Thrane and Thrane A S TU5160 Sailor System 5000 150W GMDSS MF/HF SSB DSC NBDP User Manual TT 3606E Installation Service Manual
Thrane & Thrane A/S Sailor System 5000 150W GMDSS MF/HF SSB DSC NBDP TT 3606E Installation Service Manual
Contents
user manual 6
Message Terminal
TT-3606E
Installation and Service Manual
Thrane & Thrane
Message Terminal
TT-3606E
Installation and Service Manual
Copyright Thrane & Thrane A/S
ALL RIGHTS RESERVED
Information in this document is subject to change without notice and does not
represent a commitment on the part of Thrane & Thrane A/S.
© 1998 Thrane & Thrane A/S. All right reserved. Printed in Denmark.
Document Number TT98-109638-A.
Release Date: 04 March 1998
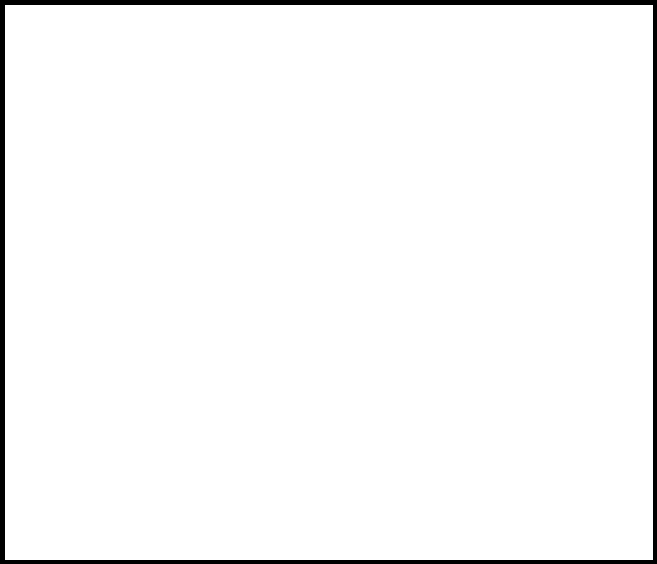
Safety Summary
The following general safety precautions must be observed during all phases of operation, service and
repair of this equipment. Failure to comply with these precautions or with specific warnings elsewhere
in this manual violates safety standards of design, manufacture and intended use of the equipment.
Thrane & Thrane A/S assumes no liability for the customers failure to comply with these requirements.
GROUND THE EQUIPMENT
To minimise shock hazard, the equipment chassis and cabinet must be connected to an electrical
ground and the cable instuctions must be followed.
DO NOT OPERATE IN AN EXPLOSIVE ATMOSPHERE
Do not operate the equipment in the presence of flammable gases or fumes. Operation of any
electrical equipment in such an environment constitutes a definite safety hazard.
KEEP AWAY FROM LIVE CIRCUITS
Operating personnel must not remove equipment covers. Component replacement and internal
adjustment must be made by qualified maintenance personnel. Do not replace components with the
power cable connected. Under certain conditions, dangerous voltages may exist even with the power
cable removed. To avoid injuries, always disconnect power and discharge circuits before touching
them.
DO NOT SERVICE OR ADJUST ALONE
Do not attempt internal service or adjustments unless another person, capable of rendering first aid
resuscitation, is present.
DO NOT SUBSTITUTE PARTS OR MODIFY EQUIPMENT
Because of the danger of introducing additional hazards, do not substitute parts or perform any
unauthorized modification to the equipment.
COMPASS SAFE DISTANCE
Minimum safety distance of 50 cm from the TT-3606E Message Terminal
This page is intentionally left blank
Table of Contents
4Mar98 Page i
Table of Contents
1 Installation............................................................................................................ 1-1
1.1 Quick system connect and checkout.................................................... 1-2
1.2 Initial inspection...................................................................................... 1-3
1.3 Storage .................................................................................................. 1-4
1.4 Repacking for shipment ........................................................................ 1-5
1.5 Cabling................................................................................................... 1-6
1.6 Mounting................................................................................................ 1-7
2 Description........................................................................................................... 2-1
2.1 Specifications......................................................................................... 2-2
2.2 Connectors ............................................................................................ 2-3
2.2.1 Keyboard connector ..................................................................... 2-3
2.2.2 Power connector .......................................................................... 2-4
2.2.3 Parallel printer port........................................................................ 2-5
2.2.4 Serial ports.................................................................................... 2-6
3 Service................................................................................................................. 3-1
3.1 Disassembling........................................................................................ 3-1
3.2 Configuration ......................................................................................... 3-3
4 Technical description........................................................................................... 4-1
4.1 Detailed specification............................................................................. 4-1
4.2 Special I/O ............................................................................................. 4-3
5 Mechanical outlines............................................................................................. 5-1
5.1 TT-3606E .............................................................................................. 5-1
5.2 Flush mount........................................................................................... 5-3
5.3 Mounting bracket................................................................................... 5-4
Table of Contents
Page ii 4Mar98
This page is intentionally left blank
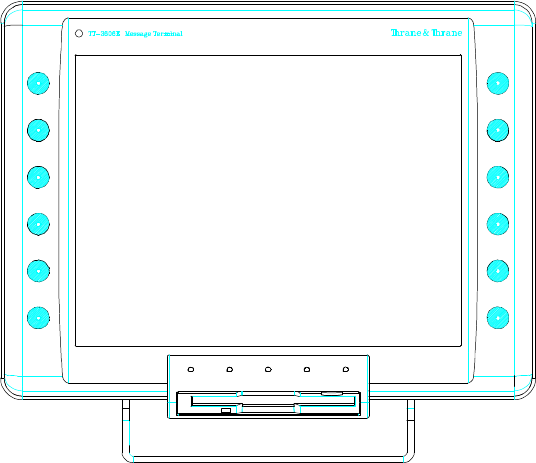
Quick system connect and checkout Installation
4Mar98 Page 1-1
11 InstallationInstallation
This chapter provides specific information about installation of the TT-3606E
Message Terminal and information about initial inspection, storage and
repacking for shipment.
