Siemens Canada Siemens Milltronics Process Instruments LR250 SITRANS LR 250 TANK LEVEL PROBING RADAR User Manual SITRANS LR250 PROFIBUS PA
Siemens Canada Ltd. - Siemens Milltronics Process Instruments SITRANS LR 250 TANK LEVEL PROBING RADAR SITRANS LR250 PROFIBUS PA
Contents
User Manual 6

SITRANS LR250 (PROFIBUS PA)
Operating Instructions, 08/2014, A5E32221386-AC 173
Service and maintenance
9
9.1
Basic safety information
WARNING
Impermissible repair of the device
• Repair must be carried out by Siemens authorized personnel only.
CAUTION
Releasing key lock
Improper modification of parameters could influence process safety.
• Make sure that only authorized personnel may cancel the key locking of devices for
safety-related applications.
9.2
Cleaning
The radar device requires no cleaning under normal operating conditions.
Under severe operating conditions, the antenna may require periodic cleaning. If cleaning
becomes necessary:
● Note the antenna material and the process medium, and select a cleaning solution that will
not react adversely with either.
● Remove the device from service and wipe the antenna clean using a cloth and suitable
cleaning solution.
NOTICE
Penetration of moisture into the device
Device damage.
• Make sure when carrying out cleaning and maintenance work that no moisture
penetrates the inside of the device.

Service and maintenance
9.3 Maintenance and repair work
SITRANS LR250 (PROFIBUS PA)
174 Operating Instructions, 08/2014, A5E32221386-AC
WARNING
Electrostatic charge
Danger of explosion in hazardous areas if electrostatic charges develop, for example, when
cleaning plastic surfaces with a dry cloth.
• Prevent electrostatic charging in hazardous areas.
9.3
Maintenance and repair work
The device is maintenance-free. However, a periodic inspection according to pertinent directives
and regulations must be carried out.
An inspection can include check of:
● Ambient conditions
● Seal integrity of the process connections, cable entries, and cover screws
● Reliability of power supply, lightning protection, and grounds
WARNING
Maintenance during continued operation in a hazardous area
There is a danger of explosion when carrying out repairs and maintenance on the device in
a hazardous area.
• Isolate the device from power.
- or -
• Ensure that the atmosphere is explosion-free (hot work permit).
WARNING
Humid environment
Danger of electric shock.
• Avoid working on the device when it is energized.
• If working on an energized device is necessary, ensure that the environment is dry.
• Make sure when carrying out cleaning and maintenance work that no moisture
penetrates the inside of the device.
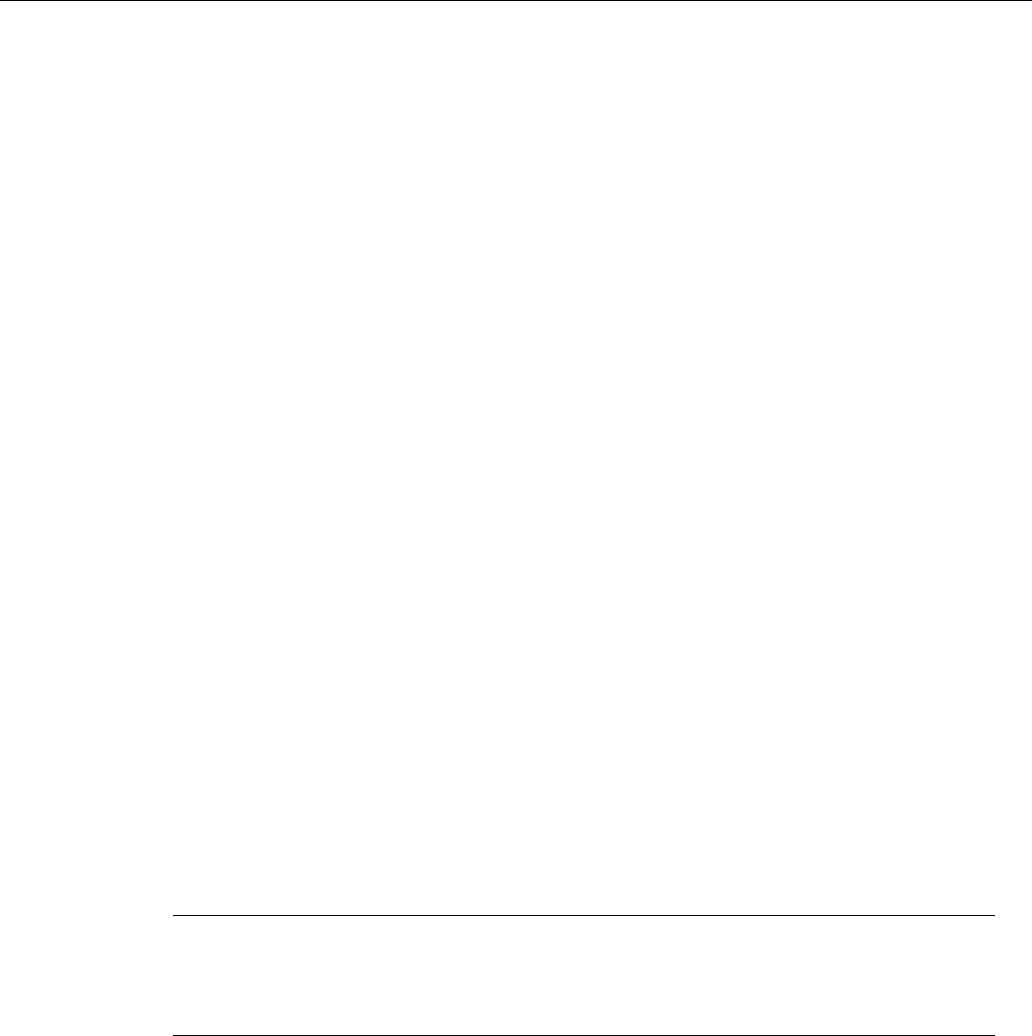
Service and maintenance
9.3 Maintenance and repair work
SITRANS LR250 (PROFIBUS PA)
Operating Instructions, 08/2014, A5E32221386-AC 175
9.3.1
Unit repair and excluded liability
All changes and repairs must be done by qualified personnel, and applicable safety regulations
must be followed. Please note the following:
● The user is responsible for all changes and repairs made to the device.
● All new components must be provided by Siemens.
● Restrict repair to faulty components only.
● Do not re-use faulty components.
9.3.2
Part replacement
If the antenna, lens, secondary O-ring, and spring washers require replacement due to damage
or failure, they may be replaced without the need for re-calibration if of the same type and size.
Replacing the antenna
Changing to a different antenna type may be performed by a Siemens authorized repair center
or personnel.
If the electronics or enclosure require replacement due to damage or failure, please ensure the
correct antenna version is used, otherwise a re-calibration will need to be performed by Siemens
authorized personnel.
Replacing the lens
1. Remove existing lens by turning it counter-clockwise until it separates from the unit.
2. Replace the O-ring between the lens and process connection with a new one.
3. Carefully thread the replacement lens, and turn it clockwise until resistance is encountered.
Do not over-tighten the lens, as this will permanently damage it.
4. For flange installation instructions, see Flanged versions (Page 36).
Note
After installation of the new lens onto the flanged encapsulated antenna version and before
mounting on the vessel/tank, some lenses may not appear to lie flush on the device, but this
is normal and will not impact performance.

Service and maintenance
9.3 Maintenance and repair work
SITRANS LR250 (PROFIBUS PA)
176 Operating Instructions, 08/2014, A5E32221386-AC
Raised-Face flange kits
Description
Process
connection
size
Part number
Replacement TFMTM 1600 PTFE Lens and Spring Washer
Kit for ASME B16.5 Class 150 raised faced
2" A5E32462817
3" A5E32462819
4" A5E32462820
6" A5E32462821
Replacement TFMTM 1600 PTFE Lens and Spring Washer
Kit for JIS B 2220 10K raised Face
50A A5E32462822
80A A5E32462823
100A A5E32462824
150A A5E32462825
Replacement TFMTM 1600 PTFE Lens and Spring Washer
Kit for EN 1092-1 PN10/16 type B1 raised face
DN50 A5E32462826
DN80 A5E32462827
DN100 A5E32462828
DN150 A5E32462829
Spare part kits
Description
Process
connection size
Part number
ISO2852, Hygienic encapsulated antenna Lens and silicon O-ring 2" A5E32572731
3" A5E32572745
4" A5E32572747
DIN11851, Hygienic encapsulated antenna Lens and silicon O-
ring
DN50 A5E32572758
DN80 A5E32572770
DN100 A5E32572772
DIN11864-1, Hygienic encapsulated antenna Lens and silicon O-
ring
DN50 A5E32572773
DN80 A5E32572779
DN100 A5E32572782
DIN11864-2/3, Hygienic encapsulated antenna Lens and silicon
O-ring
DN50 A5E32572785
DN80 A5E32572790
DN100 A5E32572791
Tuchenhagen, Hygienic encapsulated antenna Lens and silicon
O-ring
Type F A5E32572794
Type N A5E32572795
Note
For more information about accessories such as clamps, seals and process connections,
please see the catalog on the product page (http://www.siemens.com/LR250).
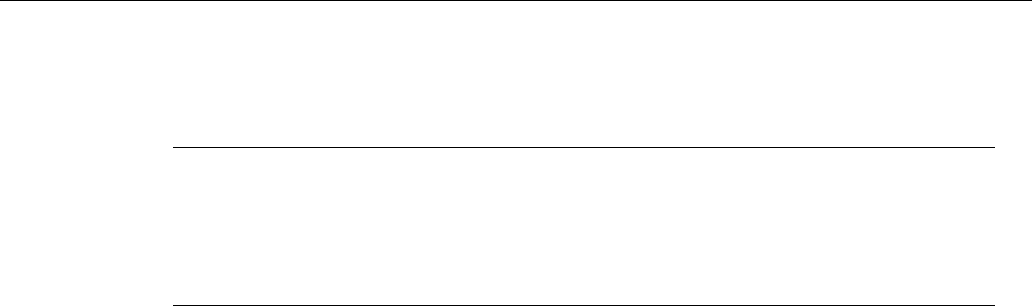
Service and maintenance
9.4 Disposal
SITRANS LR250 (PROFIBUS PA)
Operating Instructions, 08/2014, A5E32221386-AC 177
9.4
Disposal
Note
Special disposal required
The device includes components that require special disposal.
• Dispose of the device properly and environmentally through a local waste disposal
contractor.

Service and maintenance
9.4 Disposal
SITRANS LR250 (PROFIBUS PA)
178 Operating Instructions, 08/2014, A5E32221386-AC

SITRANS LR250 (PROFIBUS PA)
Operating Instructions, 08/2014, A5E32221386-AC 179
Diagnosing and troubleshooting
10
10.1
Communication troubleshooting
1. Check the following:
– There is power at the device.
– The LCD shows the relevant data.
– The device can be programmed using the handheld programmer.
– If any fault codes are being displayed see Acyclic Extended Diagnostics (General Fault
Codes) (Page 286) for a detailed list.
2. Verify that the wiring connections are correct.
3. Check the PROFIBUS address and make sure all devices are at unique PROFIBUS
addresses.
4. See the table below for specific symptoms.
Symptom
Corrective action
The device cannot be programmed via the
handheld programmer.
• Make sure
Write Protection (6.2.1.)
is set to the
unlock value.
You try to set a SITRANS LR250
parameter via remote communications but
the parameter remains unchanged.
• Ensure
Remote Lockout (6.1.1.)
is disabled.
• Ensure
Write Protection (6.2.1.)
is set to the unlock
value.
• See Resetting the PROFIBUS address to 126
(Page 97) to disable an address lock.
The PLC value equals the display value
but does not correspond to actual material
level.
• Ensure Scaling in AIFB1 is correctly entered.
• Ensure High Calibration Point is correctly entered.
• View the echo profile to see if the wrong echo is
being selected. If so, see Operation Troubleshooting
(Page 184) for possible causes and corrective action.
The PLC value is not equal to the
displayed value (regardless of actual
material level).
• Confirm you are looking at the right spot in the PLC.
• Ensure scaling has not been programmed into the
PLC: all scaling should be performed by the LR250.
• Check the network to ensure the PLC is
communicating with the LR250.
If you continue to experience problems go to our website and check the FAQs for SITRANS
LR250:
Product page (http://www.siemens.com/LR250), or contact your Siemens representative.

Diagnosing and troubleshooting
10.2 Device status icons
SITRANS LR250 (PROFIBUS PA)
180 Operating Instructions, 08/2014, A5E32221386-AC
10.2
Device status icons
Icon
Priority
Level
Meaning
1 • Maintenance alarm
• Measurement values are not valid
2 • Maintenance warning: maintenance demanded immediately
• Measured signal still valid
3 • Maintenance required
• Measured signal still valid
1 • Process value has reached an alarm limit
2 • Process value has reached a warning limit
3 • Process value has reached a tolerance limit
1 • Configuration error
• Device will not work because one or more parameters/components is incorrectly configured
2 • Configuration warning
• Device can work but one or more parameters/components is incorrectly configured
3 • Configuration changed
• Device parameterization not consistent with parameterization in project. Look for info text.
1 • Manual operation (local override)
• Communication is good; device is in manual mode.
2 • Simulation or substitute value
• Communication is good; device is in simulation mode or works with substitute values.
3 • Out of operation
• Communication is good; device is out of action.
• No data exchange
• Write access enabled
• Write access disabled
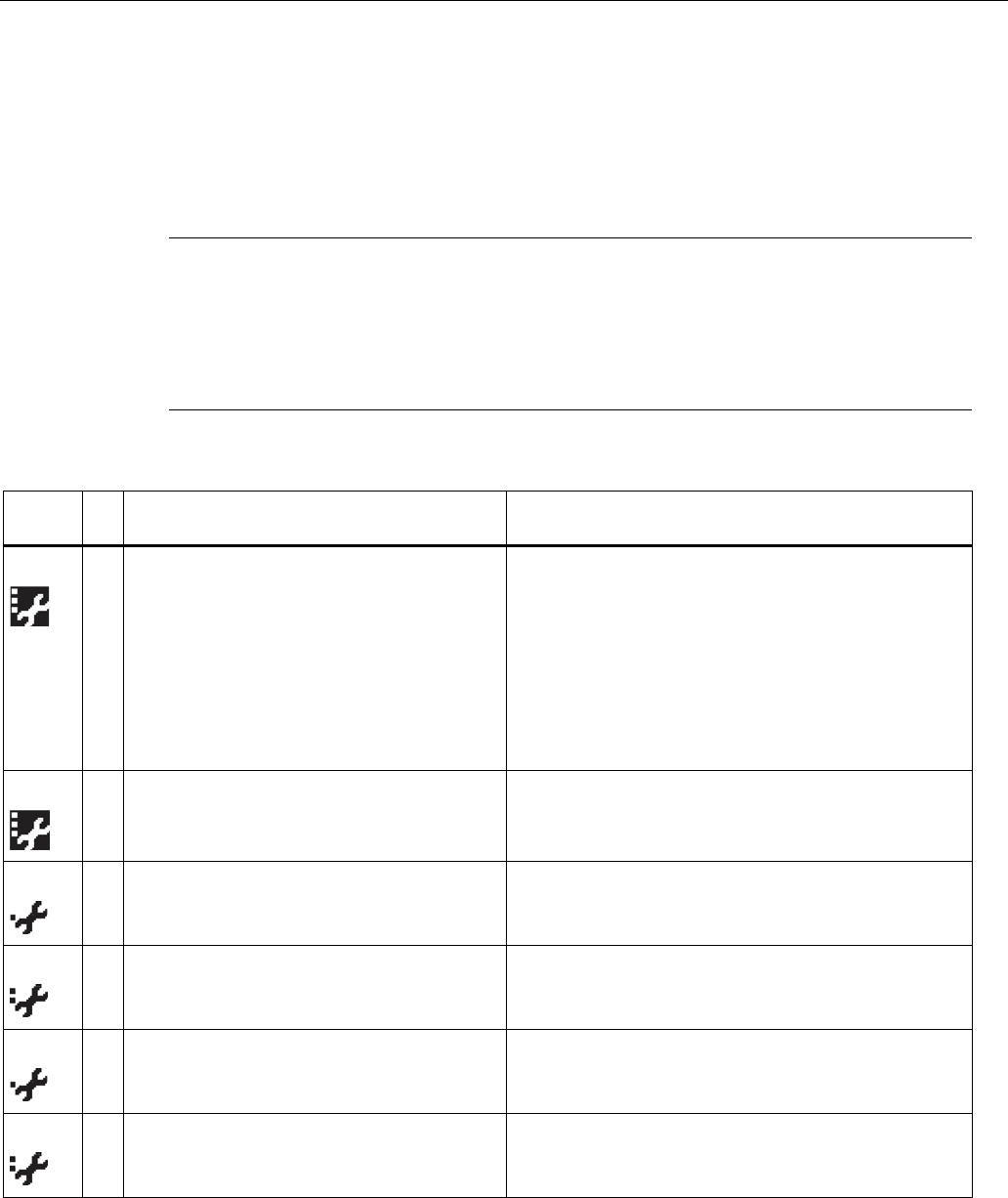
Diagnosing and troubleshooting
10.3 General fault codes
SITRANS LR250 (PROFIBUS PA)
Operating Instructions, 08/2014, A5E32221386-AC 181
10.3
General fault codes
Note
• The status icon shown associated with each fault is the default icon in Condensed Mode.
• If more than one fault is present, the device status indicator and text for each fault
alternate at 2 second intervals.
• Some faults cause the device to go to Fail-safe mode (Fault 52). These are indicated with
an asterisk (*).
Code/
Icon
Meaning
Corrective Action
S: 0
* The device was unable to get a measurement
within the Fail-safe LOE Timer period. Possible
causes: faulty installation, antenna material
buildup, foaming/other adverse process
conditions, invalid configuration range.
• Ensure installation details are correct.
• Ensure no antenna material buildup. Clean if
necessary.
• Adjust process conditions to minimize foam or other
adverse conditions.
• Correct configuration range.
• If fault persists, contact your local Siemens
representative.
S: 2
* Unable to collect profile because of a power
condition that is outside the operating range of
the device.
Repair required: contact your local Siemens
representative.
S: 3
Device is nearing its lifetime limit according to
the value set in
Reminder 1 (Required) (4.2.5.)
.
Replacement is recommended.
S: 4
Device is nearing its lifetime limit according to
the value set in
Reminder 2 (Demanded)
(4.2.6.)
.
Replacement is recommended.
S: 6
Sensor is nearing its lifetime limit according to
the value set in
Reminder 1 (Required) (4.3.5.)
.
Replacement is recommended.
S: 7
Sensor is nearing its lifetime limit according to
the value set in
Reminder 2 (Demanded)
(4.3.6.)
.
Replacement is recommended.
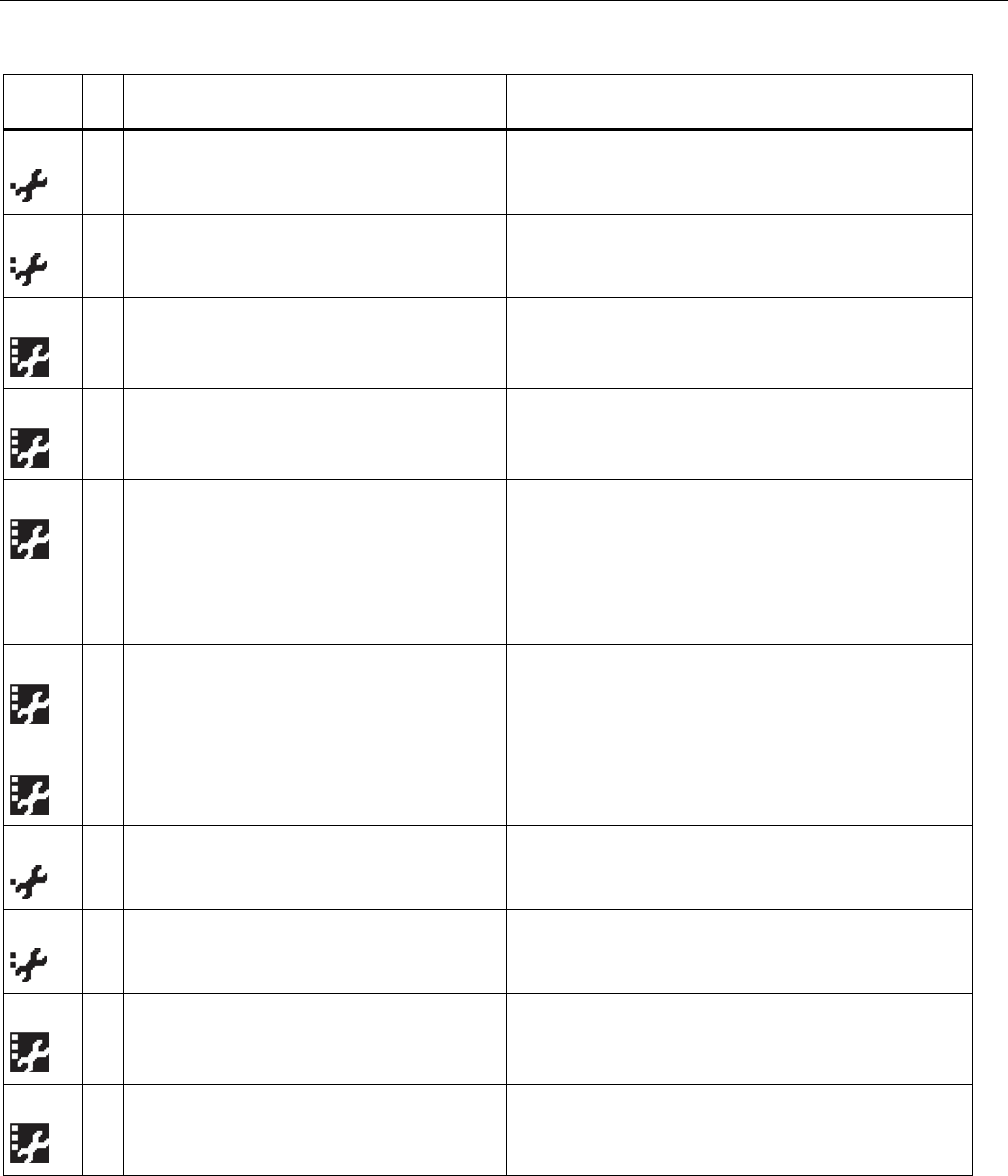
Diagnosing and troubleshooting
10.3 General fault codes
SITRANS LR250 (PROFIBUS PA)
182 Operating Instructions, 08/2014, A5E32221386-AC
Code/
Icon
Meaning
Corrective Action
S: 8
Service interval as defined in
Reminder 1
(Required) (4.4.5.)
has expired.
Perform service.
S: 9
Service interval as defined in
Reminder 2
(Demanded) (4.4.6.)
has expired.
Perform service.
S: 10
Input parameters
Low Calibration Point (1.6.)
and
High Calibration Point (1.7.)
are the same.
• Check calibration settings of device.
• Ensure settings for High Calibration Point and Low
Calibration Point are different.
S: 11
Internal temperature sensor failure. Repair required: contact your local Siemens
representative.
S: 12
Internal temperature of device has exceeded
specifications: it is operating outside its
temperature range.
• Relocate device and/or lower process temperature
enough to cool device.
• Inspect for heat-related damage and contact your
local Siemens representative if repair is required.
• Fault code will persist until a manual reset is
performed using SIMATIC PDM or the LCD interface.
S: 14
Input Scaling (2.6.5.)
Upper and lower values
for AIFB1 are the same.
• Check configuration for AIFB1.
• Ensure that Upper Value and Lower Value (Input
Scaling) are not the same.
S: 15
Input Scaling (2.6.5.)
Upper and lower values
for AIFB2 are the same.
• Check configuration for AIFB2.
• Ensure that Upper Value and Lower Value (Input
Scaling) are not the same.
S: 17
Calibration interval as defined in
Reminder 1
(Required) (4.5.5.)
has expired.
Perform calibration.
S: 18
Calibration interval as defined in
Reminder 2
(Demanded) (4.5.6.)
has expired.
Perform calibration.
S: 28
* Internal device failure caused by a RAM
memory error.
Repair required: contact your local Siemens
representative.
S: 29
* EEPROM damaged. Repair required: contact your local Siemens
representative.

Diagnosing and troubleshooting
10.3 General fault codes
SITRANS LR250 (PROFIBUS PA)
Operating Instructions, 08/2014, A5E32221386-AC 183
Code/
Icon
Meaning
Corrective Action
S: 31
* Flash error. Repair required: contact your local Siemens
representative.
S: 32
IDENT number conflict. Ensure value of the Ident number selector is correct for
the network configuration. If it is correct, the device needs
to be re parameterized by the PLC.
S: 33
* Factory calibration for the internal temperature
sensor has been lost.
Repair required: contact your local Siemens
representative.
S: 34
* Factory calibration for the device has been lost. Repair required: contact your local Siemens
representative.
S: 35
* Factory calibration for the device has been lost. Repair required: contact your local Siemens
representative.
S: 36
* Unable to start microwave module. Repair required: contact your local Siemens
representative.
S: 37
* Measurement hardware problem. Repair required: contact your local Siemens
representative.
S: 38
* Microwave module hardware failure: unable to
calculate distance measurement.
Repair required: contact your local Siemens
representative.
S: 43
* Factory calibration for the radar receiver has
been lost.
Repair required: contact your local Siemens
representative.

