Siemens Canada Siemens Milltronics Process Instruments LR250 SITRANS LR 250 TANK LEVEL PROBING RADAR User Manual SITRANS LR250 FOUNDATION FIELDBUS
Siemens Canada Ltd. - Siemens Milltronics Process Instruments SITRANS LR 250 TANK LEVEL PROBING RADAR SITRANS LR250 FOUNDATION FIELDBUS
Contents
User Manual 3
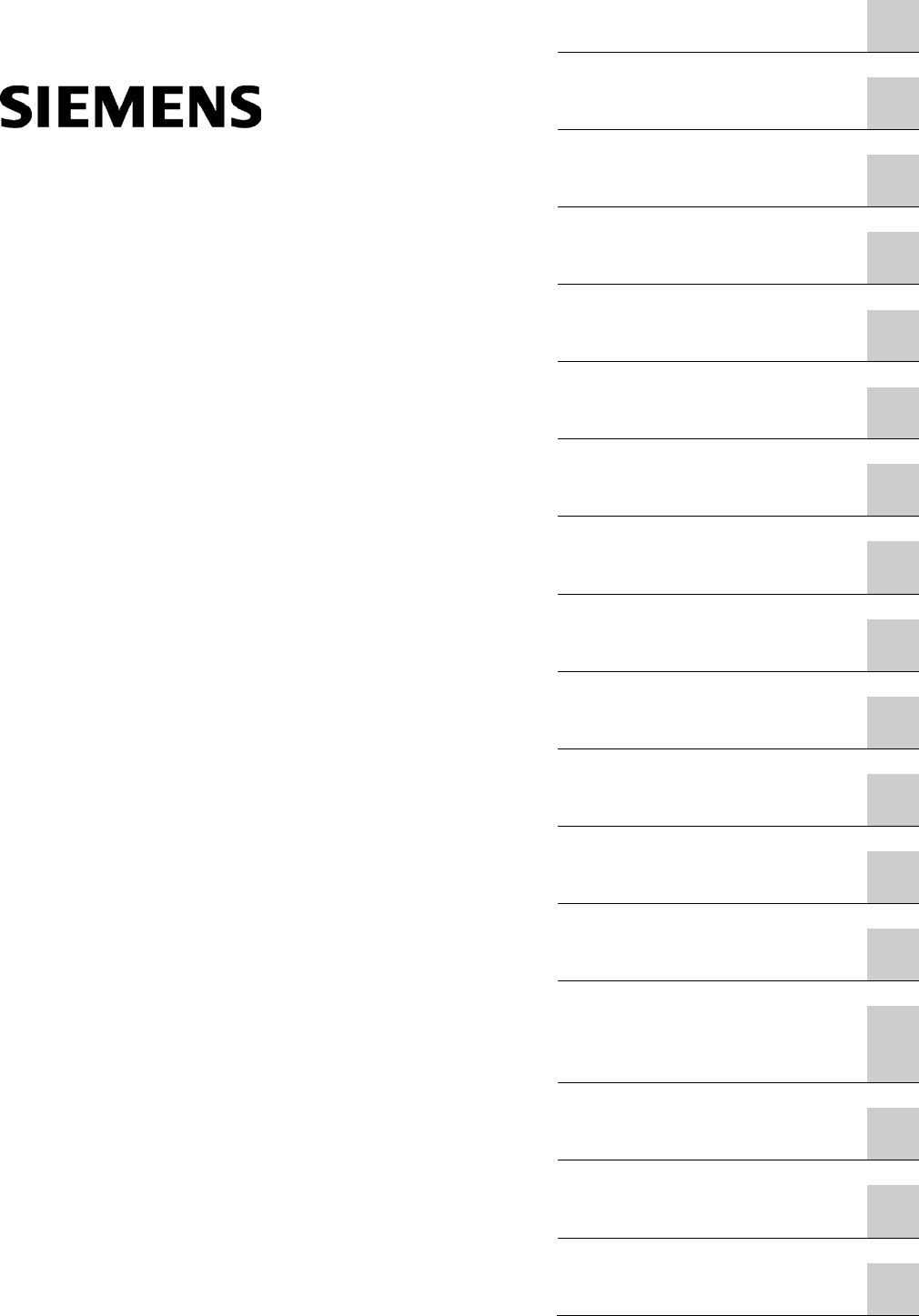
SITRANS LR250 (FOUNDATION
FIELDBUS)
___________________
___________________
___________________
___________________
___________________
___________________
___________________
___________________
___________________
___________________
___________________
___________________
___________________
___________
___________________
___________________
___________________
SITRANS
Radar Transmitters
SITRANS LR250 (FOUNDATION
FIELDBUS)
Operating Instructions
08/2014
A5E32221411-AC
Introduction
1
Safety information
2
Description
3
Installing/mounting
4
Connecting
5
Commissioning
6
Remote operation
7
Parameter reference
8
Service and maintenance
9
Diagnosing and
troubleshooting
10
Technical data
11
Dimension drawings
12
Appendix A: Technical
reference
A
Appendix B:
Communications via
Foundation Fieldbus
B
Appendix C: Certificates and
support
C
List of abbreviations
13
LCD menu structure
14
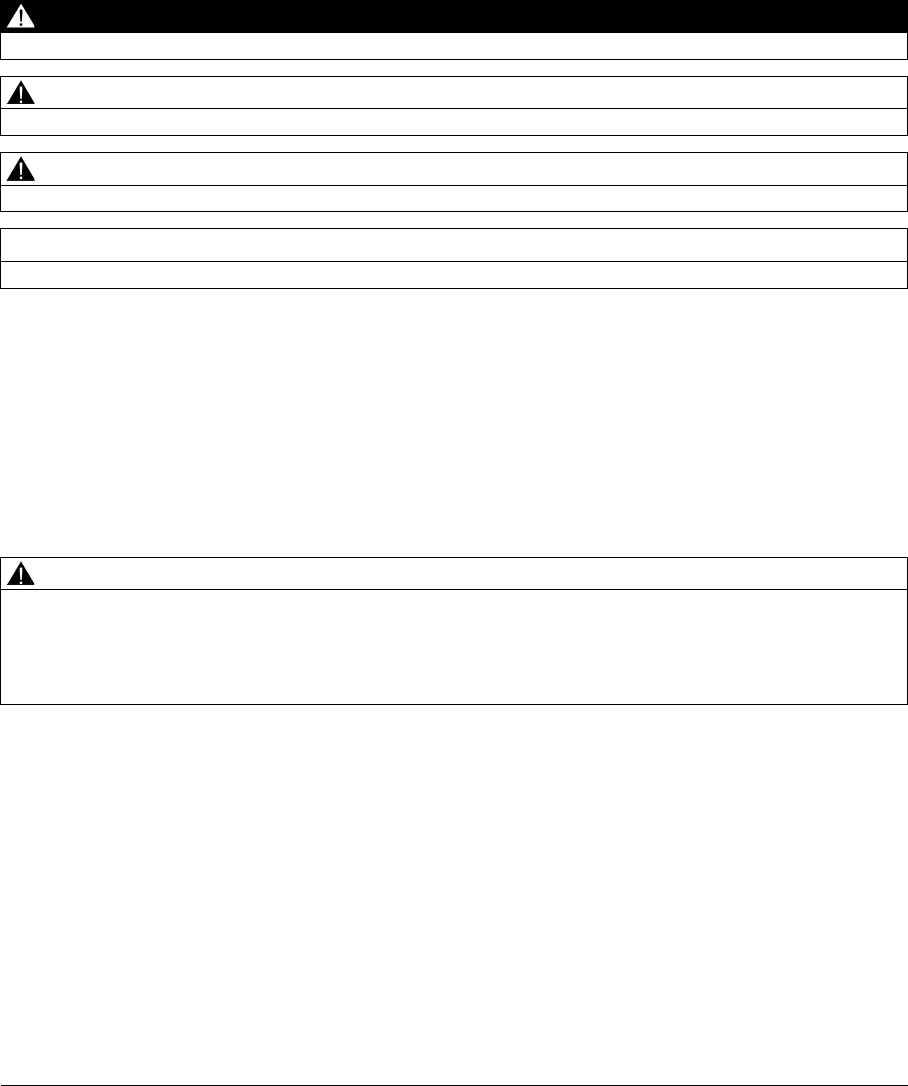
Siemens AG
Industry Sector
Postfach 48 48
90026 NÜRNBERG
GERMANY
Order number: A5E32221411
Ⓟ 05/2014 Subject to change
Copyright © Siemens AG 2014.
All rights reserved
Legal information
Warning notice system
This manual contains notices you have to observe in order to ensure your personal safety, as well as to prevent
damage to property. The notices referring to your personal safety are highlighted in the manual by a safety alert
symbol, notices referring only to property damage have no safety alert symbol. These notices shown below are
graded according to the degree of danger.
DANGER
indicates that death or severe personal injury
will
result if proper precautions are not taken.
WARNING
indicates that death or severe personal injury
may
result if proper precautions are not taken.
CAUTION
indicates that minor personal injury can result if proper precautions are not taken.
NOTICE
indicates that property damage can result if proper precautions are not taken.
If more than one degree of danger is present, the warning notice representing the highest degree of danger will be
used. A notice warning of injury to persons with a safety alert symbol may also include a warning relating to property
damage.
Qualified Personnel
The product/system described in this documentation may be operated only by
personnel qualified
for the specific task
in accordance with the relevant documentation, in particular its warning notices and safety instructions. Qualified
personnel are those who, based on their training and experience, are capable of identifying risks and avoiding
potential hazards when working with these products/systems.
Proper use of Siemens products
Note the following:
WARNING
Siemens products may only be used for the applications described in the catalog and in the relevant technical
documentation. If products and components from other manufacturers are used, these must be recommended
or approved by Siemens. Proper transport, storage, installation, assembly, commissioning, operation and
maintenance are required to ensure that the products operate safely and without any problems. The permissible
ambient conditions must be complied with. The information in the relevant documentation must be observed.
Trademarks
All names identified by ® are registered trademarks of Siemens AG. The remaining trademarks in this publication may
be trademarks whose use by third parties for their own purposes could violate the rights of the owner.
Disclaimer of Liability
We have reviewed the contents of this publication to ensure consistency with the hardware and software described.
Since variance cannot be precluded entirely, we cannot guarantee full consistency. However, the information in this
publication is reviewed regularly and any necessary corrections are included in subsequent editions.
SITRANS LR250 (FOUNDATION FIELDBUS)
Operating Instructions, 08/2014, A5E32221411-AC 3
Table of contents
1 Introduction ........................................................................................................................................... 11
1.1 LR250 FF manual usage ............................................................................................................. 11
1.2 Purpose of this documentation .................................................................................................... 11
1.3 Document history ......................................................................................................................... 11
1.4 Firmware revision history ............................................................................................................. 12
1.5 Designated use ............................................................................................................................ 12
1.6 Checking the consignment ........................................................................................................... 13
1.7 Transportation and storage .......................................................................................................... 13
1.8 Notes on warranty ........................................................................................................................ 13
2 Safety information ................................................................................................................................. 15
2.1 Preconditions for safe use ........................................................................................................... 15
2.1.1 Safety marking symbols ............................................................................................................... 15
2.1.2 Laws and directives ..................................................................................................................... 15
2.1.3 FCC Conformity ........................................................................................................................... 15
2.1.4 Conformity with European directives ........................................................................................... 16
2.1.5 CE Electromagnetic Compatibility (EMC) Conformity.................................................................. 17
2.2 Improper device modifications ..................................................................................................... 17
2.3 Requirements for special applications ......................................................................................... 18
2.4 Use in hazardous areas ............................................................................................................... 18
3 Description ............................................................................................................................................ 19
3.1 SITRANS LR250 overview ........................................................................................................... 19
3.2 Programming ................................................................................................................................ 20
3.3 Applications .................................................................................................................................. 20
3.4 Approvals and certificates ............................................................................................................ 20
4 Installing/mounting ................................................................................................................................ 21
4.1 Basic safety information ............................................................................................................... 21
4.1.1 Pressure applications ................................................................................................................... 22
4.1.1.1 Pressure Equipment Directive, PED, 97/23/EC ........................................................................... 23
4.2 Installation location requirements ................................................................................................ 24
4.3 Proper mounting........................................................................................................................... 26
4.3.1 Nozzle design ............................................................................................................................... 27

Table of contents
SITRANS LR250 (FOUNDATION FIELDBUS)
4 Operating Instructions, 08/2014, A5E32221411-AC
4.3.2 Nozzle location ............................................................................................................................ 28
4.3.3 Orientation in a vessel with obstructions ..................................................................................... 31
4.3.4 Mounting on a Stillpipe or Bypass Pipe ...................................................................................... 32
4.3.5 Device orientation ....................................................................................................................... 33
4.4 Installation instructions ................................................................................................................ 34
4.4.1 Threaded versions ...................................................................................................................... 36
4.4.2 Flanged versions ......................................................................................................................... 37
4.4.3 Hygienic versions ........................................................................................................................ 39
4.5 Disassembly ................................................................................................................................ 40
5 Connecting ............................................................................................................................................41
5.1 Basic safety information .............................................................................................................. 41
5.2 Connecting SITRANS LR250 ...................................................................................................... 42
5.3 Wiring setups for hazardous area installation ............................................................................. 46
5.3.1 Configuration with Foundation Fieldbus for hazardous areas .................................................... 46
5.3.2 Intrinsically safe wiring ................................................................................................................ 48
5.3.2.1 Intrinsically safe wiring (FM/CSA) ............................................................................................... 48
5.3.3 Non-sparking wiring .................................................................................................................... 51
5.3.4 Non-incendive wiring (US/Canada only) ..................................................................................... 51
5.4 Instructions specific to hazardous area installations ................................................................... 52
5.4.1 (Reference European ATEX Directive 94/9/EC, Annex II, 1/0/6) ............................................... 52
6 Commissioning ......................................................................................................................................55
6.1 Basic safety information .............................................................................................................. 55
6.2 Operating via the handheld programmer .................................................................................... 55
6.2.1 Power up ..................................................................................................................................... 56
6.2.2 Handheld programmer functions ................................................................................................. 56
6.2.2.1 The LCD display .......................................................................................................................... 57
6.2.2.2 Handheld programmer (Part No. 7ML1930-1BK) ....................................................................... 59
6.2.3 Programming ............................................................................................................................... 60
6.2.3.1 Quick Start Wizard via the handheld programmer_note ............................................................. 65
6.2.3.2 Auto False Echo Suppression ..................................................................................................... 69
6.2.3.3 Requesting an Echo Profile ........................................................................................................ 70
6.2.3.4 Device Address ........................................................................................................................... 71
6.3 Application examples .................................................................................................................. 71
6.3.1 Liquid resin in storage vessel, level measurement ..................................................................... 72
6.3.2 Horizontal vessel with volume measurement.............................................................................. 74
6.3.3 Application with stillpipe .............................................................................................................. 76
7 Remote operation ..................................................................................................................................79
7.1 Operating via AMS Device Manager ........................................................................................... 79
7.1.1 Functions in AMS Device Manager ............................................................................................. 79
7.1.2 Key features of AMS Device Manager Rev. 9.0 ......................................................................... 81
7.1.2.1 Pull-down menu access .............................................................................................................. 82

Table of contents
SITRANS LR250 (FOUNDATION FIELDBUS)
Operating Instructions, 08/2014, A5E32221411-AC 5
7.1.3 Adding a new device .................................................................................................................... 82
7.1.3.1 Electronic Device Description (EDD) ........................................................................................... 82
7.1.4 Master Reset ................................................................................................................................ 84
7.1.5 Scan Device ................................................................................................................................. 84
7.1.6 Sensor calibration ........................................................................................................................ 85
7.1.7 Configuring a new device ............................................................................................................. 85
7.1.7.1 Quick Start Wizard via AMS Device Manager ............................................................................. 85
7.1.8 Changing parameter settings using AMS Device Manager ......................................................... 91
7.1.9 Configure/Setup (Level Transducer Block-LTB) .......................................................................... 92
7.1.9.1 Identification (LTB) ....................................................................................................................... 92
7.1.9.2 Operation (LTB) ........................................................................................................................... 93
7.1.9.3 Setup (LTB) .................................................................................................................................. 95
7.1.9.4 Linearization (LTB) ....................................................................................................................... 97
7.1.9.5 Signal processing ......................................................................................................................... 99
7.1.9.6 Maintenance & Diagnostics (LTB) ............................................................................................. 104
7.1.9.7 Communication (LTB) ................................................................................................................ 107
7.1.10 Configure/Setup (Liquid Crystal Display Block-LCD)................................................................. 107
7.1.10.1 Identification (LCD) .................................................................................................................... 107
7.1.10.2 Operation (LCD) ......................................................................................................................... 108
7.1.10.3 Setup (LCD) ............................................................................................................................... 109
7.1.10.4 Communication (LCD) ............................................................................................................... 109
7.1.11 Configure/Setup (Diagnostic Transducer Block-DIAG) ............................................................. 110
7.1.11.1 Identification (DIAG) ...................................................................................................................
110
7.1.11.2 Operation (DIAG) ....................................................................................................................... 110
7.1.11.3 Communication (DIAG) .............................................................................................................. 111
7.1.12 Configure/Setup (Resource Block - RESOURCE) ..................................................................... 111
7.1.12.1 Identification (RESOURCE) ....................................................................................................... 111
7.1.12.2 Wizards (RESOURCE) .............................................................................................................. 112
7.1.12.3 Operation (RESOURCE) ........................................................................................................... 113
7.1.12.4 Maintenance & Diagnostics (RESOURCE) ............................................................................... 116
7.1.12.5 Communication (RESOURCE) .................................................................................................. 118
7.1.12.6 Security (RESOURCE) .............................................................................................................. 119
7.1.13 Device Diagnostics (Level Transducer Block - LTB) ................................................................. 119
7.1.13.1 Alarms & Errors (LTB) ................................................................................................................ 120
7.1.13.2 Extended Diagnostics (LTB) ...................................................................................................... 123
7.1.14 Device Diagnostics (Liquid Crystal Display Block - LCD) .......................................................... 124
7.1.14.1 Alarms & Errors (LCD) ............................................................................................................... 124
7.1.15 Device Diagnostics (Diagnostic Transducer Block - DIAG) ....................................................... 124
7.1.15.1 Alarms & Errors (DIAG) ............................................................................................................. 124
7.1.16 Device Diagnostics (Resource Block - RESOURCE) ................................................................ 124
7.1.16.1 Alarms & Errors (RESOURCE) .................................................................................................. 124
7.1.16.2 Extended Diagnostics (RESOURCE) ........................................................................................ 127
7.1.17 Process Variables (Level Transducer Block - LTB) ................................................................... 128
7.1.18 Password Protection .................................................................................................................. 129
7.1.18.1 User Manager utility ................................................................................................................... 129
7.1.19 AMS menu structure ..................................................................................................................
130
8 Parameter reference ........................................................................................................................... 143

Table of contents
SITRANS LR250 (FOUNDATION FIELDBUS)
6 Operating Instructions, 08/2014, A5E32221411-AC
8.1 Alphabetical parameter list ........................................................................................................ 191
9 Service and maintenance ..................................................................................................................... 197
9.1 Basic safety information ............................................................................................................ 197
9.2 Cleaning .................................................................................................................................... 197
9.3 Maintenance and repair work .................................................................................................... 198
9.3.1 Unit repair and excluded liability ............................................................................................... 199
9.3.2 Part replacement ....................................................................................................................... 199
9.4 Disposal .................................................................................................................................... 201
10 Diagnosing and troubleshooting ........................................................................................................... 203
10.1 Device status icons ................................................................................................................... 204
10.2 General fault codes ................................................................................................................... 205
10.3 Operation troubleshooting ......................................................................................................... 210
11 Technical data ..................................................................................................................................... 213
11.1 Power ........................................................................................................................................ 213
11.2 Performance .............................................................................................................................. 213
11.3 Interface .................................................................................................................................... 215
11.4 Mechanical ................................................................................................................................ 215
11.5 Environmental ........................................................................................................................... 218
11.6 Process ..................................................................................................................................... 218
11.7 Approvals .................................................................................................................................. 219
11.8 Programmer (infrared keypad) .................................................................................................. 220
12 Dimension drawings ............................................................................................................................. 221
12.1 Threaded horn antenna............................................................................................................. 221
12.2 Threaded horn antenna with extension ..................................................................................... 224
12.3 Flanged horn antenna ............................................................................................................... 226
12.4 Flanged horn antenna with extension ....................................................................................... 228
12.5 Flanged encapsulated antenna (2"/DN50/50A sizes only) ....................................................... 230
12.6 Flanged encapsulated antenna (3"/DN80/80A sizes and larger) .............................................. 232
12.7 Hygienic encapsulated antenna (2" ISO 2852 sanitary clamp) ................................................ 234
12.8 Hygienic encapsulated antenna (3" ISO 2852 sanitary clamp) ................................................ 235
12.9 Hygienic encapsulated antenna (4" ISO 2852 sanitary clamp) ................................................ 236
12.10 Hygienic encapsulated antenna (DN 50 nozzle/ slotted nut to DIN 11851) .............................. 237
12.11 Hygienic encapsulated antenna (DN 80 nozzle/ slotted nut to DIN 11851) .............................. 238

Table of contents
SITRANS LR250 (FOUNDATION FIELDBUS)
Operating Instructions, 08/2014, A5E32221411-AC 7
12.12 Hygienic encapsulated antenna (DN 100 nozzle/ slotted nut to DIN 11851) ............................ 239
12.13 Hygienic encapsulated antenna (DN 50 aseptic slotted nut to DIN 11864-1) ........................... 240
12.14 Hygienic encapsulated antenna (DN 80 aseptic slotted nut to DIN 11864-1) ........................... 241
12.15 Hygienic encapsulated antenna (DN 100 aseptic slotted nut to DIN 11864-1) ......................... 242
12.16 Hygienic encapsulated antenna (DN 50 aseptic flange to DIN 11864-2) .................................. 243
12.17 Hygienic encapsulated antenna (DN 80 aseptic flange to DIN 11864-2) .................................. 244
12.18 Hygienic encapsulated antenna (DN 100 aseptic flange to DIN 11864-2) ................................ 245
12.19 Hygienic encapsulated antenna (DN 50 aseptic clamp to DIN 11864-3) .................................. 246
12.20 Hygienic encapsulated antenna (DN 80 aseptic clamp to DIN 11864-3) .................................. 247
12.21 Hygienic encapsulated antenna (DN 100 aseptic clamp to DIN 11864-3) ................................ 248
12.22 Hygienic encapsulated antenna (Tuchenhagen Type N) .......................................................... 249
12.23 Hygienic encapsulated antenna (Tuchenhagen Type F) ........................................................... 250
12.24 Threaded PVDF antenna ........................................................................................................... 251
12.25 Threaded connection markings .................................................................................................. 252
12.26 Raised-Face flange per EN 1092-1 for flanged horn antenna ................................................... 253
12.27 Raised-Face flange per EN 1092-1 for flanged encapsulated antenna..................................... 255
12.28 Flat-Face flange ......................................................................................................................... 258
12.29 Aseptic/hygienic flange DN50, DN80, DN100 for DIN 11864-2 ................................................. 261
12.30 Process connection tag (pressure rated versions) .................................................................... 264
A Appendix A: Technical reference ......................................................................................................... 265
A.1 Principles of operation ............................................................................................................... 265
A.2 Echo processing......................................................................................................................... 266
A.2.1 Process Intelligence ................................................................................................................... 266
A.2.2 Echo Selection ........................................................................................................................... 266
A.2.3 CLEF Range .............................................................................................................................. 269
A.2.4 Measurement Response ............................................................................................................ 270
A.2.5 Echo Threshold .......................................................................................................................... 270
A.2.6 Echo Lock .................................................................................................................................. 271
A.2.7 Auto False Echo Suppression .................................................................................................... 271
A.2.8 Measurement Range ................................................................................................................. 273
A.2.9 Damping ..................................................................................................................................... 273
A.2.10 Loss of Echo (LOE) .................................................................................................................... 274
A.2.10.1 LOE Timer .................................................................................................................................. 274
A.3 Maximum Process Temperature Chart ...................................................................................... 274
A.4 Process Pressure/Temperature derating curves ....................................................................... 276
A.4.1 Pressure Equipment Directive, PED, 97/23/EC ......................................................................... 277

Table of contents
SITRANS LR250 (FOUNDATION FIELDBUS)
8 Operating Instructions, 08/2014, A5E32221411-AC
A.4.2 Horn antenna ............................................................................................................................ 278
A.4.3 Flanged horn antenna ............................................................................................................... 279
A.4.4 Flanged encapsulated antenna ................................................................................................. 284
A.4.5 PVDF antenna ........................................................................................................................... 286
A.4.6 Hygienic encapsulated antenna ................................................................................................ 287
B Appendix B: Communications via Foundation Fieldbus ........................................................................ 291
B.1 Field Communicator 375 (F375) ............................................................................................... 291
C Appendix C: Certificates and support ................................................................................................... 293
C.1 Certificates ................................................................................................................................ 293
C.2 Technical support ...................................................................................................................... 293
13 List of abbreviations ............................................................................................................................. 295
14 LCD menu structure ............................................................................................................................. 296
Glossary .............................................................................................................................................. 301
Index ................................................................................................................................................... 307

Table of contents
SITRANS LR250 (FOUNDATION FIELDBUS)
Operating Instructions, 08/2014, A5E32221411-AC 9

SITRANS LR250 (FOUNDATION FIELDBUS)
Operating Instructions, 08/2014, A5E32221411-AC 11
Introduction
1
1.1
LR250 FF manual usage
Note
This manual applies to the SITRANS LR250 (FOUNDATION™ Fieldbus) only.
FOUNDATION™ Fieldbus is a trademark of Fieldbus Foundation.
Follow these operating instructions for quick, trouble-free installation, and maximum accuracy
and reliability of your device.
We always welcome suggestions and comments about manual content, design, and
accessibility. Please direct your comments to:
Technical publications (mailto:techpubs.smpi@siemens.com)
1.2
Purpose of this documentation
These instructions contain all information required to commission and use the device. It is your
responsibility to read the instructions carefully prior to installation and commissioning. In order to
use the device correctly, first review its principle of operation.
The instructions are aimed at persons mechanically installing the device, connecting it
electronically, configuring the parameters and commissioning it, as well as service and
maintenance engineers.
1.3
Document history
The following table notes major changes in the documentation compared to the previous edition.
Edition
Remark
January 2014 • Flanged encapsulated antenna version added.
August 2014 • Hygienic encapsulated antenna version added.
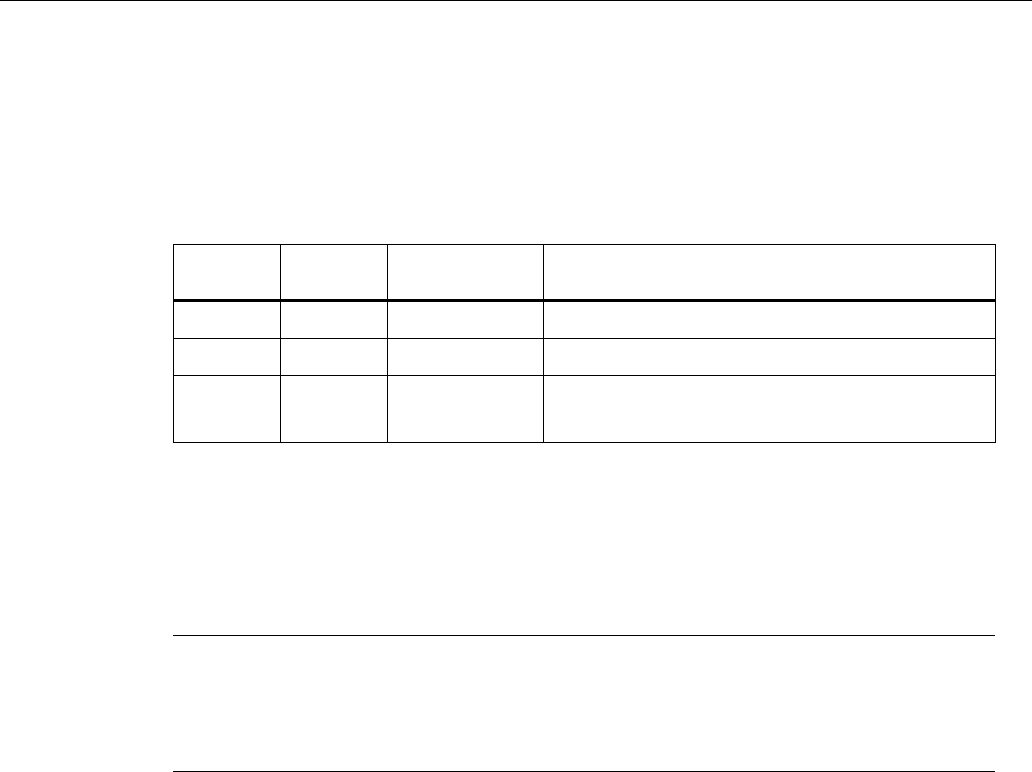
Introduction
1.4 Firmware revision history
SITRANS LR250 (FOUNDATION FIELDBUS)
12 Operating Instructions, 08/2014, A5E32221411-AC
1.4
Firmware revision history
This history establishes the correlation between the current documentation and the valid
firmware of the device.
The documentation of this edition is applicable for the following firmware:
Firmware
rev.
PDM EDD
rev.
Date
Changes
1.01.00 1.01.00 25 Feb 2010 • Initial release.
1.01.04 1.01.00 2 Aug 2011 • Threaded PVDF antenna supported.
1.01.05 1.01.00 31 Oct 2012 • Antenna parameter removed.
• Quickstart on local display enhancements.
1.5
Designated use
Use the device to measure process media in accordance with the information in the operating
instructions.
Note
Use in a domestic environment
This is a Class A Group 1 equipment intended for use in industrial areas.
In a domestic environment this device may cause radio interference.
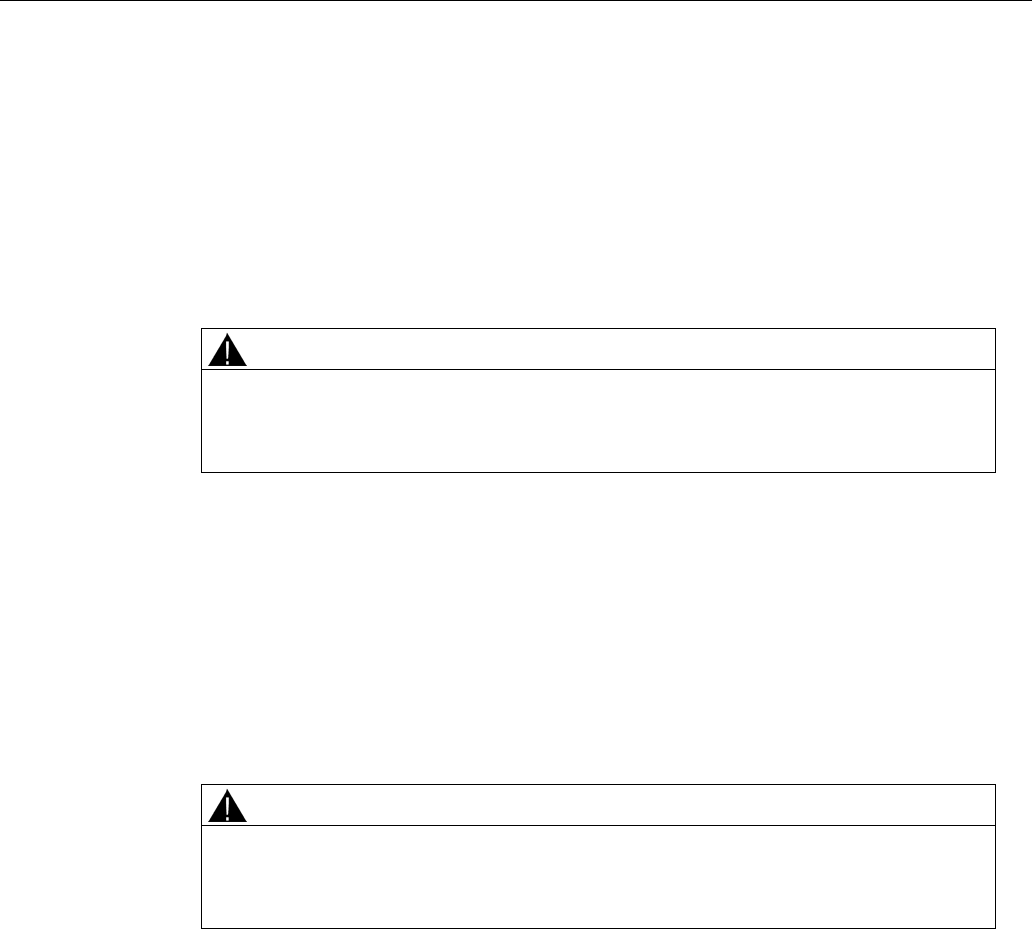
Introduction
1.6 Checking the consignment
SITRANS LR250 (FOUNDATION FIELDBUS)
Operating Instructions, 08/2014, A5E32221411-AC 13
1.6
Checking the consignment
1. Check the packaging and the device for visible damage caused by inappropriate handling
during shipping.
2. Report any claims for damages immediately to the shipping company.
3. Retain damaged parts for clarification.
4. Check the scope of delivery by comparing your order to the shipping documents for
correctness and completeness.
WARNING
Using a damaged or incomplete device
Danger of explosion in hazardous areas.
• Do not use damaged or incomplete devices.
1.7
Transportation and storage
To guarantee sufficient protection during transport and storage, observe the following:
● Keep the original packaging for subsequent transportation.
● Devices/replacement parts should be returned in their original packaging.
● If the original packaging is no longer available, ensure that all shipments are properly
packaged to provide sufficient protection during transport. Siemens cannot assume liability
for any costs associated with transportation damages.
CAUTION
Insufficient protection during storage
The packaging only provides limited protection against moisture and infiltration.
• Provide additional packaging as necessary.
1.8
Notes on warranty
The contents of this manual shall not become part of or modify any prior or existing agreement,
commitment or legal relationship. The sales contract contains all obligations on the part of
Siemens as well as the complete and solely applicable warranty conditions. Any statements
regarding device versions described in the manual do not create new warranties or modify the
existing warranty.
The content reflects the technical status at the time of publishing. Siemens reserves the right to
make technical changes in the course of further development.
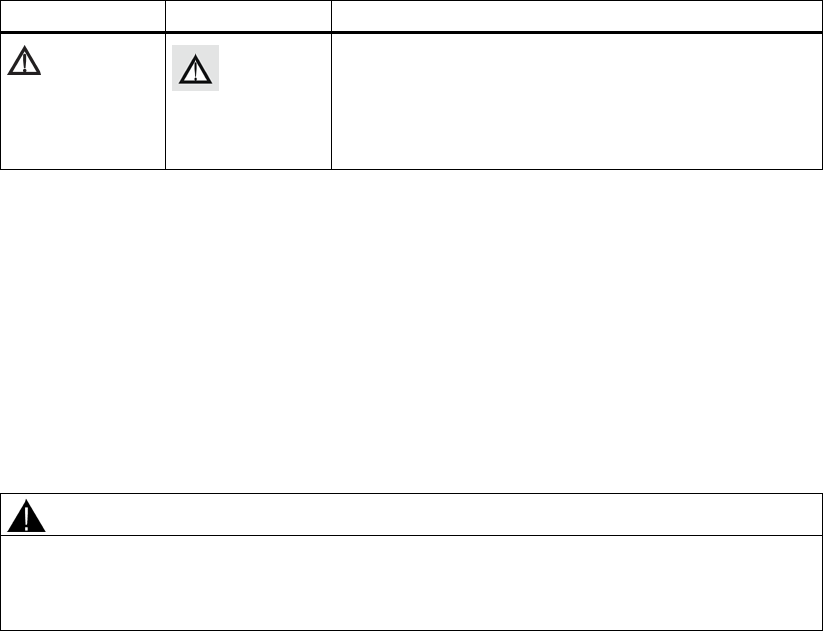
SITRANS LR250 (FOUNDATION FIELDBUS)
Operating Instructions, 08/2014, A5E32221411-AC 15
Safety information
2
2.1
Preconditions for safe use
This device left the factory in good working condition. In order to maintain this status and to
ensure safe operation of the device, observe these instructions and all the specifications
relevant to safety.
Observe the information and symbols on the device. Do not remove any information or symbols
from the device. Always keep the information and symbols in a completely legible state.
2.1.1
Safety marking symbols
In manual
On product
Description
(Label on product:
yellow
background.)
WARNING: refer to accompanying documents (manual) for
details.
2.1.2
Laws and directives
Observe the test certification, provisions and laws applicable in your country during connection,
assembly and operation.
2.1.3
FCC Conformity
US Installations only: Federal Communications Commission (FCC) rules
WARNING
Changes or modifications not expressly approved by Siemens Milltronics could void the
user’s authority to operate the equipment.
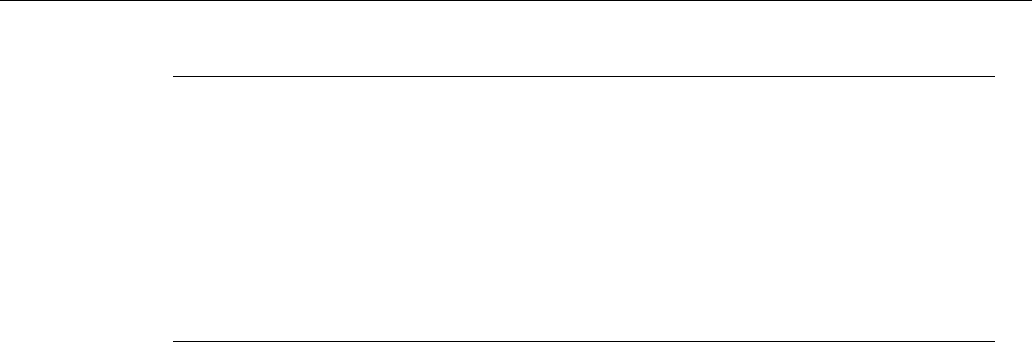
Safety information
2.1 Preconditions for safe use
SITRANS LR250 (FOUNDATION FIELDBUS)
16 Operating Instructions, 08/2014, A5E32221411-AC
Note
• This equipment has been tested and found to comply with the limits for a Class A digital
device, pursuant to Part 15 of the FCC Rules. These limits are designed to provide
reasonable protection against harmful interference when the equipment is operated in a
commercial environment.
• This equipment generates, uses, and can radiate radio frequency energy and, if not
installed and used in accordance with the instruction manual, may cause harmful
interference to radio communications. Operation of this equipment in a residential area is
likely to cause harmful interference to radio communications, in which case the user will
be required to correct the interference at his own expense.
2.1.4
Conformity with European directives
The CE marking on the device symbolizes the conformity with the following European directives:
Electromagnetic
compatibility EMC
2004/108/EC
Directive of the European Parliament and of the Council on the
approximation of the laws of the Member States relating to
electromagnetic compatibility and repealing Directive
89/336/EEC.
Low voltage directive LVD
2006/95/EC
Directive of the European Parliament and of the Council on the
harmonisation of the laws of Member States relating to
electrical equipment designed for use within certain voltage
limits.
Atmosphère explosible
ATEX
94/9/EC
Directive of the European Parliament and the Council on the
approximation of the laws of the Member States concerning
equipment and protective systems intended for use in
potentially explosive atmospheres.
Radio and
telecommunications terminal
equipment R&TTE
1999/5/EC
Directive of the European Parliament and of the Council on
radio equipment and telecommunications terminal equipment
and the mutual recognition of their conformity.
The applicable directives can be found in the EC conformity declaration of the specific device.
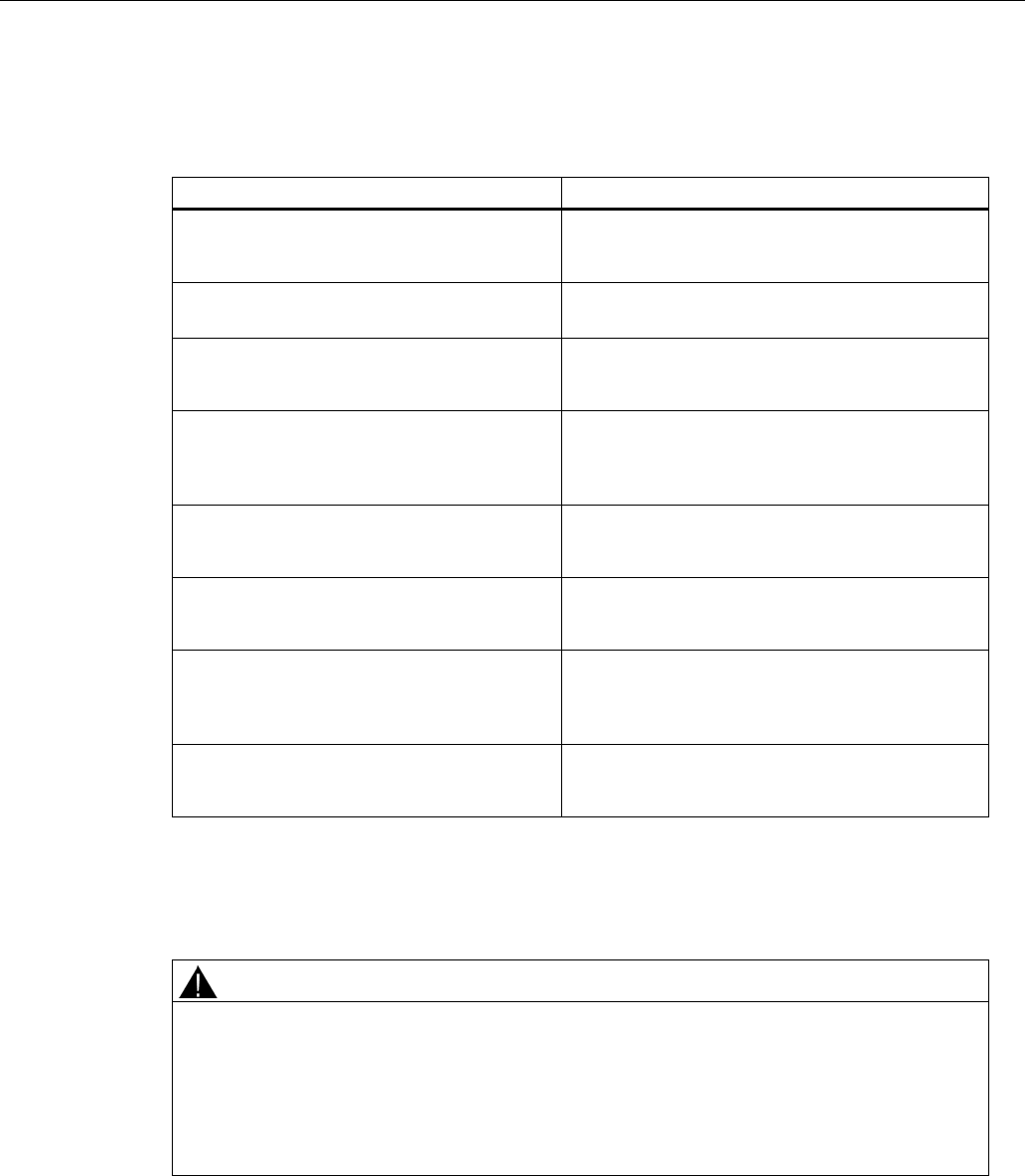
Safety information
2.2 Improper device modifications
SITRANS LR250 (FOUNDATION FIELDBUS)
Operating Instructions, 08/2014, A5E32221411-AC 17
2.1.5
CE Electromagnetic Compatibility (EMC) Conformity
This equipment has been tested and found to comply with the following EMC Standards:
EMC Standard
Title
CISPR 11:2009 + A1:2010/EN
55011:2009 + A1:2010, CLASS A
Limits and methods of measurements of radio
disturbance characteristics of industrial, scientific,
and medical (ISM) radio-frequency equipment
EN 61326:2013
(IEC 61326:2012)
Electrical Equipment for Measurement, Control and
Laboratory Use – Electromagnetic Compatibility.
EN61000-4-2:2009 Electromagnetic Compatibility (EMC) Part 4-2:
Testing and measurement techniques –
Electrostatic discharge immunity test.
EN61000-4-3:2006 + A1:2008 + A2:2010 Electromagnetic Compatibility (EMC) Part 4-3:
Testing and measurement techniques – Radiated,
radio-frequency, electromagnetic field immunity test
2006 + A1:2008 + A2:2010.
EN61000-4-4:2004 + A1:2010 Electromagnetic Compatibility (EMC) Part 4-4:
Testing and measurement techniques – Electrical
fast transient/burst immunity test.
EN61000-4-5:2006 Electromagnetic Compatibility (EMC) Part 4-5:
Testing and measurement techniques – Surge
immunity test.
EN61000-4-6:2010 Electromagnetic Compatibility (EMC) Part 4-6:
Testing and measurement techniques – Immunity to
conducted disturbances, induced by radio-
frequency fields.
EN61000-4-8:2010 Electromagnetic Compatibility (EMC) Part 4-8:
Testing and measurement techniques – Power
frequency magnetic field immunity test.
2.2
Improper device modifications
WARNING
Improper device modifications
Danger to personnel, system and environment can result from modifications to the device,
particularly in hazardous areas.
• Only carry out modifications that are described in the instructions for the device. Failure
to observe this requirement cancels the manufacturer's warranty and the product
approvals.
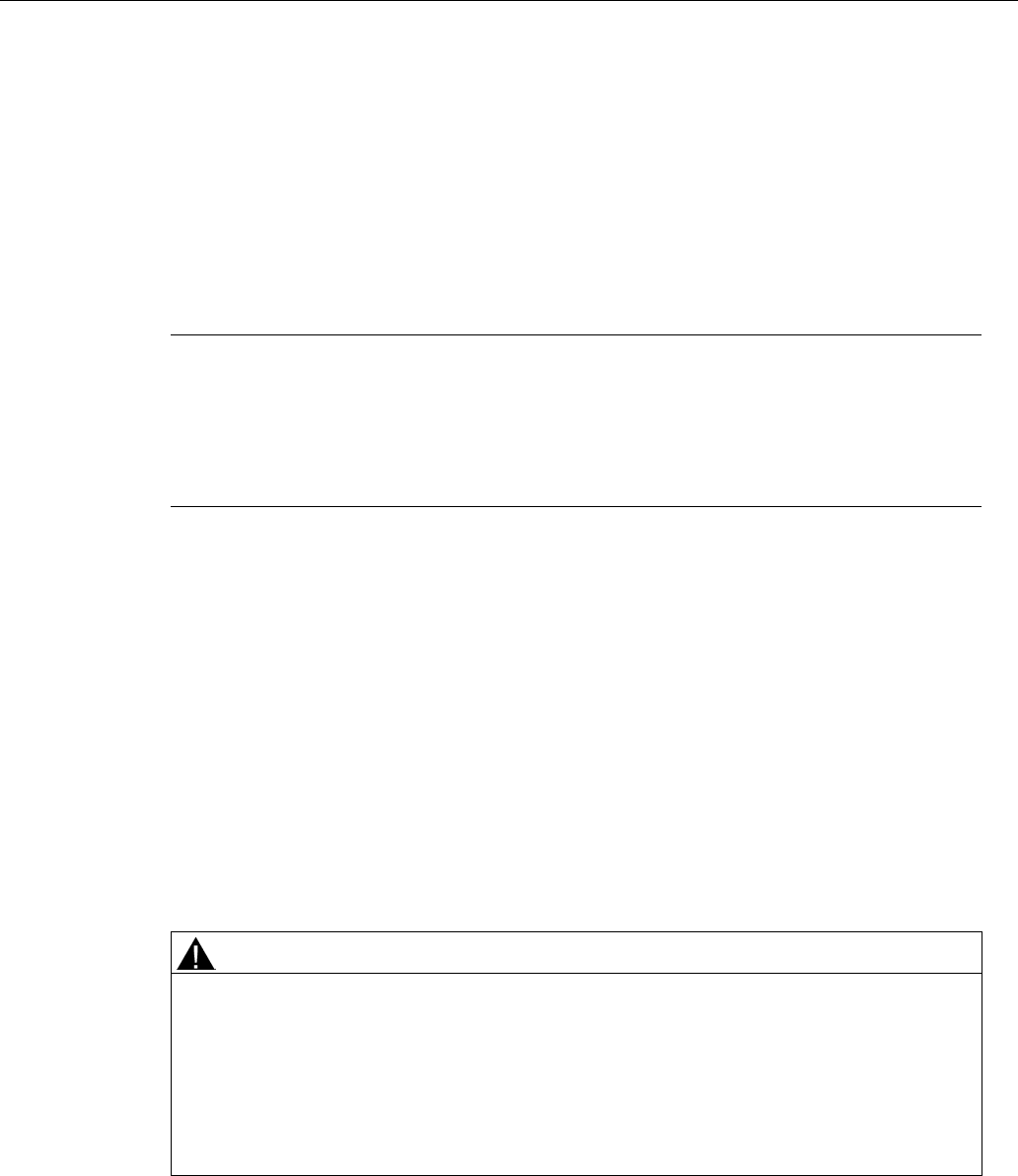
Safety information
2.3 Requirements for special applications
SITRANS LR250 (FOUNDATION FIELDBUS)
18 Operating Instructions, 08/2014, A5E32221411-AC
2.3
Requirements for special applications
Due to the large number of possible applications, each detail of the described device versions
for each possible scenario during commissioning, operation, maintenance or operation in
systems cannot be considered in the instructions. If you need additional information not covered
by these instructions, contact your local Siemens office or company representative.
Note
Operation under special ambient conditions
We highly recommend that you contact your Siemens representative or our application
department before you operate the device under special ambient conditions as can be
encountered in nuclear power plants or when the device is used for research and
development purposes.
2.4
Use in hazardous areas
Qualified personnel for hazardous area applications
Persons who install, connect, commission, operate, and service the device in a hazardous area
must have the following specific qualifications:
● They are authorized, trained or instructed in operating and maintaining devices and systems
according to the safety regulations for electrical circuits, high pressures, aggressive, and
hazardous media.
● They are authorized, trained, or instructed in carrying out work on electrical circuits for
hazardous systems.
● They are trained or instructed in maintenance and use of appropriate safety equipment
according to the pertinent safety regulations.
WARNING
Loss of safety of device with type of protection "Intrinsic safety Ex i"
If the device has already been operated in non-intrinsically safe circuits or the electrical
specifications have not been observed, the safety of the device is no longer ensured for use
in hazardous areas. There is a danger of explosion.
• Connect the device with type of protection "Intrinsic safety" solely to an intrinsically safe
circuit.
• Observe the specifications for the electrical data on the certificate.
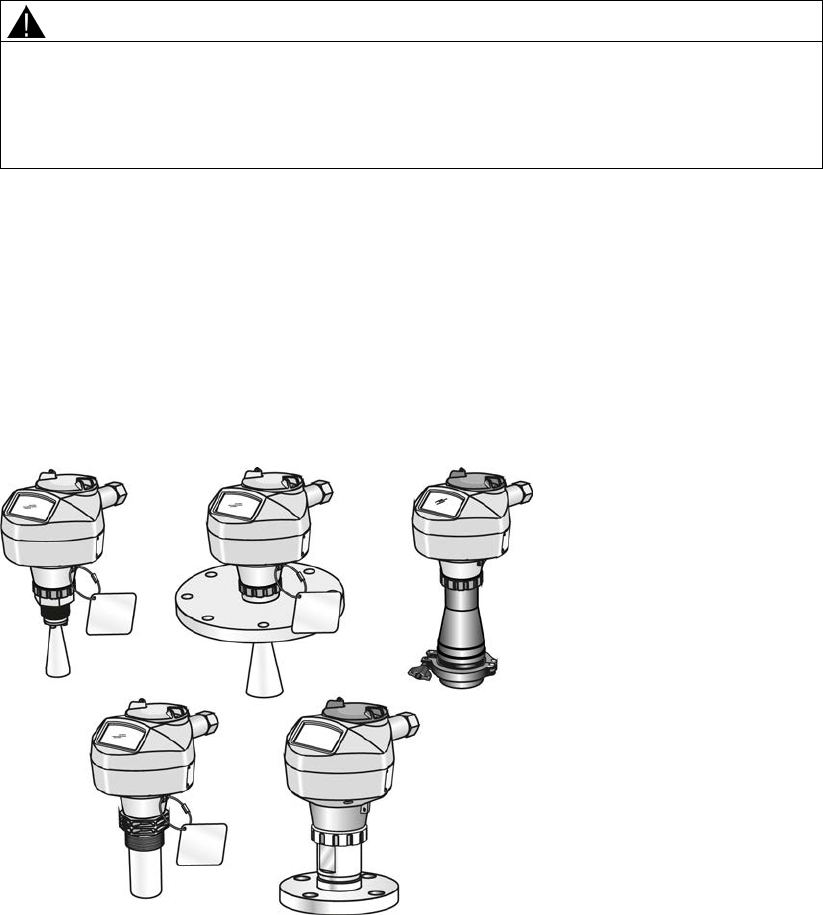
SITRANS LR250 (FOUNDATION FIELDBUS)
Operating Instructions, 08/2014, A5E32221411-AC 19
Description
3
3.1
SITRANS LR250 overview
WARNING
Loss of protection
Danger to personnel, system and environment can result from improper use of the device.
• SITRANS LR250 is to be used only in the manner outlined in this manual, otherwise
protection provided by the device may be impaired.
SITRANS LR250 is a 2-wire 25 GHz pulse radar level transmitter for continuous monitoring of
liquids and slurries in storage vessels including high pressure and high temperature, to a range
of 20 meters (66 feet). It is ideal for small vessels, material such as chemicals, food, beverages,
solvents (including those of corrosive or aggressive nature), and low dielectric media.
The device consists of an electronic circuit coupled to an antenna and either a threaded or
flange type process connection.
This device supports Foundation Fieldbus (FF) communication protocol. Signals are processed
using Process Intelligence which has been field proven in over 1,000,000 applications worldwide
(ultrasonic and radar). This device can be configured as an FF (H1) Link Master.

