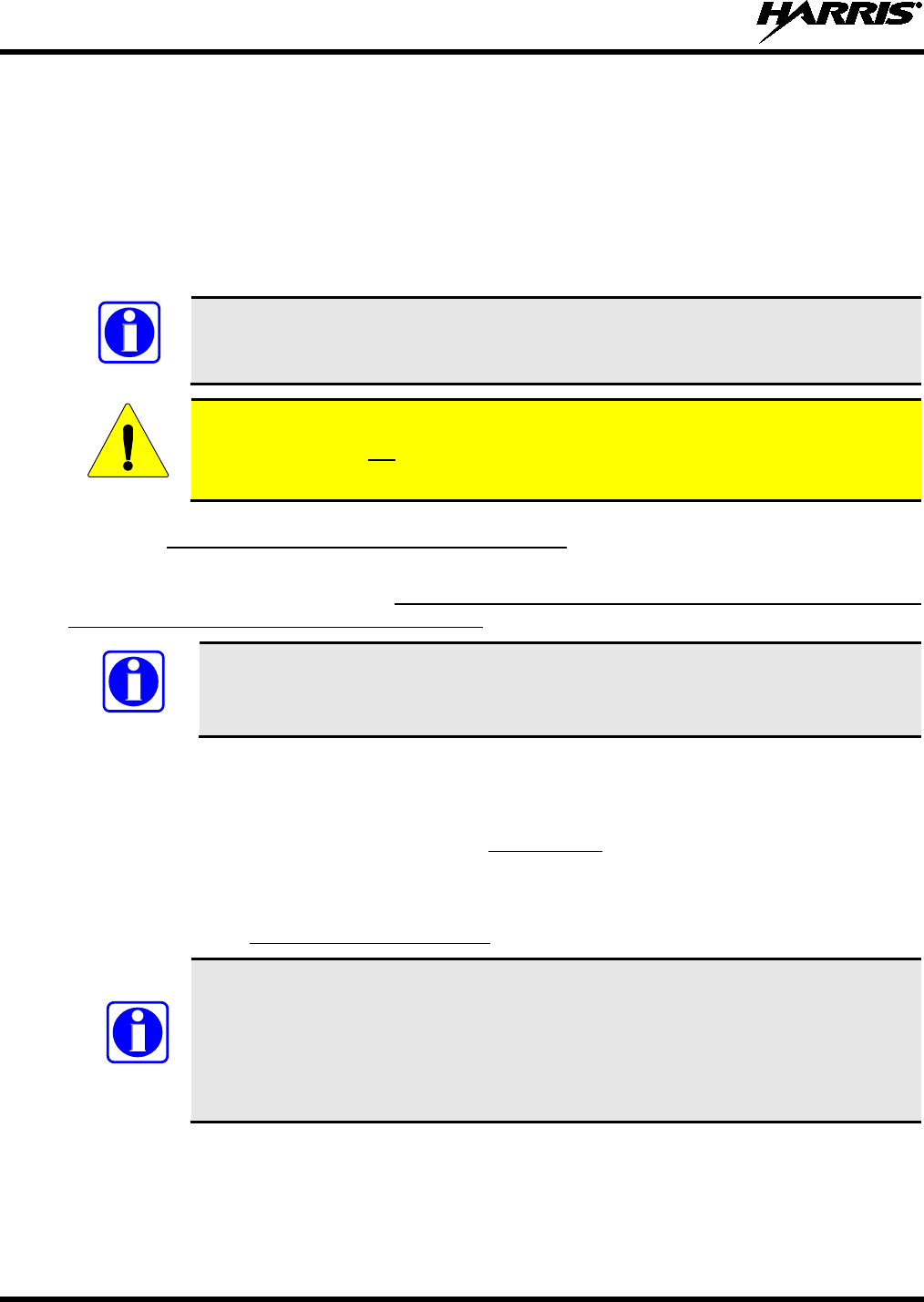
MM-018337-001, Rev. B
62
8. Cut excess length from the red wire and splice the fuse holder into it, near the location of the
unswitched 12-volt DC power source connection point.
9. Label this fuse holder and red wire appropriately (e.g., “CH-721 Main Power: 5-AMP FUSE”).
10. Using an appropriate electrical terminal, connect the red wire to the unswitched DC power source. A
⅜-inch ring terminal is included with the cable for this purpose, but another terminal type (not
supplied) may be used if required.
11. Obtain the 5-amp AGC fuse included with the cable, and install it into the fuse holder.
NOTE
Do not share the control head’s fuse with any other device. Doing so can cause excess
current to flow through the fuse, causing it to blow unnecessarily.
CAUTION
The fuse rating for the control head’s red wire is 5 amperes. The 3-amp fuse included
with the cable must not be used for fusing the control head’s main DC power. It fuses
the head’s white wire.
10.4.2 Connect DC Power Cable’s White Wire
A review of the information presented in Section 9.1 (page 52) may be beneficial at this time. As required
per the chosen power-up configuration, connect the white wire by following one of the three procedures
presented in the respective sub-section that follows.
NOTE
Only the control head’s white wire must be connected to the ignition or switched
power sense. When this vehicle line is asserted (i.e., power switched on), the control
head automatically powers-up the VRMS via the CAN connection.
10.4.2.1 Control Head and Radio Turn on with Vehicle’s Ignition Switch/Key
With this wiring configuration, the control head and the VRMS automatically turn on and off with the
vehicle’s ignition switch/key. The white wire of the control head’s DC Power Cable is sometimes referred
to as the “white ignition switch wire” or the “ignition sense input wire.” In this configuration, the white
wire connects to a switched power source, typically identified as “Accessory” power, that switches on and
off with the vehicle’s ignition switch/key. When using this configuration, the CH-721 control head’s
on/off/volume control must be left in the on position for automatic power-up/down to function properly.
NOTE
The white ignition sense wire must be connected to a power source that switches from
approximately zero volts to appro
ximately +13.6 volts when the vehicle’s ignition
switch/key is turned from the OFF position to the ACCESSORY and RUN positions.
Use of a switched power source that is subject to voltage changes as a result of other
actions, such as opening a vehicle door, may result in undesirable radio operation and/or
a degradation of radio performance.
1. Locate the vehicle’s switched ignition or “Accessory” power connection point that will be used for
the switched ignition 12-volt DC power source. This point is typically located at or near the vehicle’s
fuse panel. It may be necessary to consult the vehicle manufacturer’s wiring diagram.
2. Route the white wire of the control head’s DC Power Cable from the back of the head to the area near
this connection point. Protect the wire from possible chafing as necessary.

MM-018337-001, Rev. B
63
3. Obtain one of the waterproof inline fuse holders (HFB-type) included with the control head’s DC
Power Cable or see the following NOTE.
4. Cut excess length from the white wire and splice the fuse holder into it, near the location of the
connection point.
5. Using an appropriate electrical terminal, connect the white wire to the switched power connection
point. An open-barrel spade terminal is included with the cable for this purpose, but another type of
terminal (not supplied) may be used as required.
6. Obtain the 3-amp AGC fuse included with the cable, and install it into the fuse holder.
7. Tie and stow all wiring as necessary so it remains out of the way of casual contact and wire chafe is
avoided.
NOTE
The waterproof inline fuse holder and AGC fuse included with the DC Power Cable
must be used if the white wire connection point is located in a harsh environment such
as in the vehicle’s engine compartment. However, if the connection point is not in a
harsh environment, such as under the vehicle’s dash panel, Vehicle Fuse and T-Tap Kit
FS24473 may be ordered and used to make the white wire connection. As shown in
Figure 10-6, this kit includes an ATM fuse holder and fuse, T-tap crimp terminals for
tapping into an existing vehicle switched power wire, and a quick-disconnect terminal.
See Section 10.4.3 on page 64 for additional information.
10.4.2.2 Control Head and Radio Turn On with a Manual Switch
With this wiring configuration, the control head and the VRMS are manually turned on and off via an
on/off switch mounted separately from the control head and VRMS, not through the vehicle’s ignition
switch/key. This configuration is used when, for example, the radio must remain on even when the igni-
tion key must be removed from the vehicle and a separate on/off switch is acceptable and/or required. In
this configuration, the white wire connects to a fused switched power source such as that provided by a
toggle switch mounted on the vehicle’s dash panel. When using this configuration, the CH-721 control
head’s on/off/volume control must be left in the on position for automatic power-up/down to function
properly.
1. Route the white wire of the control head’s DC Power Cable from the back of the head to an area near
the location of the panel-mounted on/off switch. Protect the wire from possible chafing as necessary.
2. Cut a short section (6 to 8 inches) off the end of the white wire and strip the ends.
3. Obtain one of the waterproof inline fuse holders (HFB-type) included with the control head’s DC
Power Cable, and crimp one half of it to one end of the short section of wire.
4. Using an appropriate electrical terminal, connect this short white wire to unswitched 12-volt DC
power source at or near the vehicle’s fuse box.
5. Cut another section of white wire from the cable. This wire must be long enough to reach from this
fuse holder to the location of the panel-mounted on/off switch.
6. Strip one end of this wire and crimp the other half of the fuse holder to this wire end.
7. Strip the other end of this wire and, using an appropriate electrical terminal, connect it to the common
terminal of the switch.
8. Connect the white wire of the power cable to the load (switched) side of the switch.
9. If not already, mount the switch to the vehicle’s dash panel, or other customer-selected location.
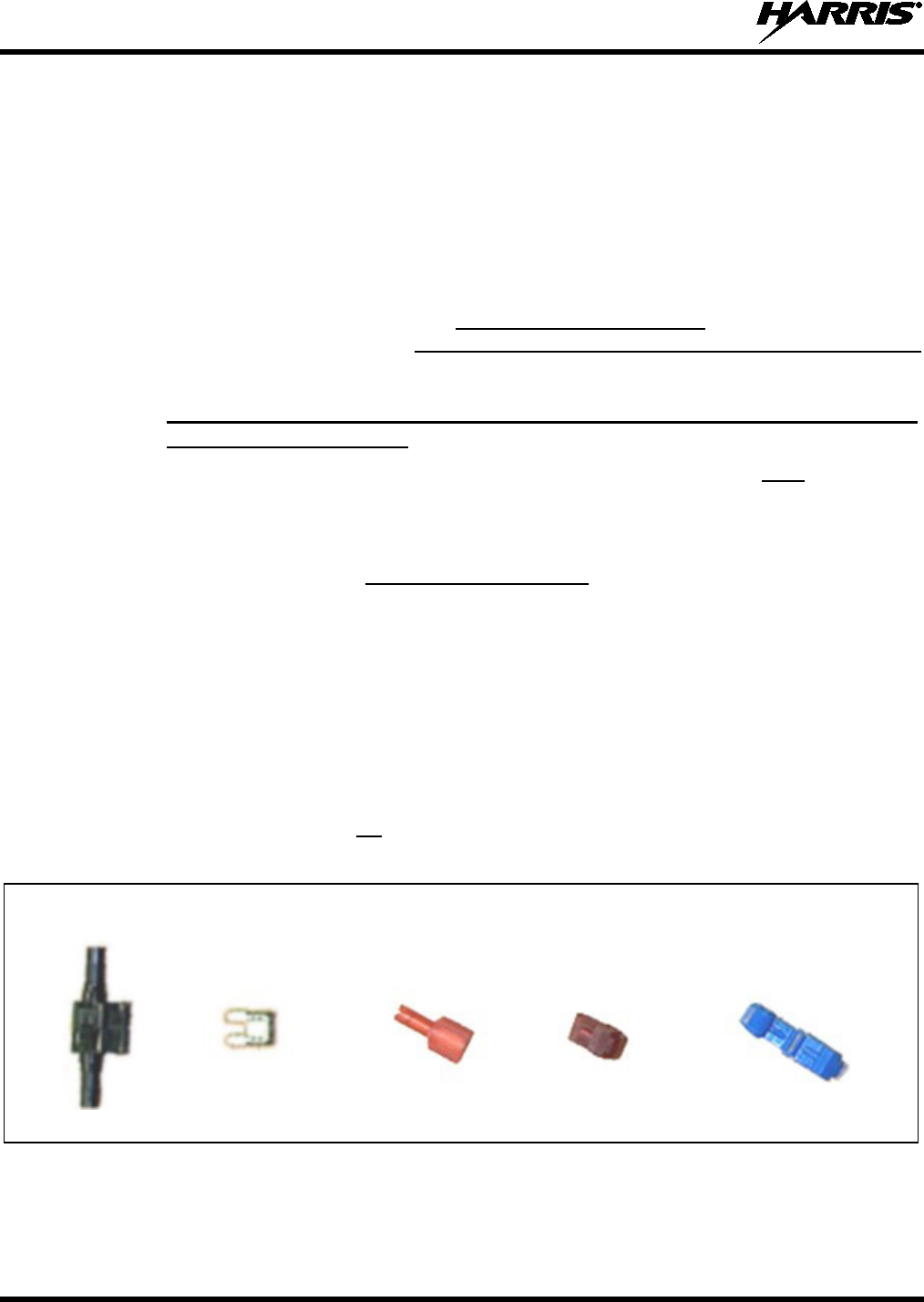
MM-018337-001, Rev. B
64
10. Obtain the 3-amp AGC fuse included with the cable, and install it into the fuse holder.
11. Tie and stow these wires as necessary so they remain out of the way of casual contact and wire chafe
is avoided.
12. Label this power switch accordingly. For example: “VRS7000 ON/OFF.”
10.4.2.3 Control Head and Radio Are “Hot Wired”
In the “hot-wired” configuration, the control head and VRMS are turned on and off only by the control
head’s on/off/volume control located on the front panel of the control head. In this configuration, the
control head’s white wire must be connected to unswitched and fused 12-volt vehicle power. Follow the
procedure presented in Section 10.4.2.1, except connect the white wire to unswitched battery power
instead of switched (“Accessory”) power.
10.4.3 Using Vehicle Fuse and T-Tap Kit (Optional) Instead of Waterproof Inline
Fuse Holder (Standard)
The waterproof inline fuse holder and AGC fuse included with the DC Power Cable must be used if the
white wire connection point is located in a harsh environment such as in the vehicle’s engine
compartment. In this case, disregard all information presented in this section, and follow one of the three
procedures presented in Section 10.4.2 to connect the white wire.
However, if the connection point is not in a harsh environment, such as under the vehicle’s dash panel,
Vehicle Fuse and T-Tap Kit FS24473 may be ordered and used to make the white wire connection. As
shown in Figure 10-6, this kit includes an ATM fuse holder and fuse, T-tap crimp terminals for tapping
into an existing vehicle switched power wire, and a quick-disconnect terminal. The following installation
procedure is recommended for this optional kit:
1. Locate the switched ignition or “Accessory” power wire (typically at or near the vehicle’s fuse block
or in a vehicle wiring harness) that will be used for the switched ignition power source. It may be
necessary to consult the vehicle manufacturer’s wiring diagram.
2. Route the white wire of the control head’s DC Power Cable from the back of the head to an area near
the switched ignition power source. At the back of the head, be sure to maintain a cable service length
of at least six (6) inches and do not loop the cable.
3. Cut a short section (6 to 8 inches) off the end of the white wire and strip each end of this short wire.
ATM 2-Amp Quick- T-Tap T-Tap
Fuse Holder ATM Disconnect Terminal for Terminal for
Fuse Terminal #22-18 AWG #16-14 AWG
(Gray) (Male Tab) Wire (Red) Wire (Blue)
(Shown Closed)
(Shown Open)
Figure 10-6: Contents of Vehicle Fuse and T-Tap Kit FS24473
4. From the Vehicle Fuse and T-Tap Kit, locate the male-tab quick-disconnect terminal and crimp it to
one end of the short wire.