Diagnosing and troubleshooting
10.4 Operation troubleshooting
SITRANS LR250 (PROFIBUS PA)
184 Operating Instructions, 08/2014, A5E32221386-AC
10.4
Operation troubleshooting
Operating symptoms, probable causes, and resolutions.
Symptom
Cause
Action
Display shows
level or target is out of range • check specifications
• check
Low Calibration Pt. (1.6.)
• increase
Confidence (2.5.9.1.)
Display shows
material build-up on antenna • clean the antenna
• re-locate SITRANS LR250
Display shows
location or aiming:
• poor installation
• flange not level
• Auto False Echo Suppression
may be incorrectly applied
• check to ensure nozzle is vertical
• ensure end of antenna protrudes from end of nozzle
• review Auto False Echo Suppression (Page 246)
• ensure Auto False Echo Suppression Range is set
correctly
Display shows
antenna malfunction:
• temperature too high
• physical damage
• excessive foam
• multiple echoes
• check temperature in
Maximum Value (3.3.2.)
• use foam deflector or stillpipe
• relocate
• use a defoamer
• set
Algorithm (2.5.7.1.)
to t
F
(trueFirst echo)
Reading does not
change, but the level
does
SITRANS LR250 processing
wrong echo, for example, vessel
wall, or structural member
• re-locate SITRANS LR250
• check nozzle for internal burrs or welds
• rotate device 90°
• use
Auto False Echo Suppression (2.5.10.1.)
• if necessary: see Auto False Echo Suppression
(Page 246)
Measurement is
consistently off by a
constant amount
• setting for
Low Calibration
Point (2.3.7.1.)
not correct
• setting for
Sensor Offset
(2.3.7.3.)
not correct
• check distance from sensor reference point to
Low
Calibration Point (2.3.7.1.)
• check
Sensor Offset (2.3.7.3.)
Screen blank power error • check nameplate rating against voltage supply
• check power wiring or source
too much load resistance • change barrier type, or
• remove something from the loop, or
• increase supply voltage
• reduce wire distance or use larger gage wire
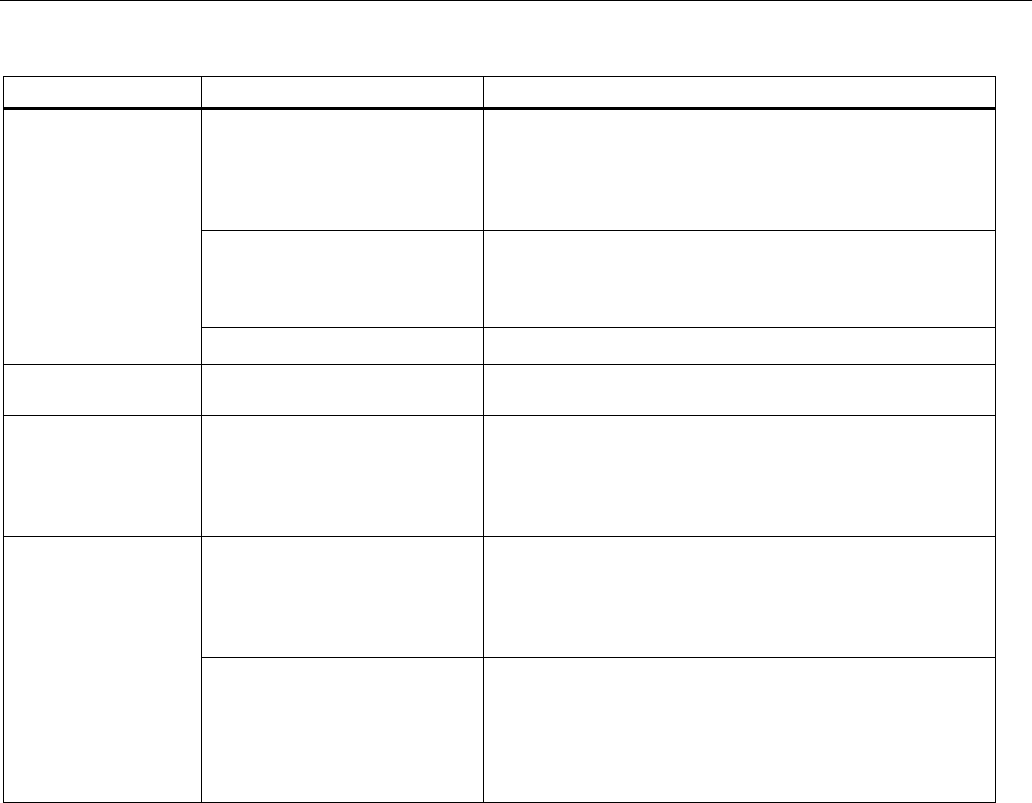
Diagnosing and troubleshooting
10.4 Operation troubleshooting
SITRANS LR250 (PROFIBUS PA)
Operating Instructions, 08/2014, A5E32221386-AC 185
Symptom
Cause
Action
Reading erratic echo confidence weak • refer to
Confidence (2.5.9.1.)
• use
Auto False Echo Suppression (2.5.10.1.)
and
Auto
False Echo Suppression Range (2.5.10.2.)
• use foam deflector or stillpipe
liquid surface vortexed • decrease
Fill Rate (2.3.8.2..)
• relocate device to side pipe
• increase confidence threshold in
Echo Threshold (2.5.7.3.)
material filling • Re-locate SITRANS LR250
Reading response
slow
Fill Rate (2.3.8.2.)
setting
incorrect
• increase measurement response if possible
Reads correctly but
occasionally reads
high when vessel is
not full
• detecting close range echo
• build up near top of vessel or
nozzle
• nozzle problem
• clean the antenna
• use
Auto False Echo Suppression (2.5.10.1.)
and
Auto
False Echo Suppression Range (2.5.10.2.)
Level reading lower
than actual material
level
• material is within Near Range
zone
• multiple echoes processed
• decrease
Near Range (2.5.1.)
(minimum value depends on
antenna type)
• raise SITRANS LR250
• ensure
Algorithm (2.5.7.1.)
is set to t
F
(First echo)
• vessel near empty and low
dK material
• ensure
Material (1.2.)
selection is LIQUID LOW DK
• set
Position Detect (2.5.7.2.)
to
Hybrid
• check the setting for
CLEF Range (2.5.7.4.):
see the table
below
Propogation Factor (2.5.3.)
for recommended
settings

Diagnosing and troubleshooting
10.4 Operation troubleshooting
SITRANS LR250 (PROFIBUS PA)
186 Operating Instructions, 08/2014, A5E32221386-AC
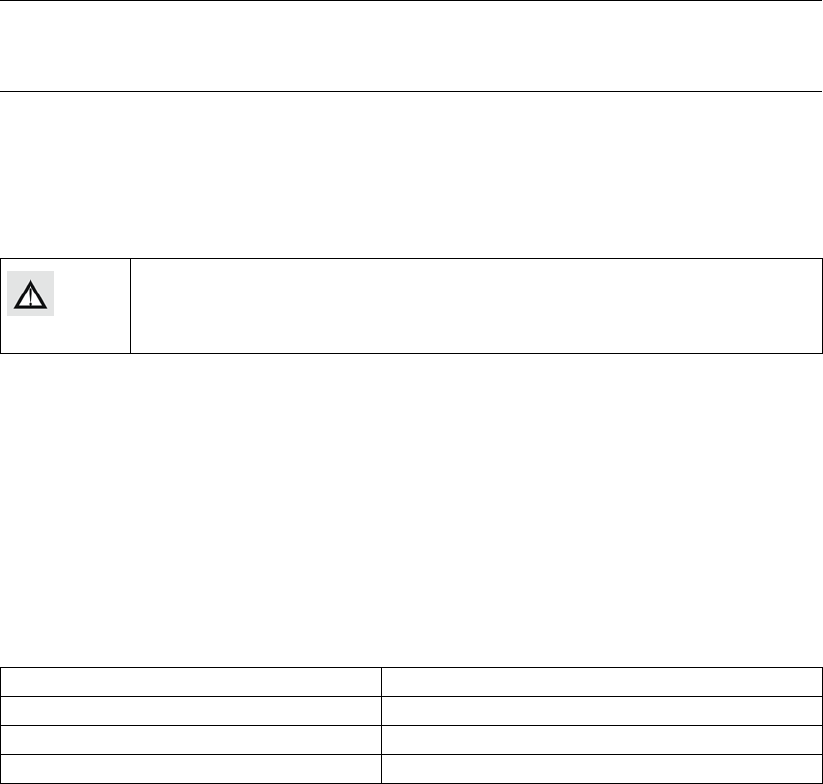
SITRANS LR250 (PROFIBUS PA)
Operating Instructions, 08/2014, A5E32221386-AC 187
Technical data
11
Note
• Siemens makes every attempt to ensure the accuracy of these specifications but
reserves the right to change them at any time.
11.1
Power
General Purpose:
Intrinsically Safe:
Non-Sparking:
Non-incendive:
Bus powered Per IEC 61158-2 (PROFIBUS PA)
Current consumed 15 mA
11.2
Performance
Reference operating conditions according to IEC 60770-1
Ambient temperature 15 to 25 °C (59 to 77 °F)
Humidity 45 to 75% relative humidity
Ambient pressure 860 to 1060 mbar a (86000 to 106000 N/m2 a)
Interference reflections minimum 20 dB lower than the main target reflections

Technical data
11.2 Performance
SITRANS LR250 (PROFIBUS PA)
188 Operating Instructions, 08/2014, A5E32221386-AC
Measurement Accuracy (measured in accordance with IEC 60770-1)
Maximum measured error =3 mm (0.12")1) 2) 3) including hysteresis and non-
repeatability
Frequency K-band
Maximum measurement range4) 1.5" antenna 10 m (32.8 ft)5)
2" threaded PVDF antenna
2"/DN50/50A Flanged encapsulated
antenna (FEA)
2", ISO 2852, DN50 DIN11864-
1/2/3, DN50
DIN11851,Tuchenhagen Types F
and N Hygienic encapsulated
antenna (HEA)
all other versions 20 m (65.6 ft)
Minimum detectable distance 50 mm (2") from end of antenna6)
Update time7) minimum 1 second, depending on settings for
Response Rate (2.3.8.1.)
and
LCD Fast Mode (4.9.).
Influence of ambient temperature < 0.003% / K (average over full temperature range,
referenced to maximum range)
Dielectric constant of material measured dK > 1.6 [antenna and application dependent8)]
Memory non-volatile EEPROM
no battery required
1) The statistical accuracy is typically 3 mm (0.12") 90% of the time, when tested in accordance
with IEC 60770-1.
2) Under severe EMI/EMC environments per IEC 61326-1 or NAMUR NE21, the device error
may increase to a maximum of 10 mm (0.4").
3) For 2" threaded PVDF antenna, Flanged encapsulated antennas and Hygienic encapsulated
antennas, the maximum measured error <500 mm from the sensor reference point =25 mm (1").
4) From sensor reference point: see Dimension drawings (Page 195) and Flanged Horn with
extension (Page 202).
5) 20 m (65.6 ft) possible in a stillpipe/bypass
6) Minimum range is antenna length +50 mm (2"). See Dimension drawings (Page 195).
7) Reference conditions:
Response Rate (2.4.1.)
set to
FAST, LCD Fast Mode (4.9.)
set to
ON
.
8) For 1.5" (40 mm) antenna and 2" (50 mm) threaded PVDF antenna, 2"/DN50/50A flanged
encapsulated antenna, and 2" ISO 2852, DN50 DIN 11864-1/2/3, DN50 DIN11851,
Tuchenhagen Types F and N hygienic encapsulated antenna the minimum dK is limited to 3
unless a stillpipe is used.
See Flanged horn antenna (Page 200).
See Flanged encapsulated antenna (3"/DN80/80A sizes and larger) (Page 206).
See Hygienic encapsulated antenna (2" ISO 2852 sanitary clamp) (Page 208).

Technical data
11.3 Interface
SITRANS LR250 (PROFIBUS PA)
Operating Instructions, 08/2014, A5E32221386-AC 189
11.3
Interface
Communication PROFIBUS PA
Configuration Remote Siemens SIMATIC PDM
Local Siemens infrared handheld programmer
Display
(local)1)
graphic LCD, with bar graph representing level
1) Display quality will be degraded in temperatures below –25 °C (–13 °F) and above +65 °C (+149
°F).
11.4
Mechanical
Process
connection:
Threaded connection 1.5" NPT (ASME B1.20.1), R (BSPT, EN 10226-1) a) or
G (BSPP, EN ISO 228-1)
or 2" NPT (ASME B1.20.1), R (BSPT, EN 10226-1) or
G (BSPP, EN ISO 228-1)
or 3" NPT (ASME B1.20.1), R (BSPT, EN 10226-1) or
G (BSPP, EN ISO 228-1)
Flange connection (flat-face)
Materials
2, 3, 4" (ASME 150 lb, 300 lb)
DN50, DN80, DN100 (PN 10/16, PN 25/40)
50A, 80A, 100A (JIS 10K)
316L /1.4404 or 316L /1.4435 stainless steel
Flange connection (raised face)
Materials
DN50, DN80, DN100, DN150 (PN 10/16, PN 25/40)
1.4404 or 1.4435 stainless steel, optional Alloy
N06022/2.4602 (Hastelloy®C-22 or equivalent)
Flanged encapsulated antenna (FEA)
connection (raised face)
Materials
2, 3, 4, 6" (ASME 150 lb); DN50, DN80, DN100,
DN150 (PN10/16); 50A, 80A, 100A, 150A (JIS 10K)
316L /1.4404 or 316L /1.4435 stainless steel
Hygienic encapsulated antenna (HEA)
connection
Materials
ISO 2852 (2, 3, 4")
DIN 11851 (DN50, DN80, DN100)
DIN 11864-1/2/3 (DN50, DN80, DN100)
Tuchenhagen (Type F [50 mm] and Type N [68 mm])
316L /1.4404 or 316L /1.4435 stainless steel
ISO 2852 (2, 3, 4")
DIN 11864-3 (DN50,
DN80, DN100)
clamp: 304/1.4301
stainless
steel

Technical data
11.4 Mechanical
SITRANS LR250 (PROFIBUS PA)
190 Operating Instructions, 08/2014, A5E32221386-AC
Tuchenhagen (Type F
[50 mm] and Type N [68
mm])
316L /1.4404 or
316L/1.4435 stainless
steel
clamp: 304/1.4301
stainless steel
nut connection:
303/1.4305
stainless steel
DIN 11851/11864-1
(DN50, DN80, DN100)
captive slotted nut
connection: 304L/1.4307
DIN 11864-2 (DN50,
DN80, DN100)
mounting nuts and bolts:
304/1.4301 stainless steel
Antenna: Horn
Materials
standard 1.5" (40 mm), 2" (50 mm), 3" (80 mm), and
4" (100 mm) horn, optional 100 mm (4") horn
extension
316L stainless steel with PTFE emitter
optional Alloy N06022/2.4602 (Hastelloy®C-22 or
equivalent) with PTFE emitter
Threaded PVDF antenna
Wetted materials
2" (50 mm)
PVDF (Polyvinylidene fluoride)
Flanged encapsulated antenna
Wetted materials
316L /1.4404 or 316L /1.4435 stainless steel
TFMTM 1600 PTFE lens
Hygienic encapsulated antenna
Wetted material
316L/1.4404 or 316L/1.4435 stainless steel
TFMTM 1600 PTFE (plus chosen seal)
Enclosure Construction aluminum, polyester powder-coated
Conduit entry 2 x M20x1.5, or 2 x ½" NPT
Ingress protection Type 4X/NEMA 4X, Type 6/NEMA 6, IP67, IP68
Weight (excluding
extensions):
1.5" threaded connection with 1.5" horn
antenna
approximately 5.1kg (11.2 lb)
2" threaded connection with 2" horn
antenna
approximately 5.5 kg (12.1 lb)
3" threaded connection with 3" horn
antenna
approximately 7.0 kg (15.4 lb)
2" threaded PVDF antenna approximately 3.3 kg (7.27 lb)
DN50 PN 10/16 or 2" 150 lb flat-face flange
with 2" horn antenna
approximately 8 kg (17.6 lb)
DN100 PN 25/40 or 4" ASME 300 lb flat-
face flange with 4" horn antenna
approximately 17.4 kg (38.3 lb)
DN50 PN 10/16 raised-face flange with 2"
horn antenna
approximately 6 kg (13.2 lb)
DN100 PN 25/40 raised-face flange with 4"
horn antenna
approximately 11.3 kg (24.9 lb)

Technical data
11.5 Environmental
SITRANS LR250 (PROFIBUS PA)
Operating Instructions, 08/2014, A5E32221386-AC 191
2" ASME 150 lb FEA approximately 7.0 kg (15.4 lb)
3" ASME 150 lb FEA approximately 10.7 kg (23.6 lb)
4" ASME 150 lb FEA approximately 13.1 kg (28.9 lb)
6" ASME 150 lb FEA approximately 17.7 kg (39 lb)
DN50 PN 10/16 FEA approximately 7.1 kg (15.7 lb)
DN80 PN 10/16 FEA approximately 10.1 kg (22.3 lb)
DN100 PN 10/16 FEA approximately 11.1 kg (24.5 lb)
DN150 PN 10/16 FEA approximately 15.9 kg (35.1 lb)
50 A JIS 10K FEA approximately 6.5 kg (14.3 lb)
80 A JIS 10K FEA approximately 9 kg (19.8 lb)
100 A JIS 10K FEA approximately 10.1 kg (22.3 lb)
150 A JIS 10K FEA approximately 16.3 kg (35.9 lb)
2" ISO2852 HEA approximately 4.7 kg (10.4 lb)
3" ISO2852 HEA approximately 6.3 kg (13.9 lb)
4" ISO2852 HEA approximately 6.8 kg (15 lb)
DN50 DIN 11864-1 HEA approximately 4.8 kg (10.6 lb)
DN80 DIN 11864-1 HEA approximately 6.7 kg (14.8 lb)
DN100 DIN 11864-1 HEA approximately 7.1 kg (15.7 lb)
DN50 DIN 11864-2 HEA approximately 5.0 kg (11 lb)
DN80 DIN 11864-2 HEA approximately 7.2 kg (15.9 lb)
DN100 DIN 11864-2 HEA approximately 7.9 kg (17.4 lb)
DN50 DIN 11864-3 HEA approximately 4.8 kg (10.6 lb)
DN80 DIN 11864-3 HEA approximately 6.6 kg (14.6 lb)
DN100 DIN 11864-3 HEA approximately 7.2 kg (15.9 lb)
DN50 DIN 11851 HEA approximately 4.8 kg (10.6 lb)
DN80 DIN 11851 HEA approximately 6.8 kg (15 lb)
DN100 DIN 11851 HEA approximately 7.2 kg (15.9 lb)
Tuchenhagen Type F HEA approximately 4.8 kg (10.6 lb)
Tuchenhagen Type N HEA approximately 4.9 kg (10.8 lb)
a)
For use with 1.5" (40 mm) horn antennas only.

Technical data
11.5 Environmental
SITRANS LR250 (PROFIBUS PA)
192 Operating Instructions, 08/2014, A5E32221386-AC
11.5
Environmental
Note
• For the specific configuration you are about to use or install, check transmitter nameplate
and see Approvals (Page 193).
• Use appropriate conduit seals to maintain IP or NEMA rating.
Location indoor/ outdoor
Altitude 5000 m (16,404 ft) max.
Ambient temperature −40 to +80 °C (−40 to +176 °F)
Relative humidity suitable for outdoor
Type 4X/NEMA 4X, Type 6/NEMA 6, IP67, IP68 enclosure (see note
above)
Installation category I
Pollution degree 4
11.6
Process
Note
The maximum temperature is dependent on the process connection, antenna materials, and
vessel pressure. For more detailed information see Maximum Process Temperature Chart
(Page 251) and Process Pressure/Temperature derating curves (Page 253).
Temperature at process
connection
Standard Horn antenna
(Threaded or Flanged):
with FKM O-ring −40 to +200 °C (−40 to +392 °F)
with FFKM O-ring −20 to +200 °C (−4 to +392 °F)
2" NPT / BSPT / G Threaded PVDF antenna: −40 to +80 °C (−40 to +176 °F)
Flanged encapsulated antenna (FEA) -40 to +170 °C (−40 to +338 °F)
Hygienic encapsulated antenna (HEA) -40 to +170 °C (−40 to +338 °F)
with FKM seals used on process
connection: -20 to +170 °C (-4 to +338
°F)
with EPDM seals used on process
connection: -40 to +120 °C (-40 to +248
°F)
Pressure (vessel) Refer to process connection tag and
Process Pressure/Temperature derating
curves (Page 253).

Technical data
11.7 Approvals
SITRANS LR250 (PROFIBUS PA)
Operating Instructions, 08/2014, A5E32221386-AC 193
11.7
Approvals
Note
The device nameplate lists the approvals that apply to your device.
Application type
LR250 version
Approval rating
Valid for:
Non-hazardous
General purpose CSAUS/C, FM, CE, RCM N. America,
Europe
Radio Europe (R&TTE), FCC, Industry Canada
Hazardous
Intrinsically safe
(Page 46)
ATEX II 1G, Ex ia IIC T4 Ga
ATEX II 1D, Ex ia ta IIIC T100 °C Da
Europe
IECEx SIR 05.0031X, Ex ia IIC T4 Ga
Ex ia ta IIIC T100 °C Da
International
FM/CSA
Class I, Div. 1, Groups A, B, C, D
Class II, Div. 1, Groups E, F, G
Class III T4
US/Canada
INMETRO DNV 12.0087 X
Ex ia IIC T4 Ga
Ex ia ta IIIC T100 °C Da IP65/IP67
-40 °C ≤ Ta ≤ +80 °C
DNV #OCP 0017
ABNT NBR IEC 60079-0:2008,
ABNT NBR IEC 60079-11:2009,
ABNT NBR IEC 60079-26:2008,
ABNT NBR IEC 60079-31:2011
Brazil
NEPSI Ex ia IIC T4 Ga
Ex iaD 20 T90 IP67 DIP A20 TA 90 ºC
China
Non-Sparking
(Page 49)
ATEX II 3 G, Ex nA IIC T4 Gc Europe
NEPSI Ex nA IIC T4 Gc China
Non-incendive
(Page 49)
FM/CSA
Class I, Div. 2, Groups A, B, C, D T5
US/Canada
Marine Lloyd's Register of Shipping
ABS Type Approval
BV Type Approval

Technical data
11.8 Programmer (infrared keypad)
SITRANS LR250 (PROFIBUS PA)
194 Operating Instructions, 08/2014, A5E32221386-AC
11.8
Programmer (infrared keypad)
Note
Battery is non-replaceable with a lifetime expectancy of 10 years in normal use.
To estimate the lifetime expectancy, check the nameplate on the back for the serial number.
The first six numbers show the production date (mmddyy), for example, serial number
032608101V was produced on March 26, 2008.
Siemens Milltronics Infrared IS (Intrinsically Safe) Handheld Programmer for hazardous and all
other locations (battery is non-replaceable).
Approvals CE
FM/CSA Class I, II, III, Div. 1, Gr. A to G T6
ATEX II 1GD Ex ia IIC T4 Ga
Ex iaD 20 T135 °C
IECEx Ex ia IIC T4 Ga
Ex iaD 20 T135 °C
INMETRO Ex ia IIC T4 Ga
Ex ia IIIC T135 °C Da
Ambient temperature −20 to +50 °C (−5 to +122 °F)
Interface proprietary infrared pulse signal
Power 3 V non-replaceable lithium battery
Weight 150 g (0.3 lb)
Color black
Part number 7ML1930-1BK
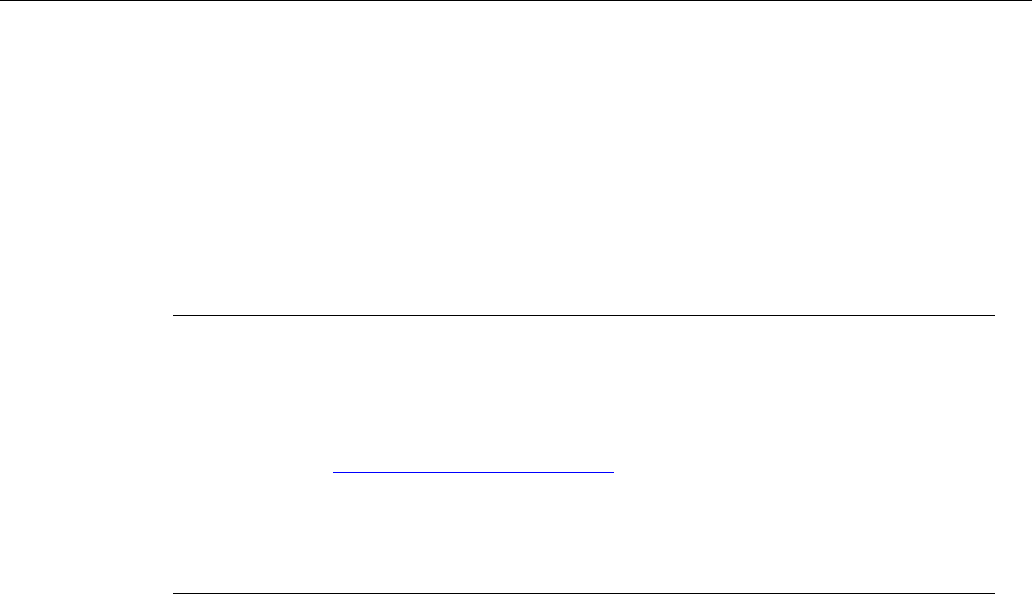
Dimension drawings
12.1 Threaded horn antenna
SITRANS LR250 (PROFIBUS PA)
Operating Instructions, 08/2014, A5E32221386-AC 195
Dimension drawings
12
12.1
Threaded horn antenna
Note
• Process temperature and pressure capabilities are dependent upon information on the
process connection tag. Reference drawing listed on the tag is available for download
from our website under
Support/Installation drawings/Level Measurement/Continuous -
Radar/LR250
:
Product page (http://www.siemens.com/LR250)
• Process connection drawings are also available for download from the
Installation
Drawings page
.
• Signal amplitude increases with horn diameter, so use the largest practical size.
• Optional extensions can be installed below the threads.

Dimension drawings
12.1 Threaded horn antenna
SITRANS LR250 (PROFIBUS PA)
196 Operating Instructions, 08/2014, A5E32221386-AC
①
½" NPT cable entry, or M20 cable gland
⑦
enclosure/electronics
②
threaded cover
⑧
retaining collar
③
2" horn
⑨
process connection tag
④
3" horn
⑩
horn
⑤
4" horn
⑪
sensor reference point
⑥
horn O.D.
Dimensions in mm (inch)

Dimension drawings
12.1 Threaded horn antenna
SITRANS LR250 (PROFIBUS PA)
Operating Instructions, 08/2014, A5E32221386-AC 197
Threaded horn dimensions
Antenna
Type
Antenna
O.D.
in mm
(inch)
Height to sensor reference point, in mm (inch) a)
Beam Angle
(°)b)
Measurement
range, in m (ft)
1-1/2" threaded
connection
2" threaded
connection
3" threaded
connection
1.5" 39.8 (1.57) 135 (5.3) N/A N/A 19 10 (32.8)
2" 47.8 (1.88) N/A 166 (6.55) 180 (7.09) 15 20 (65.6)
3" 74.8 (2.94) N/A 199 (7.85) 213 (8.39) 10 20 (65.6)
4" 94.8 (3.73) N/A 254 (10) 268 (10.55) 8 20 (65.6)
a) Height from bottom of horn to sensor reference point as shown: see dimension drawing.
b) -3dB in the direction of the polarization axis. For an illustration, see Polarization reference point
(Page 31).
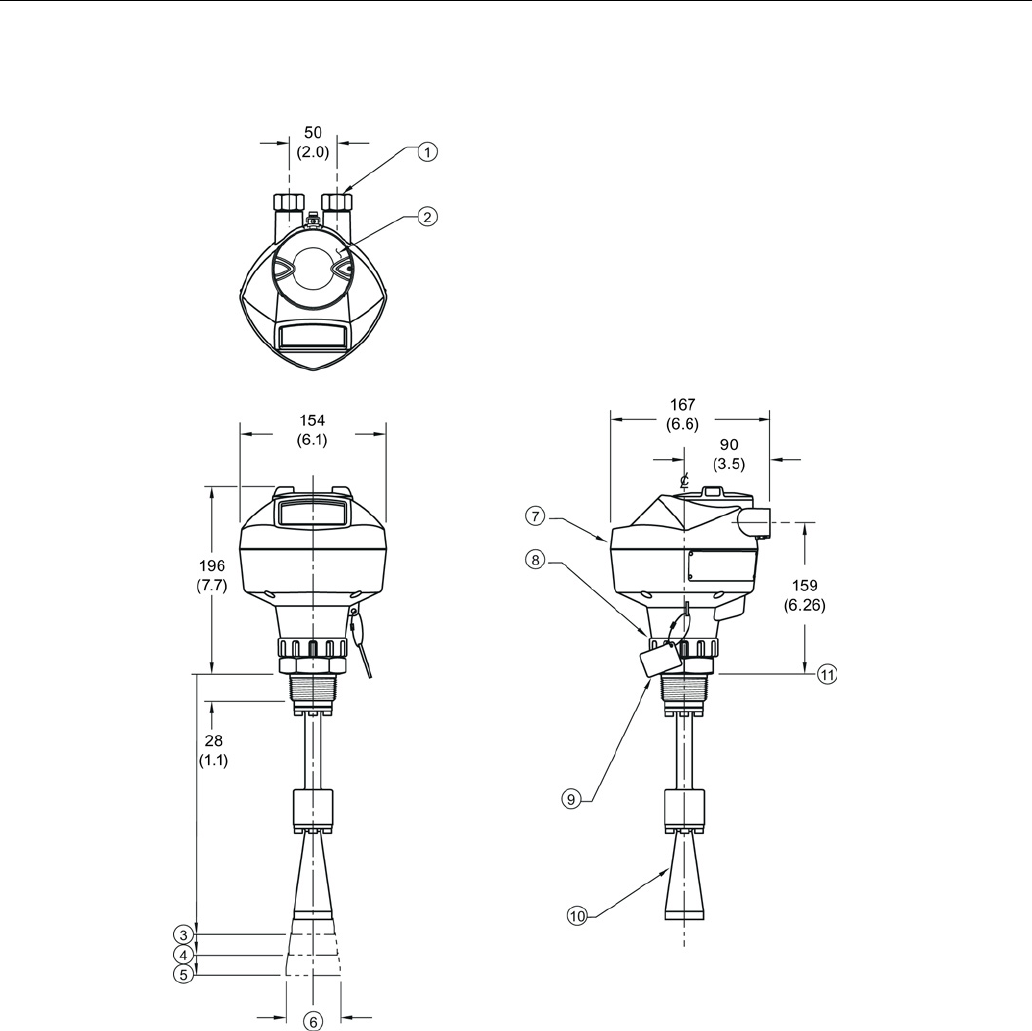
Dimension drawings
12.2 Threaded horn antenna with extension
SITRANS LR250 (PROFIBUS PA)
198 Operating Instructions, 08/2014, A5E32221386-AC
12.2
Threaded horn antenna with extension
①
½" NPT cable entry, or M20 cable gland
⑦
enclosure/electronics
②
threaded cover
⑧
retaining collar
③
2" horn
⑨
process connection tag
④
3" horn
⑩
horn
⑤
4" horn
⑪
sensor reference point
⑥
horn O.D.
Dimensions in mm (inch)

Dimension drawings
12.2 Threaded horn antenna with extension
SITRANS LR250 (PROFIBUS PA)
Operating Instructions, 08/2014, A5E32221386-AC 199
Threaded horn with extension dimensions
Antenna
Type
Antenna
O.D.
in mm
(inch)
Height to sensor reference point, in mm (inch) a)
Beam Angle
(°) b)
Measurement
range
in m (ft)
1-1/2" threaded
connection
2" threaded
connection
3" threaded
connection
1.5" 39.8 (1.57) 235 (9.25) N/A N/A 19 10 (32.8)
2" 47.8 (1.88) N/A 266 (10.47) 280 (11.02) 15 20 (65.6)
3" 74.8 (2.94) N/A 299 (11.77) 313 (12.32) 10 20 (65.6)
4" 94.8 (3.73) N/A 354 (13.94) 368 (14.49) 8 20 (65.6)
a) Height from bottom of horn to sensor reference point as shown: see dimension drawing.
b) -3dB in the direction of the polarization axis. For an illustration, see Polarization reference point
(Page 31).