Description
3.2 Programming
SITRANS LR250 (FOUNDATION FIELDBUS)
20 Operating Instructions, 08/2014, A5E32221411-AC
3.2
Programming
This device is very easy to install and configure via a graphical local user interface (LUI). You
can modify the built in parameters either locally via the Siemens infrared handheld programmer,
or from a remote location using one of the following options:
● FF host system
● AMS Device Manager
3.3
Applications
● liquids and slurries
● bulk storage vessels
● simple process vessels
● corrosive and aggressive
● hygienic/sanitary
3.4
Approvals and certificates
Note
For further details see Approvals (Page 219).
SITRANS LR250 is available with approvals for General purpose, sanitary or hygienic and for
hazardous areas. In all cases, check the nameplate on your device, and confirm the approval
rating.
Process Connections
A wide range of process connections and antenna options are available to suit virtually any
vessel configuration.
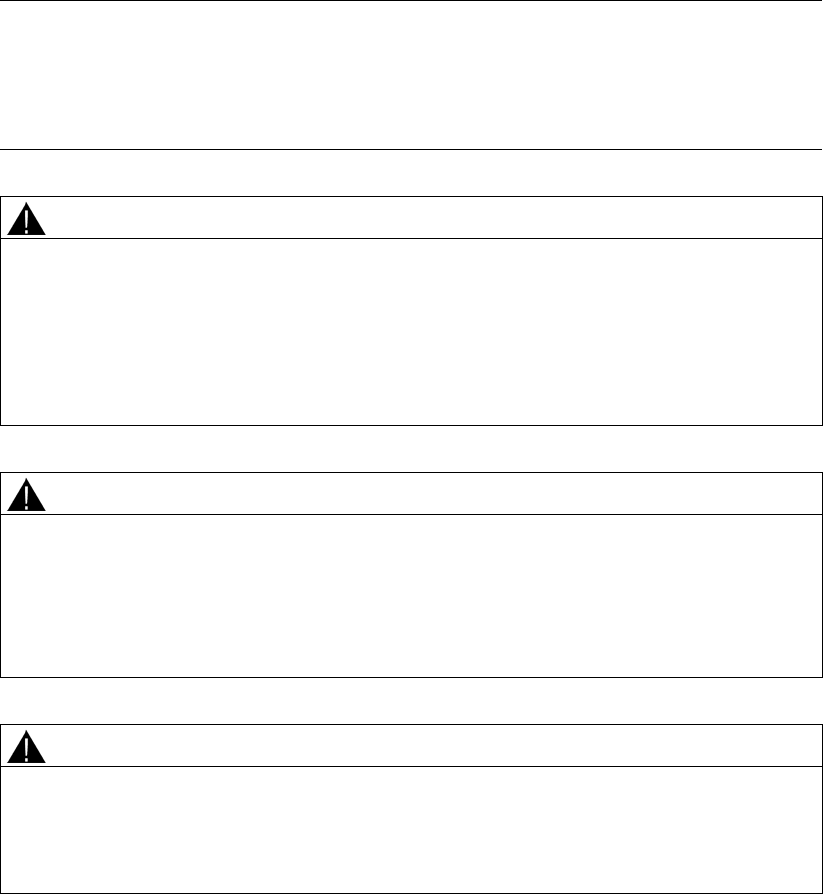
SITRANS LR250 (FOUNDATION FIELDBUS)
Operating Instructions, 08/2014, A5E32221411-AC 21
Installing/mounting
4
4.1
Basic safety information
Note
Material compatibility
Siemens can provide you with support concerning selection of sensor components wetted by
process media. However, you are responsible for the selection of components. Siemens
accepts no liability for faults or failures resulting from incompatible materials.
WARNING
Unsuitable connecting parts
Danger of injury or poisoning.
In case of improper mounting hot, toxic and corrosive process media could be released at
the connections.
• Ensure that connecting parts (such as flange gaskets and bolts) are suitable for
connection and process media.
WARNING
Exceeded maximum ambient or process media temperature
Danger of explosion in hazardous areas.
Device damage.
• Make sure that the maximum permissible ambient and process media temperatures of
the device are not exceeded.
WARNING
Open cable inlet or incorrect cable gland
Danger of explosion in hazardous areas.
• Close the cable inlets for the electrical connections. Only use cable glands or plugs
which are approved for the relevant type of protection.
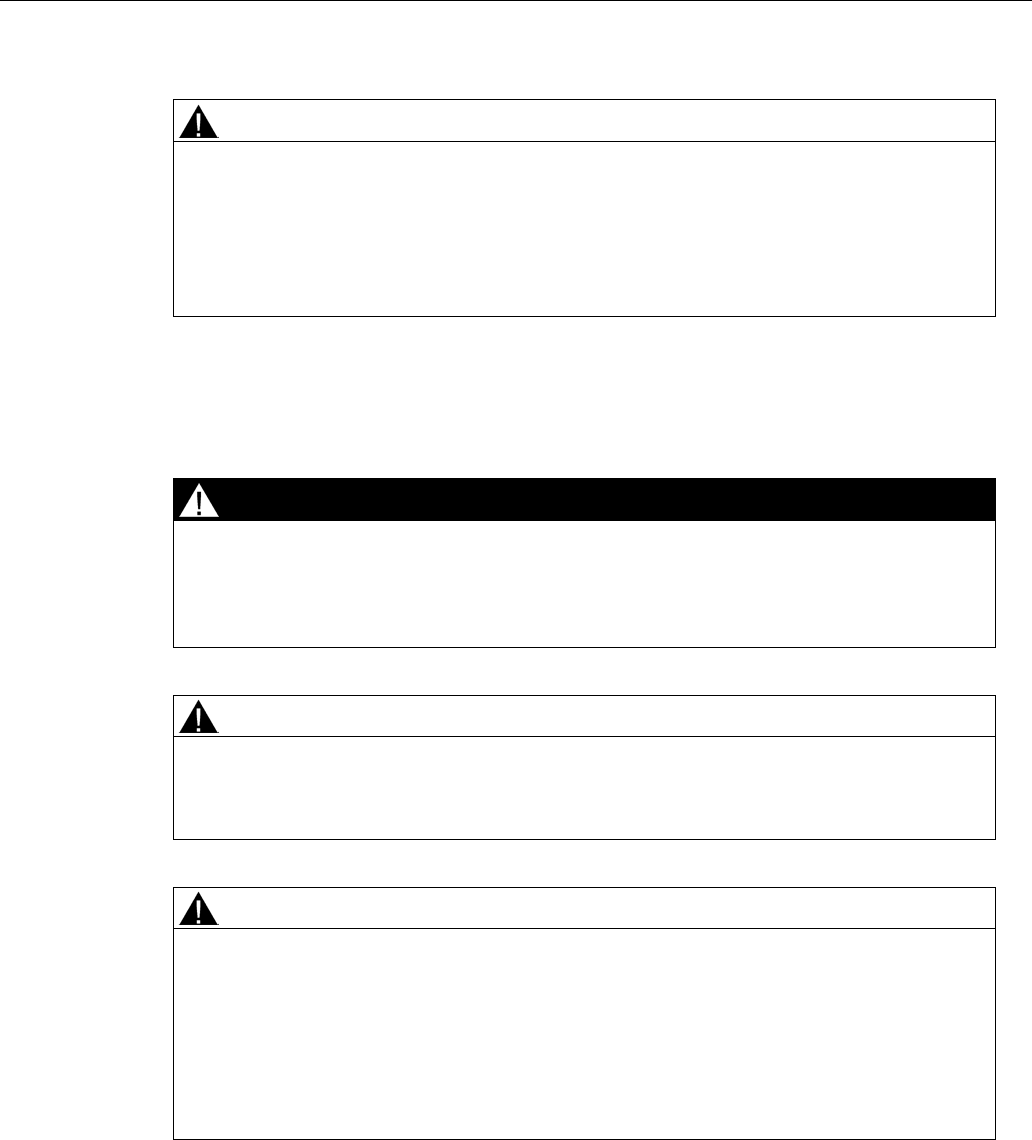
Installing/mounting
4.1 Basic safety information
SITRANS LR250 (FOUNDATION FIELDBUS)
22 Operating Instructions, 08/2014, A5E32221411-AC
WARNING
Incorrect conduit system
Danger of explosion in hazardous areas as result of open cable inlet or incorrect conduit
system.
• In the case of a conduit system, mount a spark barrier at a defined distance from the
device input. Observe national regulations and the requirements stated in the relevant
approvals.
4.1.1
Pressure applications
DANGER
Pressure applications
Danger to personnel, system and environment will result from improper disassembly.
• Never attempt to loosen, remove, or disassemble process connection while vessel
contents are under pressure.
WARNING
Pressure applications
Danger to personnel, system and environment can result from improper installation.
• Improper installation may result in loss of process pressure.
WARNING
Exceeded maximum permissible operating pressure
Danger of injury or poisoning.
The maximum permissible operating pressure depends on the device version. The device
can be damaged if the operating pressure is exceeded. Hot, toxic and corrosive process
media could be released.
• Make sure that the device is suitable for the maximum permissible operating pressure of
your system.
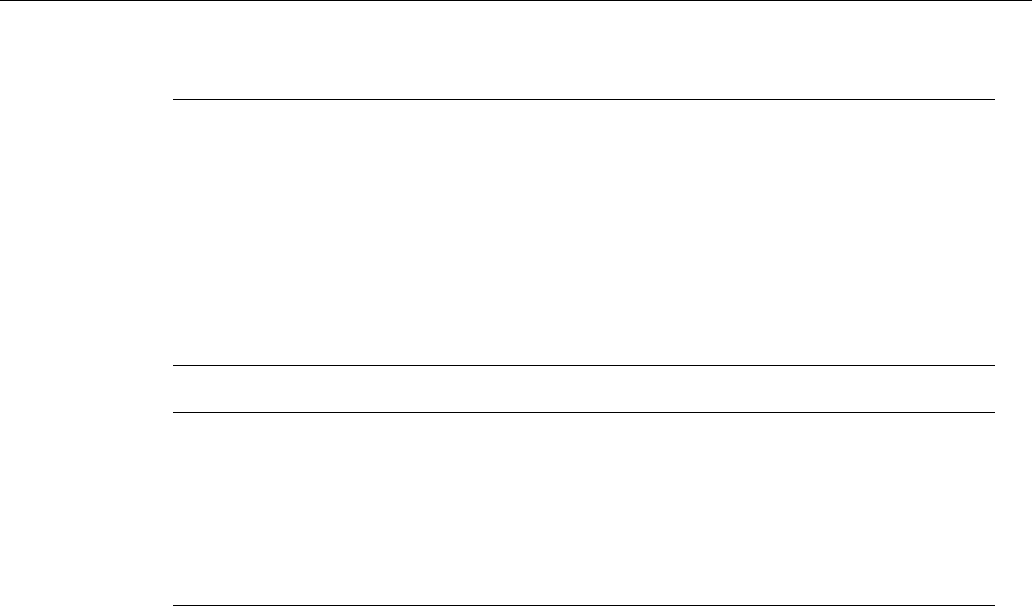
Installing/mounting
4.1 Basic safety information
SITRANS LR250 (FOUNDATION FIELDBUS)
Operating Instructions, 08/2014, A5E32221411-AC 23
Note
• The process connection tag shall remain with the process pressure boundary assembly.
(The process pressure boundary assembly comprises the components that act as a
barrier against pressure loss from the process vessel: that is, the combination of process
connection body and emitter, but normally excluding the electrical enclosure). In the
event the device package is replaced, the process connection tag shall be transferred to
the replacement unit.
• SITRANS LR250 units are hydrostatically tested, meeting or exceeding the requirement
of the ASME Boiler and Pressure Vessel Code and the European Pressure Equipment
Directive.
Note
• The serial numbers stamped in each process connection body, (flange, threaded, or
sanitary), provide a unique identification number indicating date of manufacture.
Example: MMDDYY – XXX (where MM = month, DD = day, YY = year, and XXX=
sequential unit produced)
• Further markings (space permitting) indicate flange configuration, size, pressure class,
material, and material heat code.
4.1.1.1
Pressure Equipment Directive, PED, 97/23/EC
Siemens Level Transmitters with flanged, threaded, or sanitary clamp type process mounts have
no pressure-bearing housing of their own and, therefore, do not come under the Pressure
Equipment Directive as pressure or safety accessories (see EU Commission Guideline 1/8 and
1/20).
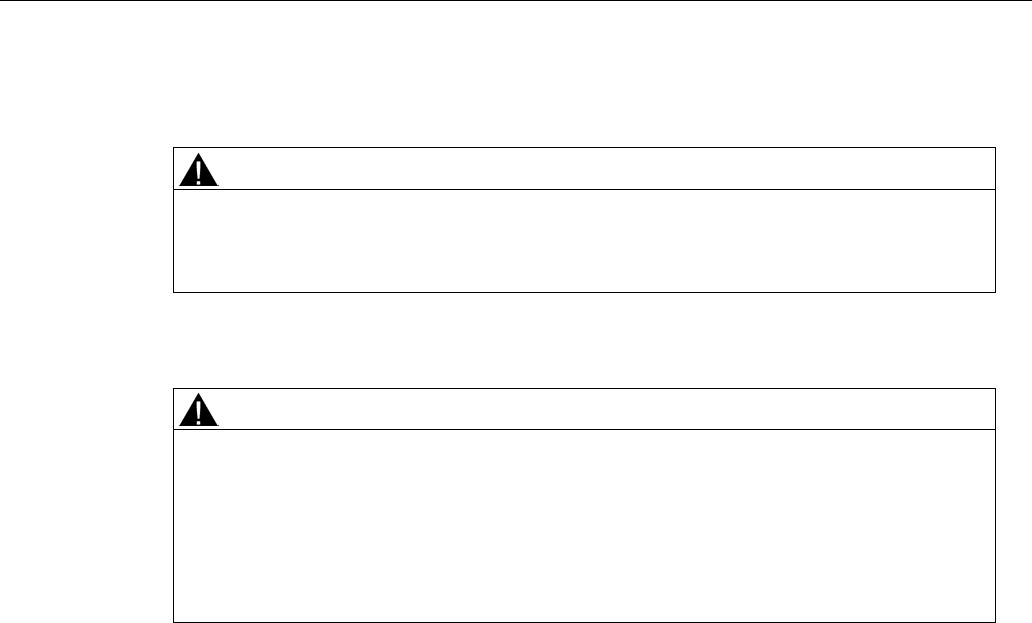
Installing/mounting
4.2 Installation location requirements
SITRANS LR250 (FOUNDATION FIELDBUS)
24 Operating Instructions, 08/2014, A5E32221411-AC
4.2
Installation location requirements
WARNING
Aggressive atmospheres
Danger to personnel, system and environment can result from unsuitable environment.
• Provide an environment suitable to the housing rating and materials of construction.
CAUTION
Direct sunlight
Device damage.
The device can overheat or materials become brittle due to UV exposure.
• Protect the device from direct sunlight.
• Make sure that the maximum permissible ambient temperature is not exceeded. Refer
to the information in Chapter "Technical data".
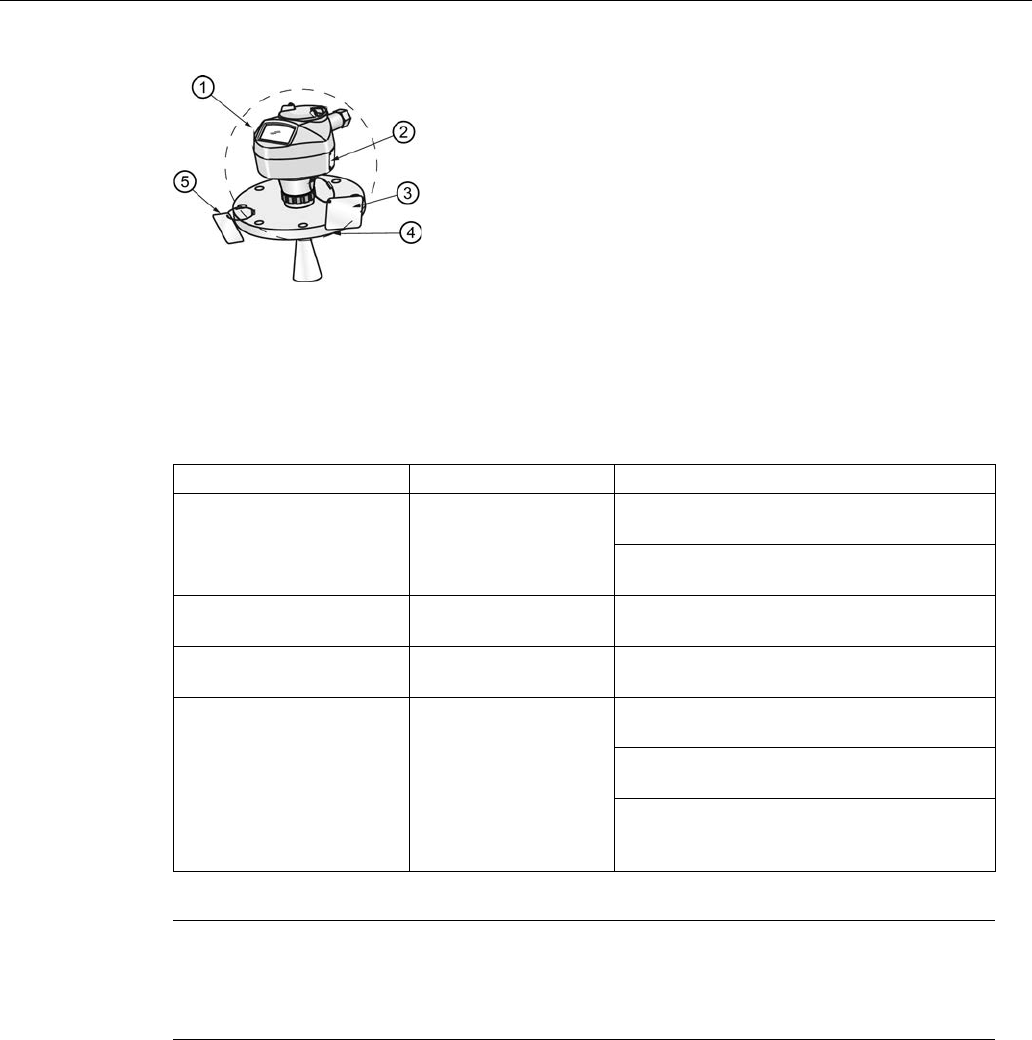
Installing/mounting
4.2 Installation location requirements
SITRANS LR250 (FOUNDATION FIELDBUS)
Operating Instructions, 08/2014, A5E32221411-AC 25
①
Ambient temperature
②
Device nameplate
③
Device tag
④
Process temperature (at process connection)
⑤
Process connection tag (contains process connection related information)
Antenna
①
③
Horn -40 to +80 °C
(-40 to +176 °F)
with FKM O-ring:-40 to +200 °C (-40 to
392 °F)
with FFKM O-ring:-20 to +200 °C (-4 to
+392 °F)
PVDF -40 to +80 °C
(-40 to +176 °F)
-40 to +80 °C
(-40 to +176 °F)
Flanged encapsulated -40 to +80 °C
(-40 to +176 °F)
-40 to +170 °C
(-40 to +338 °F)
Hygienic encapsulated -40 to +80 °C
(-40 to +176 °F)
-40 to +170 °C
(-40 to +338 °F)
with FKM seals used on process connection:
-20 to +170 °C (-4 to +338 °F)
with EPDM seals used on process
connection:
-40 to +120 °C (-40 to +248 °F)
Note
Details about the process connection, process temperature and materials are laser etched
into the body of the flanged and hygienic versions. All other SITRANS LR250 versions have
details listed on a tag.
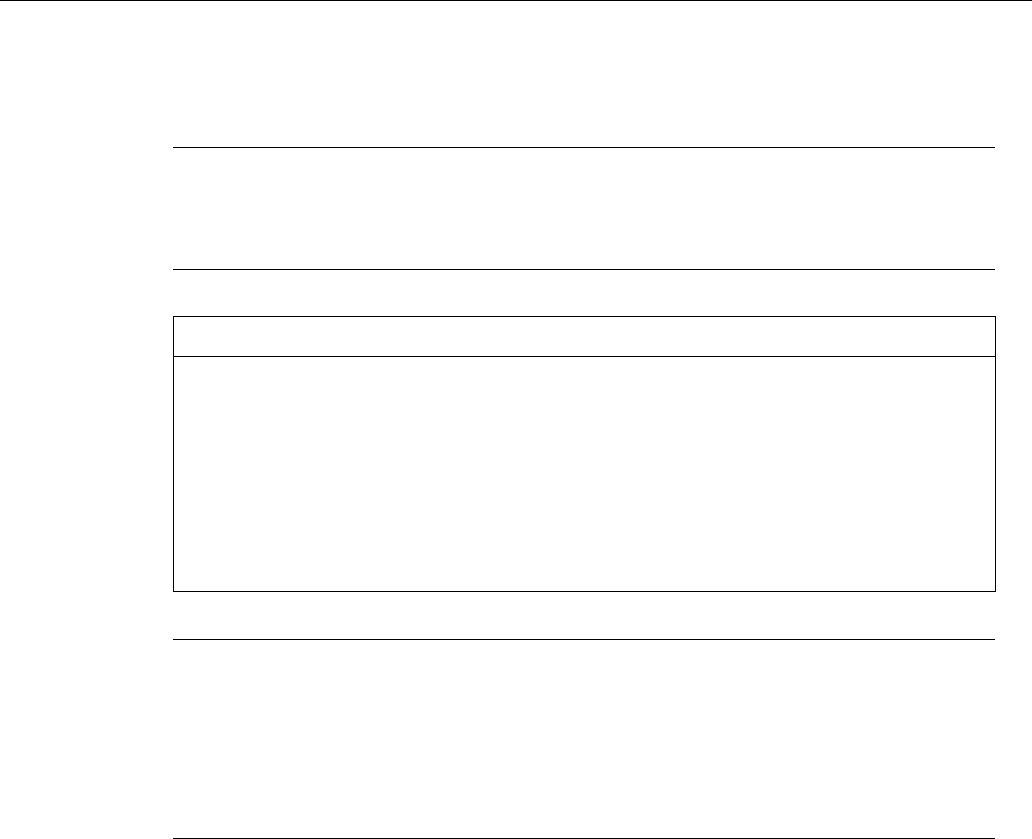
Installing/mounting
4.3 Proper mounting
SITRANS LR250 (FOUNDATION FIELDBUS)
26 Operating Instructions, 08/2014, A5E32221411-AC
4.3
Proper mounting
Note
• Correct location is key to a successful application.
• Avoid reflective interference from vessel walls and obstructions by following guidelines in
this chapter.
NOTICE
Incorrect mounting
The device can be damaged, destroyed, or its functionality impaired through improper
mounting.
• Before installing ensure there is no visible damage to the device.
• Make sure that process connectors are clean, and suitable gaskets and glands are
used.
• Mount the device using suitable tools. Refer to the information in Installation instructions
(Page 34) for installation torque requirements.
Note
• On devices with a removable head, there is no limit to the number of times a device can
be rotated without damage.
• When mounting, orient the front or back of the device towards the closest vessel wall or
obstruction.
• Do not rotate the enclosure after programming and vessel calibration, otherwise an error
may occur, caused by a polarity shift of the transmit pulse.
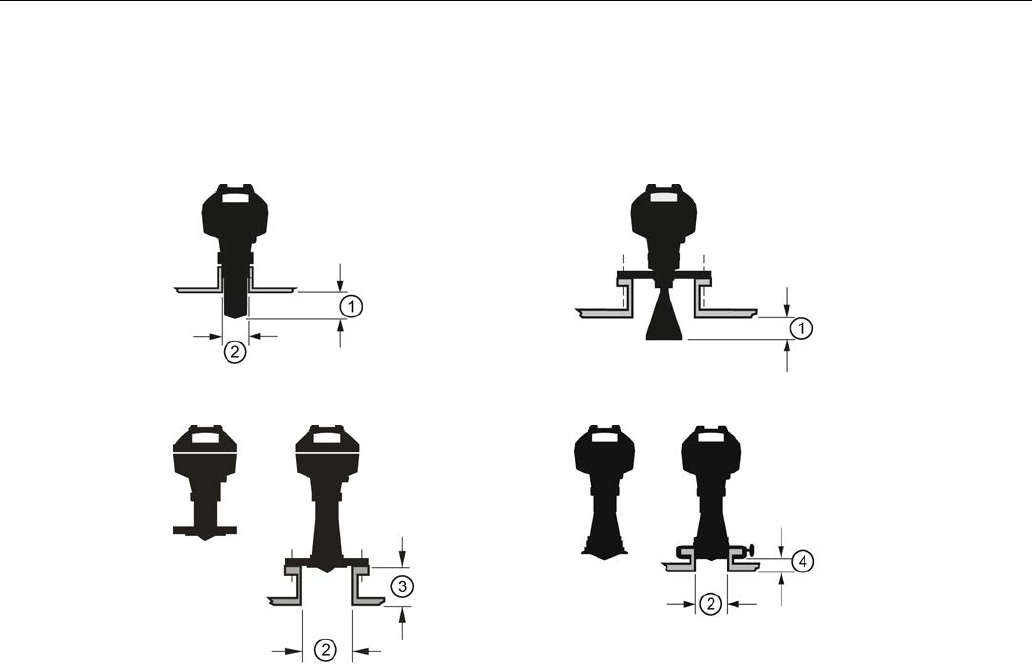
Installing/mounting
4.3 Proper mounting
SITRANS LR250 (FOUNDATION FIELDBUS)
Operating Instructions, 08/2014, A5E32221411-AC 27
4.3.1
Nozzle design
Threaded PVDF antenna
Stainless steel horn antenna
Flanged encapsulated antenna (FEA)
Hygienic encapsulated antenna (HEA)
① Minimum clearance: 10 mm (0.4")
② Minimum diameter: 50 mm (2")
③ Maximum nozzle length
④ Maximum length/diameter ratio 1:1
● The end of the antenna must protrude a minimum of 10 mm (0.4") to avoid false echoes
being reflected from the nozzle1).
● Minimum recommended nozzle diameter for the threaded PVDF antenna is 50 mm (2").
● An antenna extension (100 mm/3.93") is available for the horn antenna only.
● The maximum nozzle length for the FEA is 500 mm (19.68") when the nozzle diameter is
DN150 (6"). Only shorter lengths are recommended for smaller diameters.
● When installing the SITRANS LR250 with hygienic process connection, it is good hygienic
practice to install the antenna in a nozzle that has a maximum length/diameter ratio of 1:1.
For example, 2" (DN50) diameter nozzle should be no longer than 2" (50 mm).
● When removing any sanitary/hygienic clamp version of the HEA to clean the lens, ensure it is
re-installed in the exact position it was removed from, to avoid re-commissioning the device.
1) Not applicable for FEA or HEA
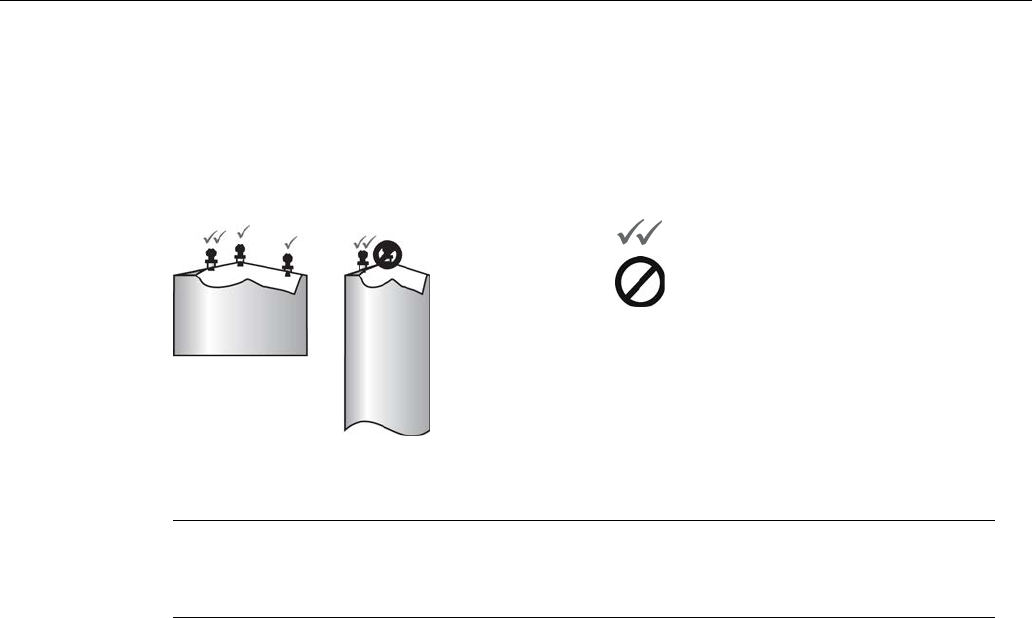
Installing/mounting
4.3 Proper mounting
SITRANS LR250 (FOUNDATION FIELDBUS)
28 Operating Instructions, 08/2014, A5E32221411-AC
4.3.2
Nozzle location
● Avoid central locations on tall, narrow vessels
● Nozzle must be vertical and clear of imperfections
Preferred
Undesirable
Beam angle
Note
• Beam width depends on antenna size and is approximate: see below.
• For details on avoiding false echoes, see Auto False Echo Suppression (Page 271).
● Beam angle is the width of the cone where the energy density is half of the peak energy
density.
● The peak energy density is directly in front of and in line with the antenna.
● There is a signal transmitted outside the beam angle, therefore false targets may be
detected.
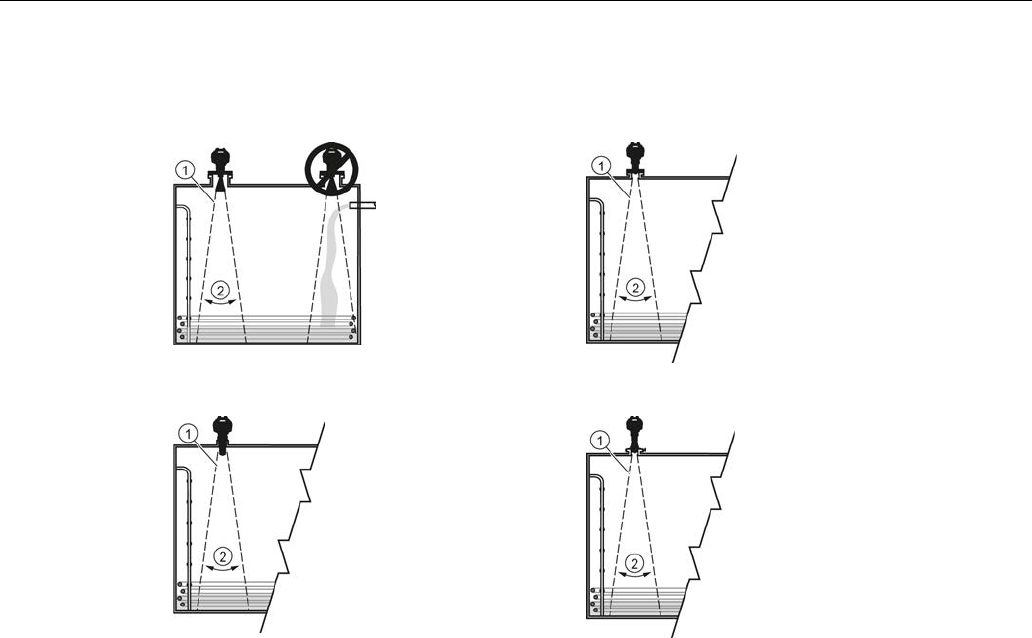
Installing/mounting
4.3 Proper mounting
SITRANS LR250 (FOUNDATION FIELDBUS)
Operating Instructions, 08/2014, A5E32221411-AC 29
Horn antenna
Flanged encapsulated antenna
Threaded PVDF antenna
Hygienic encapsulated antenna
① Emission cone
② Beam angle
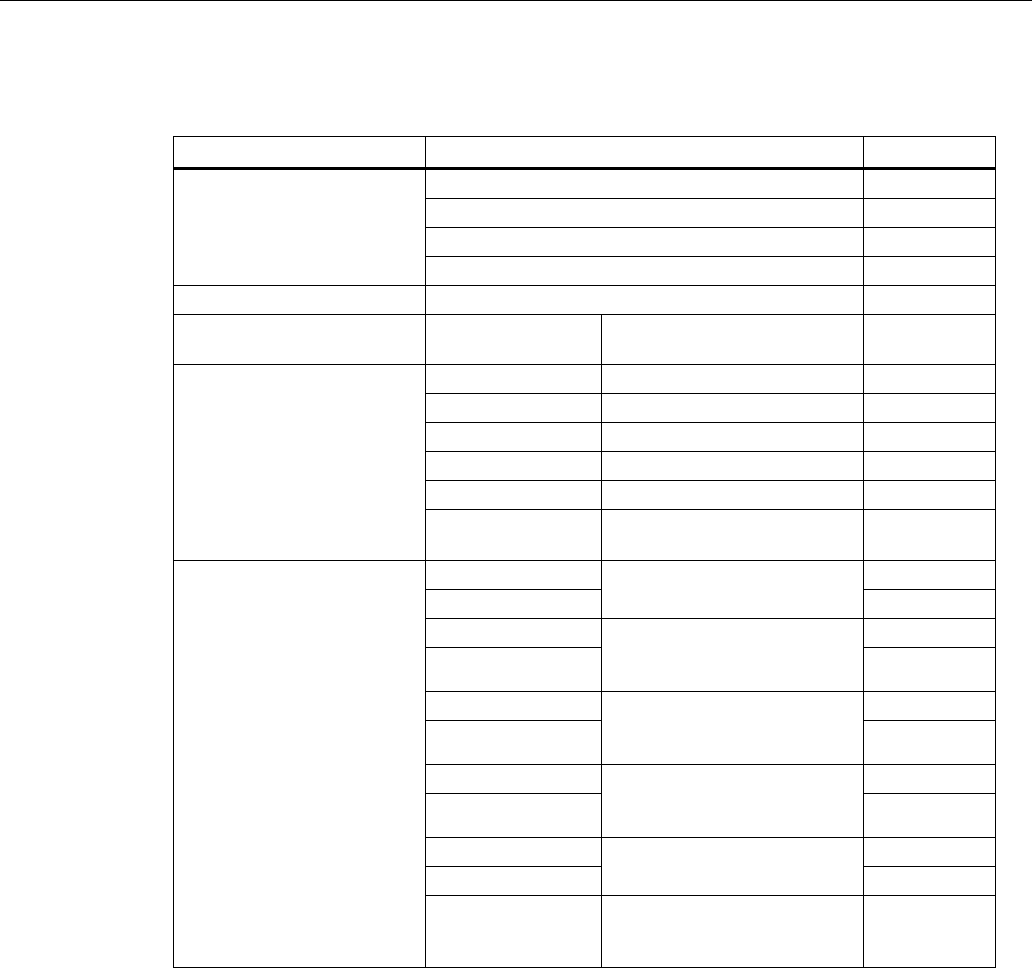
Installing/mounting
4.3 Proper mounting
SITRANS LR250 (FOUNDATION FIELDBUS)
30 Operating Instructions, 08/2014, A5E32221411-AC
Emission cone type and beam angle
Antenna type
Antenna size
Beam angle
Horn 1.5" 19°
2" 15°
3" 10°
4" 8°
Threaded PVDF 19°
Process connection
size
Process connection type
Flanged encapsulated 2" Class 150 ASME B16.5 12.8°
3, 4, 6" Class 150 ASME B16.5 9.6°
50A 10K JIS B 2220 12.8°
80A/100A/150A 10K JIS B 2220 9.6°
DN50 PN10/16 EN1092-1 12.8°
DN80/DN100/DN15
0
PN10/16 EN1092-1 9.6°
Hygienic encapsulated 2" Sanitary Clamp according to
ISO 2852
12.8°
3, 4" 9.6°
DN50 Aseptic/Hygienic nozzle/slotted
nut according to DIN 11864-1
[Form A]
12.8°
DN80/DN100 9.6°
DN50 Aseptic/Hygienic flanged
according to DIN 11864-2
[Form A]
12.8°
DN80/DN100 9.6°
DN50 Aseptic/Hygienic Clamp
according to DIN 11864-
3 [Form A]
12.8°
DN80/DN100 9.6°
DN50 Hygienic nozzle/slotted nut
according to DIN 11851
12.8°
DN80/DN100 9.6°
Type F (50 mm)
and Type N
(68 mm)
Tuchenhagen Varivent 12.8°
Emission cone
● Keep emission cone free of interference from obstructions such as ladders, pipes, I-beams,
or filling streams.
Access for programming
● Provide easy access for viewing the display and programming via the handheld programmer.
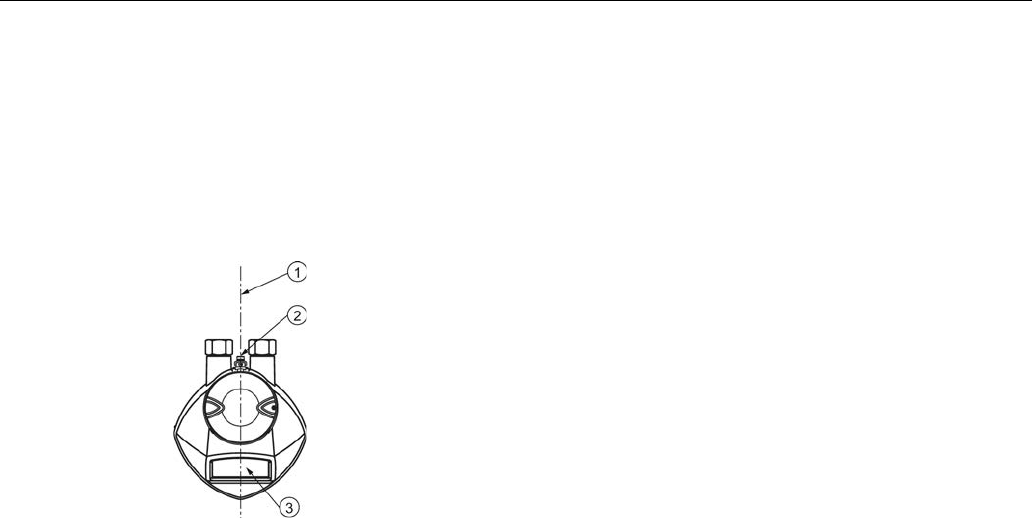
Installing/mounting
4.3 Proper mounting
SITRANS LR250 (FOUNDATION FIELDBUS)
Operating Instructions, 08/2014, A5E32221411-AC 31
4.3.3
Orientation in a vessel with obstructions
Polarization reference point
For best results on a vessel with obstructions, or a stillpipe with openings, orient the front or
back of the device toward the obstructions. For an illustration, see Device orientation (Page 33).
①
Polarization axis
②
Polarization reference point
③
Display
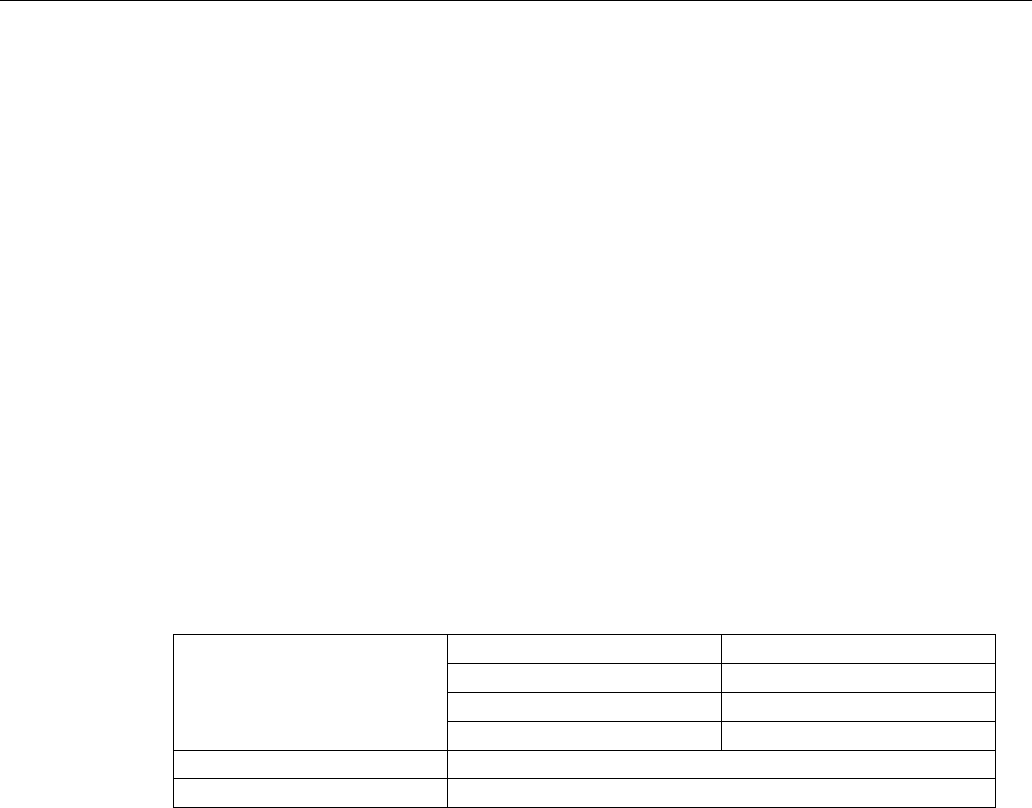
Installing/mounting
4.3 Proper mounting
SITRANS LR250 (FOUNDATION FIELDBUS)
32 Operating Instructions, 08/2014, A5E32221411-AC
4.3.4
Mounting on a Stillpipe or Bypass Pipe
A stillpipe or bypass pipe is used for products with a low dK, or when vortex or extremely
turbulent conditions exist. It can also be used to provide optimum signal conditions on foaming
materials. See Dielectric constant of material measured in Performance (Page 213) for more
information.
● The pipe diameter must be matched with the antenna size. Use the largest antenna size that
will fit the stillpipe/bypass pipe1). See Threaded Horn dimensions (Page 221), Raised-Face
Flange per EN 1092-1 (Page 255), Flanged encapsulated dimensions or Hygienic
encapsulated dimensions.
● One continuous length of metallic pipe is preferred, without joints.
● Any false reflections created by joints/welds/imperfections will lead to inaccuracies of the
measurement.
● Joints (if unavoidable) must be machined to ± 0.25 mm (± 0.010") and must have welded
connecting sleeve on the outside.
● If using any hygienic process connections in conjunction with a stillpipe/bypass, please
ensure that the antenna/lens are cleanable in accordance with the applicable approval.
1) Mounting in a pipe greater than 100 mm (4") can cause large errors, and therefore is not
recommended.
Suitable pipe diameters: Horn antenna 40 to 100 mm (1.5 to 4")
PVDF antenna 50 mm (2") only
Flanged encapsulated antenna 50 to 100 mm (2 to 4")
Hygienic encapsulated antenna 50 to 100 mm (2 to 4")
Not recommended: > 100 mm (4")
Bypass vent: Required at the upper end of the bypass 1)
1) To equalize pressure and keep the liquid level in the bypass constant with the liquid level in the
vessel.
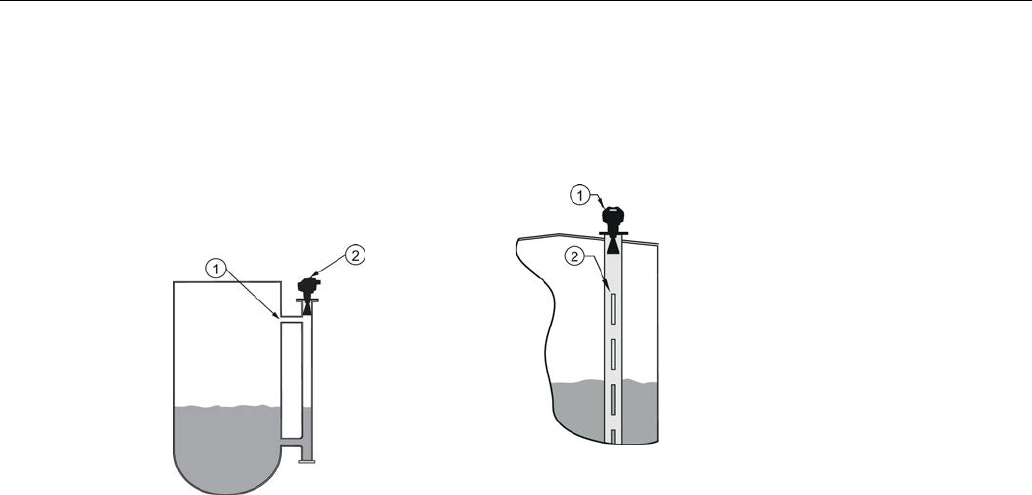
Installing/mounting
4.3 Proper mounting
SITRANS LR250 (FOUNDATION FIELDBUS)
Operating Instructions, 08/2014, A5E32221411-AC 33
4.3.5
Device orientation
Bypass pipe installation
Stillpipe installation
① Vent ① Align front or back of device with stillpipe slots1)
② Align front or back of device with
vents1)
② Slots
1) Horn antenna version shown as example
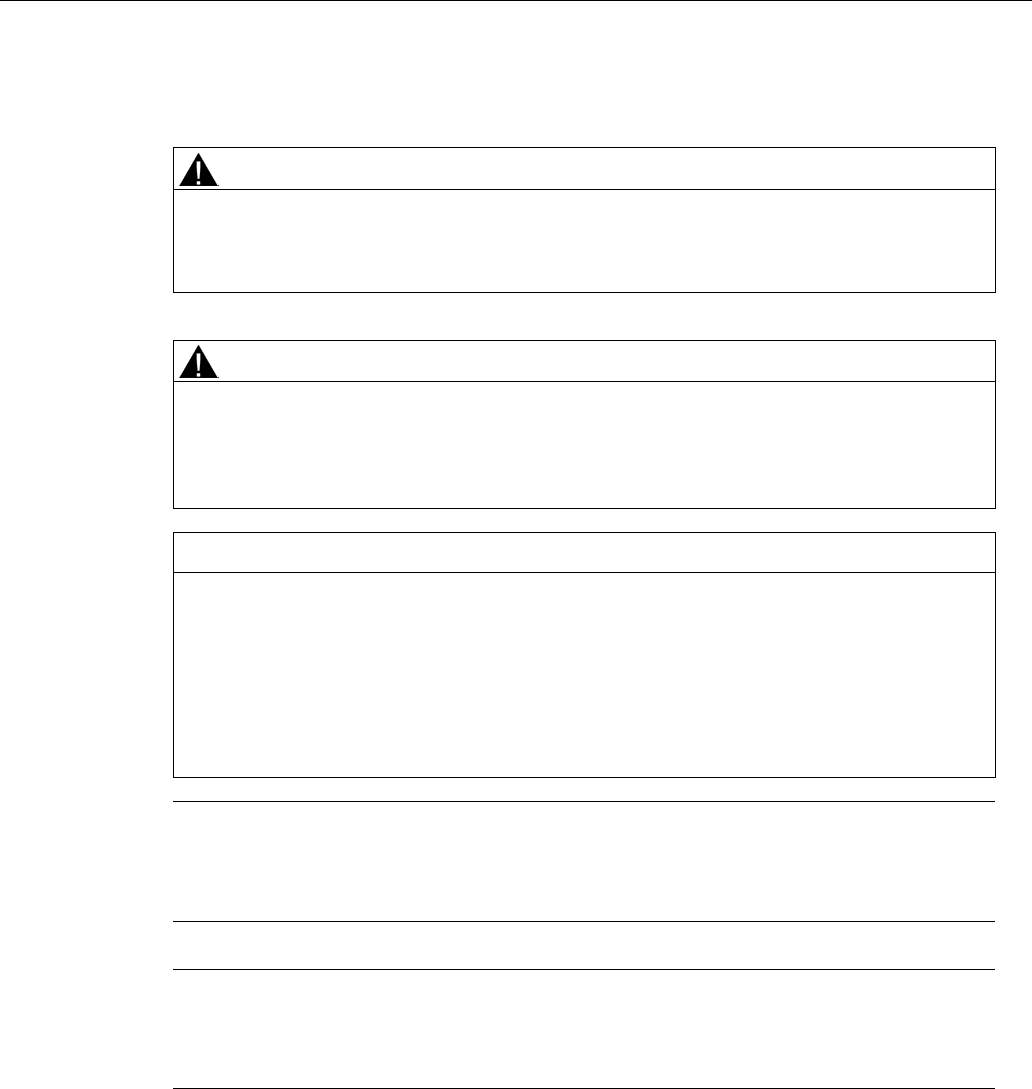
Installing/mounting
4.4 Installation instructions
SITRANS LR250 (FOUNDATION FIELDBUS)
34 Operating Instructions, 08/2014, A5E32221411-AC
4.4
Installation instructions
WARNING
Pressure applications
Danger to personnel, system and environment can result from improper installation.
• Improper installation may result in loss of process pressure.
WARNING
Improper installation
Danger to personnel, system and environment can result from improper installation.
• Installation shall only be performed by qualified personnel and in accordance with local
governing regulations.
NOTICE
Device handling
Damage to device may result from improper handling.
• Handle the device using the enclosure, not the process connection or tag, to avoid
damage.
• Take special care when handling the threaded PVDF and Hygienic or Flanged
encapsulated antennas. Any damage to the antenna surface, particularly to the tip/lens,
could affect performance. (For example, do not sit device on its lens antenna.)
Note
• For European Union and member countries, installation must be according to
ETSI EN 302372.
• Refer to the device nameplate for approval information.
Note
The outer part of the lens on the flanged encapsulated antenna version may not appear to lie
flush before installation and this is normal. This will flatten after installation and will not
impact the performance of the device.
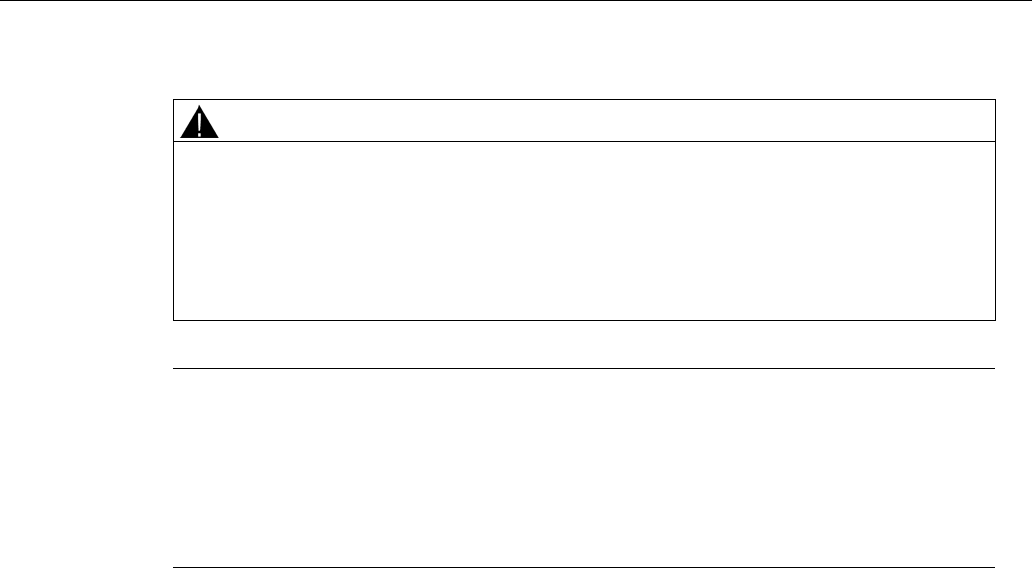
Installing/mounting
4.4 Installation instructions
SITRANS LR250 (FOUNDATION FIELDBUS)
Operating Instructions, 08/2014, A5E32221411-AC 35
WARNING
Pressure applications
Danger of injury or poisoning.
It will be necessary to use PTFE tape or other appropriate thread sealing compound, and to
tighten the process connection beyond hand-tight. (The maximum recommended torque for
Threaded versions is 40 N-m (30 ft.lbs.) See Flanged versions (Page 37) for FEA
recommended torque values.)
Note
• On devices with a removable head, there is no limit to the number of times a device can
be rotated without damage.
• When mounting, orient the front or back of the device towards the closest vessel wall or
obstruction.
• Do not rotate the enclosure after programming and vessel calibration, otherwise an error
may occur, caused by a polarity shift of the transmit pulse.
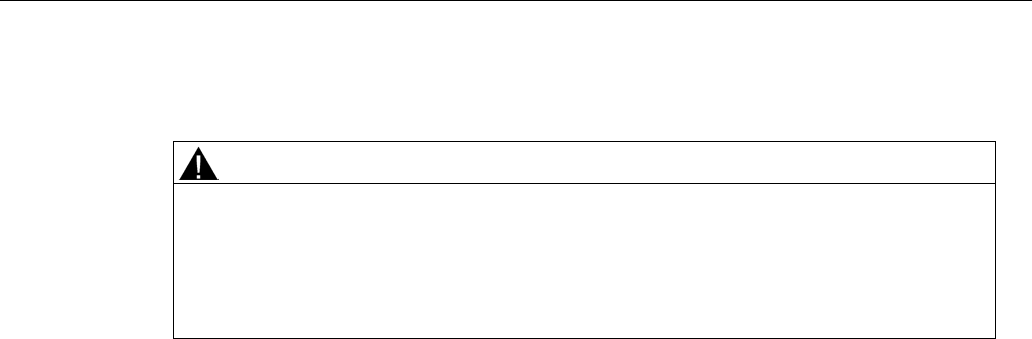
Installing/mounting
4.4 Installation instructions
SITRANS LR250 (FOUNDATION FIELDBUS)
36 Operating Instructions, 08/2014, A5E32221411-AC
4.4.1
Threaded versions
WARNING
Pressure applications
Danger of injury or poisoning.
It may be necessary to use PTFE tape or other appropriate thread sealing compound, and
to tighten the process connection beyond hand-tight. (The maximum recommended torque
for Threaded versions is 40 N-m (30 ft.lbs.)
1. Before inserting the device into its mounting connection, check to ensure the threads are
matching, to avoid damaging them.
2. Simply screw the device into the process connection, and hand tighten, or use a wrench.
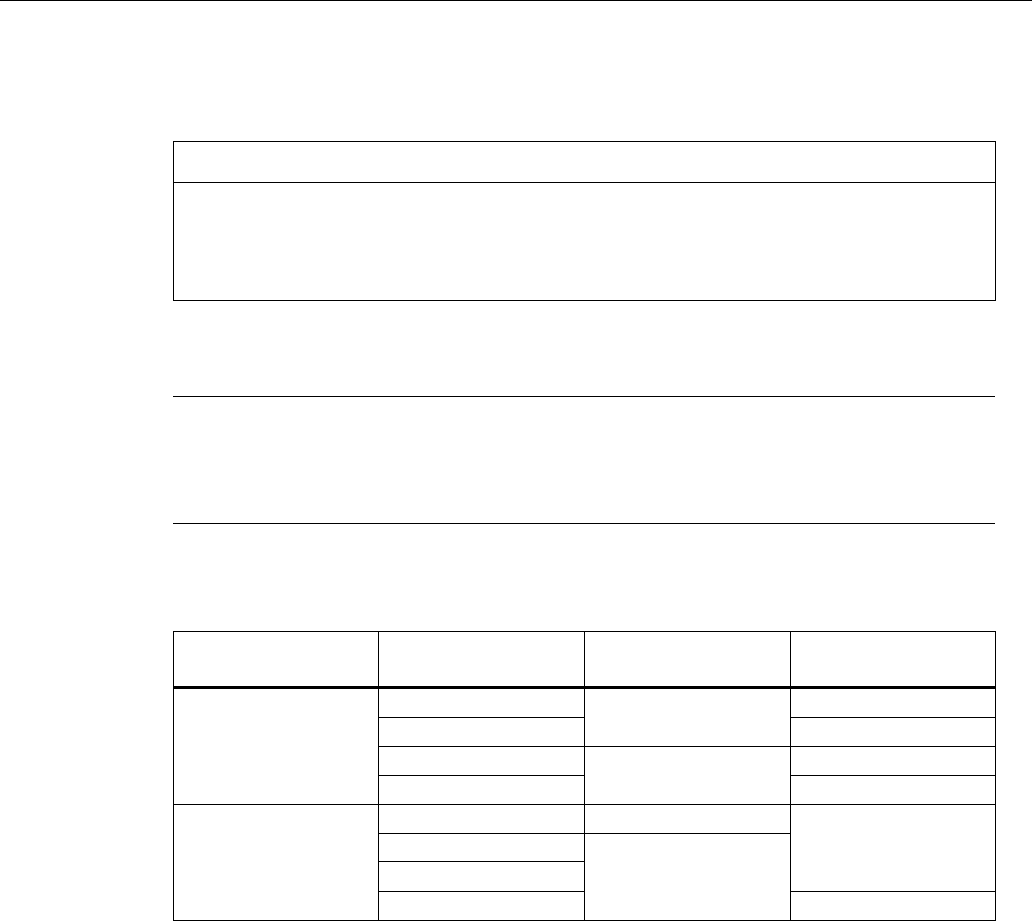
Installing/mounting
4.4 Installation instructions
SITRANS LR250 (FOUNDATION FIELDBUS)
Operating Instructions, 08/2014, A5E32221411-AC 37
4.4.2
Flanged versions
NOTICE
Improper materials
The user is responsible for the selection of bolting and gasket materials (except for Flanged
encapsulated antenna) which will fall within the limits of the process connection and its
intended use, and which are suitable for the service conditions.
Special Instructions for Flanged encapsulated antenna only
Note
• Use spring washers
• Lens assembly acts as integral gasket, no other required
• Use recommended torque values for tightening bolts
Flange bolting: recommended torque
Pressure class
Nominal pipe size
(NPS)
Number of bolts
Recommended torque
(Nm)
ASME B16.5, Class
150
2" 4 30 – 50
3" 50 – 70
4" 8 40 – 60
6" 70 – 90
EN1092-1, PN16 /
JIS B 2220, 10K
DN50/50A 4 30 – 50
DN80/80A 8
DN100/100A
DN150/150A 60 – 80
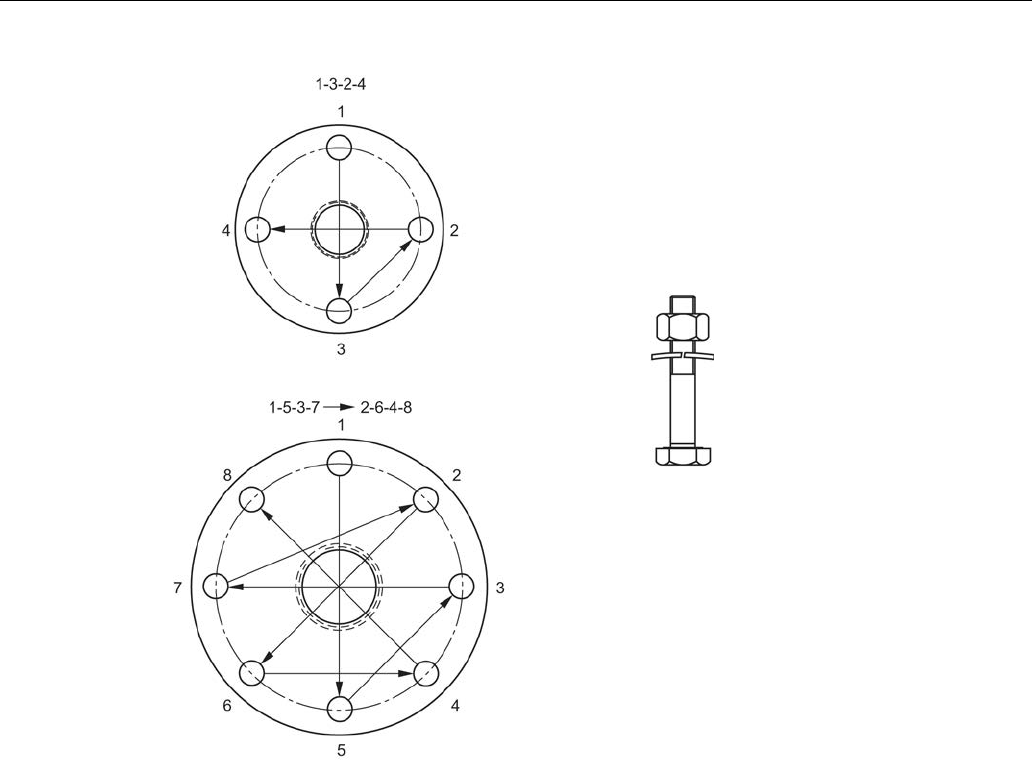
Installing/mounting
4.4 Installation instructions
SITRANS LR250 (FOUNDATION FIELDBUS)
38 Operating Instructions, 08/2014, A5E32221411-AC
Flange bolting instructions:
1. Use cross-pattern sequence as shown.
2. Check uniformity of the flange gap.
3. Apply adjustments by selective tightening if required.
4. Torque incrementally until desired value is reached.
5. Check/re-torque after 4 to 6 hours.
Recommendations for flange bolting:
● Check bolts periodically, re-torque as required.
● Use new lens, O-ring and spring washers after removal from installation.
For instructions on replacing the lens, see Part replacement (Page 199).
See Flanged Horn with extension (Page 226), Raised-Face Flange per EN 1092-1 (Page 255),
Flat-Face Flange (Page 258), and Flanged encapsulated antenna (3"/DN80/80A sizes and
larger) (Page 232) for dimensions.
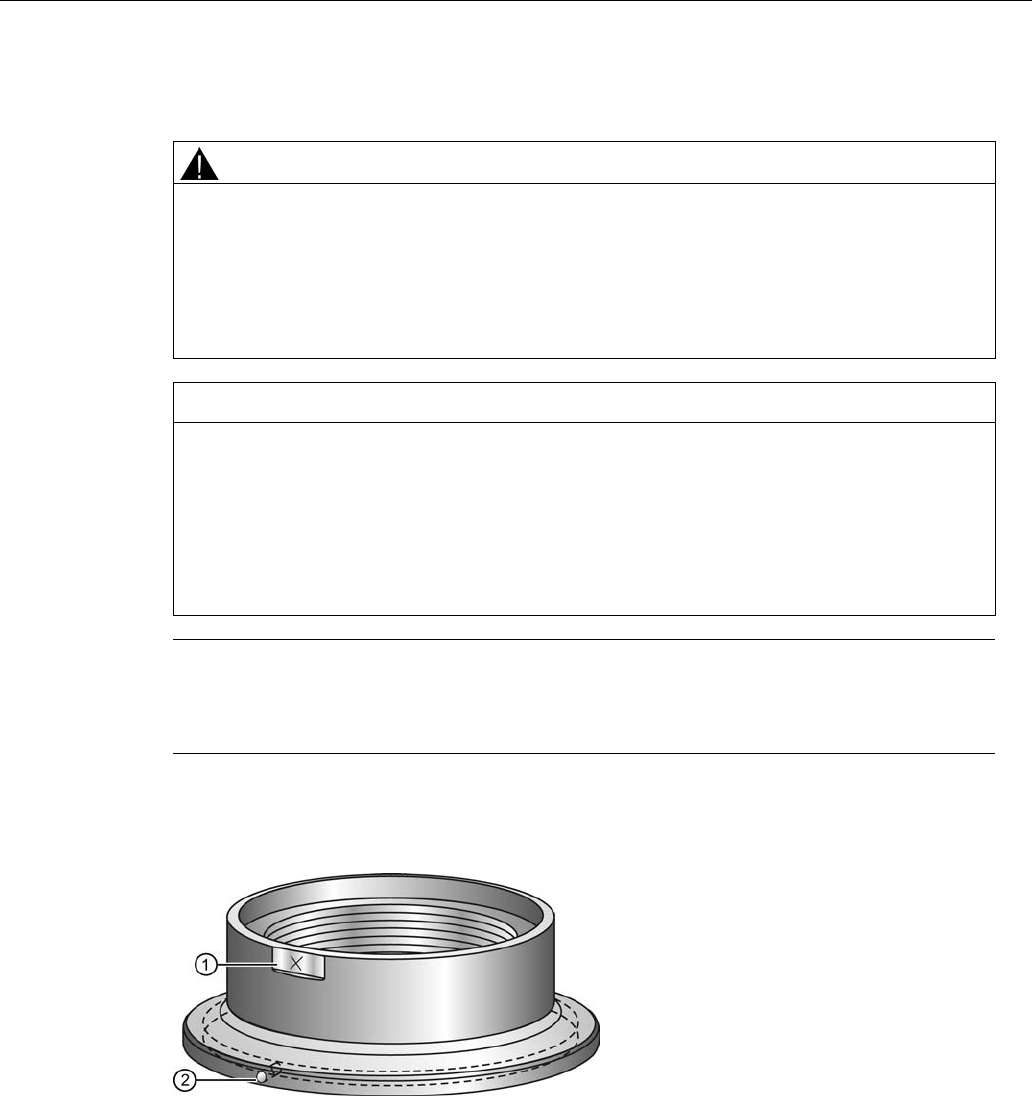
Installing/mounting
4.4 Installation instructions
SITRANS LR250 (FOUNDATION FIELDBUS)
Operating Instructions, 08/2014, A5E32221411-AC 39
4.4.3
Hygienic versions
WARNING
Loss of sanitary approvals
Loss of sanitary approvals can result from improper installation/mounting.
• Take special care when installing in hygienic or sanitary applications. Comply with
installation/mounting guidelines to ensure cleanliness and the ability to keep the wetted
parts in a position to be readily cleanable. (See relevant EHEDG/3A documentation - not
supplied).
NOTICE
Loss of sanitary approvals
• For 3-A Sanitary Approved device installation where the customer tank process
connection exists, a leak detection port of minimum 2.4 mm diameter must be provided
at the lowest point in the process connection where leakage can occur.
• If leakage is detected at any time while the device is installed, then the device process
connection parts must be disassembled and thoroughly cleaned prior to gasket
replacement and reassembly.
Note
• For Hygienic encapsulated antenna, the lens acts as a gasket/seal and should be used in
conjunction with a cleanable seal as required by the specific process connections (for
example, DIN 11864-3).
Hygienic encapsulated antenna leak detection port
① Orientation mark for leak detection port
② Leak detection port
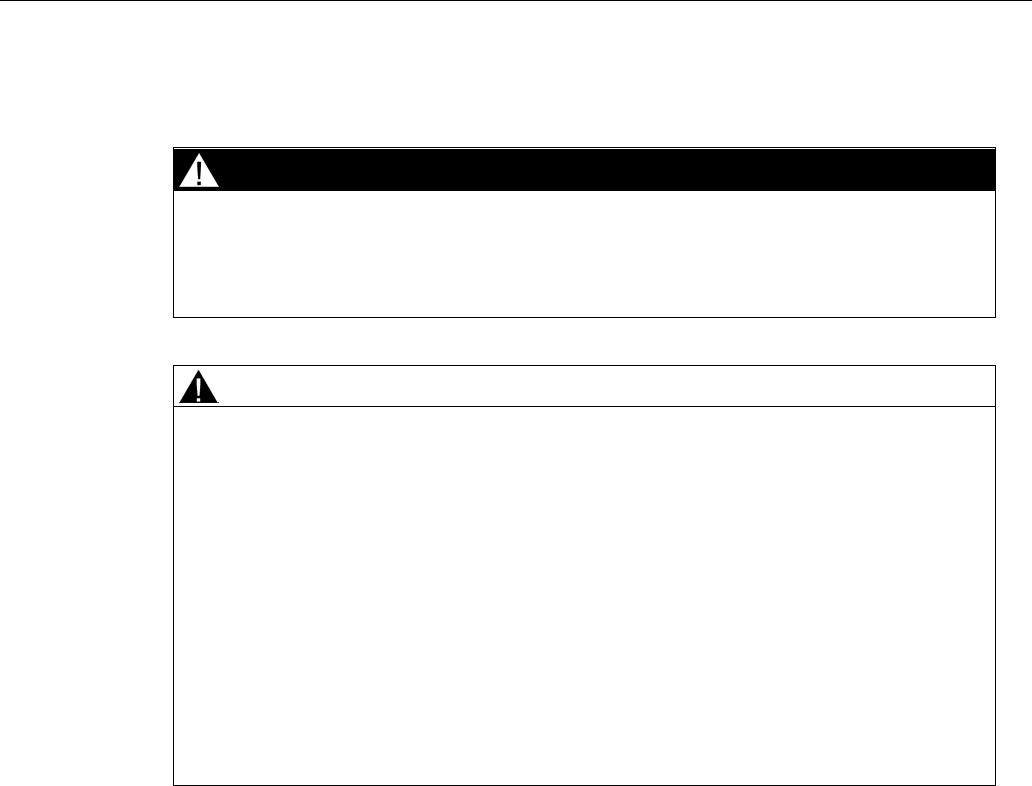
Installing/mounting
4.5 Disassembly
SITRANS LR250 (FOUNDATION FIELDBUS)
40 Operating Instructions, 08/2014, A5E32221411-AC
4.5
Disassembly
DANGER
Pressure applications
Danger to personnel, system and environment will result from improper disassembly.
• Never attempt to loosen, remove, or disassemble process connection while vessel
contents are under pressure.
WARNING
Incorrect disassembly
The following dangers may result through incorrect disassembly:
- Injury through electric shock
- Danger through emerging media when connected to the process
- Danger of explosion in hazardous area
In order to disassemble correctly, observe the following:
• Before starting work, make sure that you have switched off all physical variables such
as pressure, temperature, electricity etc. or that they have a harmless value.
• If the device contains dangerous media, it must be emptied prior to disassembly. Make
sure that no environmentally hazardous media are released.
• Secure the remaining connections so that no damage can result if the process is started
unintentionally.
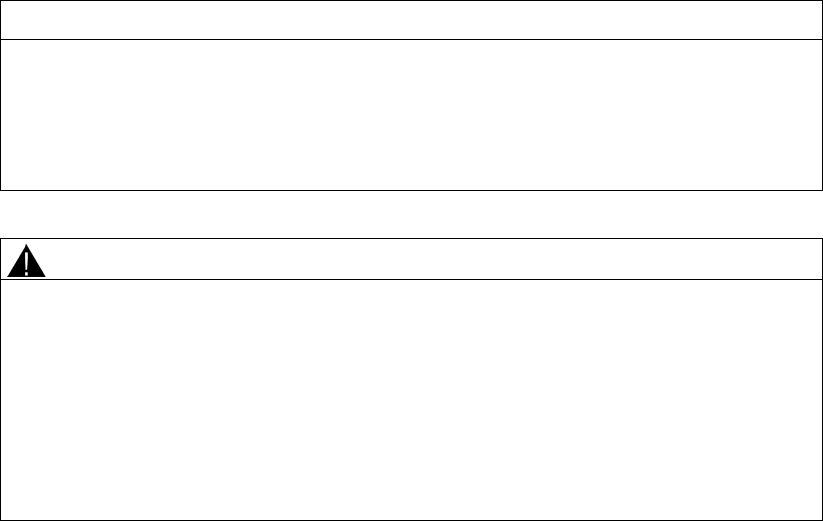
SITRANS LR250 (FOUNDATION FIELDBUS)
Operating Instructions, 08/2014, A5E32221411-AC 41
Connecting
5
5.1
Basic safety information
NOTICE
Condensation in the device
Damage to device through formation of condensation if the temperature difference between
transportation or storage and the mounting location exceeds 20 °C (68°F).
• Before taking the device into operation let the device adapt for several hours in the new
environment.
WARNING
Missing PE/ground connection
Danger of electric shock.
Depending on the device version, connect the power supply as follows:
•
Power plug
: Ensure that the used socket has a PE/ground conductor connection. Check
that the PE/ground conductor connection of the socket and power plug match each
other.
•
Connecting terminals
: Connect the terminals according to the terminal connection
diagram. First connect the PE/ground conductor.
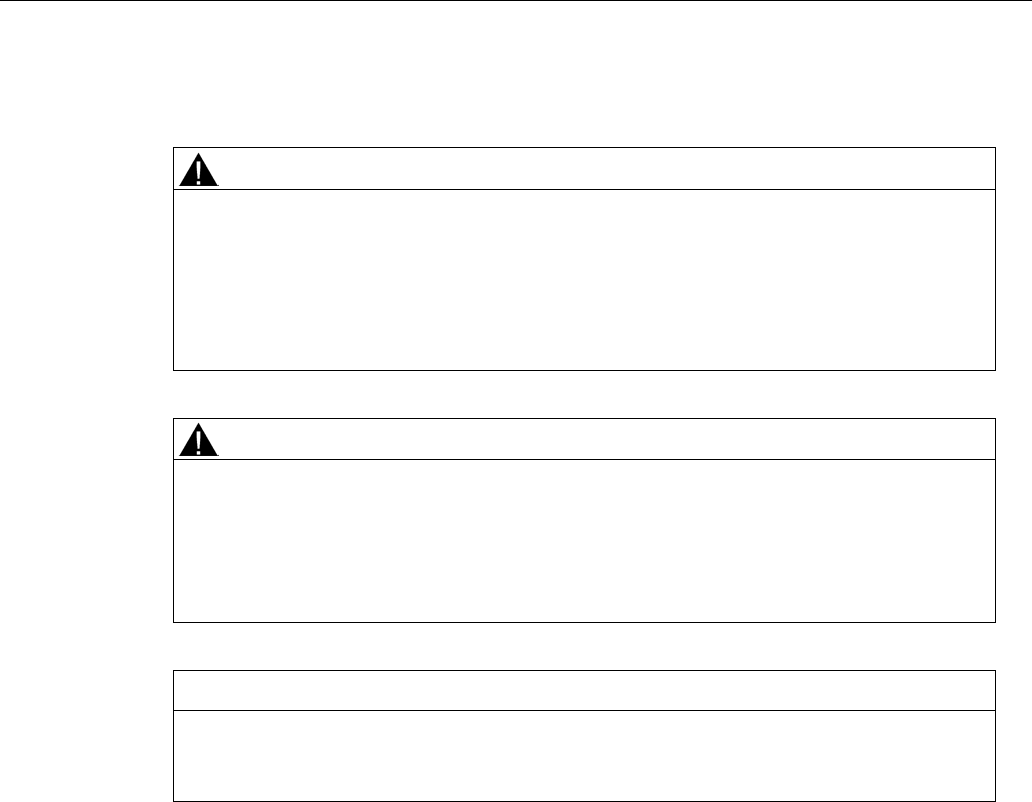
Connecting
5.2 Connecting SITRANS LR250
SITRANS LR250 (FOUNDATION FIELDBUS)
42 Operating Instructions, 08/2014, A5E32221411-AC
5.2
Connecting SITRANS LR250
WARNING
Incorrect connection to power source
Danger to personnel, system and environment can result from improper power connection.
• The DC input terminals shall be supplied from a source providing electrical isolation
between the input and output, in order to meet the applicable safety requirements of
IEC 61010-1.
• All field wiring must have insulation suitable for rated voltages.
WARNING
Loss of protection
Loss of approvals can result from improper installation.
• Check the nameplate on your device, to verify the approval rating.
• Use appropriate conduit seals to maintain IP or NEMA rating.
• See Wiring setups for hazardous area installation (Page 46).
NOTICE
Improper cables and conduit
• Separate cables and conduits may be required to conform to standard instrumentation
wiring practices or electrical codes.
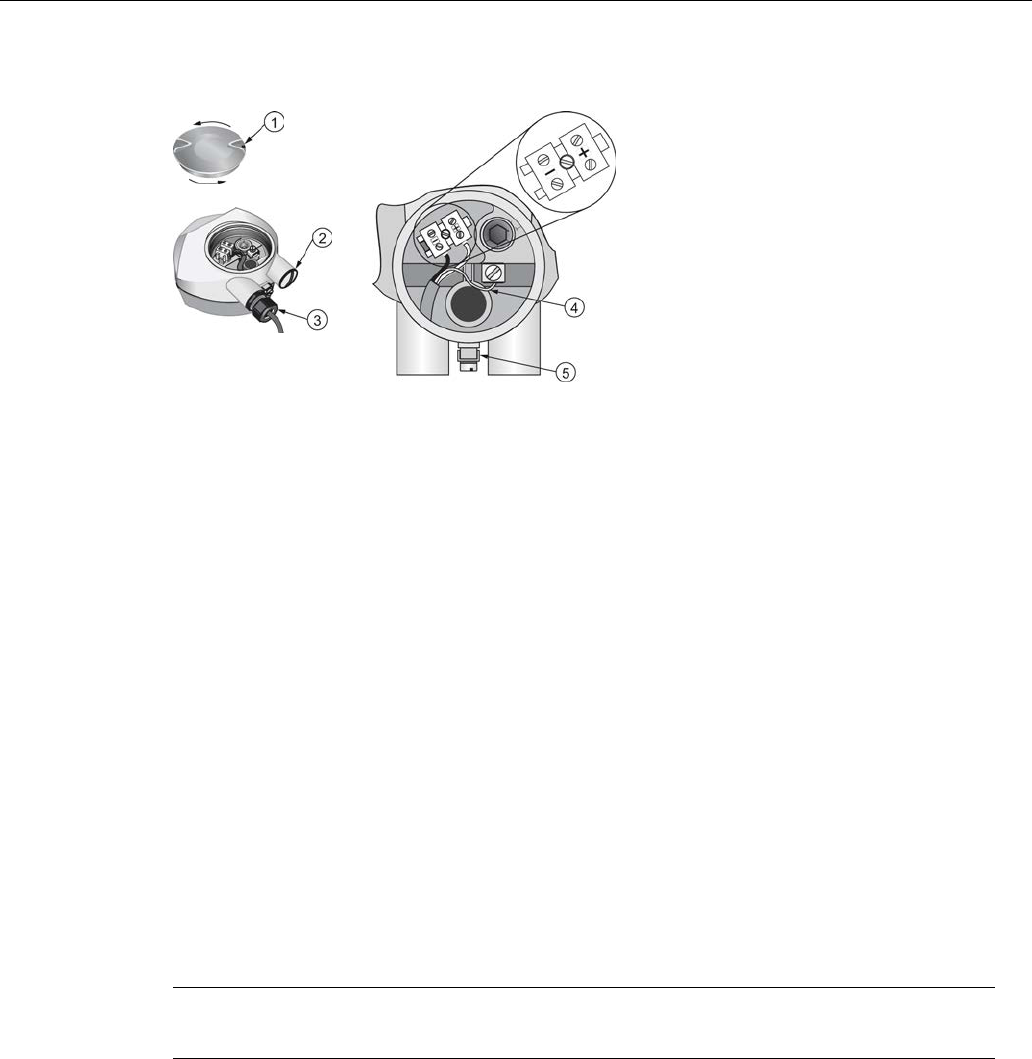
Connecting
5.2 Connecting SITRANS LR250
SITRANS LR250 (FOUNDATION FIELDBUS)
Operating Instructions, 08/2014, A5E32221411-AC 43
① Use a 2 mm Allen key to loosen the lid-lock set screw c) ④ Cable shield
② Plug (IP68) ⑤ Ground terminal
③ Optional cable glanda) b)(or NPT cable entry)b)
a)May be shipped with the device.
b)If cable is routed through conduit, use only approved suitable-size hubs for waterproof
applications.
c)Not applicable to 3-A Sanitary approved device.
Wiring instructions
1. Strip the cable jacket for approximately 70 mm (2.75") from the end of the cable, and thread
the wires through the gland. (If cable is routed through conduit, use only approved suitable-
size hubs for waterproof applications.)
2. Connect the wires to the terminals as shown: SITRANS LR250 (FF) is not polarity sensitive.
3. Ground the device according to local regulations.
4. Tighten the gland to form a good seal.
5. Close the lid and secure the locking screw before programming and device configuration.
Note
Lid-lock set screw not applicable to 3-A Sanitary approved device.
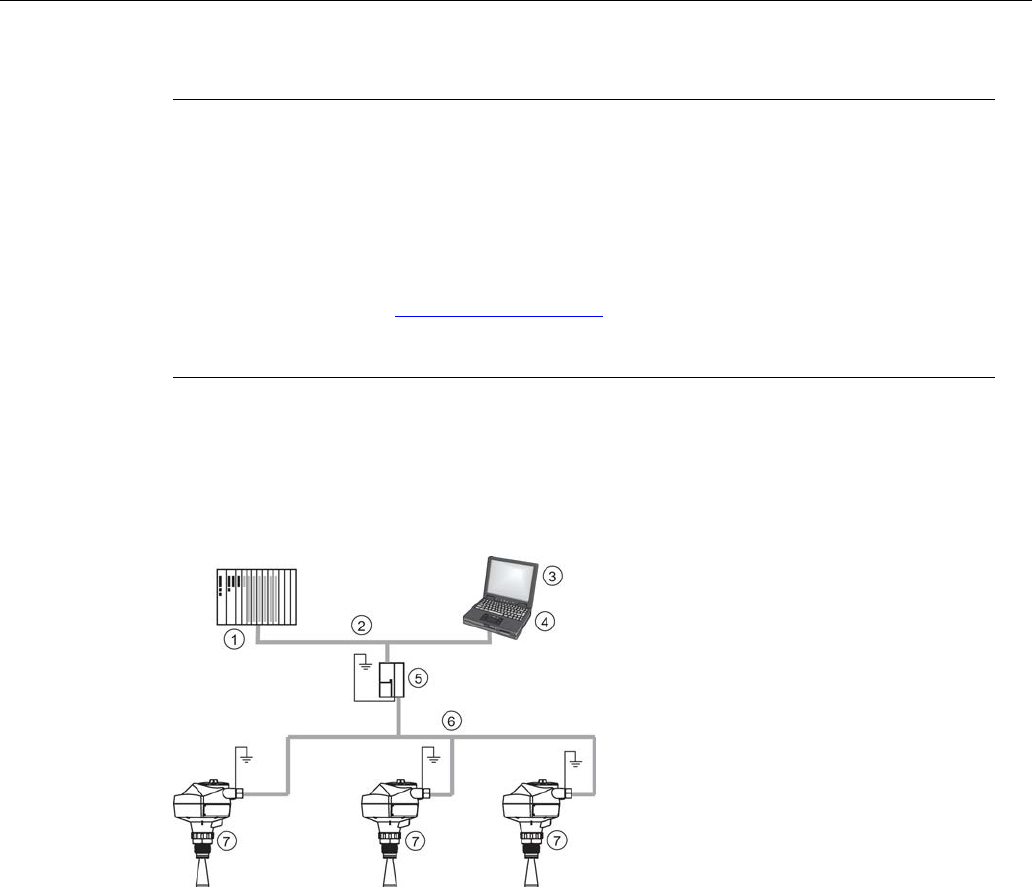
Connecting
5.2 Connecting SITRANS LR250
SITRANS LR250 (FOUNDATION FIELDBUS)
44 Operating Instructions, 08/2014, A5E32221411-AC
Note
• Foundation Fieldbus (H1) must be terminated at both extreme ends of the cable for it to
work properly.
• For optimum EMC protection, it is recommended that the FF H1 cable shield be
connected to ground at every node.
• Please refer to the Foundation Fieldbus System Engineering Guidelines (AG-181)
Revision 2.0, for information on installing FF (H1) devices available from:
Foundation Fieldbus (http://www.fieldbus.org/)
• If a Weidmüller or other current limiting junction box is connected to this device, please
ensure that the current limit is set to 40 mA or higher.
Basic Configuration with Foundation Fieldbus (H1)
Configuration via Gateway
①
Controller
⑤
Rosemount 3420 HSE/H1Gateway
②
FF (HSE)
⑥
FF (H1)
③
Configurator software
⑦
LR250 FF
④
PC/laptop
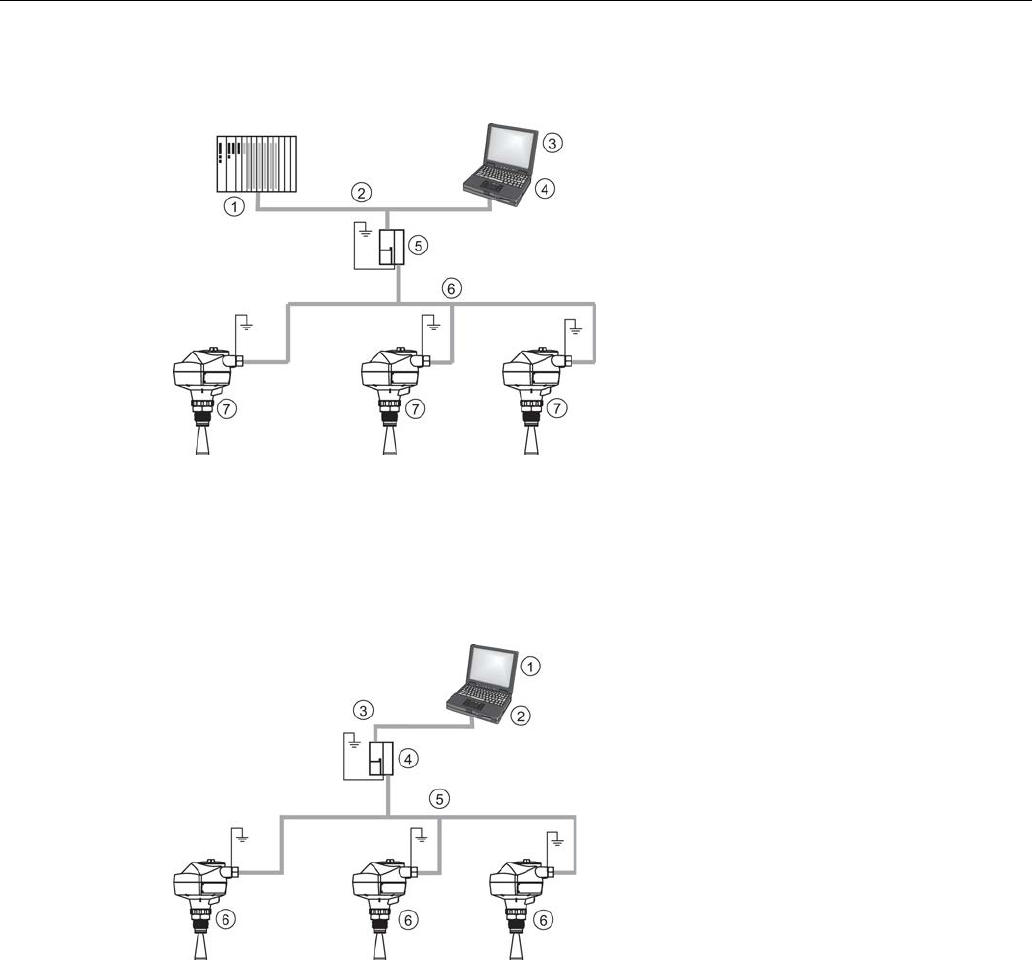
Connecting
5.2 Connecting SITRANS LR250
SITRANS LR250 (FOUNDATION FIELDBUS)
Operating Instructions, 08/2014, A5E32221411-AC 45
Configuration via Linking Device
①
Controller
⑤
HSE/H1 Linking Device
②
FF (HSE)
⑥
FF (H1)
③
Configurator software
⑦
LR250 FF
④
PC/laptop
Configuration via PCI/PCMCIA Card
①
Configurator software
④
H1 Interface
②
PC/laptop
⑤
FF (H1)
③
PCI/PCMCIA bus
⑥
LR250 FF
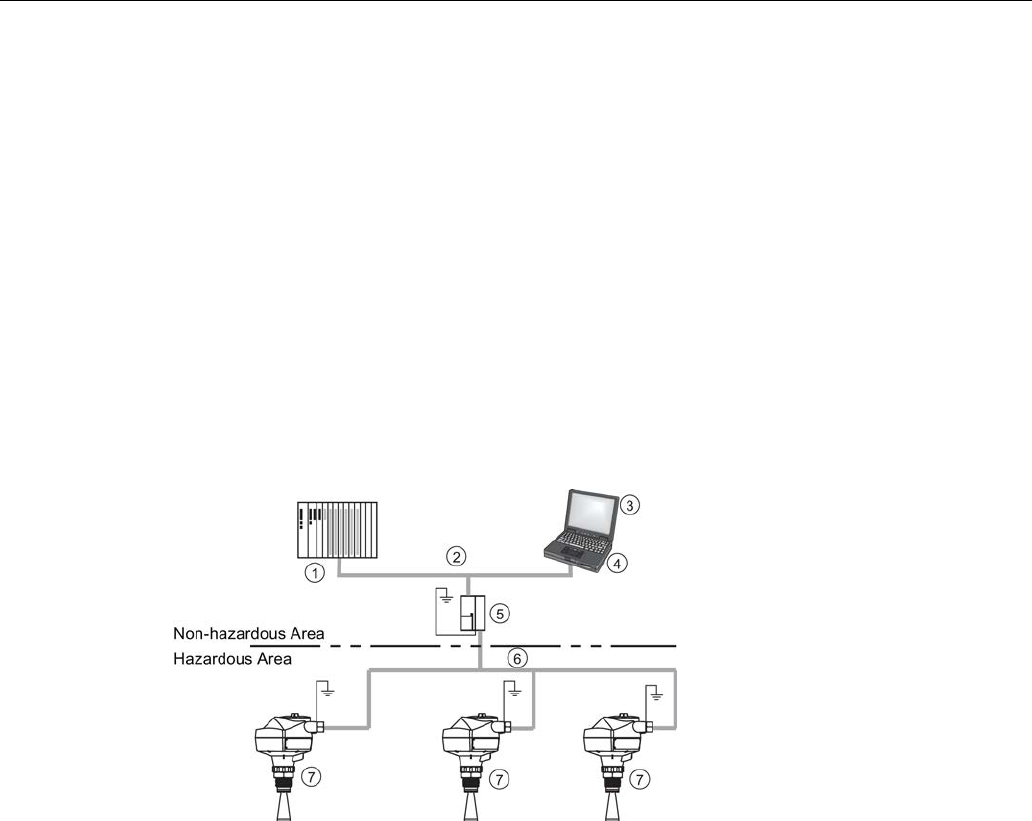
Connecting
5.3 Wiring setups for hazardous area installation
SITRANS LR250 (FOUNDATION FIELDBUS)
46 Operating Instructions, 08/2014, A5E32221411-AC
5.3
Wiring setups for hazardous area installation
There are three wiring options for hazardous area installations:
● Intrinsically safe wiring (Page 48)
● Non-sparking wiring (Page 51)
● Non-incendive wiring (US/Canada only) (Page 51)
In all cases, check the nameplate on your instrument, confirm the approval rating, and perform
installation and wiring according to your local safety codes.
5.3.1
Configuration with Foundation Fieldbus for hazardous areas
Configuration via Gateway
①
Controller
⑤
Ex ia type HSE/H1
②
FF (HSE)
⑥
FF (H1)
③
Configurator software
⑦
LR250 FF
④
PC/laptop
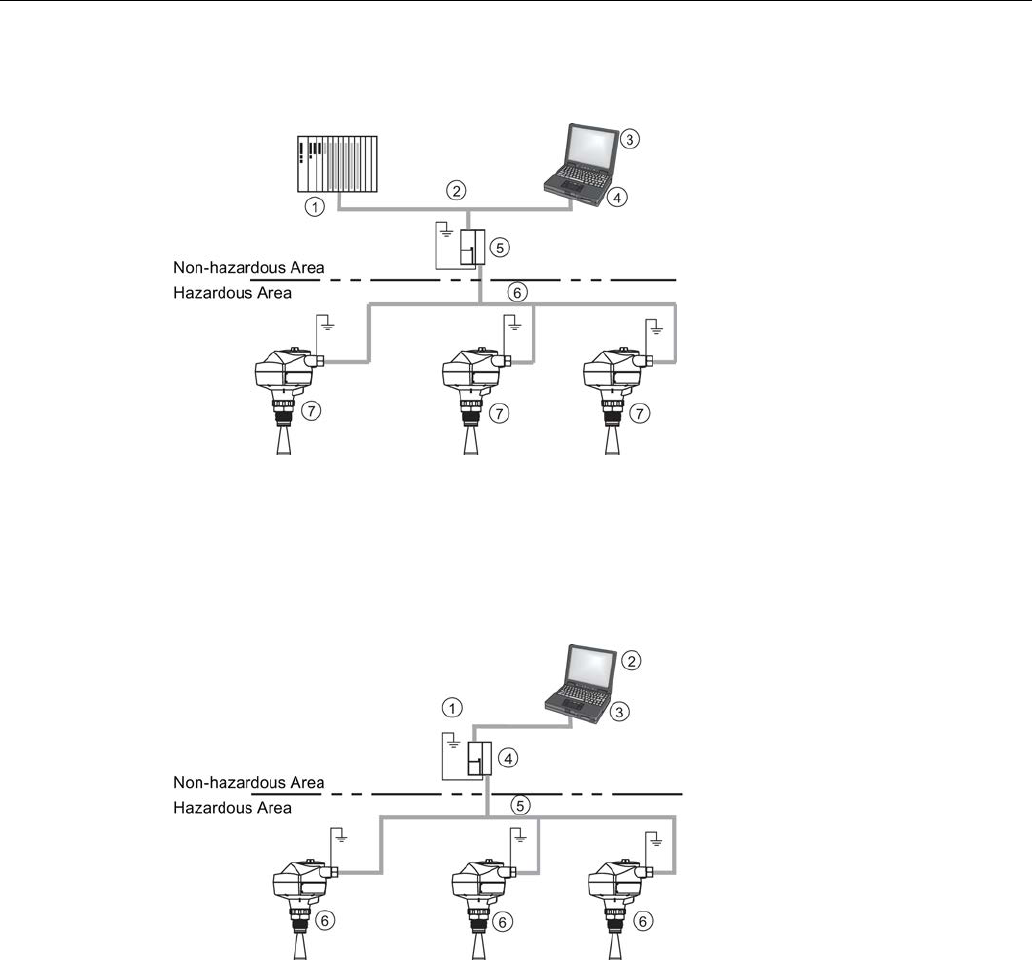
Connecting
5.3 Wiring setups for hazardous area installation
SITRANS LR250 (FOUNDATION FIELDBUS)
Operating Instructions, 08/2014, A5E32221411-AC 47
Configuration via Linking Device
①
Controller
⑤
Ex ia type HSE/H1 Linking Device
②
FF (HSE)
⑥
FF (H1)
③
Configurator software
⑦
LR250 (FF)
④
PC/laptop
Configuration via PCI/PCMCIA Card
①
PCI/PCMCIA bus
④
Ex ia type H1 Interface
②
Configurator software
⑤
FF (H1)
③
PC/laptop
⑥
LR250 FF
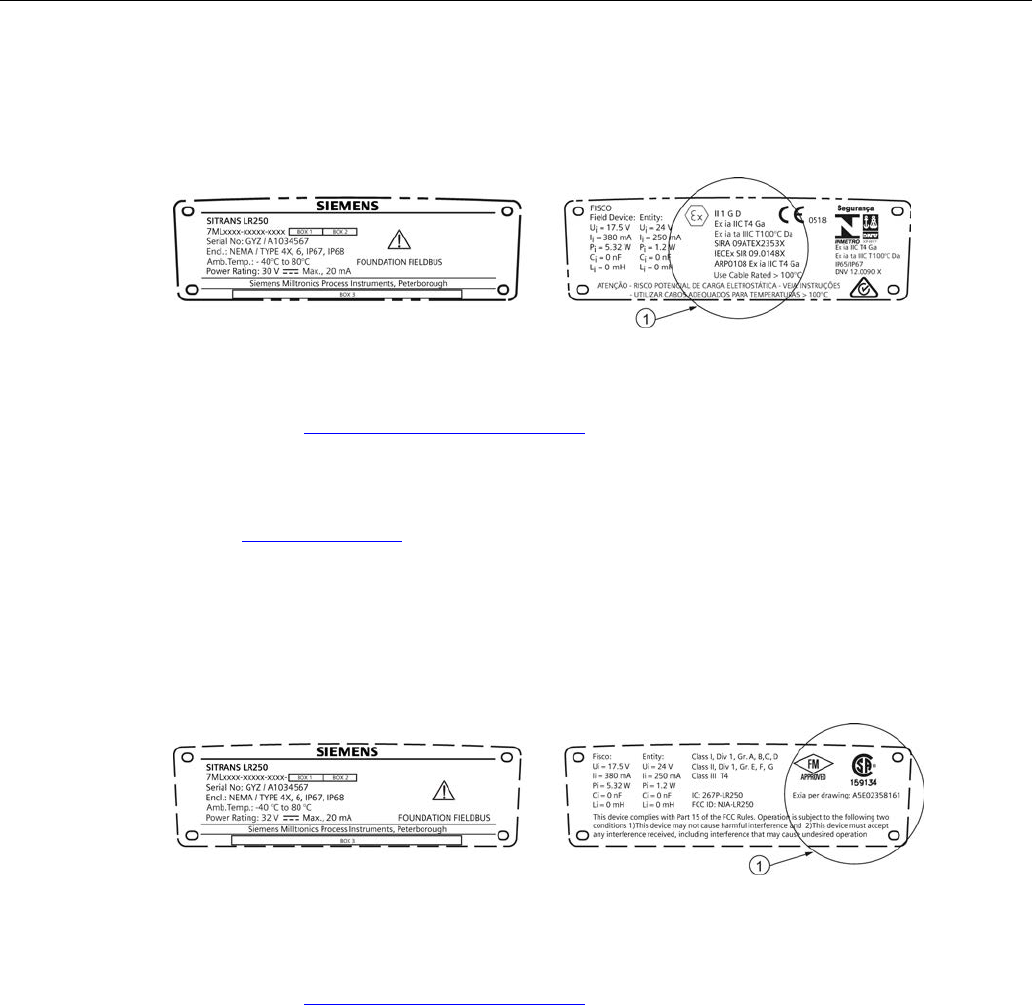
Connecting
5.3 Wiring setups for hazardous area installation
SITRANS LR250 (FOUNDATION FIELDBUS)
48 Operating Instructions, 08/2014, A5E32221411-AC
5.3.2
Intrinsically safe wiring
Device nameplate (ATEX/IECEx/RCM)
①
ATEX certificate
The ATEX certificates listed on the nameplate can be downloaded from our website:
Product page (http://www.siemens.com/LR250)
Go to
Support > Approvals / Certificates.
The IECEx certificate listed on the nameplate can be viewed on the IECEx website. Go to:
IECEx (http://iecex.iec.ch/)
Click on
Certified Equipment
and enter the certificate number
IECEx SIR 09.0148X.
5.3.2.1
Intrinsically safe wiring (FM/CSA)
Device nameplate (FM/CSA)
①
Connection drawing number
The FM/CSA Intrinsically Safe connection drawing number A5E02358161 can be downloaded
from our website at:
Product page (http://www.siemens.com/LR250)
Go to
Support > Installation Drawings > Level Measurement > SITRANS LR250
.
● For wiring requirements: follow local regulations.
● Approved dust-tight and water-tight conduit seals are required for outdoor NEMA 4X / type 4X
/ NEMA 6, IP67, IP68 locations.
● Refer to Instructions specific to hazardous area installations (Page 52).
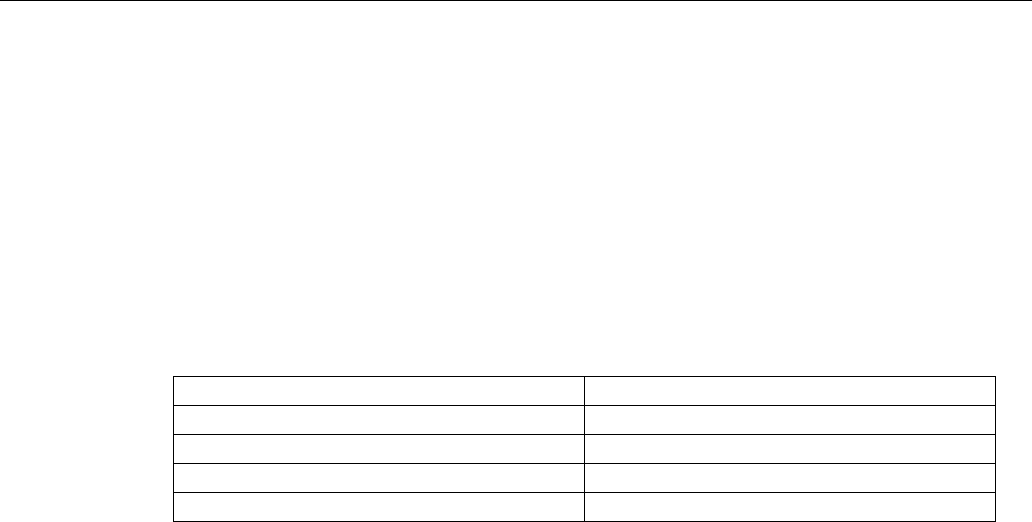
Connecting
5.3 Wiring setups for hazardous area installation
SITRANS LR250 (FOUNDATION FIELDBUS)
Operating Instructions, 08/2014, A5E32221411-AC 49
Entity concept:
The Entity Concept allows interconnection of intrinsically safe apparatus to associated apparatus
not specifically examined in such combination. The criteria for interconnection is that the voltage
and current which intrinsically safe apparatus can receive and remain intrinsically safe,
considering faults, must be equal to or greater than the output voltage (Uo) and output current
(Io) levels which can be delivered by the associated apparatus, considering faults and applicable
factors. In addition, the maximum unprotected capacitance (Ci) and Inductance (Li) of the
intrinsically safe apparatus, including interconnecting wiring, must be equal to or less than the
capacitance and inductance which can be safely connected to associated apparatus.
Under the entity evaluation concept, SITRANS LR250 has the following characteristics:
(input voltage) Ui = 24 V
(input current) Ii = 250 mA
(input power) Pi = 1.2 W
(internal capacitance) Ci = 0
(internal inductance) Li = 0
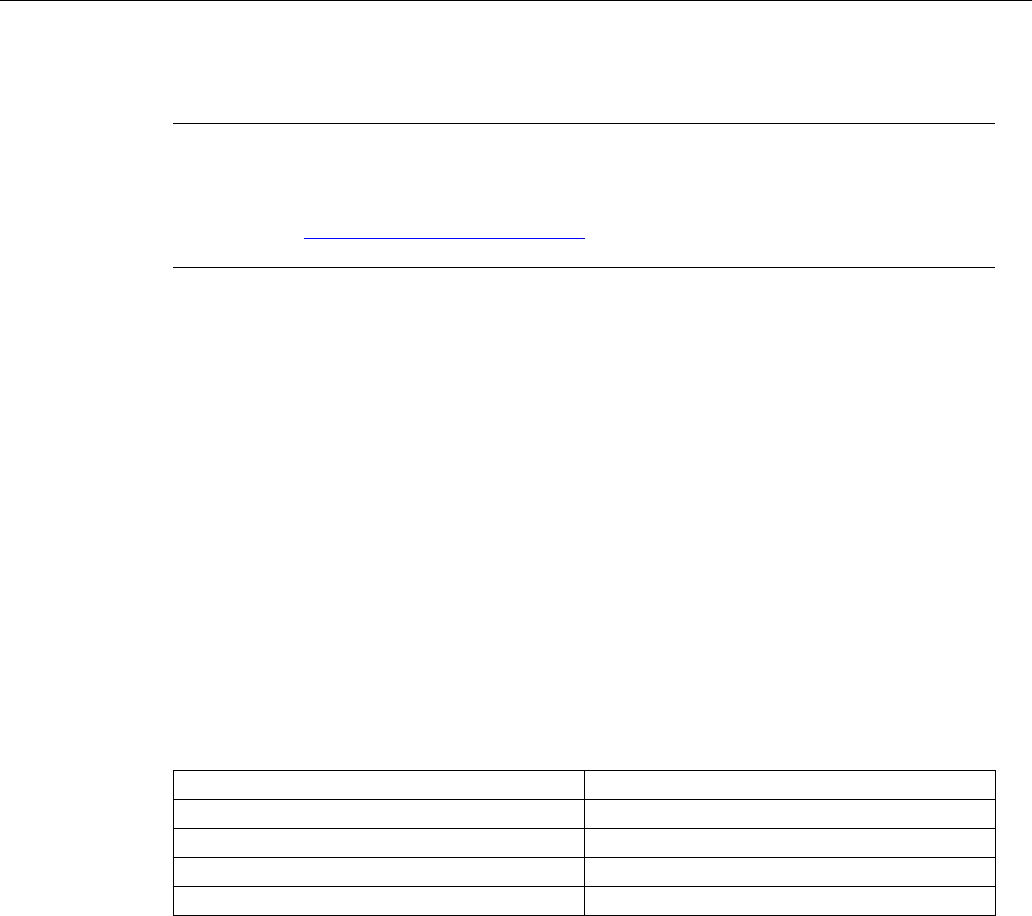
Connecting
5.3 Wiring setups for hazardous area installation
SITRANS LR250 (FOUNDATION FIELDBUS)
50 Operating Instructions, 08/2014, A5E32221411-AC
FISCO Concept
Note
For complete details and instructions regarding the FISCO Concept The FM/CSA connection
drawing number A5E02358161 can be downloaded from our website at:
Product page (http://www.siemens.com/LR250)
Go to
Support
>
Installation Drawings
>
Level Measurement
>
SITRANS LR250
.
The FISCO Concept allows interconnection of intrinsically safe apparatus to associated
apparatus not specifically examined in such combination. The criteria for interconnection is that
the voltage (Ui or Vmax), the current (Ii, or Imax) and the power (Pi, or Pmax) which intrinsically
safe apparatus can receive and remain intrinsically safe, considering faults, must be equal to or
greater than the voltage (Uo or Voc or Vi), the current (lo or Isc or li), and the power (Po or
Pmax) levels which can be delivered by the associated apparatus, considering faults and
applicable factors. In addition, the maximum unprotected capacitance (Ci) and inductance (Li) of
each apparatus (other than the termination) connected to the fieldbus must be less than or equal
to 5 nF and 10 μH respectively.
In each segment only one active device, normally the associated apparatus, is allowed to
provide the necessary energy for the fieldbus system. The allowed voltage Uo (or Voc or Vt) of
the associated apparatus is limited to the range of 14V dc to 24V dc. All other equipment
connected to the bus cable has to be passive, meaning that they are not allowed to provide
energy to the system, except for a leakage current of 50 μA for each connected device.
Separately powered equipment needs a galvanic isolation to assure that the Intrinsically Safe
fieldbus circuit remains passive.
Under the FISCO evaluation concept, SITRANS LR250 has the following characteristics:
(input voltage) Ui = 17.5 V
(input current) Ii = 380 mA
(input power) Pi = 5.32 W
(internal capacitance) Ci = 0
(internal inductance) Li = 0
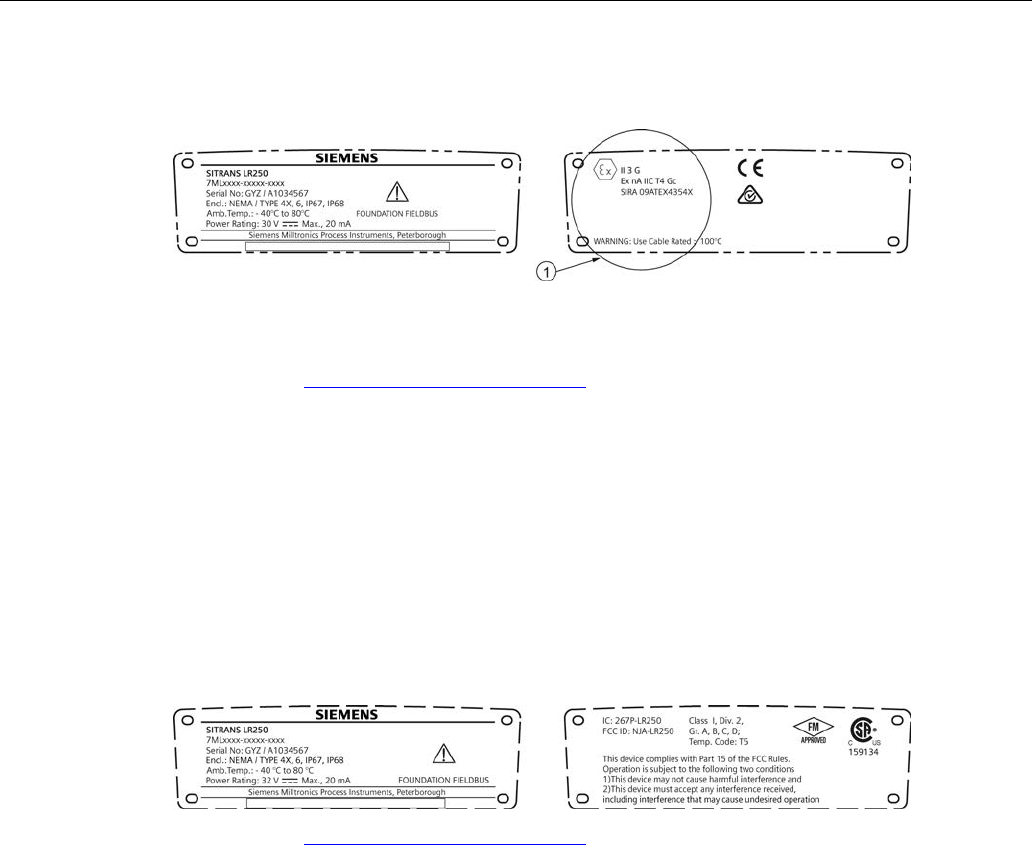
Connecting
5.3 Wiring setups for hazardous area installation
SITRANS LR250 (FOUNDATION FIELDBUS)
Operating Instructions, 08/2014, A5E32221411-AC 51
5.3.3
Non-sparking wiring
①
ATEX certificate
The ATEX certificate listed on the nameplate can be downloaded from our website:
Product page (http://www.siemens.com/LR250)
Go to:
Support > Installation drawings > Level measurement > SITRANS LR250
.
● For wiring requirements follow local regulations.
● Approved dust-tight and water-tight conduit seals are required for outdoor NEMA 4X / type 4X
/ NEMA 6, IP67, IP68 locations.
5.3.4
Non-incendive wiring (US/Canada only)
FM/CSA Class 1, Div 2 connection drawing number 23650673 can be downloaded from our
website:
Product page (http://www.siemens.com/LR250)
Go to
Support > Installation Drawings > Level Measurement > SITRAINS LR250.
● For wiring requirements: follow local regulations.
● Approved dust-tight and water-tight conduit seals are required for outdoor NEMA 4X / type 4X
/ NEMA 6, IP67, IP68 locations.
● Refer to Instructions specific to hazardous area installations (Page 52).