Figure 1TT-3606E Message Terminal
Installation Quick system connect and checkout
Page 1-2 4Mar98
1.11.1 Quick system connect and checkoutQuick system connect and checkout
The following brief outline may be used to get the TT-3606E Message terminal
up and running
• Unpack system components
• Connect the TT-3606E to the keyboard
• Connect the TT-3606E to a DC power source
The TT-3606E should then start the actual application program. Please refer the
manual for the specific application program.
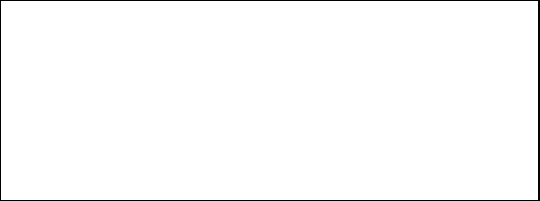
Initial inspection Installation
4Mar98 Page 1-3
1.21.2 Initial inspectionInitial inspection
WARNING
To avoid hazardous electrical shock, do not perform electrical tests if there
is any sign of shipping damage to any portion of the front or rear panel or
the outer cover. Read the safety summary at the front of this manual before
installing or operating the 3606E Message Terminal.
Inspect the shipping carton immediately upon receipt for evidence of
mishandling during the transit. If the shipping carton is severely damaged or
water stained, request that the carrier's agent be present when opening the
carton. Save the carton packing material for future use.
Contents of the shipment should be as listed in the enclosed packing list. If the
contents are incomplete, if there is mechanical damage or defect, or if the
3606E Message Terminal does not work properly, notify your dealer.
After you unpack the 3606E Message Terminal, inspect it thoroughly for hidden
damage and loose components or fittings.
²Inspect the cable harness for stress, loose or broken wires, or broken cable
tires.
²Examine all the components for loose or missing hardware. Tighten all
loose hardware.
Installation Storage
Page 1-4 4Mar98
1.31.3 StorageStorage
The 3606E may be stored or shipped in temperatures within the limits -40° C to
+80° C. It is advisable to protect 3606E from extreme temperature variation
which can cause excessive condensation. It is recommended that the 3606E is
unpacked immediately on delivery.
Repacking for shipment Installation
4Mar98 Page 1-5
1.41.4 Repacking for shipmentRepacking for shipment
The shipping carton for the 3606E has been carefully designed to protect the
Message Terminal and its accessories during shipment. This carton and its
associated packing material should be used when repacking for shipment.
Attach a tag indicating the type of service required, return address, model
number and full serial number. Mark the carton FRAGILE to ensure careful
handling.
If the original shipping carton is not available, the following general instructions
should be used for repacking with commercially available material.
1. Wrap the 3606E in heavy paper or plastic. Attach a tag indicating the type of
service required, return address, model number and full serial number.
2. Use a strong shipping container, e.g. a double walled carton of 160 kg test
material.
3. Protect the front- and rear panel with cardboard and insert a 7 cm to 10 cm
layer of shock absorbing material between all surfaces of the equipment and
the sides of the container.
4. Seal the shipping container securely.
5. Mark the shipping container FRAGILE to ensure careful handling.
Installation Cabling
Page 1-6 4Mar98
1.51.5 CablingCabling
For any installation it is required that all attached cables are shielded and
equipped with shielded connectors, which are properly connected to the shield
of the cable. Furthermore every shield should have a low impedance connection
to an electrical ground.
Before using the TT-3606E Message Terminal for the first time check out that
all cables are correctly wired and fastened.
Please notice that the DC-input range applies to the DC voltage measured at the
pin's on the power connector on the 3606E. This means that the power cable
characteristic should be taken into account. The cable should allow the DC,
measured at the input pin's on the 3606E power connector, to stay within limits
even though it has to carry a current of 3 A.
Please notice, that the wires must be properly connected in the connector and
all pin’s for each power input must be connected to the respective wire.
A cable using 2 mm2 (AWG 14) wire's of length 4 m fulfils the requirements.
Please notice, that the cable connections must be properly installed.
Mounting Installation
4Mar98 Page 1-7
1.61.6 MountingMounting
The TT-3606E Message Terminal may be mounted in several ways.