Dimension drawings
12.3 Flanged horn antenna
SITRANS LR250 (PROFIBUS PA)
200 Operating Instructions, 08/2014, A5E32221386-AC
12.3
Flanged horn antenna
①
½" NPT cable entry, or M20 cable gland
⑥
flange
②
threaded cover
⑦
name-plate
③
horn
⑧
retaining collar
④
horn O.D.
⑨
process connection tag
⑤
enclosure/electronics
⑩
sensor reference point
Dimensions in mm (inch)

Dimension drawings
12.3 Flanged horn antenna
SITRANS LR250 (PROFIBUS PA)
Operating Instructions, 08/2014, A5E32221386-AC 201
Flanged Horn dimensions
Nominal horn
size
in mm (inch)
Horn O.D.
in mm (inch)
Height to sensor reference point, in mm
(inch)a)
Beam angle
(°)b)
Measurement range,
in m (ft)
Stainless steel flange:
raised or flat-face
Optional alloy
flange c)
50 (2) 47.8 (1.88) 135.3 (5.32) 138.3 (5.44) 15
20 (65.6)
80 (3) 74.8 (2.94) 168.3 (6.62) 171.3 (6. 74) 10
100 (4) 94.8 (3.73) 223.3 (8.79) 226.3 (8.90) 8
a)Height from bottom of horn to sensor reference point as shown: see Flanged horn antenna with
extension (Page 202). See also Raised-Face flange per EN 1092-1 for flanged horn antenna
(Page 228), or Flat-Face flange (Page 233).
b) -3dB in the direction of the polarization axis (see Polarization reference point (Page 31) for an
illustration).
c) Optional alloy N06022/2.4602 (Hastelloy® C-22 or equivalent). See Raised-Face Flange
Dimensions (Page 228).
Note
Heights to sensor reference point are for stainless steel flanges. For optional alloy
N06022/2.4602 (Hastelloy© C-22 or equivalent) see Flanged Horn dimensions above.
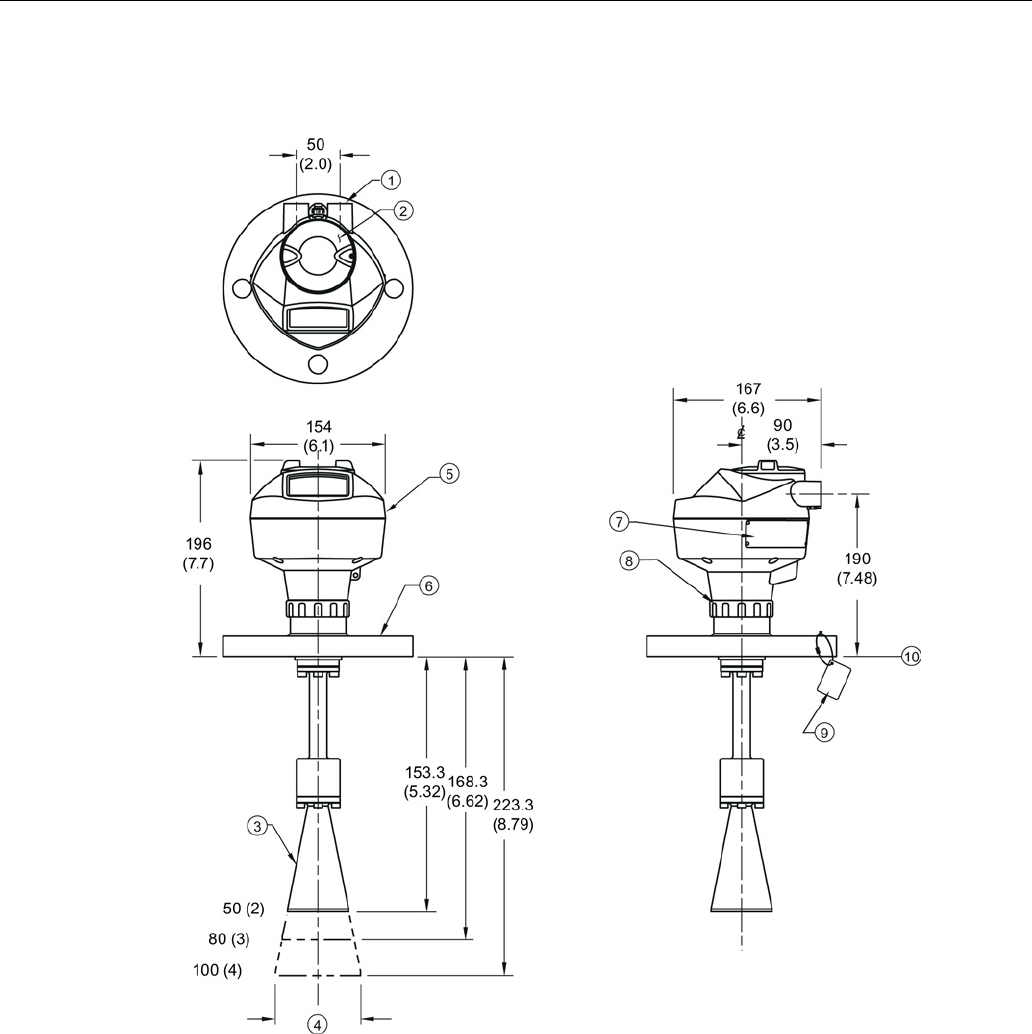
Dimension drawings
12.4 Flanged horn antenna with extension
SITRANS LR250 (PROFIBUS PA)
202 Operating Instructions, 08/2014, A5E32221386-AC
12.4
Flanged horn antenna with extension
①
½" NPT cable entry, or M20 cable gland
⑥
flange
②
threaded cover
⑦
name-plate
③
horn
⑧
retaining collar
④
horn O.D.
⑨
process connection tag
⑤
enclosure/electronics
⑩
sensor reference point
Dimensions in mm (inch)

Dimension drawings
12.4 Flanged horn antenna with extension
SITRANS LR250 (PROFIBUS PA)
Operating Instructions, 08/2014, A5E32221386-AC 203
Flanged horn with extension dimensions
Nominal horn
size
in mm (inch)
Horn O.D. in mm
(inch)
Height to sensor reference point,, in mm
(inch) a)
Beam angle
(°)b)
Measurement range,
in m (ft)
Stainless steel flange:
raised or flat-face
Optional alloy
flange c)
50 (2) 47.8 (1.88) 235.3 (9.26) 238.3 (9.38) 15
20 (65.6)
80 (3) 74.8 (2.94) 268.3 (10.56) 271.3 (10.68) 10
100 (4) 94.8 (3.73) 323.3 (12.73) 326.3 (12.85) 8
a)Height from bottom of horn to sensor reference point as shown: See also Raised-Face flange
per EN 1092-1 for flanged horn antenna (Page 228) or Flat-Face Flange. (Page 233)
b) -3dB in the direction of the polarization axis (see Polarization reference point (Page 31) for an
illustration).
c) Optional alloy N06022/2.4602 (Hastelloy® C-22 or equivalent). See Raised-Face flange per EN
1092-1 for flanged horn antenna (Page 228).
Note
Heights to sensor reference point are for stainless steel flanges. For optional alloy
N06022/2.4602 (Hastelloy© C-22 or equivalent) see Flanged Horn dimensions above.

Dimension drawings
12.5 Flanged encapsulated antenna (2"/DN50/50A sizes only)
SITRANS LR250 (PROFIBUS PA)
204 Operating Instructions, 08/2014, A5E32221386-AC
12.5
Flanged encapsulated antenna (2"/DN50/50A sizes only)
①
½" NPT cable entry, or M20 cable gland
⑥
flange
②
threaded cover
⑦
see table below
③
see table below
⑧
see table below
④
enclosure
⑨
sensor reference point
⑤
retaining collar
⑩
see table below
Dimensions in mm (inch)

Dimension drawings
12.5 Flanged encapsulated antenna (2"/DN50/50A sizes only)
SITRANS LR250 (PROFIBUS PA)
Operating Instructions, 08/2014, A5E32221386-AC 205
Flanged encapsulated antenna (2"/DN50/50A) dimensions
Flange size
③ mm (inch)
⑦ mm (inch)
⑧ mm (inch)
⑩ mm (inch)1)
2"/DN50/50A 263 (10.35) 223 (8.78) 274 (10.79) 11 (0.43)
1) Height from tip of lens to sensor reference point as shown.
Flange size
Flange class
Flange O.D.
[mm (inch)]
Antenna
aperture size
[mm (inch)]
Beam angle
(°)1)
Measurement
range
[m (ft)]
2" 150 LB 152 (5.98) 50 (1.97) 12.8 10 (32.8)2)
DN50 PN10/16 165 (6.50)
50A 10K 155 (6.10)
1) -3 dB in the direction of the polarization axis.
2) 20m if installed in stillpipe
See Raised-Face Flange per EN 1092-1, (Page 230)and Polarization reference point (Page 31).

Dimension drawings
12.6 Flanged encapsulated antenna (3"/DN80/80A sizes and larger)
SITRANS LR250 (PROFIBUS PA)
206 Operating Instructions, 08/2014, A5E32221386-AC
12.6
Flanged encapsulated antenna (3"/DN80/80A sizes and larger)
①
½" NPT cable entry, or M20 cable gland
⑥
retaining collar
②
threaded cover
⑦
see table below
③
see table below
⑧
see table below
④
enclosure
⑨
sensor reference point
⑤
flange
⑩
see table below
Dimensions in mm (inch)
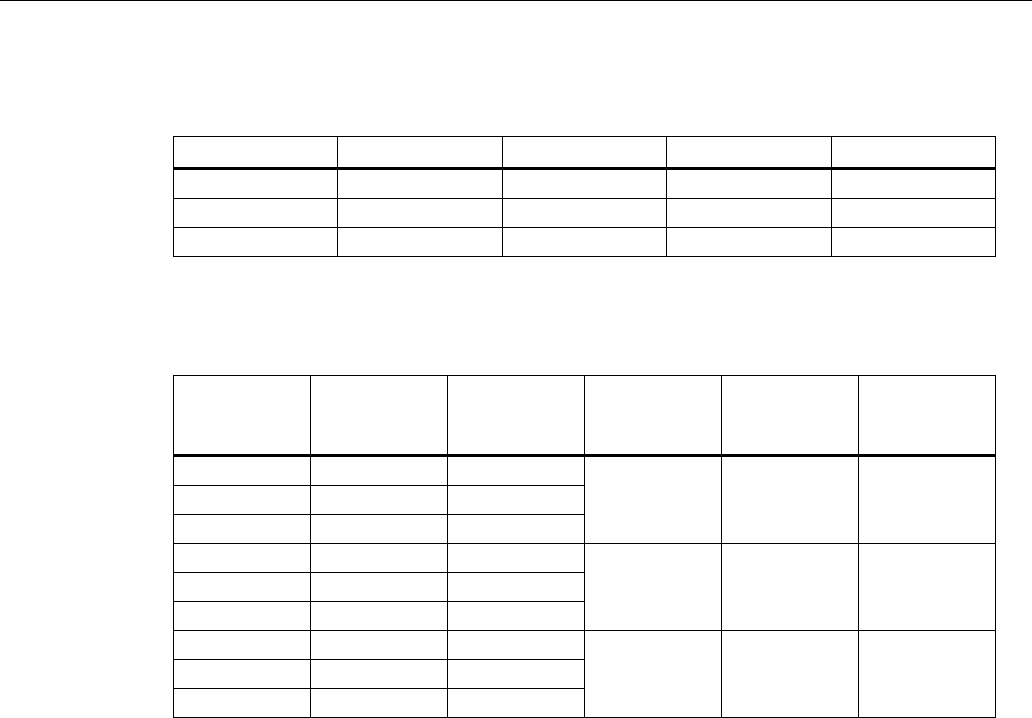
Dimension drawings
12.6 Flanged encapsulated antenna (3"/DN80/80A sizes and larger)
SITRANS LR250 (PROFIBUS PA)
Operating Instructions, 08/2014, A5E32221386-AC 207
Flanged encapsulated antenna (3"/DN80/80A and larger) dimensions
Flange size
③ mm (inch)
⑦ mm (inch)
⑧ mm (inch)
⑩ mm (inch)1)
3"/DN80/80A 328 (12.91) 288 (11.34) 343 (13.50) 15 (0.59)
4"/DN100/100A 328 (12.91) 288 (11.34) 343 (13.50) 13 (0.51)
6"/DN150/150A 333 (13.11) 293 (11.54) 348 (13.70) 15 (0.59)
1) Height from tip of lens to sensor reference point as shown. See also Raised-Face Flange per EN
1092-1.
Flange size
Flange class
Flange O.D.
[mm (inch)]
Antenna
aperture size
[mm (inch)]
Beam angle
(°)1)
Measurement
range
[m (ft)]
3" 150 LB 190 (7.48) 75 (2.95) 9.6 20 (65.6)
DN80 PN10/16 200 (7.87)
80A 10K 185 (7.28)
4" 150 LB 230 (9.06) 75 (2.95) 9.6 20 (65.6)
DN100 PN10/16 220 (8.66)
100A 10K 210 (8.27)
6" 150 LB 280 (11.02) 75 (2.95) 9.6 20 (65.6)
DN150 PN10/16 285 (11.22)
150A 10K 280 (11.02)
1)
-3 dB in the direction of the polarization axis.
See Raised-Face Flange per EN 1092-1 (Page 230), and Polarization reference point (Page 31).
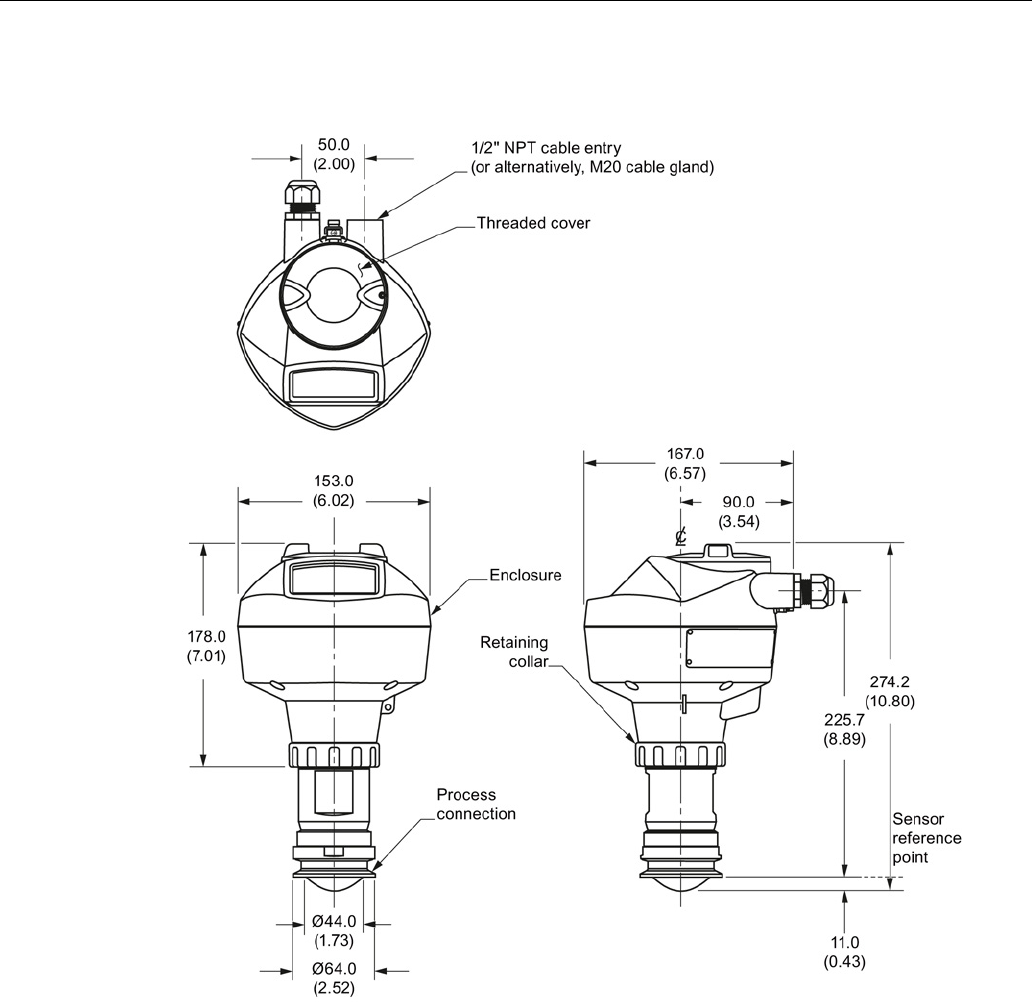
Dimension drawings
12.7 Hygienic encapsulated antenna (2" ISO 2852 sanitary clamp)
SITRANS LR250 (PROFIBUS PA)
208 Operating Instructions, 08/2014, A5E32221386-AC
12.7
Hygienic encapsulated antenna (2" ISO 2852 sanitary clamp)
Dimensions in mm (inch)

Dimension drawings
12.8 Hygienic encapsulated antenna (3" ISO 2852 sanitary clamp)
SITRANS LR250 (PROFIBUS PA)
Operating Instructions, 08/2014, A5E32221386-AC 209
12.8
Hygienic encapsulated antenna (3" ISO 2852 sanitary clamp)
Dimensions in mm (inch)

Dimension drawings
12.9 Hygienic encapsulated antenna (4" ISO 2852 sanitary clamp)
SITRANS LR250 (PROFIBUS PA)
210 Operating Instructions, 08/2014, A5E32221386-AC
12.9
Hygienic encapsulated antenna (4" ISO 2852 sanitary clamp)
Dimensions in mm (inch)
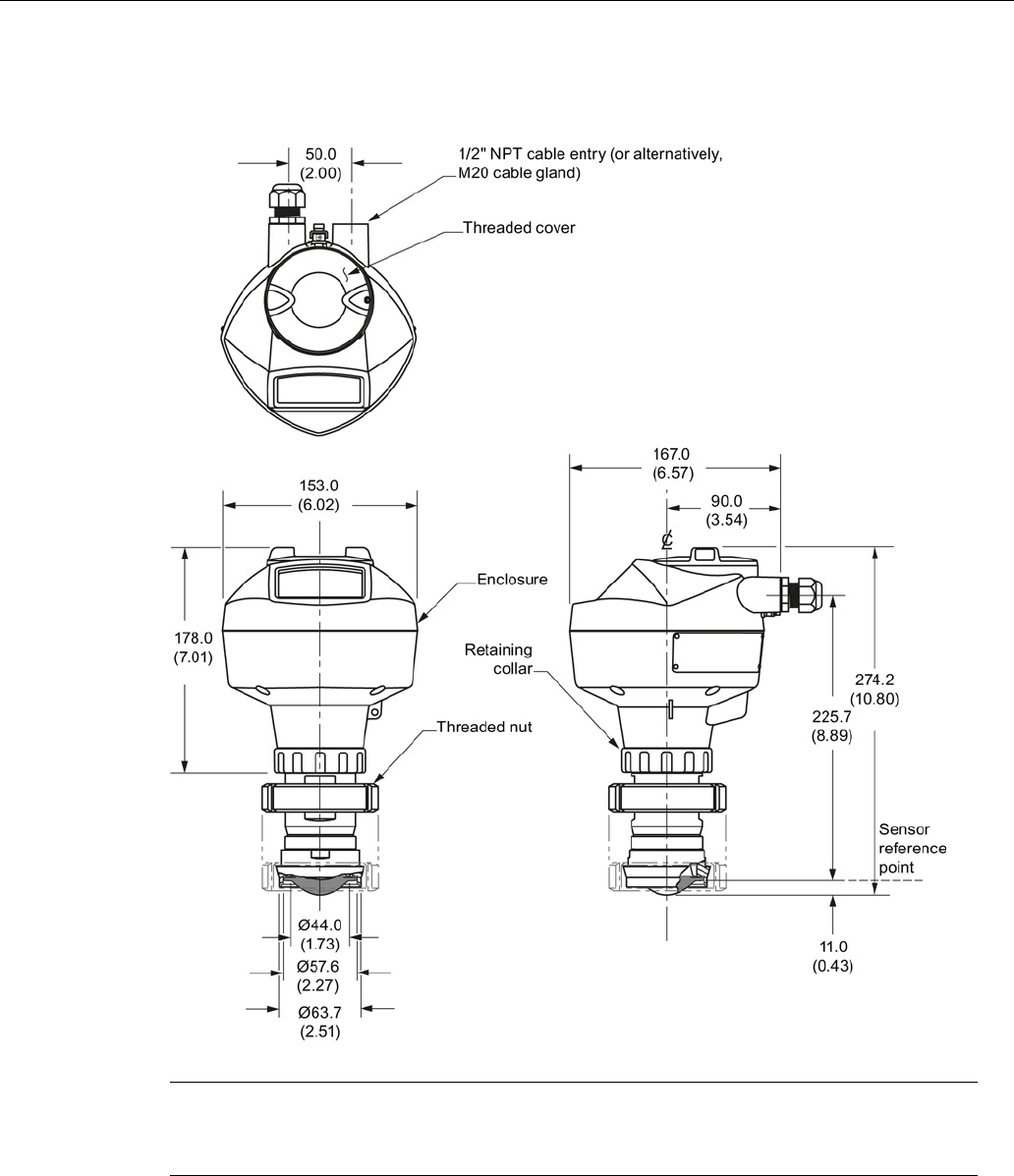
Dimension drawings
12.10 Hygienic encapsulated antenna (DN 50 nozzle/slotted nut to DIN 11851)
SITRANS LR250 (PROFIBUS PA)
Operating Instructions, 08/2014, A5E32221386-AC 211
12.10
Hygienic encapsulated antenna (DN 50 nozzle/slotted nut to DIN
11851)
Dimensions in mm (inch)
Note
Cut out of process connection and placement of threaded nut are shown for illustration
purposes only.

Dimension drawings
12.11 Hygienic encapsulated antenna (DN 80 nozzle/slotted nut to DIN 11851)
SITRANS LR250 (PROFIBUS PA)
212 Operating Instructions, 08/2014, A5E32221386-AC
12.11
Hygienic encapsulated antenna (DN 80 nozzle/slotted nut to DIN
11851)
Dimensions in mm (inch)
Note
Cut out of process connection and placement of threaded nut are shown for illustration
purposes only.
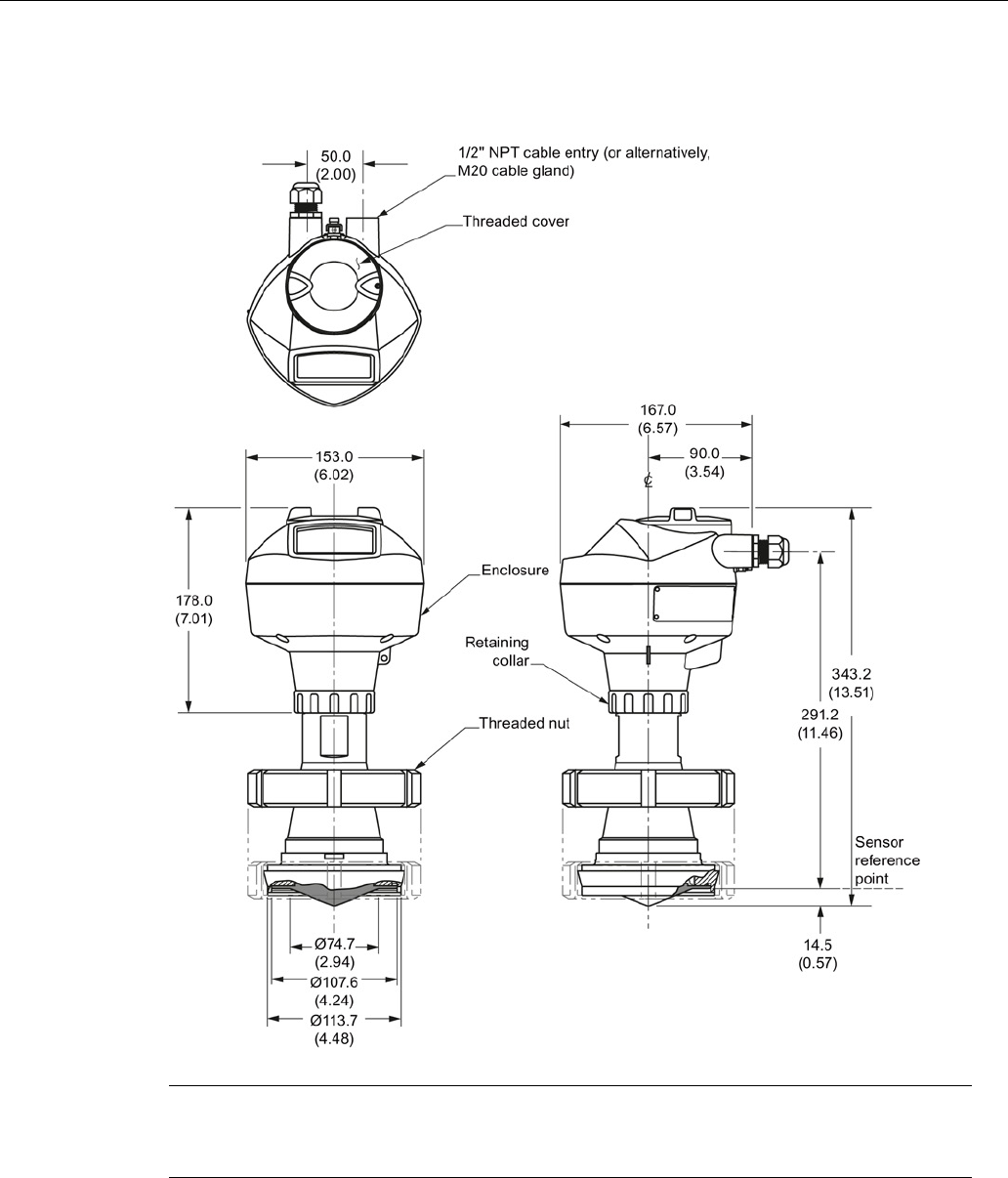
Dimension drawings
12.12 Hygienic encapsulated antenna (DN 100 nozzle/slotted nut to DIN 11851)
SITRANS LR250 (PROFIBUS PA)
Operating Instructions, 08/2014, A5E32221386-AC 213
12.12
Hygienic encapsulated antenna (DN 100 nozzle/slotted nut to DIN
11851)
Dimensions in mm (inch)
Note
Cut out of process connection and placement of threaded nut are shown for illustration
purposes only.