Connecting
5.4 Instructions specific to hazardous area installations
SITRANS LR250 (FOUNDATION FIELDBUS)
52 Operating Instructions, 08/2014, A5E32221411-AC
5.4
Instructions specific to hazardous area installations
5.4.1
(Reference European ATEX Directive 94/9/EC, Annex II, 1/0/6)
The following instructions apply to equipment covered by certificate number
SIRA 06ATEX2353X and 09ATEX4354X:
1. For use and assembly, refer to the main instructions.
2. The equipment is certified for use as Category 1GD equipment per SIRA 06ATEX2353X, and
Category 3G equipment per SIRA 09ATEX4354X.
3. The equipment may be used with flammable gases and vapors with apparatus group IIC, IIB
and IIA and temperature classes T1, T2, T3 and T4.
4. The equipment has a degree of ingress protection of IP67 and a temperature class of
T100 oC and may be used with flammable dusts.
5. The equipment is certified for use in an ambient temperature range of –40 oC to +80 oC.
6. The equipment has not been assessed as a safety related device (as referred to by
Directive 94/9/EC Annex II, clause 1.5).
7. Installation and inspection of this equipment shall be carried out by suitably trained personnel
in accordance with the applicable code of practice (EN 60079-14 and EN 60079-17 in
Europe).
8. The equipment is non-repairable.
9. The certificate numbers have an ’X’ suffix, which indicates that special conditions for safe use
apply. Those installing or inspecting this equipment must have access to the certificates.
10.If the equipment is likely to come into contact with aggressive substances, then it is the
responsibility of the user to take suitable precautions that prevent it from being adversely
affected, thus ensuring that the type of protection is not compromised.
– Aggressive substances: e.g. acidic liquids or gases that may attack metals, or solvents
that may affect polymeric materials.
– Suitable precautions: e.g. establishing from the material’s data sheet that it is resistant to
specific chemicals.

Connecting
5.4 Instructions specific to hazardous area installations
SITRANS LR250 (FOUNDATION FIELDBUS)
Operating Instructions, 08/2014, A5E32221411-AC 53
Special conditions for safe use (denoted by X after the certificate number)
● Parts of the enclosure may be non-conducting and may generate an ignition-capable level of
electrostatic charge under certain extreme conditions. The user should ensure that the
equipment is not installed in a location where it may be subjected to external conditions (such
as high-pressure steam), which might cause a build-up of electrostatic charge on non-
conducting surfaces.
● Aluminium, magnesium, titanium or zirconium may be used at the accessible surface of the
equipment. In the event of rare incidents, ignition sources due to impact and friction sparks
could occur. This shall be considered when the SITRANS LR250 FF is being installed in
locations that specifically require Equipment Protection level Ga or Da.
● The equipment shall be infallibly bonded according to the relevant code of practice.
● The end use must ensure that the explosion protection and ingress protection of IP64 is
maintained at each entry to the enclosure by use of a blanking element or cable entry device
that meets the requirements of the protection concepts type 'n' or increased safety 'e' or
flameproof 'd'.