If the mounting bracket is not used, the TT-3606E Message Terminal may be
flush mounted in a consol by using the 4 screw holes on the rear.
The mounting bracket may be used either to mount the TT-3606E Message
Terminal on a horizontal surface or a vertical surface. In both cases the angle
can be adjusted in steps of 7.5°. This is done by loosening the hand wheels
slightly and then move the upper part of the TT-3606E Message Terminal into
the wanted angle. Please remember to tighten the handwheels again.
When assembling the mounting bracket together with the TT-3606E Message
Terminal it is important that the small indications on the cylinders are in-line with
the indications on the rear of TT-3606E Message Terminal.
When installing the TT-3606E on a vertical surface it is necessary to mount the
mounting bracket opposite the way it is mounted for horizontal installation.
Please refer to the chapter describing the detailed mechanical outlines of the
TT-3606E Message Terminal and mounting bracket.
Installation Mounting
Page 1-8 4Mar98
This page is intentionally left blank
Mounting Description
4Mar98 Page 2-1
22 DescriptionDescription
This chapter describes the TT-3606E Message Terminal. This encompasses
specifications as well as provides specific information about the available
features and interfaces.
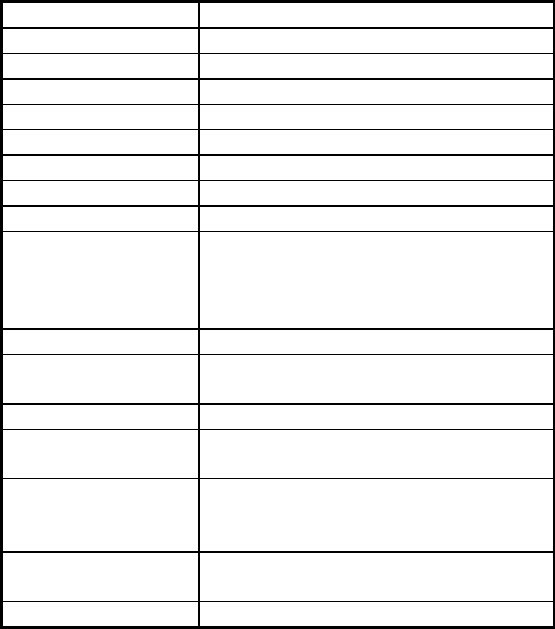
Description Specifications
Page 2-2 4Mar98
2.12.1 SpecificationsSpecifications
Processor 386SX-40MHz
RAM 2 MB
Flash DISK 2 MB
Display 10.4” Color TFT flatpanel, 640x480
Floppy drive 3.5”
Keyboard i/f 5-pin mini-DIN
Parallel printer port 25 pin SubD female connector
Serial port COM1 9 pin SubD male connector, DTE type
Serial port COM2 9 pin SubD male connector, DTE type
Environmental Meets or exceeds all INMARSAT specifications for
the Inmarsat-C Network for SOLAS with distress call
functions. (CN114 and IEC 945 requirements). Meets
CE-marking (1997) requirements.
Power Source 10 to 32 V floating DC, 15 pin SubD female
Power Consumption App. 20 Watts, maximum
App. 13 Watts, typical
Fuse Internal automatic recovering poly fuse
Ambient Temperature -20°C to 55°C operating
-40°C to 80°C storage.
Compass safe distance 50 cm
(measured in accordance with the standards
specified in ISO/R 694, Method B)
Dimensions H x W x D 221x 297 x 114.5 mm w/o bracket
256 x 297 x 114.5 mm w bracket at vertical position
Weight 3.1 kg (including mounting bracket)
Table 1TT-3606E Message Terminal
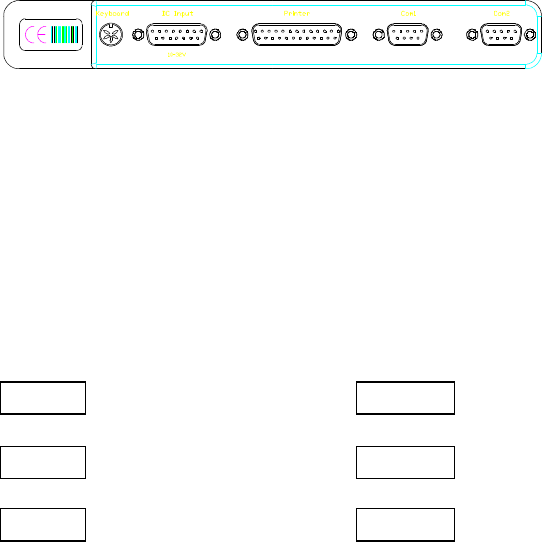
Connectors Description
4Mar98 Page 2-3
2.22.2 ConnectorsConnectors
This section describes the functions and pin assignments of connectors found
on the rear of the TT-3606E. Figure 2 shows the connector part of the TT-
3606E Message Terminal.
Figure 2Rear connectors
2.2.1 Keyboard connector
The figure below indicates the pin assignment of the keyboard connector as
seen from the rear of the TT-3606E Message Terminal.