Dimension drawings
12.13 Hygienic encapsulated antenna (DN 50 aseptic slotted nut to DIN 11864-1)
SITRANS LR250 (PROFIBUS PA)
214 Operating Instructions, 08/2014, A5E32221386-AC
12.13
Hygienic encapsulated antenna (DN 50 aseptic slotted nut to DIN
11864-1)
Dimensions in mm (inch)
Note
Cut out of process connection and placement of threaded nut are shown for illustration
purposes only.
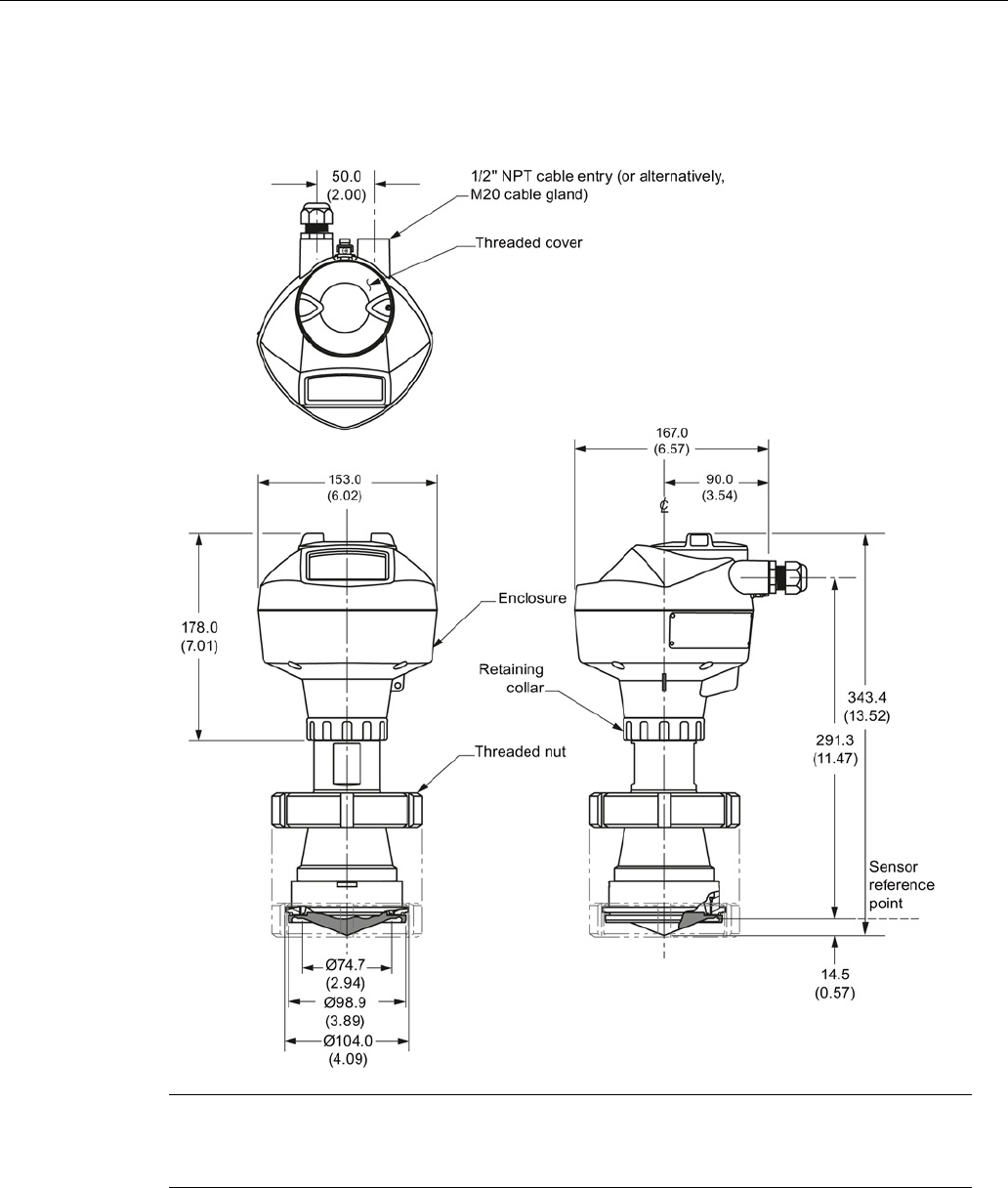
Dimension drawings
12.14 Hygienic encapsulated antenna (DN 80 aseptic slotted nut to DIN 11864-1)
SITRANS LR250 (PROFIBUS PA)
Operating Instructions, 08/2014, A5E32221386-AC 215
12.14
Hygienic encapsulated antenna (DN 80 aseptic slotted nut to DIN
11864-1)
Dimensions in mm (inch)
Note
Cut out of process connection and placement of threaded nut are shown for illustration
purposes only.

Dimension drawings
12.15 Hygienic encapsulated antenna (DN 100 aseptic slotted nut to DIN 11864- 1)
SITRANS LR250 (PROFIBUS PA)
216 Operating Instructions, 08/2014, A5E32221386-AC
12.15
Hygienic encapsulated antenna (DN 100 aseptic slotted nut to DIN
11864- 1)
Dimensions in mm (inch)
Note
Cut out of process connection and placement of threaded nut are shown for illustration
purposes only.
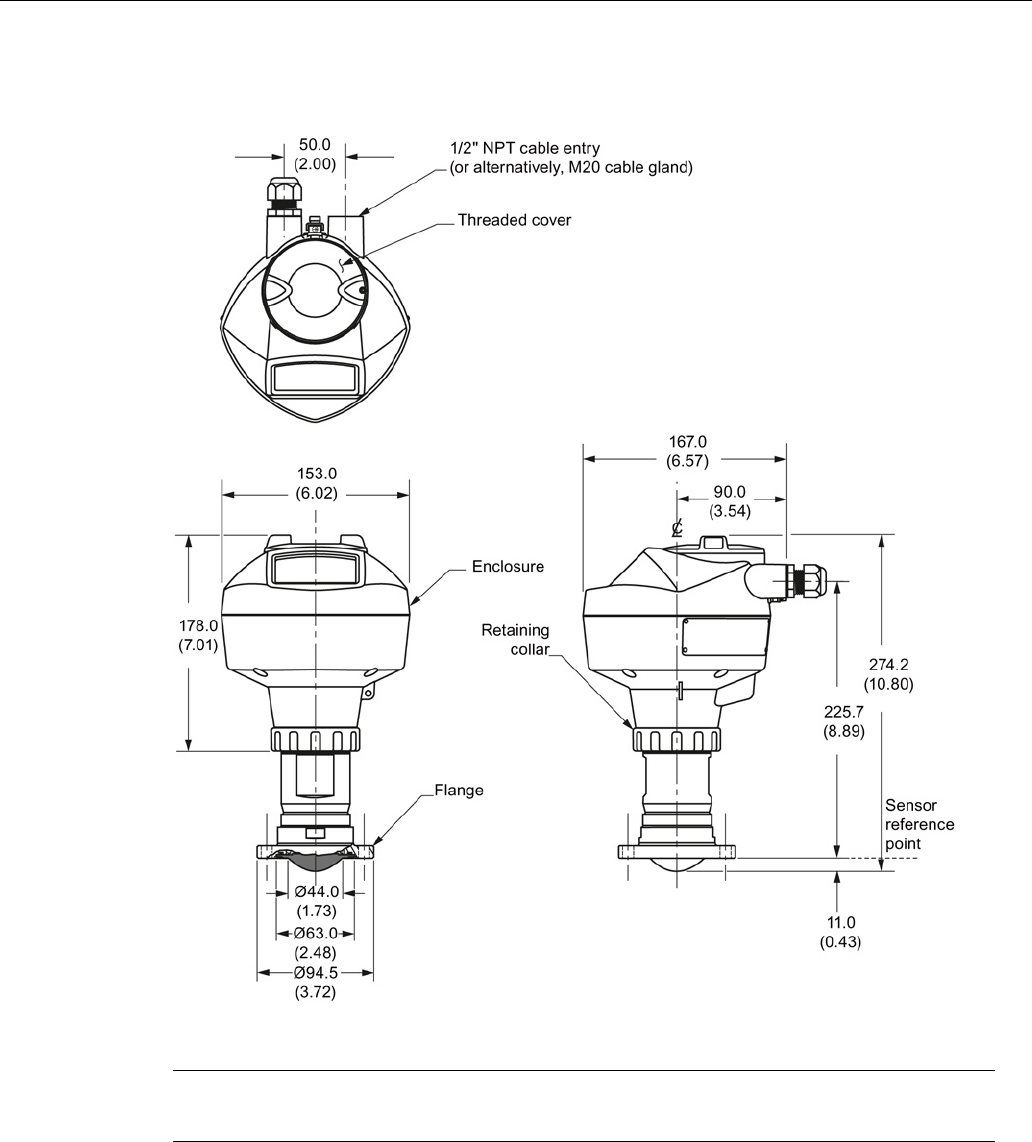
Dimension drawings
12.16 Hygienic encapsulated antenna (DN 50 aseptic flange to DIN 11864-2)
SITRANS LR250 (PROFIBUS PA)
Operating Instructions, 08/2014, A5E32221386-AC 217
12.16
Hygienic encapsulated antenna (DN 50 aseptic flange to DIN 11864-2)
Dimensions in mm (inch)
Note
Cut out of process connection and flange are shown for illustration purposes only.

Dimension drawings
12.17 Hygienic encapsulated antenna (DN 80 aseptic flange to DIN 11864-2)
SITRANS LR250 (PROFIBUS PA)
218 Operating Instructions, 08/2014, A5E32221386-AC
12.17
Hygienic encapsulated antenna (DN 80 aseptic flange to DIN 11864-2)
Dimensions in mm (inch)
Note
Cut out of process connection and flange are shown for illustration purposes only.

Dimension drawings
12.18 Hygienic encapsulated antenna (DN 100 aseptic flange to DIN 11864-2)
SITRANS LR250 (PROFIBUS PA)
Operating Instructions, 08/2014, A5E32221386-AC 219
12.18
Hygienic encapsulated antenna (DN 100 aseptic flange to DIN 11864-
2)
Dimensions in mm (inch)
Note
The cut out of the process connection and the flange are shown for illustration purposes
only.

Dimension drawings
12.19 Hygienic encapsulated antenna (DN 50 aseptic clamp to DIN 11864-3)
SITRANS LR250 (PROFIBUS PA)
220 Operating Instructions, 08/2014, A5E32221386-AC
12.19
Hygienic encapsulated antenna (DN 50 aseptic clamp to DIN 11864-3)

Dimension drawings
12.20 Hygienic encapsulated antenna (DN 80 aseptic clamp to DIN 11864-3)
SITRANS LR250 (PROFIBUS PA)
Operating Instructions, 08/2014, A5E32221386-AC 221
Dimensions in mm (inch)
Note
Cut out of process connection is shown for illustration purposes only.

Dimension drawings
12.20 Hygienic encapsulated antenna (DN 80 aseptic clamp to DIN 11864-3)
SITRANS LR250 (PROFIBUS PA)
222 Operating Instructions, 08/2014, A5E32221386-AC
12.20
Hygienic encapsulated antenna (DN 80 aseptic clamp to DIN 11864-3)
Dimensions in mm (inch)
Note
Cut out of process connection is shown for illustration purposes only.
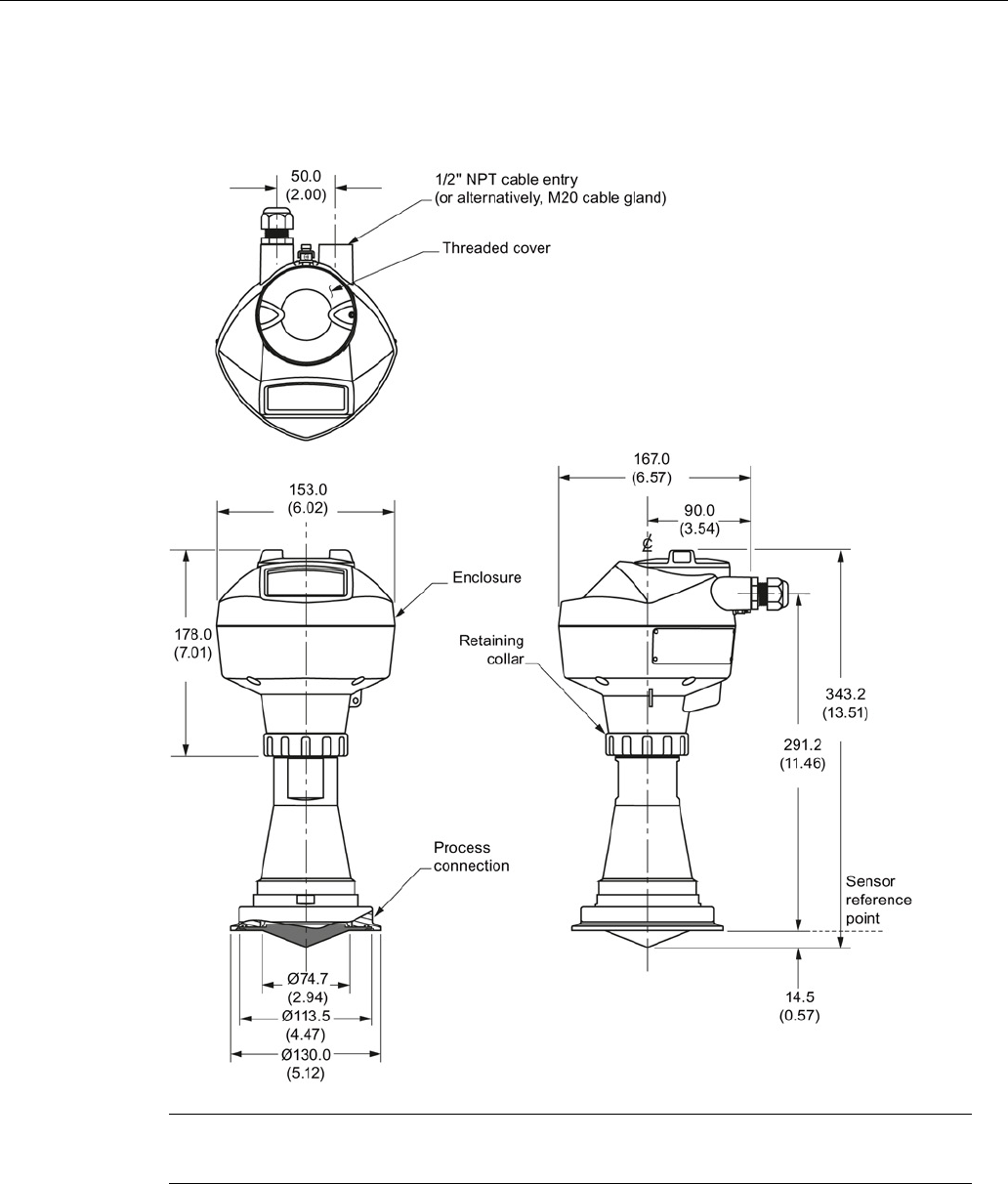
Dimension drawings
12.21 Hygienic encapsulated antenna (DN 100 aseptic clamp to DIN 11864-3)
SITRANS LR250 (PROFIBUS PA)
Operating Instructions, 08/2014, A5E32221386-AC 223
12.21
Hygienic encapsulated antenna (DN 100 aseptic clamp to DIN 11864-
3)
Dimensions in mm (inch)
Note
Cut out of process connection is shown for illustration purposes only.
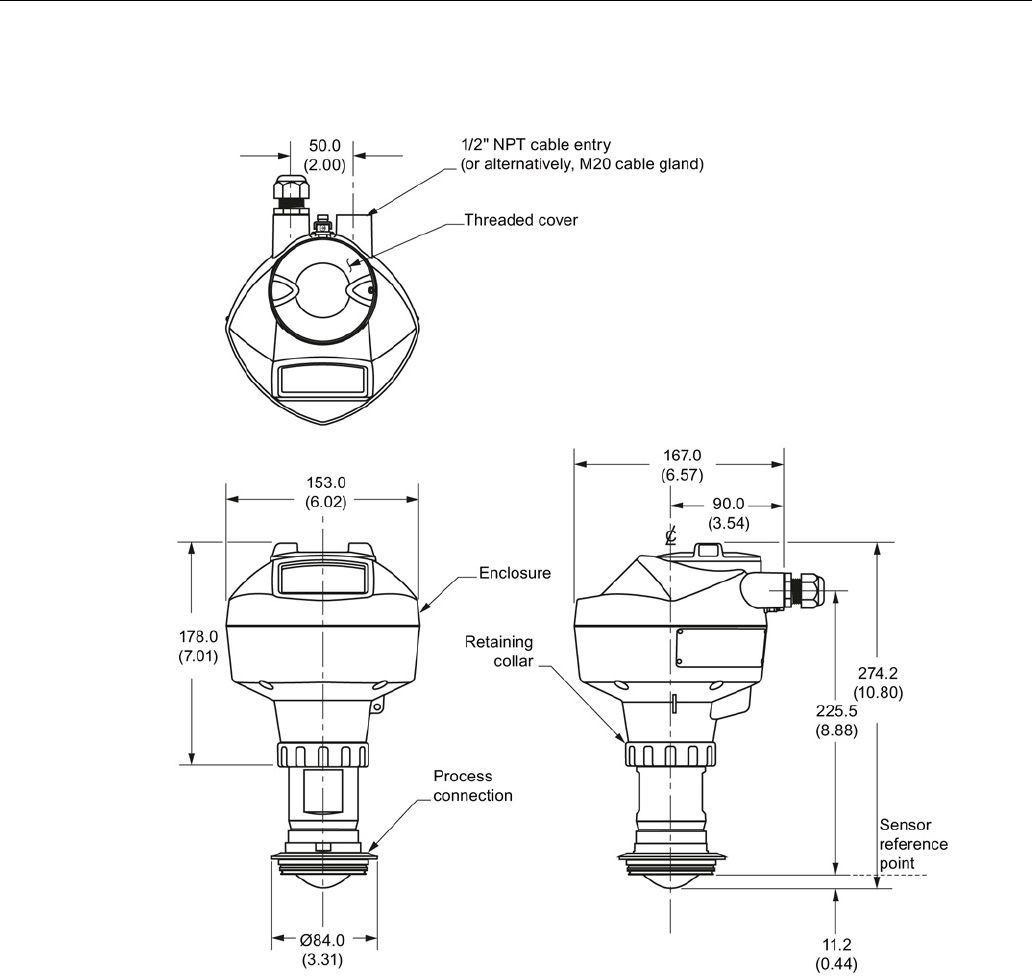
Dimension drawings
12.22 Hygienic encapsulated antenna (Tuchenhagen Type N)
SITRANS LR250 (PROFIBUS PA)
224 Operating Instructions, 08/2014, A5E32221386-AC
12.22
Hygienic encapsulated antenna (Tuchenhagen Type N)
Dimensions in mm (inch)

Dimension drawings
12.23 Hygienic encapsulated antenna (Tuchenhagen Type F)
SITRANS LR250 (PROFIBUS PA)
Operating Instructions, 08/2014, A5E32221386-AC 225
12.23
Hygienic encapsulated antenna (Tuchenhagen Type F)
Dimensions in mm (inch)

Dimension drawings
12.24 Threaded PVDF antenna
SITRANS LR250 (PROFIBUS PA)
226 Operating Instructions, 08/2014, A5E32221386-AC
12.24
Threaded PVDF antenna

Dimension drawings
12.25 Threaded connection markings
SITRANS LR250 (PROFIBUS PA)
Operating Instructions, 08/2014, A5E32221386-AC 227
Threaded PVDF antenna dimensions
Nominal antenna
size
Antenna O.D.
Height to sensor
reference point a)
Beam angle b)
Measurement
range
50 mm (2") 49.5 mm (1.94") 121 mm (4.76") 19 degrees 10 m (32.8 ft)c)
a) Height from bottom of antenna to sensor reference point as shown: see dimension drawing.
b) -3dB in the direction of the polarization axis. See Polarization reference point (Page 31) for an
illustration.
c) 20m when installed in stillpipe.
12.25
Threaded connection markings
With the exception of the threaded PVDF antenna, threaded connection markings are found on
the flat face/faces of the process connection.
Serial number: a unique number allotted to each process connection, including the date of
manufacture (MMDDYY) followed by a number from 001 to 999, (indicating the sequential unit
produced).
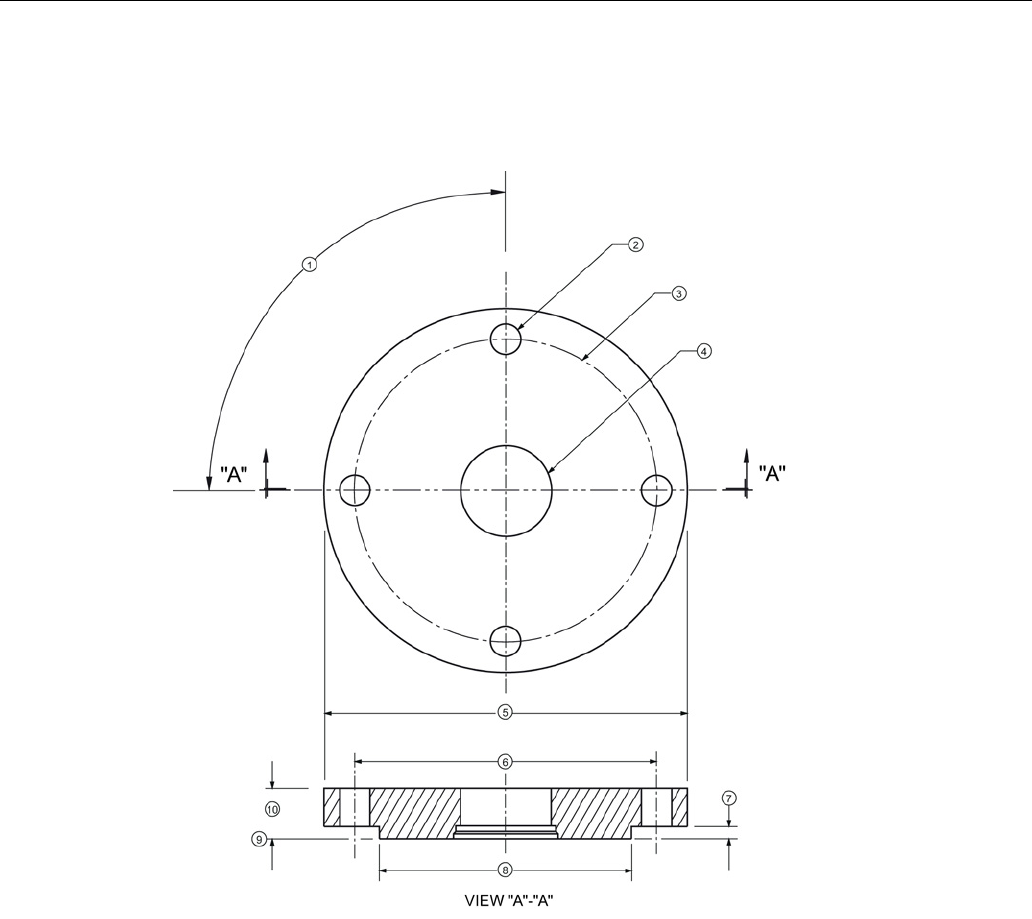
Dimension drawings
12.26 Raised-Face flange per EN 1092-1 for flanged horn antenna
SITRANS LR250 (PROFIBUS PA)
228 Operating Instructions, 08/2014, A5E32221386-AC
12.26
Raised-Face flange per EN 1092-1 for flanged horn antenna
Stainless steel or optional alloy N06022/2.4602 (Hastelloy® C-22)
①
angle of adjacent bolt holes
⑥
bolt hole circle diameter
②
bolt hole diameter
⑦
facing height
③
bolt hole circle diameter
⑧
facing diameter
④
waveguide mounting hole
⑨
sensor reference point
⑤
Flange O.D.
⑩
thickness

Dimension drawings
12.26 Raised-Face flange per EN 1092-1 for flanged horn antenna
SITRANS LR250 (PROFIBUS PA)
Operating Instructions, 08/2014, A5E32221386-AC 229
Raised-Face flange dimensions
Pipe size
Flange bolt
hole pattern
⑤
Flange
O.D.
(mm)
③
Bolt hole
circle Ø
(mm)
②
Bolt hole Ø
(mm)
No. of bolts
①
Angle of
adjacent
bolt holes
⑧
Facing Ø
(mm)
⑩
Thickness
(mm)
DN50 PN10/PN16 165 125 18 4 90 102 18
DN80 PN10/PN16 200 160 18 8 45 138 20
DN100 PN10/PN16 220 180 18 8 45 158 20
DN150 PN10/PN16 285 240 22 8 45 212 22
DN50 PN25/PN40 165 160 18 4 90 138 20
DN80 PN25/PN40 200 160 18 8 45 138 24
DN100 PN25/PN40 235 190 22 8 45 162 24
DN150 PN25/PN40 300 250 26 8 45 218 28
Raised-Face flange markings
Blind Flange Markings (Optional
Manufacturer’s Logo [optional]; Flange
Standard; Nominal Size; Material; Heat
Code)
Machining Identification
Welded Assembly Identification a)
Serial no.
Logo
Flange series
Flange
series
Heat Code
no.
Facing
Manufacturer’s logo; EN 1092-1 05 ‘B1’;
‘DN50’ ‘PN16’ ‘1.4404 or 1.4435’
A1B2C3
mmddyyx
xx xxxxx xxxxx A1B2C3 RF
a) When flange material is alloy N06022/2.4602, additional material and heat code identification
is provided.
The flange markings are located around the outside edge of the flange.
Serial number: a unique number allotted to each flange, including the date of manufacture
(MMDDYY) followed by a number from 001 to 999 (indicating the sequential
unit produced).
Flange series:
the Siemens Milltronics drawing identification.
Heat code: a flange material batch code identification.