Connecting
5.4 Instructions specific to hazardous area installations
SITRANS LR250 (FOUNDATION FIELDBUS)
54 Operating Instructions, 08/2014, A5E32221411-AC
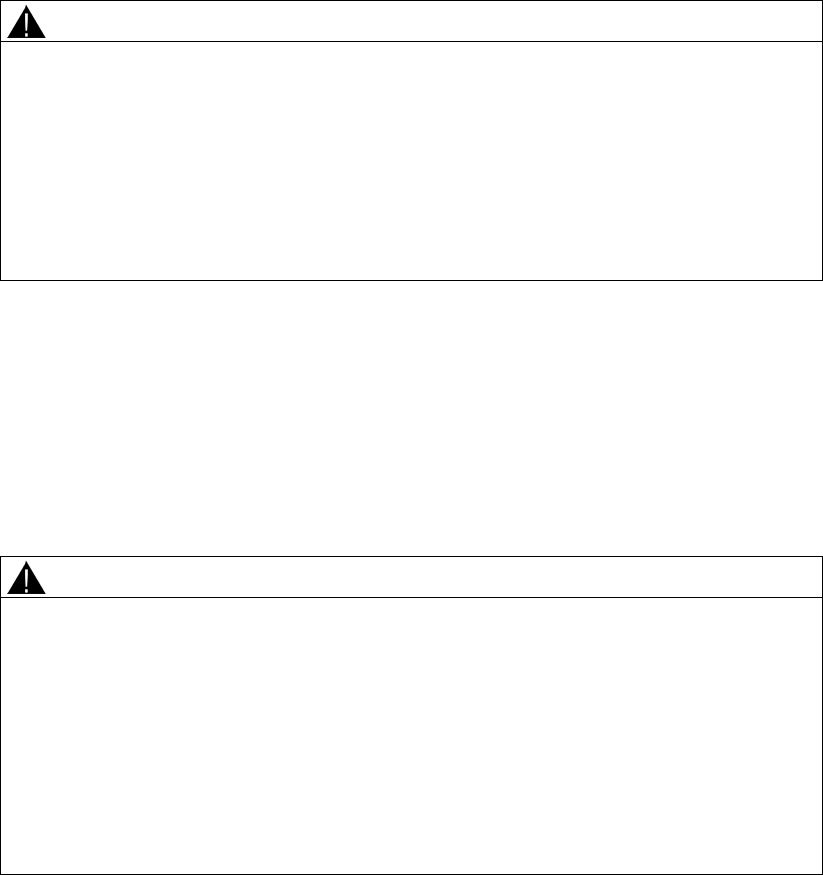
SITRANS LR250 (FOUNDATION FIELDBUS)
Operating Instructions, 08/2014, A5E32221411-AC 55
Commissioning
6
6.1
Basic safety information
WARNING
Loss of explosion protection
Danger of explosion when device is not properly commissioned
If opening device
• Isolate from power.
- or -
• Ensure that the atmosphere is explosion-free (hot work permit).
Ensure device is properly closed before returning to operation.
6.2
Operating via the handheld programmer
The handheld programmer used with this device contains lithium batteries that are non-
replaceable.
Lithium batteries are primary power sources with high energy content designed to provide the
highest possible degree of safety.
WARNING
Potential hazard
Lithium batteries may present a potential hazard if they are abused electrically or
mechanically. Observe the following precautions when handling and using lithium batteries:
• Do not short-circuit, recharge or connect with false polarity.
• Do not expose to temperatures beyond the specified temperature range.
• Do not incinerate.
• Do not crush, puncture or open cells or disassemble.
• Do not weld or solder to the battery’s body.
• Do not expose contents to water.
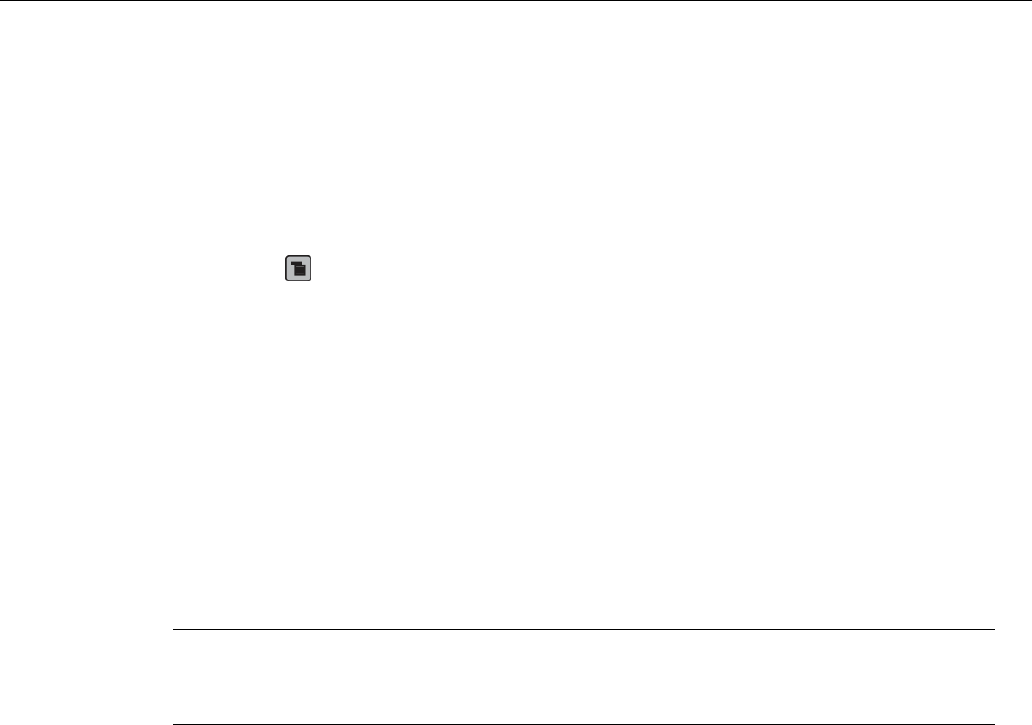
Commissioning
6.2 Operating via the handheld programmer
SITRANS LR250 (FOUNDATION FIELDBUS)
56 Operating Instructions, 08/2014, A5E32221411-AC
6.2.1
Power up
Power up the device. A transition screen showing first the Siemens logo and then the current
firmware revision is displayed while the first measurement is being processed. SITRANS LR250
automatically starts up in Measurement mode. The first time the device is configured, you will be
prompted to select a language (English, German, French, Spanish or Chinese).To change the
language again, see
Language (7.)
.
Press
Mode
to toggle between Measurement and Program mode.
[If the SITRANS LR250 FF is to be used in an FF application, configure using a network
configuration tool, such as DeltaV or NI-FBUS Configurator. See Quick Start Wizard via AMS
Device Manager (Page 85).]
Follow these steps to configure the device via the LUI:
● Complete the Quick Start Wizard [see Quick Start Wizard via the handheld programmer
(Page 65)]. Completing the Quick Start Wizard or writing any parameter via the LUI causes
the device to begin measuring. The Resource Block (RES) and Level Transducer Block (LTB)
will move to Automatic mode.
● AIFB 1 and AIFB 2 will remain Out of Service (as displayed on the LCD). These blocks can
only be configured and scheduled using a network configuration tool. For more details, see
System Integration in manual Foundation Fieldbus for Level Instruments (7ML19985MP01).
Note
The last step of the Quick Start run from the LUI will place the RESOURCE block in
Automatic mode.
6.2.2
Handheld programmer functions
The radar device carries out its level measurement tasks according to settings made via
parameters. The settings can be modified locally via the Local User Interface (LUI) which
consists of an LCD display and a handheld programmer.
A Quick Start Wizard provides an easy step-by-step procedure to configure the device for a
simple application. Access the wizards:
● locally [see Quick Start Wizard via the handheld programmer (Page 65)]
● or from a remote location [see Quick Start Wizard via AMS Device Manager (Page 85)]
For more complex setups see Application Examples (Page 71), and for the complete range of
parameters see Parameter Reference (Page 143).
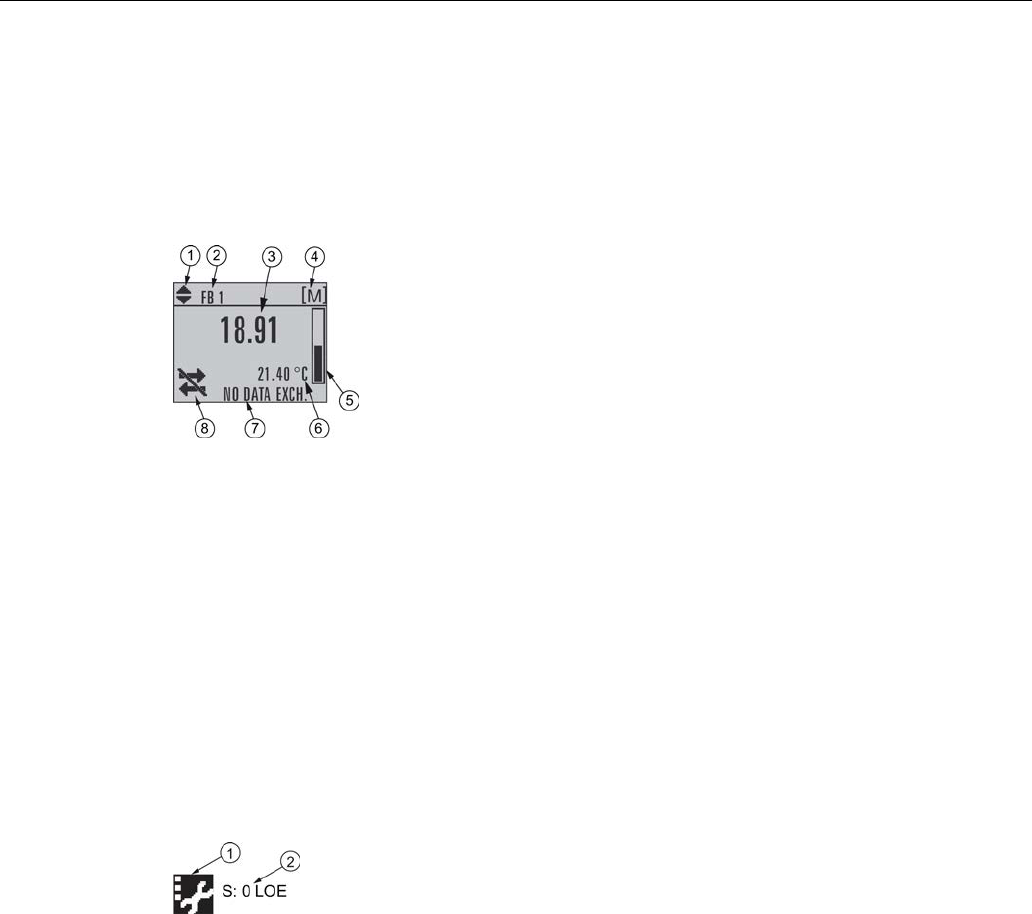
Commissioning
6.2 Operating via the handheld programmer
SITRANS LR250 (FOUNDATION FIELDBUS)
Operating Instructions, 08/2014, A5E32221411-AC 57
6.2.2.1
The LCD display
Measurement mode display
Normal operation
①
toggle indicator
a)
for analog input function blocks (AIFB 1/AIFB 2, displayed as FB1/FB2)
②
identifies which block is source of displayed value
③
Measured value (level, space, distance, or volume)
④
Units
⑤
Bar graph indicates level
⑥
Secondary region indicates on request b) electronics temperature, echo confidence, loop
current, or distance
⑦
Text area displays status messages
⑧
Device status indicator, see Device status icons (Page 204)
a)
Press UP or DOWN arrow to switch.
b) In response to a key press request. For details, see Handheld programmer (Part No. 7ML1930-1BK)
(Page 59) for key functions in Measurement mode.
Fault present
①
service required icon appears
②
Device status indicator, see Device status icons (Page 204)
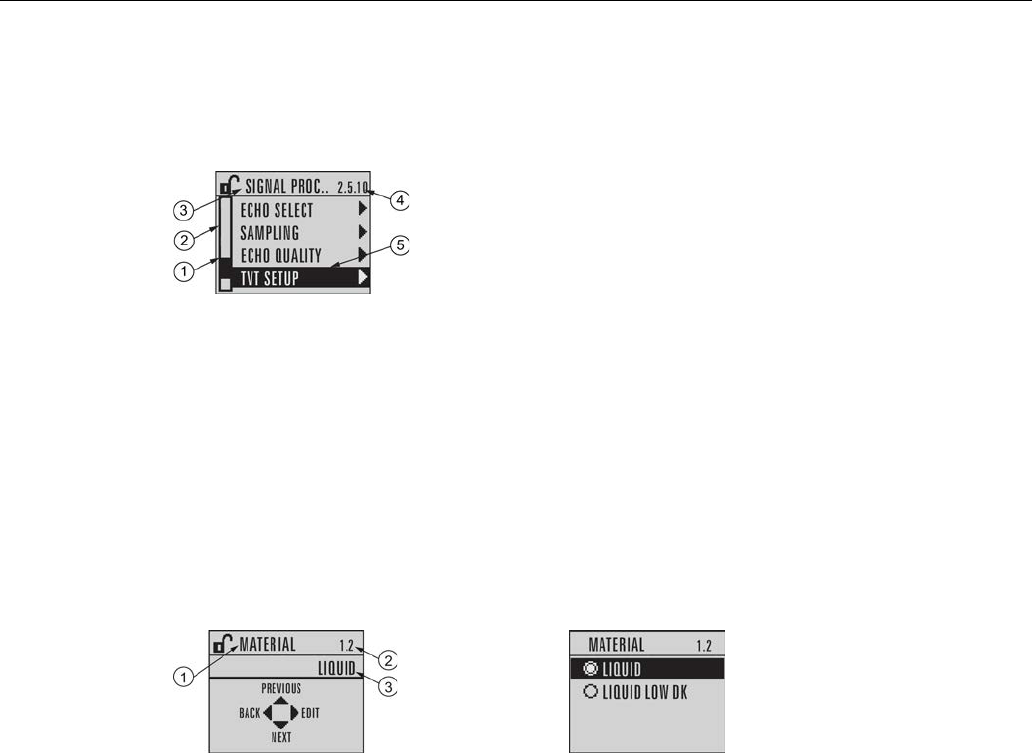
Commissioning
6.2 Operating via the handheld programmer
SITRANS LR250 (FOUNDATION FIELDBUS)
58 Operating Instructions, 08/2014, A5E32221411-AC
PROGRAM mode display
Navigation view
①
Item band
④
Current item number
②
Menu bar
⑤
Current item
③
Current menu
● A visible menu bar indicates the menu list is too long to display all items.
● A band halfway down the menu bar indicates the current item is halfway down the list.
● The depth and relative position of the item band on the menu bar indicates the length of the
menu list, and approximate position of the current item in the list.
● A deeper band indicates fewer items.
Parameter view
Edit view
① Parameter name ② Parameter number ③ Parameter value/selection
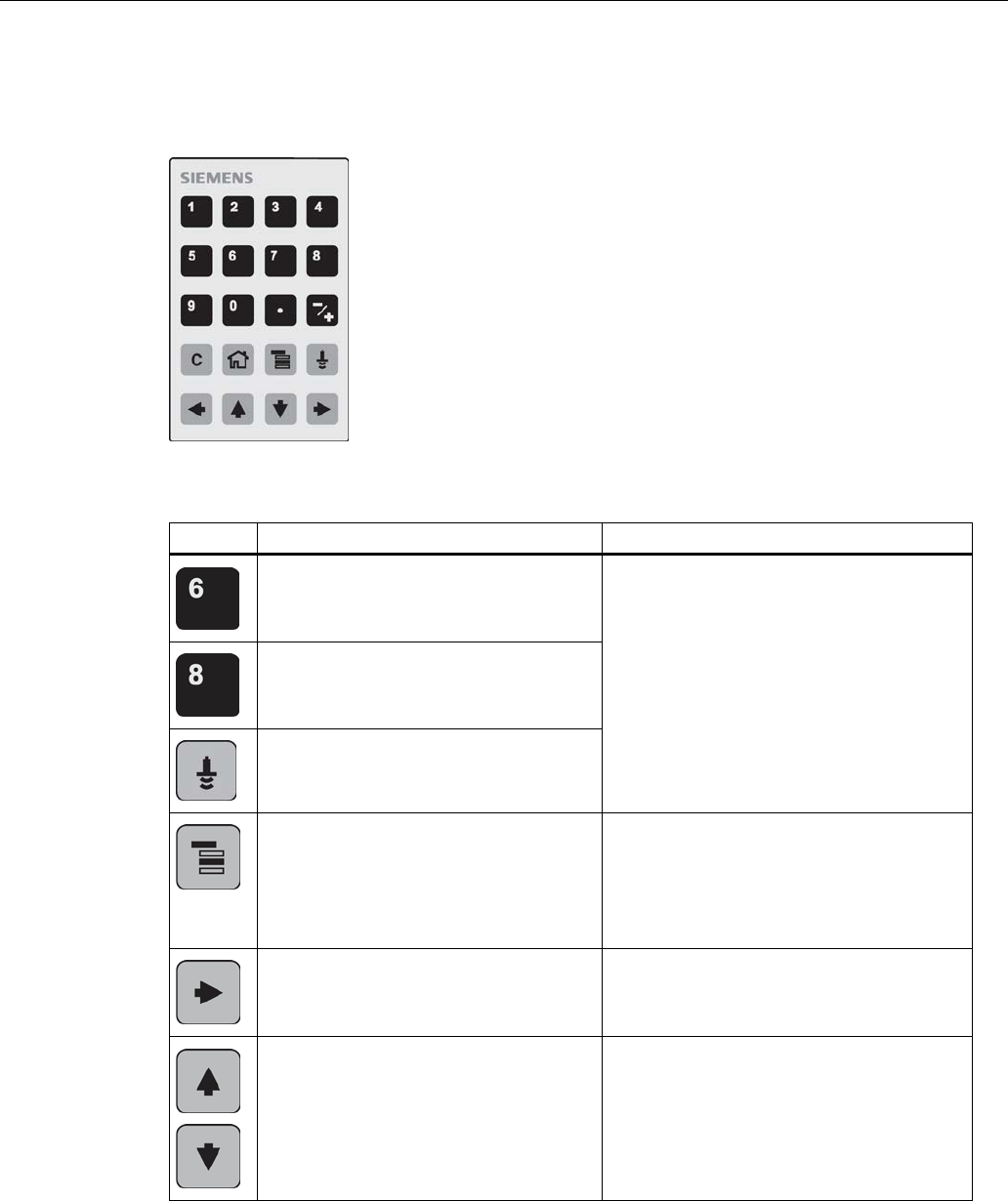
Commissioning
6.2 Operating via the handheld programmer
SITRANS LR250 (FOUNDATION FIELDBUS)
Operating Instructions, 08/2014, A5E32221411-AC 59
6.2.2.2
Handheld programmer (Part No. 7ML1930-1BK)
The programmer is ordered separately.
Key functions in measurement mode
Key
Function
Result
Updates internal enclosure temperature
reading.
New value is displayed in LCD secondary
region.
Updates echo confidence value.
Updates distance measurement.
Mode
opens PROGRAM mode. Opens the menu level last displayed in this
power cycle, unless power has been cycled
since exiting PROGRAM mode or more than
10 minutes have elapsed since PROGRAM
mode was used. Then top level menu will be
displayed.
RIGHT arrow
opens PROGRAM mode. Opens the top level menu.
UP
or
DOWN arrow
toggles between
AIFB 1 and AIFB 2.
Identifies which AIFB is the source of the
displayed value.
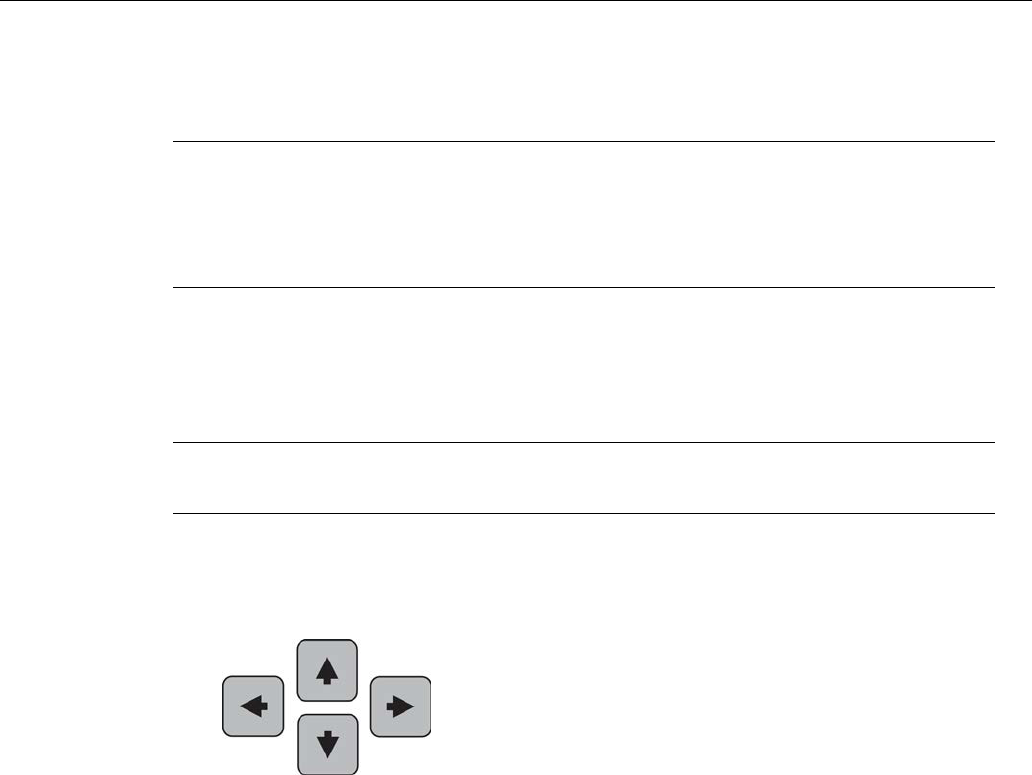
Commissioning
6.2 Operating via the handheld programmer
SITRANS LR250 (FOUNDATION FIELDBUS)
60 Operating Instructions, 08/2014, A5E32221411-AC
6.2.3
Programming
Note
• While the device is in PROGRAM mode the output remains active and continues to
respond to changes in the device.
• The device automatically returns to Measurement mode after a period of inactivity in
PROGRAM mode (between 15 seconds and 10 minutes, depending on the menu level).
Change parameter settings and set operating conditions to suit your specific application. For
remote operation see Operating via AMS Device Manager (Page 79).
Parameter menus
Note
For the complete list of parameters with instructions, see Parameter reference (Page 143).
Parameters are identified by name and organized into function groups. See LCD menu structure
(Page 296).
1. QUICK START
2. SETUP
2.1. IDENTIFICATION
2.2. DEVICE
............
2.4. LINEARIZATION
2.4.1. VOLUME
2.4.1.1. VESSEL SHAPE
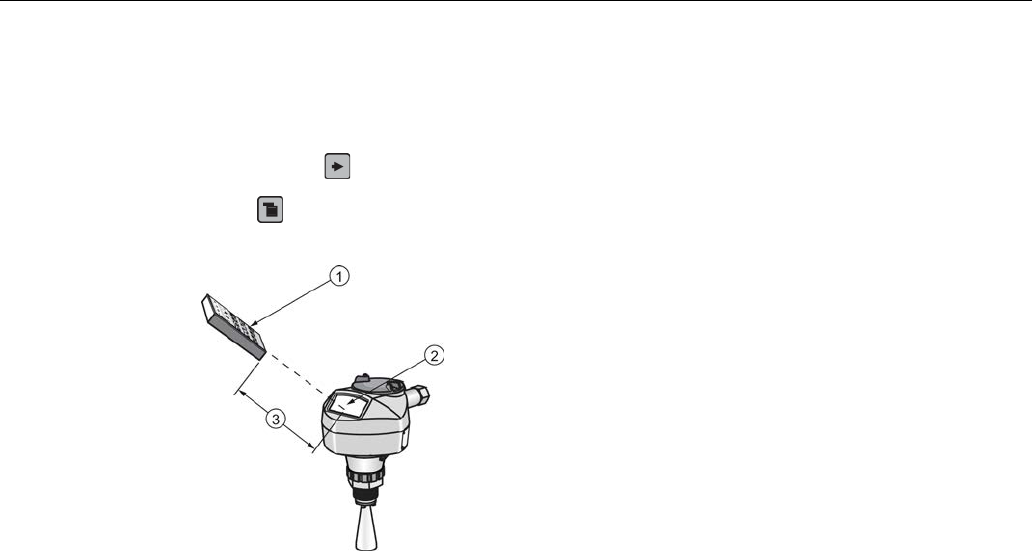
Commissioning
6.2 Operating via the handheld programmer
SITRANS LR250 (FOUNDATION FIELDBUS)
Operating Instructions, 08/2014, A5E32221411-AC 61
1. Enter PROGRAM mode
● Point the programmer at the display from a maximum distance of 300 mm (1 ft).
●
RIGHT arrow
activates PROGRAM mode and opens menu level 1.
●
Mode
opens the menu level last displayed in PROGRAM mode within the last 10 minutes,
or menu level 1 if power has been cycled since then.
① Handheld programmer ② Display ③ Maximum distance: 300 mm ( 1 ft)
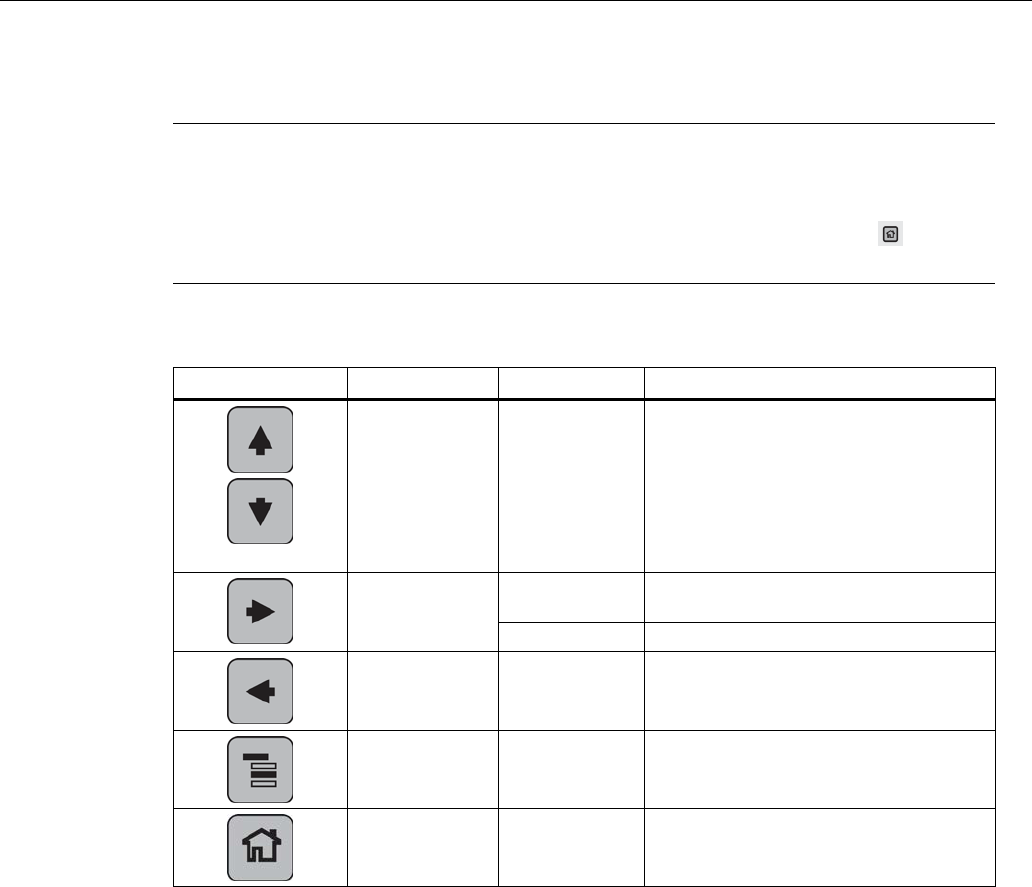
Commissioning
6.2 Operating via the handheld programmer
SITRANS LR250 (FOUNDATION FIELDBUS)
62 Operating Instructions, 08/2014, A5E32221411-AC
2. Navigating: key functions in Navigation mode
Note
• In Navigation mode
ARROW
keys move to the next menu item in the direction of the
arrow.
• For Quick Access to parameters via the handheld programmer, press Home , then
enter the menu number, for example:
Volume (2.4.1.), press 2.4.1.
Key
Name
Menu level
Function
UP
or
DOWN
arrow
menu or
parameter
Scroll to previous or next menu or
parameter
RIGHT arrow
menu Go to first parameter in the selected
menu, or open next menu.
parameter Open
Edit
mode.
LEFT arrow
menu or
parameter
Open parent menu.
Mode
menu or
parameter
Change to
MEASUREMENT
mode.
Home
menu or
parameter
Open top level menu: menu 1.
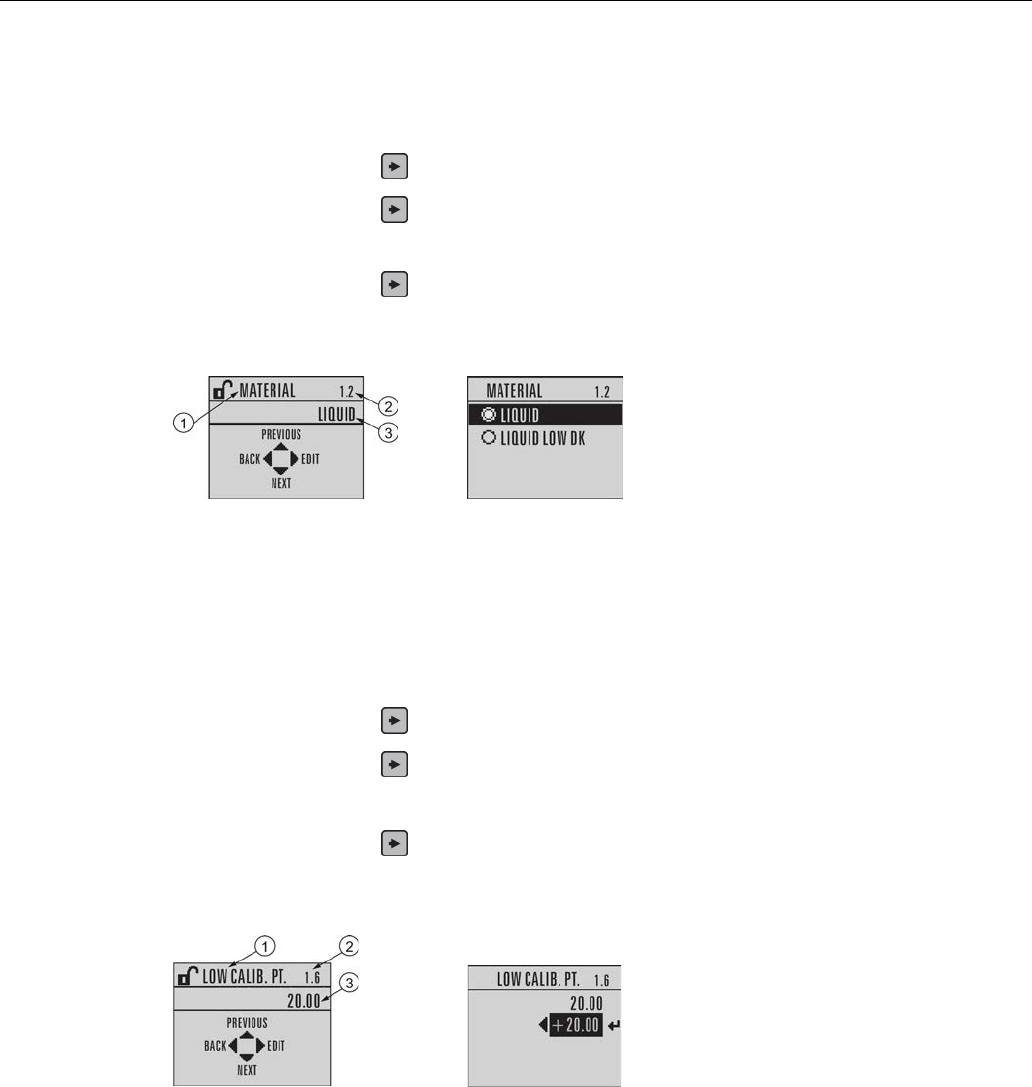
Commissioning
6.2 Operating via the handheld programmer
SITRANS LR250 (FOUNDATION FIELDBUS)
Operating Instructions, 08/2014, A5E32221411-AC 63
3. Editing in PROGRAM mode
● Navigate to the desired parameter.
● Press
RIGHT
arrow
to open parameter view.
● Press
RIGHT arrow
again to open
Edit
mode. The current selection is highlighted. Scroll
to a new selection.
● Press
RIGHT arrow
to accept it. The LCD returns to parameter view and displays the new
selection.
① Parameter name ② Parameter number ③ Current selection
4. Changing a numeric value
● Navigate to the desired parameter.
● Press
RIGHT arrow
to open parameter view. The current value is displayed.
● Press
RIGHT arrow
again to open
Edit
mode. The current value is highlighted.
● Key in a new value.
● Press
RIGHT arrow
to accept it. Press RIGHT arrow to accept it.The LCD returns to
parameter view and displays the new selection.
① Parameter name ② Parameter number ③ Current selection
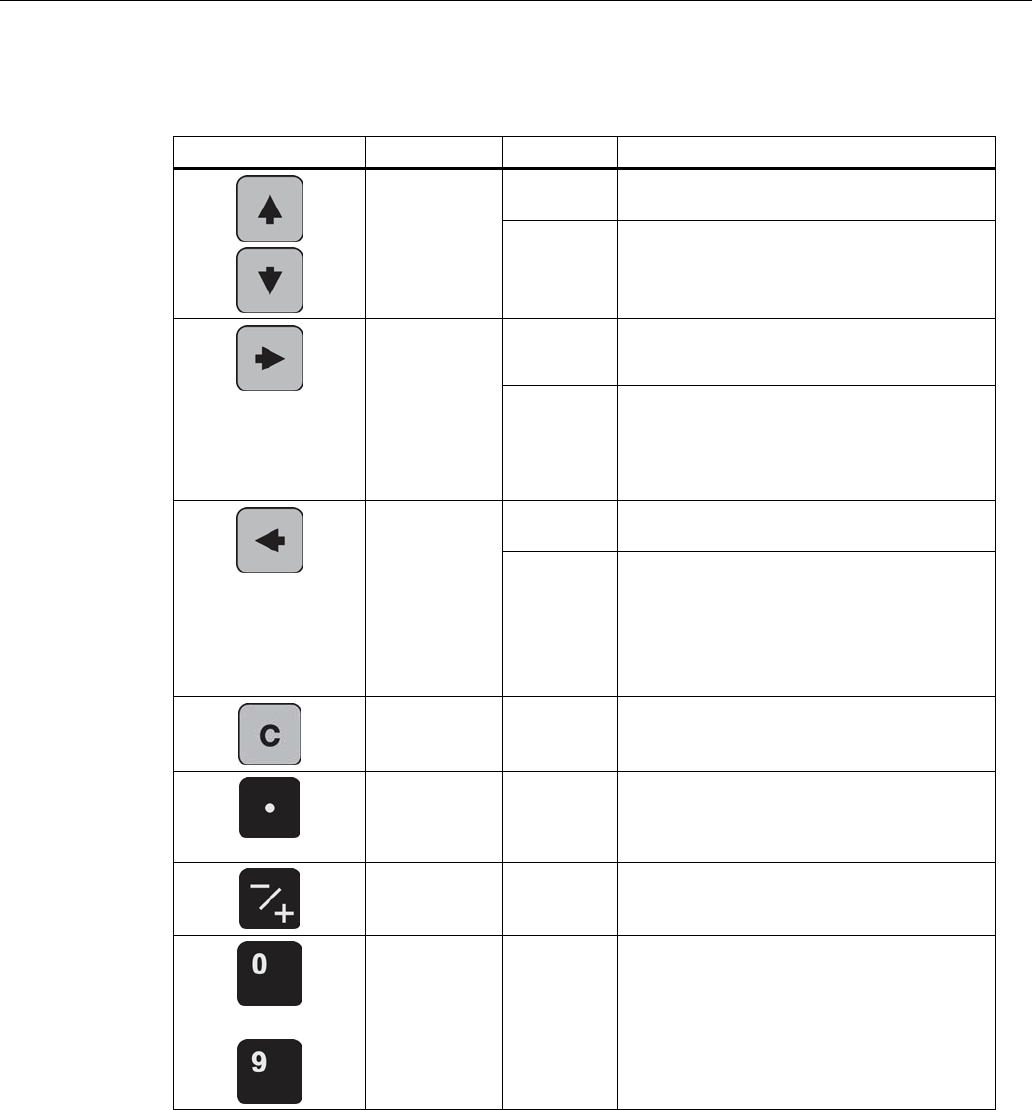
Commissioning
6.2 Operating via the handheld programmer
SITRANS LR250 (FOUNDATION FIELDBUS)
64 Operating Instructions, 08/2014, A5E32221411-AC
Key functions in edit mode
Key
Name
Function
UP
or
DOWN
arrow
Selecting
options
Scrolls to item.
Numeric
editing
• Increments or decrements digits
• Toggles plus and minus sign
RIGHT arrow
Selecting
options
• Accepts the data (writes the parameter)
• Changes from
Edit
to
Navigation
mode
Numeric
editing
• Moves cursor one space to the right
• or, with cursor on Enter sign, accepts the
data and changes from
Edit
to
Navigation
mode
LEFT arrow:
Selecting
options
Cancels
Edit
mode without changing the
parameter.
Numeric
editing
• Moves cursor to plus/minus sign if this is
the first key pressed
• or moves cursor one space to the left
• or with cursor on the Enter sign, cancels
the entry.
Clear
Numeric
editing
Erases the display.
Decimal point
Numeric
editing
• Enters a decimal point
• Captures the current path [see
Secondary
Value (4.11.)
]
Plus or minus
sign
Numeric
editing
Changes the sign of the entered value.
to
Numeral
Numeric
editing
Enters the corresponding character.
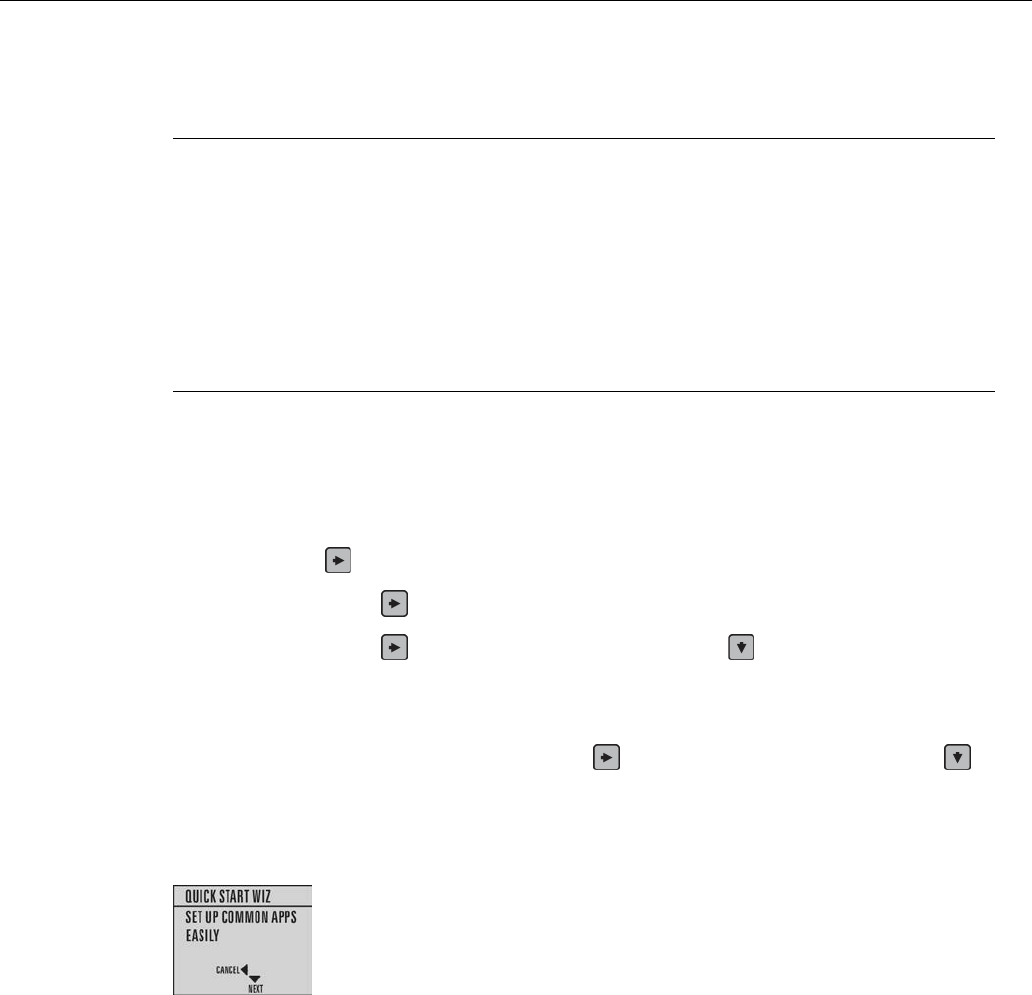
Commissioning
6.2 Operating via the handheld programmer
SITRANS LR250 (FOUNDATION FIELDBUS)
Operating Instructions, 08/2014, A5E32221411-AC 65
6.2.3.1
Quick Start Wizard via the handheld programmer_note
Note
• A reset to factory defaults should be performed before running the Quick Start Wizard if
the device has been used in a previous application. See
Master Reset (4.1.)
.
• The Quick Start wizard settings are inter-related and changes apply only after you select
Finish
in the Wizard Complete step.
• Do not use the Quick Start wizard to modify parameters: see instead Parameter
reference (Page 143). (Perform customization for your application only after the Quick
Start has been completed).
• Default settings in the parameter tables are indicated with an asterisk (*).
1. Quick Start
1.1. Quick Start Wiz
● Point the programmer at the display from a maximum distance of 300 mm (1 ft), then press
RIGHT arrow
to activate PROGRAM mode and open menu level 1.
● Press
RIGHT arrow
twice to navigate to menu item 1.1 and open parameter view.
● Press
RIGHT arrow
to open Edit mode or
DOWN arrow
to accept default values and
move directly to the next item.
● To change a setting, scroll to the desired item or key in a new value.
● After modifying a value, press
RIGHT arrow
to accept it and press
DOWN arrow
to
move to the next item.
● Quick Start settings take effect only after you select
Finish.
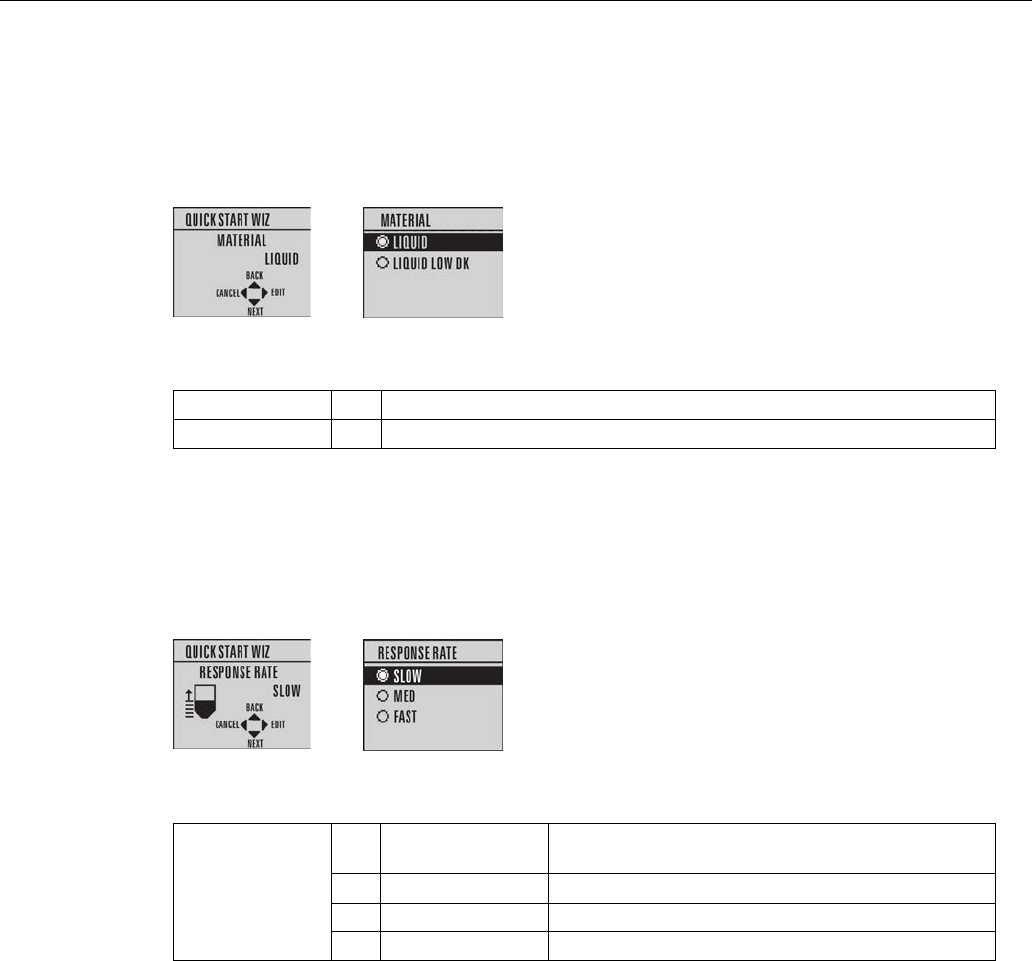
Commissioning
6.2 Operating via the handheld programmer
SITRANS LR250 (FOUNDATION FIELDBUS)
66 Operating Instructions, 08/2014, A5E32221411-AC
Material
Selects the appropriate echo processing algorithms for the material [see
Position Detect
(2.5.7.2.)
for more detail].
Options
* LIQUID
LIQUID LOW DK a) (low dielectric liquid – CLEF algorithm enabled)
a) dK < 3.0
Response rate
Sets the reaction speed of the device to measurement changes in the target range. Use a
setting just faster than the maximum filling or emptying rate (whichever is greater).
Options
Response rate
(2.3.8.1.)
Fill rate per Minute (2.3.8.2.)/
Empty rate per Minute (2.3.8.3.)
* SLOW 0.1 m/min (0.32 ft/min)
MED 1.0 m/min (3.28 ft/min)
FAST 10.0 m/min (32.8 ft/min)
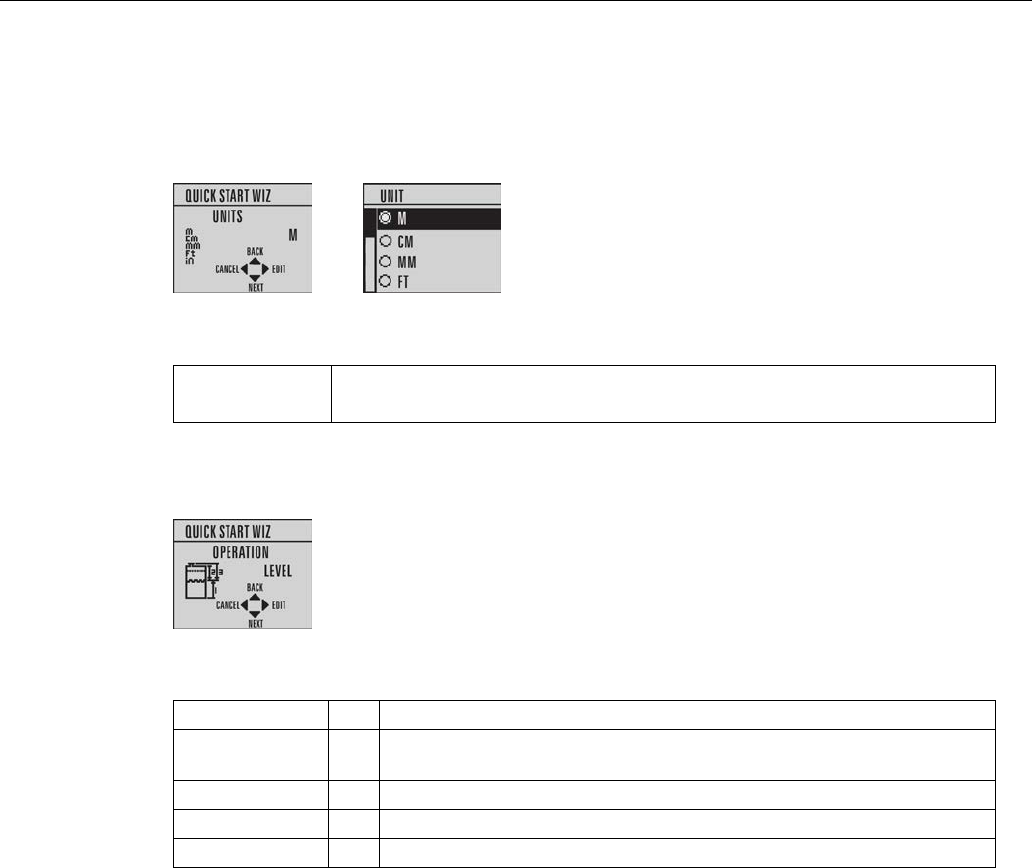
Commissioning
6.2 Operating via the handheld programmer
SITRANS LR250 (FOUNDATION FIELDBUS)
Operating Instructions, 08/2014, A5E32221411-AC 67
Units
Sensor measurement units.
Options
m, cm, mm, ft, in
Default: m
Operation
Operation
Description
NO SERVICE Measurement and associated loop current are not updated, and the device
defaults to Fail-safe mode a).
LEVEL * Distance to material surface referenced from Low calibration point
SPACE Distance to material surface referenced from High calibration point
DISTANCE Distance to material surface referenced from Sensor reference point
a)
See Material Level (2.3.5.) for more detail.
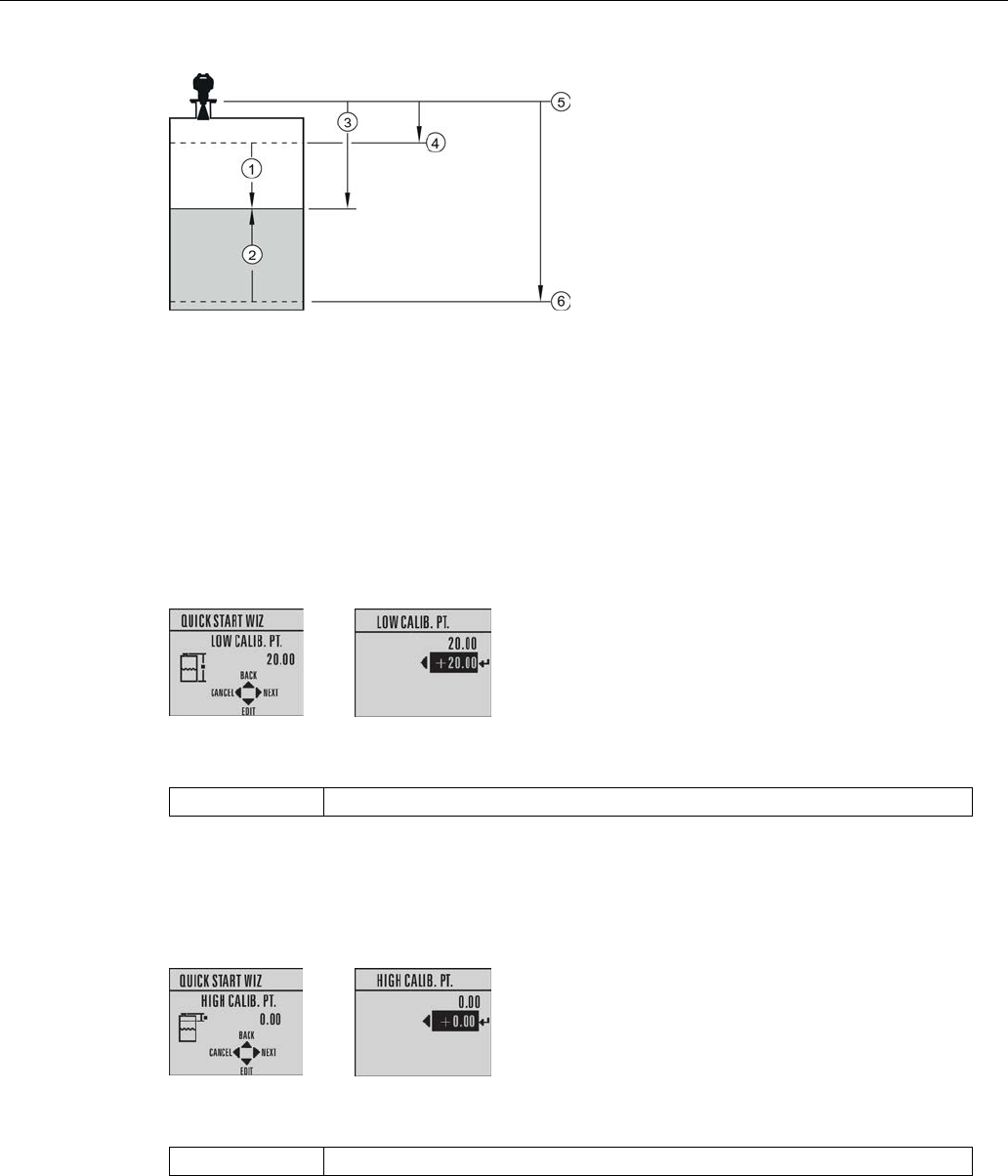
Commissioning
6.2 Operating via the handheld programmer
SITRANS LR250 (FOUNDATION FIELDBUS)
68 Operating Instructions, 08/2014, A5E32221411-AC
①
Space
④
High calibration point (process full level)
②
Level
⑤
Sensor reference point a)
③
Distance
⑥
Low calibration point (process empty level)
a) The point from which High and Low Calibration points are referenced: see
Dimension
Drawings
.
Low calibration point
Distance from Sensor Reference to Low Calibration Point: usually process empty level. (See
Operation
for an illustration.)
Values
Range: 0.00 to 20.00 m
High calibration point
Distance from Sensor Reference Point to High Calibration Point: usually process full level. (See
Operation
for an illustration.)
Values
Range: 0.00 to 20.00 m
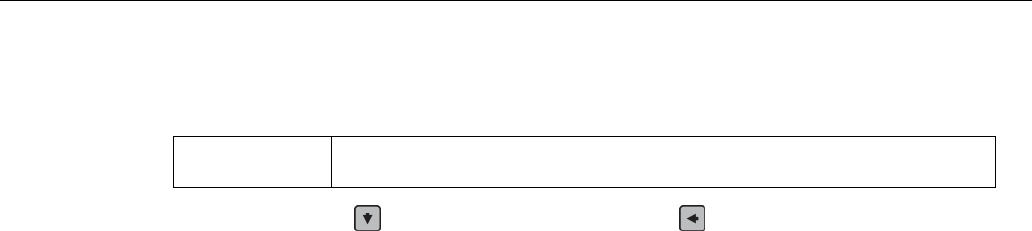
Commissioning
6.2 Operating via the handheld programmer
SITRANS LR250 (FOUNDATION FIELDBUS)
Operating Instructions, 08/2014, A5E32221411-AC 69
Wizard complete
Options
BACK, CANCEL, FINISH (Display returns to 1.1 Quick Start Wiz menu when
Quick Start is successfully completed.)
Press
DOWN arrow (Finish).
Then press
LEFT arrow
to return to
Measurement
mode.
SITRANS LR250 is now ready to operate.
6.2.3.2
Auto False Echo Suppression
If you have a vessel with known obstructions, we recommend using Auto False Echo
Suppression to prevent false echo detection. See
TVT (Auto False Echo Suppression)
Setup (2.5.10.)
for instructions.
This feature can also be used if the display shows a false high level, or the reading is fluctuating
between the correct level and a false high level.
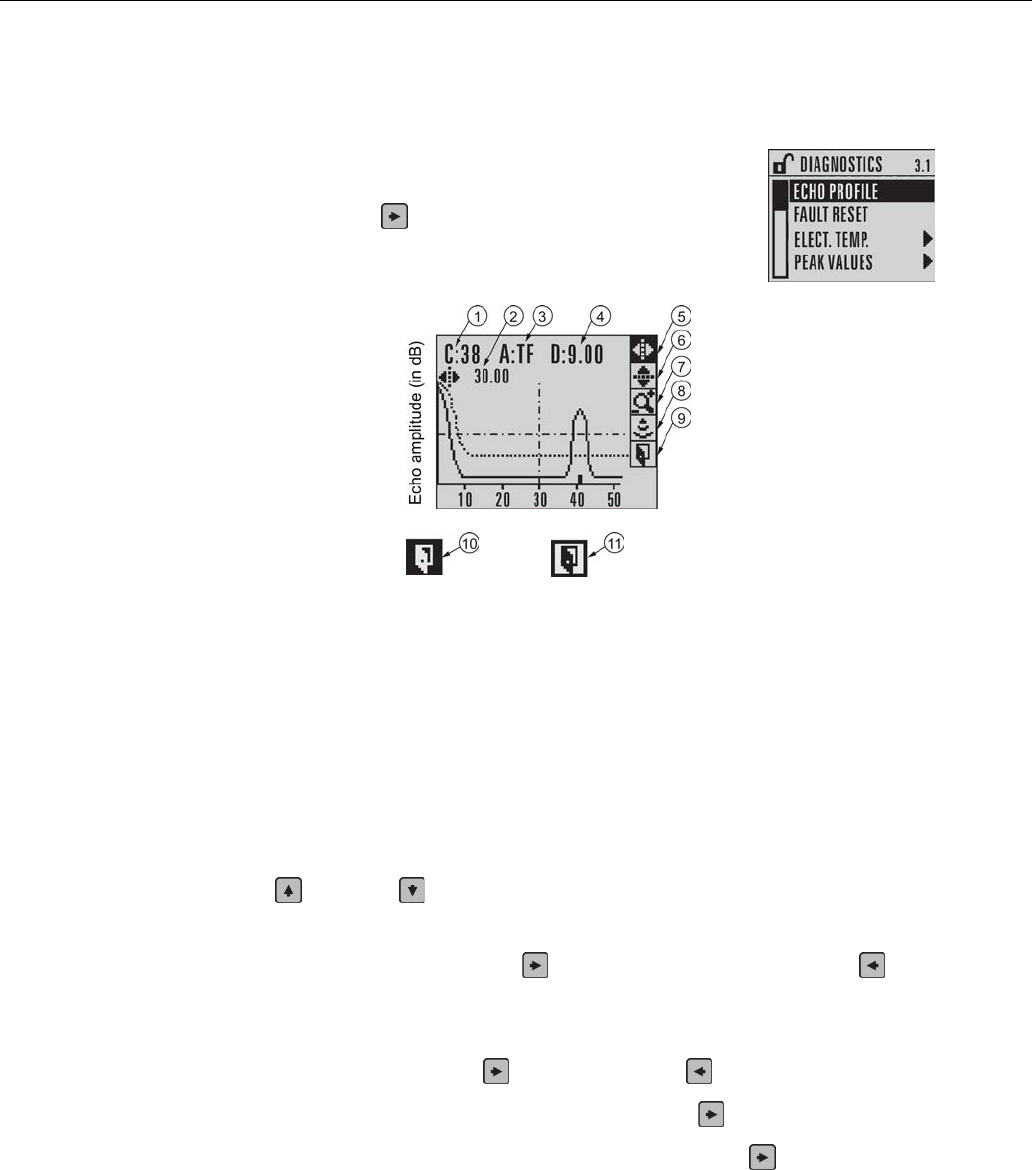
Commissioning
6.2 Operating via the handheld programmer
SITRANS LR250 (FOUNDATION FIELDBUS)
70 Operating Instructions, 08/2014, A5E32221411-AC
6.2.3.3
Requesting an Echo Profile
• In
PROGRAM
mode, navigate to:
Level Meter > Diagnostics
(3.) > Echo Profile (3.1
.)
• Press
RIGHT arrow
to request a profile.
① Confidence ⑦ Zoom
② Distance from Low Calibration Point to vertical cross-hair ⑧ Measure
③ Algorithm: t
F
(trueFirst) ⑨ Exit
④ Distance from flange face to target ⑩ Exit icon selected
⑤ Pan left/right - selected ⑪ Exit icon deselected
⑥ Pan up/down
● Use
UP
or
DOWN arrow
to scroll to an icon. When an icon is highlighted, that feature
becomes active.
● To move a cross-hair, press
RIGHT arrow
to increase the value,
LEFT arrow
to
decrease.
● To Zoom into an area, position the intersection of the cross-hairs at the center of that area,
select
Zoom
, and press
RIGHT arrow.
Press
LEFT arrow
to Zoom out.
● To update the profile, select
Measure
and press
RIGHT arrow.
● To return to the previous menu, select
Exit
then press
RIGHT arrow.
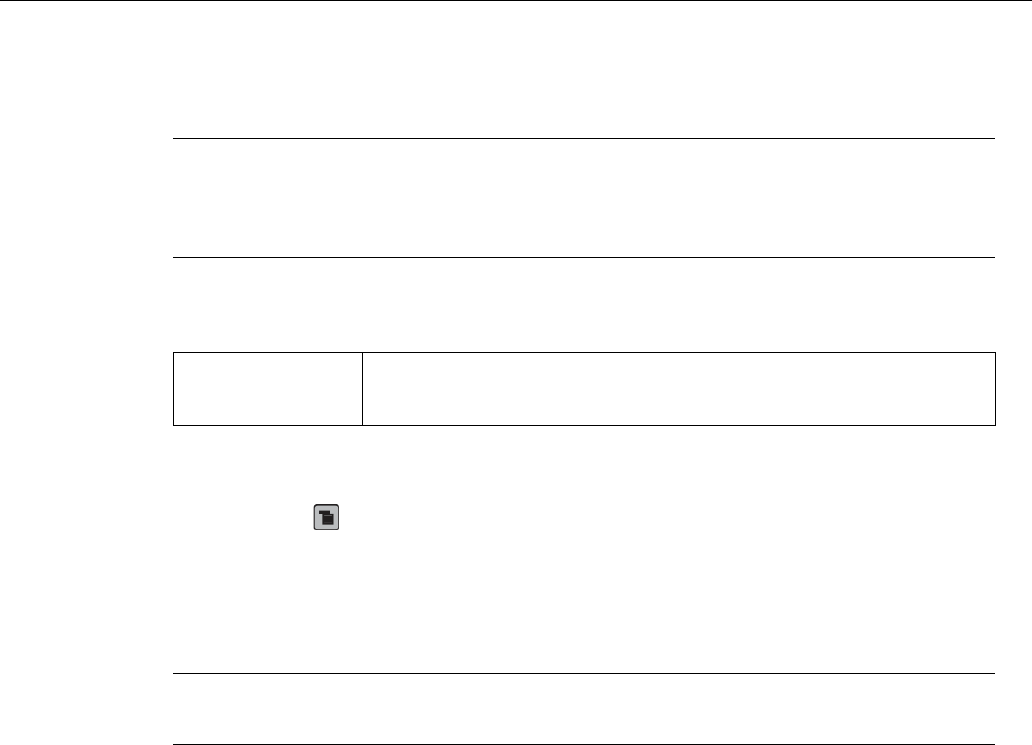
Commissioning
6.3 Application examples
SITRANS LR250 (FOUNDATION FIELDBUS)
Operating Instructions, 08/2014, A5E32221411-AC 71
6.2.3.4
Device Address
Note
The address can only be changed from a remote master such as NI-FBUS Configurator or
DeltaV. See Addressing in manual Foundation Fieldbus for Level Instruments
(7ML19985MP01) for further details.
Read only. The unique address of the device on the network.
Values
Temporary range during initial commissioning: 248 - 251. Permanent range
after commissioning complete (written to non-volatile memory in the device):
16-247
● In PROGRAM mode, navigate to:
Level Meter > Communication (5.) > Device Address (5.2.)
to view the device address.
● Press
Mode
to return to Measurement mode.
6.3
Application examples
Note
In the applications illustrated below, values are for example purposes only.
You can use these examples as setup references. Enter the values in the parameter tables to
select the corresponding functions.
Configure the basic settings using the Quick Start wizard parameters. (These parameters are
inter-related, and changes take effect only after you select
FINISH
in final step: Wizard
Complete.)
In each example, after performing a Quick Start, navigate to the other required parameters
(either via the handheld programmer or via AMS Device Manager) and enter the appropriate
values.
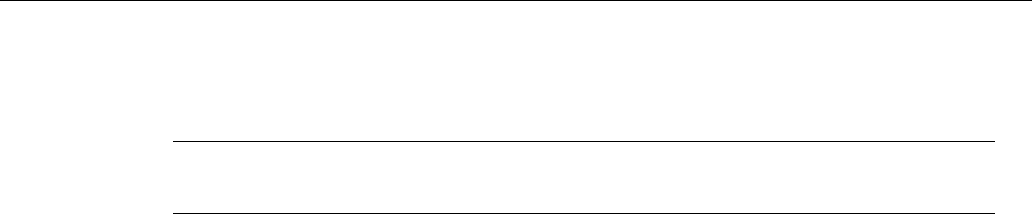
Commissioning
6.3 Application examples
SITRANS LR250 (FOUNDATION FIELDBUS)
72 Operating Instructions, 08/2014, A5E32221411-AC
6.3.1
Liquid resin in storage vessel, level measurement
Note
Minimum distance from flange face to target is limited by
Near Range (2.5.1.)
.
To obtain level measurement/4 to 20 mA output proportional to resin levels:
● Low Calibration Pt. = 5 m (16.5 ft) from sensor reference point
● High Calibration Pt.= 0.5 m (1.64 ft) from sensor reference point
● Max.fill/empty rate = 0.2 m/min (0.65 ft/min)
In the event of a loss of echo:
● SITRANS LR250 is to go into Fail-safe High after 2 minutes.
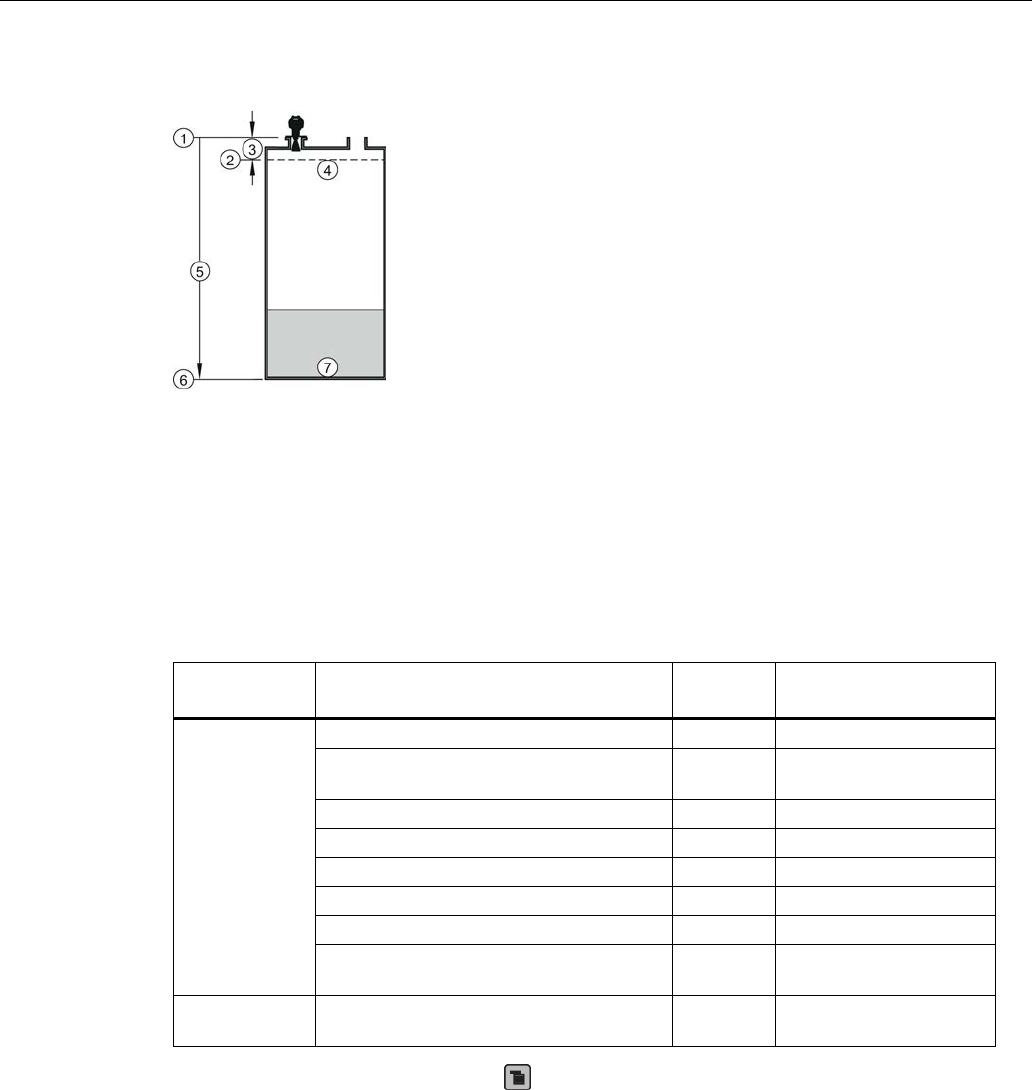
Commissioning
6.3 Application examples
SITRANS LR250 (FOUNDATION FIELDBUS)
Operating Instructions, 08/2014, A5E32221411-AC 73
① Sensor reference point ⑤ 5 m
② High calibration point ⑥ Low calibration point
③ 0.5 m ⑦ 0% level
④ 100% level
Parameter type
Parameter No. /Name
Options/
Values
Function
Quick Start
Wizard
parameters
Introduction
NEXT
Continue with Wizard.
Language
NEXT
Continue with current
language.
Material
LIQUID
Response Rate
MED
Medium =1 m/minute
Units
M
meters
Low Calibration Point
5
5 m (16.4 ft)
High Calibration Point
0.5
0.5 m (1.64 ft)
Wizard Complete
FINISH
Transfers Quick Start
settings to device.
Independent
parameters
Loss of Echo (LOE) Timer (2.3.6.)
120
120 seconds
Return to
Measurement
: press
Mode
to start normal operation.
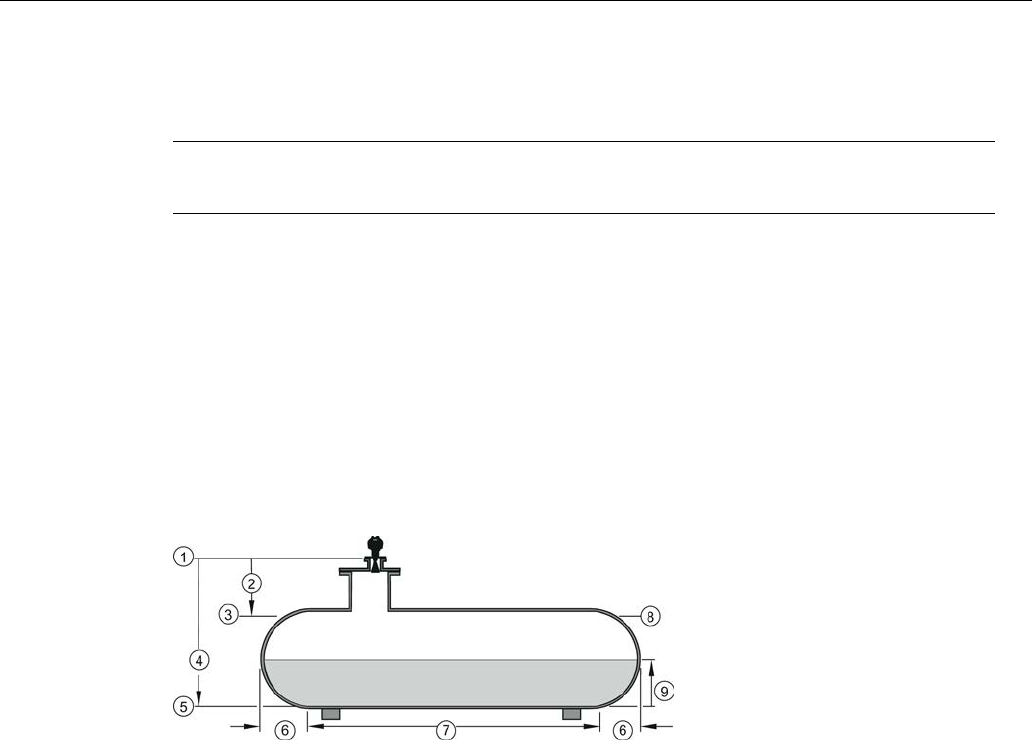
Commissioning
6.3 Application examples
SITRANS LR250 (FOUNDATION FIELDBUS)
74 Operating Instructions, 08/2014, A5E32221411-AC
6.3.2
Horizontal vessel with volume measurement
Note
The minimum distance from the flange face to the target is limited by
Near Range (2.5.1.)
.
To obtain level measurement proportional to vessel volume in a chemical vessel:
● Low Calibration Point = 3.5 m (11.48 ft) from sensor reference point
● High Calibration Point = 0.5 m (1.64 ft) from sensor reference point
● Max. fill/empty rate = 0.2 m/min (0.65 ft/min)
● Select vessel shape, Parabolic Ends, and enter values for A and L, to obtain a volume
reading instead of level.
In the event of a loss of echo:
● SITRANS LR250 is to report a status of BAD or UNCERTAIN after 120 seconds (2 minutes).
①
Sensor reference point
⑥
A = 0.8 m
②
0.5 m
⑦
L = 6 m
③
High calibration point
⑧
100% = 8000 L
④
3.5. m
⑨
Volume reading
⑤
Low calibration point