N/C † … Clock
n
+5V „ ƒ Ground
N/C ‚ • Data
Figure 3Keyboard connector
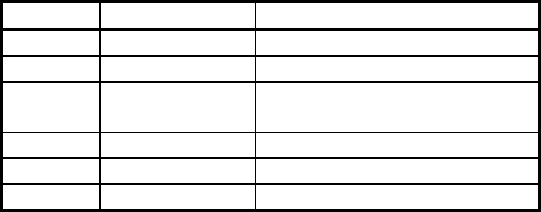
Description Connectors
Page 2-4 4Mar98
2.2.2 Power connector
The power input connector is a standard 15 pin SubD male connector, located
on the rear panel of the TT-3606E and the pin assignments are as indicated
below. The Remote ON/OFF input makes it possible to place an eventual on/off
switch at any location.
Pin Name Signal Description
1,2,9,10 + supply 10-32 VDC (Battery Positive input)
4,5,12,13 - supply DC Return (Battery Negative input)
6Remote ON/OFF ON if connected to “- supply”
OFF if floating
7,8 SGND Chassis (Secondary GND)
Ground GND Shield
3,11,14,15 NC
Table 2Power connector
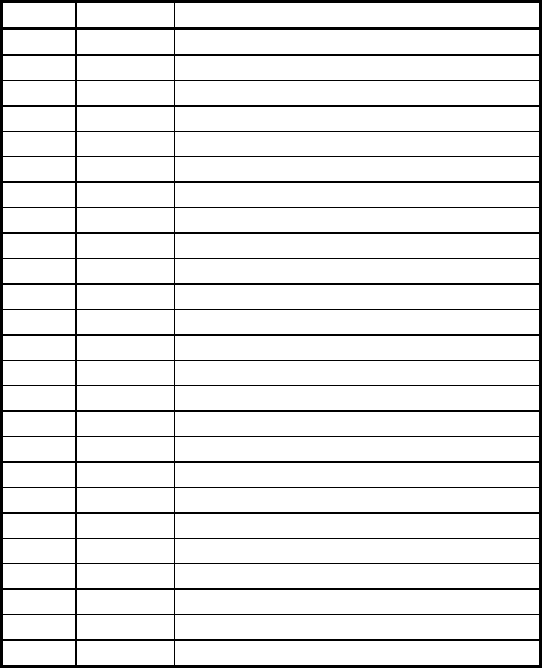
Connectors Description
4Mar98 Page 2-5
2.2.3 Parallel printer port
The parallel printer port is a standard 25 pin SubD female connector, located on
the rear panel of the TT-3606E and the pin assignments are as indicated below.
Pin Name Signal Description
1STRB Strobe
2DAT0 Data Bit 0
3DAT1 Data Bit 1
4DAT2 Data Bit 2
5DAT3 Data Bit 3
6DAT4 Data Bit 4
7DAT5 Data Bit 5
8DAT6 Data Bit 6
9DAT7 Data Bit 7
10 ACKN Acknowledge
11 BUSY Printer Busy
12 PE Paper End (out of paper)
13 SEL Printer Selected
14 ALFD Auto Line Feed
15 ERR Printer Error
16 INIT Initialise Printer
17 SLCT Select Printer
18 GND Ground
19 GND Ground
20 GND Ground
21 GND Ground
22 GND Ground
23 GND Ground
24 GND Ground
25 GND Ground
Table 3Parallel port
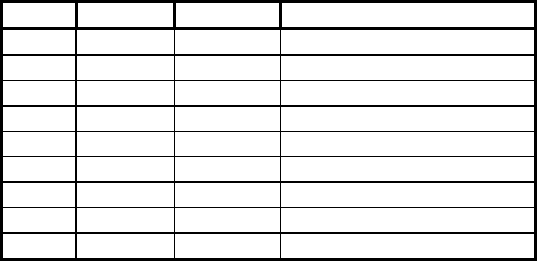
Description Connectors
Page 2-6 4Mar98
2.2.4 Serial ports
The serial ports are standard 9 pin SubD male connectors, located on the rear
panel of the TT-3606E and the pin assignments are as indicated below.
Pin Name Direction Signal Description
1DCD input Data Carrier Detect
2RxD input Received Data
3TxD output Transmitted Data
4DTR output Data Terminal Ready
5GND Ground
6DSR input Data Set Ready
7RTS output Request To Send
8CTS input Clear To Send
9RI input Ring Indicator
Table 4Serial ports
The serial ports comply with the EIA/TIA-232 standard.
For full operating specifications for the serial interface, you are kindly requested
to refer to the CCITT Rec. V24 and the EIA/TIA-232 specifications.
To interface the TT-3606E to any DCE type of device such as for example the
TT-3020C/22C/D Transceiver use a 1:1 RS-232 cable.
At a baud rate of 4800 this cable should not exceed 100 meters.
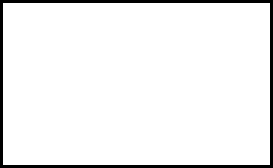
Disassembling Service
4Mar98 Page 3-1
33 ServiceService
This chapter describes how to disassemble and to service to a level of changing
boards/parts.
3.13.1 DisassemblingDisassembling
If you have to disassemble the TT-3606E Message Terminal it is important, that
you follow the procedure described in this section. Otherwise you will find it very
difficult and you risk to permanently damage the Message Terminal.