Dimension drawings
12.27 Raised-Face flange per EN 1092-1 for flanged encapsulated antenna
SITRANS LR250 (PROFIBUS PA)
230 Operating Instructions, 08/2014, A5E32221386-AC
12.27
Raised-Face flange per EN 1092-1 for flanged encapsulated antenna
Stainless steel
①
angle of adjacent bolt holes
⑤
flange O.D.
②
bolt hole diameter
⑥
facing height
③
bolt hole circle diameter
⑦
facing diameter
④
antenna
⑧
flange thickness

Dimension drawings
12.27 Raised-Face flange per EN 1092-1 for flanged encapsulated antenna
SITRANS LR250 (PROFIBUS PA)
Operating Instructions, 08/2014, A5E32221386-AC 231
Raised-Face flange dimensions
Pipe size
Flange class
⑤
Flange
O.D.
[mm
(inch)]
③
Bolt hole
circle Ø
[mm
(inch)]
②
Bolt hole
Ø [mm
(inch)]
No. of bolt
holes
①
Angle of
adjacent
bolt holes
⑦
Facing Ø
[mm
(inch)]
⑨
Flange
thickness
[mm
(inch)]
⑥
Flange
facing
thickness
[mm
(inch)]
2" 150 LB 152
(5.98)
120.7
(4.75)
19 (0.75) 4 90 92.1
(3.63)
20.6
(0.81)
1.5 (0.06)
3" 190
(7.48)
152.4
(6.00)
127 (5.00) 25.9
(1.02)
2 (0.08)
4" 230
(9.06)
190.5
(7.50)
8 45 157.2
(6.19)
2 (0.08)
6" 280
(11.02)
241.3
(9.50)
22.2
(0.87)
215.9
(8.50)
26.9
(1.06)
1.5 (0.06)
DN50 PN10/16 155
(6.10)
125 (4.92) 18 (0.71) 4 90 102 (4.02) 18 (0.71) 2 (0.08)
DN80 200
(7.87)
160 (6.30) 8 45 138 (5.43) 20 (0.79)
2 (0.08)
DN100 220
(8.66)
180 (7.09) 158 (6.22) 2 (0.08)
DN150 285
(11.22)
240 (9.45) 22 (0.87) 212 (8.35) 22 (0.87) 2 (0.08)
50A 10K 155
(6.10)
120 (4.72) 19 (0.75) 4 90 96 (3.78) 16 (0.63) 2 (0.08)
80A 185
(7.28)
150 (5.91) 8 45 126 (4.96) 18 (0.71)
2 (0.08)
100A 210
(8.27)
175 (6.89) 151 (5.94) 2 (0.08)
150A 280
(11.02)
240 (9.45) 23 (0.91) 212 (8.35) 22 (0.87) 2 (0.08)

Dimension drawings
12.27 Raised-Face flange per EN 1092-1 for flanged encapsulated antenna
SITRANS LR250 (PROFIBUS PA)
232 Operating Instructions, 08/2014, A5E32221386-AC
Raised-Face flange markings
Blind Flange Markings (Optional
Manufacturer’s Logo [optional]; Flange
Standard; Nominal Size; Material; Heat
Code)
Machining Identification
Welded Assembly Identification
Serial no.
Logo
Flange series
Flange
series
Heat Code
no.
Facing
Manufacturer’s logo; EN 1092-1 05 ‘B1’;
‘DN50’ ‘PN16’ ‘1.4404 or 1.4435’
A1B2C3
mmddyyx
xx xxxxx xxxxx A1B2C3 RF
The flange markings are located around the outside edge of the flange.
Serial number: a unique number allotted to each flange, including the date of manufacture
(MMDDYY) followed by a number from 001 to 999 (indicating the sequential
unit produced).
Flange series: the Siemens Milltronics drawing identification.
Heat code: a flange material batch code identification.
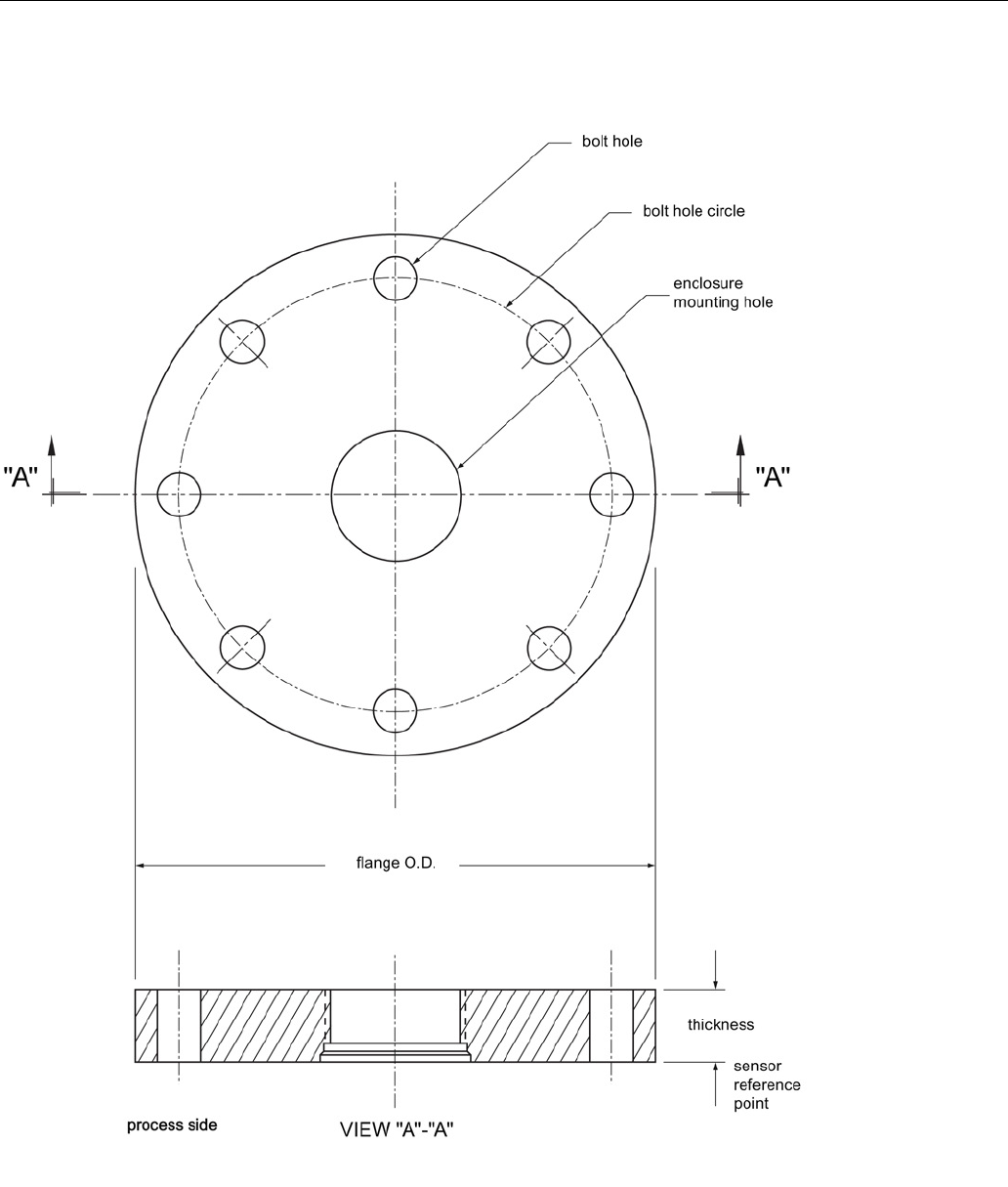
Dimension drawings
12.28 Flat-Face flange
SITRANS LR250 (PROFIBUS PA)
Operating Instructions, 08/2014, A5E32221386-AC 233
12.28
Flat-Face flange

Dimension drawings
12.28 Flat-Face flange
SITRANS LR250 (PROFIBUS PA)
234 Operating Instructions, 08/2014, A5E32221386-AC
Flat-Face flange dimensions
Flange size a)
Flange class
Flange O.D.
Bolt hole circle
Ø
Bolt hole Ø
No. of bolt
holes
Thickness
2" ASME 150 lb 6.0" 4.75" 0.75" 4 0.88"
3" ASME 150 lb 7.5" 6.0" 0.75" 4 0.96"
4" ASME 150 lb 9.0" 7.50" 0.75" 8 1.25"
2" ASME 300 lb 6.50" 5.00" 0.75" 8 1.12"
3" ASME 300 lb 8.25" 6.62" 0.88" 8 1.38"
4" ASME 300 lb 10.00" 7.88" 0.88" 8 1.50"
DN50 EN PN16 165 mm 125 mm 18 mm 4 24.4 mm
DN80 EN PN16 200 mm 160 mm 18 mm 8 31.8 mm
DN100 EN PN16 220 mm 180 mm 18 mm 8 31.8 mm
DN50 EN PN40 165 mm 125 mm 18 mm 4 25.4 mm
DN80 EN PN40 200 mm 160 mm 18 mm 8 31.8 mm
DN100 EN PN40 235 mm 190 mm 22 mm 8 38.1 mm
50A JIS 10K 155 mm 120 mm 19 mm 4 23.8 mm
80A JIS 10K 185 mm 150 mm 19 mm 8 24.4 mm
100A JIS 10K 210 mm 175 mm 19 mm 8 28.5 mm
a) A 2" flange is designed to fit a 2" pipe: for actual flange dimensions see Flange O.D. Flange
markings located around the outside edge of the flat faced flange identify the flange assembly on
which the device is mounted.
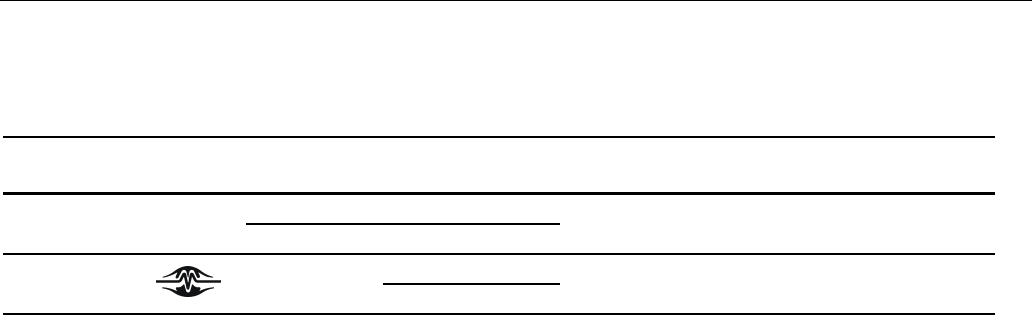
Dimension drawings
12.28 Flat-Face flange
SITRANS LR250 (PROFIBUS PA)
Operating Instructions, 08/2014, A5E32221386-AC 235
Flat-Face flange markings
Flat Face Flange Identification
Welded Assembly
Identification
Serial No. Logo Flange series Material Heat
code
Flange
series
Heat code
no.
Series Nominal size
MMDDYYXXX 25556 2 150 316L/ 1.4404 or
316L/ 1.4435
A1B2C3 25546 A1B2C3
DN80 PN16
Serial number:
A unique number allotted to each flange, including the date of manufacture
(MMDDYY) followed by a number from 001 to 999 (indicating the sequential
unit produced).
Flange series:
The Siemens Milltronics drawing identification.
Nominal size:
The flange size followed by the hole pattern for a particular flange class. For
example:
• A 2 inch ASME B16.5 150 lb class flange (North America)
• A DN80 EN 1092-1 PN16 class flange (Europe)
Material:
The basic flange material (AISI or EU material designation). North American
material codes are followed by European ones. For example, material
designation 316L/1.4404.
Heat code:
A flange material batch code identification.

Dimension drawings
12.29 Aseptic/hygienic flange DN50, DN80, DN100 for DIN 11864-2
SITRANS LR250 (PROFIBUS PA)
236 Operating Instructions, 08/2014, A5E32221386-AC
12.29
Aseptic/hygienic flange DN50, DN80, DN100 for DIN 11864-2
Aseptic/hygienic flange DN50
Dimensions in mm (inch)
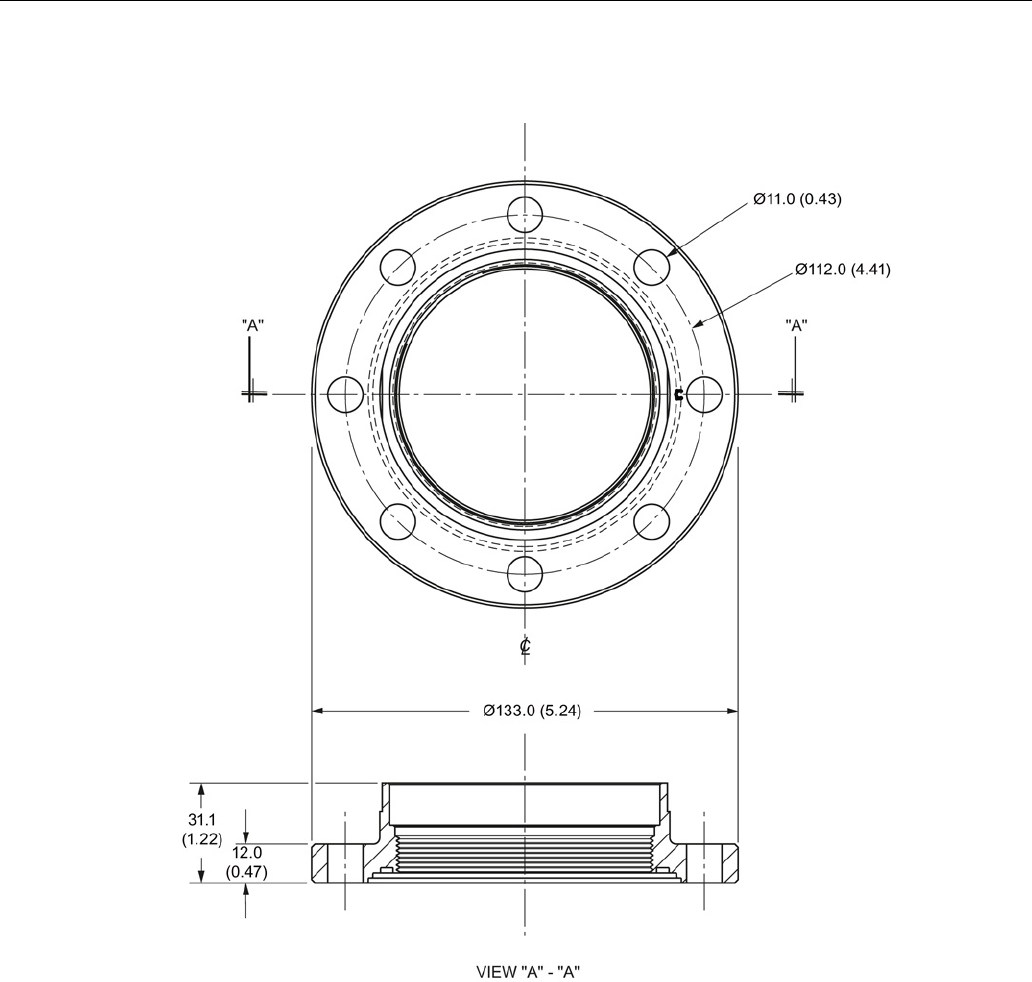
Dimension drawings
12.29 Aseptic/hygienic flange DN50, DN80, DN100 for DIN 11864-2
SITRANS LR250 (PROFIBUS PA)
Operating Instructions, 08/2014, A5E32221386-AC 237
Aseptic/hygienic flange DN80
Dimensions in mm (inch)

Dimension drawings
12.29 Aseptic/hygienic flange DN50, DN80, DN100 for DIN 11864-2
SITRANS LR250 (PROFIBUS PA)
238 Operating Instructions, 08/2014, A5E32221386-AC
Aseptic/hygienic flange DN100
Dimensions in mm (inch)

Dimension drawings
12.30 Process connection tag (pressure rated versions)
SITRANS LR250 (PROFIBUS PA)
Operating Instructions, 08/2014, A5E32221386-AC 239
12.30
Process connection tag (pressure rated versions)
For pressure-rated versions only, the process connection label lists the following information:
Process connection tag (pressure rated versions)
Item
Sample Text
Comments/Explanation
SERIAL #
GYZ / 00000000 Pressure Boundary Assembly
NOMINAL PIPE SIZE (DN)
4 INCH / 100mm Nominal Pipe Size
INSTRUMENT MAWP (PS)
11.0
BAR
Maximum Allowable Working Pressure at
Design Temperature for the device
DESIGN TEMP. (TS)
200
ºC
Maximum Allowable Working Temperature
MINIMUM PROCESS
15.9
BAR
AT
40
ºC
Minimum Wetted Process Conditions
TEST PRESSURE (PT)
22.7
BAR
Production Test Pressure
TEST DATE
10/11/11 Date of Pressure Test (Year/Month/Day)
CONNECTION SERIES
ASME B16.5 Flange Series: dimensional pattern based on
ASME B16.5 flange standards
PROCESS SERIES
25546 Pressure Tag Family Series
WETTED NON-METALLICS
TFM Antenna Emitter
WETTED METALLICS
316L Process Connection Material(s)
WETTED SEALS
FKM Seal Material(s)
● Minimum Wetted Process Conditions: the minimum pressure and temperature to which the
device assembly may be exposed in the process, and continue to provide a pressure-
retaining function.
● Pressure Tag Family Series: the identification number used to indicate specific process
connection information relating to operating conditions.
● For Flanged encapsulated antenna: this information is laser-etched on antenna body
BACK FACE
Sample Text
Comments/Explanation
CRN 0Fxxxxx.5 Canadian Registration Number (CRN)

Dimension drawings
12.30 Process connection tag (pressure rated versions)
SITRANS LR250 (PROFIBUS PA)
240 Operating Instructions, 08/2014, A5E32221386-AC

SITRANS LR250 (PROFIBUS PA)
Operating Instructions, 08/2014, A5E32221386-AC 241
Appendix A: Technical reference
A
Note
Where a number follows the parameter name [for example,
Master Reset (4.1.)
] this is the
parameter access number via the handheld programmer. See Parameter Reference
(Page 107) for a complete list of parameters.
A.1
Principles of operation
SITRANS LR250 is a 2-wire 25 GHz pulse radar level transmitter for continuous monitoring of
liquids and slurries. (The microwave output level is significantly less than that emitted from
cellular phones.) Radar level measurement uses the time of flight principle to determine distance
to a material surface. The device transmits a signal and waits for the return echo. The transit
time is directly proportional to the distance from the material.
Pulse radar uses polarized electromagnetic waves. Microwave pulses are emitted from the
antenna at a fixed repetition rate, and reflect off the interface between two materials with
different dielectric constants (the atmosphere and the material being monitored).
Electromagnetic wave propagation is virtually unaffected by temperature or pressure changes,
or by changes in the vapor levels inside a vessel. Electromagnetic waves are not attenuated by
dust.
SITRANS LR250 consists of an enclosed electronic circuit coupled to an antenna and process
connection. The electronic circuit generates a radar signal (25 GHz) that is directed to the
antenna.
The signal is emitted from the antenna, and the reflected echoes are digitally converted to an
echo profile. The profile is analyzed to determine the distance from the material surface to the
sensor reference point. See Dimension drawings (Page 195). This distance is used as a basis
for the display of material level and mA output.

Appendix A: Technical reference
A.2 Echo processing
SITRANS LR250 (PROFIBUS PA)
242 Operating Instructions, 08/2014, A5E32221386-AC
A.2
Echo processing
A.2.1
Process Intelligence
The signal processing technology embedded in Siemens radar level devices is known as
Process Intelligence
.
Process intelligence provides high measurement reliability regardless of the dynamically
changing conditions within the vessel being monitored. The embedded Process Intelligence
dynamically adjusts to the constantly changing material surfaces within these vessels.
Process Intelligence is able to differentiate between the true microwave reflections from the
surface of the material and unwanted reflections being returned from obstructions such as seam
welds or supports within a vessel. The result is repeatable, fast and reliable measurement. This
technology was developed as result of field data gained over some twenty years from more than
1,000,000 installations in many industries around the world.
Higher order mathematical techniques and algorithms are used to provide intelligent processing
of microwave reflection profiles. This "knowledge based" technique produces superior
performance and reliability.
A.2.2
Echo Selection
Time Varying Threshold (TVT)
A Time Varying Threshold (TVT) hovers above the echo profile to screen out unwanted
reflections (false echoes).
In most cases the material echo is the only one which rises above the default TVT.
In a vessel with obstructions, a false echo may occur. See Auto False Echo Suppression
(Page 246) for more details.

Appendix A: Technical reference
A.2 Echo processing
SITRANS LR250 (PROFIBUS PA)
Operating Instructions, 08/2014, A5E32221386-AC 243
①
default TVT
②
echo profile
③
material level
④
echo marker
The device characterizes all echoes that rise above the TVT as potential good echoes. Each
peak is assigned a rating based on its strength, area, height above the TVT, and reliability,
amongst other characteristics.
Algorithm (2.5.7.1.)
The true echo is selected based on the setting for the Echo selection algorithm. Options are
t
rue
F
irst Echo,
L
argest Echo, or
b
est of
F
irst and
L
argest.
Position Detect (2.5.7.2.)
The echo position detection algorithm determines which point on the echo will be used to
calculate the precise time of flight, and calculates the range using the calibrated propagation
velocity (see
Propagation Factor (2.5.3.)
for values). There are three options:
●
Center
●
Hybrid
●
CLEF
(Constrained Leading Edge Fit)

Appendix A: Technical reference
A.2 Echo processing
SITRANS LR250 (PROFIBUS PA)
244 Operating Instructions, 08/2014, A5E32221386-AC
Center
Uses center of the echo.
Hybrid
Uses the Center algorithm for the top part of the vessel, and the CLEF algorithm for the part
nearest the vessel bottom, according to the setting for
CLEF range
.
CLEF (Constrained Leading Edge Fit)
● Uses the leading edge of the echo.
● Is used mainly to process the echo from materials with a low dK value.
In an almost empty flat-bottomed vessel, a low dK material may reflect an echo weaker than the
echo from the vessel bottom. The echo profile shows these echoes merging. The device may
then report a material level equal to or lower than empty.
The CLEF algorithm enables the device to report the level correctly.
Example: CLEF off: Position set to Hybrid
Vessel height: 1.5 m; CLEF range set to 0 (
Center
algorithm gives the same result.)
①
default TVT
②
material echo
③
vessel bottom echo selected
④
echo marker

Appendix A: Technical reference
A.2 Echo processing
SITRANS LR250 (PROFIBUS PA)
Operating Instructions, 08/2014, A5E32221386-AC 245
Example: CLEF enabled
Vessel height: 1.5 m; CLEF range set to 0.5 m
①
default TVT
②
material echo selected
③
vessel bottom echo
④
echo marker
A.2.3
CLEF Range
Determines the level below which the CLEF algorithm will be used. Above this level the Center
algorithm is used when Hybrid is selected in
Position Detect (2.5.7.2.)
. CLEF Range is
referenced from Low Calibration Point (process empty level).
①
CLEF range
④
Low calibration point
②
(Center algorithm applied)
⑤
Sensor reference point
③
High calibration point
⑥
Low Calibration Point (process empty
level)

Appendix A: Technical reference
A.2 Echo processing
SITRANS LR250 (PROFIBUS PA)
246 Operating Instructions, 08/2014, A5E32221386-AC
A.2.4
Echo Threshold
Confidence (2.5.9.1.)
describes the quality of an echo. Higher values represent higher quality.
Echo Threshold
defines the minimum confidence value required for an echo to be accepted as
valid and evaluated.
A.2.5
Echo Lock
If the echo selected by
Algorithm
is within the Echo Lock window, the window is centered about
the echo, which is used to derive the measurement. In radar applications, two measurement
verification options are used:
Lock Off
SITRANS LR250 responds immediately to a new selected echo (within the restrictions set by the
Maximum Fill / Empty Rate), but measurement reliability is affected.
Material Agitator
A new measurement outside the Echo Lock Window must meet the sampling criteria before the
window will move to include it.
The other available options,
Maximum Verification
and
Total Lock
are not recommended for
radar.
A.2.6
Auto False Echo Suppression
Note
• For detailed instructions on using this feature via PDM see Auto False Echo Suppression
(Page 88).
• For detailed instructions on using this feature via the handheld programmer see
Auto
False Echo Suppression (2.5.10.1.).
Auto False Echo Suppression is designed to learn a specific environment (for example, a
particular vessel with known obstructions), and in conjunction with Auto False Echo Suppression
Range to remove false echoes appearing in front of the material echo.
The material level should be below all known obstructions at the moment when Auto False Echo
Suppression learns the echo profile. Ideally the vessel should be empty or almost empty, and if
an agitator is present, it should be running.
The device learns the echo profile over the whole measurement range and the TVT is shaped
around all echoes present at that moment.

Appendix A: Technical reference
A.2 Echo processing
SITRANS LR250 (PROFIBUS PA)
Operating Instructions, 08/2014, A5E32221386-AC 247
Auto False Echo Suppression Range (2.5.10.2.)
Auto False Echo Suppression Range specifies the range within which the learned TVT is
applied. Default TVT is applied over the remainder of the range.
The learned TVT screens out the false echoes caused by obstructions. The default TVT allows
the material echo to rise above it.
Auto False Echo Suppression Range must be set to a distance shorter than the distance to the
material level when the environment was learned, to avoid the material echo being screened out.
Example before Auto False Echo Suppression
①
default TVT
⑤
high calibration point = 0
②
false echo
⑥
obstruction at 1.3. m
③
material echo
⑦
material level at 3.2 m
④
sensor reference point

Appendix A: Technical reference
A.2 Echo processing
SITRANS LR250 (PROFIBUS PA)
248 Operating Instructions, 08/2014, A5E32221386-AC
Example after Auto False Echo Suppression
Auto False Echo
Suppression
Range set to 2 m
① Learned TVT ④ Default TVT
② False echo ⑤ Material echo
③ Auto False Echo Suppression Range ⑥ Echo marker
A.2.7
Measurement Range
Near Range (2.5.1.)
Near Range programs SITRANS LR250 to ignore the zone in front of the antenna. The default
blanking distance is 50 mm (1.97") from the end of the antenna.
Near Range allows you to increase the blanking value from its factory default. But
Auto False
Echo Suppression (2.5.10.1.)
is generally recommended in preference to extending the blanking
distance from factory values.
Far Range (2.5.2.)
Far Range can be used in applications where the base of the vessel is conical or parabolic. A
reliable echo may be available below the vessel empty distance, due to an indirect reflection
path.
Increasing Far Range to 30% or 40% can provide stable empty vessel readings.

Appendix A: Technical reference
A.2 Echo processing
SITRANS LR250 (PROFIBUS PA)
Operating Instructions, 08/2014, A5E32221386-AC 249
A.2.8
Measurement Response
Note
Units are defined in
Units (2.3.1.)
and are in meters by default.
Response Rate (2.3.8.1.)
limits the maximum rate at which the display and output respond to
changes in the measurement. There are three preset options: slow, medium, and fast.
Once the real process fill/empty rate (m/s by default) is established, a response rate can be
selected that is slightly higher than the application rate. Response Rate automatically adjusts the
filters that affect the output response rate.
Response Rate (2.3.8.1)
Fill Rate (2.3.8.2)/Empty Rate (2.3.8.3)
*
Slow
0.1 m/min (0.32 ft/min) 10 s
Medium
1.0 m/min (3.28 ft.min) 10 s
Fast
10.0 m/min (32.8 ft/min) 0 s
A.2.9
Damping
Filter Time Constant (2.6.8.1)
smooths out the response to a sudden change in level. This is an
exponential filter and the engineering unit is always in seconds.
In 5 time constants the output rises exponentially: from 63.2% of the change in the first time
constant, to almost 100% of the change by the end of the 5th time constant.
Damping example
time constant = 2 seconds
input (level) change = 2 m

Appendix A: Technical reference
A.2 Echo processing
SITRANS LR250 (PROFIBUS PA)
250 Operating Instructions, 08/2014, A5E32221386-AC
A.2.10
Loss of Echo (LOE)
A loss of echo (LOE) occurs when the calculated measurement is judged to be unreliable
because the echo confidence value has dropped below the echo confidence threshold.
Confidence (2.5.9.1.)
describes the quality of an echo. Higher values represent higher quality.
Echo Threshold (2.5.7.3.)
defines the minimum confidence value required for an echo to be
accepted as valid and evaluated.
If the LOE condition persists beyond the time limit set in
LOE Timer (2.3.6.)
the LCD displays the
Service Required icon, and the text region displays the fault code
S: 0
and the text
LOE
.
If two faults are present at the same time, the fault code, error text, and error icon for each fault
are displayed alternately. For example, Loss of Echo and faulty power supply:
Upon receiving a reliable echo, the loss of echo condition is aborted, the Service Required icon
and error message are cleared, and the reading returns to the current level.
A.2.10.1
LOE Timer
LOE Timer (2.3.6.)
determines the length of time a Loss of Echo (LOE) condition will persist
before a Fail-safe state is activated. The default is 100 seconds. Fail-safe Mode determines the
level to be reported when the Fail-safe timer expires.
A.2.10.2
Fail-safe Behavior
The purpose of the Fail-safe setting is to put the process into a safe mode of operation in the
event of a fault or failure. The value to be reported in the event of a fault is selected so that a
loss of power or loss of signal triggers the same response as an unsafe level.
Fail-safe mode may be triggered by a loss of echo, a bad configuration, or certain device faults.
You can select one of three possible values to be reported when a Fail-safe mode is activated.
Mode
Mode (2.6.9.1.)
determines the material level to be reported when
LOE Timer (2.3.6.)
expires.
Mode (2.6.9.1.)
SUB VALUE Use substitute value.
Value (2.6.9.2.)
used as output value.
LAST VALUE * Last value (Store last valid output value).
USE BAD VALUE Use bad value (Calculated output value is incorrect).