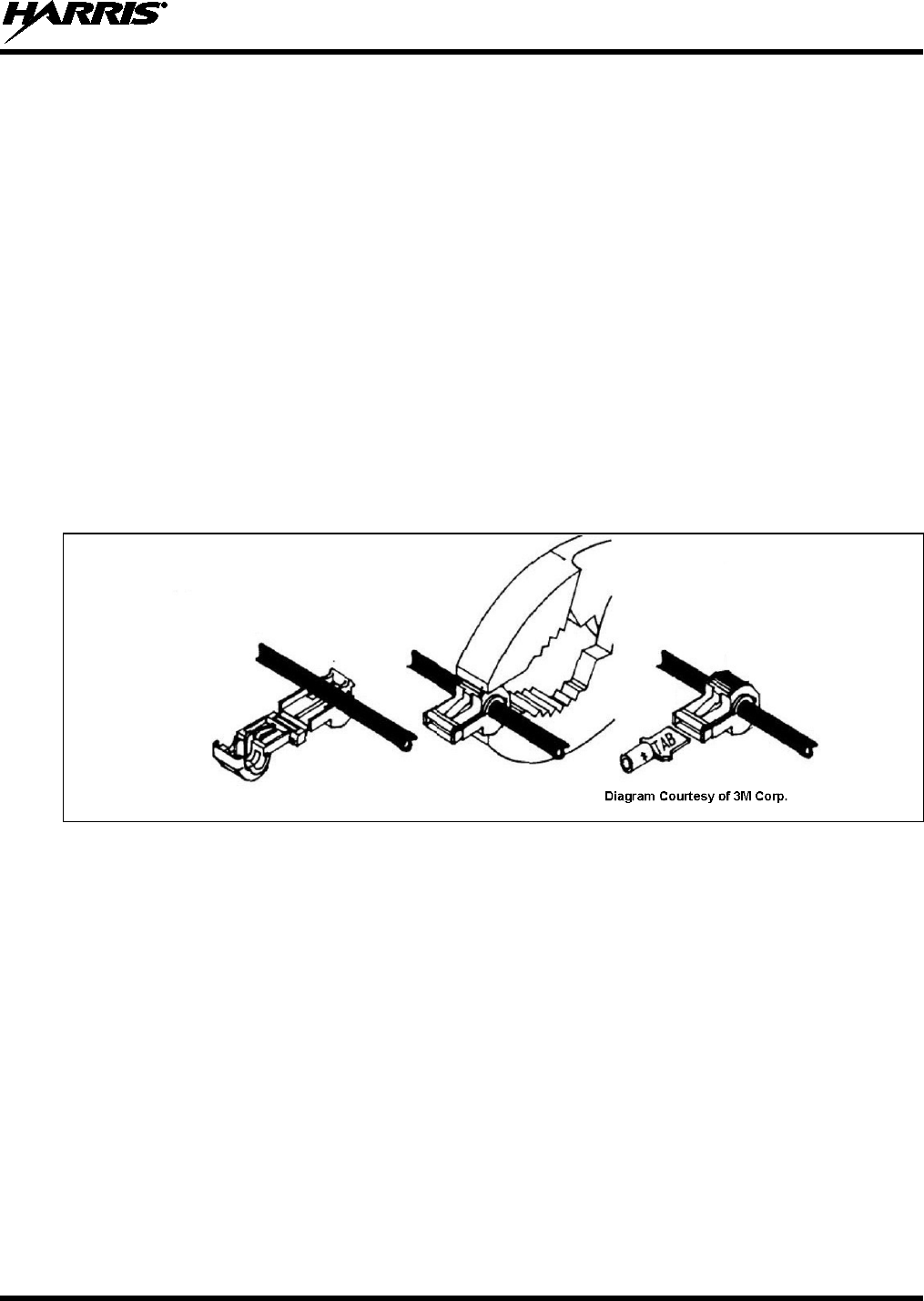
MM-018337-001, Rev. B
65
5. From the same kit, locate the ATM fuse holder and crimp it to the other end of the short wire. The
holder has built-in crimpable joints.
6. Cut the excess length from the white wire of the control head’s power cable, strip it, and crimp it to
the other side of the ATM fuse holder.
7. Pull enough of the switched ignition source wire out of the vehicle’s wiring harness so one of the
T-tap terminals may be attached to it.
8. Two T-tap terminals are included in the kit. Based on the gauge of wire, select the proper terminal
size: Red is for use with a 22 to 18-AWG wire, and blue is for use with an 18 to 14-AWG wire.
9. Attach the selected T-tap terminal by fitting the wire into its wire groove and snapping the two halves
together with a pair of pliers as shown in Figure 10-7.
10. Push the male-tab quick-disconnect terminal into the T-tap terminal’s inlet until it is fully engaged.
11. Install the 2-amp ATM fuse into the fuse holder. It is recommended that a piece of electrical tape be
wrapped around the fuse connection to keep the fuse from being jostled out of the holder.
12. Tie and stow these wires as necessary so they remain out of the way of casual contact and wire chafe
is avoided.
Figure 10-7: Attaching T-Tap Terminals to a Switched Power Wire
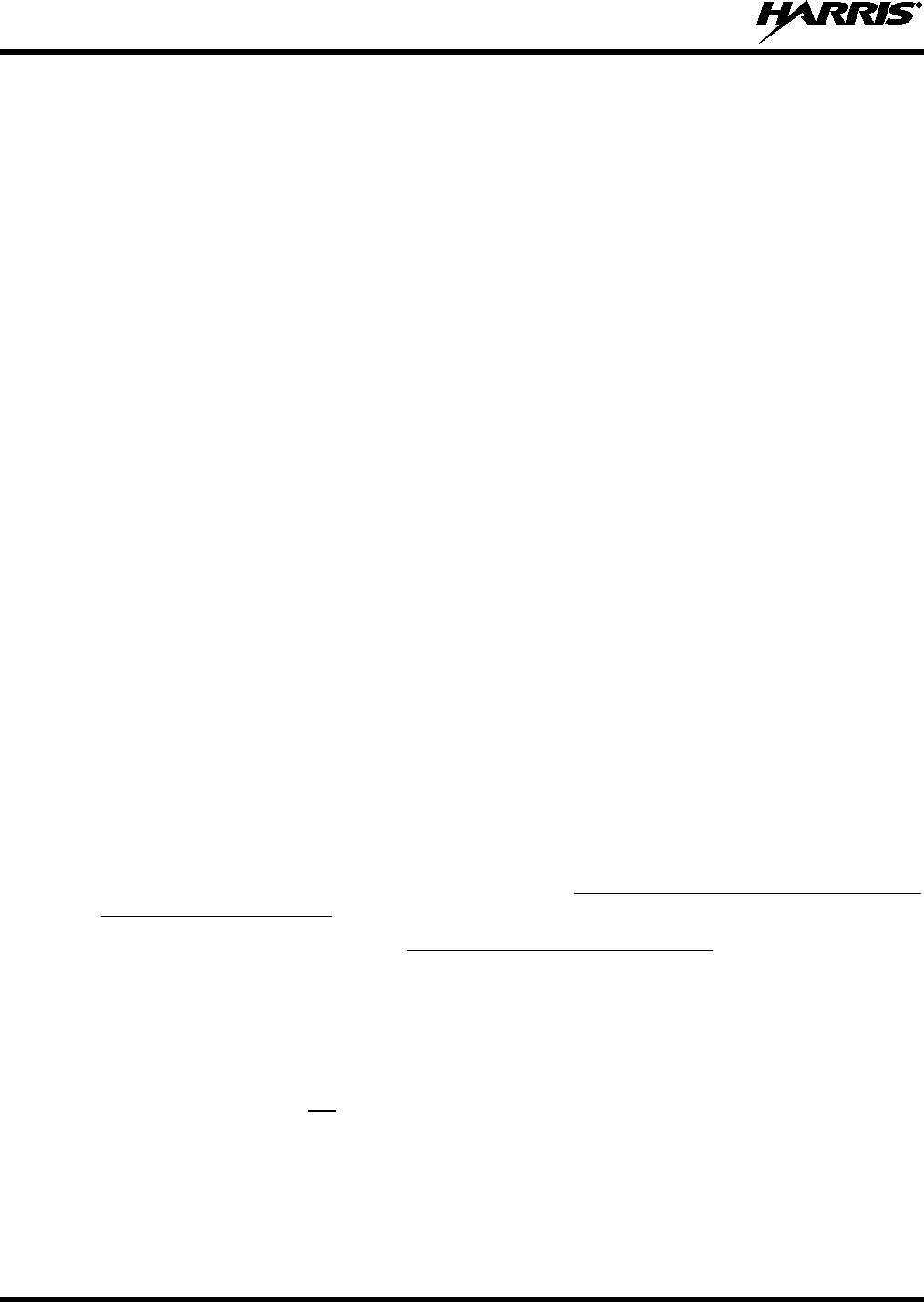
MM-018337-001, Rev. B
66
11 SPEAKER INSTALLATION
Select a location for the speaker that will allow for proper listening range with a moderate volume setting.
Total speaker cable length (of both cables) is approximately five (5) feet. Therefore, to include service
loops in the cables, the speaker must be mounted within approximately 4.5 feet of the control head.
1. Install the speaker (Item 12 in Table 4-4) using the hardware and mounting bracket supplied with it.
Also refer to the instructions included in the speaker for additional mechanical installation
information.
2. Route the speaker’s cable to the rear of the control head.
3. Mate the Speaker Cable (Item 13 in Table 4-4) to the 2-pin connector at the rear of the control head
by visually aligning the ¾-moon-shaped keys of the connectors, and then pushing and turning the
outer locking ring of the cable connector clockwise until it stops. A mild click will be sensed to
confirm proper mating.
4. Connect the speaker’s 2-pin plastic connector to the respective mating connector on the Speaker
Cable.
5. Route the cables out of the way of casual contact, and tie and stow as necessary.
12 MICROPHONE ATTACHMENT
There are several versions of microphones available for use with the CH-721 control head. Each has a
17-pin flush-mount type connector that mates with the microphone (“mic”) connector on the front panel
of the control head. The mic’s connector includes a captive thumbscrew that secures it to the mic
connector on the front panel of the control head. A microphone clip is included with each microphone.
The radio can be configured to provide a monitor function when the microphone is cradled in the clip.
Connect the mic to the control head and install the clip as follows:
1. Grasp the mic’s connector with a thumb and index finger on the sides of the connector just adjacent to
the thumbscrew.
2. Position connector just in front of the control head’s mic connector so its male pins can engage
straight into the female (socket) pins of the control head’s mic connector. The thumbscrew must be
oriented directly below the hanging mic cable.
3. Mate the two connectors by pressing them fully together. Do not apply any force to the thumbscrew
when mating the connectors.
4. Tighten the thumbscrew finger-tight. Do not use a screwdriver to tighten it.
5. Using the microphone clip as a template, drill mounting holes in the surface of the selected location.
6. Select a mounting surface location that has clearance for the mic when it is clipped to the clip, and
then attach the microphone clip to the surface. Use self-locking hardware (i.e., machine screws with
washers and locking nuts), self-drilling screws, or other appropriate hardware as necessary. Tighten
securely. Microphones used with the CH-721 control head have integrated hookswitches. Therefore,
the microphone clip does not need to be grounded.
7. Clip the microphone to the clip.
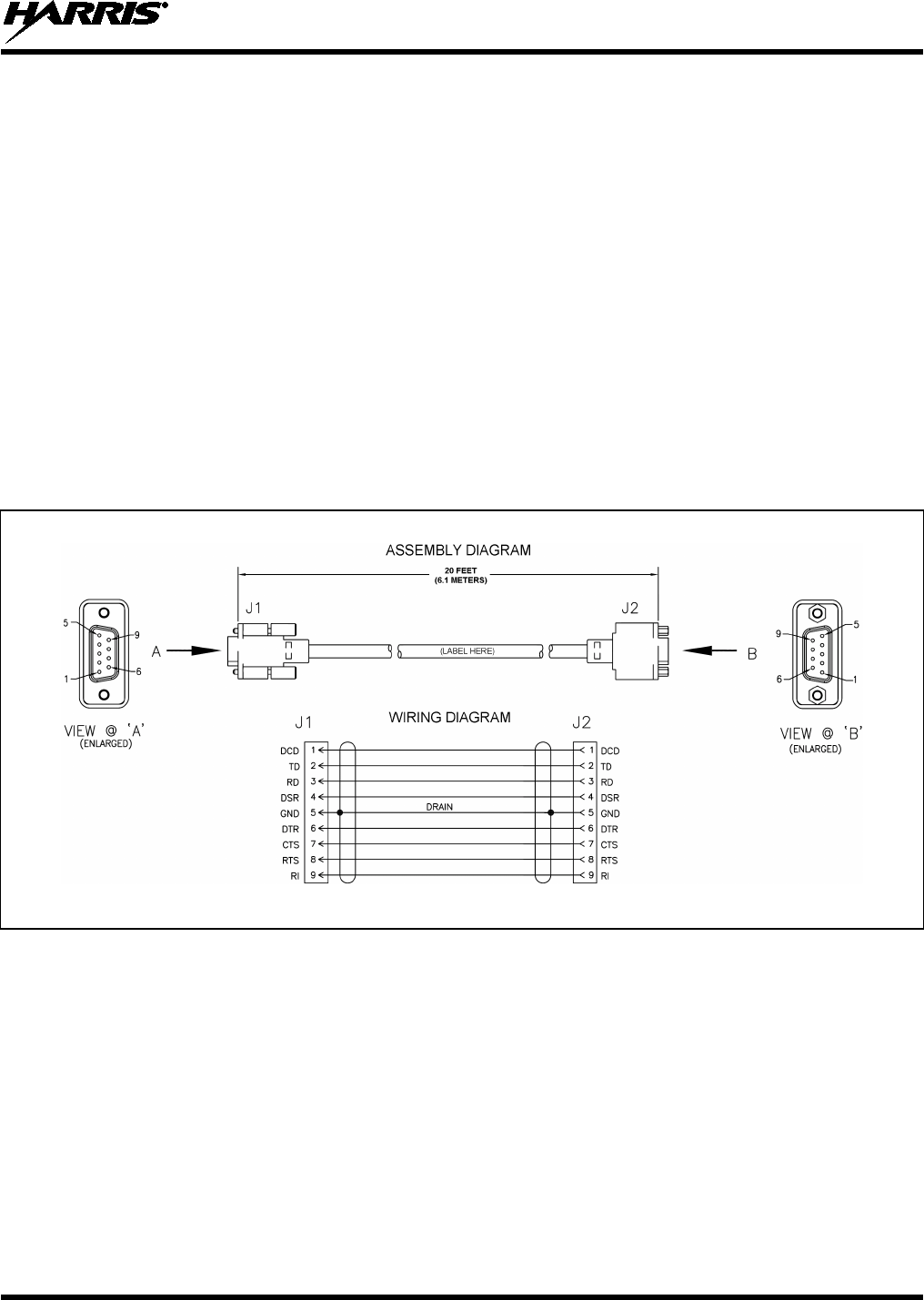
MM-018337-001, Rev. B
67
13 OPTIONAL CABLES
13.1 SERIAL PROGRAMMING CABLE CA-013671-020
Serial Programming Cable CA-013671-020 (20 feet long) can be used to program and configure the
VRMS and VRBS via a Personal Computer. This cable can also be used to extend the length of GPS
NMEA-formatted serial data connections. The cable’s assembly and wiring diagrams are shown in Figure
13-1 below.
To program and configure the VRMS, the cable’s male DB-9 connector (J1) mates to the female DB-9
serial port connector on the rear of the VRMS. To program and configure the VRBS, the cable’s male
DB-9 connector (J1) mates to the female DB-9 serial port connector of Interface Cable CA-012349-003.
Alternately, if the cable is being used to carry GPS NMEA-formatted serial data from the VRMS, its male
DB-9 connector mates to connector P5 of Interface Cable CA-012349-003.
The cable’s female DB-9 connector (J2) mates to a PC’s male DB-9 serial port connector. If the utilized
PC is not equipped with a DB-9 serial port connector, the use of a suitable adapter is required, such as
USB-to-RS-232 Adapter Cable CN24741-0001. As of the publication of this manual, CN24741-0001 is
available via the Customer Resource Center; refer to Section 3.6 on page 21 for contact information.