Commissioning
6.3 Application examples
SITRANS LR250 (FOUNDATION FIELDBUS)
Operating Instructions, 08/2014, A5E32221411-AC 75
Parameter type
Parameter Name
Options/
Values
Function
Quick Start
Wizard
parameters
Introduction
NEXT
Continue with Wizard.
Language
NEXT
Continue with current language.
Material
LIQUID
Response Rate
MED
Medium =1 m/minute
Units
M
meters
Low Calibration Point
3.5
3.5 m (11.48 ft)
High Calibration Point
0.5
0.5 m (1.64 ft)
Wizard Complete
FINISH
Transfers Quick Start settings to
device.
Independent
parameters
Vessel Shape (2.4.1.1.)
PARABOLIC
ENDS
Defines vessel shape.
PV (volume/level) Units
(2.3.3.)
L
liters
Level Unit (2.3.2.)
M
meters
Maximum Volume (2.4.1.2.)
8000
8000 liters
Dimension A (2.4.1.3.)
0.8
0.8 m (2.62 ft)
Dimension L (2.4.1.4.)
6
6 m (19.68 ft)
Loss of Echo (LOE) Timer
(2.3.6.)
120
120 seconds
Return to
Measurement:
press
Mode
to start normal operation.
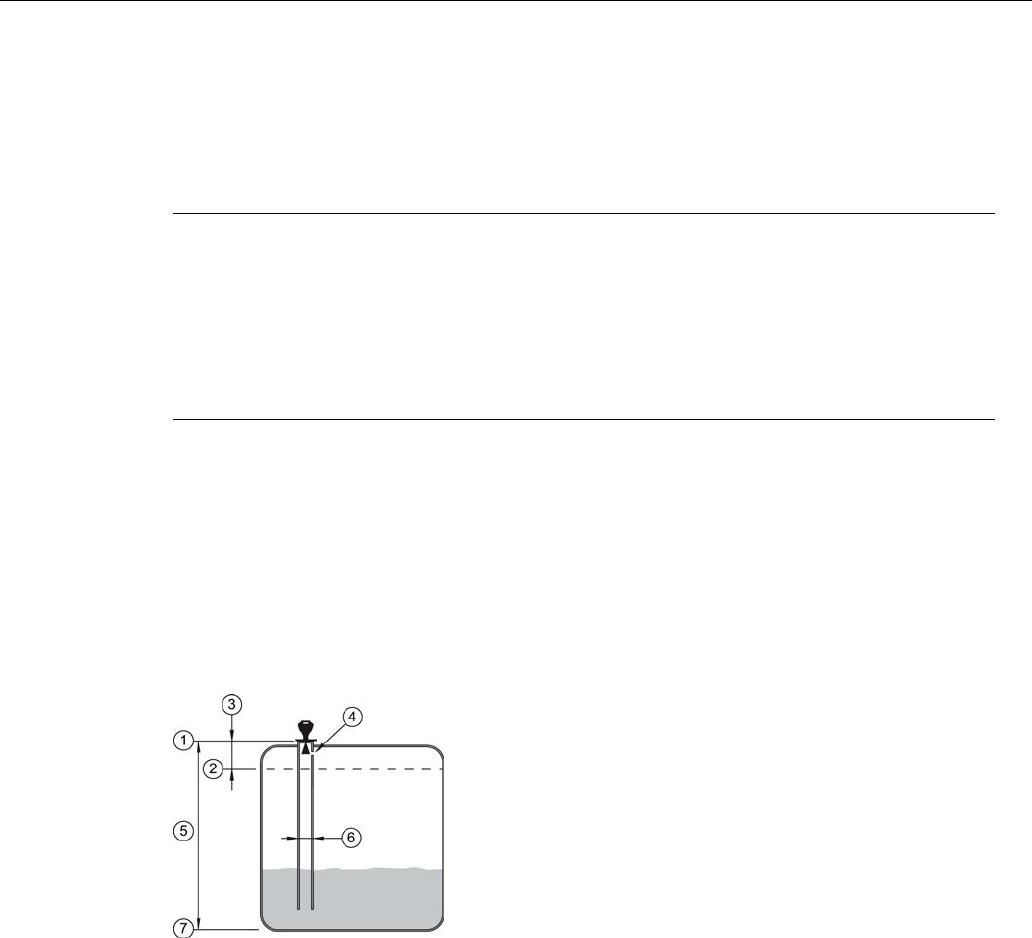
Commissioning
6.3 Application examples
SITRANS LR250 (FOUNDATION FIELDBUS)
76 Operating Instructions, 08/2014, A5E32221411-AC
6.3.3
Application with stillpipe
A stillpipe is recommended for products with a dK of less than 3, or if extremely turbulent or
vortex conditions exist. This mounting arrangement can also be used to provide optimum signal
conditions on foaming materials.
Note
•
Near Range (2.5.1.)
(Blanking) will be set at the factory. Check the process connection
tag for specific values.
• Suitable pipe diameters are 40 mm (1.5") to 100 mm (4").
• The pipe diameter must be matched with the antenna size. Use the largest antenna size
that will fit the stillpipe/bypass pipe. See Dimension drawings (Page 221).
• See Mounting on a Stillpipe or Bypass Pipe (Page 32) for installation guidelines.
This application is to obtain a level measurement and corresponding 4 to 20 mA output
proportional to the oil level in a fuel storage vessel.
● Low Calibration Pt. is 5 m (16.4 ft) from the sensor reference point.
● High Calibration Pt. is 0.5 m (1.64 ft) from the sensor reference point.
● The stillpipe inside diameter is 50 mm (1.96").
● The maximum rate of filling or emptying is about 0.1 m (4")/min.
① Sensor reference point ⑤ 5 m
② High calibration point ⑥ 50 mm I.D.
③ 0.5 m ⑦ Low calibration point
④ Vent hole
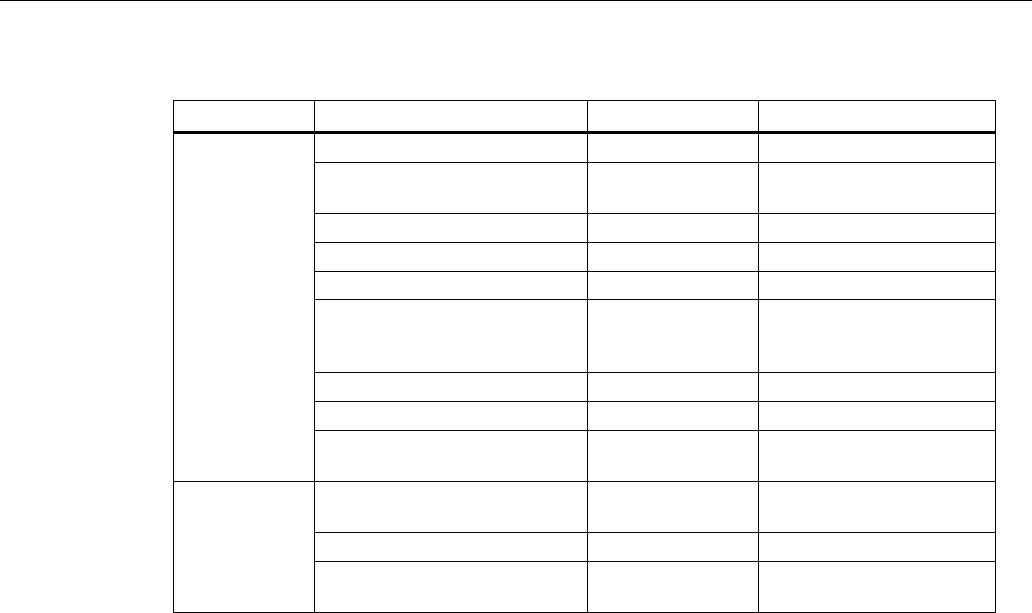
Commissioning
6.3 Application examples
SITRANS LR250 (FOUNDATION FIELDBUS)
Operating Instructions, 08/2014, A5E32221411-AC 77
Parameter type
Parameter No./Name
Options/Values
Function
Quick Start
Wizard
parameters
Introduction
NEXT
Continue with Wizard.
Language
NEXT
Continue with current
language.
Material
LIQUID LOW DK
Response Rate
MED
Medium =1 m/minute
Units
M
meters
Operating mode
LEVEL
Level is reported as
Volume when a vessel
shape is selected.
Low Calibration Point
5
5 m (16.4 ft)
High Calibration Point
0.5
0.5 m (1.64 ft)
Wizard Complete
FINISH
Transfers Quick Start
settings to device.
Independent
parameters
Propagation Factor (2.5.3.)a)
0.988
P.F. for a 50 mm (1.96")
I.D. stillpipe
Position Detect (2.5.7.2.)
HYBRID
CLEF Range (2.5.7.4.)a) 4.3 Low calibration point -
0.7 m = 4.3 m (14.1 ft)
a) The recommended values for the propagation factor and for CLEF range are dependent on the
stillpipe diameter. See Propagation Factor/Stillpipe Diameter for values.
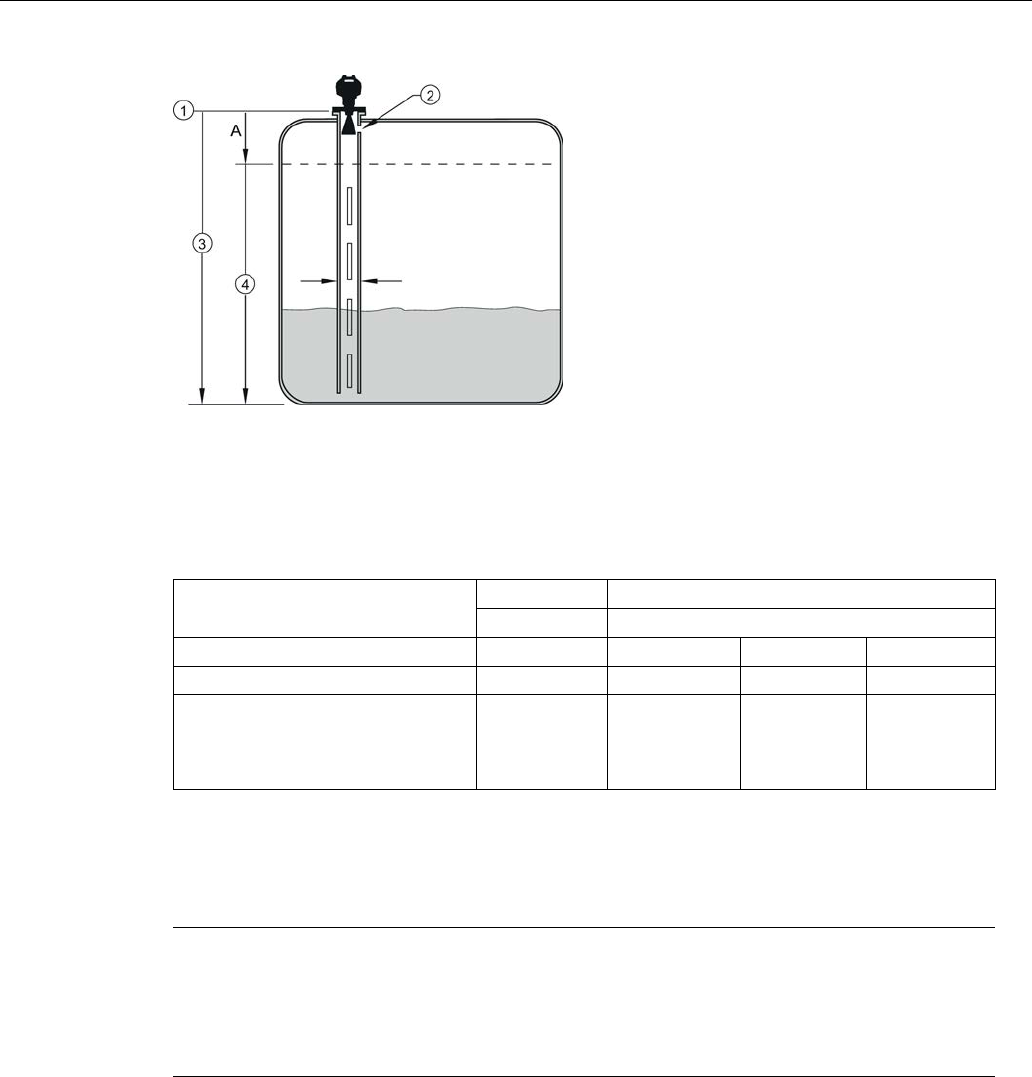
Commissioning
6.3 Application examples
SITRANS LR250 (FOUNDATION FIELDBUS)
78 Operating Instructions, 08/2014, A5E32221411-AC
①
sensor reference point
③
low calibration point
②
air gap
④
CLEF range 2.5.7.4.
A
700 or 1000 mm (see CLEF Range settings in table below)
Propagation Factor/Stillpipe Diameter
Values
Range 0.3 to 1.0 depending on pipe size
Default 1.0000
Nominal Pipe Size
a) 40 mm (1.5") 50 mm (2") 80 mm (3") 100 mm (4")
Propagation Factor
0.9844 0.988 0.9935 0.9965
CLEF Range (2.5.7.4.) settings
Low
calibration
point - 700
mm (2.29 ft)b)
Low
calibration
point - 700
mm (2.29 ft)b)
Low
calibration
point - 1000
mm (3.28 ft)b)
Low
calibration
point - 1000
mm (3.28 ft)b)
a) Since pipe dimensions may vary slightly, the propagation factor may also vary.
b) CLEF range covers the whole measurement range except first 700 or 1000 mm from sensor
reference point
Note
Flanged and Hygienic encapsulated antenna
For Flanged encapsulated antenna (7ML5432) and Hygienic encapsulated antenna
(7ML5433) match the process connection size to the pipe diameter. For example, DN 80/3"
flange to DN 80/3" pipe.
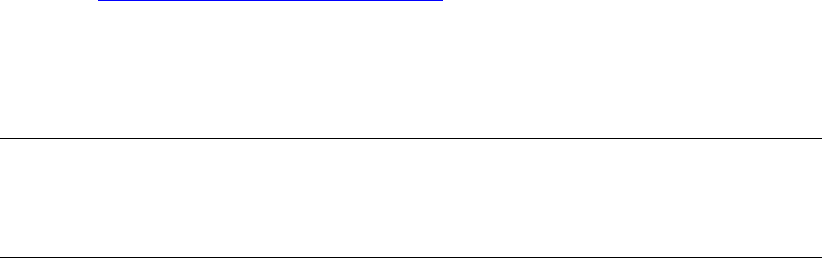
SITRANS LR250 (FOUNDATION FIELDBUS)
Operating Instructions, 08/2014, A5E32221411-AC 79
Remote operation
7
7.1
Operating via AMS Device Manager
AMS Device Manager is a software package that monitors the process values, alarms and
status signals of the device. Please consult the operating instructions or online help for details
on using AMS Device Manager. You can find more information at:
Emerson (http://www.emersonprocess.com/AMS/)
7.1.1
Functions in AMS Device Manager
Note
Do not use the handheld programmer at the same time as AMS Device Manager, or erratic
operation may result. To disable operation via the handheld programmer, see
Local
Operation (6.2.3.).
AMS Device Manager can be used to monitor the process values, alarms and status signals of
the device. It allows you to display, compare, adjust, verify, and simulate process device data.
Configuration and monitoring of the device is completed via parameters organized into three
main function groups:
● Configure/Setup
● Device Diagnostics (read only)
● Process Variables (read only)
Each function group is further divided into four blocks:
● Level Transducer Block (LTB)
● Liquid Crystal Display Block (LCD)
● Diagnostic Block (DIAG)
● Resource Block (RESOURCE)
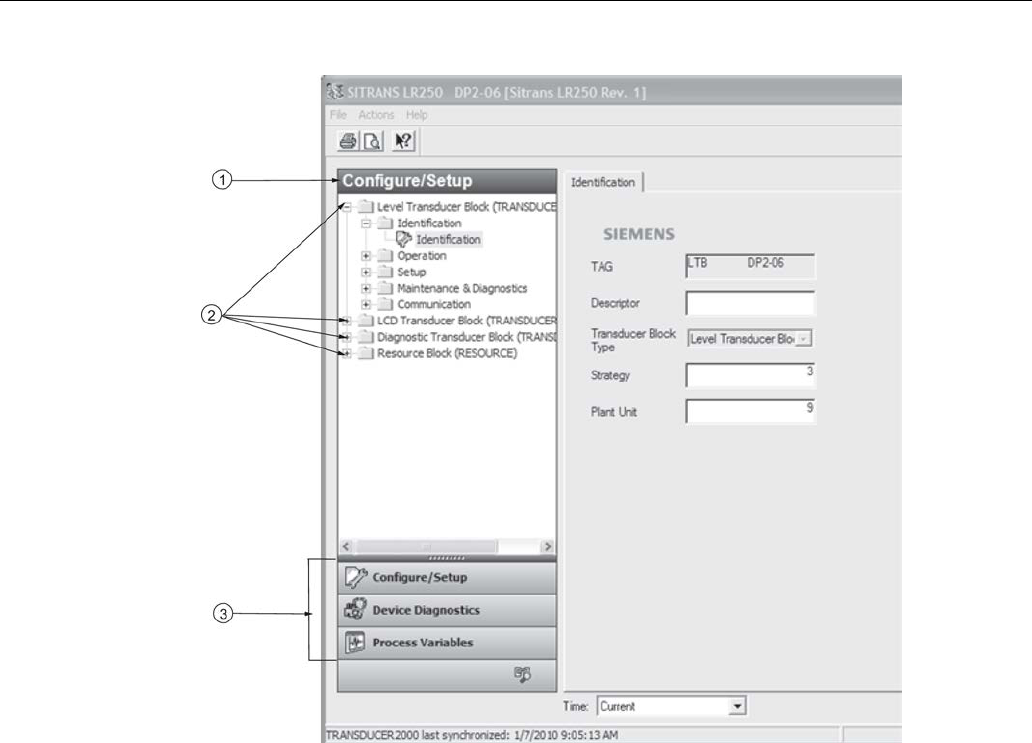
Remote operation
7.1 Operating via AMS Device Manager
SITRANS LR250 (FOUNDATION FIELDBUS)
80 Operating Instructions, 08/2014, A5E32221411-AC
①
Active function group
②
Blocks within each function group
③
Functions groups available
In general, process parameters are accessed through the Level Transducer Block, and device
parameters are accessed through the Resource Block.
See AMS Menu Structure (Page 130) for a chart, and Changing parameter settings using AMS
Device Manager (Page 91) for more details.
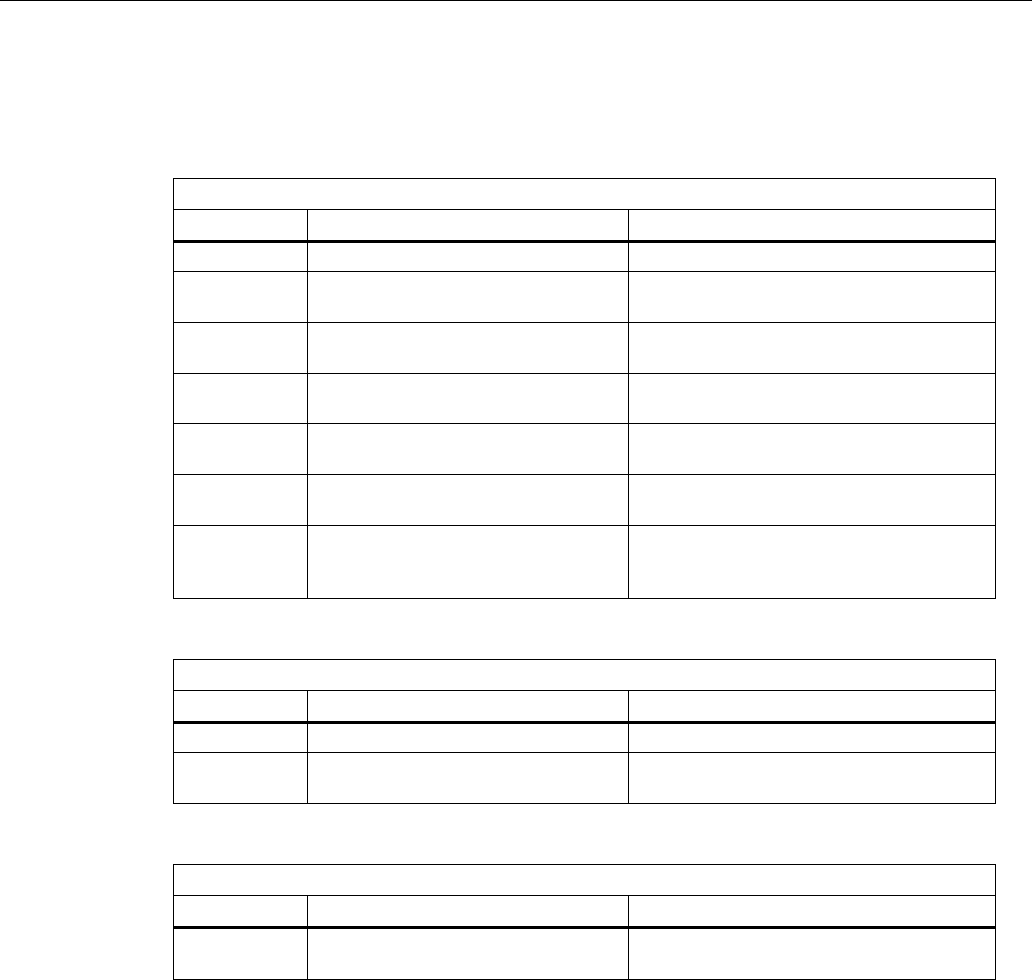
Remote operation
7.1 Operating via AMS Device Manager
SITRANS LR250 (FOUNDATION FIELDBUS)
Operating Instructions, 08/2014, A5E32221411-AC 81
7.1.2
Key features of AMS Device Manager Rev. 9.0
The graphic interface in the radar device makes monitoring and adjustments easy.
CONFIGURE/SETUP function group
Block
Feature
Function
LTB Echo Profile (Page 103) Echo profile viewing
LTB TVT (time varying threshold)
(Page 100)
Screen out false echoes
LTB Linearization (LTB) (Page 97) Volume measurement in an irregular
vessel
LTB Maintenance & Diagnostics (LTB)
(Page 104)
Set schedules and reminders for sensor
maintenance and service
RESOURCE Quick Start Wizard via AMS Device
Manager (Page 85)
Device configuration for simple applications
RESOURCE Maintenance & Diagnostics
(RESOURCE) (Page 116)
Set schedules and reminders for device
maintenance and calibration
RESOURCE Security (RESOURCE) (Page 119) Protect security and communication
parameters from modification by the
maintenance user
DEVICE DIAGNOSTICS function group
Block
Feature
Function
LTB Alarms & Errors (LTB) (Page 120) Monitor process errors and alarms
RESOURCE Alarms & Errors (RESOURCE)
(Page 124)
Monitor device errors and alarms
PROCESS VARIABLES function group
Block
Feature
Function
LTB Process Variables (Level Transducer
Block-LTB) (Page 128)
Monitor process variables and level
trend

Remote operation
7.1 Operating via AMS Device Manager
SITRANS LR250 (FOUNDATION FIELDBUS)
82 Operating Instructions, 08/2014, A5E32221411-AC
7.1.2.1
Pull-down menu access
①
Action menu items
A pull-down menu under
Actions
gives alternative access to several features.
7.1.3
Adding a new device
7.1.3.1
Electronic Device Description (EDD)
Note
SITRANS LR250 requires the EDD for AMS Device Manager version 9.0.
Check the product page of our website at: www.siemens.com/LR250
(http://www.siemens.com/LR250), under
Downloads
, for the latest version of EDD: SITRANS
LR250 FF - Foundation Fieldbus - AMS V9.0.
1. Check that you have the latest version of the EDD for AMS Device Manager that matches the
firmware revision of your device. See
Firmware Revision (2.2.2.)
, and if necessary download
it from the product page listed above. Save the files to your computer, and extract the zipped
file to an easily accessed location.
2. Launch
AMS Device Manager – Add Device Type
, browse to the unzipped EDD file and
select it.
3. The device is shipped with a unique tag, consisting of a manufacturer id and serial number.
The device tag can only be read from the device. It is not necessary to change the device tag
to make the device operational, however if you wish to change it, use AMS Device Manager.
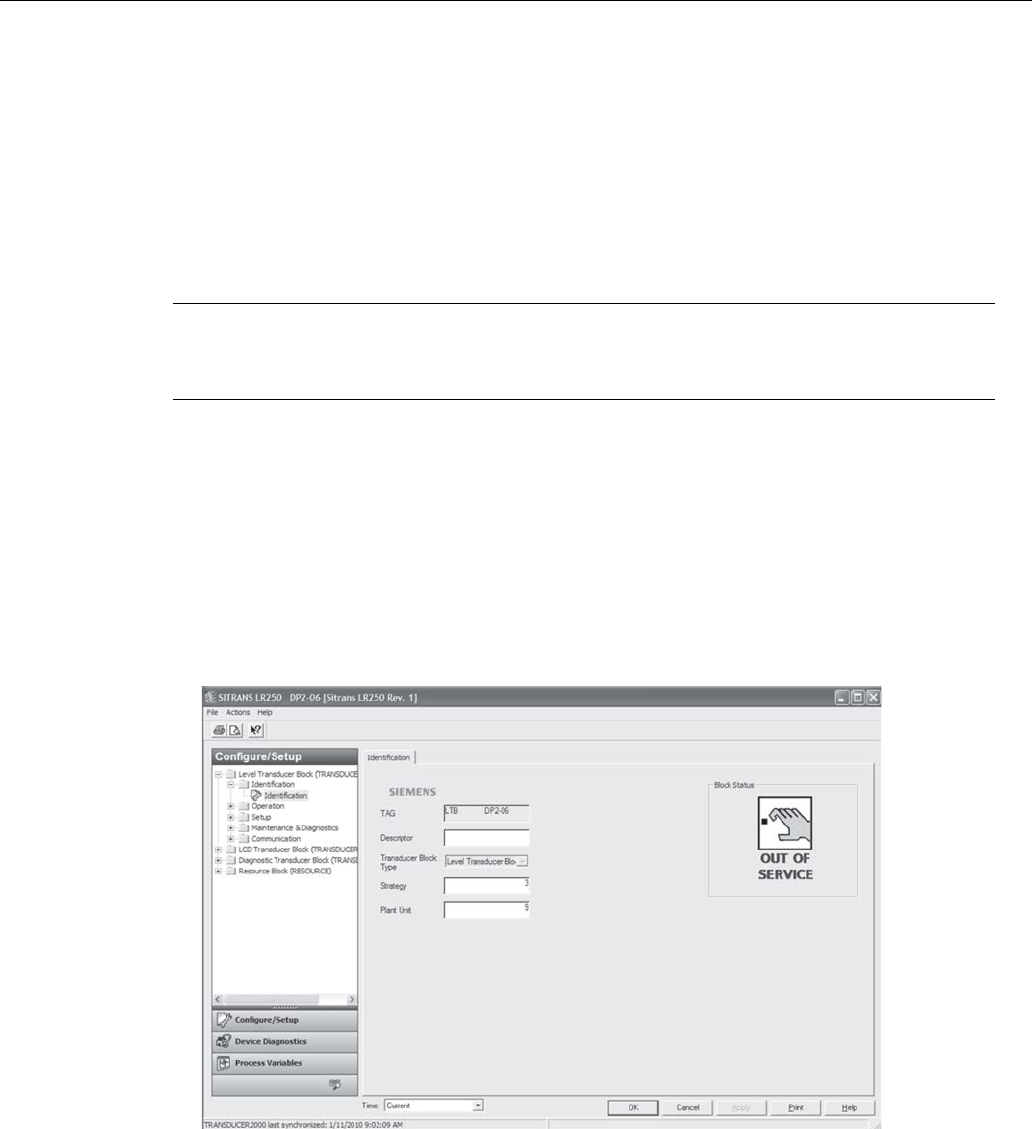
Remote operation
7.1 Operating via AMS Device Manager
SITRANS LR250 (FOUNDATION FIELDBUS)
Operating Instructions, 08/2014, A5E32221411-AC 83
Set Device Tag via AMS Device Manager:
1. Launch
AMS Device Manager – AMS Device Manager
.
2. From the Device Connection View, right click on the FF Network icon and select
Rebuild
Hierarchy
.
3. Right click on the device icon, and choose
Rename
from the menu.
4. Enter a device tag and press
Enter
.
Note
The Device Tag described above is separate from the Tag that describes each block type
(as shown in the Identification folder of each block).
Startup
1. Launch
AMS Device Manager – AMS Device Manager
. (If AMS already running, go to step 4.
2. From the Device Connection View, right click on the FF Network icon and select
Rebuild
Hierarchy
.
3. Double-click the device icon to open the startup screen. The startup screen shows device
identification details, and a navigation window on the left-hand side of the screen. (The Block
Status will show Out of Service at initial startup.)
4. Next, complete a master reset.
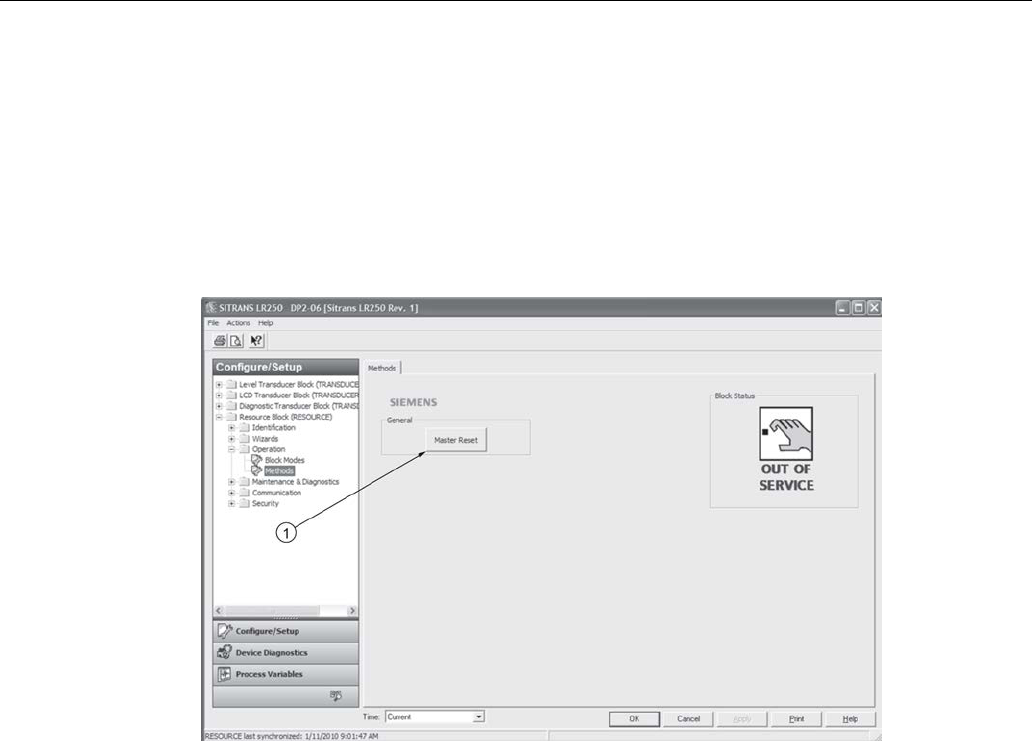
Remote operation
7.1 Operating via AMS Device Manager
SITRANS LR250 (FOUNDATION FIELDBUS)
84 Operating Instructions, 08/2014, A5E32221411-AC
7.1.4
Master Reset
A master reset is recommended before first configuring a new device. (Block Status must be Out
of Service to perform a Master Reset.)
1. Navigate to
Configure/Setup > Resource > Operation > Methods
and click to open the dialog
window.
2. In the
General
field, click on
Master Reset
and click Next to perform reset to factory defaults.
Click Next to accept default reset to
Factory Defaults
.
①
Master Reset
3. Click FINISH then restart AMS to reload settings. Next, scan the device.
7.1.5
Scan Device
Scan Device uploads parameters from the device (synchronizes parameters) to AMS Device
Manager.
1. Open the pull-down menu
Actions – Scan Device
(upload parameters from the device to
AMS).
2. The next step when adding a new device is to configure and calibrate the device via the
Quick Start Wizard.
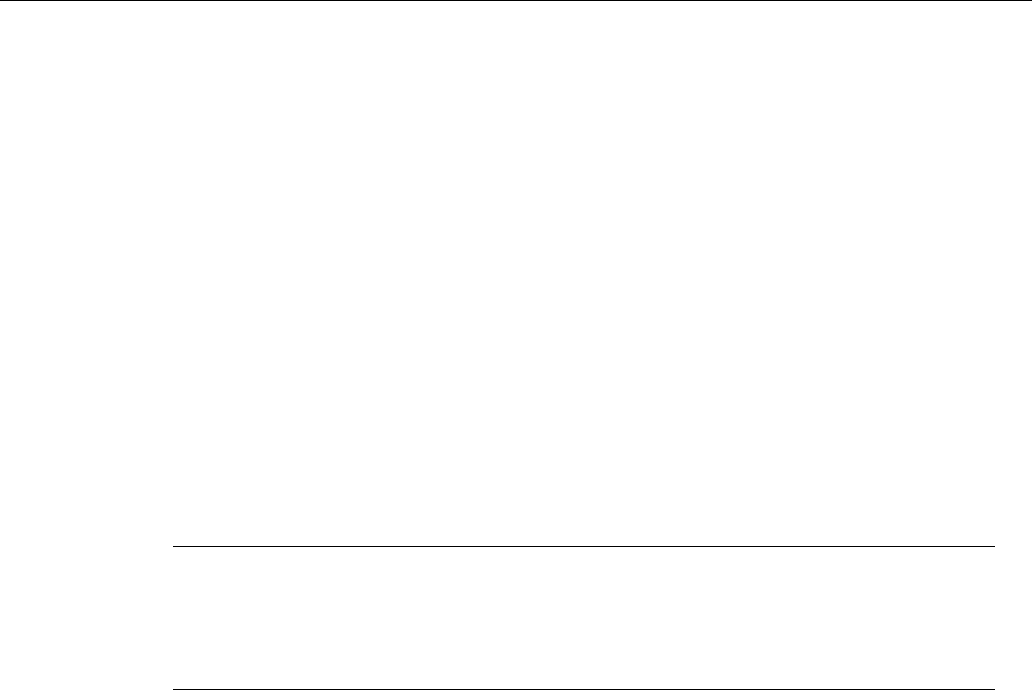
Remote operation
7.1 Operating via AMS Device Manager
SITRANS LR250 (FOUNDATION FIELDBUS)
Operating Instructions, 08/2014, A5E32221411-AC 85
7.1.6
Sensor calibration
The LR250 FF does not need to be calibrated, only configured using the Quick Start Wizard
below.
7.1.7
Configuring a new device
Configure a new device using the Quick Start Wizard, found in the
Resource Block
of the
function group
Configure/Setup
.
7.1.7.1
Quick Start Wizard via AMS Device Manager
The Quick Start Wizard groups together all the settings you need to configure a device for most
applications.
Please consult the operating instructions or online help for details on using AMS Device
Manager.
Note
Use Quick Start Wizard via AMS Device Manager for initial configuration of a device on an
FF network. If device is not on an FF network, initial configuration should be completed via
the Quick Start Wizard from the LUI. [See Quick Start Wizard via the handheld programmer
(Page 65).]