Appendix A: Technical reference
A.3 Maximum Process Temperature Chart
SITRANS LR250 (PROFIBUS PA)
Operating Instructions, 08/2014, A5E32221386-AC 251
Value
Value (2.6.9.2.)
defines the material level to be reported if the option
Use substitute value
is
selected in
Mode (2.6.9.1.)
.
The two Analog Input Function blocks are set separately.
To set a user-defined value
● Navigate to the Level Meter > Setup > desired Analog Input (1 or 2).
● Set
Mode (2.6.9.1.)
to
Use substitute value
.
● Go to
Value (2.6.9.2.)
and enter the desired value.
A.3
Maximum Process Temperature Chart
WARNING
Exceeded maximum internal and process temperatures
Danger of device malfunction
• Internal temperature must not exceed +80 ° C (+176 °F).
• Process temperature must not exceed limits specified by the antenna type.
Note
• The chart below is for guidance only.
• The chart does not represent every possible process connection arrangement. For
example, it will NOT apply if you are mounting SITRANS LR250 directly on a metallic
vessel surface.
• The chart does not take into consideration heating from direct sunlight exposure.

Appendix A: Technical reference
A.3 Maximum Process Temperature Chart
SITRANS LR250 (PROFIBUS PA)
252 Operating Instructions, 08/2014, A5E32221386-AC
Maximum Process Temperatures versus allowable ambient
① Internal enclosure temperature
② Ambient temperature
③ Process temperature (at process
connection)
Where the chart does not apply, please use your own judgement regarding the use of SITRANS
LR250.
If the internal temperature exceeds the maximum allowable limit, a sun shield or a longer nozzle
may be required.
See
Minimum Value (3.3.1.)
and
Maximum Value (3.3.2.)
to monitor the Internal Temperature.

Appendix A: Technical reference
A.4 Process Pressure/Temperature Derating Curves
SITRANS LR250 (PROFIBUS PA)
Operating Instructions, 08/2014, A5E32221386-AC 253
A.4
Process Pressure/Temperature Derating Curves
WARNING
• Never attempt to loosen, remove or disassemble process connection or device housing
while vessel contents are under pressure.
• Materials of construction are chosen based on their chemical compatibility (or inertness)
for general purposes. For exposure to specific environments, check with chemical
compatibility charts before installing.
• The user is responsible for the selection of bolting and gasket materials which will fall
within the limits of the flange and its intended use and which are suitable for the service
conditions.
• Improper installation may result in loss of process pressure and/or release of process
fluids and/or gases.
Note
• The process connection tag shall remain with the process pressure boundary assembly.
(The process pressure boundary assembly comprises the components that act as a
barrier against pressure loss from the process vessel: that is, the combination of process
connection body and emitter, but normally excluding the electrical enclosure). In the
event the device package is replaced, the process connection tag shall be transferred to
the replacement unit.
• SITRANS LR250 units are hydrostatically tested, meeting or exceeding the requirements
of the ASME Boiler and Pressure Vessel Code and the European Pressure Equipment
Directive.
• The serial numbers stamped in each process connection body, (flange, threaded, or
sanitary), provide a unique identification number indicating date of manufacture.
Example: MMDDYY – XXX (where MM = month, DD = day, YY = year, and XXX=
sequential unit produced)
• Further markings (space permitting) indicate flange configuration, size, pressure class,
material, and material heat code.
Pressure Equipment Directive, PED, 97/23/EC
Siemens Level Transmitters with flanged, threaded, or sanitary clamp type process mounts have
no pressure-bearing housing of their own and, therefore, do not come under the Pressure
Equipment Directive as pressure or safety accessories (see EU Commission Guideline 1/8 and
1/20).

Appendix A: Technical reference
A.4 Process Pressure/Temperature Derating Curves
SITRANS LR250 (PROFIBUS PA)
254 Operating Instructions, 08/2014, A5E32221386-AC
A.4.1
Horn antenna
1.5", 2" and 3" [NPT, G (BSPP), R (BSPT)] Threaded Versions
① Atmospheric
P Allowable operating pressures
T Allowable operating temperatures

Appendix A: Technical reference
A.4 Process Pressure/Temperature Derating Curves
SITRANS LR250 (PROFIBUS PA)
Operating Instructions, 08/2014, A5E32221386-AC 255
A.4.2
Flanged horn antenna
JIS B 2220, 10K: 50A, 80A, and 100A
① Atmospheric
P Allowable operating pressures
T Allowable operating temperatures
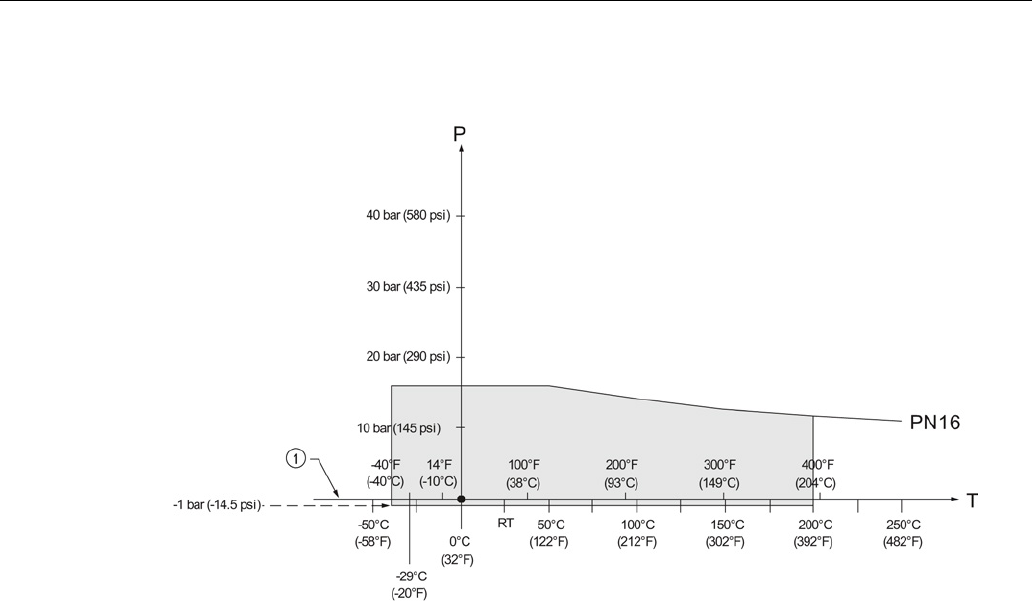
Appendix A: Technical reference
A.4 Process Pressure/Temperature Derating Curves
SITRANS LR250 (PROFIBUS PA)
256 Operating Instructions, 08/2014, A5E32221386-AC
EN1092-1, PN16: DN50, DN80, DN100, and DN150
① Atmospheric
P Allowable operating pressures
T Allowable operating temperatures

Appendix A: Technical reference
A.4 Process Pressure/Temperature Derating Curves
SITRANS LR250 (PROFIBUS PA)
Operating Instructions, 08/2014, A5E32221386-AC 257
EN1092-1, PN40: DN50, DN80, DN100, and DN150
① Atmospheric
P Allowable operating pressures
T Allowable operating temperatures

Appendix A: Technical reference
A.4 Process Pressure/Temperature Derating Curves
SITRANS LR250 (PROFIBUS PA)
258 Operating Instructions, 08/2014, A5E32221386-AC
ASME B16.5, Class 150: 2", 3", and 4" NPS
① Atmospheric
P Allowable operating pressures
T Allowable operating temperatures

Appendix A: Technical reference
A.4 Process Pressure/Temperature Derating Curves
SITRANS LR250 (PROFIBUS PA)
Operating Instructions, 08/2014, A5E32221386-AC 259
ASME B16.5, Class 300: 2", 3", and 4" NPS
① Atmospheric
P Allowable operating pressures
T Allowable operating temperatures

Appendix A: Technical reference
A.4 Process Pressure/Temperature Derating Curves
SITRANS LR250 (PROFIBUS PA)
260 Operating Instructions, 08/2014, A5E32221386-AC
A.4.3
Flanged encapsulated antenna
ASME B16.5, Class 150: 2", 3", 4", and 6" NPS
①
Atmospheric
P
Allowable operating pressures
T
Allowable operating temperatures
JIS B 2220, 10K: 50A, 80A, 100A, and 150A
①
Atmospheric
P
Allowable operating pressures
T
Allowable operating temperatures
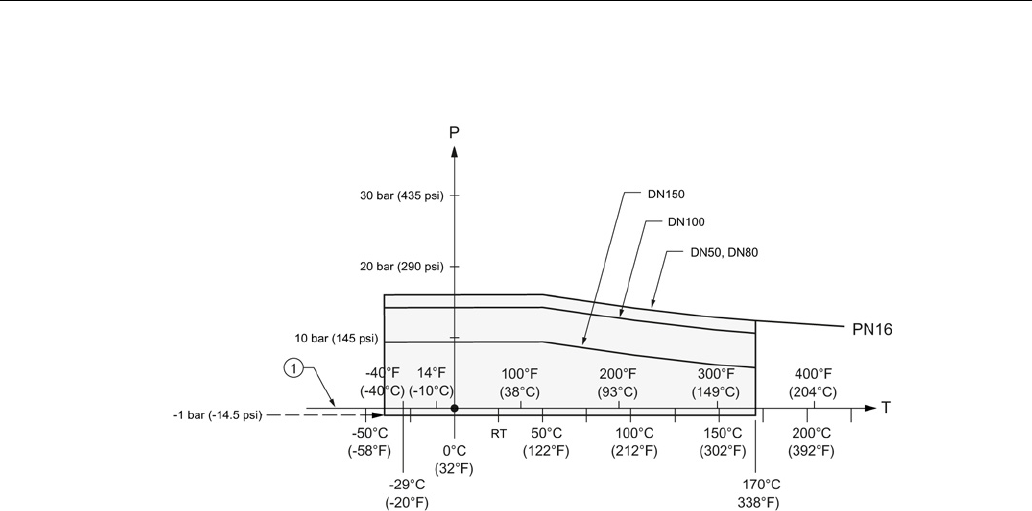
Appendix A: Technical reference
A.4 Process Pressure/Temperature Derating Curves
SITRANS LR250 (PROFIBUS PA)
Operating Instructions, 08/2014, A5E32221386-AC 261
EN1092-1, PN10/16: DN50, DN80, DN100, and DN150
①
Atmospheric
P
Allowable operating pressures
T
Allowable operating temperatures

Appendix A: Technical reference
A.4 Process Pressure/Temperature Derating Curves
SITRANS LR250 (PROFIBUS PA)
262 Operating Instructions, 08/2014, A5E32221386-AC
A.4.4
PVDF antenna
ASME B1.20.1 2" NPT, EN ISO 228-1 2" G (BSPP), EN 10226-1 2" R (BSPT)
① Atmospheric
P Allowable operating pressures
T Allowable operating temperatures

Appendix A: Technical reference
A.4 Process Pressure/Temperature Derating Curves
SITRANS LR250 (PROFIBUS PA)
Operating Instructions, 08/2014, A5E32221386-AC 263
A.4.5
Hygienic encapsulated antenna
DIN 11851 Sanitary/Hygienic nozzle/slotted nut: DN50, DN80, and DN100
DIN 11864-1 Aseptic/Hygienic nozzle/slotted nut: DN50, DN80, and DN100
① Atmospheric
P Allowable operating pressures
T Allowable operating temperatures

Appendix A: Technical reference
A.4 Process Pressure/Temperature Derating Curves
SITRANS LR250 (PROFIBUS PA)
264 Operating Instructions, 08/2014, A5E32221386-AC
DIN 11864-2 Aseptic/Hygienic flanged: DN50, DN80, and DN100
① Atmospheric
P Allowable operating pressures
T Allowable operating temperatures
Note
For pressure applications, all attachment hardware must be suitably rated.

Appendix B: PROFIBUS PA profile structure
B.1 PROFIBUS Level Device Design
SITRANS LR250 (PROFIBUS PA)
Operating Instructions, 08/2014, A5E32221386-AC 265
DIN 11864-3 Aseptic/Hygienic clamp: DN50, DN80, and DN100
IS0 2852 Sanitary/Hygienic clamp: 2", 3", and 4"
Tuchenhagen Varivent face seal clamp: Type N (68 mm) and Type F (50 mm)
① Atmospheric
P Allowable operating pressures
T Allowable operating temperatures
Note
For pressure applications, all clamps must be rated accordingly.

Appendix B: PROFIBUS PA profile structure
B.1 PROFIBUS Level Device Design
SITRANS LR250 (PROFIBUS PA)
266 Operating Instructions, 08/2014, A5E32221386-AC
Appendix B: PROFIBUS PA profile structure
B
B.1
PROFIBUS Level Device Design
The device follows the profile block model and is implemented as a Profile 3.0, Class B, PA
device. Standard profile parameters are used to program the level transducer block.
B.2
Block Model
The Block Model represents how measured values are recorded and processed. All data is
viewed from the perspective of the DCS or PLC, so information from the sensor is an input.
The functions of the device are divided into blocks with different areas of responsibility. The
blocks are configured by parameters.
The device is implemented with one Physical Block, one Transducer Block (TB), and two Analog
Input Function Blocks (AIFB1 and AIFB2).
Physical Block
The Physical Block handles functionality and descriptions relating to the device as a whole: for
example, LCD Contrast (functionality) and Firmware Revision and Tag (descriptions).

Appendix B: PROFIBUS PA profile structure
B.2 Block Model
SITRANS LR250 (PROFIBUS PA)
Operating Instructions, 08/2014, A5E32221386-AC 267
Transducer Block (TB)
The Transducer Block carries out adjustments to the sensor, such as level calibration and
volume calibration. It supplies the measurement value [Primary Value (PV), Secondary Value 1
(SV1), or Secondary Value 2 (SV2)] utilized by either or both of the AIFBs.
Analog Input Function Blocks AIFB1 and AIFB2
The two AIFBs are completely independent of each other. They utilize the measurement value
output from the Transducer Block [Primary Value (PV), Secondary Value 1 (SV1), or Secondary
Value 2 (SV2)] and apply any required quality checks, scaling, and Fail-safe operation
selections. The Analog Input Function Block output supplies the measured value and associated
status information to the PROFIBUS PA network via cyclic data transfer.
B.2.1
Description of the blocks
B.2.1.1
Transducer Block function groups
The figure below shows the signal flow of measured values from the sensor through the
Transducer Block into the output value:
● Primary Value (PV): Level or Volume
● Secondary Value 1 (SV1): Level
● Secondary Value 2 (SV2): Distance
The Transducer Block implements all of the basic parameters (see
diagram below), including
level to volume calculation, if that option has been selected.

Appendix B: PROFIBUS PA profile structure
B.2 Block Model
SITRANS LR250 (PROFIBUS PA)
268 Operating Instructions, 08/2014, A5E32221386-AC
Transducer Block
B.2.1.2
How the transducer block works:
1. The sensor technology block selects the proper echo. For an explanation of sensor
technology, see Appendix A: Technical Reference (Page 241).
The sensor value (in sensor units) is checked to see if it is within its measuring limits. If the
limit is exceeded, this results in a
Bad
status and the error message
Failure in measurement
.
The sensor value is stored in Sensor Value.
The analog signal from the sensor is transformed into a digital representation.
A Sensor Offset (default 0) compensates for changes to the sensor reference point, if
necessary.
2. Level Calibration is a linear transfer function that converts a sensor value to a level value.

Appendix B: PROFIBUS PA profile structure
B.2 Block Model
SITRANS LR250 (PROFIBUS PA)
Operating Instructions, 08/2014, A5E32221386-AC 269
① Distance/SV2 ⑥ Level
② High level point (default: 100%) ⑦ Low level point (default: 0%)
③ Sensor value a) ⑧ Level offset c)
④ High calibration point ⑨ Secondary value 1
⑤ Sensor reference point b) ⑩ Low calibration point
a) Referenced from Sensor Reference Point.
b)
Sensor Offset (2.3.7.3.)
is a constant offset that can be added to or subtracted from sensor
reference point to compensate if the sensor has been changed.
c) Level Offset (default O) can compensate for specific vessel configurations.
3. Linearization can be carried out to accommodate complex vessel shapes, or to provide level
to volume conversion.
4. The Transducer Block provides three possible outputs:
– Primary Value (PV) / Level or Volume
– Secondary Value 1 (SV1) / Level
– Secondary Value 2 (SV2) / Distance (sensor units)

Appendix B: PROFIBUS PA profile structure
B.2 Block Model
SITRANS LR250 (PROFIBUS PA)
270 Operating Instructions, 08/2014, A5E32221386-AC
Electronics temperature
The Transducer Block monitors the internal temperature of the device electronics. A change in
temperature can provide advance warning of a possible device failure, and allow for preventive
maintenance.
If a temperature limit is exceeded, the output value is unchanged but the output status changes.
(The permitted limits correspond to those of the permitted ambient temperature.)
Peak indicators allow you to check the maximum and minimum temperatures that have
occurred. To see peak temperature values, Open the menu
View – Device Diagnostics
, select
Device Status
, and click on the tab
Device Status
.
B.2.1.3
Analog Input Function Blocks 1 and 2
The input to the AIFB is a value with a status. See Transducer Block function groups (Page 267)
for a graphic representation.
Output conversion
The Analog Input Function Blocks can modify the output value.
Scaling
Output Scaling
(2.6.6.)
allows you to scale the output to any desired units.
Fail-safe
If the status of the input (TB output value or Simulation Value) is
bad
, the fault logic can output
either the last usable measured value, or a given substitute value. Set
Fail-safe Mode (2.6.9.)
and, if desired, define a value in
Value (2.6.9.2.)
.
Device/input simulation
You can define a simulated value to be input to the AIFB instead of the output value from the
Transducer Block. The simulated value allows the AIFB to be tested independently of the
characteristics of the environment.
Actual Mode: Device / Output Simulation
Actual Mode allows you to select one of three possible outputs.
Actual Mode
(2.6.2.)
Description
Output value
AUTO automatic the automatically-recorded measured value
MAN manual a manually-set fixed simulation value
O/S function block disabled the preset safety value.
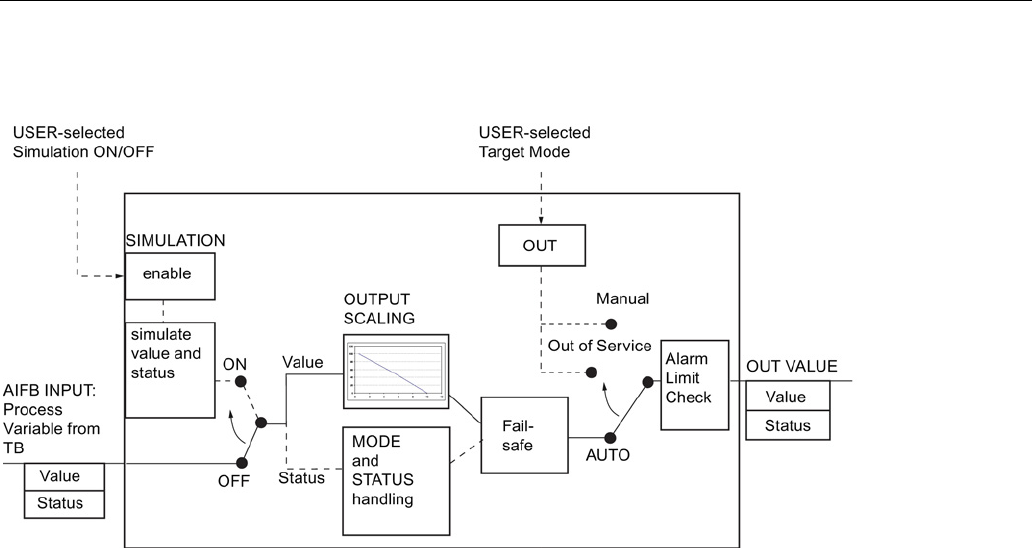
Appendix B: PROFIBUS PA profile structure
B.2 Block Model
SITRANS LR250 (PROFIBUS PA)
Operating Instructions, 08/2014, A5E32221386-AC 271
AIFB function groups
Analog Input Function Block function groups (simulation, mode and status)
Measured values are processed within an Analog Input Function Block to produce the device
output. See AIFB function groups (Page 271). The output is communicated via cyclic transfer to
PROFIBUS PA and displayed on the LCD.

Appendix B: PROFIBUS PA profile structure
B.2 Block Model
SITRANS LR250 (PROFIBUS PA)
272 Operating Instructions, 08/2014, A5E32221386-AC
How an Analog Input Function Block works
The AIFB provides a linear conversion to any desired units.
1. The AIFB Input value is the processed output value of the Transducer Block, in Transducer
Block units.
2. The user selects the desired AIFB output units and scaling is applied.
3. Damping may be applied based on a time constant provided by the user. See Damping
(Page 249) for details.
4. The status of the input value from the Transducer Block is checked. If the status is Bad, a
Fail-safe condition occurs. The output is determined by the setting for Failsafe Mode.
5.
Actual Mode (2.6.2.)
allows the entire AI block to be overridden by a Manual Output value.
See
Actual Mode (2.6.2.)
for details.
6. The value is checked against the user-defined warning and alarm limits. The upper and lower
limits are defined in units corresponding to the Output range, and a limit hysteresis can be
used to adjust the sensitivity. See
Alarms and Warnings (2.6.7.)
for details.
7. The output value (OUT) is communicated via cyclic data transfer.

Appendix B: PROFIBUS PA profile structure
B.2 Block Model
SITRANS LR250 (PROFIBUS PA)
Operating Instructions, 08/2014, A5E32221386-AC 273

SITRANS LR250 (PROFIBUS PA)
Operating Instructions, 08/2014, A5E32221386-AC 275
Appendix C: Communications via PROFIBUS
C
SITRANS LR250 (PROFIBUS PA) is a Profile Version 3.01, Class B, PA device. It supports
Class 1 Master for cyclic and acyclic data exchange, and Class 2 for acyclic services. The full
range of SITRANS LR250 functions is available only over a PROFIBUS PA network.
PROFIBUS PA is an open industrial protocol. Full details about PROFIBUS PA can be obtained
from PROFIBUS International at:
PROFIBUS PA (http://www.profibus.com/)
C.1
Device configuration
To use PROFIBUS PA, you will need a PC configuration tool: we recommend SIMATIC PDM.
Please consult the operating instructions or online help for details on using SIMATIC PDM. You
can find more information at:
SIMATIC PDM (www.siemens.com/simatic-pdm)
C.1.1
SIMATIC PDM
SIMATIC PDM is a software package used to commission and maintain SITRANS LR250 and
other process devices. For more detail see Functions in SIMATIC PDM (Page 75).
C.1.1.1
Electronic Device Description
In order to use
Process Device Manager (PDM)
with PROFIBUS PA, you will need the
Electronic Device Description for SITRANS LR250. For details see Electronic Device Description
(EDD) (Page 76).
C.2
Network configuration
To configure a PROFIBUS PA Class 1 Master (for example, a PLC), you will need a
GSD
file.
C.2.1
The GSD file
The GSD file
SIEM8150.gsd
is available from the SITRANS LR250 product page on our web
site. Go to the product page of our website and click on
Support > Software Downloads:
Product page (http://www.siemens.com/LR250)
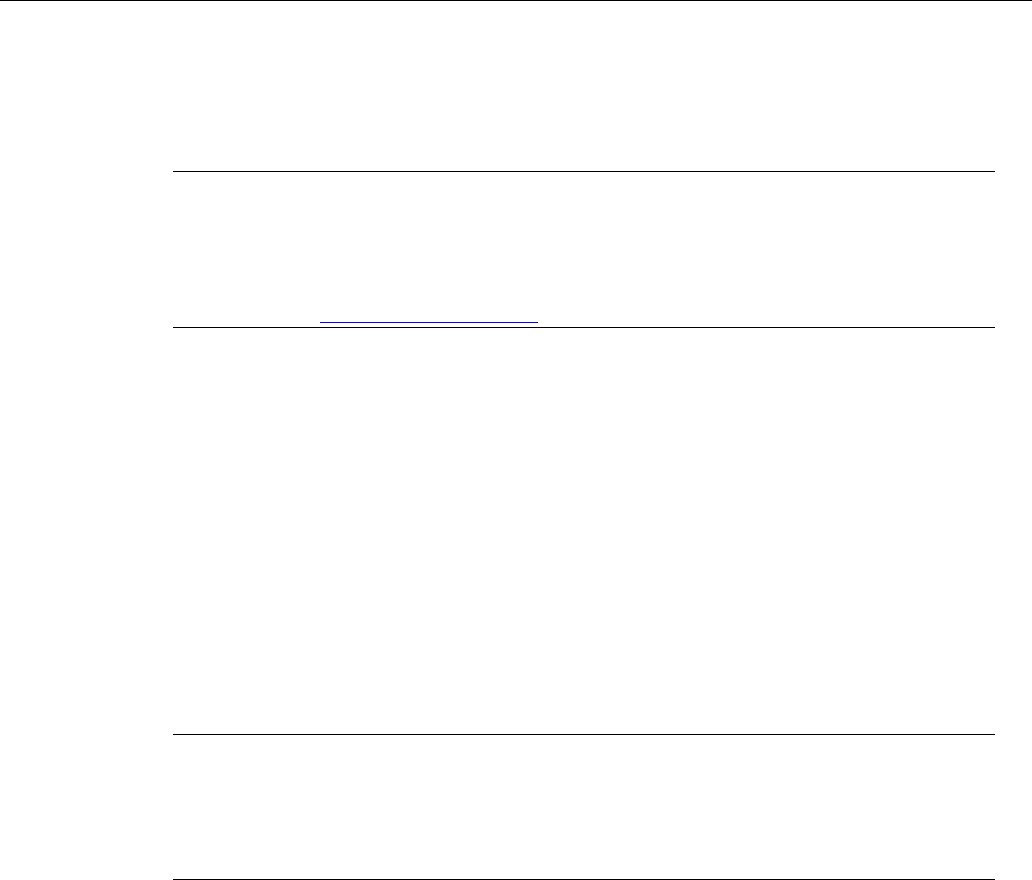
Appendix C: Communications via PROFIBUS
C.3 Bus termination
SITRANS LR250 (PROFIBUS PA)
276 Operating Instructions, 08/2014, A5E32221386-AC
C.3
Bus termination
Note
PROFIBUS PA cable shield MUST be terminated at both ends of the cable for it to work
properly. Please refer to the PROFIBUS PA User and Installation Guidelines (order number
2.092), available from:
PROFIBUS PA (http://www.profibus.com/)
C.4
Power demands
To determine how many devices can be connected to a bus line, calculate the combined
maximum current consumption of all the connected devices: 15 mA for SITRANS LR250. Allow
a current reserve for safety.
C.5
PROFIBUS address
A unique PROFIBUS address identifies each device on the network. To set the PROFIBUS
address see
Device Address (5.1.)
.
Note
• It is possible to change the device address via a Class 1 master (for example, a PLC) and
lock the device address to prevent further changes.
• If this Address Lock is on, the PA address cannot be changed. This lock can be
disabled only by performing an Address Reset.
Resetting the PROFIBUS address to 126
● Via SIMATIC PDM:
1. Open the menu
Device – Master Reset
and click on
Reset Address to 126
.
2. Click on OK: the address will be reset to 126, and if the address lock was on, it will be
disabled.
● Via the handheld programmer:

Appendix C: Communications via PROFIBUS
C.6 Operating as a profile device
SITRANS LR250 (PROFIBUS PA)
Operating Instructions, 08/2014, A5E32221386-AC 277
1. Navigate to
Service (4.) > Master Reset (4.1.)
. (You can enter the numeric value instead of
navigating via the Arrow keys.)
2. Press
RIGHT Arrow
to open Edit Mode then scroll down to
DEV ADDRESS
and press
RIGHT
Arrow
to select it. The address will be reset to 126, and if the address lock was on, it will be
disabled.
3. Press
LEFT
Arrow to exit.
C.6
Operating as a profile device
Every manufactured PROFIBUS product has a unique PROFIBUS identification number which
identifies it to the system. PROFIBUS Profile Standard version 3.01 also defines a Profile Model
which can identify a product as a generic profile device on the network.
SITRANS LR250 can be identified in one of three ways:
Device Identification
Profile Model
STD PROFILE
Standard Profile (uses generic GSD for 2 AIFB [ident # = 0x9701]
*
MANUFACTURER
Manufacturer-specific (uses Siemens EDD and GSD file, which
identifies the LR250 [PROFIBUS PA]) [ident # = 0x8150]
STD – AIFB 1 ONLY
Standard Profile AIFB 1 only (uses generic GSD for 1 AIFB) [ident #
= 0x9700]
Defining the device as Profile-specific as opposed to Manufacturer-specific makes it possible to
exchange the device for any other device of the same profile type without changing the GSD file.
To set up SITRANS LR250 as a profile device see
PROFIBUS Ident Number (5.2.)
.
C.6.1
Configuring a new device
See Configuring a new device (Page 77).
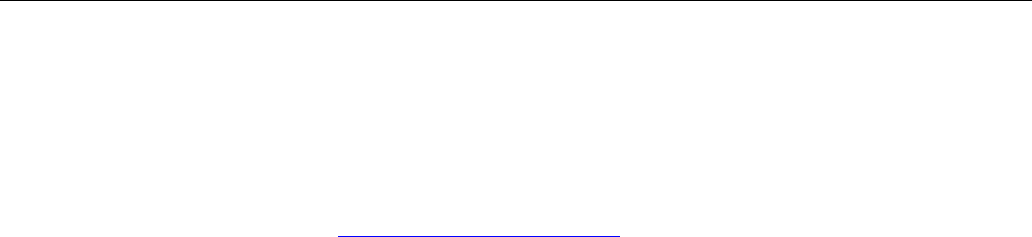
Appendix C: Communications via PROFIBUS
C.7 Cyclic versus acyclic data
SITRANS LR250 (PROFIBUS PA)
278 Operating Instructions, 08/2014, A5E32221386-AC
C.6.2
Configuring PROFIBUS PA with an S7-300/ 400 PLC
1. If SITRANS LR250 is not listed in the STEP 7 device catalog, you can download the EDD
files from the Siemens Web site and add them to your computer using the device integration
procedure specific to your host software (eg. Step 7, or PDM, etc.) version. Go to the product
page of our website and click on
Support > Software Downloads:
Product page (http://www.siemens.com/LR250)
2. Add the SITRANS LR250 "rack": click and drag the SITRANS LR250 folder from the
hardware catalog.
3. Fill the rack with desired modules, by dragging and dropping them from the hardware catalog.
4. After configuring PROFIBUS PA in steps 2 and 3, download it to the PLC.
5. Add code to the PLC program to read data consistently using the SFC14.
C.7
Cyclic versus acyclic data
When you request data from a device via PROFIBUS PA, you have two choices. Cyclic data is
provided at every bus scan: acyclic data is requested and provided as needed.
Input information is always requested at every bus scan and is set up as cyclic data.
Configuration information is only needed periodically and is set up as acyclic data.

Appendix C: Communications via PROFIBUS
C.7 Cyclic versus acyclic data
SITRANS LR250 (PROFIBUS PA)
Operating Instructions, 08/2014, A5E32221386-AC 279
C.7.1
Cyclic data
When you configure SITRANS LR250 on the PROFIBUS PA bus, there are two slots available
for modules.
Note
Each of the slots has to have a module defined in it.
Slot 0 always transmits
AIFB1
information; slot 1 defaults to Free Place, but can be changed to
AIFB2
information. If you do not wish to have data transmitted, then you must use a
Free Place
module in that slot.
Each of the two Analog Input Function Blocks can be set up to return
Level, Distance, or
Volume
. Within the function blocks, the values are scaled according to the user requirements
[see Analog Input Function Blocks 1 and 2 (Page 270) for details].
AIFB1
and
AIFB2
return 5 bytes of data each:
Floating Point
Status
AIFB1
byte 1 byte 2 byte 3 byte 4 byte 5
AIFB2
byte 6 byte 7 byte 8 byte 9 byte 10
The first 4 bytes are the floating point representation (IEEE) of the variable. The variables are
the outputs of the function block. The 5th byte is the status word and the list of possible values is
given in the chart below.
The 5 bytes must be read consistently, in a contiguous chunk: they cannot be read byte by byte,
and cannot suffer an interrupt. If you are using an S7-300 / 400, you will need to use SFC14
DPRD_DAT: Read Consistent Data of a Standard PD Slave.

Appendix C: Communications via PROFIBUS
C.8 Status byte
SITRANS LR250 (PROFIBUS PA)
280 Operating Instructions, 08/2014, A5E32221386-AC
C.8
Status byte
In PROFIBUS PA there are two possible types of status byte:
●
status byte
: originally defined in Profile Standard V3.0
●
condensed status
: an alternative status byte defined in Profile Standard V3.01
You can choose which type of status byte will be returned, by enabling or disabling
Condensed
Status (3.4.)
: see
Enable (3.4.1.)
for details. When Condensed Status is disabled, Status Byte
will be returned, and the following codes will be used.
Status Codes for good quality
Values in hex
notation
Description
0x80 Data is GOOD.
0x84 A parameter in the function block has been changed: status active for 10 s
0x89 Active low warning.
0x8A Active high warning.
0x8D Active low alarm.
0x8E Active high alarm.
Status Codes for Uncertain Quality
Values in hex
notation
Description
0x4B Value is a substituted value (normally used in Failsafe).
0x4C/0x4F Initial value.
0x47 Last usable value.
Status Codes for Bad Quality
Values in hex
notation
Description
0x10 The LOE timer has expired: this could be caused by LOE or by a sensor
malfunction: value is BAD.
0x01 There is an error in the configuration of the function blocks in PROFIBUS
PA a).
0X1F The function block, or the transducer block, has been placed out of
service.
a) This could happen when a firmware download has been done, but a system reset has not been
done. This could also happen if the function blocks are not configured properly using the handheld
programmer, PDM or acyclic services.

Appendix C: Communications via PROFIBUS
C.9 Condensed status
SITRANS LR250 (PROFIBUS PA)
Operating Instructions, 08/2014, A5E32221386-AC 281
C.9
Condensed status
These codes are available when Condensed Status is enabled. See
Condensed Status (3.4.)
for
more details.
Condensed Status (GOOD)
Hex value
Status - GOOD
Description
0x80 GOOD – ok No error or special condition is associated with this value.
0x84 GOOD – update event Set if the value is good and the block has an active Update
event. (This status remains active for 20 seconds.)
0x86 GOOD – active
advisory alarm
Set if the value is good and the block has an active Alarm.
0x80
...0x8E
GOOD – limit check/
update event
See Status Codes for Good Quality (Page 280).
0xA0
...0xA3
GOOD – initiate fail
safe
This fault is not generated by the product, but can be
simulated.
0xA4
...0xA7
GOOD – maintenance
required
Value is valid. Maintenance is recommended within a
medium-term period.
0xA8
...0xAB
GOOD – maintenance
demanded
Value is valid. Maintenance is demanded within a short- term
period.
0xBC
...0xBF
GOOD – function
check
Device performs internal function check without influencing
the process. Value is valid.

Appendix C: Communications via PROFIBUS
C.9 Condensed status
SITRANS LR250 (PROFIBUS PA)
282 Operating Instructions, 08/2014, A5E32221386-AC
Condensed Status (UNCERTAIN)
Hex value
Status - UNCERTAIN
Description
0x45 UNCERTAIN –
substitute set
Output of Failsafe logic only.
0x4F UNCERTAIN – initial
value
Default value as long as no measured value is available or
until a diagnosis is ma
de that affects the value and the status
accorded to it.
0x68
...0x6B
UNCERTAIN –
maintenance
demanded
Usability of the process value depends on the application.
Value is potentially invalid. Cause can be determined by
reading the extended diagnostics a). Maintenance is
demanded within a short-term period.
0x73 UNCERTAIN –
simulated value, start
Indicates the start of a simulation.
Simulation of a measured value or Input FB mode changes
from AUTO to MAN.
• This status remains active for at least 10 seconds:
– after enabling simulation
– after setting the FB to MAN mode
– after a restart (e.g. power down cycle) if the simulation
is enabled or the FB is in MAN mode
– after passivation is cleared if simulation is
enabled or the FB is in MAN mode
• In MAN mode the status remains until a subsequent write
command overwrites the OUT value after the 10 seconds
have expired.
• In simulation mode the written status is buffered and
appears in the value flow after 10 seconds. However the
new written SIMULATE parameter with its status can be
read before the 10 seconds have expired.
0x74
...0x77
UNCERTAIN –
simulated
value, end
Indicates the end of a simulation.
Simulation of a measured value is disabled or Input FB mode
changes from MAN to AUTO.
This Status remains active for 10 seconds after simulation
ends.
While this status is active there is no reliable process value.
Measured values and their status are updated
afterwards.
See Acyclic Extended Diagnostics (General Fault Codes) (Page 286).

Appendix C: Communications via PROFIBUS
C.10 Diagnostics
SITRANS LR250 (PROFIBUS PA)
Operating Instructions, 08/2014, A5E32221386-AC 283
Condensed Status (BAD)
Hex value
Status - BAD
Description
0x00 BAD – non specific Proxy determines that a device does not communicate.
0x23 BAD – passivated
(diagnostics
alerts disabled)
Configured failsafe value is used, accompanied by this
status.
0x24
...0x27
BAD – maintenance
alarm, more
diagnosis available
No measurement available because of a failure.
0x25 BAD – process
related, no
maintenance
No measurement available because of invalid process
conditions.
0x3C
...0x3F
BAD – function check
/ local override, value
not usable
Occurs during cleaning or calibration process.
C.10
Diagnostics
All diagnostic information shown below is viewable via PDM.
C.10.1
Diagnosis reply (available cyclically)
During DPV0 data exchange, the PROFIBUS PA slave will notify the Master when a serious
error occurs. The Master will then send a Diagnosis request. The reply to this request is normally
logged in the PLC and is referred to as the "Hex values."
The reply may contain two parts. The first part is 6 bytes long and is defined by the PROFIBUS
standard. If there is a second part, it is called the ’extended cyclic diagnosis’ and it is 8 bytes
long. The last 4 bytes of the extended diagnostic message give the error diagnosis [see
Extended Mode Diagnosis (Page 284) and Condensed Mode Diagnosis (Page 285)].
The same information is also available acyclically via the Diagnosis Object.

Appendix C: Communications via PROFIBUS
C.10 Diagnostics
SITRANS LR250 (PROFIBUS PA)
284 Operating Instructions, 08/2014, A5E32221386-AC
C.10.2
Diagnosis object (available cyclically or acyclically)
This consists of four bytes.
In PROFIBUS PA there are two options for the Diagnosis Object:
● Extended Mode Diagnosis (Page 284)
● Condensed Mode Diagnosis (Page 285)
You can choose which of these will be returned, by enabling or disabling Condensed Status.
See
Enable (3.4.1.)
. When Condensed Status is disabled
Extended Mode Diagnosis
will be
returned, and the following codes will be used.
C.10.3
Extended mode diagnosis
Extended Mode Diagnosis
Hex values
Byte
Bit
Description
Indication class
a)
0x01000000
0
0 Electronics failure R
0x02000000 1 Mechanical failure R
0x04000000 2 Motor Temperature too high R
0x08000000 3 Electronics temperature too high R
0x10000000 4 Memory error R
0x20000000 5 Measurement failure R
0x40000000 6 Device not initialized (no calibration) R
0x80000000 7 Self calibration failed R
0x00010000
1
0 Zero point error (limit position) R
0x00020000 1 Power supply failure (electrical, pneumatic) R
0x00040000 2 Configuration invalid R
0x00080000 3 New startup carried out (Warm Start) A
0x00100000 4 Restart carried out (Cold Start) A
0x00200000 5 Maintenance required R
0x00400000 6 Characterization invalid R
0x00800000 7 Set to 1 (one), if the Ident_Number of the running
cyclic data transfer and the value of Physical
Block IDENT__NUMBER_SELECTOR parameter
are different.
R
2 0 to 7 Reserved for use within the PNO
3 0 to 6 Reserved for use within the PNO
0x00000080 7 More diagnosis information is available
a)
R
indicates the message remains active as long as the reason for the message exists.
A
indicates the message will automatically reset after 10 seconds.
Values of the DIAGNOSIS bit:
0
= not set;
1
= set

Appendix C: Communications via PROFIBUS
C.10 Diagnostics
SITRANS LR250 (PROFIBUS PA)
Operating Instructions, 08/2014, A5E32221386-AC 285
C.10.4
Condensed mode diagnosis
Condensed Mode Diagnosis
Hex values
Byte
Bit
Description
Indication class
a)
0x01000000
0
0 Electronics failure R
0x02000000 1 Mechanical failure R
0x04000000 2 Motor Temperature too high R
0x08000000 3 Electronics temperature too high R
0x10000000 4 Memory error R
0x20000000 5 Measurement failure R
0x40000000 6 Device not initialized (no calibration) R
0x80000000 7 Self calibration failed R
0x00080000
2
3 New startup carried out (Warm Start) R
0x00100000 4 Restart carried out (Cold Start) R
0x00200000 5 Maintenance required R
0x00400000 6 Reserved for use within the PNO A
0x00800000
7
Set to 1 (one), if the Ident_Number of the running
cyclic data transfer and the value of Physical
Block IDENT__NUMBER_SELECTOR parameter
are different.
A
0x00010000
3
0 Failure of the device or armature R
0x00020000 1 Maintenance demanded R
0x00040000 2 Device is in function check mode, or simulation,
or under local control e.g. maintenance
R
0x00080000 3 The process conditions do not allow the return of
valid values. (Set if a value has the quality
Uncertain - Process related, no maintenance or
Bad - Process related, no maintenance.)
R
4 to 7 Reserved for use within the PNO
4 0 to 6 Reserved for use within the PNO
0x80000000 7 0: There is no more information available
1: More diagnosis information is available in
DIAGNOSIS_EXTENSION
a)
R
indicates the message remains active as long as the reason for the message exists.
A
indicates the message will automatically reset after 10 seconds.

Appendix C: Communications via PROFIBUS
C.10 Diagnostics
SITRANS LR250 (PROFIBUS PA)
286 Operating Instructions, 08/2014, A5E32221386-AC
C.10.5
Acyclic extended diagnostics (general fault codes)
In addition to the extended diagnostics available by cyclic data exchange (shown above), further
extended diagnostics are available via acyclic communications. This consists of six bytes. See
Diagnosis reply (available cyclically) (Page 283) for information on the location of the
Extended
Diagnostics.
Note
Certain fault codes (identified by an asterisk [*] in the table below) will persist until a manual
reset has been performed [see
Fault Reset (3.2.)
].

Appendix C: Communications via PROFIBUS
C.10 Diagnostics
SITRANS LR250 (PROFIBUS PA)
Operating Instructions, 08/2014, A5E32221386-AC 287
Acyclic Extended Diagnostics /General Fault Codes
LCD display
Meaning
Corrective Action
Byte
Bit
S:0
The device was unable to get a
measurement within the Failsafe LOE
Timer period. Possible causes: faulty
installation, antenna material buildup,
foaming/other adverse process
conditions, invalid calibration range.
• Ensure installation details are correct.
• Ensure no antenna material
buildup. Clean if necessary.
• Adjust process conditions to minimize
foam or other adverse conditions.
• Correct range calibration.
• If fault persists, contact your local
Siemens representative.
0
0
S:2
Unable to collect profile because of a
power condition that is outside the
operating range of the device.
Repair required. Contact your local
Siemens representative.
2
S:3
Device is nearing its lifetime limit
according to the value set in
Maintenance Required Limit.
Replacement is recommended. 3
S:4
Device is nearing its lifetime limit
according to the value set in
Maintenance Demanded Limit.
Replacement is recommended. 4
S:6
Sensor is nearing its lifetime limit
according to the value set in
Maintenance Required Limit.
Replacement is recommended. 6
S:7
Sensor is nearing its lifetime limit
according to the value set in
Maintenance Demanded Limit.
Replacement is recommended. 7
S:8
Service interval as defined in
Maintenance Required Limit has expired.
Perform service
0
S:9
Service interval as defined in
Maintenance Demanded Limit
has expired.
Perform service. 1
S:10
Input parameters High Calibration Point
and Low Calibration Point are the same.
• Check calibration settings of device.
• Ensure settings for High Calibration
Point and Low Calibration Point are
different.
3
S:11
Internal temperature sensor failure. Repair required. Contact your local
Siemens representative.
4
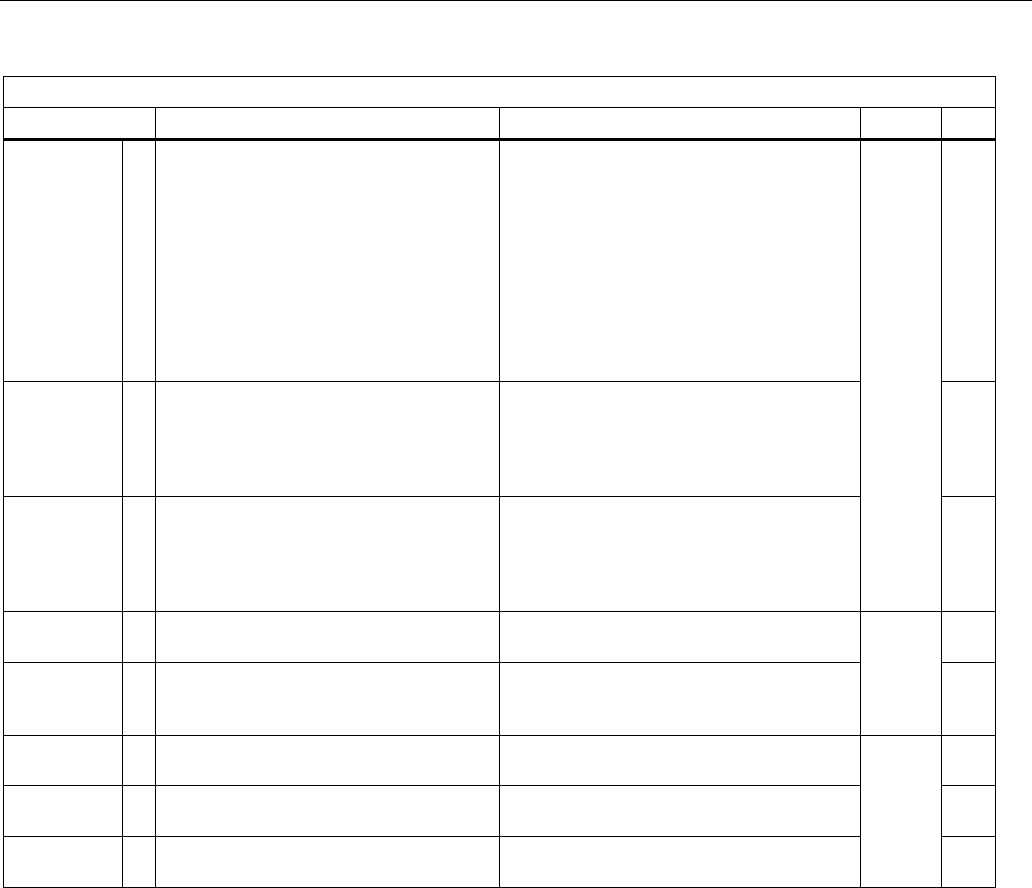
Appendix C: Communications via PROFIBUS
C.10 Diagnostics
SITRANS LR250 (PROFIBUS PA)
288 Operating Instructions, 08/2014, A5E32221386-AC
Acyclic Extended Diagnostics /General Fault Codes
LCD display
Meaning
Corrective Action
Byte
Bit
S:12
* Internal temperature of the device has
exceeded
specifications: it is operating outside its
temperature range.
• Relocate device and/or lower process
temperature enough to cool device.
• Inspect for heat-related damage and
contact your local Siemens
representative if repair is
required.
• Fault code will persist until a manual
reset is performed using PDM or the
LCD interface.
1
5
S:14
Upper and lower input values (Process
Value Scale) for AIFB1 are the same.
• Check configuration for AIFB1.
• Ensure that Upper Value and Lower
Value (Process Value Scale) are not
the same.
6
S:15
Upper and lower input values
(Process Value Scale) for AIFB2
are the same.
• Check configuration for AIFB2.
• Ensure that Upper Value and Lower
Value (Process Value Scale) are not
the same.
7
S:17
Calibration interval as defined in
Maintenance Required Limit has expired.
Perform calibration.
2
1
S:18
Calibration interval as defined in
Maintenance Demanded Limit has
expired.
Perform calibration. 2
S:28
Internal device failure caused by a RAM
memory error.
Repair required: contact your local
Siemens representative.
3
4
S:29
EEPROM damaged. Repair required: contact your local
Siemens representative.
5
S:31
Flash error. Repair required: contact your local
Siemens representative.
7

Appendix C: Communications via PROFIBUS
C.10 Diagnostics
SITRANS LR250 (PROFIBUS PA)
Operating Instructions, 08/2014, A5E32221386-AC 289
Acyclic Extended Diagnostics /General Fault Codes
LCD display
Meaning
Corrective Action
Byte
Bit
S:32
IDENT number conflict. Ensure value of the Ident number selector
is correct for the network configuration. If it
is correct, the device needs to be re-
parameterized by the PLC.
4
0
S:33
Factory calibration for the internal
temperature sensor has been lost.
Repair required: contact your local
Siemens representative.
1
S:34
Factory calibration for the device has
been lost.
Repair required: contact your local
Siemens representative.
2
S:35
Factory calibration for the device has
been lost.
Repair required: contact your local
Siemens representative.
3
S:36
Unable to start microwave module. Cycle power. If fault persists, contact your
local Siemens representative.
4
S:37
Measurement hardware problem. Cycle power. If fault persists, contact your
local Siemens representative.
5
S:38
Microwave module hardware failure:
unable to calculate distance
measurement.
Cycle power. If fault persists, contact your
local Siemens representative.
6
S:43
Factory calibration for the radar receiver
has been lost.
Repair required: contact your local
Siemens representative.
5 3
C.10.6
Acyclic data
SITRANS LR250 supports up to four simultaneous connections by a Class 2 Master (C2
connection). It supports one connection by a Class 1 Master (C1 connection).
In order for a Class 1 Master to read parameters from a device, it needs to know the slot and
absolute index of the parameter.
The parameters are all listed in SIMATIC PDM under Help. If you do not have SIMATIC PDM
you can download the EDD (Electronic Device Description) and reference the HTML help file
directly.
To find the slot and index numbers via SIMATIC PDM, go to Help > Communications, and select
the appropriate block from the list. For each parameter, the slot and the relative index is listed.
For example.