(Made From PS-CA-013671 Rev. -)
Figure 13-1: Serial Data Cable CA-013671-020
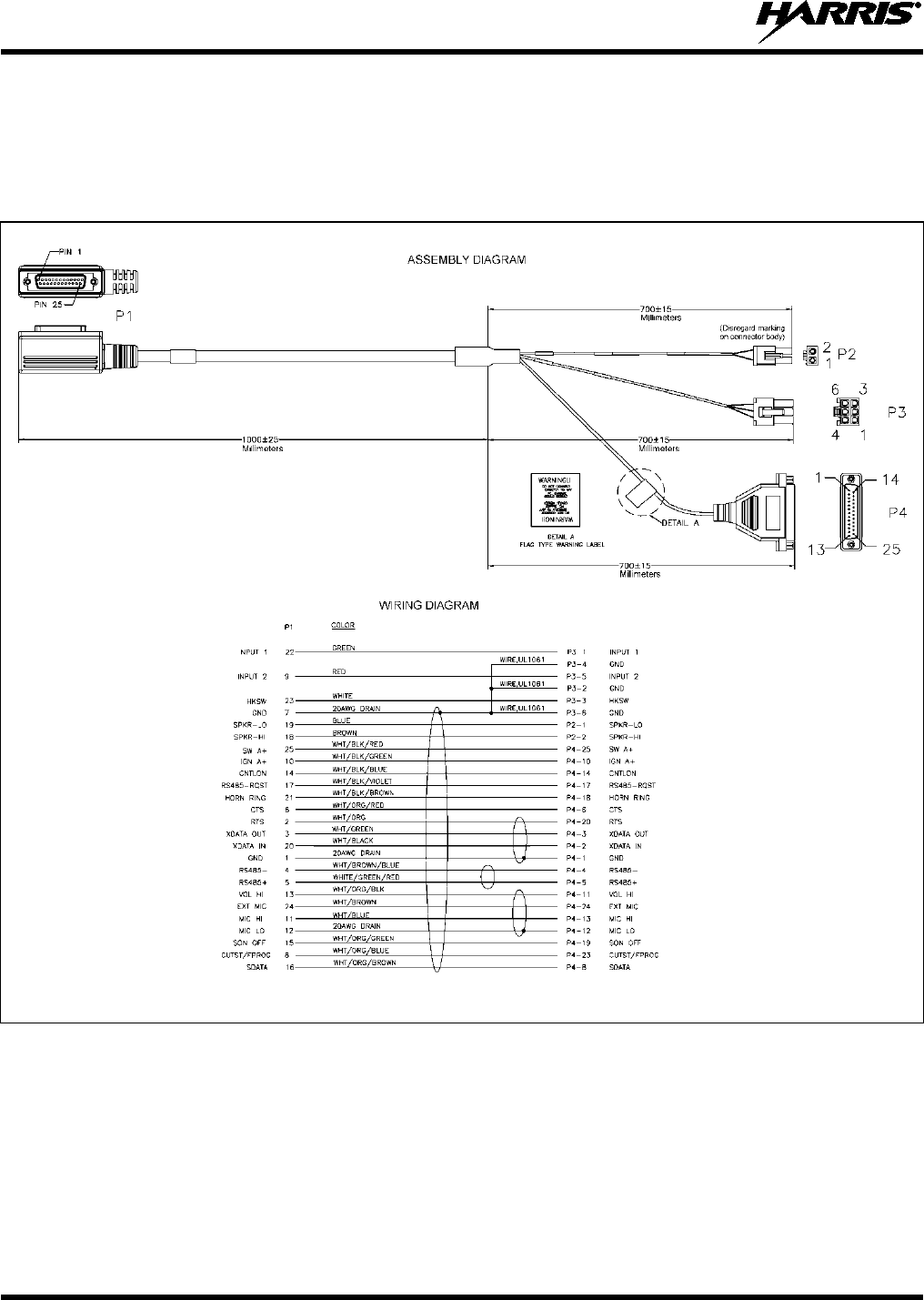
MM-018337-001, Rev. B
68
13.2 CH-721 OPTION CABLE CA-011854-001
CH-721 Option Cable CA-011854-001 can be used to connect optional equipment to the 25-pin
D-subminiature (DB-25) connector on the rear of the CH-721. This cable expands the connections
available at the 25-pin connector to three (3) separate connectors. The cable’s assembly and wiring
diagrams are shown in Figure 13-2 below.
(Made From PS-CA-011854 Rev. D)
Figure 13-2: CH-721 Option Cable CA-011854-001
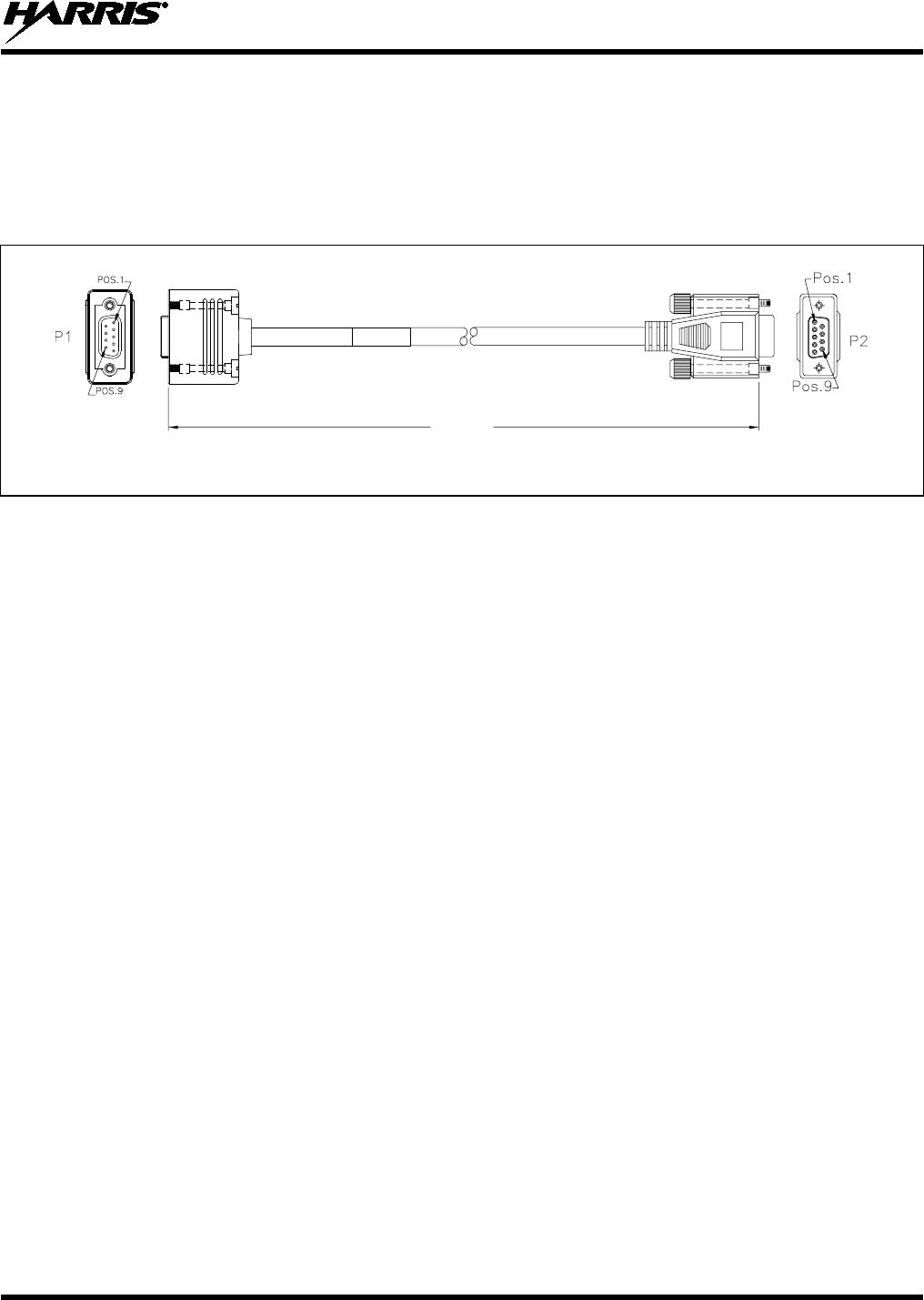
MM-018337-001, Rev. B
69
13.3 CH-721 SERIAL PROGRAMMING CABLE CA-104861
Serial Programming Cable CA-104861 (5 feet) can be used to program and configure the CH-721 control
head via a Personal Computer. This cable has a female DB-9 connector on one end for connection to the
PC’s serial port connector and a male DB-9 connector on the other end for connection to the serial port
connector on the rear of the head. The cable’s assembly diagram and wiring list are shown in Figure 13-3
below.
5 FEET
(1.524 METERS)
ASSEMBLY DIAGRAM
(Made From PS-CA-104861 Rev. A)
Figure 13-3: Programming Cable CA-104861
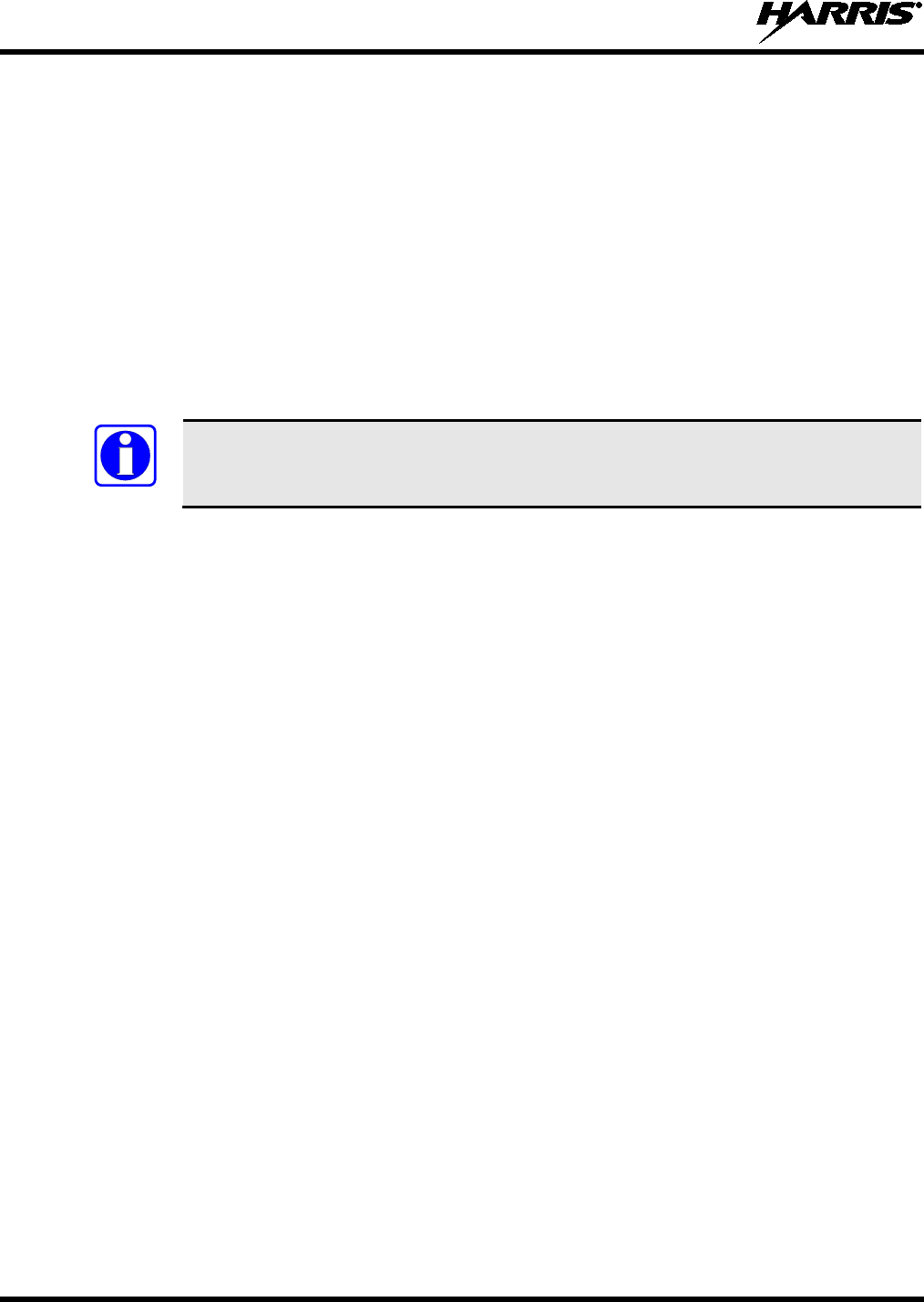
MM-018337-001, Rev. B
70
14 GPS NMEA-FORMATTED SERIAL DATA
CONNECTION
To obtain GPS NMEA-formatted serial data from the VRMS, follow this procedure to complete serial
data connections:
1. Connect the DB-9 female connector labeled “GPS” of Interface Cable to the computer’s serial port
DB-9 male connector—either directly or extended via a serial cable. Serial Programming Cable
CA-013671-020 (20 feet) can be used to extend the length; see Section 13.1 for additional
information. Tighten the screws firmly, and then route the cabling as required. If the computer is not
equipped with a DB-9 serial port connector, the use of a suitable adapter is required, such as
USB-to-RS-232 Adapter Cable CN24741-0001.
2. Follow the manufacturer’s instructions on processing the NMEA-formatted GPS data from the radio.
NOTE
Industry software to process GPS information through this interface is not supported by
Harris.
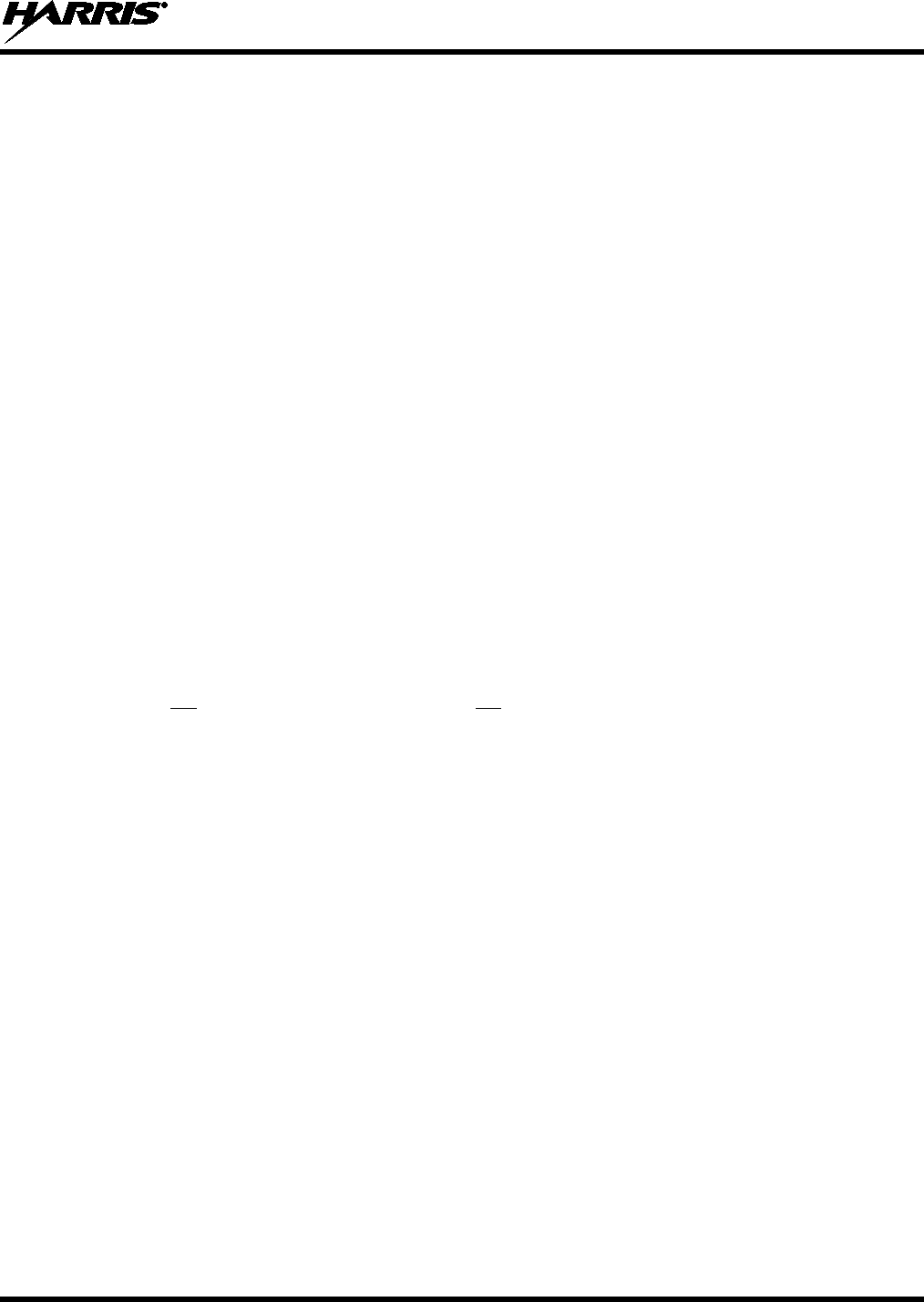
MM-018337-001, Rev. B
71
15 INITIAL POWER-UP TEST
1. At the main inline fuse holders located near the vehicle battery (or DC power access point), insert a
15-amp AGC fuse into the fuse holder for VRMS main power. The fuse is included with the
respective DC Power Cable (installed per Section 9.2.1.2).
2. Insert another 15-amp AGC fuse into the fuse holder for VRBS main power. The fuse is included
with the respective DC Power Cable (installed per Section 9.2.1.2).
3. If not already, insert a 5-amp AGC fuse into the fuse holder for the CH-721 control head’s main
power fuse. The fuse is included with the respective DC Power Cable.
4. If not already, near the vehicle’s fuse panel, install a 3-amp AGC fuse in the respective inline fuse
holder. The fuse is included with the respective DC Power Cable. However, if Vehicle Fuse and
T-Tap Kit FS24473 was used to make the control head’s ignition/switched power connection, install
the 2-amp ATM fuse included with the T-tap kit.
5. Tie and stow all fuse holders and wiring to prevent excess vibration/movement.
6. Carefully reconnect the vehicle’s battery ground cable.
7. If not already, temporarily connect the two mobile antenna cables from the vehicle-mounted antennas
to the female TNC RF connector at the rear of the two radios. These are temporary connections until
test procedures in Section 16 are complete.