Remote operation
7.1 Operating via AMS Device Manager
SITRANS LR250 (FOUNDATION FIELDBUS)
86 Operating Instructions, 08/2014, A5E32221411-AC
Quick Start Wizard steps
Note
• Complete the steps in order. Click on
Apply
after revising parameters in each step, or
CANCEL
to exit step without saving changes. (Note:
Apply
will write changes to the
device.
OK
will write changes to the device and exit to the Device Connection View.
CANCEL
will exit to the Device Connection View without applying changes.)
• Do not use the Quick Start Wizard to modify individual parameters: see instead Changing
parameter settings using AMS Device Manager (Page 91). (Perform customization only
after the Quick Start has been completed.)
• Values set using the Quick Start Wizard via AMS Device Manager are saved and recalled
each time it is initiated (unlike the Quick Start Wizard initiated via the handheld
programmer).
• To run the Quick Start Wizard for this device, the RESOURCE block must first be set to
Out of Service (OOS) mode, before any configuration changes (changes to parameters
affecting block output) can be written. (Setting RESOURCE block to OOS also sets LTB
to OOS.)
• After completing steps 1-4, review all settings in Step 5 - Summary. Return to steps1-4 if
further changes are required.
• After completing the Quick Start Wizard from AMS, you must manually place the
RESOURCE block in Automatic mode.
Launch
AMS Device Manager
and double-click the device icon from the Device Connection
View to open the startup screen. Navigate to
Configure/Setup
> Resource Block > Wizards >
Quick Start
, and click on
Step 1 - Identification
.
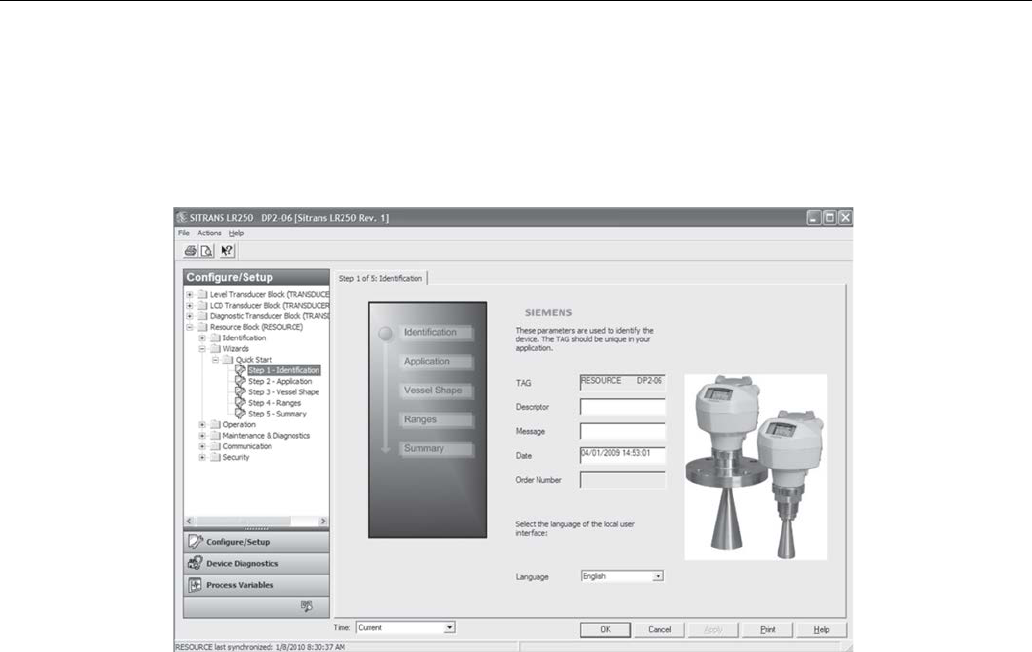
Remote operation
7.1 Operating via AMS Device Manager
SITRANS LR250 (FOUNDATION FIELDBUS)
Operating Instructions, 08/2014, A5E32221411-AC 87
Step 1 - Identification
You can accept the default values without modification. (Descriptor, Message, and Installation
Date
fields can be left blank.) If desired, make changes then click on
Apply
. (The
Apply
button is
activated when a parameter is modified.) Go to Step 2.
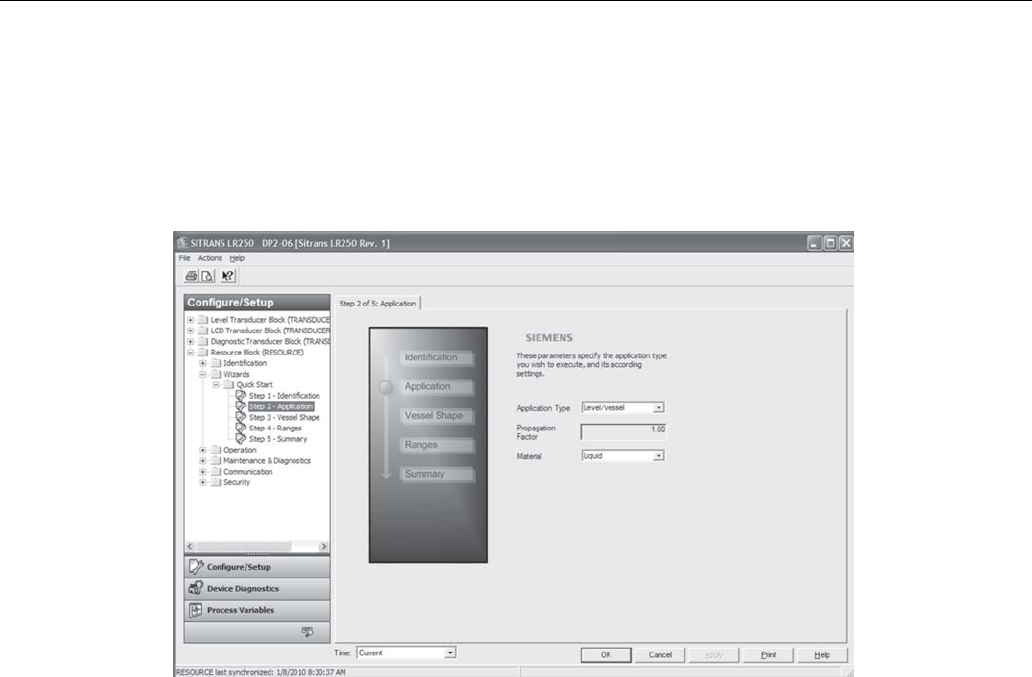
Remote operation
7.1 Operating via AMS Device Manager
SITRANS LR250 (FOUNDATION FIELDBUS)
88 Operating Instructions, 08/2014, A5E32221411-AC
Step 2 - Application Type
Click on
Step 2 - Application Type
in the navigation window. Select the Application Type (level or
volume), Propagation Factor (if using a stillpipe application), and the Material. For a Low
Dielectric Liquid application in a stilling well, see example Application with Stillpipe. Click on
Apply
to save settings then go to Step 3.
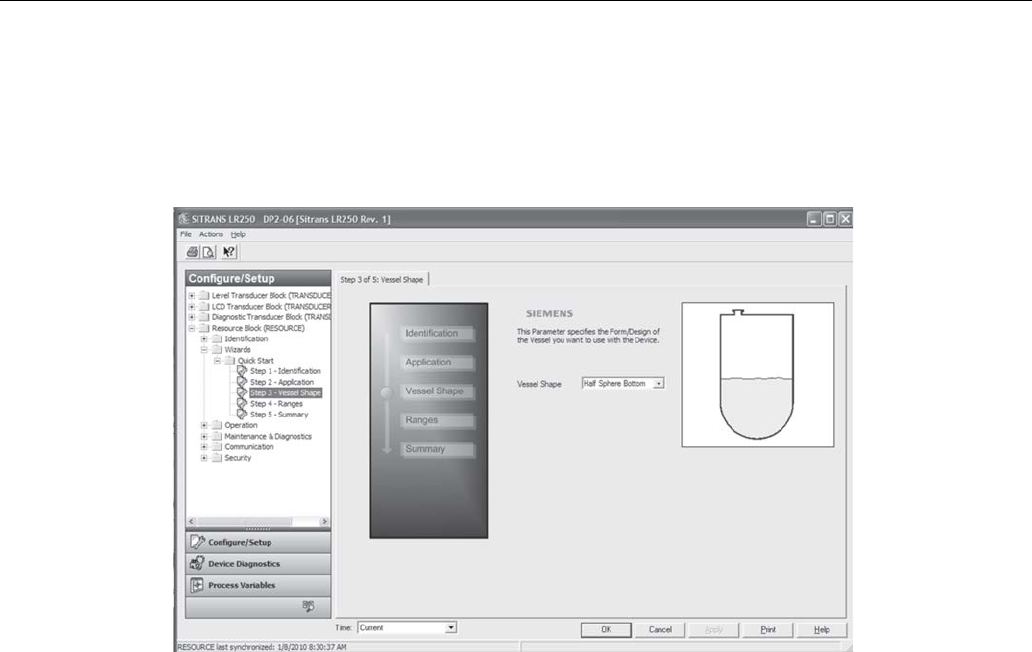
Remote operation
7.1 Operating via AMS Device Manager
SITRANS LR250 (FOUNDATION FIELDBUS)
Operating Instructions, 08/2014, A5E32221411-AC 89
Step 3 - Vessel Shape
Click on
Step 3 - Vessel Shape
in the navigation window. Select the vessel shape. To describe a
more complex shape, select
Linearization Table
in the Vessel Shape field and see Linearization
(LTB) (Page 97) for more details. Click on
Apply
to save settings then go to Step 4.
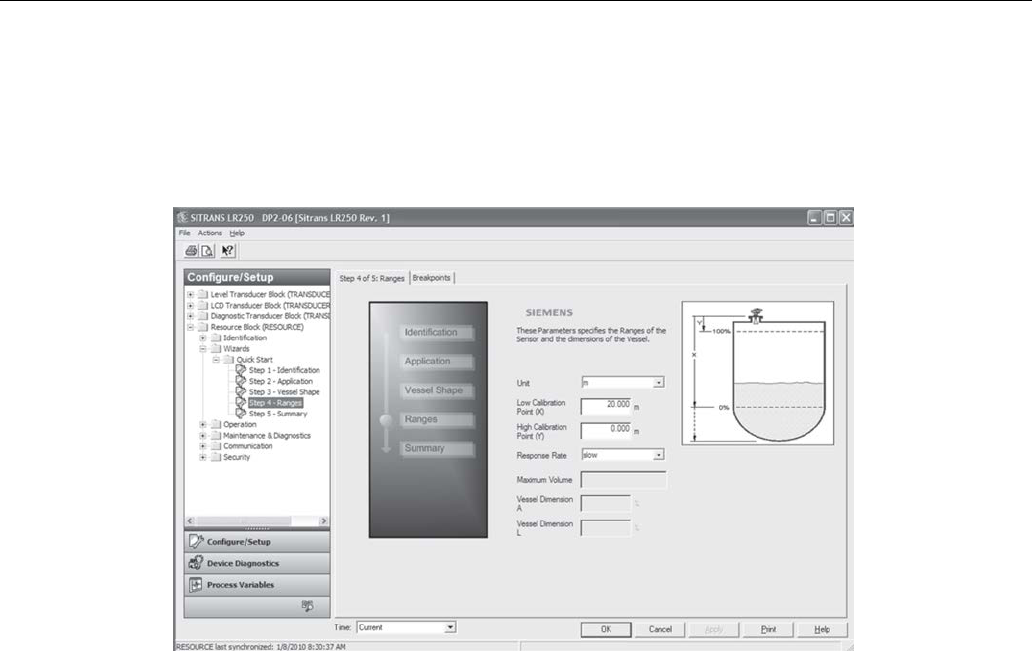
Remote operation
7.1 Operating via AMS Device Manager
SITRANS LR250 (FOUNDATION FIELDBUS)
90 Operating Instructions, 08/2014, A5E32221411-AC
Step 4 - Ranges
Click on
Step 4 - Ranges
in the navigation window. On the tab Step 4 of 5 Ranges: set the
parameters, and click on
Apply
to save settings. If necessary, click on the Breakpoints tab, set
the parameters, and click on
Apply
to save settings. Go to Step 5.
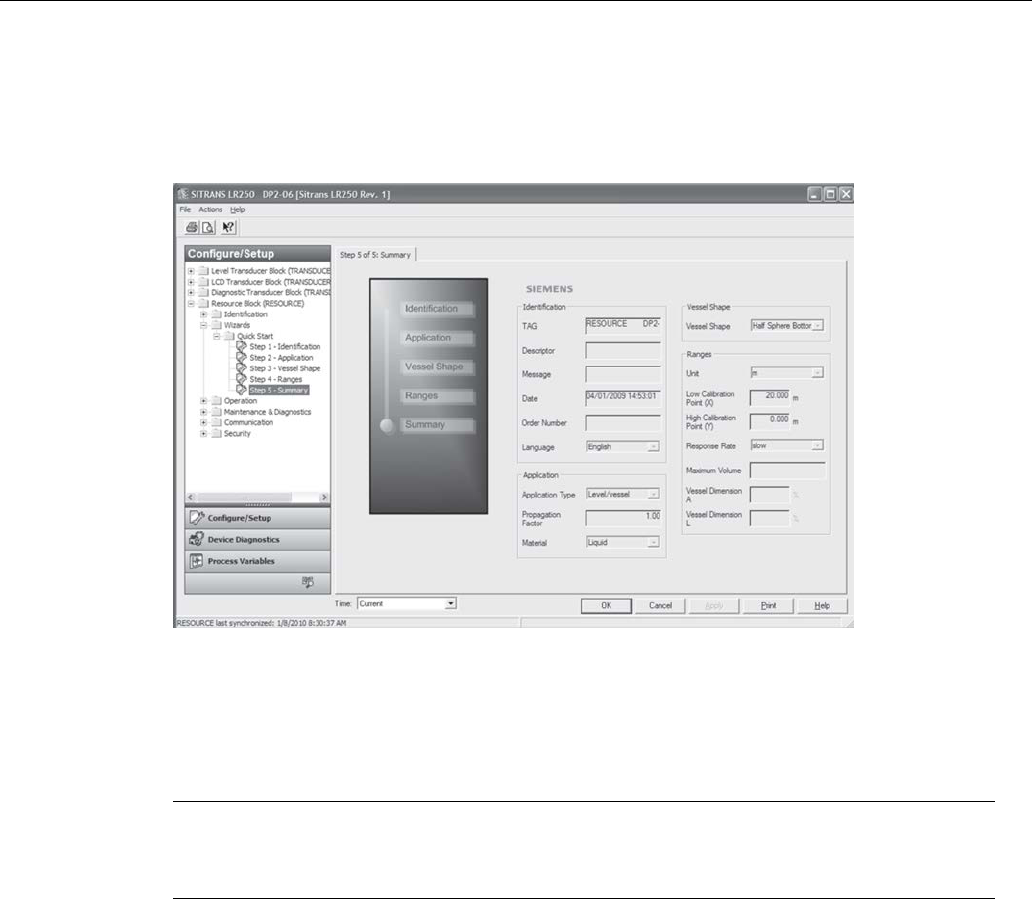
Remote operation
7.1 Operating via AMS Device Manager
SITRANS LR250 (FOUNDATION FIELDBUS)
Operating Instructions, 08/2014, A5E32221411-AC 91
Step 5 - Summary
Click on
Step 5 - Summary
in the navigation window. Check parameter settings. Return to
individual steps if further changes are necessary.
The Quick Start Wizard is now complete.
7.1.8
Changing parameter settings using AMS Device Manager
Note
• For a complete list of parameters, see Parameter Reference (Page 143).
• For more detailed explanations of the parameters listed below see the pages referenced.
1. Adjust parameter values in the parameter value field in
Configure/Setup
view, then click on
Apply
to write the new values to the device. The parameter field will display in yellow until the
value has been written to the device.
2. Click on
OK
only if you wish to update all parameters and exit device view.
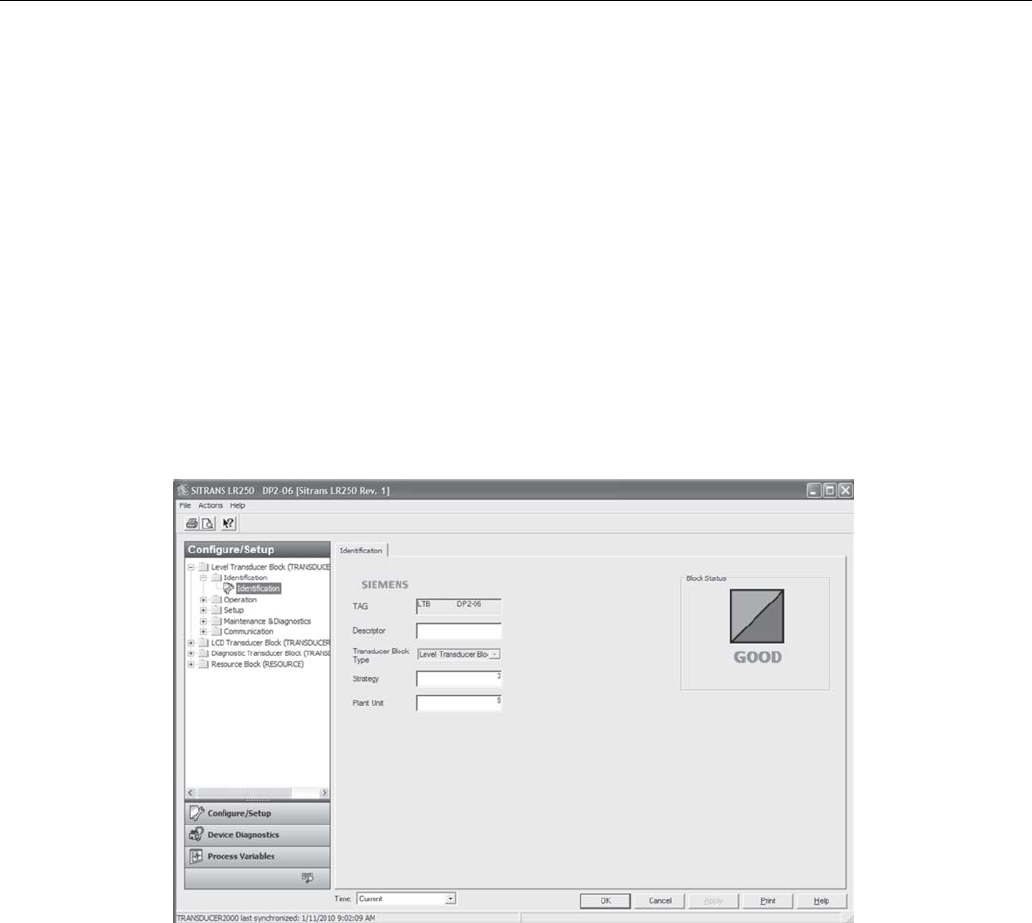
Remote operation
7.1 Operating via AMS Device Manager
SITRANS LR250 (FOUNDATION FIELDBUS)
92 Operating Instructions, 08/2014, A5E32221411-AC
7.1.9
Configure/Setup (Level Transducer Block-LTB)
7.1.9.1
Identification (LTB)
Navigate to
Configure/Setup > LTB > Identification
.
Identification:
● TAG: Read only. Description for the associated block: device tag prefixed by block type.
● Descriptor [see
Descriptor (2.1.2.)
]
● Transducer Block Type: Read only. Identifies the type of transducer block.
● Strategy: Used to identify grouping of blocks.
● Plant Unit: The identification number of the plant unit. For example, can be used in the host
for sorting alarms.
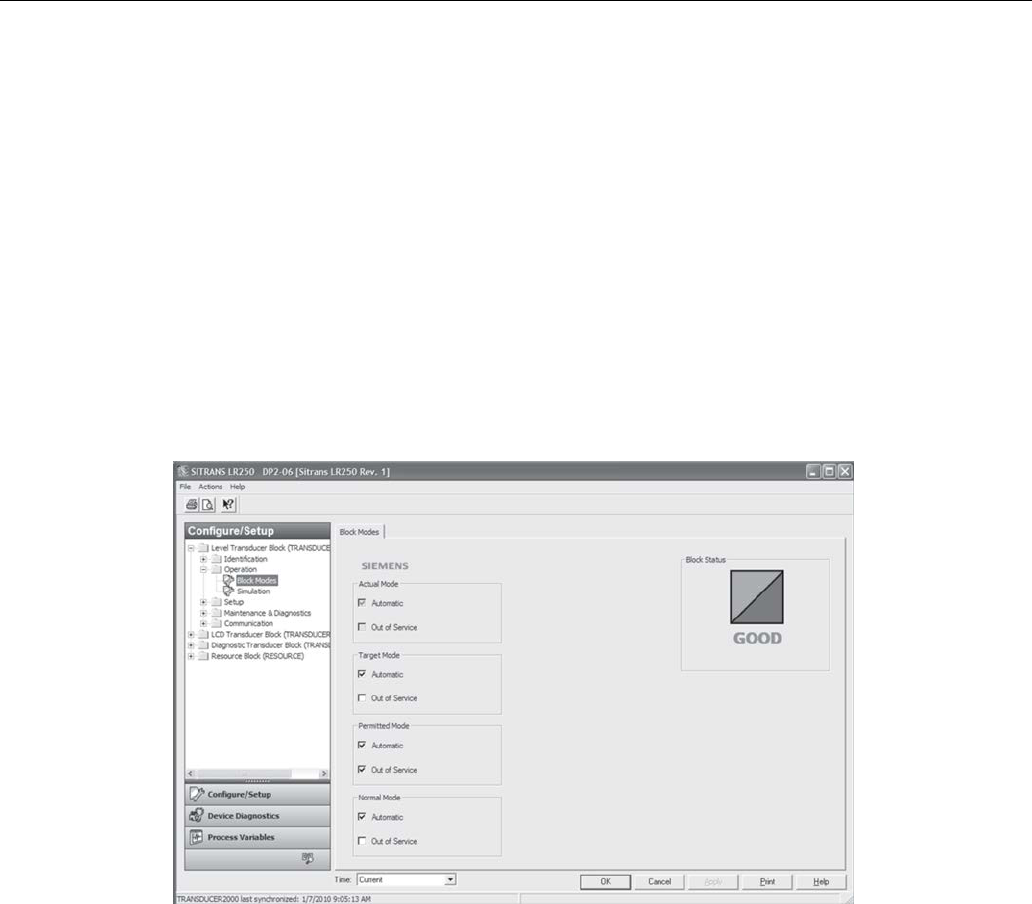
Remote operation
7.1 Operating via AMS Device Manager
SITRANS LR250 (FOUNDATION FIELDBUS)
Operating Instructions, 08/2014, A5E32221411-AC 93
7.1.9.2
Operation (LTB)
Navigate to
Configure/Setup > LTB > Operation
.
Click on Block Modes to open the dialog window for access to:
Block Modes:
● Actual Mode: This is the current mode of the block, which may differ from the target based on
operating conditions. Its value is calculated as part of the block execution.
● Target Mode [see
Mode (2.6.2.)
]
● Permitted Mode: Defines the modes that are allowed for an instance of the block. The
permitted mode is configured based on application requirements.
● Normal Mode: This is the mode that the block should be set to during normal operating
conditions.
Click on
Simulation
to open the dialog window for access to:
Simulation (Input)
Allows you to simulate the sensor value which is input to the Level Transducer Block. This tests
everything between the Level Transducer Block and Output.
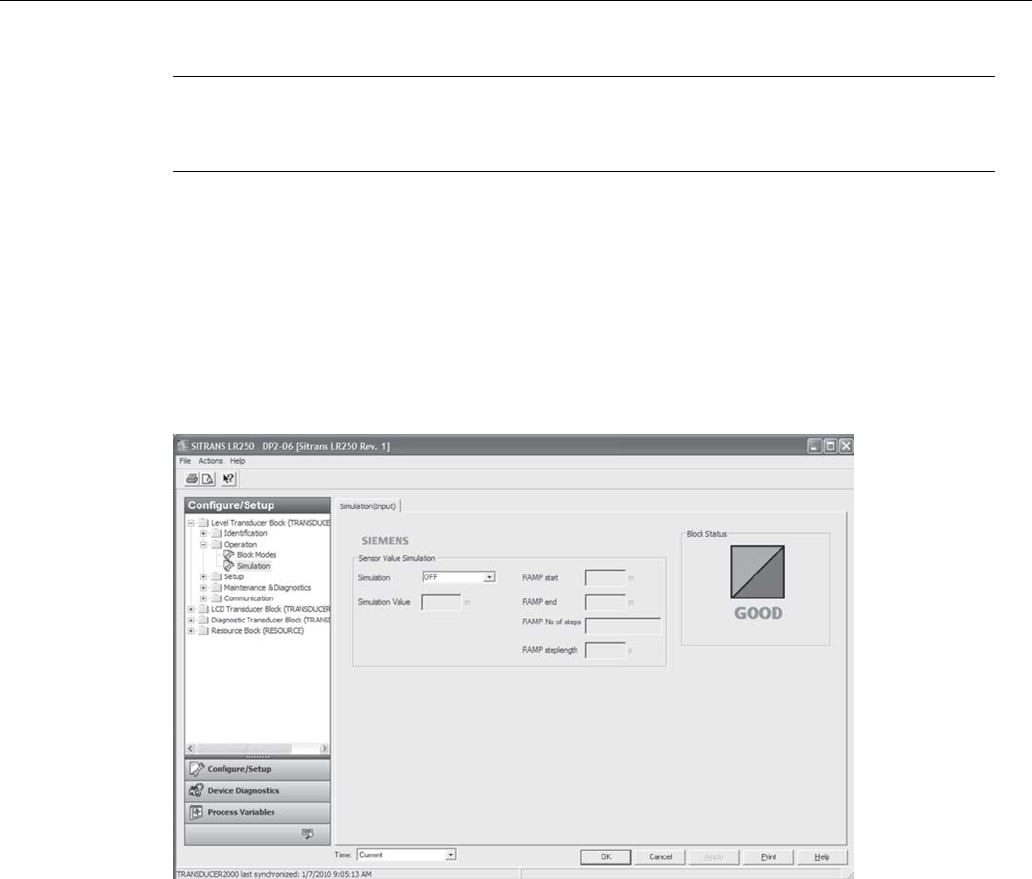
Remote operation
7.1 Operating via AMS Device Manager
SITRANS LR250 (FOUNDATION FIELDBUS)
94 Operating Instructions, 08/2014, A5E32221411-AC
Note
To activate simulation via AMS Device Manager or the 375 Field Communicator, simulation
must also be set to Enabled on the device. See
Simulate Enable (4.12.)
.
● Simulation
● Simulation Value
● RAMP start
● RAMP end
● RAMP No of steps
● RAMP steplength
1. To enable simulation select
Fixed value
or
Ramp
in the Simulation field.
2. If you select Fixed value, enter a Simulation Value.
3. If you select Ramp, enter the ramp start, end, number of steps, and steplength.
4. Click
Apply
.
5. After simulation is complete, set Simulation to
OFF
and click
Apply
.
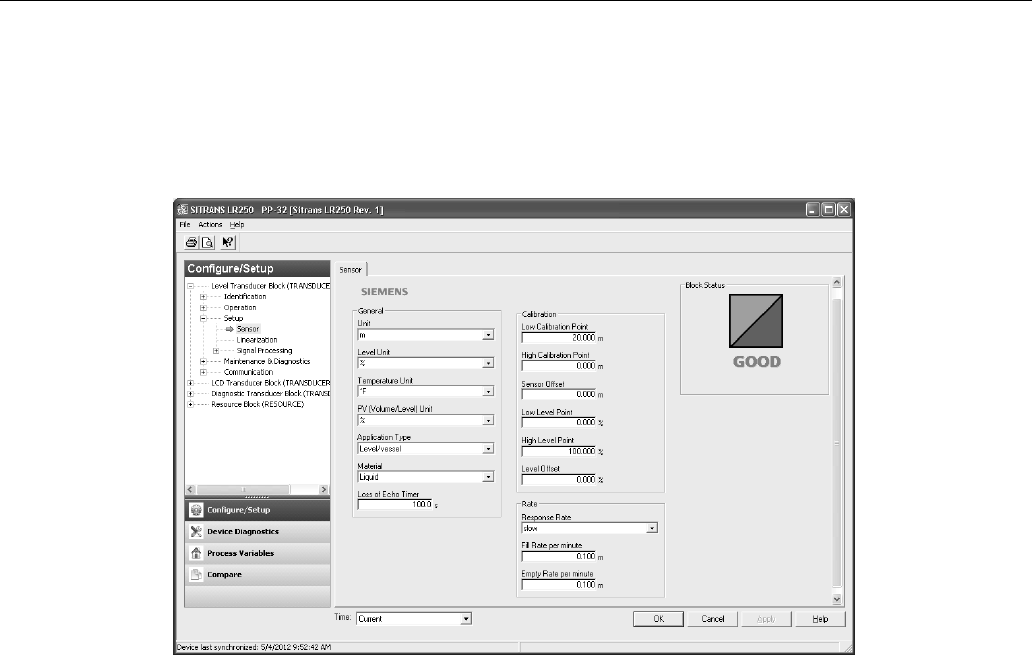
Remote operation
7.1 Operating via AMS Device Manager
SITRANS LR250 (FOUNDATION FIELDBUS)
Operating Instructions, 08/2014, A5E32221411-AC 95
7.1.9.3
Setup (LTB)
Sensor (LTB)
Navigate to
Configure/Setup > LTB > Setup
and click on
Sensor
for access to:
General
[see
Sensor (2.3.)
for details]
● Unit [see
Unit (2.3.1.)
]
● Level Unit [see
Level Unit (2.3.2.)
]
● Temperature Unit [see
Temperature Units (2.3.4.)
]
● PV (Volume/Level) Unit [see
PV (volume/level) Units (2.3.3.)
]
● Application Type (available only via AMS Device Manager)
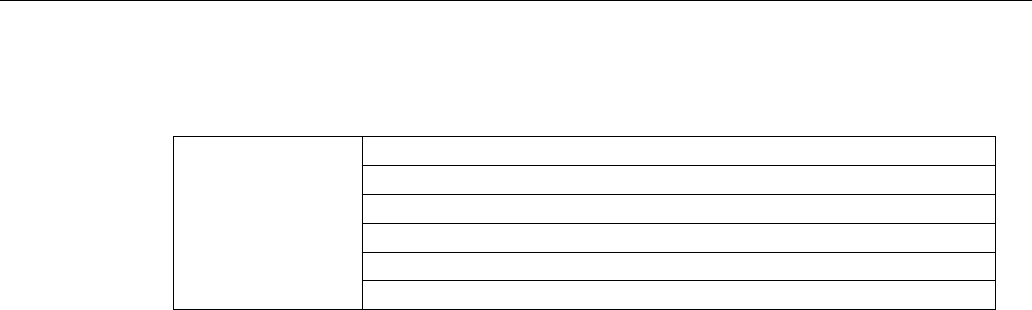
Remote operation
7.1 Operating via AMS Device Manager
SITRANS LR250 (FOUNDATION FIELDBUS)
96 Operating Instructions, 08/2014, A5E32221411-AC
Defines the application type.
Values
Level/vessel (default)
Level/stillpipe
Level/bypass pipe
Volume/vessel
Volume/stillpipe
Volume/bypass pipe
● Material [see
Material (2.3.5.)
]
● Loss of Echo Timer (see
Loss of Echo (LOE) Timer (2.3.6.)
]
Calibration
[see
Calibration (2.3.7.)
for details]
● Low Calibration Point [see
Low Calibration Point (2.3.7.1.)
]
● High Calibration Point [see
High Calibration Point 2.3.7.2.)
]
● Sensor Offset [see
Sensor Offset (2.3.7.3.)
]
● Low Level Point [see
Low Level Point (2.3.7.4.)
]
● High Level Point [see
High Level Point (2.3.7.5)
]
● Level Offset [see
Level Offset (2.3.7.6.)
]
Rate
[see
Rate (2.3.8.)
]
● Response Rate [see
Response Rate (2.3.8.1.)
]
● Fill Rate per Minute [see
Fill Rate per Minute (2.3.8.2.)
]
● Empty Rate per Minute [see
Empty Rate per Minute (2.3.8.3.)
]
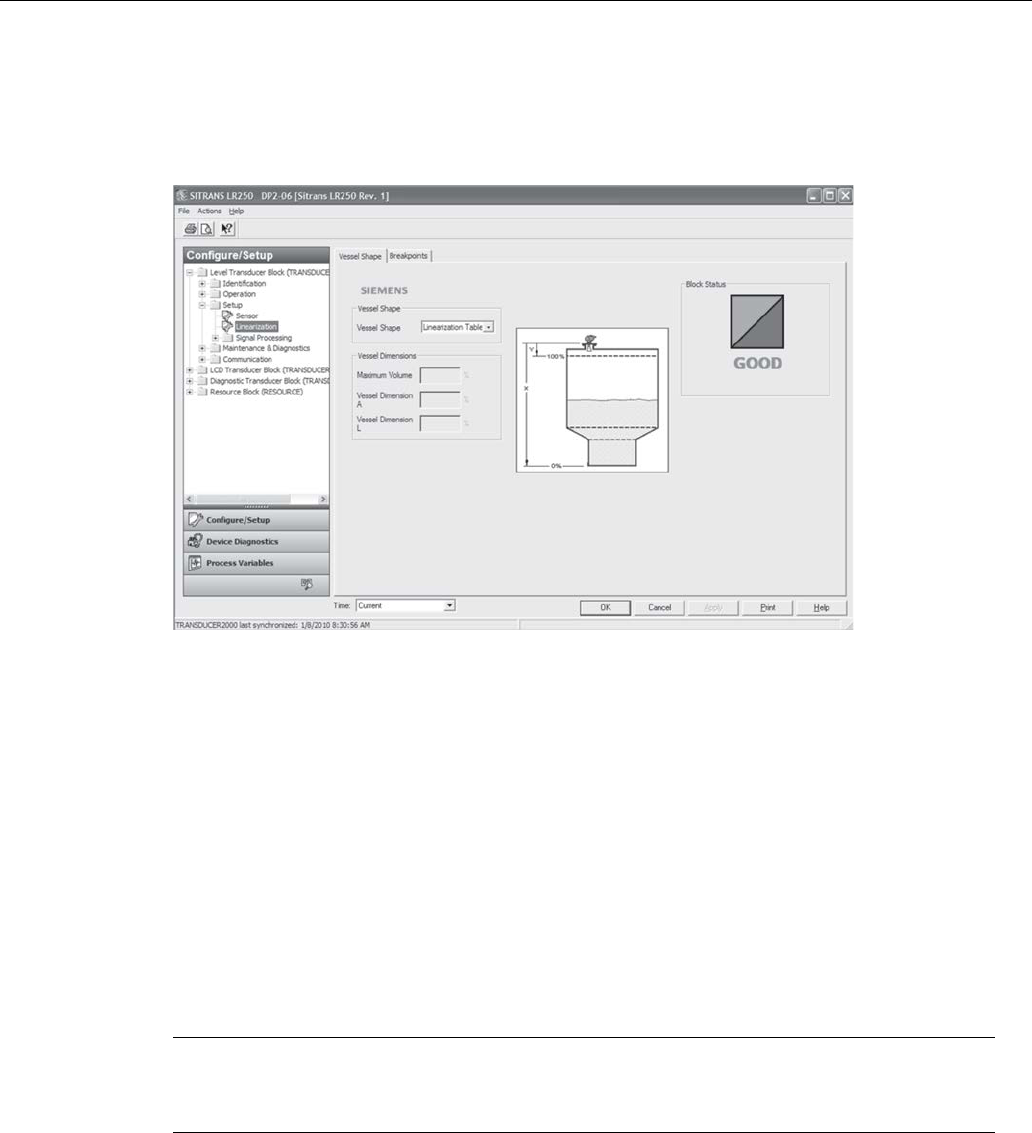
Remote operation
7.1 Operating via AMS Device Manager
SITRANS LR250 (FOUNDATION FIELDBUS)
Operating Instructions, 08/2014, A5E32221411-AC 97
7.1.9.4
Linearization (LTB)
You can use the linearization feature to define a more complex vessel shape and enter up to 32
level breakpoints where the corresponding volume is known. See
Linearization (2.4.)
.
Navigate to
Configure/Setup > LTB > Setup > Linearization
and click on
Linearization
. Click on
the Vessel Shape tab to access the parameters listed:
Vessel Shape
● Vessel Shape [see
Vessel Shape (2.4.1.1.)
]
Vessel Dimensions
● Maximum Volume [see
Maximum Volume (2.4.1.2.)
]
● Vessel Dimension A [see
Dimension A (2.4.1.3.)
]
● Vessel Dimension L [see
Dimension L (2.4.1.4.)
]
OR
Click on
Breakpoints
tab for access to level and volume breakpoints.
Note
This parameter becomes accessible only after
Linearization Table
has been selected in
Vessel Shape
above.
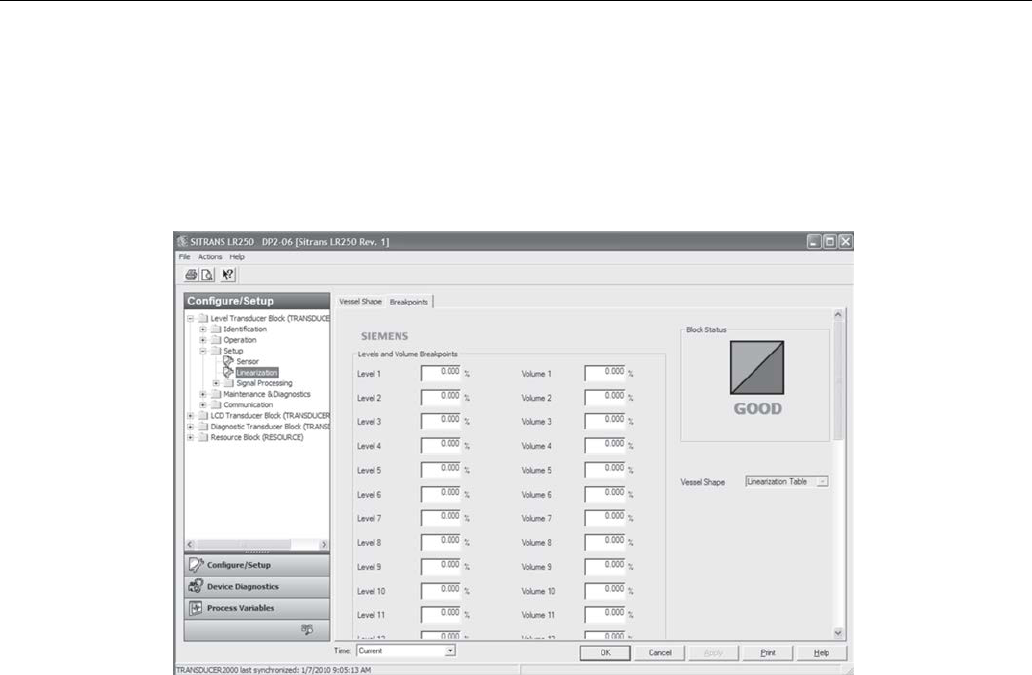
Remote operation
7.1 Operating via AMS Device Manager
SITRANS LR250 (FOUNDATION FIELDBUS)
98 Operating Instructions, 08/2014, A5E32221411-AC
Level and Volume Breakpoints [see XY Index (2.4.1.5.)]
● Level 1 .... Level 32
● Volume 1 ... Volume 32
● Vessel Shape
1. The default for level values is percent: if you want to select units instead, go to
Configure/Setup > LTB > Setup > Sensor > Level Unit
, and select the desired unit.
2. Go to
Configure/Setup > LTB > Setup > Sensor > PV (Volume/Level) Unit
, and select the
desired volume units.
3. From the Vessel Shape tab of
Configure/Setup > LTB > Setup > Linearization
, select
Linearization Table
option in the Vessel Shape field.
4. Click on the Breakpoints tab and enter values for level and volume breakpoints in table.
The values corresponding to 100% and 0% levels must be entered. The breakpoints can be
ordered from top to bottom, or the reverse.
After completing the above steps you will need to configure AIFB 1 and/or AIFB 2. [See
AIFB 1
(2.6.)
and
AIFB 2 (2.7.)
]
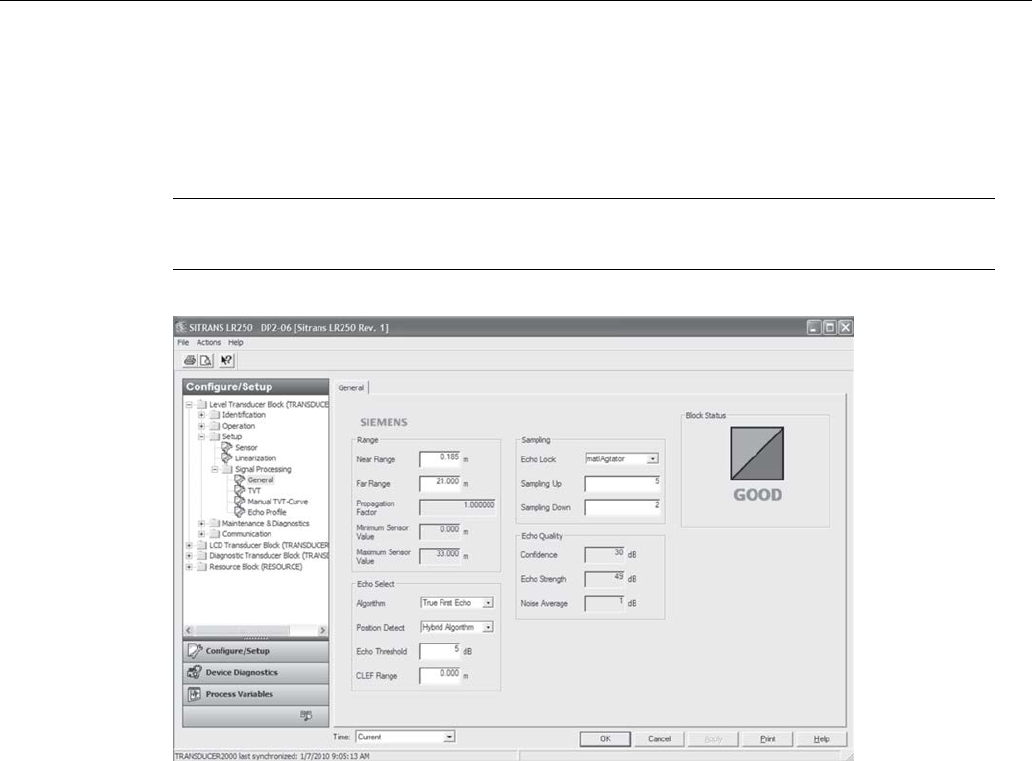
Remote operation
7.1 Operating via AMS Device Manager
SITRANS LR250 (FOUNDATION FIELDBUS)
Operating Instructions, 08/2014, A5E32221411-AC 99
7.1.9.5
Signal processing
Signal Processing (LTB)
Note
For more detailed explanations of the parameters listed below see the pages referenced.
General
Navigate to
Configure/Setup > LTB > Setup > Signal Processing
and click on General for access
to:
Range
[see
Signal Processing (2.5.)
]
● Near Range [see
Near Range (2.5.1.)
]
● Far Range [see
Far Range (2.5.2.)
]
● Propogation Factor [see
Propogation Factor (2.5.3.)
]
● Minimum Sensor Value [see
Minimum Sensor Value (2.5.4.)
]
● Maximum Sensor Value [see
Maximum Sensor Value (2.5.5.)
]