Appendix C: Communications via PROFIBUS
C.10 Diagnostics
SITRANS LR250 (PROFIBUS PA)
290 Operating Instructions, 08/2014, A5E32221386-AC
AIFB 1
Index
Parameter
Datatype
1 Static Revision No. UNSIGNED_INTEGER (2)
Each block has a slot number and an Index Offset value.
Block Name
Slot
Index Offset
Physical block 0 16
Transducer block 0 77
AIFB 1 1 16
AIFB 2 2 16
To get the absolute index for any parameter, add the Index Offset for the appropriate block to
the relative index for that parameter. The parameter takes the slot number of the block in which
it is located.
For example:
● Parameter
Static Revision Number
has relative index = 1 and is located on AIFB1.
● It has Absolute Index = 17 (relative index 1 + index offset 16).
● It is located at Slot 1 (the slot number for AIFB 1).
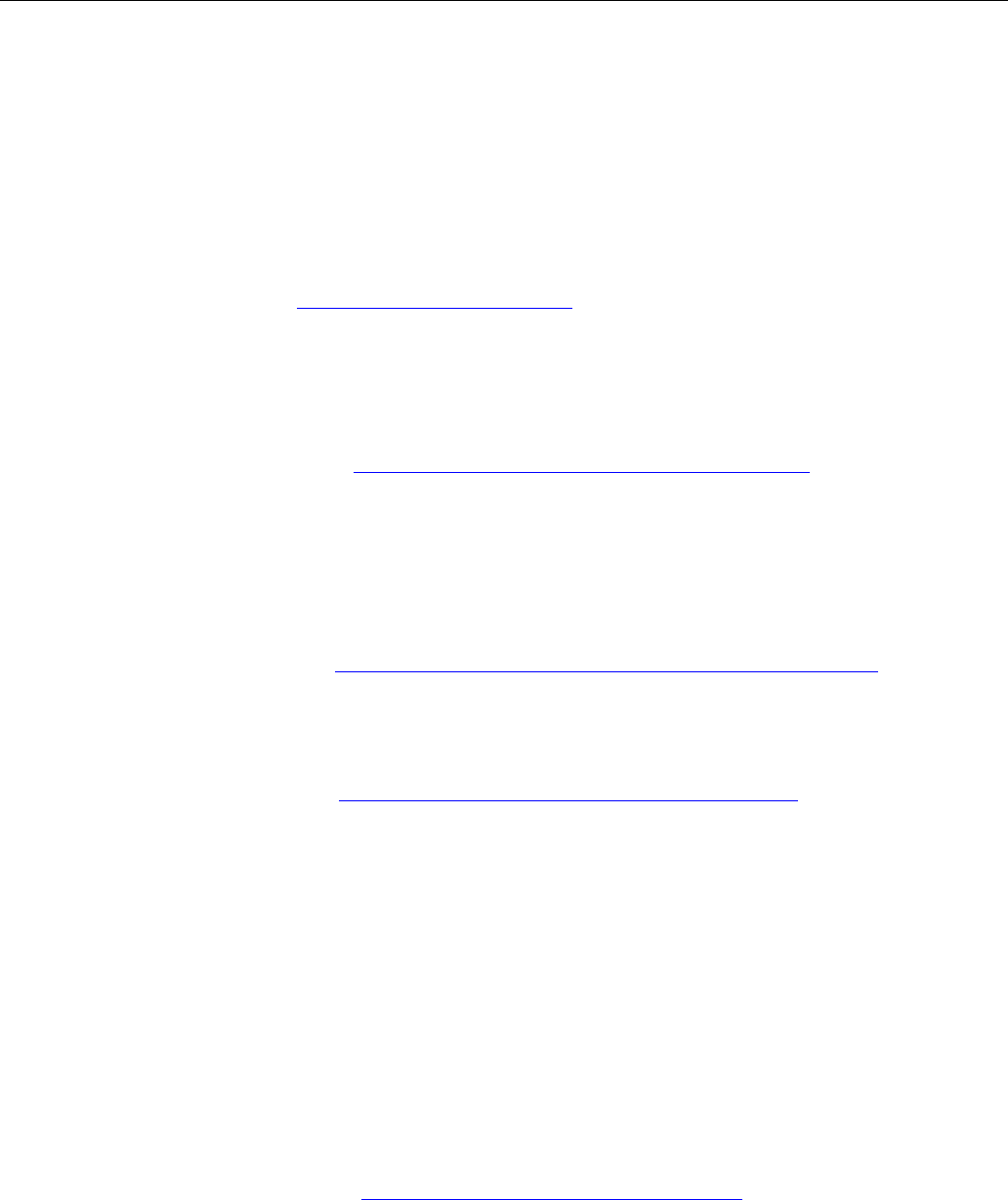
Appendix D: Certificates and Support
D.1 Certificates
SITRANS LR250 (PROFIBUS PA)
Operating Instructions, 08/2014, A5E32221386-AC 291
Appendix D: Certificates and Support
D
D.1
Certificates
Certificates can be downloaded from our website at:
Product page (http://www.siemens.com/LR250).
D.2
Technical support
If you have any technical questions about the device described in these Operating Instructions
and do not find the right answers, you can contact Customer Support:
● Via the Internet using the
Support Request:
Support request (http://www.siemens.com/automation/support-request)
● Via Phone:
– Europe: +49 (0)911 895 7222
– America: +1 423 262 5710
– Asia-Pacific: +86 10 6475 7575
Further information about our technical support is available on the Internet at
Technical support (http://support.automation.siemens.com/WW/view/en/16604318)
Service & Support on the Internet
In addition to our documentation, we offer a comprehensive knowledge base online on the
Internet at:
Service & Support (http://www.siemens.com/automation/service&support)
There you will find:
● The latest product information, FAQs, downloads, tips and tricks.
● Our newsletter, providing you with the latest information about your products.
● Our bulletin board, where users and specialists share their knowledge worldwide.
● You can find your local contact partner for Industry Automation and Drives Technologies in
our partner database.
● Information about field service, repairs, spare parts and lots more under "Services."
Additional Support
Please contact your local Siemens representative and offices if you have additional questions
about the device
Find your contact partner at:
Local contact person (http://www.siemens.com/automation/partner)

SITRANS LR250 (PROFIBUS PA)
Operating Instructions, 08/2014, A5E32221386-AC 293
List of abbreviations
13
Short form
Long form
Description
Units
3-A 3-A Sanitary Standards, Inc.
AIFB Analog Input Function Block
CE / FM / CSA Conformité Européene / Factory Mutual
/ Canadian Standards Association
safety approval
Ci Internal capacitance F
D/A Dialog to analog
DCS Distributed Control System control room apparatus
dK dielectric constant
EDD Electronic Device Description
EHEDG European Hygienic Engineering Design
Group
FEA Flanged Encapsulated Antenna
FDA Food and Drug Administration
HEA Hygienic Encapsulated Antenna
Ii Input current mA
Io Output current mA
IS Intrinsically Safe safety approval
Li Internal inductance mH
mH milliHenry 10-3 H
μF microFarad 10-6 F
μs microsecond 10-6 s
PED Pressure Equipment Directive safety approval
pF pico Farads 10-12 F
ppm parts per million
PV Primary Variable measured value
PVDF Polyvinylidene fluoride
SELV Safety extra low voltage
SV Secondary Variable equivalent value
TB Transducer Block
TFM1600 PTFE Modified PTFE polytetrafluoroethylene
with perfluoropropyl
vinyl ether (PPVE)
modifier
TVT Time Varying Threshold sensitivity threshold
Ui Input voltage V
Uo Output voltage V

List of abbreviations
SITRANS LR250 (PROFIBUS PA)
294 Operating Instructions, 08/2014, A5E32221386-AC

LCD menu structure
SITRANS LR250 (PROFIBUS PA)
Operating Instructions, 08/2014, A5E32221386-AC 295
LCD menu structure
14
Note
• In Navigation mode,
ARROW keys (
)
navigate the menu in the direction of
the arrow. See Parameter Reference (Page 107) for detailed information and
instructions.

LCD menu structure
SITRANS LR250 (PROFIBUS PA)
296 Operating Instructions, 08/2014, A5E32221386-AC
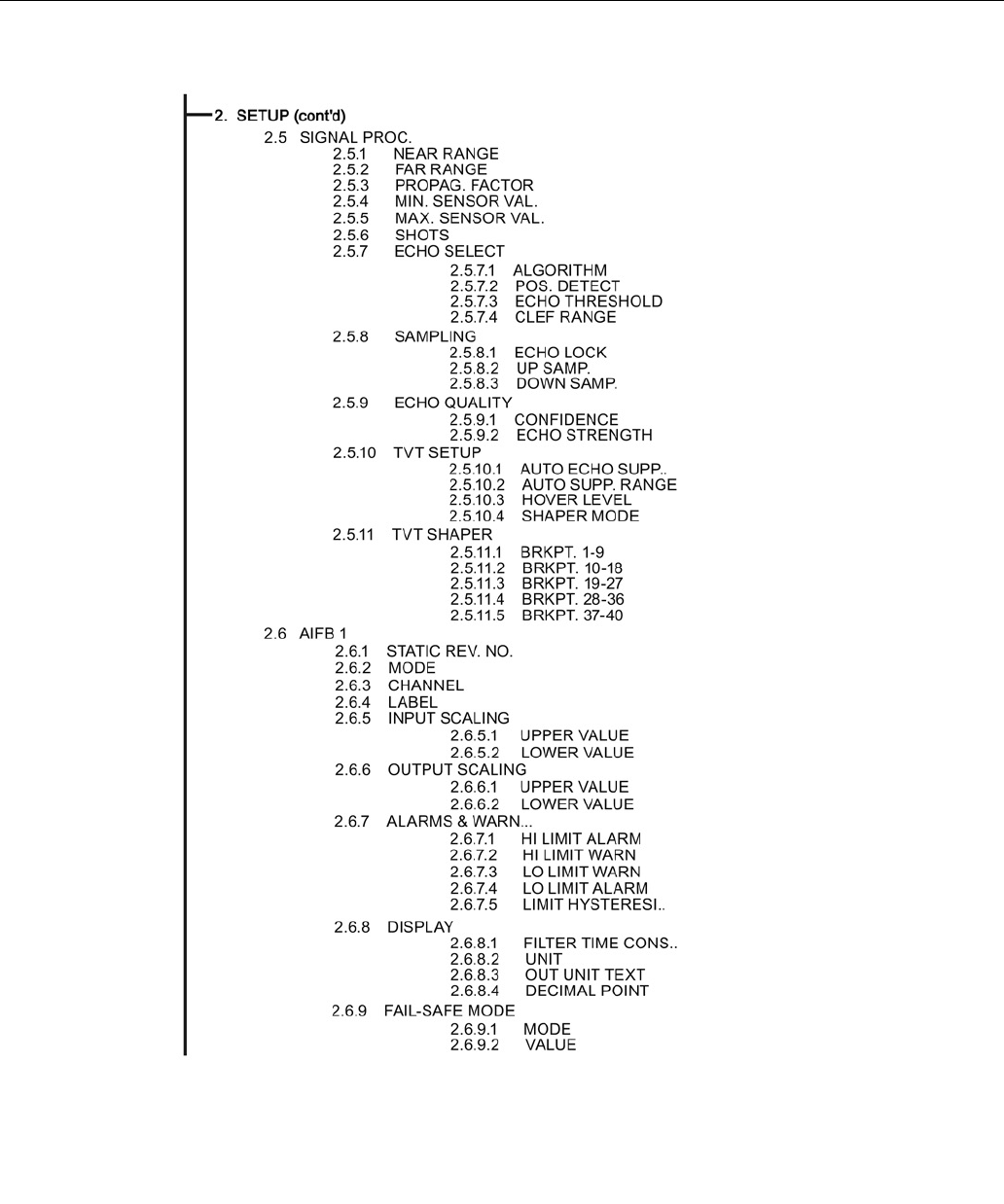
LCD menu structure
SITRANS LR250 (PROFIBUS PA)
Operating Instructions, 08/2014, A5E32221386-AC 297

LCD menu structure
SITRANS LR250 (PROFIBUS PA)
298 Operating Instructions, 08/2014, A5E32221386-AC
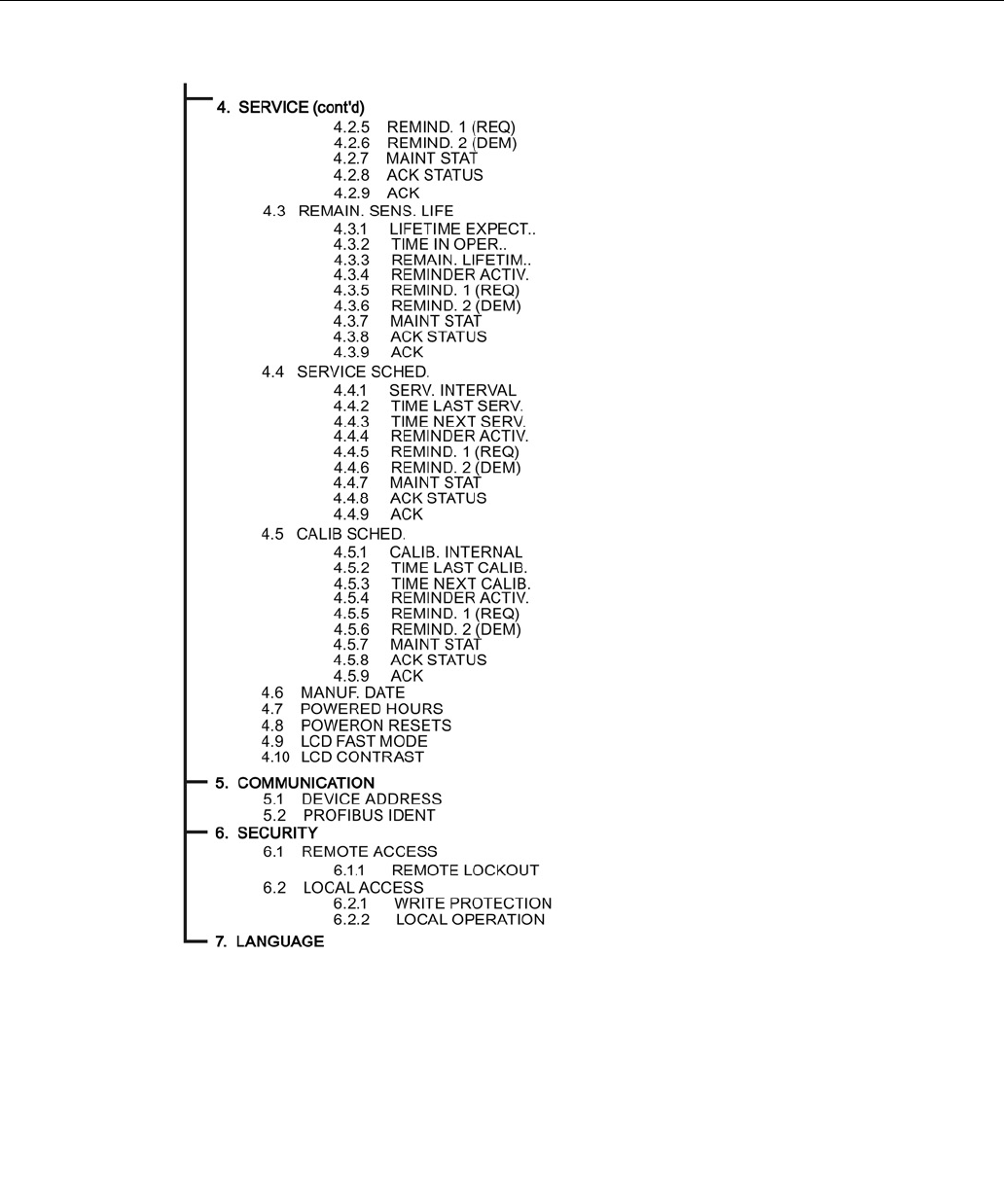
LCD menu structure
SITRANS LR250 (PROFIBUS PA)
Operating Instructions, 08/2014, A5E32221386-AC 299

LCD menu structure
SITRANS LR250 (PROFIBUS PA)
300 Operating Instructions, 08/2014, A5E32221386-AC
SITRANS LR250 (PROFIBUS PA)
Operating Instructions, 08/2014, A5E32221386-AC 301
Glossary
accuracy
degree of conformity of a measure to a standard or a true value.
agitator
mechanical apparatus for mixing or aerating. A device for creating turbulence.
algorithm
a prescribed set of well-defined rules or processes for the solution of a problem in a finite
number of steps.
ambient temperature
the temperature of the surrounding air that comes in contact with the enclosure of the device.
antenna
an aerial which sends out and receives a signal in a specific direction. There are four basic types
of antenna in radar level measurement, horn, parabolic, rod, and waveguide.
attenuation
a term used to denote a decrease in signal magnitude in transmission from one point to another.
Attenuation may be expressed as a scalar ratio of the input magnitude to the output magnitude
or in decibels.
Auto False-Echo Suppression
a technique used to adjust the level of a TVT to avoid the reading of false echoes. (See TVT.)
Auto-False Echo Suppression Distance
defines the endpoint of the TVT distance. (See TVT.) This is used in conjunction with auto false
echo suppression.
beam angle
the angle diametrically subtended by the one-half power limits (-3 dB) of the microwave beam.
beam spreading
the divergence of a beam as it travels through a medium.
blanking
a blind zone extending away from the reference point plus any additional shield length.The
device is programmed to ignore this zone.
capacitance
the property of a system of conductors and dielectrics that permits the storage of electricity when
potential differences exist between the conductors. Its value is expressed as the ratio of a
quantity of electricity to a potential difference, and the unit is a Farad.
confidence
see Echo Confidence.
damping
term applied to the performance of a device to denote the manner in which the measurement
settles to its steady indication after a change in the value of the level.
dB (decibel)
a unit used to measure the amplitude of signals.
derating
to decrease a rating suitable for normal conditions according to guidelines specified for different
conditions.
dielectric
a nonconductor of direct electric current. Many conductive liquids/electrolytes exhibit dielectric
properties; the relative dielectric constant of water is 80.
dielectric constant (dK)
the ability of a dielectric to store electrical potential energy under the influence of an electric field.
Also known as Relative Permittivity. An increase in the
dielectric constant is directly proportional to an increase in signal amplitude. The value is usually
given relative to a vacuum /dry air: the dielectric constant of air is 1.
echo
a signal that has been reflected with sufficient magnitude and delay to be perceived in some
manner as a signal distinct from that directly transmitted. Echoes are frequently measured in
decibels relative to the directly transmitted signal.
Echo Confidence
describes the quality of an echo. Higher values represent higher quality. Echo Threshold defines
the minimum value required for an echo to be accepted as valid and evaluated.
Echo Lock Window
a window centered on an echo in order to locate and display the echo’s position and true
reading. Echoes outside the window are not immediately processed.
Echo Marker
a marker that points to the processed echo.
Echo Processing
the process by which the radar unit determines echoes.
Echo Profile
a graphical display of a processed echo.
Echo Strength
describes the strength of the selected echo in dB referred to 1 μV rms.
false Echo
any echo which is not the echo from the desired target. Generally, false echoes are created by
vessel obstructions.
frequency
the number of periods occurring per unit time. Frequency may be stated in cycles per second.
hertz (Hz):
unit of frequency, one cycle per second. 1 Gigahertz (GHz) is equal to 109 Hz.
horn antenna
a conical, horn-shaped antenna which focuses microwave signals. The larger the horn diameter,
the more focused the radar beam.
inductance
the property of an electric circuit by virtue of which a varying current induces an electromotive
force in that circuit or in a neighboring circuit. The unit is a Henry.
microwaves
the term for the electromagnetic frequencies occupying the portion of the radio frequency
spectrum from 1 GHz to 300 GHz.
multiple echoes
secondary echoes that appear as double, triple, or quadruple echoes in the distance from the
target echo.
Near Blanking
see Blanking.
nozzle
a length of pipe mounted onto a vessel that supports the flange.
parameters
in programming, variables that are given constant values for specific purposes or processes.
polarization
the property of a radiated electromagnetic wave describing the time-varying direction and
amplitude of the electric field vector.
polarization error
the error arising from the transmission or reception of an electromagnetic wave having a
polarization other than that intended for the system.
PROFIBUS PA
one of the PROFIBUS family of protocols, specifically tailored for the needs of process industries
(PA = Process Automation).
propagation factor (pf)
where the maximum velocity is 1.0, pf is a value that represents a reduction in propagation
velocity as a result of the wave travelling through a pipe or
medium.
pulse radar
a radar type that directly measures distance using short microwave pulses. Distance is
determined by the return transit time.
radar
radar is an acronym for RAdio Detection And Ranging. A device that radiates electromagnetic
waves and utilizes the reflection of such waves from distant objects to determine their existence
or position.
range
distance between a transmitter and a target.
range extension
the distance below the zero percent or empty point in a vessel.
relative permittivity
see dielectric constant.
repeatability
the closeness of agreement among repeated measurements of the same variable under the
same conditions.
shot
one transmit pulse or measurement.
speed of light
the speed of electromagnetic waves (including microwave and light) in free space. Light speed is
a constant 299, 792, 458 meters per second.
stilling-well
see stillpipe.
stillpipe
a pipe that is mounted inside a vessel parallel to the vessel wall, and is open to the vessel at the
bottom.
TVT (Time Varying Threshold)
a time-varying curve that determines the threshold level above which echoes are determined to
be valid.
two wire radar
a low-energy radar. Can be loop powered, analog, intrinsically safe 4 to 20 mA, or a digital
(BUS) transmitter.
waveguide antenna
a hollow, metallic tube that transmits a microwave signal to the product target.
Index
A
Abbreviations and identifications list, 291
access control
local access, 166
remote access, 166
Acknowledge Faults
via PDM, 93
activating SITRANS LR250, 54
acyclic diagnostics
fault codes, 282
agitator blade detection
avoiding, 126
antenna
replacement, 175
antenna types
flanged encapsulated antenna, 205, 207
flanged horn antenna, 201
flanged horn antenna with extension, 203
threaded horn, 195
threaded PVDF antenna, 227
Auto False Echo Suppression
explanation, 246
setup, 128
setup via LUI, 130
TVT Shaper adjustment, 86
via PDM, 85, 88
B
beam angle
flanged encapsulated antenna, 205, 207
flanged horn, 201, 203
threaded horn, 197, 199
threaded PVDF antenna, 227
blanking (see Near Range), 248
bolting instructions, 37
bus address (device address)
resetting to 126, 276
bus termination, 276
bypass pipe
see stillpipe, 32
C
cables
requirements, 42
Calibration Interval, 161
calibration schedules via PDM, 91
cleaning
instructions, 173
CLEF (Constrained Leading Edge Fit)
explanation, 244
CLEF range
setup, 125
Condensed Status
explanation, 280
conduits
requirements, 42
configuration
network, 275
new device via PDM, 77
PLC with PROFIBUS PA, 44
Quick Start via LUI, 63
Correct usage, (See improper device modifications)
cyclic data
versus acyclic data, 278
D
damping
Filter Time Constant setup, 136
Damping
explanation, 249
data logging
time-based echo profile storage, 86
Device Address, 165
reset via LUI, 67
device description
Electronic Device Description, 275
Device Description (DD)
see EDD, 76
device namepate
Intrinsically Safe (FM/CSA), 47
device nameplate
FM/CSA Class 1 Div. 2 28, 49

Index
SITRANS LR250 (PROFIBUS PA)
308 Operating Instructions, 08/2014, A5E32221386-AC
Intrinsically Safe (ATEX/IECEx), 46
Device Reset
see Master Reset, 146
Device Status
icons, 180
view via PDM, 101
diagnosis reply, 282
Diagnostics
maintenance settings, 138
via PDM, 98
dimensions
flanged encapsulated antenna, 205, 207
flanged horn, 201, 203
flat face flange, 234
raised face flange
, 229, 231
threaded horn with extension, 197, 199
threaded PVDF antenna, 227
E
echo confidence
parameter setup, 127
echo processing
Process Intelligence, 242
Echo Profile
data logging, 86
view via LUI, 66
view via PDM, 85
Echo Profile Utilities
Auto False Echo Suppression, 84
Echo Profile, 84
TVT Shaper, 84
echo selection
Algorithm, 243
CLEF (Constrained Leading Edge Fit), 244
Position Detect, 243
time varying threshold (TVT), 242
Echo Setup
quick access via PDM, 91
EDD
updating, 77
EDD (electronic device description), 275
edit mode
handheld programmer, 59
key functions, 62
Electronic Device Description (EDD)
required for PROFIBUS PA, 76
updating, 77
Empty rate
setup, 115
enable/disable local operation, 166
enable/disable remote operation, 166
enclosure
opening, 43
F
factory defaults
Master Reset, 146
Factory Defaults
reset via PDM, 97
Fail-safe
Behavior explanation, 250
Mode explanation, 250
Value explanation, 251
Fail-safe Mode FB1
setup, 137
false echo
see Auto False Echo Suppression, 246
Far Range
explanation, 248
setup, 121
fault codes
acyclic diagnostics, 282
acyclic extended diagnostics, 285
general fault codes, 181
Fill Rate
setup, 114
Filter Time Constant
explanation, 249
flange
bolting instructions, 37
flange markings
flat face, 234
raised face, 229, 232
flange sizes
flat face, 234
raised face
, 229, 231
flanged encapsulated antenna
dimensions, 207
flanged horn
dimensions, 201, 203
Function Blocks
view process variables via PDM, 99

Index
SITRANS LR250 (PROFIBUS PA)
Operating Instructions, 08/2014, A5E32221386-AC 309
function keys
edit mode, 62
navigation mode, 59
Function keys
measurement mode, 57
G
GSD file, 276
H
handheld programmer
edit mode, 60, 62
measurement mode, 57
navigation, 59
programming, 58
hazardous area installations
instructions, 50
wiring requirements, 45
hysteresis
setup, 136
I
Identifications and abbreviations
list, 291
Improper device modifications, 16
installation
hazardous area requirements, 45
requirements, 34
warnings and notes, 34
internal temperature
monitoring, 251
K
key functions
edit mode, 62
navigation mode, 59
L
Language, 167
LCD display
contrast adjustment, 164
echo profile viewing, 66
fast mode, 164
measurement mode, 55
lens
replacement, 175
lid-lock set screw, 43
Limit Hysteresis
setup, 136
Lithium batteries
Safety, 53
Local Operation
enable/disable, 166
Local User Interface (LUI), 55
LOE Timer
explanation, 250
setup, 111
loop voltage vs. loop resistance
power supply requirements, 47
loss of echo (LOE)
explanation, 250
Loss of Echo (LOE)
explanation, 250
LUI (Local User Interface
contrast adjustment, 55
M
maintenance
calibration schedules, 92
repairs, 173
replacing antenna, 175
replacing lens, 175
service schedules, 92
Maintenance, 174
maintenance settings
Calibration Interval, 161
see Diagnostics, 138
see Remaining Sensor Lifetime, 153
Service Interval, 156
Master Reset
factory defaults, 146
reset PROFIBUS address (to 126), 146
standard defaults, 146
Measurement Response
explanation, 249
mounting

Index
SITRANS LR250 (PROFIBUS PA)
310 Operating Instructions, 08/2014, A5E32221386-AC
bypass requirements, 32
handheld programmer access, 30
housing construction, 24, 31
nozzle design, 27, 253
nozzle location, 28, 253
on vessel with obstructions, 31
sunshield recommended, 31
N
nameplate
Intrinsically Safe (ATEX/IECEx), 46
Intrinsically Safe (FM/CSA), 47
Near Range
explanation, 248
setup, 121
O
operating principles
cleaning, 241
Operation
level, distance, space, 108
Output limits
setup, 135
Output Scale
setup, 134
overview, 19
P
parameters
reset via PDM, 83
password protection
via PDM, 104
PDM
see SIMATIC PDM, 75
peak values
electronics temperature, 102
sensor peak values FB1 and FB2, 103
PED (Pressure Equipment Directive), 23, 253
performance
specifications, 187
pipe sizes
flange mounting
, 229, 231
polarization reference point, 31
power consumption, 276
power source
requirements, 41
pressure applications, 23
Pressure Equipment Directive, 23, 253
Process Intelligence, 242
process temperature
maximum, 251
Process Variables
view via PDM, 98
PROFIBUS address
reset to 126, 146
PROFIBUS address 145, 276
PROFIBUS Ident Number, 165
programmer
handheld, 57
programming
adjust parameters via PDM, 83
via the handheld programmer, 58
programming LR250
enter program mode, 59
via handheld programmer, 59
propogation factor
values, 122
Q
Qualified personnel, 17
Quick Start Wizard
via LUI, 63
via SIMATIC PDM, 78
R
raised face flange markings, 228, 230
reading erratic
troubleshooting, 185
reading incorrect
troubleshooting, 185
reading response slow, 185
Remote Lockout, 166
repair
cautions, 175
excluded liability, 175
reset
see Master Reset, 146
Response Rate

Index
SITRANS LR250 (PROFIBUS PA)
Operating Instructions, 08/2014, A5E32221386-AC 311
explanation, 249
setup, 114
S
Scope of delivery, 11
sensor reference point
flanged encapsulated antenna, 205, 207
flanged horn, 201, 203
flat faced flange, 234
raised face flange, 228, 230
threaded horn, 197, 199
threaded PVDF horn, 227
Service Interval, 156
service schedules via PDM, 91
settings
adjust parameters via LUI, 62
adjust parameters via PDM, 58, 83
sidepipe
see bypass pipe, 32
SIMATIC PDM
functions and features, 75
overview, 275
Rev 5.2, SP1 features, 76
Rev 6.0, SP4 features, 76
Simulate Analog Input
via PDM, 94
Simulate Input
via PDM, 96
Simulate Output
via PDM, 95
Simulation
via PDM, 93
SITRANS LR250
operating principles, 241
startup
transition screen, 54
status byte
status codes, 279
status codes, 279
stillpipe
mounting requirements, 32
Support
contact information, 289
T
technical data, 187
ambient temperature, 192
antenna, 190
enclosure, 190
environmental, 192
performance, 187
pressure, 192
process connections, 189
process temperature, 192
weight, 190
technical support
contact information, 289
temperature de-Rating
curves, 253
threaded connection markings, 227
threaded horn antenna
dimensions, 197, 199
threaded PVDF antenna
dimensions, 227
trend view
via PDM, 100
troubleshooting
communication, 179
operation, 184
TVT (time varying threshold)
explanation, 242
TVT Shaper
manual adjustment via PDM, 87
via PDM, 84
V
vessel shape
selection, 116
W
Wear
powered hours, 93
poweron resets, 93
view via PDM, 93
wiring
cables, 42
hazardous areas, 45
Write Locking
via PDM, 96
Write Protection, 166

Index
SITRANS LR250 (PROFIBUS PA)
312 Operating Instructions, 08/2014, A5E32221386-AC

Index
SITRANS LR250 (PROFIBUS PA)
Operating Instructions, 08/2014, A5E32221386-AC 313