8. If the VRMS is equipped with the GPS receiver option, permanently connect the antenna cable from
the GPS antenna (or mobile/GPS combo antenna) to the female SMA connector on the rear panel of
the radio. The male SMA connector on most GPS antenna cables has a 5/16-inch hex collar, so the
use of a wrench of this same size is normally required for tightening. However, some may have
collars with only knurled surfaces, so a standard wrench or torque wrench cannot be used. In either
case, do not over tighten the connector and do not twist the cable when tightening.
9. If the installation is wired so the vehicle’s ignition key/switch turns the radio on and off, turn the
switch to the Accessory or Run position.
10. If the control head is not already powered up, do so by rotating its on/off/volume control clockwise
out of the detent position.
11. Verify the control head has powered-up by observing its display. If the display is not lit, refer to
Section 9.1 as necessary.
As long as the software configuration parameters have been loaded, successful installation is almost
immediately realized:
• After a short boot-up sequence, the control head displays login information and/or a talk group.
• If no errors are displayed, the installation is most-likely properly wired.
• If an error is displayed, recheck all cable connections, verify all fuses are properly installed, and
verify battery power is getting to the radios’ main power fuses. If problems persist, contact the
Technical Assistance Center (see page 21).
• Consult the Operator’s Manual for operational information. Refer to Section 3.5 on page 21 as
necessary.
Refer to the following section for performance test information.
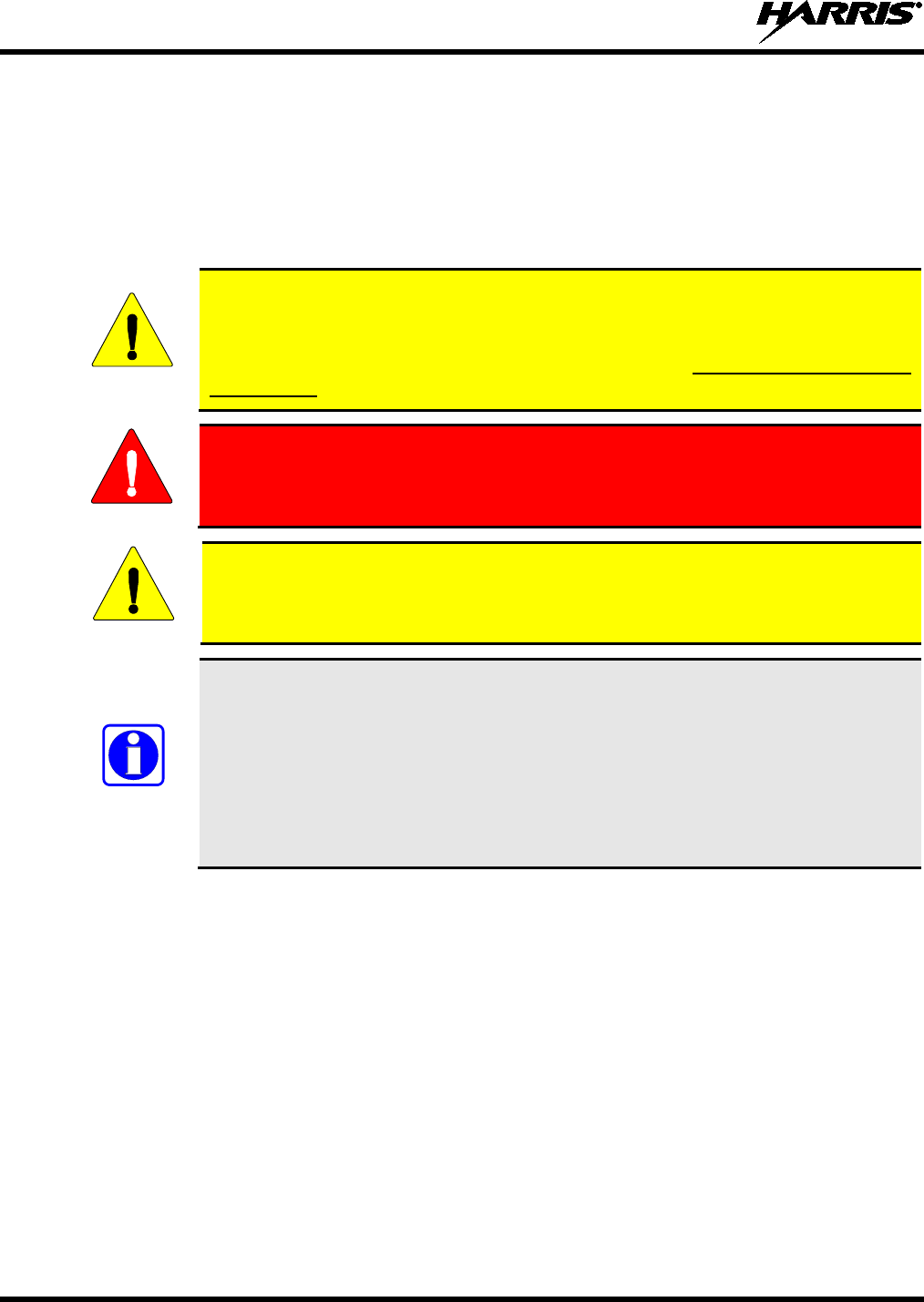
MM-018337-001, Rev. B
72
16 PERFORMANCE TESTS
This section includes procedures to verify the performance of the installation’s antennas. Procedures
include:
• VRMS and VRBS Testing by Transmitting into a 50-Ohm RF Load/Terminator (“Dummy Load”)
• VRMS and VRBS Testing by Transmitting into the Respective Radio Antennas
CAUTION
The accuracy of test results depends upon a DC power source in the range of 13.6 volts
DC ±10%, with a current capacity of greater than 15 amps. Make sure the vehicle’s
battery is fu
lly charged by running the engine for a few minutes before the test, and
keep the engine running during the test procedures. Abide by
the following
WARNING!
WARNING
If the vehicle’s engine must remain running, the vehicle location should be well
ventilated so exhaust fumes from the engine do not cause harm!
CAUTION
If a vehicle equipped with a VRS7000 requires jump-starting, the radio installation’s
four (4) fuses should be removed from the fuse holders prior to jump-starting. Doing
so will prevent damage to the VRS7000 and CH-721.
NOTE
Prior to installation, VRMS and VRBS transmit RF output power levels should be
configured appropriately. The wide range of power levels indicated in the following
procedures take into account such things as: customer’s requirements; measurement
errors, especially to include uncalibrated equipment; cabling losses; and temperature
variations. By no means should the result from Performance Testing in this section be
construed as the exact value of power level outputs from the VRS7000 radio
equipment, as values are set and more accurately measured in the factory. The values
obtained in these test procedures determine a successful installation only.

MM-018337-001, Rev. B
73
16.1 REQUIRED TEST EQUIPMENT
Table 16-1: Test Equipment Required for Performance Tests
TEST EQUIPMENT MODEL / PART NUMBER & DESCRIPTION
Peak-Reading
Wattmeter Bird Electronic Corp. Model 4314B (or equivalent) with Type N female
connectors at input and output ports.
100-Watt
RF Wattmeter
Slug
Bird Electronic Corp. Element 100E, 100-watt, 400 - 1000 MHz (or
equivalent).
5-Watt
RF Wattmeter
Slug
Bird Electronic Corp. Element 5E, 5-watt, 400 -
1000 MHz (or
equivalent).
RF Coaxial
Jumper Cable
Pasternack Enterprises PE3661-36 (or equivalent) 50-Ohm Coaxial
Cable with TNC male connector and Type N
male connector,
approximately three (3) feet in length. The utilized cable must have
VSWR below 1.5:1 within the RF passband.
Type N Male-to-TNC
Female RF Adapter
Pasternack Enterprises PE9090 or Amphenol Connex 242130 (or
equivalent) Type N male to TNC female adapter. Required to connect
the cable of the vehicle-mounted antennas to the wattmeter.
Type N Female-to-
TNC Male RF
Adapter
Pasternack Enterprises PE9089 or Amphenol Connex 242131 (or
equivalent) Type N female to TNC male adapter. Required to connect
a female TNC connector to a 50-ohm RF load/terminator.
Two (2)
50-Ohm RF
Loads/Terminators
(“Dummy Loads”)
Pasternack Enterprises PE6106 (or equivalent) 50-ohm RF terminator
rated at greater than 50 watts power, with Type N male connector.
Two 50-ohm RF terminators are required.
Vehicle-Mounted
Antennas Tests are performed with the vehicle-mounted antennas.
16.2 VRMS TRANSMITTING INTO A 50-OHM LOAD/TERMINATOR
1. At the rear of the VRMS, disconnect the antenna cable from the 800 MHz bandpass filter’s antenna
connector (TNC connector labeled “OUTPUT”). If it is not already, label this cable as the “VRMS
Antenna” cable. This should be the cable from the highest (vehicle rooftop-mounted) antenna.
2. Using the Type N male to TNC male coaxial jumper cable, connect the antenna connector on the rear
of the 800 MHz bandpass filter (connector labeled “ANTENNA”) to the wattmeter’s input connector.
Refer to Figure 16-1 as necessary.
3. Connect a 50-ohm RF load/terminator to the wattmeter’s output connector.
4. At the rear of the VRBS, disconnect the antenna cable from the VRBS. If it is not already, label this
cable from the antenna as the “VRBS Antenna” cable. This should be the cable from the lowest
(vehicle trunk lid-mounted) antenna.
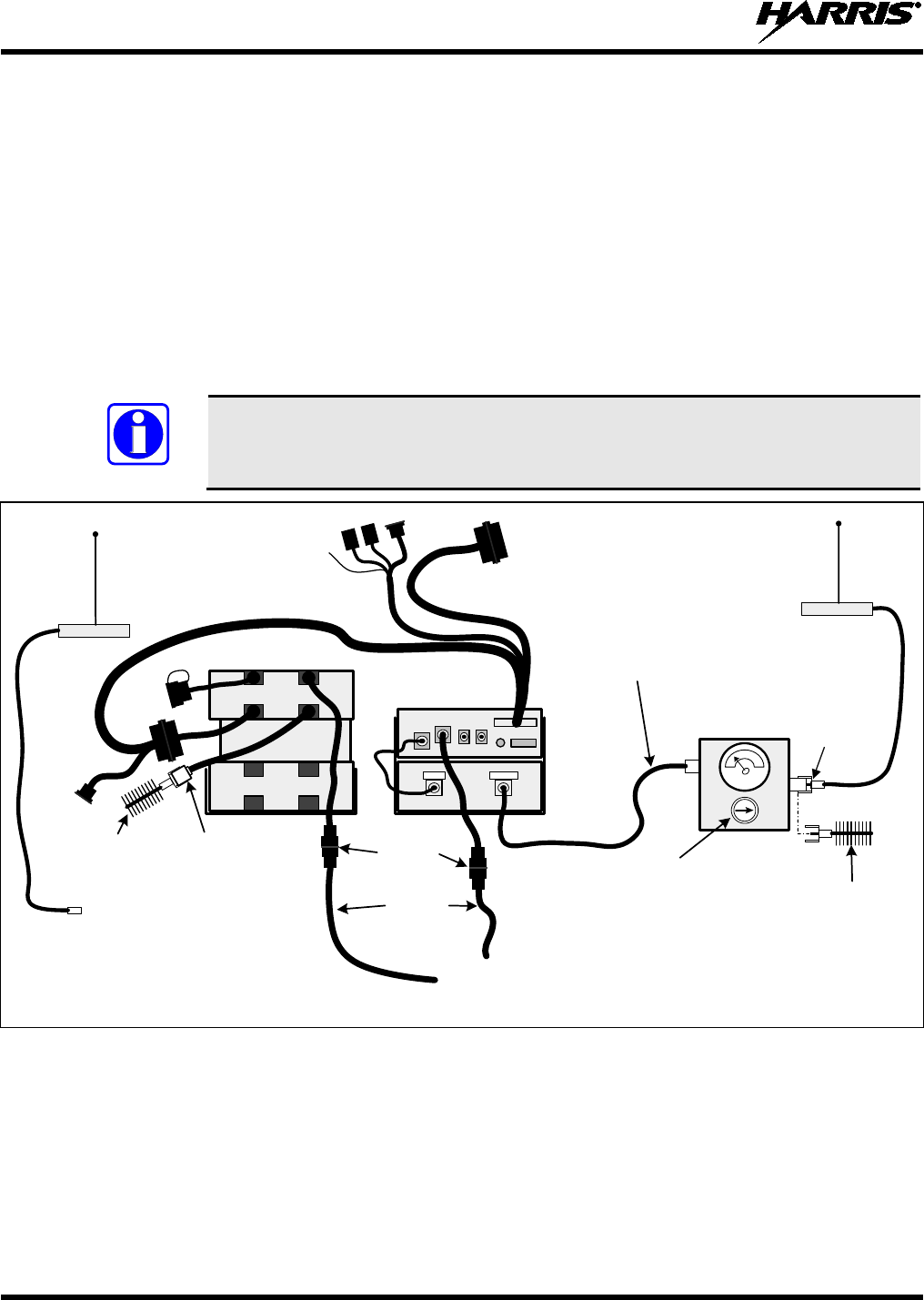
MM-018337-001, Rev. B
74
5. Connect the other 50-ohm RF load/terminator to the VRBS. Use the Type N female to TNC male RF
adapter. Refer to Figure 16-1 as necessary.
6. If not already, turn on the VRS via the CH-721’s on/off volume control (or externally-mounted
switch). The front panel of the CH-721 is shown in Figure 10-1 on page 56. The VRS powers-up in
the mobile-only mode (vehicular repeater disabled).
7. For the VRS7010, set it to an 800 MHz test conventional channel.
For the VRS7020, set it to a 700 MHz test conventional channel.
For the VRS7030, set it to a VHF test conventional channel.
8. Insert the 100-watt slug into the wattmeter and position the slug to measure forward RF output power.
Rotate it as necessary. The arrow on the face of the slug must point away from the VRMS antenna
jack and towards the 50-ohm load/terminator for forward power measurements.
NOTE
It is recommended that a test conventional RF channel be allocated for this testing.
This same channel should be used during the antenna test procedure presented in the
next section.
IN
OUT
Rear View of
VRMS7010/
7020/7030
3-Pin
DC Power
Connectors
DC Power
Cables
From 13.6-Volt
Fused Power
Source
TNC Male-to-Type N Male
Coaxial Jumper Cable
CAN Cable and
GPS Antenna
Cable connections
not are indicated.
Vehicle-Mounted
Antenna for
VRMS7010/7020/7030
(highest antenna)
Type N Male-to-
TNC Female
RF Adapter
Peak-
Reading
Wattmeter
50-Ohm RF Load/
Terminator
(“Dummy Load”)
Wattmeter Slug
(see text)
Rear View of
VRBS7010/7020/7030
Interface
Cable
Vehicle-Mounted
Antenna for
VRBS7010/7020/7030
(lowest antenna)
50-Ohm RF Load/
Terminator
(“Dummy Load”)
Type N Female-
to-TNC Male
RF Adapter
(VRBS Antenna Cable
Disconnected During
VRMS Transmitter and
Antenna Tests)
Option
Connectors
RADIO ANTENNA
Antenna’s
Coaxial
Cable
Antenna’s
Coaxial
Cable
Figure 16-1: Wattmeter Connections for VRMS7010/VRMS7020/VRMS7030 Antenna Tests
9. Set the wattmeter to measure peak RF power.
10. Key the VRMS transmitter via the microphone’s PTT button.
11. For an 800 MHz band transmission (VRMS7010), compare the wattmeter’s reading with the target
RF output power range of between 22.1 and 55.5 watts (35 watts ±2 dB). This transmit output power
range assumes the VRMS7010 is currently configured for high-power transmit.