Remote operation
7.1 Operating via AMS Device Manager
SITRANS LR250 (FOUNDATION FIELDBUS)
100 Operating Instructions, 08/2014, A5E32221411-AC
Echo Select
[see
Echo Select (2.5.7.)
]
● Algorithm [see
Algorithm (2.5.7.1.)
]
● Position Detect [see
Position Detect (2.5.7.2.)
]
● Echo Threshold [see
Echo Threshold (2.5.7.3.)
]
● CLEF Range [see
CLEF (Contrained Leading Edge Fit) Range (2.5.7.4.)
]
Sampling
[see
Sampling (2.5.8.)
]
● Echo Lock [see
Echo Lock (2.5.8.1.)
]
● Sampling Up [see
Up Sampling (2.5.8.2.)
]
● Sampling Down [see
Down Sampling (2.5.8.3.)
]
Echo Quality
[see
Echo Quality (2.5.9.)
]
● Confidence [see
Confidence (2.5.9.1.)
]
● Echo Strength [see
Echo Strength (2.5.9.2.)
]
● Noise Average
Displays the average ambient noise (in dB above 1 μV rms) of a noise profile. Noise level is a
combination of transient noise and receiving circuitry. After a measurement, the values from
the previous noise shot will be displayed.
TVT (time varying threshold)
A time-varying curve that determines the threshold level above which echoes are determined to
be valid.
Modify the TVT to screen out false echoes [see Time Varying Threshold (TVT) (Page 266), and
Auto False Echo Suppression (2.5.10.1.)
].
Navigate to
Configure/Setup > LTB > Setup > Signal Processing
and click on
TVT
. Click on one
of the two tabs to access the parameters listed:
TVT Setup
● Auto False Echo Suppression [see
Auto False Echo Suppression (2.5.10.1.)
]
● Auto False Echo Suppression Range [see
Auto False Echo Suppression Range (2.5.10.2.)
]
● Hover Level [see
Hover Level (2.5.10.3.)
]
● Shaper Mode [see
Shaper Mode (2.5.10.4.)
]
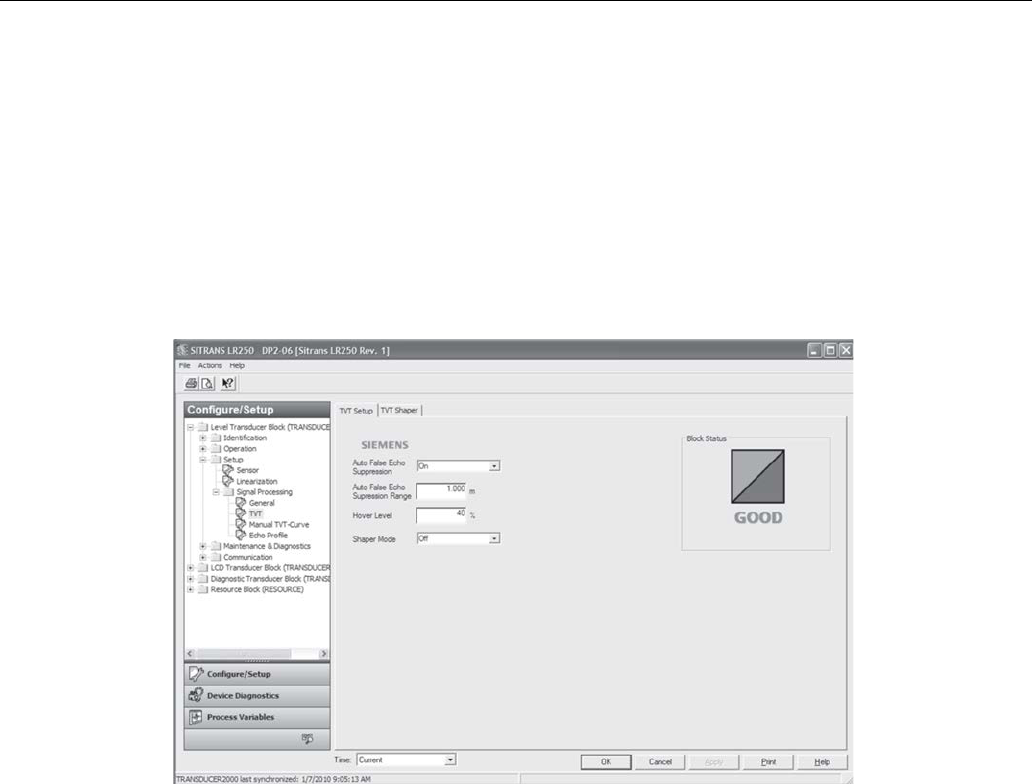
Remote operation
7.1 Operating via AMS Device Manager
SITRANS LR250 (FOUNDATION FIELDBUS)
Operating Instructions, 08/2014, A5E32221411-AC 101
Auto False Echo Suppression
1. Determine Auto False Echo Suppression Range. Measure the actual distance from the
sensor reference point to the material surface using a rope or tape measure.
2. Subtract 0.5 m (20") from this distance, and use the resulting value.
3. Open the menu
Configure/Setup > LTB > Setup > Signal Processing > TVT
and set Auto
False Echo Suppression Range.
4. From the same menu, set Auto False Echo Suppression to learn. The device will
automatically revert to On (Use Learned TVT) after a few seconds.
TVT Shaper
[see
TVT Shaper (2.5.11.)
]
● Breakpoints 1 to 40
● Shaper Mode
1. Open the menu
Configure/Setup > LTB > Setup > Signal Processing > TVT
and click on the
TVT Setup tab
2. Turn Shaper Mode to
On
to activate Breakpoints 1 to 40 on the TVT Shaper tab
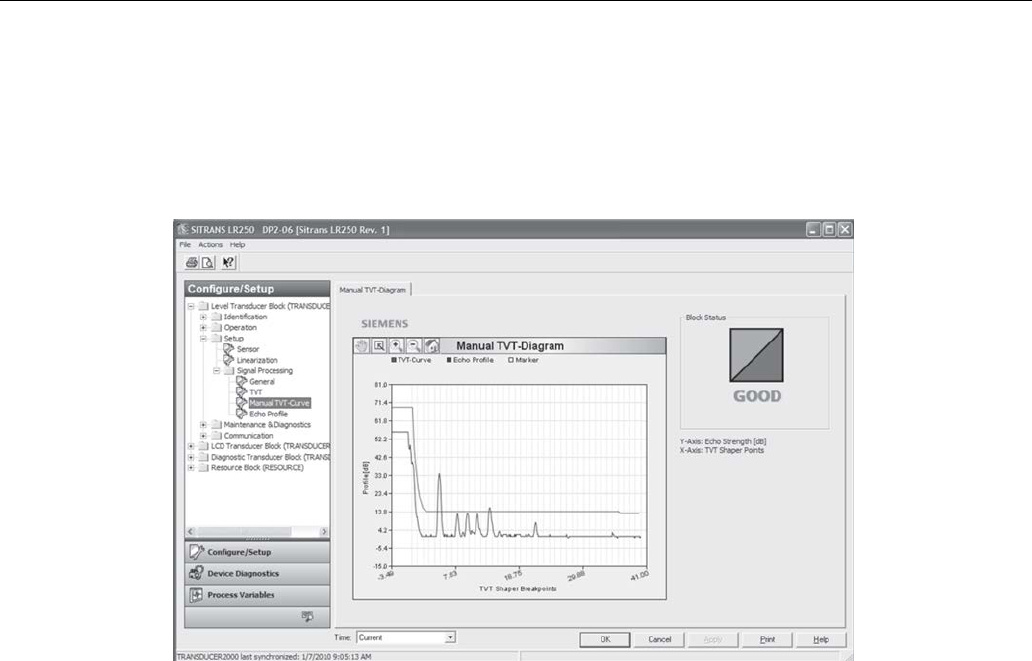
Remote operation
7.1 Operating via AMS Device Manager
SITRANS LR250 (FOUNDATION FIELDBUS)
102 Operating Instructions, 08/2014, A5E32221411-AC
Manual TVT curve
Displays the effects of the TVT shaper modifications.
Navigate to
Configure/Setup > LTB > Setup > Signal Processing
and click on
Manual TVT
Curve
.
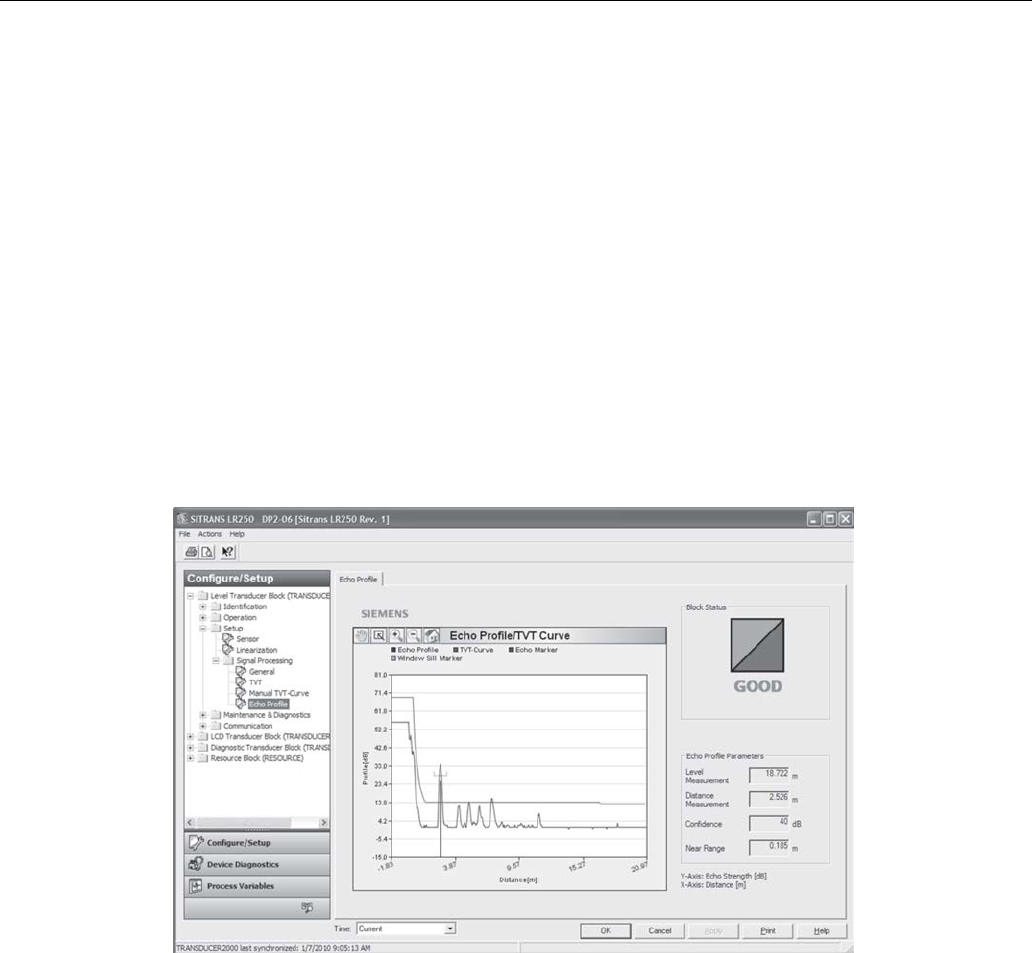
Remote operation
7.1 Operating via AMS Device Manager
SITRANS LR250 (FOUNDATION FIELDBUS)
Operating Instructions, 08/2014, A5E32221411-AC 103
Echo Profile
Displays the current echo profile.
Navigate to
Configure/Setup > LTB > Setup > Signal Processing
and click on
Echo Profile
to
view the current echo profile and to access:
Echo Profile Parameters
[see
Echo Profile (3.1.)
]
● Level Measurement [see
Measured Values (2.8)
]
● Distance Measurement [see
Measured Values (2.8.)
]
● Confidence [see
Confidence (2.5.9.1.)
]
● Near Range (see
(Near Range 2.5.1.)
]
To view a previous profile, click the drop-down arrow on the
Time
field and select the desired
profile (note: available only using AMS version 10.1or later).
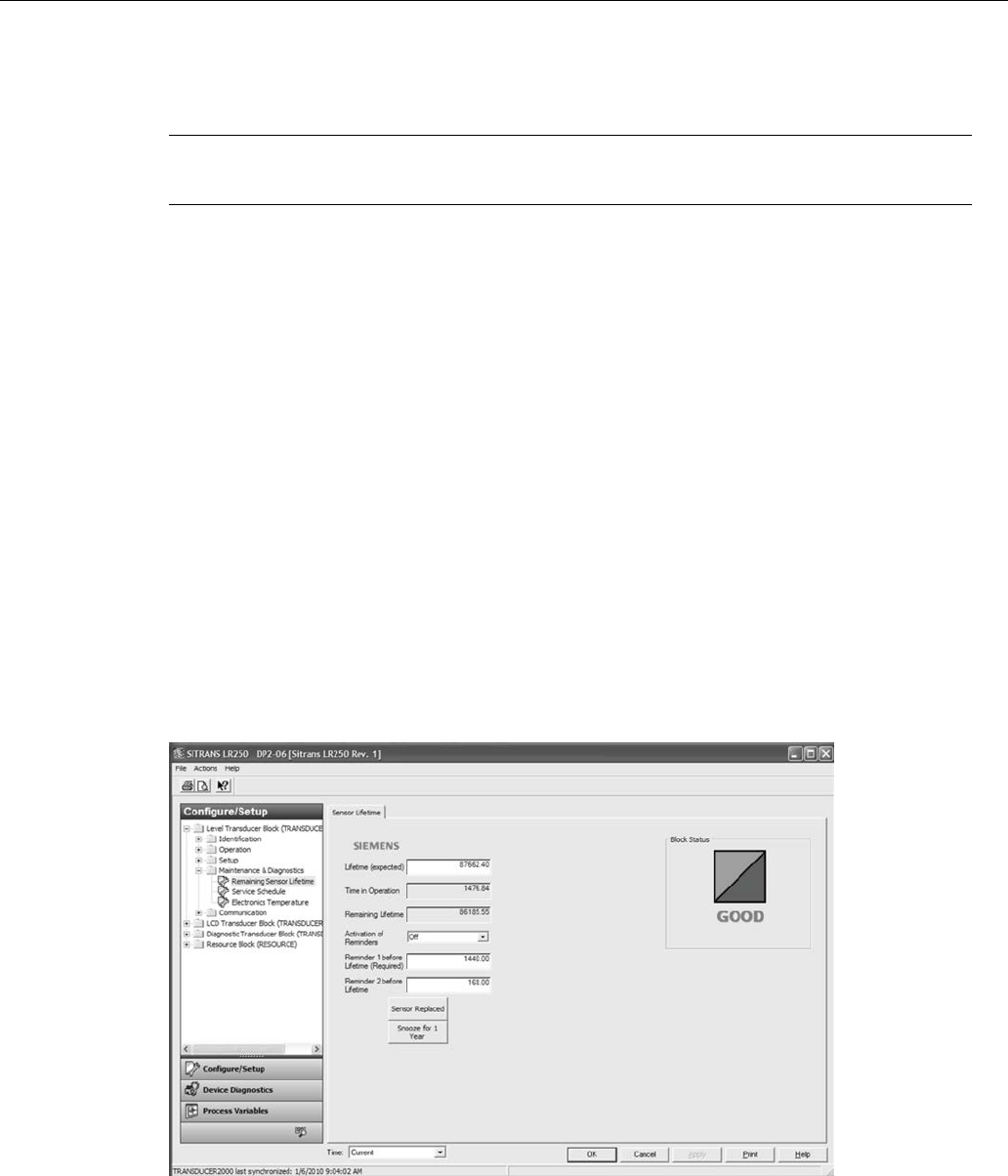
Remote operation
7.1 Operating via AMS Device Manager
SITRANS LR250 (FOUNDATION FIELDBUS)
104 Operating Instructions, 08/2014, A5E32221411-AC
7.1.9.6
Maintenance & Diagnostics (LTB)
Note
For more detailed explanations of the parameters listed below see the pages referenced.
Navigate to
Configure/Setup > LTB > Maintenance and Diagnostics
for access to:
Remaining Sensor Lifetime
[see
Remaining Sensor LIfetime (4.3.)
]
● Lifetime (expected) [see
Lifetime (expected) (4.3.1.)
]
● Time in Operation [see
Time in Operation (4.3.2.)
]
● Remaining Lifetime [see
Remaining Lifetime (4.3.3.)
]
● Activation of Reminders [see
Activation of Reminders (4.3.4.)
]
● Reminder 1 before Lifetime (Required) [see
Reminder 1 before Lifetime (Required) (4.3.5.)
]
● Reminder 2 before Lifetime (Demanded) [see
Reminder 2 before Lifetime (Demanded)
(4.3.6.)
]
1. Open the window
Remaining Sensor Lifetime
2. After modifying values/units as required, click on
Apply
to accept the change.
● Click on
Sensor Replaced
to reset Time in Operation to 0 hours
● Click on
Snooze for 1 Year
to add a year to the Total Expected Sensor Life
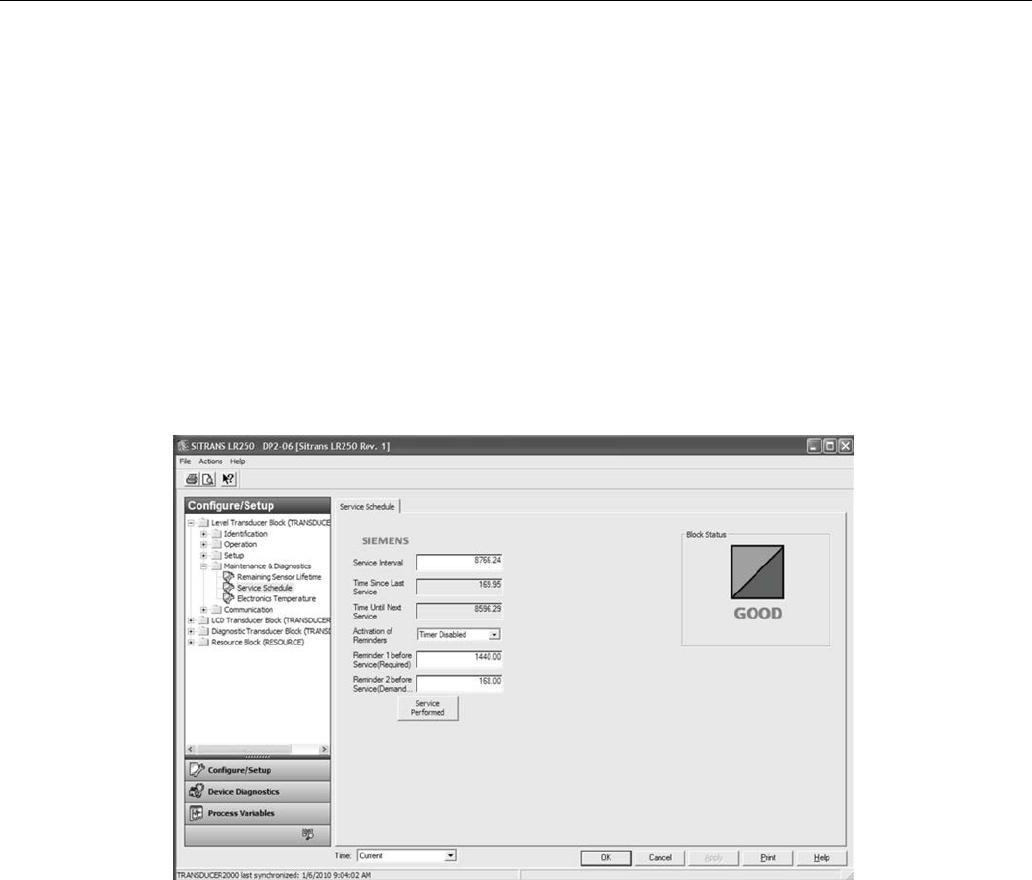
Remote operation
7.1 Operating via AMS Device Manager
SITRANS LR250 (FOUNDATION FIELDBUS)
Operating Instructions, 08/2014, A5E32221411-AC 105
Service Schedule
[see
Service Schedule (4.4.)
]
● Service Interval [see
Service Interval (4.4.1.)
]
● Time Since Last Service [see
Time Since Last Service (4.4.2.)
]
● Time Until Next Service [see
Time Until Next Service (4.4.3.)
]
● Activation of Reminders [see
Activation of Reminders (4.4.4.)
]
● Reminder 1 before Lifetime (Required) [see
Reminder 1 before Service (Required) (4.4.5.)
]
● Reminder 2 before Lifetime (Demanded) [see
Reminder 2 before Service (Demanded)
(4.4.6.)
]
● Click on
Service Performed
to reset Time Since Last Service to 0 hours
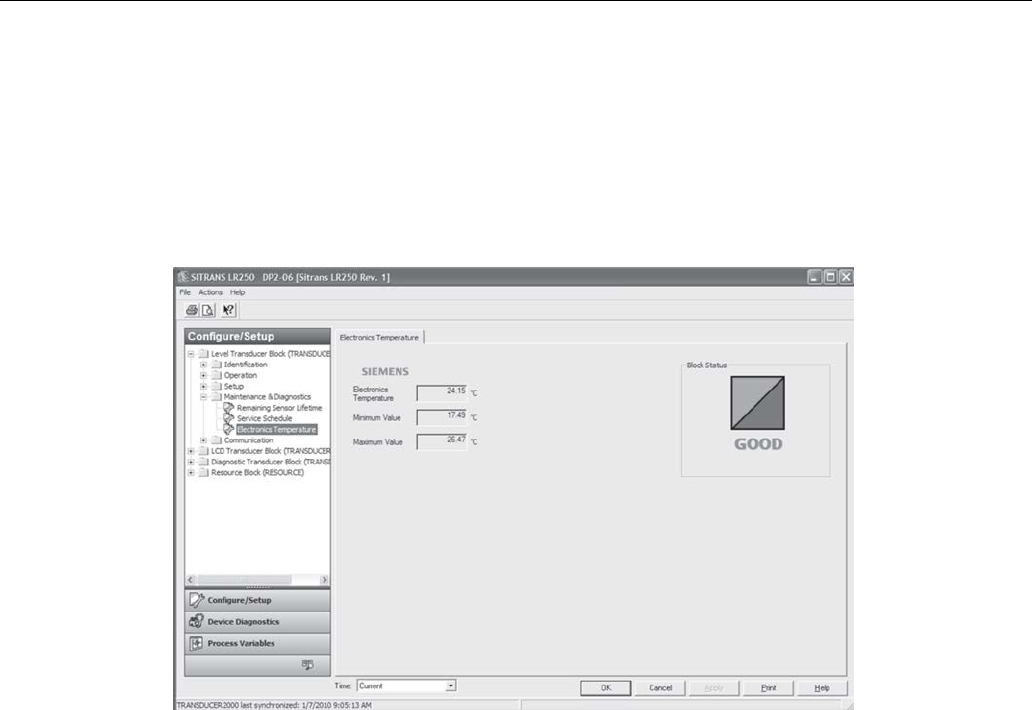
Remote operation
7.1 Operating via AMS Device Manager
SITRANS LR250 (FOUNDATION FIELDBUS)
106 Operating Instructions, 08/2014, A5E32221411-AC
Electronics Temperature
[see
Electronics Temperature (3.3.)
]
● Electronics Temperature: Displays the current internal temperature of the device
● Minimum Value [see
Minimum Value (3.3.1.)
]
● Maximum Value [see
Maximum Value (3.3.2.)
]
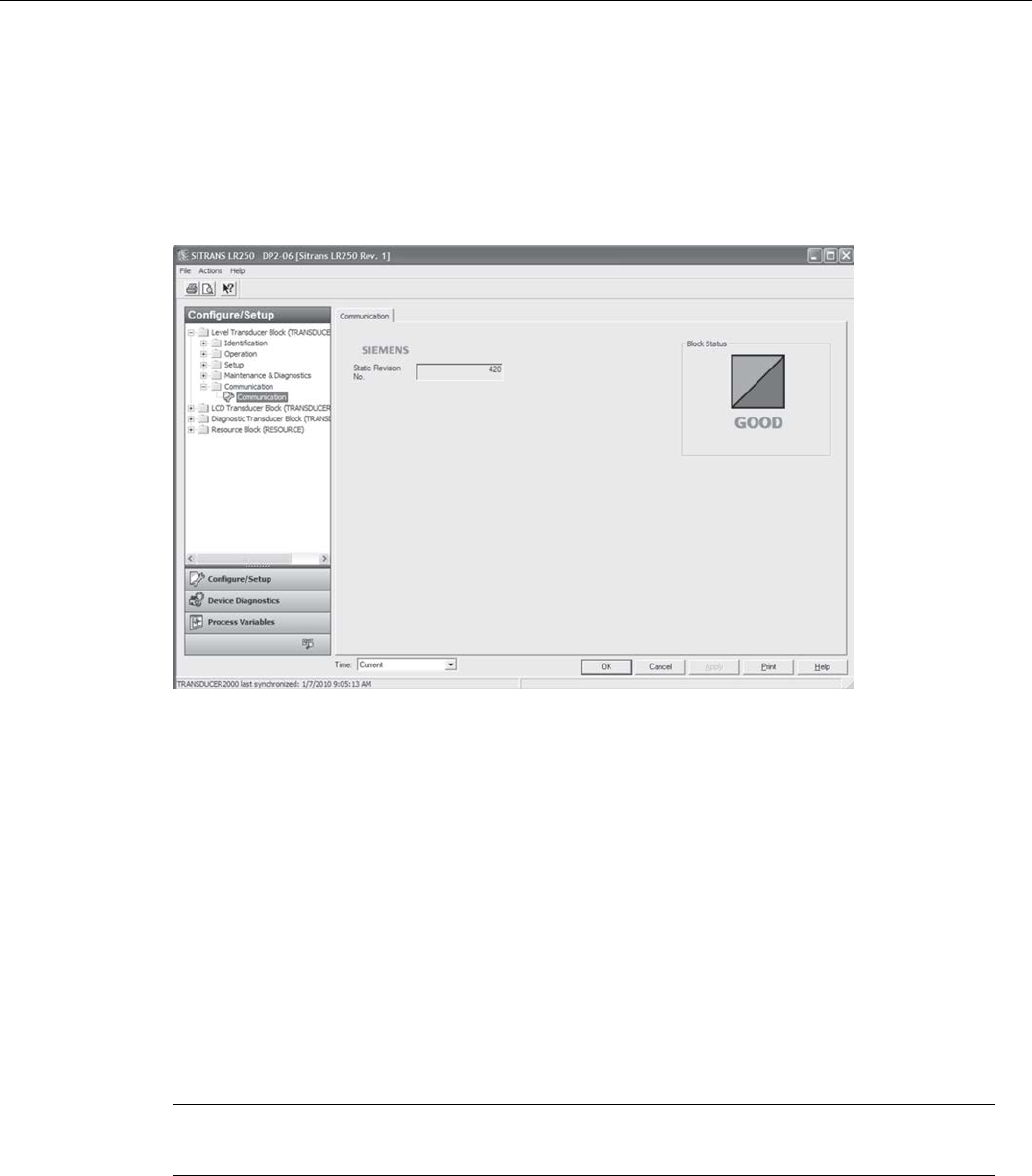
Remote operation
7.1 Operating via AMS Device Manager
SITRANS LR250 (FOUNDATION FIELDBUS)
Operating Instructions, 08/2014, A5E32221411-AC 107
7.1.9.7
Communication (LTB)
Navigate to
Configure/Setup > LTB > Communication
for access to:
Communication:
● Static Revision No. [see
Static Revision Number (2.6.1.)
]
7.1.10
Configure/Setup (Liquid Crystal Display Block-LCD)
7.1.10.1
Identification (LCD)
Navigate to
Configure/Setup > LCD > Identification
.
Identification:
● TAG
● Descriptor
● Transducer Block Type
● Strategy
● Plant Unit
Note
For descriptions of Identification parameters see Identification (LTB) (Page 92).
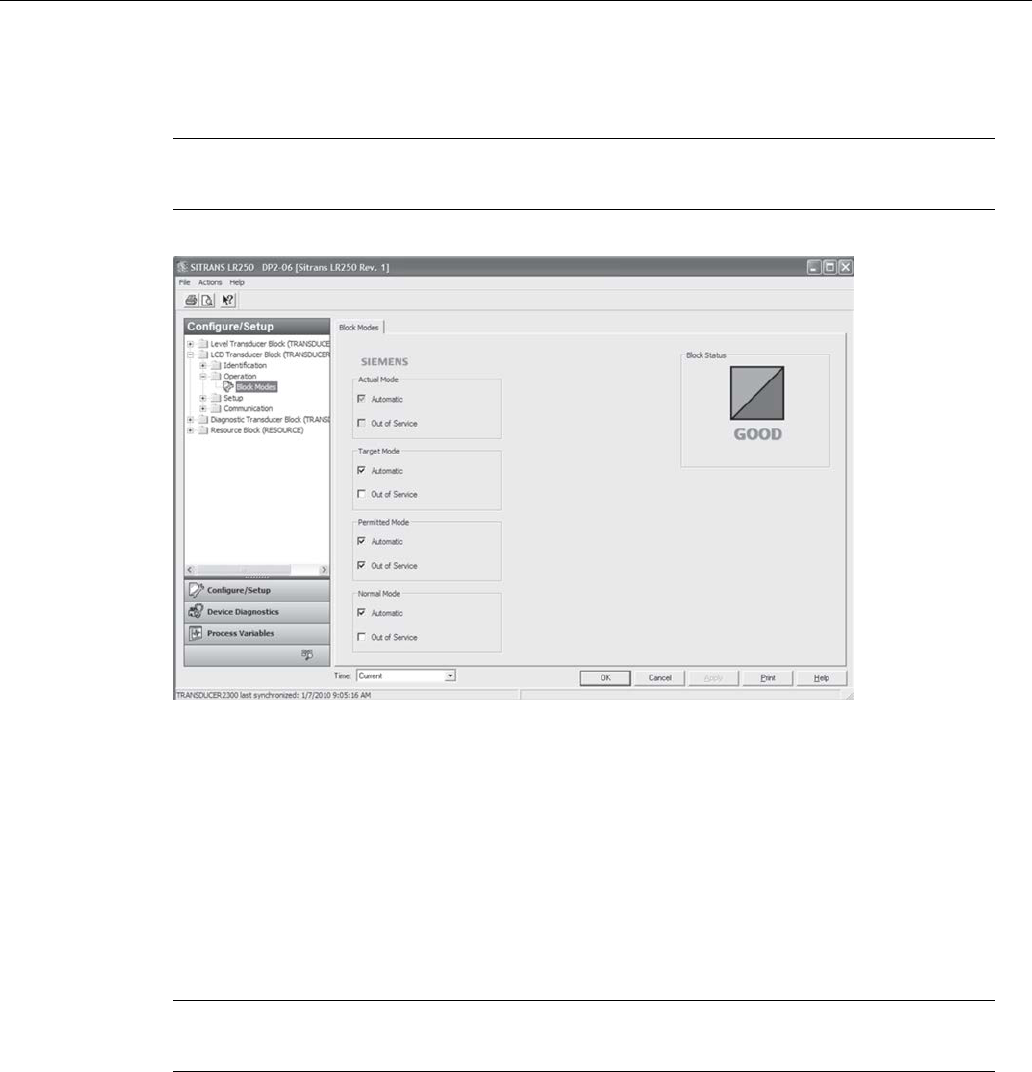
Remote operation
7.1 Operating via AMS Device Manager
SITRANS LR250 (FOUNDATION FIELDBUS)
108 Operating Instructions, 08/2014, A5E32221411-AC
7.1.10.2
Operation (LCD)
Note
For more detailed explanations of the parameters listed below see the pages referenced.
Navigate to
Configure/Setup > LCD > Operation
.
Click on
Block Modes
to open the dialog window for access to:
Block Modes:
● Actual Mode
● Target Mode
● Permitted Mode
● Normal Mode
Note
For descriptions of Block Modes see Operation (LTB) (Page 93).
To disable updating of the LCD remotely, Actual Mode of this block should read
Out of Service
.
This is done by setting Target Mode to
Out of Service
.
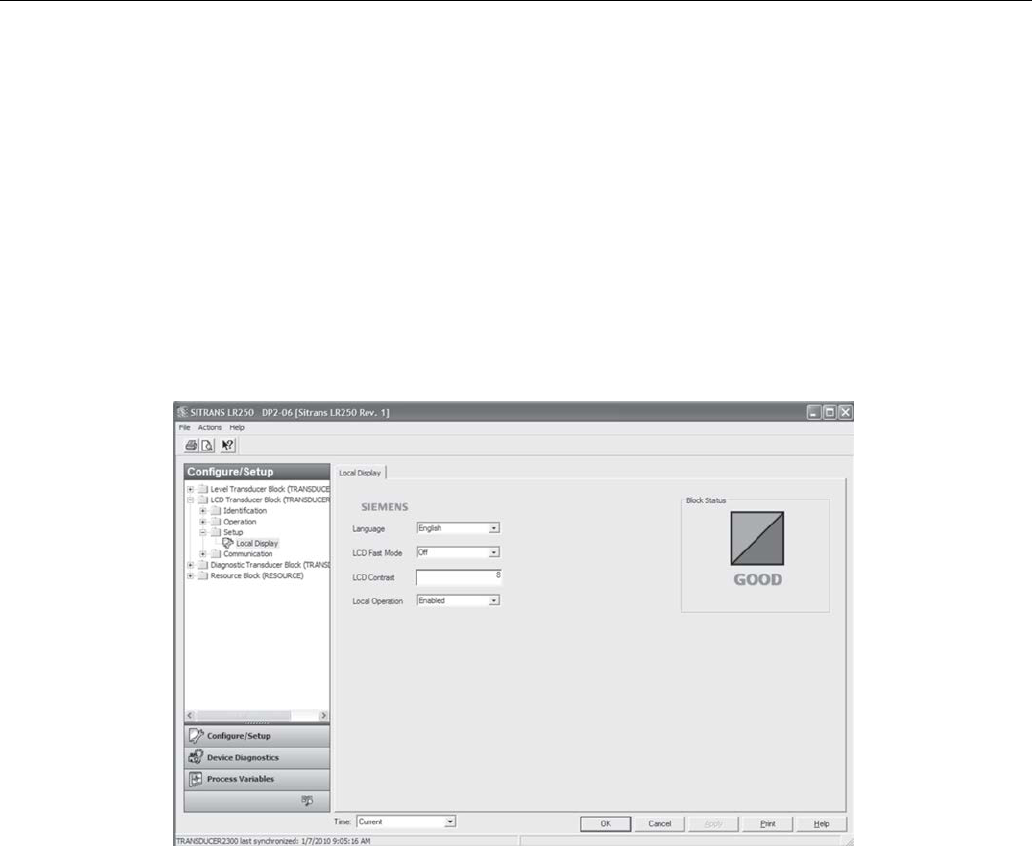
Remote operation
7.1 Operating via AMS Device Manager
SITRANS LR250 (FOUNDATION FIELDBUS)
Operating Instructions, 08/2014, A5E32221411-AC 109
7.1.10.3
Setup (LCD)
Navigate to
Configure/Setup > LCD > Setup > Local display
for access to:
Local Display
Language [see
Language (7.)
]
LCD Fast Mode [see
LCD Fast Mode (4.9.)
]
LCD Contrast [see
LCD Contrast
(4.10.)
]
Local Operation [see
Local Operation (6.2.3.)
]
If local operation is disabled remotely and no communication activity exists for 30 seconds, the
parameter is made visible again locally.
7.1.10.4
Communication (LCD)
Navigate to
Configure/Setup > LCD > Communication
for access to:
Communication:
● Static Revision No. [See
Static Revision Number (2.6.1.)
]
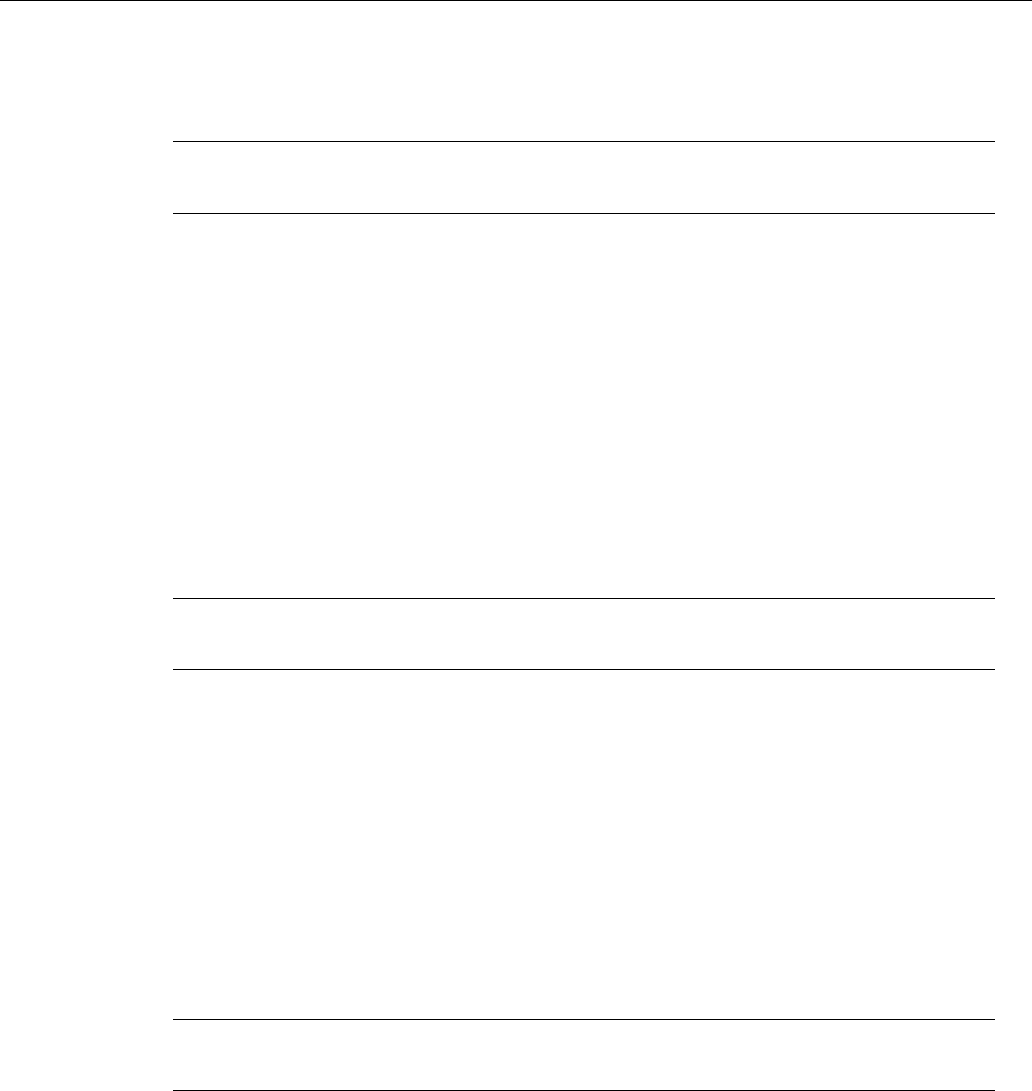
Remote operation
7.1 Operating via AMS Device Manager
SITRANS LR250 (FOUNDATION FIELDBUS)
110 Operating Instructions, 08/2014, A5E32221411-AC
7.1.11
Configure/Setup (Diagnostic Transducer Block-DIAG)
Note
Parameters in the Diagnostic Transducer Block used solely by factory personnel.
7.1.11.1
Identification (DIAG)
Navigate to
Configure/Setup > DIAG > Identification
.
Identification
:
● TAG
● Descriptor
● Transducer Block Type
● Strategy
● Plant Unit
Note
For descriptions of Identification parameters see Identification (LTB) (Page 92).
7.1.11.2
Operation (DIAG)
Navigate to
Configure/Setup > DIAG > Operation
.
Block Modes:
● Actual Mode
● Target Mode
● Permitted Mode
● Normal Mode
Note
For descriptions of Block Modes see Operation (LTB) (Page 93).
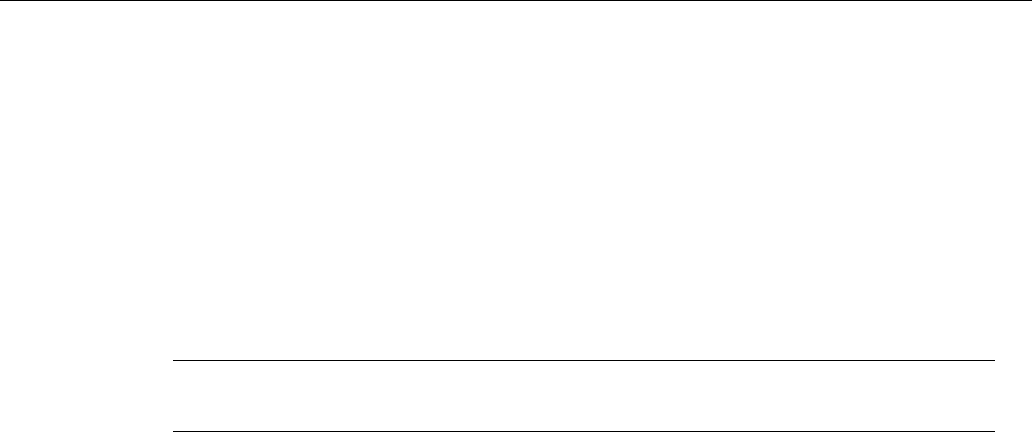
Remote operation
7.1 Operating via AMS Device Manager
SITRANS LR250 (FOUNDATION FIELDBUS)
Operating Instructions, 08/2014, A5E32221411-AC 111
7.1.11.3
Communication (DIAG)
Navigate to
Configure/Setup > DIAG > Communication
.
Communication:
● Static Revision No. [see
Static Revision Number (2.6.1.)
]
7.1.12
Configure/Setup (Resource Block - RESOURCE)
Note
For more detailed explanations of the parameters listed below see the pages referenced.
7.1.12.1
Identification (RESOURCE)
Navigate to
Configure/Setup > RESOURCE > Identification
for access to:
Identification
● TAG: Read only. Description for the associated block: device tag prefixed by block type.
● Descriptor [see
Descriptor (2.1.2.)
]
● Message [see Message
(2.1.3.)
]
● Date (Installation Date): The user entered date on which the device was installed in the
system.
● Strategy: Used to identify grouping of blocks.
● Plant Unit: The identification number of the plant unit. For example, can be used in the host
for sorting alarms.
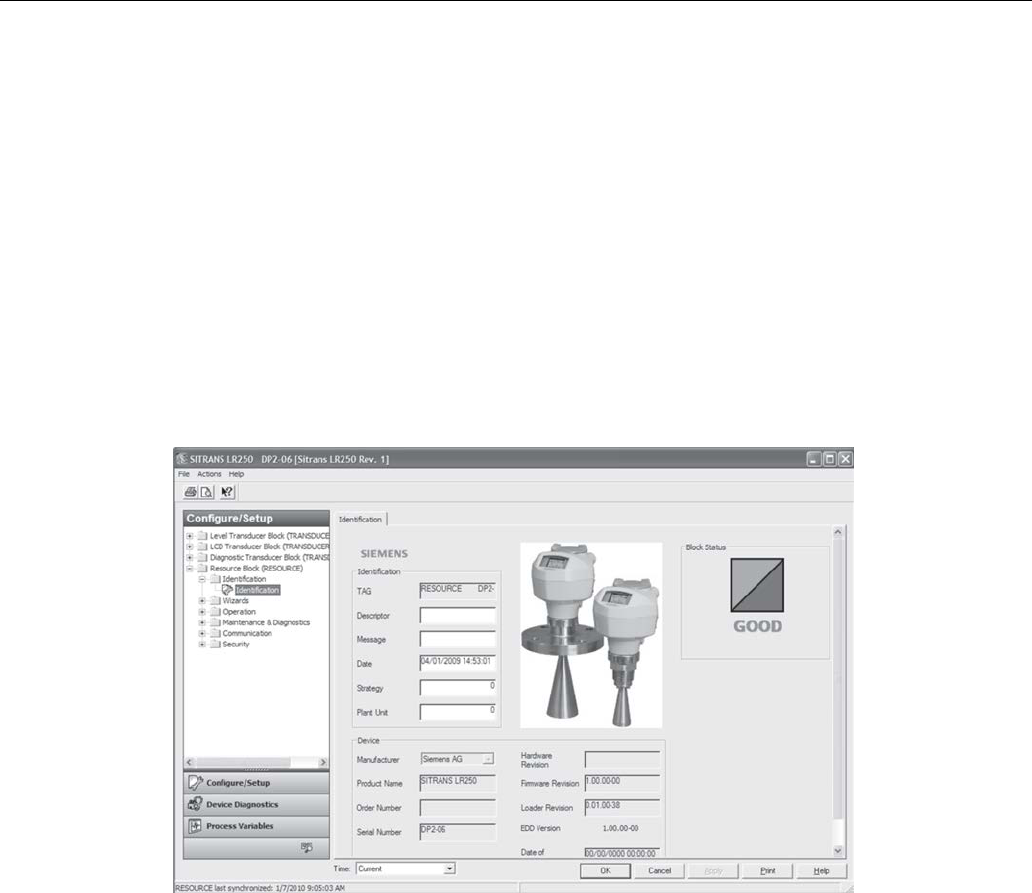
Remote operation
7.1 Operating via AMS Device Manager
SITRANS LR250 (FOUNDATION FIELDBUS)
112 Operating Instructions, 08/2014, A5E32221411-AC
Device (read only)
● Manufacturer (see
Manufacturer (5.3.)
]
● Product Name: The manufacturer’s product name for this device.
● Order Number: The manufacturer’s order number (MLFB) for this device.
● Serial Number: The manufacturer’s unique serial number for this device.
● Hardware Revision [see
Hardware Revision (2.2.1.)
]
● Firmware Revision [see
Firmware Revision (2.2.2.)
]
● Loader Revision [see
Loader Revision (2.2.3.)
]
● EDD Version: The version of the EDD currently installed.
● Date of Manufacturing [see
Manufacture Date (4.6.)
]
7.1.12.2
Wizards (RESOURCE)
Navigate to
Configure/Setup > RESOURCE > Wizards > Quick Start
for access to Quick Start
steps [see Quick Start Wizard via AMS Device Manager (Page 85)].
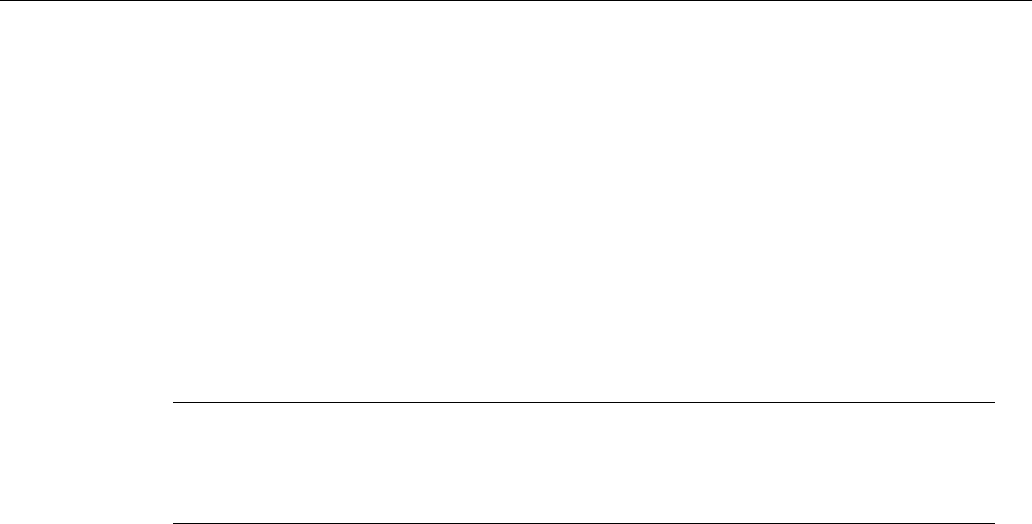
Remote operation
7.1 Operating via AMS Device Manager
SITRANS LR250 (FOUNDATION FIELDBUS)
Operating Instructions, 08/2014, A5E32221411-AC 113
7.1.12.3
Operation (RESOURCE)
Navigate to
Configure/Setup > RESOURCE > Operation
.
Click on
Block Modes
to open the dialog window for access to:
Block Modes:
● Actual Mode
● Target Mode
● Permitted Mode
● Normal Mode
Note
• For descriptions of Block Modes see Operations (LTB) (Page 93).
• If the RESOURCE block is set to Out of Service, the LTB, and AIFB blocks are forced to
Out of Service also, but the LCD and DIAG blocks remain in Automatic mode
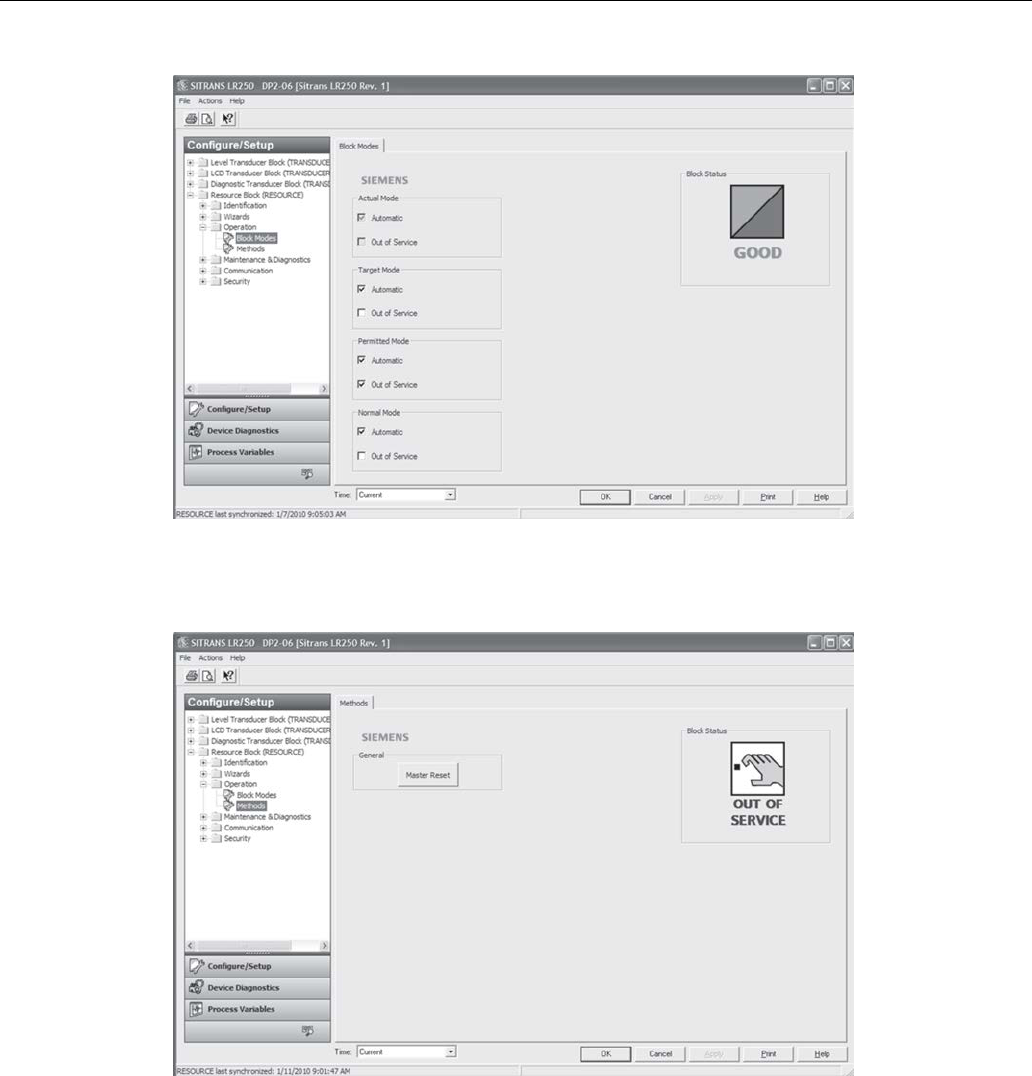
Remote operation
7.1 Operating via AMS Device Manager
SITRANS LR250 (FOUNDATION FIELDBUS)
114 Operating Instructions, 08/2014, A5E32221411-AC
Click on
Methods
to open the dialog window for access to:
General:
● Master Reset: see
Master Reset (4.1.)
1. Ensure the Block Status is Out of Service.
2. Click the Master Reset button, then click Next to perform a reset.
3. Select the Reset Type
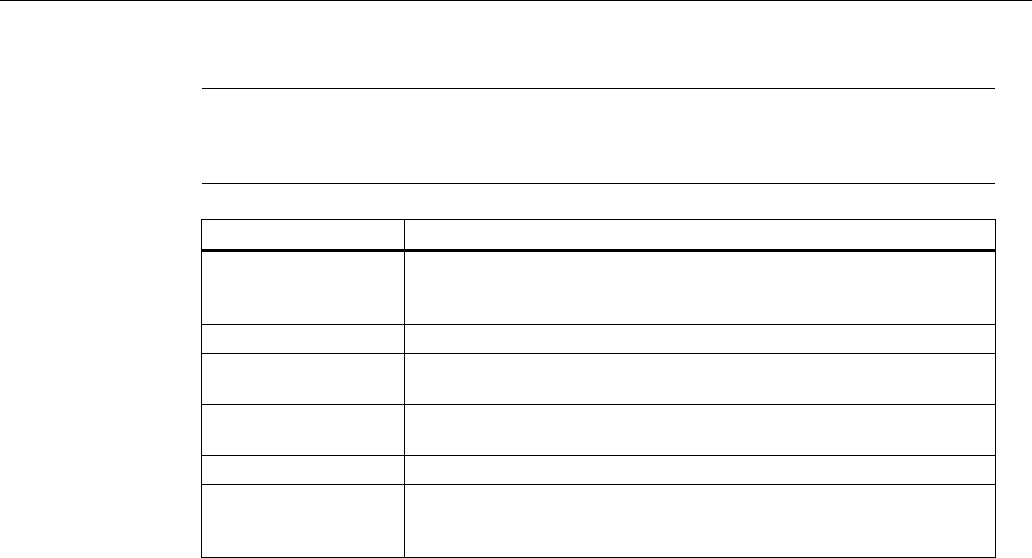
Remote operation
7.1 Operating via AMS Device Manager
SITRANS LR250 (FOUNDATION FIELDBUS)
Operating Instructions, 08/2014, A5E32221411-AC 115
Note
The following parameters are not reset by any reset type: Write Protection, PIN to Unlock,
Auto False Echo Suppression Range, Learned TVT.
Reset Type
Result
Factory Defaults a) Default. Resets all user parameters to the manufacturer’s default
settings. Following this type of reset, complete reprogramming is
required.
Standard Defaults Resets all parameters to standard default settings.
Informational Resets parameters such as Block Descriptor, Strategy, Device
Install Date, Device Message.
Functional a) Resets parameters that control device behavior and functionality
(such as Low Calibration Point).
Warm Start Has the same effect as recycling power to the device.
FF Object Dictionary Resets the FF standard block profile parameters (such as block
tags) to their specified defaults. This option also clears any function
block parameters and device schedule b) set by the user.
a) The only difference between Factory Defaults and Functional reset is that Factory Defaults
resets maintenance parameters, such as device and sensor wear, calibration and maintenance
timers. Functional reset does not reset these parameters.
b) See Data transmission in manual
Foundation Fieldbus for Level Instruments
(7ML19985MP01)
for further details.
4. Click Next, then FINISH to complete the Master Reset.
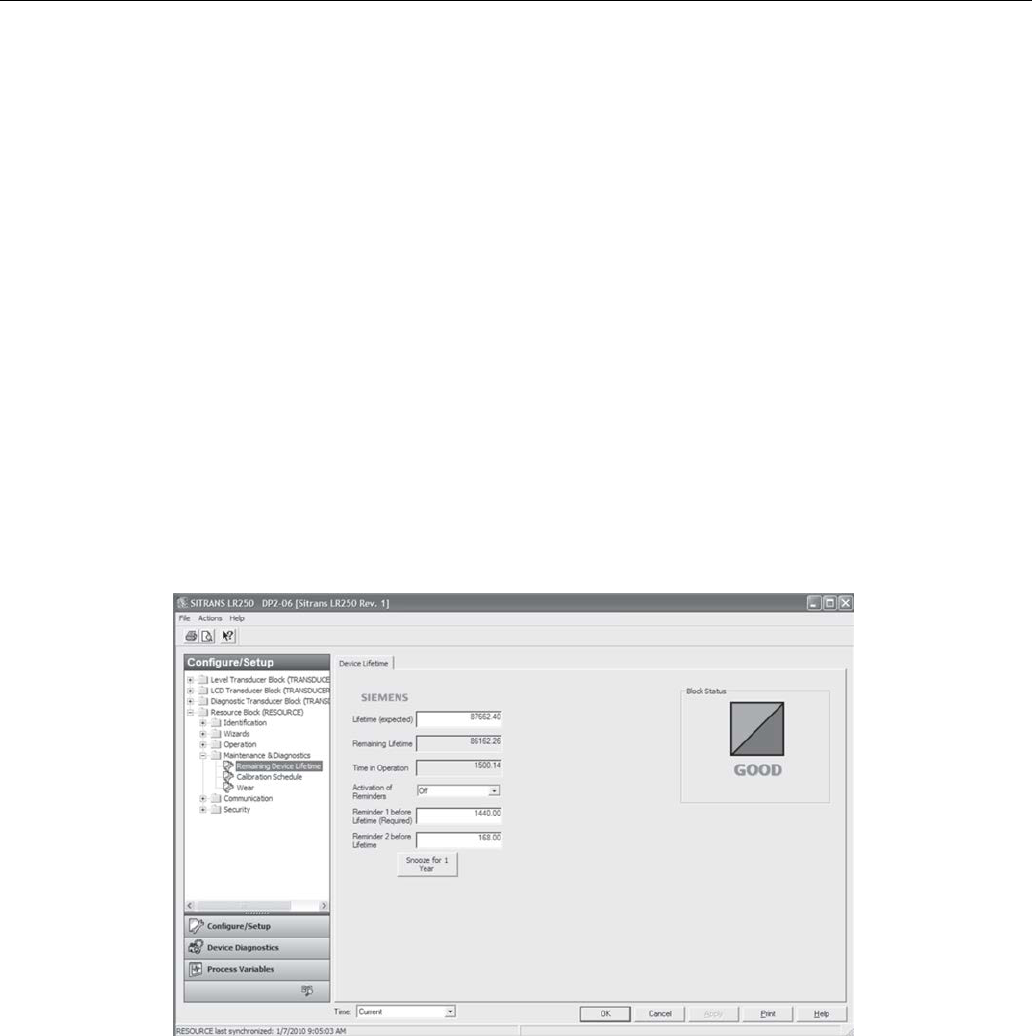
Remote operation
7.1 Operating via AMS Device Manager
SITRANS LR250 (FOUNDATION FIELDBUS)
116 Operating Instructions, 08/2014, A5E32221411-AC
7.1.12.4
Maintenance & Diagnostics (RESOURCE)
Navigate to
Configure/Setup > RESOURCE > Maintenance & Diagnostics
for access to:
Remaining Device Lifetime
[see
Remaining Device Lifetime (4.2.)
]
● Lifetime (expected) [see
Lifetime (expected (4.2.1.)
]
● Remaining Lifetime (read only) [see
Remaining Lifetime (4.2.3.)
]
● Time in Operation (read only) [see
Time in Operation (4.2.2.)
]
● Activation of Reminders [see
Activation of Reminders (4.2.4.)
]
● Reminder 1 before Lifetime (Required) [see
Reminder 1 before Lifetime (Required) (4.2.5.)
]
● Reminder 2 before Lifetime (Demanded) [see
Reminder 2 before Lifetime (Demanded)
(4.2.6.)
]
1. Open the window
Remaining Device Lifetime
2. After modifying values/units as required, click on
Apply
to accept the change.
● Click on
Snooze for 1
Year
to add a year to the Total Expected Device Life.
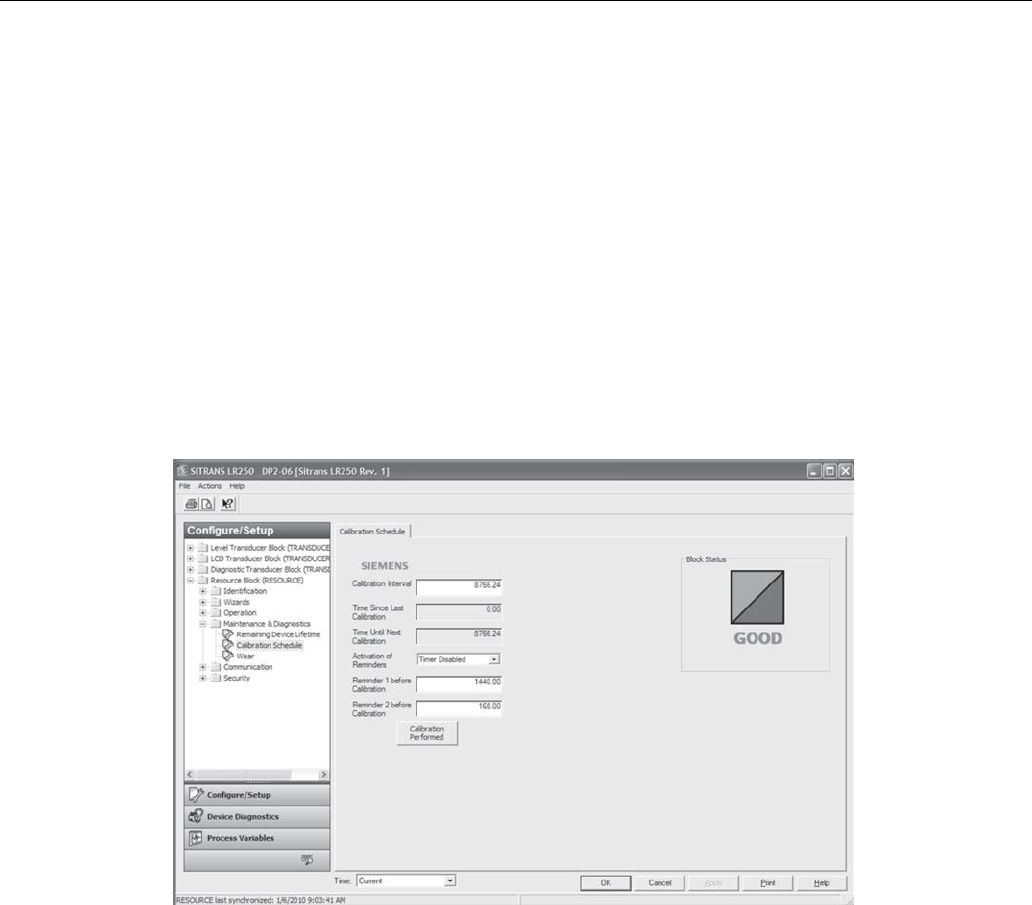
Remote operation
7.1 Operating via AMS Device Manager
SITRANS LR250 (FOUNDATION FIELDBUS)
Operating Instructions, 08/2014, A5E32221411-AC 117
Calibration Schedule
[see
Calibration Schedule (4.5)
]
● Calibration Interval [see
Calibration Interval (4.5.1.)
]
● Time Since Last Calibration [see
Time Since Last Calibration (4.5.2.)
]
● Time Until Next Calibration (read only) [see
Time Until Next Calibration (4.5.3.)
]
● Activation of Reminders [see
Activation of Reminders (4.5.4.)
]
● Reminder 1 before Calibration (Required) [see
Reminder 1 before Calibration (Required)
(4.5.5.)
]
● Reminder 2 before Calibration (Demanded) [see
Reminder 2 before Calibration (Demanded)
(4.5.6.)
]
● Click on
Calibration Performed
to reset Time Since Last Calibration to 0 hours.
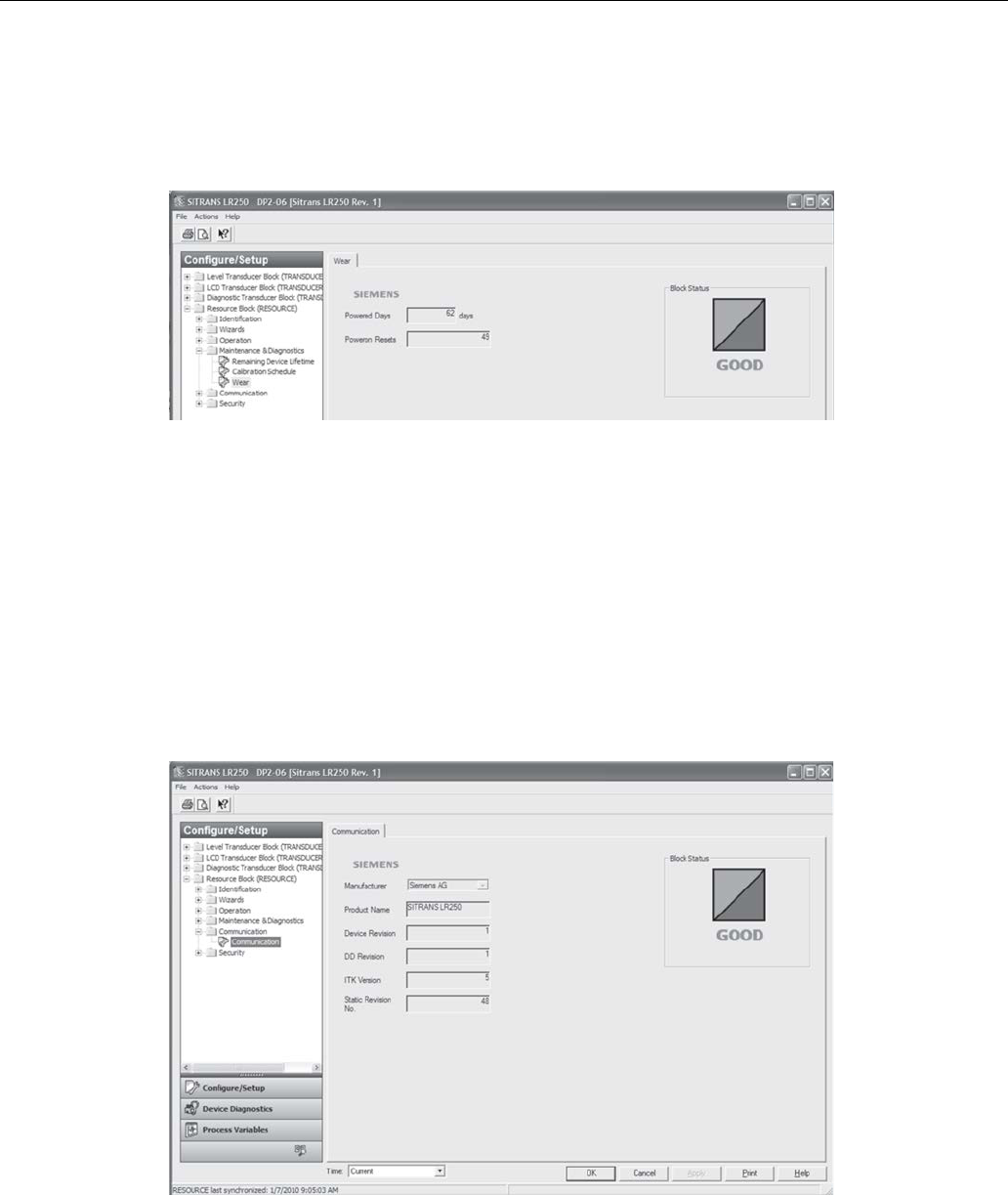
Remote operation
7.1 Operating via AMS Device Manager
SITRANS LR250 (FOUNDATION FIELDBUS)
118 Operating Instructions, 08/2014, A5E32221411-AC
Wear
● Powered Days (read only) [see
Powered Hours (4.7.)
]
● Poweron Resets (read only) [see
Power-on Resets (4.8.)
]
7.1.12.5
Communication (RESOURCE)
● Navigate to
Configure/Setup > RESOURCE > Communication
to read the following:
● Manufacturer [see
Manufacturer (5.3.)
]
● Product Name: the manufacturer’s product name for this device.
● Device Revision [see
Device Revision (5.5.)
]
● DD Revision: revision of the DD (also called EDD) associated with this device.
● ITK Version [see
ITK Version (5.6.)
]
● Static Revision No. [see
Static Revision Number ( 2.6.1.)
]

Remote operation
7.1 Operating via AMS Device Manager
SITRANS LR250 (FOUNDATION FIELDBUS)
Operating Instructions, 08/2014, A5E32221411-AC 119
7.1.12.6
Security (RESOURCE)
Navigate to
Configure/Setup > RESOURCE > Security
to access:
Local Access
● Local Write Protected [see
Write Protection (6.2.1.)
]
● PIN to Unlock [see
PIN to Unlock (6.2.2.)
]
See also Password Protection (Page 129).
7.1.13
Device Diagnostics (Level Transducer Block - LTB)
Note
For explanations of the alarms and errors listed below, see Parameter Description charts for
the respective block in manual
Foundation Fieldbus for Level Instruments
(7ML19985MP01).

Remote operation
7.1 Operating via AMS Device Manager
SITRANS LR250 (FOUNDATION FIELDBUS)
120 Operating Instructions, 08/2014, A5E32221411-AC
7.1.13.1
Alarms & Errors (LTB)
Navigate to
Device Diagnostics > LTB > Alarms & Errors
.
Click on
Block Error
to open the dialog window to read the following:
Failures
● Input Failure
● Output Failure
● Memory Failure
● Lost Static Data
● Lost Non-Volatile Data
● Readback Check
● Device Fault State
● Block Configuration
● Link Configuration
● Other
Maintenance
● Maintenance Required
● Maintenance Demanded
Information
● Simulation Active
● Local Override
● Power Up
● Out of Service
XD Error
● Transducer Error
Click on
Block Alarm
to open the dialog window to read the following:
Unacknowledged
● Unacknowledged
Alarm State
● Alarm State
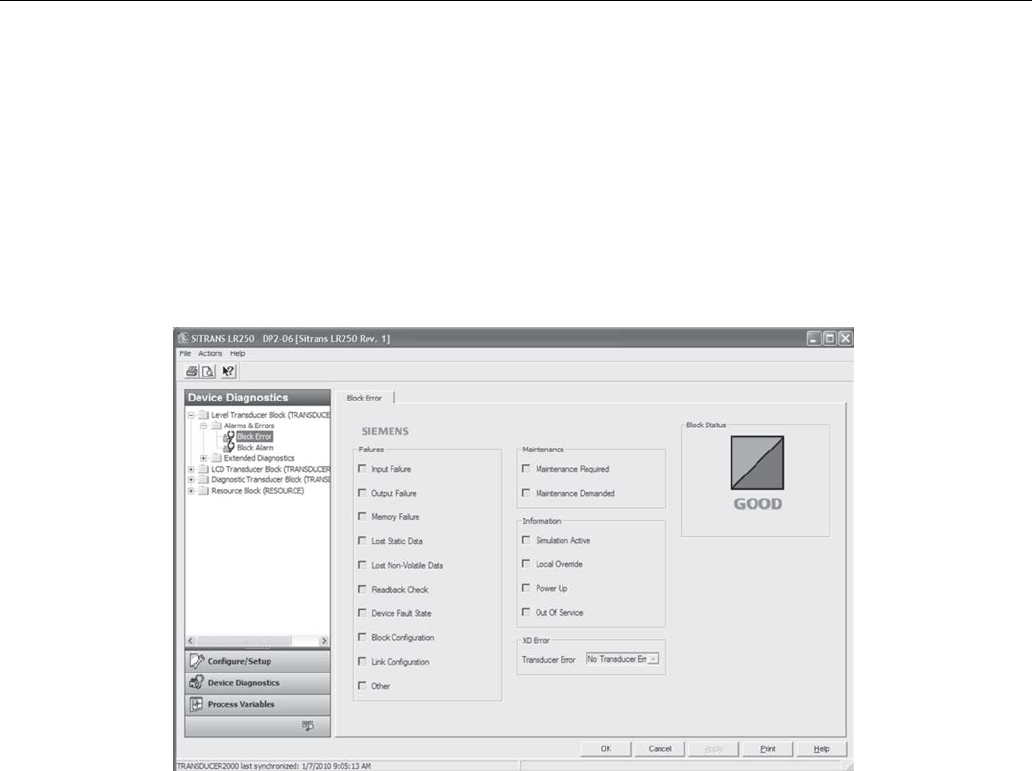
Remote operation
7.1 Operating via AMS Device Manager
SITRANS LR250 (FOUNDATION FIELDBUS)
Operating Instructions, 08/2014, A5E32221411-AC 121
Time Stamp
● Time Stamp
Subcode
● Subcode
Value
● Value
1. From the
Block Error
tab, check the
Maintenance
window to display the level of maintenance
alarm that is active.
2. From the
Block Alarm
tab, check the
Alarm State
window to display the level of maintenance
alarm that has been acknowledged.
3. From the
Block Alarm
tab, in the
Unacknowledged
window, select
Acknowledged
to
acknowledge an alert.
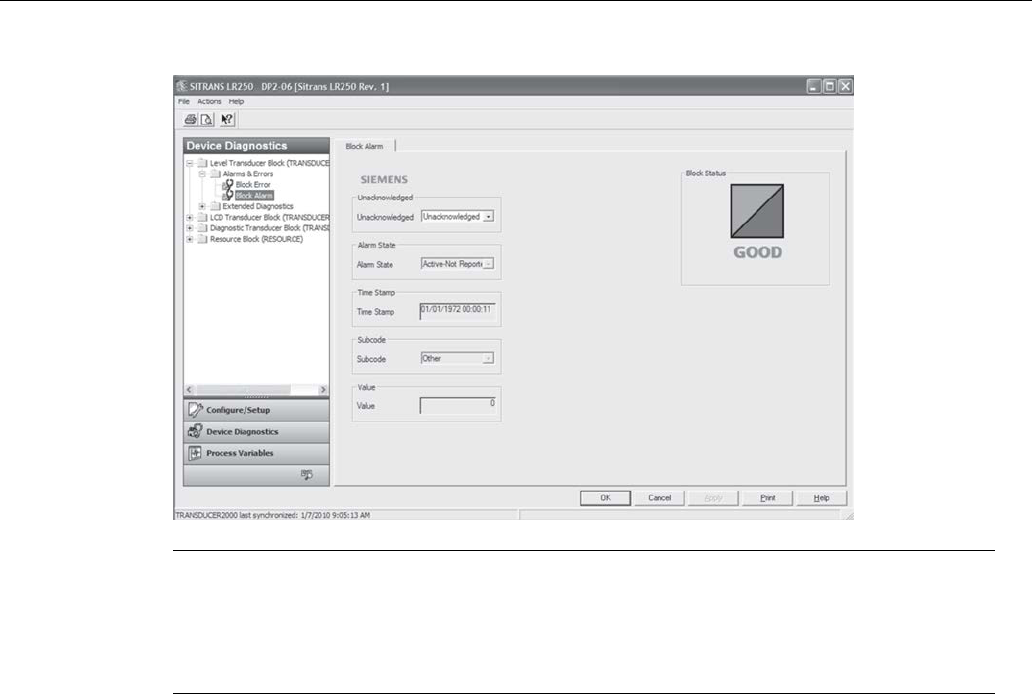
Remote operation
7.1 Operating via AMS Device Manager
SITRANS LR250 (FOUNDATION FIELDBUS)
122 Operating Instructions, 08/2014, A5E32221411-AC
Note
Acknowledging a maintenance reminder from the device (see
Acknowledge
(4.2.9.)
,
(4.3.9.)
,
(4.4.9.)
,
(4.5.9.)
will not set the Block Alarm to Acknowledged in AMS. The maintenance
alarm will cause an FF block alert, and the block alert can only be acknowledged via a
remote host such as NI-FBUS Configurator or AMS Device Manager (as in step 3 above).