WARNING
Do not try to disassemble the TT-
3606E Message Terminal yourself.
This operation must only be
performed by qualified service
personnel.
The unit is assembled out of three parts:
1. Rear plate holding the floppy drive
2. Intermediate plate holding the different PCB’s on the rear side and the flat
panel on the front side.
3. Plastic front holding the softkey construction and the display window.
To get access to the main PCB, backlight PCB (piggy bag on the main PCB)
and computer board the following steps should be followed:
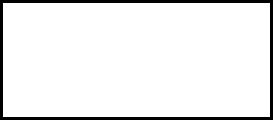
Service Disassembling
Page 3-2 4Mar98
WARNING
To avoid hazardous electrical shock,
do not touch the two high voltage
outputs of the backlight inverter.
1. Make sure the mounting bracket is removed
2. Unscrew the 12 counter sunk screws on the rear and the 8 Sub-D stays.
3. Gently divide the front part and rear part from each other so that the flex
cable connecting the floppy with the main PCB on the intermediate plate can
be removed by releasing the zero-insertion force cable connector mounted
on the main PCB (J15).
If it is necessary to remove/replace the main PCB it is necessary to remove the
backlight inverter first in order to get access to two of the screws holding the
main PCB.
To further get access to the display or soft key PCB’s placed just behind the
softkeys the following steps further have to be followed
1. Dismantle the cables attached to J2 and J3 (just left and right of J15).
These cables establish the connections from the main PCB on the
intermediate plate and to the softkey PCB’s attached to the plastic front.
2. Remove the plastic front from the intermediate plate by unscrewing the 14
counter sunk screws.
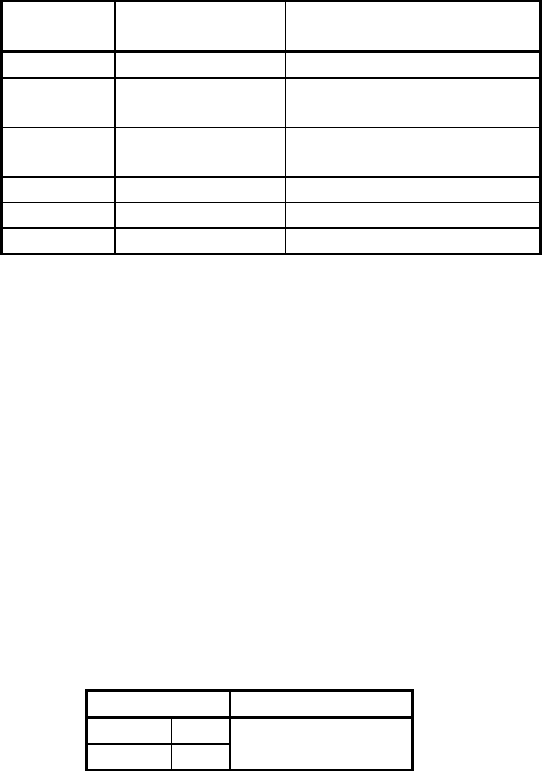
Configuration Service
4Mar98 Page 3-3
3.23.2 ConfigurationConfiguration
The main PCB, which is shown in figure 4, contains the following jumpers,
measurement points and adjustment possibilities:
Reference Factory setting or
value/range
Function
W1 Open If closed the computer is reset
W2 Closed Connecting/disconnecting power
supply from rest of circuitry
W3 120 kHz, ± 2 kHz Switch frequency of switch mode
power supply
TP1 0 - 3.6 V DC Output of light sensor
TP2 0 - 3 V DC Output to softkey back light
R38 120 kHz, ± 2 kHz Adjustment of switch frequency
Table 5Configuration
The jumper W2 can be used to remove the connection between the switch
mode power supply and the rest of the circuitry including computer as well as
backlight inverter. The pin assignments for W2 are as follows. Please notice
that ground connection can only be disconnected when the PCB is NOT
mounted on the intermediate plate.
W2 pin no Function
1 2 + 12 V DC, ± 20 %
3 4
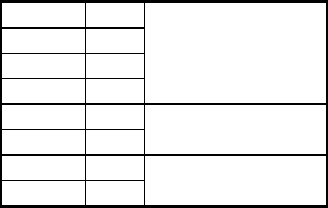
Service Configuration
Page 3-4 4Mar98
5 6 Ground
7 8
9 10
11 12
13 14 + 5 V DC, ± 10 %
15 16
17 18 No Connection
19 20
Table 6Jumper W2
The CMOS-setup in the computer may be reset to default by moving the jumper
marked “CLEAR CMOS” on the computer board from position 1-2 to position 2-
3 and then back to position 1-2.