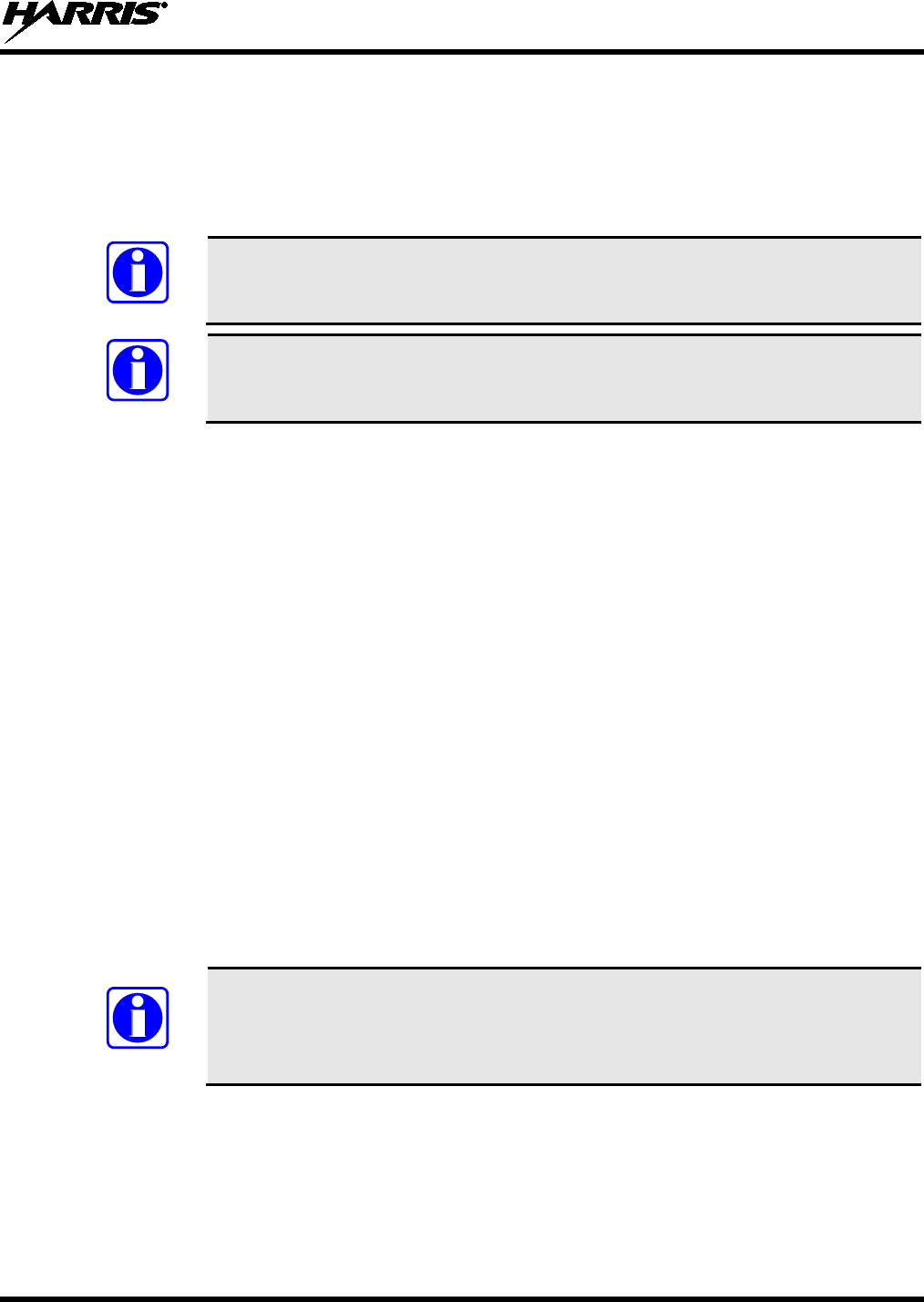
MM-018337-001, Rev. B
75
For a 700 MHz band transmission (VRMS7020), compare the wattmeter’s reading with the target RF
output power range of between 15.1 and 23.9 watts (19 watts ±1 dB). This transmit output power
range assumes the VRMS7020 is currently configured for high-power transmit.
For a VHF band transmission (VRMS7030), compare the wattmeter’s reading with the target RF
output power range of between 39.8 and 63 watts (50 watts ±1 dB). This transmit output power range
assumes the VRMS7030 is currently configured for high-power transmit.
NOTE
As stated in the NOTE on page 72, the wide power level range takes into account
errors caused by test cable loss, etc.
NOTE
Transmit only for as long as needed to take the measurement, then immediately
disable the transmission.
12. If the wattmeter reading is within the range, record the measured value in the appropriate space on
the data collection form near the end of this manual (page 81).
If the wattmeter reading is outside the range, verify the VRS power supply voltage (i.e., battery
voltage) is within the specified range, recheck all connections and measure the RF output power
again. If this fails to produce a reading within the range, replace it and repeat this procedure. If
problems persist, contact the Technical Assistance Center (see page 21).
13. Un-key the transmitter by releasing the microphone’s PTT button.
16.3 VRMS TRANSMITTING INTO ITS ANTENNA
1. To verify transmit output power of the VRMS, perform the test procedure presented in the previous
section (Section 16.2).
2. Disconnect the 50-ohm load/terminator from the wattmeter.
3. Connect the cable from the vehicle-mounted VRMS antenna (cable labeled “VRMS Antenna”) to the
wattmeter’s output connector, as shown in Figure 16-1.
4. If not already, turn on the VRS via the CH-721’s on/off volume control (or externally-mounted
switch). The front panel of the CH-721 is shown in Figure 10-1 on page 56. The VRS powers-up in
the mobile-only mode (vehicular repeater disabled).
5. Set the VRS (and thus its VRMS) to a test conventional channel. Use the same channel that was used
when performing the previous procedure.
NOTE
It is recommended that a test conventional channel
be allocated for this testing.
Otherwise, interference with other radio users in the system may occur. Also, during
transmissions, always observe the RF exposure-related
safety information
presented in Section 1.2 of this manual (begins on page 6).
6. Insert the 100-watt slug into the wattmeter and position the slug to measure forward RF output power.
Rotate it as necessary. The arrow on the face of the slug must point away from the VRMS and
towards the antenna for forward power measurements.
7. Set the wattmeter to measure peak RF power.
8. Key the transmitter via the microphone’s PTT button.
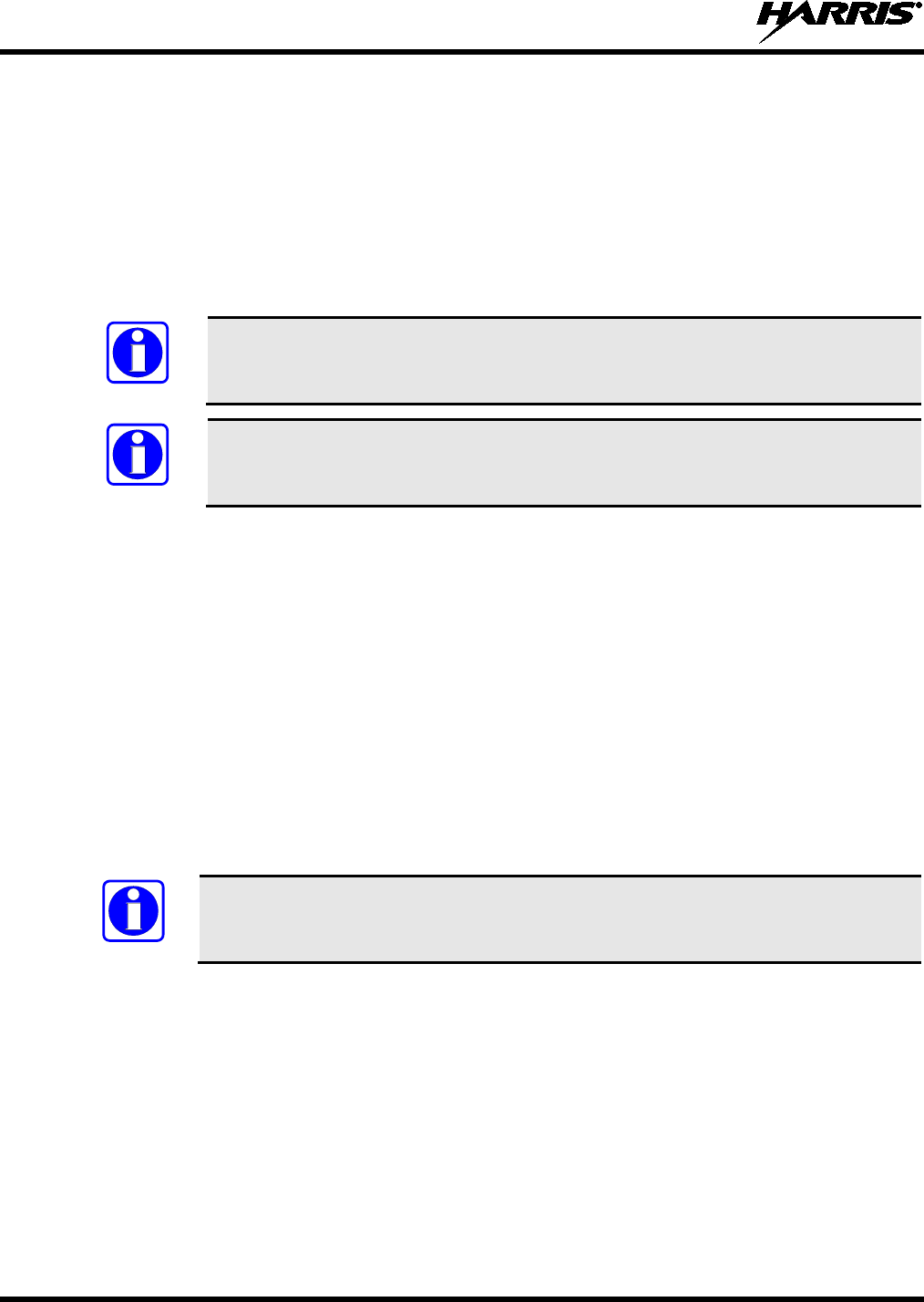
MM-018337-001, Rev. B
76
9. For an 800 MHz band transmission (VRMS7010), compare the wattmeter’s reading with the target
RF output power range of between 22.1 and 55.5 watts (35 watts ±2 dB). This transmit output power
range assumes the VRMS7010 is currently configured for high-power transmit.
For a 700 MHz band transmission (VRMS7020), compare the wattmeter’s reading with the target RF
output power range of between 15.1 and 23.9 watts (19 watts ±1 dB). This transmit output power
range assumes the VRMS7020 is currently configured for high-power transmit.
For a VHF band transmission (VRMS7030), compare the wattmeter’s reading with the target RF
output power range of between 39.8 and 63 watts (50 watts ±1 dB). This transmit output power range
assumes the VRMS7030 is currently configured for high-power transmit.
NOTE
As stated in the NOTE on page 72, the wide power level range takes into account
errors caused by test cable loss, etc.
NOTE
Transmit only for as long as needed to take the measurement, then immediately
disable the transmission.
10. If the wattmeter reading is within the range, record the value in the appropriate space on the data
collection form near the end of this manual (page 81).
If the wattmeter reading is outside the range, verify the VRMS power supply voltage (i.e., battery
voltage) is within the specified range, recheck all connections, and measure the forward power again.
If this fails to produce a reading within the range, check all cabling and connections, and repeat the
testing procedure to this point. In the event the wattmeter reading still falls outside the range, replace
the antenna, make sure all connections are seated firmly, and repeat the testing procedure. If problems
persist, contact the Technical Assistance Center (see page 21).
11. Position the wattmeter’s 100-watt slug to measure reverse (reflected) RF power from the antenna. The
arrow on the face of the slug must point away from the antenna and towards the VRMS to measure
reverse power.
12. Key the transmitter via the microphone’s PTT button.
13. Compare the wattmeter reading with the RF power output range of 2 watts or less.
NOTE
Transmit only for as long as needed to take the measurement, then immediately disable
the transmission.
14. If the wattmeter reading is within the range, record the value in the appropriate space on the data
collection form near the end of this manual (page 81).
If the wattmeter reading is outside the range, make sure the antenna is consistent with the specified
frequency range of the VRMS. Recheck all antenna connections, and measure the reverse power
again. If this fails to produce a reading within the range, replace the antenna and repeat the entire
antenna test procedure. Any value exceeding the maximum allowable reflected power value will
result in a diminished RF output signal. If problems persist, contact the Technical Assistance Center
(see page 21).
15. Un-key the transmitter by releasing the microphone’s PTT button.
16. Disconnect the coaxial cable jumper and wattmeter.
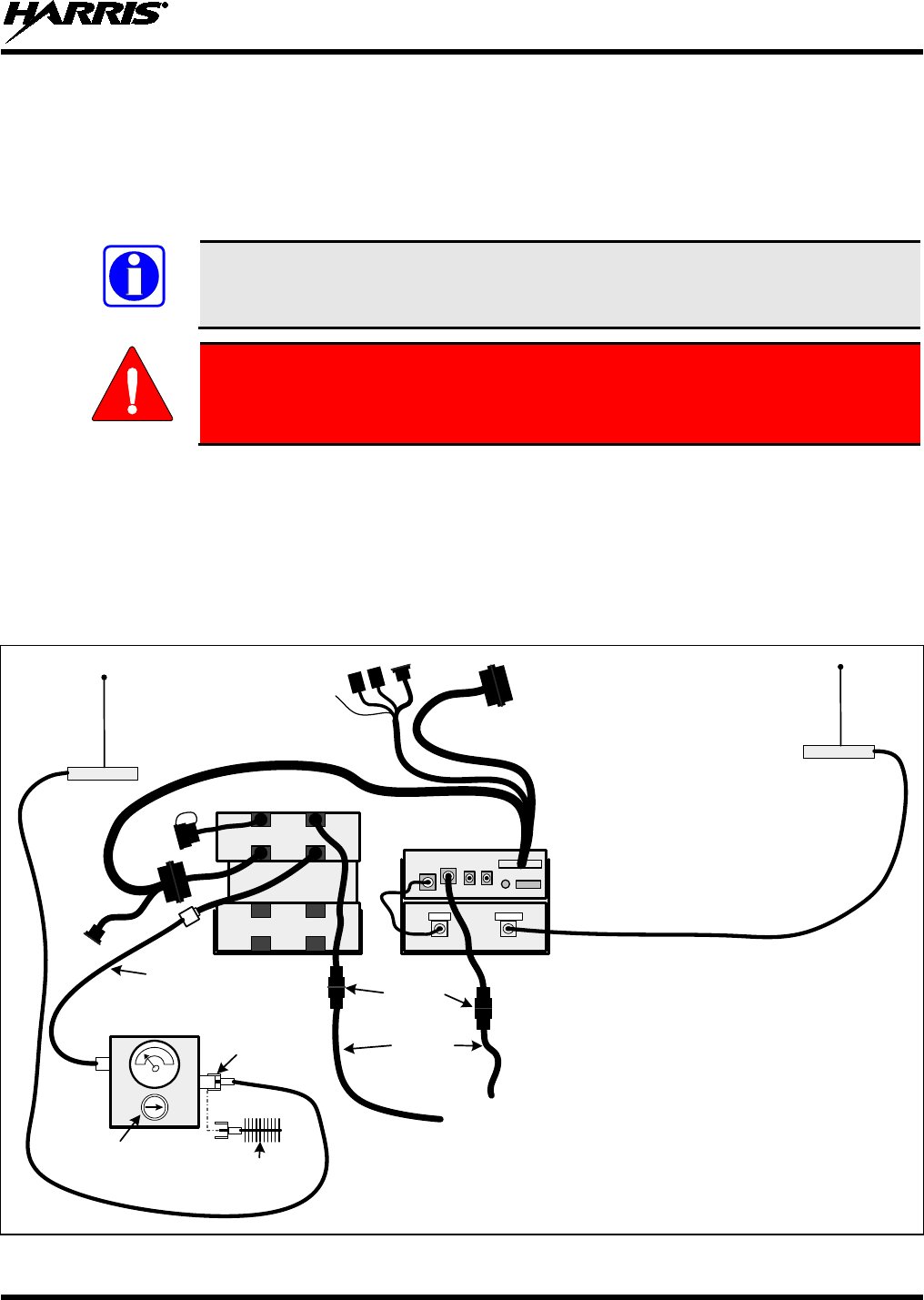
MM-018337-001, Rev. B
77
17. For the VRMS7010 and the VRMS7020, permanently connect the cable from the vehicle-mounted
VRMS antenna to the bandpass filter’s antenna connector (labeled “ANTENNA”) by mating the two
TNC connectors together. Use a pair of soft-jaw pliers to gently tighten this connection. Do not over
tighten and do not twist the antenna cable.
18. Make several test calls on the radio system to verify VRMS operation. Before making the calls, select
another conventional channel(s), as required to verify operation.
NOTE
To prevent RF leakage and ensure peak performance, make sure the RF connectors are
tight, but do not over-tighten so connector damage will not occur.
WARNING
Improper installation of the RF cables may lead not only to poor radio
performance but also to harmful exposure to RF electromagnetic energy.
16.4 VRBS TRANSMITTING INTO A 50-OHM LOAD/TERMINATOR
1. If it is not already, disconnect the VRBS antenna cable at the rear of the VRBS. Label this cable from
the antenna as the “VRBS Antenna” cable. This should be the cable from the lowest (vehicle trunk lid
mounted) antenna.
2. Using the Type N male to TNC male coaxial jumper cable, connect the antenna connector at the rear
of the VRBS to the wattmeter’s input connector. See Figure 16-2.
IN
OUT
Rear View of
VRMS7010/
7020/7030
3-Pin
DC Power
Connectors
DC Power
Cables
From 13.6-Volt
Fused Power
Source
TNC Male-to-Type N Male
Coaxial Jumper Cable
CAN Cable and
GPS Antenna
Cable connections
not are indicated.