Remote operation
7.1 Operating via AMS Device Manager
SITRANS LR250 (FOUNDATION FIELDBUS)
Operating Instructions, 08/2014, A5E32221411-AC 123
7.1.13.2
Extended Diagnostics (LTB)
Navigate to
Device Diagnostics > LTB > Extended Diagnostics
to read the following:
Detailed Error Info
● Loss of Echo
● No Tech Power
● Sensor Lifetime Limit1
● Sensor Lifetime Limit2
● Device Service Limit1
● Device Service Limit2
● LTB Scale
● Internal Temp Sensor
● Internal Temp High
● Internal Temperature Calibration
● Velocity Calibration
● Receiver Init Calibration
● Receiver Calibration
● Tech Module Hardware
● Tech Module Ramp
● Receiver Frequency Calibration
● Safe Process Data Corrupt
● Profile Clipped
● Too Few Shots Taken
● Measurement Error
● No Shots Taken
● Measurement Was Corrupted
● DMA Error
● Sensor Value too High
● Sensor Value too Low

Remote operation
7.1 Operating via AMS Device Manager
SITRANS LR250 (FOUNDATION FIELDBUS)
124 Operating Instructions, 08/2014, A5E32221411-AC
7.1.14
Device Diagnostics (Liquid Crystal Display Block - LCD)
7.1.14.1
Alarms & Errors (LCD)
Navigate to
Device Diagnostics > LCD > Alarms & Errors
to read Block and Alarm errors. [Errors
displayed are the same for each block (LTB, LCD, DIAG, RESOURCE). See Alarms & Errors
(LTB) (Page 120) for full listing.]
7.1.15
Device Diagnostics (Diagnostic Transducer Block - DIAG)
7.1.15.1
Alarms & Errors (DIAG)
Navigate to
Device Diagnostics > DIAG > Alarms & Errors
to read Block and Alarm errors.
[Errors displayed are the same for each block (LTB, LCD, DIAG, RESOURCE). See Alarms &
Errors (LTB) (Page 120) for full listing. See AMS Device Manager instruction manual to work
with alarms and errors.]
7.1.16
Device Diagnostics (Resource Block - RESOURCE)
7.1.16.1
Alarms & Errors (RESOURCE)
Navigate to
Device Diagnostics > RESOURCE > Alarms & Errors
.
Click on
Block Error
tab to open the dialog window to read the following:
Failures
● Input Failure
● Output Failure
● Memory Failure
● Lost Static Data
● Lost Non-Volatile Data
● Readback Check
● Device Fault State
● Block Configuration
● Link Configuration
● Other

Remote operation
7.1 Operating via AMS Device Manager
SITRANS LR250 (FOUNDATION FIELDBUS)
Operating Instructions, 08/2014, A5E32221411-AC 125
Maintenance
● Maintenance Required
● Maintenance Demanded
Information
● Simulation Active
● Local Override
● Power Up
● Out of Service
Click on
Block Alarm
tab to open the dialog window to read the following:
Unacknowledged
● Unacknowledged
Alarm State
● Alarm State
Time Stamp
● Time Stamp
Subcode
● Subcode
Value
● Value
Values available on
Block Alarm
tab are also available for
Write Alarm
with one exception: the
Value parameter on the Write Alarm tab is a
Discrete Value
. Click on
Alarm Summary
tab to
open the dialog window to read the following:
Current
● Discrete Alarm
● Block Alarm
Unacknowledged
● Discrete Alarm Unacknowledged
● Block Alarm Unacknowledged
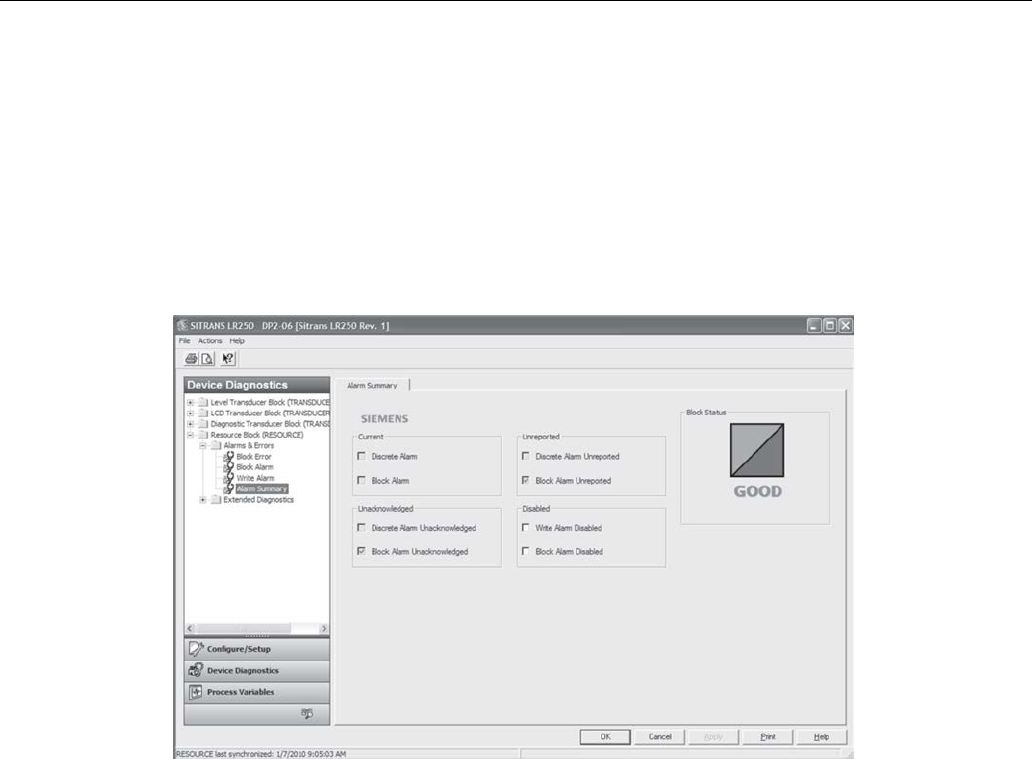
Remote operation
7.1 Operating via AMS Device Manager
SITRANS LR250 (FOUNDATION FIELDBUS)
126 Operating Instructions, 08/2014, A5E32221411-AC
Unreported
● Discrete Alarm Unreported
● Block Alarm Unreported
Disabled
● Write Alarm Disabled
● Block Alarm Disabled

Remote operation
7.1 Operating via AMS Device Manager
SITRANS LR250 (FOUNDATION FIELDBUS)
Operating Instructions, 08/2014, A5E32221411-AC 127
7.1.16.2
Extended Diagnostics (RESOURCE)
Navigate to
Device Diagnostics > RESOURCE > Extended Diagnostics
to read the following:
Detailed Error Info
● Device Lifetime Limit1
● Device Lifetime Limit2
● Calibration Schedule Limit1
● Calibration Schedule Limit2
● Memory RAM
● Memory EEPROM
● Memory EEPROM Flags
● Memory Flash
● Corrupt Stack
● High Stack
● Data Safe Read
● Data Safe Write
● Board Voltage
● ADC Failed
● Seq. Corrupt
● Seq. CP
● Seq. Duration
● BC Corrupt
● BC Start
● BC Stop
● BC Duration
● CPU Fault
● Data Bus
● Addr Bus
● Spurious SW Interrupt
● Spurious HW Interrupt
● Time Base Failure
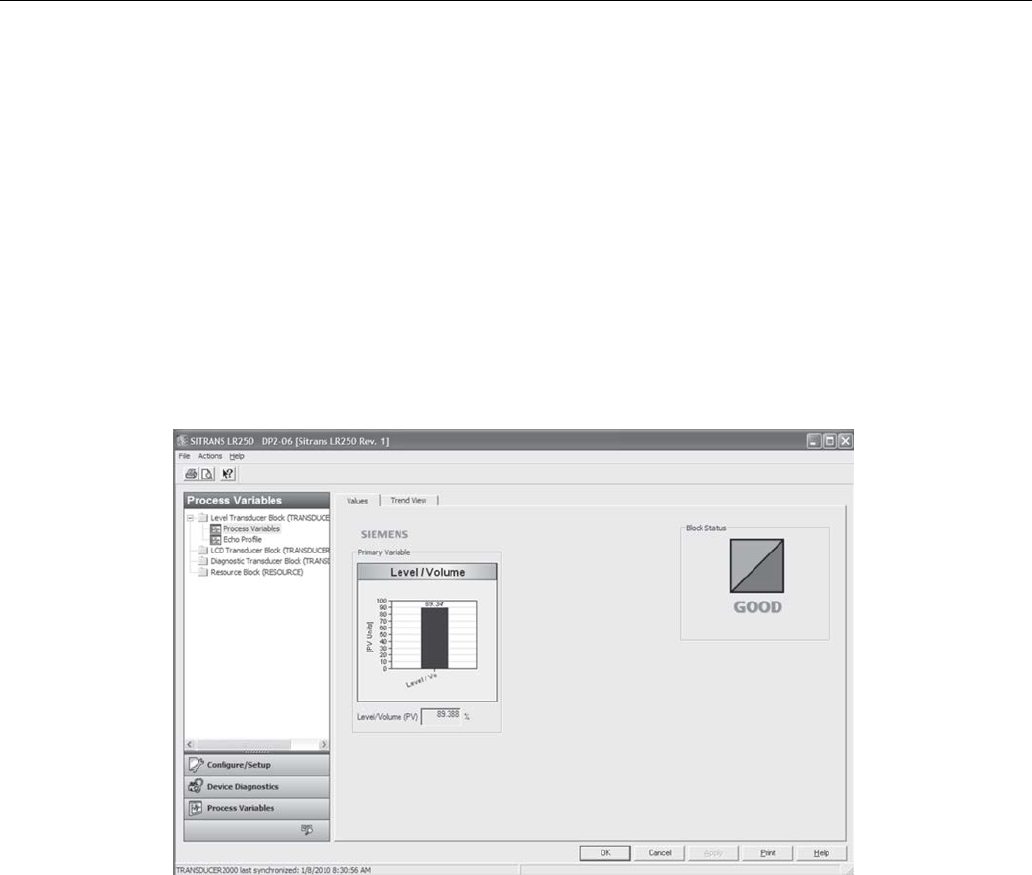
Remote operation
7.1 Operating via AMS Device Manager
SITRANS LR250 (FOUNDATION FIELDBUS)
128 Operating Instructions, 08/2014, A5E32221411-AC
7.1.17
Process Variables (Level Transducer Block - LTB)
To compare outputs in real time navigate to
Process Variables > LTB
.
Click on
Process Variables
then the
Values
tab to read the following:
Primary Variable
[see
Main Output (PV - Primary Value) (2.8.1.)
]
● Level/Volume (PV)
The primary variable and the channel 1 output from the transducer block. For level
applications, chart range is affected by High and Low Level Point values set in
Configure/Setup > LTB > Setup > Sensor
. For volume applications, chart range is 0 to Max.
Volume, set in
Configure/Setup > LTB > Setup > Linearization
.
Click on
Trend View
tab to read the following:
Trend Values
● Level/Volume (PV)
The primary variable and the channel 1 output from the transducer block.
Click on
Echo Profile
to open the dialog window to read the following:
Echo Profile
• Level Measurement [see
Measured Values (2.8.)
]
• Distance Measurement [see
Measured Values (2.8.)
]
• Confidence [see
Confidence (2.5.9.1.)
]
• Near Range [see
Near Range (2.5.1.)
]
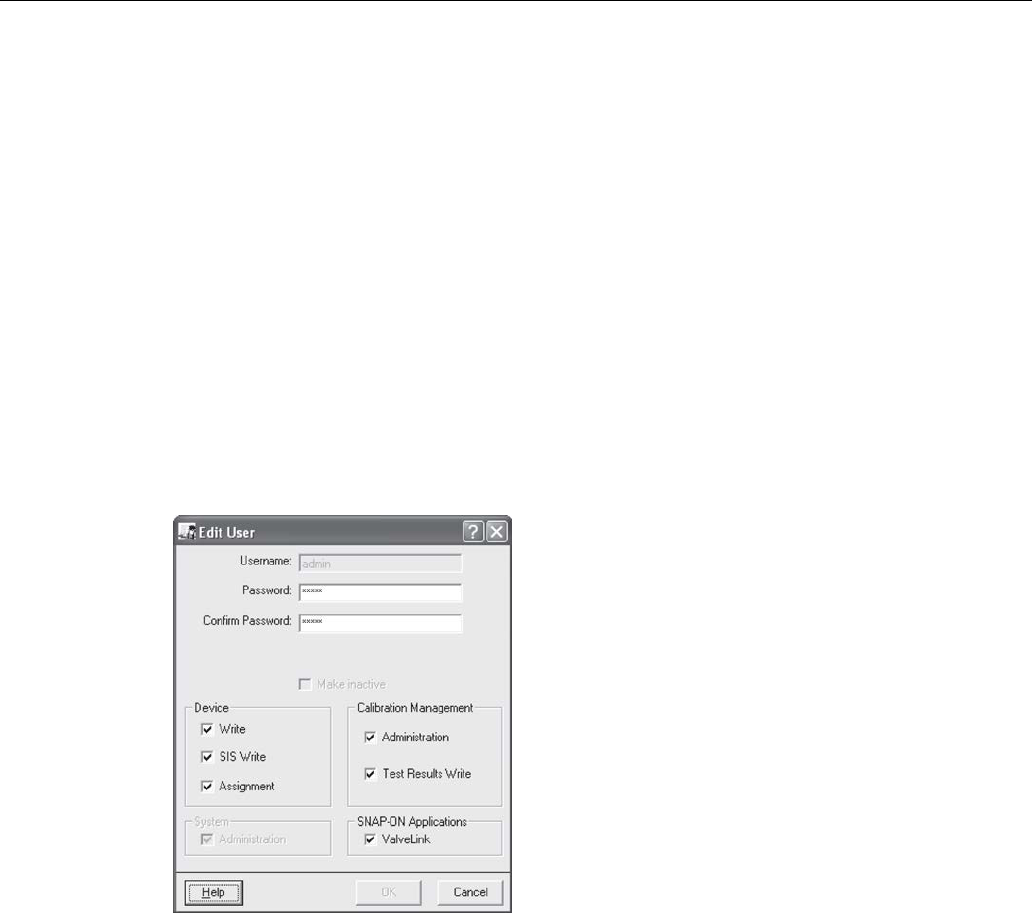
Remote operation
7.1 Operating via AMS Device Manager
SITRANS LR250 (FOUNDATION FIELDBUS)
Operating Instructions, 08/2014, A5E32221411-AC 129
7.1.18
Password Protection
7.1.18.1
User Manager utility
Usernames, passwords, and permissions, are assigned to users by an AMS Device Manager
administrator, using the User Manager utility on the Server Plus Station. Only a user with AMS
Device Manager System Administration rights can log in to User Manager.
To configure a new user/edit existing user:
1. From the Windows taskbar select:
Start > AMS Device Manager > User Manager
.
2. In the User Manager window click on
Add User
.
The Add User Wizard dialog allows you to:
● select a user type, standard (AMS Device Manager) or Window user.
● enter the username and password, and set permissions
● edit existing users
An AMS Device Manager administrator can configure the user to require a password. The use of
passwords is recommended. A password should be assigned to the ’admin’ username
immediately after installing AMS Device Manager.
Each user is given an AMS Device Manager username and password and required to enter
them when they start AMS Device Manager. Access to functions depends on the level of
permissions granted.
Login types
● standard, local, or domain
A standard user can change their password in AMS Device Manager. A Local or Domain
Windows user cannot change their password using AMS Device Manager and must request
their network administrator to do so.
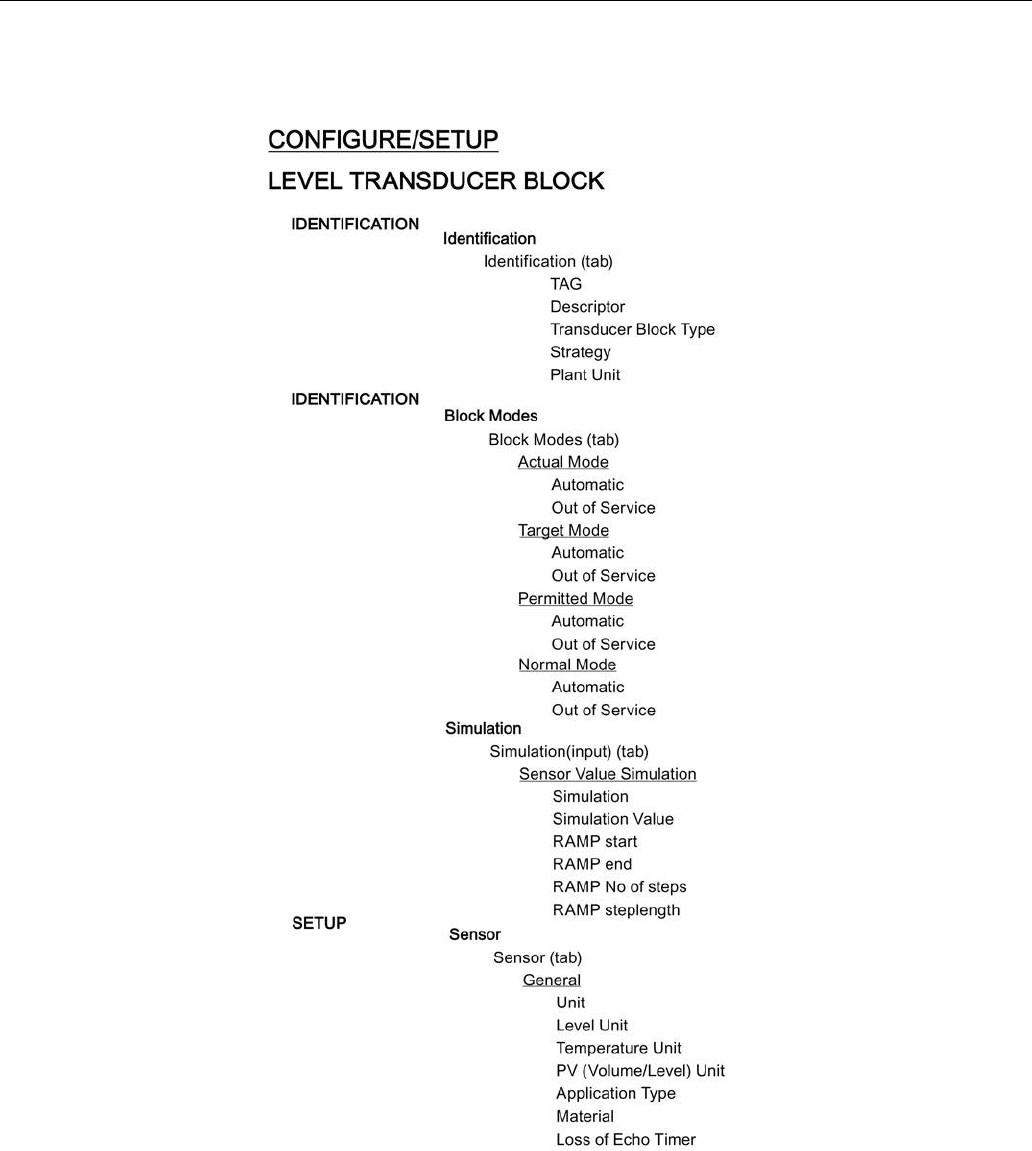
Remote operation
7.1 Operating via AMS Device Manager
SITRANS LR250 (FOUNDATION FIELDBUS)
130 Operating Instructions, 08/2014, A5E32221411-AC
7.1.19
AMS menu structure
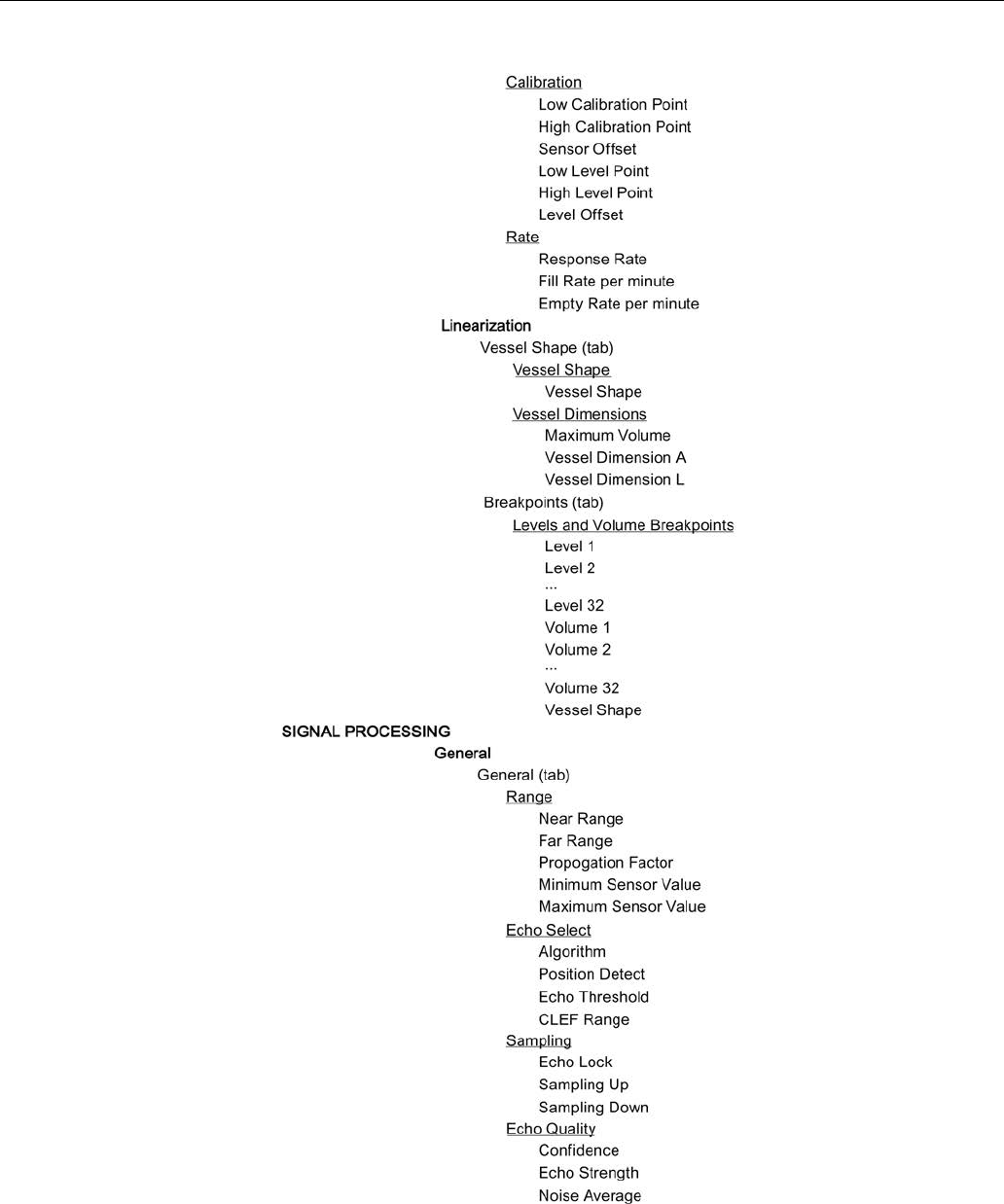
Remote operation
7.1 Operating via AMS Device Manager
SITRANS LR250 (FOUNDATION FIELDBUS)
Operating Instructions, 08/2014, A5E32221411-AC 131
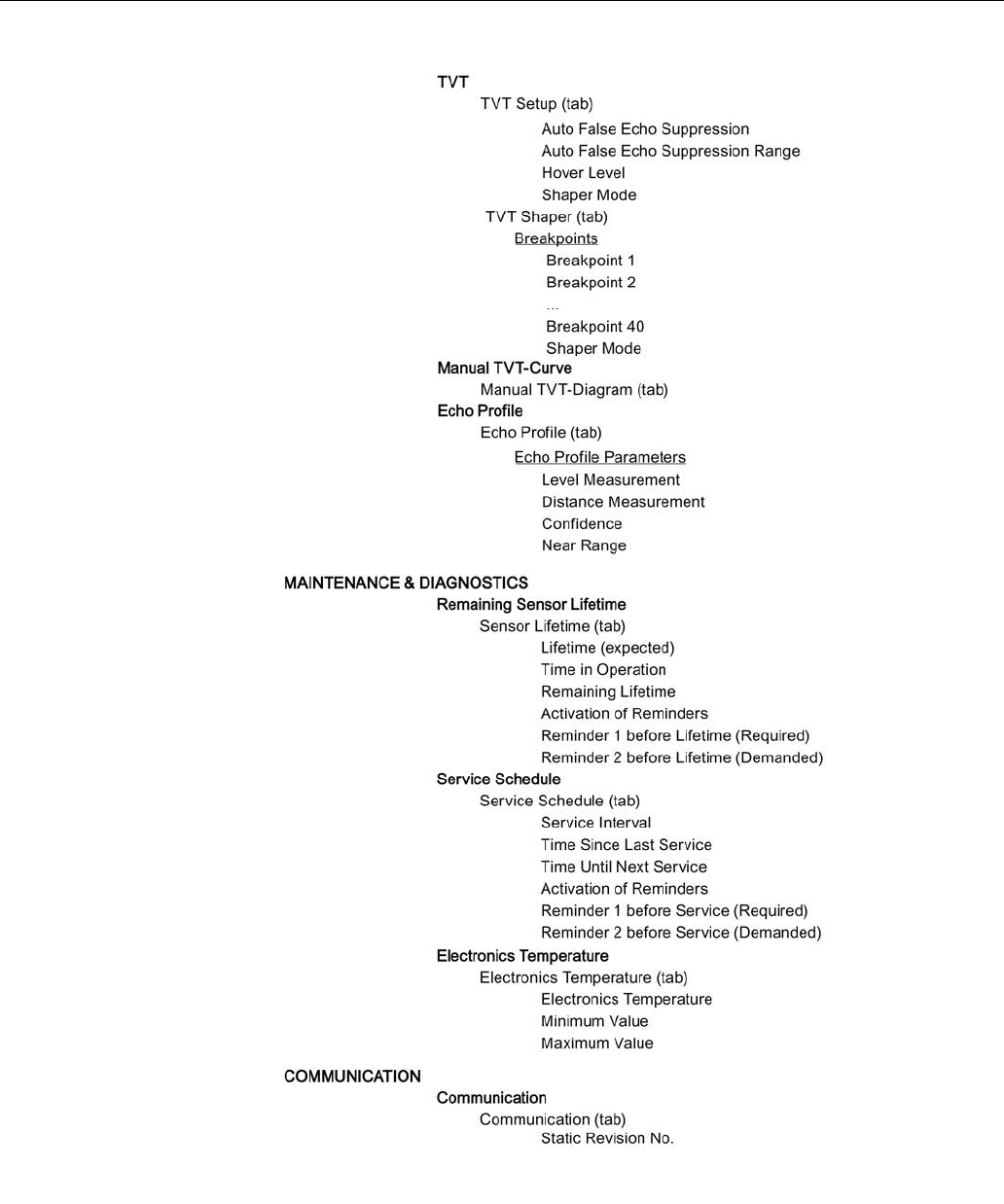
Remote operation
7.1 Operating via AMS Device Manager
SITRANS LR250 (FOUNDATION FIELDBUS)
132 Operating Instructions, 08/2014, A5E32221411-AC
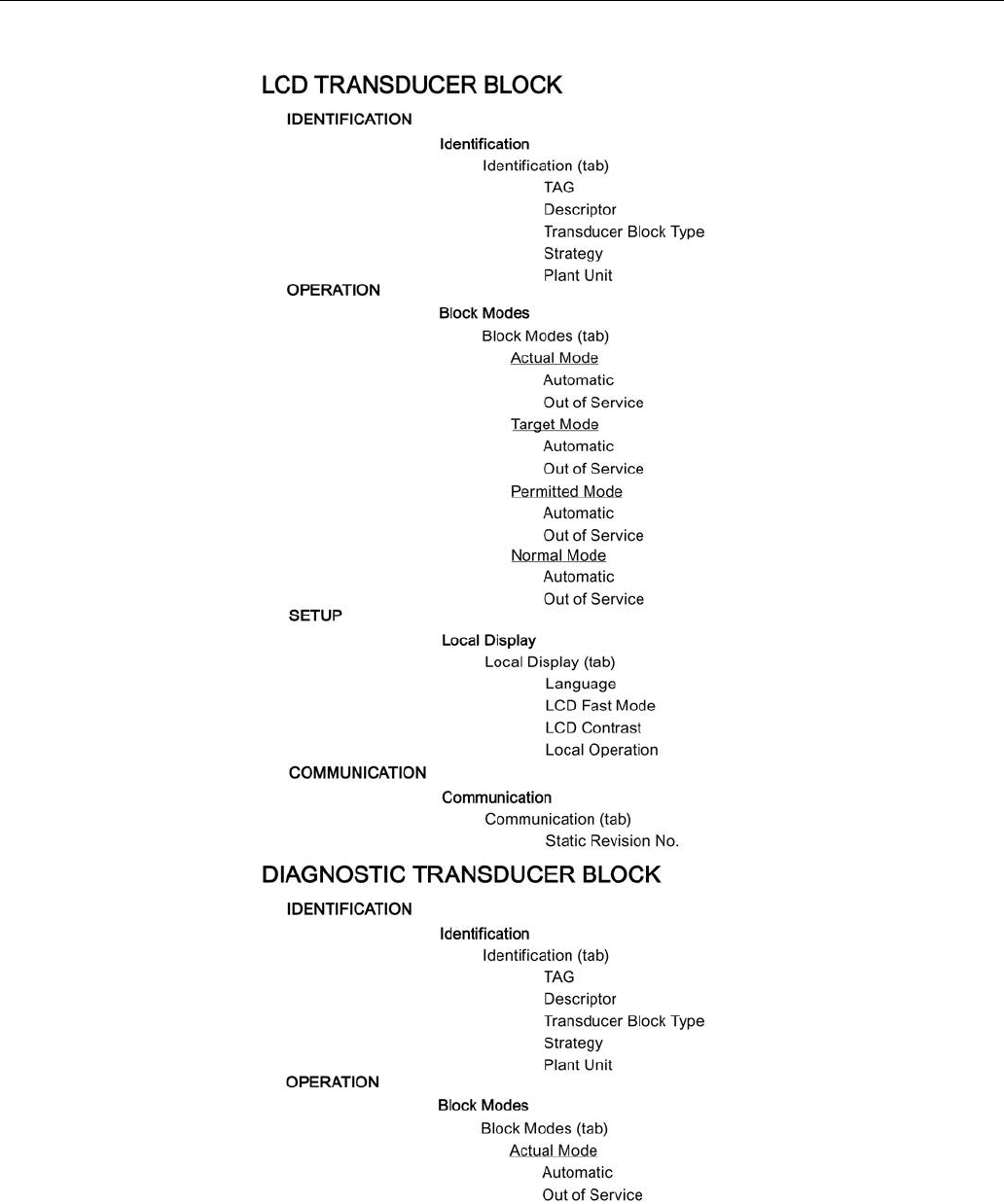
Remote operation
7.1 Operating via AMS Device Manager
SITRANS LR250 (FOUNDATION FIELDBUS)
Operating Instructions, 08/2014, A5E32221411-AC 133
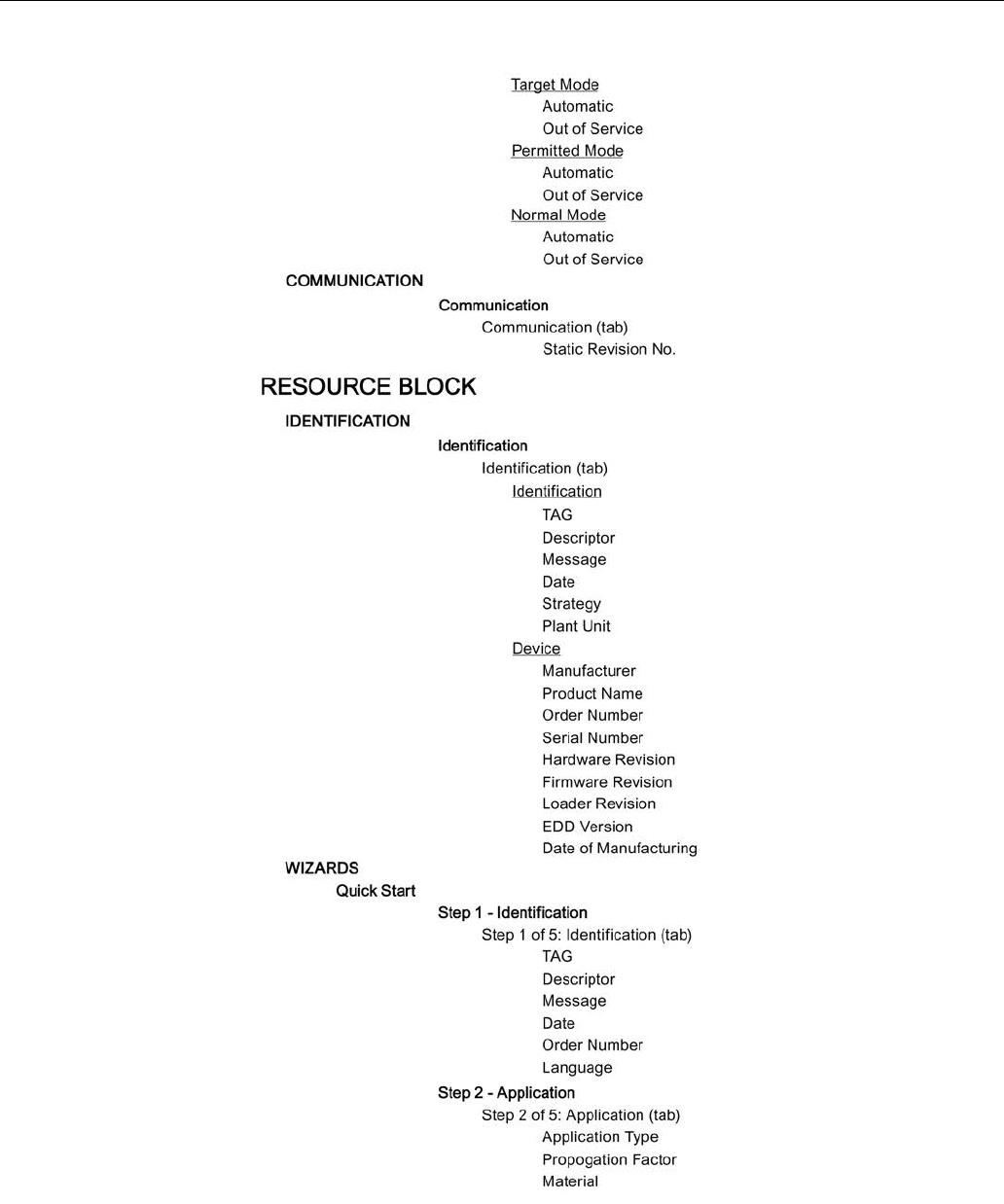
Remote operation
7.1 Operating via AMS Device Manager
SITRANS LR250 (FOUNDATION FIELDBUS)
134 Operating Instructions, 08/2014, A5E32221411-AC
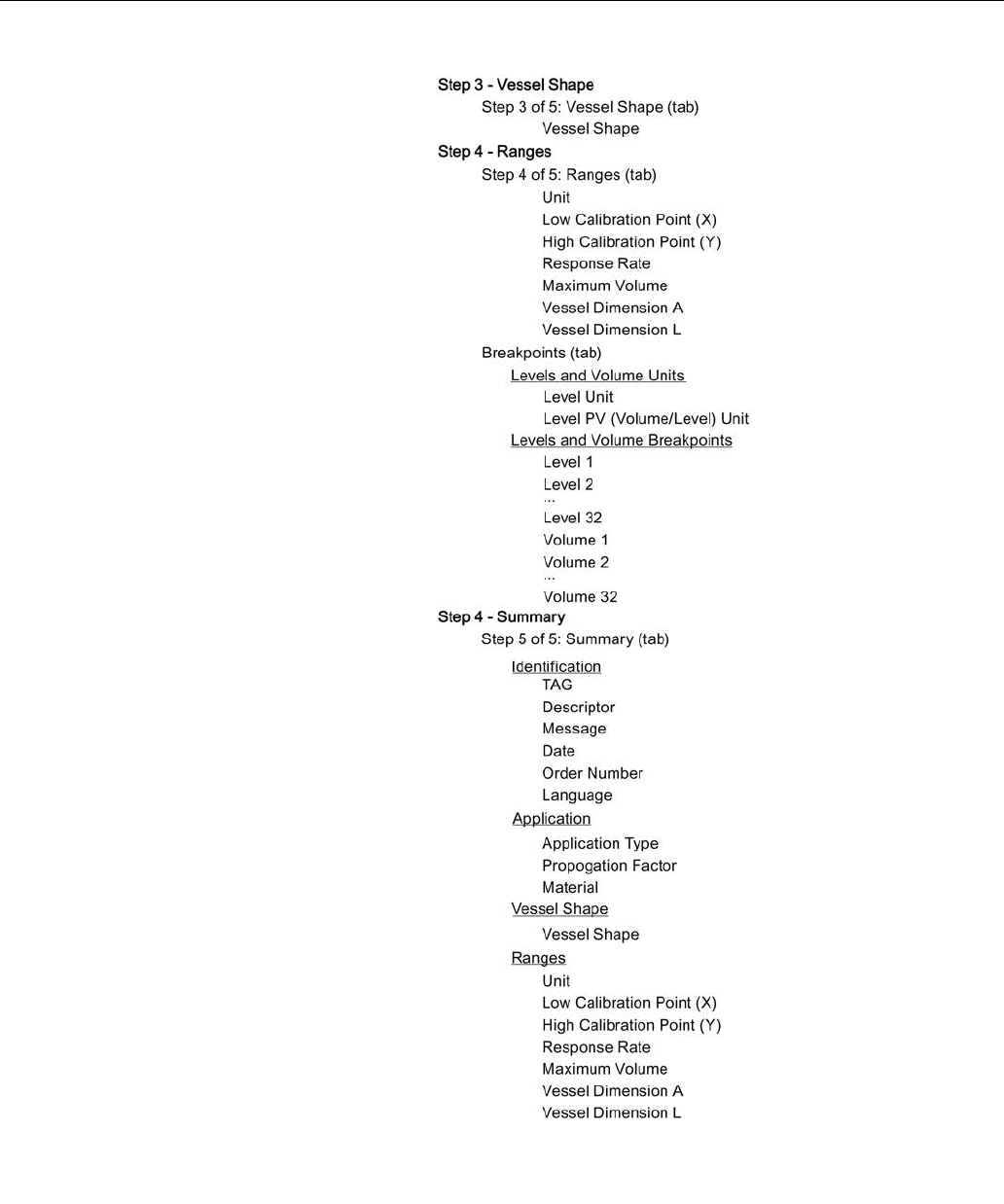
Remote operation
7.1 Operating via AMS Device Manager
SITRANS LR250 (FOUNDATION FIELDBUS)
Operating Instructions, 08/2014, A5E32221411-AC 135
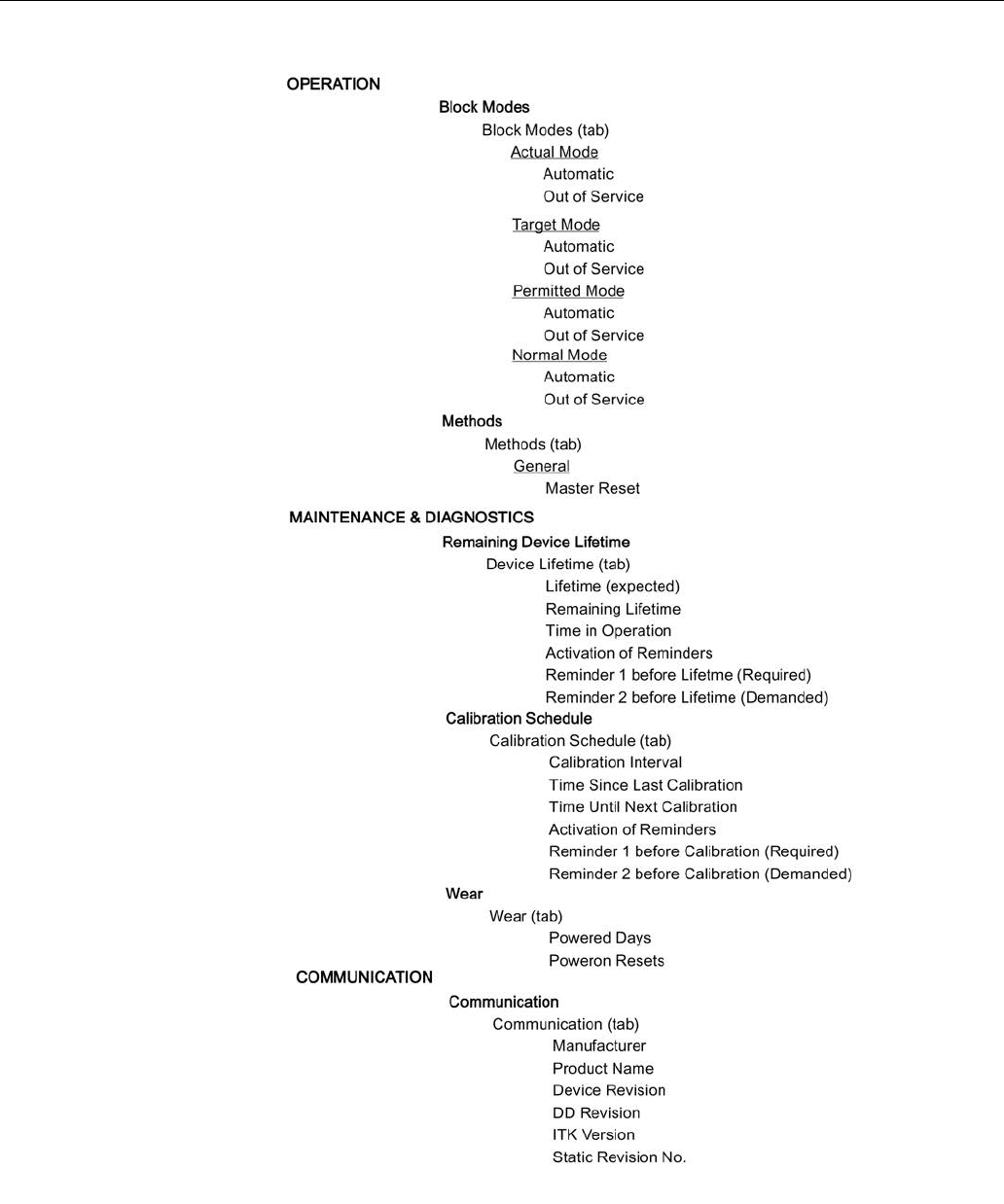
Remote operation
7.1 Operating via AMS Device Manager
SITRANS LR250 (FOUNDATION FIELDBUS)
136 Operating Instructions, 08/2014, A5E32221411-AC
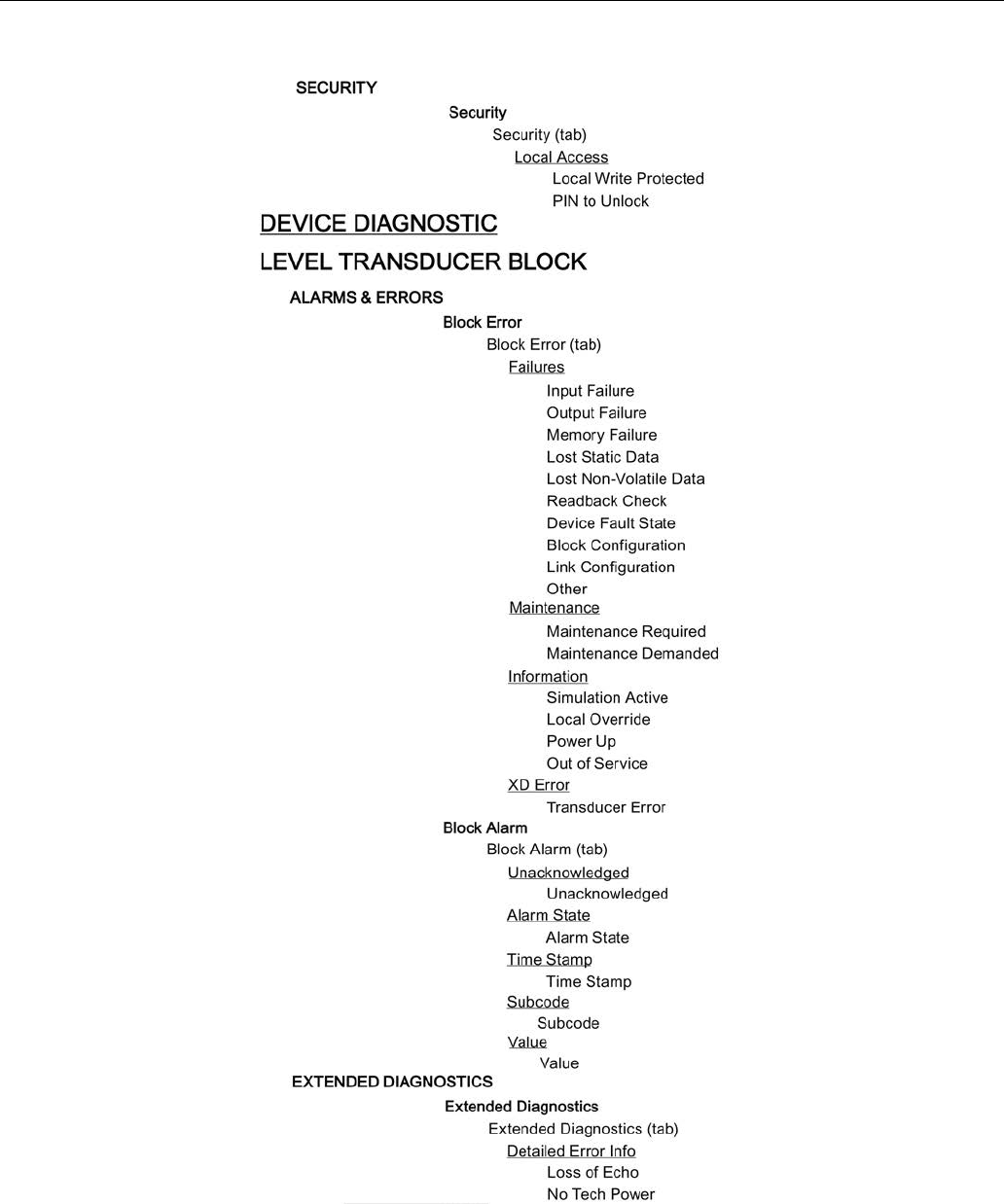
Remote operation
7.1 Operating via AMS Device Manager
SITRANS LR250 (FOUNDATION FIELDBUS)
Operating Instructions, 08/2014, A5E32221411-AC 137
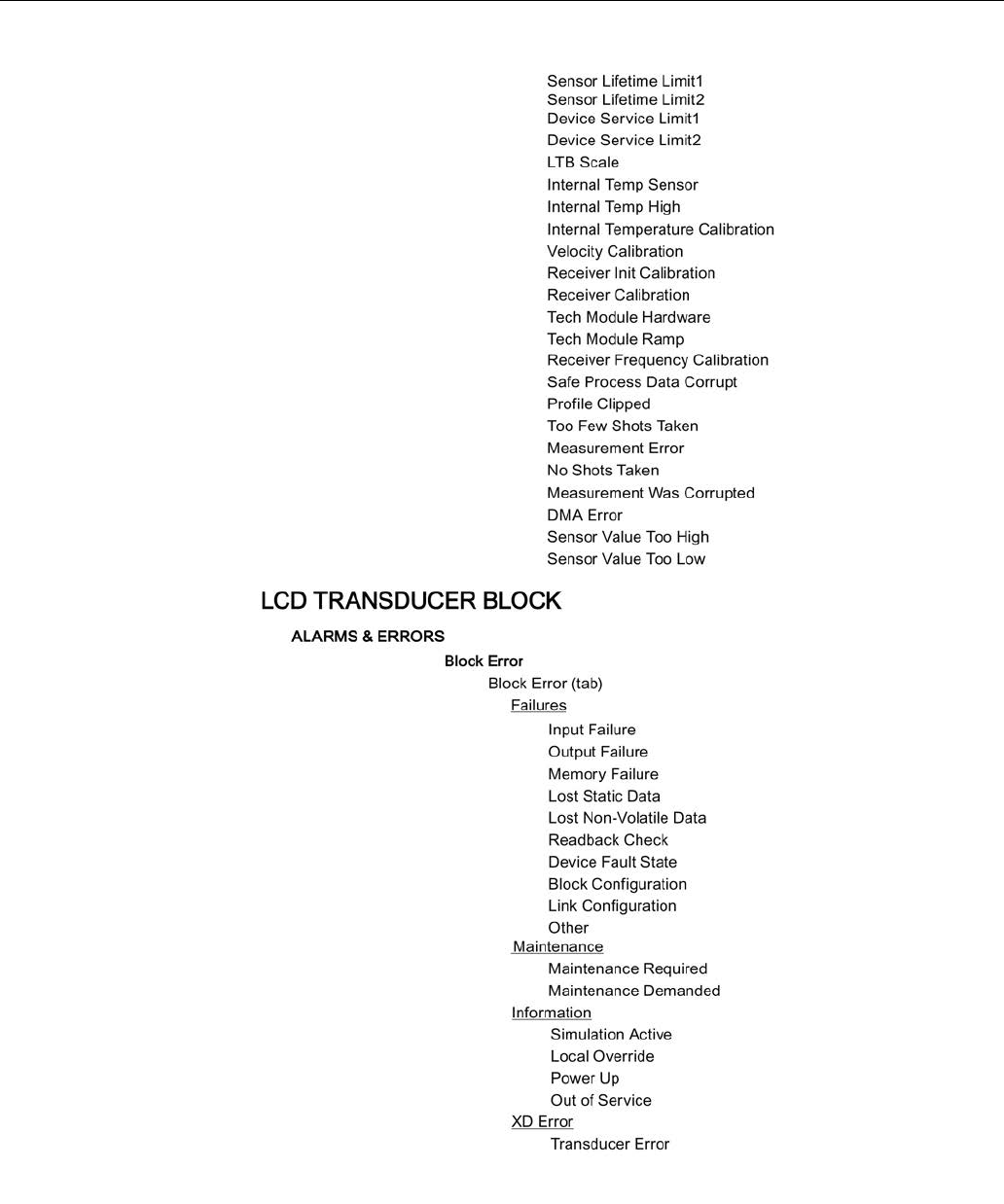
Remote operation
7.1 Operating via AMS Device Manager
SITRANS LR250 (FOUNDATION FIELDBUS)
138 Operating Instructions, 08/2014, A5E32221411-AC
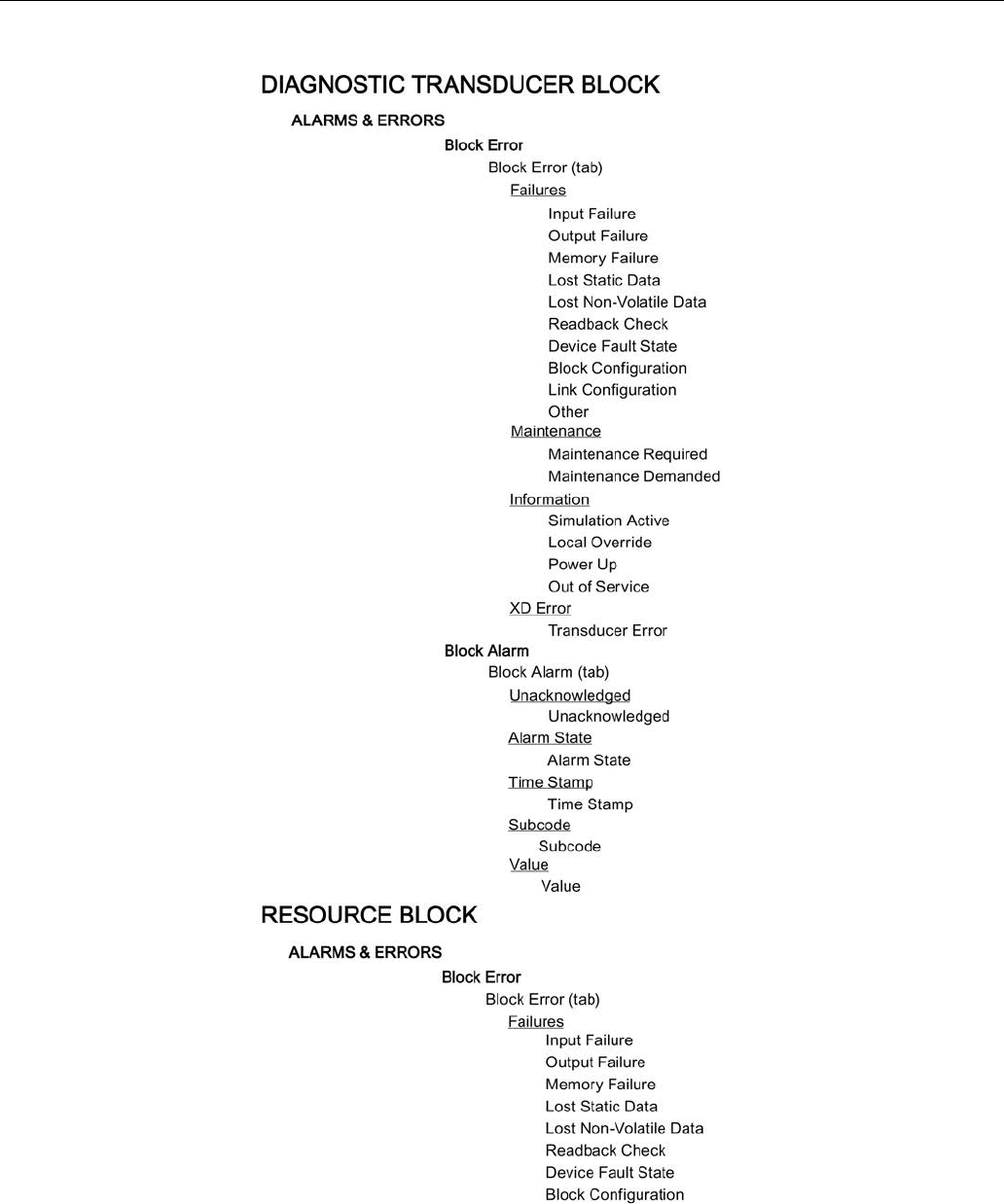
Remote operation
7.1 Operating via AMS Device Manager
SITRANS LR250 (FOUNDATION FIELDBUS)
Operating Instructions, 08/2014, A5E32221411-AC 139
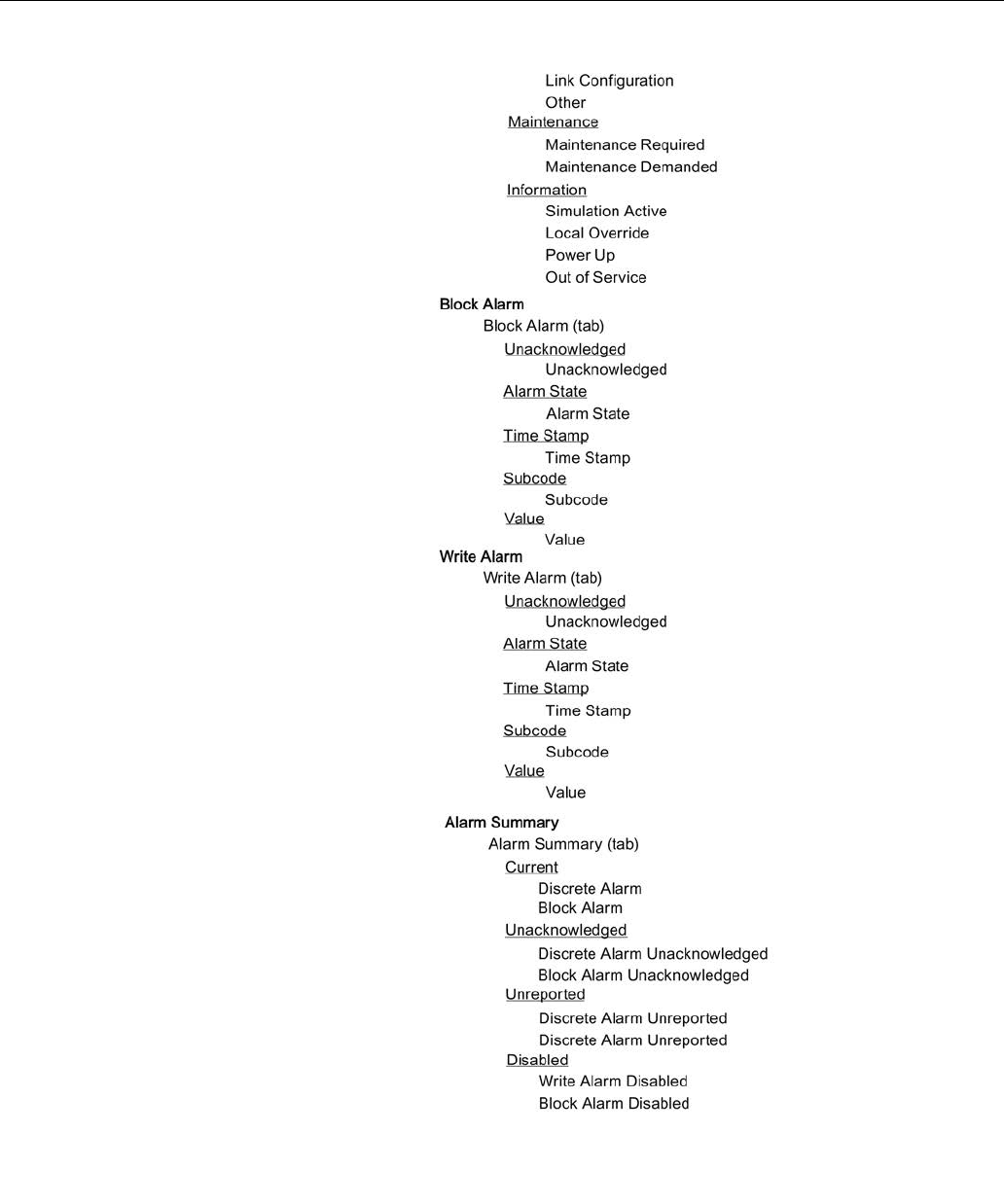
Remote operation
7.1 Operating via AMS Device Manager
SITRANS LR250 (FOUNDATION FIELDBUS)
140 Operating Instructions, 08/2014, A5E32221411-AC
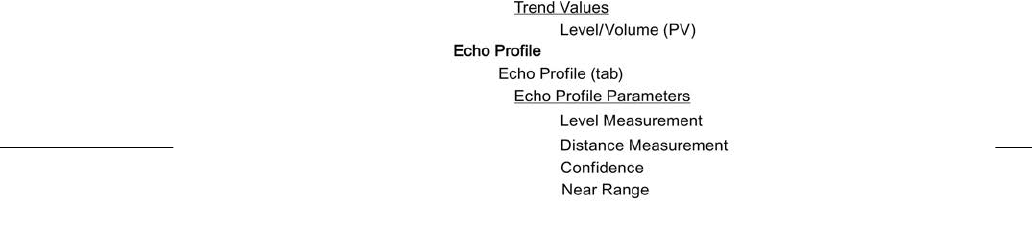
Remote operation
7.1 Operating via AMS Device Manager
SITRANS LR250 (FOUNDATION FIELDBUS)
Operating Instructions, 08/2014, A5E32221411-AC 141