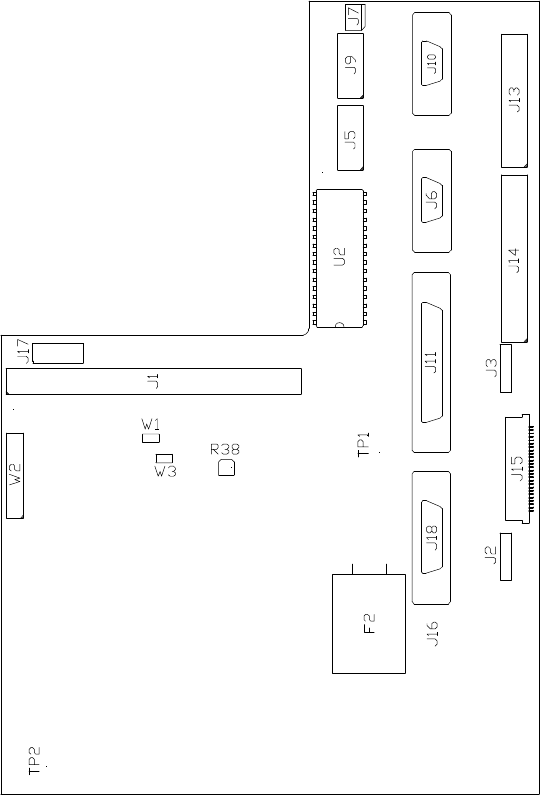
Configuration Service
4Mar98 Page 3-5
Figure 4Main PCB
Service Configuration
Page 3-6 4Mar98
This page is intentionally left blank
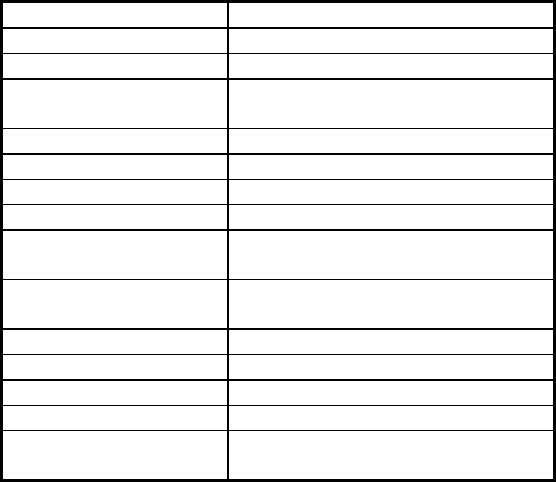
Detailed specification Technical description
4Mar98 Page 4-1
44 Technical descriptionTechnical description
This chapter gives a detailed description of the TT-3606E Message Terminal.
4.14.1 Detailed specificationDetailed specification
The hardware platform of TT-3606E Message Terminal is PC - compatible. The
table below gives a more detailed specification of the computer part. Whether or
not these hardware features are used dependents on the installed application
program.
Processor 386SX-40MHz
Data bus 16-bit
Processing ability 32-bit
Shadow RAM Support for system and video BIOS up to 256 kB
in 32 kB blocks
Display memory 512 kB DRAM
IDE HDD interface Supports up to two IDE (AT bus) HDD’s
FDD interface Supports up to two FDDs
Parallel port Bi-directional (SPP/ECP/EPP modes)
Serial ports Two RS-232 (both use 16C550 UART with 16-
byte FIFO). Up to 115.200 baud.
Real time clock ALI M6117B internal RTC, battery for up to 10
years data retention
DMA channels 7
Interrupt levels 15
Keyboard interface PS/2
Bus speed 8 MHz
Flash DISK DiskOnChip2000 from M-Systems.
Address: DC000-DDFFF
Table 7Detailed specification
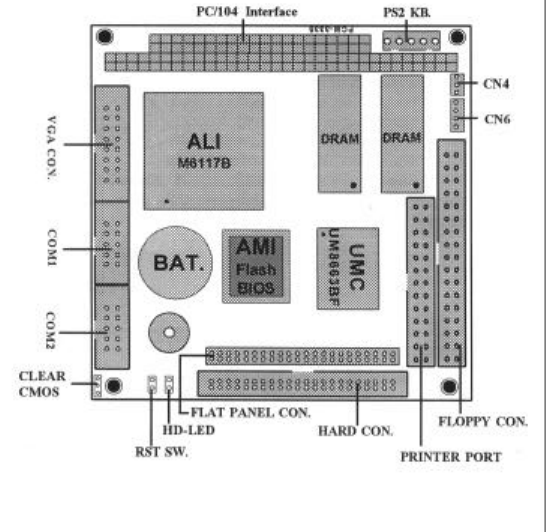
Technical description Detailed specification
Page 4-2 4Mar98
Figure 5 shows the physical outline of the computer board:
Figure 5Computer board
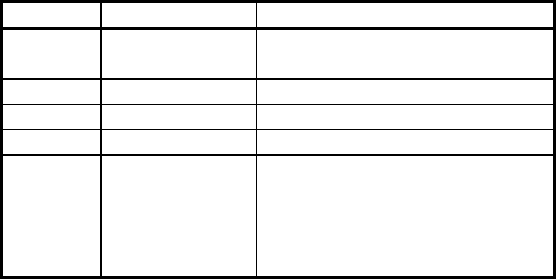
Special I/O Technical description
4Mar98 Page 4-3
4.24.2 Special I/OSpecial I/O
Special I/O ports have been implemented in the TT-3606E Message Terminal in
order to be able to support some extra features compared to a standard PC.