Vehicle-Mounted
Antenna for
VRMS7010/7020/7030
(highest antenna)
Type N Male-to-
TNC Female
RF Adapter
Peak-Reading
Wattmeter
50-Ohm RF Load/
Terminator
(“Dummy Load”)
Wattmeter Slug
(see text)
Rear View of
VRBS7010/7020/7030
Interface
Cable
Vehicle-Mounted
Antenna for
VRBS7010/7020/7030
(lowest antenna)
Option
Connectors
RADIO ANTENNA
Antenna’s
Coaxial
Cable
Antenna’s
Coaxial
Cable
Figure 16-2: Wattmeter Connections for VRBS7010/VRBS7020/VRBS7030 Antenna Tests
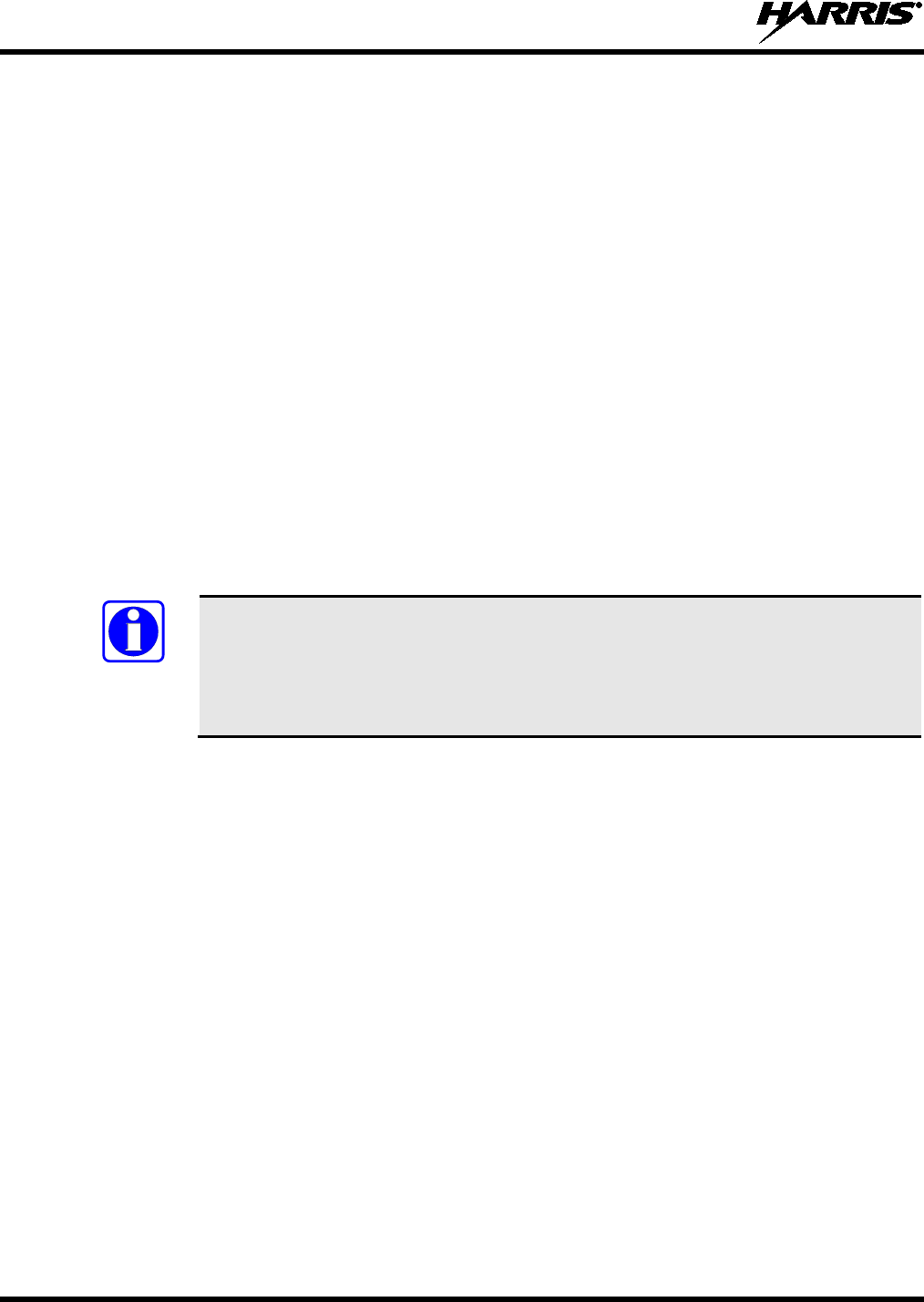
MM-018337-001, Rev. B
78
3. Connect a 50-ohm RF load/terminator to the wattmeter’s output connector.
4. Insert a 5-watt slug into the wattmeter and position the slug to measure forward RF output power.
Rotate it as necessary. The arrow on the face of the slug must point away from the VRBS and towards
the 50-ohm load/terminator for forward power measurements.
5. Set the wattmeter to measure peak RF power.
6. If not already, turn on the VRS7000 via the CH-721’s on/off volume control (or externally-mounted
switch). The front panel of the CH-721 is shown in Figure 10-1 on page 56. The VRS7000 powers-
up in the mobile-only mode (vehicular repeater disabled). Refer to the operator’s manual as
necessary.
7. Switch the VRS to a P25 trunked radio network (i.e., make a “system” change if necessary) that it has
access to and is within radio range. Use a test trunked system if available.
8. Enable/Activate the extended coverage (XCOV) vehicular repeater mode as follows:
a. Press the control head’s MENU button.
b. Use the control head’s •/•• Ramp Control to scroll through the menu until “P25 Menu”
appears in the middle line of the display.
c. Press the MENU button again. After a short delay, “VR Standby” will appear in the display,
indicating the VRS7000 is operating in XCOV vehicular repeater mode and waiting for (client)
radios to connect to it. When one or more radios connect, the display changes to “VR Active.”
NOTE
Within twelve (12) seconds of enabling the XCOV vehicular repeater mode, the VRBS
should begin transmitting control channel information. For the VRBS7010, this occurs
on a 700 MHz RF channel. For the VRMS7020, this occurs on an 800 MHz RF
channel. For the VRMS7030, this can occur on either a 700 or an 800 MHz RF
channel.
9. Compare the wattmeter’s reading with the target RF output power range of between 2.4
and 3.8 watts (3 watts ±1 dB). This transmit output power range assumes the VRBS is currently
configured for maximum transmit power. The VRBS may be configured with a lower RF output
power (range = ¼ to 3 watts) per its VRB radio configuration.
10. If the wattmeter reading is within the range, record the measured value in the appropriate space on
the data collection form near the end of this manual (page 81).
If the wattmeter reading is outside the range, verify the VRS’s power supply voltage (i.e., battery
voltage) is within the specified range, recheck all connections and measure the RF output power
again. If this fails to produce a reading within the range, replace it and repeat this procedure. If
problems persist, contact the Technical Assistance Center (see page 21).
11. At the control head, disable P25 vehicular repeater mode. The VRBS should immediately stop
transmitting, as indicated by the wattmeter.
16.5 VRBS TRANSMITTING INTO ITS ANTENNA
1. To verify transmit output power of the VRBS, perform the test procedure presented in the previous
section (Section 16.4).
2. Disconnect the 50-ohm load/terminator from the wattmeter.
3. Connect the cable from the vehicle-mounted VRBS antenna (cable labeled “VRBS Antenna”) to the
wattmeter’s output connector. See Figure 16-2.
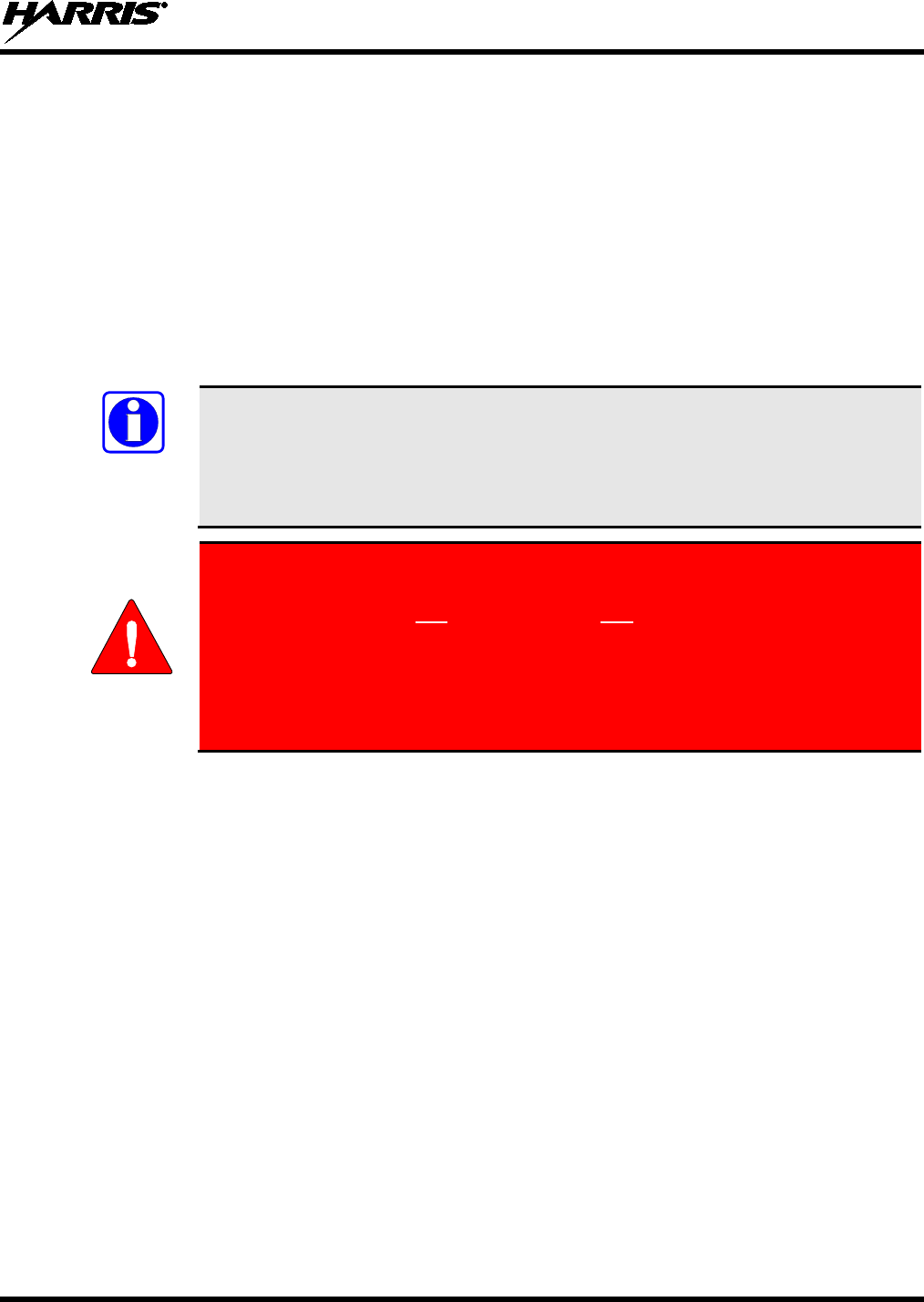
MM-018337-001, Rev. B
79
4. Insert a 5-watt slug into the wattmeter and position the slug to measure forward RF output power.
Rotate it as necessary. The arrow on the face of the slug must point away from the VRBS and towards
the 50-ohm load/terminator for forward power measurements.
5. Set the wattmeter to measure peak RF power.
6. If not already, turn on the VRS7000 via the CH-721’s on/off volume control (or externally-mounted
switch). The front panel of the CH-721 is shown in Figure 10-1 on page 56. The VRS7000 powers-
up in the mobile-only mode (vehicular repeater disabled).
7. Enable the extended coverage (XCOV) P25 vehicular repeater mode. Refer to step 8 in the previous
section (Section 16.4) as necessary. If no radios are connected to the VRS7000, “VR Standby” is
indicated in the control head’s display. When one or more radios connect, the display changes to
“VR Active.”
NOTE
Within twelve (12) seconds of enabling the XCOV vehicular repeater mode, the VRBS
should begin transmitting control channel information. For the VRBS7010, this occurs
on a 700 MHz RF channel. For the VRMS7020, this occurs on an 800 MHz RF
channel. For the VRMS7030, this can occur on either a 700 or an 800 MHz RF
channel.
WARNING
Since the VRBS
automatically begins transmitting soon after enabling the
vehicular repeater mode, before enabling this mode, an antenna must be
connected to the VRBS and VRMS antennas and personnel should be at least the
minimum safe distance from these two (2) antennas. Minimum safe distances
from the VRMS antenna are listed in Table 1-1 on page 8 for the VRMS7010 and
the VRMS7020. Minimum safe distances from the VRMS7030 antenna are listed
in Table 1-2 (on page 10). Minimum safe distances from the VRBS7010/-
VRBS7020/VRBS7030 antenna are listed in Table 1-3 (on page 10).
8. Compare the wattmeter’s reading with the target RF output power range of between 2.4
and 3.8 watts (3 watts ±1 dB). This transmit output power range assumes the VRBS is currently
configured for maximum transmit power. The VRBS may be configured with a lower RF output
power (range = ¼ to 3 watts) per its VRB radio configuration.
9. If the wattmeter reading is within the range, record the value in the appropriate space on the data
collection form near the end of this manual (page 81).
If the wattmeter reading is outside the range, first verify the VRBS antenna’s driven element is
properly trimmed. Before making any antenna adjustments, be sure to disable P25 vehicular
repeater mode so the VRBS will stop transmitting. Next, verify VRBS power supply voltage (i.e.,
battery voltage) is within the specified range, recheck all connections, and measure the forward power
again. If this fails to produce a reading within the range, check all cabling and connections, and repeat
the testing procedure to this point. In the event the wattmeter reading still falls outside the range,
replace the antenna, make sure all connections are seated firmly, and repeat the testing procedure. If
problems persist, contact the Technical Assistance Center (see page 21).
10. At the CH-721, disable the P25 vehicular repeater mode. The VRBS should immediately stop
transmitting, as indicated by the wattmeter.
11. Position the wattmeter’s 5-watt slug to measure reverse (reflected) RF power from the antenna. The
arrow on the face of the slug must point away from the antenna and towards the VRBS to measure
reverse power.
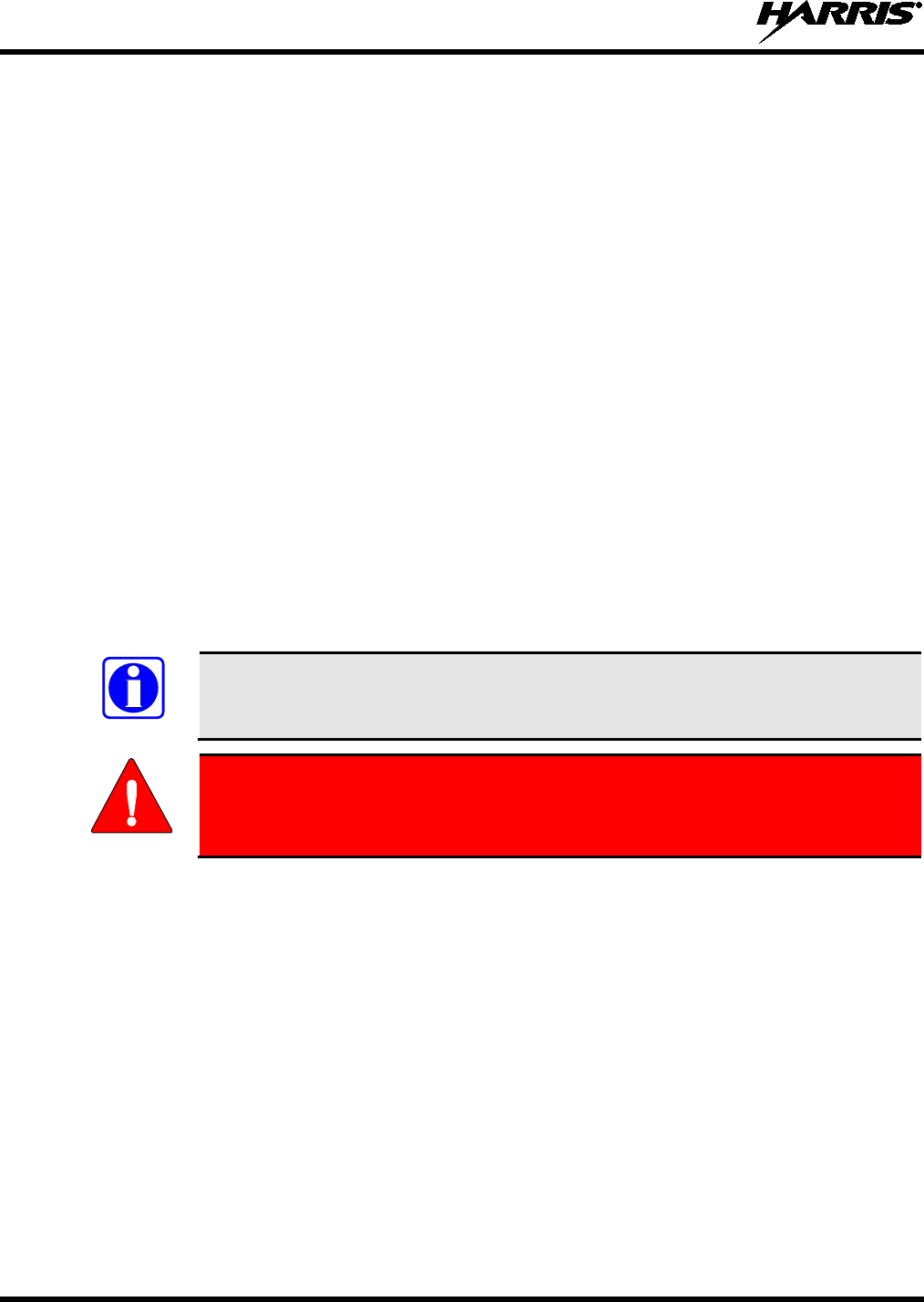
MM-018337-001, Rev. B
80
12. At the CH-721, enable P25 vehicular repeater mode. Within twelve (12) seconds, the VRBS should
begin transmitting control channel information on a 700 MHz RF channel.
13. Compare the wattmeter reading with the RF power output range of less than ½ watt.
14. If the wattmeter reading is within the range, record the value in the appropriate space on the data
collection form near the end of this manual (page 81).
If the wattmeter reading is outside the range, first verify the VRBS antenna’s driven element is
properly trimmed. Before making any antenna adjustments, be sure to disable P25 vehicular
repeater mode so the VRBS will stop transmitting. Verify VRBS power supply voltage (i.e.,
battery voltage) is within the specified range, recheck all connections, and measure the forward power
again. If this fails to produce a reading within the range, check all cabling and connections, and repeat
the testing procedure to this point. In the event the wattmeter reading still falls outside the range,
replace the antenna, make sure all connections are seated firmly, and repeat the testing procedure. If
problems persist, contact the Technical Assistance Center (see page 21).
15. At the CH-721, disable P25 vehicular repeater mode. The VRBS should immediately stop
transmitting, as indicated by the wattmeter.
16. Disconnect the coaxial cable jumper and wattmeter.
17. Permanently connect the cable from the vehicle-mounted VRBS antenna to the VRBS antenna
connector at the rear of the VRBS. Mate the two TNC connectors together. Use a pair of soft-jaw
pliers to gently tighten this connection. Do not over tighten and do not twist the cable.
18. Re-enable extended coverage (XCOV) P25 vehicular repeater mode and make several test calls
between P25 radios connected to the VRS7000.
NOTE
To prevent RF leakage and ensure peak performance, make sure the RF connectors are
tight, but do not over-tighten so connector damage will not occur.
WARNING
Improper installation of the RF cables may lead not only to poor radio
performance but also to harmful exposure to RF electromagnetic energy.
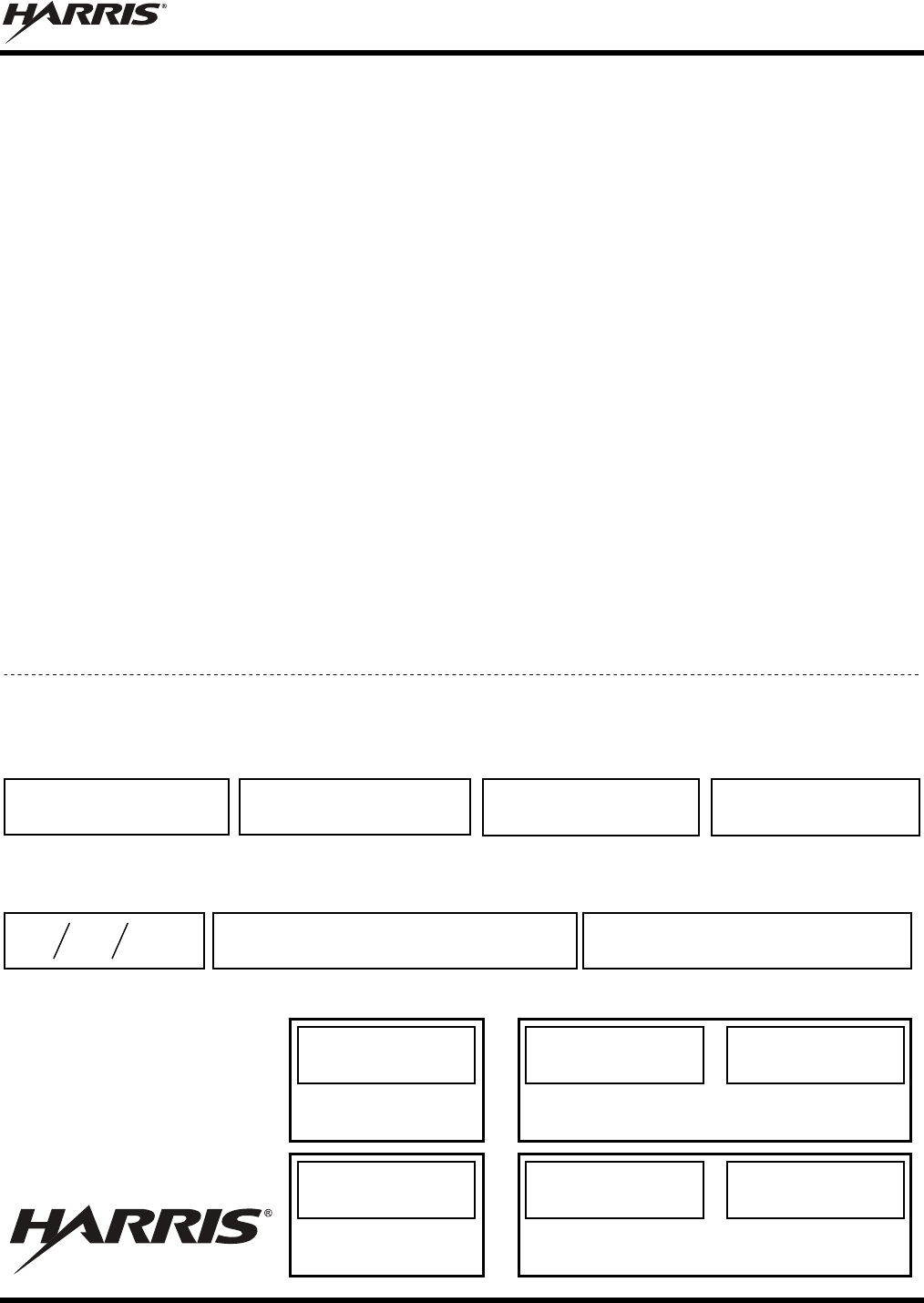
MM-018337-001, Rev. B
81
16.6 TEST PERFORMANCE DATA FORM
Enter the information requested on this data collection form. Clip this form and file it as a permanent record of
the tested performance of the installed VRS7010/VRS7020/VRS7030.
Clip
Here
Company Performing Installation Technician Performing Test
Date of Test
(mm/dd/yyyy)
VRMS
Serial Number VRBS Antenna
Make and Model Number
VRBS Power Into
50-Ohm Load
Watts
VRBS Forward Power
with Antenna VRBS Reflected Power
with Antenna
Watts
Watts
VRMS Power Into
50-Ohm Load
Watts
VRMS Forward Power
with Antenna VRMS Reflected Power
with Antenna
Watts
Watts
VRBS
Serial Number VRMS Antenna
Make and Model Number
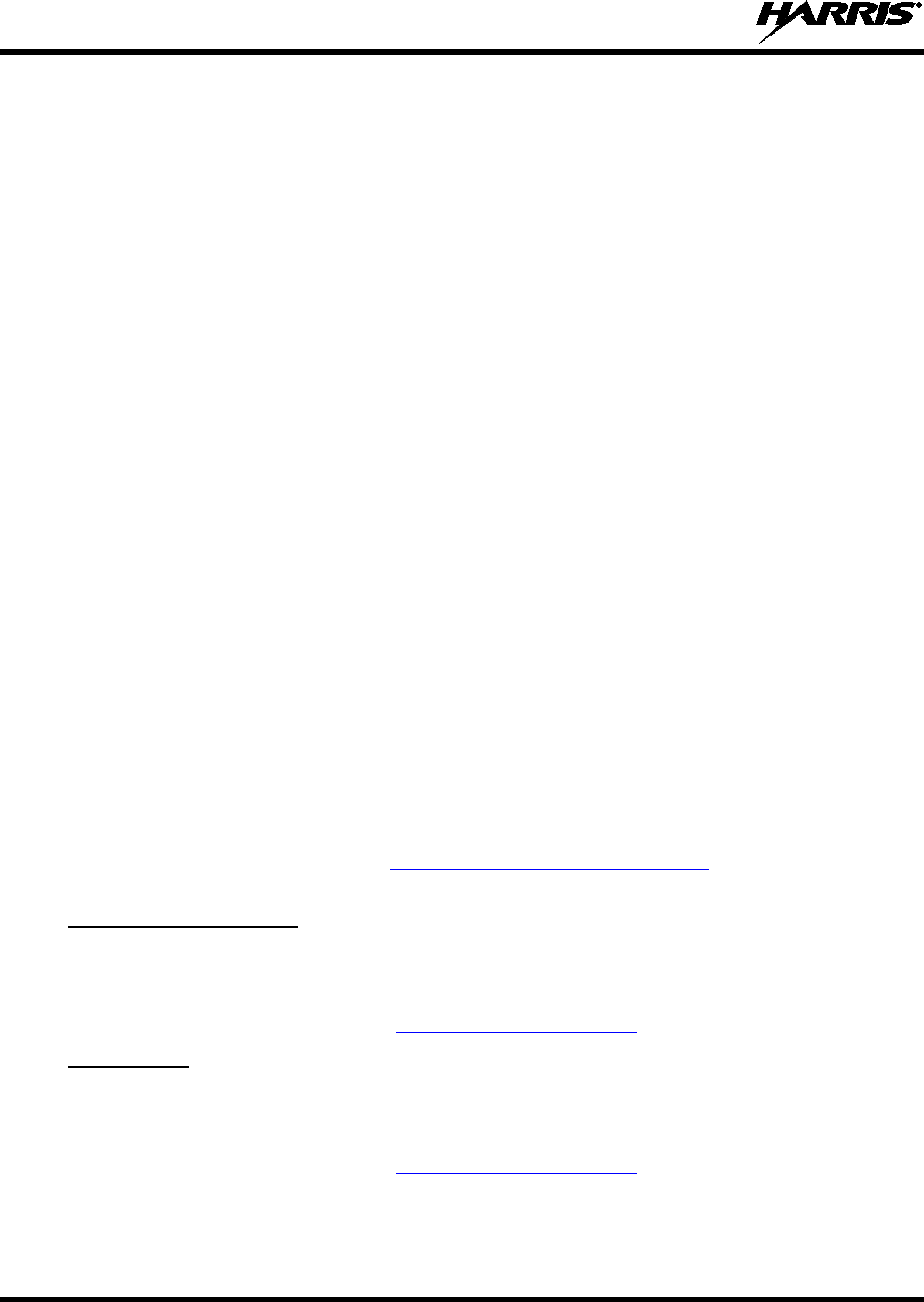
MM-018337-001, Rev. B
82
17 COMPLETE THE INSTALLATION
Double-check the following items before considering the installation completed:
• Verify all newly installed mechanical hardware is mounted securely and all respective mounting
hardware is tight.
• Verify all electrical interconnections are connected properly and the associated connector attachment
hardware is tight. Pay special attention to all RF antenna cables!
• Verify all related fuses are correctly installed, properly rated, and correctly labeled.
• Verify all electrical cables and wiring are tied, stowed, and protected so they are out of the way of
casual contact, away from sources of extreme heat, and wire chafing cannot occur. Pay special
attention to all RF antenna cables!
• To prevent fumes from entering the vehicle’s passenger compartment, seal the hole/grommet/wire
combination at the firewall with a silicon-based sealer.
• Verify all vehicle components are properly reinstalled such as kick panels, headliners, and seats.
• If the installation includes a separately-mounted on/off power switch for manually turning the V-TAC
mobile radio (and possibly others systems) on and off, verify it is labelled accordingly. For example:
“Radio ON/OFF.”
• Remove all tools and unused hardware from the vehicle.
• Verify the test performance data has been recorded on the data collection form shown in this manual.
• Consult with the radio system administration personnel and placard/post required minimum antenna
separation distances in plain view of all VRS7000 user/operator positions.
18 WARRANTY REGISTRATION
Please register this product within ten (10) days of purchase. Registration validates the warranty coverage,
and enables Harris to contact you in case of any safety notifications issued for this product.
Registration can be made on-line at www.pspc.harris.com/CustomerService or by contacting Harris
Warranty Administration at the following:
United States and Canada:
• Phone Number: 1-800-368-3277, Option 4 (toll free)
• Fax Number: 1-434-455-6821
• E-mail: WarrantyClaims@Harris.com
International:
• Phone Number: 1-434-455-6403
• Fax Number: 1-434-455-6676
• E-mail: WarrantyClaims@Harris.com
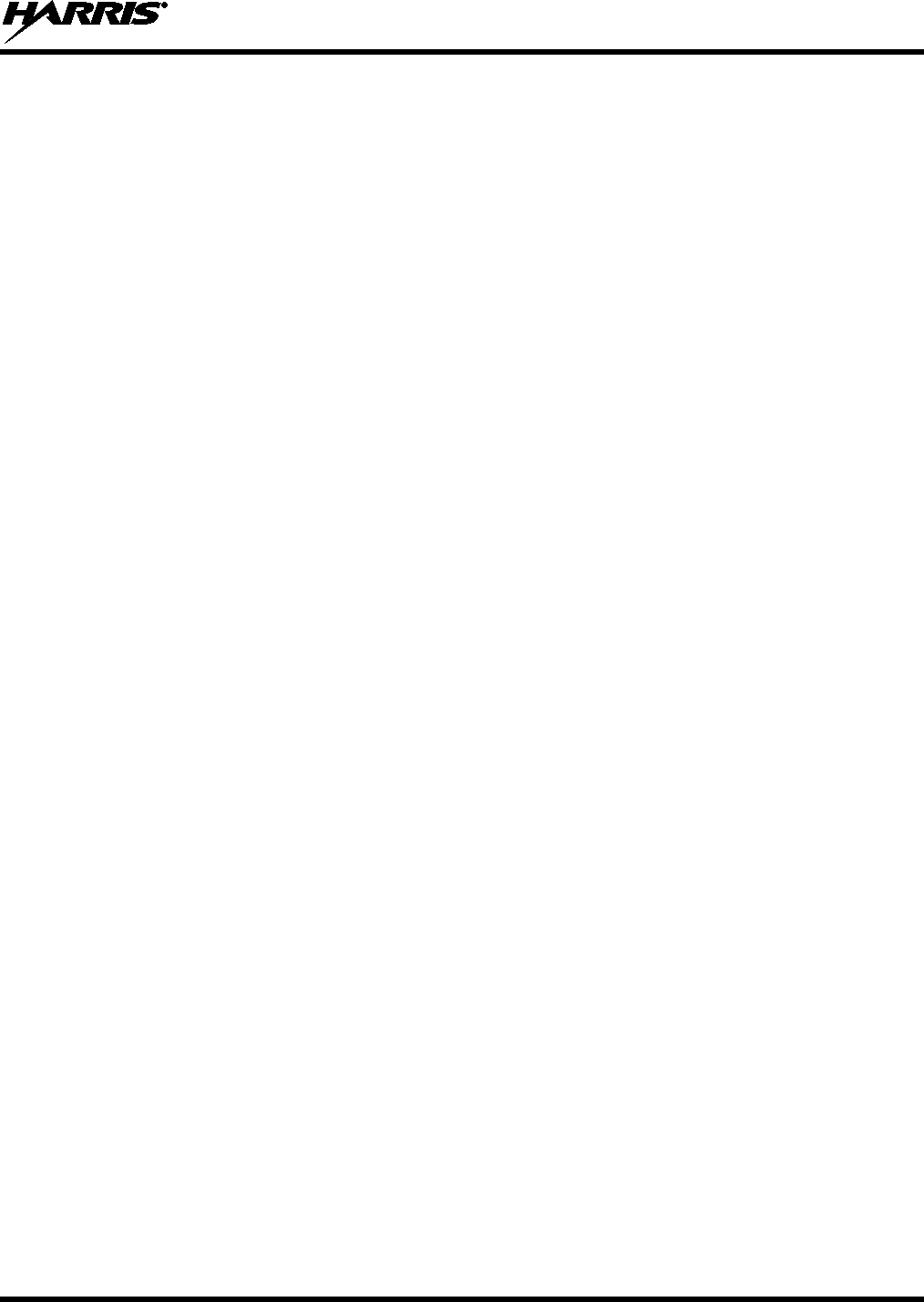
MM-018337-001, Rev. B
83
19 WARRANTY
A. Harris Corporation, a Delaware Corporation, through its RF Communications Division (hereinafter
"Seller") warrants to the original purchaser for use (hereinafter "Buyer") that Equipment manufactured
by or for the Seller shall be free from defects in material and workmanship, and shall conform to its
published specifications. With respect to all non-Seller Equipment, Seller gives no warranty, and only
the warranty, if any, given by the manufacturer shall apply. Rechargeable batteries are excluded
from this warranty but are warranted under a separate Rechargeable Battery Warranty (ECR-7048).