These are
• 12 softkeys
• Disk change signal from floppy
• Backlight control of TFT flat-panel as well as softkeys
• Watchdog
• Light sensor
• Reset of external keyboard
The table below indicates the diffent I/O ports
Address Direction Function
300h input status of softkey right and
disk change signal
301h input status of softkey left
302h output light sensor sample and hold
302h input light sensor output
303h output control of
display backlight level
softkey backlight level
watch dog
keyboard reset
Table 8Special I/O ports
The light level surrounding the equipment is determined by the light sensor
circuitry. A sample/hold of the light level is done by writing to this port two times.
The sampled value can then be determined by reading this port afterwards.
An 8-bit A/D-converter is used with a reference level of 5V (corresponds to A/D
value FFh). The linear light sensor gives an output in the range from 0V to
3,60V, thus the light level is in the range from 00h to approximately C0h
(255*5V/3,75V).
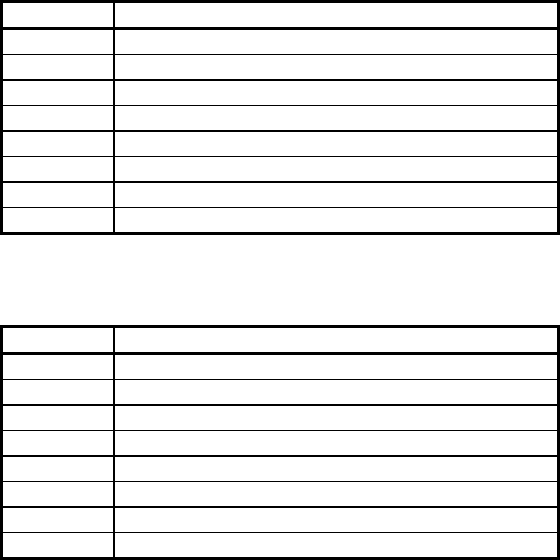
Technical description Special I/O
Page 4-4 4Mar98
The tables below indicate the precise function of each bit in the remaining ports.
300h Indicates
0 (LSB) 0 if right softkey 1 is pressed else 1 (upper)
10 if right softkey 2 is pressed else 1
20 if right softkey 3 is pressed else 1
30 if right softkey 4 is pressed else 1
40 if right softkey 5 is pressed else 1
50 if right softkey 6 is pressed else 1 (lower)
6Always “1”
7 (MSB) Always “1”
Table 9Softkey right
301h Indicates
0 (LSB) 0 if left softkey 1 is pressed else 1 (upper)
10 if left softkey 2 is pressed else 1
20 if left softkey 3 is pressed else 1
30 if left softkey 4 is pressed else 1
40 if left softkey 5 is pressed else 1
50 if left softkey 6 is pressed else 1 (lower)
6Status of disk change signal from floppy
7 (MSB) Always “1”
Table 10 Softkey left
The hardware does not provide any deglicth secuitry for the softkeys. This is to
be implemented in software. The keys are physically placed outside line
3,7,11,15,19 and 23, if there is a total of 25 lines on the display.
The “disk change signal “ is a hardware signal from the floppy drive which
during access to the floppy indicates (goes to 0) whether or not the floppy has
been changed. Can be used in the application software to only read the FAT-
table, when the floppy has actual changed.
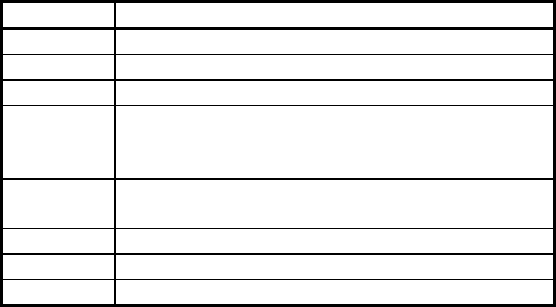
Special I/O Technical description
4Mar98 Page 4-5
303h Function
0 (LSB) If 0 display backlight off else on
1if 1 display backlight control selected, CS
2If 1 softkey backlight control selected, CS
3If toggled from 1 to 0 to 1 the light level of the selected
backlight(s) is(are) changed 1 unit (out of 100), /INC.
Direction depends on bit 4
4If 0 the light level is decreased when toggeling bit 3 (/DWN)
else increased
5Watch dog toggled when changing this bit
6If 0 watchdog is disabled else enabled
7 (MSB) External keyboard enabled if 0 and disabled/reset if 1
Table 11 Control port (all 0 except bit 1,2 after power up)
The control port is used to set/reset the different bits in the connected register.
After power up all bits in this register defaults to “0” except bit 1 and 2 which set
to 1. This implies that the the display backlight is turned on, the watchdog is
disabled and the external keyboard is enabled.
After the unit has booted, the application can enable the watchdog, if the
application program supports a watchdog surveillance circuitry. If enabled it
must be toggled every 0,5 second by changing the appropriate bit as indicated
above otherwise the unit will reset and reboot.
The reset possibility of the external keyboard can be used by the application
software for keyboard surveillance purposes.