B. Seller’s obligations set forth in Paragraph C below shall apply only to failures to meet the above
warranties occurring within the following periods of time from date of sale to the Buyer and are
conditioned on Buyer’s giving written notice to Seller within thirty (30) days of such occurrence:
1. for fuses and non-rechargeable batteries, operable on arrival only.
2. for parts and accessories (except as noted in B.1), ninety (90) days.
3. for P7300, P7200, P7100IP, P5400, P5300, P5200, P5100, P3300, M7300, M7200 (including
V-TAC), M7100IP, M5300 and M3300 radios, two (2) years, effective 10/01/2007.
4. for Unity® XG-100P, three (3) years.
5. for all other equipment of Seller’s manufacture, one (1) year.
C. If any Equipment fails to meet the foregoing warranties, Seller shall correct the failure at its option (i)
by repairing any defective or damaged part or parts thereof, (ii) by making available at Seller’s factory
any necessary repaired or replacement parts, or (iii) by replacing the failed Equipment with equivalent
new or refurbished Equipment. Any repaired or replacement part furnished hereunder shall be
warranted for the remainder of the warranty period of the Equipment in which it is installed. Where
such failure cannot be corrected by Seller’s reasonable efforts, the parties will negotiate an equitable
adjustment in price. Labor to perform warranty service will be provided at no charge during the
warranty period only for the Equipment covered under Paragraph B.3 and B.4. To be eligible for no-
charge labor, service must be performed at Seller’s factory, by an Authorized Service Center (ASC)
or other Servicer approved for these purposes either at its place of business during normal business
hours, for mobile or personal equipment, or at the Buyer’s location, for fixed location equipment.
Service on fixed location equipment more than thirty (30) miles from the Service Center or other
approved Servicer’s place of business will include a charge for transportation.
D. Seller’s obligations under Paragraph C shall not apply to any Equipment, or part thereof, which (i) has
been modified or otherwise altered other than pursuant to Seller’s written instructions or written
approval or, (ii) is normally consumed in operation or, (iii) has a normal life inherently shorter than the
warranty periods specified in Paragraph B, or (iv) is not properly stored, installed, used, maintained or
repaired, or, (v) has been subjected to any other kind of misuse or detrimental exposure, or has been
involved in an accident.
E. The preceding paragraphs set forth the exclusive remedies for claims based upon defects in or
nonconformity of the Equipment, whether the claim is in contract, warranty, tort (including
negligence), strict liability or otherwise, and however instituted. Upon the expiration of the warranty
period, all such liability shall terminate. The foregoing warranties are exclusive and in lieu of all other
warranties, whether oral, written, expressed, implied or statutory. NO IMPLIED OR STATUTORY
WARRANTIES OF MERCHANTABILITY OR FITNESS FOR PARTICULAR PURPOSE SHALL
APPLY. IN NO EVENT SHALL THE SELLER BE LIABLE FOR ANY INCIDENTAL,
CONSEQUENTIAL, SPECIAL, INDIRECT OR EXEMPLARY DAMAGES.
This warranty applies only within the United States.
Harris Corporation Harris Corporation
RF Communications Division RF Communications Division
221 Jefferson Ridge Parkway 1680 University Avenue
Lynchburg, VA 24501 Rochester, NY 14610
1-800-528-7711 1-585-244-5830 ECR-7047L
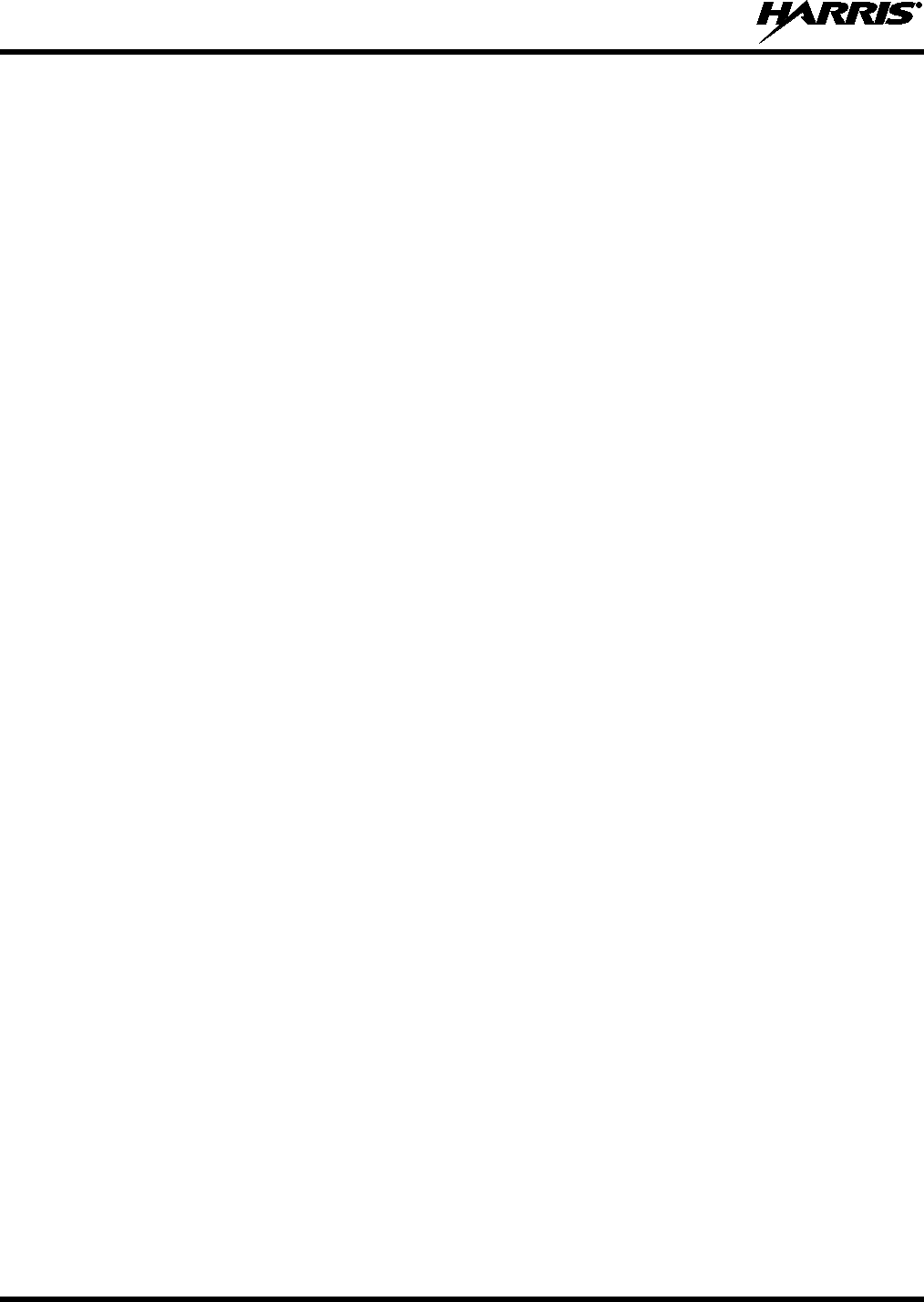
MM-018337-001, Rev. B
84
(This Page Intentionally Blank)
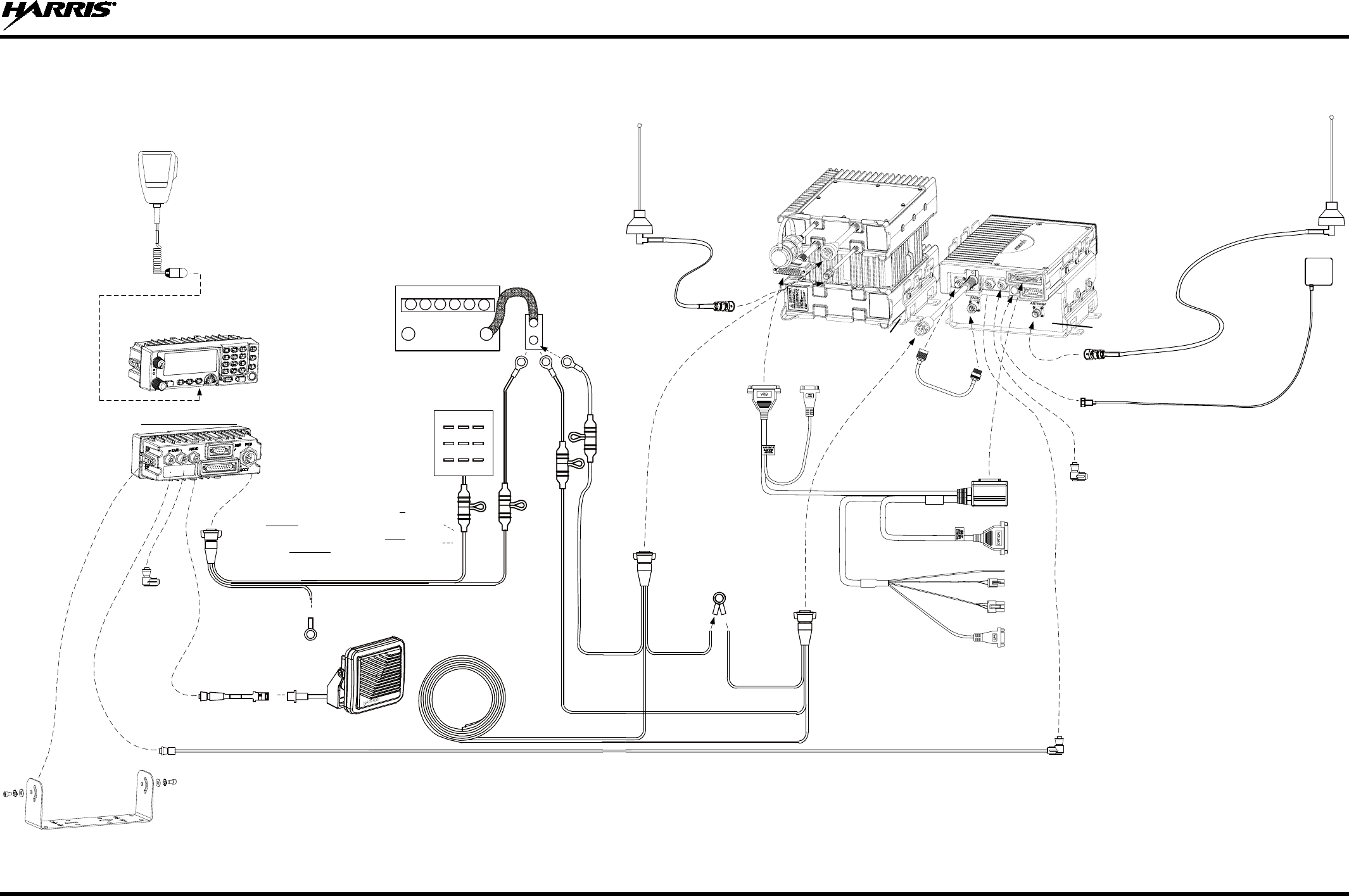
MM-018337-001, Rev. B
85
CAN TERMINATOR
CD-014027-001
[SUPPLIED WITH
INSTALLAITON KIT]
MALE TNC RF
CONNECTOR
(SUPPLIED
WITH
ANTENNA)
VEHICLE-MOUNTED
GPS ANTENNA
(OPTIONAL OR MAY
BE INTEGRATED IN
MOBILE ANTENNA)
DC POWER CABLE
CA-012365-001
(SUPPLIED WITH
INSTALLATION KIT)
CH-721 SYSTEM MODEL CONTROL HEAD
CU23218-0004
(MAMW-CP9F)
CH-721 MOUNTING
BRACKET KIT
KT-008608
[SUPPLIED WITH
INSTALLATION KIT]
• IF IGNITION SENSE ON/OFF FUNCTIONALITY IS REQUIRED,
CONNECT WHITE WIRE OF CONTROL HEAD’S DC POWER CABLE
TO A SWITCHED 13 VDC POWER SOURCE USING THE SUPPLIED
FUSE AND FUSE HOLDER.
• IF IGNITION SENSE ON/OFF FUNCTIONALITY IS NOT REQUIRED,
CONNECT WHITE WIRE OF CONTROL HEAD’S DC POWER CABLE
TO AN UNSWITCHED 13 VDC POWER SOURCE USING THE
SUPPLIED FUSE AND FUSE HOLDER.
WATERPROOF CAP
FM-104859-001 (NOT SHOWN)
FOR DB-9 SERIAL CONNECTOR
[SUPPLIED WITH INSTALLATION KIT]
WATERPROOF CAP
FM-104859-002 (NOT SHOWN)
FOR DB-25 ACCESSORY CONNECTOR
[SUPPLIED WITH INSTALLATION KIT]
REAR VIEW OF CONTROL HEAD
NEG POS
BLACK
RED
WHITE
RED
VEHICLE-
MOUNTED
VRBS
ANTENNA
RED RED
5-AMP
FUSE
& FUSE
HOLDER
(YELLOW)
3-AMP FUSE &
FUSE HOLDER
(YELLOW)
TWO
15-AMP
FUSES &
FUSE
HOLDERS
(ORANGE)
RED
WHITE
RED
RING
TERMINALS
VEHICLE
DC POWER
DISTRIBUTION
BLOCK
(E.G., “POWER
ACCESS POINT”)
VEHICLE BATTERY
+-
NOTE: BATTERY GROUND (-)
CONNECTION NOT INDICATED.
CAN
TERMINATOR
CD-014027-001
[SUPPLIED
WITH
INSTALLATION
KIT]
RED
WHITE
BLACK
(SHORT AS POSSIBLE)
RING TERMINAL
(CONNECT TO VEHICLE
CHASSIS GROUND)
SPEAKER CABLE
MAMROS0034-NN006
[SUPPLIED WITH
INSTALLATION KIT]
EXTERNAL SPEAKER
LS102824V10
[SUPPLIED WITH
INSTALLATION KIT] WHITE WIRES (2)
OF DC POWER
CABLES (LABELED
AND COILED NEAR
VEHICLE’S FUSE BOX)
DC POWER CABLE CA-012616-001
(SUPPLIED WITH INSTALLATION KIT)
VEHICLE FUSE
BOX, ETC.
WHITE (2X)
STANDARD MICROPHONE
MC-101616-040 OR
MC-101616-041
(INCLUDED WITH
MAMW-MC7Z)
OR
NOISE-CANCELING
MICROPHONE
MC-103334-050 OR
MC-103334-051
(INCLUDED WITH
MAMW-NMC9D)
DC POWER CABLE
CA-012365-001
(SUPPLIED WITH
INSTALLATION KIT)
RING
TERMINALS
(CONNECT TO
VEHICLE
CHASSIS
GROUND)
BLACK
RED
RED
WHITE
INTERFACE CABLE
CA-012349-003
(SUPPLIED WITH
INSTALLATION KIT)
MALE TNC RF CONNECTOR
(SUPPLIED WITH ANTENNA)
VEHICLE-MOUNTED
VRMS ANTENNA
RED
VRBS
(REAR VIEW)
VRBS7010 (700 MHz) = RU-017933-010
VRBS7020 (800 MHz) = RU-017933-020
VRBS7030 (700/800 MHz) = RU-017933-030
CAN CABLE CA-009562-030 (30 FEET LONG)
[SUPPLIED WITH INSTALLATION KIT]
MALE SMA RF CONNECTOR
(SUPPLIED WITH ANTENNA)
VRMS
(REAR VIEW)
EXTENSION BRACKET
FM-018205
(QTY. = 2)
BASE BRACKET
1000003678
RF CABLE
CA-018378
(SUPPLIED WITH
INSTALLATION KIT;
NOT USED WITH
VRMS7030)
(DB-9 CONNECTOR
FOR VRB RADIO
PROGRAMMING)
(COMMON
GROUND POINT
FOR BOTH
RADIOS)
M7300 MOBILE RADIO
VRMS7010 = RU-144750-061
VRMS7020 = RU-144750-061
VRMS7030 = RU-144750-041
BANDPASS FILTER
VRMS7010 = FL-017938-010
VRMS7020 = FL-017938-020
BASE BRACKET
1000003678
RADIO
20 WIRING DIAGRAM FOR VRS7000 AND CH-721
VRS7000 AND CH-721
WIRING DIAGRAM