The display as well as the softkey backlight is controlled using electronic
potentiometers. Both are controlled by using three signals:
CS : Chip Select
/INC: Increment
/DWN: Up/down selection
Technical description Special I/O
Page 4-6 4Mar98
If CS is “1” the electronic potentiometer is selected and the /INC and /DWN
signals can be used to adjust the electronic potentiometer and thus the light
level. If CS is “0” these two signals will not imply any change. Every time the
/INC-bit is toggled the potentiometer is adjusted 1/100 of its maximum value.
The direction is controlled by the /DWN-bit. If it is 0 the light level is decreased
where as a 1 will imply an increase when the /INC bit is toggled.
In this way the application can control the potentiometers to obtain any of its 100
different positions/levels.
The /INC bit may not be changed more often than every 4 µsec.
Both potentiometers can be adjusted simultaneously in the same direction by
setting both CS bits to “1”.
To make sure that the position of the potentiometers are known by the
application software after power up both potentiometers should be initialised with
100 pulses in either up or down. It is recommended to decrease both backlights
to the minimum level at power up.
The relation between light level and potentiometer position is not identical for the
display backlight and the softkey backlight. For the softkey back light there is a
1:1 relation. With respect to the display backlight there is a 1:1 relation from
potentiometer position 100 (maximum light) down to approximately 60. Below 60
the display backlight level will not change.
In order to completely turn off the backlight it is necessary to use the display
backlight on/off bit and set it to 1.
A way to cope with the display backlight characteristic is to have two display
setups/styles: one used during daylight (bright colors, but not red) and one used
during night (red characters and graphics on a black background).
Special I/O Technical description
4Mar98 Page 4-7
Technical description Special I/O
Page 4-8 4Mar98
This page is intentionally left blank
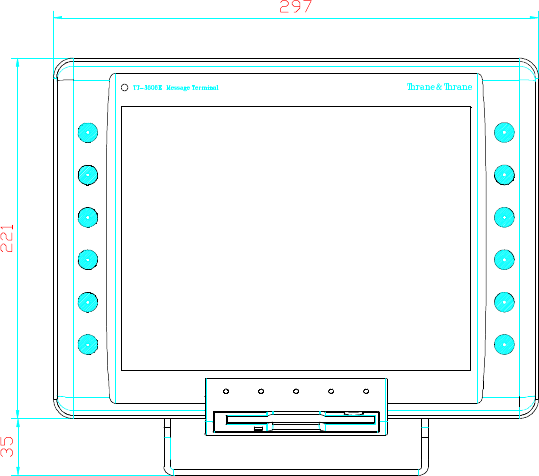
Index
4Mar98 Page 5-1
55 Mechanical outlinesMechanical outlines
This chapter shows the dimensions of the TT-3606E Message Terminal as well
as the mounting stencils for the different ways of mounting the TT-3606E
Message Terminal.
5.15.1 TT-3606ETT-3606E
Figure 6 and 7 shows the dimensions of the TT-3606E Message Terminal.
Figure 6TT-3606E Message Terminal
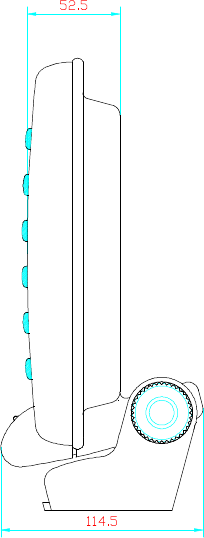
Mechanical outlines
Page 5-2 4Mar98
Figure 7TT-3606E Message Terminal
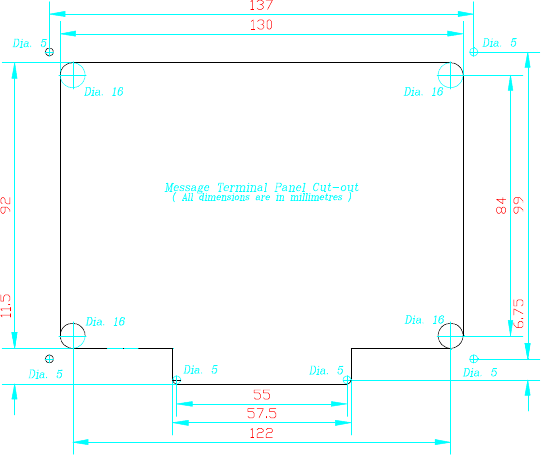
Index
4Mar98 Page 5-3
5.25.2 Flush mountFlush mount
Figure 8 indicates the dimension of the panel cut-out and position of mounting
holes when mounting the TT-3606E Message Terminal in a consol.
Figure 8TT-3606E Message Terminal
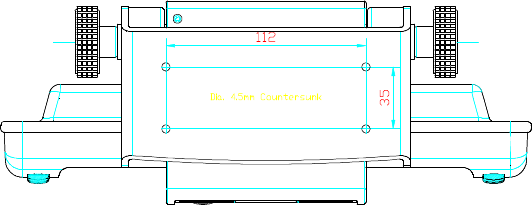
Mechanical outlines
Page 5-4 4Mar98
5.35.3 Mounting bracketMounting bracket
Figure 9 indicates the position of the mounting holes for the mounting bracket.
Figure 9TT-3606E Message Terminal